"Construction" Gallery
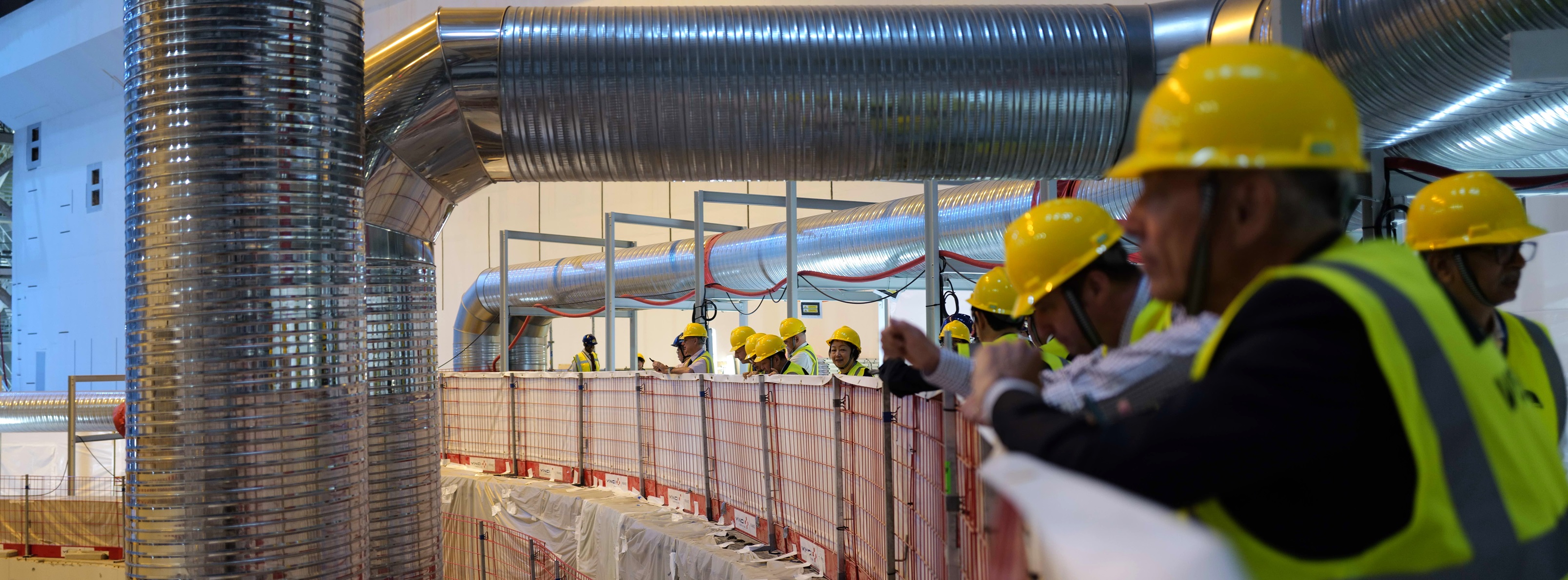
Council views recently added sector module
2025-06-19 - Representatives to the Thirty-Sixth Meeting of the ITER Council (IC-36) stand at the top of the tokamak pit, looking down on the never-before-seen sight of TWO sector modules.
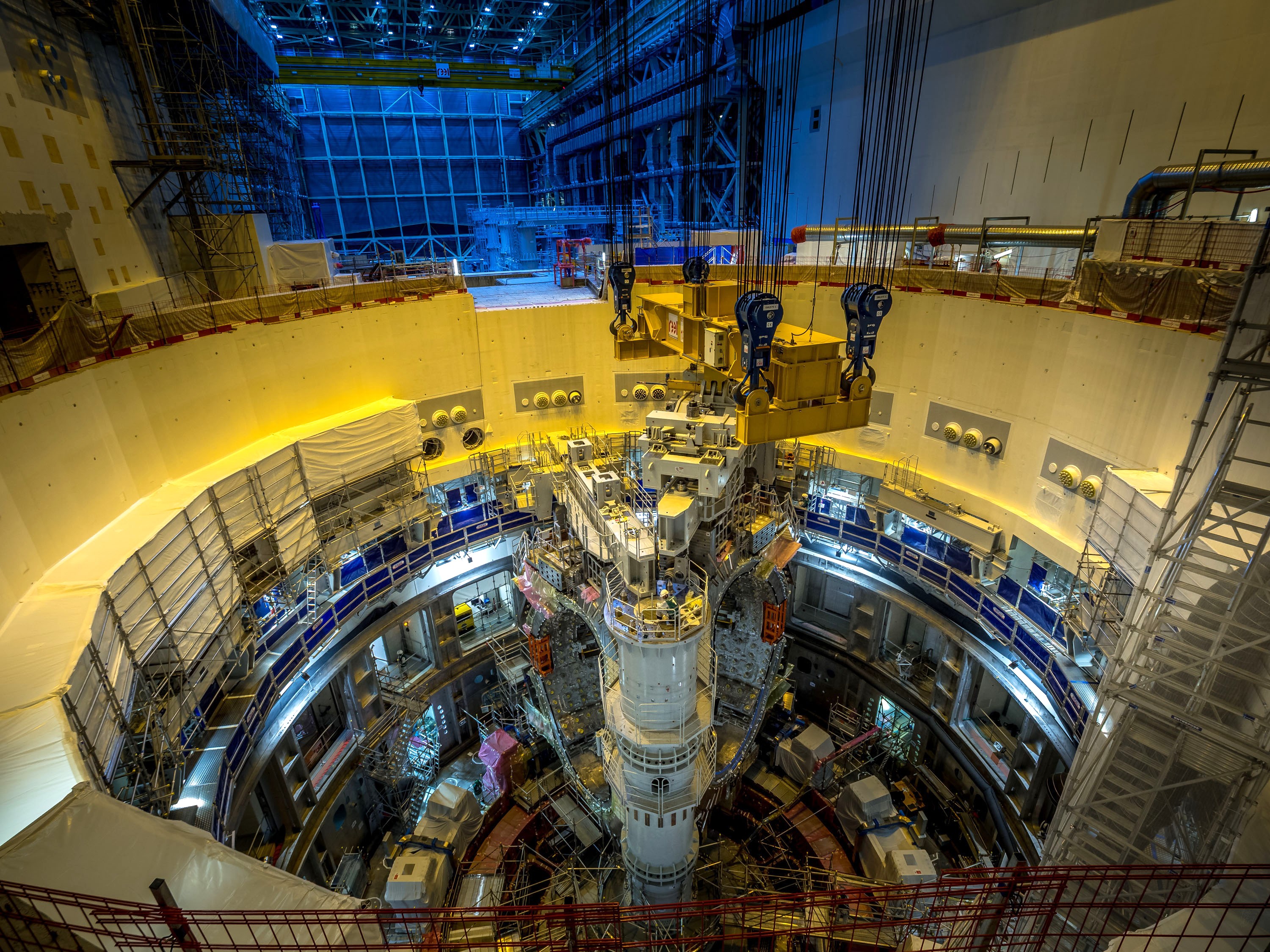
From above
2025-06-18 - The two sector modules as viewed from the rim of the tokamak pit. They represent two-ninths of the ITER vacuum vessel.
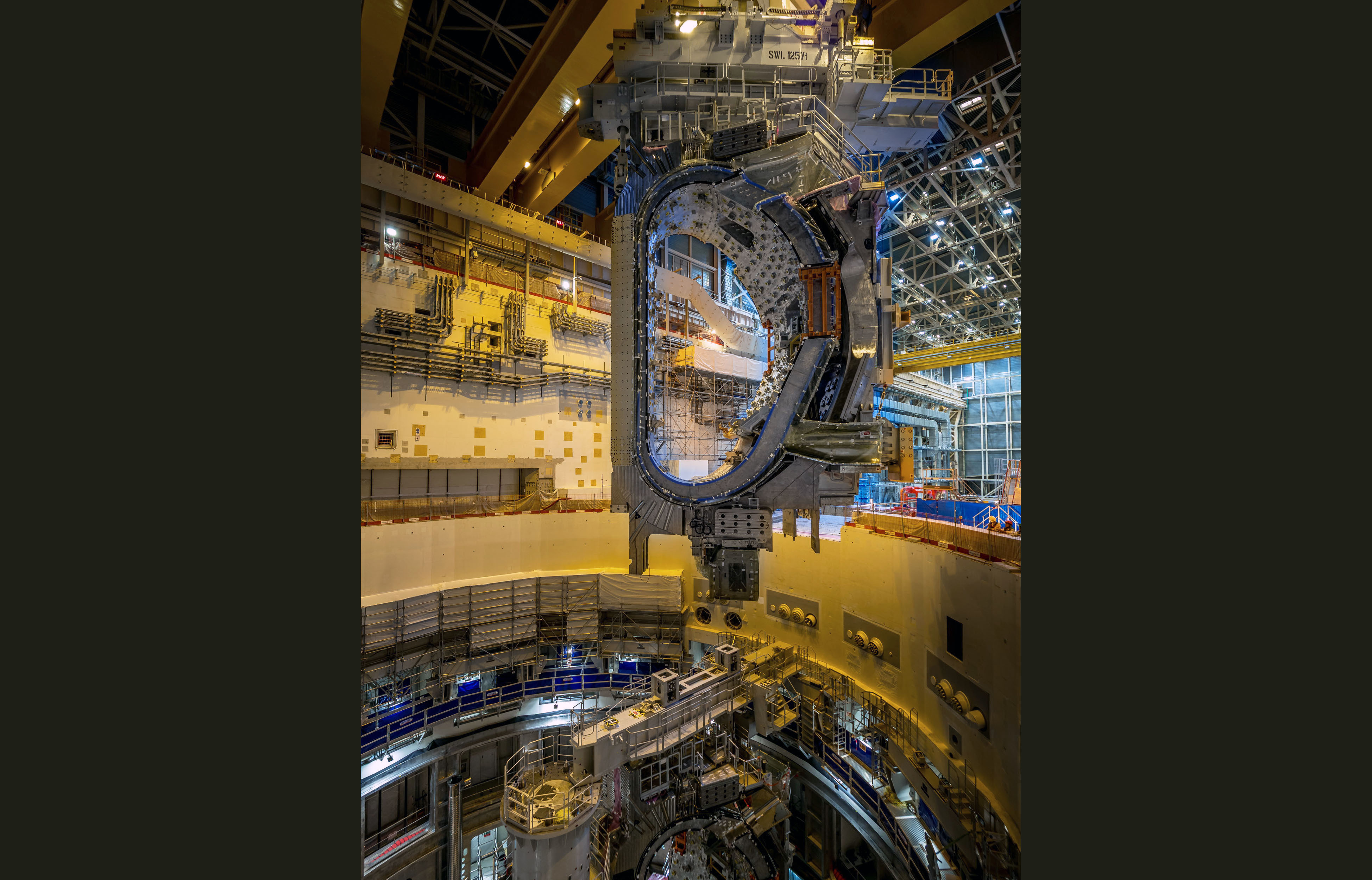
Above the pit
2025-06-18 - The 1,380-tonne load is suspended above bay #6 in the tokamak pit and will soon start to descend.
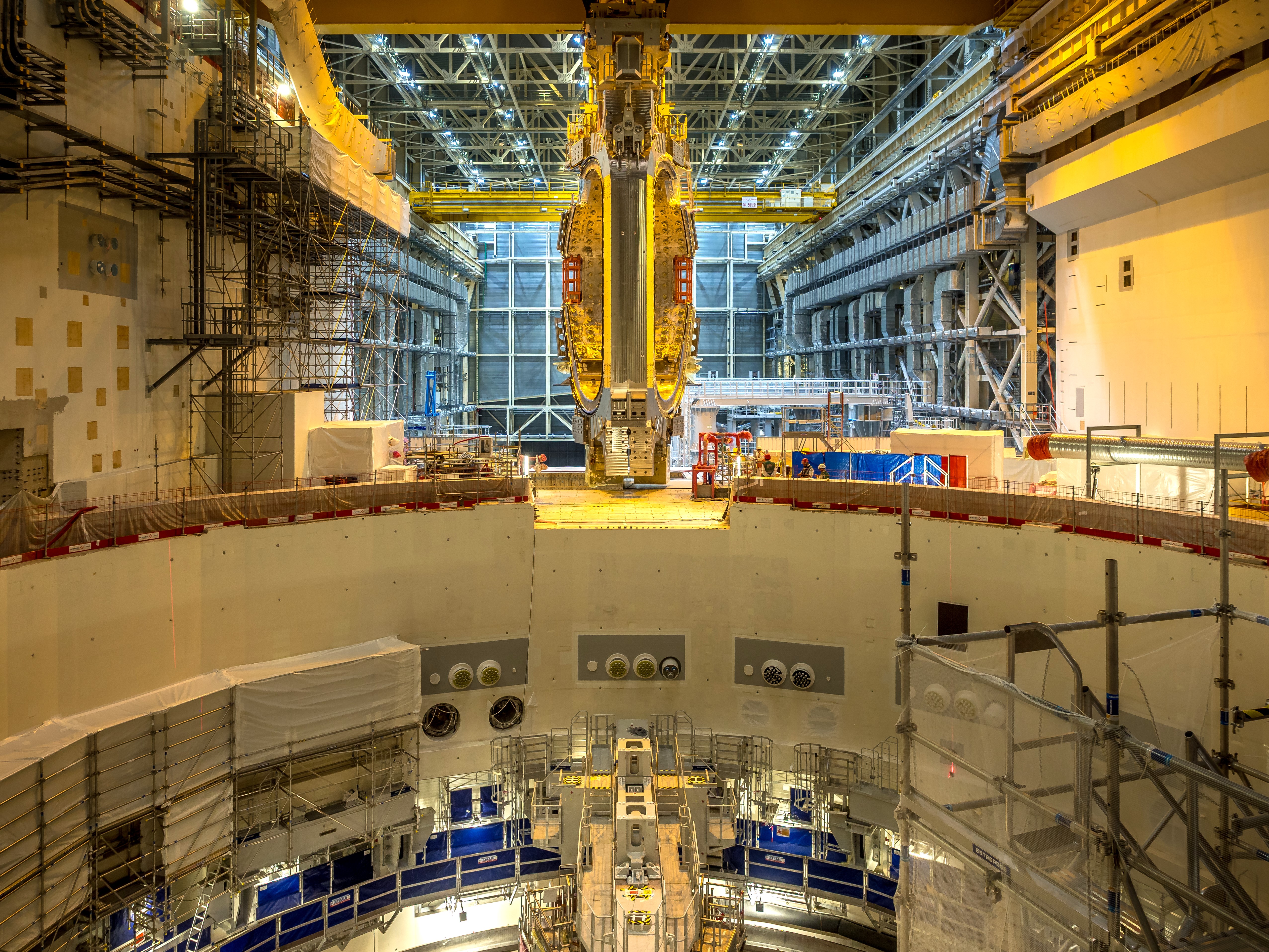
Over the wall
2025-06-18 - Above and below: sector module #6 is about to join sector module #7 in the tokamak assembly pit.
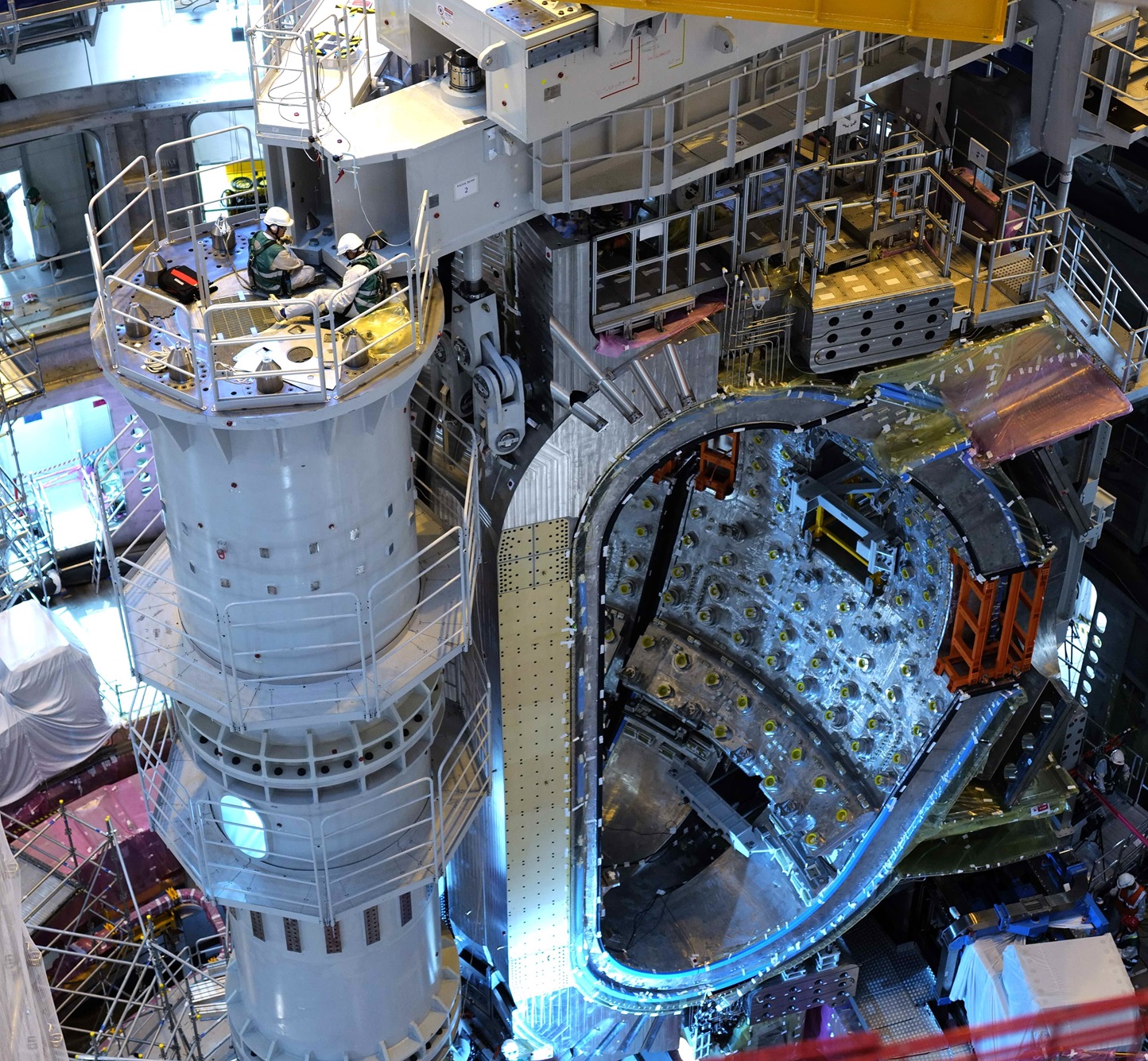
Just a few more centimetres
2025-06-18 - The radial beam supporting new sector module #6 is still a few centimetres above the one that has been in the pit since April. These workers from the CNPE consortium are watching closely as it travels the last bit of distance.
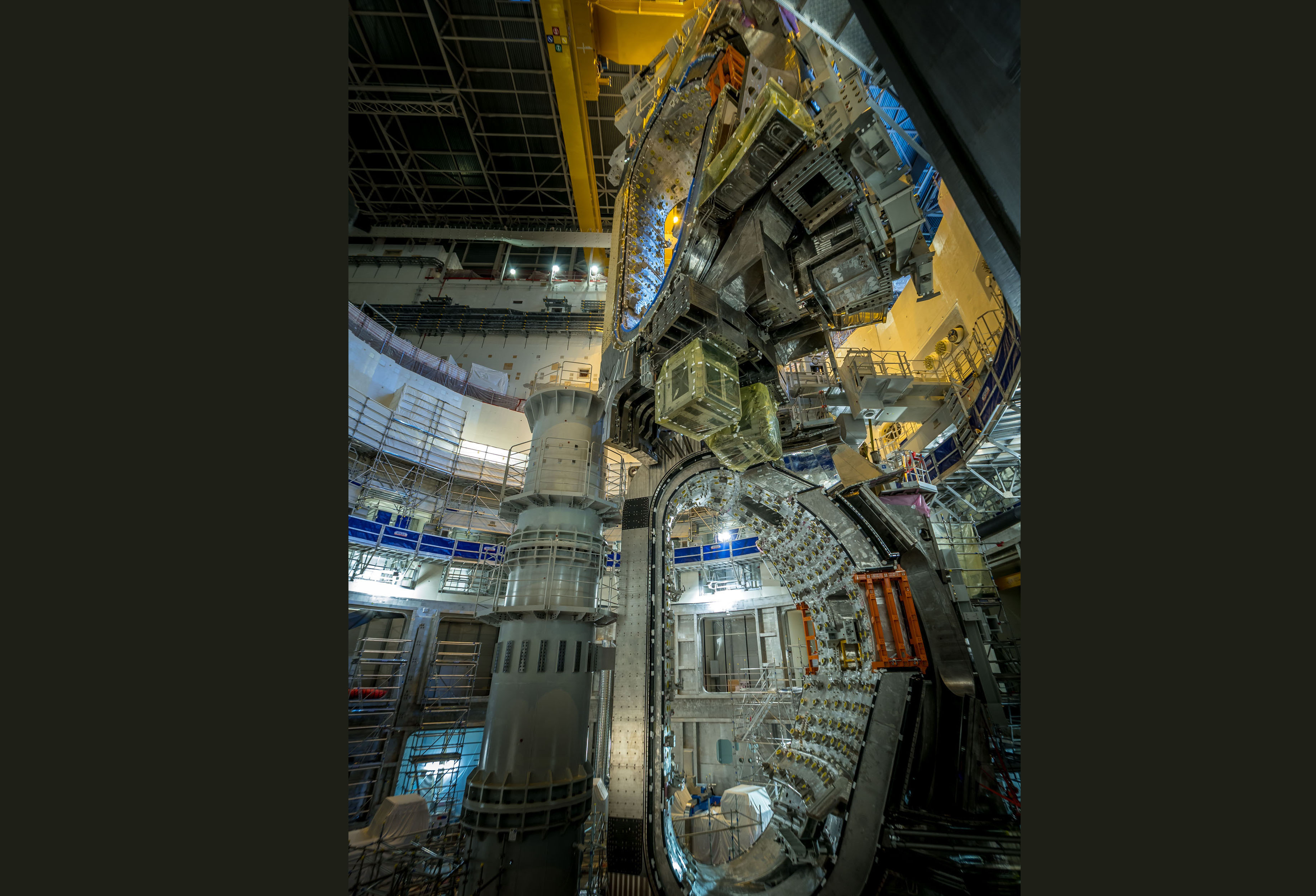
Close now
2025-06-18 - The cranes have pivoted sector module #6 above the pit to the orientation required for its slow descent.
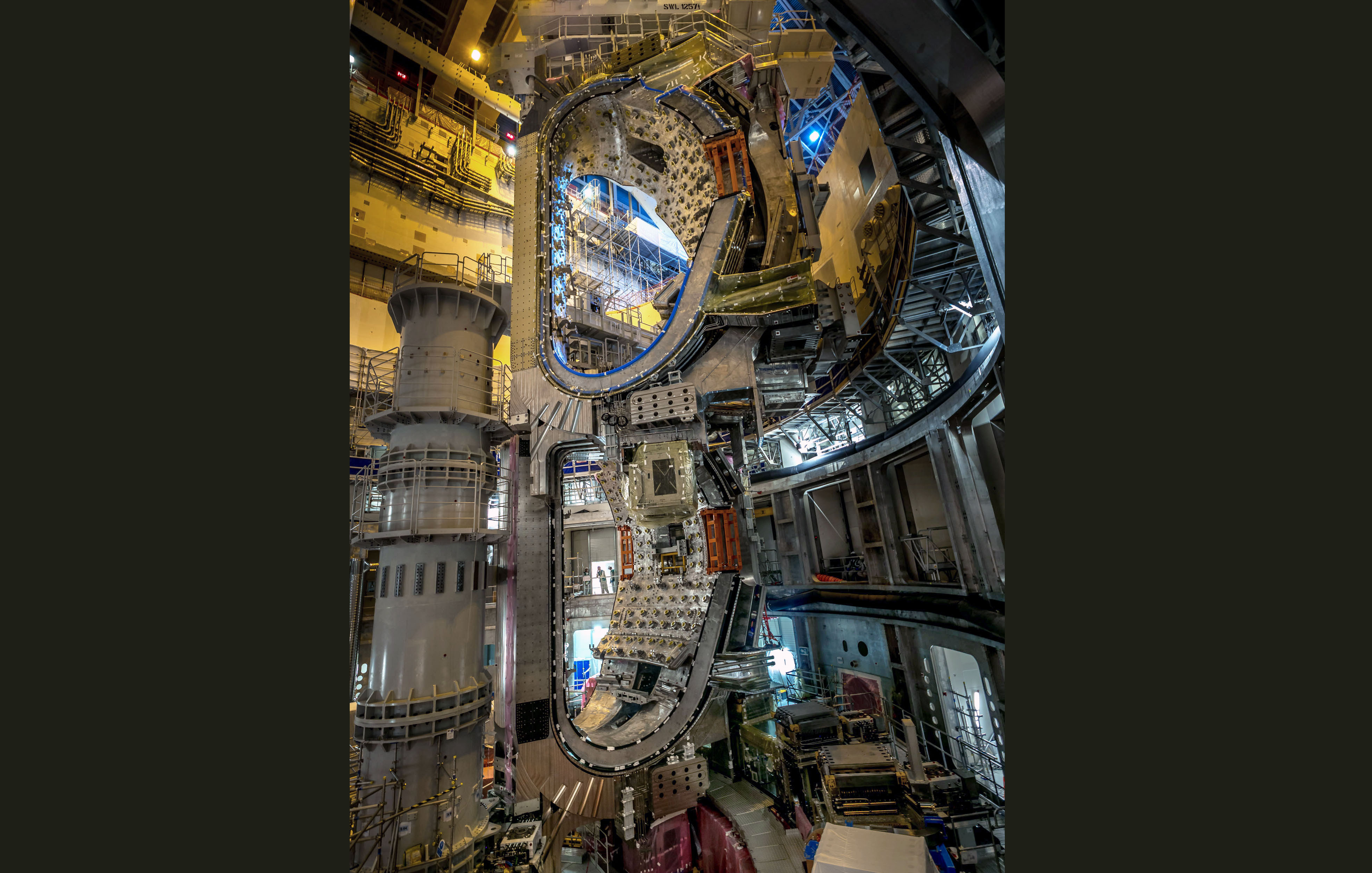
Slowly
2025-06-18 - Descending slowly: the new sector module had to be lowered especially slowly to avoid the pendulum effect. The two sectors are only 15 cm apart.
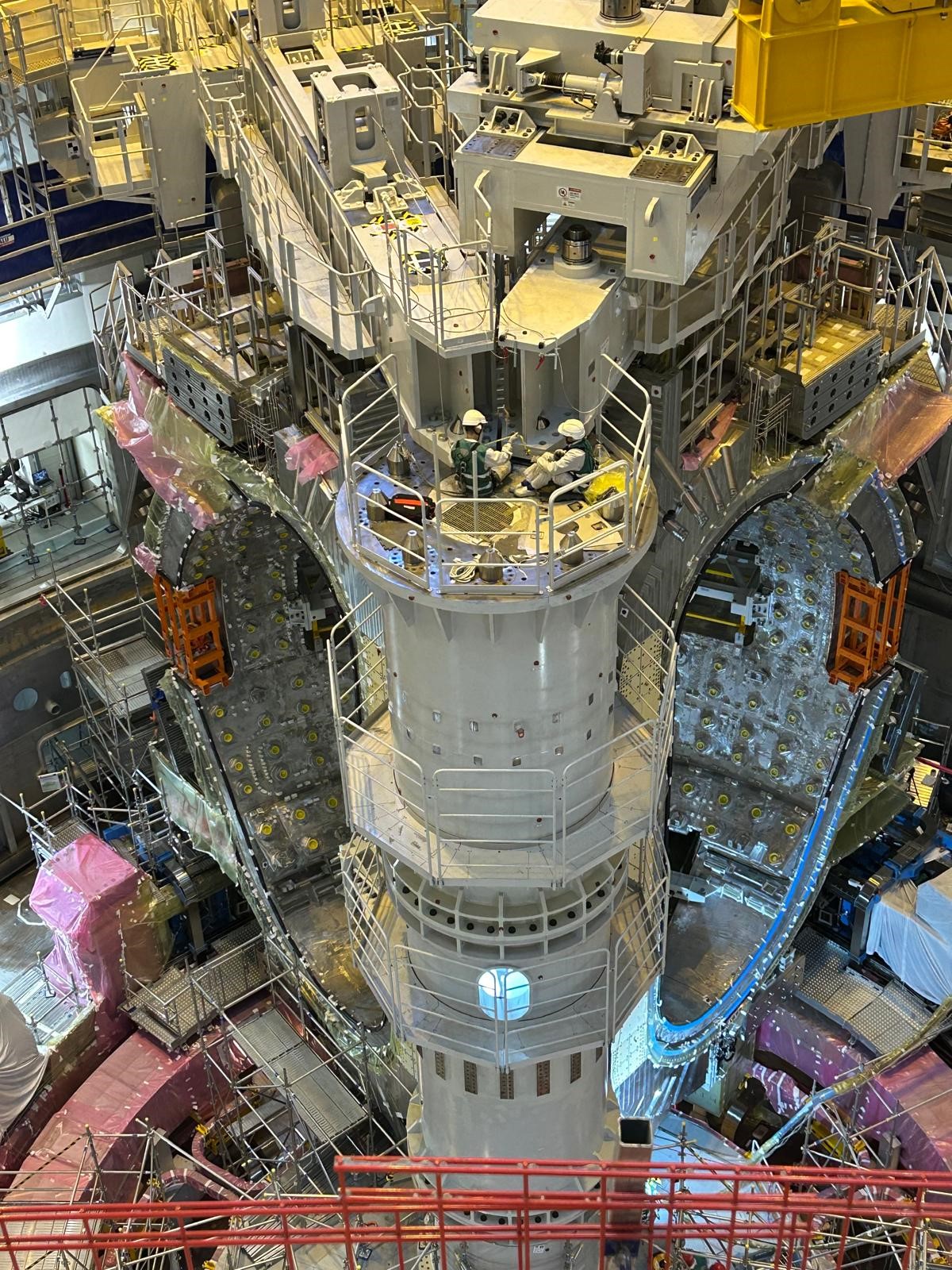
Sector module #6 installed in the pit
2025-06-18 - Sector module #6 slowly descends to take its place next to sector module #7 in the pit.
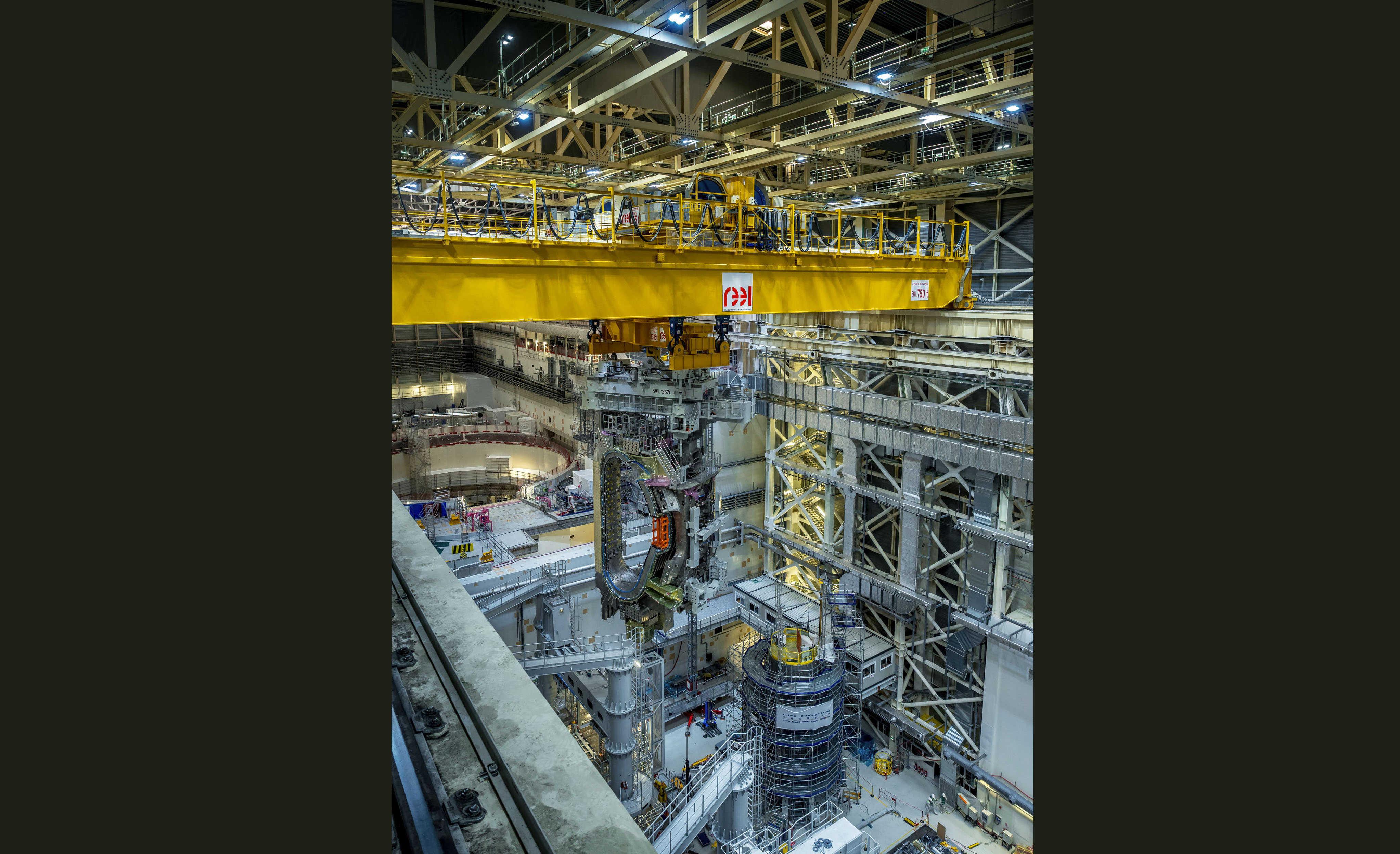
Pivoting toward the pit
2025-06-17 - The cranes are pivoting the sector module 90° in the clockwise direction so it can go over the tokamak pit wall narrow end first.
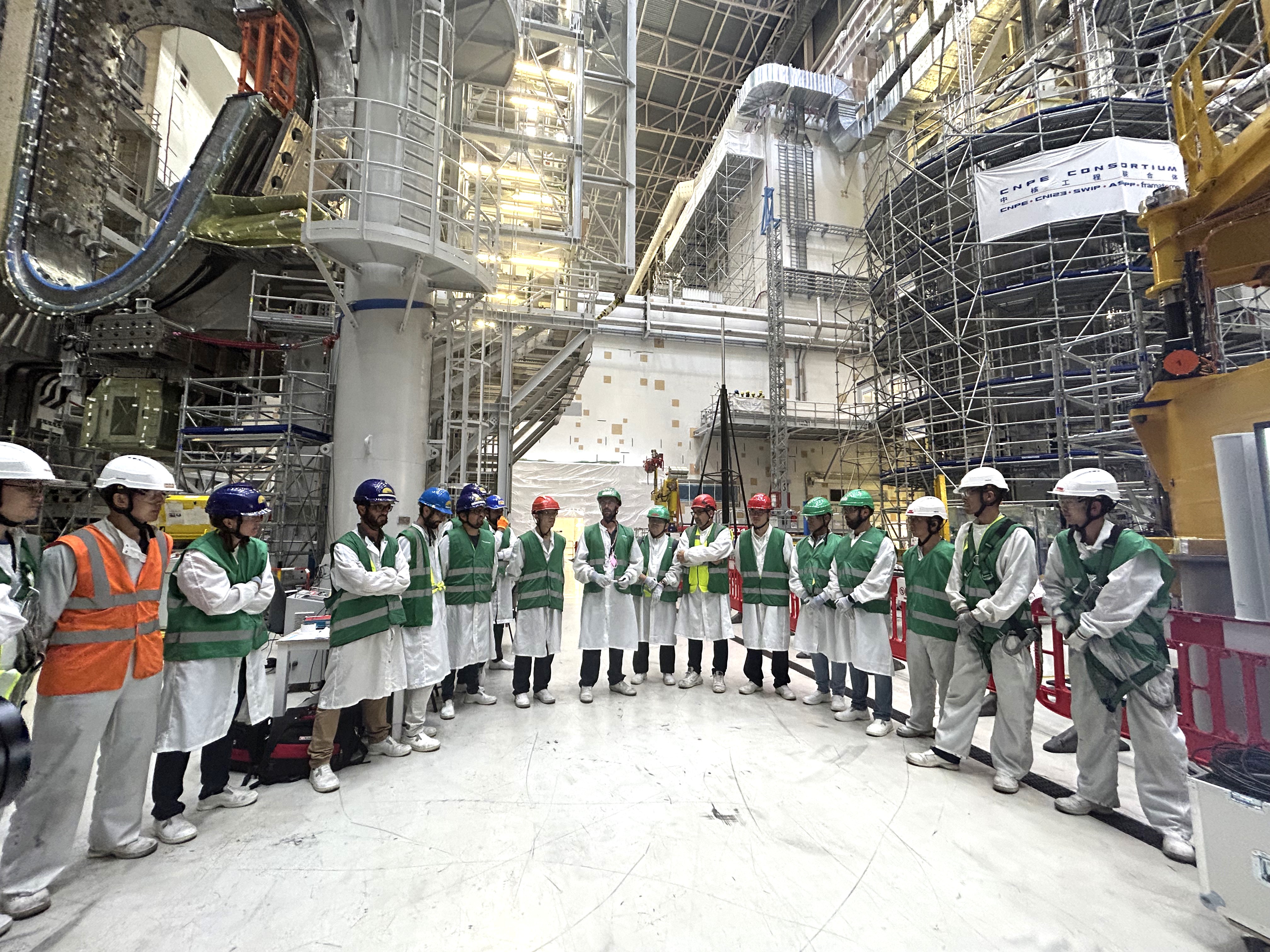
Meeting before the big lift
2025-06-17 - Burning the midnight oil: the assembly team meets at the beginning of a 12-hour night shift. Earlier, the 1,380-tonne load had been raised 50 cm and the pins attaching it to the assembly tool were released. All is go for its transfer to the pit.
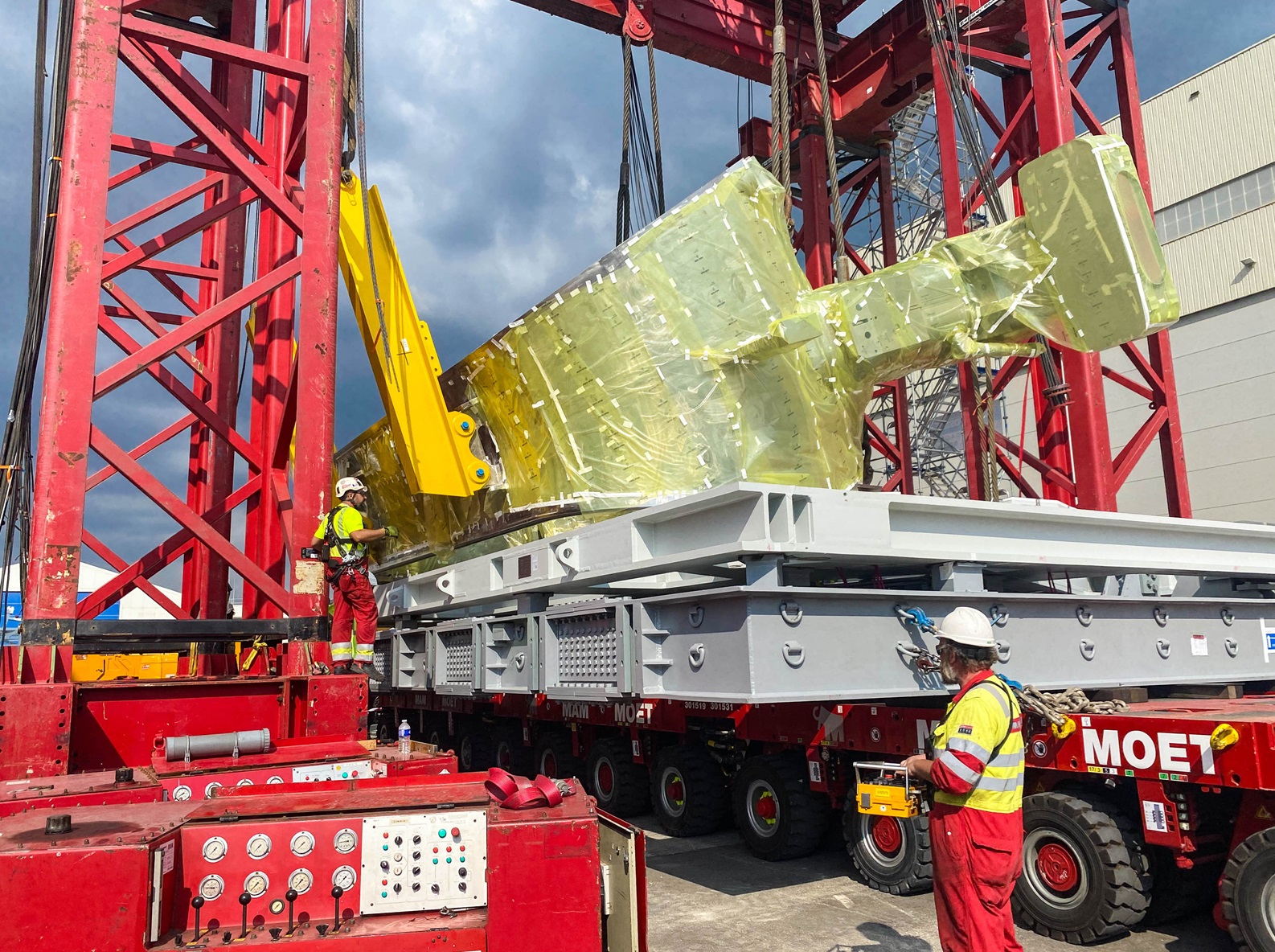
Back down
2025-06-17 - Ensuring the perfect landing: the sector had to land on supporting blocks with only 3 cm of margin.
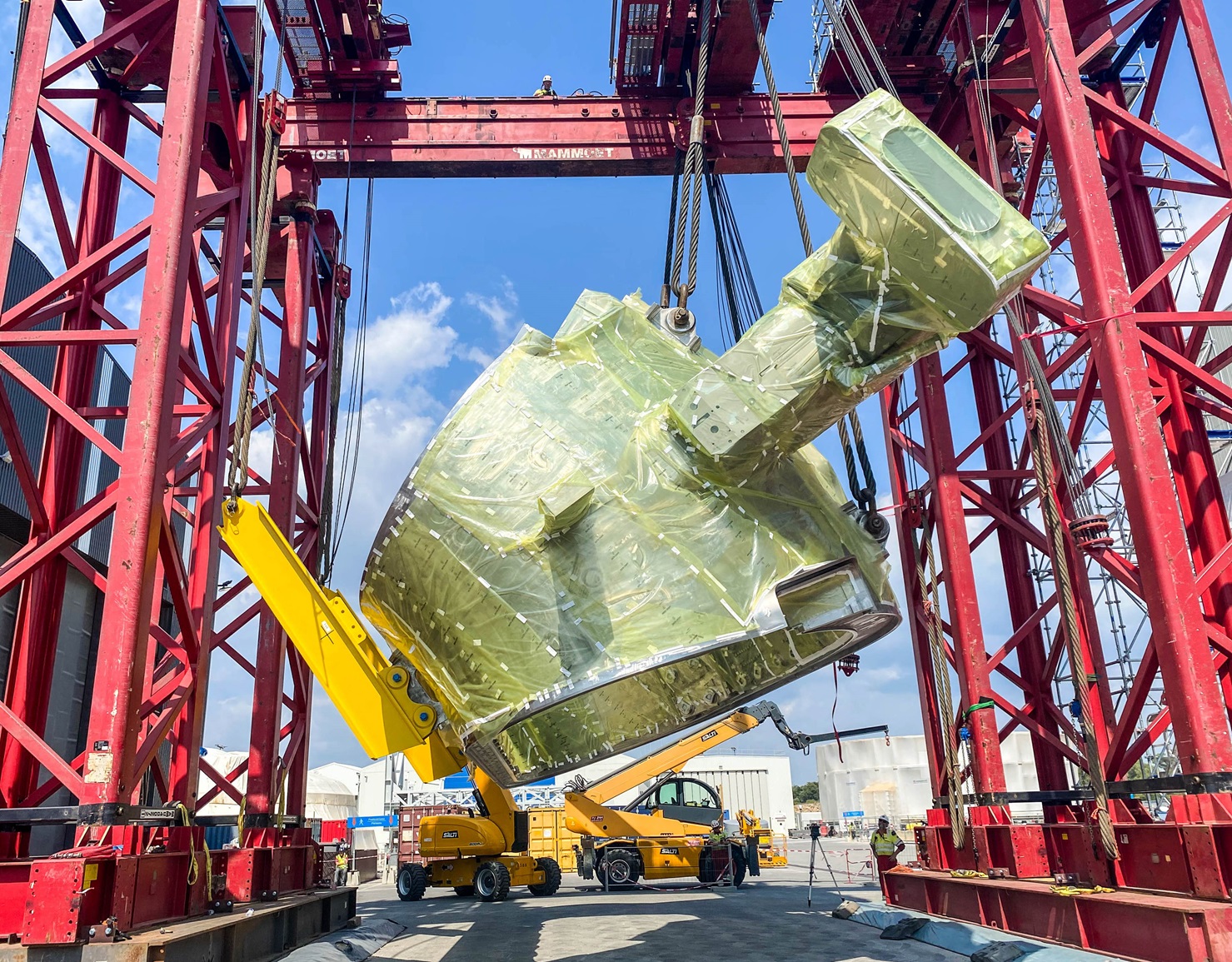
Rotation underway
2025-06-17 - It took 11 hours to raise, rotate and set back down vacuum vessel sector #4. By devising an outdoor solution, time was saved and extra congestion in the indoor assembly spaces was avoided.
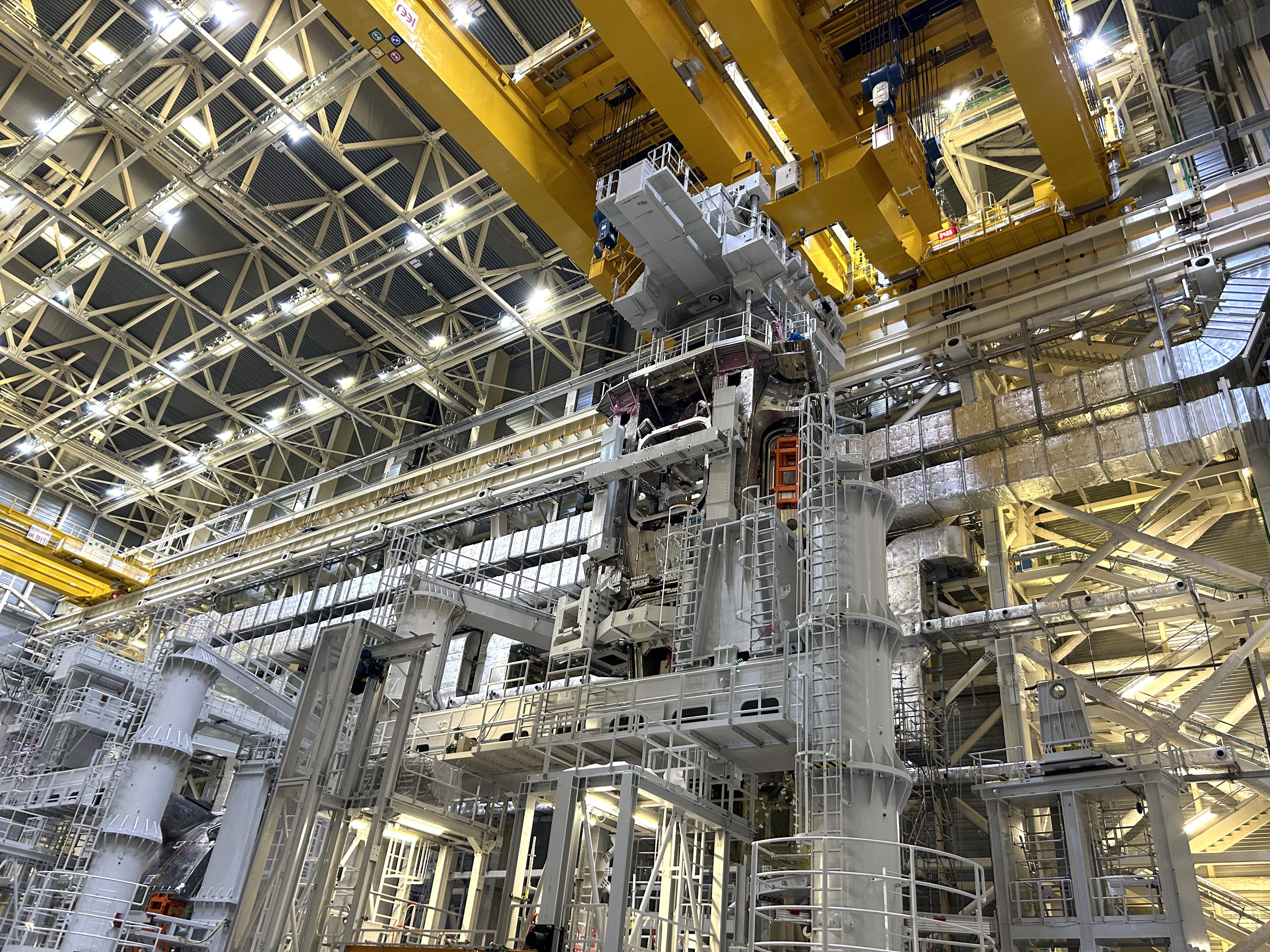
Moving vertically out of the tool
2025-06-17 - The overhead cranes are lifting the load to its highest point so that it can pass over the tool’s crossbar and head to the centre of the Assembly Hall.
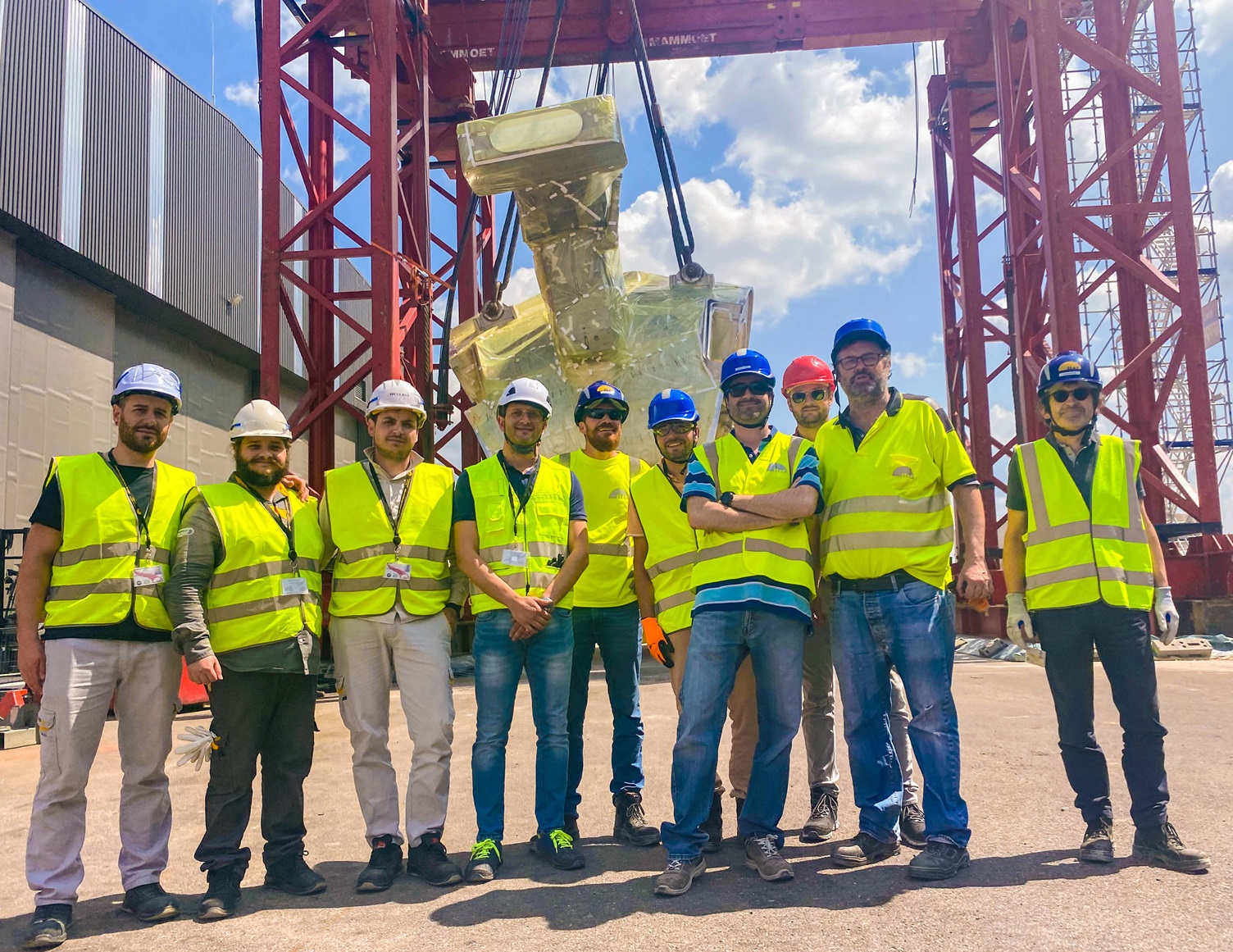
The team behind the outdoor rotation
2025-06-17 - The team that made it happen, including Alex Martin, second from right.
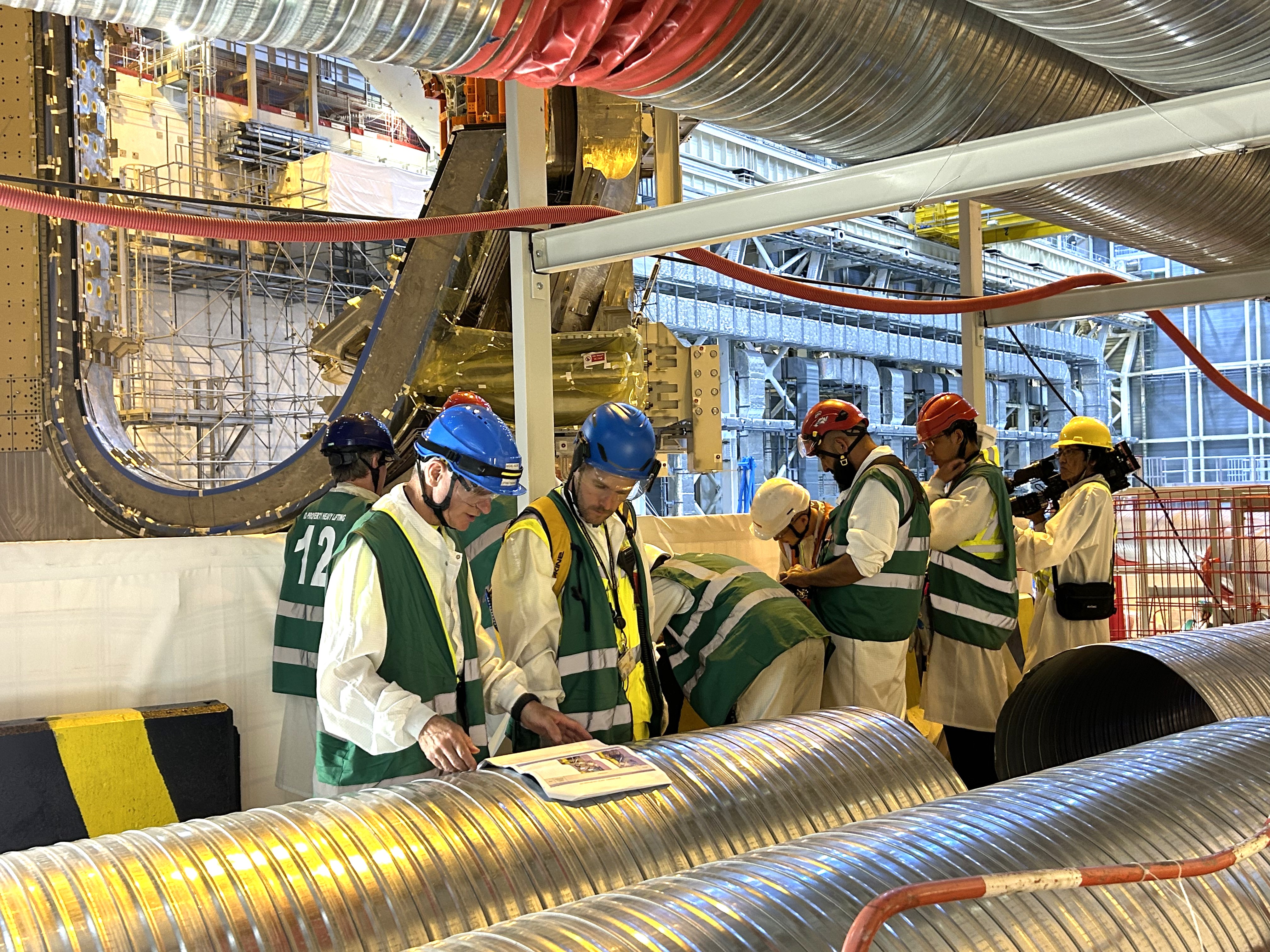
On shift during an important operation
2025-06-17 - Verifying that all is proceeding according to plan.
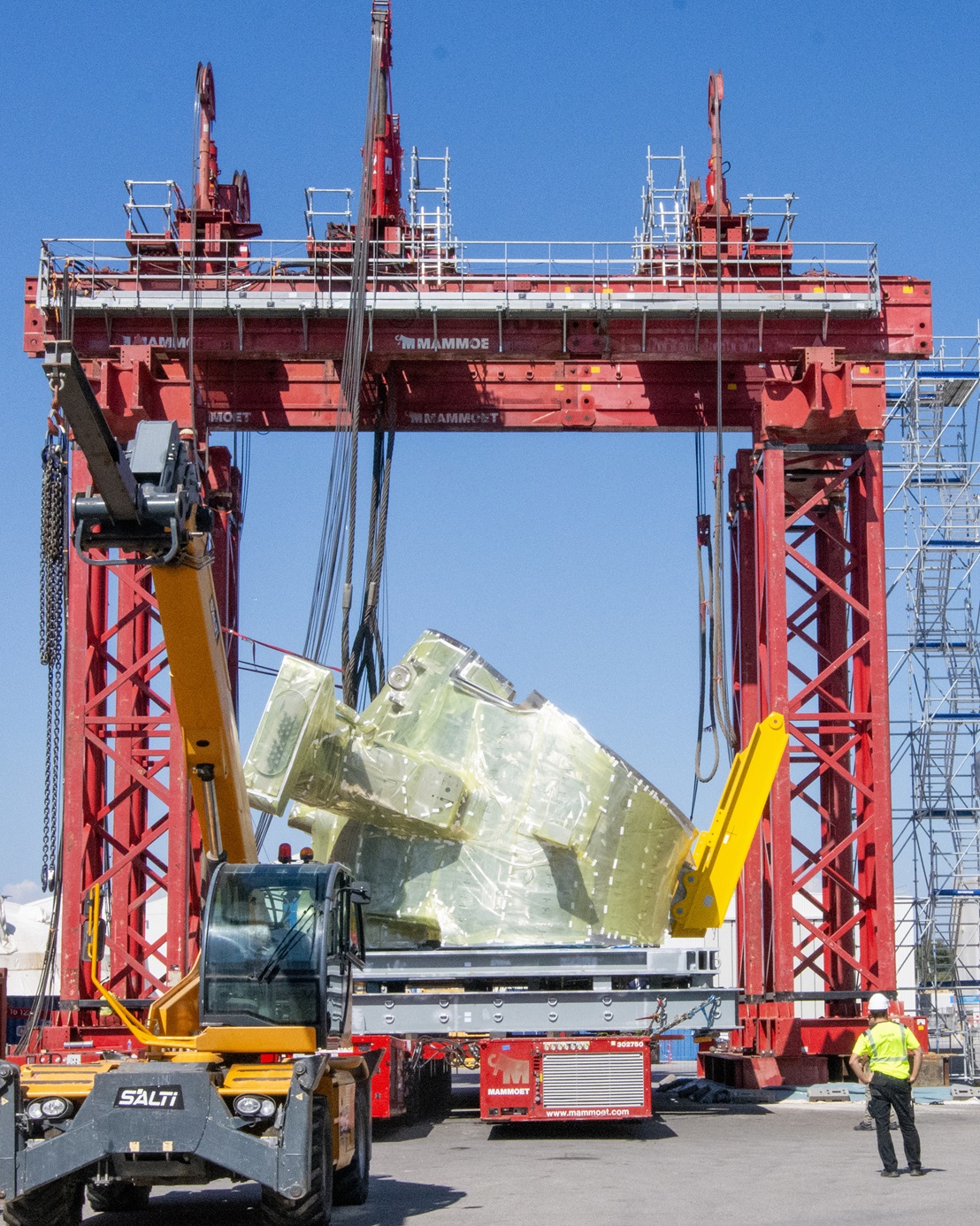
Sector in place for its Amanar vault
2025-06-17 - Covered in protective plastic for its day outdoors, sector #4 has been positioned under the gantry crane.
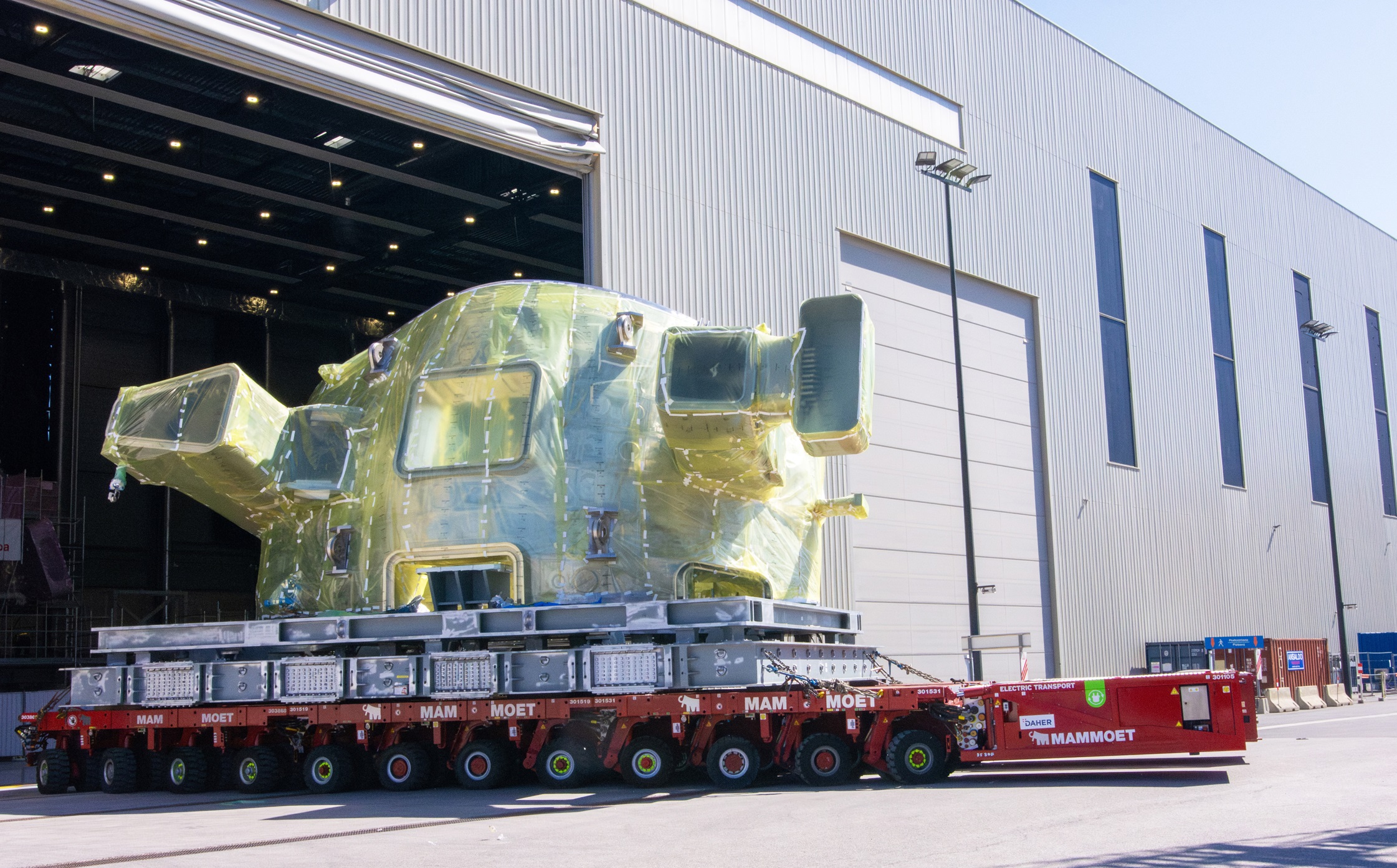
Outdoor rotation planned
2025-06-16 - This vacuum vessel sector from Europe, sector #4, must be rotated so that the bevel edges on the inaccessible side can be repaired. A gantry crane has been installed outdoors for the operation.
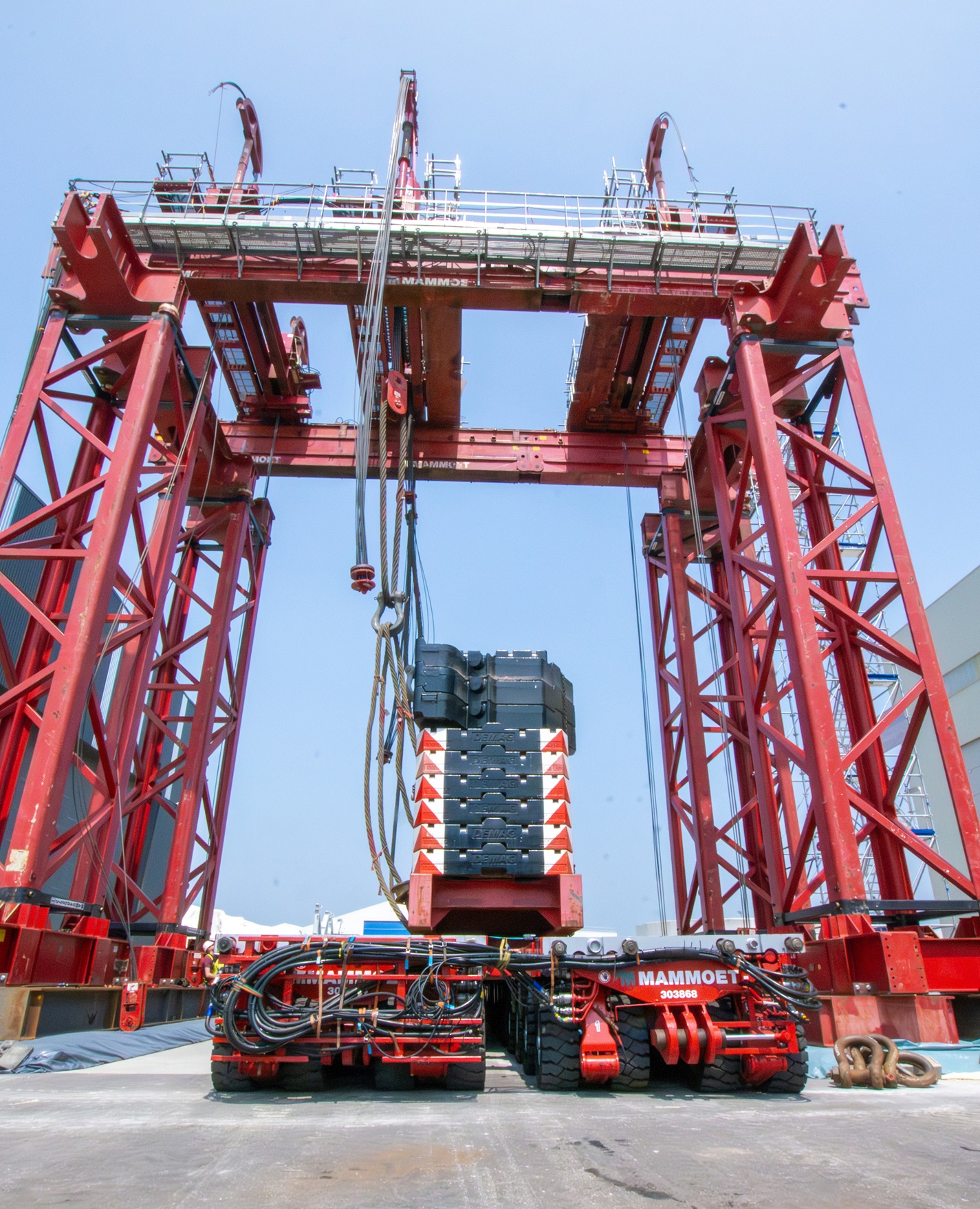
Testing the specialized gantry crane
2025-06-04 - A gantry crane has been installed outside of the Cryostat Workshop for a special operation—the lifting and rotation of vacuum vessel sectors that require repair on their second sides. The crane was load tested in early June.
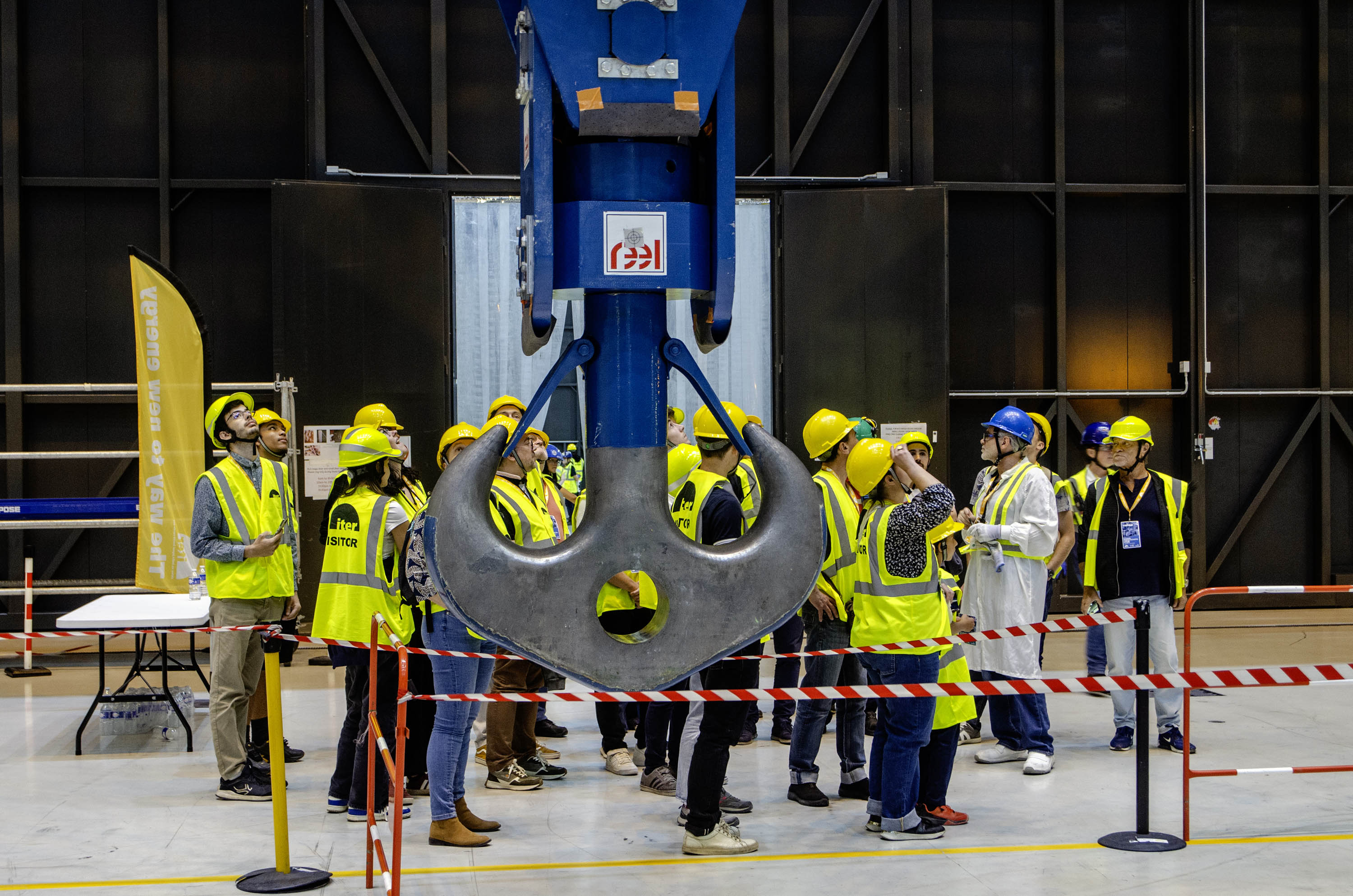
Large hooks
2025-05-17 - The size of the overhead crane hooks must have surprised more than one visitor on 17 May 2025 during the semi-annual ITER Open Doors Day. The combined lift capacity of the largest overhead bridge cranes is 1,400 tonnes.
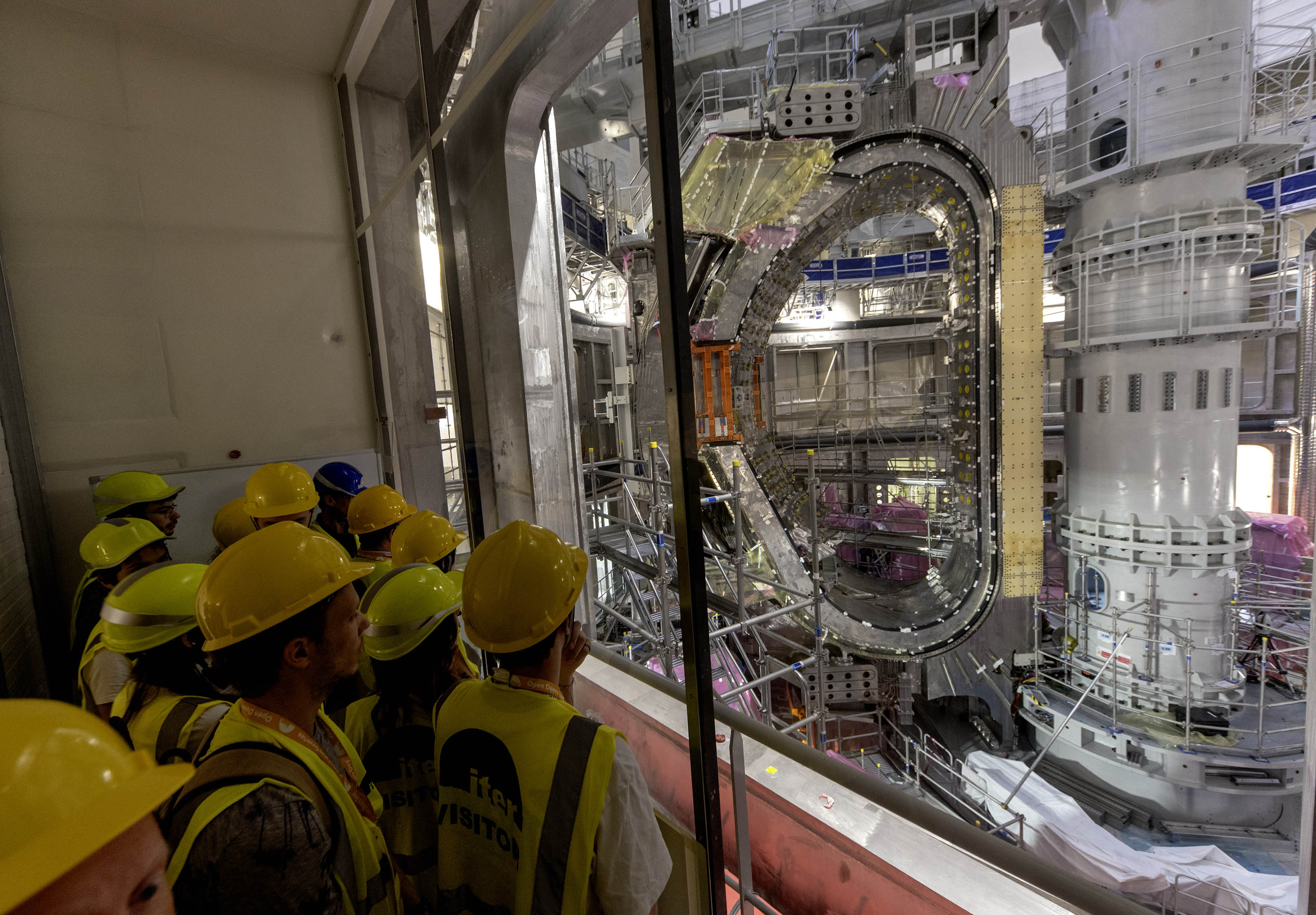
Front-row view
2025-05-17 - The first Open Doors Day of 2025 was well-timed ... only one month before the first of nine vacuum vessel sectors had been lowered into the tokamak pit.
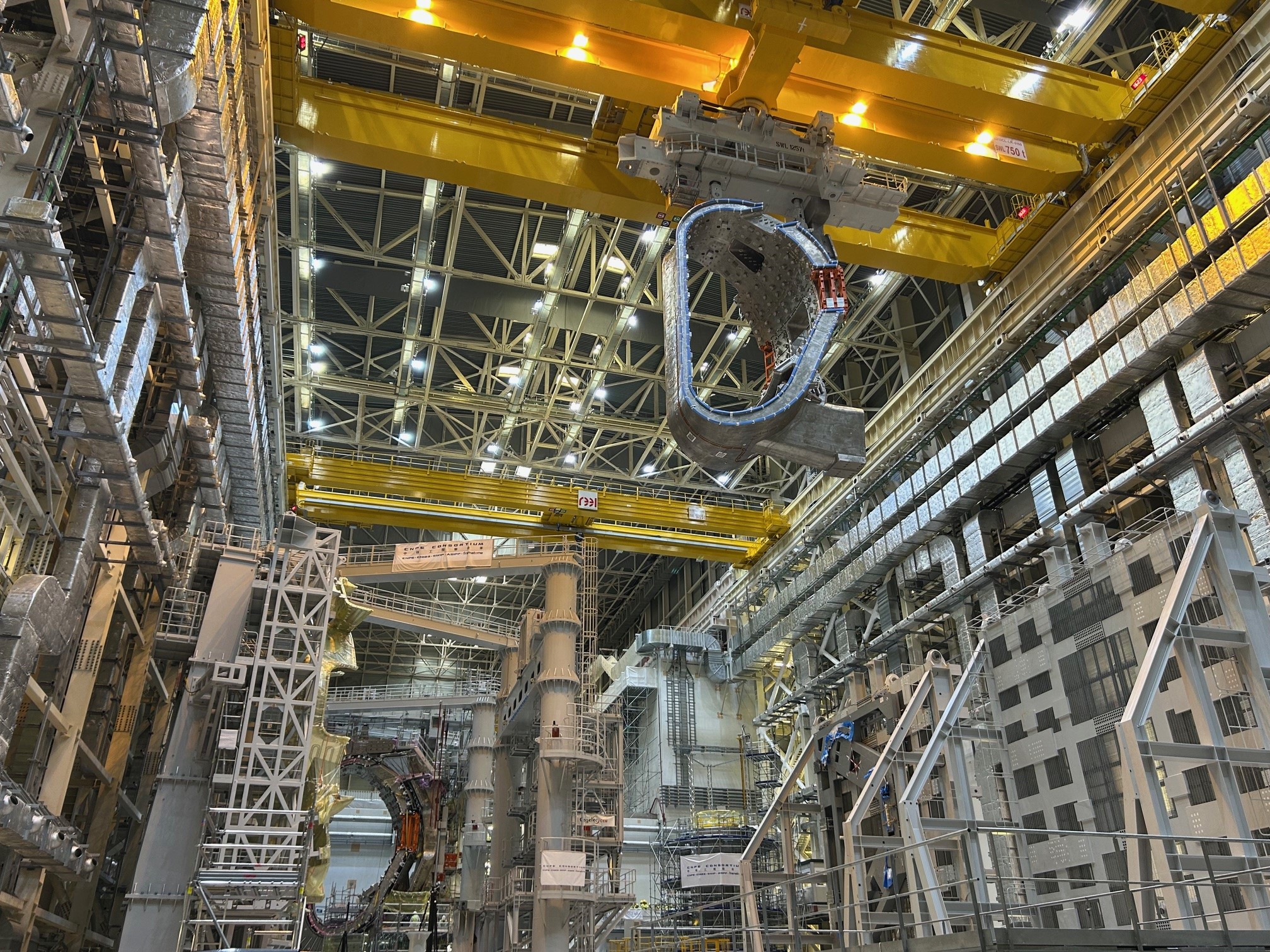
Up in the air
2025-05-15 - The overhead cranes winch the 440-tonne sector right up to the ceiling so that it will be able to pass over the front crossbar of the SSAT sub-assembly tool. The radial beam will be supported in the tool; the suspended sector will also be propped from below.

Transfer of sector #5 to tooling
2025-05-15 - On Thursday 15 May, vacuum vessel sector #5 is extracted from the upending tool (right) and transferred across the Assembly Hall to the standing tool where it will associated with other key machine components to become sector module #5.
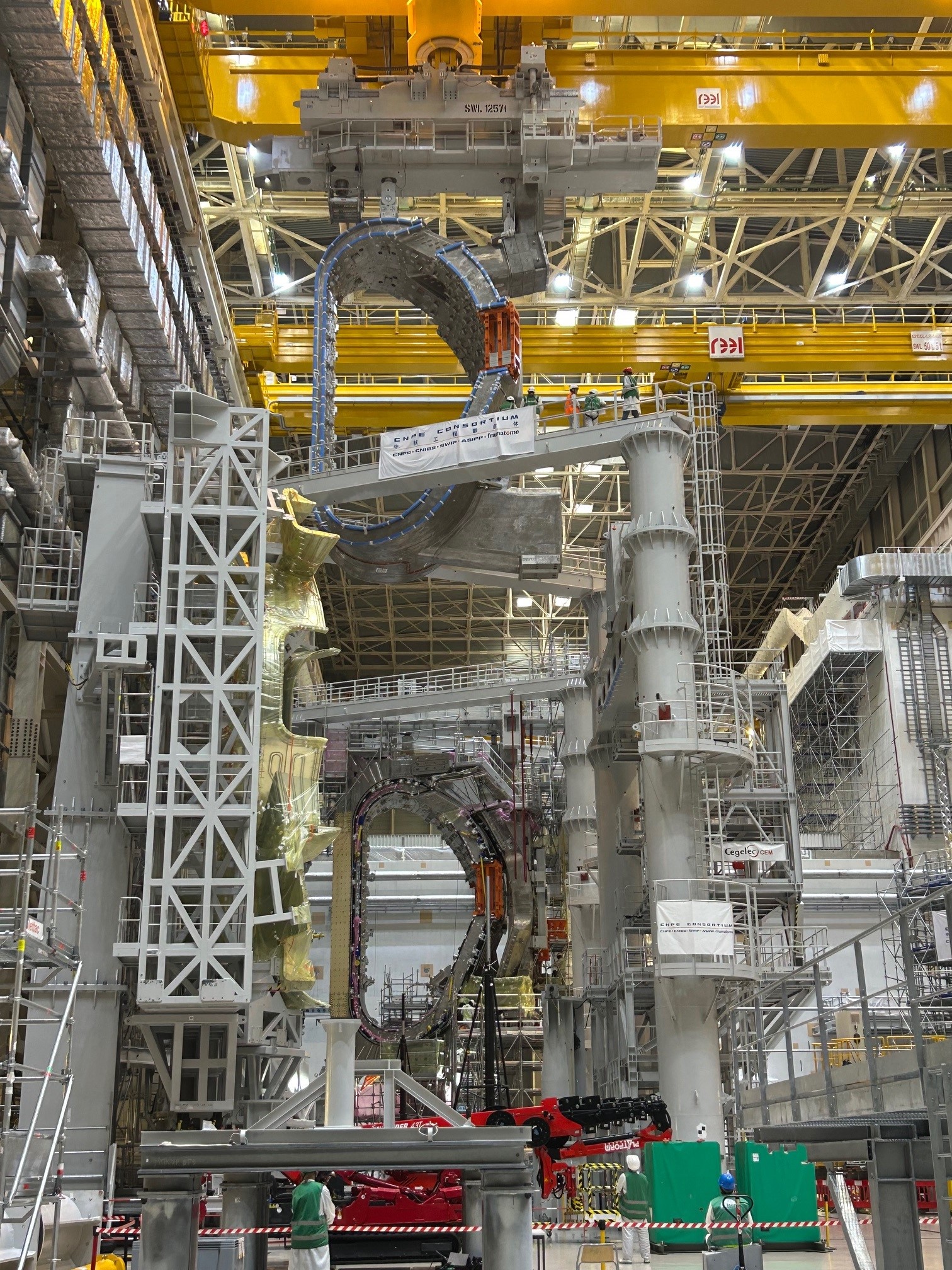
Tools are full
2025-05-15 - Vacuum vessel sector #5 is lowered in the tool that was vacated earlier this month by completed sector module #7. The association of sector #5 with its thermal shield and a pair of toroidal field coils will take approximately six months.
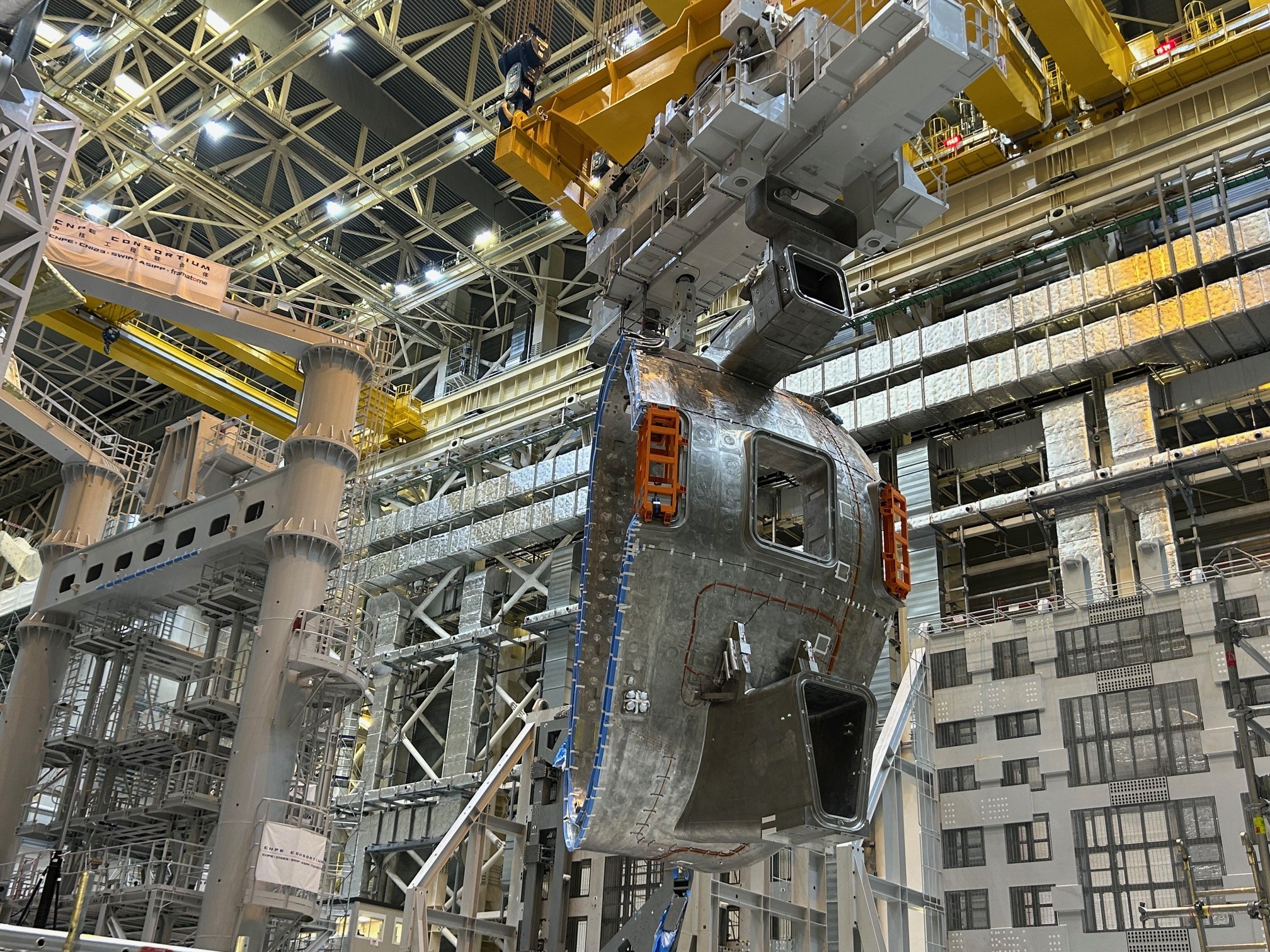
Attached to a radial beam
2025-05-15 - The radial beam (directly above the component) plays an important role. The sector remains attached to it all through the sub-assembly process... as it is extracted from the upending tool, as it is received into the sector sub-assembly tool, as it is transferred into the pit, and during in-pit vacuum vessel welding.
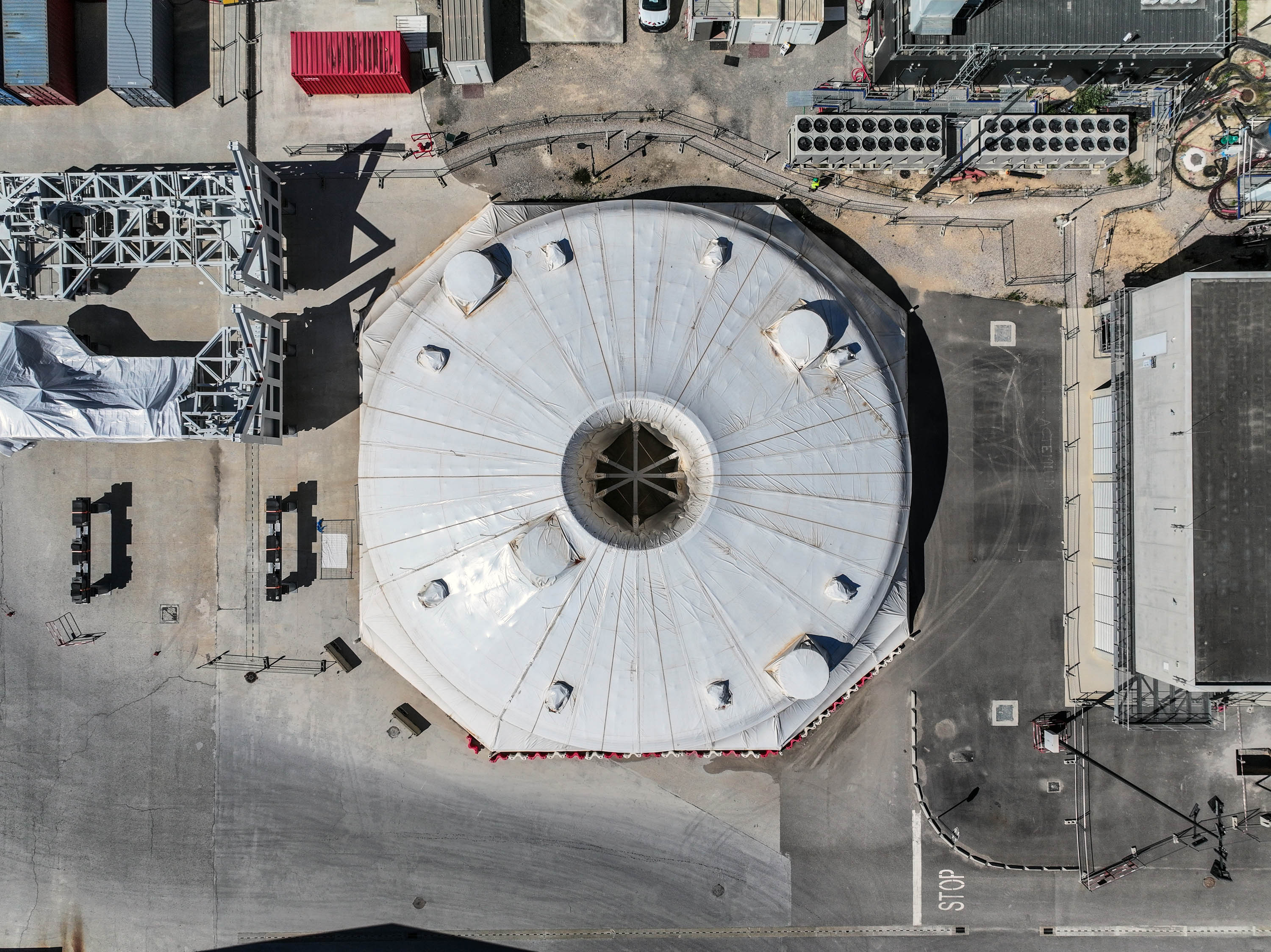
Top lid awaits
2025-05-14 - A drone hovers above a 665-tonne component stored on the ITER platform—the top lid of the ITER cryostat. In the top right quadrant of the photo, a worker in yellow (look closely!) gives a sense of the component's scale. (Photo EJF Riche - ITER Organization)
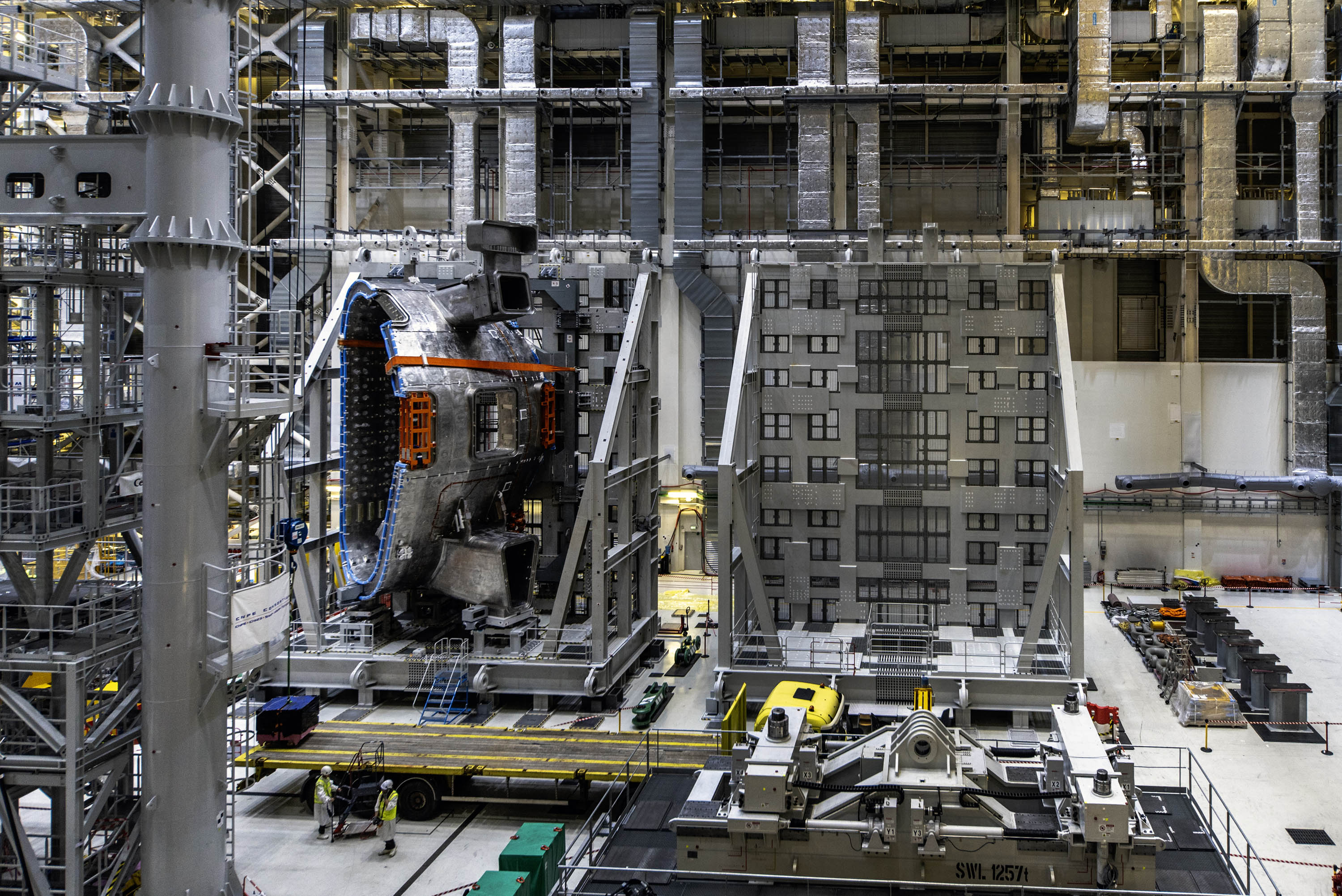
Two upending tools
2025-05-12 - ITER's two upending tools stand side by side in the Assembly Hall, with one hosting a 440-tonne vacuum vessel sector. For an idea of their actual size, see the two workers in yellow at the bottom left of the frame.
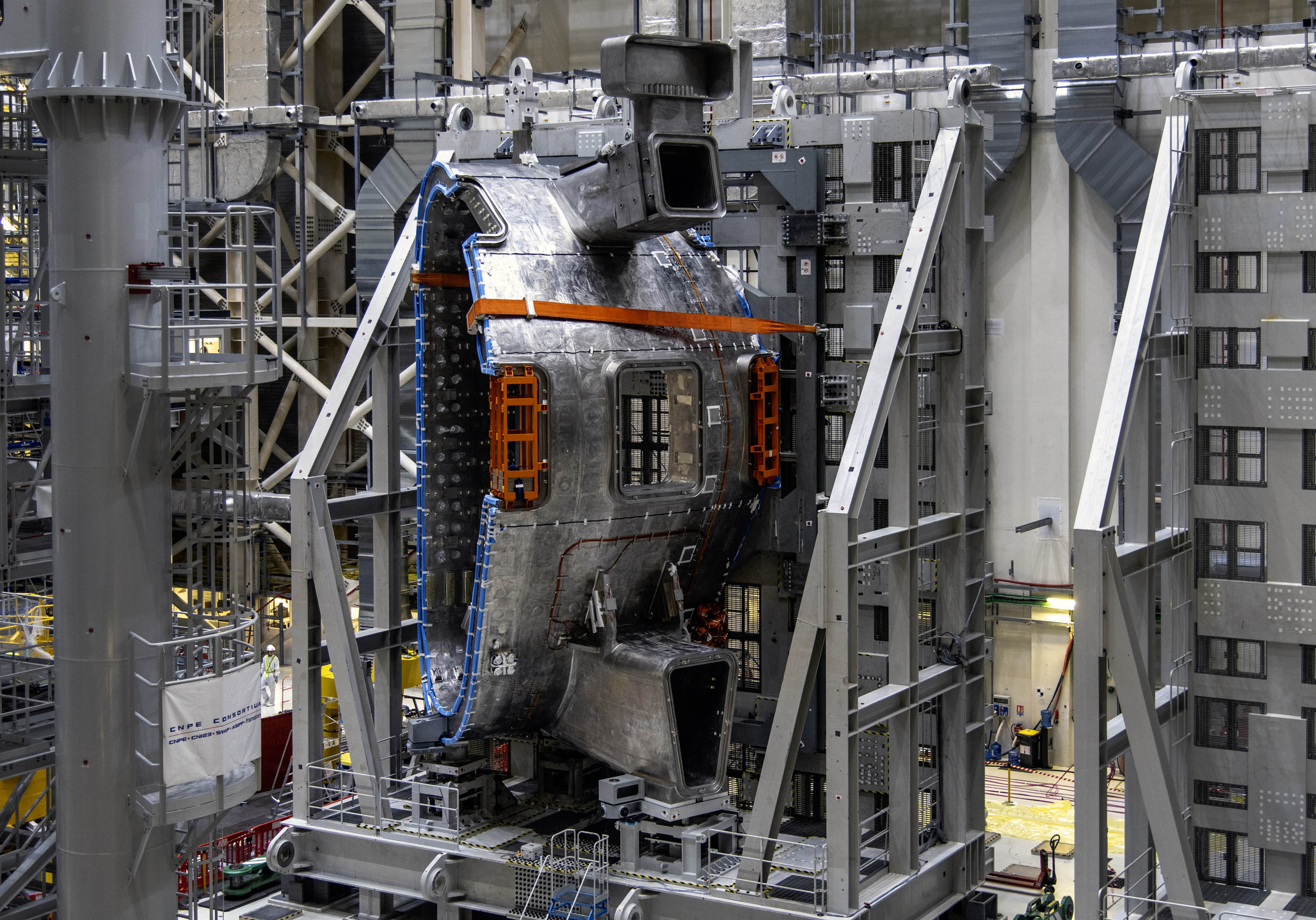
Sector #5 is vertical
2025-05-09 - A specialized upending tool is used to raise sector #5 to vertical. In the next phase of operations, the overhead cranes will lift the 440-tonne component into the sub-assembly tool that was recently vacated by sector module #7 (now installed in the tokamak pit).
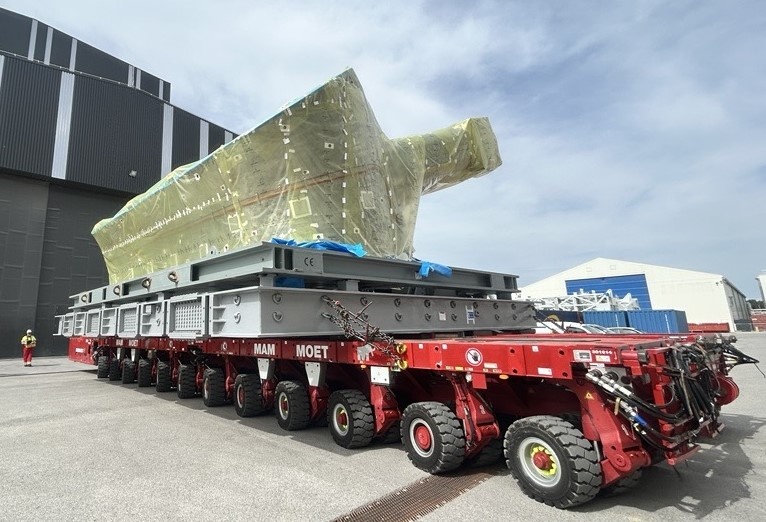
Next sector for sub-assembly
2025-05-02 - Vacuum vessel sector #5 leaves the former Cryostat Workshop for the ITER Assembly Hall, where it will be raised to vertical and installed in sub-assembly tooling.
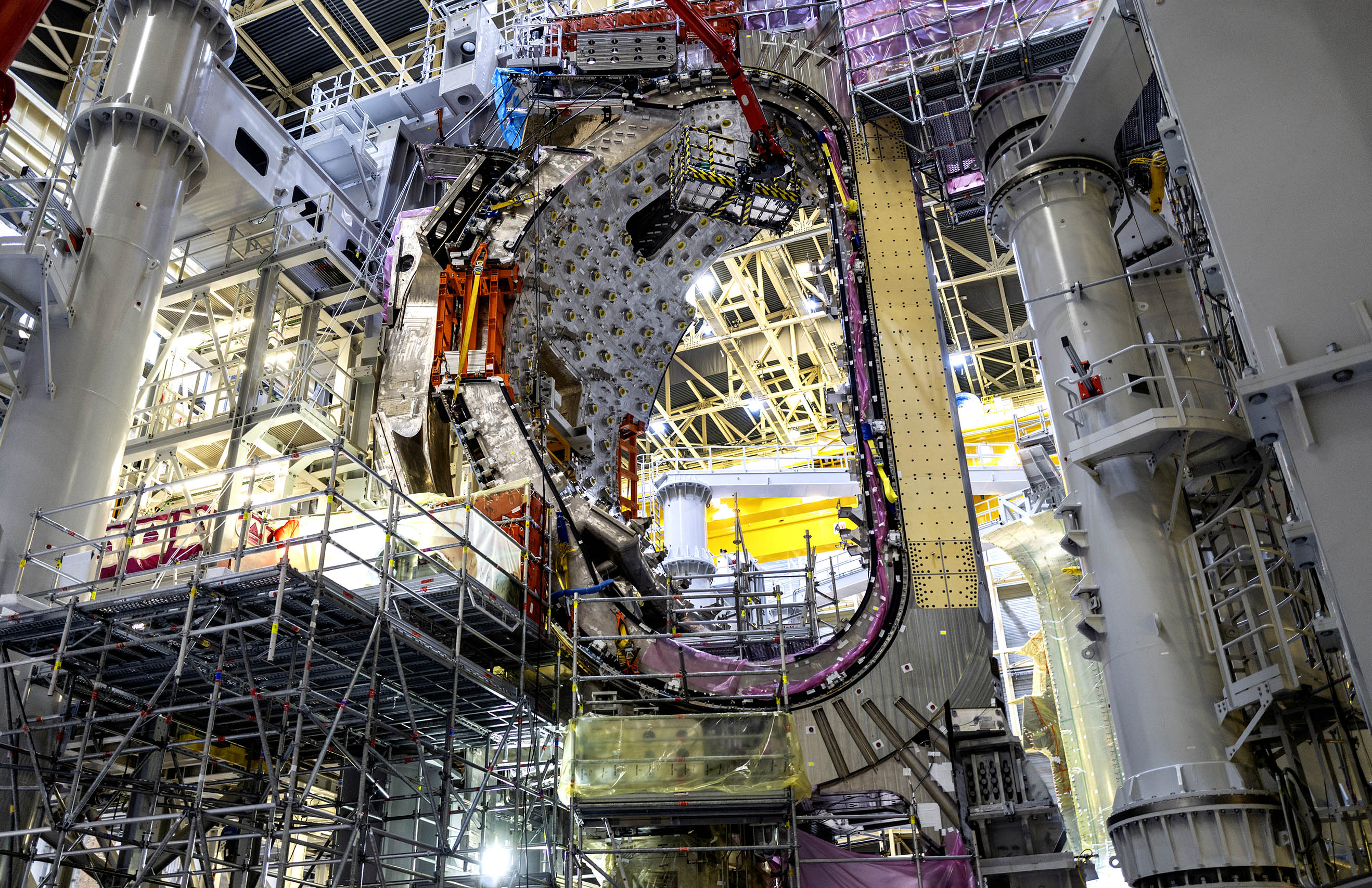
Next in line
2025-04-29 - This sector module is next in line for insertion in the tokamak pit. The assembly suspended in vertical tooling is composed of vacuum vessel sector #6 at the centre, which is surrounded by a thin layer of thermal shielding and two toroidal field coils that form an enveloping superstructure. This 1,200-tonne module will be transferred into the assembly pit in July.
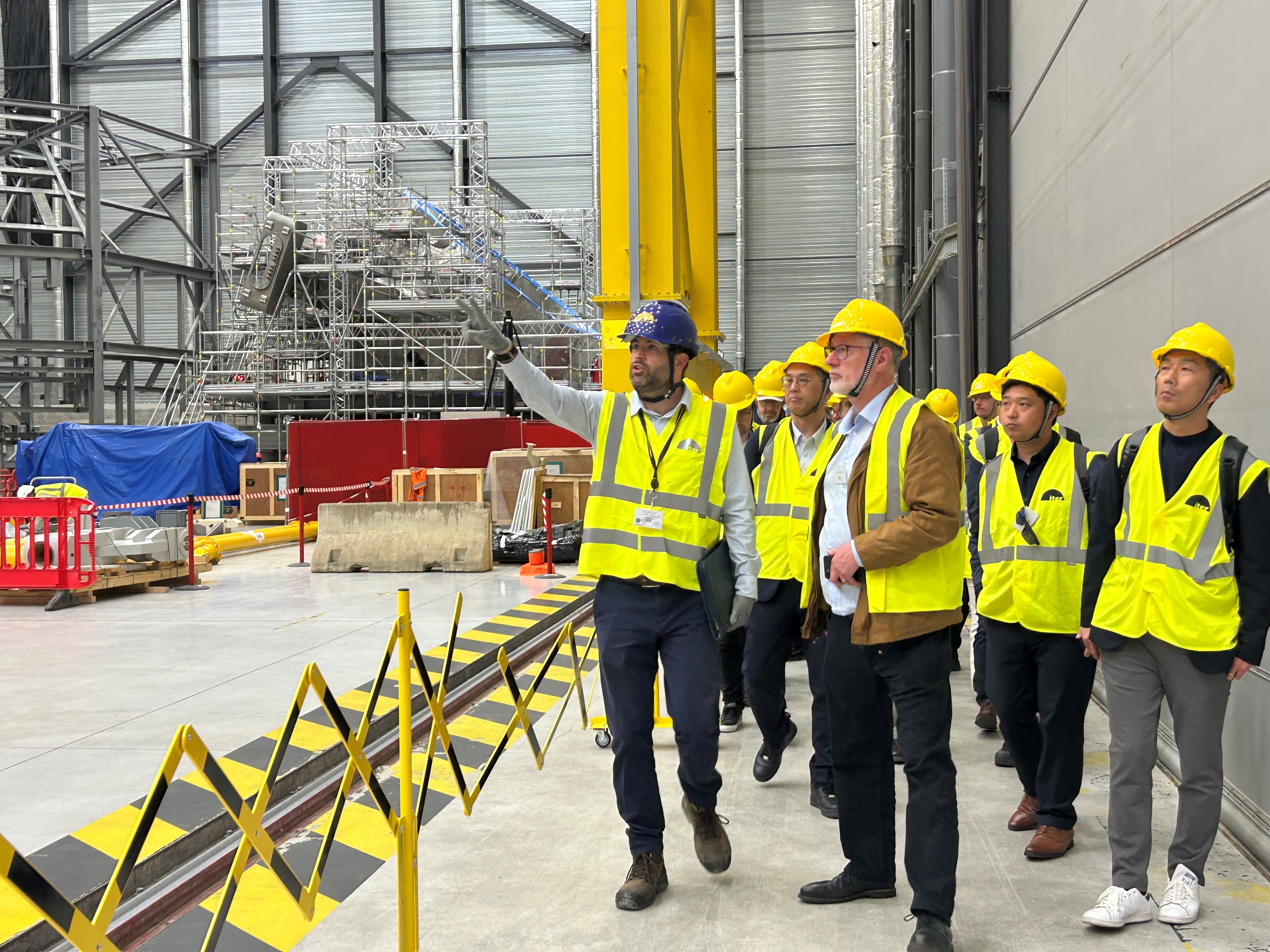
Seeing ITER before talking business
2025-04-24 - Participants to the 2025 ITER Business Forum visit the ITER worksite on Tuesday 23 April, one day before the conference program officially gets underway. Here, the group is touring the Cryostat Workshop, where several vacuum vessel sectors are stored horizontally.
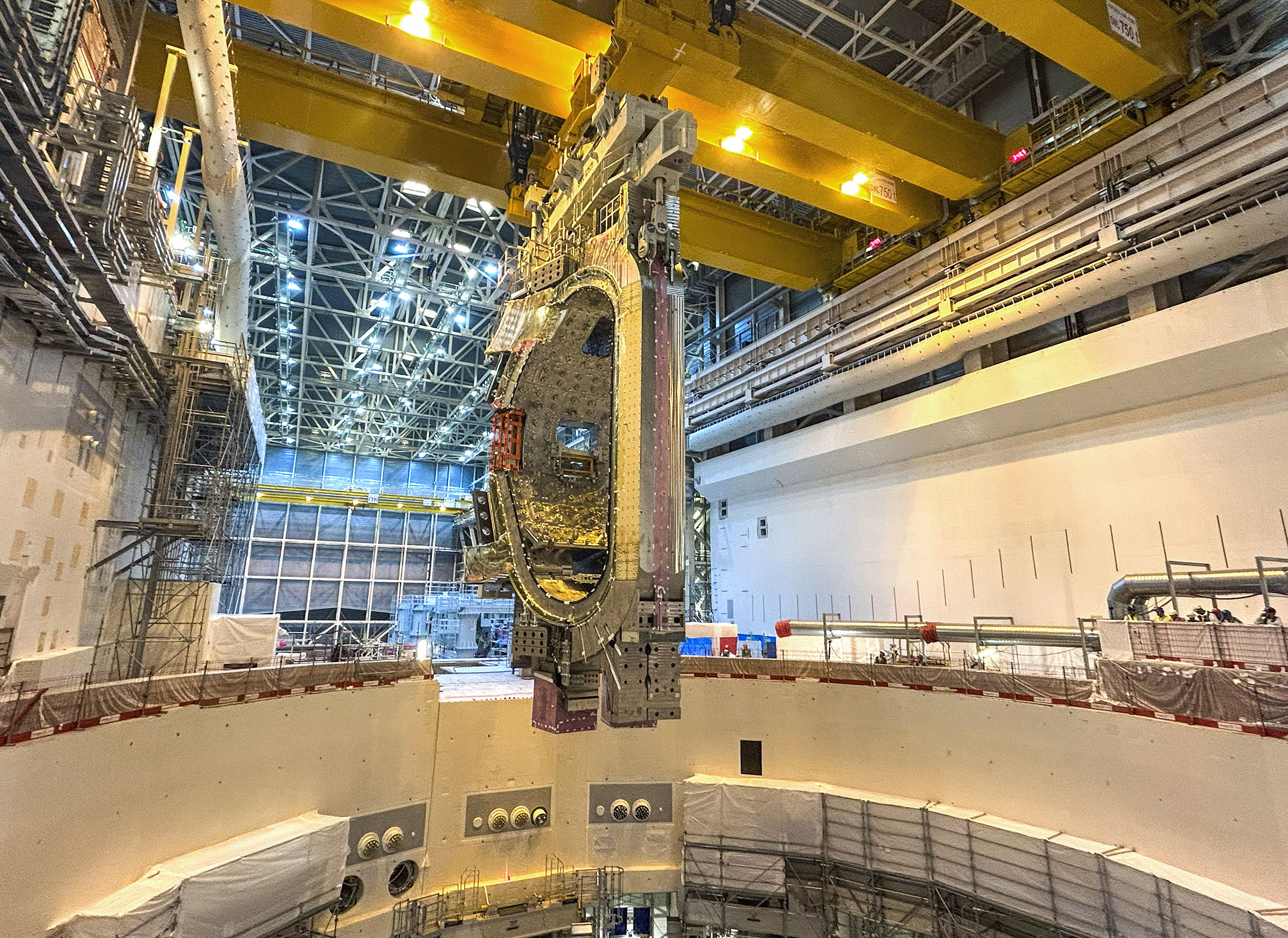
The most delicate moment
2025-04-14 - The module commences its descent into the 30-metre-deep tokamak pit. This last phase of the transfer is also the most delicate as the “pendulum effect” increases with the length of the cables.
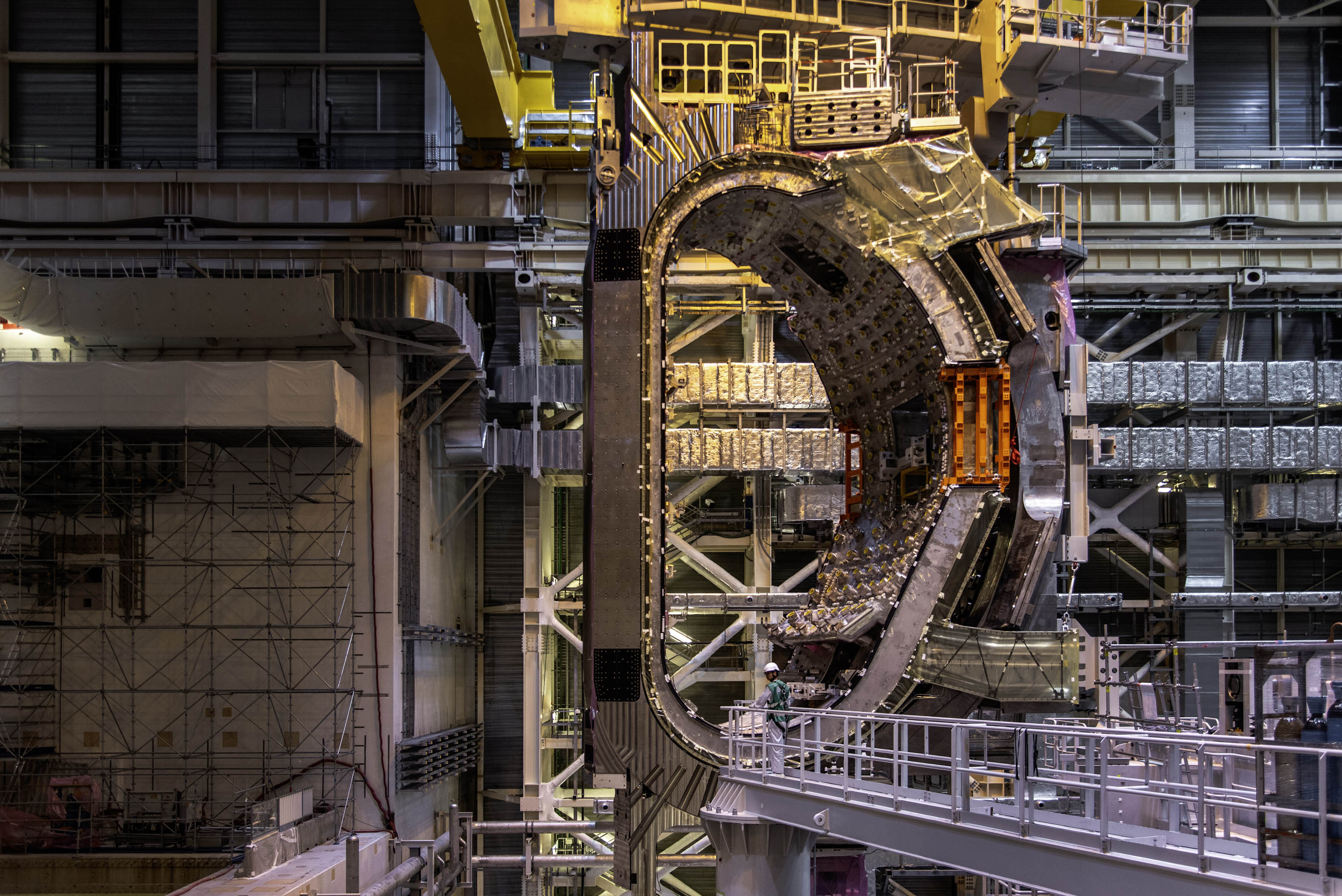
Can you spot the spotter?
2025-04-11 - Dwarfed by the 18-metre-tall module, this “spotter” in his green vest monitors the approach of the load as it nears the wall separating the Assembly Hall from the tokamak pit.
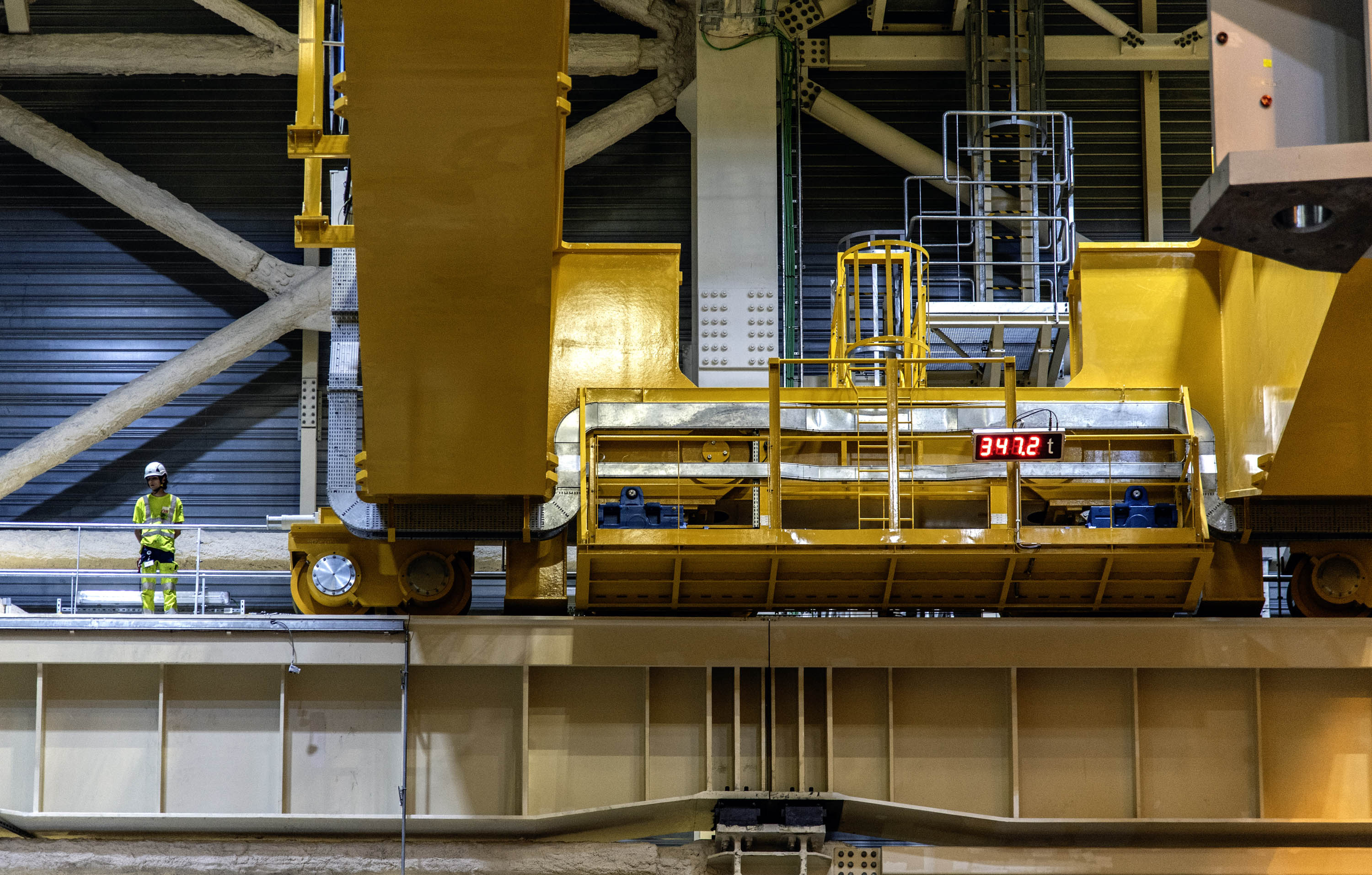
Sharing the load
2025-04-11 - The load is split between the four hooks of the double overhead travelling crane. The math is easy: the total load (including rigging) amounts to four times 347 tonnes, 100 tonnes below the nominal lifting capacity of the crane.
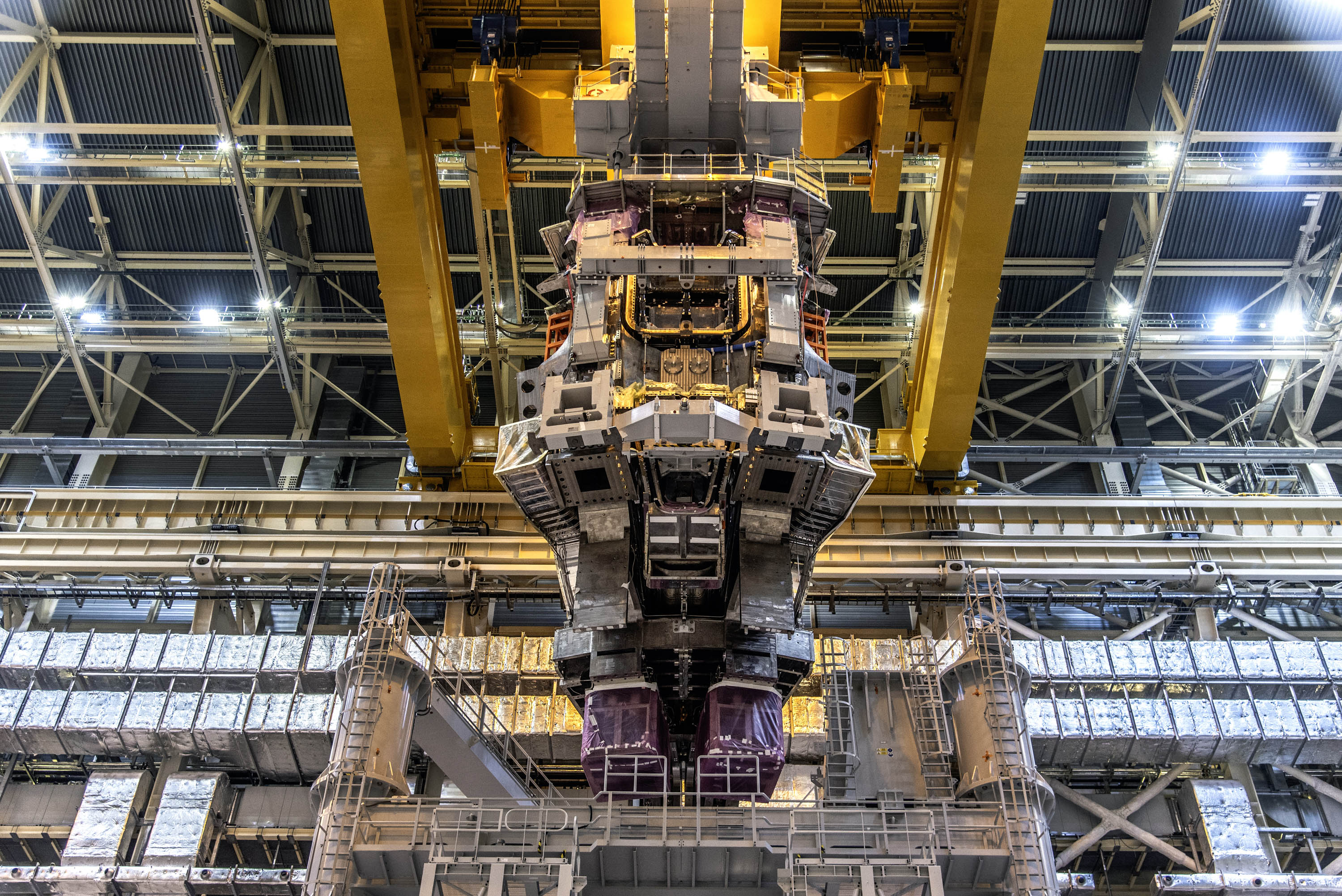
Sector module #7 from below
2025-04-11 - This view from below illustrates the extreme complexity of a sector module. Wrapped in pink plastic are the “feet” of the toroidal field coils that will be bolted to gravity supports at the bottom of the tokamak pit.

Sector module #7 installed in pit
2025-04-10 - The first of nine modules required to form the ITER plasma chamber is installed in the tokamak assembly pit on 10 April. Sector module #7 was created from one vacuum vessel sector, its thermal shield and two toroidal field coils in 6 months and 10 days; for reference, the first time this sub-assembly operation was carried out it took 18 months to accomplish.
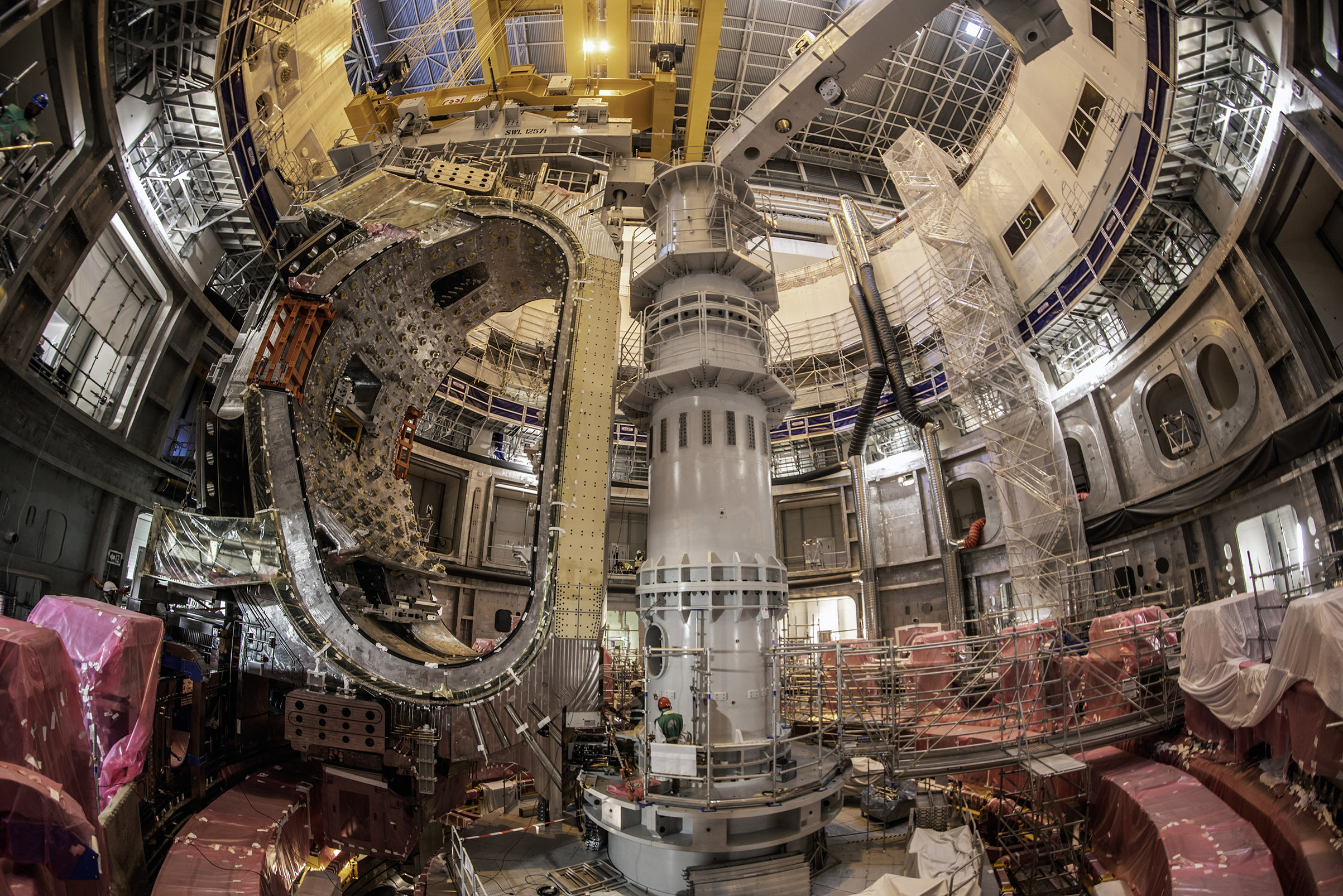
One-ninth of the vacuum vessel lowered into the pit
2025-04-10 - On 10 April, three weeks ahead of schedule, sector module #7 is lowered into the tokamak pit. Eight more sector assemblies—massive components comprised of a vacuum vessel sector, its thermal shield, and two D-shaped toroidal field coils—will join this first unit to form the torus-shaped ITER vacuum vessel.
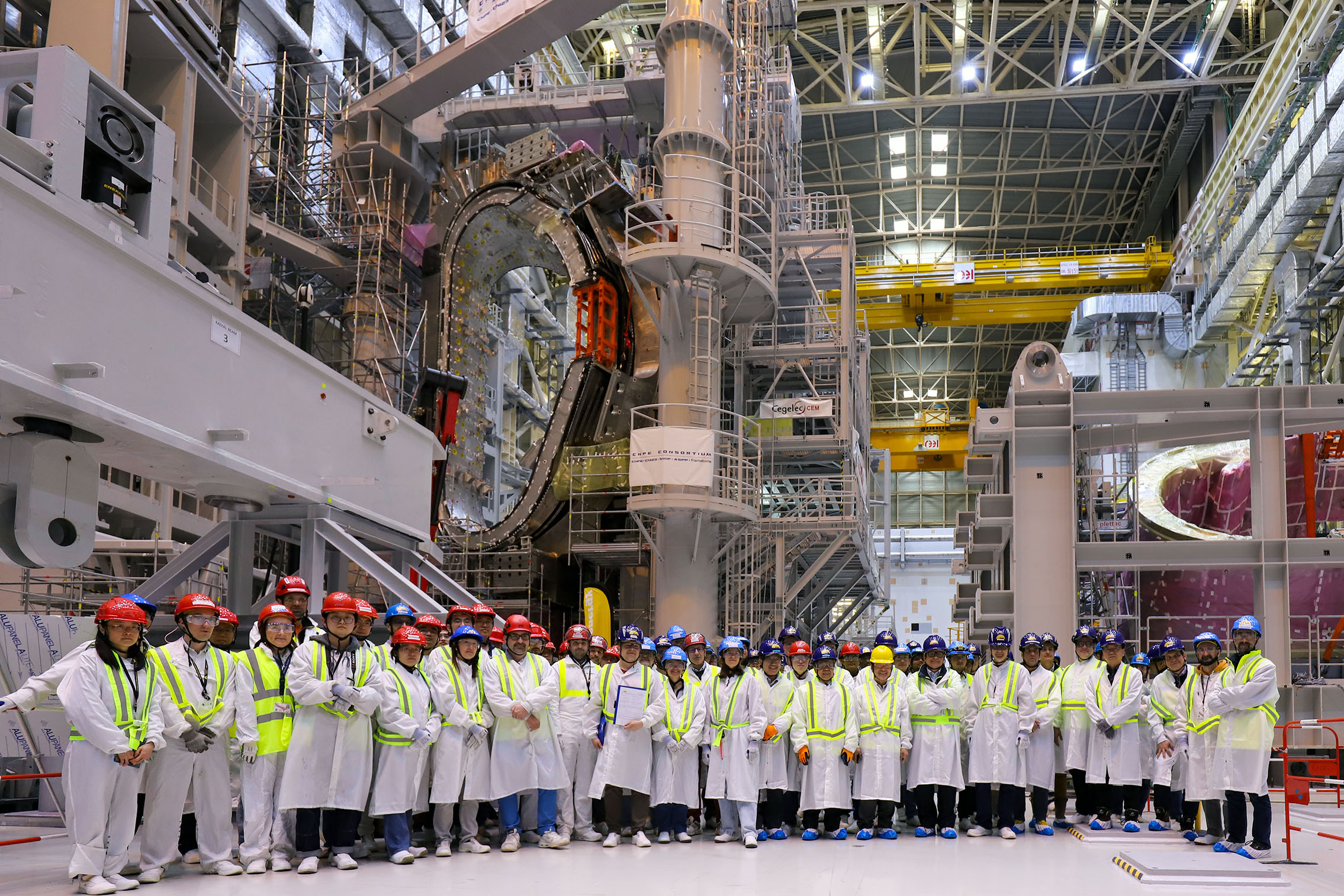
Sector module #7 completed
2025-03-28 - It took only 6 months and 10 days to assemble a 440-tonne vacuum vessel, its corresponding thermal shield and two 330-tonne toroidal field coils into a vacuum vessel module. On Friday 28 March, the teams that contributed to this remarkable achievement gathered at the foot of the completed module to celebrate.
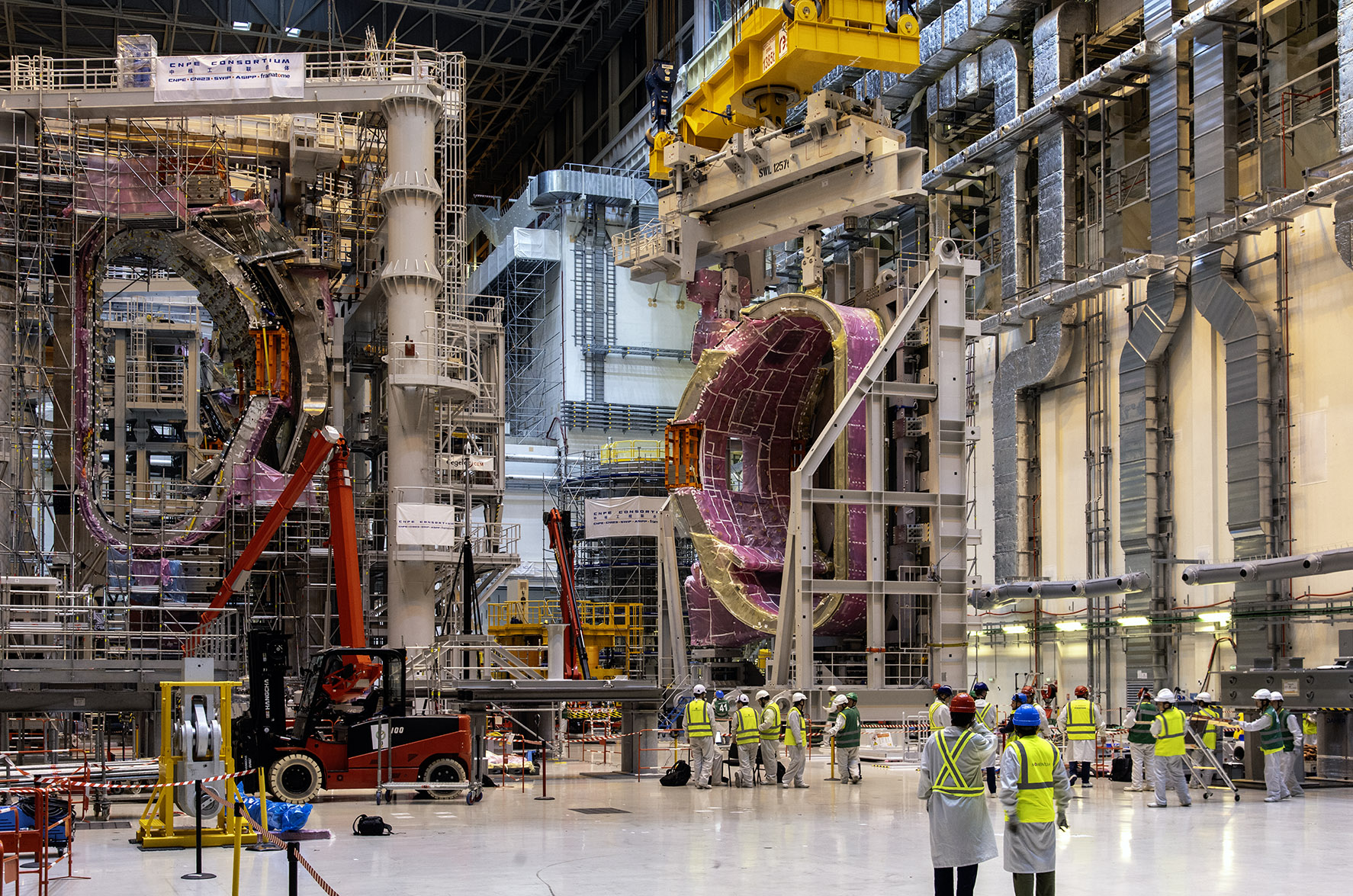
Two giant sectors
2025-03-18 - Sector 8, on the right, is a "bare" vacuum vessel sector. Sector 7, on the left, has been ensconced in its thermal shield and associated with two vertical magnet coils (toroidal field coils) to form a "sector module assembly." This assembly will be ready for permanent placement in the tokamak pit in April—the first of nine sector module assemblies that will form the vacuum vessel and its surrounding toroidal field magnet superstructure.
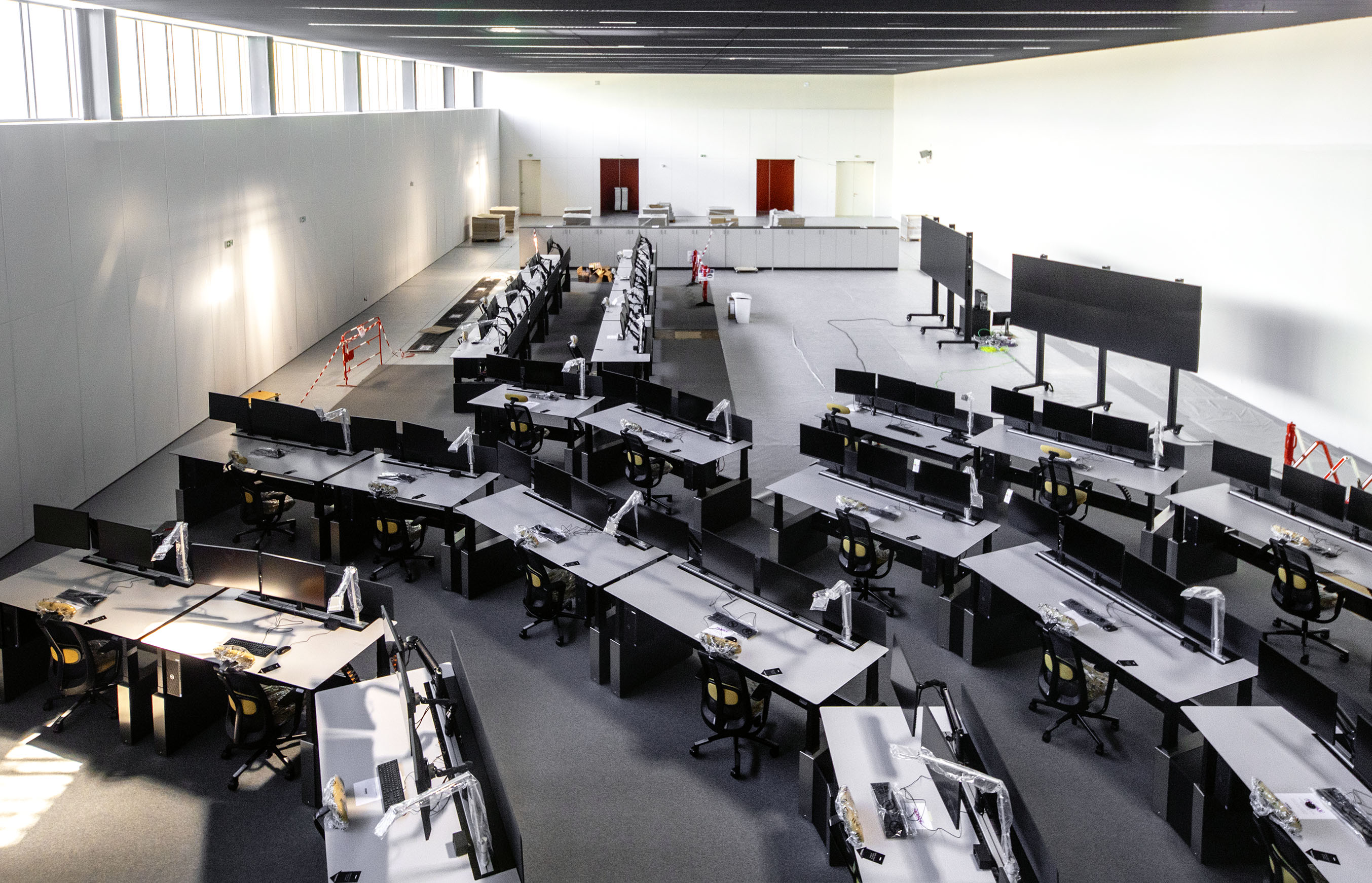
Equipping the control room
2025-03-18 - 30 operator stations in the ITER control room are now equipped with keyboards, mice and computer screens. This configuration will cover needs for the next seven to eight years.
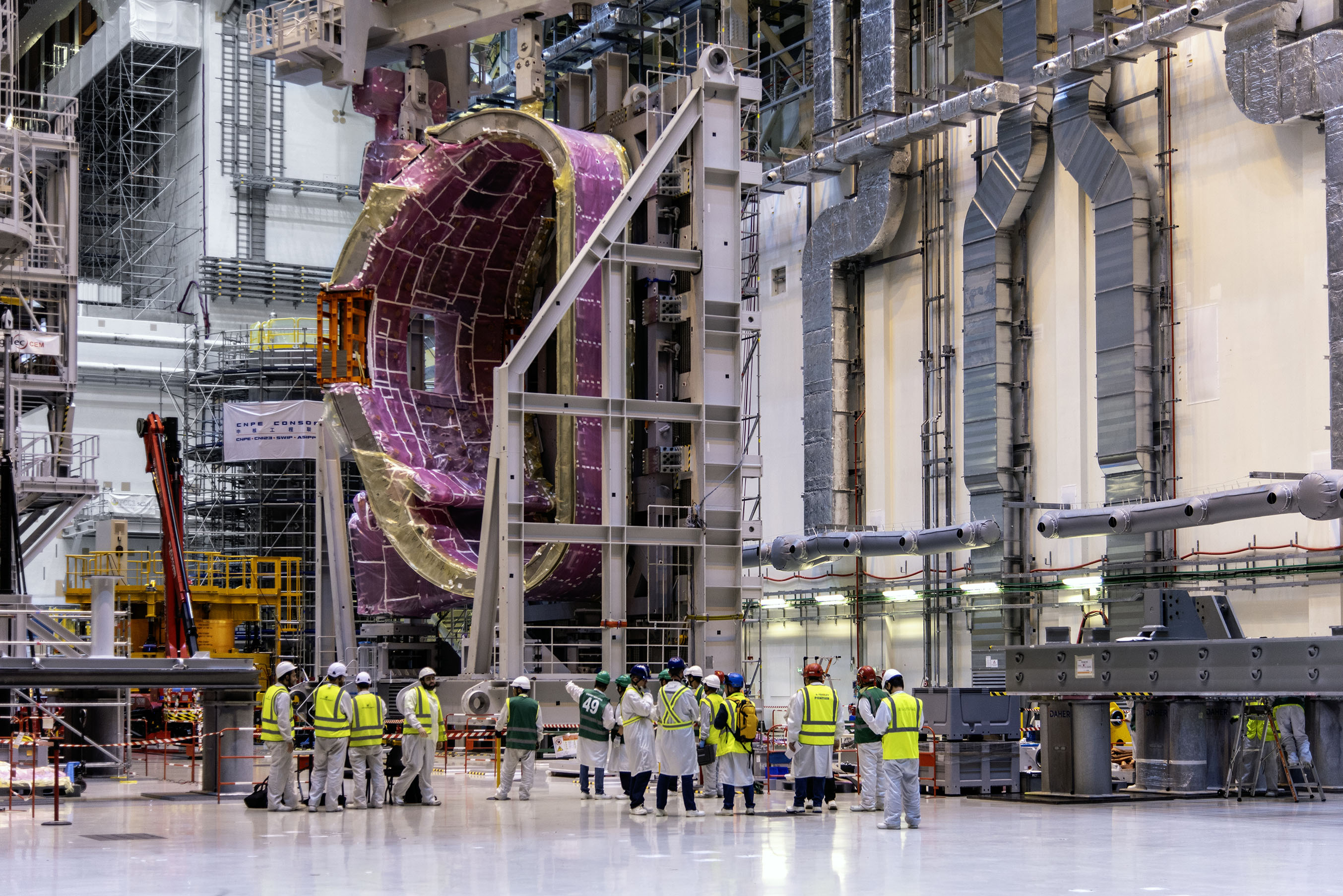
Sector 8 returns from the pit
2025-03-18 - After a brief stay in the tokamak pit, sector #8 has been returned to the upending tool, whose rigging has been prepared to receive its repaired side facing down. The sector will be "downended" and returned to the Cryostat Workshop for further remediation.
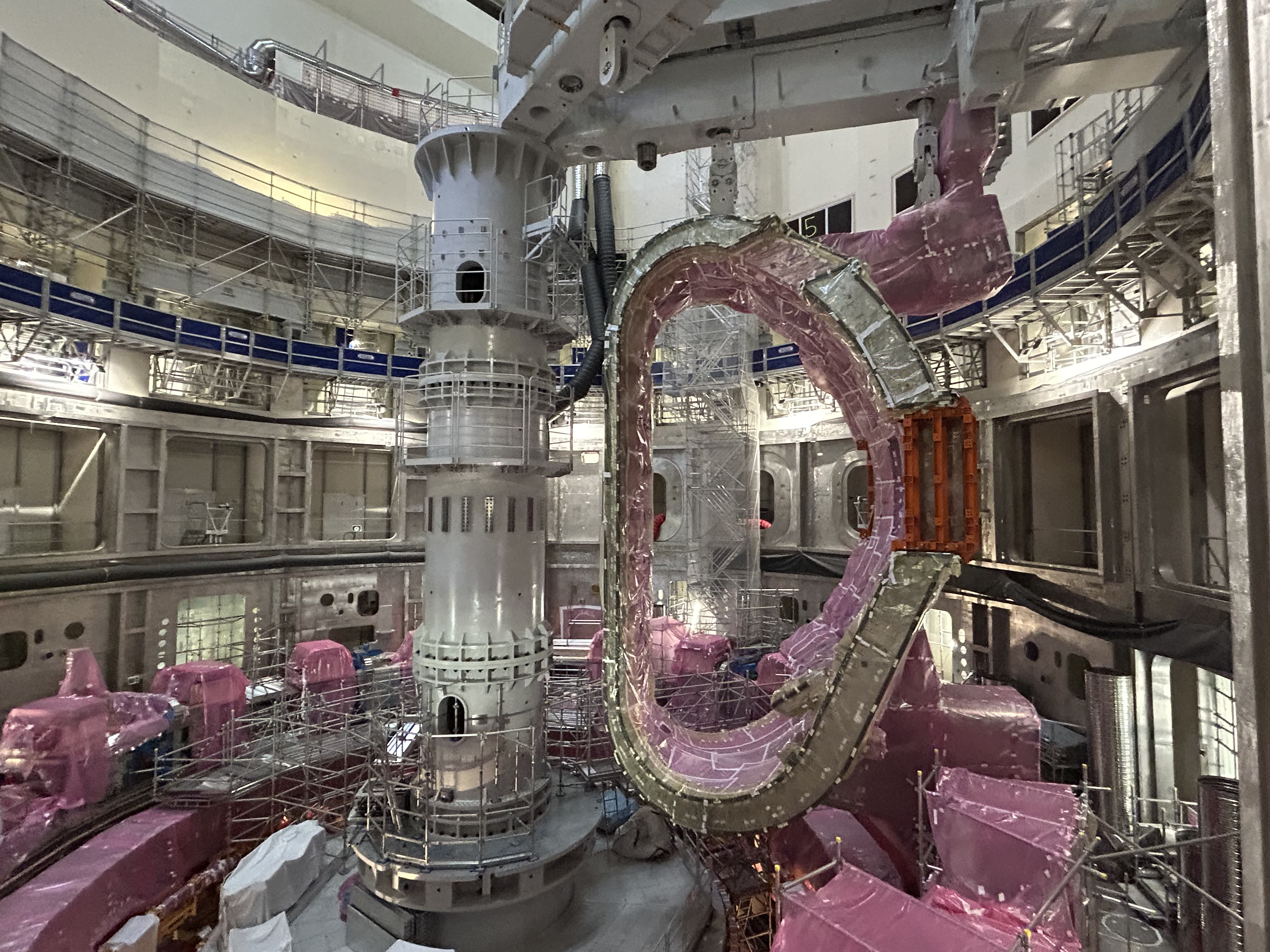
A short visit
2025-03-04 - This vacuum vessel sector is temporarily occupying one of the bays reserved for sector modules in the tokamak pit. Next month, though, a completed sector module assembly (a sector + vertical coils + thermal shield) will be permanently lowered into bay #7.
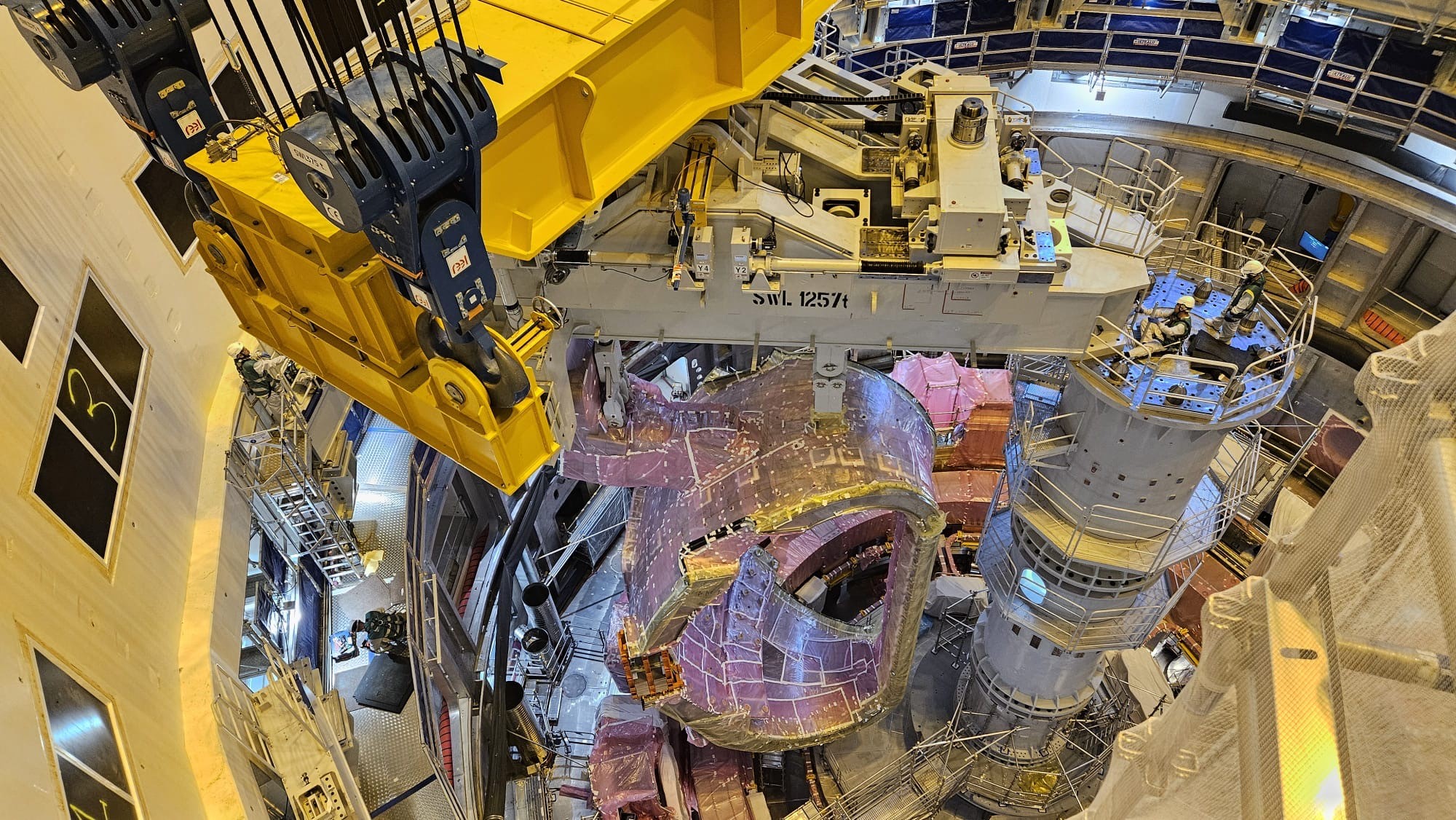
Temporarily in the pit
2025-03-04 - On Tuesday 4 March, sector #8 of the vacuum vessel is temporarily "parked" in the tokamak pit. The handling operation that will ensue has been designed to reverse the bevel joint region that will be exposed when the component is returned to a horizontal position.
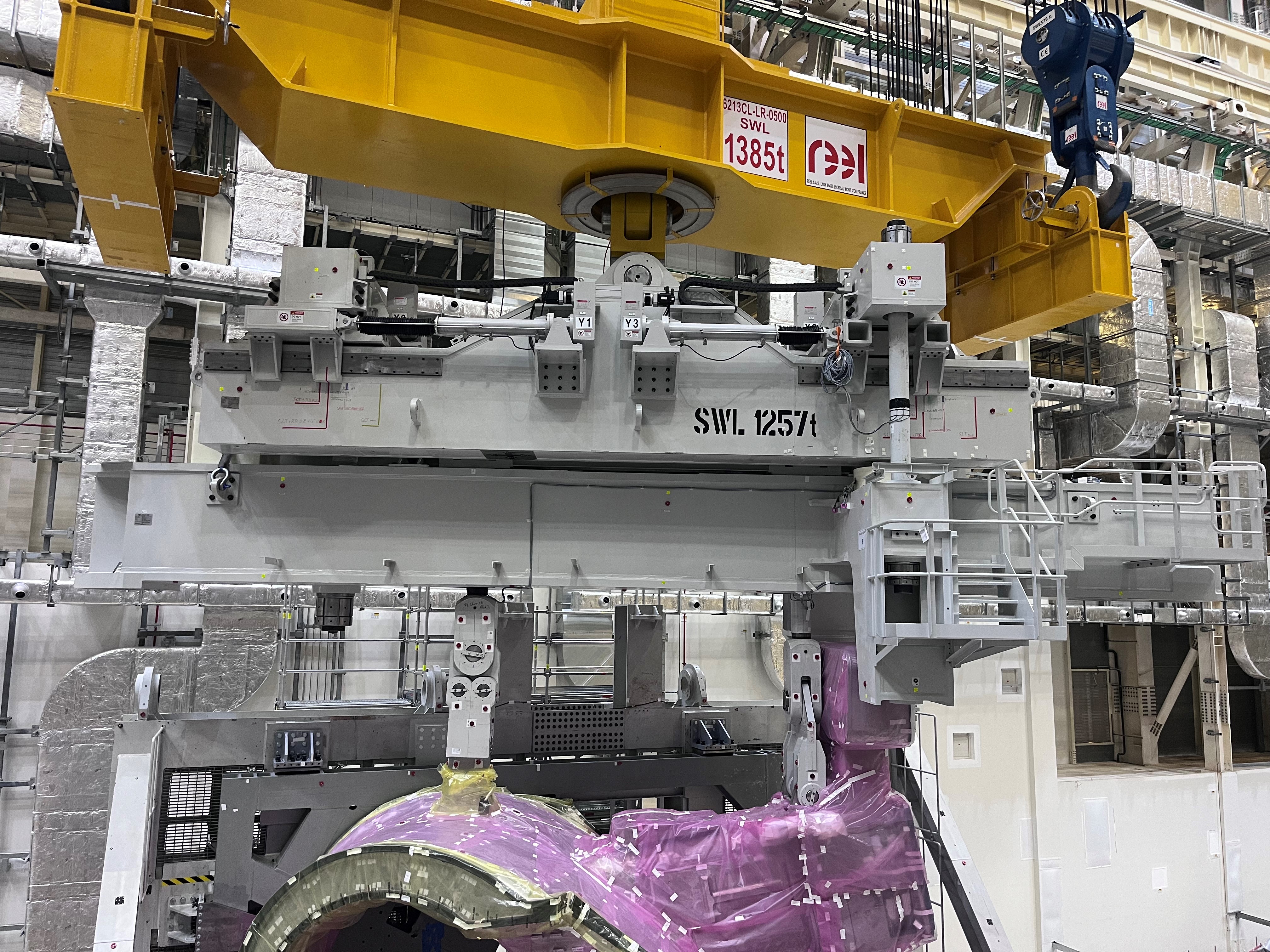
Dedicated rigging
2025-03-04 - The overhead cranes cannot "grasp" major loads directly; instead, several elements of rigging intervene between the cranes and the components to be lifted. The dual crane heavy lifting beam (in yellow) allows the cranes to work in tandem and facilitates the rotation of components. The sector lift tool (in grey, with the marking SWL 1257t) interfaces with the radial beam suspending the sector and is equipped with a system to balance the load.
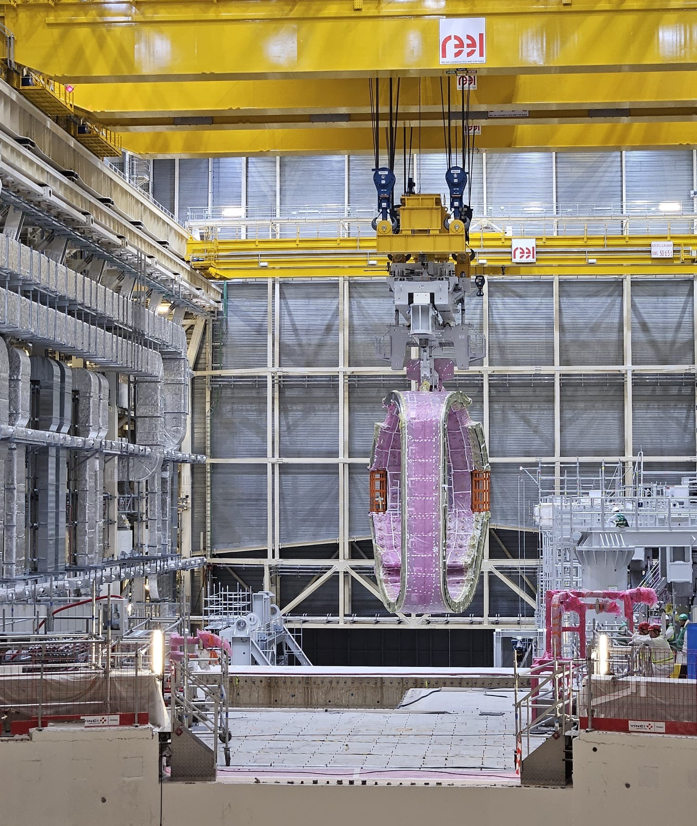
Travelling slowly
2025-03-04 - Two overhead cranes work together to transport the sector out of the upending tool, across the Assembly Hall, and into the tokamak pit.
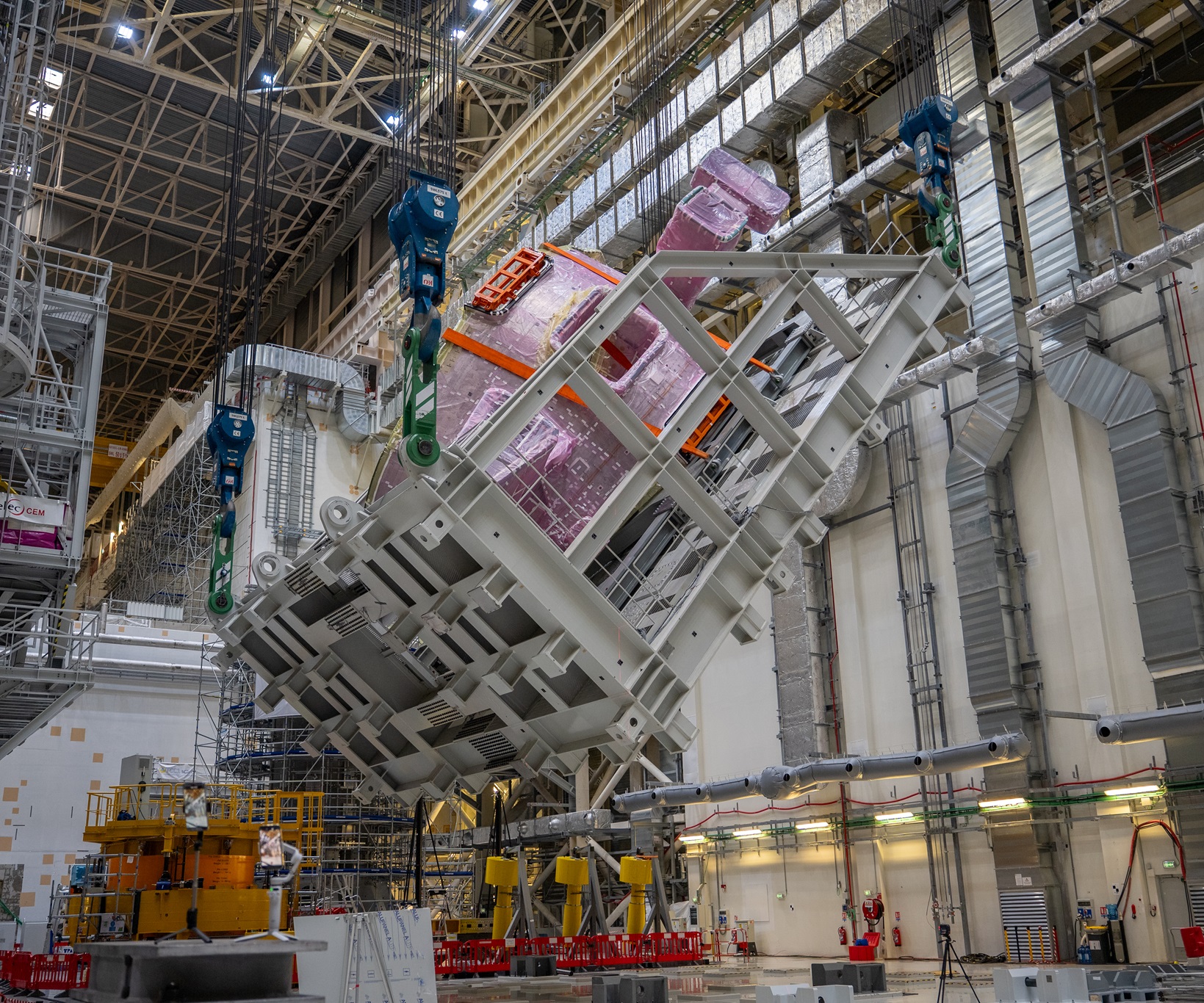
Pivoting
2025-02-21 - The upending tool is a 240-tonne steel frame that is designed to cradle components that are twice its weight. Vacuum vessel sector #8 and its transport frame weigh more that 440 tonnes.

A few metres
2025-02-21 - Thick cables connect the overhead bridge cranes to the four corners of the upending tool—the sturdy steel cradle that has been designed to raise some of ITER's heaviest components to vertical. Little by little, as the cables strain, the cradle leaves the ground with sector #8 lashed securely inside.
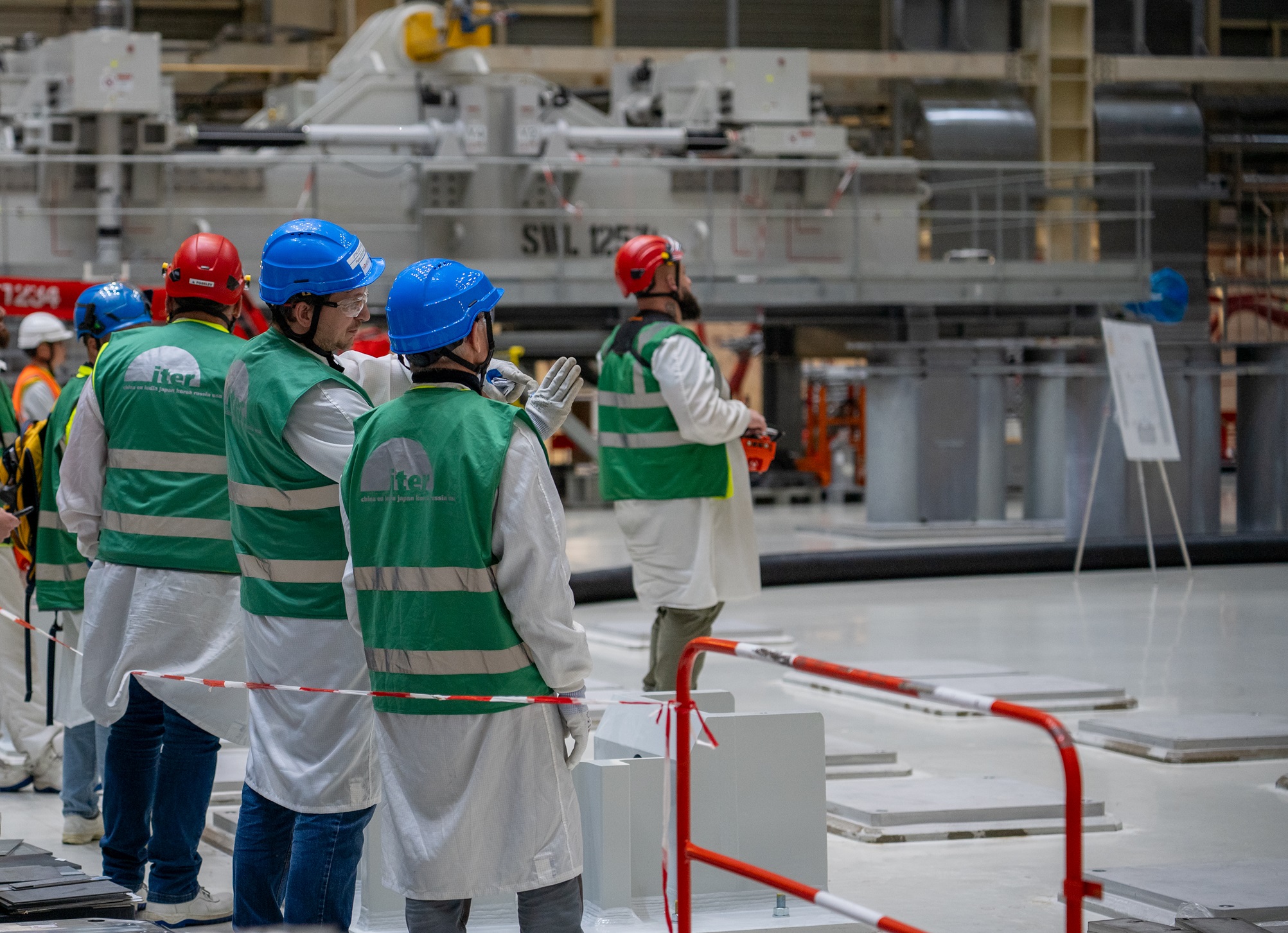
Driving the overhead cranes
2025-02-21 - The team watches as the operator manoeuvres the cranes by joystick. The carefully planned operation lasts about 1.5 hours.
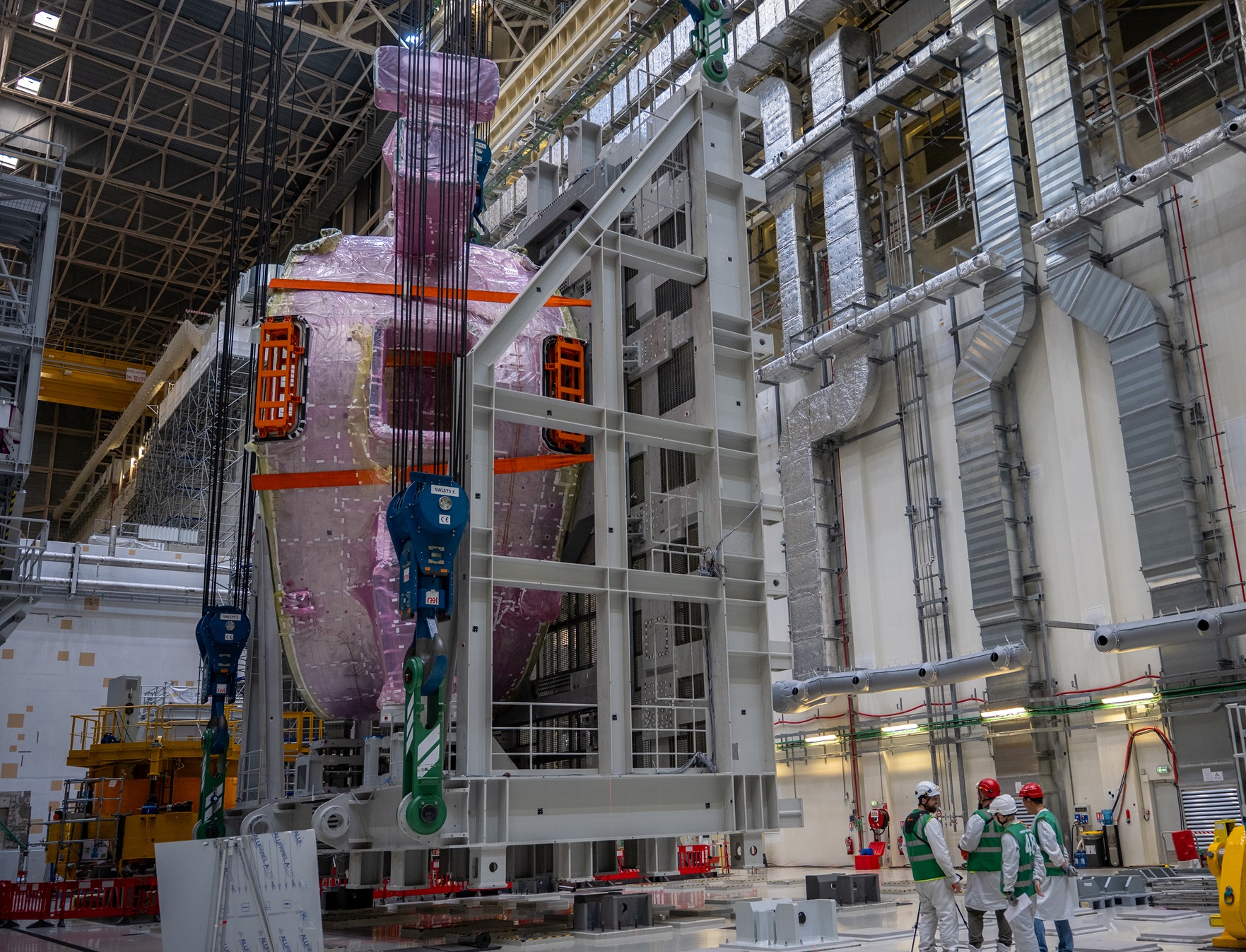
Vertical
2025-02-21 - Sector #8 is now in its vertical orientation, ready to be lifted out of the upending tool and transferred, temporarily, to the tokamak pit. It will be back soon, facing the opposite direction.
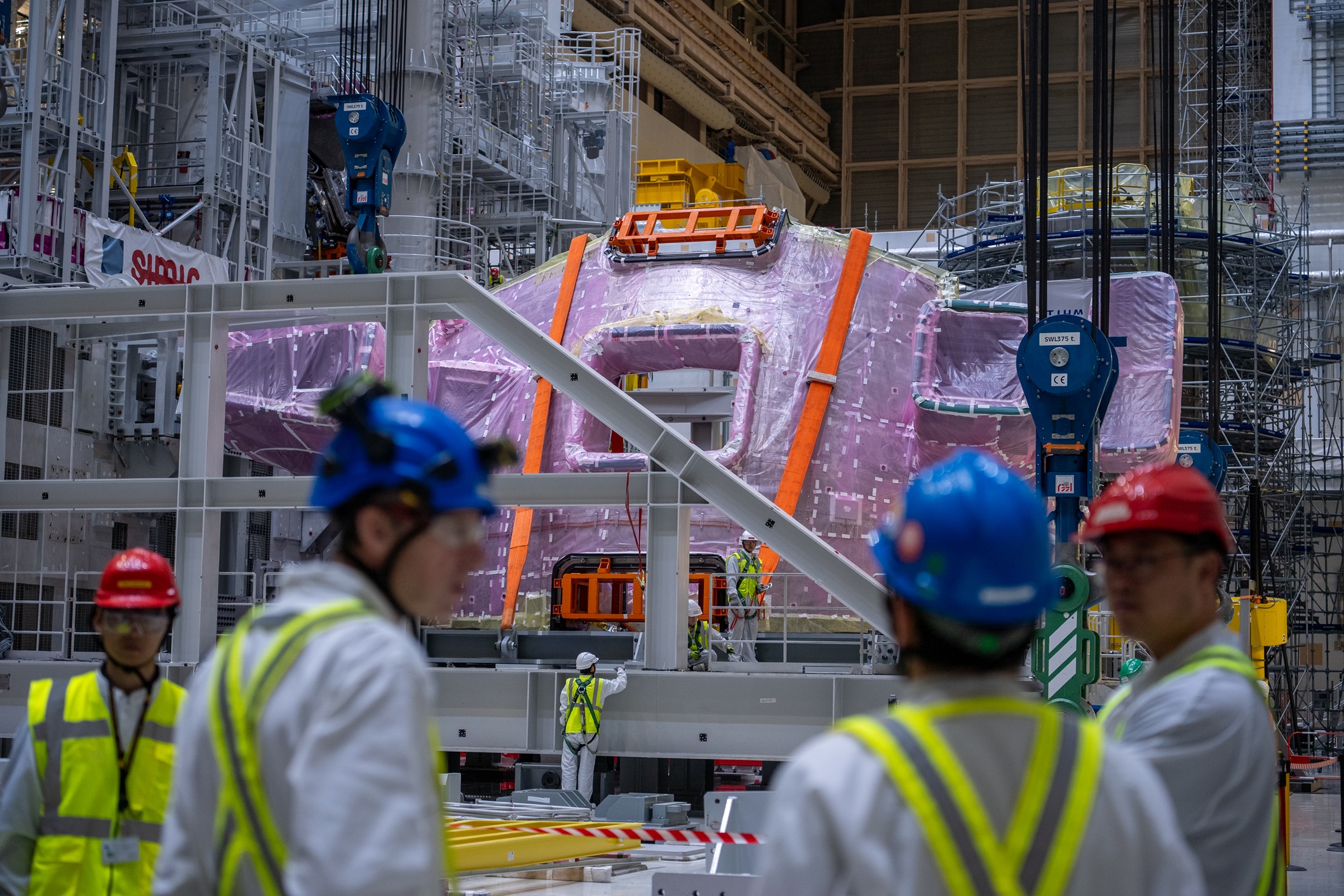
Starting the operation
2025-02-21 - The team in the Assembly hall prepares to upend vacuum vessel sector #8. "Upending" the sector means bringing it to vertical.
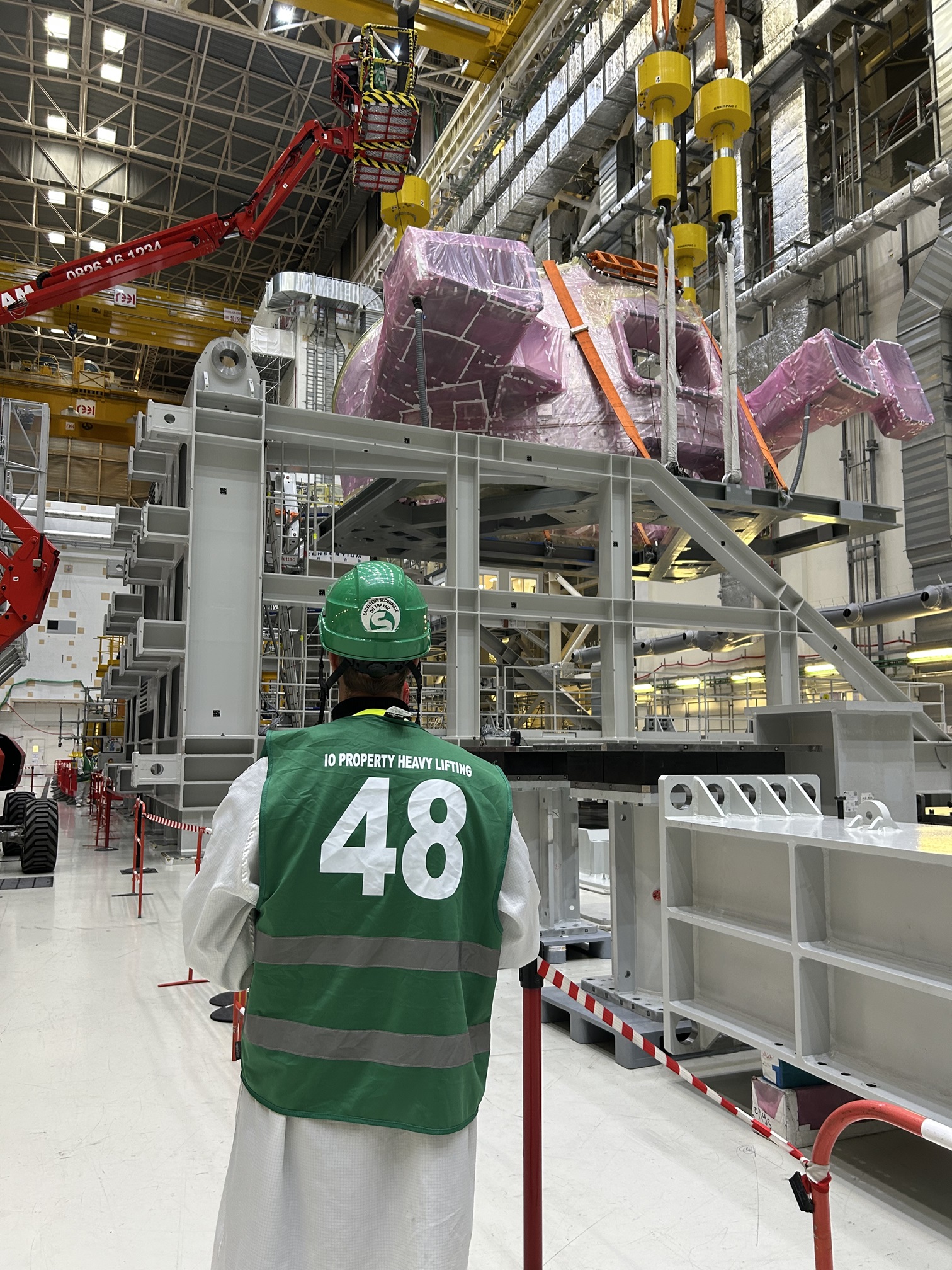
To flip a sector...
2025-02-17 - Step 1 of flipping a 440-tonne vacuum vessel sector: place it horizontally, on its frame, inside of the upending tool.
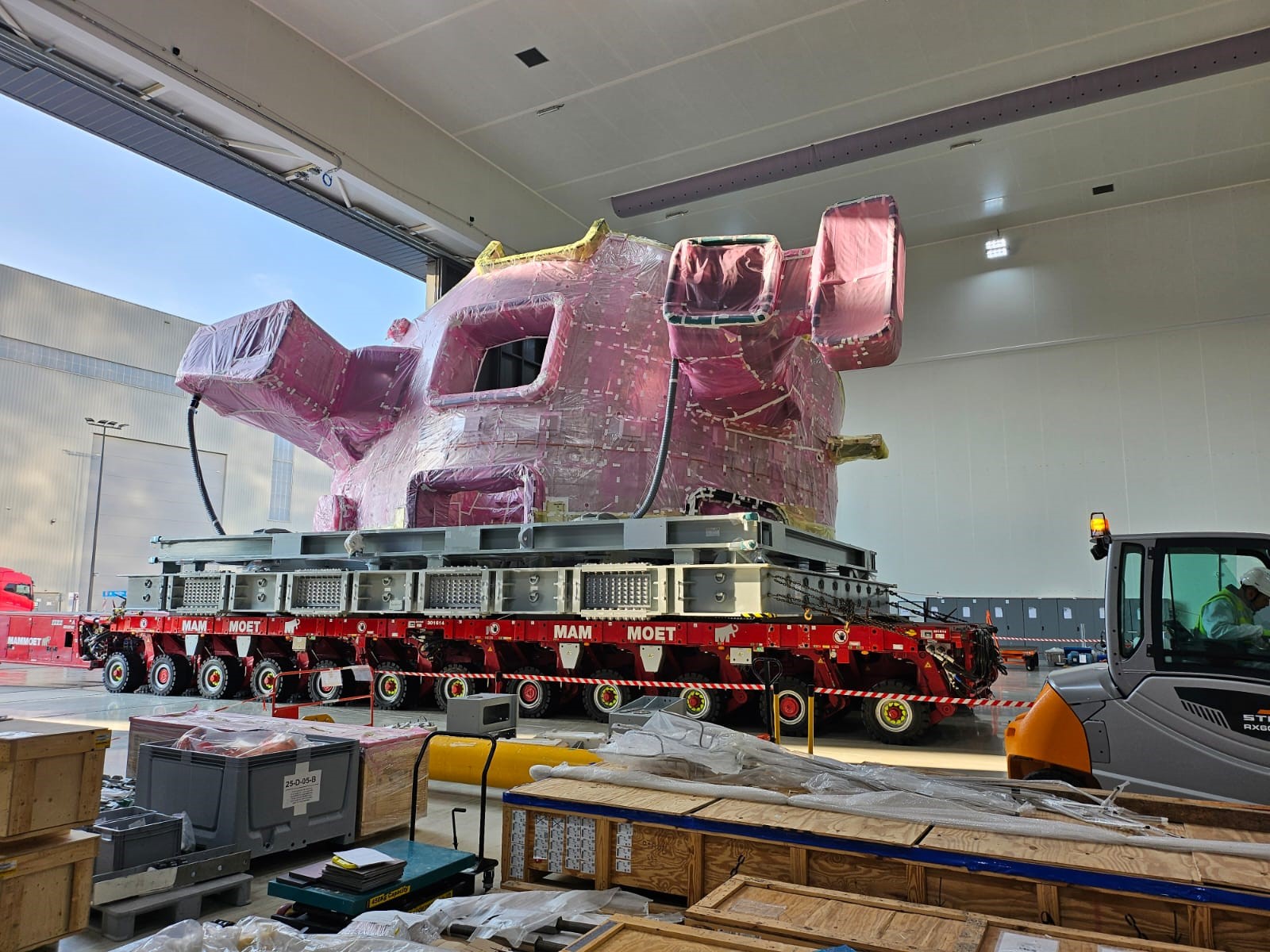
Sector 8 arrives for lifting and turning
2025-02-07 - Sector #8 arrives on its transport frame at the Cleaning Facility—an antechamber to the Assembly Hall. When it leaves again, its other side will be exposed.
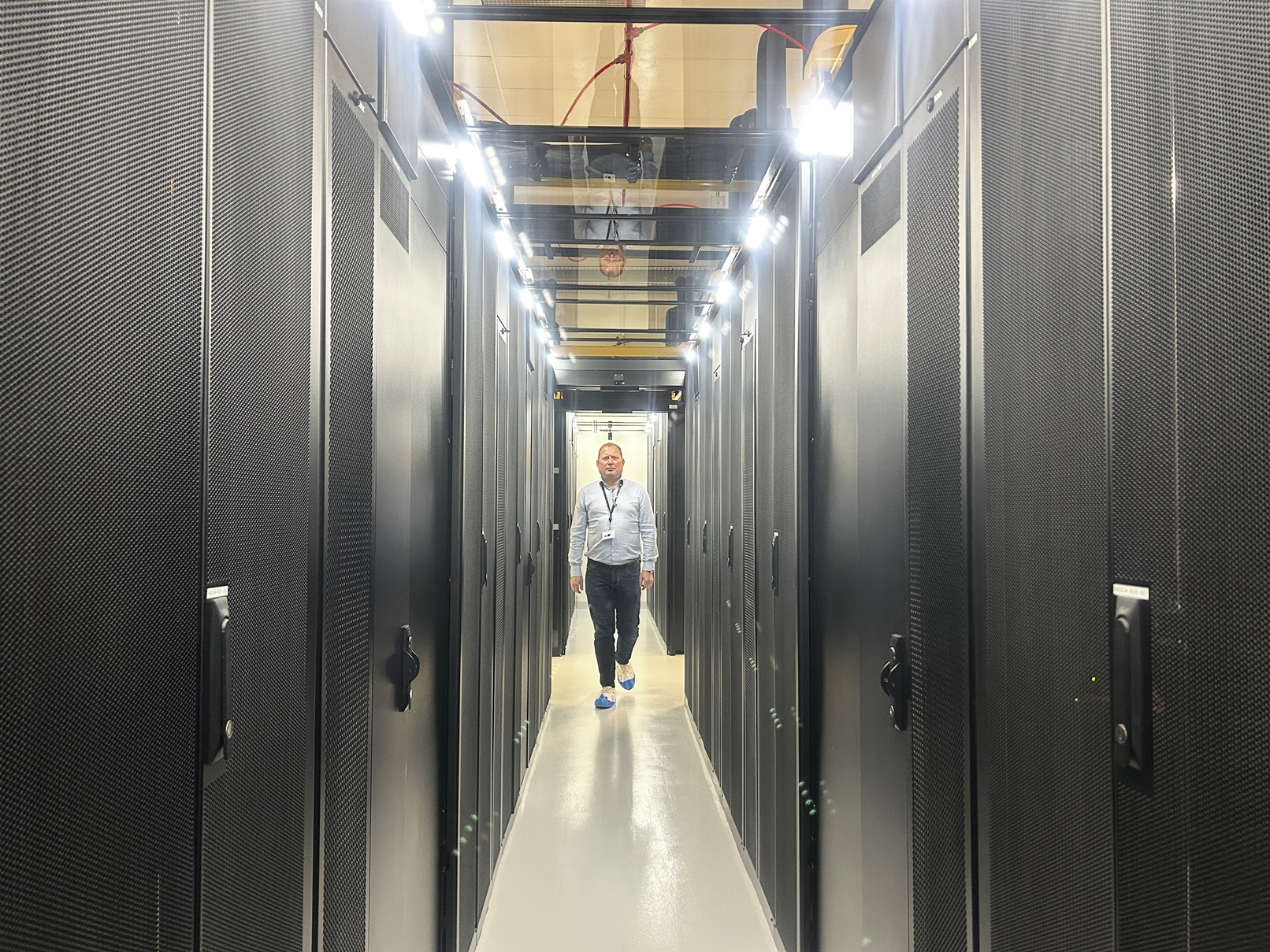
Scientific Data and Computer Centre coming on line
2025-02-03 - Peter Kroul—from the IT System and Operation Section—is in the Scientific Data and Computer Centre, where ITER data will be stored, secured, processed and distributed throughout the lifetime of the machine. Data storage and management will begin in 2025 when the centre starts receiving data from various ITER plant systems.
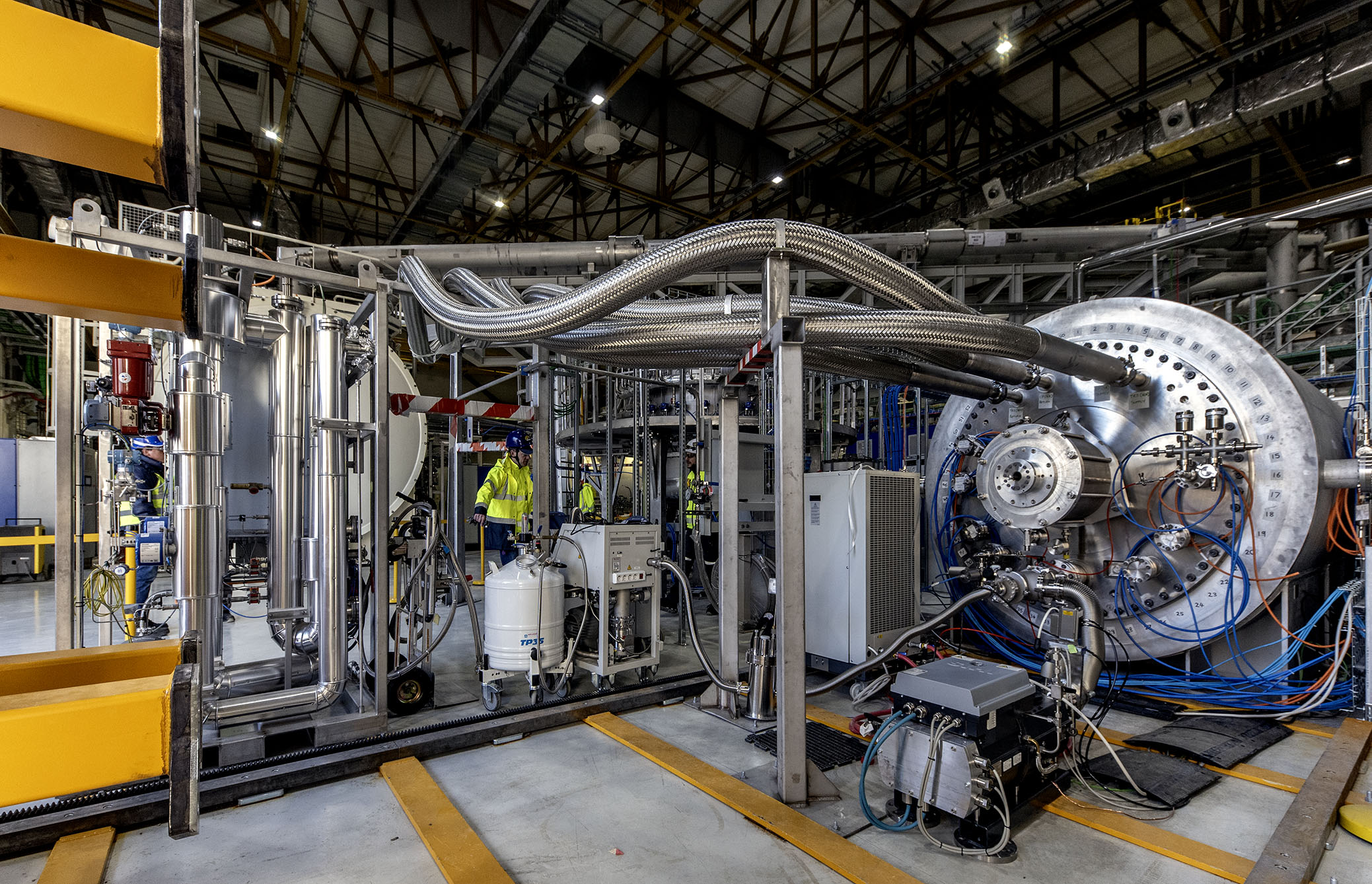
A test bench for cryopumps
2025-01-14 - Like all ITER components, the torus and cryostat cryopumps that will create the vacuum conditions needed for ITER operation are subjected to comprehensive factory acceptance tests before shipment. But because this is not sufficient to guarantee that they will perform as expected during actual tokamak operation, a test facility has been created to bring the cryopumps to cryogenic temperatures (4 K or minus 269 °C). Engineers will be able to test a whole range of cryopump processes in the new facility, which is located in the ITER cryoplant for convient access to cryogenic fluids.
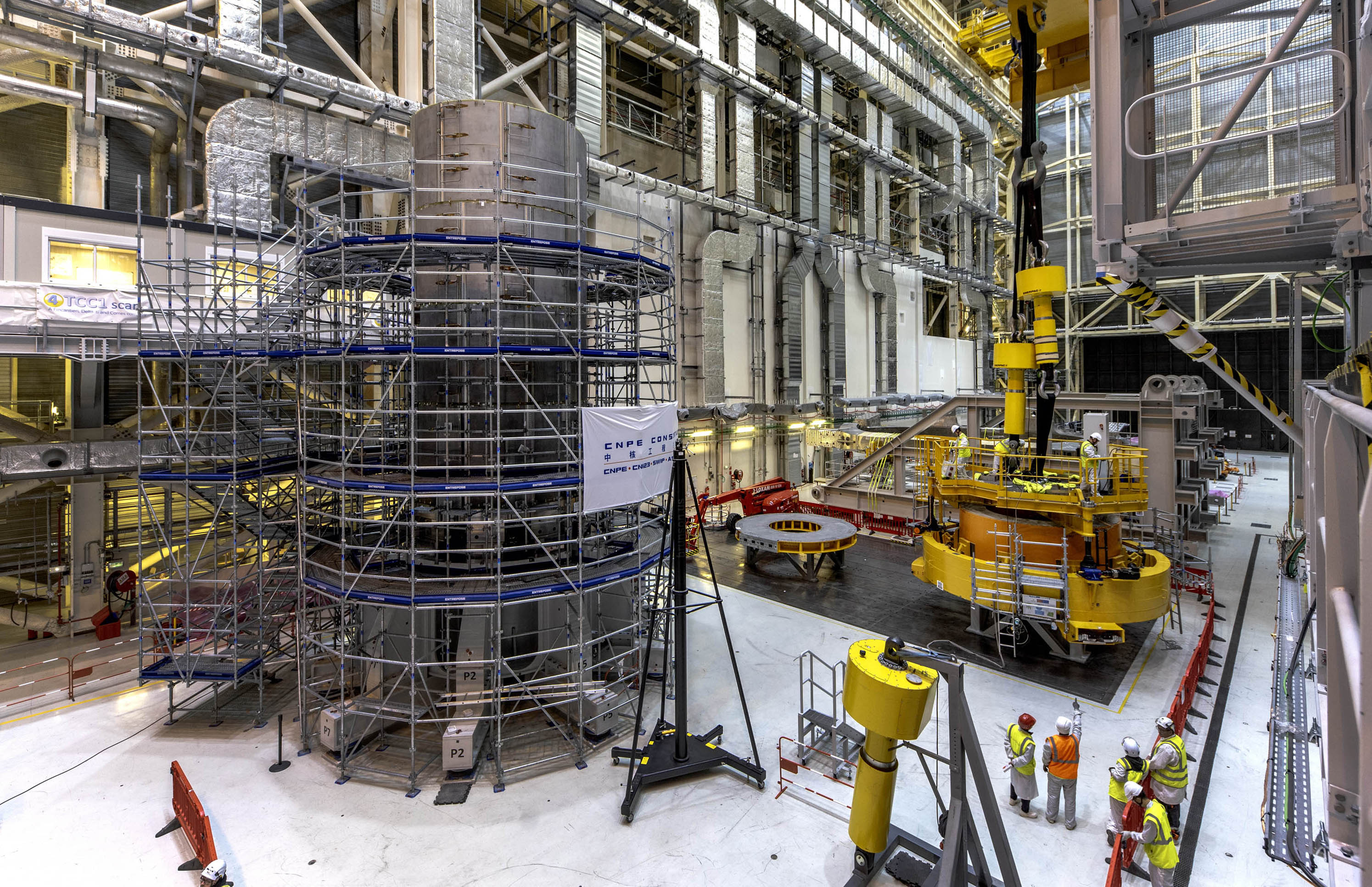
Central solenoid: only two more to go
2025-01-13 - With a fourth module now in place, the massive, tower-like superconducting magnet being assembled in the ITER Assembly Hall now reaches approximately two-thirds of its final height.
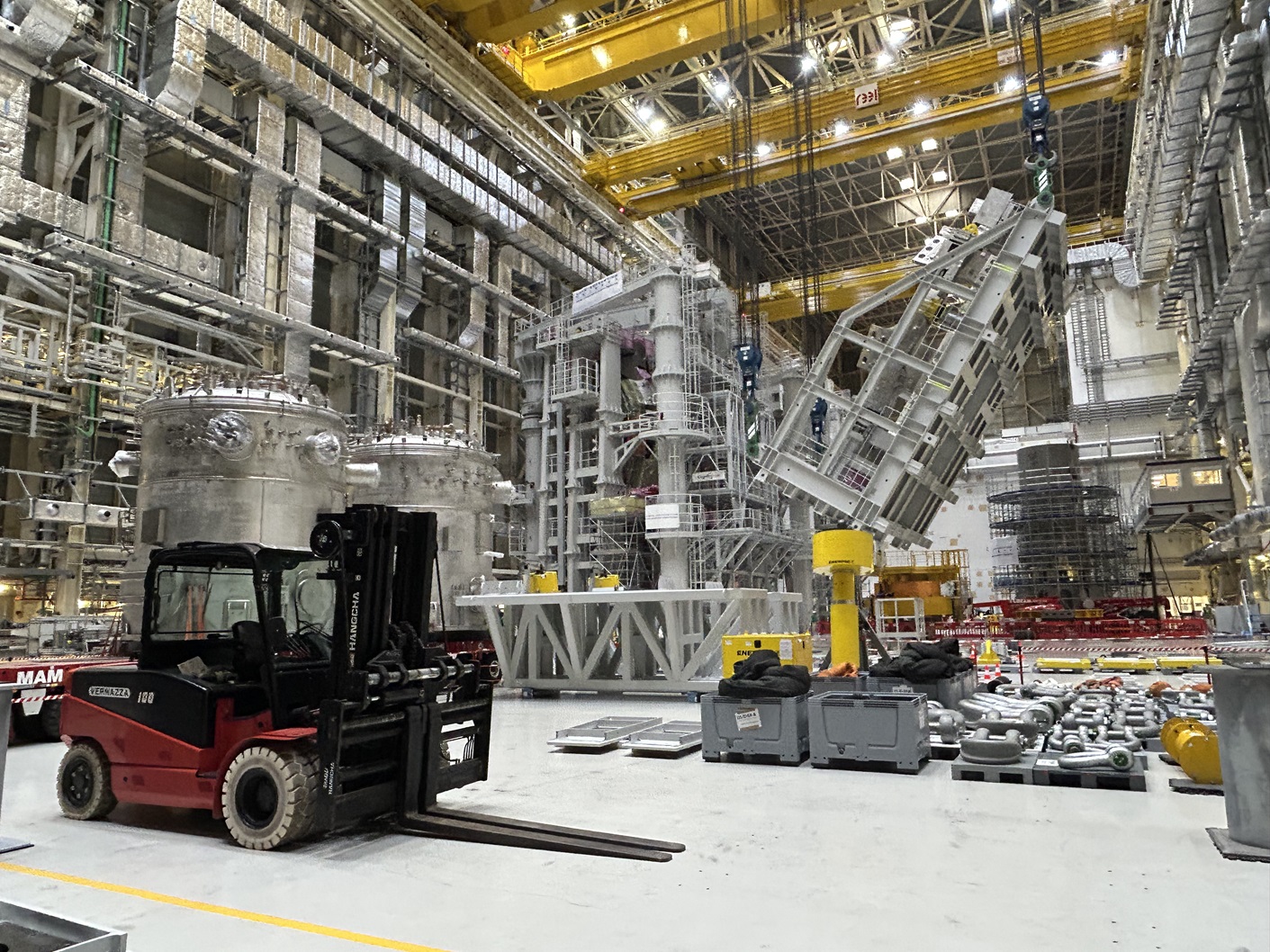
Upending 330 tonnes
2025-01-13 - ITER's bespoke upending tool is seen here in action as it pivots a 330-tonne toroidal field coil from horizontal to vertical. Once vertical, it will be lifted by the overhead cranes and brought to the tool hosting vacuum vessel sector 6, where it will be rotated toward the sector and attached.
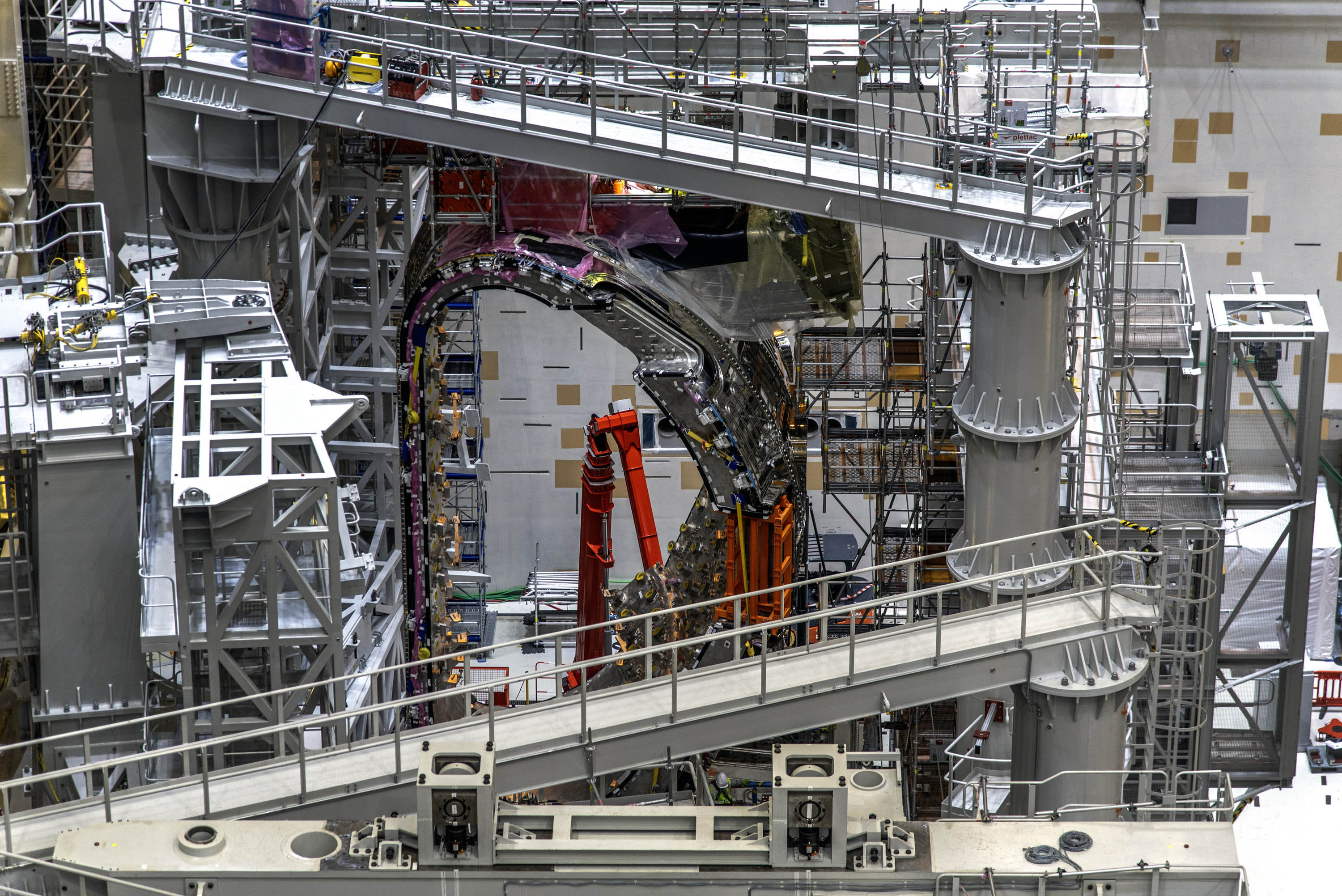
Thermal jacketing
2025-01-09 - If you look closely, you'll see a thin layer of polished stainless steel thermal shield closely jacketing vacuum vessel sector 6. Installed between the vacuum vessel and the superconducting magnets, it will act to minimize heat loads transferred by thermal radiation and conduction from warm to cold components.
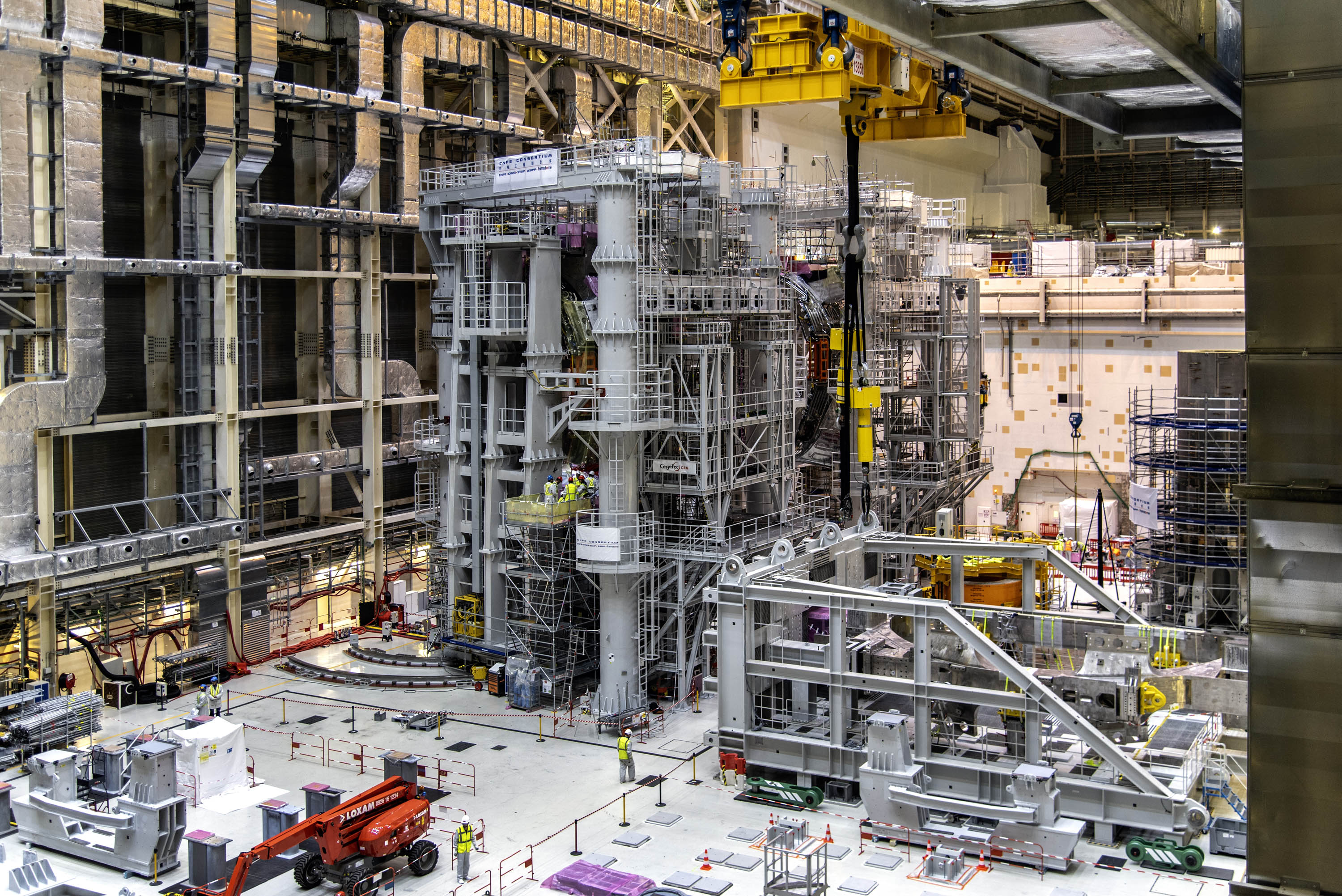
Sector sub-assembly progressing
2025-01-09 - A 330-tonne toroidal field coil is lying in a cradle tool that will be used to upend it to vertical; the rotation is carried out mid-air. Workers from the Chinese consortium CNPE can be seen in the tall tooling at left, where the sub-assembly of vacuum vessel sector #7 (a process by which the sector is assembled with its thermal shield and two toroidal field coils) is near completion.
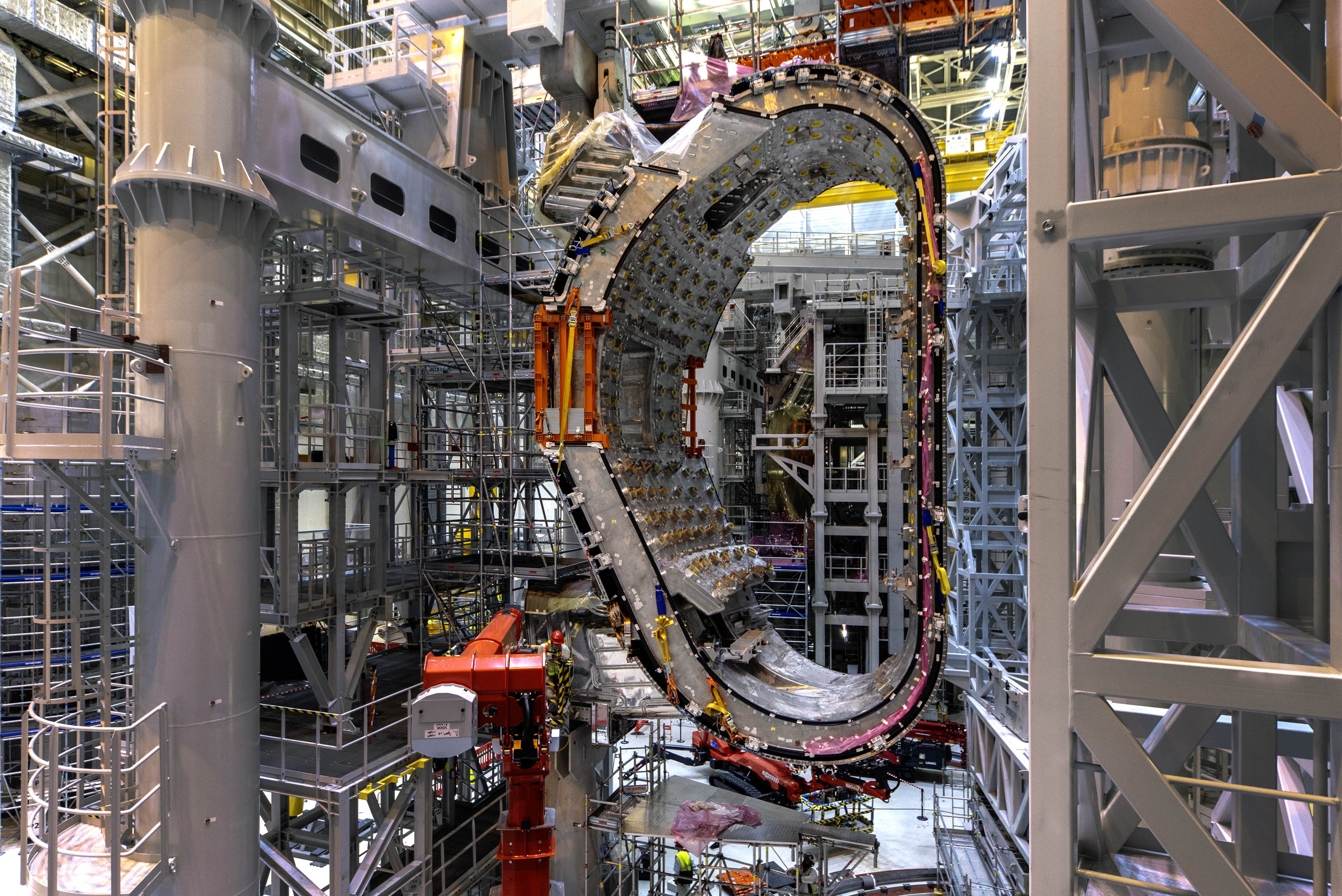
Wings to close on sector 6
2025-01-09 - Suspended in tooling, vacuum vessel sector 6 awaits the attachment of a toroidal field coil on each of its sides. The magnet coils will be positioned in the wings of the tool and rotated inward.
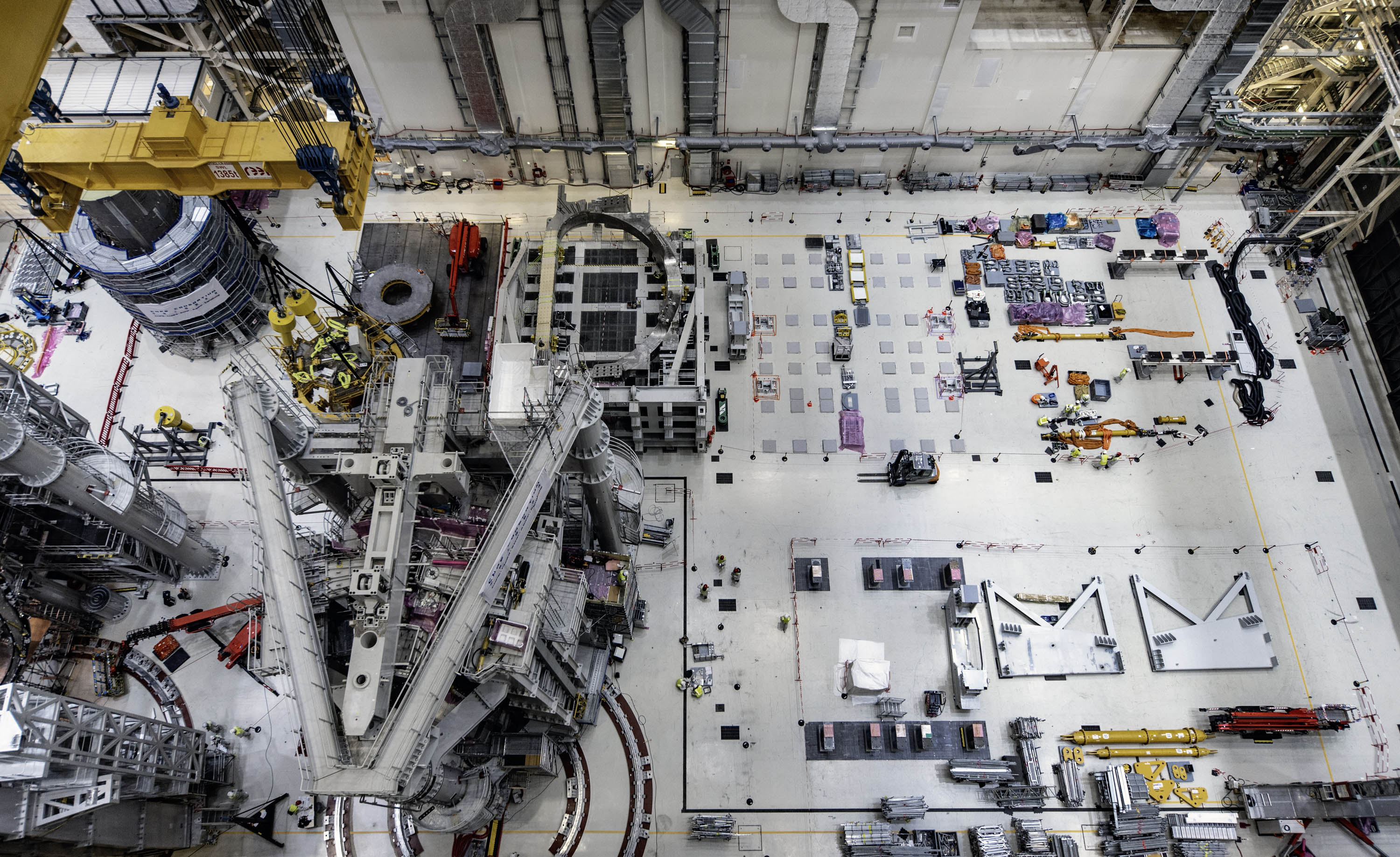
Second upending tool coming
2025-01-09 - On the floor of the Assembly Hall, a space has been prepared for a second upending tool; reception pads are clearly visible. Having two identical tools—one specializing in the handling of toroidal field coils and the newest in vacuum vessel sectors—the need for regular tool reconfiguration will be avoided, which could amount to weeks saved in the assembly schedule.
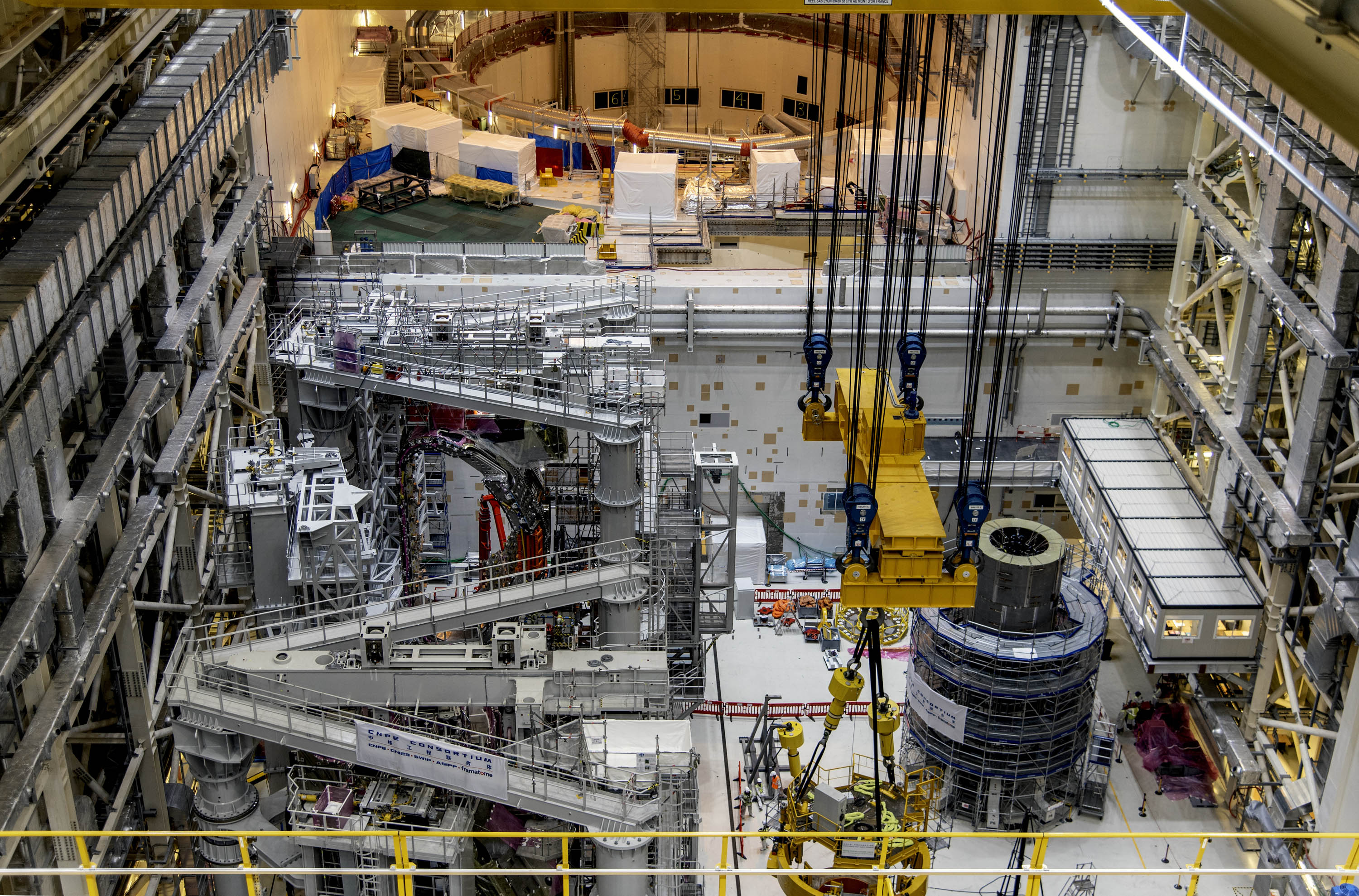
Assembly activities, from above
2025-01-09 - In this view from the rafters, we look down into the vacuum vessel sub-assembly tools, where two sectors are being assembled into modules (left). The tokamak pit is at the top of the image. To the right, a fourth central solenoid module has just been added to the growing stack.
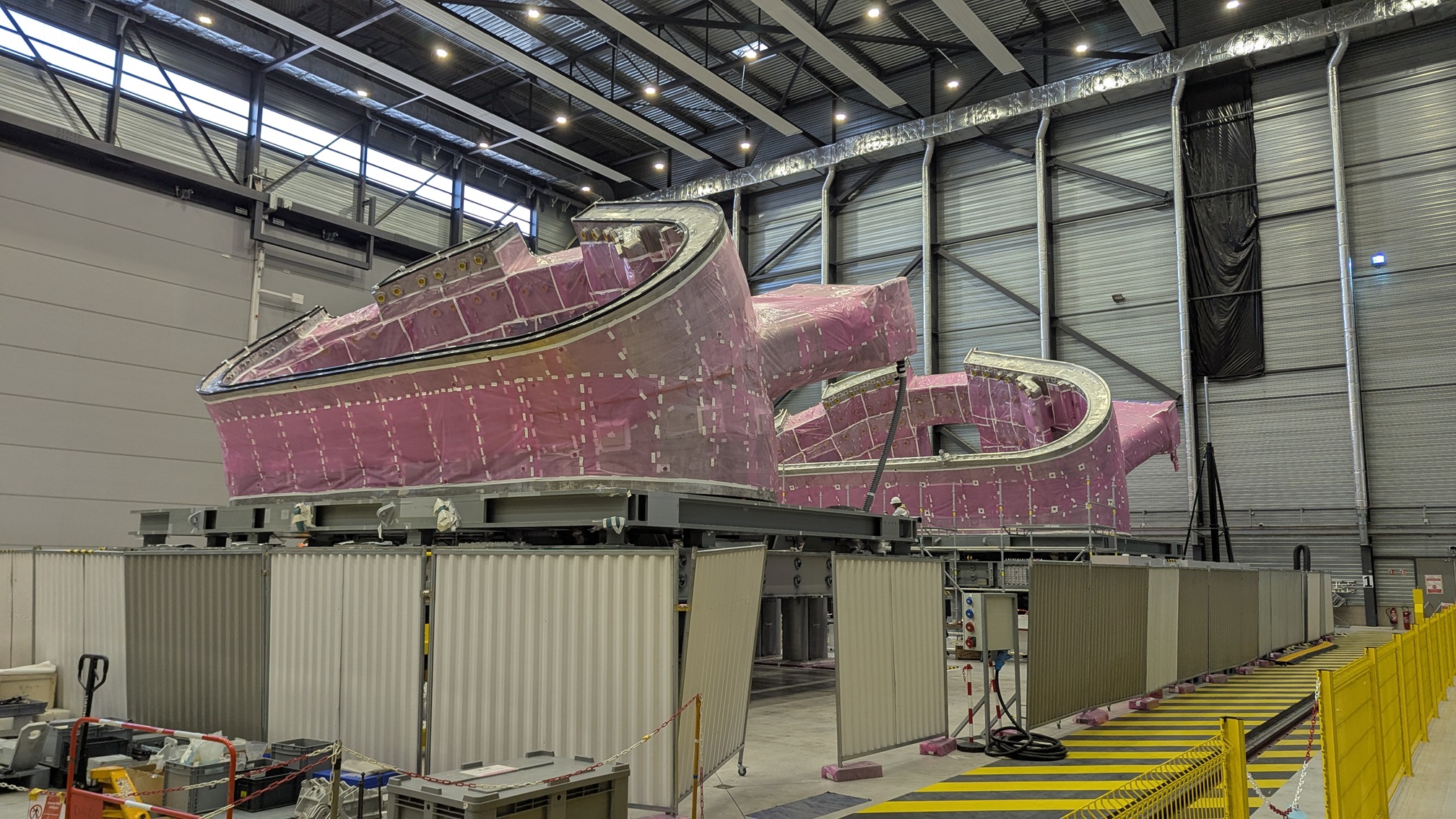
Sectors galore
2024-12-27 - Five of the nine required ITER vacuum vessel sectors are on site. Two are in tooling in the Assembly Hall; three others are being held in the former Cryostat Workshop (including the two pictured).
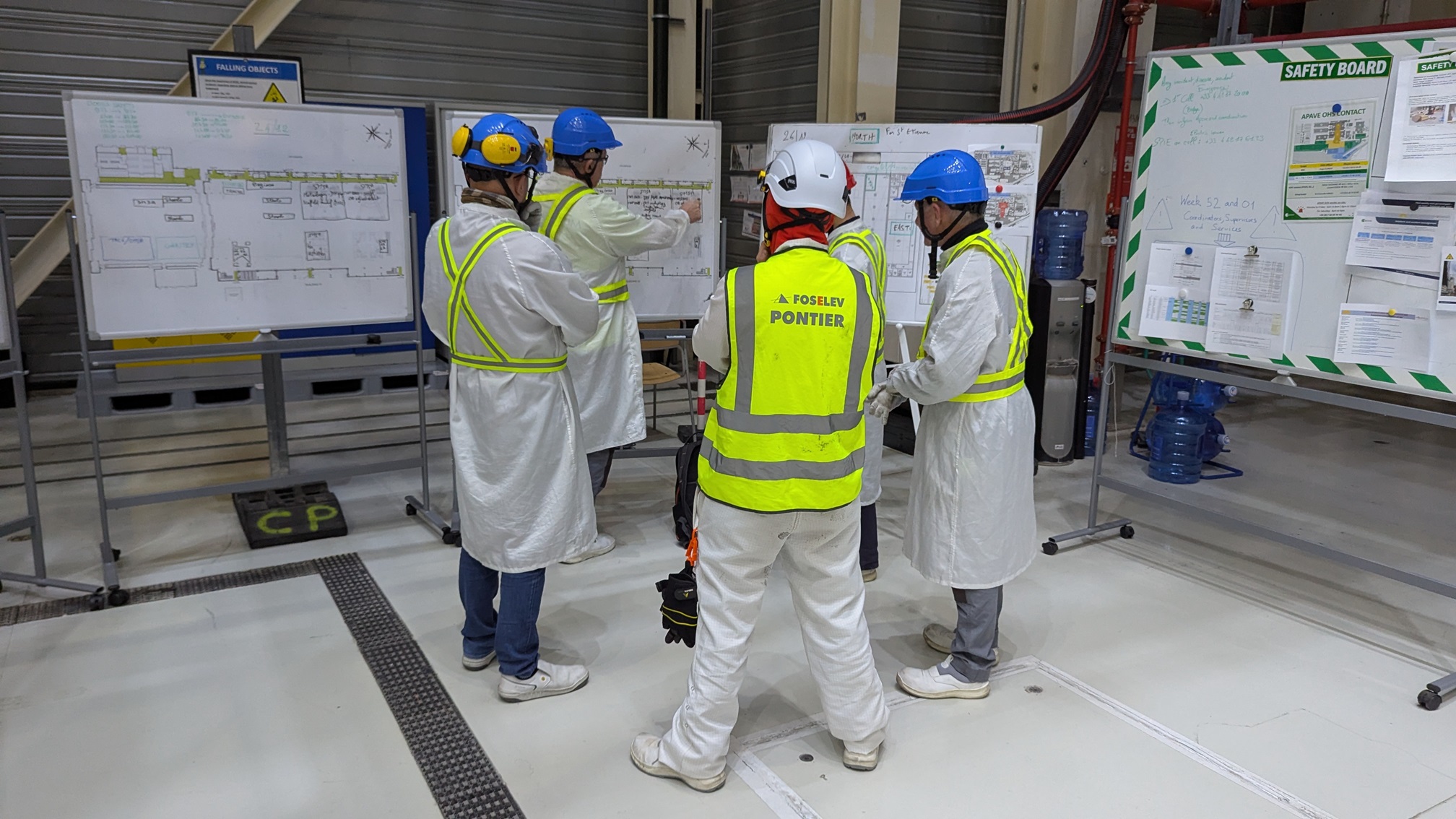
Work never stops on the platform
2024-12-27 - Offices may have been closed at ITER for the end-of-year holidays, but on the worksite the teams remained active. In the Assembly Hall, where tokamak components are prepared for installation, every day began with a coordination meeting.

Don't step here
2024-12-27 - Scaffolding is installed above poloidal field coil #5 to protect it while assembly teams re-install support thermal shield panels.
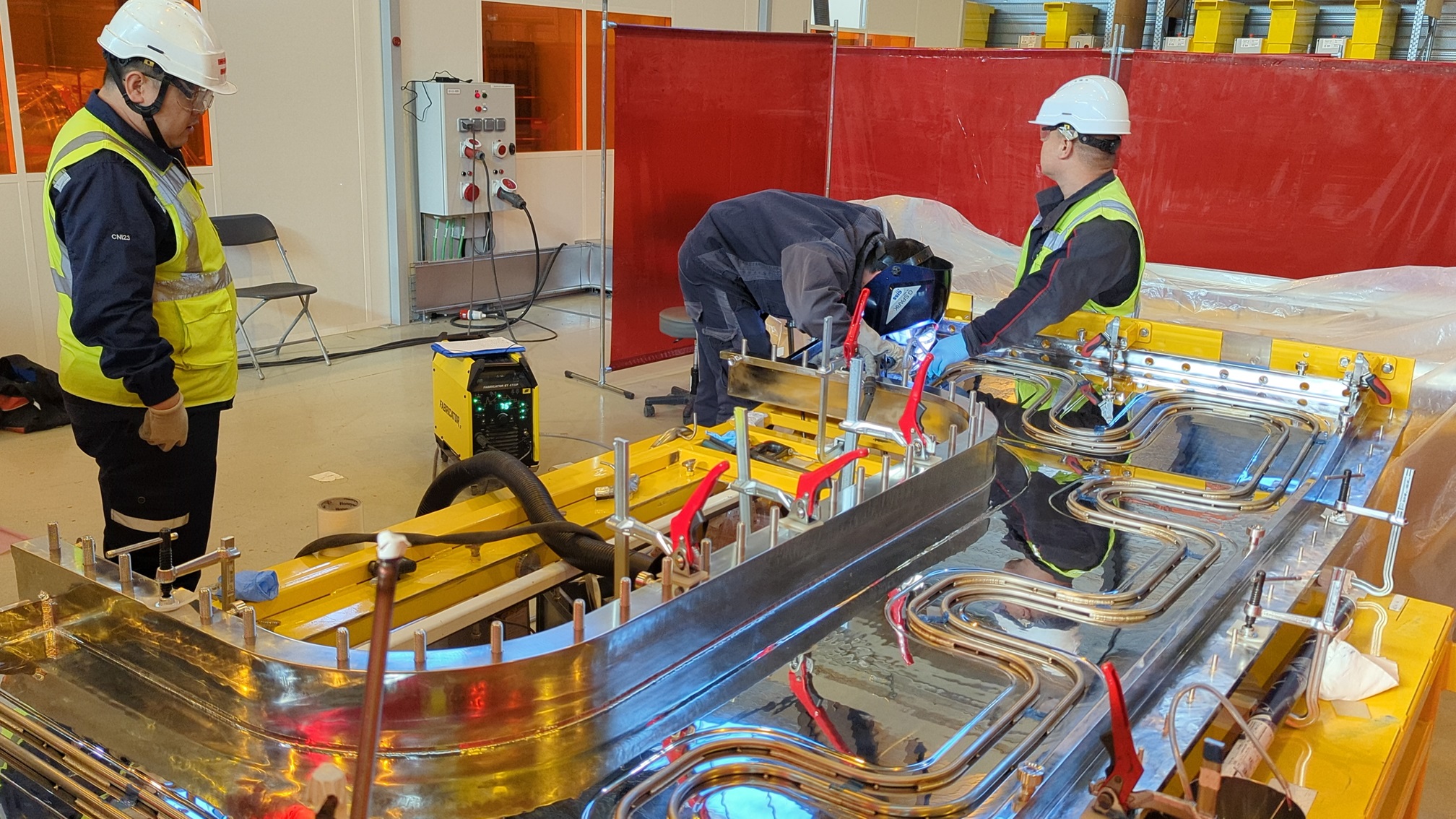
Repairs advancing
2024-12-27 - New piping is welded on a segment of support thermal shield panel at ITER. The panel will be lowered into the tokamak pit and installed as a thermal barrier between the toroidal field coil gravity supports and the vacuum vessel.
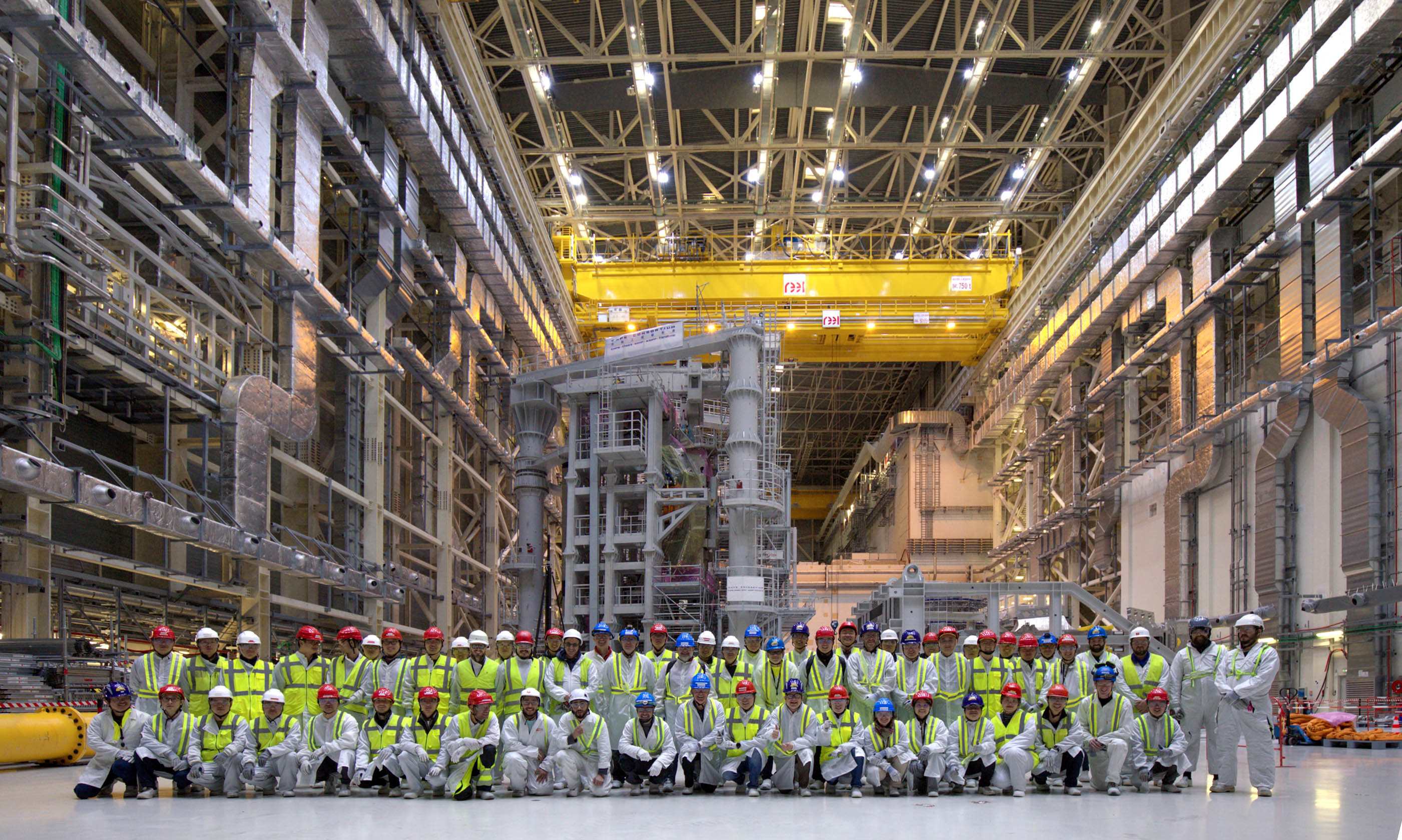
No stopping this team
2024-12-27 - Personnel from the ITER Organization, ITER's Construction Management-as-Agent, and the CNPE assembly consortium stayed busy at the end of the year.
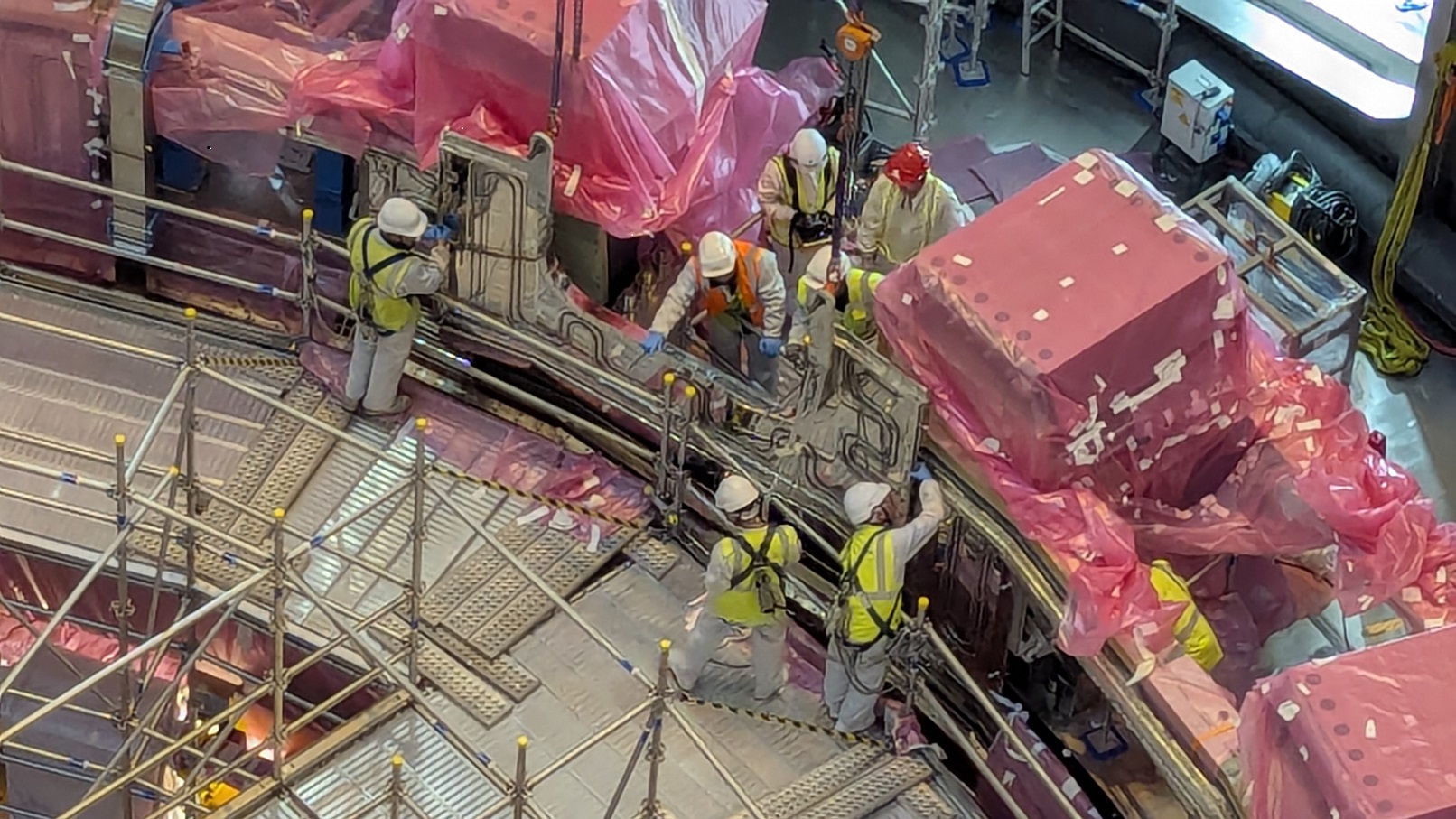
Thermal shield panel aligned in pit
2024-12-26 - A support thermal shield panel is installed and aligned in the pit. When corrosion cracking was discovered in some vacuum vessel thermal shield panels, the decision was made to replace all thermal shield cooling pipes. Support thermal shield panels, which weigh approximately 700 kg each, were easy to remove from the pit and repair. Now, after the removal of old pipes, machining, the welding of new pipes, and metrology, the panels are being reinstalled.
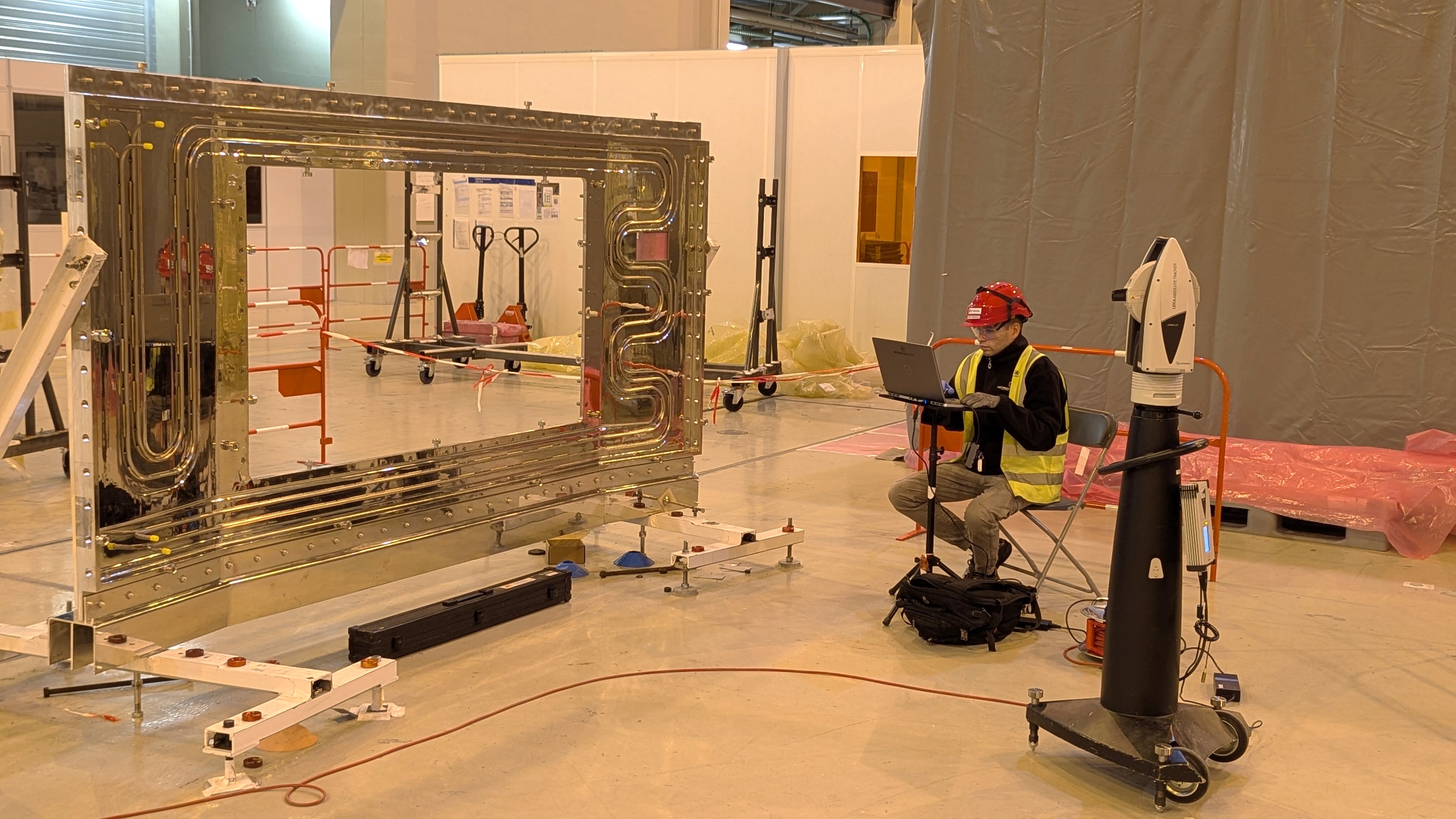
Metrology after repair
2024-12-26 - Support thermal shield panel #17 is surveyed by a metrologist after repair and before installation in the tokamak pit.

First activity from the main control room
2024-12-19 - All smiles. In the main ITER control room, not yet fully equipped, a small ceremony takes place in December 2024 to mark the first time a CODAC command (for Control, Data Access and Communication) is sent to a plant system. In the future, some 80 operators, engineers and researchers will work from this space to monitor plasma, tokamak and plant system parameters in real-time.
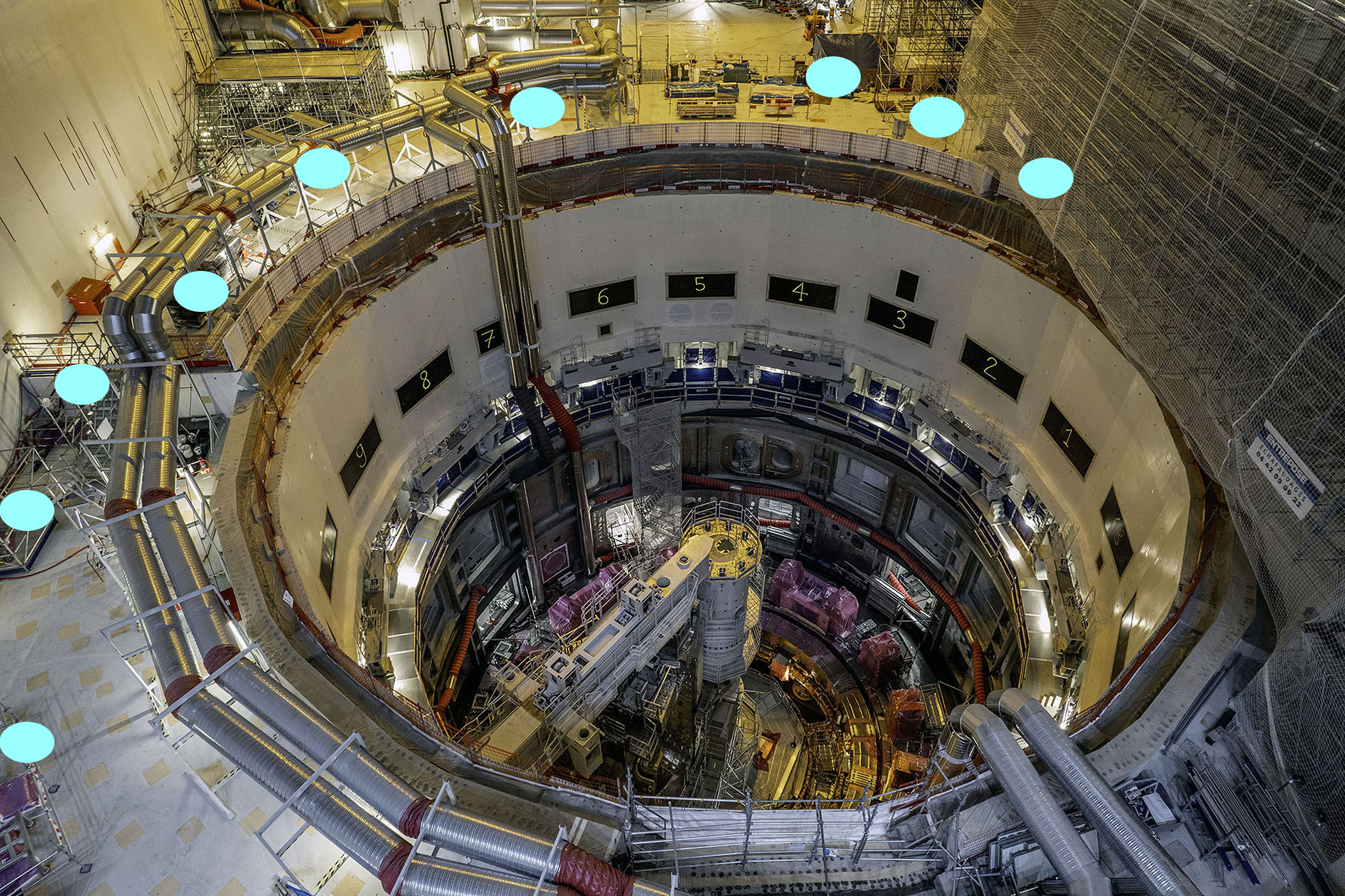
Backfilling penetrations
2024-12-19 - Some 4,600 "penetrations" (or openings) provide passage for pipes, cables, diagnostics and HVAC between the buildings and rooms of the Tokamak Complex. Each one needs to be carefully backfilled with concrete after cutouts have been reserved for equipment. Right now, the teams are working on openings on the rim of the tokamak pit (marked by blue ovals in the image).
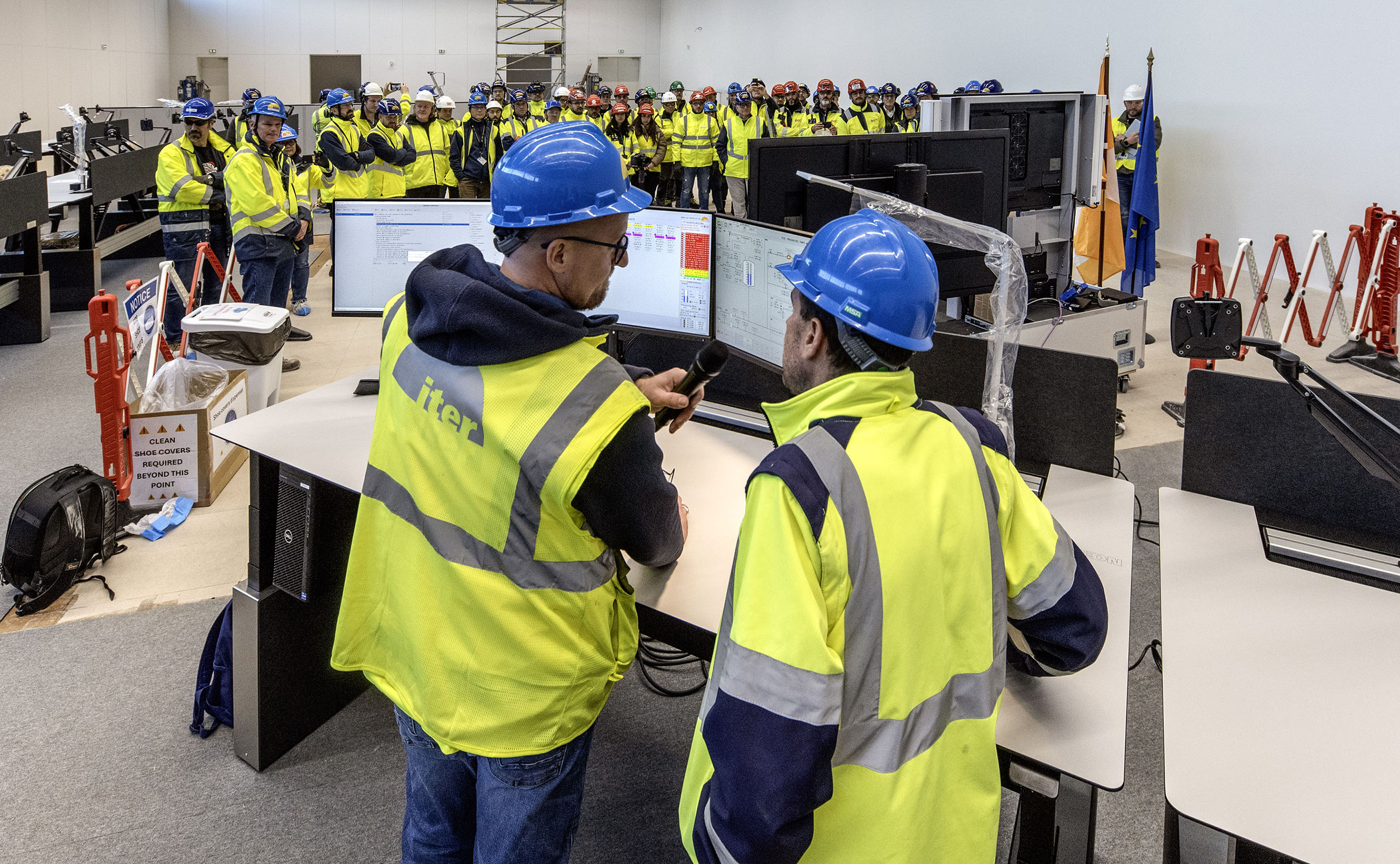
First command issued from control room
2024-12-19 - On Thursday 19 December, the ITER main control room issues its first CODAC command to a plant system, a decisive milestone towards tokamak operation. A powerful pump is activated, and water starts rushing into one of the cooling loops of the reactive power compensation installation.
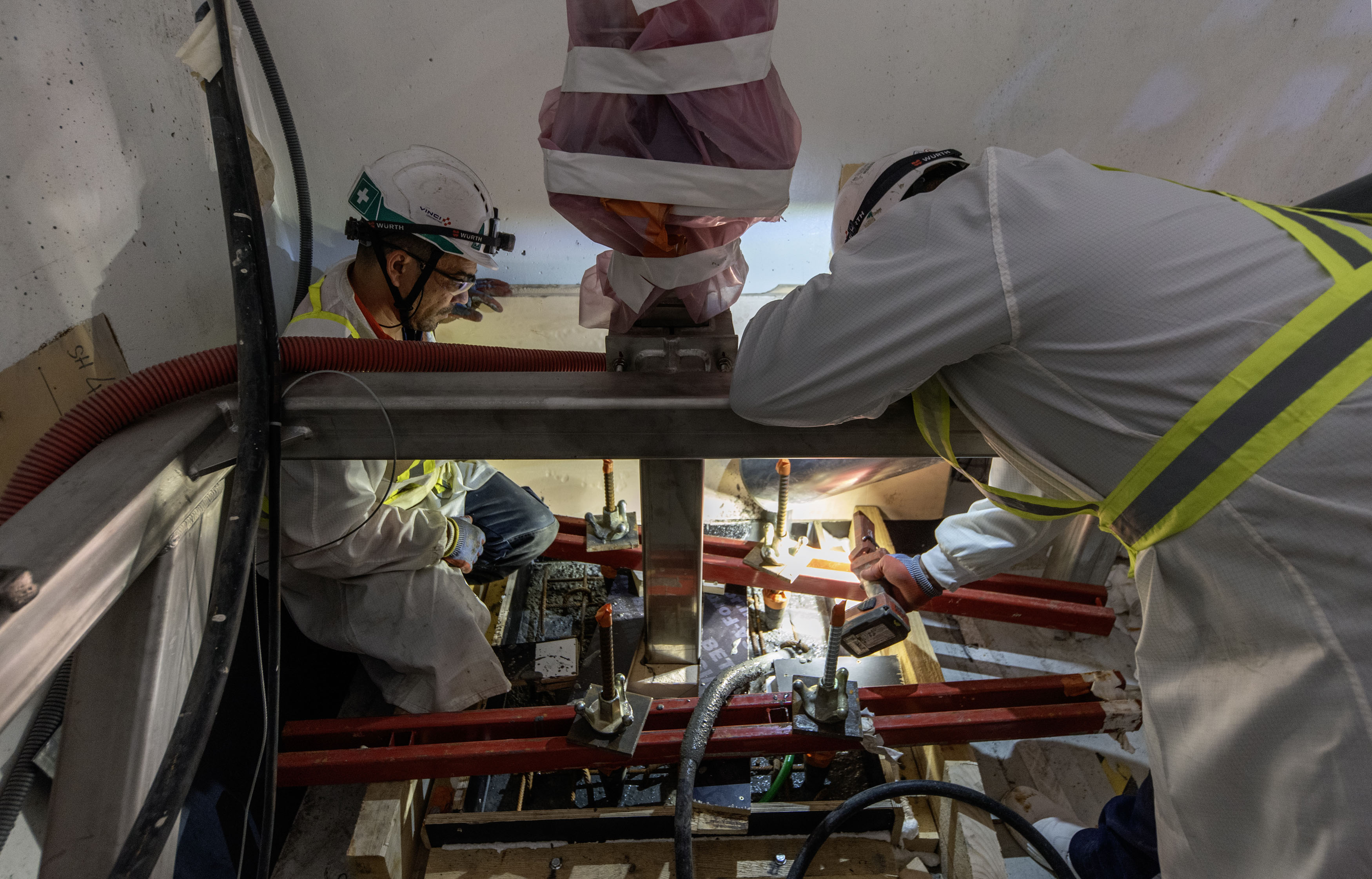
One week to cure the concrete
2024-12-16 - The opening is now filled and the high-density concrete is being vibrated so that it settles in a homogeneous manner through the rebar. "Curing” will take one week; full compressive strength will be obtained in 28 days.

Bringing concrete to difficult areas
2024-12-16 - For some backfilling operations, no truck, pump or piping can easily access the zone. In these cases, solutions have been devised to bring the required concrete to where it is needed through a carefully orchestrated series of transfers of concrete to skips. In this image, one of the small skips delivered by cargo lift is emptied into a larger one that will be lifted and positioned above the opening to be filled.

How do electronics react to magnetic fields?
2024-12-04 - Components installed in the ITER Tokamak Complex will be exposed to magnetic fields to varying degrees. To test the resistance of these components before operation, and to avoid the risk of dysfunction, samples of valves, circuit breakers, and electric and electromechanical components are being subjected to maximum expected field levels in a test facility on the ITER site that was designed and built in China. See "How do electronics react to magnetic fields?" in the ITER video gallery.
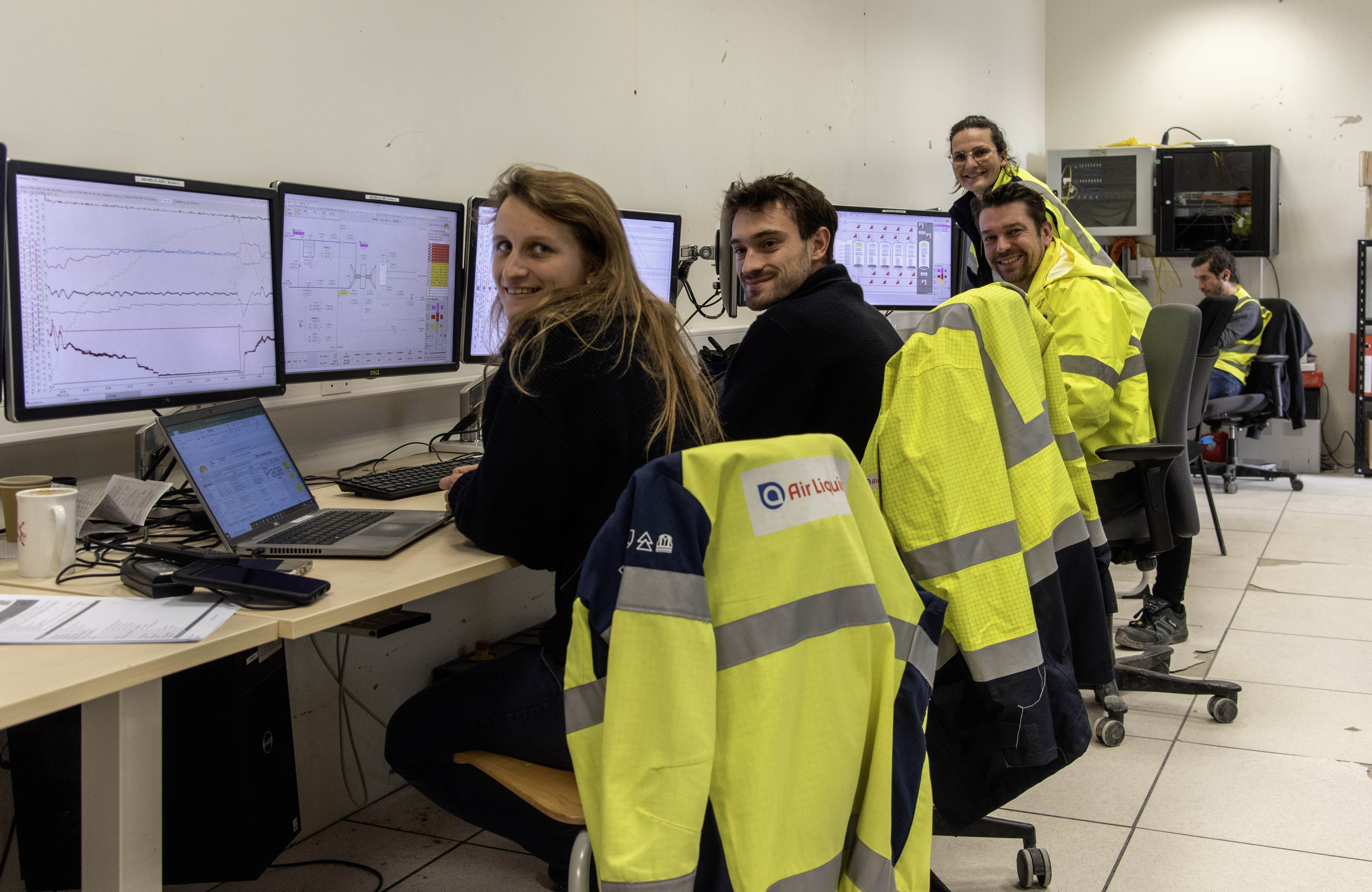
Temporary control room for the cryoplant
2024-12-02 - Pending the availability of the Control Building, cryoplant activities are managed from temporary control rooms staffed with ITER and Air Liquide staff.
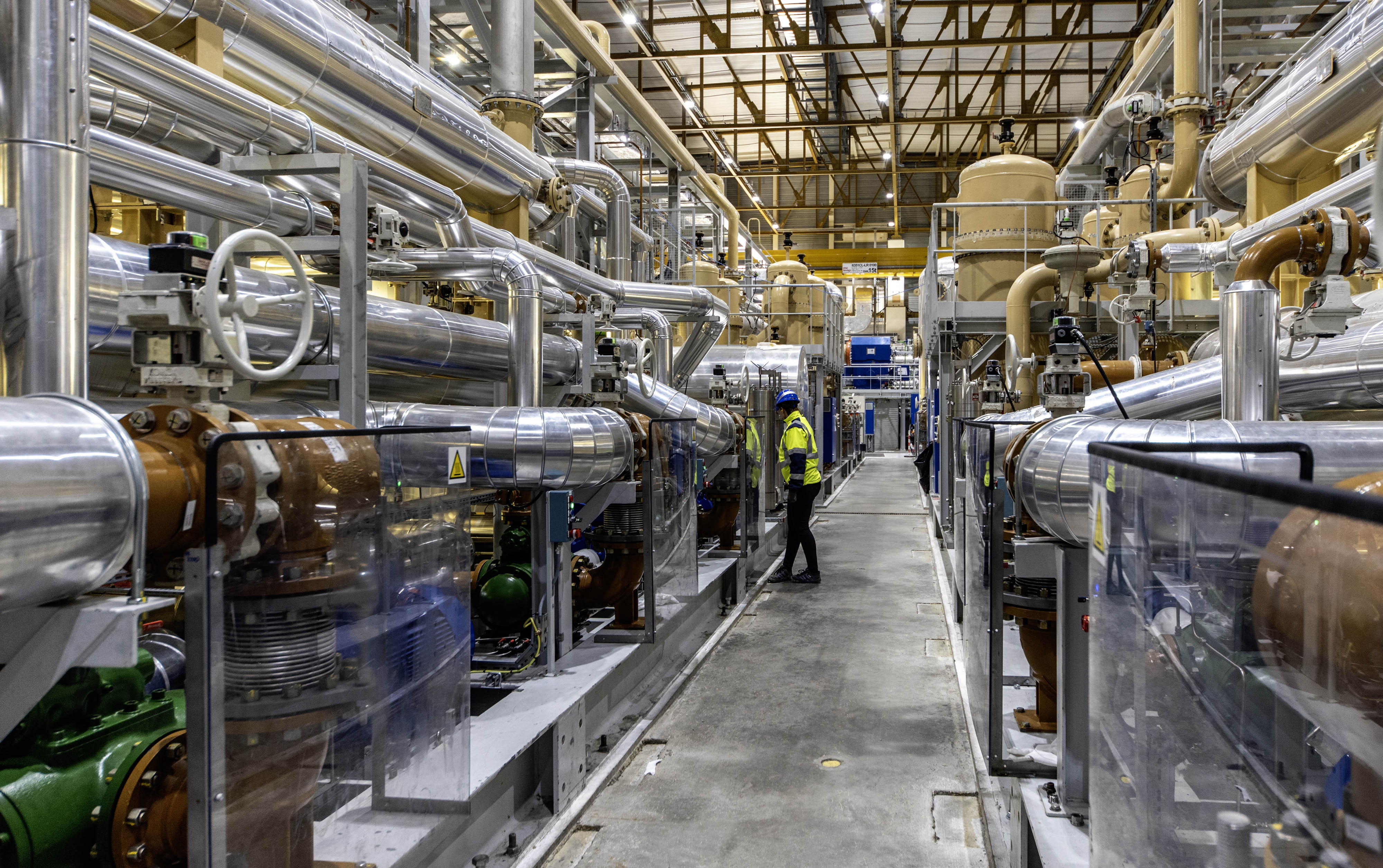
12 compressors at work in the cryoplant
2024-12-02 - Twelve megawatt class-compressors, out of a total 18, are presently at work in the ITER cryoplant. Liquid helium at 4 K (minus 269 °C) is needed for the tokamak’s magnetic system and cryopumps, but also for the planned cold test facility, whose commissioning will begin in July next year.
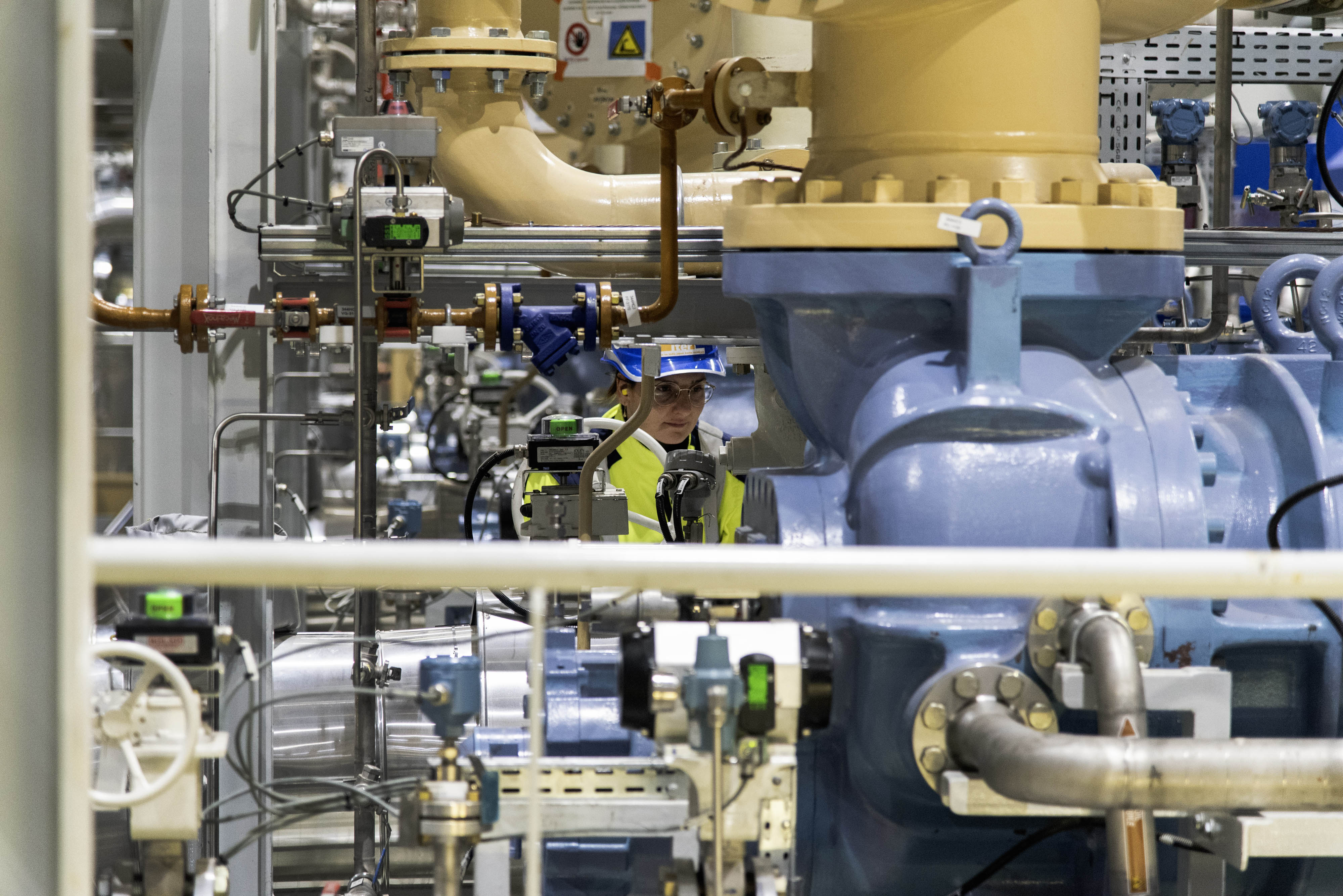
Cryoplant tests underway
2024-12-02 - The ongoing tests mimic the variations of the loads that the tokamak’s magnetic system will exert on the liquid helium flux. "This is quite unusual in the world of large cryogenic facilities, where loads are generally stable,” explains Marie Cursan, a project engineer in the Cryogenic System Project.
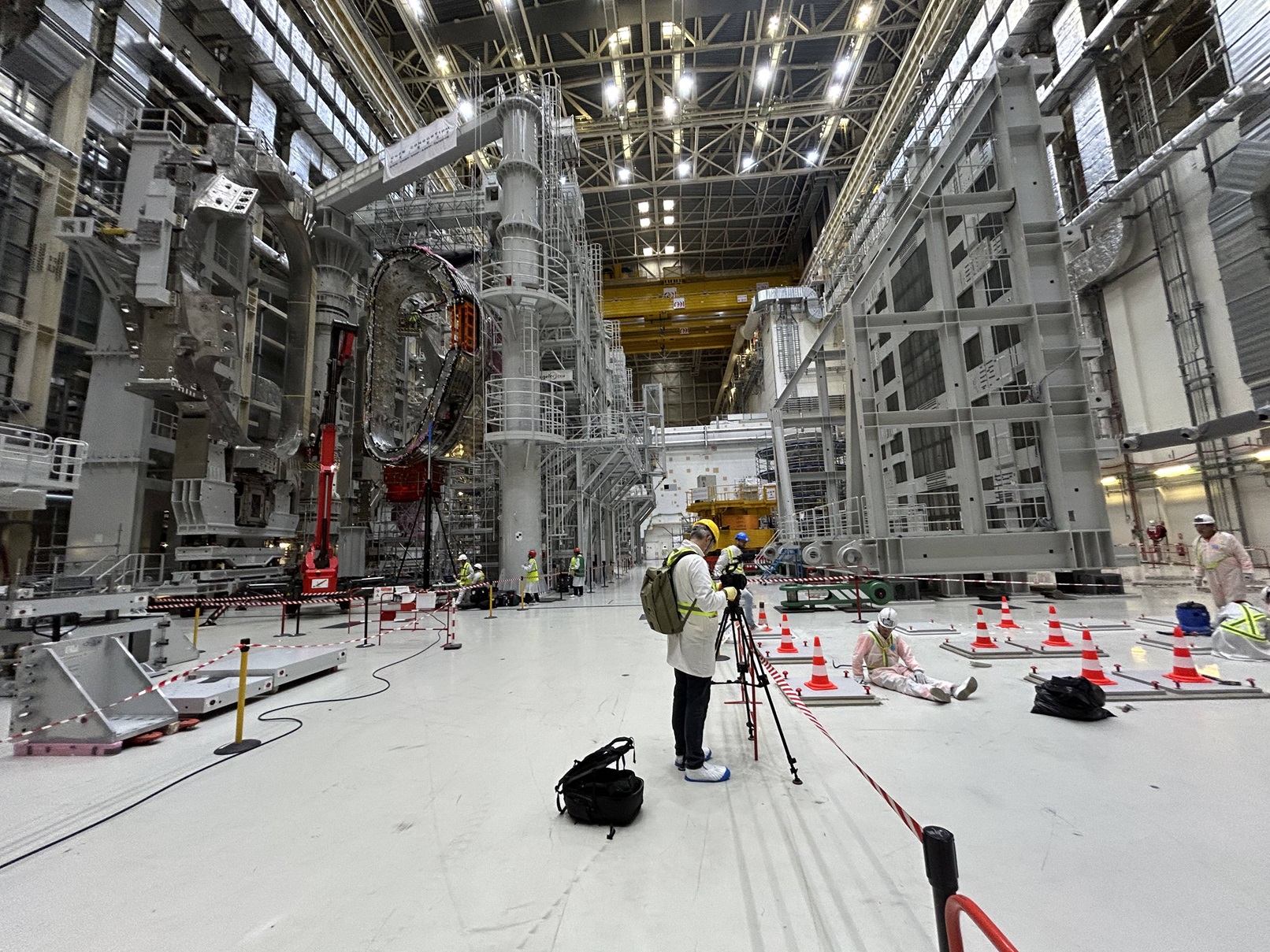
Preparing to receive a second upending tool
2024-11-25 - Next to the first upending tool (seen standing on end, at right) reception pads are being prepared for the arrival of a second tool early next year. Two tools will save time in vacuum vessel assembly.
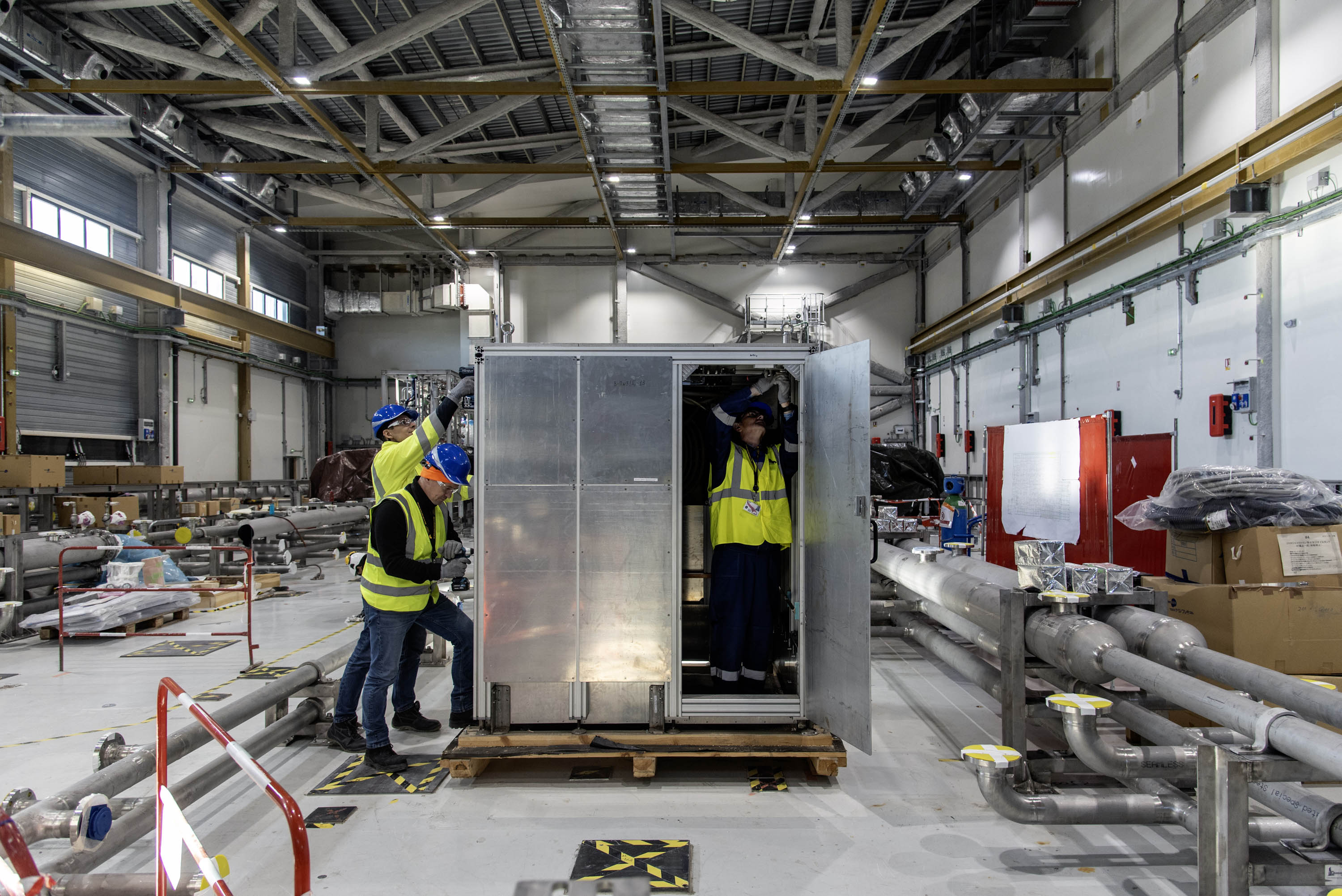
First gyrotron sets
2024-11-19 - On the south side of the Radiofrequency Building, a small team of technicians from GYCOM, the Russian gyrotron manufacturer, is at work installing cubicles and preparing the support structures and ancillaries for the first gyrotron set to be installed in the coming months.
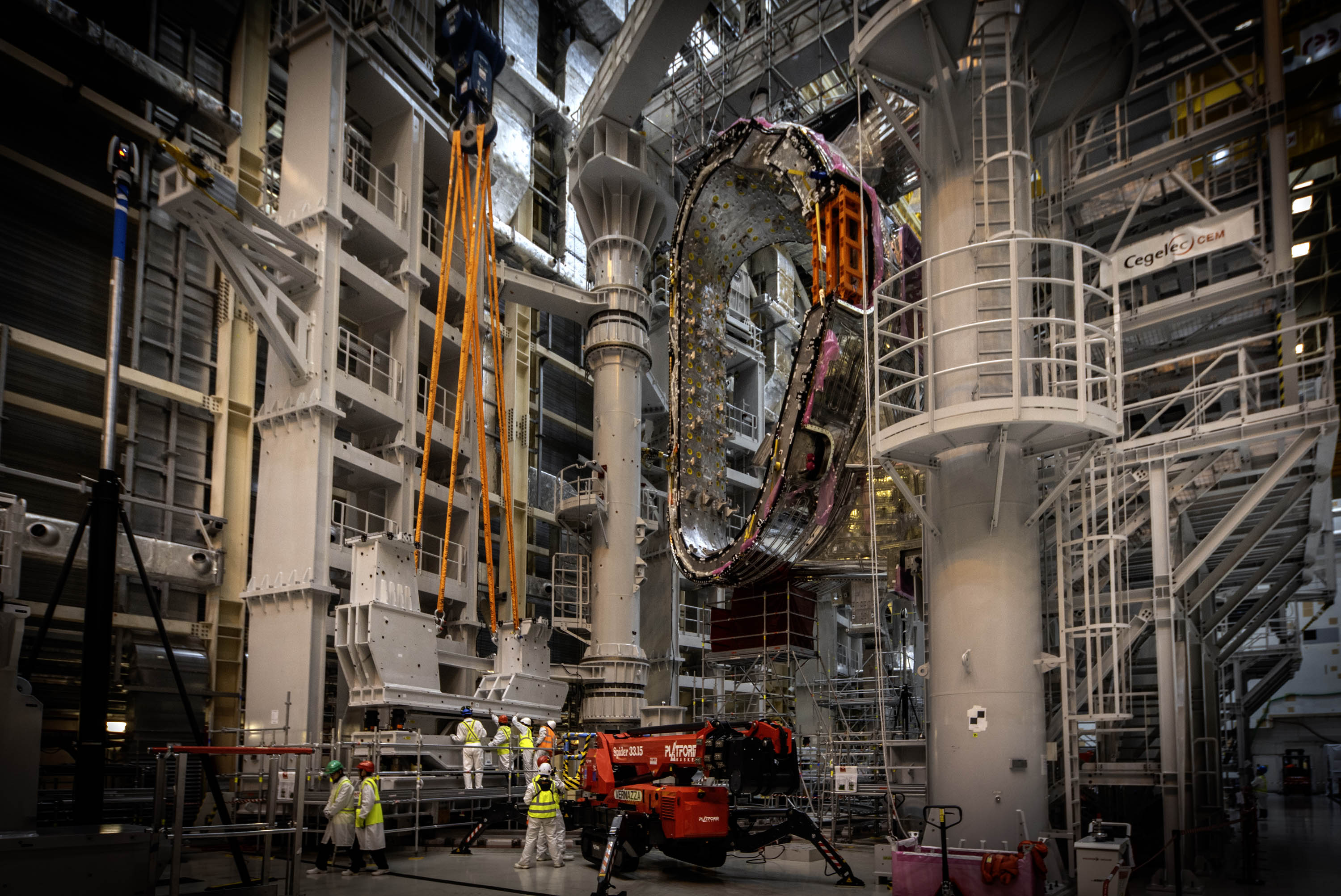
Sector 7: thermal shield in place
2024-11-19 - With thermal shield panels already in place around sector #7, workers are installing the lower adapters on the wings of the tool for the pair of toroidal field coils that will be rotated inward towards the sector.
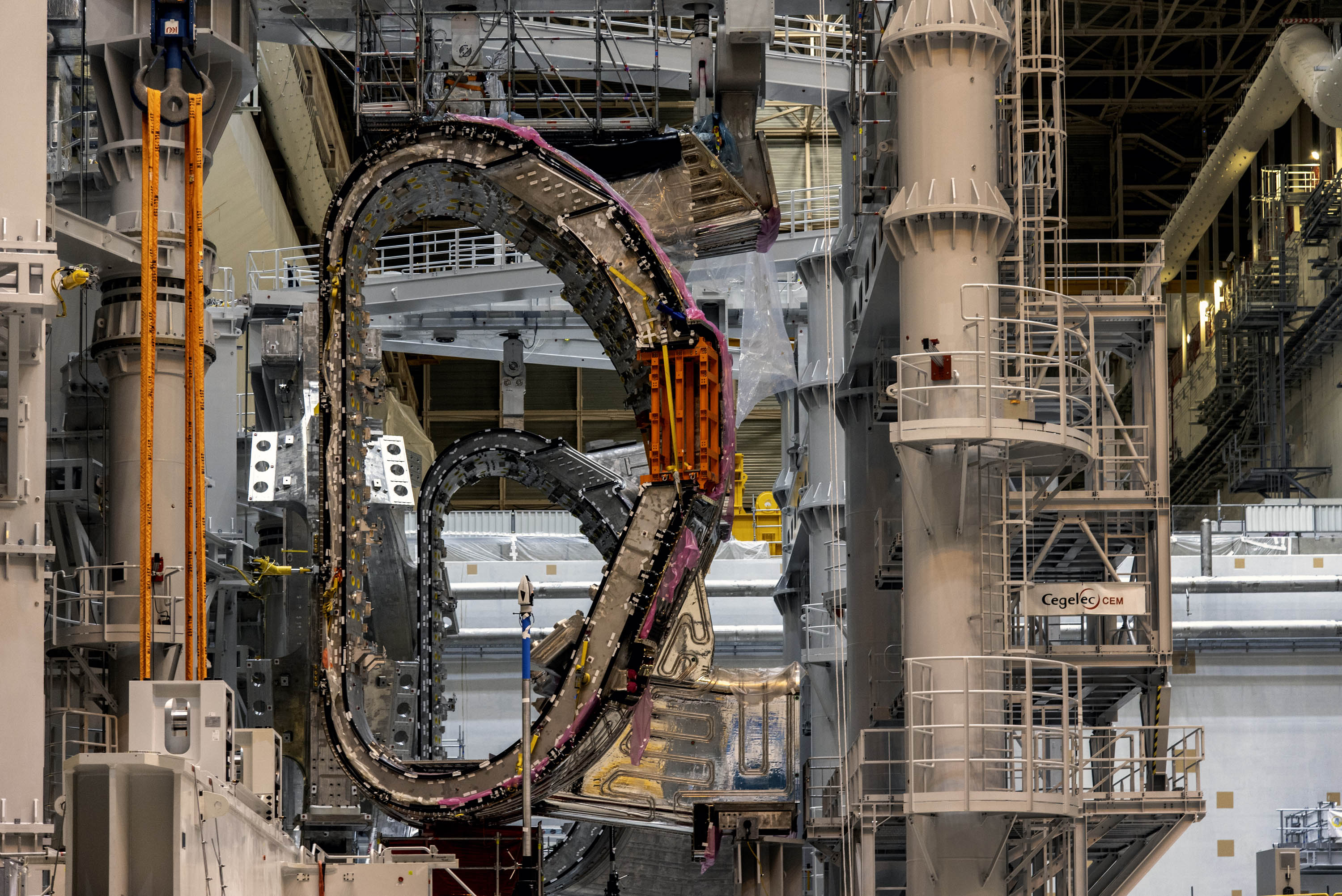
With experience, the process will be faster
2024-11-18 - The assembly teams have already benefitted from the assembly, and disassembly, of the vacuum vessel #6 which had to be removed from the tokamak pit for repair. That experience, as well as improvements made in the overhead cranes, the process workflow, and contract management, should result in the acceleration of the sub-assembly process for each sector by a factor of 2.5 or 3.
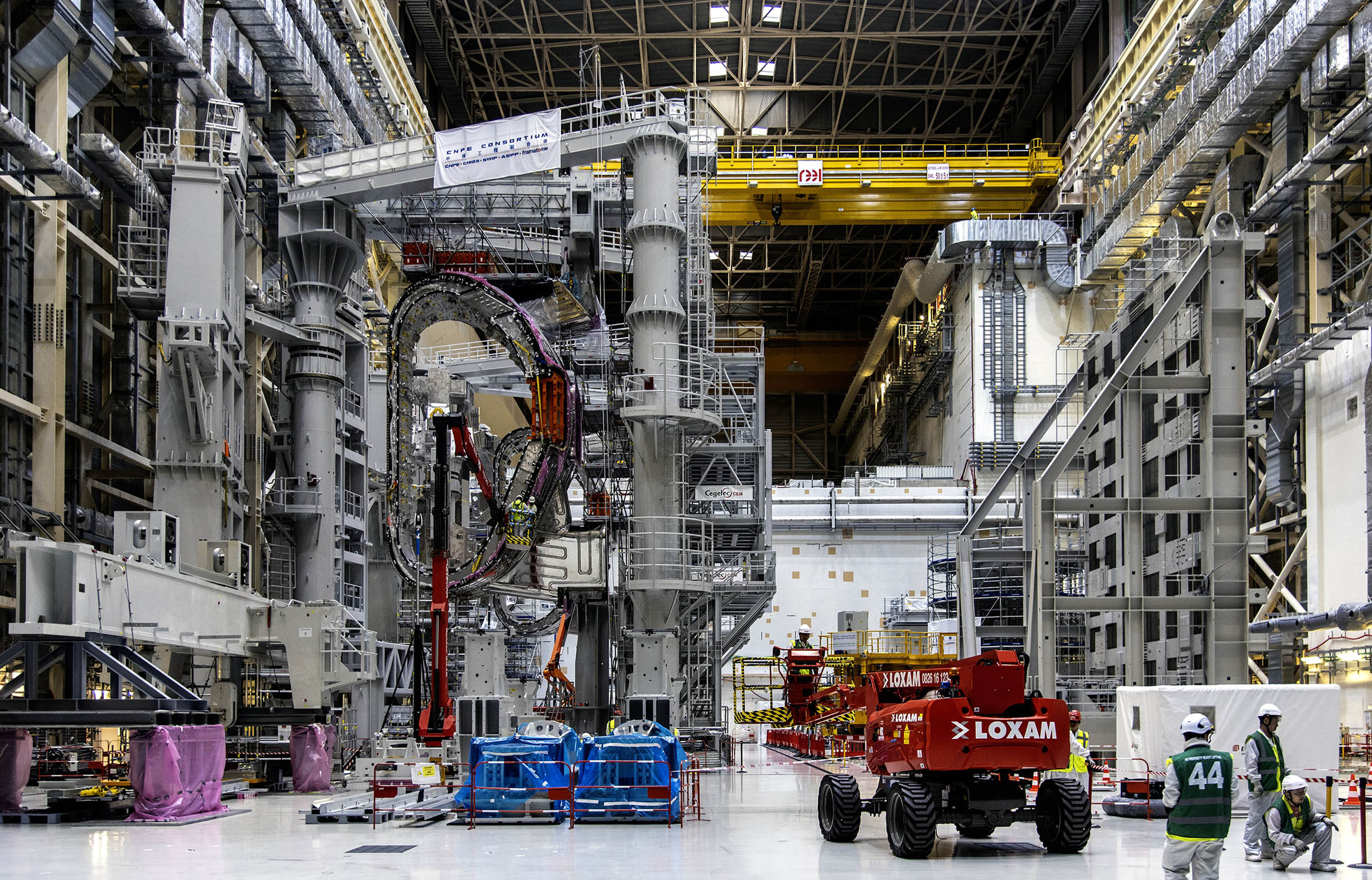
Two sectors in sub-assembly tooling
2024-11-18 - Two giant sectors of the ITER vacuum vessel are suspended vertically in tooling. One has been fully repaired and is being re-assembled into a "sector module" (with thermal shield panels and two D-shaped superconducting magnets). The other is in the last stage of repair.

Last stage of repair for sector #6
2024-11-12 - Sector module #6, which was extracted from the tokamak pit in July 2023, is presently in the last stages of repair, with one side already completed and the other to be finalized in the coming days.
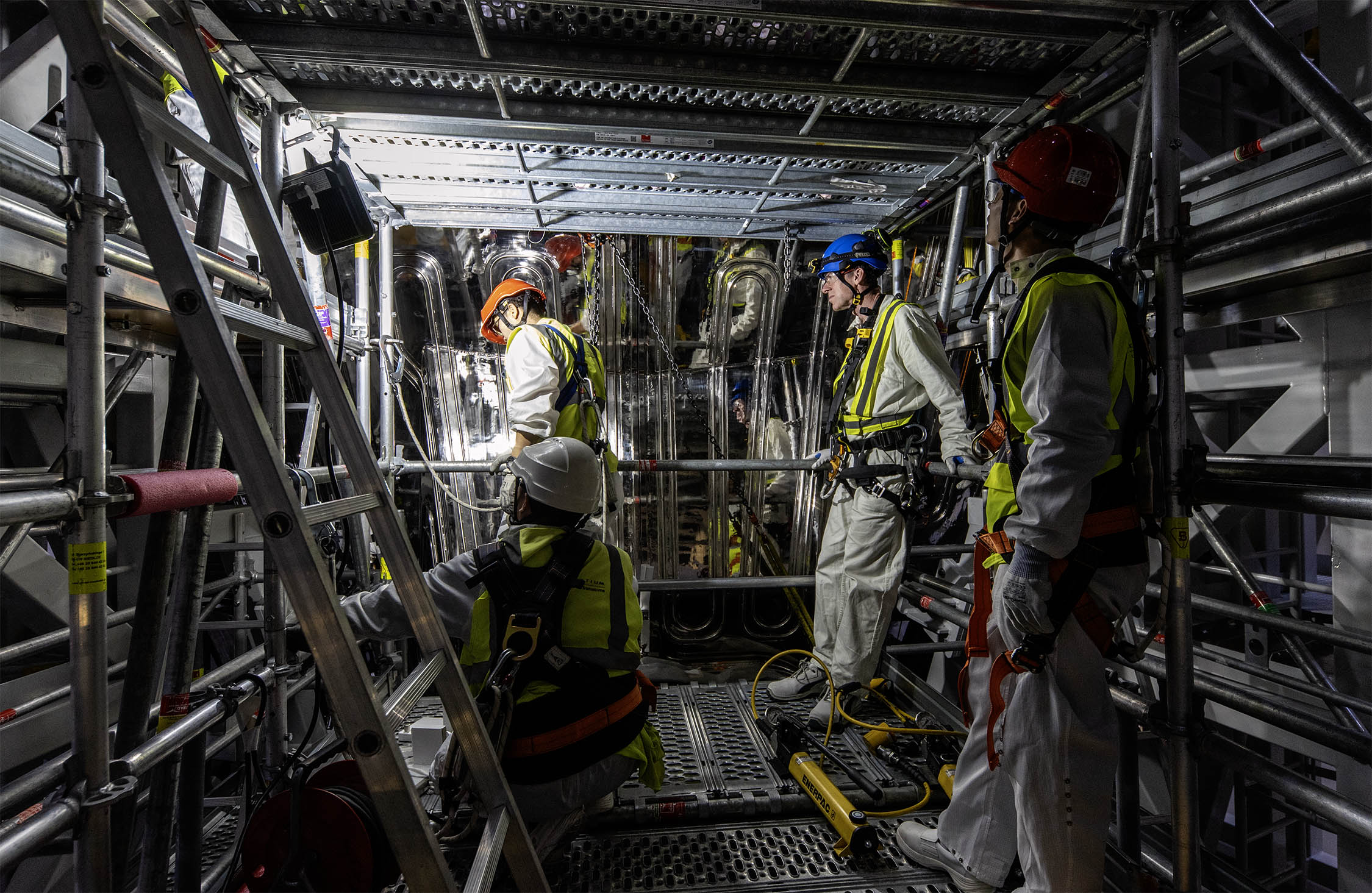
Sector 7 will be the first to re-enter the pit
2024-11-12 - Assembly operations on sector module #7 began in September 2024 and should be completed in the first quarter of 2025—a seven-and-a-half month process compared to the 18 months spent on the initial assembly of sector module #6.
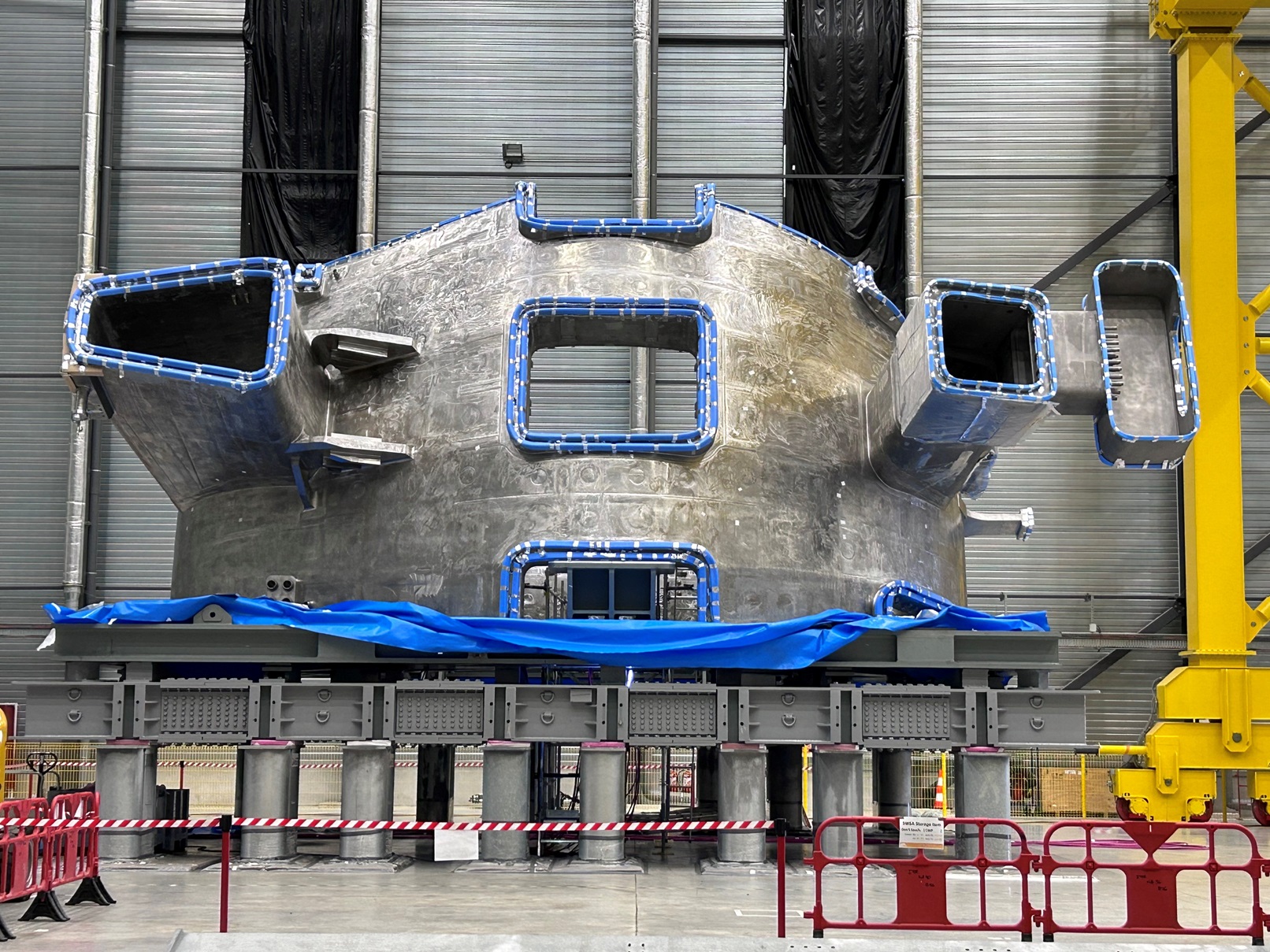
Sector 5, unveiled
2024-11-08 - The first vacuum vessel sector delivered by Europe, sector 5, arrived two weeks ago. Since then, it has been settled into a space in the former Cryostat Workshop on its transport frame and unpacked.
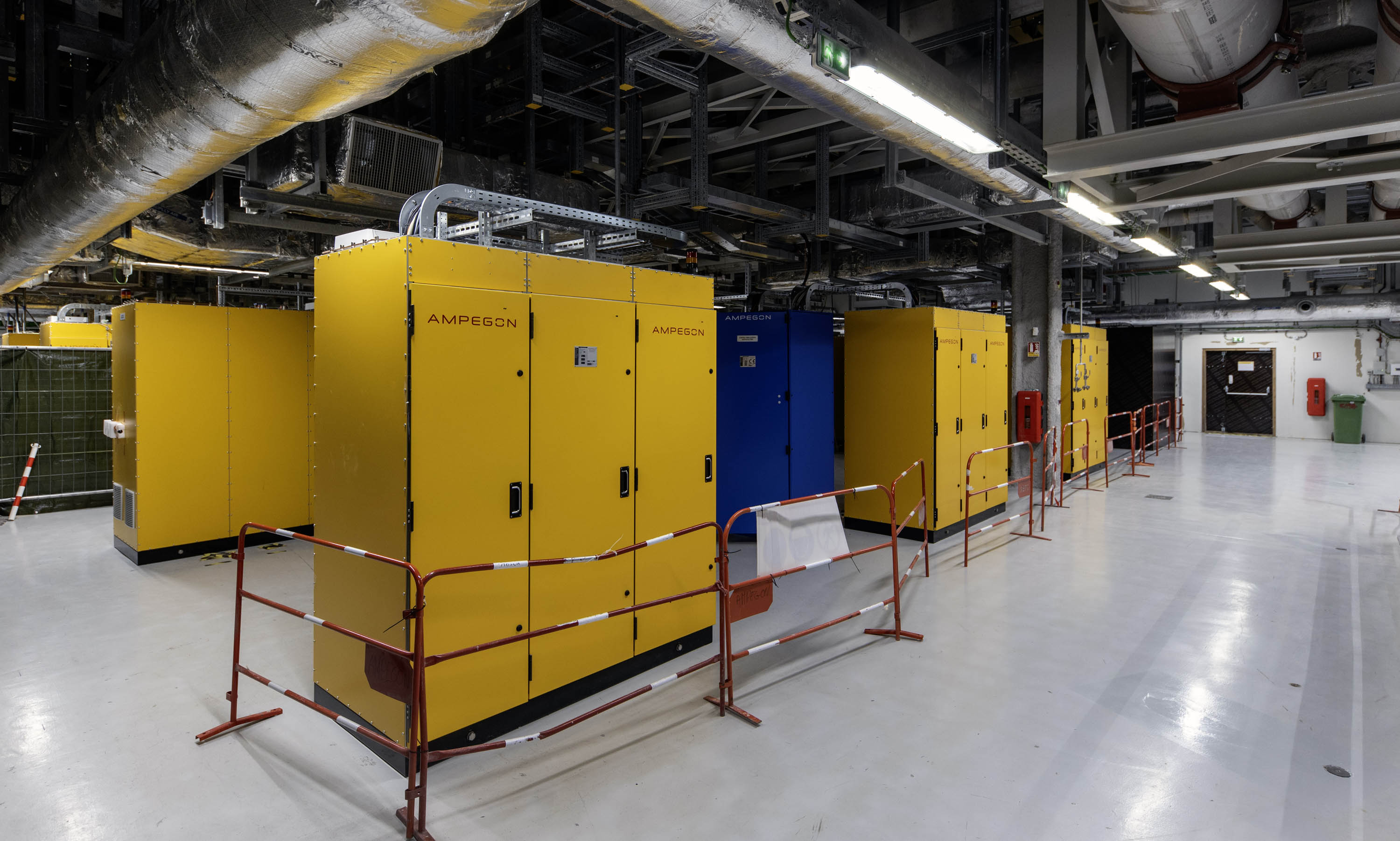
Radiofrequency Building: adding equipment
2024-11-04 - Inside the Radiofrequency Building, the main high voltage power supplies (delivered by Europe) occupy a large portion of the first level. The first wave-generating gyrotrons will be added soon.
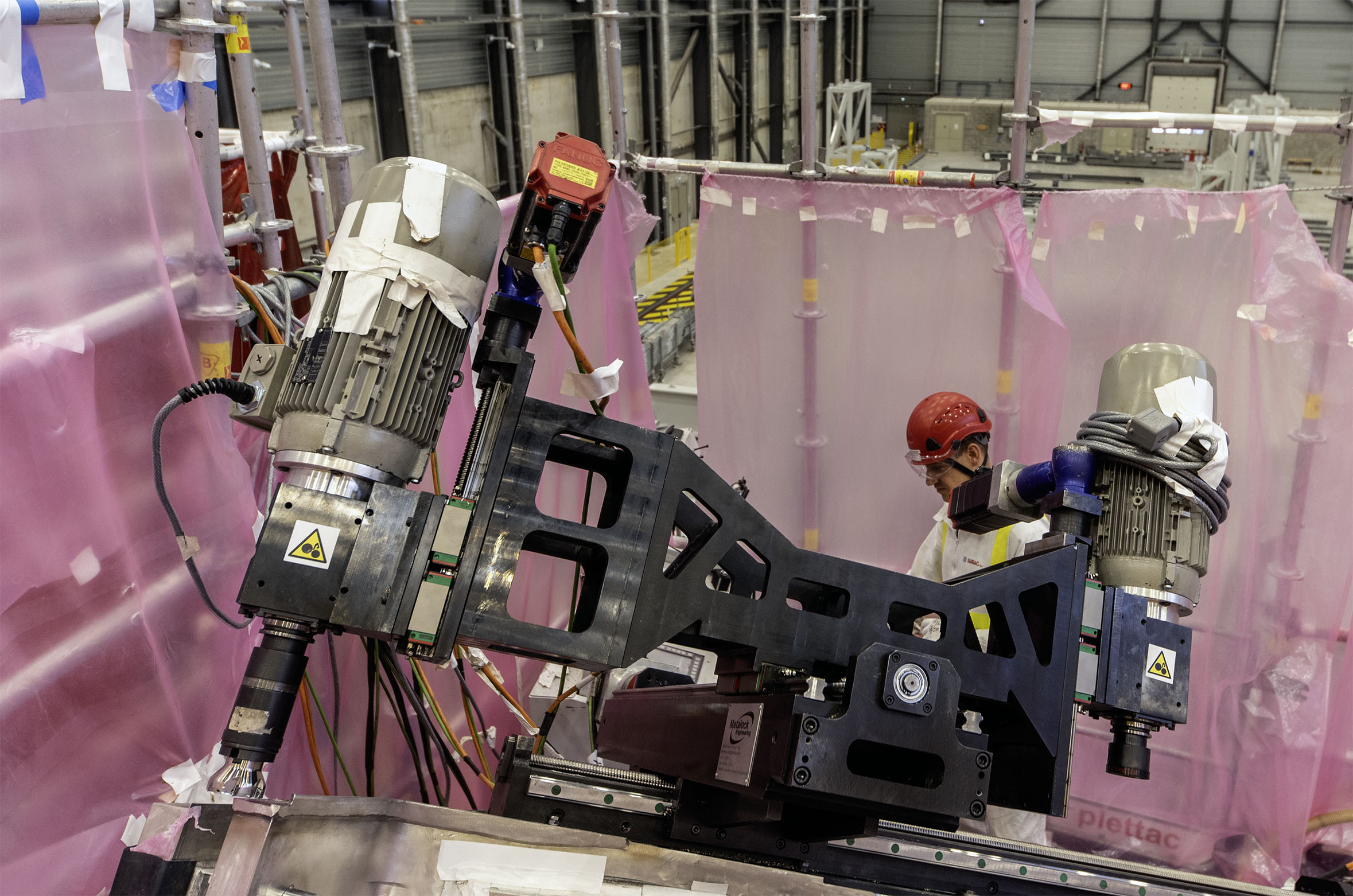
Automatic welding robot at work on sector 8
2024-10-28 - Following close to three months of metal build-up, machining has started on the bevels of vacuum vessel sector #8. Two machining tools, driven by computer numerical control are presently at work. Three others are scheduled to join in the coming weeks.
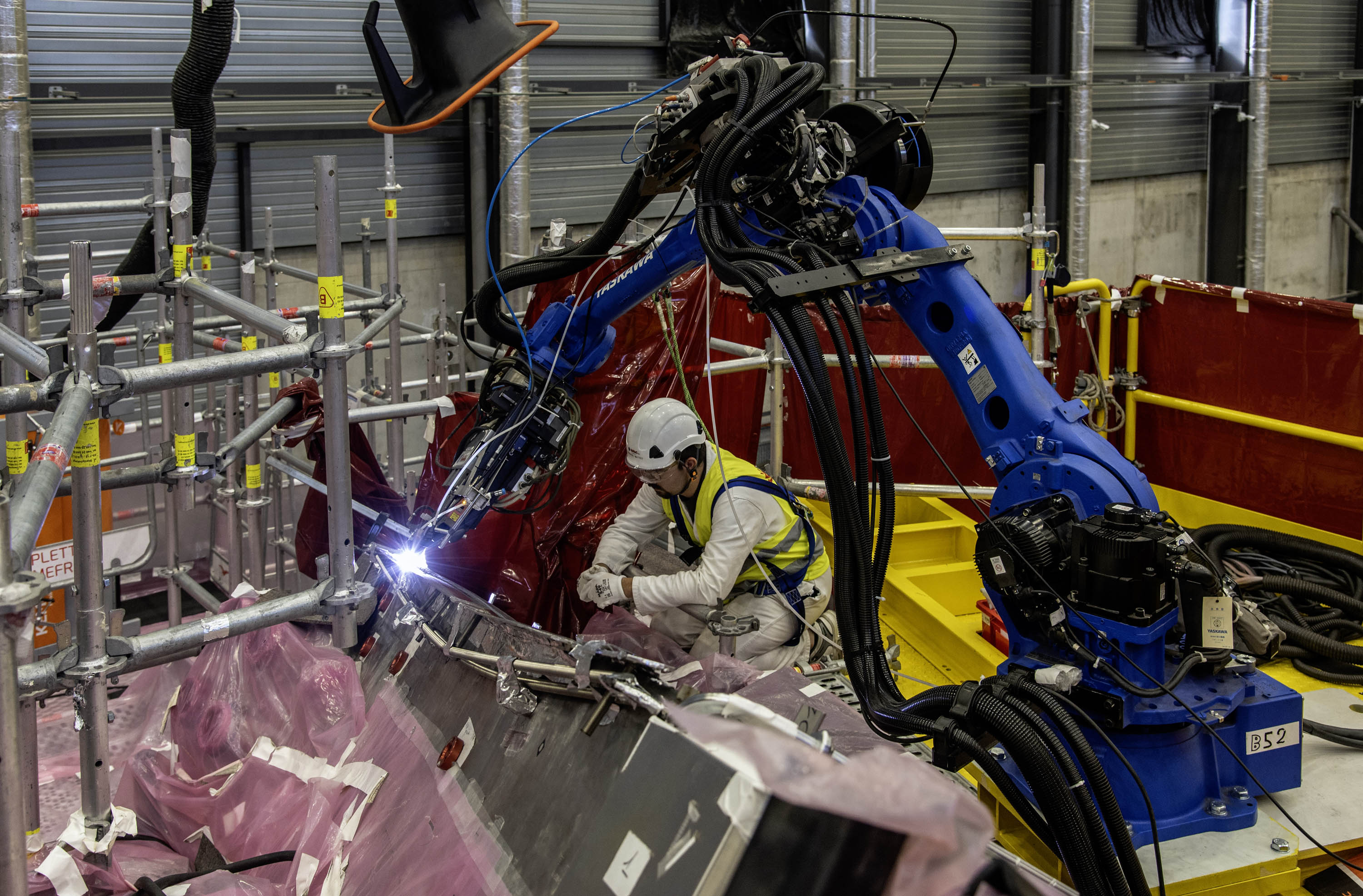
First the robots, then the hands
2024-10-28 - Adapted and equipped for the specific task of metal filling and build-up, the welding robot has now completed its task on one side of vacuum vessel sector #8. The mechanized process, however, represents only 25 percent of the total metal build-up required. For reasons of accessibility and flexibility, the remaining 75 percent must be done manually.
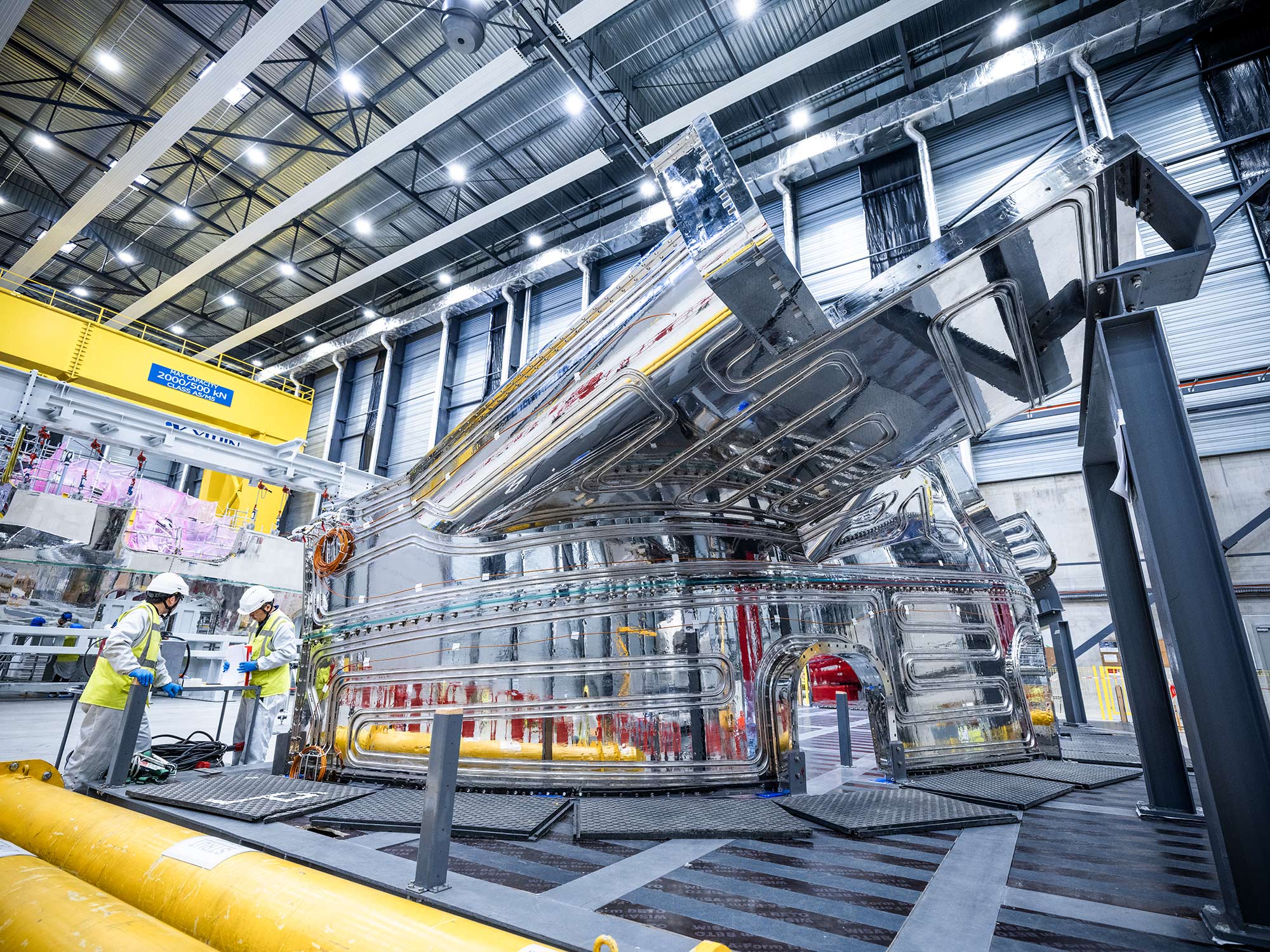
To "jacket" a sector
2024-10-25 - This vacuum vessel thermal shield with a surface of polished stainless steel will perfectly "jacket" a vacuum vessel sector. The piping visible in this photo on the component's surface is new—part of repairs undertaken this year on all thermal shield elements. (Low-res photo courtesy of Jan Hosan, https://www.hosan.eu/portfolio/iter/.)
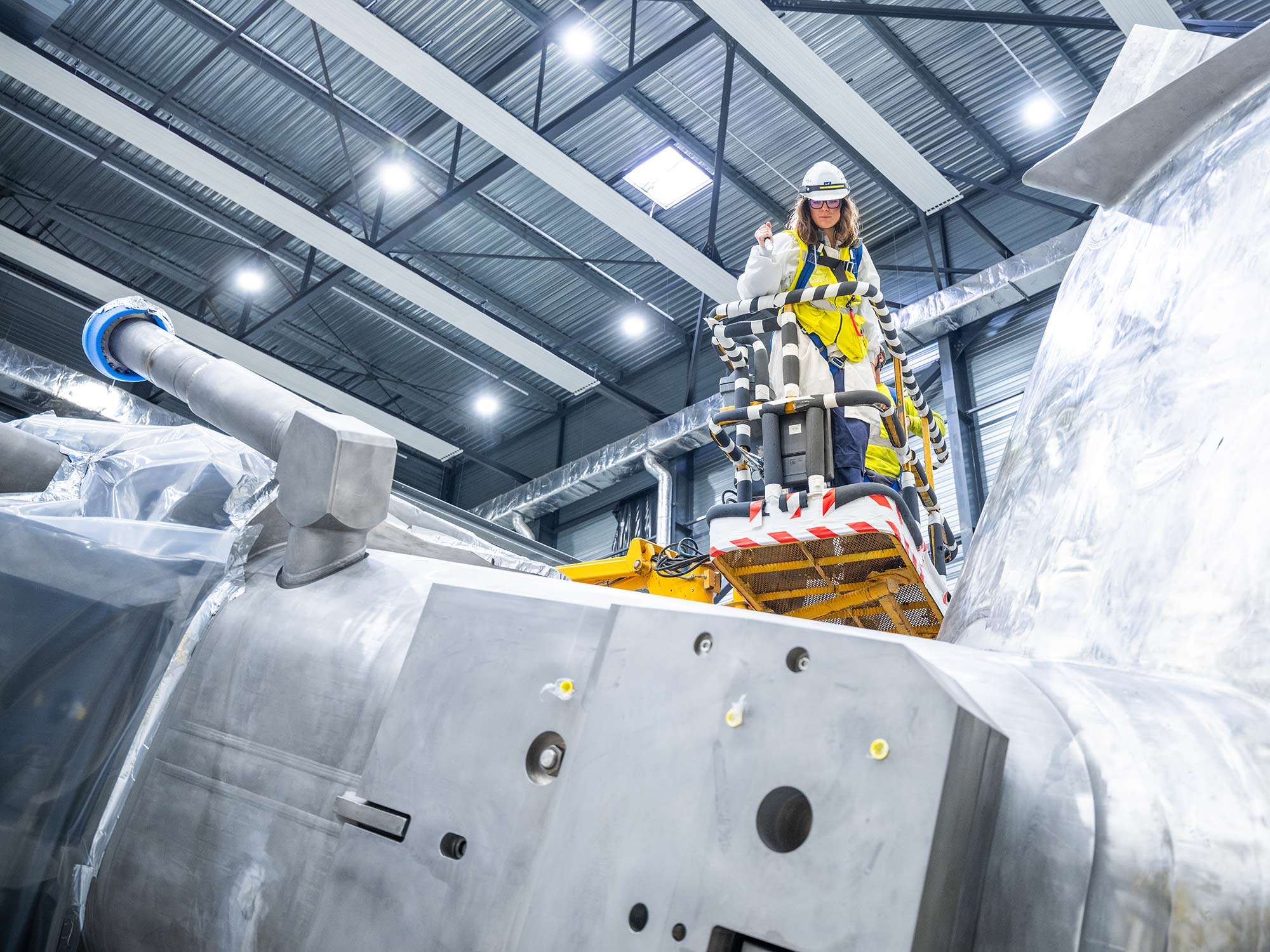
Inspection
2024-10-25 - This 440-tonne vacuum vessel sector lies on its side in the former Cryostat Workshop. On delivery, ITER teams take over inspection and preservation activities. (Low-res photo courtesy of Jan Hosan, https://www.hosan.eu/portfolio/iter/.)
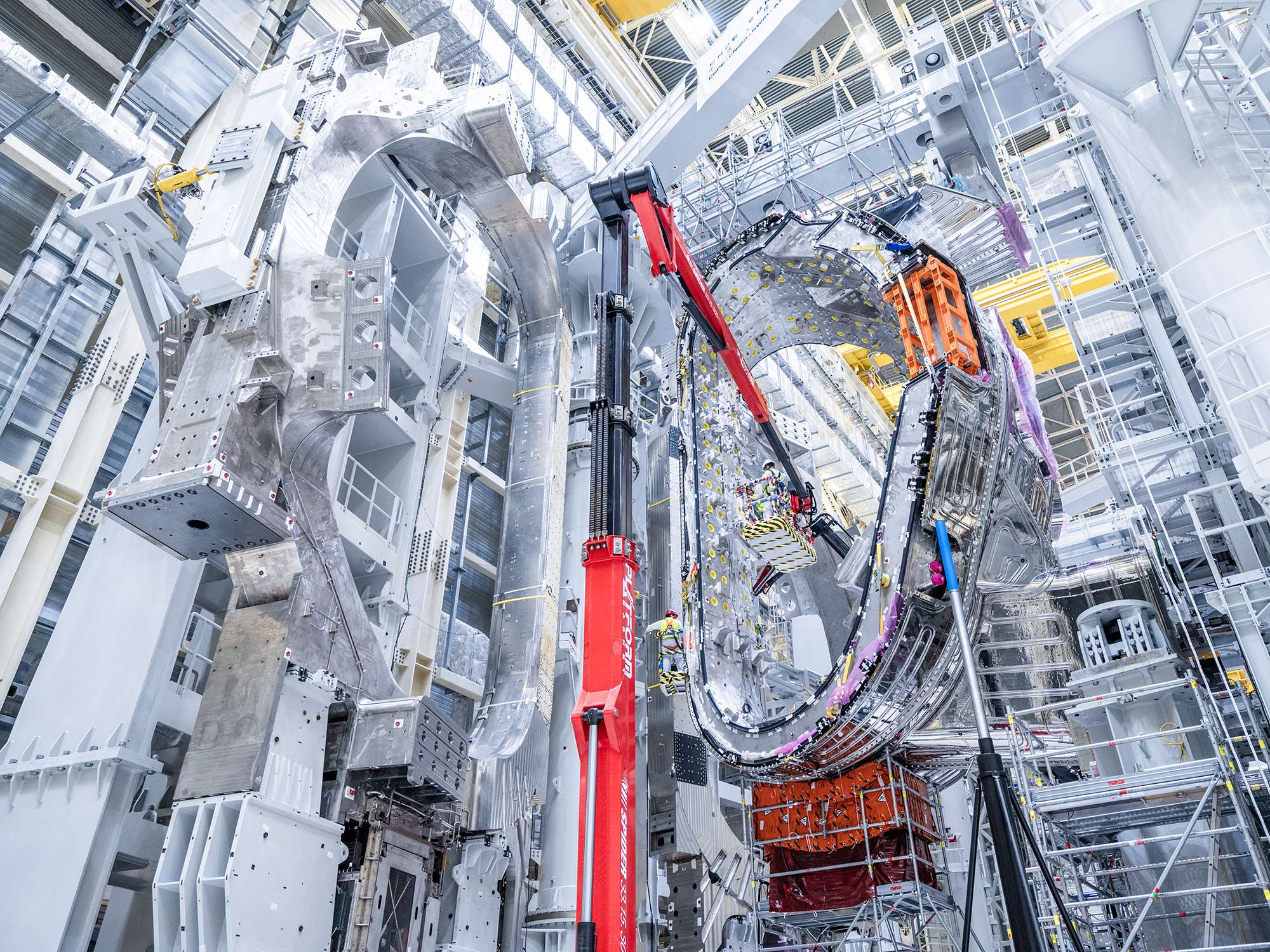
About to rotate
2024-10-25 - The toroidal field coil and its superstructure (left) is about to be rotated inward towards the sector. Actuators at the bottom of the rotating wing allow adjustments to be made at the millimetre level to ensure alignnment. (Low-res photo courtesy of Jan Hosan, https://www.hosan.eu/portfolio/iter/.)
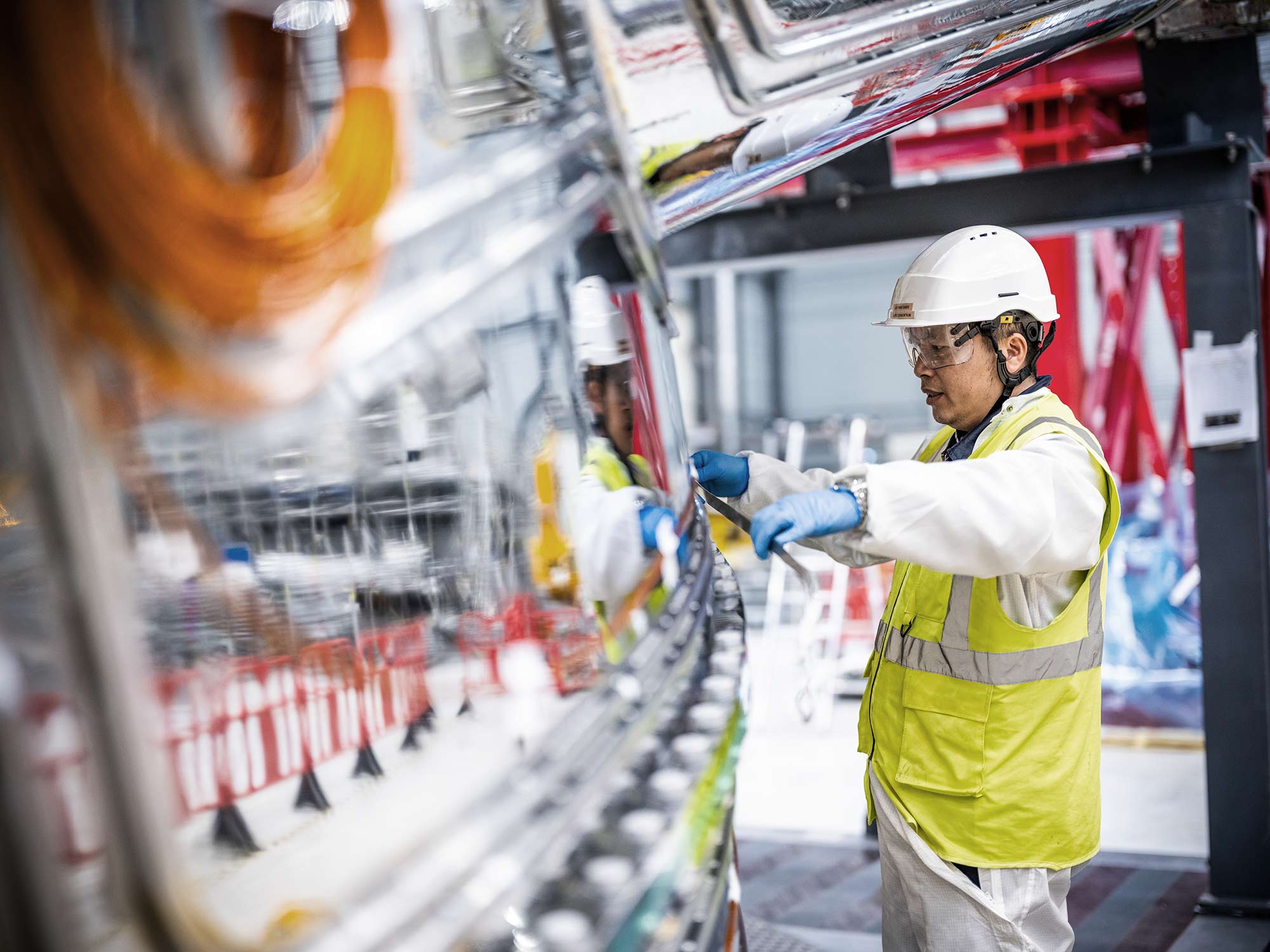
Last measurements
2024-10-25 - A few last measurements are made by hand before the thermal shield sector is transported to the Assembly Hall. (Low-res photo courtesy of Jan Hosan, https://www.hosan.eu/portfolio/iter/.)
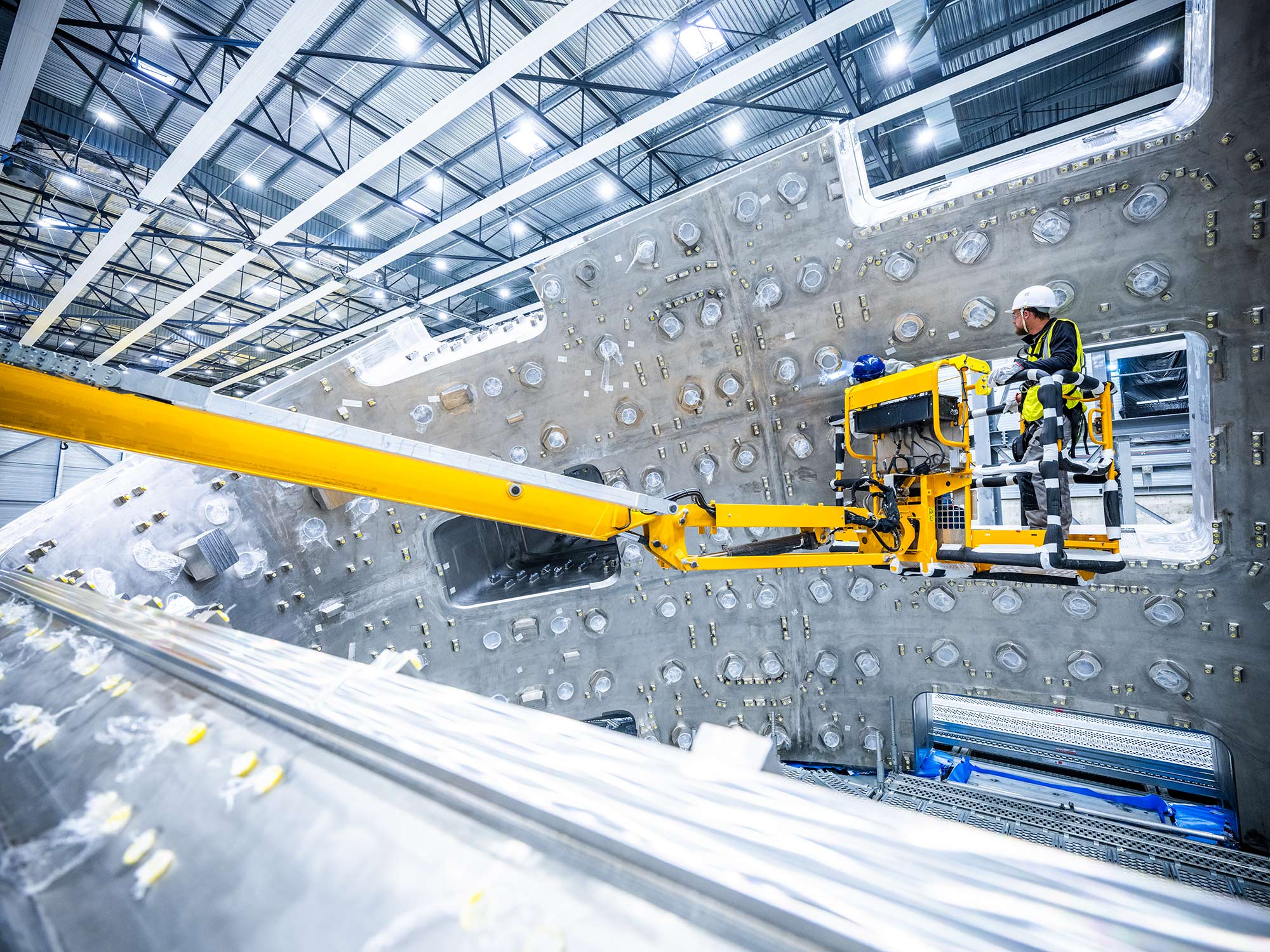
Inner wall
2024-10-25 - The inner wall of the vacuum vessel is equipped with cartridges in sets of four. Each set is designed to receive the bolts of a blanket shield block. (Low-res photo courtesy of Jan Hosan, https://www.hosan.eu/portfolio/iter/.)
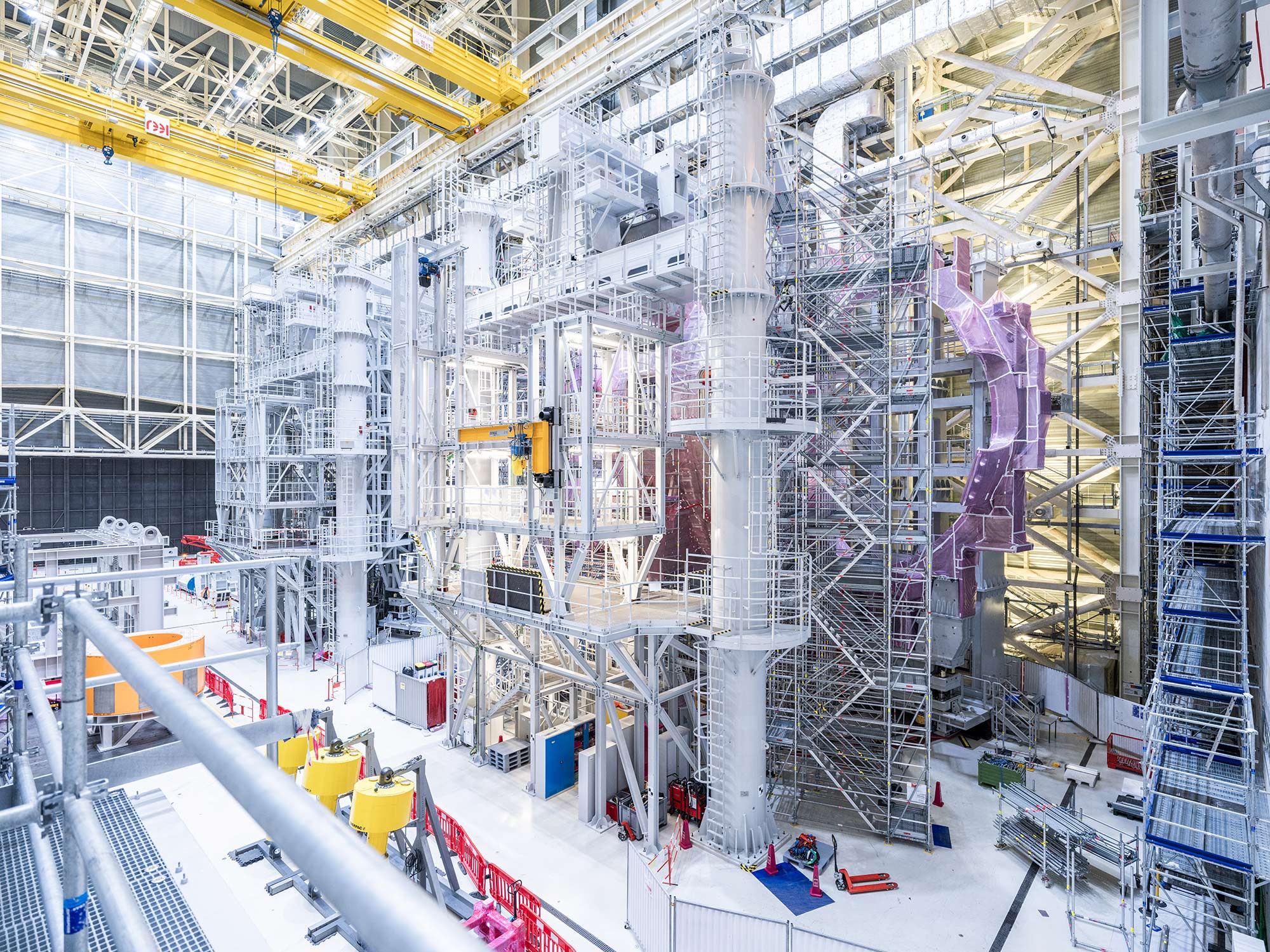
A jungle of scaffolding
2024-10-25 - Behind the scaffolding, workers from the CNPE Consortium are creating sector modules 6 and 7 (assembly of the vacuum vessel sectors with toroidal field coils and vacuum vessel thermal shielding). (Low-res photo courtesy of Jan Hosan, https://www.hosan.eu/portfolio/iter/.)
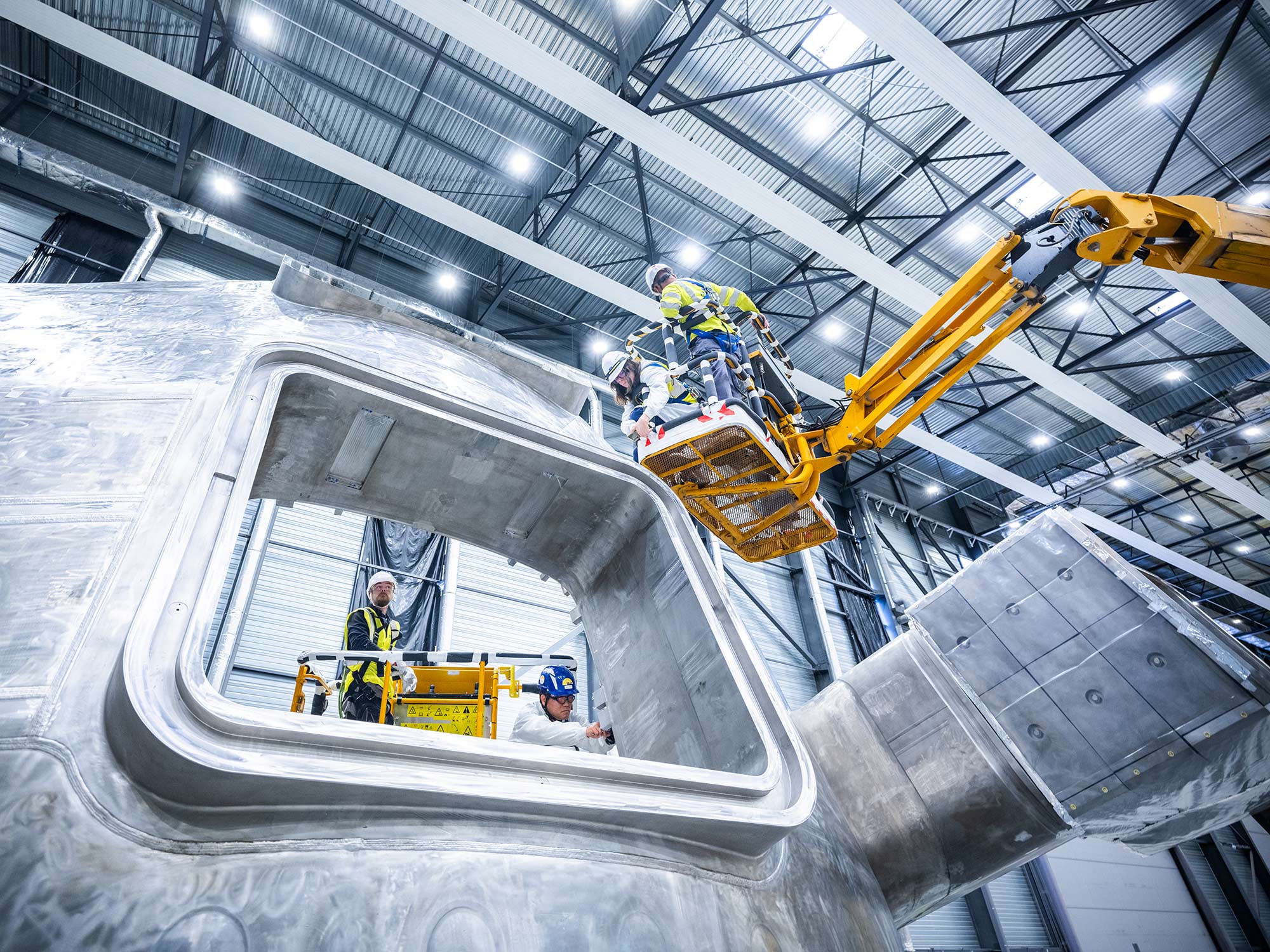
Through the window
2024-10-25 - A vacuum vessel sector—one-ninth of the torus-shaped plasma chamber—comes equipped with ports and port stubs. These are the openings through which equipment for fuelling, heating, diagnostics and disruption mitigation can be installed. (Low-res photo courtesy of Jan Hosan, https://www.hosan.eu/portfolio/iter/.)
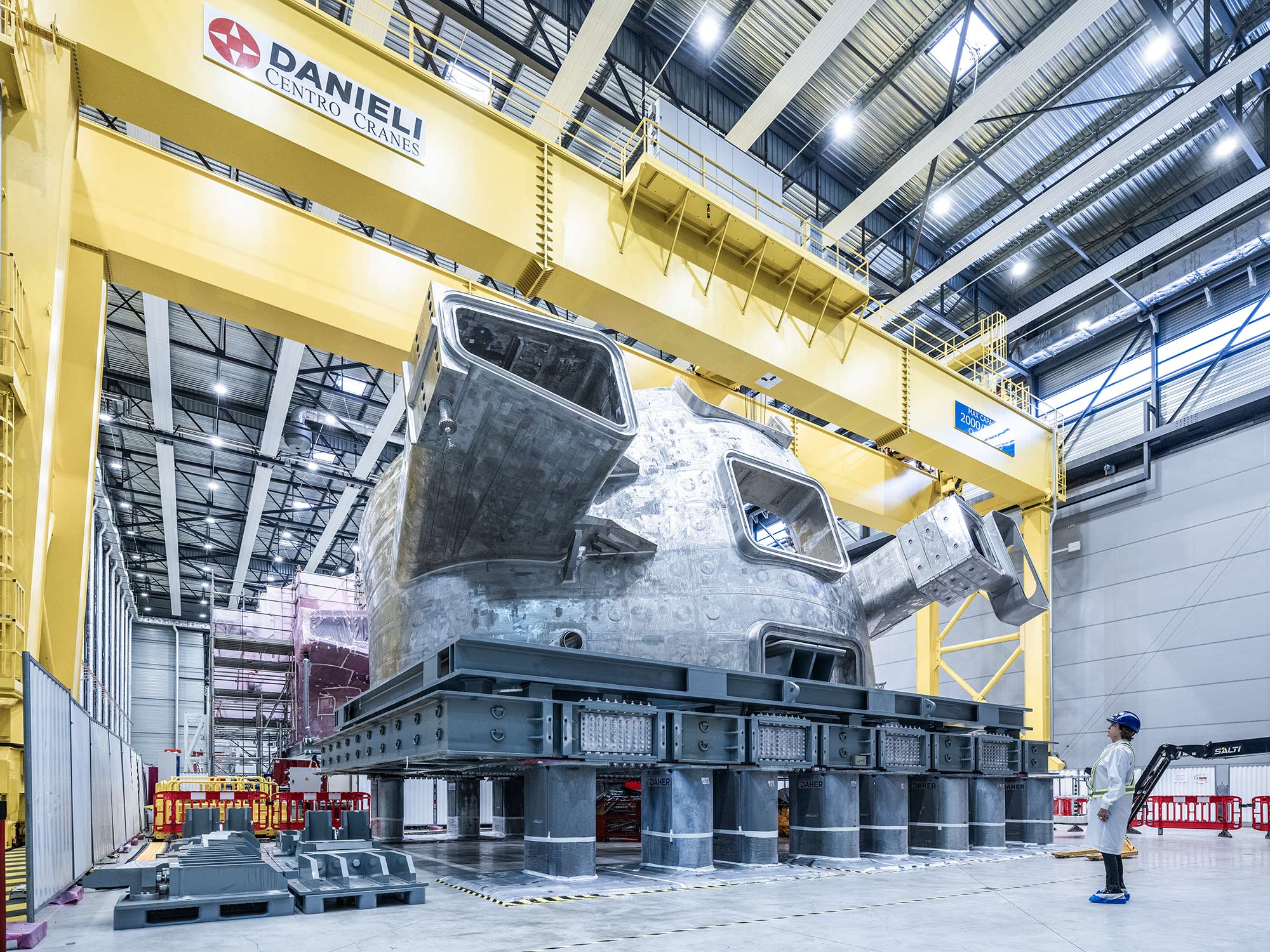
Parking lot
2024-10-25 - Behind one vacuum vessel sector there is another waiting to be unwrapped. These heavy components are moved, on their platforms, by self-propelled modular transporters (SPMTs). (Low-res photo courtesy of Jan Hosan, https://www.hosan.eu/portfolio/iter/.)
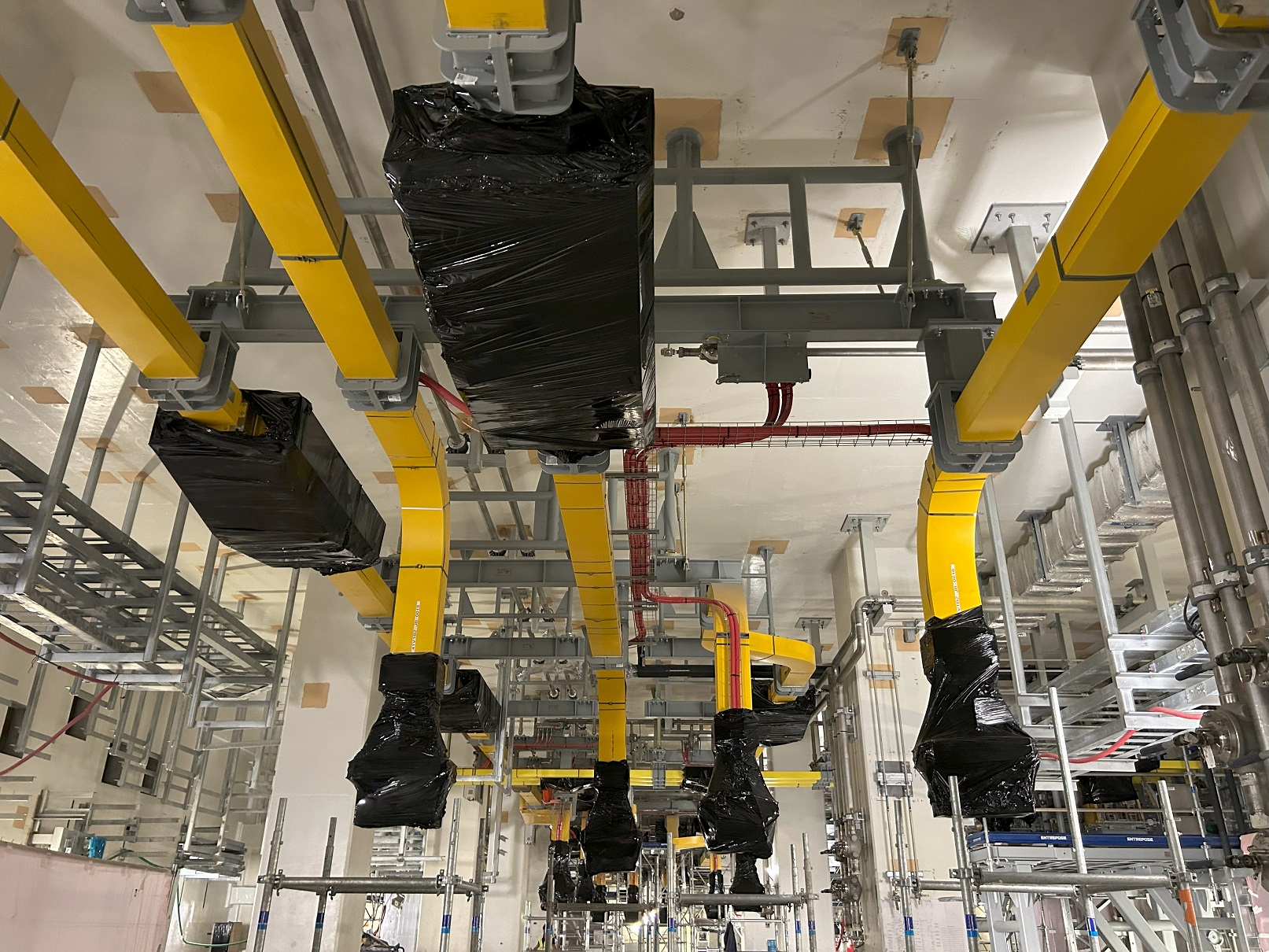
Yellow busbars
2024-09-18 - These electrical busbars, sized to deliver up to 70 kA of current, have been installed on ceiling supports in the Diagnostics Building at L5 level.

Thermal shield panel: ready for reintegration
2024-09-17 - A repaired thermal shield panel is inspected in the former Cryostat Workshop. It will soon join vacuum vessel sector #7 in sub-assembly tooling.

Highly polished
2024-09-17 - The original silver coating has been removed and the surface has been polished to mirror-like perfection (less than 80 microns rugosity). Ultra-high polishing ensures a similar performance (low emissivity) as the former silver coating.

Sector #7 is the first to be repaired
2024-09-15 - The first-repaired sector of the ITER vacuum vessel is sector #7 (pictured). The bevel joint region has been brought back to its nominal dimensions and the work to create a sector module (sector + thermal shield panels + toroidal field coils) can proceed.
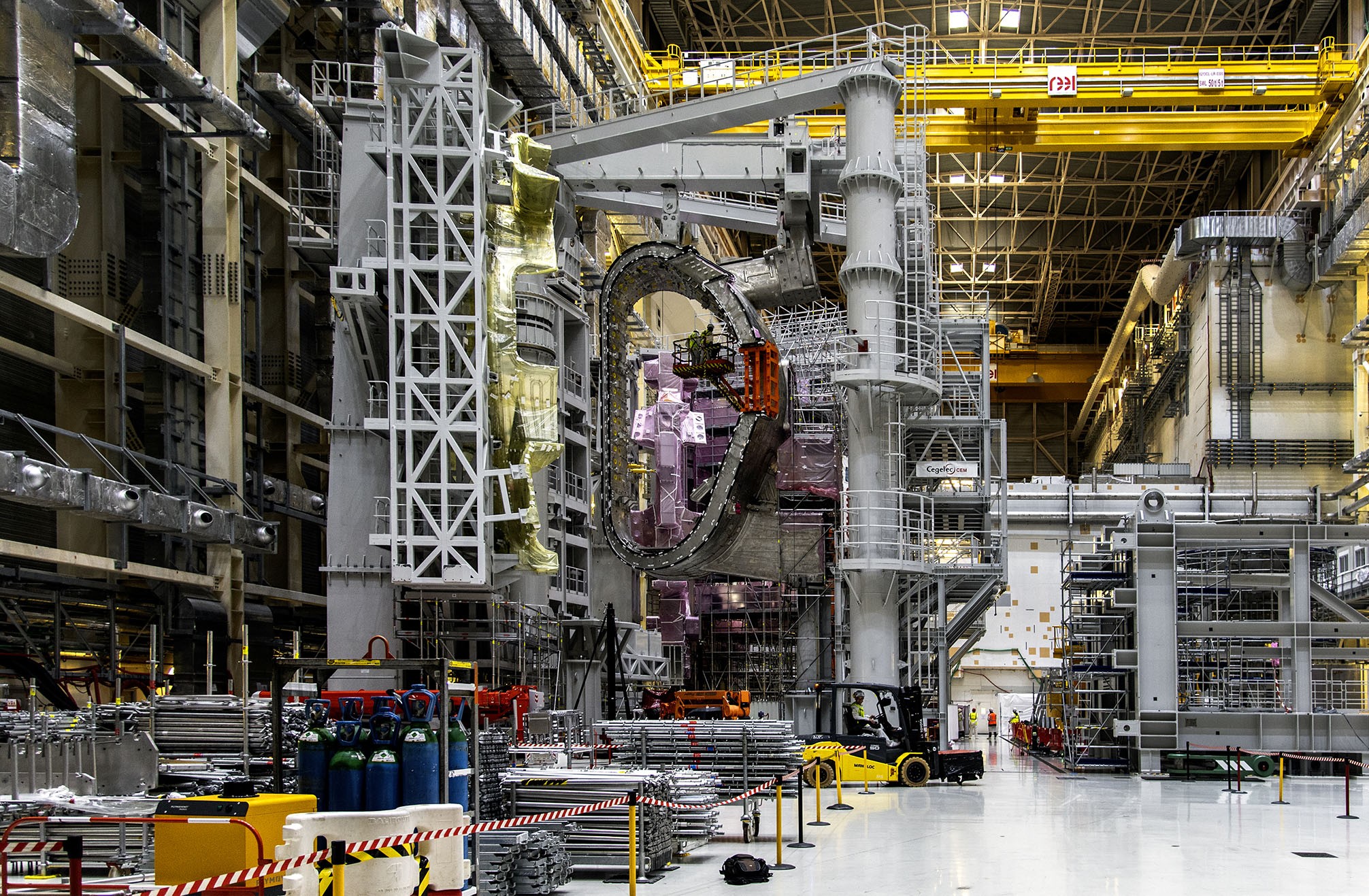
Vacuum vessel assembly restarts
2024-09-15 - Close to two years have passed since vacuum vessel assembly was halted when defects were identified in the ITER tokamak's vacuum vessel sectors and thermal shield. In September 2024, sector module assembly restarts.
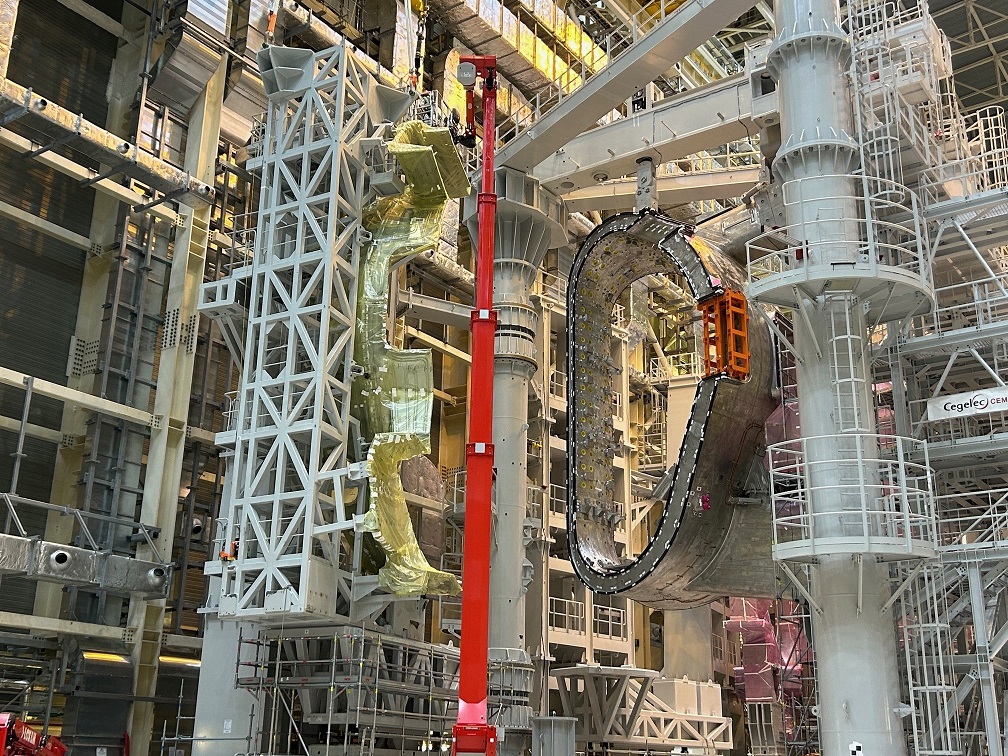
Ready to rotate
2024-09-13 - A thermal shield panel (protected in yellow) has been installed on the wings of the assembly tool to be rotated toward sector #7. The sector is now free of the dense scaffolding that had kept it hidden for the better part of the year.

Busbar bridges, ready for equipment
2024-09-12 - Two 50-metre-long ''busbar bridges'' span the distance between the Magnet Power Conversion buildings and the Tokamak Building to carry busbars and other electrical equipment. Installation works have begun.
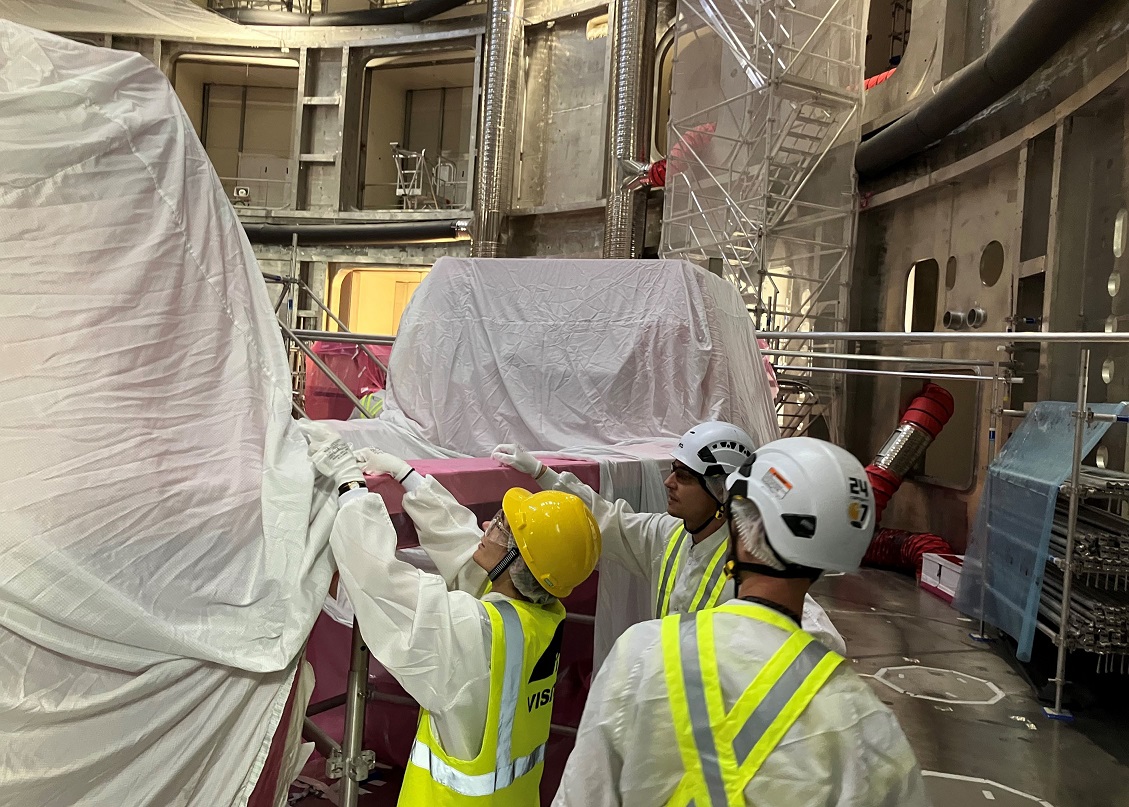
Keeping components clean
2024-09-06 - ITER is working with outside provider OHB (Germany) to implement specific cleaning and protective protocols for ITER components that must be kept free of contamination while construction work is taking place all around. In this picture, textile coverings are being installed on components in the Tokamak pit.

Repairs on sector #8
2024-09-05 - In the former Cryostat Workshop, the bevel joint region of vacuum vessel sector #8 (side one) is being repaired while the 440-tonne component is in a horizontal position. It will need to be "flipped" and the sequence of operations repeated on the other side.

Nearly 5 km of busbars
2024-09-04 - Russia is supplying approximately five kilometres of DC busbars—amounting to 500 tonnes of material—for the power supply system of the superconducting magnets. Approximately 70% of the busbar lengths (402 out of 570) have been received on site.

Getting crowded
2024-09-04 - A 1.5-tonne boomerang-shaped busbar destined for the central solenoid feeder system is installed in the Tokamak Building with the help of a small overhead crane.

Water falling
2024-07-18 - Cooling water and heat rejection systems have entered routine operation to support the plant system processes that require continuous water cooling for commissioning. A sheet of water is visible in this cooling tower as it falls through corrugated plastic fill as part of the cooling process.

Graphic ducts
2024-07-18 - In the Fast Discharge & Switching Network Resistors Building, exhaust ducts are being connected to a central chimney. In the case of a quench, when superconducting magnets lose their superconductivity, excess energy is diverted here as a protective mechanism.
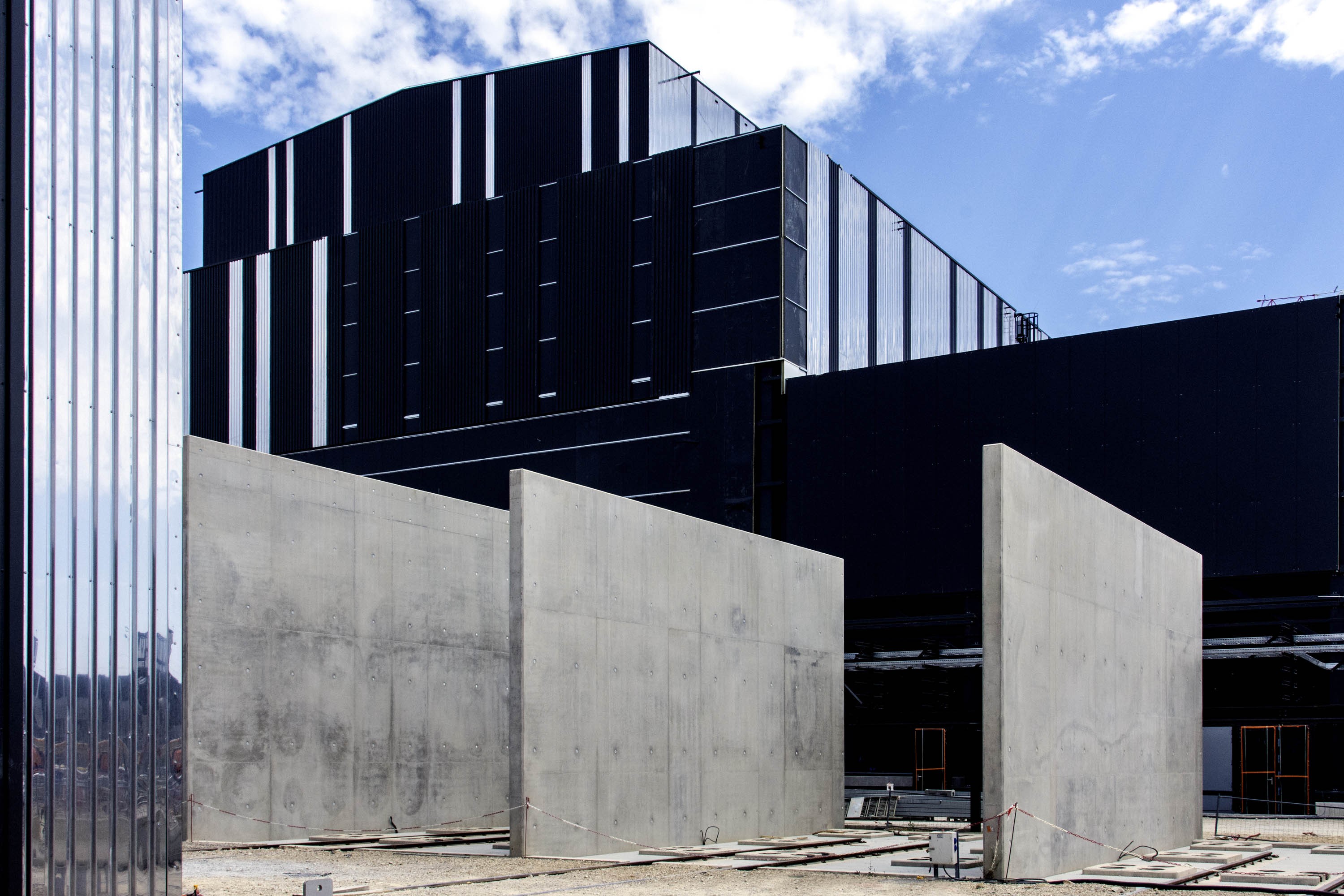
Cladding stage
2024-07-18 - In July, cladding work continues on the High Voltage Building (right) while the low-voltage building (left, nearly out of the frame) already displays its final black and silver covering.
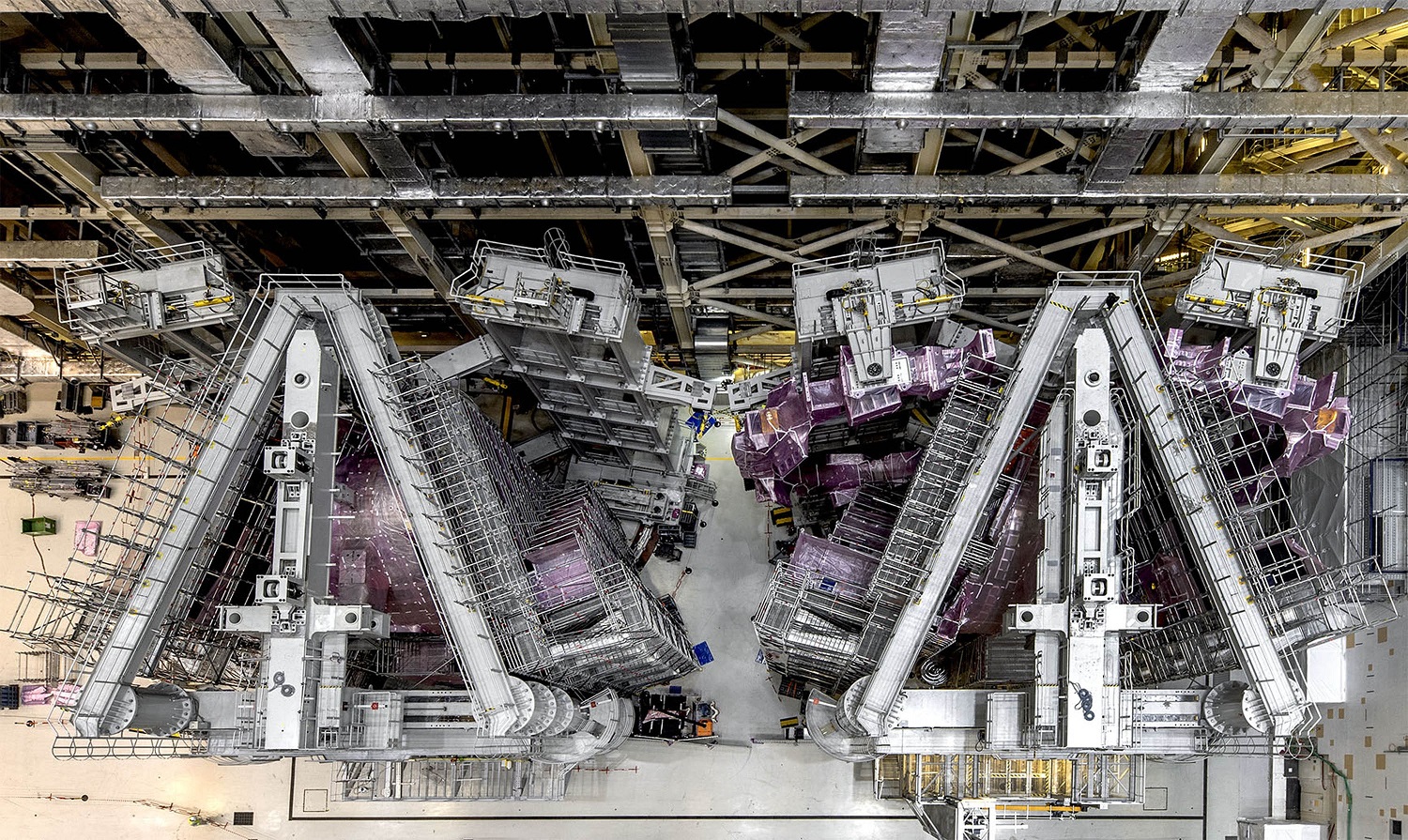
Seen from the rafters
2024-07-18 - Vacuum vessel sectors #7 and #6 supported in vertical tooling as their joint regions are repaired. Work on sector #7 (left) is expected to be completed in late August.
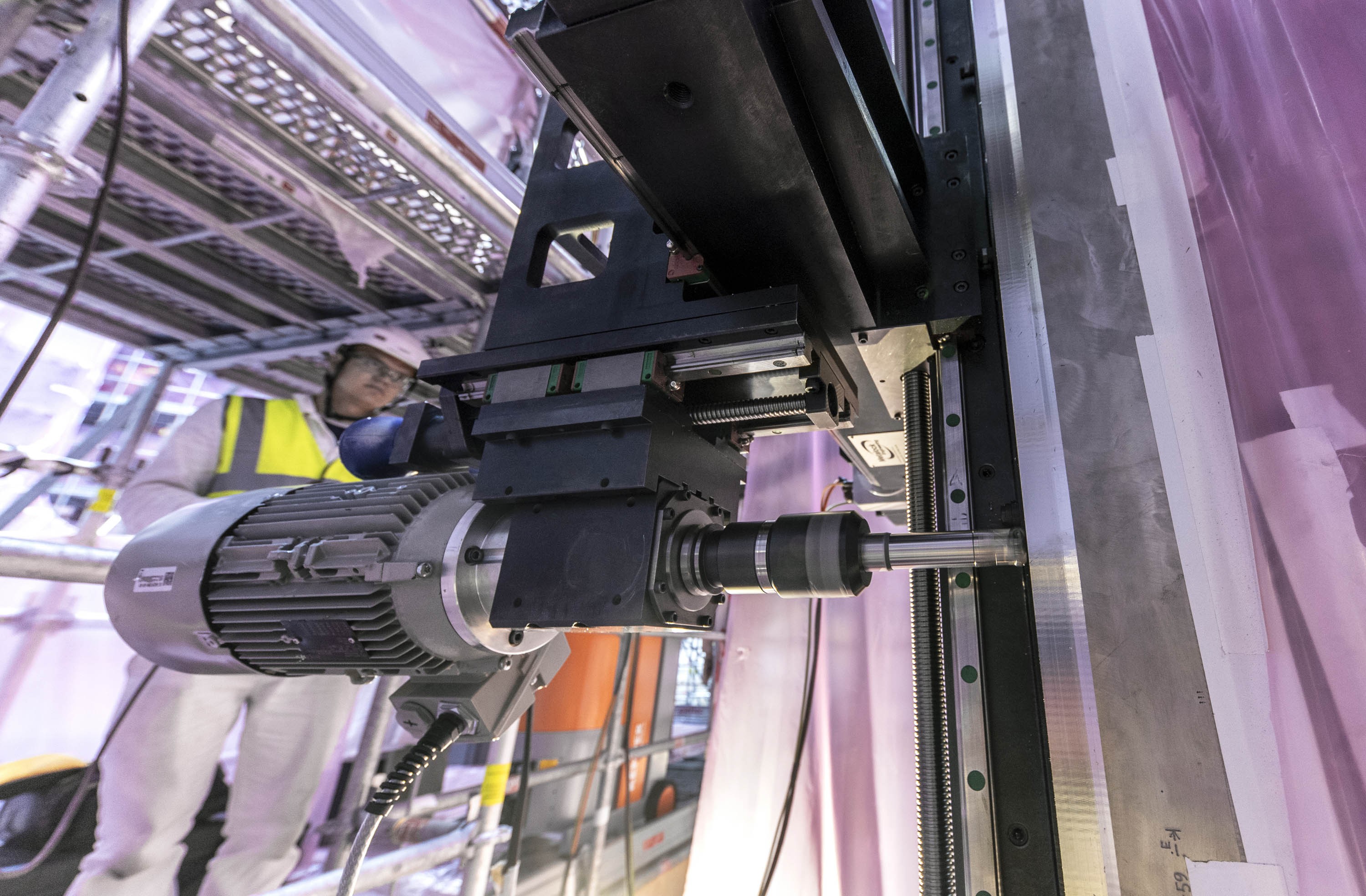
Shaving
2024-07-15 - A close-up of one of the milling machines working along the bevel region of sector #7.

Horizontal repair for sector #8
2024-07-15 - As both sub-assembly tools in the Assembly Hall are mobilized for the repair of sectors #6 and #7, there is no other option than to repair sector #8 in a horizontal position. Repairs have started on the first side of sector #8 in the former Cryostat Workshop.
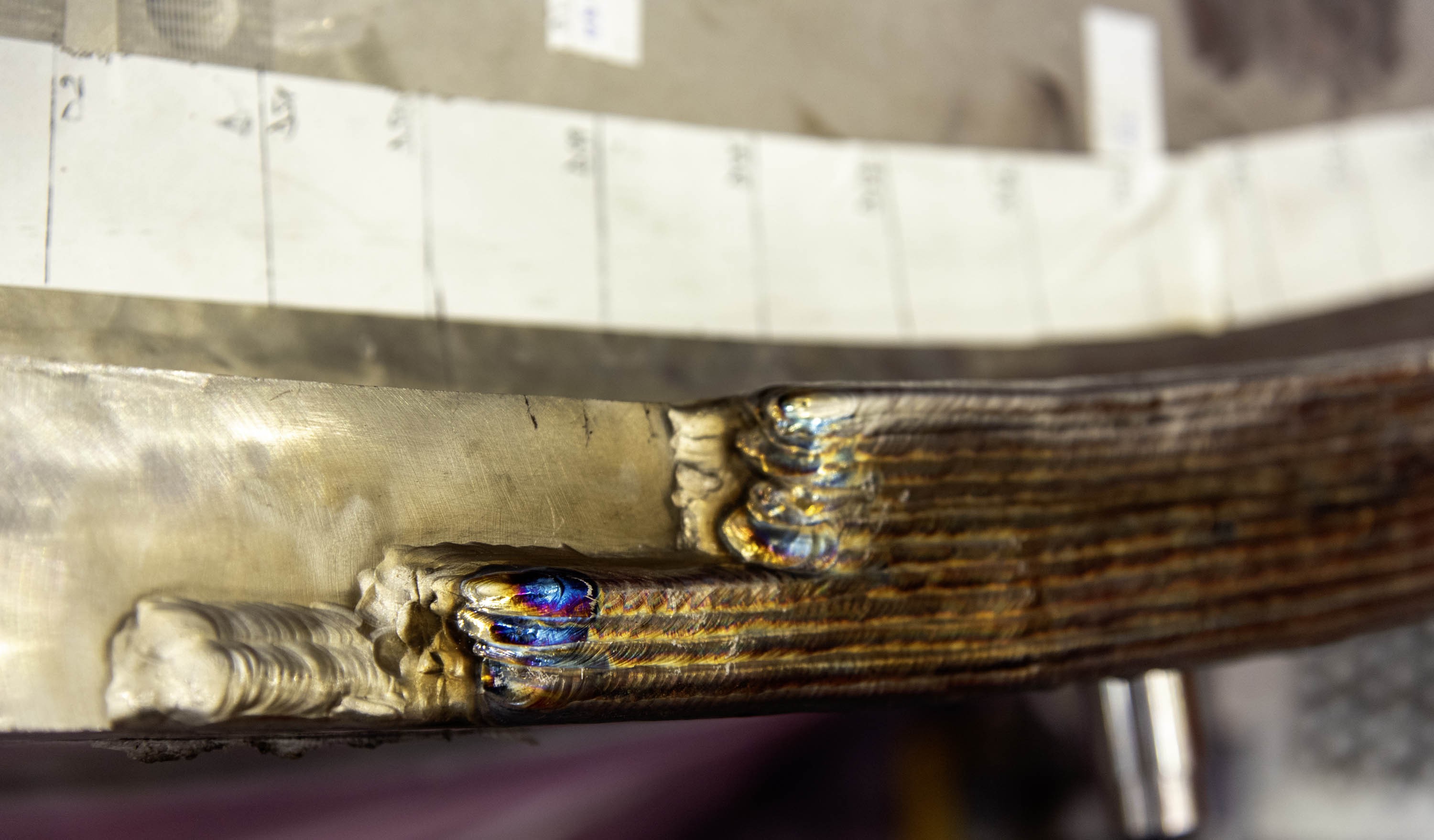
Metal build-up
2024-07-15 - Metal build-up (here on sector #8) is a delicate operation that demands extreme concentration to achieve uniformity, homogeneity and reliability.
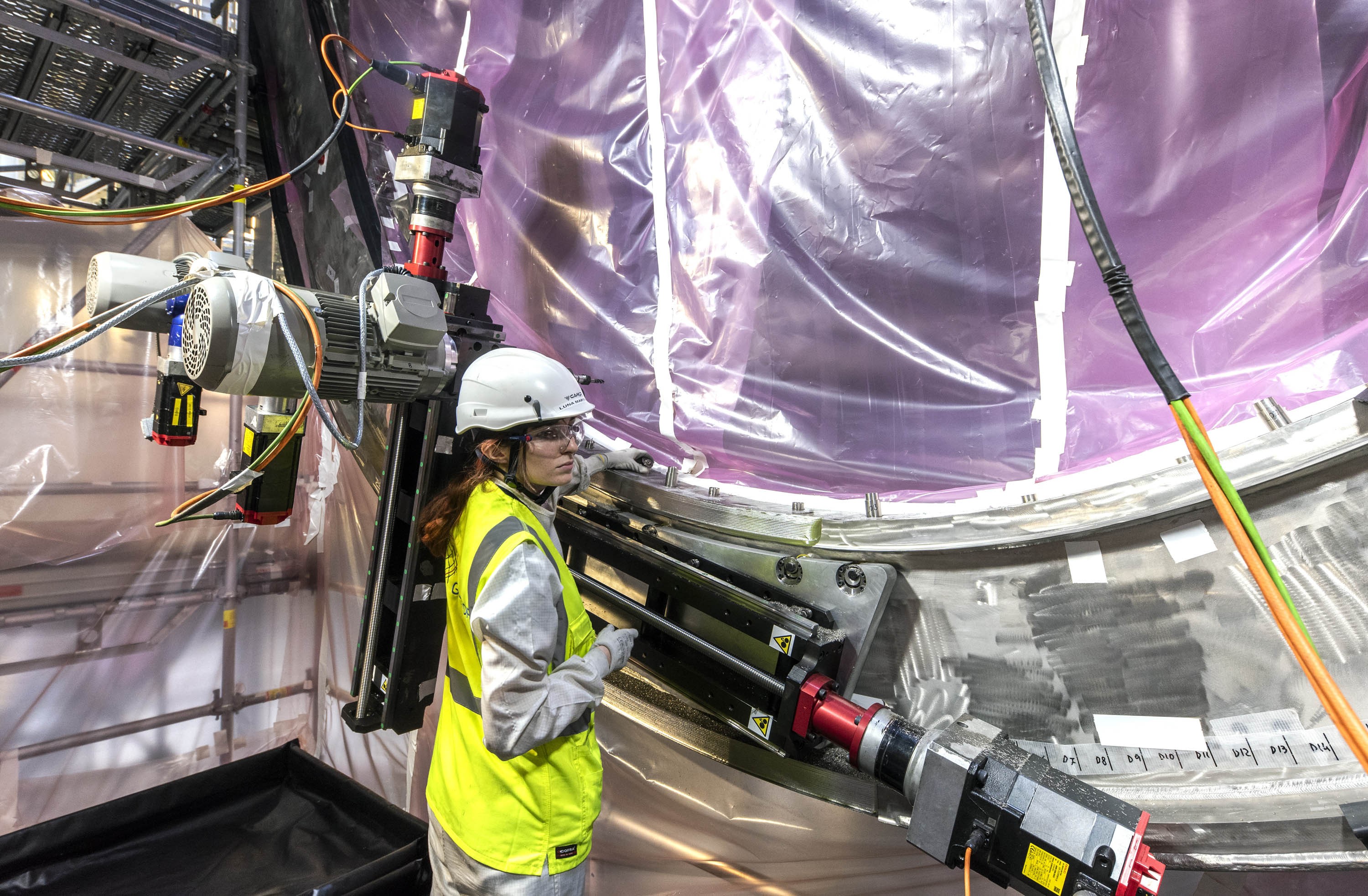
An essential role
2024-07-15 - Metrology is playing an essential role in the repair of ITER vacuum vessel sectors, including in the positioning, with micrometric precision, of the milling machines responsible for shaving off excess material.

Restoring vacuum vessel geometry
2024-07-15 - Up to three automatic milling machines can be positioned along a sector's joint (bevel) region to shave off excess material and return the component to nominal. Work on sector #6 (photo) will conclude this autumn.

Automatic welding on sector #8
2024-07-15 - Whereas approximately 24 kgs of metal fill are needed for sectors #7 and #6, the quantity required for sector #8 is significantly higher. As a consequence, with the exception of a few initial passes (pictured here), the process will be automated.
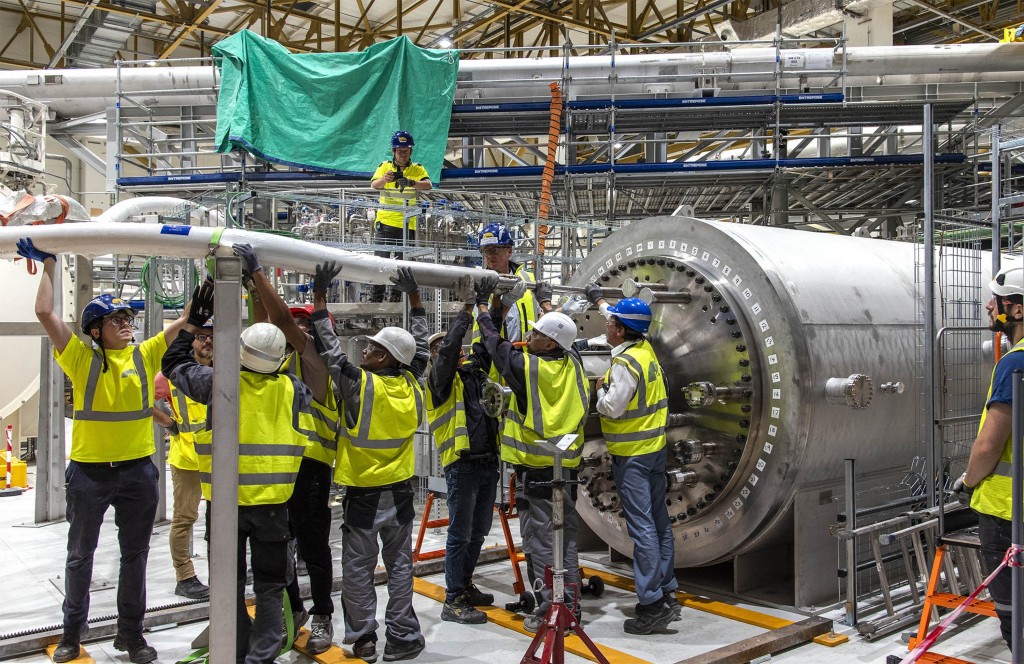
Preparing for cryopump cold tests
2024-07-02 - In a test facility inside the ITER cryoplant, torus and cryostat cryopumps can be tested through a whole range of operating temperatures and pumping scenarios. Testing will begin with a pre-production component that will not be installed in the ITER machine (photo).
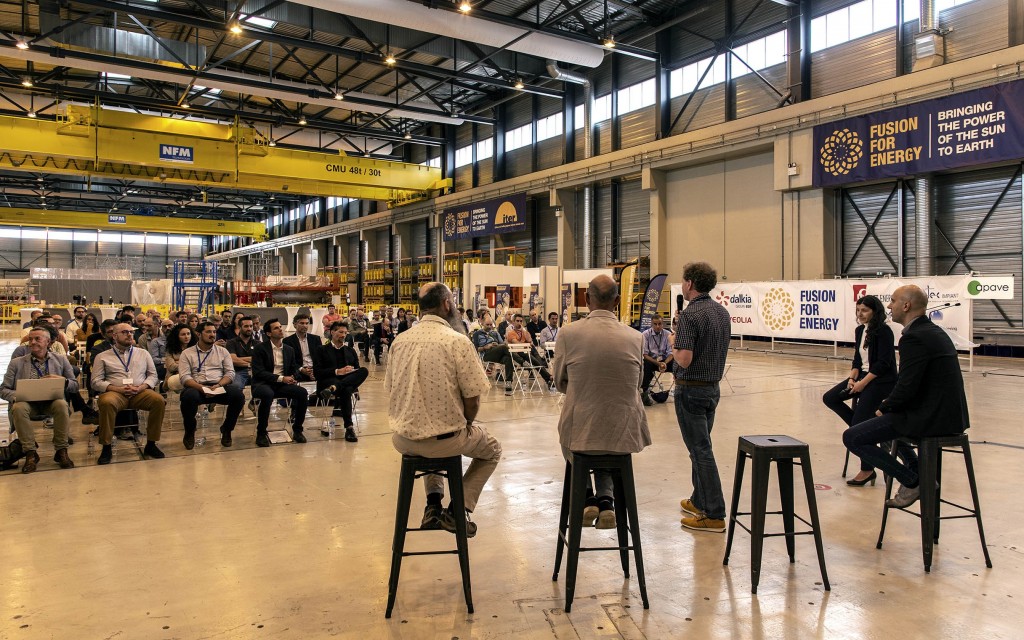
European poloidal field coils: the end of an era
2024-06-20 - With the completion of poloidal field coil #3 (PF3) in April, the ten-year effort to procure six ring-shaped coils for ITER came to a close. On 20 June, Fusion for Energy (the European Domestic Agency), the ITER Organization, and industry representatives celebrate a massive accomplishment and the end of an era. See: https://www.iter.org/newsline/-/4054
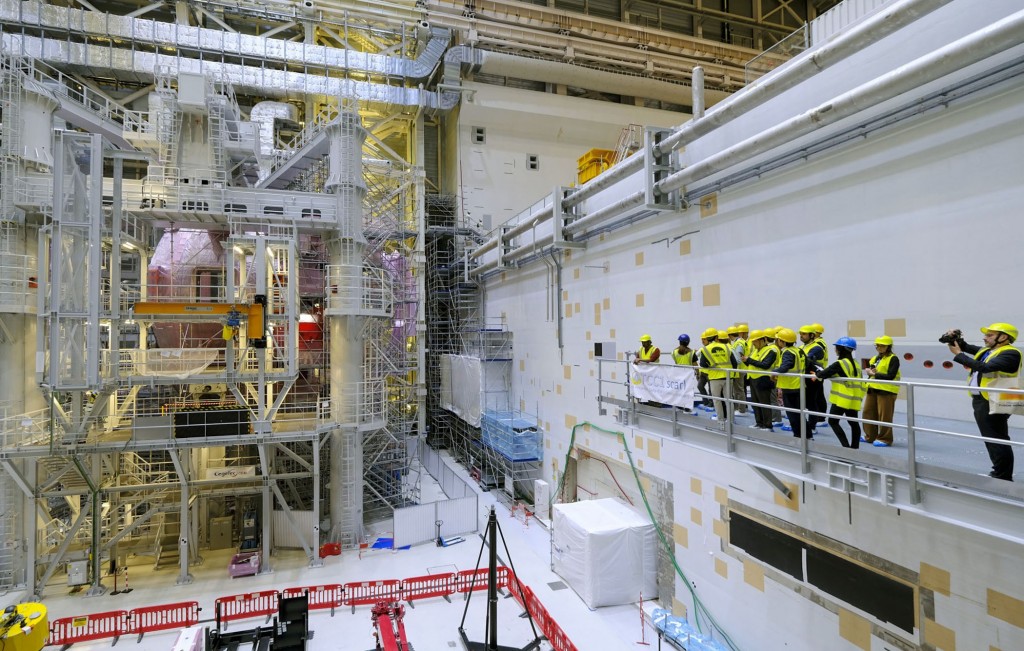
Hundreds learn more about ITER machine assembly
2024-05-27 - Participants to ITER's Private Sector Fusion Workshop in late May had the opportunity to visit the Assembly Hall and the Tokamak pit in small groups. A new visitors platform in the Assembly Hall provides for excellent viewing. Find out more at: https://www.iter.org/whatsnew/423 (Photo Christian Lünig)
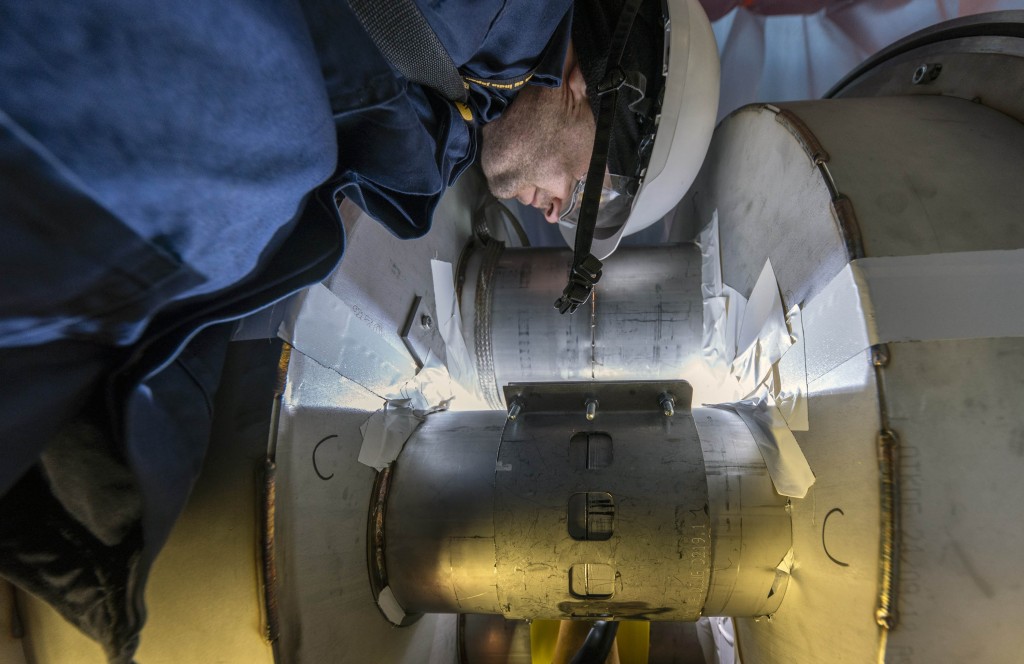
Welding two cryoline spools
2024-05-17 - The welders' task is difficult, the space constricted, the body contortions sometimes painful but the work gets done, millimetre after millimetre. The cryoline network spans several kilometres.
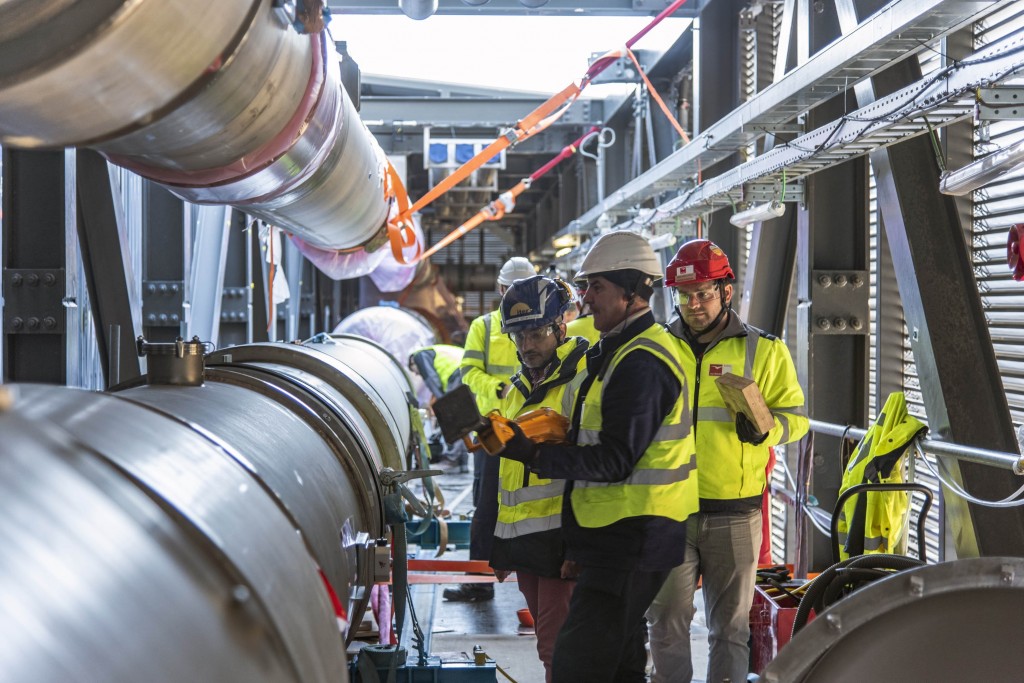
A challenging operation
2024-05-17 - One of the most challenging operations of the whole cryoline installation process: the precise positioning of a 9-tonne spool designed to decouple displacements between the cryobridge and the Tokamak Building in case of a seismic event.
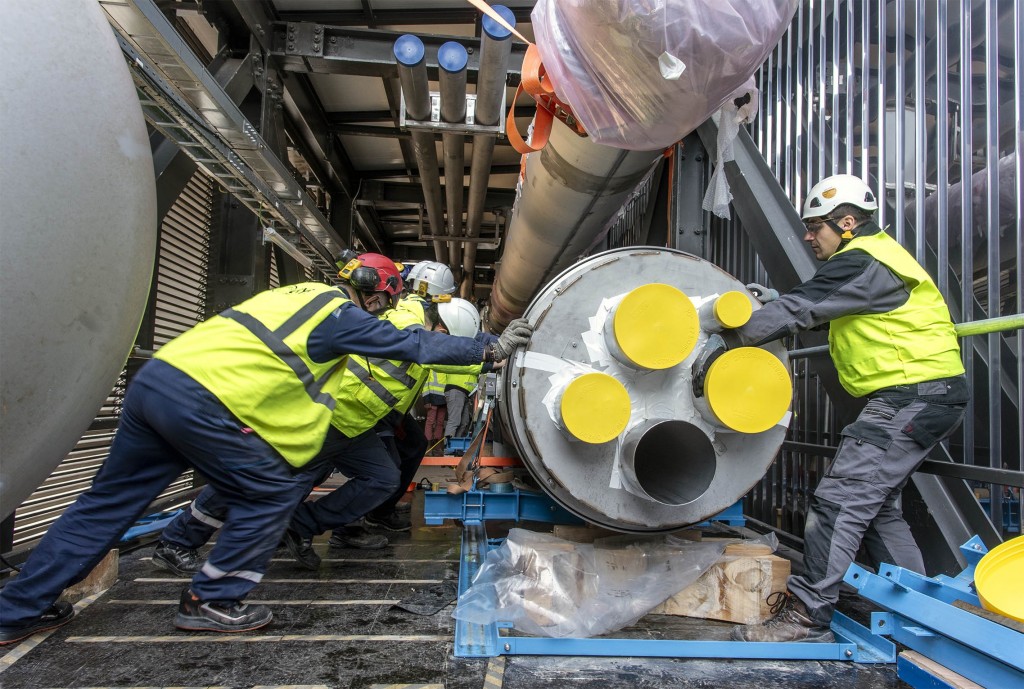
Pushing and pulling
2024-05-17 - Measuring between 6 and 9 metres in length and weighing between 2.2 and 9 tonnes, the cryoline spools need to be perfectly aligned before welding operations can begin. Sometimes, a bit of pushing and pulling is necessary...

Activity on the cryobridge
2024-05-17 - In the bridge that connects the cryoplant to the Tokamak Complex, contractors are installing multipurpose cryolines, spool by spool.

Final coil leaves moves into storage
2024-04-30 - The last poloidal field coil manufactured on site by the European Domestic Agency is moved into storage on 30 April. The completion of PF3—one of the two largest ring-shaped coils, measuring 24 metres in diameter—marks the high point of technical and organizational expertise accumulated since manufacturing began in the Winding Facility in late March 2017.
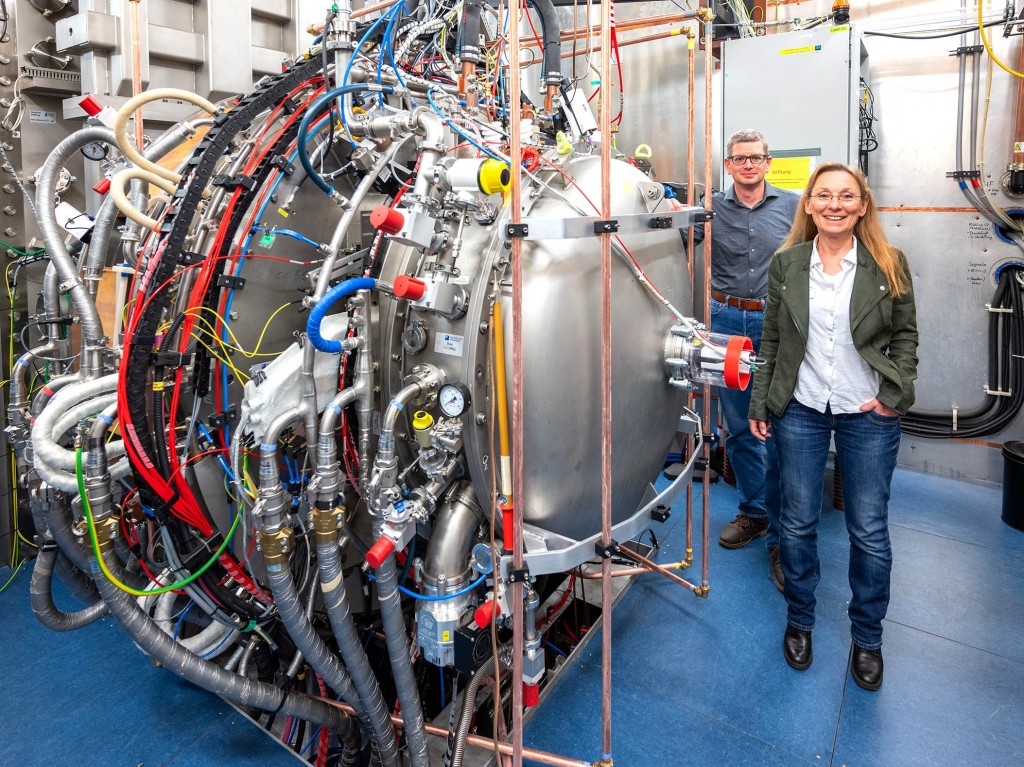
ELISE achieves target values for ITER
2024-04-29 - Researchers at the Max Planck Institute for Plasma Physics in Garching, Germany, have generated the ion current densities required for ITER neutral beam injection on the ELISE testbed—a negative ion source prototype that is half the size of ITER's. This experimental first is good news for the development of reliable, high-performance heating neutral beam injectors for ITER. See more at https://www.iter.org/newsline/-/4032.
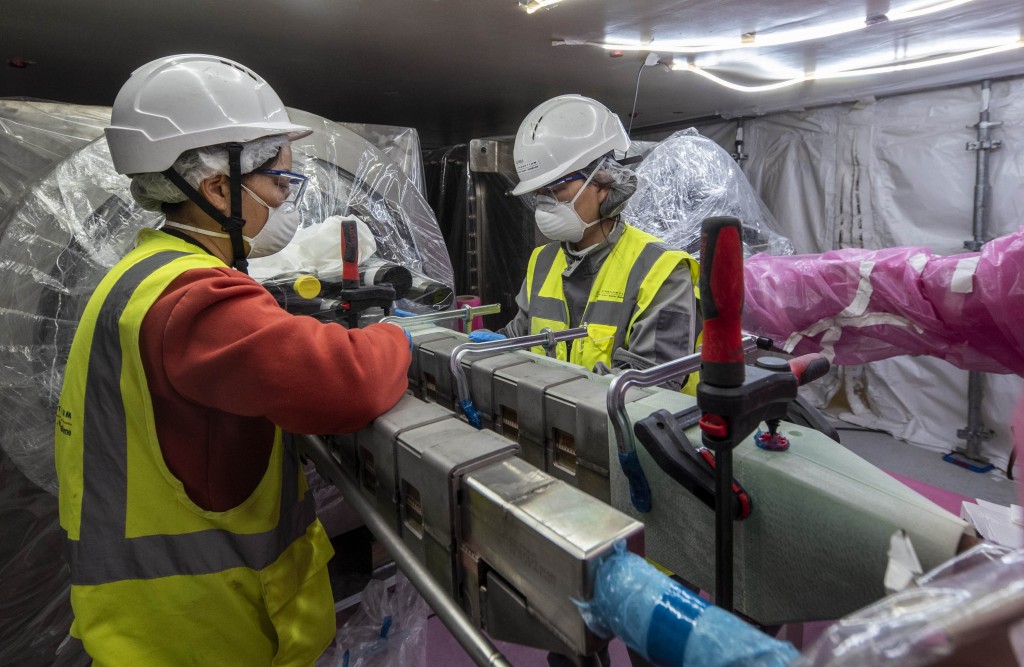
Precise work: creating feeder joints
2024-04-18 - Twenty-one magnet feeders must be installed at B2 basement level, each one formed from three segments. Here, highly trained workers from the CNPE consortium are finalizing the joints connecting two segments of the feeder that will deliver cryogens and electricity to the lowest central solenoid module.
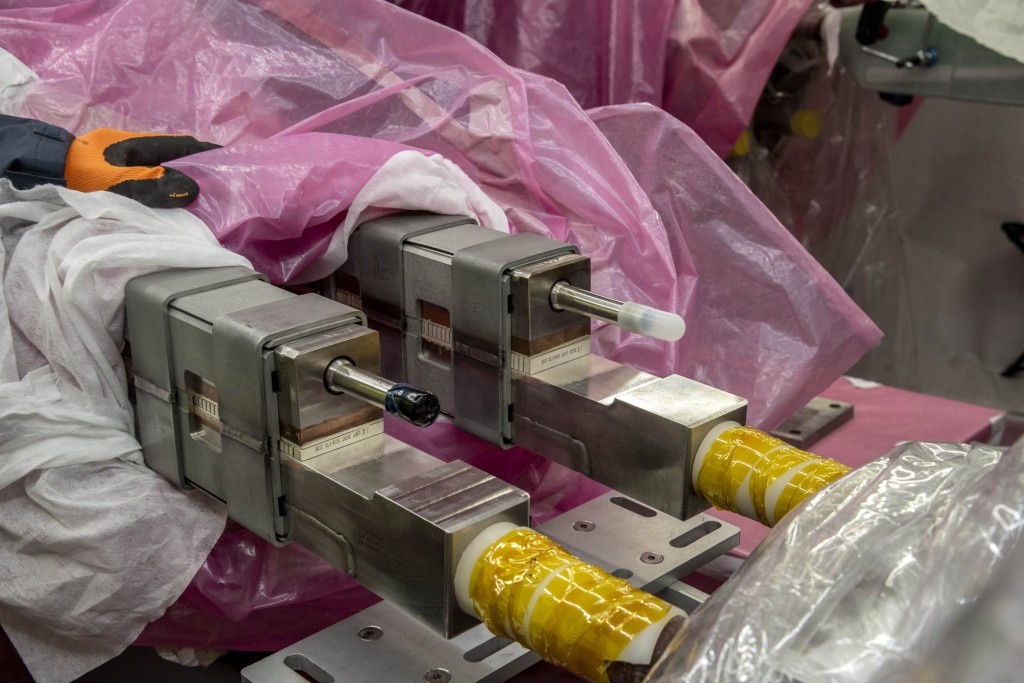
Close-up of feeder joints
2024-04-18 - The criticality of the superconducting feeder joints stems from the fact that they can only be truly tested once the machine is up and running. Hence the exceptionnaly demanding qualification programs for the technicians who realize joint assemblies.

Completion of PF3
2024-04-16 - On 16 April 2024, workers from Fusion for Energy, ITER Organization, APAVE, ASG, S&I, MAMMOET and CNIM operators celebrate the completion of PF3. The 24-metre-in-diameter coil is equipped with 17 lifting accessories (red).
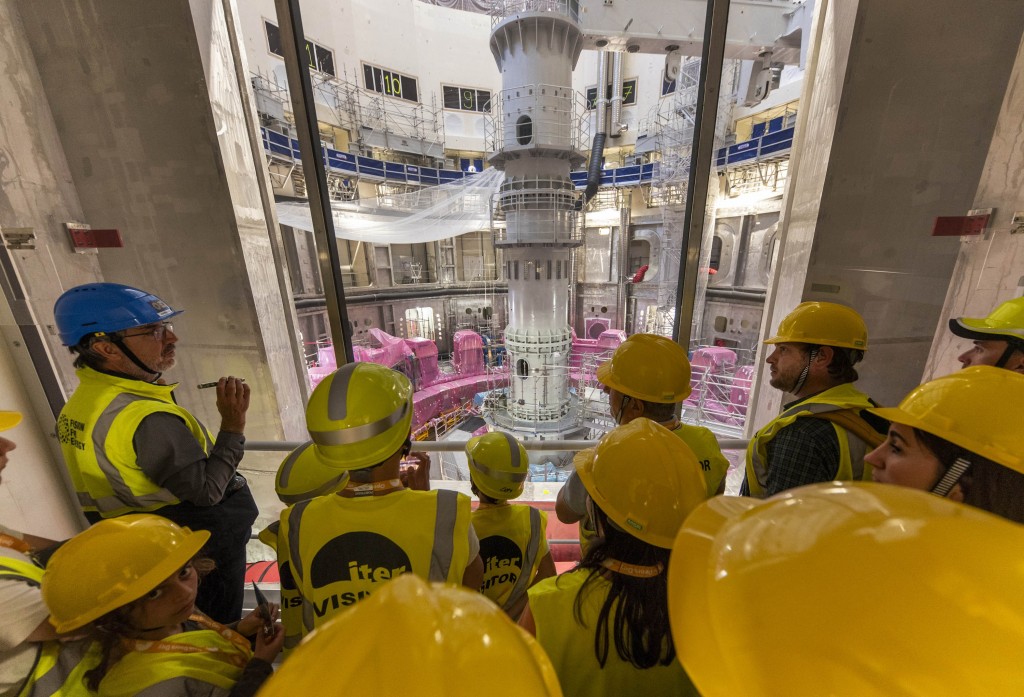
Peeking in on Tokamak assembly
2024-04-13 - During a public event on 13 April, groups were taken into one of two port cells leading to the Tokamak pit, where guides explained what has already been installed and what we are expecting next.

Work ahead
2024-04-11 - One of the main tasks ahead is the completion of superconducting electrical connections. This will involve welding, ultrasonic weld inspection, helium leak testing, electrical installation and high voltage testing.
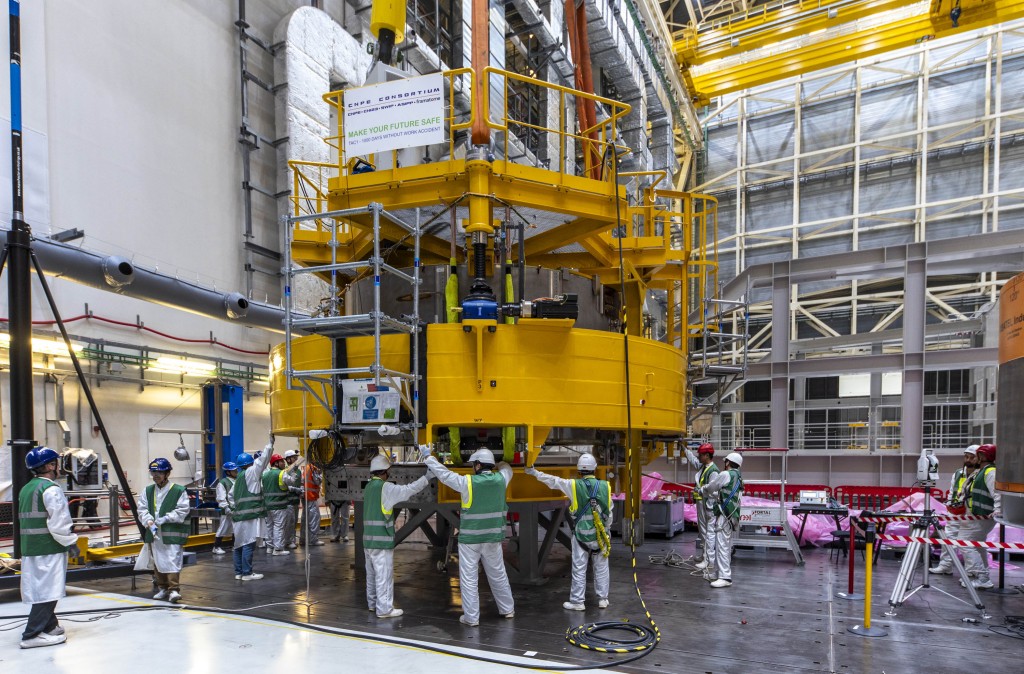
Lifting central solenoid module #3
2024-04-11 - The specialized lifting tool, in yellow, exerts radial pressure to "grasp" the cylindrical module. Redundent lifting slings and support blocks are installed ensure to ensure operation security.

Almost there
2024-04-11 - Module 3 will be positioned on the two-module stack with a slight radial offset to provide room for equipment and connection work.
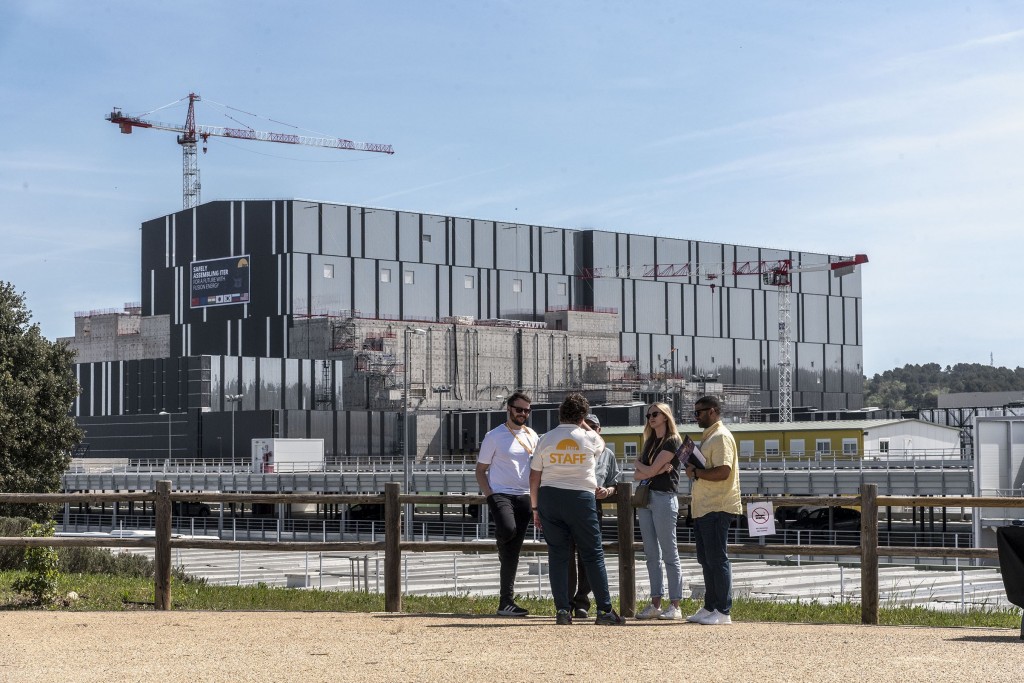
An imposing sight
2024-04-11 - Over the years, the view from the Visitors Centre has evolved. Today, building construction on the platform is largely completed and the Tokamak Complex has become the worksite's most iconic feature.

Heading to the stack
2024-04-11 - The third independent superconducting magnet for the ITER central solenoid has been lifted off its temporary platform and is heading toward the stack.
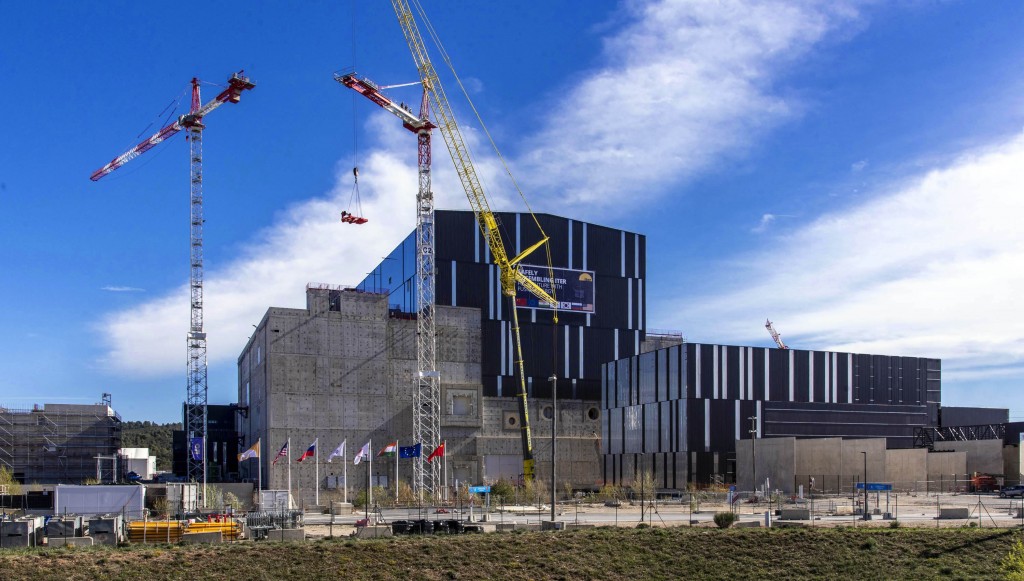
Longstanding crane dismantled
2024-04-03 - Erected in 2014 to construct the Tokamak Complex, crane C2 is dismantled in early April after 10 years of service. The 84-metre-tall crane operated continuously, for two or three shifts per day (16-24 hours), with no accident or major lift incident.
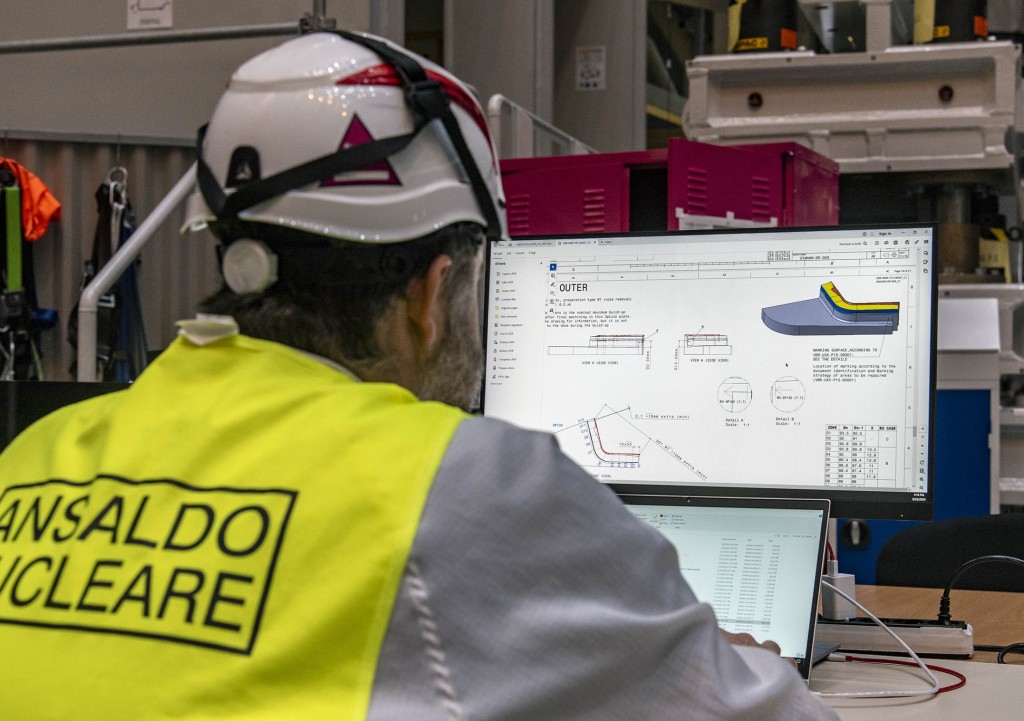
Precision
2024-03-22 - With a precision of 0.05 millimetres, laser metrology has mapped the geometry of every section of the bevel affected by dimensional non-conformities. For each section the data obtained is made available to the welder, both as a printed document and as markings embossed on the component itself.

Up close with welders
2024-03-22 - A team of four welders has started on the dimensional repairs of vacuum vessel sector #7. Here, a welder checks the temperature of the weld pass he has just completed. It must fall to 116 °C before he can start another pass.
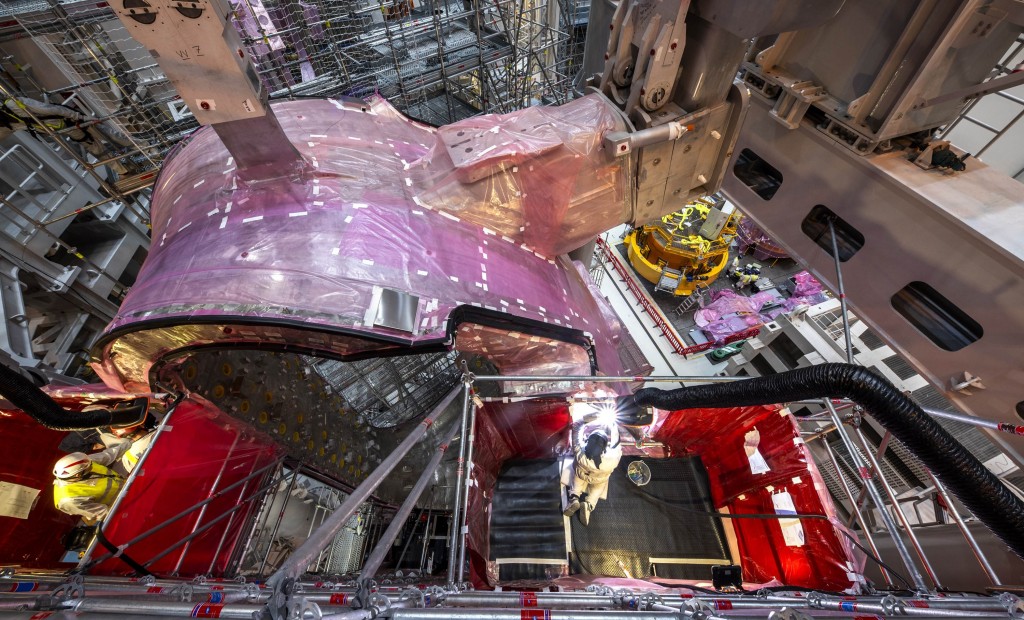
Welders, seen from above
2024-03-22 - Operating from protruding platforms located at different levels of the scaffolding, four welders have started the long and patient task of metal build-up on the regions of the sector 7 bevel affected by dimensional non-conformities.
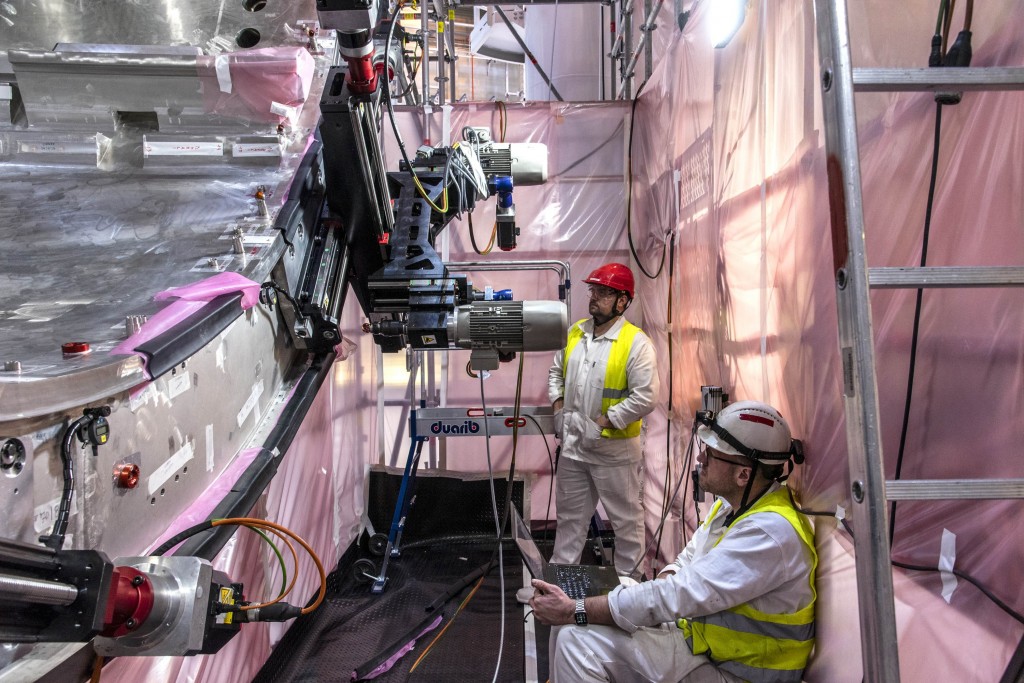
Specialized tools
2024-03-22 - Machining tools are programmed to follow a precise trajectory along the bevel area. Here, specialists from Metalock Engineering UK, contractor to the SIMANN consortium (SIMIC/Ansaldo Nucleare), are fine-tuning the initial positioning of the tools prior to actual machining. See https://www.iter.org/newsline/-/4017 for more information.
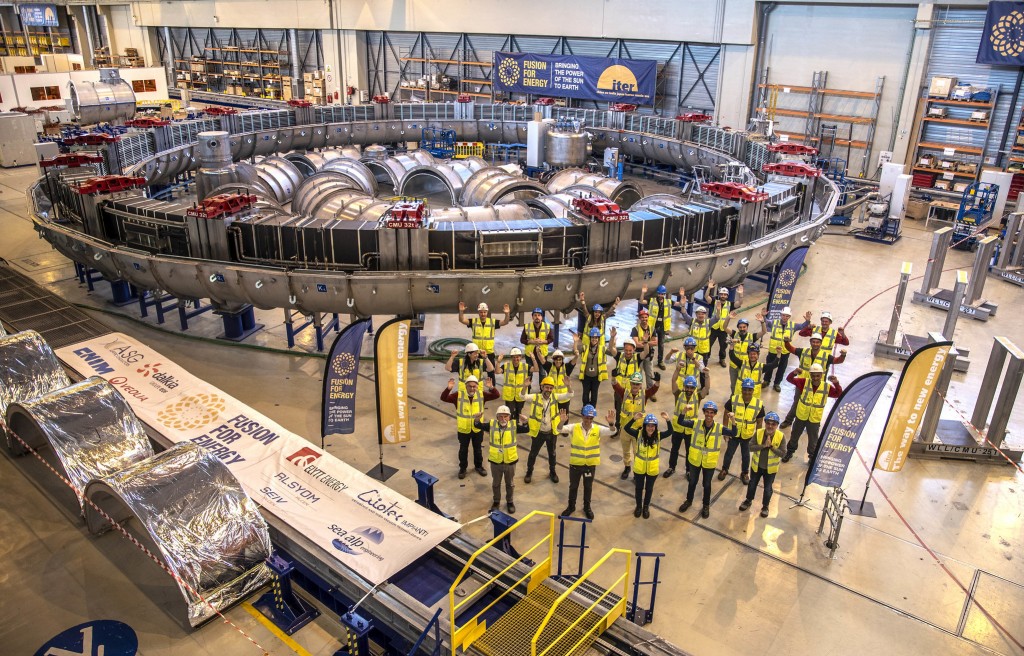
PF3 successfully completes cold tests
2024-03-21 - Poloidal field coil #3—the final coil to be supplied by Europe—completes cold tests in March 2023.

Last ring coil in cold test chamber
2024-03-14 - In the European coil winding facility on site, poloidal field coil #3 is undergoing a test campaign inside a cryostat (pictured) designed to perform a cold test at 80K. While not the final operating temperature of 4 K, tests at 80 K provide important information to the manufacturing team and quality inspectors.
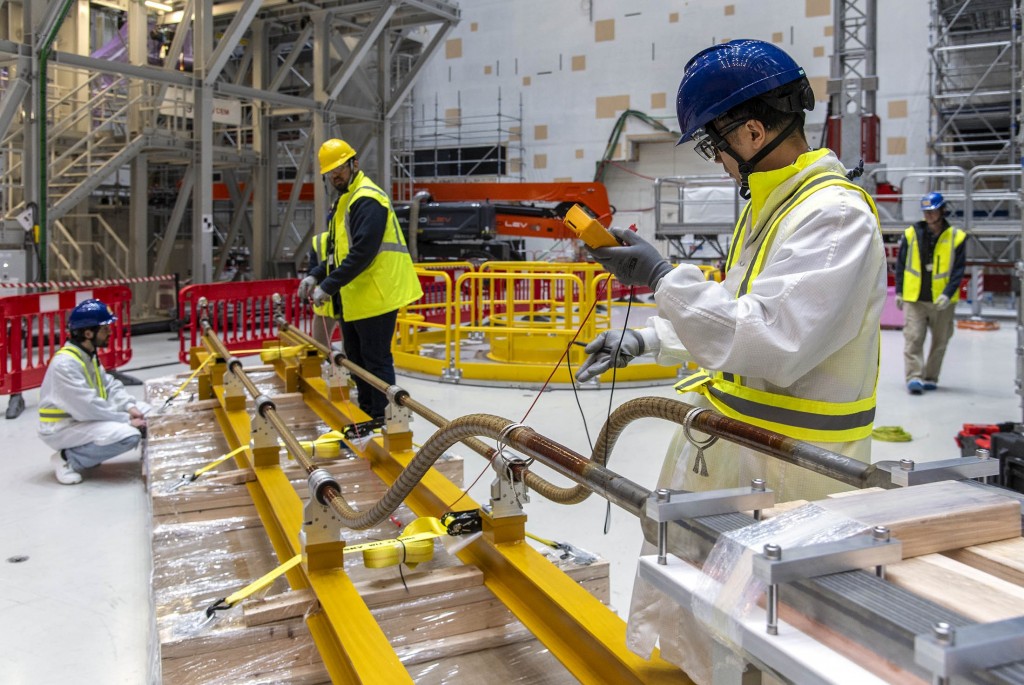
Current carriers
2024-02-29 - Experts from the ITER Magnet Project are carrying out the electrical site acceptance test of central solenoid busbar lead extensions prior to preparing them for installation in the central solenoid stack.

Central solenoid stacking: update
2024-02-29 - Two central solenoid modules are already installed on the bespoke assembly platform in the ITER Assembly Hall. Bottom left, is a multi-purpose work platform used for work on top of the stack. To the right, are helium-cooled busbar lead extensions that feed 40 kA electric current to the magnets. A third module (in pink) will be installed in the coming weeks.

Measuring precisely
2024-02-23 - In order to precisely identify the bevel regions that need to be rectified, metrologists from the SIMANN (SIMIC-Ansaldo) consortium are performing ultra-precise measurements on both sides of vacuum vessel sector #7.

Flags
2024-02-23 - Flags of the seven ITER Members, and the ITER Organization, stand out against the imposing facade of the Tokamak Complex.

Thermal shield repair
2024-02-21 - Vacuum vessel thermal shield sets are being inspected on site (here, using endoscopy techniques) and tested for corrosion cracking. Only the panels with superficial defects are being shipped to India for repair by INOX-CVA. So far, that's five of nine sets.

Disassembled, for now
2024-02-21 - Once repaired, and in a few cases re-manufactured, vacuum vessel thermal shield panels will be reassembled on site with vacuum vessel sectors and toroidal field coils to form the modules that, once joined, constitute the doughnut-shaped plasma chamber.
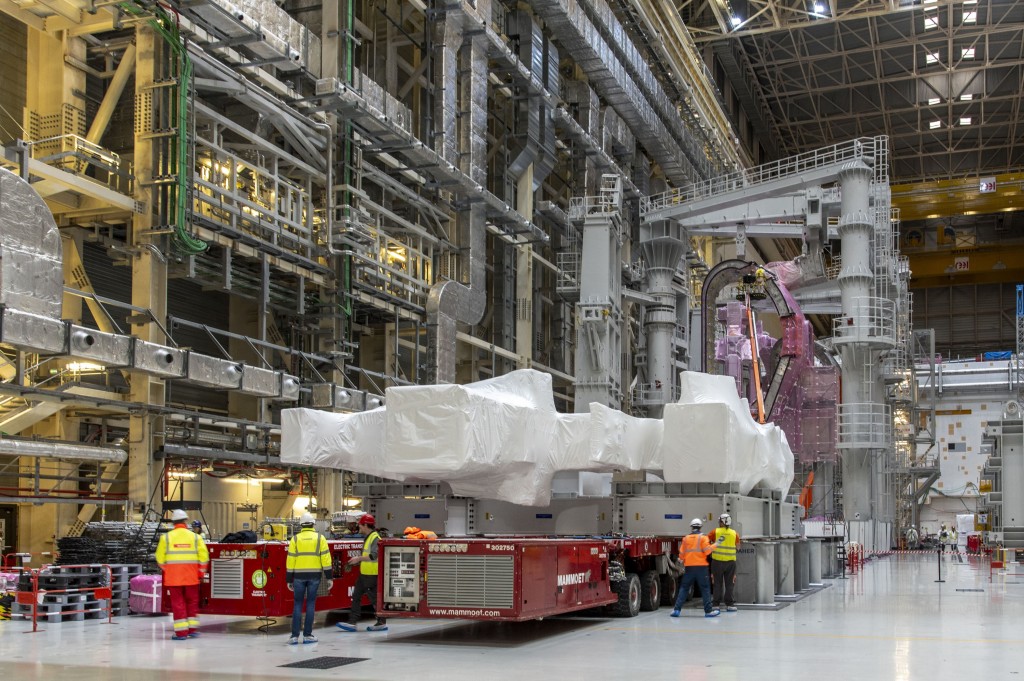
Component transfer goes electric
2024-02-16 - In February, a toroidal field coil (330 tonnes) was moved for the first time from the Assembly Hall by a modular trailer (SPMT) equipped with an electric power pack. Designed by Dutch specialist Mammoet for ITER, it reduces the noise and eliminates the pollution of diesel-type trailers. See more at https://www.iter.org/newsline/-/4001.

"Equivalent power and much bigger torque"
2024-02-16 - Identical in aspect and dimension to the diesel version, the electric power pack unit developed by Mammoet for ITER can sustain two days of standard operation on site before requiring a charge. See: https://www.iter.org/newsline/-/4001
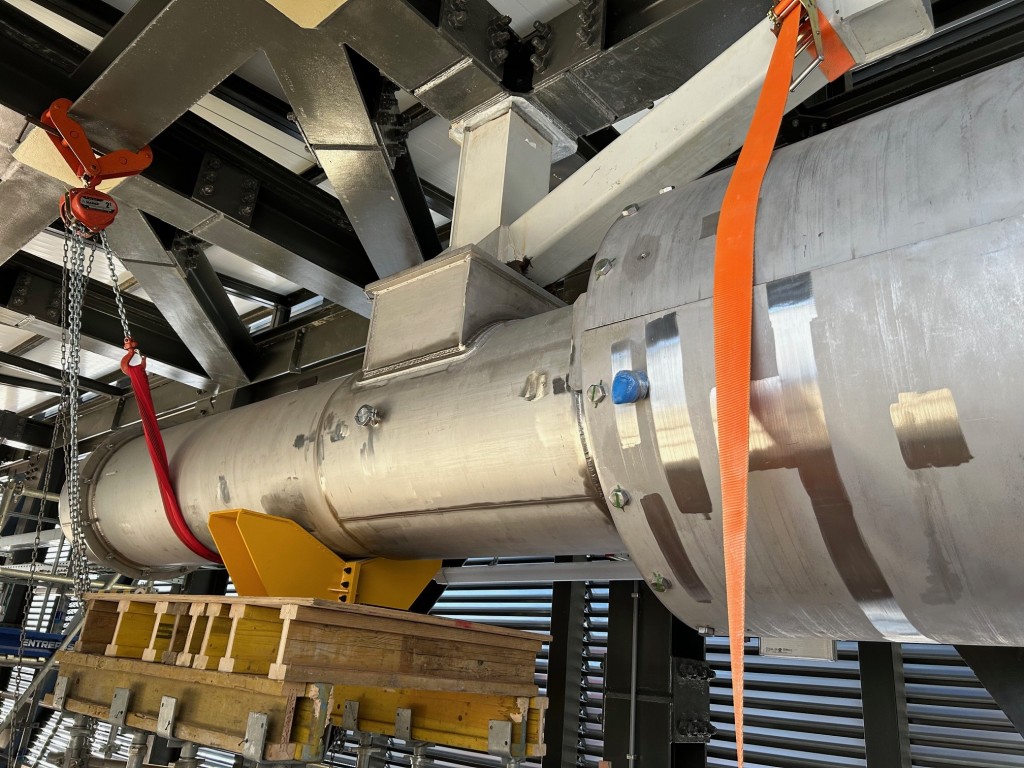
In the cryobridge
2024-02-14 - A process line is installed in the bridge that connects the ITER cryoplant to the Tokamak Complex. Approximately five kilometres of cryolines are necessary to distribute gas and liquid helium to the different "clients".

Plant components in the cryobridge
2024-02-14 - In the completed cryobridge, teams are installing mechanical components like this segment of cryogenic line.
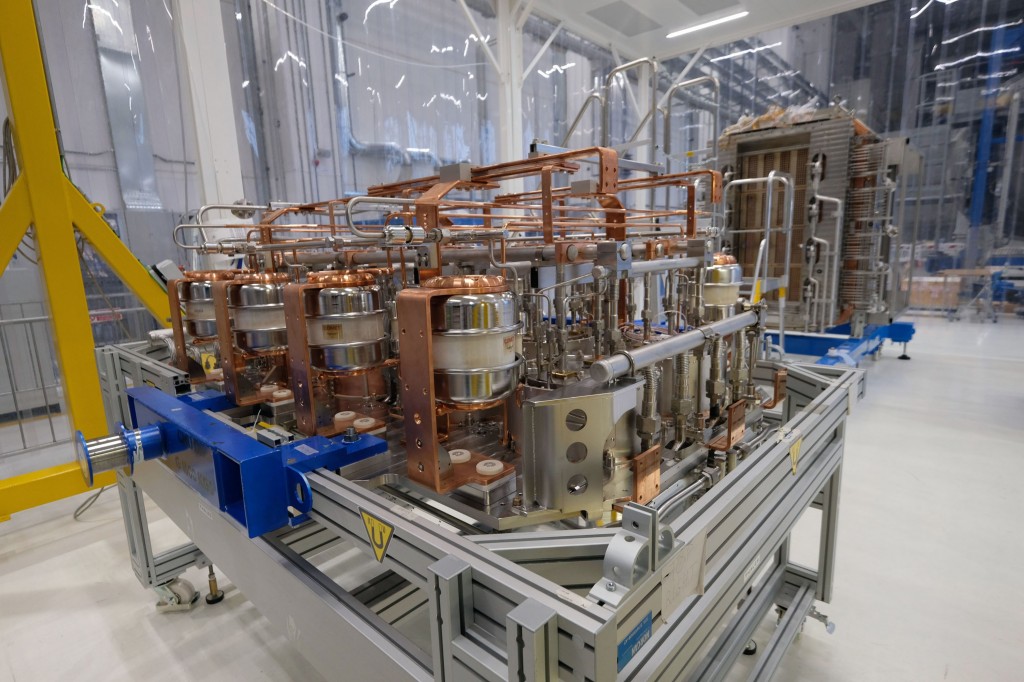
Back side
2024-02-09 - The rear side of the ion beam source is visible before final assembly. © Luca Lotto
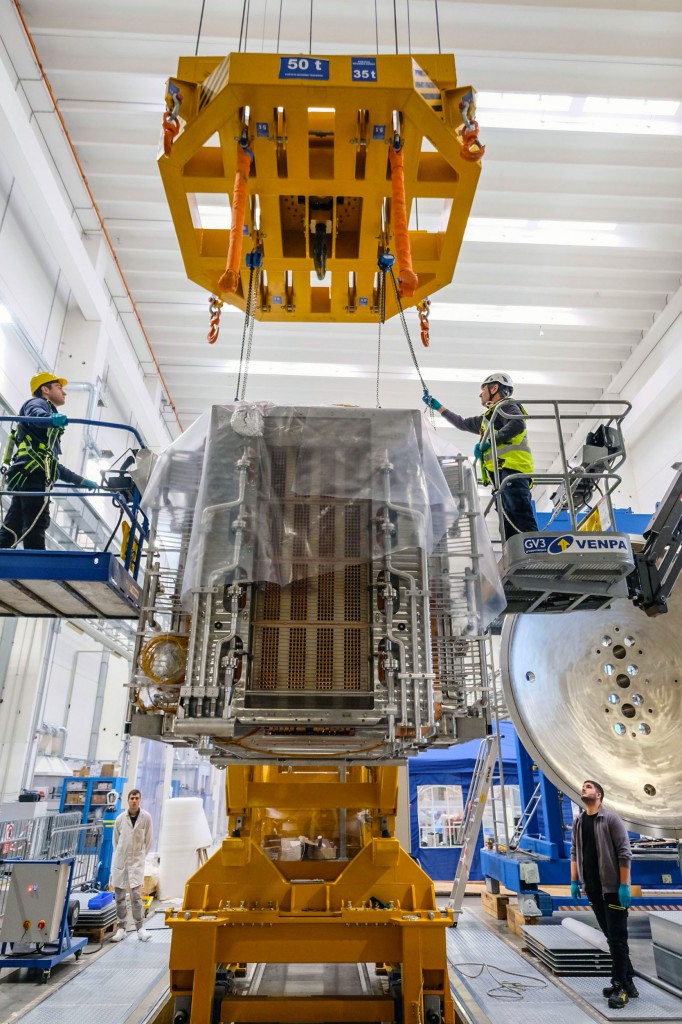
Lifting
2024-02-09 - The beam source is lifted for re-installation. During the shutdown there were approximately 60 procurements for new or revised components for beam source enhancement. © Luca Lotto
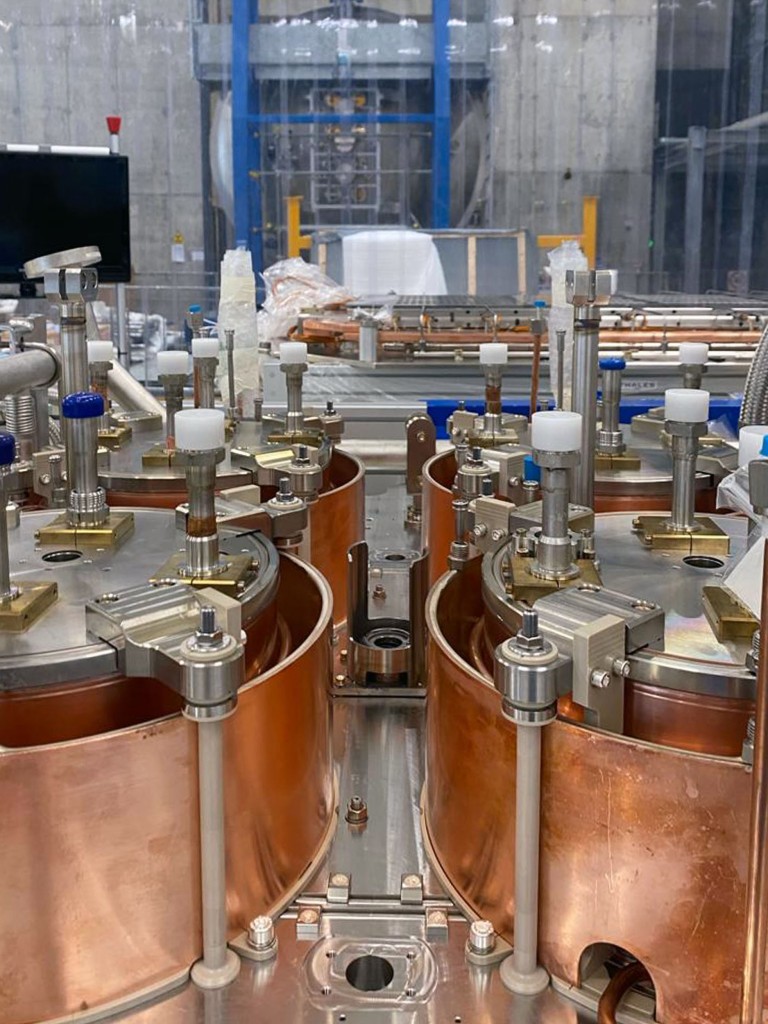
SPIDER re-assembly underway
2024-02-09 - Assembly of the beam source at Consorzio RFX. In the background is the SPIDER bunker. © Maria Teresa Orlando
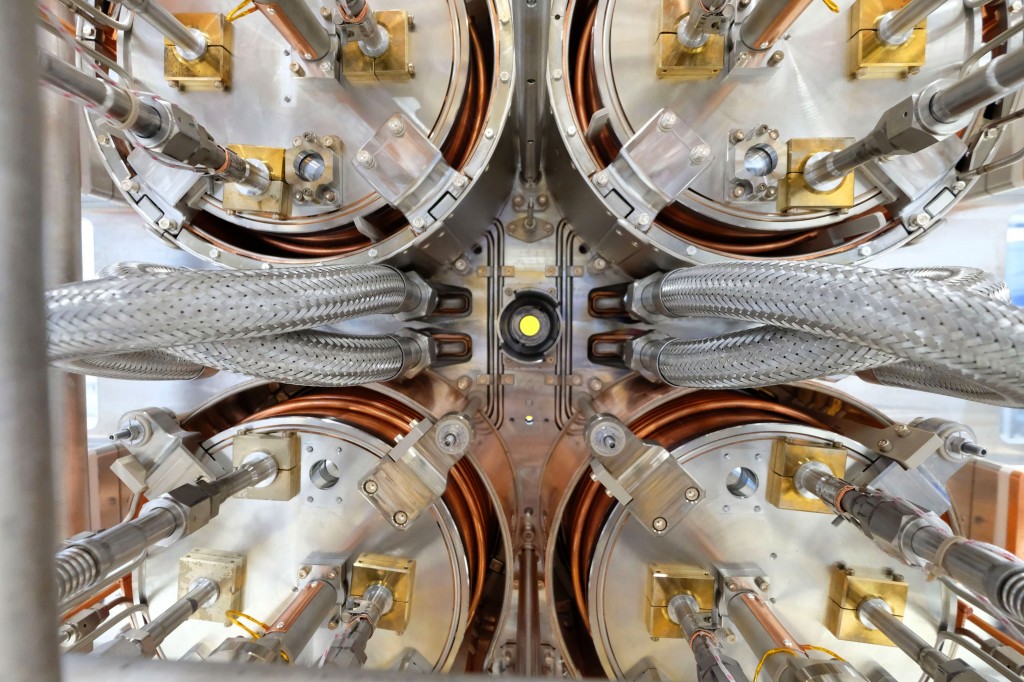
Close-up
2024-02-09 - A close-up view of four of SPIDER's eight radiofrequency drivers, each one surrounded by a ferromagnetic shield. © Luca Lotto

After upgrades, SPIDER set to restart
2024-02-09 - The SPIDER beam source is the world's most powerful negative ion source. It was removed in December 2021 for engineering upgrades, and has now been re-installed in the vacuum vessel of the SPIDER test bed at Consorzio RFX. © Luca Lotto See: https://www.iter.org/newsline/-/3994

Component repair
2024-02-08 - Vacuum vessel bevel repair will be carried out at the ITER site by a consortium called SIMANN comprising the Italian firms SIMIC S.p.A. and Ansaldo Nucleare. Operations on sectors #6 and #7 (pictured) will be performed in parallel.
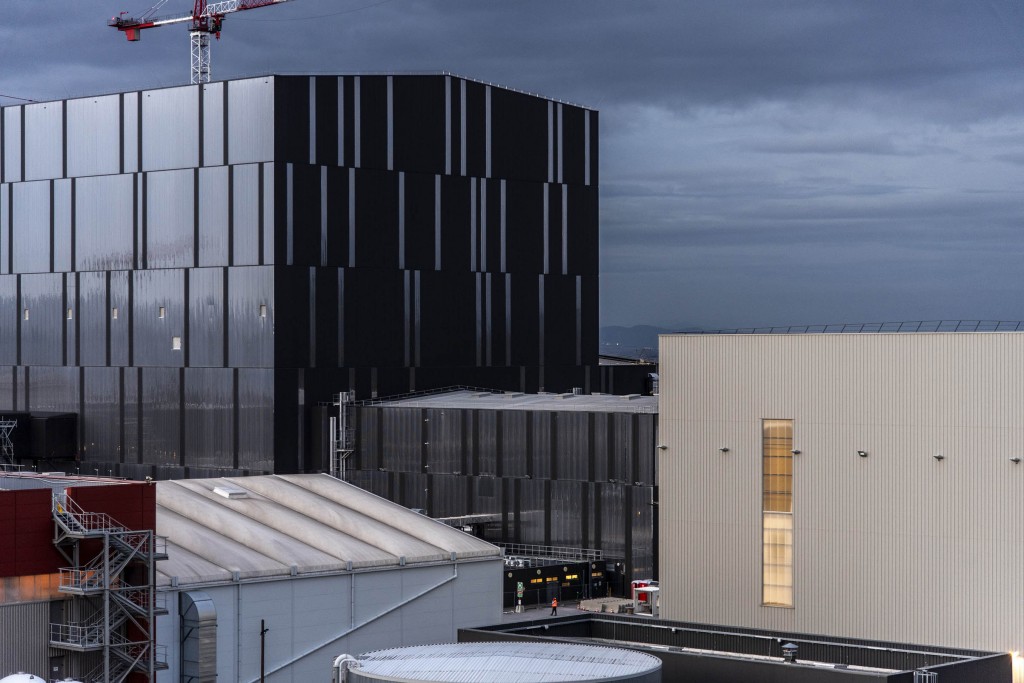
Mammoth
2024-02-08 - One worker in an orange jacket provides the scale we need to understand the size of some of the ITER buildings.

Vacuum vessel metrology
2024-02-08 - In the ITER Assembly Hall, metrologists from the SIMANN (SIMIC-Ansaldo) consortium are performing ultra-precise measurements on the bevel joint region of vacuum vessel sector #7.
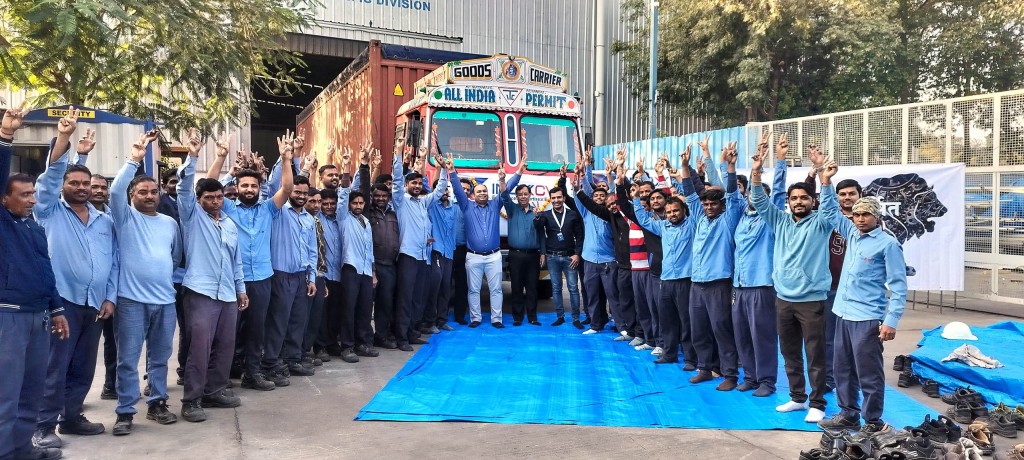
First repaired elements leave Indian factory
2024-02-03 - On the basis of a repair contract concluded with the ITER Organization in 2023, INOX-CVA India began on the repair of two vacuum vessel thermal shield sets. The first repaired elements left the factory in Vadodara this week for shipment to ITER.

Bevel repair
2024-02-02 - Sector #7, seen from below. The bevel region of a vacuum vessel sector describes the joint region on either side that must be welded to the next sector.
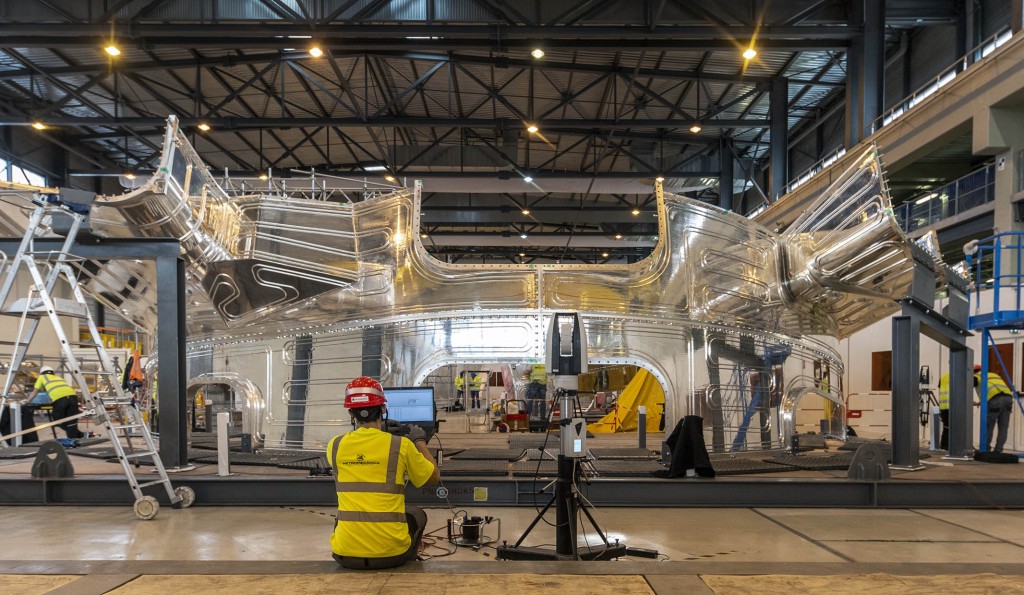
Supporting ITER units for all metrology needs
2024-01-26 - Metrology is involved in every step of ITER machine assembly, including the repair works underway on critical components. The size of thermal shield segments, measuring around 15 metres by 10 metres in area, is one of the challenges for metrologists, obliging them to take laser observations from multiple instrument locations. (See more at https://www.iter.org/newsline/-/3992)

Scanning before thermal shield repair
2024-01-26 - A vacuum vessel thermal shield outboard segment is surveyed before repairs. Capturing flange features (hole cylinders) helps to define the as-built reference model.
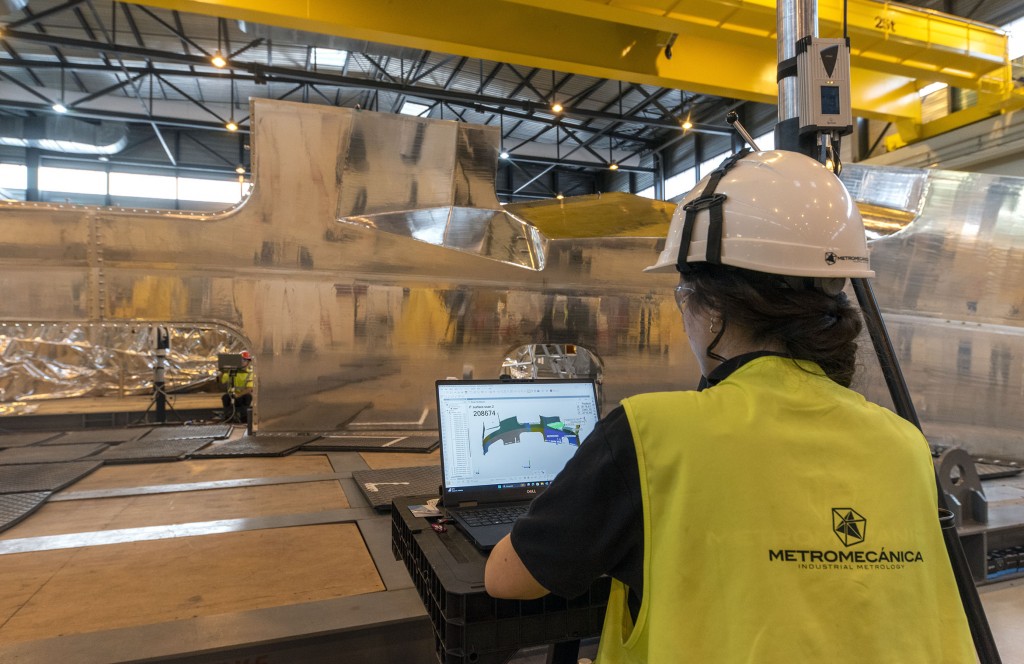
Assessing structural changes caused by repair
2024-01-26 - Metrologists are being called on to assess the structural changes resulting that may result from repairs—but in order to do so, they have to quantify several sources of variation such as support structure pressure and temperature. Here, a metrologist performs a shell scan using ATS600.

Repairing the sectors
2024-01-23 - Vacuum vessel sectors #6 and #7 are positioned in the Assembly Hall tooling for repair and early activities are underway. A third sector (#8) was moved from the Assembly Hall to the now-vacated Cryostat Workshop for repair in a horizontal position. Tooling will have to be adapted.

Qualifying procedures
2024-01-23 - The vacuum vessel sectors have been stripped of thermal shielding and toroidal field magnets as preparation for repair. Repair operations will begin in parallel by the end of February/beginning of March when all tests and qualification procedures are complete.
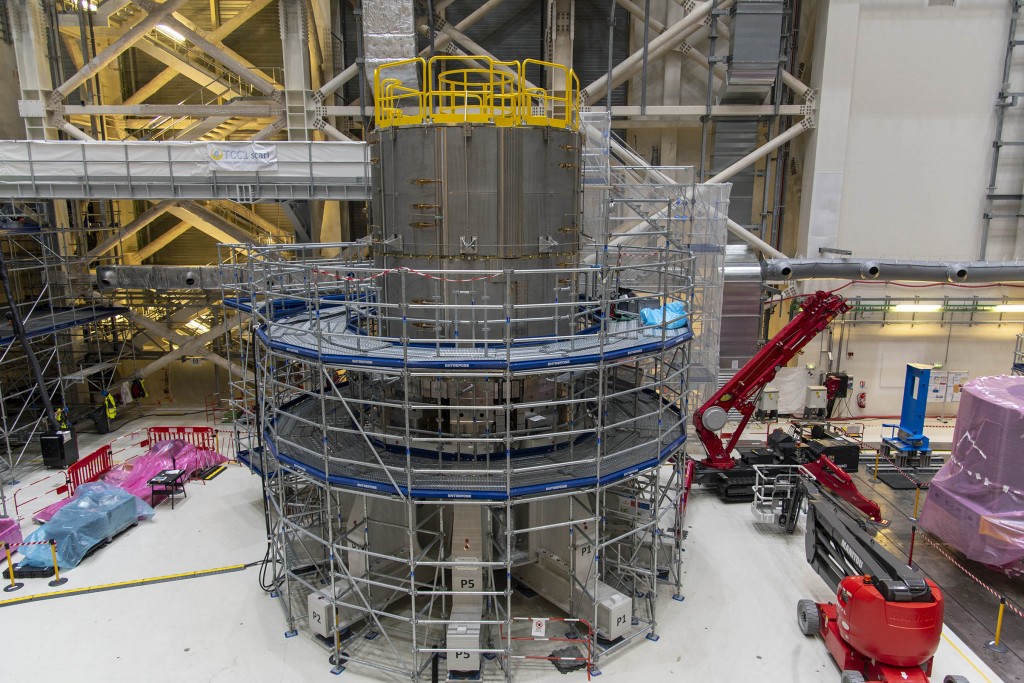
The stack
2024-01-18 - The second central solenoid module is now fully installed on the first and the team is preparing for the placement of the next module.
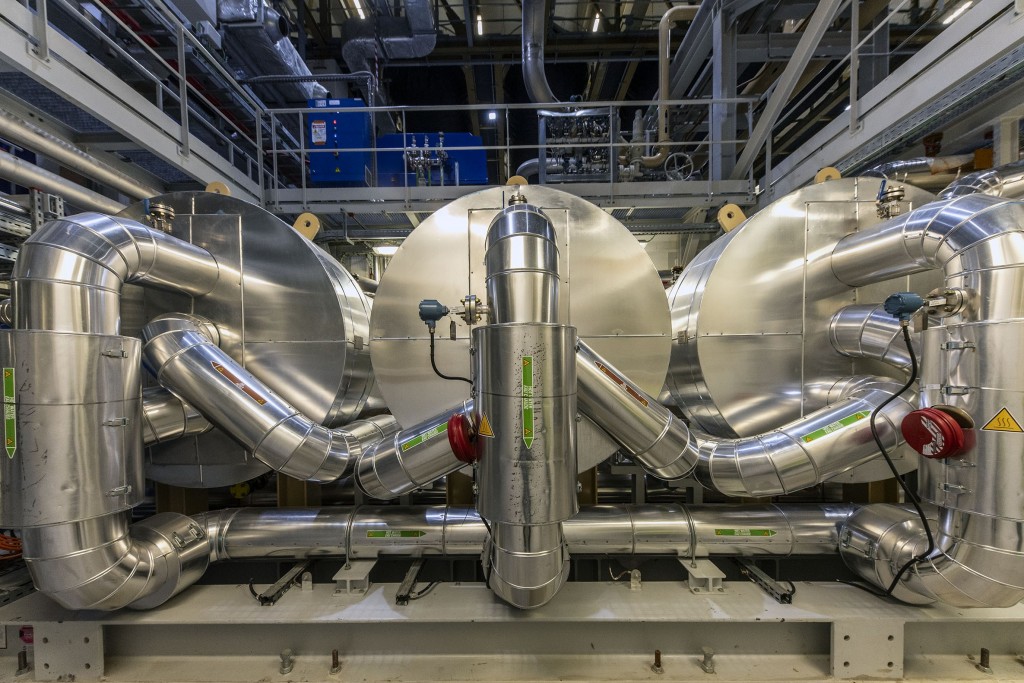
Recouping energy from the cryoplant
2024-01-18 - In the ITER cryoplant, 12 additional heat exchangers have been installed in the liquid helium plant to recover the heat generated by the helium compression process. (Three are pictured here.) This energy-saving initiative has been the beneficiary of an important financial subsidy from the French utility EDF.

Finding infinitesimal needles in a haystack
2024-01-16 - This photo, from summer 2022, shows how sections of thermal shield cooling pipe showing corrosion were removed and sent to CERN to be sliced, polished, and X-ray tomographed in a unique campaign to discover the extent of cracking. There will be an update on repair works soon in the ITER Newsline.
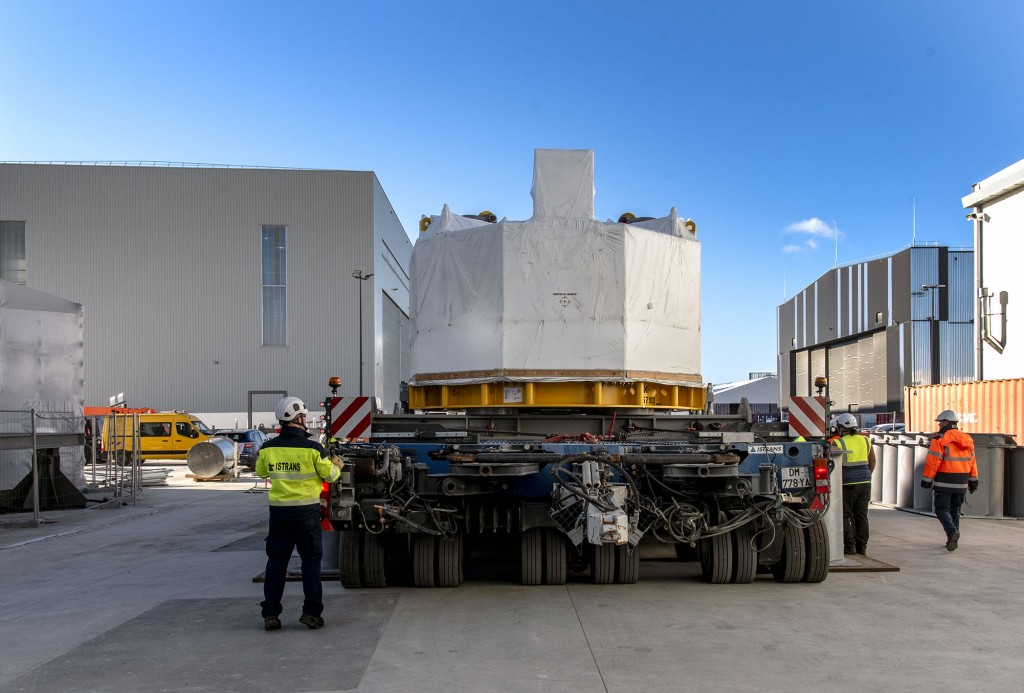
Deliveries continue
2023-12-22 - This 110-tonne central solenoid module is the fourth (of seven) to be delivered to ITER by the US Domestic Agency.

Very last toroidal field coil
2023-12-15 - The team celebrates as the delivery of toroidal field coil #18 from Europe marks the very end of the toroidal field procurement program. Nineteen magnets in all—each weighing approximately 330 tonnes (the weight of a large jetliner)—have been delivered to the ITER site.

Dispatchers
2023-12-01 - Dozens of connections, large and small, protrude from the boiler-like component. Auxiliary cold boxes act like dispatchers, receiving the different fluids from the cryogenic termination cold box located inside the cryoplant and redistributing them throughout the ITER machine.

Up and over
2023-12-01 - The auxiliary cold box is lifted over the wall into the Tokamak Building where it will be pre-positioned in a gallery at L3 level.

Supplied by India, manufactured in Switzerland
2023-12-01 - Pending their final installation, three auxiliary cold boxes—part of the cryogenic distribution system—have been pre-positioned in the Tokamak Building. Two others are expected next year. The components were procured by ITER India and designed and manufactured by Linde Kryotechnik AG in Switzerland.
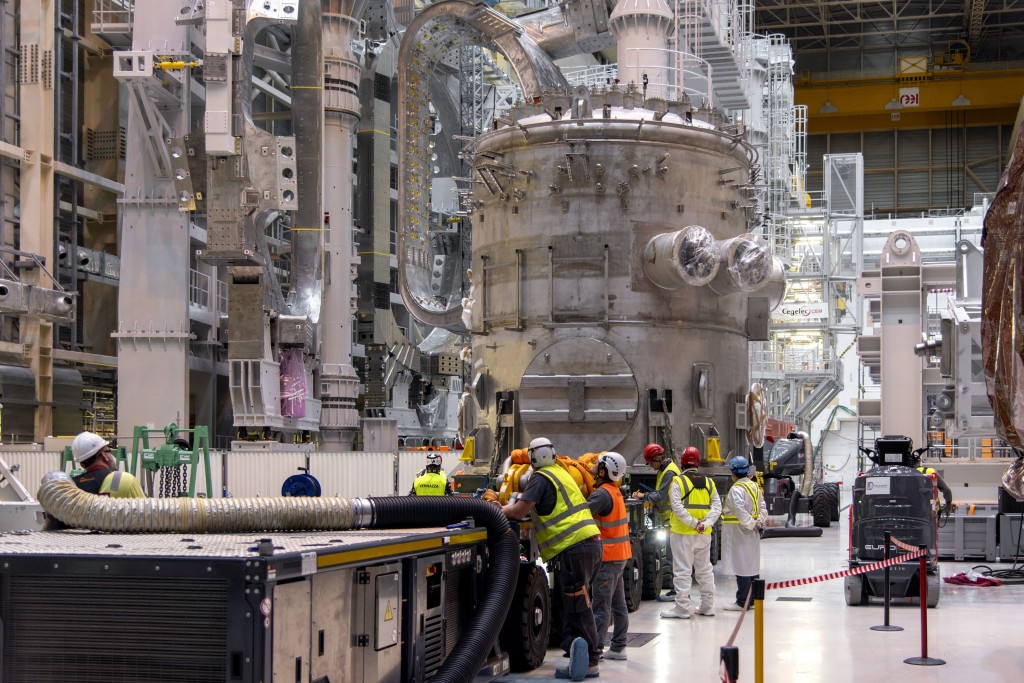
First of five "auxiliary cold boxes"
2023-12-01 - This 28-tonne "auxiliary cold box"—part of the distribution system for cryogenic fluids—is being transferred into the Assembly Hall for lifting. https://www.iter.org/newsline/-/3972
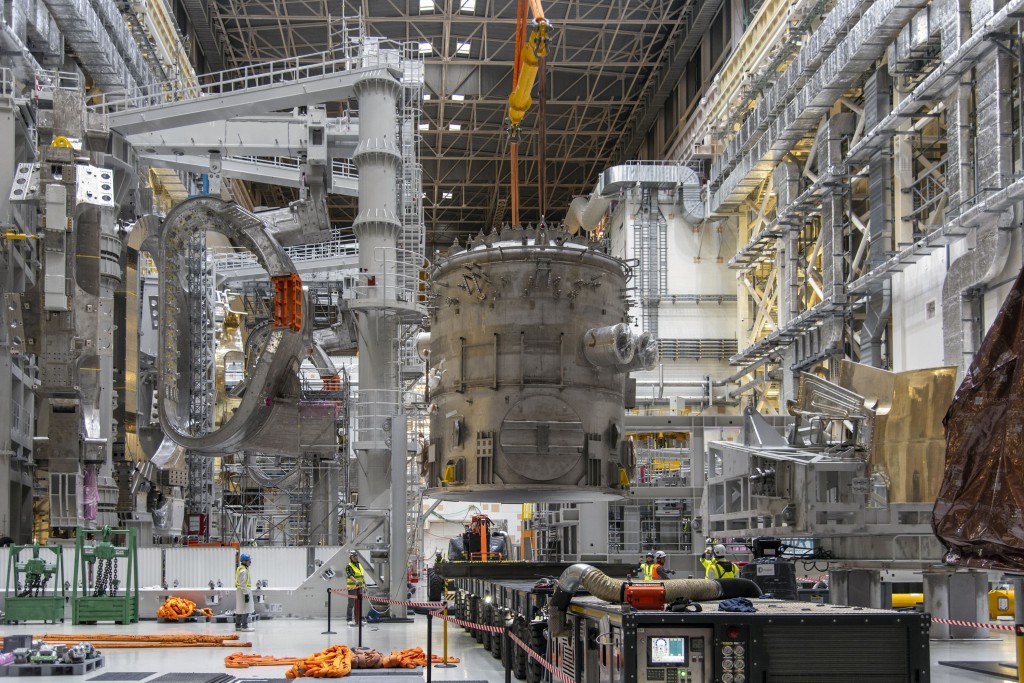
Heading across
2023-12-01 - The load is lifted by overhead crane from the truck bed and carried to the other end of the Assembly Hall, where it will be lifted over the wall.

Lowered through
2023-12-01 - Near the machine assembly, a large opening permits access to the L3 level of the Tokamak Building.

Holiday panettone
2023-11-28 - Vacuum vessel sector #8 has been wrapped in three layers of plastic protection for storage. The shiny top layer, and the form of the component in its horizontal orientation, make it resemble a panettone, that Italian sweet bread hat is enjoyed throughout southern Europe at Christmas and New Year.

Change of banner
2023-11-24 - The banner on the facade of the imposing Tokamak Building has been changed. For over three years, a banner had declared collective pride celebrating the delivery of the building. Now that the machine has entered the assembly phase, the message is one of commitment: "Safely assembling ITER."
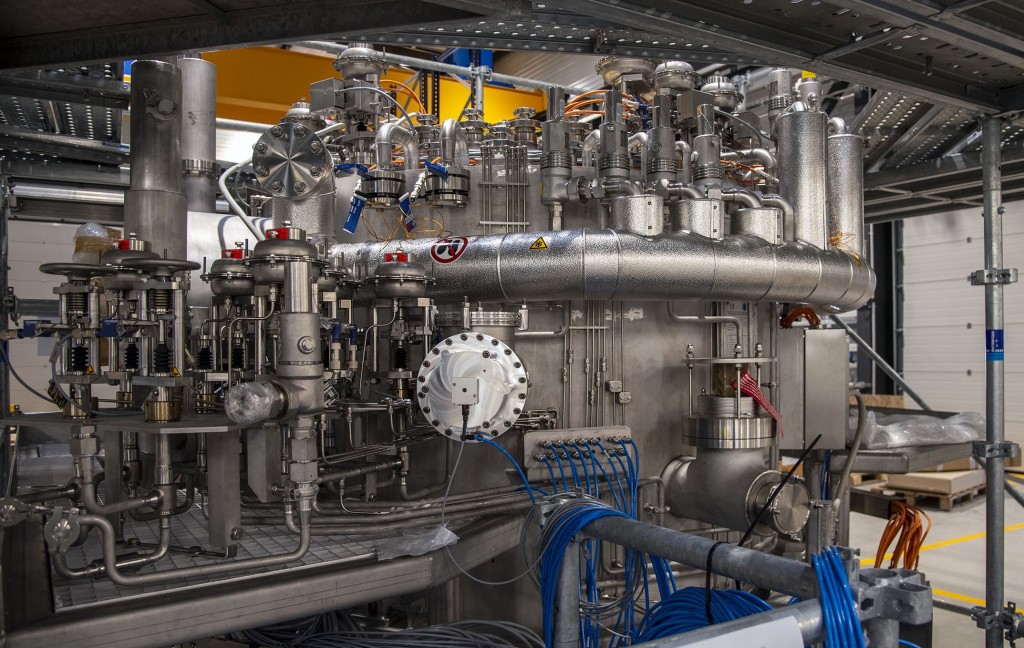
Vacuum equipment testing
2023-11-23 - In the Vacuum Lab on site, the first cold valve box procured by Europe is undergoing site acceptance tests. (More at https://www.iter.org/newsline/-/3958)

Coming down
2023-11-07 - The D-shaped toroidal field coil (TF13) has been removed from sector module #6 and placed in the "upending" tool (photo). The tool will return the coil to the horizontal position it was delivered in, so it can be removed from the Assembly Hall and placed in storage.
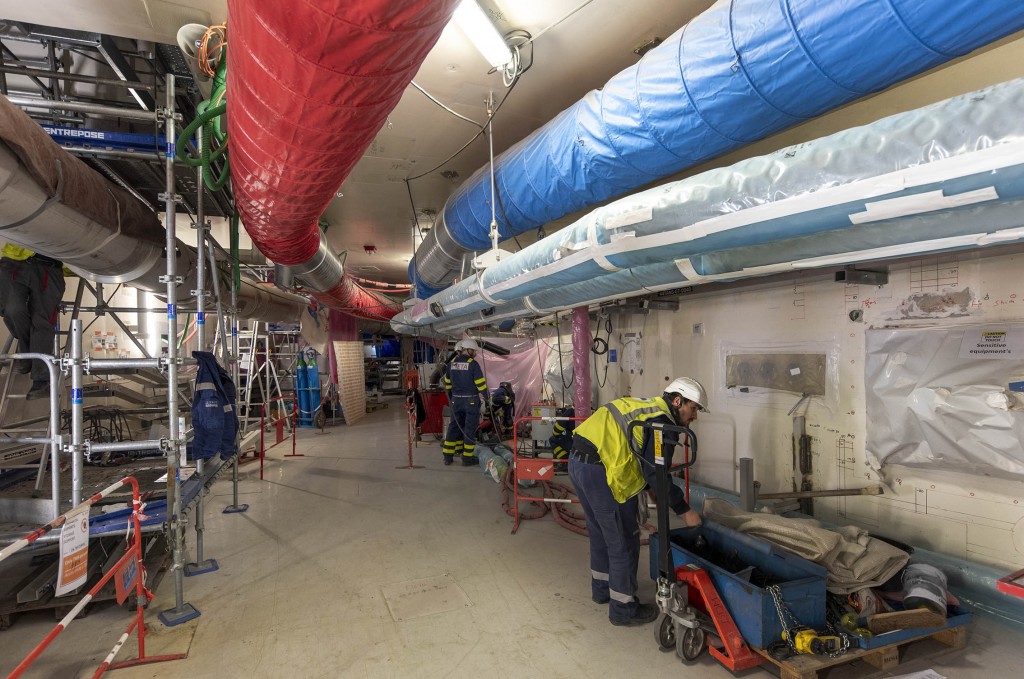
Little by little
2023-11-07 - When all equipment is installed in the galleries of the Tokamak Complex, walking room will be tight!

Cavernous galleries
2023-11-07 - In the bowels of the Tokamak Complex, plant systems are being installed little by little. The red and blue ducts that are part of a temporary HVAC system installed by works contractors to keep the building conditions at nominal.
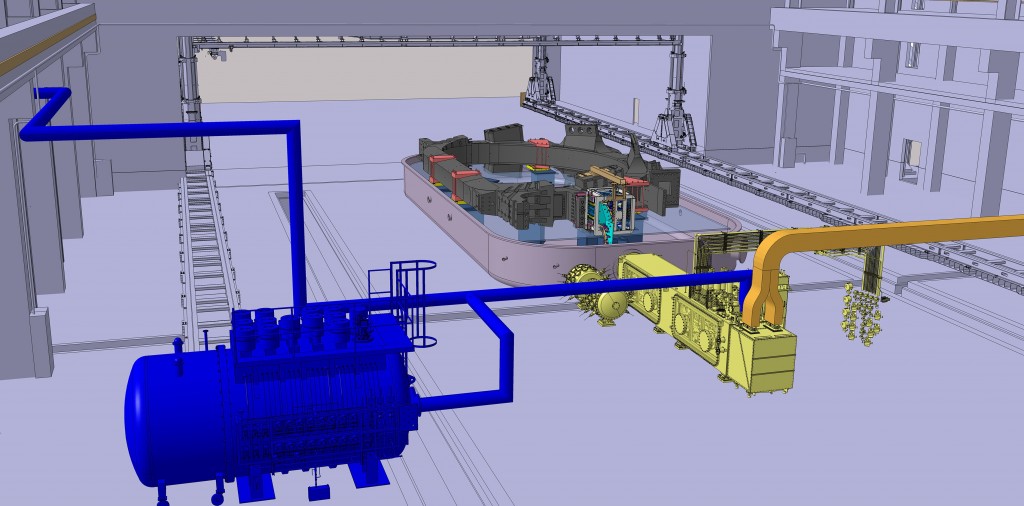
Toroidal field coils will be tested at 4 K
2023-11-06 - While repairs are ongoing on the vacuum vessel and thermal shield, a window has opened to test "as many toroidal field coils" as possible at 4 K (-269° C). "A 4 K test is about much more than just testing a coil ... it's about validating a whole infrastructure (the power supply system, the cryogenics, the feeders, the control-command system ...). Along with minimizing risks, this partial commissioning will be like a general rehearsal that will save us a considerable amount of time," says Project Leader David Grillot. More at https://www.iter.org/newsline/-/3954.

Smallest poloidal field coil also
2023-11-06 - The cold test infrastructure will be dimensioned for the D-shaped toroidal field coils, but the smallest poloidal field coil, PF1, is also a good fit and can be tested.

New project launched: a 4 K magnet cold test facility
2023-11-02 - This is the dedicated, fully matrixed project team that has been established to set up the magnet cold testing facility in less than two years. The plan is to test at least one toroidal field coil from each manufacturer. (Each cold test takes from 4 to 6 months.)
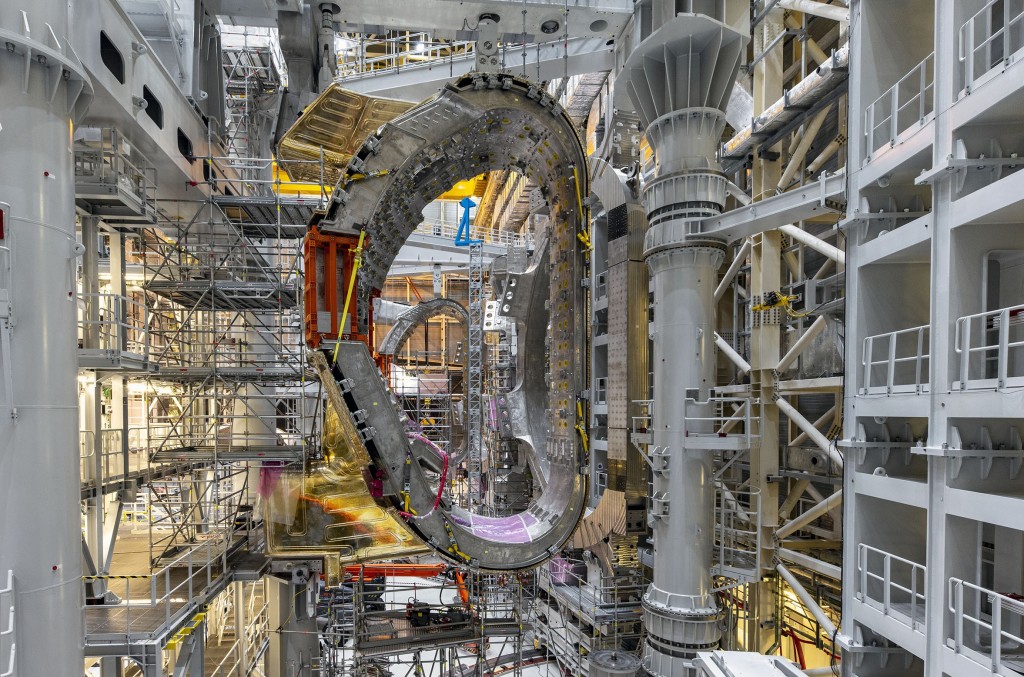
Disassembling sector module #6
2023-11-01 - To prepare vacuum vessel sector #6 (foreground) for repair, teams are removing the two toroidal field coils and the thermal shield panels that created sector module #6. One coils has been removed so far.

Advancing R&D for neutral beam injection
2023-10-27 - A cooperation agreement signed in 2020 between the ITER Organization, Consorzio RFX (host to the test facility) and EUROfusion formalized the involvement of European experts in the ITER Neutral Beam Test Facility. In October 2023, some of these experts were at ITER.

Neutral beam experts at ITER
2023-10-26 - On 26 and 27 October 2023, EUROfusion experts working to support the R&D for the ITER neutral beam injection system at Consorzio RFX and IPP Garching meet at ITER. Each one presents research updates in poster form.

About to shine
2023-10-24 - The High Voltage Building (left), which will house part of the power supply for the neutral beam injection heating system, is being "dressed" in its final layer of silver and black cladding and will soon match the other large buildings on site.

Ring-coil fabrication: spreader beam no longer needed
2023-10-12 - In the Poloidal Field Coils Winding Facility, a spreader beam (lifting capacity: 48 tonnes) was used under the overhead crane to balance the weight of the individual double pancake windings as they were transferred from the winding table. This phase of fabrication is over, and the spreader beam was dismantled in October.

Last pour for Tritium Building
2023-10-12 - The last significant concrete pour, on Thursday 12 October, was to create a 60-centimetre-thick slab for the aedicula sitting on top of the Trititum Building. The seven-storey building is now completely framed out, from B2 basement level to Level 5 and roof structures.
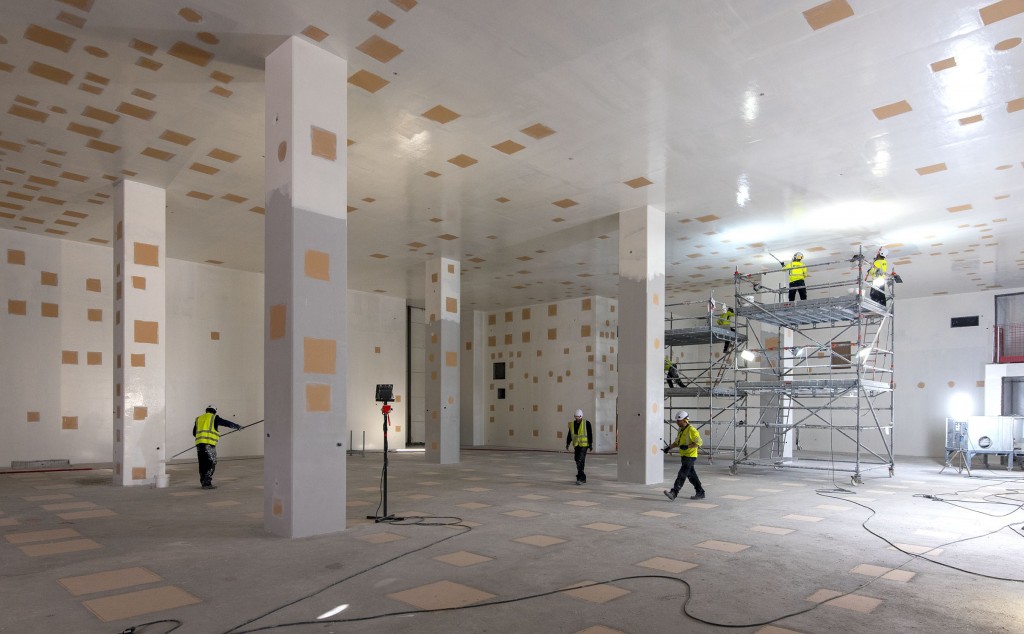
Painting inside the Tritium Building
2023-10-12 - Paint work is progressing inside the Tritium Building (pictured: the vault annex at level L4). This vast space (40,000 cubic metres) will accommodate equipment for the tokamak cooling water and tritium breeding systems.

Building use will change
2023-10-06 - The last ring coil in construction, PF3, is barely visible at the far end of the European coil winding facility. What is evident is that the building is being used in a new way as equipment is moved out. In the foreground, thermal shield panels are stored awaiting replacement or repair. Photo: ITER Organization/EJF Riche
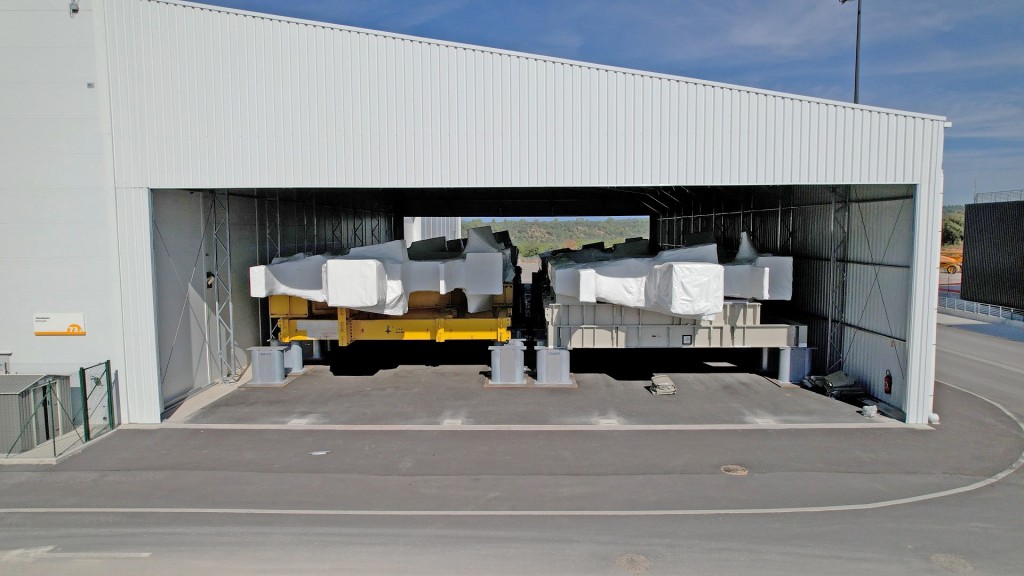
Magnet storage on site
2023-10-06 - Two toroidal field coils rest on their sides in storage. They will be called back into the Assembly Hall when repair is completed on the vacuum vessel sectors and thermal shield. Photo: ITER Organization/EJF Riche

Elements of the thermal shield
2023-10-06 - Contractors are cleaning a silver-coated element of the vacuum vessel thermal shield. Under the terms of repair contracts signed this year the thermal shield panels will either be repaired or replaced. Photo: ITER Organization/EJF Riche

Coils in storage
2023-09-29 - In this image, we see two poloidal field coils in storage on the ITER site: PF4 (foreground, ø24 metres) and PF6 (ø9 metres). Photo: ITER Organization/EJF Riche
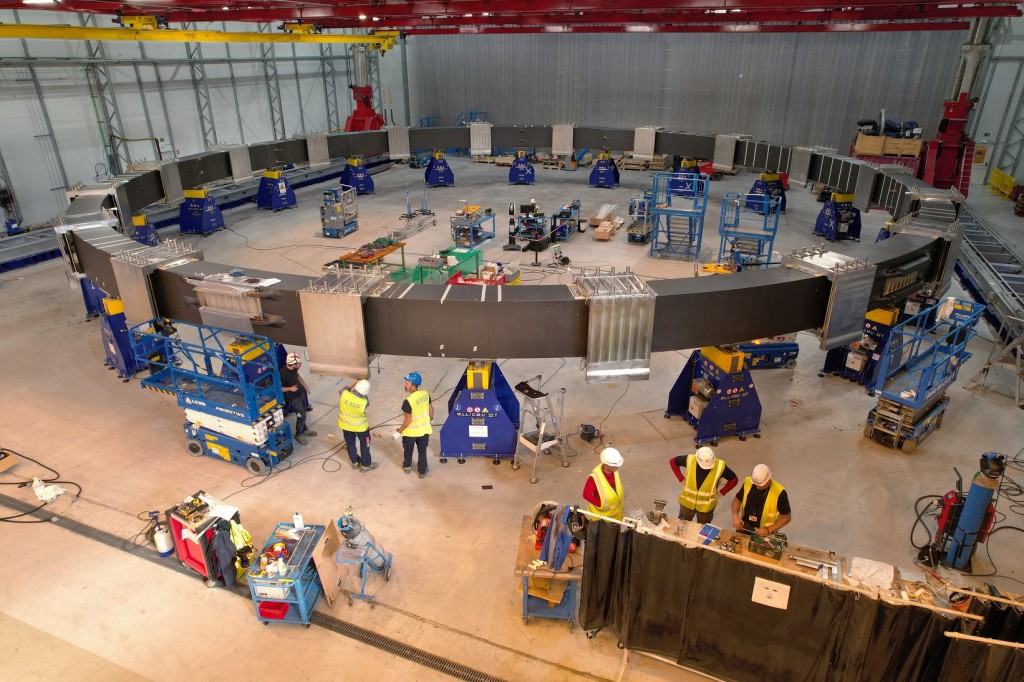
Last ring coil
2023-09-29 - In the European winding facility, teams are putting the finishing touches on poloidal field coil #3 (PF3). This is the last coil expected. Progressively, the building is being handed over for other assembly purposes. Photo: ITER Organization/EJF Riche
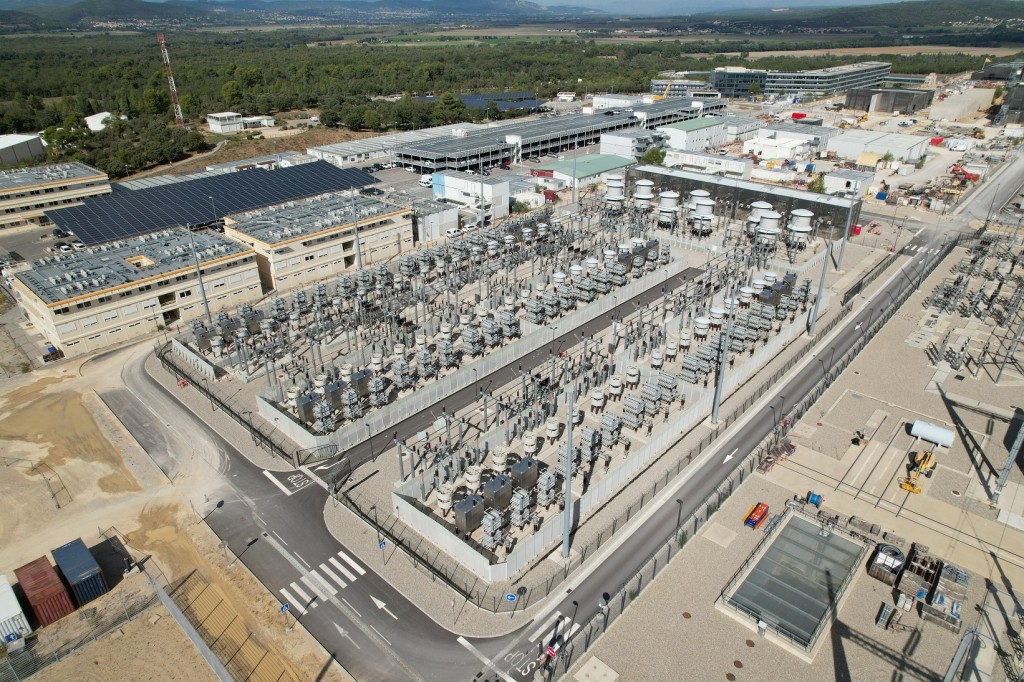
Reactive power compensation
2023-09-28 - The reactive power compensators area accommodates reactors, capacitors, resistors and sensors that aim to smooth the flow of AC current both inside the ITER installation and in the immediate vicinity. Photo: ITER Organization/EJF Riche
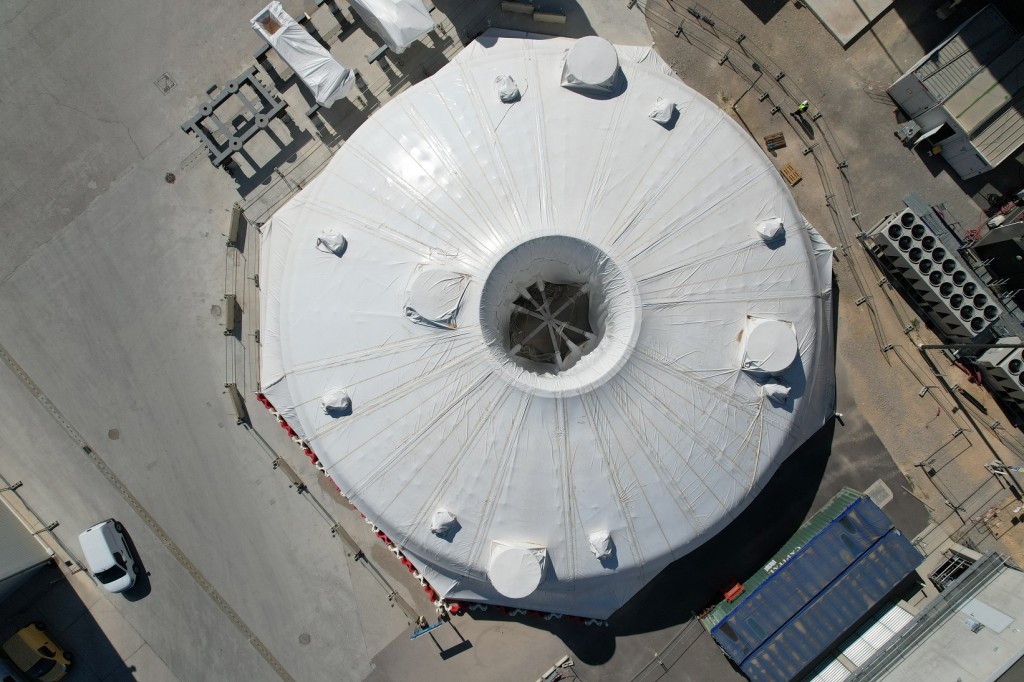
Stored outdoors
2023-09-27 - A drone flies over the top lid of the cryostat, which is stored on the platform under layers of protective covering. Photo: ITER Organization/EJF Riche
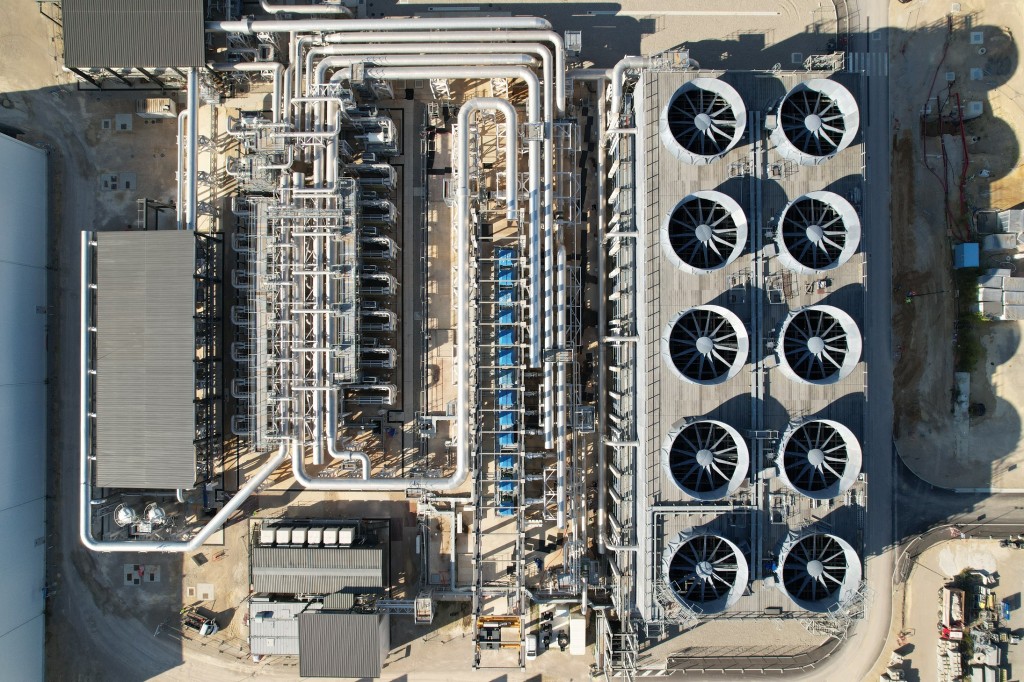
Heat rejection system, from the sky
2023-09-27 - The cooling water system is striking from above, with its neatly arranged pumps and pipes and its 10 cooling towers at right. Photo: ITER Organization/EJF Riche
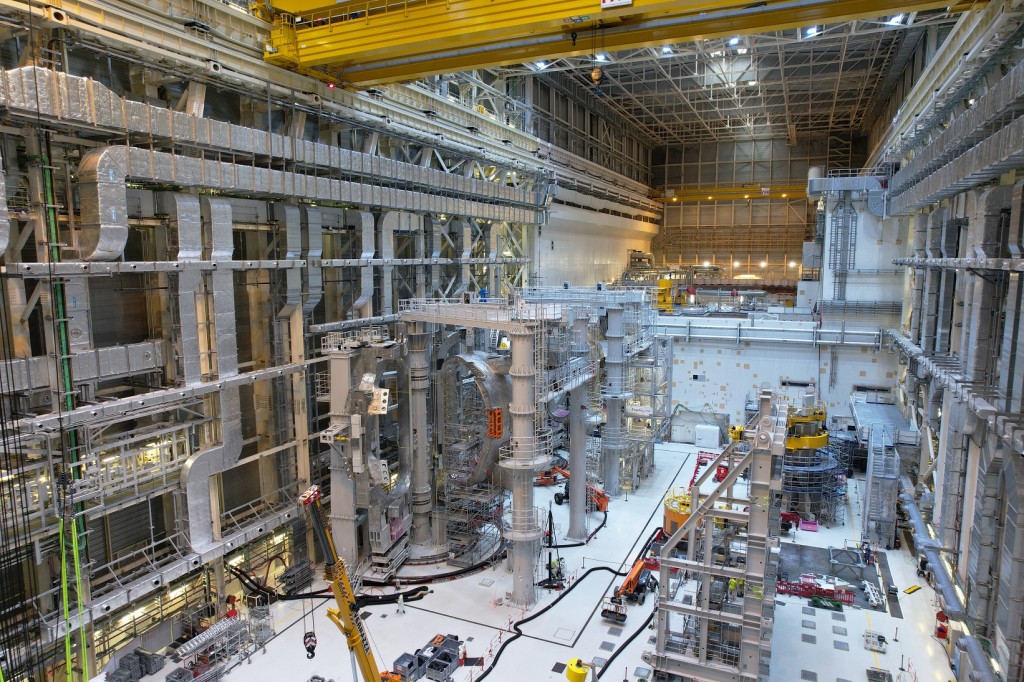
A busy hall
2023-09-27 - Looking across the Assembly Hall toward the wall that hides the Tokamak pit. The central solenoid stacking area is visible at right (round yellow tool). Photo: ITER Organization/EJF Riche
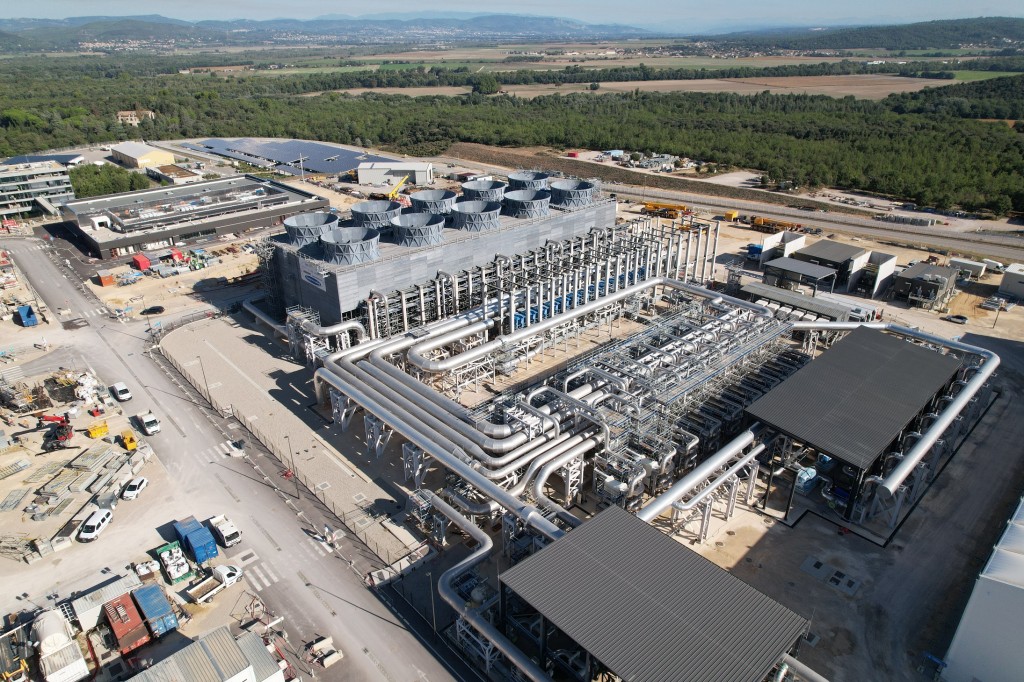
Systems vs integrated commissioning
2023-09-27 - ITER's approach to commissioning makes a clear distinction between system commissioning (underway now on many plant systems including the heat rejection system, pictured) and integrated commissioning. Integrated commissioning is a carefully orchestrated process that occurs only after all components and systems have been tested independently. Photo: ITER Organization/EJF Riche
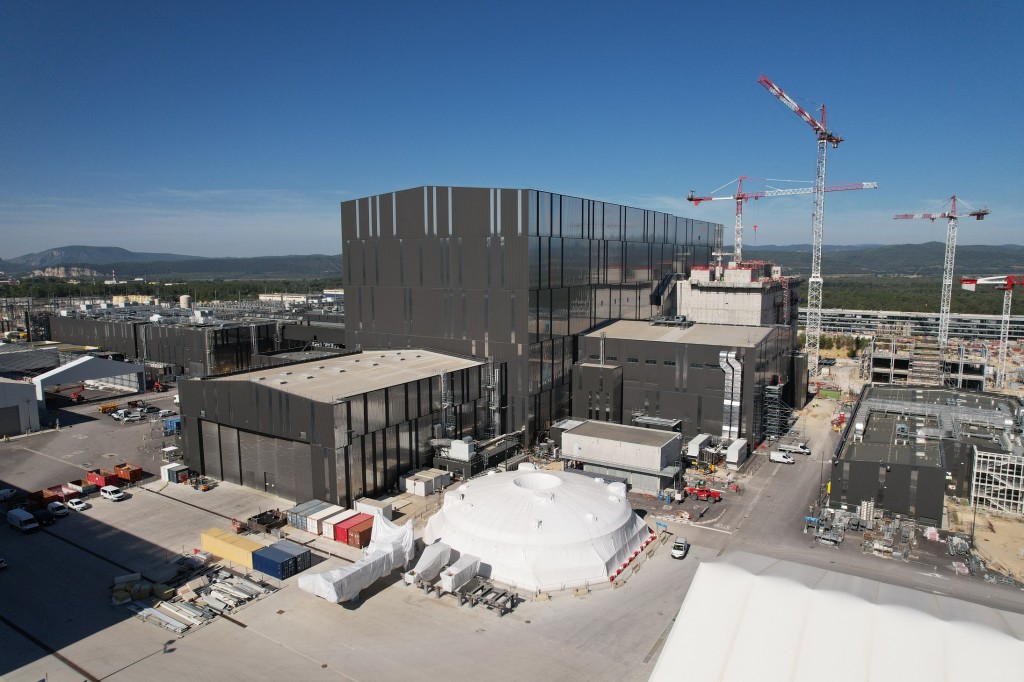
Components stored outside
2023-09-27 - Two large sections of the ITER cryostat, the top lid (photo) and the upper cylinder (not pictured) are stored on the ITER platform in weather-tight coverings. Their size (30 metres in diameter) makes them easier to store outside than inside. Photo: ITER Organization/EJF Riche
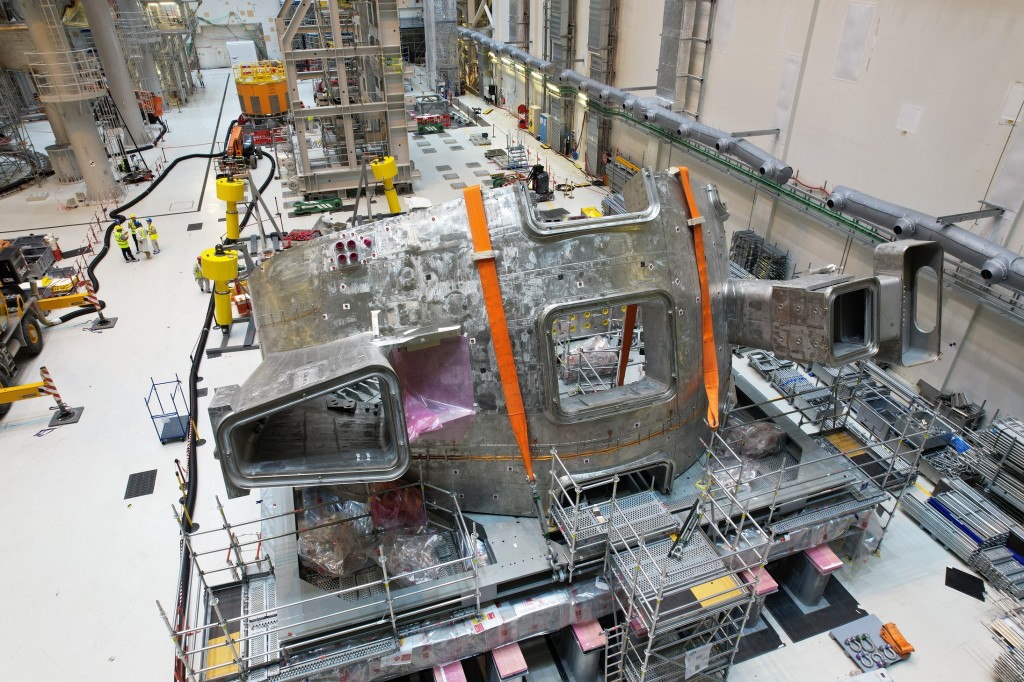
Waiting its turn
2023-09-27 - After dimensional non-conformities were found in the bevel (field joint) region of the three vacuum vessel sectors that have been delivered to ITER (#6, #7 and #8), sector #8 was removed from assembly tooling. It will be the last of the three to be repaired. Photo: ITER Organization/EJF Riche

Hovering over the assembly theatre
2023-09-27 - The drone hovers above the different "extensions" of the assembly theatre: left, the Cleaning Facility; bottom right, the Radiofrequency Building; top right, the now-completed Tritium Building. Photo: ITER Organization/EJF Riche
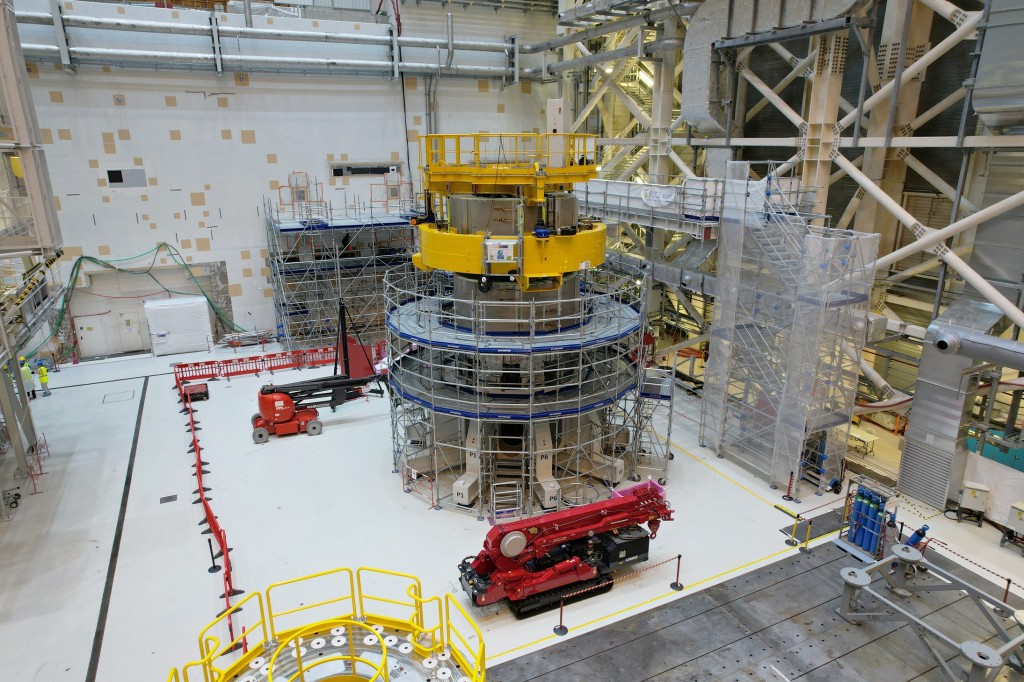
Stacking area
2023-09-27 - In this clearly delimited area, the central solenoid stack is rising. Two magnet modules are in place; four others will join them. Photo: ITER Organization/EJF Riche

Closeup
2023-09-27 - Commissioning is currently underway on the many integrated parts of the heat rejection system. Photo: ITER Organization/EJF Riche

The pit
2023-09-26 - Looking straight down into the 30-metre-deep Tokamak pit, which will house the world's largest tokamak. Photo: ITER Organization/EJF Riche

The cold factory
2023-09-26 - All equipment has been installed in the ITER cryoplant and commissioning is underway. The cryoplant will provide the extensive cryogenic power needed to cool the ITER magnets, thermal shield and cryopumps. Photo: ITER Organization/EJF Riche
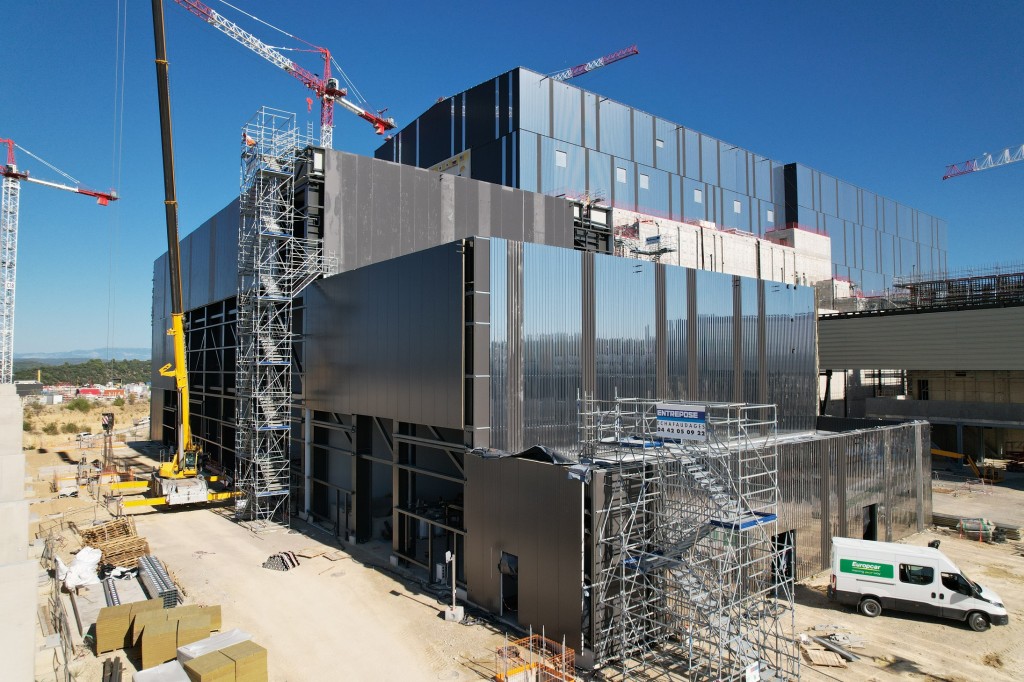
Near complete
2023-09-26 - Work has progressed quickly on the High Voltage Building, the neutral beam power supply building closest to the neutral beam injectors in the Tokamak Complex. Photo: ITER Organization/EJF Riche
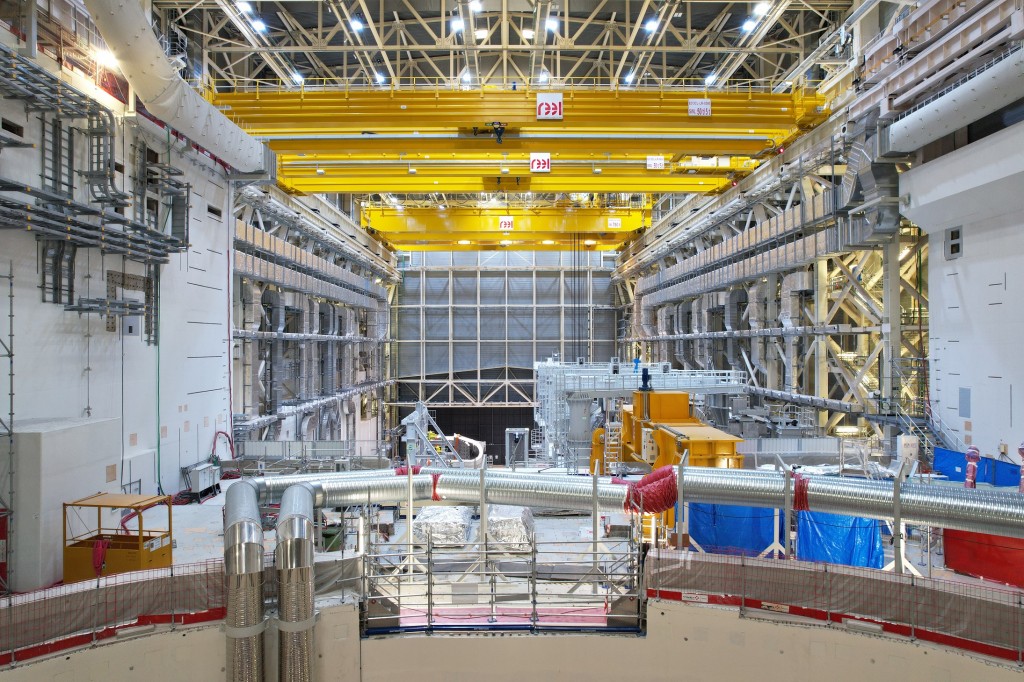
Workhorses
2023-09-26 - The workhorses of the machine are the overhead cranes, capable of working together to respectively lift 100 tonnes (the set in the foreground) and 1,500 tonnes (the set in the background). Photo: ITER Organization/EJF Riche
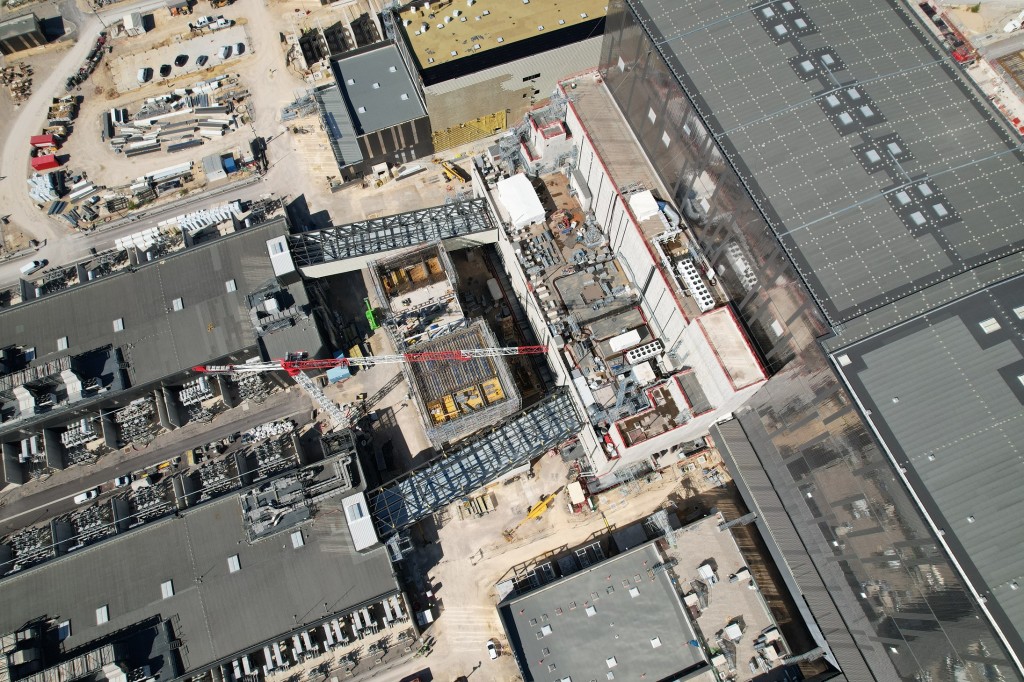
More bridges
2023-09-26 - Two bridges are in construction to link the Magnet Power Conversion buildings (left) to the Tokamak Complex. Photo: ITER Organization/EJF Riche
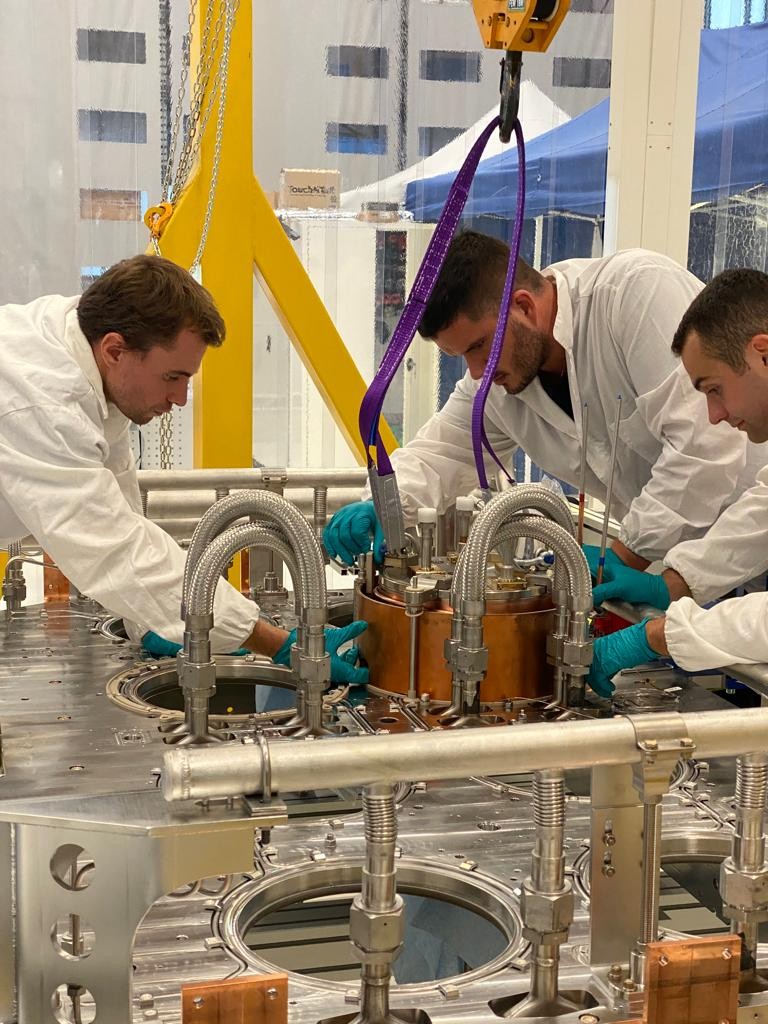
SPIDER re-assembly underway
2023-09-15 - The NBTF team is proceeding with the re-assembly of SPIDER after a key set of improvements were implemented (pictured, one of the test bed's radiofrequency drivers). SPIDER operated from 2018 to 2021 and is planning new experiments from 2024 on.
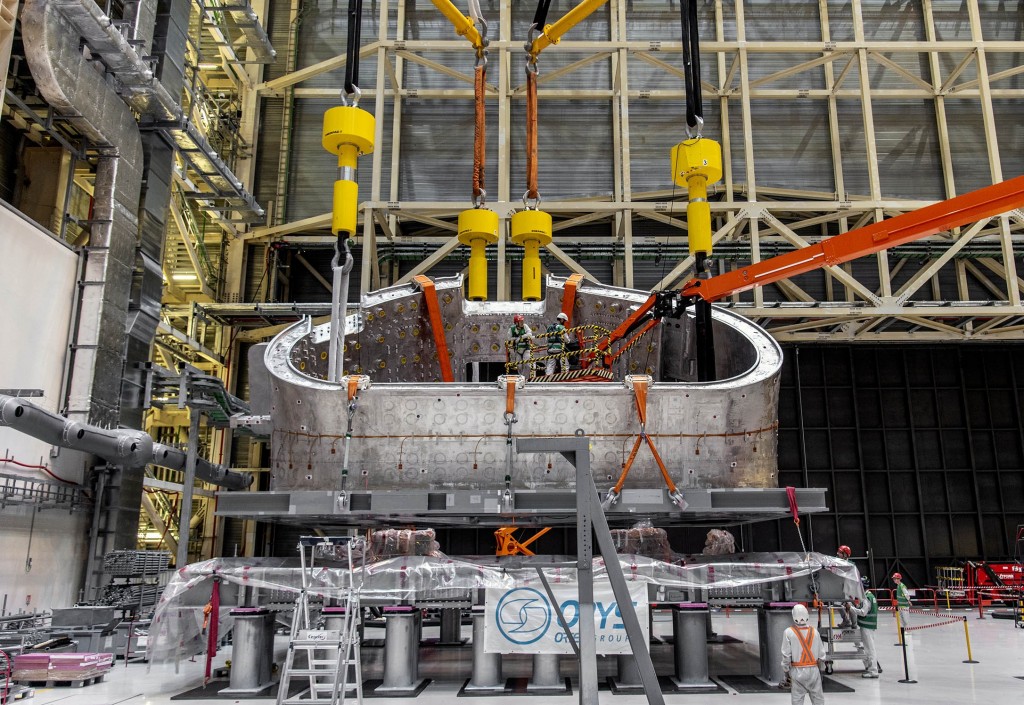
Sector #8 on the move
2023-09-15 - After spending just about one year in vertical tooling, vacuum vessel sector #8 has been returned to a horizontal orientation for removal from the Assembly Hall and repair.

Inside the MITICA bunker
2023-09-13 - Inside of the MITICA bunker with the vacuum vessel on the right and the last part of the 1MV transmission line in blue. When it enters operation, MITICA will be a 1:1-scale ITER neutral beam injector, the first to operate at ITER requirements (up to the full acceleration voltage of 1 MV and full power of 16.5 MW.

Window on the (ITER) world
2023-09-13 - This new viewpoint into the Tokamak pit is proving popular with visitors.
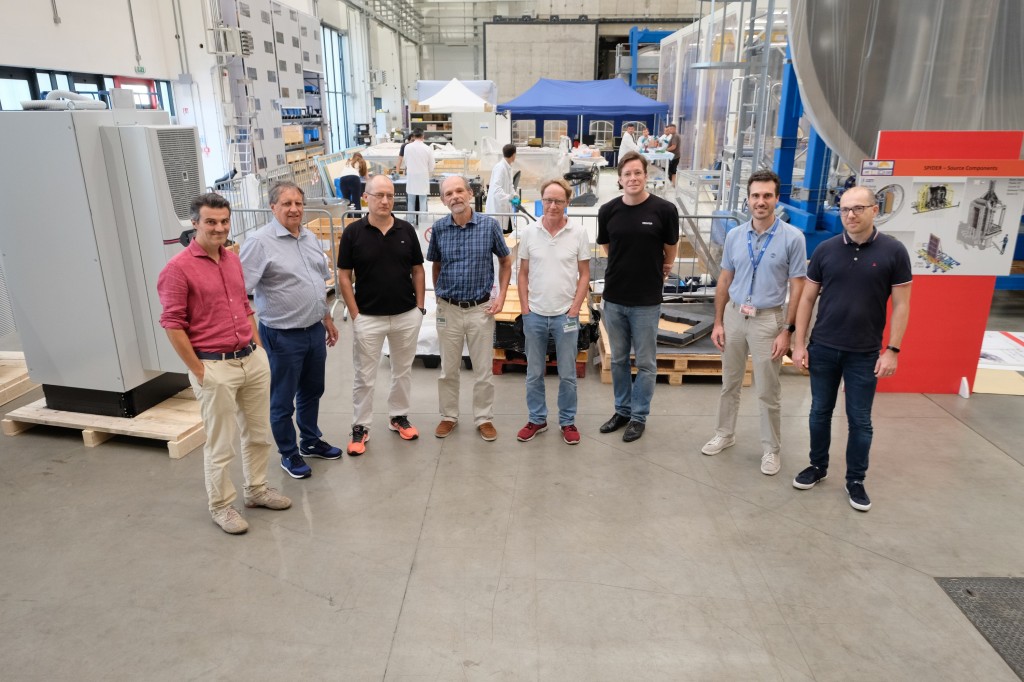
A team from IPP (Germany) visits the facility
2023-09-13 - Engineers and physicists from the Neutral Beam Injection Group at the Max Planck Institute for Plasma Physics together with members of the Neutral Beam Test Facility Team in the experimental hall. At IPP, two test facilities have for years been supporting the development of the radio-frequency-driven ion source for ITER neutral beam injection.
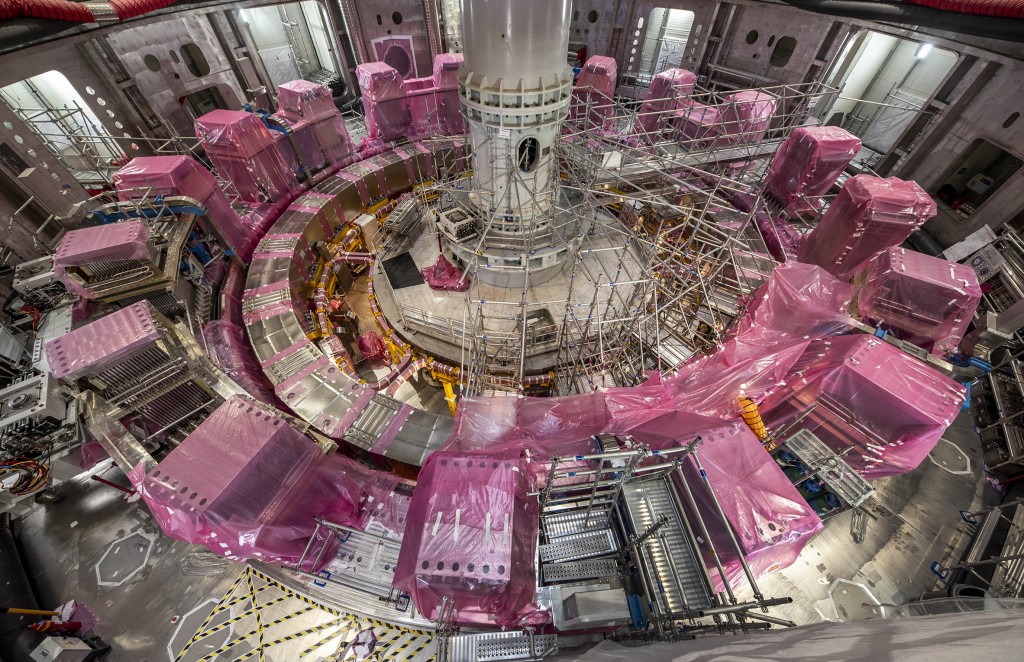
Protected in pink
2023-09-07 - Eighteen supports for the toroidal field magnets are protected in pink plastic. Just inside the circle formed by the supports is poloidal field magnet #5.

Central solenoid: now a two-module stack
2023-09-05 - Lifted by a bespoke tool exercising pressure through radial compression, a second 110-tonne central solenoid module is positioned on the assembly platform above the first. (A third waits its turn on the left.)
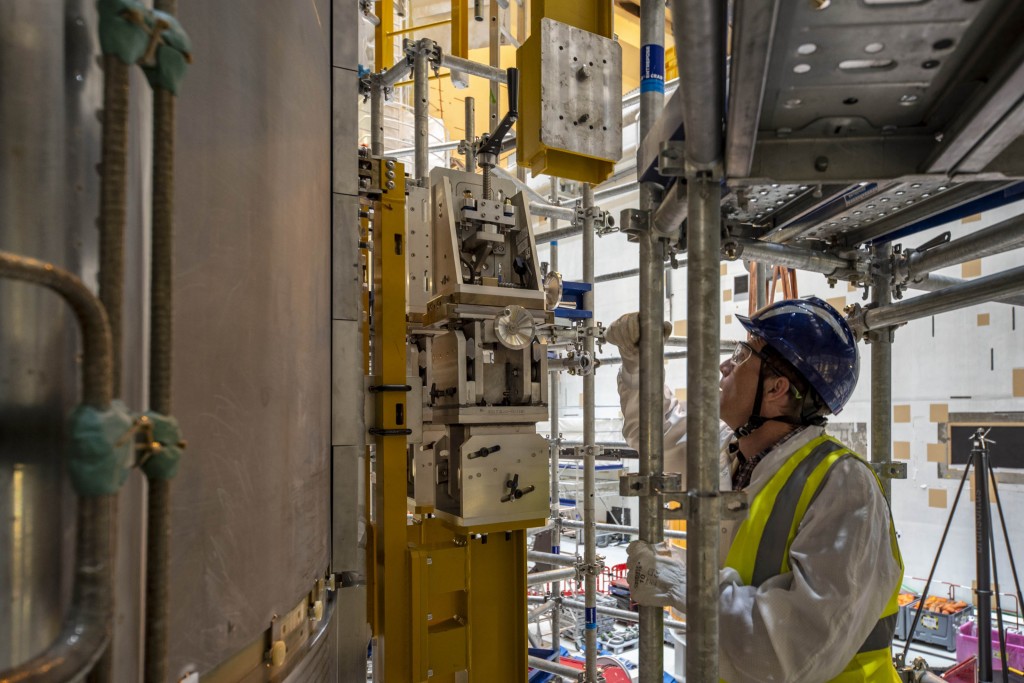
Pin-point precision
2023-09-05 - It takes a whole range of tools to position the 110-tonne component with the required precision: once cranes and ''synch hoists'' have done the heavy job, a complex system of subtle adjustment devices allows micrometric movements in pitch, roll and spin.
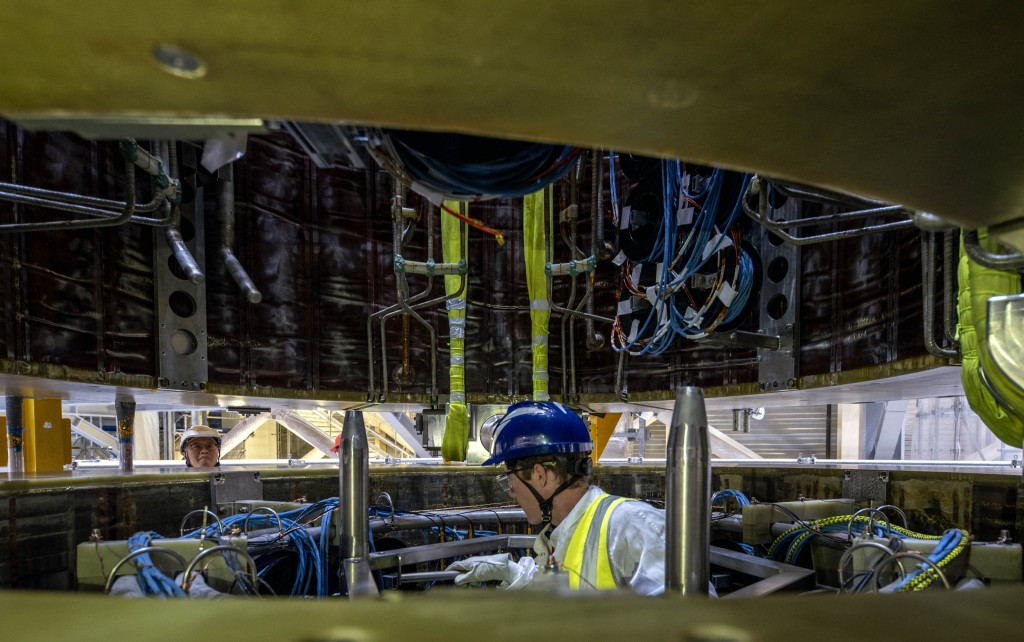
Small adjustments
2023-09-05 - Stacking cylindrical devices and connecting their fragile electrical and cryogenics leads demands a particular attention to concentricity and straightness.
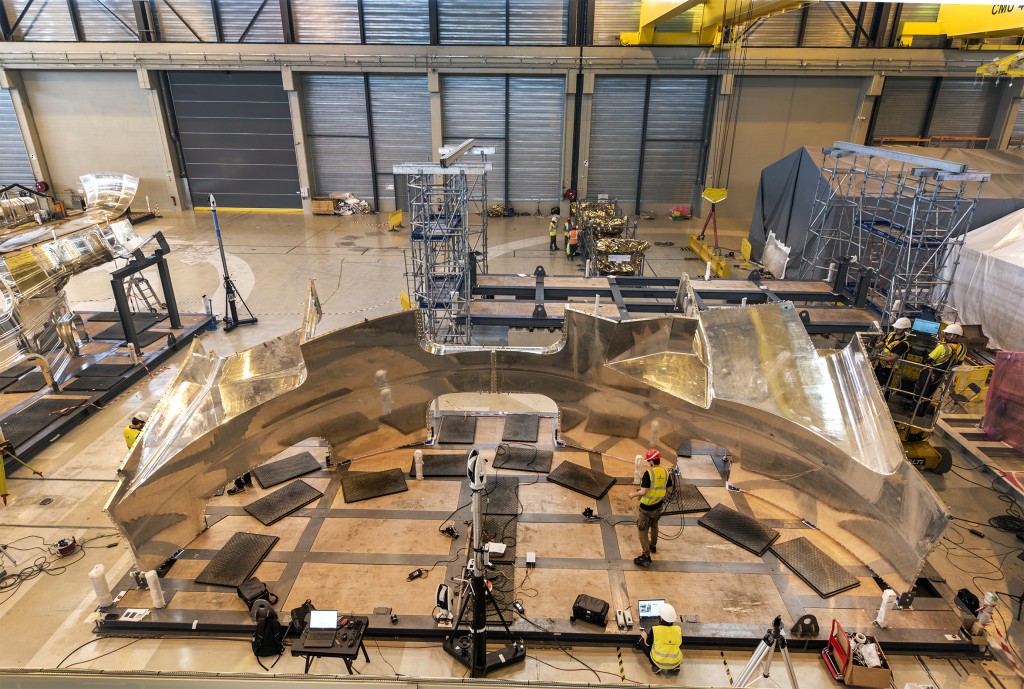
Recording as-built dimensions
2023-08-30 - This segment of thermal shield must be dismantled into four individual panels. Before that takes place, teams of metrologists record all of its as-built dimensions.
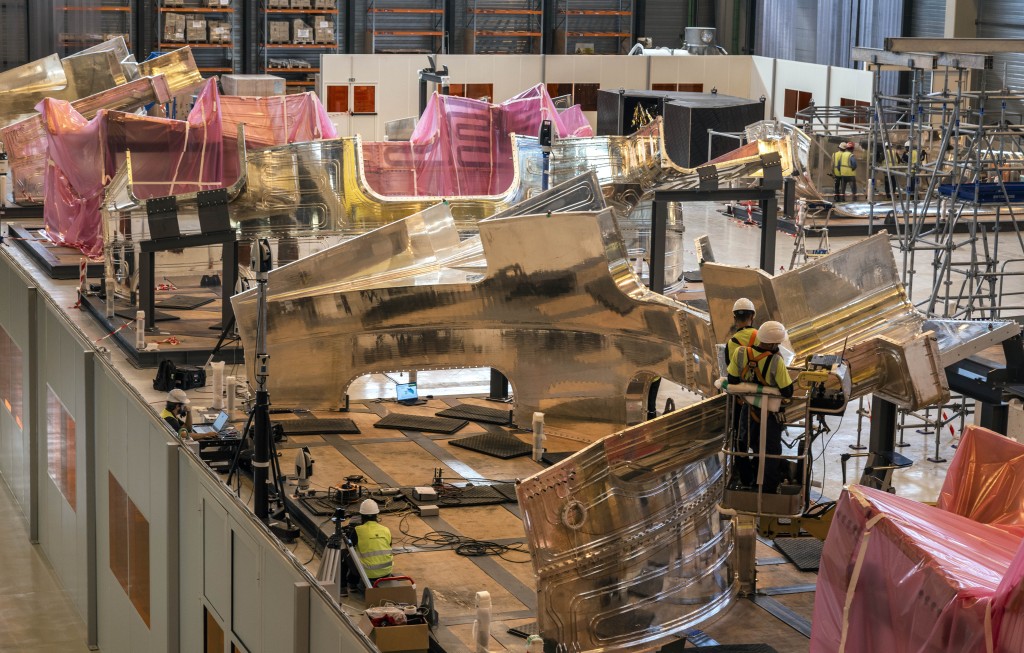
Thermal shield repair/replacement contracts signed
2023-08-30 - For vacuum vessel thermal shield sectors showing no sign of stress corrosion cracking, the panels can be repaired. The initial scope of the repair contract is for two sector sets to be disassembled at ITER, repaired at the contractor's premises, and returned. For thermal shield sectors already compromised by damage, complete re-fabrication is necessary.

Thermal shield: metrology underway
2023-08-30 - Metrology is underway on outboard segments of thermal shield at one end of the Poloidal Field Coils Winding Facility on site.
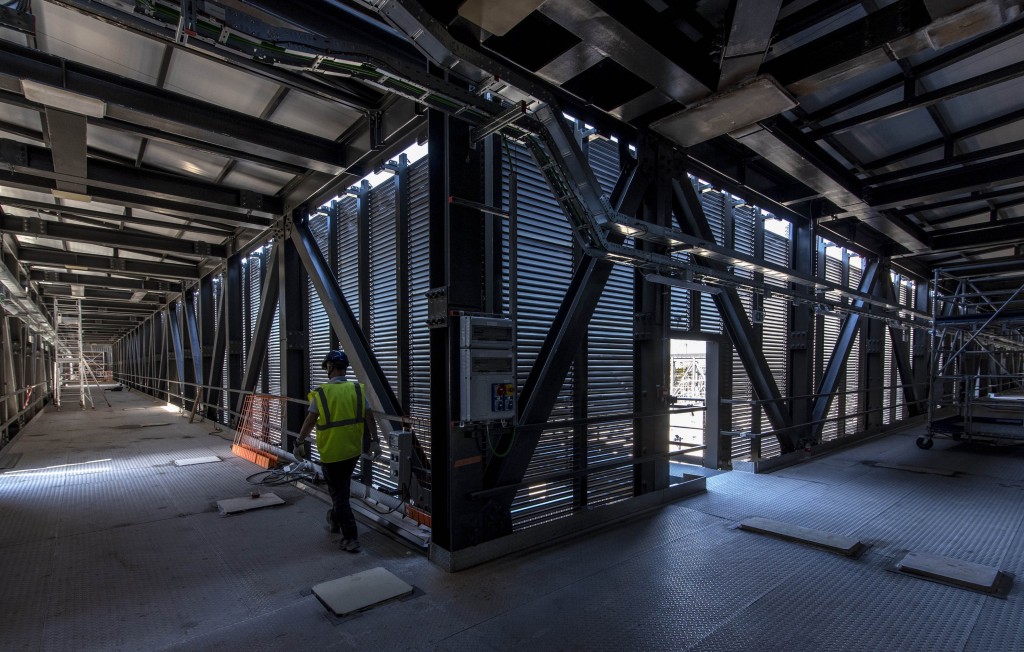
Inside the cryobridge
2023-08-29 - In order to connect the cryolines coming from the cryoplant to those already installed in the Tokamak Building, the cryobridge runs for 130 metres, first crossing the boulevard and then making a sharp left turn to run along the Assembly Hall. This employee is inside the cryobridge, walking towards the cryoplant.
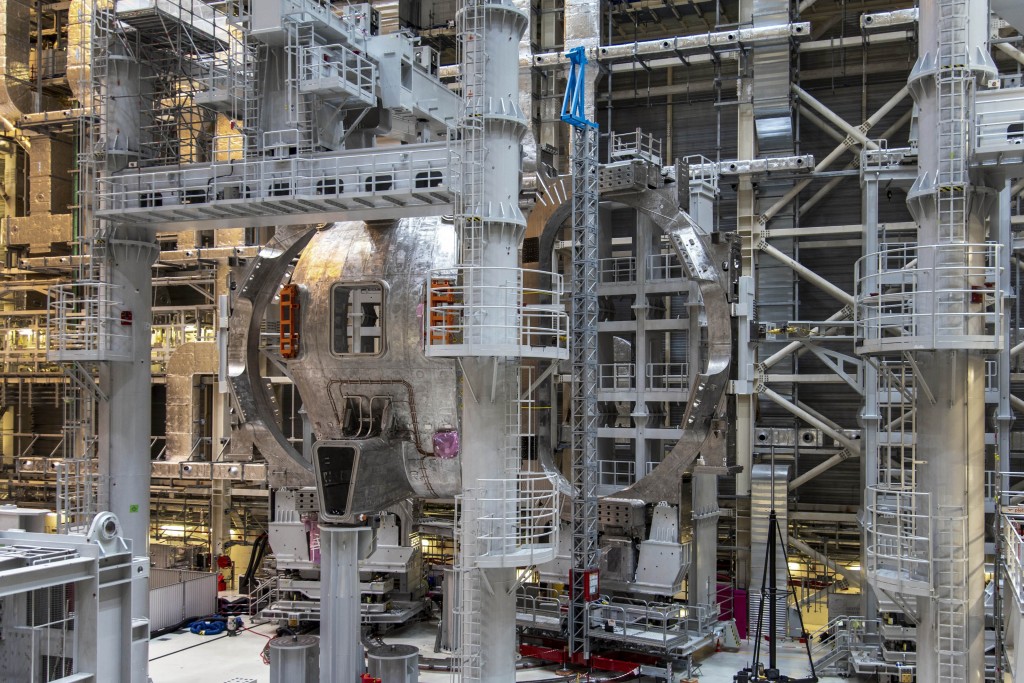
Same tool, different operation
2023-08-29 - The assembly of sector module #7 was almost finalized when the decision to stop the process and to dismantle was taken at the end of 2022. The reverse operation—the disassembly of the different elements making up a sector—is underway to prepare for repair work. (https://www.iter.org/newsline/-/3882
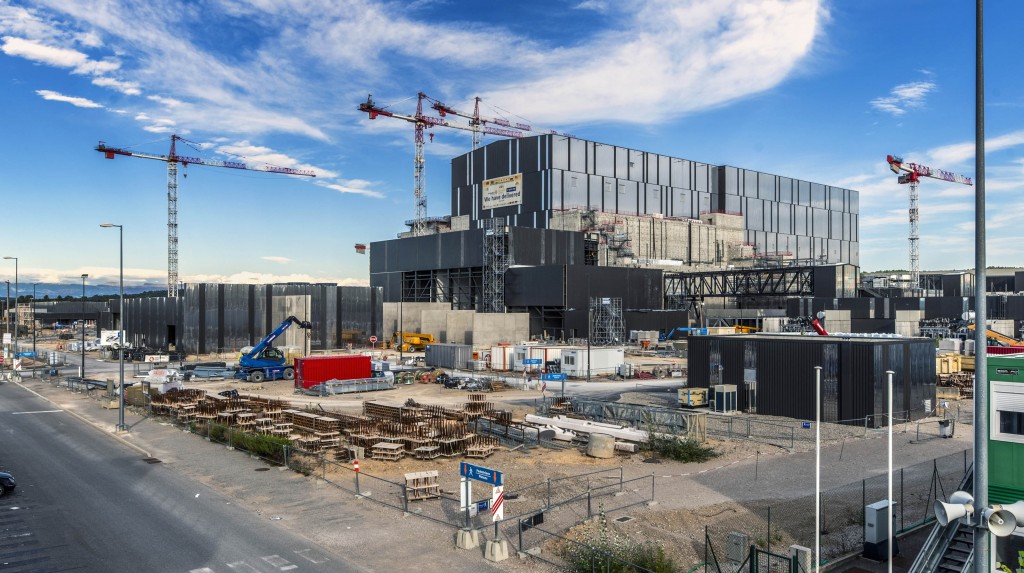
New buildings emerge
2023-08-29 - The concrete facade of the Tokamak Complex is now obscured by the High Voltage Building for neutral beam power supply (black, centre). Other fast-evolving features on the platform include the structure of a new bridge for the transfer of electrical power to the magnets (right) and the low-voltage Neutral Beam Power Supply Building (left).
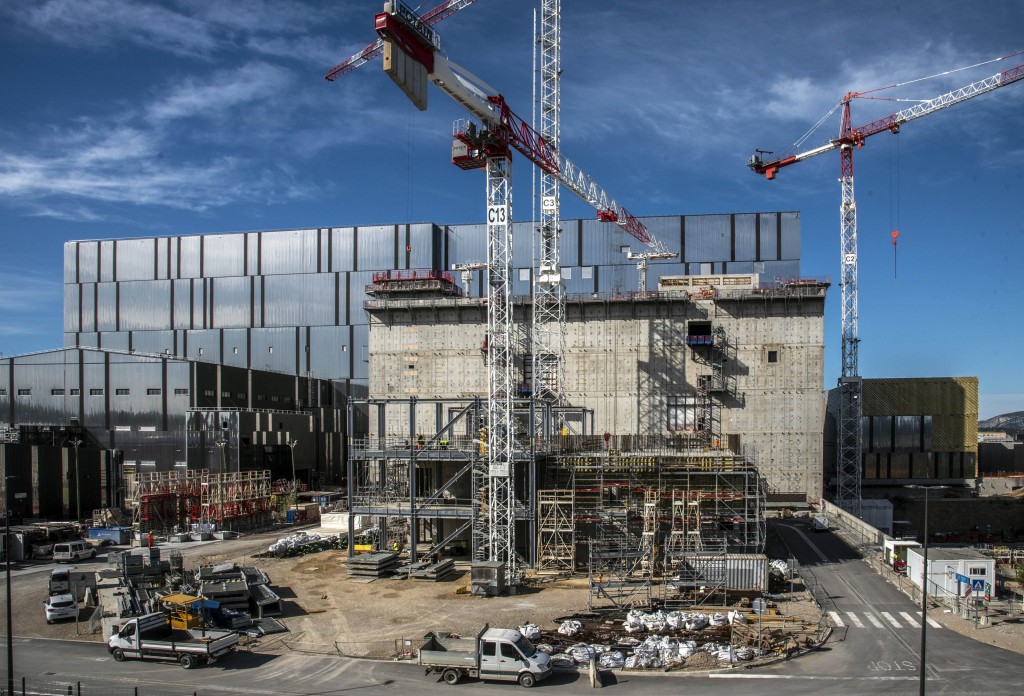
Tritum Building: end of civil works
2023-08-29 - Civil works on the seven-storey concrete Tritium Building are nearly complete and the tall cranes will soon be dismantled. Teams are working on the last level, L5, to complete all kinds of finishing works, including waterproofing.

Sector module #8
2023-08-29 - Vacuum vessel sector #8, seen here in a horizontal position on the upending tool, was removed from vertical tooling when it became evident that sector #6 (already in the pit) would need to be removed and repaired alongside sector #7. Sector #8 will be repaired horizontally in the former Cryostat Workshop.

Late summer 2023
2023-08-29 - With cladding, the two buildings for neutral beam power supplies (centre and left of centre) are looking close to finalized. In between them is a technical area designed to house 10 high voltage transformers.
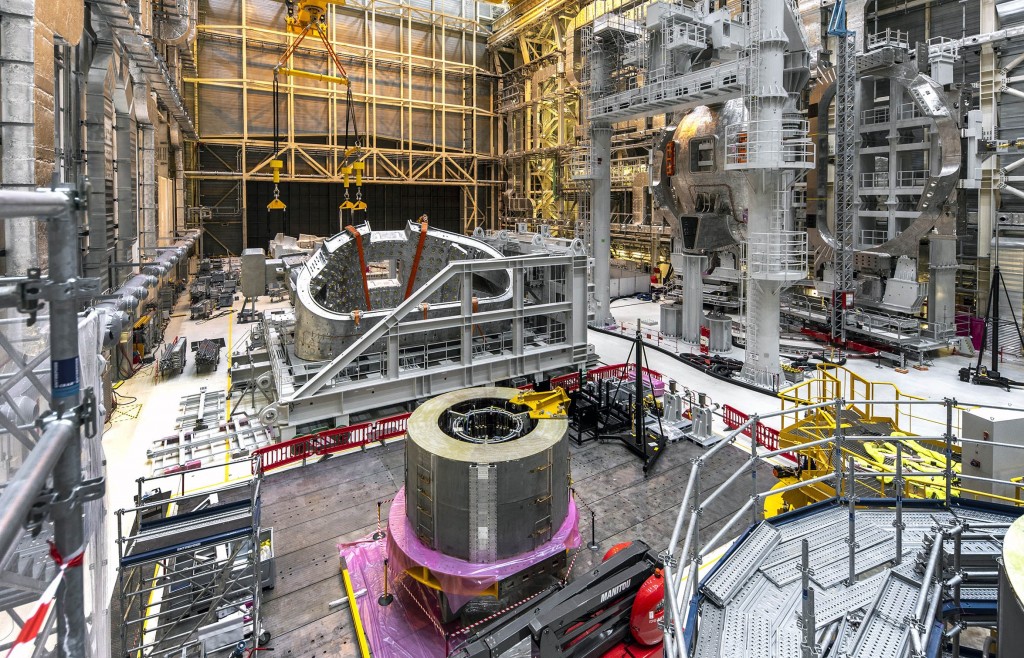
Next cylindrical magnet in line
2023-08-29 - This cylindrical, 110-tonne central solenoid magnet, delivered by the United States Domestic Agency, has been unwrapped to prepare for its installation on the dedicated assembly platform in the right corner of the photo.
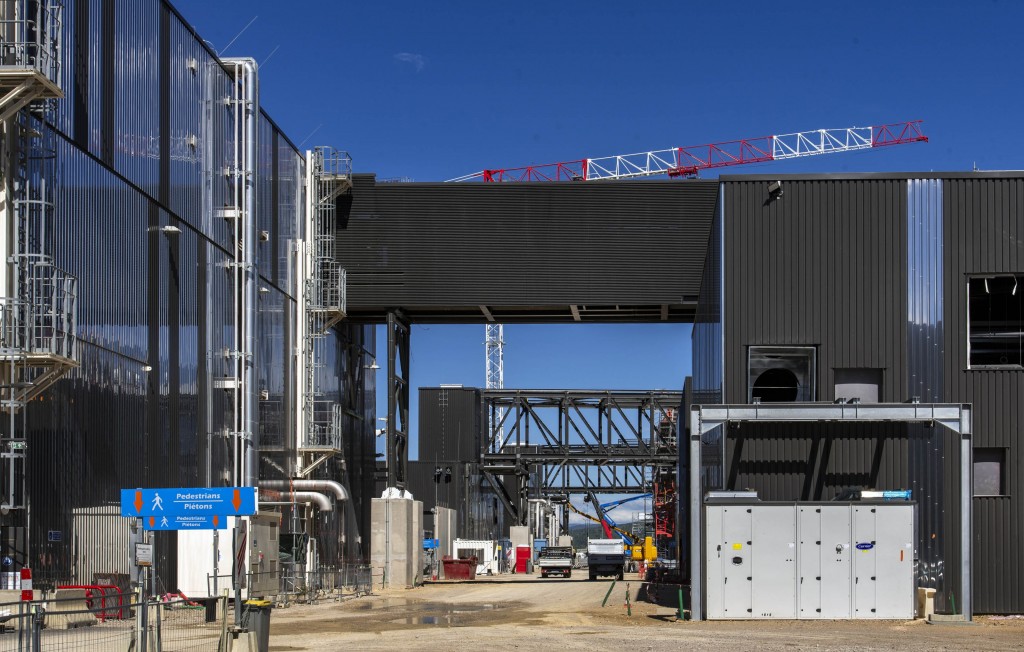
New bridges
2023-08-29 - In addition to the cryobridge (foreground, for the distribution of cryogenic lines) there are now two other bridges spanning the main boulevard of the platform They are busbar bridges, for the transport of electrical busbars from the Magnet Power Conversion buildings to the Tokamak Complex.
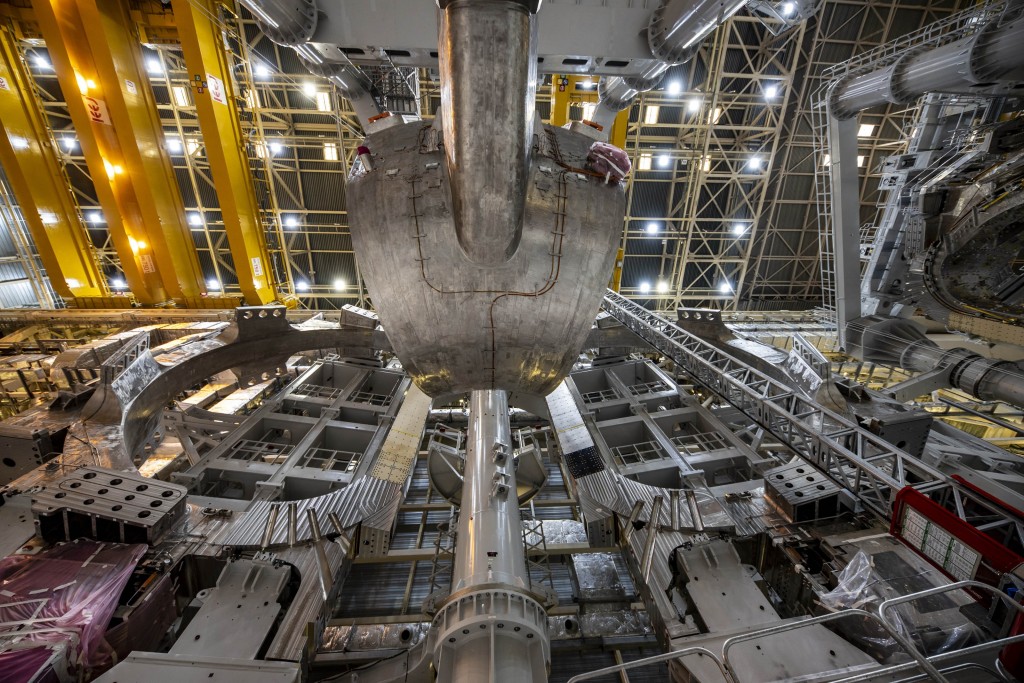
Disassembly works
2023-08-29 - Disassembly of sector module #7 is well advanced; thermal shield panels have been removed and toroidal field coils have been dissociated. In this striking view taken from under the tool, the sector's "underbelly" is clearly visible, as are the toroidal field coils on either side in the tool "wings."
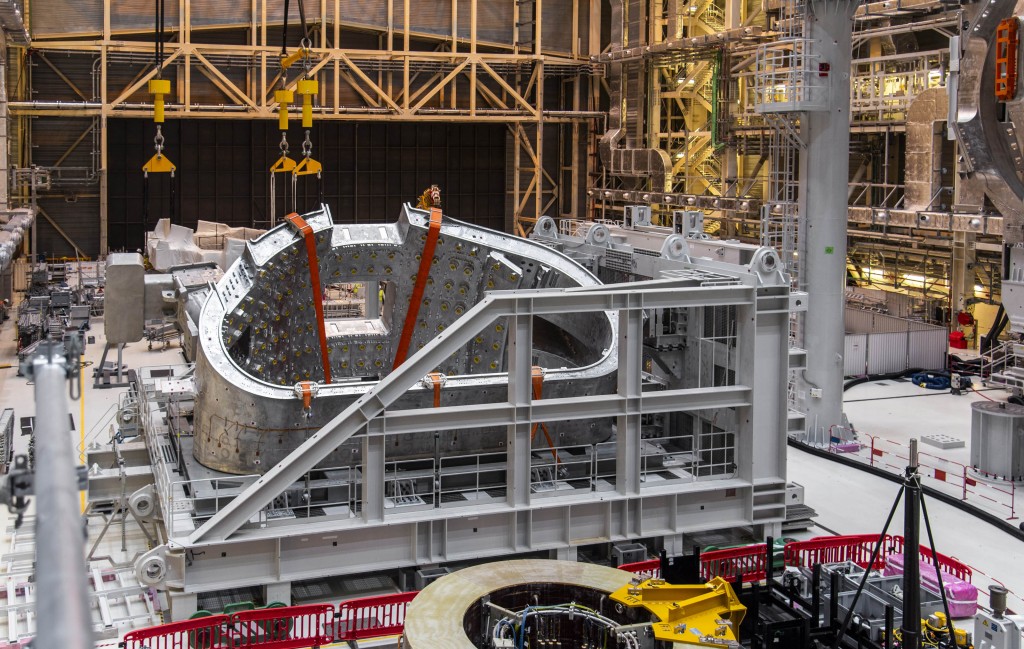
Things in reverse
2023-08-29 - The "upending tool" had to turn into a "downending tool" in order to remove sector #8 from the sector sub-assembly tool where it had been positioned. This unplanned for operation required study and measurements.
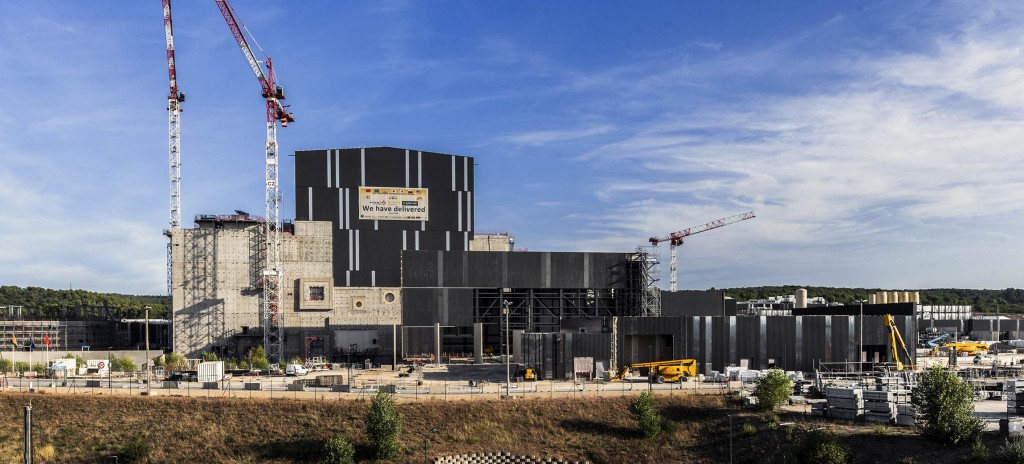
Late August
2023-08-29 - Despite the heat waves of July and August, progress made over the summer is observable in every corner of the ITER platform. The last major addition to the construction platform will be the Hot Cell Facility, a large building will go up where the two cranes are standing, at left.
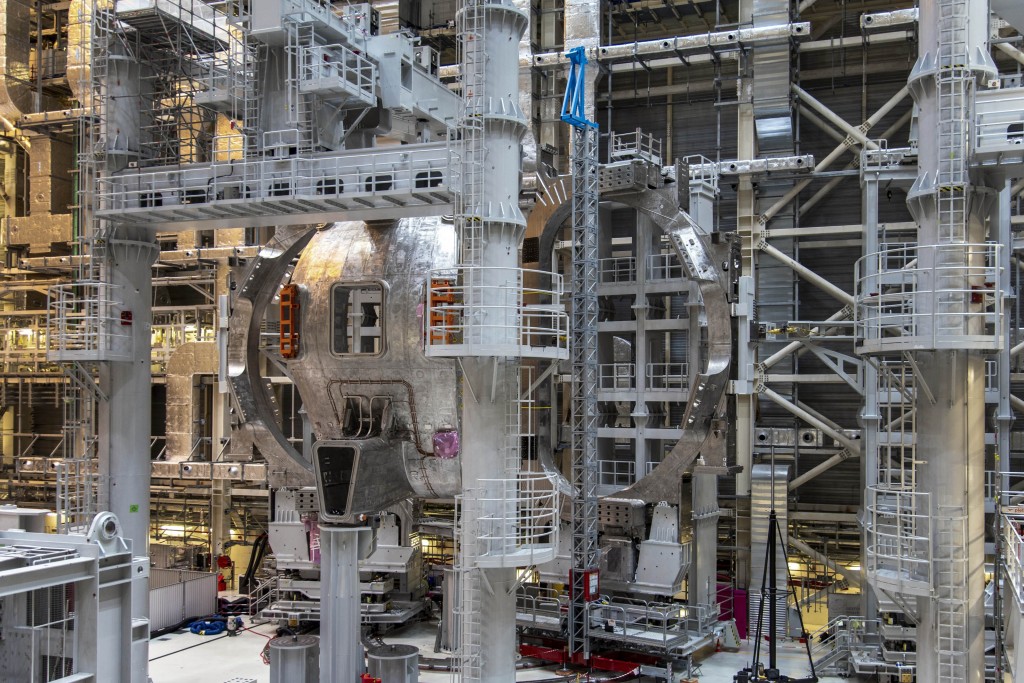
Disassembling sector #7
2023-08-29 - To prepare for the repair of the bevel region of vacuum vessel sector #7, the two toroidal field magnets have been removed from the sector into the wings of the tool.
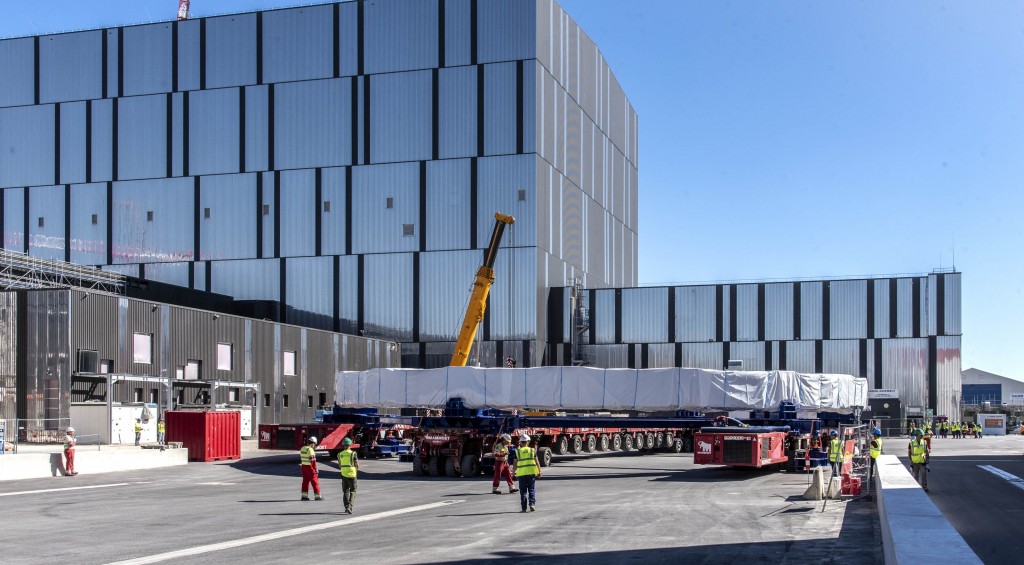
PF4 moved to storage
2023-08-08 - On 8 August, poloidal field coil #4 (24 metres in diameter, 350 tonnes) is moved from the European Poloidal Field Coils Winding Facility to storage on site. Only one coil, PF3, remains to be completed by Europe.

Preparing for the Scientific Data and Computer Centre
2023-07-22 - Cooling and electrical equipment has been installed outside of Headquarters for the ITER Scientific Data and Computer Centre. The Centre will handle a data load of 50 gigabyte per second during full deuterium-tritium operation.

Thermal shield panels
2023-07-21 - These are some of the 27 vacuum vessel thermal shield panels that must be repaired or replaced to correct stress corrosion cracking in the cooling pipes. In September, the ITER Newsline will have a full report on repair strategies and contracts.
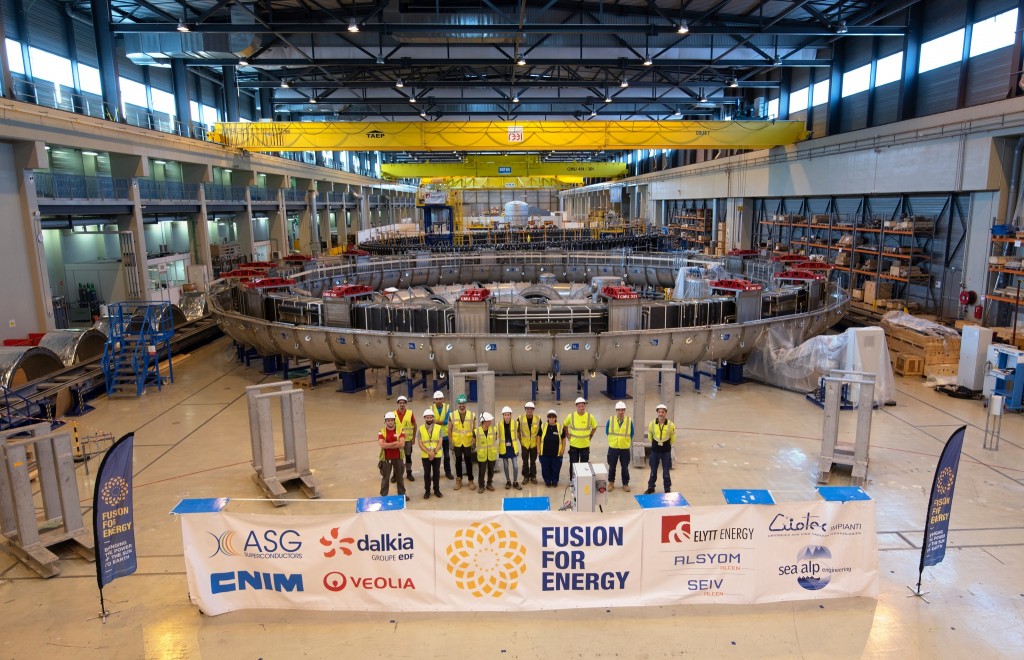
5 of 6 ring magnets completed
2023-07-07 - With the successful conclusion of cold testing, poloidal field coil #4 (PF4) is ready to leave the European winding facility. Only one more coil remains to be finalized: PF3.

Back in tooling
2023-07-05 - In order to carry out this reverse operation—sector module #6 from the Tokamak pit and re-placing it in tooling in the Assembly Hall—metrologists were part of the preparation and execution teams.
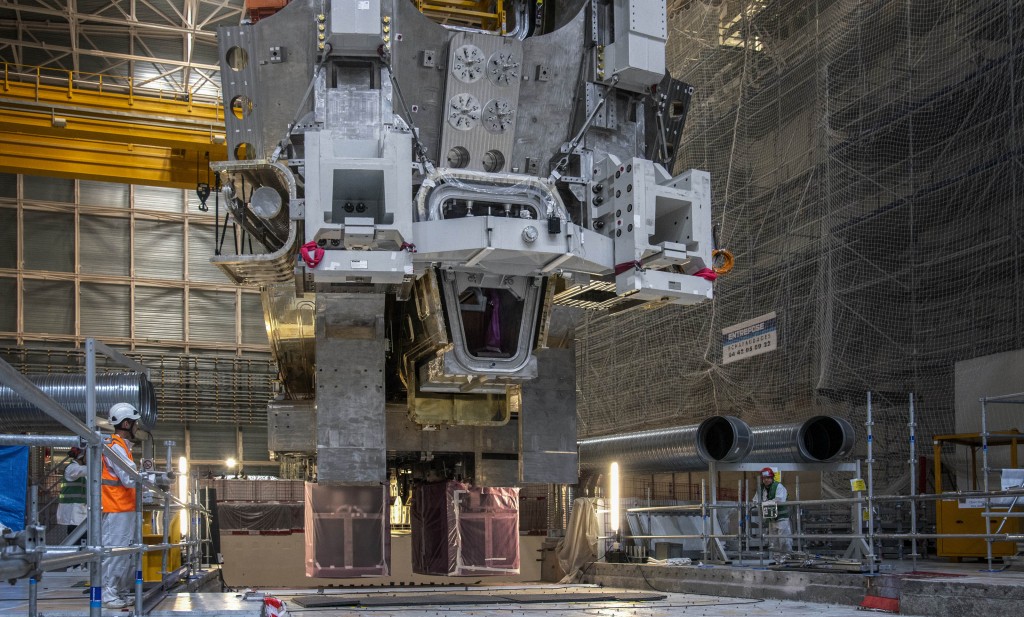
Carefully now
2023-07-05 - One of the most delicate passages: the toroidal field coil termination boxes (wrapped in protective pink plastic) are the most sensitive and delicate parts of the assembly. When passing the wall that separates the assembly pit from the Assembly Hall, the vertical clearance is less than 20 centimetres.
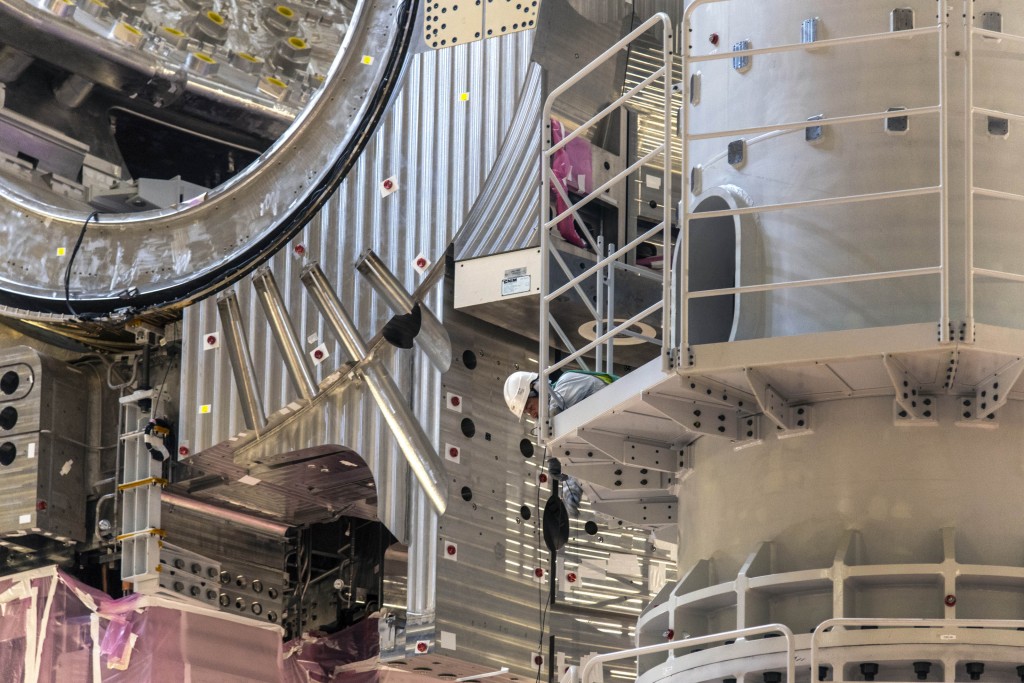
Eagle eyes
2023-07-05 - Although the lift operation relied heavily on sensors and strategically positioned cameras, "spotters" played a crucial role in overall safety and precision.
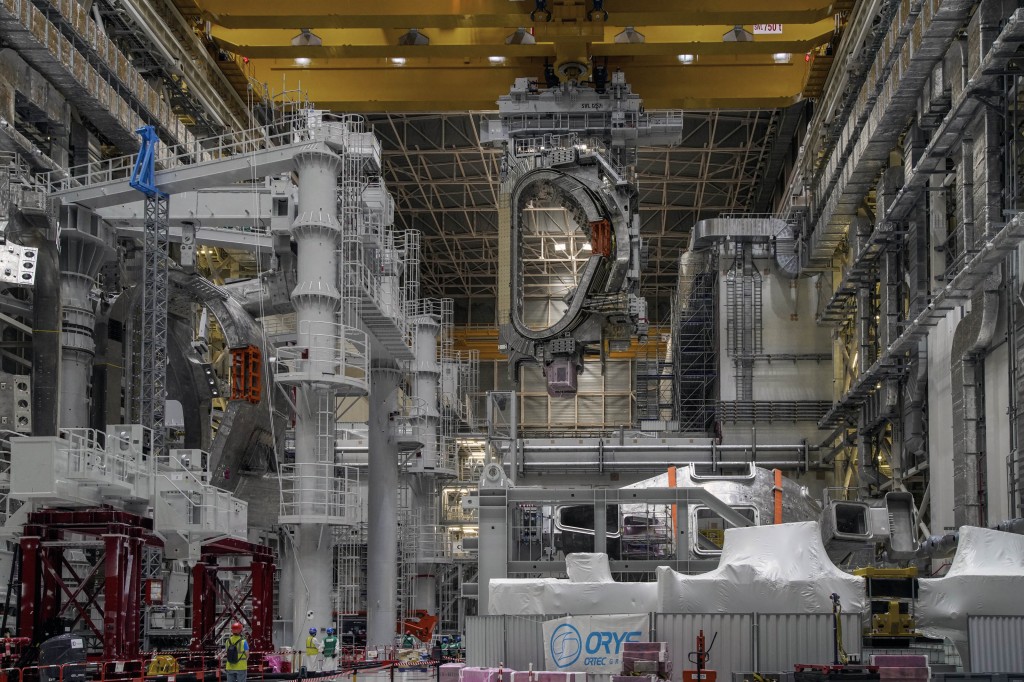
Reverse operation
2023-07-05 - Lessons learned during the May 2022 installation of the sector module were essential to the reverse operation. So too was the fact that the same team was on deck... (Photo Kenichi Ueno, ITER)

Step by step
2023-07-05 - From detaching the module from its moorings in the assembly pit to lifting and transporting it to the sub-assembly tool, more than one hundred different steps had to be defined, validated and integrated into the lift procedure.

Back towards the Assembly Hall
2023-07-05 - Sector module #6 follows the same path out of the assembly pit as it did 15 months ago on its way in.
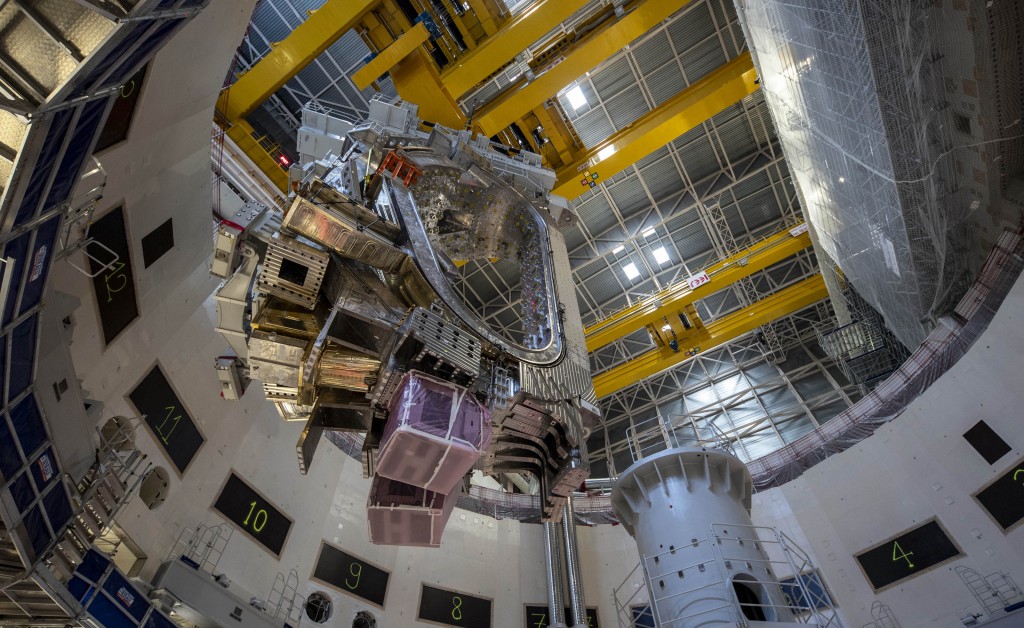
Sector module #6 removed
2023-07-05 - Sector module #6 (1,350 tonnes) is removed from the Tokamak pit on 5 July 2023.
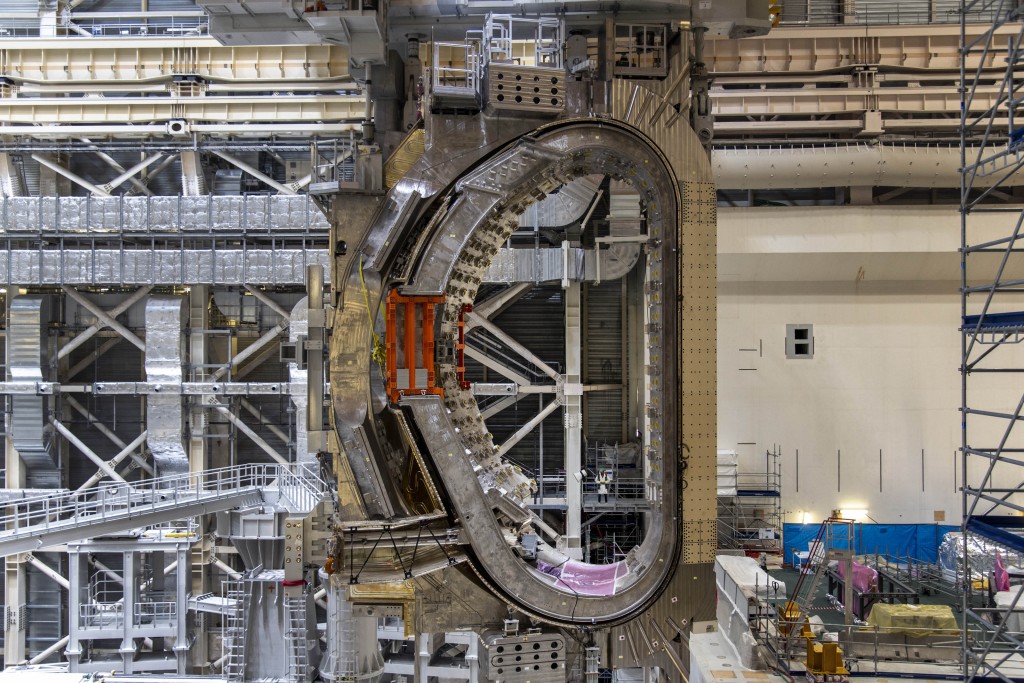
Rotating
2023-07-05 - The load has now passed the wall and will be rotated 90 degrees to face the sector sub-assembly tool closest to the wall.
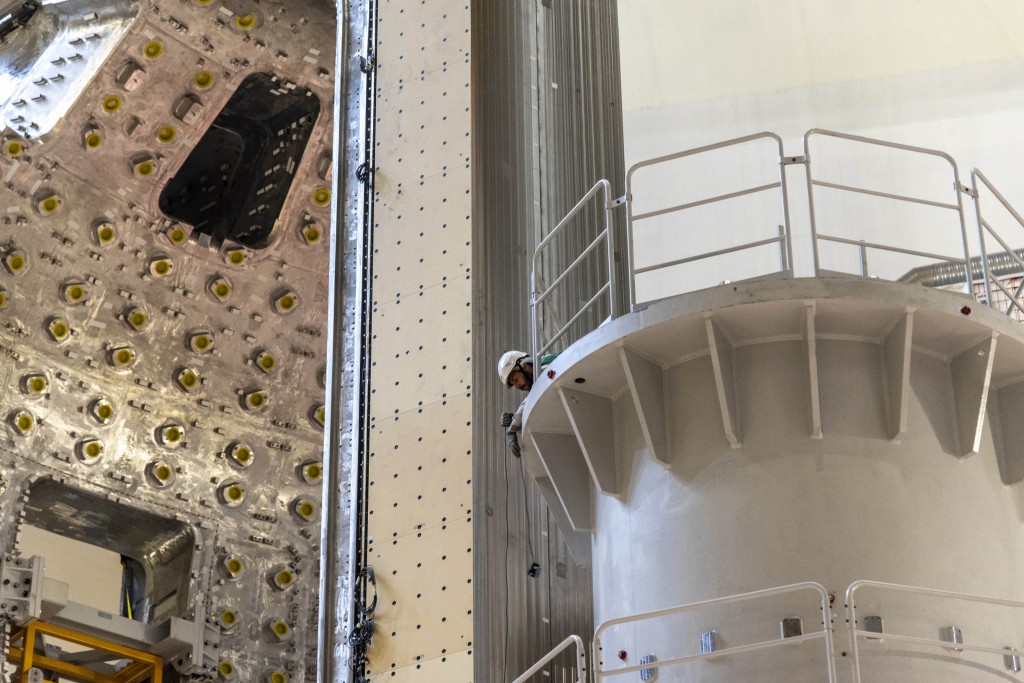
A few centimetres
2023-07-05 - At its narrowest, the clearance between the module and the central column does not exceed a few centimetres. The lift is paused at regular intervals to slow the swinging effect.

Into tool
2023-07-05 - The last leg of the reverse operation for sector module #6: after removal from the Tokamak pit, the component is lowered into one of the twin sector sub-assembly tools to be disassembled and prepared for repair.
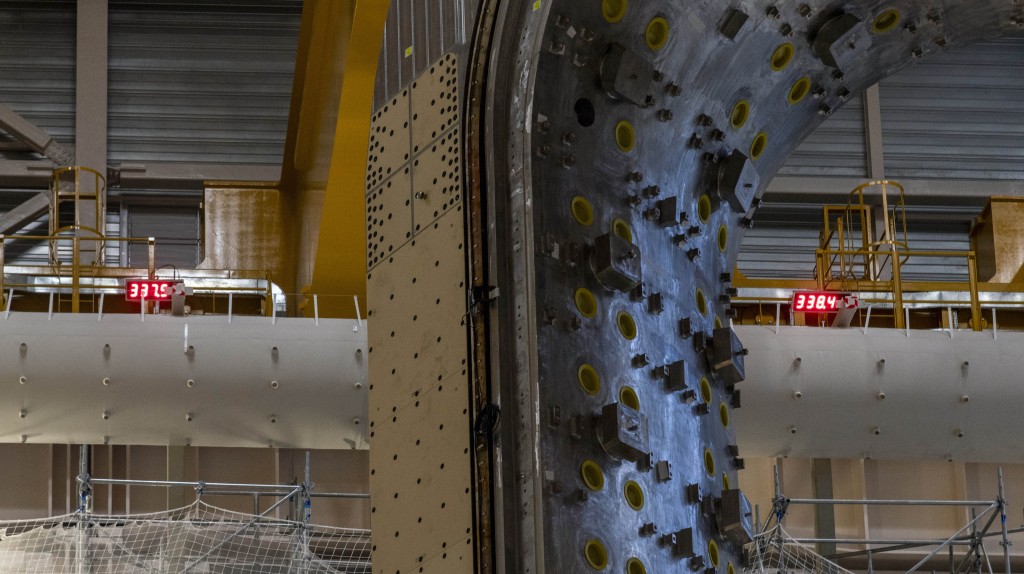
Watching the weight
2023-07-05 - The load supported by each of the four crane hooks is displayed in real time on small screens, so the math is easily done: the module weighs slightly in excess of 1,350 tonnes.
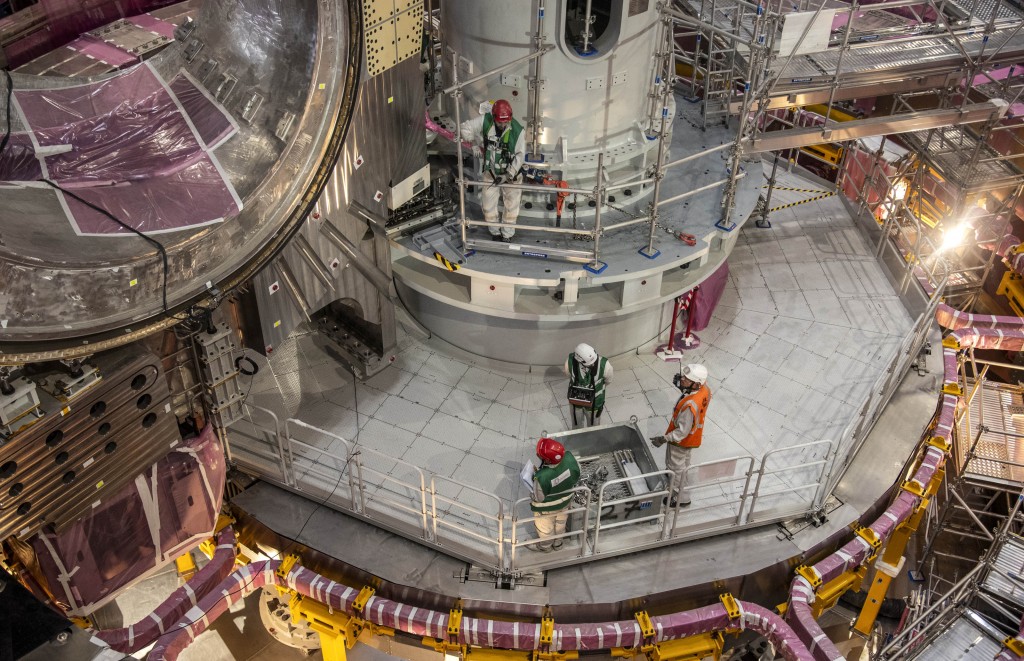
Final instrument checks
2023-07-04 - "A lift-off is not exactly the reverse of a landing," says Daniel Coelho, the ITER assembly engineer who will coordinate the lift operation. Procedures have had to be adapted and additional guiding systems have had to be manufactured and installed.

Planning removal
2023-07-03 - The paperwork is done. Every tool and system has been checked. A "functional briefing" has reminded everyone involved of how the operation will proceed and clarified the chain of command. This week, the delicate and complex "extraction" of vacuum vessel sector module #6 from the assembly pit (in the background) will take place.
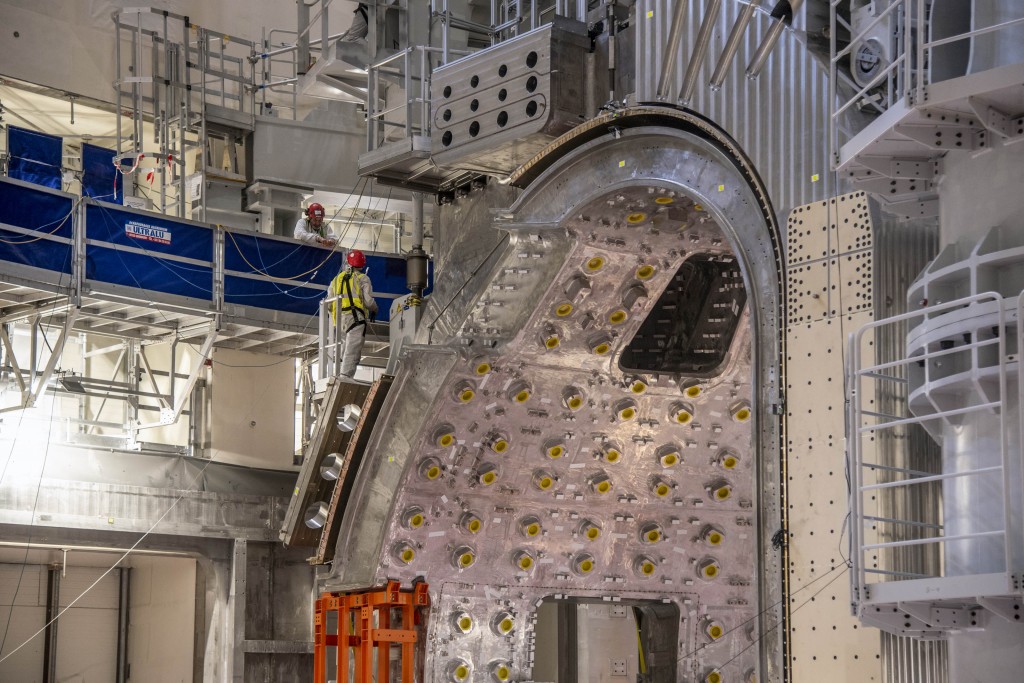
Reverse lift imminent
2023-06-28 - Late June, technicians were busy preparing sector module #6 for removal from the pit.

June 2023
2023-06-28 - The ITER machine assembly pit, in late June 2023. (At the base of the column, a worker with a blue hard hat provides a sense of scale.)
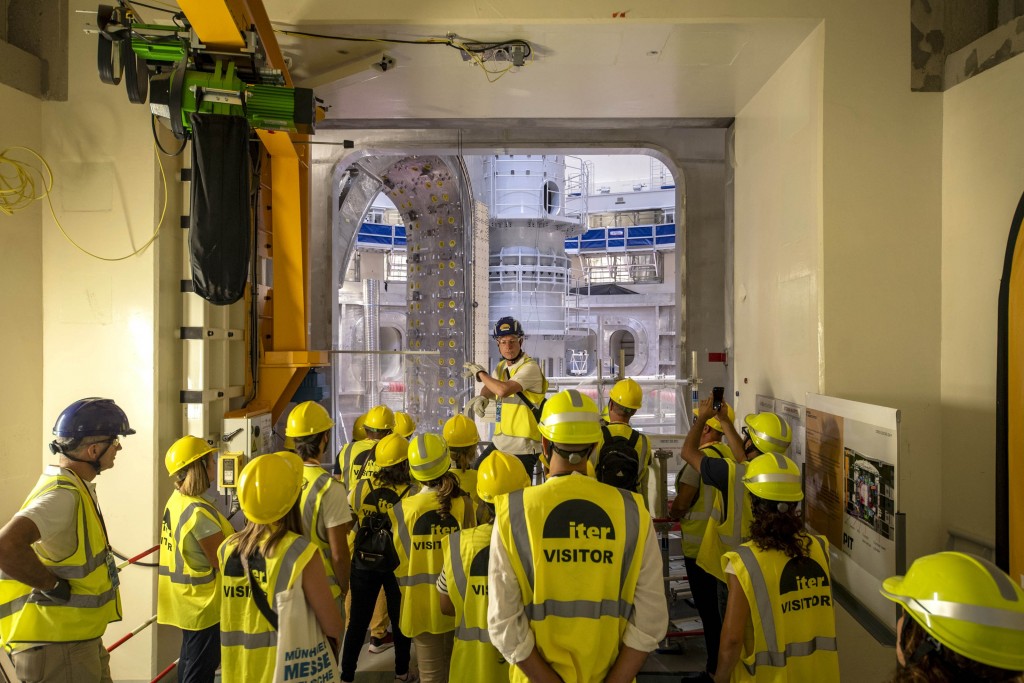
A window into the Tokamak pit
2023-06-24 - On Saturday 24 June, Open Doors Day groups are taken through a port cell to the edge of the Tokamak pit. They are among the last people to see sector module #6 in place in the pit, since it is scheduled for removal (within days) for repair.
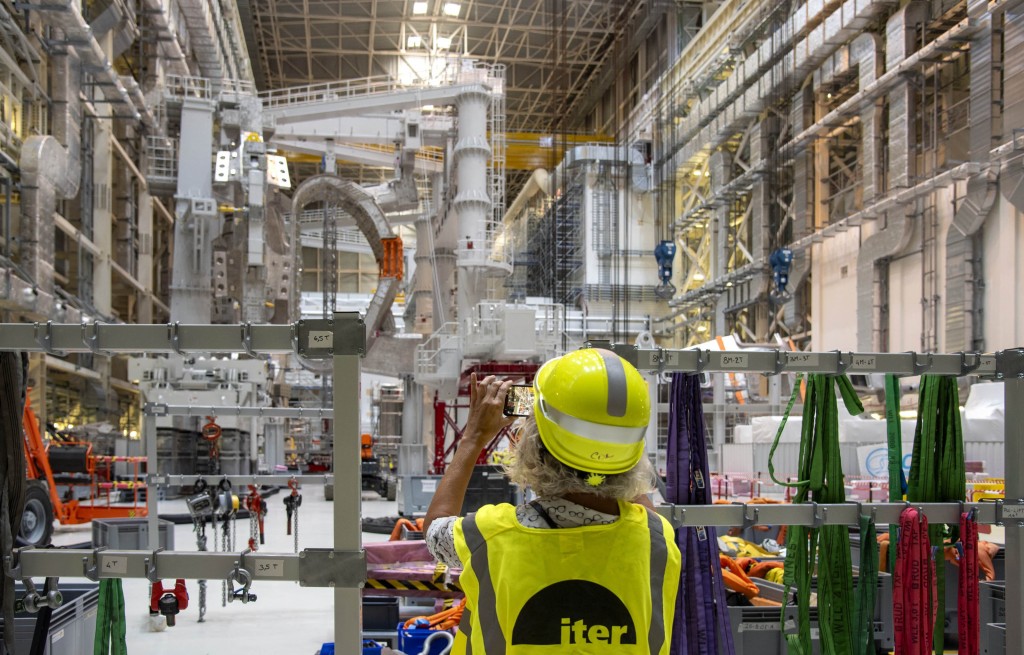
Sector tools
2023-06-24 - In the background, vacuum vessel sector #7 is suspended in tooling, and its two D-shaped toroidal field coils have been removed to the wings. The second tool, further to the back of the Hall, awaits sector module #6 from the machine pit.
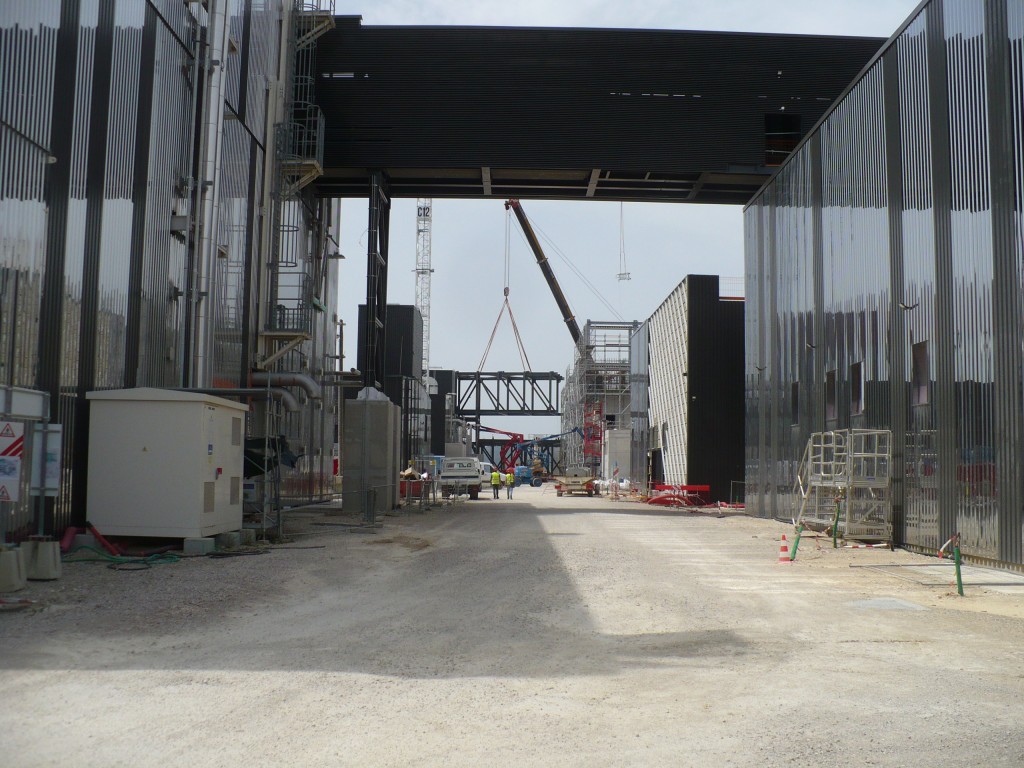
Overhead
2023-06-20 - The completed cryobridge is 13 metres above the platform. Two other bridges along this road will house electrical busbars (one can be seen in construction in the background).
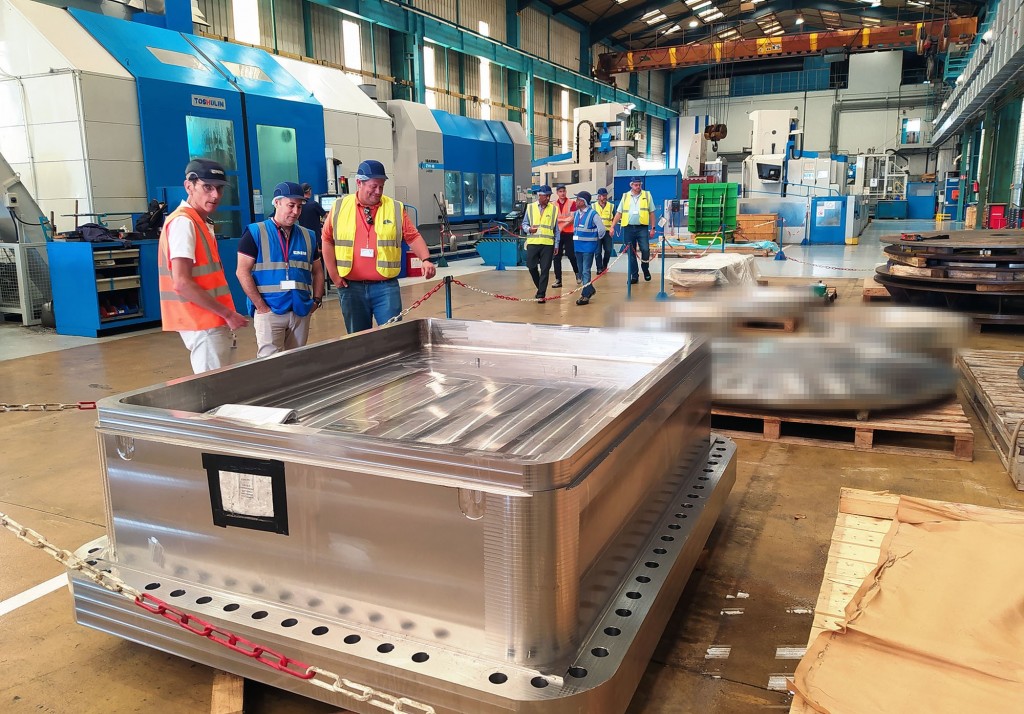
Diagnostic port plugs: 1st units near completion
2023-06-19 - Part of 23 vacuum vessel ports, " diagnostic port plug structures" will house diagnostics, integrated services, and other hardware. Two types are planned and the first units are coming off line.
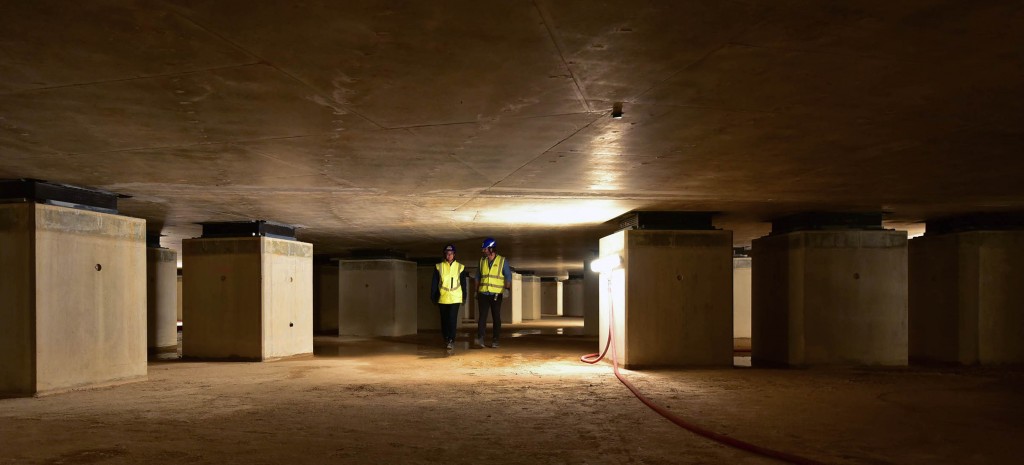
Under the Tokamak Complex
2023-06-01 - Underneath the concrete slab that supports the Tokamak Complex is a vast, dimly lit space whose only features are squat, pillar-like structures called "plinths." Sandwiched between the top of the pillars and the slab above, flexible seismic pads ensure that in the event of an earthquake, the integrity of the building will be protected from sudden and strong horizontal accelerations.
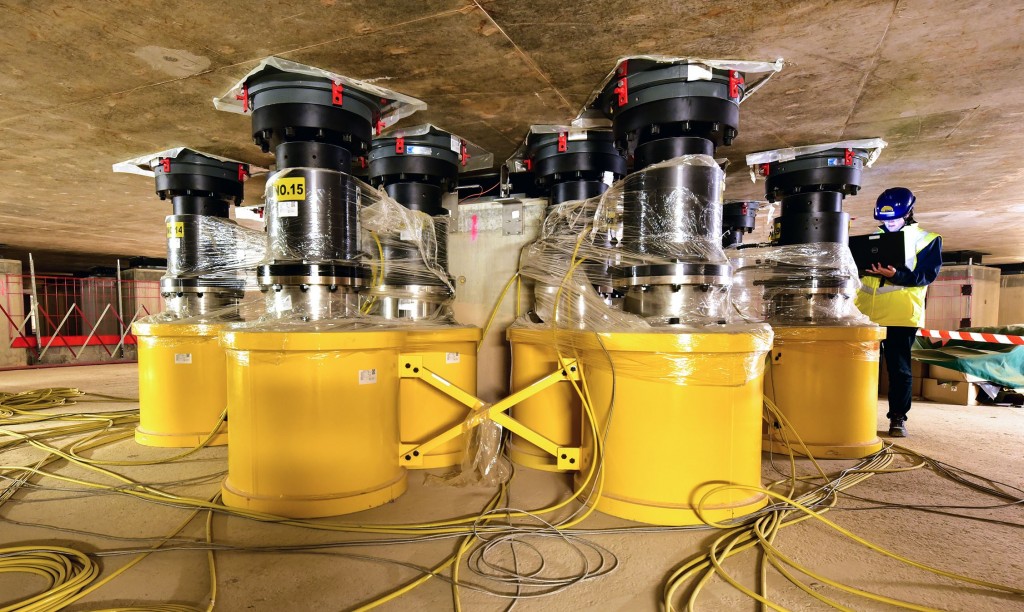
Extra support from below
2023-06-01 - A temporary propping system is in place to support the central column tool (in the centre of the Tokamak pit) during machine assembly. These propping elements have been installed under the concrete slab of the Tokamak Complex, directly under the machine.
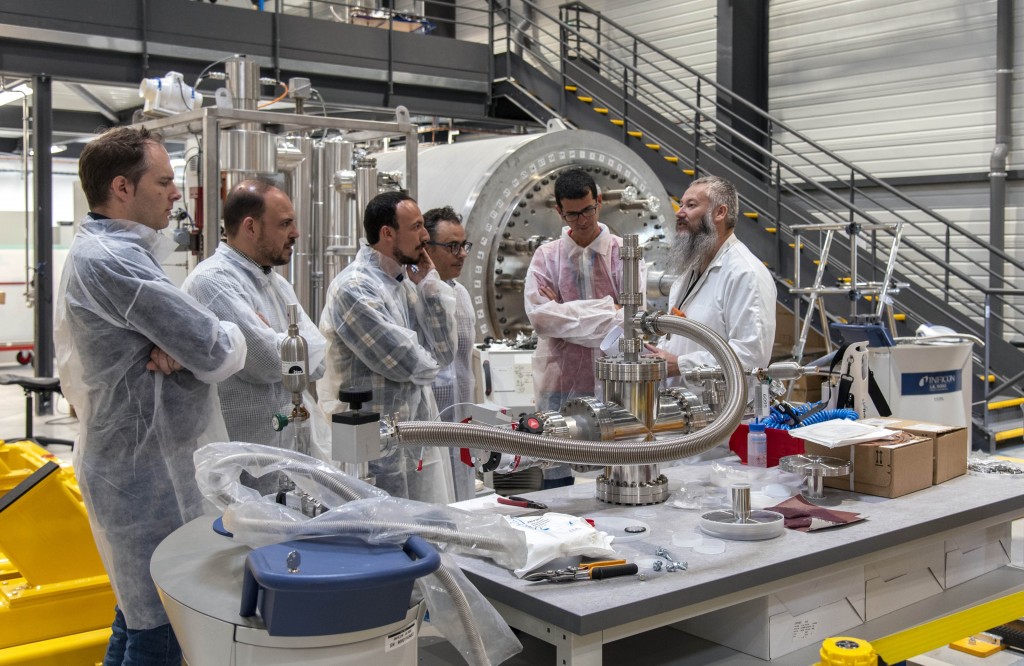
Highlighting the imporance of vacuum systems
2023-05-31 - The ITER vacuum team organizes regular workshops to highlight the criticality of vacuum standards and quality with technical responsible officers, quality assurance specialists, and resident inspectors working at ITER and in the Domestic Agencies.
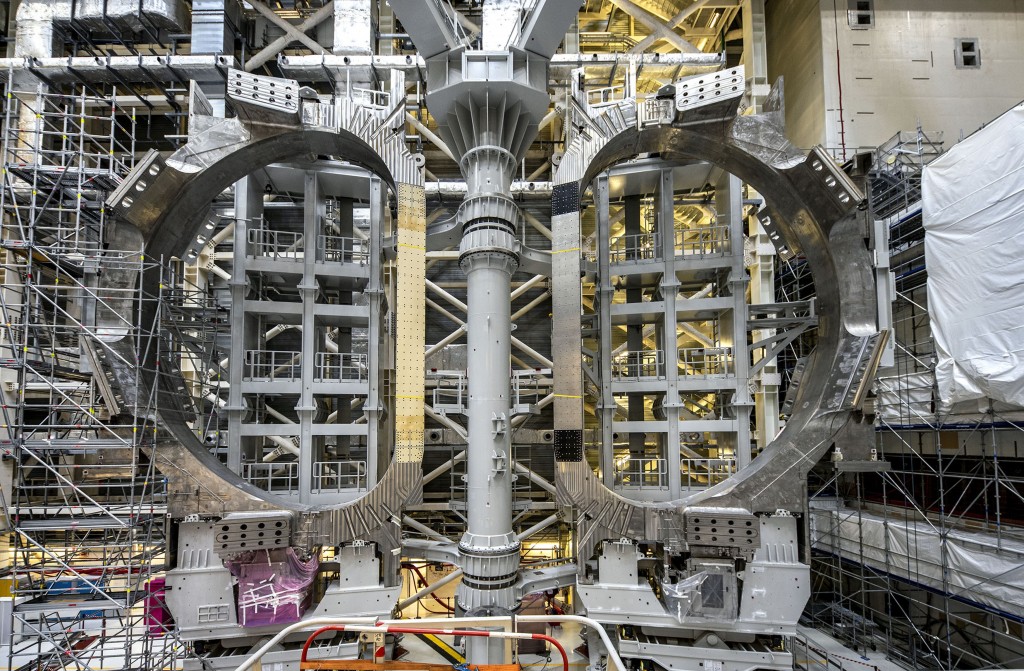
Preparing for repair work
2023-05-11 - The same tools that were used for assembling the vacuum vessel sector modules from 1 sector, 2 toroidal field coils and thermal shield panels, is now being used for disassembly. In this photo, two toroidal field coils are temporarily held after disassembly on the wings of vertical tool SSAT-2.

Beginning to re-centralize control stations
2023-05-09 - Since 2018, small control rooms around the site have been established to support local testing and commissioning of plant equipment. With the opening of the temporary main control room (T-MCR) in late 2022 (https://www.iter.org/newsline/-/3845), some of these distributed functions are being brough back in and centralized (https://www.iter.org/newsline/-/3880).

Musical chairs
2023-05-08 - The view inside the Assembly Hall now gives a clear indication of what will happen soon: to the left sector #7 stands in the tall assembly tool SSAT-1, ready for repairs once the outboard thermal shield panel is removed. To the right, sector #8 is solidly attached to the upending tool, waiting to be moved from vertical to horizontal and transported to another building.

Cold test ends
2023-05-06 - The cold test of poloidal field coil #4 (PF4) has ended. Stay tuned for the lifting of the lid of the cryogenic chamber.
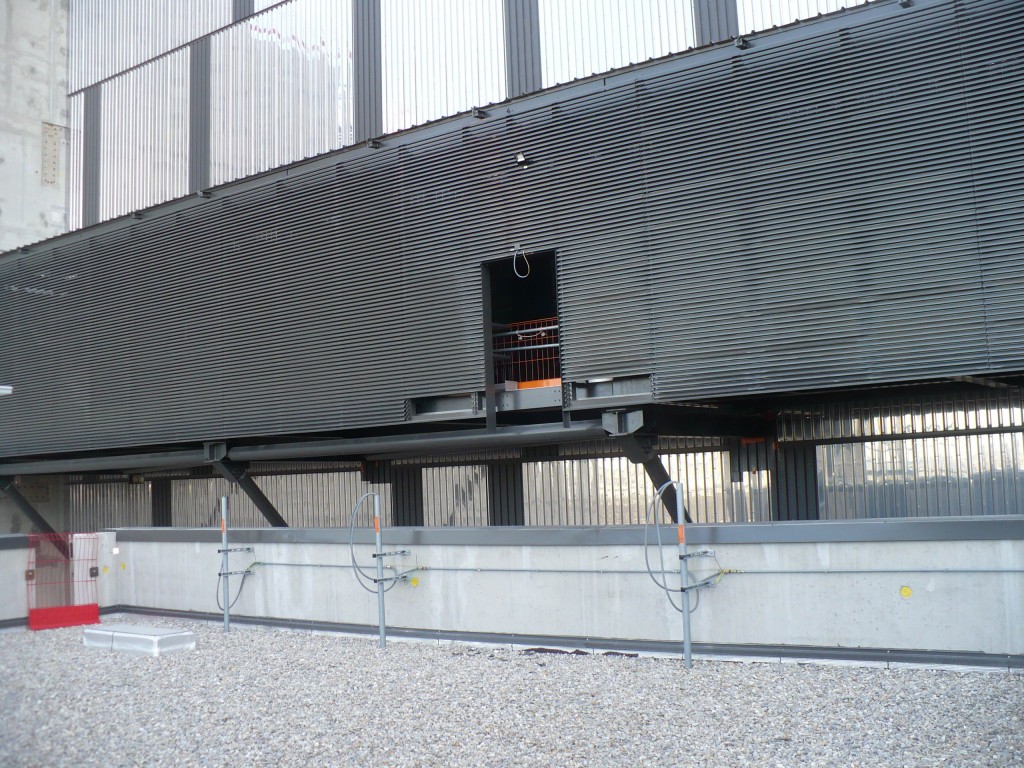
Sturdy yet flexible
2023-05-04 - Cryogenic process lines will be sheltered in this cryobridge, designed to withstand 200 tonnes of dead load and the "pushing and pulling" of the lines.
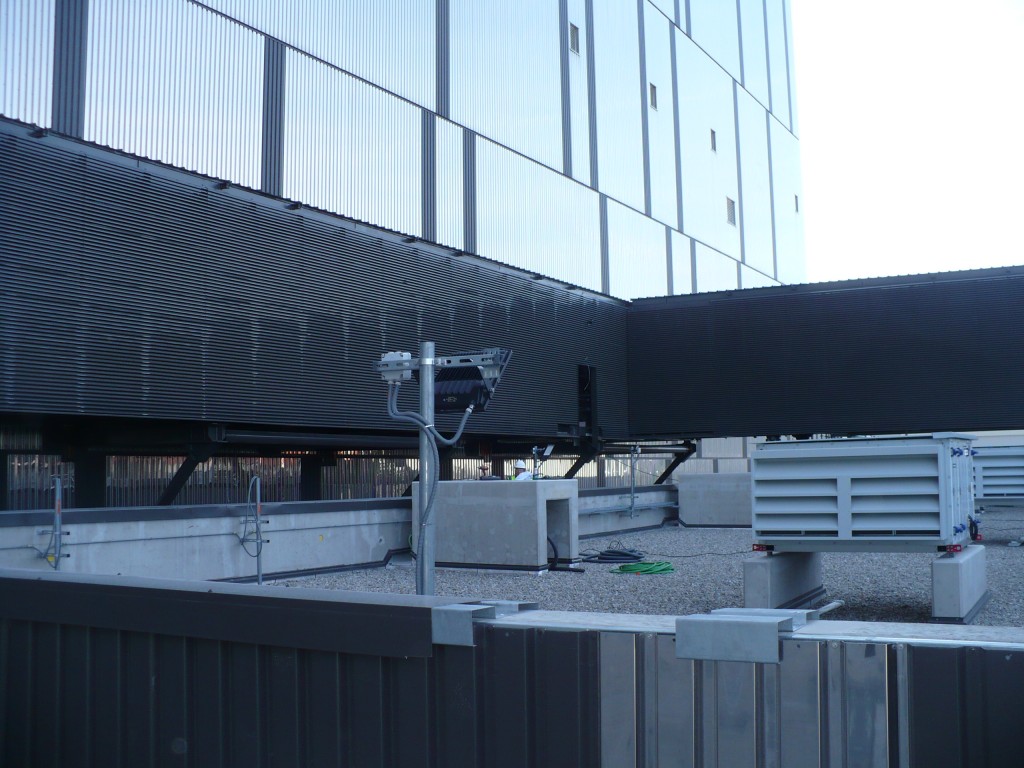
Bridge with an angle
2023-05-04 - A covered bridge runs 70 metres from the cryoplant to the Assembly Hall, before abruptly turning left at a 90-degree angle to run parallel to the Assembly Hall for another 60 metres in order to reach the Tokamak Complex. Its purpose? To carry gas and liquid helium to "clients" (superconducting magnets, thermal shield, cryopumps).

An unusual vision
2023-04-06 - On its way to the storage location, some 50 metres away from the Cryostat Workshop, the flying saucer-shaped component passes the Cleaning Facility and adjacent Assembly Hall, whose architectural design add a futuristic touch to the scene.

Coordination is the key
2023-04-06 - Success was achieved through the close collaboration the ITER Organization, global logistics provider DAHER, and transport platform operator Mammoet. The company Cegelec played an important role in designing systems and processes to synchronize the movements of the six individual transport platforms, and risk manager Apave was responsible for the overall safety of the transfer.

Team huddle
2023-04-06 - Coordination and anticipation are key for a successful, smooth and safe operation. As the transport trailer power packs warm up, a last briefing brings together the operators and responsible officers from the dozen companies and organizations involved in the top lid transfer.

Huge
2023-04-06 - As it sat at the far end of the Cryostat Workshop, the top lid certainly felt like a large component. But as it slowly came out of the building amidst the roar of the power packs, it seemed to have dramatically grown in size. The 30-metre-in-diameter, 10-metre-tall load dwarfed everything around it.
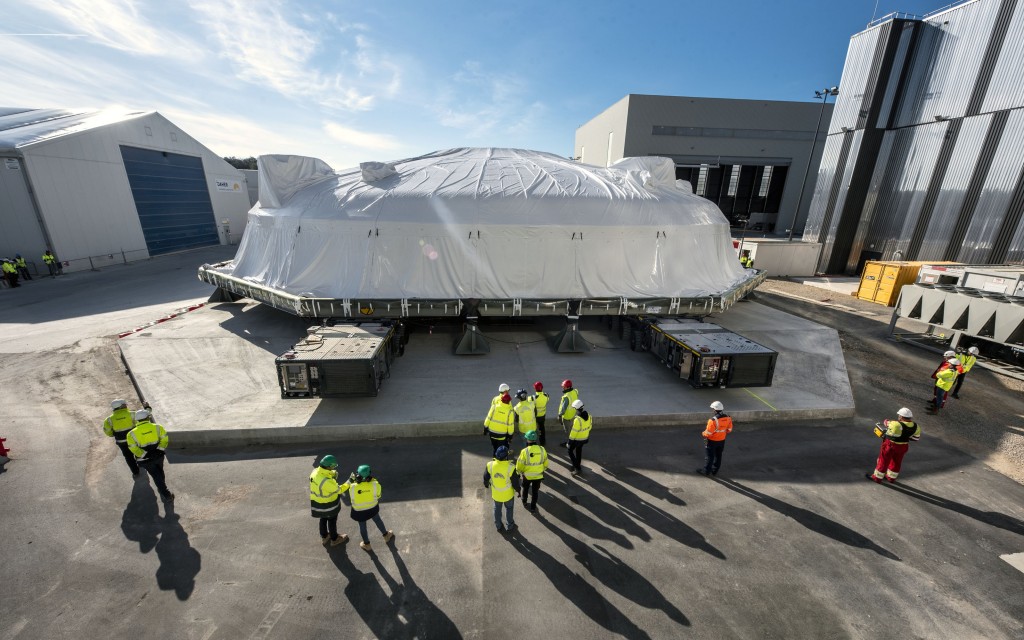
900 tonnes of dead weight
2023-04-06 - A heavy duty, 50-centimetre-thick reinforced slab was recently constructed to accommodate the combined load of the top lid, support frame and transport platforms in the last phase of the operation. At approximately 900 tonnes, their total weight is equivalent to that of three Airbus A380s.
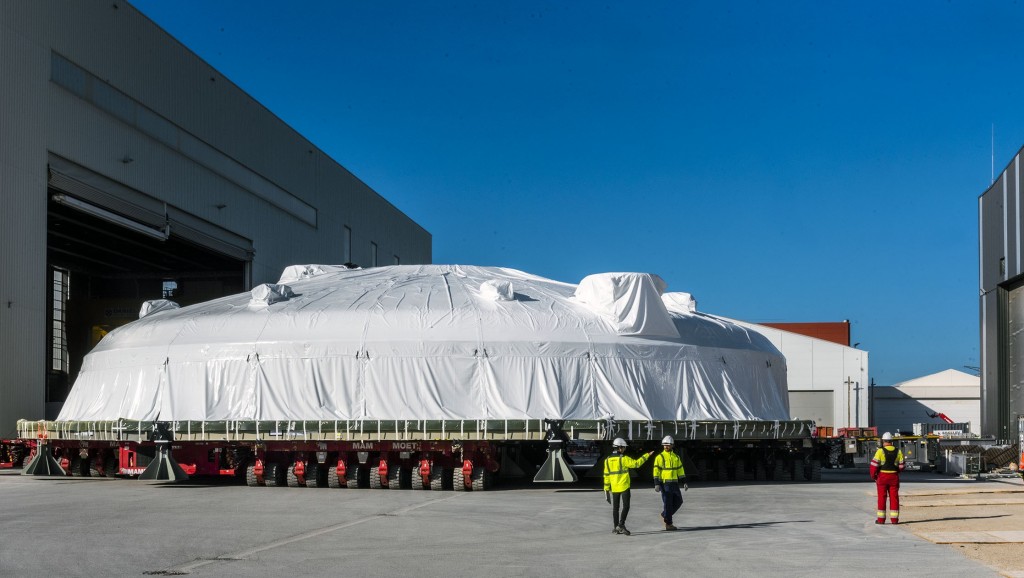
6 self-propelled modular transporters
2023-04-06 - Six self-propelled modular transport platforms, each equipped with a 500 HP power pack, worked in unison to move the cryostat top lid (665 tonnes) and its massive support frame.

Winding facility: progressive handover begins
2023-04-03 - As poloidal field coil manufacturing activities wind down, the European Domestic Agency is progressively handing over the building to the ITER Organization, which will use the space for assembly activities. On 3 April, approximately 25% of the shop floor was officially transferred. See more at: https://www.iter.org/newsline/-/3865

Wow!
2023-04-01 - Push aside the plastic curtain at the end of a long corridor and .... wow! The size of the future ITER machine is suddenly apparent to all the senses.
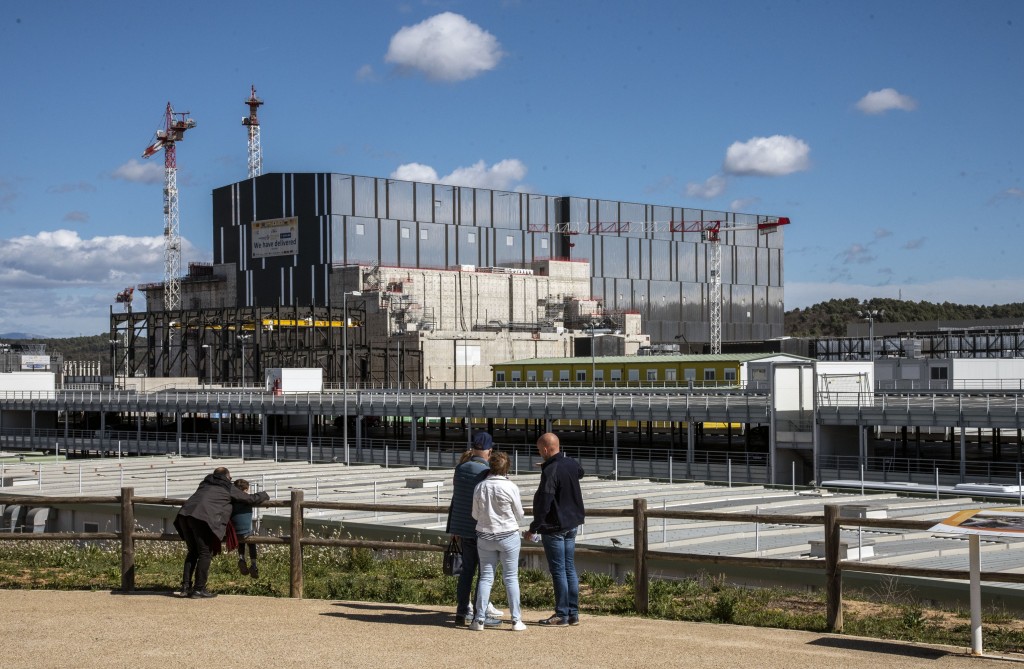
Best view
2023-04-01 - One of the best views of the Tokamak Complex and the ITER Assembly Hall is from the belvedere of the Visitors Centre.
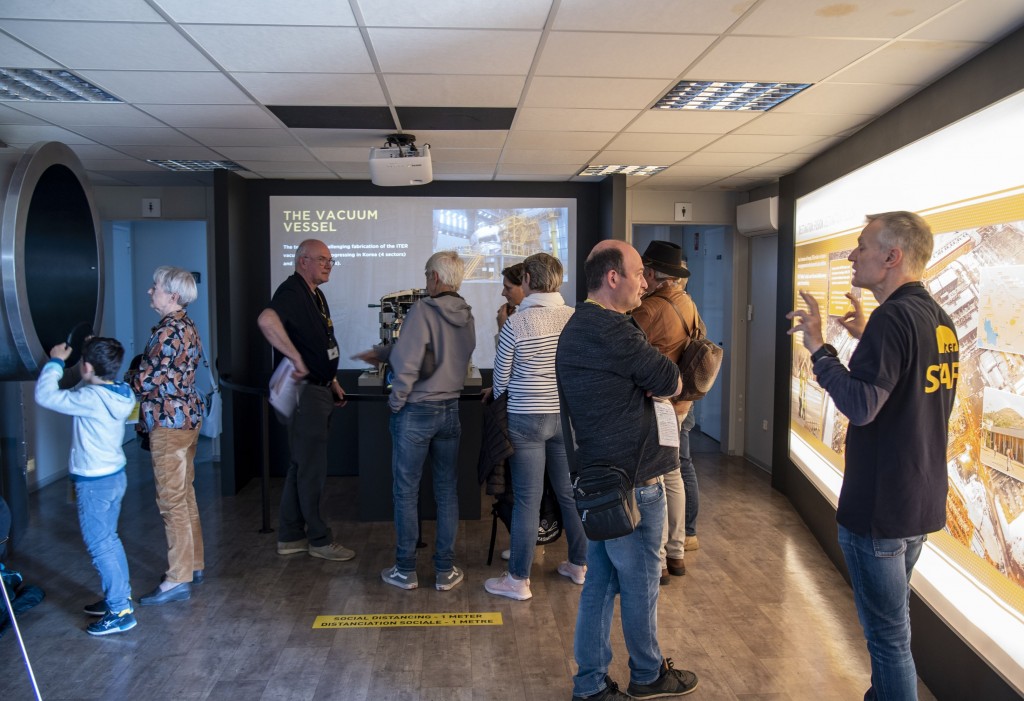
The Visitors Centre
2023-04-01 - Inside the Visitors Centre there are lots of ways to learn more about ITER--films, posters, mockups ... and of course the explanations of volunteer guides!

An exciting stop
2023-04-01 - Welcome to the Assembly Hall, where major ITER components are unwrapped and prepared for installation in the machine pit.

Ready to move
2023-04-01 - The Open Doors Day on 1 April was the last occasion to see the cryostat top lid in the Cryostat Workshop; it will be moved to outdoor storage next week.
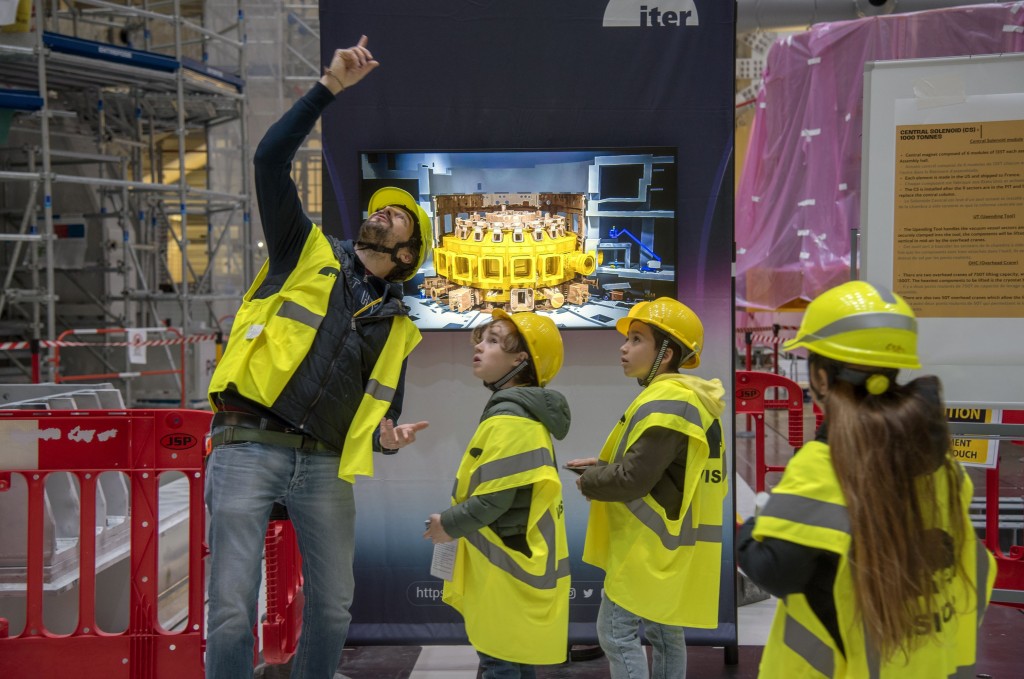
Look up!
2023-04-01 - There is lots to see in the ITER Assembly Hall, including overhead! These young visitors are taking part in the ITER Open Doors Day that was organized on 1 April.

A guest from inside the house!
2023-04-01 - ITER Director-General Pietro Barabaschi (far right) takes part in one of the early bus tours of the day ... as a visitor, not a guide!
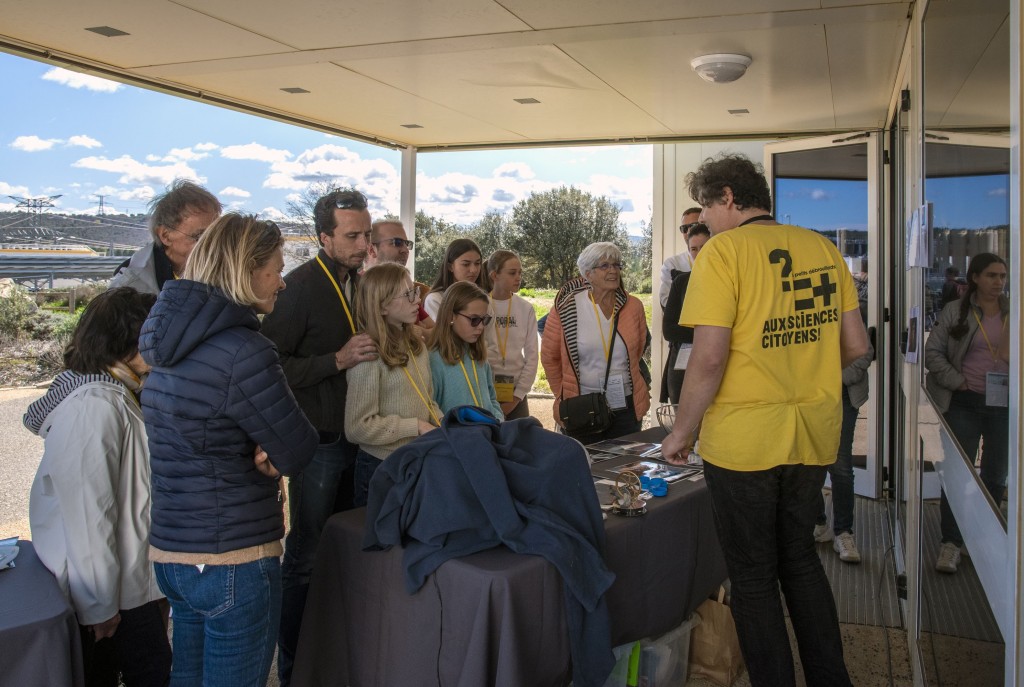
Welcoming visitors on site
2023-04-01 - The ITER Visitors Centre dominates the work site, and is a good place to start for visitors. (Pictured, a member of the French science association "Les Petits Débrouillards" ("Little Crafty Ones") during a display of magnetism at ITER's Open Doors Day event on 1 April.)
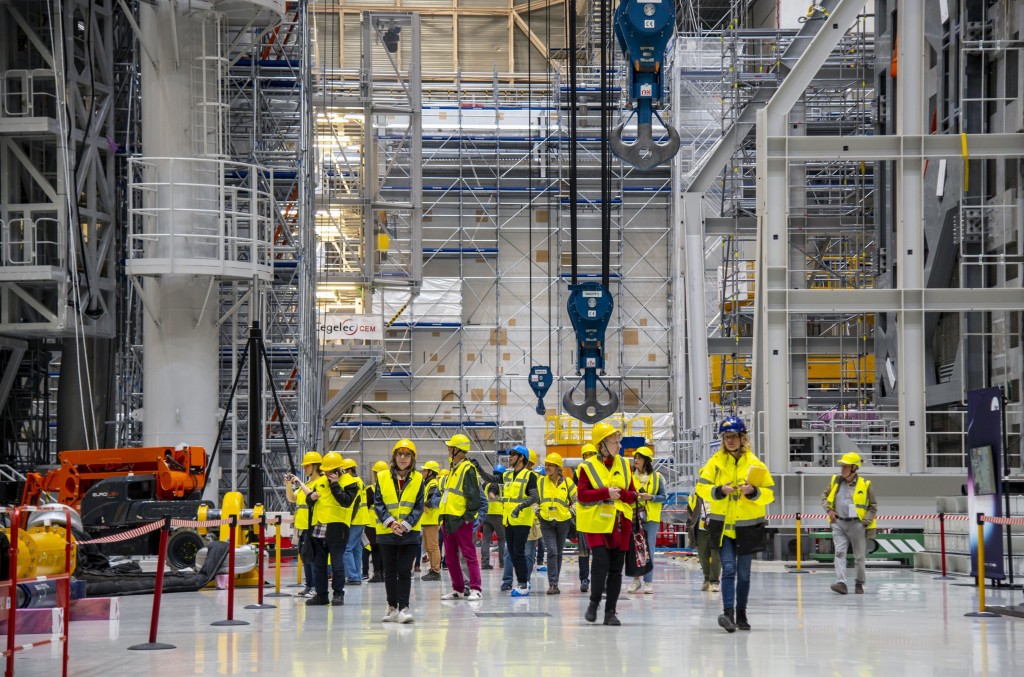
50 ... or less
2023-04-01 - Fifty people climb aboard every site tour bus, but once in the Assembly Hall they are broken into four smaller groups so that everyone can hear the guide.
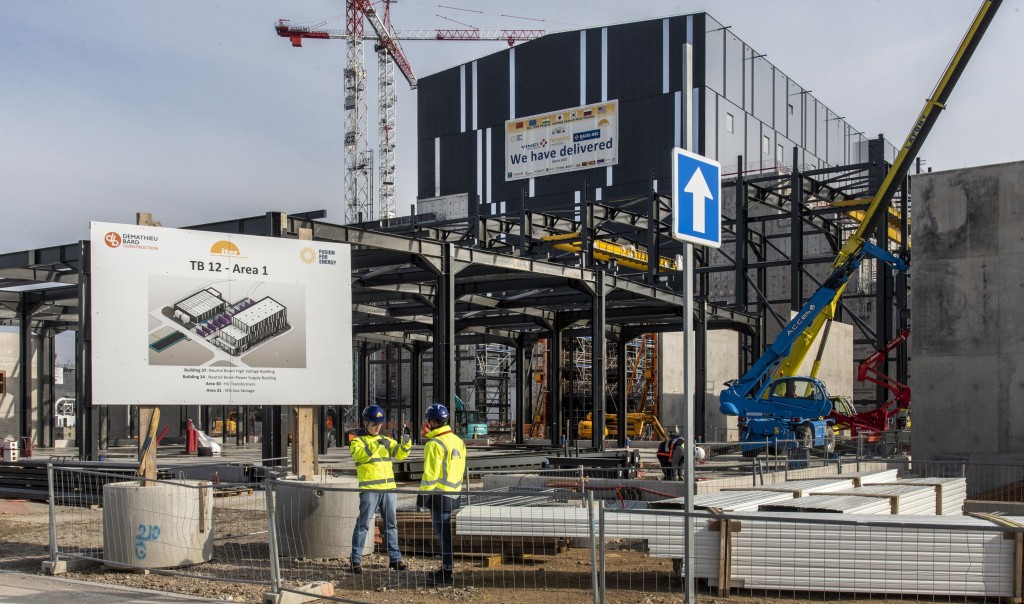
40% complete
2023-03-17 - Civil works for the neutral beam power supply infrastructure are now 40% complete, thanks to the teams of the European Domestic Agency. ITER's Hans Decamps, the electrical engineer responsible for the project (left) is seen here discussing with Aleksei Fedotov, the technical responsible officer for the Japanese contribution.
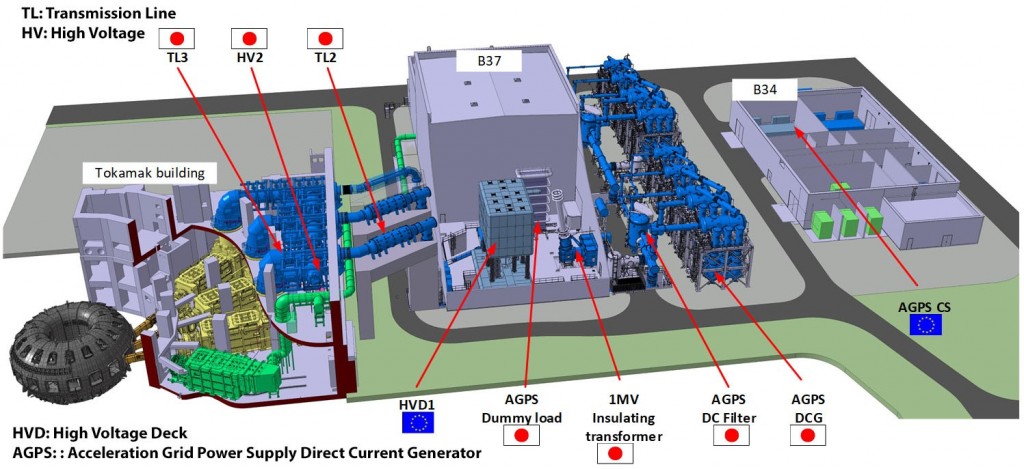
Europe and Japan contributing
2023-03-17 - Procurement for the neutral beam power supply infrastructure is shared between Europe and Japan.

High Voltage Building
2023-03-17 - The steel frames for the twin high voltage halls of the heating neutral beam system (25 metres tall) are anchored in massive concrete slabs. For each heating neutral beam injector the building will accommodate one 9-metre-tall high-voltage deck sitting on its 6-metre-tall insulating supports, as well as the even-taller bushing (16 metres) for the giant insulating transformer.
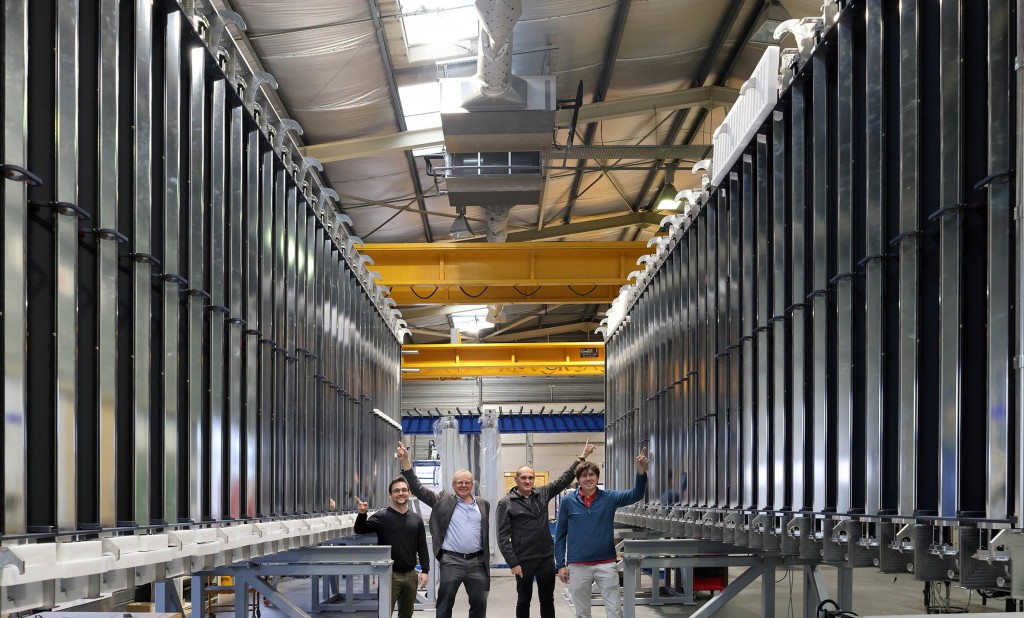
MITICA cryopump passes site acceptance tests
2023-03-12 - These huge panels coated with charcoal are part of the cryopump that will allow high vacuum to be created in the full-size ITER neutral beam injector MITICA (part of the ITER Neutral Beam Test Facility in Padua, Italy.) See more at: https://www.iter.org/newsline/-/3856
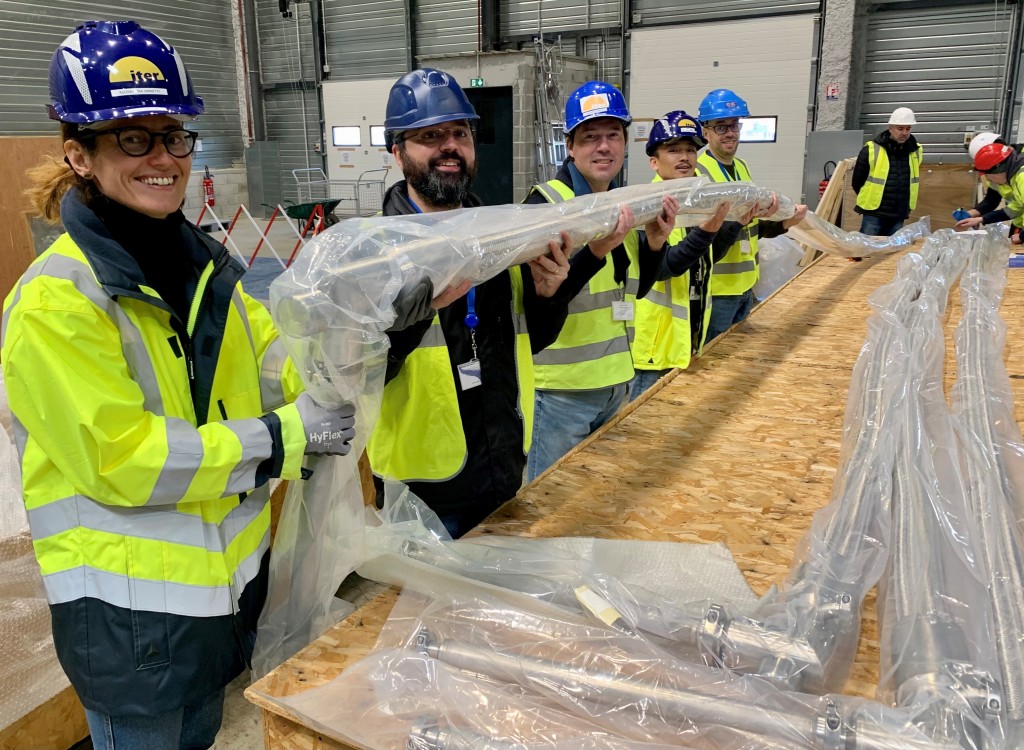
Small but essential parts
2023-03-06 - 32 sets of cryojumpers—semi flexible cryogenic pipes that distribute gaseous and liquid helium from the cold valve boxes to the torus and cryostat cryopumps—have been delivered by the European Domestic Agency.
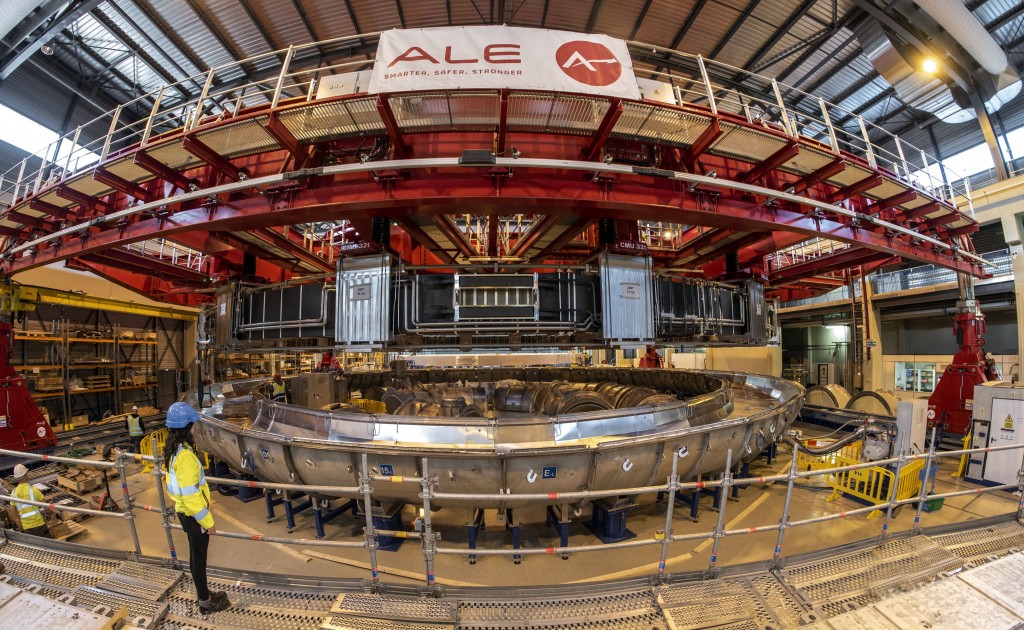
Last step for PF4
2023-02-20 - Only one step remains for completed poloidal field coil PF4—cold testing. Cold testing will take several months, as the coil is slowly brought to a target temperature of 80 K (-193 °C), stabilized, then brought back to room temperature. Tests are planned during every stage of the process.

Cryostat lid storage location
2023-02-20 - In the foreground, an octagonal concrete platform that has been reinforced for the weight of the cryostat top lid and its platform (almost 1,000 tonnes, combined).
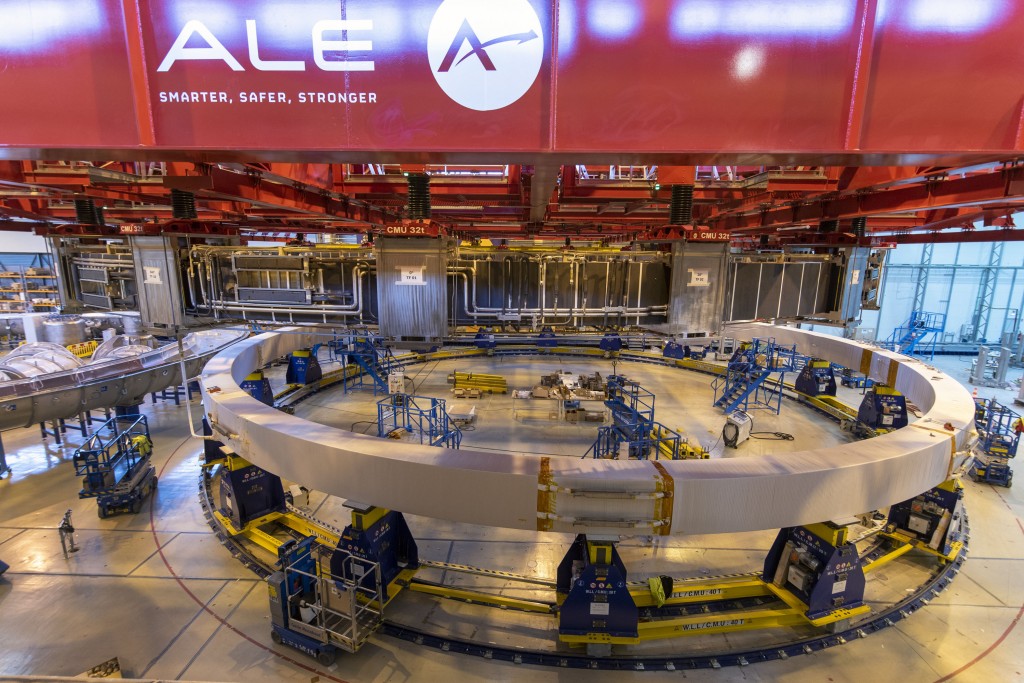
One over the other
2023-02-20 - The last two poloidal field coils to be produced in the European winding facility on site are now quite advanced. In this picture, as coil PF4 (black, at top) heads to cold testing, it passes over the PF3 winding pack (white).
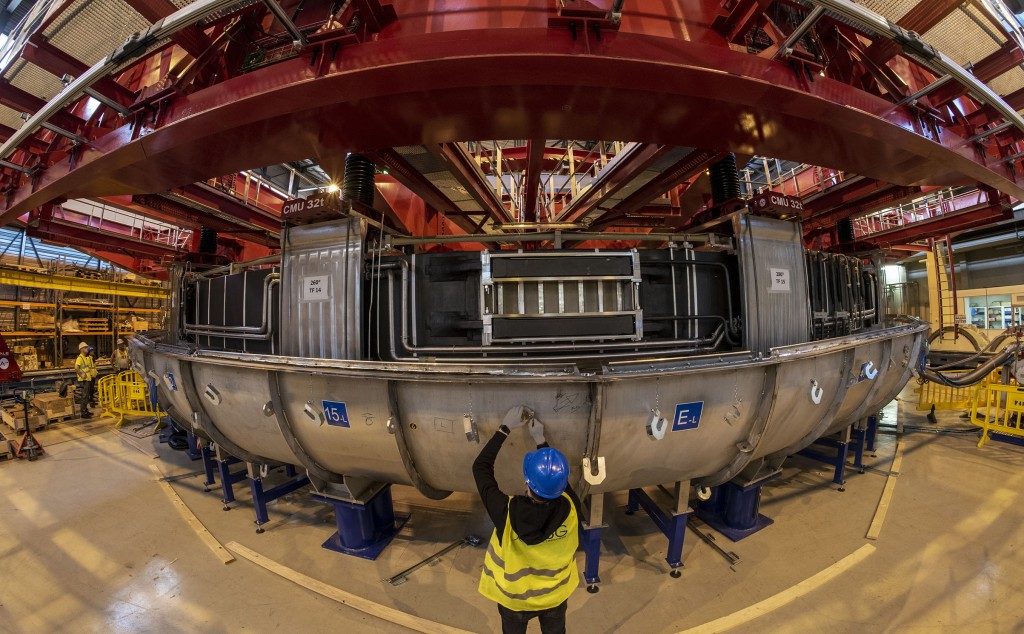
Reproducing a daunting environment
2023-02-20 - Inside the cryostat, the coil will experience extreme cold, intense pressure, high voltage and considerable thermal stresses—a foretaste of its life to come in the daunting environment of a burning plasma.
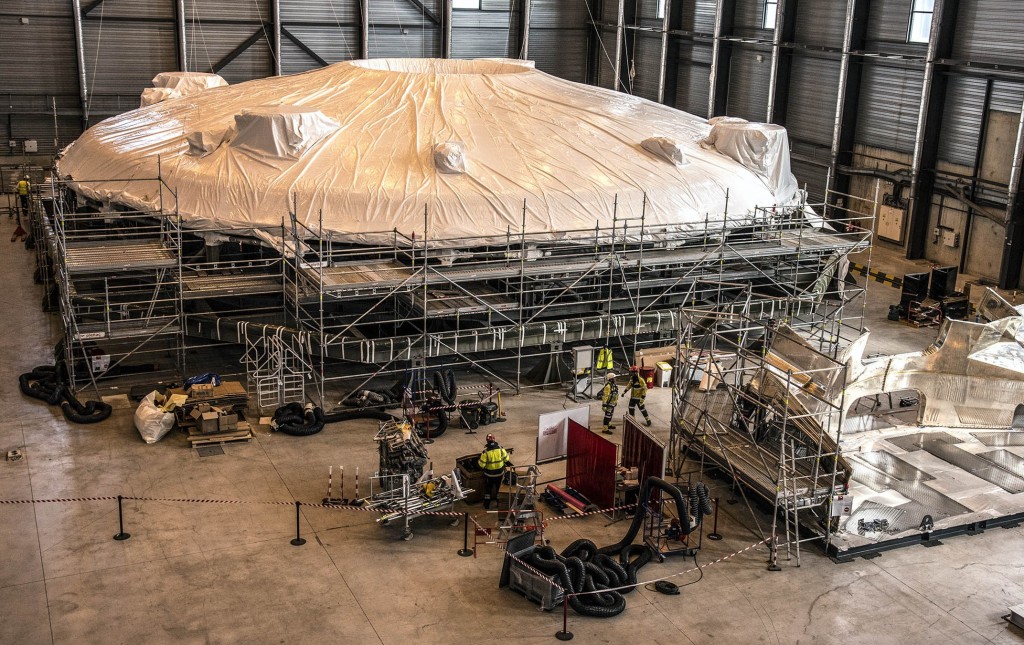
Top lid wrapping
2023-02-20 - The top lid needs to be protected for outdoor storage. After two layers of volatile corrosion inhibitor (VCI) material were applied, a thick cover (1.5 tonnes) is being added to ensure appropriate protection. More at: https://www.iter.org/newsline/-/3844
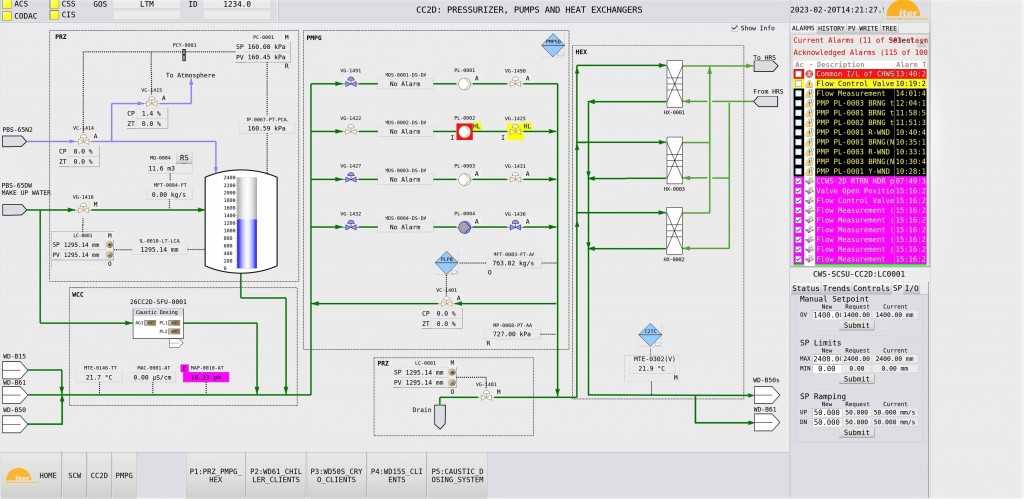
Five days a week
2023-02-18 - Two systems are already operational on site and run from this temporary control room—electrical distribution and utilities like compressed air and demineralized water from the Site Services Building. From this remote location, operators are also helping to commission the cryoplant, the heat rejection system and reactive power compensation.
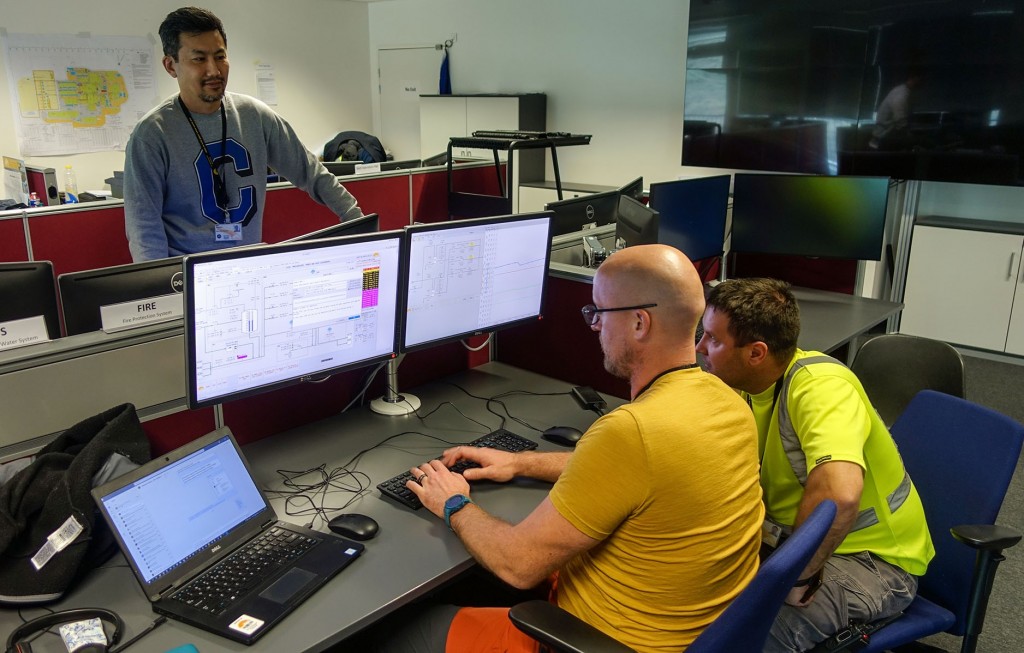
Temporary main control room goes live
2023-02-18 - On the second floor of the ITER Headquarters building, a temporary main control room is now operating five days a week. it uses the same CODAC workstation—with the same human-machine interface—that will be moved to the main control room when it opens in the Control Building.
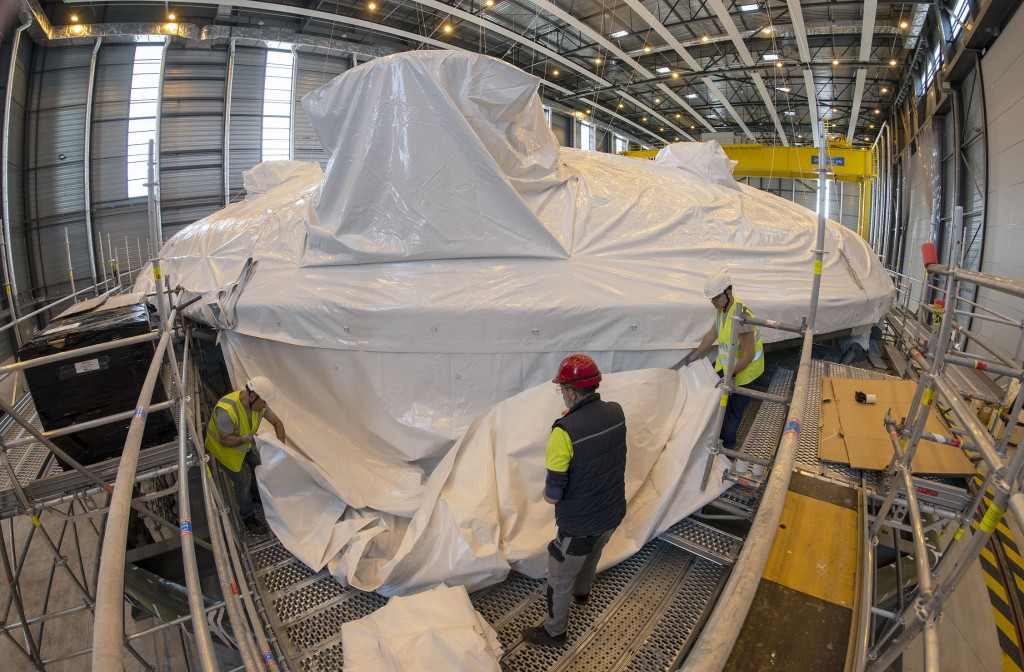
Monitoring closely
2023-02-15 - Three cameras inside of the wrapping will allow the cryostat team to monitor the state of the component for the duration of its storage outdoors.
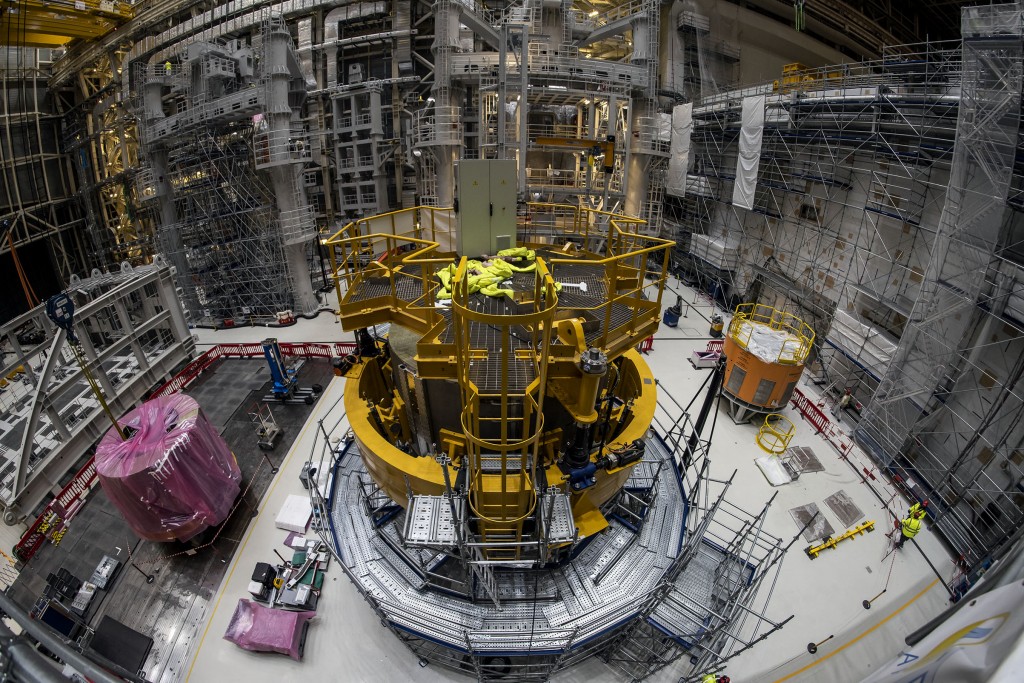
Electrical connections to complete
2023-01-26 - The central solenoid team is working with assembly contractors to complete the superconducting electrical connections of module 1. This involves welding, ultrasonic weld inspection, helium leak testing, electrical installation and high voltage testing.
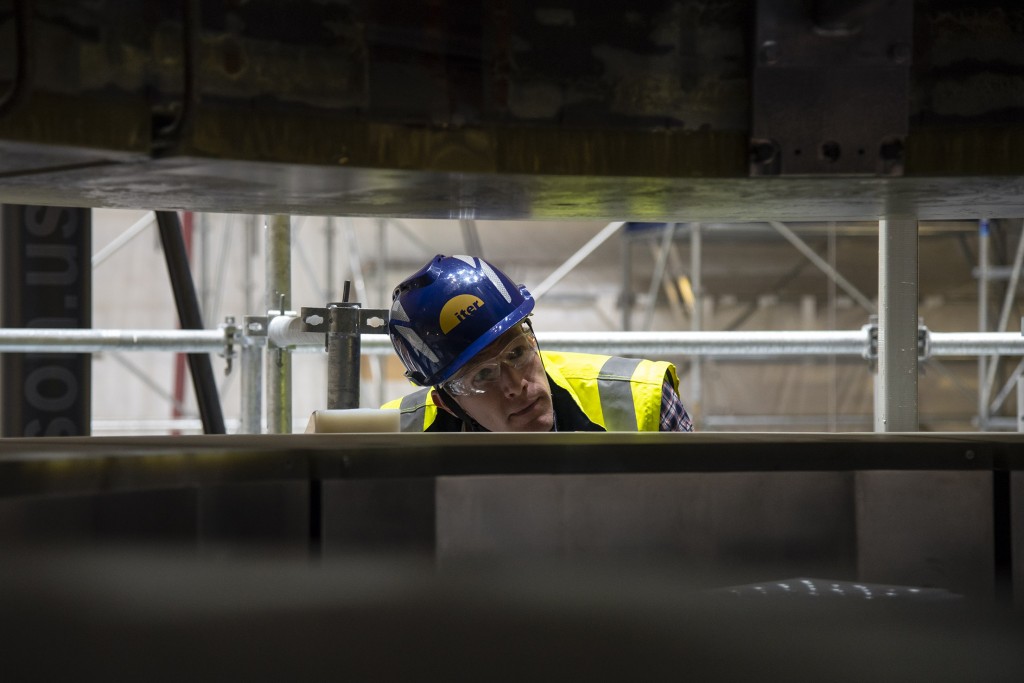
Oversight
2023-01-26 - American Carl Cormany from ITER's Magnet Section works closely with the contractor team as it carries out the many assembly steps required on module one.
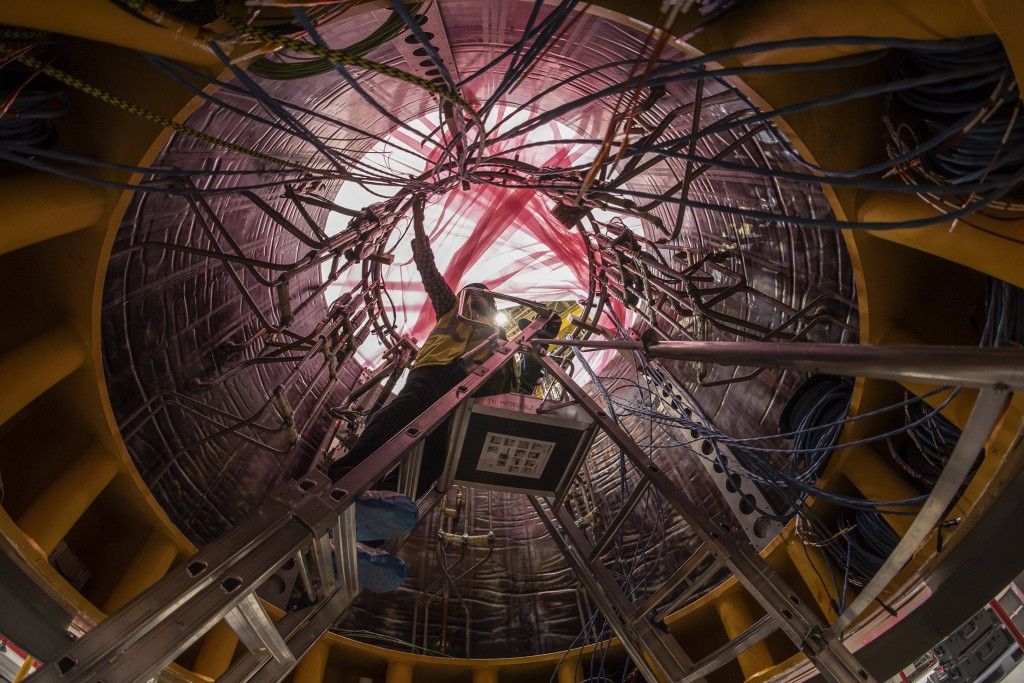
5 other modules to come
2023-01-26 - At the end of the module stacking process, the central solenoid tower will be 18 metres tall. Five other modules like the one in this photo will be added one after the other.
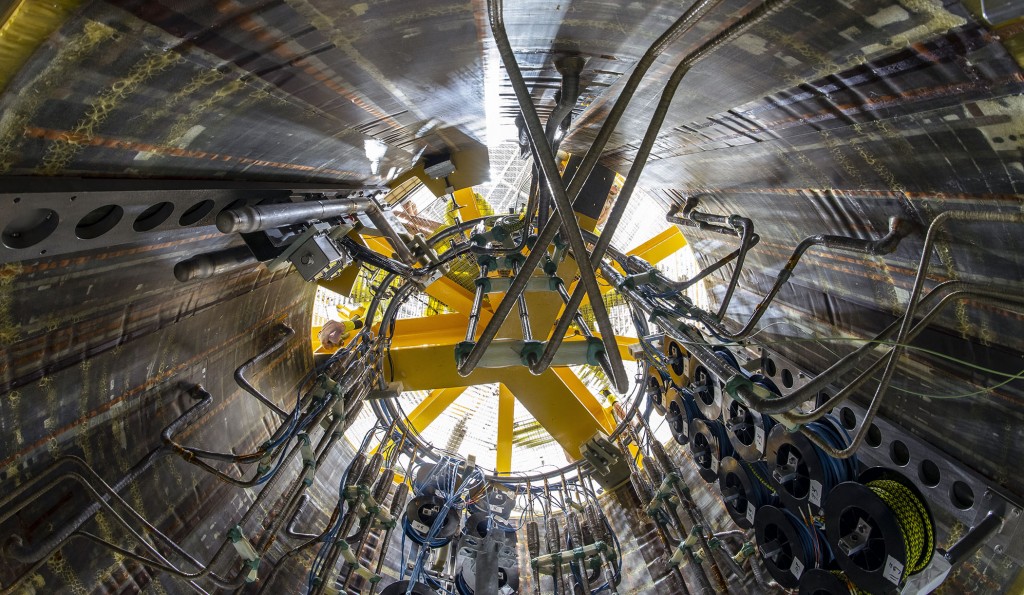
Inside the cylinder
2023-01-26 - The first of six cylindrical superconducting magnets for the central solenoid is positioned on a dedicated assembly platform at ITER. This picture was taken inside the cylinder, among the helium input pipes and electrical connections.
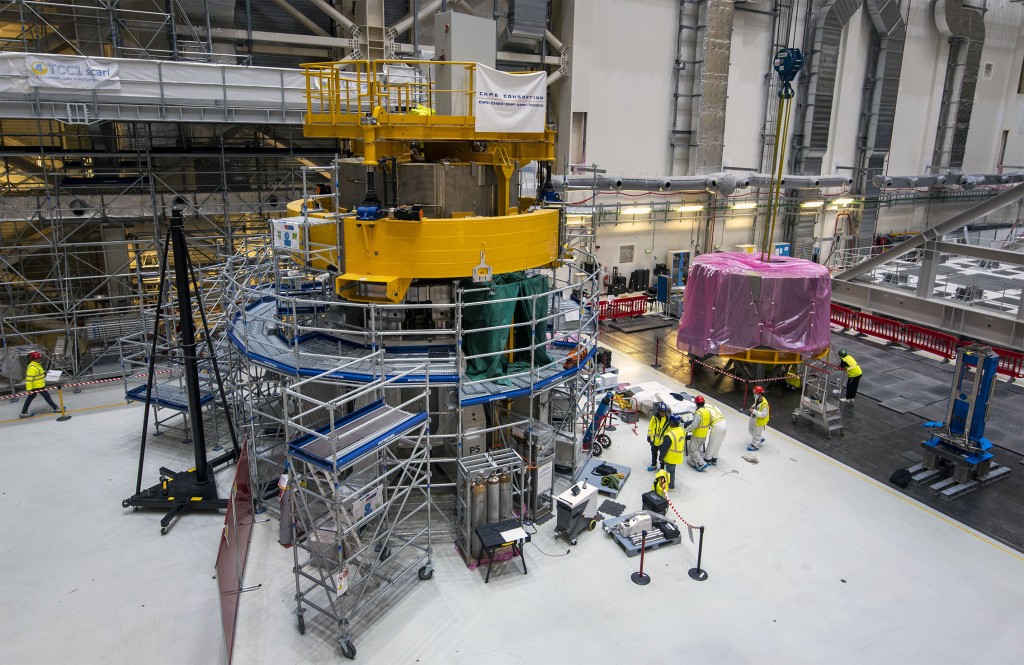
Up and up
2023-01-26 - In one corner of the ITER Assembly Hall, work has started on the central solenoid magnet tower. The first module now sits atop nine lower key blocks on a dedicated assembly platform. Five more modules will bring the tower to well over 20 metres (platform included), rivalling the height of a seven-storey residential building.
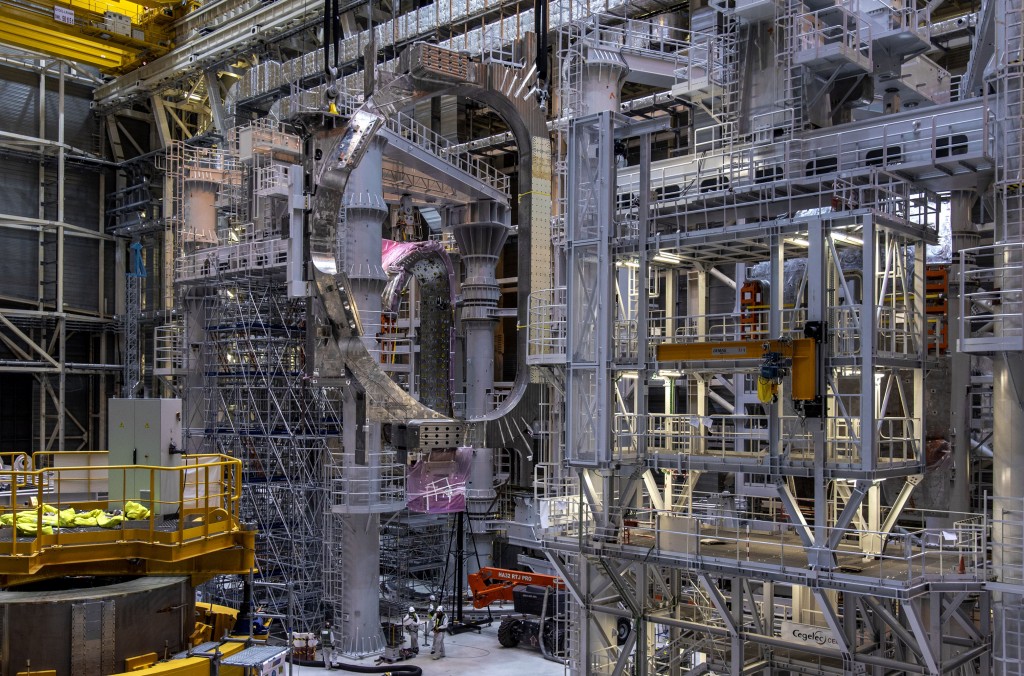
Squeezing through
2023-01-25 - The coil now enters the narrow space between SSAT-1 and SSAT-2. Limited clearance was the main challenge of the operation.
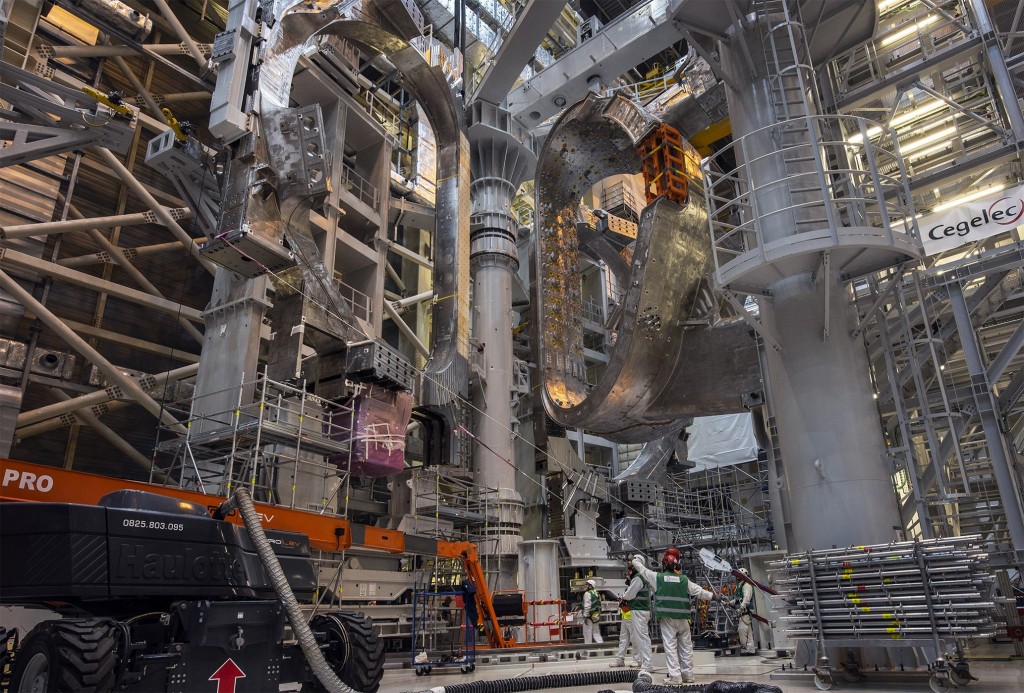
Pull!
2023-01-25 - As the crane hook slowly rotates to align the component, operators use a pair of "Tirfor" devices with a relatively low but sufficient pulling capacity (800 kilograms). Precise positioning is achieved by working the two "Tirfor" units one against the other.
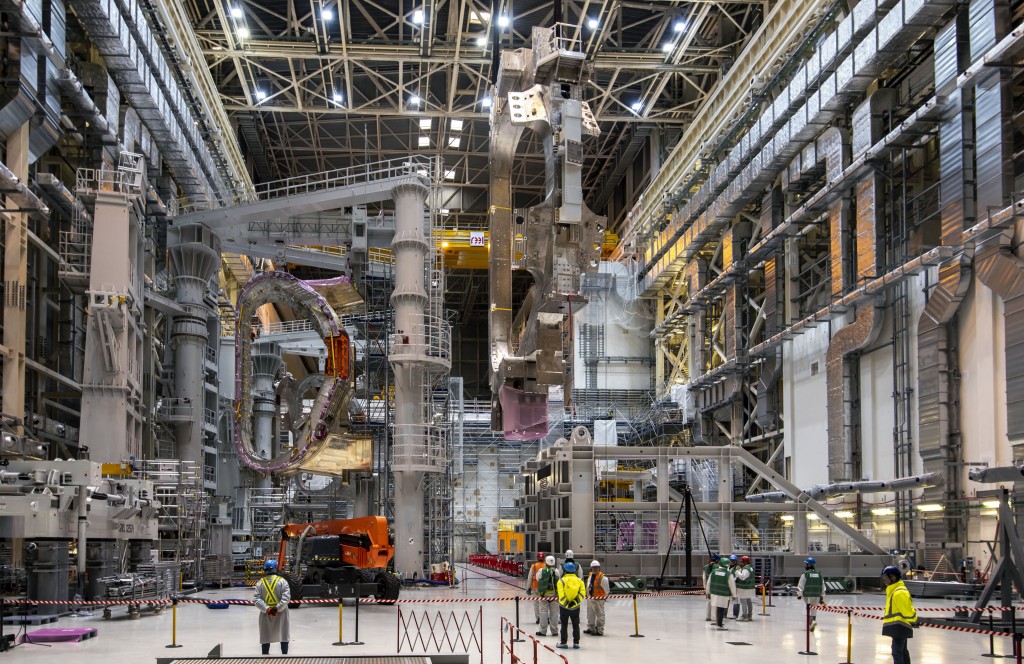
Musical chairs
2023-01-25 - January's faultless transfer of two 17-metre tall, 330-tonne toroidal field coils marked the first act of a giant, slow-motion game of musical chairs aimed at making thermal shield panels and vacuum vessel sectors ready for repairs.
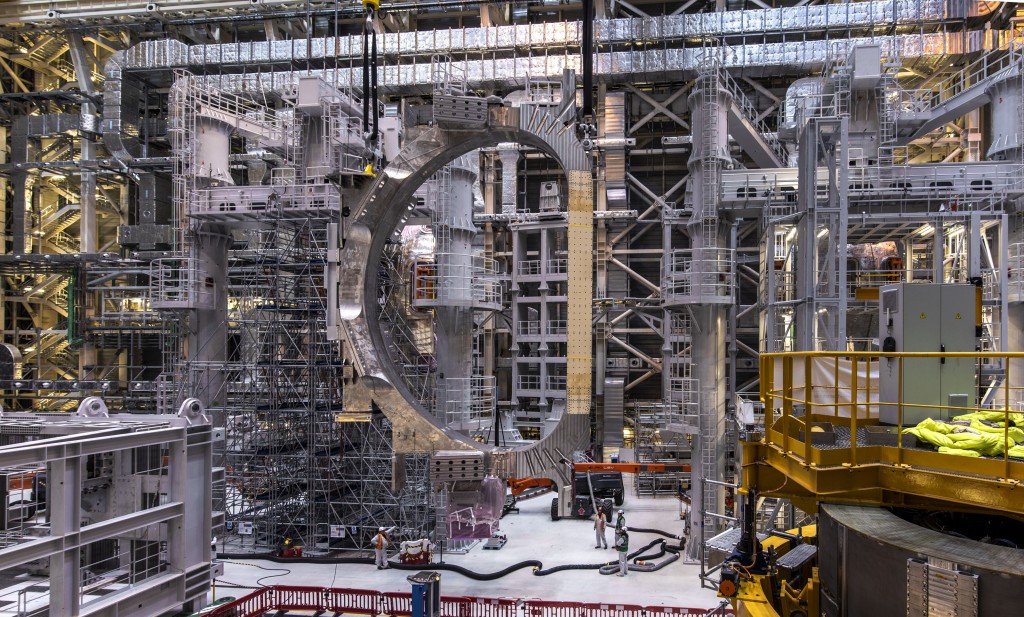
Moving a huge component
2023-01-25 - Halfway between the two sub-assembly tools, toroidal field coil TF8 is being readied for a 90-degree pivot. Operators standing next to the component give a sense of scale...
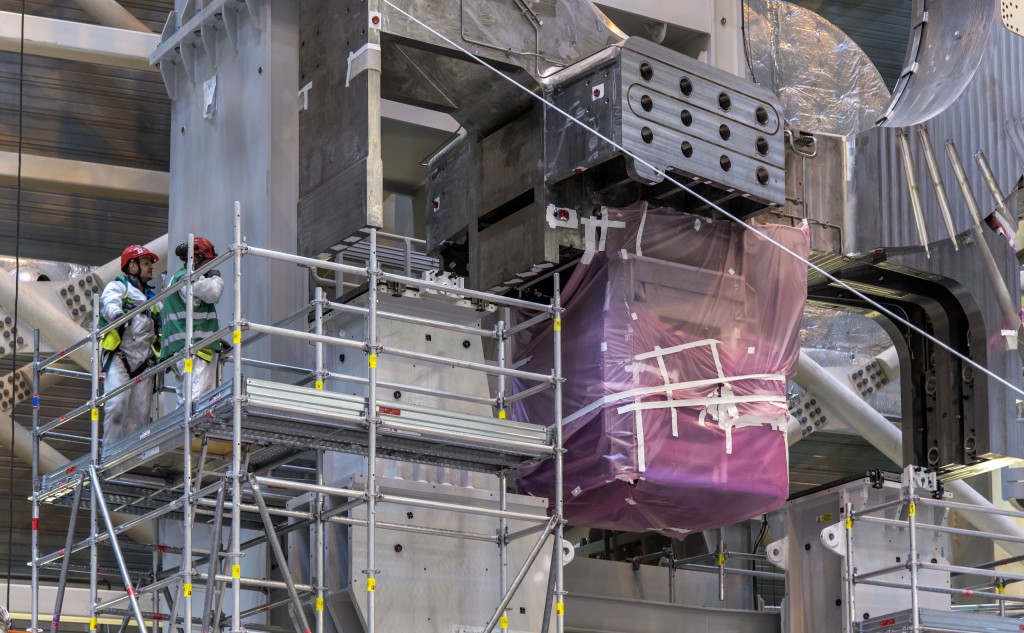
Almost there
2023-01-25 - The coil has now almost landed on its supports in SSAT-2. Synchronous hoist systems ("Synchoists") in the rigging, guiding devices, and customized shims contribute to the final positioning.
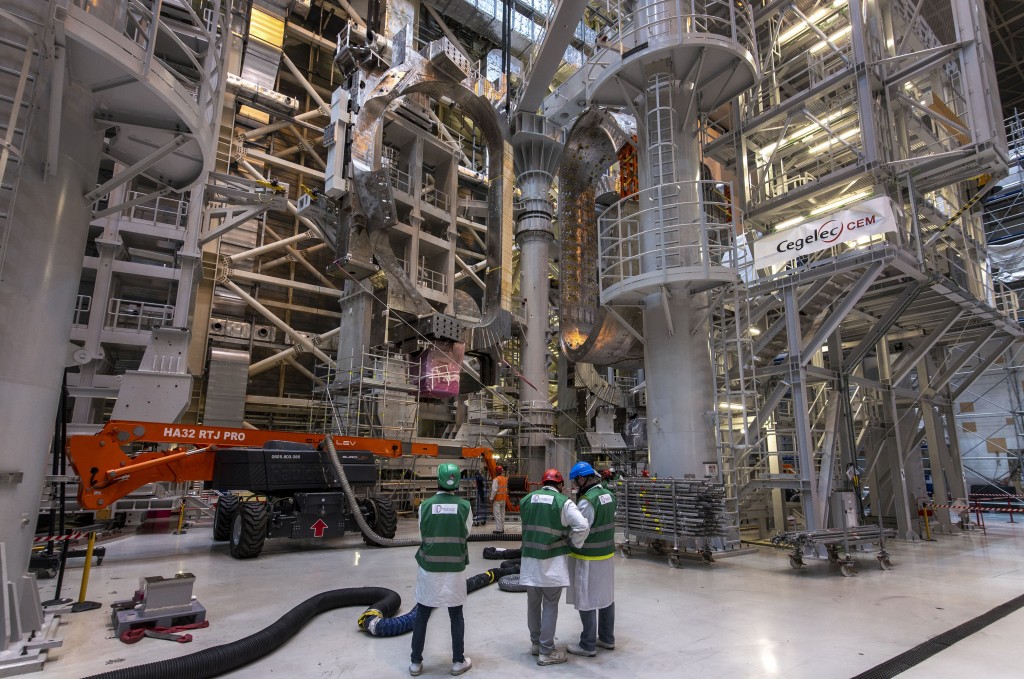
Activity in the Assembly Hall
2023-01-25 - There is activity in and around the double sector sub-assembly tools (SSATs) in the Assembly Hall, as component transfers are planned in relation to upcoming repair work.

Close up
2023-01-25 - Hanging a few centimetres above the floor, the connexion box (wrapped in pink plastic) is the most fragile part of a toroidal field coil. Note the precision of the steel machining on the larger coil case.
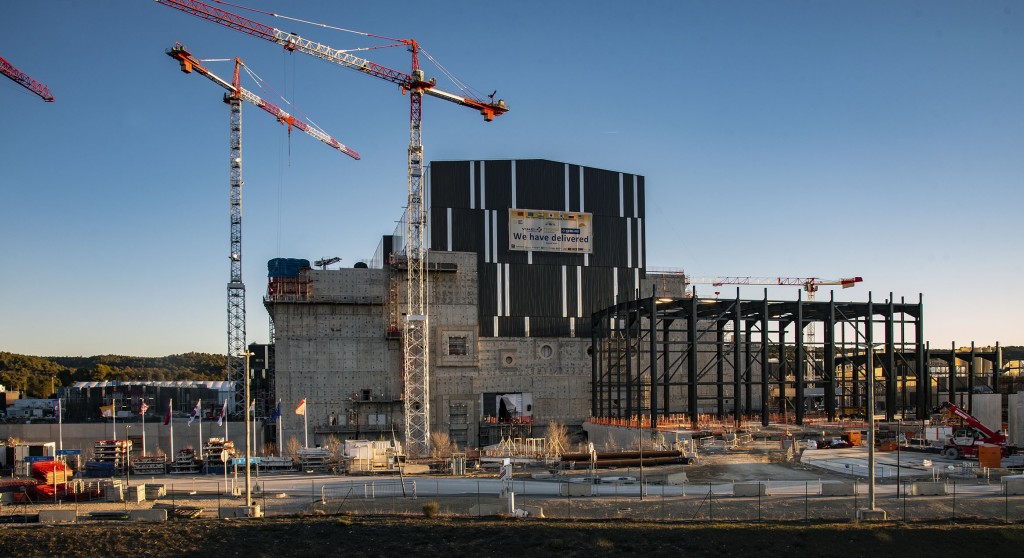
January 2023
2023-01-20 - The Tritium Building (concrete structure, left) is now at height. To the right, the structural beams of the High Voltage Building for neutral beam power supply are in place.
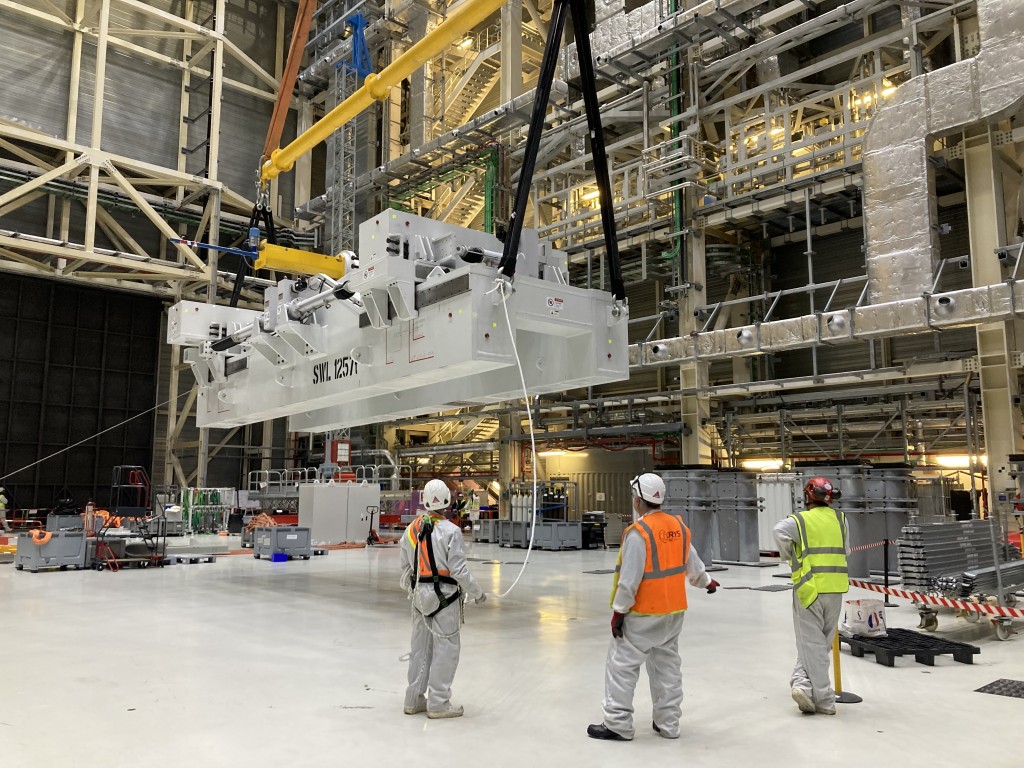
Tool back in action soon
2023-01-16 - This specialized sector lift tool will be back in action this year as vacuum vessel sector #6 is removed from the Tokamak pit for repair. It interfaces with the radial beam that supports the D-shaped sector.
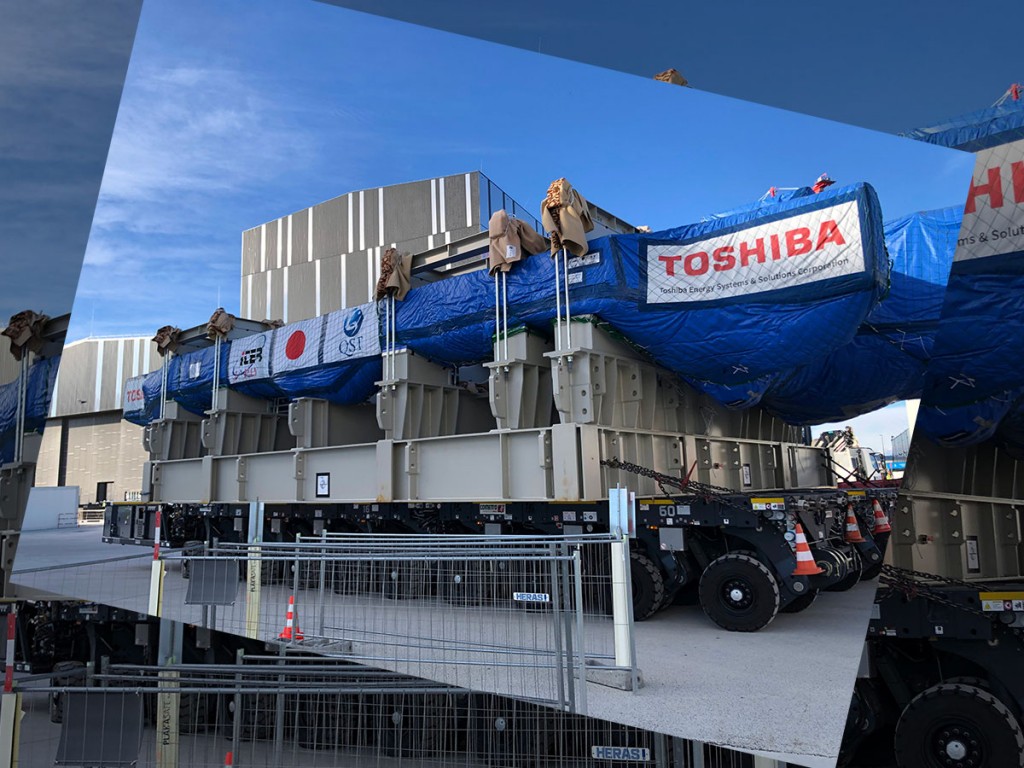
Important arrival
2023-01-13 - Another toroidal field coil has arrived at ITER—this one from ITER Japan. Only four more of these D-shaped coils are expected (out of 19).
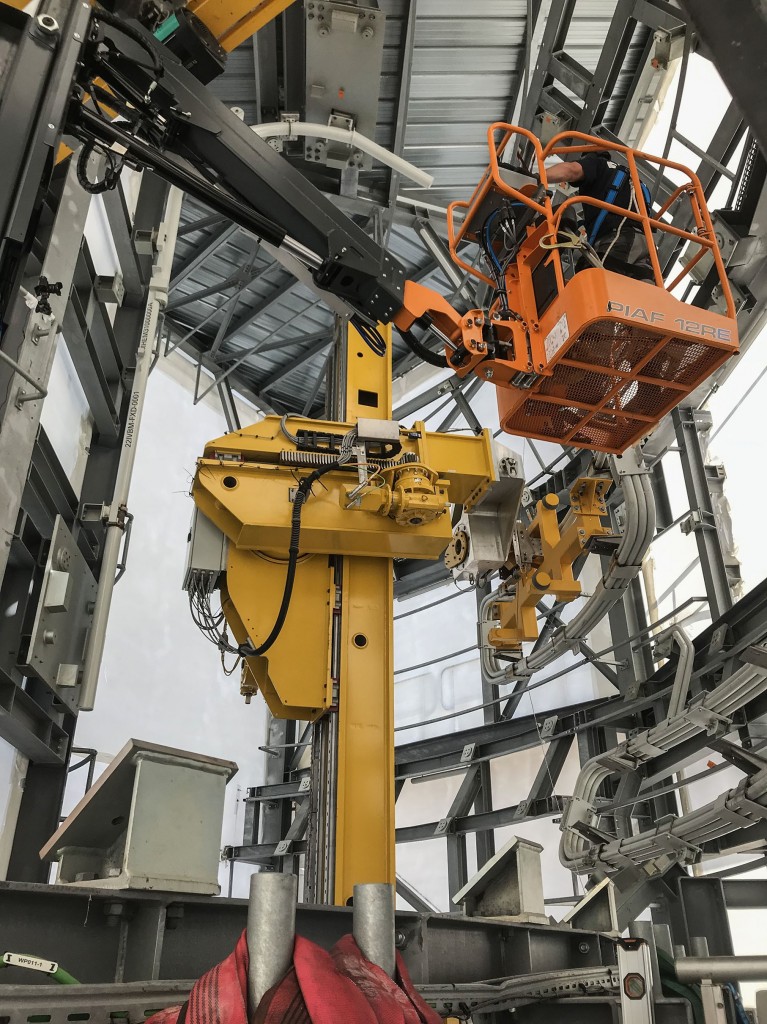
Manipulator arms: super strong and ultra precise
2023-01-10 - This is the in-vessel tower crane developed by CNIM Systèmes Industriels, a remote-controlled mobile manipulator that travels 360° around the interior of the vacuum vessel on dedicated rails. It can carry internal components weighing up to 5 tonnes and position them at any location inside the vacuum vessel to better than 0.5 mm accuracy. Two of these manipulators are planned.
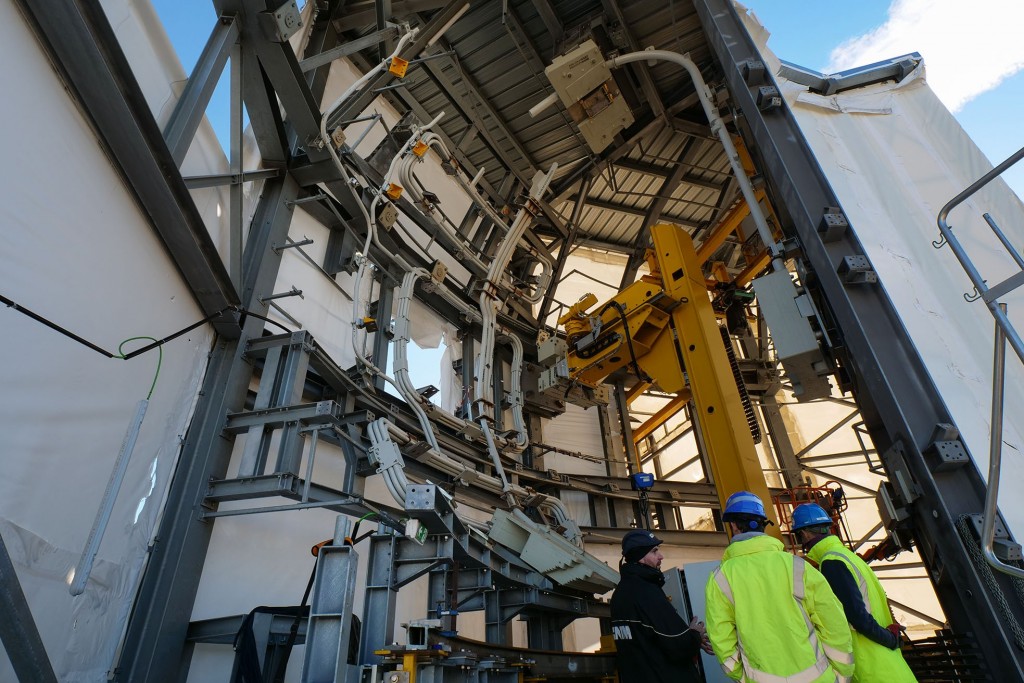
Tools for in-vessel component installation
2023-01-10 - At this Trial, Test and Training Facility at CNIM Systèmes Industriels (Toulon, France), bespoke mechanical handling solutions have been developed for the installation of components on the inner wall of the ITER vacuum vessel. In 2022 and early 2023, the entire suite of tools passed acceptance testing ''with flying colours.'' (Read more at https://www.iter.org/newsline/-/3835.)
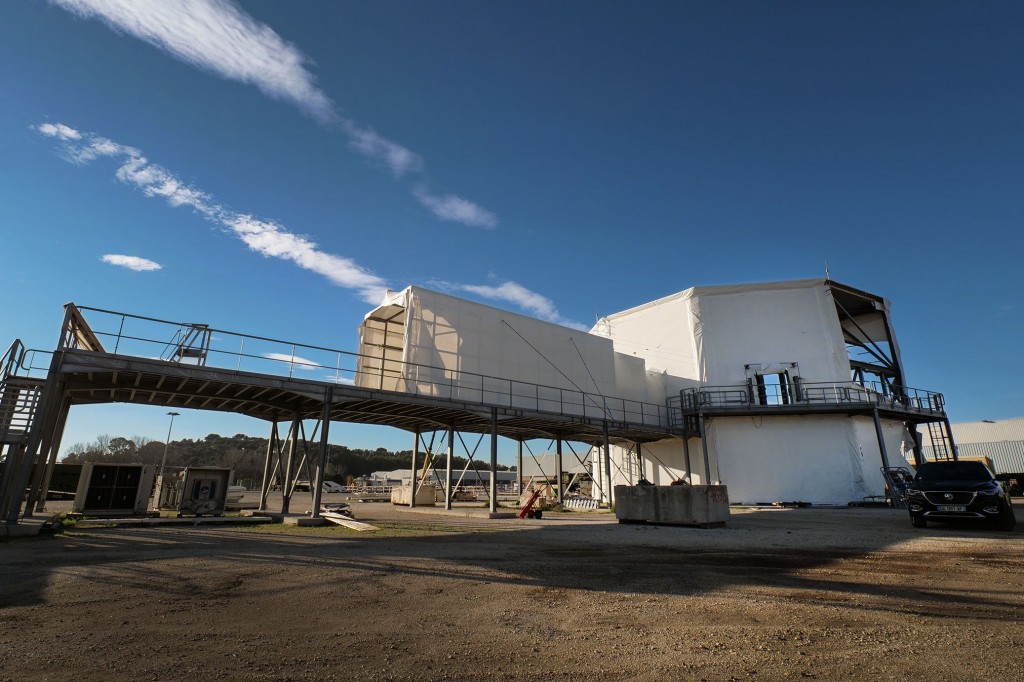
To be transferred to ITER
2023-01-10 - This scale-one Trial, Test and Training Facility reproduces one-third of the ITER vacuum vessel and a single port cell corridor. It will be transferred along with all tools and mockups to ITER for operator training and procedure development.
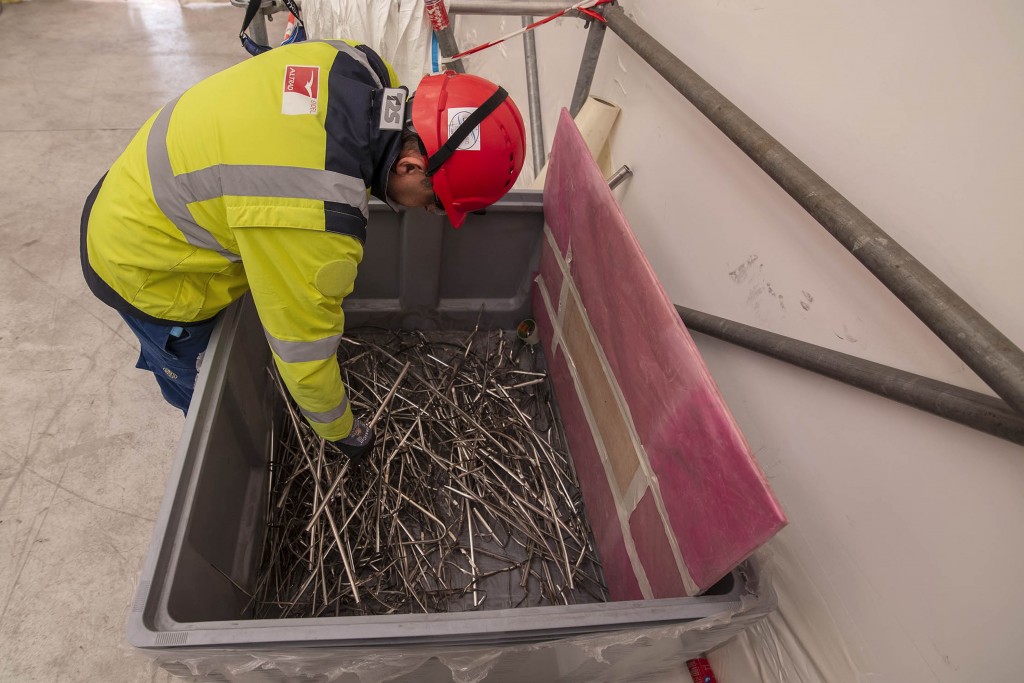
Pipe removal trials
2023-01-09 - Under a tent in the Cryostat Workshop, contractors are stripping piping from a panel of thermal shielding as part of strategy trials. (In the photo, you see some of the pipes that have been removed.) In total, 23 kilometres of piping snake along the surface of the 27 vacuum vessel thermal shield segments and will be removed and replaced.
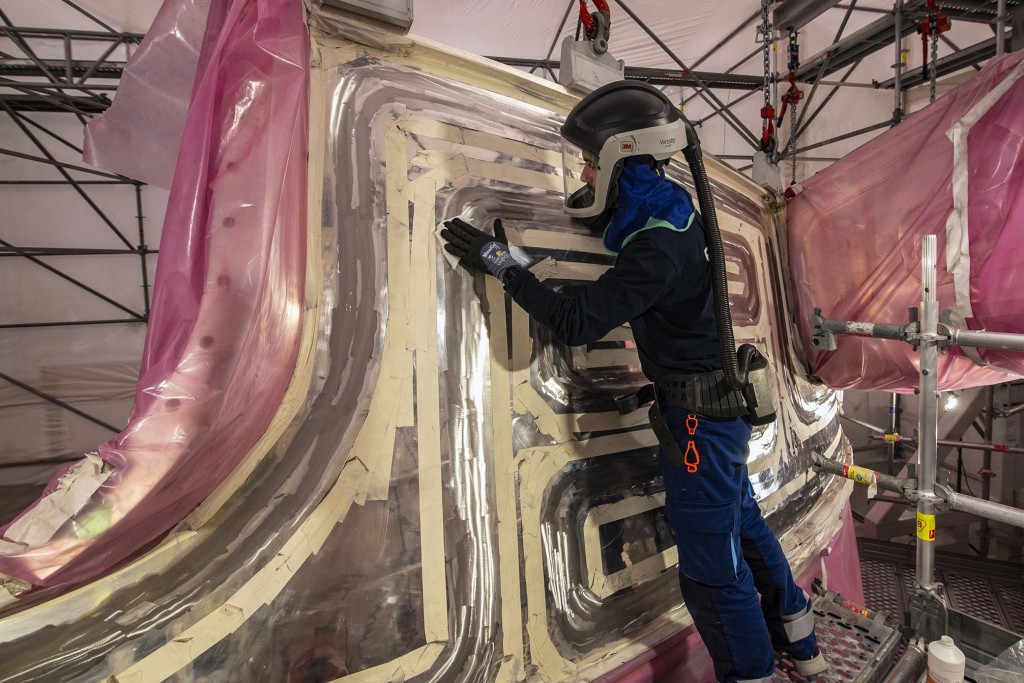
Cleaning the surface
2023-01-09 - A worker in protective gear cleans the surface of an outboard thermal shield panel that has had its cooling pipes removed; soon a new set of pipes will be attached. With a different steel formulation, lower-energy welding techniques, and a slightly different welding wire the new process will avoid the risk of "stress corrosion cracking."
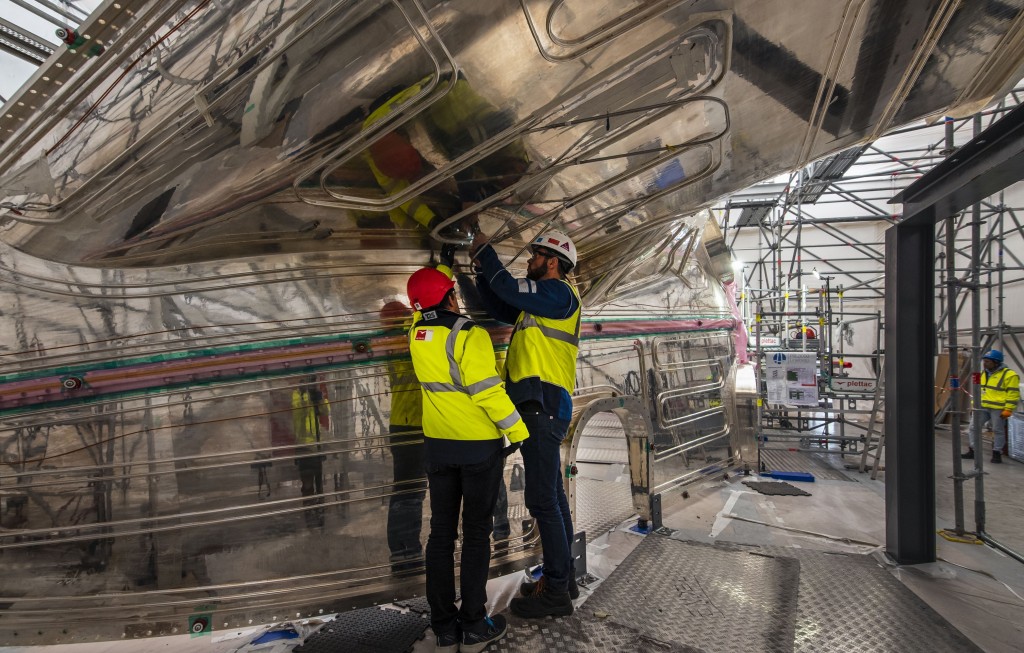
Investigation and analysis
2023-01-09 - Following months of discussion, tests and analysis, a clear picture of the repairs to be executed on the thermal shield is now emerging. The decision has been taken to remove and replace all cooling pipes (23 kilometres in total).

Questions to answer
2023-01-09 - How does the removal of cooling pipes from a thermal shield panel impact the component's dimensions, rigidity and capacity to accommodate a new set of piping? This is what experts have been busy evaluating.
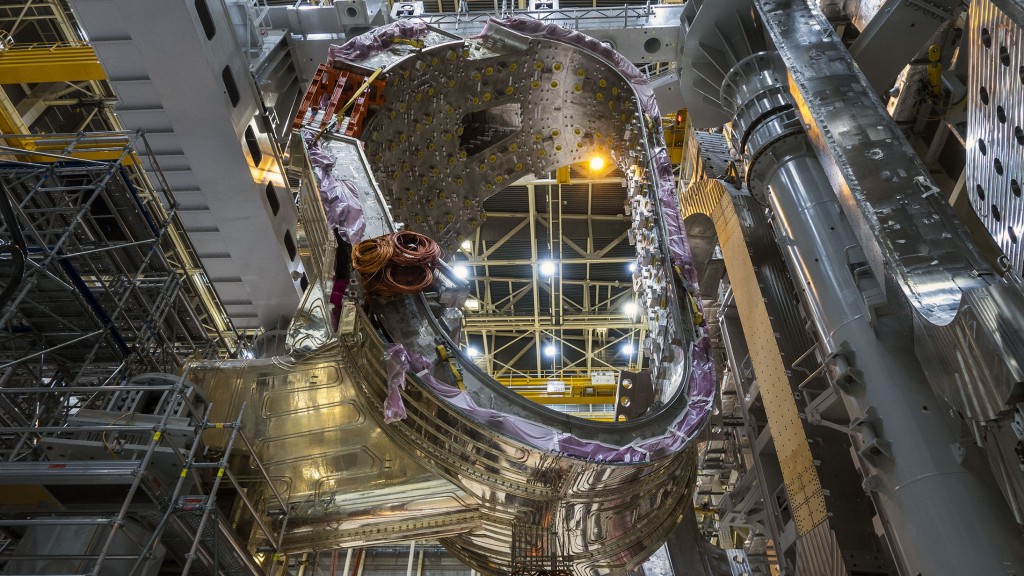
Deviations on the outer shell
2023-01-08 - During the formation of the D-shaped sector in factory, welding deformations created deviations from nominal on the outer shell of the sectors. Schematically (very schematically...), valleys must be filled and hills must be shaved in order to restore the geometry to nominal.
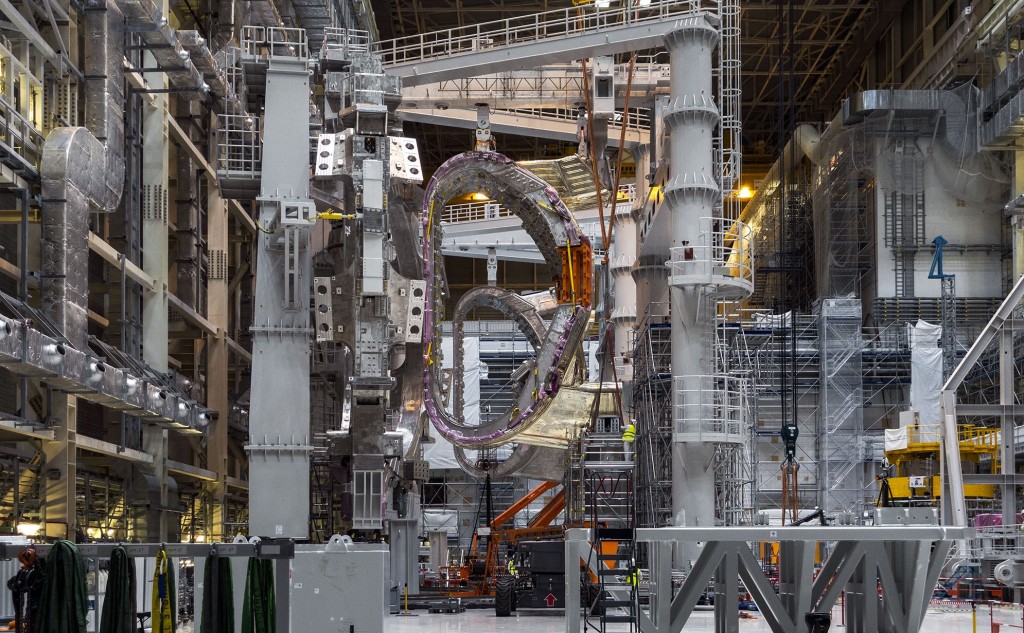
Repair of the sectors
2023-01-08 - The logistics are already planned for the repair of dimensional non-conformities on the three vacuum vessel sectors: sector #1(7) will stay where it is in the SSAT-1 vertical tool; sector #8 (currently in SSAT-2) will be removed and placed horizontally on a repair platform; sector #6 will be removed from the pit and installed in the SSAT-2 vertical tool.
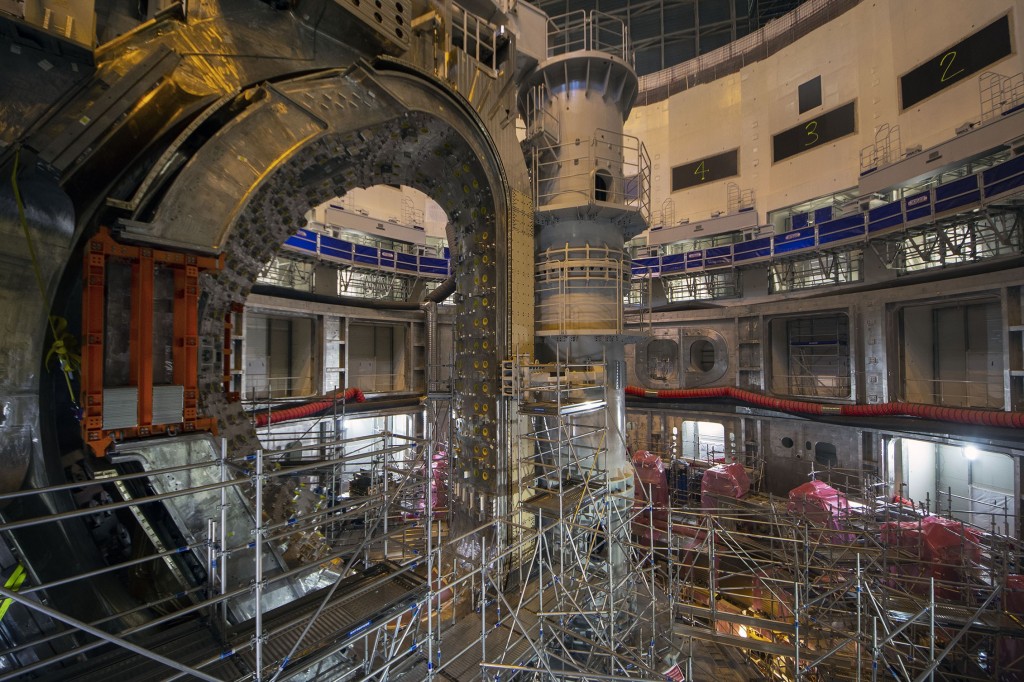
To be removed
2023-01-08 - In late May/early June, one of the twin sub-assembly tools will be ready to accommodate vacuum vessel module #6. The component will be lifted out of the Tokamak pit and placed in tooling to be stripped of its thermal shield panels and toroidal field coils in order to be ready for repair in late 2023.
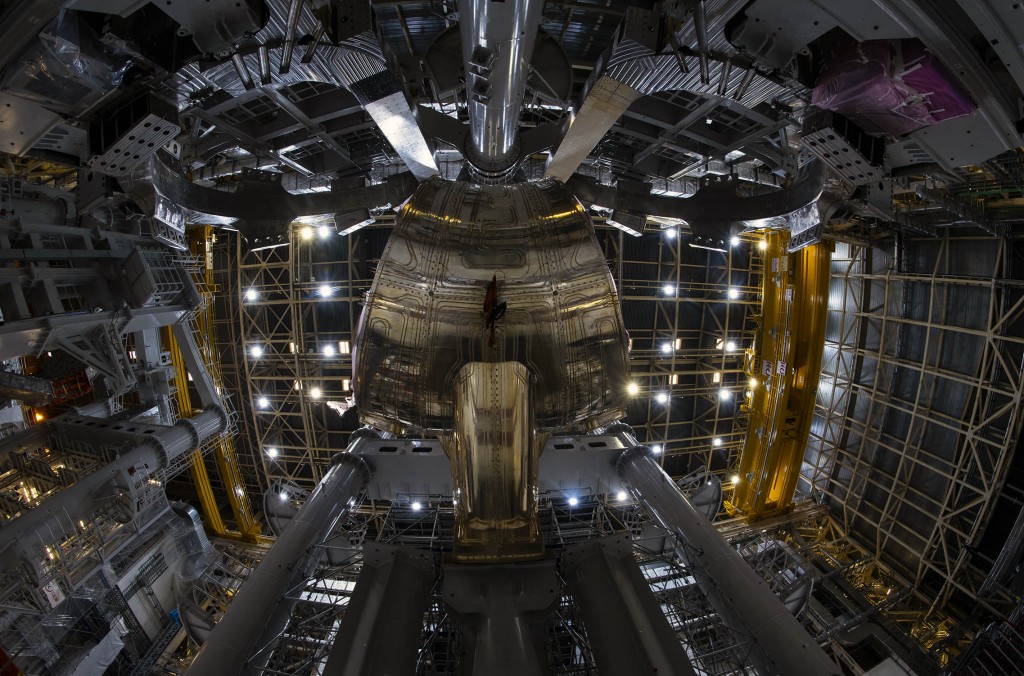
This sector will remain in tooling
2023-01-06 - Sector#1(7) remains in vertical tooling, where it is being disassembled in order to prepare for repairs on both the thermal shield segments and the geometry of vacuum vessel field joints. Notice the D-shaped coils that are now back on the tool wings.

Investigating repair strategies
2022-12-19 - Under a plastic tent set up in the Cryostat Workshop teams, including metrologists, are investigating repair solutions for the ITER Tokamak's thermal shield panels. See more at: https://www.iter.org/newsline/-/3830

Toroidal field coil alignment
2022-12-15 - The assembly tolerances required to align a pair of toroidal field coils in the Tokamak pit are shown in this image. The measurement of deviations from ideal "as-designed" parts on a computer screen to "as-built" coils ready for installation at ITER is a vital part of the assembly strategy. See more at: https://www.iter.org/newsline/-/3826

Last structural beams are up
2022-12-12 - Thirteen structural beam sets—nine tall and four small—are in place for the High Voltage Building. Part of the infrastructure that will house neutral beam power supply, this tall building will house state-of-the-art high voltage components including HV decks and HV deck bushings.

Moon on the rise
2022-12-07 - The moon on the rise is captured through the metal structure of the neutral beam power supply's High Voltage Building. (Photo courtesy of Tony Donné, EUROfusion)
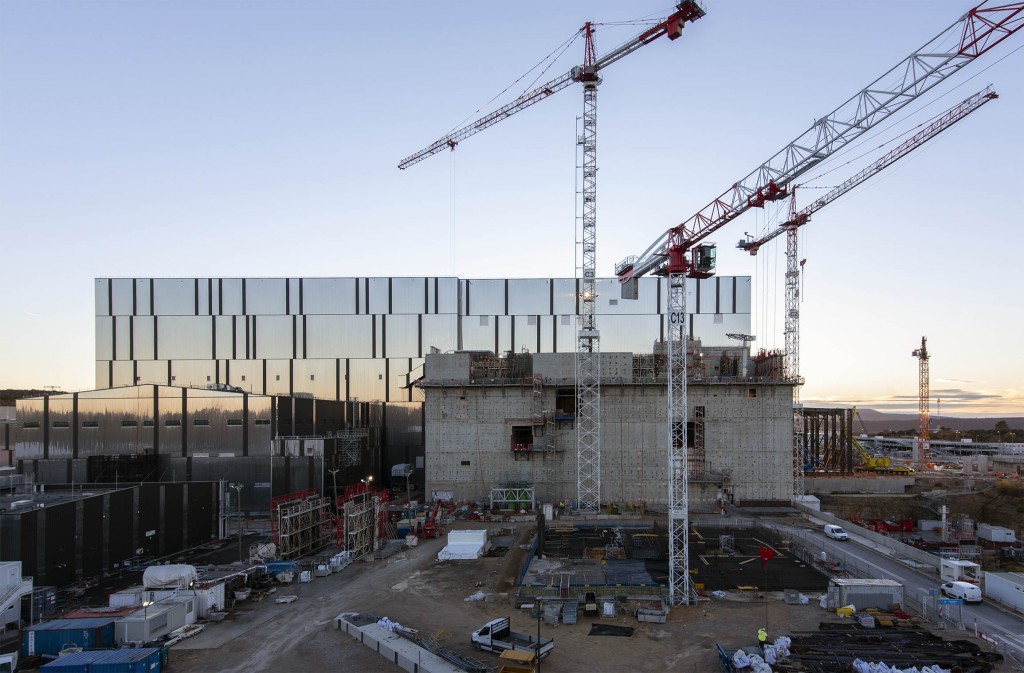
Progress on the Tritium Building
2022-12-06 - European contractors are currently pouring concrete at level 5 (L5) of the Tritium Building. This will bring the structure to full height.

25 metres tall
2022-12-06 - The tallest galleries of the High Voltage Building (in construction, far right) will stand 25 metres above platform level.

Step-by-step validation
2022-12-06 - Plant commissioning is proceeding step by step, as individual cryoplant sub-systems are tested and validated.
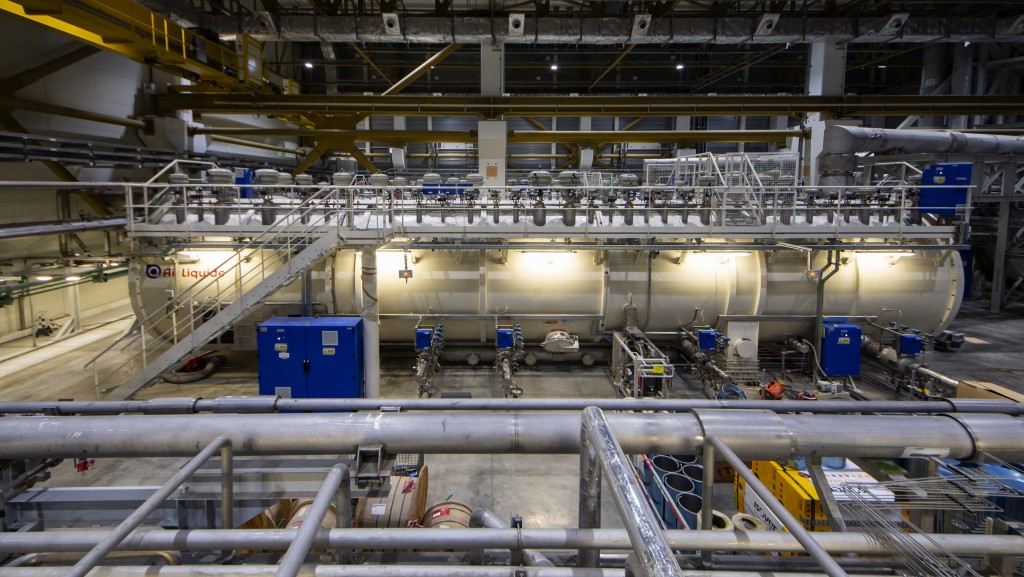
Cold boxes
2022-12-06 - One of three "cold boxes" in the cryoplant that will cool and liquefy the large volumes of helium needed by ITER's cryogenic "clients" (the magnets, thermal shield and cryopumps).

From above
2022-12-06 - From the rafters, with a view all the way through to the Tokamak Pit at the far end. Machine components visible in this photo include an element of the vacuum vessel thermal shield (bottom left), a D-shaped toroidal field coil (lying horizontally); the start of the central solenoid stack (middle right), and a sector of the vacuum vessel (mainly hidden in vertical tooling, middle left).

Tritium Building: nearly there
2022-12-06 - We can expect a topping-out ceremony for the Tritium Building in 2023, as the last level is completed. (This tradition originating from Eastern Europe consists of placing a small tree atop a completed construction project.)

Two buildings emerging
2022-11-29 - Both neutral beam power supply buildings are emerging on site. The steel frame going up in front of the Tokamak Complex is the High Voltage Building. In the bottom right corner of the photo is the (lower voltage) Neutral Beam Power Supply Building.
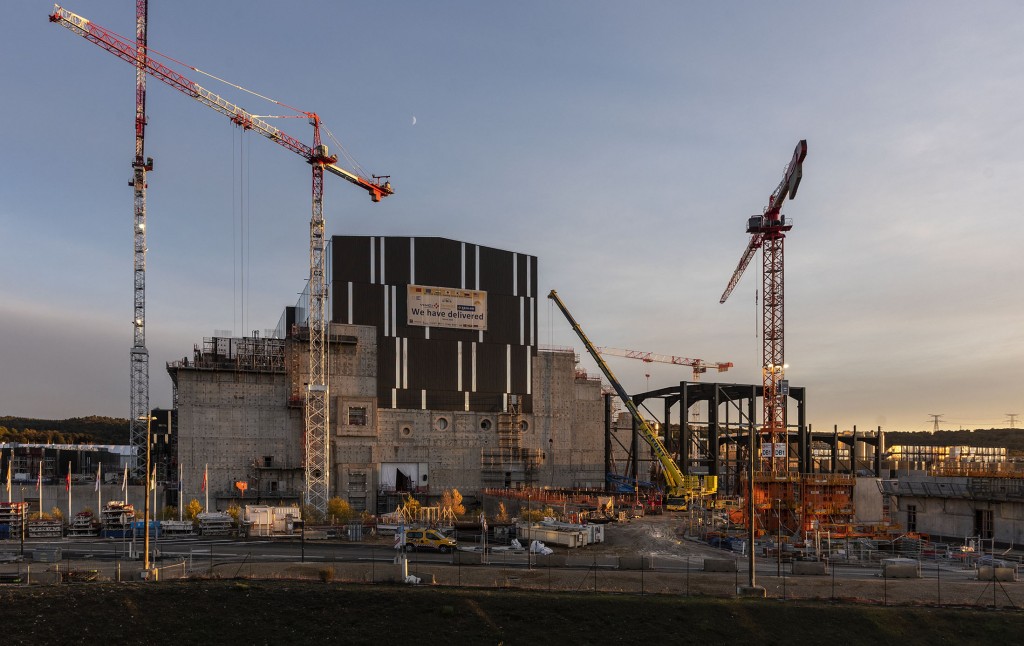
New building emerging
2022-11-29 - Against the concrete structure of the Tokamak Complex, the frame of a new building is emerging: the tall High Voltage Building that will house the high voltage equipment for neutral beam injection. See more information at: https://www.iter.org/construction/NeutralBeamPower.
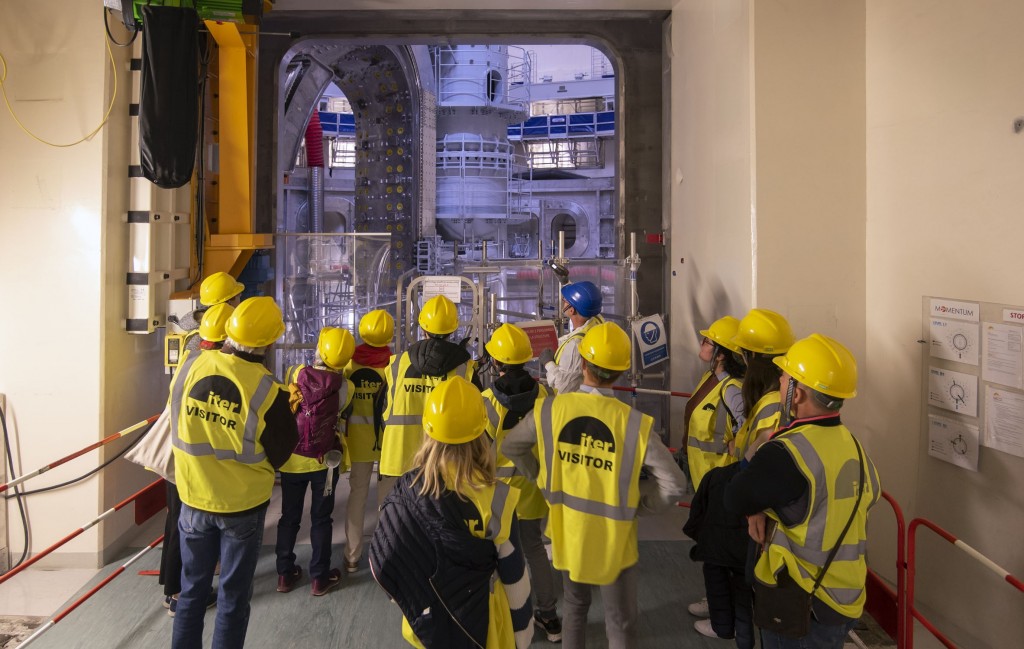
Couldn't be closer
2022-11-26 - A port cell has been specially prepared to receive visitors on Saturday 26 November during ITER's latest Open Doors Day. Impossible for a visitor to get any closer to the machine assembly pit.
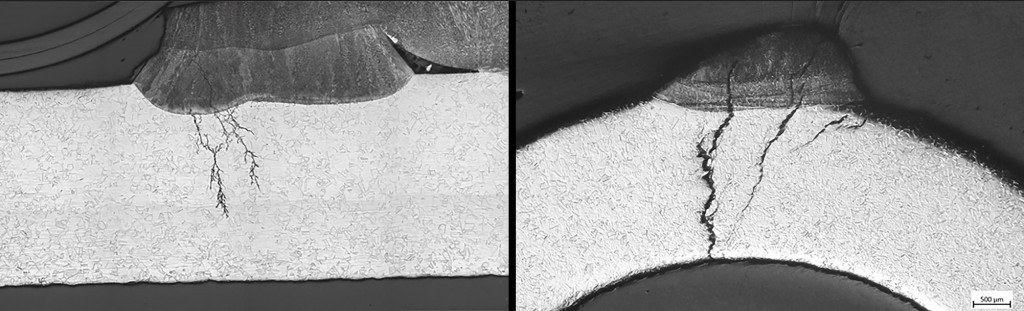
Close up
2022-11-21 - Investigative techniques (high-resolution CT scanning, scanning electron microscope, energy-dispersive X-ray spectrometer, and metallographic observation) revealed cracks in thermal shield cooling pipes such as the ones pictured here. At left, the crack is 1.5 mm deep. At right it is 2.2 mm deep and crosses the full width of the pipe.

Defects identified
2022-11-21 - In November 2022, the ITER Organization announces that it had identified issues in key tokamak components, the thermal shield (stress corrosion cracks in cooling pipes) and three vacuum vessel sectors (dimensional non-conformities). These defect are repairable; repair strategies are under investigation now. (In this picture, the thermal shield and its snaking cooling pipes are visible sandwiched between the magnet and the sector.)

Sector non-conformities
2022-11-21 - Deviations during the welding process of the vacuum vessel sectors led to dimensional ''non-conformities'' on the outer shells of the three sectors that have been delivered to ITER, affecting the geometry of the field joints where the sectors are to be welded together. Repairs will have to be carried out.
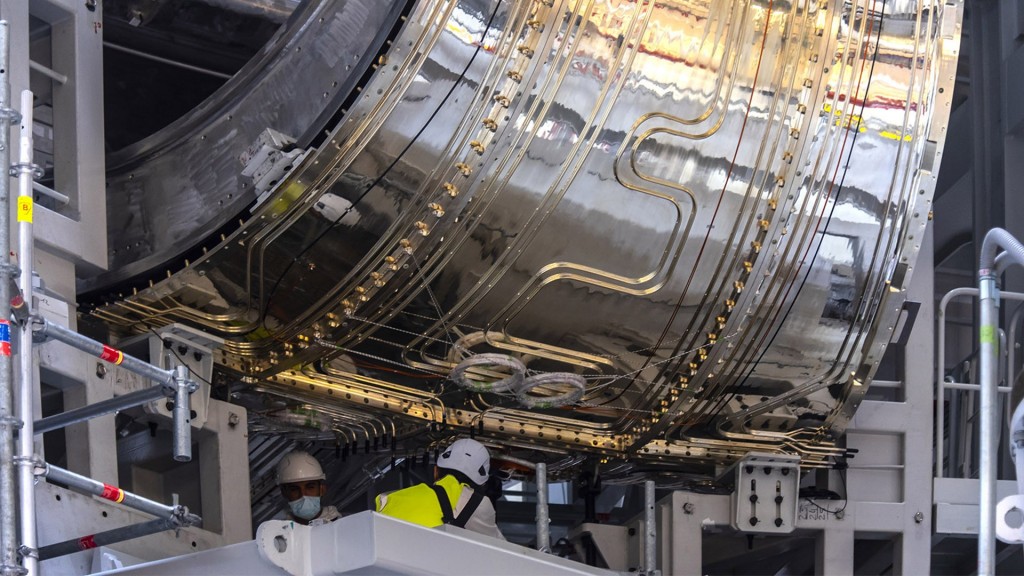
Root cause
2022-11-21 - A total of approximately 23 kilometres of piping are welded to the surface of the thermal shield panels. In three instances, stress caused by the bending and welding of the cooling fluid pipes to the thermal shield panels, compounded by a slow chemical reaction due to the presence of chlorine residues, caused "stress corrosion cracking" near the pipe welds.
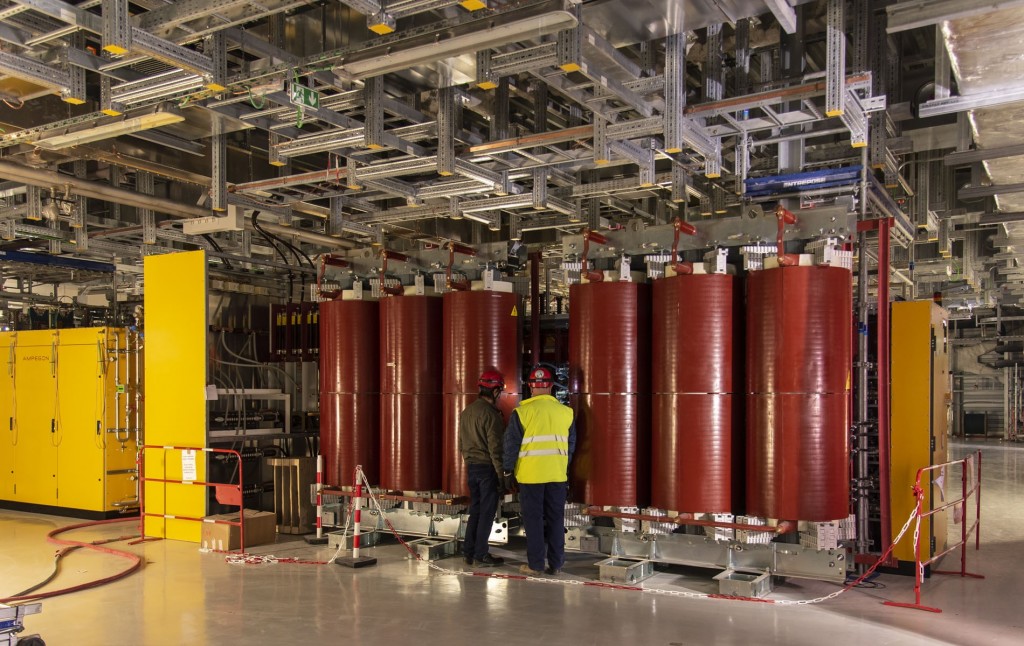
RF power supplies and transformers
2022-11-09 - One of the two sets of high-voltage power supplies for the electron cyclotron resonance heating (ECRH) system is already installed on the second floor of the Radio Frequency Building. The red cylinders are ~6MW cast-resin multi-secondary transformers that feed the power modules to the left (yellow).
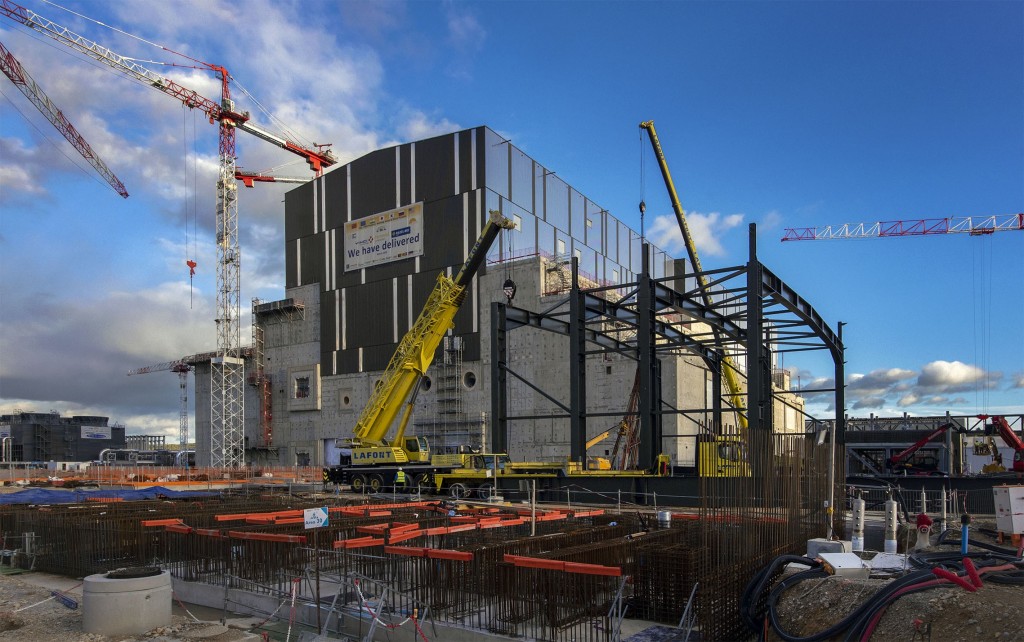
First steel frames
2022-11-03 - Of 13 steel frames planned for the 84-metre-long Neutral Beam High Voltage Building, 4 have been anchored in place. At 15 metres tall, they correspond to the (smaller) diagnostic neutral beam bay of the building. The next-in-series will rise 25 metres in height.
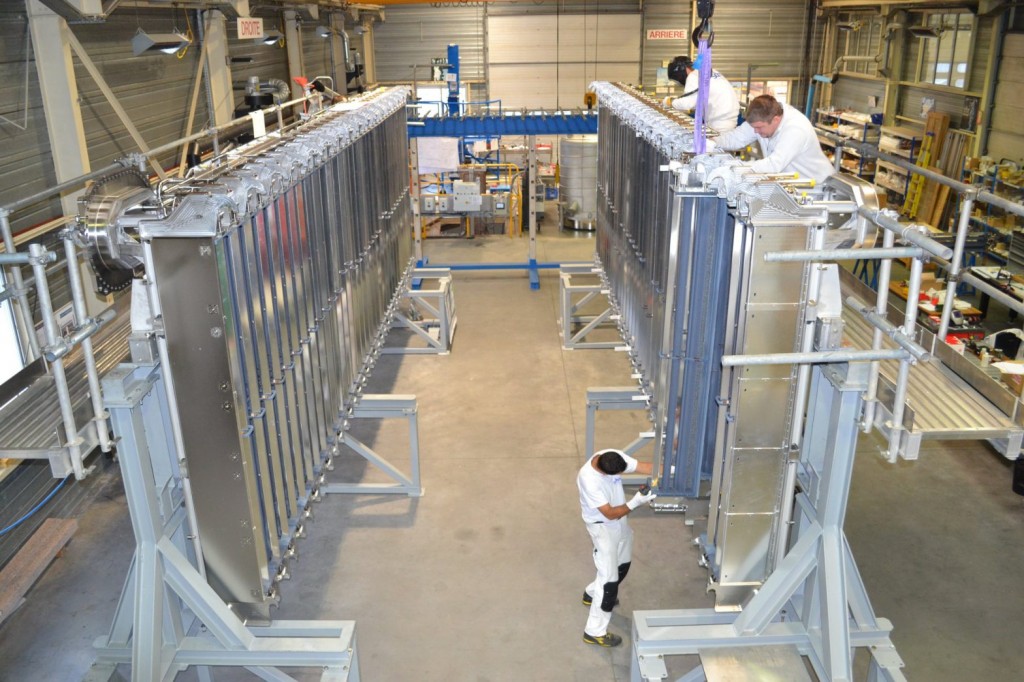
Final assembly and testing for MITICA cryopump
2022-10-22 - European Domestic Agency contractor SDMS (France) is completing the final mounting and testing of the MITICA cryopump's two pumping assemblies, which consist of frames with 32 pumping sections each. In this photo, technicians are positioning one pumping section. © SDMS

Heavy duty "shape sorter"
2022-10-17 - At level 3 (L3) of the Tokamak Building, the teams are ready to play a heavy-duty version of "Shape Sorter": the cylindrical object to introduce in the circular opening measures 8 metres in length, 1 metre in diameter and weighs 5.5 tonnes.

Tokamak Building cryolines: 75% installed
2022-10-17 - With the insertion of this massive elbow-shaped spool, total cryoline installation inside the Tokamak Building is now close to 75% complete. Inserted into a wall opening, the spool will connect the cryolines installed inside the building to those coming from the cryoplant along the elevated ''cryobridge.''

Bottom-up assembly
2022-10-17 - In the heart of the Tokamak Building, this 30-metre-deep pit is the stage for ITER machine assembly. Assembly is progressing bottom to top. October 2022

Not just pipes
2022-10-17 - Procured by India, manufactured by INOX-CVA in India and Air Liquide in France, cryolines are more than just pipes: they are high-tech, vacuum-insulated components that, for the most complex of them, host several multi-process pipes transporting different cooling fluids in and out of the ITER Tokamak.

Manual alignment
2022-10-17 - Whatever the size or weight of a cryoline spool, the most delicate sequences of final alignment are done manually. Here, an operator delicately guides the 5.5-tonne spool into the wall opening, whose diameter is only a few millimetres larger than that of the component.

A 90-minute operation
2022-10-17 - Operating under the supervision of ITER Organization specialists Lahcene Benkheira and Adrien Forgeas, workers from contractors ENDEL, ORYS and Cryodiffusion finalized the complex operation in 90 minutes.
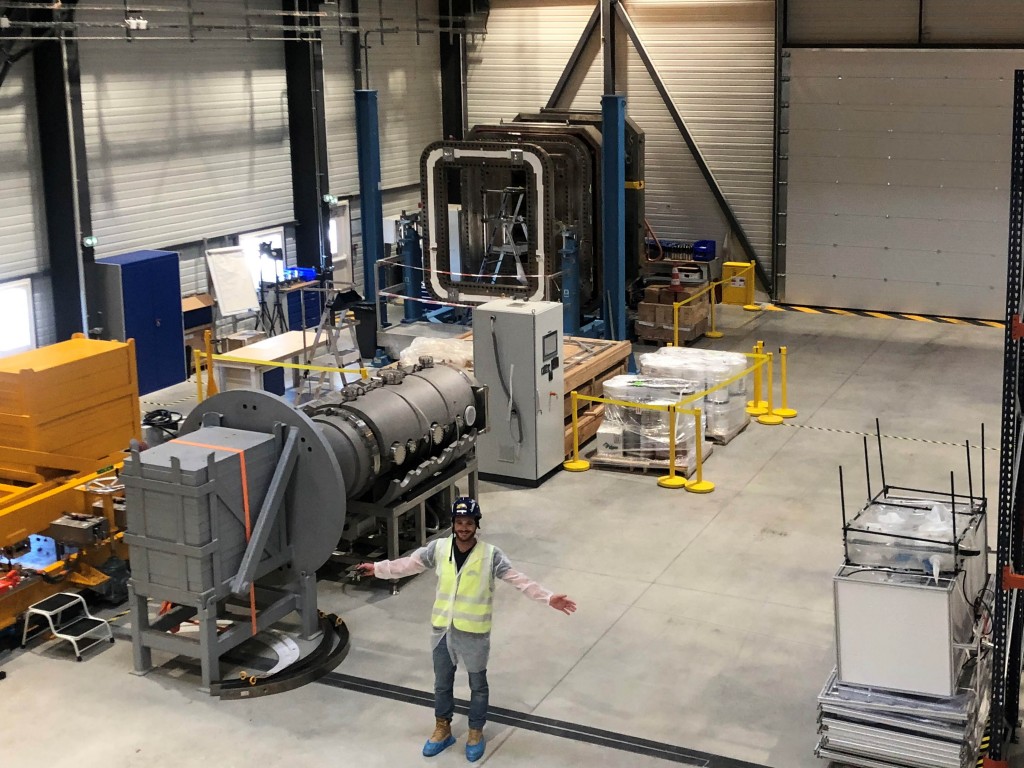
Laboratory facility, open since January 2022
2022-10-15 - Facility Management Officer Guillaume Roux was involved in every stage of development of this new 740m² laboratory facility on site, which will be used both by the vacuum and tritium teams.
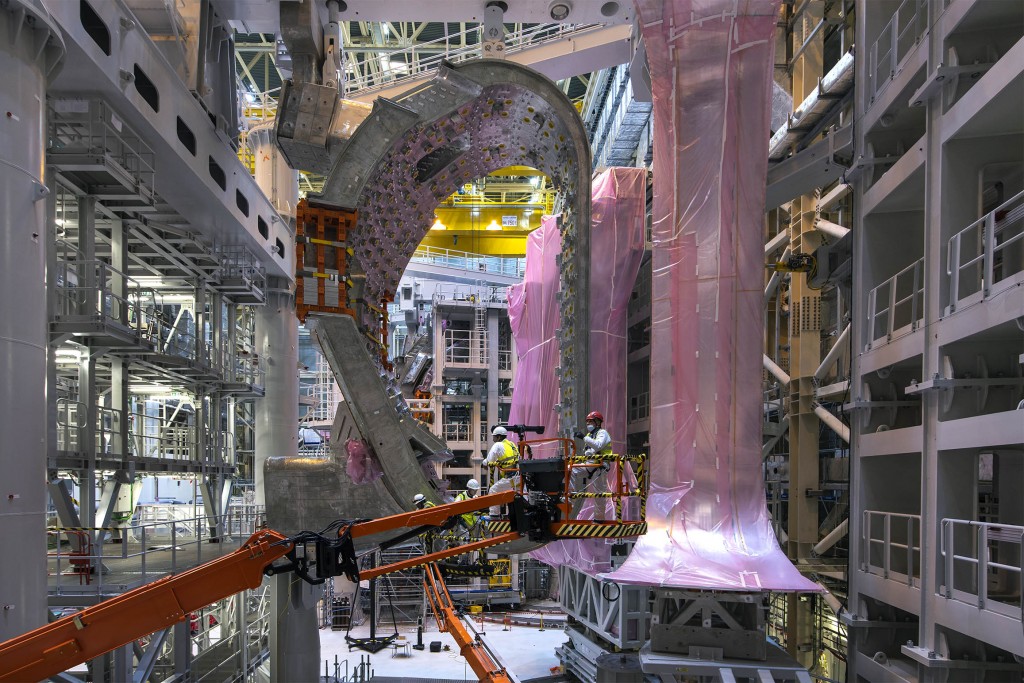
Sector module: in work
2022-10-06 - Vacuum vessel sector #8 is suspended in the centre of the sub-assembly tool, as thermal shield panels (protected in pink wrap) wait on the wings to be rotated and attached. Note the pillar at bottom left that supports the 440-tonne sector under its lower port stub extension.
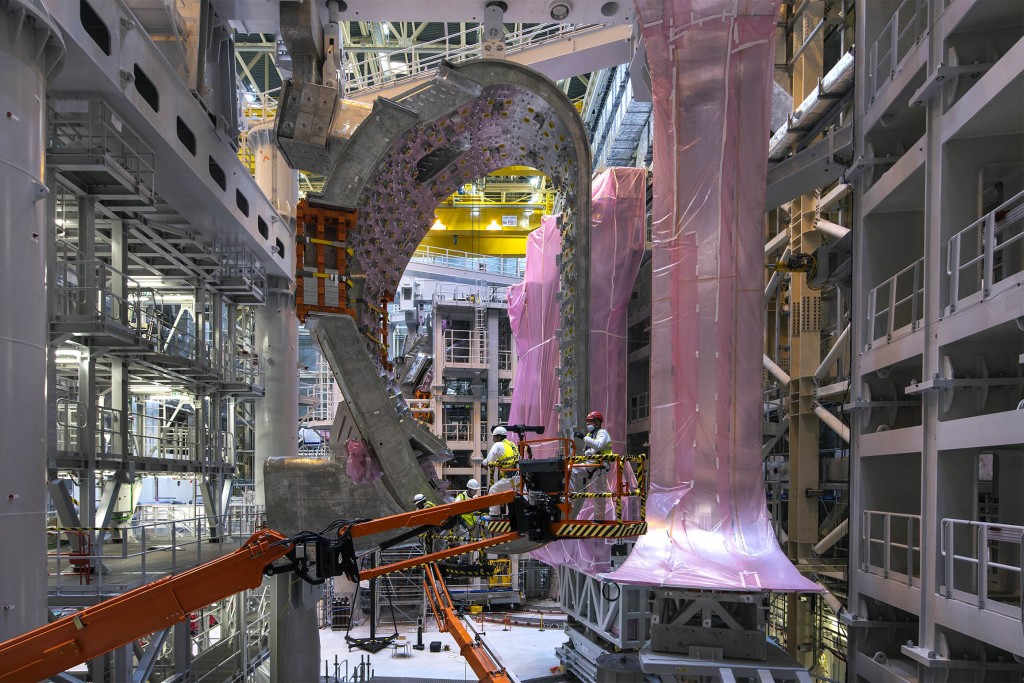
Preparing sector #7
2022-10-06 - Measurements are taken before, during and after the activities to assemble sector #7 with panels of thermal shielding (pink) and, later, two toroidal field coils.

Three in a row
2022-10-04 - Three bridges will cross over this major artery of the ITER worksite: the cryobridge (in construction, pictured) and two bridges from the Magnet Power Conversion buildings (background, with the black boxes as starting points).
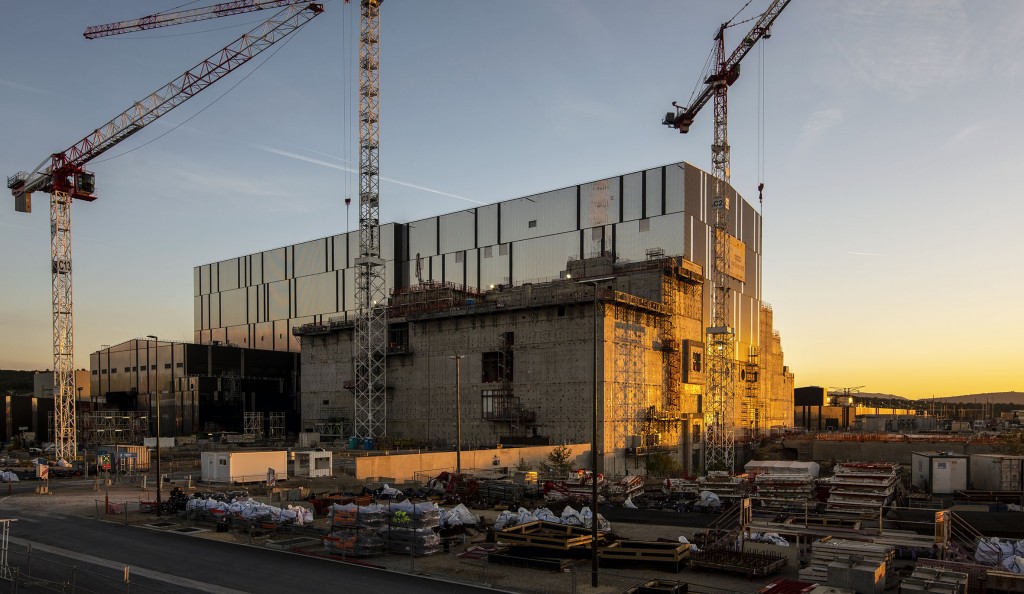
As the day ends ...
2022-10-04 - The last rays of sun illuminate the facade of the Tokamak Complex in early October 2022.
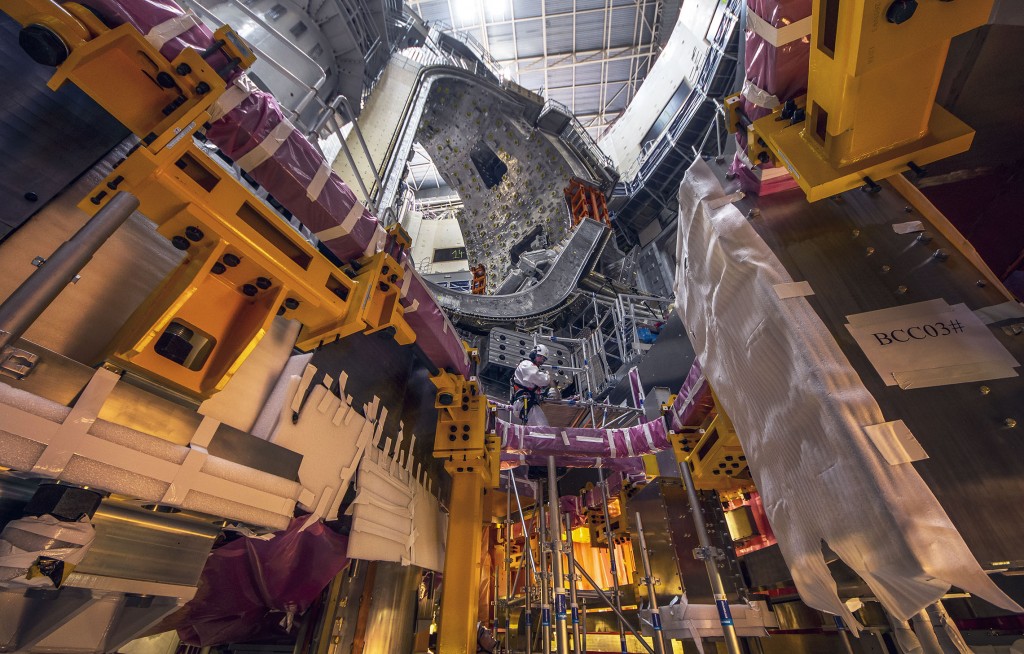
Down under
2022-09-21 - There is a whole world at the bottom of the Tokamak pit—one which we rarely enter. In this image, we can distinguish the bottommost poloidal field coil (PF6, left, with white coverings to protect openings from dust) and one kidney-shaped bottom correction coil (wrapped in pink, overhead).
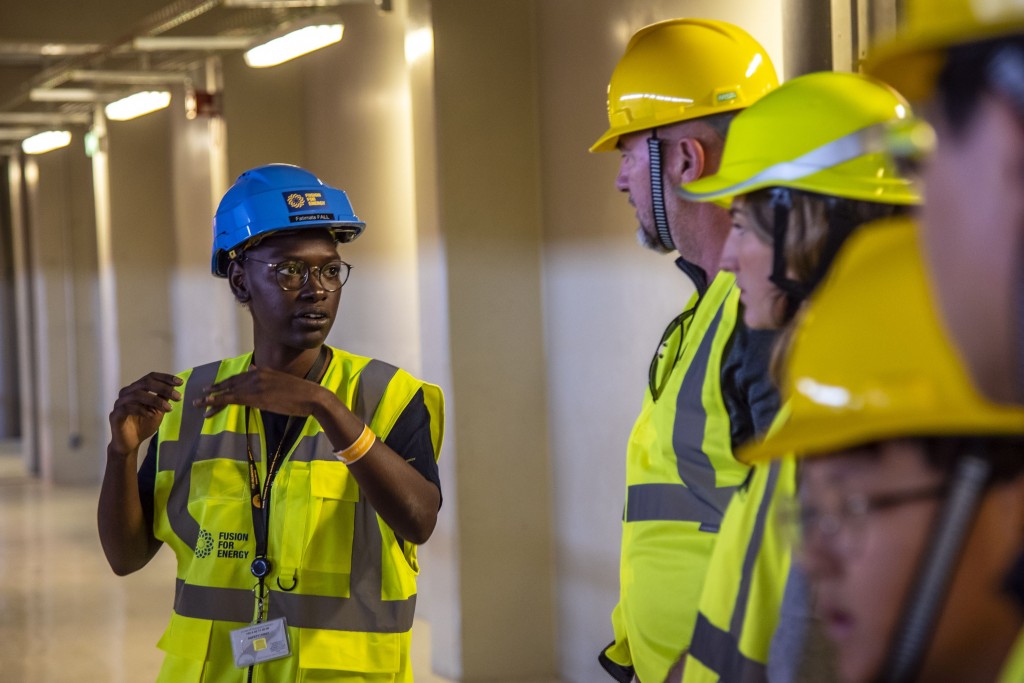
Colleagues teaching colleagues
2022-09-17 - Standing above the production line, in the visitors gallery, is the best way to understand the entire process. It also helps to have an expert guide to talk you through the steps ...

"Really impressive"
2022-09-17 - On 17 September, staff and contractors were able to bring their families on site and share their work environment. One of the most impressive sights of the visit: a 440-tonne vacuum vessel sector suspended in tooling.

First stop: the European winding facility
2022-09-17 - Families participating in the first-ever ITER Family Open Doors Day in September are guided through the poloidal field winding facility, where the two largest coils are still in fabrication.
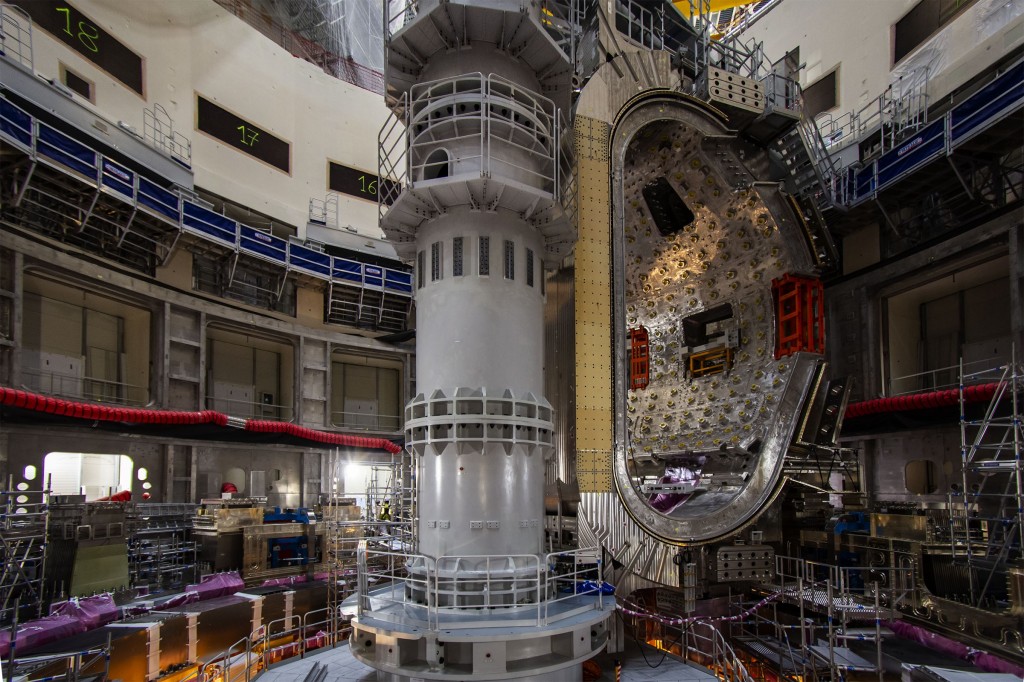
Final alignment
2022-09-15 - Sector module #6, following alignment in the Tokamak pit, which was achieved in September by the assembly and metrology teams.
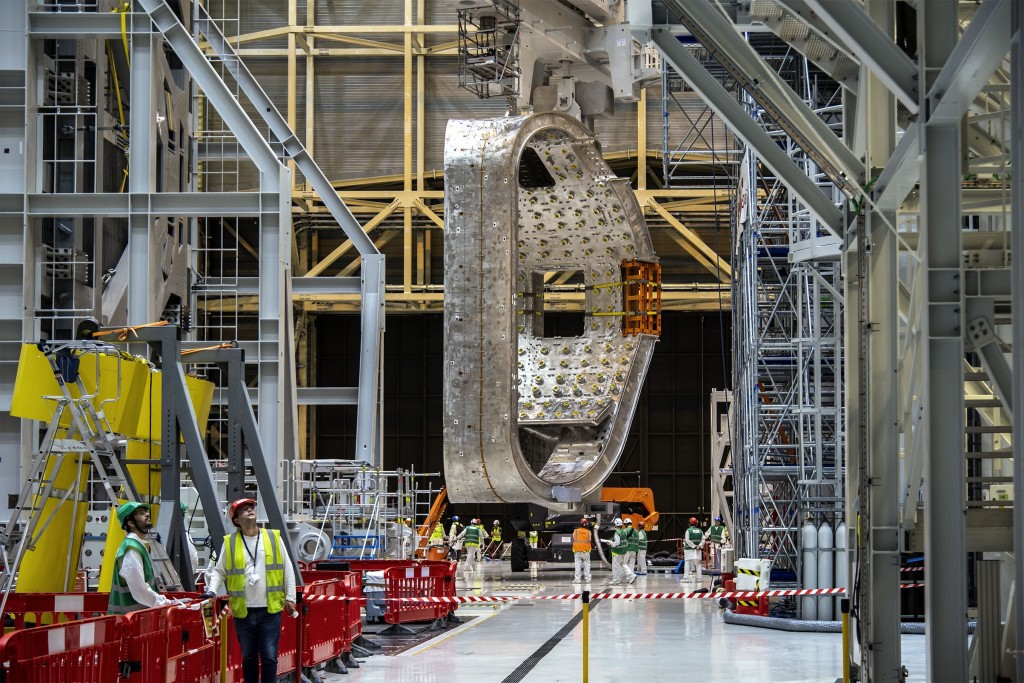
Out of one tool, into another
2022-09-12 - The 440-tonne sector is lifted out of the upending cradle and rotated before insertion into the V-shaped opening of the SSAT tool (sector sub-assembly tool).
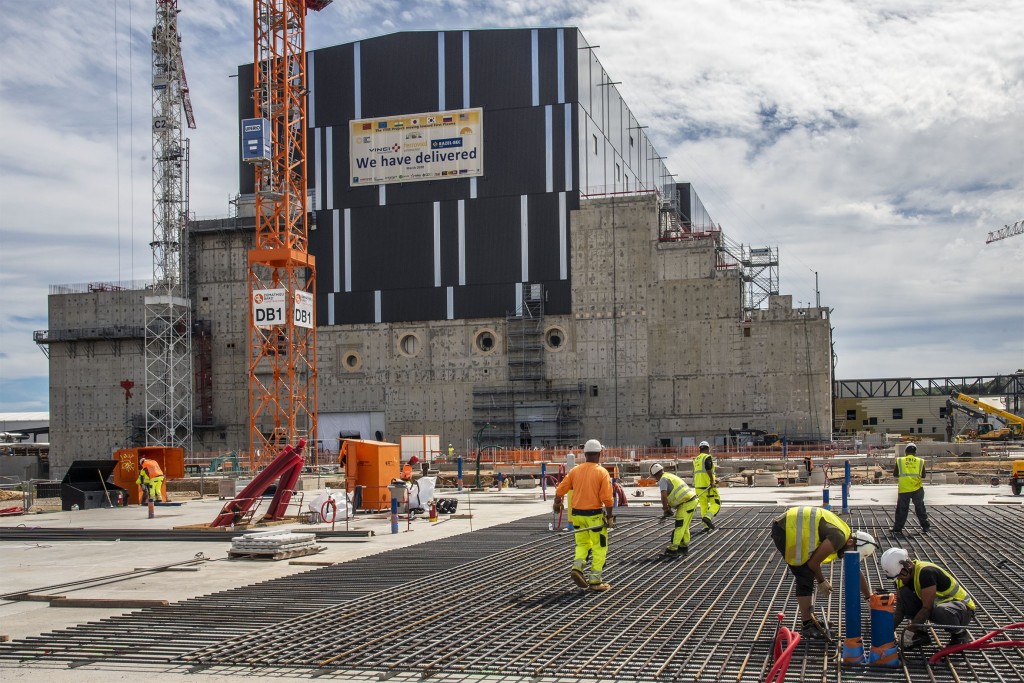
For low-voltage equipment
2022-09-12 - Workers are laying rebar for the basemat for Building 34, the Neutral Beam Power Supply Building. Located at the far side of the neutral beam power supply area, it will house AC/DC rectifiers, DC/AC conversion systems, and other low-voltage power supply equipment.

Sector #8: Moved into tooling
2022-09-12 - On 12 September, vacuum vessel sector #8, from Korea, is transferred from the upending tool (left) to the available sector sub-assembly tool on the other side of the Assembly Hall. The twin assembly tools are now both occupied, one with sector #1(7) and one with sector #8.
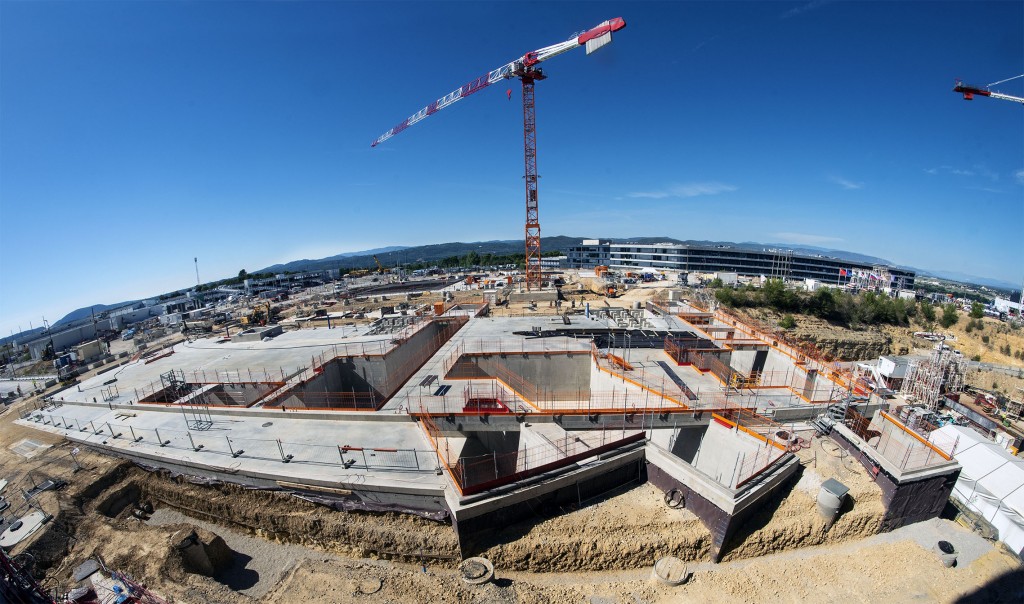
High Voltage Supply Building
2022-09-12 - The structure of the High Voltage Supply Building is emerging, with three "branches" heading toward the Tokamak Building and showing the trajectory that the transmission lines will follow. The building is 86 metres long and 30 metres wide.
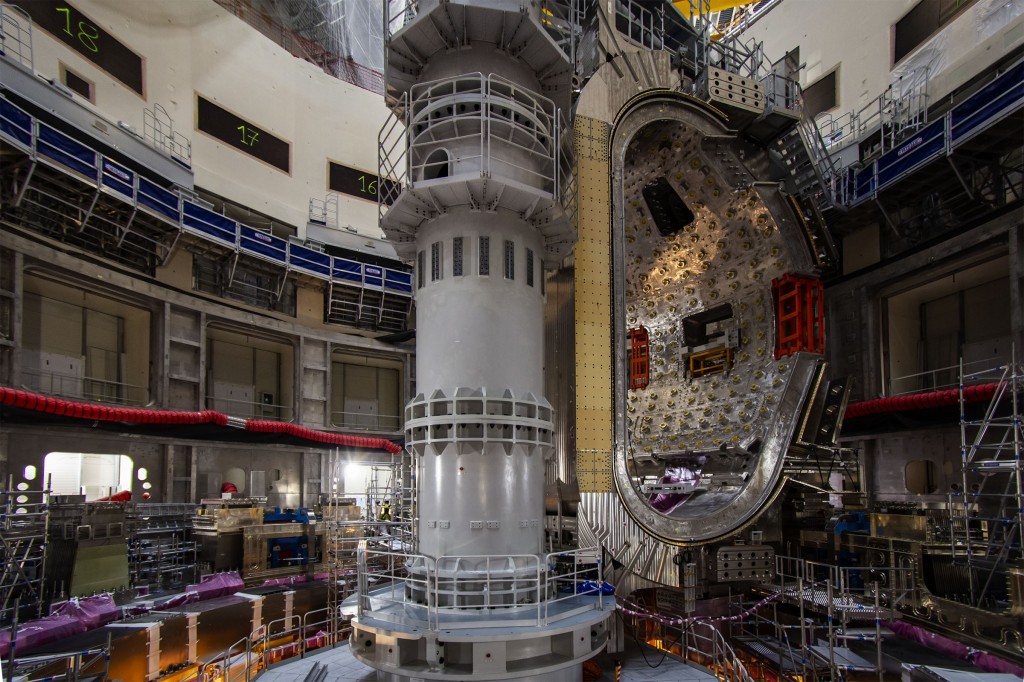
Sturdy
2022-09-09 - The in-pit assembly tool enters action for the first time, supporting the sector module built around vacuum vessel sector #6.

Coil alignment achieved
2022-09-09 - The toroidal field coils that are part of the first vacuum vessel sector module have been aligned to their final position in the pit and are ready to be bolted to the toroidal field coil gravity supports.

Shining performance
2022-09-09 - The shinier a thermal shield's silver coating, the better its thermal radiation performance. Here, the right-hand outboard segment for vacuum vessel sector #8 is hand polished before being moved into position on the vacuum vessel sub-assembly tool.

Early September in the Assembly Hall
2022-09-08 - The long view of the ITER Assembly Hall, with component pre-assembly in the foreground and the machine well in the background. On the right, vacuum vessel sector #8 from Korea is in the upending tool, ready for transfer across the hall to tooling.
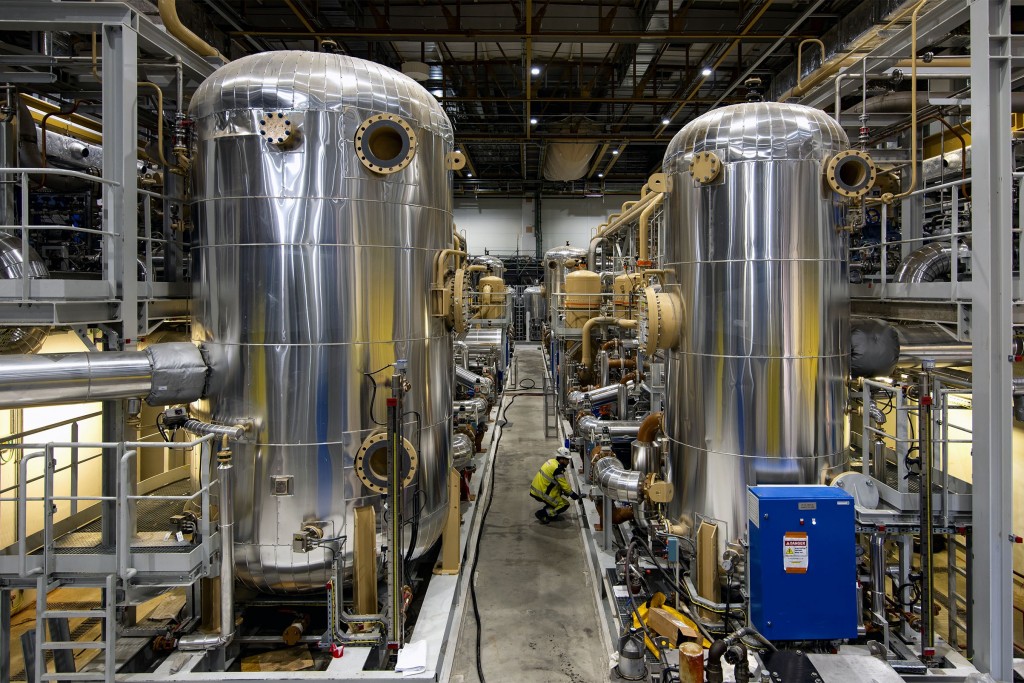
Commissioning in a spotless environment
2022-09-08 - In the ITER cryoplant, the commissioning and dynamic testing of the nitrogen vaporization system have been successfully initiated to support the startup of the liquid helium plant system. Other activities underway include oil filling (some 60,000 litres) and cleaning procedures to prepare for operation.

Winding station: 7 years of faithful service
2022-09-08 - Thirty production double pancakes for four poloidal field coils were created on the winding table installed in the building by Sea Alp Engineering (Italy). With no more to produce, the table was dismantled in August 2022. (See: https://www.iter.org/newsline/-/3791)

Tools galore
2022-09-08 - In this view from the rafters, major pieces of the assemlby "toolkit" are laid out before us.

First "footprint" visible
2022-09-07 - The "footprint" of the High Voltage Supply Building is now clear. Also visible are the two distinct rooms dedicated to the high voltage decks and high voltage deck bushings for each heating neutral beam injector.

Central solenoid assembly begins
2022-09-07 - Six independent modules make up the 1,000-tonne, 18-metre-tall central solenoid. This summer, the first module was positioned with millimetric precision on the bespoke assembly platform (centre) in the Hall in order to assemble the extensions that will later connect to the magnet feeders. (Positioning accuracy is +/-1mm in plane.) A second module is covered in pink, at right.
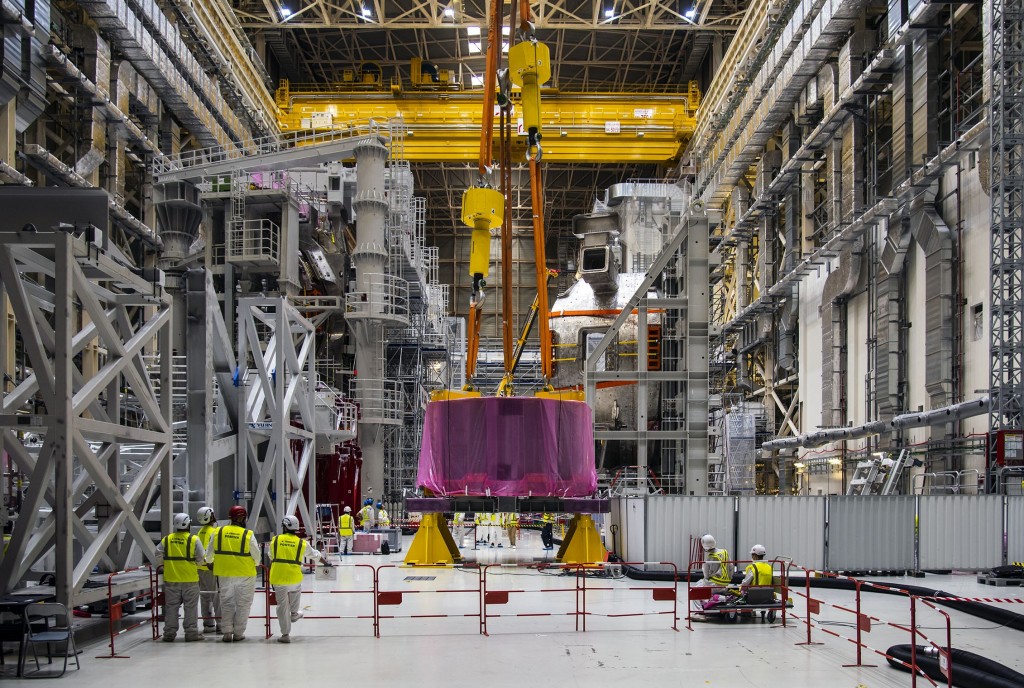
Busy cranes
2022-09-06 - A 110-tonne central solenoid module hangs from one set of overhead cranes. The Assembly Hall is equipped with two sets: the heavy-duty 750-tonne cranes that work together to lift loads of 1,500 tonnes, and a smaller set of 50-tonne auxiliary cranes.

Second module moved to assembly zone
2022-09-06 - On 6 September, the second central solenoid module, which had been delivered in October 2021, joined the first in the dedicated assembly zone at the far end of the Assembly Hall. The remaining five modules (including one spare) are in the final stages of fabrication at General Atomics in California and expected at ITER by mid-2023.
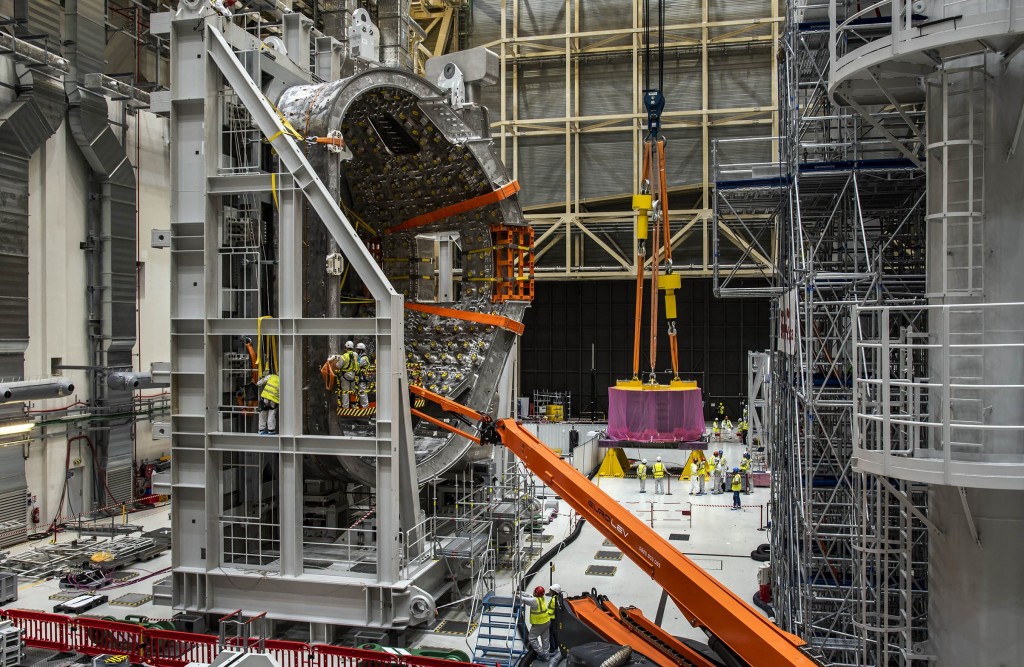
Third sector to be moved
2022-09-06 - For the first time in its existence, vacuum vessel sector #8 is in a vertical position. (At the factory, during D-shape assembly, and during transport, the ITER vacuum vessel sectors are always horizontal.) Sector #8 is the third section of the vacuum vessel to be delivered. Six more sectors are expected, one from Korea and five from Europe. This image also features, in the background, the second central solenoid module (wrapped in pink plastic) being lifted to its assembly zone at the far end of the Assembly Hall.
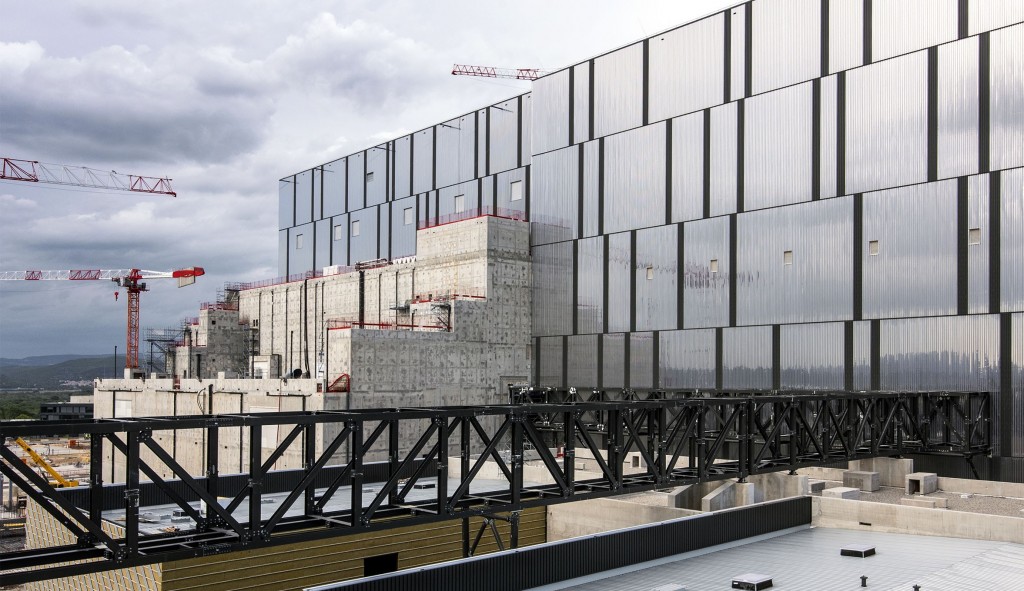
Right angle
2022-08-30 - To reach and enter the opening in the concrete wall of the Tokamak Complex, the cryobridge has to make a 90-degree turn. This has added complexity to the design of the structure, as the pressurized flow of cryogenic fluids at this location will cause intense traction forces.

First bridge on site
2022-08-30 - Three bridges will cross this major artery on the ITER platform. The first, connecting the cryoplant to the Tokamak Complex, is under construction now.

Coil PF4 in its mould
2022-07-25 - In July, contractors to the European Domestic Agency carry out the vacuum pressure impregnation (VPI) of poloidal field coil #4. During the process, epoxy resin is injected at a temperature of 50 °C, then heated to 140 °C by a strong electrical current fed to the conductors (the Joule effect) and by electrical resistances positioned around the mould. VPI confers rigidity to the winding pack and ensures electrical insulation.
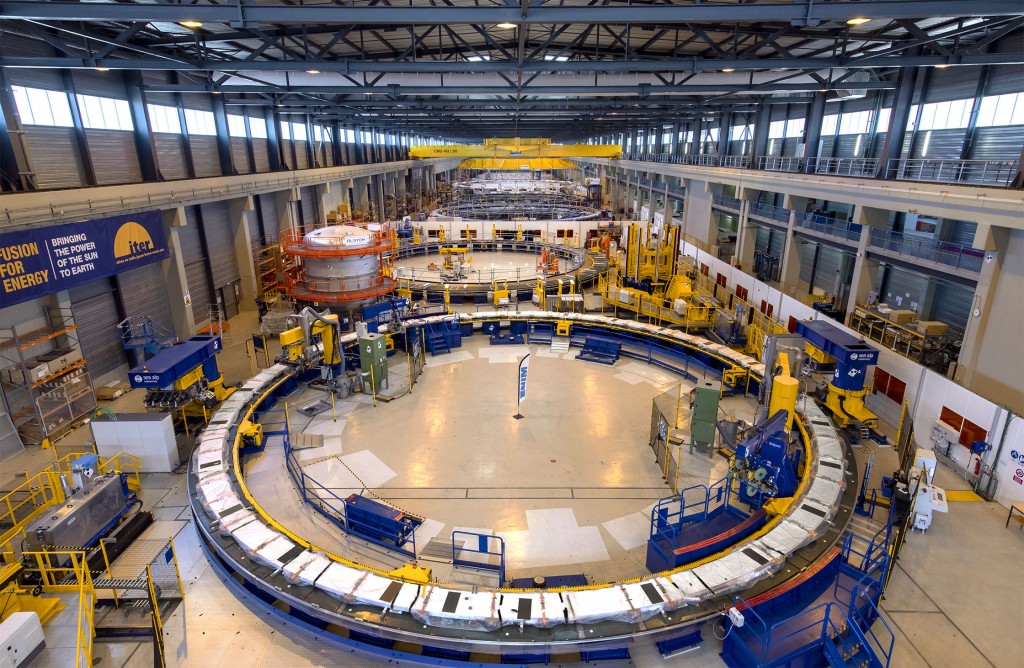
The long view
2022-07-21 - The coil production line in the 250-metre, on-site production facility where the European Domestic Agency for ITER, Fusion for Energy, is producing four poloidal field coils. Two have been finalized (including one already installed in the Tokamak pit) and two others are in the last stages of production.

Module moves
2022-07-20 - A specially designed tool is used to move the first 110-tonne module to the central solenoid assembly platform in July.

Early engineering studies in Korea for an important tool
2022-07-18 - Before ITER's giant vacuum vessel sector sub-assembly tools could be manufactured, the team at SFA Engineering Corp., Korea, built this 2010 mockup at one-fifth scale to perform structural and functional tests, and to demonstrate the global kinematics of the system. See the story here: https://www.iter.org/newsline/-/3778
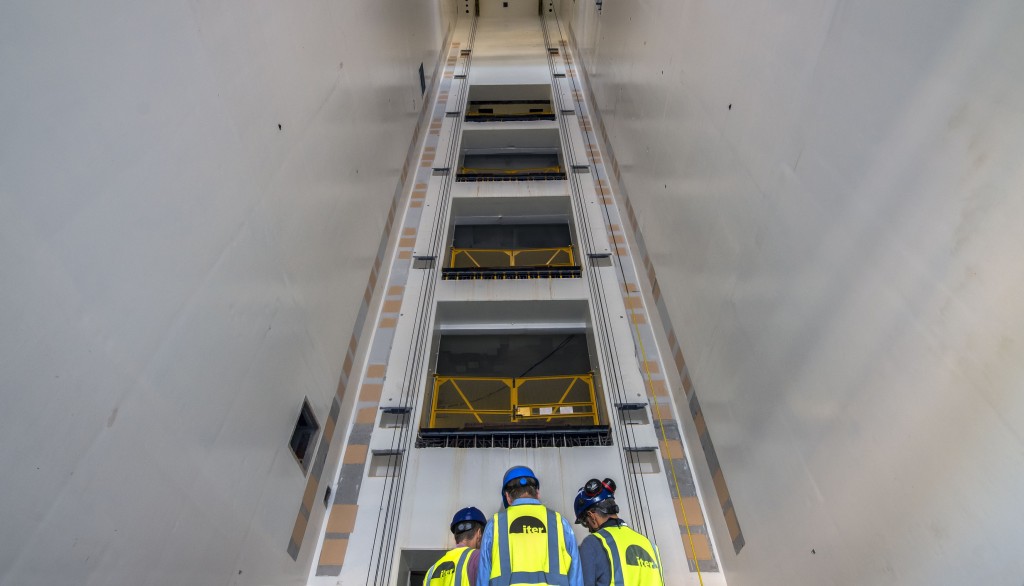
Elevator shaft (large)
2022-07-06 - When fully operational, this lift will transport the casks from ITER's ITER cask and plug remote handling system (for activated components) between the Tokamak Building to the Hot Cell facility. For the time being, a temporary cargo lift has been installed to deliver loads to the different levels of the Tokamak Building.

Seeing with their own eyes
2022-07-06 - During a management walkthrough on 6 July, magnet expert Min Liao (left) and the head of the Machine Construction Department Xavier Bravo (right) brief ITER Director-General (interim) Eisuke Tada (centre) on the latest progress in the assembly of the second vacuum vessel module.
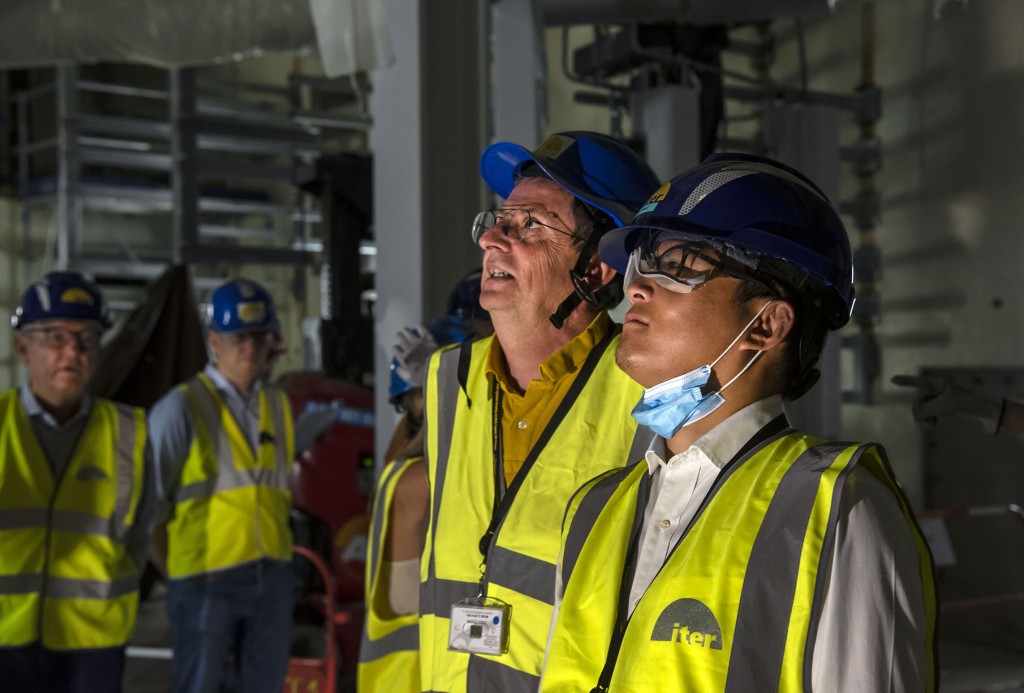
Always impressive
2022-07-06 - Walking through the ITER installation, its massive structures and complex networks, alien-looking components and dizzying vistas, is always impressive.

Management walkthrough
2022-07-06 - For a comprehensive overview of issues and progress on the worksite, senior management does a monthly "walkthrough" of all buildings. It's about keeping in touch with challenges, progress on challenges, and also the day-to-day determination of the teams.

Touring operational units
2022-07-06 - The compressed air and demineralized water units of the Site Services Building are in operation. Commissioning Coordinator Adrien Deydier is seen here giving a facility tour to management.

Ten towers
2022-07-06 - The most visible part of the heat rejection zone—the cooling towers—are captured by Swiss photographer Luca Zanier (https://www.zanier.ch/) in early July. Commissioning activities are underway.
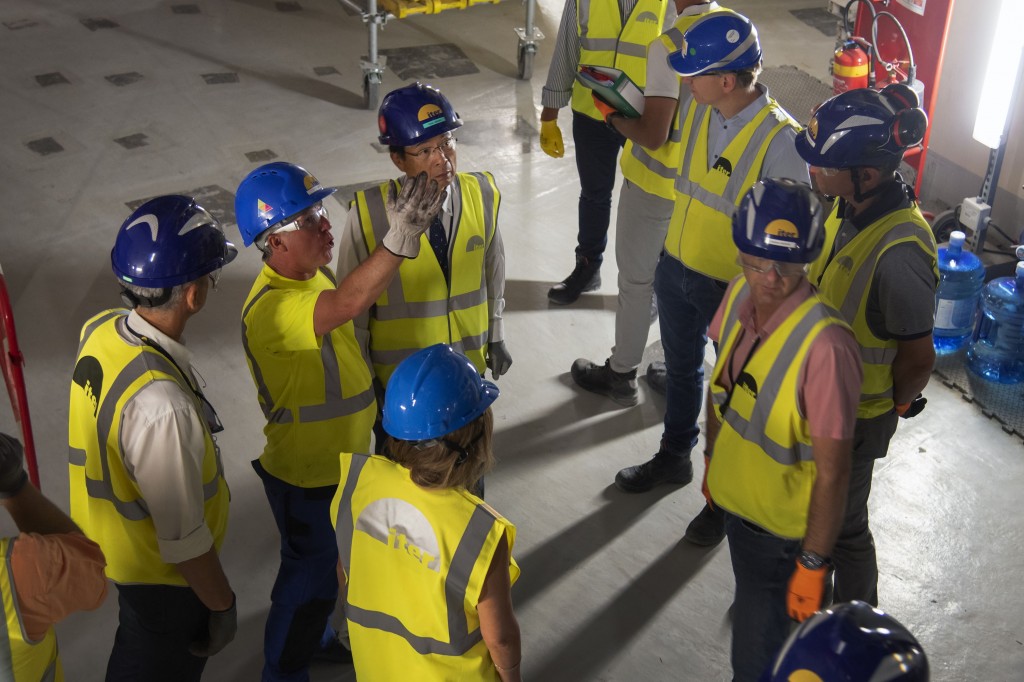
The importance of work performed today
2022-07-06 - "It is important to properly plan and execute the commissioning of systems, of course. But also, the ability to achieve the project's objectives depends vitally on the quality of the workmanship and the decisions made in the course of the present phase." (Head of the Science & Operation Domain, Tim Luce. See more at https://www.iter.org/newsline/-/3774)
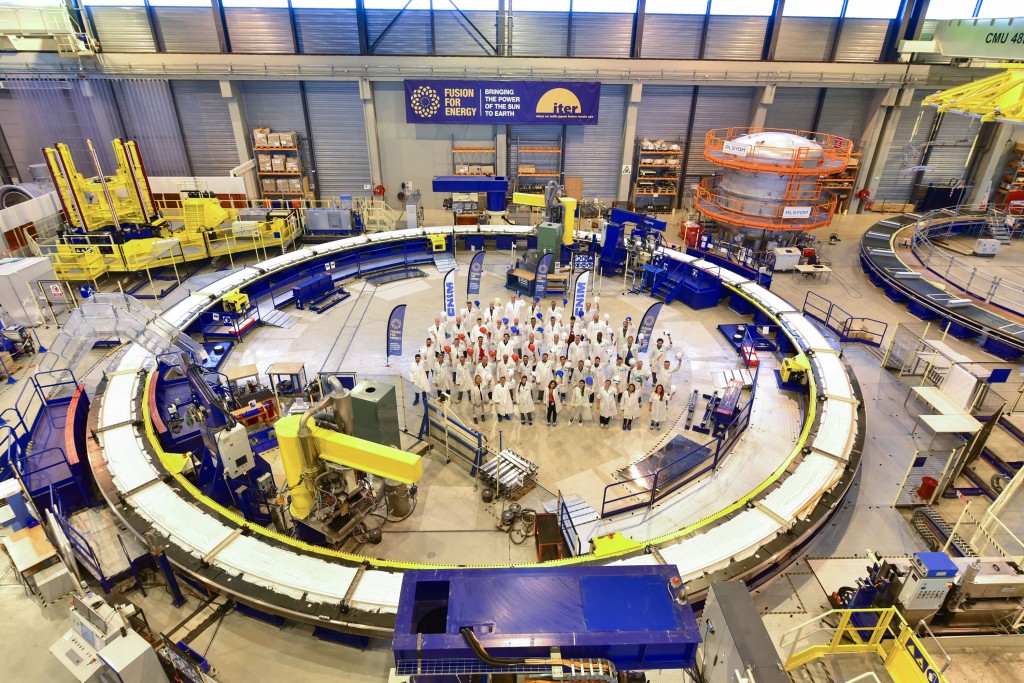
Last double pancake!
2022-06-23 - After close to five years of intense activity, the winding table at the south end of the European poloidal field coil factory on site is now empty. In June, the final circular conductor arrangement ("double pancake") required for the last ring-shaped coil was finalized and moved to the next workstation. Since production began in August 2017, 30 double pancakes have been produced for four poloidal field coils.
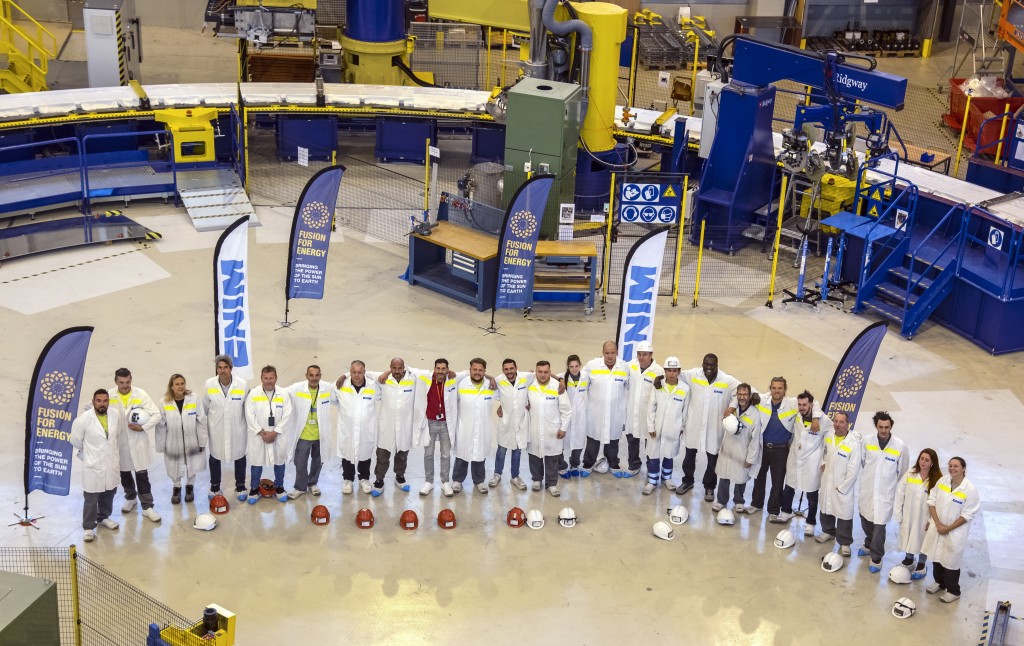
Relief and satisfaction
2022-06-23 - Members of the CNIM team (Toulon, France) celebrate the end of double pancake winding. CNIM was the European subcontractor responsible for manufacturing and cold testing. © F4E

Now at L4
2022-06-14 - Workers are advancing at level L4 of the Tritium Building (L5 will be the last storey). The civil works are scheduled for completion in summer 2023.
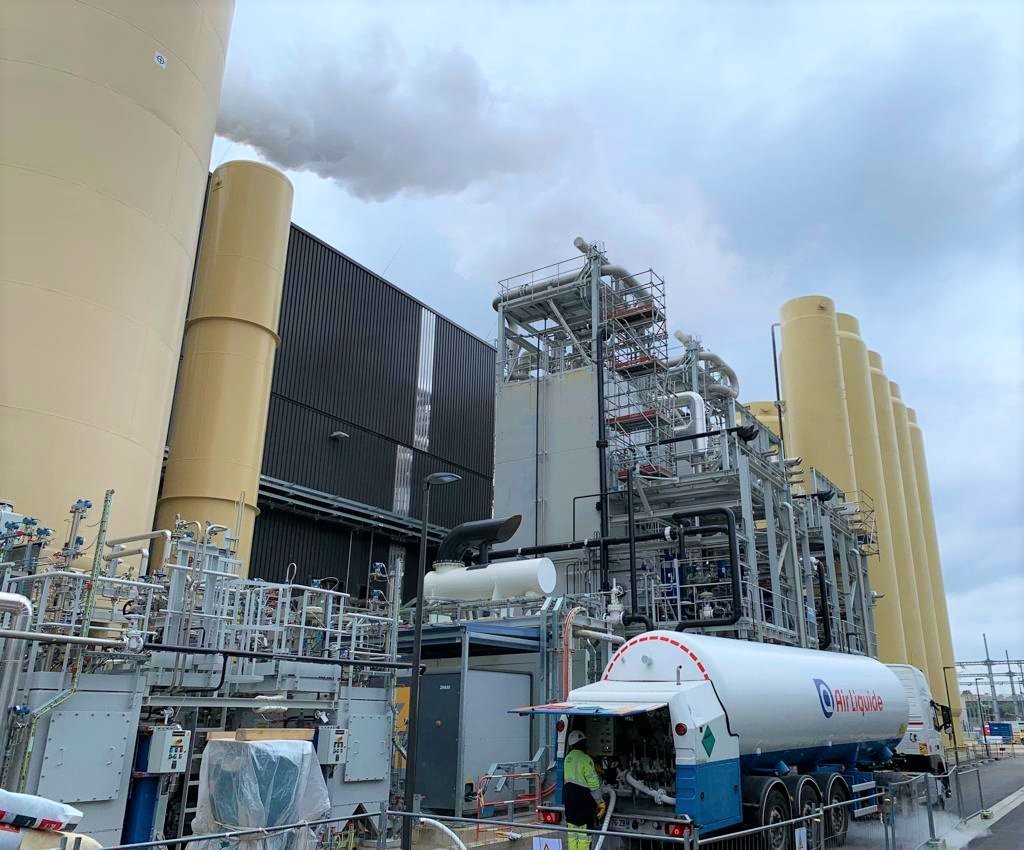
Nitrogen tank fill up
2022-06-14 - Cryoplant commissioning is underway. In June 2022, 12 trailers delivered enough liquid nitrogen to fill the tank to 80% of its capacity.

Repelling down the module
2022-06-09 - The first section of the ITER vacuum vessel has been in place in the assembly pit since 11 May. This "rope access technician" is positioning fiducial targets on the surfaces of the component to be used in laser metrology.
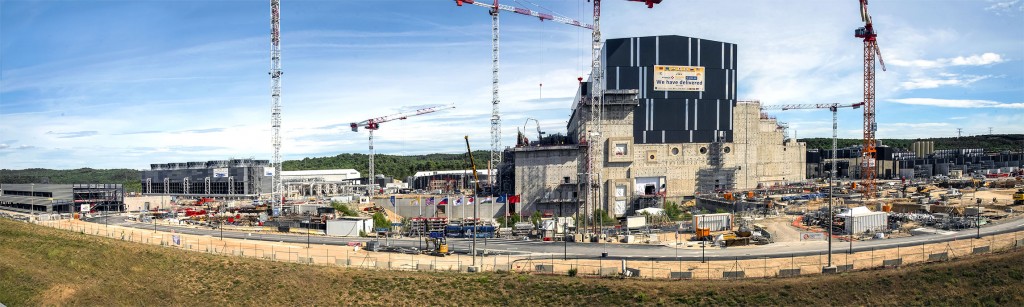
June view
2022-06-08 - From the roof of ITER Headquarters, the Tokamak Complex stands out as the major feature of the ITER construction site. After a pause while European construction teams concentrated on delivering the Tokamak Building crane gallery (centre), work is proceeding at level L4 of the Tritium Building (located to the left of the Tokamak Building). On the right side of the Complex, behind the red crane, infrastructure for neutral beam power supply is emerging.

25 metres tall
2022-06-08 - At 25 metres tall Building 37, the High Voltage Supply Building, will partially obscure the Tokamak Complex (as seen from ITER Headquarters), rising several metres higher than the four transmission line openings that are visible in the concrete facade.
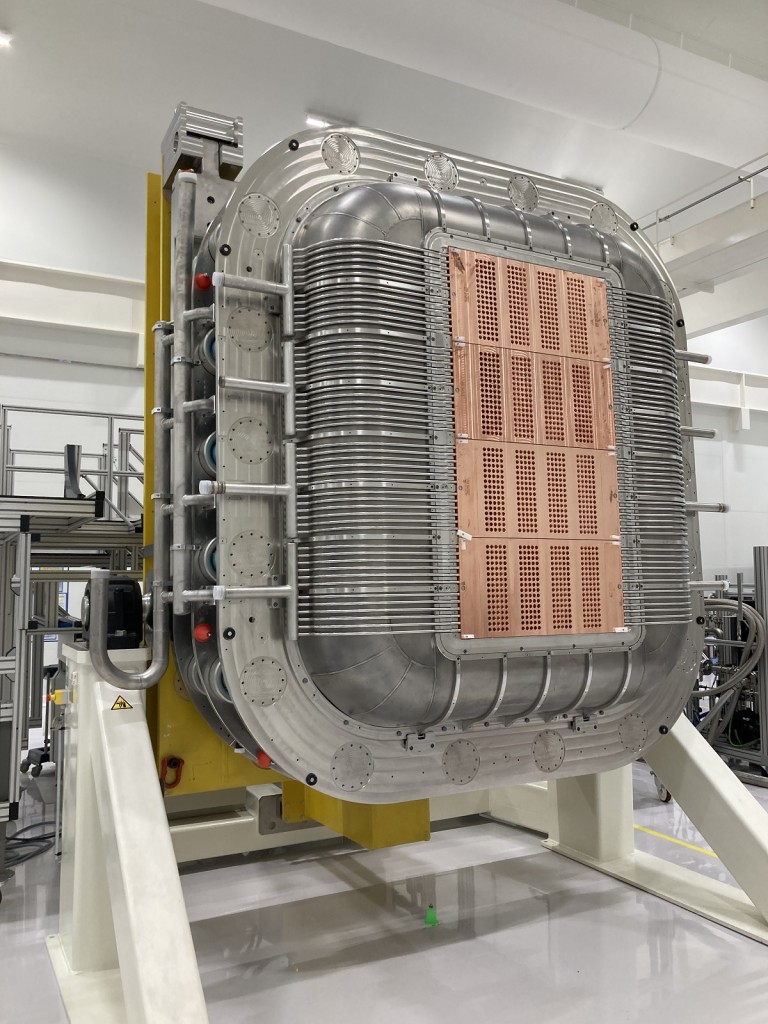
MITICA beam source: 90% complete
2022-06-02 - The European Domestic Agency Fusion for Energy (F4E) is procuring the beam source for MITICA. Composed of a radio frequency ion source and a seven-grid accelerator, the beam source is being assembled at ALSYMEX (Tarbes, France) from components produced at approximately 20 European companies. © F4E

In the clean room at ALSYMEX
2022-06-01 - Segments of the MITICA beam source accelerator components prior to being assembled at ALSYMEX. May 2022 © ALSYMEX

Home at last
2022-05-13 - The sector module has now been lowered to its supports, arriving "home" after a long and complex journey.

One-ninth
2022-05-13 - Although only one-ninth of the Tokamak's torus-shaped vacuum vessel, the sector module dwarfs everything around it. Eight other similar operations, plus welding, will be necessary to close the torus.
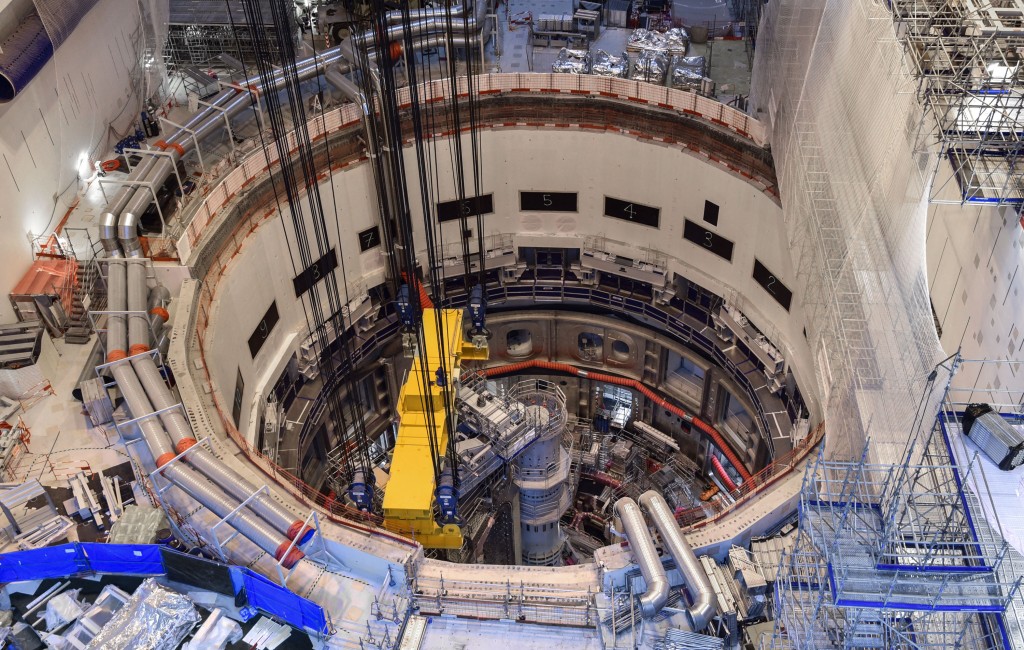
Particularly complex rigging
2022-05-13 - The complex rigging required for the lifting of the sector module is clearly visible is this view from high above: the yellow structure is the Dual Crane Heavy Lifting Beam (DCHLB) that synchronizes the four hooks of the cranes into a single lift point, enabling the rotation of the load. The grey device below is the Sector Lifting Tool. Connected to both the DCHLB and the radial beam, this tool can precisely align the load with the cranes.

Over the wall, with only 20 cm to spare
2022-05-11 - The massive component—representing one-ninth of the ITER plasma chamber—was extracted from its assembly tool, rotated, transferred over the bioshield wall (with only 20 cm to spare), and lowered into the Tokamak pit.

A particularly complex rigging
2022-05-11 - Particularly complex rigging is on display during the transport of the first vacuum vessel sector module into the pit. Between the blue cable hooks and the component itself (deep in the pit) we see the Dual Crane Heavy Lifting Beam (DCHLB, in yellow) that synchronizes the four hooks of the cranes into a single lift point and enables the rotation of the load, and the grey Sector Lifting Tool. This last rigging attachment connects to both the DCHLB and the radial beam to precisely align the load with the cranes.
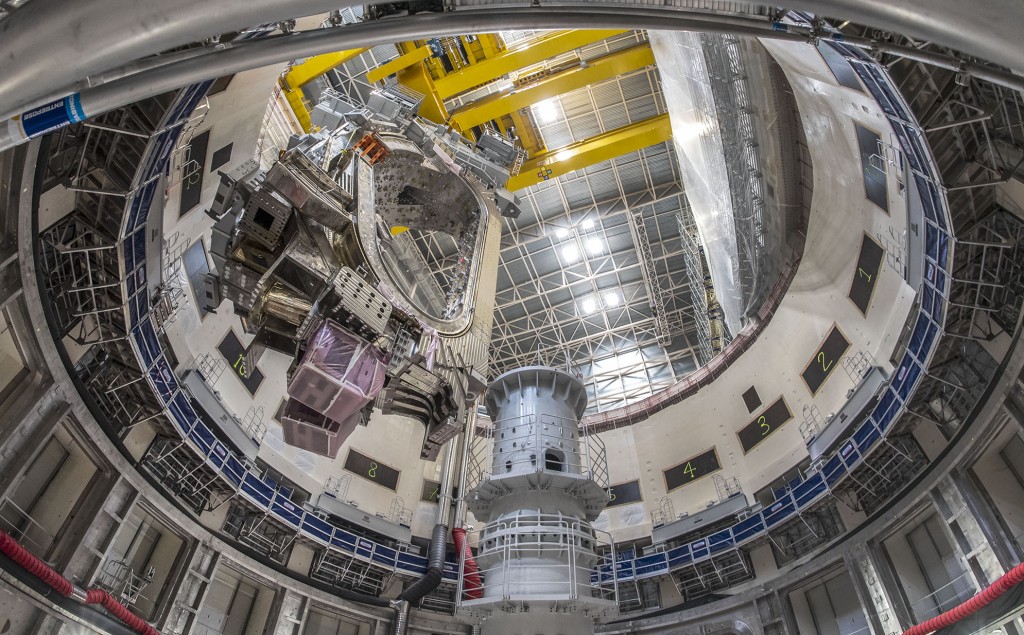
Most complex lift to date
2022-05-11 - The 1,380-tonne assembly (component plus rigging) is six storeys high and weighs the equivalent of four fully loaded Boeing 747s. The lift operation achieved today was the most complex of ITER machine assembly to date.
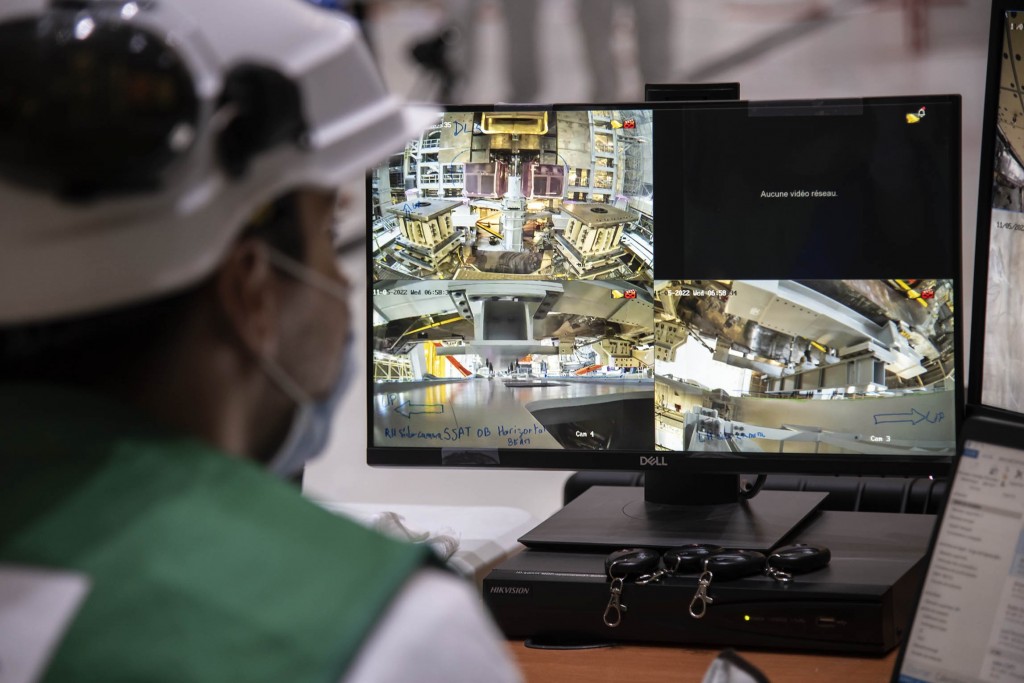
Eyes everywhere
2022-05-11 - As the sector module is slowly lifted from the sub-assembly tool, an operator closely monitors the feedback from three of the seven video cameras positioned at strategic locations inside the tool.
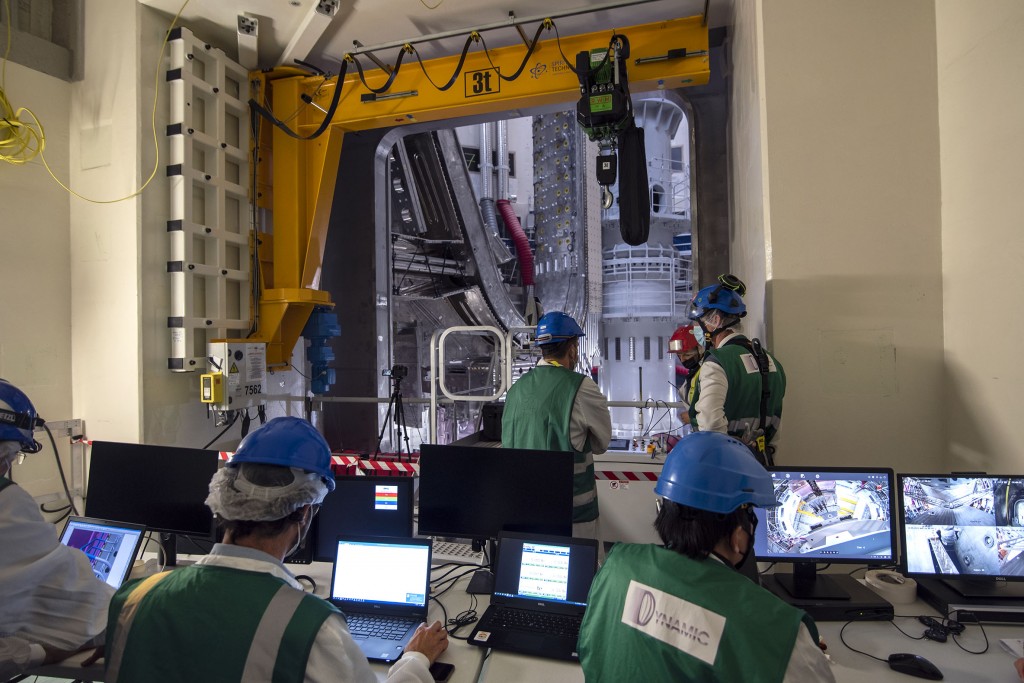
Months of practice and preparation
2022-05-11 - From one of the "command centres," looking through a port cell window out into the Tokamak pit, where the first section of the ITER plasma chamber is slowly descending toward waiting supports. The DYNAMIC consortium (Ansaldo Nucleare; Endel Engie; Orys Group ORTEC; SIMIC; Ansaldo Energia; and Leading Metal Mechanic Solutions SL) is ITER's TAC2 assembly contractor (for Tokamak Assembly Contractor 2), in charge of sector sub-assembly, and assembly of the main vessel and ports including welding.
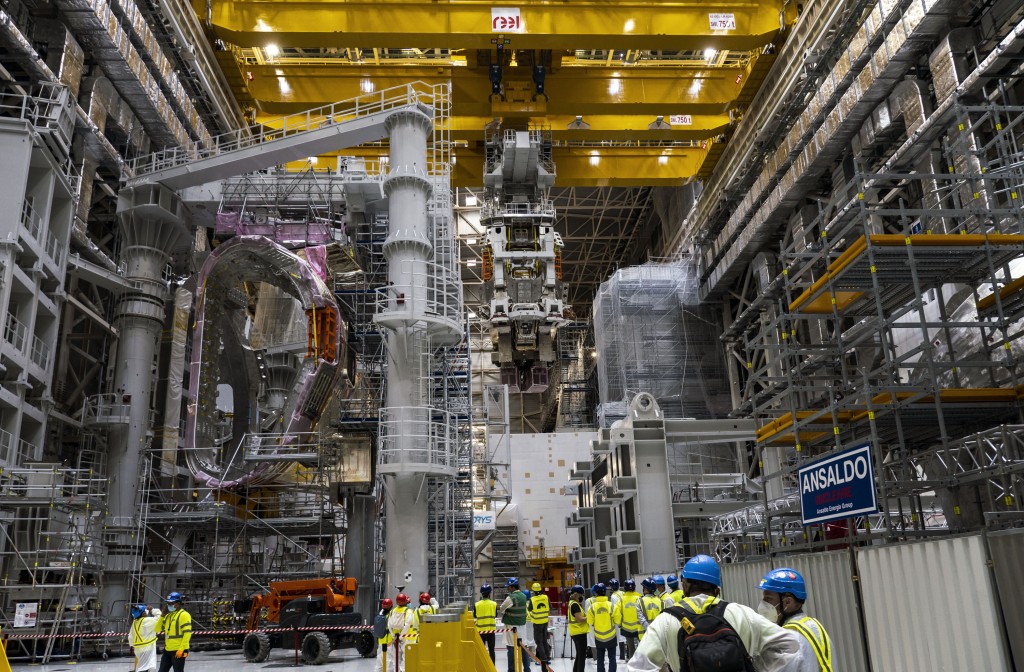
Right in the axis
2022-05-11 - Extracted from the sub-assembly tool, the component has rotated 90 degrees and is now heading towards the wall separating the Assembly Hall from the Tokamak pit.
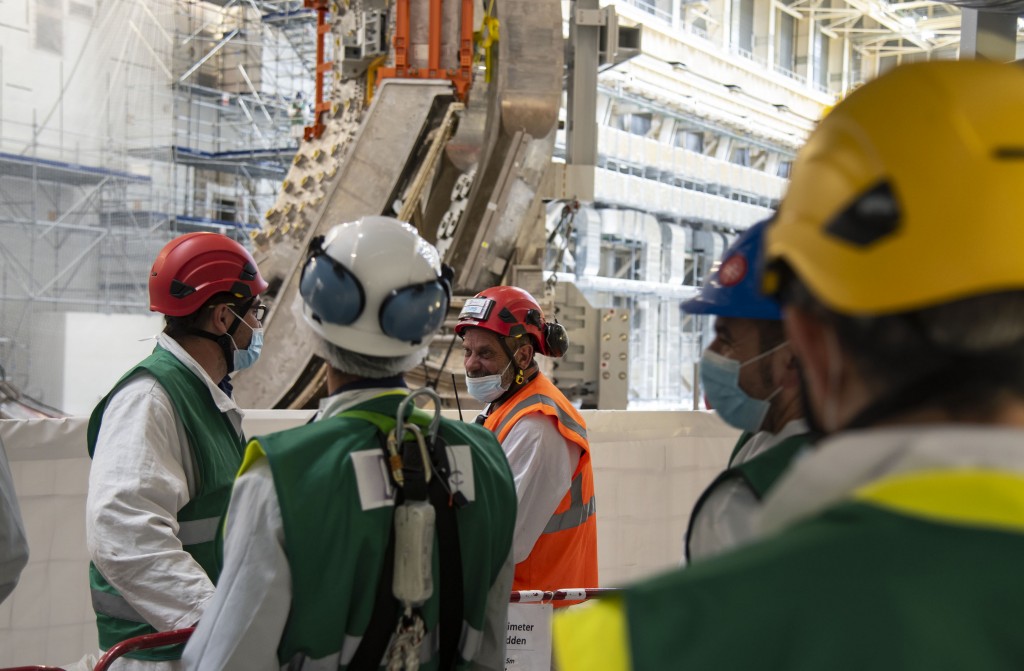
Coordination
2022-05-11 - The perfect coordination of a 50-person team belonging to half a dozen different companies and organizations was key to the operation's success. Lift coordinator for this operation is Daniel Coelho, ITER assembly engineer.
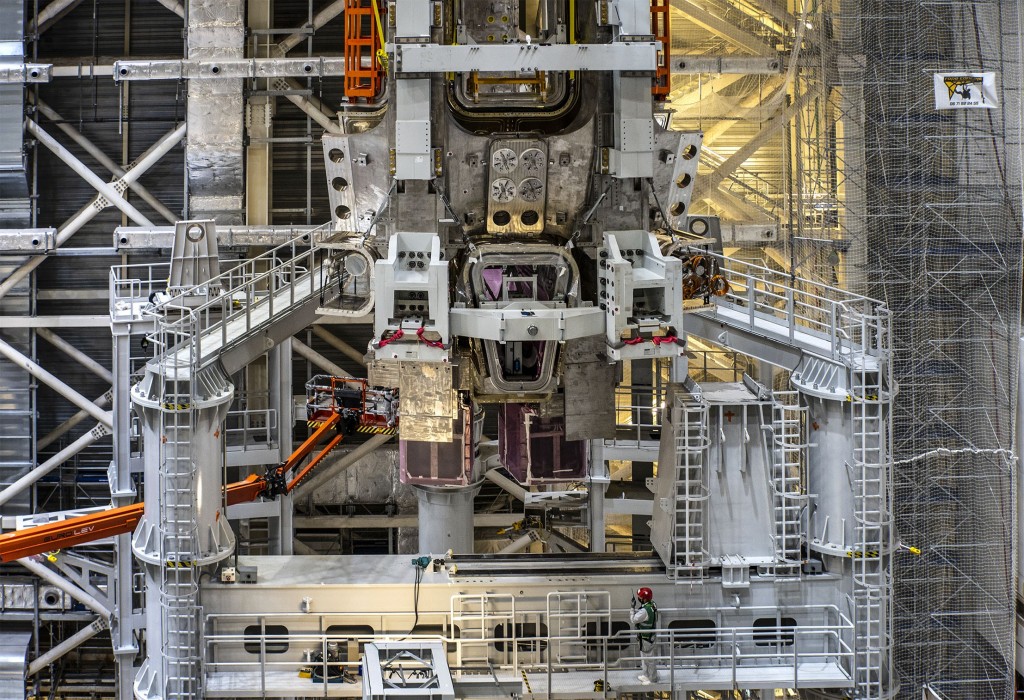
A very slow lift-off
2022-05-11 - As one of a dozen "spotters" communicates by walkie-talkie with the operators in charge of the lift, the 1,380-tonne sector module commences its journey to the assembly pit.

Seven centimetres of clearance
2022-05-11 - During the descent to its mooring position, at the bottom of the Tokamak assembly pit, the distance between the vertical section of the D-shaped component and the central column never exceeded 7 centimetres.
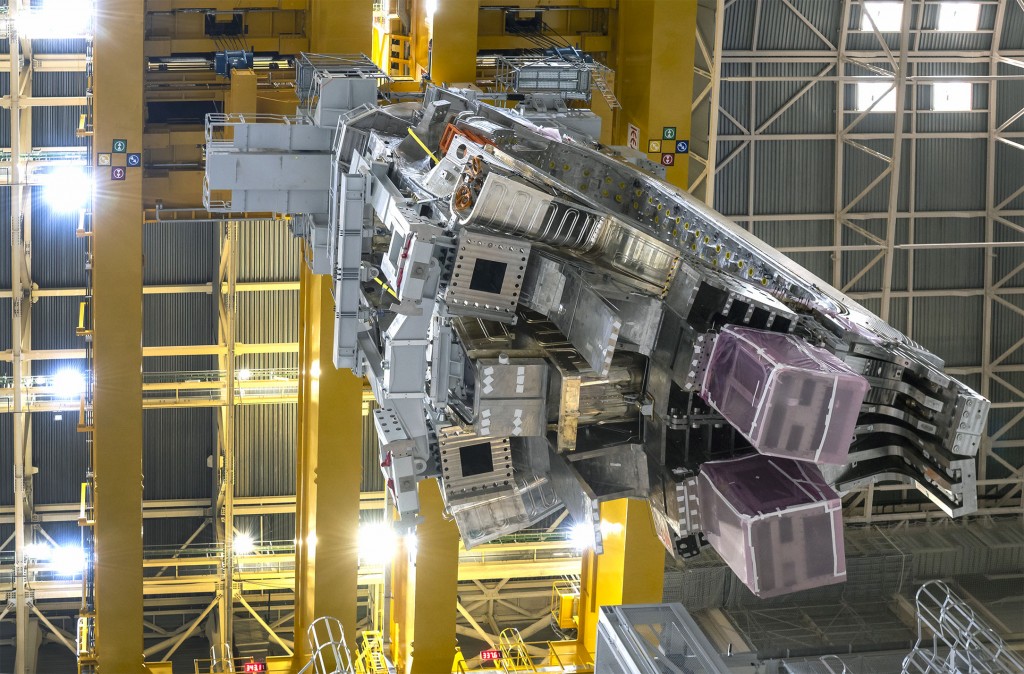
The first of nine similar "sub-assemblies"
2022-05-11 - The "piece" of the ITER machine installed today is a modular assembly, formed from one 40° vacuum vessel sector fitted with silver-coated thermal shields, and two D-shaped vertical superconducting electromagnets called toroidal field coils. Eight other similar assemblies will form the complete chamber and surrounding toroidal field coil superstructure.
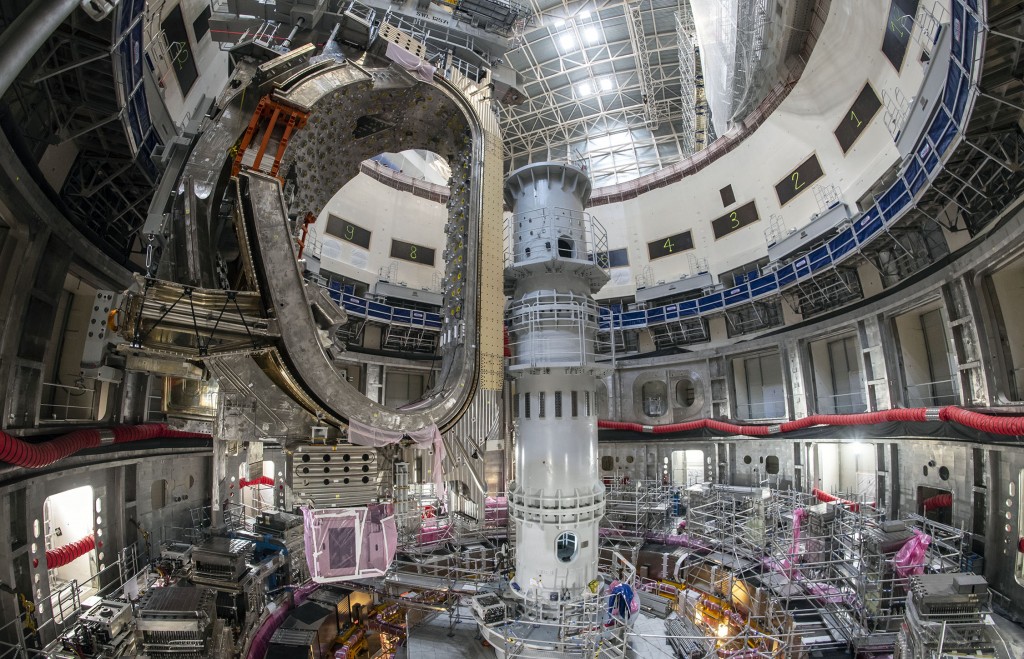
ITER achieves major lift
2022-05-11 - On 11 May 2022, the ITER Organization team achieves a major assembly milestone: lifting the first sub-section of the ITER plasma chamber out of tooling and lowering it into the machine well.

Watching the instruments
2022-05-05 - Although it represented only a fraction of what the actual operation will require, the "pre-lifting" of the sector assembly on Thursday 5 May permitted the thorough testing of every instrument that will be involved in the major move to come.

Pre-lift: a success
2022-05-05 - The pre-lift operation on Thursday 5 May was a partial rehearsal for the big lift to come, testing the tools, sequences, and coordination. For the ITER Organization and DYNAMIC teams that participated, it was a success.
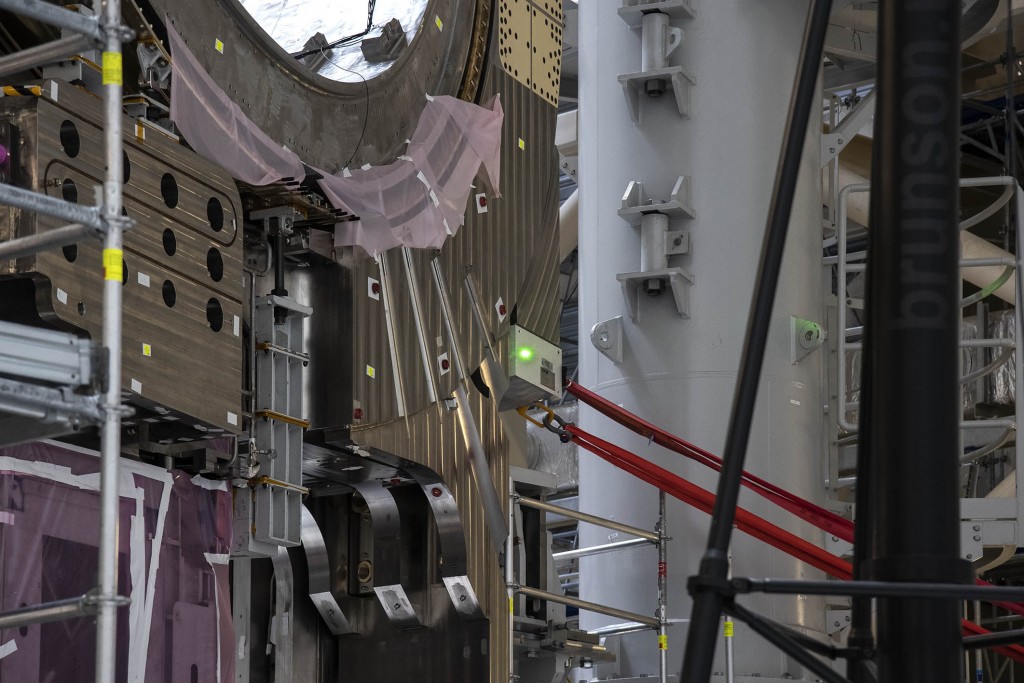
There they are
2022-05-05 - On 5 May, in a pre-lift test, the sector module is lifted 50 centimetres above its supports. This small distance is visible below the rectangular structure illuminated by the green pointer's beam at the centre of the image.

Showing their numbers
2022-05-05 - During sector module lift tests on 5 May 2022, the overhead bridge cranes display their numbers—each of the crane's four hooks is supporting a load of approximately 345 tonnes (only two of them are visible in this image). The total weight of the sector module plus its rigging apparatus is in the range of 1,380 tonnes—the equivalent of four fully loaded Boeing 747s. See the story at: https://www.iter.org/newsline/-/3754.
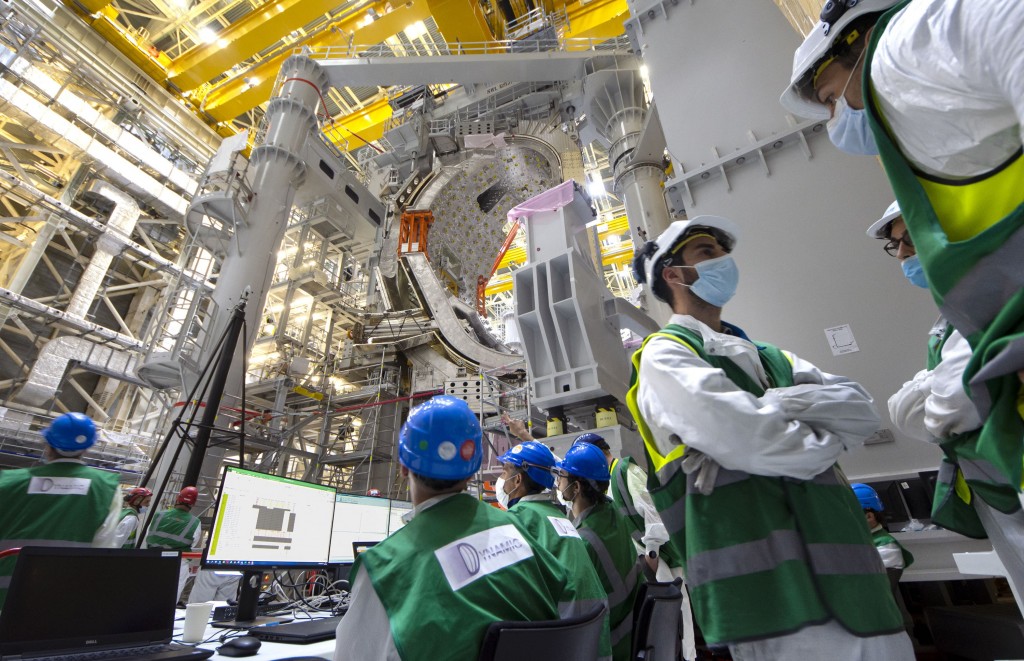
Only 50 cm, but ...
2022-05-05 - Lifting the 1,380-tonne load (module + rigging) a mere 50 centimetres required the participation of dozens of specialists from the ITER Organization and the DYNAMIC SNC consortium (in charge of the TAC2 machine assembly contract covering the main vessel and ports, sector sub-assembly with toroidal field coils and vacuum vessel thermal shielding, and welding.
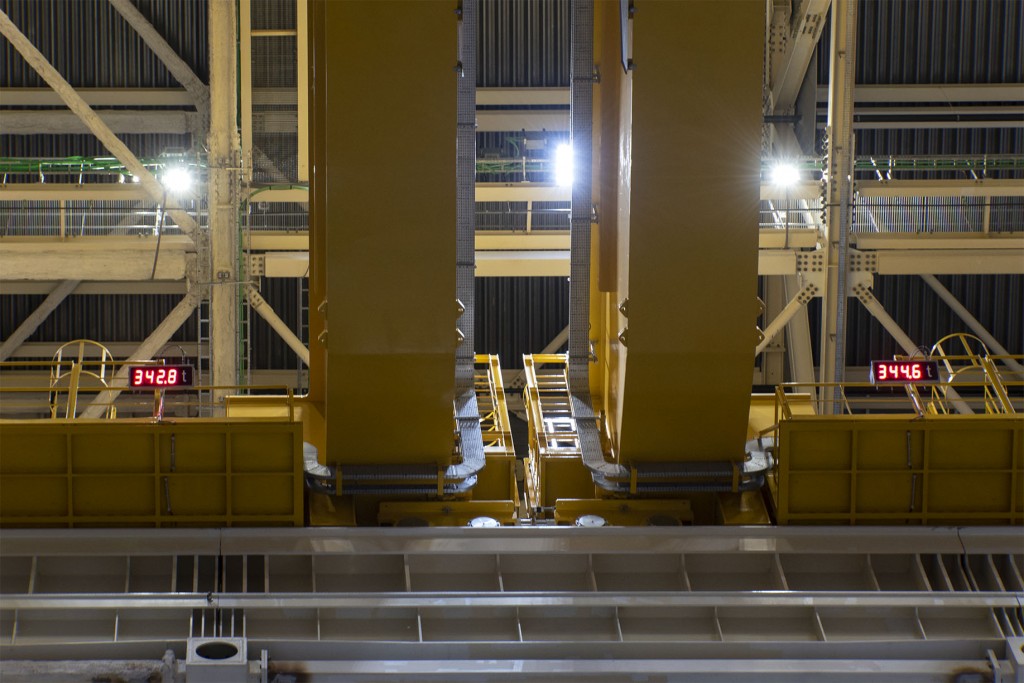
Wow
2022-05-05 - Each of the bridge crane's four hooks can be seen to support loads of approximately 345 tonnes (two totals are visible in this image). The total weight of the sector module plus its rigging apparatus is in the range of 1,380 tonnes—the equivalent of four fully loaded Boeing 747s.
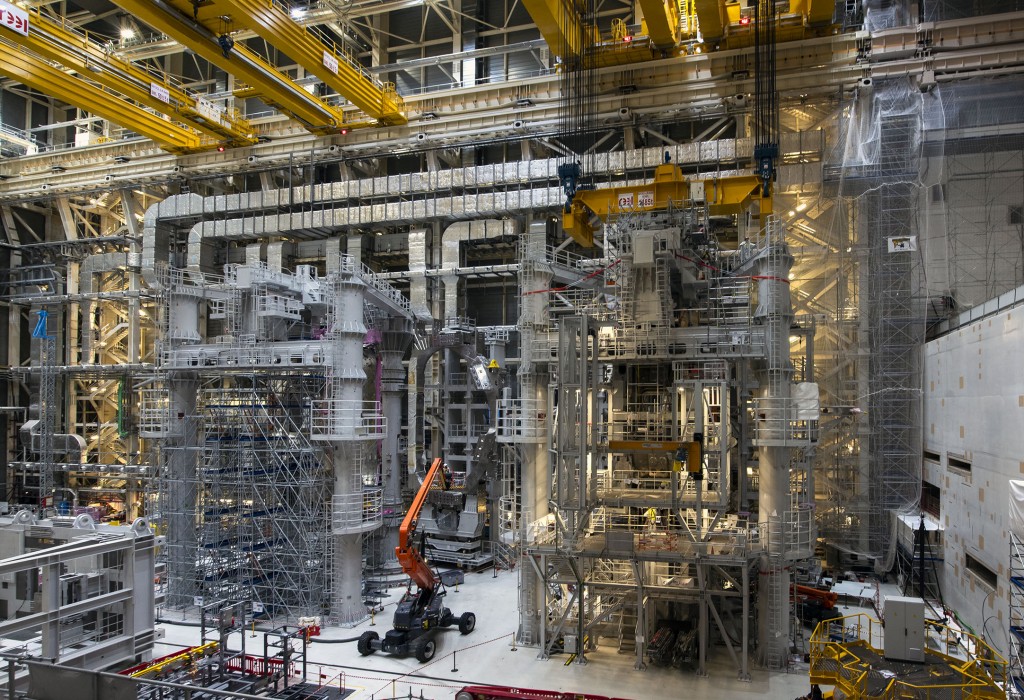
The golden hour
2022-05-02 - Evening is upon us and the teams working to prepare sector module #6 for transfer have turned on some extra lighting ...
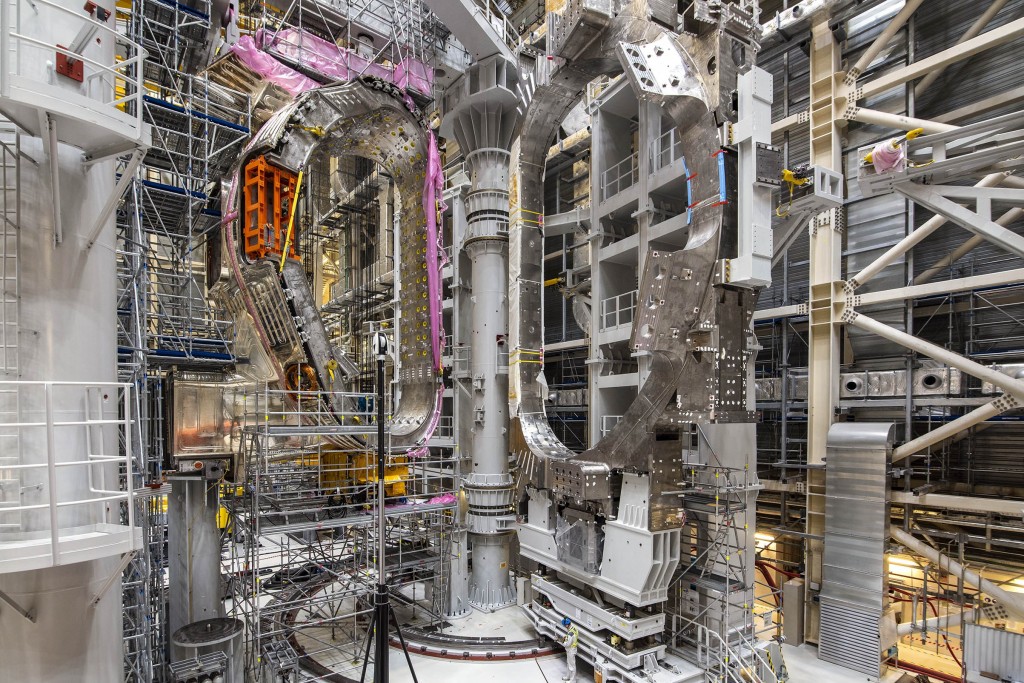
A second sub-assembly underway
2022-04-29 - Toroidal field coil #9 (TF9) from Europe has been mounted on one of the standing tools. Through the rotary motion of the wing, the coil will be brought toward the vacuum vessel sector at the centre and attached.

Commissioning the liquid nitrogen (LN2) plant
2022-04-29 - As part of LN2 plant commissioning, this liquid nitrogen tank is being filled to 80% of its capacity to verify the rate of evaporation, which should not exceed 0.16 percent of the total volume per day. The tank in the photo has a capacity of 300 cubic metres.
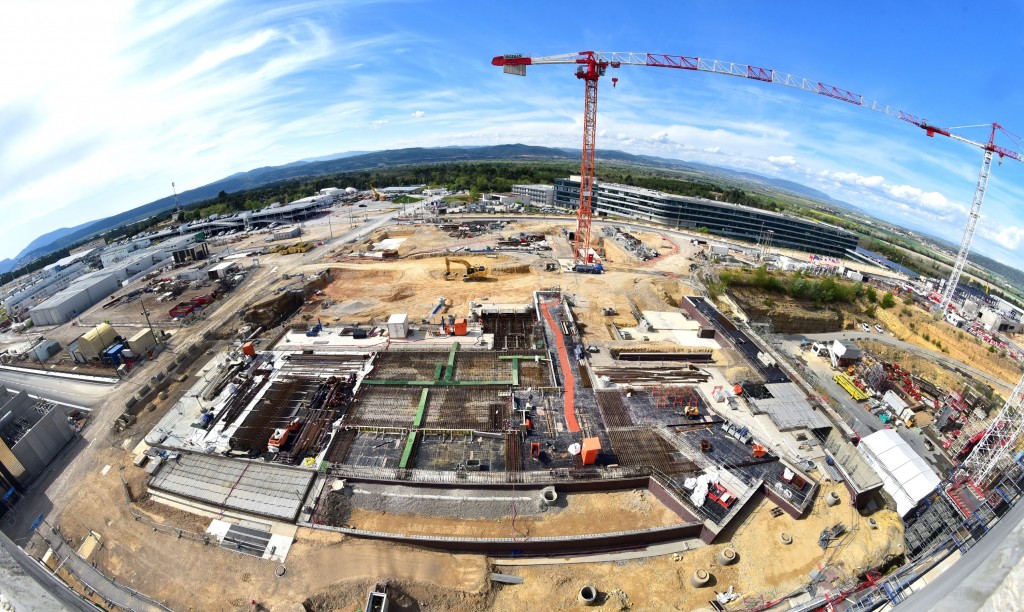
Neutral beam heating power supply: buildings rising
2022-04-25 - From the roof of the Diagnostics Building, we are looking directly down at the site of the future ITER Neutral Beam Power Supply buildings, currently under construction by European Domestic Agency (Fusion for Energy) contractors.
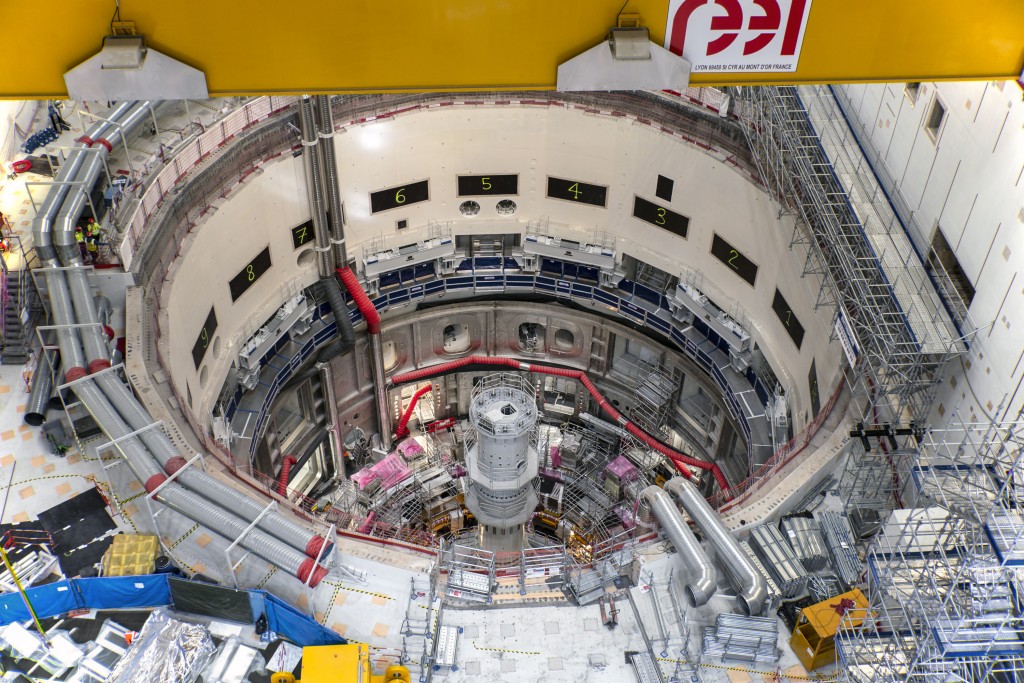
"The beam" is in place
2022-04-25 - A new scaffolding element called "the beam" has been installed above the Tokamak pit (to the right). This 28-metre-long structure will allow for the installation of the cable trays and ventilation ducts.

Neutral beam heating power supply: buildings rising
2022-04-25 - From the roof of the Diagnostics Building, we are looking directly down at the site of the future ITER Neutral Beam Power Supply buildings, currently under construction by European Domestic Agency (Fusion for Energy) contractors.
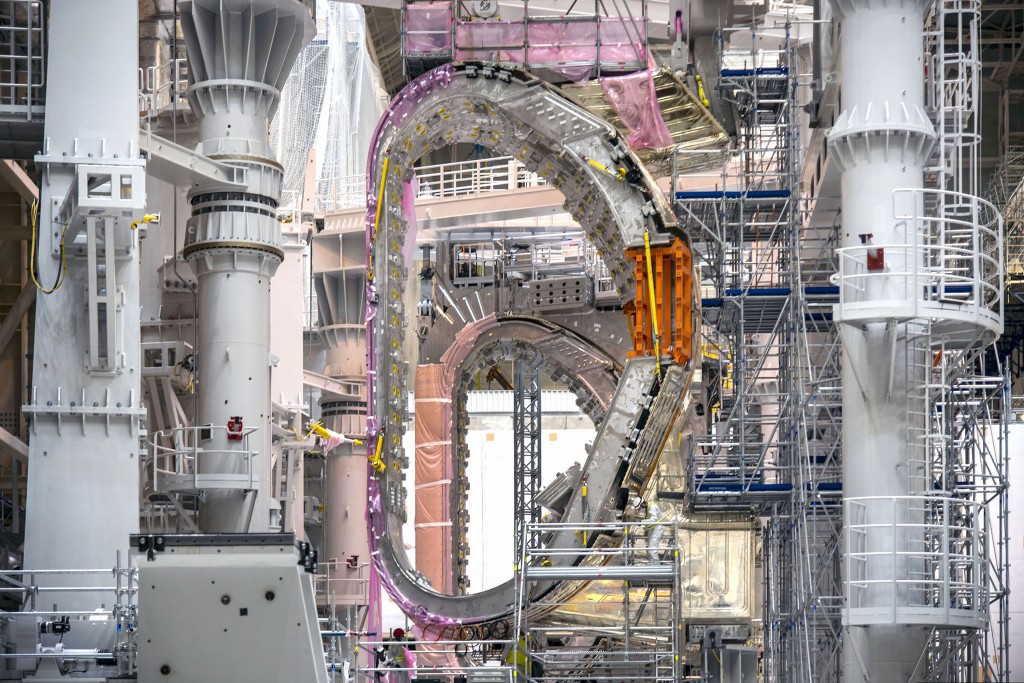
Sector assembly line
2022-04-25 - Thermal shield panels have been pivoted to the vacuum vessel sector in the foreground and attached. A toroidal field coil from Europe is already held vertically in tooling, ready to be transferred across and installed on one of the tool's wings.

Roads finalized
2022-04-25 - This paved road running to the east of the Tokamak Complex is one of the last to be realized under Fusion for Energy's TB16 contract, which covered the realization of service trenches, precipitation drainage, and site adaptation works such as roads and lighting.

Bustling
2022-04-25 - The busy ITER Assembly Hall. Only 97 metres long and 60 metres wide ... and a lot of pre-assembly activities to house.
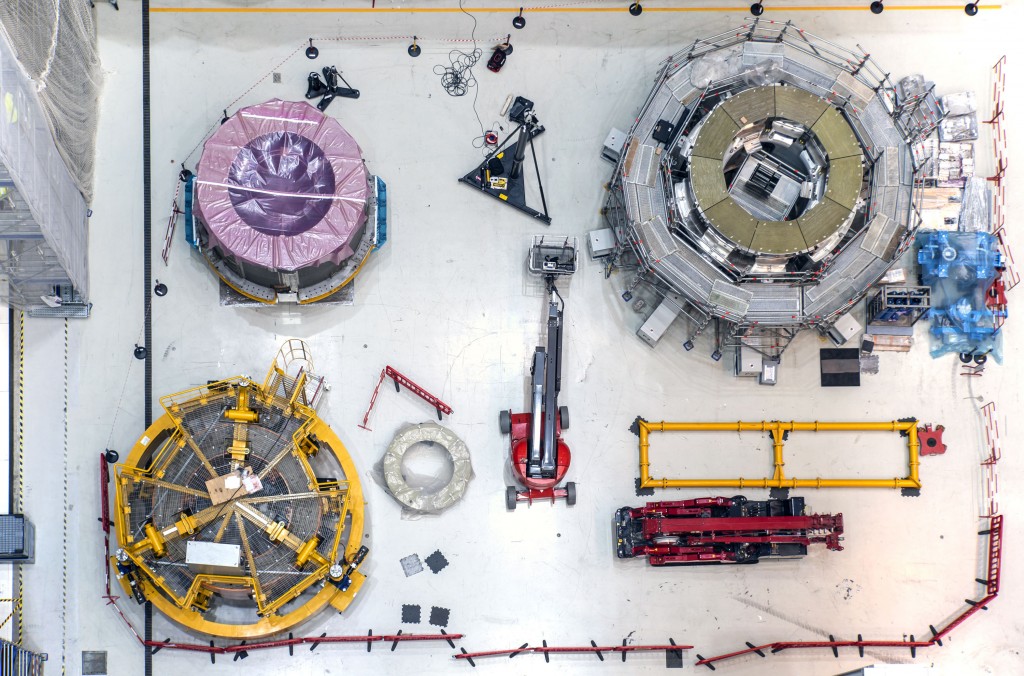
A, B then C
2022-04-25 - The purpose-built central solenoid module lift tool (bottom left) is ready to exert a radial force on the first 110-tonne magnet module (top left) in order to lift it to the central solenoid assembly platform (top right). This operation is planned before the end of April 2022.
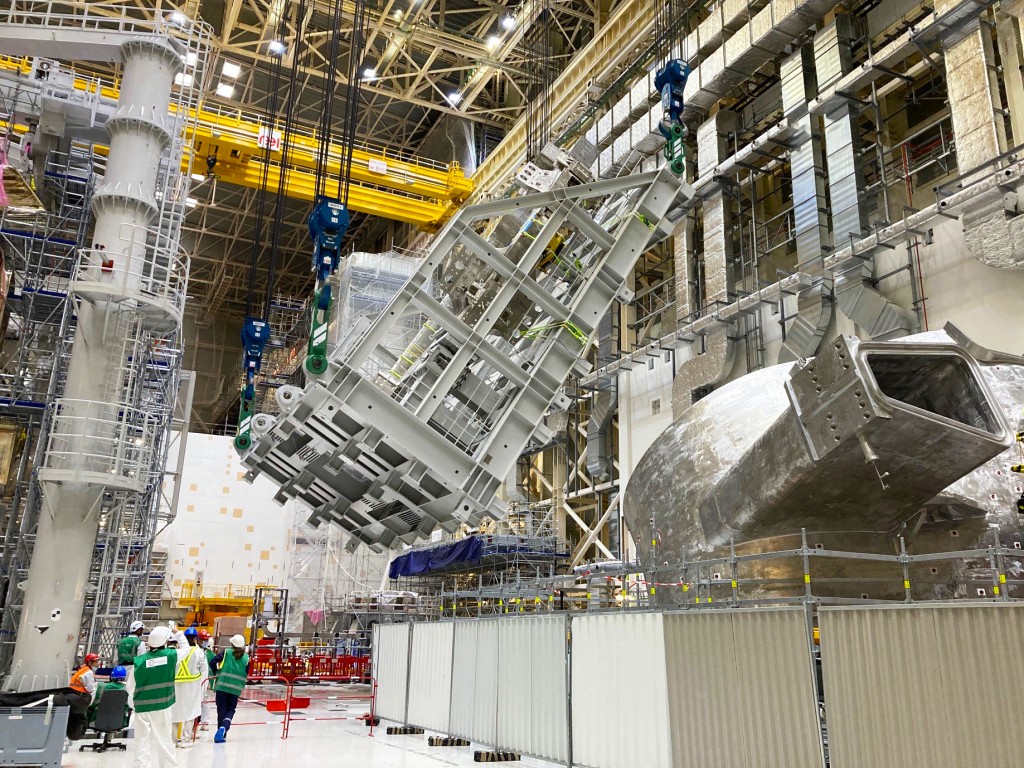
Toroidal field coil #9 goes vertical
2022-04-25 - In the ITER Assembly Hall, the overhead bridge cranes are used to raise a 330-tonne toroidal field coil, tightly lashed inside the upending frame, to vertical. The coil will be moved across the Hall to join vacuum vessel sector #1(7).

At the centre of it all
2022-04-22 - Two workers stand in the central Tokamak pit, a 30-metre-tall x 30-metre-wide space where the assembly of the ITER machine is proceeding from bottom up.

MITICA advancing
2022-04-15 - Workers verify MITICA accelerator components at ALSYMEX. April 2022 © F4E

Poloidal field coil #4 in fabrication
2022-04-14 - Eight double pancakes have been stacked and joined and now poloidal field coil #4 (PF4) is being prepared for vacuum pressure impregnation, which confers electrical insulation to the magnet and creates a rigid assembly.
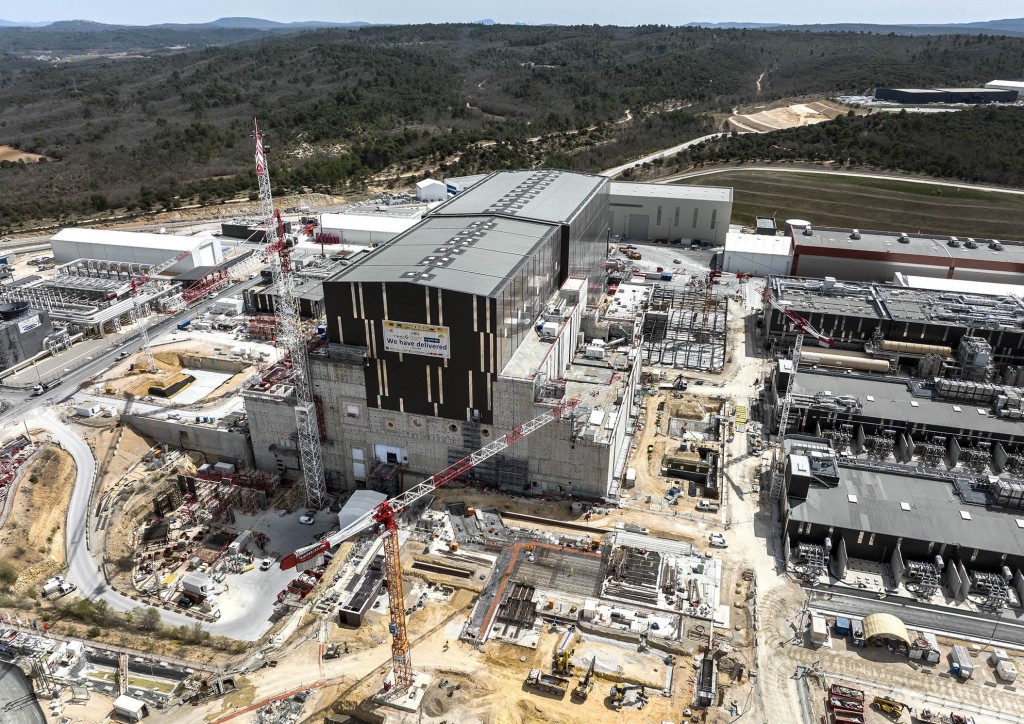
A complex area
2022-04-14 - In April 2022, a drone captures the platform from above. The large Neutral Beam Power Supply zone (in construction, front and centre) is one of the largest remaining areas still to be finalized on the ITER platform.
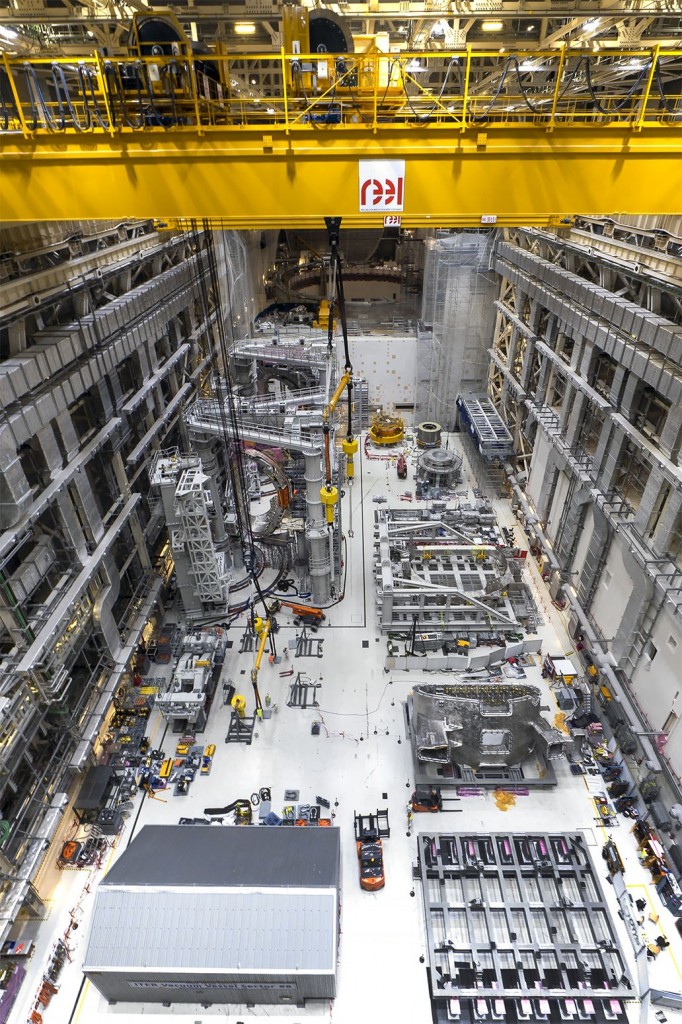
From the upper galleries
2022-04-08 - At 55 metres above the floor, the gangway offers a spectacular view of the Assembly Hall's ever-changing landscape. In this 6,000-square-metre building, components are unloaded, received, equipped, and handled prior to being lifted into the Tokamak assembly pit.
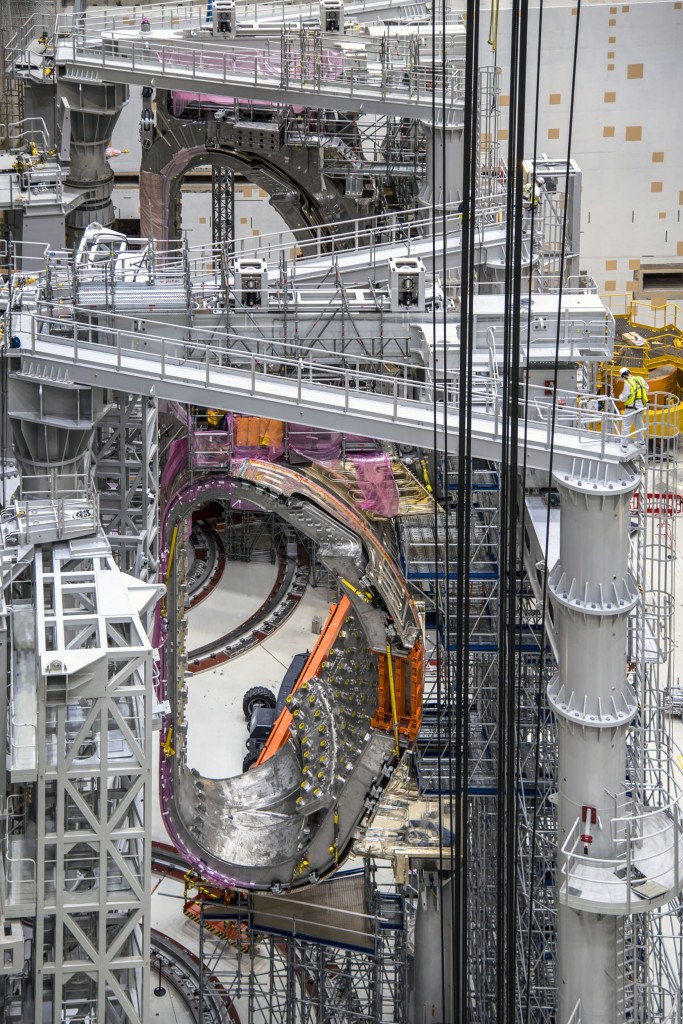
All it takes
2022-04-08 - A vacuum vessel sector, two toroidal field coils, thermal shield segments... that's all it takes to assemble a 1,250-tonne "sector module." In the Assembly Hall, barely visible in the background, sector module #6 is ready to be installed in the Tokamak pit; in the foreground, sector module #1(7) has entered the pre-assembly process.

Central solenoid "corner"
2022-04-08 - Delivered in September 2021, the first of the six modules required for the central solenoid magnet sits between the lifting fixture (holding an orange mockup) and the assembly platform (grey). The six modules will be stacked one atop the other in order to form the 18-metre tall, 1,000-tonne magnet.
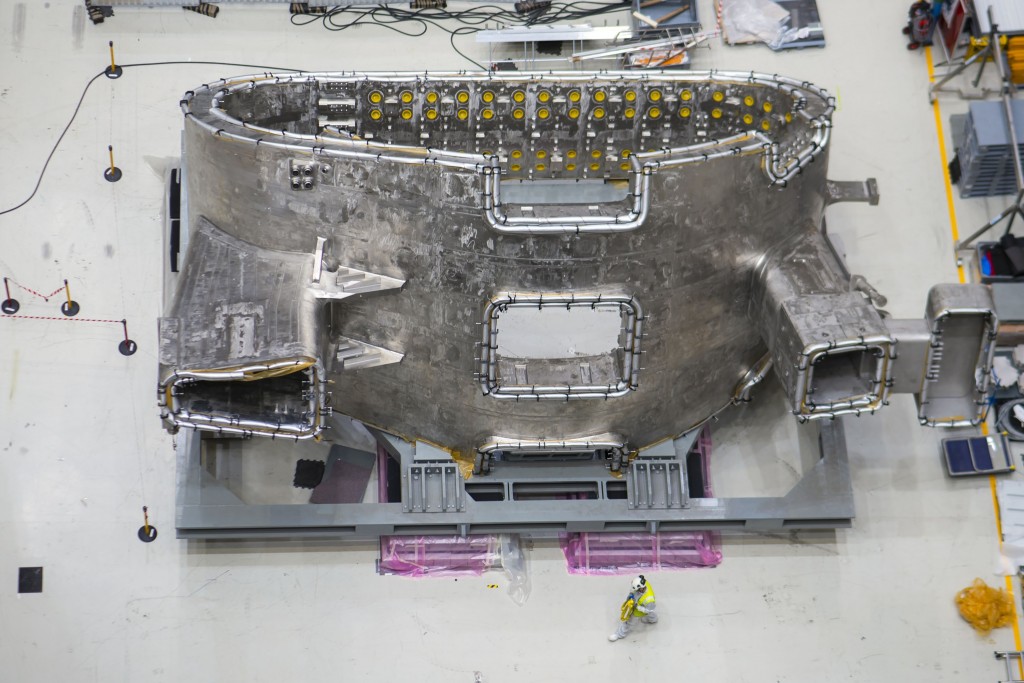
Sector #8 uncovered
2022-04-08 - Sector #8, recently delivered by the Korean Domestic Agency, has been removed from its transport housing and placed on temporary supports.
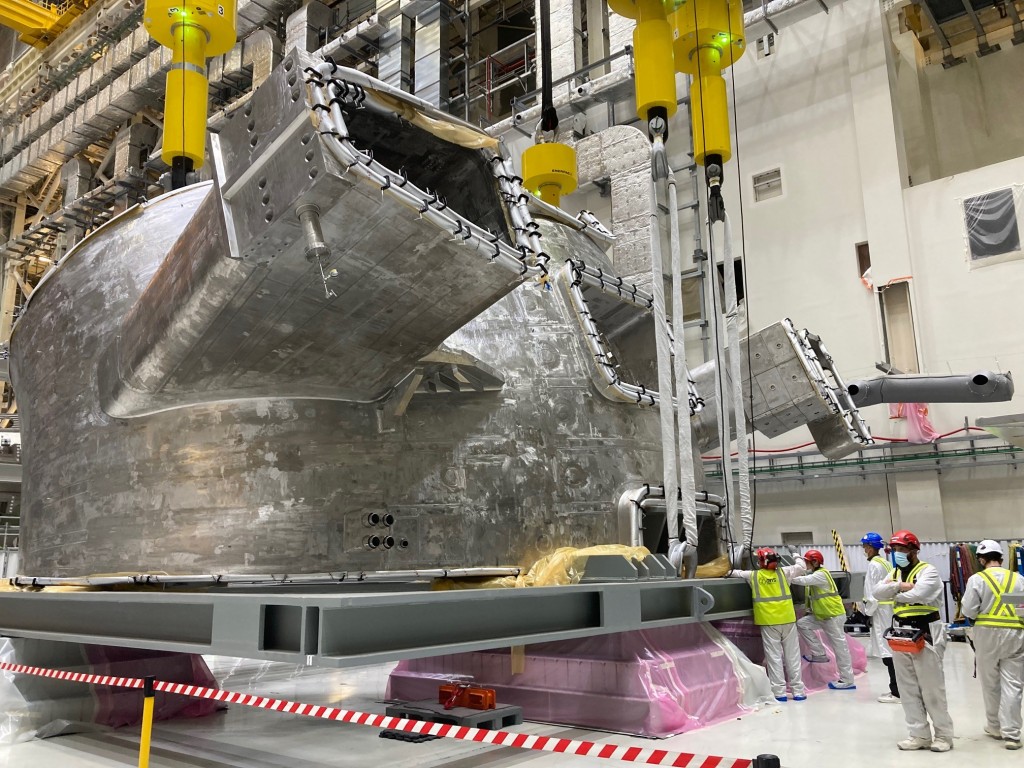
Third time around
2022-04-07 - Like sectors #6 and #1(7), this vacuum vessel sector (#8) will be first be inspected, then equipped with fasteners, instrumentation and diagnostics before moving on to a vertical position in sub-assembly tooling. With repetition, these operations are carried out with ever more efficiency.
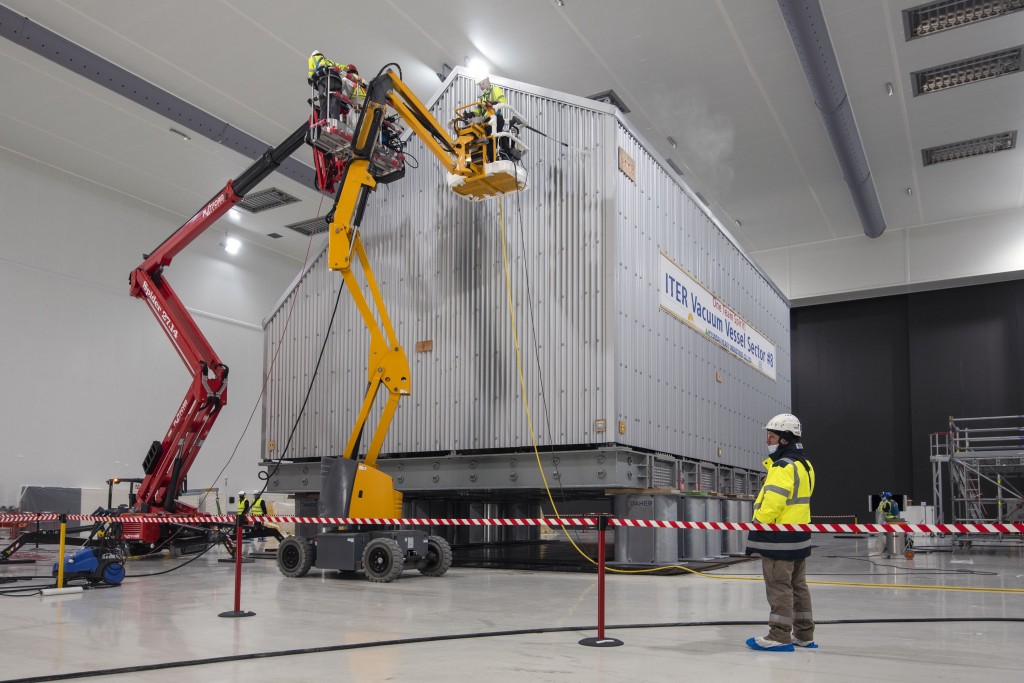
Before the double doors open
2022-04-01 - Before the double doors into the Assembly Hall open to admit vacuum vessel sector #8, from Korea, the transport container is cleaned with high-power washers.
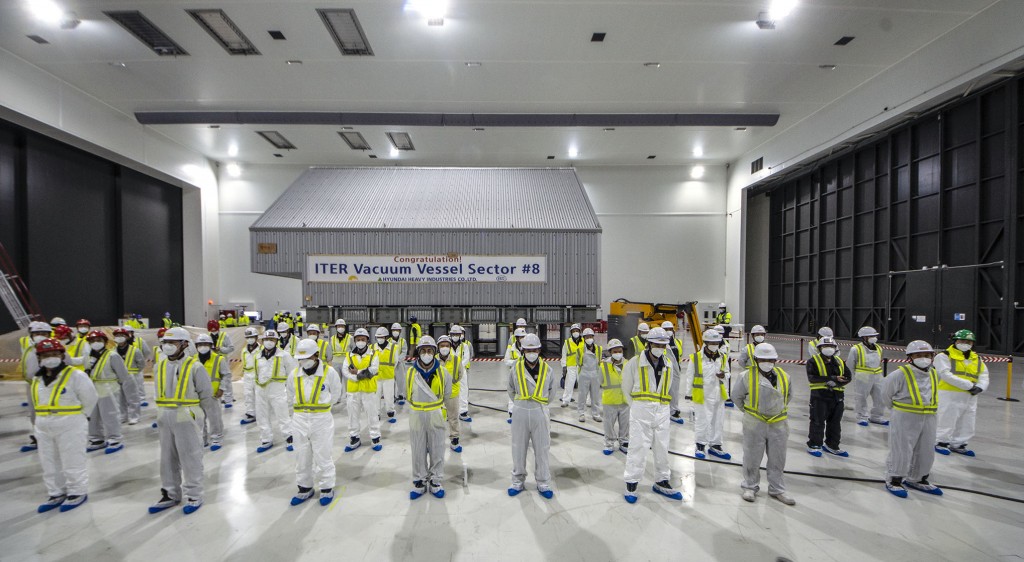
Start of shift
2022-04-01 - It is a bit after 1:00 p.m. in the vast ITER Cleaning Facility and second-shift workers from the CNPE consortium are assembled for their daily briefing. As they stand to attention, a foreman in a green helmet, bullhorn in hand, communicates the objectives of the day, describes the co-activity they will encounter, and emphasizes the importance of strictly observing safety rules. The CNPE consortium is one of two ITER machine assembly contractors.
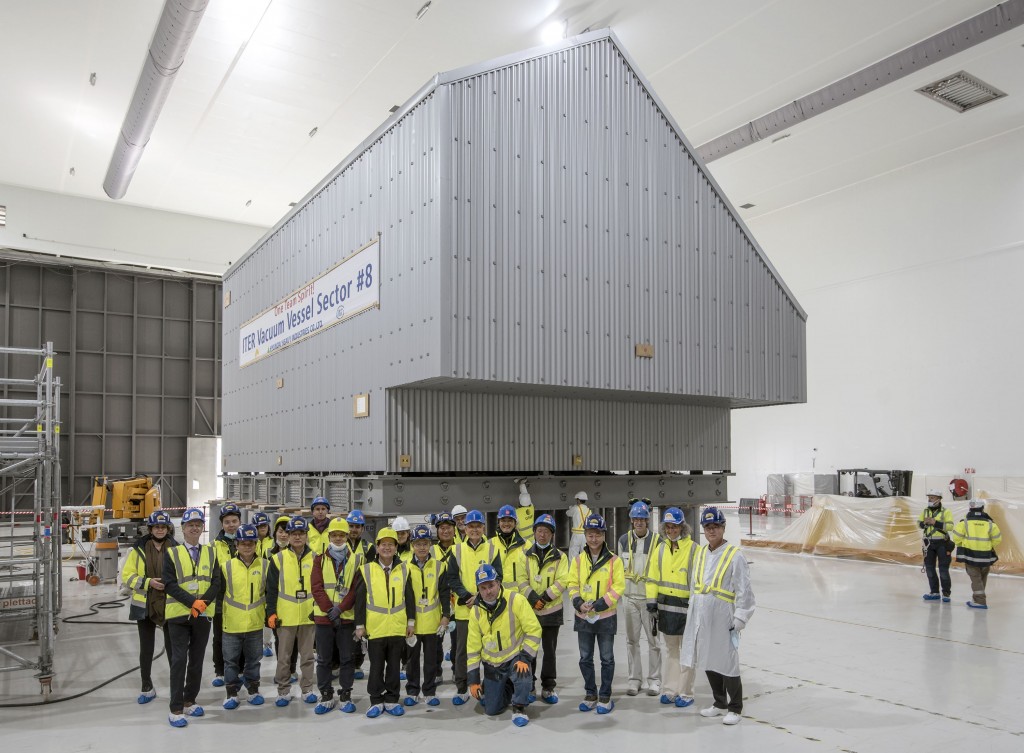
Sector #8 enters the stage
2022-04-01 - Vacuum vessel sector #8, recently arrived from Korea, is the third sector to enter the ITER assembly buildings (pictured: the Cleaning Facility). The project is expecting six more sectors (one from Korea and five from Europe).

Early installation for optical diagnostics
2022-03-31 - Recently installed diagnostics supports at the L1 level of the Tokamak Building, showing some of the detail of how the supports are bolted to the ceiling by first welding threaded studs to steel plates embedded in the ceiling concrete. This allows for high accuracy in the installation of the optical beamlines.
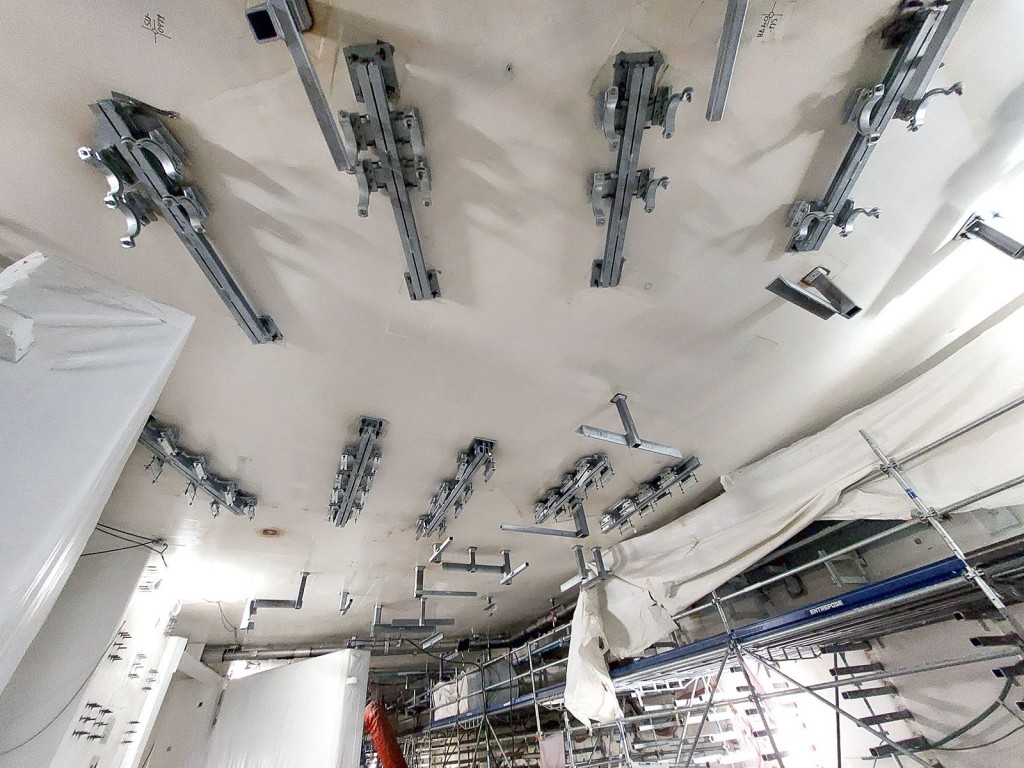
"Hugging" the ceiling
2022-03-31 - Supports installed on the ceiling in the B1 level of the Tokamak Building, showing the ''ceiling hugging'' nature, which keeps the diagnostic systems very close to the ceiling and above other installed equipment.

Diagnostics: installing captive components now
2022-03-31 - Support elements for diagnostic pipes, cables and lines are received at the workshop of the installation contractor on the ITER site, before they are assembled and installed in the Tokamak Complex. Any captive components (soon to be boxed in by other systems or components) must be installed now.
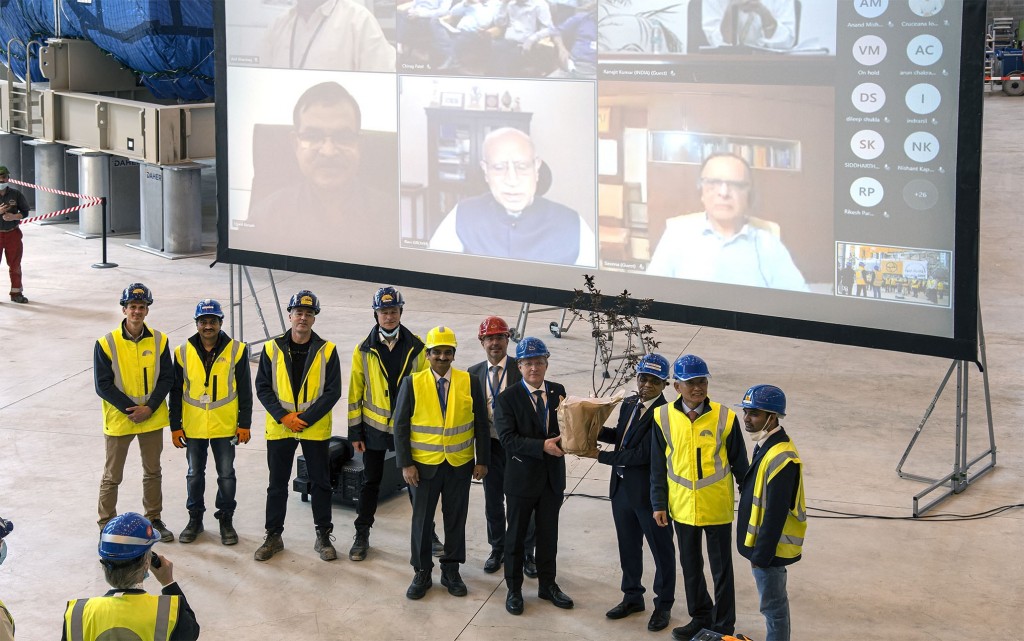
In person and through video link...
2022-03-24 - Gathered in the Cryostat Workshop on site or present virtually through a video connection with India, the designers, manufacturers, machining experts, metrology specialists and welders involved in the realization of the ITER cryostat bore testimony to the magnitude and complexity of the international venture.

"Final closing piece"
2022-03-24 - ITER Head of Construction Youngeek Jung speaks at a ceremony on 24 March 2022 in the Cryostat Workshop. Speaking of the completed cryostat lid, which has been prepared for storage, he said, "When it next appears, it will be the final closing piece of the largest fusion machine humans have ever dared to build."

Compressed air for cryoplant commissioning first
2022-03-18 - Connecting the compressed air distribution network to the cryoplant was an essential step in the testing of the facility's 1,500 pneumatic actuators and hundreds of control valves. An integrated team composed of ITER operators and European staff from Fusion for Energy and Engage have been working closely together to achieve this milestone. The demineralized water system will be next, and progressively, one by one, all the clients throughout the installation on the platform will be served.
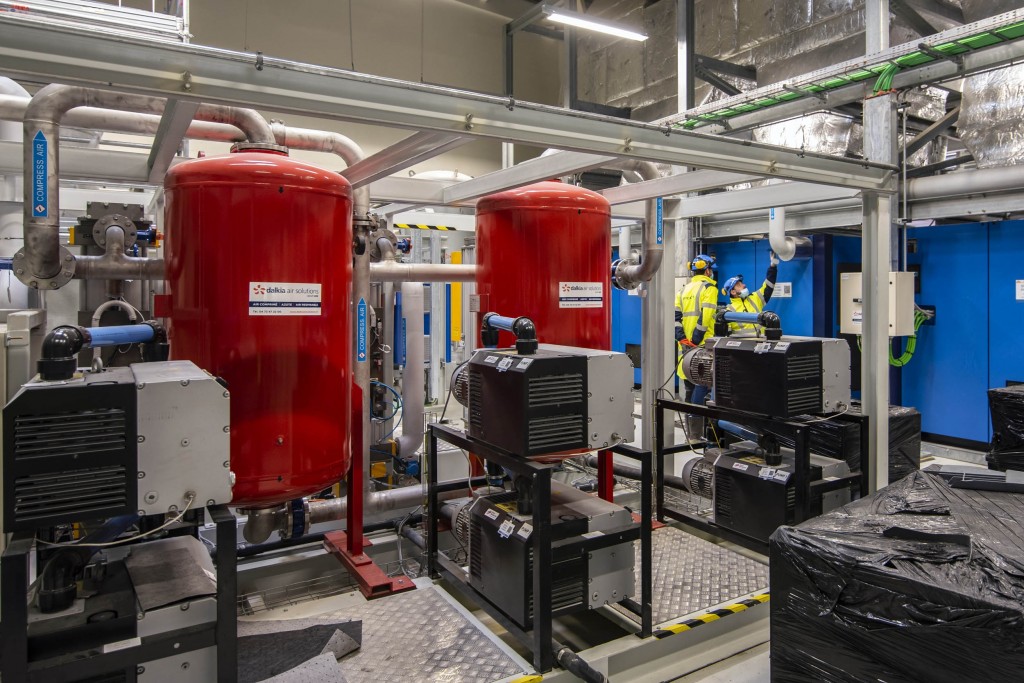
Site Services Building: beginning to serve clients
2022-03-18 - The Site Services Building is beginning to service its first utility clients on the ITER platform. Densely packed with a demineralized water plant, chiller systems, air compressors, dozens of pumps and kilometres of piping, the facility produces and distributes compressed and breathable air (for operators in ventilated nuclear suits), demineralized water for cooling circuits and detritiation systems, and cold water for air conditioning systems.
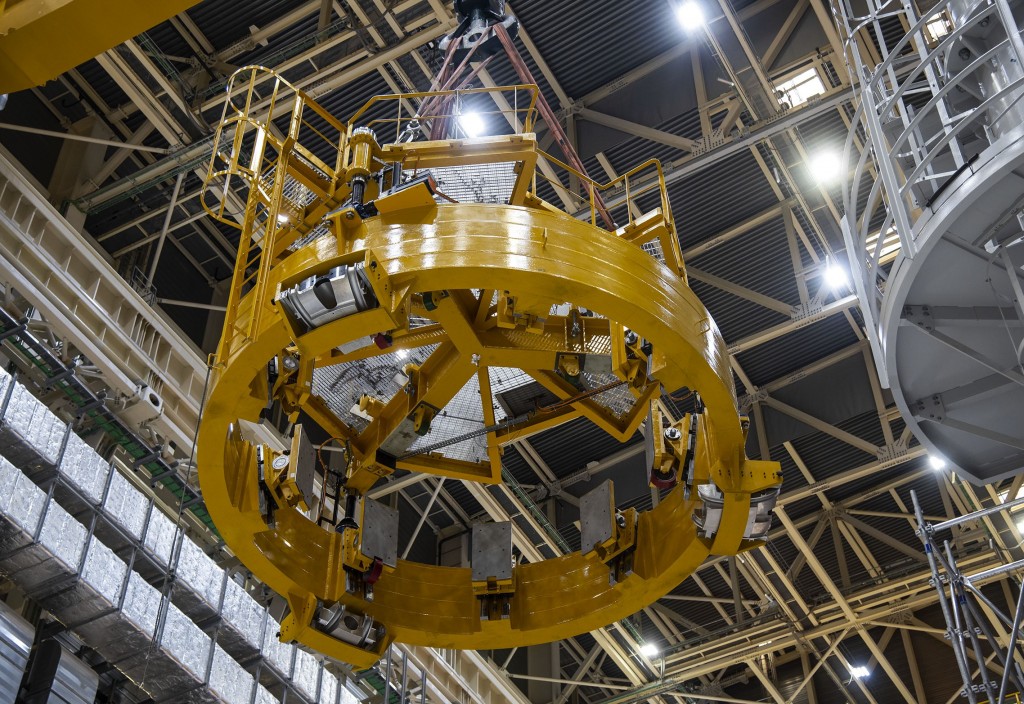
A gripping tool for central solenoid assembly
2022-03-17 - This unique tool was designed by US ITER to clutch 110-tonne central solenoid modules and hold them in its grip by exerting a strong radial force. The modules cannot be lifted in a traditional manner because it is impossible to add hooks and other lift fixtures to the superconductors.

"The beam"
2022-03-15 - This 28-metre-long scaffolding structure known as ''the beam'' will be installed above the Tokamak pit to allow for the completion of cable trays and ventilation ducts.

Taking care of scaffolding
2022-03-15 - A dedicated team on site takes care of the assembly and disassembly of all scaffolding. For scaffolding operations in the Tokamak pit, such as this assembly around the central column of the in-pit column tool, a carbon-free kit is necessary. The team now has almost 100 tonnes of carbon-free material on hand after developing and procuring it especially for ITER's needs.

Scaffolding: always changing
2022-03-15 - Scaffolding. Imagine you have a massive Lego kit with 1,600 different types of references and you need to build hundreds of one-of-a-kind structures while facing challenging deadlines ...

Demand for scaffolding is increasing
2022-03-15 - As construction and assembly accelerate at ITER, the demand for scaffolding is increasing. There are currently about 800 scaffolds in use on the site and every month there are more than 300 new scaffolding jobs that need to be done, without considering the modification and dismantling tasks.
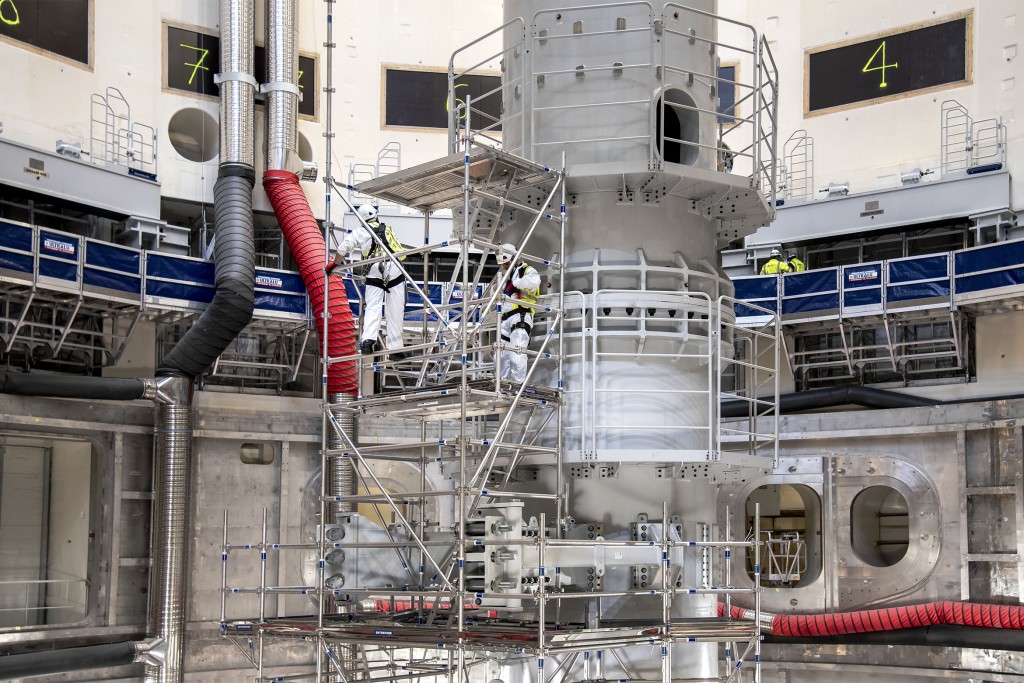
Central column
2022-03-15 - Inside of the Tokamak pit, where the central column tool is ready to receive the first 1,200-tonne section of the vacuum vessel. The beam connected to the top of the section will brace between the central column and the surrounding wall.
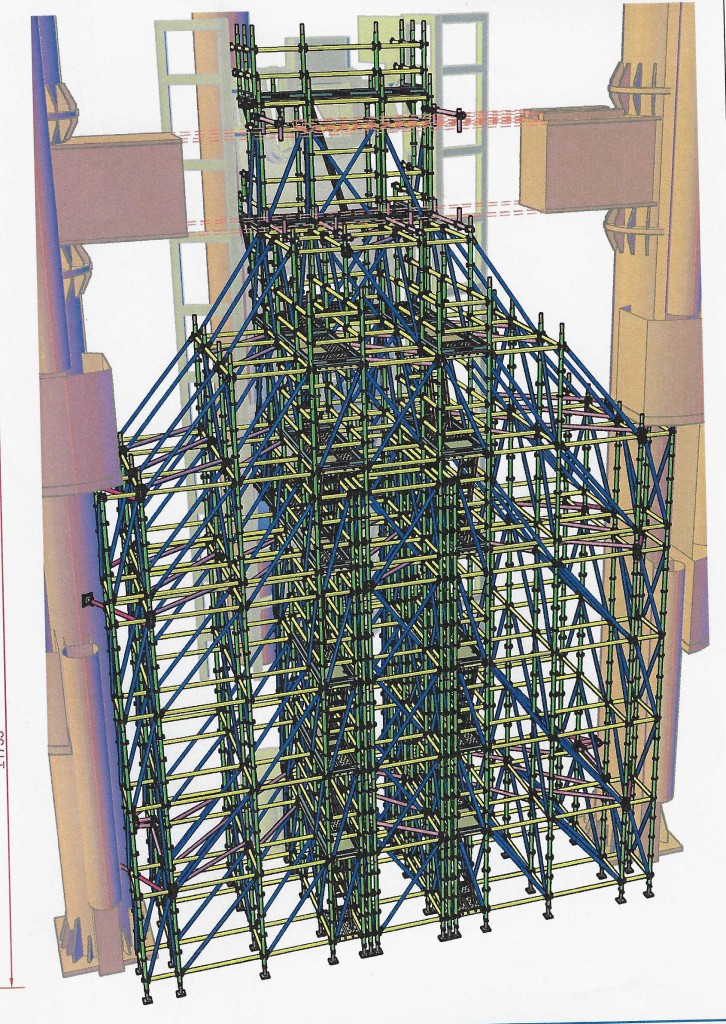
Custom designed for the SSAT1 tool
2022-03-15 - This scaffolding was specifically designed to give contractors access to all parts of the sector sub-assembly tool SSAT1 in the Assembly Hall. The ITER construction team works with Construction Management-as-Agent contractor MOMENTUM and scaffolding contractor Entrepose Echafaudages to design and build these specialized projects.

The most complex of the sections
2022-03-10 - The top lid is also the most structurally complex of the four sections that make up the ITER cryostat. Curved in three directions like a skull cap, it is strengthened by an array of stiffeners and ribs. Here, from left to right: Dipen Shah, from Indian manufacturer Larsen & Toubro; Guillaume Vitupier, leader of the ITER cryostat group; and Girish Kumar Gupta, ITER cryostat engineer.

Thanks to ...
2022-03-10 - The steel elements were manufactured by Larsen & Toubro (India) for the Indian Domestic Agency. Welding and assembly were carried out in the Cryostat Workshop by MAN Energy Solutions (Germany). The 665-tonne component will be stored outdoors from October 2022 on in order to make room in this workshop for other machine assembly activities.

Lid completed
2022-03-10 - Approximately one year after work started on the ITER cryostat top lid, the team has completed the 665-tonne component. Only some cleaning and final verification checks remain.

From the top
2022-03-09 - In March, the commissioning team transfers water from the hot basin to two cells of the cooling tower for the first time, using vertical turbine pump #13. In the picture, we can see the water in the towers by spray nozzles to the fill packs (which increase the heat exchange surface).

Six years of activity come to a close
2022-03-08 - Final checks before the component is handed over to the ITER Organization late March. The finalization of the top lid concludes six years of work in the Cryostat Workshop for the assembly and welding of the four large ITER cryostat sections.

300 specialized joints
2022-03-01 - Approximately 300 superconducting feeder joints need to be created as part of assembling the magnet feeders on site at ITER. These highly critical joints require special qualification and training to carry out.
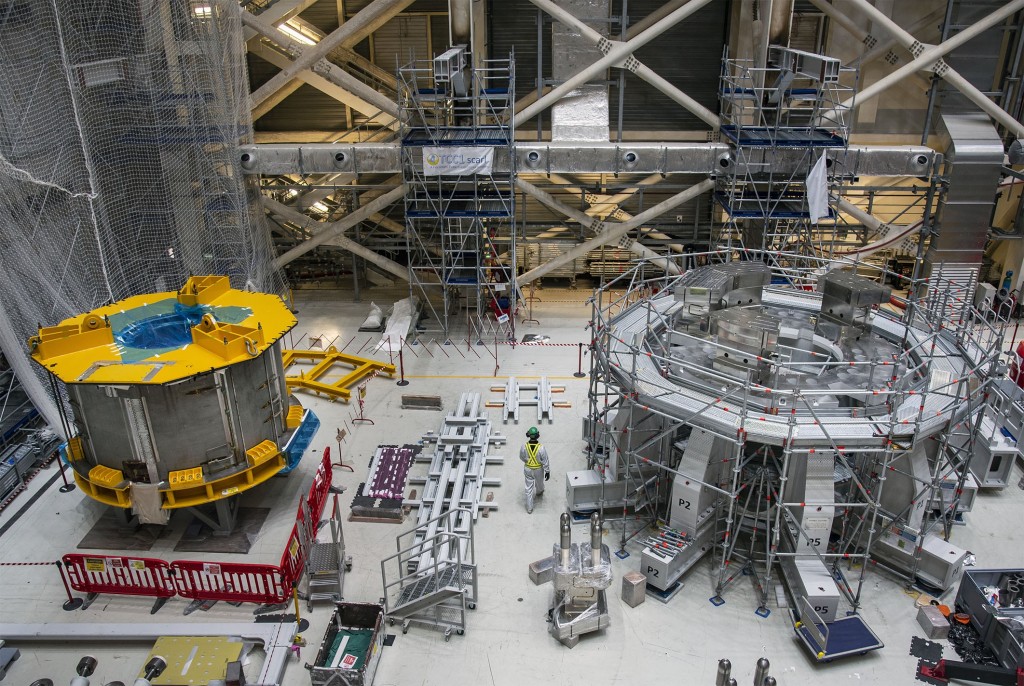
In one corner of the Assembly Hall
2022-02-28 - This is the first ITER central solenoid module to enter the assembly process. As the yellow lifting tools and devices are progressively removed from the module on the left, the platform to the right is being equipped for the first assembly steps.
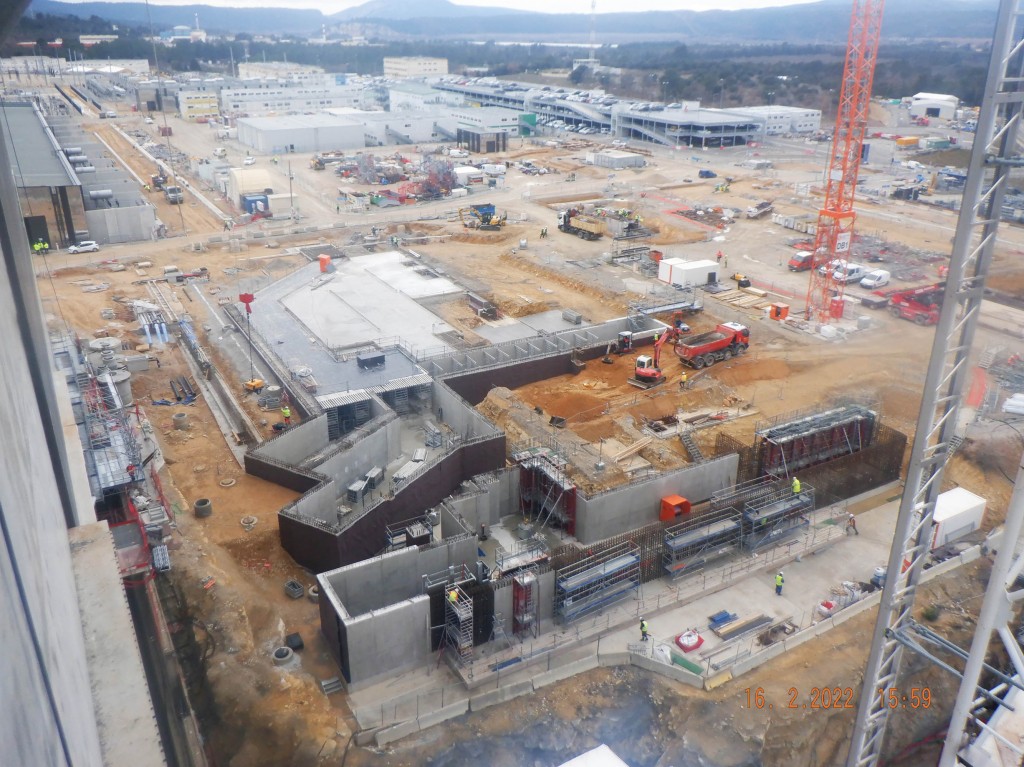
Coming out of the ground: Neutral Beam Power Supply buildings
2022-02-21 - Not often seen from above: the neutral beam power supply buildings, which are under construction next to the Tokamak Complex. Work on the foundations is advancing well.
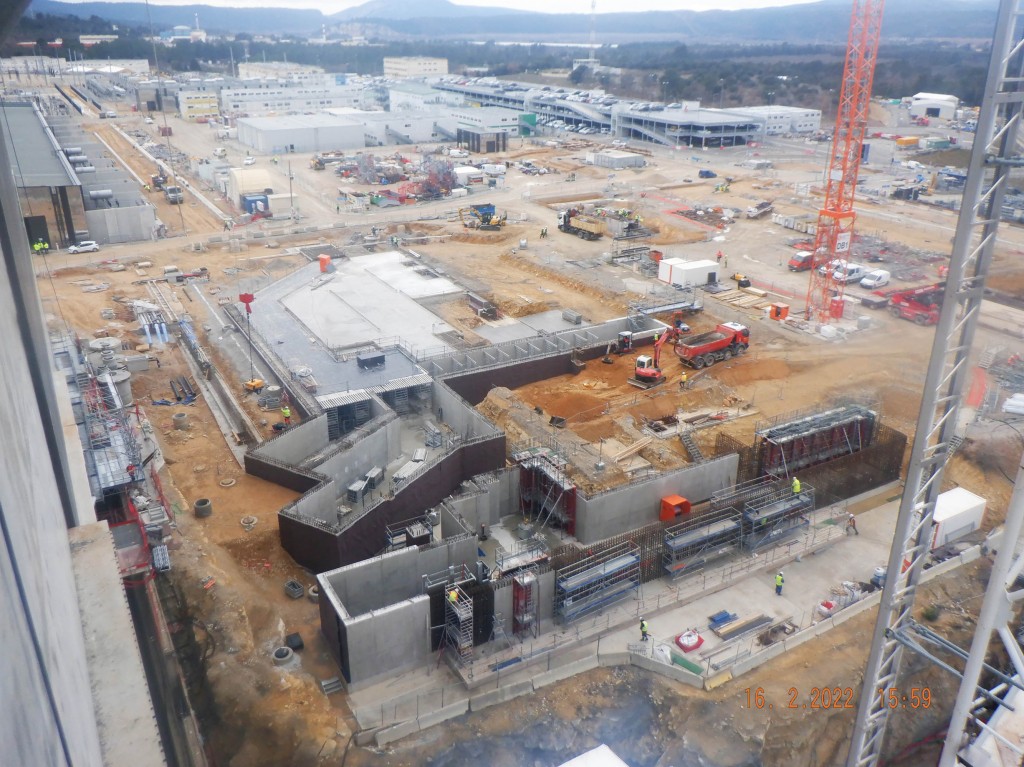
Coming out of the ground: Neutral Beam Power Supply buildings
2022-02-21 - Seen from above: work underway on the galleries and foundation slabs of the Neutral Beam Power Supply Buildings. Work is progressing as planned.
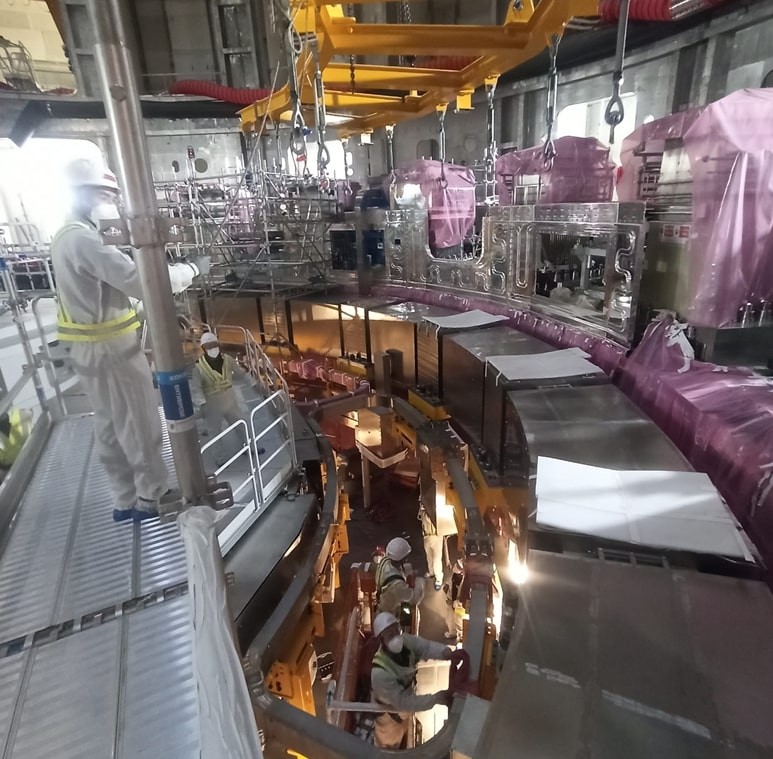
Another bottom coil
2022-02-15 - A small superconducting magnet, a bottom correction coil, is inserted into the space at the bottom of the Tokamak pit between ring coil PF6 (hidden under staging at left) and PF5 (right).
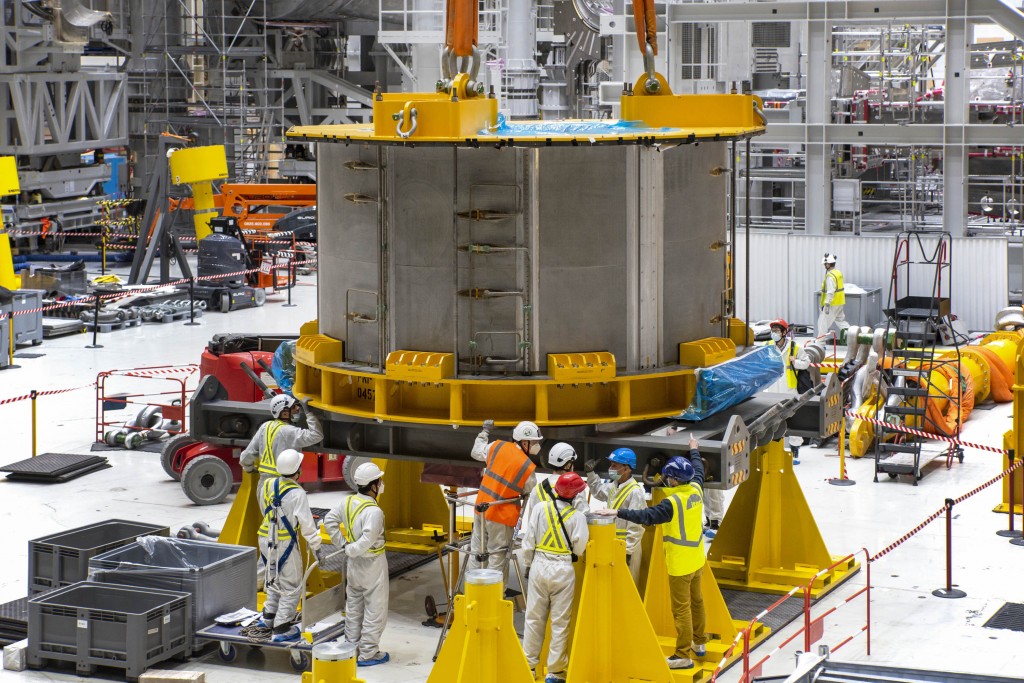
Careful preparation
2022-02-10 - The team spent more than one hour preparing the load for the lift. It was essential to avoid any contact between the rigging and the electrical connections on the central solenoid module.
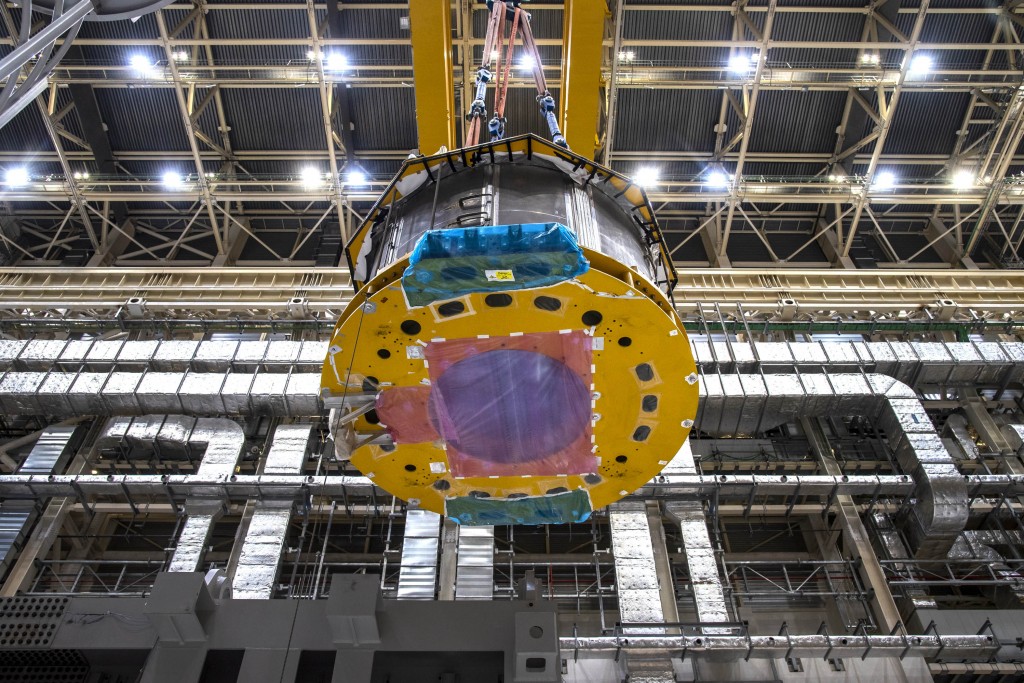
Travelling
2022-02-10 - Once six modules are stacked and assembled, the ITER central solenoid will be placed at the very centre of the Tokamak pit where the central column (a temporary assembly tool) presently stands.
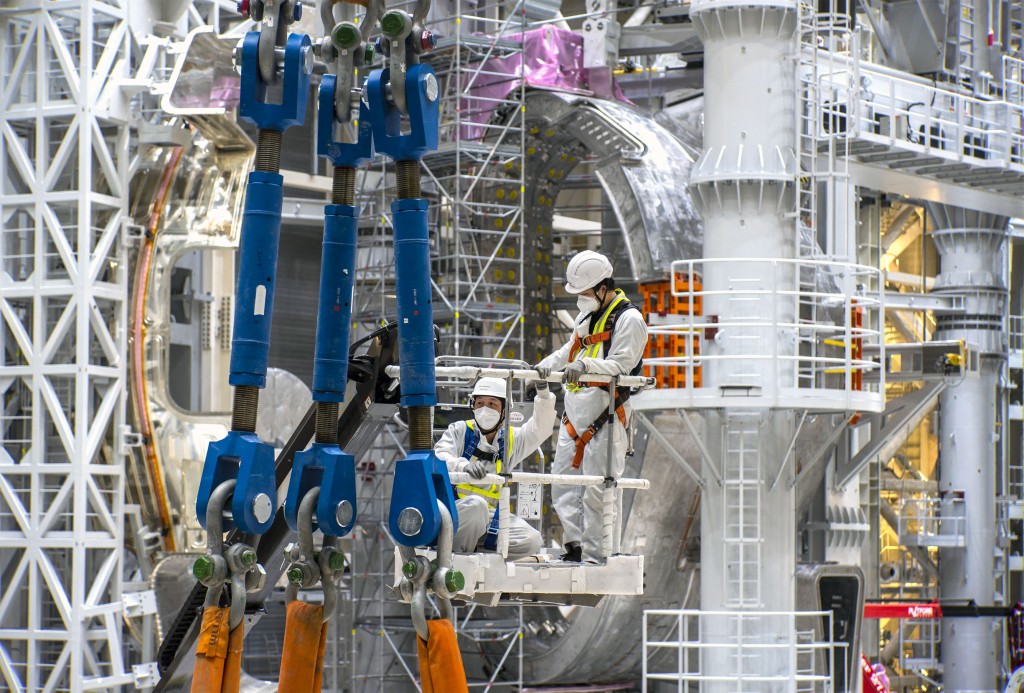
Tasks in the Assembly Hall
2022-02-10 - The two main machine assembly contractors (CNPE and DYNAMIC) have learned to share tooling and common services in an efficient manner as they execute work packages under the oversight of ITER Organization and MOMENTUM (Construction Management-as-Agent) teams.

A simple table
2022-02-10 - Equipment and tests will be performed on this simple ''table'' before the module is moved over to the assembly platform, visible on the right side of the image.

Sector alley
2022-02-10 - Against the backdrop of vacuum vessel sector assembly, CNPE* consortium members are preparing to move a 100-tonne central solenoid module. (China Nuclear Power Engineering = China Nuclear Industry 23 Construction Company Ltd.; Southwestern Institute of Physics; Institute of Plasma Physics, Chinese Academy of Sciences ASIPP; and Framatome).
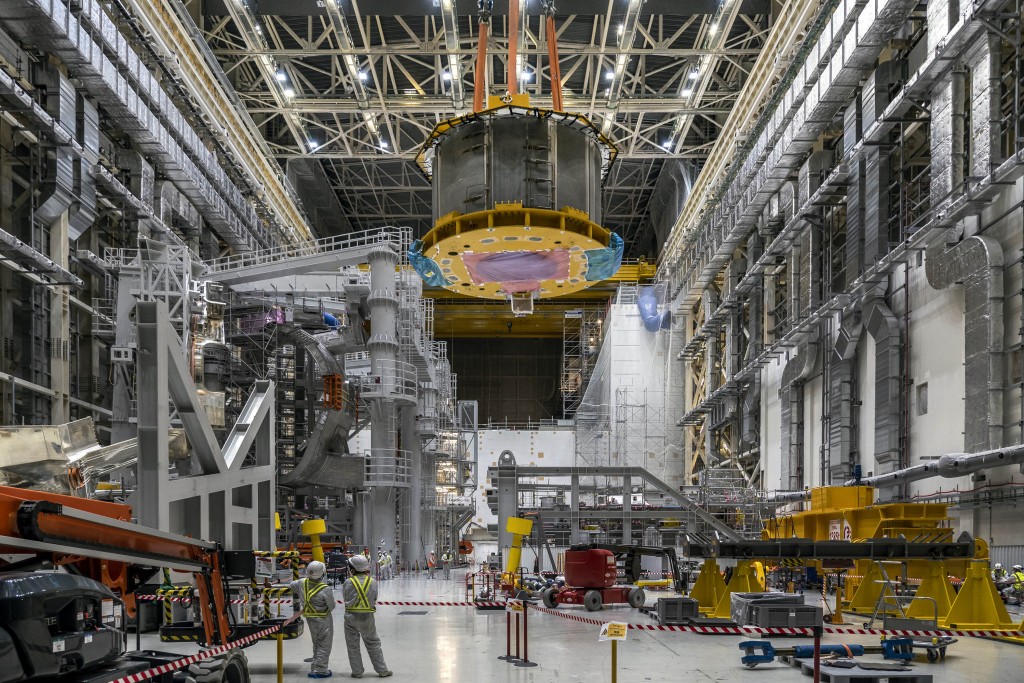
First central solenoid module aloft
2022-02-10 - A 110-tonne central solenoid module is moved to the far end of the Assembly Hall for tests on its instrumentation, sensors and superconducting joints.

Powerful ducts
2022-02-10 - Against the backdrop of the travelling module are ducts belonging to the Assembly Hall's powerful HVAC system. The Assembly Building will be operated as a clean space for the duration of machine assembly.

Careful adjustment
2022-02-10 - The workers in the cherry picker will adjust strap lengths, millimetre by millimetre, so that the 110-tonne central solenoid module will be perfectly balanced and the lift perfectly vertical.

Implementing every step of the process
2022-02-04 - Another commissioning task is testing the control software for the heat rejection system. Laura de Frutos Bolzoni (centre) is the engineer responsible for integrating the cooling water system with CODAC (ITER's central control system). Thomas Pralus (left) and Thierry Menguy (right) also work in the Operations Division with responsibility for cooling water commissioning.
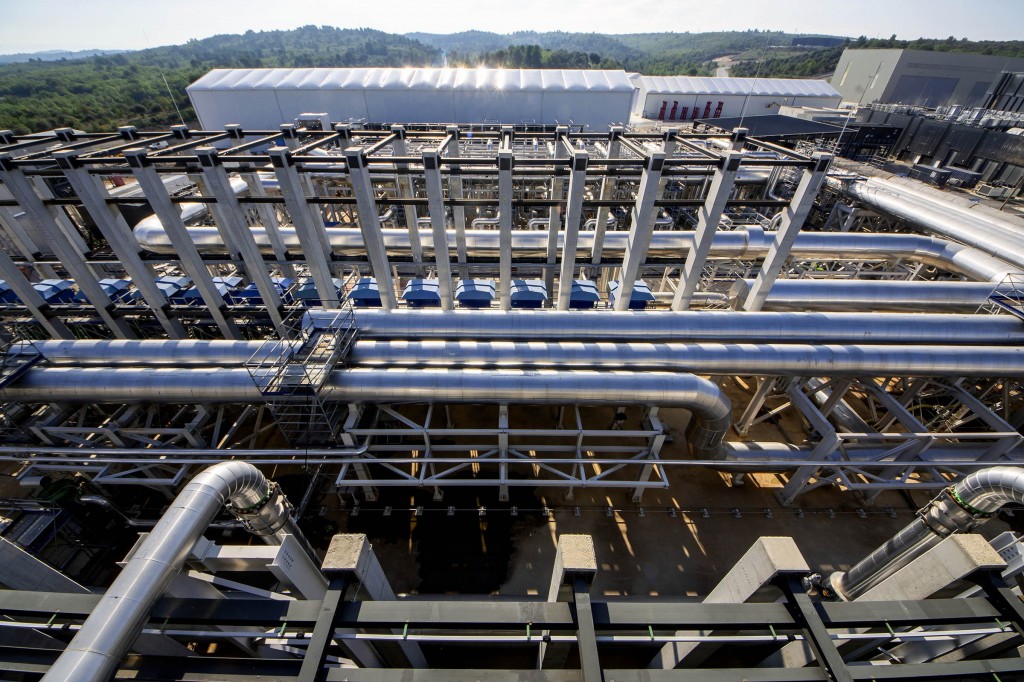
Step-by-step commissioning
2022-02-04 - One big remaining task for the team is testing the 10 cooling towers. A lot of cold commissioning has already been done there, including all the instrumentation of the cooling tower fans; the next step is to start the fans.
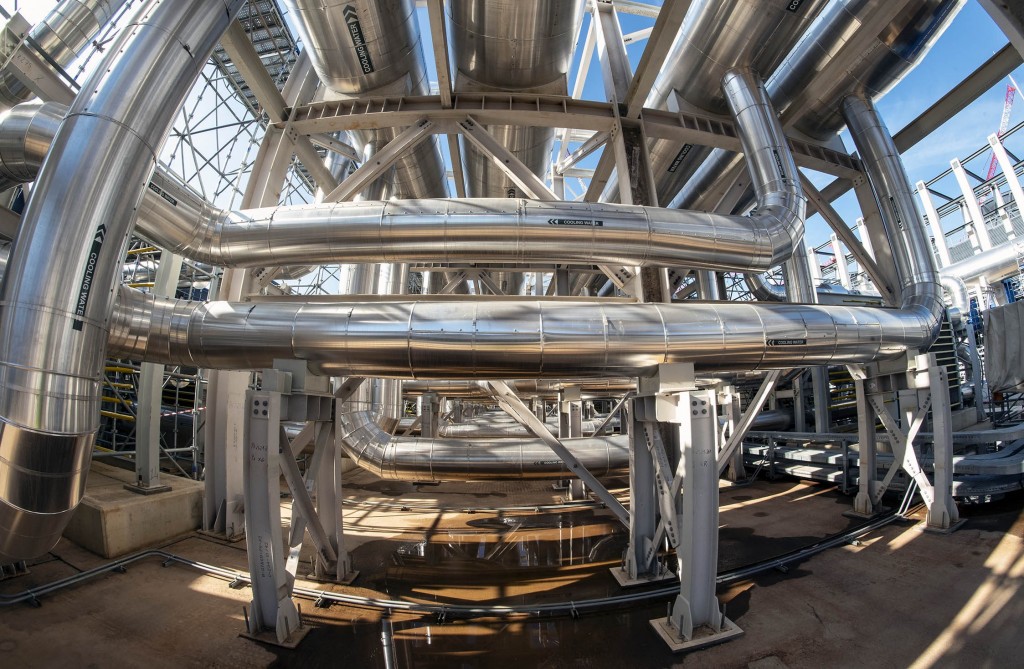
Commissioning the heat rejection system
2022-02-04 - Commissioning of the heat rejection system is well underway, clearing the path for all "client" systems. The team started by performing loop checks, testing of input/output signals, starting up motors and pumps, and circulating water through the basins.

Keeping track of all parts
2022-02-03 - This small part, an elbow joint, must be manufactured, inspected, transported, received in an ITER warehouse, inspected again, logged into the system and finally stored before the time comes for it to be integrated into the ITER machine. ITER's Integrated Material & Logistics Management Group is currently managing the storage of 1.5 million parts and components.

ITER's largest warehouse
2022-02-03 - The main ITER warehouse on site, where components are stored according to specific requirements such as temperature and humidity control. On average, four or five shipments arrive at the main warehouse each day.

Calling down
2022-02-03 - Work is underway on the second vacuum vessel sub-assembly, with technicians at every level.

Joining conductor "terminations"
2022-01-20 - Conductor lengths have to be joined at their ends. In this photo, the European teams are preparing a termination "joggle" by bending the conductor to align with another conductor end.

Spool after spool
2022-01-20 - Fifty-six spools, each weighing 16 tonnes and containing 900 metres of jacketed superconducting cable, have already been used in the onsite manufacturing of the ITER poloidal field coils.

Final double pancakes for PF3
2022-01-20 - This is a double pancake for poloidal field coil #3, the last one of four to be manufactured in this on-site European winding facility. It is 24 metres in diameter.
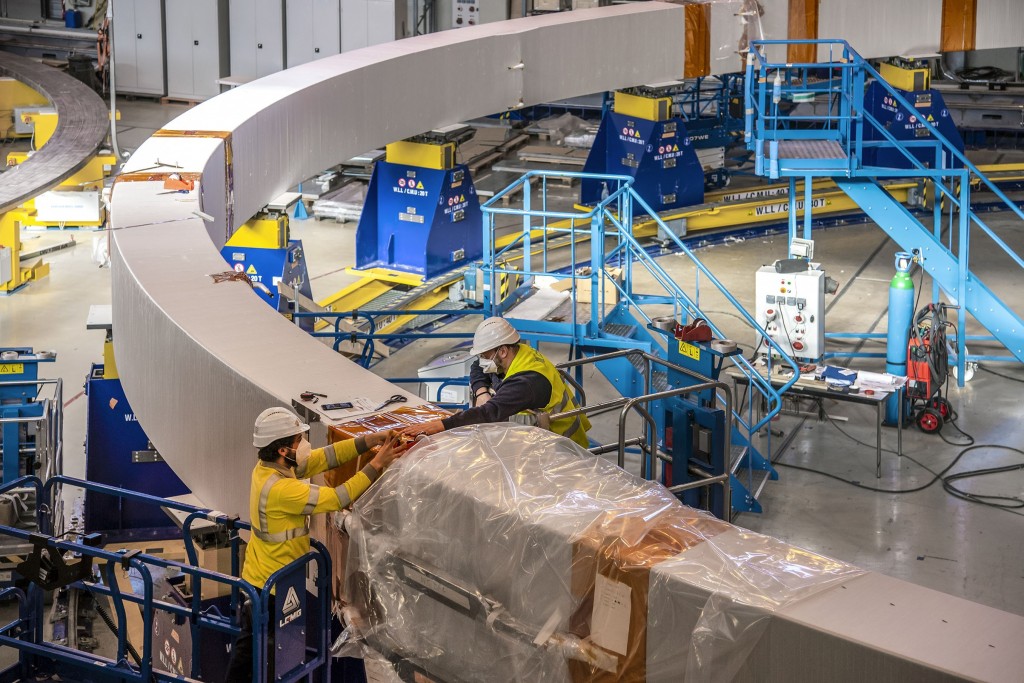
Manual wrapping, nine layers
2022-01-20 - Prior to final resin impregnation, coils are manually wrapped with nine successive layers of glass-Kapton tape that provide efficient electrical insulation. (In the photo is coil PF4.)
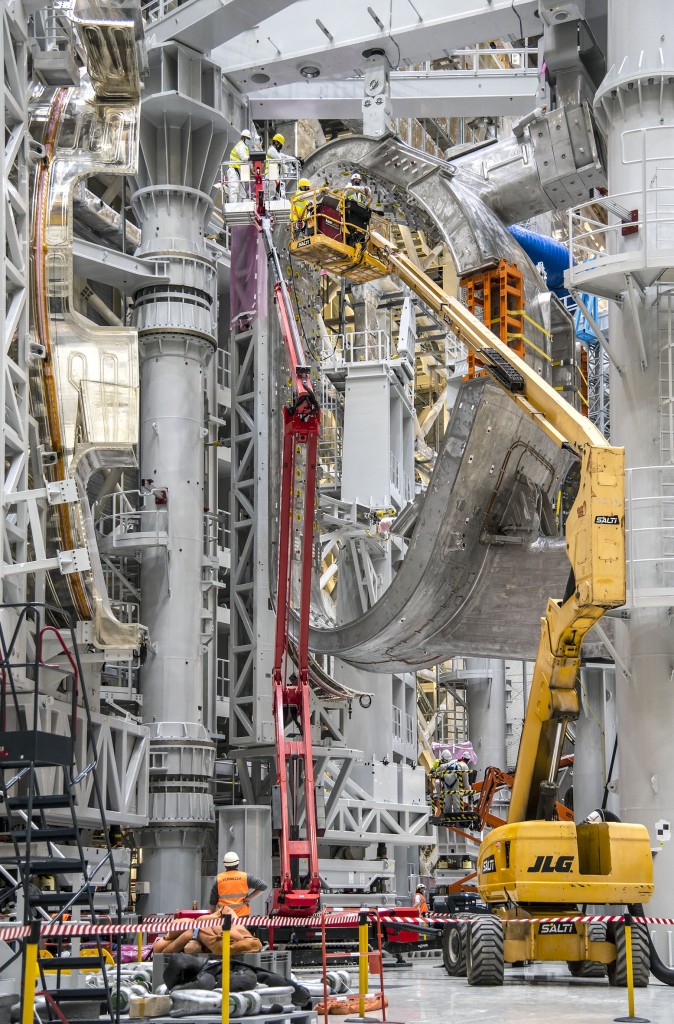
Working at height
2022-01-19 - Scaffolding surrounds the docked sector to give access to every level of the giant component. Still, a bucket truck can be useful ...
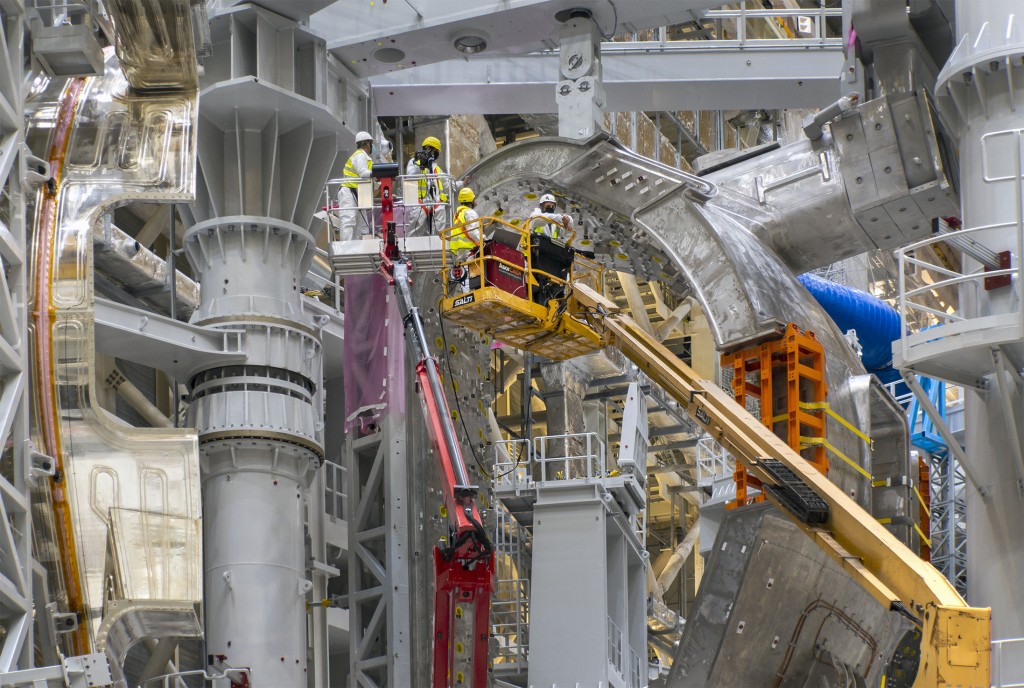
Working on a 2nd sub-assembly
2022-01-19 - The teams are working on the second vacuum vessel sub-assembly. In this tool we see sector #1(which will be placed next to sector #6 in the pit in position 7) and an outboard thermal shield panel on the left. The thermal shield will be rotated toward the vacuum vessel sector and attached in place.
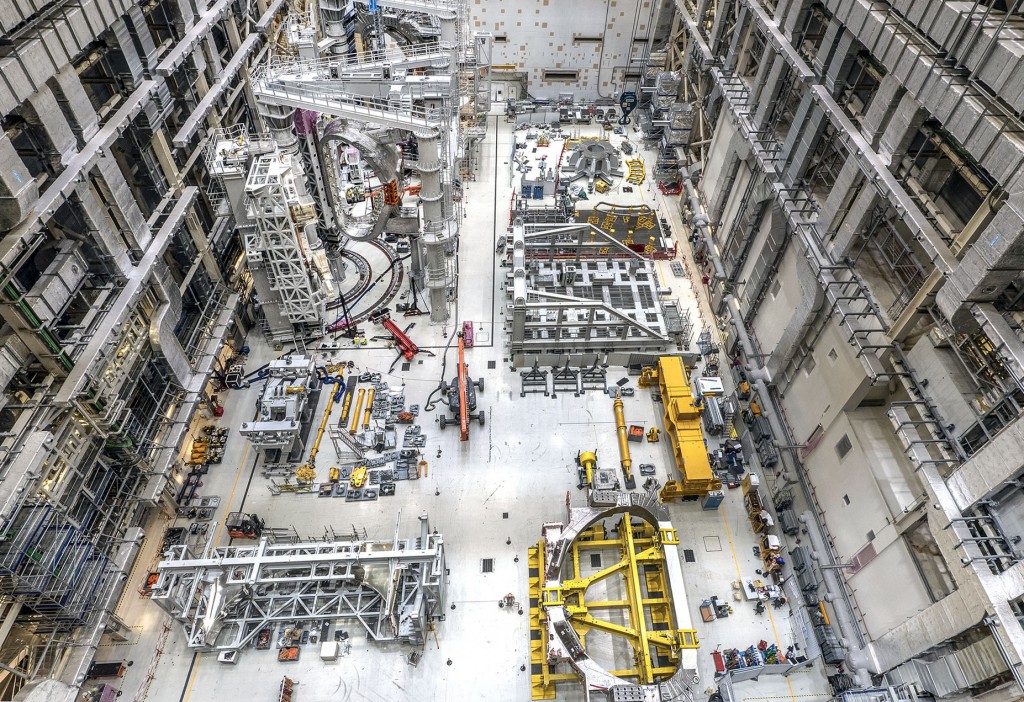
Pieces all aligned
2022-01-17 - Like Erector set or Meccano parts, components and tools for ITER machine assembly cover the floor of the vast hall that serves as an antechamber to the Tokamak pit.

Adjusting a correction coil
2022-01-05 - Workers from the CNPE Consortium are seen here carrying out metrology measurements at the bottom of the Tokamak pit, adjusting a kidney-shaped bottom correction coil on its yellow temporary supports. Final positioning will be possible only when all vacuum vessel modules are in place.

Focused
2022-01-03 - A metrology instrument has been fixed to a port cell (right), with its camera trained on the centre of the assembly pit. During the assembly phase and beyond, metrology processes ensure that the machine and its supporting systems are dimensionally compliant.

Second sector assembly underway
2022-01-03 - A second 440-tonne vacuum vessel sector, #1(7), is positioned vertically in the tooling for sub-assembly with other major components (a pair of vertical coils and thermal shield panels). Far to the right, the first completed sub-assembly (around sector #6) waits for transfer this month into the Tokamak pit.

New laboratory building on site
2022-01-03 - This 700 m² facility will be equipped for vacuum and tritium laboratory activities, including the assembly and testing of delivered components, performance trials, welding and grinding and maintenance. It was erected in just one year.

2 sectors of 9
2022-01-03 - One sub-assembly is ready (far end), another is in the early stages. A third vacuum vessel sector sub-assembly will be built around Korean sector #8, which will leave Hyundai Heavy Industries later this month. Nine sectors in all will form the ITER machine torus (4 from Korea and 5 from Europe).
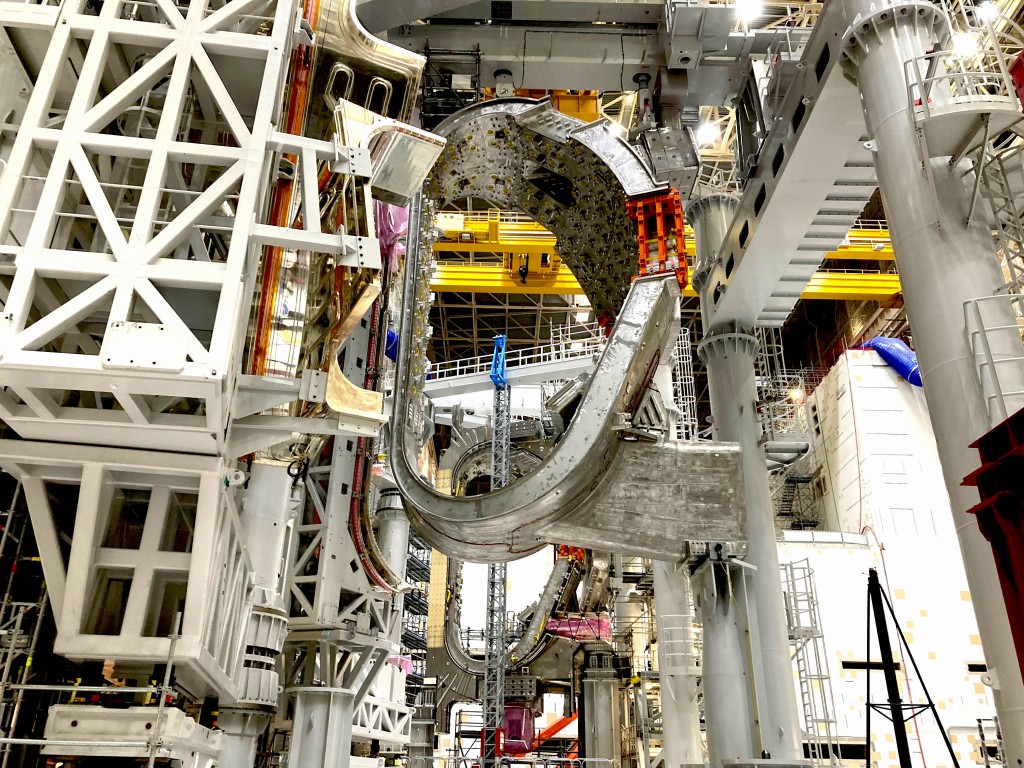
Two tools in a row
2021-12-21 - In December, for the first time, each sector-sub assembly tool (SSAT) had its own vacuum vessel sector...
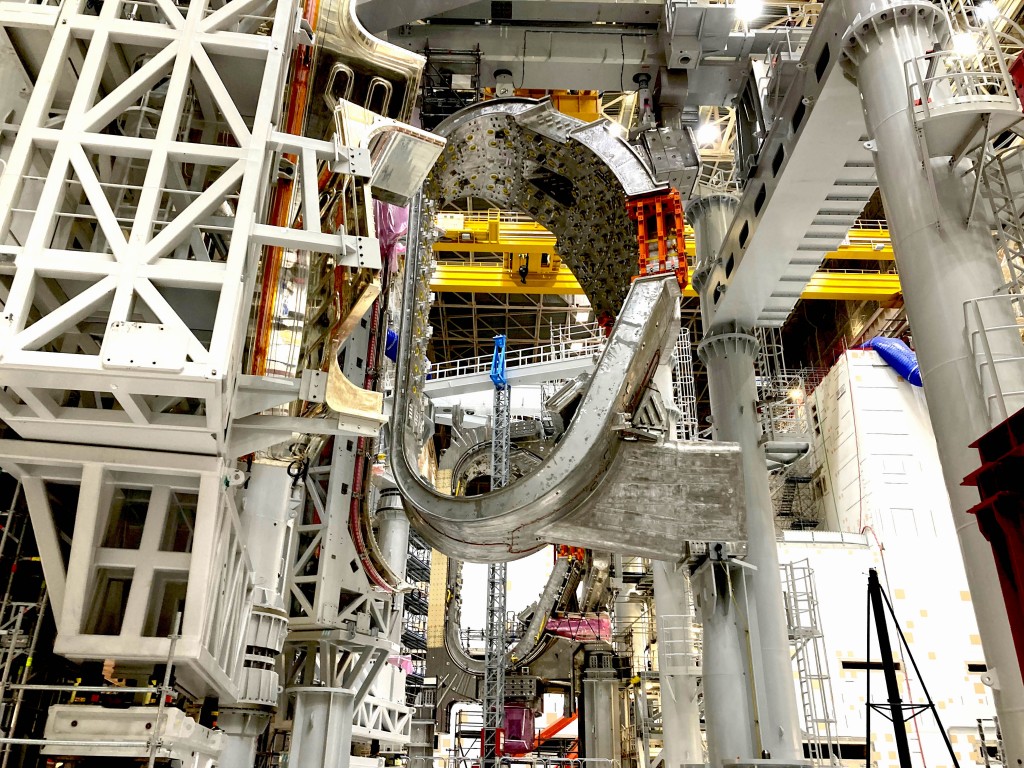
Assembly row
2021-12-21 - TWO vacuum vessels sectors are docked in Assembly Hall tooling. One has completed the pre-assembly sequence (far end); the other is at the start. Two identical sub-assembly tools were planned to keep this critical stage of machine assembly moving.
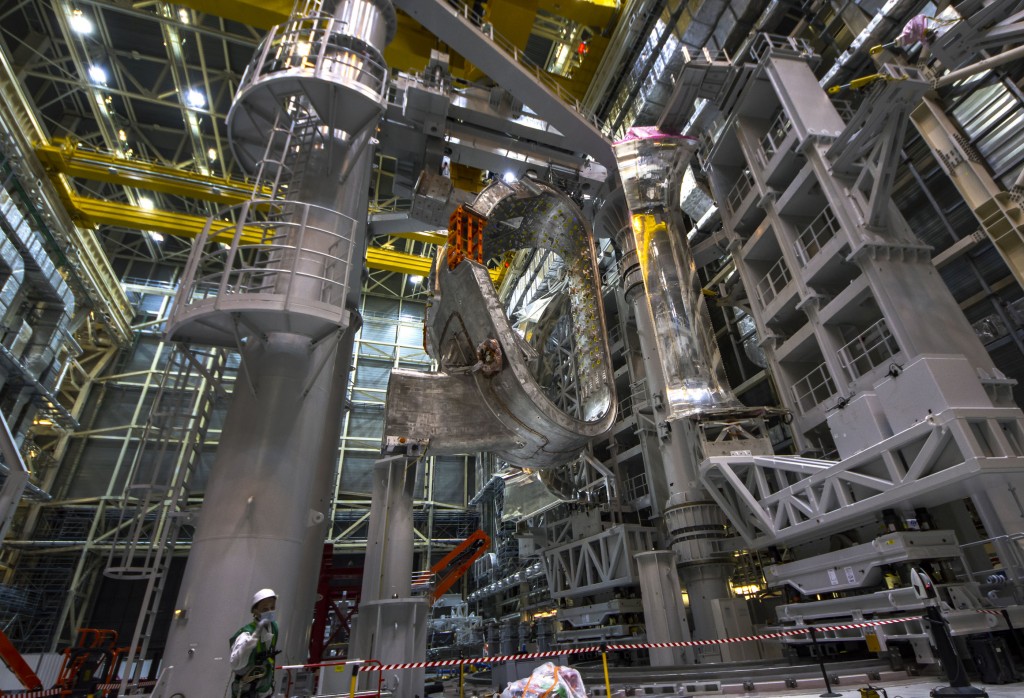
Second sector docked
2021-12-20 - Sector #1(7) has been docked in the sub-assembly tool SSAT1. Work begins now to pair the sector with approximately 880 tonnes of additional components (two magnet coils and thermal shielding), creating a perfect 40-degree section of the ITER torus.
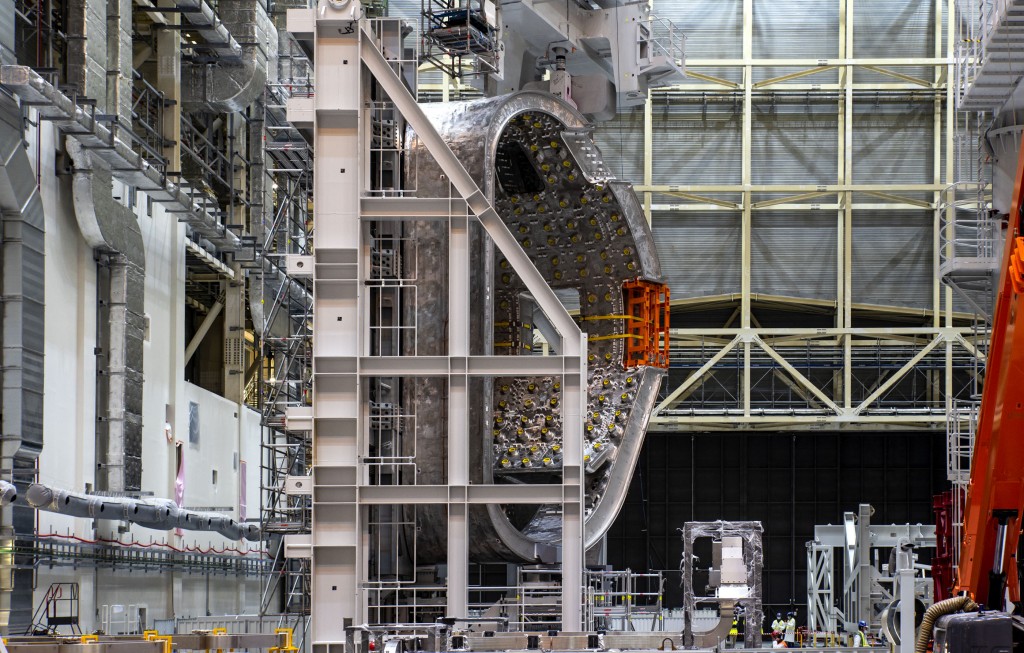
Transfer day
2021-12-20 - On 20 December 2021, the second vacuum vessel sector to arrive from Korea (called #1(7)) is lifted out of the upending tool and into the standing assembly tooling.
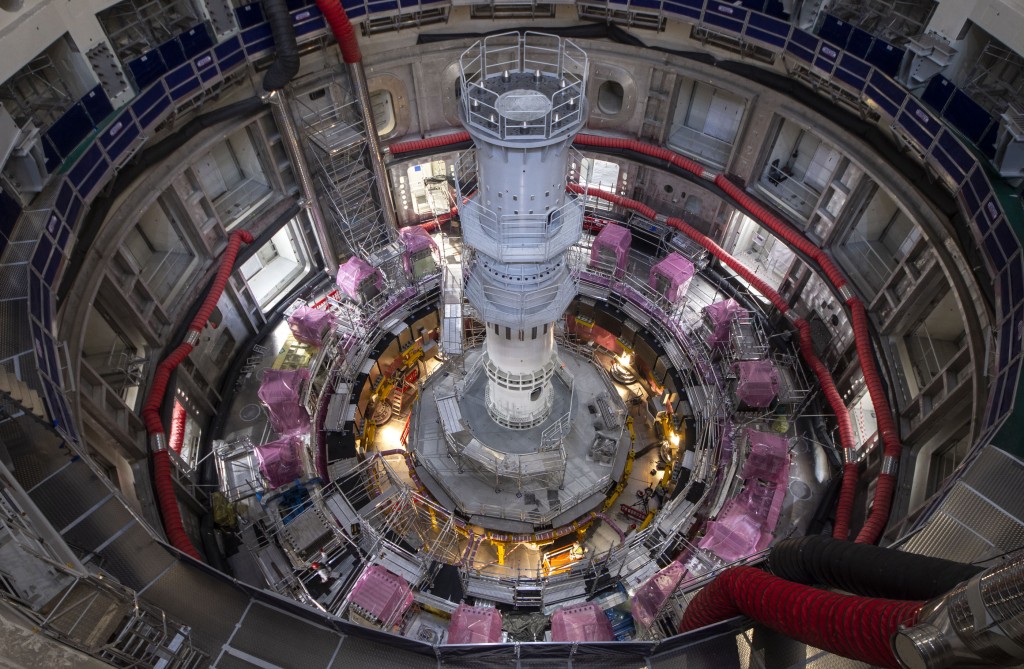
The well-named column tool
2021-12-20 - The central column of the in-pit column tool is in place. The nine radial beams will arrive next, each one designed to support a vacuum vessel sub-assembly by sharing the weight of the load between the central column and the concrete wall of the pit.

Up and into the SSAT tool
2021-12-20 - A vacuum vessel sector is slowly lowered into a sector sub-assembly tool (SSAT #1). Two identical tools allow the assembly team to go twice as fast.
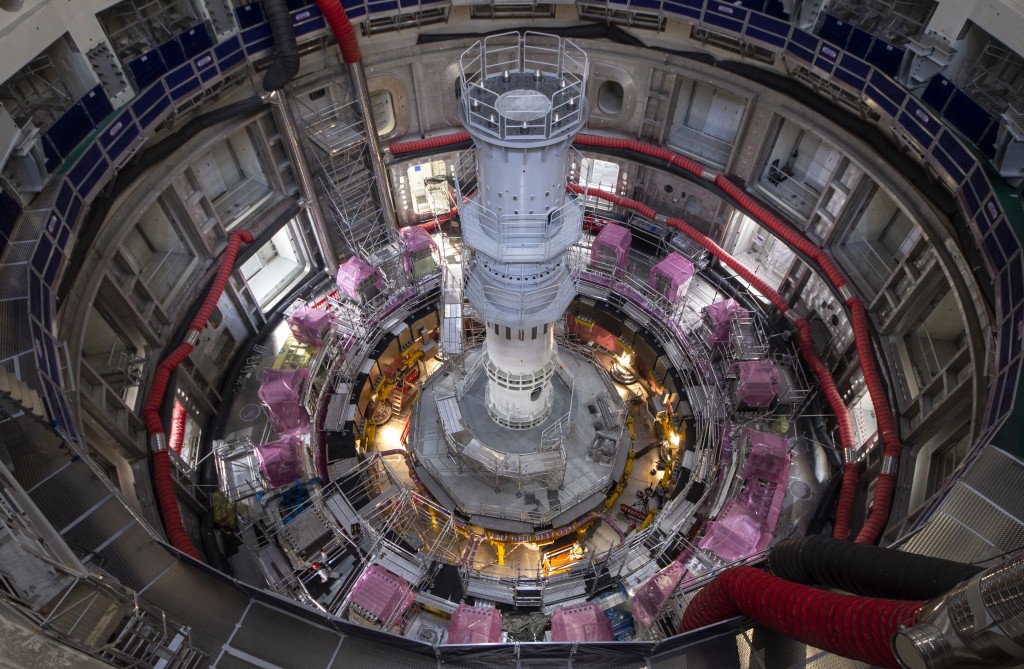
Pit is ready
2021-12-20 - The 30-metre-deep Tokamak pit is ready to receive its first 40-degree vacuum vessel section. As the sections begin to fill up the space the hollow central column, equipped with ladders and access ports, will be used to reach different levels of the emerging torus.
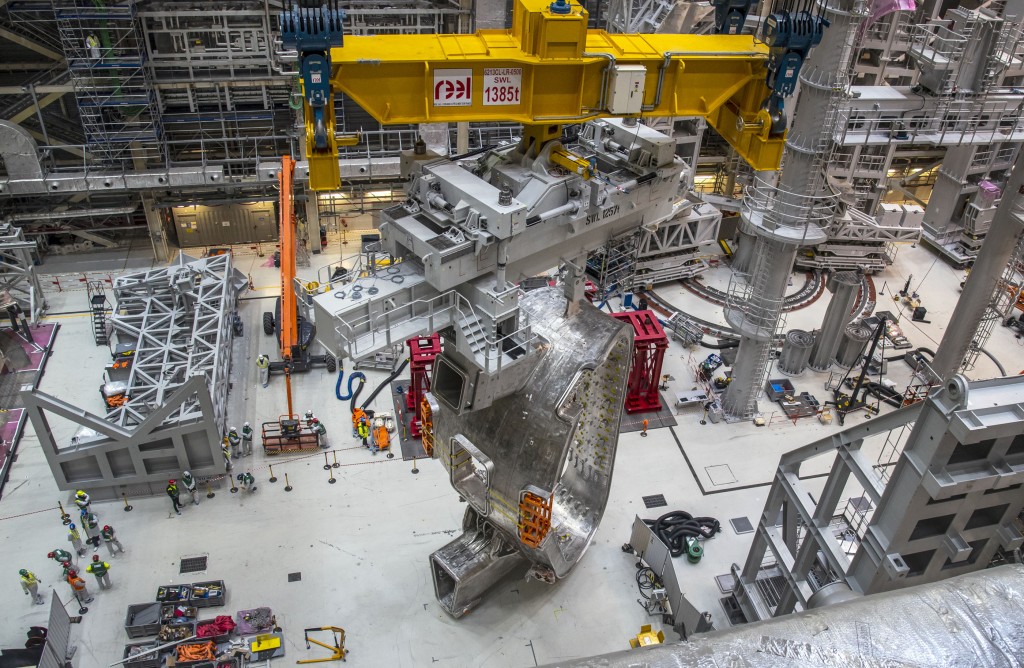
Complex rigging
2021-12-20 - The rigging for a vacuum vessel sector (440 tonnes) is particularly complex. For more information, see this article: https://www.iter.org/newsline/-/3592
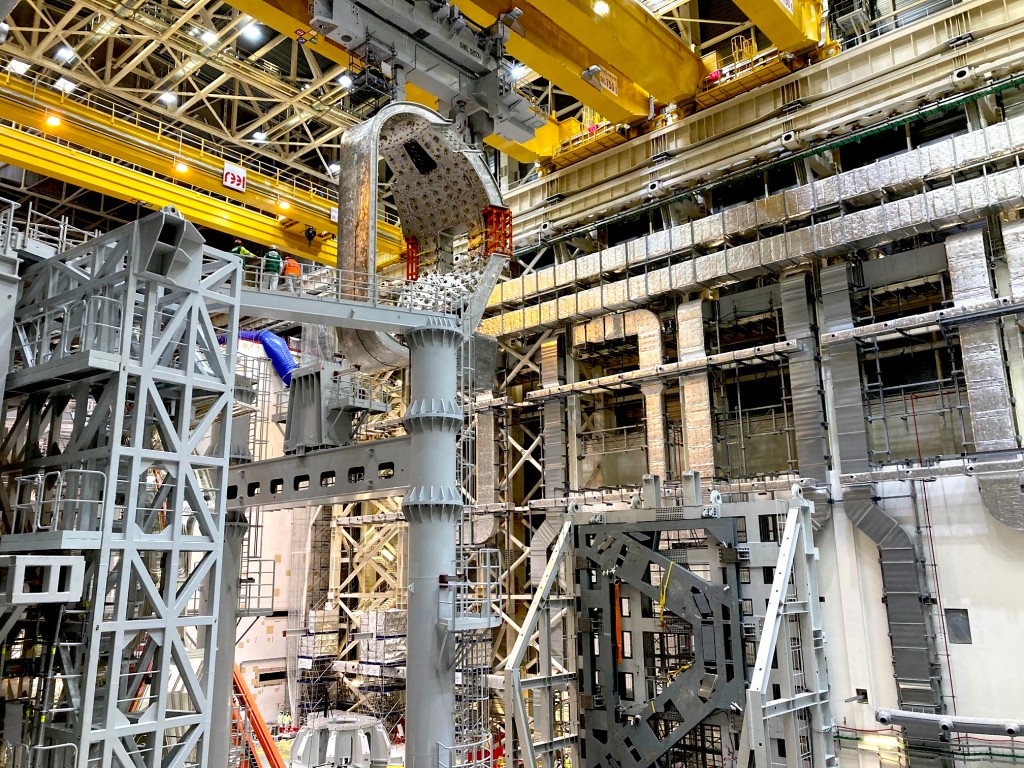
Strong back
2021-12-20 - The standing sub-assembly tool will support the weight of the 440-tonne component for several months, as thermal shielding and two toroidal field coils are attached.
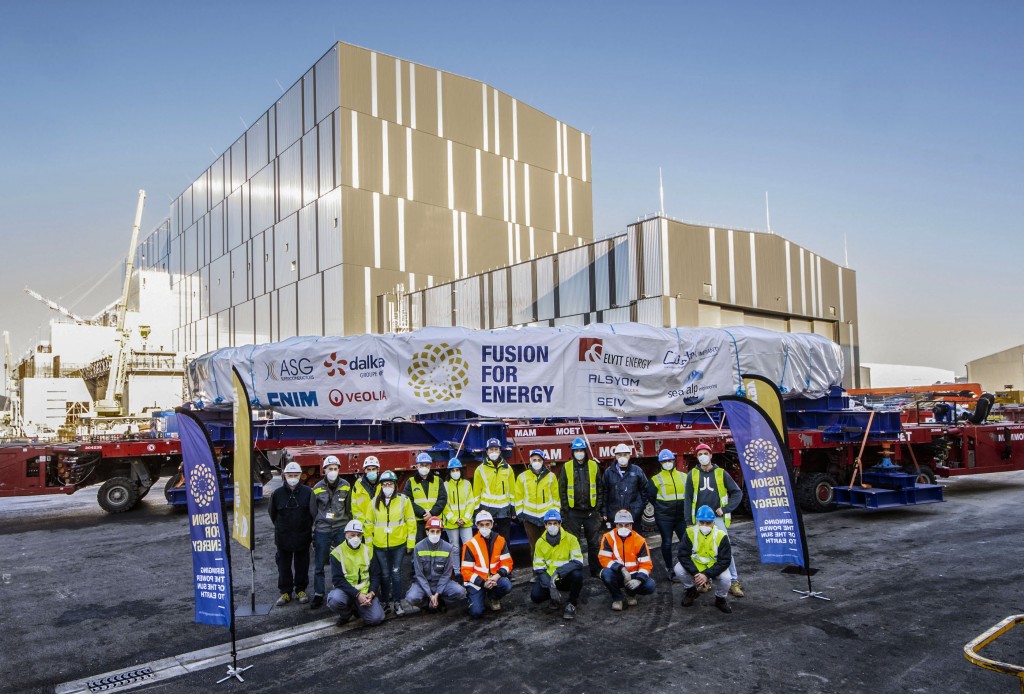
Another ring magnet delivered
2021-12-17 - Poloidal field coil #2 is removed from the winding facility after its completion and moved into storage. PF2 is the second ring magnet to be produced by the European Domestic Agency on site.
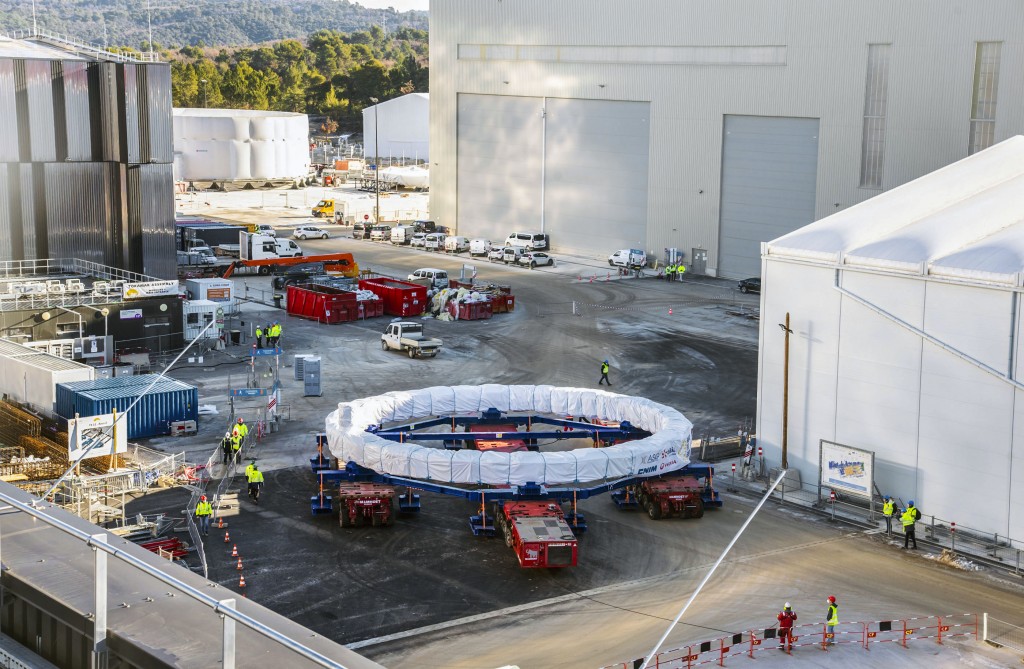
Making way for others
2021-12-17 - Poloidal field coil #2 (PF2) is moved into storage to make way for the assembly of two other ring coils, PF4 and PF3. Both are in production now.
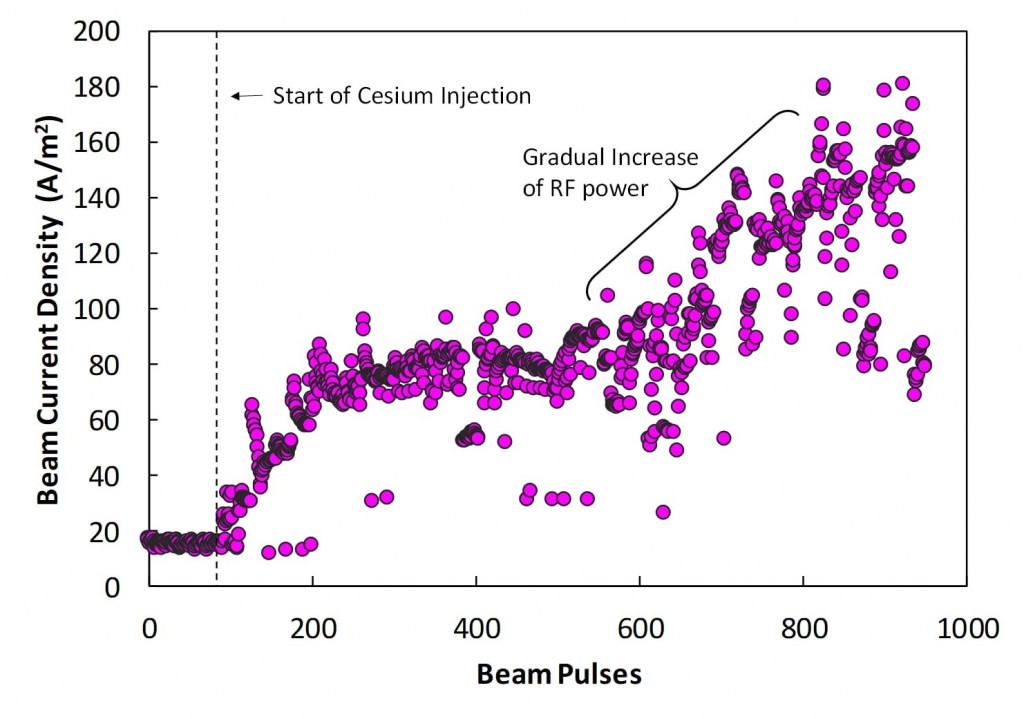
Testing operation in cesium
2021-12-15 - One of the highlights of SPIDER's first campaign was operation in cesium. (Cesium is used as a catalyst to get negative ions out of hydrogen using a technique that has been known for years but never tested on a large-scale ion source.) Experiments demonstrated that cesium injection was effective, even with reduced source power.)
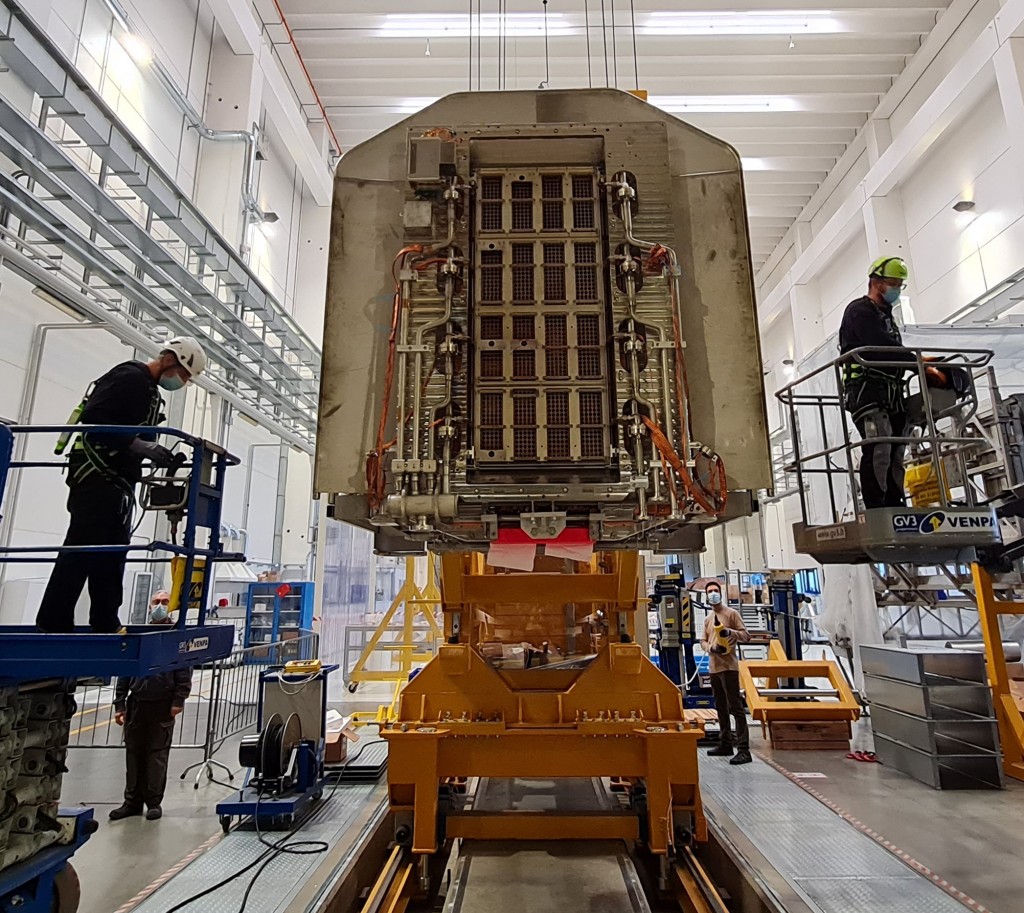
One-year engineering shutdown for SPIDER
2021-12-15 - The SPIDER testbed is now entering an engineering upgrade phase. During a one-year shutdown, improved diagnostics and other upgrades will be installed to allow for future testing at full intensity and for the required duration—1000 seconds for hydrogen, and one hour for deuterium.

Maintenance period begins for SPIDER
2021-12-15 - The SPIDER ion source is removed in December 2021 from the vacuum vessel and concrete bunker for engineering maintenance. Photo courtesy of Consorzio RFX
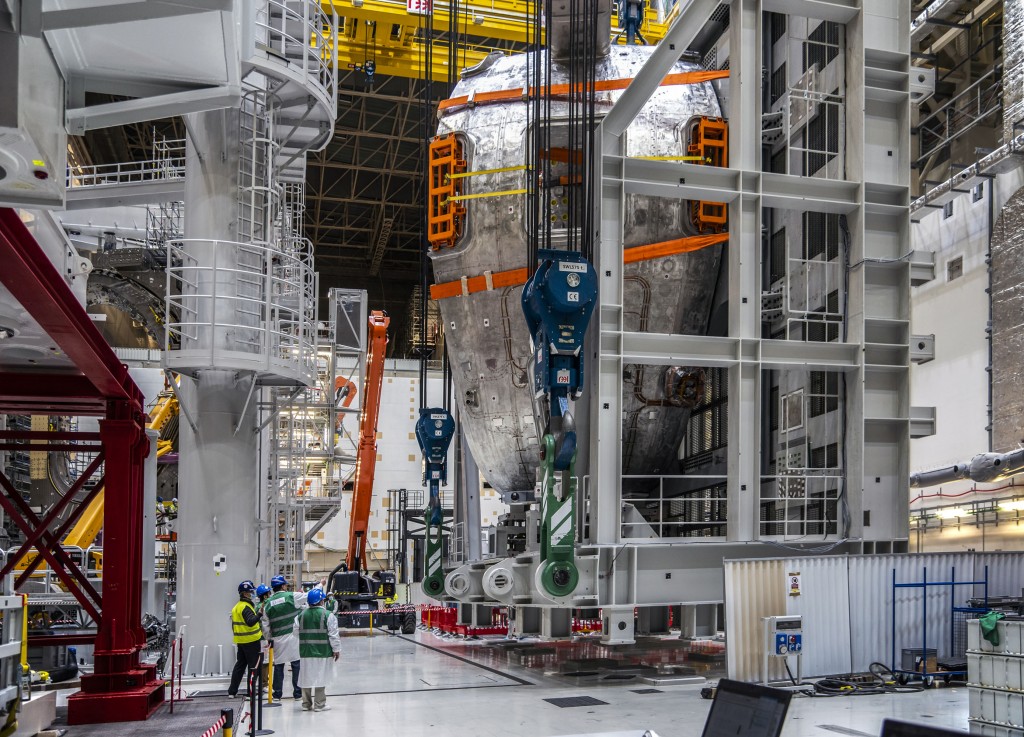
Lower slowly
2021-12-08 - Once vertical, the upending tool and its load are returned to the shop floor. The tool has been specifically designed to upend 9 vacuum vessel sectors and 18 toroidal field coils, or 27 lifts in all. This is number four.

One week later
2021-12-08 - One week later, the crane rigging is altered to bring the upending tool to vertical.

Horizontal to vertical
2021-12-08 - The upending tool raises ITER's heaviest components (vacuum vessel sectors and toroidal field coils) from horizontal to vertical. In this photo, it is sector #1(7) from Korea.
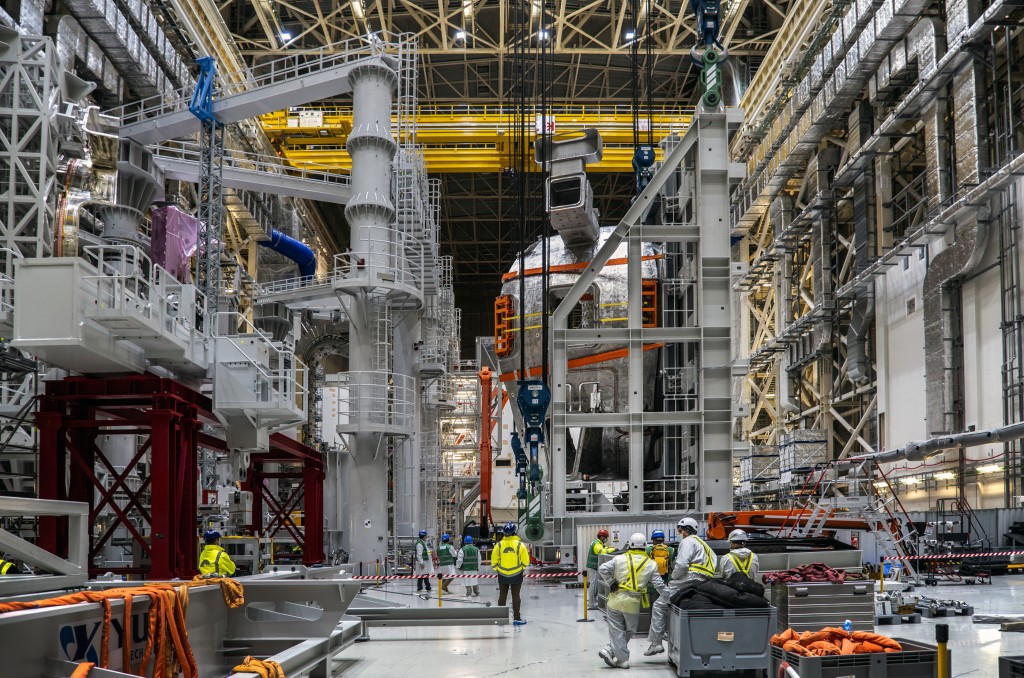
Next?
2021-12-08 - Next up: the sector will be lifted out of the tool, rotated, and installed on the assembly tool we see at left.
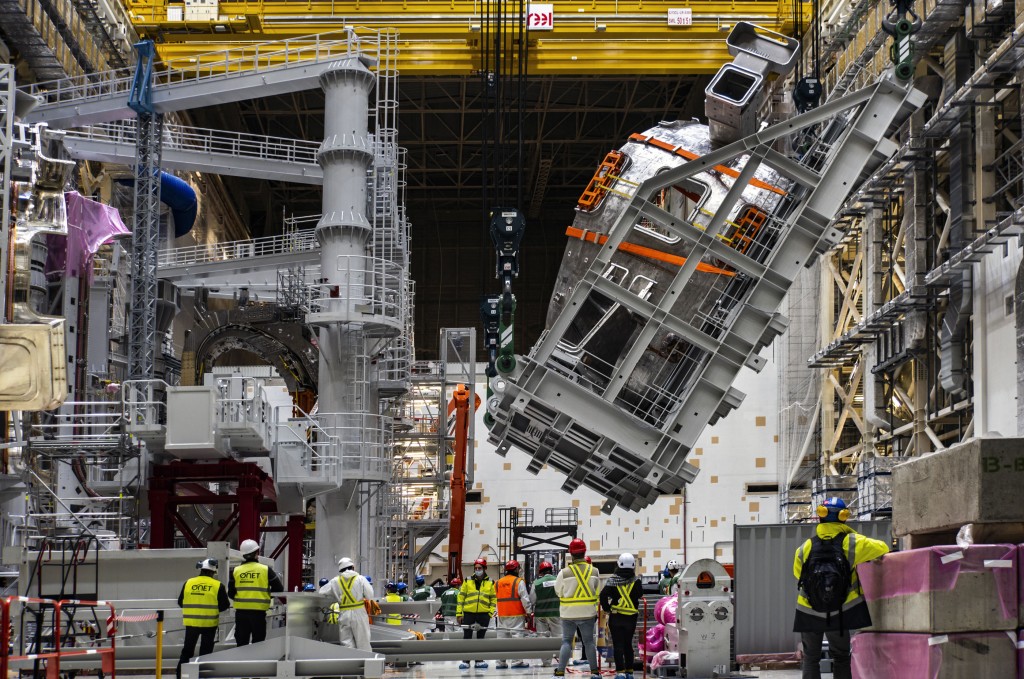
Hefty
2021-12-08 - The tool weighs 250 tonnes itself. Adding the vacuum vessel sector and rigging, that's nearly 700 tonnes under the cranes.
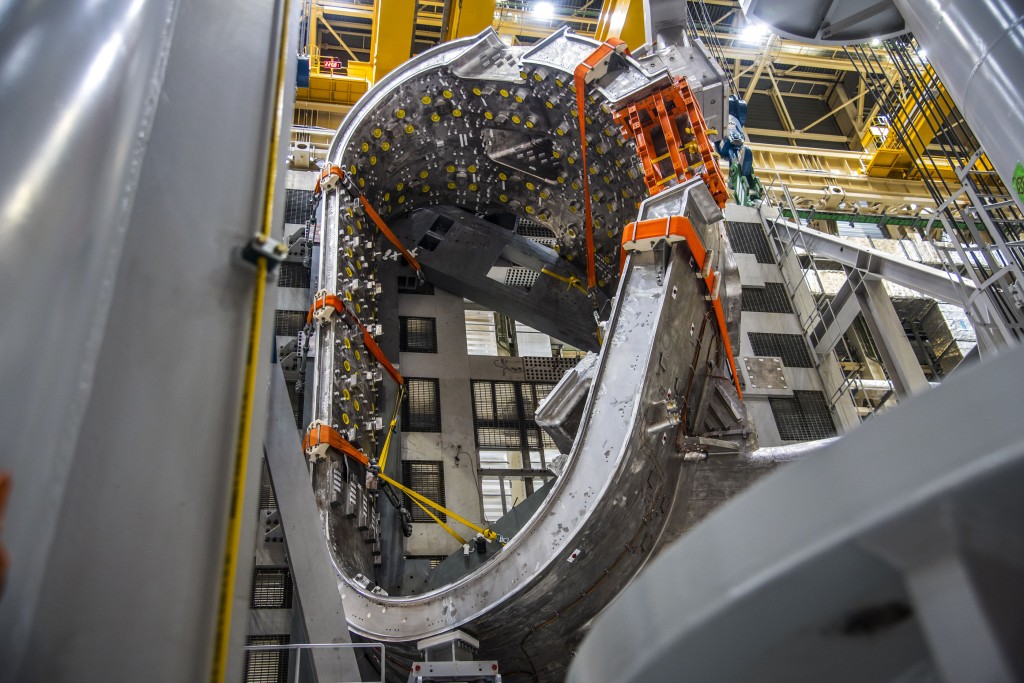
Hold tight
2021-12-08 - The component is lashed tightly so that it doesn't budge an inch during the upending operation.
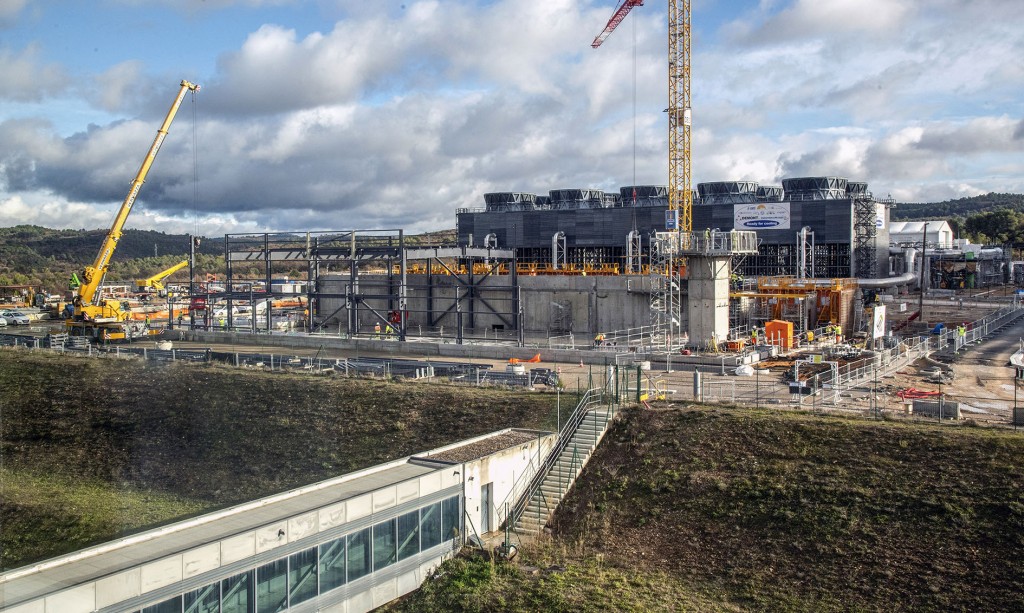
Control Building: 24-hour presence
2021-12-08 - The Control Building, going up now on the ITER site, will be the daily work environment for the operators, researchers, and engineers running ITER physics experiments or the routine 24-hour operation and control functions of the machine and plant.
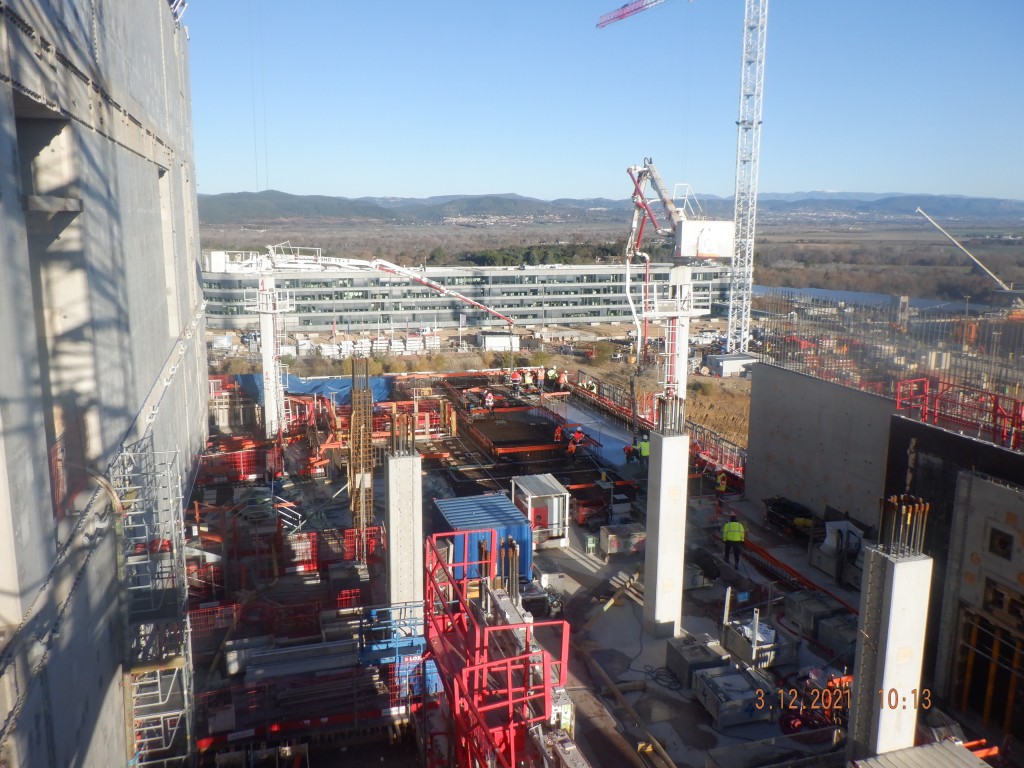
Rising
2021-12-03 - The exterior walls of the Tritium Building (level L3) are rising. Two other levels will follow: L4 and L5.
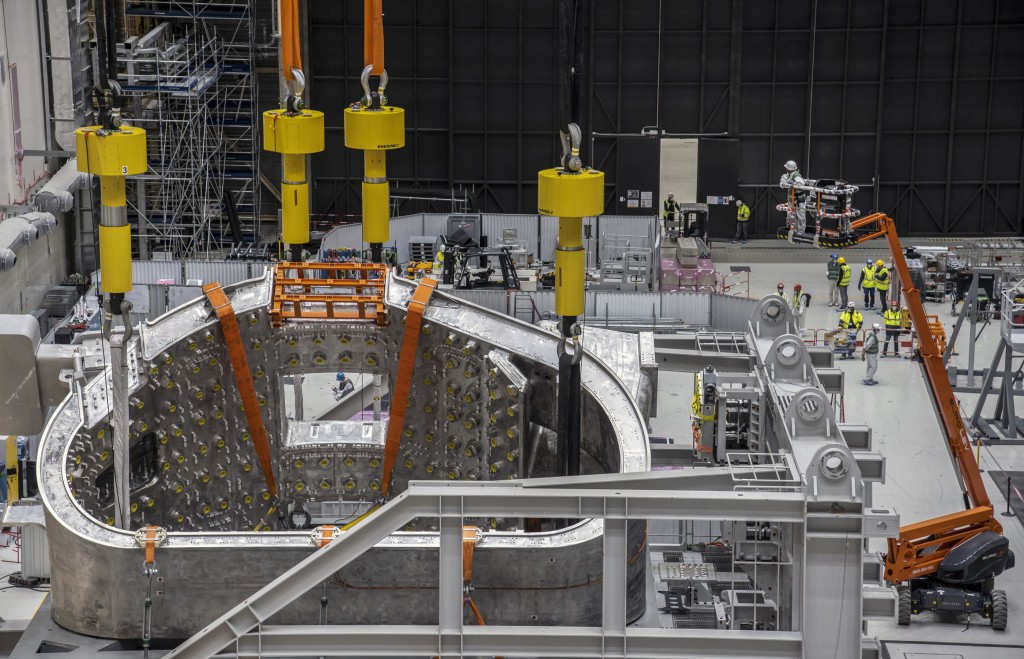
Fine tuning
2021-12-02 - The vacuum vessel sector is now inside the upending tool. Fine-tuning of the lifting system was performed by four hydraulic ''sync hoists'' attached to a pair of load-balancing beams suspended to the crane hooks.
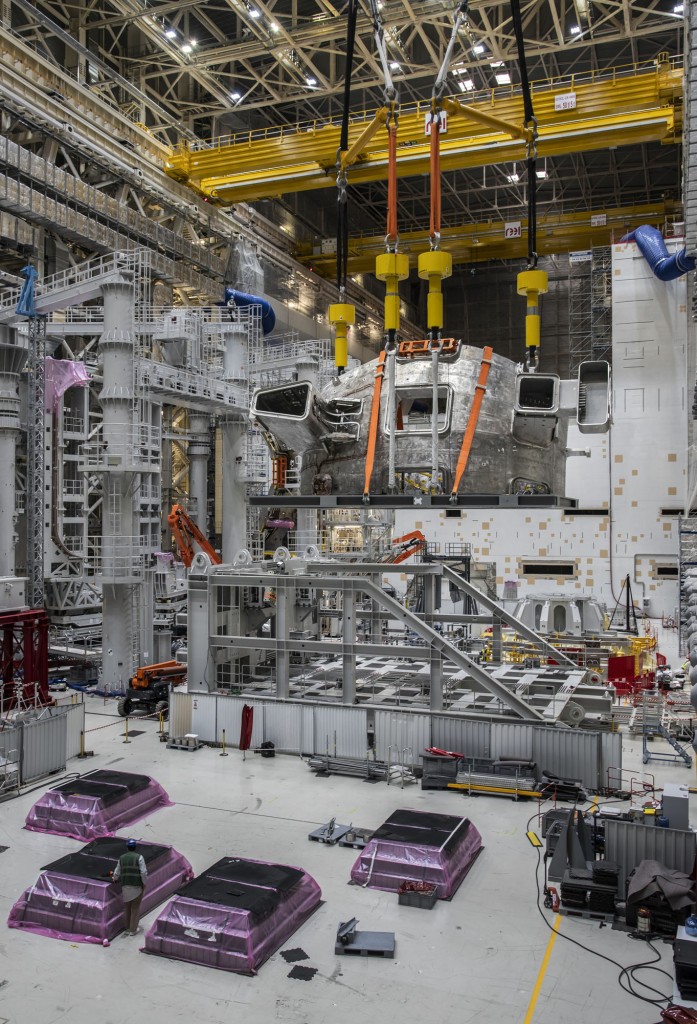
Into its cradle
2021-12-02 - The 440-tonne sector, securely strapped to its staging platform, is lowered into the upending tool. Next week, it will be raised to vertical.
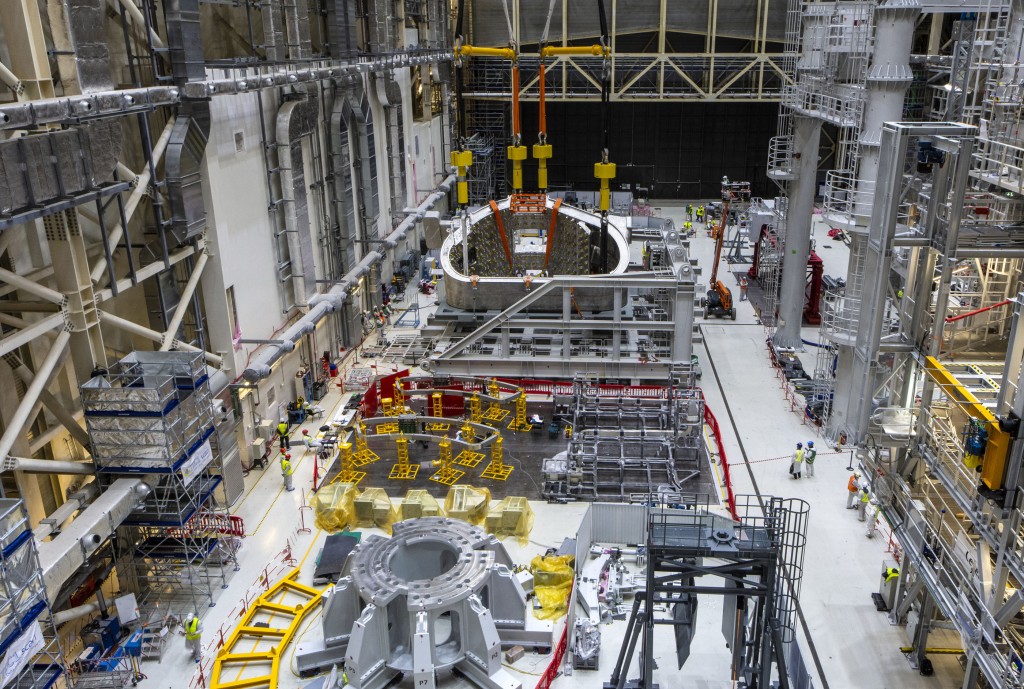
A busy hall
2021-12-02 - On the far end, sector #1(7) is inserted into the upending tool, right across from the tall sector sub-assembly tool that is its next destination. In the middle, two bottom correction coils are prepped for installation in the Tokamak pit. In the foreground, the central solenoid assembly platform is ready for the first module.
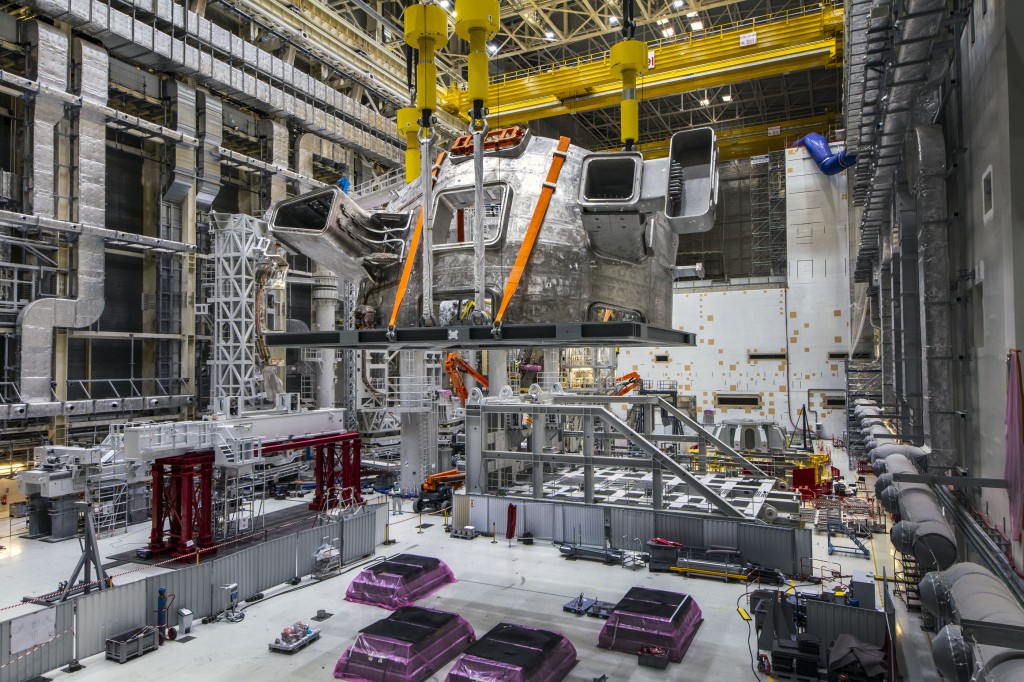
Second sector on the move
2021-12-02 - Vacuum vessel sector #1(7) is on the move. On Thursday 2 December it was lifted into the upending tool. See the full story in the ITER Newsline on 6 December.

Neutraliser
2021-11-29 - On the right is the neutraliser panel—one of the MITICA beam line components under construction for the European Domestic Agency at AVS, Spain.
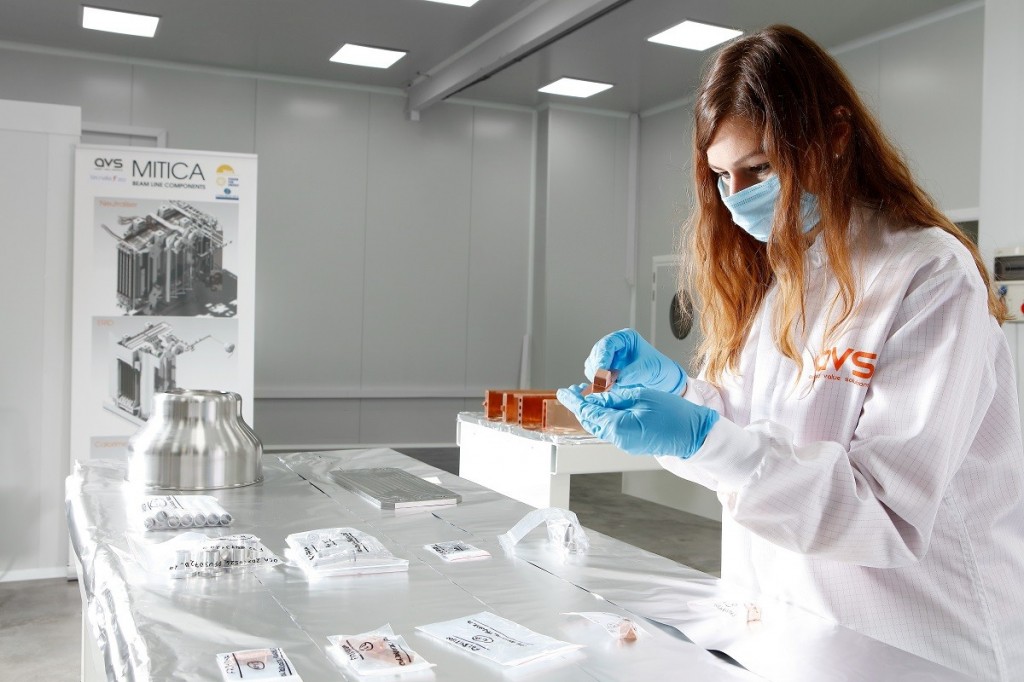
Building a beam line in Europe
2021-11-29 - Following a conclusive manufacturing readiness review, European contractor AVS—Tecnalia (Spain) is proceeding with the manufacturing of the beam line components for MITICA—the full-size prototype of the 1 MV heating neutral beam injectors at ITER. See more at https://www.iter.org/construction/NBTF.

MITICA calorimeter tubes in fabrication
2021-11-29 - Performing dimensional measurements on one of the 200 calorimeter tubes to be produced for MITICA. (AVS, Spain)
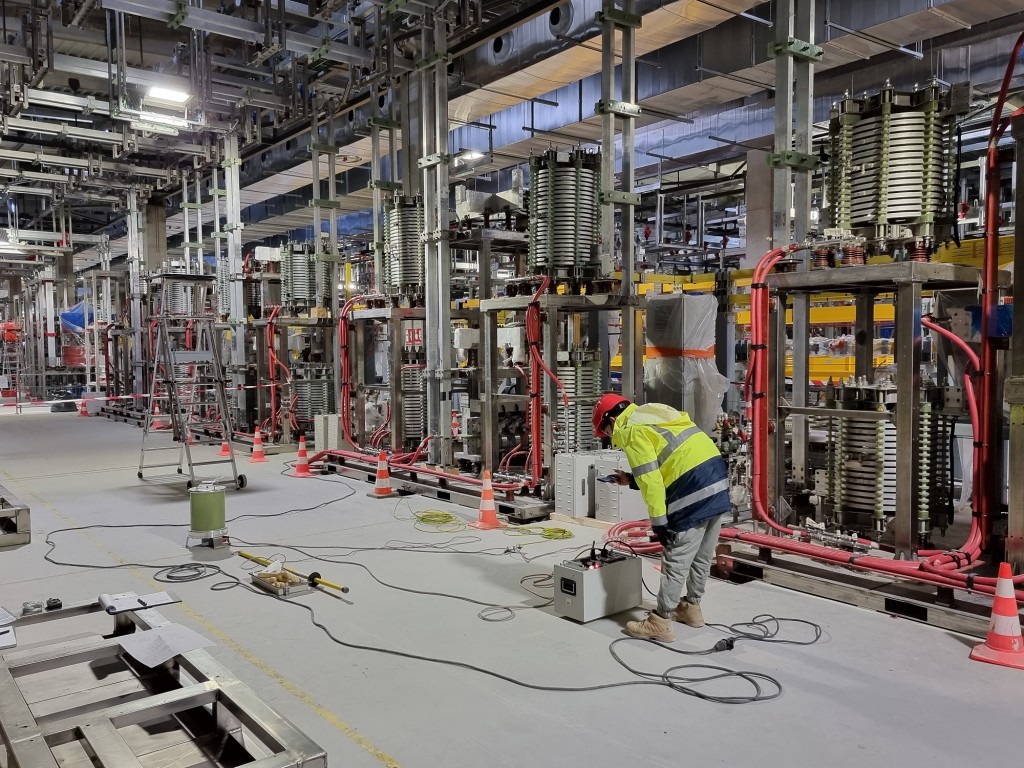
Converter tests
2021-11-26 - This Korean-built AC/DC converter is undergoing insultation voltage tests in one of the Magnet Power Conversion buildings.
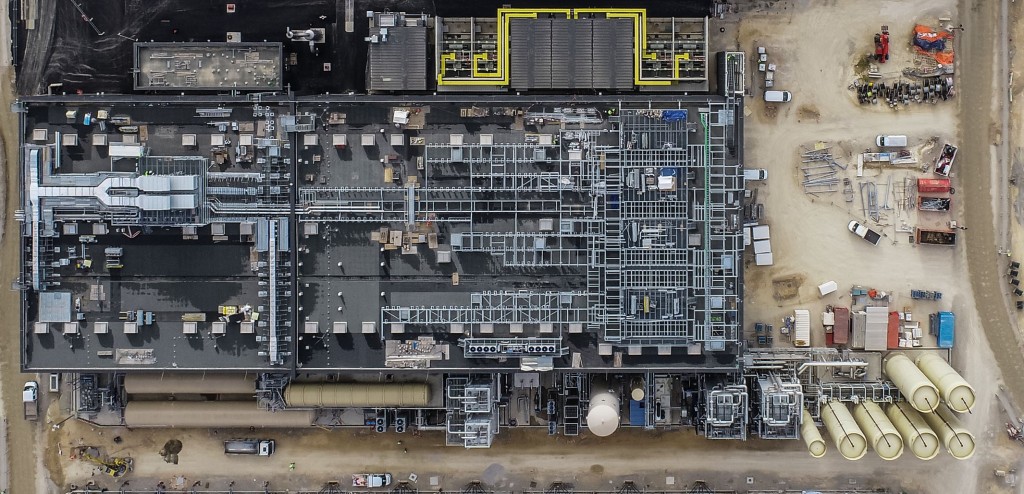
Cryoplant, from above
2021-11-25 - Despite being water cooled, the large power machines inside the cryoplant will dissipate considerable amounts of heat (on the order of 20 MW). HVAC ducts on the building's roof are tasked with extracting it. The yellow elements at the top of this drone photograph are busbars feeding electrical power to the installation.
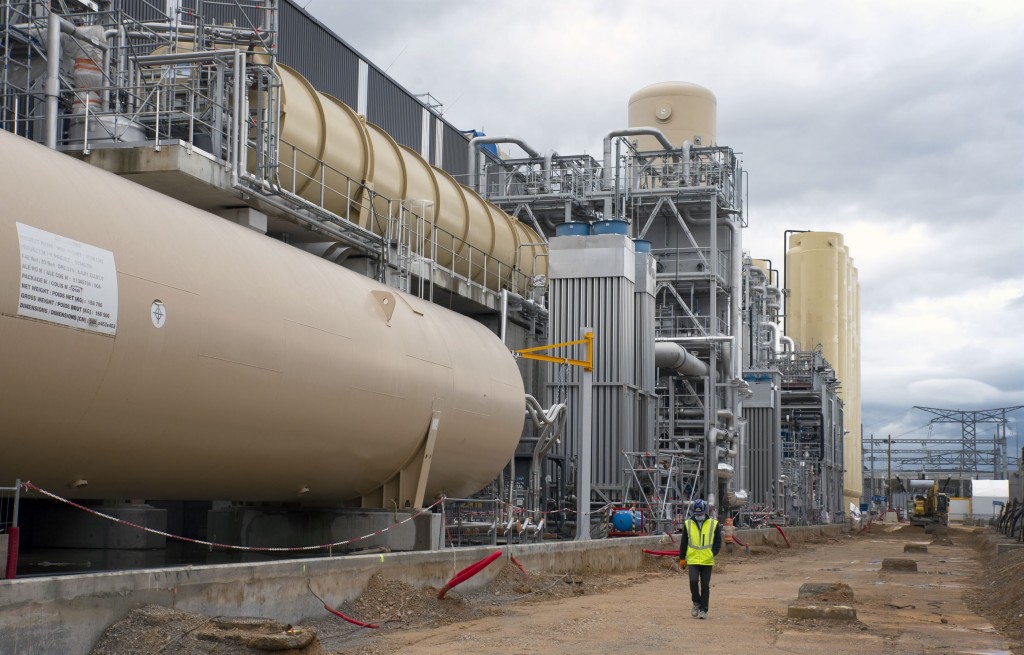
Tanks galore
2021-11-25 - Tanks line the exterior of the building. From left to right: one of two quench tanks; a 200,000-litre helium storage tank; atmospheric vaporizers; one out of two 80 K cold boxes (for the cooling of the cryostat shielding system); a vertical liquid nitrogen storage tank; and seven vertical tanks for nitrogen and helium storage.

Attention to detail
2021-11-25 - Ensuring the cleanliness of the equipment inside the installation is an integral part of the pre-commissioning process. Here, workers are busy dusting and cleaning pipes between one of the cryoplant's 18 screw compressors (foreground) and the 1 MW electrical motor that drives it.

Cryoplant: temporary control room
2021-11-25 - For the next two years, cryoplant commissioning operations and equipment testing will be managed from this temporary control room. At a later stage, cryoplant operation and monitoring will be moved to the main ITER control room (which is presently under construction).

5,000 tonnes of equipment
2021-11-25 - As tall as a seven-storey building and covering the equivalent of two soccer fields, the ITER cryoplant is located south of the Tokamak Complex. The largest single-unit cryogenic installation in the world, it is tasked with a daunting mission: to provide cooling fluids to 10,000 tonnes of superconducting magnets, eight massive cryopumps, and thousands of square metres of thermal shielding. Approximately 5,000 tonnes of equipment have been installed and commissioning is about to start.
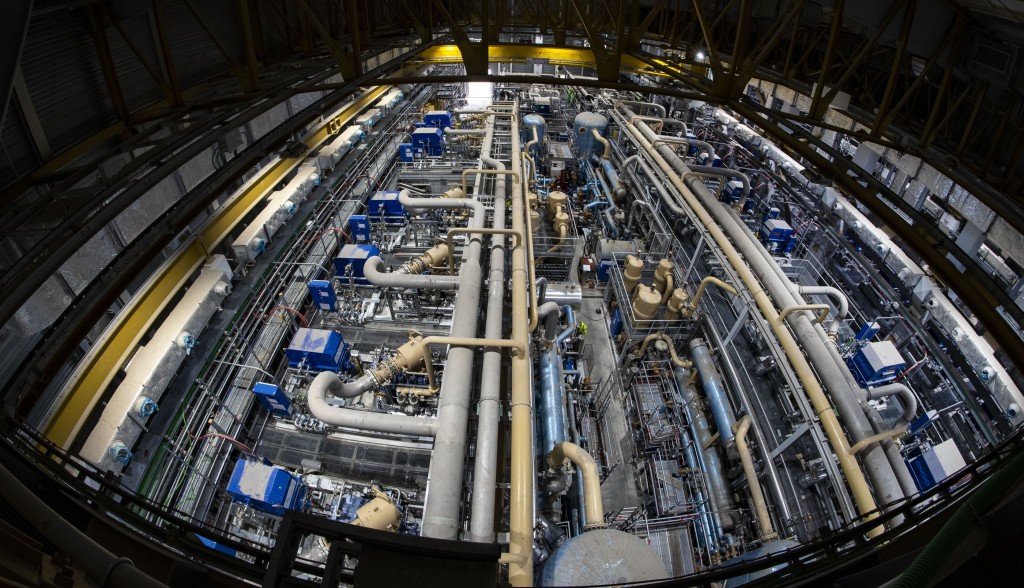
Cryoplant: first steps towards commissioning
2021-11-25 - Over the past three and a half years, some 5,000 tonnes of equipment (tanks, compressors, piping, valves, truck-size electrical motors and Zeppelin-like gas bags) were installed in the cryoplant. Now, a two-year commissioning period opens.
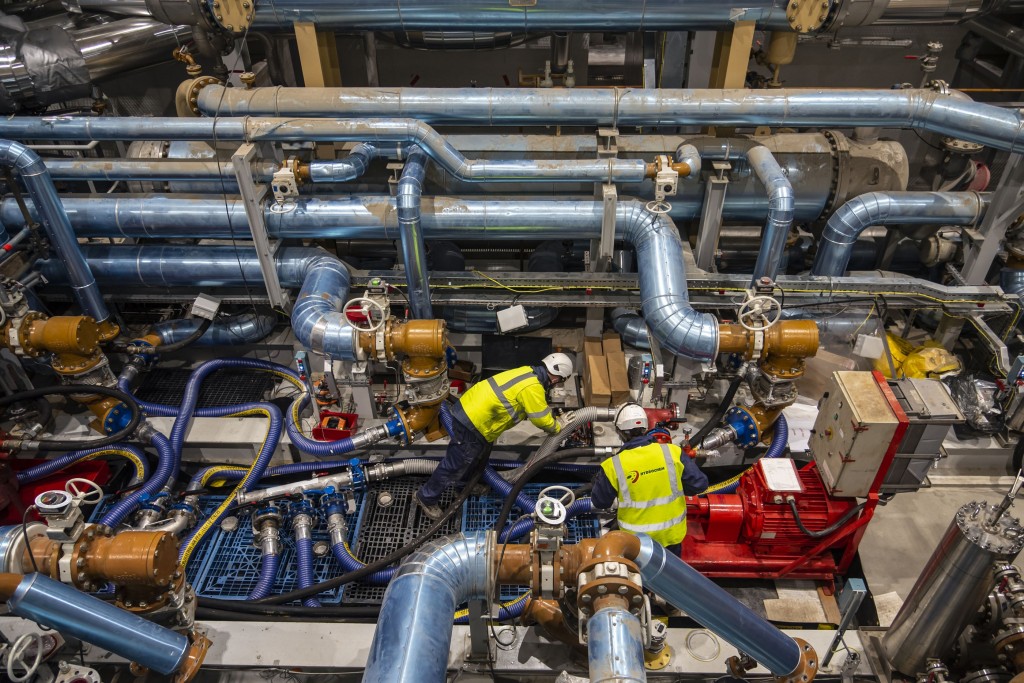
Pre-commissioning
2021-11-25 - As part of cryoplant pre-commissioning, operators are testing and verifying control-command systems, performing leak tests, and ensuring cleanliness, helium purity and the safety of the equipment.
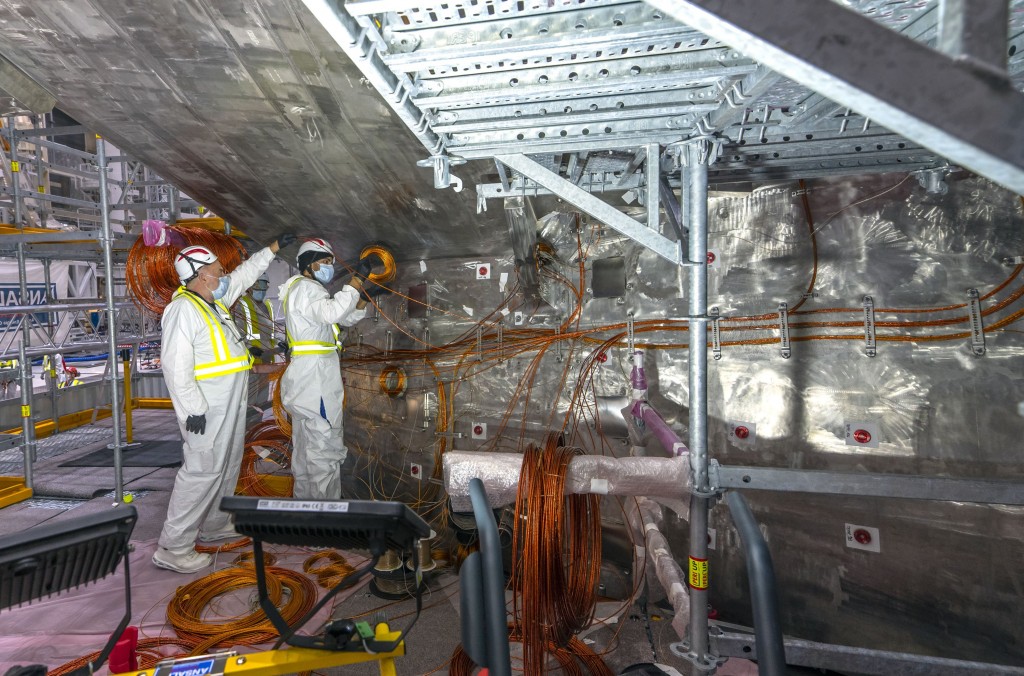
Sector #1(7): prep work underway
2021-11-19 - In order to support the instrumentation that monitors the main electromagnetic parameters of the plasma, several hundred welded attachments (i.e., bosses or clips) need to be precisely fitted to every vacuum vessel sector. (Pictured: Korean sector #1(7))

Faster the second time around
2021-11-19 - Experience and lessons learned brought the total duration of preparation works on the second vacuum vessel sector down from 36 weeks to an expected 15 to 17 weeks.
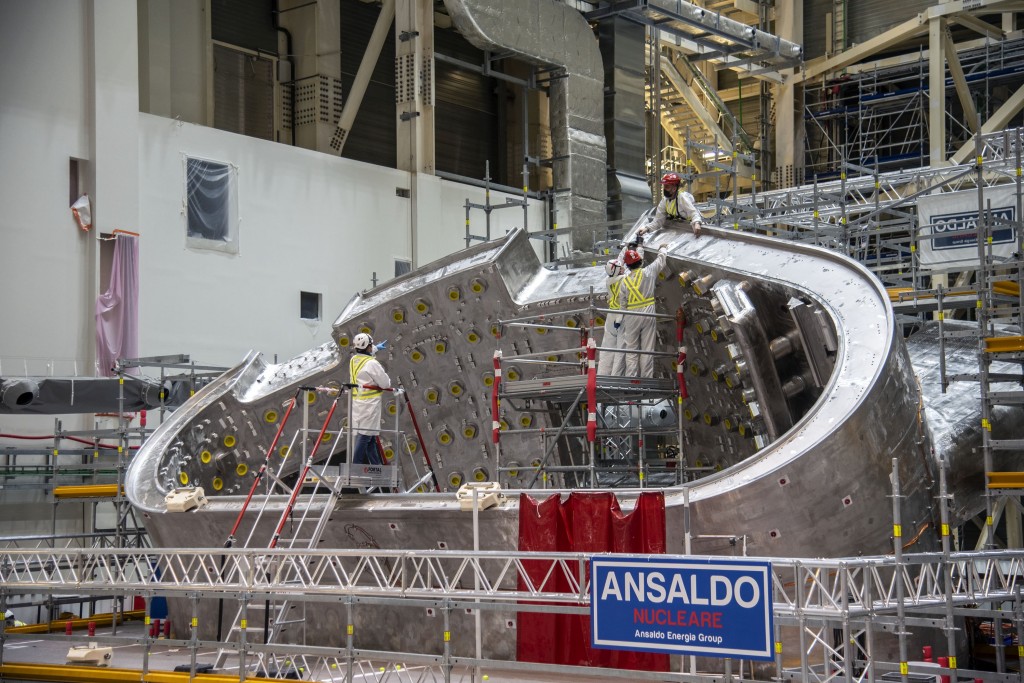
Second sector in the wings
2021-11-19 - Another imminent operation at ITER: the lifting of the second Korean sector, #1(7), into the assembly tooling. The teams were able to prep this sector for lifting in half the time as the first.
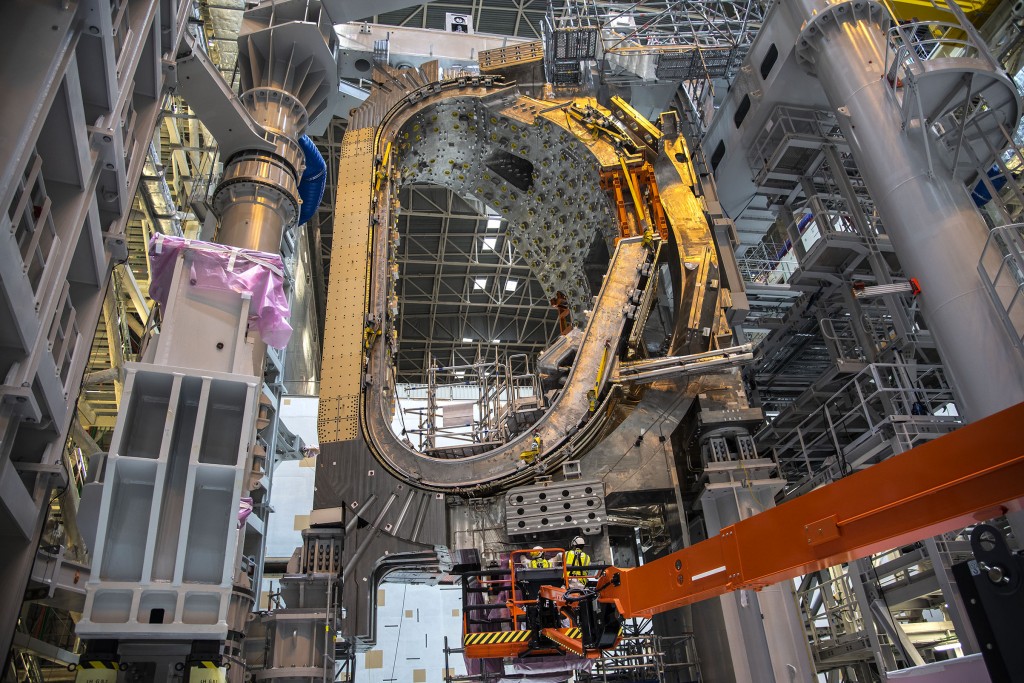
Only six more "steps"
2021-11-18 - The path to lowering the first vacuum vessel sub-assembly into the Tokamak pit was set out in 27 distinct construction work packages, and 21 of these have now been achieved. The transfer of the sub-assembly into the Tokamak pit will be a major project milestone.
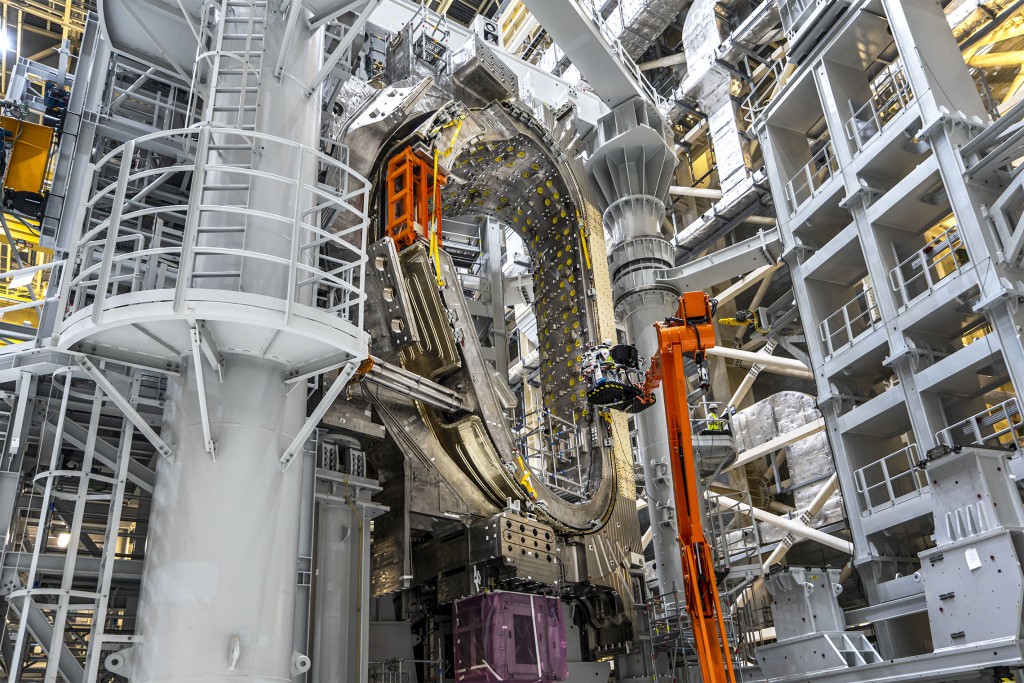
Next lift into pit: 1,250 tonnes
2021-11-15 - ITER's first vacuum vessel sub-assembly is nearly ready for transfer into the Tokamak pit. Together, the sub-assembly components weigh 1,250 tonnes.

Awesome
2021-11-15 - Workers look small when they stand at the foot of this unique and spectacular D-shaped structure.
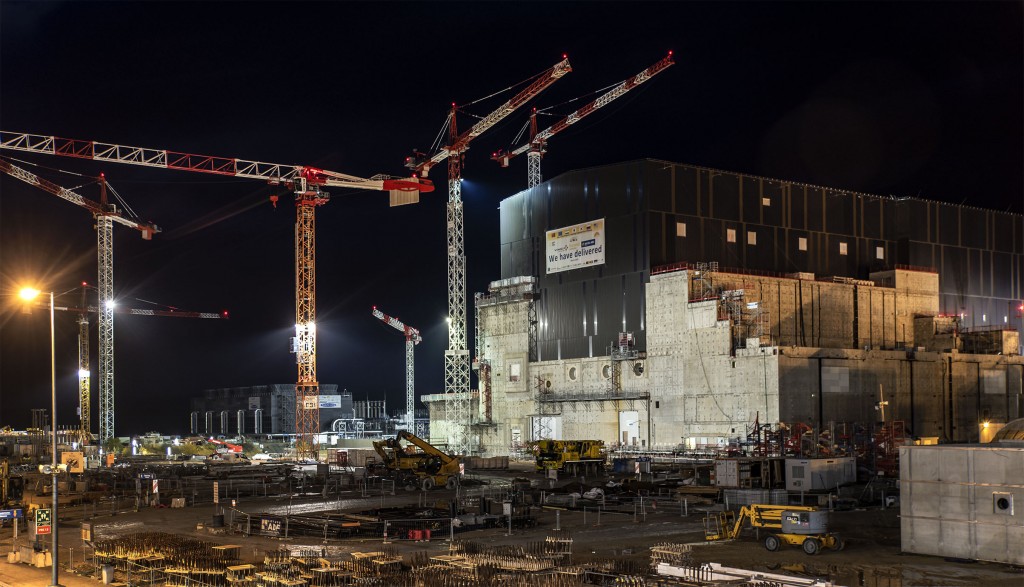
At night
2021-11-12 - The Tokamak Complex, at the heart of the construction site, is captured at night by the ITER photographer. The ITER worksite hardly ever sleeps; when employees leave their offices and head home, the night shift begins for dozens of workers and specialists.
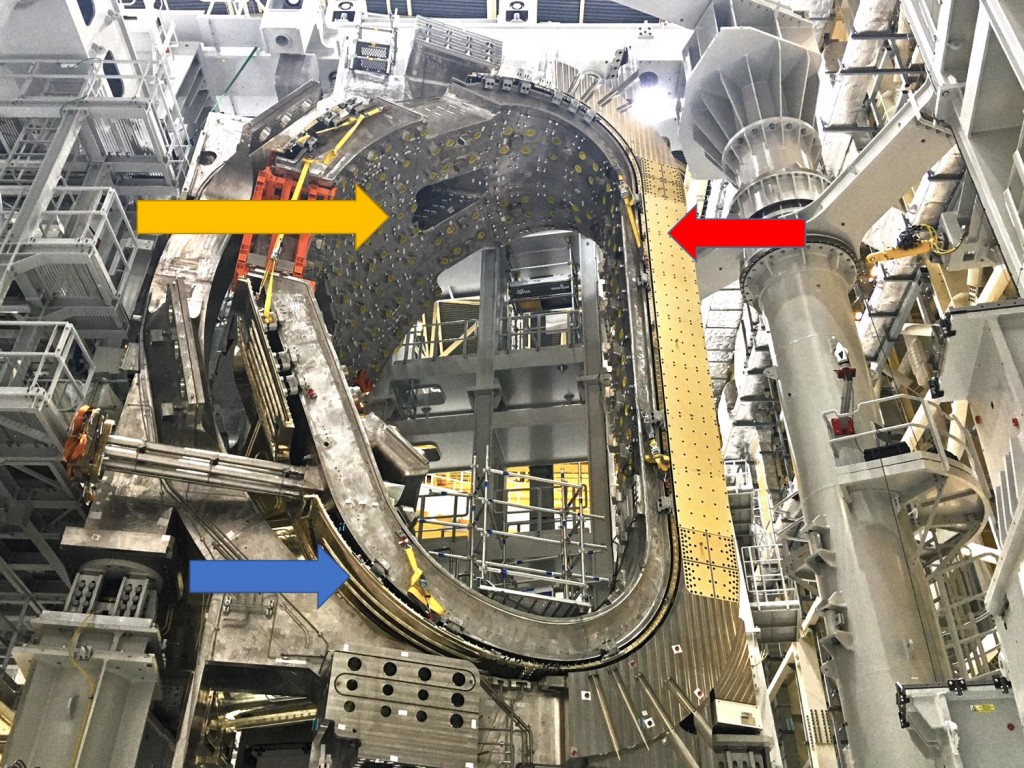
One-ninth of the chamber revealed
2021-11-12 - Part of the scaffolding around the first vacuum vessel sub-assembly has been removed, revealing one-ninth of the ITER vacuum chamber. Follow the arrows to make out the three parts of the 1,200-tonne assembly: the vacuum vessel sector (yellow), one of two toroidal field coils (red), and the thermal shield for sector #6 (blue).

Science on SPIDER
2021-11-11 - The SPIDER testbed was inaugurated in 2018 and it produced its first beam in 2019. Stay tuned for a December 2021 update in the ITER Newsline on the science underway since.
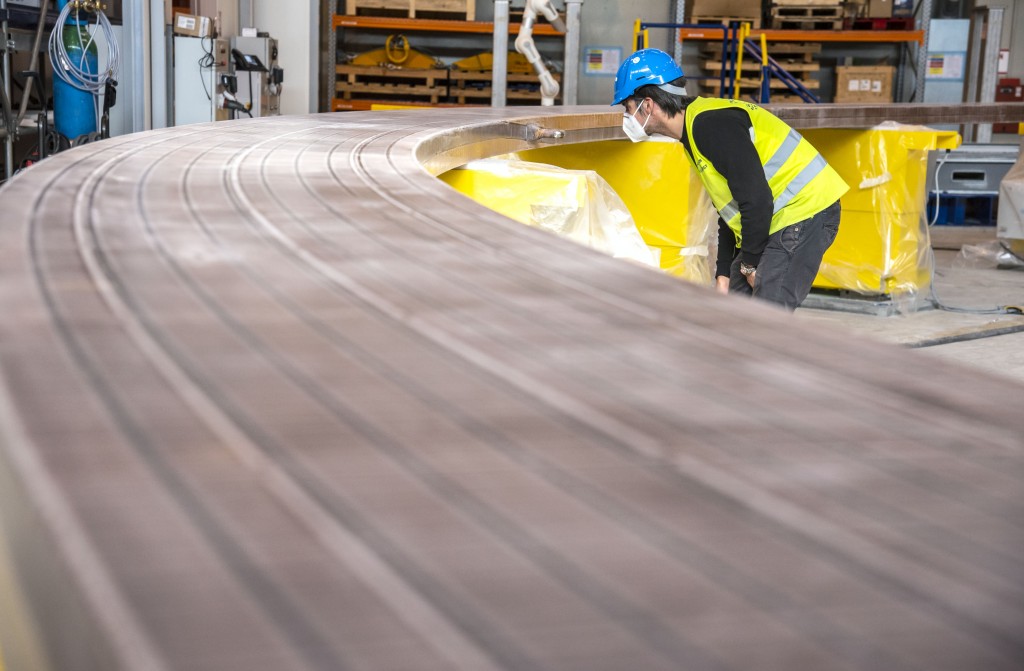
After impregnation
2021-11-09 - After impregnation, the double pancake is structurally rigid and the coil turns are electrically insulated from one another.

Fusion for Energy
2021-11-09 - The European agency for ITER, Fusion for Energy, is procuring 5 of the 6 poloidal field coils for the project; (a sixth, PF1, is procured by Russia). Four are too big to travel by road and are manufactured instead in Europe's on-site winding facility.
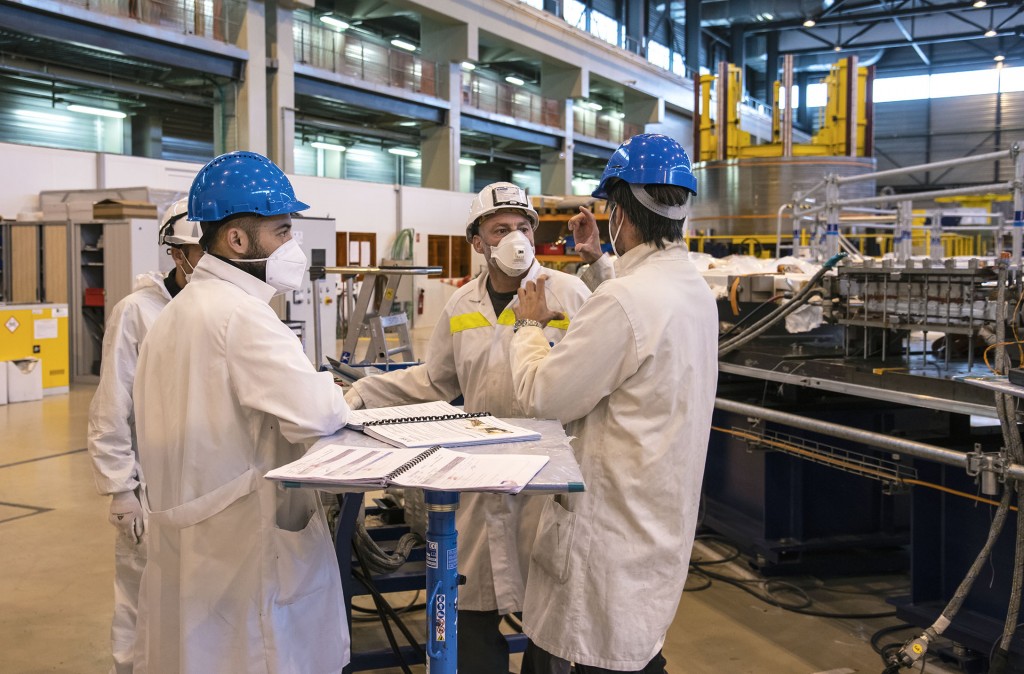
Takes a team
2021-11-09 - The successful completion of the coils is dependent on the collaboration of many actors, including the European Domestic Agency (Fusion for Energy, procuring party), ASG Superconductors (engineering integration), Dalkia (site and infrastructure), and CNIM (fabrication).

PF2 nears finalization
2021-11-09 - The last "medium size" poloidal field coil undergoes inspection in Europe's on-site winding facility. With a diameter of 17 metres it is bigger than coils #1 and #6 (9/10 metres in diameter) and smaller than coils #4 and #3 (24 metres in diameter).

Custom fit
2021-11-09 - All tooling had to be expanded for the two coils measuring 24 metres in diameter—PF4 and PF3. (The first two coils had a diameter of 17 metres.)
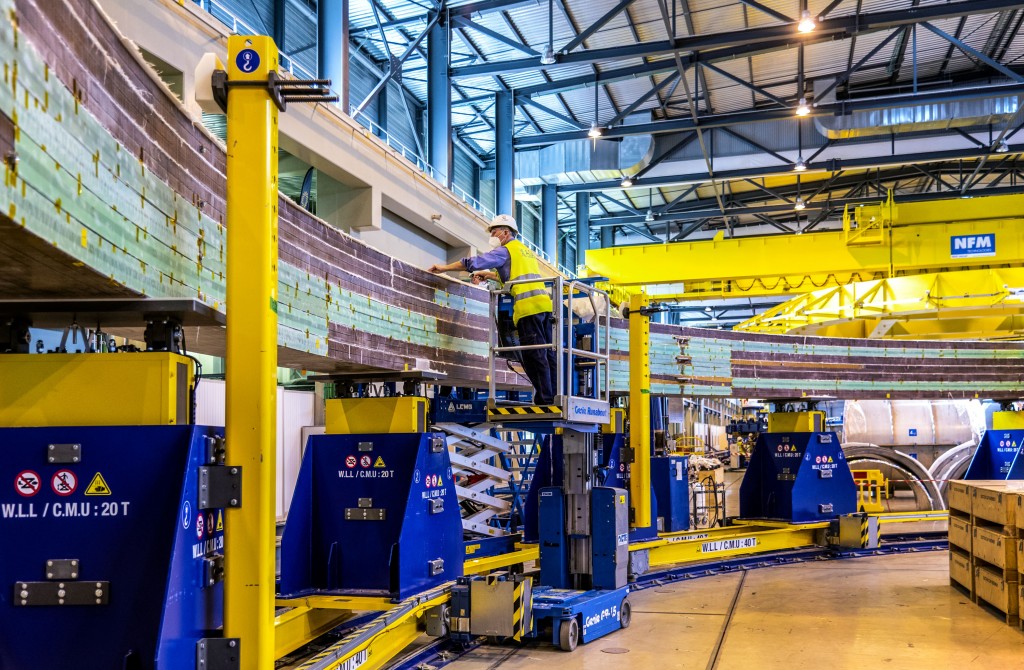
Stacking PF4
2021-11-09 - Seven out of eight double pancakes for coil #4 (PF4) are now stacked. This technician is carrying out dimensional verifications.
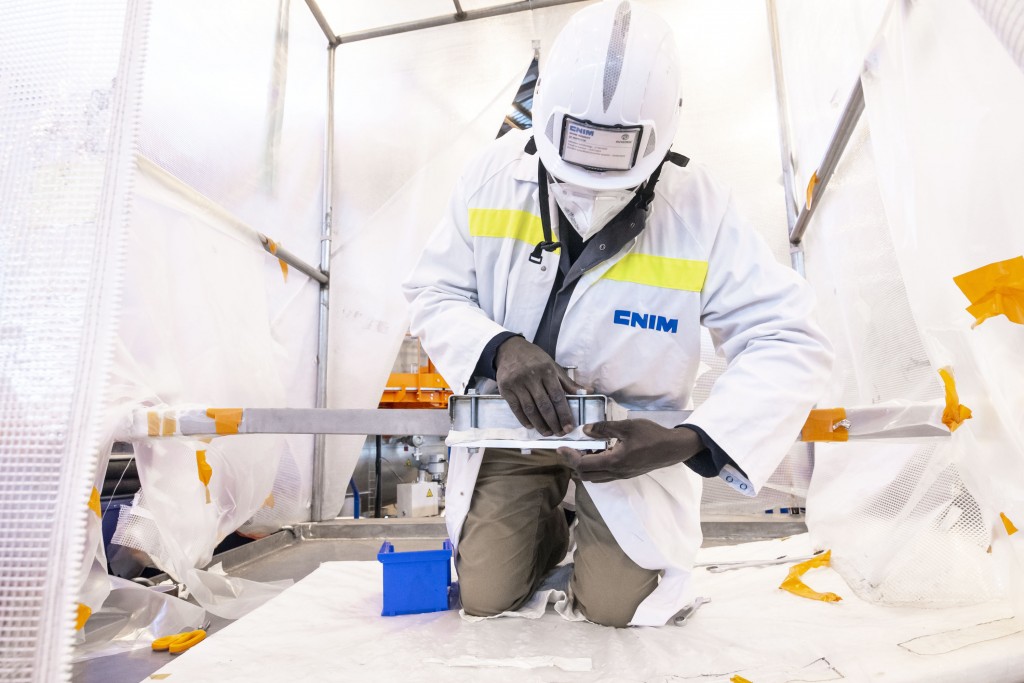
Critical tests
2021-11-09 - Helium tests are underway at critical points along the sixth double pancake for PF3, which is in production in Europe's on-site coil winding facility.

Resin time for this double pancake
2021-11-09 - A double pancake has been sealed tightly into its resin chamber. Epoxy resin, injected over the course of several hours, will fill all gaps and harden the glass insulation tape under the effect of heat and pressure. A 36-hour "curing" phase at 140 °C completes the process.
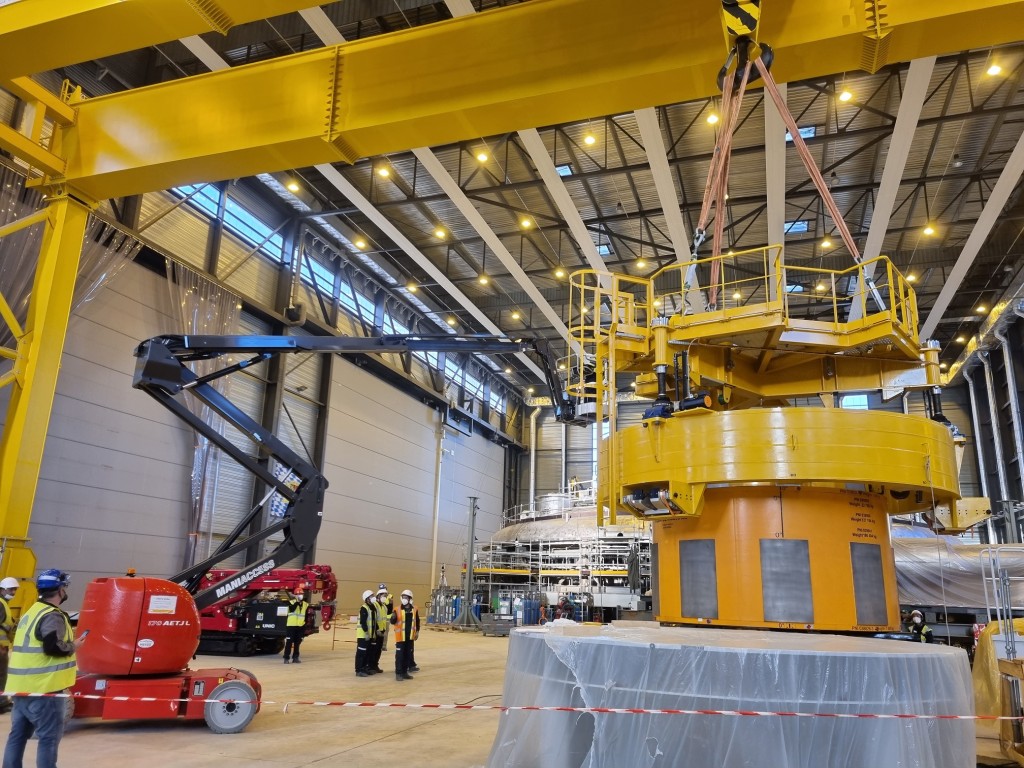
A purpose built tool for cylindrical magnets
2021-11-04 - In yellow, the purpose built central solenoid lift tool. Manufactured by Robatel (France) for the US Domestic Agency, it will move soon from storage in the Cryostat Workshop to the central solenoid work station in the Assembly Hall.
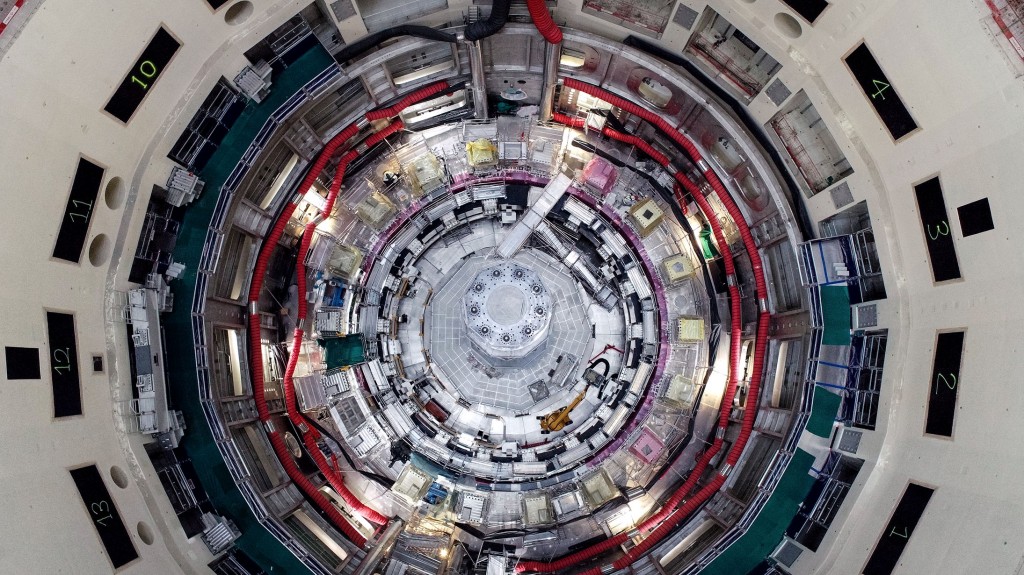
Dizzying
2021-10-29 - A drone hovers over the ITER Tokamak pit and captures a dizzying array of components, tools, staging platforms and equipment. This view of the lower machine will be impossible in a few weeks, when the first vacuum vessel sub-assembly is inserted. © Les Nouveaux Médias/SNC ENGAGE
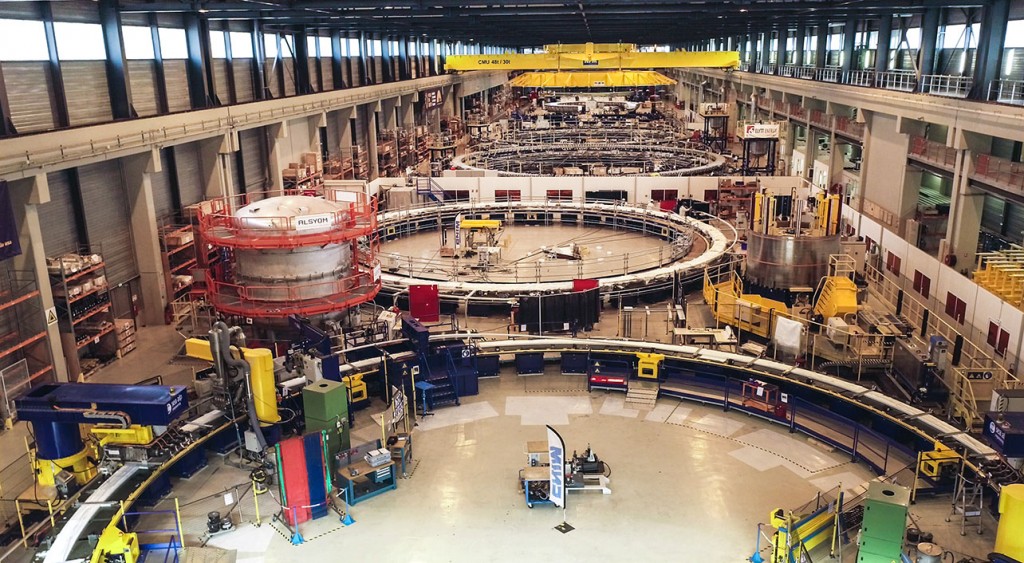
Busy factory
2021-10-29 - In this 250-metre-long facility, European contractors are currently producing the building blocks (the individual double pancakes) for the last of four poloidal field magnets—PF3, which has a diameter of 24 metres. © Les Nouveaux Médias/SNC ENGAGE
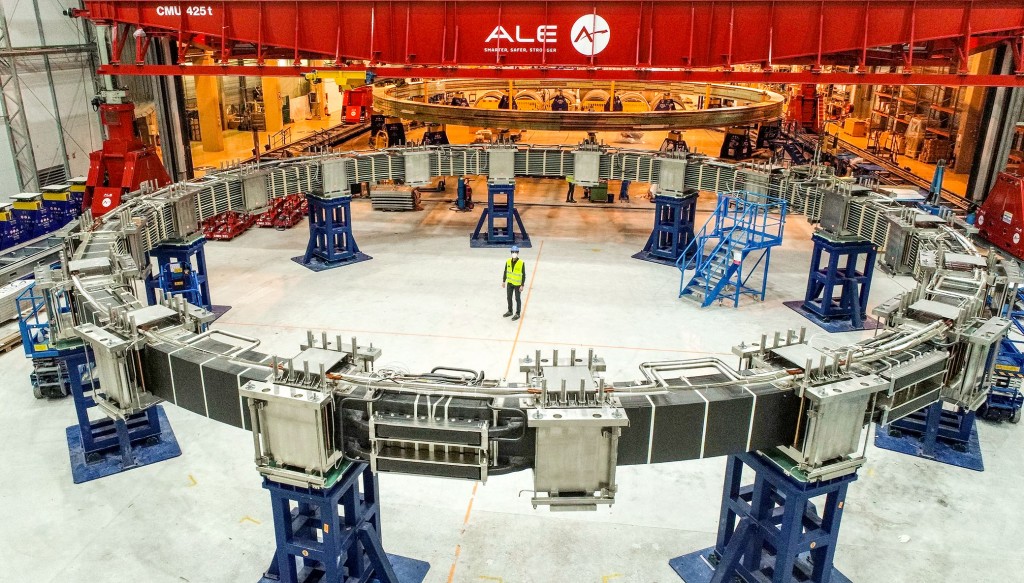
Second ring coil completed on site
2021-10-29 - In the Poloidal Field Coils Winding Facility on site, European contractors have completed a second ring-shaped magnet. Poloidal field coil #2 (PF2) is 17 metres in diameter, like PF5 that preceded it. © Les Nouveaux Médias/SNC ENGAGE
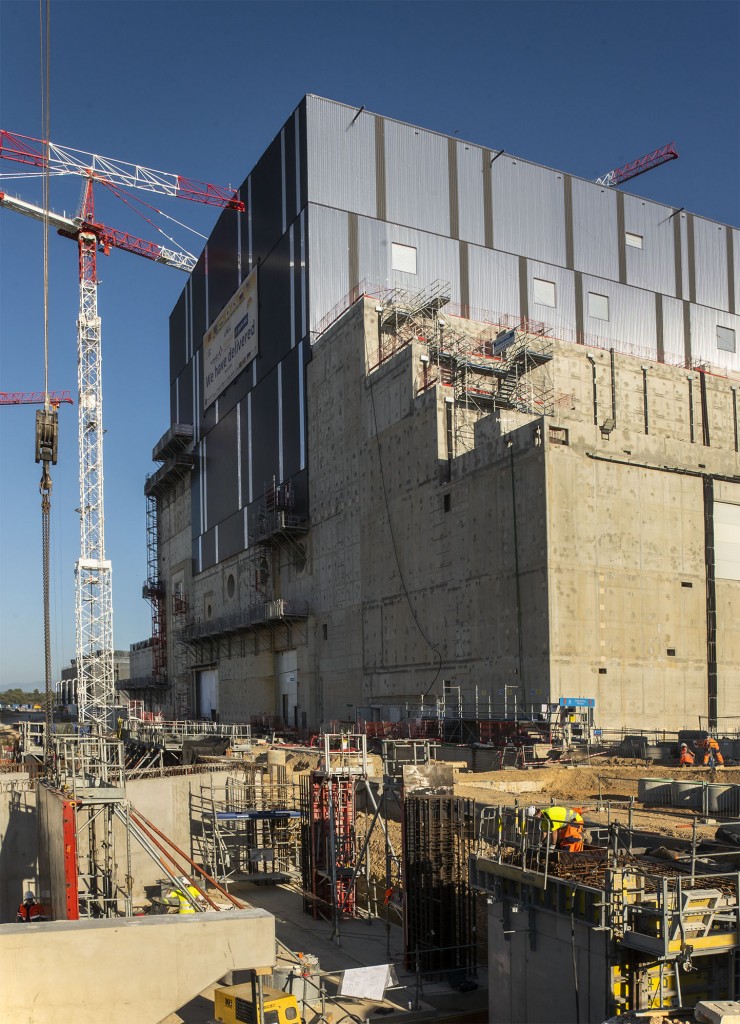
Neutral beam power supplies
2021-10-25 - In front of the Diagnostics Building, construction is underway on two new buildings dedicated to the power supplies for the neutral beam injection system.

A large area
2021-10-25 - Infrastructure for the neutral beam power supply system will be installed over an area measuring 11,700 m².
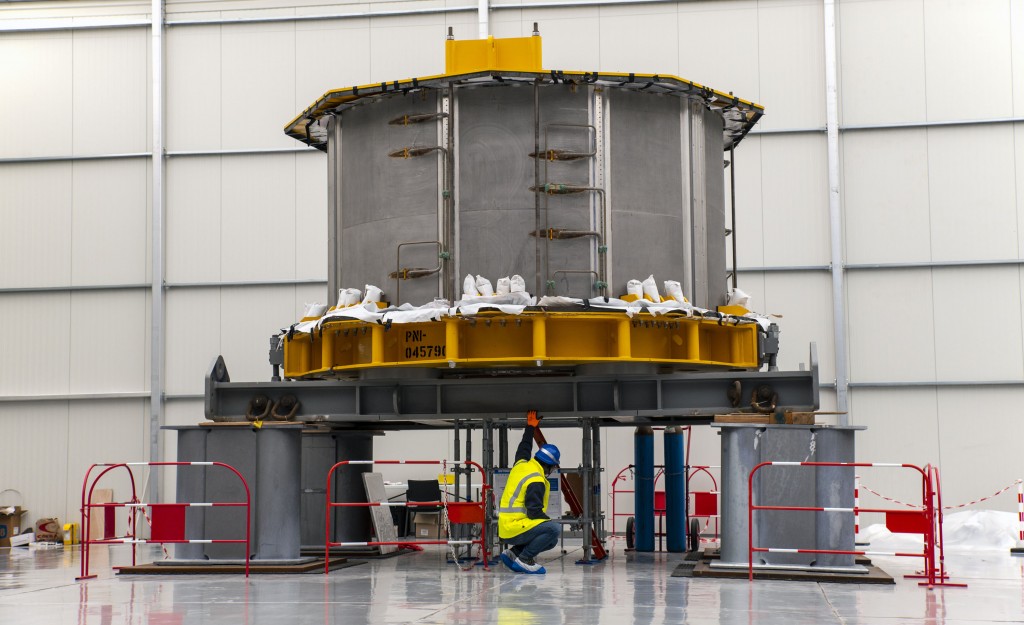
Central solenoid assembly to begin in January 2022
2021-10-21 - Delivered to ITER in September, the first central solenoid module is undergoing a battery of tests and verifications—metrology, sensors, electrical insulation inspection, etc. Assembly of the 18-metre tall, 1,000-tonne central solenoid is set to begin in January 2022.
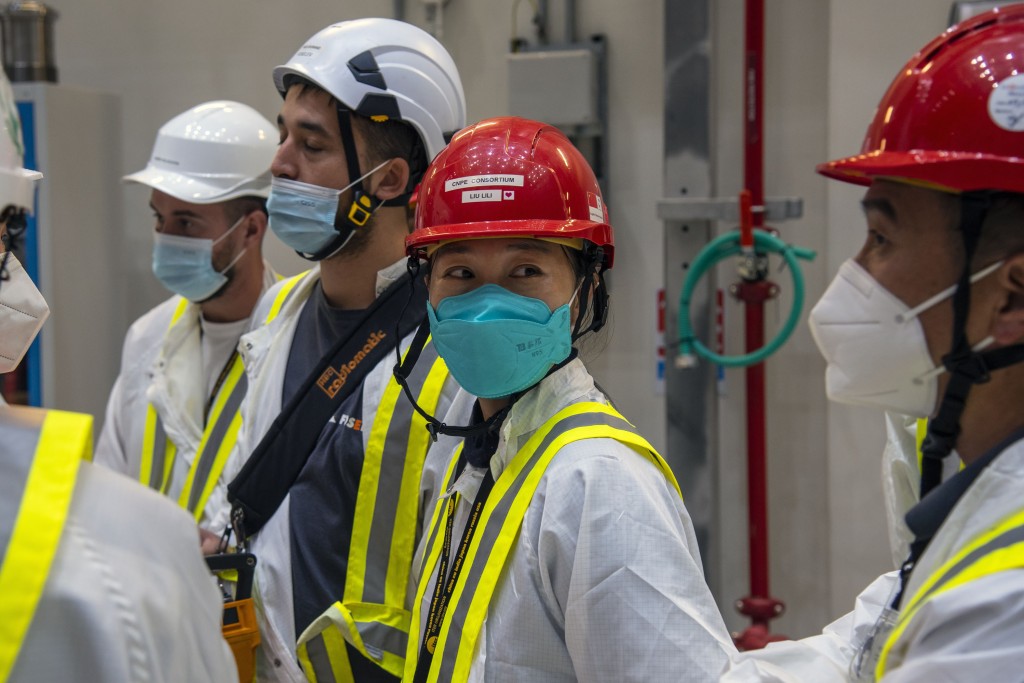
Teamwork
2021-10-21 - ITER Organization teams are working with the Tokamak Assembly Contract (TAC1) consortium CNPE for the correction coil lift operations. See more on assembly contractors here: https://www.iter.org/construction/TokamakAssembly
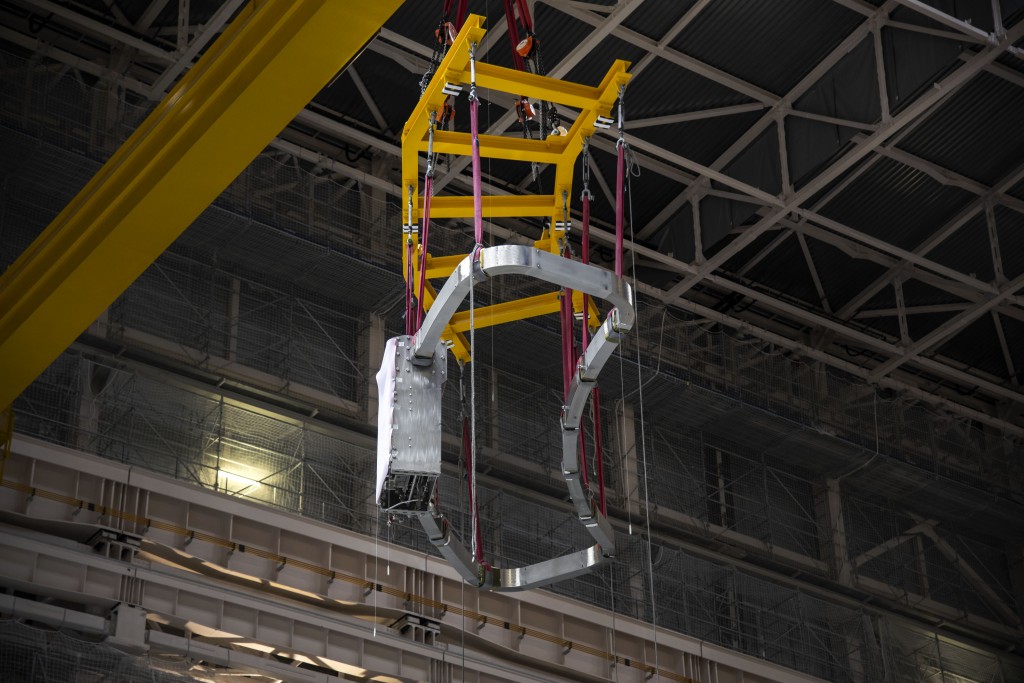
Kidney-shaped
2021-10-21 - Correction coils are manufactured in unusual shapes to fit into the space between the poloidal and toroidal field magnets. At the bottom and the top of the machine, the coils are rectangles that curve inward to espouse the torus shape of the vacuum vessel.

Over the top
2021-10-21 - Once completed, the sector sub-assemblies will be lifted vertically out of the SSAT tool. The required height above the tool for this operation helps to explain the height of the bridge cranes in the Assembly Hall. © Les Nouveaux Médias/SNC ENGAGE
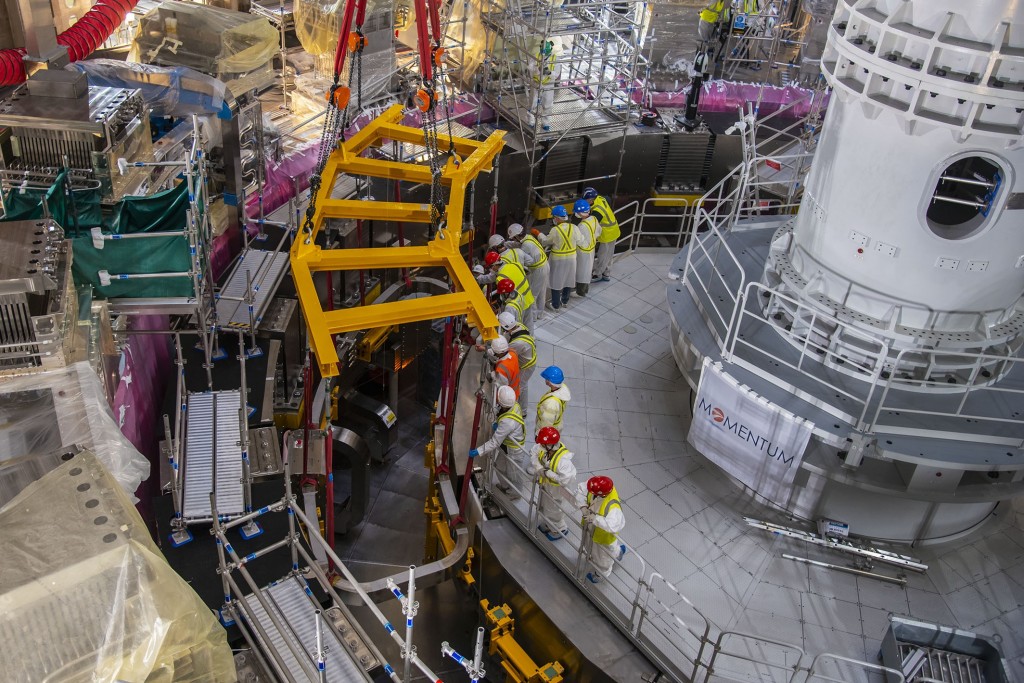
Success
2021-10-21 - The lowering of the BCC/4 coil onto its temporary supports goes smoothly, thanks to detailed preparation that included metrology, reverse engineering and accurate positioning. In the final machine geometry, the correction coils will be attached to the toroidal field coil superstructure.

First correction coil lifted
2021-10-21 - The lift operation for correction coil BCC/4 gets off to a start at 10:30 a.m. on 21 October. The total load under the crane is 5.3 tonnes including lift accessories.

Different types of rigging
2021-10-21 - For each lift, the rigging is adapted to the load. Here the rigging (in yellow) for this bottom correction coil allows for a smooth and balanced transfer, with no tilting.
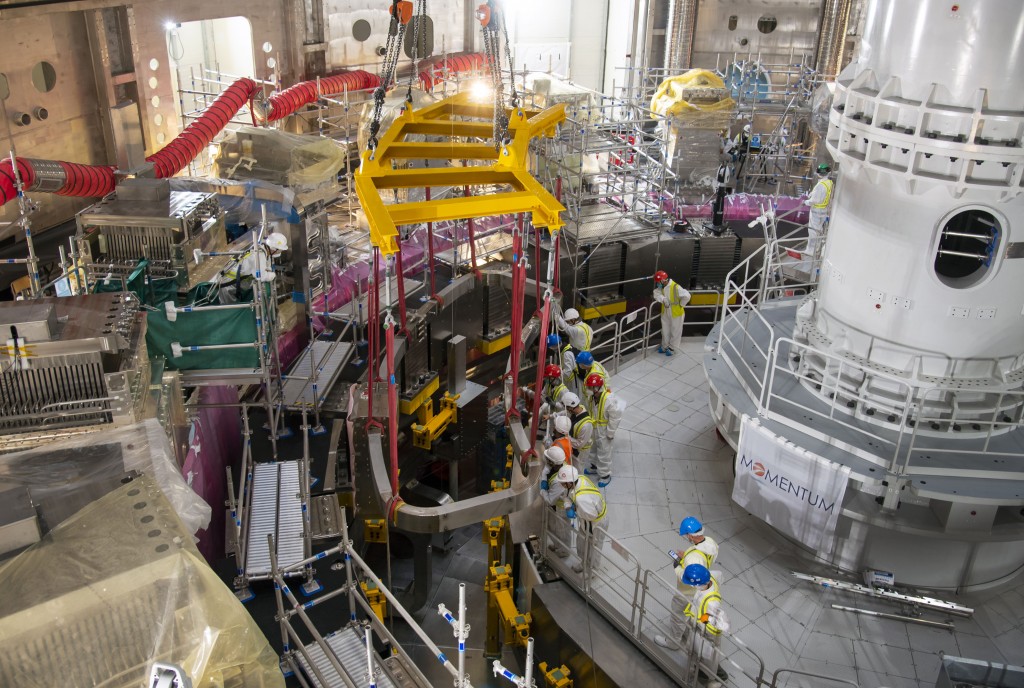
Just a sliver of space
2021-10-21 - Final touch down is the most critical part of the lift. The "sliver" of space between poloidal field coil #5, poloidal field coil #6, lower magnet feeders, and staging platforms does not exceed 25 mm for BCC/4 (pictured) and 15 mm for BCC/5.
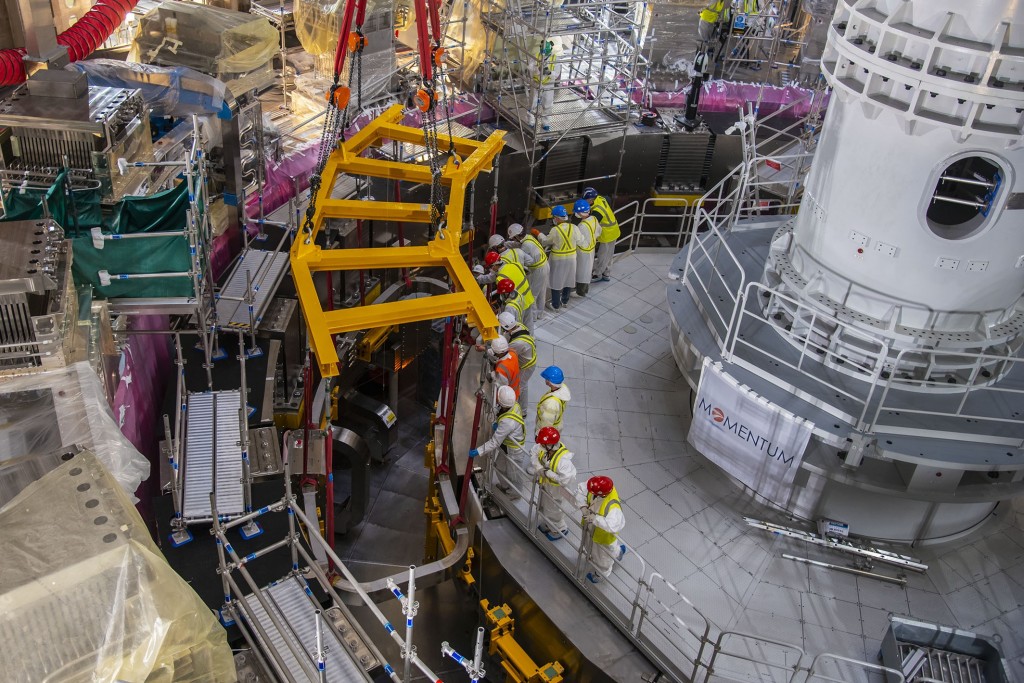
First correction coil lowered
2021-10-21 - The lowering of the BCC/4 coil onto its temporary supports goes smoothly in October, thanks to detailed preparation that included metrology, reverse engineering and accurate positioning. In the final machine geometry, the correction coils will be attached to the toroidal field coil superstructure.

Central solenoid assembly platform
2021-10-20 - The assembly platform for the ITER central solenoid has been positioned in the Assembly Hall (load capacity: 1,300 tonnes). Six modules will be stacked on top of this platform inside of a strong supporting structure. © Les Nouveaux Médias/SNC ENGAGE

Second tool enters action
2021-10-20 - On the sector sub-assembly tool #2 (SSAT2), we are counting down the days until the first sub-assembly (built around vacuum vessel sector #6) is transferred to the Tokamak pit. Meanwhile, on SSAT1, assembly contractors have mounted the inboard segment of the thermal shield. On this tall tool, a sub-assembly unit will be built around vacuum vessel sector #7.
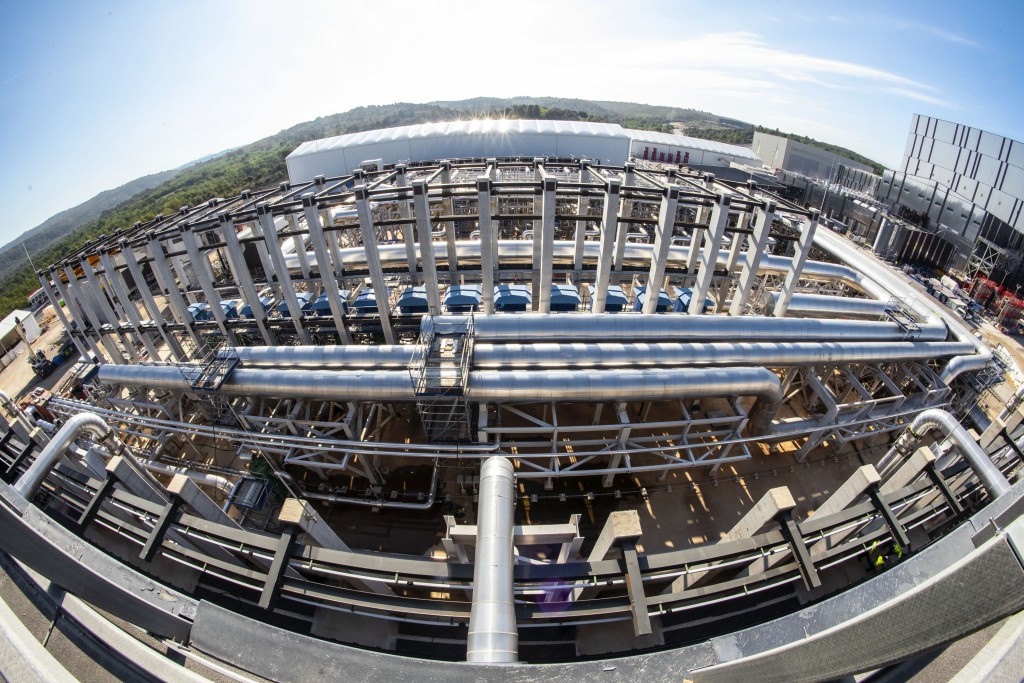
Cooling plant: next step, commissioning
2021-10-15 - Approximately 6,000 tonnes of equipment for the ITER cooling plant have been supplied by India and installed by ITER Organization contractors. The next step is plant commissioning.

First client: the cryoplant
2021-10-15 - The ITER cryoplant will be one of the first "clients" to require cooling water, which is why the cooling plant team has started commissioning that part of the plant first. Pictured, is the pumping station that will service the cryoplant.
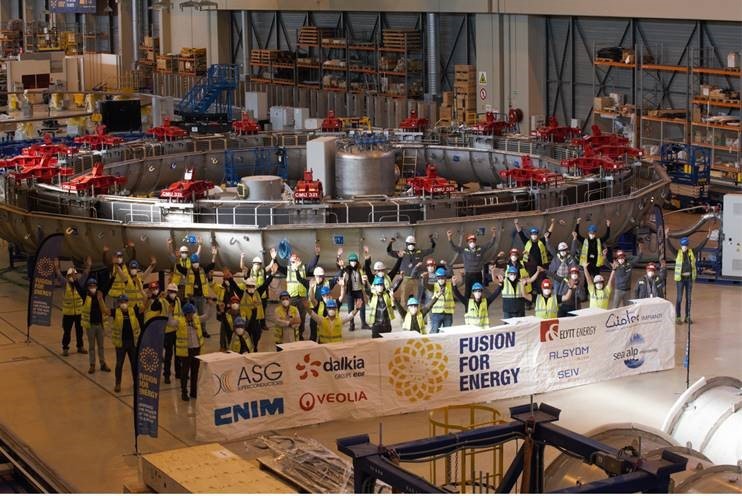
PF2: Successful cold tests
2021-10-15 - Cryotests on PF2 have successfully concluded and the team gathers in celebration. (The 200-tonne coil is seen here in its open vacuum chamber.)

Insulation
2021-10-15 - Teams are completing the insulation of the pipes connecting 17 heat exchangers to the cooling water plant.

Chemistry matters
2021-10-15 - The chemical injection system adds chemicals to the pipes and cooling towers to prevent scaling, bacteria and legionella from growing.

Working on L3 of the Tritium Building
2021-10-15 - Two levels of the Tritium Building have been erected; in this photo we can see the teams active on the basemat for L3. When it is completed, the Tritium Building will rise to the height of the concrete segment of the Tokamak Building in the background.
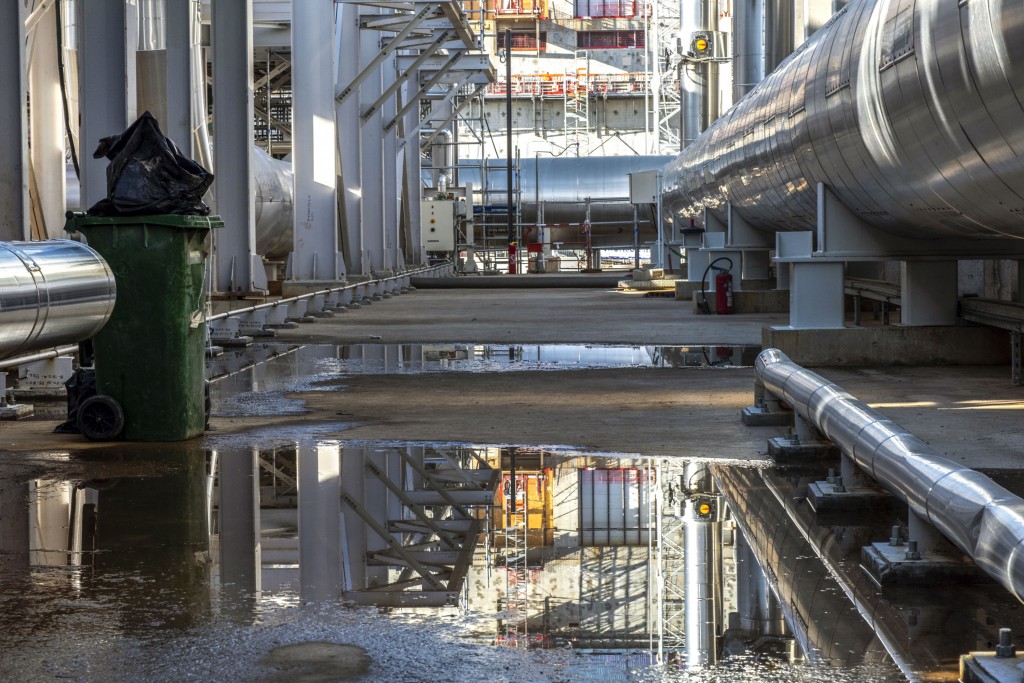
Cooling plant responsibilities
2021-10-15 - The Indian Domestic Agency is responsible for the design and fabrication of the heat rejection system. The ITER Organization is responsible for equipment installation and system commissioning.
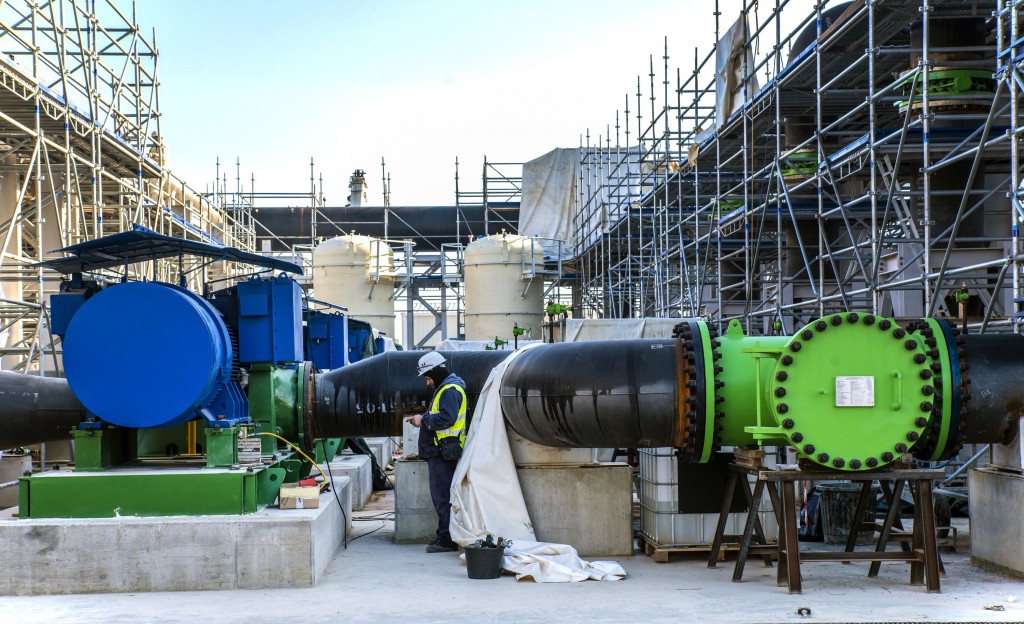
Different loops
2021-10-15 - Cooling water circulates in the ITER installation in three separate loops: the tokamak loop, the auxiliary plant loop, and the balance of site. (Pictured in this photo is the loop #1 pumping station.)
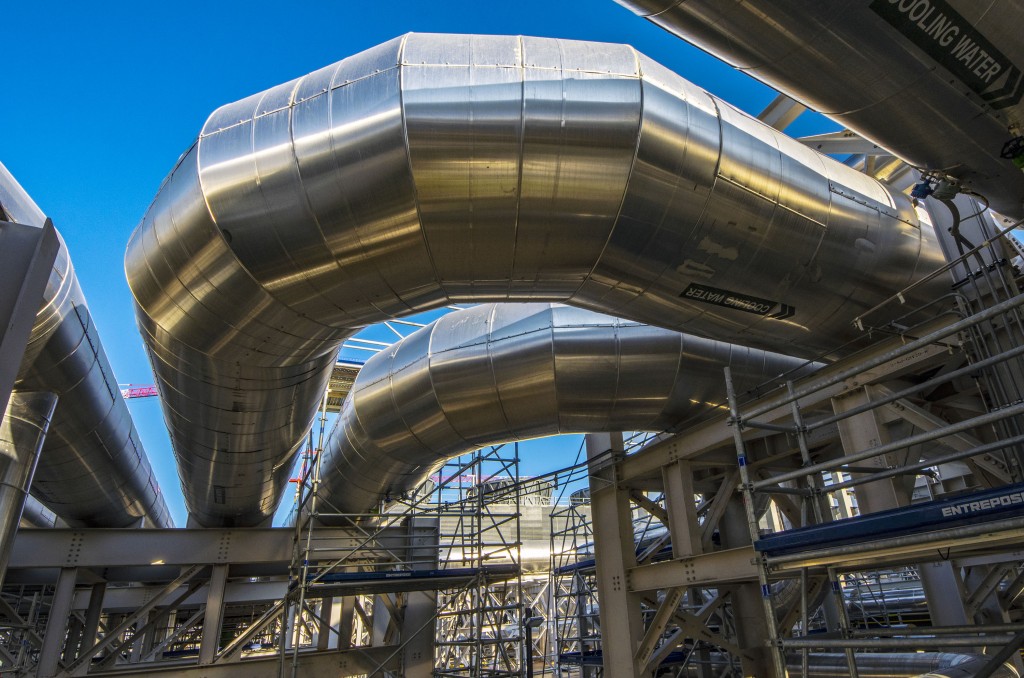
Maximum flow
2021-10-15 - At peak flow (during a plasma pulse) the cooling plant is designed to handle 7,700 cubic metres of water per second.

I&C
2021-10-15 - The "E-house" is where signals from the cooling water plant are tied into the overall network of instrumentation and control for ITER, which is monitored from the ITER control room.
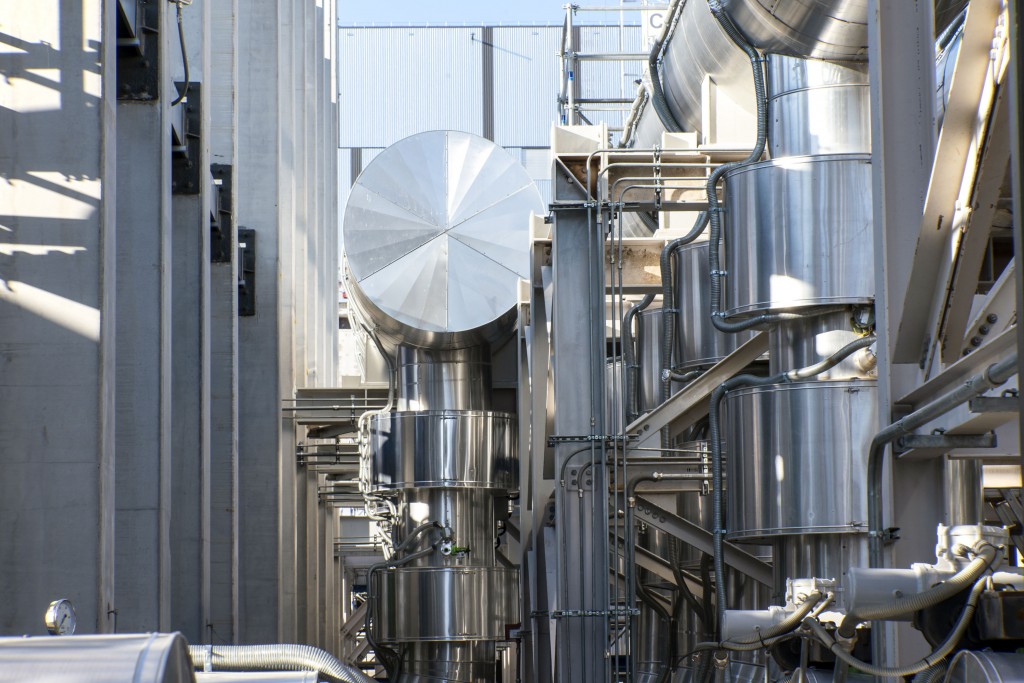
Large valves
2021-10-15 - Valves like these control the flow of cooling water through the heat exchangers.

First correction coils
2021-10-07 - Two out of six bottom correction coils have completed site acceptance tests are are in line for pit insertion. The Chinese Domestic Agency is supplying 18 correction coils in all (six bottom, six side and six top).

Cooling plant: nearly fully installed
2021-10-06 - Equipment procured by India has been installed in the 6,000 m² cooling tower area on the northern corner of the ITER site, including heat exchangers (photo), chemical treatment equipment, pumps, piping and cooling towers.
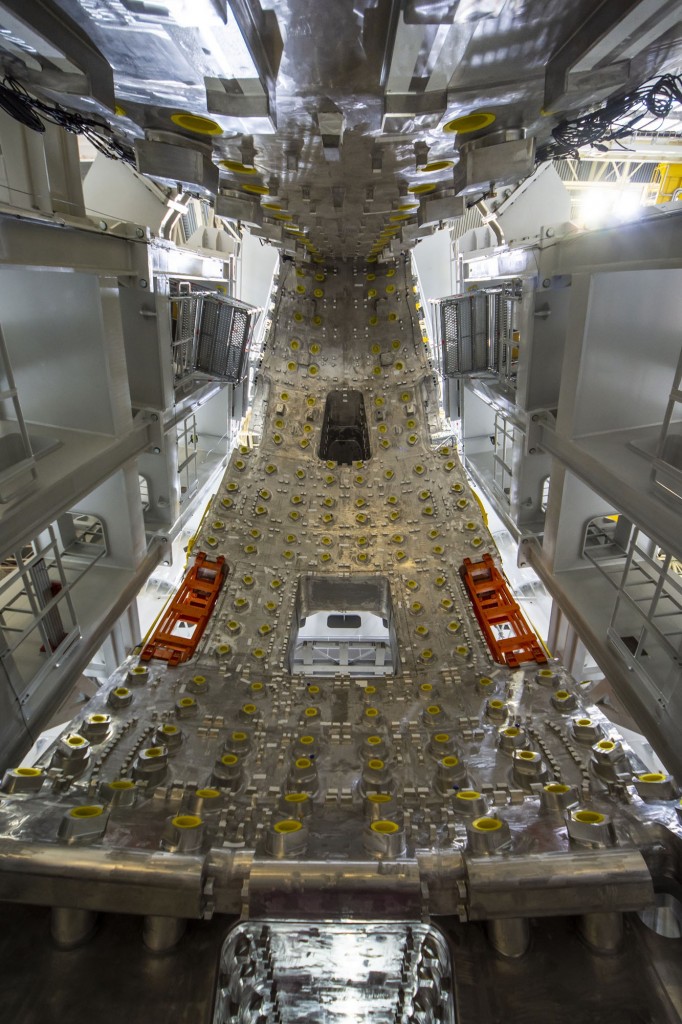
Sub-assembly #1: final alignment achieved
2021-10-05 - Final alignment has been achieved for the first building block of the ITER plasma chamber—four major components, totalling 1,250 tonnes, have been aligned to within 1 mm of tolerance in the radial, toroidal and vertical directions. (Picture taken inside of the sub-assembly group.)
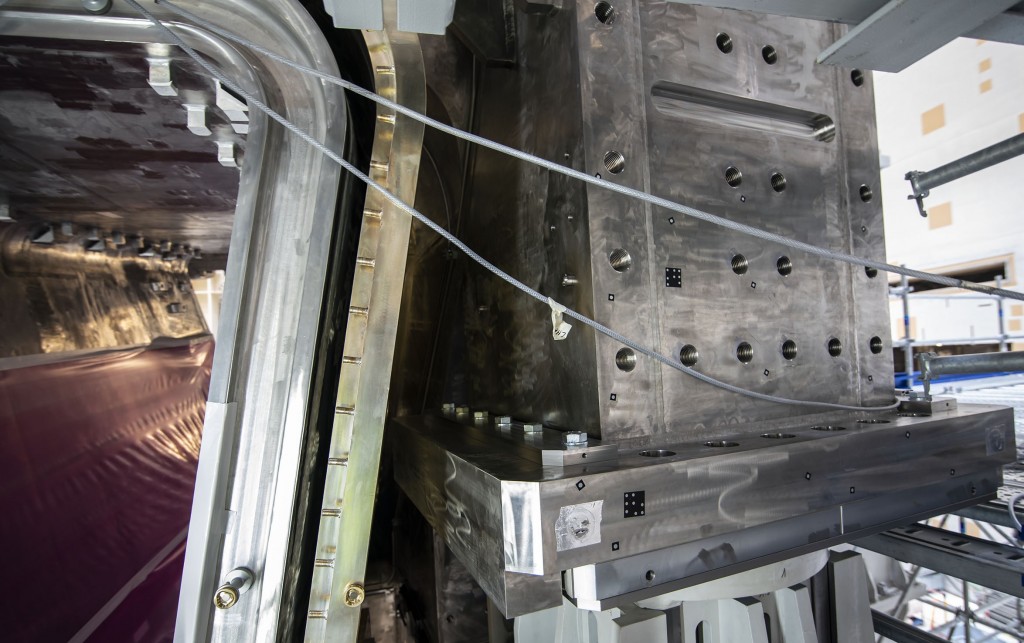
Assembly precision
2021-10-05 - The elements of the first vacuum vessel sub-assembly are positioned precisely relative to one another. To the right, the bottom of one of the toroidal field coils (TF13); in the centre, the much thinner silver-plated thermal shield; and to the left, the opening of the vacuum vessel sector lower port stub extension.
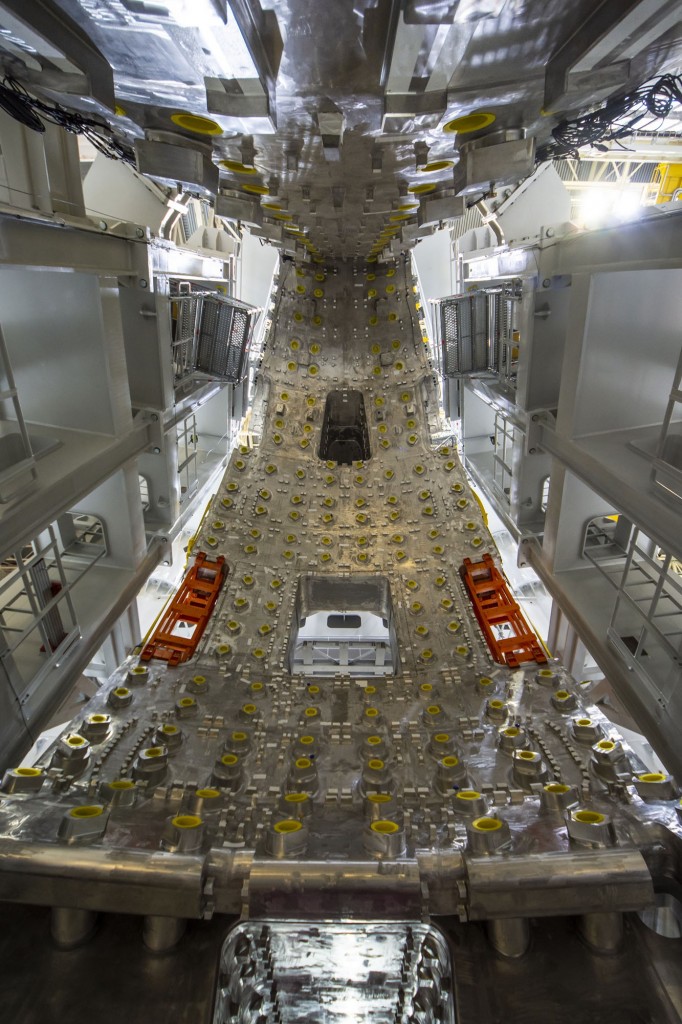
Major alignment achievement
2021-10-04 - The four major components of the first building block of the ITER plasma chamber have been precisely aligned (here, a view of the vacuum vessel taken from inside the sub-assembly). This major achievement smooths the way for the similar assembly of eight other sub-assemblies in the months and years ahead.
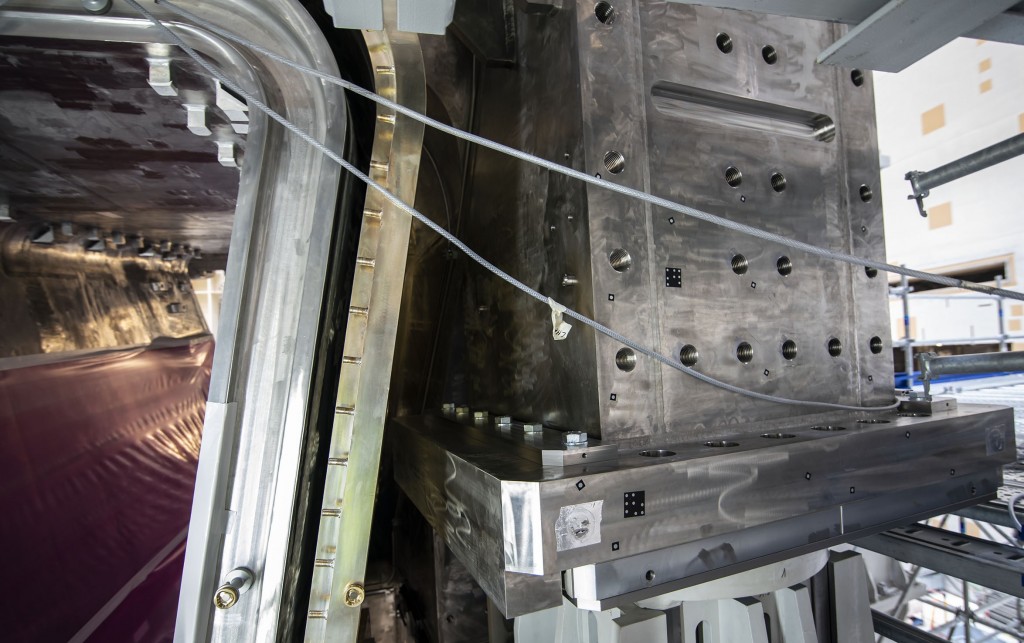
Precision is vital
2021-10-04 - Precision in assembling and positioning the vacuum vessel sub-assembly components is paramount; any deviation from required tolerances in any component would result in knock-on issues in the sub-assembly and the finalized torus.

New thermal shield set
2021-10-01 - Contractors have unpacked the three thermal shield panels that will be mounted onto vacuum vessel sector #1(7)—the second sector to be equipped. (Pictured: the inboard sector.) All nine sets of vacuum vessel thermal shielding are on site. © Christian Luenig
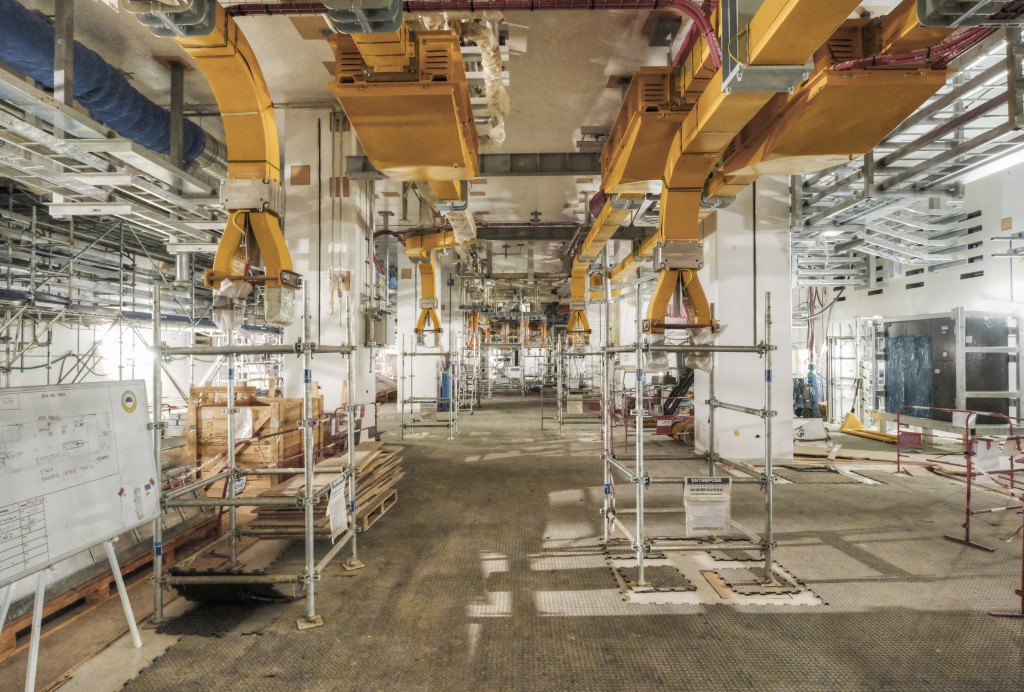
Yellow highways
2021-09-29 - High-current busbars connect tokamak coils with their power supplies, thyristor converters, and powerful switching devices and resistors for the extraction of energy from the magnet system. © Christian Luenig
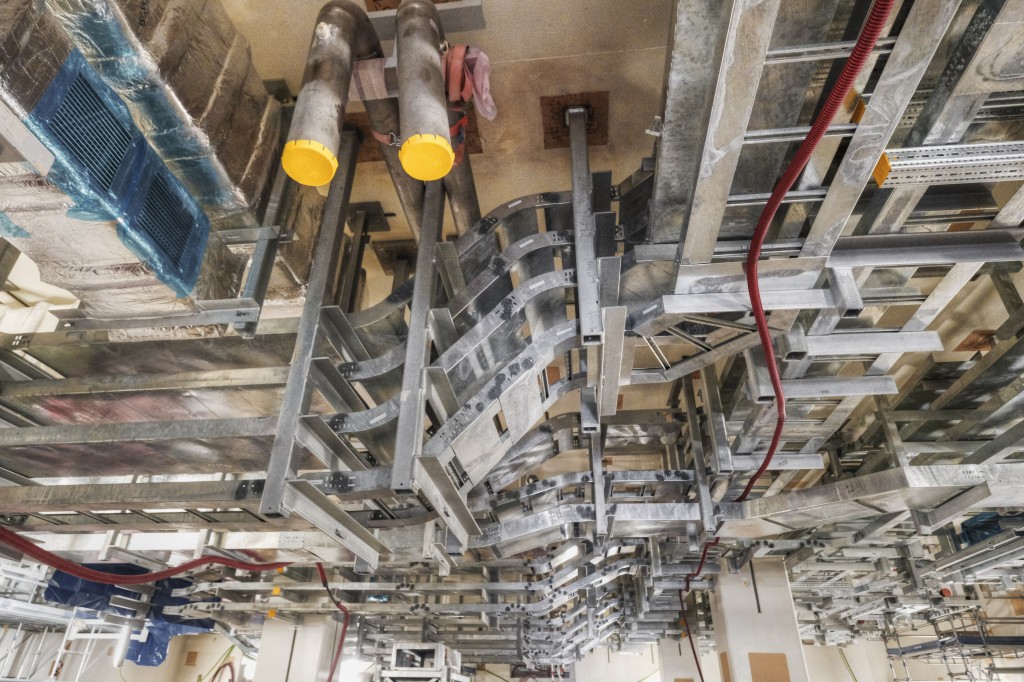
Embedded plates, supporting equipment
2021-09-29 - Ventilation, cable trays ... all equipment is soldered to metal plates that have been embedded in the floors, walls and ceilings of the Tokamak Complex. © Christian Luenig
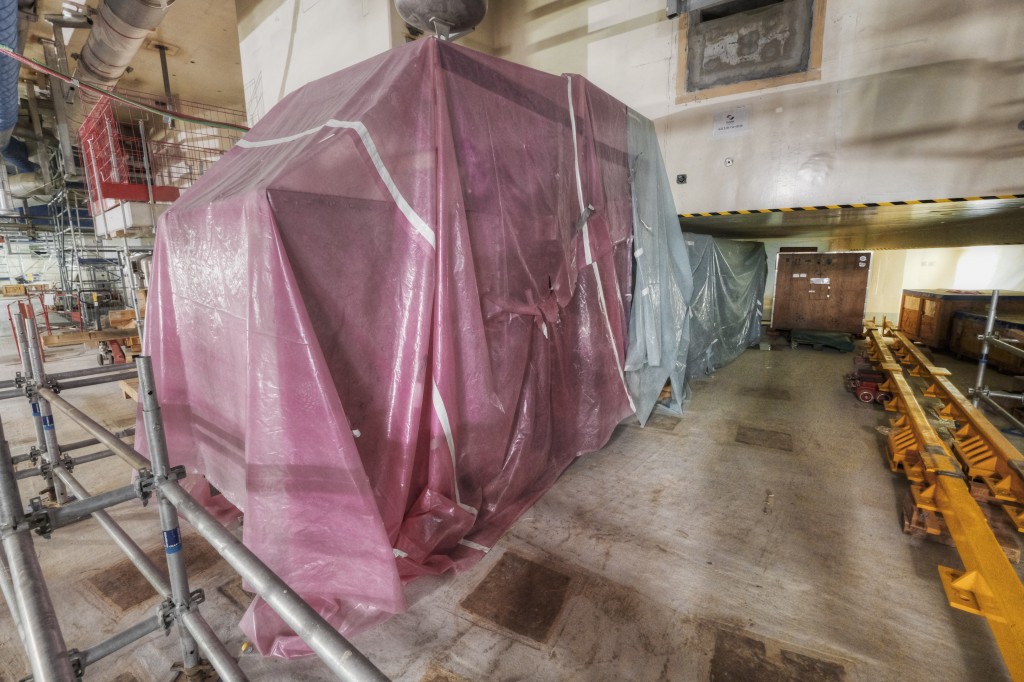
Installed and protected
2021-09-29 - This is the back end of a magnet feeder—a "coil termination box" that has been installed in the lowest level of the Tokamak Building and protected with plastic. © Christian Luenig

Elevator shaft
2021-09-29 - ITER's cask and plug remote handling system will transport components between the Tokamak Building and the Hot Cell Complex. We are looking at the elevator shaft for the lift that will service the casks at upper, equatorial and lower machine levels. © Christian Luenig (www.arbeitsblende.de)

Hidden corridor
2021-09-29 - To exit the ground floor of the Tokamak pit, you have to pass under poloidal field coil #5. © Christian Luenig
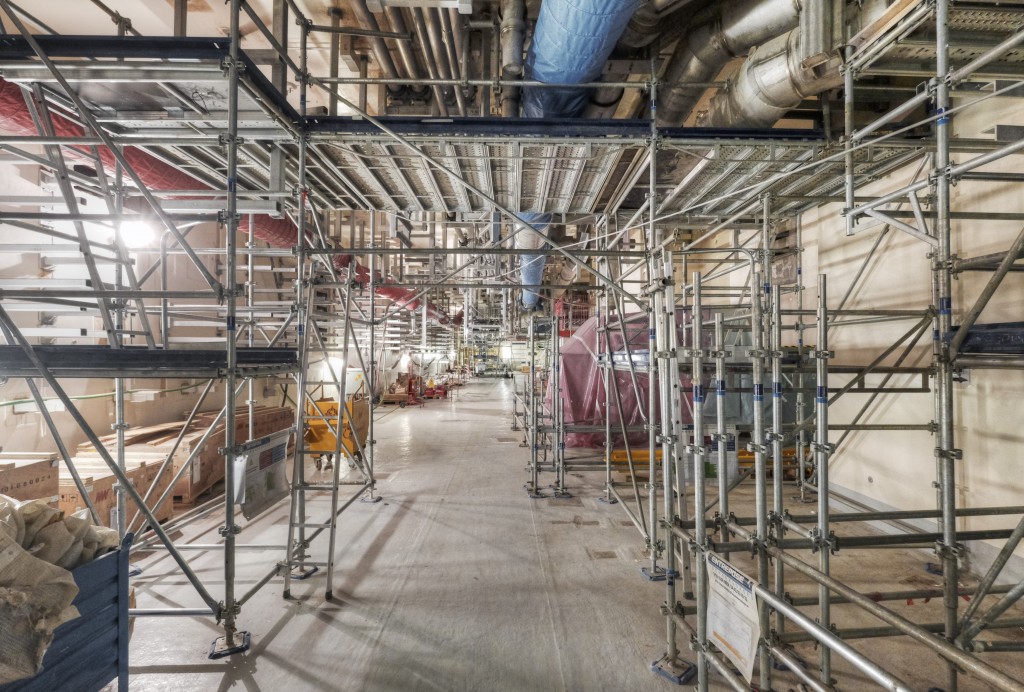
Filling up
2021-09-29 - Back in 2016 we published this GIF, showing how the galleries of the Tokamak Complex would fill up with equipment: https://www.iter.org/newsline/-/2570. Well, the reality corresponds to the plan... © Christian Luenig
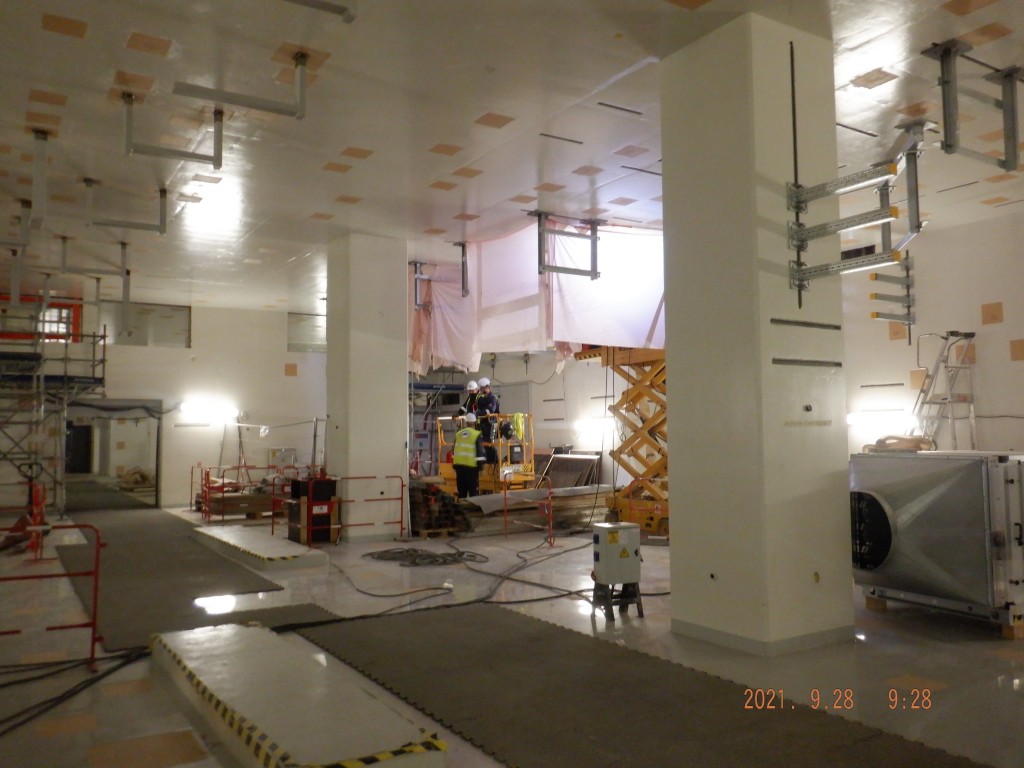
Readying the supports
2021-09-28 - All through the Diagnostic Building, plant assembly teams are installing ceiling supports for equipment.
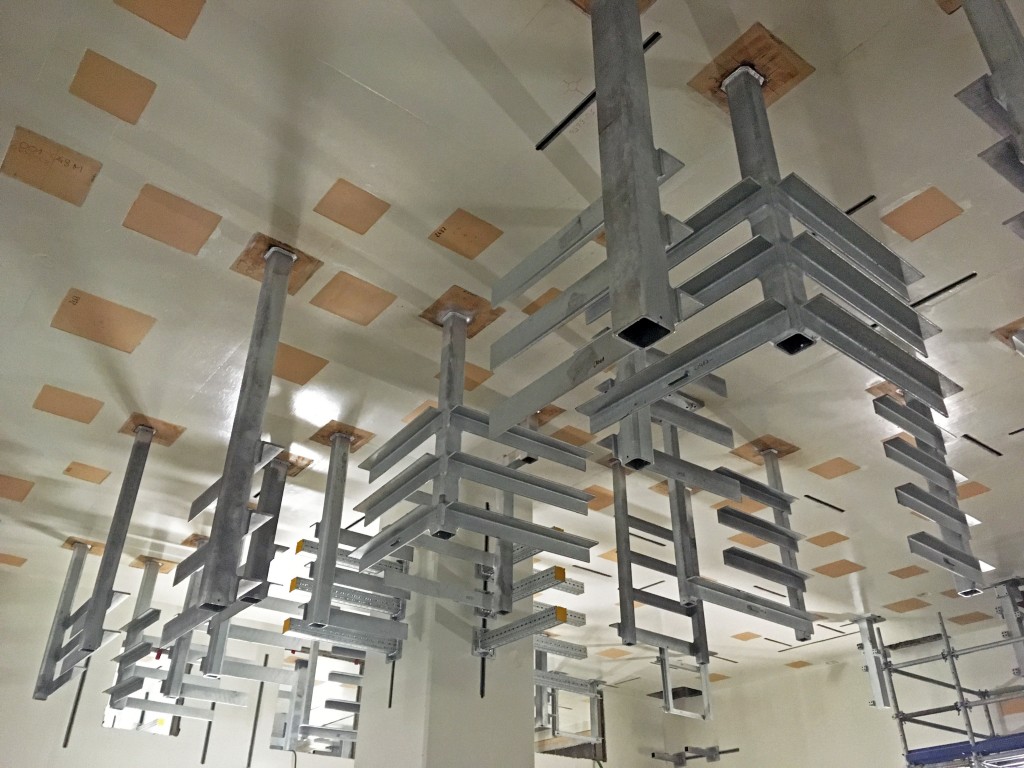
Cable tray supports
2021-09-25 - Cable tray supports are welded to the embedded plates in the ceiling of the Tokamak Complex. Over 100,000 plates have been pre-positioned in the concrete in anticipation of systems installation.

Plasma cutting tool
2021-09-22 - Precisely aligned, the nozzle of the robot's cutting head delivers a super heated jet of hydrogen-nitrogen-argon plasma.
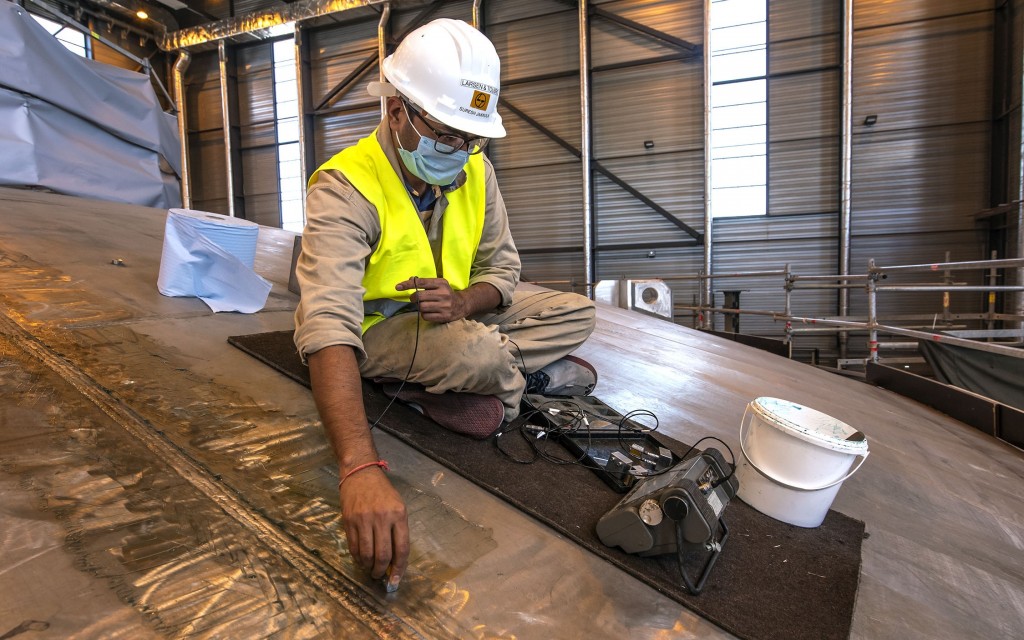
50% of welding finalized
2021-09-22 - Every radial joint must be leak tested on both surfaces of the steel plate (top and underside), a process that takes about two days. 50% of cryostat lid welding has now been finalized.

Like a fire-breathing dragon
2021-09-22 - This plasma-jet cutting tool is performing precise machining on the cryostat lid. The ultra hot (30 000 °C) hydrogen-nitrogen-argon plasma slices through steel like butter.

Visiting the heart of ITER
2021-09-17 - It is still possible to enter the Tokamak Building to view machine assembly close up. In this photo, European Union Commissioner for Energy Kadri Simson is accompanied by ITER Director-General Bernard Bigot.
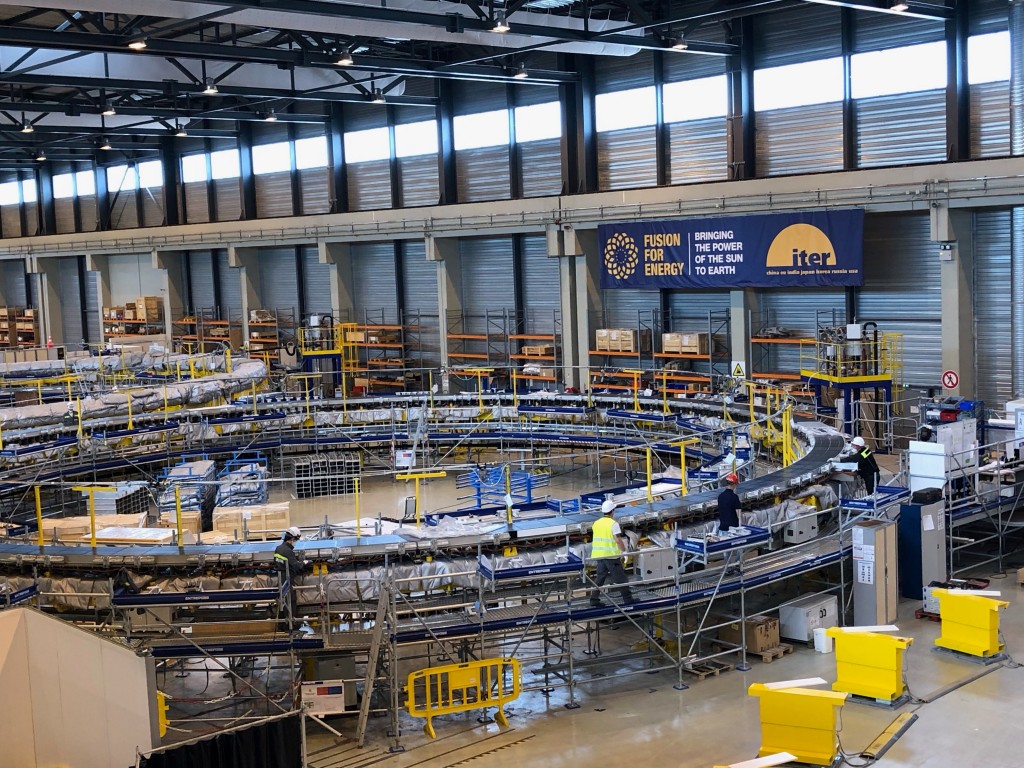
PF4 is underway
2021-09-16 - In Europe's on-site facility for poloidal field coil manufacturing, the teams are creating the individual double pancakes for PF4, a coil that is 24 metres in diameter. After PF5 (installed in the pit) and PF2 (nearly completed), PF4 will be the third ring-shaped magnet to leave the facility.

Ring coil PF5 installed successfully
2021-09-16 - The coil slowly descends into the assembly pit on 16 September 2021. It will make a long pause for final metrology before being delicately deposited on its temporary supports.

Ring coil PF5 is in place
2021-09-16 - The coil has now reached its "parking position," where it will remain for a few years. When all vacuum vessel sectors are in place, it will be raised approximately 1.5 metres to its permanent position.

Planarity checks
2021-09-16 - Lifting and positioning huge components, like this 17-metre-in-diameter poloidal field coil (PF5) demands a perfect balancing of the lifting hooks and a constant check for planarity. The metrology teams are essential.

Another major magnet installed
2021-09-15 - Right on time, the assembly teams lower poloidal field coil #5 into the Tokamak pit. This magnet, which is captive under the machine, needed to be in place before the first vacuum vessel sub-assembly is lowered late next month.
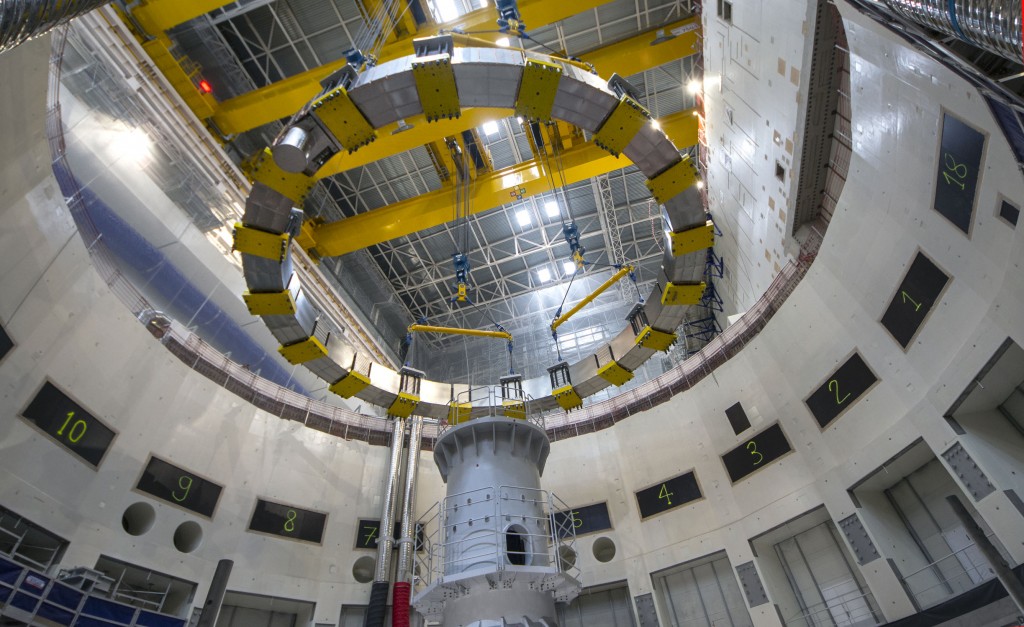
A pause for metrology
2021-09-15 - Part of the way down, the load is paused in order for metrologists to take measurements. It must be positionned at the bottom within a few millimetres of tolerance.
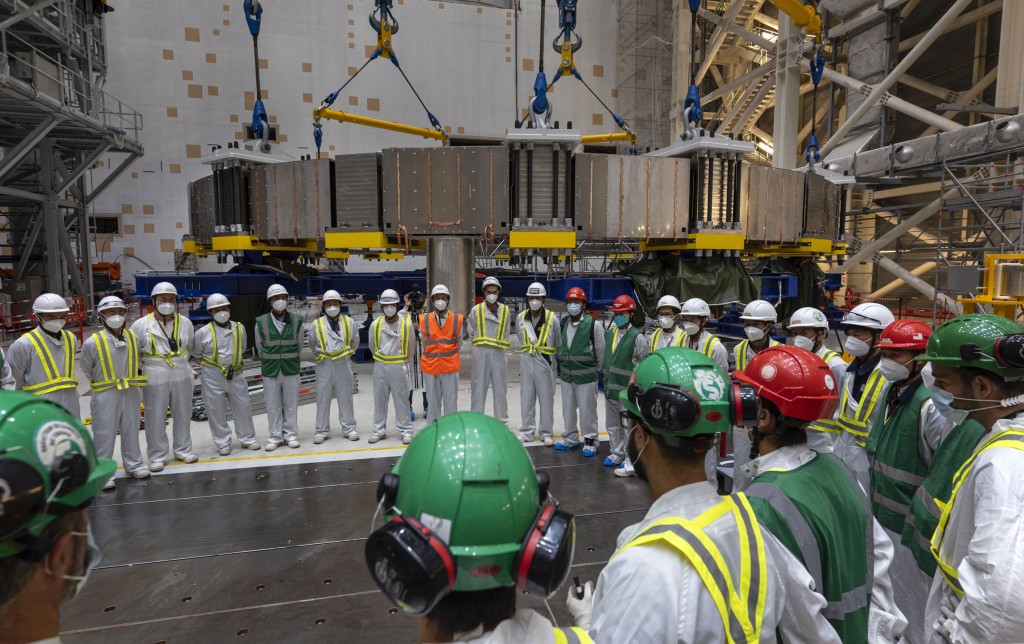
Early morning briefing
2021-09-15 - Approximately 20 workers from the machine assembly consortium CNPE, two crane operators and four ITER Organization supervisors were involved in the operation.
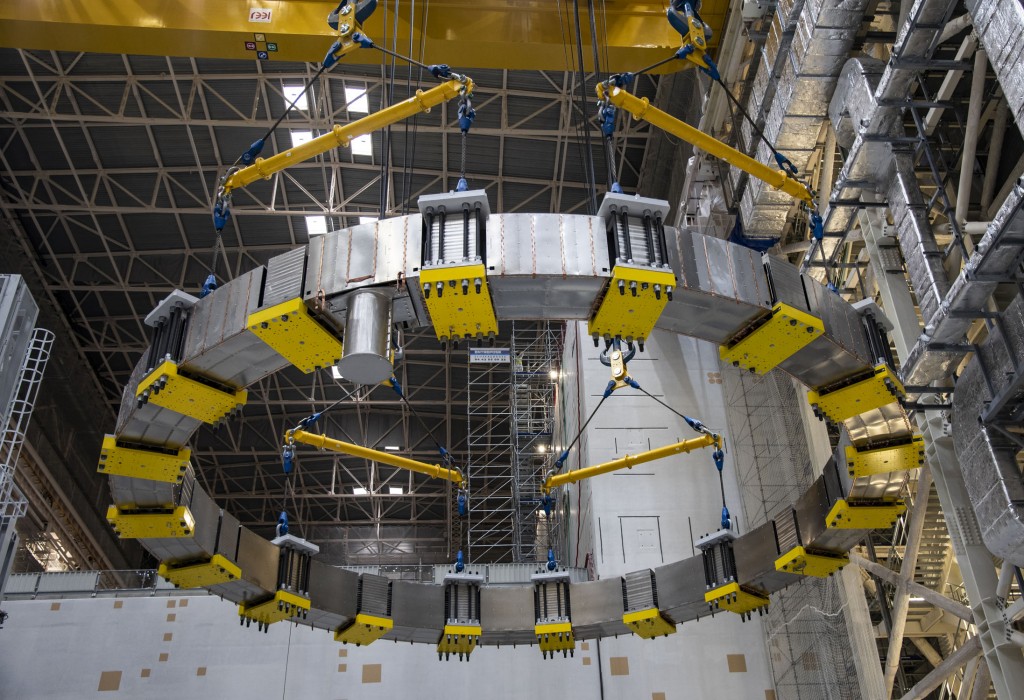
Created on site by Europe
2021-09-15 - Poloidal field coil #5 is the first magnet to exit the Poloidal Field Coils Winding Facility, a production facility created on site by the European Domestic Agency for the realization of four of the five ring-shaped magnets under its responsibility. (The fifth, poloidal field coil #6) was produced at the Chinese institute ASIPP under an agreement with Europe.)
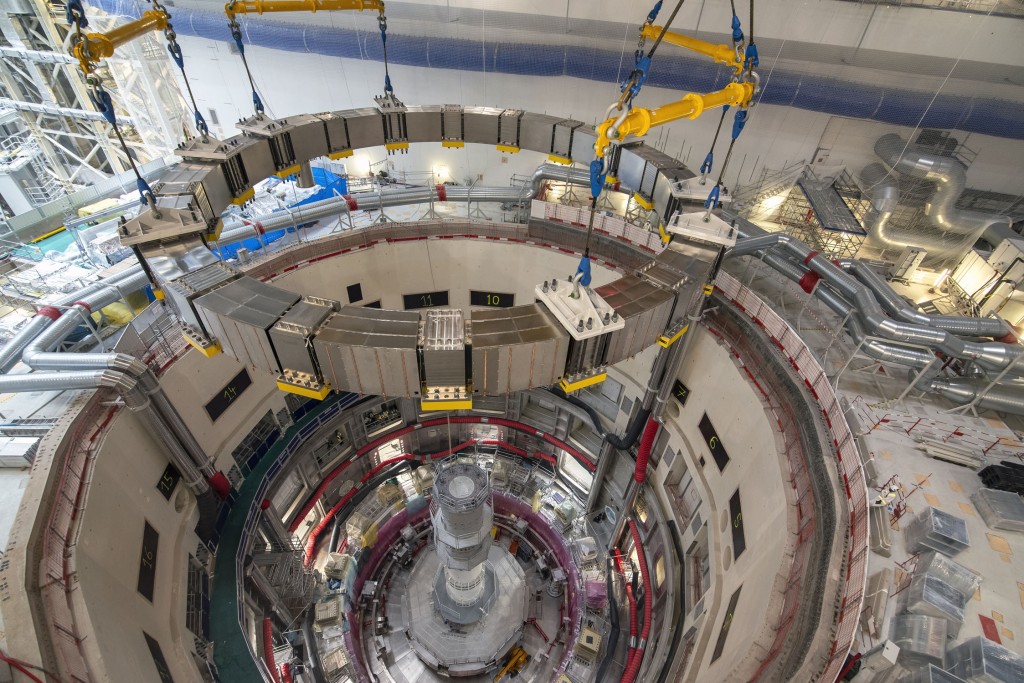
Altitude 35 metres
2021-09-15 - The coil is now approximately 35 metres above its final position. Its diameter is just a few centimetres smaller than the lower cryostat thermal shield that is visible (wrapped in protective pink plastic) at the bottom of the pit.

Planarity check
2021-09-15 - Poloidal field coil #5: Lifting and positioning a 17-metre-in-diameter steel coil demands a perfect balancing of the lifting hooks and a constant check for planarity.
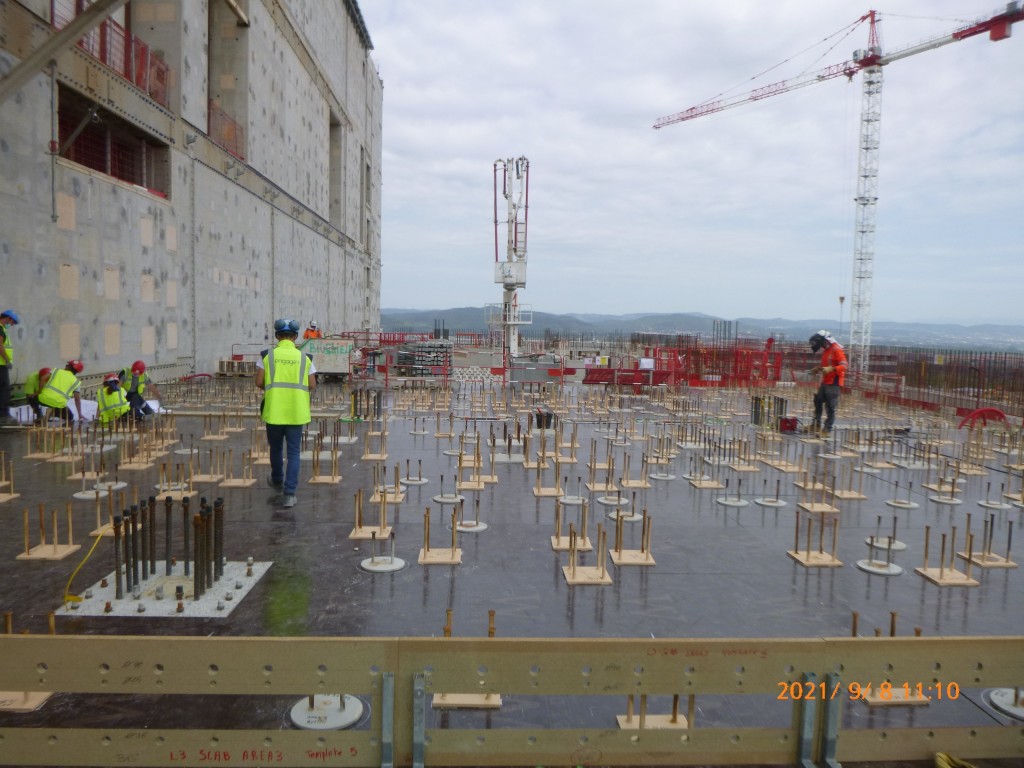
Planned completion: 2023
2021-09-09 - Work on the Tritium Building resumed this year. The final level (L5) should be completed in the spring of 2023. While most of the functions of the Tritium Building are directly linked to full-power operation at ITER, the building also hosts equipment that must be in place by First Plasma.

Home at last
2021-09-09 - The first central solenoid module to arrive on site enters the antechamber of the Assembly Hall, where it will be stored until the second module arrives.

Using the column for access
2021-09-08 - At the base of the central column tool, the first work platform has been installed. Platforms will be installed at three other levels, with access possible through the hollow interior of the column (equipped with ladders).
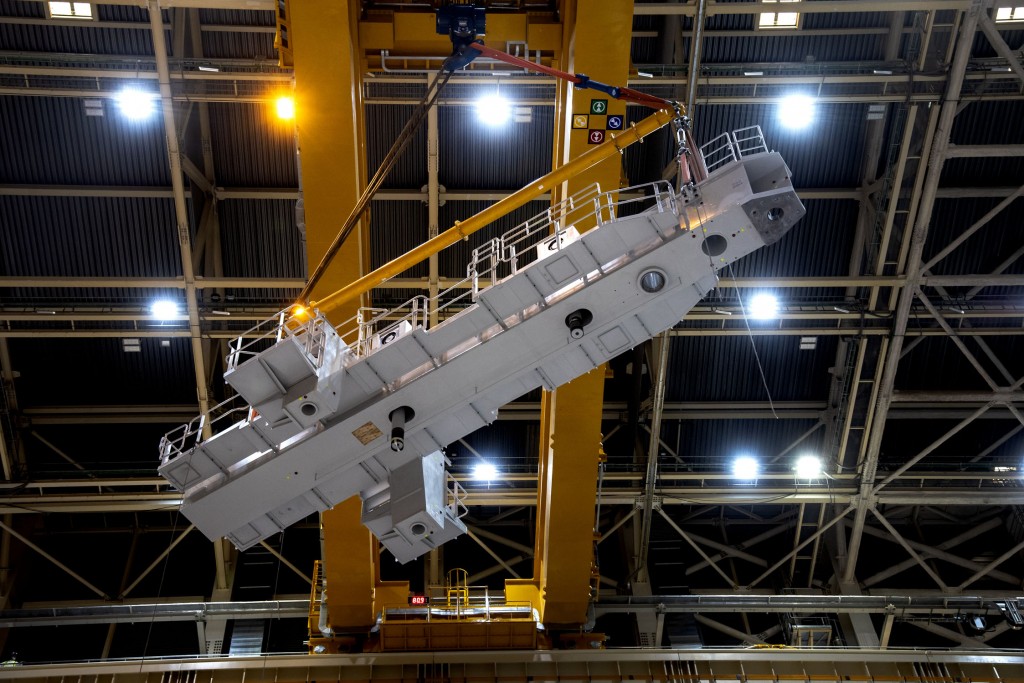
A spaceship?
2021-09-07 - The shape of an in-pit radial beam is strongly evocative of slim spaceship—the bow turned toward its destination, an upper deck gangway, and openings in its hull like rocket exhausts.
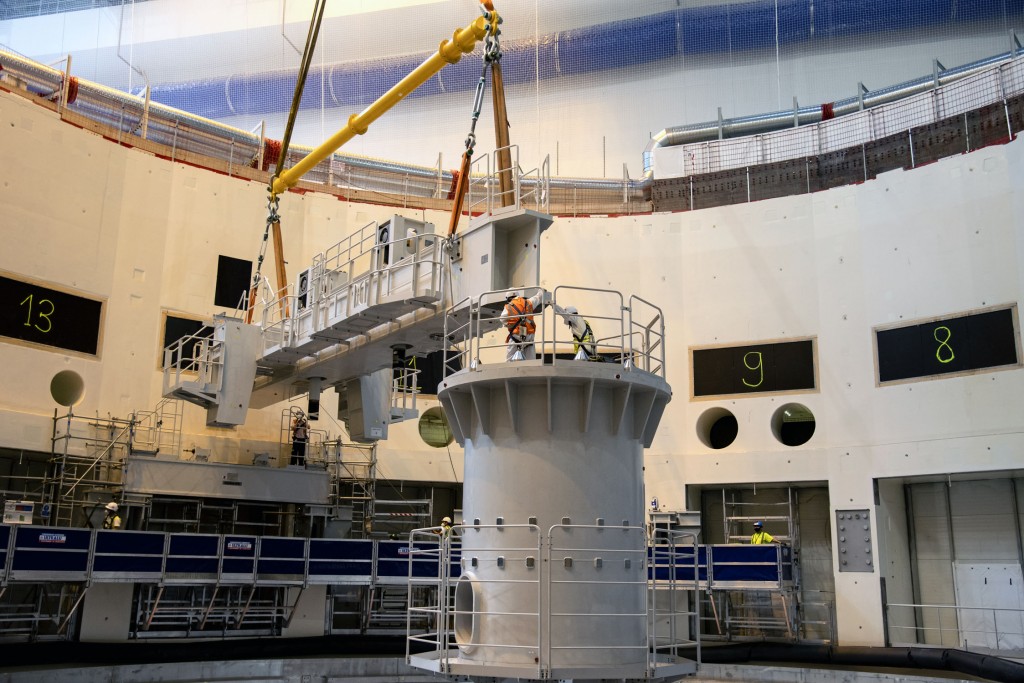
Good fit
2021-09-07 - The test operation demonstrated that the docking and bolting of the test beam fell within the required tolerances.
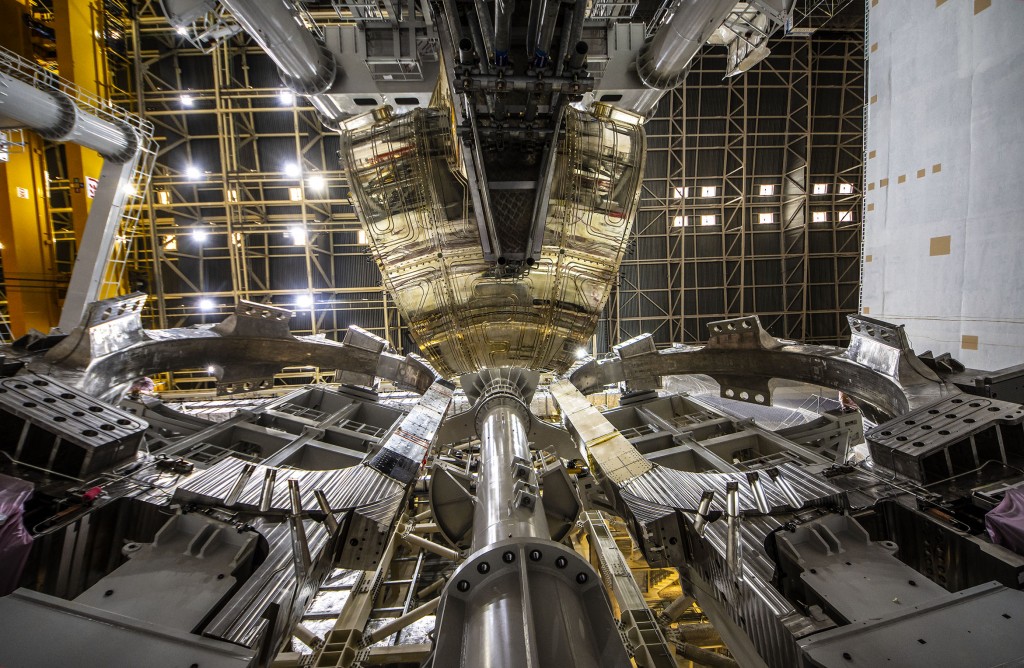
ITER's largest tools
2021-09-07 - This tall three-pillared sector sub-assembly tool (SSAT) weighs 700 tonnes, and is capable of supporting a vertical vacuum vessel sector (440 tonnes, centre) and two toroidal field coils (2 x 350 tonnes, left and right). Impressive.
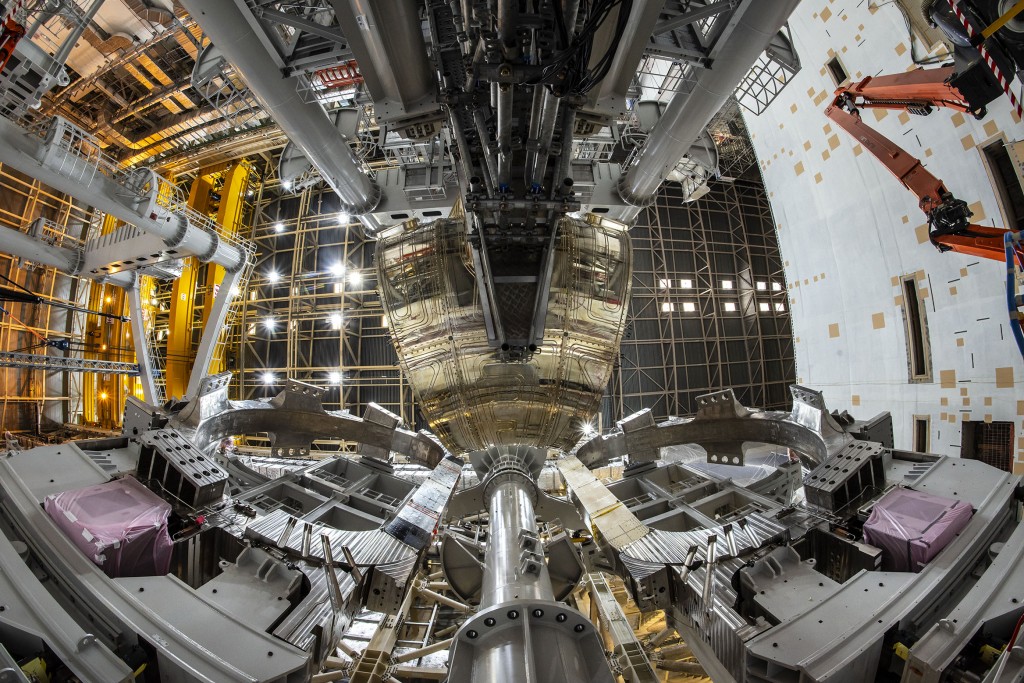
First sub-assembly underway
2021-09-07 - The assembly teams are creating the first vacuum vessel sub-assembly in one of the tall tools in the Assembly Hall. Vacuum vessel sector #6, seen from below covered by its shiny thermal shield, will be paired with toroidal field coils TF11 (left) and TF12 (right). The completely integrated unit, weighing 1,200 tonnes, will be lowered into the Tokamak pit in late October.
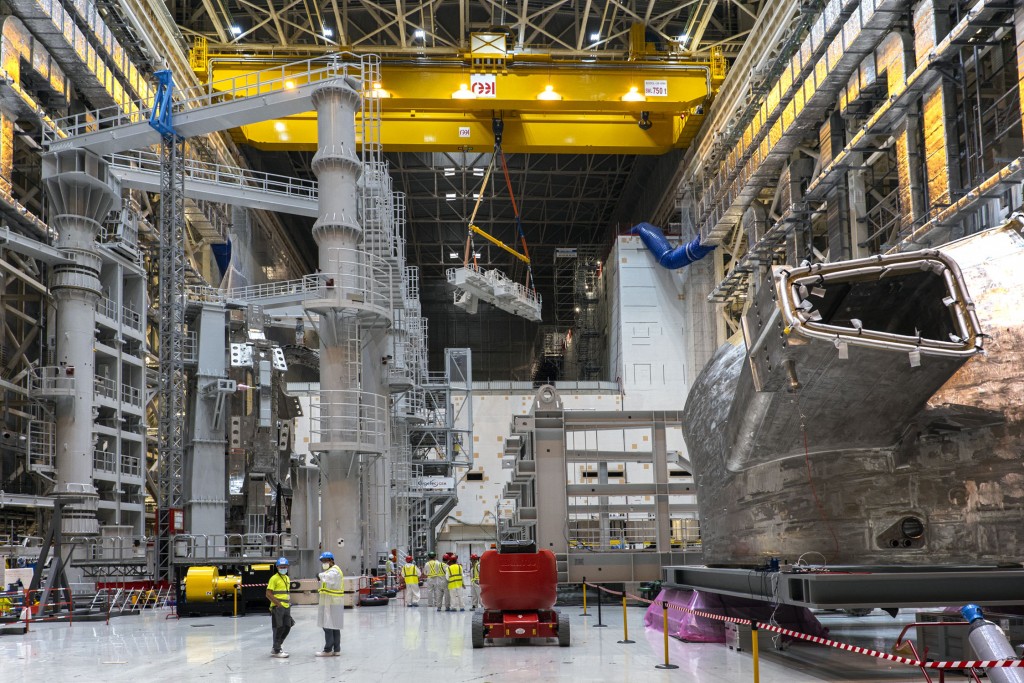
Preparing for a big lift next month
2021-09-07 - The first vacuum vessel sector should be ready for transfer to the pit late October, fully assembled with its thermal shielding and two toroidal field coils. It will travel into place under a radial beam that will brace its its weight between the column and the wall. In early September, this docking operation was tested without load.
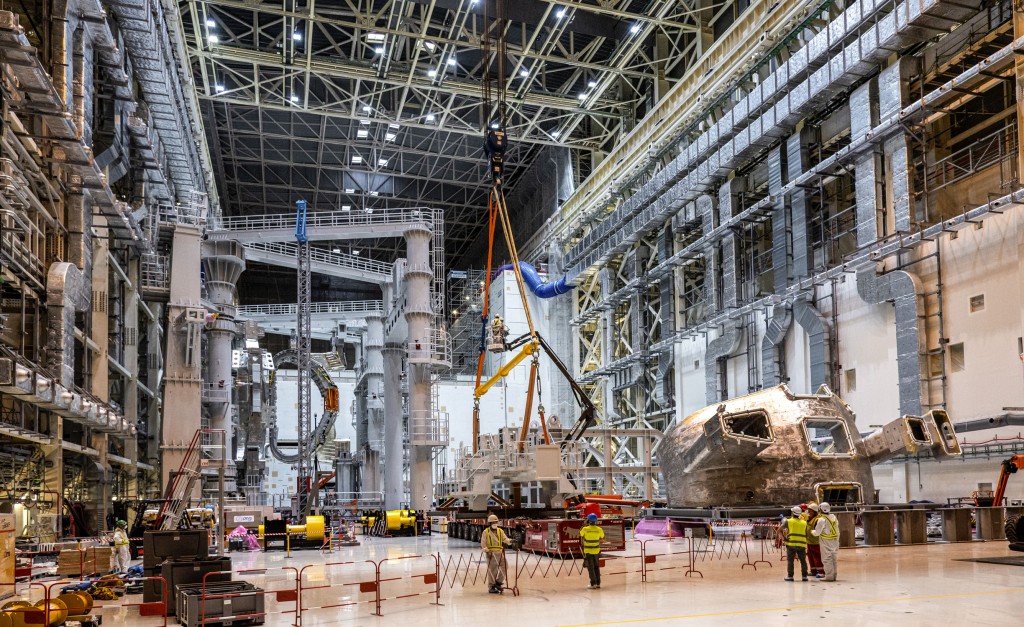
The antechamber of the tokamak
2021-09-07 - Before being assembled in the Tokamak pit, all large components are brought through this space: the ITER Assembly Hall. Their sojourn in this space can be long or short, depending on the number of pre-assembly activities required to prepare the components for lifting.
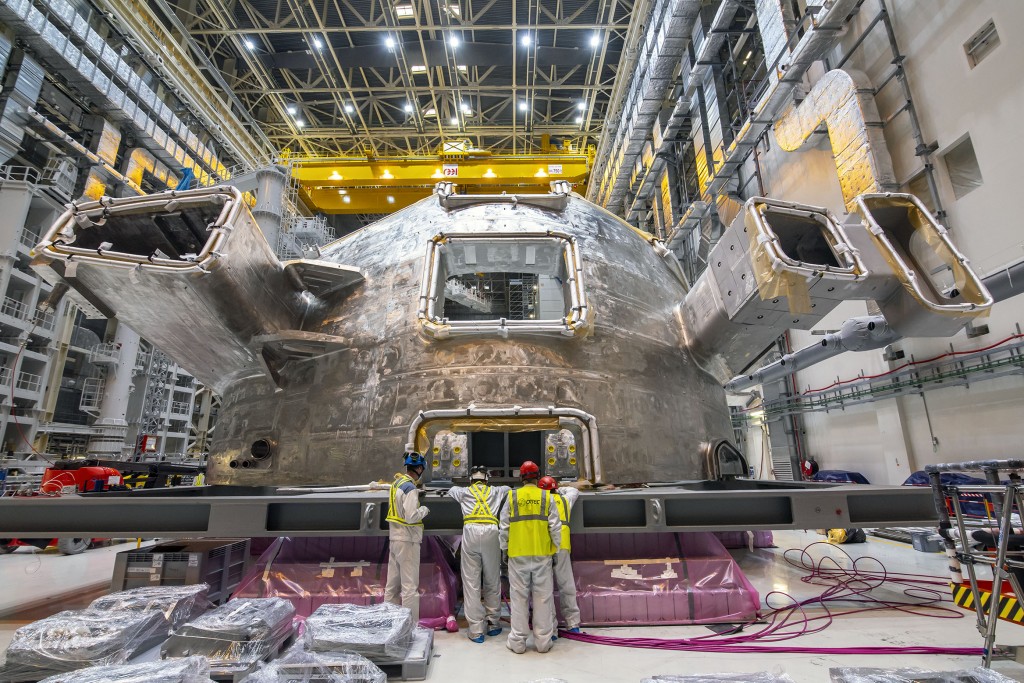
Unpacked
2021-09-07 - The latest vacuum vessel sector to arrive at ITER—sector #1(7)—has been positioned in the Assembly Hall and unwrapped.
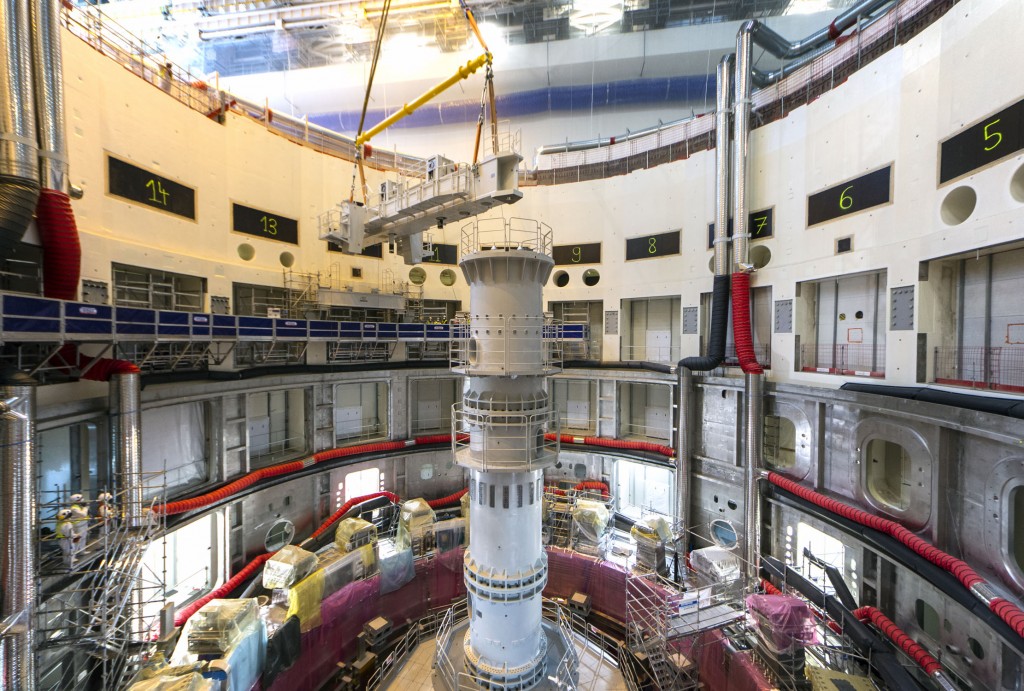
Testing a radial beam
2021-09-07 - Radial beams will arrive in the pit supporting each vertical vacuum vessel sub-assembly as it travels by overhead crane. Their precise positioning is paramount for the alignment of the machine torus. A test operation, in September, demonstrated that tolerances were respected.
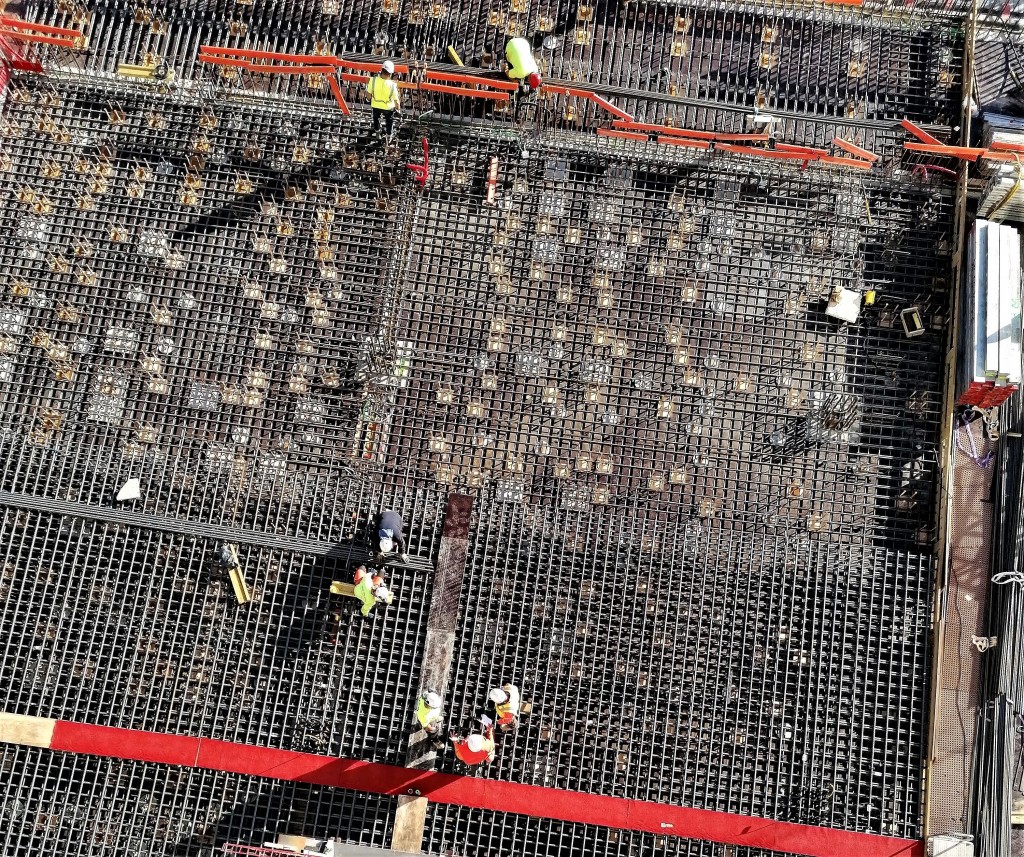
Tritium Building advancing
2021-09-03 - Work is underway on the L3 level of the Tritium Building. (September 2021)

Central column in place
2021-09-01 - Formed from a central column and nine radial beams, the in-pit column tool will support, align and stabilize vacuum vessel sub-assemblies as they are joined and welded. The tool is designed to support a nominal weight of 5,400 tonnes.
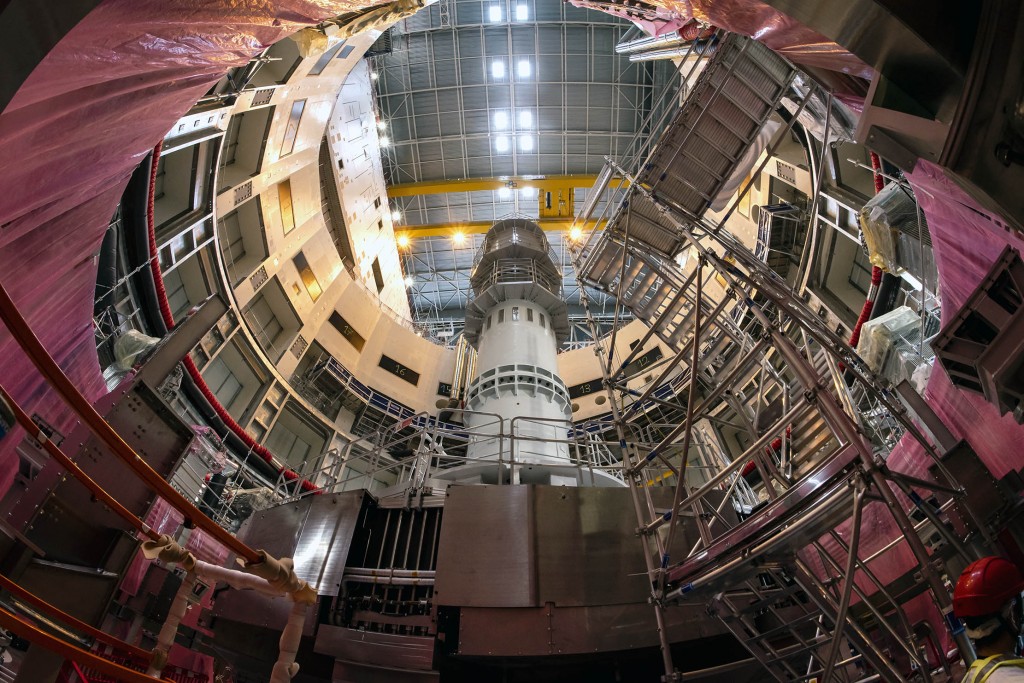
Central column
2021-09-01 - A central column is being erected in the centre of the Tokamak pit. It will help support the vacuum vessel sector sub-assemblies as they are welded together.

Preserving installed components
2021-09-01 - Between installation and operation, machine components and plant equipment must be kept in good condition through preservation activities. Here, a worker performs a white cloth test to check for moisture on a cryostat support bearing during a preservation inspection.

Revealed
2021-08-30 - The metal housing is lifted and ... voilà! ... the 440-tonne sector is revealed.

Inspection underway
2021-08-30 - Delivered on Friday 27 August, sector #1(7) was unpacked the next day. In this image, members of the vacuum vessel team are carrying out a first visual inspection prior to removing the component's protective plastic wrapping.
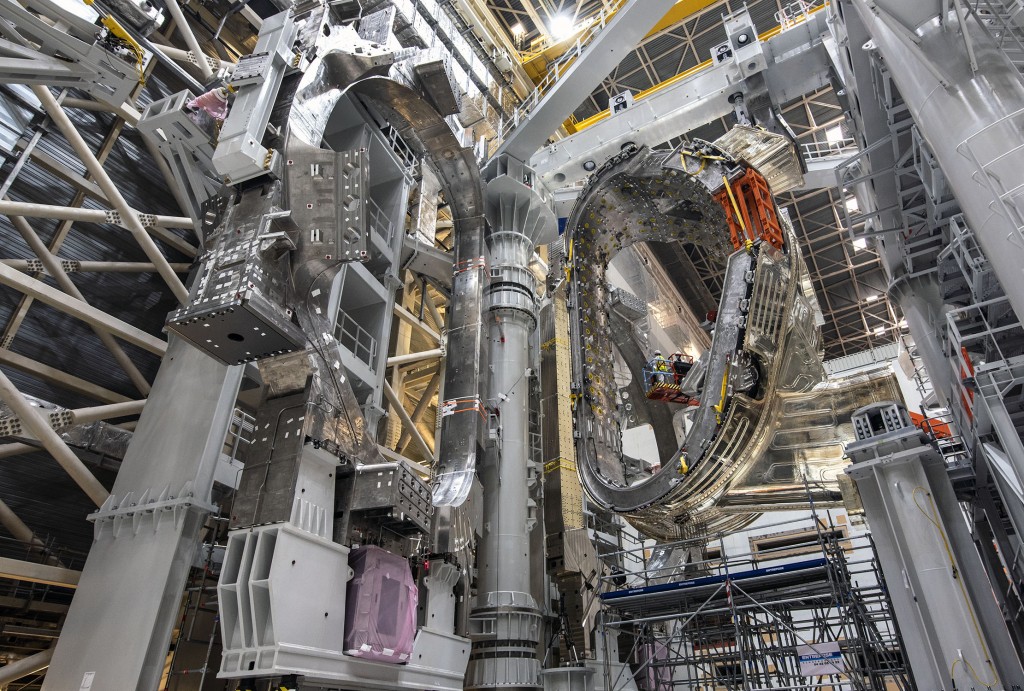
Rotation is next step
2021-08-30 - For now, this D-shaped magnet coil (left) is supported from below. Once it is rotated to the vacuum vessel sector (right) and attached, the load can be transferred.
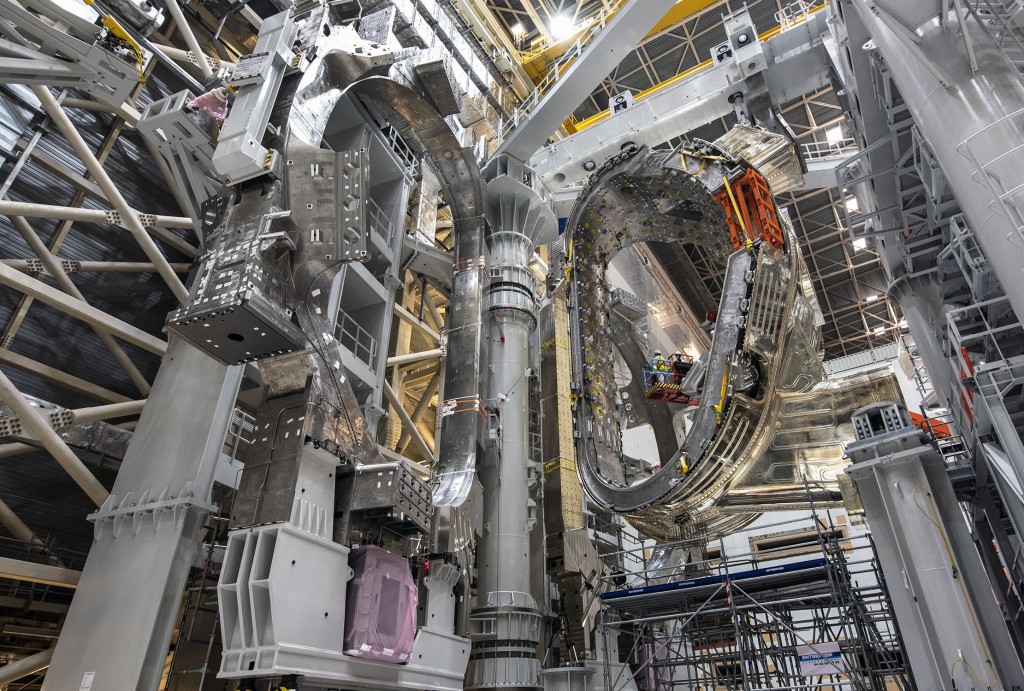
First building block takes shape
2021-08-30 - With the scaffolding now removed, the three constitutive components of the first sub-assembly are revealed in all their technological splendour and complexity: to the right, the 40° vacuum vessel sector encased in its silver-plated thermal shield panels; to the left, toroidal field coil #12. (Toroidal field coil #13 is only partly visible through the sector's D-shaped opening.)

Second vacuum vessel sector received
2021-08-27 - Vacuum vessel sector #1(7) from Korea enters the Cleaning Facility. It is just a few hundred metres from its final destination.

Shiny surfaces
2021-08-24 - If you look closely into this V-shaped tool, you'll see the components that must be associated: the triangular form of the vacuum vessel sector (centre, shiny) already covered in panels of thermal shielding, and toroidal field coils on wings to either side. At the top of the image, poloidal field coil #5 stands ready for installation in the pit.

Assembling a puzzle
2021-08-24 - A vacuum vessel sector sub-assembly tool is photographed from an overhead crane. All the pieces are in place to assemble the first section of the ITER vacuum vessel.
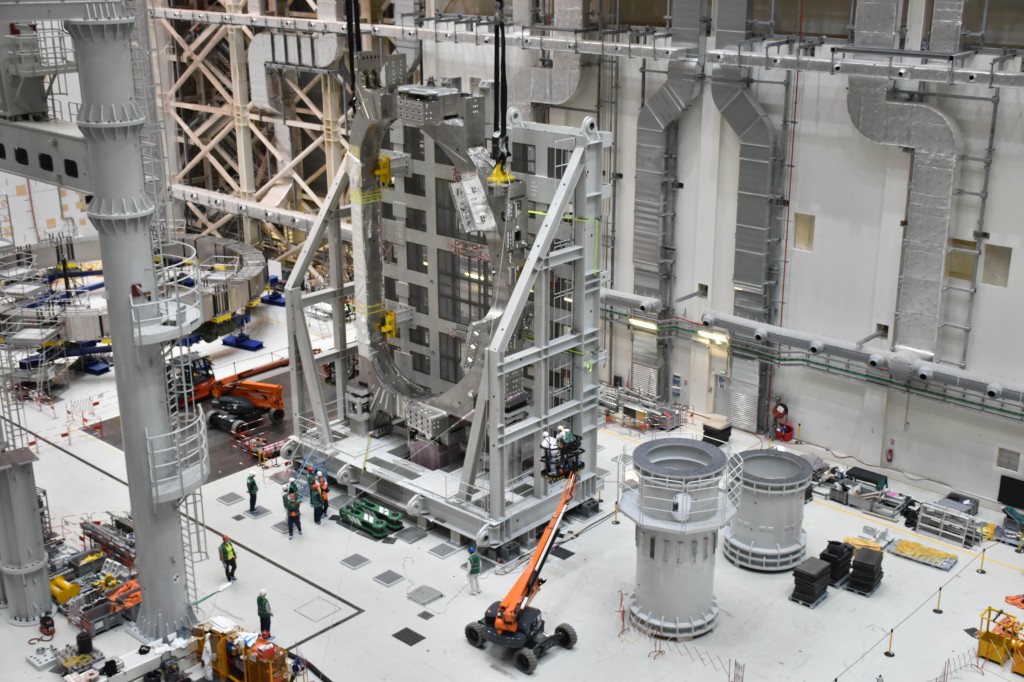
Ready for coil number 2
2021-08-12 - Two days after the transfer of coil TF12 to the standing tool, its twin—TF13—was raised to vertical and delivered to the opposite wing. Vacuum vessel sector #6 now has a toroidal field coil on each side.
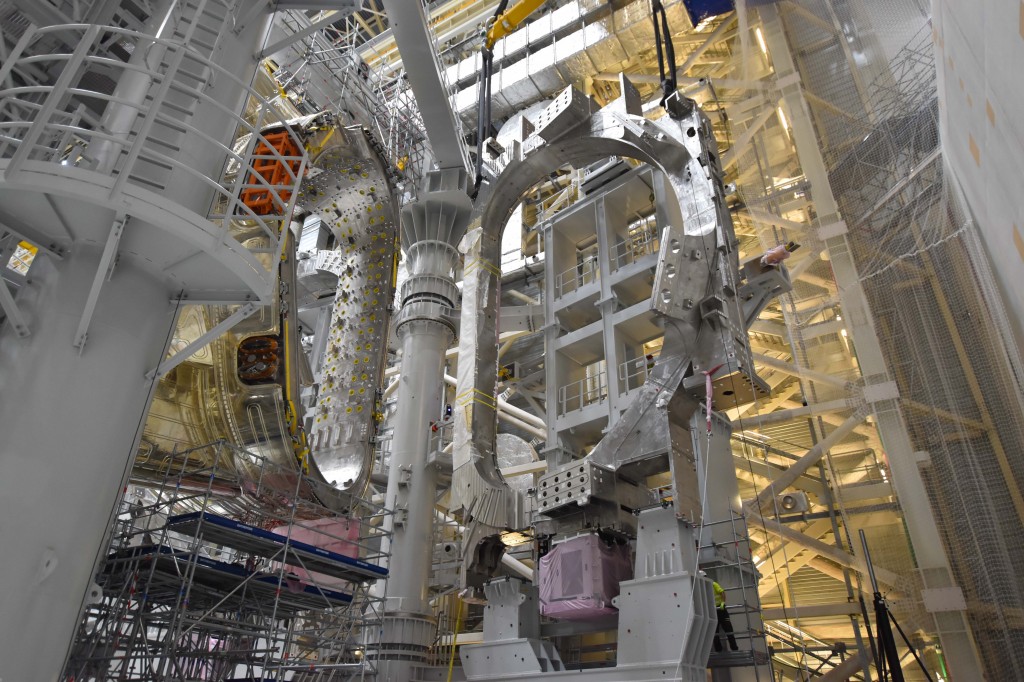
Second vertical coil delivered to tool
2021-08-12 - To the right of the image, the newly installed toroidal field coil. To the left, vacuum vessel sector #6. (A second vertical coil is out of sight to the left.)
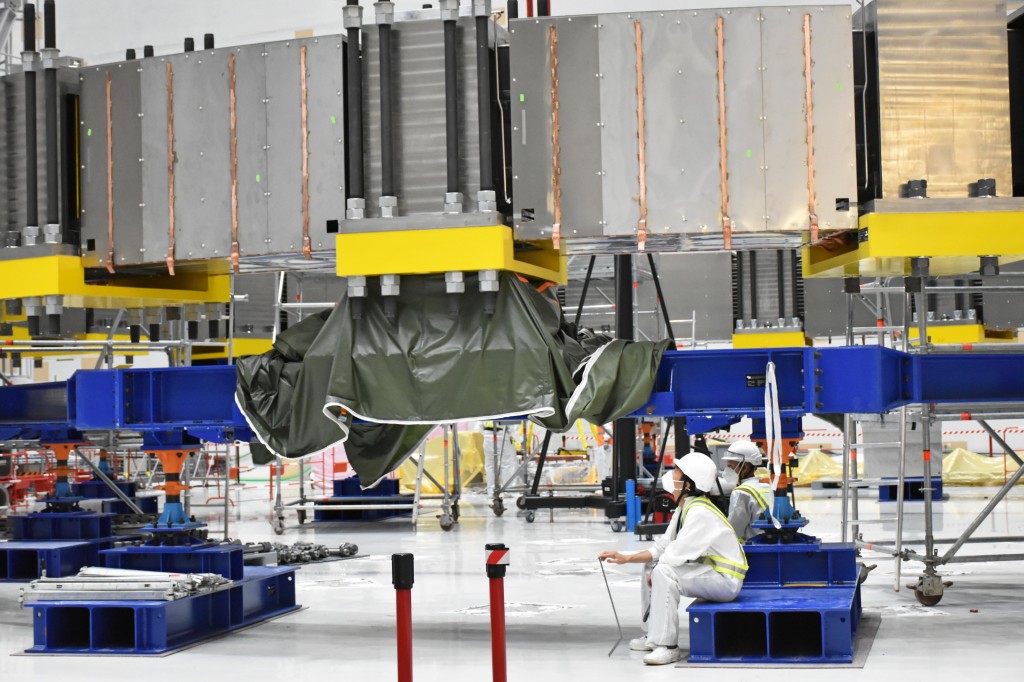
Horizontal coil PF5 ready for positioning
2021-08-10 - A major lift operation will take place in mid-September, as the second poloidal field coil (PF5, pictured) is installed in the Tokamak pit.

From one tool to the other
2021-08-10 - Since 15 June, this toroidal field coil had been stored vertically on one of the wings of SSAT1 (the first vacuum vessel sector sub-assembly tool to be erected in the Assembly Hall). On 10 August, it was moved by overhead crane to the SSAT2 tool, where teams are preparing to create the first vacuum vessel sub-assembly.

Vertical coil moved into place
2021-08-10 - Toroidal field coil #12 (supplied by Japan) is moved out of temporary storage on one standing assembly tool and into the other, where all the action is ready to begin. To form a sub-assembly ready for installation in the machine pit, a vacuum vessel sector must be pre-assembled with two toroidal field coils and panels of thermal shielding.
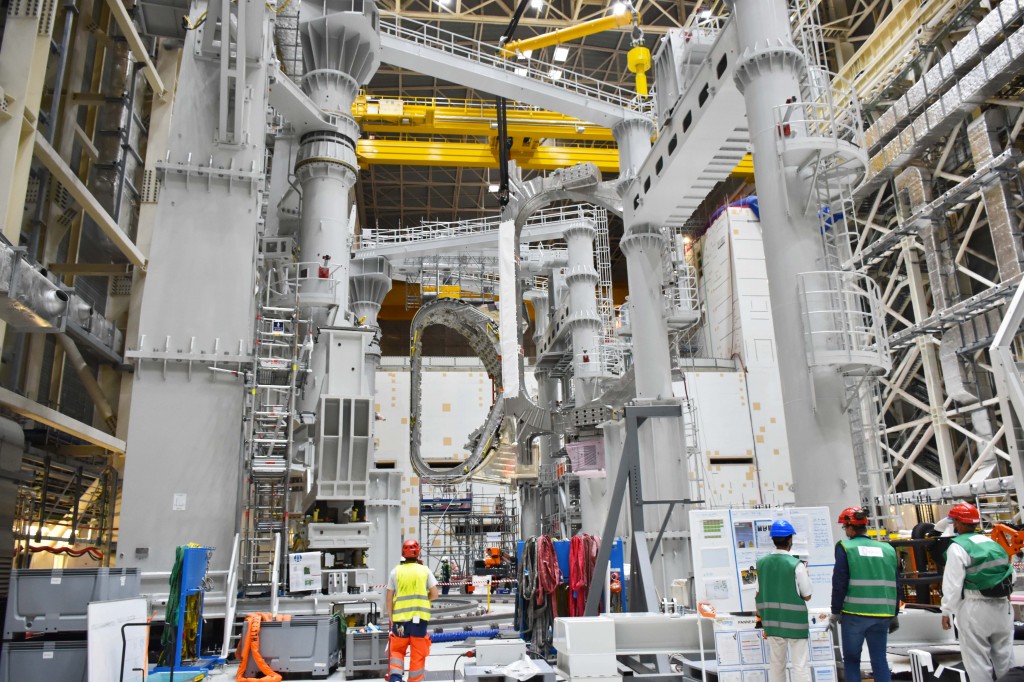
Vertical ballet
2021-08-10 - Toroidal field coil #12 (TF12) is rotated in mid-air to approach its final destination on the wind of the standing tool in the proper position.
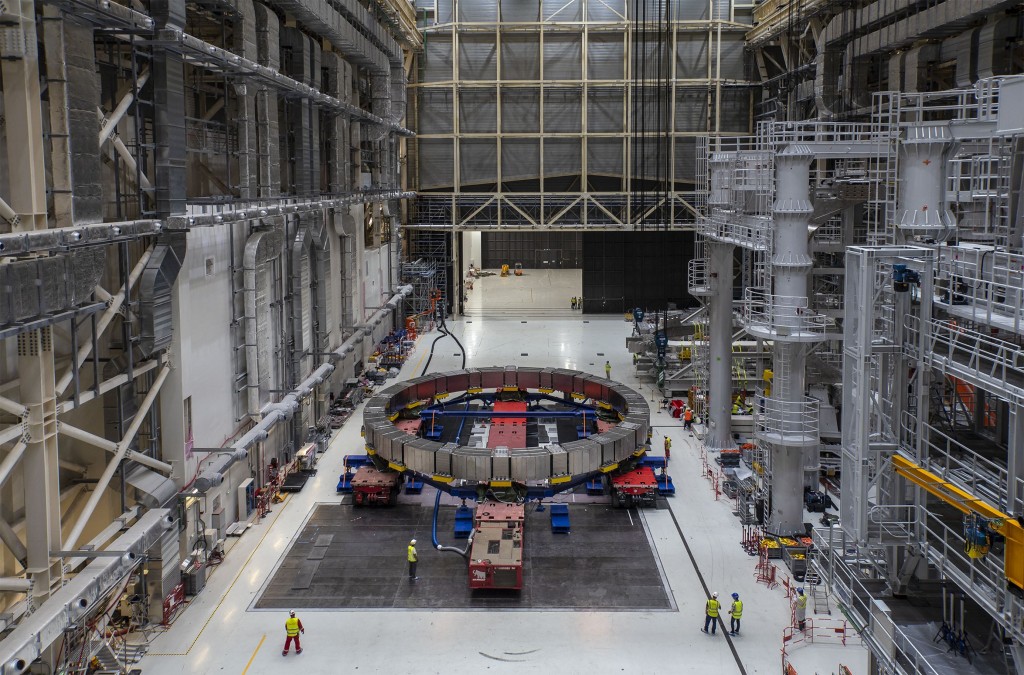
PF5 enters pre-assembly theatre
2021-07-27 - Metrology and rigging must be performed on poloidal field coil #5 before it can be installed in September in the Tokamak pit.

Second ring coil in line for installation
2021-07-26 - Manufactured on site by Europe, poloidal field coil #5 left the production line in April. The component was three and a half years in the making. On 26 July 2021, it was brought into the Assembly Hall, to be prepped for installation in the Tokamak pit.
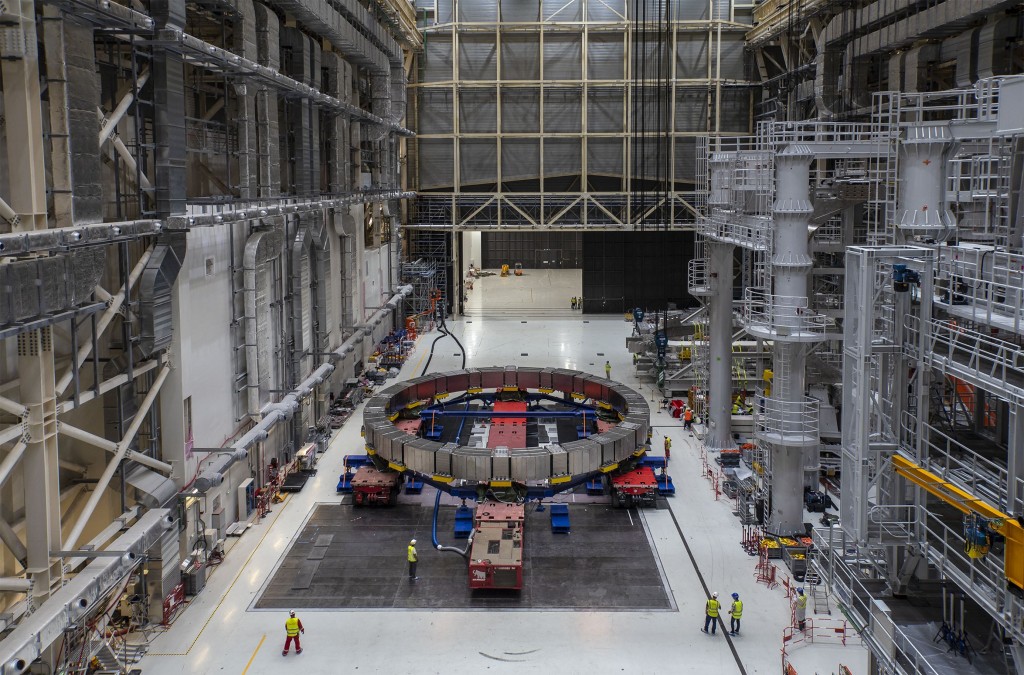
Next major component to be installed
2021-07-26 - A lead actor enters the stage: poloidal field coil #5, 17 metres in diameter, is one the six ring-shaped coils required for the machine.
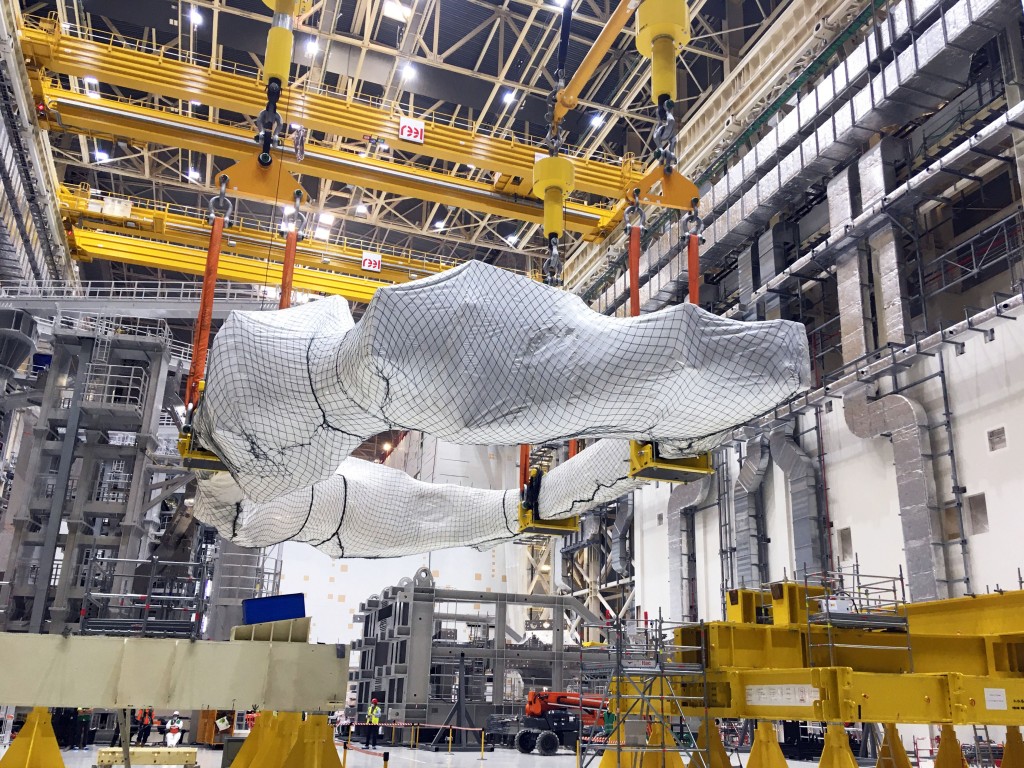
A quick swap
2021-07-12 - The overhead cranes of the Assembly Hall were required to move this toroidal field coil (TF3, from Europe) from its transport frame to a storage frame.
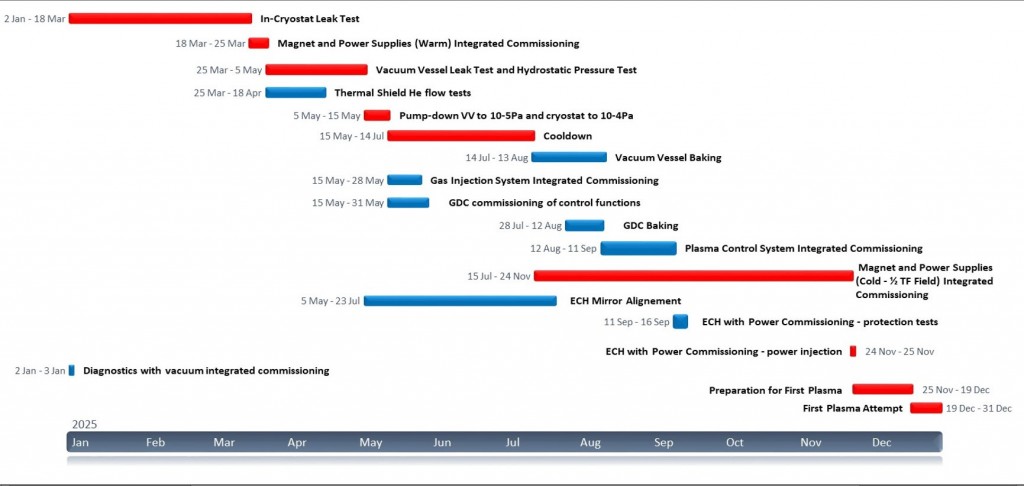
Integrated commissioning at ITER
2021-07-12 - ITER's approach to commissioning makes a clear distinction between system commissioning and integrated commissioning. This chart shows the highest-level tasks for Integrated Commissioning 1, which concludes with First Plasma. Read more at: https://www.iter.org/newsline/-/3641
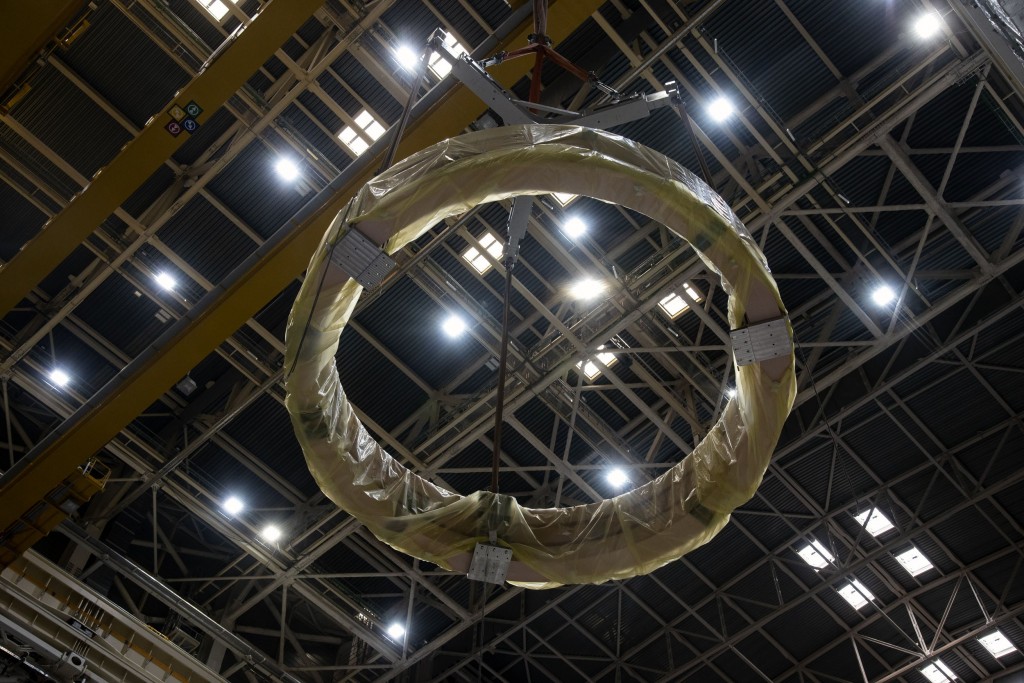
First pre-compression rings installed
2021-07-08 - A set of three spare pre-compression rings made of glass fibre/epoxy composite are installed in the Tokamak pit on Thursday 8 July. Two other sets of three rings will tightly hold the toroidal field coils at top and bottom with a radial force of 7,000 tonnes per coil to push back against expansion forces during operation.

Tight space
2021-07-08 - The set of three spare pre-compression rings was installed in the tight space between the bottom cylinder of the central column tool and the recently installed poloidal field coil #6.

Musical chairs
2021-07-02 - A toroidal field coil (TF13) lays horizontal on a frame in the Assembly Hall. Soon, it will be moved to the upending tool to be raised to vertical.
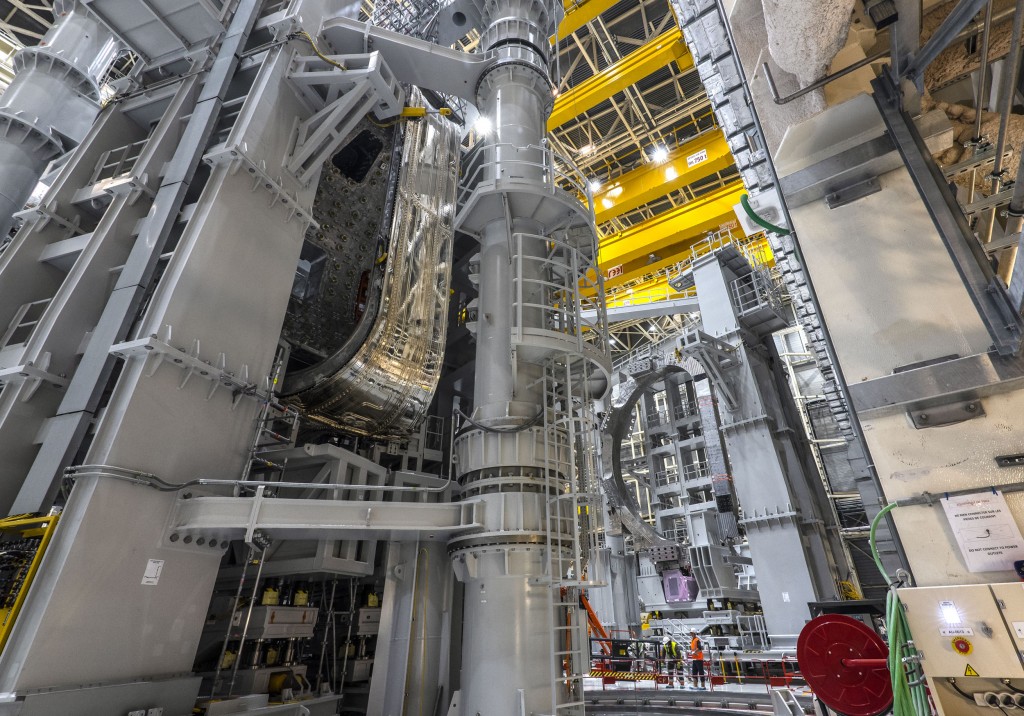
Sub-assembly progressing
2021-07-02 - In the Assembly Hall, the first vacuum vessel sector sub-assembly operation is underway. On the left tool, a vacuum vessel sector has been paired with thermal shielding. On the right, one D-shaped toroidal field coil waits to be transferred over. (Another is ready for vertical upending and installation.) A sub-assembly marries one sector, inboard and outboard thermal shield panels, and two toroidal field coils.

Creating a "sub-assembly"
2021-07-02 - This coil, TF13, will join TF12 on the sector sub-assembly tooling to be matched with vacuum vessel sector #6 and thermal shielding. Both coils were supplied by Japan.

The pit, early July
2021-07-02 - Sixteen of the eighteen toroidal field coil gravity supports are in place in a circle on the cryostat base. Next to be installed? A set of three pre-compression rings around the central column.

Metrology underway
2021-06-29 - Metrology is a constant presence in the Tokamak Complex, whether for construction or assembly tasks. © Les Nouveaux Médias/SNC ENGAGE
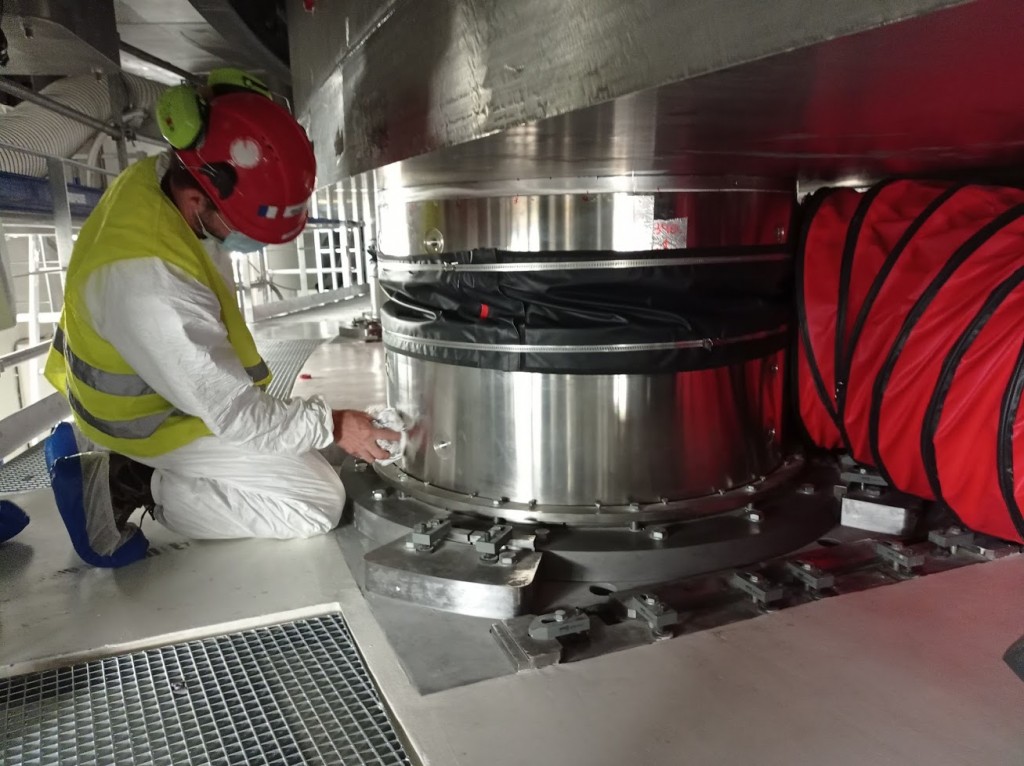
Preserving all installed components
2021-06-28 - Preservation activities are defined for each component that needs to be maintained in good condition prior to entering service. In this photo, a worker performs a "white cloth test" to check for moisture on a cryostat support bearing during a preservation inspection.
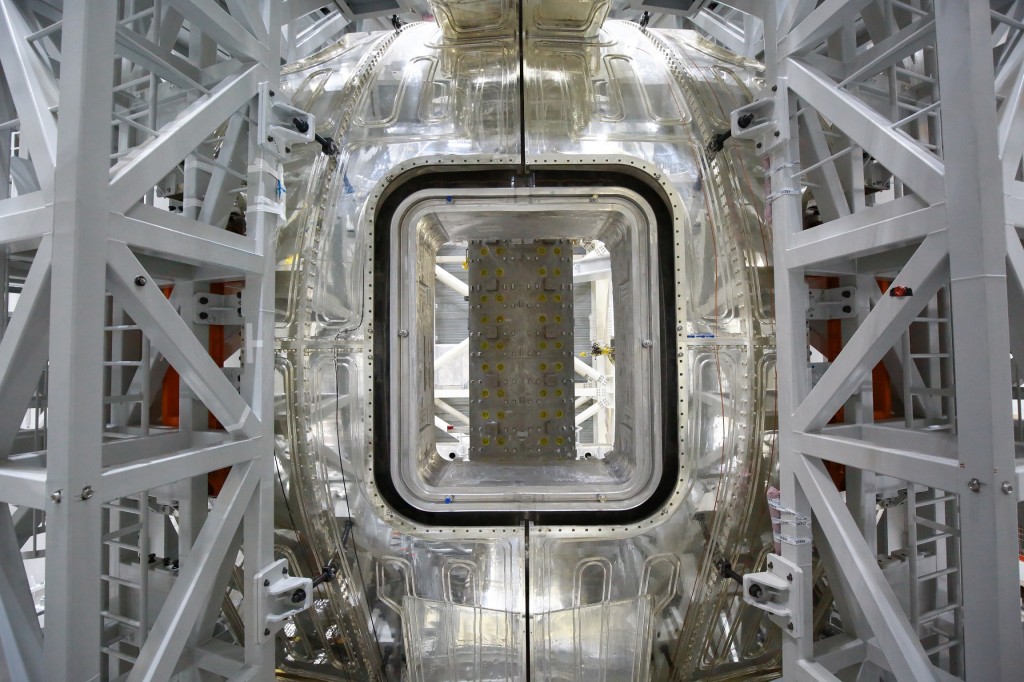
Rotated inward
2021-06-26 - The outboard thermal shield sections have been rotated in by the tooling, and they match perfectly. (Photo courtesy of Chang Hyun Noh.)
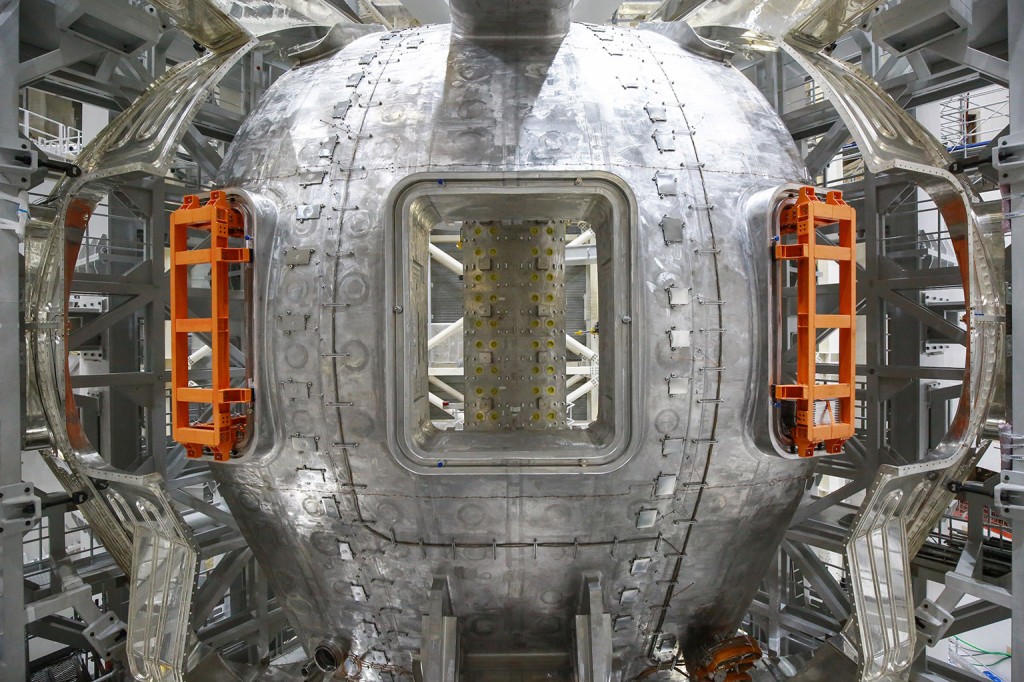
Seen from the back
2021-06-23 - A 40-degree sector of the ITER vacuum vessel is photographed in the sub-assembly tool from behind. Two outboard panels of thermal shielding are ready to be rotated inward and affixed, perfectly matching the shape and openings of the sector. (Courtesy of Chang Hyun Noh.)

Open, for now
2021-06-22 - One of the 46 nuclear doors of the Tokamak Complex, designed to create a radiation barrier. © Les Nouveaux Médias/SNC ENGAGE
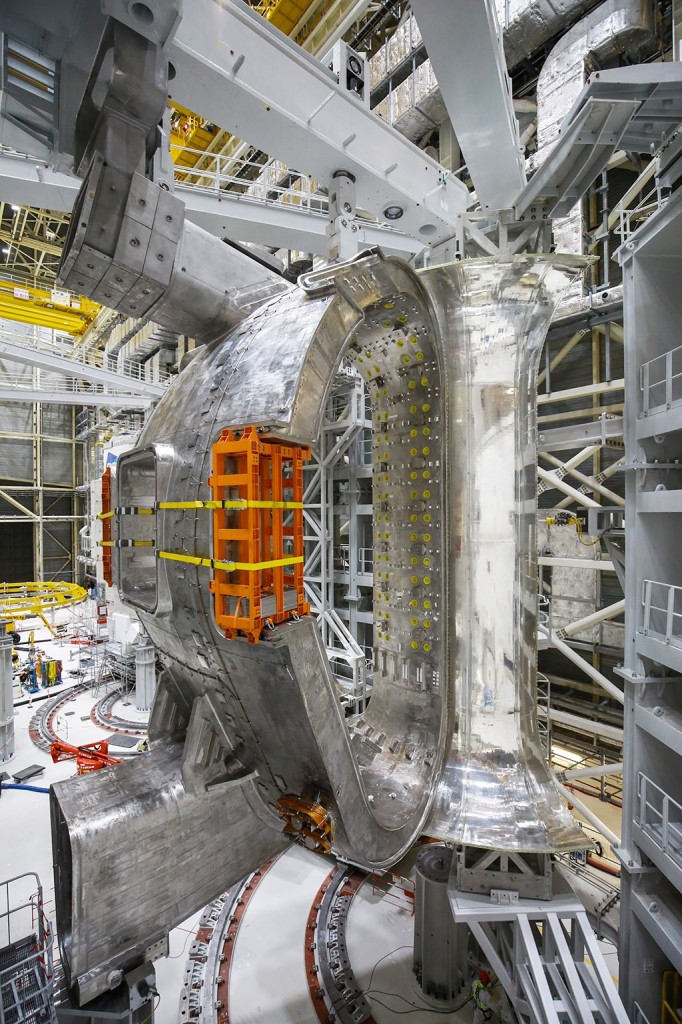
Specialized tool required
2021-06-21 - The thermal shield is designed to fit like a glove. Little by little, the tool introduces the inboard panel behind the vacuum vessel.
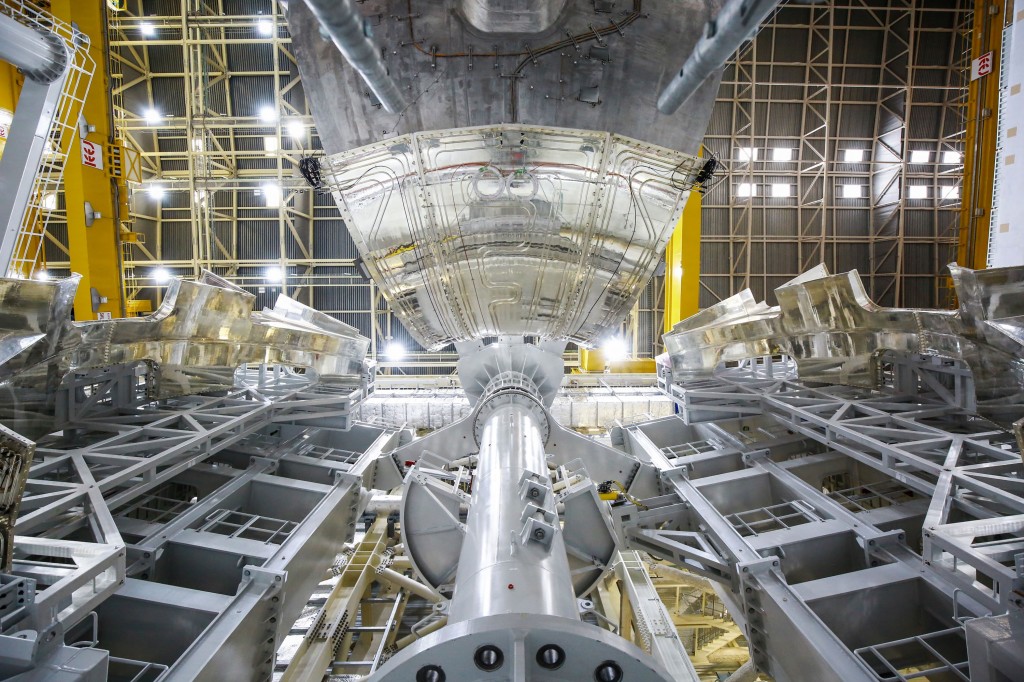
From below
2021-06-21 - Seen from under the sector. The right and left outboard sectors are already attached on the wings of the tool; they will be rotated inward to meet and match perfectly, leaving no part of the vacuum vessel visible.

Thermal shield installed
2021-06-21 - You have to look twice to see it: the inboard thermal shield section has been clamped to vacuum vessel sector #6. Only its colour, shiny silver, permits us to distinguish it from the background grey of the vacuum vessel.
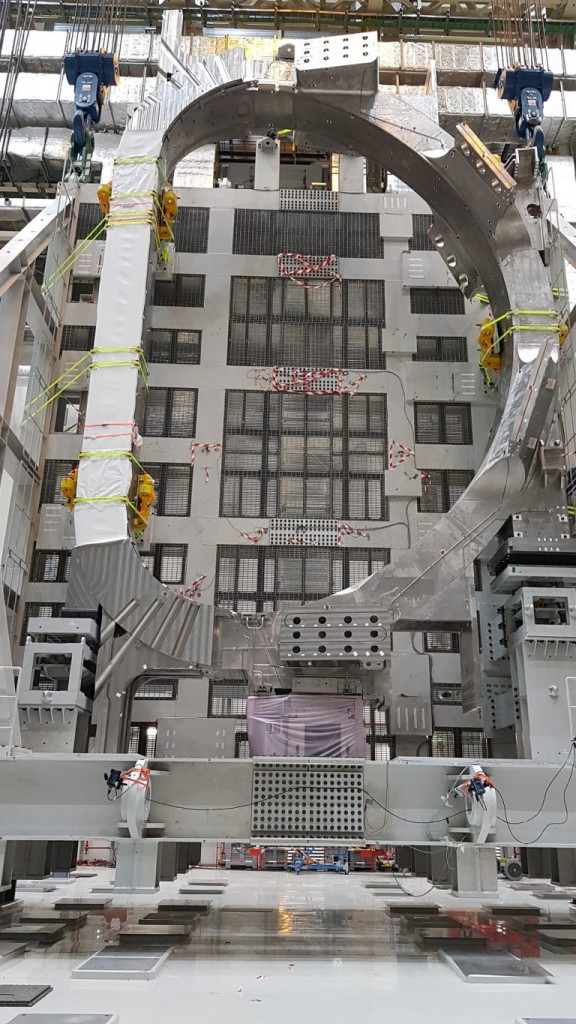
Real-time photogrammetry
2021-06-17 - Two cameras at the bottom of the lifting frame collect data every 5 seconds during the two-hour lift operation of toroidal field coil #12. This real-time photogrammetry permits operators to verify that the deformation of component as it is raised to vertical does not exceed limits.
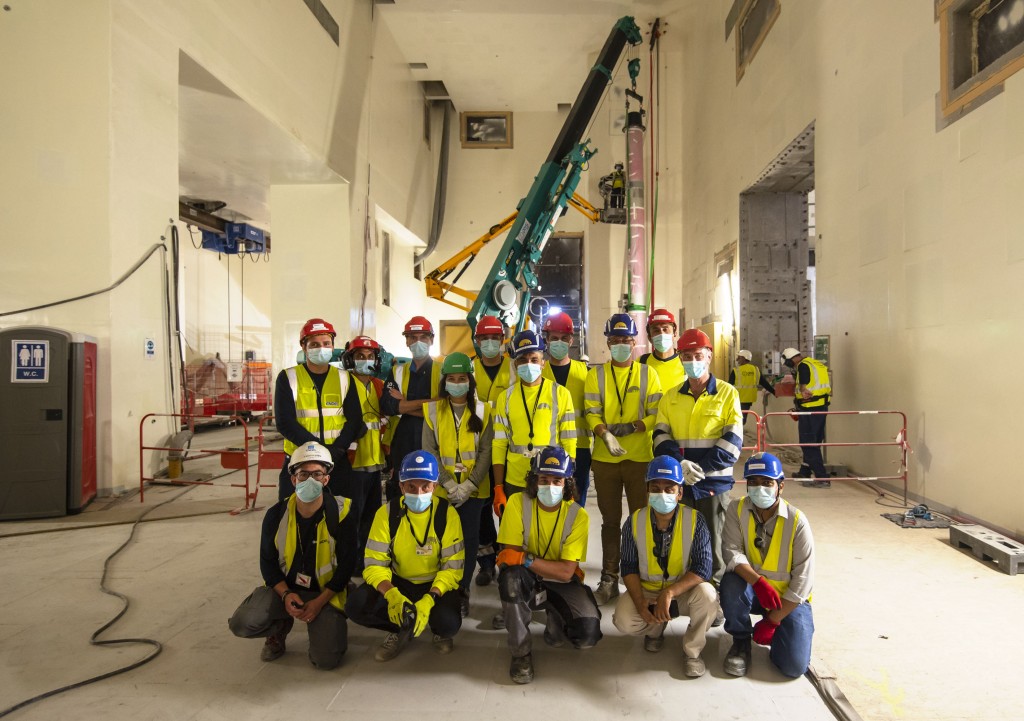
Just tall enough
2021-06-16 - This L3 gallery is just tall enough to permit the handling, by telescopic spider crane, of the 1.5-tonne, 11-metre-long spool. On 16 June it is inserted into the narrow ''south shaft'' connecting L3 to B2, which is designed to host this cryoline plus one other.

Equipment installation
2021-06-16 - In this tall gallery at the top of the Tokamak Complex (level L3), teams are installing cryolines—both horizontally and vertically (in shafts, photo). Painting has been completed at all levels.

Vertical
2021-06-16 - "Vertical cryolines" will connect the cryoline network in the basement (B2 level) with those on level L3. A first vertical spool is installed in the south shaft at L3 on 16 June.

The team in charge
2021-06-15 - Responsible for the operation today is the DYNAMIC SNC consortium (Ansaldo Nucleare; Endel Engie; Orys Group ORTEC; SIMIC; Ansaldo Energia; and Leading Metal Mechanic Solutions SL). As TAC-2 contractor (for Tokamak Assembly Contract 2) for the ITER Organization, DYNAMIC is in charge of the assembly of the main vessel and ports, sector sub-assembly with toroidal field coils and vacuum vessel thermal shielding, and welding.
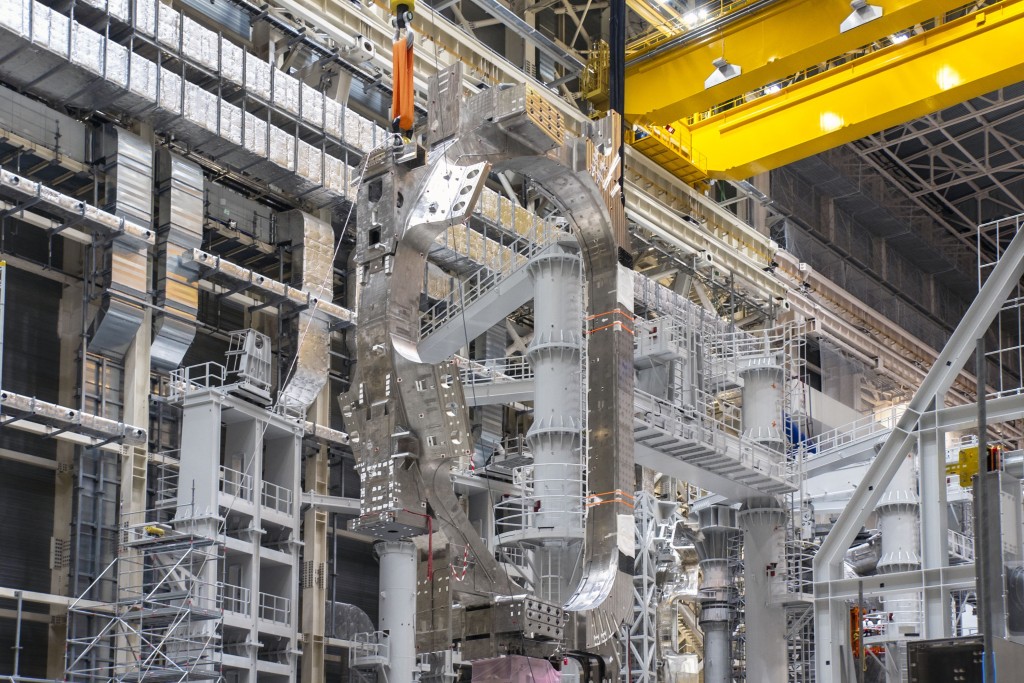
Crossing the Hall
2021-06-15 - Toroidal field coil #12 (supplied by Japan) crosses the Hall to be installed on the left wing of the first sector sub-assembly tool (SSAT-1). The component will remain in this temporary location for about a month, before it is moved to the other sector sub-assembly tool (SSAT-2) for the actual pre-assembly operations.

"Outside and beyond"
2021-06-15 - The high voltage power supply equipment planned for the ITER neutral beam injection system is "outside and beyond anything that's ever been done in terms of electrical engineering." See more at https://www.iter.org/newsline/-/3554. © Les Nouveaux Médias/SNC ENGAGE

Smooth
2021-06-15 - The operation went smoothly, with no show-stopper, no physical mismatching, and no major adjustments required. It was an important rehearsal for the identical sequences to follow. In only two weeks, TF13 (also from Japan) will follow the same path.
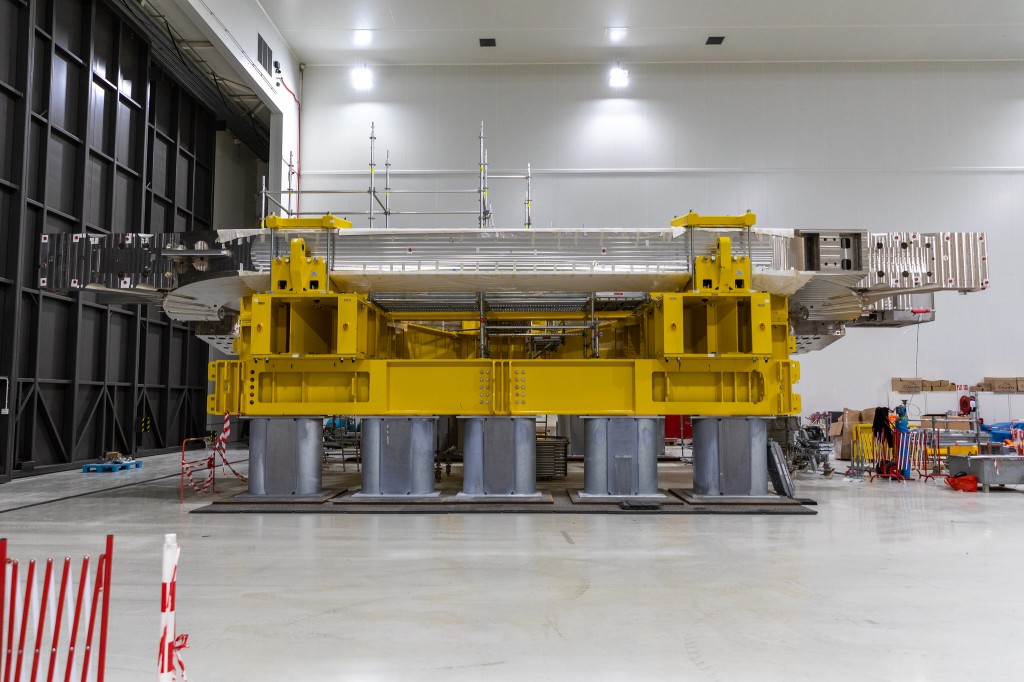
Next in line
2021-06-15 - A second toroidal field is ready to enter the Assembly Hall: TF11 from Japan. © Les Nouveaux Médias/SNC ENGAGE

Ready to remove
2021-06-15 - Time to lift the 320-tonne vertical coil from its upending frame and transfer it over to one of the sector sub-assembly tools on the opposite side of the Hall.
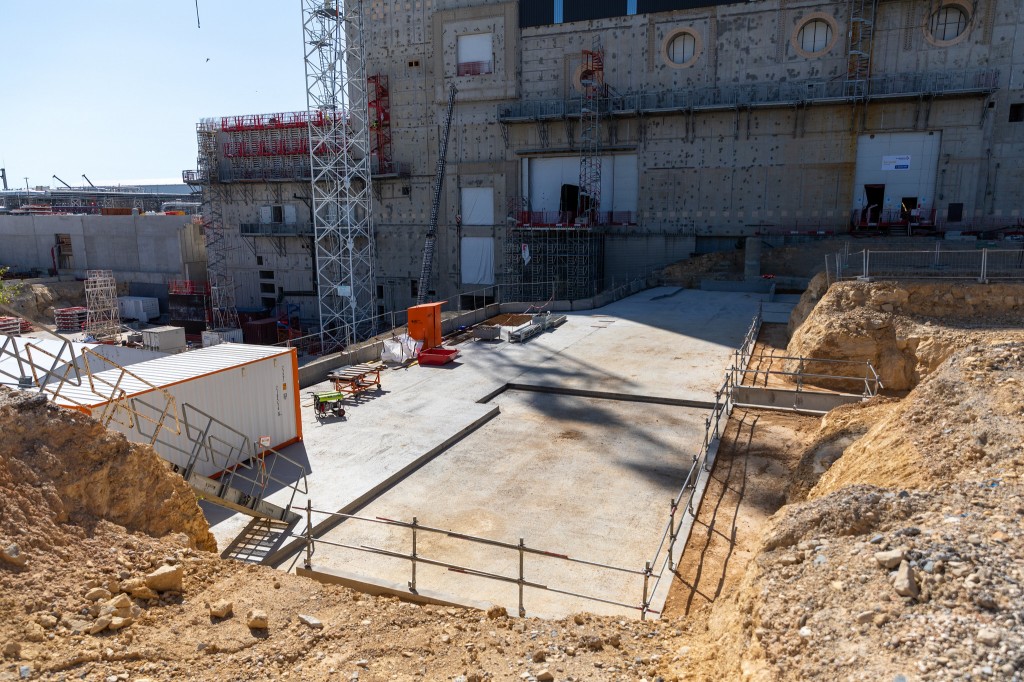
Neutral beam power buildings: status June 2021
2021-06-15 - European contractor Demathieu Bard Construction is building the neutral beam power supply area (two buildings and one technical area). Work is advancing well. © Les Nouveaux Médias/SNC ENGAGE
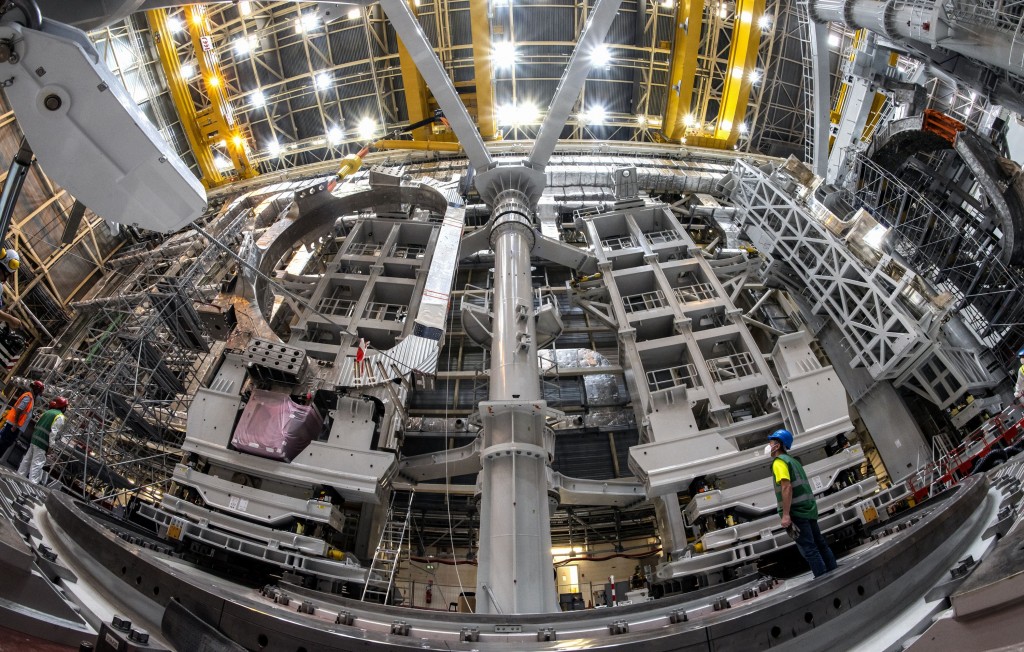
First toroidal field coil in tooling
2021-06-15 - In a series of operations that started on Wednesday 9 June and concluded six days later, TF12 was successfully attached to the left wing of one the twin sector sub-assembly tools (SSAT-1). The 320-tonne coil will be moved to SSAT-2 in about a month for the start of pre-assembly operations with vacuum vessel sector #6 (visible to the far right).

Connected by bridges
2021-06-15 - The neutral beam power supply buildings are going up near the Tokamak Complex. Transmission lines will enter the L3 level of the Tokamak Building through the north wall. © Les Nouveaux Médias/SNC ENGAGE

Satisfaction
2021-06-09 - The team can be satisfied with work well done. The next step is to "detach" toroidal field coil #12 from the upending tool and perform the balancing of the load under the cranes, before it is moved to the sector sub-assembly tooling.

Ready to go
2021-06-09 - The teams are ready to perform the first "upending" of a D-shaped toroidal field coil (TF12). The upending tool (light grey) can handle both vacuum vessel sectors and vertical coils.
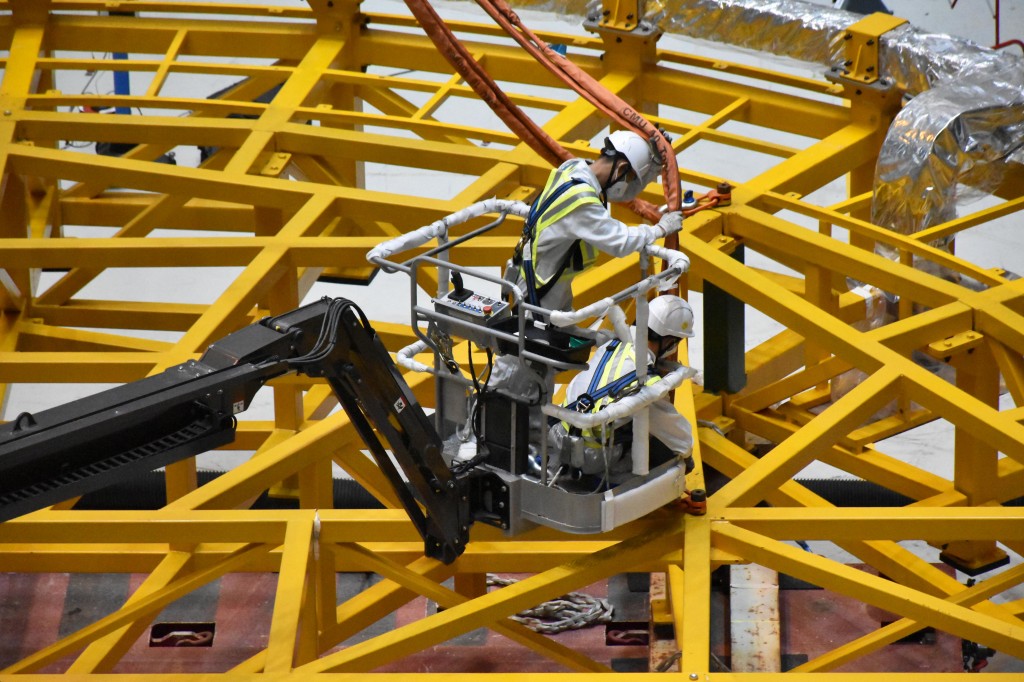
Points d'attache
2021-06-09 - Technicians attach crane hooks to the transport frame in order to lift the component and free the modular transporter.

Watching from below
2021-06-09 - Watching as the 200-tonne upending frame and its 360-tonne load are raised to vertical.

Temporary rest area
2021-06-09 - The newly arrived load is transferred to a temporary laydown area. Later, in the order determined by assembly sequences, it will be transferred to the Tokamak pit.

First of 18
2021-06-09 - Eighteen "D"-shaped toroidal field magnets placed around the vacuum vessel produce a magnetic field whose primary function is to confine the plasma particles.
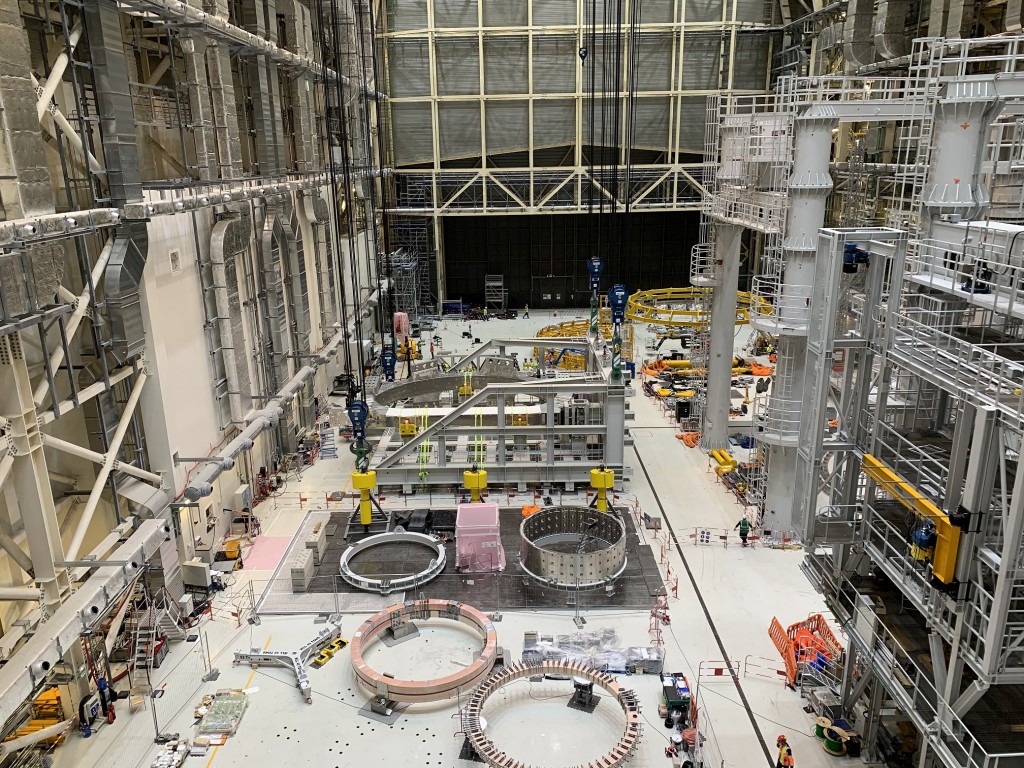
A vast hall
2021-06-09 - The upending tool is located in the middle of the Assembly Hall, not far from the sector sub-assembly tools.
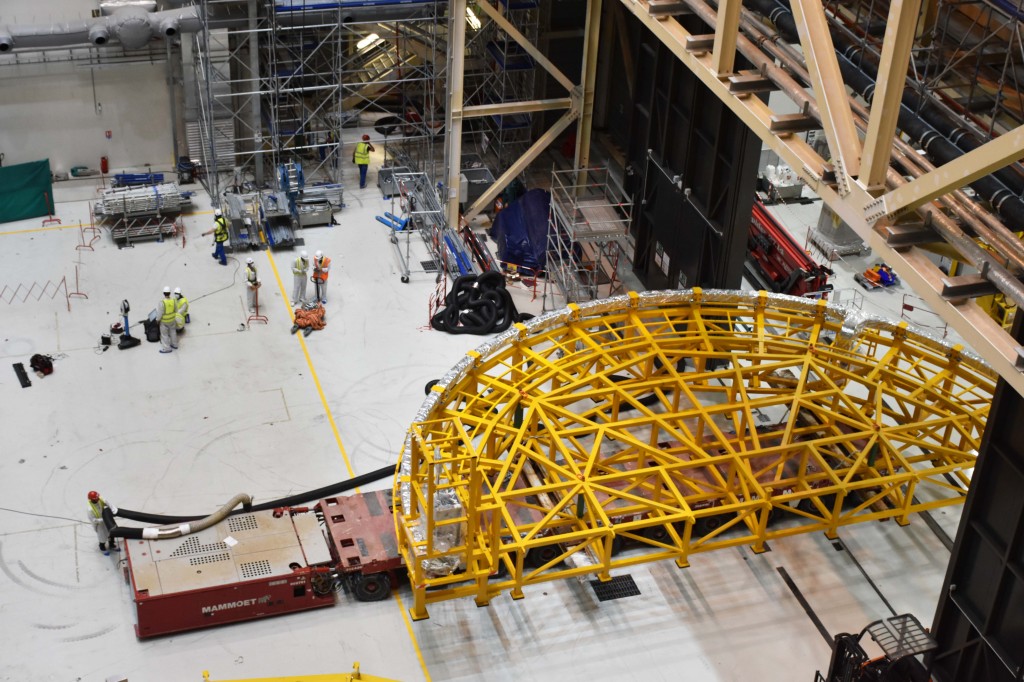
Open sesame
2021-06-09 - The massive doors of the Assembly Hall open to admit a semi-circular feeder component on its self-propelled modular transporter.
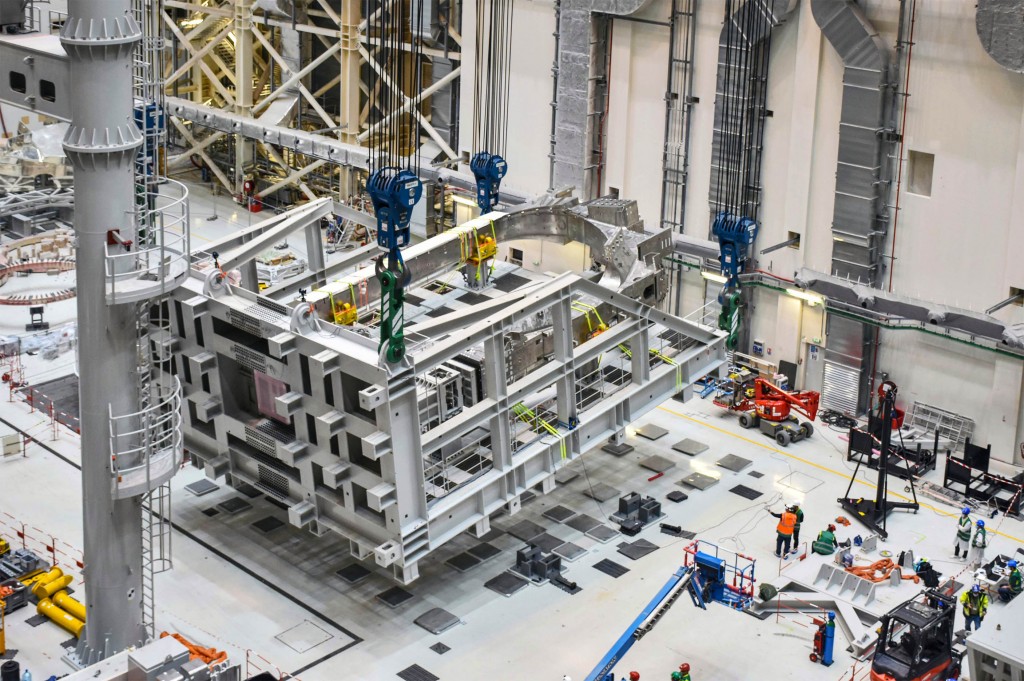
Let's go
2021-06-09 - By coordinating the cables of the four lift points, the overhead crane operators first lift the load and then start to tilt it.

Up it goes
2021-06-09 - The new feeder element (wrapped in silver) and its transport frame are lifted off the transporter. In the foreground, another (unwrapped) feeder component awaits its turn in the assembly pit.
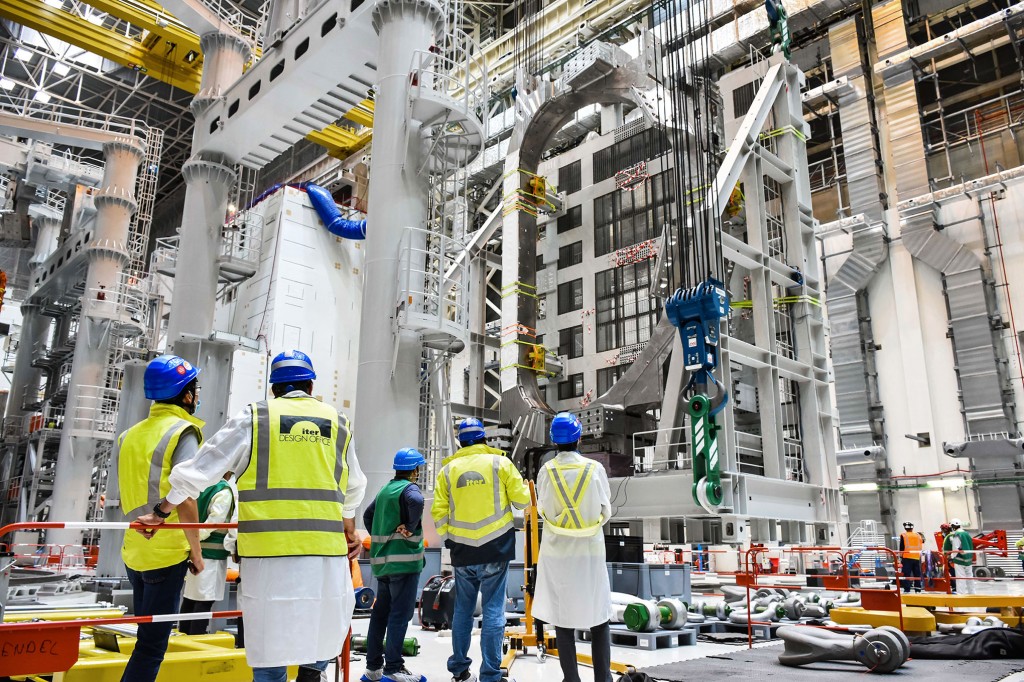
For the first vacuum vessel sub-assembly
2021-06-09 - Seventeen metres tall and 9 metres wide, this D-shaped coil (TF12, procured by Japan) is one of two that will be matched with a 40-degree sector of the ITER vacuum vessel. Sector #6 is already in the SSAT assembly tooling; TF12 will be transferred to the tooling next week.
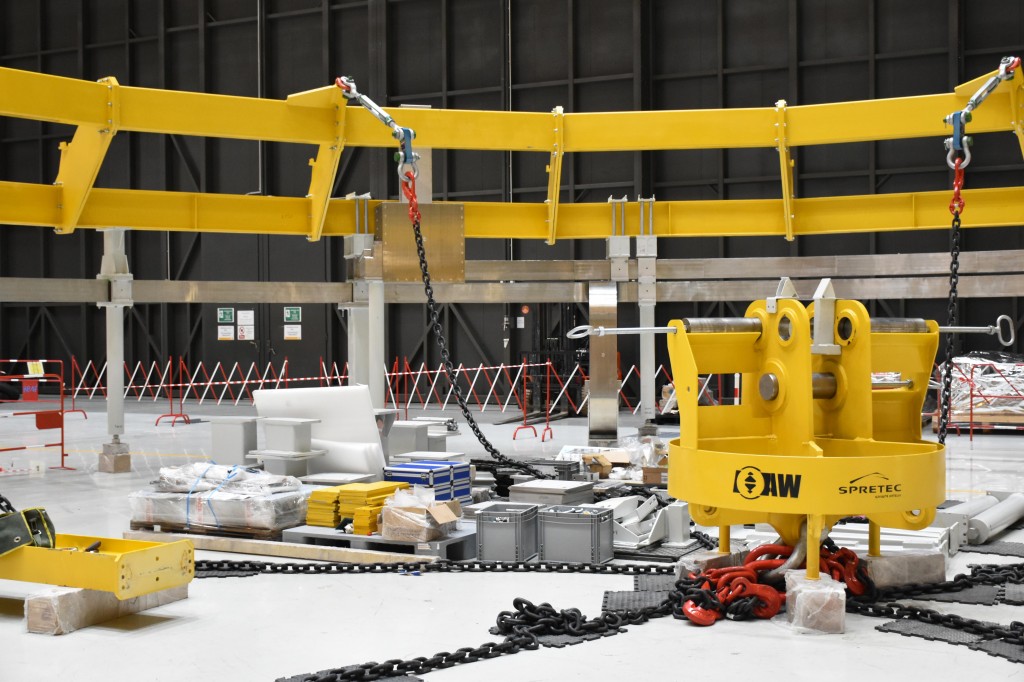
Near ready
2021-06-09 - This correction coil feeder element is already in the lift frame that will be used for its transfer into the pit.

First coil in tool
2021-06-09 - In a series of operations that started on 9 June and concluded six days later, TF12 was successfully attached to the left wing of one the twin sector sub-assembly tools (SSAT-1). The 320-tonne coil will be moved to SSAT-2 in about a month for the actual pre-assembly operations.

Stacking rings
2021-06-08 - Assembly contractors are preparing for the lift of two sets of three pre-compression rings. © Les Nouveaux Médias/SNC ENGAGE

First "arc"
2021-06-07 - Two welders from MAN Energy Solutions (subcontractor to India's Larsen & Toubro) work in parallel on opposite sides of the component's "skin" to create the ''first arc'' of the welding campaign.

MITICA cryopump: another qualification milestone
2021-06-07 - A mockup pumping section is inspected by a European Domestic Agency metrologist at SDMS France. The MITICA cryopump will have 64 pumping sections; now that qualification tests have been completed, series manufacturing can start.

Top lid welding kicks off
2021-06-07 - The alignment of the twelve 30-degree segments has been confirmed and all preparatory activities completed. The four- to five-month campaign to weld the cryostat top lid begins on 7 June 2021.
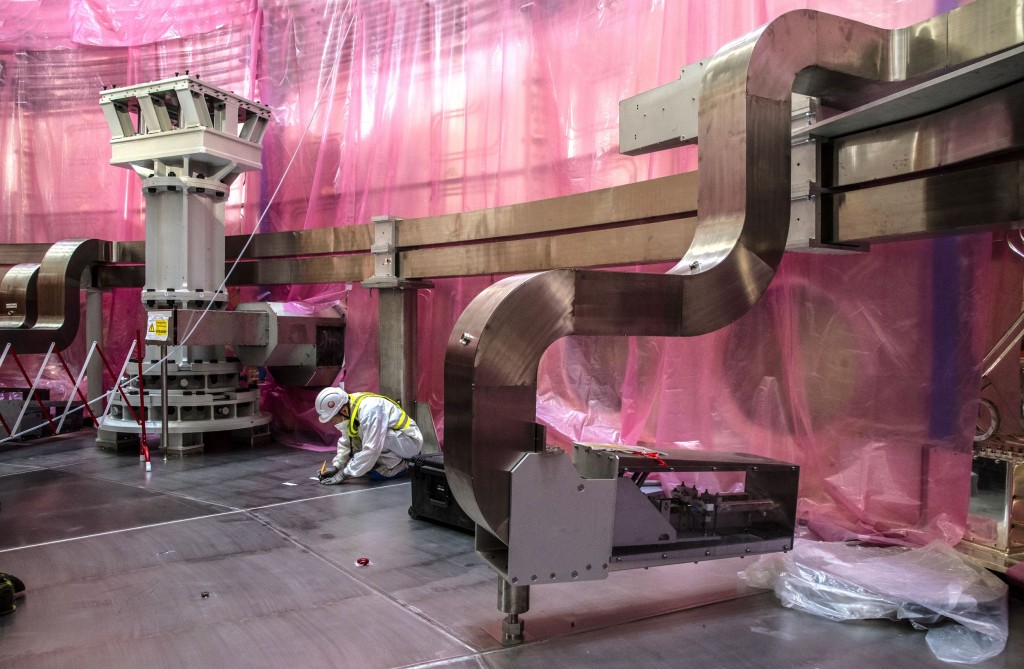
It's happening in the pit
2021-06-04 - The structure to the left of this image is one of the six temporary supports for the 17-metre-in-diameter poloidal field coil #5 (PF5), which is scheduled for installation in late July/early August. To the right, the side correction coil feeder rests in a temporary position; later, it will be lifted several metres to its final location.
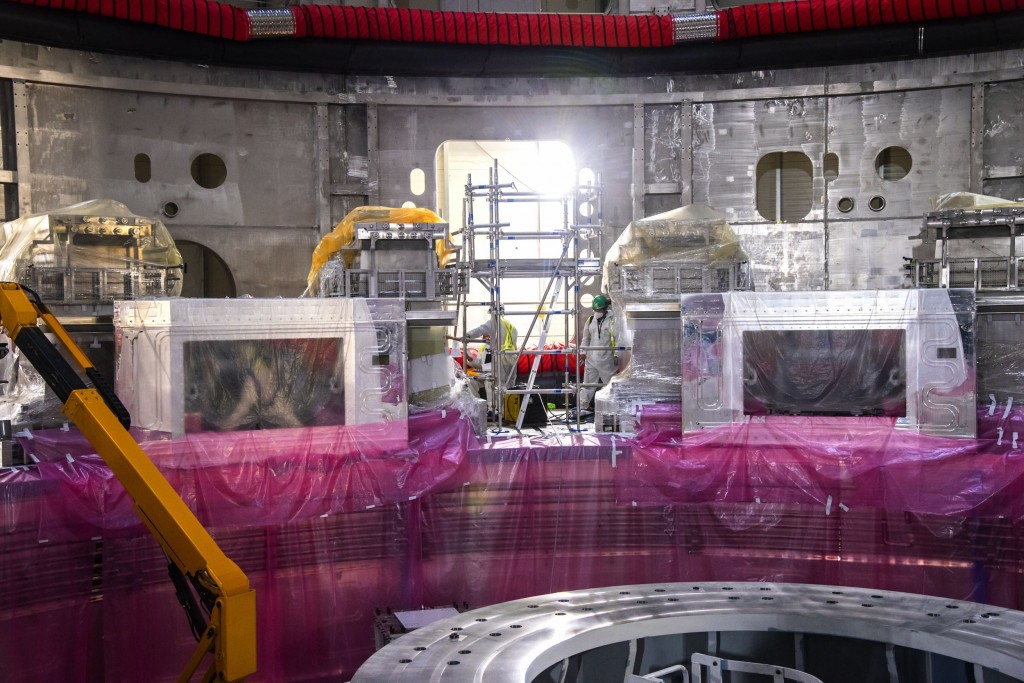
Looking like microwave ovens
2021-06-04 - Two "front full" support thermal shield panels are in place in front of the toroidal field coil gravity supports. A "front open" panel will be precisely fitted between them. The system is designed to shield the magnets at cryogenic temperature from the warmth coming from the cryostat base and transmitted by the gravity supports.

Limited space
2021-06-04 - The ITER Tokamak pit is alive with activity as workers, tools and components compete for limited space. Coordination is paramount.
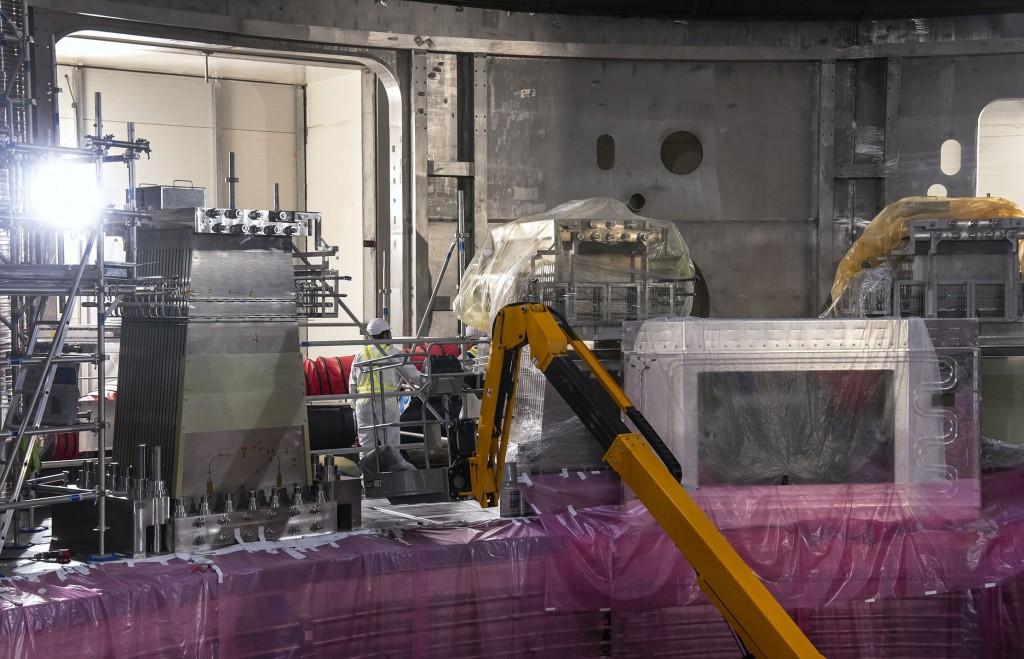
Managing a wide temperature gradient
2021-06-04 - Gravity supports create the bridge between the toroidal field coils operating at 4 K (minus 269 °C) and the cryostat base at room temperature (approximate). This makes for a huge temperature gradient that must be smoothly distributed throughout the 2.65-metre-tall, 20-tonne component.

A unique place
2021-06-04 - Nothing in the world remotely resembles the ITER "assembly pit." What we see here are the first steps of a prodigious undertaking: the construction, from the bottom up, of the most complex machine ever designed.

Thermal insulation
2021-06-04 - Thermal insulation between the different components of the ITER Tokamak is paramount. Here, workers prepare one of the 18 "support thermal shield" panels that will be fitted tightly to the massive toroidal field coil gravity supports. Each silver-plated panel measures approximately 1.6 m by 3.3 m and weighs 730 kg.
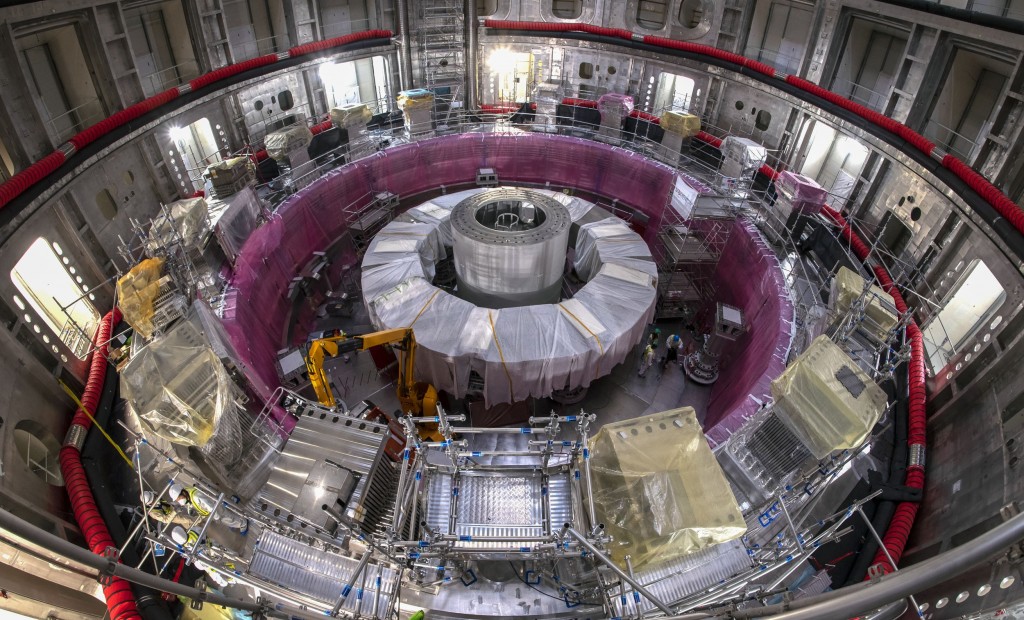
Bottom to top
2021-06-04 - ITER machine assembly is proceeding from bottom to top. After the 1,250-tonne cryostat base comes: the lower cryostat components; nine large, 40° vacuum vessel sectors (pre-assembled with thermal shield panels and a pair of toroidal field coils); components at the top of the machine; and finally the cryostat lid.

In the Tokamak pit
2021-06-04 - Metrology is an essential tool for installing components to within tight tolerances, controlling the interfaces berween the different elements, and keeping the right distances between surfaces in order to avoid clashes.
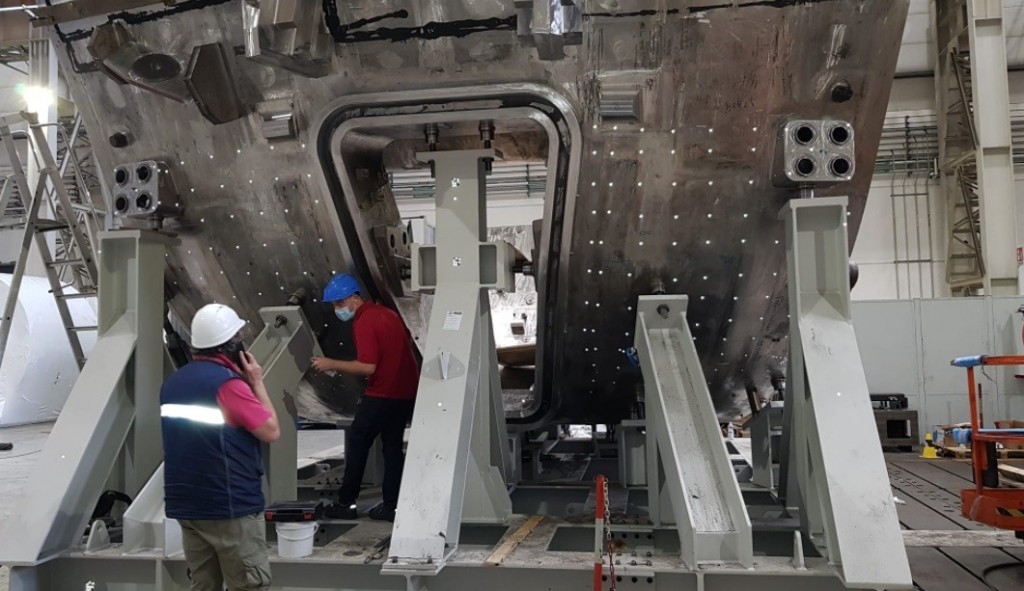
Verifying component shape
2021-05-27 - Photogrammetry is one of the techniques used to inspect and validate the shape of components. The bright points in the picture are photogrammetry targets placed on the outer shell of a vacuum vessel segment before final machining. Mangiarotti, Italy, May 2021.
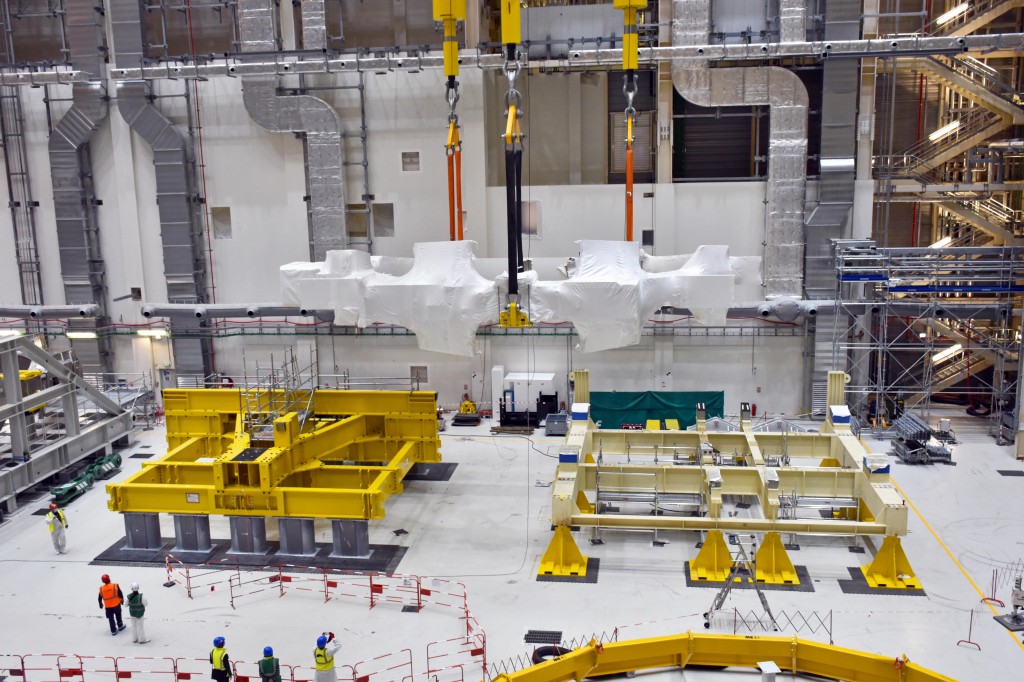
17 metres
2021-05-21 - When raised to vertical, the 360-tonne toroidal field coils will stand 17 metres tall.

Knocking at the door
2021-05-21 - Toroidal field coil #13 (from Japan) has been unwrapped in the Cleaning Facility. It will be the second coil mounted on the sector sub-assembly tooling, joining vacuum vessel sector #6 and pairing with toroidal field coil #12.

One to another
2021-05-21 - At the entrance of the Assembly Hall, a "swap" is performed: toroidal field coil #8, from Japan, is transferred from its travel frame (right) to a temporary support frame (left) for storage.
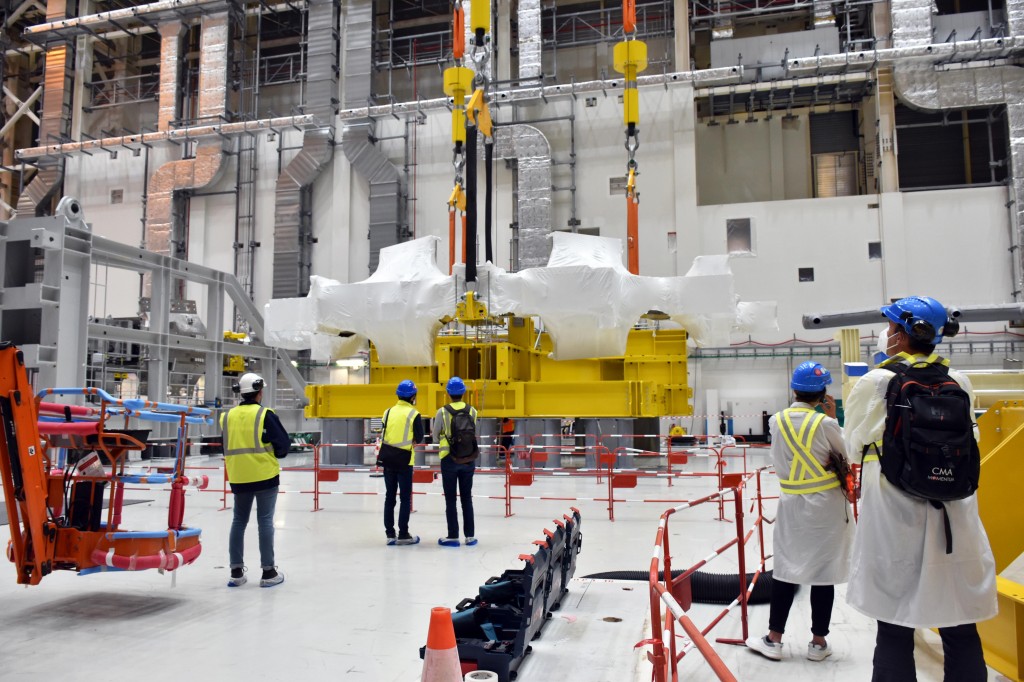
Coil meets frame
2021-05-21 - The operation goes smoothly, as the 360-tonne magnet coil is positioned on its support frame.

Preparing the transfer
2021-05-21 - The teams meet ahead of the transfer operation, which is carried out by one of the two 750-tonne overhead cranes in the Assembly Hall.

How to create a sector sub-assembly
2021-05-18 - Two toroidal field coils as well as panels of thermal shielding must be associated with each vacuum vessel sector before the new unit, call a sector sub-assembly, can be transferred to the Tokamak pit. (In the background, we can see sector #6, from Korea, already in the sector sub-assembly (SSA) tooling.)
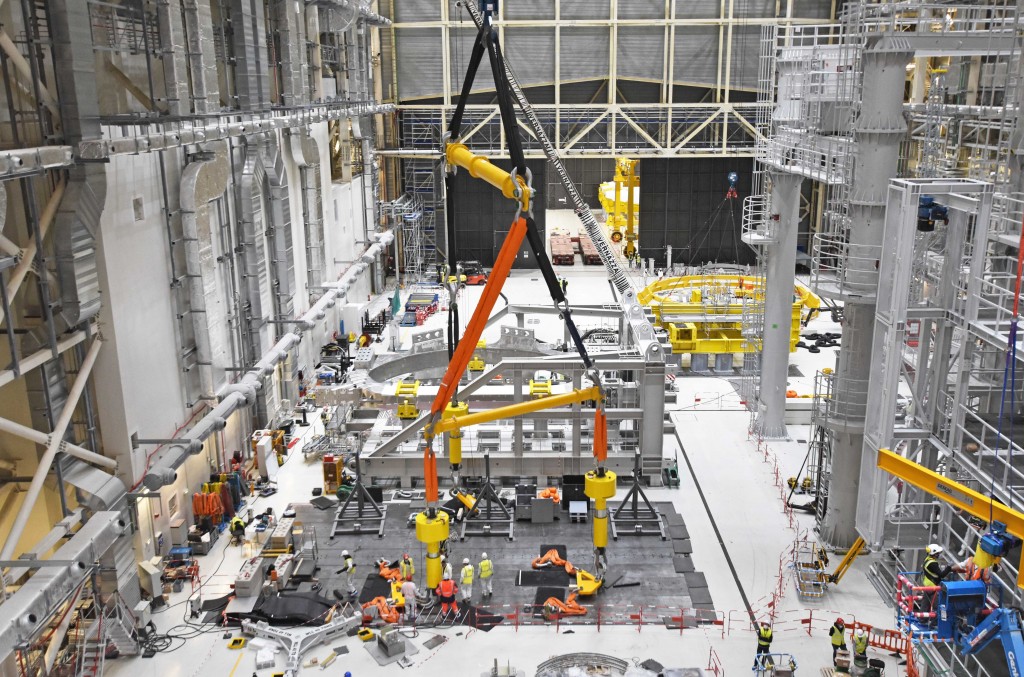
Upending tool in action again
2021-05-18 - This time, the upending tool will secure and raise to vertical one of the D-shaped toroidal field coils--TF12 from Japan. Once vertical, the coil will be installed on a giant sector sub-assembly tool in the Assembly Hall, to be paired with the first vacuum vessel sector.
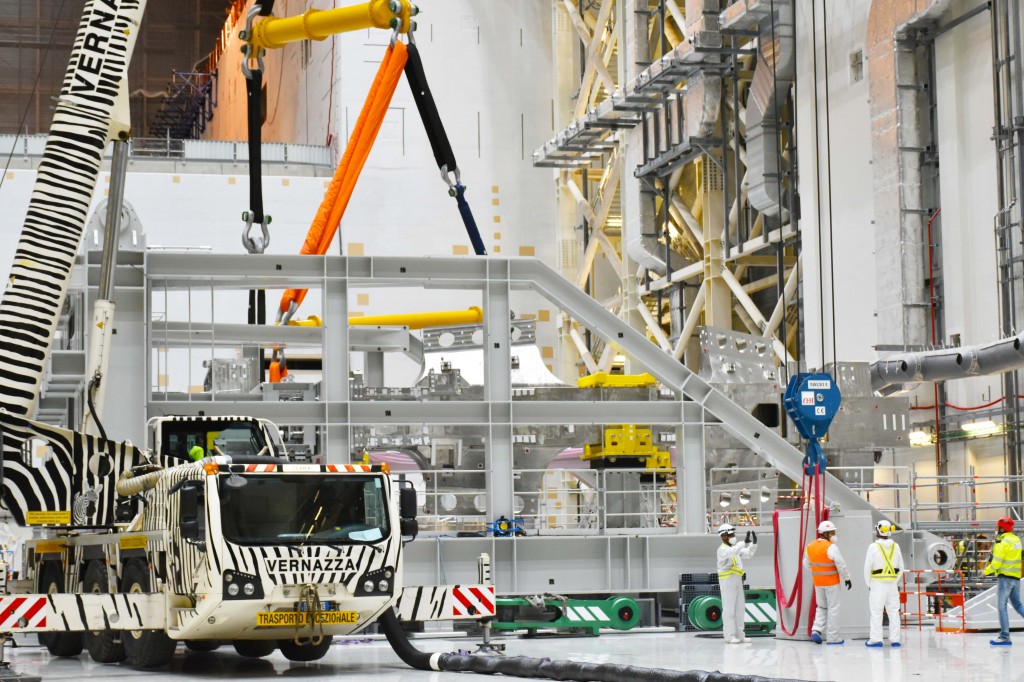
27 assembly-phase lifts
2021-05-18 - The upending tool will enter into action 27 times during ITER assembly (not counting lift tests) in order to upend 18 toroidal field coils and 9 vacuum vessel sectors.
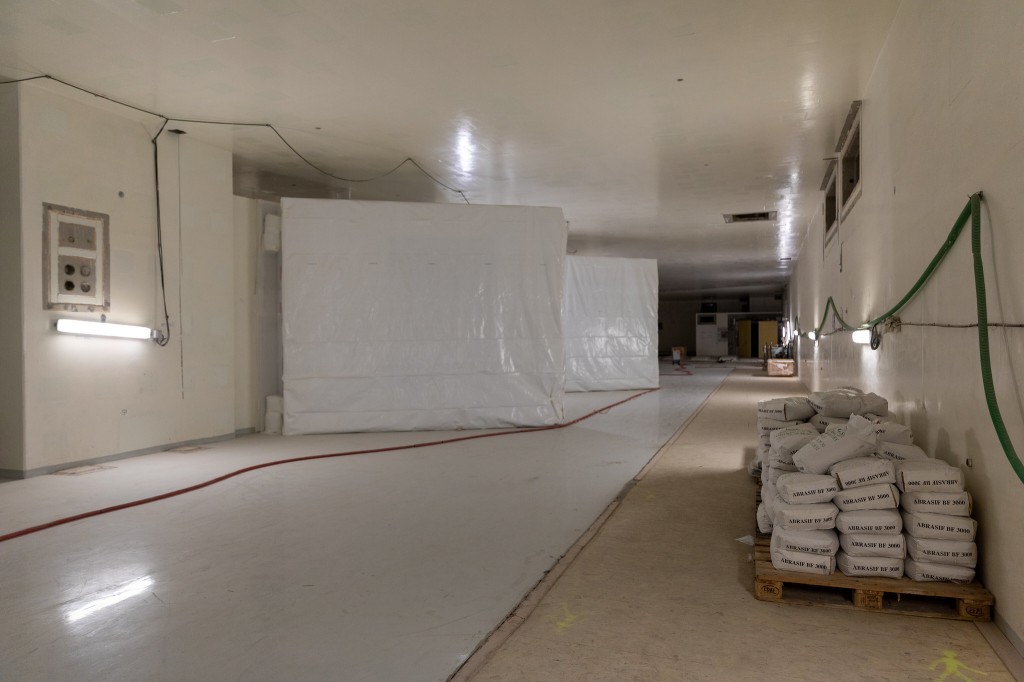
Non-nuclear doors
2021-05-17 - European Domestic Agency contractors have 300 non-nuclear doors like these to install in the Tokamak Complex. © Les Nouveaux Médias/SNC ENGAGE

Semi-circular feeder
2021-05-15 - On 15 May 2021, this 10-tonne circular feeder was inserted in the assembly pit. This in-pit component will connect to a cryostat feedthrough in order to deliver electrical power to the six side correction coils located at the mid section of the machine.

When completed
2021-05-14 - This is what the future neutral beam power supply area will look like when completed. © Les Nouveaux Médias/SNC ENGAGE
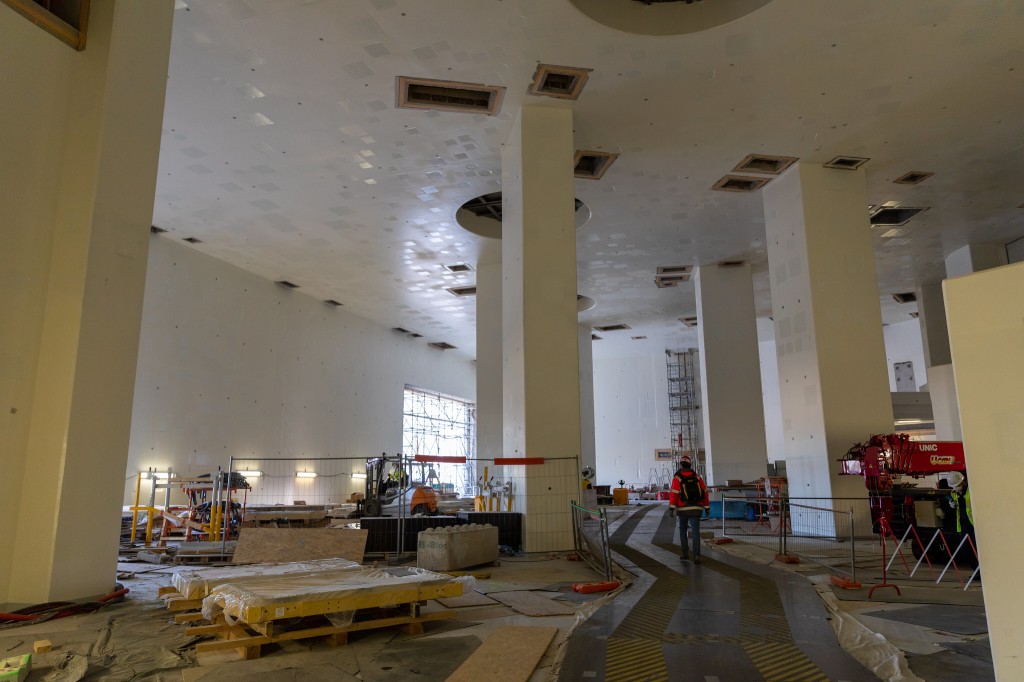
Injecteur room
2021-05-14 - The heating neutral beam injectors (2) and the diagnostic neutral beam injector (1) will be located in this room of the Tokamak Complex. Power supply will arrive through the openings in the ceiling. © Les Nouveaux Médias/SNC ENGAGE
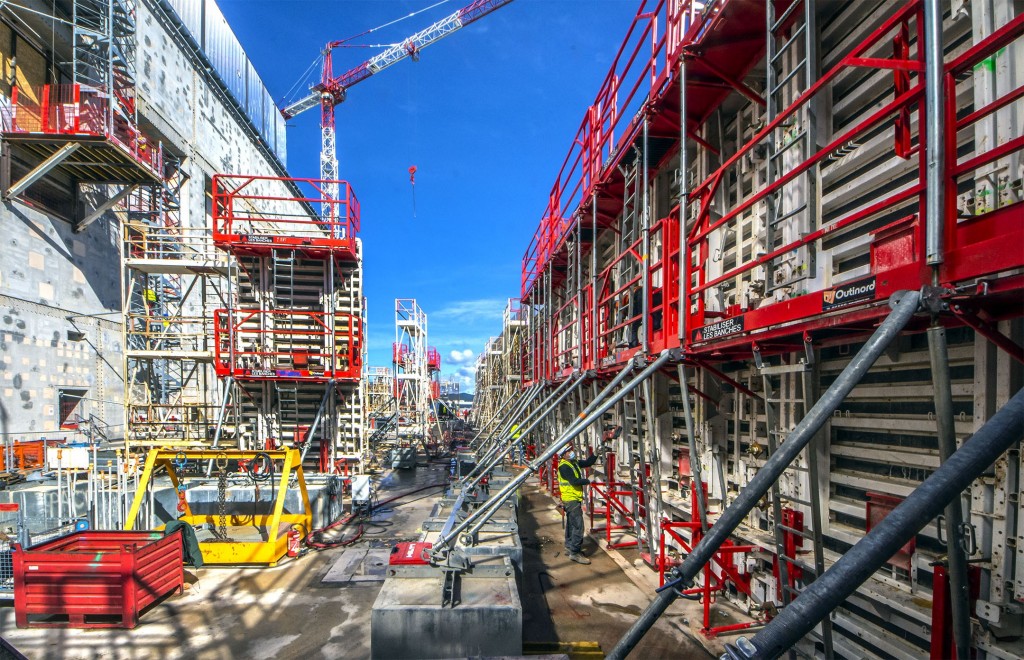
Work resumes on the Tritium Building
2021-05-07 - Work has started again on the Tritium Building, one of the three structures of the Tokamak Complex. Activity is underway at the L2 level.
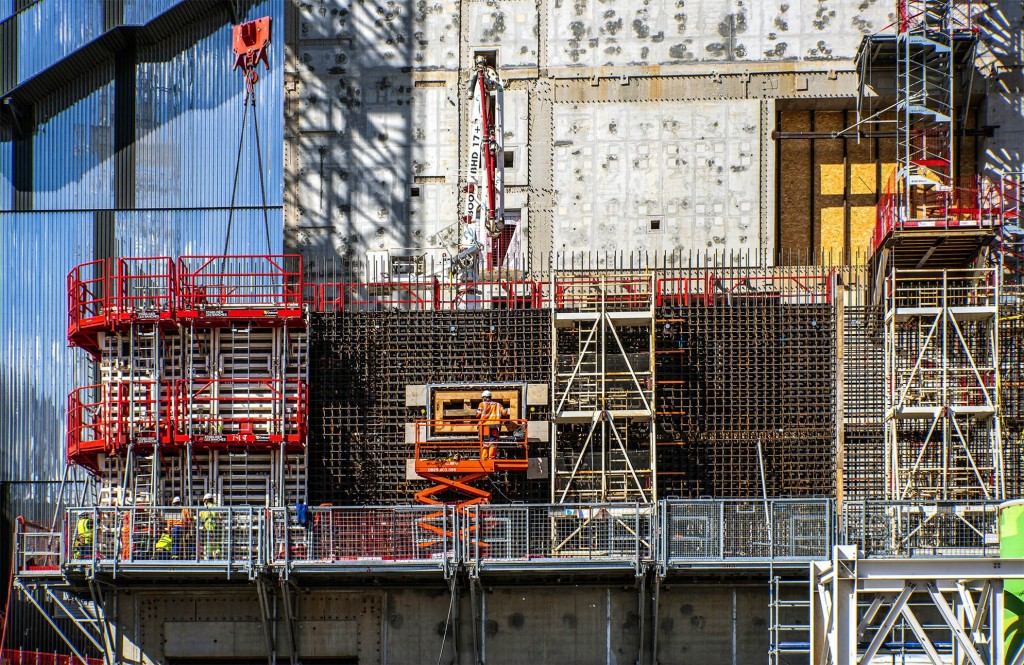
Framing and pouring
2021-05-07 - Just like in the Tokamak Building, several areas of the Tritium Building will require concrete walls with exceptionally dense steel reinforcement.
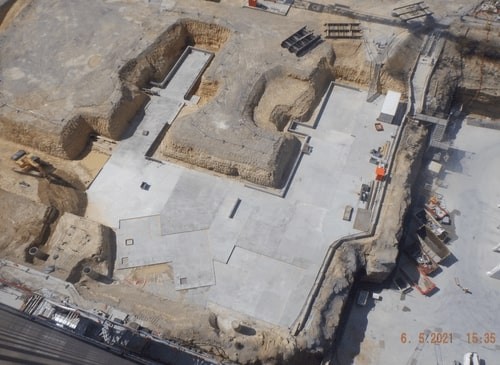
Heating and diagnostic neutral beam power supply
2021-05-05 - Two buildings and a technical area will host the transformers, generators, rectifiers, inverters, high-voltage decks and their bushings designed to feed 1 MeV ultra high voltage to two heating neutral beam injectors and a smaller level of energy to the one diagnostic neutral beam injector.
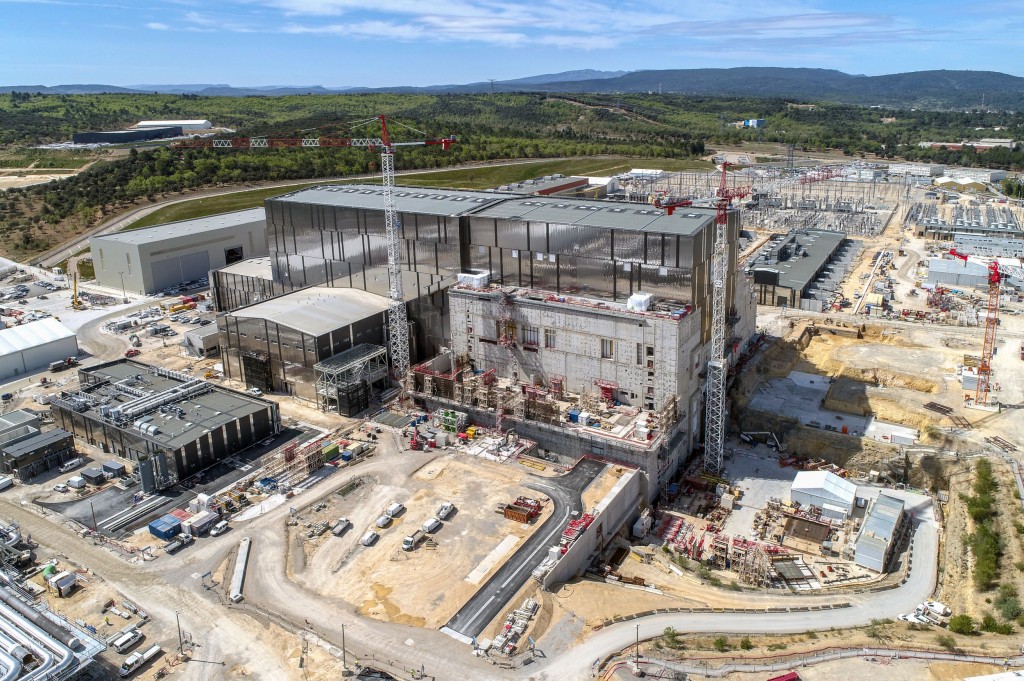
Europe finalizes work inside the Tokamak Building
2021-05-05 - Civil engineering and finishing works are nearly completed in the Tokamak Building (tall building, right); the last area will be painted this summer. Contractors are 80% of the way though installing 300 shielding and confinement doors. Photo: ITER Organization/EJF Riche

Neutral beam power supply
2021-05-05 - In front of the Tokamak Complex, work is underway on two buildings that will host the ITER neutral beam power supply installation and its array of transformers, generators, rectifiers, inverters and other exotic electrical devices designed to feed 1 MeV ultra high voltage to the injectors—something that is ''outside and beyond anything that's ever been done in terms of electrical engineering.''
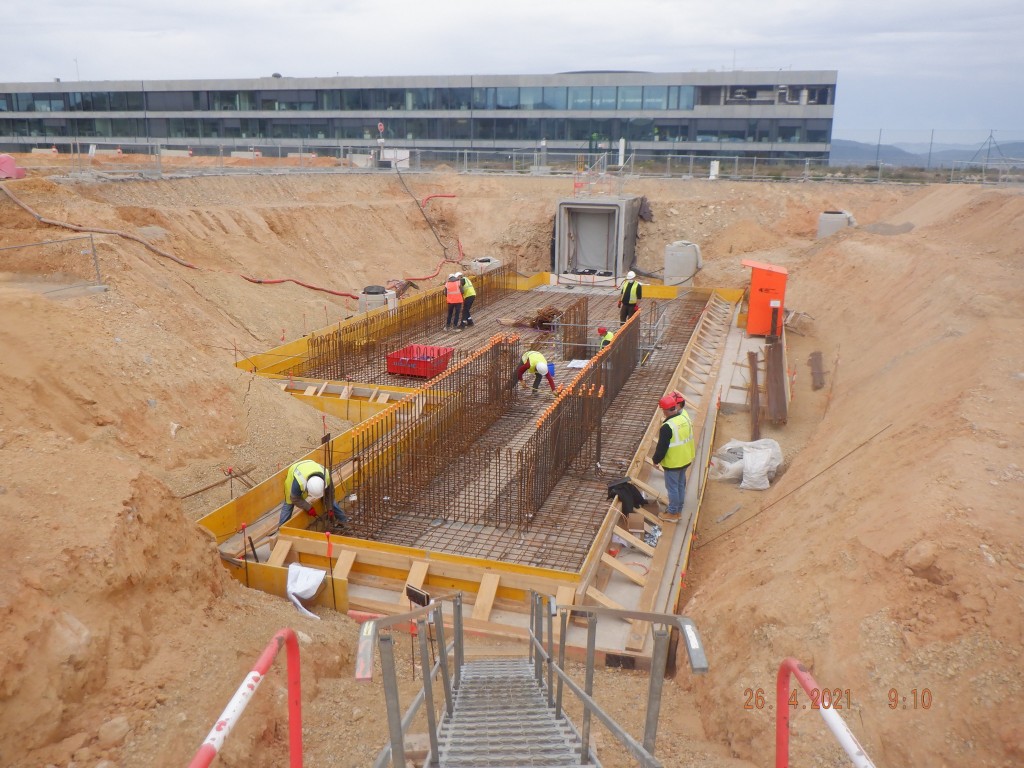
Starting on the Control Building
2021-04-30 - Work has started on the site of the ITER Control Building. A tunnel (and bridge) connect the ITER Control Building with Headquarters.
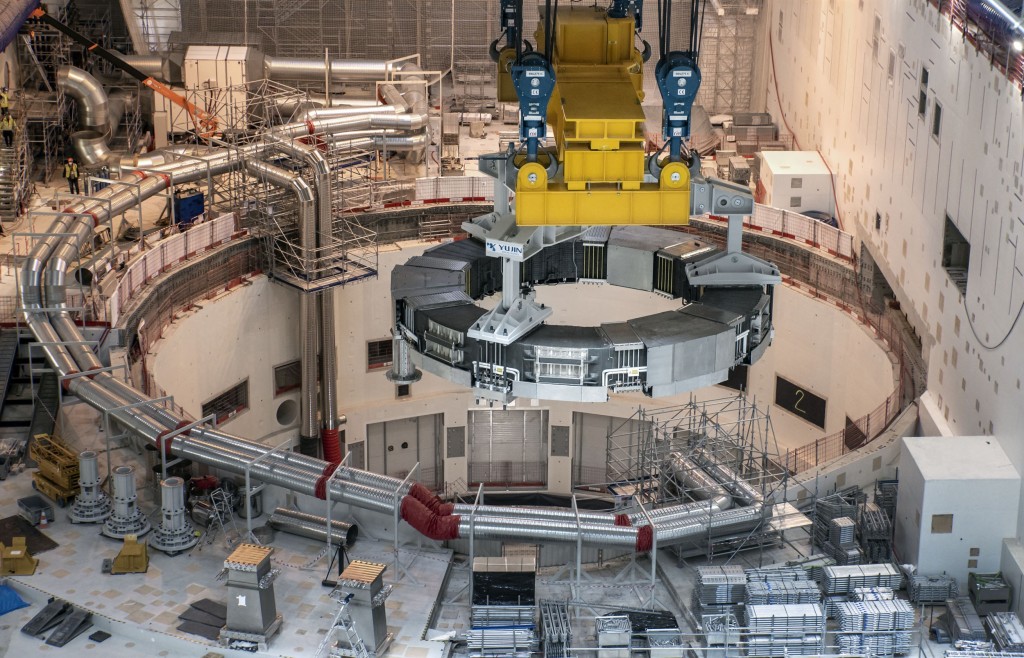
Stabilizing attachments
2021-04-26 - A special lift attachment between the load and the bridge cranes ensures that this component, poloidal field coil #6 (PF6), is kept stable (no tilt) for the duration of the transfer.

Teams prepare ITER games?
2021-04-26 - Arranged unexpectedly in a configuration that can only remind us of the Olympic Games, six pre-compression rings in the ITER Assembly Hall are being prepped for installation.
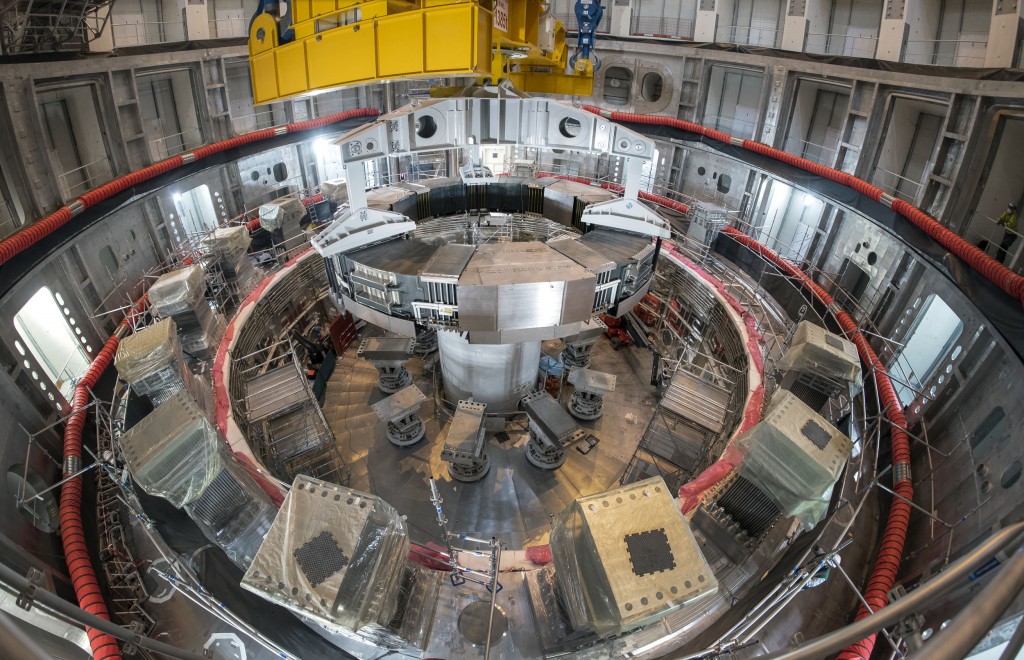
Nearly there
2021-04-21 - PF6 slowly arrives at its destination. The coil will remain on temporary supports until the vacuum vessel has been assembled and welded; then, it will be anchored to the toroidal field coil superstructure.
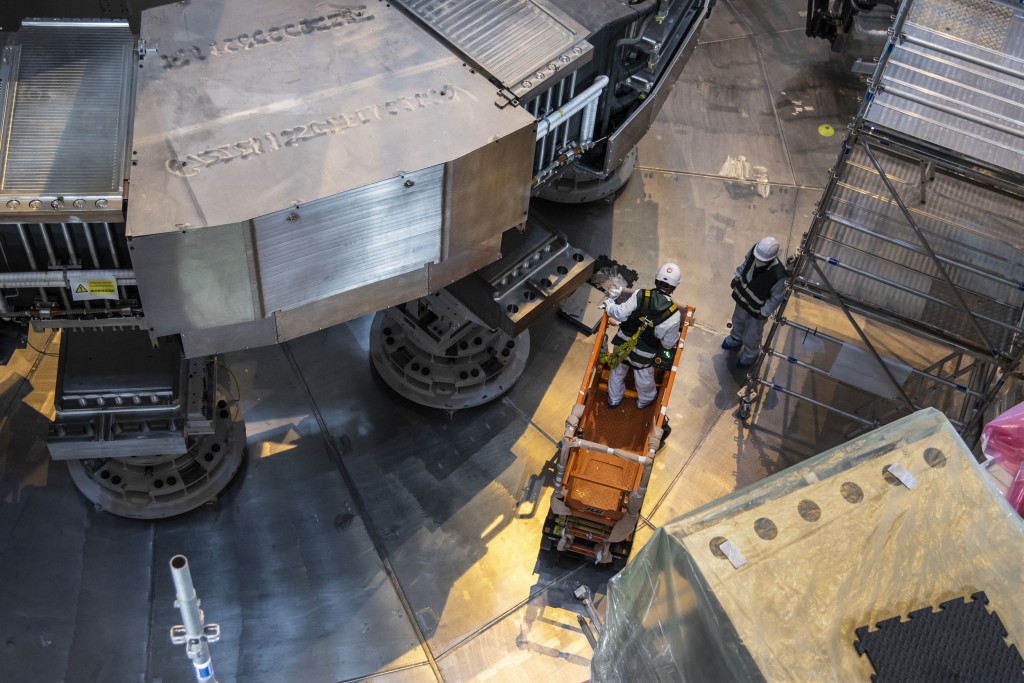
Last check
2021-04-21 - The journey is not complete yet. Operators check the coil's position as it hovers 10 centimetres above the temporary supports.

Just passing through
2021-04-21 - On its way to the assembly pit the poloidal field coil passes vacuum vessel sector #6, safely docked in one of the sector sub-assembly tools.

First ITER magnet lowered into pit
2021-04-21 - This 400-tonne component—poloidal field coil #6 (PF6)—is the first superconducting magnet to enter the Tokamak pit. It will rest on temporary supports until the vacuum vessel is assembled and welded; at that point PF6 can be adjusted into its final position.
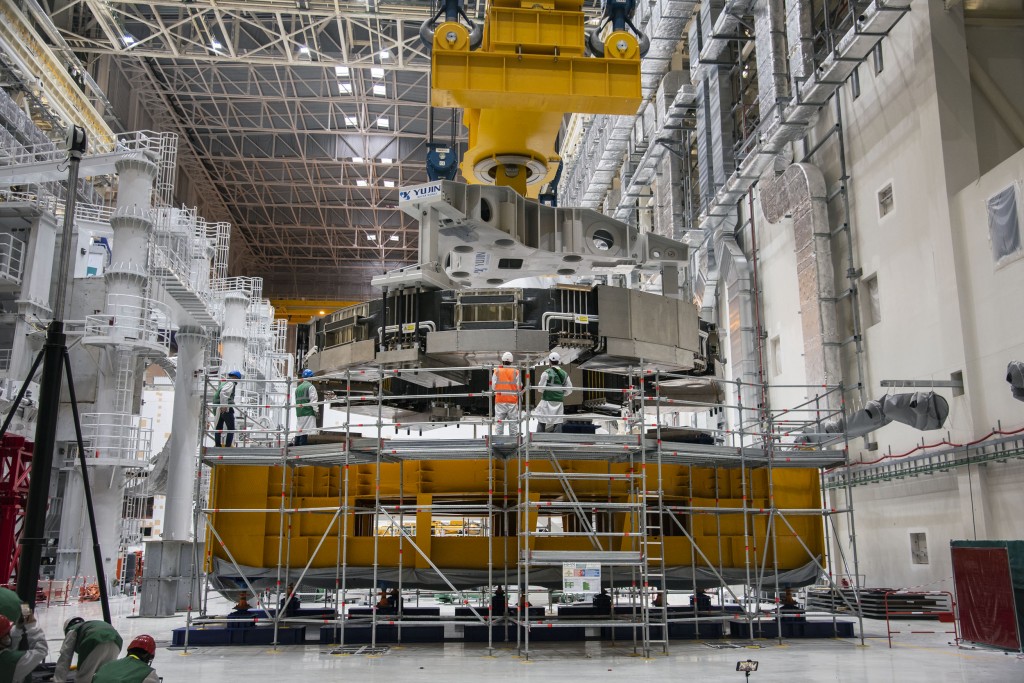
Lifting off
2021-04-21 - Lift-off begins. One day earlier, pre-lift trials had been run to assess the risk of not compensating the slight imbalance in the component's centre of gravity caused by a one-tonne feeder on one side. The slight tilting of the coil did not exceed one degree and remained within tolerance.
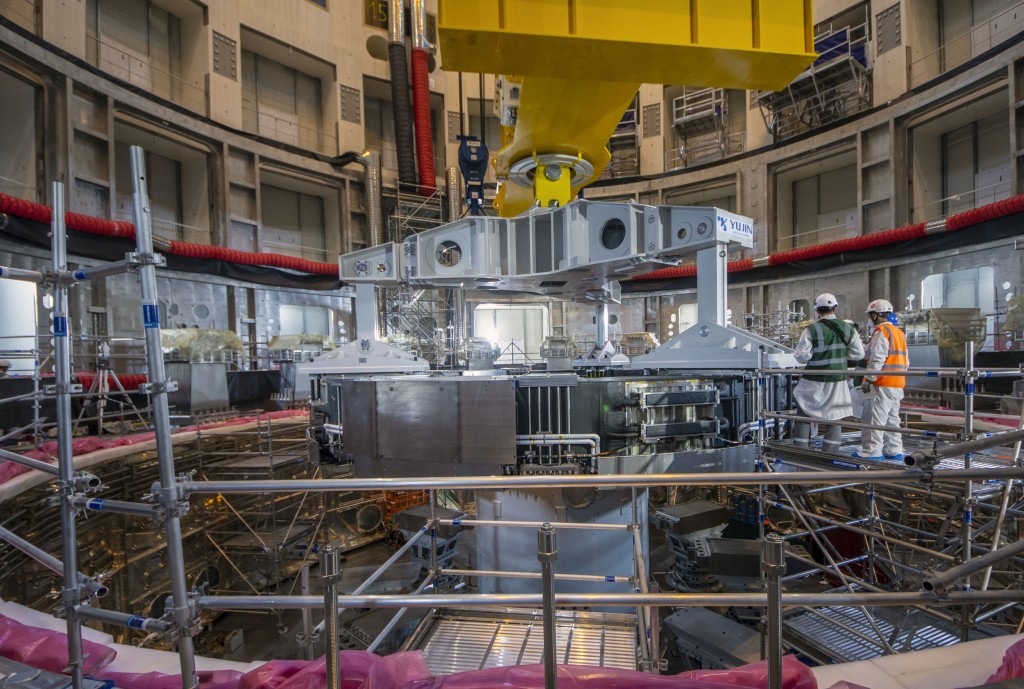
4 mm of tolerance
2021-04-21 - The rotating mechanism of the dual crane heavy lifting beam (in yellow) is clearly visible in this image of the PF6 coil arriving at the bottom of the assembly pit. The coil is installed to within 4 mm of tolerance.

Weighty
2021-04-21 - On the screen in red flashes the weight under one of the four crane hooks. The total load was approximately 480 tonnes (330-tonne coil plus rigging).

25 metres overhead
2021-04-21 - Ring magnet PF6 travels at a cruising altitude of 25 metres. Eight hours are required for the installation operation on 21 April 2021.
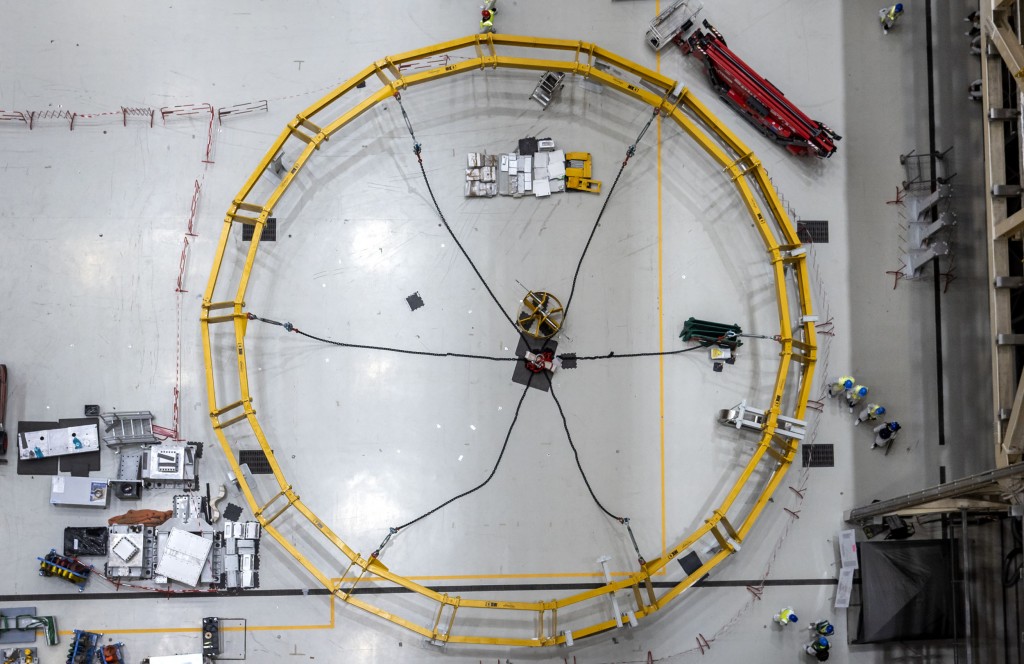
Lifting attachment
2021-04-20 - Used in January for the installation of the lower cryostat thermal shield (https://www.iter.org/newsline/-/3547), this ring-shaped lifting attachment will serve next for the installation of ring-shaped in-cryostat feeders. For the moment it is stored in the Assembly Hall.

Into storage
2021-04-16 - Officially handed over to the ITER Organization and safely placed in storage, PF5 will wait its turn in the machine assembly sequence.

36 axels, 144 wheels
2021-04-16 - Three self-propelled modular transporters, piloted in sync and powered by 1000 HP hydraulic power packs took care of the transfer.
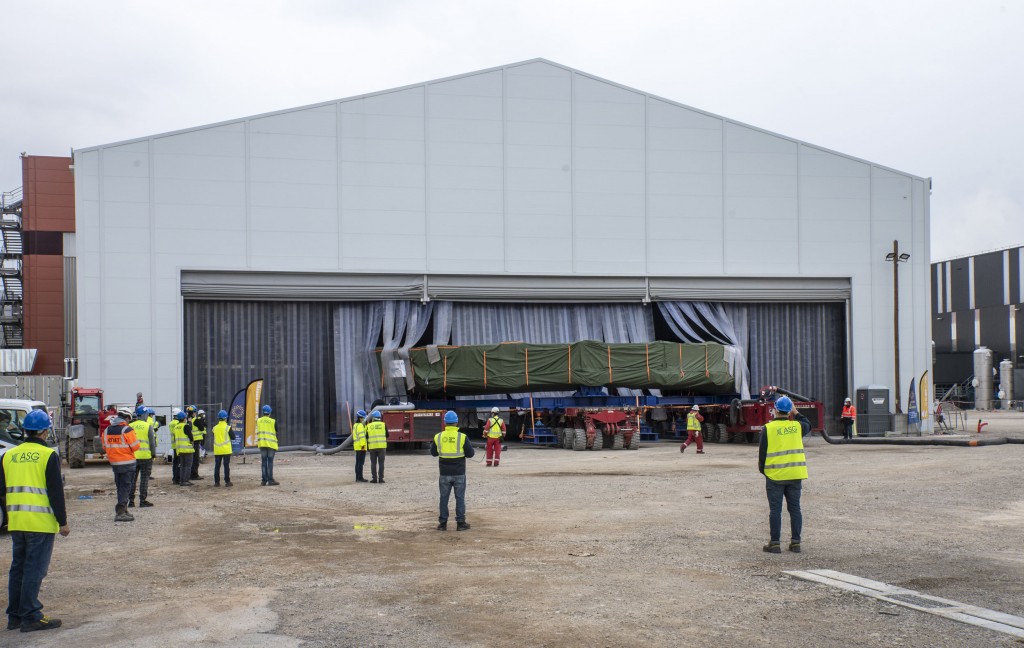
First coil exits manufacturing facility
2021-04-16 - The 340-tonne, 17-metre-in-diameter coil slowly exits the European winding facility on 16 April 2021.

Europe completes poloidal field coil #5
2021-04-16 - On Friday 16 April, the first ITER ring magnet to be manufactured by European Domestic Agency contractors on site—poloidal field coil #5 (PF5)—has been moved into temporary storage to await assembly.

State of play in the pit (mid-April 2021)
2021-04-15 - This diagram identifies the components that are visible on the floor of the Tokamak pit in mid-April 2021.

Charcoal as an excellent adsorbant
2021-04-15 - Inside of the MITICA test bed, a large sorption cryopump will be installed in the beam line vessel with cold surfaces to adsorb all particles. At SDMS in France. the surfaces (230 cryopanels) have been coated with charcoal for its excellent adsorption properties. Photo: F4E (Adsorption: the adhesion of atoms, ions or molecules from a gas, liquid or dissolved solid to a surface.)

Just large enough
2021-04-14 - This opening in the Tritium Building is just large enough for feeder elements to pass. This one (the coil termination box for poloidal coil #4 ) is 17 metres long.

Building the feeders, segment by segment
2021-04-14 - This cryostat feedthrough is one of two feeder components introduced into the basement of the Tokamak Complex on 14 April. Called the STR3 feedthrough, it will supply supercritical helium at 4.5 K to the toroidal field coil cases and other coil structures (central solenoid, correction coils).

Reactive power compensation: site acceptance tests
2021-04-08 - Protected by fire-resistant work wear, headpiece and face shield, this ITER electrical engineer is testing one of the 8-metre-tall thyristor-controlled reactors that is part of the reactive power compensation and harmonic filtering system. Site acceptance tests of all system equipment on arrival from China ensures a no-default situation despite the long journey and subsequent handling.
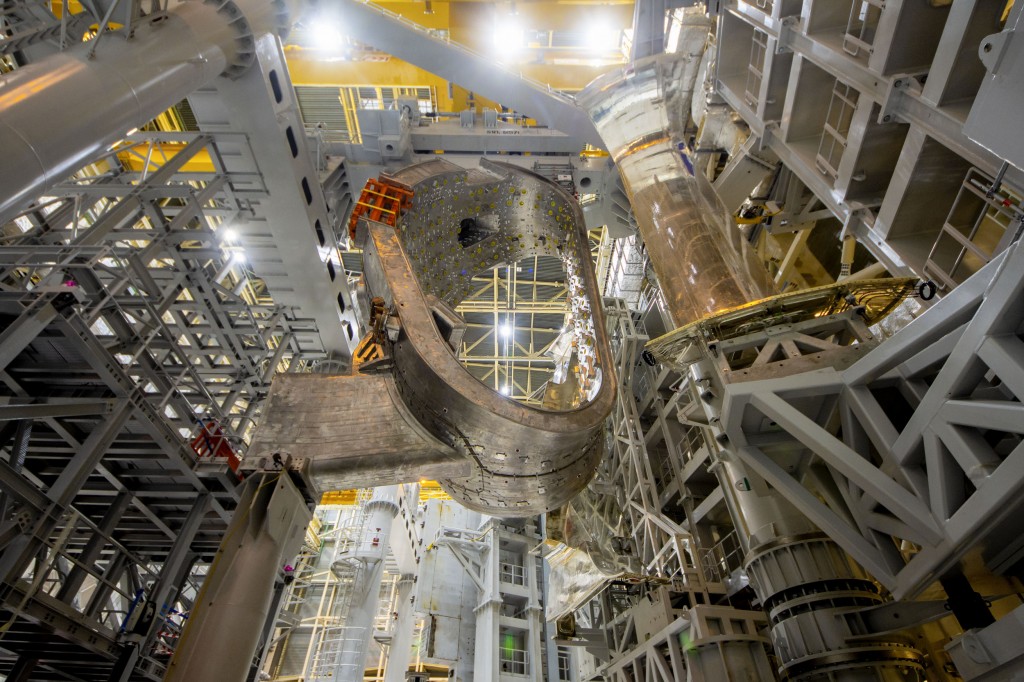
Final position
2021-04-06 - Seen from below, the component is in its final position, supported from above by a radial beam (soon to be detached from the crane) and from below by a pillar under the lower port stub extension.
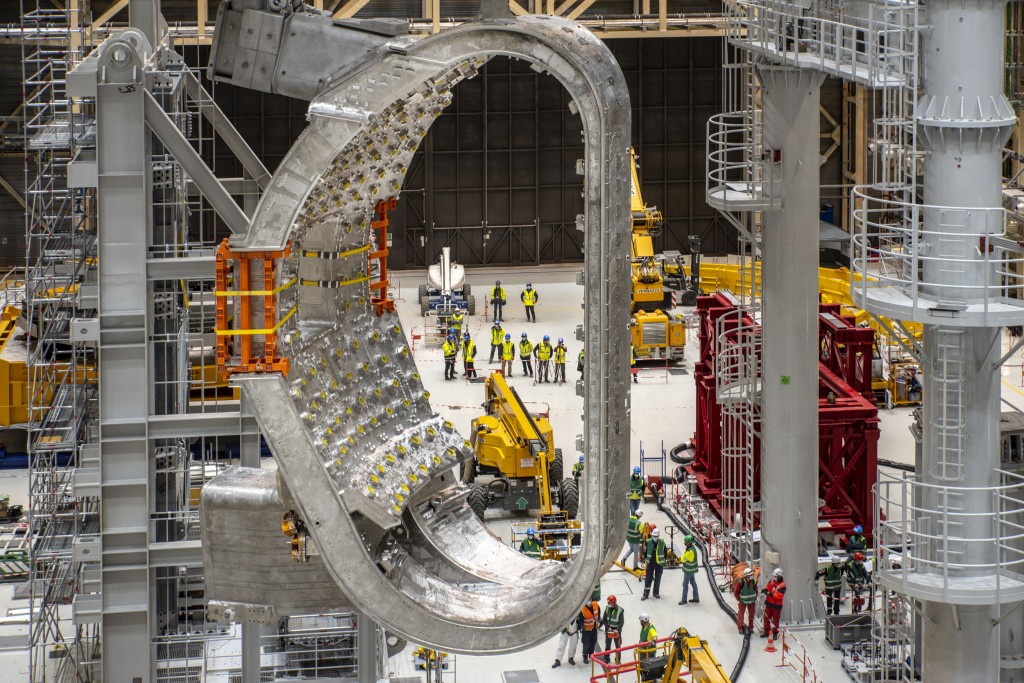
Mammoth
2021-04-06 - The double-walled, D-shaped sector is 13.8 metres tall, 6.6 metres deep, and 7.8 metres wide.

To the end of the building
2021-04-06 - On Tuesday 6 April, sector #6 was removed from the upending tool and carried by overhead crane to the end of the Assembly Hall and sector sub-assembly tool #2. Several bespoke attachments interfaced between the crane and the component.
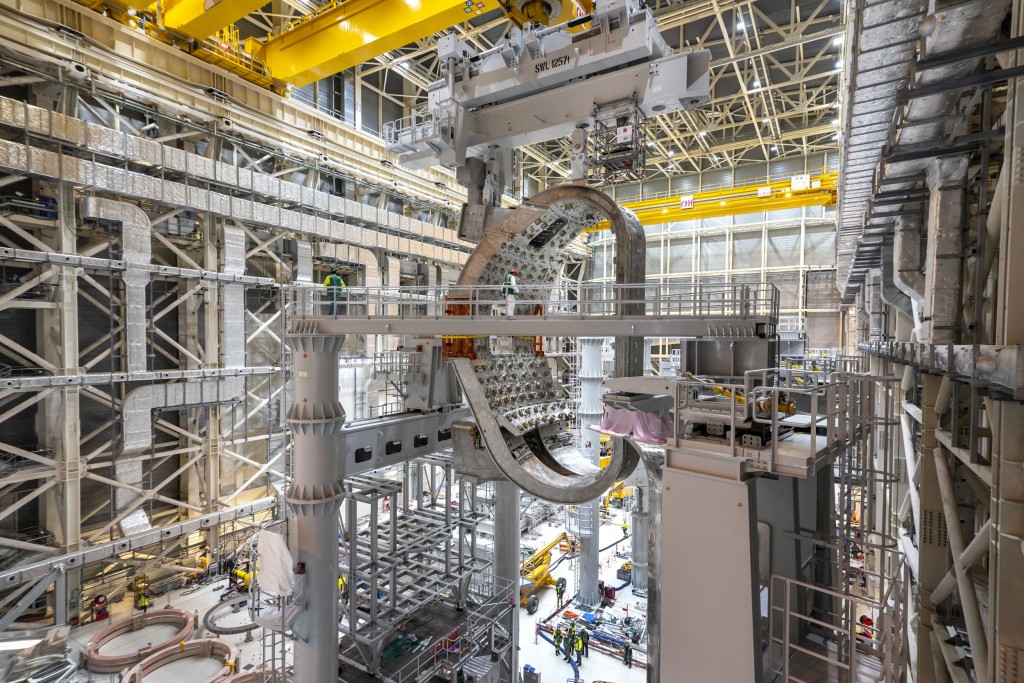
From above
2021-04-06 - Sector #6 is inserted from above into the V-shaped sector sub-assembly tool.

First sector safely docked
2021-04-06 - Supported by a radial beam above, vacuum vessel sector #6 is now safely docked in the sector sub-assembly tool (SSAT#2).
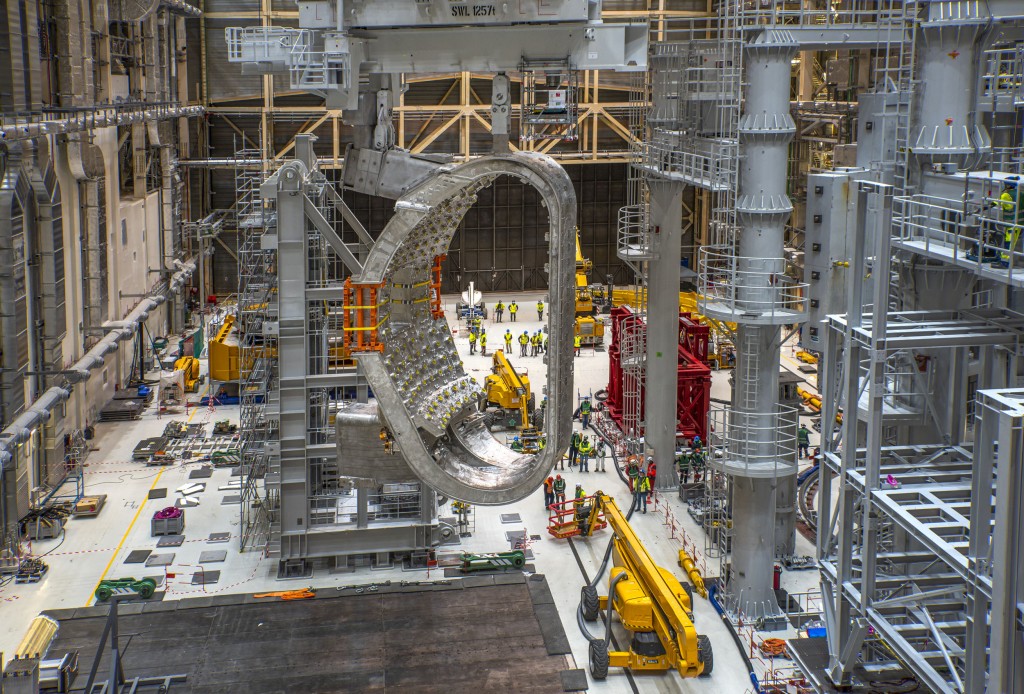
Transferred to SSAT tool #1
2021-04-06 - The first 440-tonne vacuum vessel sector (#6 from Korea) has been transferred to sector sub-assembly tool (SSAT) #1, closest to the Tokamak pit. Two identical tools stand side by side in the Assembly Hall to double the speed at which vacuum vessel sub-assemblies can be created.
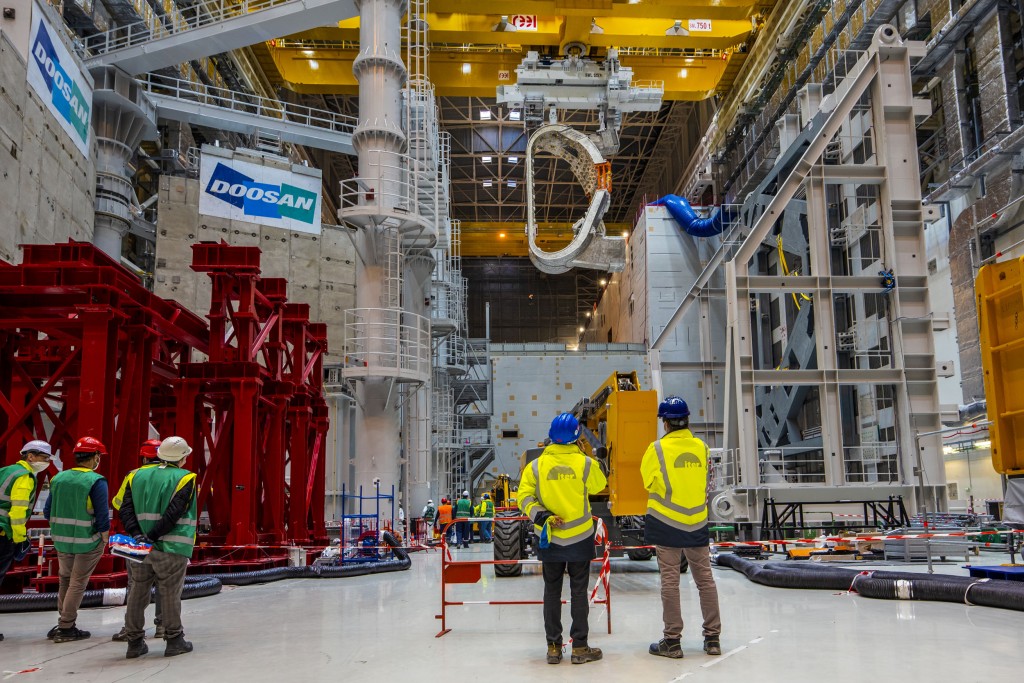
Without a hitch
2021-04-06 - The upending, transfer and tool installation sequence performed on vacuum vessel sector #6 will be repeated eight other times. The first operation was prepared carefully, and went off without a hitch.
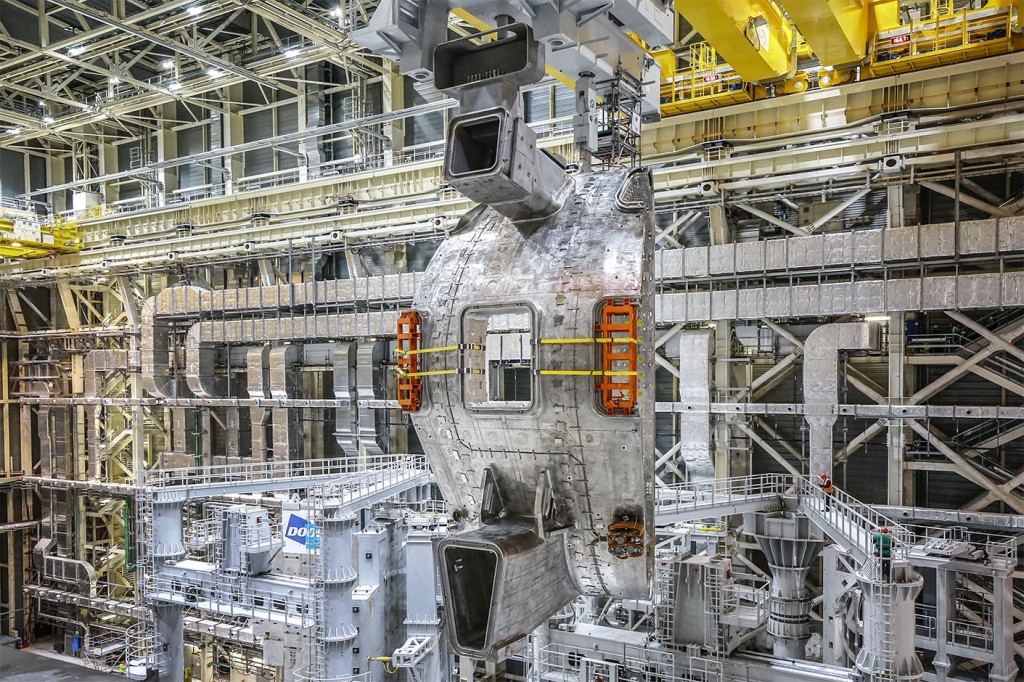
Perfect
2021-04-06 - The lifting of this 440-tonne vacuum vessel sector and its positioning in the sector sub-assembly tool was a master class of coordination and precision.
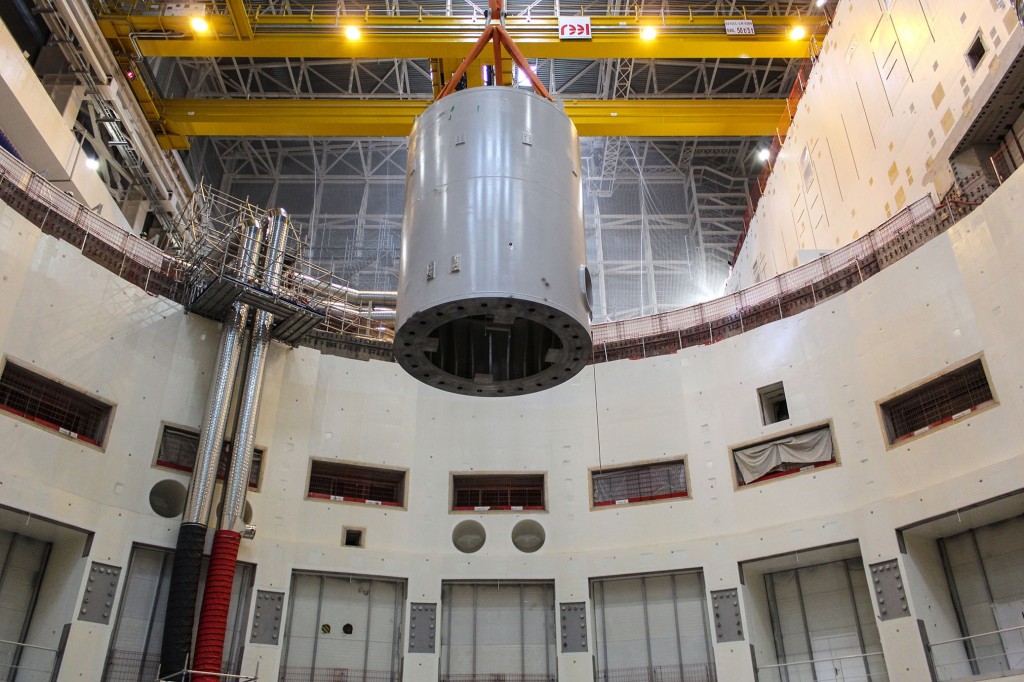
Hollow, but reinforced
2021-03-27 - The central column is hollow (although heavily reinforced with ribbing). Cat ladders and port holes will allow access to different levels of the vacuum vessel during assembly.

First piece
2021-03-27 - The bottom cylinder of the tool was installed in the pit on 27 March 2021. Four other segments will be added to form the +20-metre-tall central column.
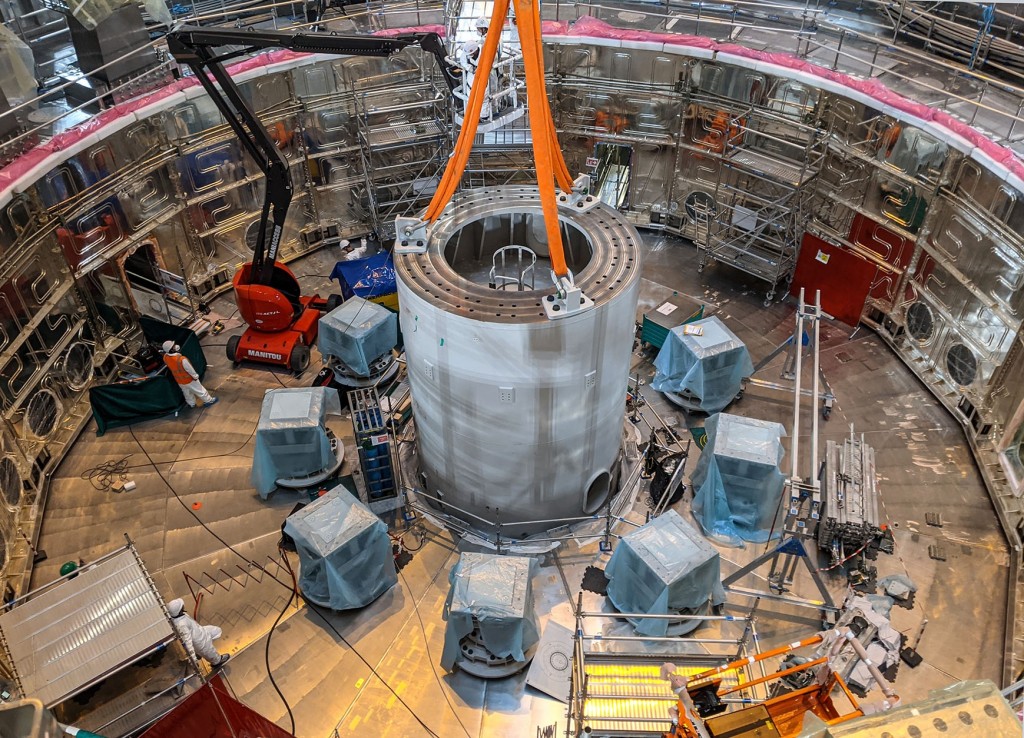
A strong base for a heavy task
2021-03-27 - On 27 March, the teams installed the bottom cylinder of the in-pit assembly tool. With a central column and radiating beams braced against the pit walls, the in-pit column tool will support all nine sectors of the vacuum vessel as they are welded together.

Ring magnet PF6 enters Assembly Hall
2021-03-26 - Poloidal field coil #6 (PF6) is the second smallest of the ITER ring magnets in terms of diameter (10 metres) but the first in the assembly sequence of the ITER Tokamak. It will be lowered onto temporary supports at the bottom of the Tokamak pit in April.
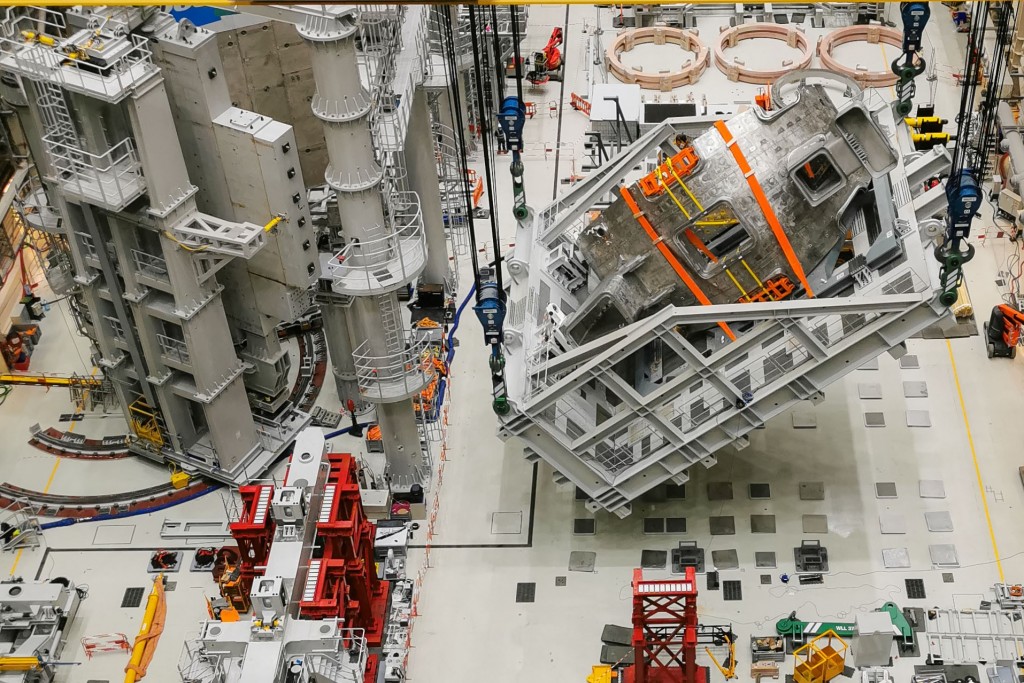
Mid-air
2021-03-26 - The tilt operation took place mid-air. At one point, the component was nine metres overhead.
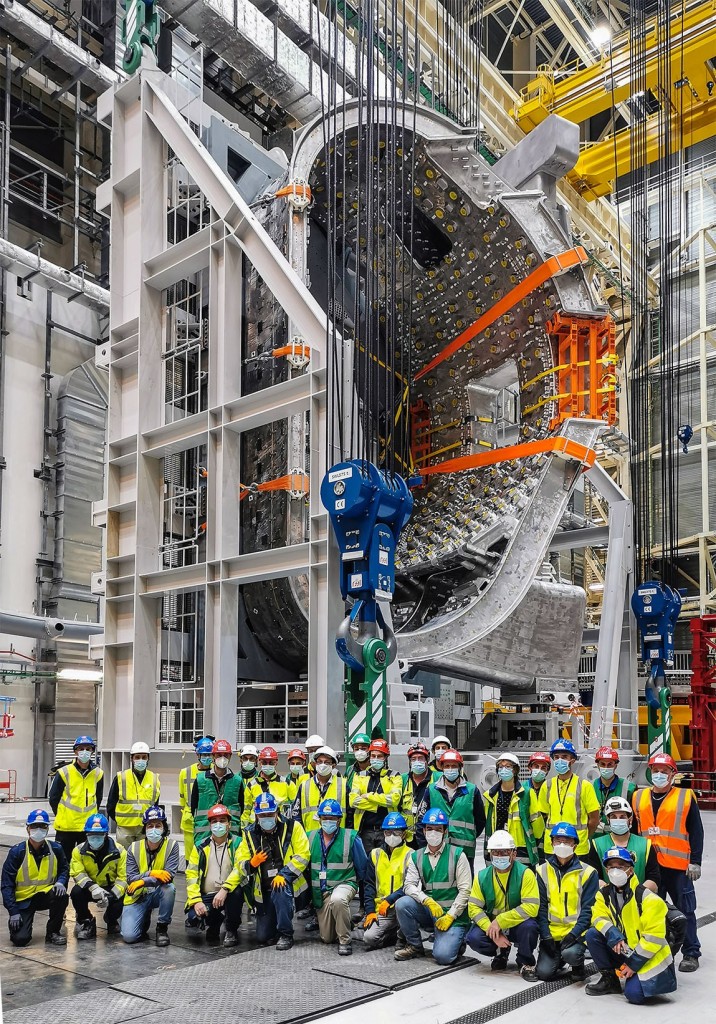
Vertical
2021-03-26 - For the first time of its existence, the 440-tonne component is in a vertical position ... and the observer can truly measure the size of the ITER plasma chamber.
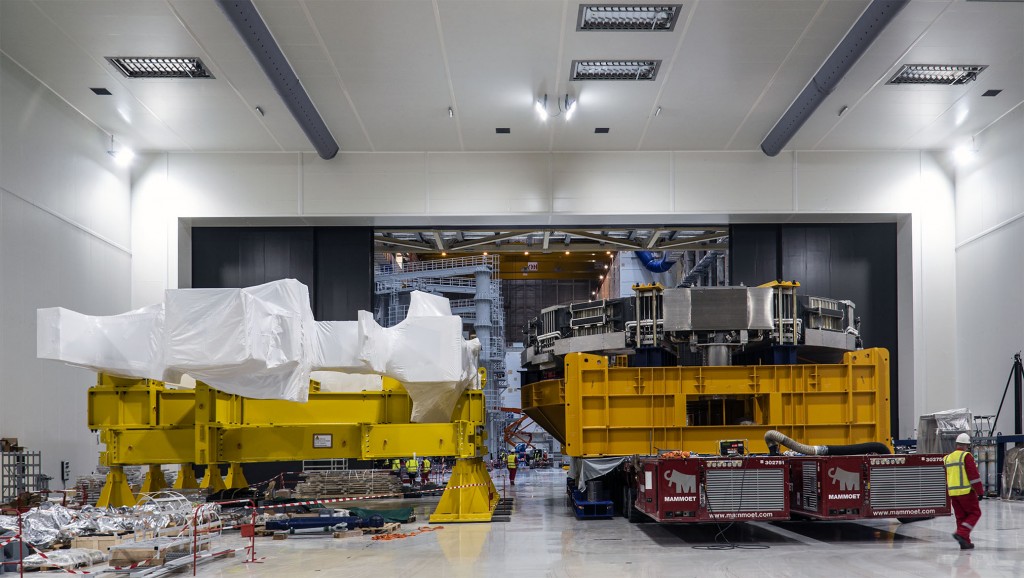
Waiting in line
2021-03-26 - Two massive machine components are waiting to enter the Assembly Hall. Left: a 360-tonne vertical coil, TF12; right: a 440-tonne ring magnet, PF6.

It takes a team
2021-03-26 - Personnel from the Dynamic consortium (machine assembly), crane operators from Foselev, security experts from APAVE, and ITER construction team members were all involved in the successful upending operation for sector #6.
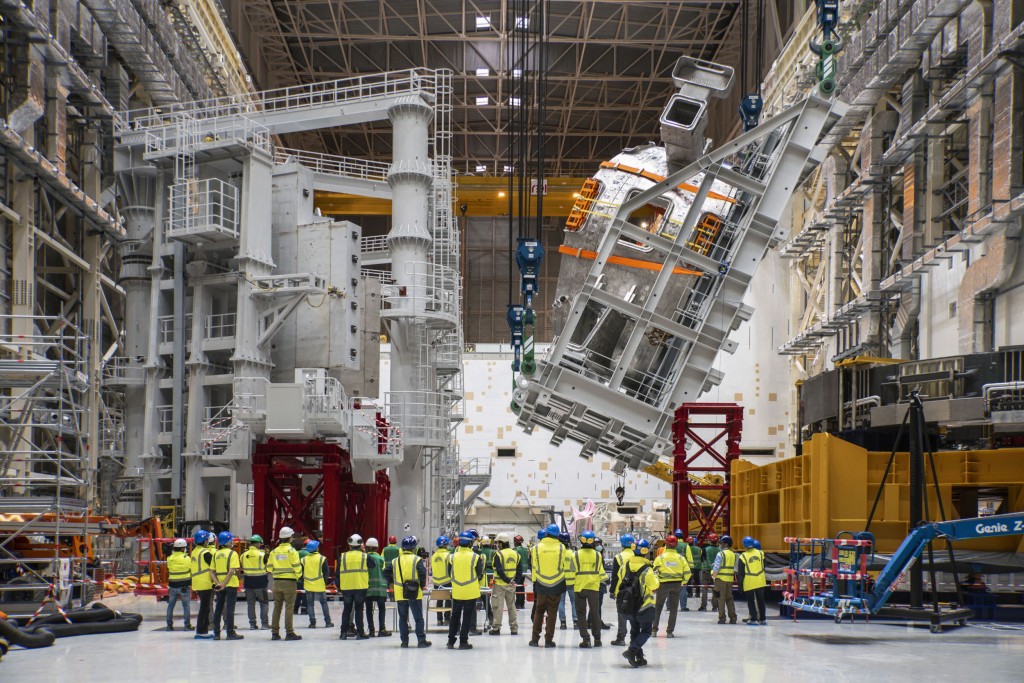
Success!
2021-03-26 - The first "upending" operation is successfully performed on sector #6 on 26 March 2021. The vacuum vessel sector, now vertical, will soon be mounted on specialized tooling in the Assembly Hall.
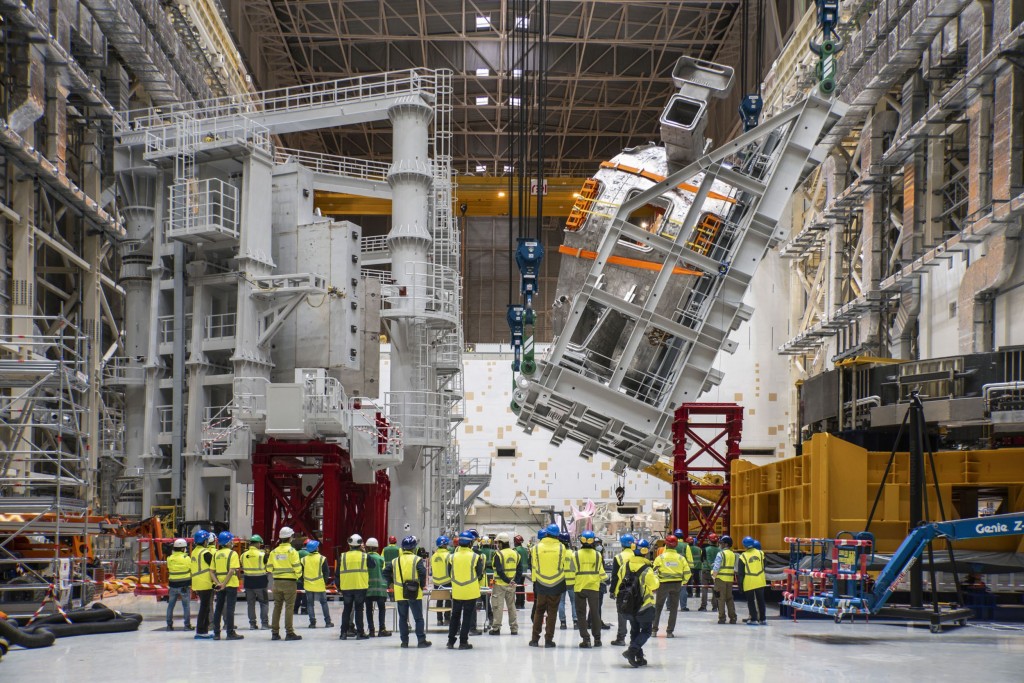
A 90° tilt in mid-air
2021-03-26 - The first vacuum vessel sector is upended on 26 March 2021, the culmination of close to one year of planning and rehearsal.
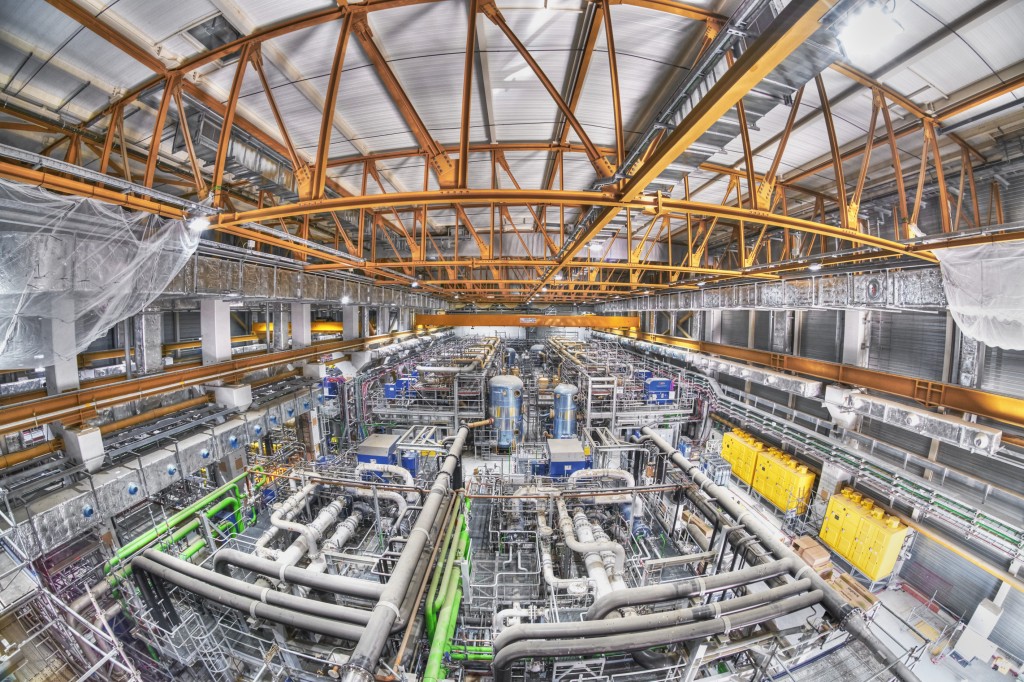
Good progress in the cryoplant
2021-03-25 - Installation work in the cryoplant is nearing completion, and commissioning activities are scheduled to begin in July 2021. Follow all progress in the plant assembly pages of the ITER website (https://www.iter.org/construction/SystemsPlantAssembly). © Christian Luenig (www.arbeitsblende.de)
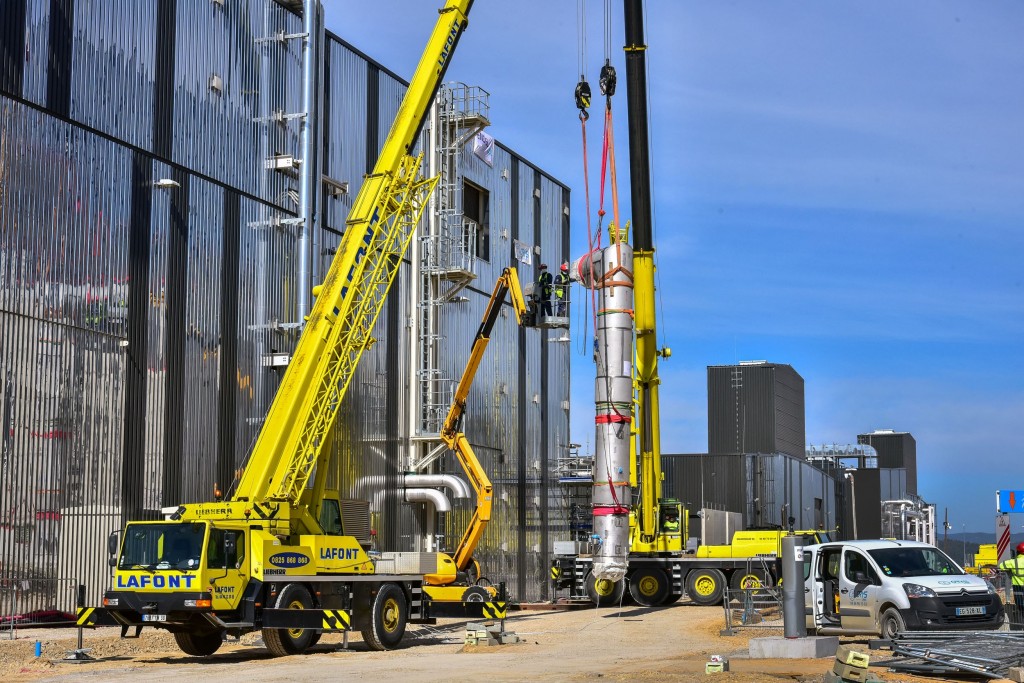
Delivers helium
2021-03-25 - The largest of the two spools installed on Thursday 25 March was 12 metres long, 1 metre in diameter and weighed 6 tonnes. It is tasked with delivering supercritical helium at 4.7 K (minus 269 °C) to the magnets.

Assembly well
2021-03-25 - ITER will be the first tokamak completely integrated into the surrounding building. The 23,000-tonne machine will be assembled here, in the 30-metre-deep Tokamak pit. © Christian Luenig
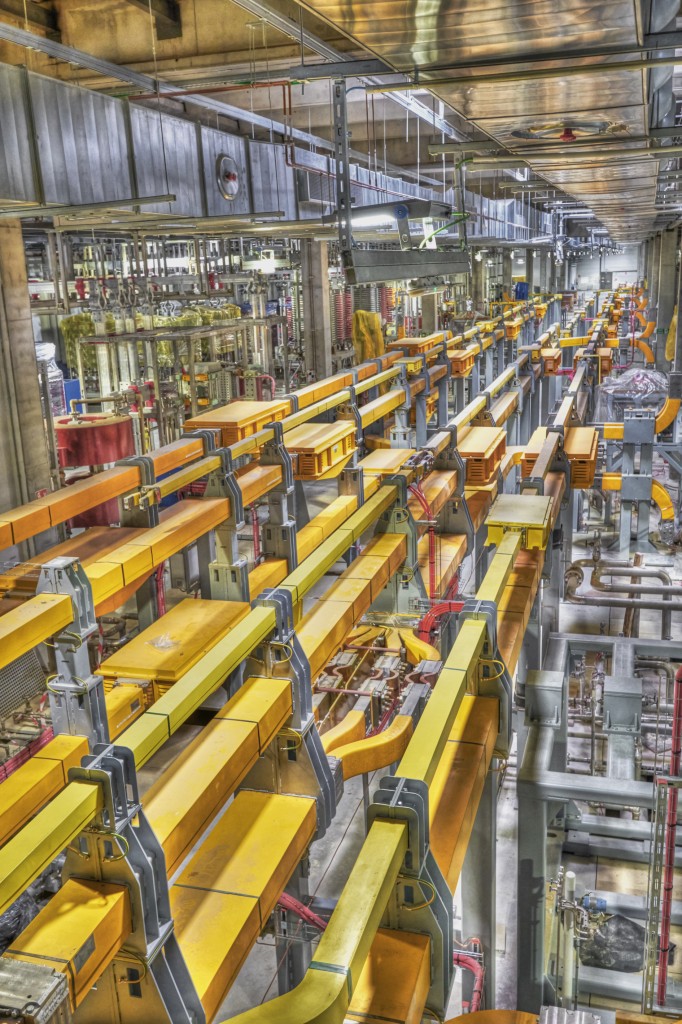
Yellow thruways
2021-03-25 - DC busbars in the Magnet Power Conversion buildings start at the AC/DC converters and run all the way through the buildings, over a bridge, and through the Tokamak Complex to the superconducting magnets. They carry very high current (up to 70 kA). © Christian Luenig

The very centre
2021-03-25 - Workers stand in the very centre of the Tokamak pit, where the central solenoid magnet will be installed late in Assembly Phase 1. Before then, though, a tall column tool will brace the vacuum vessel sectors as they are installed and welded. © Christian Luenig
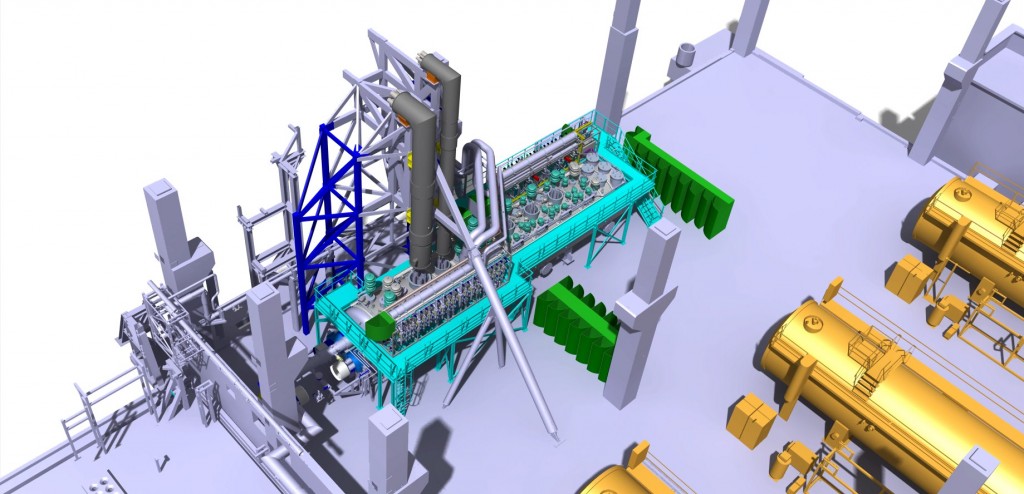
Dark grey elements
2021-03-25 - The two elements in dark grey have now been installed. At the bottom, they connect to the cryoplant's termination cold box (which acts as a dispenser of cooling fluids). At the top, other spools will connect to carry the cooling fluids across a bridge to the Tokamak Building.

Upending operation
2021-03-25 - This specialized upending frame will be used to raise two types of large components—vacuum vessel sectors (440 tonnes) and toroidal field coils (360 tonnes)—from their horizontal delivery configuration to vertical for subsequent installation on the sector sub-assembly tools. The "tilt" operation is carried out in coordination with the overhead cranes.

Carefully
2021-03-25 - The cryoline spools are delicate pieces of high technology that can only tolerate a certain level of acceleration during transport and lift. Shock recorders allowed operators to control every step of the process.

Strong hands
2021-03-25 - A huge hook has just disengaged from a load deposited in the Tokamak pit. The back-and-forth ballet of the overhead cranes is accelerating. © Christian Luenig (www.arbeitsblende.de)

Swaths of yellow
2021-03-25 - Busbars in the Magnet Power Conversion buildings make a good backdrop for the artistic photos of (©) Christian Luenig

Down the alley
2021-03-25 - A large cryoline spool, with several process pipes inside its metal case, is transported along the cryoplant to be installed through the roof of the far end, near the Tokamak Building.
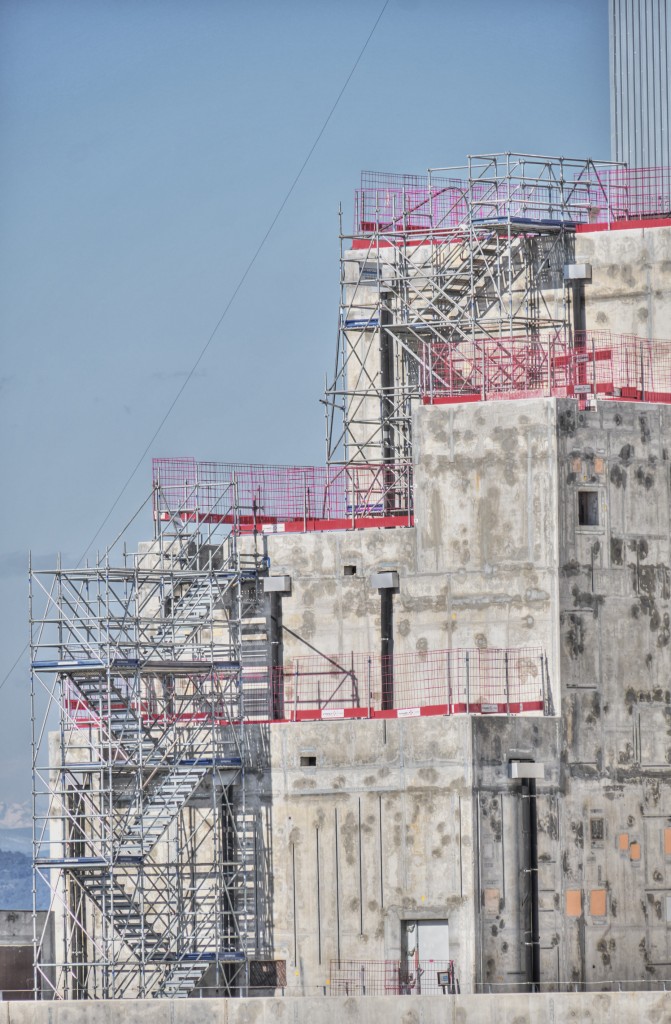
Massive
2021-03-25 - A corner of the Tokamak Complex, a seven-storey structure that will house not only the ITER Tokamak, but also more than 30 different plant systems that are necessary for machine operation. Photo: © Christian Luenig (www.arbeitsblende.de)
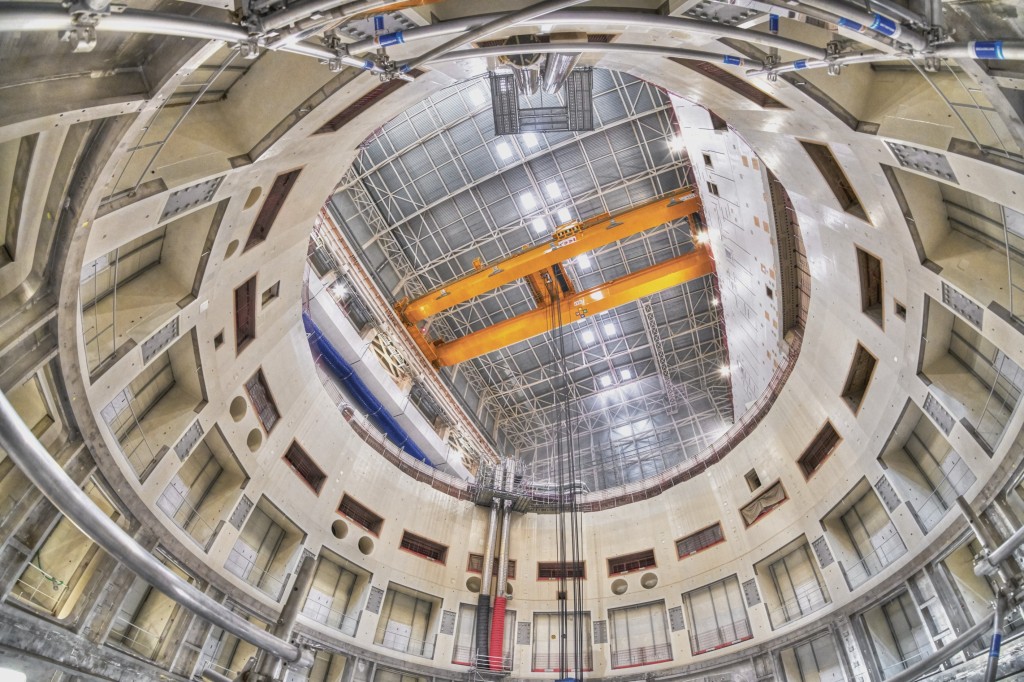
Strong hands
2021-03-25 - The heavy-lift bridge cranes have been operating in the complete assembly space (Assembly Hall + Tokamak Building) since March 2020.

Through the roof
2021-03-25 - A massive steel structure supports the 6-tonne component that has come through the roof. It needs to be precisely aligned with the connections on top of the cryoplant's termination cold box.

Top lid taking shape
2021-03-24 - The 665-tonne top lid section is taking shape in the Cryostat Workshop. MAN Energy Solutions (sub-contractor to India's Larsen & Toubro) is in charge of welding. Photo: © Christian Luenig (www.arbeitsblende.de)
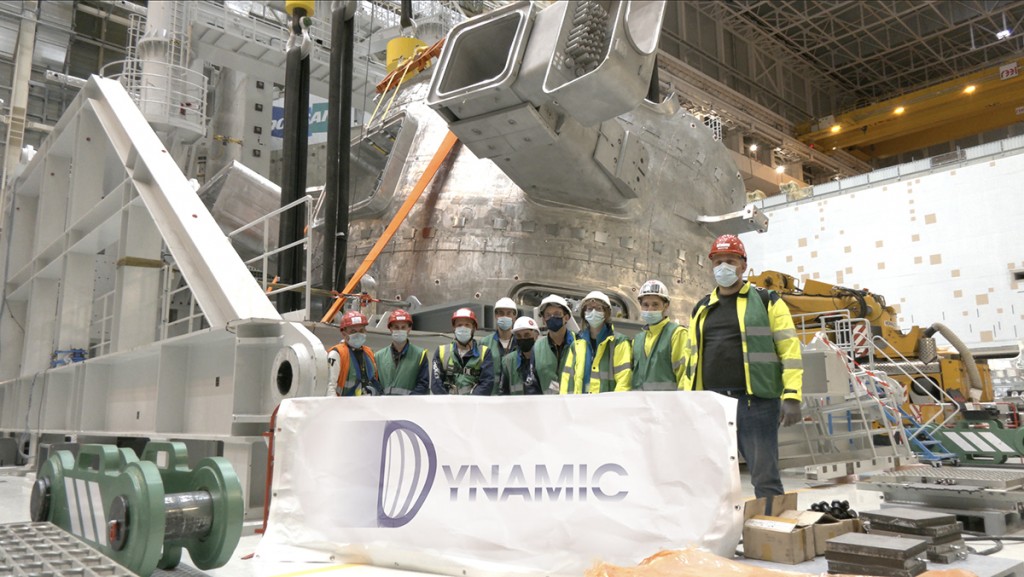
Machine assembly partners
2021-03-24 - The ITER Organization is collaborating with two consortia for the assembly of the core machine: the CNPE Consortium (China Nuclear Power Engineering; China Nuclear Industry 23 Construction Company Ltd.; Southwestern Institute of Physics; Institute of Plasma Physics, Chinese Academy of Sciences ASIPP; and Framatome) and the DYNAMIC SNC consortium (Ansaldo Nucleare; Endel Engie; Orys Group ORTEC; SIMIC; Ansaldo Energia; and Leading Metal Mechanic Solutions SL).

Last of four
2021-03-23 - The cryostat top lid is the last of four cryostat sections to be produced on site in the Cryostat Workshop. It should be completed by the end of 2021. © Christian Luenig (www.arbeitsblende.de)

Basins
2021-03-23 - Below platform level, deep basins will receive the water coming in from different cooling circuits. © Christian Luenig
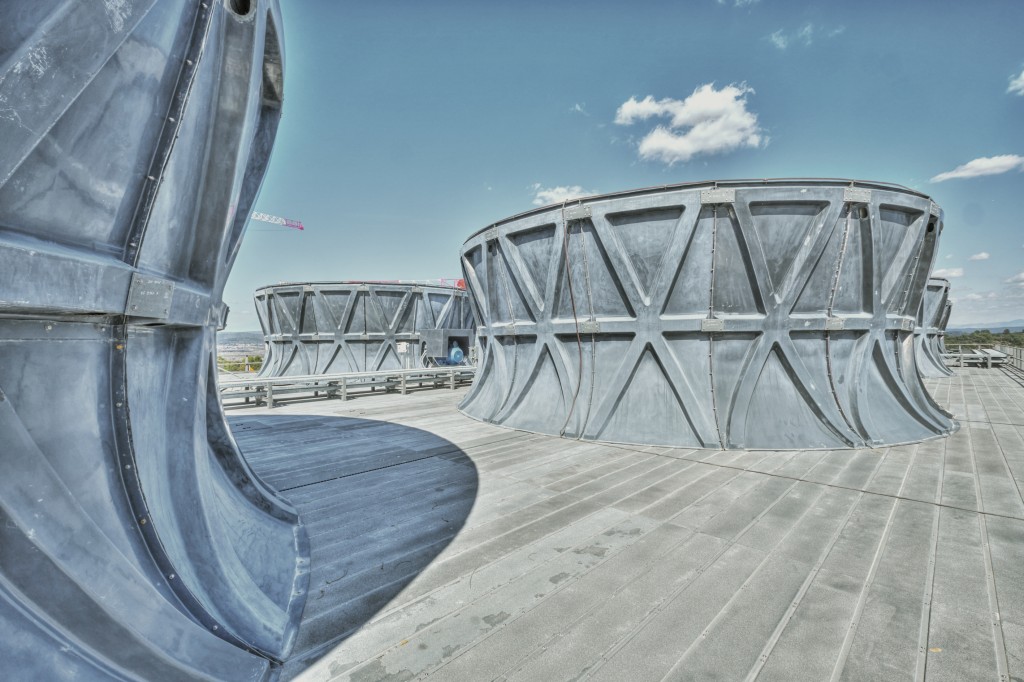
The roof
2021-03-23 - Behind each cylinder are powerful fan blades that will create an upward draft to cool the water released from the top. © Christian Luenig

Top lid enters stage
2021-03-23 - The top lid will be formed from: 12 lid segments, one centre cylinder and one centre cover. In this photo, welding is performed by a specialist from MAN Energy Solutions (sub-contractor to the Indian firm Larsen & Toubro). © Christian Luenig (www.arbeitsblende.de)
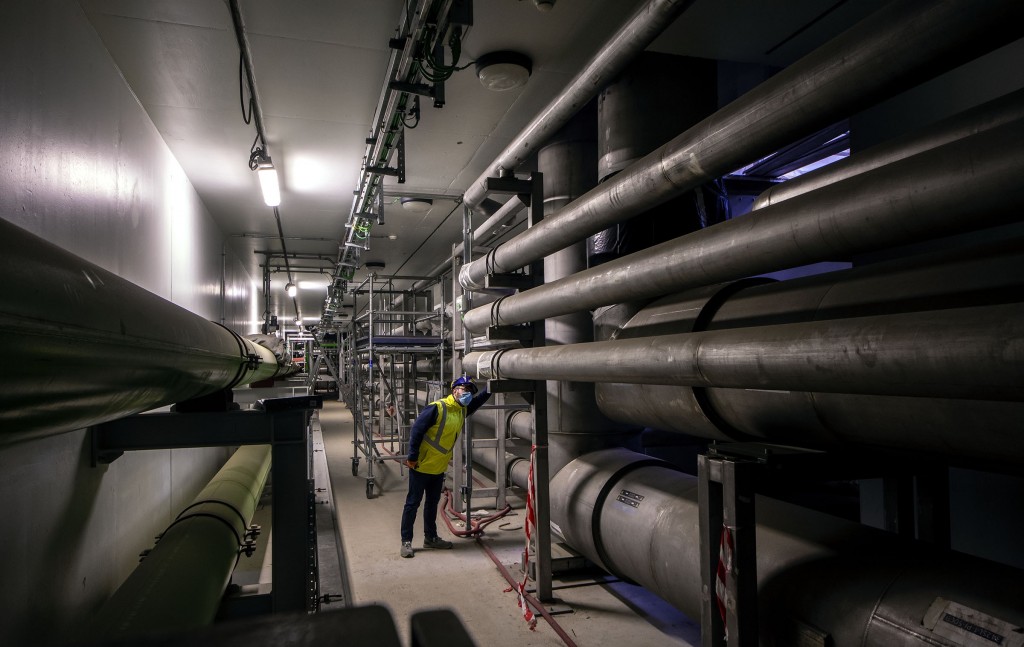
Point of departure
2021-03-23 - Cryolines originating in the cryoplant deliver cooling fluids to some essential elements of the ITER machine—the superconducting magnets, the cryopumps and the different parts of the thermal shield.

A field of pipes
2021-03-23 - Pipes, pumps and heat exchangers are photographed from the top of the heat rejection system cooling towers. © Christian Luenig

Mostly empty
2021-03-23 - Under the cooling towers, once the water droplets have passed through a labyrinth of fill packs to cool, they fall back into the basins. The lower part of the cooling tower building is largely empty and open to the wind. © Christian Luenig
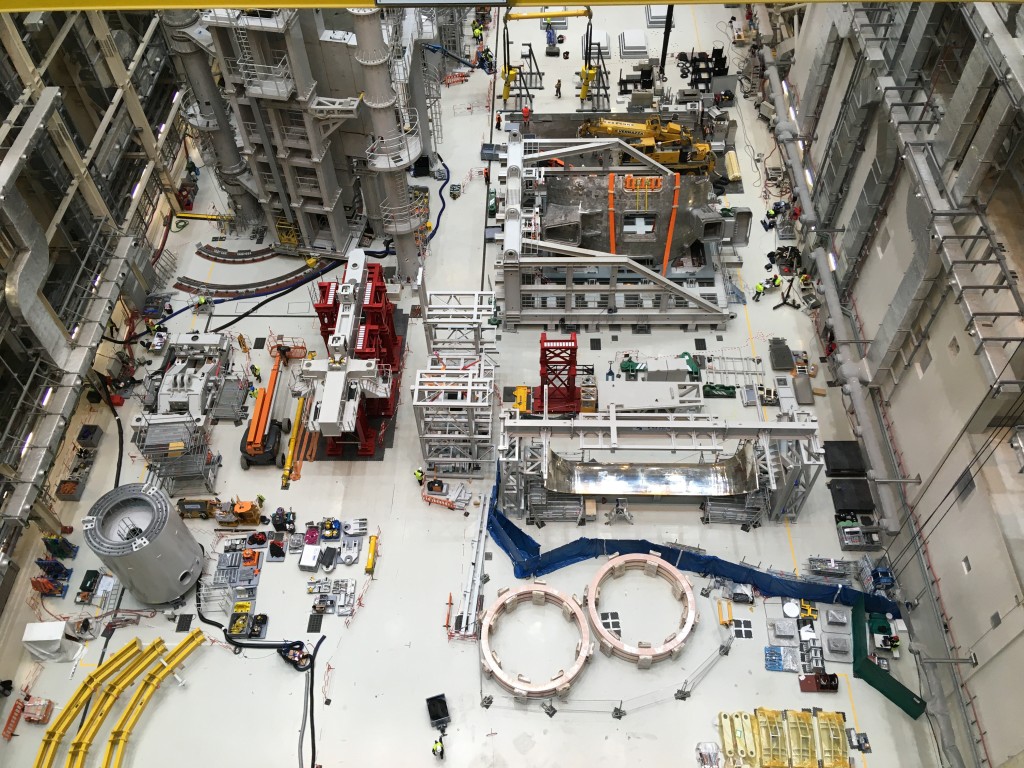
Bird's eye view
2021-03-22 - A bird's eye view of the assembly and installation projects running in parallel in the ITER Assembly Hall. Top right: vacuum vessel sector #6, lashed to its frame, has been positioned in the upending tool; bottom right: pre-compression rings await their turn in the assembly pit; bottom left: the base cylinder of the in-pit assembly tool, ready for lifting; top left: on a red stand, the radial beam that will attach to the top of the vacuum vessel sector once it is lifted to its vertical orientation.
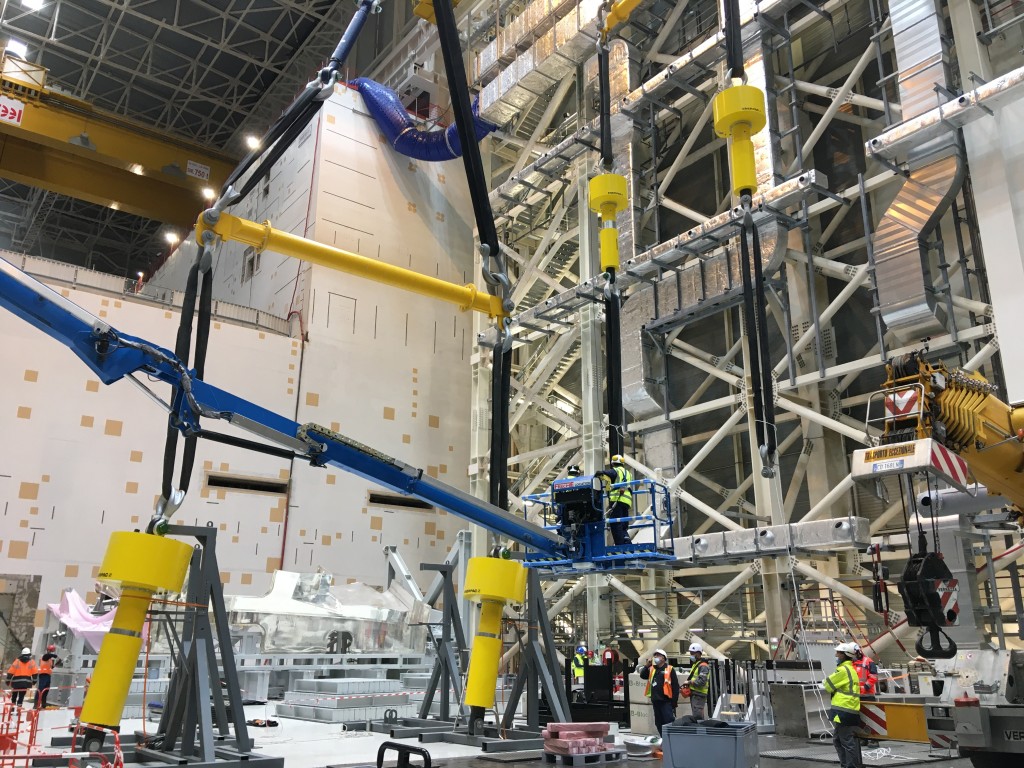
Big lift to come
2021-03-22 - The assembly teams are preparing the overhead cranes, and all their interfacing parts, for the next big lift: bringing the first 440-tonne vacuum vessel sector from horizontal to vertical.
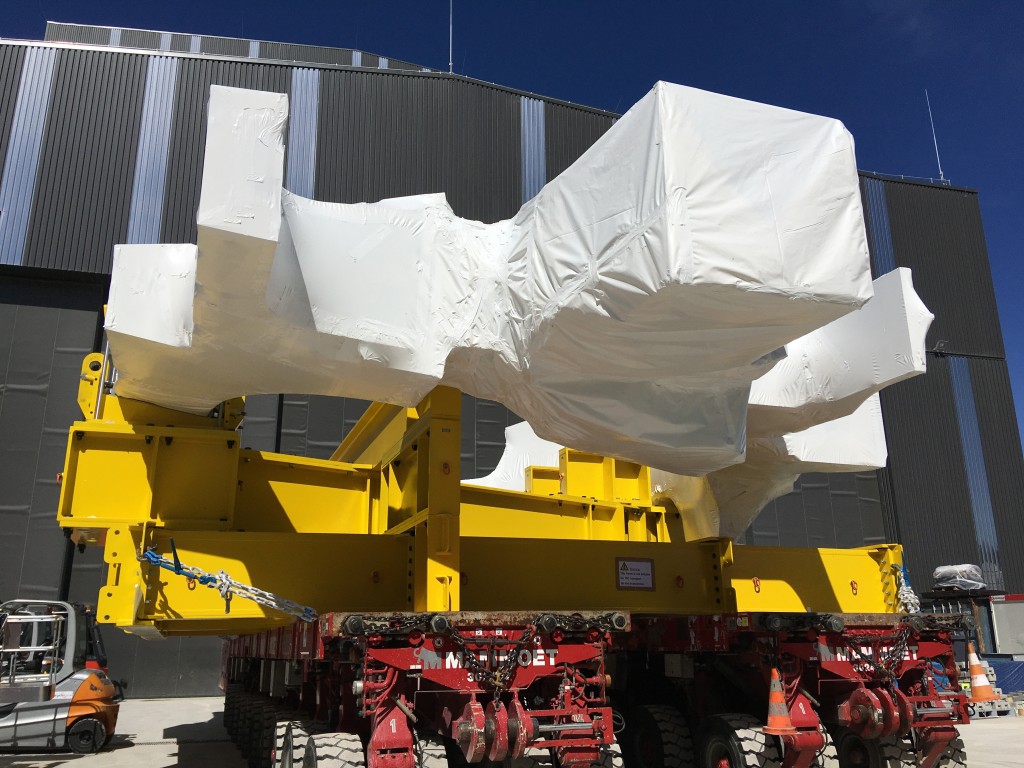
Coil enters assembly antechamber
2021-03-22 - This 360 magnet coil—toroidal field coil #12, from Japan—is leaving a temporary storage facility and entering the Cleaning Facility.
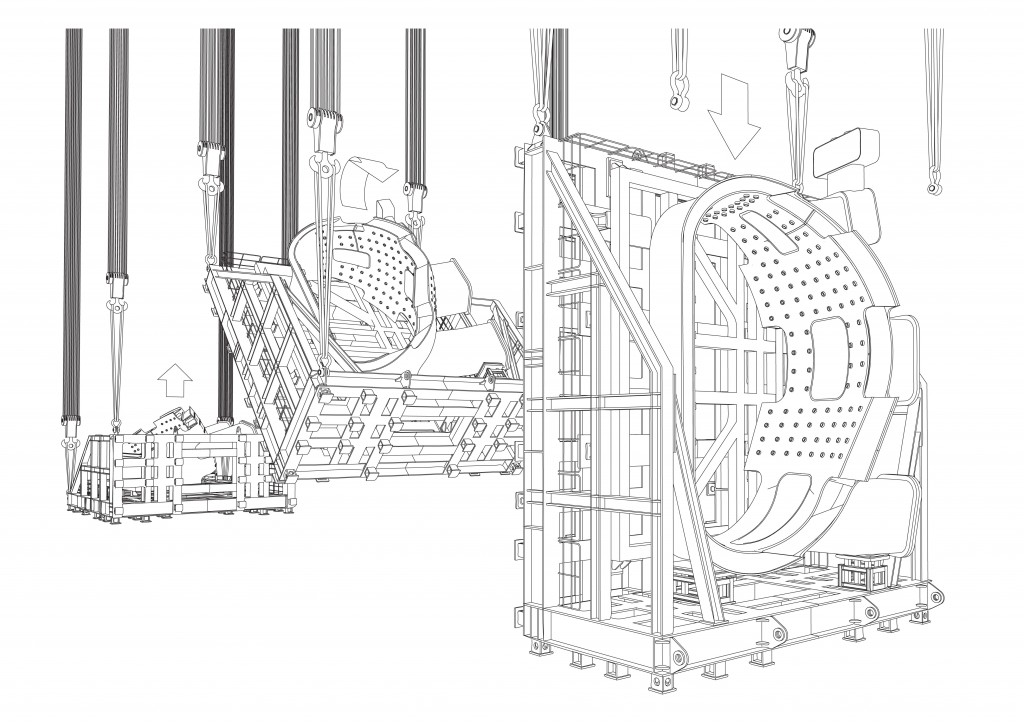
Upending operation
2021-03-21 - This specialized upending frame will be used to raise two types of large components—vacuum vessel sectors (440 tonnes) and toroidal field coils (360 tonnes)—from their horizontal delivery configuration to vertical for subsequent installation on the sector sub-assembly tools. The "tilt" operation is carried out in coordination with the overhead cranes.

Heavy base for a strong task
2021-03-20 - Close to 6 metres tall and weighing approximately 70 tonnes, this is the first segment of the in-pit column tool, the bottom cylinder. Hollow inside, it will permit access to different levels of the vacuum vessel during in-pit welding operations. Four other segments will follow to build the full column.
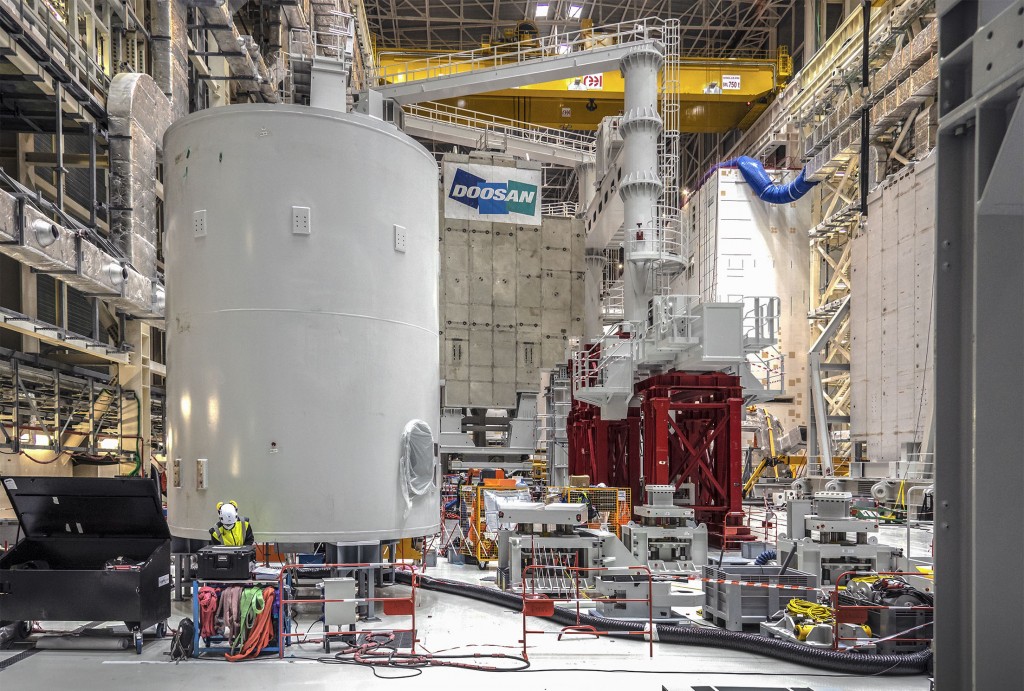
First element of the central column
2021-03-10 - Close to 6 metres tall and weighing approximately 70 tonnes, this is the first segment of the in-pit column tool, the bottom cylinder. Hollow inside, it will permit access to different levels of the vacuum vessel during in-pit welding operations. Four other segments will follow to build the full column.
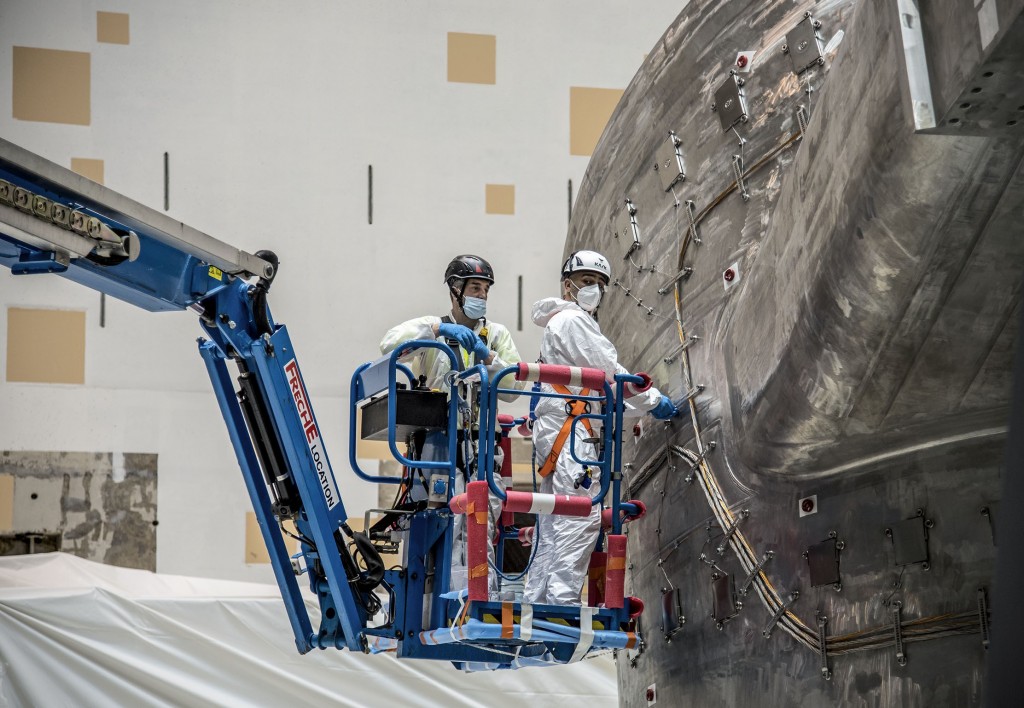
Little "bosses"
2021-03-10 - Approximately 700 ''bosses'' have been welded to the outer skin of vacuum vessel sector #6 in precise locations, for the attachment of instrumentation, instrumentation cables, and cable trays. Over the workers' heads are some of the magnetic sensor cases, attached with four ''bosses'' each; elsewhere, we see the routing of cables and instrumentation wires.

Concentric circles of support
2021-03-10 - Half of the toroidal field magnet supports (covered in yellow) have been installed in the pit. Anchored in a circle to the cryostat base, they will support the outer edge of each toroidal field coil.
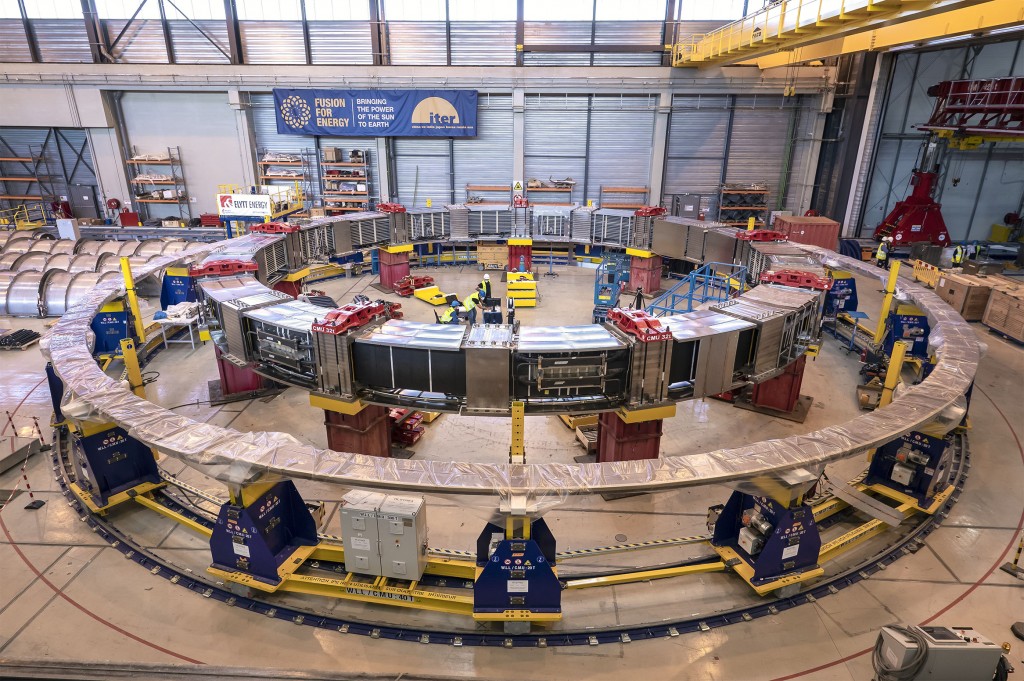
Two sizes
2021-03-10 - Poloidal field coil #5 (PF5) is the second ring coil procured by the European Domestic Agency. Here PF5 is seen inside of one of the double pancakes that has been wound for PF4, which is a larger coil (24 metres in diameter vs 17 metres in diameter).
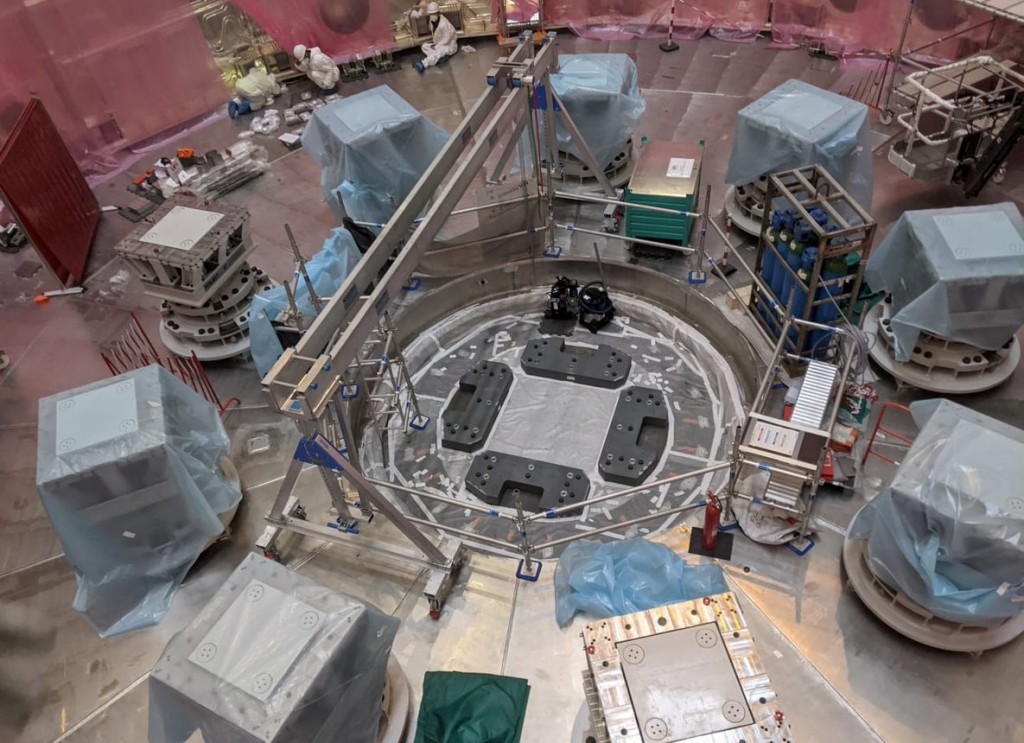
Shear keys
2021-03-10 - At the bottom of the pit, the assembly teams are preparing for the installation of a tall central column, part of the in-pit assembly tool that will support the vacuum vessel during welding. The first segment of the column, the lower cylinder, will be anchored to the concrete basemat through these four shear keys.

In-pit assembly tool
2021-03-09 - Formed from a central column and nine radial beams, this tool is installed inside of the Tokamak pit to support, align and stabilize vacuum vessel sub-assemblies as they are joined and welded. With the central column anchored to the Tokamak Building basemat and the radial beams supported between the column and the concrete bioshield, the in-pit assembly tool is designed to support a nominal weight of 5,400 tonnes.
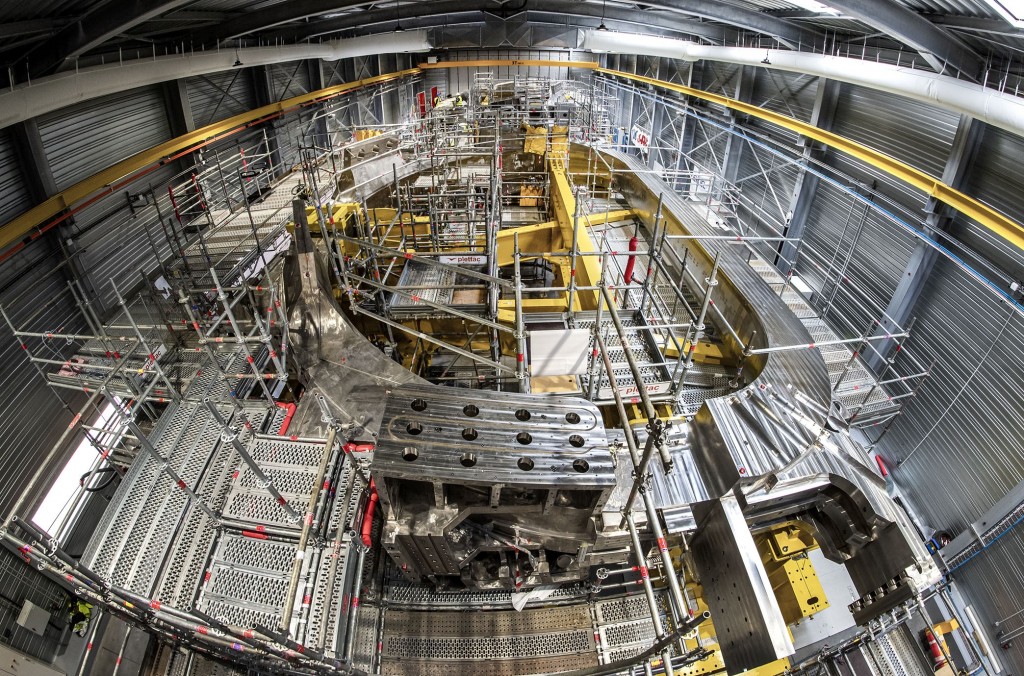
Prepping the toroidal field coils
2021-03-06 - A pair of toroidal field coils supplied by Japan is being prepped for pre-assembly. The process adds approximately 10 tonnes of equipment, some of it temporary, to their already considerable mass.

Sort and connect
2021-03-06 - The ITER Tokamak is an experimental machine whose parameters will be closely monitored by a vast array of diagnostics devices. Sorting and connecting the low-voltage cables that transport data from sensors on the toroidal field coils is a delicate operation that is performed during the assembly prep works.

7 segments assembled
2021-03-02 - Seven of 12 segments have been assembled on the work platform—enough for us to appreciate the size and shape of the cryostat top lid.

440 tonnes
2021-03-02 - Planned for mid-March, the first upending operation will be quite spectacular. Once raised to vertical, this 440-tonne vacuum vessel sector will stand just over 11 metres tall.

Keeping clean
2021-03-02 - A close-up of the lower cryostat work area. A strict cleanliness protocol is in effect, to keep dust and sub-microscopic particles off of the components.

Preparing for lift off
2021-03-02 - Strong orange lashing lines will help to keep vacuum vessel sector #6 securely attached to its lifting frame during the 90-degree upending procedure.

Major tools, all in a row
2021-03-01 - Some of the major assembly tools are visible in this photo: the sector sub-assembly tools (22 metres tall, right); the upending tool (in its raised position, left); and the ITER bridge cranes.

3 handling devices
2021-02-28 - Under the overhead crane, the 90-tonne "dual crane heavy lifting beam" (yellow) provides a single connection for the next-layer of lifting attachment. The second layer—the sector lifting tool—interfaces at three points with toroidal field coil lifting beam. The lifting beam (also called a radial beam) connects directly to the top of the vacuum vessel sector (which is represented here by the dummy load).
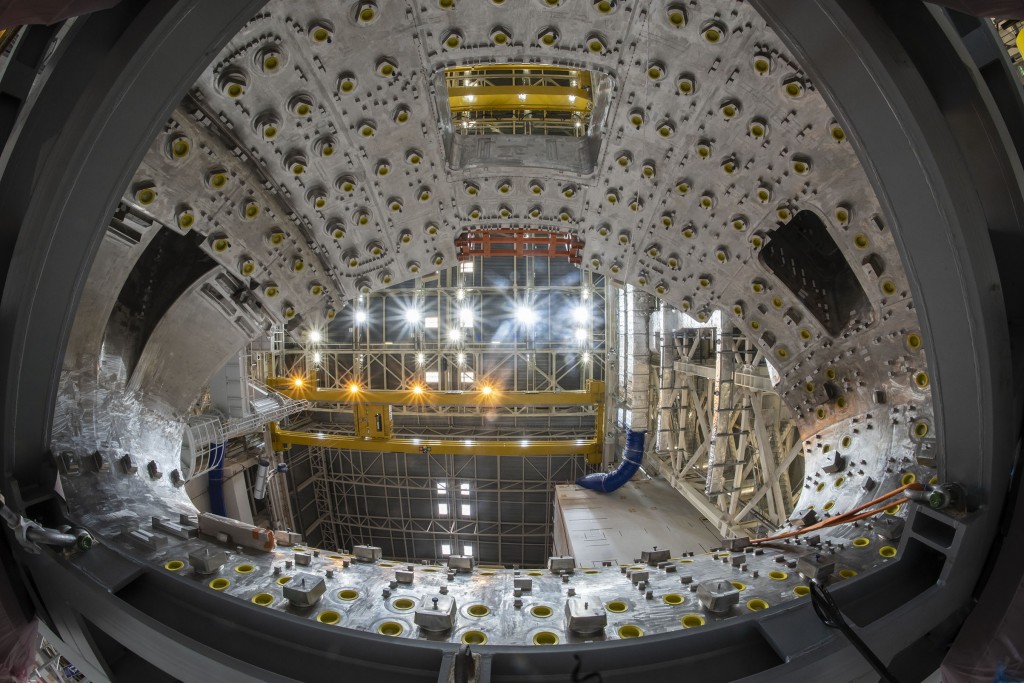
Inside sector #6
2021-02-26 - Stub keys and flexible support housings dot the inner surface of vacuum vessel sector #6. Flexible support cartridges will lock into these housings and act as bolts securing the blanket modules to the vacuum vessel. This massive component is now ready to be upended and positioned on one of the twin giant sector sub-assembly tools.
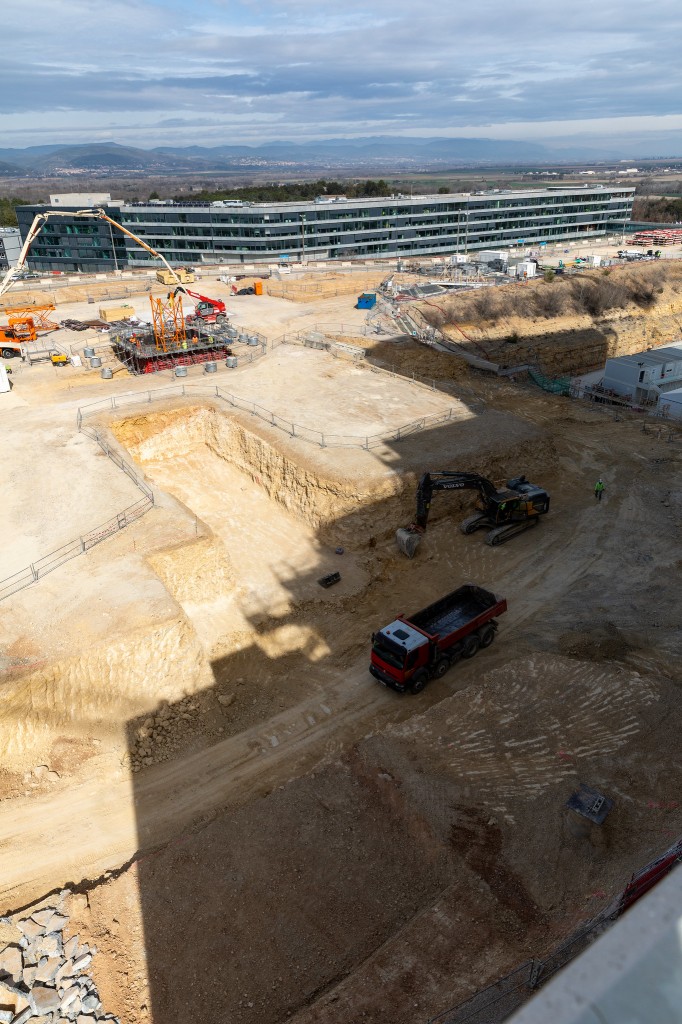
Careful construction
2021-02-26 - Standing close to the Tokamak Building (to which they connect by bridges and transmission lines), the buildings are designed to resist fire, outside explosions and seismic events. © Les Nouveaux Médias/SNC ENGAGE

Ring game
2021-02-26 - Seen on the shop floor: six pre-compression rings as well as their lift tool and a seventh test coil.
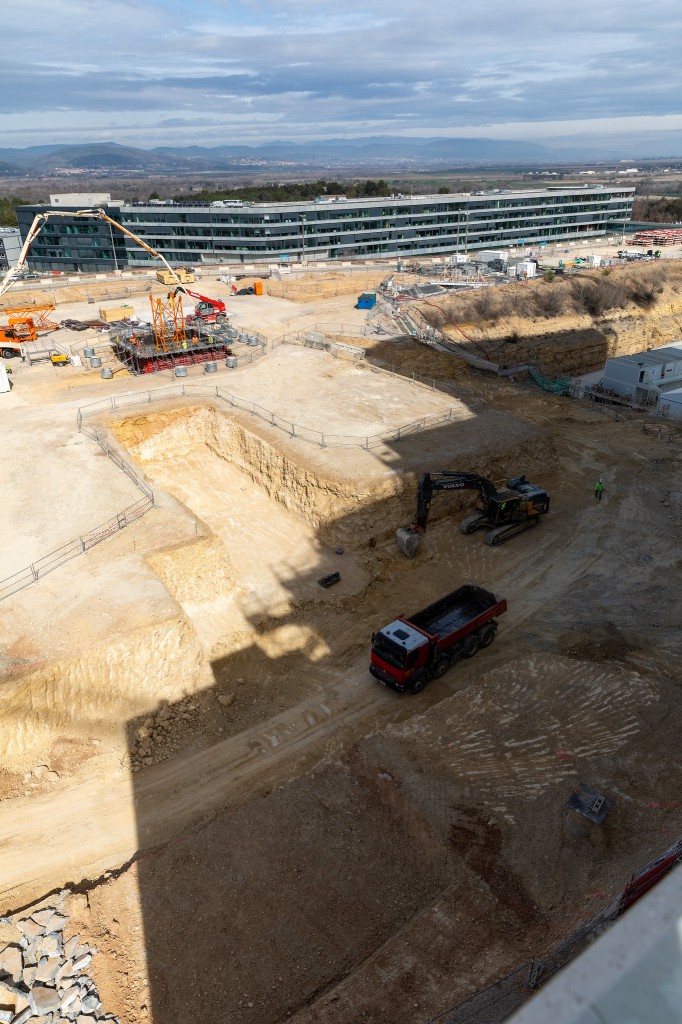
New construction zone for neutral beam power
2021-02-26 - Between the Tokamak Complex and ITER Headquarters, a new construction project is underway. Two buildings and a technical zone for the neutral beam power supplies are planned. © Les Nouveaux Médias/SNC ENGAGE
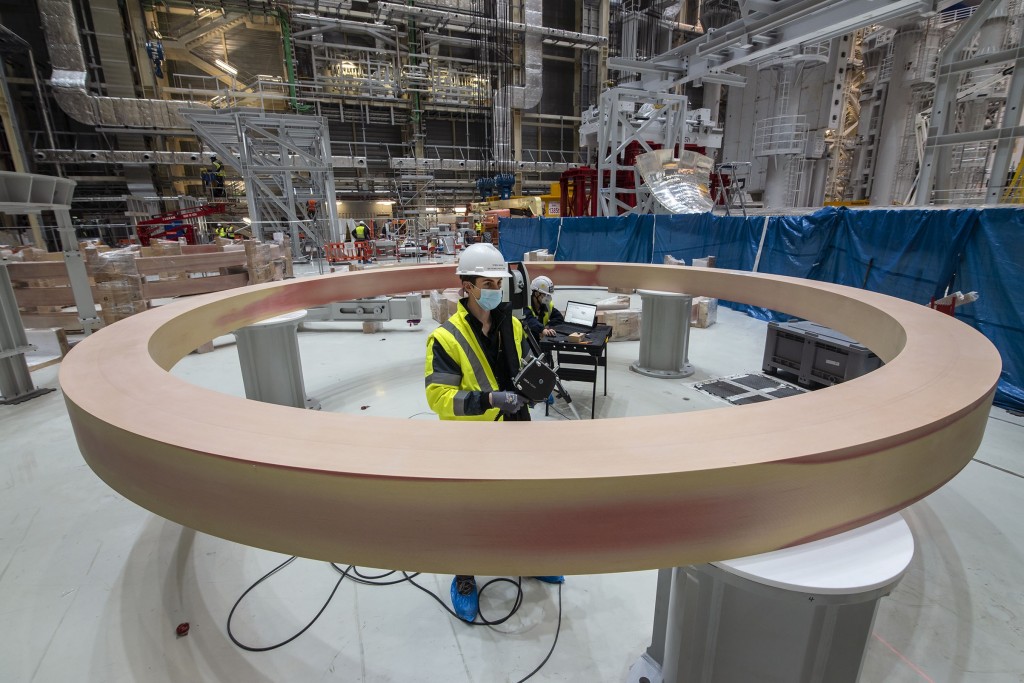
Pre-compression rings: preparing to install six
2021-02-26 - Metrology operations are underway on the first of six pre-compression rings to be positioned in the assembly pit at the end of the month. The rings have an inner diameter of 5 metres.
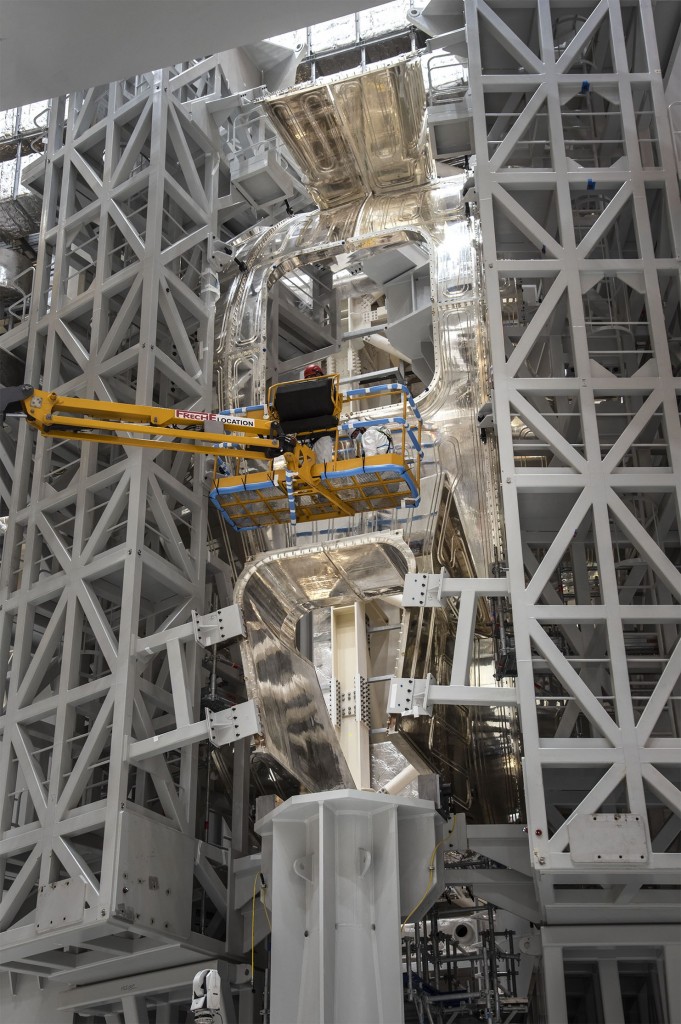
Perfect alignment
2021-02-26 - Perfect alignment between two vacuum vessel thermal shield outboard panels was achieved during recent alignment tests.
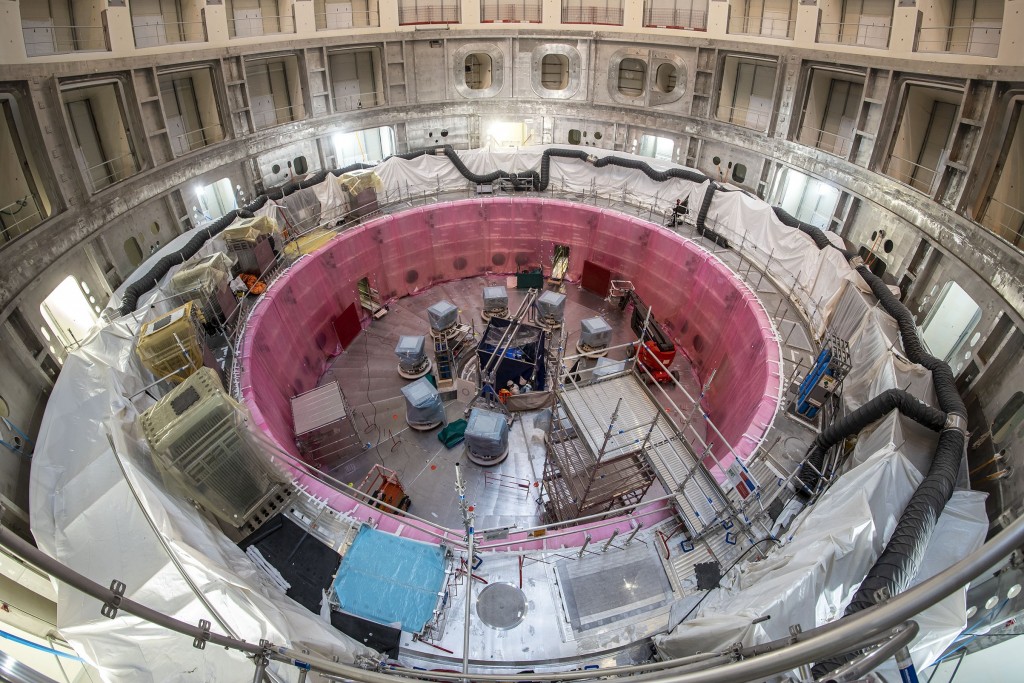
Filling up
2021-02-26 - The lower part of the assembly pit is getting more crowded by the day. On the rim of the cryostat base (the "pedestal"), five toroidal gravity supports are now installed. At the bottom level, six temporary supports for poloidal field coil #6 are arranged in a perfect circle. In the middle, drilling is underway to prepare for the bolting of the 600-tonne "central column" on to a massive circular embedded plate.

Lashed tightly
2021-02-26 - Vacuum vessel sector #6 is tightly lashed to its support frame. It will lifted and placed inside the upending tool on its frame, and then lifted to vertical. © Les Nouveaux Médias/SNC ENGAGE

A busy month
2021-02-26 - March will be a busy month in the assembly theatre. In every corner of the vast Assembly Hall, teams are preparing for the upcoming operations (the upending of the first vacuum vessel sector, the installation of part of the in-pit column tool, the installation of the first pre-compression rings...).
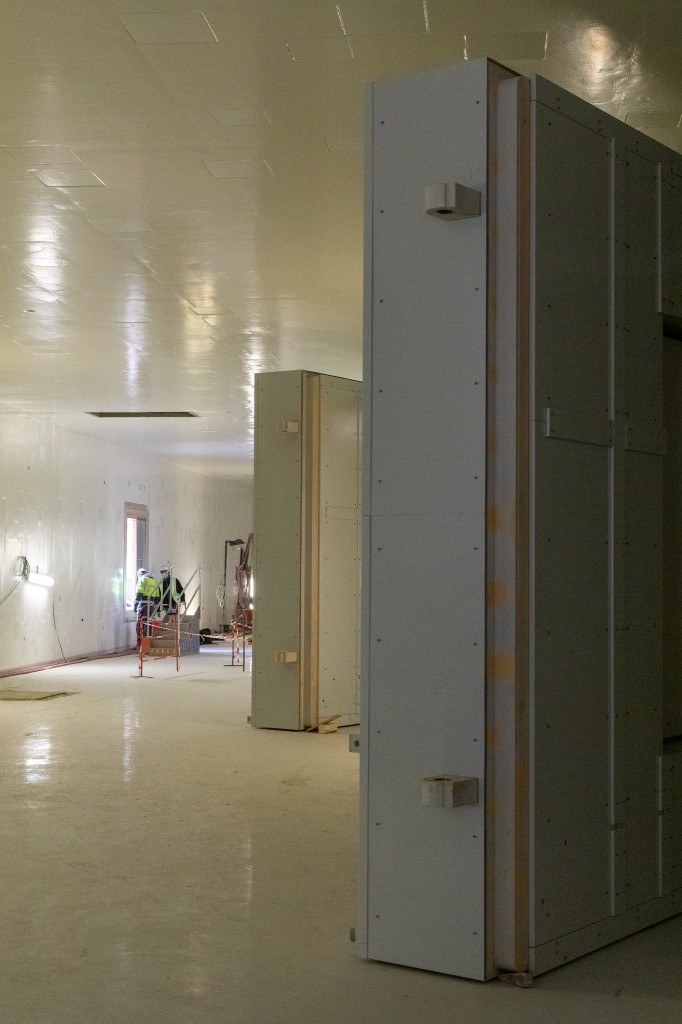
Near the Tokamak
2021-02-26 - To the right, ITER port cells leading in to the Tokamak (and sealed by massive nuclear doors); to the left, a completed gallery area, fully painted. © Les Nouveaux Médias/SNC ENGAGE

Handing over to systems installation
2021-02-25 - In the lower galleries of the Tokamak Complex, where the civil works are near finalized, the rooms have been handed over to the ITER assembly teams for systems installation. Follow all systems installation news on this page: https://www.iter.org/construction/systemsplantassembly. © Les Nouveaux Médias/SNC ENGAGE
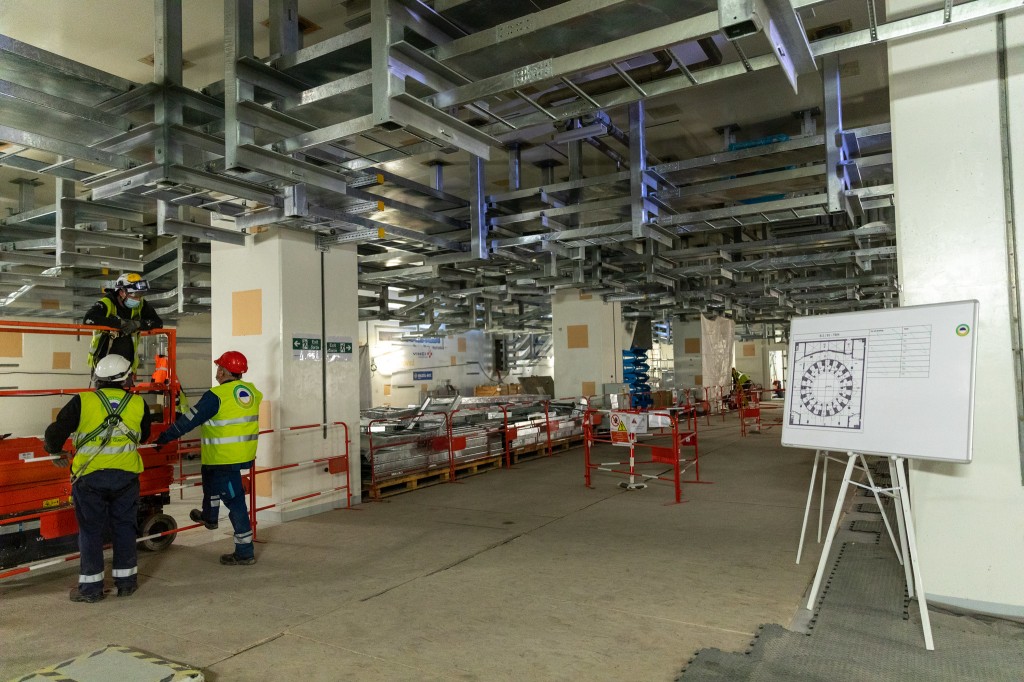
Starting from the ceiling
2021-02-25 - In the lower basement of the Tokamak Complex (level B2) the installation of equipment is progressing in a counter clockwise manner, room by room around the Tokamak assembly pit. © Les Nouveaux Médias/SNC ENGAGE
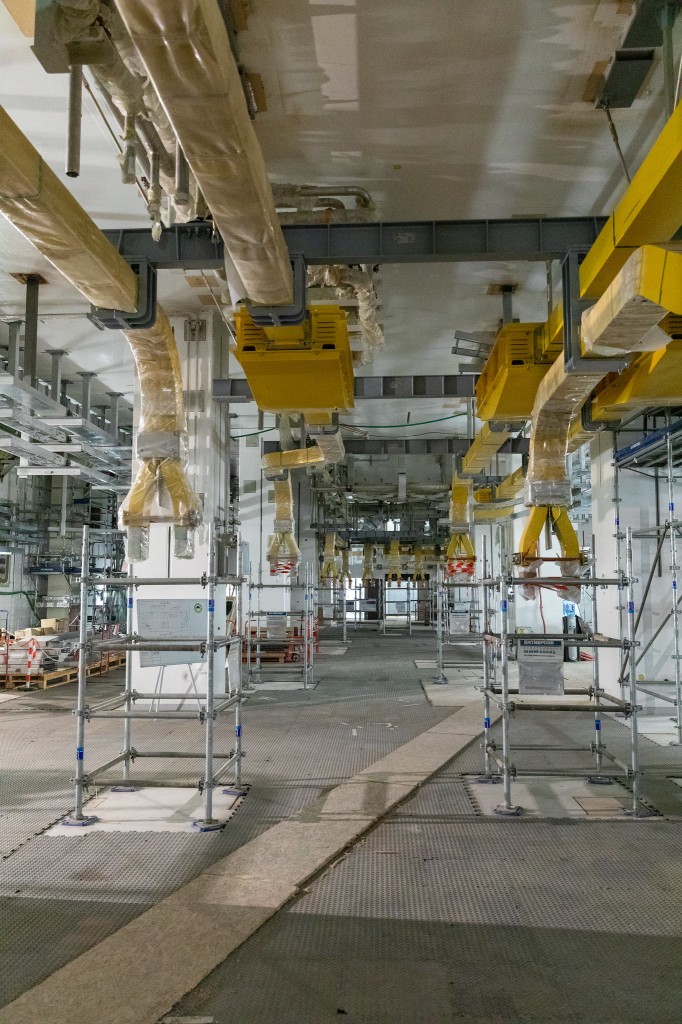
Busbars and more in the Tokamak Complex
2021-02-25 - The installation of cryolines, cooling water lines, cable trays, heating/ventilation/air conditioning (HVAC) equipment, and busbars is underway. © Les Nouveaux Médias/SNC ENGAGE

Not so small
2021-02-23 - The man in the middle of the image helps us to put the size of the temporary supports for poloidal field coil #6 into perspective. They are quite large ... and strong enough to support 400 tonnes.
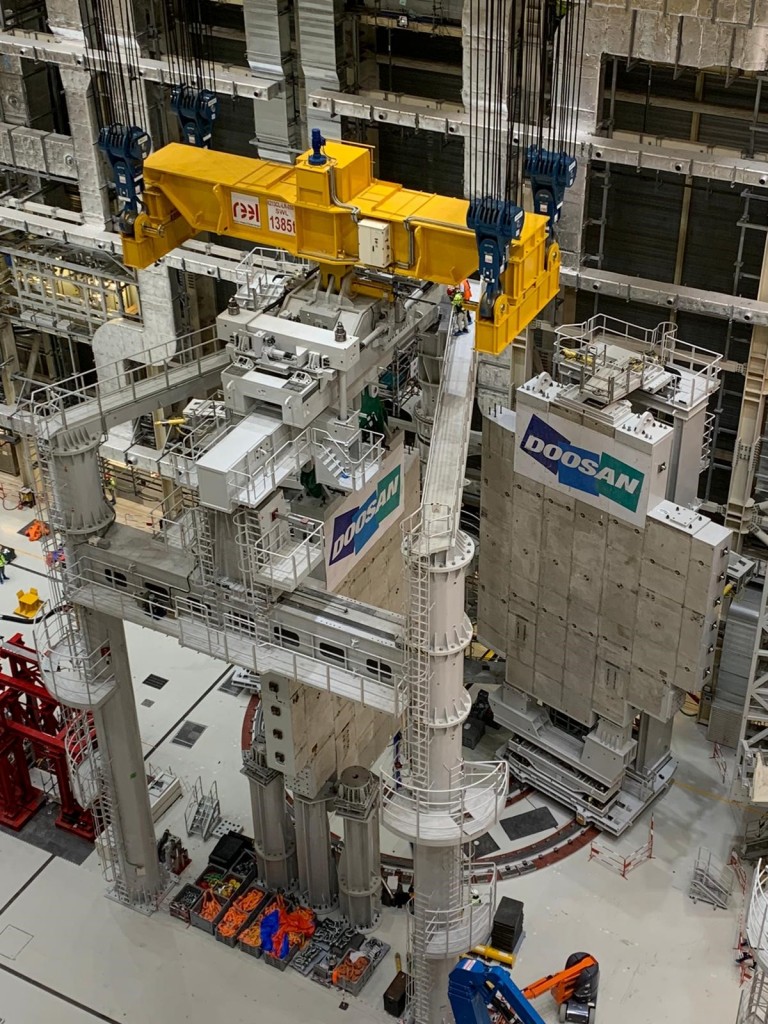
Practising a major operation
2021-02-18 - Dummy loads have been transferred from the upending tool to one of the sector sub-assembly tools. The assembly contractors are preparing and practicing for the upending of vacuum vessel #6 next month.
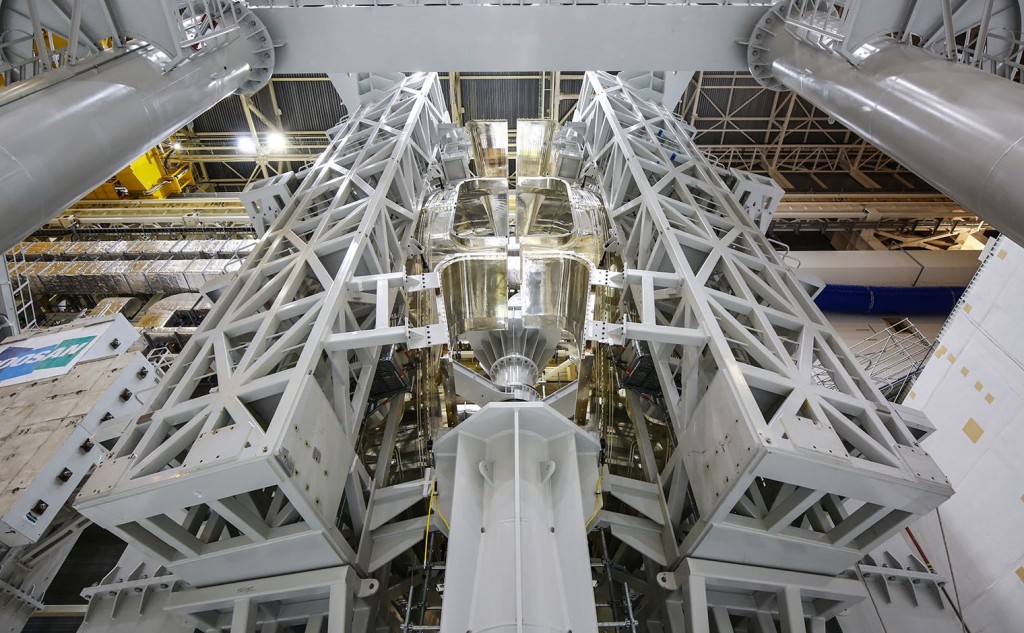
Just right
2021-02-16 - The success of another trial operation: the two wings of the sector sub-assembly tool are rotated inward with their two outboard segments of vacuum vessel thermal shielding, and the precision of their alignment is measured.
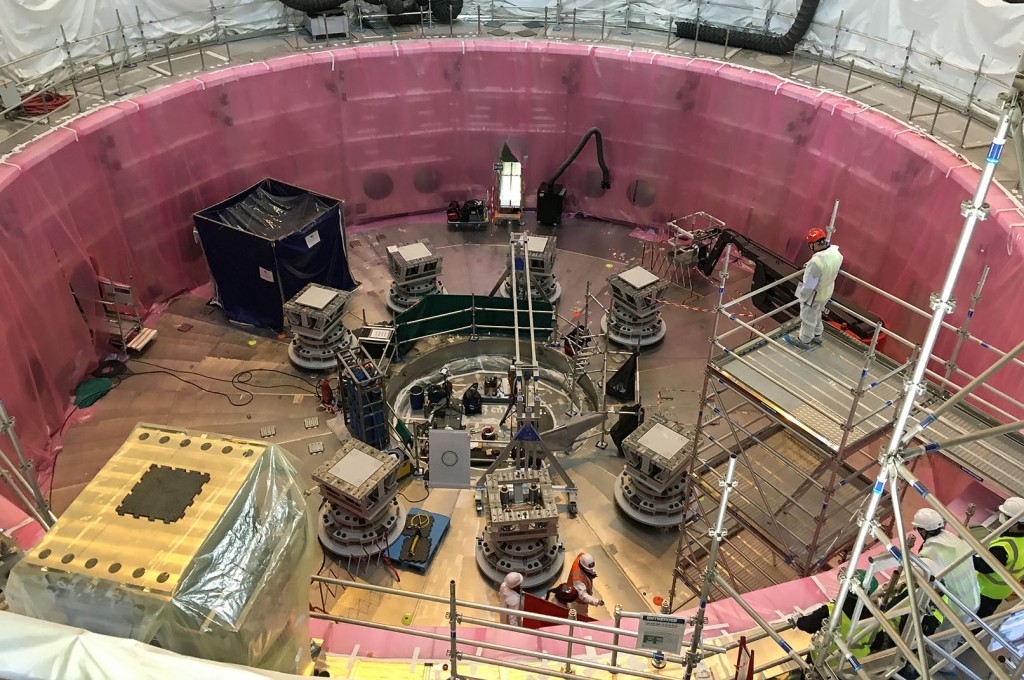
Temporary magnet supports
2021-02-15 - A new circle is being formed by temporary supports being installed for poloidal field coil #6. In April, the 400-tonne magnet will be lowered onto these supports, where it will remain until the completion of vacuum vessel assembly. The wider circle, in pink, is the lower cryostat thermal shield, which was installed in January 2021. See: https://www.iter.org/newsline/-/3547.
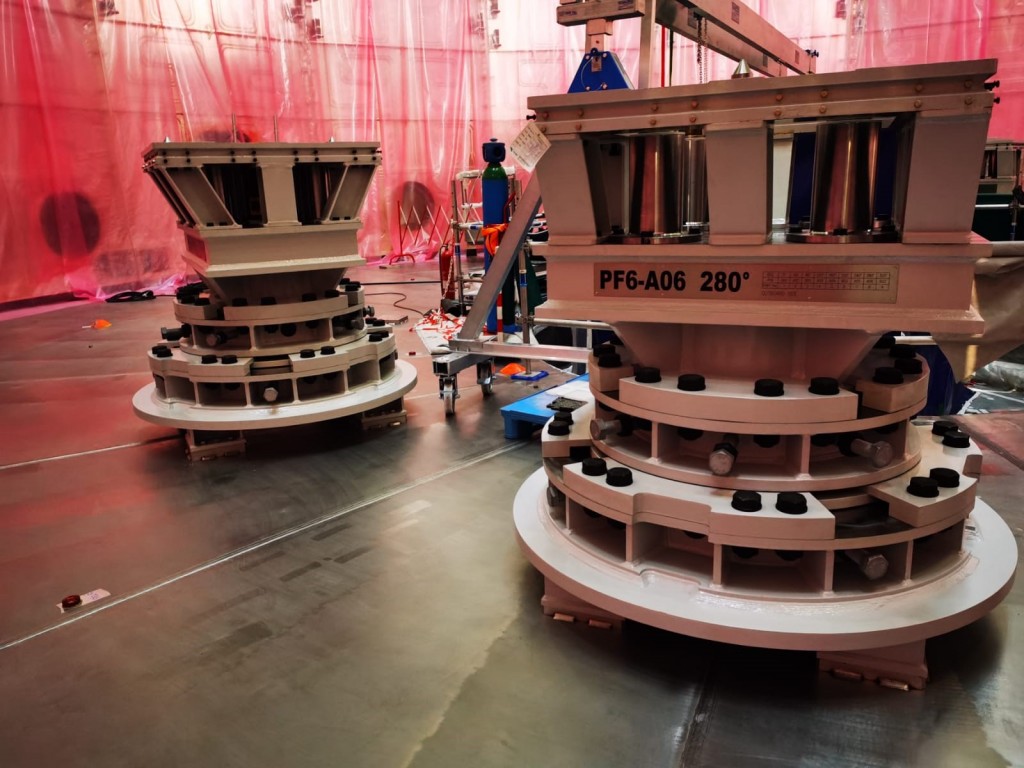
Close up
2021-02-13 - A close up of the support units for poloidal field coil #6 that have been bolted to the cryostat base. Each of the nine supports weighs approximately 5 tonnes and contains vertical actuators.

SSAT tool #2 in action
2021-02-12 - Thermal shield fitting tests are being carried out on sector sub-assembly tool (SSAT) #2. The outboard panels of vacuum vessel thermal shielding were first mounted on the wings of the tool; then, the wings rotated slowly inward to test the alignment of the panels. Metrology is underway.
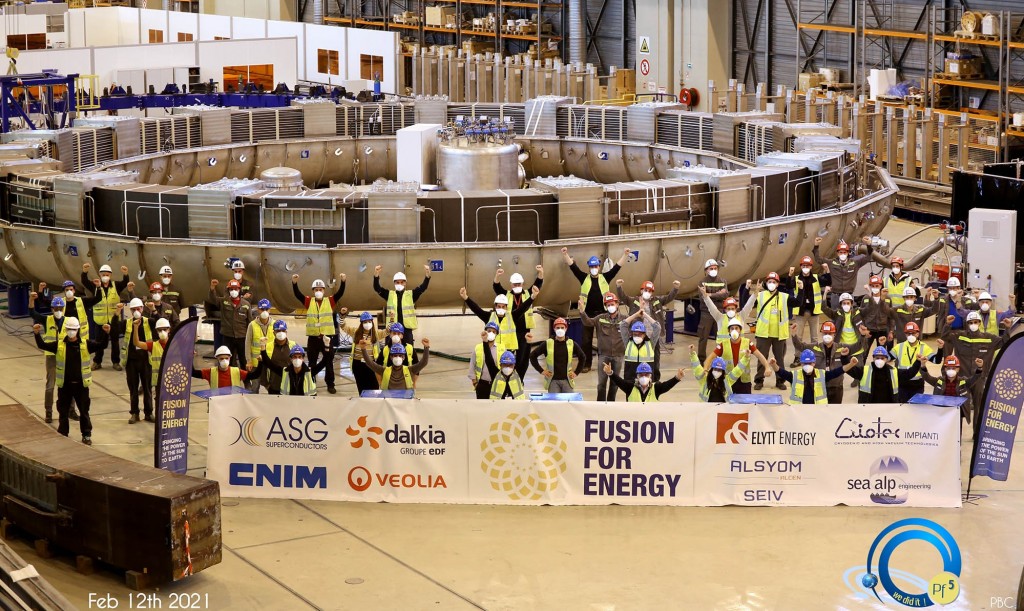
PF5 completes cold testing
2021-02-12 - Following in the footsteps of poloidal field coil #6 (PF6), which completed all tests in December 2020, PF5 is the second ring-shaped coil out of six to check all the boxes. During the final-phase thermal tests, the coil was inserted into a dedicated cryogenic chamber and cooled down to approximately 80 K (-193 °C), then cycled between cooldown and warmup.
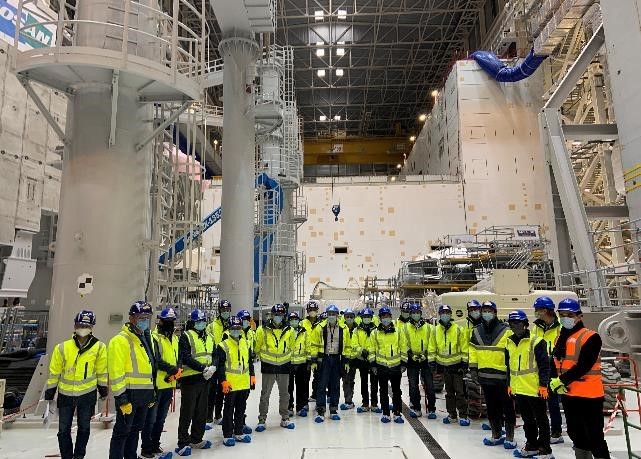
Group visit
2021-02-12 - A group of senior managers makes a tour of the pre-assembly activities underway in the Assembly Hall.

Before rotation
2021-02-11 - The outboard thermal shield sectors have been mounted on the tools and a last metrology session is underway before the components rotated inward.
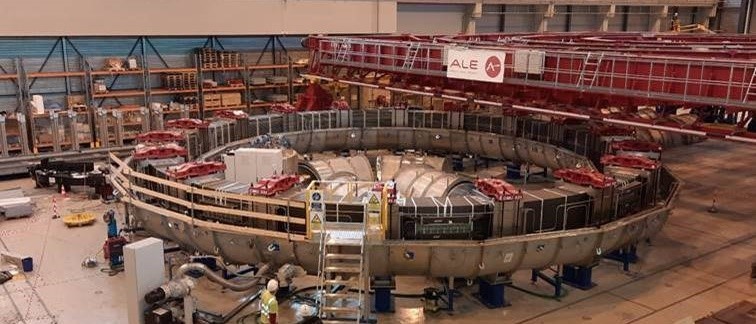
PF5 passes cold tests
2021-02-10 - In the European workshop on site, poloidal field coil #5 has completed cold testing and will be removed from its cryogenic chamber.

Top lid segments unveiled
2021-02-09 - Perfectly aligned on the workshop floor, the major elements of the cryostat top lid will soon be positioned inside the supporting frame in the background of this photograph (the central cylinder is hidden by the frame).
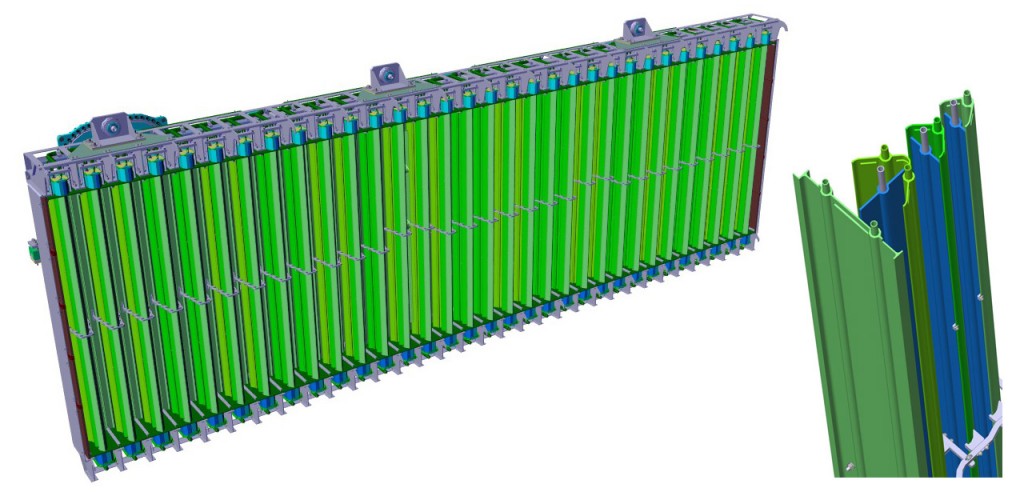
MITICA cryopump: components completed
2021-02-09 - An important part of accelerating neutral beam particles is the cryopump, whose charcoal-coated panels trap unwanted particles. The French firm Ravanat was charged by the European Domestic Agency with delivering the main components of the cryopump: the cryopanels (blue) and the thermal radiation shields (green). Fabrication ended in December 2020.

12 plus 2
2021-02-09 - Specialists from MAN Energy Solutions (contractor to Larsen & Toubro, cryostat manufacturer) are finalizing the installation of the support frame, prior to starting on assembly and welding. The top lid is composed of 12 triangular segments, plus a central disk and a central lid.
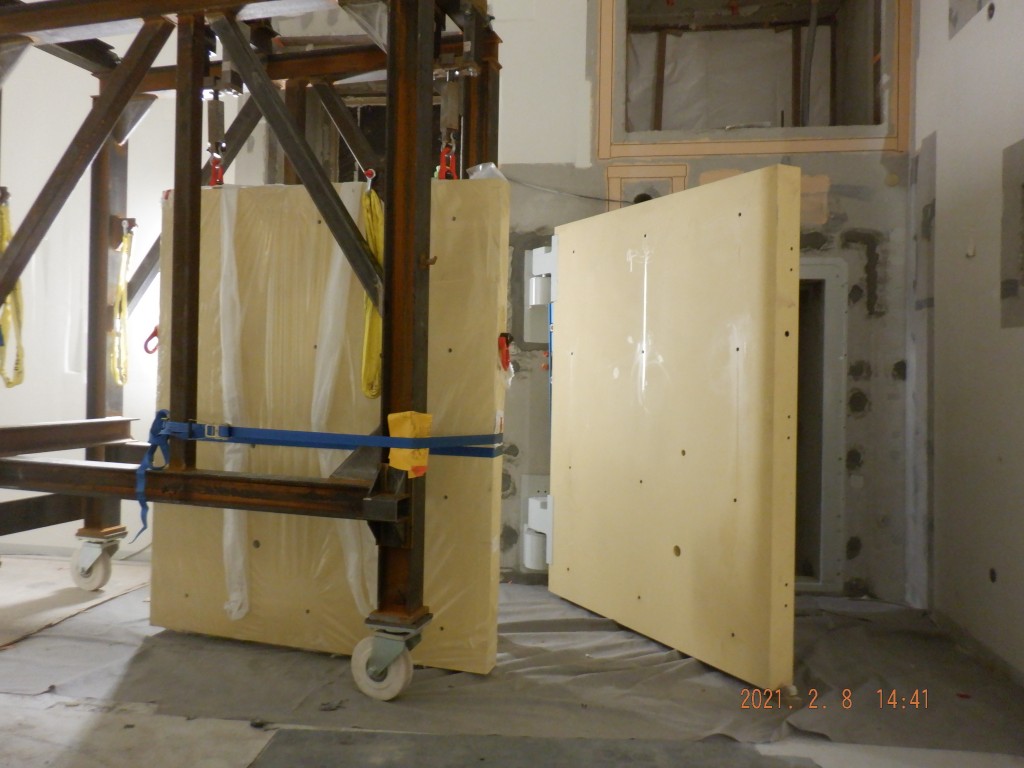
Standard doors
2021-02-08 - There are many areas of the Tokamak Complex where standard doors are required.
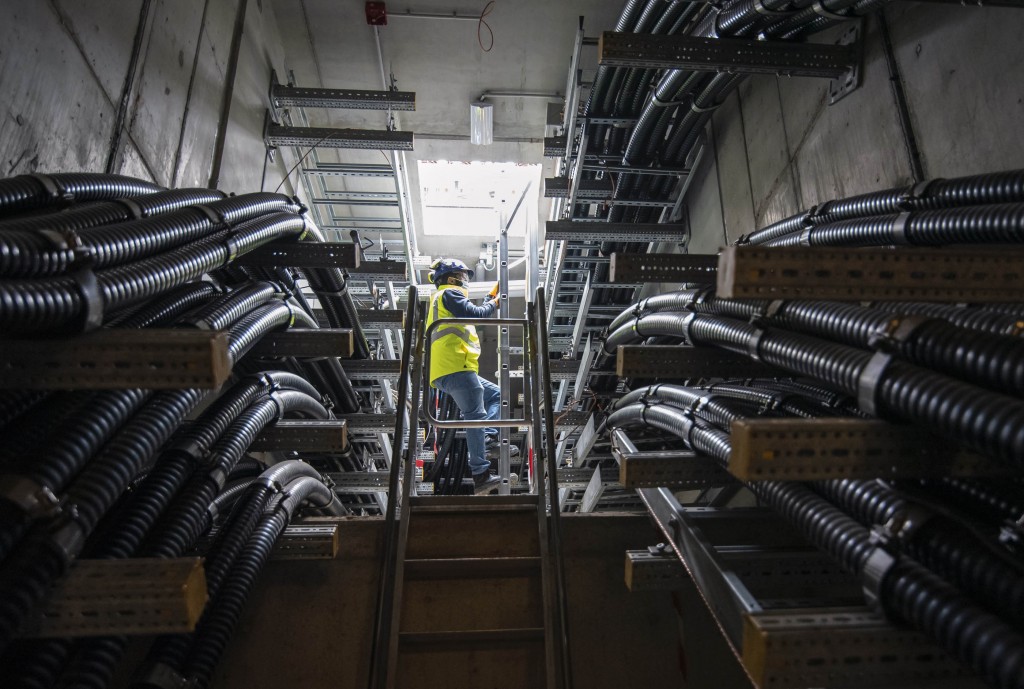
A creature?
2021-02-04 - More than 4.5 kilometres of cable galleries run underneath the ITER platform. In certain places, where the cables bend towards the surface, the impression is that of tentacles belonging to a creature lurking in the depths.
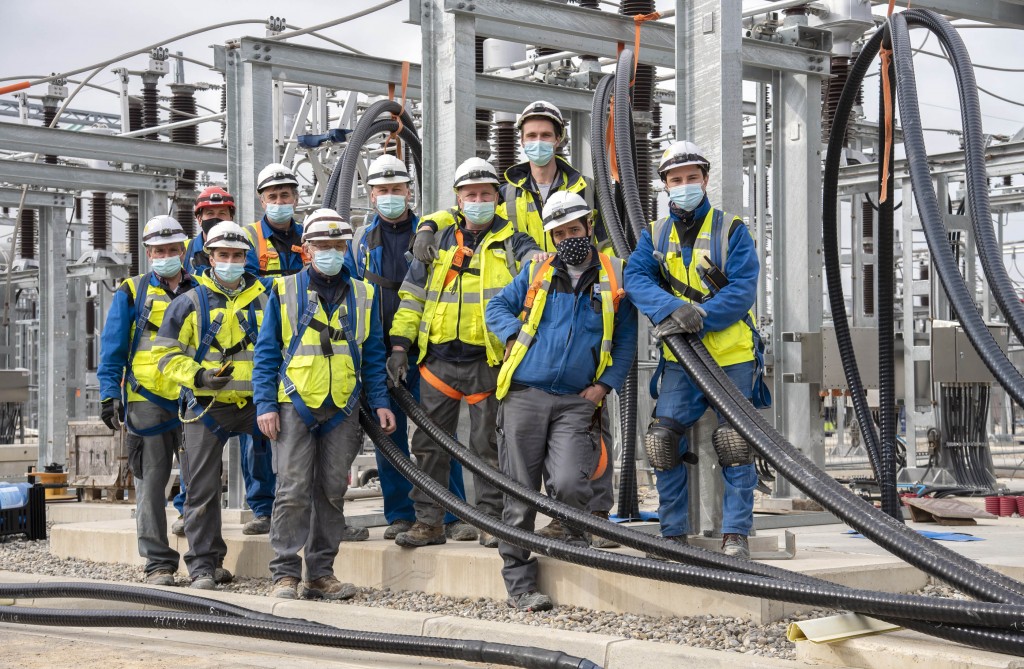
Cable pulling team
2021-02-04 - Some 53 kilometres of 66 kV cables must be installed in the underground galleries of the ITER worksite to connect converters in the electrical switchyard to equipment inside the magnet power conversion buildings. This team from the Italian-Slovakian contractor Busbar4F is carrying out the work.

As thick as an arm
2021-02-04 - Seven centimetres in diameter, the 66 kV cables transport 300 times the voltage of a standard household cord.

8 metres tall
2021-02-04 - In this high-ceilinged space called "the cathedral," cable trays are installed nearly 8 metres high. From here, cables head in all directions, eventually reaching the four corners of the platform.

Top lid: start of assembly
2021-02-02 - All of the segents of the cryostat top lid have reached ITER and the Indian Domestic Agency teams in the Cryostat Workshop can begin assembly and welding.
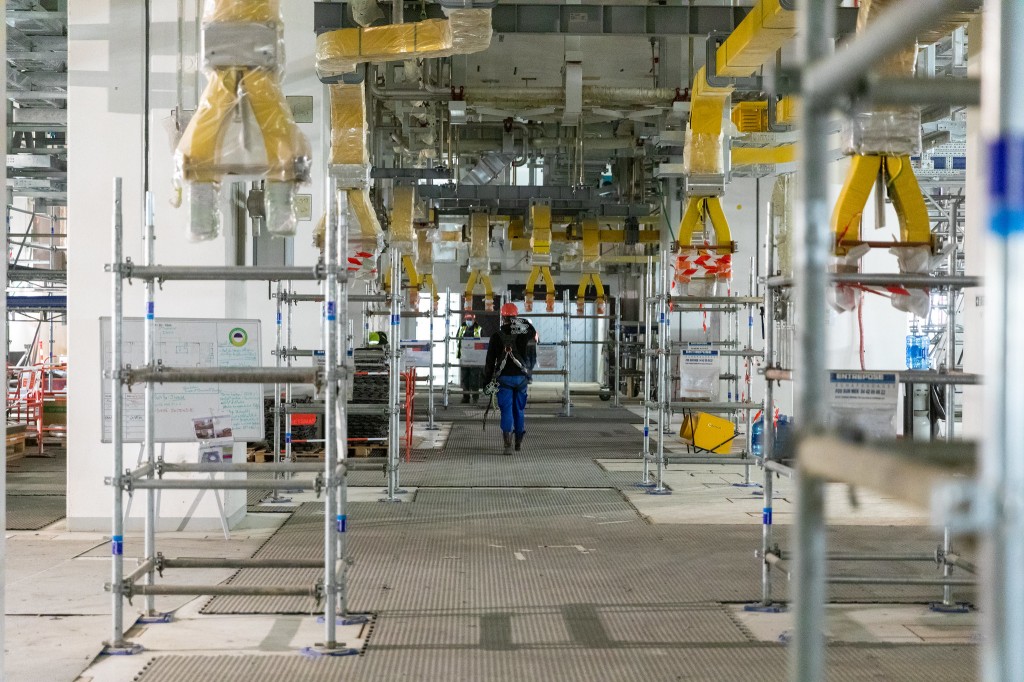
Installing equipment
2021-01-28 - About 50 contractors are currently working under the Tokamak Complex assembly Contracts (TCC) and a Balance of Plant contract for multi-process lines. © Les Nouveaux Médias/SNC ENGAGE
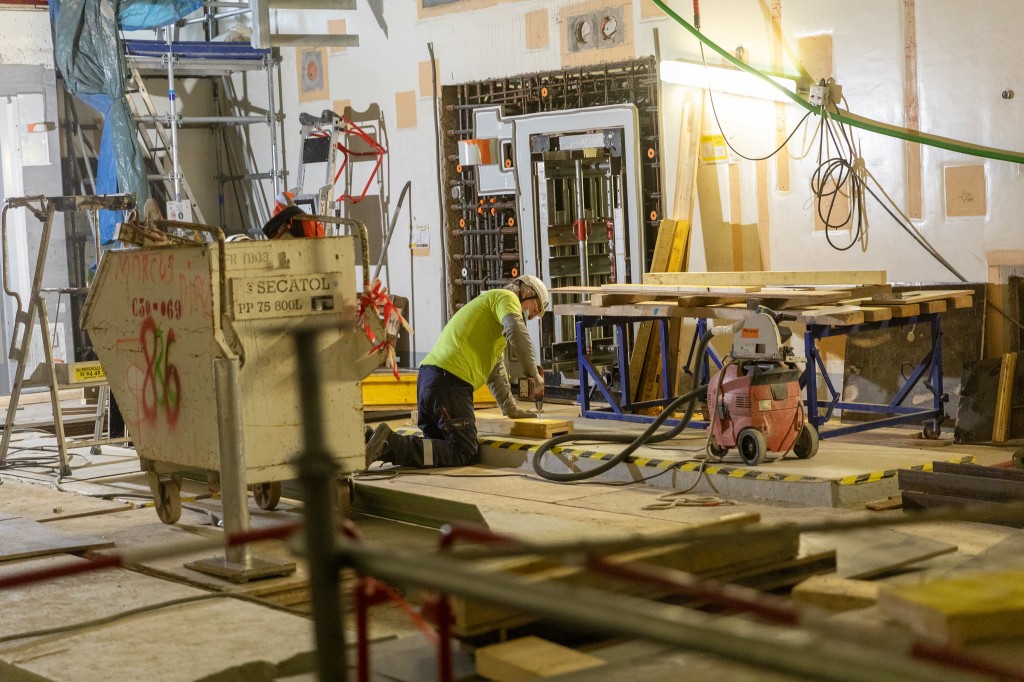
Down in the bowels of the Tokamak Complex
2021-01-28 - Deep in the Tokamak Complex, European contractors are finishing civil works tasks. © Les Nouveaux Médias/SNC ENGAGE

PF6 enters an ITER storage facility
2021-01-27 - The coil was transferred from the European coil winding facility on site to an ITER storage facility to be prepared for assembly.
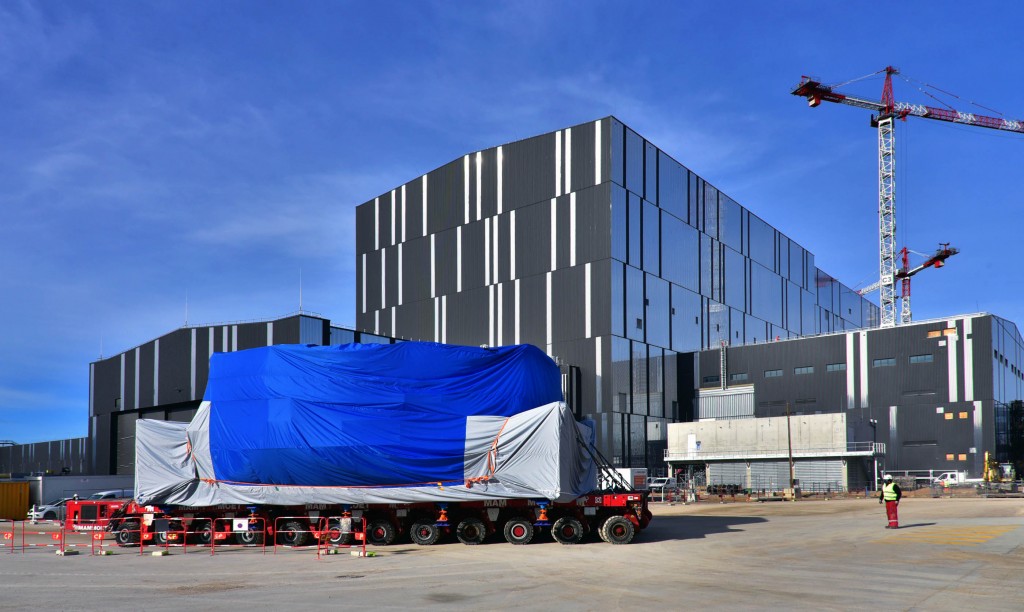
First poloidal field coil handed over
2021-01-27 - On 27 January 2021, the first of six poloidal field coils is handed over to the ITER Organization by the European Domestic Agency, Fusion for Energy. Poloidal field coil #6 (PF6) is a 400-tonne magnet that will be the first to be assembled into the ITER machine pit.

Pending installation
2021-01-27 - Some light equipment work (such as the addition of protective covers) will be performed while the component is in storage.

400-tonne coil moves to temporary storage
2021-01-27 - Poloidal field coil #6 is transported from the European winding facility on site to a temporary storage facility. It will be the first magnet coil to be inserted into the Tokamak pit in April 2021. Three other ring coils are in various stages of fabrication on site.

Heading in
2021-01-26 - The load is seen here as it approaches an opening on the Tritium Building side of the Tokamak Building. Twenty-one feeders will be situated at the bottom of the machine, and another 10 at the top.

Out in the galleries
2021-01-26 - The coil terminal box is the part of the magnet feeder that sits farthest from the machine core. Nine metres in length, shaped like a shipping container, the box houses warm-to-cold electrical transition equipment, remote control helium supply valves, and sensors for coil instrumentation.

Magnet feeder segment installed in Tritium Building
2021-01-26 - On 26 January 2021, the coil terminal box serving toroidal field coils #12 and #13 is lifted and moved inside the basement of the Tokamak Building. Each magnet feeder comprises three elements: a coil terminal box, a cryostat feedthrough (segment passing through the bioshield and cryostat) and an in-cryostat feeder (segment connecting to the magnets).
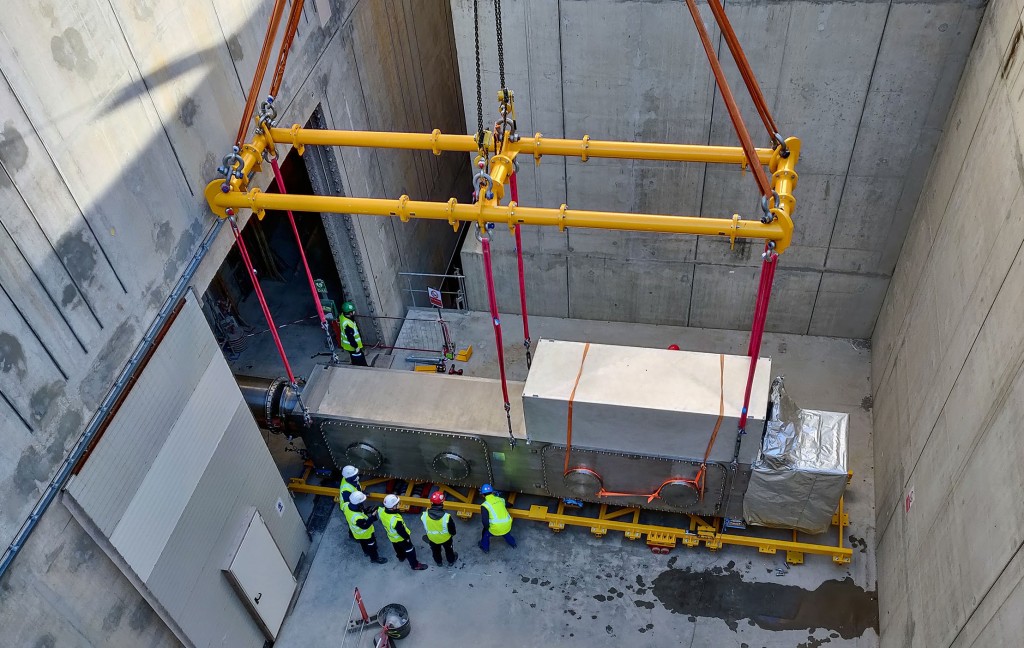
Roll it in
2021-01-26 - This backend feeder component has been lowered to B2 basement level in the Tritium Building and will now move on rollers to its final position.
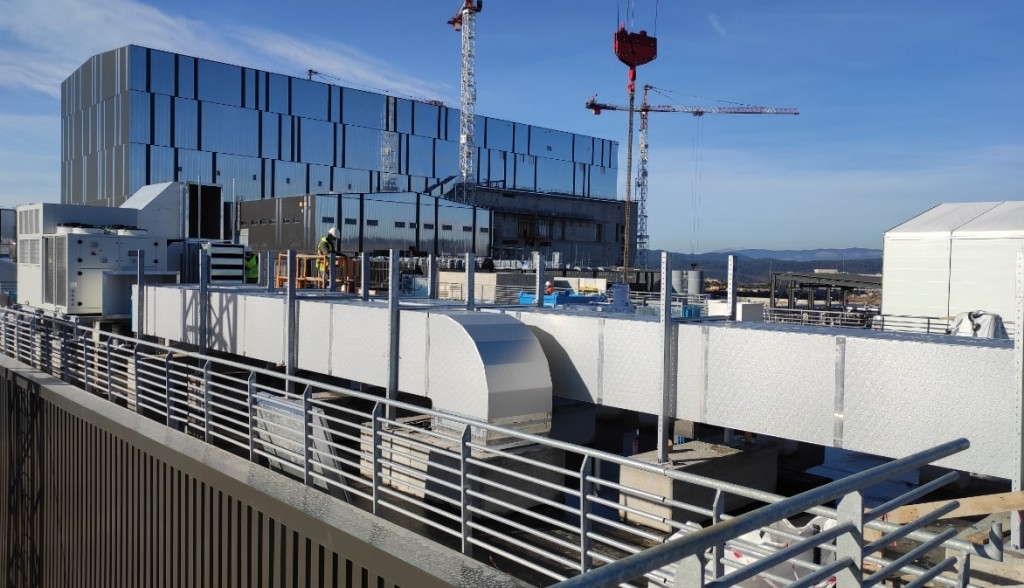
Rooftop HVAC installation
2021-01-25 - All HVAC equipment has now been installed on the roof of the Tokamak Assembly Preparatory Building.

Fabricating the double pancakes for PF4
2021-01-22 - Data fed by approximately one hundred sensors is displayed on large screens and closely examined by the Fusion for Energy team responsible for the impregnation of the first of the eight double pancakes required for poloidal field coil #4.
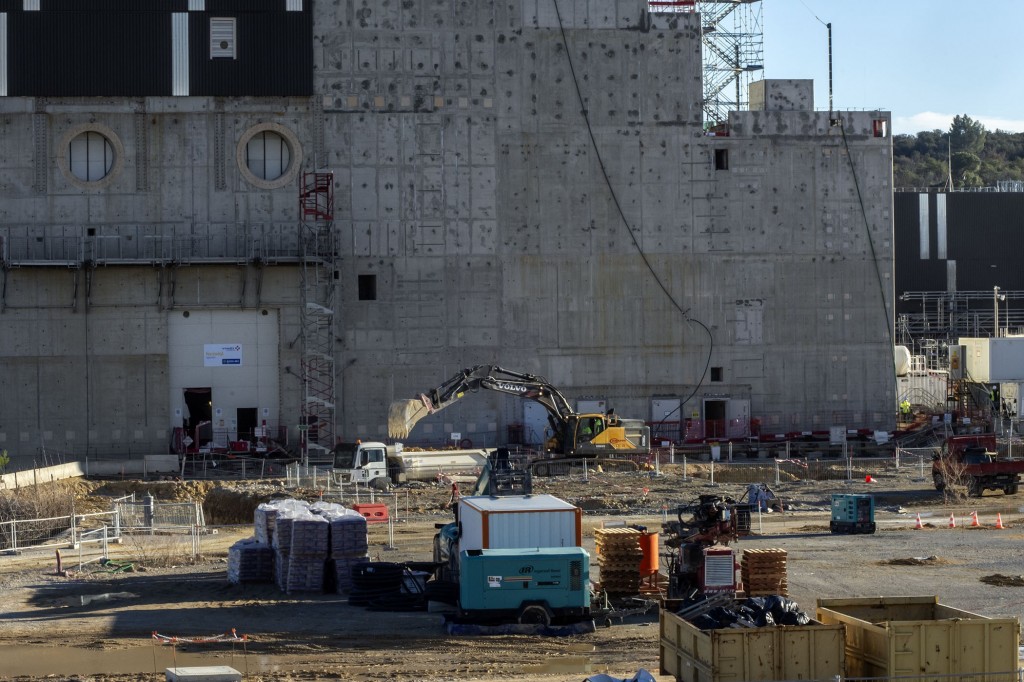
Work begins on a new set of buildings
2021-01-21 - On a level area in front of the Tokamak Complex, karst investigation and excavation has started for a series of buildings (two buildings and one technical area) that will be dedicated to the power supply of the neutral beam heating system.

Work begins on a new set of buildings
2021-01-21 - On a level area in front of the Tokamak Complex, karst investigation and excavation has started for a series of buildings (two buildings and one technical area) that will be dedicated to the power supply of the neutral beam heating system.
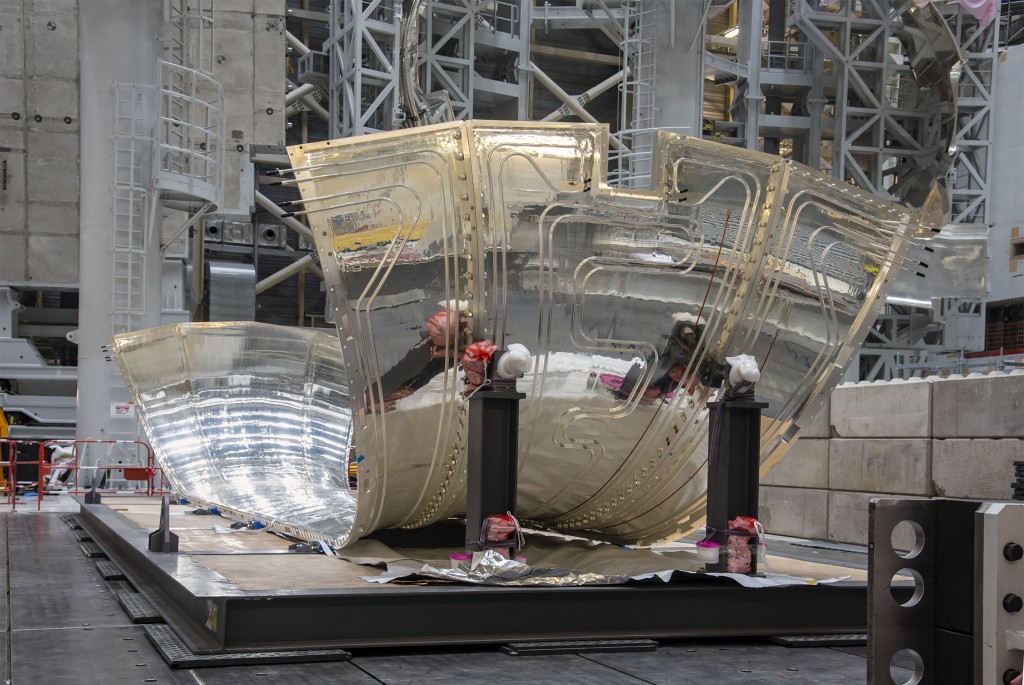
Intricate
2021-01-20 - Delicate cooling pipes snake along the outer surface of the inboard sector of vacuum vessel thermal shielding.

Like a glove
2021-01-20 - The lower cryostat thermal shield, partially draped in pink cloth, fits the depression of the cryostat base like a glove.

Another shiny element
2021-01-20 - Another element of thermal shielding—this time the inboard shielding element for vacuum vessel sector #6—is being prepped in a laydown area in the Assembly Hall.
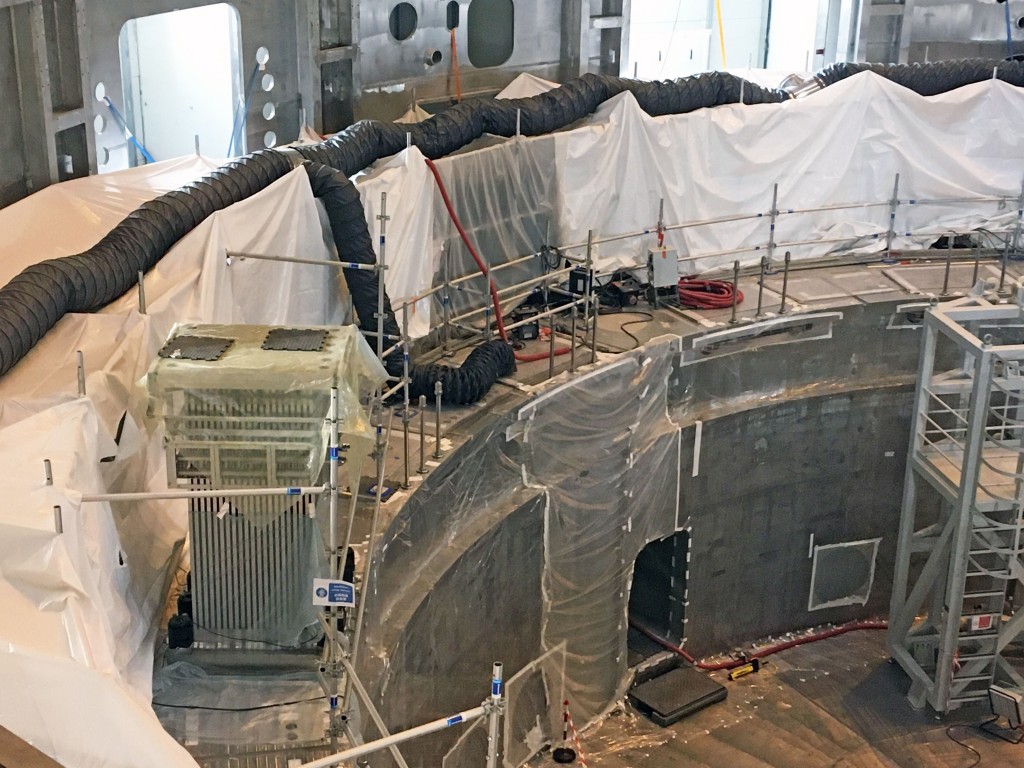
Gravity supports: first unit
2021-01-15 - The first toroidal field coil gravity support is installed on the pedestal of the cryostat base. It stands 2.65 metres tall.

Well done
2021-01-14 - As the load is transferred from the crane to an array of hydraulic jacks, a full-day operation comes to an end. A few more adjustments ... then final metrology ... and the day can be declared a success.
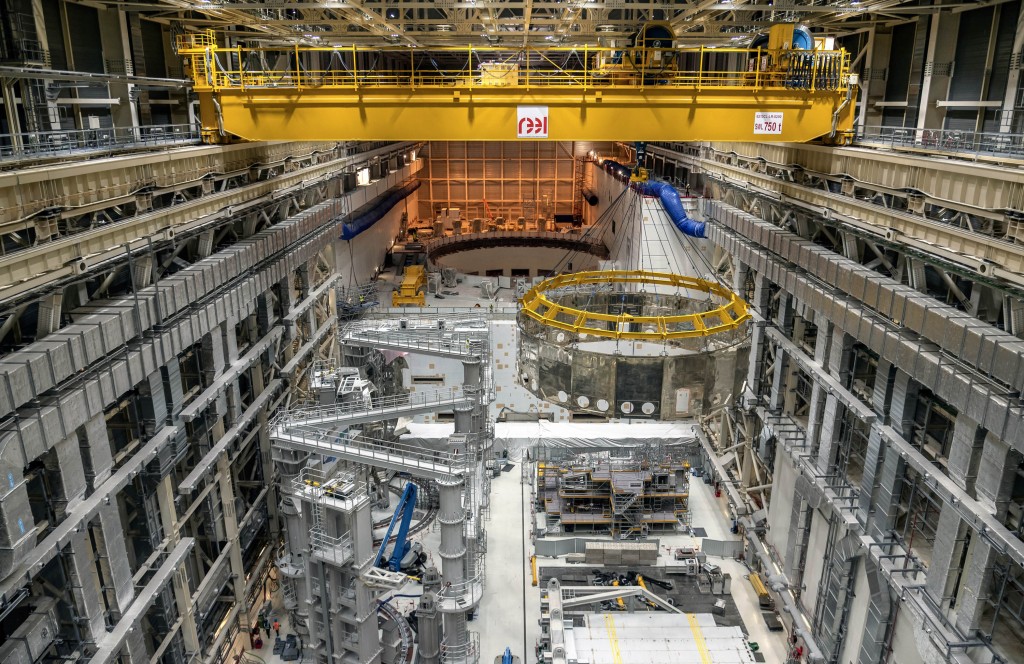
Travelling 100 metres
2021-01-14 - The 50-tonne lower cryostat thermal shield travelled approximately 100 metres to the Tokamak pit at a cruising altitude of 23 metres.

Segments arriving
2021-01-14 - Inside of the Cryostat Workshop, the latest top lid elements to arrive are unpacked.
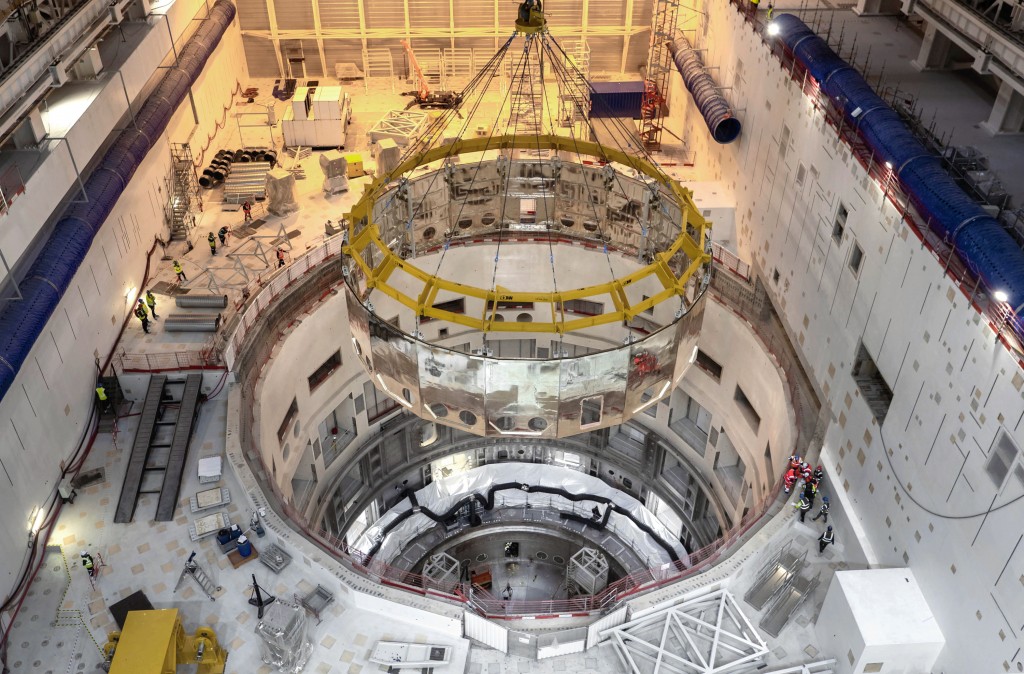
Ready for lowering
2021-01-14 - The component has travelled the length of the assembly theatre and is now positioned right above the pit. Two alignment tools, visible at the bottom of the large circular opening, will guide its final trajectory.

One hook, 18 attachment interfaces
2021-01-14 - Attached to the overhead crane by a single hook, the "strong back" is connected to the thin component (10 millimetres) by way of 18 attachment interfaces equally distributed around its circumference. This type of rigging is designed to provide both rigidity and stability.

Corrected!
2021-01-14 - After a bit of rope pulling to realign the load, the final descent can begin. The temporary rails (in grey against the silvery backdrop of the component) are now ready to slide into the tower-like alignment tools all the way to the bottom of the pit. The protruding bolts of the gravity support (left) were passed without incident.

Attached to a "strong back"
2021-01-14 - Attached to its ''strong back,'' the 50-tonne lower cryostat thermal shield has reached cruising speed (2 metres/minute). Its silvery surface reflects the colours, lights and distorted shapes of the environment.
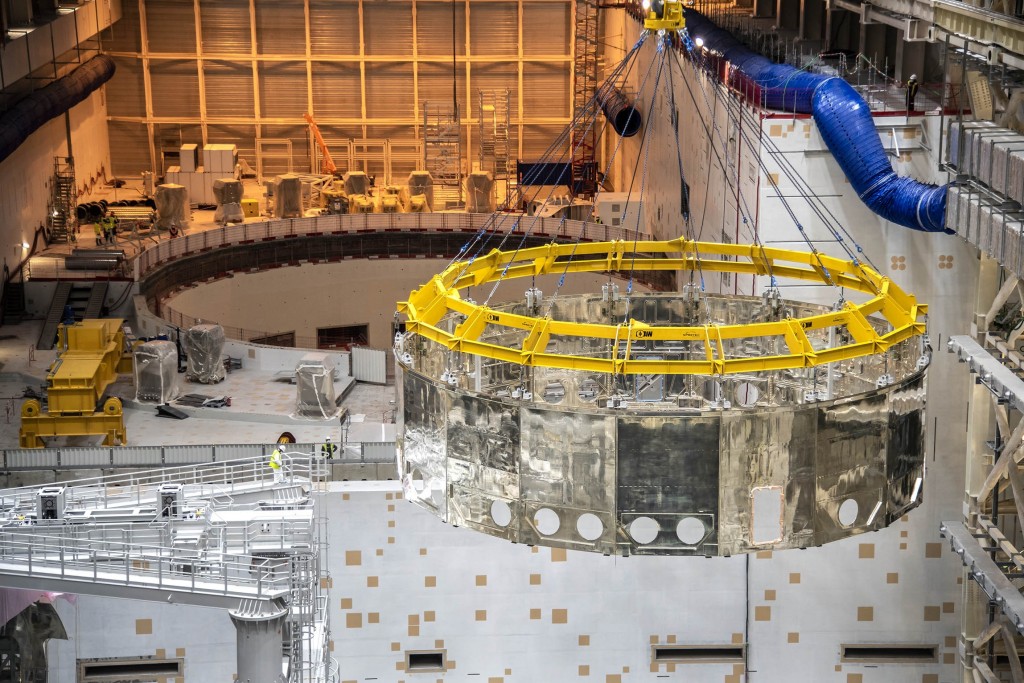
Close
2021-01-14 - The component's trajectory brings it to within a few metres of the vacuum vessel sector assembly tools (at left). A team member is stationed at the top of one tool to keep a watchful eye.

Realignment needed
2021-01-14 - The lower cryostat thermal shield is now well engaged in the assembly pit. A slight rotation has been identified and re-alignment will be necessary before the component engages its final descent.
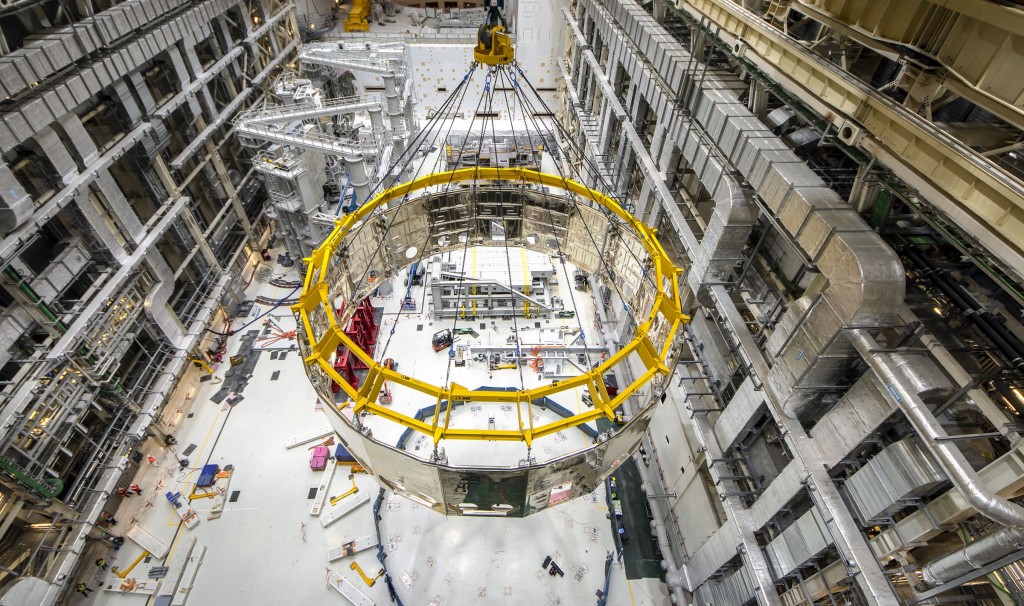
Up it goes
2021-01-14 - A few minutes after take-off, the component has reached its cruising altitude of 23 metres and is now aligned with its destination—the mouth of the assembly pit at the opposite end of the assembly theatre.
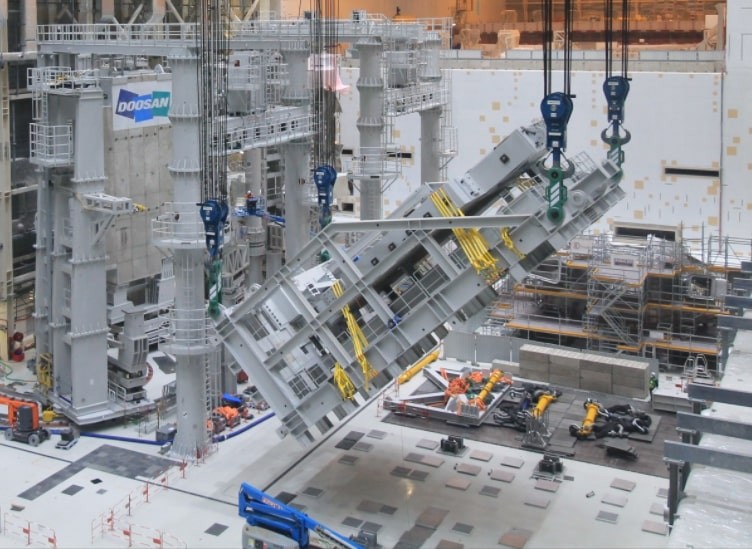
Putting the tool through its paces
2021-01-12 - Operators are practicing with a dummy load to prepare for the upending operations to come—the tilting from horizontal to vertical of vacuum vessel sectors and toroidal field coils.

Tall gravity supports: in line for installation
2021-01-12 - Eighteen of these toroidal field coil gravity supports must be positioned on the cryostat base. This one is about to be transferred into the Tokamak pit.

Practicing
2021-01-11 - By overhead crane, the teams are transferring two dummy loads (representing approximately 700 tonnes) to the tool in its upright position, practicing for when the upending tool will handle some of ITER's heaviest components: toroidal field coils or vacuum vessel sectors.
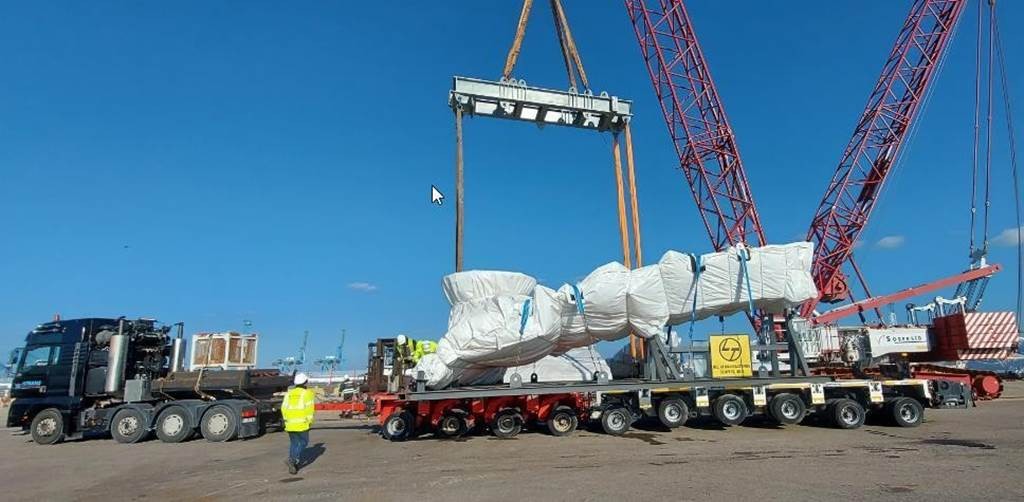
Final lid segments arriving
2021-01-11 - The last segments of the 665-tonne cryostat lid (including the central disk) have arrived in France.
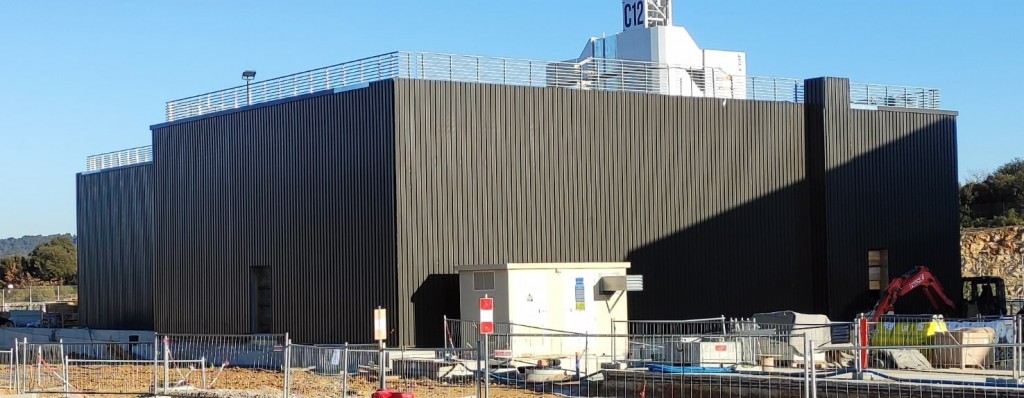
TAPB building, finished on time
2021-01-08 - The Tokamak Assembly Preparation Building (TAPB) construction team completed this building to nuclear specifications in nine months. The team was recognized by a 2020 ITER Award, winning in the "Balance-of-Plant Systems" category in December.
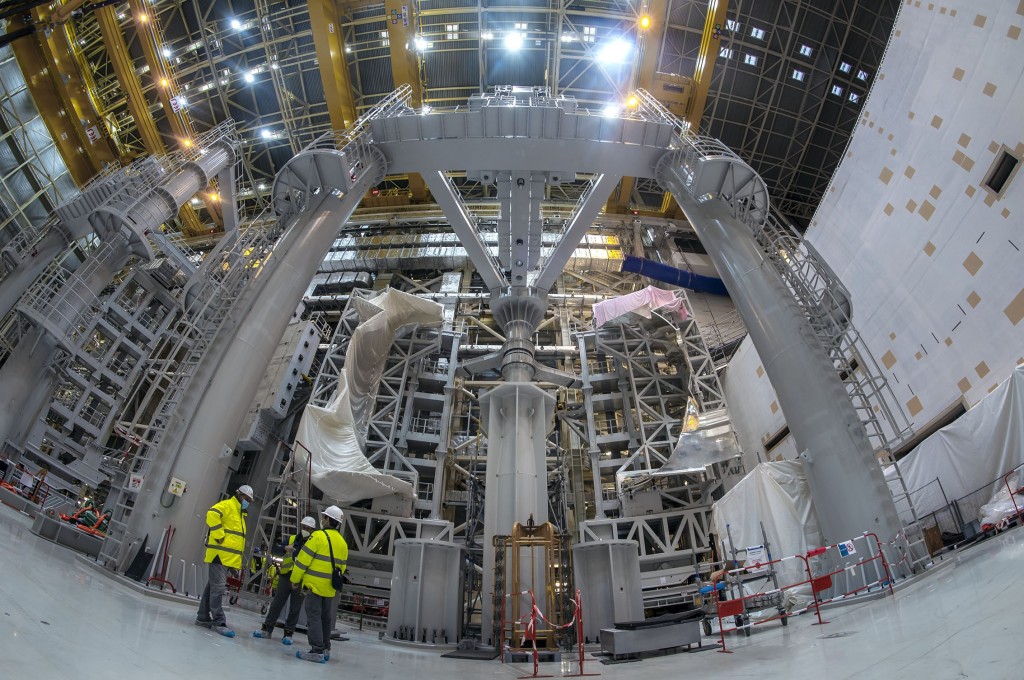
Two segments of the thermal shield are mounted
2021-01-08 - With two outboard thermal shield panels now mounted on one of the giant pre-assembly tools, thermal shield assembly trials can begin.
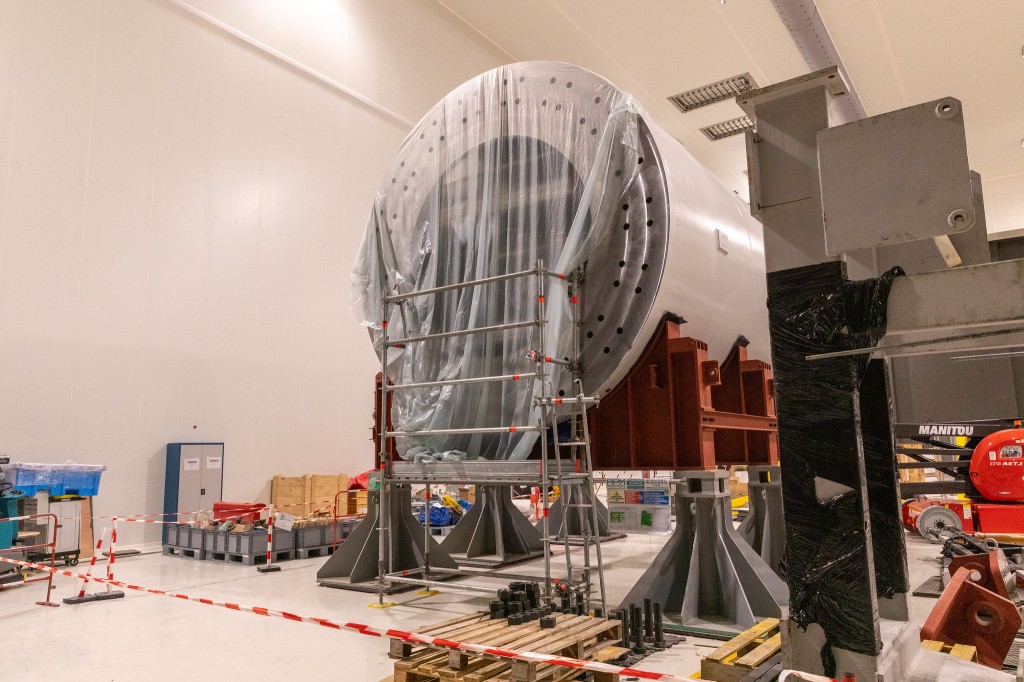
In-pit assembly tool
2020-12-22 - Stairs installed inside of the central column of the in-pit assembly tool will allow assembly teams to access different levels of scaffolding inside of the vacuum vessel. © Les Nouveaux Médias/SNC ENGAGE

Special openings
2020-12-22 - These special openings are designed for the neutral beam injectors. © Les Nouveaux Médias/SNC ENGAGE

Near the ceiling first
2020-12-22 - Systems installation begins near the ceiling, on pre-installed trays and supports. © Les Nouveaux Médias/SNC ENGAGE

The Tokamak Complex is changing
2020-12-22 - In the galleries around the Tokamak pit, walking in a counter clockwise direction. Parts of the Tokamak Complex are taking on a finished air. © Les Nouveaux Médias/SNC ENGAGE

Under the surface
2020-12-22 - Our eyes are mostly focused on work happening above the platform ... but a lot is happening just under the surface to ensure that power, water and services are distributed around the platform. © Les Nouveaux Médias/SNC ENGAGE

Equipment installation advances
2020-12-22 - In the heat rejection zone, the ITER Organization is installing equipment supplied by the Indian Domestic Agency. Follow all installation and commissioning news on the assembly pages of the ITER website (https://www.iter.org/construction/assembly). © Les Nouveaux Médias/SNC ENGAGE

A big job
2020-12-22 - Room by room, level by level, the raw concrete of the Tokamak Complex is being covered with coats of smooth, shiny white paint. An estimated 150 tonnes of resin, primer and paint are required. © Les Nouveaux Médias/SNC ENGAGE

Filling penetrations
2020-12-22 - One of the last construction activities is to seal the openings (or penetrations) in the walls. The penetrations must be filled while letting equipment pass. © Les Nouveaux Médias/SNC ENGAGE

Next tool to be installed
2020-12-22 - In December, part of the central column of the in-pit assembly tool is moved to the antechamber of the Assembly Hall. © Les Nouveaux Médias/SNC ENGAGE

Neutral beam cell
2020-12-22 - In this large open space on the northwest side of the Tokamak Building, the bus-sized neutral beam injectors will be installed. © Les Nouveaux Médias/SNC ENGAGE
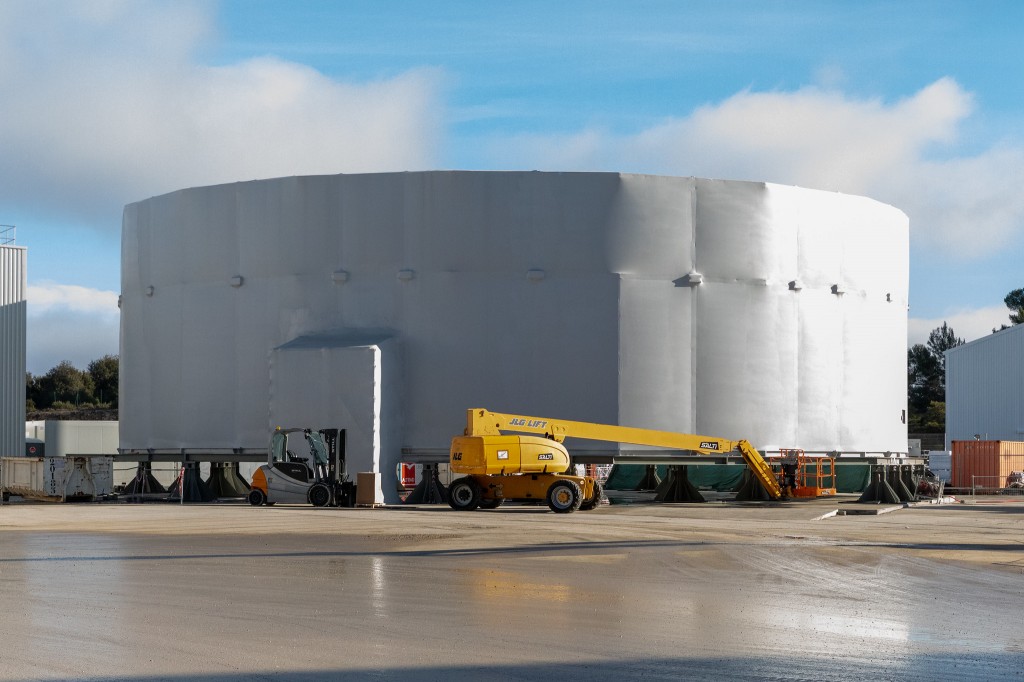
Still in its cocoon
2020-12-22 - The cryostat upper cylinder is still waiting in its protective cocoon to be called into the Assembly Hall. The lower cylinder was installed in August 2020. © Les Nouveaux Médias/SNC ENGAGE
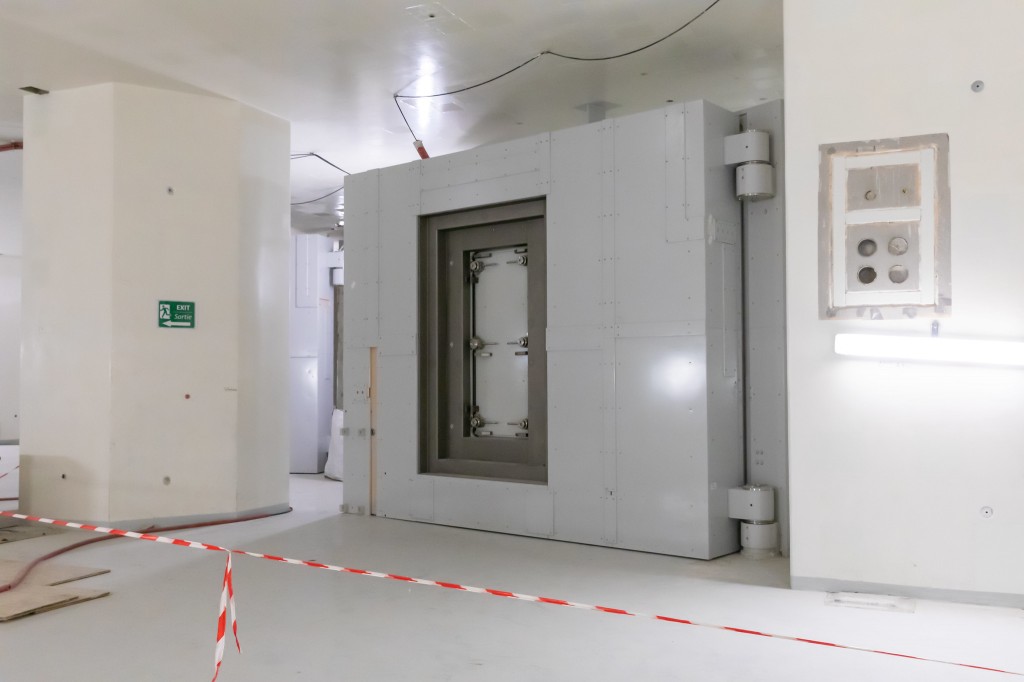
Finalizing the nuclear doors
2020-12-22 - Following the installation of 46 nuclear doors to seal off the port cells surrounding the ITER Tokamak, European Domestic Agency teams are progressing on the finishing work, including painting. © Les Nouveaux Médias/SNC ENGAGE

Space needed
2020-12-22 - The need for storage and workshop spaces is high on the ITER site and every ounce of space must be utilized. This additional building just went up near the European Poloidal Field Coils Winding Facility. © Les Nouveaux Médias/SNC ENGAGE

Anticipation
2020-12-17 - The yellow busbars that cross the Diagnostics Building to provide power to the superconducting magnets cannot be re-routed. All other systems must be designed around this constraint and installed on supports welded to embedded plates on the walls and the ceiling.

Backfilling penetrations
2020-12-17 - Some 4,600 penetrations, or openings, will provide passage for pipes, cables, diagnostics and HVAC equipment between the rooms and buildings of the Tokamak Complex. The example in this photo illustrates how the penetrations must be backfilled with concrete, while providing passageway for in/out cooling water pipes.
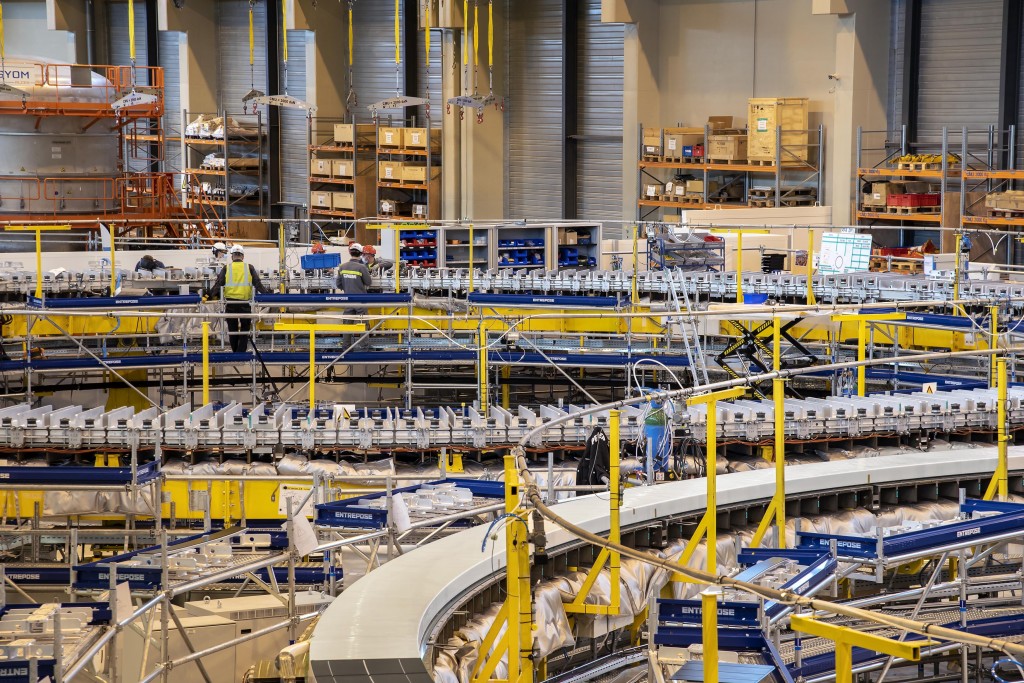
The middle poloidal field coils are larger
2020-12-15 - The tooling has been widened, and work is underway on the first double pancakes of PF4 (24 metres in diameter). PF4 and PF3 (not yet started) are the largest poloidal field coils of the ITER machine.

Soon: installation of the lower cryostat thermal shield
2020-12-15 - Inside of the Tokamak pit, three tower-like alignment tools have been installed for the installation of the lower cylinder thermal shield.

A whole battery of tests
2020-12-15 - In addition to thermal testing, PF6 has successfully passed global leak tests, electrical tests, and high voltage tests.

For a careful lift
2020-12-15 - As soon as a double pancake for PF4 is completed, it is transferred carefully with the help of this circular spreader beam (40 tonnes) to the impregnation, and then the assembly tables.

Coil #6: ready for installation
2020-12-14 - Poloidal field coil #6—the bottommost ring coil of the ITER machine and the first in line for installation—has completed all testing on site in the European winding facility. Pictured: representatives from the European Domestic Agency (procuring agency), China's ASIPP (manufacturer), and ASG Superconductors (engineering integrator).
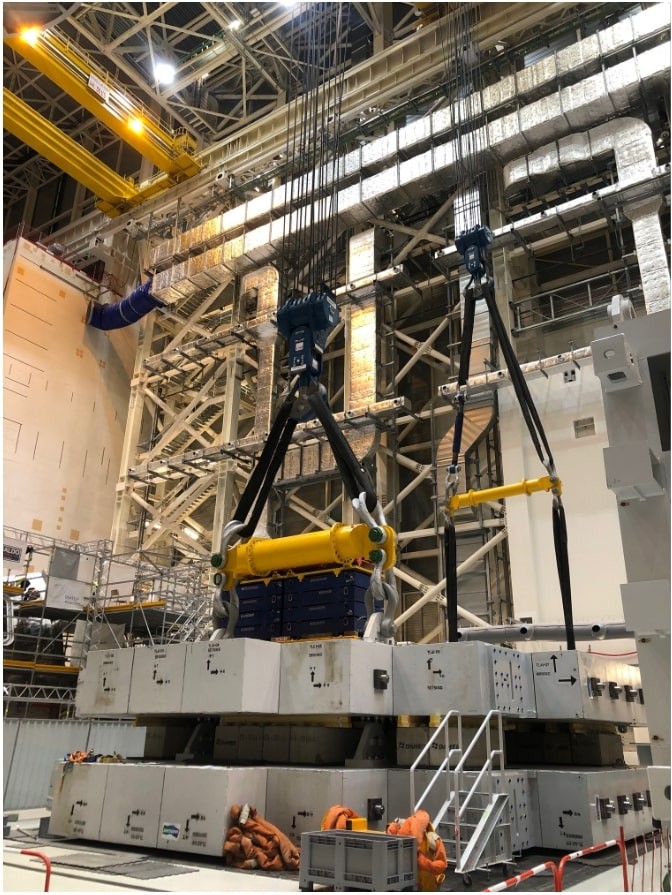
Cable stretching
2020-12-12 - New cables on the 750-tonne overhead cranes are prepared for use through some "stretching" exercises.
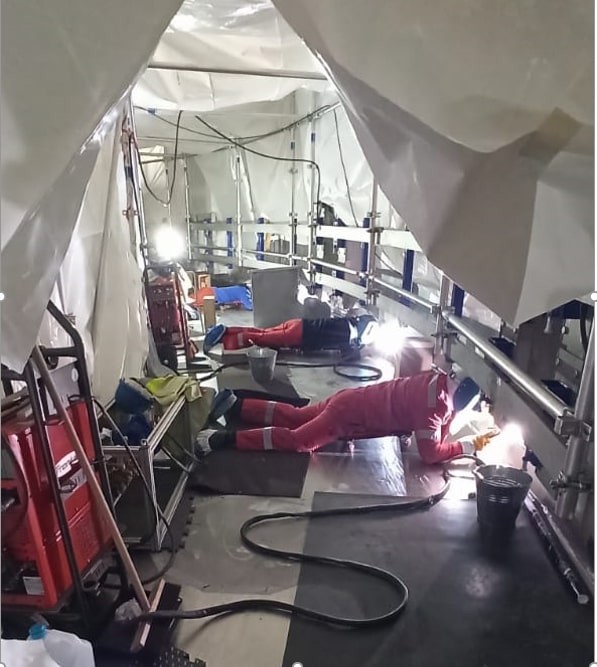
Advancing carefully
2020-12-12 - The Larsen & Toubro/MAN Energy Solution teams continue to weld the cryostat base and lower cylinder together in the Tokamak pit. It is a precise and careful job, which is carried out by highly qualified technicians.

Down into the basement
2020-12-11 - The first feeder component is introduced directly into the B2 basement level of the Tokamak Building. Approximately 100 components must be introduced to build the 31 ITER magnet feeders.

After three months in the chamber
2020-12-10 - During thermal testing, the coil was inserted into a dedicated cryogenic chamber and cooled down to approximately 80 K (-193 °). Three full cooldown and warmup cycles were performed, each one requiring approximately one month.

Yellow busbars
2020-12-10 - In the lowest basement level of the Diagnostics Building (B2), a labyrinth of busbars is being installed. Some five kilometres of these specialized power transfer devices will be needed to connect the magnets to the source of their power several hundred metres away.

Cold testing poloidal field coil #5
2020-12-09 - A second poloidal field coil—PF5—enters its cryogenic chamber on site for cold testing.
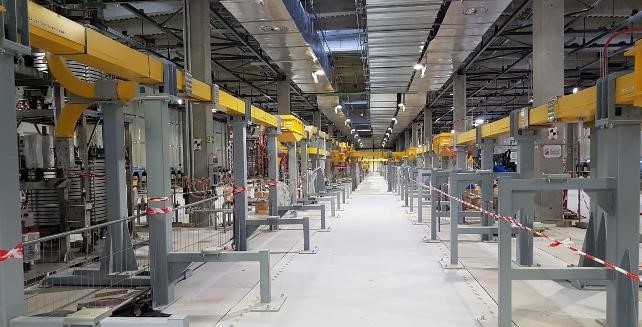
Good progress
2020-12-09 - n one of the twin Magnet Power Conversion buildings (B33), 100% of supports, busbars, links, and plates have been installed, together with cooling water hoses and junction boxes.
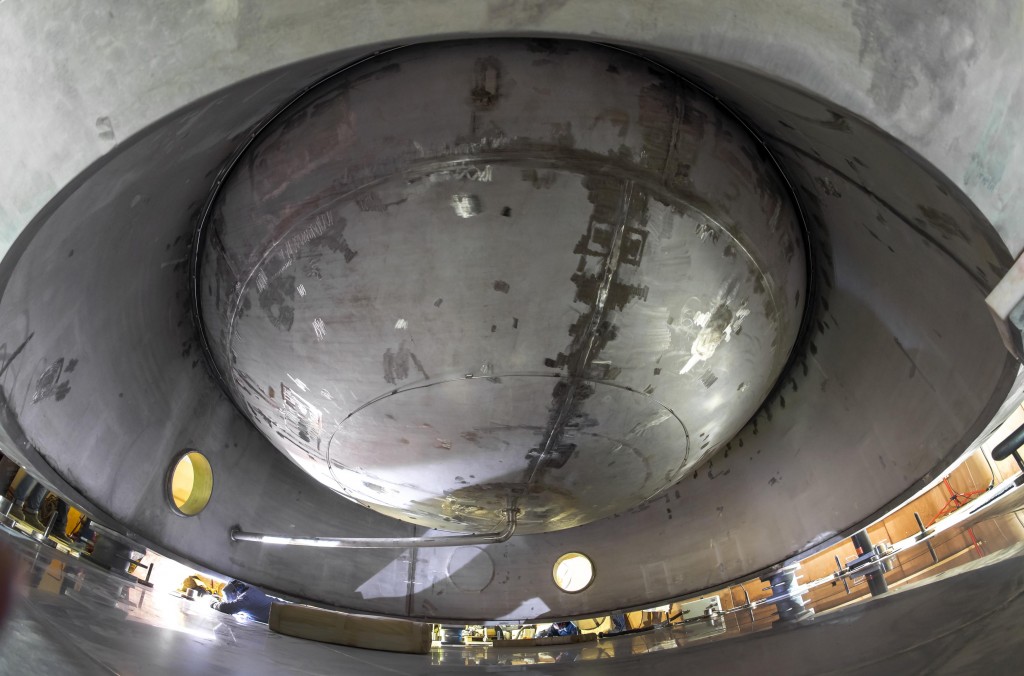
Drain tank lifted
2020-12-08 - One of the tokamak cooling water tanks in the Tokamak Complex is lifted so that contractors can weld a new leak-tight anchorage system.

Connecting
2020-12-08 - Here are the connection boxes between busbar lengths in the Magnet Power Conversion buildings.

Cooling manifold installation
2020-12-07 - On the inner surface of the lower cryostat thermal shield, workers have begun installing cooling manifold pipes.

Radial beams
2020-12-04 - One of the nine radial beams that will support the vacuum vessel sectors are they are loaded onto the assembly tooling, and support the full vacuum vessel assemblies as they are transferred and installed in the pit.

Into the depths
2020-11-27 - For five days in late November, a diver explored the depths of the heat rejection basins, inspecting the critical zones of the massive concrete structure that had been "overfilled" for structural testing.
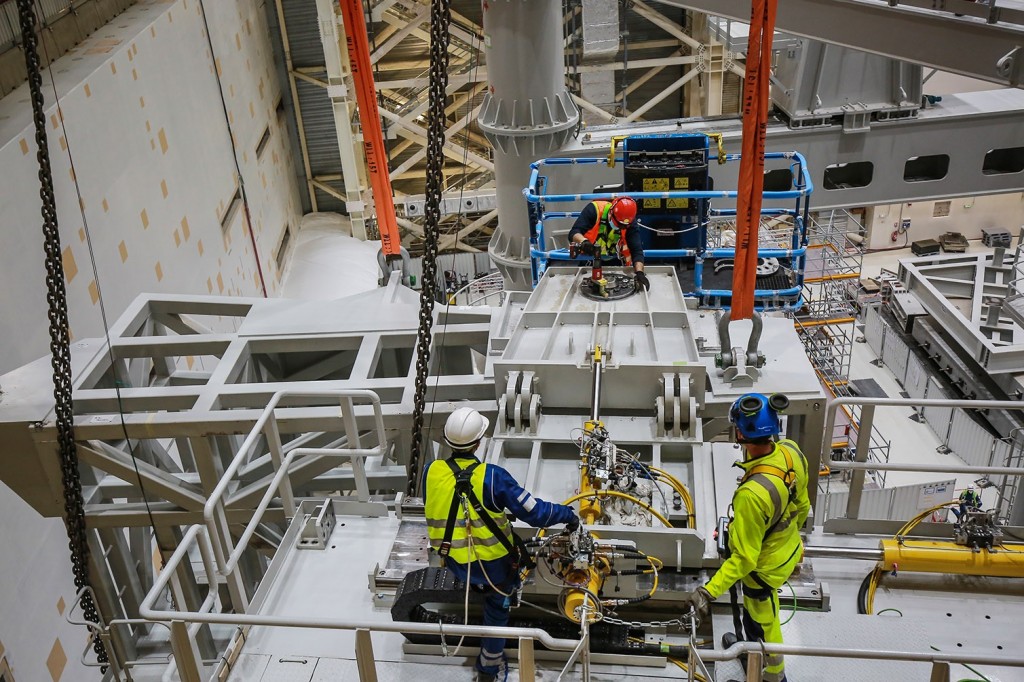
Seen from the top
2020-11-25 - This picture is taken from the top of the tool, as the thermal shield panel and its structure are "docked."
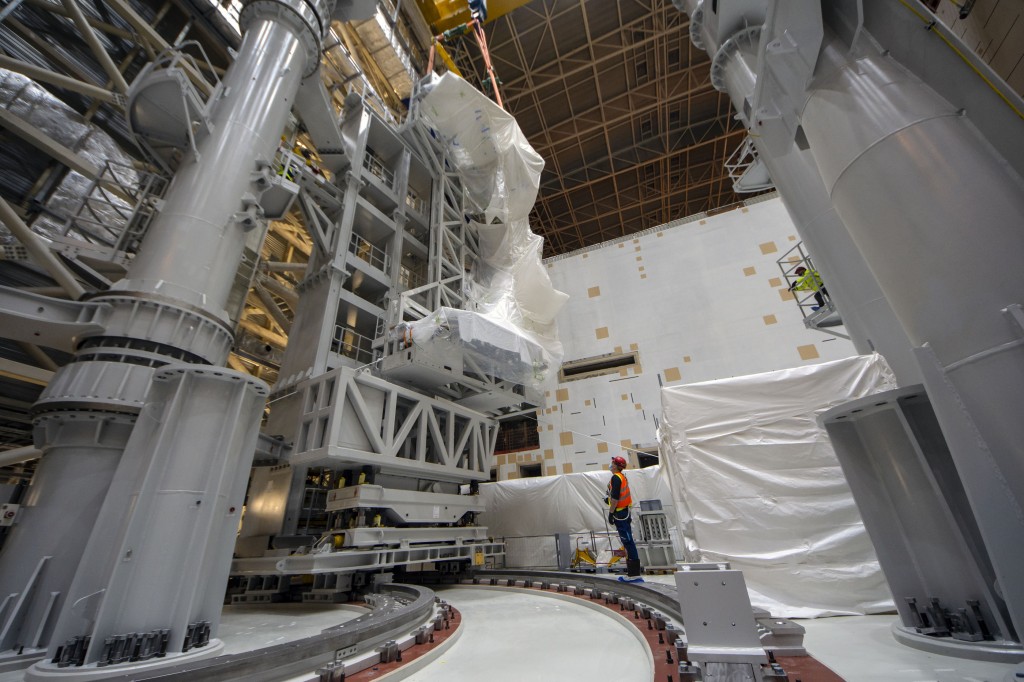
Lift frame goes along
2020-11-25 - A specially designed frame accompanied the thermal shield panel during the lift. Both thermal shield and lifting frames are supplied to the ITER Project by Korea.
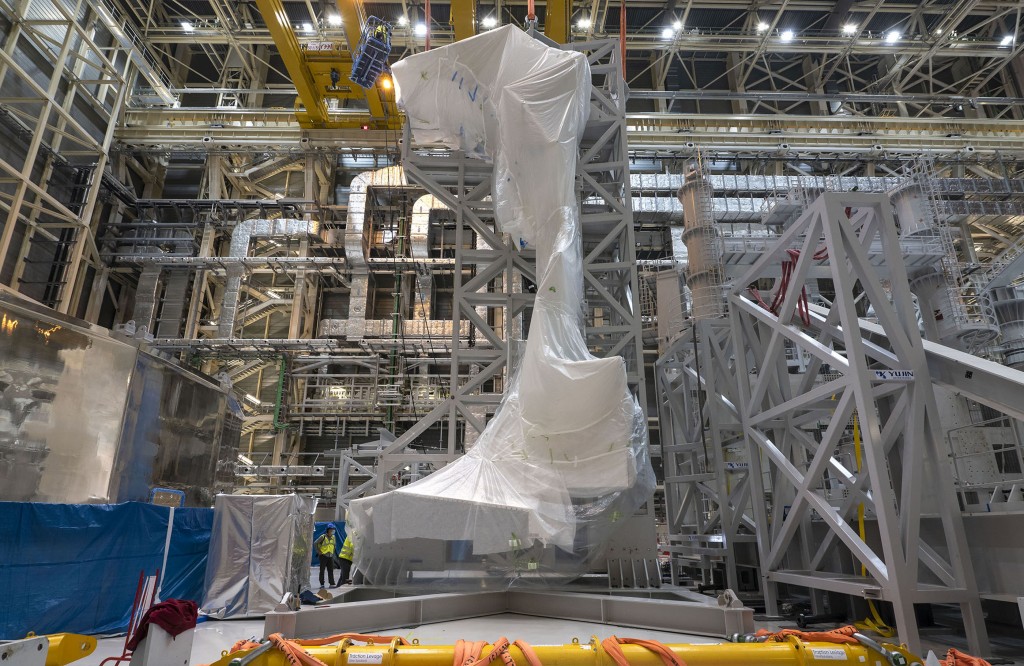
A protective "shell"
2020-11-25 - The vacuum vessel thermal shield is like a shell that encloses the vacuum vessel and protects the magnetic system from thermal radiation. At the pre-assembly stage, each vacuum vessel sector will be fitted with the three panels of thermal shield: two outboard (left and right) and one inboard.
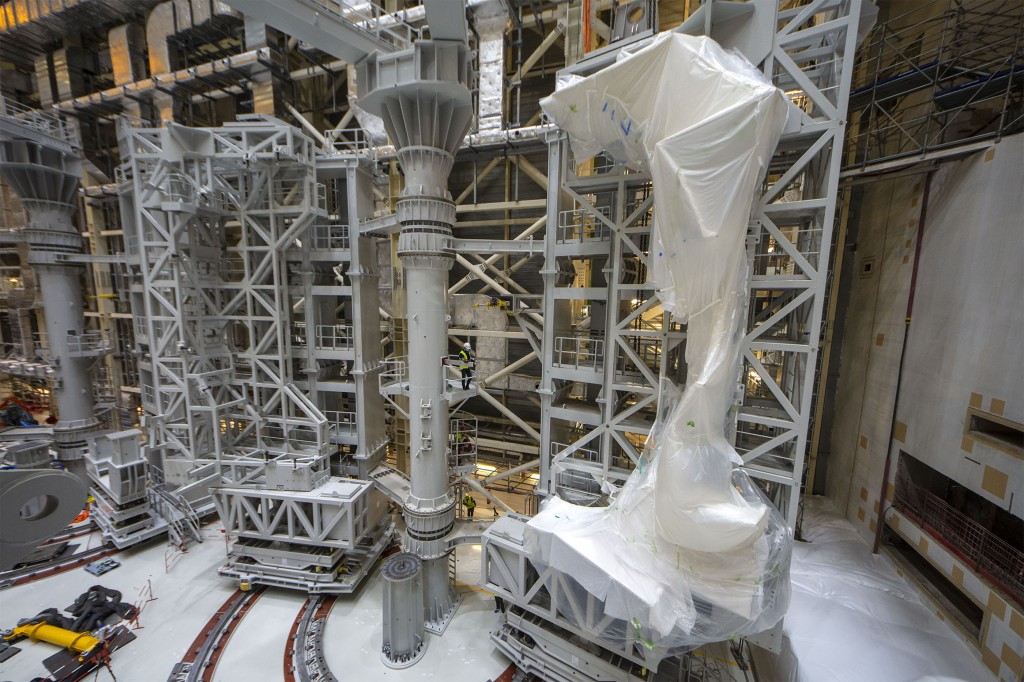
First component upended
2020-11-25 - A panel of outboard thermal shield for vacuum vessel sector #6 has been installed on one of the sector sub-assembly tools. For the giant tool, it represented the first ''embrace'' of an actual machine component.
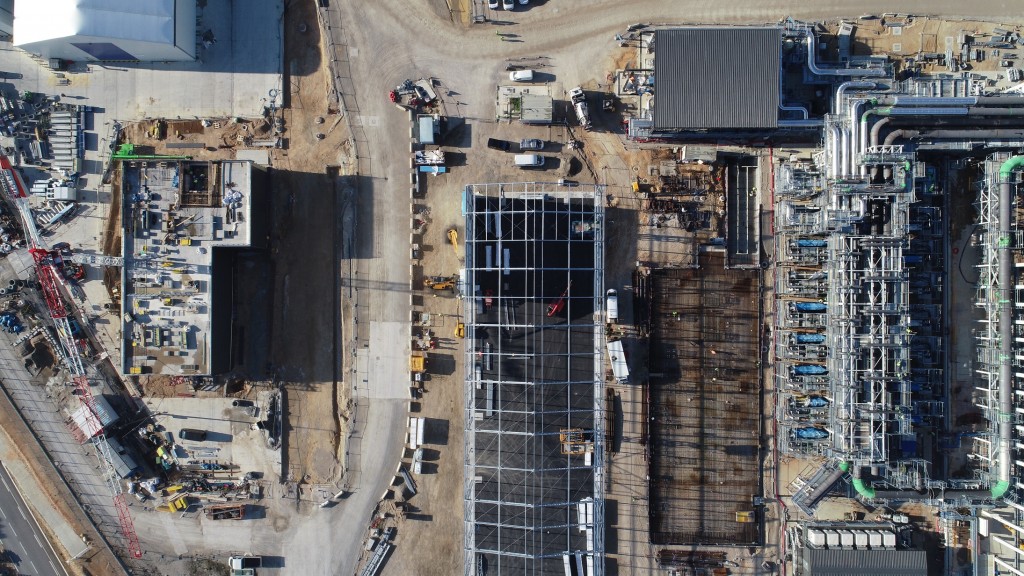
New structures
2020-11-24 - On the northeastern corner of the platform, several new structures have emerged. Left: the Tokamak Assembly Preparatory Building; right: a new storage facility. Photo: ITER Organization/EJF Riche

Fearless photographer
2020-11-23 - The ITER photographer climbed the equivalent of 20 stories to get this comprehensive shot of pre-assembly activities underway.

Inside and outside
2020-11-23 - All kinds of activity is underway to prepare the first vacuum vessel sector for pre-assembly.

Both 17 metres in diameter: PF5 and PF2
2020-11-23 - PF5 undergoes laser dimensional inspection before insertion into its cryogenic chamber. In the background, PF2 (the second coil produced on site) has been enclosed inside the coil impregnation station. Photo: ITER Organization/EJF Riche
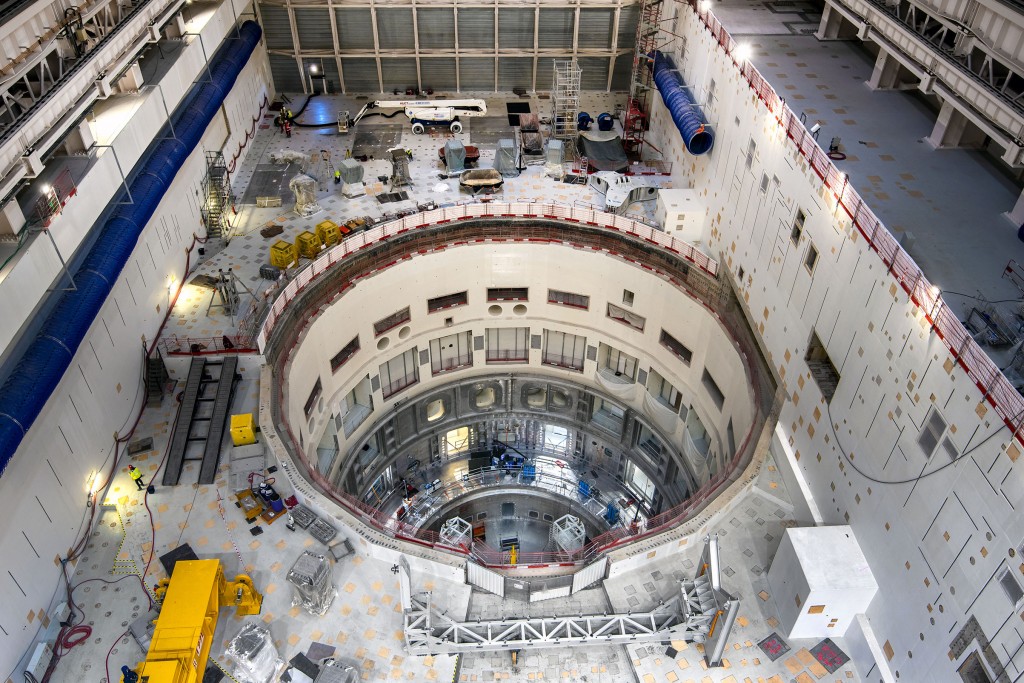
Up in the rafters
2020-11-23 - Taken from a height of approximately 55 metres, this photo captures the crane hall of the Tokamak Building and the deep machine assembly well.

By zone
2020-11-23 - From above, we have a clear view of the different work zones of the Assembly Hall. The component the furthest from the Tokamak pit (the lower cylinder thermal shield, top) will be the next one installed.
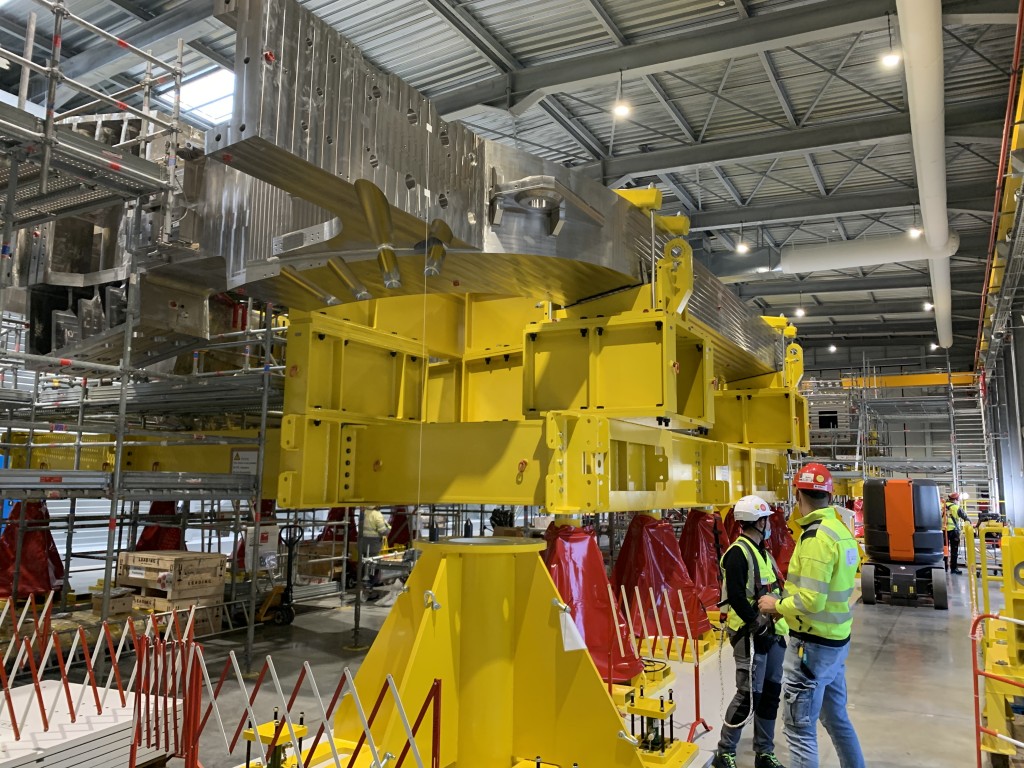
Lying in wait
2020-11-17 - The two toroidal field coils received from Japan will be needed next year in the first vacuum vessel sub-assembly to be mounted on the giant standing tools in the Assembly Hall. Until then there is plenty to do: leak testing the welds in the helium piping and adding handling and pre-assembly equipment.

Chunky accessories
2020-11-17 - A huge crane requires huge accessories. These are some of the attachments of the ITER bridge cranes.
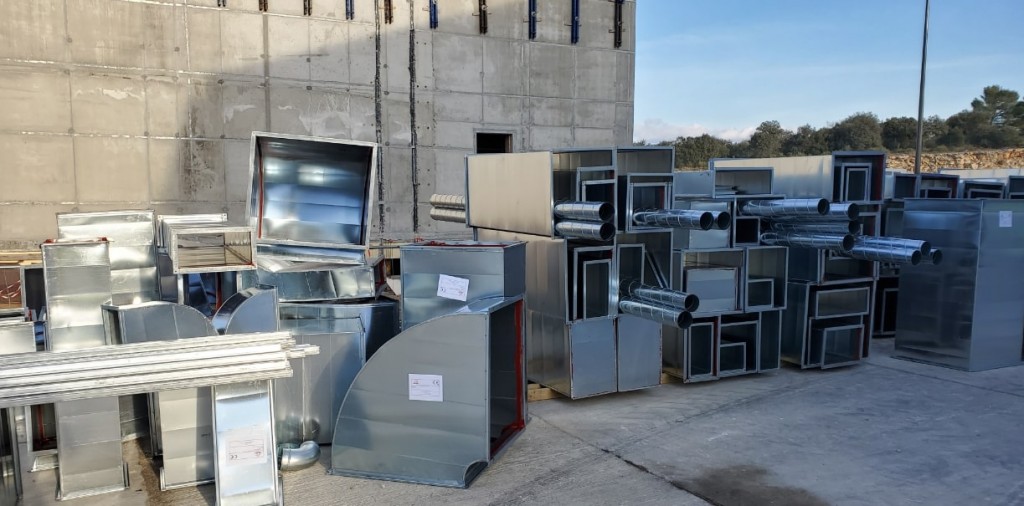
Aeration
2020-11-13 - HVAC ducts are delivered for the B1 (first basement) level of the Tokamak Complex.

Tall supports
2020-11-13 - Some of the gravity supports for the toroidal field coils are stored in the Assembly Hall. They will be installed one by one on the pedestal of the cryostat base.

720 tonnes
2020-11-13 - Two 360-tonne dummy loads have now been loaded onto the upending tool for trials that are preparing for the first component lifts.
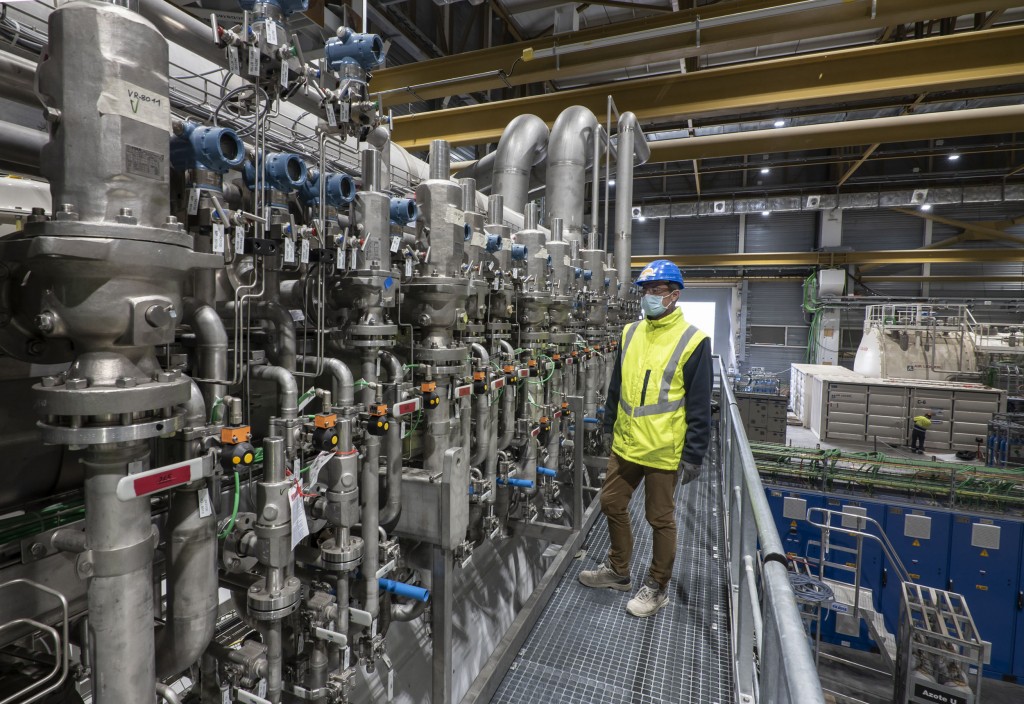
Two important roles
2020-11-12 - The cryogenic termination cold box has two roles: collecting and distributing cryogenic fluids produced in the cryoplant to the Tokamak Building, and warming up the fluids when it's time to bring clients back to room temperature for maintenance. Pictured: David Grillot, the head of ITER Cryogenic System Section.

The cryogenic termination cold box
2020-11-12 - Procured by ITER India and manufactured by the Swiss company Linde Kryotechnik AG, the cryogenic termination cold box is a massive structure packed with pipes, valves, electrical feedthroughs and pneumatic actuators. Photo: ITER Organization/EJF Riche
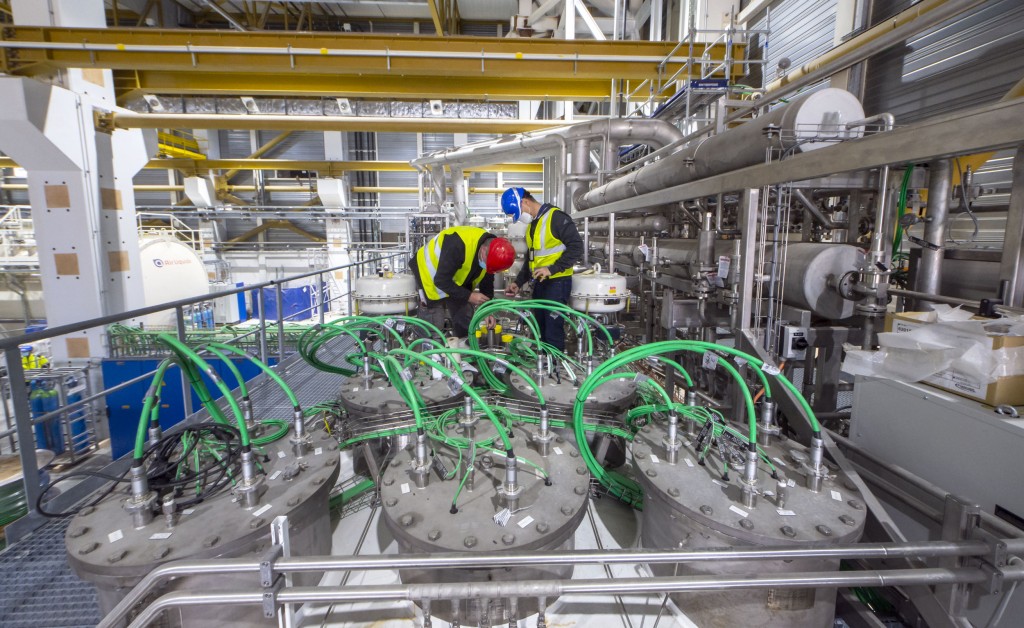
The cryoplant's "cryogenic termination cold box"
2020-11-12 - ITER technical responsible officer Hyun Sik Chang (right) and a technician from the Swiss company Linde Kryotechnik AG, perform the cleanliness check protocol on the multiprocess cryolines of the cryogenic termination cold box. This box collects the cooling fluids from the cryoplant and redirects them to the Tokamak Building over an elevated bridge.
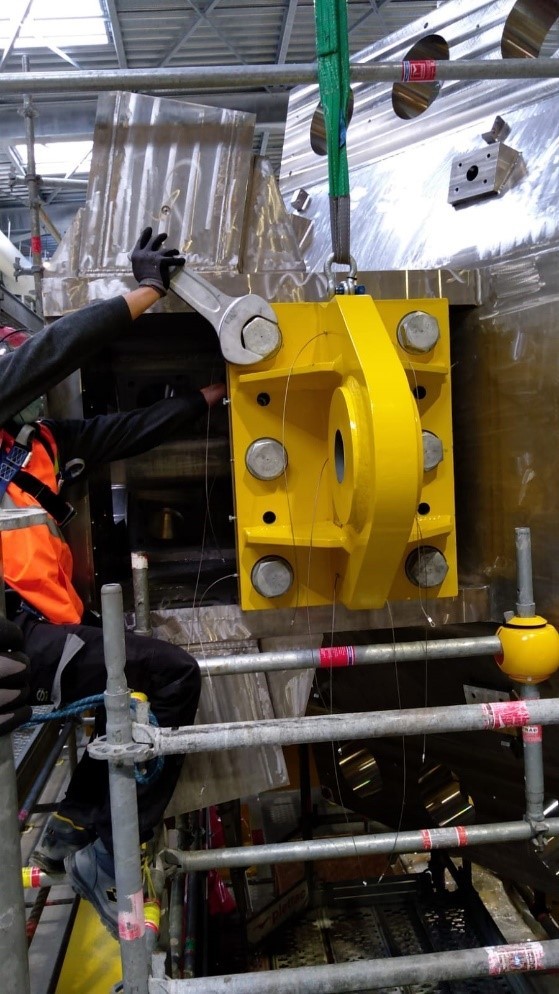
How to lift
2020-11-11 - These lifting lugs were pre-installed on toroidal field coil #12. For now, the coil is in a preparatory area not far from the Assembly Hall.
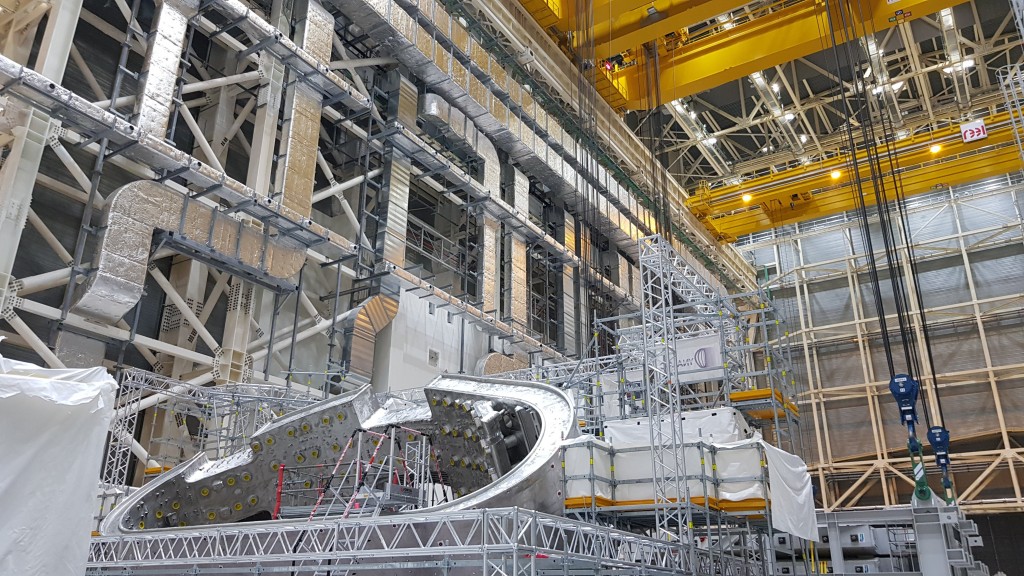
Practicing every step
2020-11-09 - Behind vacuum vessel sector #6, operators are practicing the lift operation that will bring the sector from horizontal to vertical. The crane is about to raise the upending frame (seen here loaded with dummy weights).
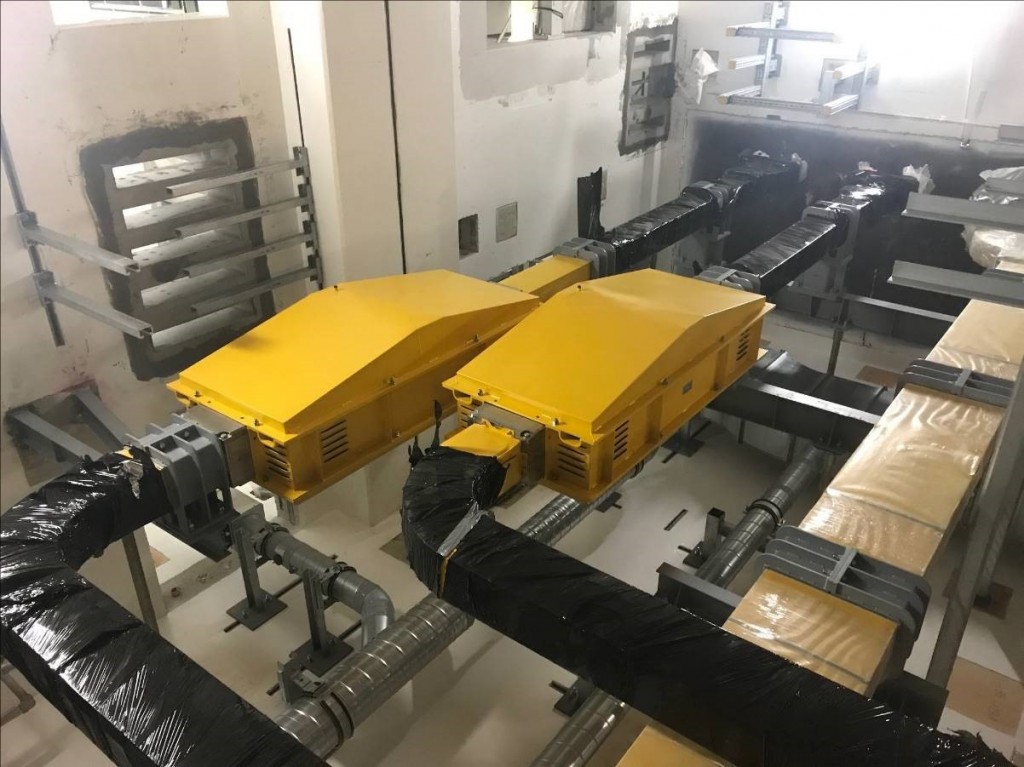
Connecting busbars
2020-11-09 - Part of the work to install several kilometres of busbars between the Magnet Power Conversion facilities and the ITER magnets, is the interconnection that joins two busbar lengths.
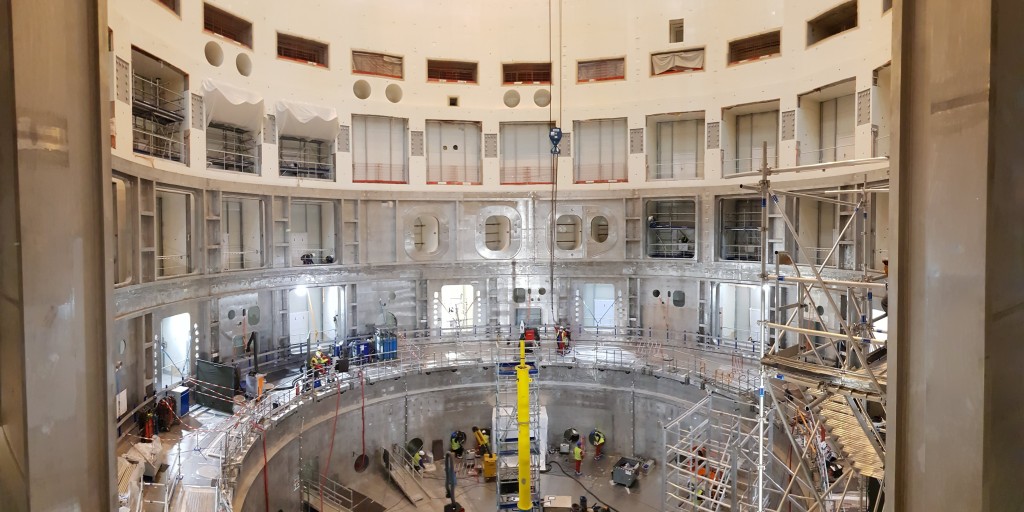
Like a candle
2020-11-09 - In this photo, the metrology tower in the centre of the pit looks a lot like a candle. Perhaps for ITER's 10 years of construction? (Building works on the platform began in August 2010.)

Progressing well
2020-11-09 - Busbars leave the Magnet Power Conversion buildings by overhead pass and cross through the Diagnostics Building to reach the magnets. Some 89% of busbar supports and 76% of planned busbars in the Diagnostics Building have been installed by assembly contractors.

Measurements at every step
2020-11-06 - As the silver-coated panels of the lower cryostat thermal shield are assembled, metrologists are constantly at hand to verify alignment.
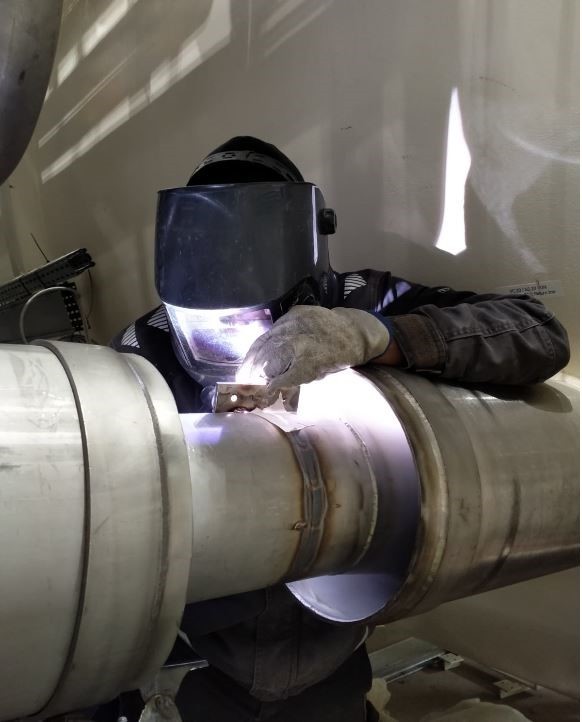
Piping interconnections
2020-11-03 - In the Cryoplant Building, a welder complete the first cryoline piping interconnection on the liquid helium plant cold box.

Inside the plant
2020-11-03 - ITER's cryoplant has been designed to operate over a wide range of ITER plasma scenarios, from short plasma pulses (a few hundred seconds) with 700 MW of fusion power, to long plasma pulses of 3,000 seconds with 365 MW of fusion power. Photo: ITER Organization/EJF Riche

Pre-compression rings
2020-11-03 - Two sets of pre-compression rings and dedicated lifting equipment are stored on site. The bottom set will be called for installation quite early in the machine assembly process.

A new tool arrives from Korea
2020-11-02 - The "sector lifting tool" is one of the interfacing components between the heavy lift cranes and some of the heaviest ITER components. The tool is equipped to perform horizontal-plane adjustments along the X and Y axis (longitudinal and transverse) in order to balance the loads before each lift.

Heat barrier
2020-10-30 - This lower cryostat thermal shield will be positioned inside of the soup-dish-shaped depression of the cryostat base to form a heat barrier.

Advancing cautiously
2020-10-30 - The progress of the welding machine (8 centimetres per minute) is closely scrutinized by a technician from MAN Energy Solutions (contractor to Larsen & Toubro, the cryostat manufacturer).

Lower cryostat thermal shield
2020-10-30 - In the ITER Assembly Hall, contractors are joining eighteen 20° segments of thermal shield into a silver circle.

First in-pit welding
2020-10-30 - The gap between the cryostat lower cylinder and the cryostat base is 40 millimetres. It will take 1 tonne of filler material to completely weld the 90 metres of circumference.

Step by step
2020-10-30 - A pass inside the six-metre-long predefined sections is approximately one millimetre thick ... and it takes close to 80 passes to fill the gap between the two components. Behind the wall, a specialist monitors the process by video screen.

The eye in the pit
2020-10-30 - At the centre of the pit, a rotating "eye" blinks red and green atop a tall structure. The eye is the central piece of a metrology system that monitors a component's potential deformations by computing data acquired from several dozen targets.
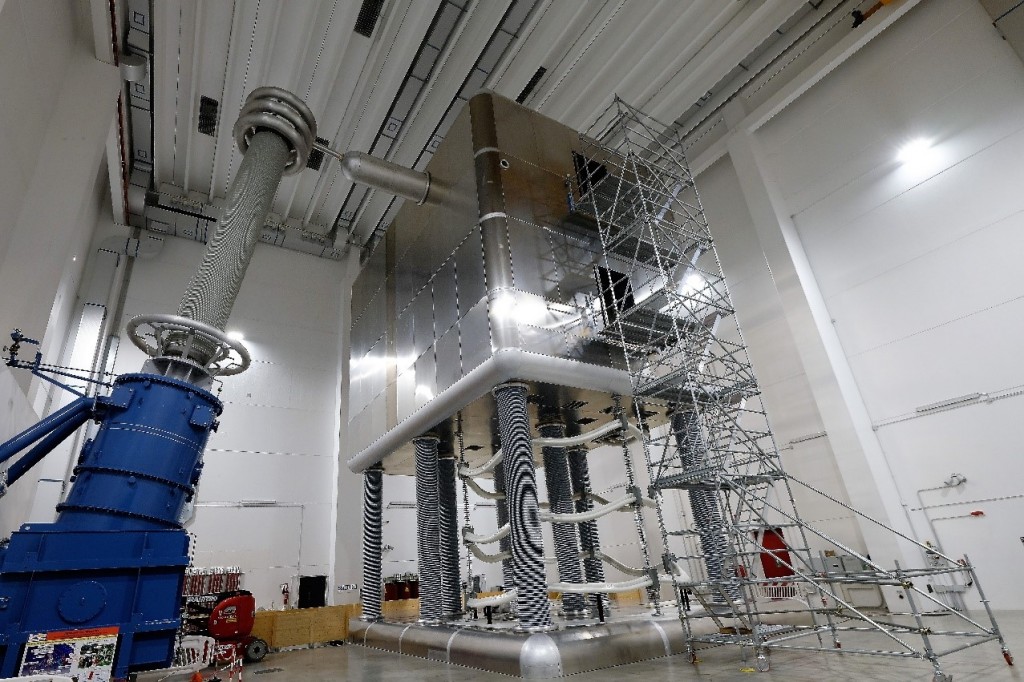
MITICA: first integrated power supply tests
2020-10-27 - In October, integrated tests on high voltage equipment supplied by Japan (left) and Europe (right) were carried out successfully at 50 kV. The next step will be testing at 1MV.
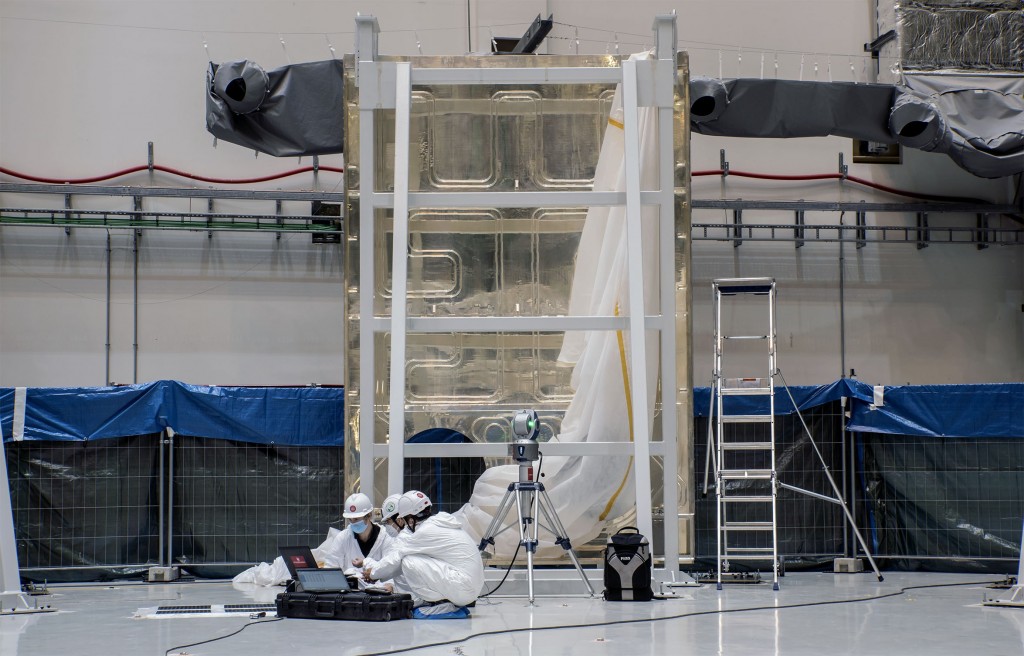
Camera in place
2020-10-27 - The first panel of the lower cryostat thermal shield is in place and metrologists verify that assembly can continue.
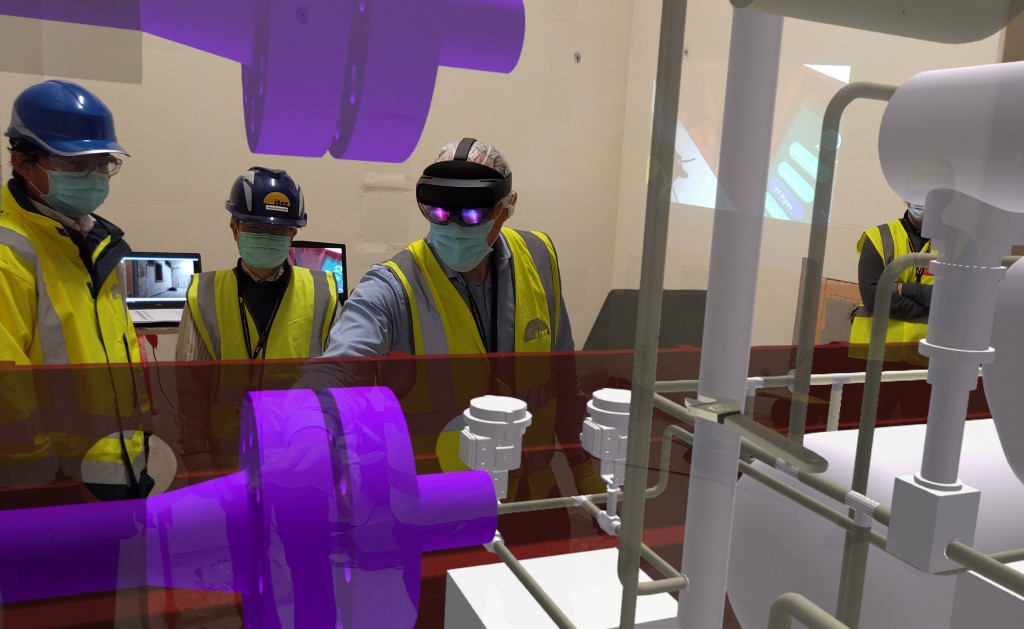
A novel technique for a novel environment
2020-10-26 - ITER is working with "augmented reality" to plan for, and visualize, complex installation and maintenance tasks in crowded environments. The novel technique is the fruit of a collaboration between the French Alternative Energies and Atomic Energy Commission (CEA) and the ITER Organization.

Barnacles?
2020-10-22 - Like barnacles colonizing a whale, small cylindrical "bosses" are being welded in precise locations to the outer shell of vacuum vessel sector #6. Bosses are like studs onto which other components can be bolted or welded, for example instrumentation and diagnostics cables.

Horizontal for now
2020-10-22 - Vacuum vessel sector #6 is on a platform across from the large assembly tool where it will be mounted (in a vertical position) during the first sector sub-assembly operation.
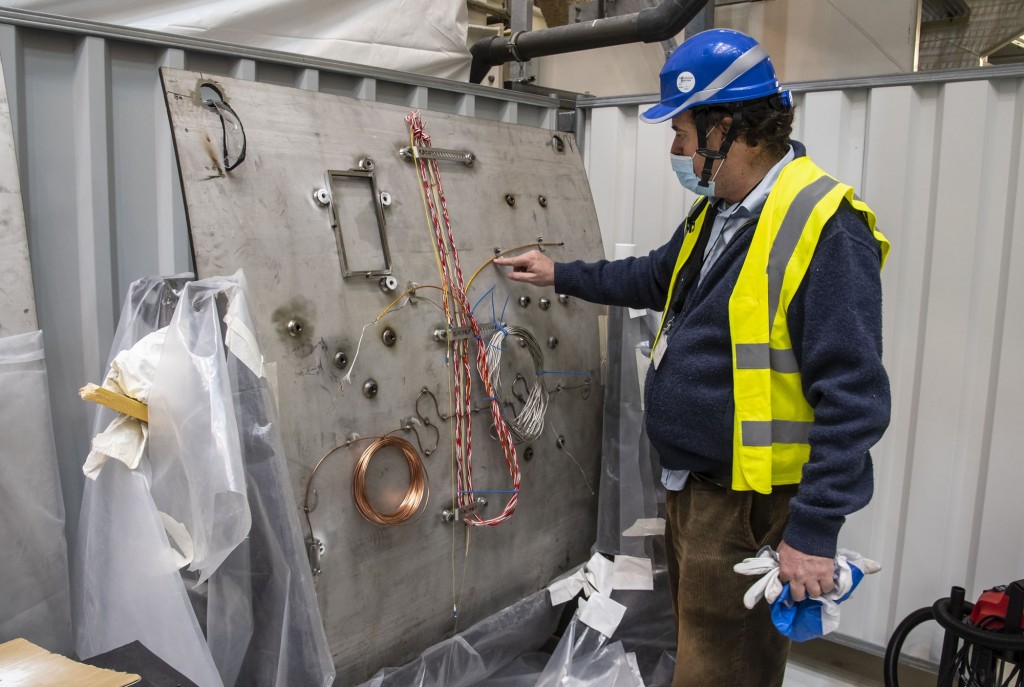
How it will look
2020-10-22 - This mockup clearly illustrates the attachment role played by the "bosses": the small rectangular frame will support a sensor; the flat hold plates are for cable looms; and another set of smaller devices provides a pathway to the "continuous flux loop," a single cable that runs along the whole circumference of the torus to measure the magnetic field.
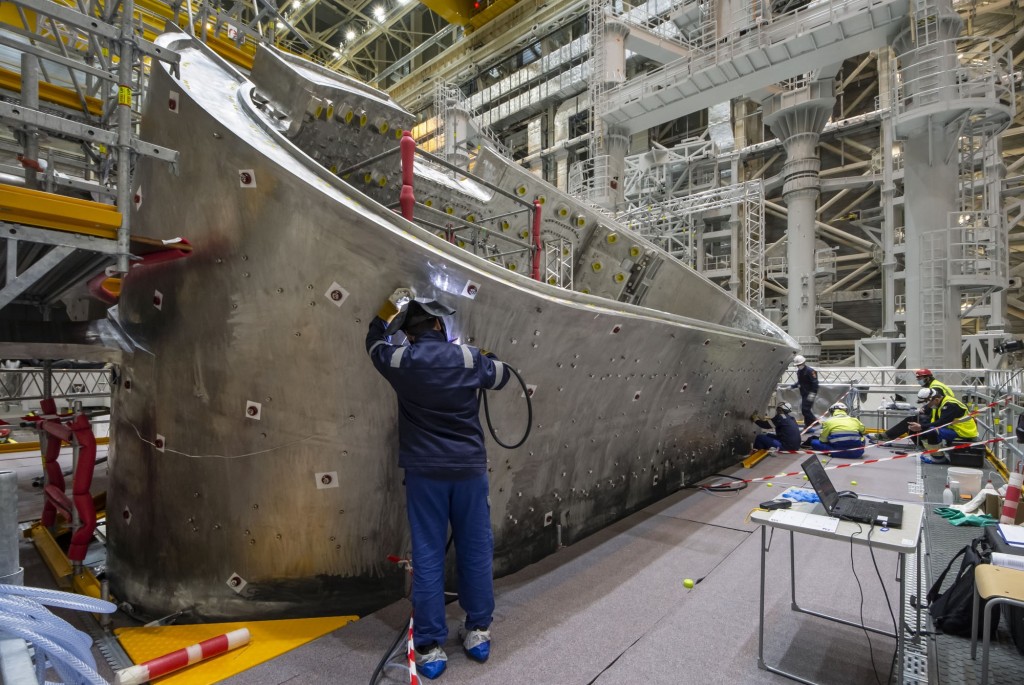
Bumps galore
2020-10-22 - The larger cylinders, bordered with white, are metrology targets. The smaller "bosses" are like clips that will hold instrumentation and diagnostics cables.

Outside and inside
2020-10-22 - Approximately 800 "bosses" need to be welded to the outer surface of each vacuum vessel sector. As for those planned on the component's inner wall, they will be installed once the vacuum vessel pre-assemblies have been lowered into the Tokamak pit.

Using "laser templating" for the first time
2020-10-22 - Implemented in ITER for the first time, "laser templating" techniques are used to project an outline of the element to be welded at its precise pre-defined position on the component's surface with a safe, low-power laser, providing the welder with a perfect template to follow.
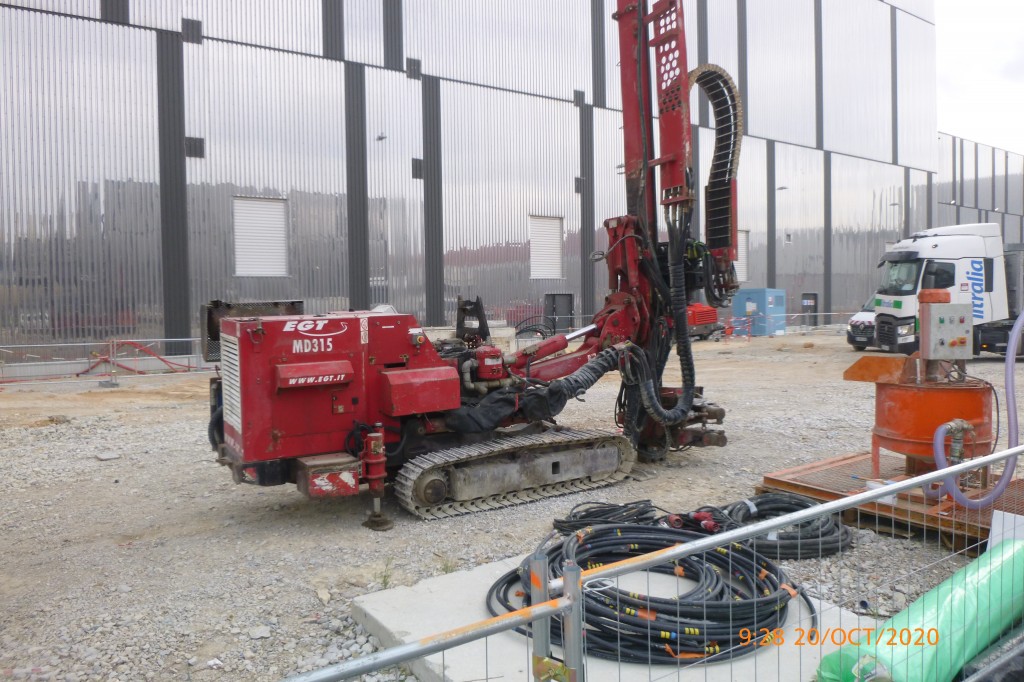
Preparations underway for a new building
2020-10-20 - Near the Assembly Hall, groundwork has started for a new building that will house electrical switching equipment. Contractors are drilling regular holes to check for karsts (fissures) in the bedrock.

In the pit
2020-10-15 - Standing inside the Tokamak pit, where the welding of the cryostat lower cylinder to the cryostat base has started. A metrology instrument is visible on the tall pole at left.
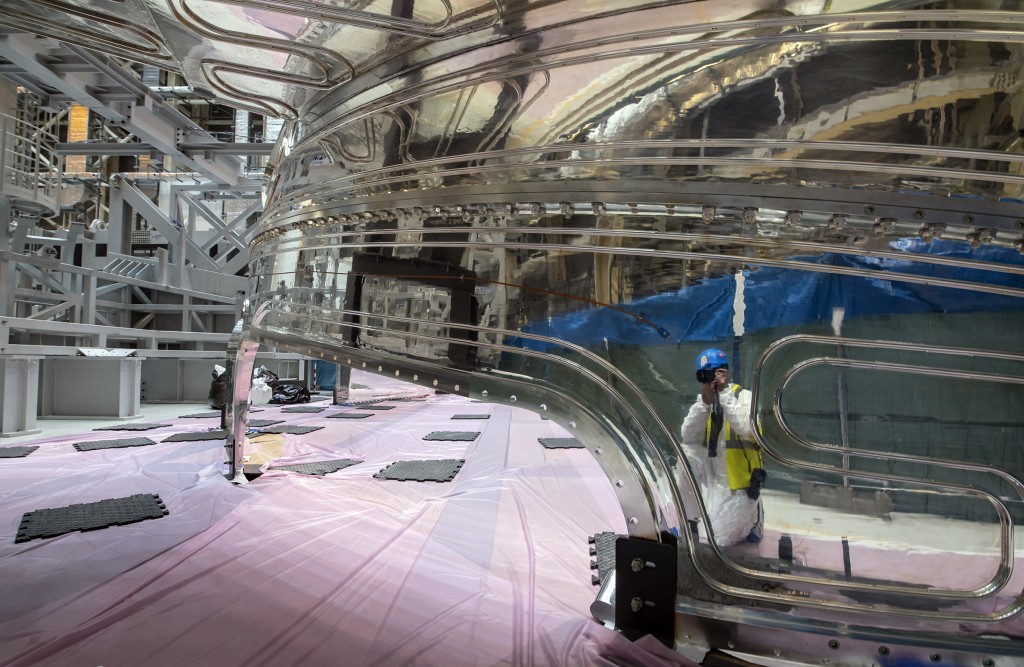
The shine
2020-10-15 - The component's shine is due to the thin layer of silver that covers its entire surface. A "low emissivity" material, silver raises an obstacle against the thermal radiation, in the form of electromagnetic waves, that a heat source generates.

Lower cryostat thermal shield
2020-10-15 - Silver-plated thermal shield panels are being arranged in a circle to form the lower section of the cryostat thermal shield, which should be lowered into the assembly pit in late November.

In the pit
2020-10-15 - Standing inside the Tokamak pit, where the welding of the cryostat lower cylinder to the cryostat base has started. A metrology instrument is visible on the tall pole at left.
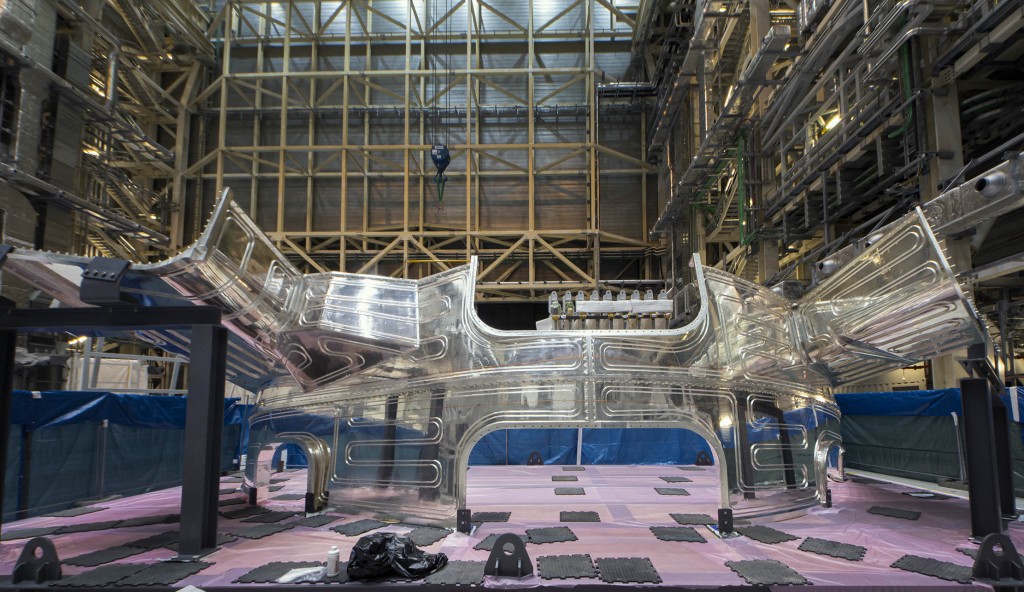
Thermal shield uncovered
2020-10-15 - Like a giant's tiara. This segment of silver-coated thermal shield will on the outside of the D-shaped vacuum vessel sector #6.
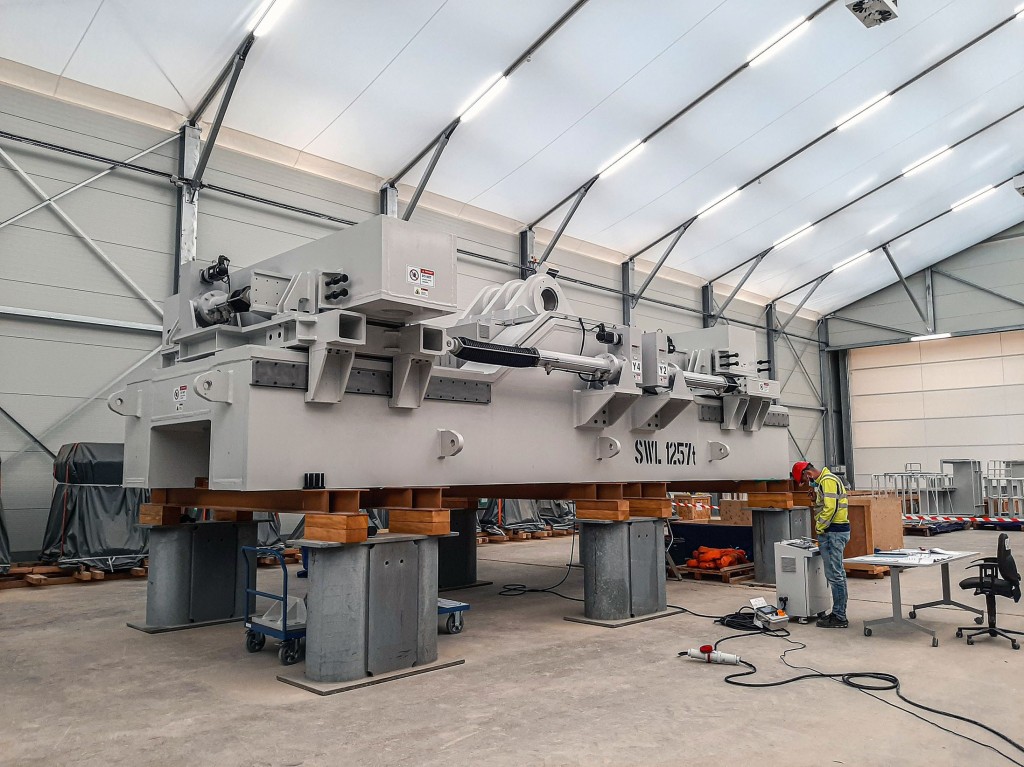
Readying an assembly tool
2020-10-15 - This sector lifting tool will be positioned between the heaviest components to be lifted into the giant sector pre-assembly tools in the Assembly Hall and the hooks of the overhead cranes. A control system can be activated through controllers and electrically driven actuators to optimally balance the loads.
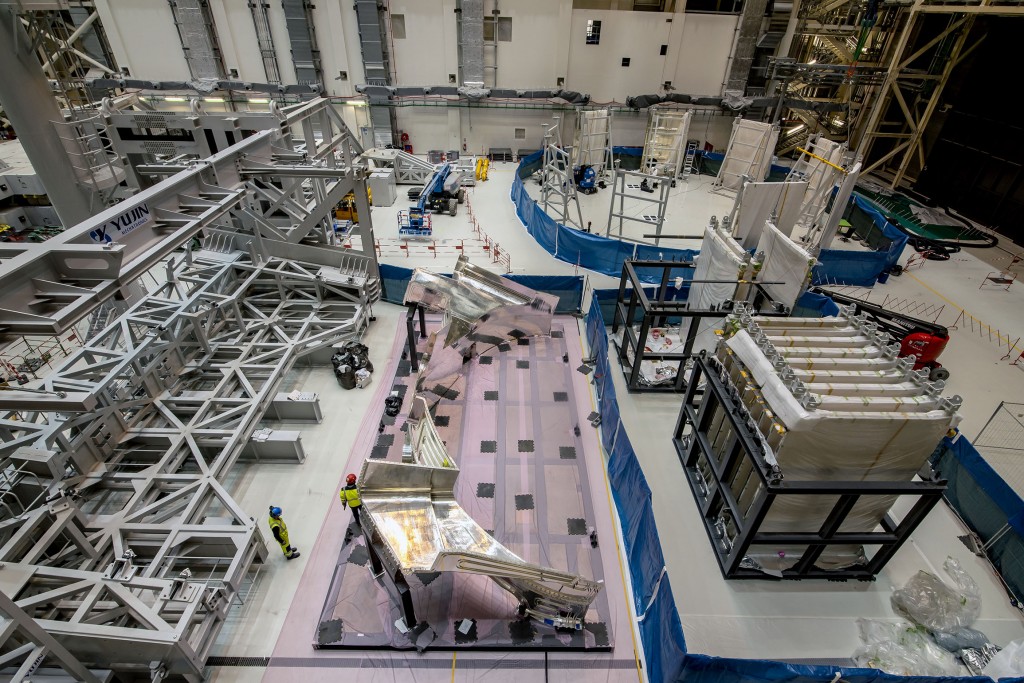
Thermal shield(s)
2020-10-15 - Seen from above, elements of the vacuum vessel thermal shield (foreground, centre) and the lower cryostat thermal shield (foreground right, and background). To the left, a lifting frame that will support vacuum vessel thermal shield sectors as they are lifted to vertical and installed on the large pre-assembly tools.
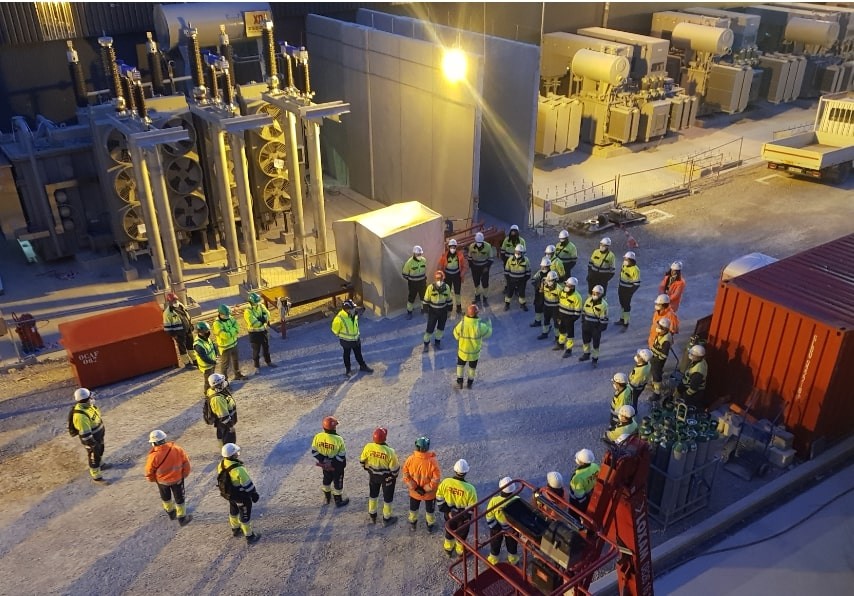
Night shift
2020-10-15 - One of the challenges of the plant assembly project is coordinating the different actors with activities in the same areas. At this coordination meeting, we can identify some of the participants by the colour of the hardhats—green for safety agents, red for foremen/women and supervisors, and white for workers.
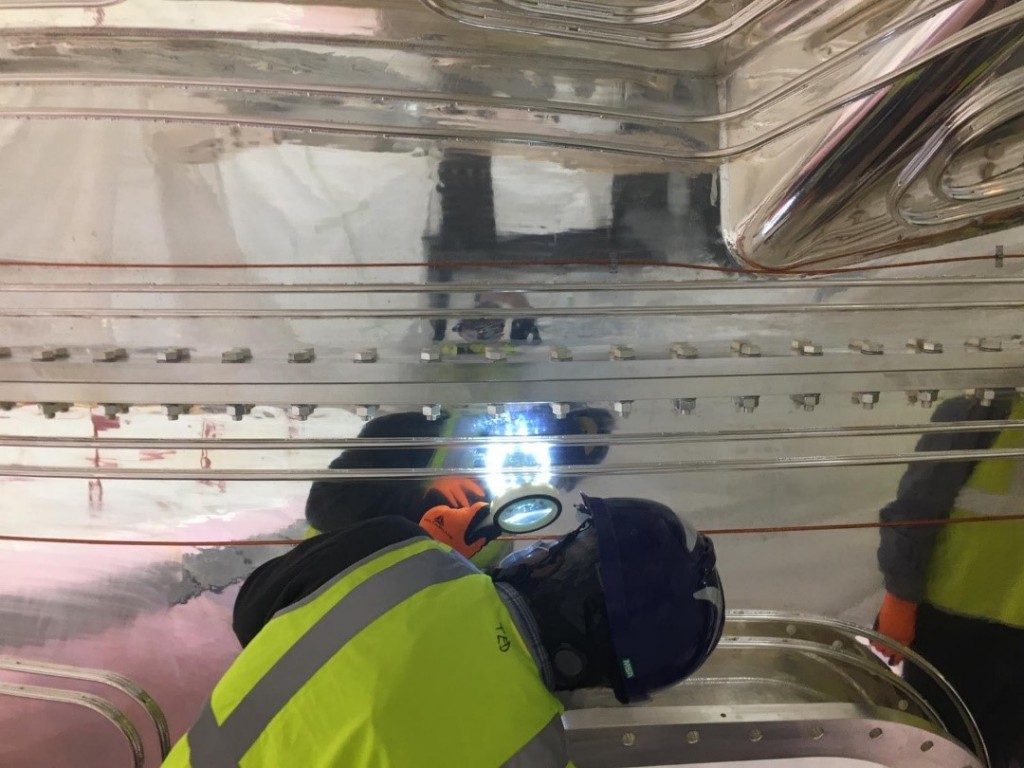
Close inspection
2020-10-14 - This outboard panel of thermal shielding is undergoing careful inspection.

Functional tests conclude on sector lifting tool
2020-10-14 - Functional tests on the "sector lifting tool" have demonstrated that the tool's controller and actuators are ready to implement operator commands during the delicate lifting operations of vacuum vessel sectors, toroidal field coils, and the finalized sector sub-assemblies.

Takes a team
2020-10-14 - Assessing the leak tightness of the heat rejection system basins involved the ITER Control Division, in charge of instrumentation and control; the Operations Division; the Mechanical Implementation Division; the Field Engineering Installation Division, and Site Coordination.
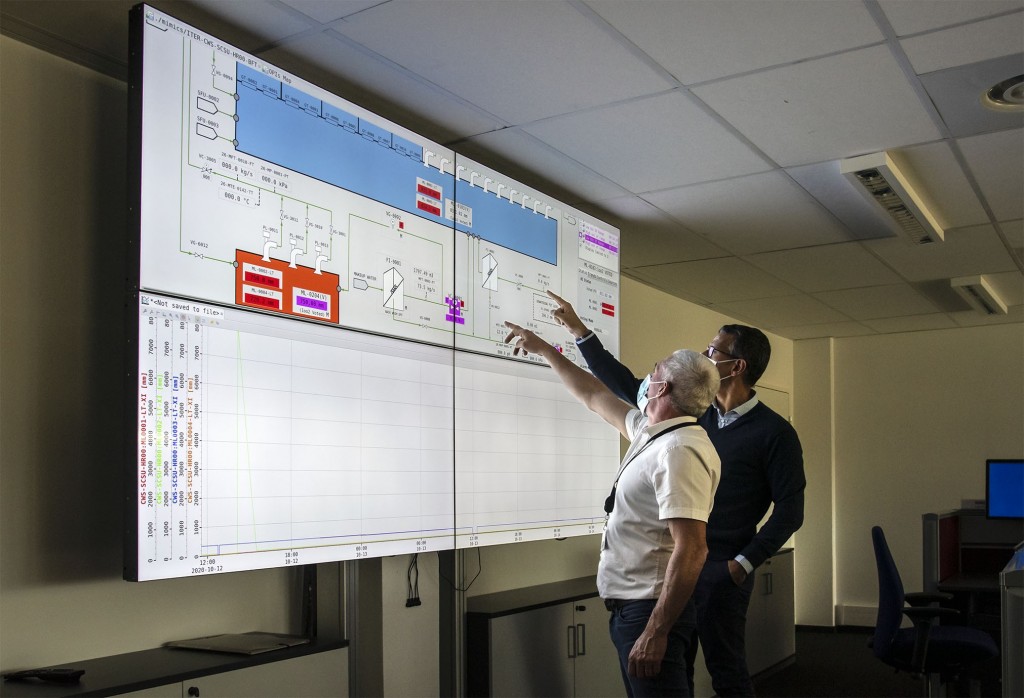
Testing the basins
2020-10-14 - The heat rejection system team begins a week-long "fill test" for the cold and hot basis of the cooling tower area. From this temporary control room, the level of the water can be monitored.
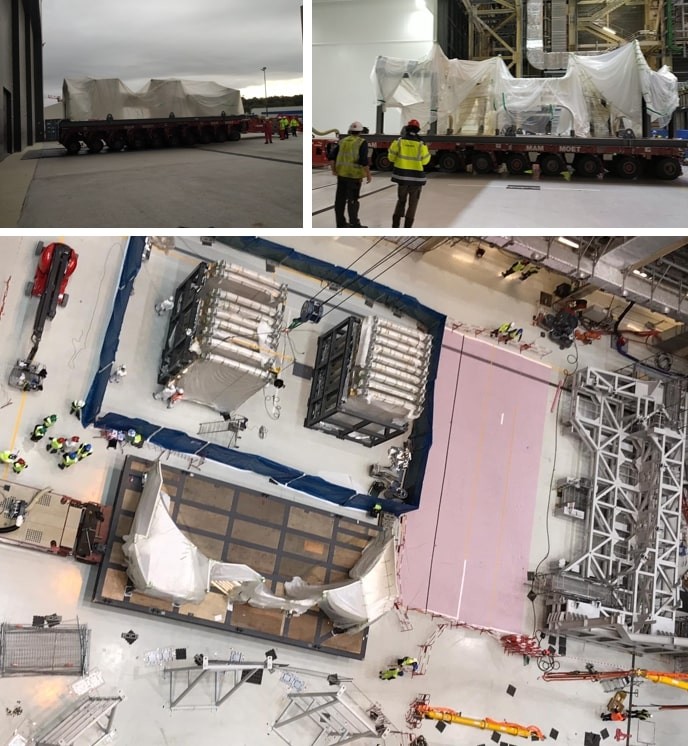
Two types of thermal shield
2020-10-14 - Panels of cryostat thermal shielding have arrived at the Assembly Hall from Korea, alongside larger sections of vacuum vessel thermal shielding.
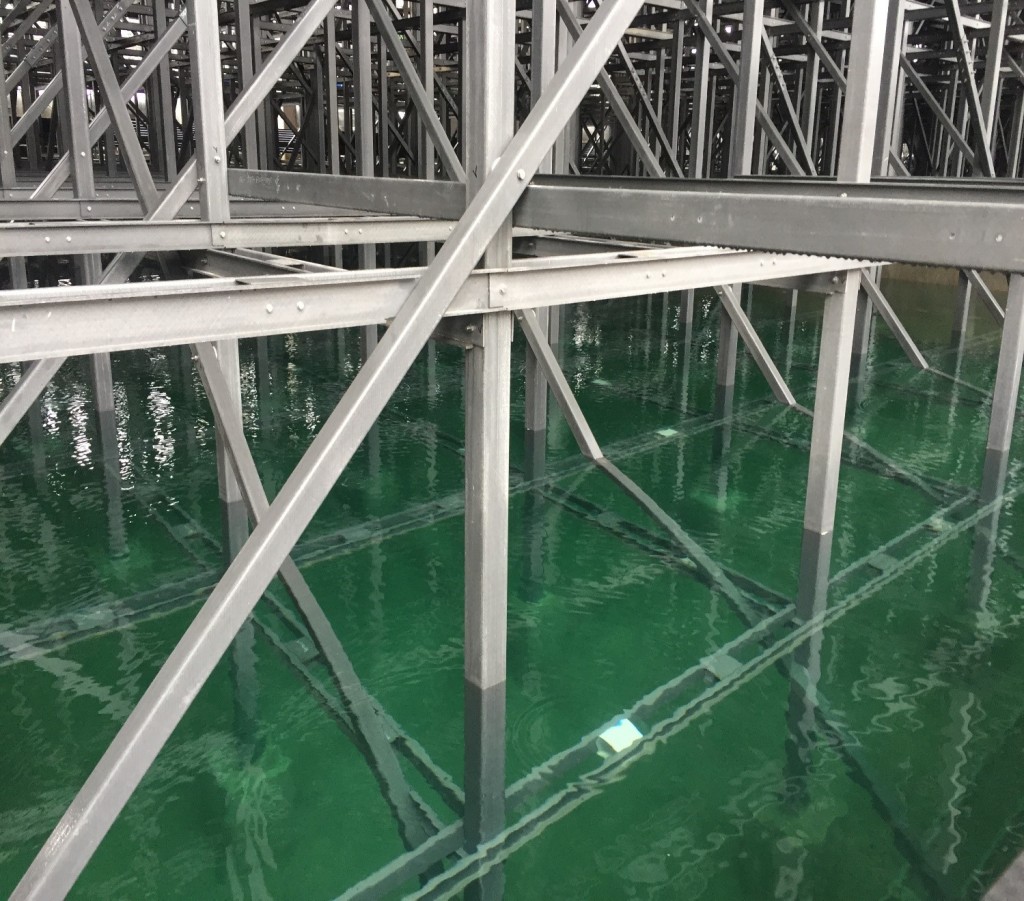
Full
2020-10-14 - After one week the heat rejection basins were full and detailed investigations could begin.

Testing the basins
2020-10-14 - Prior to turning over the heat rejection system to the ITER commissioning team, a leak tightness test was organized for the system's cold and hot basins. The basins were filled to capacity, and even a little beyond, to test their leak tightness and structural solidity.
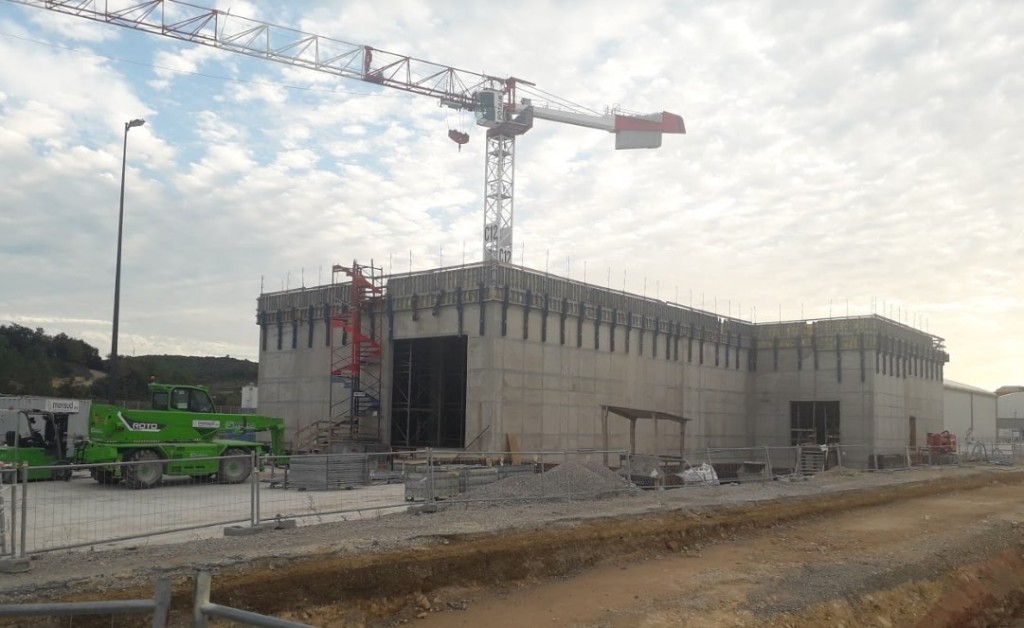
TAPB: fully erected
2020-10-12 - In a northeastern corner of the platform, not far from the Assembly Hall, the Tokamak Assembly Preparatory Building is fully erected. It is a one-story building, with a full basement.

The only circles
2020-10-09 - These unusual openings are for a very specific component—the injectors of the ITER neutral beam heating system. © Les Nouveaux Médias/SNC ENGAGE

Painting time
2020-10-09 - Nuclear doors, and the floors under them, are being coated with the same smooth, shiny white paint as the other areas of the Tokamak Complex. © Les Nouveaux Médias/SNC ENGAGE
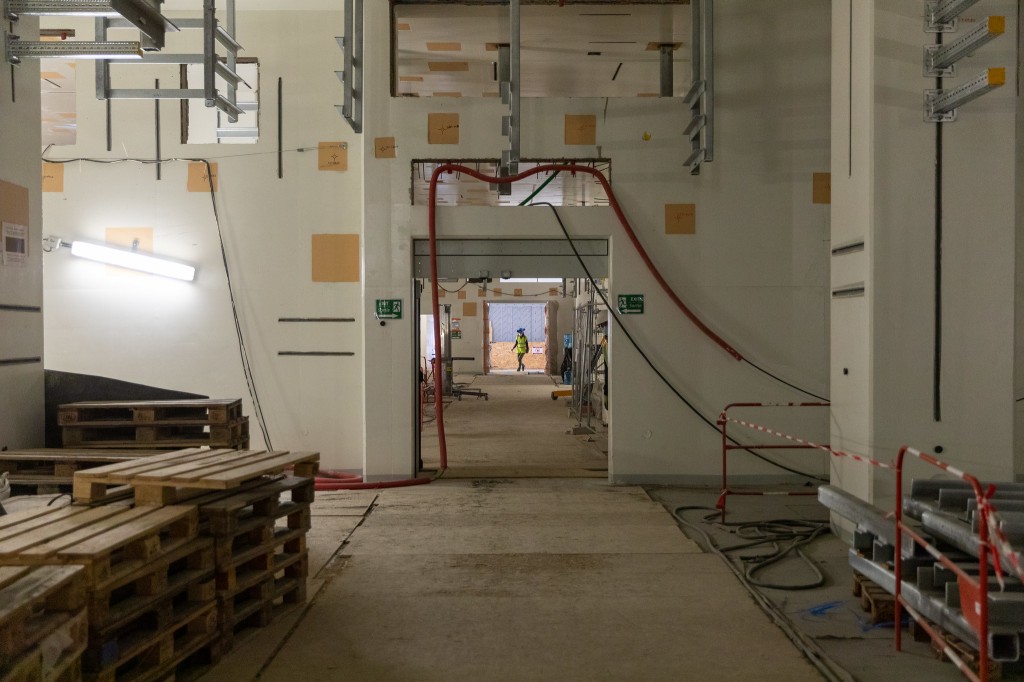
One after another
2020-10-09 - Room after room in the Tokamak Complex will house the equipment needed to run the machine. The ceiling racks will hold cables and cable trays. © Les Nouveaux Médias/SNC ENGAGE
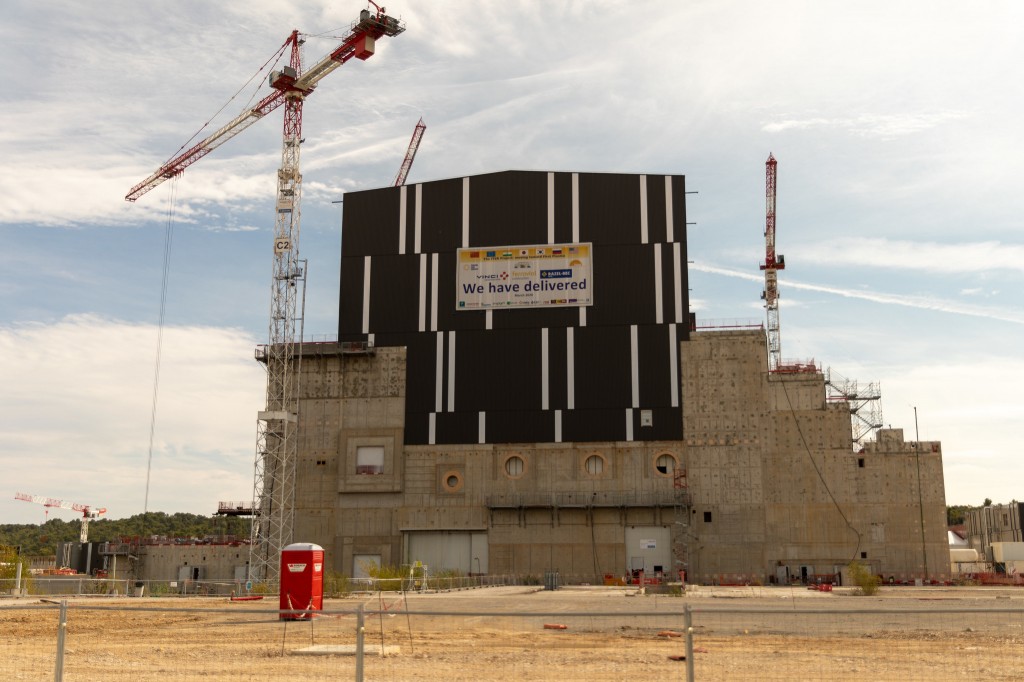
All clear
2020-10-09 - In front of the Tokamak Complex, land has been cleared for the construction of two small buildings and a technical area. All are dedicated to the power supply of ITER's massive neutral beam injection heating system. © Les Nouveaux Médias/SNC ENGAGE

Waiting its turn
2020-10-09 - Protected from humidity and the weather, the upper cylinder waits for its turn in the Tokamak pit. © Les Nouveaux Médias/SNC ENGAGE

A constellation of plates
2020-10-09 - We can guess at the number of components that will be installed in this large room by the number of anchor plates on the walls, ceiling and floor. © Les Nouveaux Médias/SNC ENGAGE

Inside and out
2020-10-09 - The equipment inside and outside of the conversion buildings is dedicated to the ITER superconducting magnets, which require power at DC voltages between 0.10 kV and 1.35 kV, depending on their size. © Les Nouveaux Médias/SNC ENGAGE
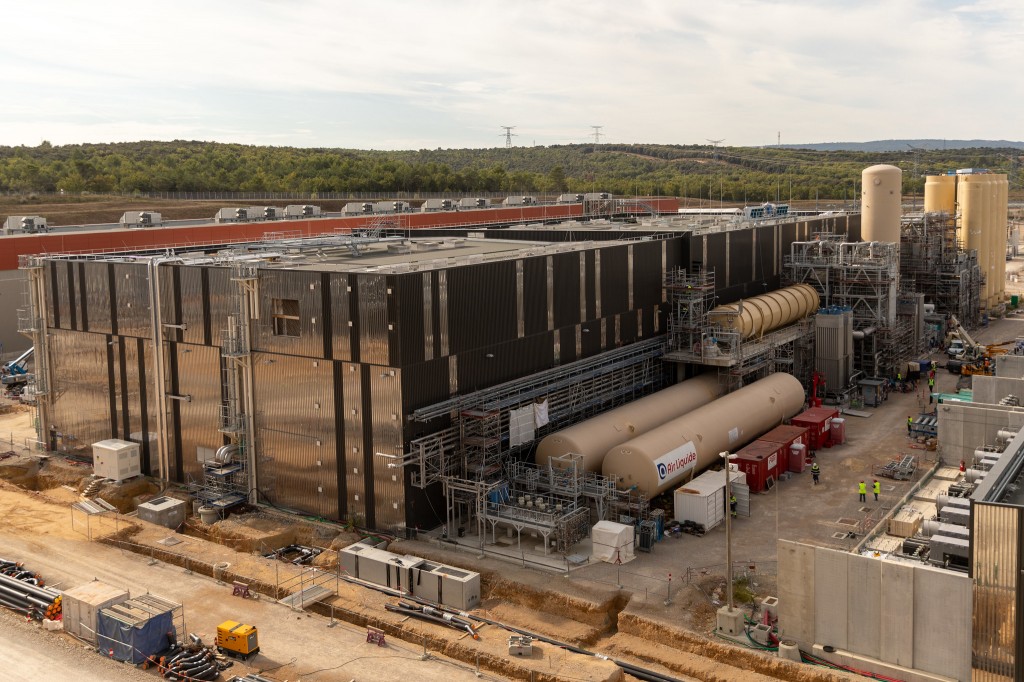
Cryoplant in October
2020-10-09 - The ITER cryoplant comprises 5,400 m² of covered buildings plus a large exterior area for the storage of helium and nitrogen. An overhead bridge (not yet constructed) will connect the cryoplant to the Tokamak Complex. © Les Nouveaux Médias/SNC ENGAGE
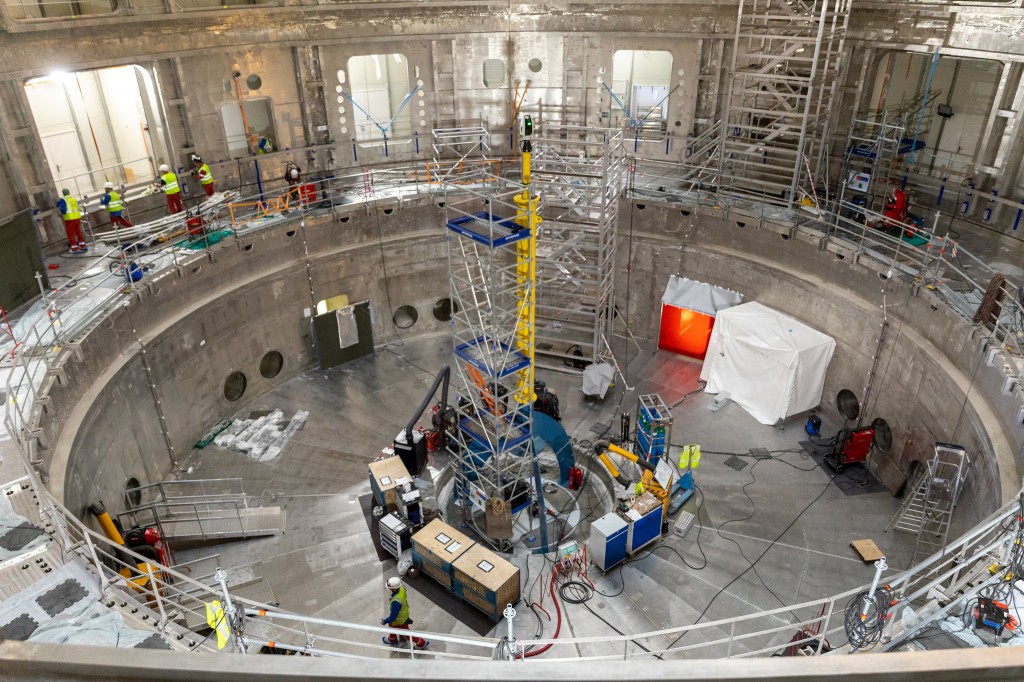
Walking inside the machine
2020-10-09 - All is silver steel at the bottom of the Tokamak pit in October 2020. © Les Nouveaux Médias/SNC ENGAGE
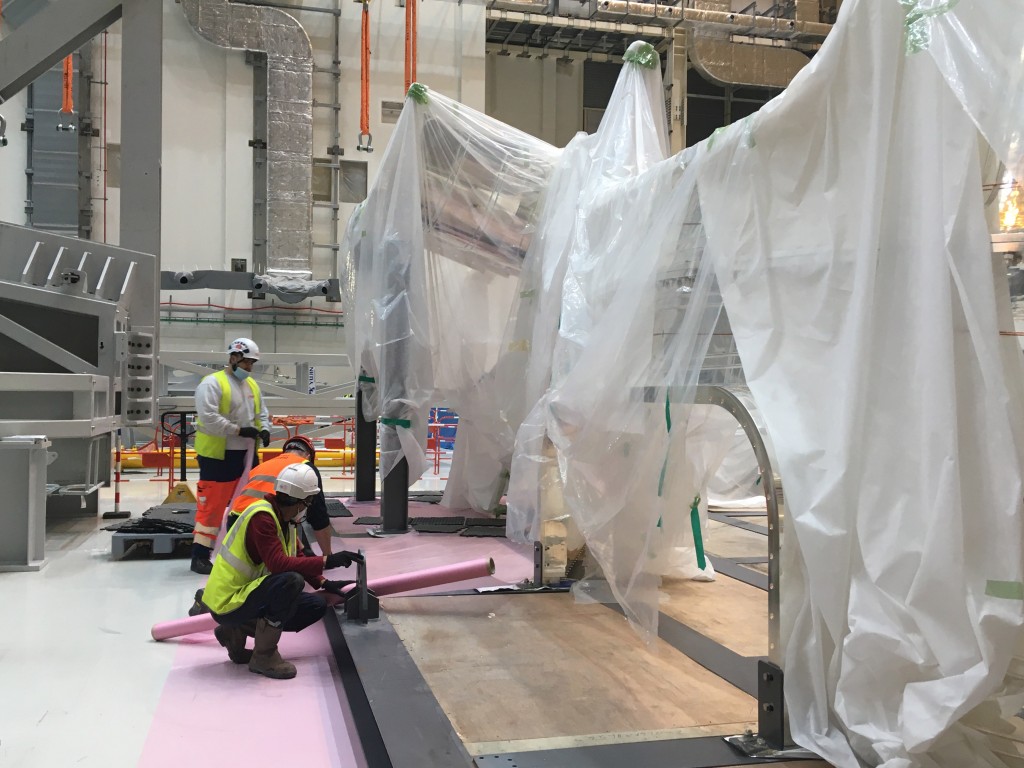
Creating a clean area
2020-10-07 - The thermal shield panels must be kept as clean as possible prior to their installation on the sector sub-assembly tools. Once the clear area is established and the component uncovered, assembly workers will only approach with gowns, hair covers, shoe covers, etc.

A big job
2020-10-07 - It will take several months to weld the cryostat upper cylinder to the cryostat base. Work started in October.
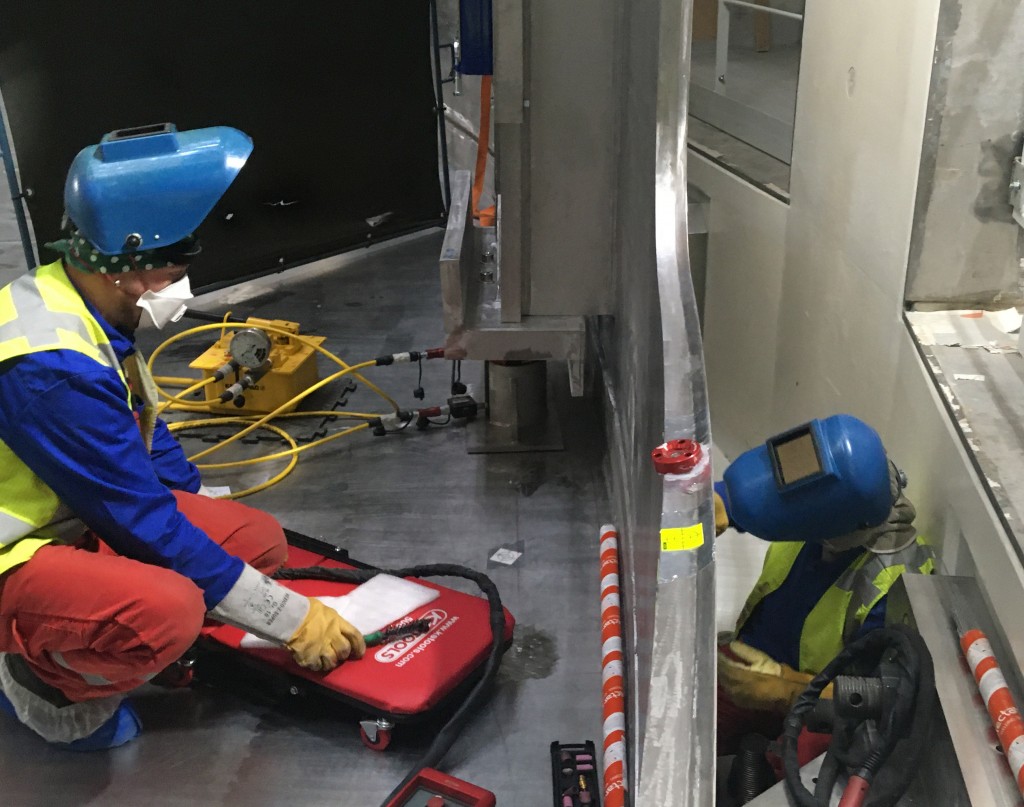
Two-sided welding
2020-10-07 - Technicians from MAN Energy Solutions (contractor to Larsen & Toubro, the enterprise chosen by the Indian Domestic Agency to manufacture the cryostat) work by pair on the in-pit welding of the cryostat.
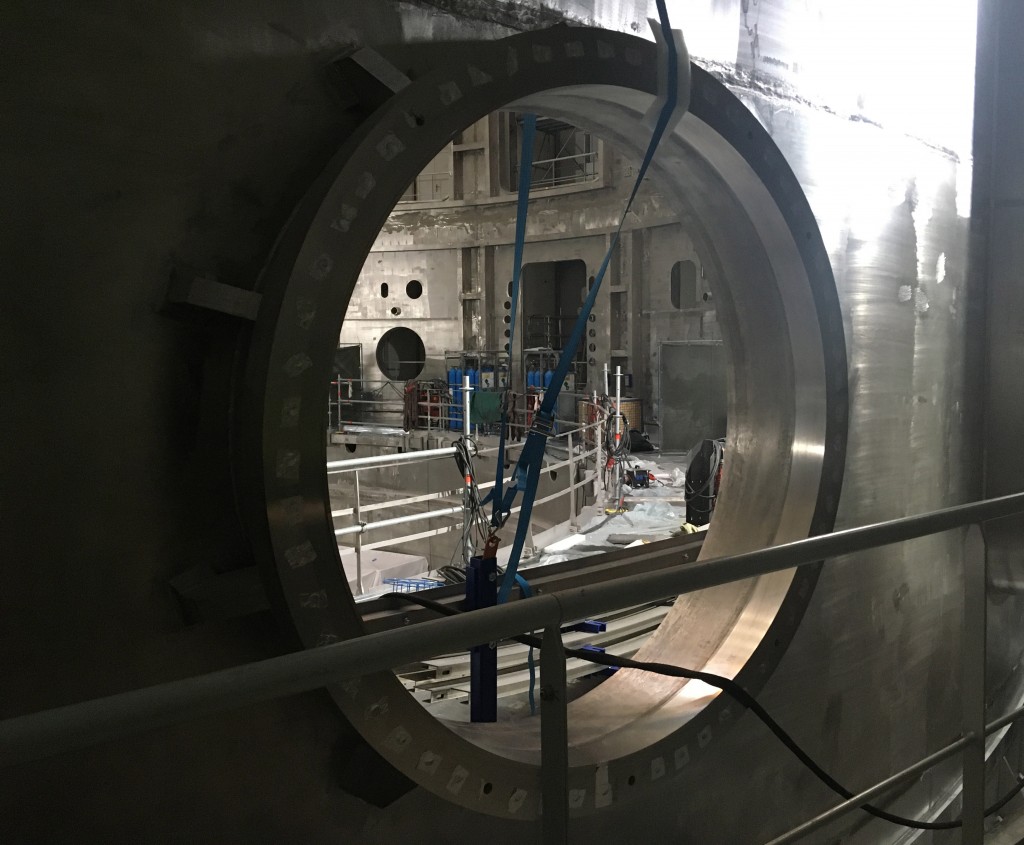
Peeking in
2020-10-07 - Looking through a penetration in the cryostat lower cylinder into the machine assembly area.
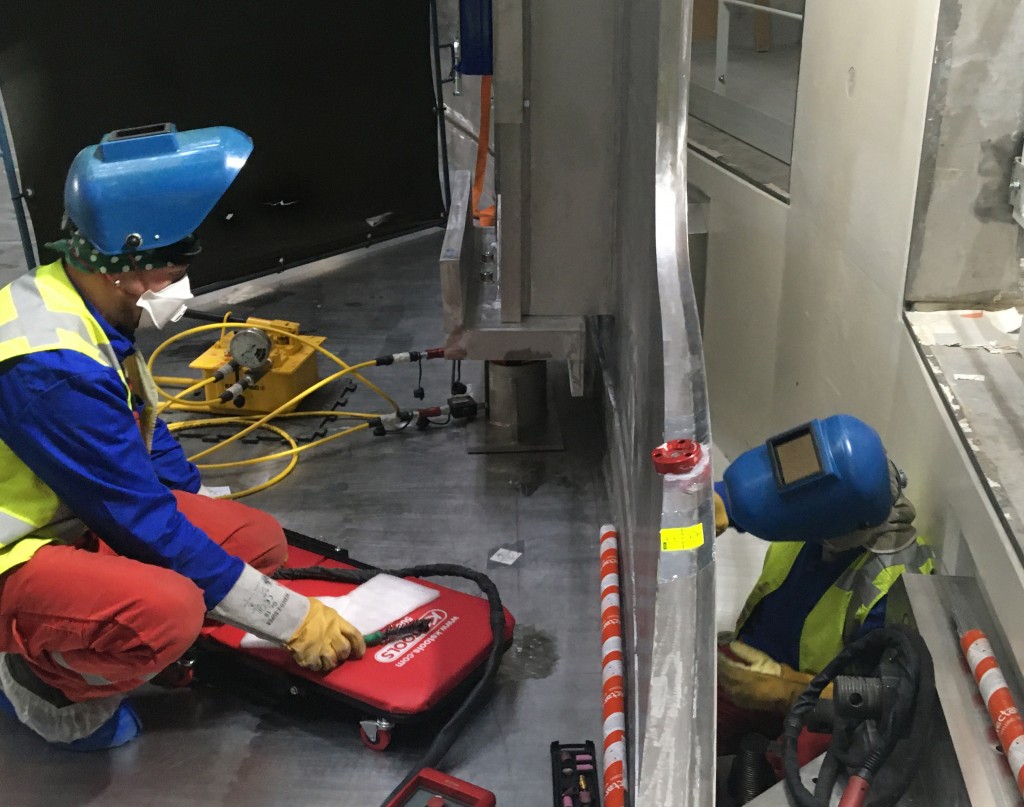
Two-sided welding
2020-10-07 - Technicians from MAN Energy Solutions (contractor to Larsen & Toubro, the enterprise chosen by the Indian Domestic Agency to manufacture the cryostat) work by pair on the in-pit welding of the cryostat.

Cryostat welding has begun
2020-10-07 - Deep in the Tokamak pit, welders working for the Indian Domestic Agency have begun root passes in the welding of the cryostat lower cylinder to the cryostat base.

Measuring the current
2020-10-05 - Arranged in three sets, there are 39 of these "current transformers" in the one-hectare Reactive Power Compensators Area (A39). Despite their name, they can be described as sensors that monitor the variations of the current.
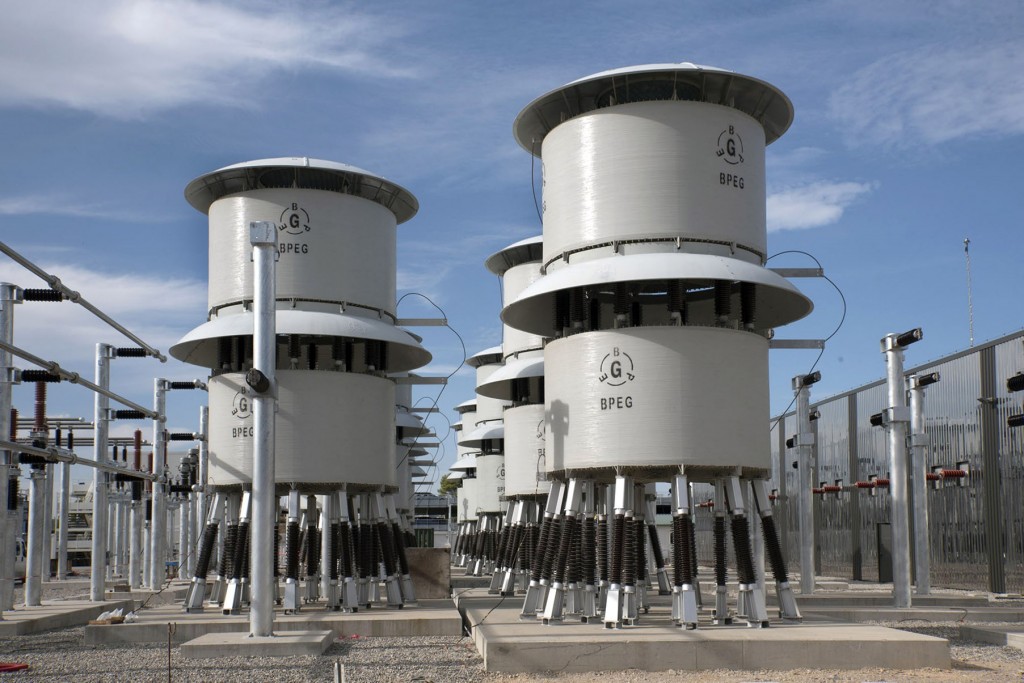
Towers
2020-10-04 - These 8-metre-tall tower-like structures are thyristor-controlled reactors. Directly connected to the thyristors inside the Reactive Power Control Building to the right, their function is to smooth the sine wave of the AC current, filtering out distortions.

Managing AC current
2020-10-04 - What can be contained in a medium-size building in a steelworks or other heavy industrial facility requires a one-hectare yard at ITER. Adjacent to the Reactive Power Control Building (background), the reactive power compensators area accommodates reactors, capacitors, resistors and sensors that aim to smooth the flow of AC current both inside the ITER installation and in the immediate vicinity.

Thyristor alley
2020-10-04 - Nine thyristors (3 metres tall and weighing over 2 tonnes each) are hosted inside the Reactive Power Control Building on the ITER site. Thyristors are power electronic devices that act like switches. ITER Organization contractors Consortium Fincantieri SI and SAET have now finalized 80% of the installation.

A new feeder element
2020-10-01 - A feeder element newly arrived from China is stored on site prior to installation. (Magnet feeders carry electricity and cryogens to the superconducting magnets.)
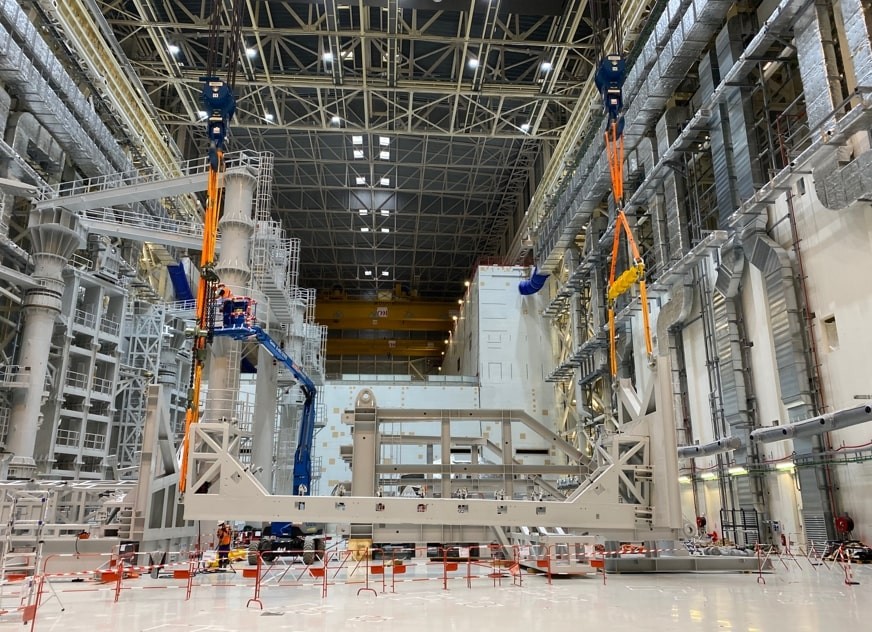
Tool in testing
2020-10-01 - Soon, three types of components will be lifted into the first Sector Sub-Assembly tools in the Assembly Hall: a vacuum vessel sector, a pair of toroidal field coils, and inboard and outboard thermal shield panels. This tool, in testing now, will lift and "upend" the inboard thermal shield panel.
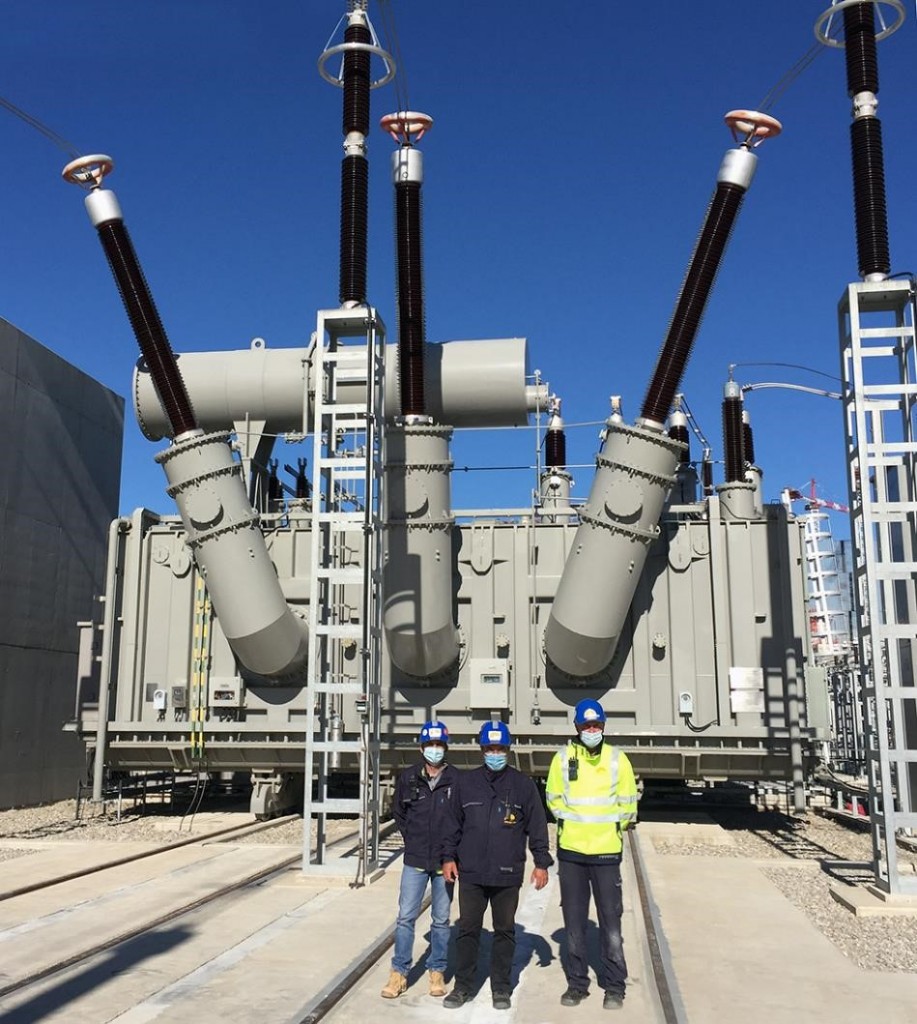
ITER fully connected
2020-09-30 - Three 400 kV transformers for the pulsed power electrical network (PPEN) have been energized. Going forward, the French operator RTE considers ITER as fully connected and operational, with all seven ITER connections at the 400kV level in operation. (There are three transformers for the pulsed power network and four for the steady state electrical network.)

A smaller upending tool
2020-09-29 - One massive upending tool (background, lying flat) will raise ITER's vacuum vessel sectors and toroidal field coils to vertical; two others will do the same for the lighter inner and outboard sectors of vacuum vessel thermal shielding. This outboard sector upending tool has just been detached from the giant SSAT tools where it was tested.
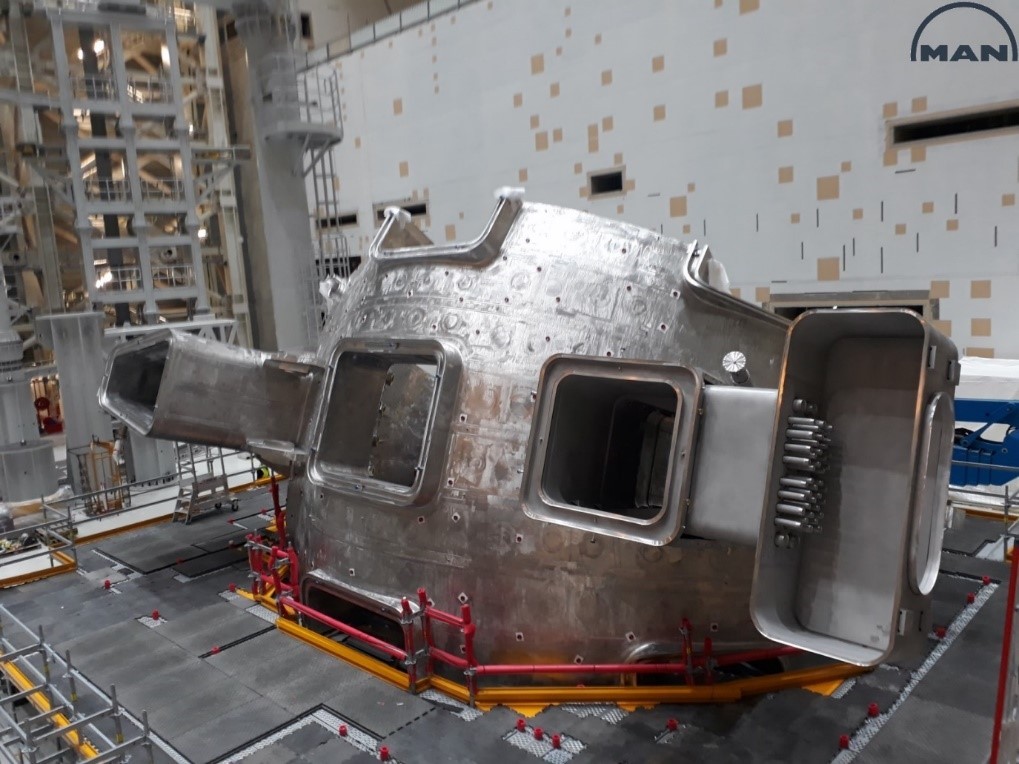
Metrology on vacuum vessel #6
2020-09-28 - The first vacuum vessel sector has passed all site acceptance tests and is now being measured from every angle by the metrology teams. (Look closely to see the metrology targets.)
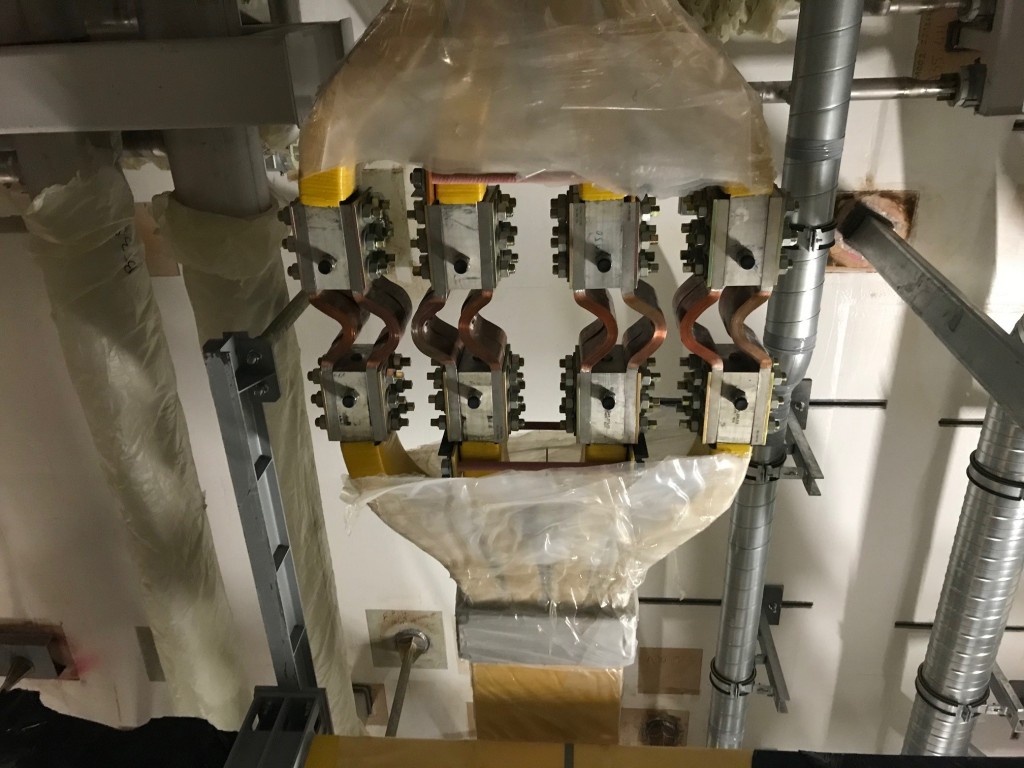
Connecting busbars
2020-09-26 - Near the ceiling of a Tokamak Building gallery, contractors have connected two busbar lengths.

New segments arrive
2020-09-24 - The first five segments of the cryostat top lid arrived from India this week.
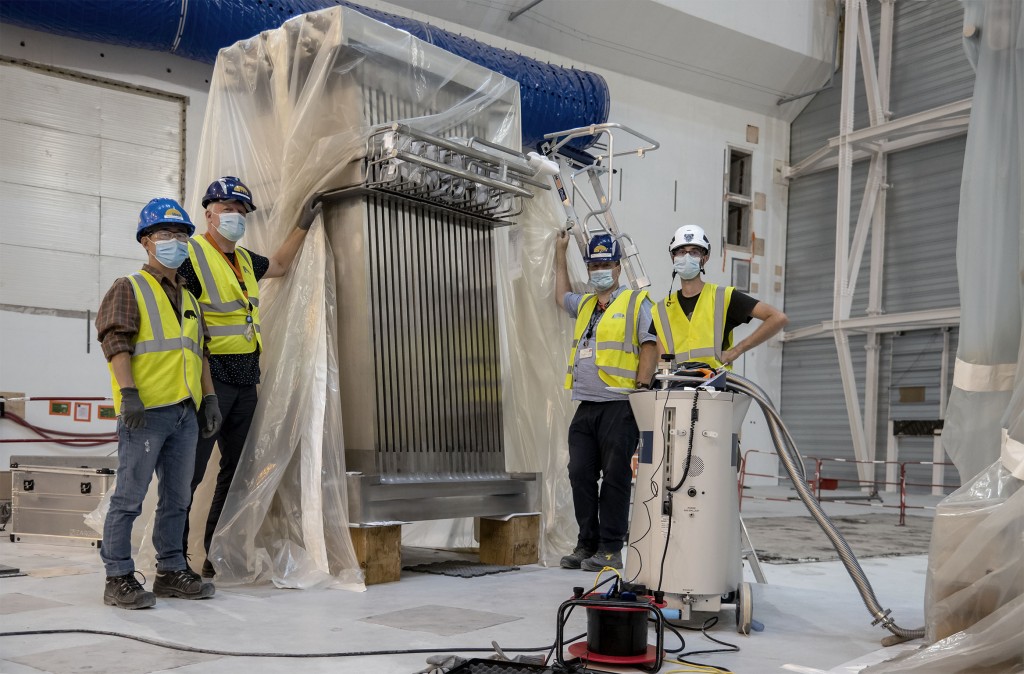
Gravity supports for the toroidal field coils
2020-09-24 - Eighteen of these 2.65-metre-tall gravity supports will be bolted to the cryostat base to support the outer edge of the toroidal field coils. The full gravity load of the ITER magnets (10,000 tonnes) will be transferred to the cryostat through these marvels of engineering delivered by China. They are next in line for delivery to the Tokamak pit.

The work to come
2020-09-24 - The top lid will be assembled from 12 triangular segments and a central disk.

A welding bubble
2020-09-24 - This worker is welding a steel pipe to its concrete passageway. One of the machine's magnet feeders will pass through this tunnel on its way to supply magnets with power and liquid helium.

Machining workshop installed on site
2020-09-22 - The new workshop will be operated by the DYNAMIC consortium, which was formed to execute one of ITER's two main machine assembly contracts, TAC2 (Tokamak Assembly Contract 2). The workshop will be a space for repairs and retrofitting, and boasts two milling machines, a large CNC (Computer Numeric Control) machine, and spaces for welding and metrology.

A new workshop
2020-09-22 - This new workshop will be operated by the DYNAMIC consortium, which was formed to execute one of ITER's two main machine assembly contracts, TAC2 (Tokamak Assembly Contract 2). The workshop will be a space for repairs and retrofitting, and boasts two milling machines, a large CNC (Computer Numeric Control) machine, and spaces for welding and metrology.

Secondary cooling circuit
2020-09-21 - The chiller plant in the Site Services Building has been turned over to the ITER Science, Controls & Operation Department (SCOD) for commissioning. Now, a commissioning team led by SCOD will start to energize the equipment, fill the pipes, and test the circuits and control interfaces of this auxiliary plant, which is one element of the chilled water system.
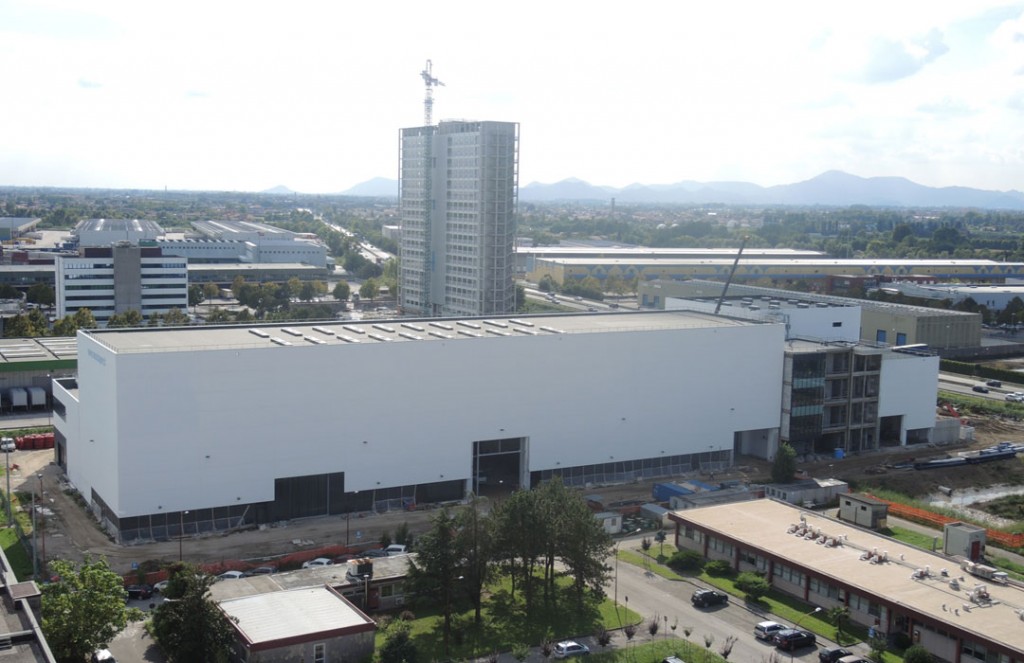
EUROfusion becomes part of the team
2020-09-18 - Under the terms of a Cooperation Agreement signed with the ITER Organization and Consorzio RFX, the European Consortium for the Development of Fusion Energy (EUROfusion) can provide select experts from European labs—up to 14 professionals per year (PPY)—to work on the neutral beam project at ITER's facility in Padua (and another 6 PPY to support the development of the half-size negative ion source ELISE in Garching). The ITER team welcomes EUROfusion's "strong commitment" and the "support of our European colleagues and experts in developing and operating the ITER facility."
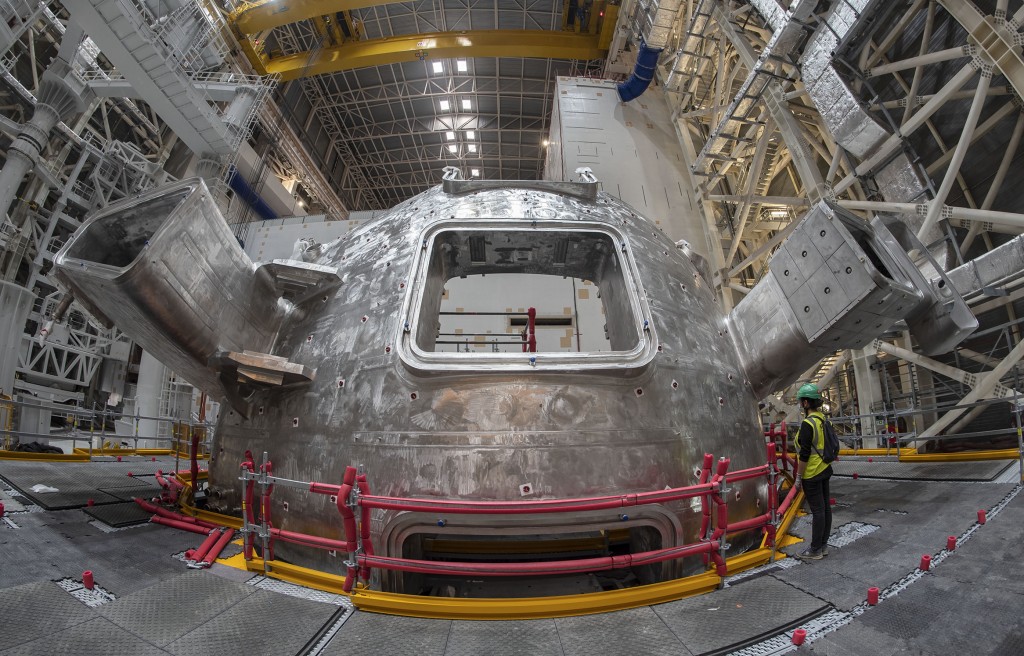
Shrek?
2020-09-17 - With the distortions of a fisheye lens, this vacuum vessel sector reminds us of Shrek—the (all-green) cartoon character with ears that look a lot like these port extensions.
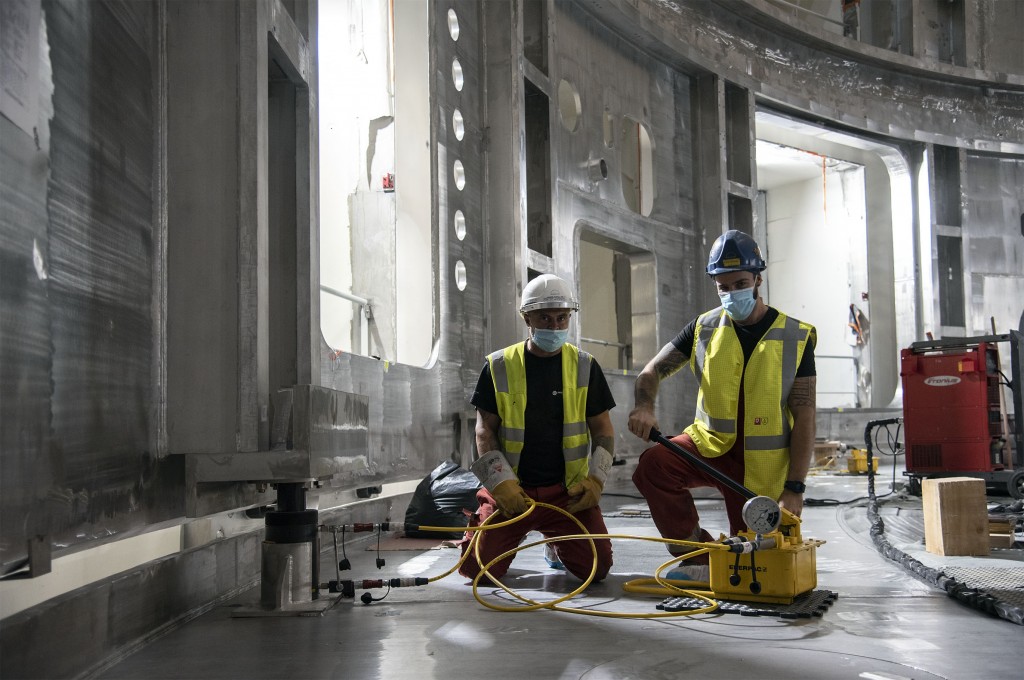
On the base pedestal
2020-09-17 - The cryostat lower cylinder is still on hydraulic jacks as final alignment activities are carried out and the first tack welds are performed.
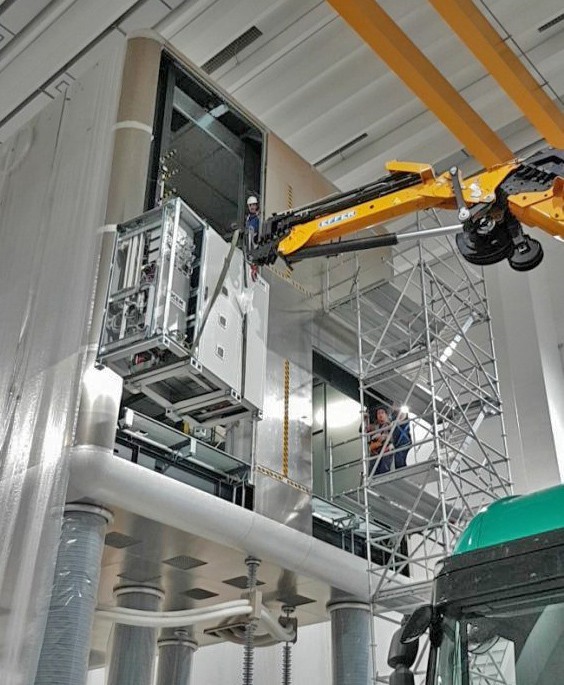
Site acceptance tests on the injector's power supplies
2020-09-15 - The European Domestic Agency has carried out successful site acceptance tests on power supply equipment installed overhead in the spectacular high voltage deck. The eight power supplies and auxiliary equipment for MITICA's ISEPS (ion source and extraction power supply) were successfully tested in September.

Forklifts and pulleys
2020-09-10 - Moving and adjusting the beams into position is a delicate operation that requires the coordinated movements of forklifts and pulley systems before they can be manually bolted to their supports.

Assembly underway
2020-09-10 - Now that ITER assembly has started, a clean corridor is the obligatory passageway into the ITER Assembly Hall leading to a check-in desk and worker changing rooms. Follow all assembly activity on the ITER website at ASSEMBLY (https://www.iter.org/construction/assembly).

Overhead
2020-09-10 - In the Diagnostics Building, teams are bolting the busbars to supports anchored in the ceiling. The environment is already crowded with cable trays and all sorts of piping and HVAC ducts.

Precision work
2020-09-10 - Once bolted to their supports, the busbar lengths must be connected to one another and to cooling water collectors. Hose connections must be installed before the whole system can be tested and commissioned.
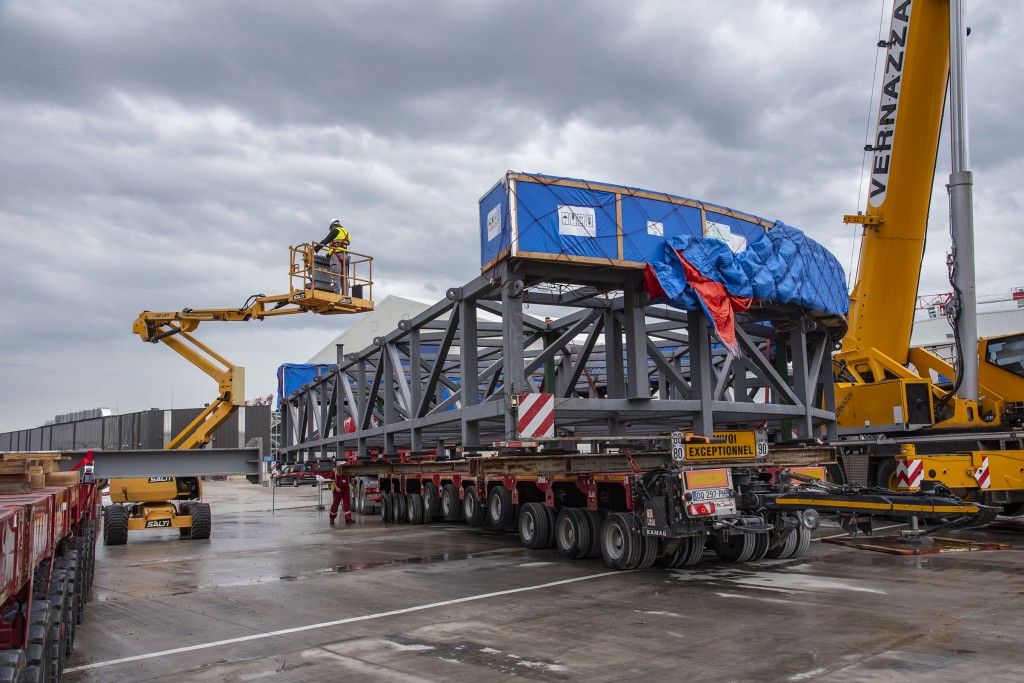
Magnet feeder elements arriving
2020-09-10 - This giant semi-circular component is destined for installation under the machine. It is part of a magnet feeder—the components that deliver cryogens and electrical power to the superconducting magnets.

Weighty components
2020-09-10 - Individual busbar segments are sometimes very long (up to 12 metres) and quite heavy, ranging from 2 to 4 tonnes in weight.
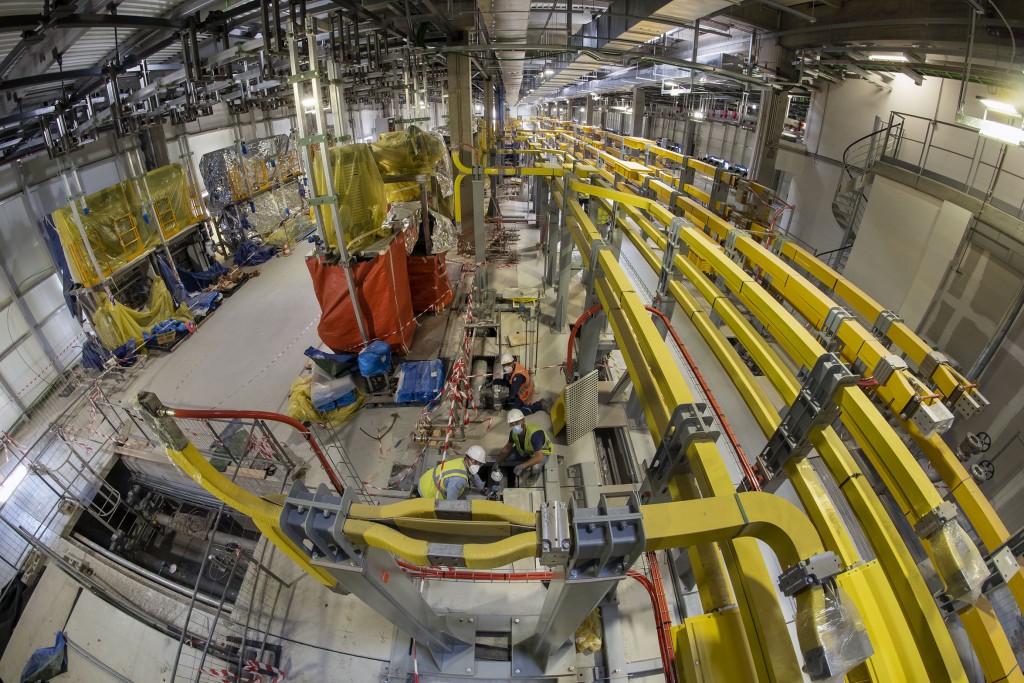
"Power cords" thicker than train rails
2020-09-09 - Originating in the Magnet Power Conversion buildings (as seen here), busbars will travel over bridges to the Tokamak Complex to deliver power to the superconducting magnets. These train-rail-sized bars can carry current 7,000 times more intense than a heavy-duty electrical cable.
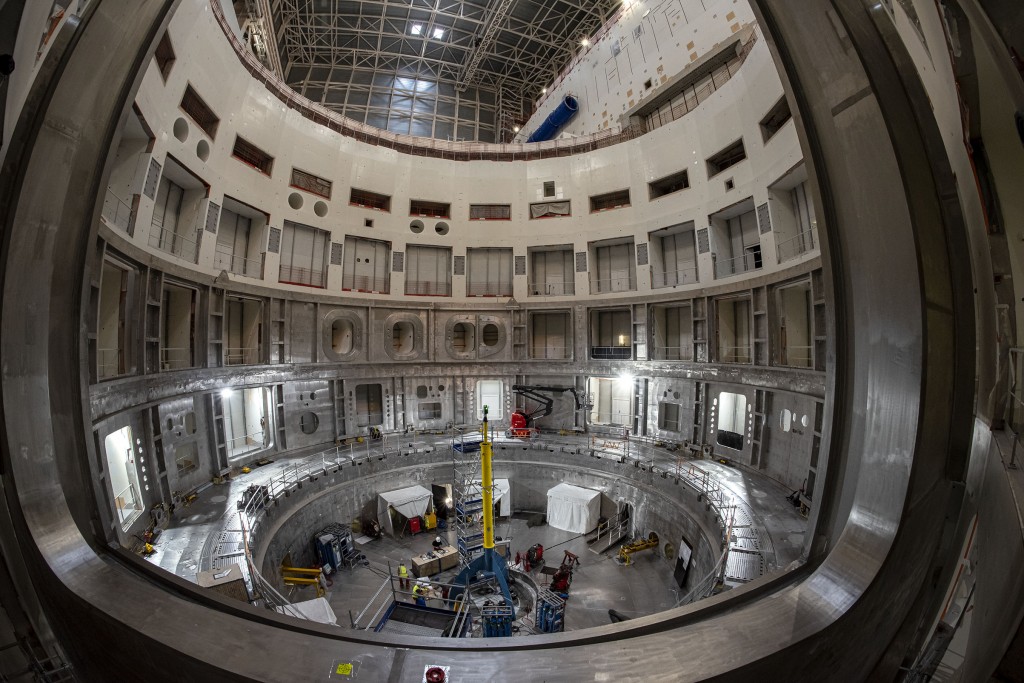
Joining two components in the pit
2020-09-09 - The assembly teams in the Tokamak pit are preparing for the root welding of the cryostat lower cylinder to the pedestal of the cryostat base. Mechanical cleaning of the bevel has been completed; next, the cylinder will be locked to the base through bridge piece welding and the alignment tool will be removed.

Counting on metrology
2020-09-09 - The cryostat lower cylinder is now positioned in the Tokamak pit above the cryostat base and the remaining gap is less than 6 millimetres. Before welding activities begin, the exact position of the lower cylinder is recorded through metrology.
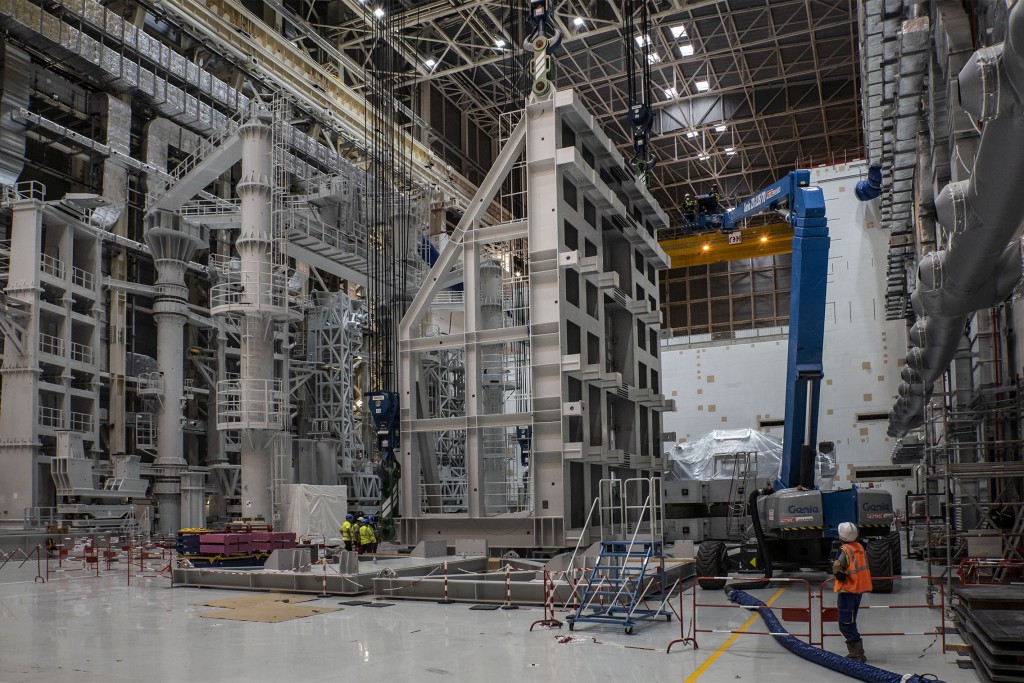
Warming up
2020-09-09 - This large tool—the "upending tool"—will lift some of ITER's heaviest components to vertical so that they can be installed in the vacuum vessel sub-assembly tools (left). Warm-up tests are underway.

That's 1,600 tonnes of steel
2020-09-09 - The two major Tokamak components already installed in the pit—the cryostat base and lower cylinder—represent 1,600 tonnes of steel. Welding operations to join the two pieces begin this week.

PF6 enters the cryogenic chamber
2020-09-08 - PF6 is now in its cryogenic chamber, as the team prepares for thermal testing at 80 K. Poloidal field coil #6 (PF6) was fabricated by the ASIPP Institute in China under contract with the European Domestic Agency, and then sent to Europe's on-site winding facility for testing.
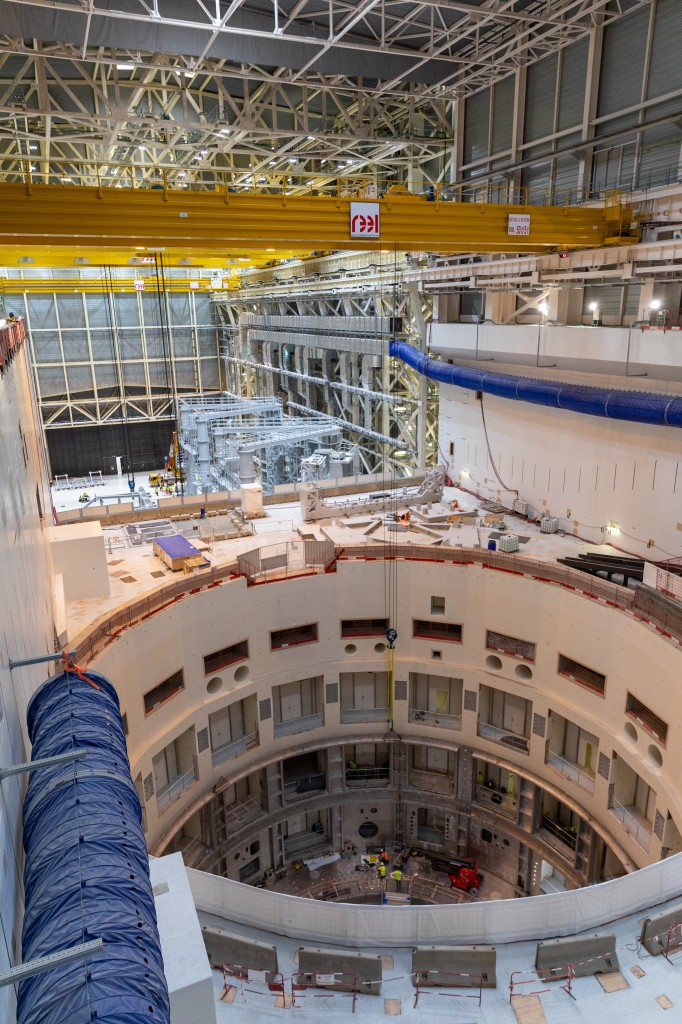
The assembly theatre
2020-09-04 - About 150 metres separates the double doors of the Assembly Hall, which open to receive components, from the Tokamak pit. All components will spend some time in the Assembly Hall for unpacking, measurement and test activities before the final lift into place. © Les Nouveaux Médias/SNC ENGAGE
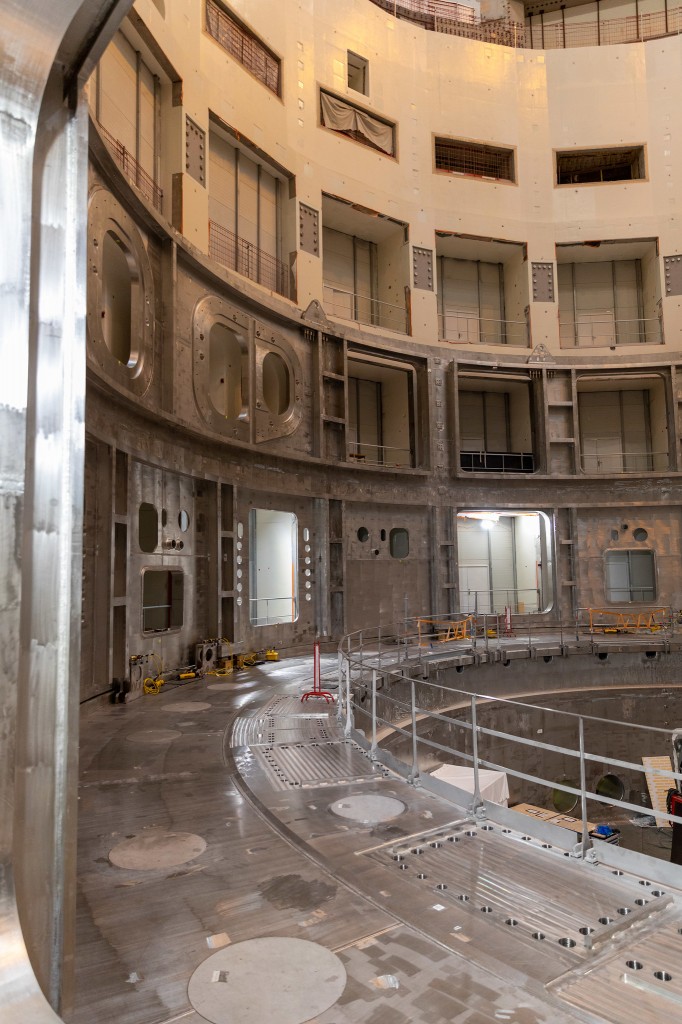
Components in the pit
2020-09-04 - Looking closely, we can distinguish the metal of the cryostat lower cylinder from the painted concrete Tokamak pit. © Les Nouveaux Médias/SNC ENGAGE
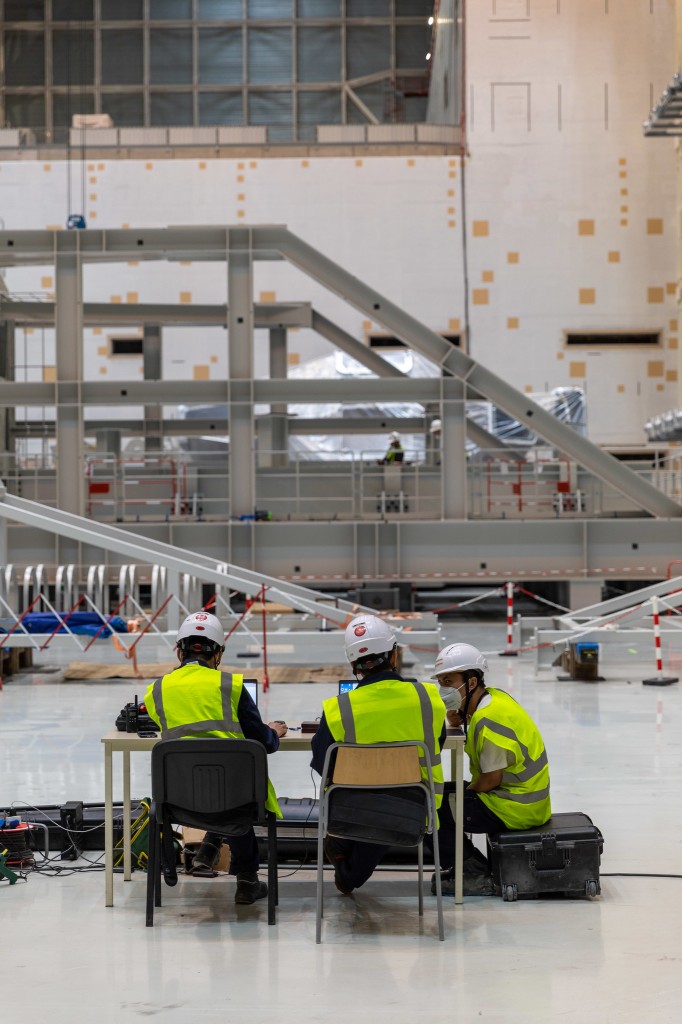
Concentrating
2020-09-04 - Contractors prepare the metrics for another round of upending tool lift tests. © Les Nouveaux Médias/SNC ENGAGE
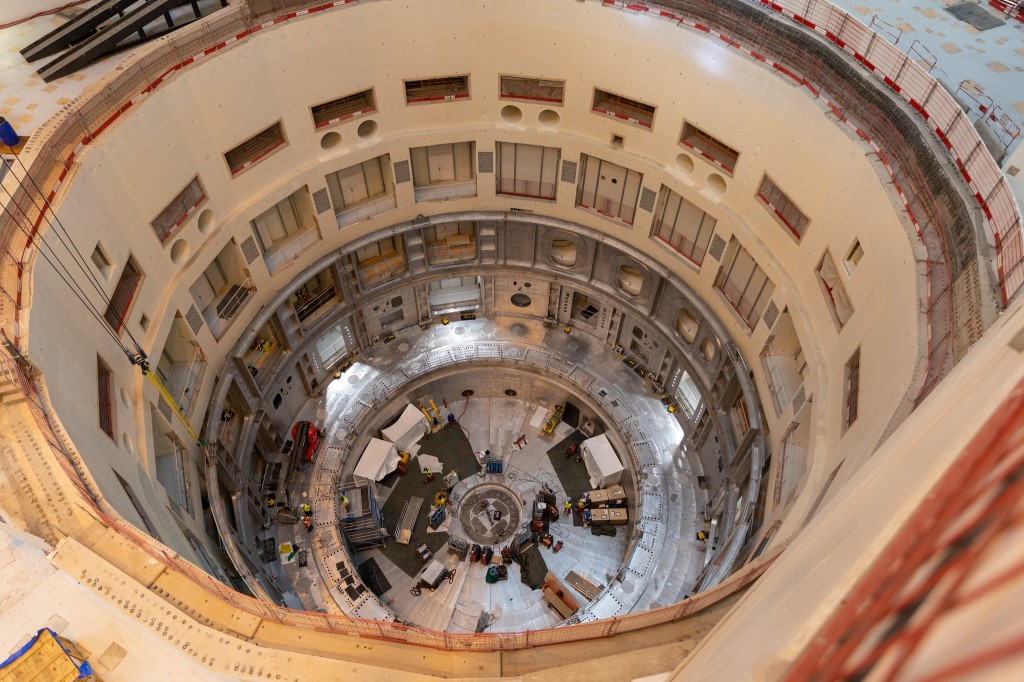
In-pit welding to start
2020-09-04 - Two cryostat sections are in place but not yet welded. Cryostat welding begins later this month. © Les Nouveaux Médias/SNC ENGAGE

Over the platform
2020-09-04 - From the roof of the Tokamak Building, looking in the northeast direction towards the new beryllium storage facility (also called the Tokamak Assembly Preparatory Building). © Les Nouveaux Médias/SNC ENGAGE

All about busbars
2020-09-04 - The interior of the Magnet Power Conversion buildings resembles a busbar forest. Busbar lengths are now being installed in the Tokamak Complex; in the year ahead, a bridge between the two buildings will be realized and the different lengths connected.
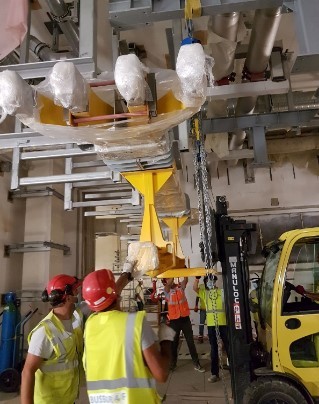
First busbars in Tokamak Complex
2020-09-03 - The first magnet busbars are being installed among cable trays and other equipment on the ceiling of this Tokamak Complex gallery. Each length weighs between 2 and 4 tonnes.

Room for manoeuvre
2020-09-03 - Moving a busbar into place in the Diagnostics Building. Equipment installation is underway in the higher areas first (the ceiling) in carefully coordinated sequences so that each piece fits without having to alter what is already installed.
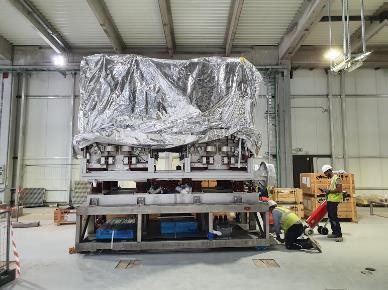
Converter arrives from Korea
2020-09-02 - In one of the Magnet Power Conversion buildings, a converter bridge has arrived from Korea. The converter changes the power from AC to DC before being supplied to the central solenoid.
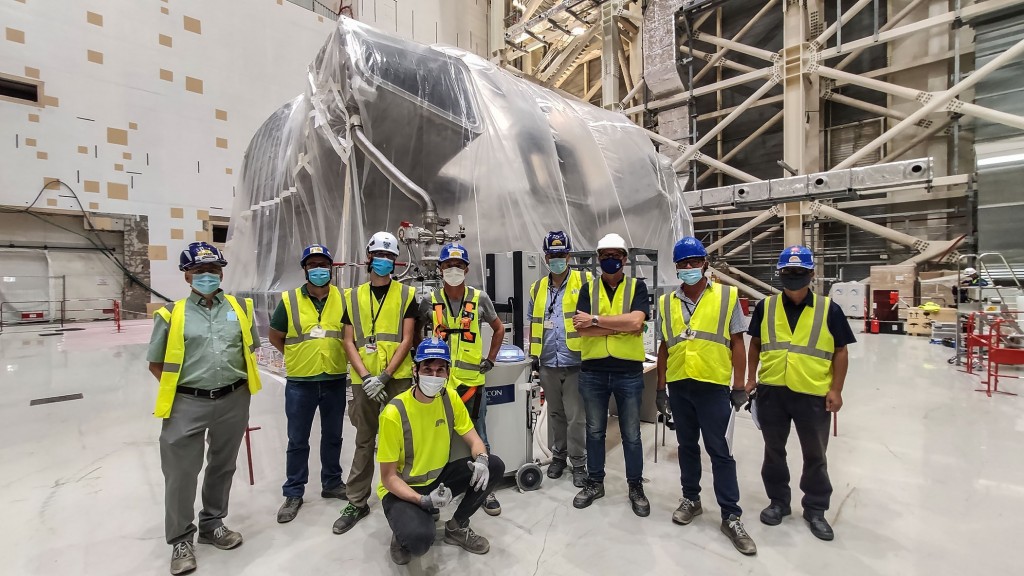
Sector #6 is leak tight
2020-09-02 - The first ITER vacuum vessel sector has passed a helium leak test on site with flying colours, confirmed to be leak tight to two orders of magnitude better than acceptance criteria.

Final position
2020-08-31 - The lower cylinder was first docked on an alignment device on 31 August; on 2 September the final alignment was performed within the required tolerances. The Indian Domestic Agency and its contractor MAN Energy Solutions will begin welding the cryostat lower cylinder to the cryostat base on 7 September.
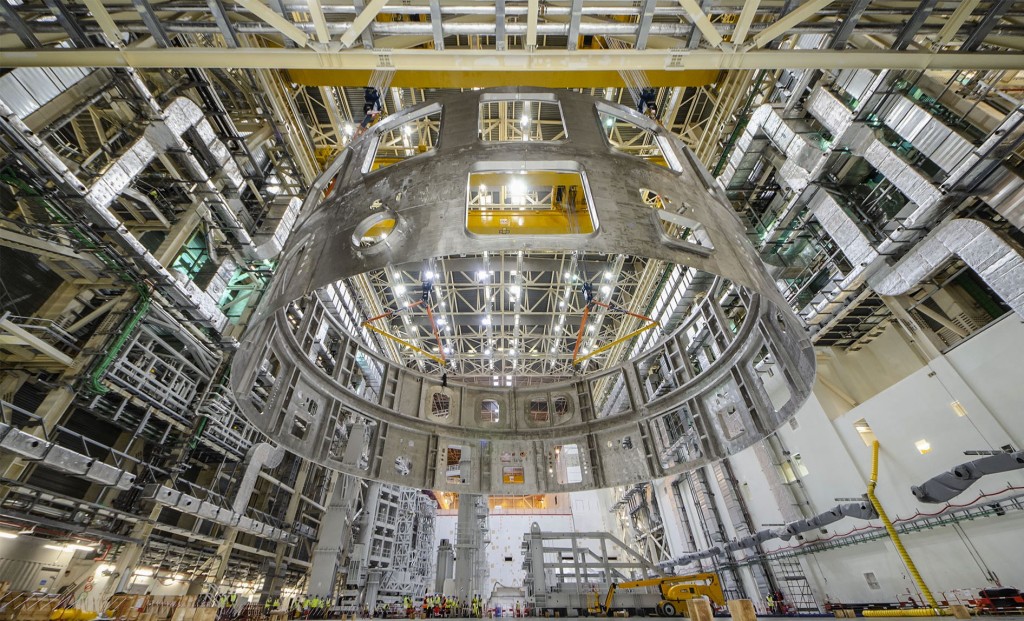
Lift off
2020-08-31 - The 375-tonne component is lifted by overhead crane and delivered to the Tokamak pit on the opposite side of the building.

Up and over
2020-08-31 - The massive component spent more than four hours suspended from the overhead cranes as it was lifted, transferred across the Assembly Hall, and lowered. Here, it clears the tallest assembly tools by just a few inches.
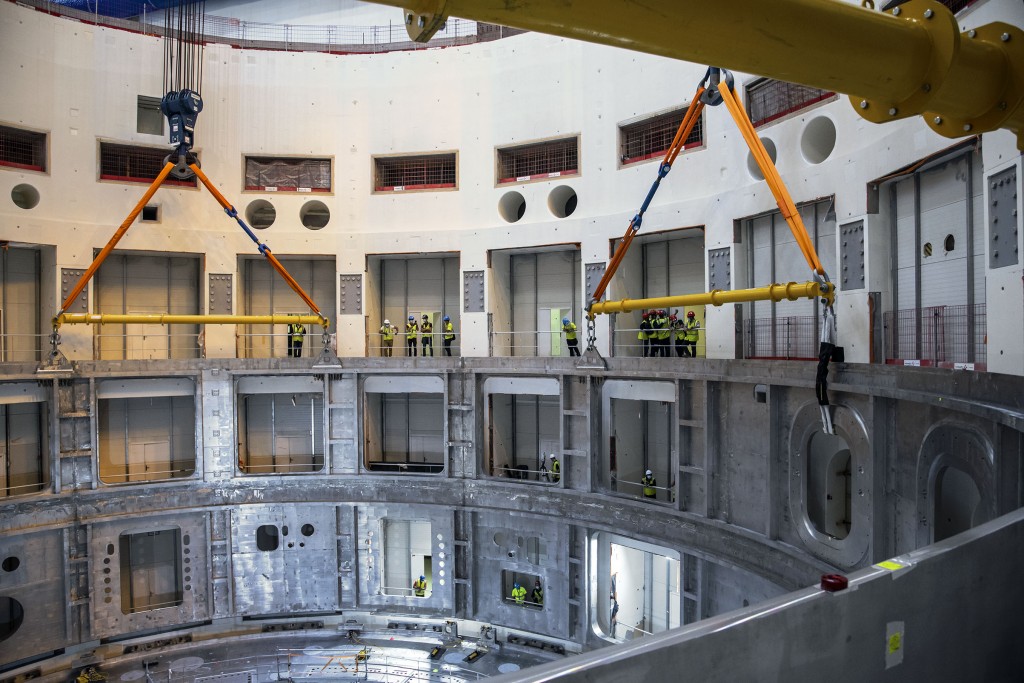
Home at last
2020-08-31 - And finally, the cryostat lower cylinder hovers just a few centimetres above the cryostat base. Teams will carry out some final measurements before settling it onto temporary supports.

Lower cylinder is aloft
2020-08-31 - This 375-tonne steel cylinder is the second section of the cryostat to be installed in the Tokamak pit. The operation, which was carried out on 31 August, went off without a hitch.

Exacting tolerances
2020-08-31 - Not only does the component have to clear the tight tolerances that separate it from the walls as it descends, but its many openings (called penetrations) have to line up precisely with corresponding openings in the bioshield.
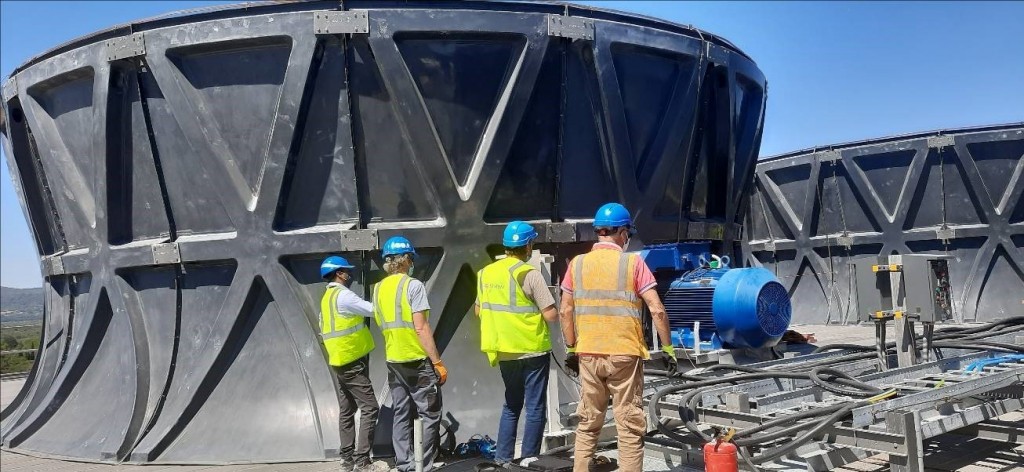
On the roof of the cooling tower building
2020-08-24 - Vibration testing is underway on the cooling towers.

Plenty of space
2020-08-22 - Just in time, the vacuum vessel sector that had recently been delivered from Korea was moved to the other side of the building, and its travel platform and casing were removed.

Full shop
2020-08-22 - The lower cylinder is just passing through. After approximately one week of preparation, metrology measurements, and trial lift tests, the 10-metre-tall lower cylinder will be lifted up and over the crowded shop floor of the Assembly Hall and lowered into the Tokamak pit.

Second cryostat section ready for insertion
2020-08-22 - The lower cylinder, which had been cocooned on the platform, is now ready for transfer into the Assembly Hall. After some light preparatory activities, it will be ready for assembly into the machine pit.

Into the airlock
2020-08-22 - The component first enters the Cleaning Facility, and the doors are shut behind it, before the rolling doors of the Assembly Hall are pulled back.
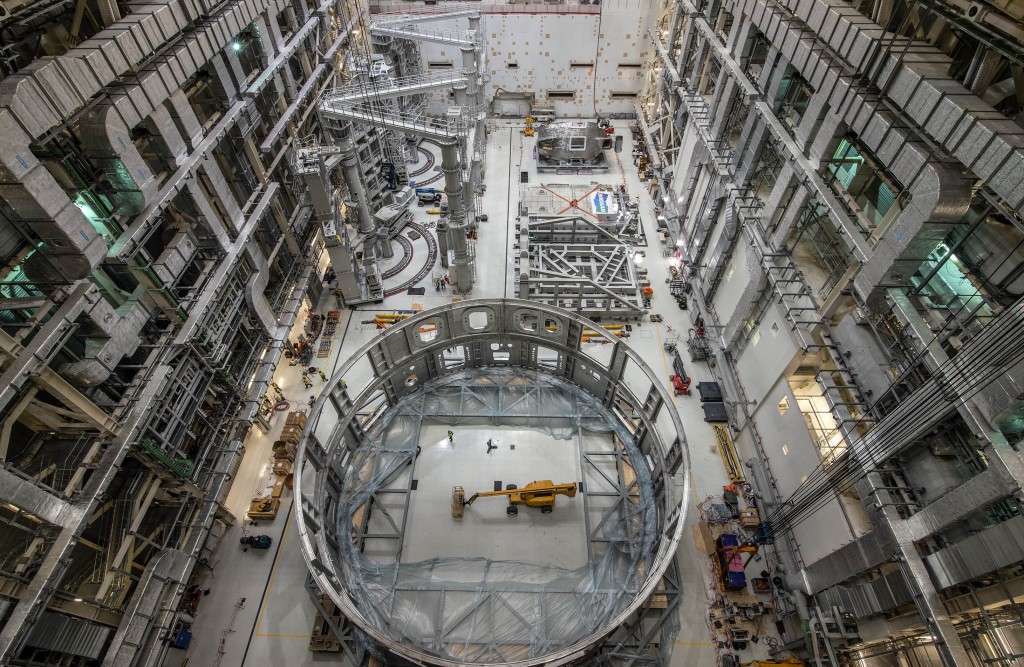
Successful transfer
2020-08-22 - On 22 August 2020, the lower cylinder travelled the short distance from the Cryostat Workshop to the Assembly Hall.
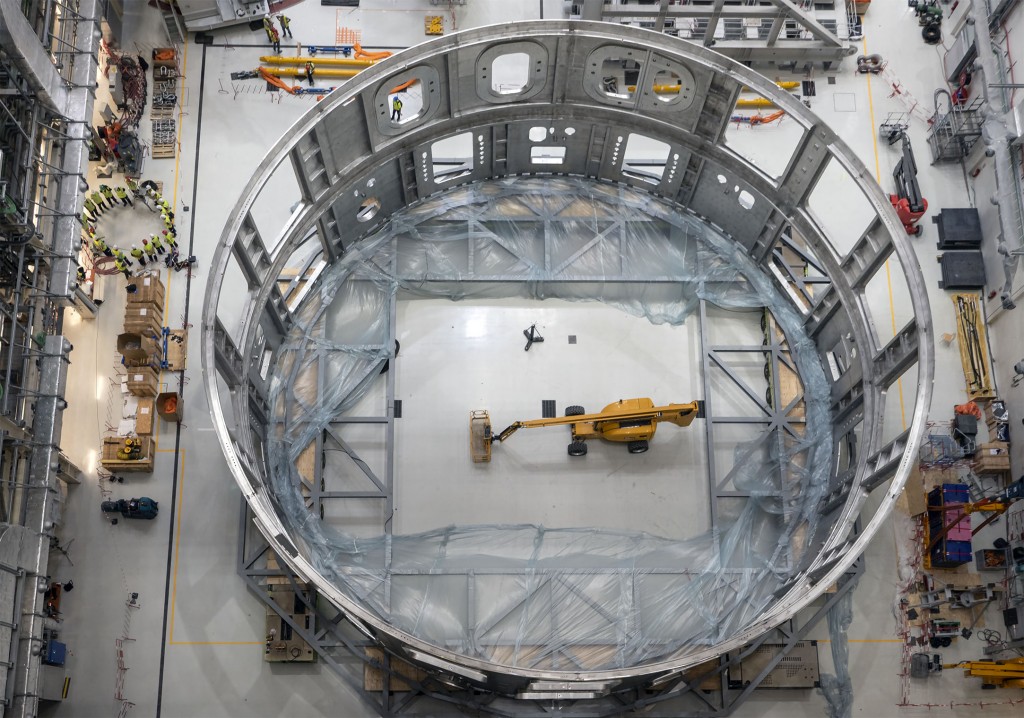
Lower cylinder
2020-08-22 - A new machine component is making a short pause in the Assembly Hall before it is inserted into the machine well: the cryostat lower cylinder. Ten metres tall, 30 metres in diameter, and 375 tonnes.

Cryostat lower cylinder: next up in line
2020-08-22 - The lightly wrapped cryostat lower cylinder—30 metres in diameter, 375 tonnes—is seen through the open doors of the Cryostat Workshop, right before its transfer into the Assembly Hall.

Transfer successful
2020-08-20 - On Friday 20 August, 490 tonnes (sector plus frame) were successfully lifted, transferred 40 metres, and redeposited on supports on the other side of the Assembly Hall.
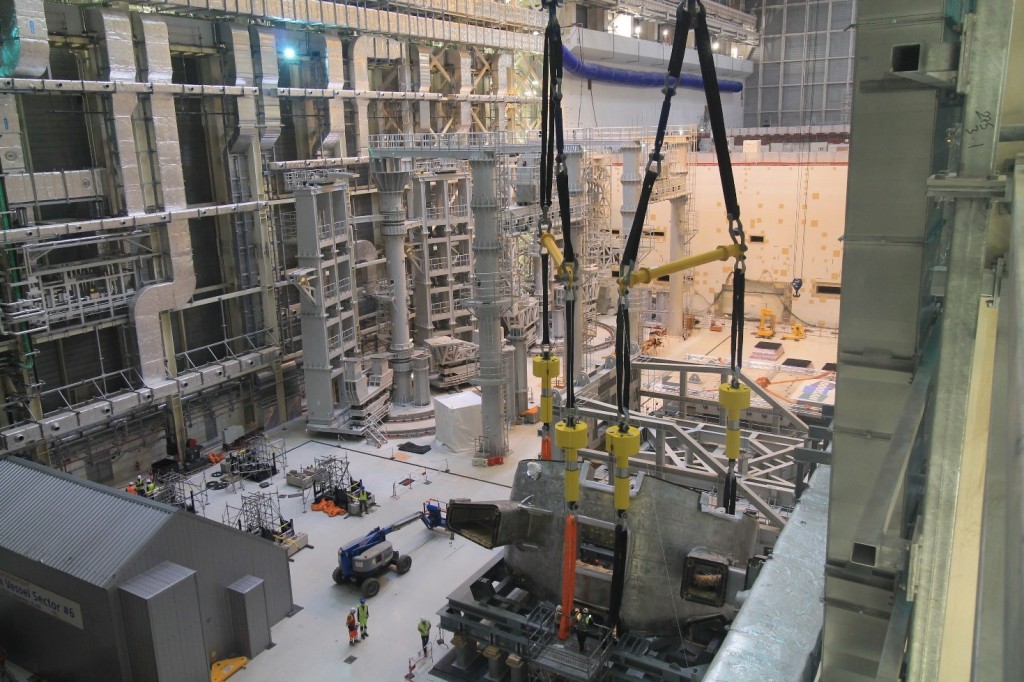
Leapfrog
2020-08-20 - The teams in the Assembly Hall are organizing the transfer of vacuum vessel sector #6 to a location on the other side of the building, across from the sector pre-assembly tools. Room must be made for the next large component expected to enter through the large double doors—the cryostat lower cylinder.

Making room
2020-08-20 - The component is now directly across from the sector sub-assembly tools (SSATs), where it will be pre-assembled with a pair of D-shaped magnet coils and thermal shield panels.
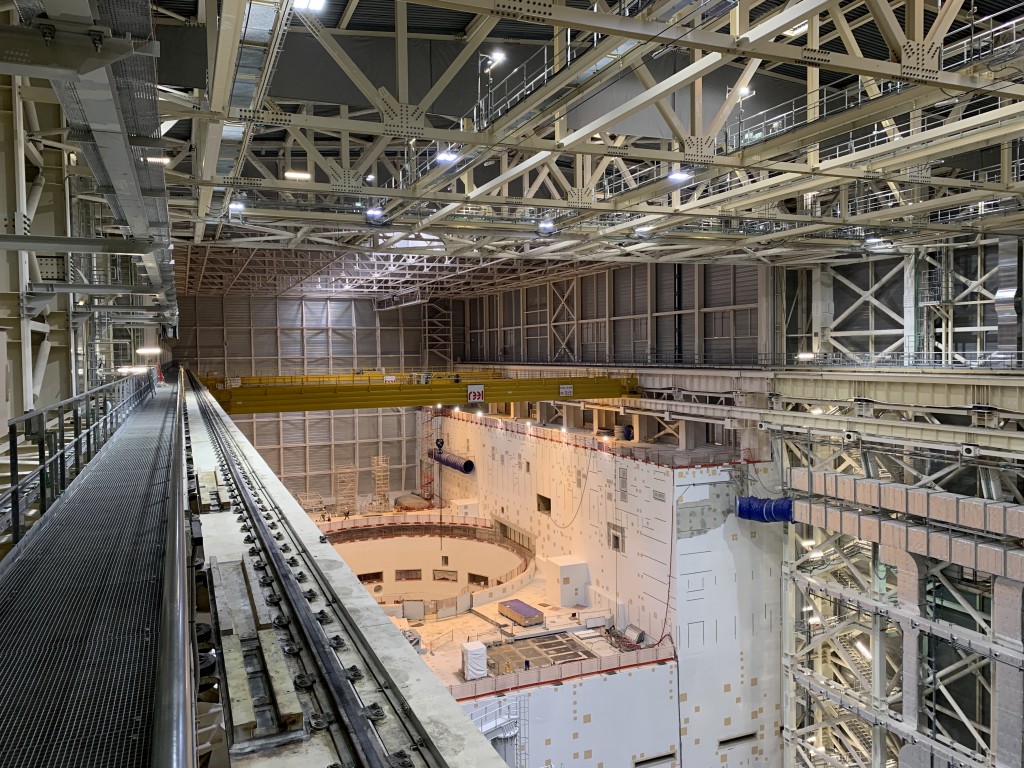
Next piece coming
2020-08-20 - From the rafters, a view of the machine assembly theatre. The first machine component, the cryostat base, has already been installed. The cryostat lower cylinder will be transferred into the Tokamak pit in early September.

Perfect fit
2020-08-19 - The gantry crane lowers the 400-tonne coil (PF6) into its cryogenic chamber. In addition to a cooldown to 77 K, the coil will be submitted to a pressure drop test, several leak tests (at cooldown and after warmup) and a 100A current test.
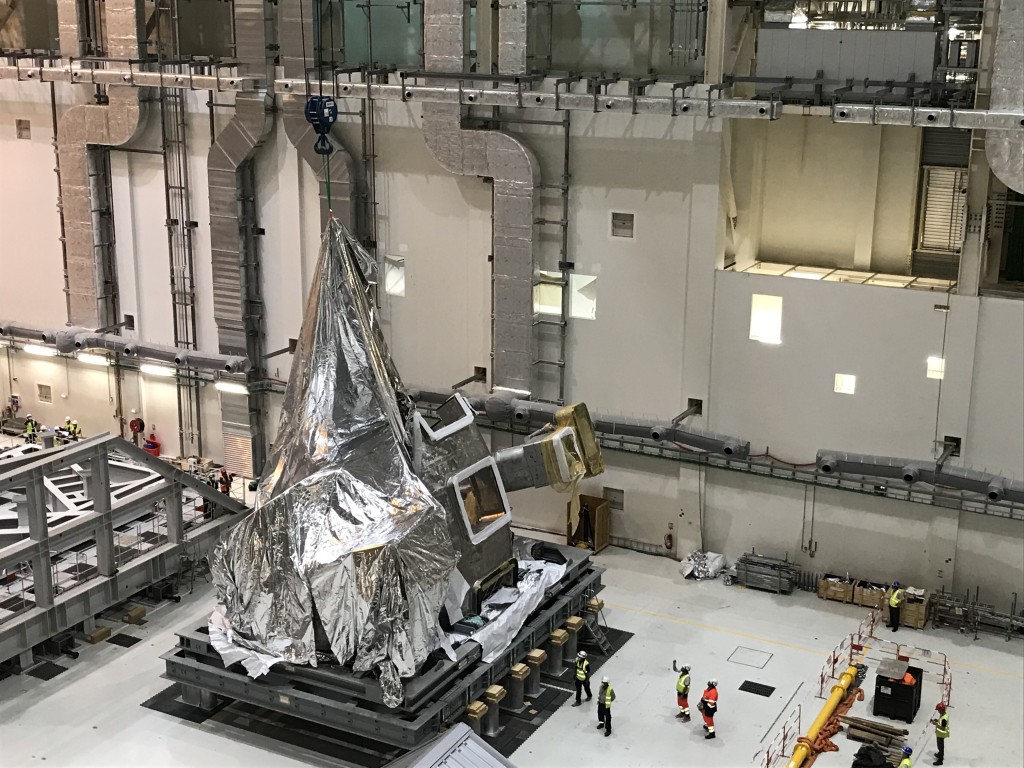
Then the other
2020-08-12 - This 440-tonne steel component travelled 10,000 km to reach ITER after it was finalized at Hyundai Heavy Industries in Korea.
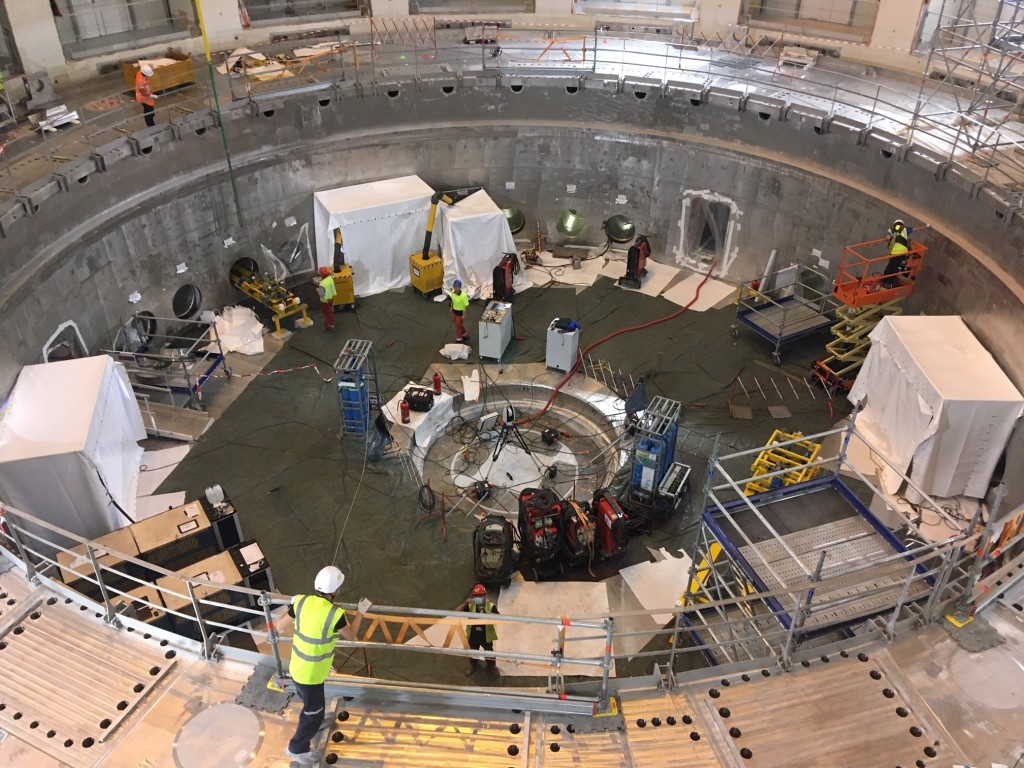
At the bottom of the assembly arena
2020-08-12 - Inside of (and on) the machine base, the assembly teams are busy with all kinds of preparatory activities. Before August ends, the lower cylinder of the cryostat will join the base in the Tokamak pit in ITER's second major lift operation.

First one
2020-08-12 - Operators use the cranes to lift the first protective layer off the steel component.
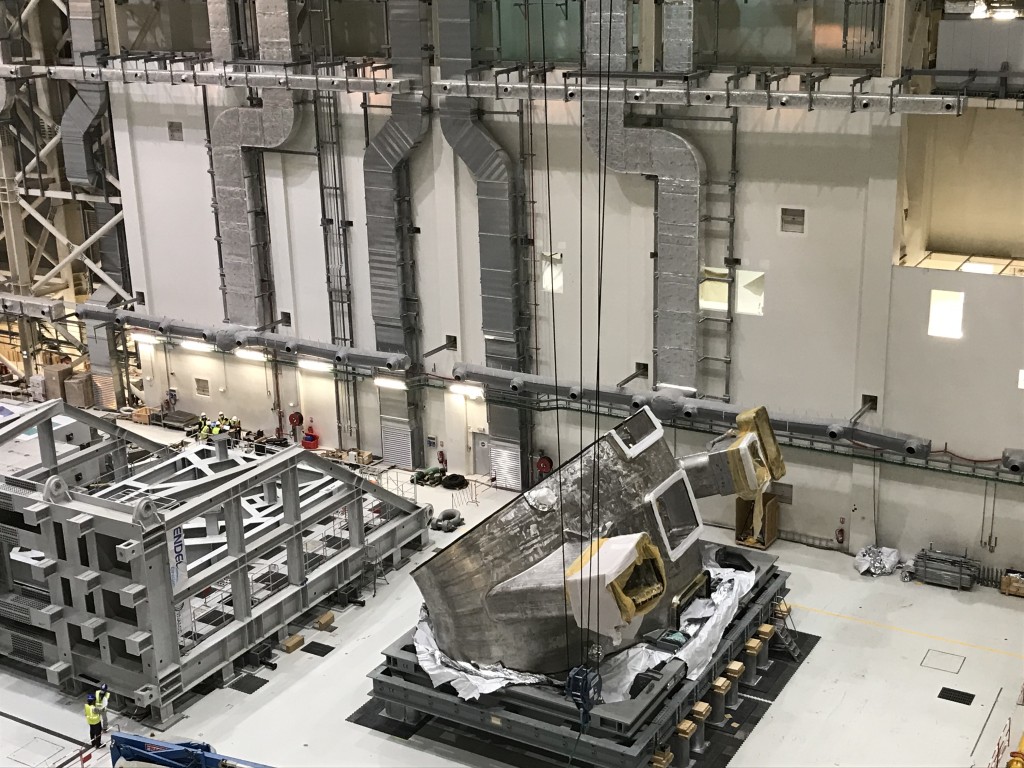
First of nine
2020-08-12 - Each vacuum vessel sector will be paired with two toroidal field coils and thermal shielding on the giant sector sub-assembly tools in the Assembly Hall. Sector #6 (pictured) will be the first to undergo this suite of assembly operations; sector #7, also from Korea, will be the next. Today, S#7 is 94% complete at Hyundai Heavy Industries.
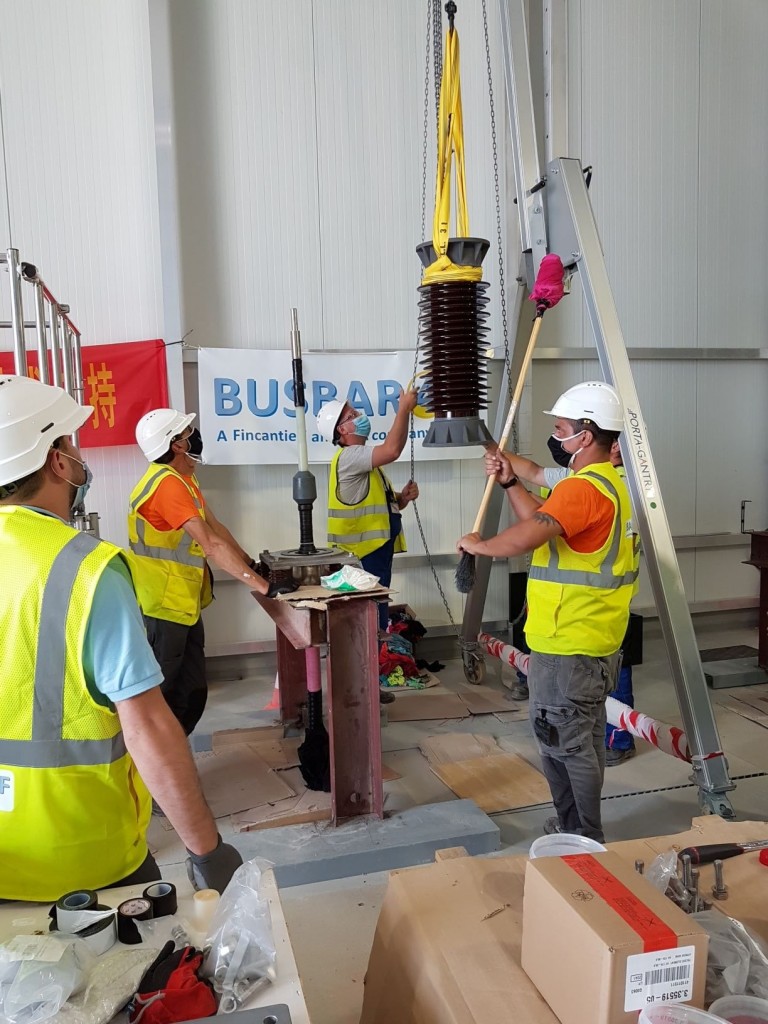
Contractors-in-training
2020-08-12 - Contractors charged with the installation of DC busbars, switching networks and fast discharge units (Balance of Plant Group 5) have spent the last months training for the work they will carry out on site. Here, members of the team lift a high voltage insulator onto a cable termination.
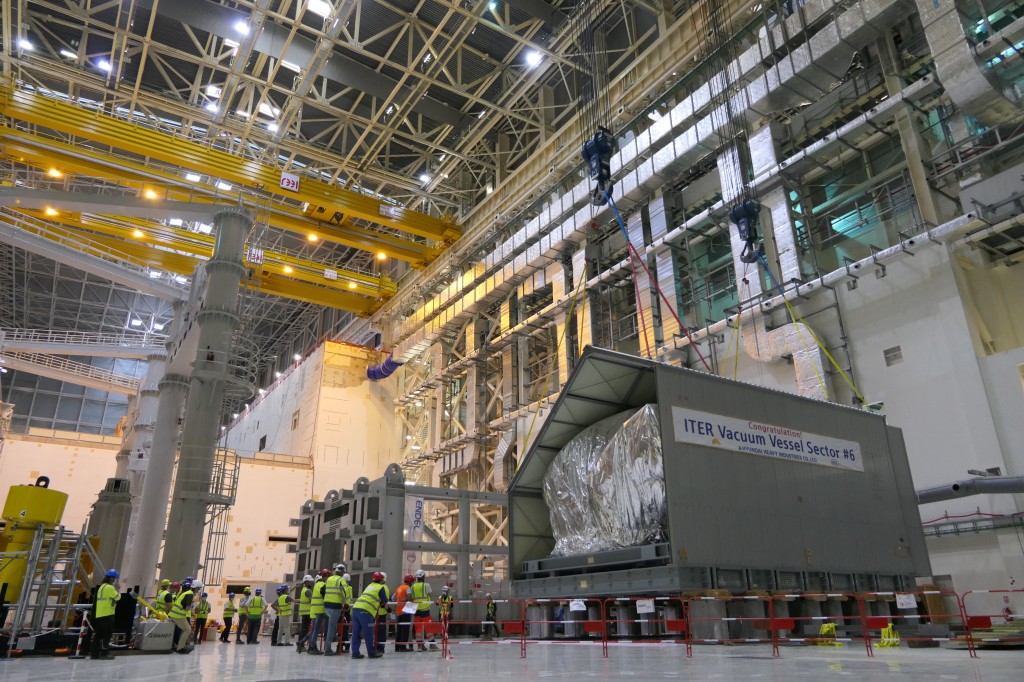
Latest arrival
2020-08-11 - The first vacuum vessel sector from Korea has been delivered to a laydown area in the Assembly Hall. After a final helium leak test and site acceptance test, the component will be ready for handover to the ITER Organization assembly contractor responsible for the vessel (TAC2) for a number of initial activities such as the installation of diagnostics, instrumentation and cable trays.
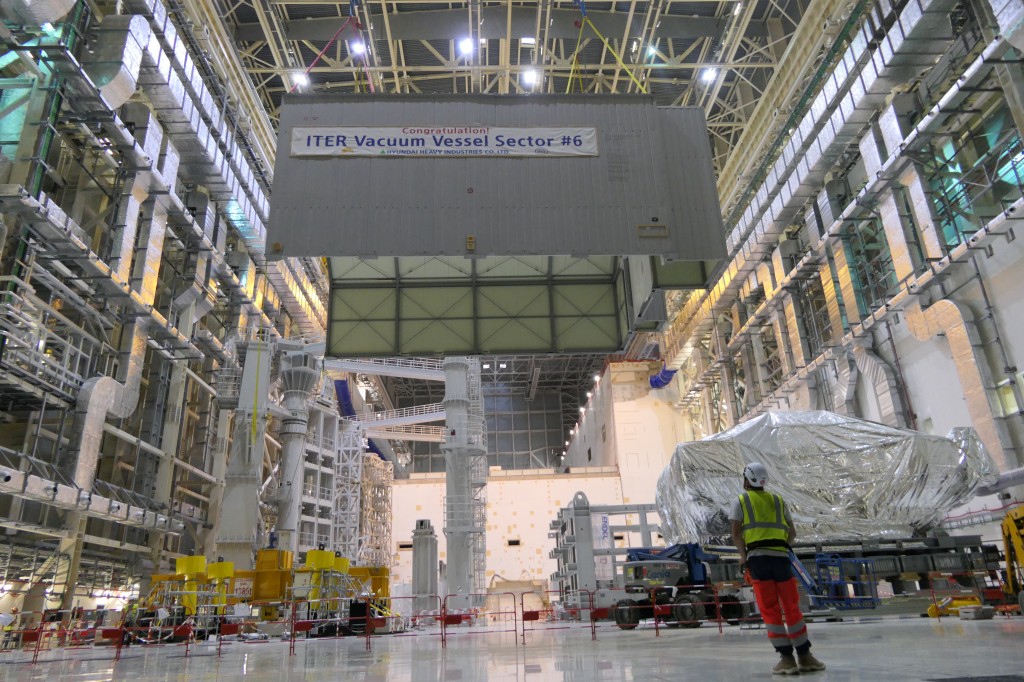
Lid off
2020-08-11 - The travel box around vacuum vessel #6 has been removed. Next in line: two layers of protective foil.
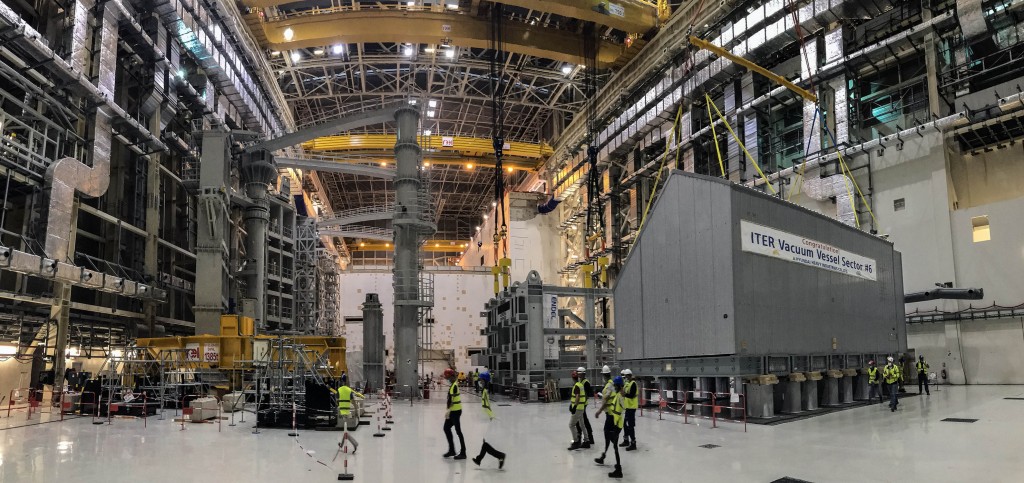
Inside the hall
2020-08-10 - A panoramic view of the Assembly Hall that shows the largest assembly tools and the newly arrived vacuum vessel sector #6. (It also, by a quirk of perspective, erases or flattens the people passing by...)
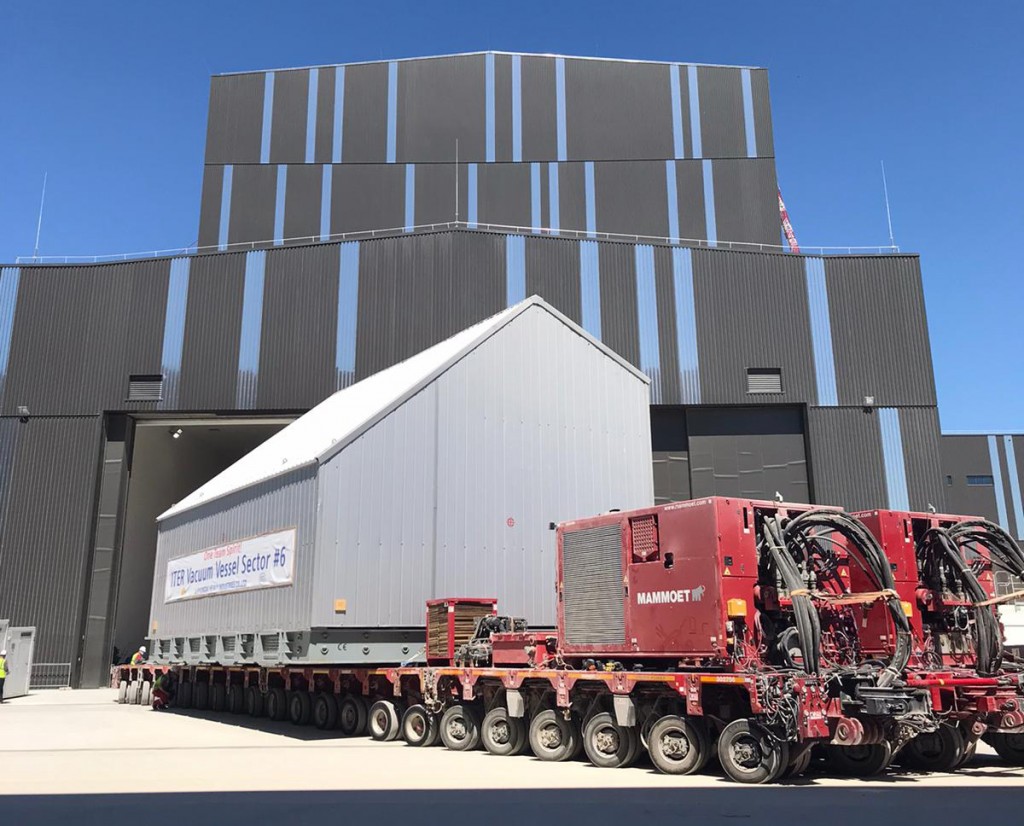
First vacuum vessel sector enters Assembly Hall
2020-08-07 - Vacuum vessel sector #6 arrives from Korea on 7 August 2020. This will be the first sector mounted on the giant sector sub-assembly tools in the Assembly Hall for pairing with thermal shield panels and a pair of toroidal field coils.
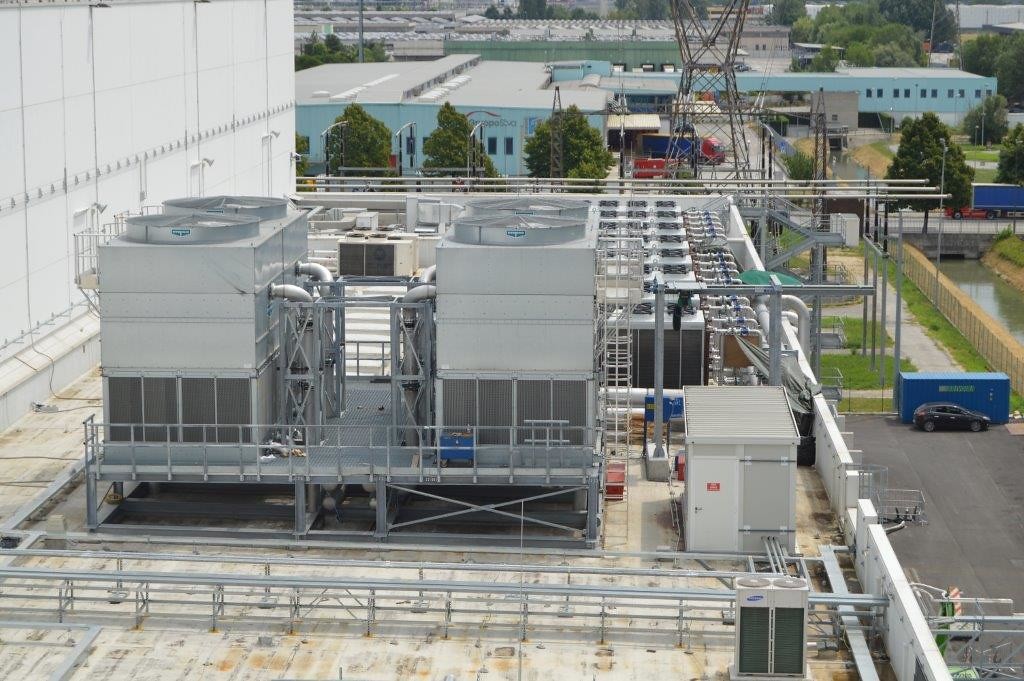
Europe completes NBTF cooling plant
2020-08-04 - In a 17,500 m² building on the premises of Consorzio RFX, in Padua, Italy, two test stands will allow the ITER Organization to test all the components of the neutral beam heating system. Europe, one of the contributing parties, has just completed the cooling plant.

Pouring has started
2020-08-03 - A full basement and one floor—the Tokamak Assembly Preparatory Building is going up not far from the Assembly Hall.
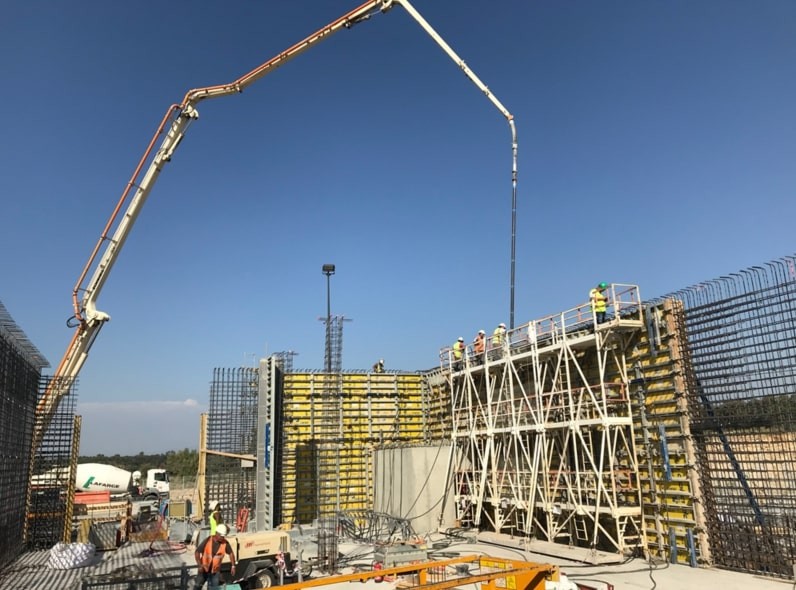
Small building rising
2020-08-03 - The Tokamak Assembly Preparatory Building (TAPB) is rising in one corner of the ITER platform. Destined to receive and store beryllium components in the future, it will first be used for assembly prep activities.

PF6 unwrapped
2020-07-31 - At one end of the European winding facility on site, poloidal field coil #6 (PF6) sits unwrapped. The team is preparing the magnet for cold testing before insertion in the Tokamak pit later this year.

Join ITER's start-of-assembly ceremony!
2020-07-27 - On 28 July, the ITER Organization will be livestreaming its start-of-assembly ceremony from 10:00 a.m. local French time. To log into the livestream, see our YouTube page.

Preparing for a kickoff event
2020-07-22 - Preparations are underway in the Assembly Hall for ITER's kickoff assembly event on 28 July 2020. French President Emmanuel Macron and government leaders from China, Europe, India, Japan, Korea, Russia and the United States will join. Tune into the livestream by clicking on the video screen at the end of the announcement (https://www.iter.org/newsline/-/3473).
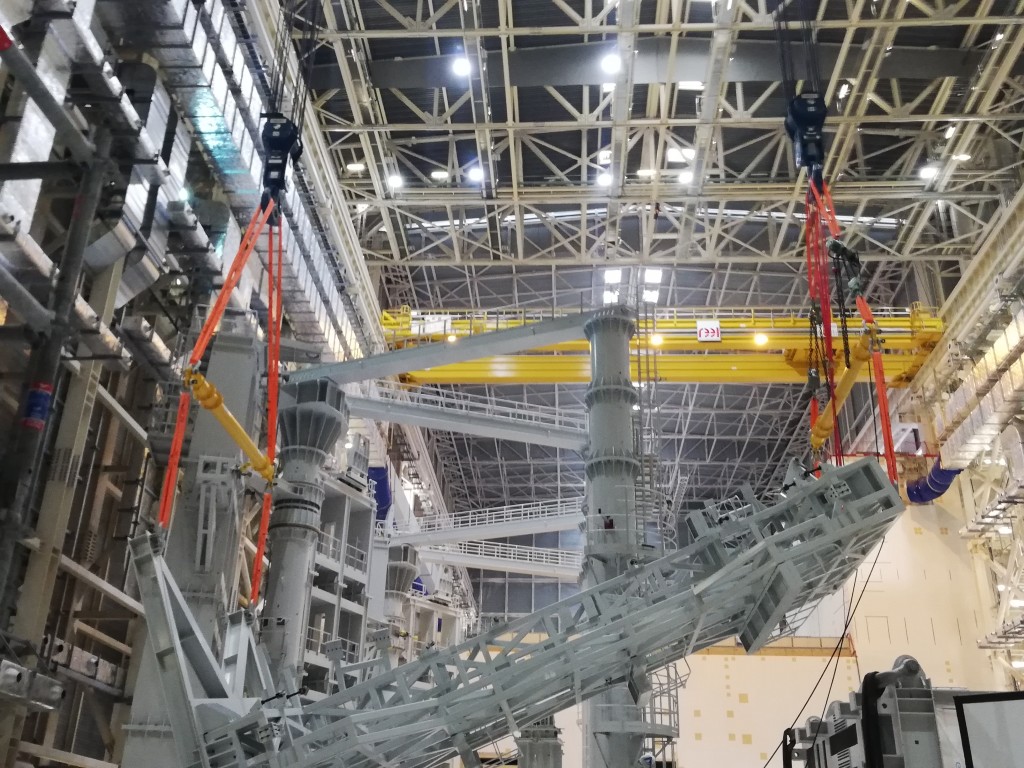
Thermal shield lift frame: tests underway
2020-07-22 - In the ITER Assembly Hall, another pair of assembly tools designed and procured by Korea—the thermal shield frames—are undergoing tests without load. These frames will support tall panels of thermal shielding as they are lifted to vertical for installation of the sector sub-assembly tools.
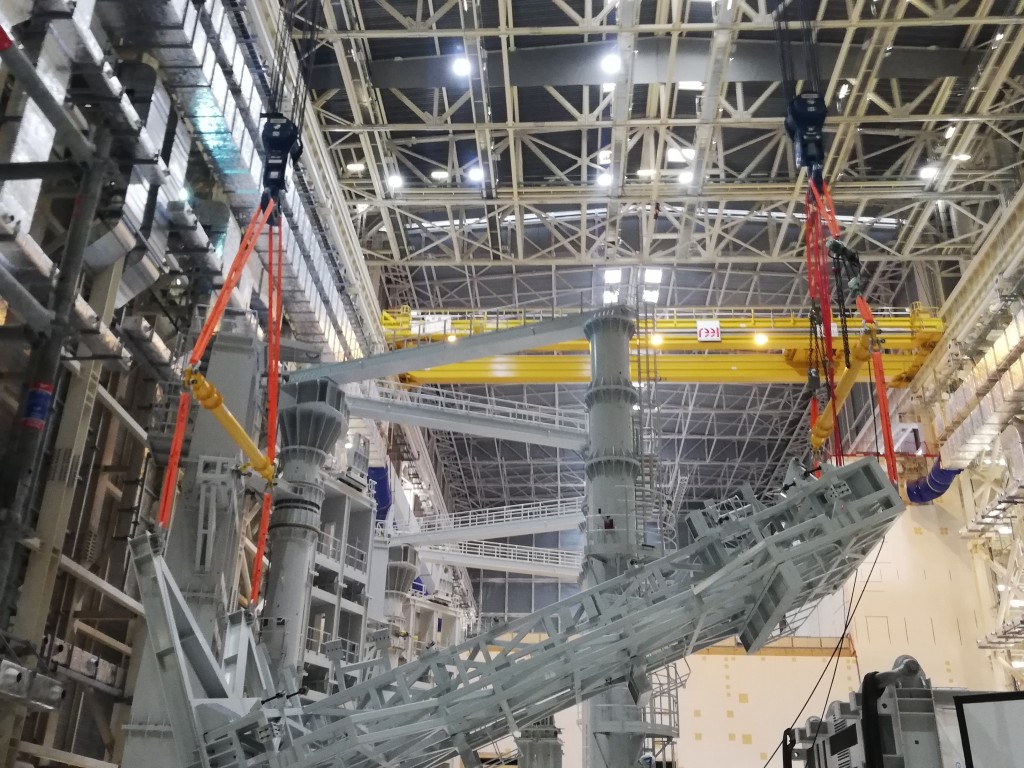
Thermal shield lift frame: tests underway
2020-07-22 - In the ITER Assembly Hall, another pair of assembly tools designed and procured by Korea—the thermal shield frames—are undergoing tests without load. These frames will support tall panels of thermal shielding as they are lifted to vertical for installation of the sector sub-assembly tools.

Three in a glance
2020-07-16 - Three poloidal field coils are now present in Europe's on-site winding facility: poloidal field coil #5 (PF5, far left, black) is being equipped with helium piping and electrical cables; PF2, of similar diameter (white, centre left) is ready for the impregnation stage; and PF6 (far right, under the crane) is being prepared for cold testing.
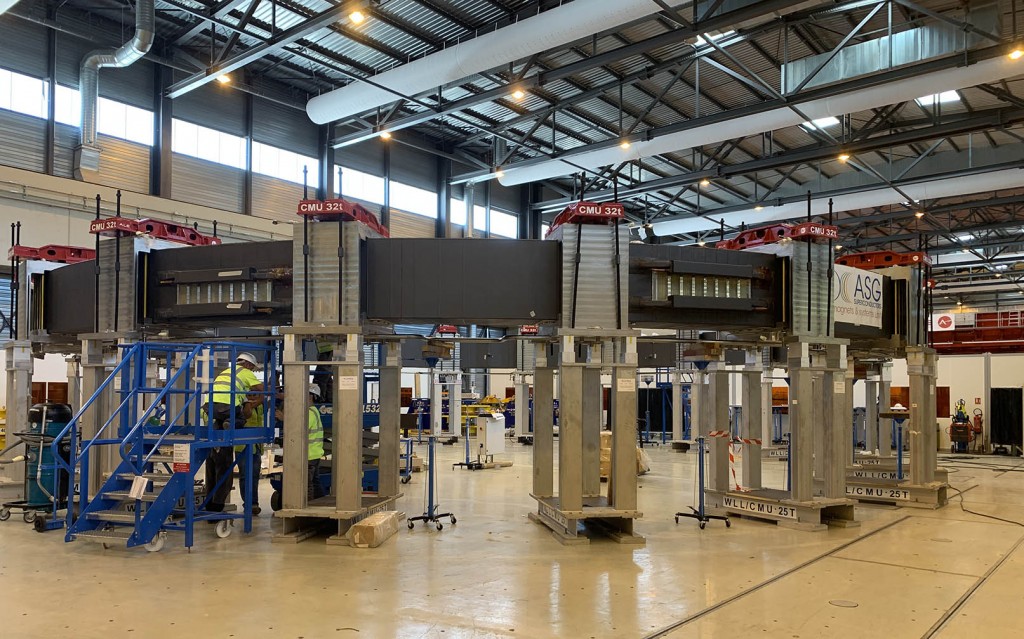
Preparing for cold testing
2020-07-09 - The first magnet coil produced in the European winding facility on site is PF5 (pictured). The teams are preparing for cold testing.
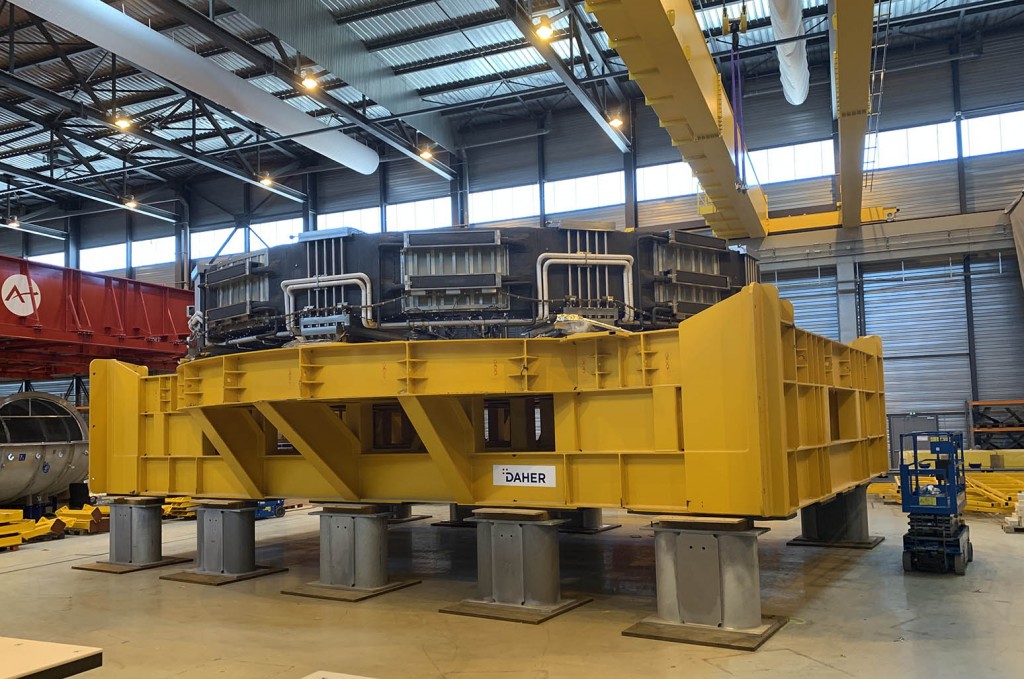
Recent arrival
2020-07-09 - Poloidal field coil #6, recently delivered from China, still sits on its transport frame.
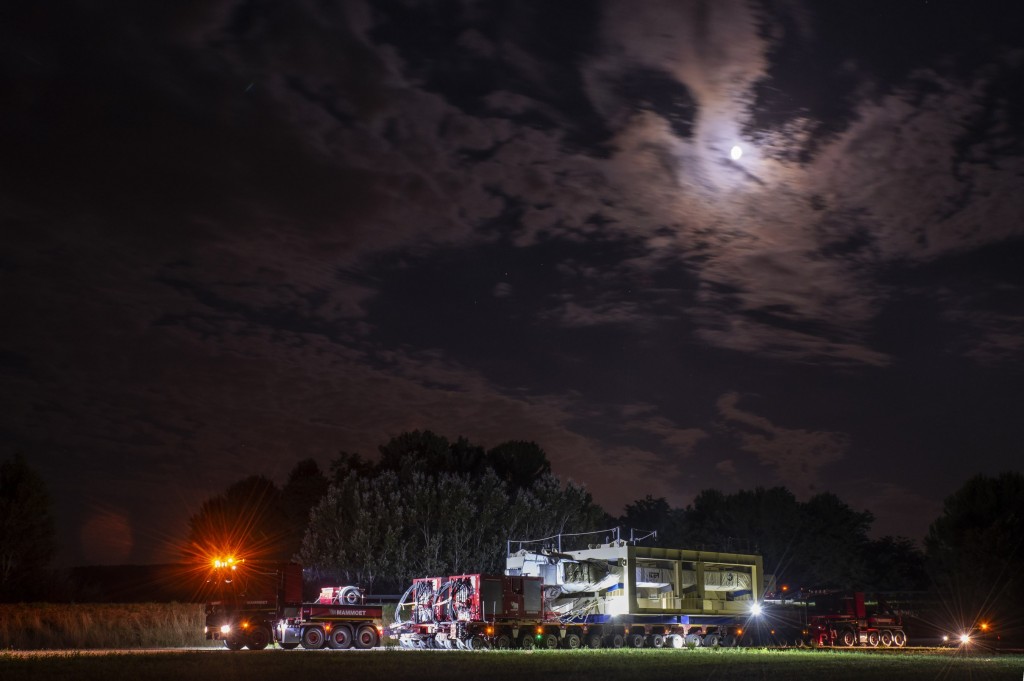
Toroidal field coil #13 arrives from Japan
2020-07-03 - A second toroidal field coil, TF13 from Japan, arrives at ITER on 3 July. TF13 will be paired with TF12 (also from Japan) and Korea's vacuum vessel sector #6 to form the first 1,200-tonne sub-assembly of ITER's vacuum vessel.
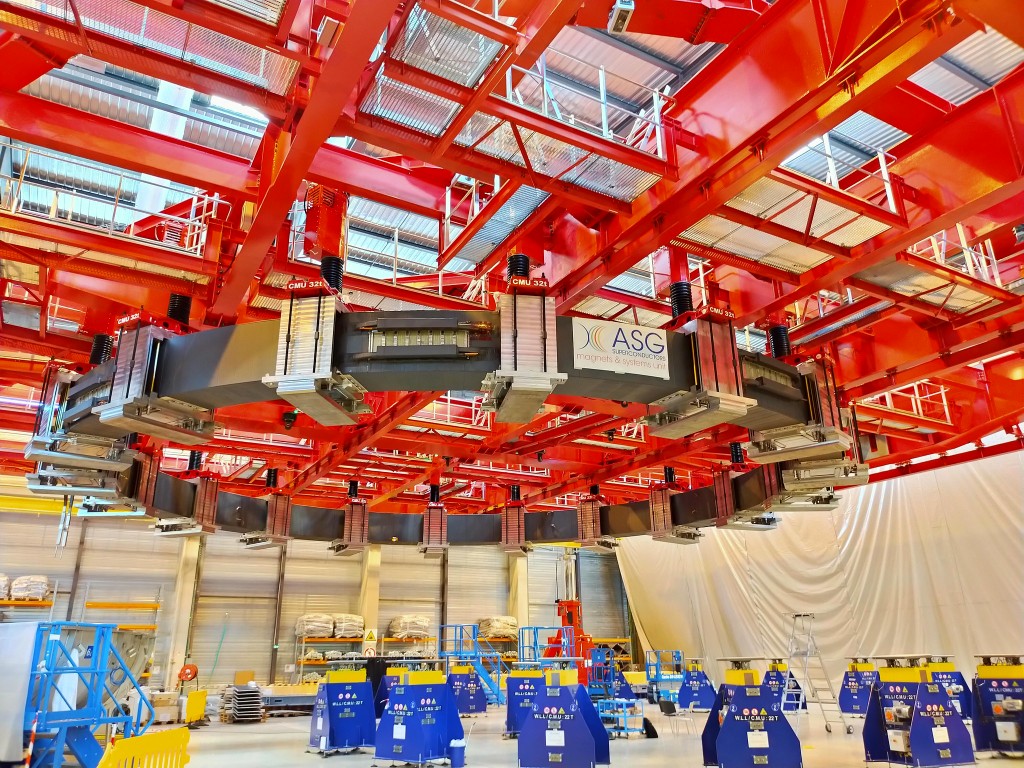
PF5 in line for cold testing
2020-06-30 - The fifth poloidal field coil (PF5) is now fully assembled, including protective plates and clamps (18). The next step is cold testing.

Top lid elements, ready to ship
2020-06-30 - In India, Larsen & Toubro has finalized all of the elements of the top lid (12 triangular segments plus a central disk). The segments will soon ship to ITER for assembly in the Cryostat Workshop.

A warehouse for coil preparation
2020-06-30 - Two coils—TF9 (Europe) and TF12 (Japan)—are now on temporary stands in a coil preparatory building not far from the Assembly Hall for pre-assembly operations.
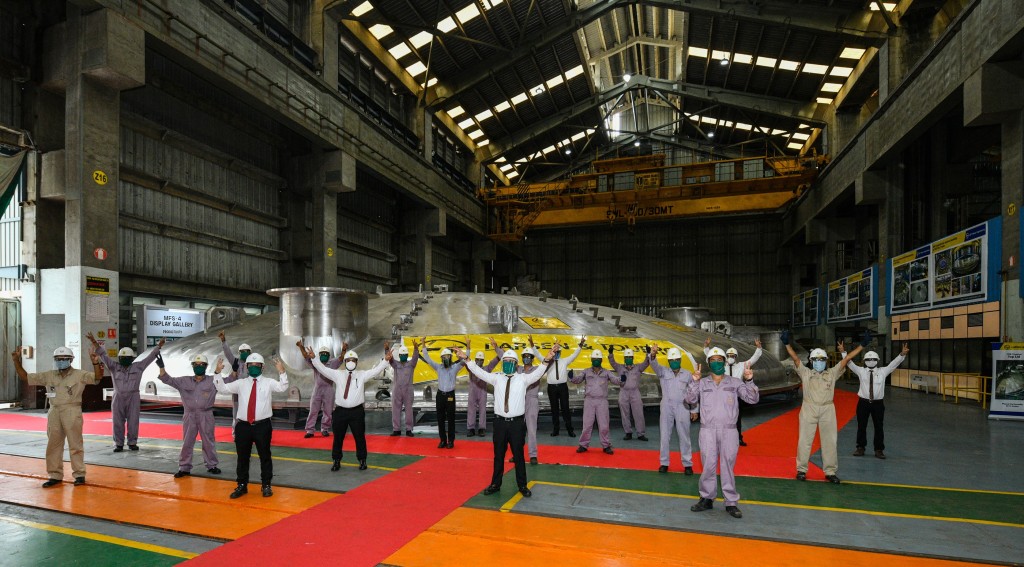
650-tonne lid, temporarily assembled
2020-06-30 - The segments of the top lid were put together at Larsen & Toubro's Hazira factory for verification, and then disassembled and packed for shipment. This brings cryostat manufacturing to an end for the Indian firm, which signed a contract back in 2012.

PF6 arrives!
2020-06-26 - Procured by Europe and manufactured in China, the ring-shaped magnet coil PF6 will be the first to be integrated into the ITER machine. The massive component arrived on site on Friday 26 June 2020 after a 10,000-kilometre voyage from its manufacturing site in Hefei, China.

PF6 arrives!
2020-06-26 - Procured by Europe and manufactured in China, the ring-shaped magnet coil PF6 will be the first to be integrated into the ITER machine. The massive component arrived on site on Friday 26 June 2020 after a 10,000-kilometre voyage from its manufacturing site in Hefei, China.
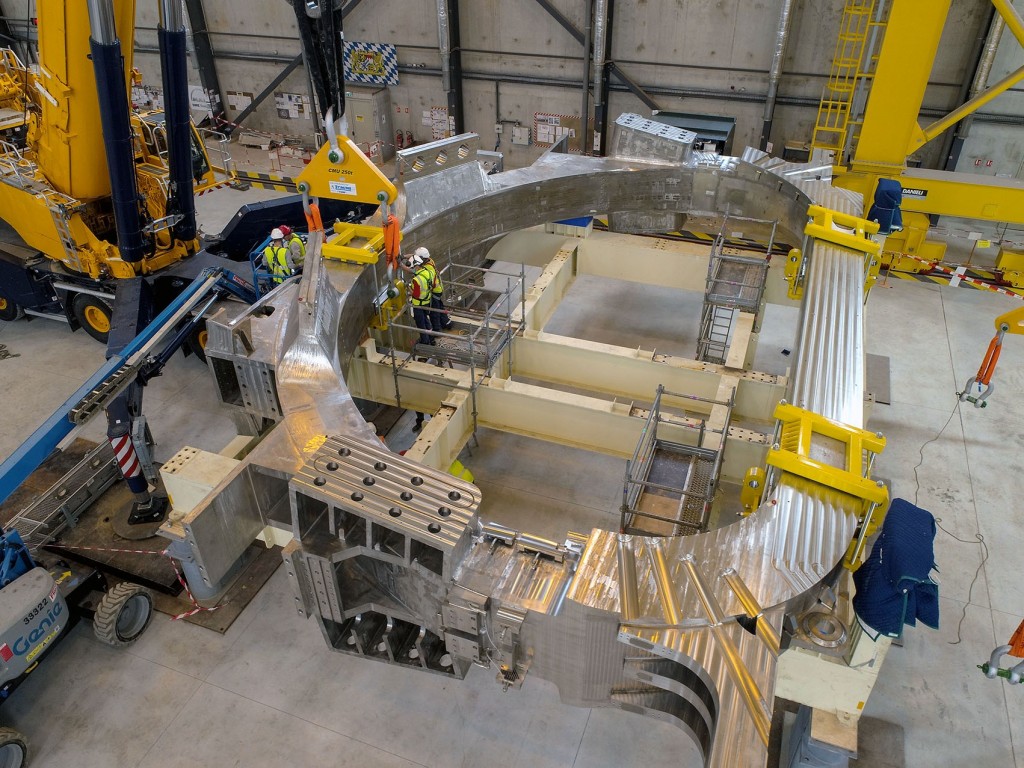
Unwrapped at ITER
2020-06-20 - This is toroidal field coil #12, from Japan, seen in an ITER workshop without its transport frame.

46 rather particular doors
2020-06-19 - Installed all around the tokamak machine at three levels, these port cell doors double in weight (from 30 to 60 tonnes) when filled with dense, neutron-blocking concrete. The last of 46 doors was installed in June by European Domestic Agency contractors.
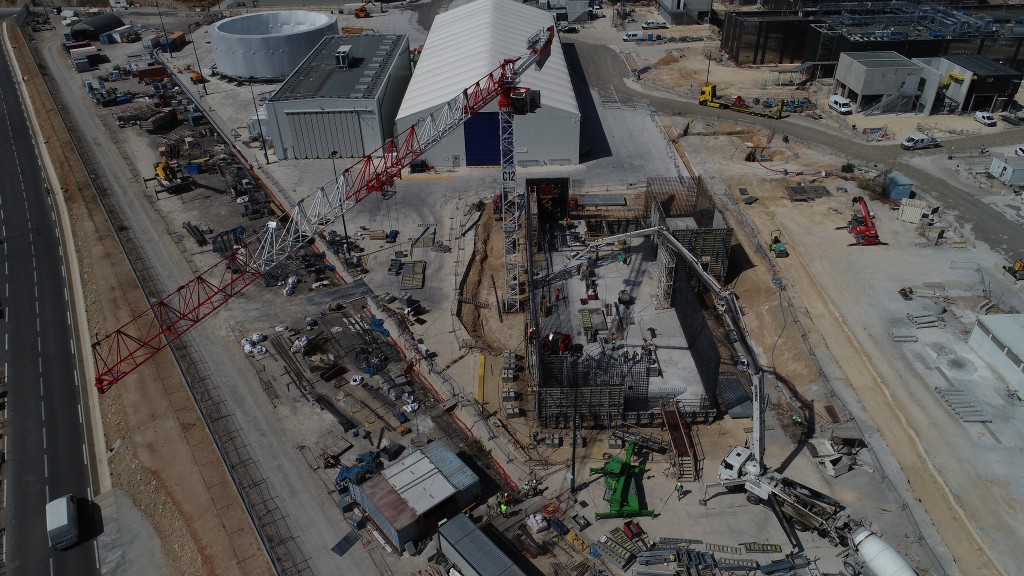
Walls rise for beryllium storage building
2020-06-15 - The building in the foreground will be used down the road to store ITER blanket components containing beryllium. Up to then, it will serve as another assembly preparatory building (hence its name: the Tokamak Assembly Preparatory Building, or TAPB). © Les Nouveaux Médias/SNC ENGAGE
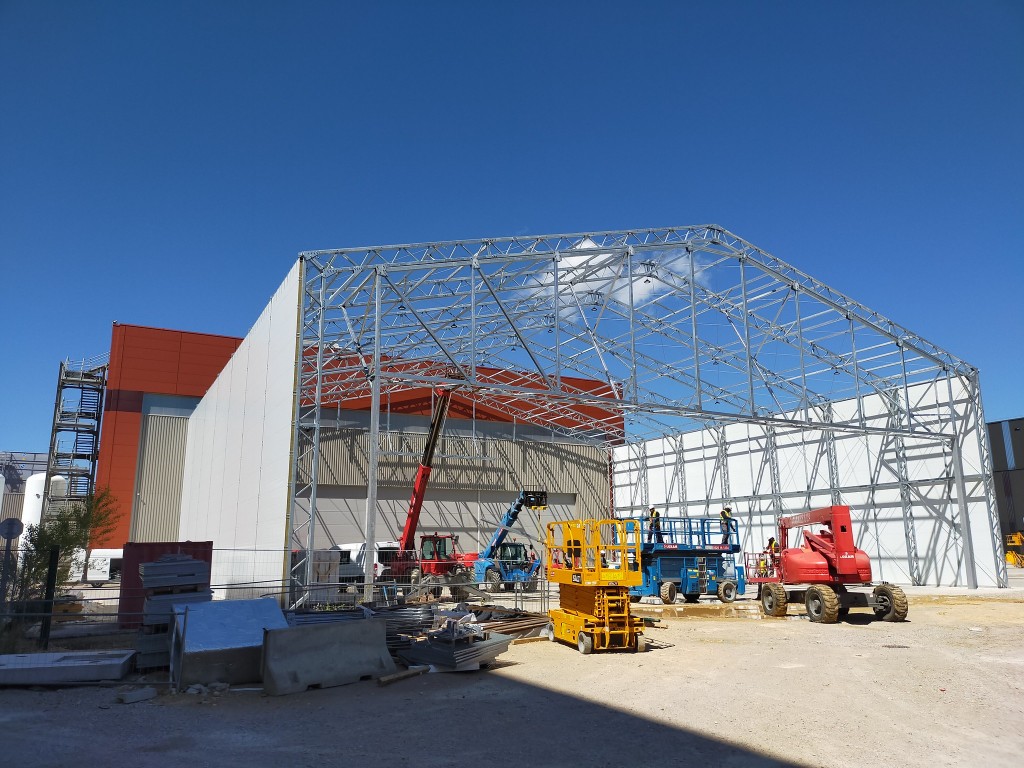
Extension going up
2020-06-15 - An extension of the Poloidal Field Coils Winding Facility will create additional space for the handling of the next set of double pancakes to be produced for poloidal field coil #4 (24 m in diameter).
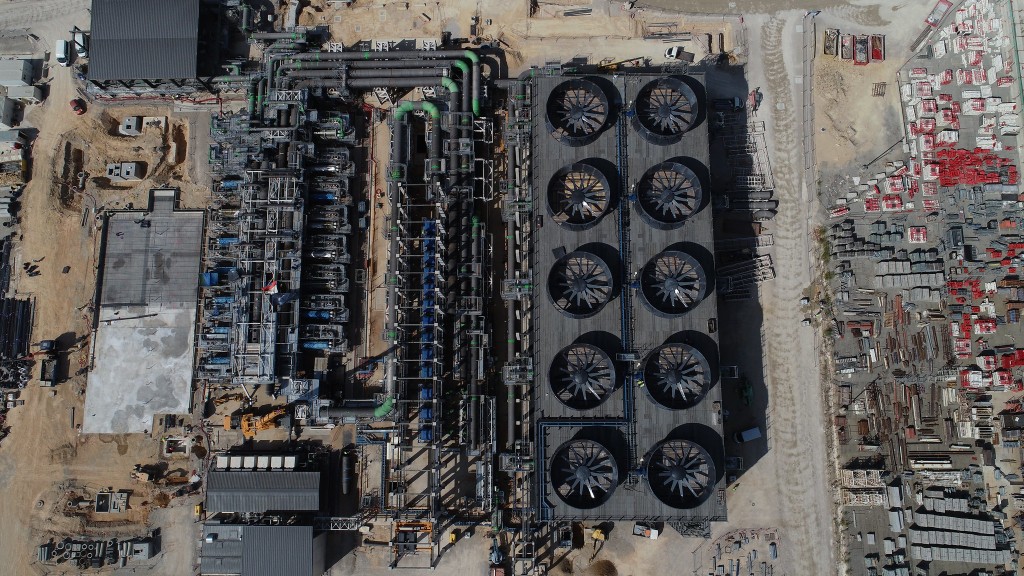
Cooling tower area
2020-06-15 - ITER's heat rejection system, including 10 cooling towers, seen from the air. © Les Nouveaux Médias/SNC ENGAGE

Understanding the use of space
2020-06-15 - A lot is happening in the Assembly Hall. This photo explains it all.

Finding your way on site
2020-06-08 - To identify the buildings and technical areas of the ITER site, please see this article: https://www.iter.org/newsline/-/3451.
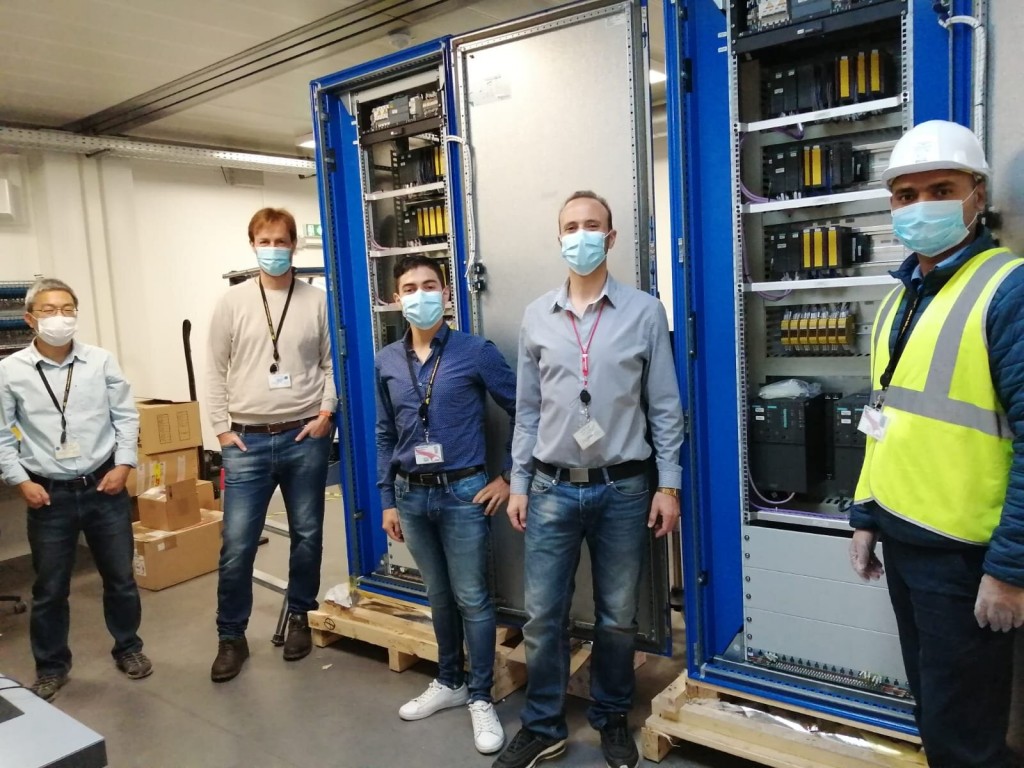
Central interlock
2020-06-08 - The ITER central interlock system will interface with 170 local interlock systems (at the level of each plant system) to ensure machine protection. Material is beginning to arrive on site.
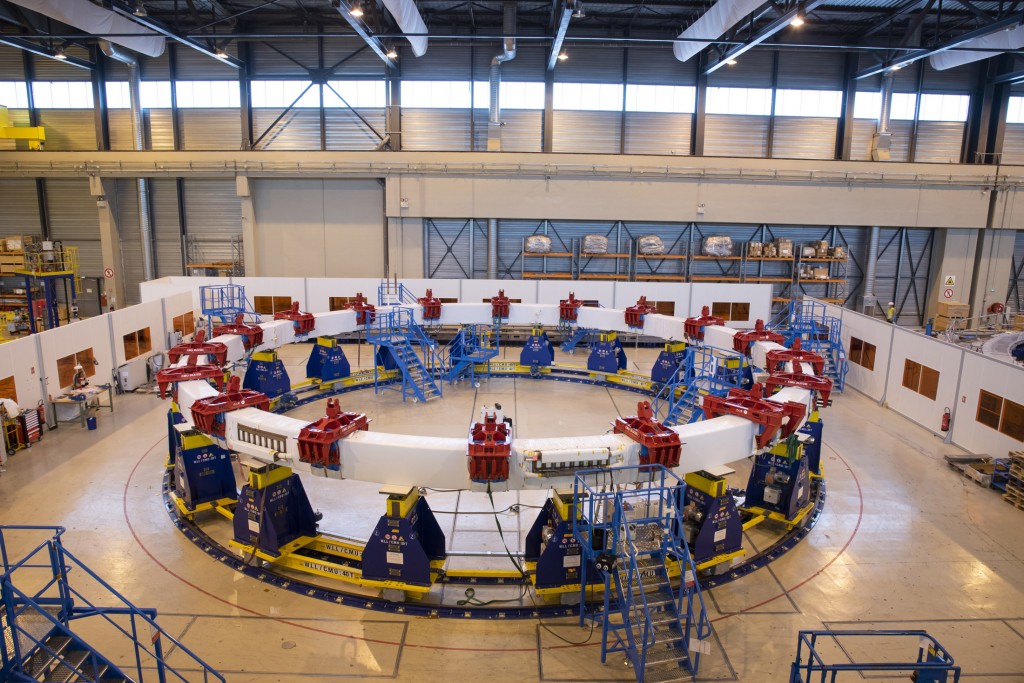
PF2: impregnation next
2020-06-04 - Nine layers of ground insulation wrapping have been applied and lifting tool interfacing elements have been attached. The next step for poloidal field coil #2 (PF2) is transport to the vacuum pressure impregnation station.
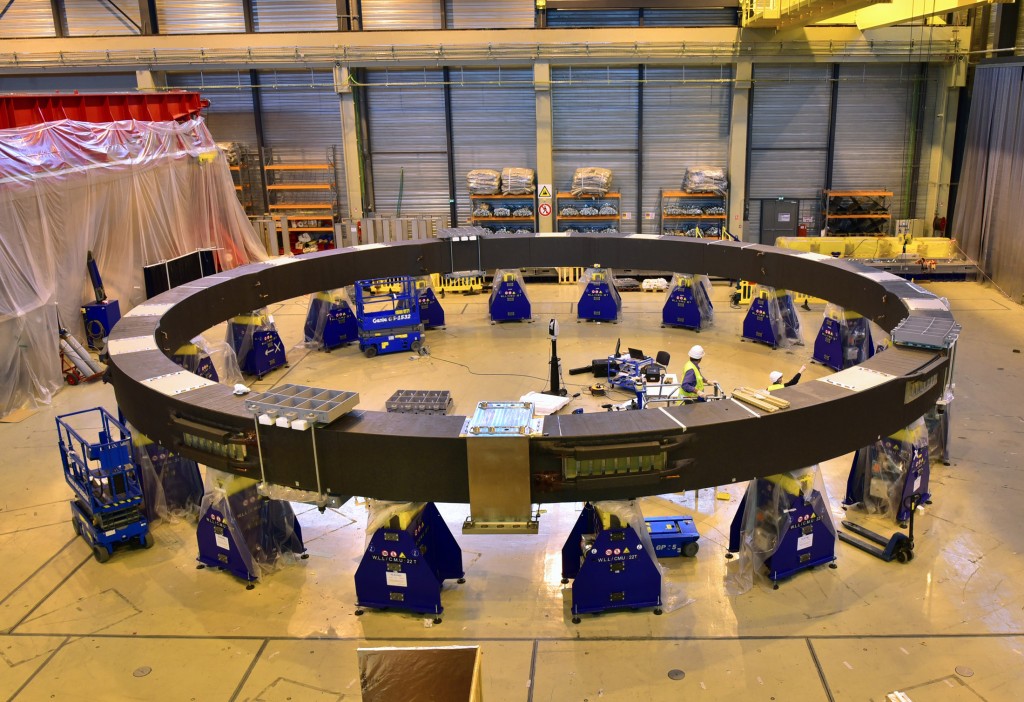
Final stages for poloidal field coil #5
2020-06-04 - The first coil produced on site by the European Domestic Agency in the Poloidal Field Winding Facility is PF5. Following successful impregnation, the hardened coil is now receiving protective plating (yellow in the picture, spaced regularly). Clamping trials (foreground) are also underway.

Winding station set up
2020-06-04 - Les stations de travail qui ont servi à la fabrication des bobines PF5 et PF2 sont en cours d'élargissement (de 17 à 24 mètres de diamètre) pour les deux prochaines bobines. La station de bobinage sur la photo tournera bientôt de nouveau pour créer les bobinages de PF4.

One of the last giants
2020-06-02 - One of the last large components enters the ITER cryoplant: a 56-tonne helium dryer.
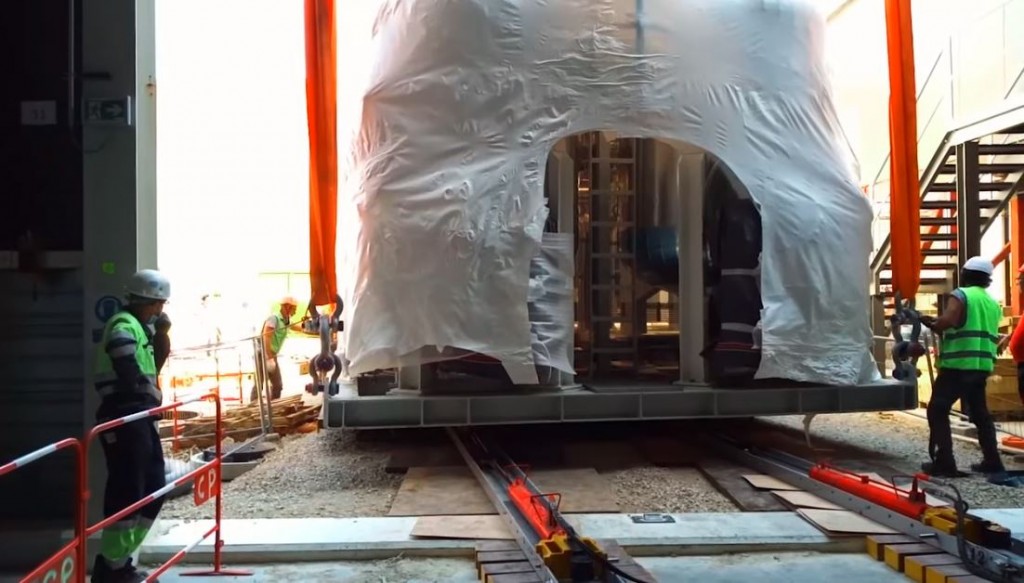
One of the last giants
2020-06-02 - One of the last large components enters the ITER cryoplant: a 56-tonne helium dryer.
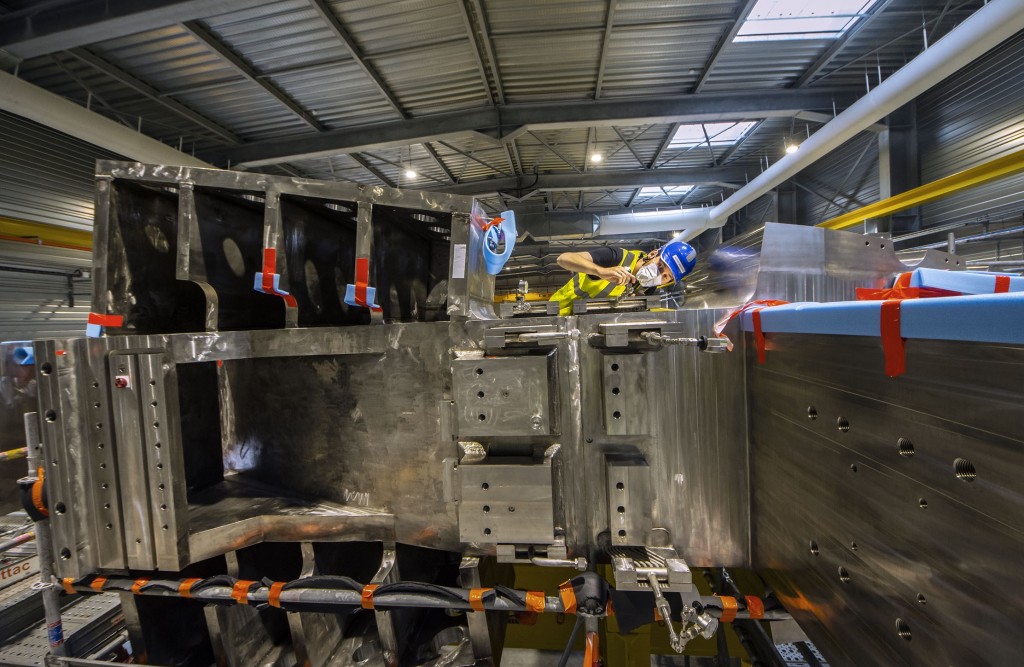
Pre-assembly work on the toroidal field coils
2020-05-28 - For the moment, the toroidal field coils already delivered to ITER are in a staging facility, where welds in the helium piping can be leak-tested and additional handling and pre-assembly equipment can be added. In this photo, TF9 from Europe.
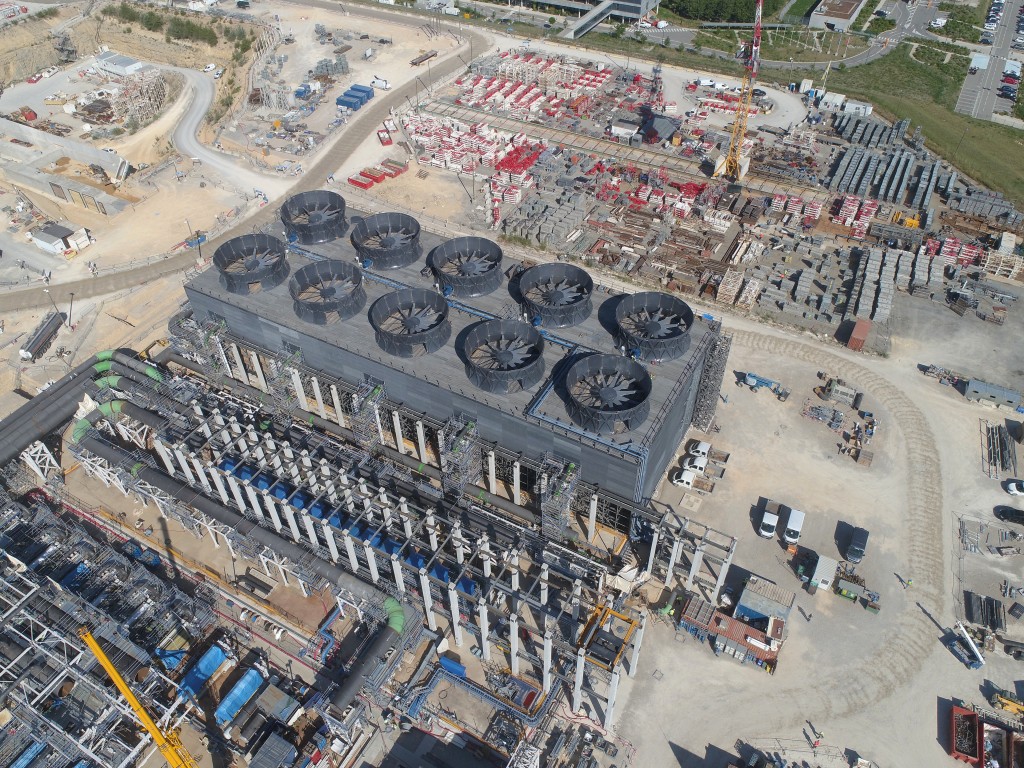
Towers equipped
2020-05-28 - Ten fans have now been installed at the top of the building, one for each cooling tower. Photo: ITER Organization/EJF Riche
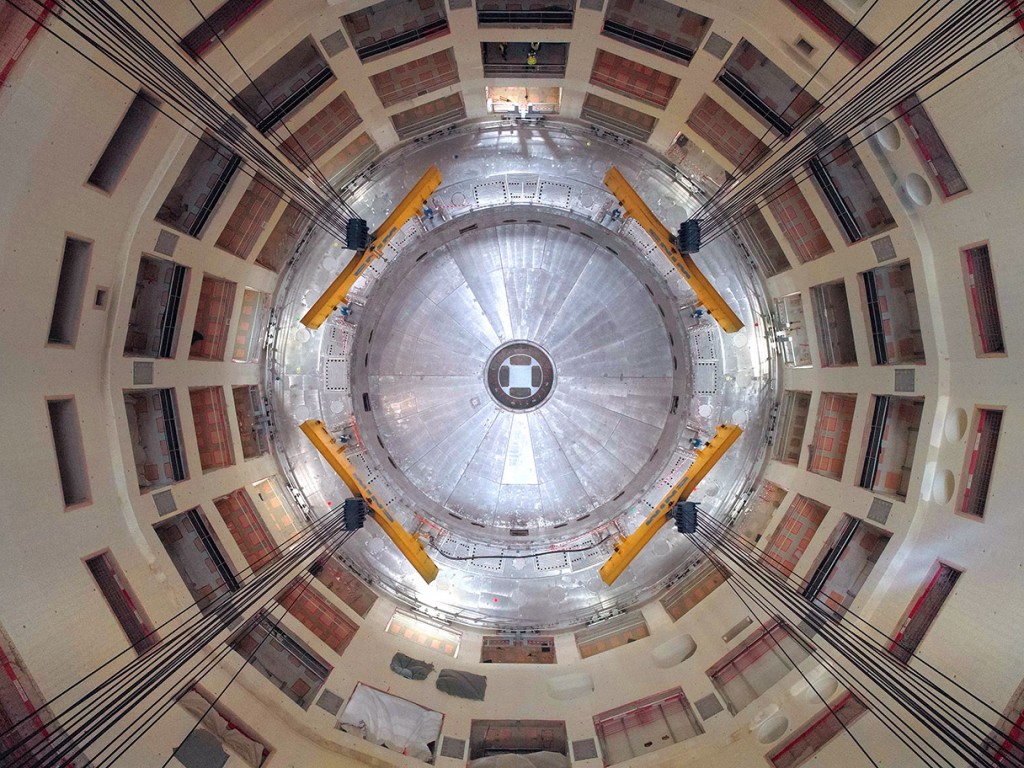
Base installed
2020-05-28 - Part one of the cryostat, the 1,250 base, was inserted into the machine assembly pit on 26 May 2020. The operation went as smoothly as planned.
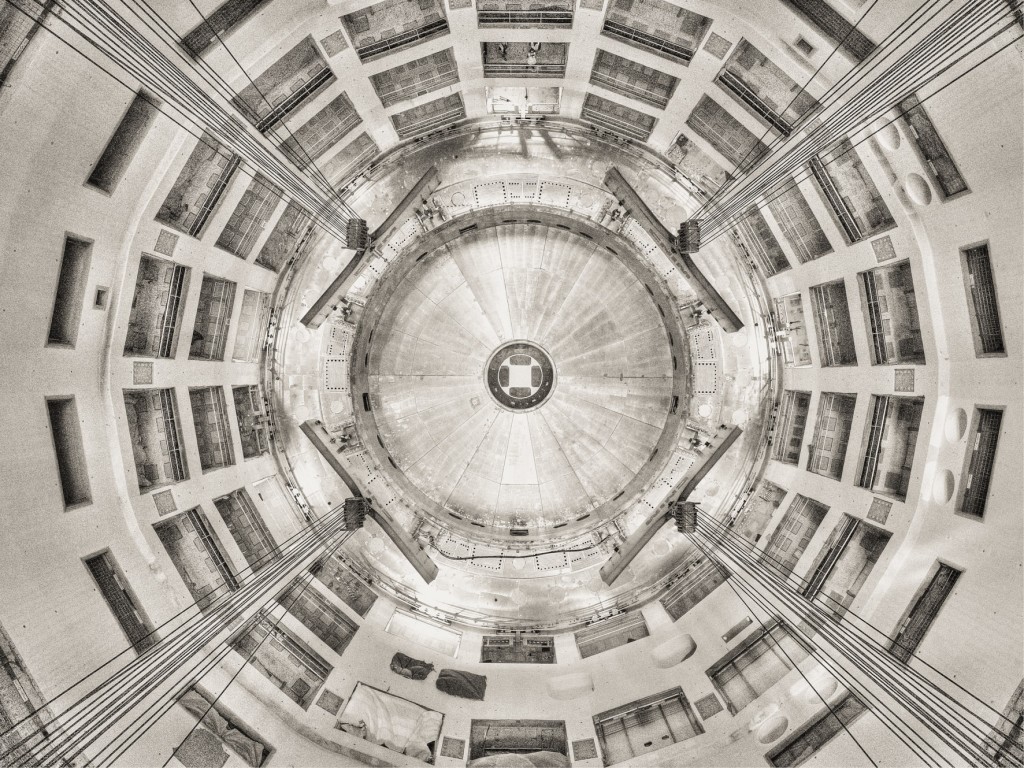
Engineering as art 3/3
2020-05-28 - An artistic adaptation of a photo of the cryostat base insertion by German photographer Christian Luenig. © Christian Luenig

First piece installed
2020-05-28 - First piece installed The first piece of the ITER Tokamak—the soup-dish-shaped base of the cryostat (1,250 tonnes)—was lowered into the Tokamak pit on 26 May. It fit perfectly. Photo: ITER Organization/EJF Riche
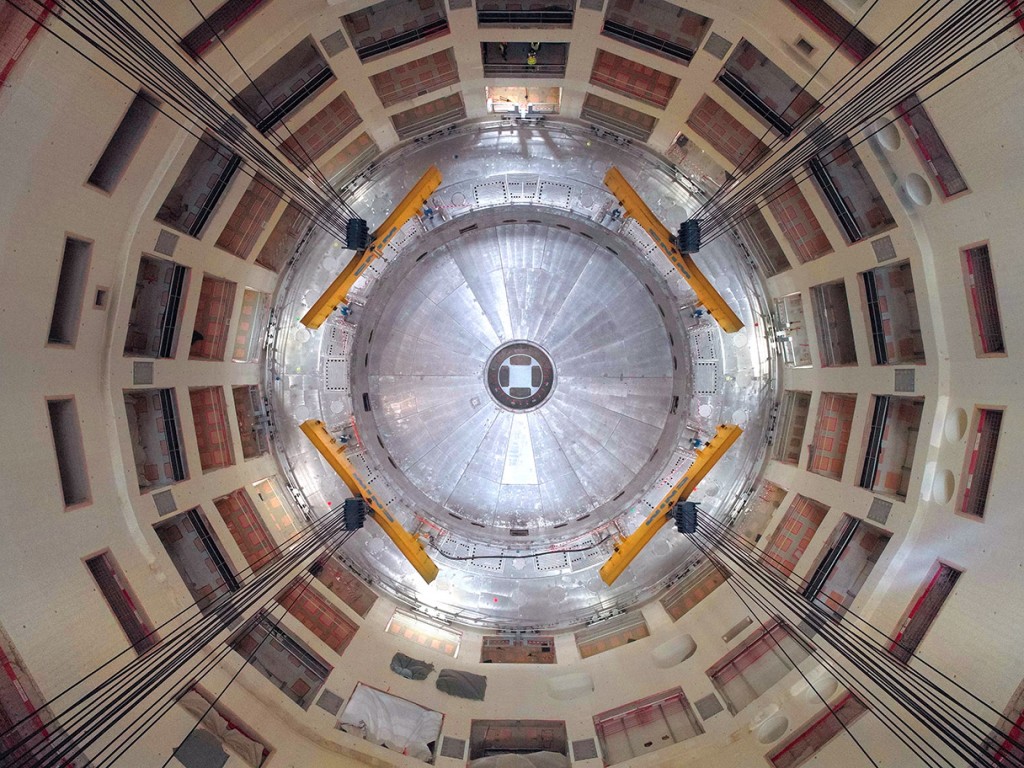
First piece installed
2020-05-28 - The first piece of the ITER Tokamak—the soup-dish-shaped base of the cryostat (1,250 tonnes)—was lowered into the Tokamak pit on 26 May. It fit perfectly. Photo: ITER Organization/EJF Riche
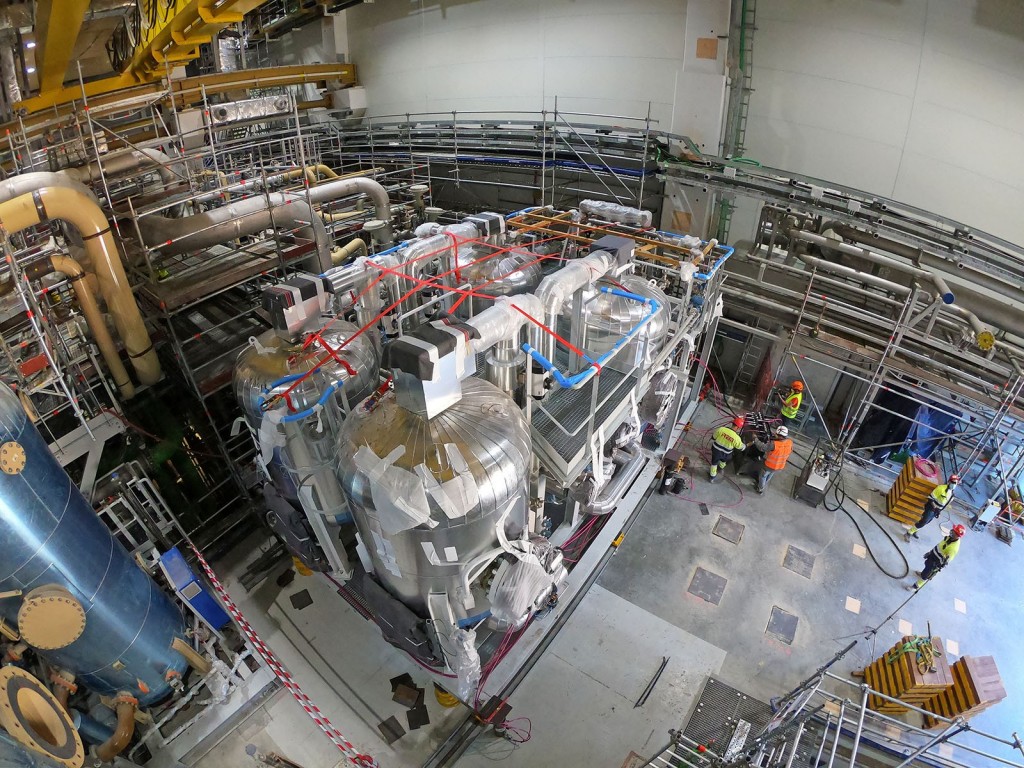
As dry as 'He' can get
2020-05-27 - Cold boxes do not like water. Before it is processed, gaseous helium needs to be perfectly dry to prevent damage. This crucial operation is the task of a 56-tonne ''helium dryer'' that was installed in the cryoplant on 27 May.
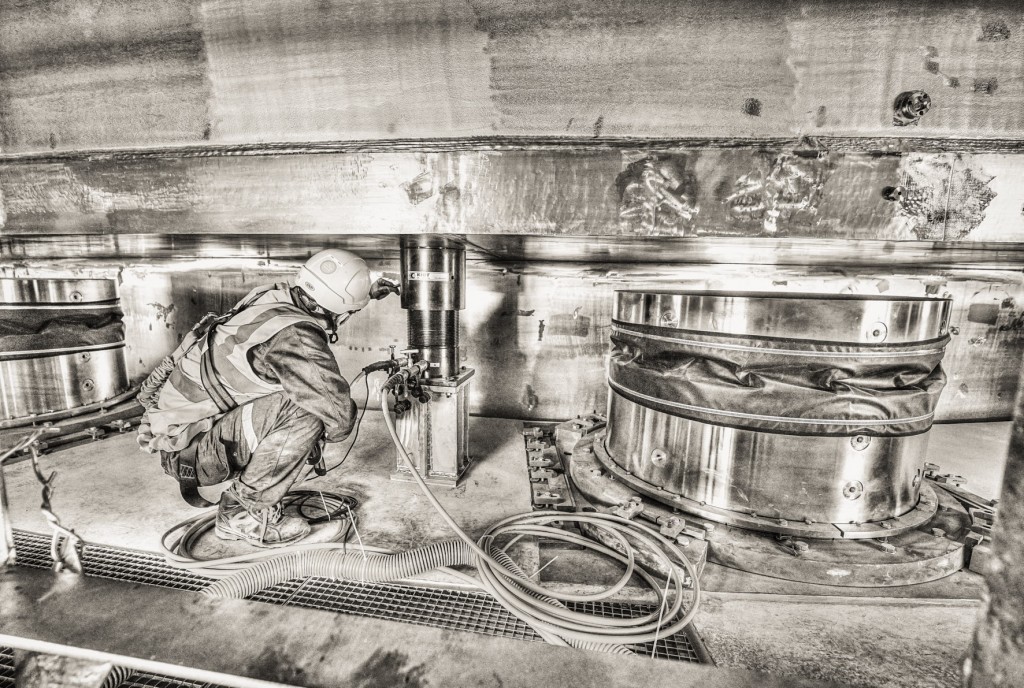
Engineering as art 2/3
2020-05-27 - An artistic adaptation of a photo of the cryostat base sitting on hydraulic jacks, by German photographer Christian Luenig. © Christian Luenig

As dry as 'He' can get
2020-05-27 - Cold boxes do not like water. Before it is processed, gaseous helium needs to be perfectly dry to prevent damage. This crucial operation is the task of a 56-tonne ''helium dryer'' that was installed in the cryoplant on 27 May.

6,000 square metres
2020-05-27 - The concrete batching plant has been removed from the platform (left) and the cooling plant is expanding into the zone. In all, it will cover a 6,000-square-metre area. Photo : ITER Organization/EJF Riche

Resting at last
2020-05-27 - Hydraulic jacks will support the 1,250-tonne component until the load is transferred to the cryostat support bearings.

Nearly there
2020-05-27 - The lower part of the component is now passing the edge of the supporting crown. A pair of hydraulic jacks, located between two bearings to the left, are ready to be pumped up to act as temporary supports for the massive load.

A bit of low tech
2020-05-26 - However sophisticated the technologies involved, there comes a moment when ancient tooling and methods come in handy. Here, a plumb bob attached to the component gives a clear visual indication of verticality.
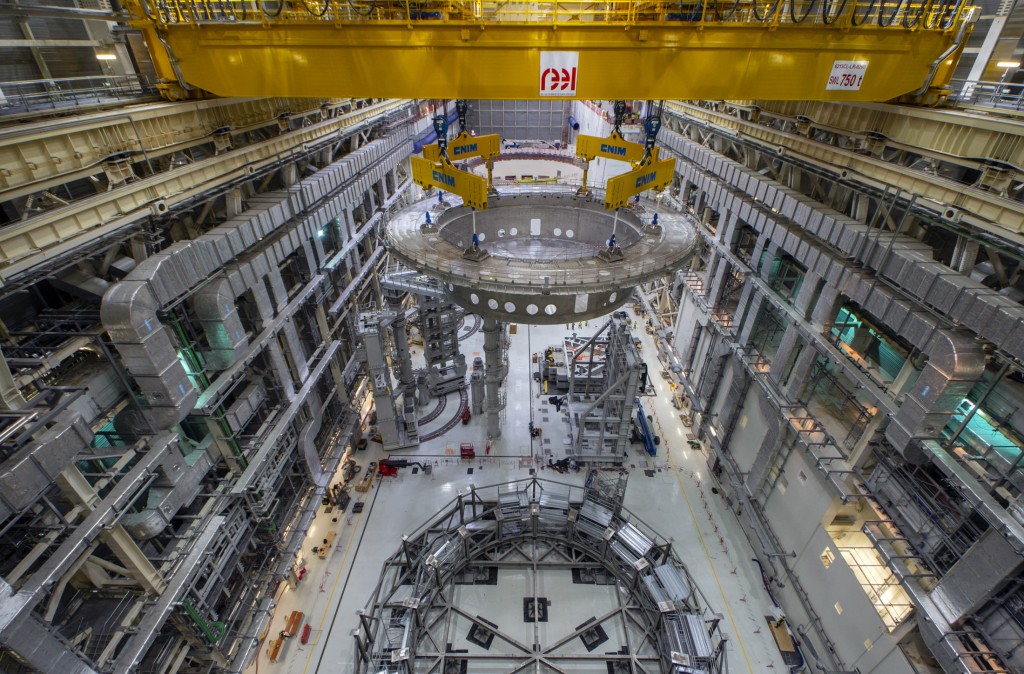
Overhead
2020-05-26 - The cryostat base travelled up and over the equipment in the Assembly Hall and into the Tokamak Building—a voyage of approximately 150 metres.
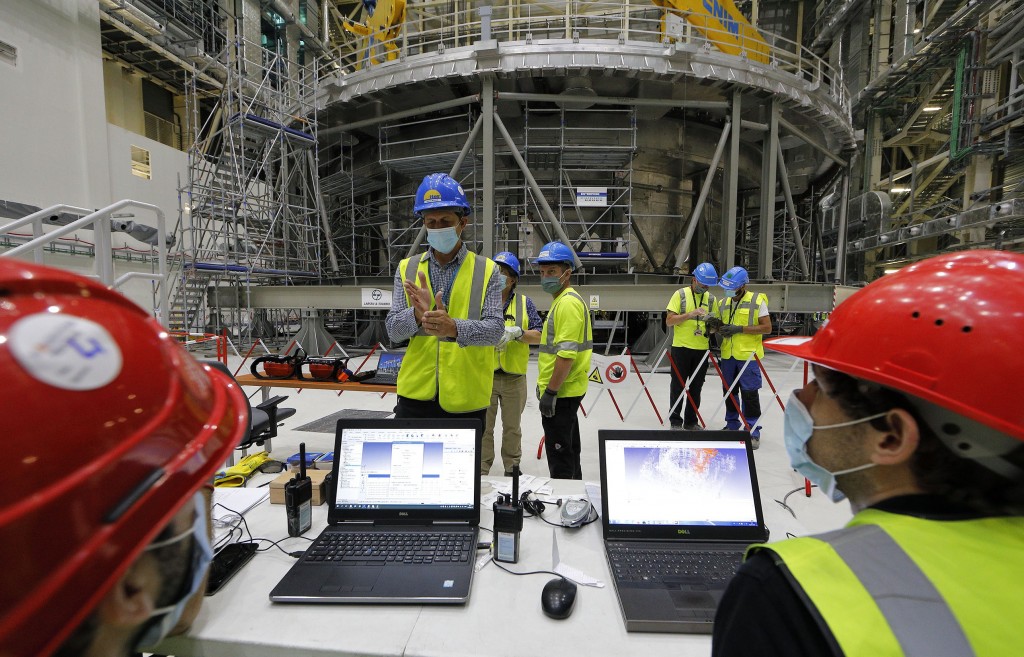
Countdown to liftoff
2020-05-26 - Following close to one week of preparation, tests, measurements and rehearsals, the teams are now confident enough to launch the actual operation. (Photo Gérard Lesénéchal - ITER Organization)

A tight fit
2020-05-26 - A tight fit At the mouth of the pit, the distance from the rim of the cryostat base to the wall is approximately 50 centimetres. It gets smaller as the component descends into the depths of the concrete cylinder, reducing to only 5 centimetres at the level of the crown.
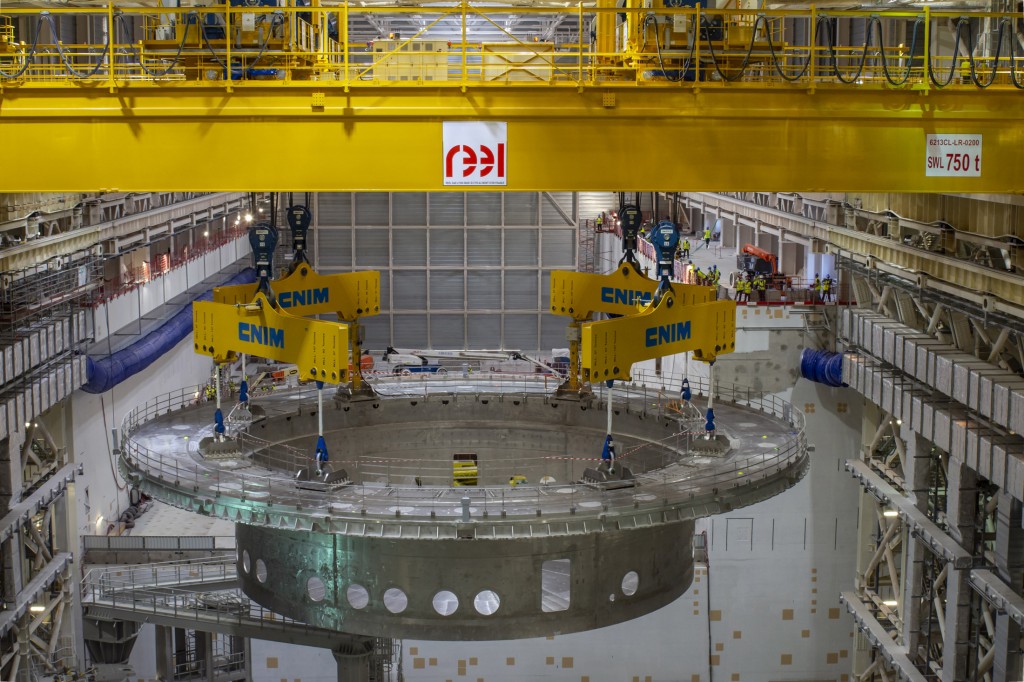
Major machine assembly milestone
2020-05-26 - On Tuesday 26 May, the first major machine component—the cryostat base—is lifted by overhead crane and lowered into the Tokamak assembly pit.
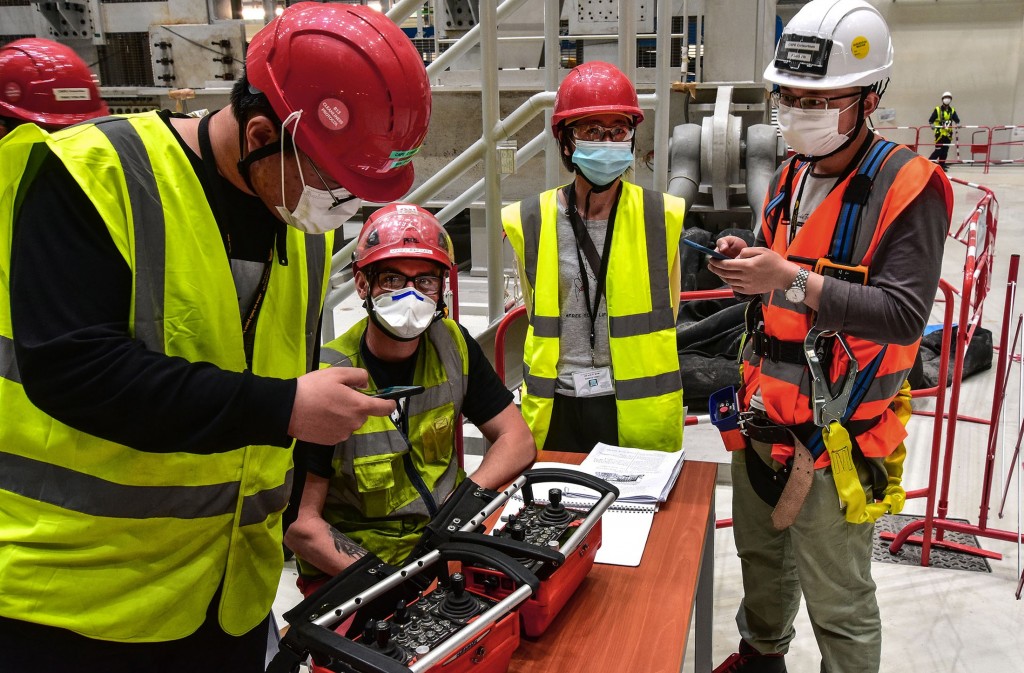
All with a joystick
2020-05-26 - Orders are transmitted to the crane system through a console equipped with a radio control transmitter. Communication between the French operator from the crane manufacturer and the Chinese movement coordinator from the CNPE consortium is done through an interpreter.

Rolling along the rails
2020-05-26 - Forty-five metres above the shop floor, the crane rails run 170 metres from the Assembly Hall to past the Tokamak pit. Photo: ITER Organization/EJF Riche

First major machine component
2020-05-26 - This first machine component was procured by the Indian Domestic Agency through the industrial giant Larsen & Toubro. Steel segments fabricated in India were assembled on site in the Cryostat Workshop by teams from Larsen & Toubro and MAN Energy Solutions (welding).

Perfectly clean
2020-05-26 - The machine assembly "well" is perfectly clean and ready to receive machine components. The 18 cylindrical cryostat support bearings are clearly visible, like jewels in the supporting crown.
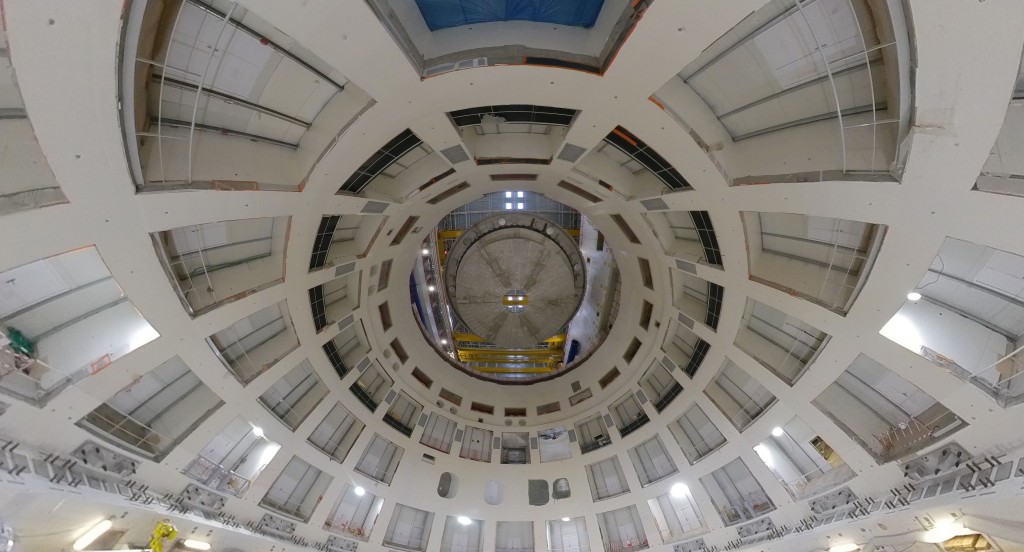
Fisheye
2020-05-26 - The slow descent of the base is photographed with a fisheye lens. Photo: ITER Organization/EJF Riche

Watching as it passes
2020-05-26 - Standing in one of the bioshield's portholes, a technician from the CNPE consortium watches in awe as the cryostat base almost brushes the inner walls of the pit.

Major machine assembly milestone
2020-05-26 - On Tuesday 26 May, the first major machine component—the cryostat base—is lifted by overhead crane and lowered into the Tokamak assembly pit.

Engineering as art 1/3
2020-05-26 - An artistic adaptation of a photo of the cryostat base lift by German photographer Christian Luenig. © Christian Luenig
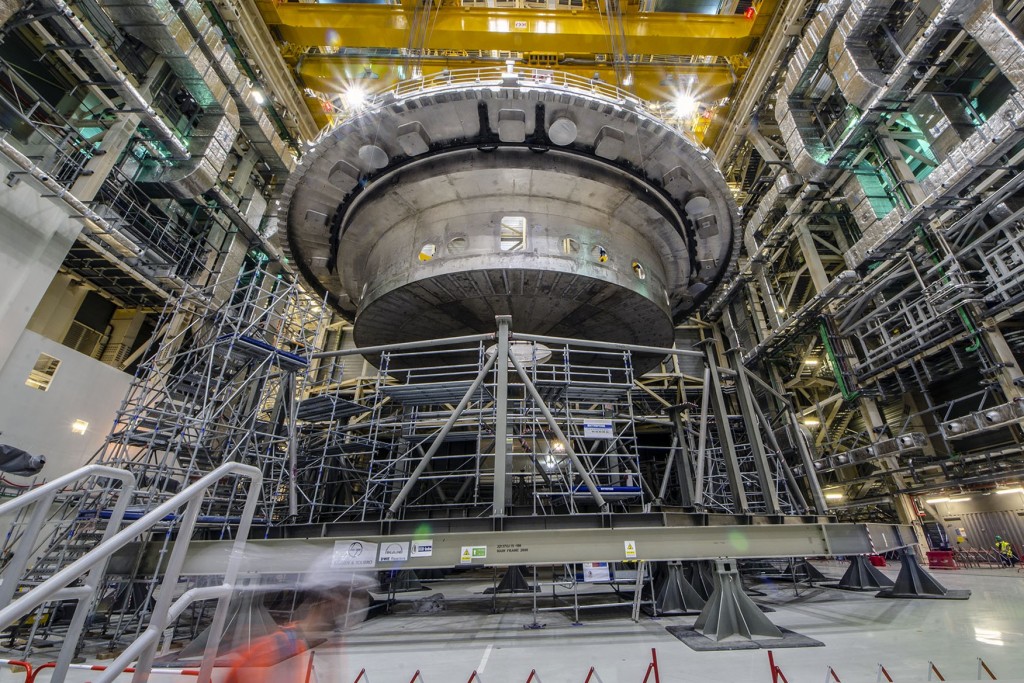
Major machine assembly milestone
2020-05-26 - On Tuesday 26 May, the first major machine component—the cryostat base—is lifted by overhead crane and lowered into the Tokamak assembly pit.
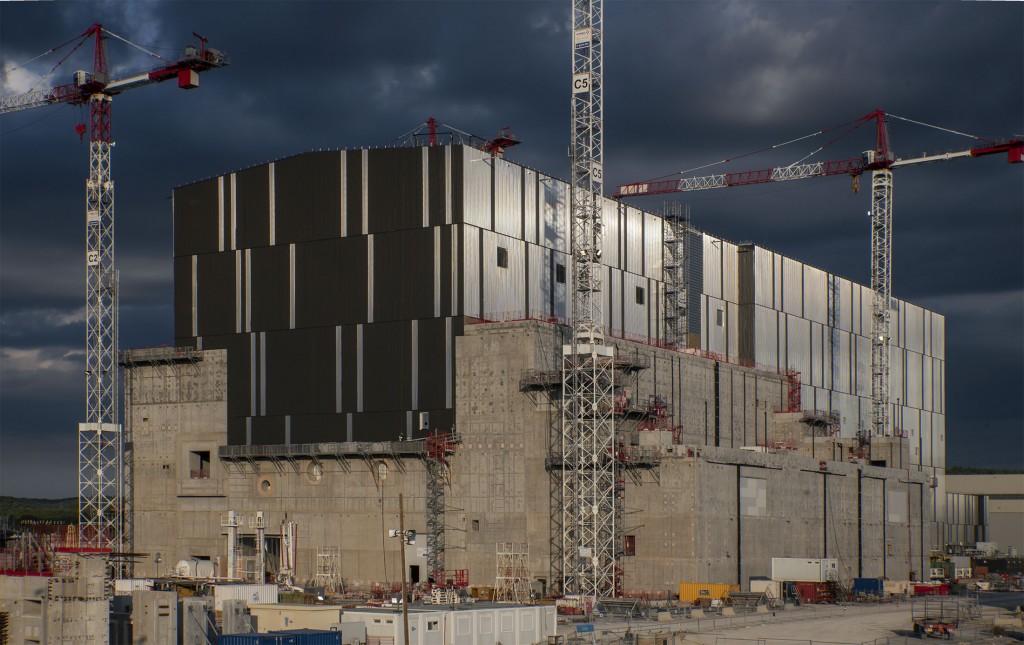
Cladding completed
2020-05-26 - Metal cladding now completely covers the crane hall of the Tokamak Building.
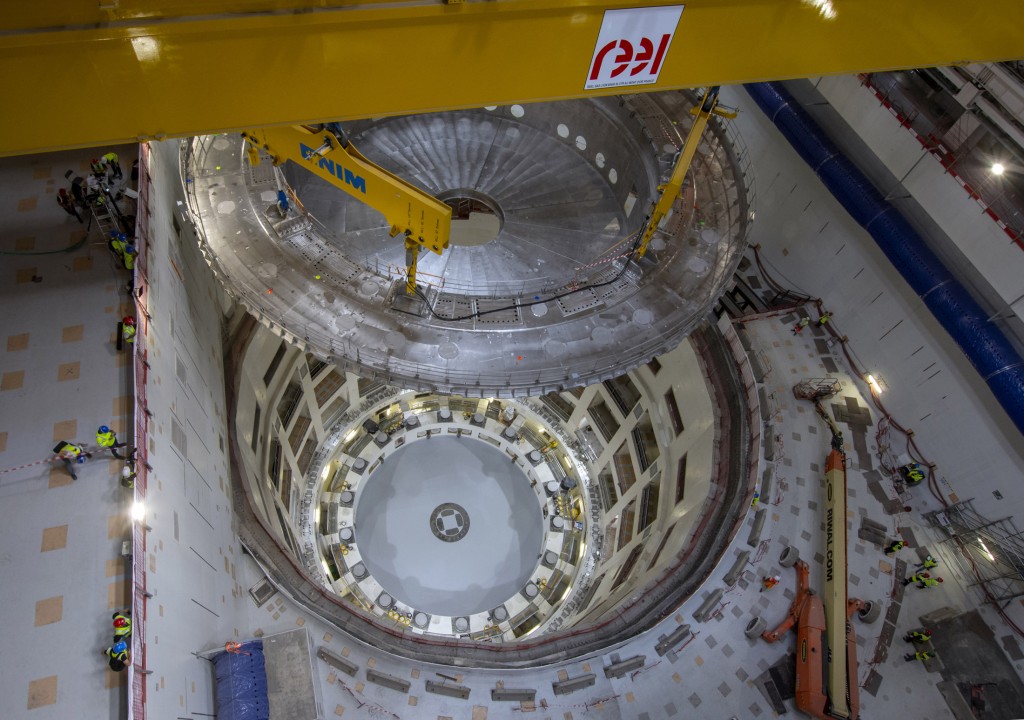
Perfect fit
2020-05-26 - The 1,250-tonne machine base has just the room it needs to enter the Tokamak pit.

Perfectly clean
2020-05-26 - Perfectly clean The machine assembly "well" is perfectly clean and ready to receive machine components. The 18 cylindrical cryostat support bearings are clearly visible, like jewels in the supporting crown.

Perfect fit
2020-05-26 - Two 750-tonne bridge cranes work together to transport, and lower, the cryostat base (1,250 tonnes). Photo: ITER Organization/EJF Riche
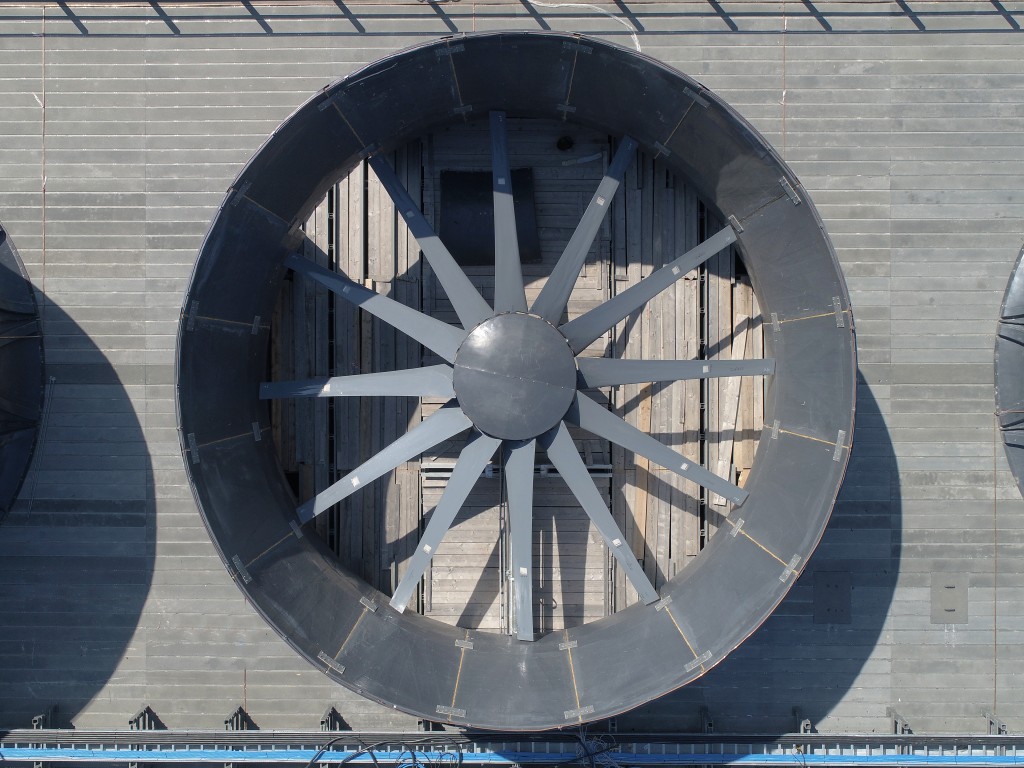
From river to droplets and mist
2020-05-25 - Large fans at the top of the cooling tower building will induce an upward airstream that accelerates the evaporation process. Photo : ITER Organization/EJF Riche

From the rafters
2020-05-25 - Seen by drone in the very rafters of the Assembly Hall, the cryostat base is ready to be lifted. Photo: ITER Organization/EJF Riche

Penultimate test
2020-05-20 - Every aspect of the lift operation has been choreographed and practiced in advance of the big day. In one critical test on 20 May, the cryostat base is lifted six metres and then set back onto its supports.

Penultimate test
2020-05-20 - Every aspect of the lift operation has been choreographed and practiced in advance of the big day. In one critical test on 20 May, the cryostat base is lifted six metres and then set back onto its supports.
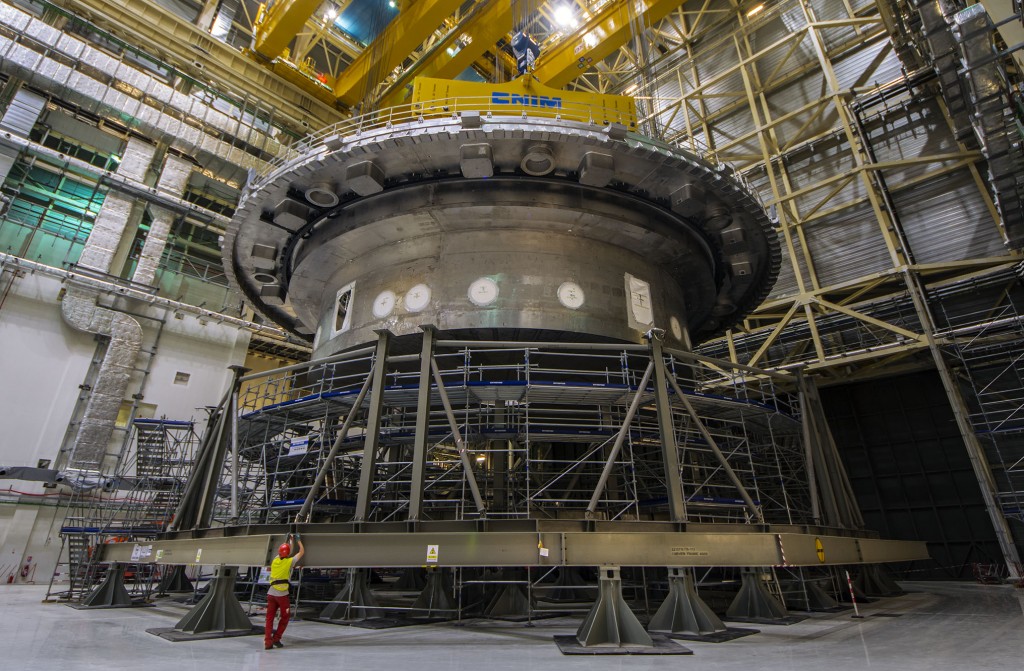
Spreading the load
2020-05-20 - Between the overhead heavy lift cranes and the component are yellow "spreader beams" that share the weight of the component and eliminate any tilt.
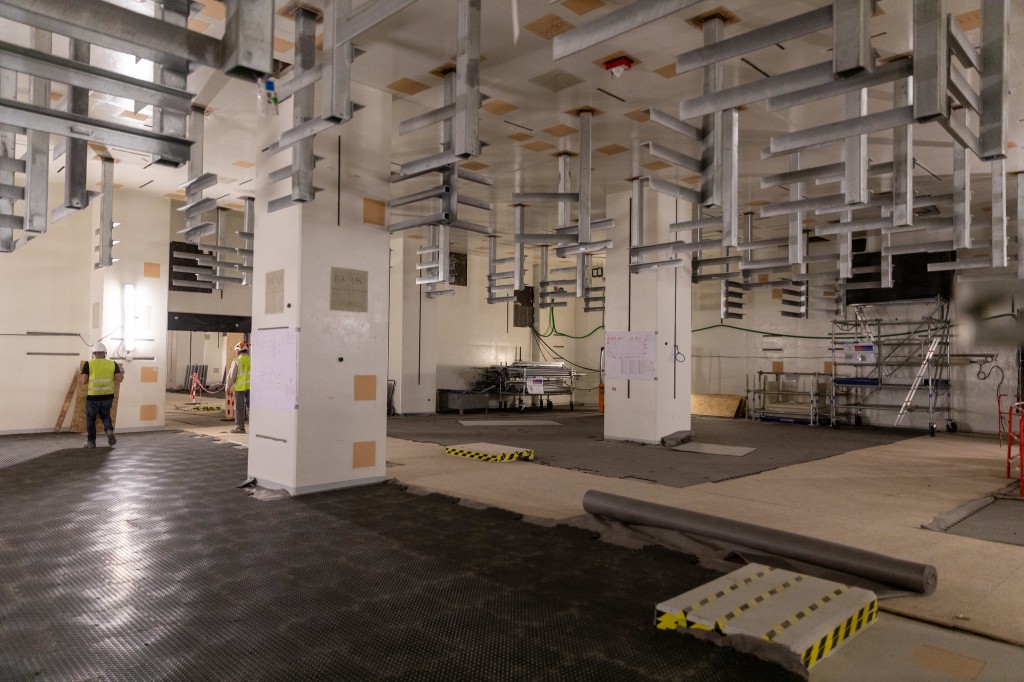
Welding equipment supports
2020-05-15 - In the vast galleries of the Tokamak Complex on every level, ten of thousands of steel plates have been embedded into the floors, ceilings and walls. Now we see why: all equipment, like these cable tray supports, has to be welded to these plates to avoid drilling into the concrete (which is forbidden in a nuclear building). © Les Nouveaux Médias/SNC ENGAGE
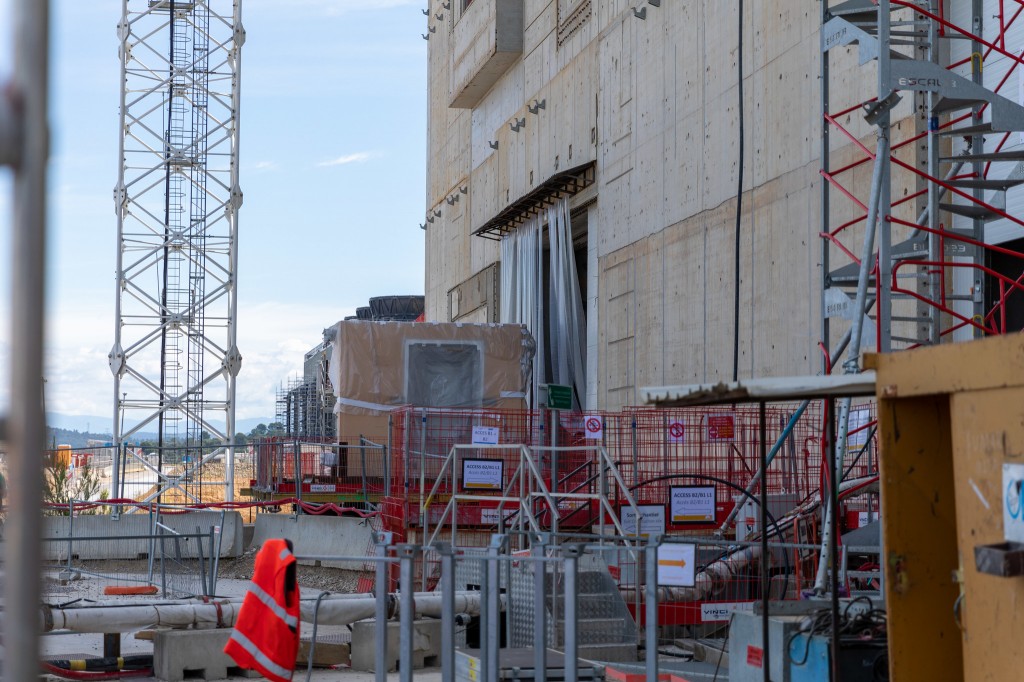
Final nuclear doors
2020-05-15 - The last nuclear doors are delivered through a Level 1 door of the Tokamak Complex. By next month, all 46 will have been installed. © Les Nouveaux Médias/SNC ENGAGE
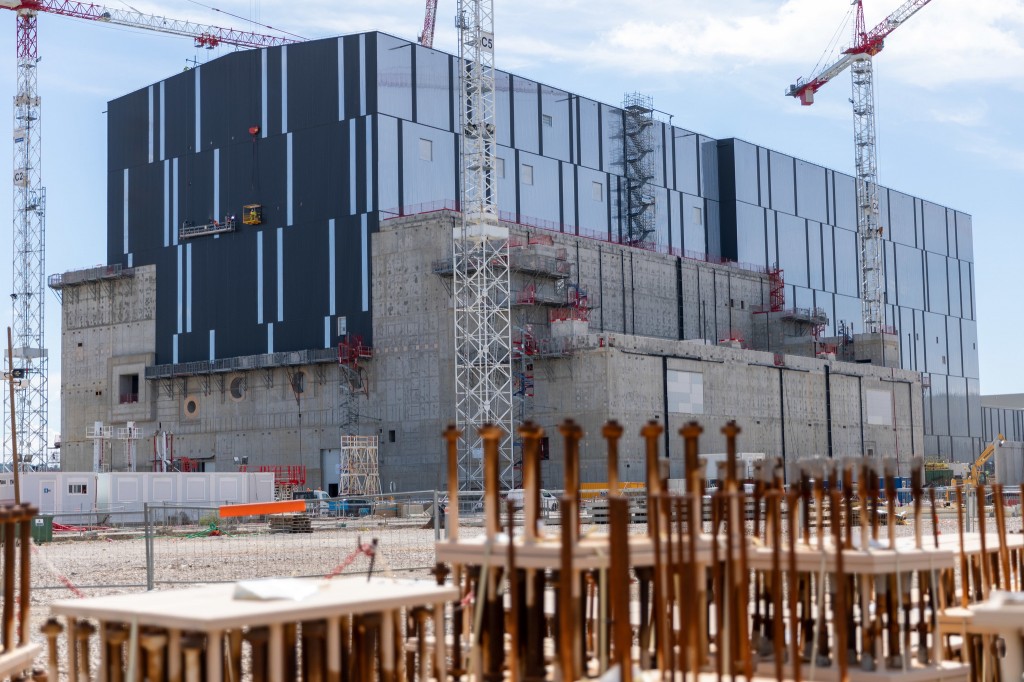
The Tokamak Complex
2020-05-15 - The Tokamak Building now mirrors the Assembly Hall. To either side of it, the Diagnostics Building (centre) and the Tritium Building (left) are still under construction. © Les Nouveaux Médias/SNC ENGAGE
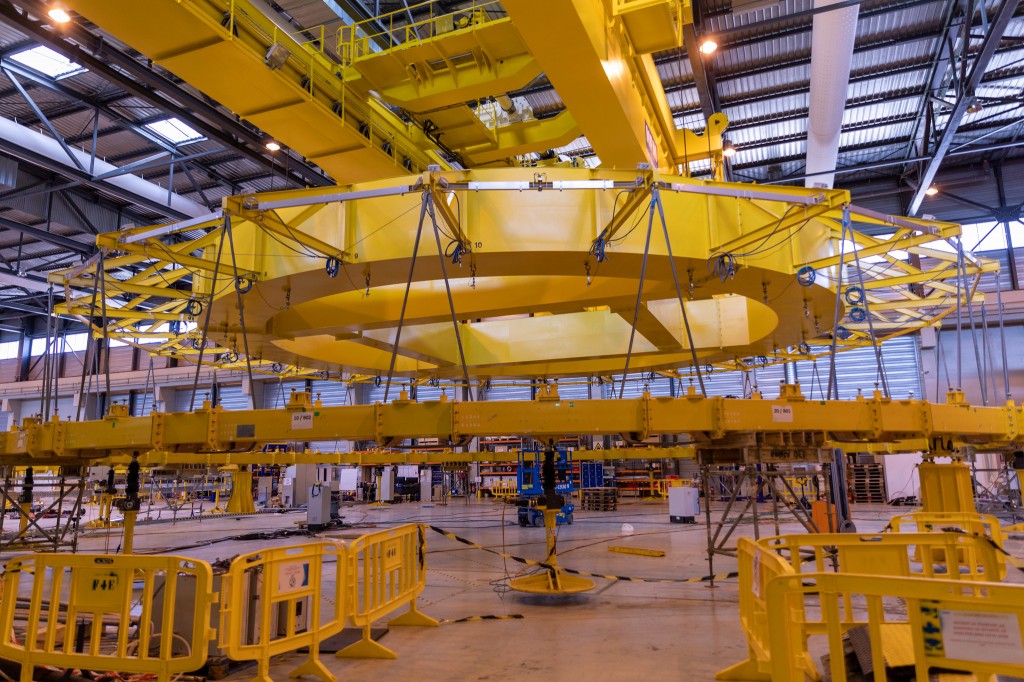
Spreader beam
2020-05-15 - This 40-tonne spreader beam supports the double pancakes at many points, allowing them to be transported without tilting. © Les Nouveaux Médias/SNC ENGAGE
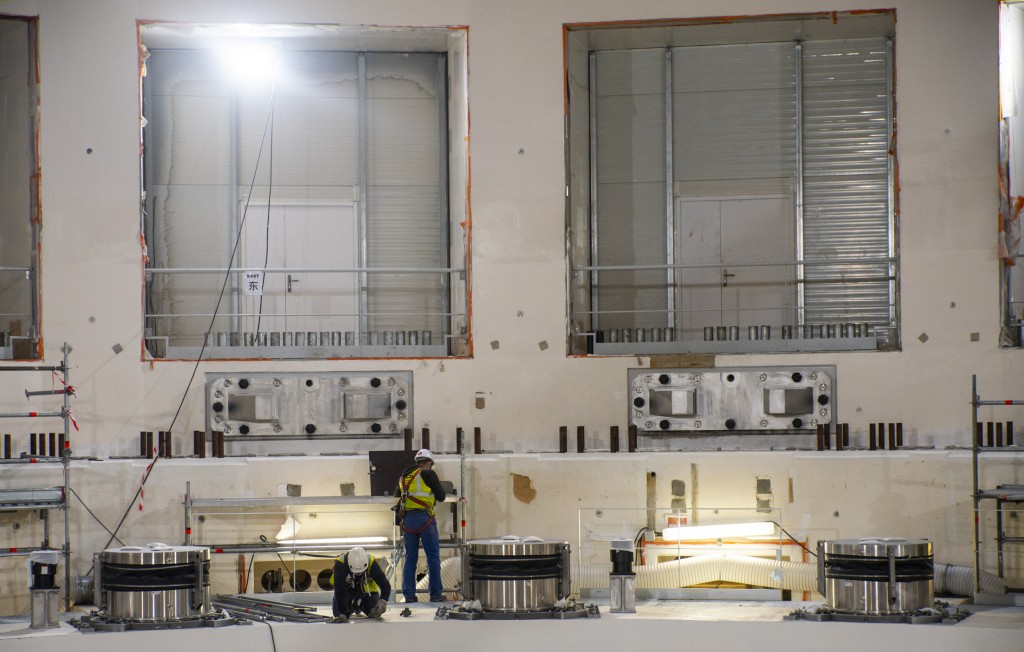
Match exactly
2020-05-13 - The pedestal of the cryostat base will be affixed to the female lugs seen here in the wall of the bioshield (steel rectangles). To meet these interfacing pieces, the base must be positioned as it is lowered with a tolerance of +/-5 mm.

Deep in the Tokamak Complex
2020-05-13 - Welding the pipes inside the multi-process cryolines is a challenging operation, sometimes performed in an extremely cramped environment.

18 cryostat bearings
2020-05-13 - A set of 18 spherical bearings, evenly spaced and deeply anchored into the "crown," will bear the full weight of the machine and, acting as ball-and-socket joints, will enable the smooth transfer of horizontal and rotational forces.

Match exactly
2020-05-13 - The pedestal of the cryostat base will be affixed to the female lugs seen here in the wall of the bioshield (steel rectangles). To meet these interfacing pieces, the base must be positioned as it is lowered with a tolerance of +/-5 mm.
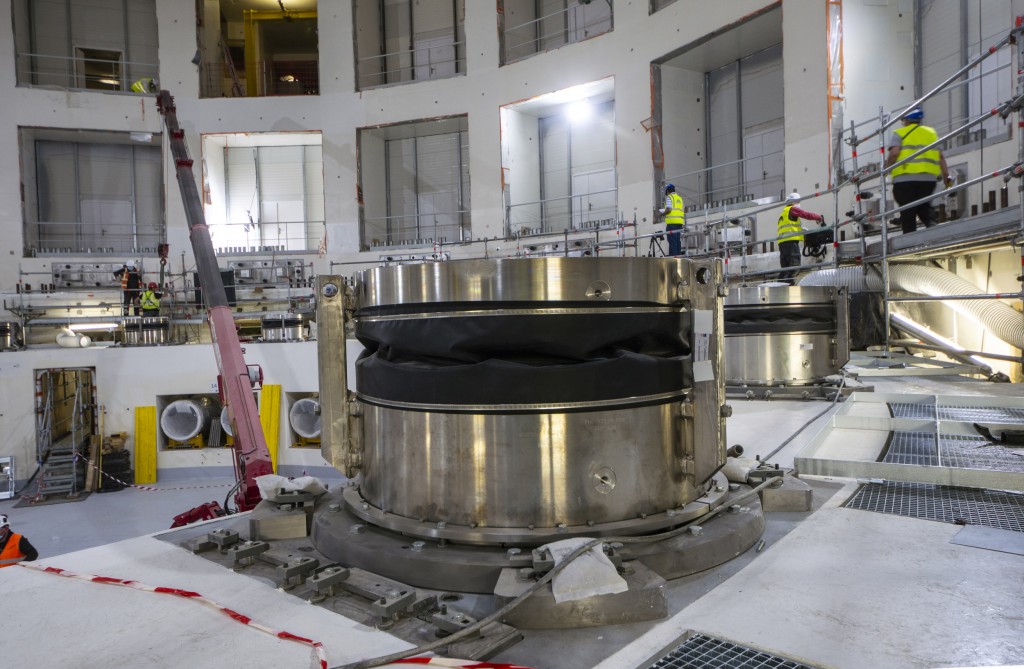
Covers off
2020-05-13 - One of the last things to do at the bottom of the Tokamak pit—uncover the cryostat bearings, which until now had been hidden under thick protective wrapping.

500 sections of cryolines to connect
2020-05-13 - Prior to welding cryoline sections, process pipes that transport the cooling fluid need to be cut and surfaced for optimal adjustment.

Managing ITER assembly
2020-05-13 - In green, the zone covered by the TAC (Tokamak Assembly) contracts, including the Tokamak Pit, the Assembly Hall and the Cleaning Facility. In light blue, the TCC (Tokamak Complex) zone plus Radio Frequency Building. In red, pink and dark blue, the areas covered by the ''Balance of Plant'' contracts.
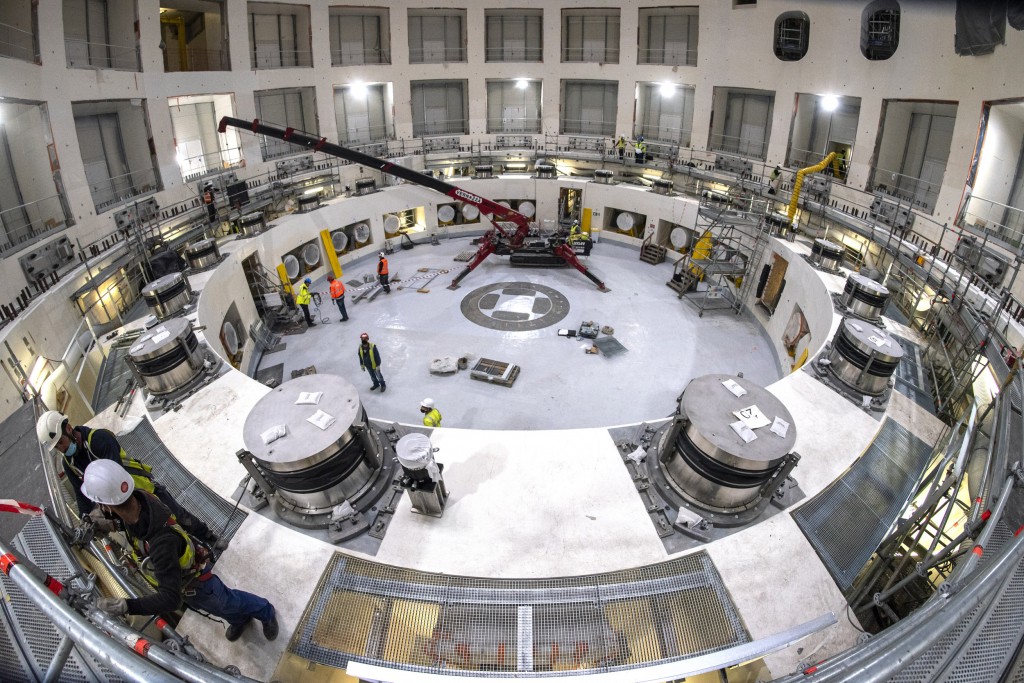
18 cryostat bearings
2020-05-13 - A set of 18 spherical bearings, evenly spaced and deeply anchored into the "crown," will bear the full weight of the machine and, acting as ball-and-socket joints, will enable the smooth transfer of horizontal and rotational forces.
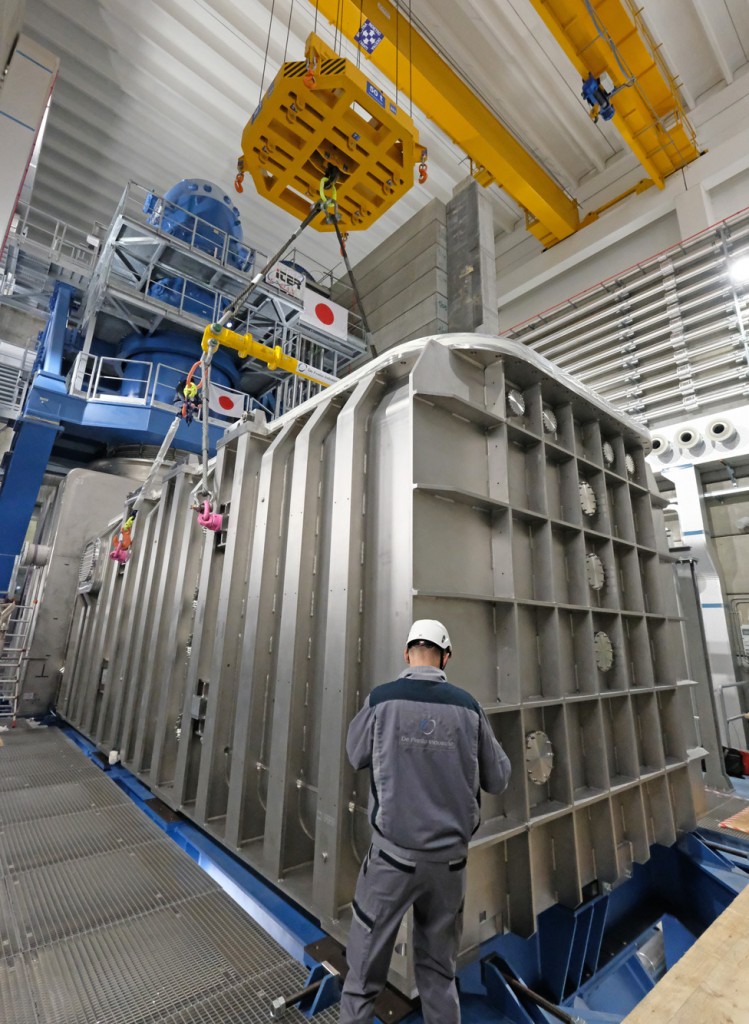
MITICA vessel is ready for handover
2020-05-10 - A technician conducts final checks on the MITICA vacuum vessel prior to handover to the ITER Organization. The vacuum vessel was delivered in two parts by European contractor De Pretto Industrie, and welded in May 2020.
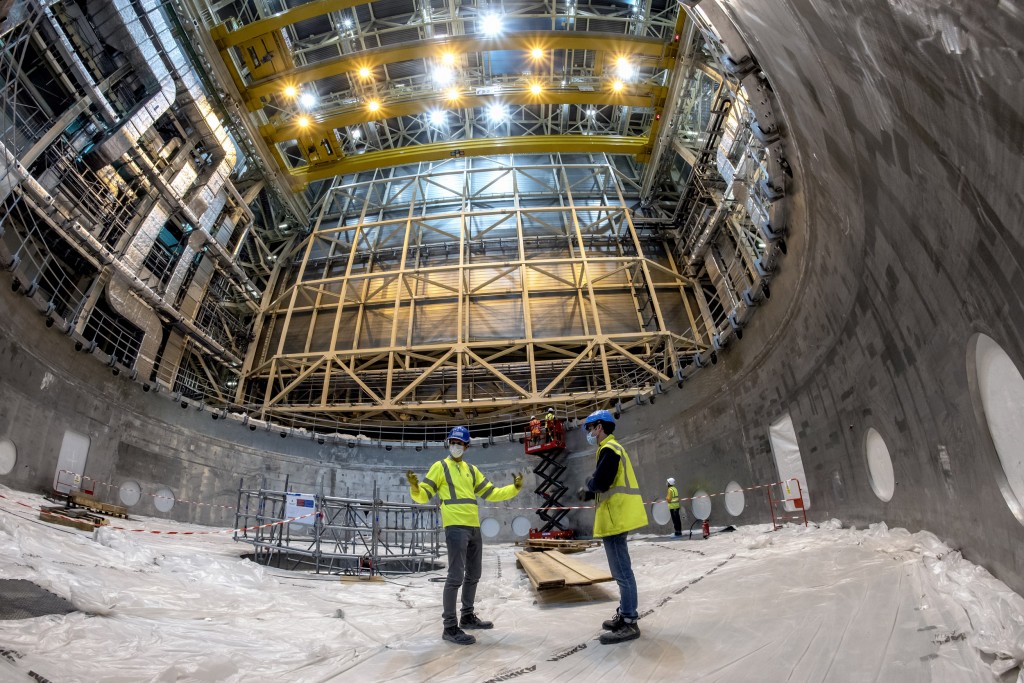
Preparing the base for lifting
2020-05-06 - Standing inside the "dish" of the cryostat base, these employees are involved in the preparations for the "big lift," when the overhead cranes raise this 1,250-load high overhead and then travel to the Tokamak pit. As a preparatory activity, the base will be raised a few centimetres in the week to come.
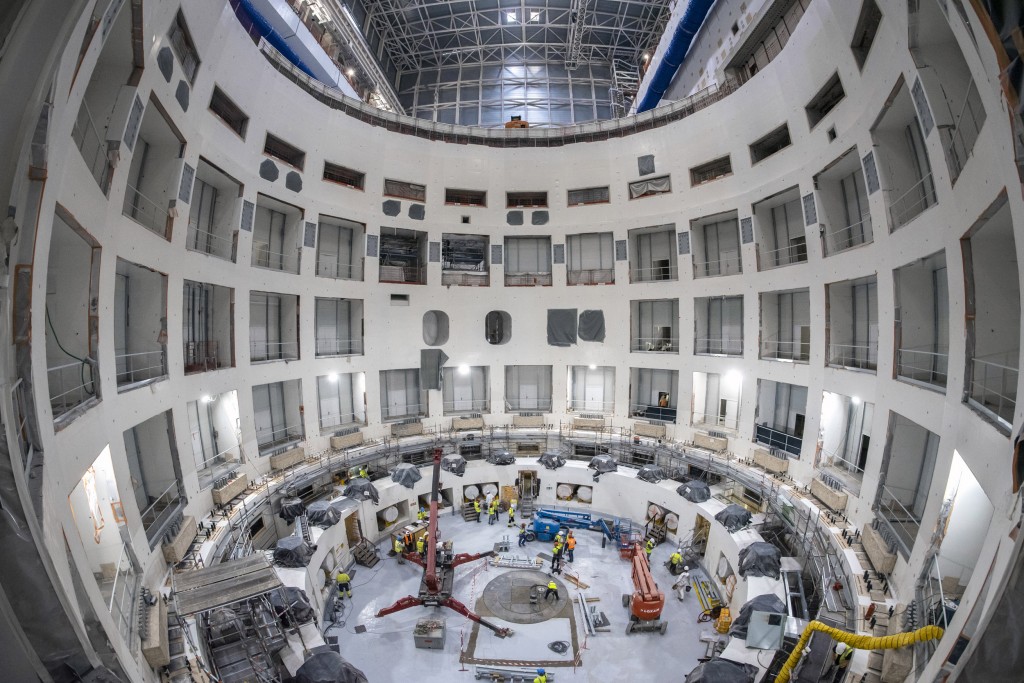
On the pit floor
2020-05-06 - Painted and cleaned, everything is nearly ready in the Tokamak pit for the first machine components. Photo: Gérard Lesénéchal

30 metres deep
2020-05-06 - Two sets of overhead cranes (2 x 750 tonnes and 2 x 50 tonnes) will be responsible for the ballet of activity as components ready for installation are picked up in the Assembly Hall and brought to the 30-metre deep Tokamak pit. Photo: Gérard Lesénéchal
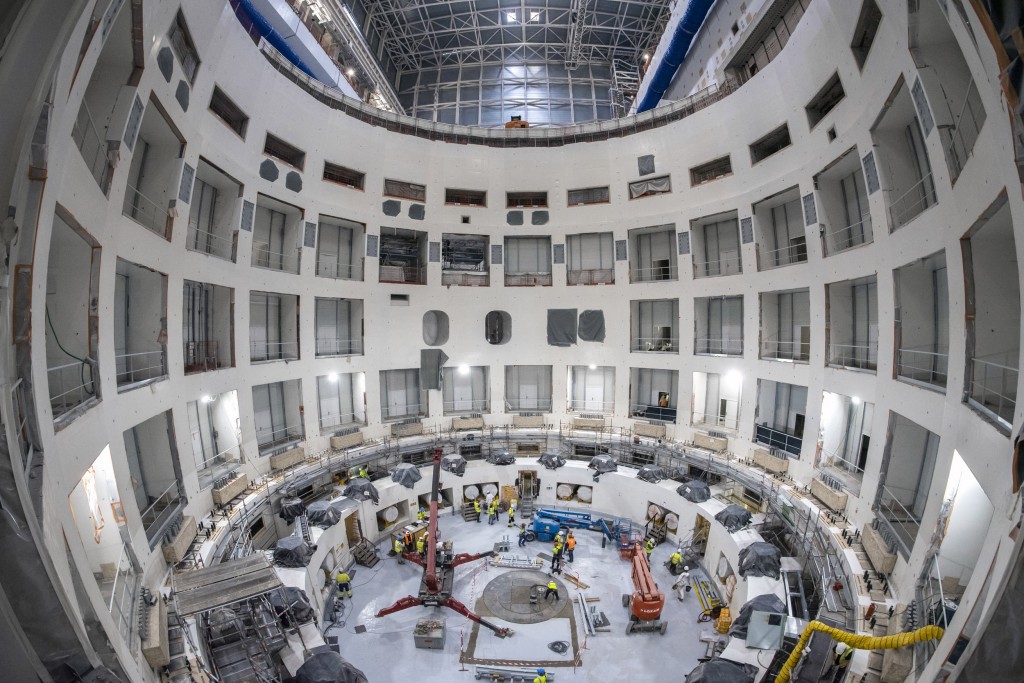
On the pit floor
2020-05-06 - Painted and cleaned, everything is nearly ready in the Tokamak pit for the first machine components. Photo: Gérard Lesénéchal

30 metres deep
2020-05-06 - Two sets of overhead cranes (2 x 750 tonnes and 2 x 50 tonnes) will be responsible for the ballet of activity as components ready for installation are picked up in the Assembly Hall and brought to the 30-metre deep Tokamak pit. Photo: Gérard Lesénéchal
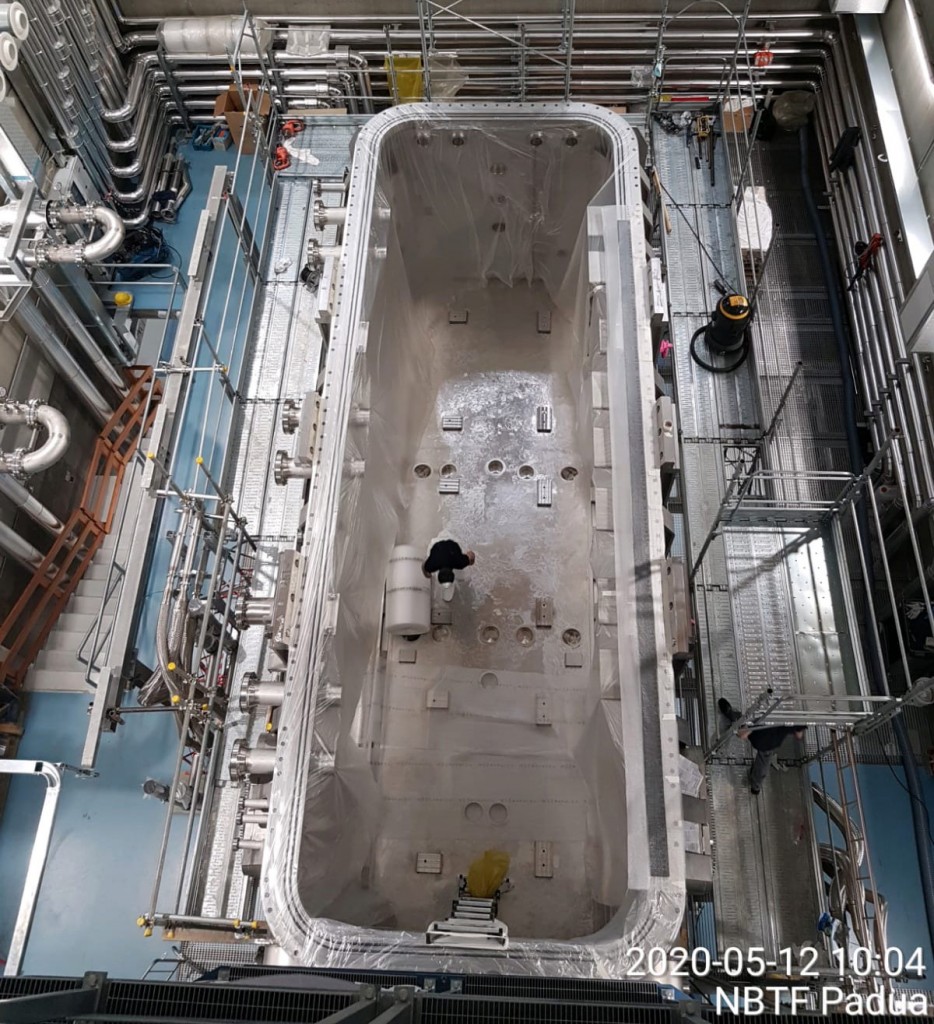
Large vacuum chamber
2020-05-04 - Looking down into the MITICA vessel before welding. The MITICA beam source, beam line components and cryogenic pumps will all be housed inside this vessel.

Assembly theatre
2020-05-04 - The ''assembly theatre'' is a vast space that encompasses the assembly and crane halls. In the foreground, the opening of the assembly pit; in the background (past the twin sector sub-assembly tools), the cryostat base is being groomed for the upcoming assembly operations.

The base of the machine
2020-05-04 - Two weeks remain before the first "big lift" of ITER assembly. Preparatory works are underway to prepare the component for handling and the Tokamak pit for receiving.
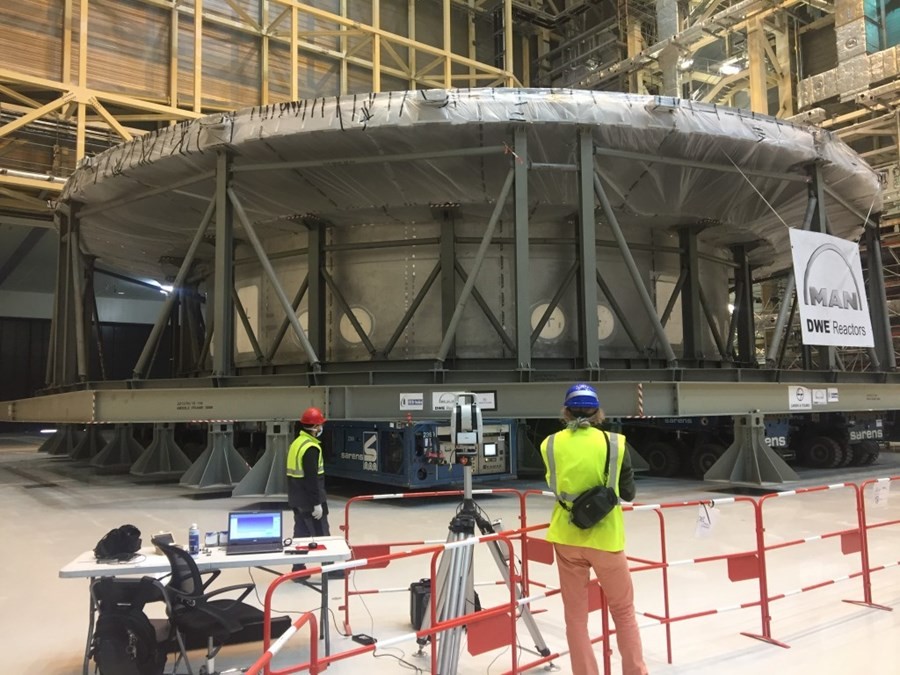
A rotational tolerance of +/- 5 mm
2020-05-04 - Because rotating the heavy cryostat base during installation would be difficult, metrologists were on hand as the base entered the Assembly Hall to make sure the transporter positioned the component exactly as it must be lifted by the overhead cranes. The team managed to achieve a rotational tolerance of +/- 5 mm.

Assembly theatre
2020-05-04 - The ''assembly theatre'' is a vast space that encompasses the assembly and crane halls. In the foreground, the opening of the assembly pit; in the background (past the twin sector sub-assembly tools), the cryostat base is being groomed for the upcoming assembly operations.

The base of the machine
2020-05-04 - Two weeks remain before the first "big lift" of ITER assembly. Preparatory works are underway to prepare the component for handling and the Tokamak pit for receiving.
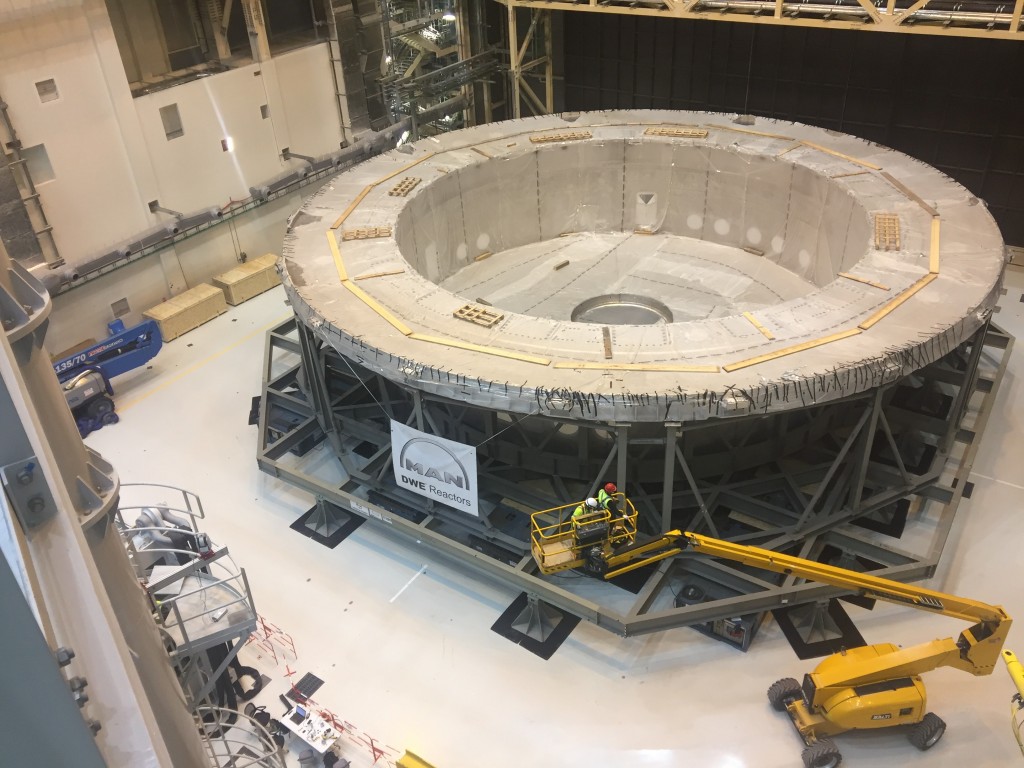
Clear lines of sight
2020-05-04 - The team anticipated the arrival of the cryostat base in the Assembly Hall by installing one instrument station high up on the nearest sector sub-assembly tool (you can see the instrument if you look closely) for a clear line of sight.

Larger width
2020-05-01 - The teams are currently setting up the work tables they will need for poloidal field coils 4 and 3, which are larger in diameter--24 metres instead of 17. © Les Nouveaux Médias/SNC ENGAGE

ITER's assembly arena
2020-05-01 - Machine components make a first stop in the Cleaning Facility (right) before entering the Assembly Hall. After pre-assembly and installation activities, the components are moved by overhead crane to the Tokamak pit. © Les Nouveaux Médias/SNC ENGAGE
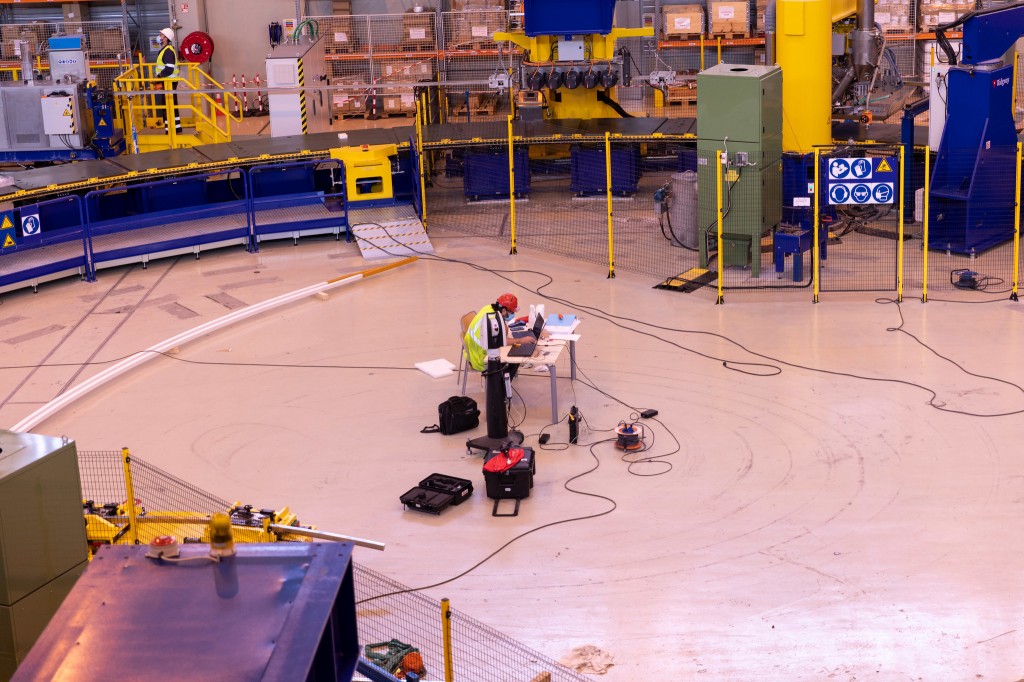
Working on a dummy
2020-05-01 - A dummy double pancake is underway for poloidal field coil #4 (PF4)—a prerequisite to starting actual fabrication this summer. © Les Nouveaux Médias/SNC ENGAGE

Cold chamber
2020-05-01 - A second cryogenic chamber is under construction for poloidal field coil #5 (PF5), which will be the second European coil to undergo cold testing. © Les Nouveaux Médias/SNC ENGAGE
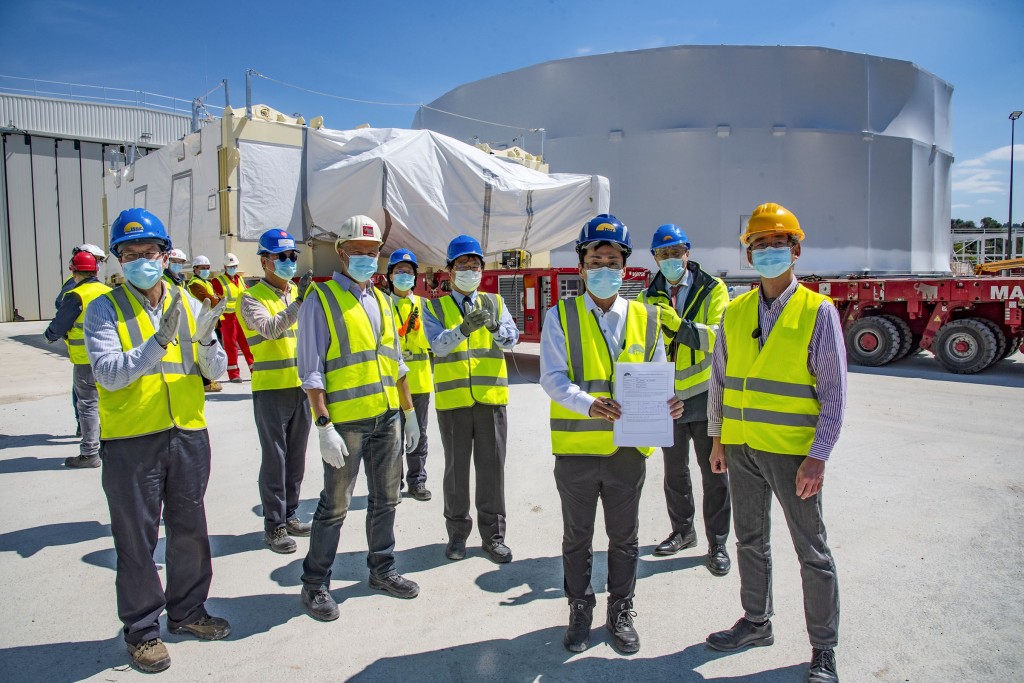
TF12 delivered
2020-04-25 - Toroidal field coil #12 (TF12) reaches the ITER site from Japan on 25 April 2020. Gathered around the certificate of acceptance are representatives of the ITER Organization and ITER Japan. In the background is the upper cylinder of the ITER cryostat moving out of India's on-site workshop to a storage location.

Not empty for long
2020-04-24 - After the cryostat base and upper cylinder were removed from the Cryostat Workshop in mid-April, the building was empty for one week. Now, one of the machine's 18 toroidal field coils—#12, supplied by the Japanese Domestic Agency—has been moved in so that construction teams can unwrap the component and prepare it for handling and pre-assembly activities.

First magnet on site
2020-04-17 - The first ITER magnet to arrive on site—toroidal field coil #12, procured by Europe—is delivered to a temporary building (background) where it will be prepared for lifting and handling.
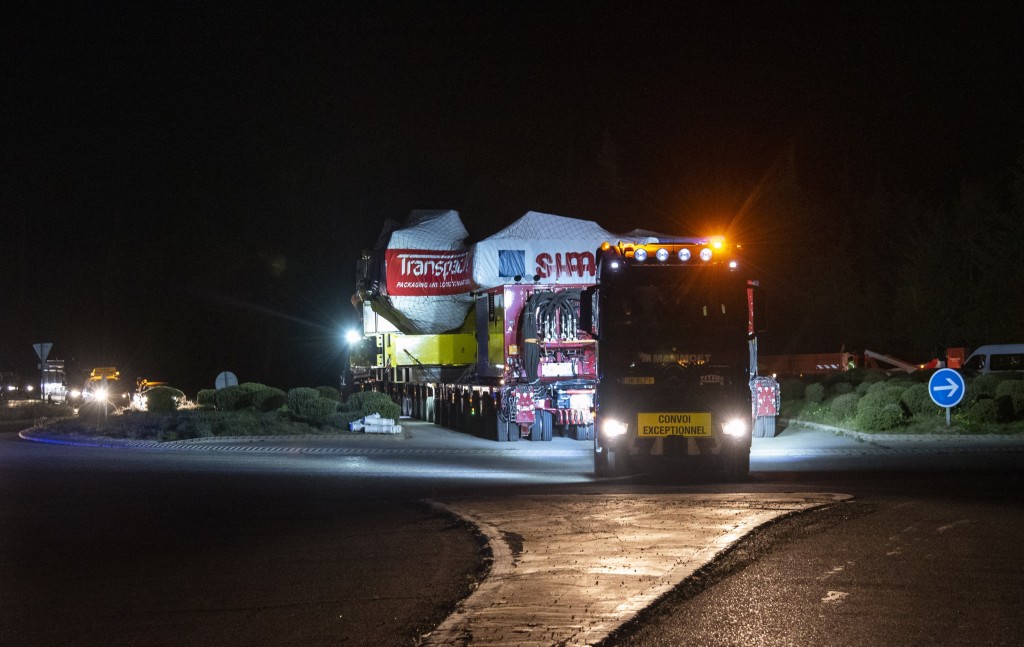
First ITER magnet arrives on site
2020-04-17 - A little before 2:00 a.m. on Friday 17 April, toroidal field coil #9 arrives at the ITER site. The 360-tonne component is one of ten toroidal field magnets to be delivered by Europe. (Japan will deliver another nine.)

Cryostat base enters building
2020-04-17 - Installation contractors have moved the cryostat base from its fabrication workshop on site into the Assembly Hall. (The big lift to the Tokamak Building will take place next month.) The Indian Domestic Agency has delivered the completed component in collaboration with main contractor Larsen & Toubro Heavy Engineering (manufacturing design, segment fabrication in India and assembly at ITER) and MAN Energy Solutions, Germany (Larsen & Toubro sub-contractor for on-site welding).
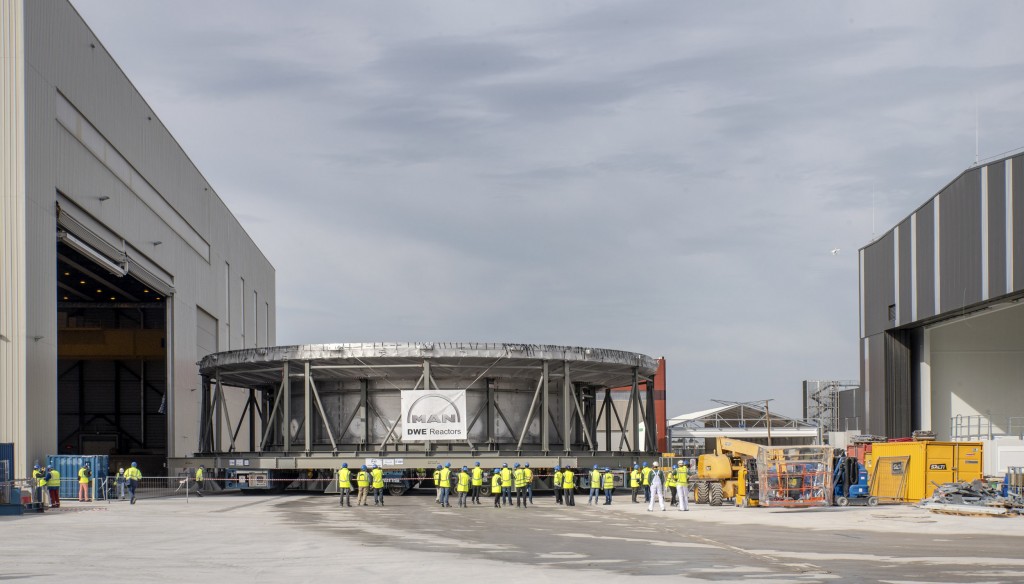
Moved next door
2020-04-17 - On Friday 17 April, the heaviest piece of the ITER machine—the cryostat base—is transferred into the ITER Assembly Hall. There, it will be prepared for the May 2020 transfer to the Tokamak Pit, where 18 ball-and-socket joints ("bearings") are waiting to receive its weight.

First machine component enters building
2020-04-17 - The cryostat base enters the Cleaning Facility on a self-propelled modular transporter that has 192 wheels. Photo: ITER Organization/EJF Riche

Cryostat base enters building
2020-04-17 - Cryostat base enters building Installation contractors have moved the cryostat base from its fabrication workshop on site into the Assembly Hall. (The big lift to the Tokamak Building will take place next month.) The Indian Domestic Agency has delivered the completed component in collaboration with main contractor Larsen & Toubro Heavy Engineering (manufacturing design, segment fabrication in India and assembly at ITER) and MAN Energy Solutions, Germany (Larsen & Toubro sub-contractor for on-site welding).

Leaving home
2020-04-17 - The cryostat base was assembled and welded in the Cryostat Workshop between September 2016 and early 2019. After site acceptance tests, responsibility for the component was transferred to the ITER Organization for pre-installation works such as the welding of cooling water bellows and skirt supports. Today is the first time the cryostat base will be leaving "home."

Safe in the Assembly Hall
2020-04-17 - The 192 wheels of the self-propelled modular transporter carried the 1,250-base carefully and successfully into the Assembly Hall. After unwrapping and preparatory works, the overhead cranes will enter into action. They were sized for this load—ITER's heaviest.
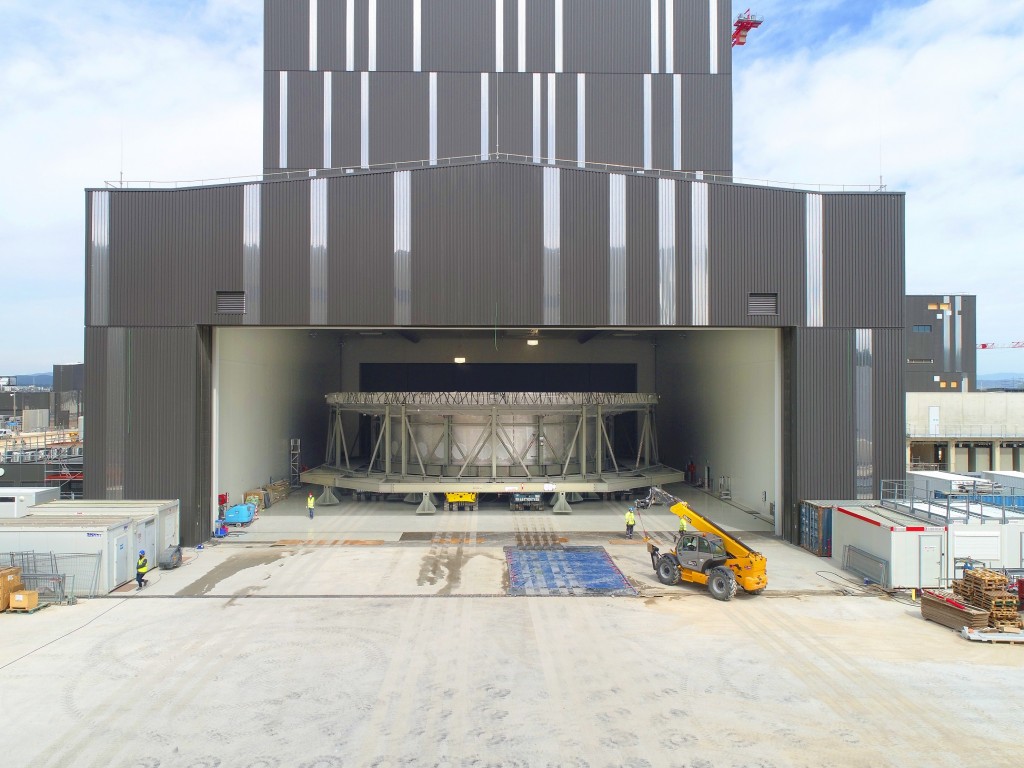
First machine component enters building
2020-04-17 - First machine component enters building The cryostat base enters the Cleaning Facility on a self-propelled modular transporter that has 192 wheels. Photo: ITER Organization/EJF Riche

Second section leaves workshop
2020-04-15 - The double doors of the Cryostat Workshop are open and teams are getting ready to remove the upper cylinder to storage. Its removal will allow the cryostat base to be moved out at the end of this week.

Ready for the weather
2020-04-15 - Further layers of plastic material will be added once the component is settled into the storage area. The synthetic skin that is formed seals the upper cylinder hermetically and protects it from weather, moisture and dust.
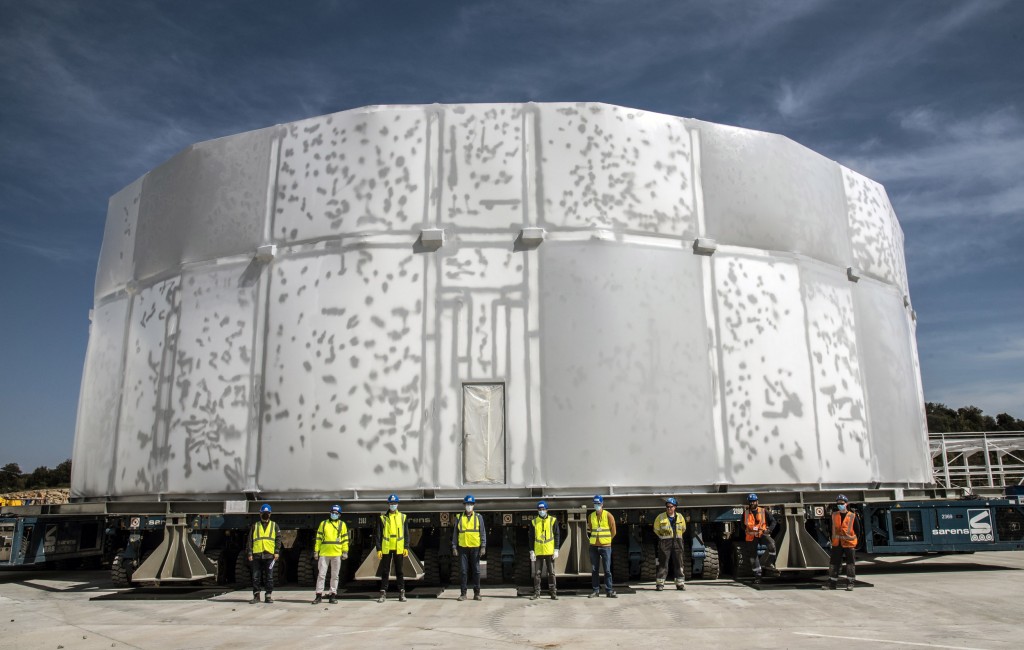
Third completed cryostat section
2020-04-15 - The cryostat upper cylinder, assembled in the Cryostat Workshop from 12 segments manufactured in India. It took less than one year to complete.

On many wheels and axles
2020-04-15 - The 430-tonne upper cylinder is cocooned and ready for storage outdoors. The component is transported out of the workshop by self-propelled modular transporter (SPMT).

Sisters
2020-04-15 - Not far from the Cryostat Workshop, two cryostat sections are now stored—the lower cylinder (right, 375 tonnes) and the upper cylinder (left, 430 tonnes).
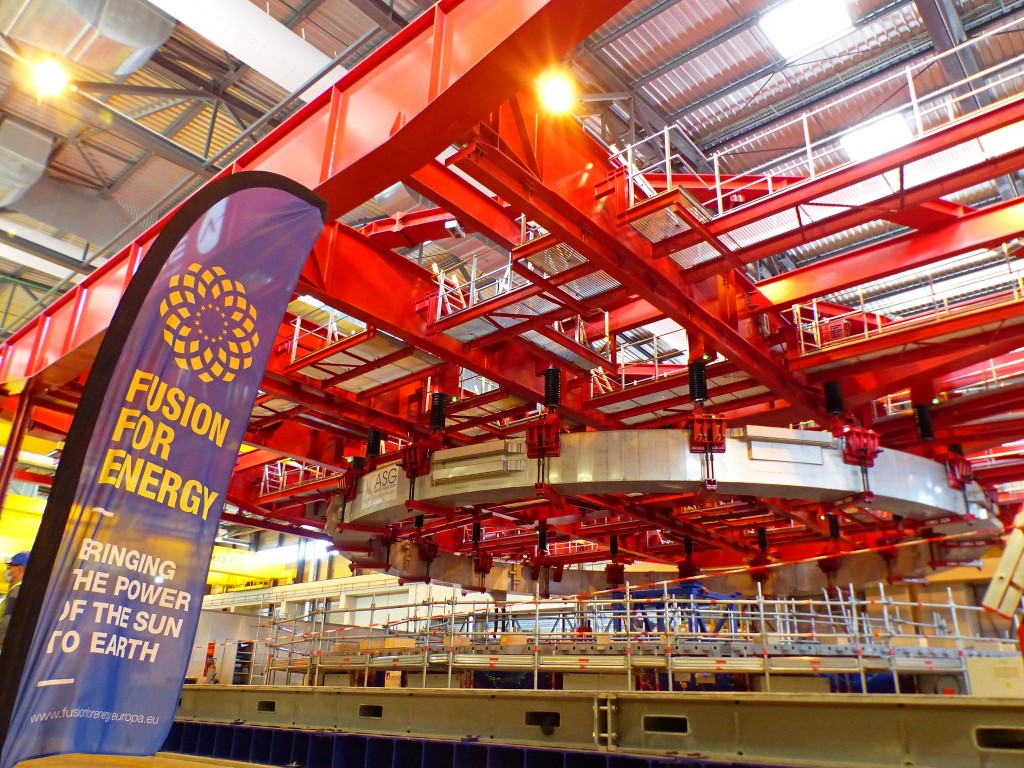
Gantry crane in action
2020-04-11 - The 280-tonne impregnated winding pick is lifted by gantry crane and transported to the assembly station where clamps and other components will be attached. When the coil leaves the building, it will weigh 342 tonnes.
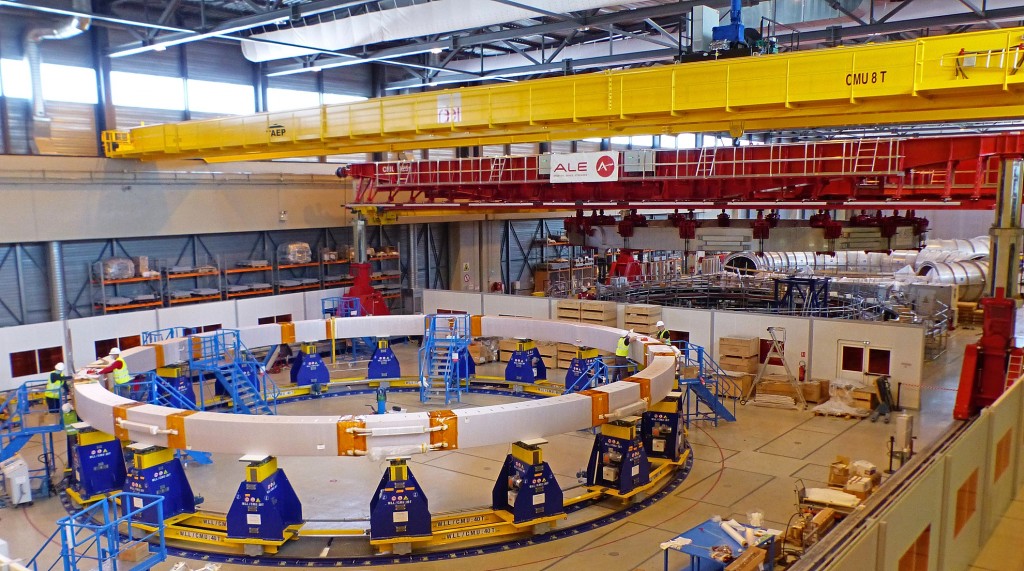
A production line
2020-04-11 - In the background, PF5 is discernible under the red gantry crane as it is moved to the final assembly station. In the foreground, European contractors are working on the ground insulation of the PF2 winding pack. In one month, a coil manufactured for Europe in China, PF6, will arrive for cold testing in one of the silver cryogenic chambers seen to the far right of the image.

Celebrating the penultimate step
2020-04-11 - Poloidal field coil #5 (PF5)—the first coil produced by Europe in its on-site winding facility—is lifted from the impregnation station to the final assembly station. Partners in the successful works are: the ASG consortium, MAMMOET (formerly ALE), Bureau Veritas (regulatory control of the gantry crane), and Fusion for Energy, the European Domestic Agency.
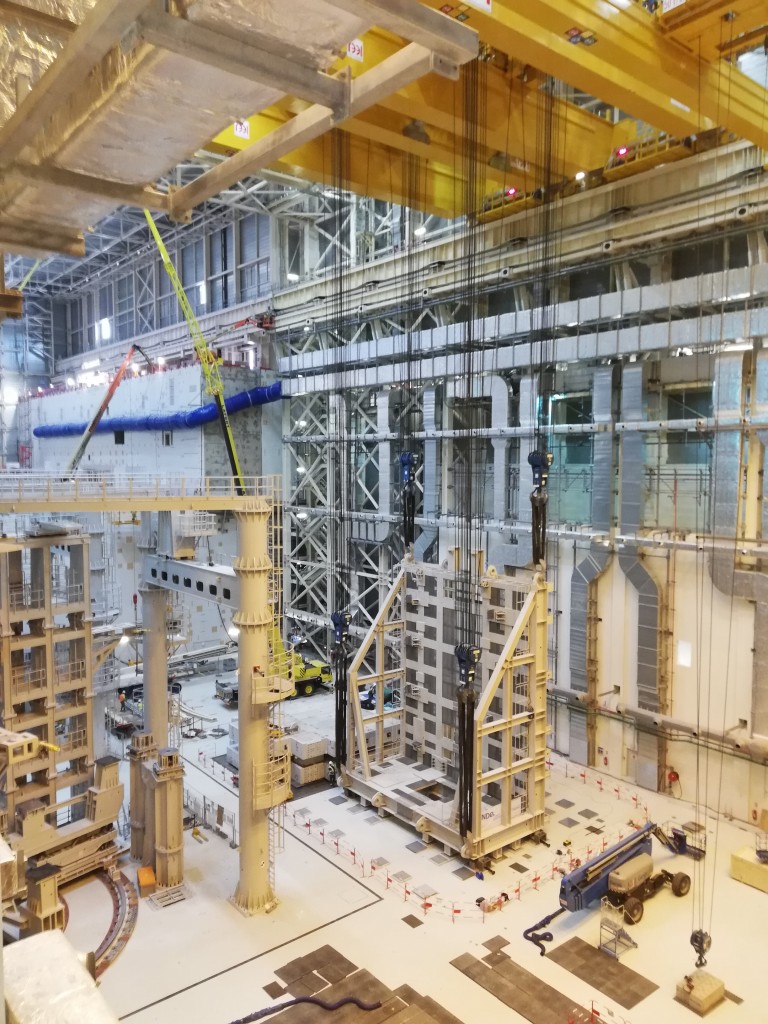
Practicing with the upending tool
2020-04-10 - The upending tool is brought to vertical by the overhead cranes during commissioning tests in the Assembly Hall.

Practicing with the upending tool
2020-04-10 - The upending tool is brought to vertical by the overhead cranes during commissioning tests in the Assembly Hall.
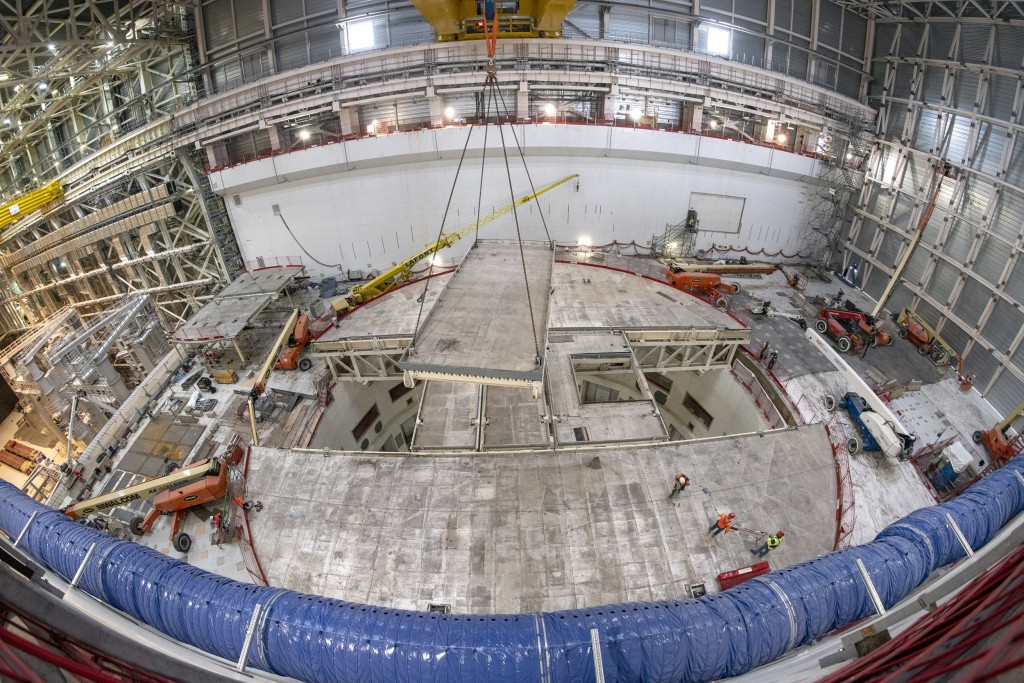
One segment at a time
2020-04-02 - The temporary lid over the assembly pit is made of 11 segments ranging in weight from 10 to over 80 tonnes.
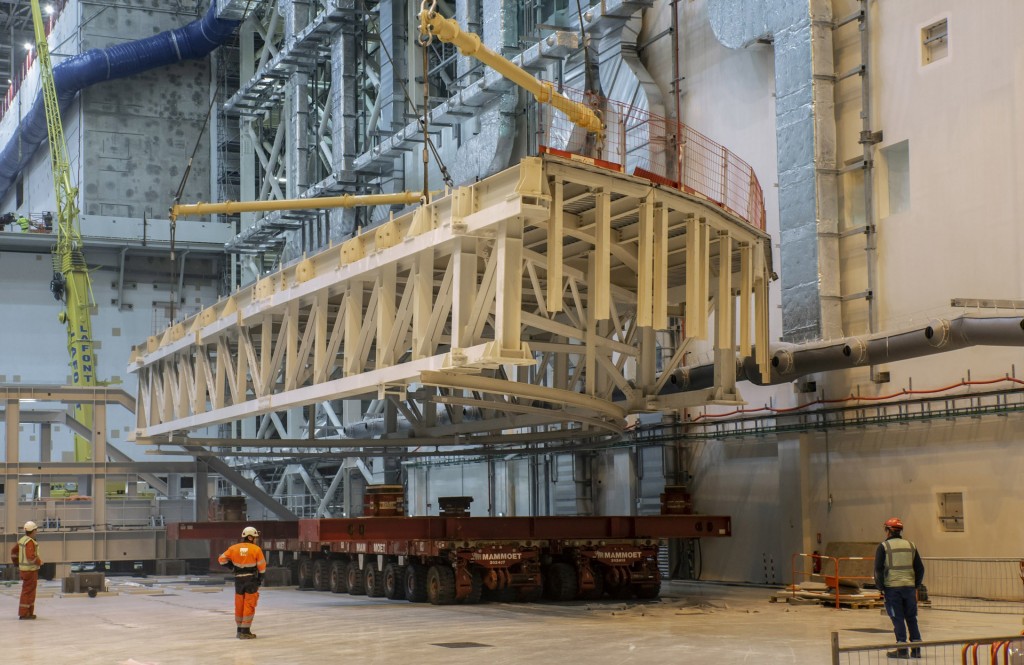
Heaviest piece
2020-04-02 - A half-moon element of the temporary lid is transported through the Assembly Hall to the waiting truck.

The lid is off
2020-04-02 - Standing at the end of the Tokamak Building, looking over the Tokamak pit toward the Assembly Hall. The temporary lid has been removed and installation activities are about to start.

11 segments in all
2020-04-02 - Once the central segment have been removed, two half-moon segments remain. At 80 tonnes each, they are the heaviest elements of the lid removal operation, which took two days to complete.
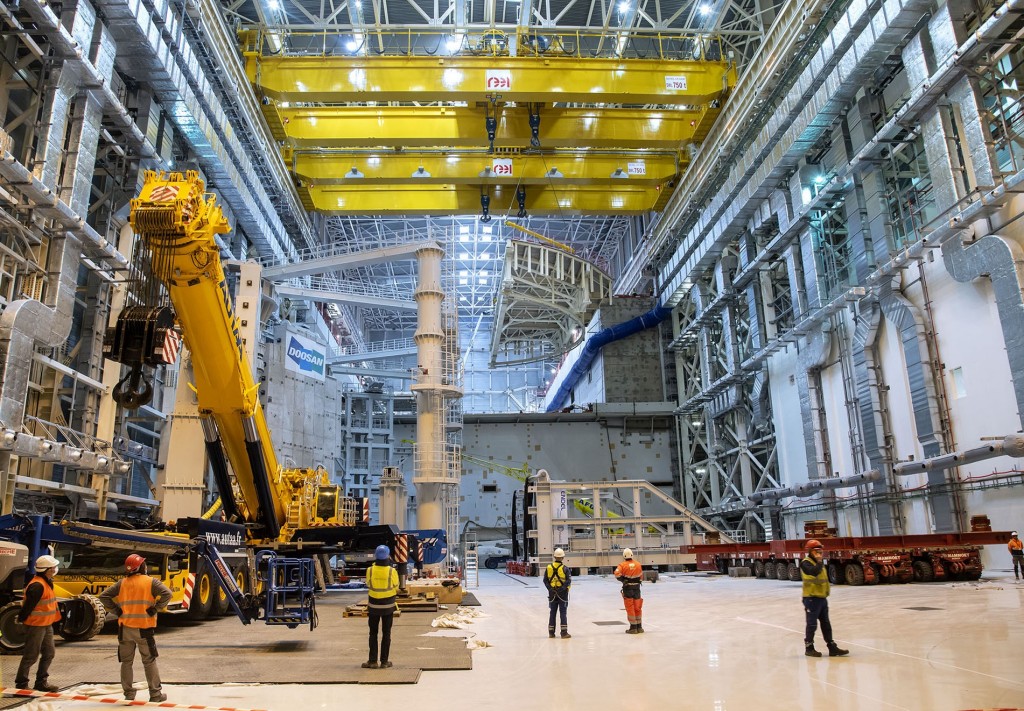
Essential activities on the worksite
2020-04-02 - Activity continues on the ITER worksite for a list of "essential activities" related to buildings and components, with the strict application of social distancing and recommended sanitary measures. For those used to working in the offices of the ITER Organization, however, approximately 95% are currently working from home.
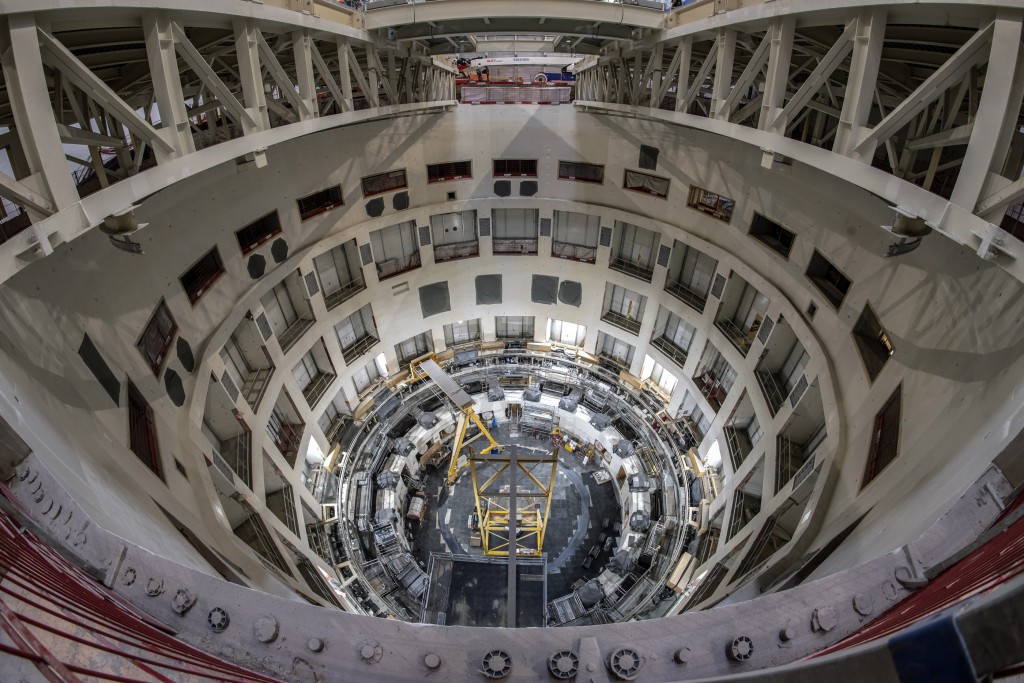
Getting ready
2020-04-02 - The Tokamak pit is nearly ready for its first machine component: 18 cryostat bearings are in place on the cryostat crown, contractors are finalizing painting and cleaning, and captive components have been installed in areas that will be blocked once the cryostat base has been lowered.
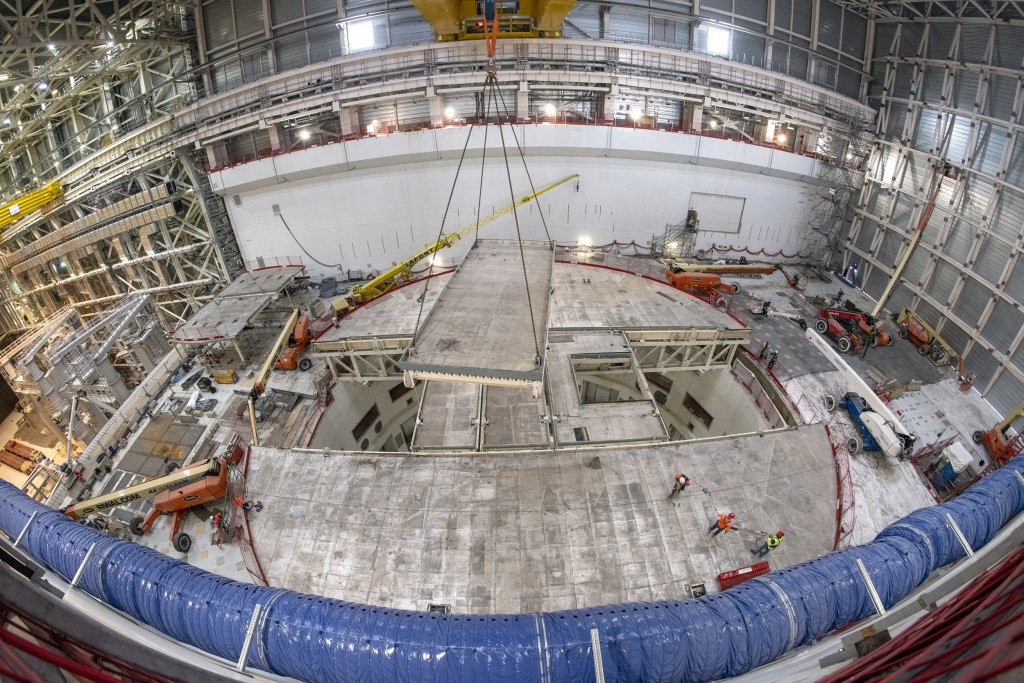
Removing the temporay lid
2020-04-02 - The temporary lid over the assembly pit is made of 11 segments ranging in weight from 10 to over 80 tonnes. They have to be removed, one by one, to make way for machine assembly.

Two hands
2020-04-02 - The two 750-tonne overhead cranes take part in the transport of the heaviest elements of the lid, from the Tokamak pit to the waiting truck.

The lid is off
2020-04-02 - Standing at the end of the Tokamak Building, looking over the Tokamak pit toward the Assembly Hall. The temporary lid has been removed and installation activities are about to start.
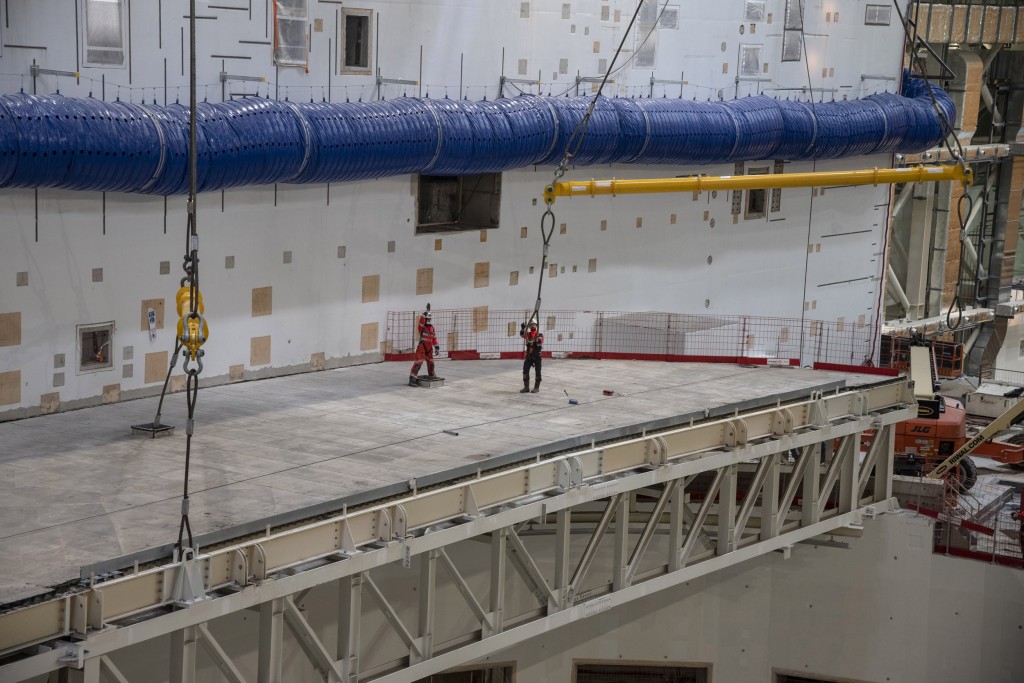
One half moon
2020-04-02 - Specialists attach a pair of hoisting beams to one of the two "half-moon" segments, bringing the total weight of the load to approximately 100 tonnes.
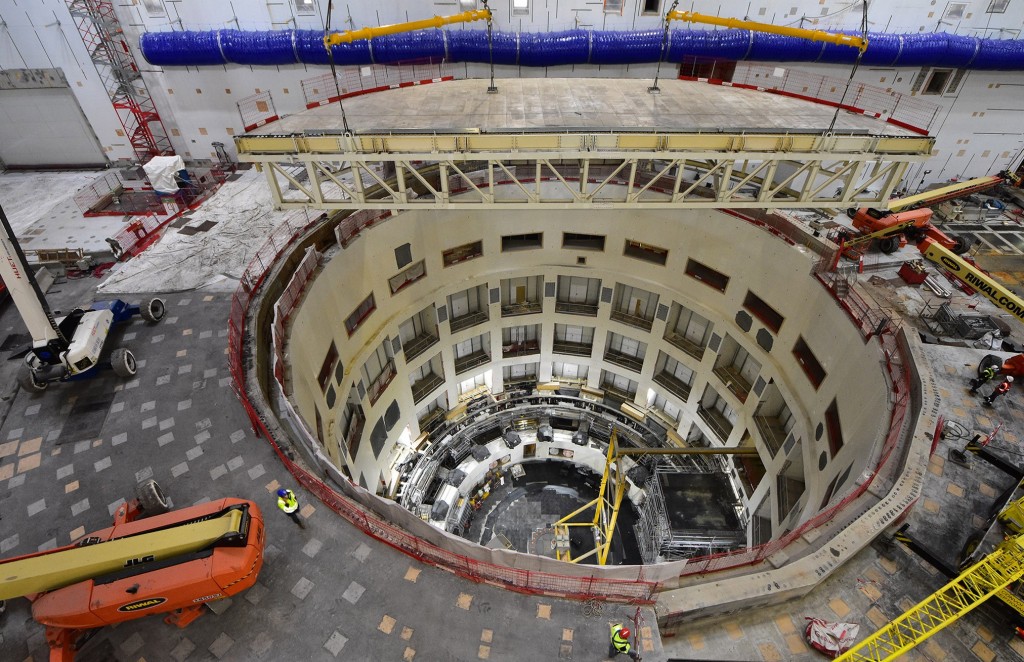
Pit revealed
2020-04-02 - As the last segment of the lid is raised, we have access to a spectacular view of the 30-metre-deep assembly pit.

Getting ready
2020-04-02 - The Tokamak pit is nearly ready for its first machine component: 18 cryostat bearings are in place on the cryostat crown, contractors are finalizing painting and cleaning, and captive components have been installed in areas that will be blocked once the cryostat base has been lowered.

Off to storage
2020-04-02 - If you look closely at the image, you will see one element of the temporary lid as it is carried over the upending tool to a waiting flatbed truck. The lid will be stored on site for reuse later in the assembly phase.
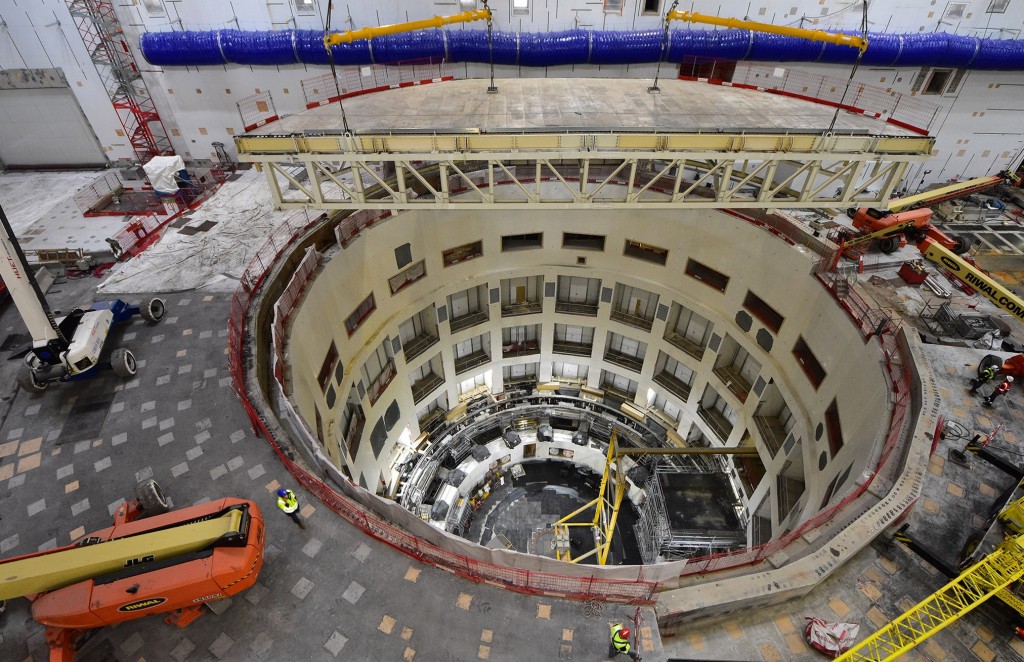
Last piece
2020-04-02 - As the last segment of the lid is raised, it reveals a spectacular view of the 30-metre-deep assembly pit.
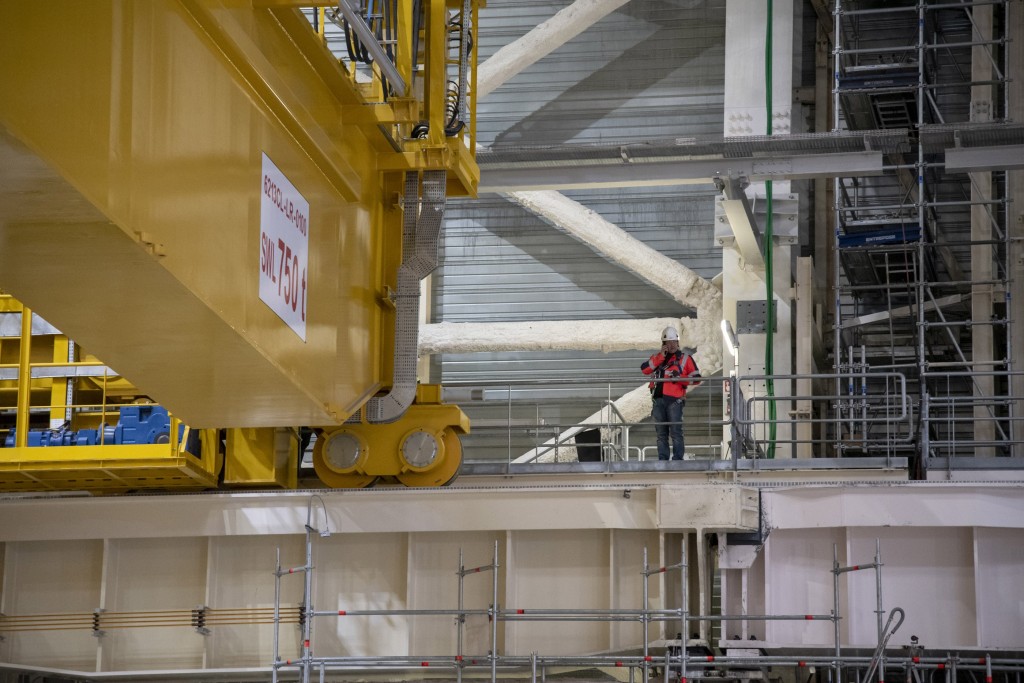
A big beam for a heavy load
2020-03-28 - The double overhead bridge crane comprises four such 47-metre-long, 155-tonne steel girders, or beams. Arranged in two pairs and working in tandem, they can lift up to 1,500 tonnes. The double overhead bridge crane was tested at 125 percent of its capacity (1,870 tonnes) in December 2017.

The numbers on the scale
2020-03-28 - The weight of the loads appears in real time on the small screens just above the rails. Figures can vary slightly depending on the positions of the loads along the beams.

Final crane path tests
2020-03-28 - Totalling approximately 1,000 tonnes, these loads are travelling the way of future ITER components, and permitting the European Domestic Agency to validate ITER Council milestone #50, for crane access in the newly completed Tokamak Building.
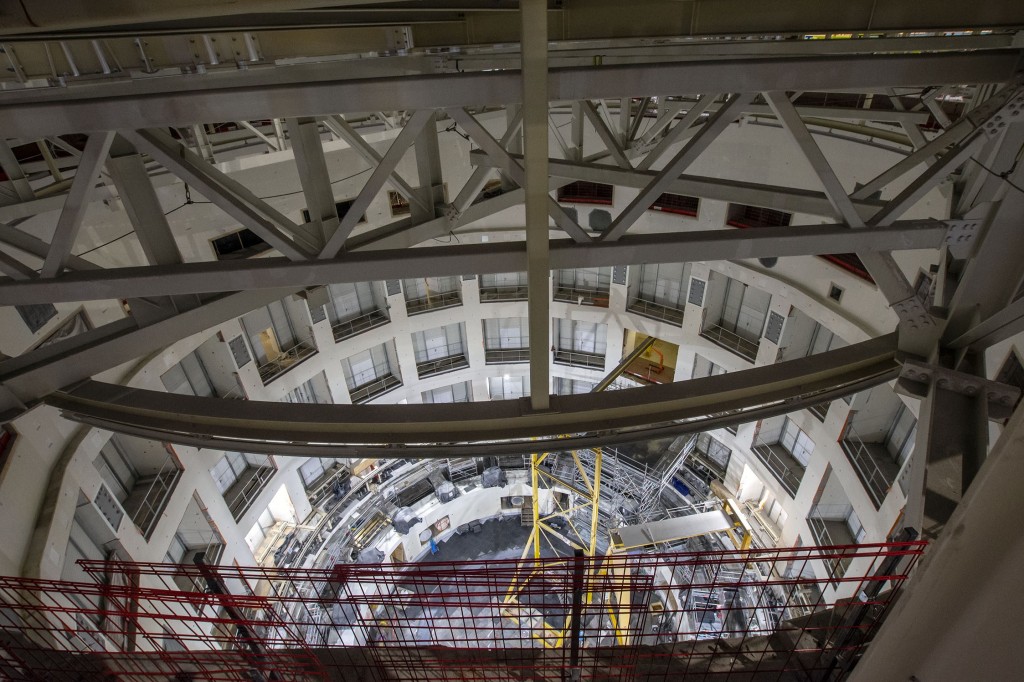
Coming next
2020-03-28 - Part of the circular lid that closes the assembly pit has already been taken down, allowing a dizzying view into the 30-metre-deep concrete cylinder. The removal of the 11 segments that make up the lid is scheduled to begin on Thursday 2 April and last through the end of the work week.

A big beam for a heavy load
2020-03-28 - The double overhead bridge crane comprises four such 47-metre-long, 155-tonne steel girders, or beams. Arranged in two pairs and working in tandem, they can lift up to 1,500 tonnes. The double overhead bridge crane was tested at 125 percent of its capacity (1,870 tonnes) in December 2017.
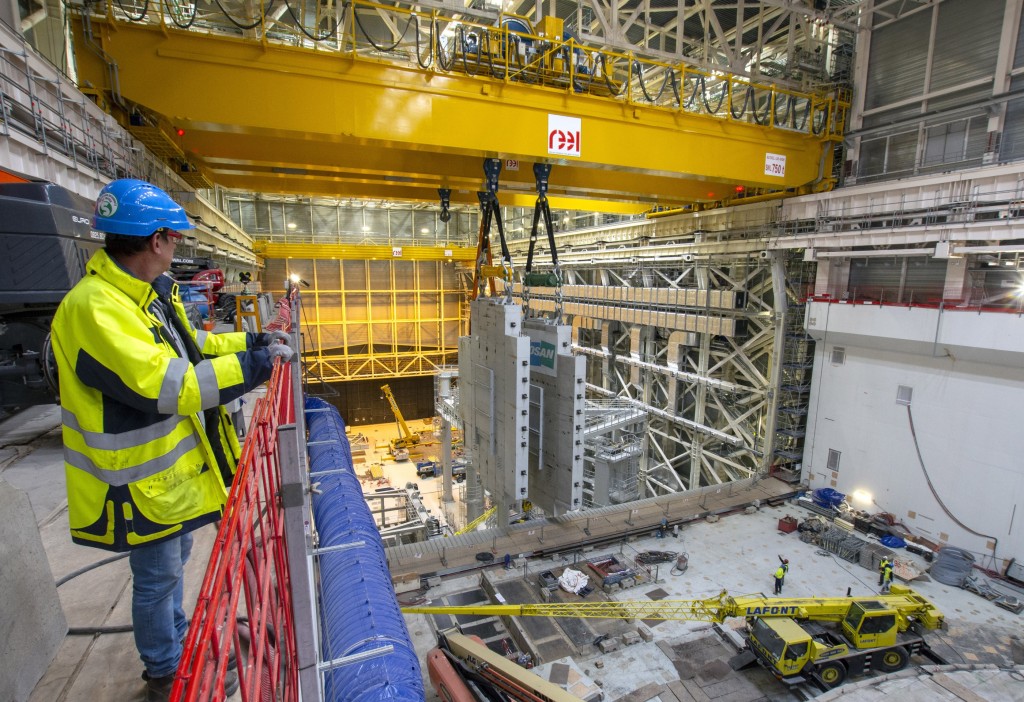
A delicate threshold
2020-03-28 - The loads are about to cross from the Assembly Hall into the Tokamak Building. The cranes will halt at the threshold to allow the loads to be moved back and forth along the crane's yellow beams to monitor the deflection of the crane runway and that of the crane hall pillars.

Testing the path before the real loads
2020-03-28 - Totaling approximately 1,000 tonnes, the mock loads are ready to undertake their 170-metre-long journey from the entrance of the Assembly Hall all the way to the opposite end of the newly created crane hall. Testing the load path, and carefully monitoring building inflection as the loads go by, are part of the last commissioning activities before machine assembly.
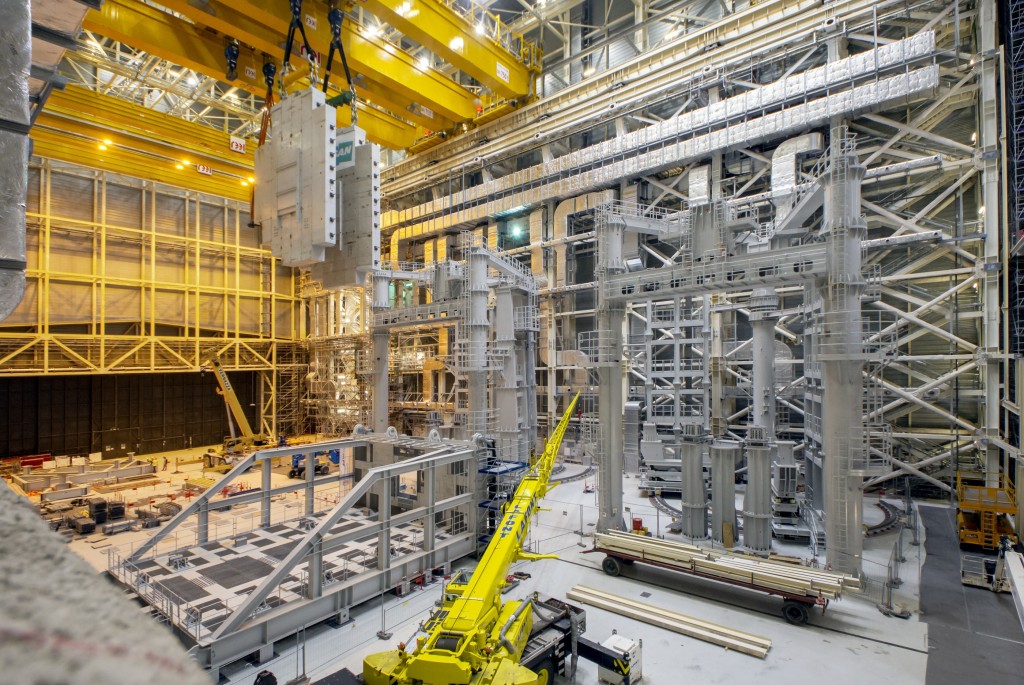
Testing the path before the real loads
2020-03-28 - Totaling approximately 1,000 tonnes, the mock loads are ready to undertake their 170-metre-long journey from the entrance of the Assembly Hall all the way to the opposite end of the newly created crane hall. Testing the load path, and carefully monitoring building inflection as the loads go by, are part of the last commissioning activities before machine assembly.

Carefully supervising
2020-03-28 - The load path operation was overseen by Roberto Lanza (left, ITER Responsible Officer for cranes and crane operations) and Duco Jensen (ITER site planning coordinator), with strong support from construction coordinator Stéphane Herpin. The operation involved personnel from the Buildings Infrastructure & Power Supplies (BIPS) Project Team; Fusion for Energy contractors VFR (Vinci, Ferrovial, Razel-Bec), REEL (cranes), Dalkia, GDES, Martifer (manufacturing and installation of the crane hall), SAMT, and Nuvia; and contractors supporting both the ITER Organization and Fusion for Energy (Engage, APAVE, Energhia, Tiresia, and MOMENTUM).

Testing the path before the real loads
2020-03-28 - Totaling approximately 1,000 tonnes, the mock loads are ready to undertake their 170-metre-long journey from the entrance of the Assembly Hall all the way to the opposite end of the newly created crane hall. Testing the load path, and carefully monitoring building inflection as the loads go by, are part of the last commissioning activities before machine assembly.
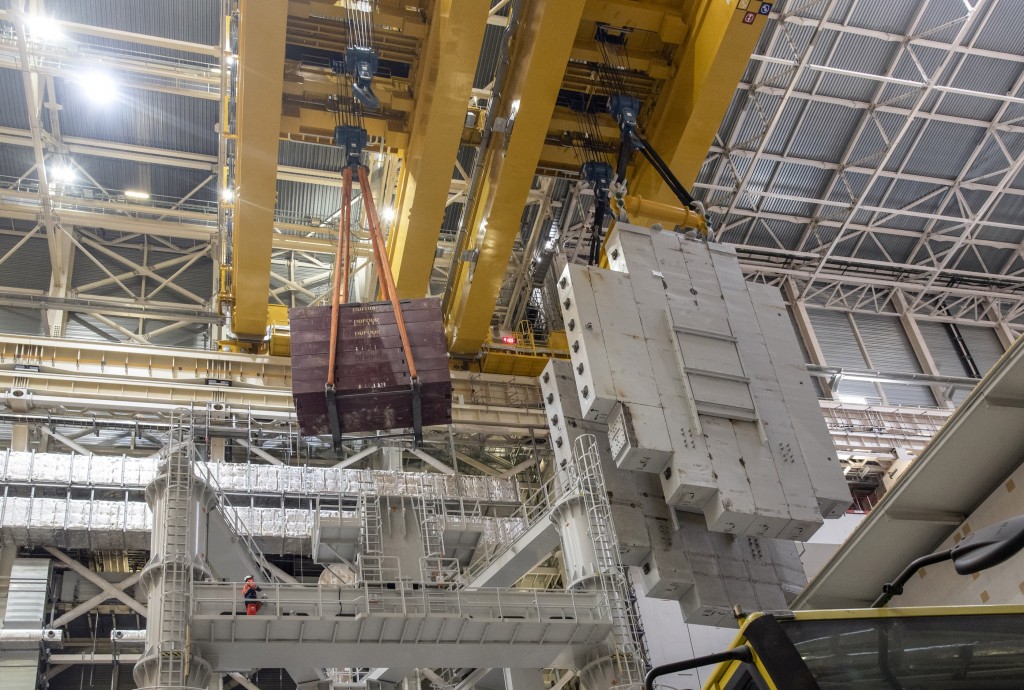
1,000 tonnes
2020-03-28 - The 840-tonne double load on the "north bridge" (right) is complemented by a 156-tonne load on the "south bridge," bringing the total to a little more than 1,000 tonnes. Calculations and modelling are used to extrapolate the effect the actual 1,500-tonne loads will have on the building's structure.
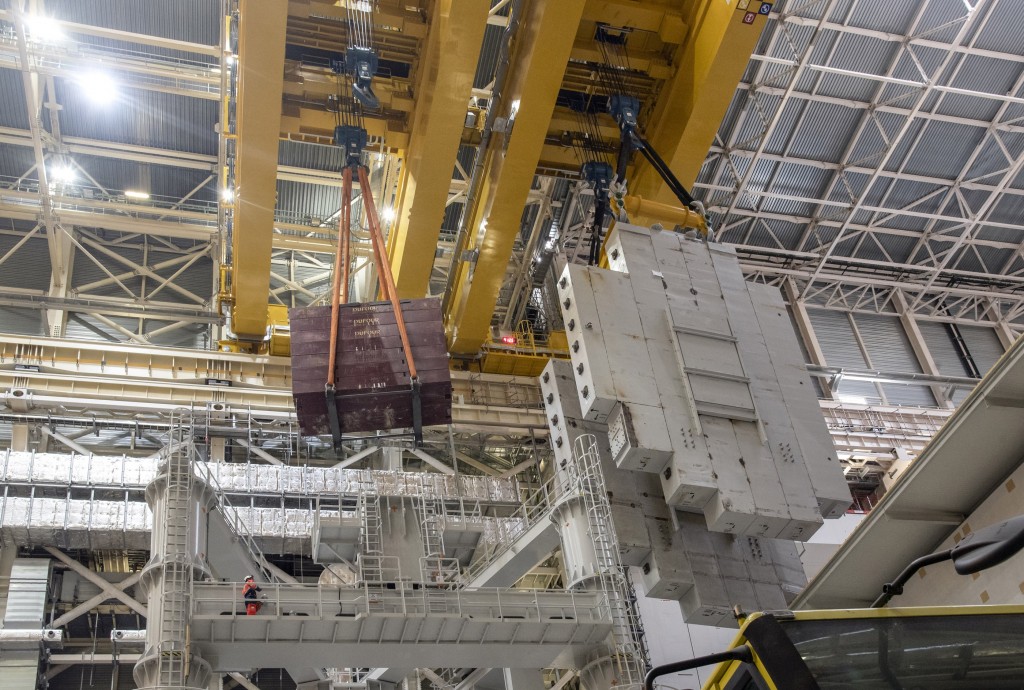
1,000 tonnes
2020-03-28 - The 840-tonne double load on the "north bridge" of the crane (right) is complemented by a 156-tonne load on the "south bridge," bringing the total to a little more than 1,000 tonnes. Calculations and modelling are used to extrapolate the effect the actual 1,500-tonne loads will have on the building's structure.

Preparing for episode one
2020-03-26 - As the European Domestic Agency puts the finishing touches on work in the Tokamak pit (painting, cleaning), ITER's Construction Management-as-Agent contractor MOMENTUM is preparing for the first episode of machine assembly: the lowering of the cryostat base.

Late into the evening
2020-03-26 - These workers, present just as Saturday turns into Sunday, are following recommended distance and personal protection measures.

Getting ready
2020-03-26 - At the bottom of the Tokamak pit, teams are preparing for the arrival of the cryostat base.

Preparing for episode one
2020-03-26 - As the European Domestic Agency puts the finishing touches on work in the Tokamak pit (painting, cleaning), ITER's Construction Management-as-Agent contractor MOMENTUM is preparing for the first episode of machine assembly: the lowering of the cryostat base.
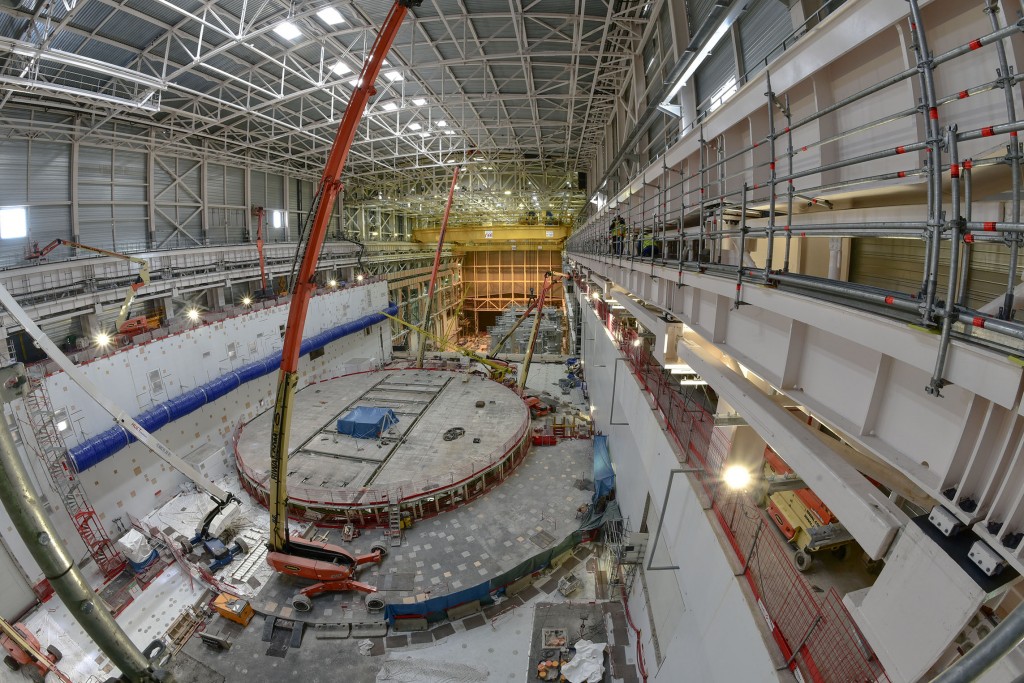
Open for assembly
2020-03-26 - There is no longer a barrier separating the Assembly Hall from the Tokamak Building. In the next step, the temporary lid over the machine assembly pit will be dismantled and removed.

Getting ready
2020-03-26 - At the bottom of the Tokamak pit, teams are preparing for the arrival of the cryostat base.

Open for assembly
2020-03-26 - There is no longer a barrier separating the Assembly Hall from the Tokamak Building. In the next step, the temporary lid over the machine assembly pit will be dismantled and removed.

MITICA vacuum vessel now complete
2020-03-23 - The second part of the MITICA beam source vacuum vessel, financed by the European Domestic Agency (F4E) and manufactured by De Pretto Industrie (Italy), has been delivered to the ITER Neutral Beam Test Facility.
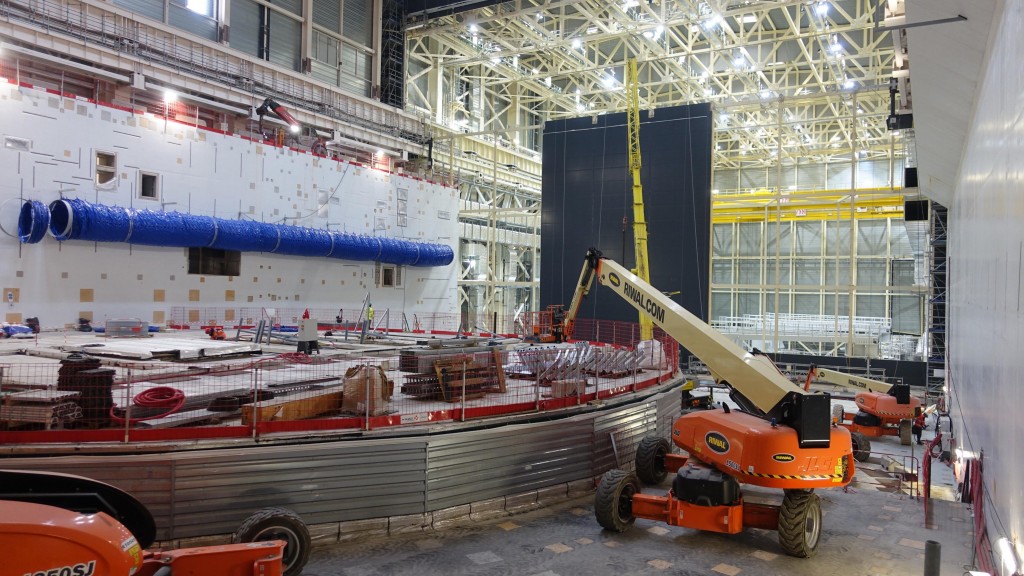
Wall comes down
2020-03-10 - The last piece of temporary wall is removed, creating a single-volume space for the pre-assembly and assembly of the ITER machine.

A very clean Cleaning Facility
2020-03-06 - The antechamber to the Assembly Hall—the Cleaning Facility—has been prepped and painted in time to receive the first ITER magnets.

75% of the way there
2020-03-03 - The civil structures of the ITER site are constructed under the responsibility of Fusion for Energy, the European Domestic Agency, in conjunction with its Architect Engineer ENGAGE. Seventy-five percent of the civil work required by First Plasma has been completed. Photo: ITER Organization/EJF Riche

Teamwork
2020-03-02 - Early tests on the upending tool are carried out under the supervision of the ITER Organization. The operation was coordinated by MOMENTUM (ITER's Construction Management-as-Agent) and involved Apave (security), contractors from the assembly consortium DYNAMIC, an operator, and an engineer from crane manufacturer REEL.
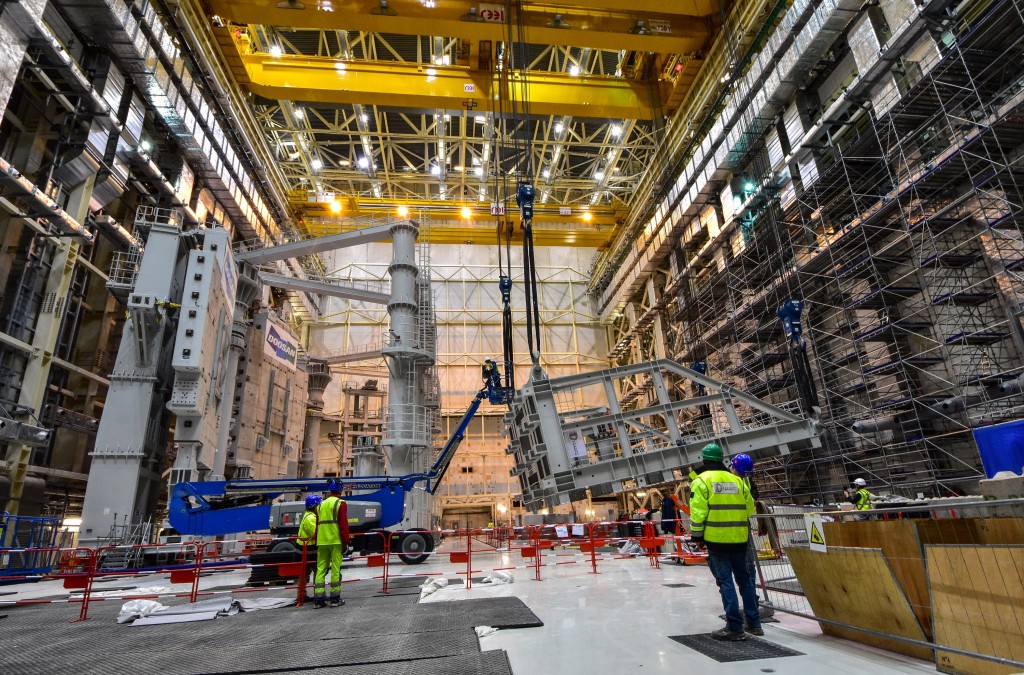
5-degree increments
2020-03-02 - In the Assembly Hall, the steel upending tool is lifted by increments of 5 degrees. A photogrammetric survey is performed between lifts in order to acquire baseline measurements and to monitor deformations.

First steps
2020-03-02 - An important step for every tool, once assembled, is testing and commissioning. This step verifies that the tool is performing according to specification and also serves to train operators.

Like a steel cradle
2020-03-02 - Procured by Korea, the upending tool is a 250-tonne steel "cradle" designed and equipped to handle vacuum vessel sectors and D-shaped toroidal field coils throughout the "pre-assembly" phase.
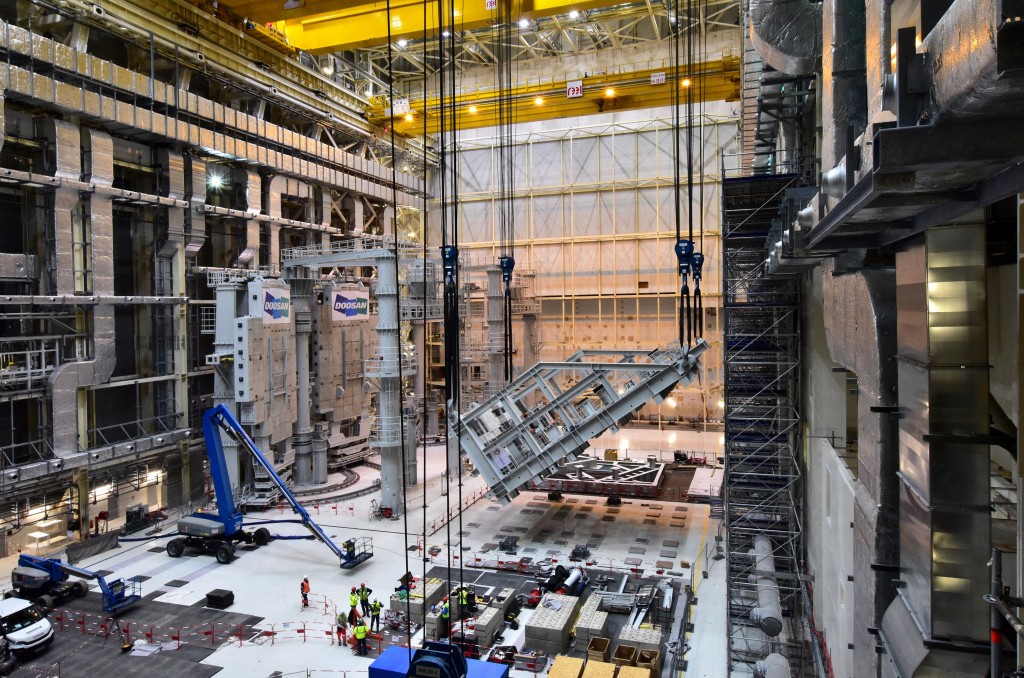
From horizontal to vertical
2020-02-28 - The largest ITER machine components (the D-shaped toroidal field coils and the vacuum vessel sectors) will be delivered in a horizontal position. They will be "upended" by the tool at right, before being installed on the SSAT pre-assembly tools at left.

5-degree increments
2020-02-28 - During tool commissioning activities, the steel cradle is lifted by increments of 5 degrees. A photogrammetric survey is performed between lifts in order to acquire baseline measurements and to monitor deformations.
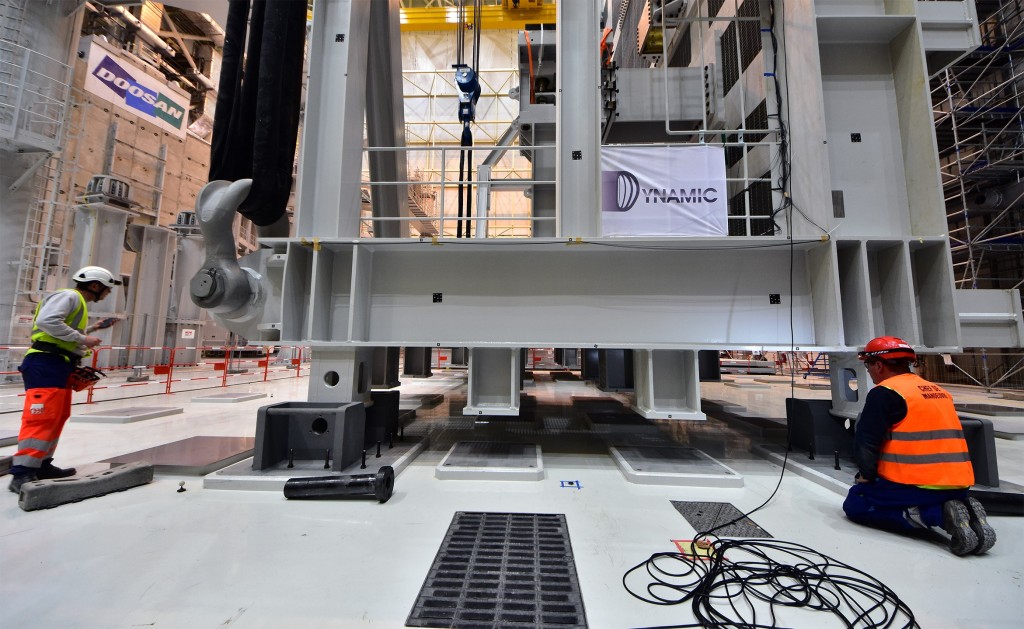
Four pins
2020-02-28 - The massive tool nears its resting position on the ground, and four 80-kilogram steel pins (left) are being readied for insertion at the four corners of the tool's base. Pins provide extra security in case of a seismic event.
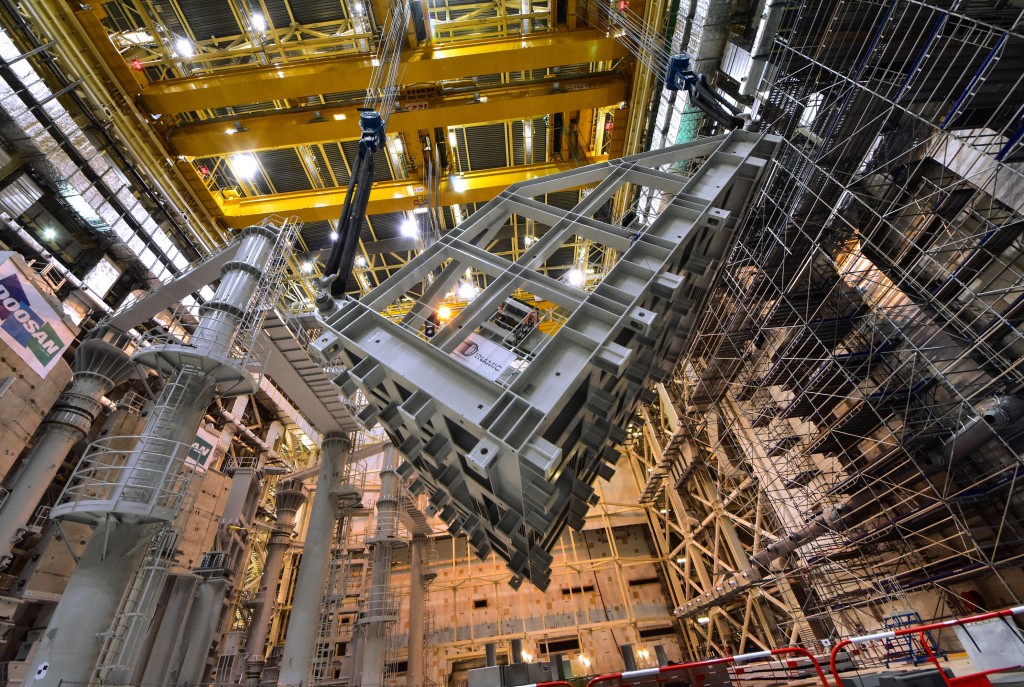
Getting ready for machine assembly
2020-02-28 - Two important activities in relation to the start of machine assembly are underway: commissioning of the upending tool (pictured) and the commissioning of the heavy lift cranes in the Tokamak Building where the crane rails have been extended over the Tokamak pit.
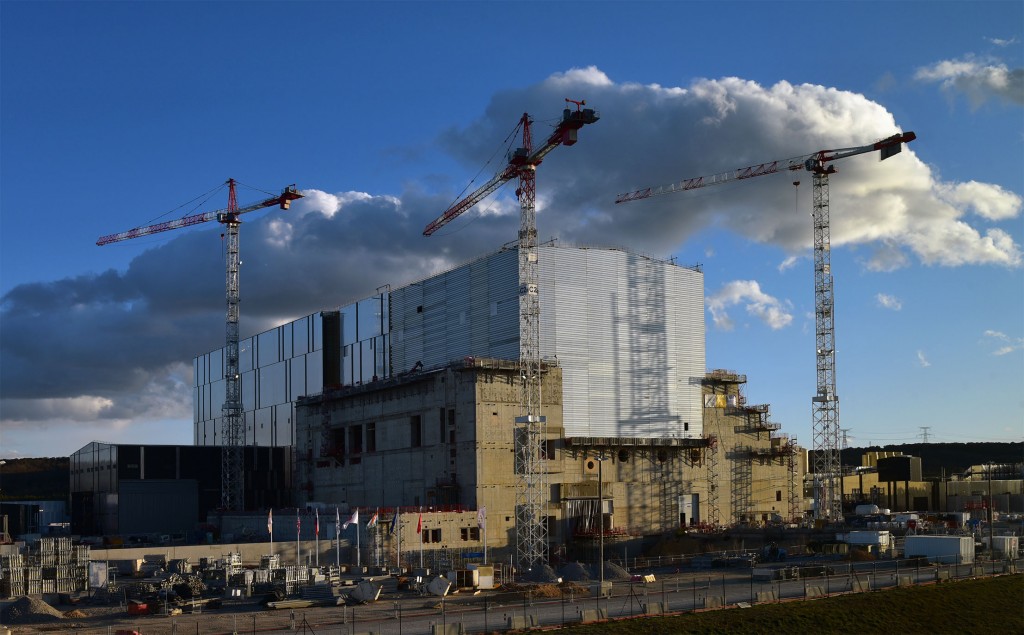
Fully contained
2020-02-26 - The volume of the crane hall (right) is now fully framed out. When the interior partition wall is removed, the buildings will form one continuous assembly space.
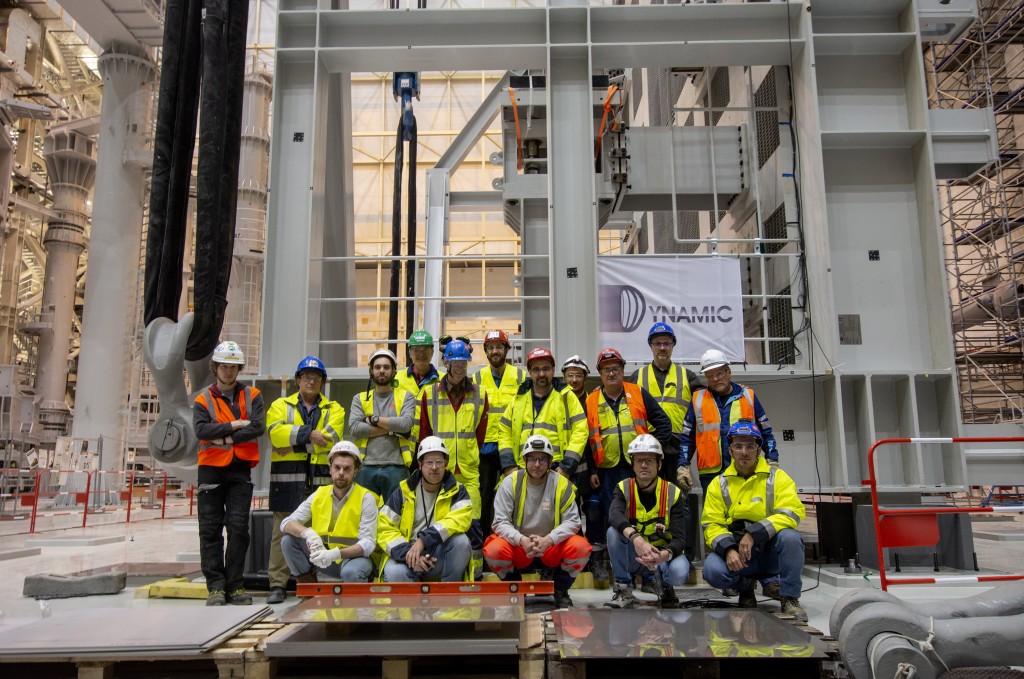
Team spirit
2020-02-25 - Under the supervision of the ITER Organization, upending tool testing was coordinated by MOMENTUM (ITER's Construction Management-as-Agent). It involved Apave (security), contractors from the assembly consortium DYNAMIC, an operator, and an engineer from crane manufacturer REEL.
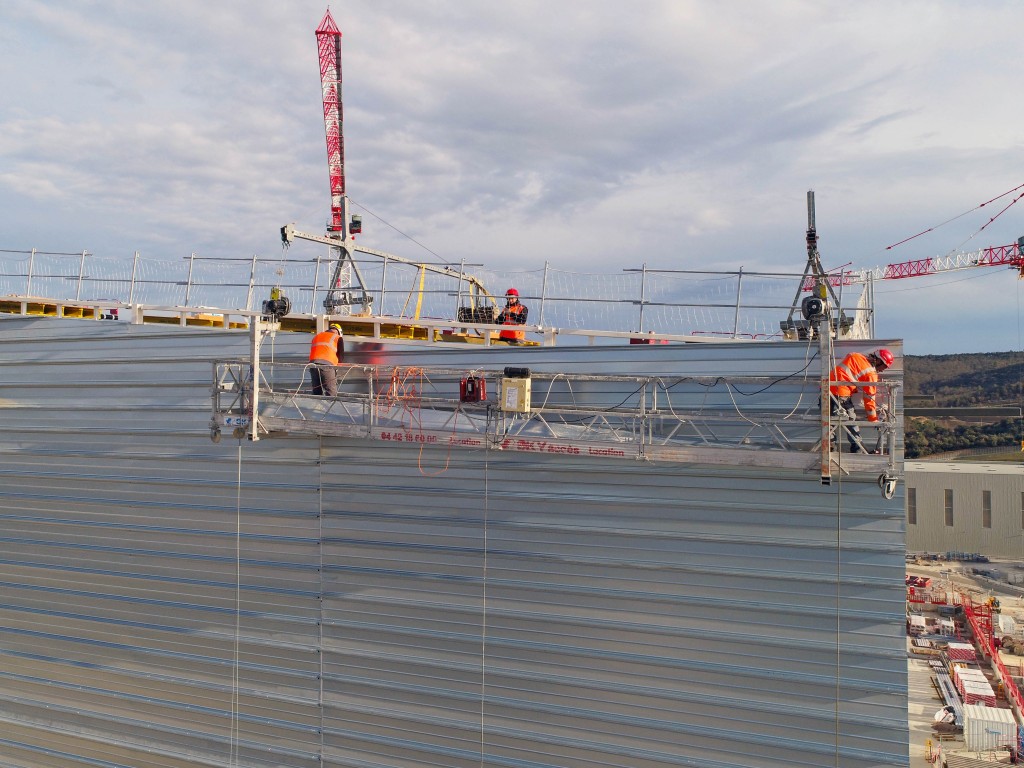
Covered completely
2020-02-25 - Natural light over the Tokamak pit is a thing of the past, as the last panel of metal cladding (layer one) is positioned on 25 February.
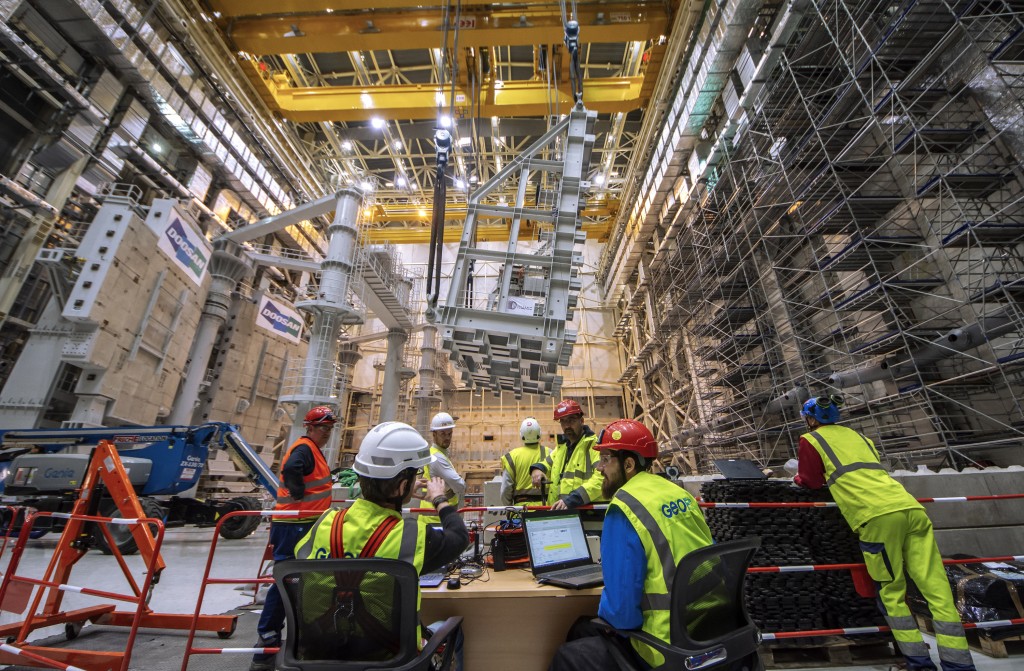
Preparing all processes
2020-02-25 - ITER specialists and contractors involved are testing "processes"—not just lifting systems and the loads to be handled, but their interaction and the whole kinematics of upending, transporting and manipulating charges that can be as heavy as four fully loaded Boeing 747s. Here, we see the upending tool in testing.
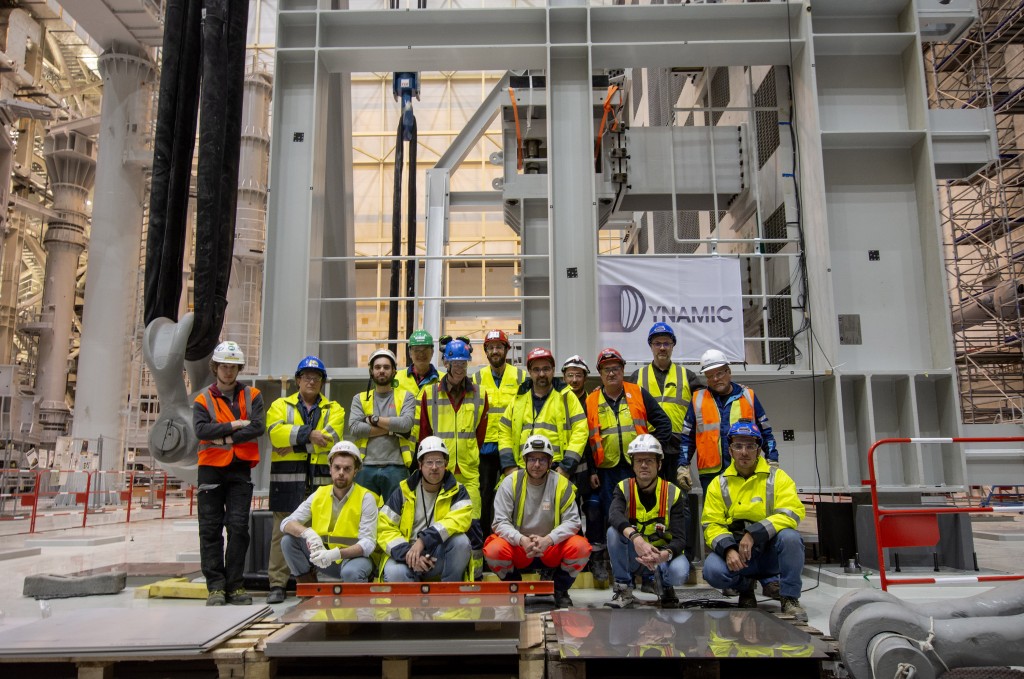
Team spirit
2020-02-25 - Under the supervision of the ITER Organization, upending tool testing was coordinated by MOMENTUM (ITER's Construction Management-as-Agent). It involved Apave (security), contractors from the assembly consortium DYNAMIC, an operator, and an engineer from crane manufacturer REEL.

From the north
2020-02-25 - The ITER site is photographed by drone in late February 2020. Photo: ITER Organization/EJF Riche

Pre-assembly preparations
2020-02-24 - The upending tool is lifted off the floor so that metrologists can measure the planarity of its support pads.

Pre-assembly preparations
2020-02-24 - The upending tool is lifted off the floor so that metrologists can measure the planarity of its support pads.

Pre-assembly preparations
2020-02-24 - The upending tool is lifted off the floor so that metrologists can measure the planarity of its support pads.

Upper cylinder assembly accomplished
2020-02-21 - Work on the upper cylinder is complete. The 430-tonne component will soon be cocooned and moved to storage outside the building.

Cleaning operation
2020-02-21 - Before cocooning the component, more than 2,500 square metres of stainless steel must be cleaned using cloth, demineralized water, a standard solvent and ... a lot of elbow grease.
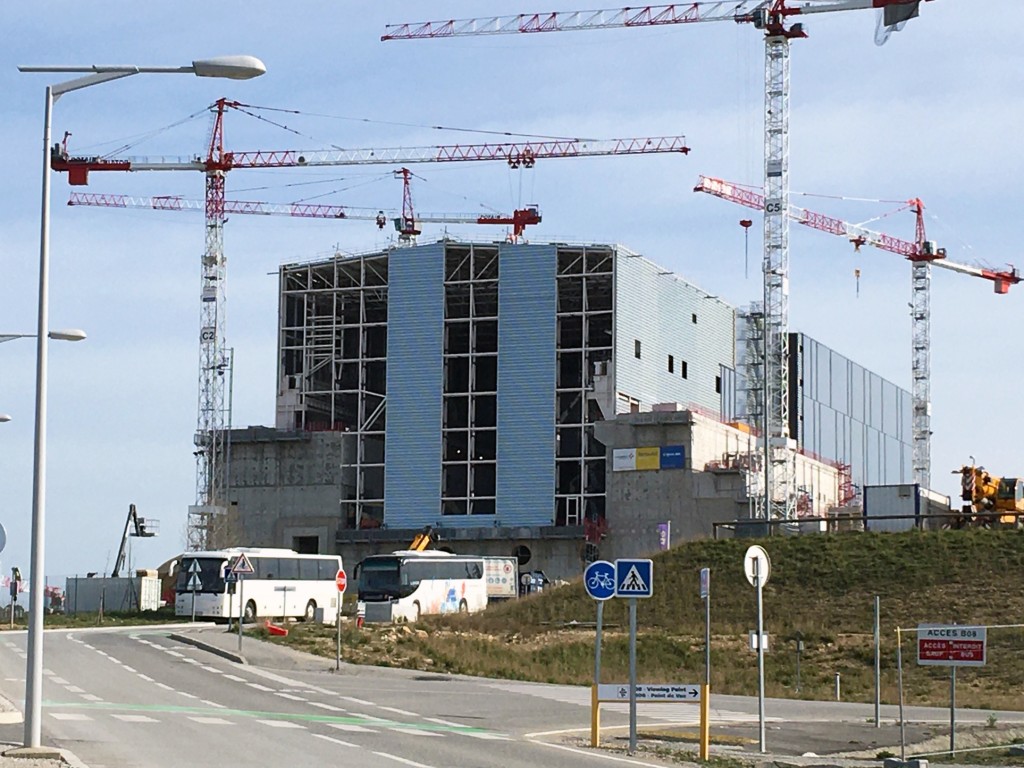
Cladding, layer one
2020-02-21 - First-level cladding is nearly complete on the Tokamak Building crane hall. At the end of construction, the building will have the same exterior treatment as the Assembly Hall.
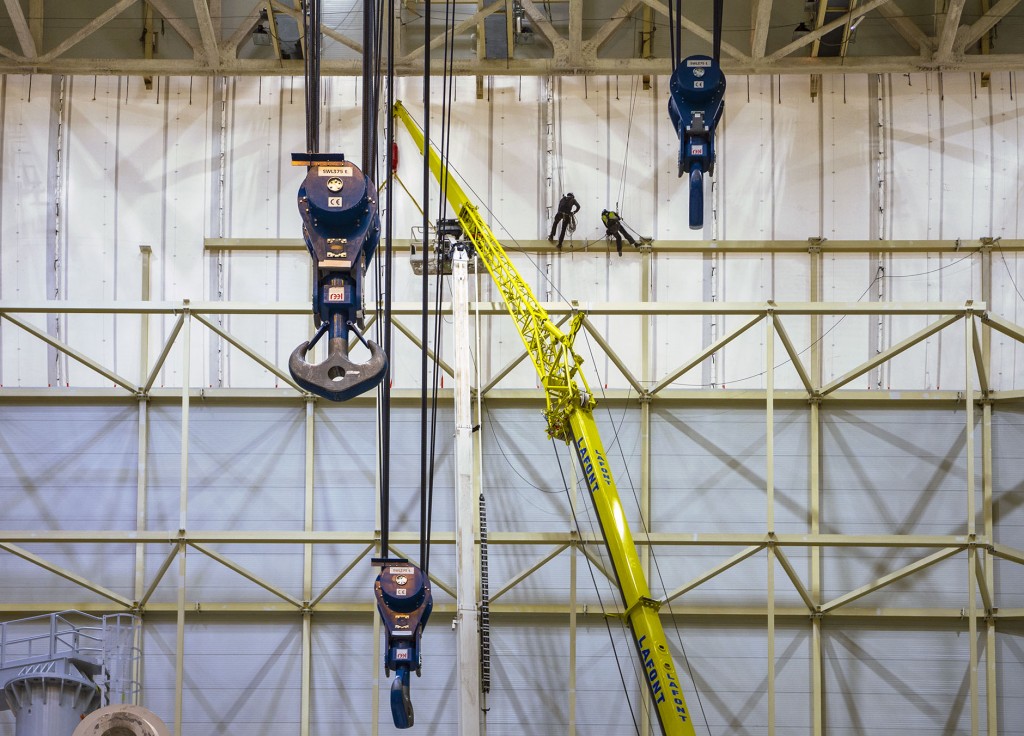
Dancers in a vertical ballet
2020-02-19 - Acrobatic workers are busy disassembling the temporary wall that separates the Assembly Hall from the Tokamak Building.

Dancers in a vertical ballet
2020-02-19 - Acrobatic workers are busy disassembling the temporary wall that separates the Assembly Hall from the Tokamak Building.
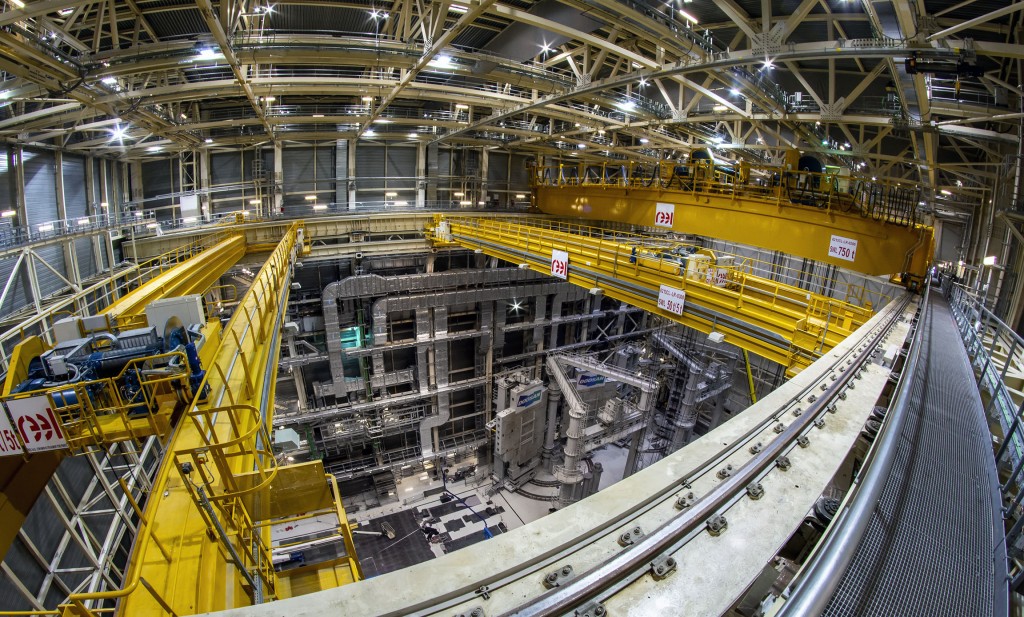
Up in the rafters
2020-02-18 - Soon, these bridge cranes will be able to travel double distance—not only the length of the Assembly Hall, but that of the adjacent building as well. Crane commissioning activities over the Tokamak pit will start once the temporary wall comes down.
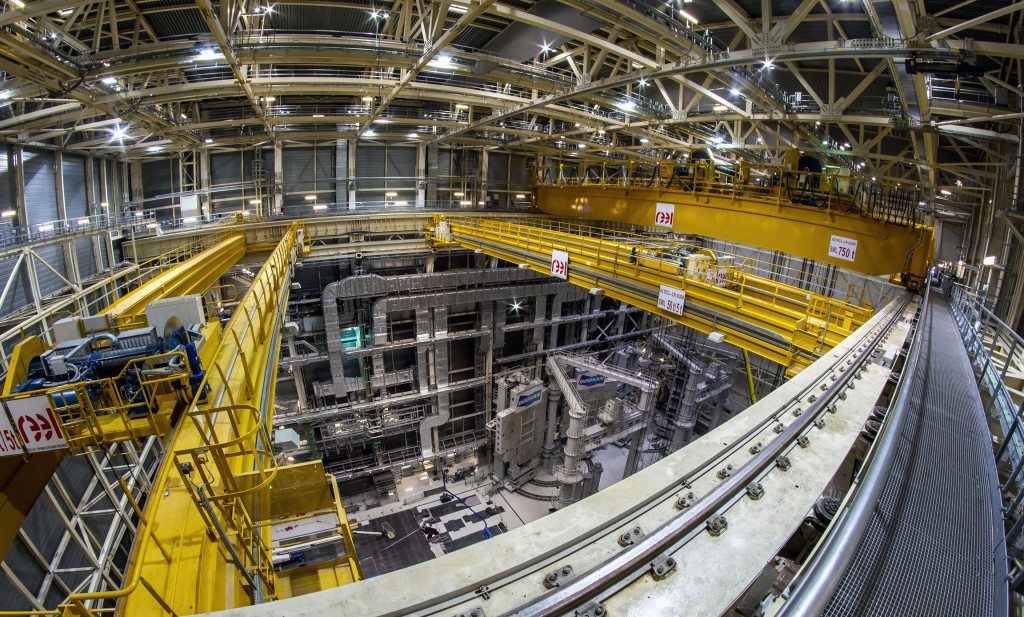
Up in the rafters
2020-02-18 - Soon, these bridge cranes will be able to travel double distance—not only the length of the Assembly Hall, but that of the adjacent building as well. Crane commissioning activities over the Tokamak pit will start once the temporary wall comes down.
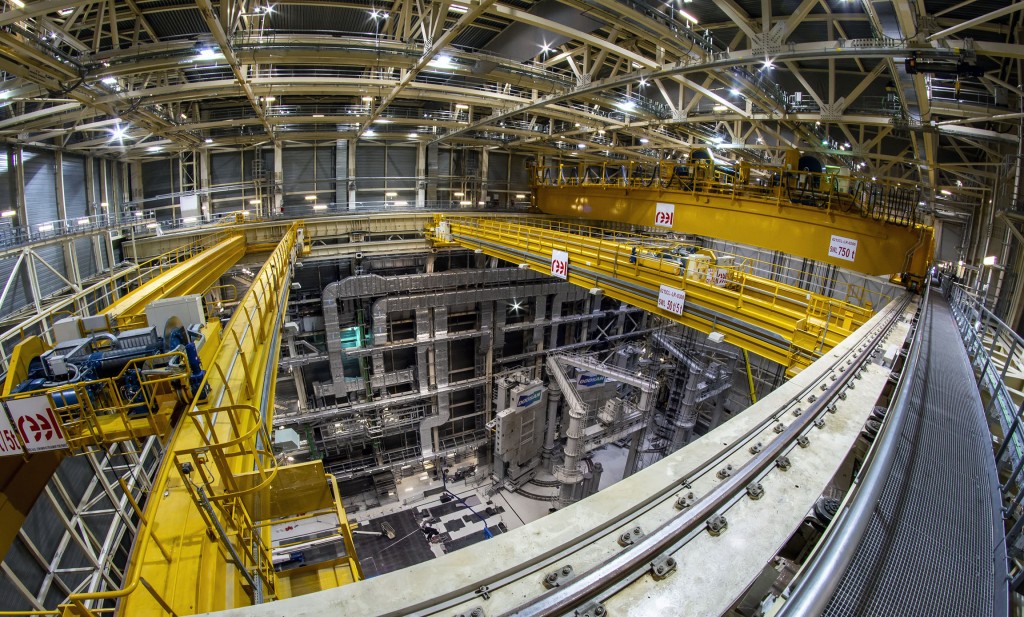
Up in the rafters
2020-02-18 - Soon, these bridge cranes will be able to travel double distance—not only the length of the Assembly Hall, but that of the adjacent building as well. Crane commissioning activities over the Tokamak pit will start once the temporary wall comes down.
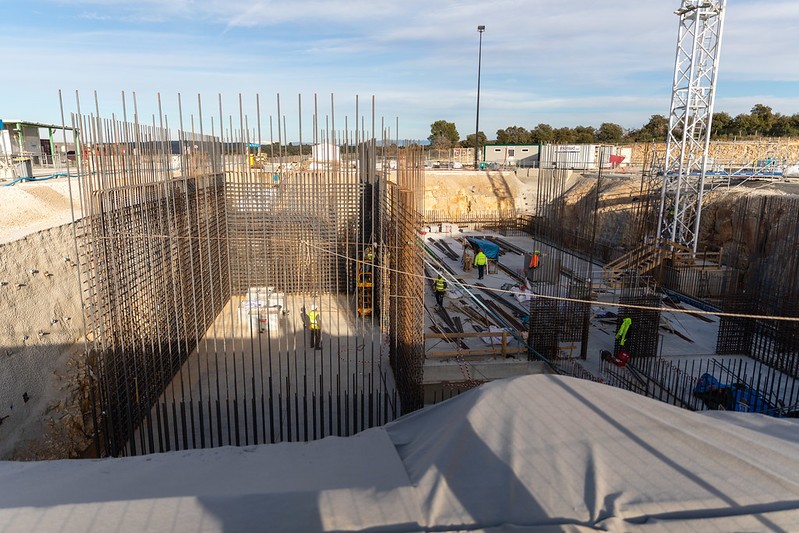
Basemat completed on new building
2020-02-15 - The basemat for the beryllium handling facility (also called the Tokamak Preparatory Activities Building) is in place and contractors are installing rebar. The building will have a full basement and one floor. © Les Nouveaux Médias/SNC ENGAGE
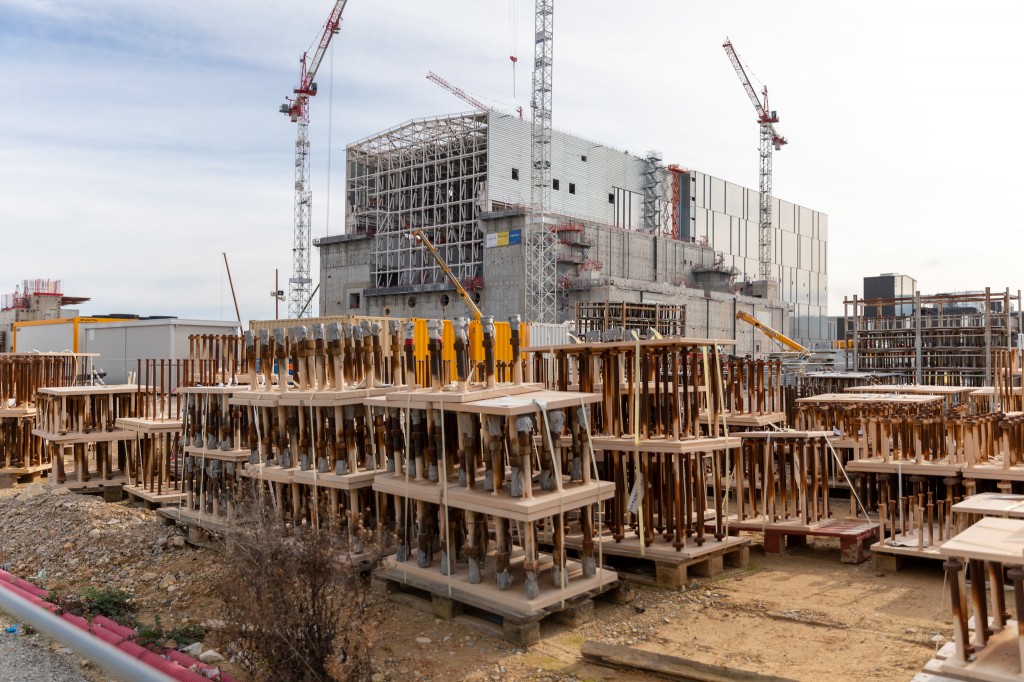
100,000 embedded plates
2020-02-15 - All of the equipment in the Tokamak Complex will be attached to embedded plates. These metal plates have long prongs that are inserted deep into the concrete walls for support. There are at least 100,000 of them. © Les Nouveaux Médias/SNC ENGAGE
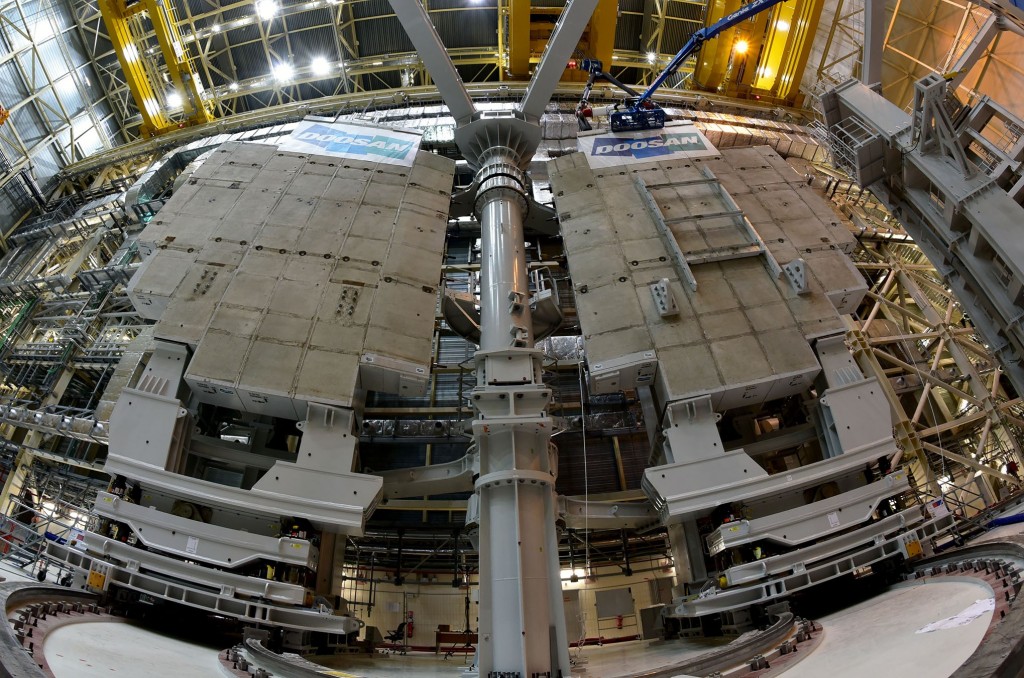
Back in service
2020-02-14 - Two 360-tonne test loads are back on the main tools of the Assembly Hall. With extra weight added, they will be used to commission the overhead cranes in the new crane hall of the Tokamak Building. The temporary wall between the buildings is coming down now.
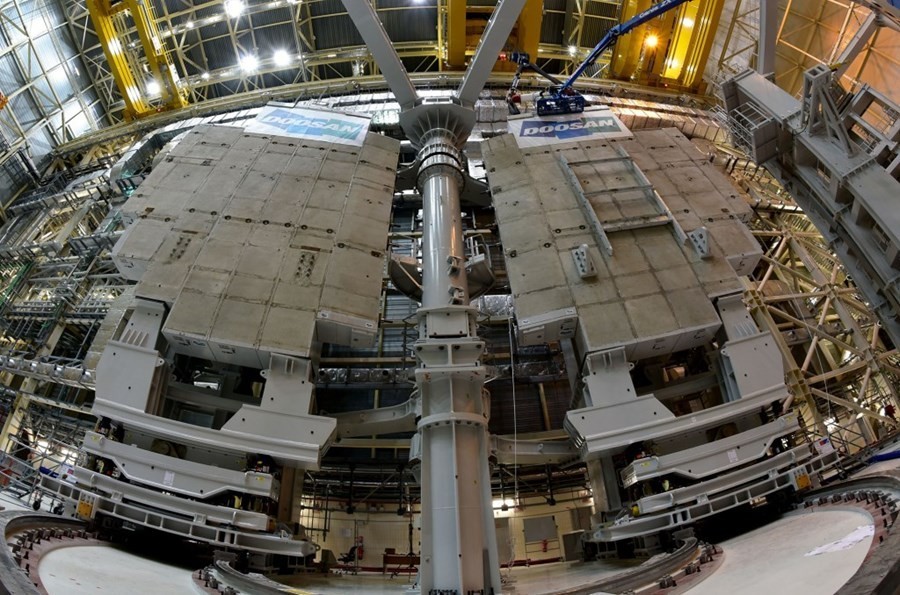
Aligning loads vertical to gravity
2020-02-14 - When two 340-tonne test loads were positioned on one of the sector sub-assembly tools in the Assembly Hall, the metrology team was there to help the operators align the loads vertical to gravity and within one millimetre. The team has established the Tokamak Complex Global Coordinate network for the alignment of components, as well as a local coordinate system in the Assembly Hall for vacuum vessel sector sub-assembly.
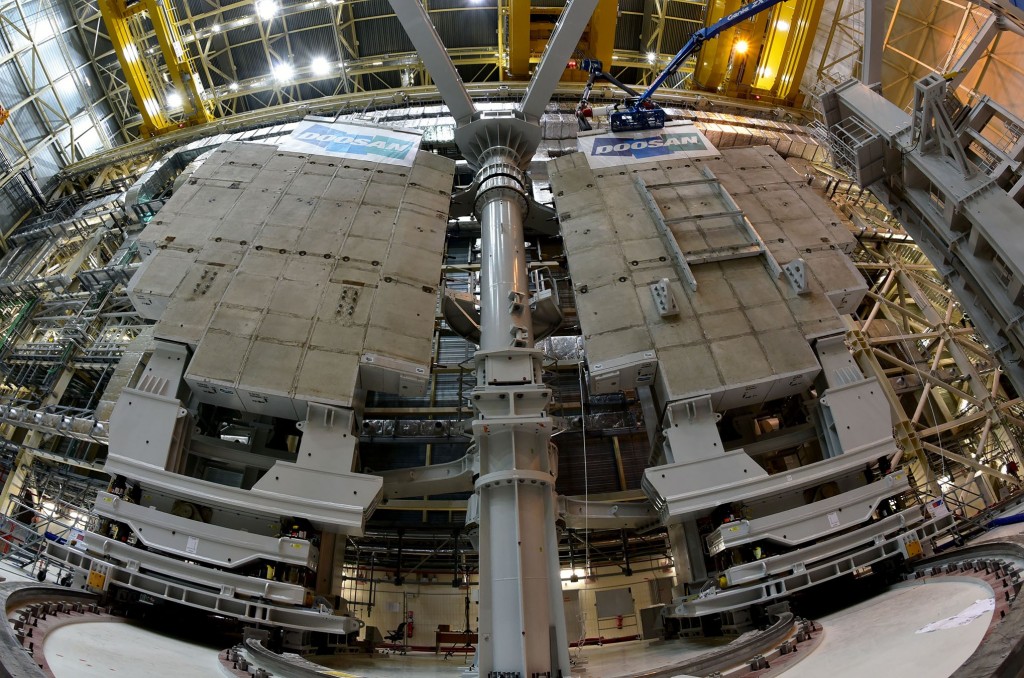
Back in service
2020-02-14 - Two 360-tonne test loads are back on the main tools of the Assembly Hall. With extra weight added, they will be used to commission the overhead cranes in the new crane hall of the Tokamak Building. The temporary wall between the buildings is coming down now.

Back in service
2020-02-14 - Two 360-tonne test loads are back on the main tools of the Assembly Hall. With extra weight added, they will be used to commission the overhead cranes in the new crane hall of the Tokamak Building. The temporary wall between the buildings is coming down now.

Cryostat base: grand opening soon
2020-02-13 - The huge cryostat base section will descend from above, supported by the overhead cranes as it is lowered 30 metres to the bottom of the pit.

Destination for the base
2020-02-13 - The last activities are underway at the bottom of the Tokamak pit to prepare for the arrival of the 1,250-tonne cryostat base. In the picture, we can distinguish three bearings (ball-and-socket joints) covered in plastic, and the different interface points along the wall.

Interface points
2020-02-13 - Female lugs on the bioshield wall will interface with male lugs on the cryostat base's pedestal rim. A high-precision drill is boring holes into one of the 18 female lugs to accommodate a steel pin.

Cryostat base: grand opening soon
2020-02-13 - The huge cryostat base section will descend from above, supported by the overhead cranes as it is lowered 30 metres to the bottom of the pit.
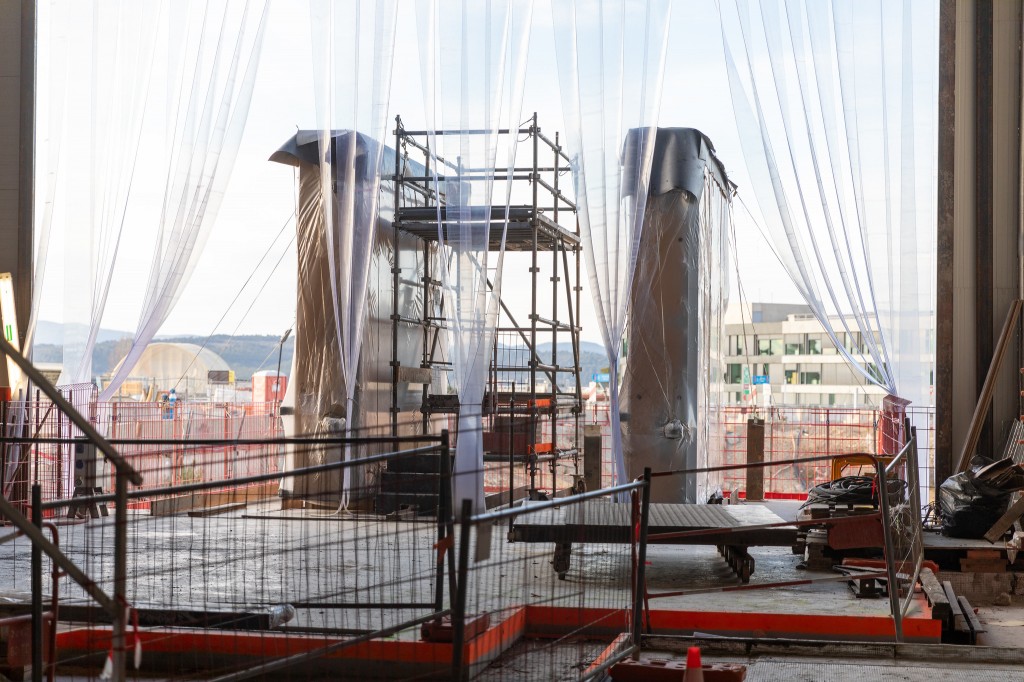
More doors
2020-02-08 - Two nuclear doors are delivered to the ground level of the Tokamak Building. © Les Nouveaux Médias/SNC ENGAGE
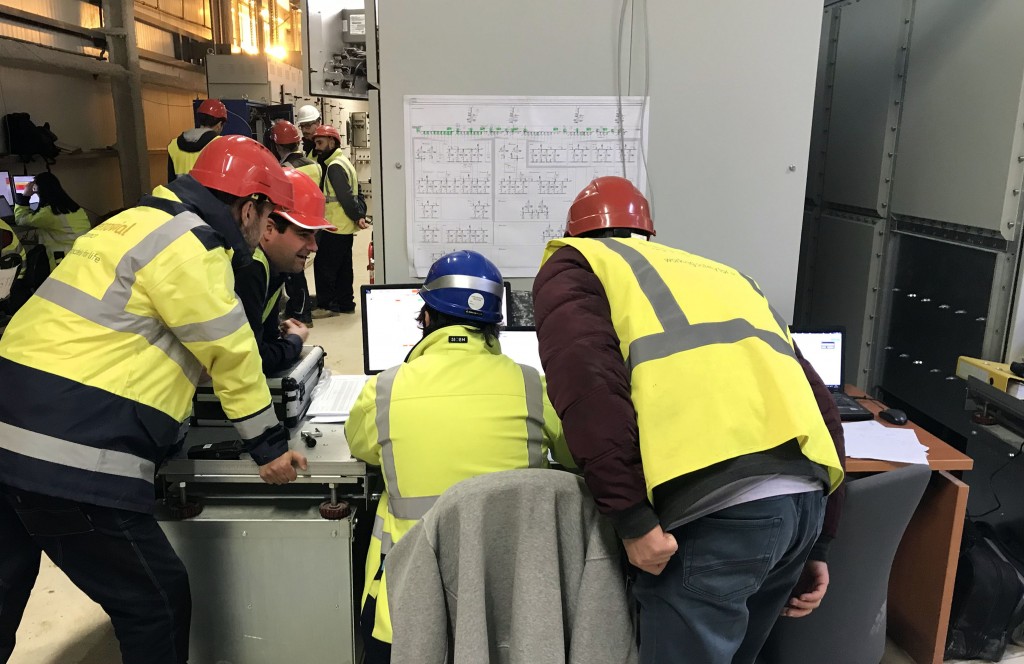
Verifying everything
2020-02-07 - Checking the protection logic for the high voltage relays during the commissioning of ITER's electrical distribution system.
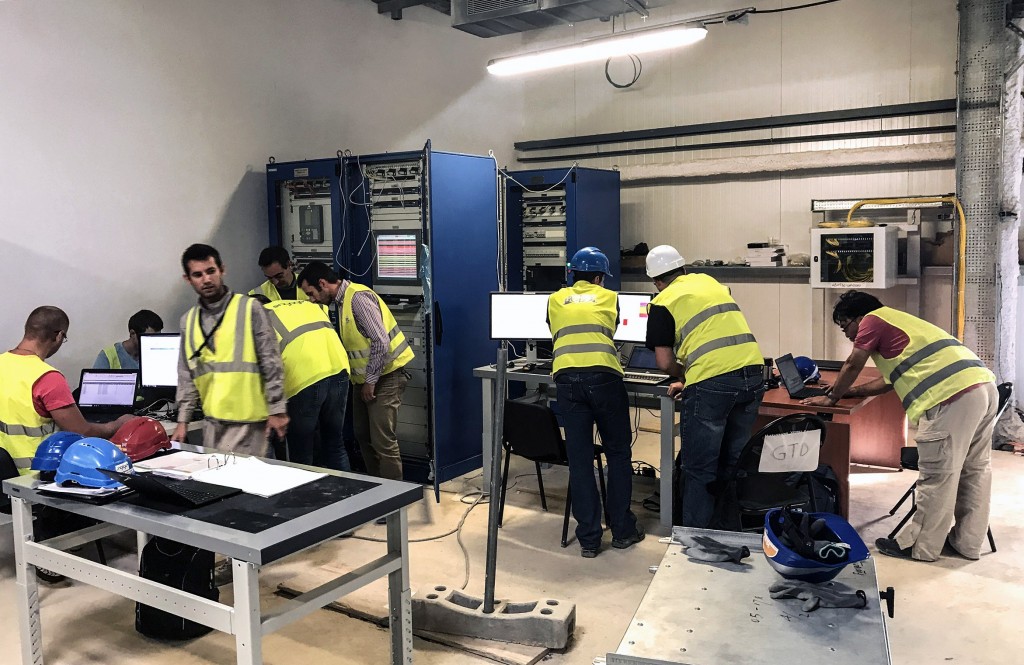
Early control room
2020-02-07 - Because the main ITER control room will not be in place until 2022, a temporary control room had to be put into place. The temporary control room is really a "virtual control room" in the sense that it is several different rooms connected together.
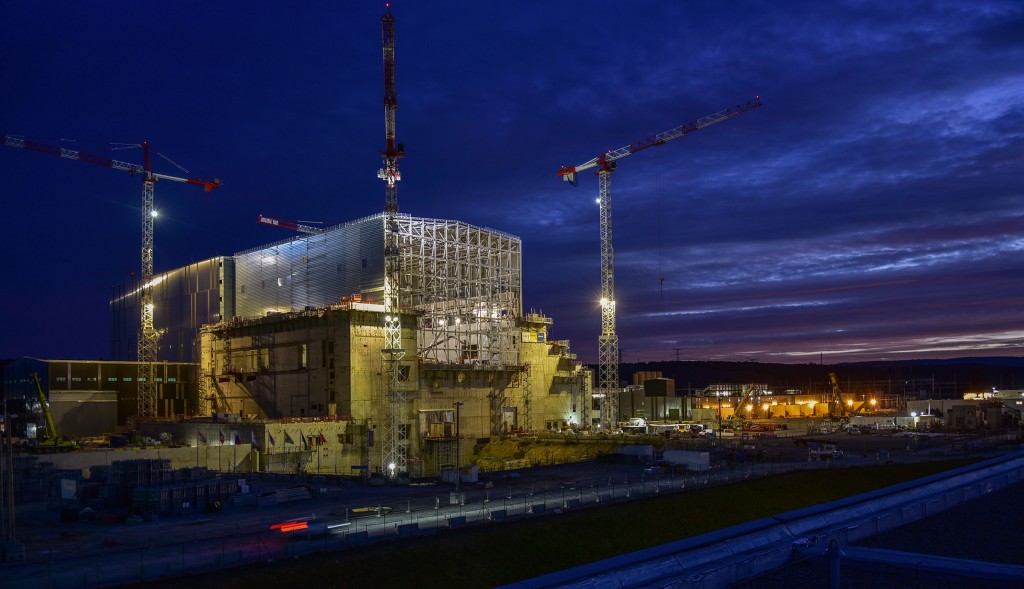
170 metres
2020-02-06 - Seeing the building from this angle, it's easy to imagine the overhead cranes travelling 170 metres from the entrance of the Assembly Hall (far left) to over the Tokamak assembly pit (far right). Cladding is advancing quickly.
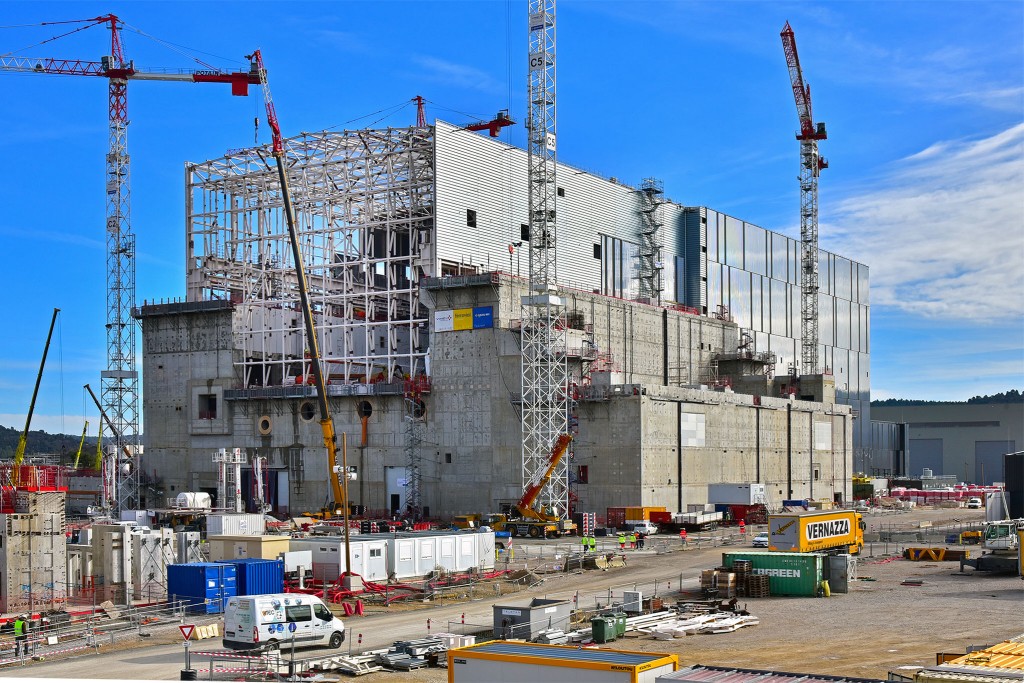
Late January: progress is swift
2020-01-30 - The frame of the crane hall is nearly complete and a first layer of cladding now covers the south wall and part of the roof.

The mechanics under the machine
2020-01-29 - The concrete crown (left) that will sit under the machine is supported by 18 radial walls (centre). 18 cryostat bearings (covered in grey) will be the interface points between the 1,250-tonne cryostat base and the crown. © Les Nouveaux Médias/SNC ENGAGE
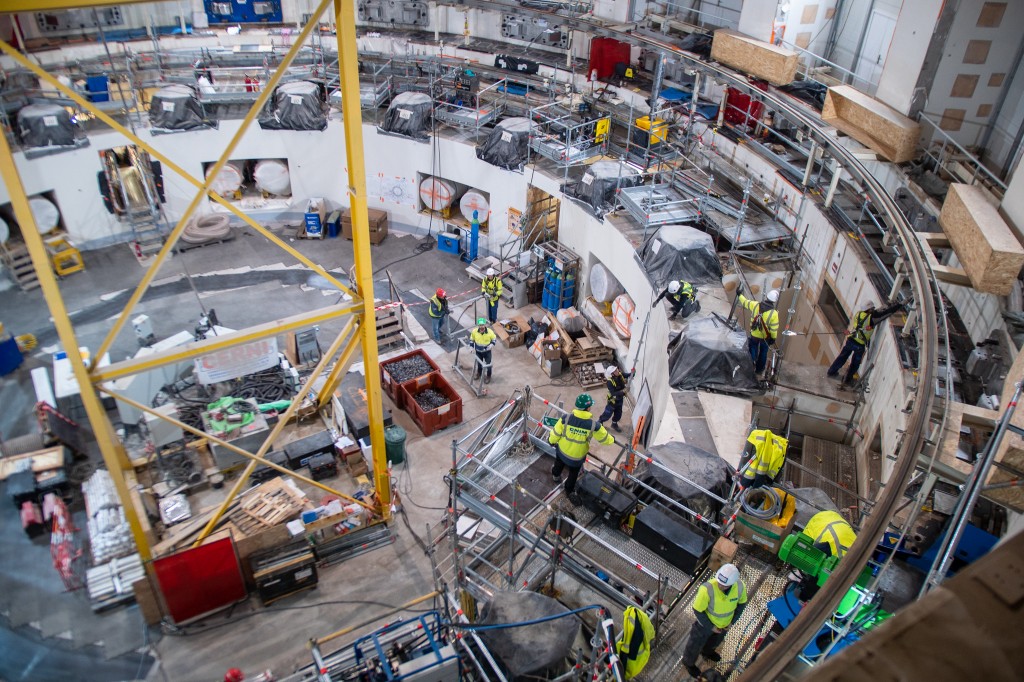
At the bottom of the pit
2020-01-29 - Teams are active at the bottom of the Tokamak pit to prepare for the insertion of the first machine component: the cryostat base. © Les Nouveaux Médias/SNC ENGAGE

Excavated and waiting
2020-01-29 - The largest construction project left to realize on the ITER site is the Hot Cell Facility, which will rise in this excavated area next to the Tokamak Building. © Les Nouveaux Médias/SNC ENGAGE

Radio Frequency Building
2020-01-29 - The structure of the three-floor Radio Frequency Building is in place, and equipment will begin arriving this summer. The ground floor (pictured) will house 12 power supplies for 24 gyrotons (external heating devices). © Les Nouveaux Médias/SNC ENGAGE
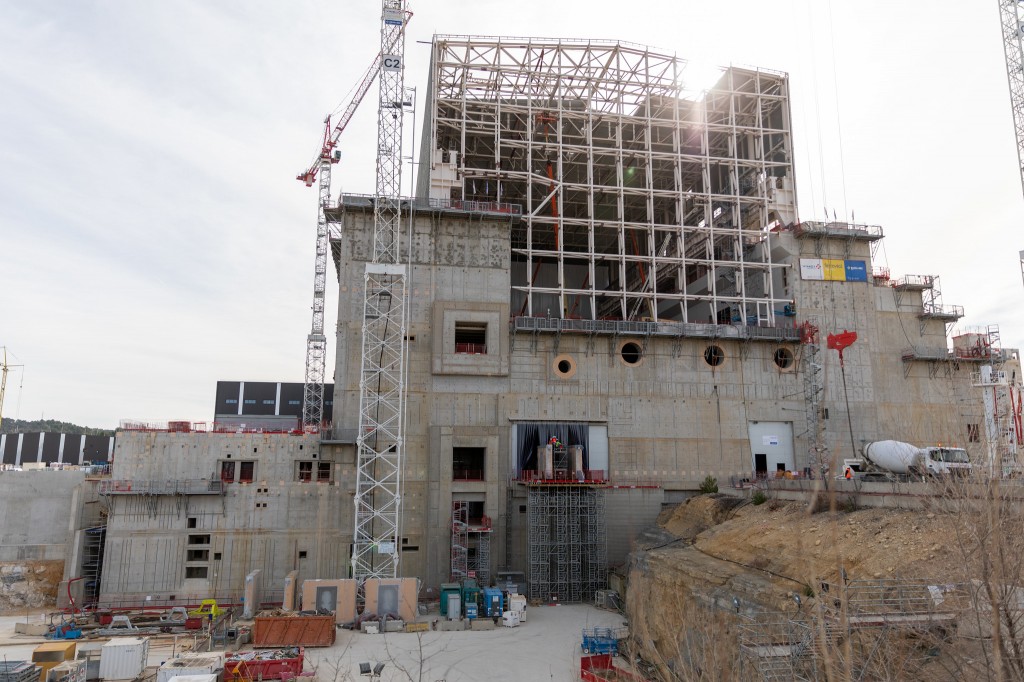
Rising sun
2020-01-27 - The sun rises on the crane hall, which is nearly entirely framed out. © Les Nouveaux Médias/SNC ENGAGE

Hinges and frames
2020-01-25 - Before each nuclear door can be installed, massive frames and hinges must be mounted at port cell exits. © Les Nouveaux Médias/SNC ENGAGE
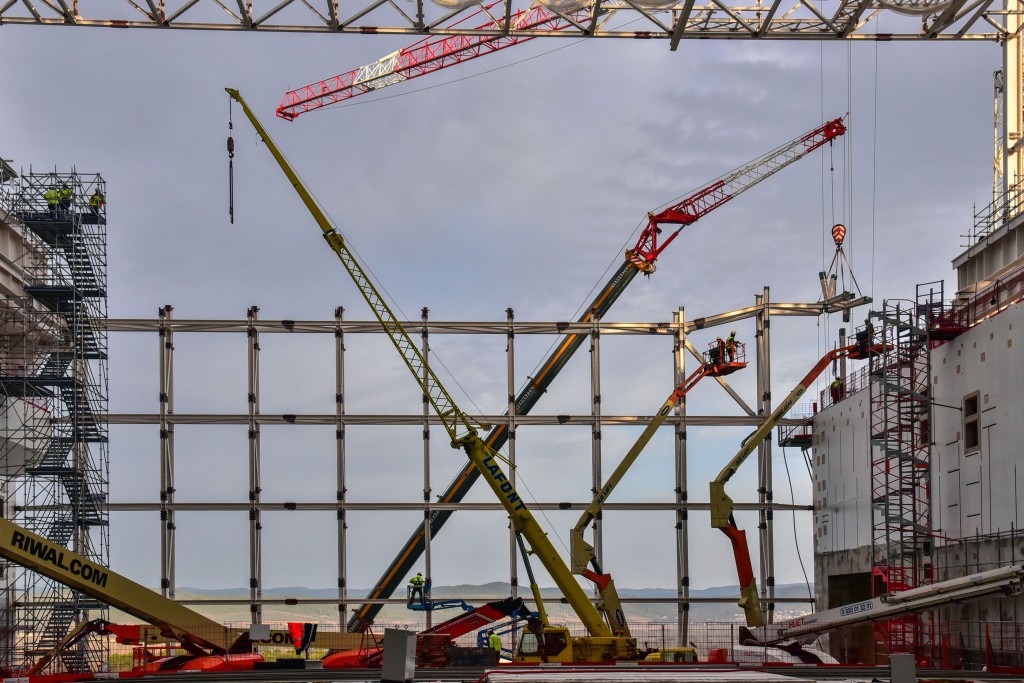
How quickly it goes!
2020-01-23 - Workers on elevated platforms install the steel framework elements of the north wall. Another four days and it will be completed.

Zigzag shape
2020-01-22 - In order to recapture the water droplets that would be otherwise scattered by the upward draft, close to 4,500 "drift eliminator" packs located at the top of each cell provide a dense, zigzagging labyrinth that forces droplets to change direction, lose velocity and fall back into the cooling tower.

Last stop
2020-01-22 - It all ends up here, in the 6,000-square-metre heat rejection zone. The squat black building to the left hosts the 10 cooling cells that are tasked with evacuating the heat generated by operation; to the right, a complex network of piping, pumps and heat exchangers connects the installation's cooling loops to the cells and the underground hot and cold basins.

Fill packs
2020-01-22 - Inside each cooling cell, stacked layers of millimetre-thick corrugated plastic sheet (''fill pack'') act like the honeycomb structure of a car radiator. (Look closely at the black ''floor.'')

First blade
2020-01-22 - Rotating at 92 rpm, a large twelve-blade fan on top of each cell induces the upward draft that optimizes the cooling process. Here, inside a newly installed fan cylinder, the fan's rotor has just been equipped with its first blade.
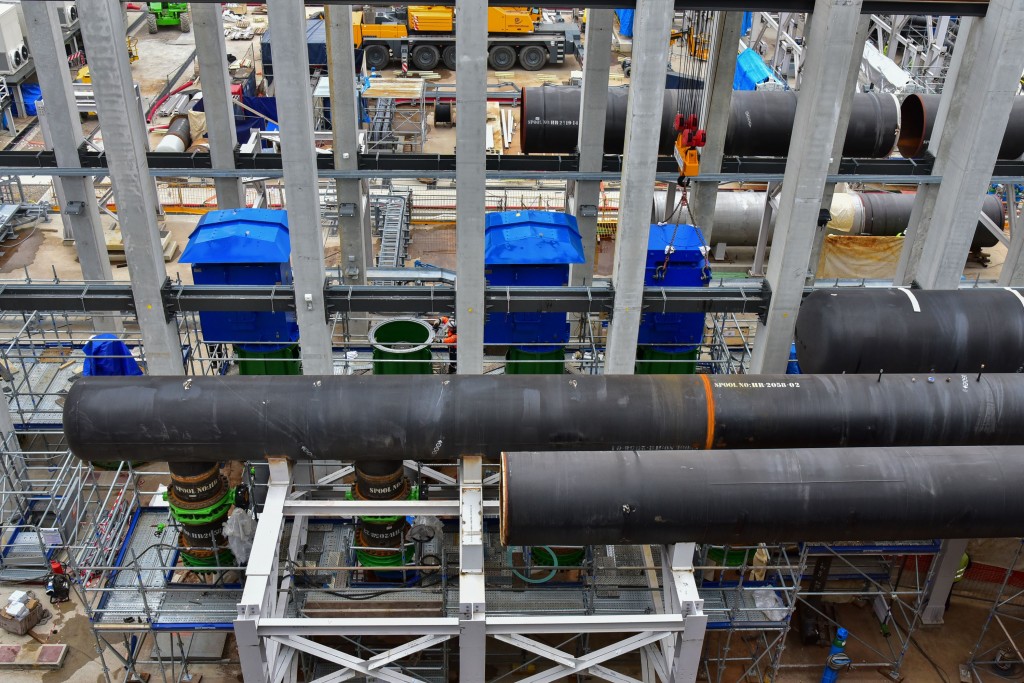
10t of water per second
2020-01-22 - Thirteen large vertical turbine pumps (in blue), each one powered by a 870 kW motor and capable of moving 10 tonnes of water per second, circulate water throughout the heat rejection system.

Cylinders, rotors and motors
2020-01-22 - A 3-tonne fan cylinder is being lifted into its final position above the cooling cell. The fan rotor (light grey), connected through a shaft to a 170 kW electrical motor (blue), is ready to be fitted with twelve 5-metre long plastic blades.
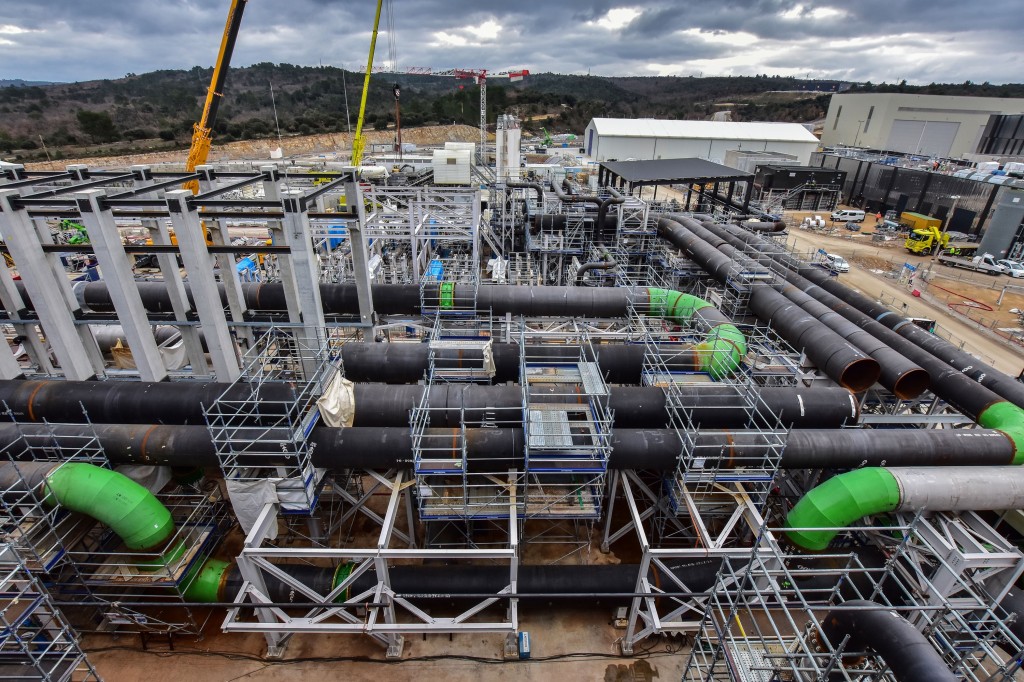
Evacuating 1 GW
2020-01-22 - Cooling water flows through approximately 5 kilometres of piping and 17 heat exchangers inside the heat rejection zone. At full power, the combined load that needs to be evacuated is on the order of one gigawatt, approximately half generated by the burning plasma inside the Tokamak.

10t of water per second
2020-01-22 - Thirteen large vertical turbine pumps (in blue), each one powered by a 870 kW motor and capable of moving 10 tonnes of water per second, circulate water throughout the heat rejection system.

Next step: large fans
2020-01-22 - At the top of the building each cooling cell is topped by a "fan cylinder." Once installed, the twelve-blade fans will induce an upward draft.

Fill packs
2020-01-22 - Inside each cooling cell, stacked layers of millimetre-thick corrugated plastic sheet (''fill pack'') act like the honeycomb structure of a car radiator. (Look closely at the black ''floor.'')

Next step: large fans
2020-01-22 - At the top of the building each cooling cell is topped by a "fan cylinder." Once installed, the twelve-blade fans will induce an upward draft.

Ready to lift
2020-01-22 - Three "fan cylinders" made of fibre-reinforced plastic are ready to be lifted and installed on the roof. Each one measures more than 11 metres in diameter and weighs approximately 3 tonnes.
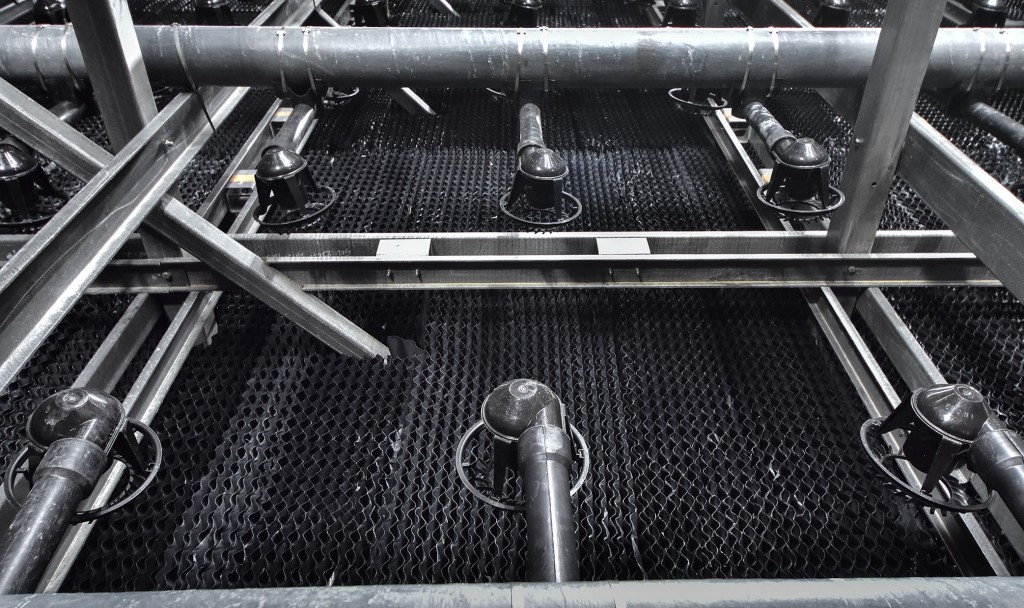
4,540 nozzles
2020-01-22 - A set of 4,540 nozzles sprays the water coming in from the installation's cooling system over the stacked fill-pack layers. If unfolded, the total heat exchange surface provided by the fill pack would be approximately 704,000 square metres, the approximate equivalent of 70 soccer pitches.
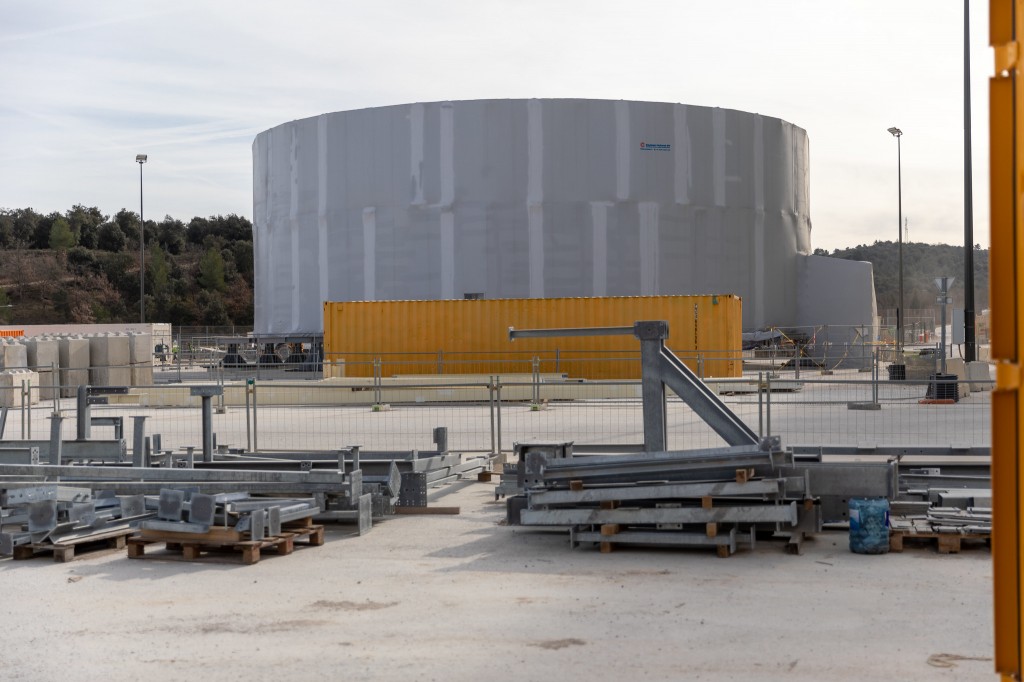
Stored on site
2020-01-20 - The cryostat lower cylinder, cleaned and stored in protective wrapping on the construction platform, will soon be joined by the upper cylinder. © Les Nouveaux Médias/SNC ENGAGE

Capable of lifting 60 tonnes
2020-01-20 - In this embedded-plate-studded galley of the Tokamak Complex, a red "leaf mounting" tool is parked. This specialized tool was created by contractor Cegelec/Sommer to move the massive port cell doors to the concrete pouring station and back to their final installation locations. It is equipped with two large holding frames that clutch the port cell door like a sandwich.© Les Nouveaux Médias/SNC ENGAGE

Utmost precision
2020-01-16 - In the densely packed environment of the buildings, laser measurement ensures that each component—whether busbar, converter or reactor—is set into place with utmost precision.
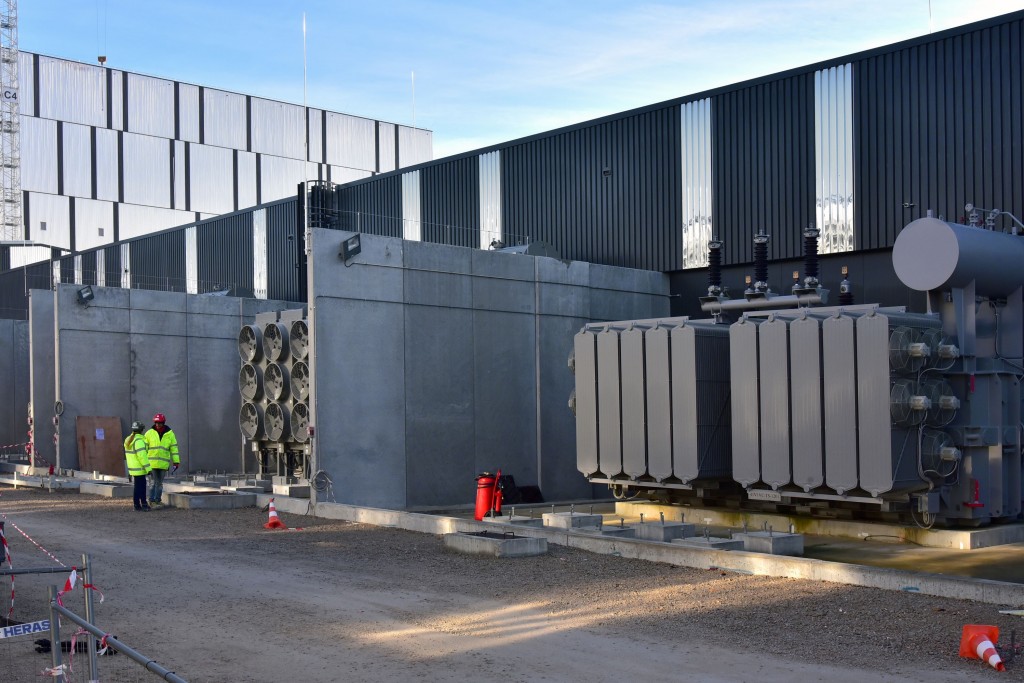
Exterior bays
2020-01-16 - Two transformers procured by Korea and China are shown outside. Depending on which "client" they serve, the transformers step down AC power from 66 kV or 22 kV to 1 kV AC. The currant then enters the building along AC busbars that connect the transformers to AC/DC converters.
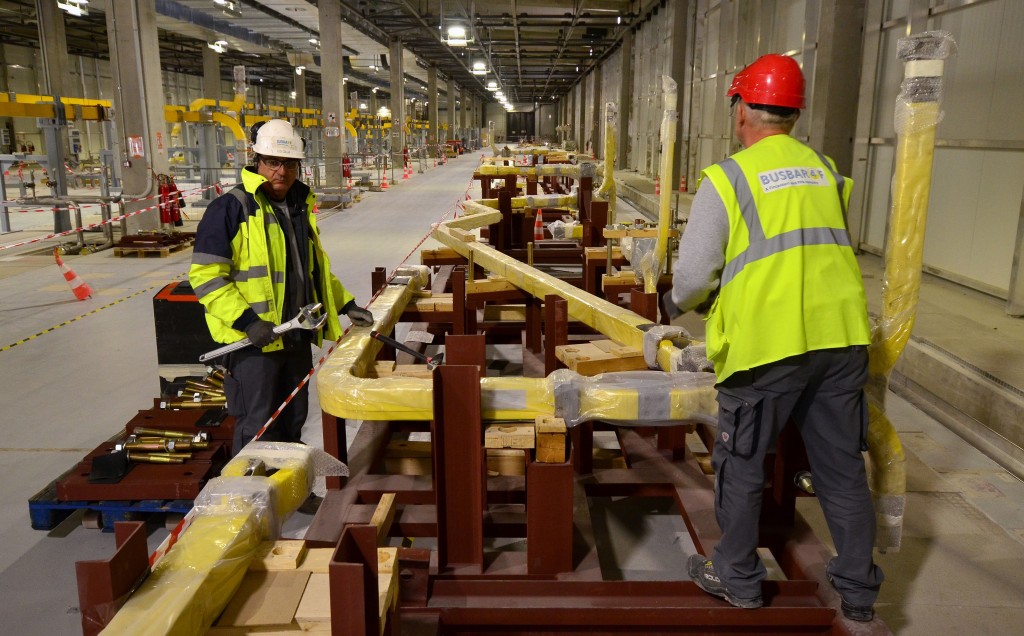
Fresh from Russia
2020-01-16 - Workers unpack a section of DC busbar that has just been delivered from Russia. The contorted shape reflects the complexity of connections in some areas of the buildings. This section is a vertical interface for a correction coil converter. Busbar installation is 92 percent complete in the first Magnet Power Conversion building, and 72 percent complete in the other.
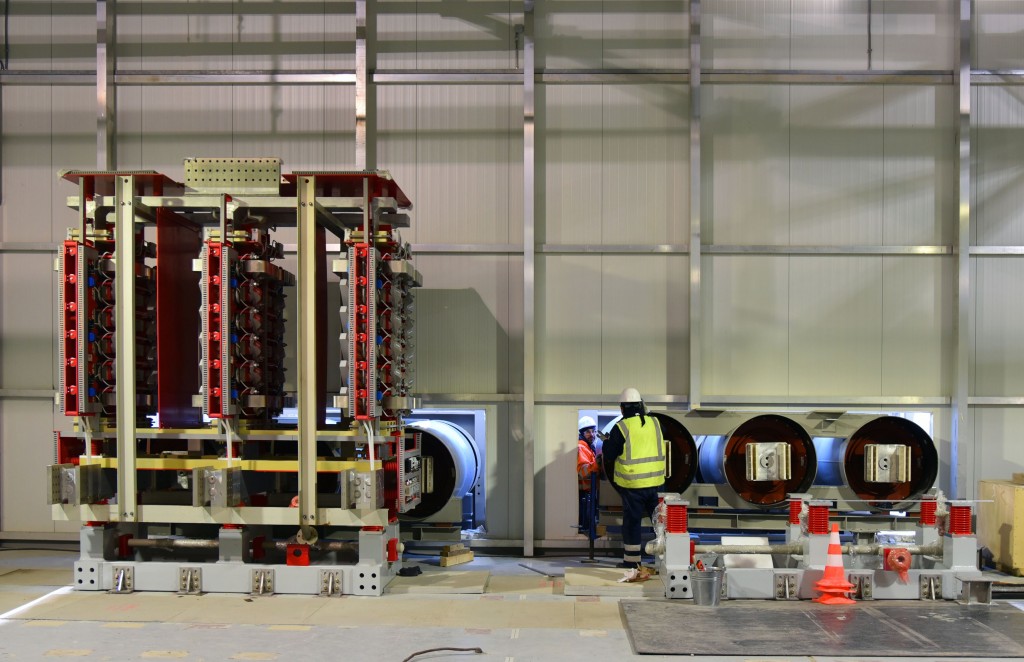
Inside and out
2020-01-16 - The first of a set of four converter modules for poloidal field coil #6 has just been installed. Connected to an outdoor transformer by way of three AC busbars, the converters are tasked with converting the 1 kV power from AC to DC. There are 12 such converters in one of the buildings, 17 in the other. The converters serving the poloidal field coils are procured by China; all others are procured by Korea.
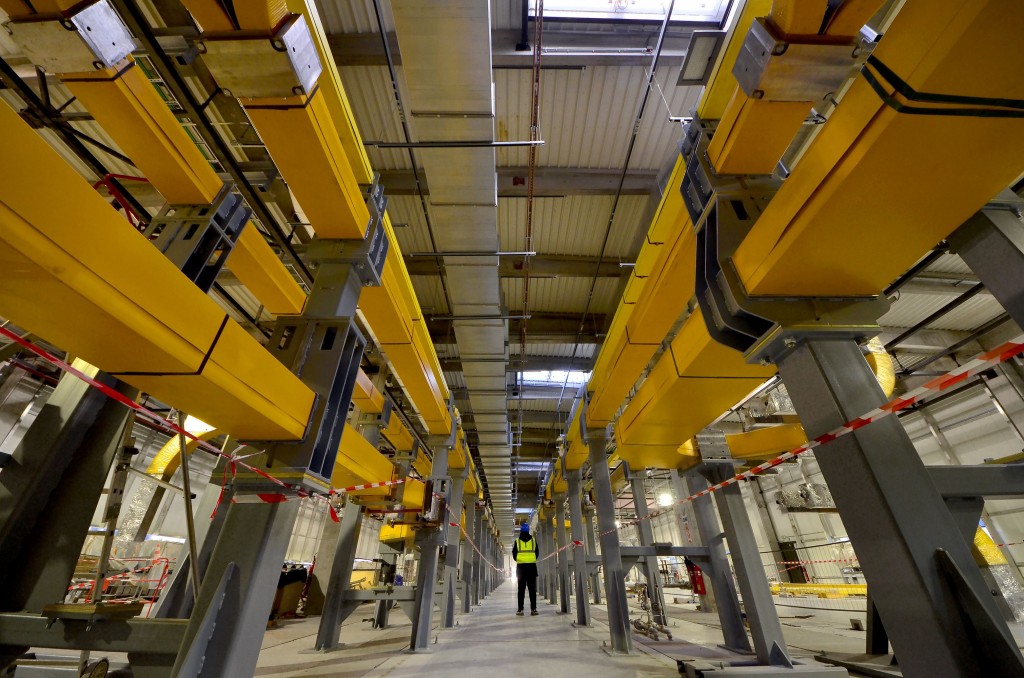
Elevated busbars
2020-01-16 - Thicker than railroad rails, steel-jacketed DC busbars are actively cooled by a constant flow of pressurized water. As many as 5 kilometres of busbars supplied by Russia will be installed, including these running half the length of the Magnet Power Conversion buildings on elevated supports.
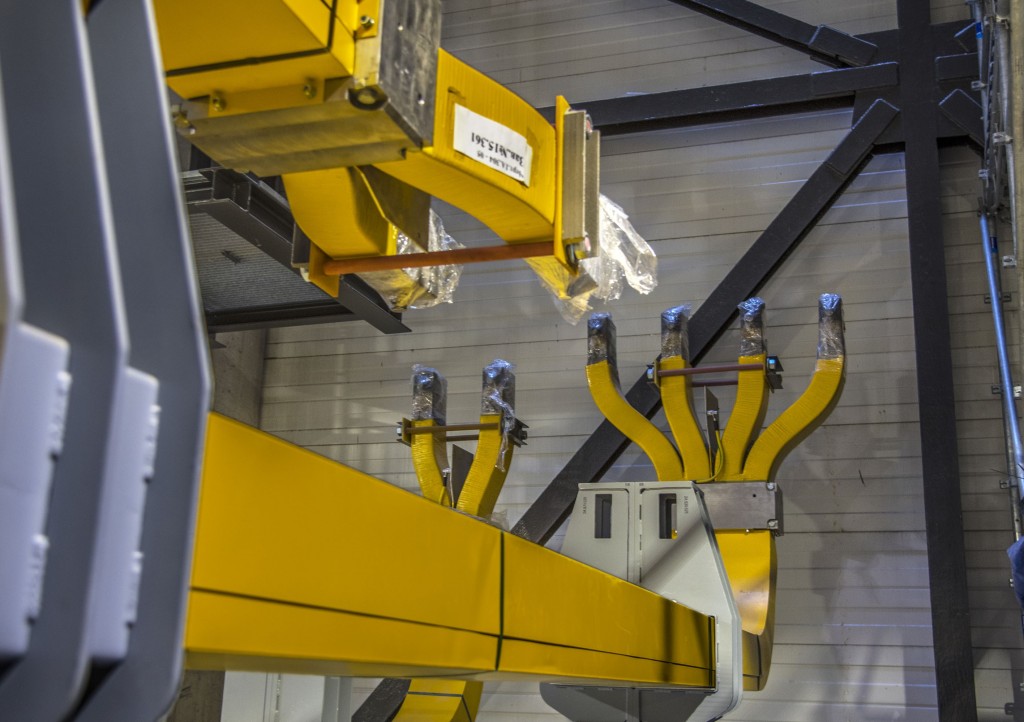
65,000 amps
2020-01-16 - High-intensity current (65,000 amps) is fed to the toroidal field coils through a double set of busbars (right). The simple set of busbars to the left is for a poloidal field coil that requires "only" 55,000 amps. Just like in daily life, DC outlet busbars have a positive and a negative polarity.

A five-kilometre network
2020-01-16 - Five kilometres of actively cooled aluminium busbars, procured by Russia, run through the twin conversion buildings. Busbars carry the high-intensity DC current that is fed to the ITER magnetic system.

Smoothing the currant
2020-01-16 - This strange contraption that looks like a giant vintage seismograph is a "reactor." Its function is to create a magnetic field that filters the small spikes in DC waveform before it is fed to the magnetic system. Korea and China are sharing procurement of the 31 reactors, each coupled with a converter or set of converters, that the system requires.
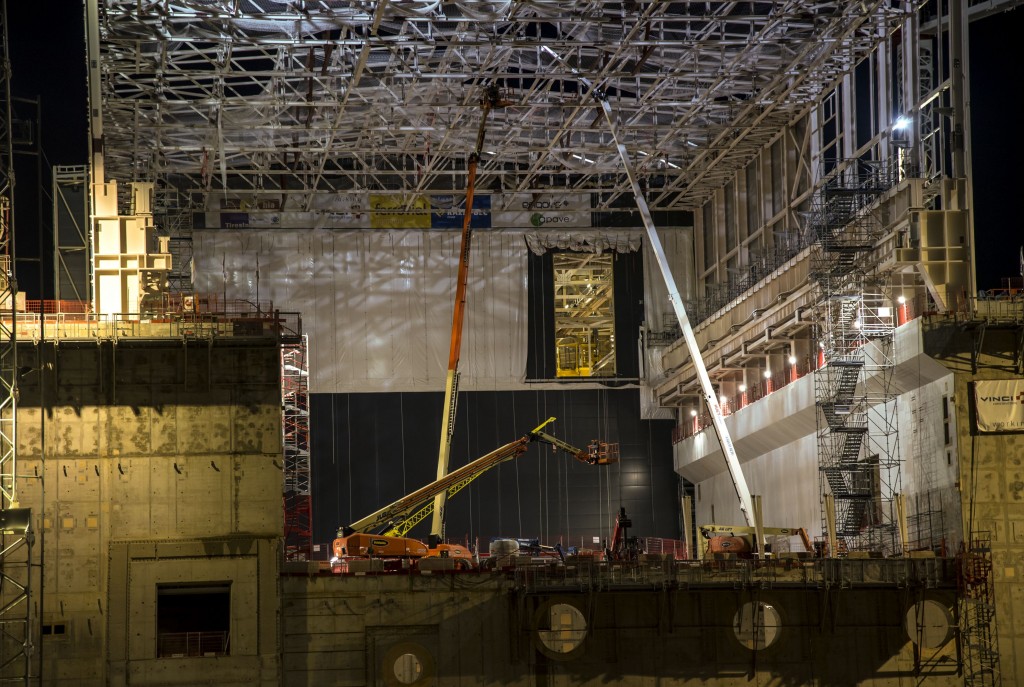
A peek
2020-01-13 - Evocative of a stage with black curtains, the vertical opening at the centre of this image offers a glimpse of the ongoing activity inside the adjacent Assembly Hall.
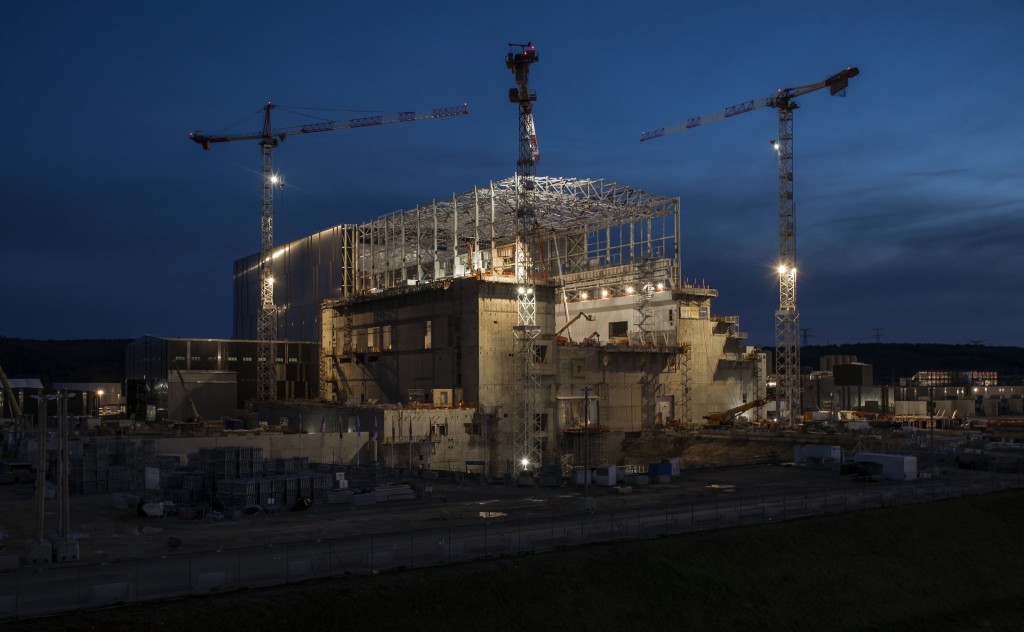
One step away
2020-01-13 - With the Tokamak Building now topped by the steel structure of its crane hall, the main building on the ITER worksite is just a step away from its final aspect.

Cooling tower installation underway
2020-01-08 - Cooling water will flow from the Tokamak machine to the heat rejection zone (pictured) at rates of up to 14 m³/s. Equipment arriving from India is being installed by ITER Organization contractors inside of infrastructure prepared by Europe.
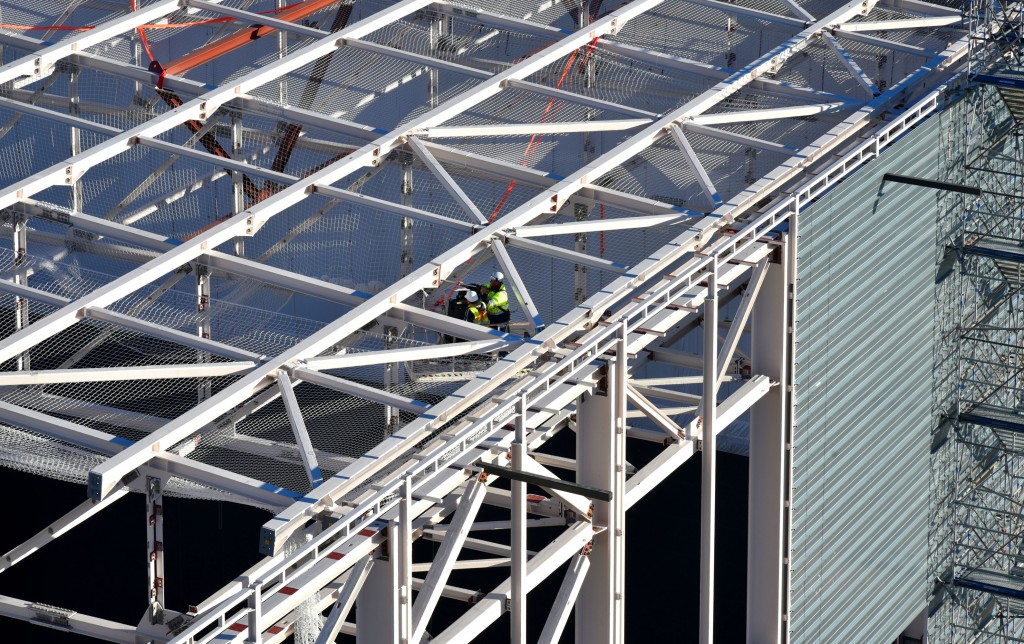
Adjusting torque
2020-01-08 - In different areas of the roof structure, teams are tightening bolts and adjusting torque. First-level cladding will completely cover the structure by late February, allowing the bridge cranes to be brought into the new volume over the Tokamak pit for testing and commissioning.
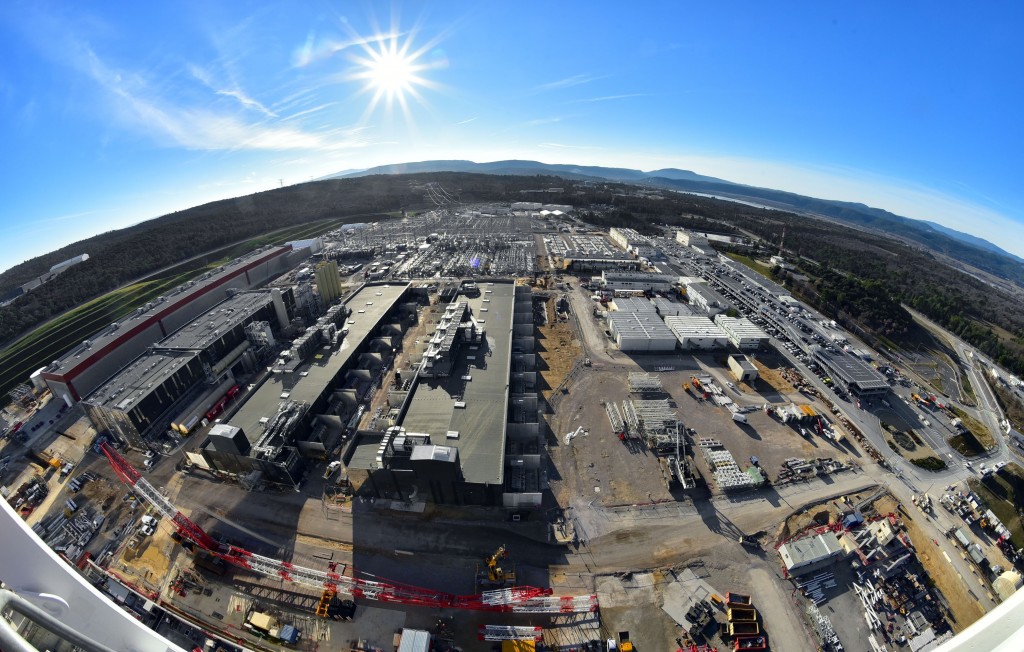
Site south
2020-01-08 - Much of the central area of the platform is dedicated to electrical power, with two identical buildings for magnet power conversion (centre), a small facility for reactive power compensation (further along to the right) and as yet unbuilt structures to house the neutral beam power supplies. Also visible is the European magnet winding facility (far left) and the ITER cryoplant (left).
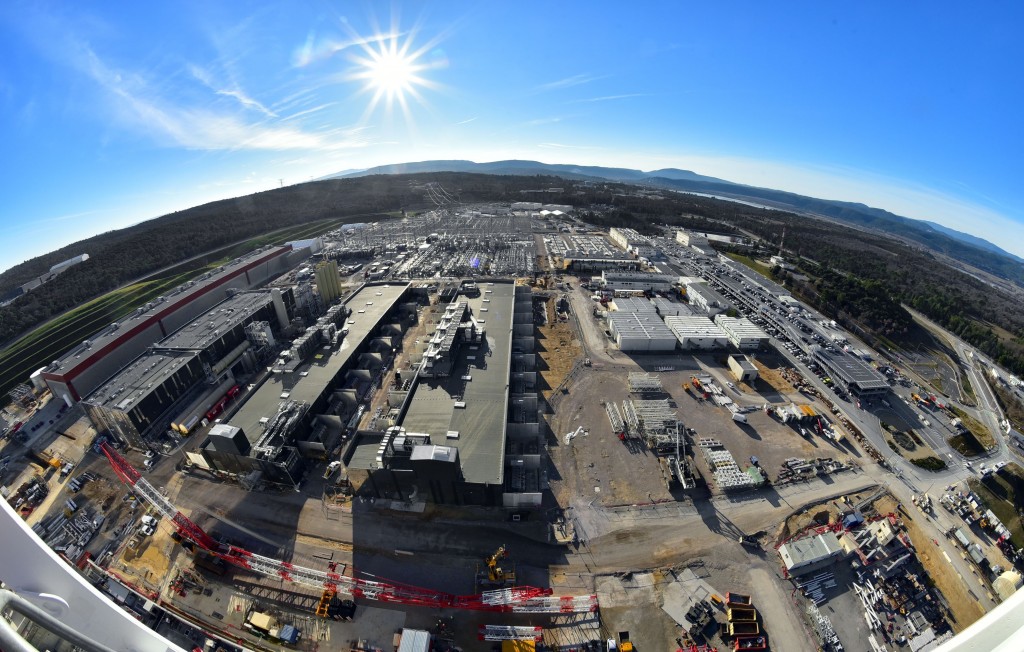
Site south
2020-01-08 - Much of the central area of the platform is dedicated to electrical power, with two identical buildings for magnet power conversion (centre), a small facility for reactive power compensation (further along to the right) and as yet unbuilt structures to house the neutral beam power supplies. Also visible is the European magnet winding facility (far left) and the ITER cryoplant (left).
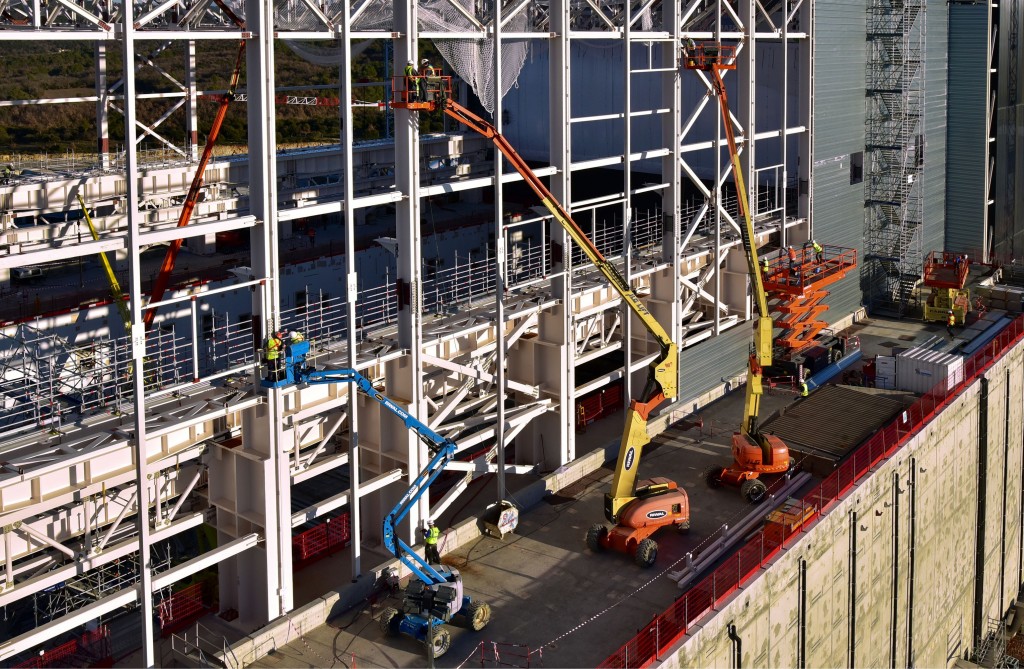
In one month
2020-01-08 - Just inside the metal frame are the massive "runway beams" that will support the weight of the bridge cranes and their heavy loads. The beams are ready to receive the crane rails; installation work begins this week.

Crane hall: framed out
2020-01-08 - The complete crane hall structure—20 tall pillars and roof modules included—weighs approximately 2,000 tonnes. Contractors are currently installing the secondary steel structure (crossbars, etc), tightening bolts, and touching up paint.

Powering the facility
2020-01-08 - A vast electrical switchyard occupies the southern third of the construction platform to transform 400 kV current from the French electrical grid into the pulsed power required by the machine, or the steady state power required by the installation. The commissioning of the electrical distribution networks has proceeded on pace with needs.
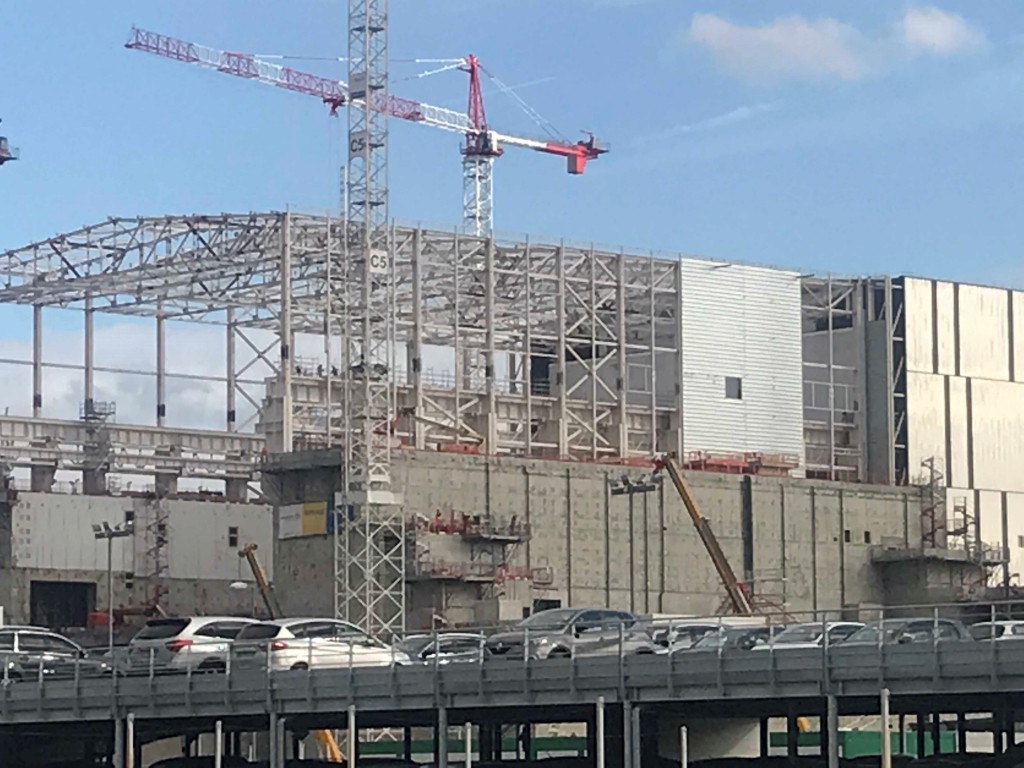
Cladding begins
2019-12-19 - The first panels of steel cladding appear on the south side of the crane hall.
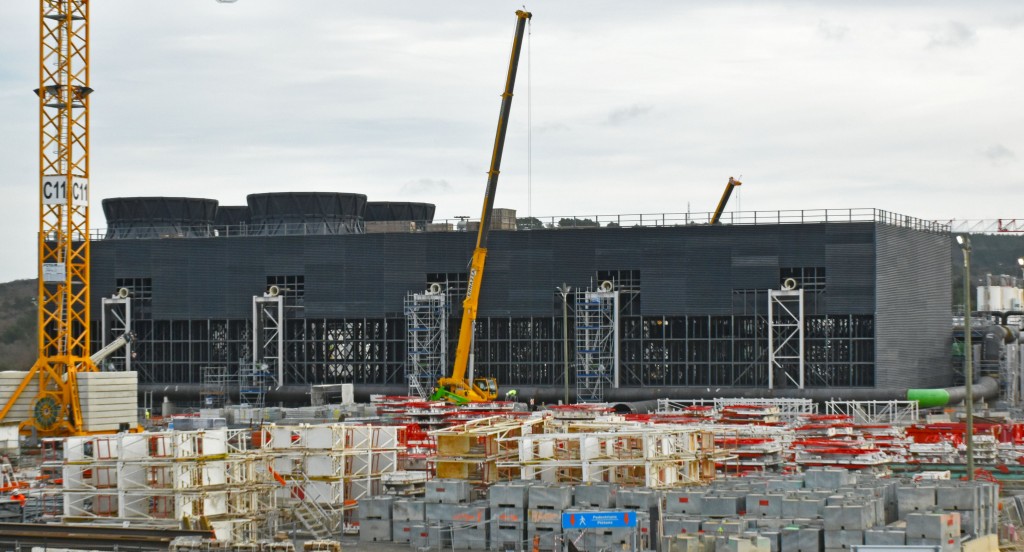
Installation of cooling fans
2019-12-16 - Ten 16 x 16-metre cooling cells will receive water from the hot basin and discharge it—once cooled—to the cold basin. Each cell is filled with hundreds of layers of corrugated plastic fill and equipped with a large fan (installation underway at the top of the building) that pulls air upward.
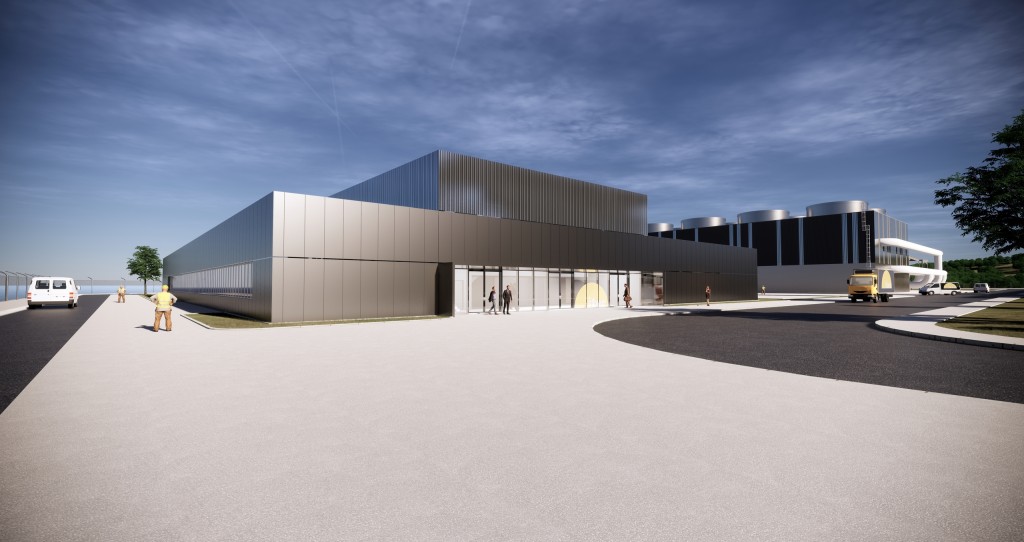
A view of the future Control Building
2019-12-16 - ITER's main control room will be situated in a non-nuclear structure on the northern corner of the platform. Work will begin on the structure in 2020. © Enia Architectes, France
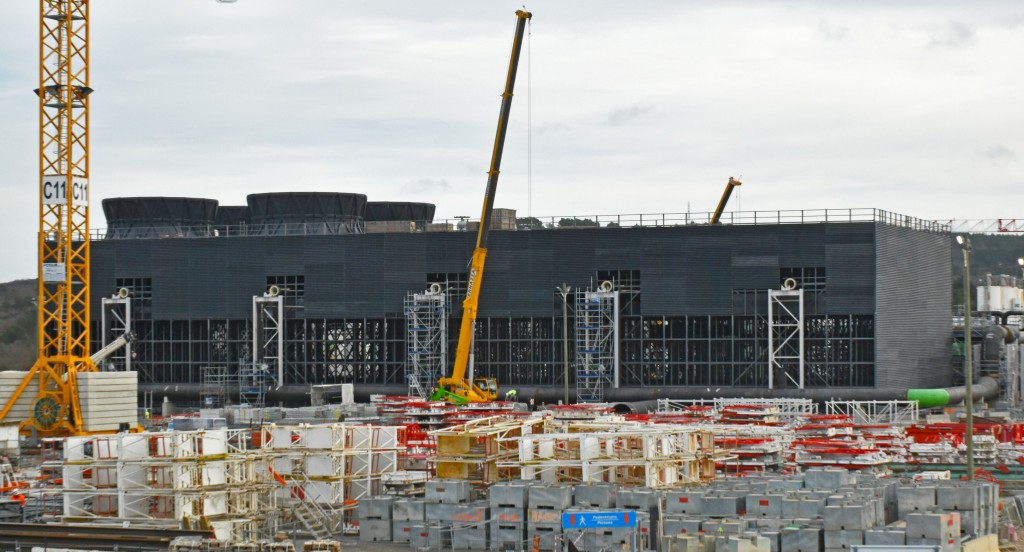
Installation of cooling fans
2019-12-16 - Ten 16 x 16-metre cooling cells will receive water from the hot basin and discharge it—once cooled—to the cold basin. Each cell is filled with hundreds of layers of corrugated plastic fill and equipped with a large fan (installation underway at the top of the building) that pulls air upward.
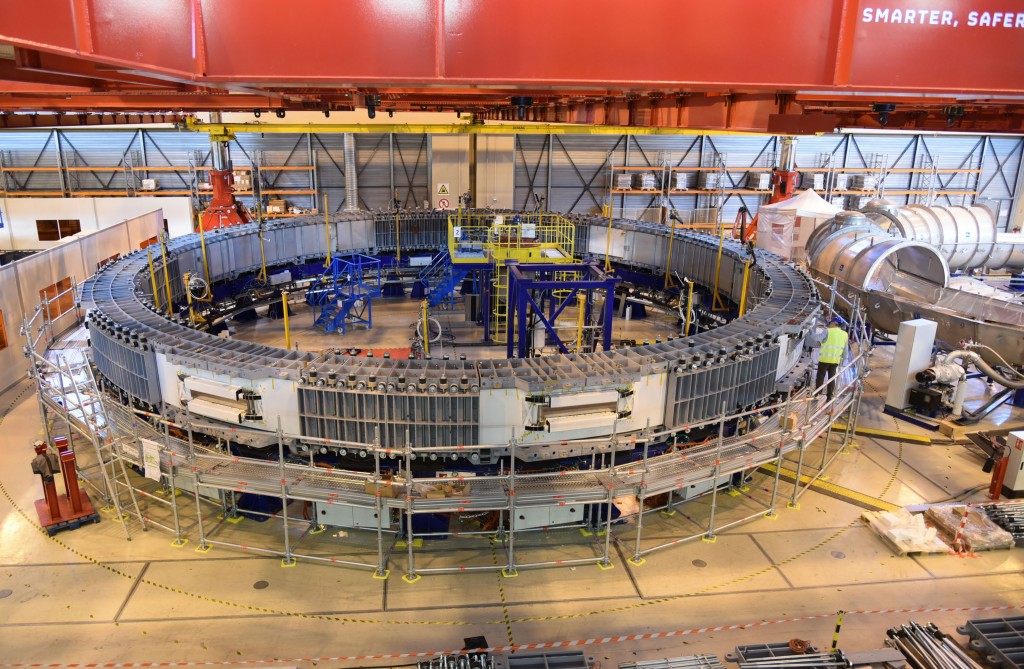
Next step for PF5: impregnation
2019-12-13 - A mould has been assembled and welded around the first on-site production coil—PF5. After the impregnation process, which will last about three weeks, the coil will be prepared for cold testing at 80 K.
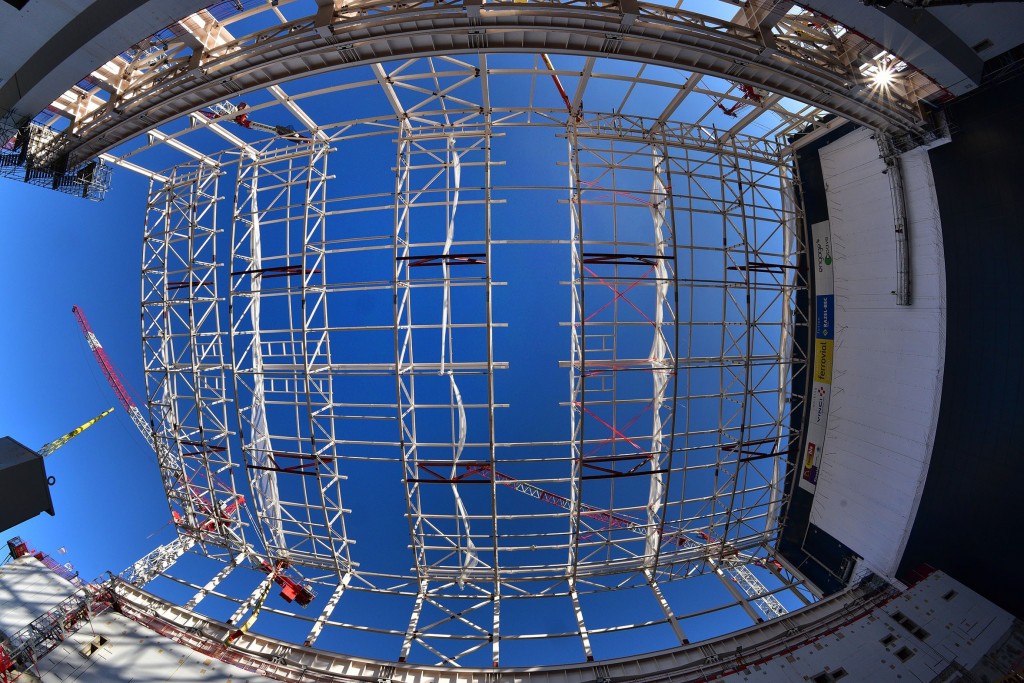
Without a hitch
2019-12-13 - The last roof module is moved into position on 11 December. The complete roof structure—20 tall pillars and roof modules included—weighs approximately 2,000 tonnes.
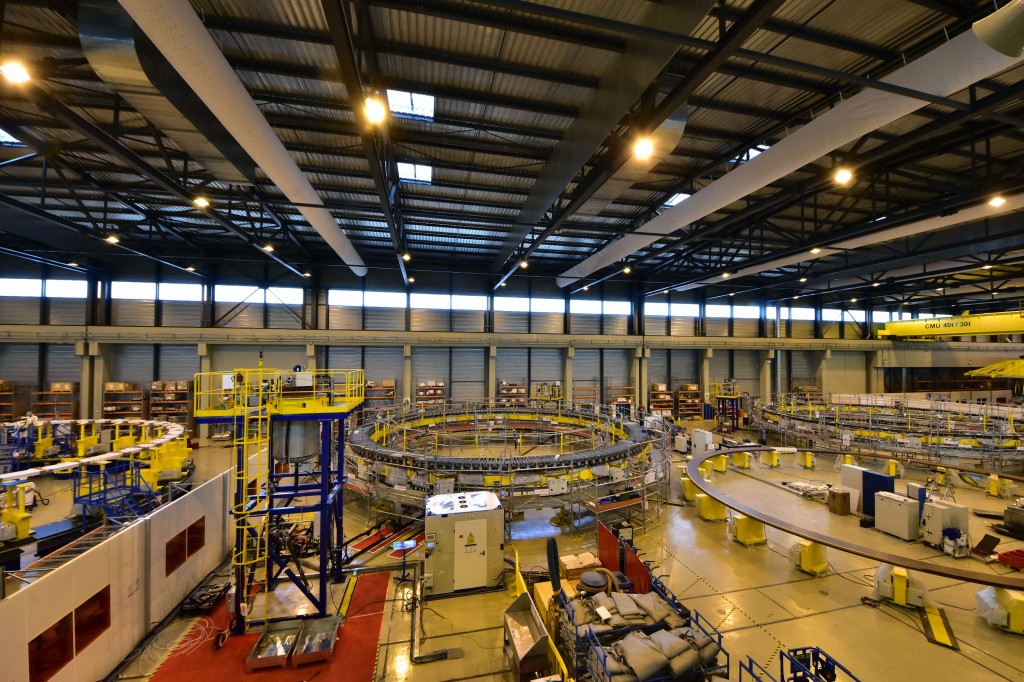
Building blocks for PF2
2019-12-13 - Work is underway to wind and impregnate the double pancake windings for poloidal field coil #2 (PF2).

Next to test: the upending tool
2019-12-13 - Tool commissioning is an important activity, during which the all specified functional requirements are demonstrated. Also, for tools sourced outside of the European Union, it is the occasion to show compliance with EU regulations.
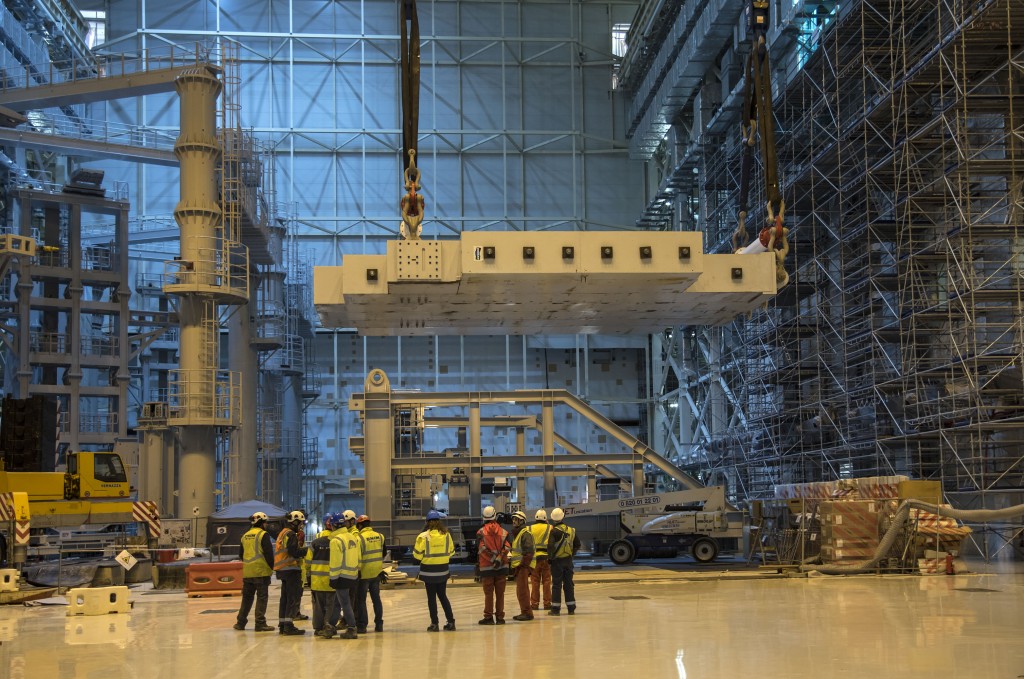
Next to test: the upending tool
2019-12-13 - Tool commissioning is an important activity, during which the all specified functional requirements are demonstrated. Also, for tools sourced outside of the European Union, it is the occasion to show compliance with EU regulations.
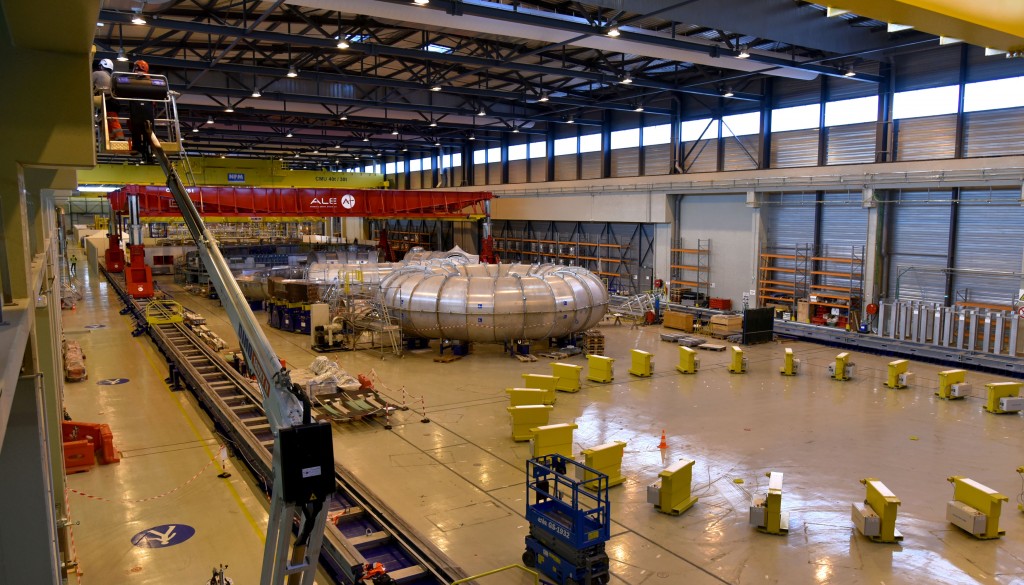
Cryogenic chambers ready
2019-12-13 - The cryogenic chamber for PF6 stands ready for the arrival of the completed coil from China early next year. The red gantry crane will be used to lift the 400-tonne component in and out of the chamber. A second chamber for PF5 has also been assembled.

Commissioning with load completed
2019-12-13 - The 360-tonne test load is lowered to the Assembly Hall floor. After six months hooked up first to one, then the other, of the sector sub-assembly tools (left), the test loads will be stored in laydown areas until called for use to commission the upending tool.

Next to test: the upending tool
2019-12-13 - Tool commissioning is an important activity, during which the all specified functional requirements are demonstrated. Also, for tools sourced outside of the European Union, it is the occasion to show compliance with EU regulations.

Winding tooling to be reconfigured
2019-12-12 - The winding tooling used for PF5 and PF2 has now been disassembled. It will be reconfigured for the winding of the last two poloidal field coils to be produced in this facility—PF3 and PF4, which have a diameter of 24 metres.

Impregnation: a three-week operation
2019-12-12 - The casing assembled around the PF5 winding pack must be absolutely leak tight. Approximately 2,200 litres of resin will be injected over 60 hours, followed by a period of "gelling" and "curing."
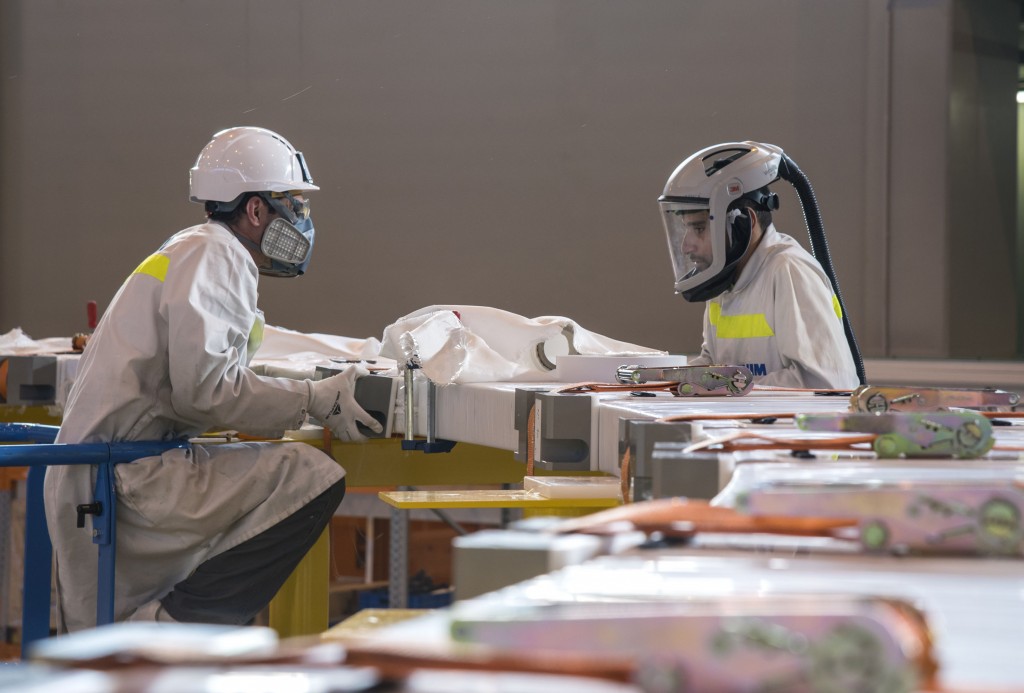
Last double pancake for PF2
2019-12-12 - The last of six double pancakes for poloidal field coil #2 (PF2) is being wrapped with insulating tape ... the final step before transfer of the double pancake to its impregnation station. The first two coils produced in the facility are not identical, although both are 17 metres in diameter. PF5 is built from 11.5 km of niobium-titanium conductor (8 double pancakes) and will weigh 342 tonnes when completed; PF2 is built from 6 km of conductor (6 double pancakes) and will weigh 204 tonnes when completed.

70 metres above ground
2019-12-04 - The preassembled modules are raised 70 metres overhead before being positioned on the waiting pillars. A second crawler crane (under construction at the right of the image) will be necessary for the last operations.
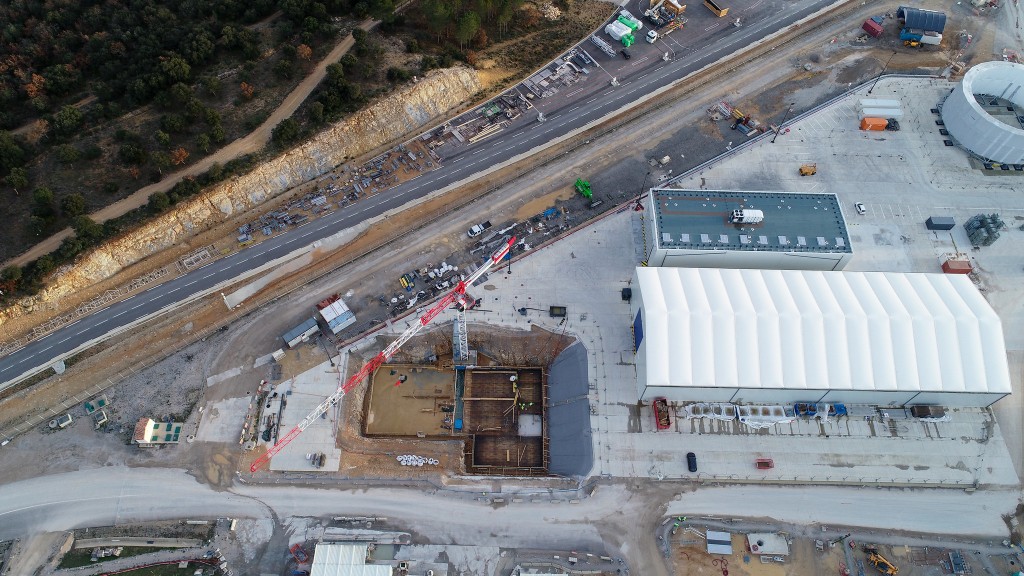
Optimizing space
2019-12-04 - Every corner of the ITER platform has been optimized. In this photo, we see the excavation underway for the Tokamak Assembly Preparatory Building (left), a storage tent, and a smaller rectangular building dedicated to preparatory activities on the toroidal field coils. © Les Nouveaux Médias/SNC ENGAGE

First of five
2019-12-04 - The five modules weigh between 62 and 78 tonnes and span a distance of 50 metres between the two rows of pillars. A giant crawler crane—with a boom spanning more than 100 metres—was put in place for the lift operation.
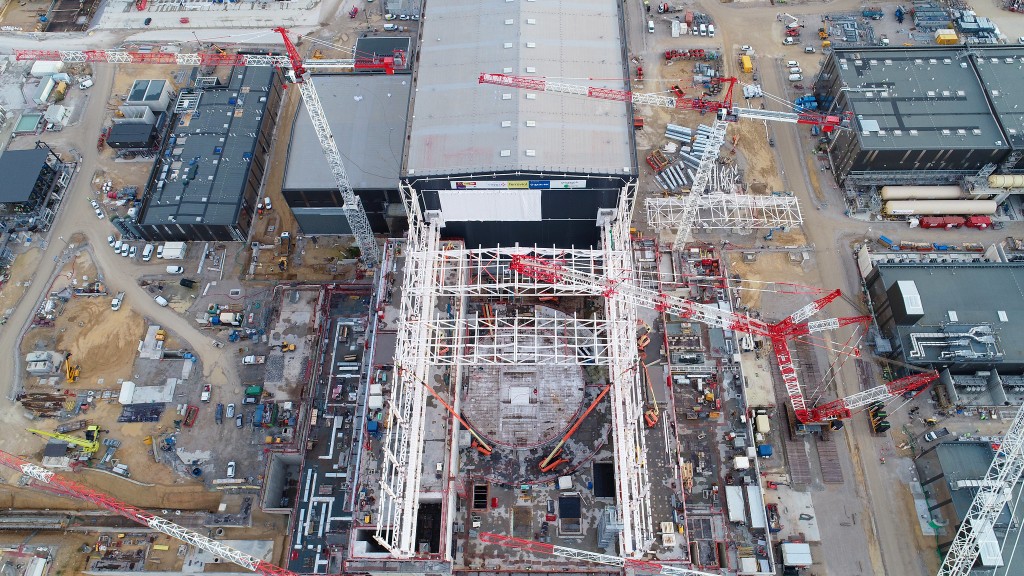
Bird's eye view
2019-12-04 - The assembly of the Tokamak Building roof, seen from above. © Les Nouveaux Médias/SNC ENGAGE

And a second
2019-12-04 - Because the first module was lifted and installed without technical incident, European Domestic Agency contractors were able to proceed with a second lift on the same day.

Ten cooling towers
2019-12-04 - The first two fan cylinders are positioned near the cooling tower facility, ready to be lifted to the top. © Les Nouveaux Médias/SNC ENGAGE

First roof module
2019-12-04 - The first module of the crane hall roof is lifted on 4 December, in an operation that begins at 7:00 a.m.

Next step: the roof modules
2019-12-03 - The pillars of the crane hall are in place on top of the Tokamak Building; next, five roof modules must be installed. These will be lifted from 4 December on.
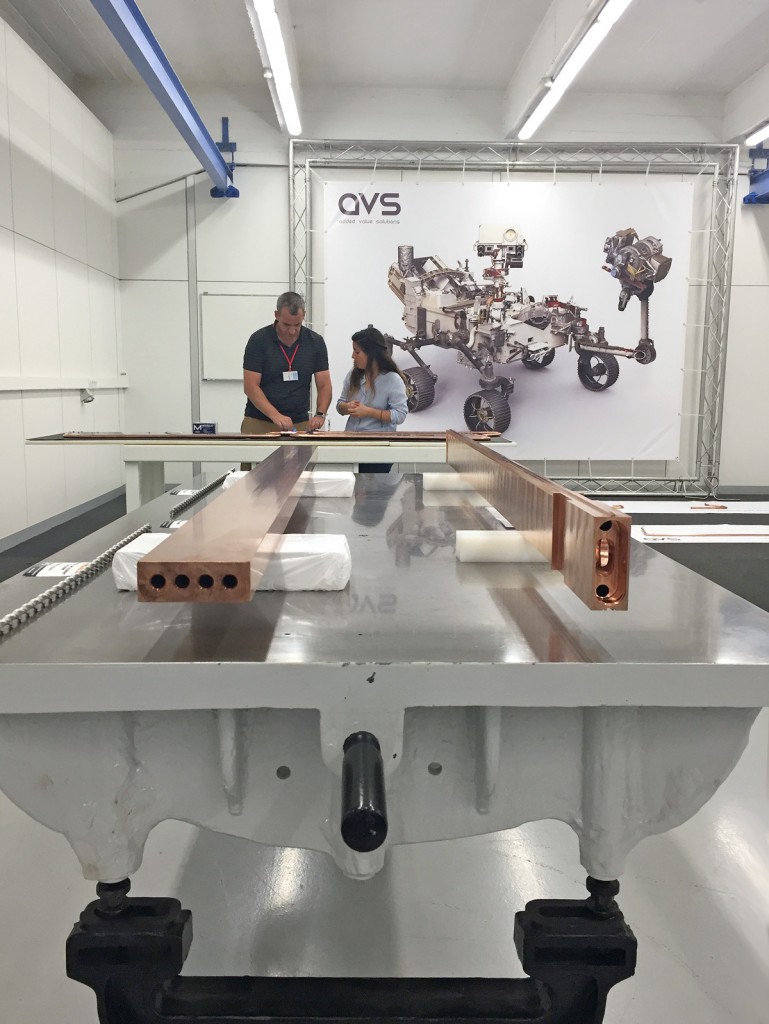
Contract signed for MITICA beam line components
2019-12-01 - The European Domestic Agency has signed a contract with the AVS/Fundación Tecnalia consortium for the manufacture of MITICA's beamline components (neutraliser, electrostatic residual dump, calorimeter and auxiliary equipment). Their main function is to remove the negative ions and guide them through, in the form of a neutralized beam, to the final target.
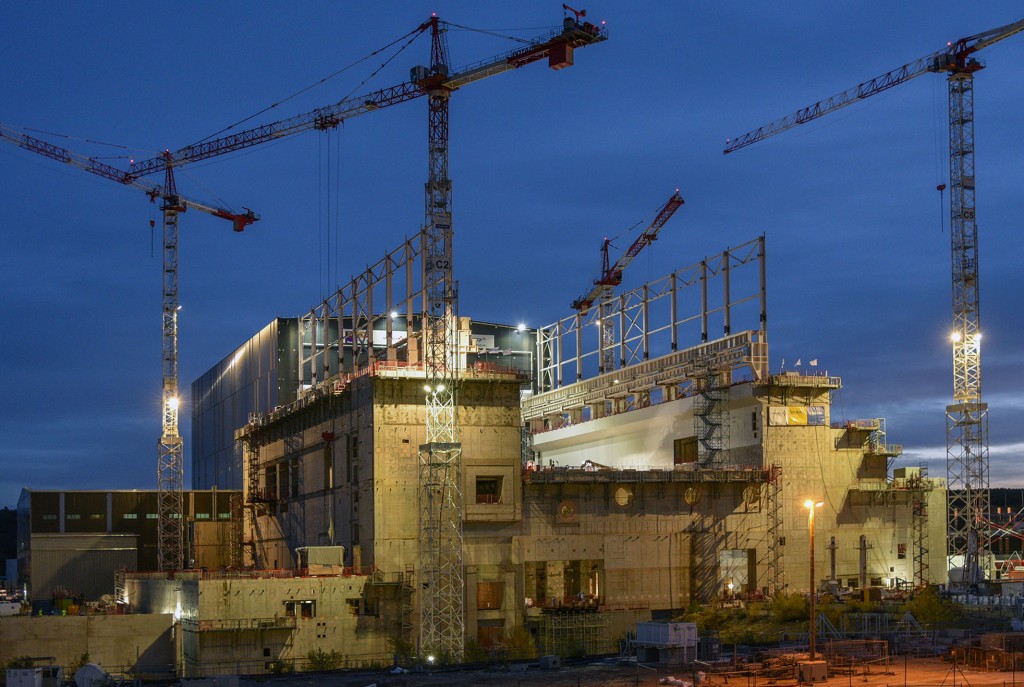
All pillars in place
2019-11-28 - Two rows of pillars, ten on each side, have been installed on the top of the Tokamak Building. Approximately one-third of the way up the pillars, are the sturdy supports for the assembly crane rails.
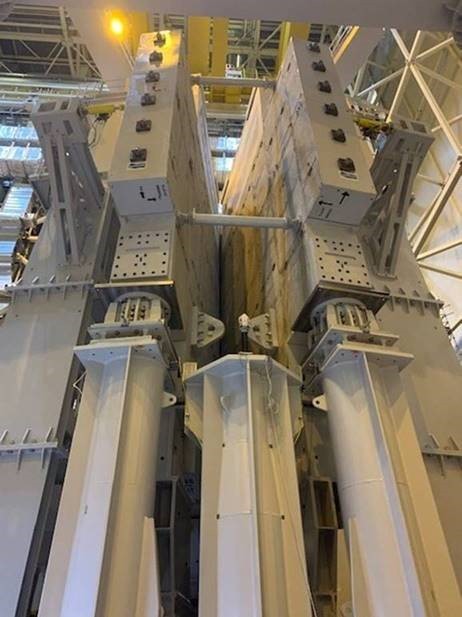
Load tests conclusive
2019-11-27 - The commissioning phase for the twin sector sub-assembly tools (SSAT) in the Assembly Hall is over. The final verification tests—with test load (photo)—demonstrated that both tools are performing to expectation.

Load tests conclusive
2019-11-27 - The commissioning phase for the twin sector sub-assembly tools (SSAT) in the Assembly Hall is over. The final verification tests—with test load (photo)—demonstrated that both tools are performing to expectation.

Load tests conclusive
2019-11-27 - The commissioning phase for the twin sector sub-assembly tools (SSAT) in the Assembly Hall is over. The final verification tests—with test load (photo)—demonstrated that both tools are performing to expectation.
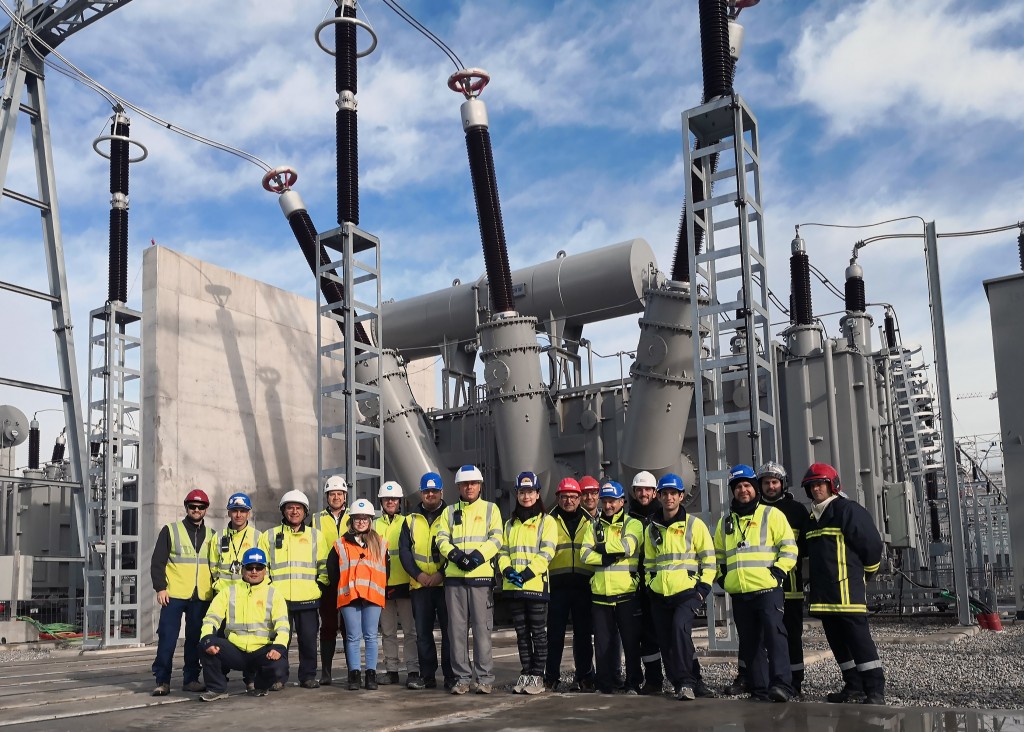
"Energization" begins for second electrical distribution network
2019-11-26 - The first of three transformers for the pulsed power electrical network (PPEN) was successfully "energized" on 26 November. Procured by China and installed by Europe, weighing close to 500 tonnes and towering 15 metres above ground, the PPEN transformers are the largest electrical components of the project.
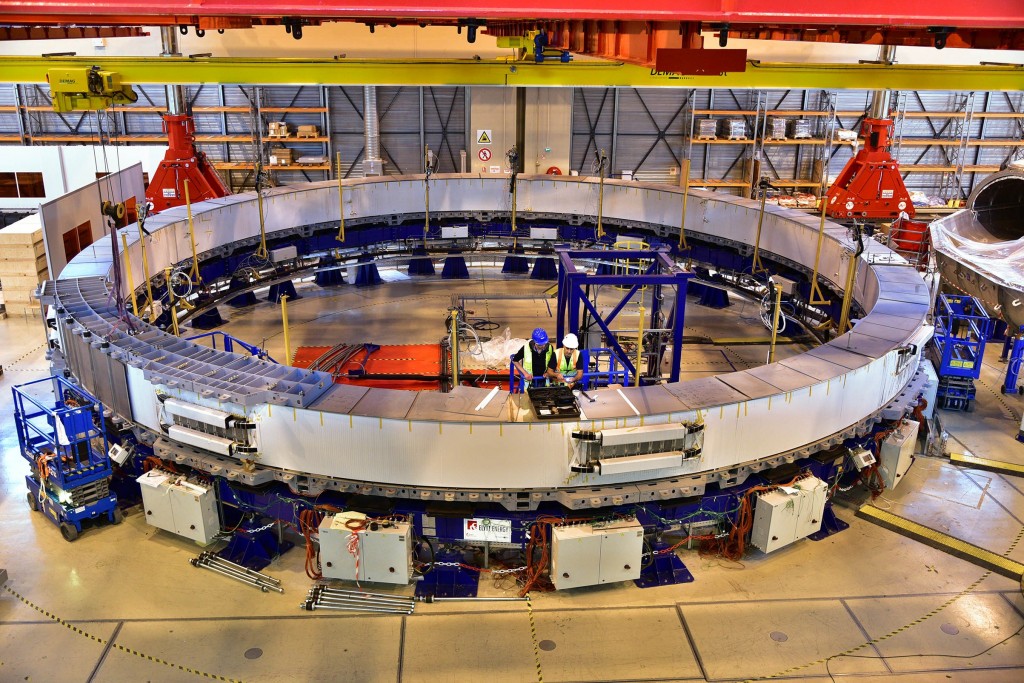
Progress on PF5—the first poloidal field coil produced on site
2019-11-25 - Poloidal field coil #5 (PF5), 17 metres in diameter, is the first coil produced by European Domestic Agency contractors in the winding facility on site. Coil vacuum pressure impregnation—when the entire winding pack is "impregnated" with epoxy resin to form a hardened assembly—is about to start.
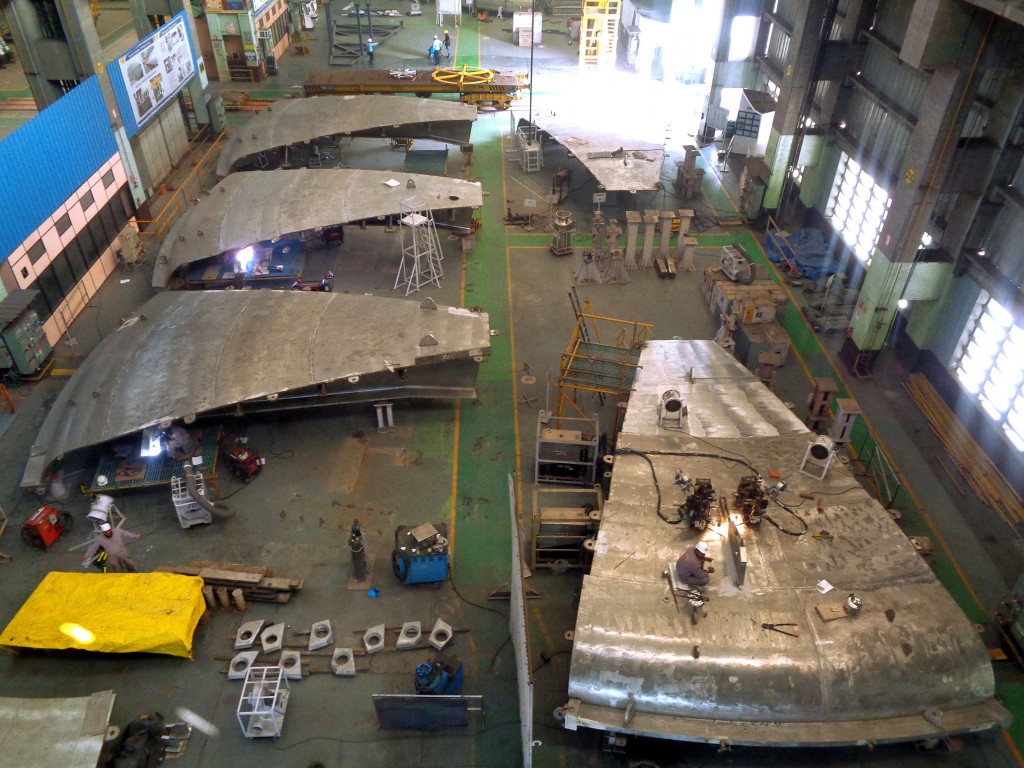
Last manufacturing tasks in India
2019-11-25 - At the Larsen & Toubro factory in Hazira, India, the elements of the top lid of the cryostat lid are in fabrication. These "pieces" make up the last of four main cryostat sectors (base, lower cylinder, upper cylinder, top lid). They will be shipped to ITER for assembly in the Cryostat Workshop.

The golden hour
2019-11-18 - Second-level pillars have risen all along the right wall of the Tokamak Building crane hall. European teams plan to pose the first roof module in December.

46 to install
2019-11-15 - All around the tokamak are galleries full of equipment, which must be closed off by nuclear doors (photo). The teams have 46 to install. © Les Nouveaux Médias/SNC ENGAGE
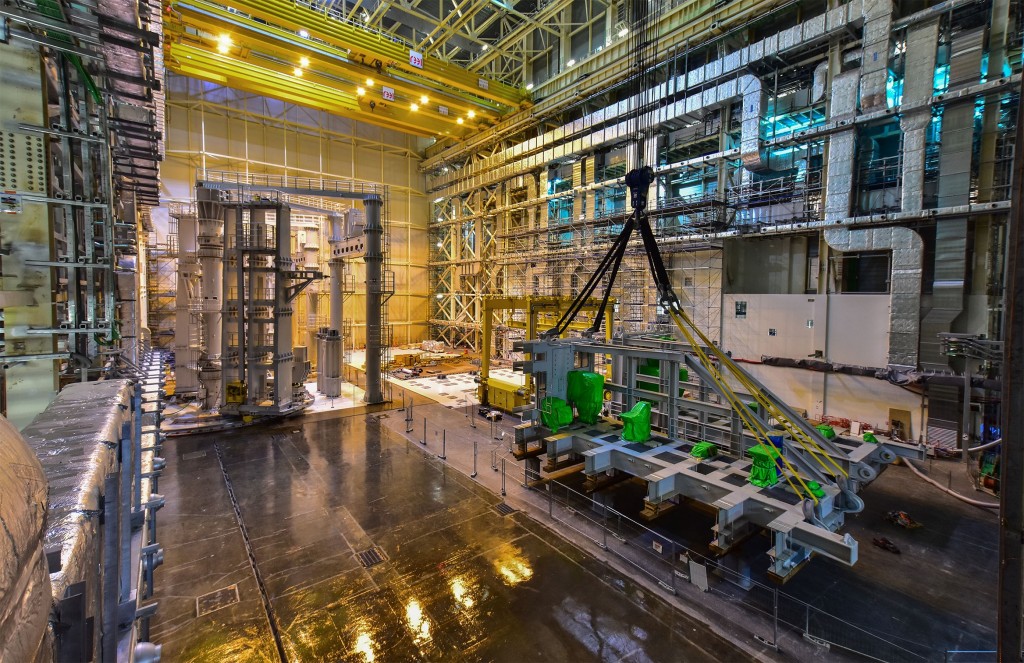
Upending tool arrives
2019-11-14 - The two halves of the upending tool (right) are headed for installation in the far right corner of the Assembly Hall, on the area of floor that has been painted.

Upending tool arrives
2019-11-14 - The two halves of the upending tool (right) are headed for installation in the far right corner of the Assembly Hall, on the area of floor that has been painted.

Upending tool arrives
2019-11-14 - The two halves of the upending tool (right) are headed for installation in the far right corner of the Assembly Hall, on the area of floor that has been painted.

PF5, ready for impregnation
2019-11-13 - A mould will be constructed tightly around the coil winding pack (built from eight double pancakes, stacked and joined). The impregnation process that follows will create a rigid assembly.
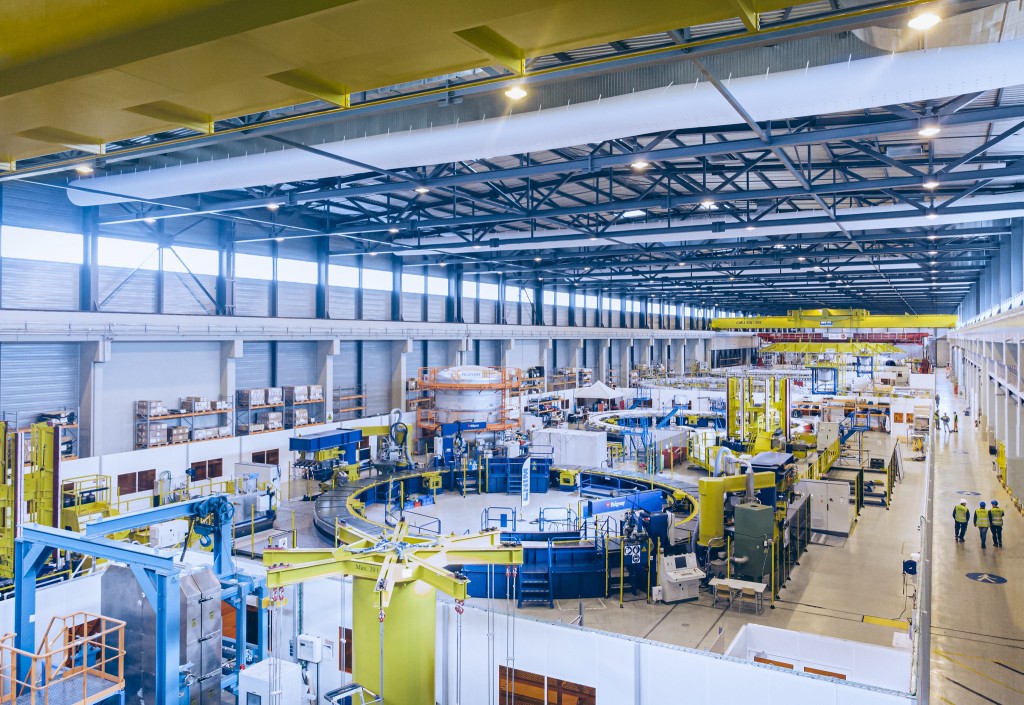
Production line
2019-11-13 - The 257-metre-long European winding facility is completely filled with workstations, from winding all the way through to cold testing.

Termination station
2019-11-12 - European Domestic Agency contractors (from CNIM, France) are working on the termination of double pancake joints.

The doors open and ...
2019-11-07 - ... the segments of the upending tool, delivered by Korea, enter. This large structure is designed to "upend" ITER's largest components (toroidal field coils and vacuum vessel sectors) from horizontal to vertical.
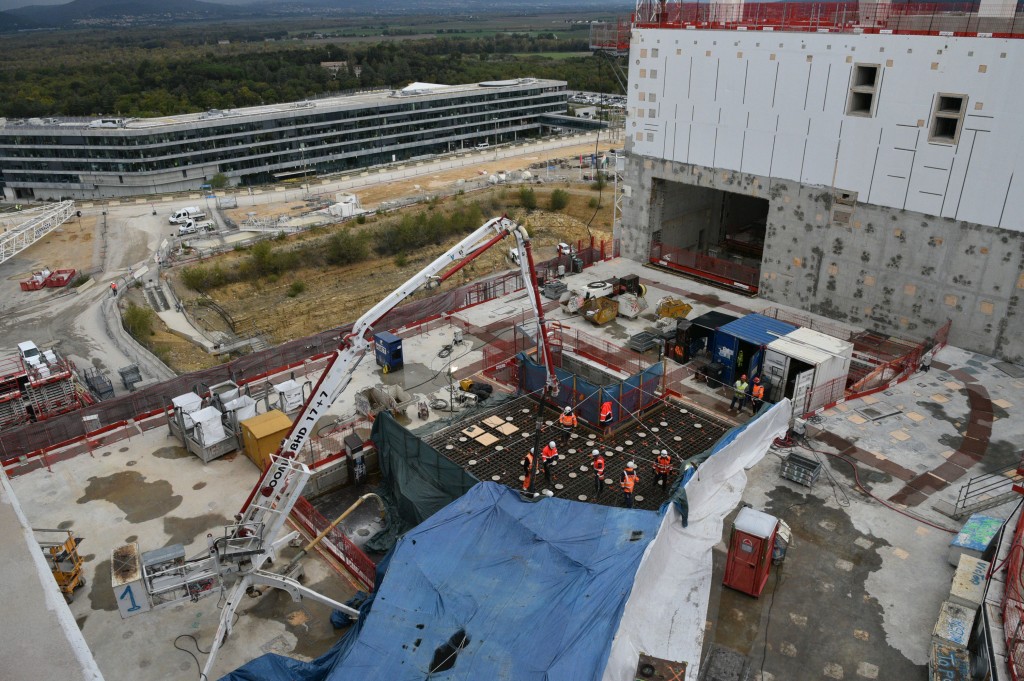
Last concrete for Tokamak Building
2019-11-07 - Forty-five metres above platform level, the final concrete pour of the Tokamak Building is achieved at L4 level on 7 November. Only the roof structure remains.

The doors open and ...
2019-11-07 - ... the segments of the upending tool, delivered by Korea, enter. This large structure is designed to "upend" ITER's largest components (toroidal field coils and vacuum vessel sectors) from horizontal to vertical.

The doors open and ...
2019-11-07 - ... the segments of the upending tool, delivered by Korea, enter. This large structure is designed to "upend" ITER's largest components (toroidal field coils and vacuum vessel sectors) from horizontal to vertical.
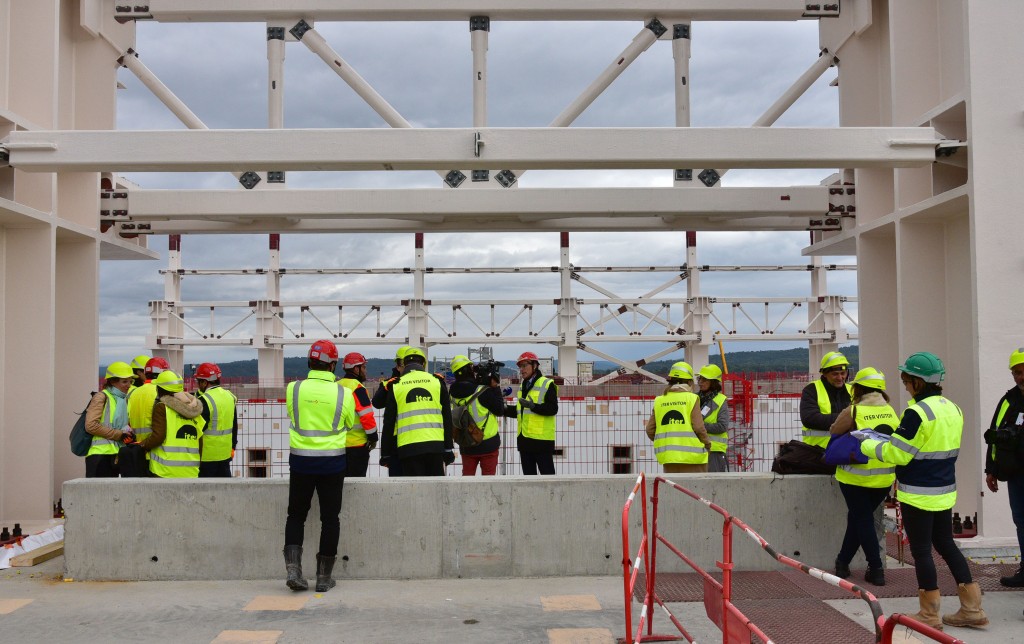
On the roof
2019-11-07 - French journalists stand on the top of the Tokamak Building, among the strong pillars of the roof structure, on the day that the ITER community celebrates the end of civil work on the Tokamak Building.

Soon, impregnation
2019-11-06 - The PF5 winding pack has been moved to the next station, in preparation for impregnation.
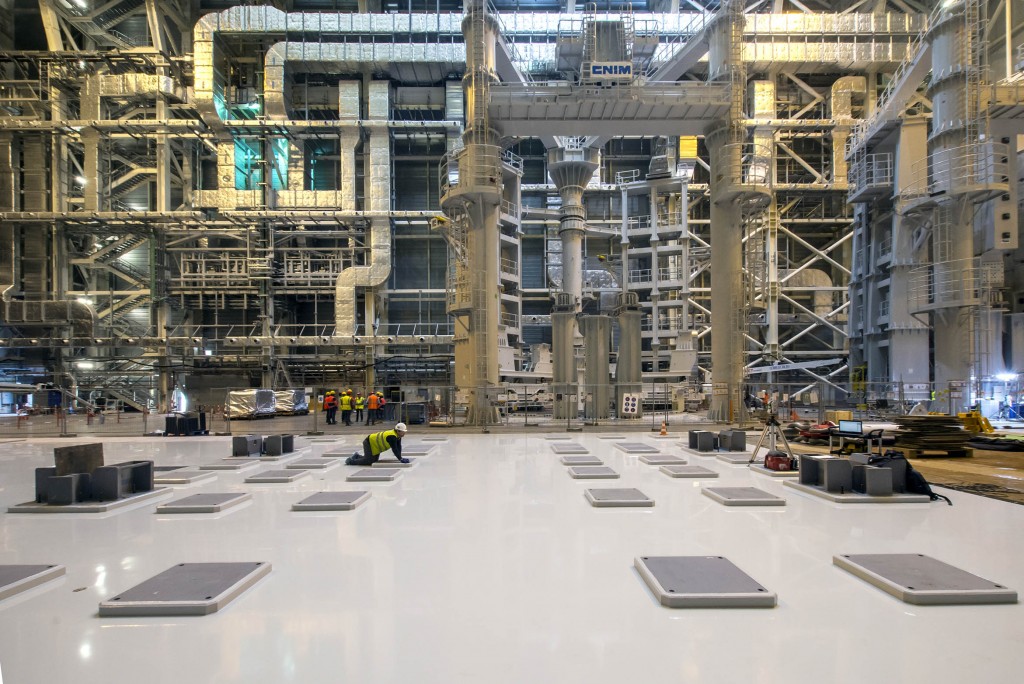
As smooth as an ice rink
2019-10-29 - European Domestic Agency contractors are currently coating the floor of the ITER Assembly Hall (6,500 m²) with epoxy resin. A hard, perfectly smooth floor that will resist erosion is one of the main conditions for maintaining cleanliness during pre-assembly operations.

First zone completed
2019-10-29 - The area to be painted has been divided into four zones. One has been completed, in time for the delivery of the upending tool from Korea next week. A total of 24 tonnes of epoxy resin will be needed to cover the full floor surface of the Hall.

Lots of electricity
2019-10-24 - The electrical substation takes up nearly half of the ITER site. Across the middle is a row of transformers—four for the steady state electrical network and three larger transformers for the pulsed power electrical network (PPEN) that will feed the magnets and heating systems during operation. The first PPEN transformer will be connected to the grid next month. Photo: ITER Organization/EJF Riche

Imagining the wall removed
2019-10-24 - The temporary wall will be removed in 2020, creating a vast open space for the transport of components between the Assembly Hall and the Tokamak pit. Photo: ITER Organization/EJF Riche
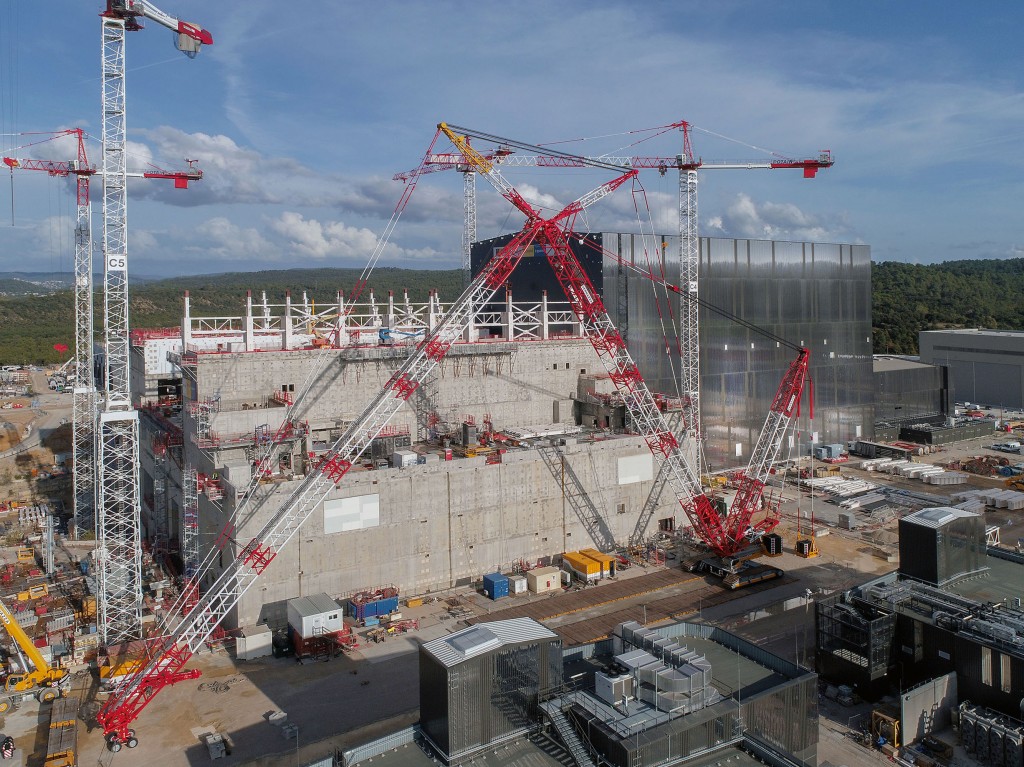
First level pillars nearly installed
2019-10-24 - Pillars are now aligned along both sides of the Tokamak Building rooftop and bracing bars are being installed between the pillars. A second crawler crane will be set up on the far side to help handle the heavy roof modules that will be installed between mid-December and mid-January. Photo: ITER Organization/EJF Riche

Under the secret cap
2019-10-24 - Hidden under the temporary lid at left is the 30-metre-deep machine well, where the major machine assembly activities kick off next year. The last concrete pour for the area around the central well is scheduled for early November. Photo: ITER Organization/EJF Riche
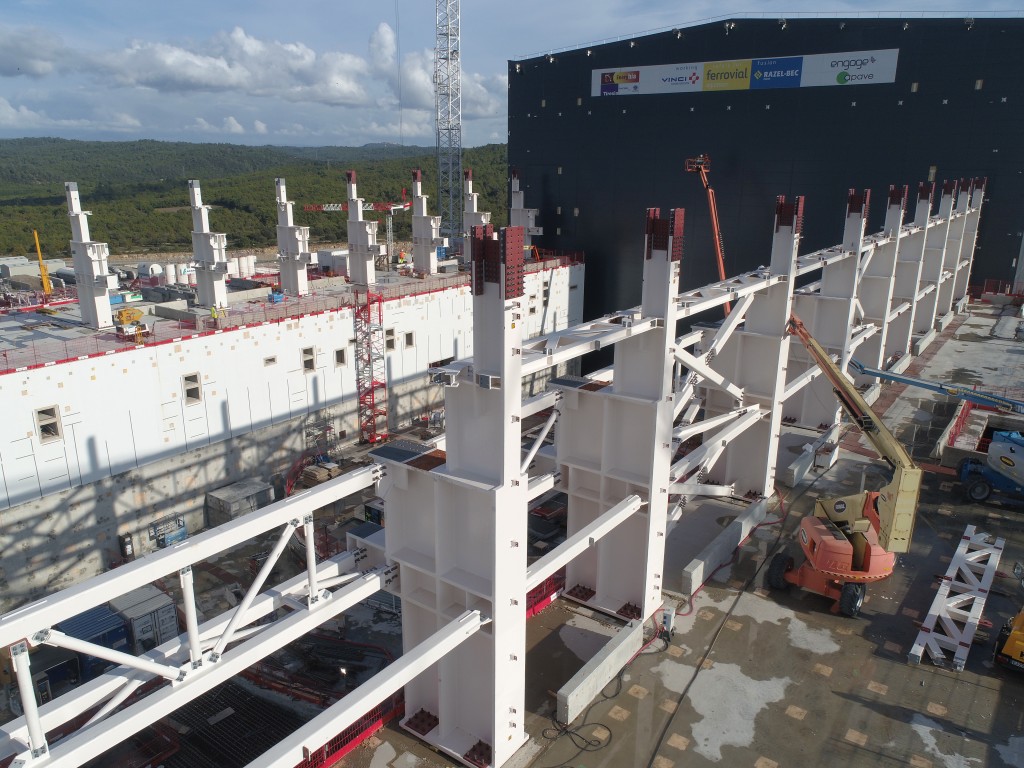
Pillars: close up
2019-10-24 - Ten on one side and ten on the other: these massive lower pillars will support the massive bridge cranes that will be used during machine assembly. Photo: ITER Organization/EJF Riche
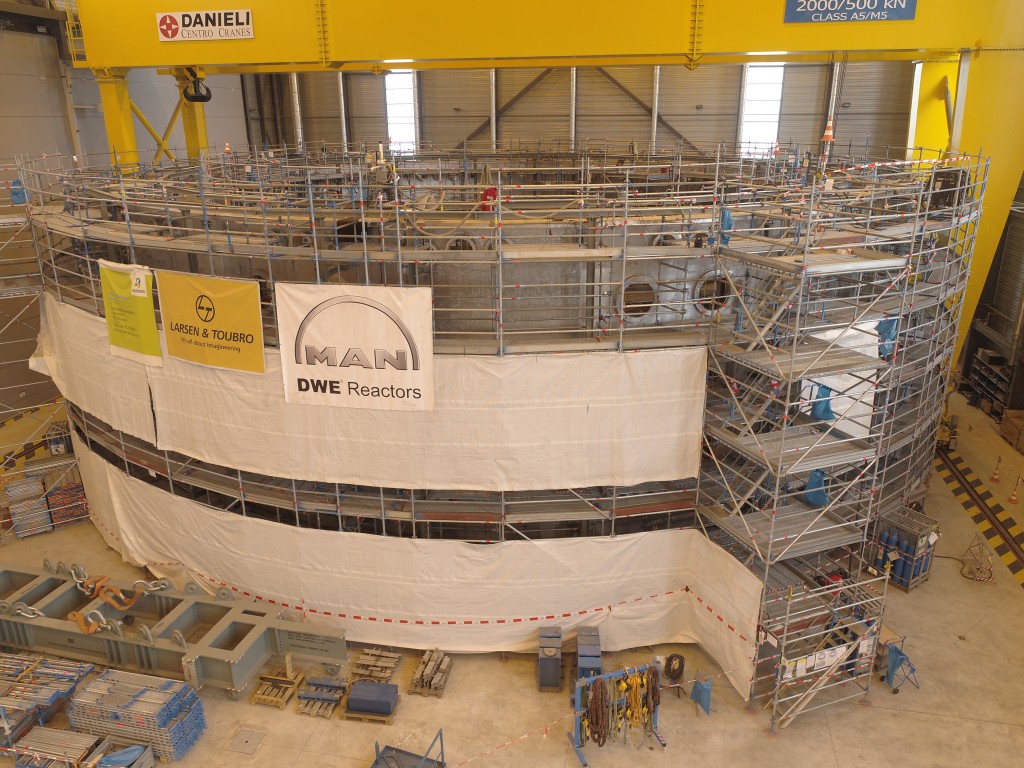
Upper cylinder advances
2019-10-22 - The assembly of the 430-tonne upper cylinder is underway in India's on-site Cryostat Workshop. Contractors Larsen & Toubro (fabrication and assembly) and MAN Energy Solutions (welding) are in charge of carrying out the assembly activities. Photo: ITER Organization/EJF Riche

Last details before the big day
2019-10-22 - The completed cryostat base is being prepped for handling and insertion into the Tokamak pit, a spectacular operation that is scheduled for early April 2020. Photo: ITER Organization/EJF Riche

Power Supplies Distribution Building
2019-10-15 - The Power Supplies Distribution Building is handed over by the European Domestic Agency to the ITER Organization in October. The equipment will contribute to distributing the current for activities across the worksite. ©F4E
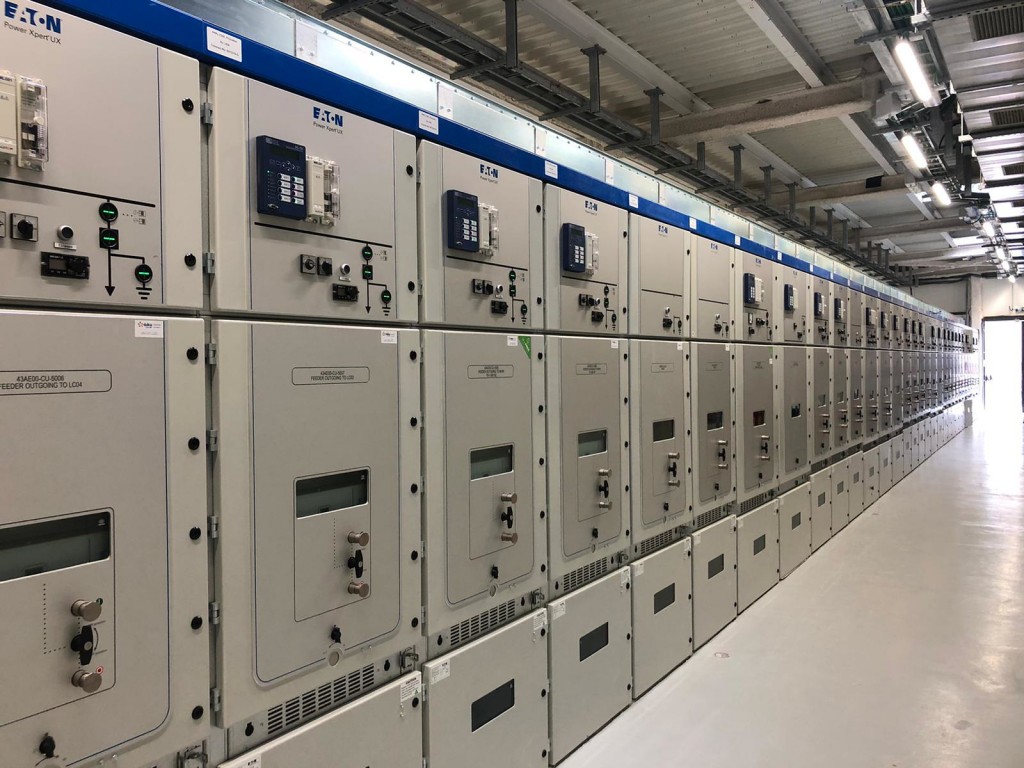
Power Supplies Distribution Building
2019-10-15 - The Power Supplies Distribution Building is handed over by the European Domestic Agency to the ITER Organization in October. The equipment will contribute to distributing the current for activities across the worksite. ©F4E

Between two clouds
2019-10-14 - Highlighted by the sun are the 10 south pillars of the crane gallery, installed at level L5 of the Tokamak Building.
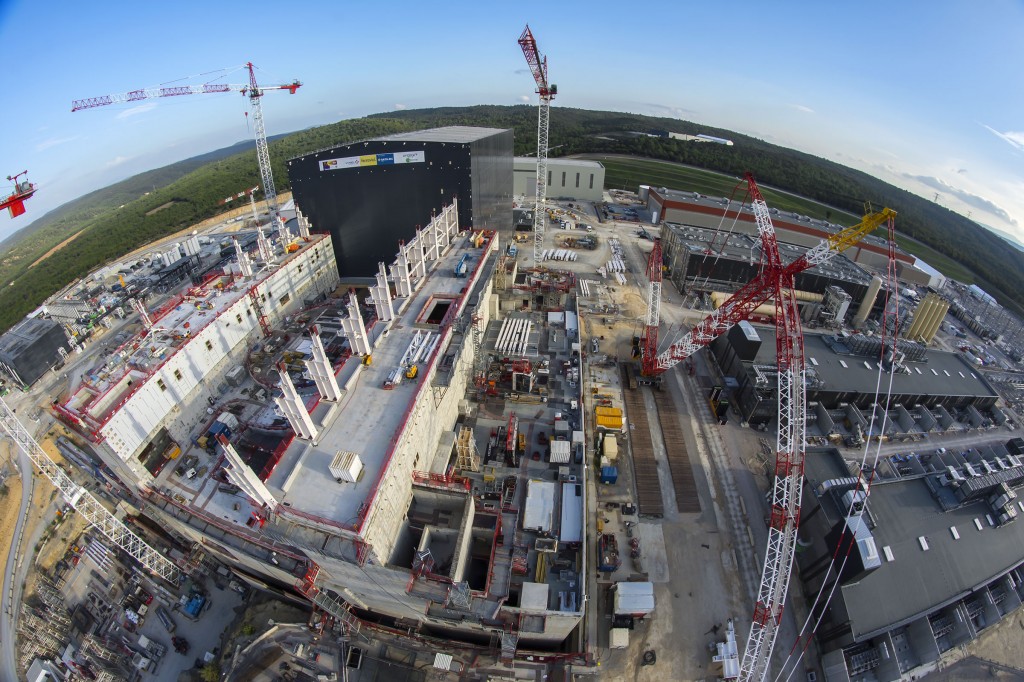
The crane hall begins to emerge
2019-10-14 - From the top of one of the worksite cranes, it is easy to imagine how the heavy lift bridge cranes will execute their back-and-forth ballet between the Assembly Hall (in black) and the Tokamak Building.

Busbars galore
2019-10-11 - Inside of the Magnet Power Conversion buildings, contractors are installing the first busbars. Approximately five kilometres of large, aluminium, water-cooled DC busbars connect the power converters to the magnets feeders.

12 pillars and counting
2019-10-07 - Two rows of pillars have now appeared at the top of the ITER Tokamak Building. When 10 have been installed on each side, contractors will begin installing second-level pillars.

First cryolines in Tokamak Complex
2019-10-02 - The cooling fluids produced by the cryoplant reach their ''clients'' in the ITER Tokamak by way of cryolines—high-technology components manufactured under Indian Domestic Agency contract partly in India and partly in France.
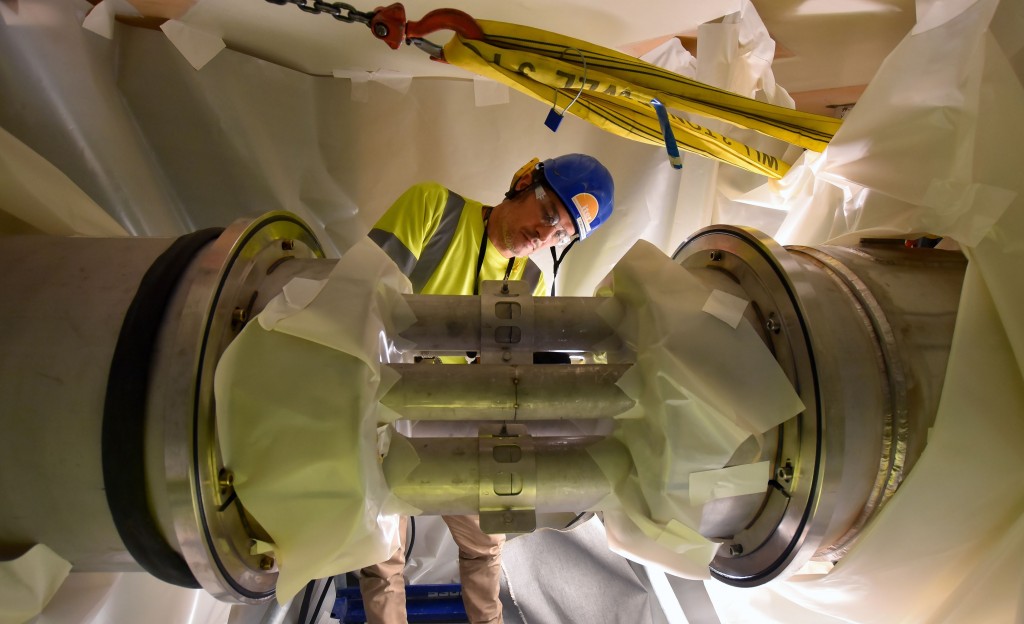
Joining two lines
2019-10-02 - This technician is joining two lengths of cryogenic line inside of the Tokamak Complex. Each "pipe" can contain up to seven individual lines.
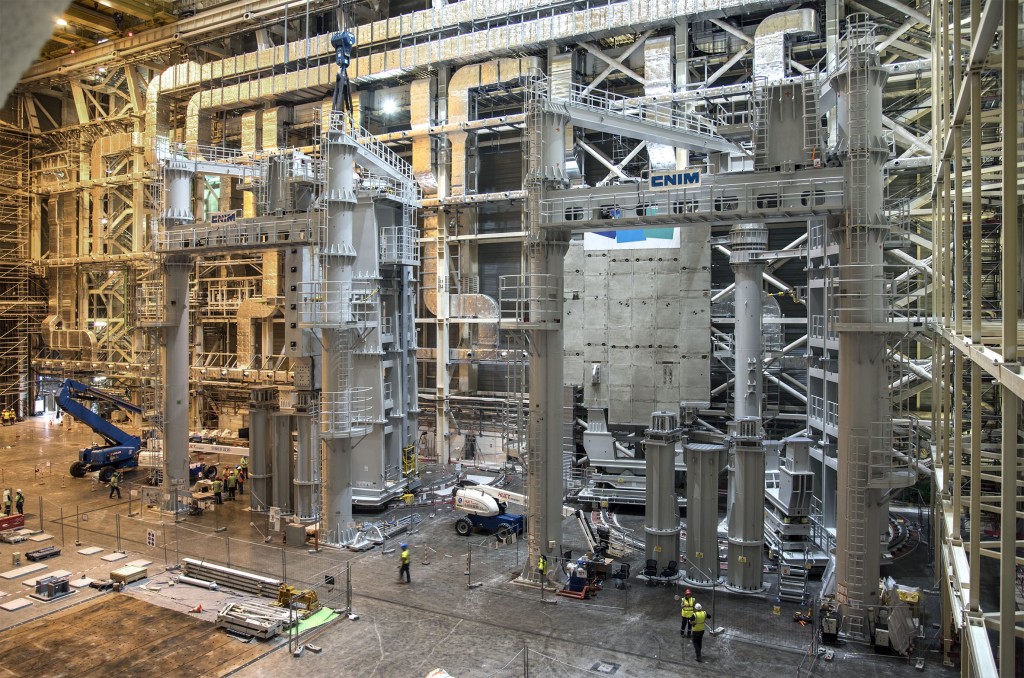
Shift of weight
2019-09-30 - In late September, the second 360-tonne load (at left) was transferred to SSAT tool #2 (on the right). After one month of functional tests on the second tool, the loads will be removed and stored until needed for the testing of the "upending" structure that has been shipped by Korea.

Shift of weight
2019-09-30 - In late September, the second 360-tonne load (at left) was transferred to SSAT tool #2 (on the right). After one month of functional tests on the second tool, the loads will be removed and stored until needed for the testing of the "upending" structure that has been shipped by Korea.

Shift of weight
2019-09-30 - In late September, the second 360-tonne load (at left) was transferred to SSAT tool #2 (on the right). After one month of functional tests on the second tool, the loads will be removed and stored until needed for the testing of the "upending" structure that has been shipped by Korea.
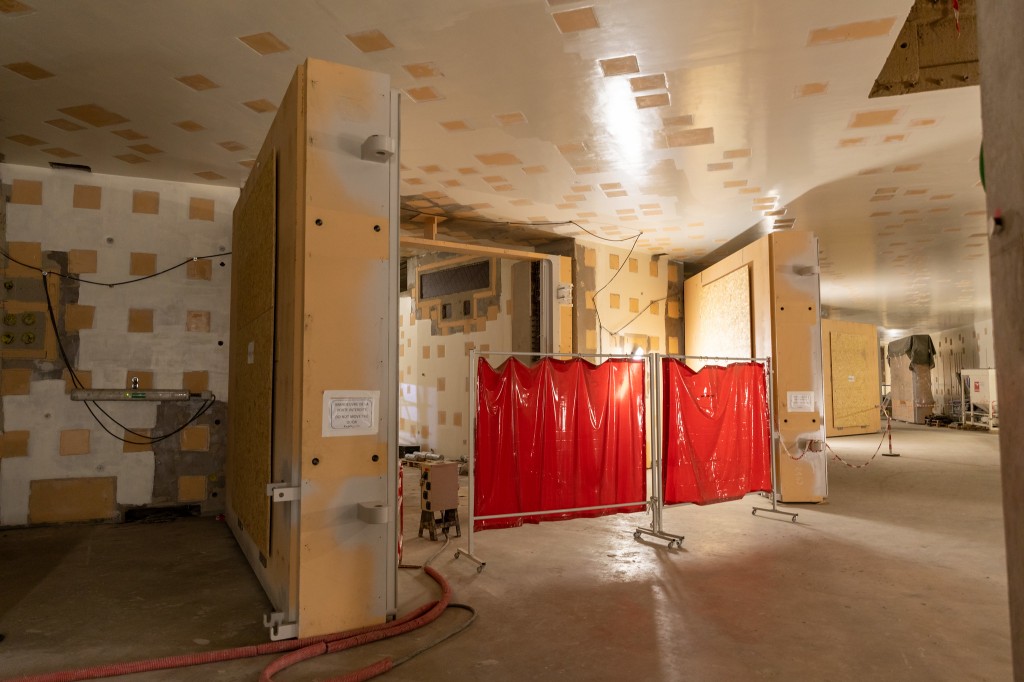
Filled with concrete
2019-09-25 - The nuclear doors are delivered hollow, and then filled with 7.5 cubic metres of heavy concrete. Special tools have been developed to handle the 60-tonne doors and mount them on their hinges. © Les Nouveaux Médias/SNC ENGAGE
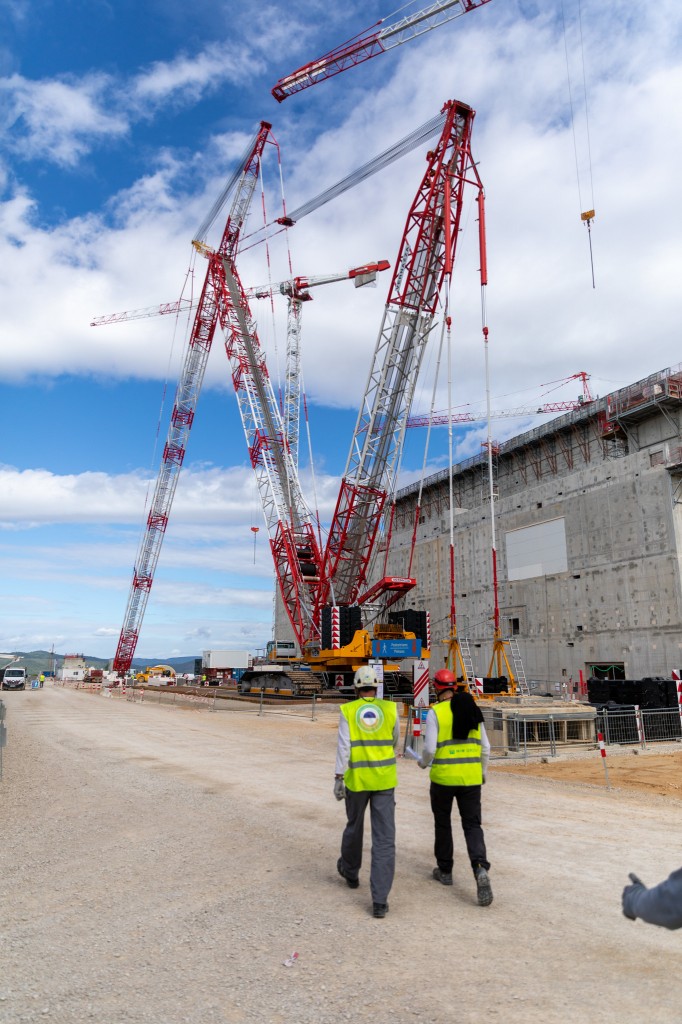
Tall enough
2019-09-25 - The boom of the new crawler crane reaches more than 100 metres. © Les Nouveaux Médias/SNC ENGAGE
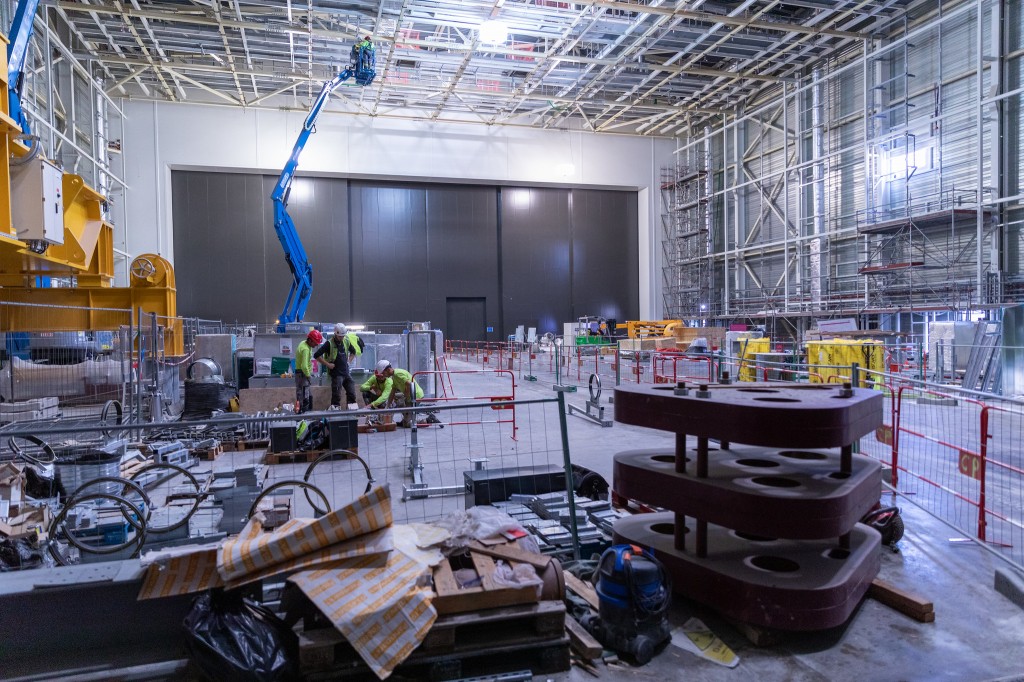
Antechamber to the Assembly Hall
2019-09-25 - After leaving storage, ITER's largest components will be submitted to a thorough cleaning process in the antechamber of the Assembly Hall, the Cleaning Facility (photo). The large doors will then open to allow the component, on its transport platform, to enter the Hall where the overhead cranes can take over. © Les Nouveaux Médias/SNC ENGAGE
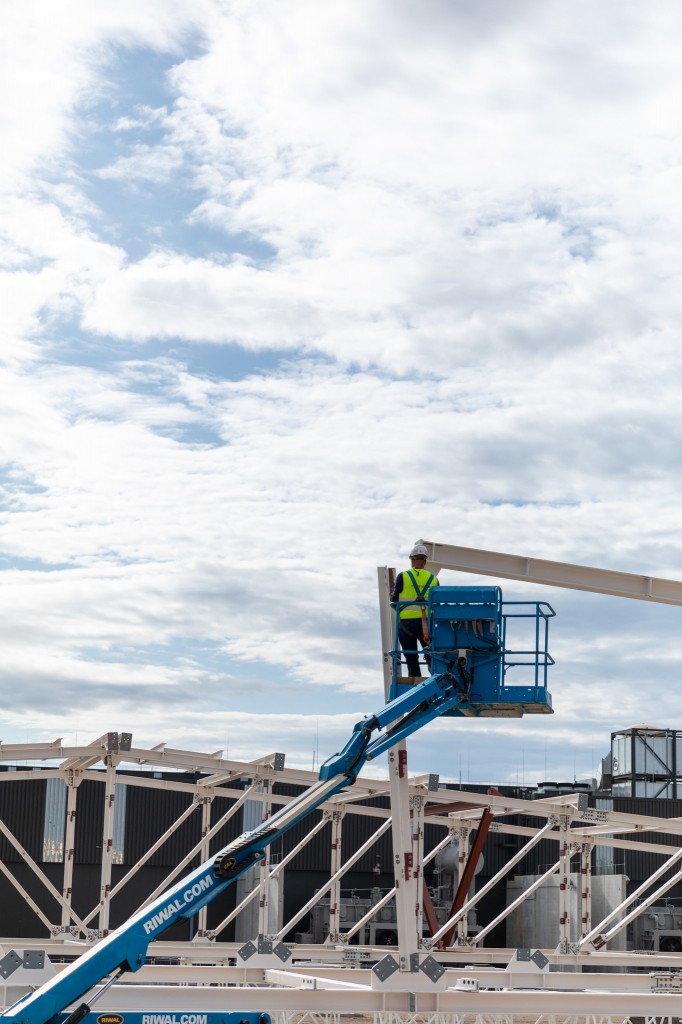
Elements of the roof structure
2019-09-25 - The first transversal roof elements will be lifted in December. © Les Nouveaux Médias/SNC ENGAGE

46 nuclear doors
2019-09-25 - Each of the galleries immediately surrounding the machine will be sealed off by a 60-tonne nuclear door (pictured). Each one has been fitted with a personnel access door. © Les Nouveaux Médias/SNC ENGAGE
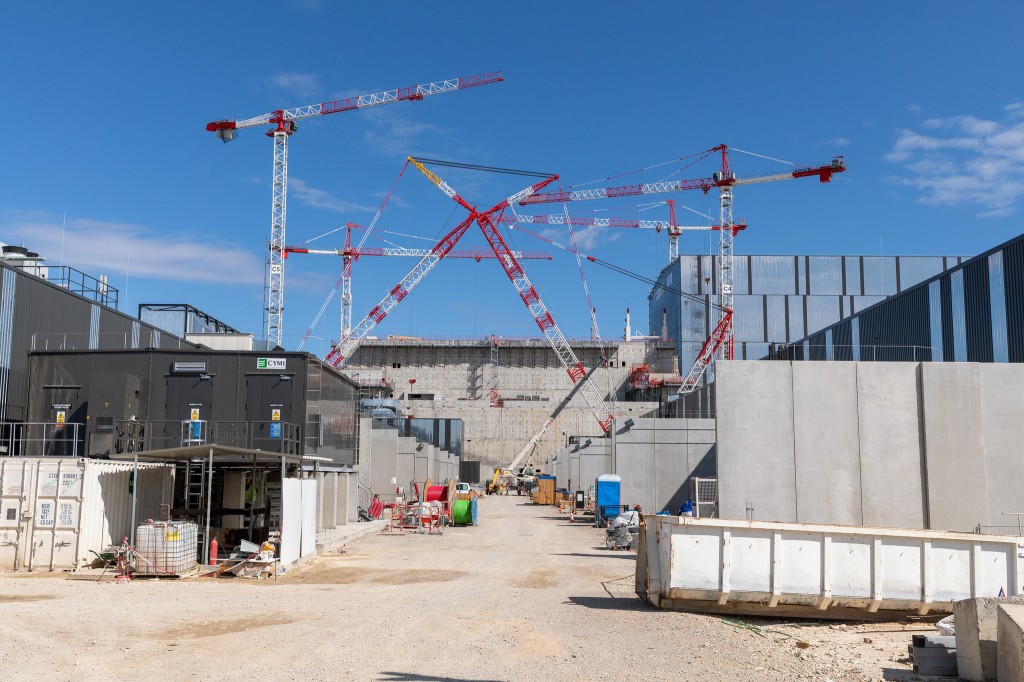
Another red and white crane
2019-09-25 - At the end of this alley of transformers, is the giant crawler crane that has been installed to lift the elements of the Tokamak Building roof. © Les Nouveaux Médias/SNC ENGAGE
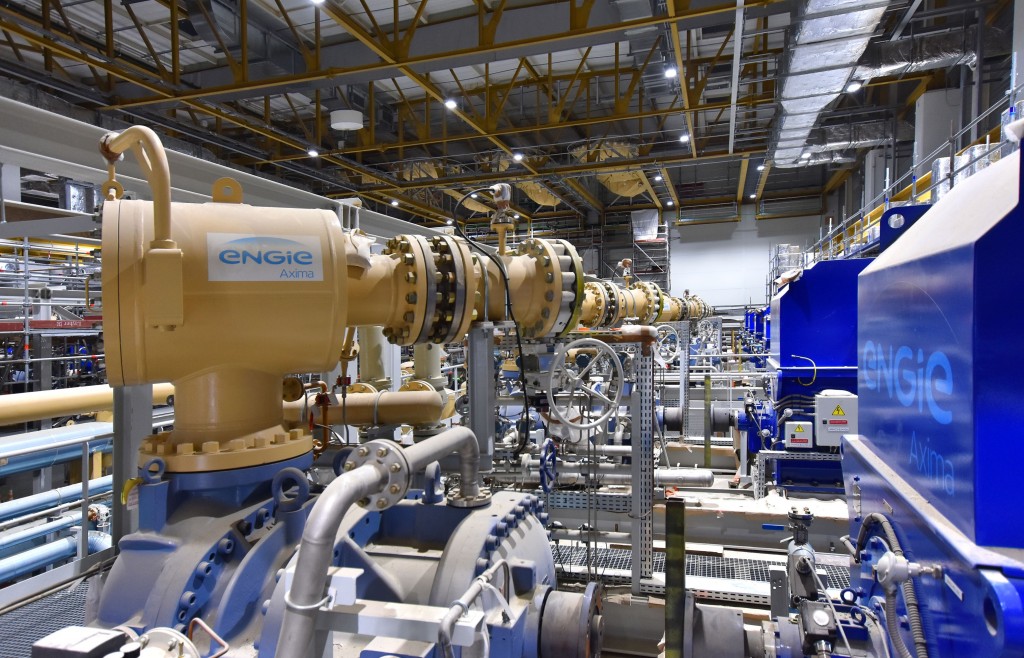
Compressor row
2019-09-23 - A total of 18 helium compressors and associated inlet filters and electrical motors are aligned on two parallel platforms inside the cryoplant.
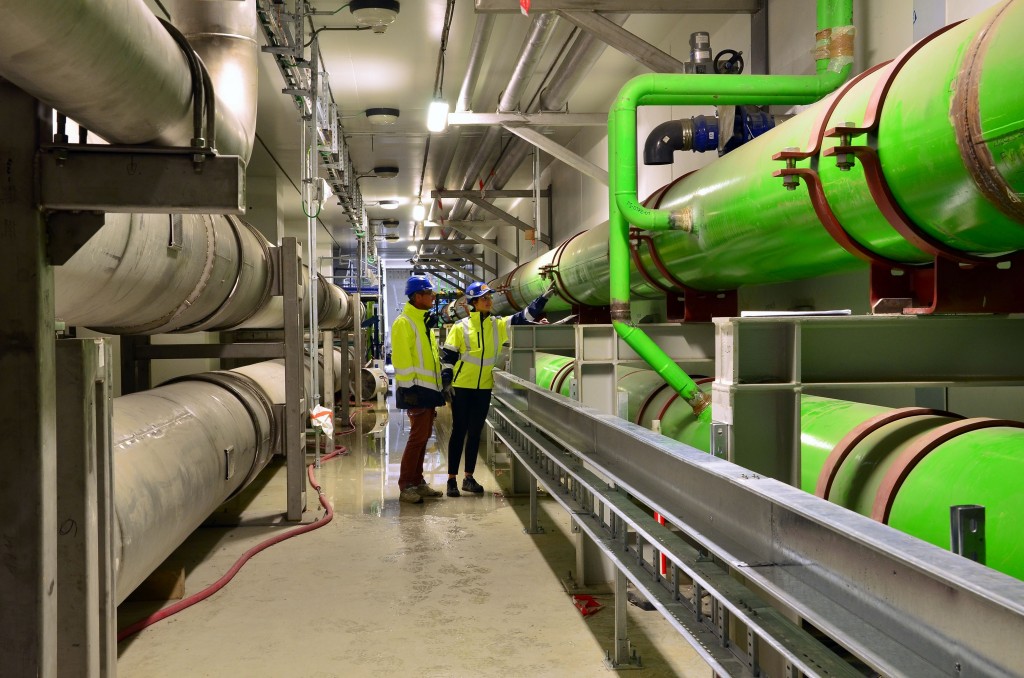
Seven kilometres of pipes
2019-09-23 - Approximately seven kilometres of pipes run through the installation, carrying helium, nitrogen and cooling water for the compressors and other equipment. Cooling water circulation in the cryoplant is in the range of 2,500 cubic metres per hour—the equivalent of an Olympic pool every 30 minutes.

Preciseness counts
2019-09-23 - Each six-tonne vertical shaft must be perfectly positioned and balanced to withstand the considerable forces that the rotation of the impeller and the flux of water exert. Horizontal deflection at the bearings cannot exceed 0.05 millimetre.

Three cold boxes plus one
2019-09-23 - Serving the ITER cold clients requires three "cold boxes" plus a fourth to connect them (the "termination cold box," to the left). The 21-metre components —each weighing about 137 tonnes with internal systems—provide an insulated environment for heat exchangers, cryogenic adsorbers, liquid helium and liquid nitrogen phase separators.

Seven kilometres of pipes
2019-09-23 - Approximately seven kilometres of pipes run through the installation, carrying helium, nitrogen and cooling water for the compressors and other equipment. Cooling water circulation in the cryoplant is in the range of 2,500 cubic metres per hour—the equivalent of an Olympic pool every 30 minutes.
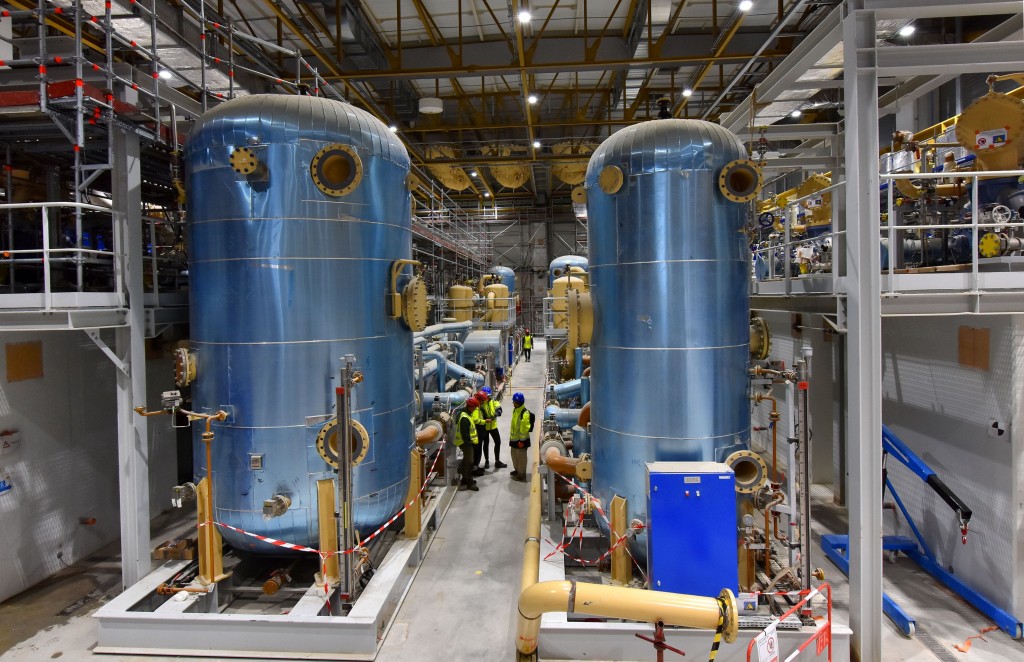
Compression station
2019-09-23 - In the liquid helium plant compression station, a narrow corridor separates the two parallel oil removal system skids. Oil is used in the helium compression process but needs to be removed entirely by a set of filters, separators, pumps etc.
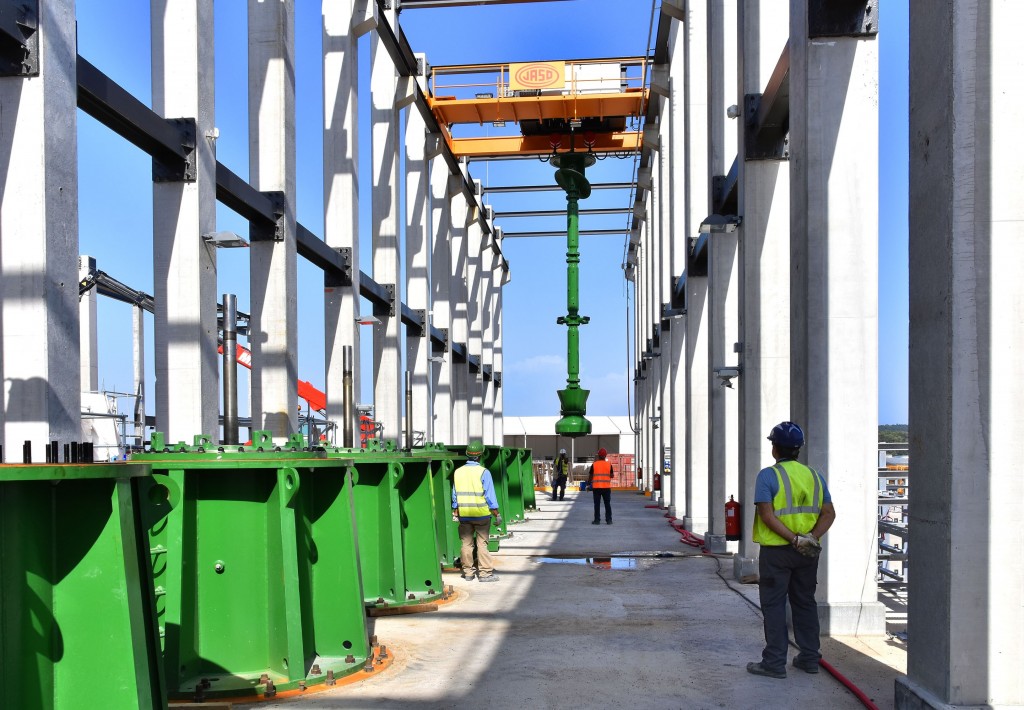
10-metre-long shafts
2019-09-23 - In the heat rejection zone, 13 vertical turbine pumps will take cooling water from deep in the hot basins and circulate it either to the cold basin, or through the installation's heat exchangers. The shafts, pictured, connect the rotor (impeller) to the motor.

Inside the cold factory
2019-09-23 - As large as two football pitches, the ITER cryoplant provides cooling fluids to 10,000 tonnes of superconducting magnets, eight massive cryopumps, and thousands of square metres of thermal shielding.
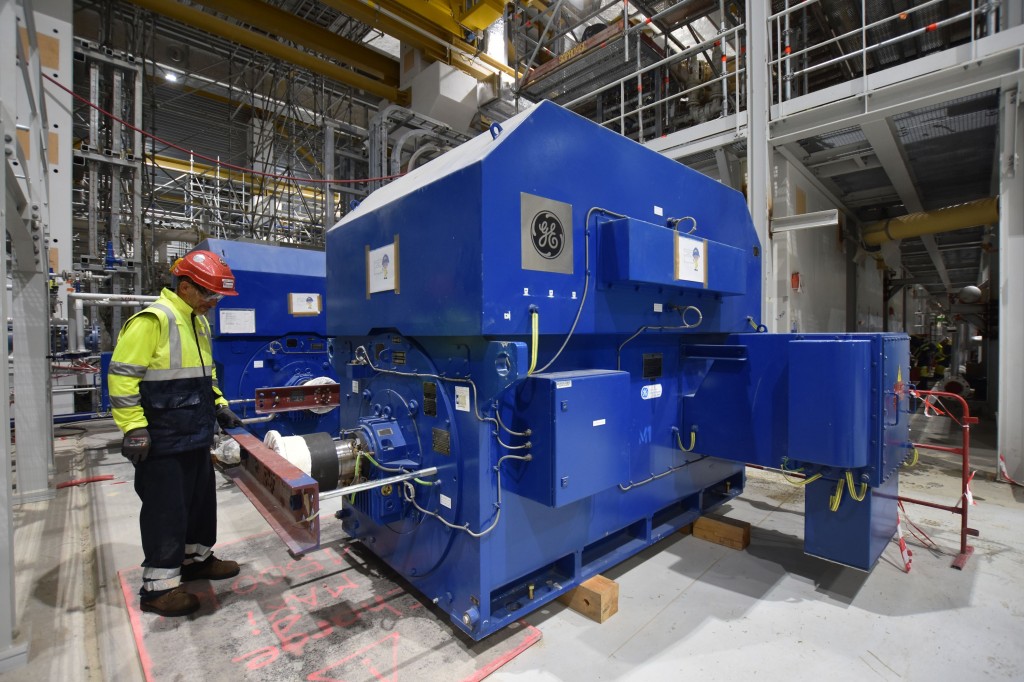
A 4.5 MW electrical engine
2019-09-23 - Packing the power of approximately 60 electric vehicles, this 4.5 MW motor feeds the multistage centrifugal nitrogen compressor.
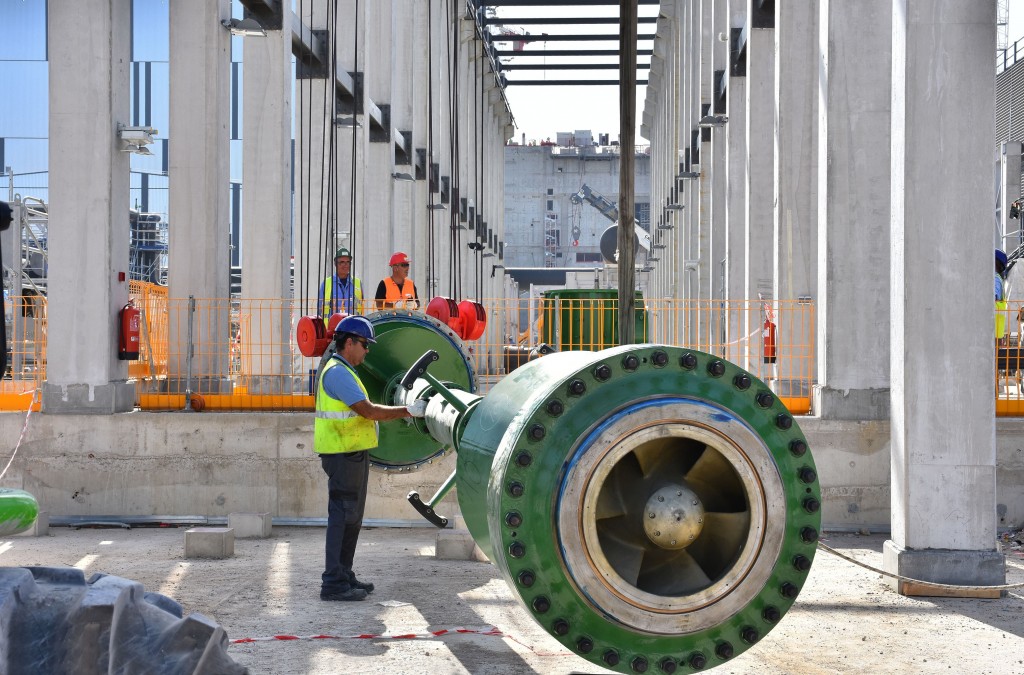
10-metre-long shafts
2019-09-23 - Thirteen vertical turbine pumps will take cooling water from deep in the hot basins and circulate it either to the cold basin, or through the installation's heat exchangers. The shafts, pictured, connect the rotor (impeller) to the motor.
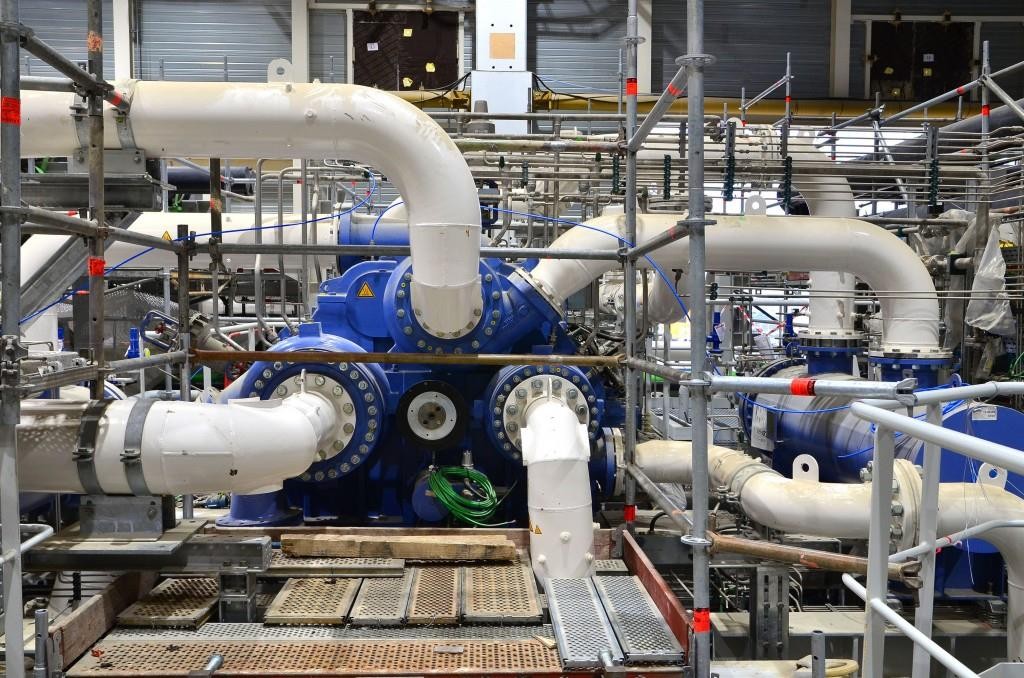
The octopus
2019-09-23 - Evocative of a monster bug or a creature from the depths, this multistage centrifugal compressor pressurizes nitrogen before liquefying it. Liquid nitrogen at 77 K (minus 196 °C) contributes to the cooling process of helium.

Inside the cold factory
2019-09-23 - As large as two football pitches, the ITER cryoplant provides cooling fluids to 10,000 tonnes of superconducting magnets, eight massive cryopumps, and thousands of square metres of thermal shielding. Approximately 50% of equipment has been installed.

To be repeated 13 times
2019-09-16 - Workers install the vertical turbine pump shafts in each pump housing. The 10-metre-long shafts connect the rotor (or impeller) to a powerful 870 kW electrical motor.
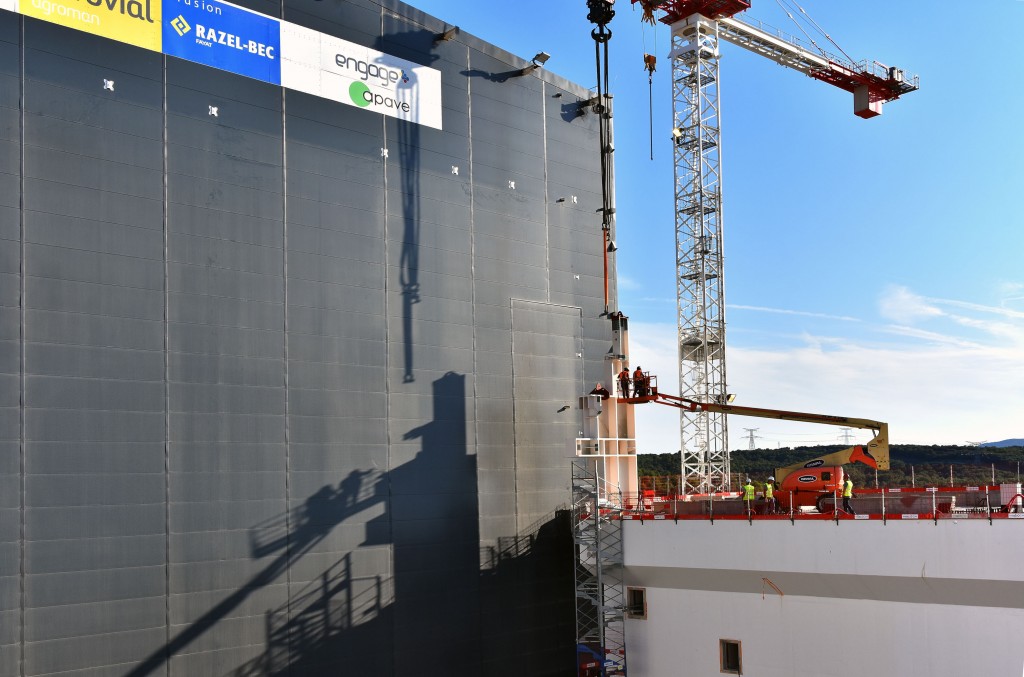
Carefully now
2019-09-11 - Twenty-four anchors in the plinth of the corbel had to be matched perfectly with 24 bolts under the pillar. A dozen specialists were on hand for the final insertion operation.
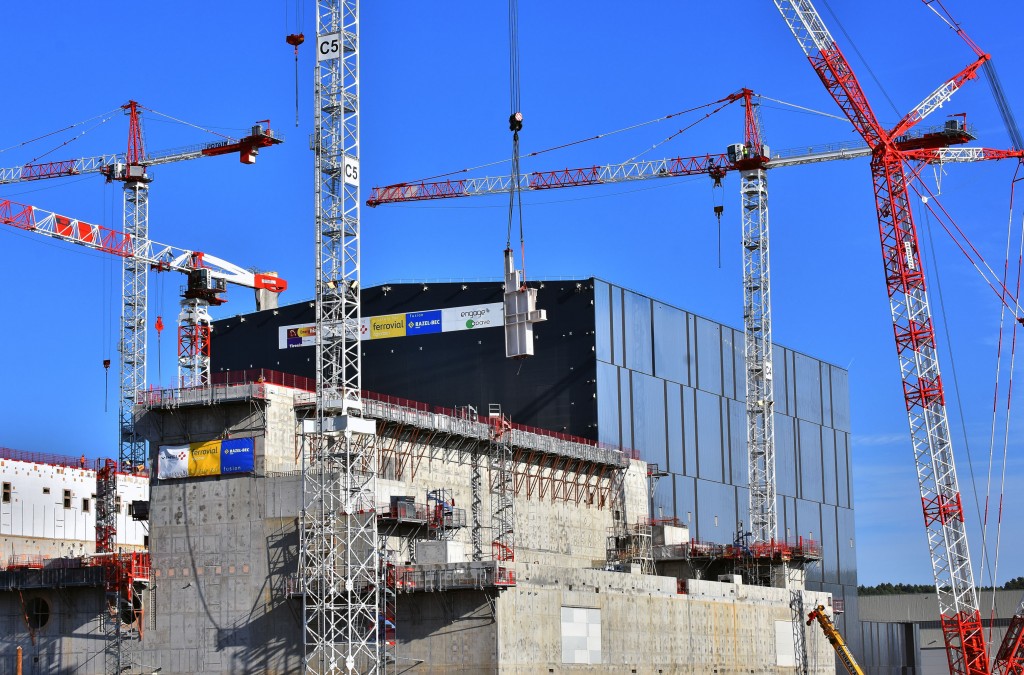
Steel pillar section #1
2019-09-11 - The first crane hall pillar section is lifted on 11 September. This is the lower, 13-metre-tall section of one pillar. An upper section, 16 metres tall, will be added later.
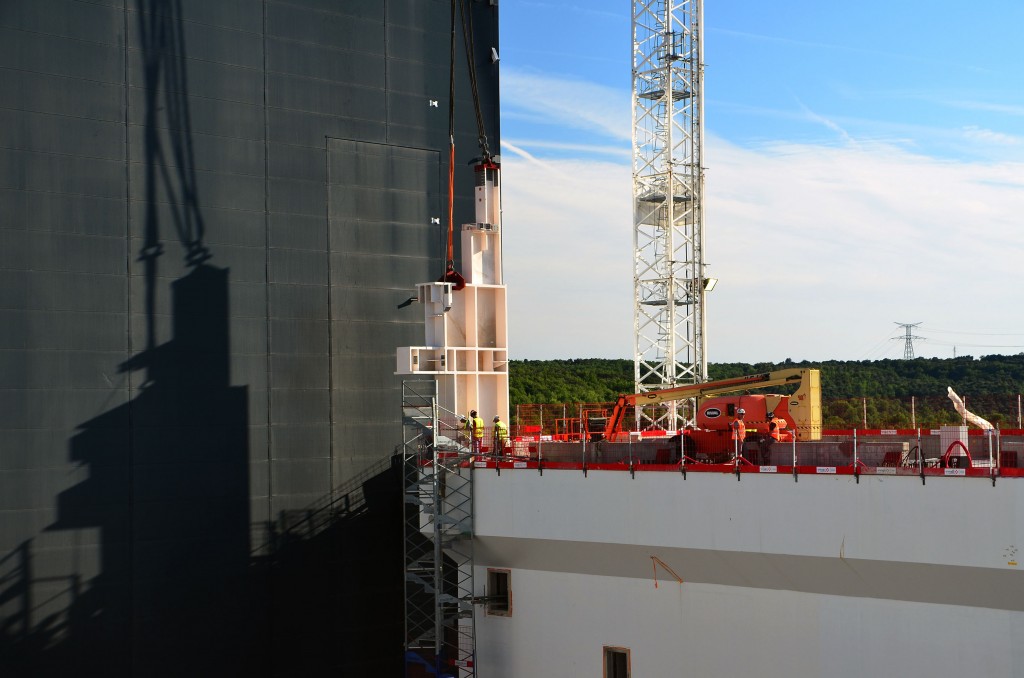
Special shelves
2019-09-11 - The shelf-like protrusions on the interior surface of the pillars will support the crane rails that must be extended out over the Tokamak pit.
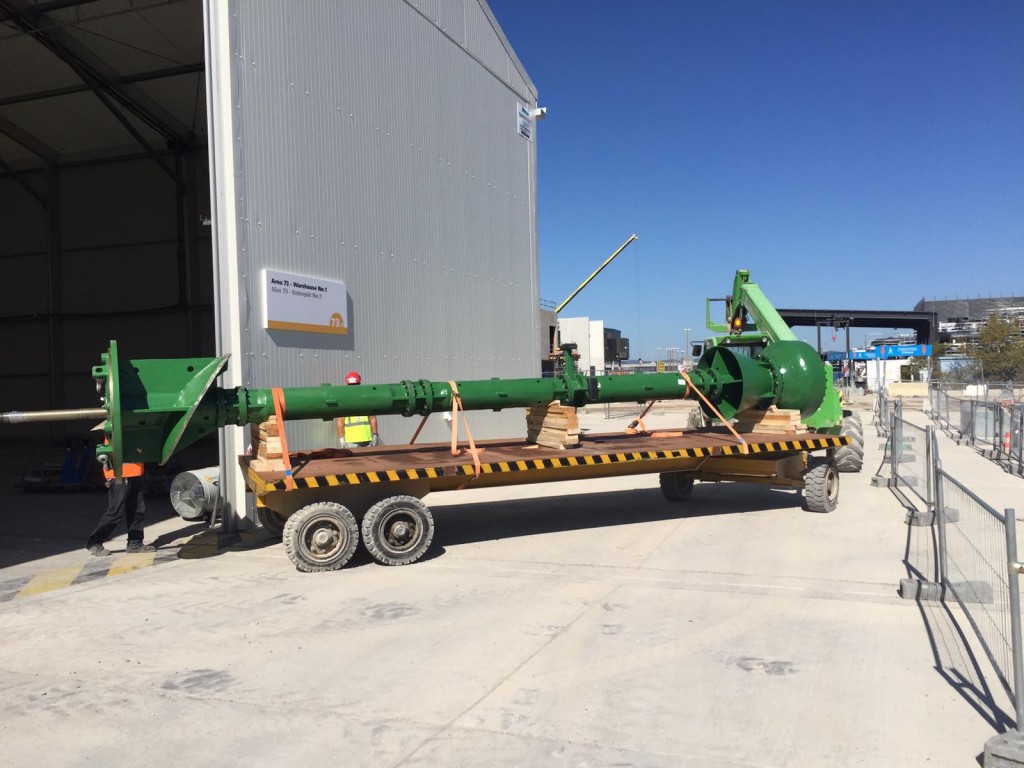
Ready for use
2019-09-11 - One of 13 vertical turbine shafts is moved from storage to the heat rejection zone for installation over the hot basin.
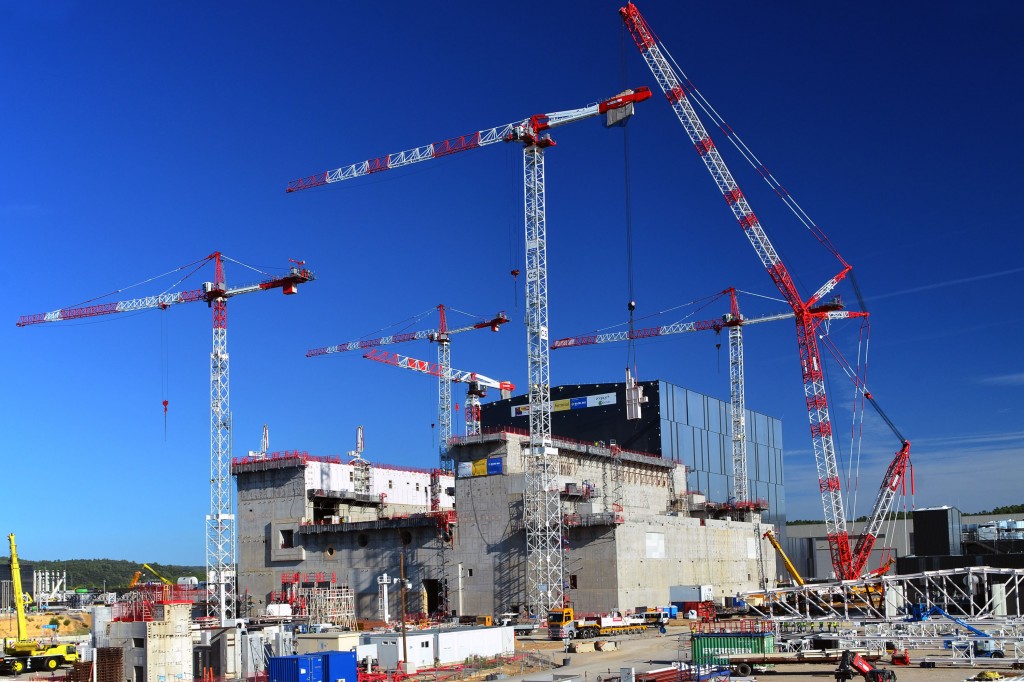
20 pillars in all
2019-09-11 - Twenty pillars (10 on either side of the Tokamak Building) will support the roof of the crane hall as well allow the overhead crane rails to be extended from the Assembly Hall into the Tokamak Building.

First crawler crane in action
2019-09-05 - On 11 September, this crawler crane began lifting pillars to the top of the Tokamak Building for the metal roof of the crane hall.
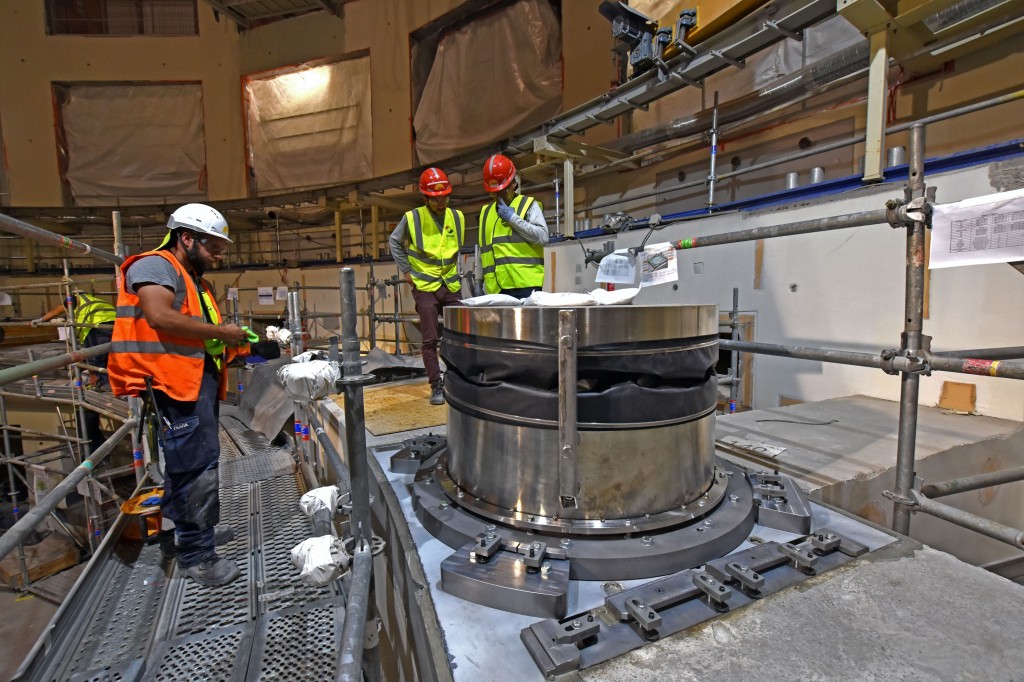
First cryostat bearing
2019-09-04 - Eighteen semi-spherical bearings anchored deep in the Tokamak support crown will act like ball-and-socket joints under the pedestal of the cryostat to allow the smooth transfer of forces generated during machine operation. The first one has been installed.
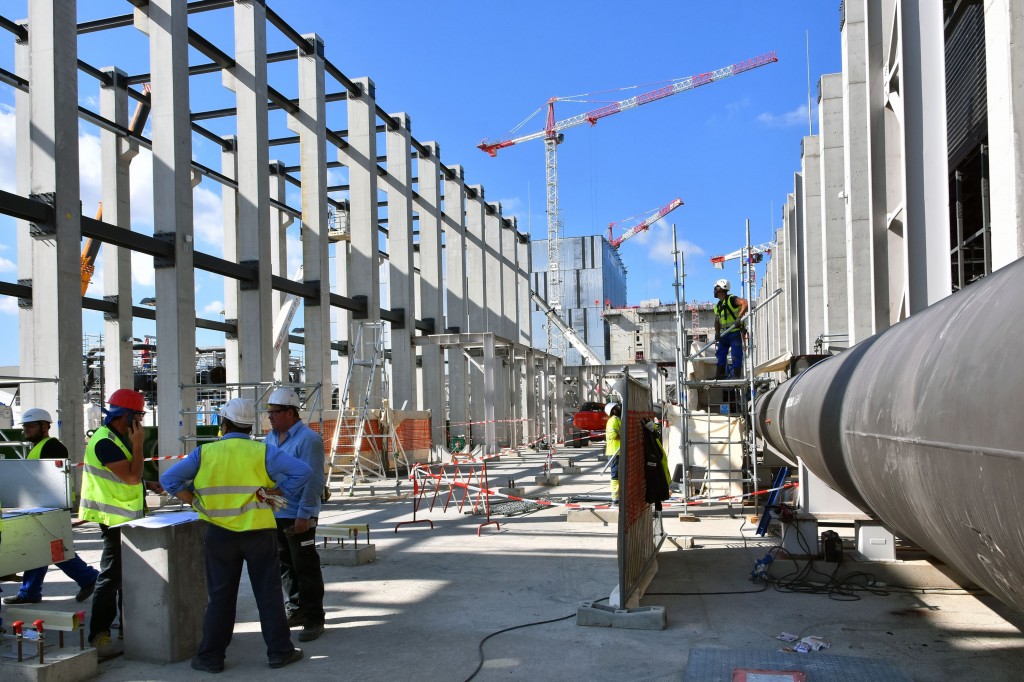
Last stop for the heat of the tokamak
2019-09-04 - Above the hot basin, contractors are supervising the installation of large lengths of piping. Over 5 km of piping is necessary to receive cooling water from the machine and plant systems and cycle it through the cooling water system, including 20-metre-tall cooling tower cells.

Pumping up
2019-09-04 - ITER Organization contractors are managing equipment installation in the cooling tower zone. The infrastructure of the zone was provided by Europe; the design and fabrication of heat rejection equipment is part of India's procurement contributions to the ITER Project.

Transfer of force through the lugs
2019-09-04 - Anchored and bolted in the wall surrounding the cryostat crown, 18 of these 2.5-tonne rectangular steel pieces ("female lugs") will play a key role in transferring horizontal forces to the bioshield structure and protecting the integrity of the machine. They will match with the "male lugs" welded on the cryostat pedestal.
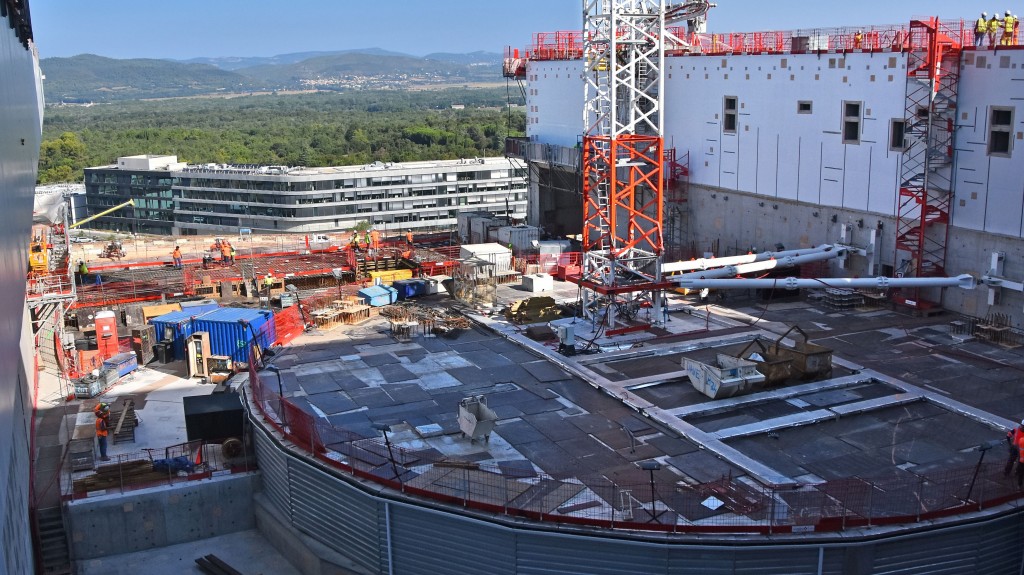
Major milestone ahead
2019-09-04 - For years, crane #1 has supported activities in the Tokamak Building from its central location, anchored at the bottom of the machine well. Before the end of the year it will be dismantled to allow for the installation of the metal walls and roof of the crane hall. Once the building has a roof, the temporary lid of the bioshield can be removed and the project will have reached a major milestone on the road to the official start of machine assembly.
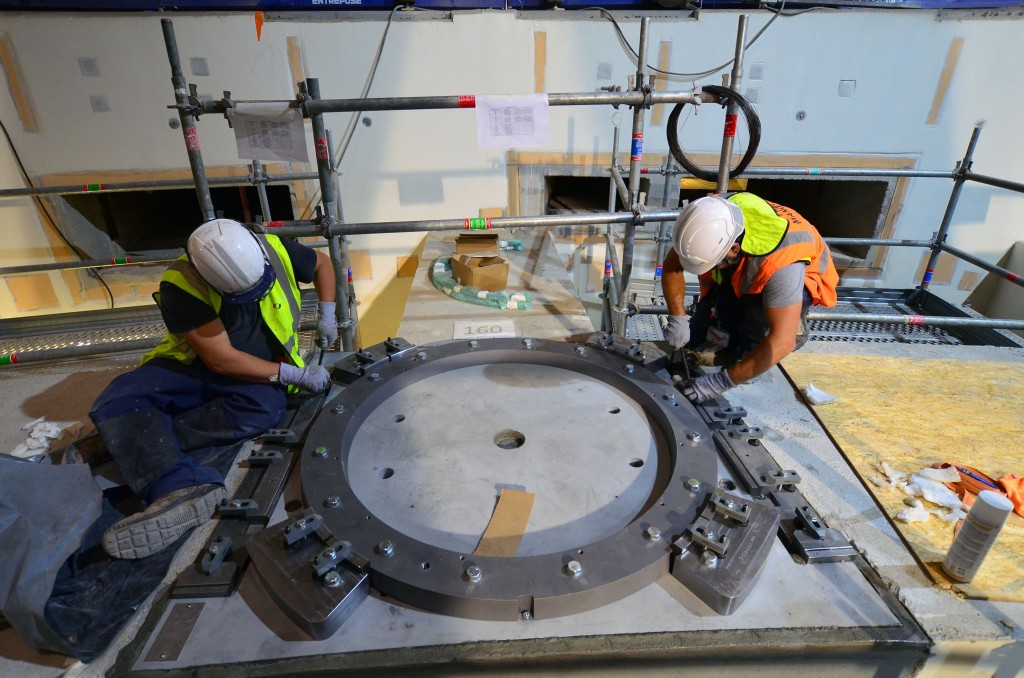
Clockwork precision for a 3.5-tonne component
2019-09-04 - As a fastening system for the bearings, a steel transition piece is half embedded in the concrete crown during the first phase of pouring. Then, a high-strength top plate (3.5 tonnes of steel) is positioned on the transition piece to receive the bearings with a mechanical blocking mechanism worthy of a Swiss watch. Permitted tolerances for the different elements of the fastening system will be less the 2 mm.
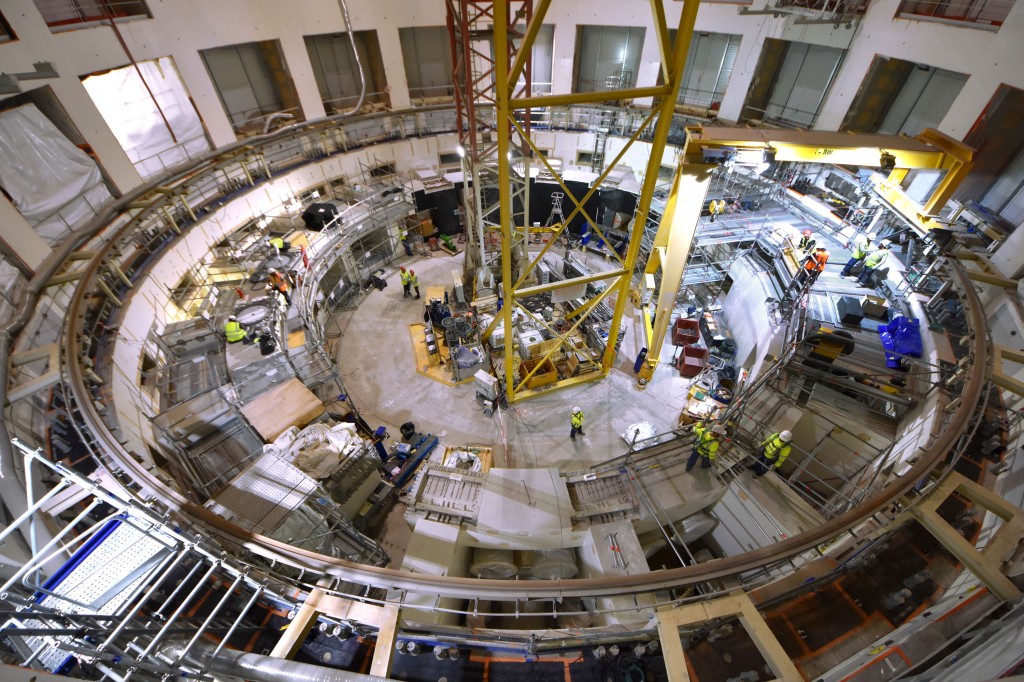
The precision of a clockmaker
2019-09-04 - Teams have been active all summer at the very bottom of the Tokamak pit, in preparation for the installation of the cryostat base. On top of the concrete crown, at the point of intersection with each of its 18 radial walls, contractors are installing a set of 18 metal bearings. (If you look closely you'll see that one has been installed in its socket and protected under black cloth, while—moving in a counter clockwise direction—other interfacing areas are in various stages of preparation.)

First cryostat bearing
2019-09-04 - First cryostat bearing Eighteen semi-spherical bearings anchored deep in the Tokamak support crown will act like ball-and-socket joints under the pedestal of the cryostat to allow the smooth transfer of forces generated during machine operation. The first one has been installed.

Rotated completely
2019-09-04 - The wings of the first sector sub-assembly tool (SSAT1) have been fully rotated inward and the tool has performed as expected. Later this month, the mock loads will be transferred to SSAT2. Both tools will enter service in 2020.

Pumping up
2019-09-04 - ITER Organization contractors are managing equipment installation in the cooling tower zone. The infrastructure of the zone was provided by Europe; the design and fabrication of heat rejection equipment is part of India's procurement contributions to the ITER Project.
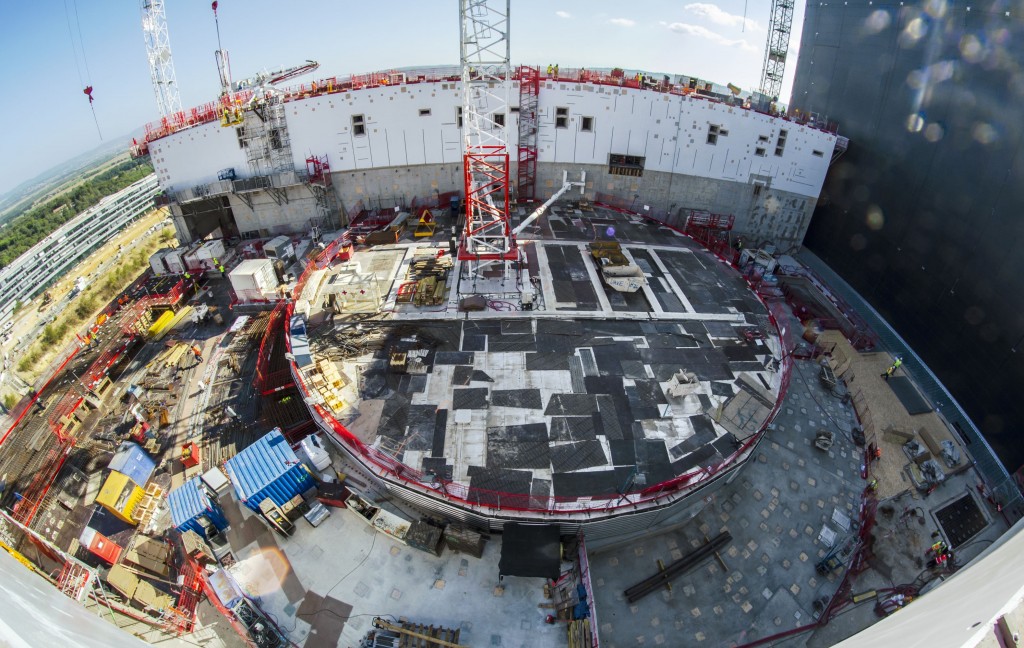
A wall in white
2019-09-04 - A thick coat of white paint has changed the look of the north wall, which stands between the Tokamak and Tritium buildings.

Crane hall coming
2019-09-04 - To the right of the Tokamak Complex, contractors are assembling one of two crawler cranes that will be used to install the metal structure of the crane hall.
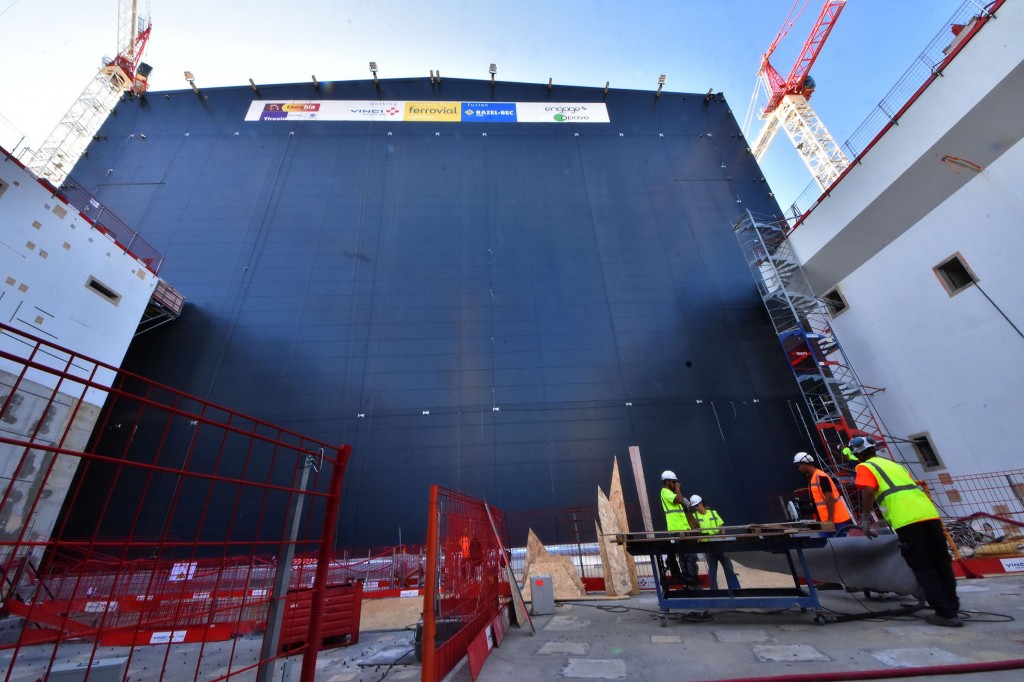
The poster is gone
2019-09-04 - A large poster of the ITER machine used to adorn the temporary wall of the Assembly Hall. It has been removed as part of the dismantling process for the wall itself.
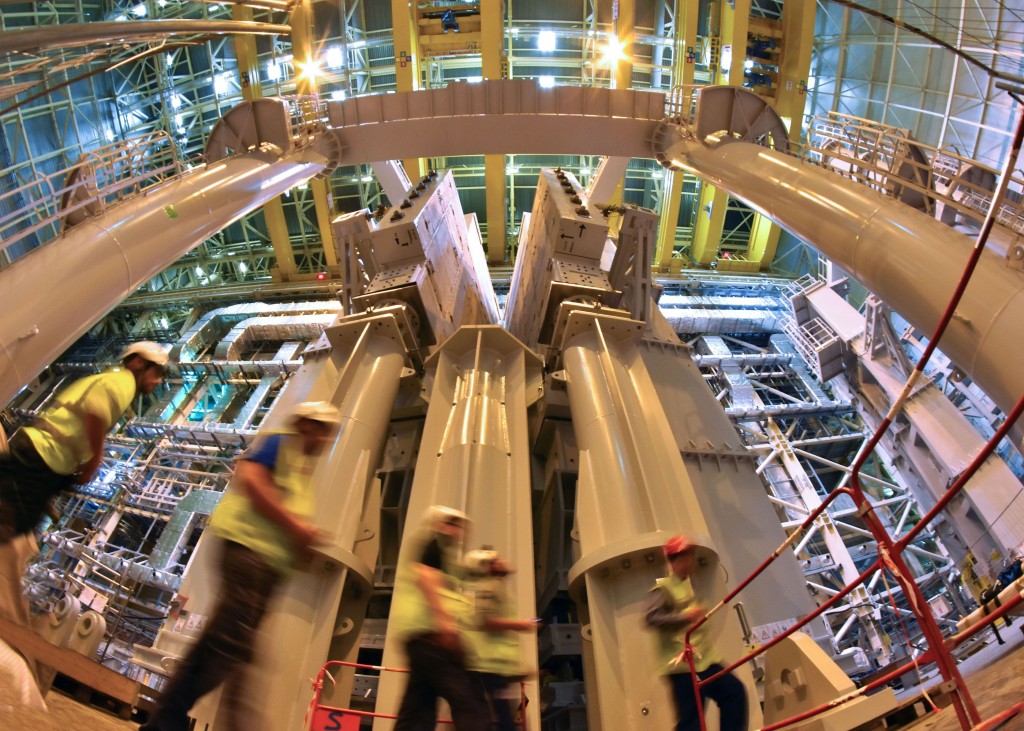
Rotated completely
2019-09-04 - The wings of the first sector sub-assembly tool (SSAT1) have been fully rotated inward and the tool has performed as expected. Later this month, the mock loads will be transferred to SSAT2. Both tools will enter service in 2020.
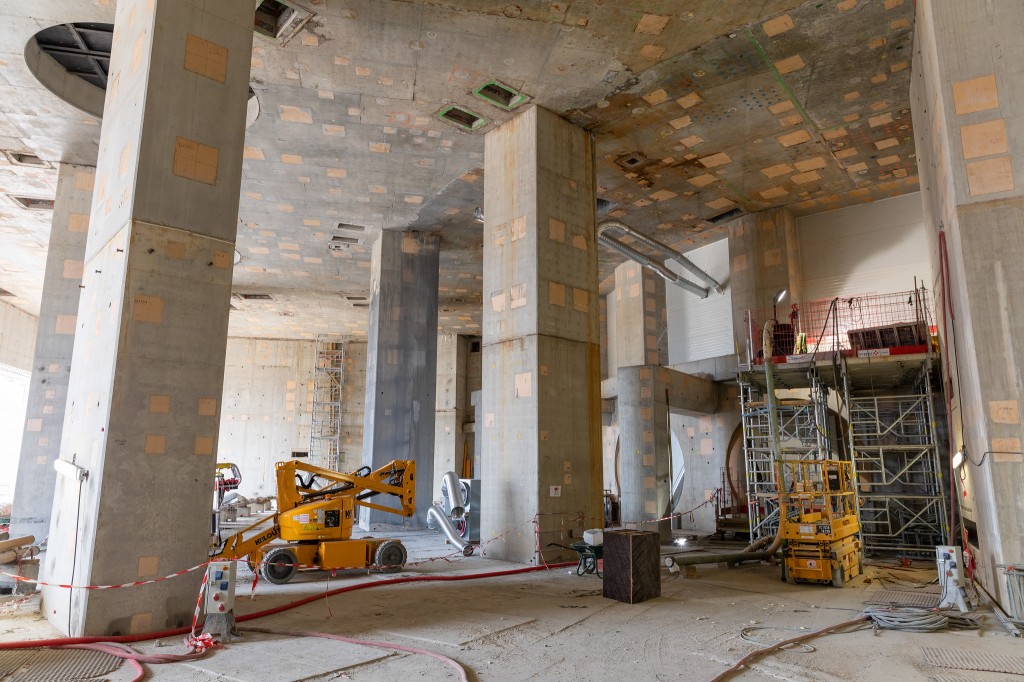
Neutral beam cells
2019-08-28 - This particular area of L3 of the Tokamak Building is reserved for the bus-sized injectors of the heating and diagnostic neutral beam systems. © Les Nouveaux Médias/SNC ENGAGE
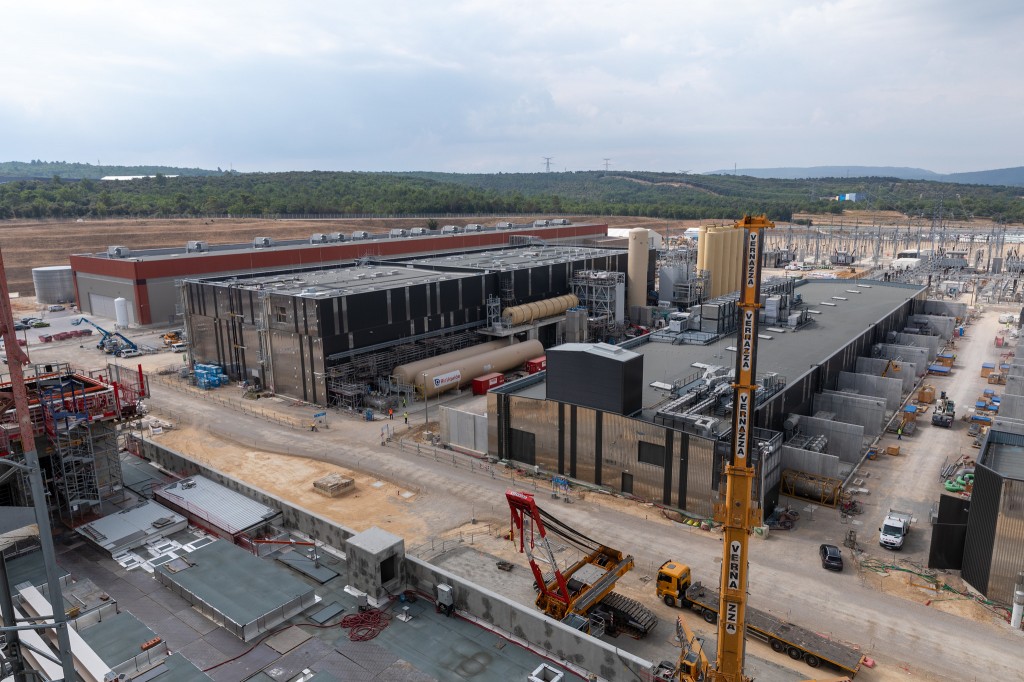
The view late August 2019
2019-08-28 - Looking south over the Poloidal Field Coils Winding Facility (red top), the ITER cryoplant, and one of the two buildings for magnet power conversion. © Les Nouveaux Médias/SNC ENGAGE
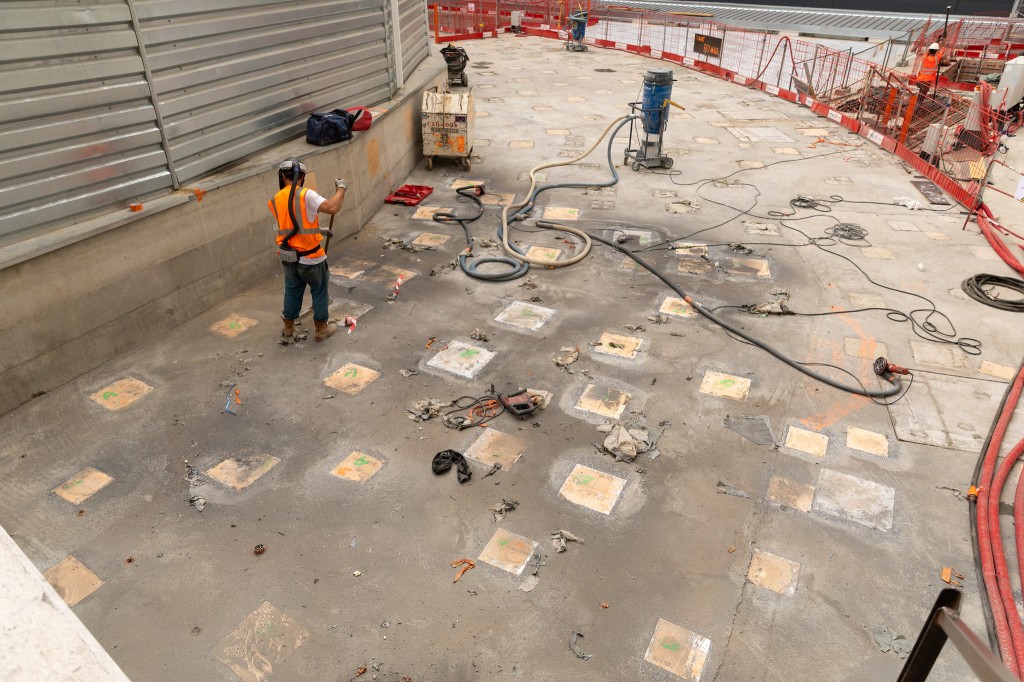
Future equipment
2019-08-28 - All around the top of the bioshield are embedded plates ready to receive equipment. © Les Nouveaux Médias/SNC ENGAGE
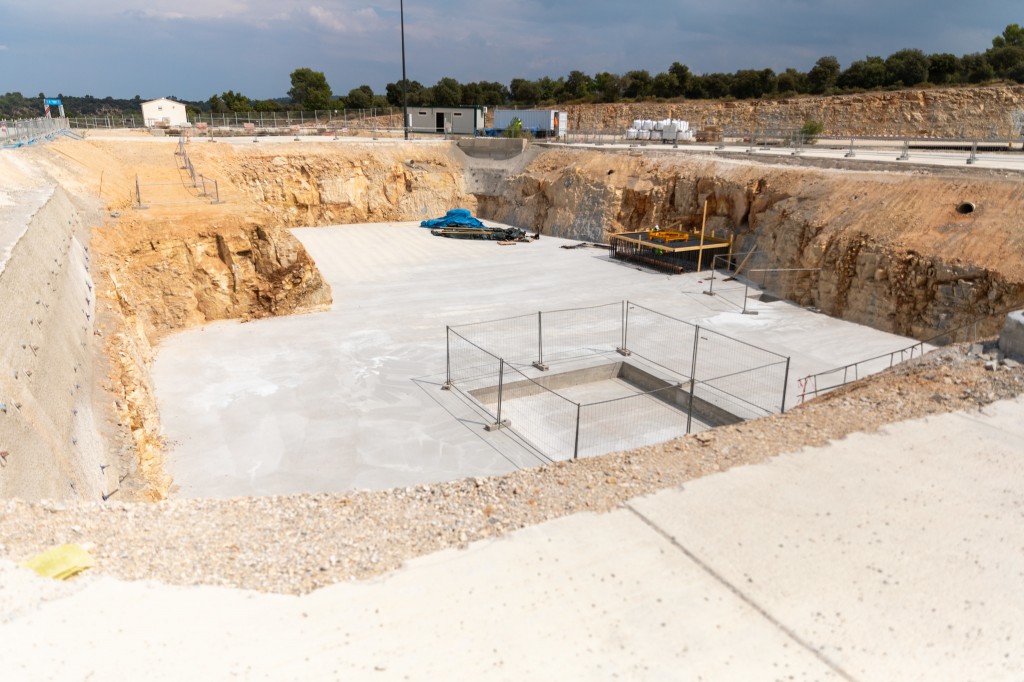
A new project
2019-08-28 - Work has begun on the foundations of the Tokamak Assembly Preparatory Building, where beryllium components will be handled and stored after their delivery to the ITER site. © Les Nouveaux Médias/SNC ENGAGE
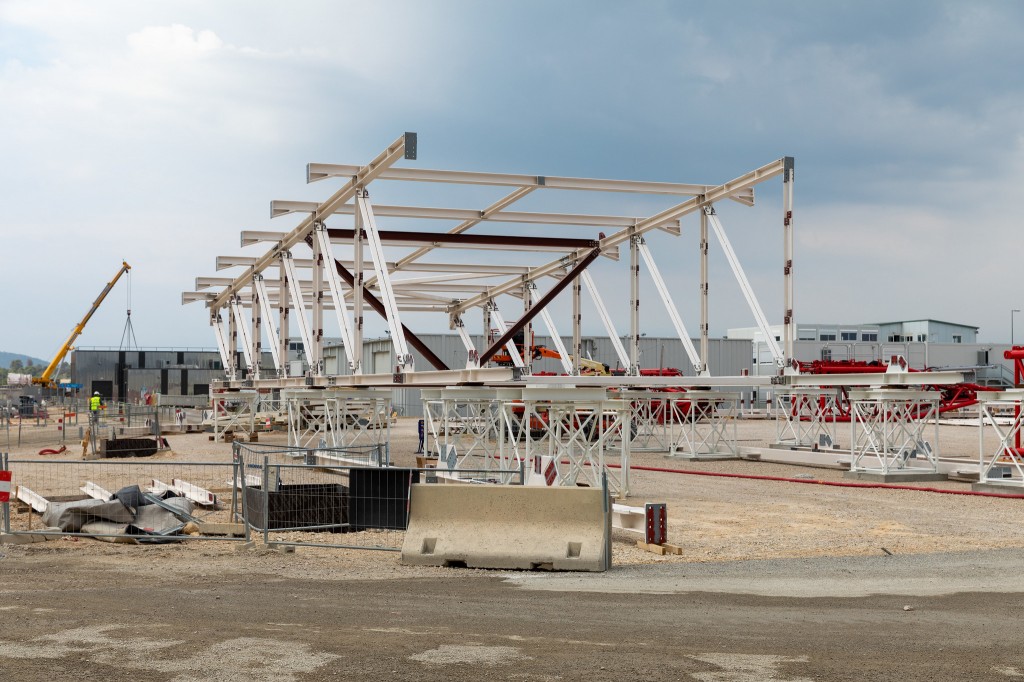
Meanwhile, on the ground ...
2019-08-28 - Teams have started to assemble the Tokamak Building roof structure from metal beams delivered over the summer. © Les Nouveaux Médias/SNC ENGAGE

Up at the top
2019-08-28 - The very top of the Tokamak Building is where pillars will soon be installed for the roof structure. Material is arriving. © Les Nouveaux Médias/SNC ENGAGE
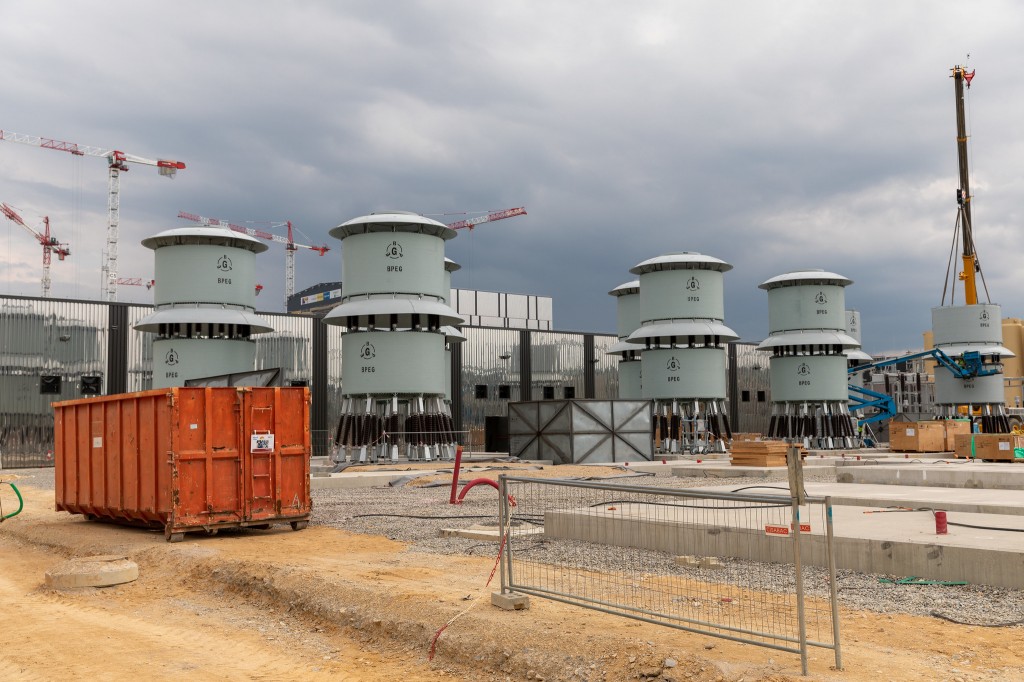
New arrivals on the platform
2019-08-28 - These alien-looking objects are harmonic filters, part of ITER's reactive power compensation and harmonic filtering system. This unique system is responsible for fast-acting reactive power compensation on the high-voltage electricity transmission network, in order to stabilize the power grid and provide the required quality of electrical power to operate ITER. © Les Nouveaux Médias/SNC ENGAGE

Basins hidden
2019-08-28 - The deep basins of the thermal rejection system were once visible in this corner of the platform. Now they have been covered over by the cooling towers (far left) and other heat removal infrastructure. © Les Nouveaux Médias/SNC ENGAGE

Tokamak Building: final concrete this year
2019-08-28 - European contractors are preparing the last concrete pours of the Tokamak Building (foreground). The work should be completed in November. © Les Nouveaux Médias/SNC ENGAGE
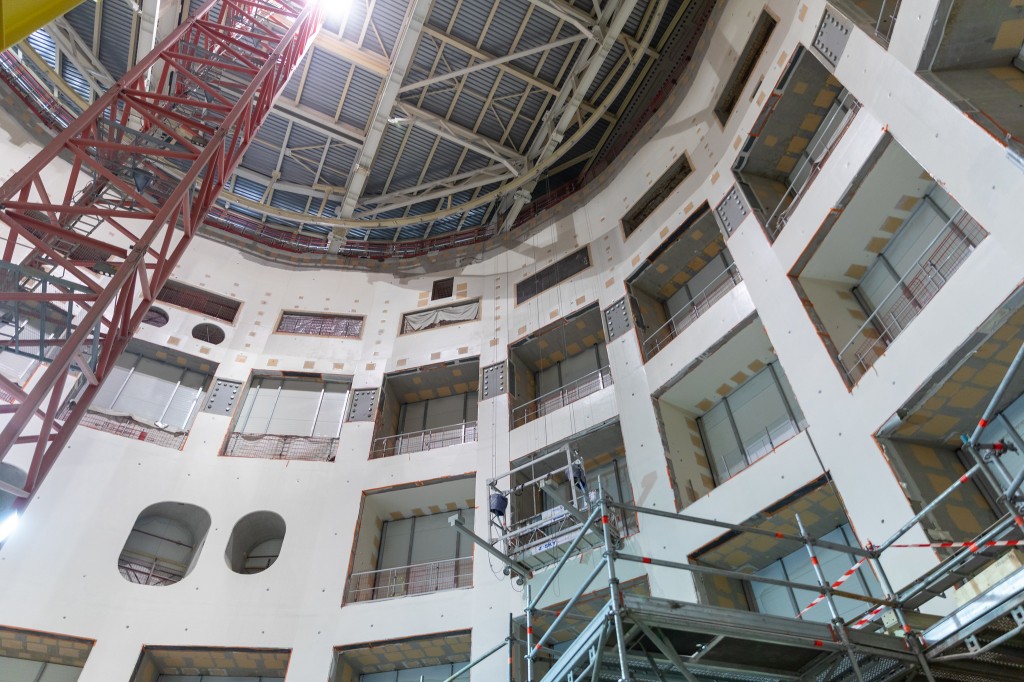
Lid still in place
2019-08-28 - As long as the Tokamak Building is open to the sky, a temporary lid will remain in place to protect the Tokamak pit from the weather. © Les Nouveaux Médias/SNC ENGAGE
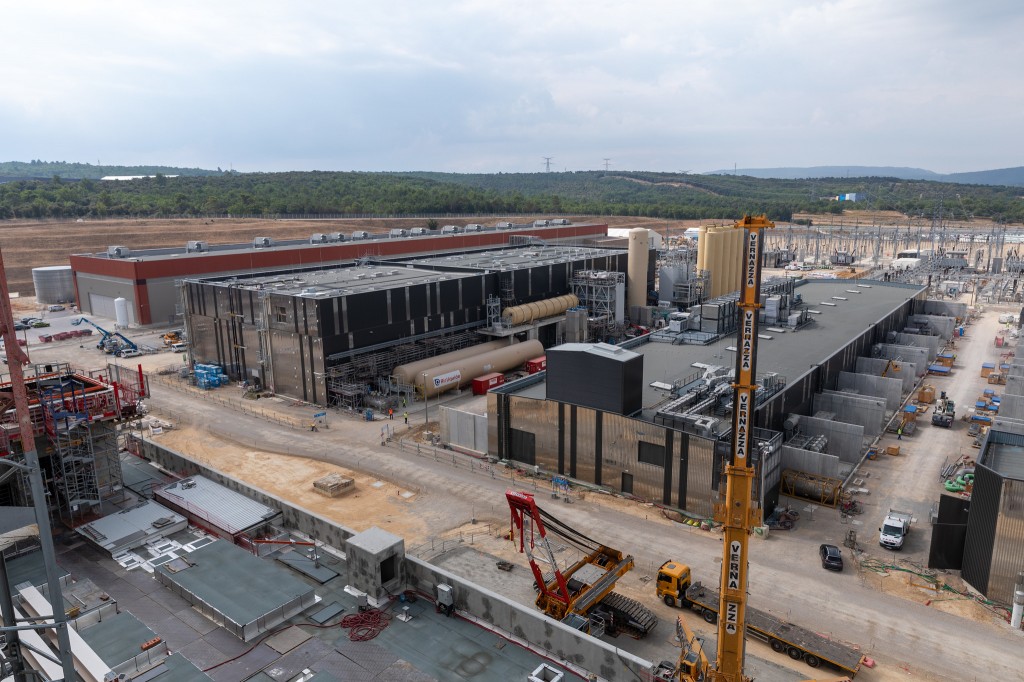
The view late August
2019-08-28 - Looking south over the Poloidal Field Coils Winding Facility (red top), the ITER cryoplant, and one of the two buildings for magnet power conversion. © Les Nouveaux Médias/SNC ENGAGE

A privileged view
2019-08-28 - A whole world exists up at Level 4 of the Tokamak Building—one with a fantastic view of the surrounding countryside ... © Les Nouveaux Médias/SNC ENGAGE

Reactive power compensation
2019-08-28 - These alien-looking objects are harmonic filters, part of ITER's reactive power compensation and harmonic filtering system. This unique system is responsible for fast-acting reactive power compensation on the high-voltage electricity transmission network, in order to stabilize the power grid and provide the required quality of electrical power to operate ITER. © Les Nouveaux Médias/SNC ENGAGE
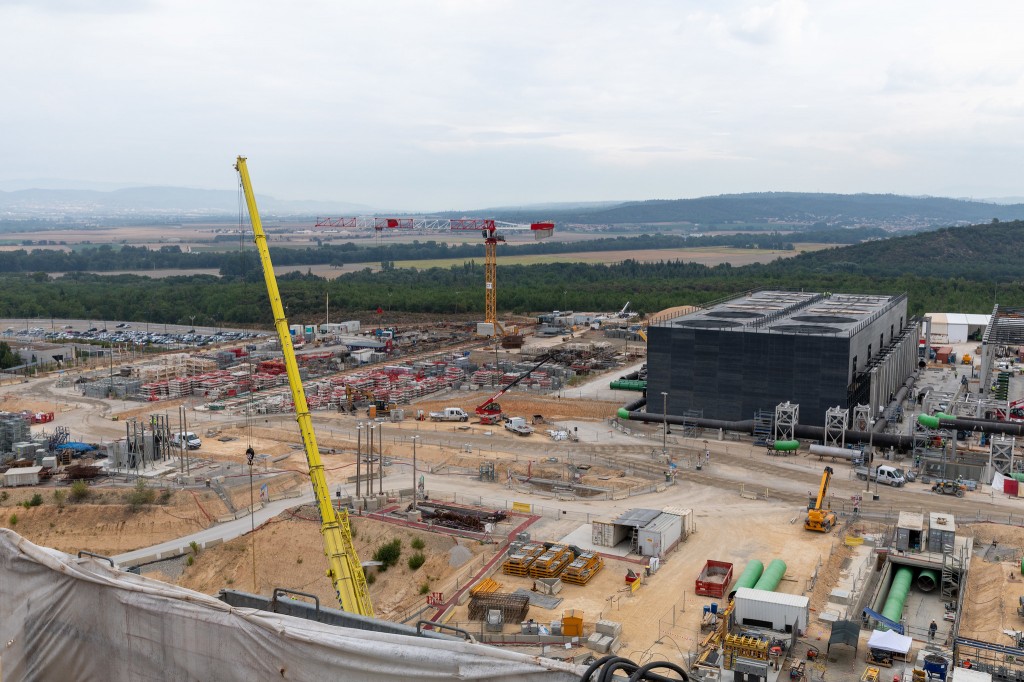
A last free corner
2019-08-28 - One of the last free spots on the platform—on the northern tip—is reserved for the Control Building. Work is scheduled to begin next year. © Les Nouveaux Médias/SNC ENGAGE
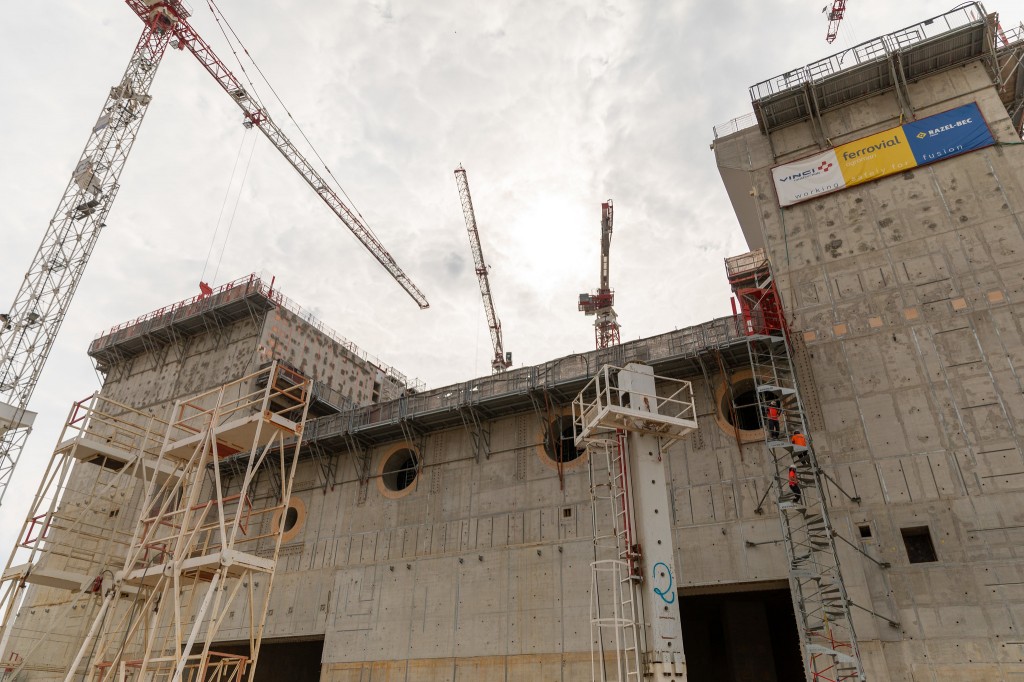
Civil works underway since 2014
2019-08-28 - The civil works of the Tokamak Complex fall under the TB03 contract signed between the European Domestic Agency and the VFR consortium (Vinci, Ferrovial, Razel Bec). Their colours are displayed at right. © Les Nouveaux Médias/SNC ENGAGE
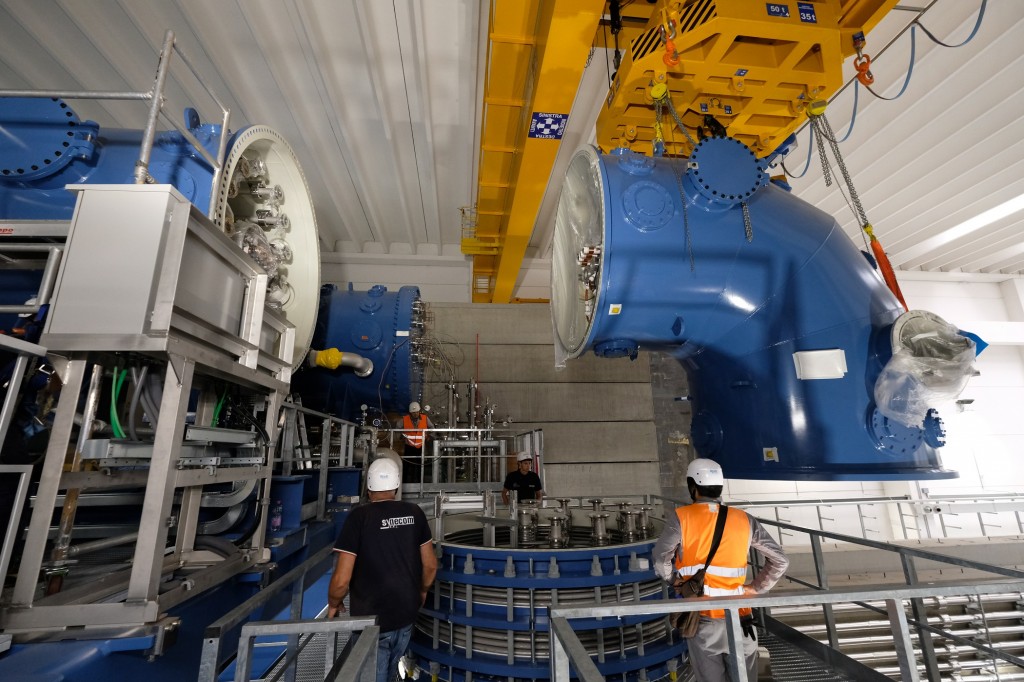
Progress on MITICA in August
2019-08-19 - In August, the last component of the MITICA 1 MV transmission line is successfully installed.

Perfect fit
2019-08-19 - All MITICA "utilities" will pass through the high voltage bushing supplied by Japan: electricity, water (for cooling) and gas (for the plasma).
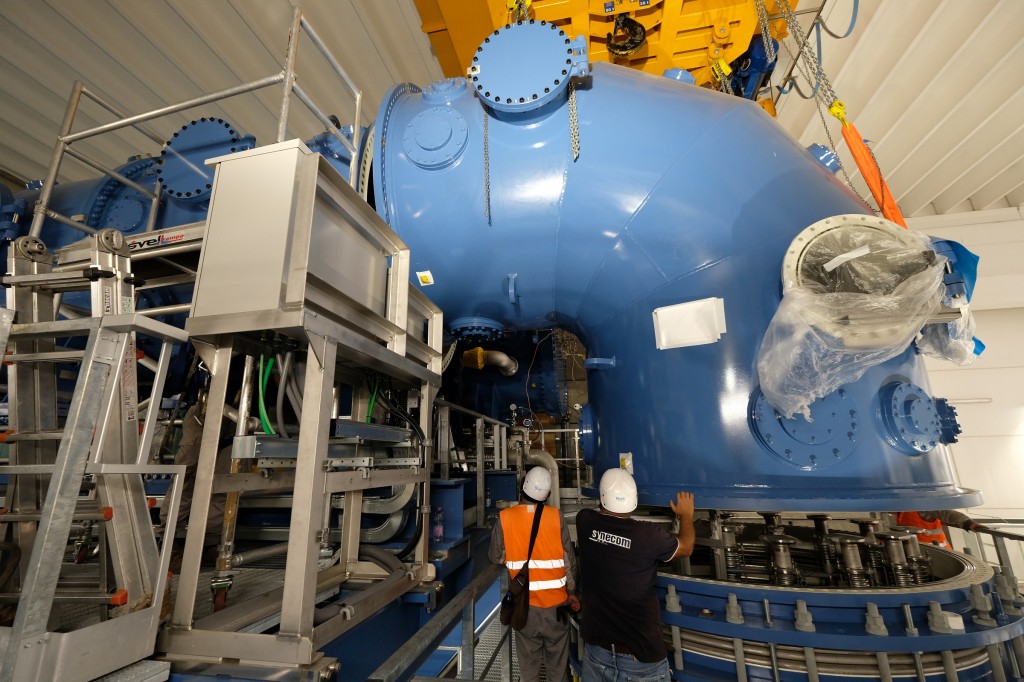
Elbow-shaped
2019-08-19 - The bend component now connects the MITICA transmission line to the high voltage bushing.

Pump station 1
2019-08-07 - Equipment provided by India has been installed in one of the two pump stations planned for the heat rejection system.
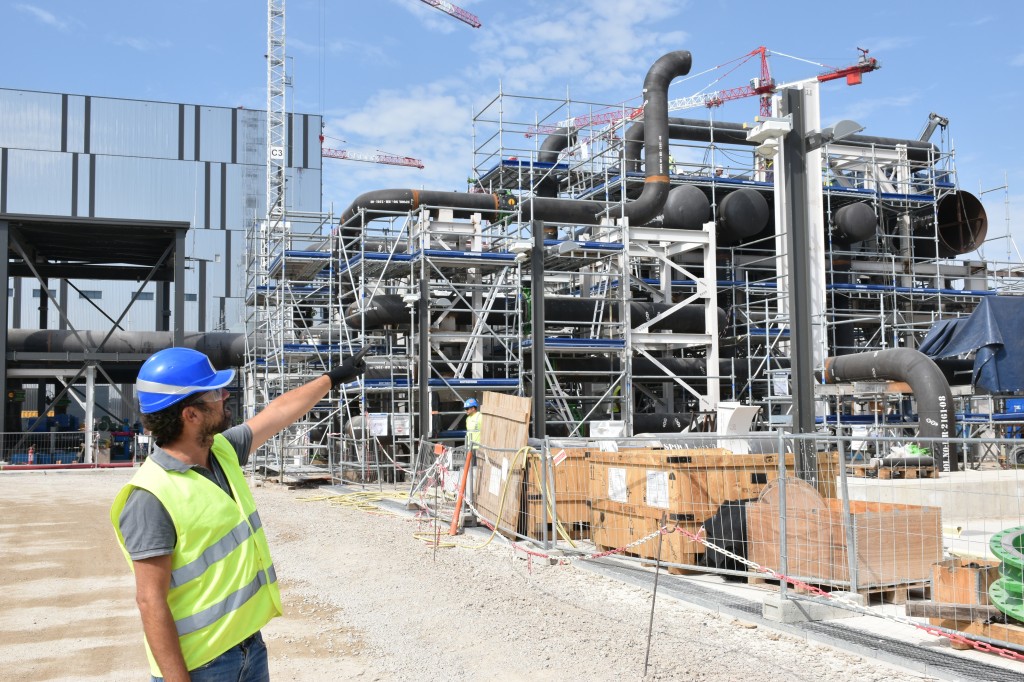
Pump station 1
2019-08-07 - Equipment provided by India has been installed in one of the two pump stations planned on site.
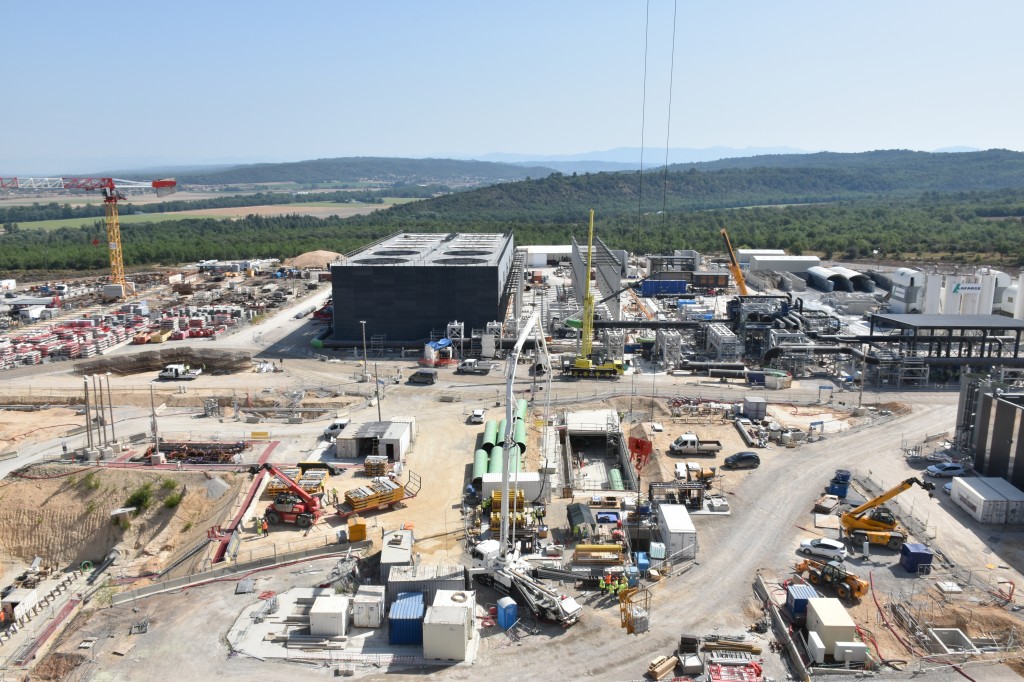
Next to be installed: large updraft fans
2019-08-06 - The cooling tower zone is taking shape. A pump station has been erected (right, near the orange crane) and large cooling fans have arrived on site for installation in the cooling tower building.
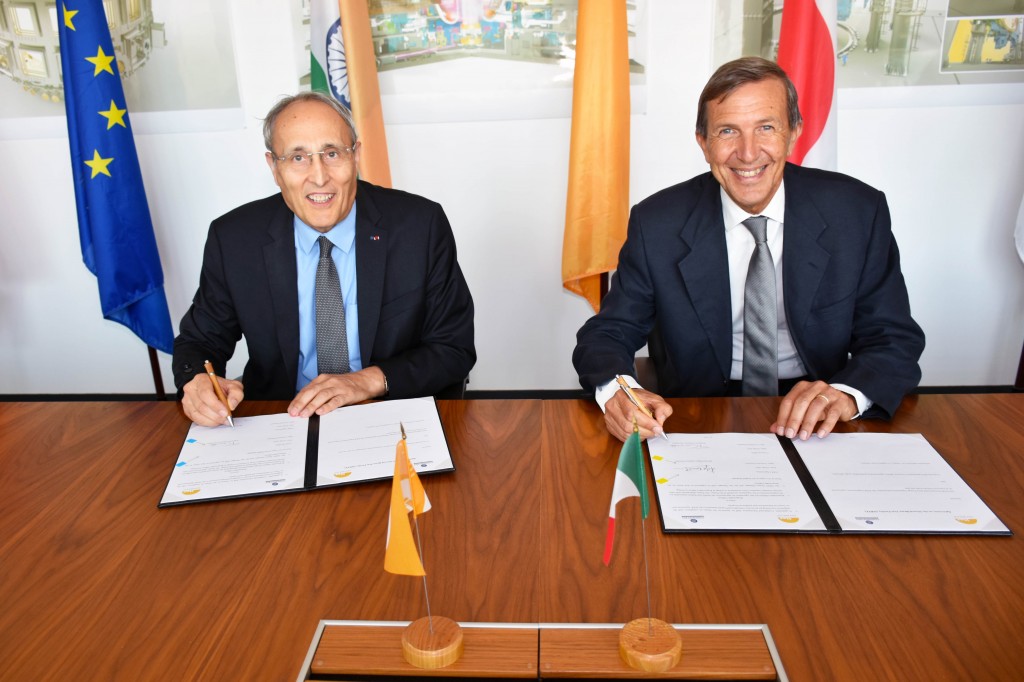
New agreement ratified for the Neutral Beam Test Facility
2019-07-25 - The ITER Organization and the Italian consortium Consorzio RFX sign a new agreement governing the construction and operation of the ITER Neutral Beam Test Facility. In a first phase, testbed results will inform the procurement of components for the ITER system. After operation starts at ITER, by 2032, the facility in Padua, Italy, will be a testbed for ongoing performance enhancement.
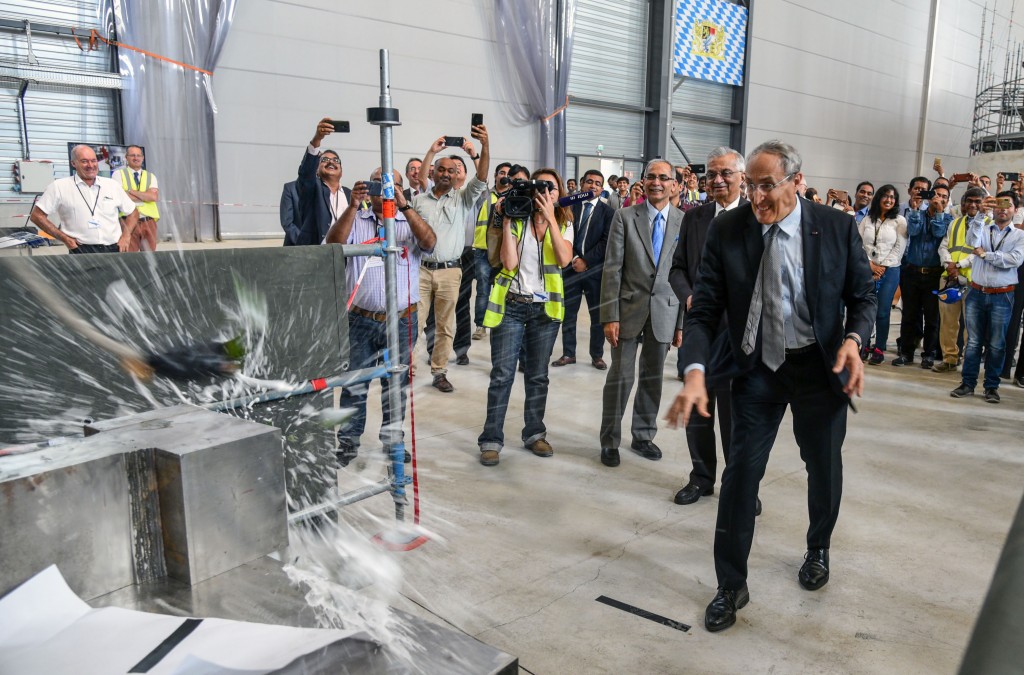
60% complete
2019-07-23 - On 23 July 2019, ITER Director-General Bernard Bigot, India's Ambassador to France Vinay Mohan Kwatra, and the former chairman of the Atomic Energy Commission of India, Anil Kakodkar, symbolically smash a bottle of French champagne on a large chunk of steel representing the ITER cryostat. Sixty percent of manufacturing has been completed, and the base and lower cylinder have been accepted by the ITER Organization.
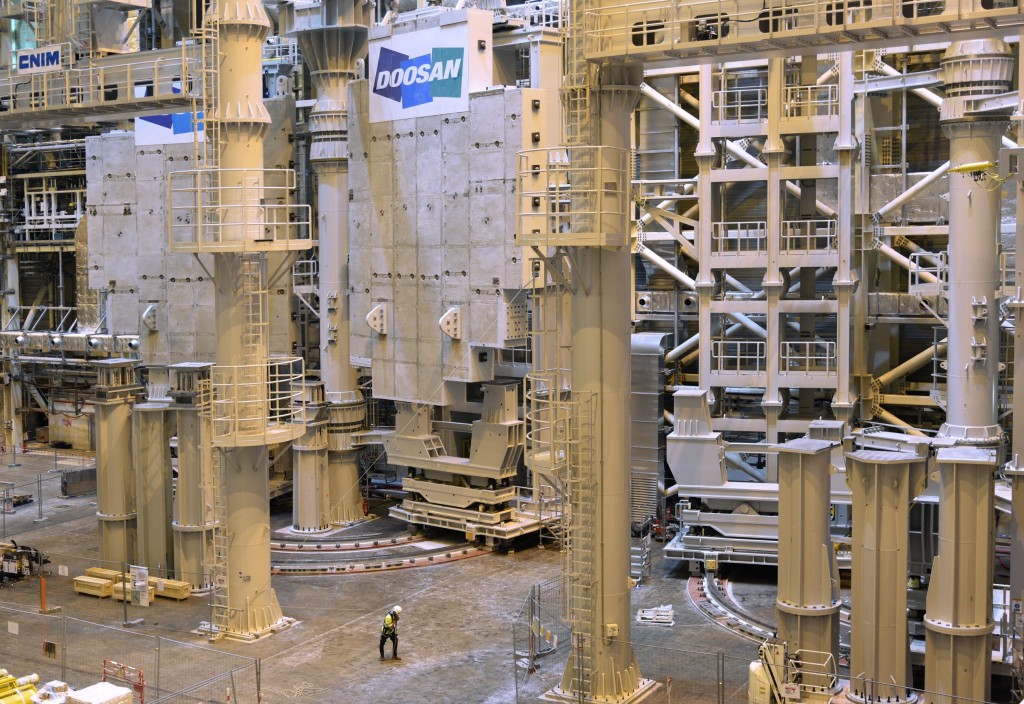
Two mounted
2019-07-23 - Two mock loads were built in Scotland by Doosan Babcock and shipped to ITER for assembly. They represent a combined weight of 700 tonnes, now mounted on the tool SSAT#1. Rotational tests begin late in July.

Celebrating together
2019-07-23 - The ITER Director-General is pictured with Praveen Bhatt, Joint General Manager for Larsen & Toubro; India's Ambassador to France, His Excellency Vinay Mohan Kwatra; and ITER's Prabhat Kumar, Deputy to the Site Construction Director.

Two mounted
2019-07-23 - Two mock loads were built in Scotland by Doosan Babcock and shipped to ITER for assembly. They represent a combined weight of 700 tonnes, now mounted on the tool SSAT#1. Rotational tests begin late in July.
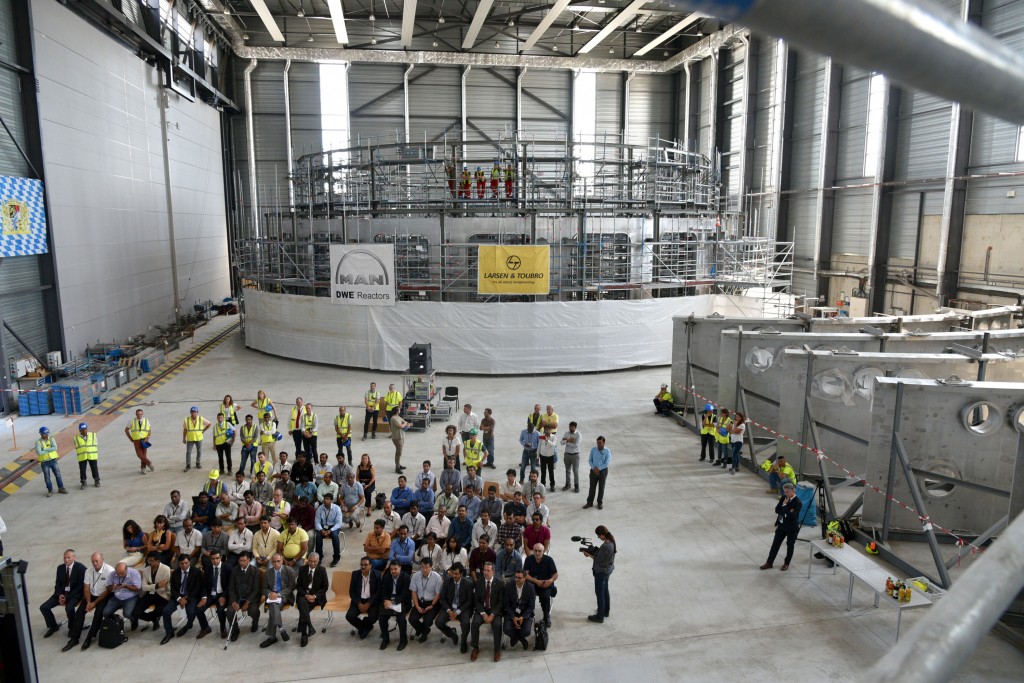
Gathered for a special celebration
2019-07-23 - A small ceremony in the Cryostat Workshop is held for representatives of all involved parties: the ITER Organization, ITER India, Larsen & Toubro, and MAN Energy Solutions. In the background, work has begun on the upper cylinder.

The hands-on team from Larsen & Toubro
2019-07-23 - Over its 80 years of existence, Larsen & Toubro Ltd. has built solar and nuclear plants, ports and airports, supertankers and submarines and played a key role is putting into Mars orbit the Mangalyaan space probe. Still, there are challenges in the fabrication of the ITER cryostat that the company had never faced. This young team is at the centre of the cryostat project, including Project Manager Patel Chiarg (third from left).
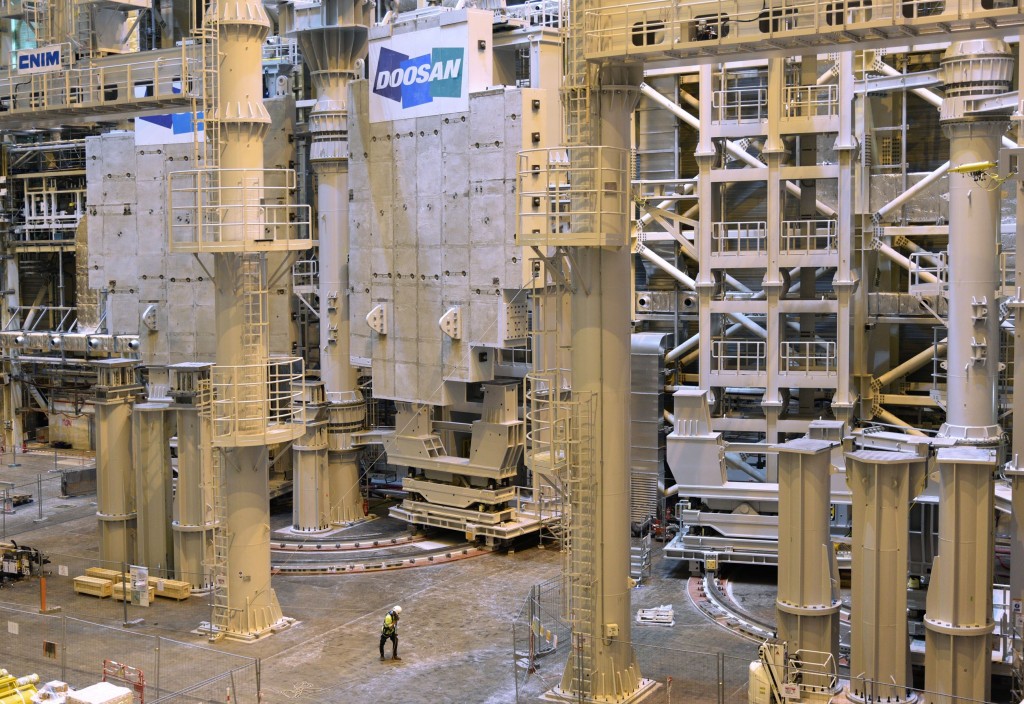
Two mounted
2019-07-23 - Two mock loads were built in Scotland by Doosan Babcock and shipped to ITER for assembly. They represent a combined weight of 700 tonnes, now mounted on the tool SSAT#1. Rotational tests begin late in July.
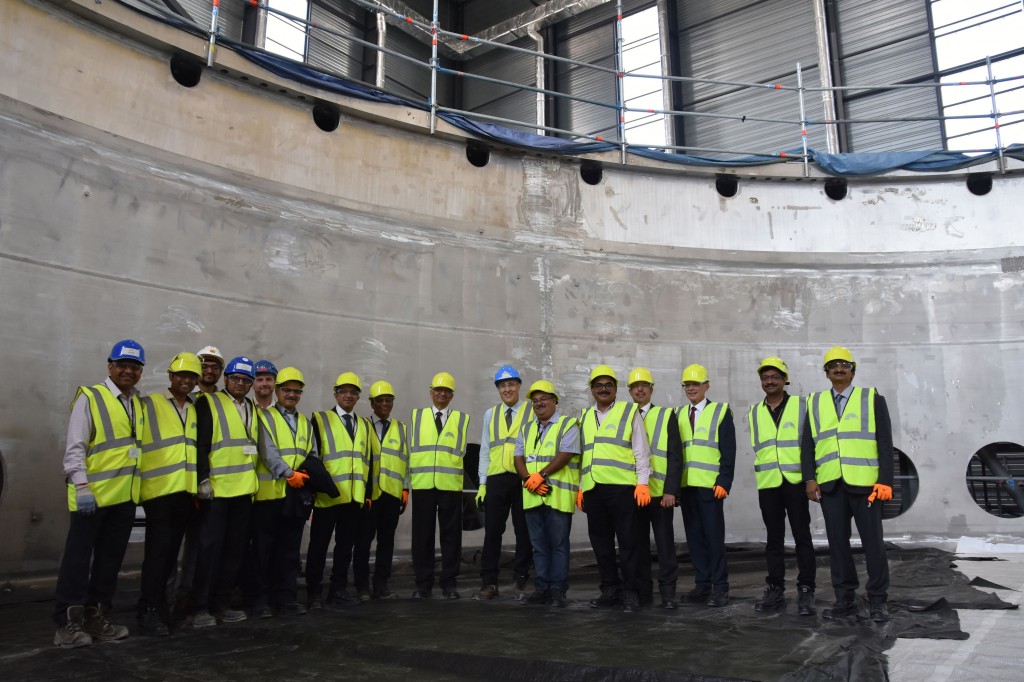
Inside of the completed base
2019-07-23 - This group is standing inside of the 1,250-tonne base, which will be the first major component installed in the Tokamak Pit next year.
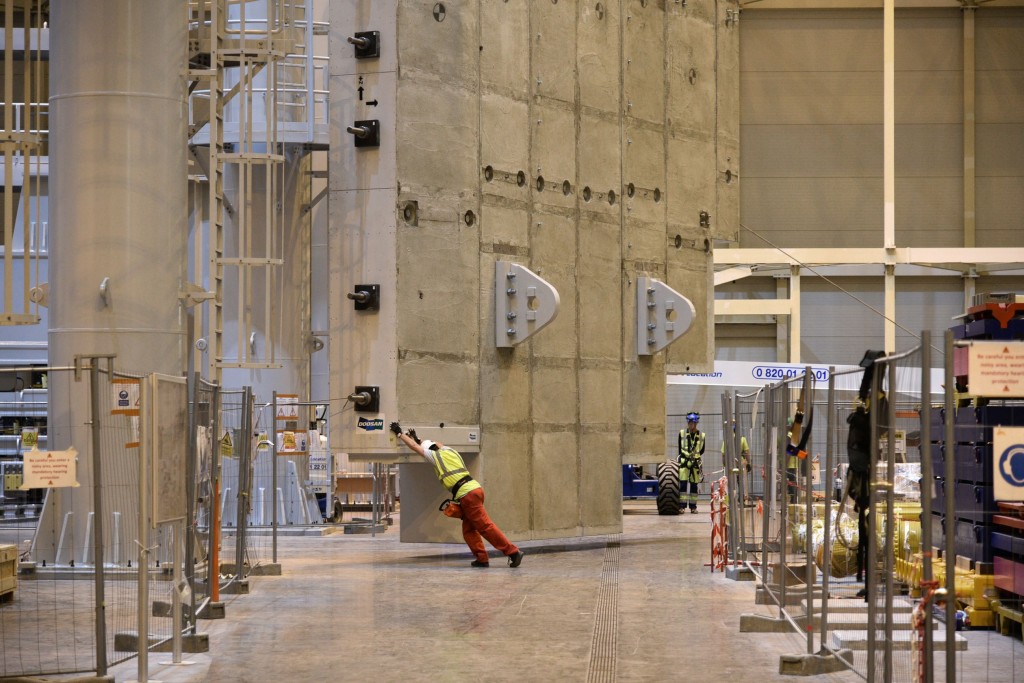
A little push by hand ...
2019-07-22 - Even in the most technical of operations, there is always a need for final adjustment by hand. Seen vertically, the loads share the D-shape of the toroidal field coils they are meant to represent. They also reproduce the centre of gravity and mass distribution of the coils.

A little push by hand ...
2019-07-22 - Even in the most technical of operations, there is always a need for final adjustment by hand. Seen vertically, the loads share the D-shape of the toroidal field coils they are meant to represent. They also reproduce the centre of gravity and mass distribution of the coils.
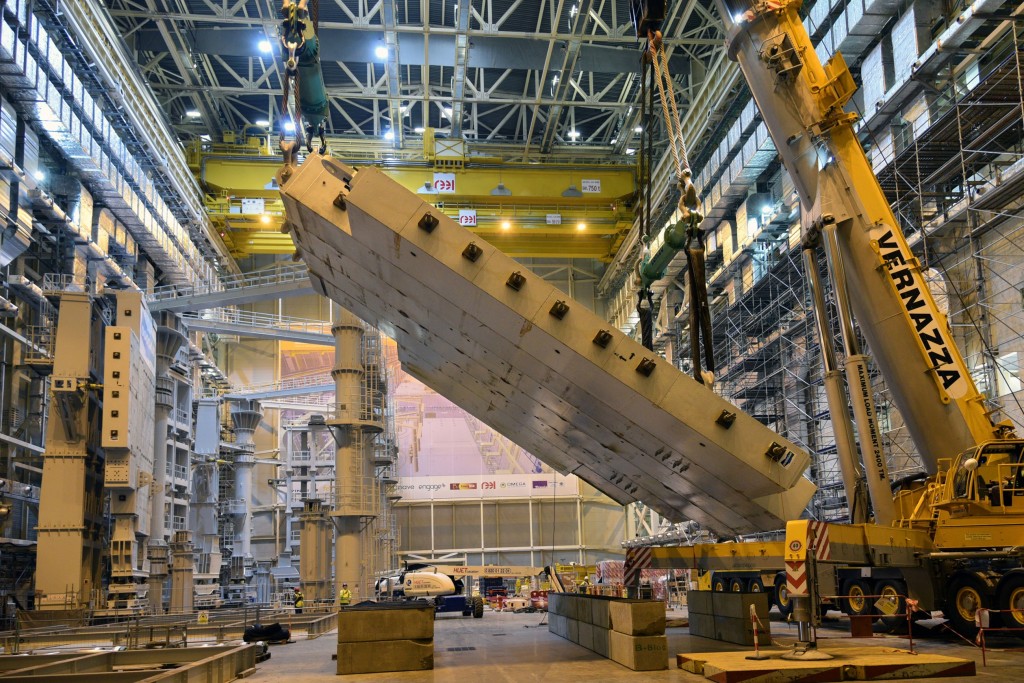
Inching up
2019-07-19 - One 350-tonne dummy load, representing a toroidal field coil, is slowly upended using both the double overhead crane at one end and a powerful telescopic crane at the other.
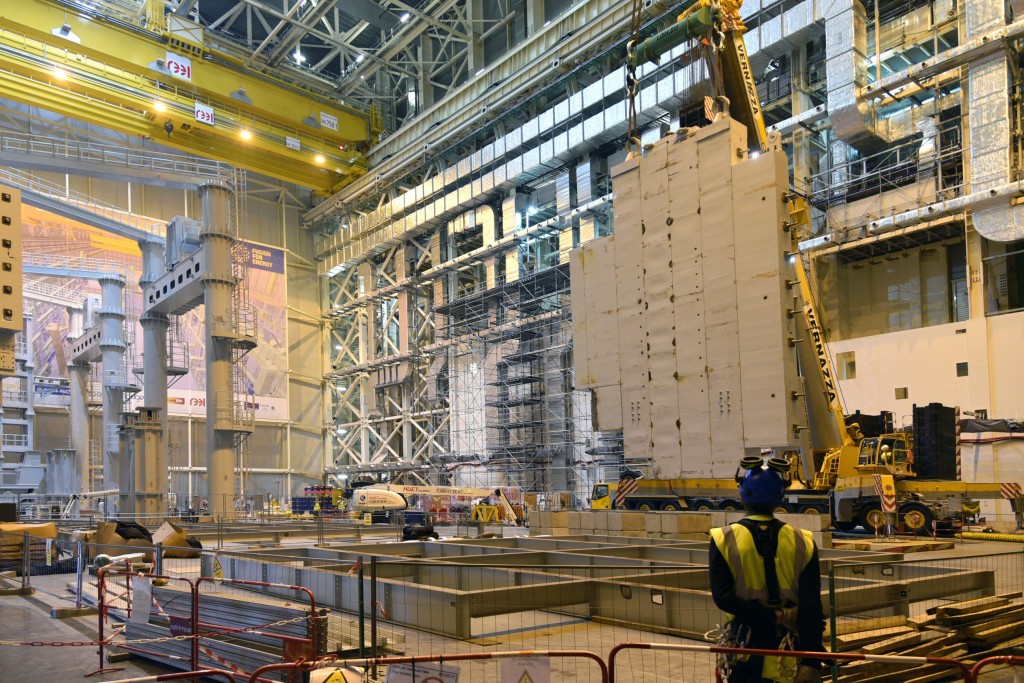
Travelling now
2019-07-19 - The upended load is carried to the first tool, to be installed on one of its wings.
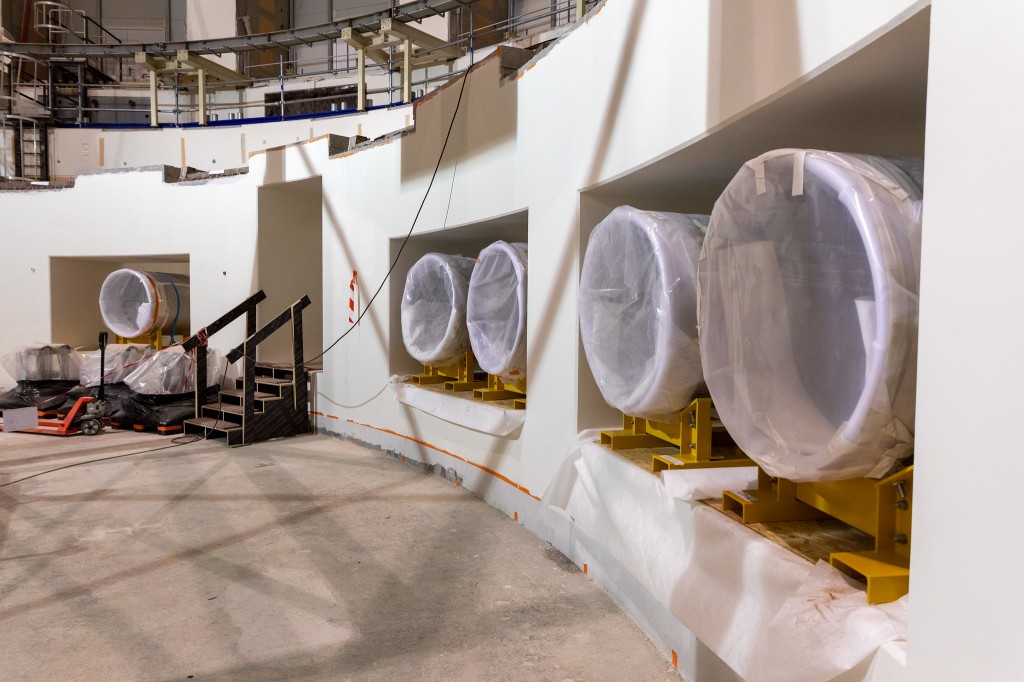
Coming in
2019-07-12 - At the bottom of the Tokamak pit, different openings allow for the arrival of electricity, cryogens and instrumentation. In the picture, placeholders have been pre-positioned. © Les Nouveaux Médias/SNC ENGAGE

Coming in
2019-07-12 - At the bottom of the Tokamak pit, different openings allow for the arrival of electricity, cryogens and instrumentation. In the picture, placeholders have been pre-positioned. © Les Nouveaux Médias/SNC ENGAGE
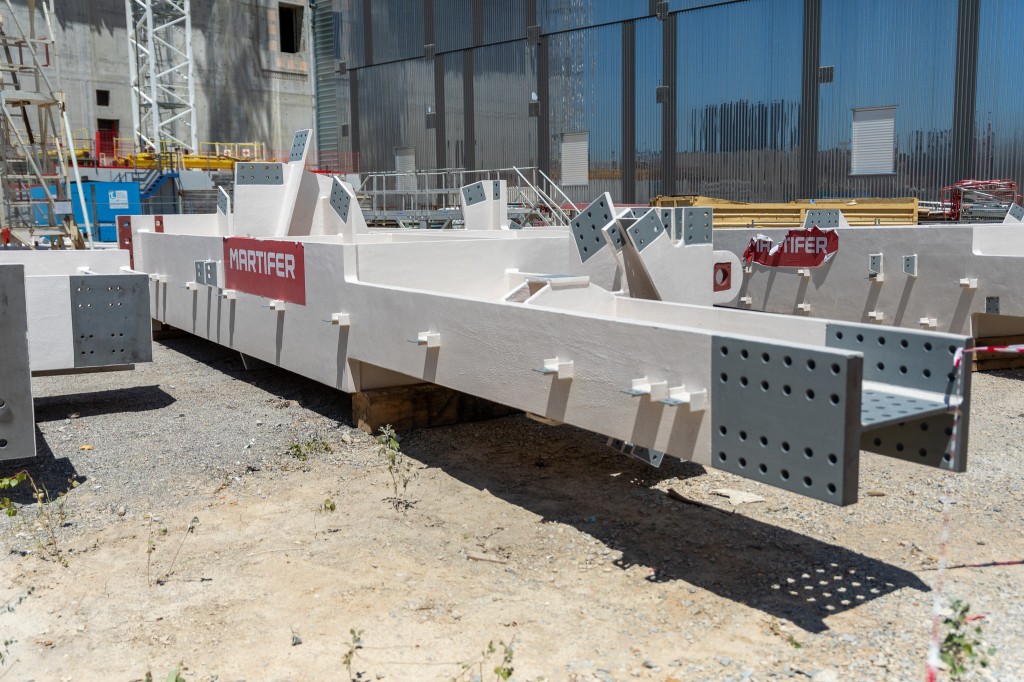
Elements of the crane hall
2019-07-12 - The pillars of the future crane hall are arriving on site. They will support the metal roof of the Tokamak Building. © Les Nouveaux Médias/SNC ENGAGE

Two mock loads
2019-07-11 - Two mock loads weighing 350 tonnes have been constructed from steel and concrete (far left) to represent the D-shaped toroidal field coils that will be mounted on the wings of the assembly tools. Lifting and installation will begin soon.

Two mock loads
2019-07-11 - Two mock loads weighing 350 tonnes have been constructed from steel and concrete (far left) to represent the D-shaped toroidal field coils that will be mounted on the wings of the assembly tools. Lifting and installation will begin soon.
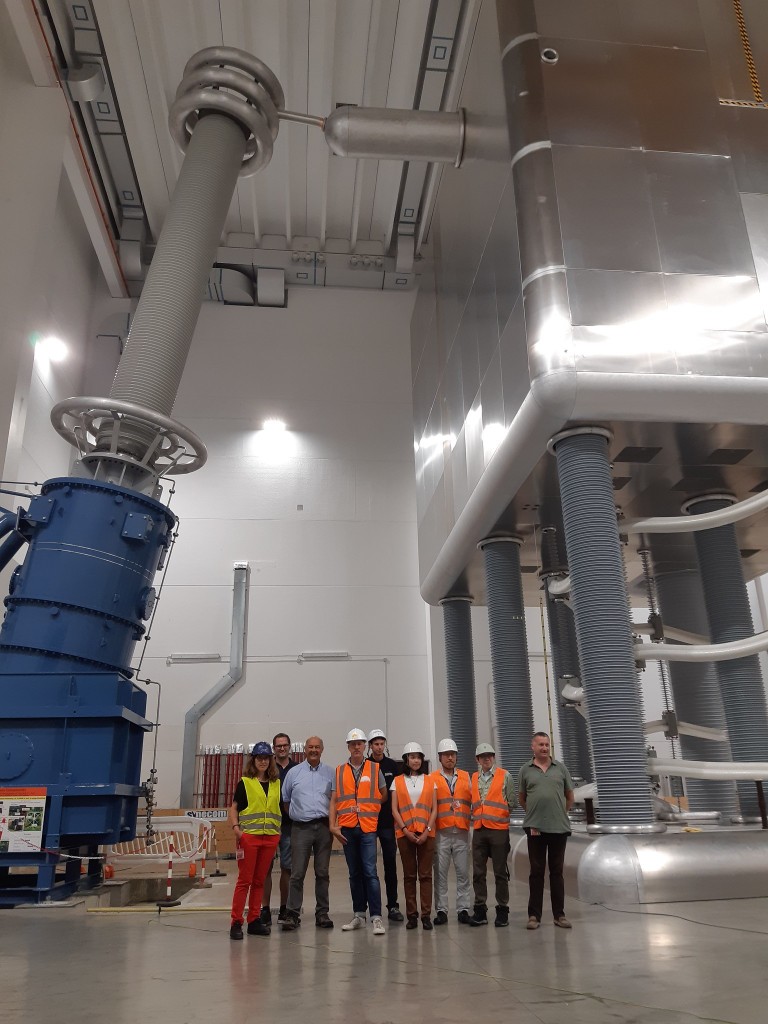
Successful high voltage tests for MITICA
2019-07-09 - Engineers from the European Domestic Agency (F4E), Consorzio RFX, ITER Japan, ITER Organization, and the companies involved in fabrication of the MITICA high voltage deck and high voltage bushing assemblies are pictured in the NBTF High Voltage Hall below the connection between the insulating transformer from Japan (left) and the high voltage deck from Europe (right) after a series of successful high voltage tests.

Capitalizing on lessons learned
2019-07-04 - The assembly and welding of the upper cylinder will follow more or less the pattern of work of the lower cylinder. Lessons learned are already bearing fruit: it took less than two weeks to install the first three segments (out of six) of upper cylinder tier one onto the frame.

Final verifications
2019-07-04 - A specialist from Indian Domestic Agency contractor MAN Energy Solutions is performing a final dimensional inspection on the "holes" that will receive the bolts of the toroidal field coil and vacuum vessel gravity supports. Match up must be close to perfect.

Wraps off
2019-07-04 - Work on the cryostat base has ended. The 1,250-tonne component, which resembles a soup dish, or an upside down hat, will remain in the Cryostat Workshop until required in the ITER machine assembly sequence.
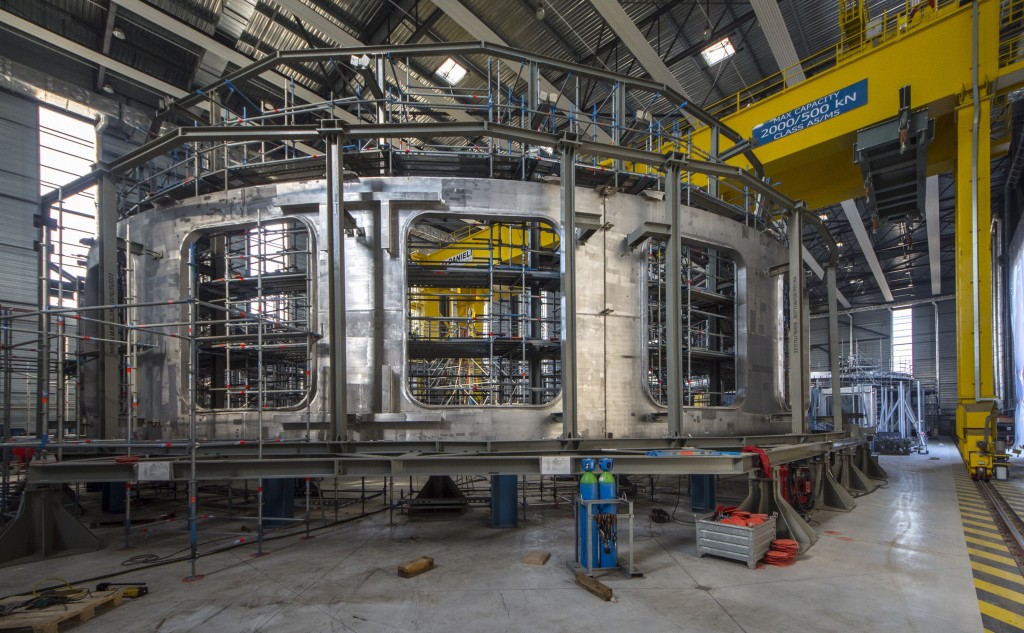
Work starts on upper cylinder
2019-07-04 - Several of the upper cylinder's first-tier segments have already been unwrapped and installed on the assembly platform.

Interfacing with the crown
2019-07-04 - This is where the cryostat base will interface with the concrete support crown of the Tokamak Pit and the bioshield inner walls. The protruding steel piece at the centre-right of the image is one of 18 "toroidal lugs" that will lock into the bioshield.
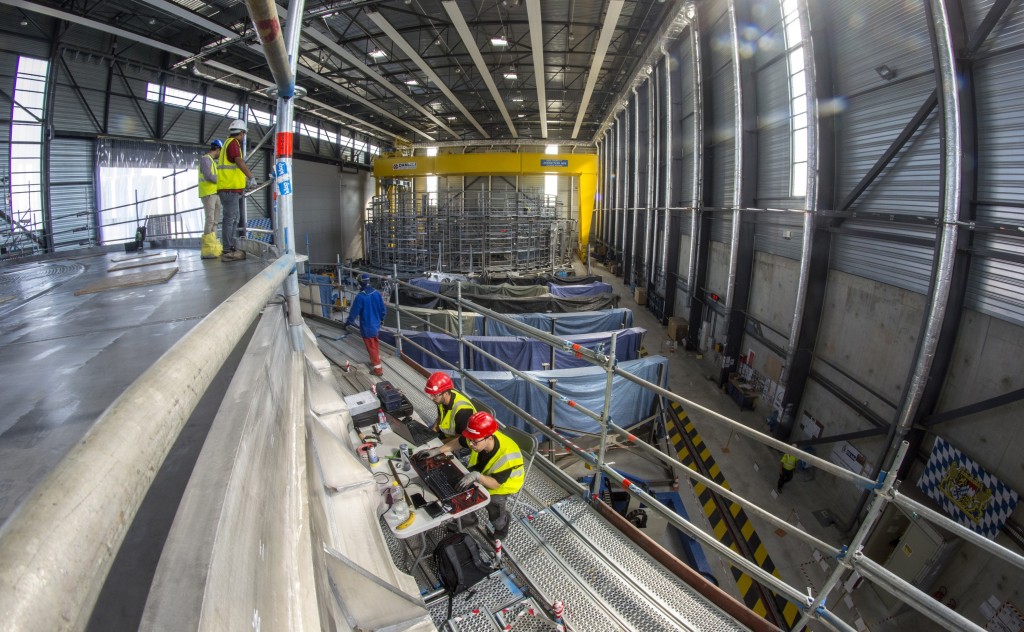
Fore, mid and aft
2019-07-04 - In the foreground, metrologists are completing a survey of the "skirt" of the base; in the middle of the Workshop, segments of the upper cylinder, freshly arrived from India; and in the background, the assembly platform for the upper cylinder.
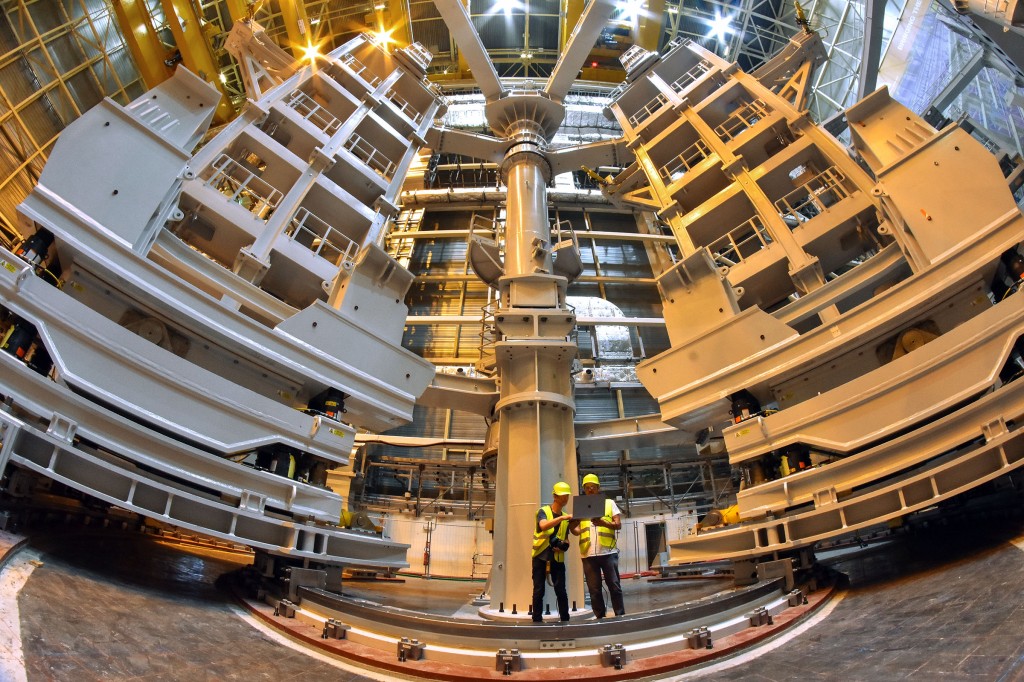
Open arms
2019-07-03 - Standing in front of one of the sub-sector assembly tools is Swiss photographer Luca Zanier, who spent two days at ITER in July in pursuit of "unusual" perspectives in industry.

The pit, all aglow
2019-07-03 - Raw concrete in the Tokamak assembly pit has given way to the smooth shiny surface of white paint. Teams have been working to complete the job in this 25,000 cubic-metre space since early March; now only finishing touches remain to prepare for machine assembly.

Open arms
2019-07-03 - Standing in front of one of the sub-sector assembly tools is Swiss photographer Luca Zanier, who spent two days at ITER in July in pursuit of "unusual" perspectives in industry.

The pit, all aglow
2019-07-03 - Raw concrete in the Tokamak assembly pit has given way to the smooth shiny surface of white paint. Teams have been working to complete the job in this 25,000 cubic-metre space since early March; now only finishing touches remain.
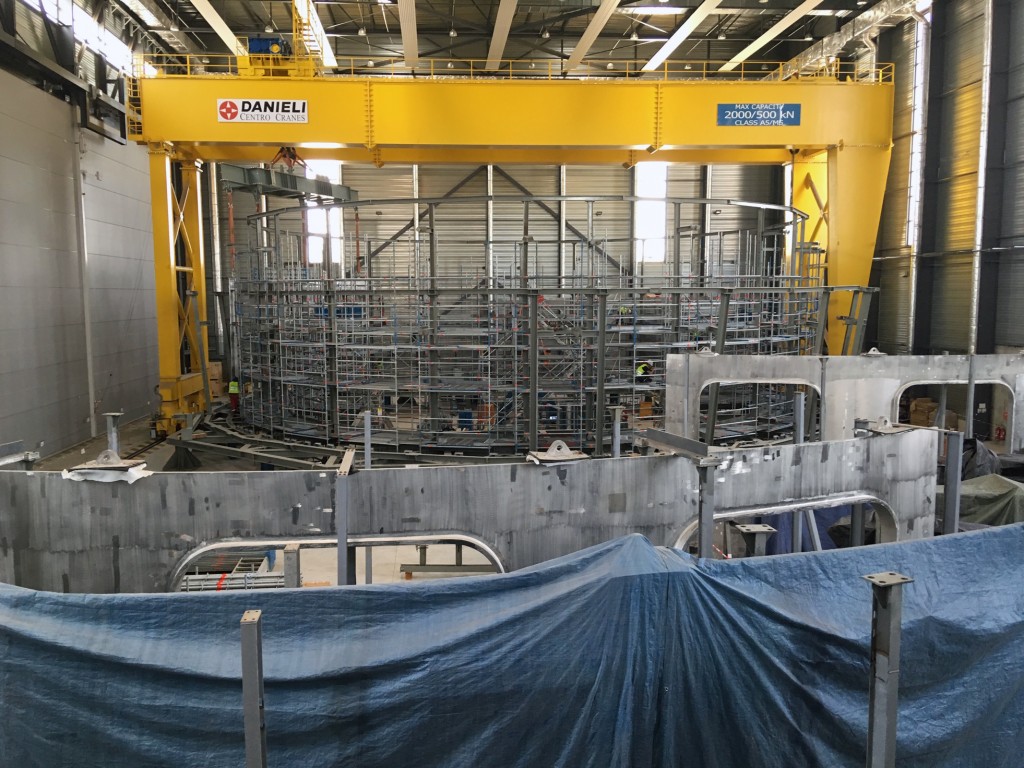
Work to start to assemble the upper cylinder
2019-07-02 - The assembly platform is in place for the upper cylinder and the first segments have arrived.
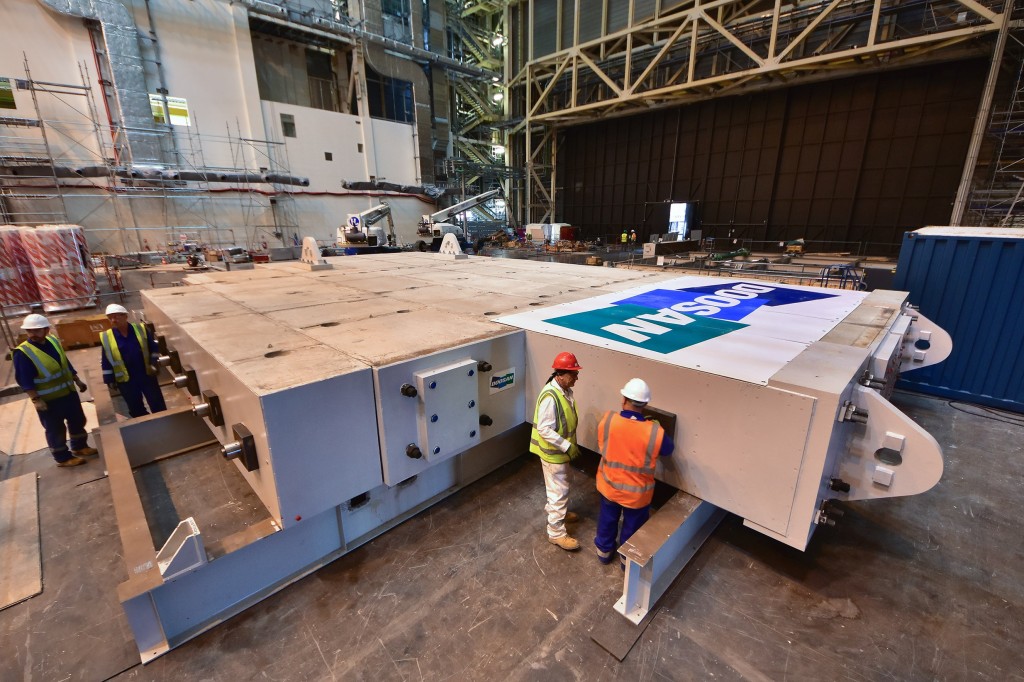
Inspecting the loads
2019-07-01 - Made of seven different steel-and-concrete modules, the dummies slightly exceed the weight of the actual coil but closely reproduce their centre of gravity and distribution of mass.
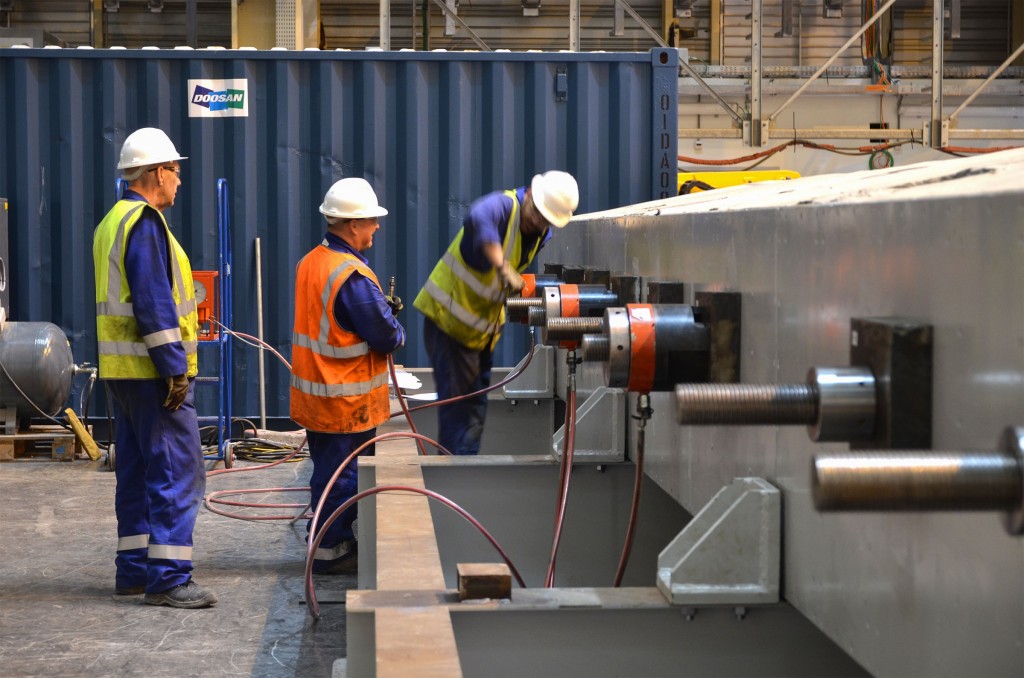
Preparing the lift
2019-07-01 - The load modules are held together by strong threaded tension bars called "Macalloys." The stress on these bars was tested recently by lifting the load several centimetres above the shop floor as part of preparatory activities for the real lift.
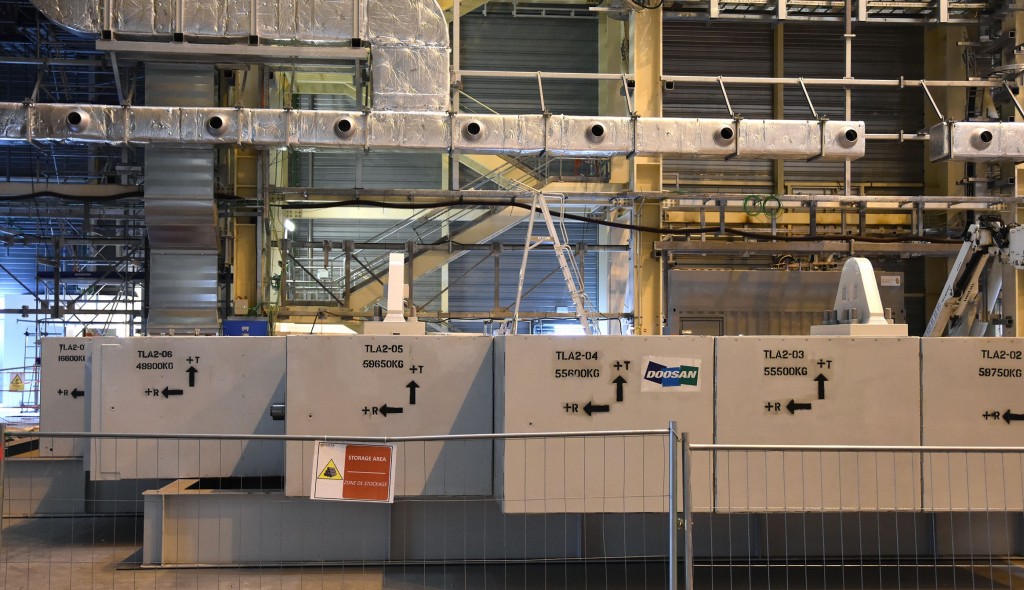
Steel and concrete modules to make the weight
2019-07-01 - Each dummy load is made of seven assembled modules of varying weights.

Tokamak-sur-mer
2019-06-30 - At the height of the heat wave, in late June, surface temperature on the ITER worksite climbed to the 50 °C range. To continue work—and protect workers—a series of measures was implemented: the morning shifts began earlier, longer pauses were granted, cool mist vaporizers were installed, and... parasols made an appearance.

New excavation
2019-06-19 - Excavation has ended for a concrete building designed for the distinct storage and handling requirements of ITER's beryllium components—in particular, the first-wall panels of the ITER blanket. But as these components are not expected on site before late 2024, the building will be used in the interim for Tokamak pre-assembly work. Photo: ITER Organization/EJF Riche
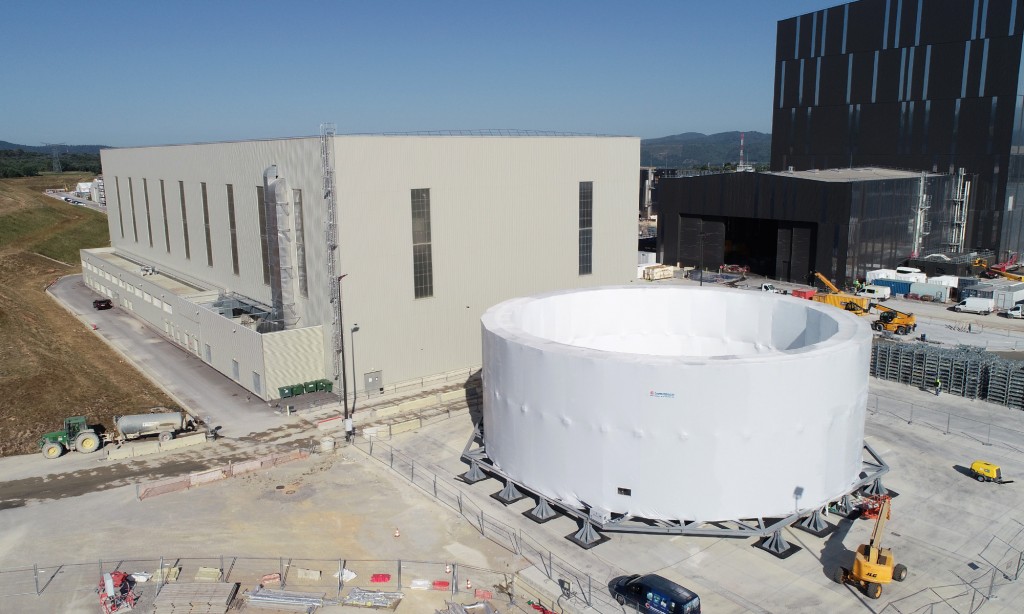
Twin underway on the inside
2019-06-19 - Nearly as wide as the building itself this "piece" of ITER—the cryostat lower cylinder—was moved outside of the Cryostat Workshop so that its near twin—the upper cylinder—can be aligned and welded. Photo: ITER Organization/EJF Riche
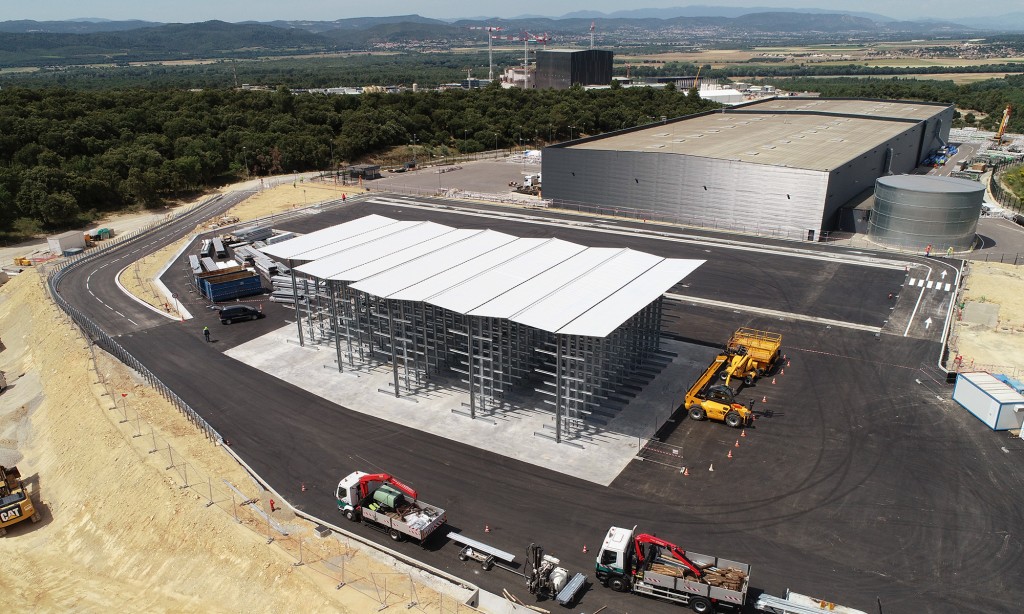
Storage on the hill
2019-06-19 - Contractors have erected a new storage facility on the hill behind ITER for the many pipes that are being delivered for ITER's cooling water networks. Photo: ITER Organization/EJF Riche
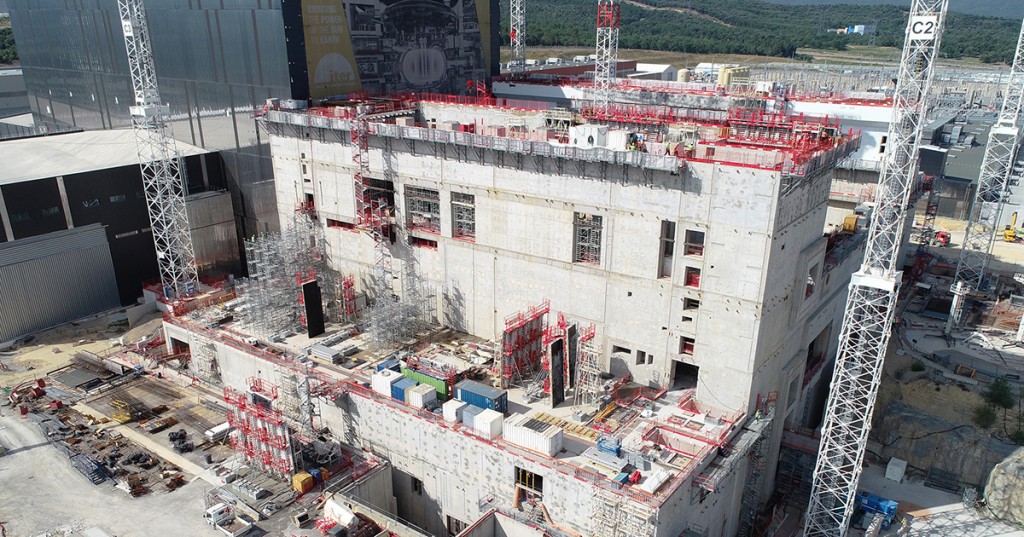
Progress in mid-June 2019
2019-06-18 - The European Domestic Agency in concentrating construction resources on the central Tokamak Building. The metal crane hall is arriving in sections, for assembly on the concrete walls beginning in September. Photo: ITER Organization/EJF Riche¶

All lined up
2019-06-18 - These segments have arrived from Larsen & Toubro, India, for the assembly of the upper cylinder. Photo: ITER Organization/EJF Riche
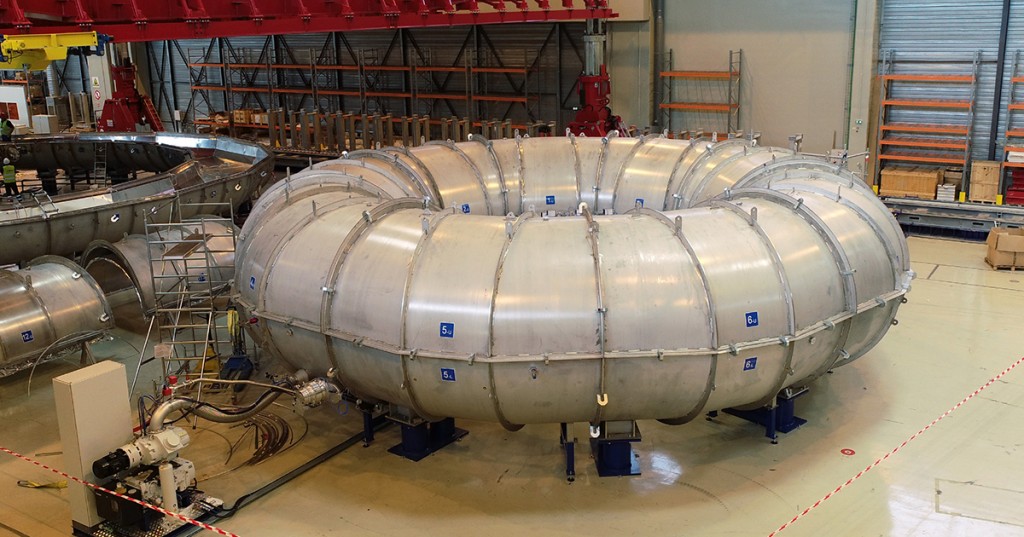
A chamber for the first-built coil
2019-06-18 - This cryogenic chamber is dimensioned especially for poloidal field coil #6 (PF6) which, at 10 metres in diameter, is the second smallest ring magnet. The coil will arrive this autumn from China, where it was manufactured on behalf of the European Domestic Agency. Cold tests will take place in this chamber at 80 K. Photo: ITER Organization/EJF Riche

Upside-down hat
2019-06-18 - The base of the cryostat is shaped like an upside-down hat. The pedestal ring will be supported by the concrete crown at the bottom of the Tokamak Pit and, in turn, the ring will support the rest of the machine. Photo: ITER Organization/EJF Riche

Through the eyes of a crane operator
2019-06-17 - Sitting in his cabin 80 metres above the ground, Alex Dumonteil enjoys a most spectacular view of the ITER construction site.
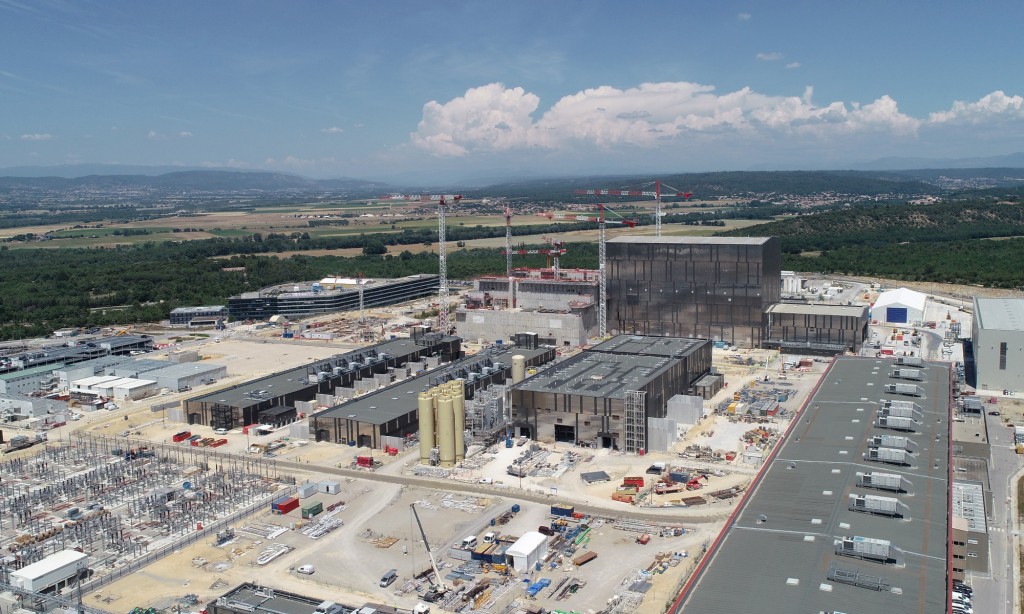
Bridges planned
2019-06-17 - The central area of the ITER construction houses facilities for magnet power conversion (two buildings, left) and cryogenics (right). Overhead bridges will be installed between these buildings and the Tokamak Complex (grey concrete) for the transport of power and cryogens like liquid helium. Photo: ITER Organization/EJF Riche
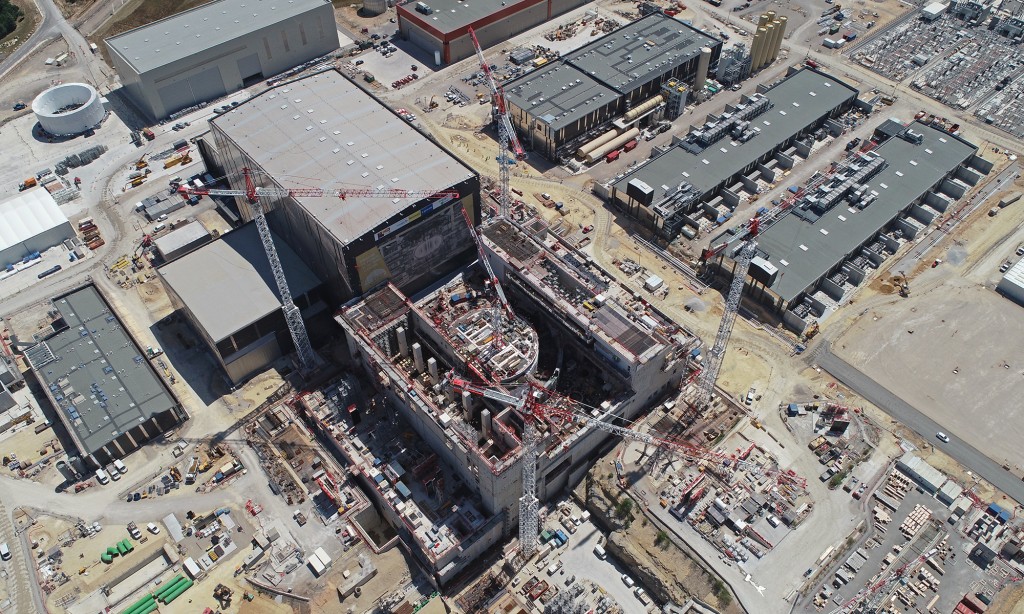
Roof frame on its way
2019-06-17 - European construction contractors are getting ready to install the metal frame of the crane hall—the structure that will complete the central Tokamak Building. The structure will "prolong" the Assembly Hall. In this photo we can see where it will sit (on the right, on top of the white corbel, and on the left, atop pillars). Photo: ITER Organization/EJF Riche
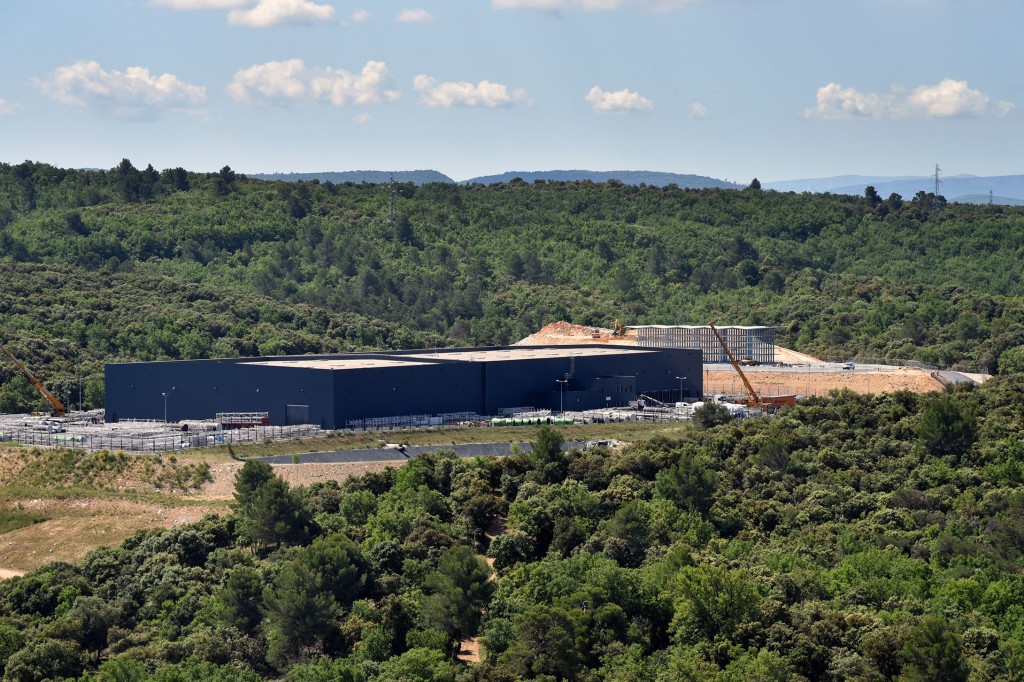
Extending storage capacity
2019-06-17 - Sitting on compacted backfill from the early worksite excavation works, the low black-clad building is ITER's largest warehouse. It provides a total of 15,000 m² of storage (9,000 m² internal, 6,000 m² external) and accommodates medium-size components waiting to be integrated into the ITER machine and plant systems. A recently erected structure in the background will provide racking for the storage of pipe lengths.
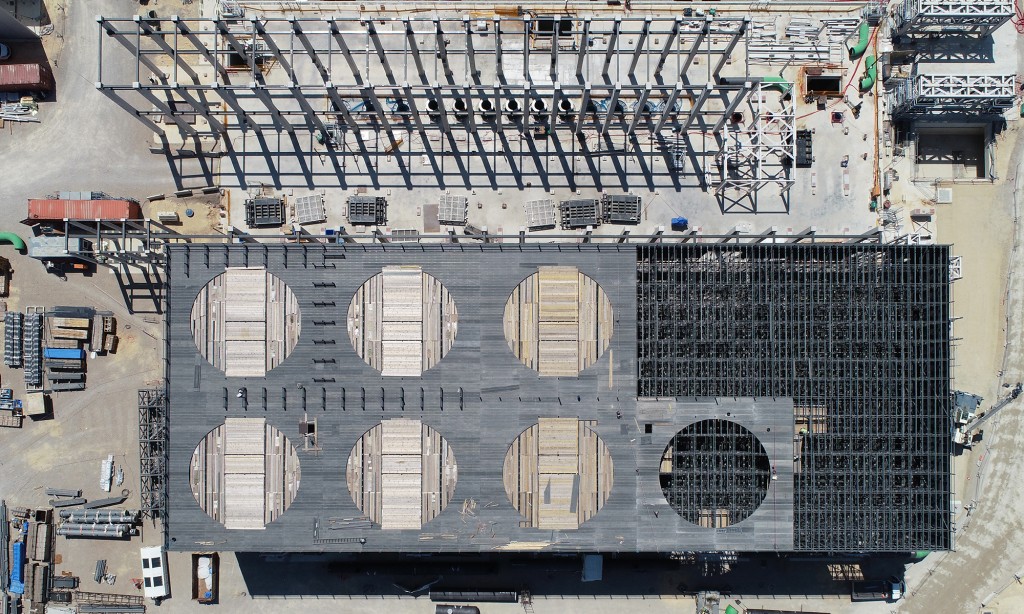
Cooling towers, from above
2019-06-17 - The infrastructure of the ITER cooling tower area, with 10 individual cells, is advancing on the northern corner of the ITER worksite. Large updraft fans will be installed in September. Photo: ITER Organization/EJF Riche
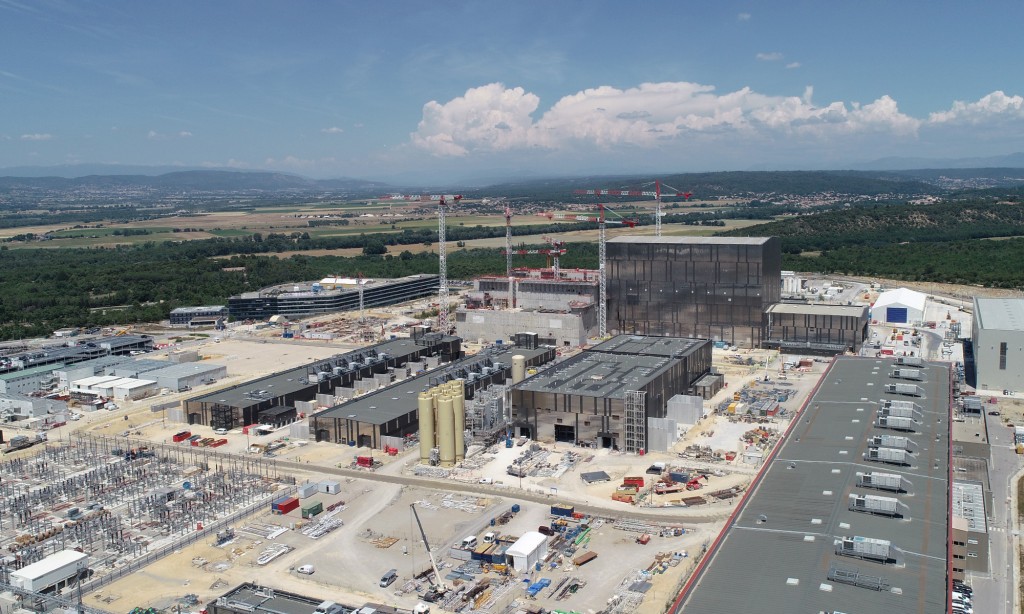
Bridges planned
2019-06-17 - The central area of the ITER construction houses facilities for magnet power conversion (two buildings, left) and cryogenics (right). Overhead bridges will be installed between these buildings and the Tokamak Complex (grey concrete) for the transport of power and cryogens like liquid helium. Photo: ITER Organization/EJF Riche

A site that never sleeps
2019-06-13 - An average of 300 trucks pass through the gates of the ITER worksite every day. Ongoing construction requires a huge amount of material—rebar to reinforce the concrete, huge formwork panels, steel columns, backfill soil, pipes by the kilometre, paint ... All the indispensable supplies for one of the world's biggest construction sites.
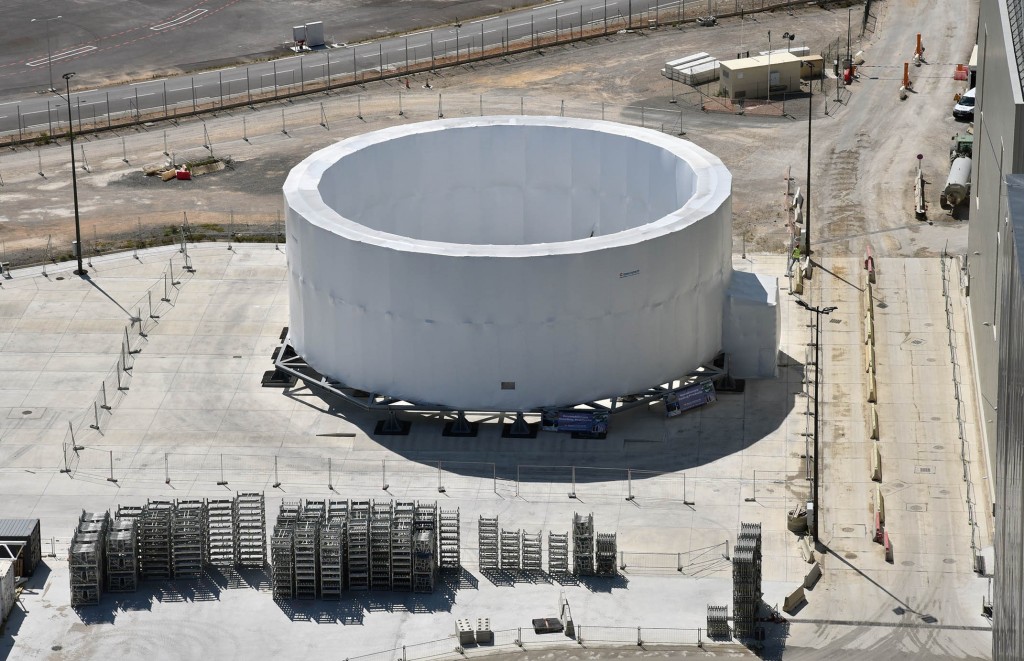
Under wrap
2019-06-13 - The lower cylinder, as seen from one of the worksite cranes. It has been safely "cocooned" and stored outside of the Cryostat Workshop to wait for its turn in the machine assembly sequence.
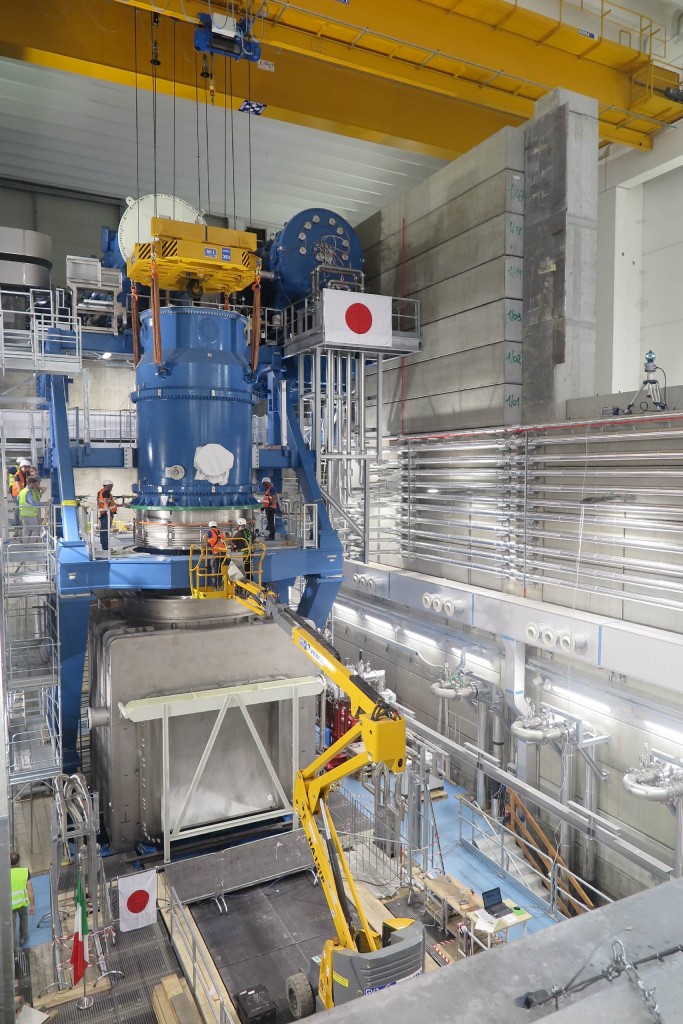
High voltage bushing installed
2019-06-13 - The 50-tonne MITICA high voltage bushing has been installed on top of the square, 57-tonne vacuum vessel.
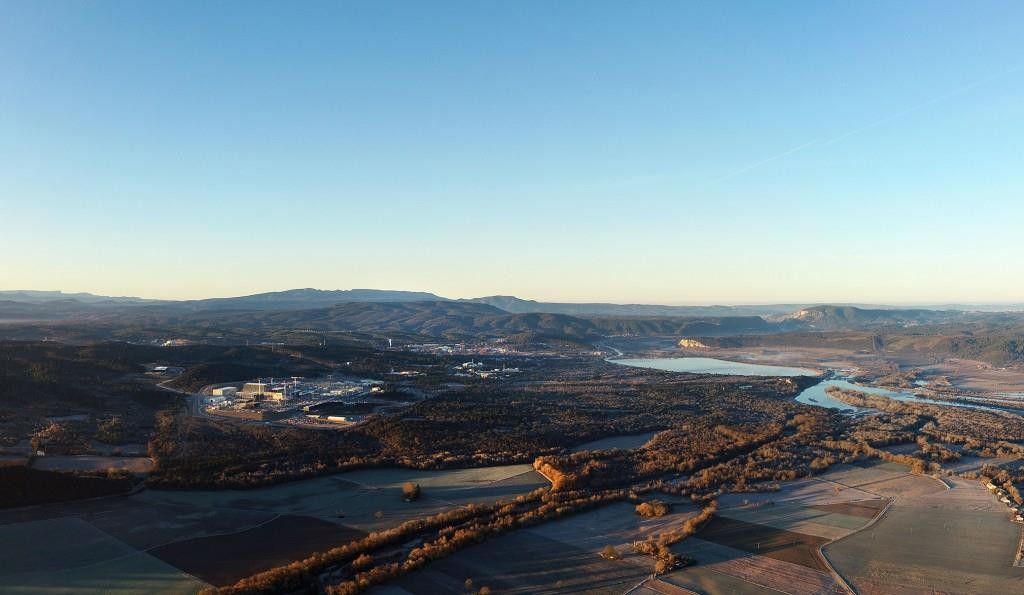
Amid field and forest
2019-06-12 - ITER is an outpost of activity in an otherwise sparsely populated region. The site was cleared more than a decade ago on land belonging to the CEA Cadarache research centre in a bend of the Durance River Valley.
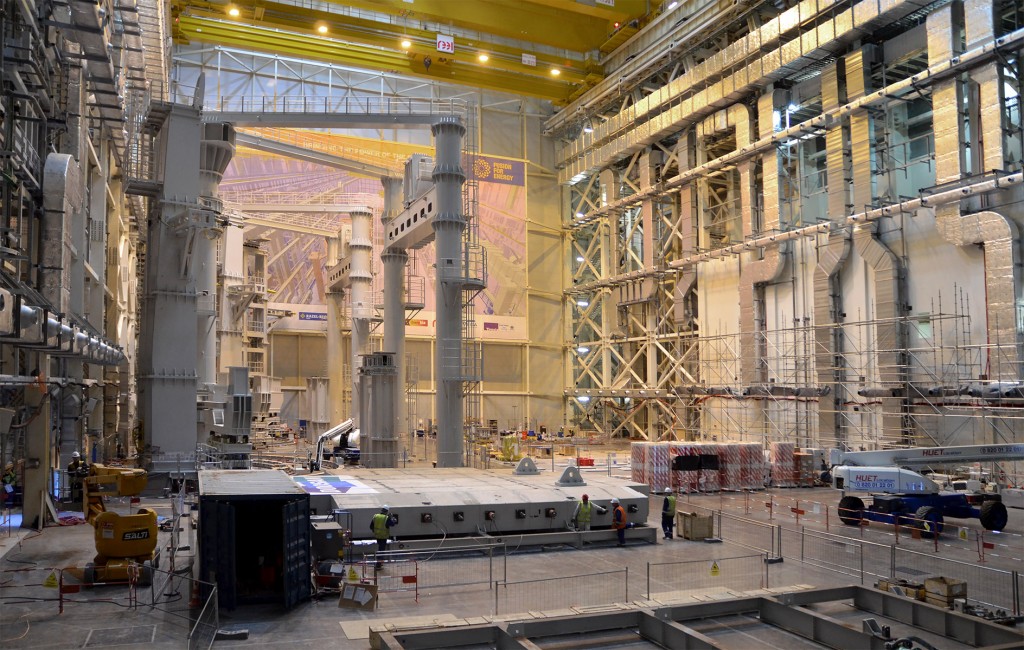
Loads prepared
2019-06-12 - Load tests are about to start on the twin sector sub-assembly tools (SSAT). The mock loads in the foreground—weighing 350 tonnes each—will be installed on the tool "wings" to measure their capacity to rotate inwards and adjust to within millimetre tolerances.
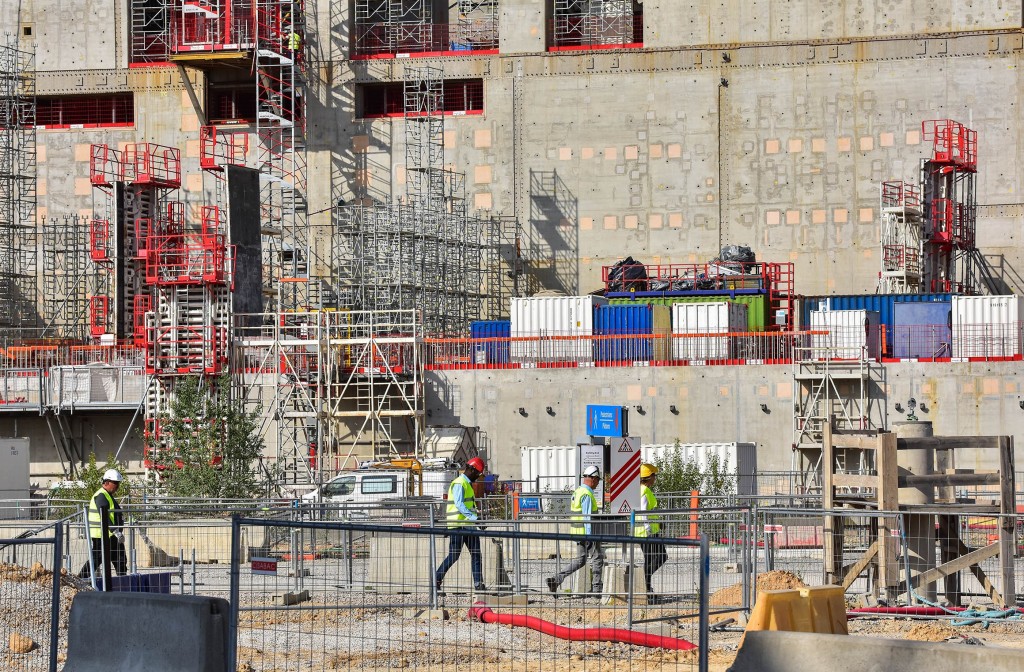
Massive concrete structure
2019-06-12 - In the five years since the completion of the Tokamak Complex foundations, the Tokamak Building has risen seven levels. Work is about to start on the metal frame that will complete the structure.

Loads prepared
2019-06-12 - Load tests are about to start on the twin sector sub-assembly tools (SSAT). The mock loads in the foreground—weighing 350 tonnes each—will be installed on the tool "wings" to measure their capacity to rotate inwards and adjust to within millimetre tolerances.

Up and over
2019-06-10 - At the Consorzio RFX facility in Padua, Italy, three ITER Members (Europe, Japan and India) have made voluntary contributions to the Neutral Beam Test Facility. In this image, for example, the high voltage bushing (top) has been procured by Japan, while the MITICA vacuum vessel (bottom) has been procured by Europe.
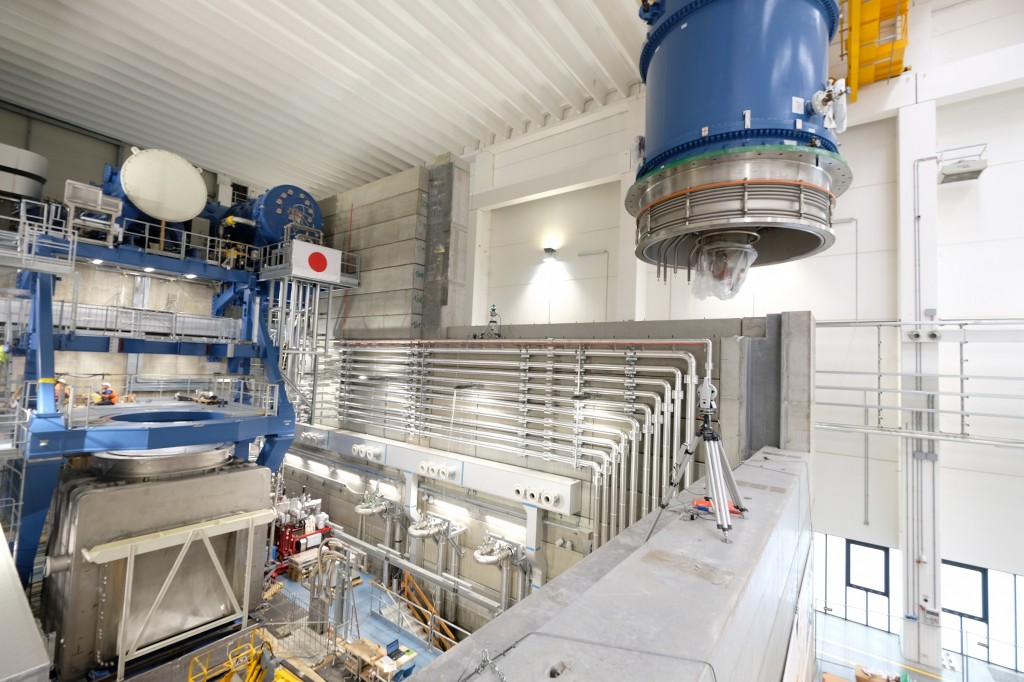
MITICA assembly advancing
2019-06-09 - The 50-tonne high voltage bushing is installed in June on the MITICA vacuum vessel. The bushing acts like a feedthrough between the transmission line and the injector.

Site services building: all equipment installed
2019-05-27 - Demineralized water, chilled air, cooling water, compressed air—these industrial services will be distributed throughout the plant from the Site Services Building. All equipment has been installed and will be maintained in a state of readiness for the first commissioning activities.
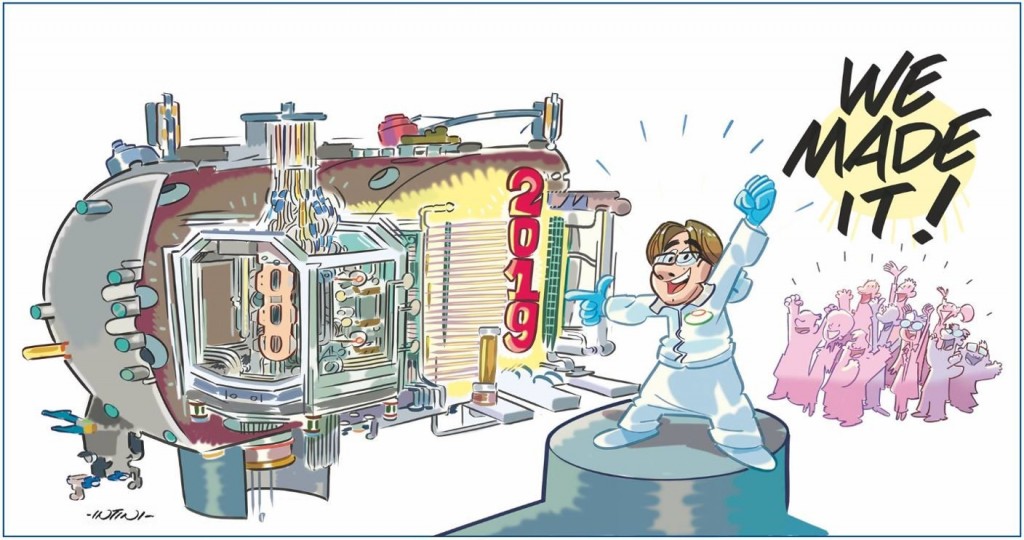
SPIDER's first beam!
2019-05-24 - One year after its inauguration, the SPIDER testbed achieves its first low-power beam. (Cartoon by Stefano Intini)
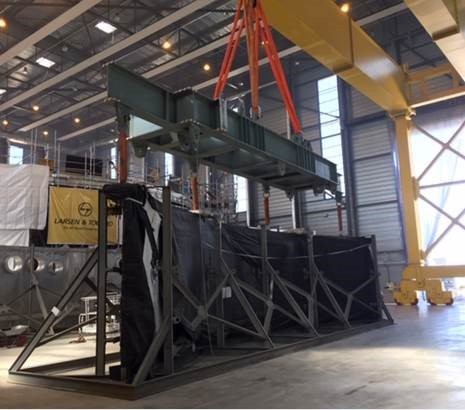
Welcome: upper cylinder segments
2019-05-24 - The first upper cylinder segments (tier one) have arrived in the on-site workshop. They were fabricated by Larsen & Toubro in Hazira, India, and shipped by the Indian Domestic Agency.
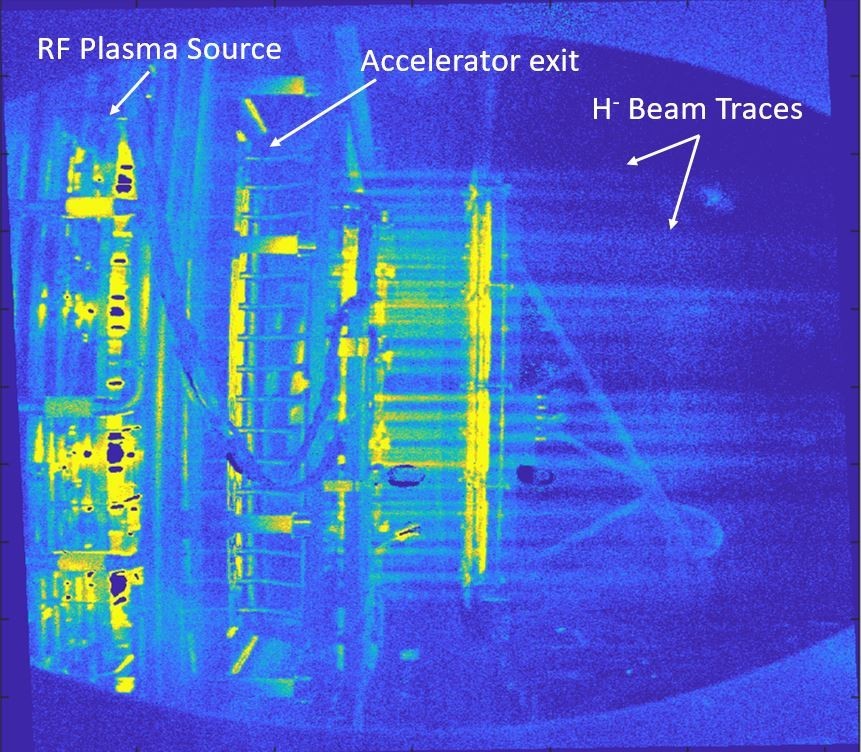
SPIDER: A beam for its first birthday
2019-05-24 - One year ago, on 11 June 2018, the world's largest negative ion source was inaugurated at the ITER Neutral Beam Test Facility with the ignition of a brief plasma in the ion source. In the twelve months of experimentation since, scientists at SPIDER have been stepping up the testbed's power in increments, integrating additional components, and adjusting the complex system of controls. Efforts were rewarded on 24 May 2019 with the first negative hydrogen ion beam.
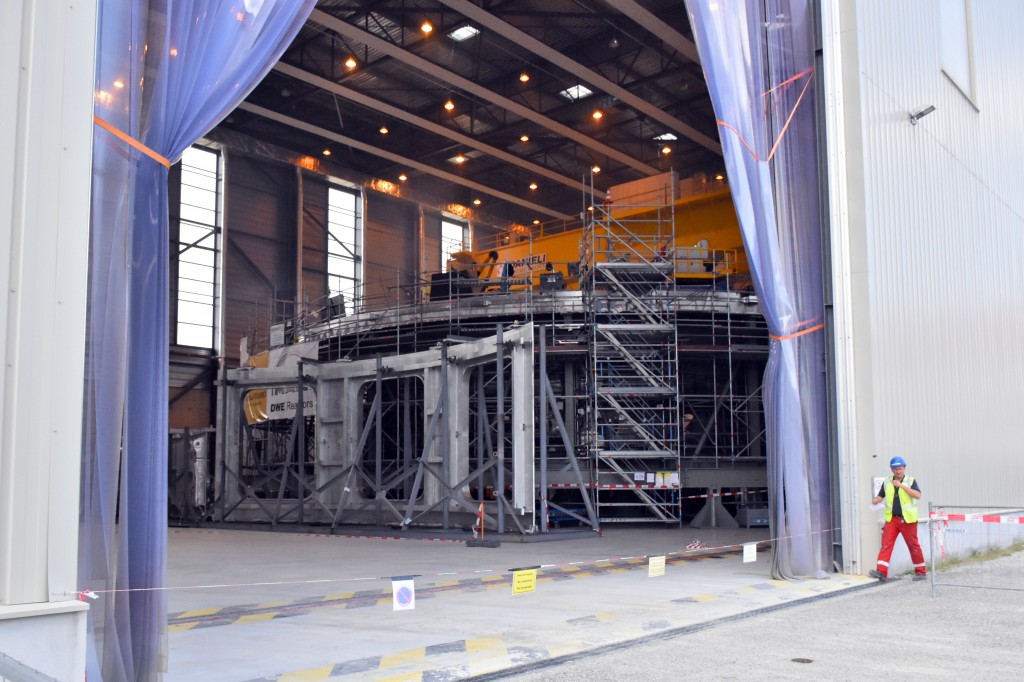
Unwrapping the new arrivals
2019-05-23 - Through the open doors of the workshop, we see the first unwrapped segment of the upper cylinder (tier one). In the background is the cryostat base.
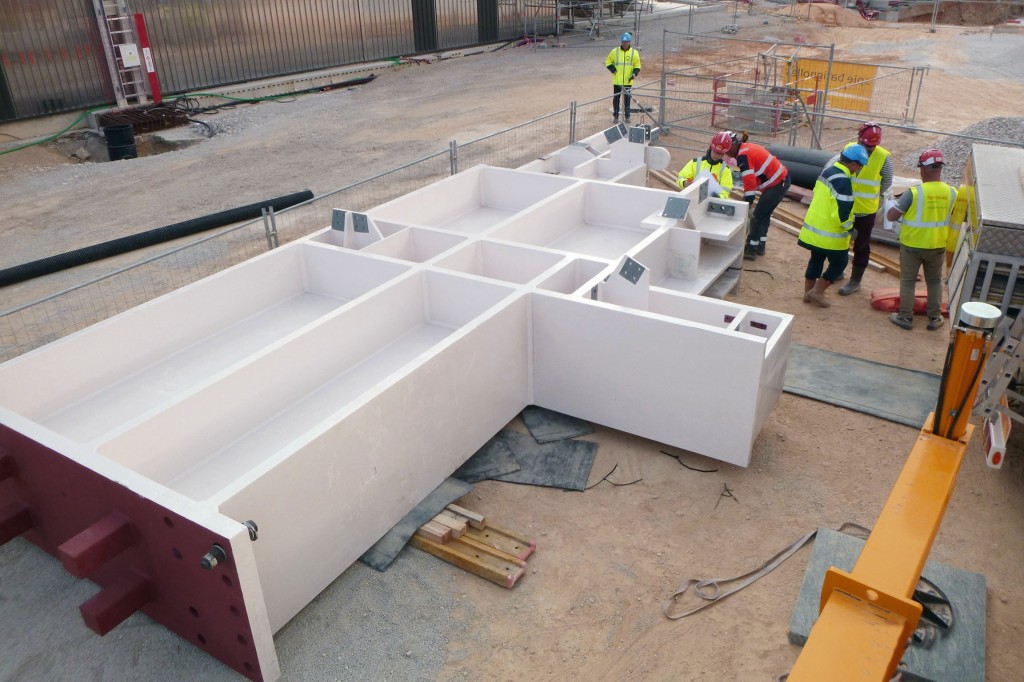
Crane hall columns
2019-05-20 - The steel pillars for the crane hall are beginning to arrive on site. Pictured is the lower segment of one pillar, which will be installed directly on the Tokamak Building.
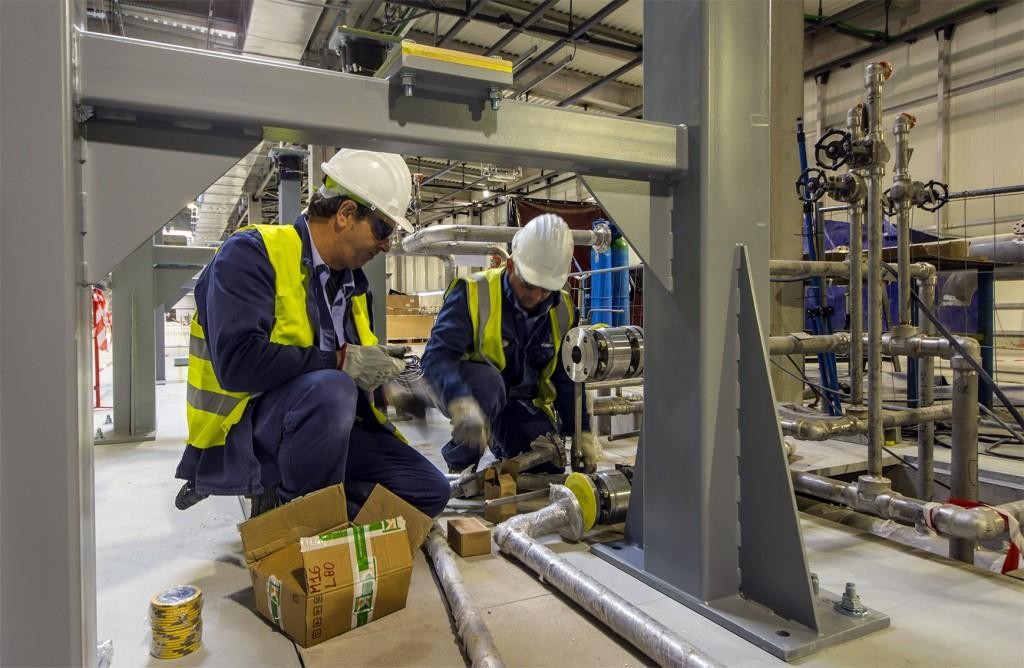
Busbar support
2019-05-20 - Inside the buildings, workers are installing supports for Russian-procured busbars that will be installed to deliver DC power to the magnets. The equipment will leave the buildings over two 50-metre-long bridges.

Equipment is arriving
2019-05-20 - Now that the civil work on the twin buildings is nearly completed, the installation of equipment can begin. Equipment is expected from China, Korea, Russia and India. Follow all installation and commissioning news on the assembly pages of the ITER website (https://www.iter.org/construction/assembly).

Magnet Power Conversion buildings: equipment is arriving
2019-05-20 - Now that the civil work on the twin Magnet Power Conversion buildings is nearly completed, the installation of equipment can begin. Equipment is expected from China, Korea and Russia.
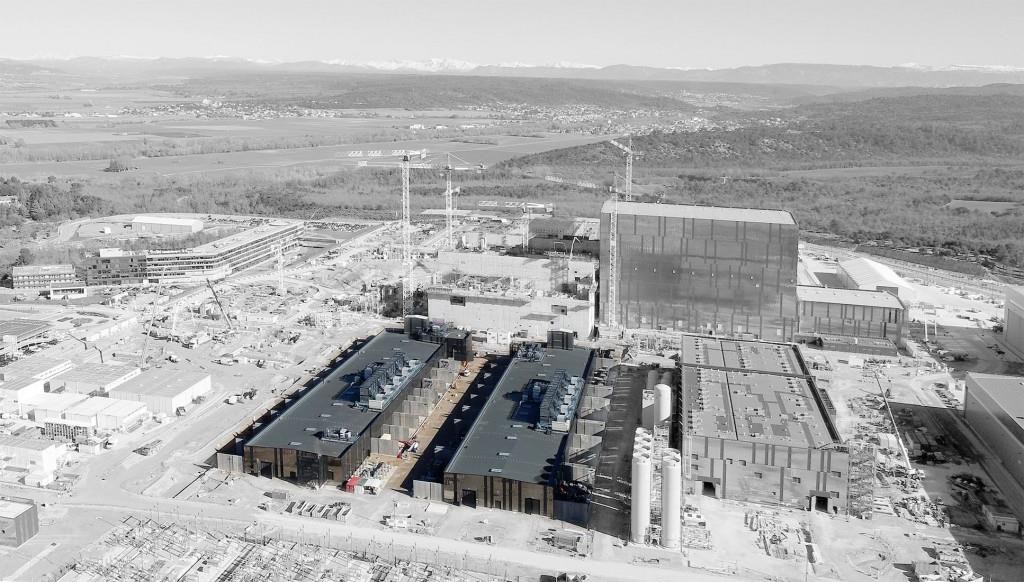
Two stand out
2019-05-20 - The twin Magnet Power Conversion buildings are highlighted in this image of the ITER worksite.

Transformer Street
2019-05-20 - Of the 32 transformers needed for First Plasma, 30 have already been delivered to ITER from China and Korea. In this photo, Chinese transformers are being installed in their dedicated bays outside of one of the twin buildings.

Transformer Street
2019-05-20 - Out of a total of 32 transformers, 30 have already been delivered to ITER from China and Korea. In this photo, Chinese transformers are being installed in their dedicated bays outside of one of the twin Magnet Power Conversion buildings.

Into the concrete maze
2019-05-18 - Open Doors Day visitors are taken to look into the Tokamak Pit through some of the port cell openings at L1 level. The openings were quickly sealed off again after the event, so that painting can continue.
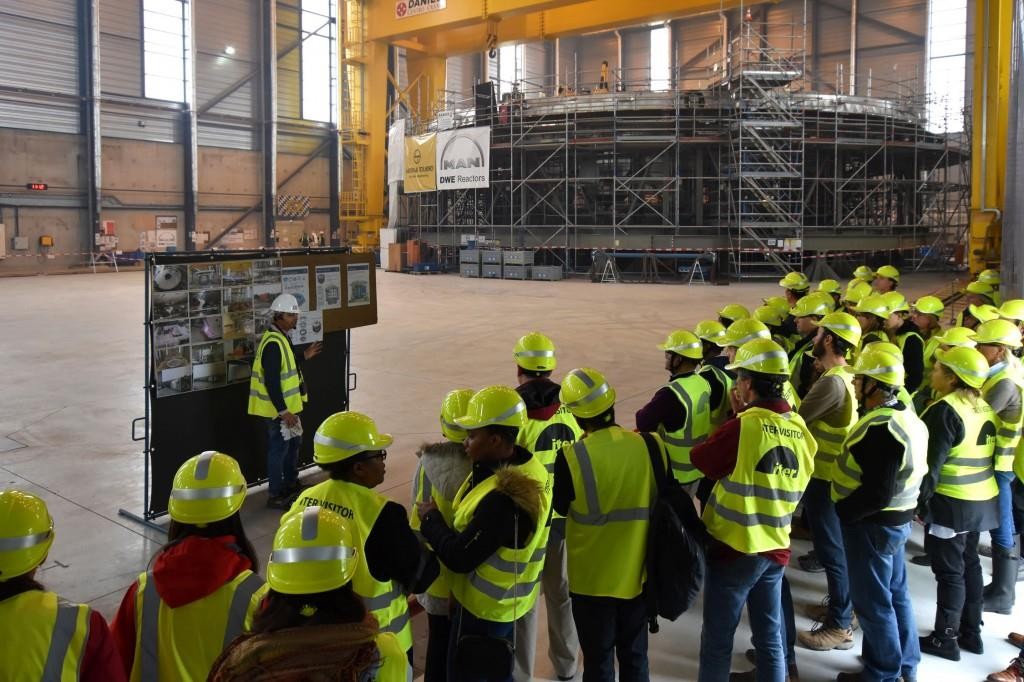
How to make a giant thermos
2019-05-18 - The Cryostat Workshop was part of the site tour offered to participants of the 14th edition of the ITER Open Doors Day event. Saroj Kumar Jha, ITER Project Associate from India, provides explanations to the first group of visitors.

Upper cylinder: settling into its new home
2019-05-18 - Contractors continue to apply plastic to the cocoon of the lower cylinder. Already, though, it is well protected from the weather.
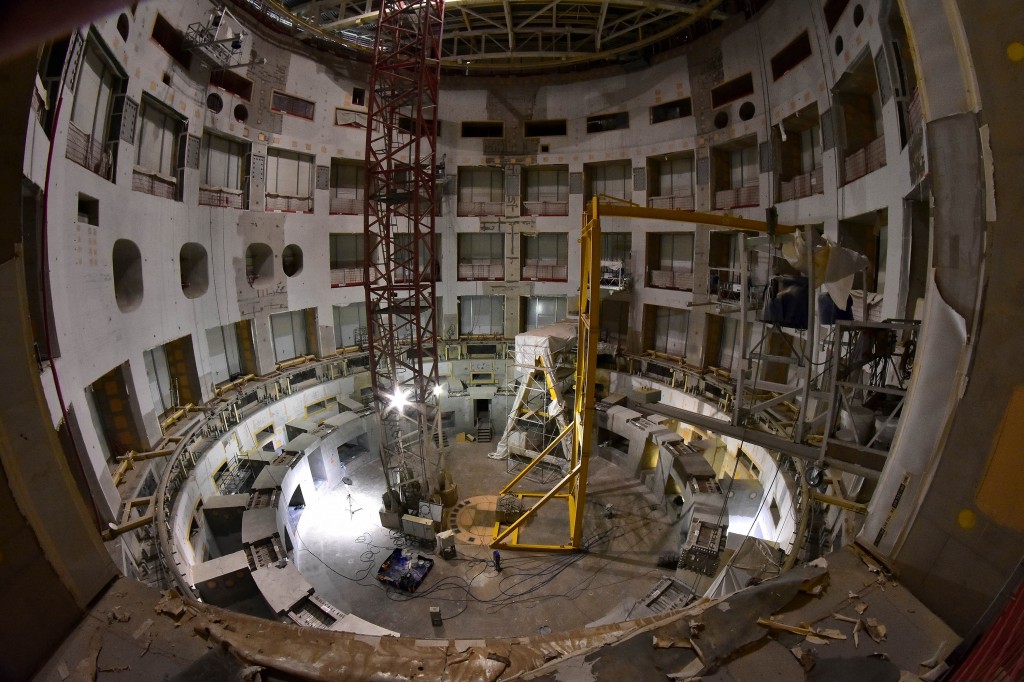
What they saw
2019-05-18 - Members of the public were treated to this view of the Tokamak Pit on 18 May. Openings are sealed off and a first coat of primer has been applied after sandblasting and other preparatory activities.
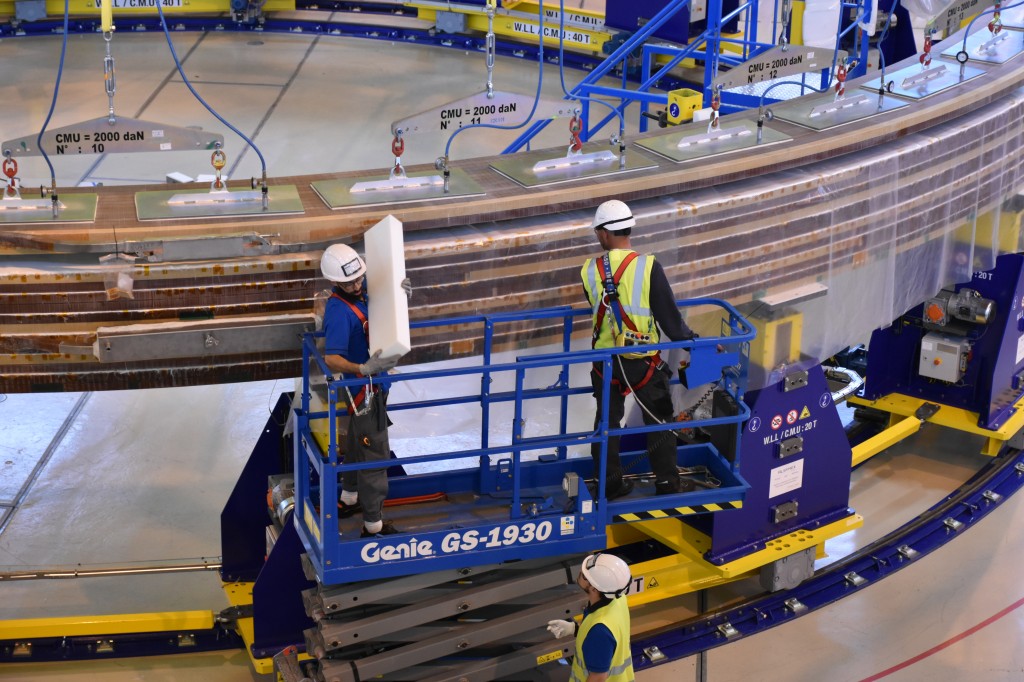
One atop the other
2019-05-16 - Stacking is proceeding well for the double pancakes of poloidal field coil #5 (PF5). The teams must then connect the pancakes to ensure the flow of cryogenic helium—both between the double layers of each pancake (an "intra pancake joint"), and between each double pancakes (an "inter pancake joint").
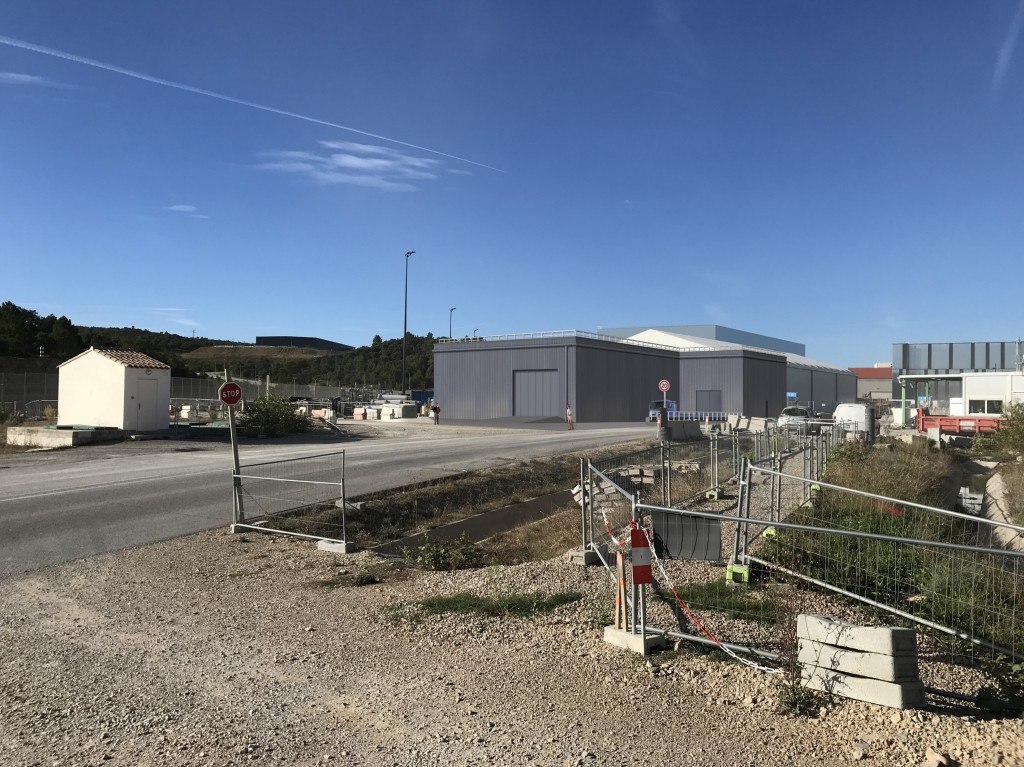
Architect's rendition
2019-05-14 - An architect's rendition of the Tokamak Assembly Preparatory Building, which will be erected before summer 2020 on the northeastern corner of the ITER construction platform.
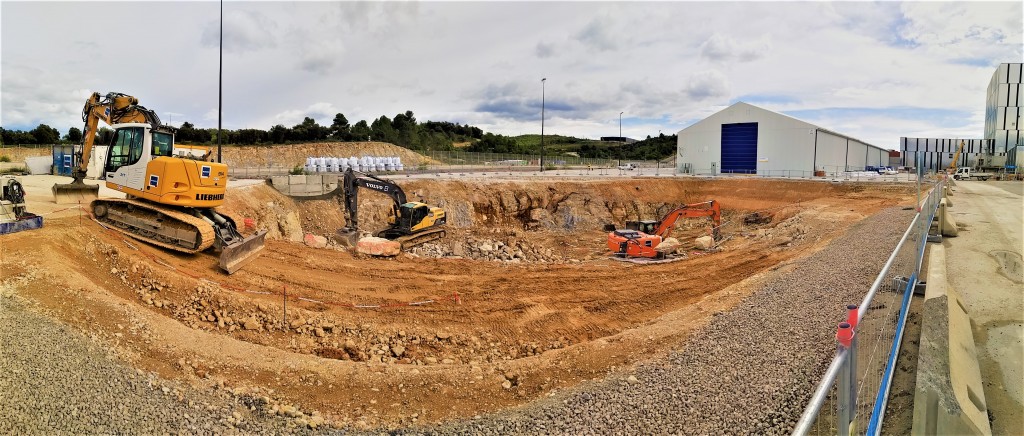
New building, two purposes
2019-05-14 - The Tokamak Assembly Preparatory Building will provide the space and systems to receive, transport, test, store, pre-assemble and export berylliated components. From 2020 to 2023—before those components arrive—the building will serve as part laboratory/part training facility for first-phase machine assembly activities. Excavation is underway on site.

Generation
2019-05-11 - What is experimental today could be the daily reality of tomorrow. For these two youngsters sitting on a rock in front of the spectacular outline of the ITER Tokamak Complex and Assembly Hall, fusion-generated electricity will be part of everyday life.
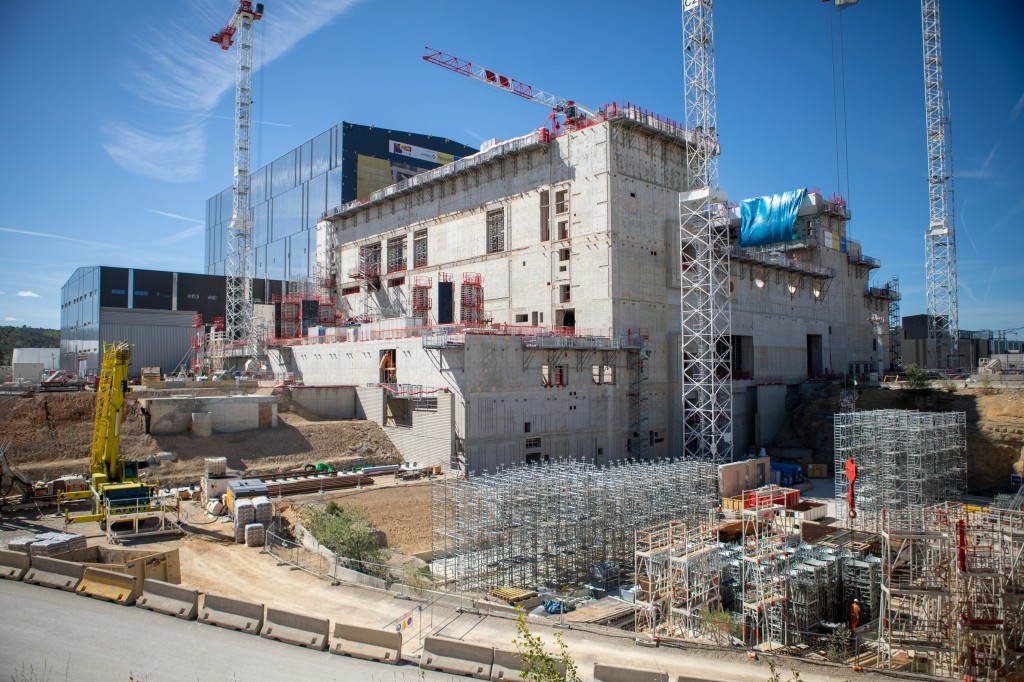
Jewel box
2019-05-10 - The concrete "box" for the machine is ready, and the roof structure will be installed by the end of the year. © Les Nouveaux Médias/SNC ENGAGE
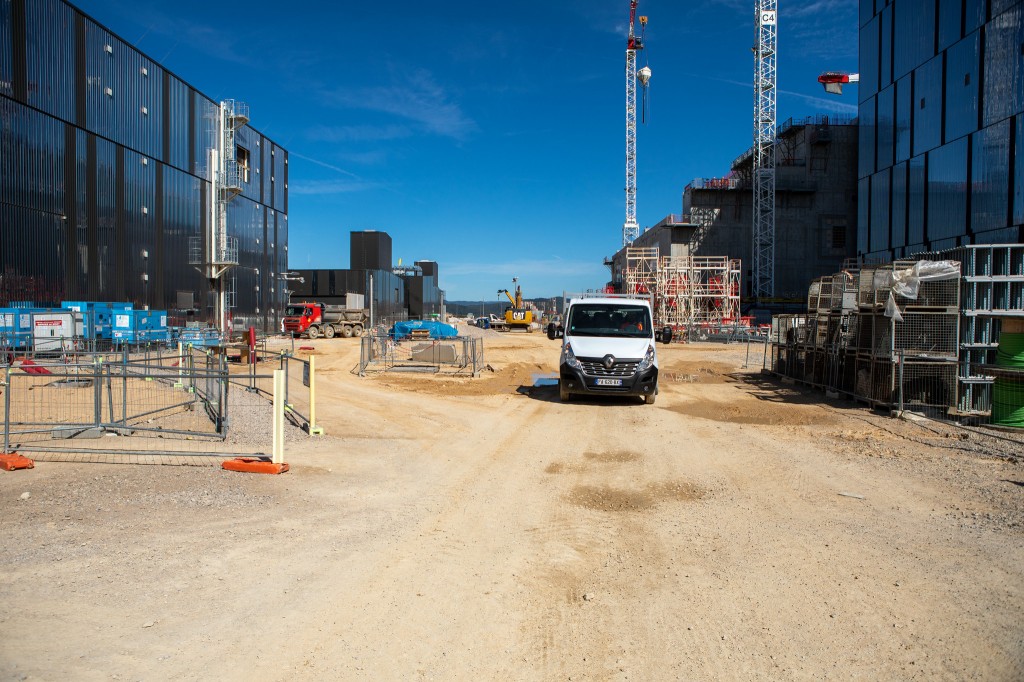
Across the road
2019-05-10 - Cryogens produced in the cryoplant (left) will travel by overhead bridge to the Tokamak Complex (concrete building at right).
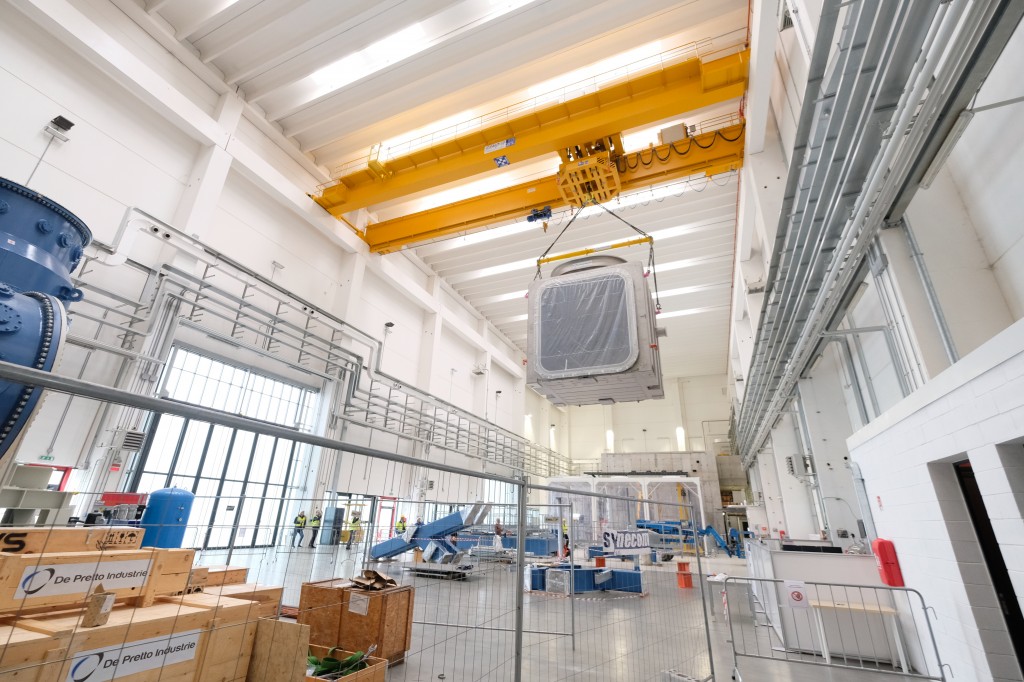
Container for the MITICA beam source
2019-05-07 - The vacuum vessel was installed at the ITER Neutral Beam Test Facility in early May. The full vacuum vessel for MITICA will weigh 67 tonnes.

Measuring the cryostat during assembly
2019-05-06 - ITER's Lionel Poncet (right) and Giacomo Calchi of the European Domestic Agency Fusion for Energy (F4E) perform a surface scan of a port opening inside the cryostat's lower cylinder. The ITER Organization and F4E enjoy an efficient resource-sharing collaboration in the area of metrology.

Looks like a balcony
2019-05-06 - More than 80 metres long and 3.2 metres wide at the top, the corbel is a massive balcony-like structure. It is designed to carry the weight of the crane hall's structure (1,800 tonnes) and to withstand considerable vertical and lateral forces transmitted by the movements of the travelling cranes.

Preparing for the crane hall
2019-05-06 - At the top of the "corbel," the anchoring system for each steel pillar is designed to withstand vertical compression loads in excess of 150 tonnes and a ''moment'' (lateral acceleration) of 220 tonnes per metre.

An unusual angle
2019-05-02 - The tallest concrete of the Tokamak Building offers a spectacular and unusual viewpoint for works underway around the central Tokamak Pit.

A "corbel" for the crane hall
2019-05-02 - This 80-metre long, 3.2-metre-wide protruding element (painted in white) is a "corbel" that will support steel pillars for the future crane hall.

Finalizing the cryostat base
2019-04-30 - Final machining works are underway on the cryostat base. Pictured are the interface holes that have been machined in the base for one toroidal field gravity support.
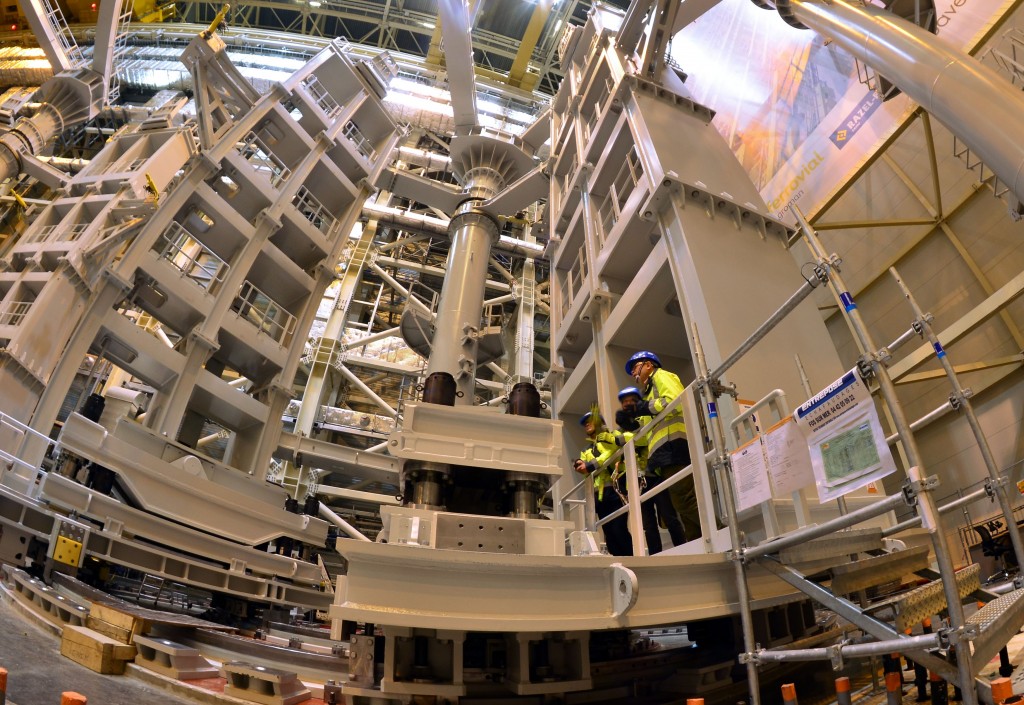
Mechanical testing underway on SSAT tools
2019-04-25 - With both sector sub-assembly tools (SSATs) now erected, mechanical load testing can start. In April, teams begin testing the movement of upper alignment units. Load testing is schedule for June.

Mechanical testing underway on SSAT tools
2019-04-25 - With both sector sub-assembly tools (SSATs) now erected, mechanical load testing can start. In April, teams begin testing the movement of upper alignment units. Load testing is schedule for June.
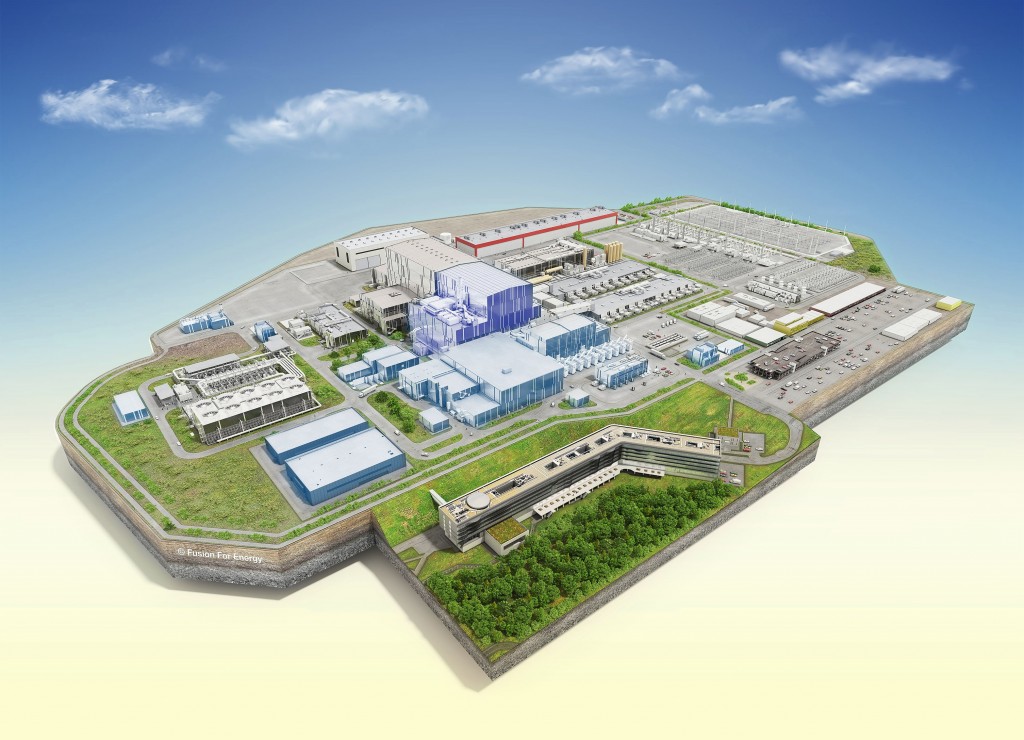
State of play on the worksite
2019-04-15 - The ITER worksite. In steel grey: the completed buildings; in purple: buildings in progress; in blue: future buildings. © Fusion for Energy 2019

Coordination for success
2019-04-15 - Anil Kumar Bhardwaj, Cryostat Group Leader, and Patrick Petit, In-Cryostat Assembly Section Leader, watch over the transfer operation. The 12-metre tall, nearly 30-metre-wide component is one of the largest "pieces" of the ITER machine. It will be stored on the construction platform until required in the assembly sequence.

Careful now
2019-04-15 - Shims are adjusted under every "foot" before the assembly platform is lowered to the ground and the SPMTs are removed. With the successful transfer of the lower cylinder out of the Cryostat Workshop space has been created for the assembly of a new frame to receive the elements of the cryostat upper cylinder, which ship this month from India and are expected in May on site.
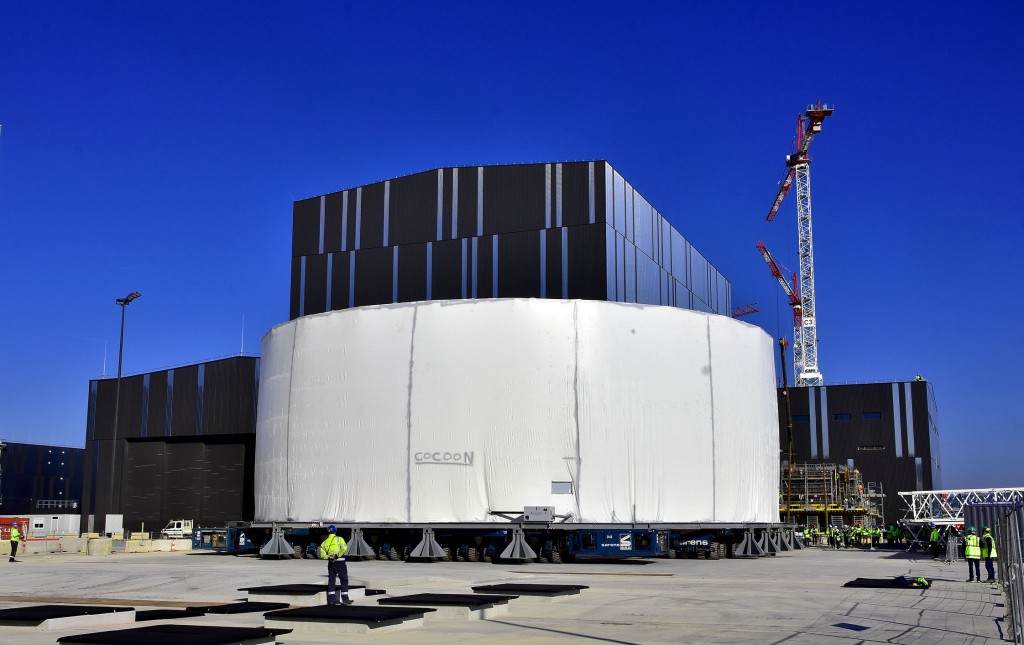
Just a short distance to travel
2019-04-15 - The 375-tonne component left the building on its assembly platform, propelled by four multi-axle SPMTs (self propelled modular transporters). Everything went smoothly.
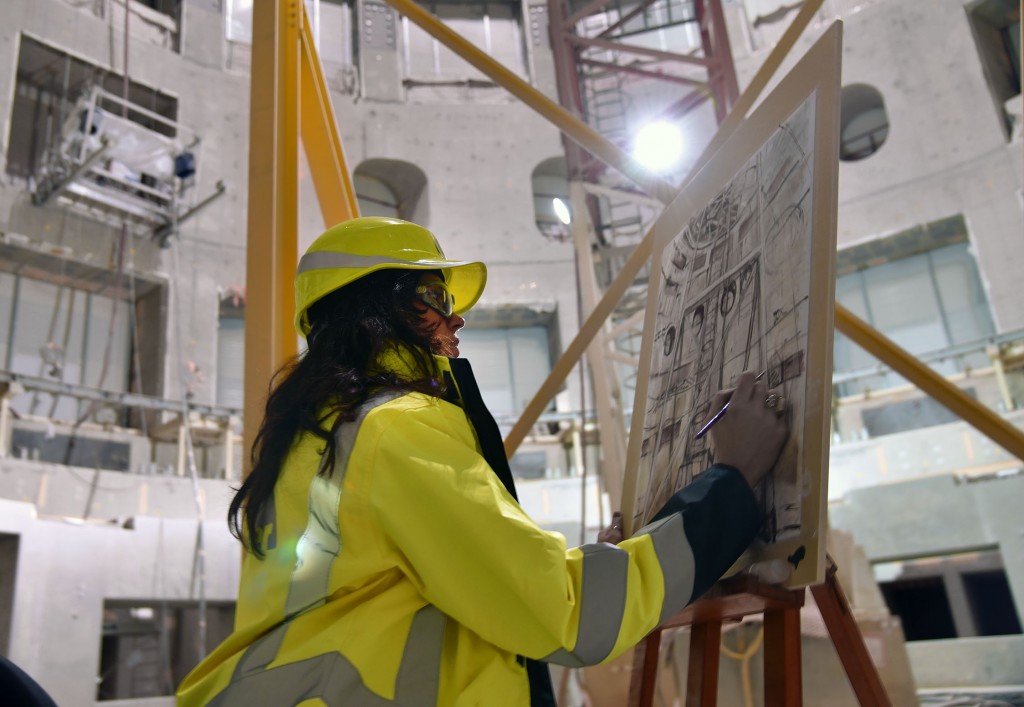
Art in the Tokamak Pit
2019-04-15 - Italian artist Michela Meneguzzi was at ITER in April for the celebration of "500 Years of Innovation: From Da Vinci to ITER." In a few hours, she was able to capture and render the colosseum-like ambiance of the Tokamak Pit in the style of Leonardo da Vinci.

Like clockwork
2019-04-15 - Participating in the transfer operation were members of the ITER Organization construction teams, ITER logistics provider DAHER, transportation specialist Sarens, ITER India and its contractor Larsen & Toubro, the European Domestic Agency and its contractor ENGAGE, and MOMENTUM—the ITER Construction Management-as-Agent contractor.
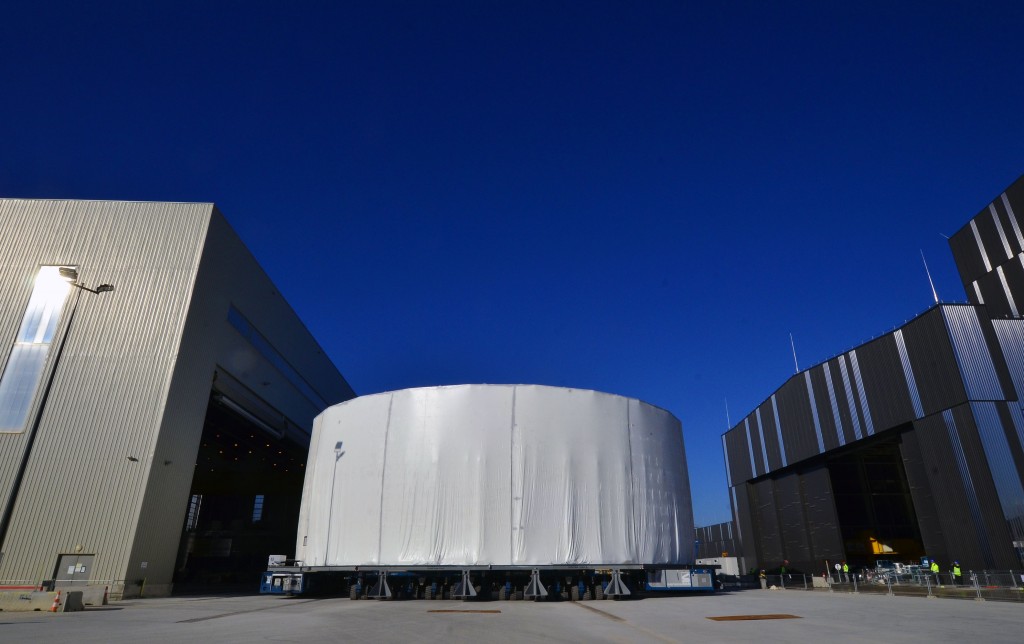
Lower cylinder transfer
2019-04-15 - On 15 April, the lower cylinder is moved out of the Cryostat Workshop to exterior storage area 73 (out of the picture frame, further to the left), where it will remain until it is time to enter the Cleaning Facility (right) for integration into the ITER machine pit.

192 wheels
2019-04-12 - A few days before the transfer, transporters were delivered and assembled. Their configuration under the 375-tonne component has been carefully planned.
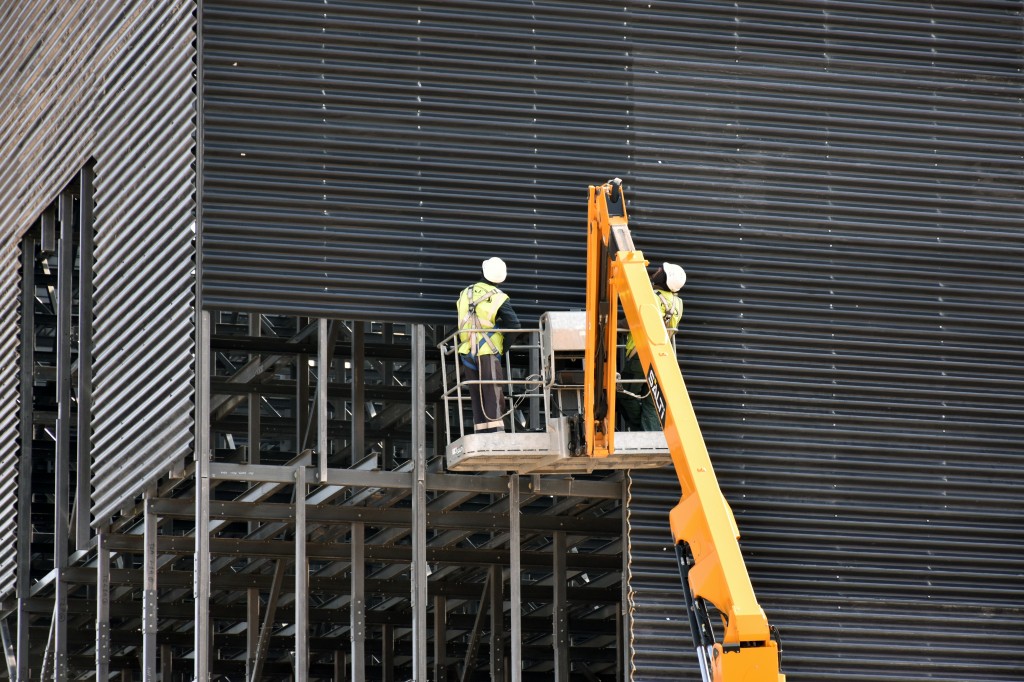
Cladding underway
2019-04-12 - The cladding of the cooling water tower is progressing. The lower sides of the structure will remain open to facilitate air flow induced by large fans on the roof. The resulting draft will cool down the water falling through thousands of corrugated plastic sheets inside the tower.
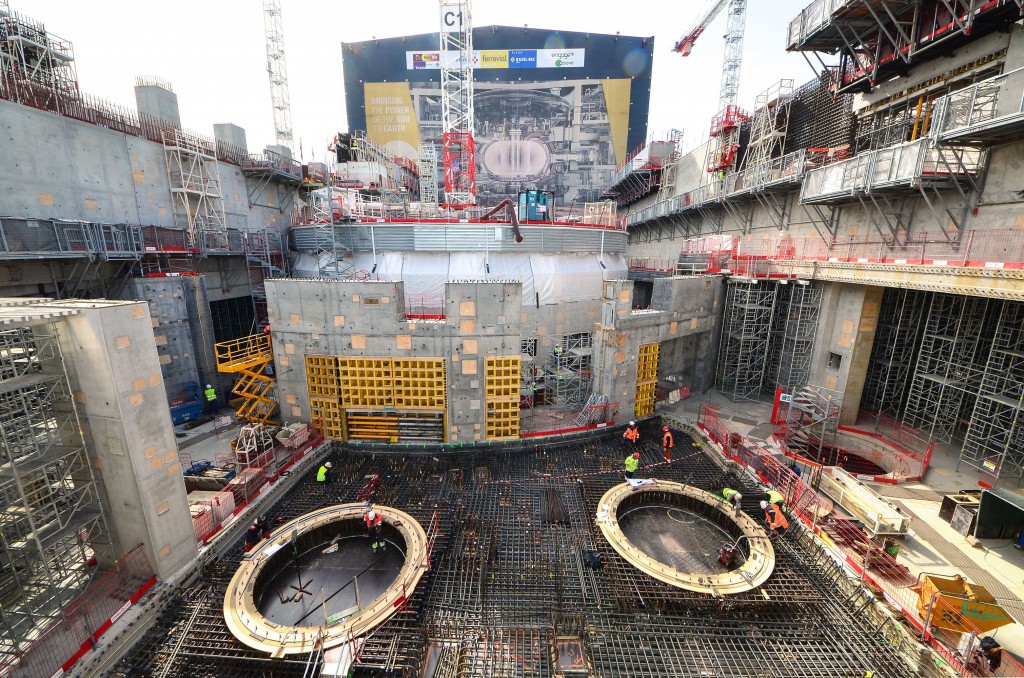
Giant power outlets for a giant appliance
2019-04-08 - These circular openings in the rebar at L3 level of the Tokamak Building are more than 3 metres in diameter each. They will allow the high-voltage bushings of the neutral beam system to deliver electrical power, cooling, and other services such as diagnostics to the injectors below.
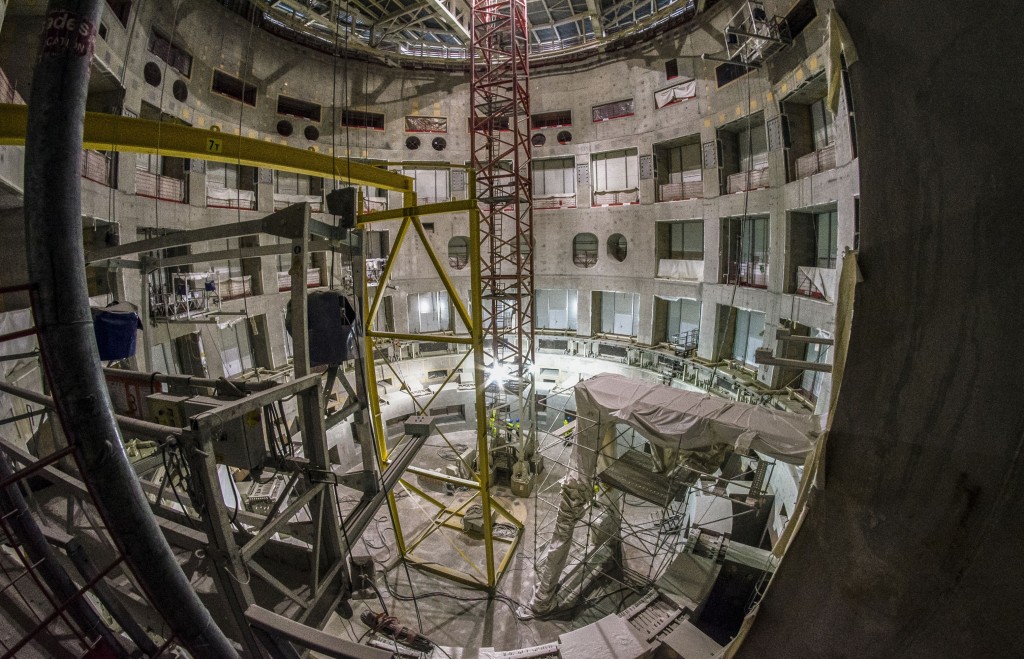
Painting to start soon
2019-04-05 - 30 tonnes of abrasive sand projected with high pressure on the inside wall of the Tokamak Pit have created the rough surface that optimizes nuclear paint adherence. The application of decontaminable "nuclear paint" will begin as soon as hot air blowers have brought the vast volume of the Pit (25,000 m³) to the required temperature of ~20 °C.
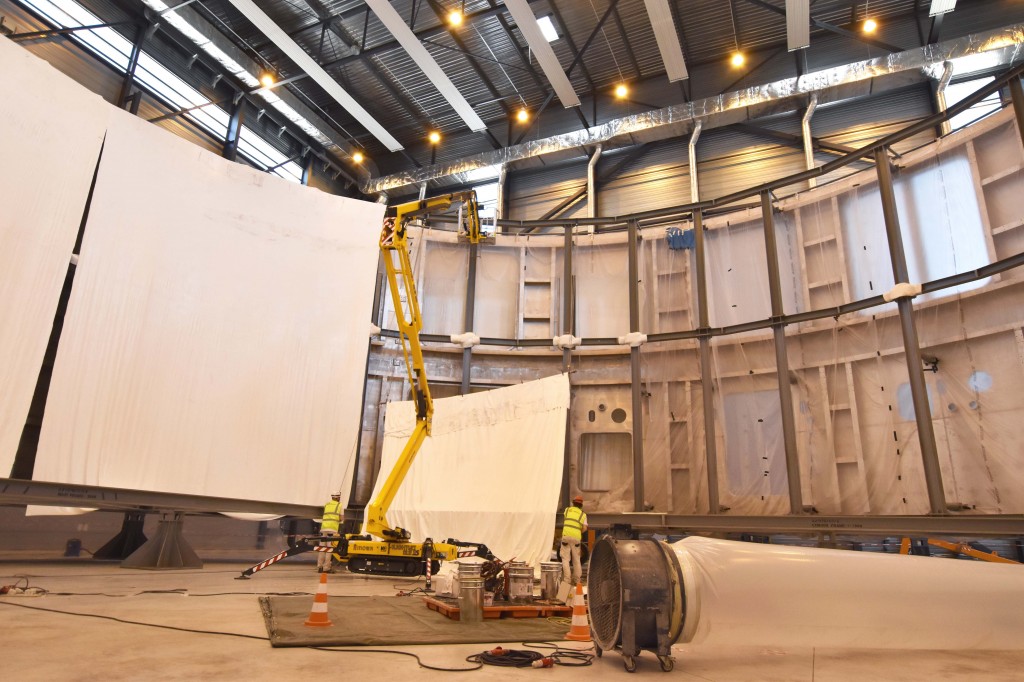
"Mothballing"
2019-04-05 - Layers of synthetic thermoplastic material are "melted" together through the application of sprayable glue. The technique, called "mothballing," is designed and implemented by Cocoon Holland, a specialist in weatherproof storage solutions.

A cocoon for the cryostat
2019-04-02 - An all-weather protection system is being installed around the lower cylinder, which will move out to storage on the platform in April.
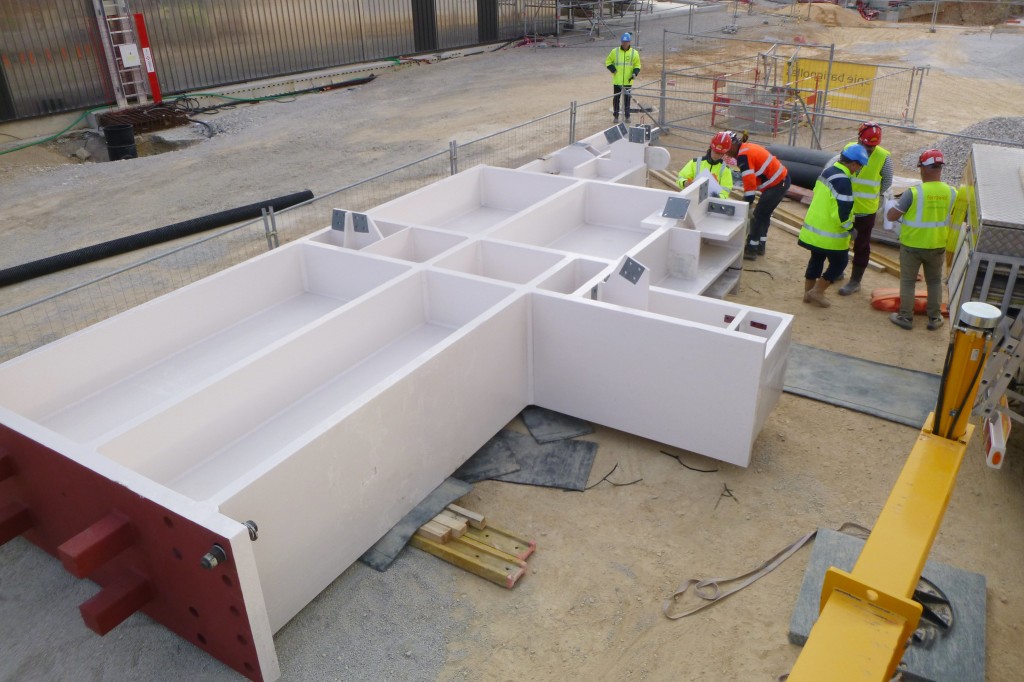
First pillars for crane hall
2019-04-02 - The first metal pillars for the upper floors of the Tokamak Building (the crane hall) have arrived on site, shipped by European supplier Martifer. Photo: F4E
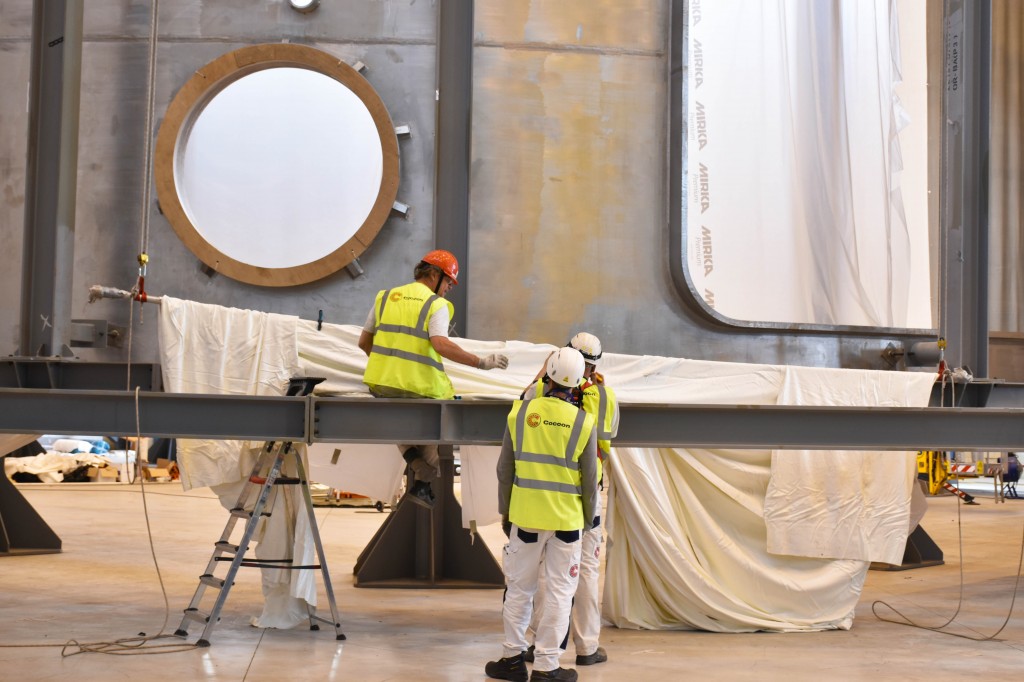
Controlled environment
2019-04-02 - Inside of the cocoon, the enclosed air will be kept constantly circulating and humidity will be maintained at a steady 38 percent—conditions that prevent the formation of corrosion or mould.
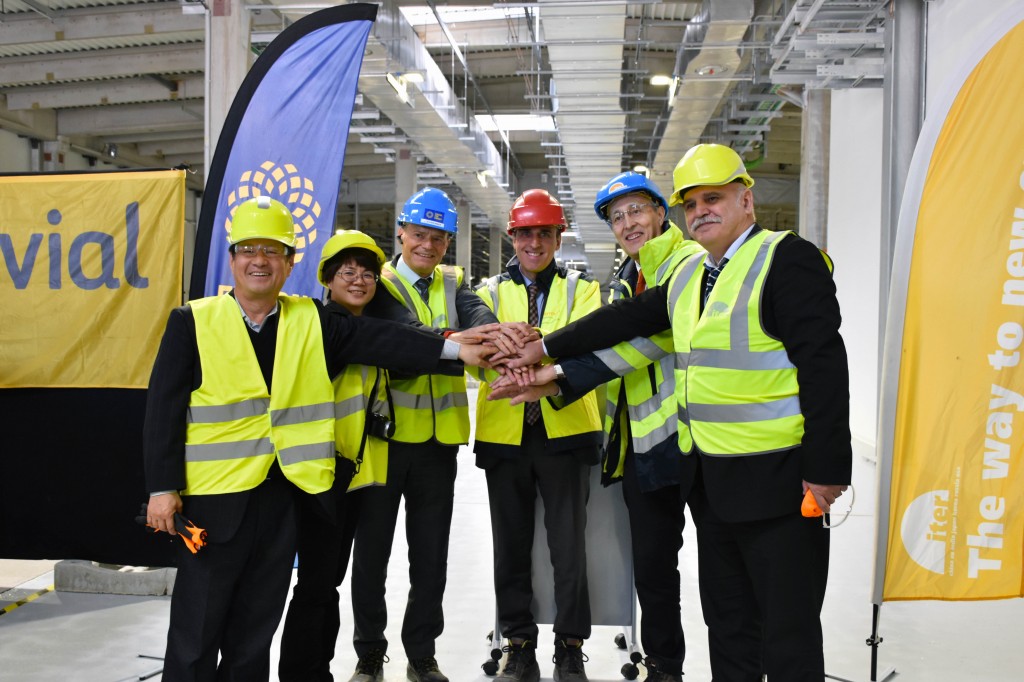
Three plant buildings handed over
2019-03-29 - The European Domestic Agency Fusion for Energy hands over three completed buildings to the ITER Organization in March: the twin Magnet Power Conversion buildings and a smaller facility for reactive power compensation. Equipment installation can now begin.

Late March 2019
2019-03-29 - Looking south over the ITER site from one of the Tokamak Complex cranes.

Pillars to rise
2019-03-29 - By summer, the first metal pillars will be rising for the Tokamak Crane Hall. The first massive machine component—the cryostat base—is schedule for installation in March 2020.
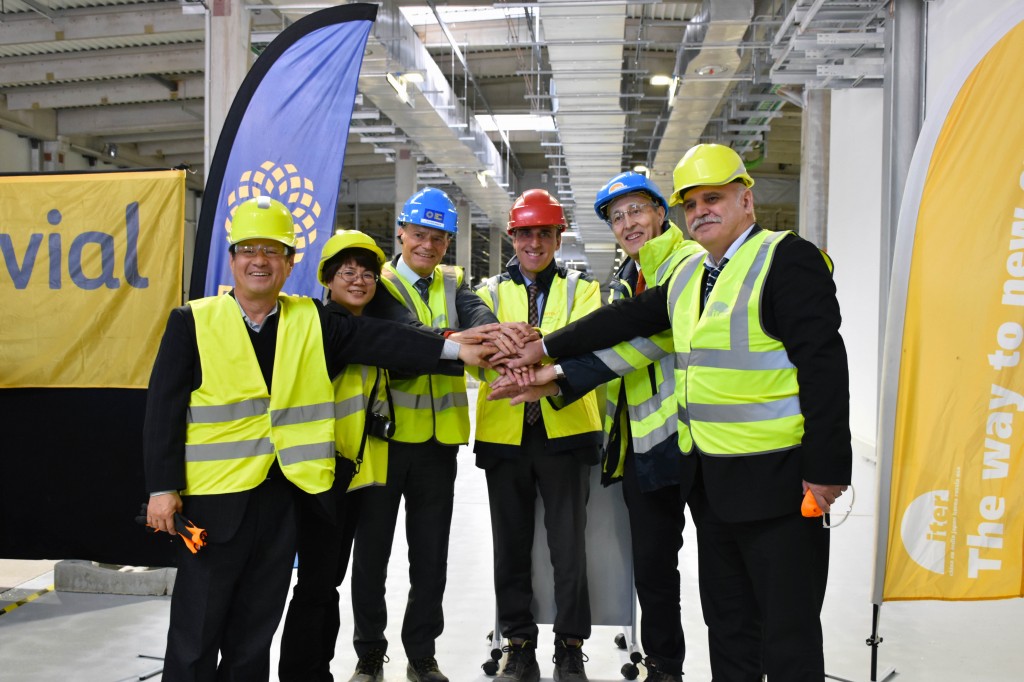
Three plant buildings handed over
2019-03-29 - The European Domestic Agency Fusion for Energy hands over three completed buildings to the ITER Organization in March: the twin Magnet Power Conversion buildings and a smaller facility for reactive power compensation. Equipment installation can now begin.

Late March 2019
2019-03-29 - Looking south over the ITER site from one of the Tokamak Complex cranes.
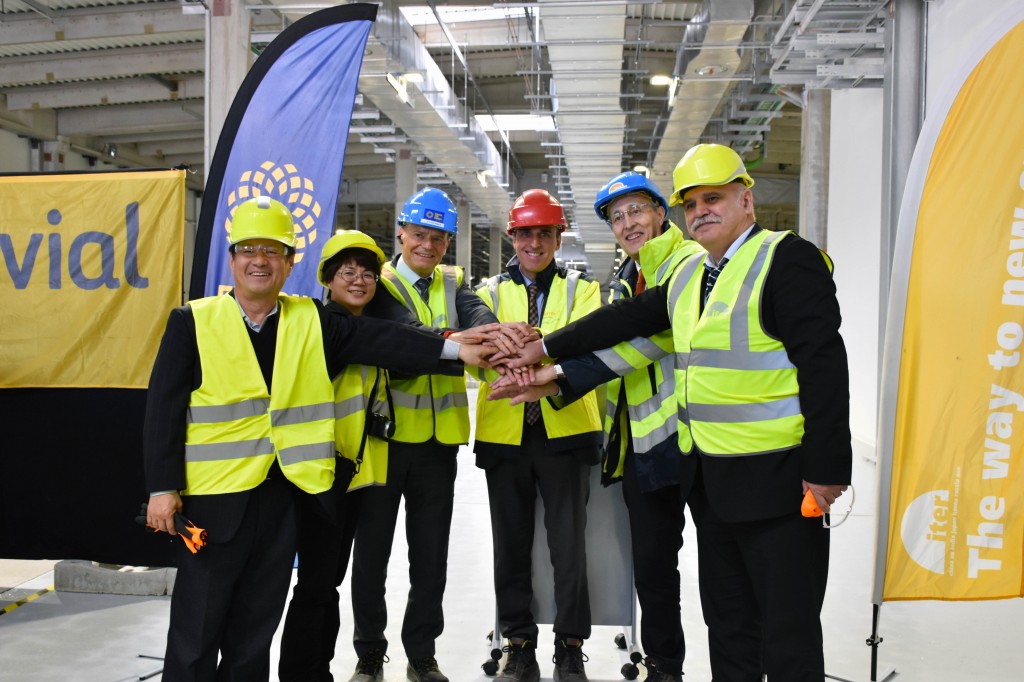
Three plant buildings handed over
2019-03-29 - The European Domestic Agency Fusion for Energy hands over three completed buildings to the ITER Organization in March: the twin Magnet Power Conversion buildings and a smaller facility for reactive power compensation. Equipment installation can now begin.
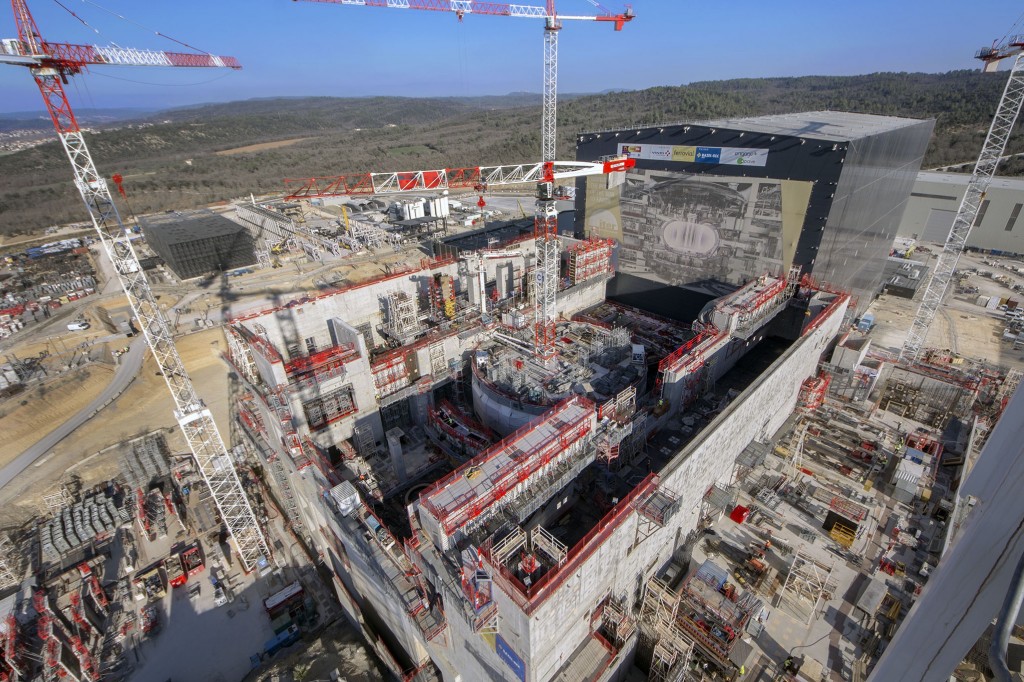
First pillar supports
2019-03-29 - European contractors are installing massive support pieces for the pillars of the Crane Hall. The first examples can be seen by visually tracing a line that extends from the wall of the Assembly Hall (right side) to the end of the Tokamak Building.
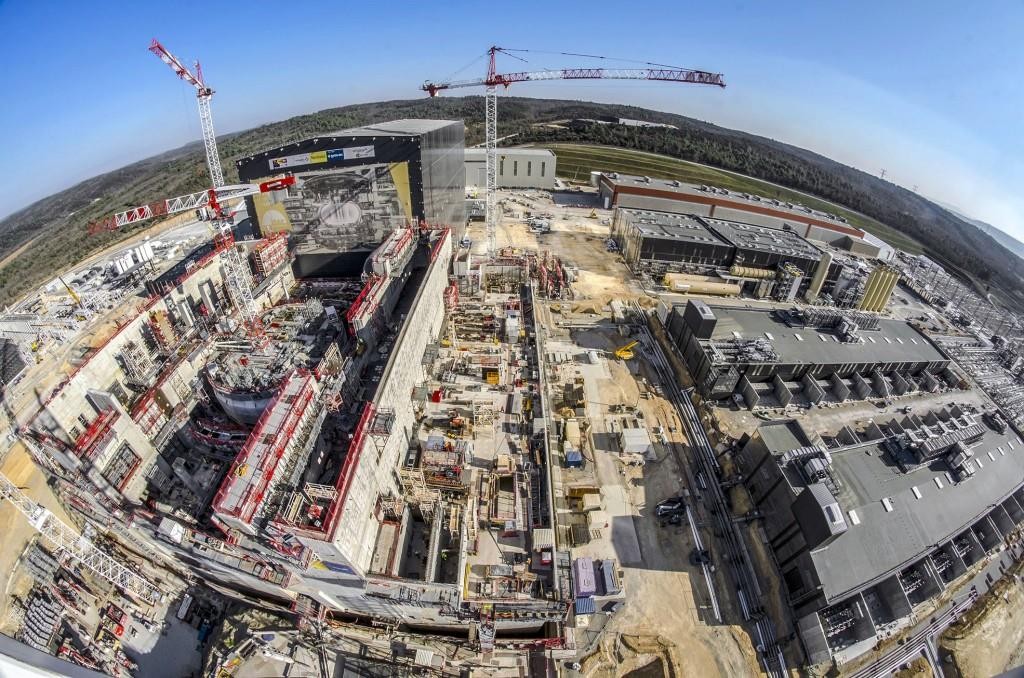
Final concrete pours
2019-03-29 - In the Tokamak Building, contractors are preparing to pour the last concrete slabs that will cover the open galleries to the left and right of the machine well.

New component at MITICA
2019-03-28 - The first part of the MITICA beam source vacuum vessel, financed by the European Domestic Agency (F4E) and manufactured by De Pretto Industrie (Italy), has been delivered to the ITER Neutral Beam Test Facility.
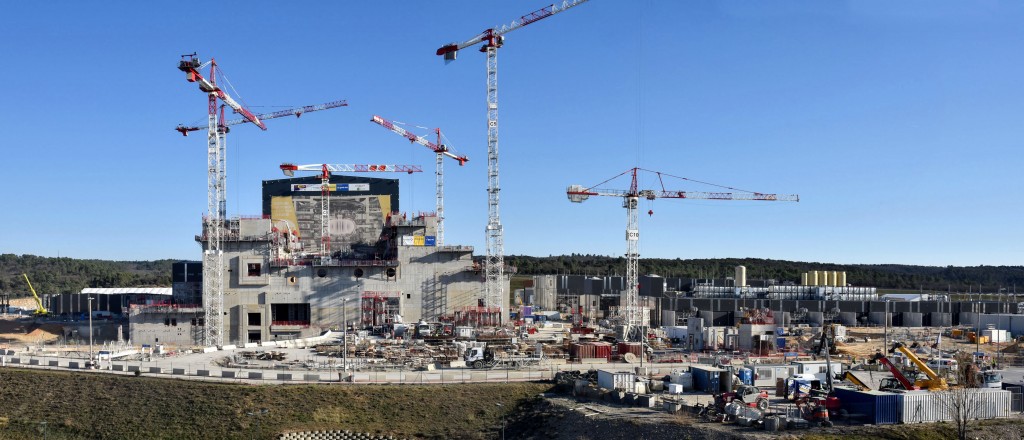
Spring on the ITER platform
2019-03-21 - The Tokamak Complex, with a cut-out in the centre for machine assembly. Large cranes will begin travelling from the Assembly Hall over the Tokamak Pit (centre) with their heavy component loads in one year—March 2020.

One last angle
2019-03-15 - The Tokamak Building has reached its maximum height ... in terms of concrete that is. The tallest corner in this image represents the last concrete level of the building that will house the ITER machine. Above that, a steel structure will enclose the area used by the overhead cranes as they deliver their component loads to the Tokamak Pit.
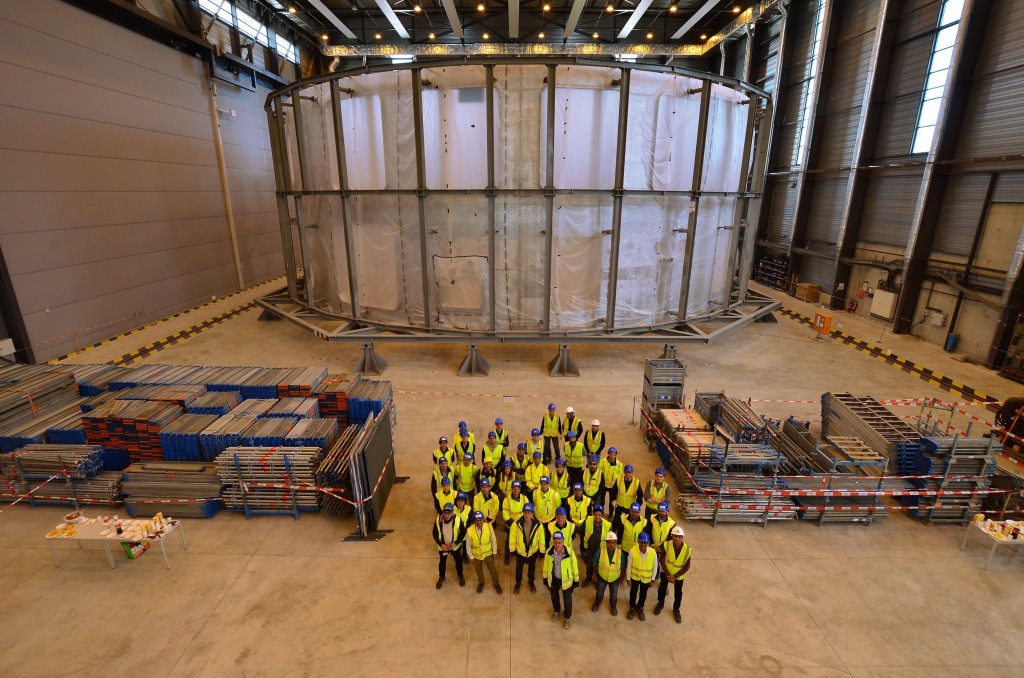
Standing tall
2019-03-14 - Representatives of the ITER Organization, which designed the cryostat and will integrate it into the machine; of the Indian Domestic Agency responsible for its procurement; of Larsen & Toubro which forged the segments; of the German company MAN Energy Solutions which performed assembly and welding gathered on 14 March to mark the completion of the lower cylinder.
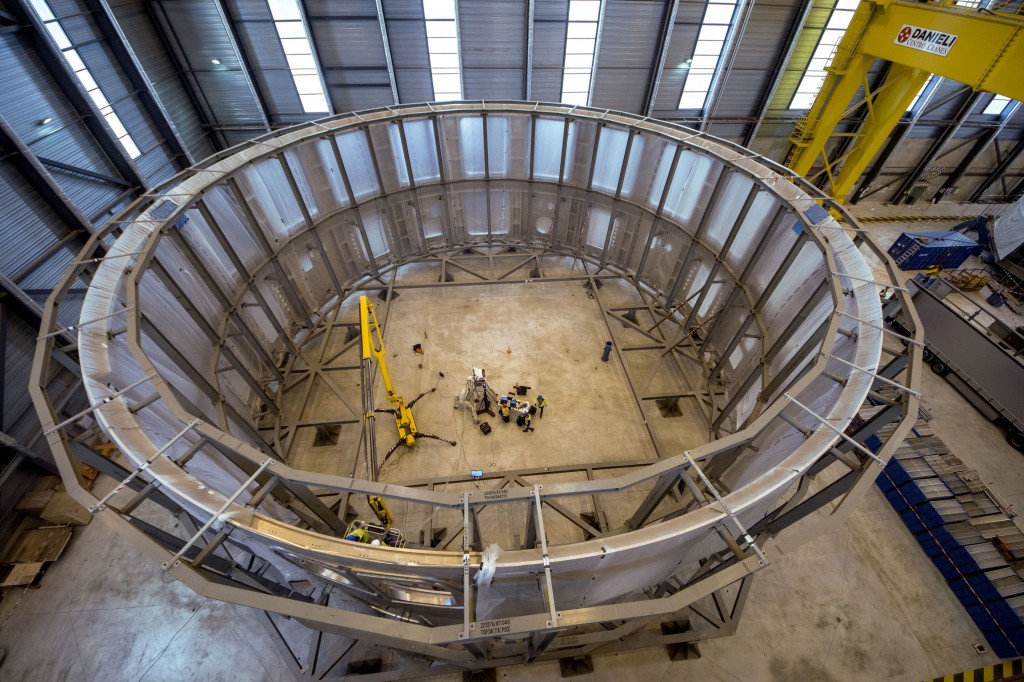
Only a veil
2019-03-14 - Scaffolding around the 10-metre-tall, 30-metre-in-diameter lower cylinder has been removed and only a veil remains. Look closely at the size of the group in the centre.

Laser mapping
2019-03-14 - The 375-tonne lower cylinder will soon be enveloped in a protective cocoon that will insulate it from dust and humidity. In the meantime, metrology specialists are using 3D laser-scanning techniques to map selected areas where the component will interface with other systems (here, a port for the neutral beam injection system). Based on the precise topography of the "as built" component, the interfaces can be reverse-engineered to fit as precisely as possible.

Windows to the machine
2019-03-14 - The openings in the cryostat correspond to openings in the vacuum vessel. They will permit auxiliary systems (heating, fuelling, cryogenics, diagnostics, vacuum ...) to reach the machine.

Work continues on cryostat base
2019-03-14 - The three parts of the base—lower sandwich structure, vertical shells, and top pedestal ring—are aligned and the last welding activities are underway. The base section should be finalized in July but, contrary to the lower cylinder, the 1,250-tonne base will remain inside the building to be equipped, under the ITER Organization's responsibility, with different ancillary elements (stoppers for the gravity supports, shims, bellows, etc.).
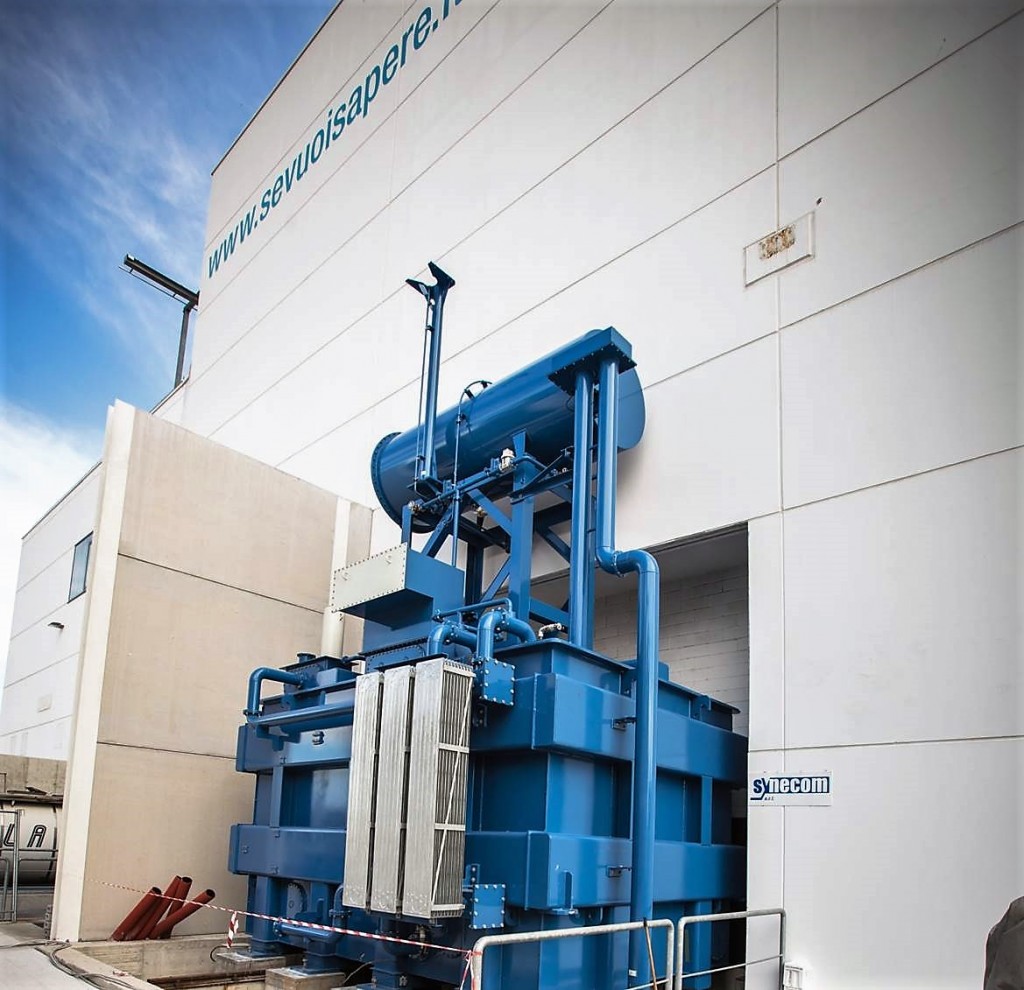
Part of the high-voltage power supplies
2019-03-10 - This I MV insulating transformer supplied by Japan is part of the high-voltage power supply system for MITICA, the full-scale ITER neutral beam injector. Acceptance tests on the power supply system will be finalized when this transformer is connected to the high voltage deck on the inside of the building.
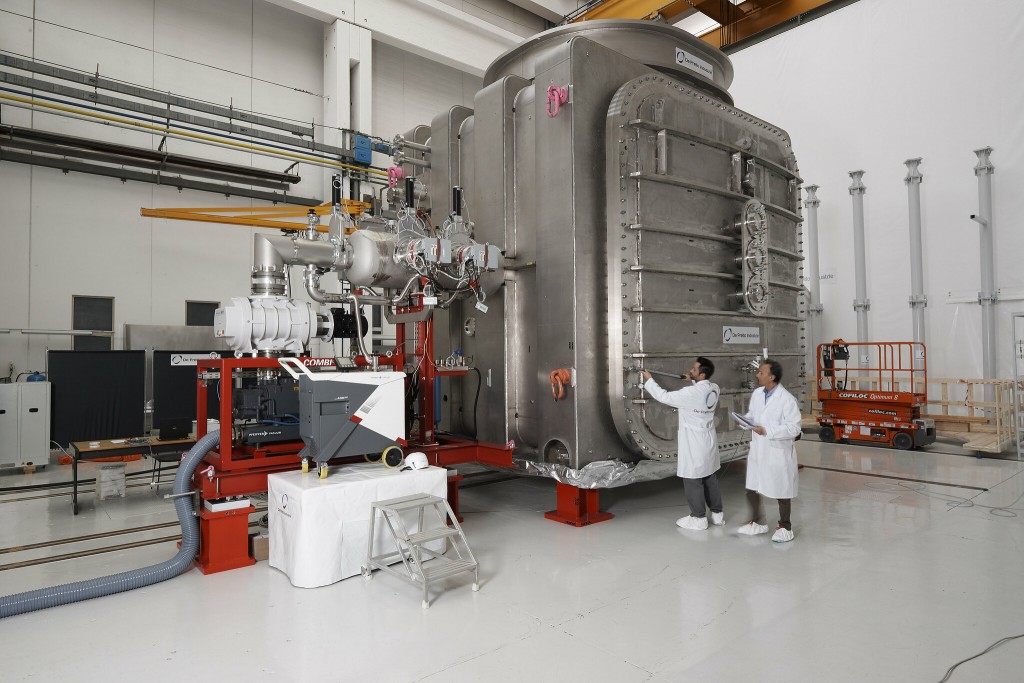
Leak-tight vessel for MITICA
2019-03-08 - Technicians perform the final acceptance tests of the MITICA beam source vacuum vessel at Pretto Industrie (Vincenza, Italy).

Cold tests at 80 K
2019-03-07 - Two cryogenic chambers are being assembled for the final stage of fabrication—cold testing at 80 K, which will permit contractors to test the behaviour of the completed coils under thermal constraint. One chamber will serve for PF5, the other for PF6 (manufactured in China on behalf of Europe and delivered at the end of 2019).

Test mockup
2019-03-07 - This "piece" of mockup coil faithfully mimics poloidal field coil #5 (PF5) and its eight stacked double pancakes. The winding pack impregnation operation will be tested first on this mockup before being carried out on PF5.
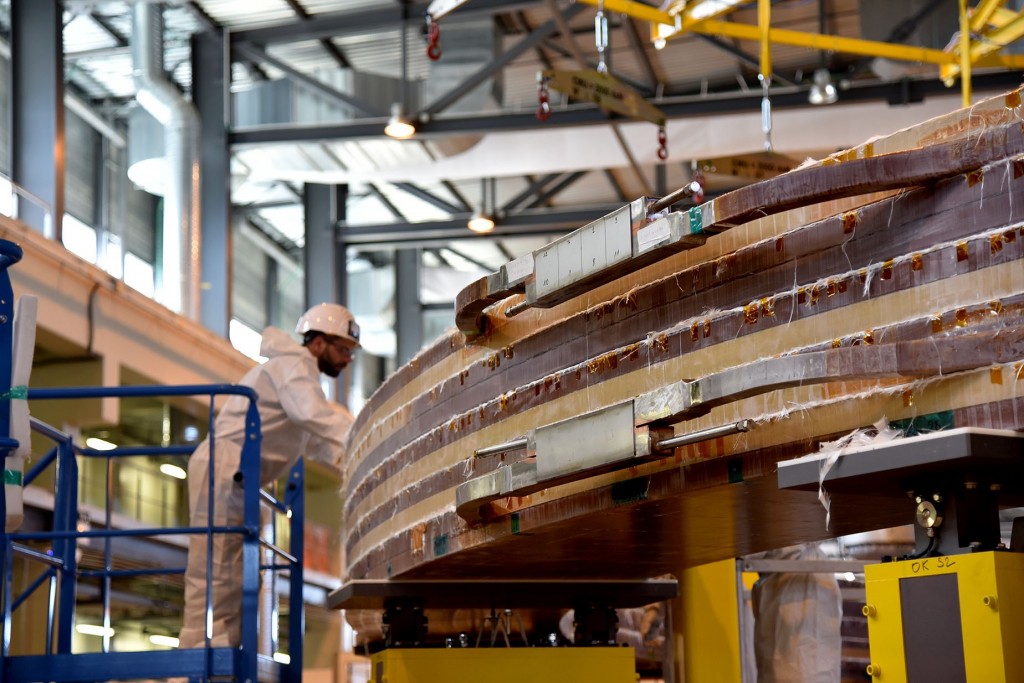
Stacking
2019-03-07 - Impregnated double pancakes are stacked and joined to form the final coil. Here we see five of PF5's eight double pancakes stacked, as well as intra- and inter-pancake joints for helium flow.

New winding activities
2019-03-07 - Winding activities have begun on PF2—the second of four coils to be produced by Europe in this manufacturing facility on site. With a few adaptations, the equipment set up to wind the first production coil, PF5, can serve again to wind the double pancakes required for PF2, as both coils measure 17 metres in diameter.
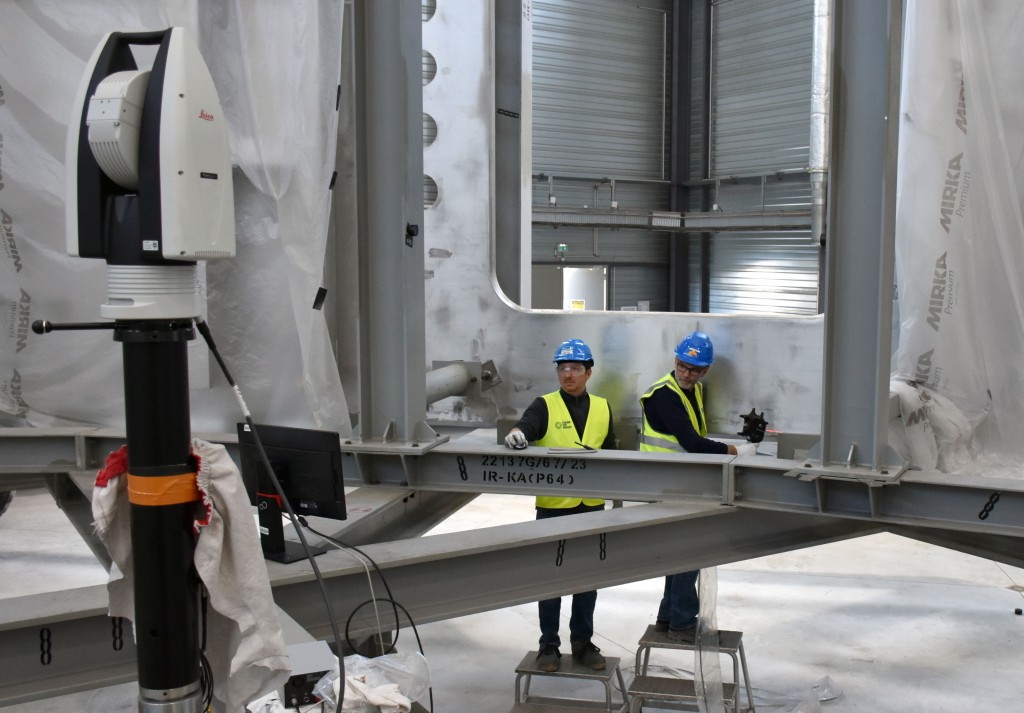
Lower cylinder: surveyed from every angle
2019-03-02 - Metrologists perform the first "as-built" survey of a finalized ITER component.

Outside the cryoplant
2019-03-01 - This complex set of hand valves and local readings of pressure, temperature and flow is part of the cooling loop that maintains the temperature inside the cryoplant's quench tanks at 100 K.

Outside the cryoplant
2019-03-01 - This complex set of hand valves and local readings of pressure, temperature and flow is part of the cooling loop that maintains the temperature inside the cryoplant's quench tanks at 100 K.
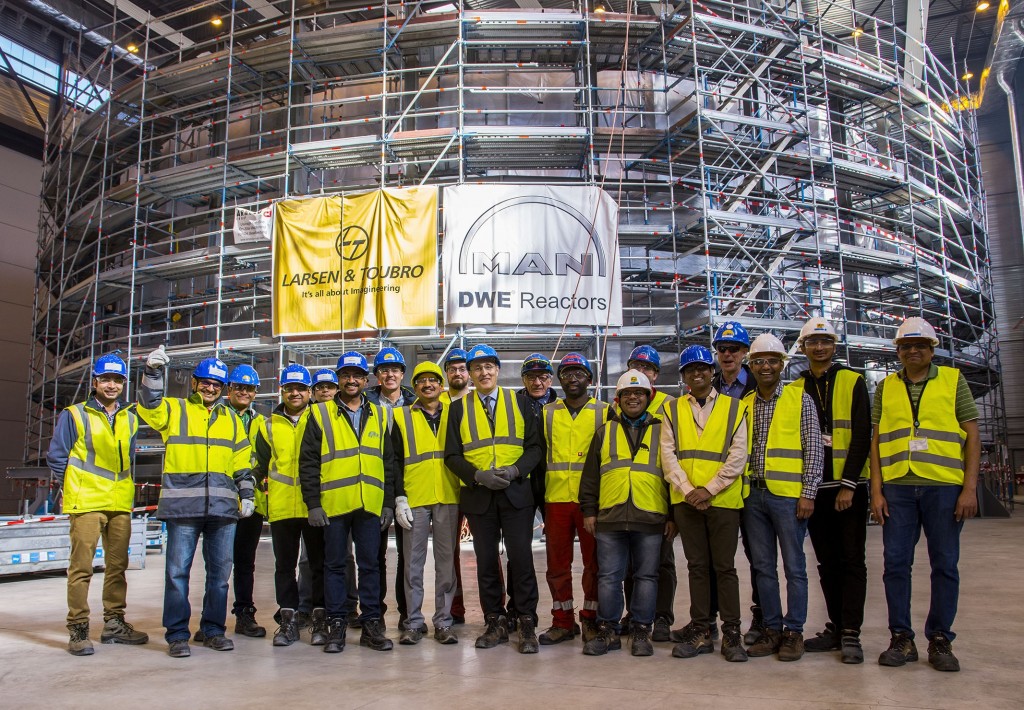
Well done
2019-02-27 - On 27 February, guests from the Indian Domestic Agency (responsible for procuring the cryostat) and from Indian contractor Larsen & Toubro (L&T) joined the ITER Director-General, ITER Organization staff, and on-site welding specialists from MAN Energy Solutions (subcontractor to L&T) to celebrate the completion of the component.

Lower cylinder: DONE
2019-02-27 - The final tests have been carried out and the 375-tonne can officially be called "completed." Scaffolding will be removed in March.
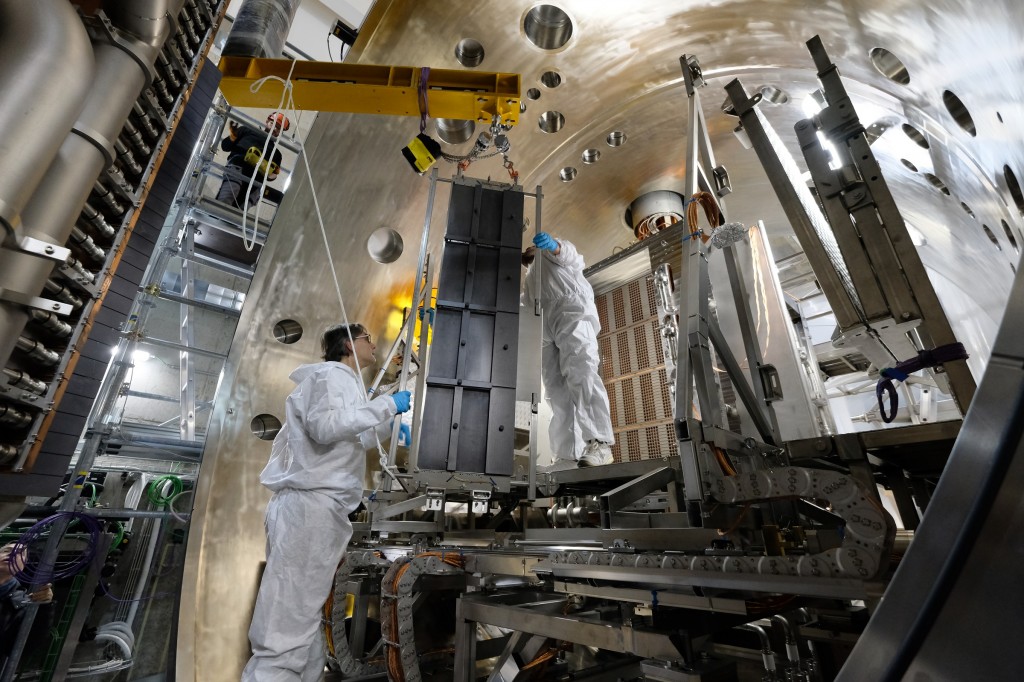
In the line of fire
2019-02-18 - The carbon-fibre panels of STRIKE stand directly in the line of the SPIDER ion beam. The power deposited on the front side of the tiles will be propagated in form of heat to the rear side, where a set of infrared cameras will detect and analyze the thermal pattern in order to reconstruct beam properties.
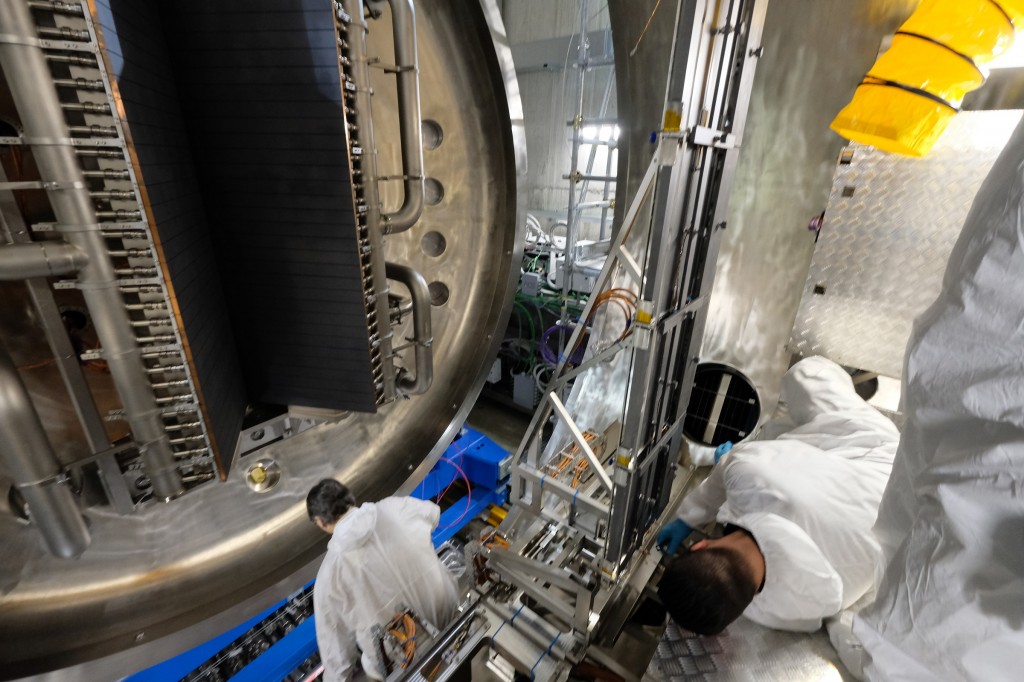
STRIKE installed
2019-02-18 - In Padua, technicians are installing the STRIKE diagnostic, which will characterize the uniformity and divergence of the SPIDER beam. Directly behind it, on the other side of the open vessel, is the actively cooled beam dump.

A pause in operations
2019-02-18 - The SPIDER vessel was opened for the installation of the STRIKE diagnostic. Plasma was generated for the first time in the beam source in June 2018 during the inauguration of the test bed.

Directly above
2019-02-15 - Looking straight down into the Tokamak Building, with the capped Tokamak Pit in the centre. Materials are lowered by crane through the openings.

Door frames
2019-02-14 - This welder is working on the installation of one of the Tokamak Building's 46 nuclear doors.
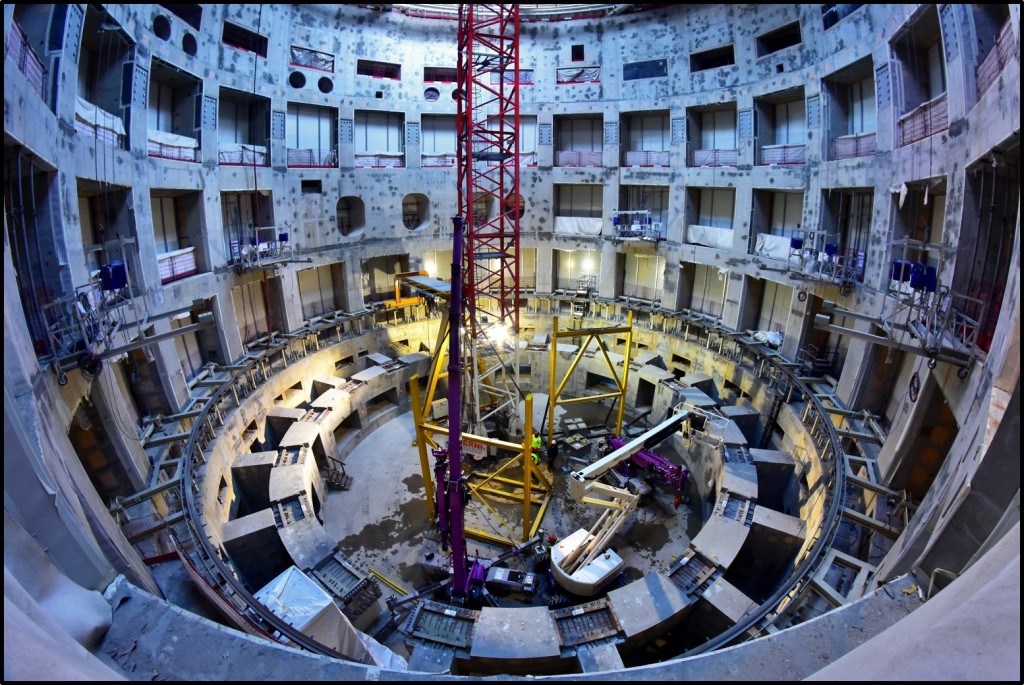
Preparing for painting
2019-02-12 - The port cells have been closed off by temporary "curtains" in order to prepare the Tokamak Pit for painting.
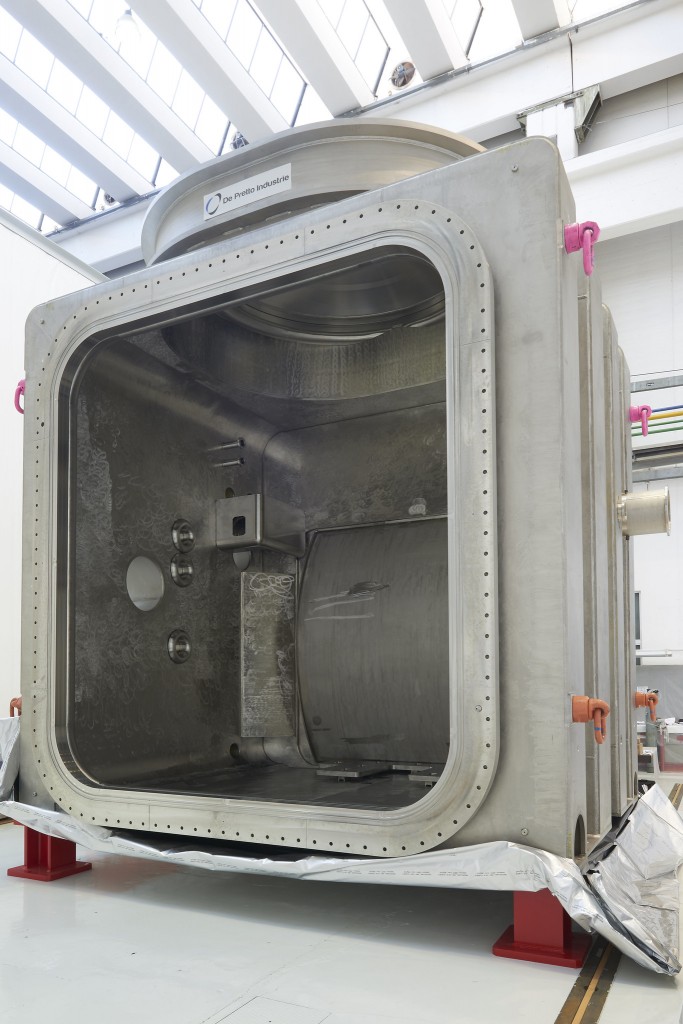
End of fabrication: MITICA vessel
2019-02-06 - At De Pretto Industrie (Italy) the 6 m x 5 m MITICA vacuum vessel and its one kilometre of welds has been inspected successfully.
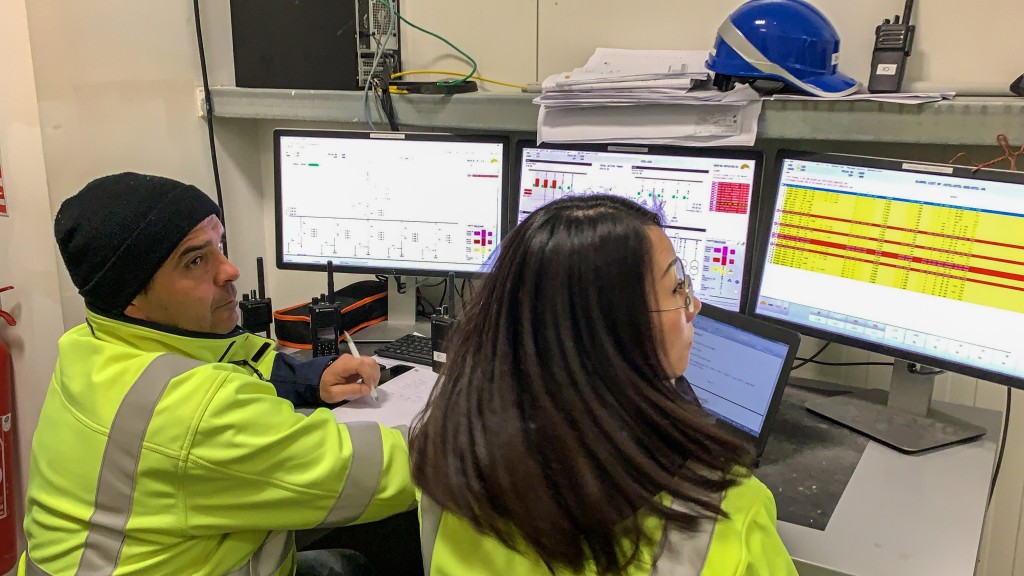
ITER's first electrical distribution system enters operation
2019-01-23 - After several months of tests and commissioning, the first ITER system—steady state electrical distribution—enters into operation on 23 January 2019. The ITER site is now independently powered by an electrical substation that draws power directly from the 400 kV French national grid.
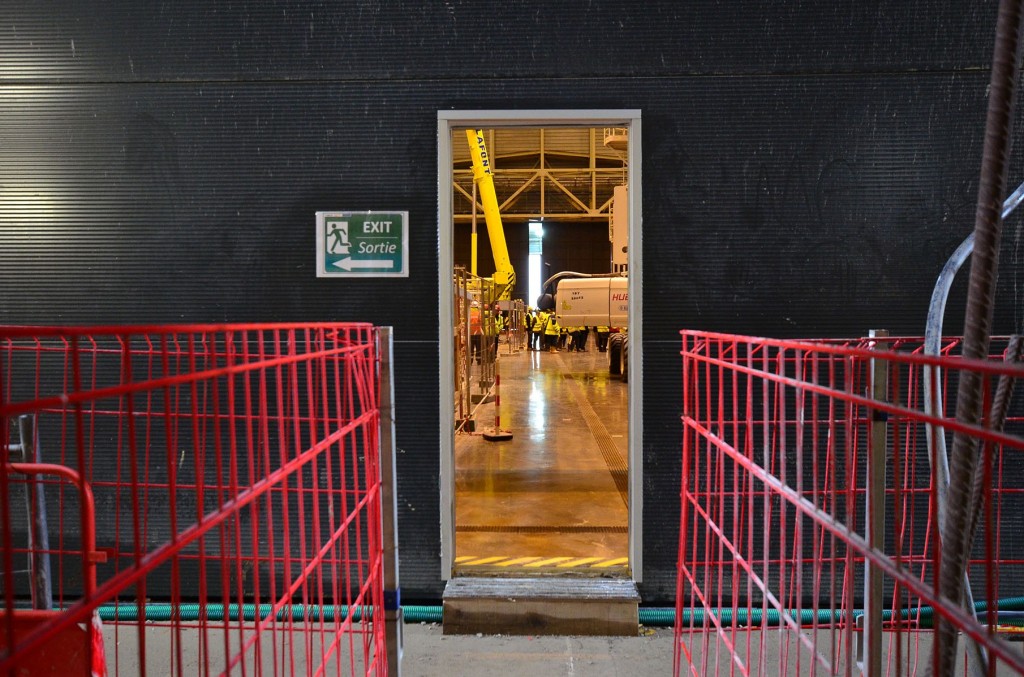
A VIP door
2019-01-18 - Between two very different worlds—the concrete labyrinth of the Tokamak Building and the vast open volume of the Assembly Hall—this small door has been created to facilitate VIP visits.
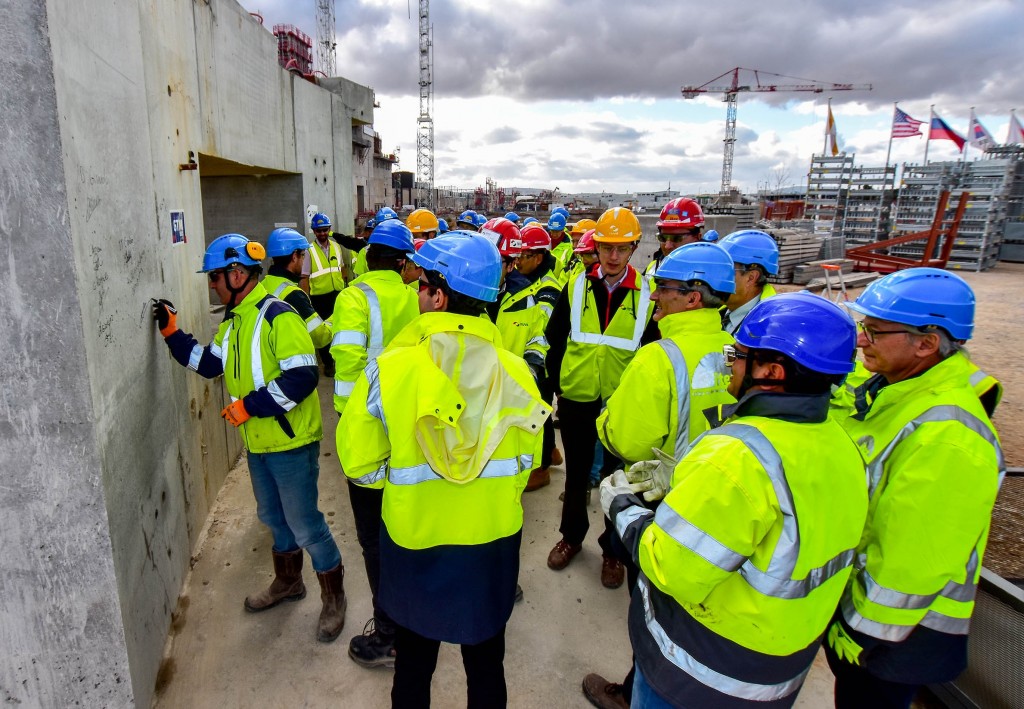
Honouring the crown mockup
2019-01-17 - Replicating a 40-degree section of the Tokamak crown—a challenging structure characterized by unique geometry, high-density steel reinforcement and high-performance concrete—this mockup was built on site to demonstrate crown constructability. Now that its mission has been fulfilled, the teams are leaving a trace of their participation by "signing" the work.
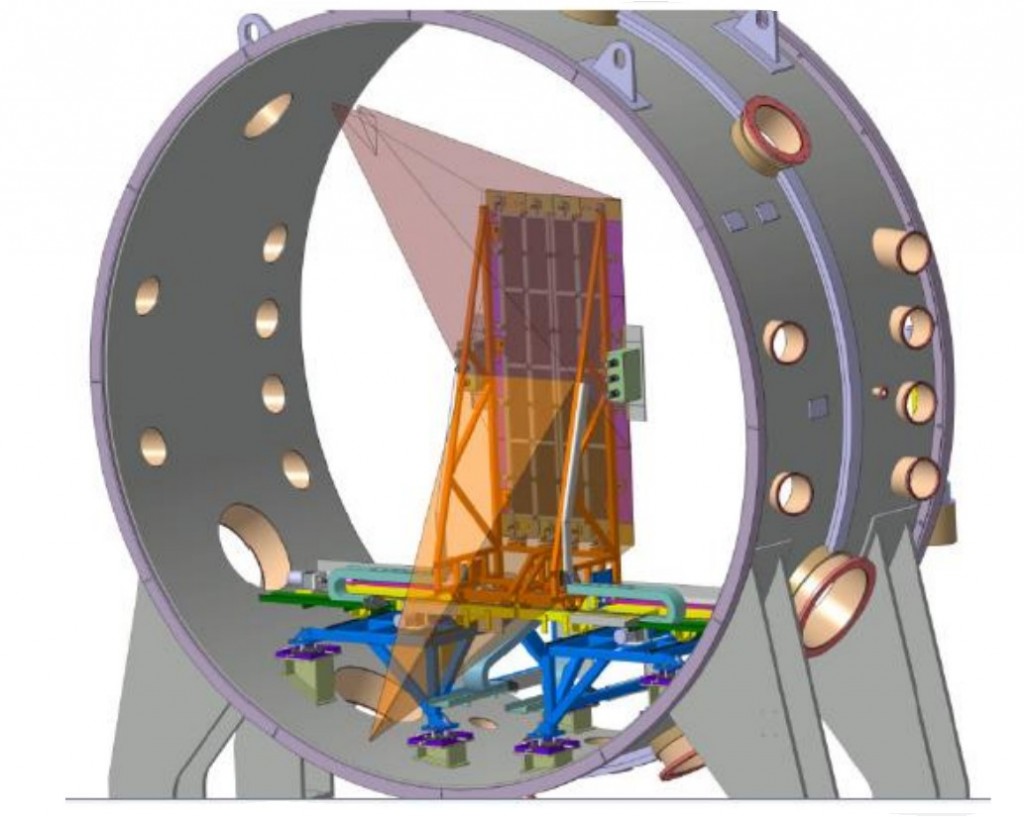
Installation of STRIKE diagnostic
2019-01-15 - Last-phase assembly activities are underway on the STRIKE calorimeter at the ITER Neutral Beam Test Facility. STRIKE is designed to measure the SPIDER beam's uniformity and divergence.
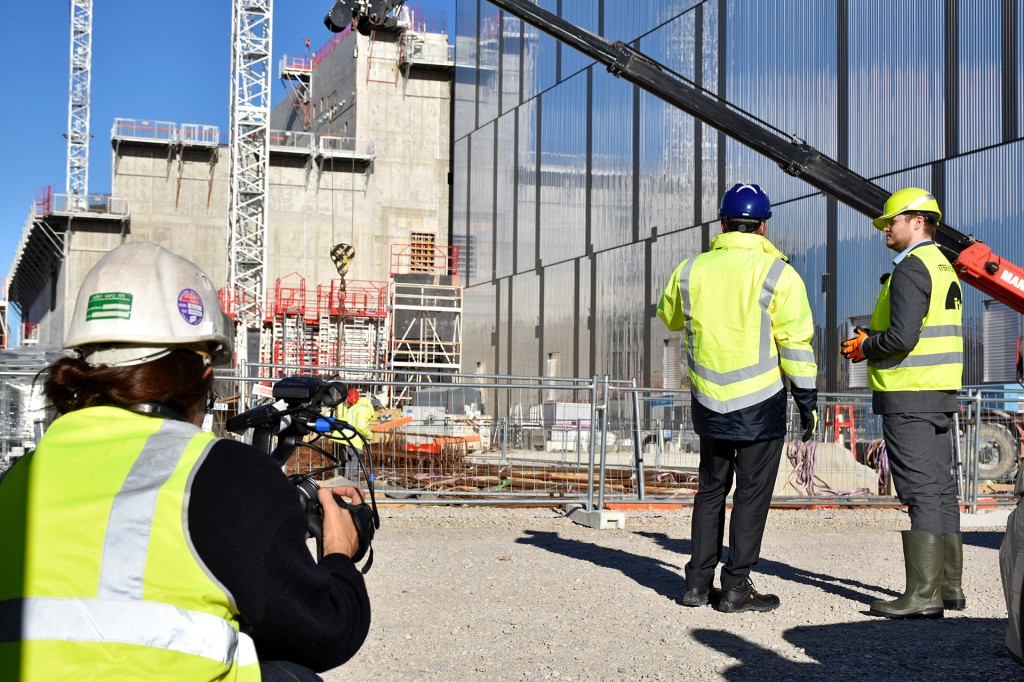
Filming on site
2019-01-14 - Dozens of international media teams film on site at ITER every year. This group has a slightly different project—preparing a human resources video in Russian to attract the best candidates to ITER positions.
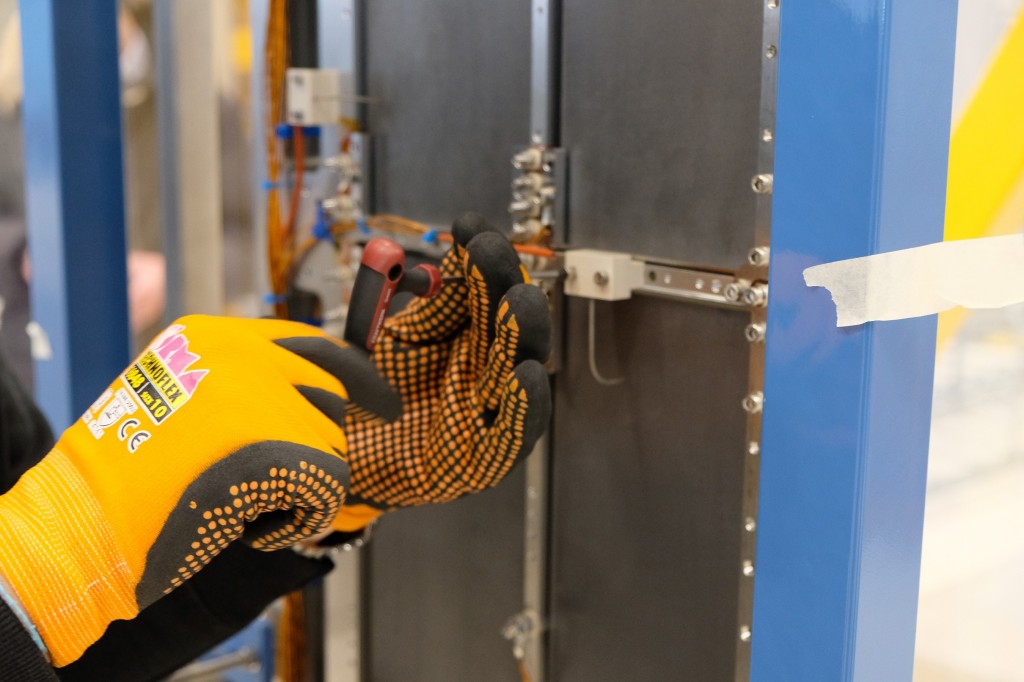
In the line of the beam
2019-01-10 - Sixteen carbon fibre composite tiles are being mounted on the structure of the STRIKE diagnostic. These tiles will face the brunt of the SPIDER negative ion beam ... for short periods of time.

Up high
2019-01-10 - At the top of the second SSAT tool, contractors are assembling the final elements.
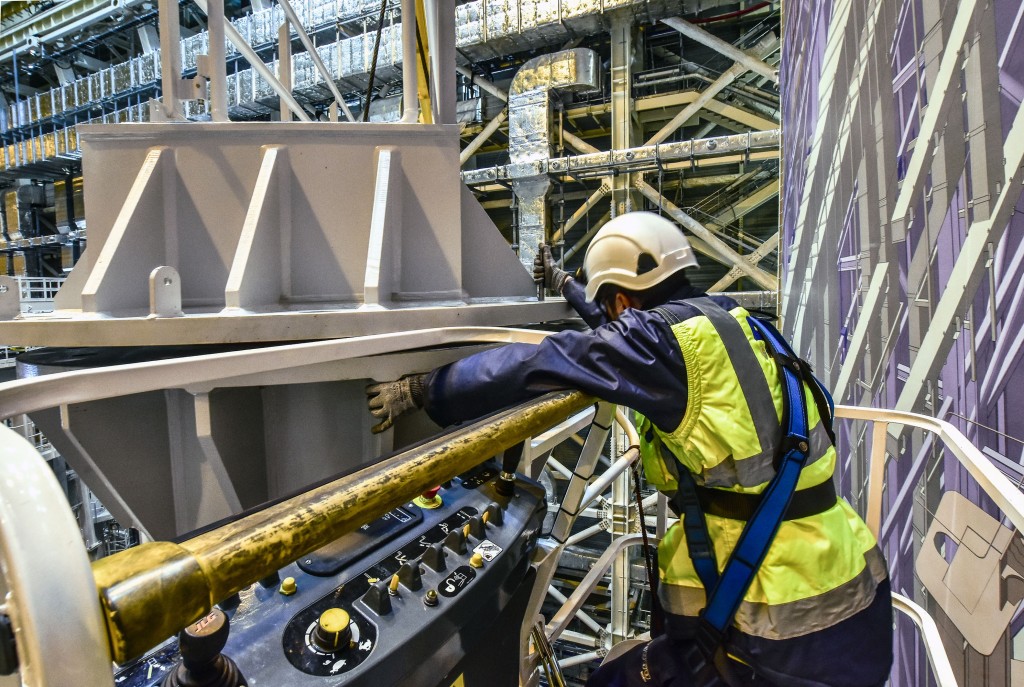
A pair of hands is still useful
2019-01-10 - Lessons learned from the first tool have reduced assembly time for SSAT-2 by approximately one-third. Still, some manual operations are still required...
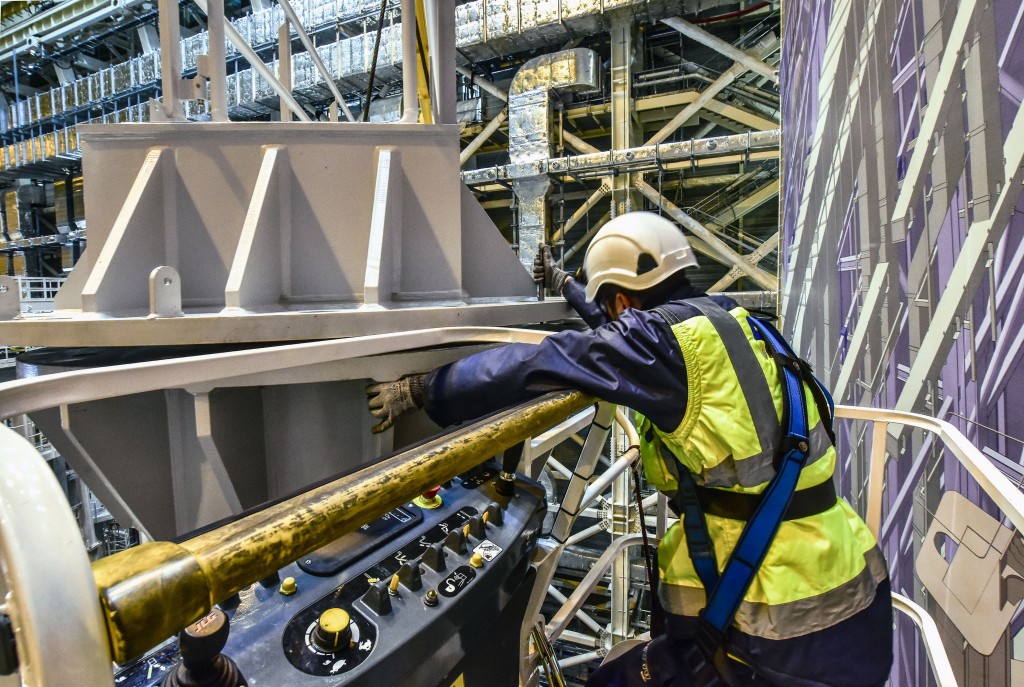
A pair of hands is still useful
2019-01-10 - Lessons learned from the first tool have reduced assembly time for SSAT-2 by approximately one-third. Still, some manual operations are still required...

Commissioning local control systems
2019-01-07 - One after another, 170 local controls systems have to be integrated into central conventional control, CODAC. In this image, members of the Controls Division are attempting for the first time to operate high voltage circuit breakers from the CODAC human/machine interface.

Infrastructure completed
2018-12-21 - On 21 December, the European Domestic Agency hands the completed cooling tower zone over to the ITER Organization for equipment installation. The areas handed over include the cold and hot basins, the water cooling pumping station, the heat exchange zone, and the water treatment facility.
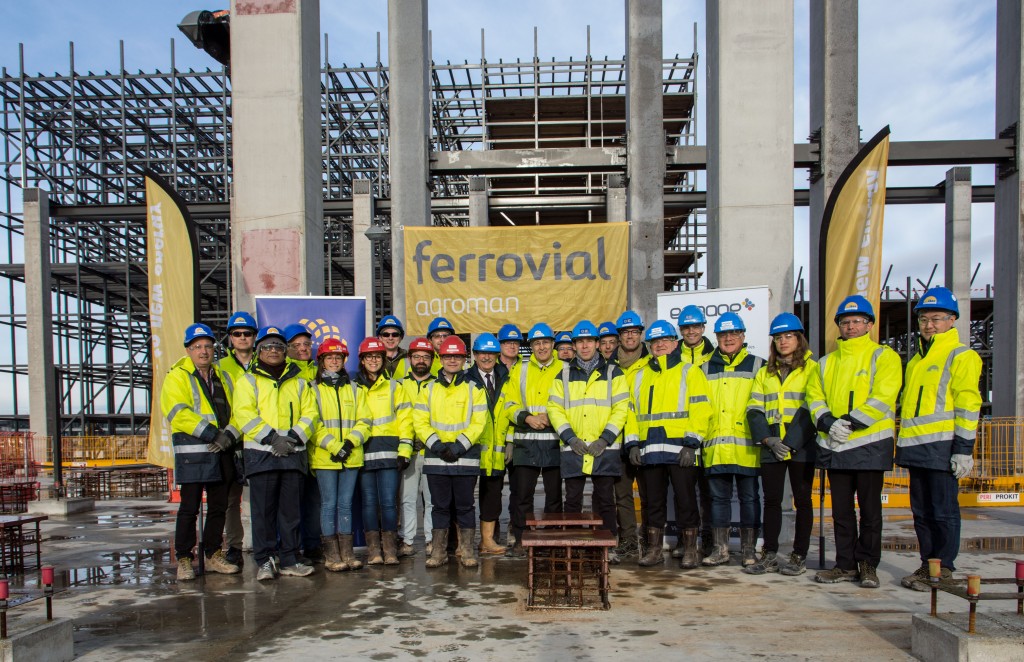
Construction completed on the cooling tower zone
2018-12-21 - The handover of the cooling tower zone from the European Domestic Agency to the ITER Organization takes place on 21 December 2018. The infrastructure is ready; now the ITER team will supervise the installation of equipment sent by the Indian Domestic Agency.

Hot basin
2018-12-21 - During the ceremony participants were given access to the underground hot basin. During the machine's operational phase, water can enter the hot basin at up to 65 °C.
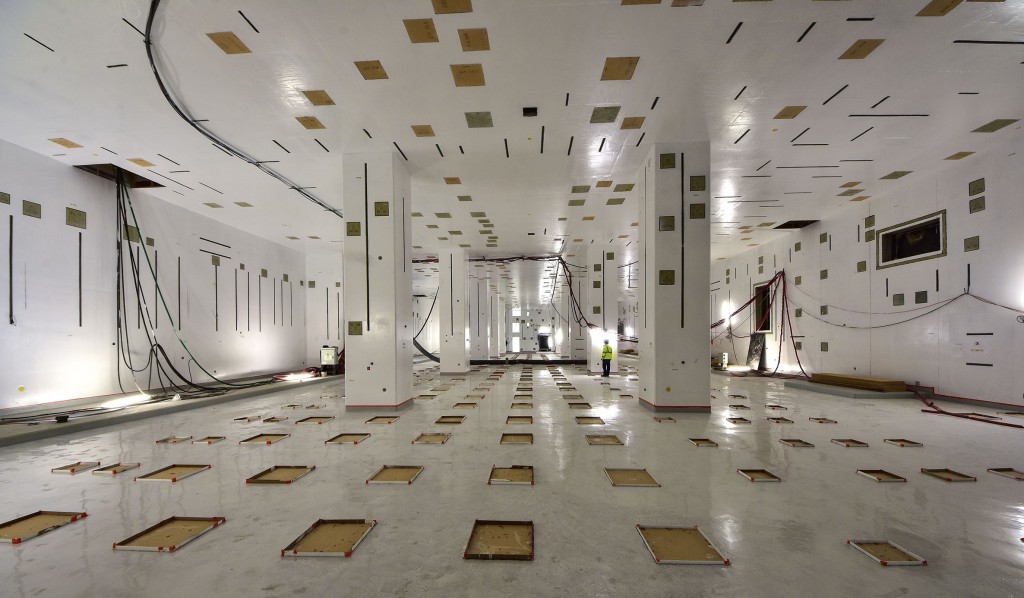
All painted in white
2018-12-14 - Now painted in white, the first level of the Diagnostic Building is ready for handover to contractors for the beginning of systems installation. The embedded plates visible on all surfaces will allow contractors to attach the supports required for installing plant systems.
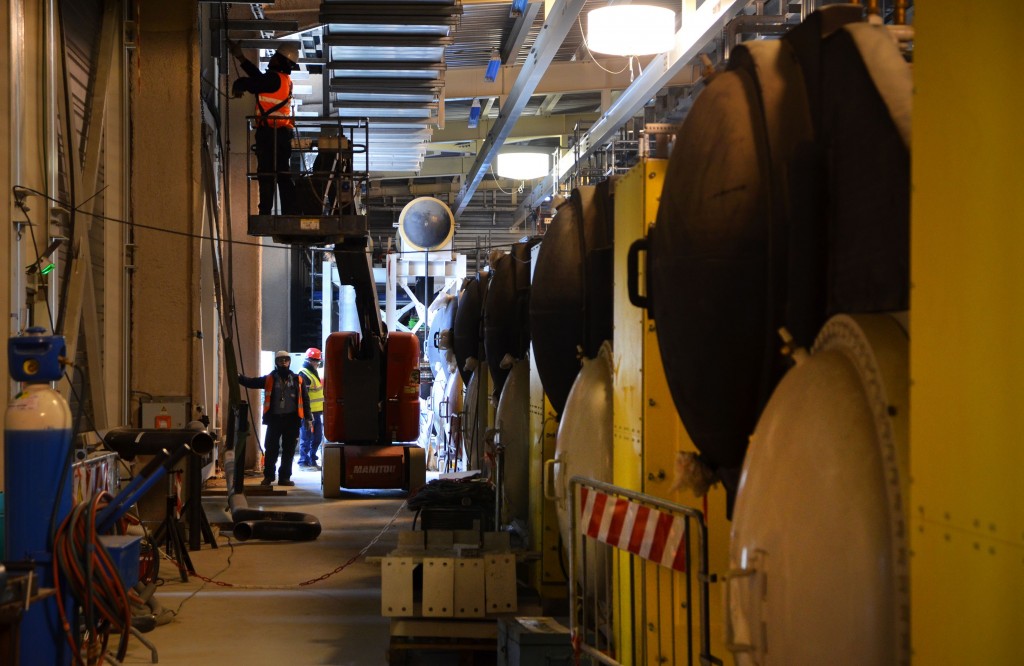
Ready to serve the installation in 2019
2018-12-12 - Installation works in the Site Services Building have been completed on time, despite a complicated context of limited space, numerous interfaces and coordination. Eight 25-tonne chillers are installed at right (plus their soft starters in yellow).
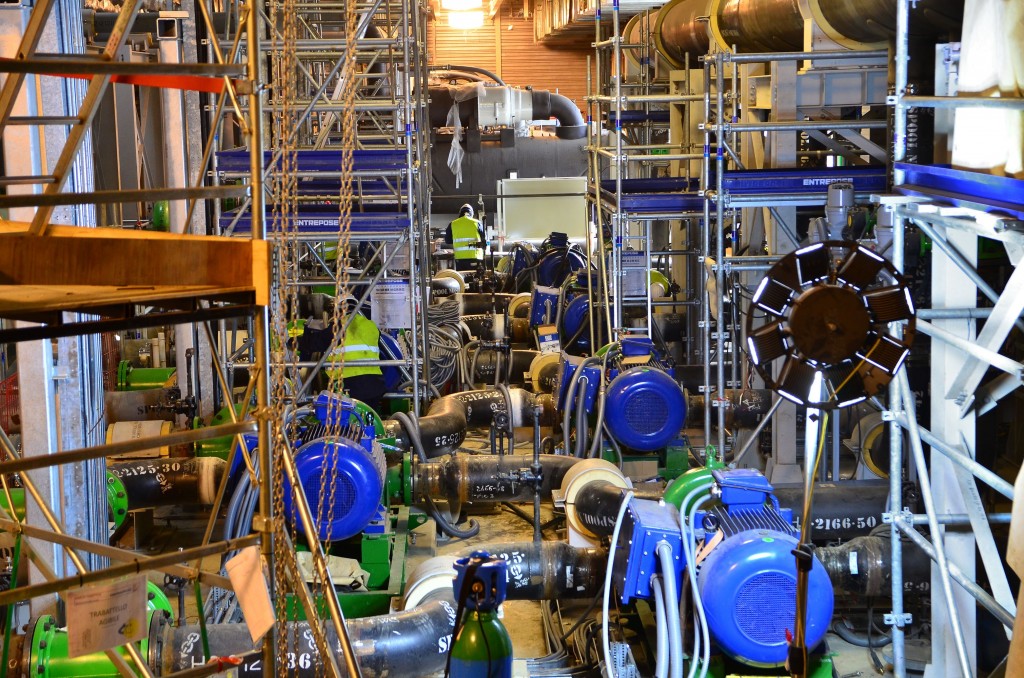
An unassuming name, a strategic building
2018-12-12 - Despite a rather unassuming name, the Site Services Building is a strategic resource for the entire installation, accommodating and distributing a large number of industrial support services and systems. All mechanical and electrical equipment (pumps, chillers, pressurizers, cabinets and chemical dosing systems) and relevant piping has been installed, and a series of hydrostatic tests have been completed successfully.
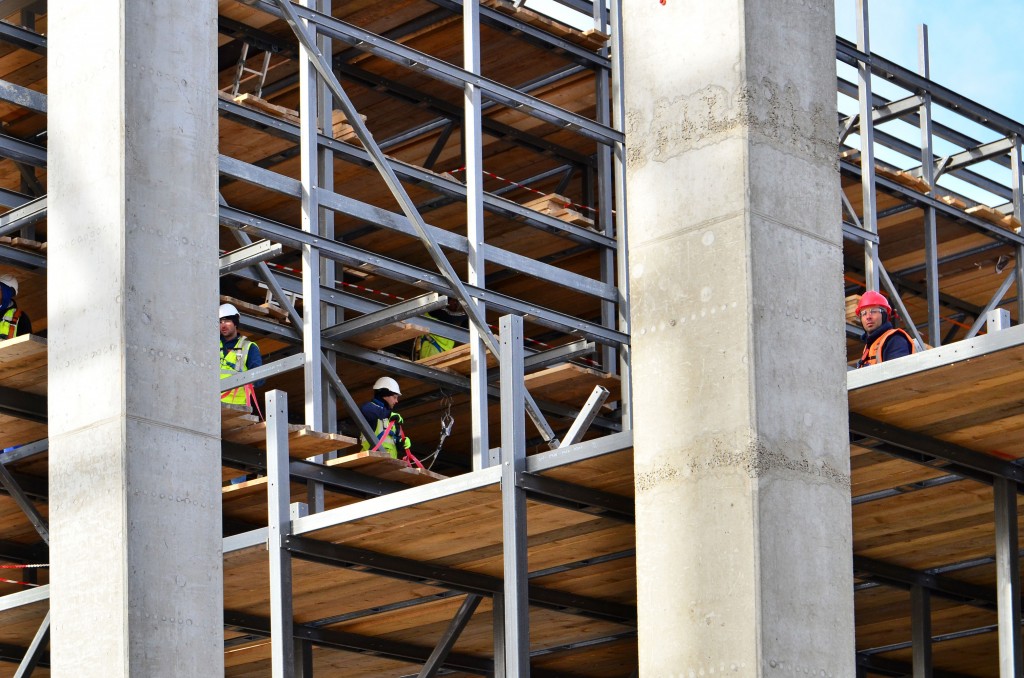
Specially designed for ITER
2018-12-12 - The cooling towers are one part of a high-performance heat rejection system that has been designed for ITER. The design and fabrication of the system is part of India's procurement contributions to the ITER Project; Europe has created the concrete basins and infrastructure; the equipment will be installed by the ITER Organization.
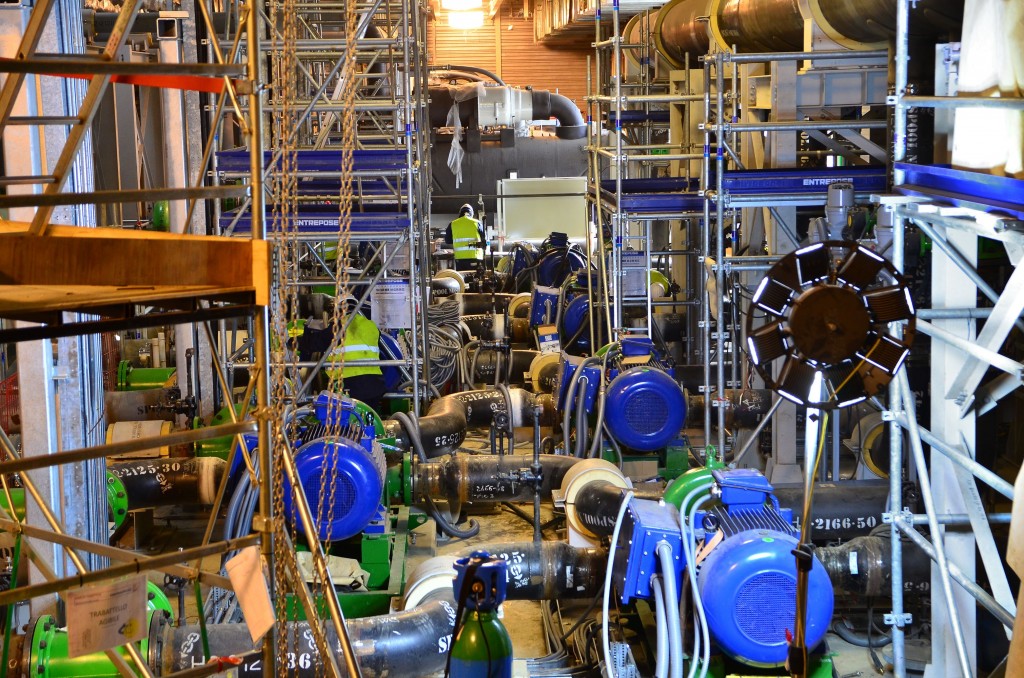
An unassuming name, a strategic building
2018-12-12 - Despite a rather unassuming name, the Site Services Building is a strategic resource for the entire installation, accommodating and distributing a large number of industrial support services and systems. All mechanical and electrical equipment (pumps, chillers, pressurizers, cabinets and chemical dosing systems) and relevant piping has been installed, and a series of hydrostatic tests have been completed successfully.
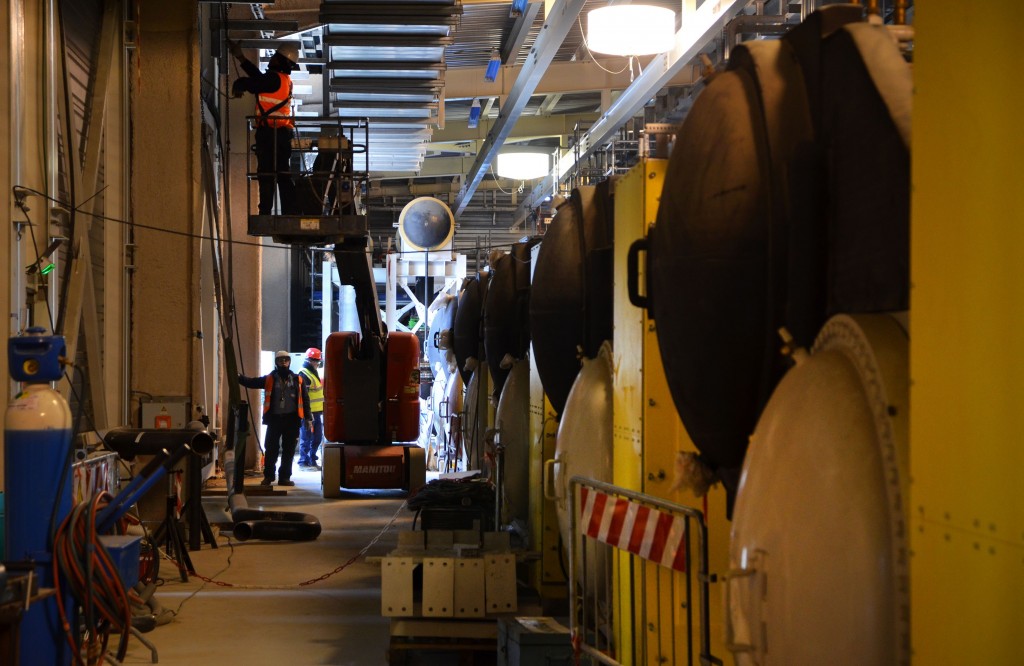
Ready to serve the installation in 2019
2018-12-12 - Installation works in the Site Services Building have been completed on time, despite a complicated context of limited space, numerous interfaces and coordination. Eight 25-tonne chillers are installed at right (plus their soft starters in yellow).

One structure, 10 cells
2018-12-12 - Each of the 20-metre-tall cooling tower cells will be filled with hundreds of layers of corrugated plastic fill and equipped with a large fan that pulls air upward. As water falls through the fill, some of it evaporates due to the strong uptake of air, removing heat. The dark-grey support structure for the cooling tower cells is made of pultruded fibre-reinforced polymer beams.
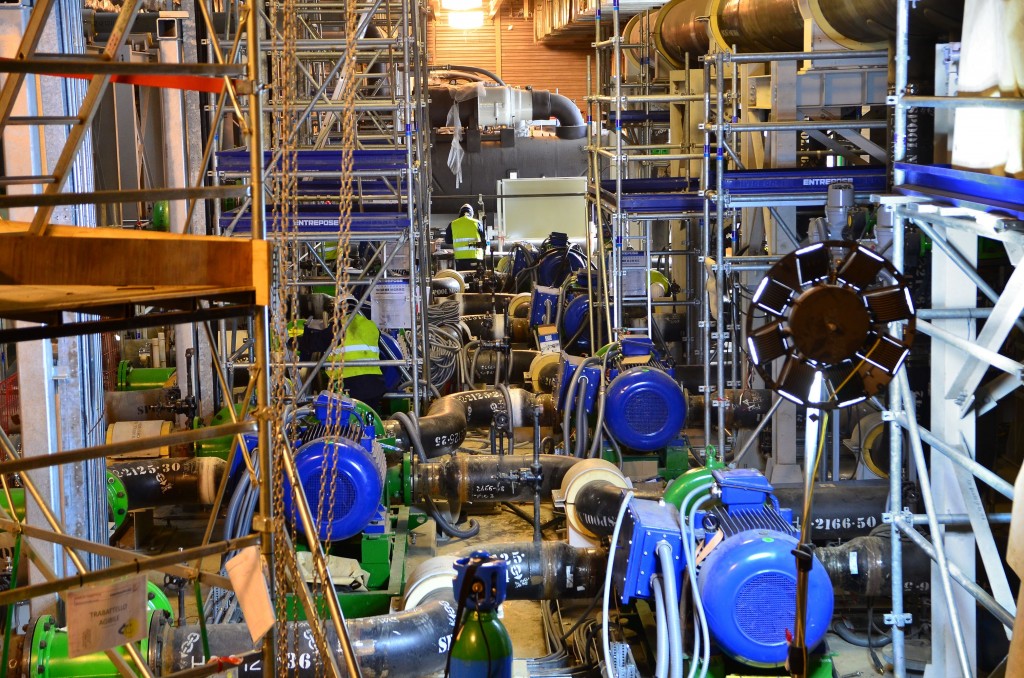
An unassuming name, a strategic building
2018-12-12 - Despite a rather unassuming name, the Site Services Building is a strategic resource for the entire installation, accommodating and distributing a large number of industrial support services and systems. All mechanical and electrical equipment (pumps, chillers, pressurizers, cabinets and chemical dosing systems) and relevant piping has been installed, and a series of hydrostatic tests have been completed successfully.
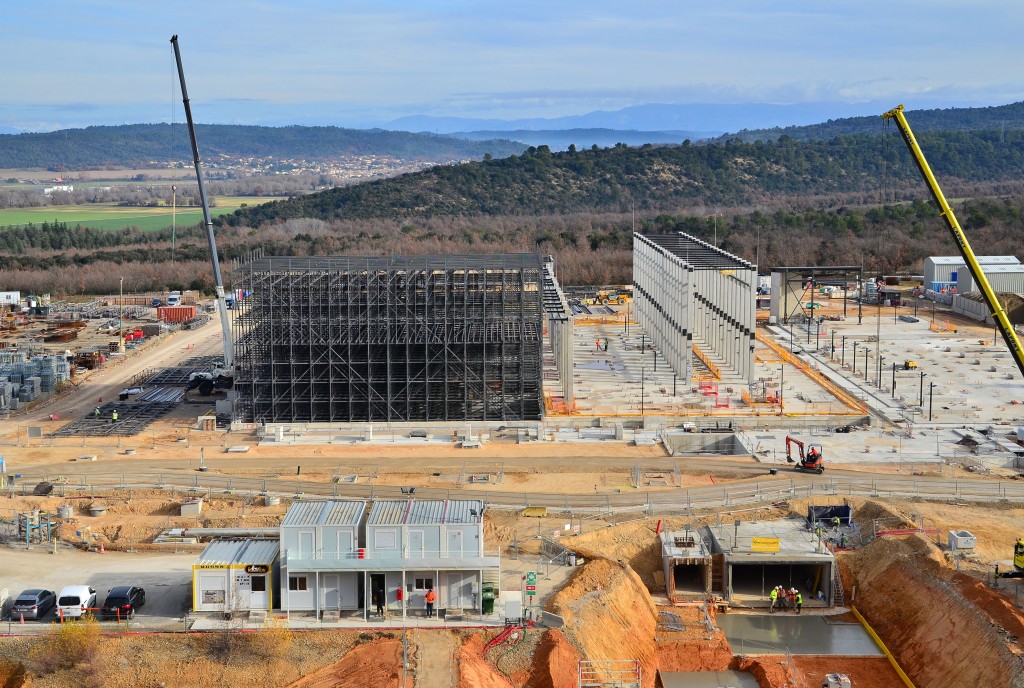
Heat rejection
2018-12-12 - On the northern tip of the worksite the 6,000 m² heat rejection zone is emerging. The most recent structure, in black, will house the 10-cell, 20-metre-tall cooling tower.

Moving out next year
2018-12-10 - Upon its completion the lower cylinder will be moved out of the Cryostat Workshop to protected storage on site. That will free the assembly platform for the next activity—the assembly of the upper cylinder from steel segments shipped by India.
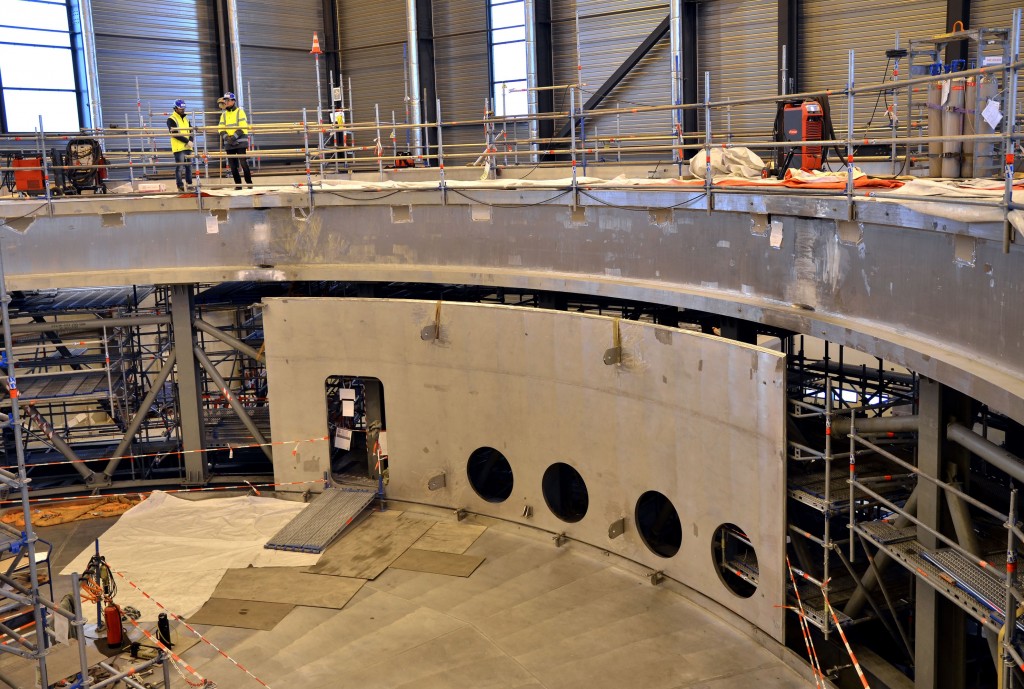
As we enter 2019 ...
2018-12-10 - The first welding activities on the cryostat base kicked off in 2016. Today the lower tier has been finalized, the pedestal ring is suspended above and, in between, teams are trial fitting the vertical wall segments.

Lower cylinder : ready in March
2018-12-10 - The lower cylinder of the cryostat is well advanced. The last seam welds should be completed in one month, and site acceptance tests are scheduled for March.
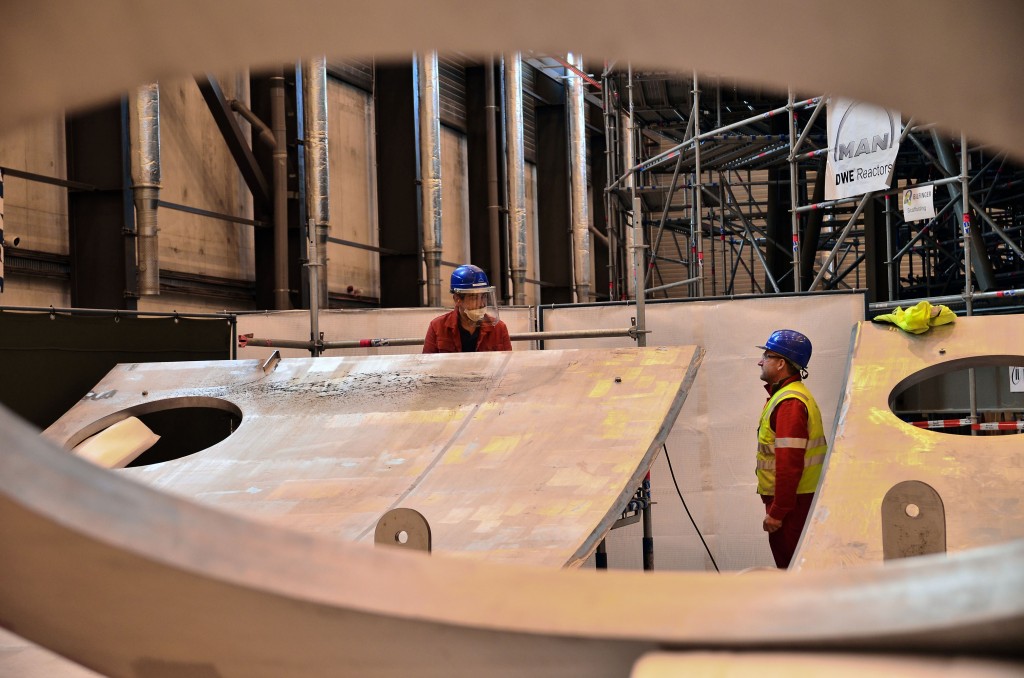
Back to the base
2018-12-10 - Back in August, the vertical shells had already been trial fitted on the bottom sandwich structure, inspected, and then disassembled for adjustment. One by one, the six segments are being re-positioned for final assembly.
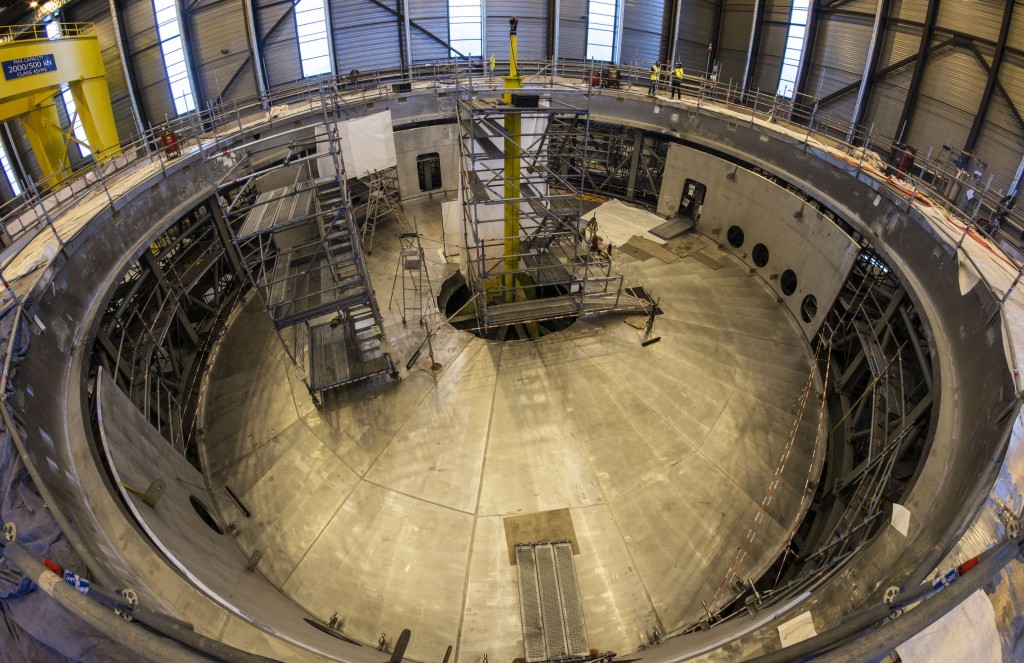
Base: final assembly stages
2018-12-10 - The components of the cryostat base—the 20-metre-in-diameter bottom disk, side shells, and 30-metre-in-diameter pedestal ring—are positioned for final assembly in the Cryostat Workshop. After welding, tests and final machining, site acceptance tests will be carried out in April 2019.

Welding: the name of the game
2018-12-10 - In total, the Indian Domestic Agency estimates that one kilometre of full penetration weld joints will have to be carried out to exacting standards on the four sections of the cryostat in the site workshop, followed by several hundred metres of weld joints to assemble the cryostat sections in the Tokamak Pit. The cryostat chamber must be completely leak free in order to achieve high vacuum within its large volume (8,500 m³).
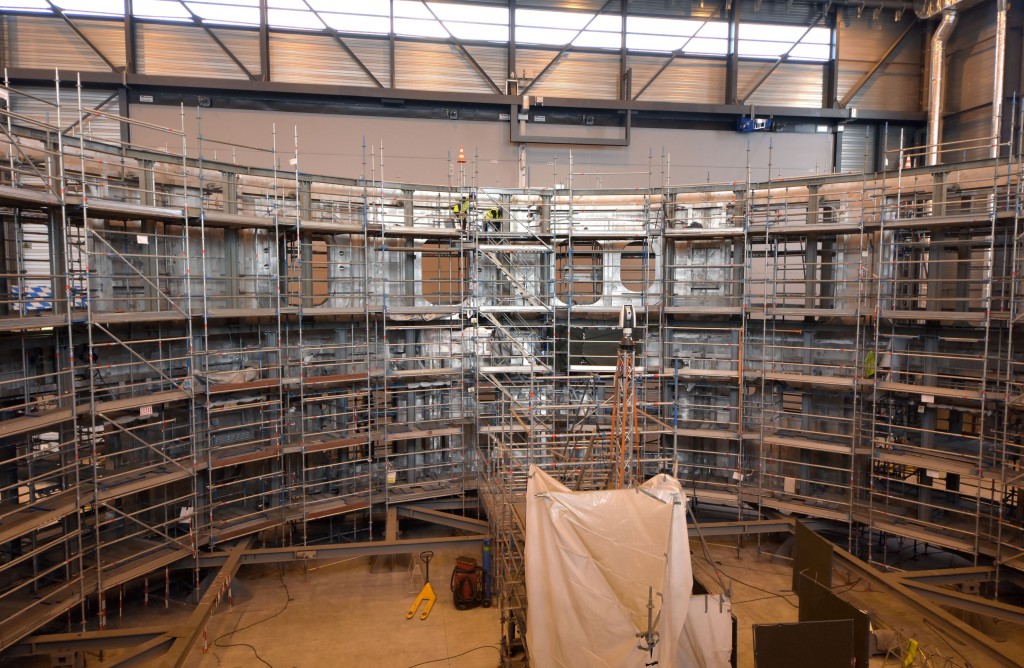
A generous volume
2018-12-10 - The ITER Tokamak and superconducting magents will all be contained within the generous volume of the cryostat. The lower cylinder is a ten-metre-tall component that will sit on the cryostat base. The upper cylinder will in turn fit perfectly on the lower cylinder and the entire assembly will be topped off with a lid.

Lower galleries
2018-12-06 - This opening in the 3.5-metre-thick bioshield was specially designed to house the part of the feeder that crosses through the bioshield and cryostat—the feedthrough. Thirty-one feeders in all will find their way through galleries like this to reach the ITER magnets.
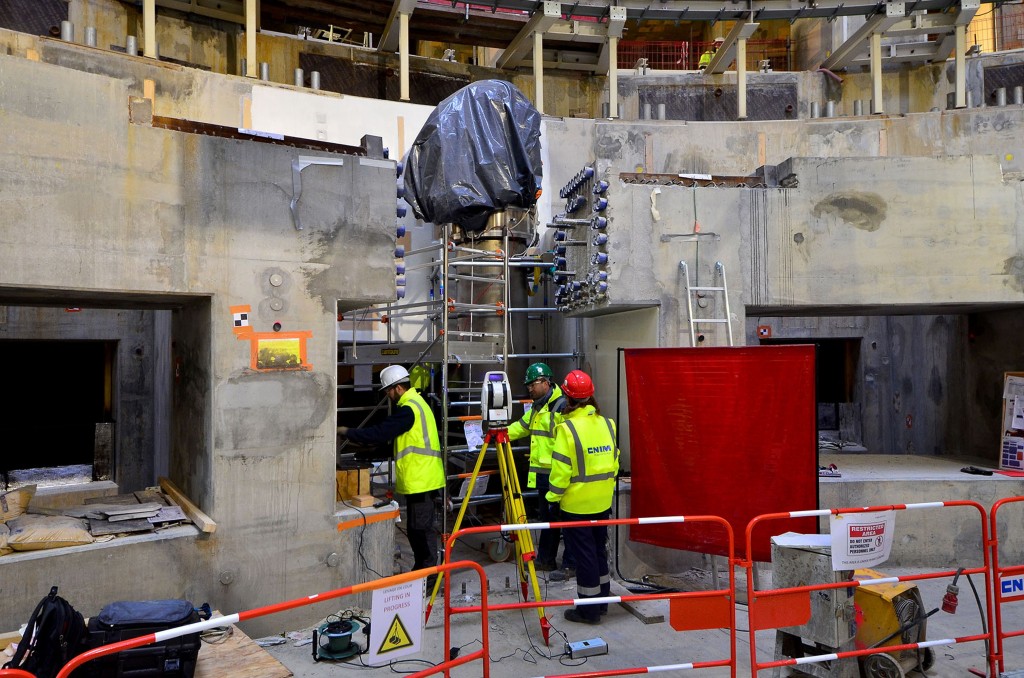
"As installed"
2018-12-06 - At the bottom of the machine assembly pit, the first metal component has been inserted into its bay. Metrologists are recording its "as-installed" position, as this component will be assembled with two other sub-assemblies to form the full magnet feeder for poloidal field coil #4. Thirty-one feeders in all will deliver electricity, cryogens and instruments to the ITER magnets.
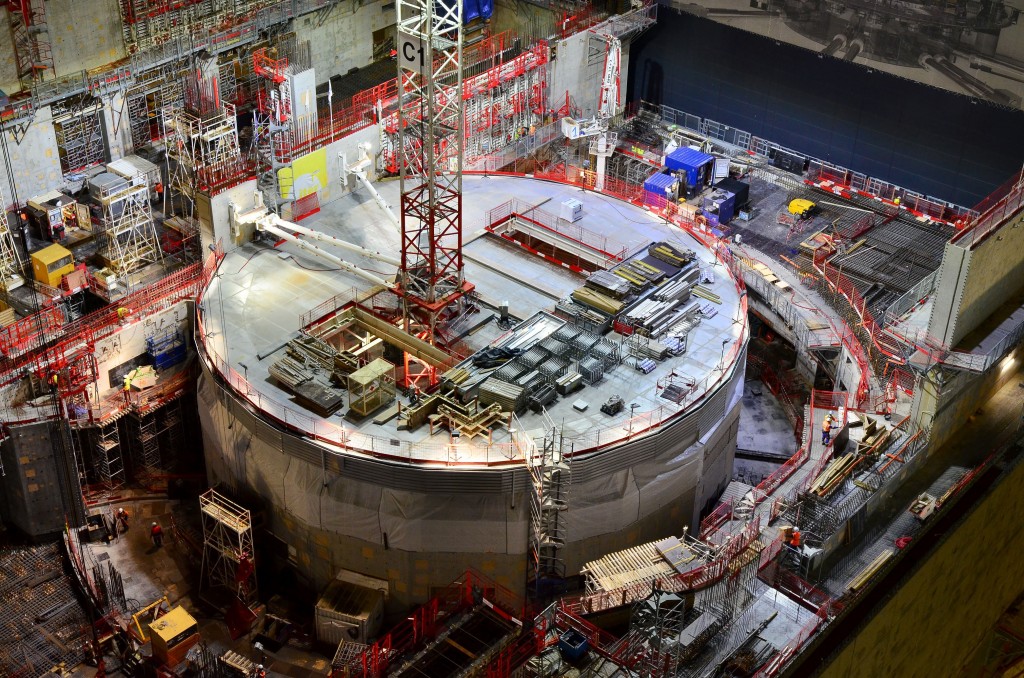
A covered well
2018-12-06 - The temporary lid on the bioshield prevents us from seeing 30 metres down onto the floor of the Tokamak Complex, where the concrete crown and radial walls are in place. In 2019, 18 steel bearings will be installed in a ring to prepare for the first big lift of ITER assembly—the lowering of the cryostat base.

Lower galleries
2018-12-06 - This opening in the 3.5-metre-thick bioshield was specially designed to house the part of the feeder that crosses through the bioshield and cryostat—the feedthrough. Thirty-one feeders in all will find their way through galleries like this to reach the ITER magnets.
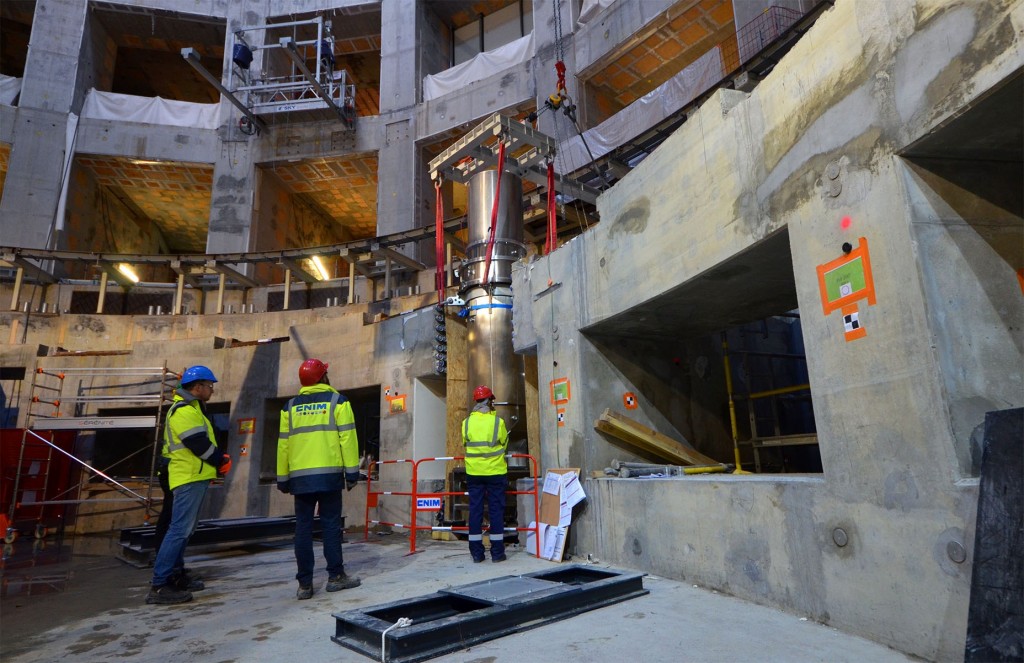
Installed!
2018-12-06 - Into the slim opening of the cryostat crown: a break in the concrete had been left by building contractors for the installation of the cryostat feedthrough for poloidal field coil #4. The operation was successfully carried out on 6 December 2018.
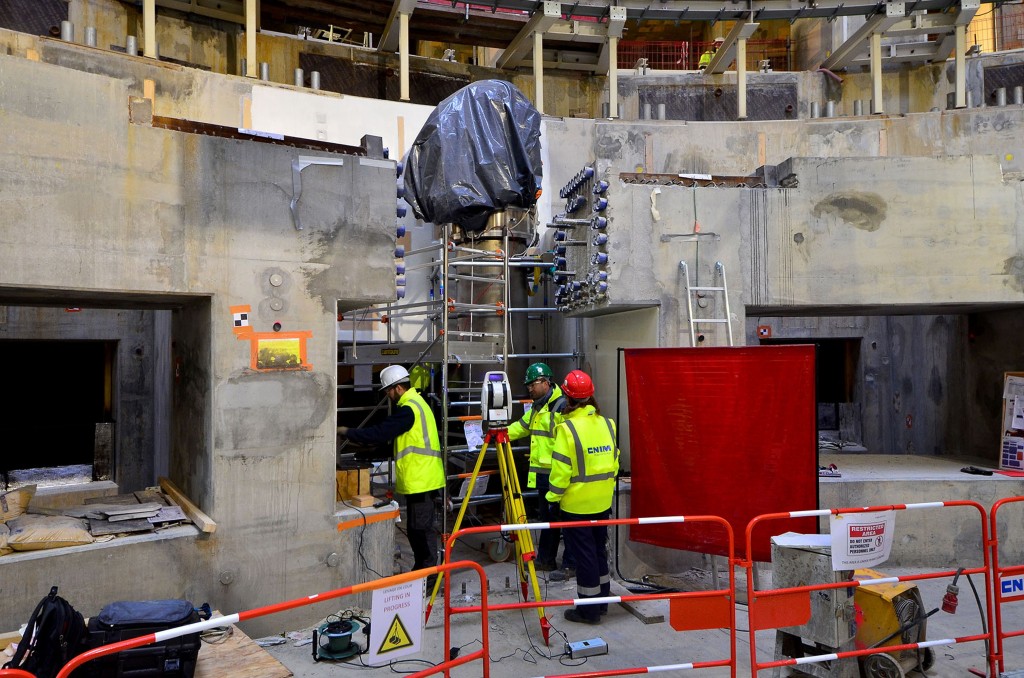
"As installed"
2018-12-06 - At the bottom of the machine assembly pit, the first metal component has been inserted into its bay. Metrologists are recording its "as-installed" position, as this component will be assembled with two other sub-assemblies to form the full magnet feeder for poloidal field coil #4. Thirty-one feeders in all will deliver electricity, cryogens and instruments to the ITER magnets.

Installed!
2018-12-06 - Into the slim opening of the cryostat crown: a break in the concrete had been left by building contractors for the installation of the cryostat feedthrough for poloidal field coil #4. The operation was successfully carried out on 6 December.
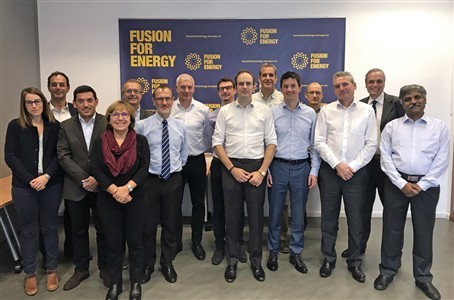
En route for the MITICA beam source
2018-12-03 - The European Domestic Agency, Fusion for Energy, has awarded a EUR 20 million contract to ALSYOM-SEIV (ALCEN group, France) for the fabrication of the MITICA beam source—a prototype of the ITER neutral beam heating beam source that will generate 40 A of negative hydrogen or deuterium ions. The equipment is expected in four years. (Pictured, representatives of Fusion for Energy, ITER Organization, Consorzio RFX, and ALSYOM-SEIV.)

Important arteries
2018-12-03 - Cable drums are lined up outside of the ITER cryoplant, where tray laying and cable pulling activities are about to start. A total of 10,000 kilometres of cables will be needed at ITER to connect components, provide power and transmit data.

Important arteries
2018-12-03 - Cable drums are lined up outside of the ITER cryoplant, where tray laying and cable pulling activities are about to start. A total of 10,000 kilometres of cables will be needed at ITER to connect components, provide power and transmit data.
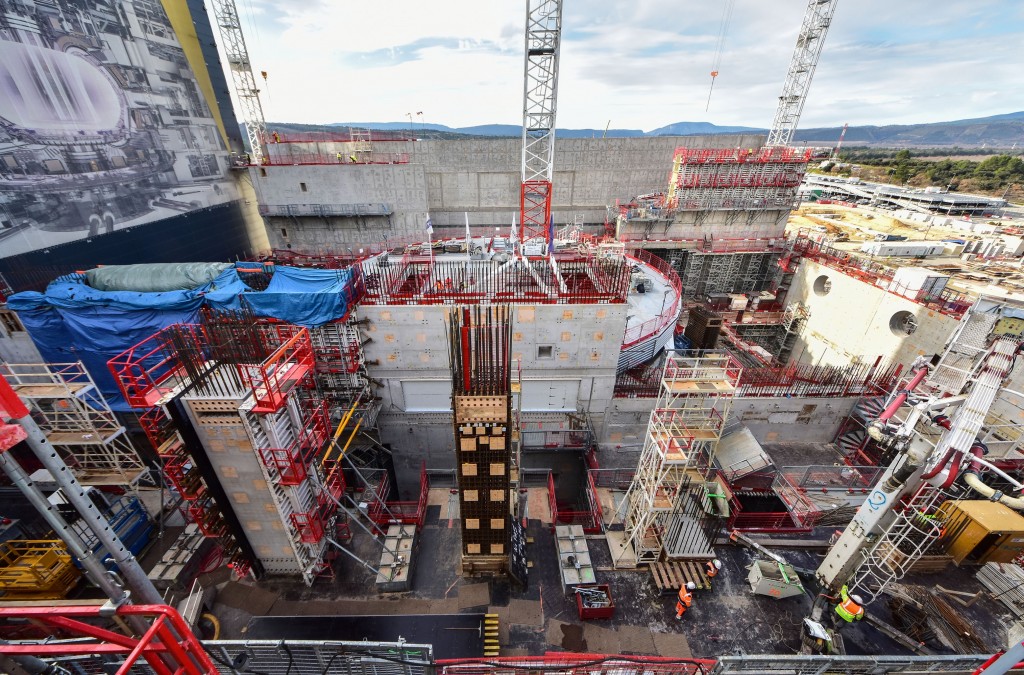
Looking over the wall
2018-11-29 - Standing now on the tall north-facing wall of the Tokamak Building, the ITER photographer is able to capture all of the activities going on around the machine well at L3 level. The space in these outlying galleries will be completely filled with equipment and systems.

Sturdy wings
2018-11-29 - Precision hydraulics will drive the lateral wings of the SSAT tools, which rotate to deliver the toroidal field coils to their installation fixtures on the vacuum vessel sector.
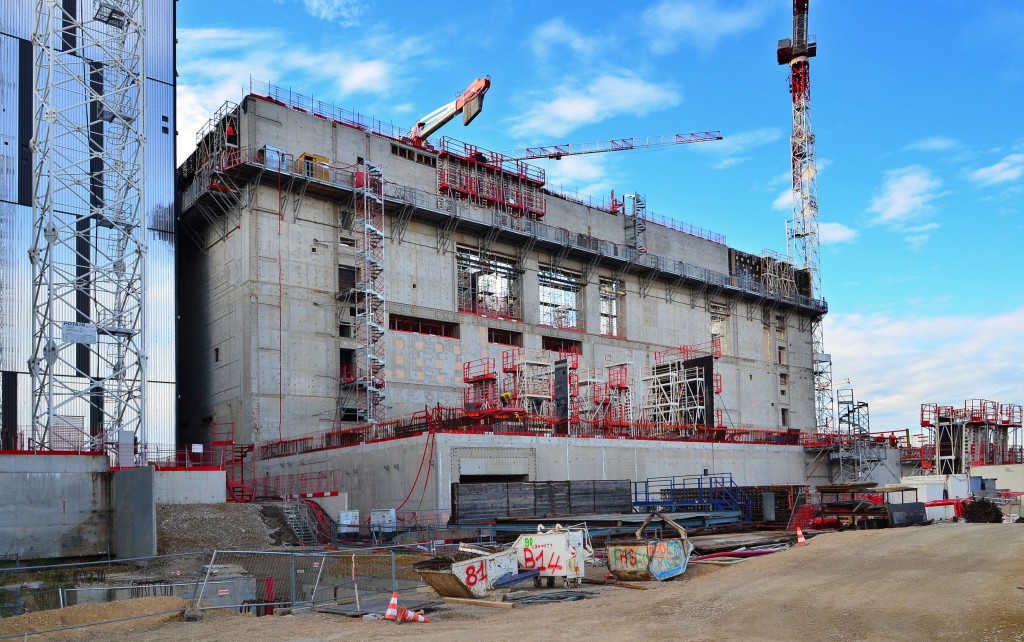
An unusual angle
2018-11-29 - The Tokamak Building, seen rising alongside the metal-clad Assembly Hall. On the other side of this north-facing wall is the circular well where the machine will be assembled. European contractors are working to close up the building over the Tokamak Pit in time for heavy assembly works to begin in March 2020.
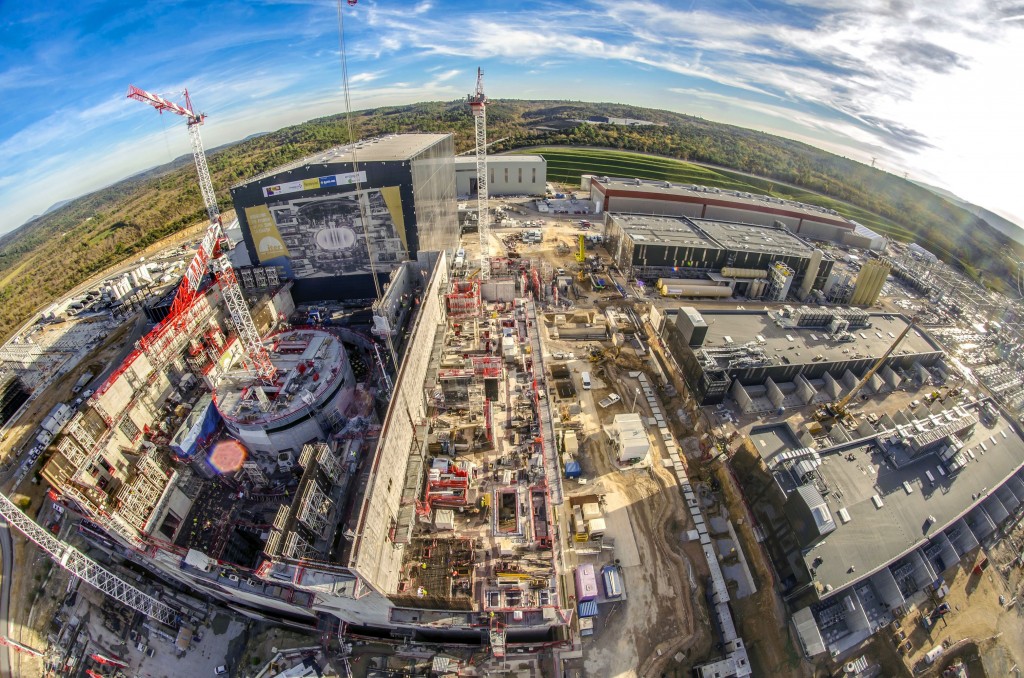
As the year ends
2018-11-29 - It was a year of major progress, as the bioshield and the cryostat crown—both strategic structures—were completed. The walls of the Tokamak Complex are rising and, all around, equipment is being moved into the plant system buildings.
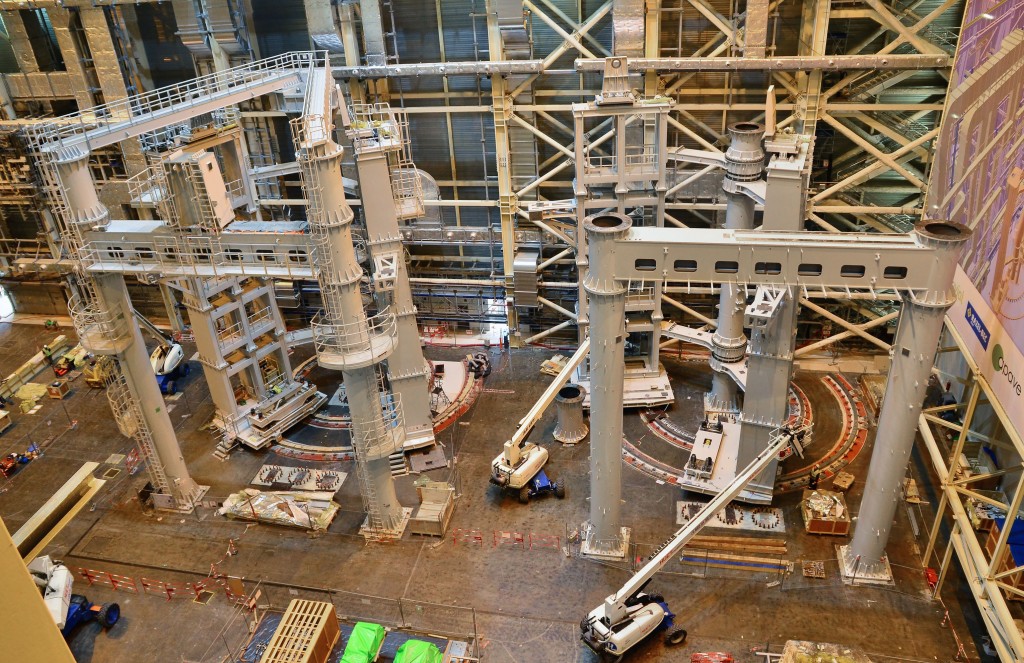
Near twins
2018-11-29 - The second SSAT tool is rising quickly in the Assembly Hall. Each of these 800-tonne behemoths can carry component assemblies of 1,200 tonnes.
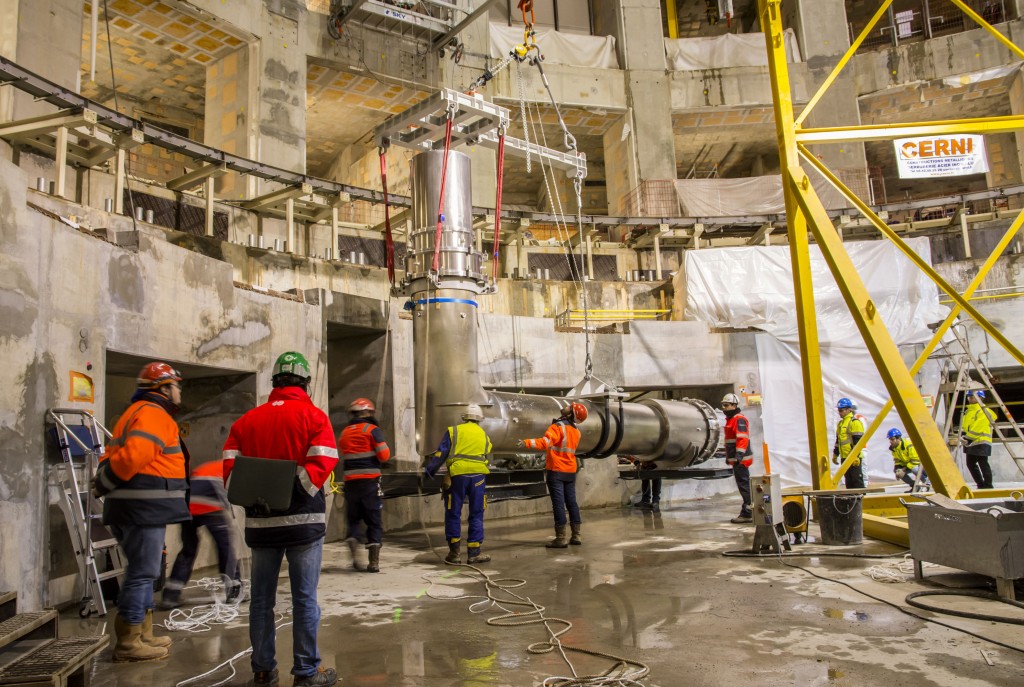
Lifelines
2018-11-27 - Feeders will reach the magnets by either crossing through the lower level of the bioshield—passing under the machine—or through the top level, passing over.
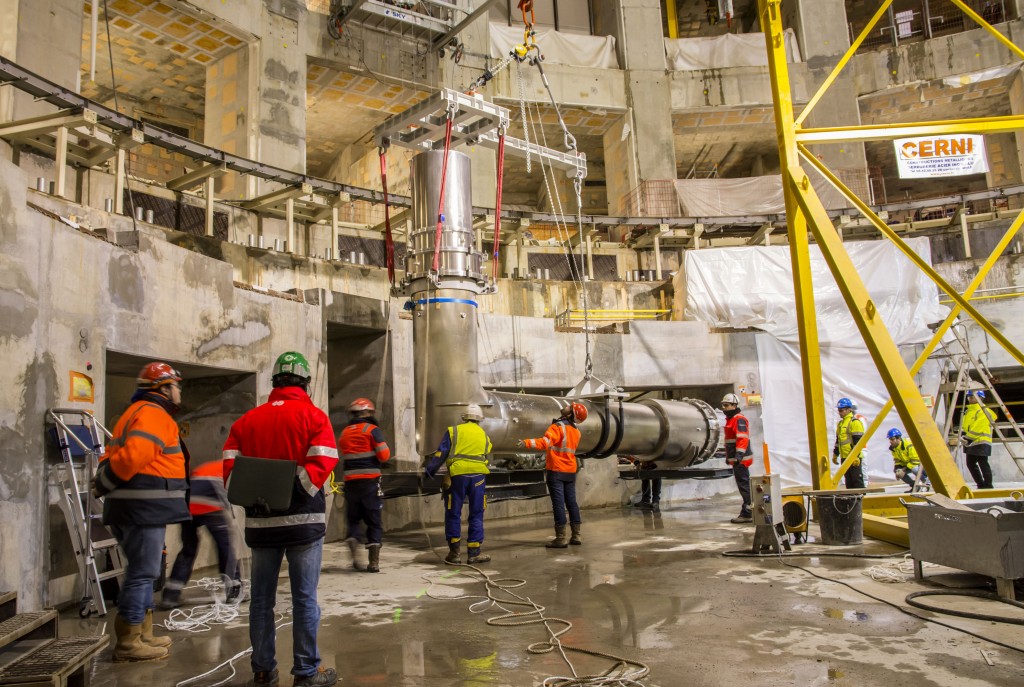
Lifelines
2018-11-27 - Feeders will reach the magnets by either crossing through the lower level of the bioshield—passing under the machine—or through the top level, passing over.

Transformer Way
2018-11-27 - Equipment from China and Korea is arriving for the Magnet Power Conversion buildings on site. Two 150-metre twin buildings will act as the AC/DC adapter that converts current coming out of the electrical distribution network into the DC current required by the magnets.
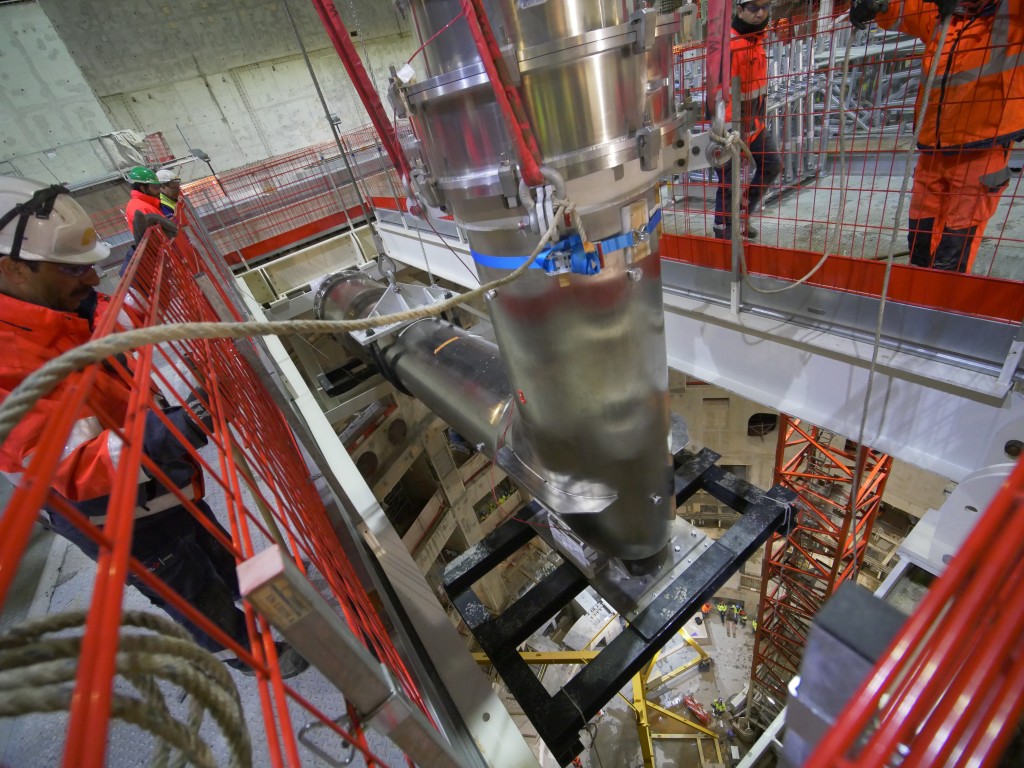
The first one
2018-11-26 - The cryostat feedthrough begins its 30-metre descent—the first metal component of the ITER machine to enter this space.
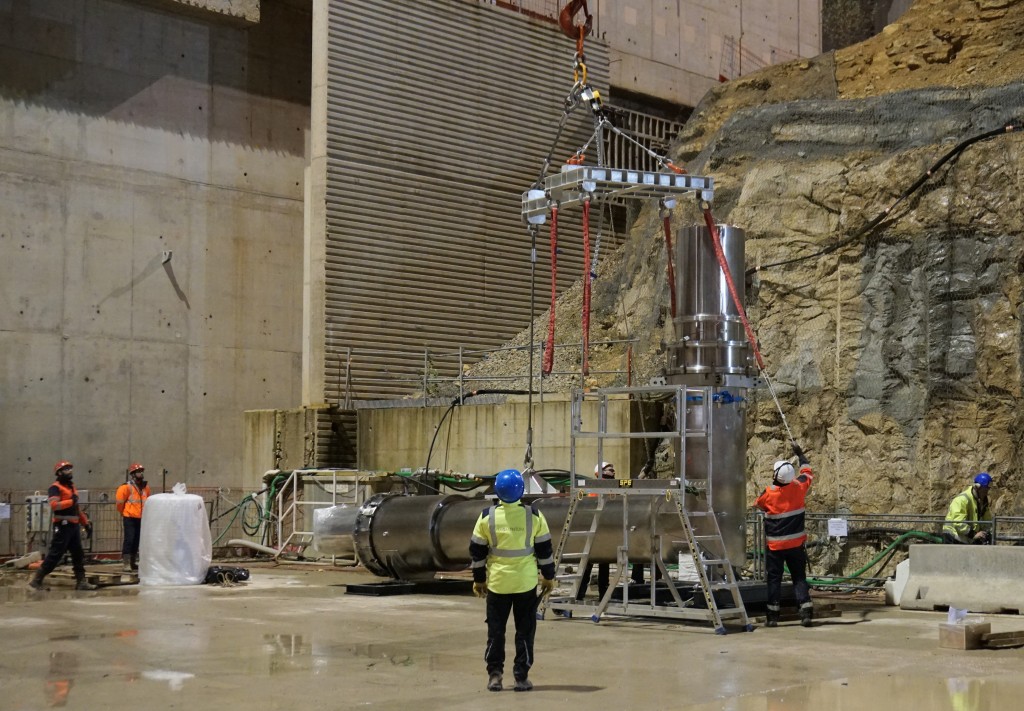
Operation underway
2018-11-26 - The Sun had just set on the ITER worksite when the cryostat feedthrough for poloidal field coil #4—a big, shiny stainless-steel pipe bent at a 90° angle—was slowly lifted from the Hot Cell zone to be deposited on the third level of the Tokamak Building.
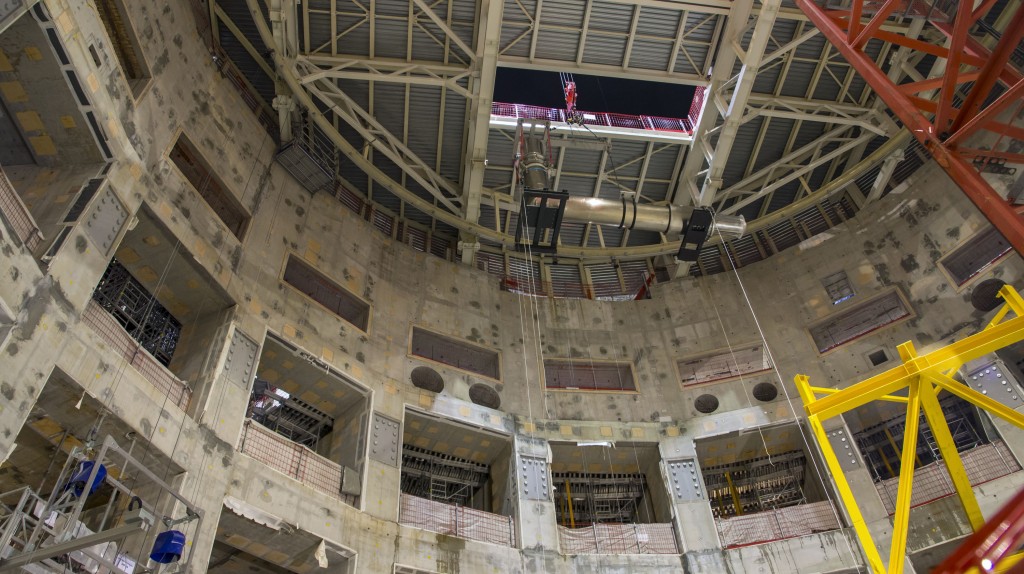
Through the opening
2018-11-26 - The magnet feeder component passes through one of the openings of the temporary bioshield lid. This lid will remain in place until the Tokamak Building roof is completed.
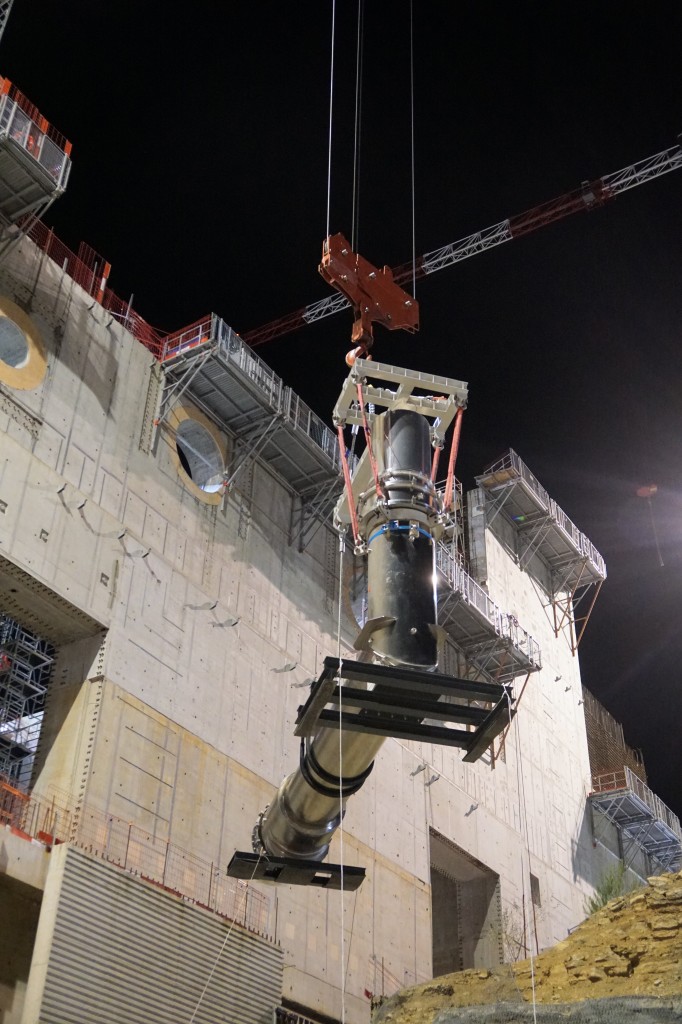
Up it goes
2018-11-26 - The 10-metre, 6.6-tonne component (part of a magnet feeder for poloidal field coil #4) is slowly lifted up and over the wall of the Tokamak Complex, to be posed near the top of the ITER bioshield. From there, it will be lowered into the pit.
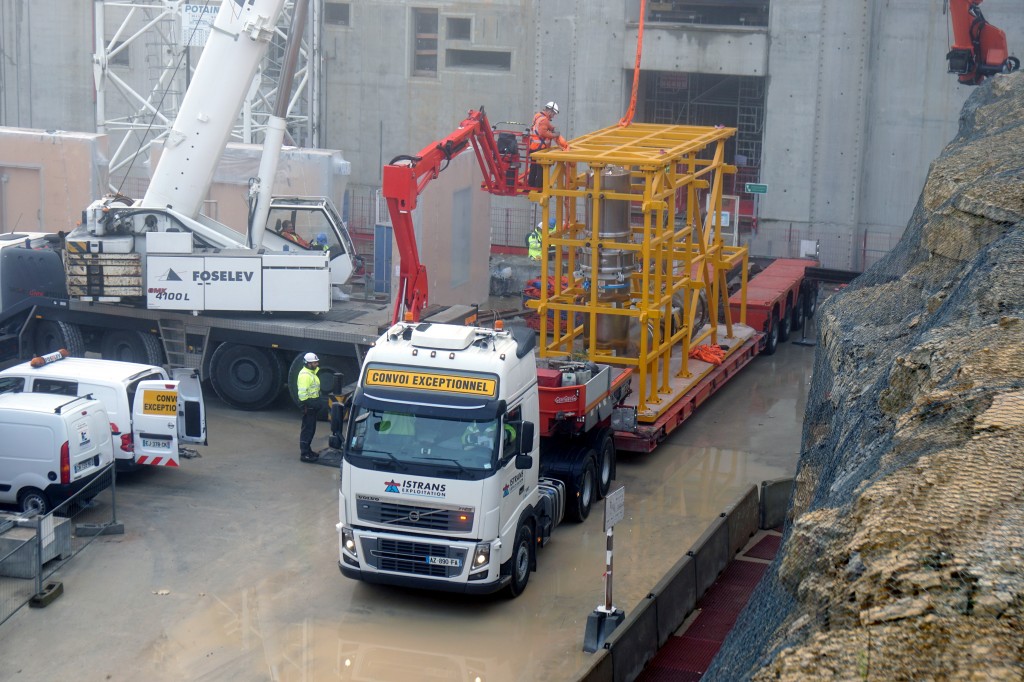
Tests completed
2018-11-26 - The first metallic component to be installed in the machine pit—a feeder component—had been delivered by China for testing to the Magnet Infrastructure Facilities for ITER (MIFI), next door on the CEA site, one year ago. On 26 November, it was positioned outside of the Tokamak Complex for lifting.
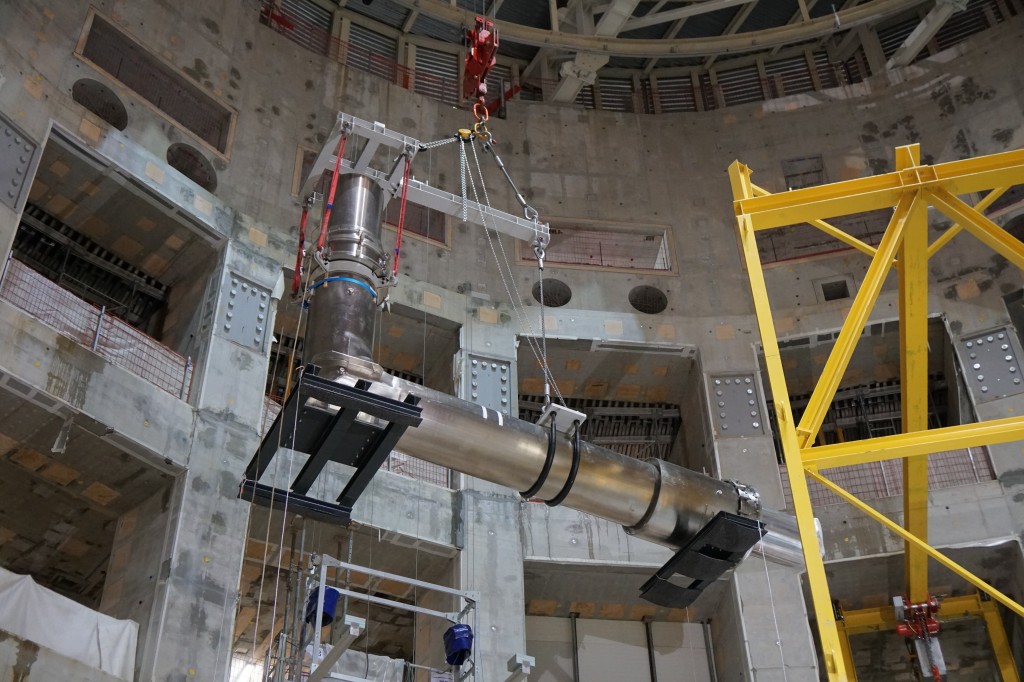
First of many
2018-11-26 - The feeder array for the ITER magnets is composed of over 100 main components. This one was scheduled for delivery ahead of the others because of its particular shape and its installation configuration at the lower level of the Tokamak Pit.
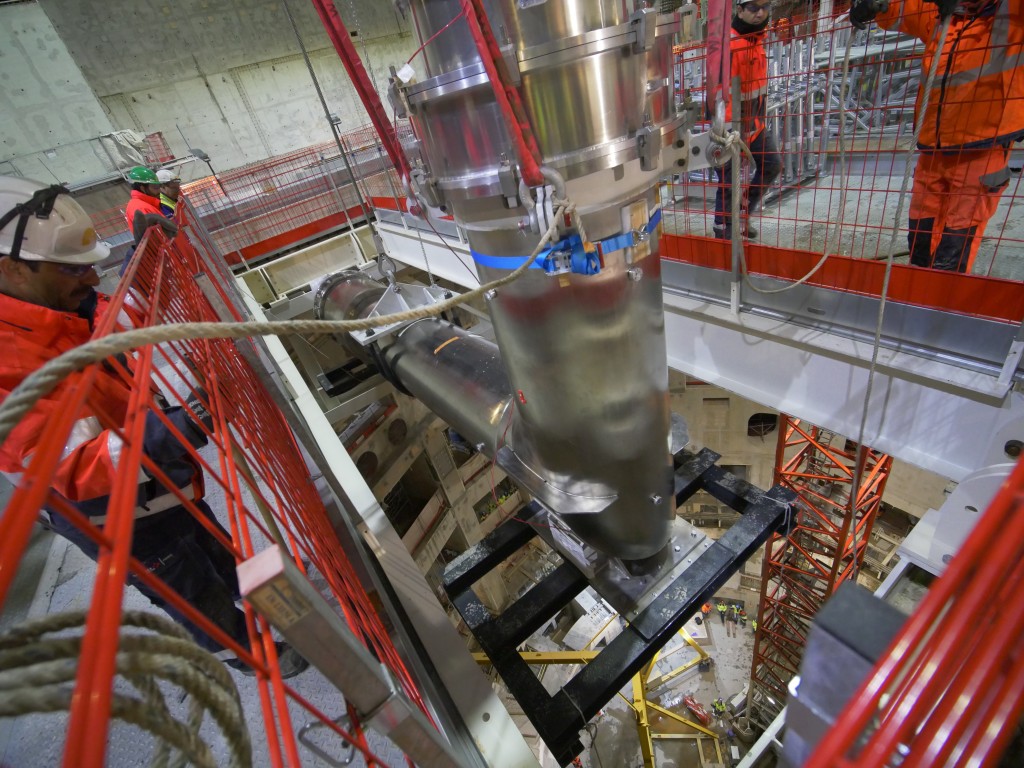
The first one
2018-11-26 - The cryostat feedthrough begins its 30-metre descent—the first metal component of the ITER machine to enter this space.

Handling frame procured in Korea
2018-11-26 - In light grey, a special handling frame that was designed and procured by the Korean Domestic Agency specifically for this operation.

Through the opening
2018-11-26 - Through the opening The magnet feeder component passes through one of the openings of the temporary bioshield lid. This lid will remain in place until the Tokamak Building roof is completed.

Up it goes
2018-11-26 - The 10-metre, 6.6-tonne component (part of a magnet feeder for poloidal field coil #4) is slowly lifted up and over the wall of the Tokamak Complex, to be posed near the top of the ITER bioshield. From there, it will be lowered into the pit.
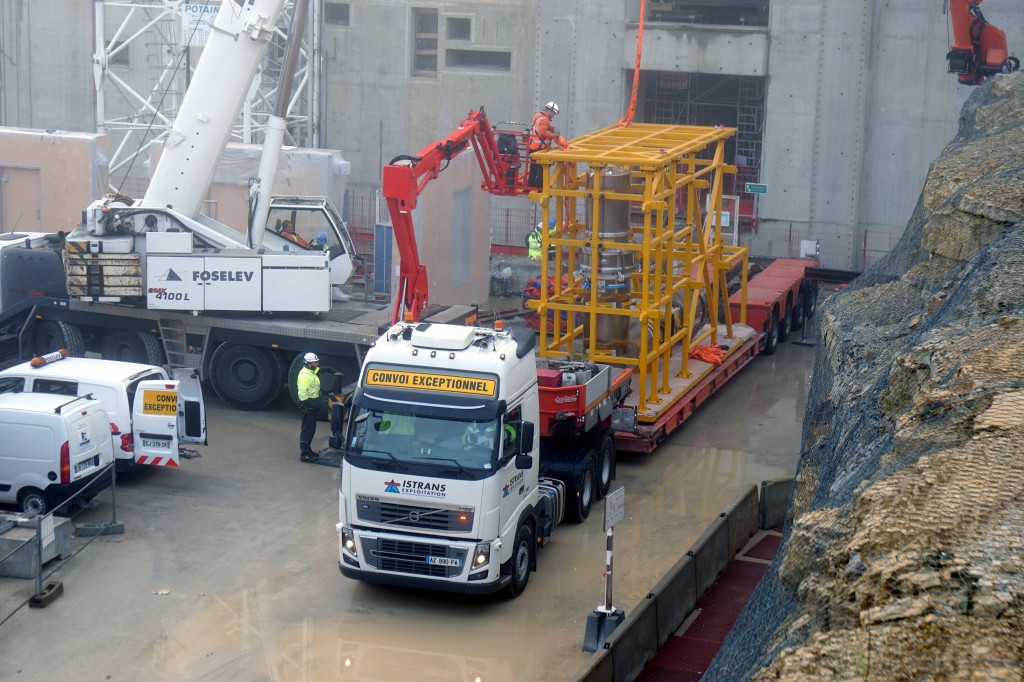
Tests completed
2018-11-26 - The first metallic component to be installed in the machine pit—a feeder component—had been delivered by China for testing to the Magnet Infrastructure Facilities for ITER (MIFI), next door on the CEA site, one year ago. On 26 November 2018, it was positioned outside of the Tokamak Complex for lifting.
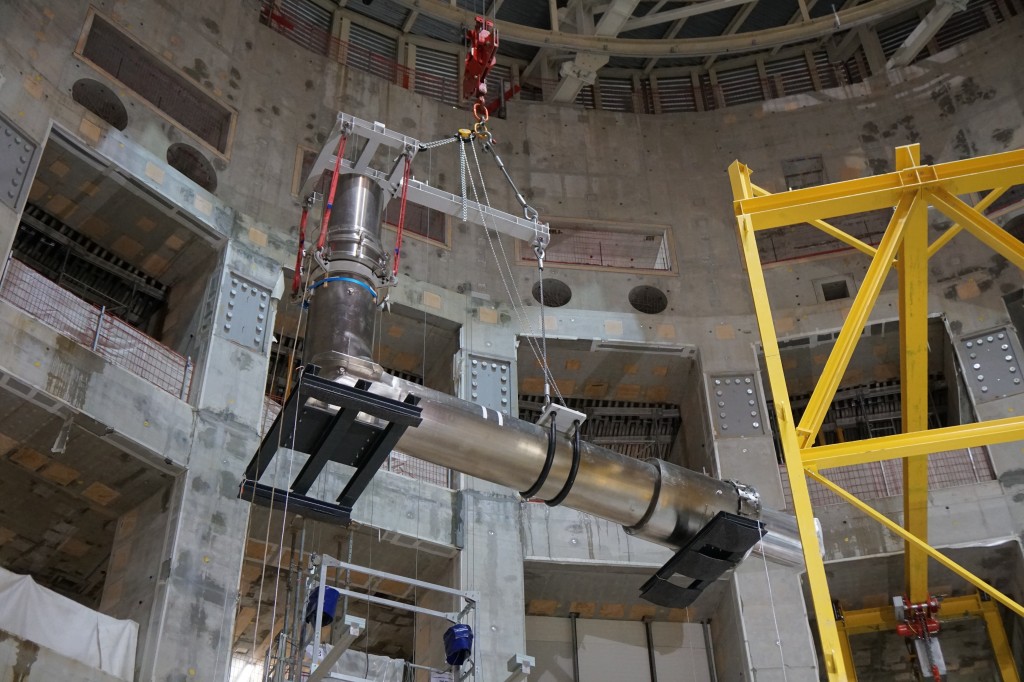
First of many
2018-11-26 - The feeder array for the ITER magnets is composed of over 100 main components. This one was scheduled for delivery ahead of the others because of its particular shape and its installation configuration at the lower level of the Tokamak Pit.
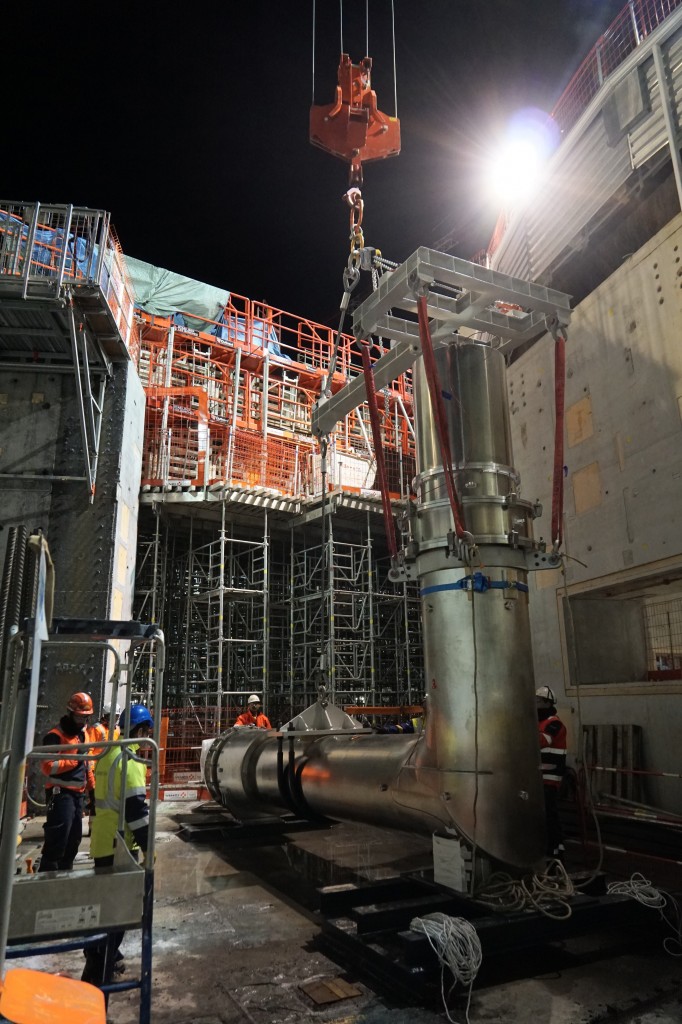
Close to home now
2018-11-26 - A quick halt near the bioshield, up at the top of the Tokamak Complex, as the team organizes the equipment for the final lift.
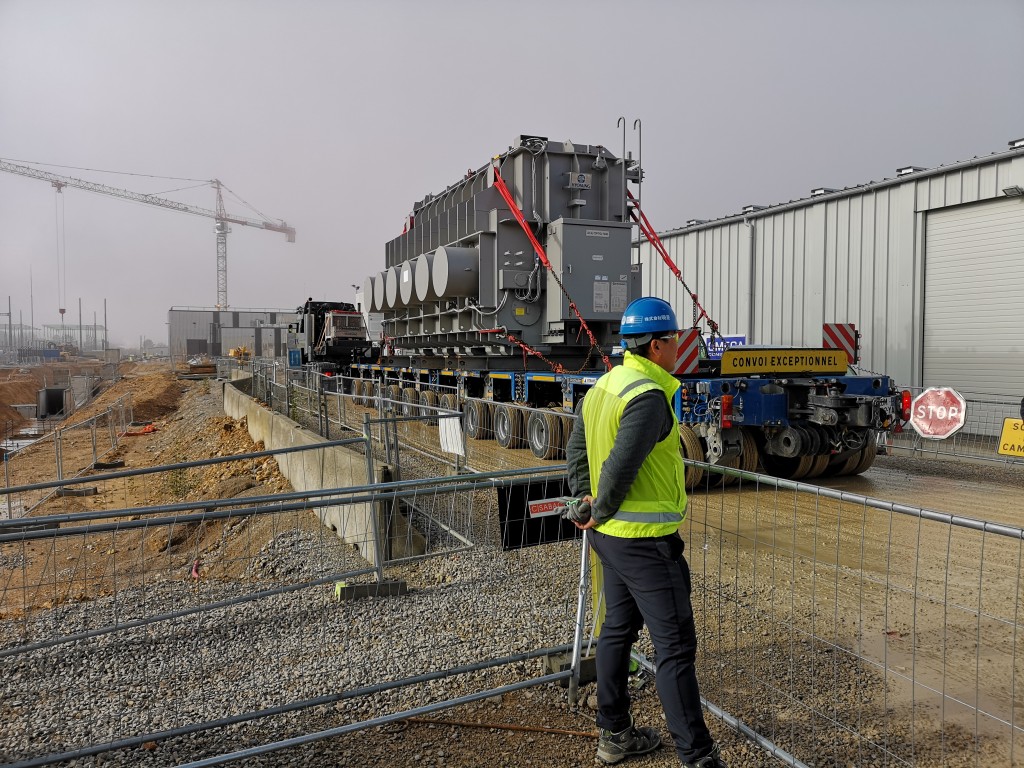
Transformers moved on site
2018-11-26 - Four transformers recently delivered to the ITER site have been moved to their final berths. In the lot, were three central solenoid converters procured by Korea and one poloidal field coil rectifier procured by China. ITER's Field Engineering Installation Division was in charge of the operation.

A special kind of house
2018-11-22 - This "electrical house" (E-houses) will accommodate dozens of instrumentation and control cubicles that relay orders from the control room to the installation's high voltage components. In November is transported to its final platform location.

A special kind of house
2018-11-22 - This "electrical house" (E-houses) will accommodate dozens of instrumentation and control cubicles that relay orders from the control room to the installation's high voltage components. In November is transported to its final platform location.
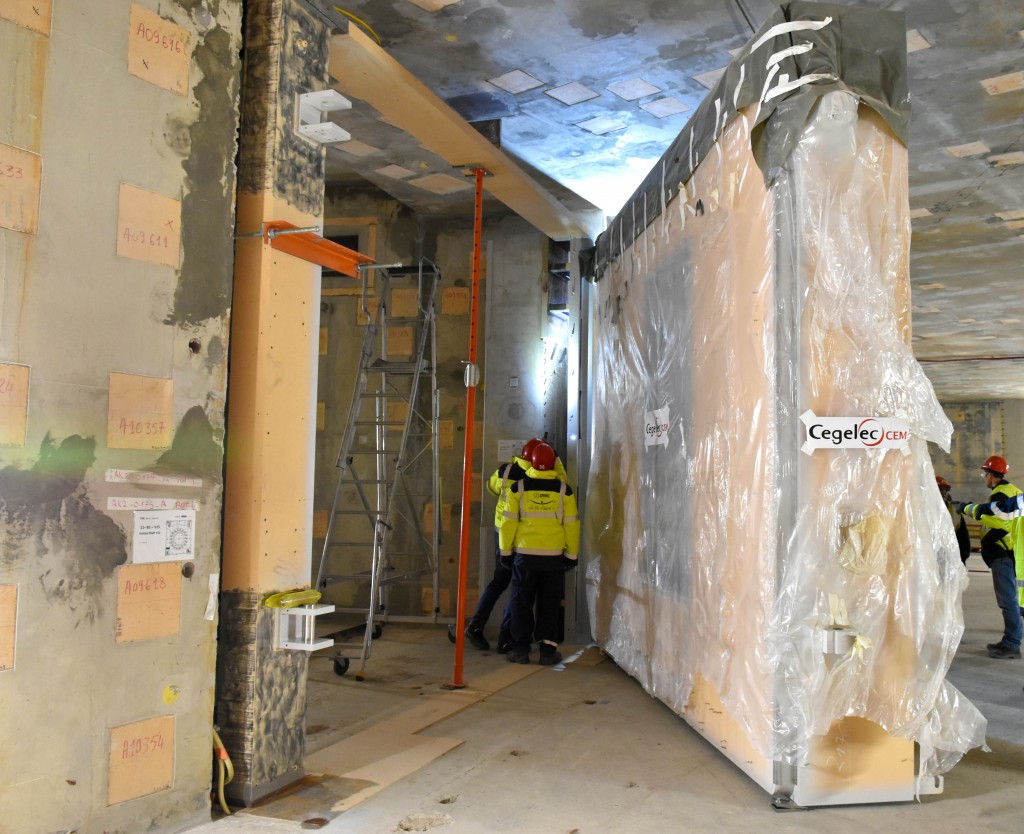
First nuclear door installed
2018-11-15 - This 60-tonne nuclear door was set into place in November—the first of 46 to be installed at the openings of port cells leading to the Tokamak. All went well, as the dedicated mounting tool successfully transferred the weight of the door to the heavy duty hinges.

Success
2018-11-15 - A remote-controlled camera positioned above helped operators to align the door with its hinges exactly. Representatives of the ITER Organization, the European consortium VFR, and sub-contractor Cegelec/Sommer were all present for this first door installation operation
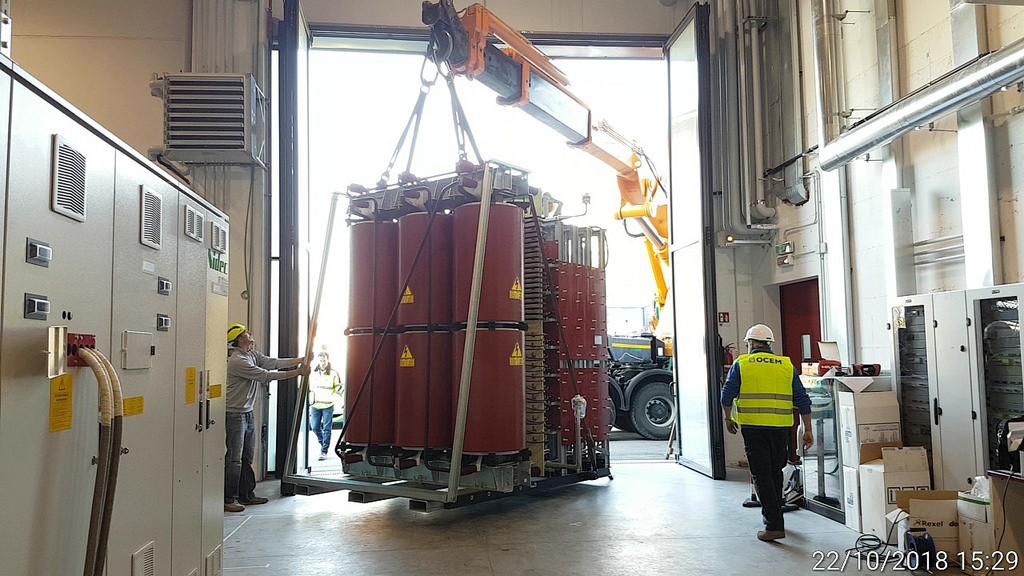
Power supply equipment for MITICA
2018-11-15 - Equipment arrives for the MITICA power sources, delivered by the European Domestic Agency. Centre: the power supply for MITICA's residual ion dump (manufactured by OCEM ET, Italy); at left, the conversion system for the acceleration grid power supply (manufactured by Nidec ASI, Italy).

Selfies in front of the Tokamak Complex
2018-11-14 - Some 135 young "doctors in fusion"—PhD students specializing in fusion science and technology in Europe—were on site in November for a three-day event organized by FuseNet and the ITER Organization. A perfect occasion for selfies ...

A peek into the Cryostat Workshop
2018-11-13 - The lower cylinder of the cryostat is seen through the open doors of the workshop.

Factory acceptance tests underway
2018-11-12 - Factory acceptance tests are underway on components of the MITICA high-voltage power supply procured and delivered by the Domestic Agencies of Europe and Japan.
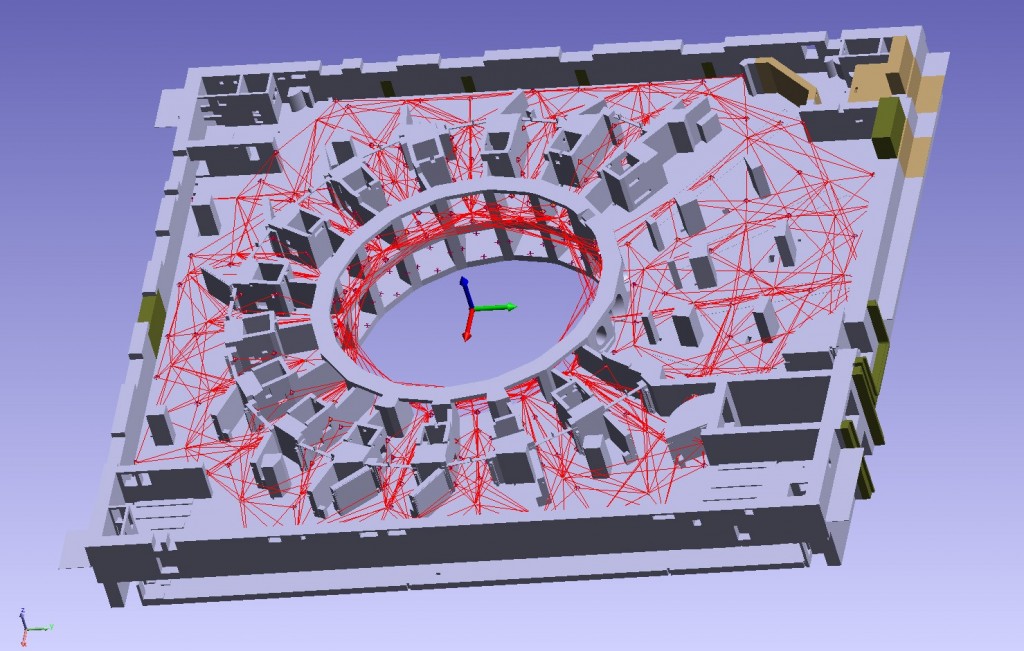
For the alignment of machine components and plant systems
2018-11-12 - A vast network of fiducial target nests installed on the concrete surfaces of the bioshield, port cells and galleries will enable installation contractors to align components to sub-millimetre accuracy. Advanced software was used to lay out the positions of each instrument station and simulate clear lines of sight to the fiducial nests. This simulated measurement geometry was used to predict the measurement uncertainty to be expected, which was subsequently qualified with real measurement data. (Pictured: one level of the Tokamak Complex)
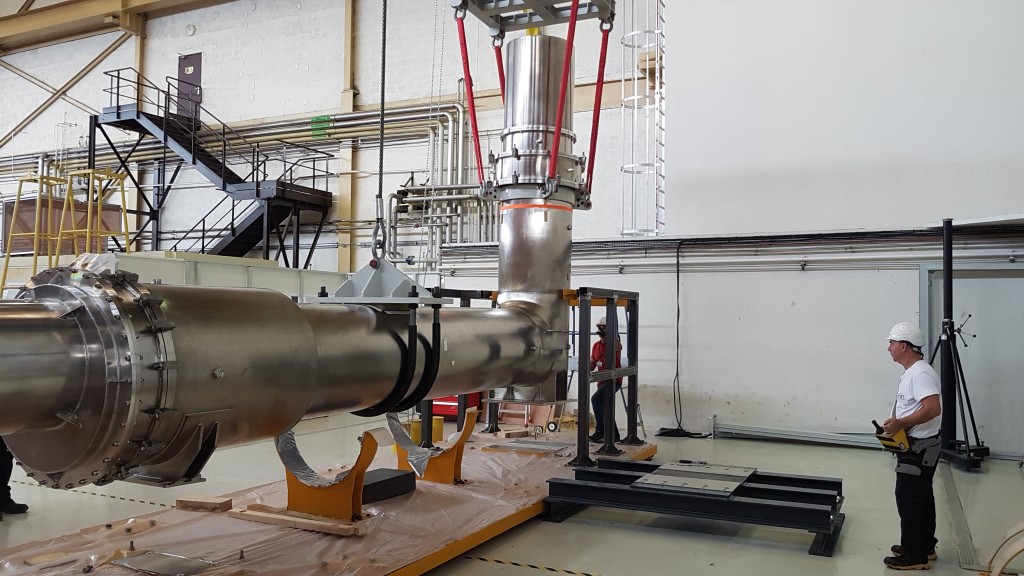
First machine component in November
2018-11-12 - This six-tonne metal component—part of a magnet feeder—will be the first piece of the machine to be lowered into the Tokamak Pit. Installation activities will take place in the third week of November.
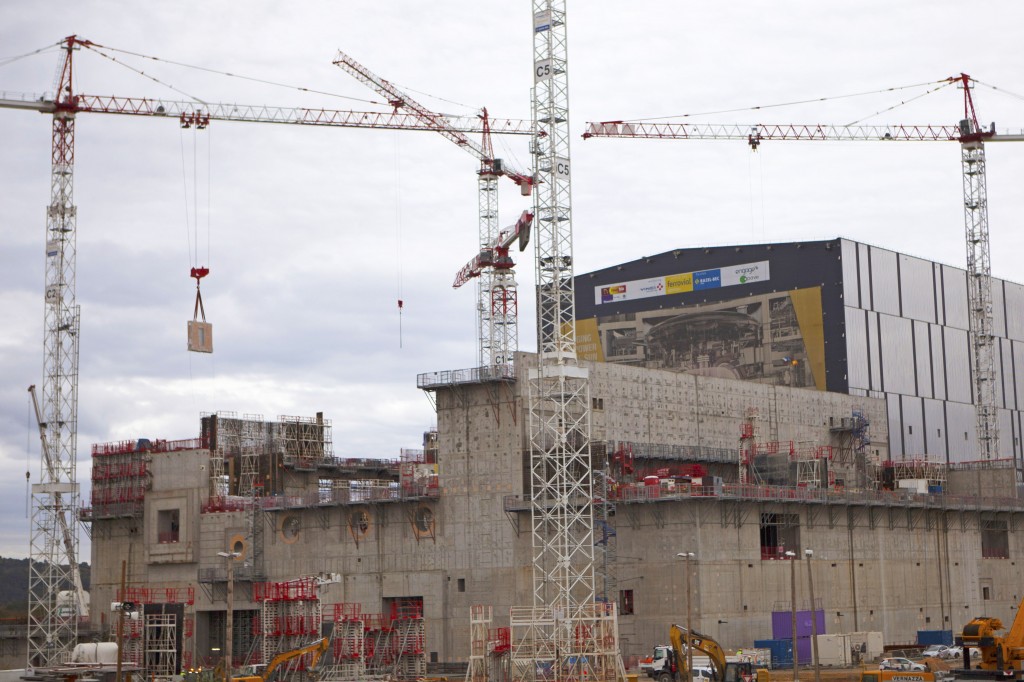
Delivering doors
2018-11-08 - One of 46 nuclear doors is lowered by crane into the Tokamak Building. Photo courtesy of Thomas Body, IPP.

Destined for the cryostat
2018-10-24 - Doric or ionic? Neither. What looks like broken columns from a Greek temple are in fact steel ingots, cooling on a bed of black sand inside the Larsen & Toubro foundry in Hazira, India. Weighing 6 to 200 metric tonnes, they are the raw material for the fabrication of cryostat segments.

Cryolines in production
2018-10-24 - INOXCVA in India is producing about half of the 5 km of cryolines needed for ITER (700 "spools") for the Indian Domestic Agency. Eighty percent have all kinds of angles, bends and turns.

Inside Medium Fabrication Shop #4
2018-10-23 - On their way back from lunch, workers at Larsen & Toubro's Hazira faility pass by ongoing works for the ITER cryostat inside Medium Fabrication Shop #4.

Visiting Larsen & Toubro
2018-10-23 - On 23 October Director-General Bernard Bigot visits Larsen & Toubro's Hazira facility, where the segments of the ITER cryostat are produced.

Drawing to a close
2018-10-23 - A formidable industrial venture that began in 2015 is nearing its end. At the Larsen & Tourbo Hazira manufacturing complex, work is underway on the two last orders the company is filling for the ITER cryostat: segments of the 430-tonne upper cylinder and 665-tonne top lid.

Welds. welds and more welds
2018-10-23 - Despite Larsen & Toubro's extensive experience in manufacturing for the nuclear and space industries, new processes and techniques had to be specifically developed for the welding of the cryostat segments. Pictured here: the welding of two segments for the top lid.
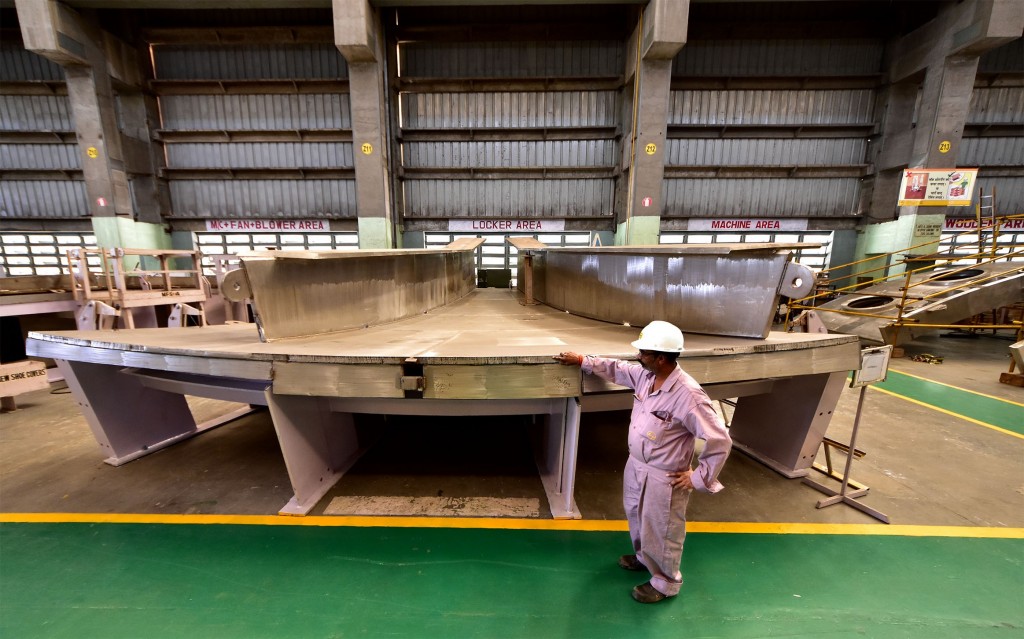
A prototype sector for the lid
2018-10-23 - The 655-tonne top lid will be the last of four cryostat sectors to leave the Larsen & Toubro factory (in segments). Before series manufacturing began, a prototype segment was manufactured in order to check potential profile distortions. All 12 top lid segments will be ready for dispatch in the summer of 2019.
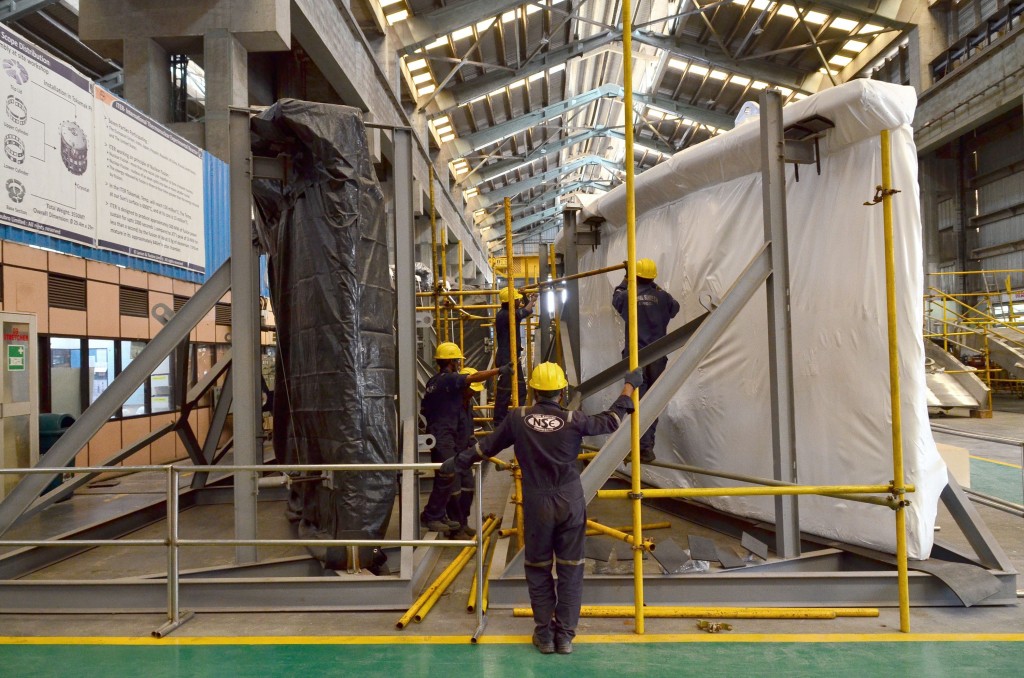
Packing is done
2018-10-23 - These tier-two upper cylinder segments are being packed and conditioned for the long journey to the ITER site. In the on-site Cryostat Workshop, Larsen & Toubro contractors will weld tier-one segments first, then position tier-two segments on top. Upper cylinder segments will begin arriving at ITER in March 2019.

Last verification
2018-10-23 - Final dimensional inspection is being conducted on an upper cylinder sector for the ITER cryostat. Seven segments are packed and ready for dispatch; another two are undergoing finishing works and inspections.

Like a leaf
2018-10-20 - This "leaf mounting tool" has been specially conceived to manoeuvre the nuclear doors that will seal off the 46 individual galleries (port cells) that spoke off from the machine pit. The doors weigh 30 tonnes on delivery, and 30 more after they have been filled with concrete.

Solid frames
2018-10-20 - At the end of each nine-metre port cell gallery, teams are creating frames to receive heavy nuclear doors. Filled with heavy concrete, the doors will play a role in shielding workers and the environment from fusion-generated radiation.
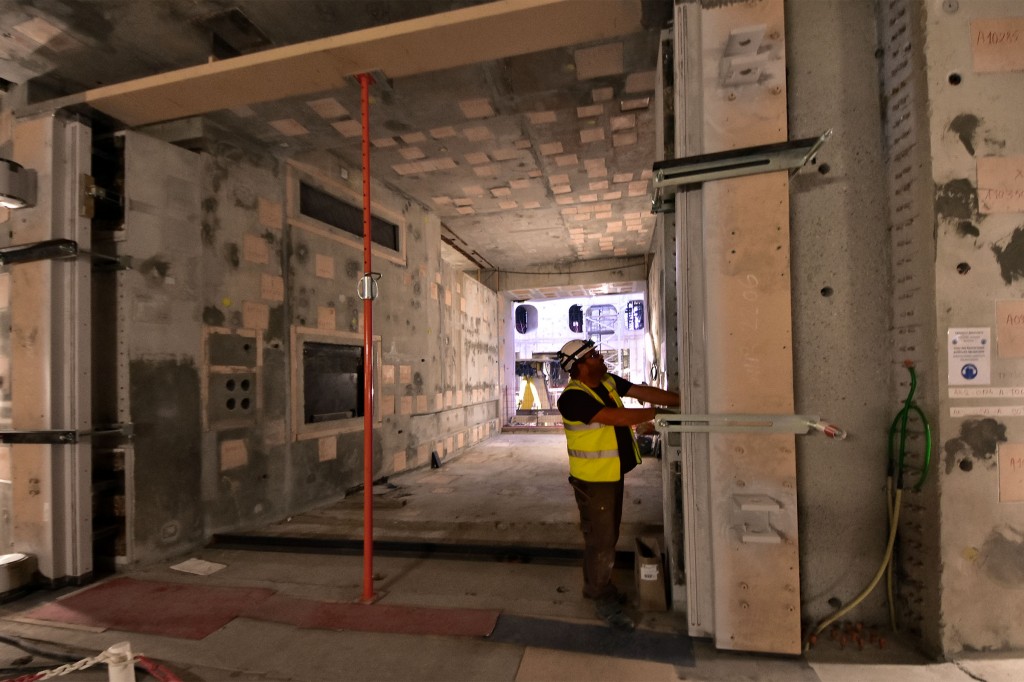
46 port cells
2018-10-19 - Extending out radially from the concrete bioshield—like so many spokes around a central hub—are nine-metre-long chambers called port cells. The port cells will accommodate heating pipes, electricity cables, diagnostic lines and maintenance systems as they pass through to the vacuum vessel from outlying galleries.
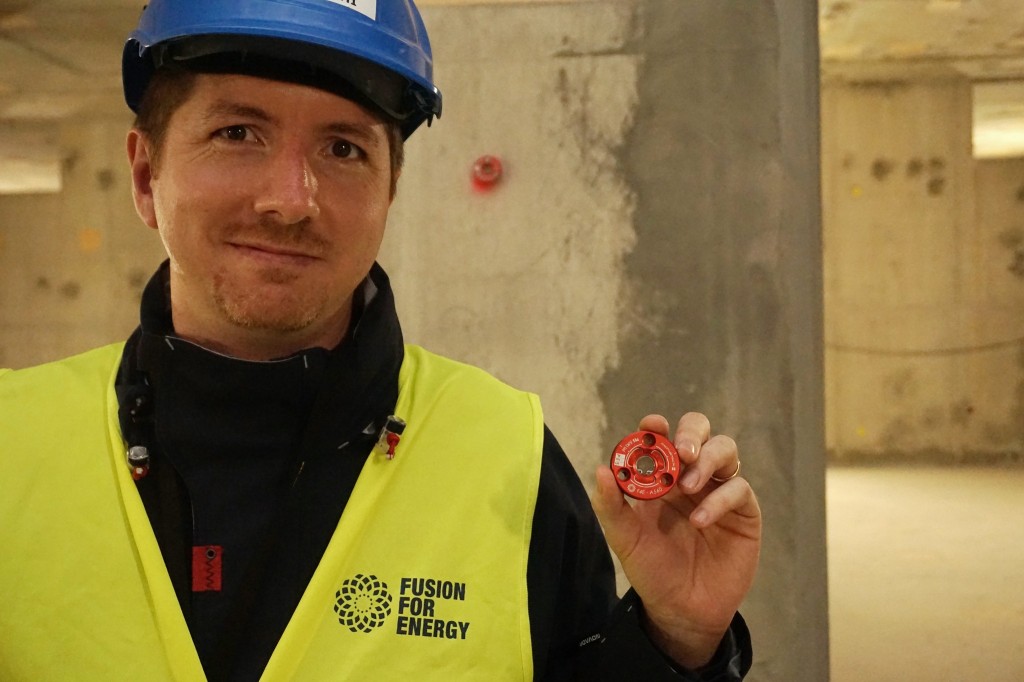
Perfectly planned points
2018-10-15 - A vast network of fiducial target nests installed on the concrete surfaces of the bioshield, port cells and galleries will provide the reference datum for the dimensional control and alignment of machine components and plant systems. European contractors are in the process of installing approximately 2,000 of them. Photo: F4E

Fiducial target nests
2018-10-15 - 2,000 of these small fiducial tests will be placed by European building contractors in accessible areas of the Tokamak Complex. The nests are used to receive spherically mounted reflectors (SMRs), which are surveyed with laser trackers to establish their coordinate values and confirm their compliance with the simulation used during the network design process. Photo: F4E
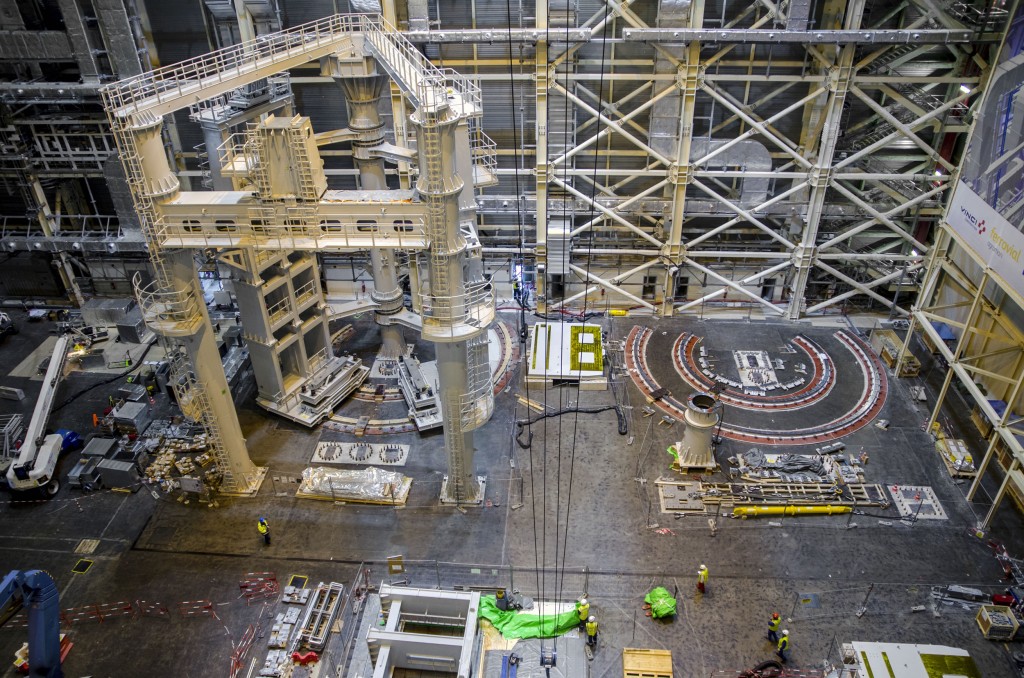
Load tests next year
2018-10-12 - Both tools will be tested with a full-weight dummy load, expected on site in March 2019. Load testing is the final tool qualification activity, allowing operators to verify the tools' ability to accurately adjust the dummy load toroidally and to six degrees of freedom within tolerances of +/- 1 millimetre.

A novel angle
2018-10-12 - This 800-tonne tool, seen from a novel angle, stands 22 metres tall and can handle a 1,200-tonne subassembly. And it will soon have an identical twin in the Assembly Hall ...

Precise alignment
2018-10-12 - Specialists are busy installing and precisely aligning the toroidal rail tracks upon which the wings of the giant tool will travel.
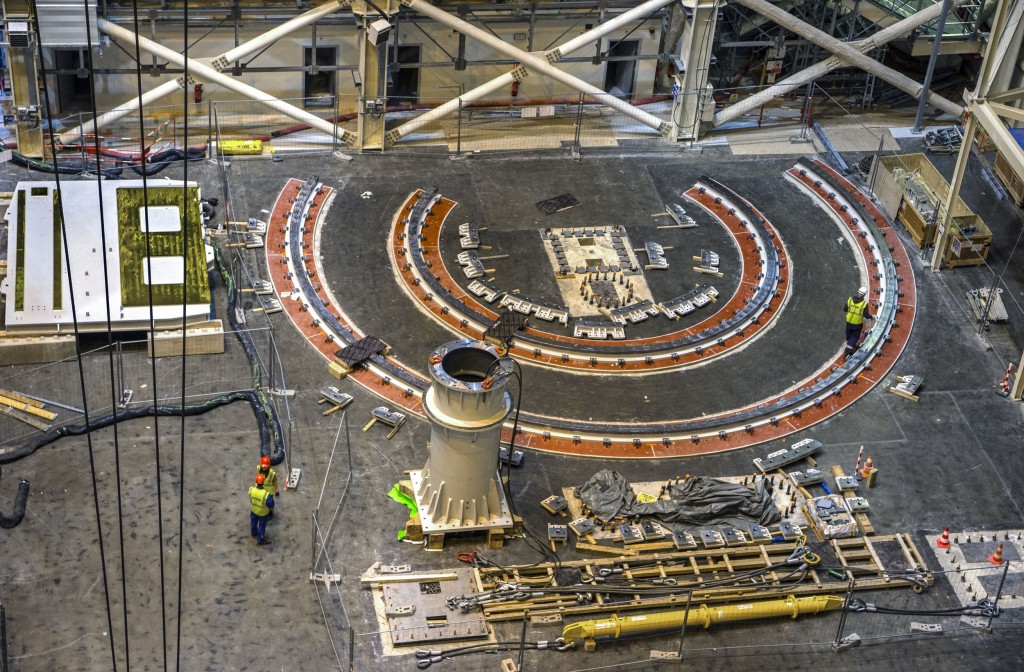
From the rafters
2018-10-12 - The technician walking along the curved rails gives us a sense of the tool's scale. The first segment of tool #2 has been positioned for installation.
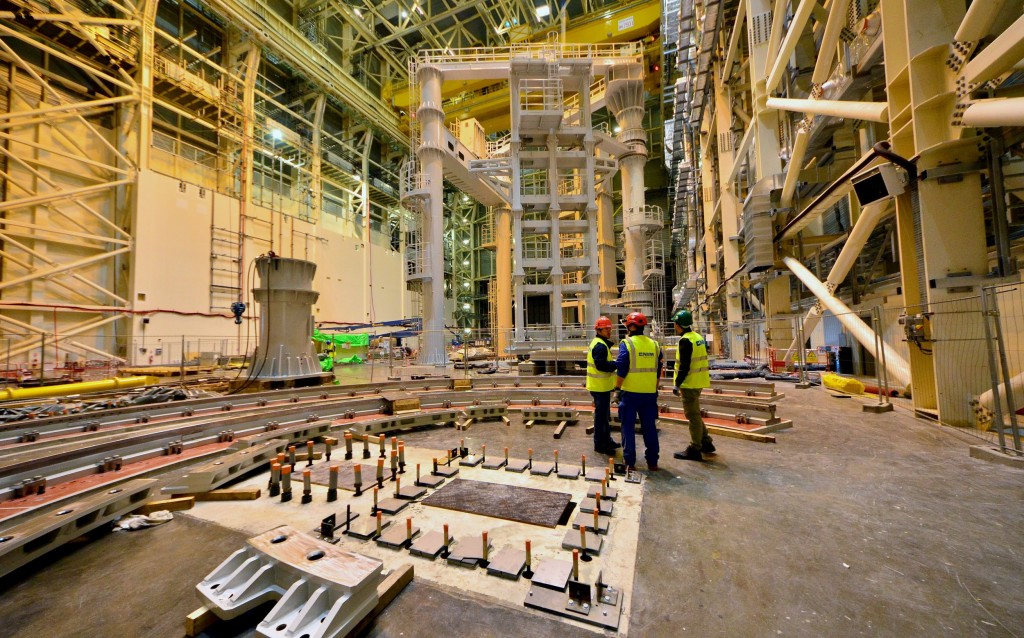
Well anchored
2018-10-12 - The tools are solidly anchored in the concrete floor of the Assembly Hall. In the foreground is the footing arrangement for the inboard column.

Tool #1
2018-10-12 - All the pieces of the first tool are in place; only hydraulic and electrical connections must be installed. Ahead are functional tests (integrated system tests without the test load), followed by full-load tests.
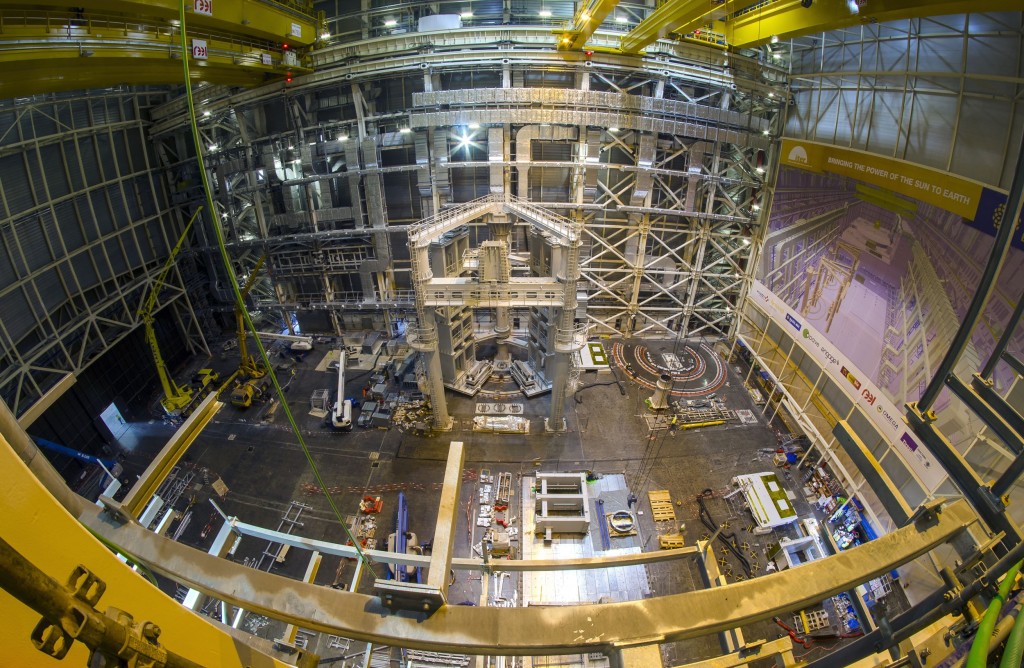
Assembly stations
2018-10-12 - On the floor of the Assembly Hall, across from the SSAT tools, other bespoke handling stations will be installed—for example, for the assembly of the central solenoid.
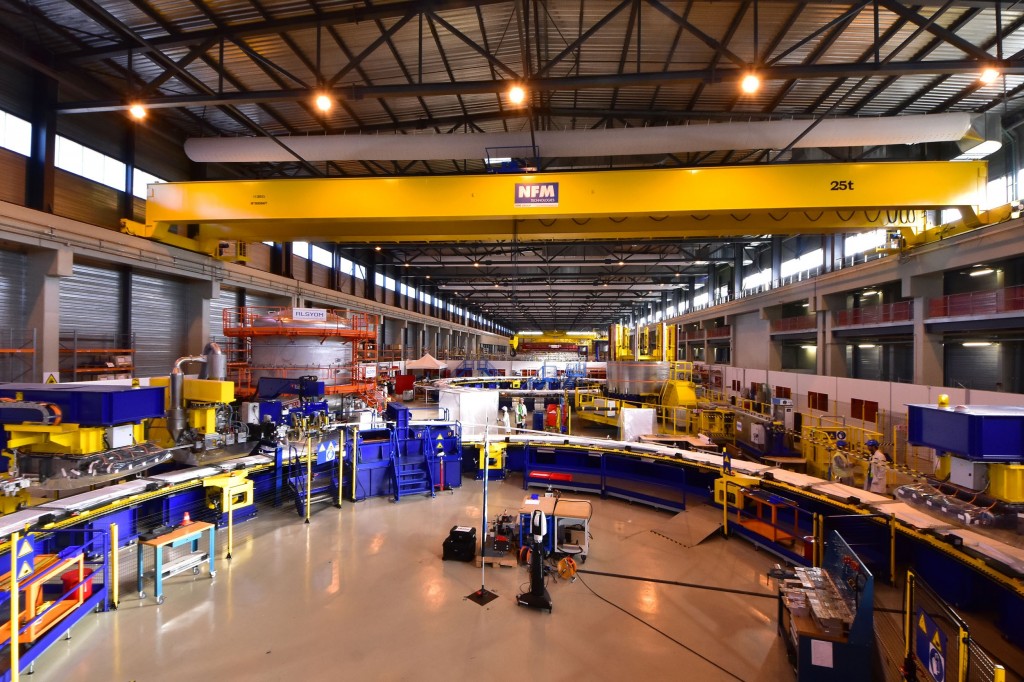
Ring magnet fabrication in full swing
2018-10-10 - Beginning with conductor winding and ending—at the other side of the 257-metre-long facility—with final assembly and cold testing, the fabrication of ITER's ring shaped magnets is a precise step-by-step process.

A precise mould
2018-10-10 - The mould is custom built around the double pancake to be impregnated. Current passed through the conductor heats the double pancake to approximately 80 degrees Celsius, all air is removed, and resin is injected slowly to fill all nooks and crannies.

Broadcast to the world
2018-10-10 - Media crews were invited to tour the ITER site in early October, including the Assembly Hall where one giant tool stands and another is going up.
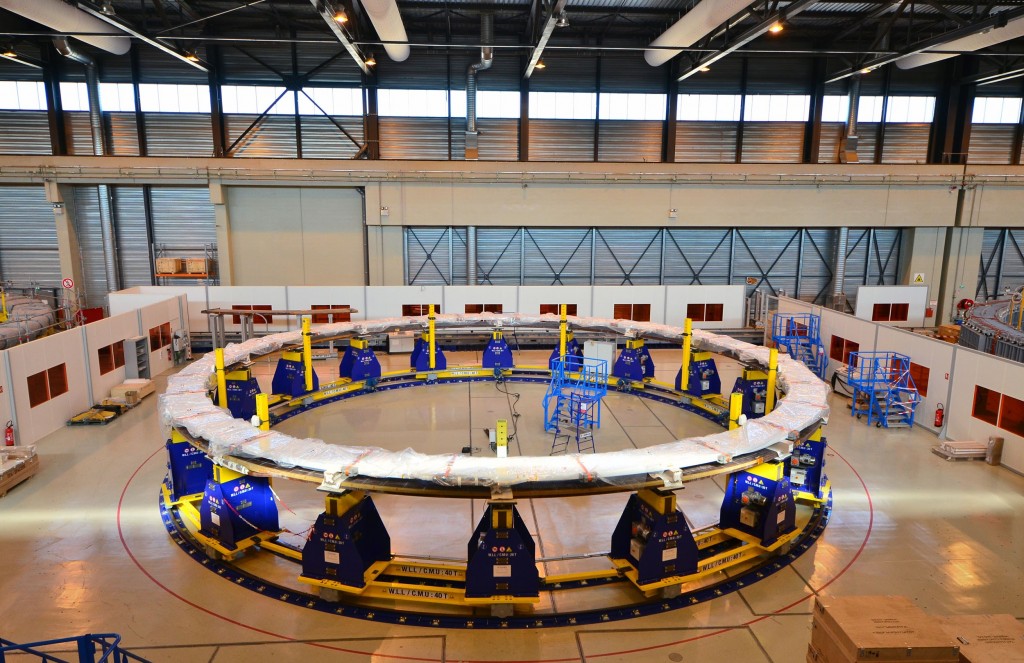
Before impregnation
2018-10-10 - Six of the eight double pancakes needed for PF5 have been wound. This staging table is used to prepare the double pancakes for the next stage—impregnation.
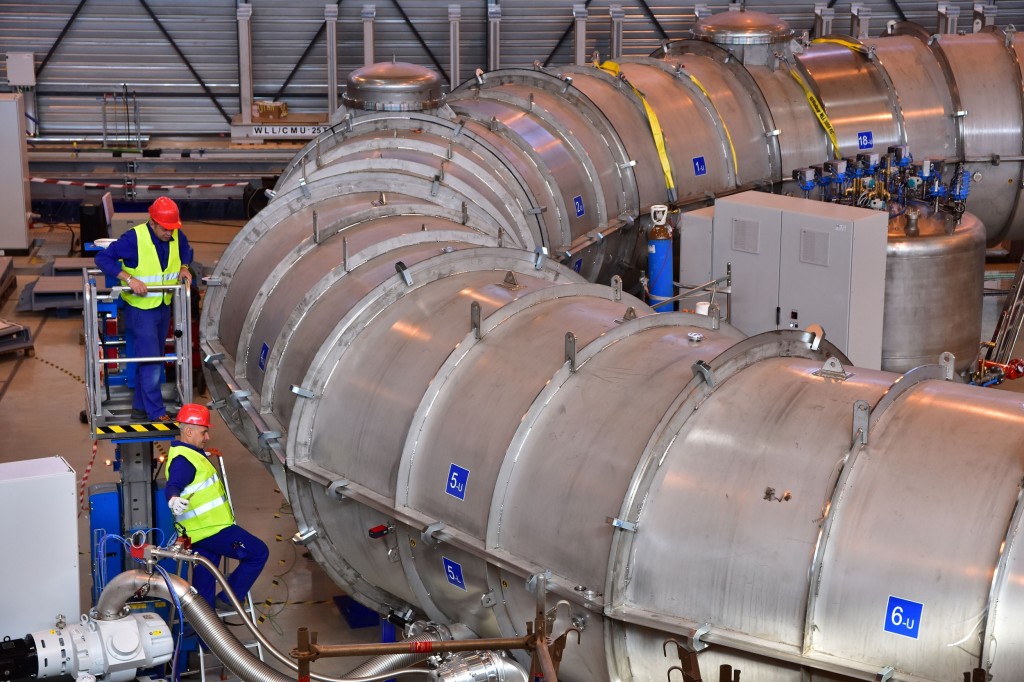
Final step: Cold testing
2018-10-10 - This cryogenic chamber will permit a final coil assembly to be tested at low temperature (approximately 80 K) in order to simulate the thermal stresses and the work conditions that will be experienced during operation. In this way, the performance of the coils will be tested before their installation in the ITER machine.

First step: winding
2018-10-10 - Two spools of niobium-titanium conductor are simultaneously fed onto the winding table to create a double pancake (a double layer of spiralled conductor.) The winding table in the picture is dimensioned for PF5 and PF2. Later, for the two larger coils PF3 and PF4 (24 metres in diameter), it will be expanded.
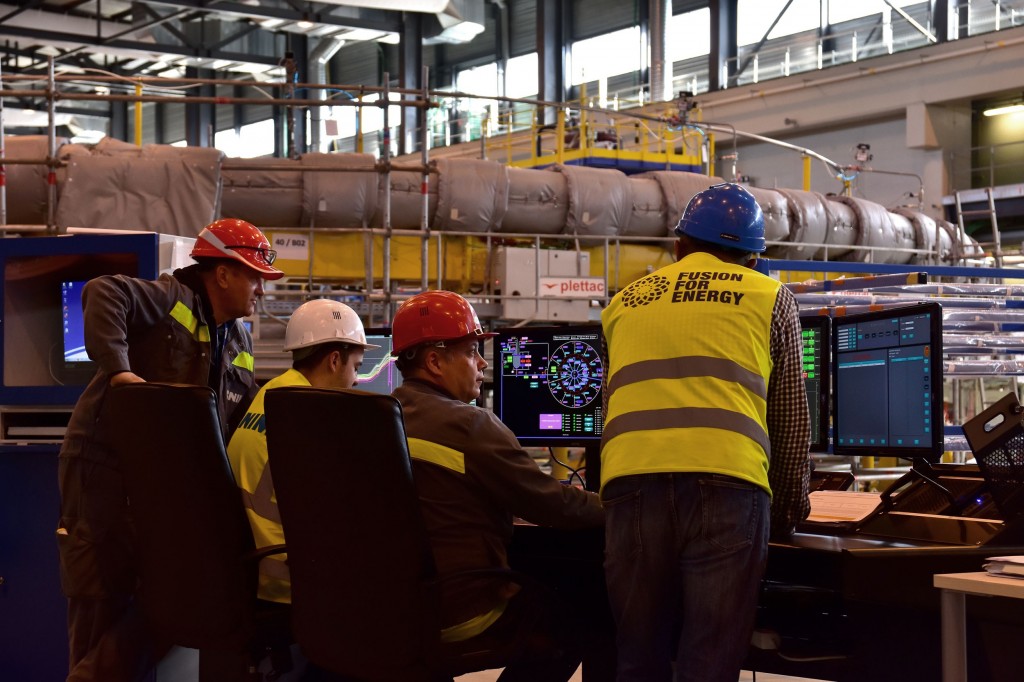
A team of 70
2018-10-10 - A team of 70 people is working daily to meet a tight production schedule. Here, the technicians are monitoring the impregnation of one double pancake.

Second step: impregnation
2018-10-10 - For the second phase of operations, the double pancake windings are transferred by overhead bridge crane to the impregnation area in the centre of the winding facility. The cranes lower the double pancakes into moulds for vacuum pressure impregnation (VPI) with epoxy resin. The resin—acting inside of a sealed mould and under the effect of heat—hardens the glass tape to bond each double pancake into a rigid assembly.
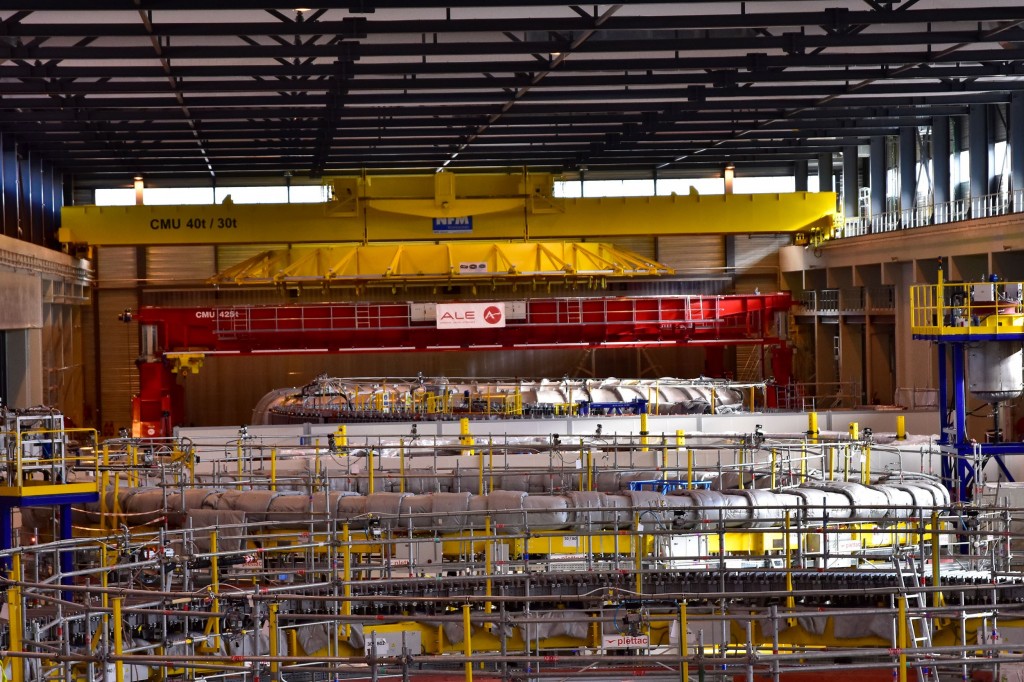
A series of workstations
2018-10-10 - Technicians are active at all of the workstations of the Poloidal Field Coils Winding Facility, either performing work on the first production unit PF5, or qualifying later stages. The European Domestic Agency reports that, all activities combined, the first coil is 42 percent complete.
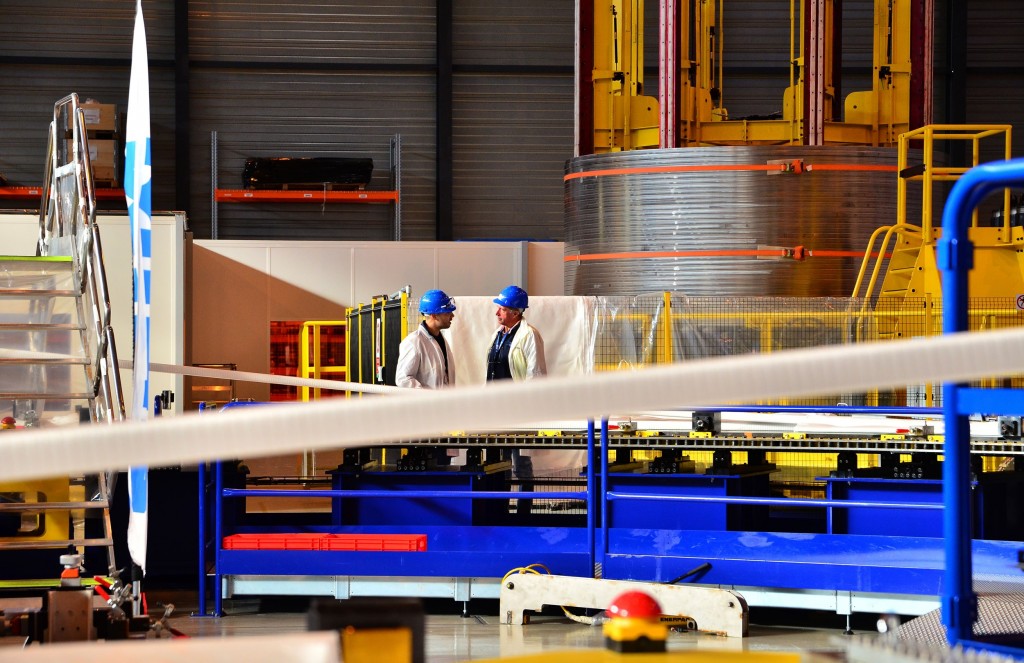
Glass-fibre tape
2018-10-10 - During the winding process the conductor is wrapped with several layers of glass-fibre tape, which insulates the conductor turns one from another.
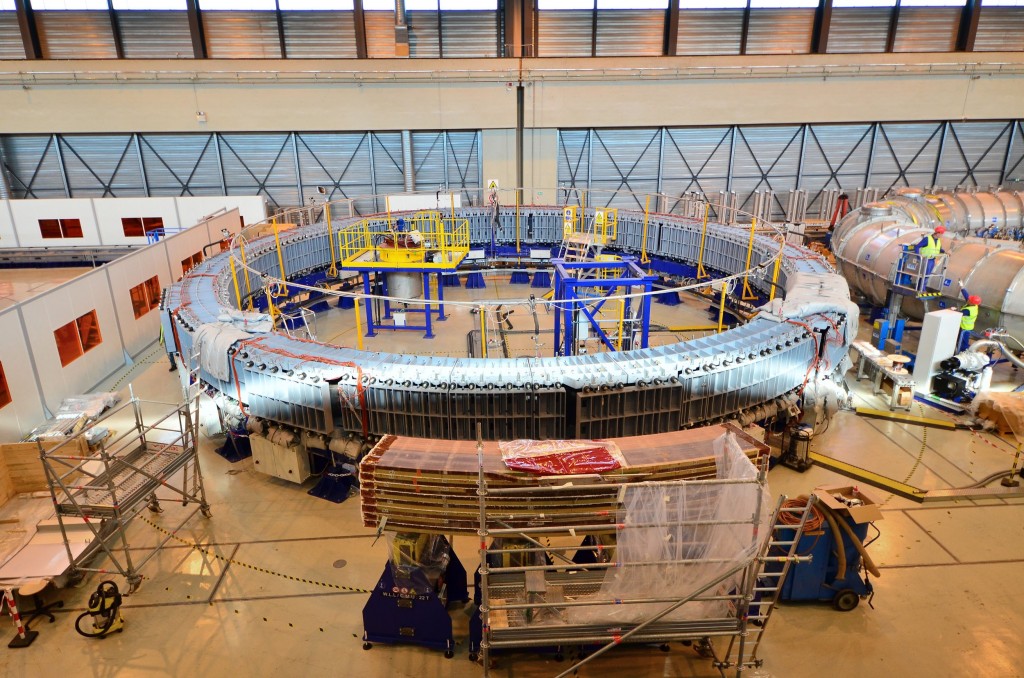
A larger mould for the stacked assembly
2018-10-10 - The rigid double pancakes will be stacked and joined electrically to form the winding pack (in the case of PF5, eight double pancakes will be stacked). The final assembly will undergo a second impregnation process in this larger mould. Notice in the foreground, a segment of mockup winding that was created from multiple layers of dummy impregnated conductor lengths to test all processes.

On the critical path
2018-10-08 - The ITER Organization and the seven Domestic Agencies are working to very detailed and closely monitored schedules to reach First Plasma in 2025. Project control metrics show that 57 percent of total First Plasma work scope has been completed (a figure that includes design activities, component manufacturing, building construction, shipping and delivery, assembly and installation). In March 2020 the Tokamak Building will have a roof and the first limited crane access will be possible between the Assembly Hall and the machine assembly pit.
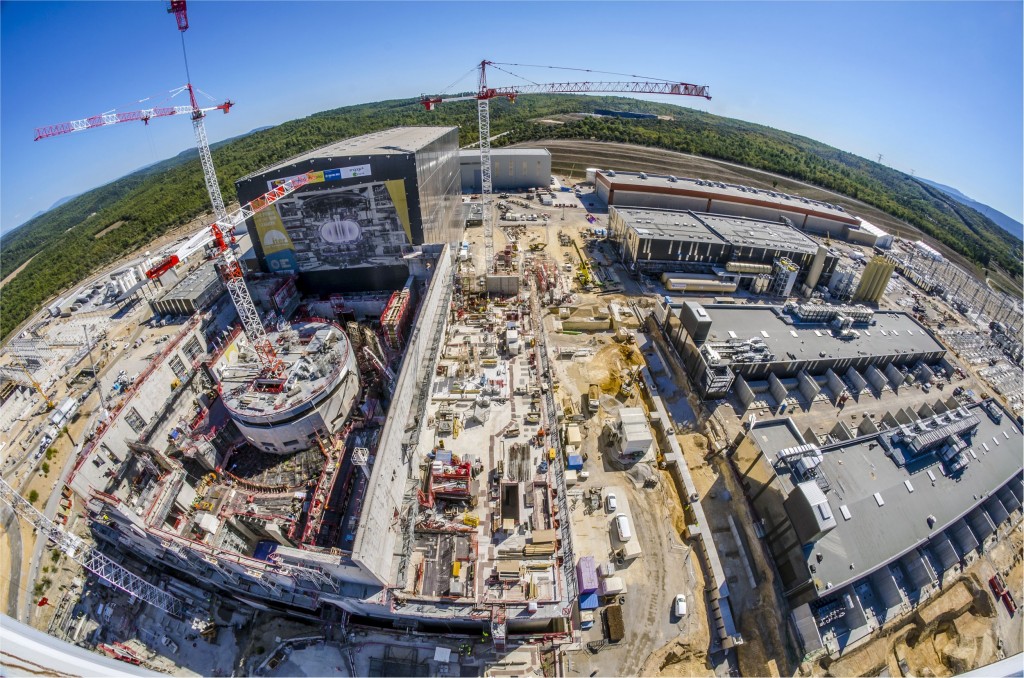
Boomtown
2018-10-08 - From the C5 crane, we can see a small town booming with activity: to the left, the 60-metre-high Assembly Hall and the circular bioshield ressembling a jewel in its box; to the right, part of the industrial infrastructure (power conversion, cryoplant, electrical switchyard) that will support machine operations.

All kinds of shapes
2018-10-08 - Seen from the main ITER office building, the facade of the Tokamak Complex is changing at a fast pace. The column of openings to the left shows where the cask and plug robotic system will move components between the Hot Cell Facility and the port openings at different levels of the machine. The four circular openings will allow the passage of the high voltage transmission lines for the neutral beam systems (diagnostic neutral beam far left, neutral beam heating three on right).
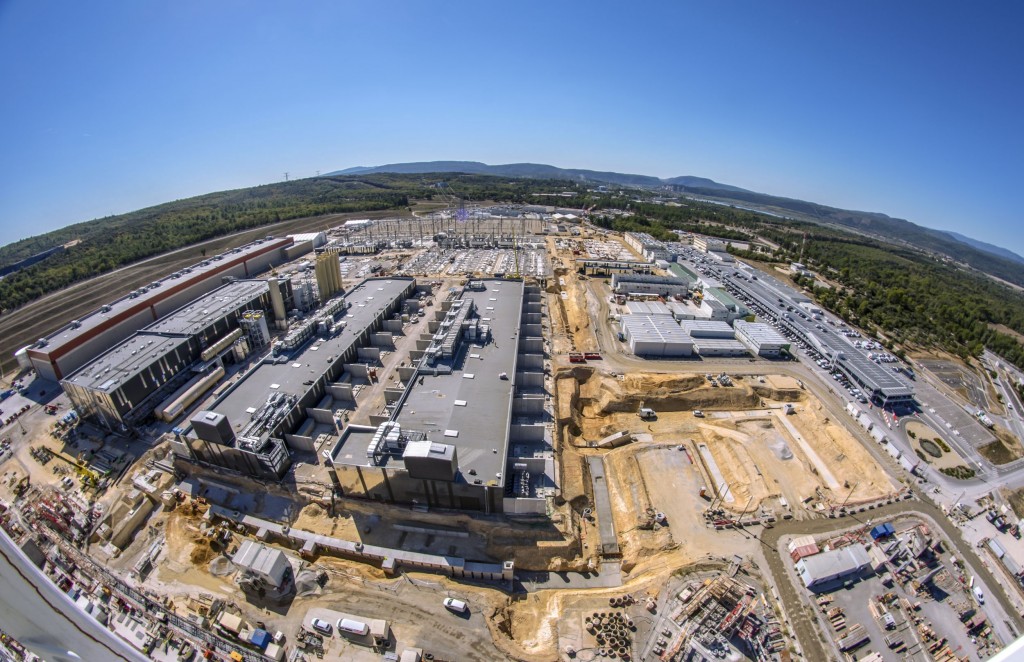
In support of
2018-10-08 - Some 30 plant systems will be installed to support the machine. On the one-kilometre-long ITER construction platform, infrastructure and buildings rose in 2018 for cryogenics (second from left), magnet power supply (twin buildings in centre), power distribution and heat rejection (not pictured).

Intricate webs of rebar
2018-10-08 - The nuclear concrete structure around the ITER machine will contain 30,000 tonnes of rebar and 150,000 m³ of concrete. The densest, thickest and most intricate rebar arrangements are located under the machine, in the concrete floor (basement), the recently completed crown, and the crown's radial walls.

In the driver's seat
2018-10-08 - The ITER Organization is based in this five-storey, 215-metre-long building in Saint Paul-lez-Durance, France. Through the bridge that connects the building to the construction worksite, machine operators will be able to pass directly on to the Control Room.

Rushing water
2018-10-05 - The cooling water circulating through the different cooling loops of the ITER installation will be directed toward the heat rejection zone through galleries like this. The maximum total flow rate during operation is 14 m³/s. © Les Nouveaux Médias/SNC ENGAGE
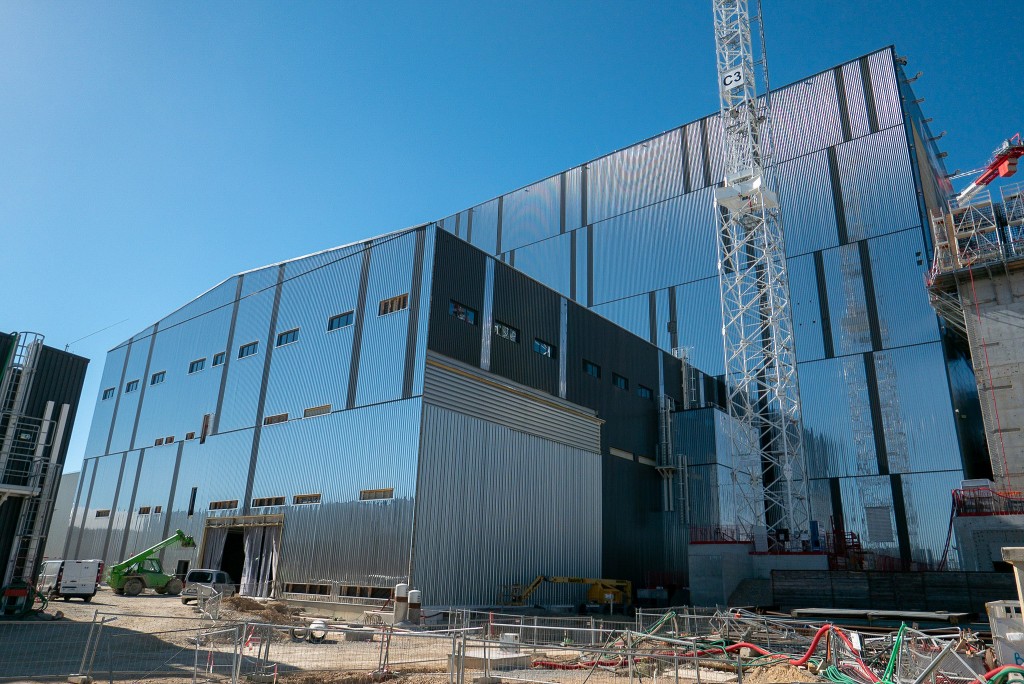
Heating building
2018-10-03 - This building to the side of the Assembly Hall will contain the power sources and wave generators for two of ITER's external heating systems—the ion cyclotron and the electron cyclotron systems. © Les Nouveaux Médias/SNC ENGAGE
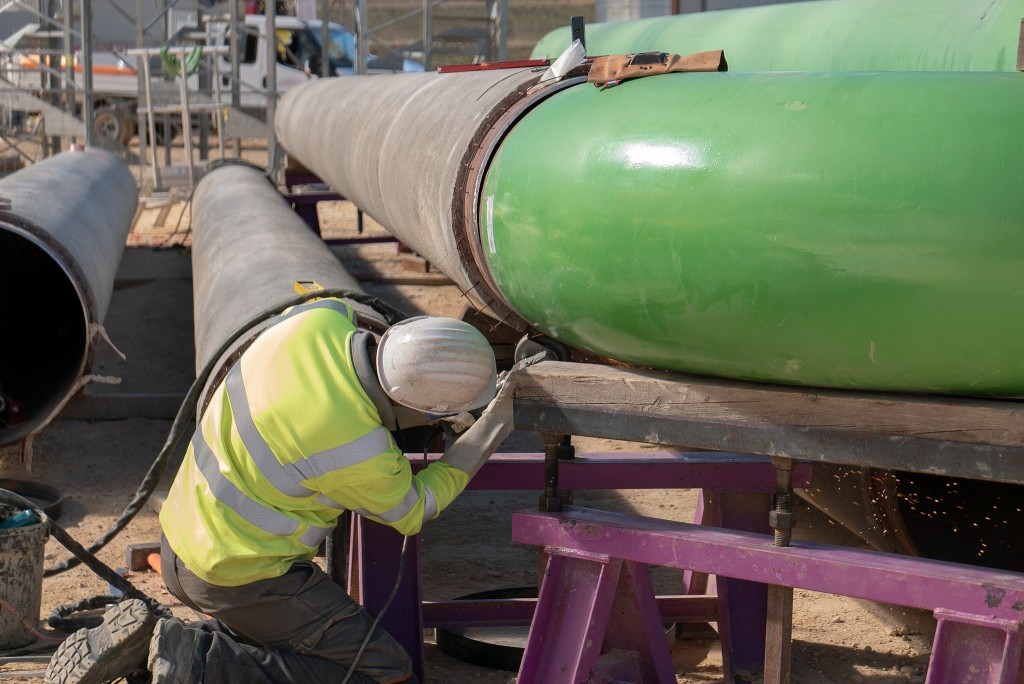
Piping from India
2018-10-03 - India is sending over 100 containers of piping for the component cooling water, chilled water and heat rejection systems. Spool assembly is one of the major installation activities on site. © Les Nouveaux Médias/SNC ENGAGE
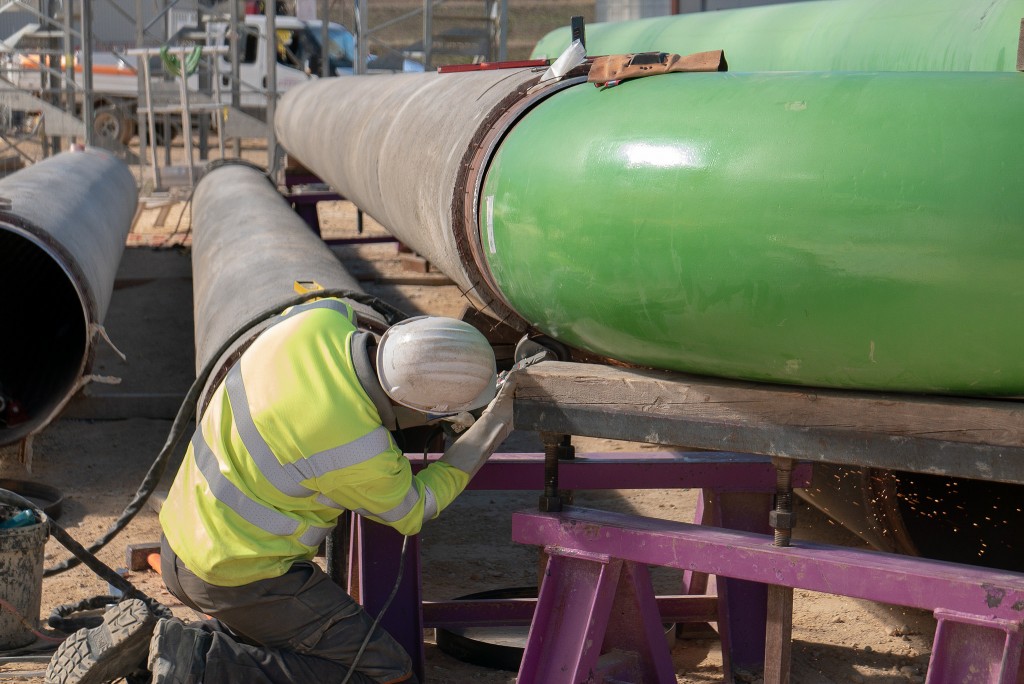
Piping from India
2018-10-03 - Piping under Indian scope for the component cooling water, chilled water and heat rejection systems represents some 100 containers worth in all. © Les Nouveaux Médias/SNC ENGAGE

First transformer is powered up
2018-09-18 - ''Electricians'' and command-control specialists from the ITER Organization and the European Domestic Agency (Fusion for Energy) succeed on 18 September in powering up the four transformers of the steady state electrical network.
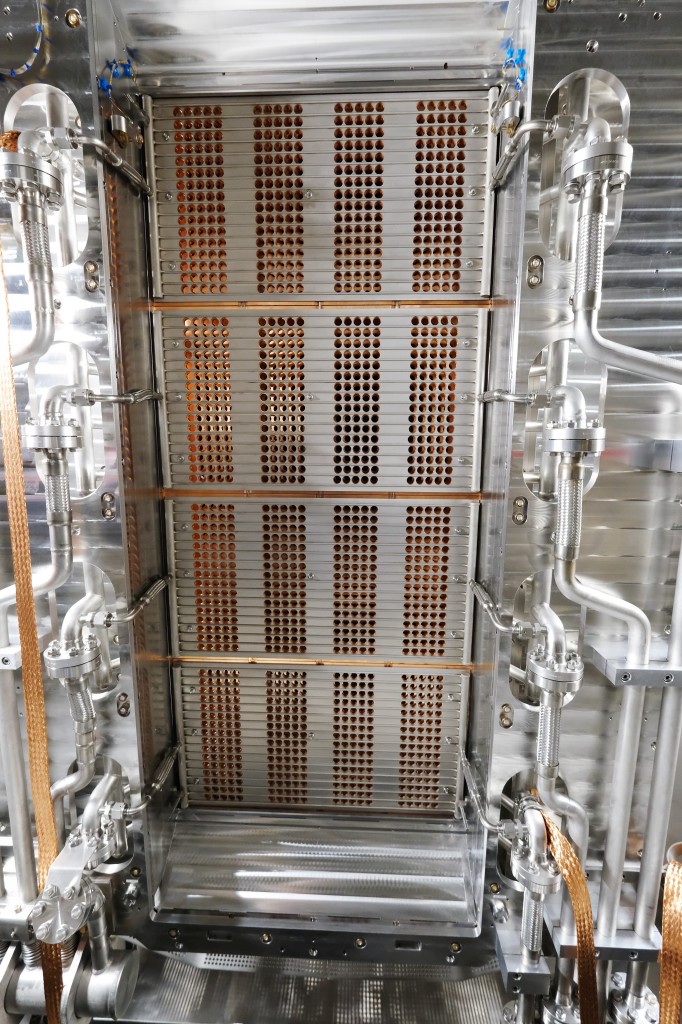
1,280 apertures
2018-09-13 - The plasma generated by the SPIDER ion source expands out through a series of grids. A potential difference between the different grids provides the extraction of the negative charges from the neutral plasma and subsequent acceleration. Pictured: the back side of the acceleration grid.
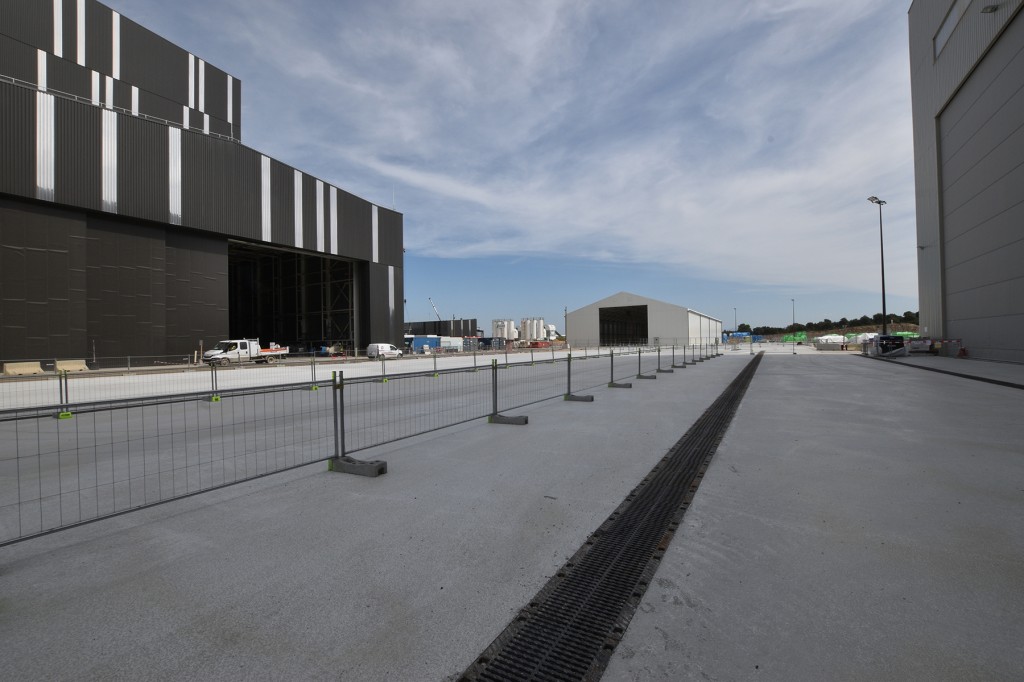
Reinforced zone
2018-09-10 - The asphalt in front of the Cryostat Workshop has been reinforced in order to receive the 375-tonne lower cylinder. Once completed this cryostat component will be stored in this exterior area under a protective "cocoon."
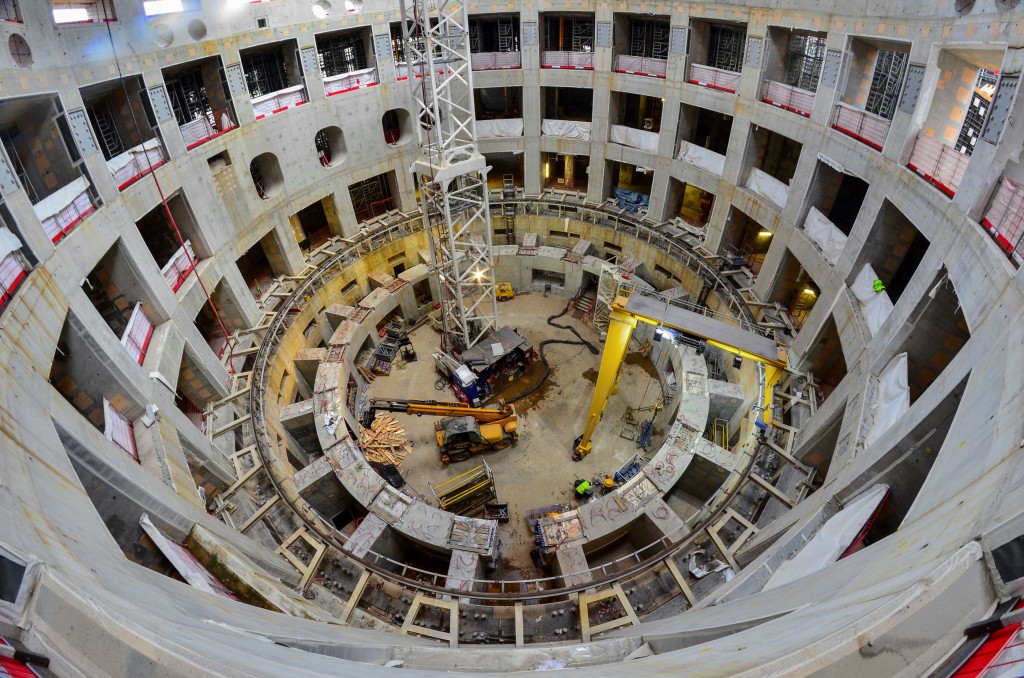
Circles of support
2018-09-06 - 800 tonnes of concrete and 224 tonnes of steel went into the concrete structure (circular and radial walls) that will support the combined mass of the machine and the enveloping cryostat. The realization opens the way to machine assembly.

The crown ... unveiled
2018-09-06 - Under the 23,000-tonne machine a crown with 18 points will be hidden. The crown was completed in four pours over four months. Only one small opening remains in the circular wall for the passage of a magnet feeder.

In September, the first structures appear
2018-09-05 - If you look closely, you'll see the first cooling tower structures rising in the fourth and fifth cooling tower cells. © Les Nouveaux Médias/SNC ENGAGE
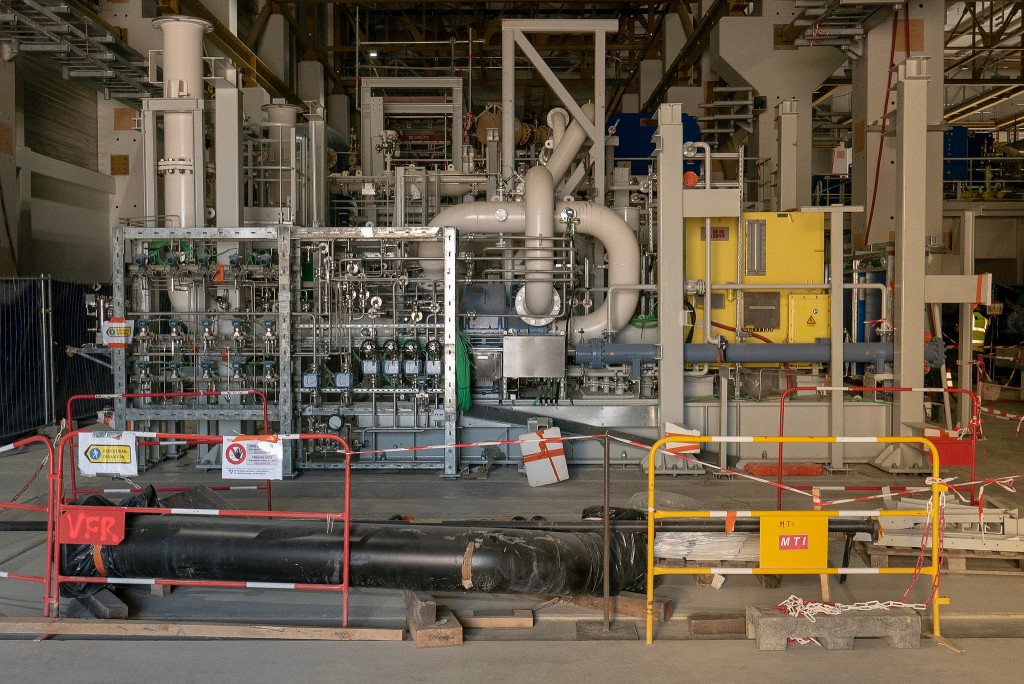
Through the open doors of the cryoplant
2018-09-05 - All machines and equipment for the Cryoplant Building have been delivered and 30% of the material has been installed. © Les Nouveaux Médias/SNC ENGAGE
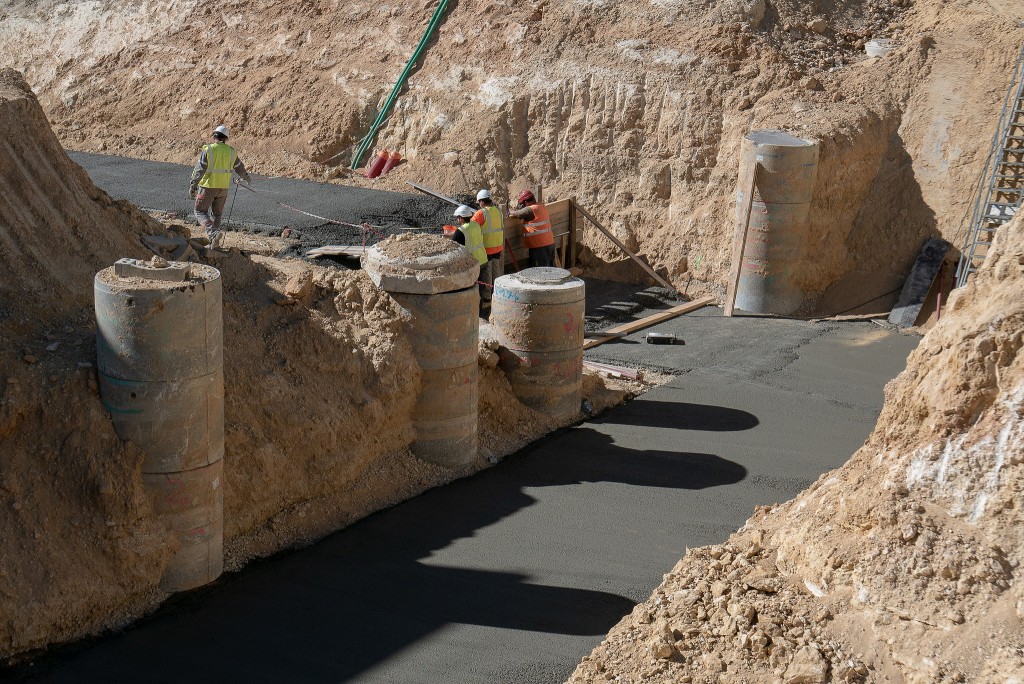
Gallery work
2018-09-05 - Service galleries for electricity and communication crisscross the platform at a depth of five metres. © Les Nouveaux Médias/SNC ENGAGE

Cooling through an evaporative process
2018-09-05 - After filtering down through the cooling towers, the water that has not evaporated will be collected in the cold basin located under the cells. © Les Nouveaux Médias/SNC ENGAGE
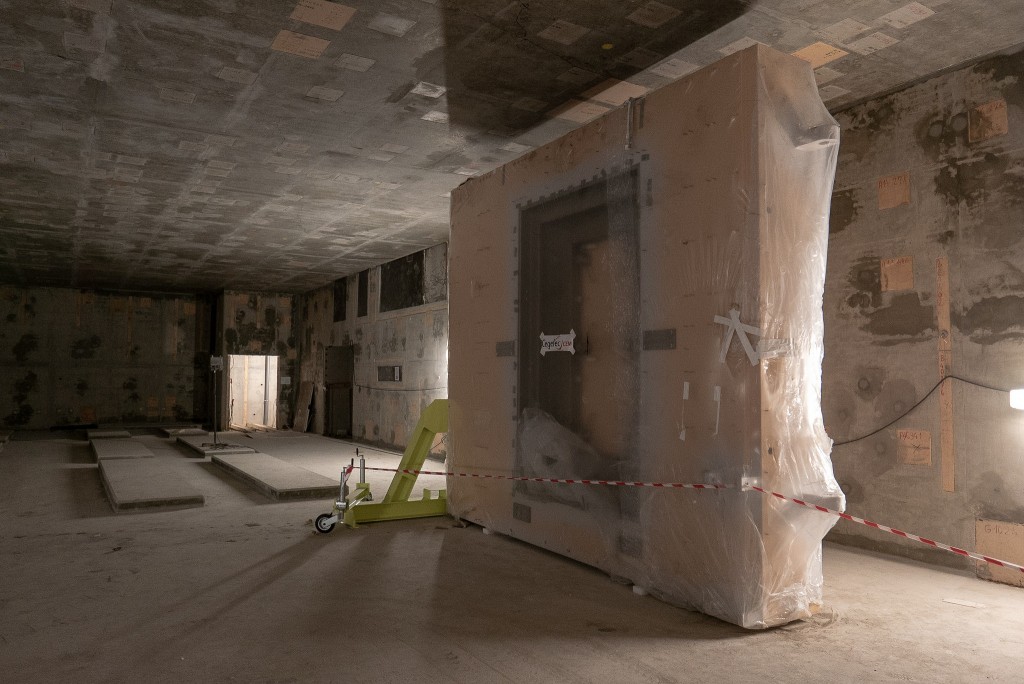
Doors delivered
2018-09-05 - Once filled with concrete this 30-tonne nuclear door will weigh 60 tonnes. Forty-six units have been ordered to close off the 46 port cells that surround the central bioshield like spokes. © Les Nouveaux Médias/SNC ENGAGE

Cooling towers
2018-09-05 - The dark-grey support structure for the cooling tower cells is made of pultruded fibre-reinforced polymer beams. © Les Nouveaux Médias/SNC ENGAGE
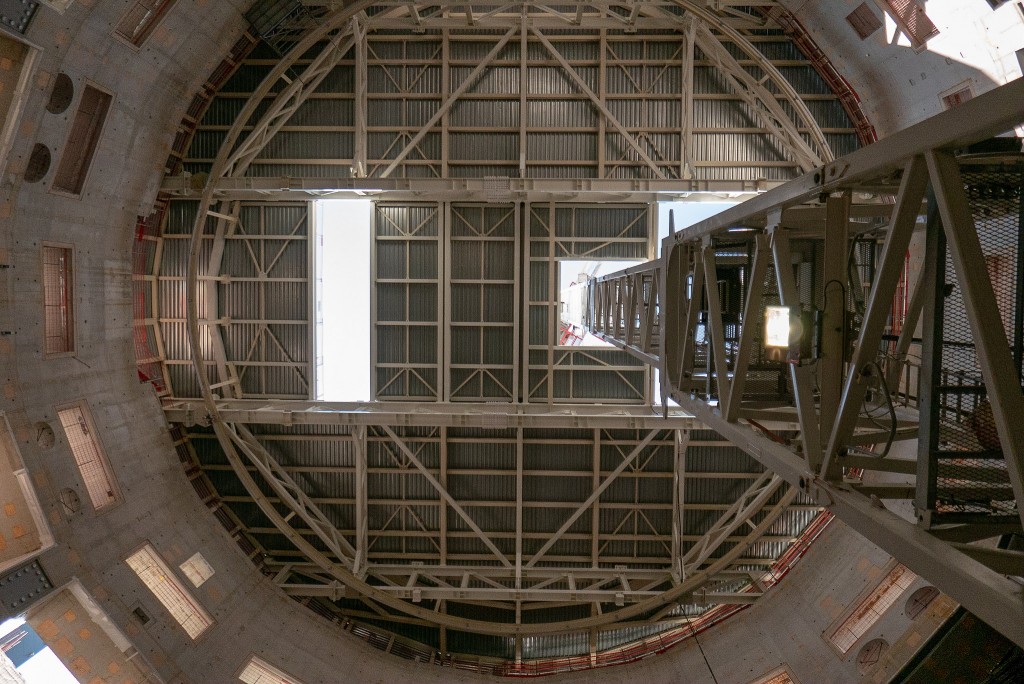
Waiting on the first piece
2018-09-05 - Looking straight up through the machine "well" where an opening in the temporary roof will allow the first machine component to be introduced in December. © Les Nouveaux Médias/SNC ENGAGE

Waiting on the first piece
2018-09-05 - Looking straight up through the machine "well" where an opening in the temporary roof will allow the first machine component to be introduced in December. © Les Nouveaux Médias/SNC ENGAGE

Soon ...two tools
2018-09-05 - The assembly of the second tool starts next month. As the wall poster shows, there will be two identical handling tools working from 2019 on to equip the vacuum vessel sectors for delivery to the machine pit.© Les Nouveaux Médias/SNC ENGAGE

Door operation
2018-09-05 - Here is one of the nine-metre-long port galleries surrounding the Tokamak Pit that will be closed off by a nuclear door. In this photo we see the start of the door frame as well as the bespoke tool designed for lifting and handling the 60-tonne doors. © Les Nouveaux Médias/SNC ENGAGE

Just the tip
2018-09-05 - From this angle, we see only the structures emerging from ground level. The ten cells of the cooling tower can be operated independently; ITER will start operation with just four. © Les Nouveaux Médias/SNC ENGAGE
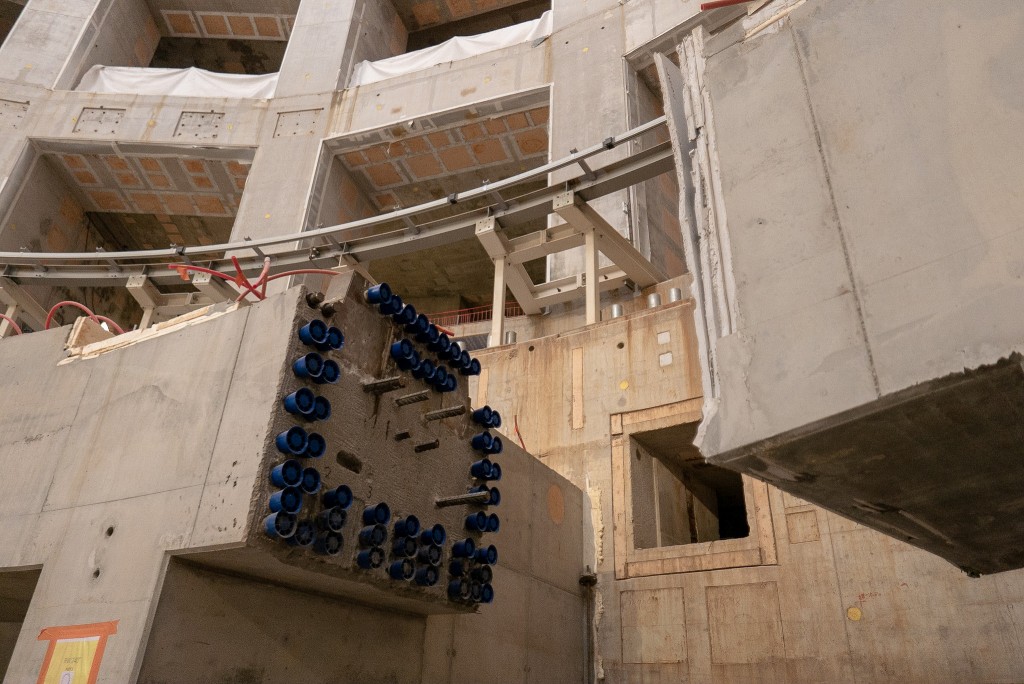
Room for the bend
2018-09-05 - The first machine element to be installed in the pit is an elbow-shaped feeder component. It will be slid into place through this break in the crown. © Les Nouveaux Médias/SNC ENGAGE
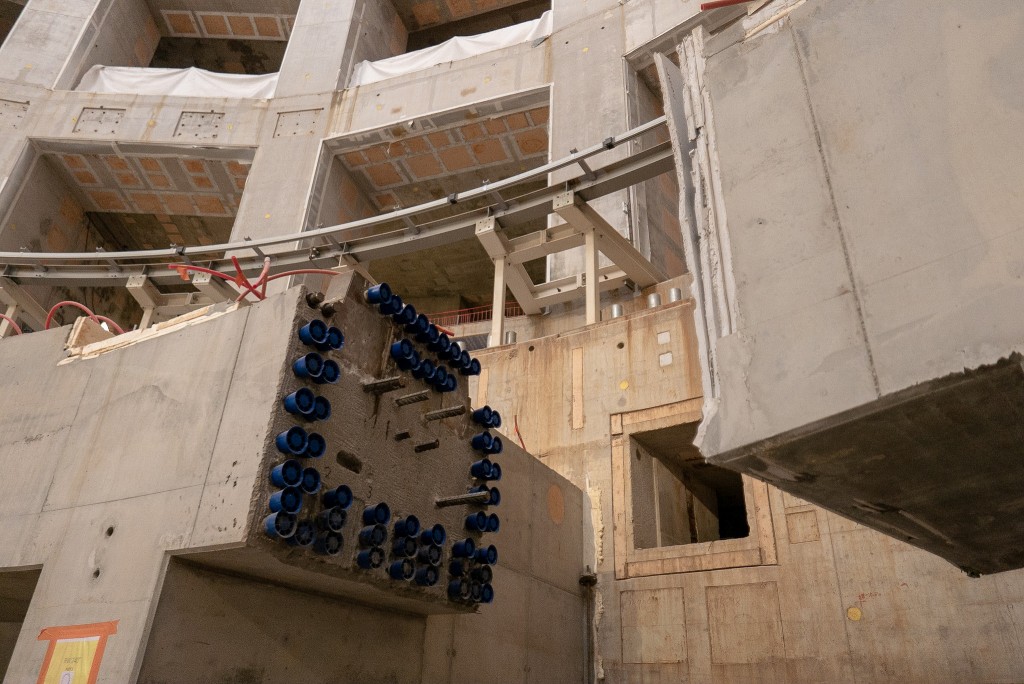
Room for the bend
2018-09-05 - The first machine element to be installed in the pit is an elbow-shaped feeder component. It will be slid into place through this break in the crown. © Les Nouveaux Médias/SNC ENGAGE
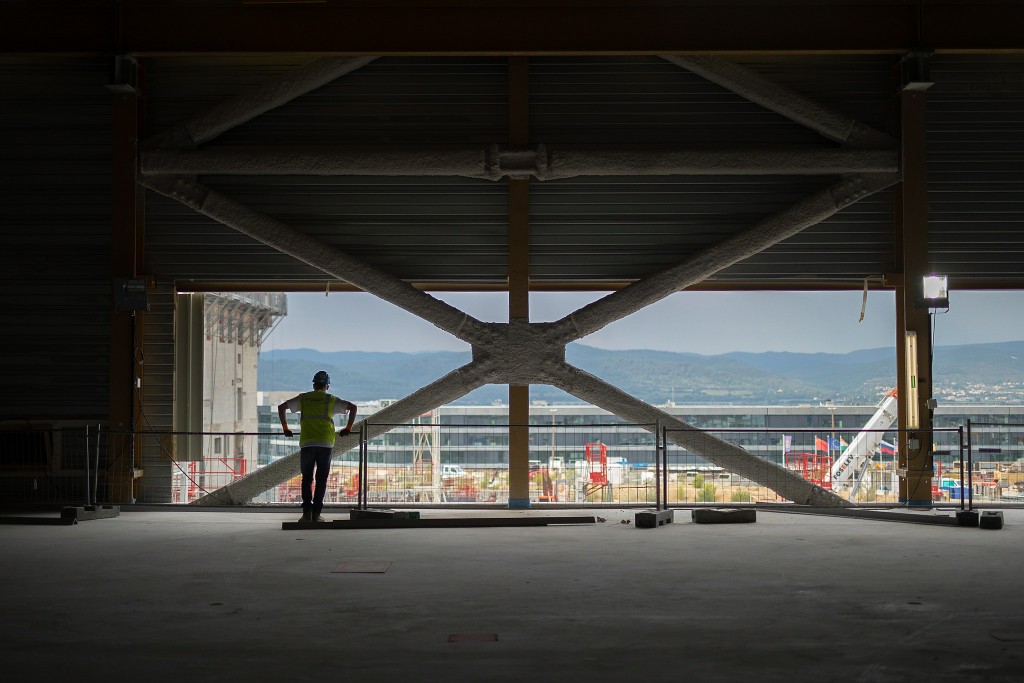
Nice view
2018-08-22 - Looking out of the third floor of the Radio Frequency Building in August. © Les Nouveaux Médias/SNC ENGAGE
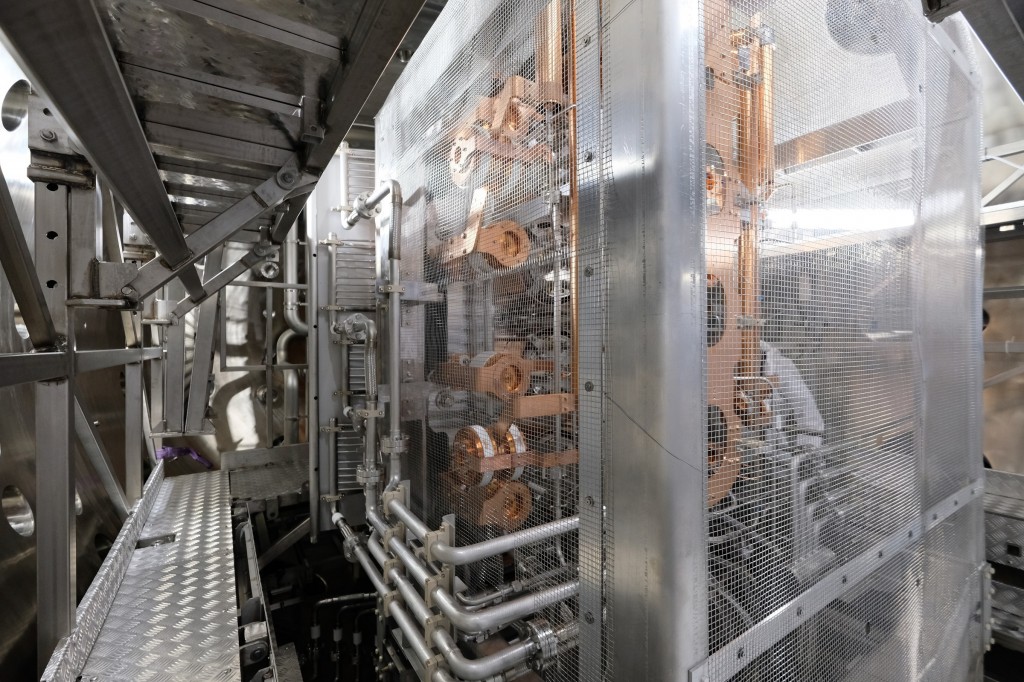
In a see-through cage
2018-08-22 - The SPIDER beam source has been fitted out with a Faraday cage. This metallic grid reduces the probability of arch discharge effects induced by the radio frequency (RF) circuit, while allowing the visual inspection of the RF drivers.
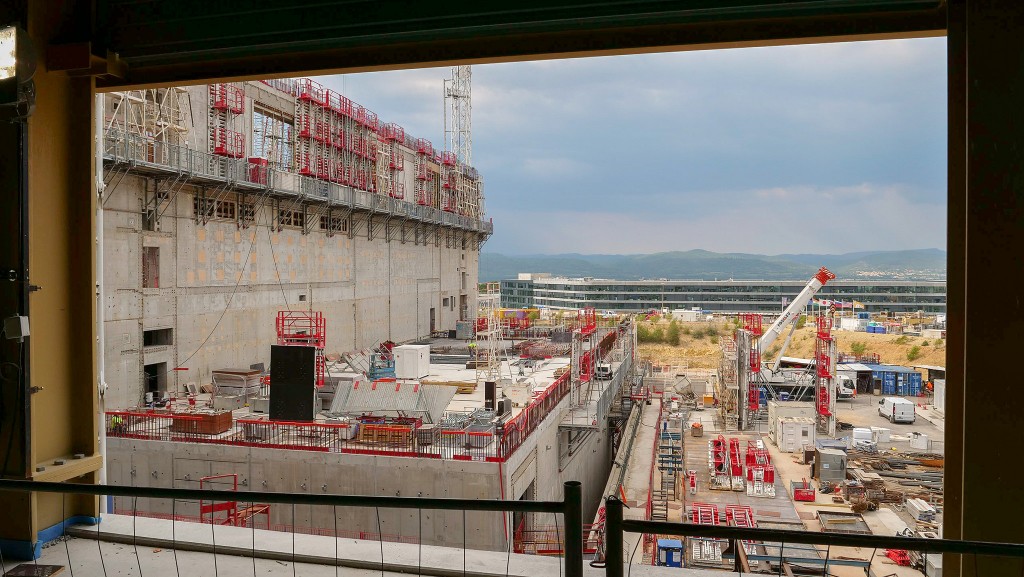
Third building
2018-08-22 - The Tritium Building (centre) is rising more slowly than the rest of the Tokamak Complex because it is not on the "critical path" to machine assembly. The gap around the building shows how the Tokamak Complex sits inside a concrete box on anti-seismic foundations. © Les Nouveaux Médias/SNC ENGAGE
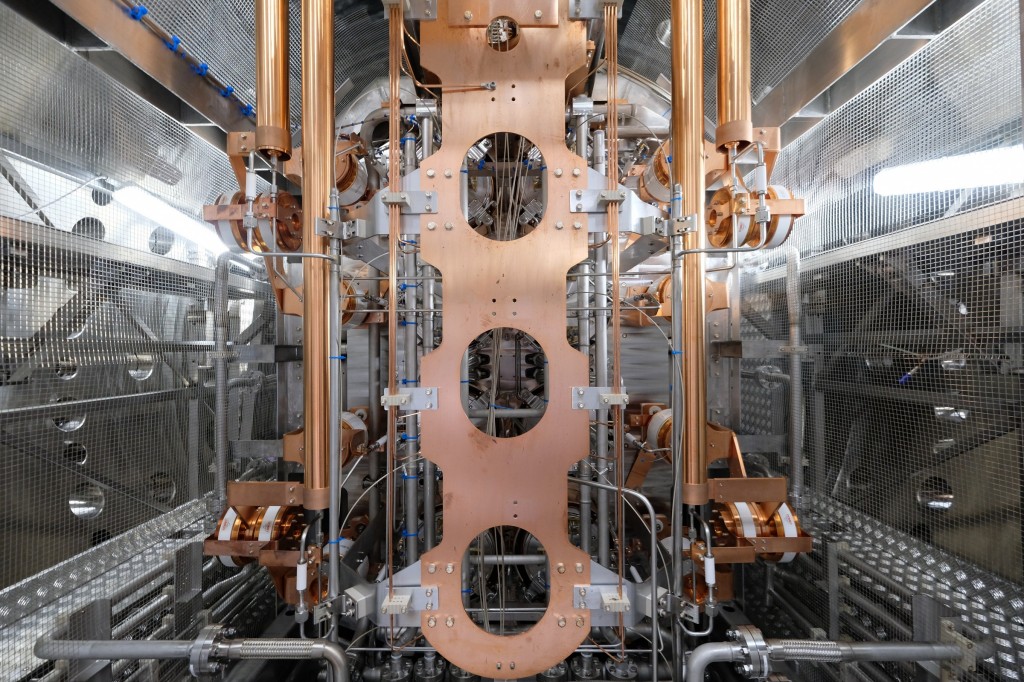
Near the source
2018-08-22 - Inside the Faraday cage, which has been installed at the rear of the ion source.
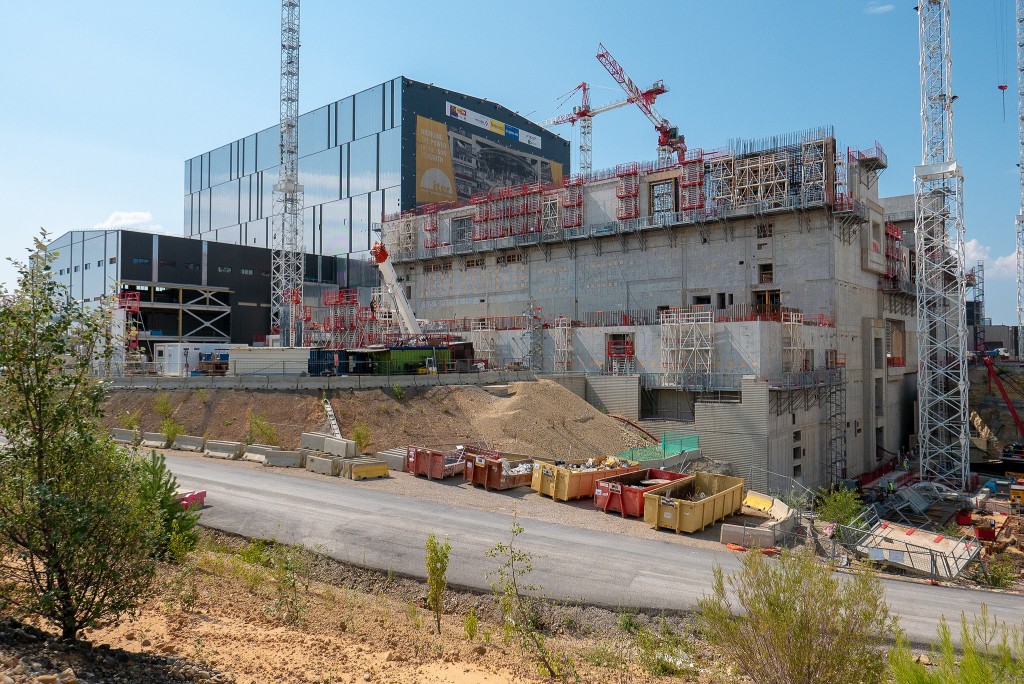
From the corner
2018-08-22 - Visible from this angle are the two basement levels of the Tokamak Complex. © Les Nouveaux Médias/SNC ENGAGE

Room ready
2018-08-16 - Painting and finishing works in the drain tank room were finalized before the tank installation. It only remains to now close the roof opening.
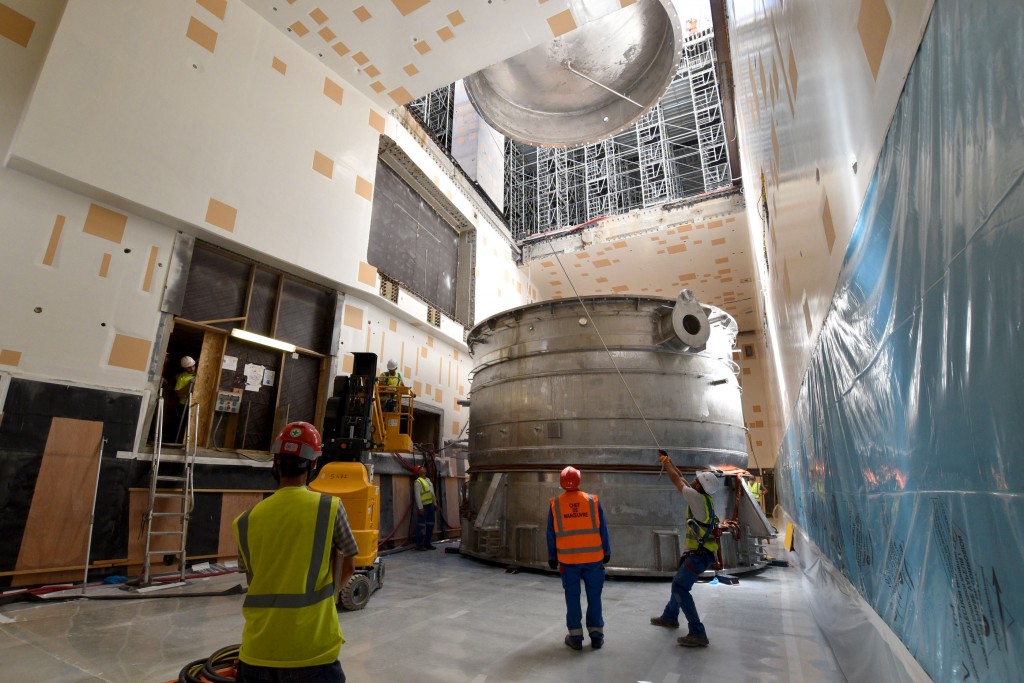
A pair
2018-08-16 - The first vapour suppression tank has been deposited and a second is being lowered through the opening in the ceiling. Once paired (one on top of the other) they will be moved to the side to make room for the next delivery.
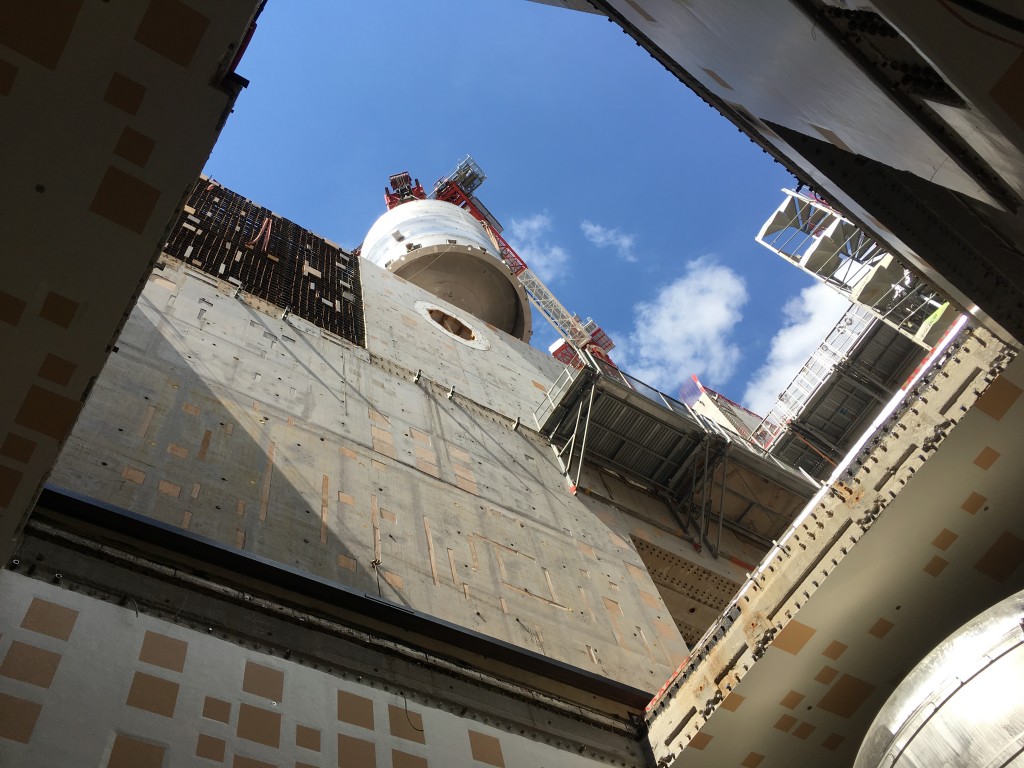
Large tanks installed at B2 level
2018-08-16 - In August, seven tanks were introduced through the roof of the drain tank room at B2 (lower basement) level.
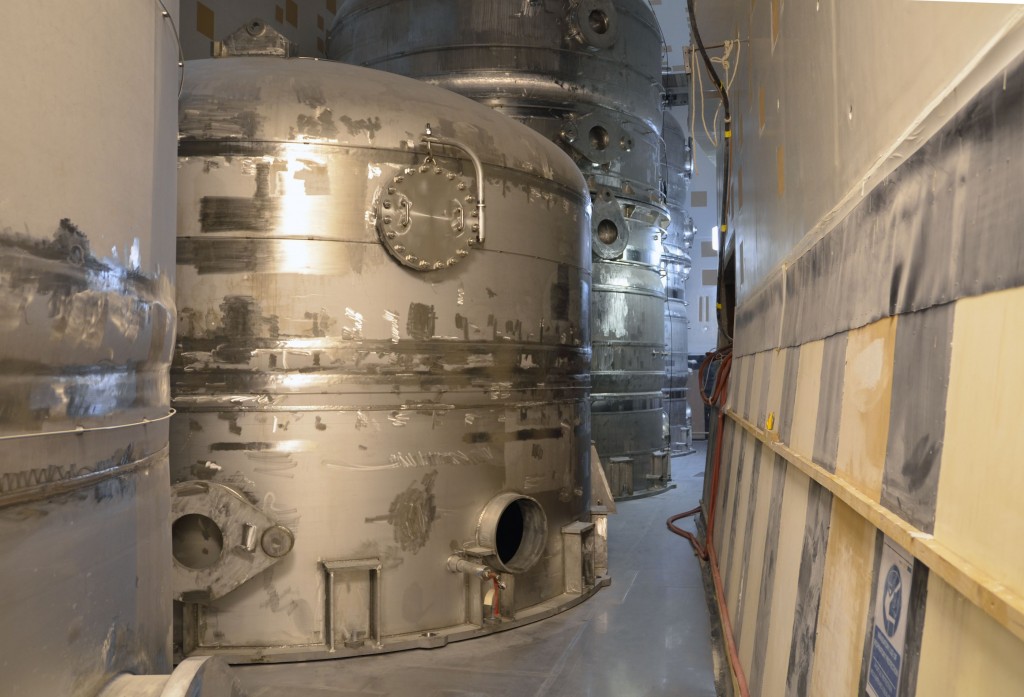
Standing room only
2018-08-16 - Once a cavernous open space, the drain tank room is now completely filled by the seven tanks. The space above the smallest tank, in the middle, will be taken up by a mezzanine supporting piping, pumps and exchangers for the vacuum vessel's primary heat transfer system.

Approaching destination
2018-08-16 - One of the Tokamak cooling water system drain tanks is transported from temporary storage to the lifting point outside of the Tokamak Complex. One after another, the tanks were lowered through an opening preserved in the ceiling of the drain tank room.
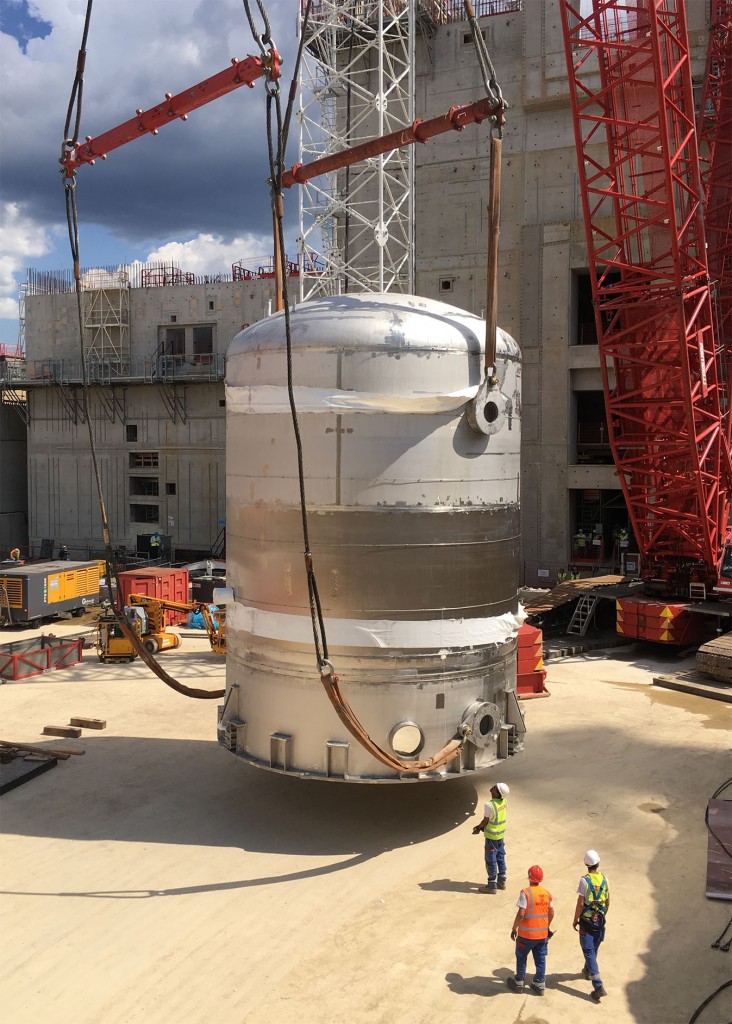
Standing tall
2018-08-16 - This tall tank for the Tokamak cooling water system had to be raised from its horizontal storage position before it could be lifted by crane up and into the Tokamak Complex.
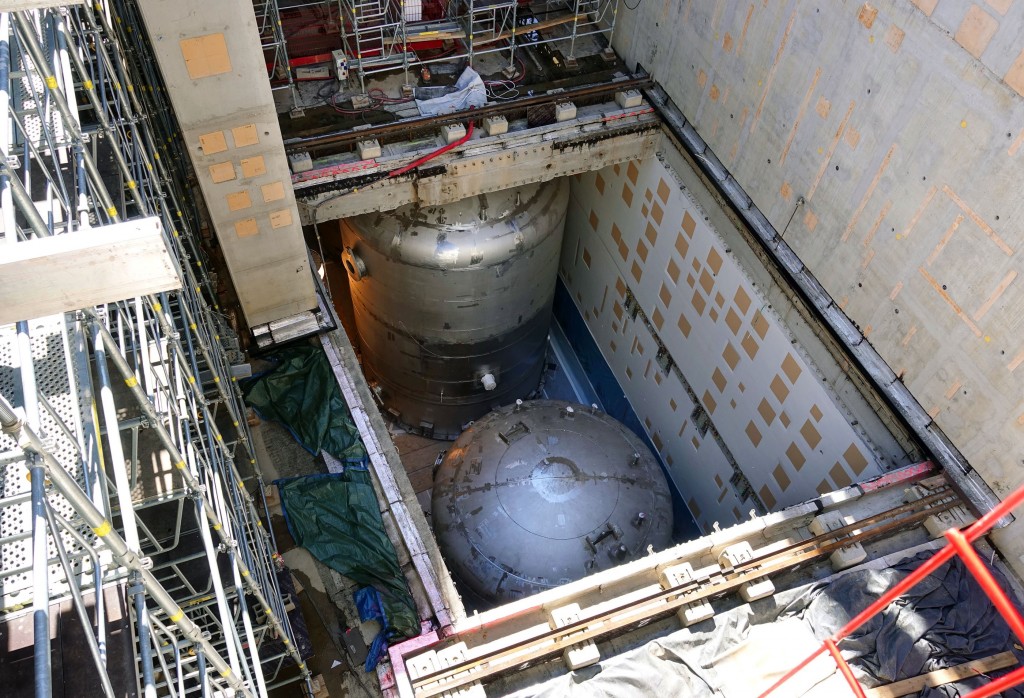
Skidding on air pads
2018-08-16 - Moving components in the 100-tonne range does not require tremendous force ... provided that the loads are placed on air pads. Once deposited on the floor, each tank (or pair of tanks) was gently drawn into its final position by manually operated cables anchored in the walls.

Big doings
2018-08-16 - In one of the most spectacular installation activities performed yet in the Tokamak Complex, three drain tanks and four vapour suppression tanks were installed during the week of 14 August—some 600 tonnes of equipment in all.
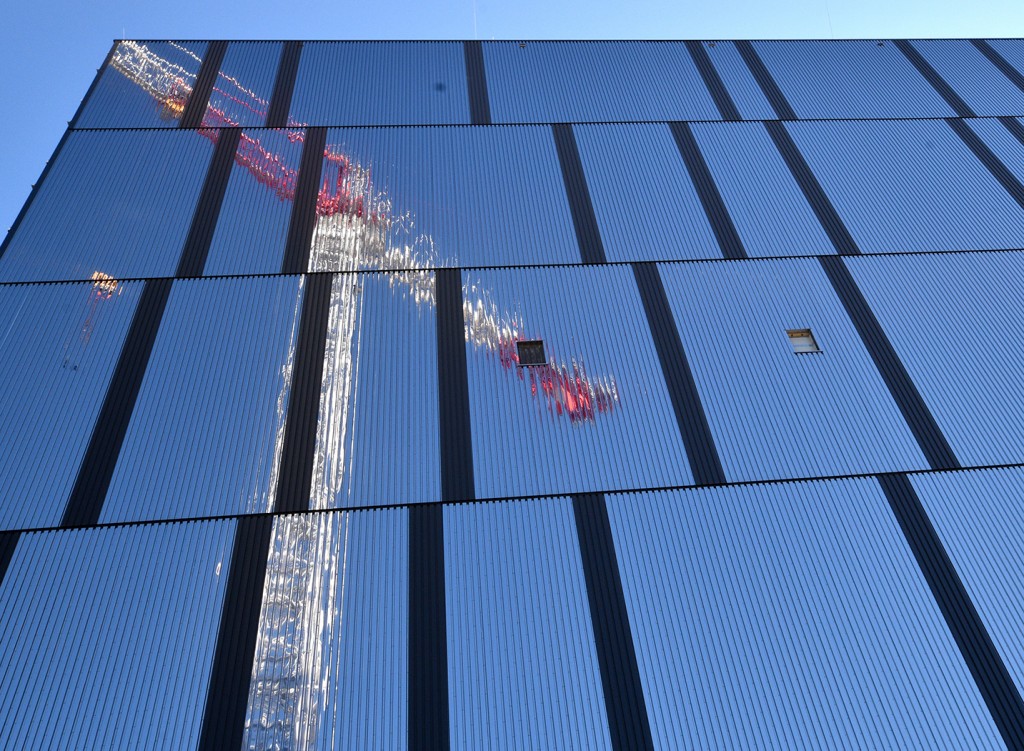
Shimmering
2018-08-14 - A worksite crane is reflected from the mirror surface of the Assembly Hall in August.

A runway for the cryostat
2018-08-10 - A section of runway-worthy tarmac has been completed in front of the Cryostat Workshop, with four times the load-bearing capacity of regular pavement. Other areas will receive the same treatment soon—for example, the road in front of the Cleaning Facility over which all components will pass.

The Tokamak Building in July
2018-07-26 - The red-and-white crane beam spins slowly over the capped bioshield in late July. Down below, teams are continuing to pour concrete for the crown wall; outside, at level 3, they are laying a special type of "neutron-absorbing" borated concrete.
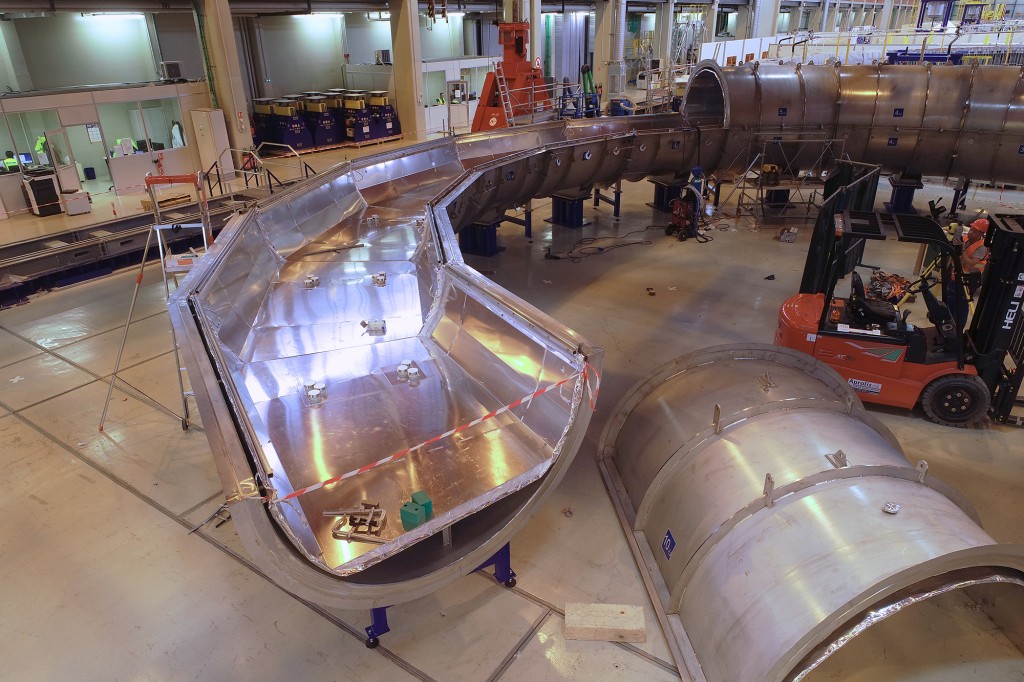
Testing performance
2018-07-26 - Finished magnets will be inserted here and cooled to low temperature (approximately 80 K, or -193 °C). Photo: ITER Organization/EJF Riche
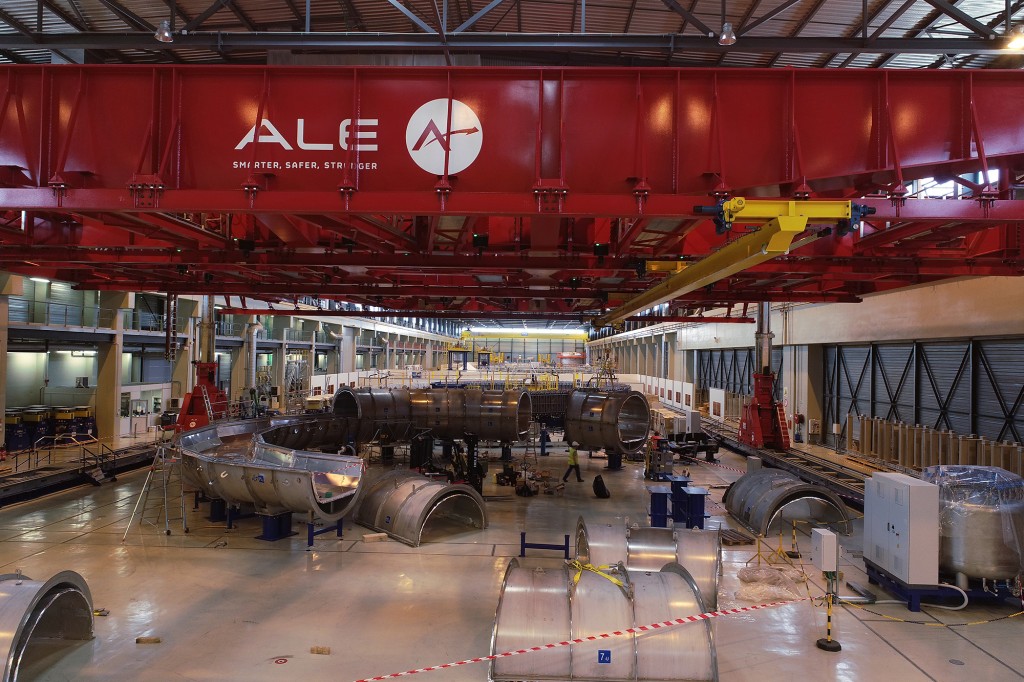
Cold testing equipment
2018-07-26 - On the far end of the building, teams are installing equipment for the cold testing (at 80 K) of the completed magnets. Photo: ITER Organization/EJF Riche
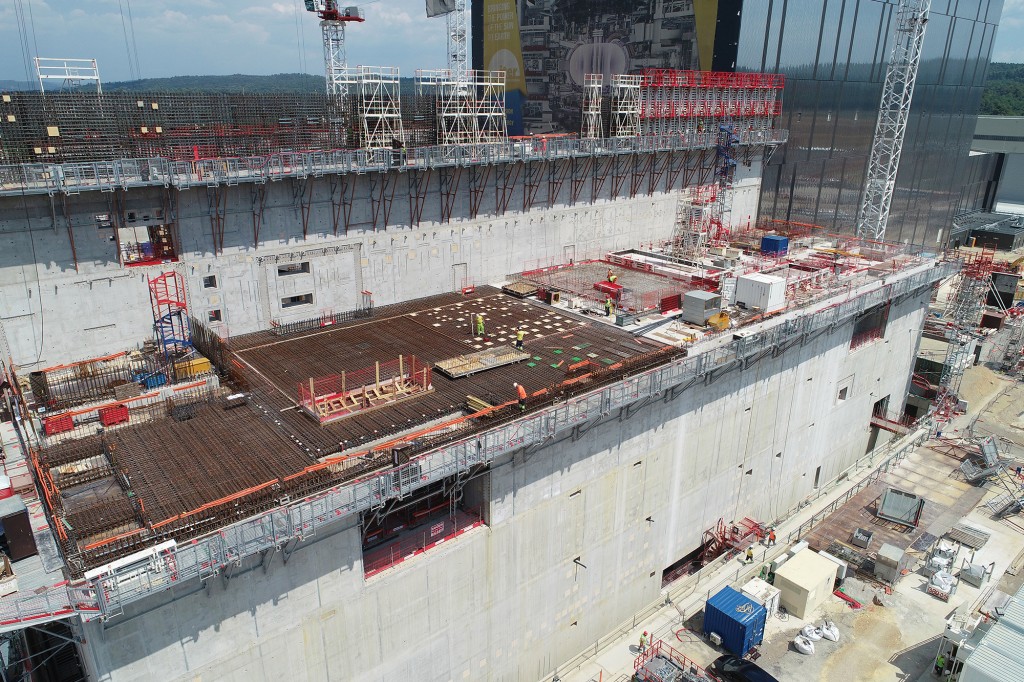
Diagnostics Building
2018-07-25 - With the last work on the roof of the three-storey Diagnostics Building, the building will be completely framed out. Photo: ITER Organization/EJF Riche
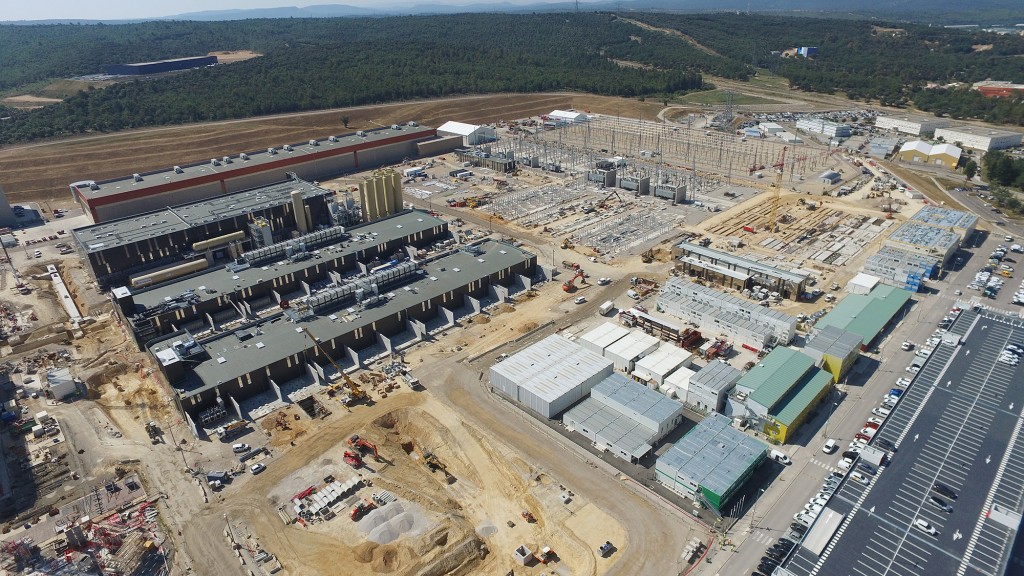
Plant system zone
2018-07-25 - Areas for cryogenics, magnet power conversion, and the arrival of electricity ... all in support of the ITER Tokamak. Photo: ITER Organization/EJF Riche
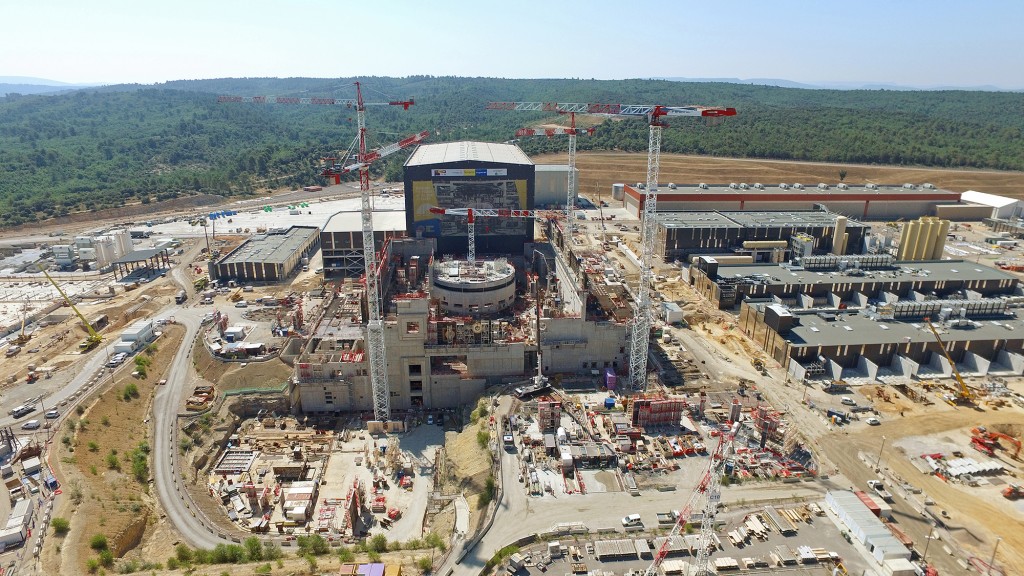
Building rising
2018-07-25 - The bioshield is 30 metres deep; only the top third appears above the concrete of the Tokamak Building. Photo: ITER Organization/EJF Riche
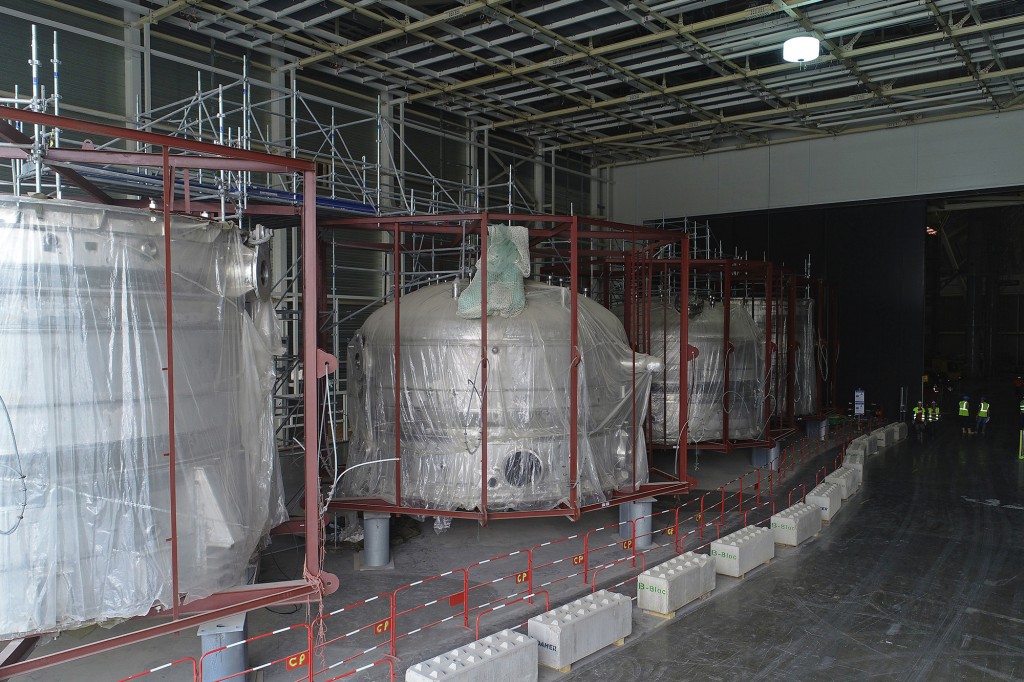
Tanks awaiting installation
2018-07-25 - For now the Cleaning Facility—at the entrance of the Assembly Hall—can be used for storage. In this picture are four tanks for the pressure suppression system of the vacuum vessel, which will be installed in the Tokamak Building in August. Photo: ITER Organization/EJF Riche
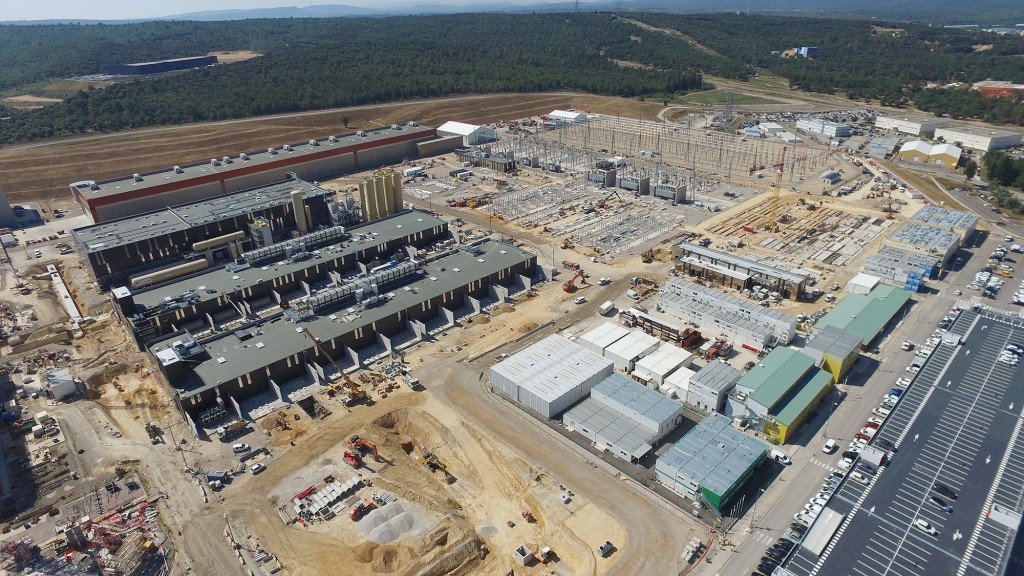
Plant system zone
2018-07-25 - Areas for cryogenics, magnet power conversion, and the arrival of electricity ... all in support of the ITER Tokamak. Photo: ITER Organization/EJF Riche
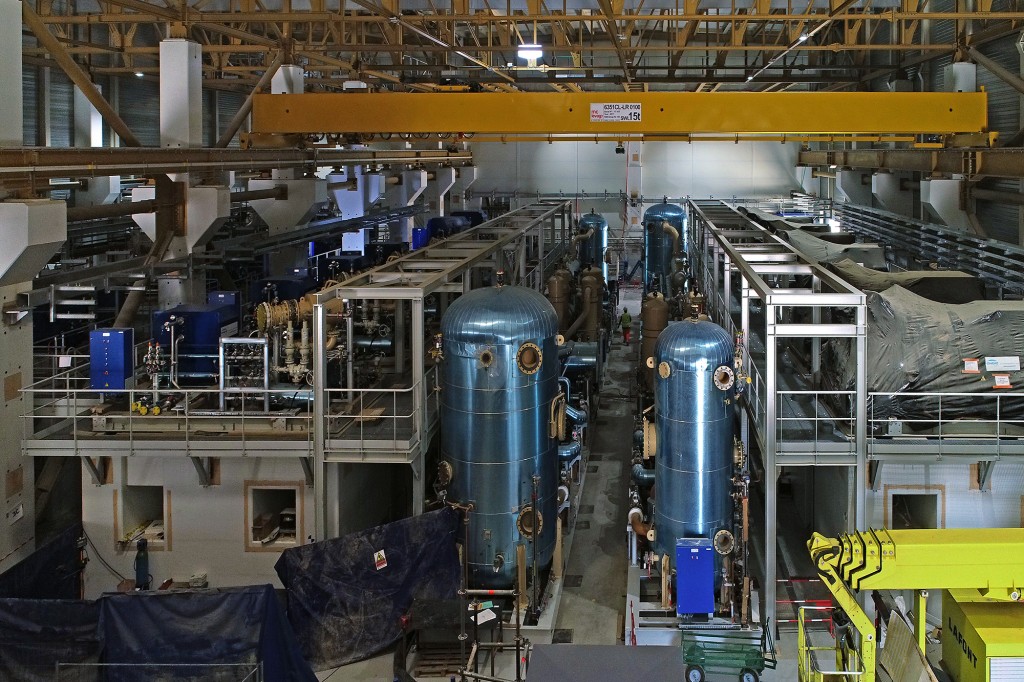
Flying above
2018-07-24 - Factory equipment, seen by drone in July. Photo: ITER Organization/EJF Riche
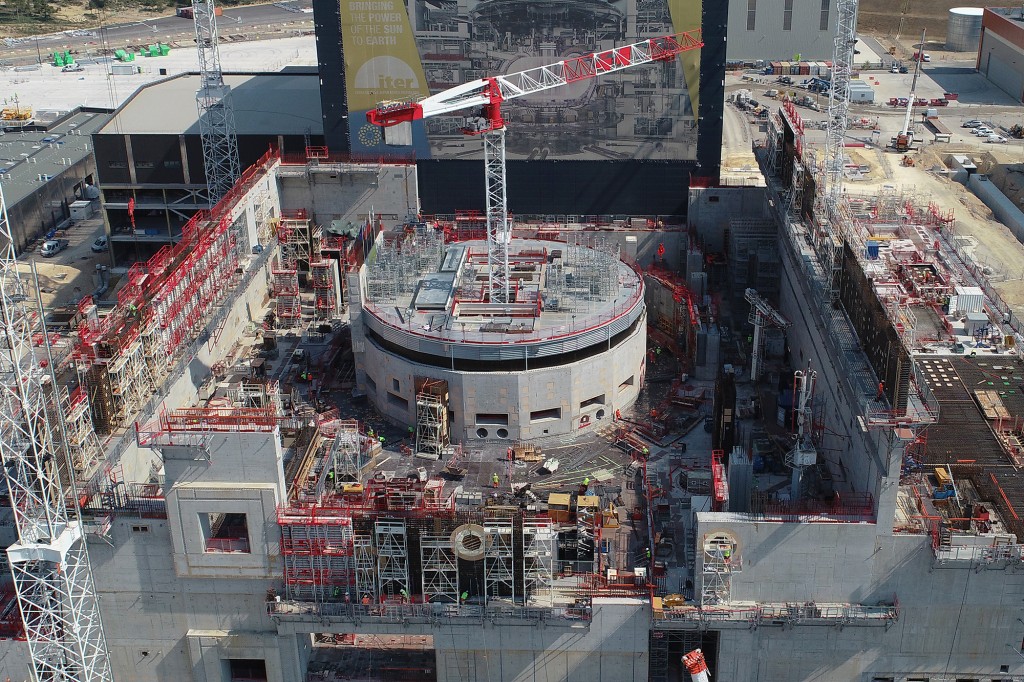
From above
2018-07-24 - The Tokamak Building, photographed from a drone. Photo: ITER Organization/EJF Riche

Disassembled for now
2018-07-24 - The tier-two base pieces were assembled, measured and disassembled for adjustment. Photo: ITER Organization/EJF Riche
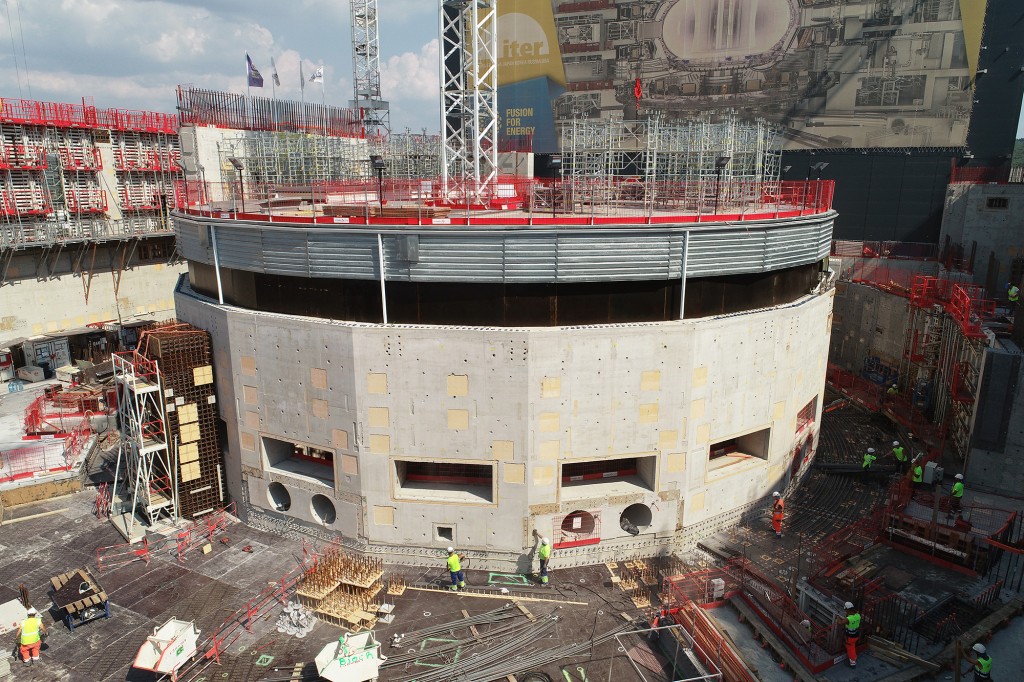
Circular?
2018-07-24 - The bioshield is not quite the circular structure we often describe, but is rather built from 18 plane surfaces, or facets. Photo: ITER Organization/EJF Riche
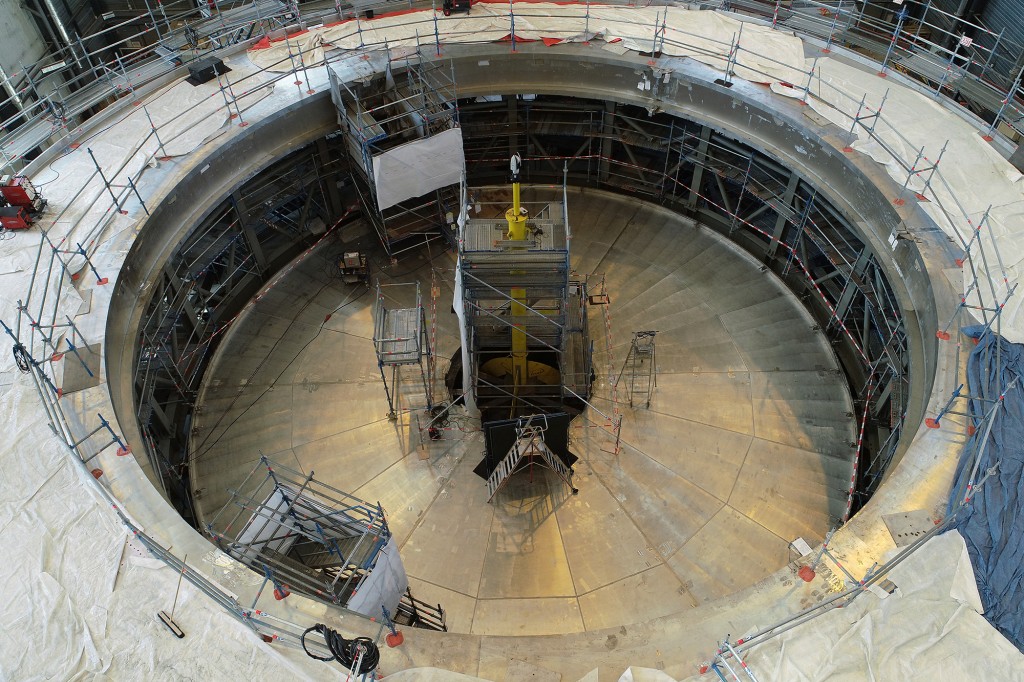
Flying over the base by drone
2018-07-24 - Looking down on the dish-like cryostat base. The lower disk and upper rim are in place, but the vertical side walls were removed for adjustment after inspection.
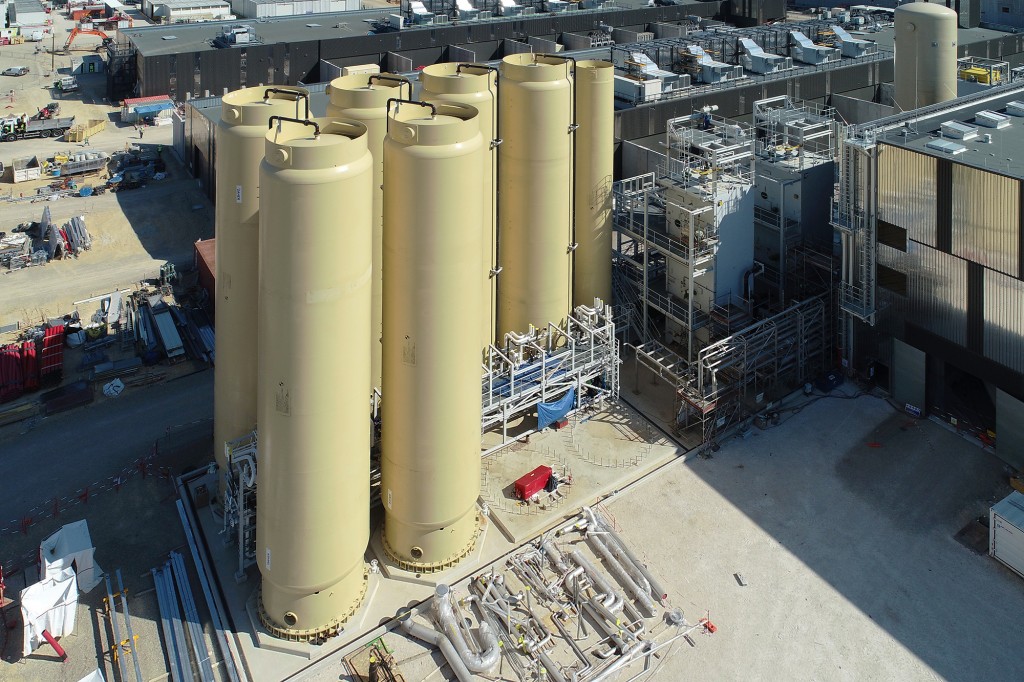
Not far
2018-07-24 - Outside storage tanks in the cryoplant area. Photo: ITER Organization/EJF Riche

Space reservations
2018-07-24 - Circular openings in the exterior walls are being reserved for the high voltage transmission lines that will feed power to the neutral beam injectors. Photo: ITER Organization/EJF Riche
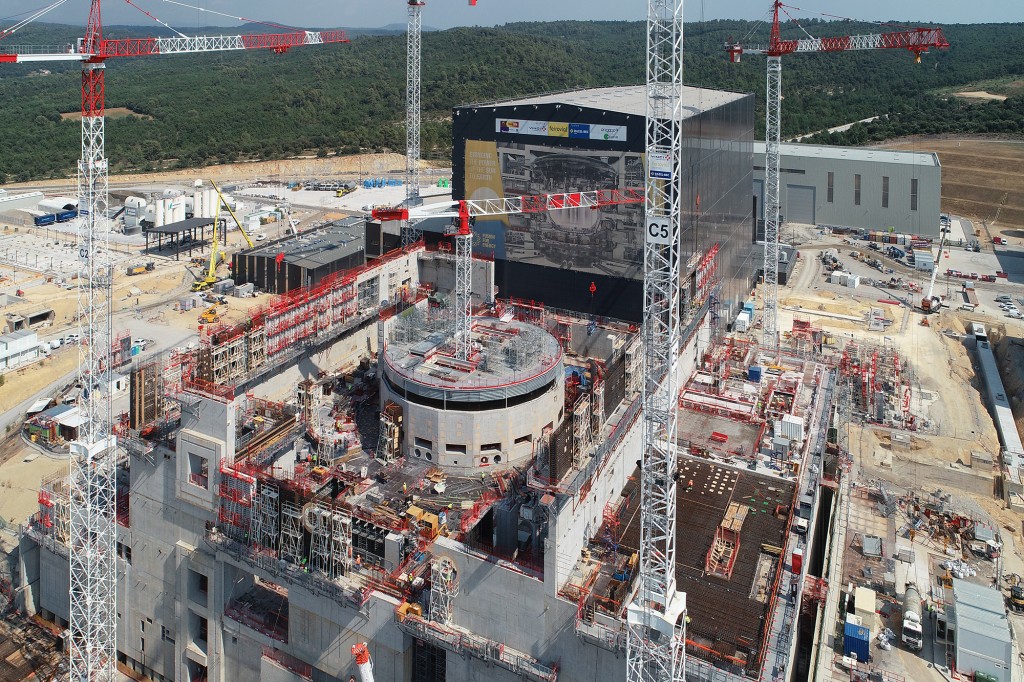
Going up
2018-07-24 - The concrete "box" is rising around the bioshield. Photo: ITER Organization/EJF Riche
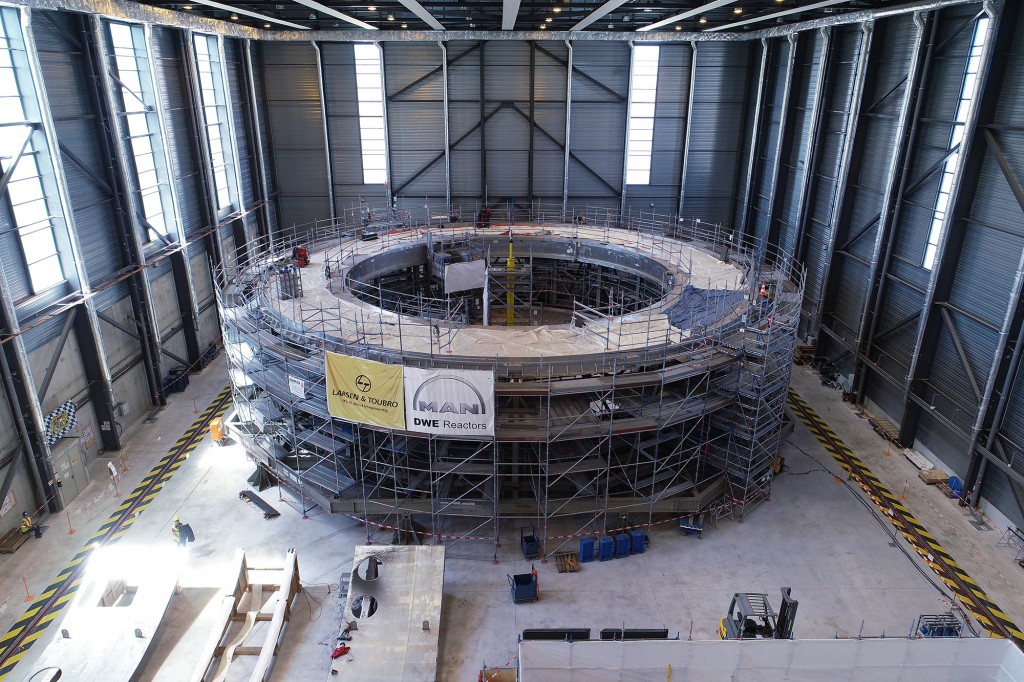
Lower cylinder
2018-07-24 - 30 metres in diameter, 10 metres in height, 375 tonnes ... and 200 metres of circular and vertical welds. Photo: ITER Organization/EJF Riche

Cryoplant gas storage
2018-07-24 - Outside storage tanks have been installed in the cryoplant area for gaseous and liquid cryogens. Photo: ITER Organization/EJF Riche

In late July
2018-07-23 - In this central arena of the construction site, teams are active three shifts a day—two full work shifts and a third, at night, dedicated to moving scaffolding and formwork in preparation for the next day's tasks. Work will continue through the traditional August holiday in France.
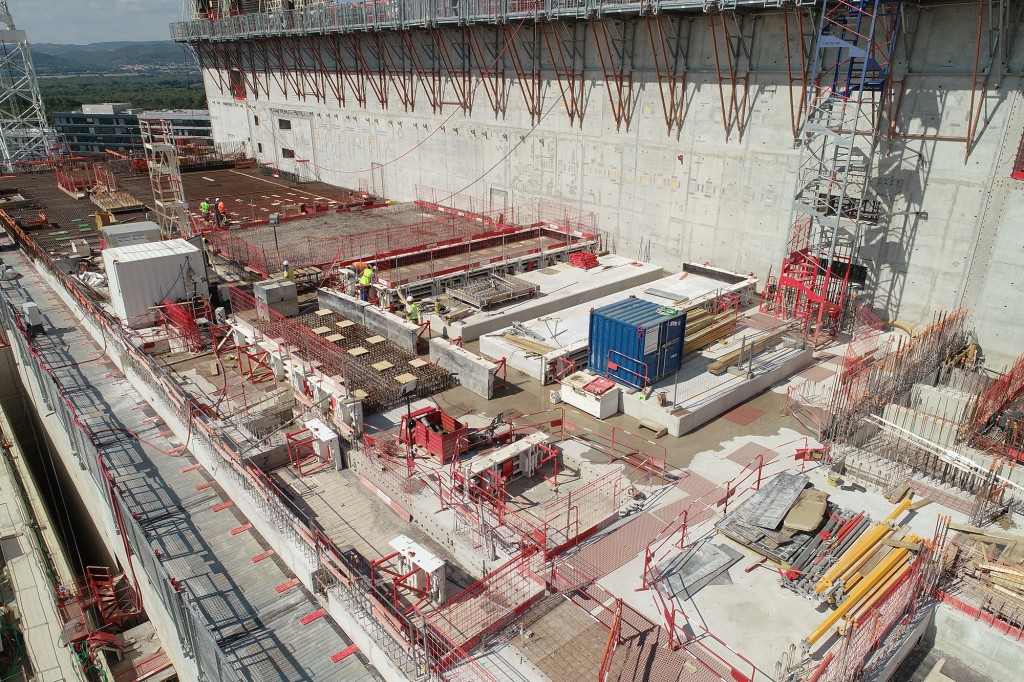
Diagnostics roof
2018-07-23 - Successive concrete pours are taking place on the roof of the Diagnostics Building. Photo: ITER Organization/EJF Riche
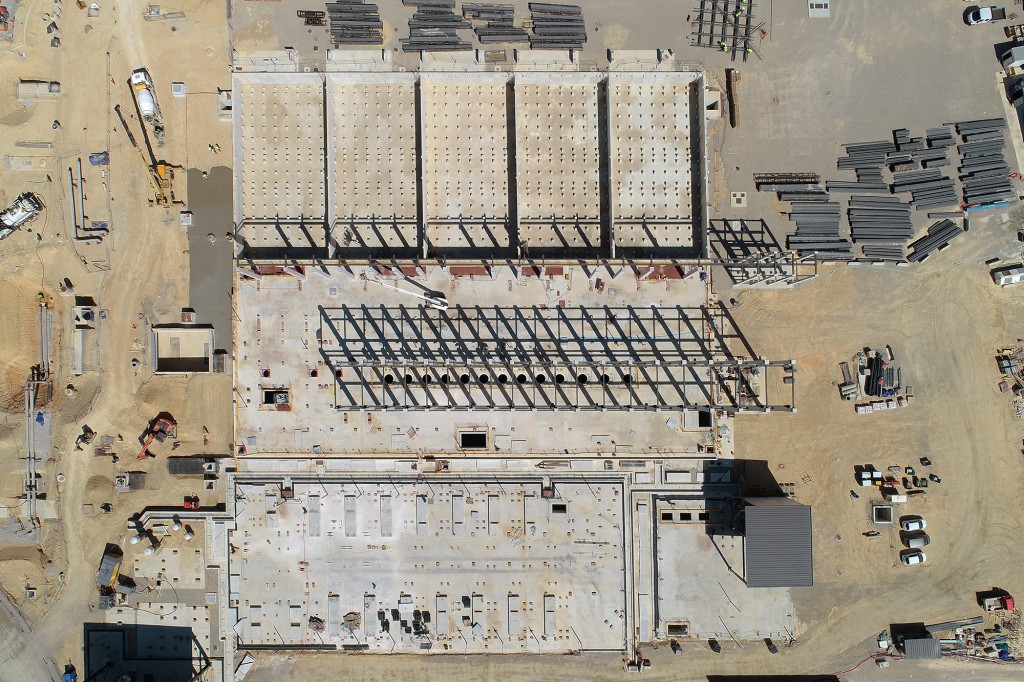
Construction as art
2018-07-23 - Graphic shadows just before midday on 23 July. Photo: ITER Organization/EJF Riche

Covered
2018-07-23 - The temporary roof prevents us from looking down into the 30-metre-deep "well" formed by the bioshield. Photo: ITER Organization/EJF Riche
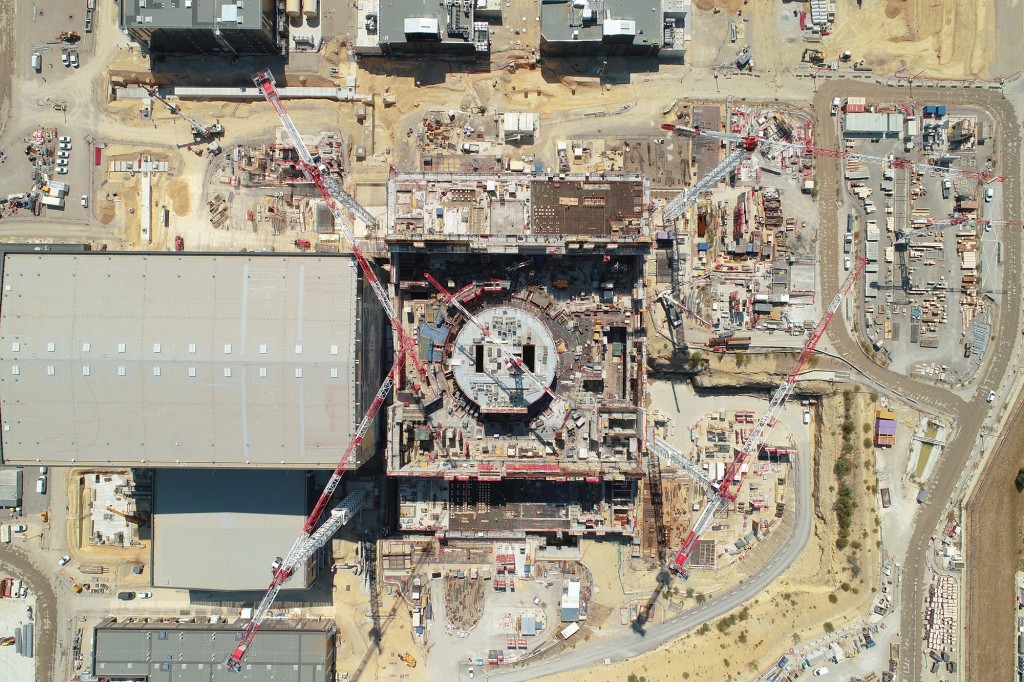
A small Sun on Earth
2018-07-23 - The jewel box is ready, now for the assembly of the jewel. Photo: ITER Organization/EJF Riche
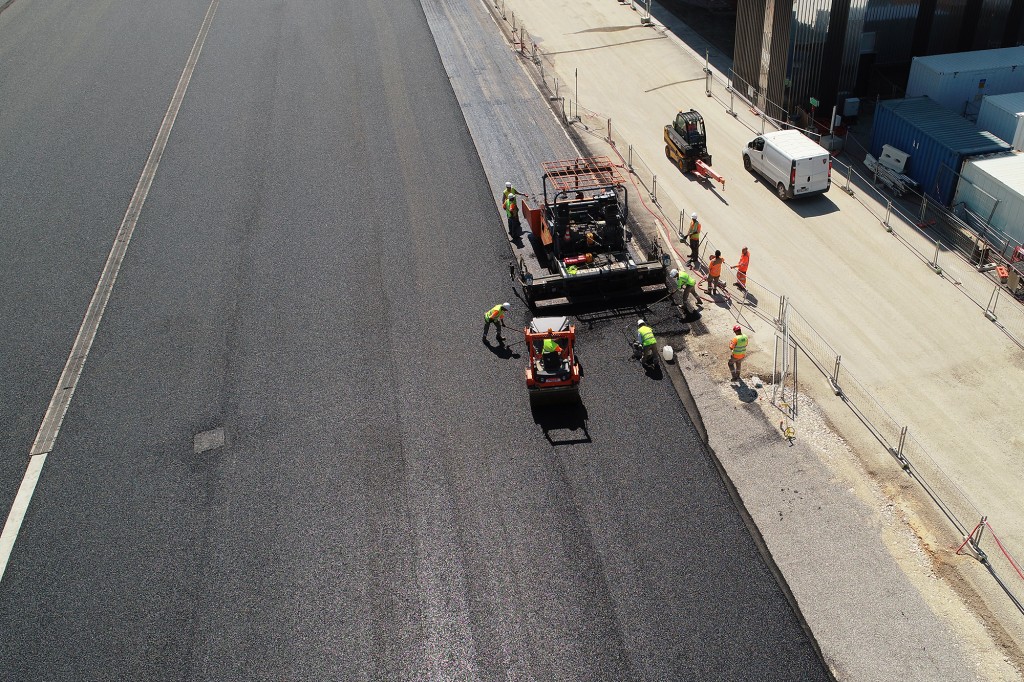
Hot work in July
2018-07-23 - Asphalting the heavy-weight storage zone. Photo: ITER Organization/EJF Riche
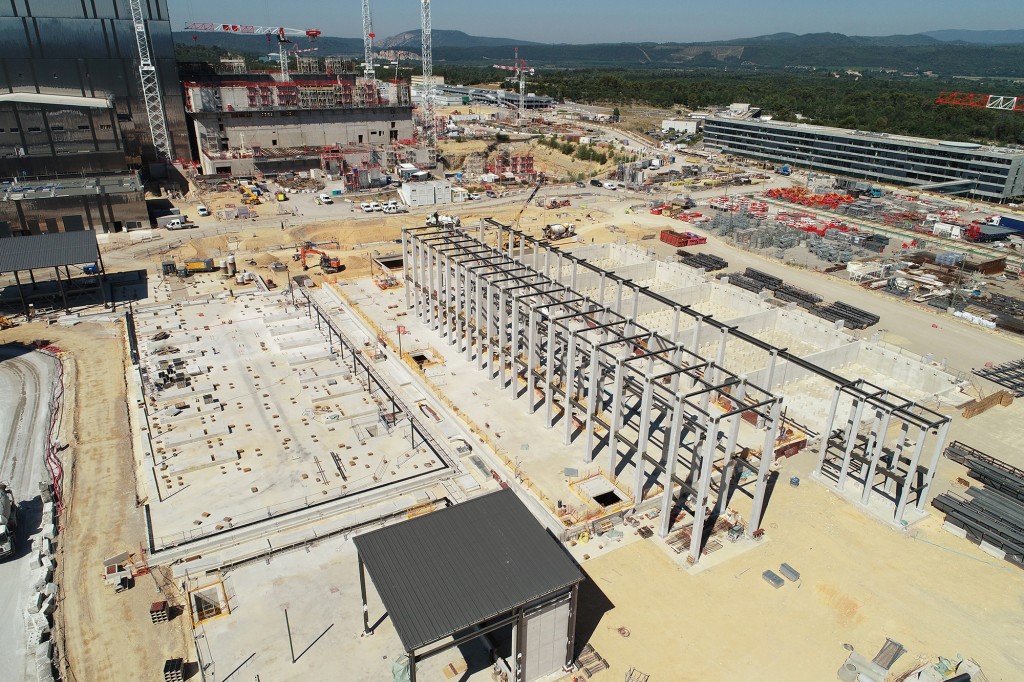
Heat rejection zone in July
2018-07-23 - All is ready in the heat rejection zone for the installation of the cooling towers. Photo: ITER Organization/EJF Riche
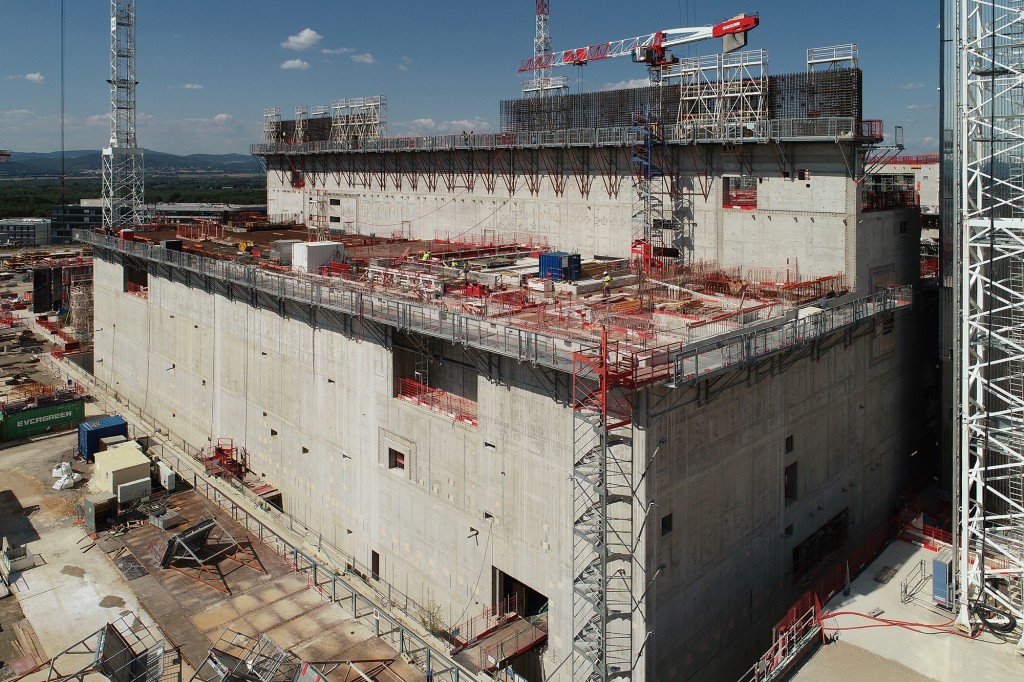
Impressive
2018-07-23 - At the far end of the Tokamak "pit" activities have started on the L1 and L2 levels of the ITER bioshield. © EJF Riche
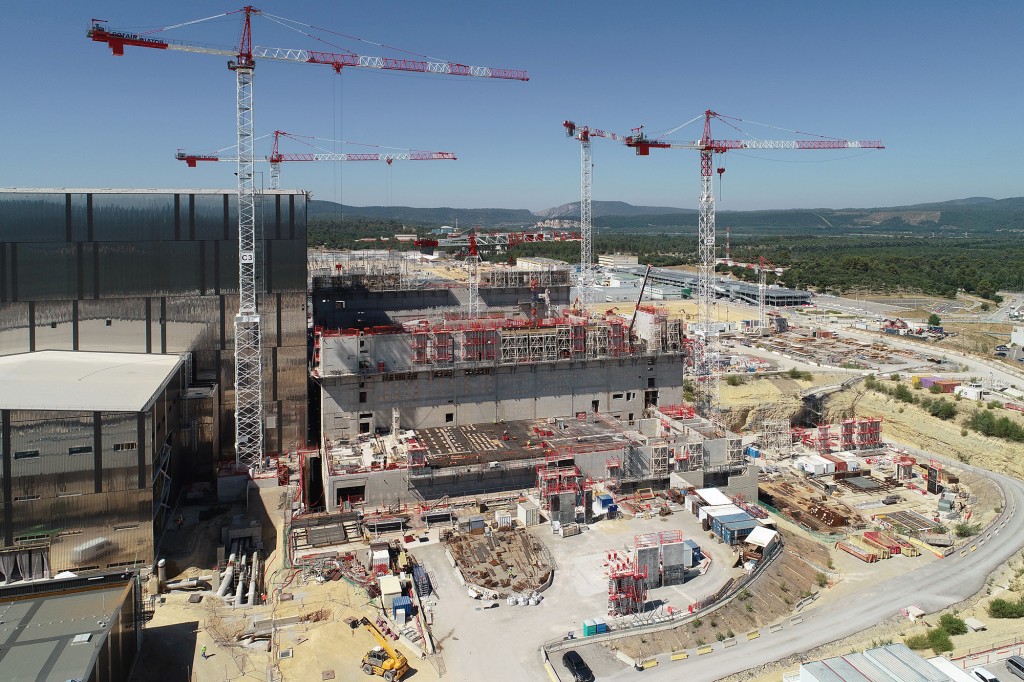
Growing
2018-07-23 - The Tokamak Building (centre) will rise as tall as the Assembly Building when finished. That's 60 metres. Photo: ITER Organization/EJF Riche

Special reinforcement
2018-07-23 - Outside of the Cryostat Workshop is an exterior storage area for heavy components. Asphalting has been going on all summer. Photo: ITER Organization/EJF Riche
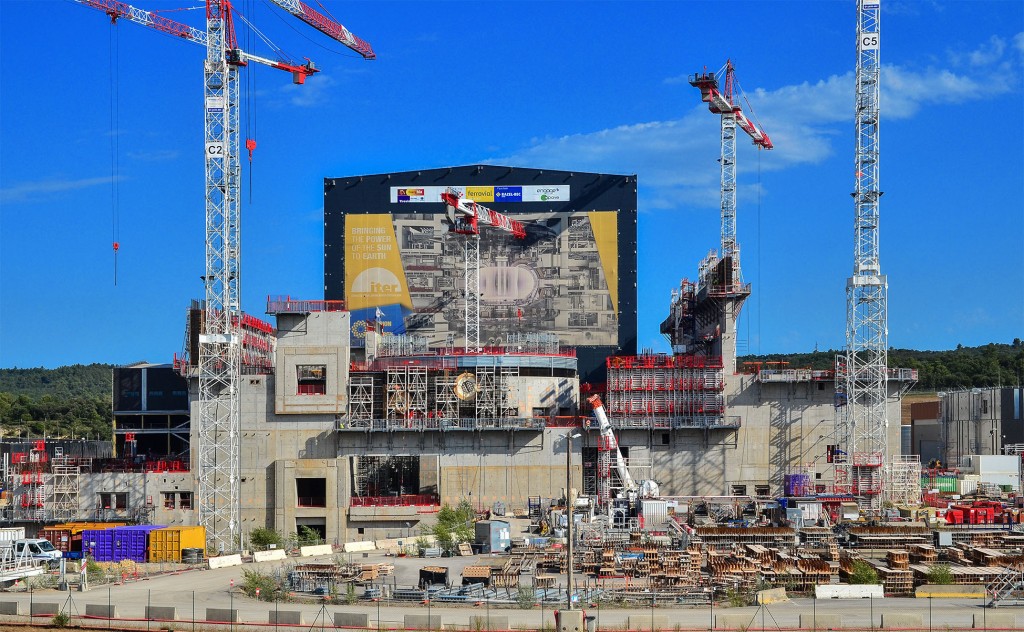
Full steam ahead
2018-07-20 - Responsible for civil engineering and construction, the European Domestic Agency is working to meet an important date on the ITER calendar—March 2020, when the first limited crane access between the Assembly Hall and the Tokamak Building is needed for major installation activities.

At the bottom
2018-07-19 - The concrete "crown" will support the machine from below and transfer forces generated during operation to the massive bioshield and the ground. The cryostat base—the first major "piece" in the assembly puzzle of the ITER machine—will "sit" on this wall, with the deep bottom of the base occupying the inner circle while the outer pedestal rim will be supported by the wall and also on the "lip" of concrete now hidden by rails for the circular crane.
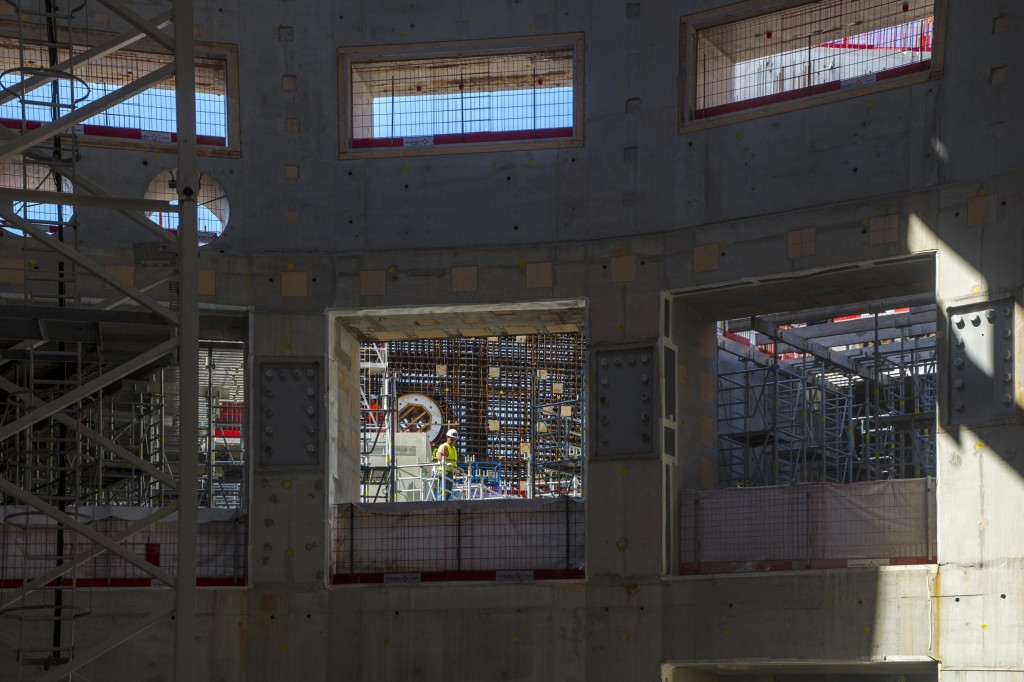
Inside looking out
2018-07-19 - Most of the openings of the bioshield are 4 x 4 metres, Near the top, though, the penetrations change shape.

Crown emerging
2018-07-18 - At the bottom of the Tokamak Pit, the crown circle and radial walls are being poured in segments. A third pour is planned later this month.

First tool up
2018-07-18 - The 800-tonne tools are designed to support charges of up to 1,200 tonnes.
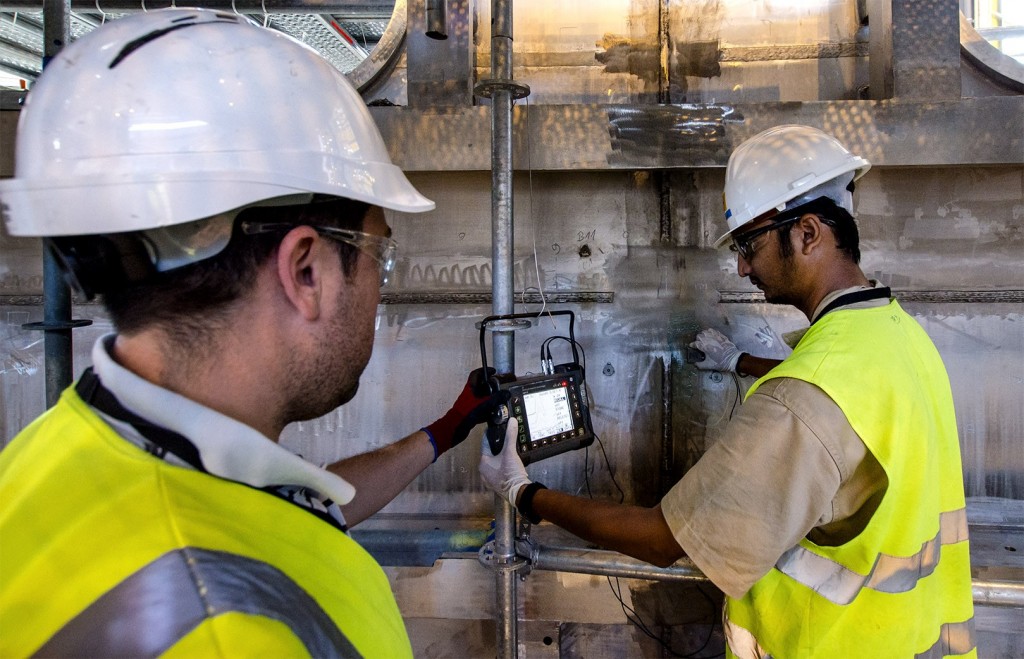
Inspection underway
2018-07-18 - It took approximately four weeks to verify half of the vacuum welds of the lower cylinder. Different specific ultrasonic examination probes are being used by Larsen & Toubro specialists to cover various angles and depth ranges.
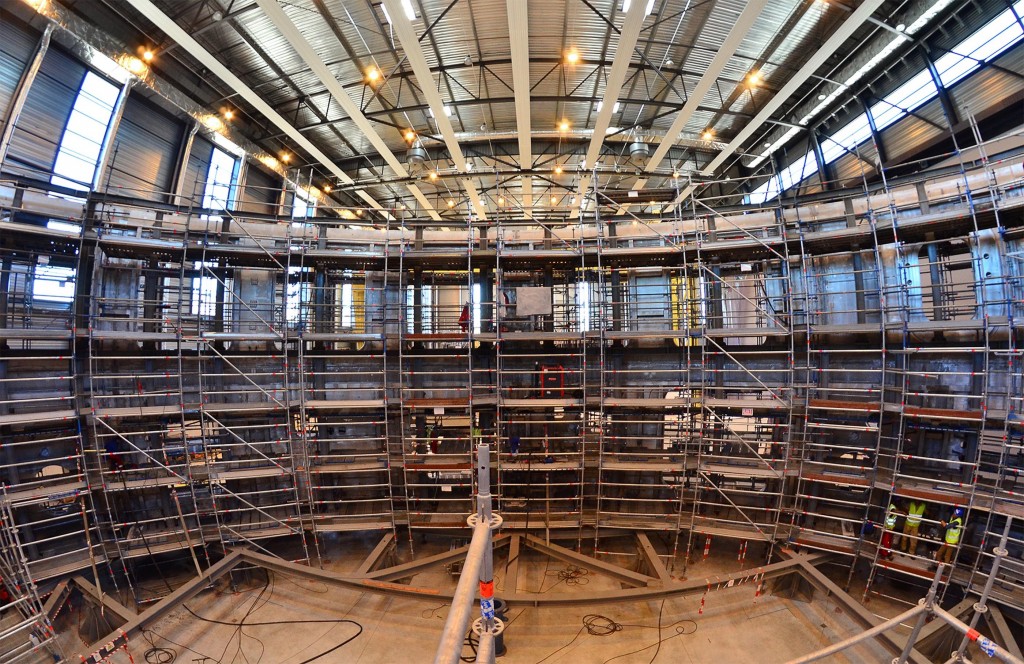
On the other side of the shop
2018-07-18 - The 10-metre-tall lower cylinder has been completely assembled and contractors are verifying the welds. This section will be moved out of the facility next year to make room for the assembly of the upper cylinder.

Turning tables and hot resin
2018-07-18 - One double pancake for PF5 is undergoing impregnation in the background, while assembly is underway on the impregnation mould for another.
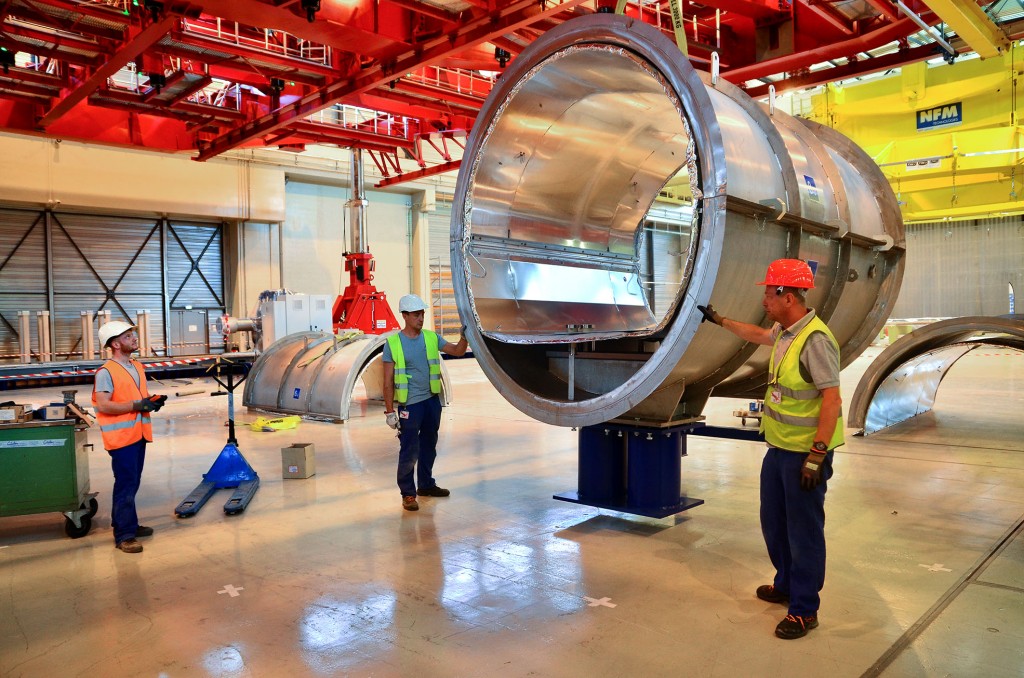
Creating a cold room
2018-07-18 - The cold test chamber has been delivered in segments. Here we see how the magnet coils will be enclosed in a tube-like structure.
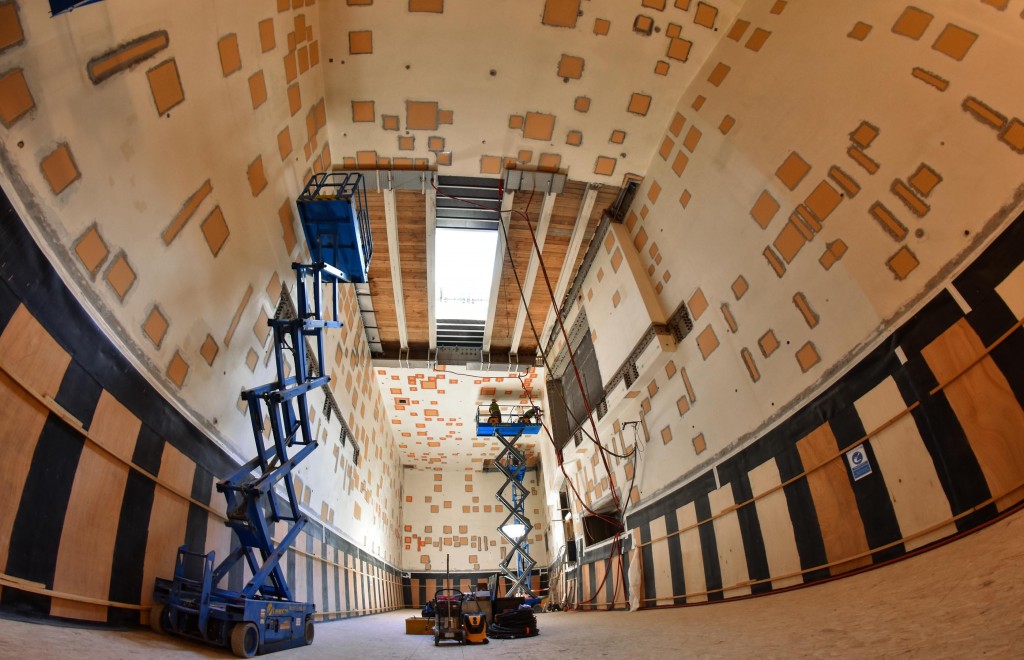
A peculiar chamber
2018-07-18 - In the bowels of the Tokamak Building the drain tank room was designed to house seven water storage tanks required for the operation of the machine's cooling water and vacuum vessel pressure suppression systems.
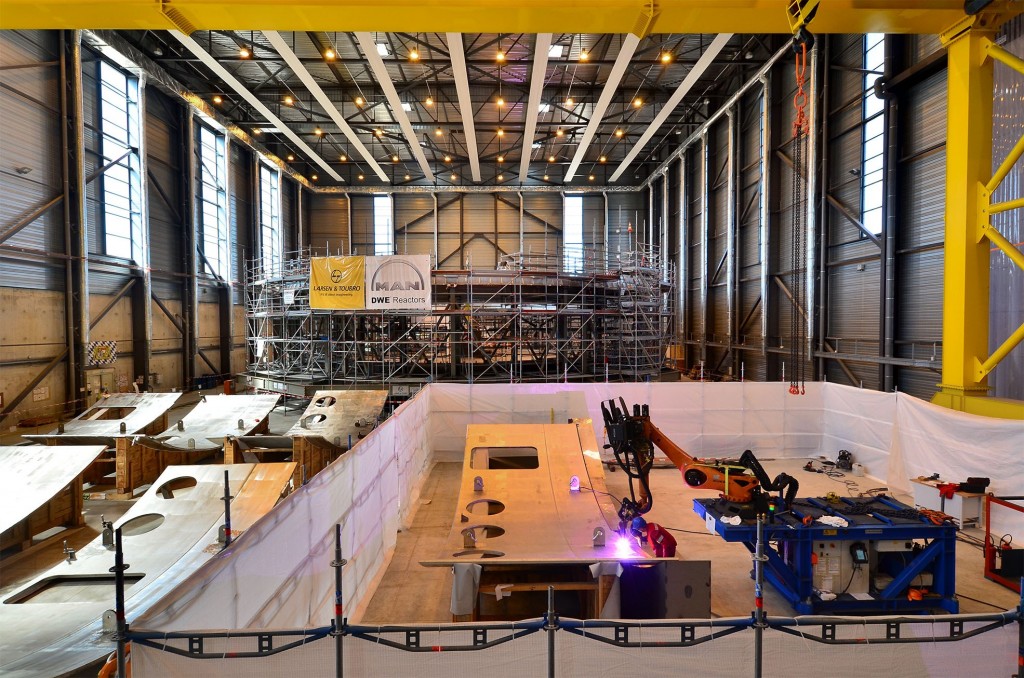
Adjusting
2018-07-18 - Following inspection, the wall segments were disassembled and adjustments are being made with a high-performance plasma torch.

Precise welding operations
2018-07-18 - This "termination box" is welded to the jacket of conductor on one end with a stainless steel pipe for liquid helium cooling exiting on the other end.
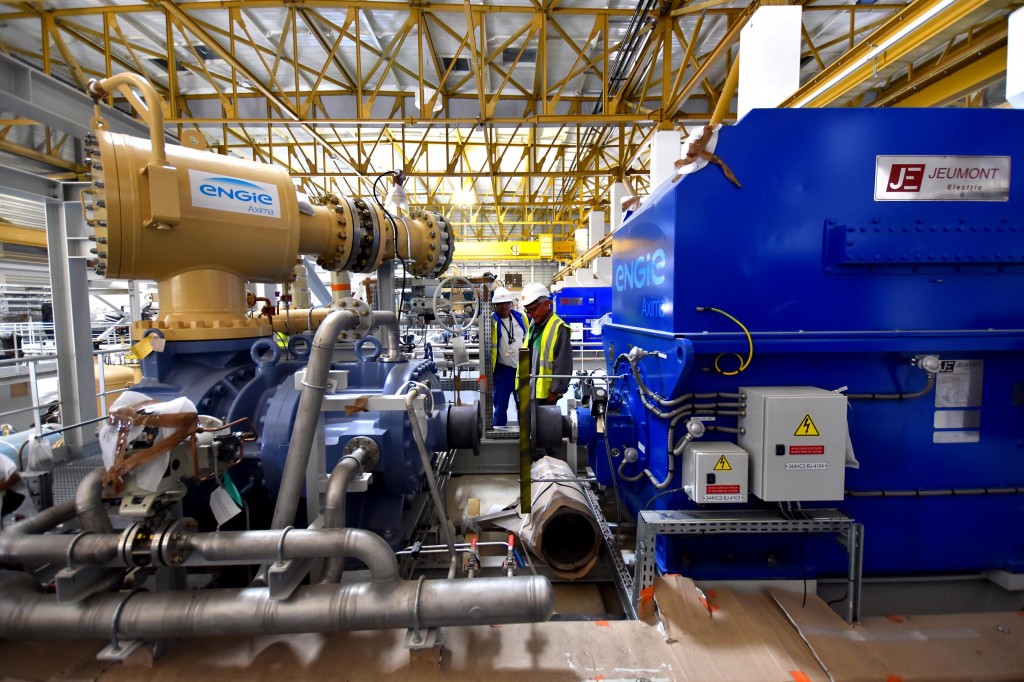
Three identical rows
2018-07-17 - Aligned in three rows, each one linked to a helium cold box, the helium compressors installed on tall concrete pads will supply the cold boxes with gaseous helium at 21.8 bars.

First industrial plant on site
2018-07-17 - The ITER cryoplant used to be a vast echoey chamber with 5,400 m² of interior space divided into two areas; now, it is filled from floor to ceiling with industrial equipment.
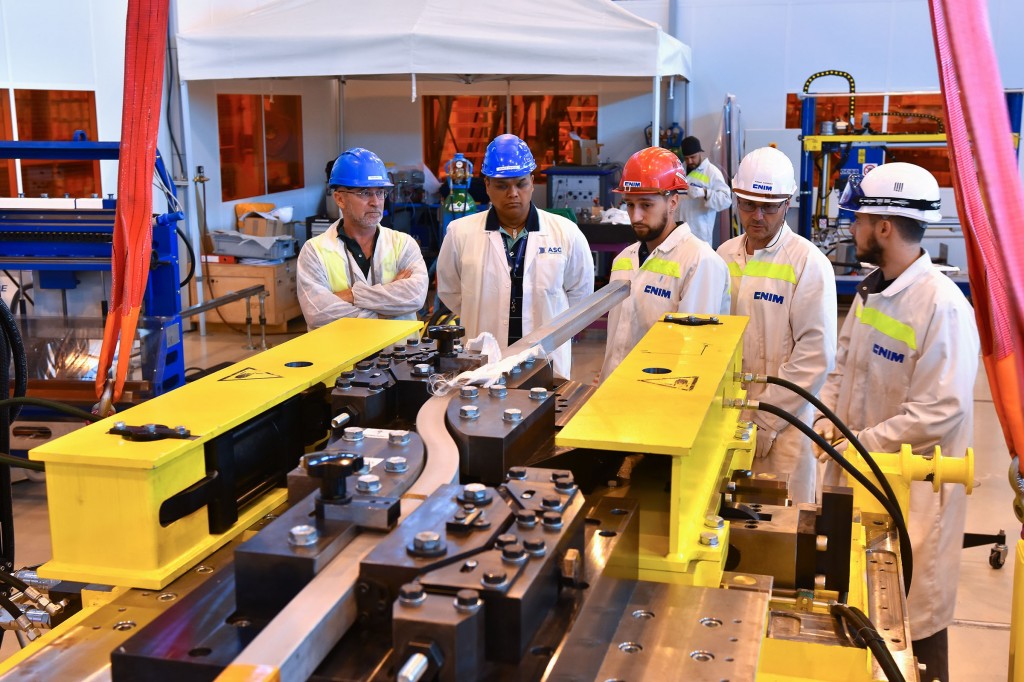
Creating a "joggle"
2018-07-17 - After completing the winding, the next step is to shape the "terminations"—the areas that connect one conductor length electrically to another, or one double pancake to another. A portion of conductor is opened, the turn insulation is removed and moulds are brought close to the double pancake to shape its end into a "termination joggle."

Strong arms
2018-07-17 - The sector sub-assembly tools (SSAT) will support a vacuum vessel sector vertically while operations that can only take place in a spacious area—the addition of large thermal shielding sections and the attachment of a pair of D-shaped toroidal field magnets—are carried out.

Nitrogen as a pre-cooler for liquid helium
2018-07-17 - For the nitrogen plant, the first phase of centrifugal compressor installation was achieved this month.
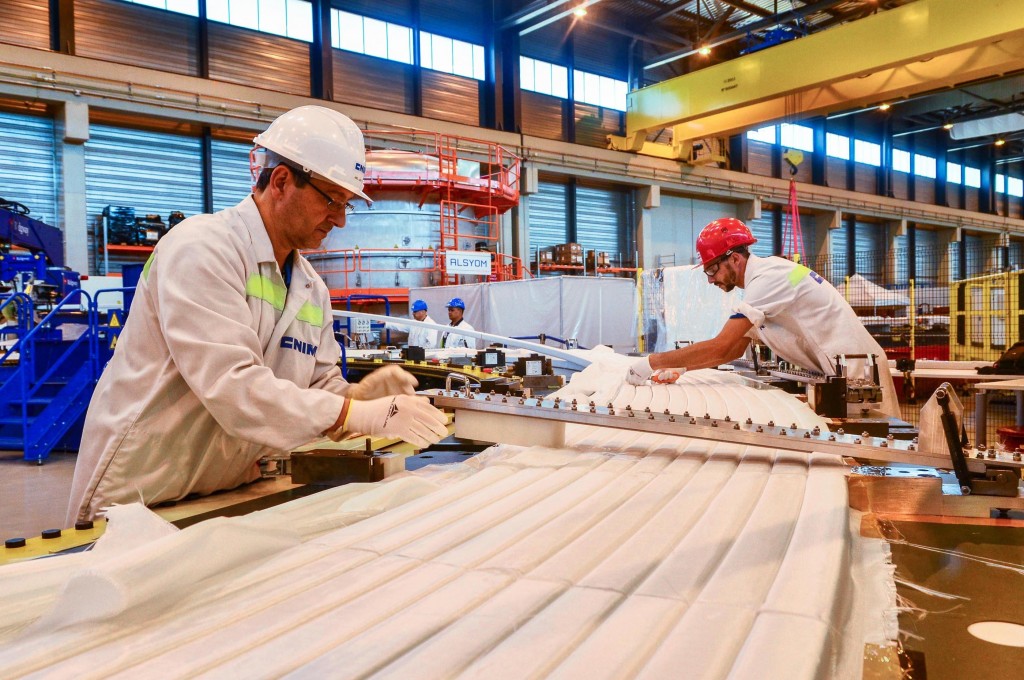
Working on double pancake number six
2018-07-17 - European contractors are winding the sixth in the series of eight double pancakes required by PF5. The winding table rotates slowly as conductor is fed simultaneously from two spools in a process known as "two-in-hand" winding.
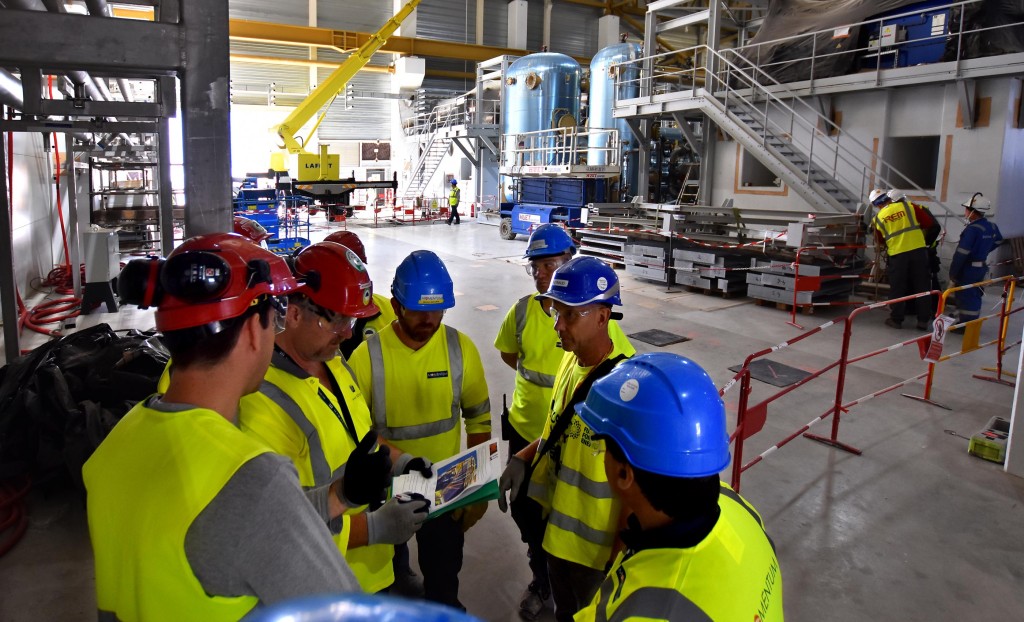
Teamwork
2018-07-17 - Close coordination is required of the different teams representing the ITER Organization, the European Domestic Agency, equipment manufacturer Air Liquide, mechanical installation contractors, and ITER's Construction Management-as-Agent.

Filling up
2018-07-17 - Most of the planned components are now installed in the Compressor Building, drastically reducing the space for circulation.
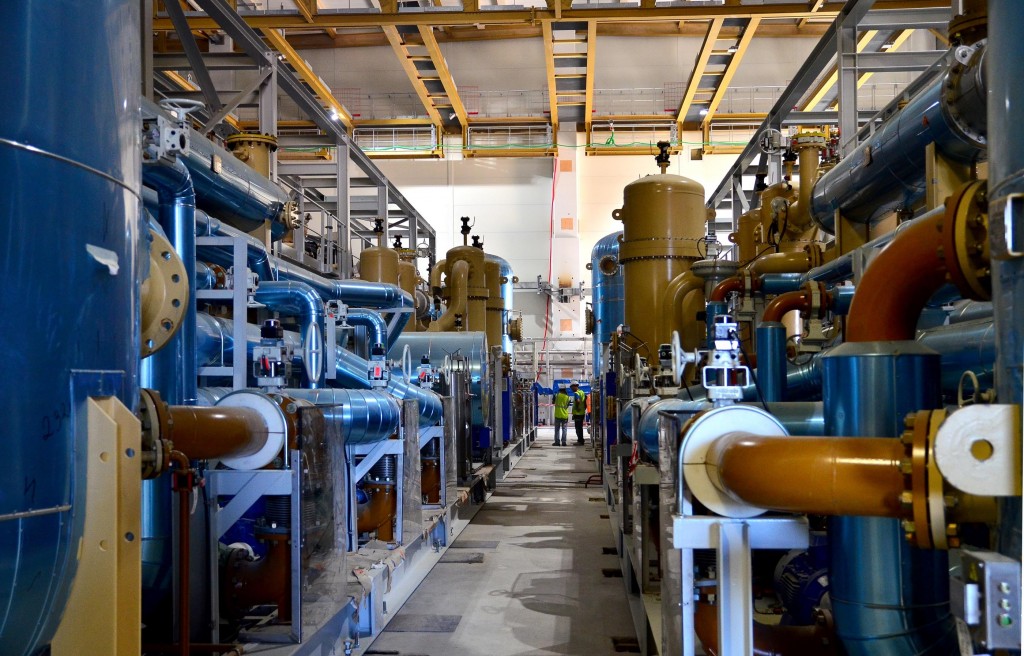
The world's largest single-platform cryoplant
2018-07-17 - The world's largest single-platform cryoplant Three parties are sharing responsibility for the plant's procurement: the ITER Organization, responsible for the liquid helium plants; Europe, in charge of the liquid nitrogen plant and auxiliary systems as well as the construction of the cryoplant infrastructure on site; and India, whose contractors are procuring the cryolines and cryodistribution components. The ITER Organization is managing installation works.
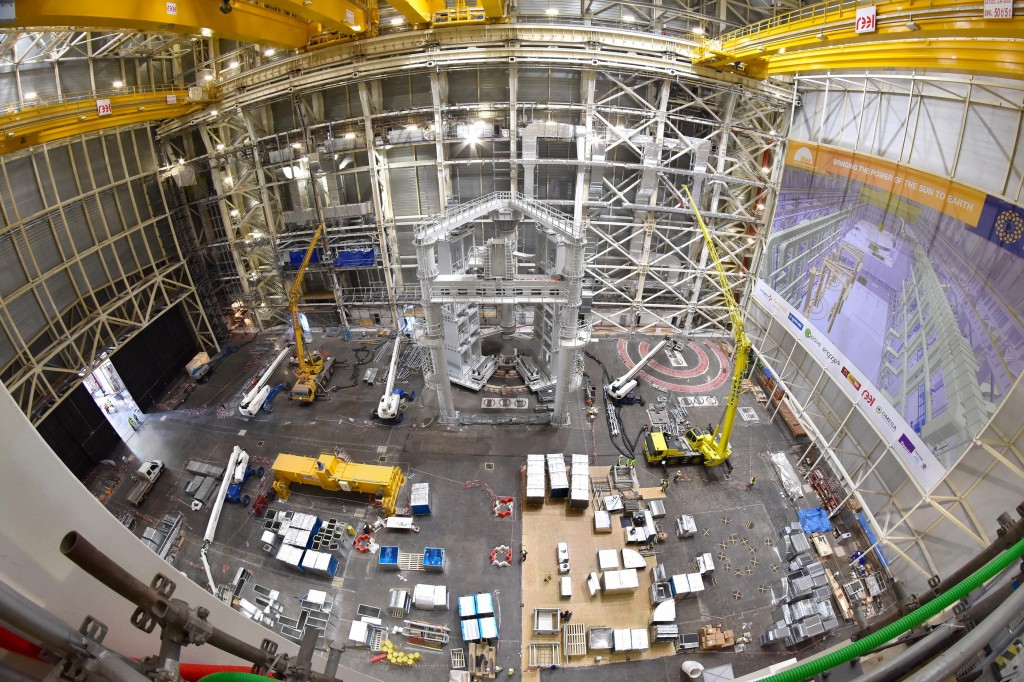
Waiting on its double
2018-07-17 - A second sector sub-assembly tool has been manufactured and tested in Korea, and then shipped to ITER for assembly. After commissioning, the first tool will enter operations with the arrival of vacuum vessel sector #6 in Q2 2019.

First industrial plant on site
2018-07-17 - The ITER cryoplant used to be a vast echoey chamber with 5,400 m² of interior space divided into two areas; now, it is filled from floor to ceiling with industrial equipment.

Installing the final work station
2018-07-17 - European contractors are installing a cold test chamber for the last phase of production: cooling the completed coil to approximately 80 K (-193 °C) in order to simulate the thermal stresses and the work conditions that will be experienced during operation.
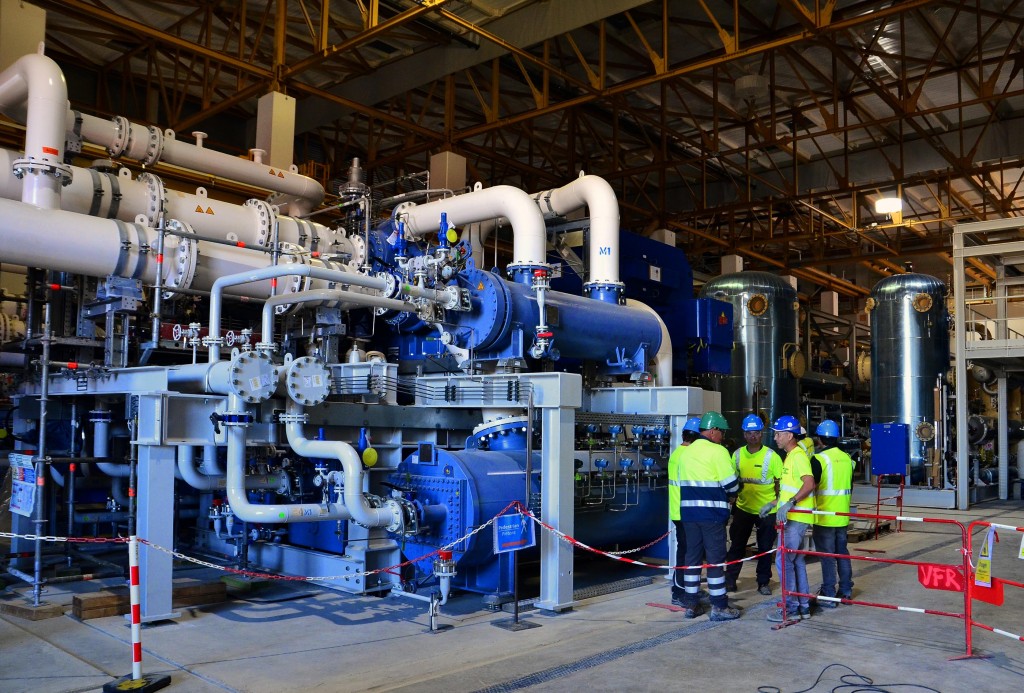
Nitrogen as a pre-cooler for liquid helium
2018-07-17 - For the nitrogen plant, the first phase of centrifugal compressor installation was achieved this month.

The world's largest single-platform cryoplant
2018-07-17 - Three parties are sharing responsibility for the plant's procurement: the ITER Organization, responsible for the liquid helium plants; Europe, in charge of the liquid nitrogen plant and auxiliary systems as well as the construction of the cryoplant infrastructure on site; and India, whose contractors are procuring the cryolines and cryodistribution components.
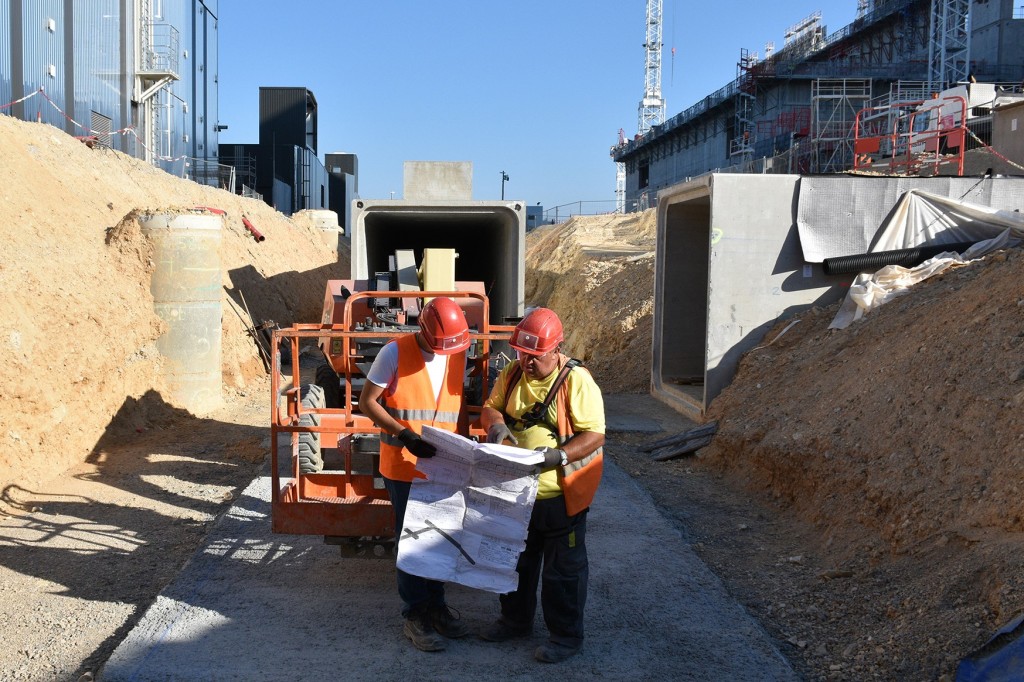
Inside the catacombs
2018-07-15 - Service galleries coming from three different areas of the platform join at a junction near the cryoplant. A five-kilometre network of underground service tunnels criss-crosses the ITER site to bring electricity and communications to the buildings.
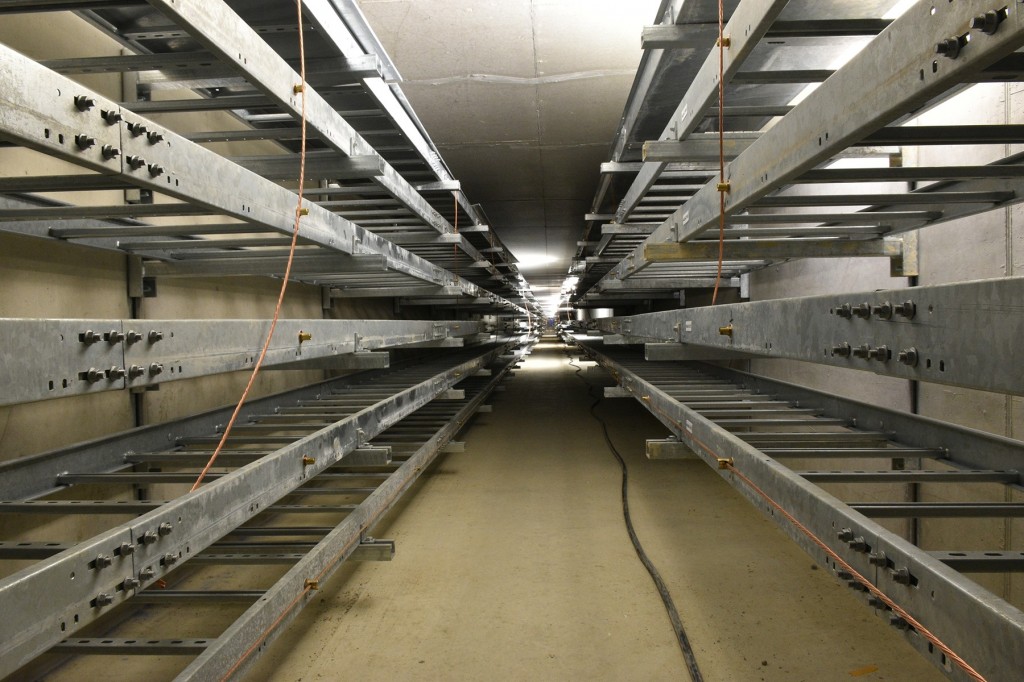
Cable trays
2018-07-15 - Some of the first underground galleries on site (near the Tokamak Complex) have already been equipped with cable trays.

Installation work for MITICA
2018-07-12 - Connecting the main cold box, on the left, with the auxiliary cold box, on the far right, with the help of cryolines. Photo: F4E
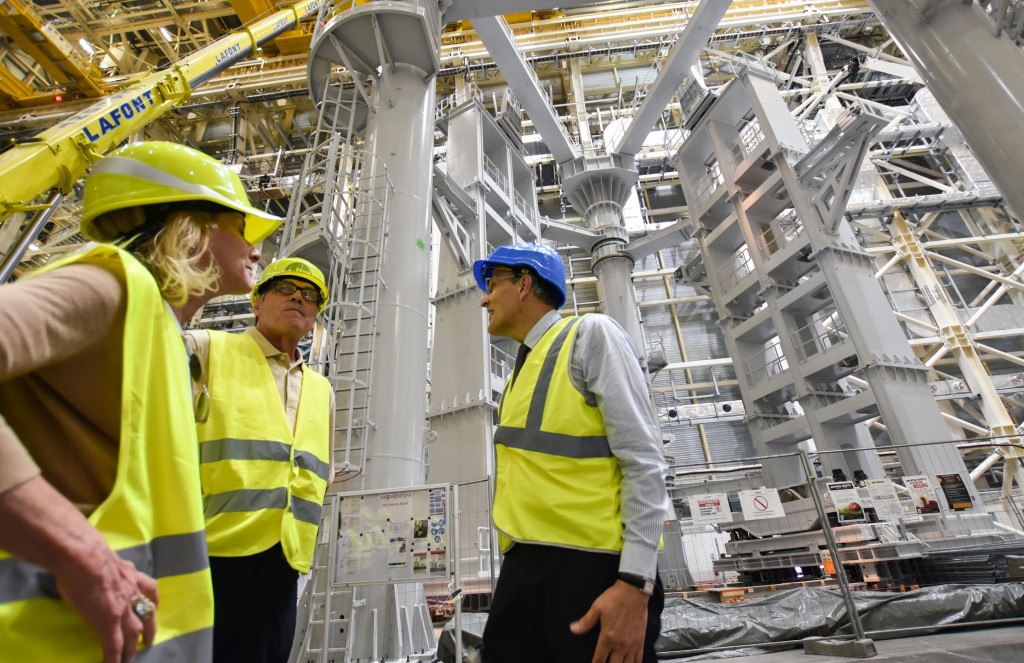
A knowledgeable guide
2018-07-11 - 13,000 visitors passed through ITER in 2017 and a similar number is expected this year. Pictured: the ITER Director-General leads a tour for US Secretary of Energy Rick Perry and US Ambassador to France Jamie McCourt.
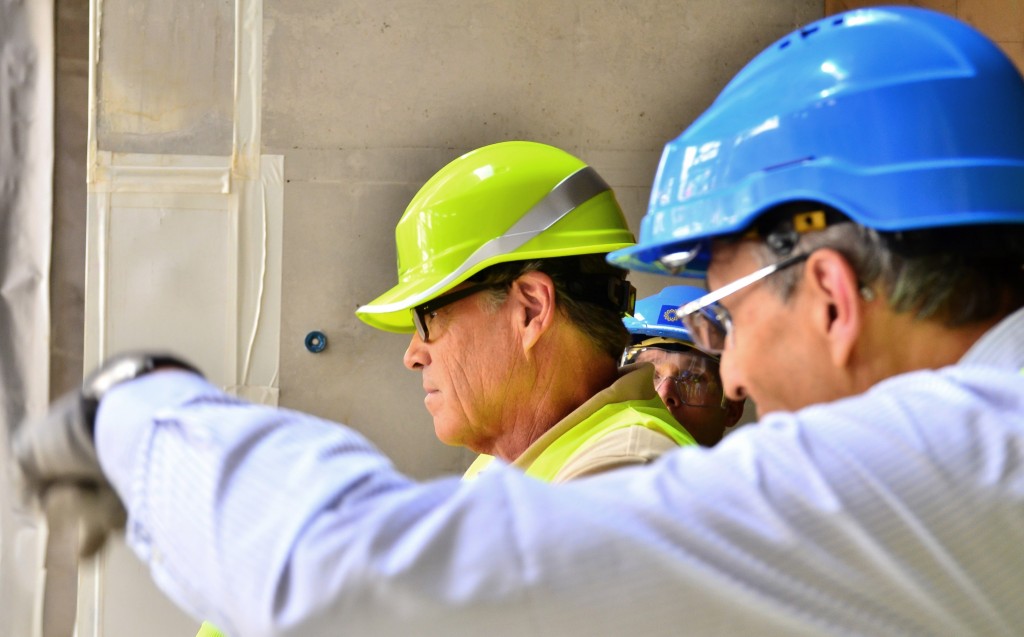
Looking through a "window" in the bioshield
2018-07-11 - The United States Department of Energy head, Secretary Rick Perry, visits ITER on 11 July as part of a US review of ITER Project progress.
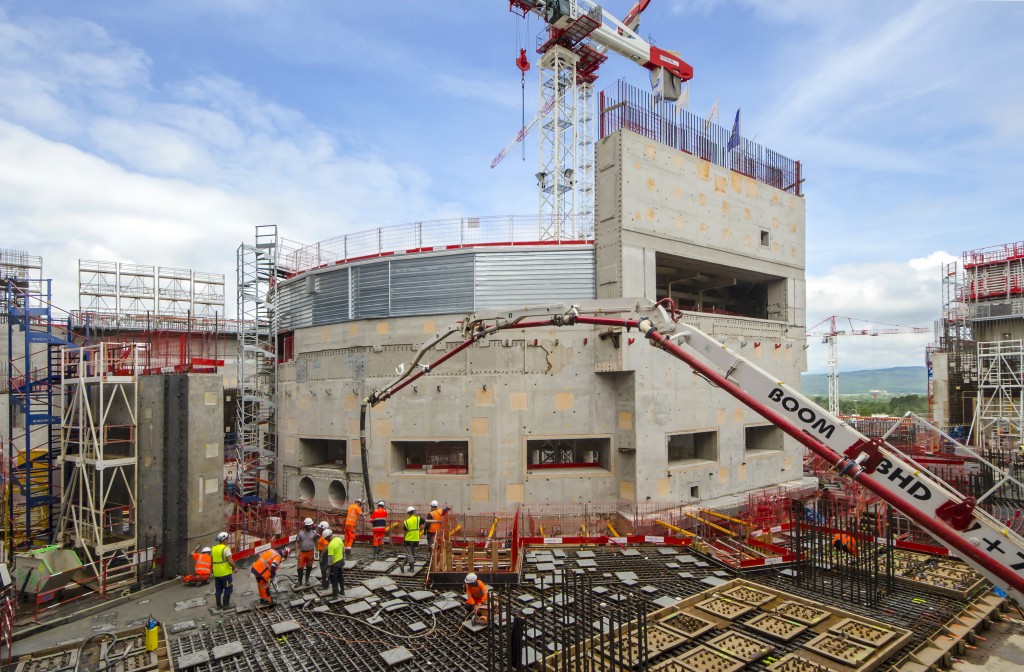
Thinking ahead to machine assembly
2018-07-10 - This wall going up on one side of the bioshield will support the crane rails that will be extended out from the Assembly Hall. A similar wall will be built on the opposite side.
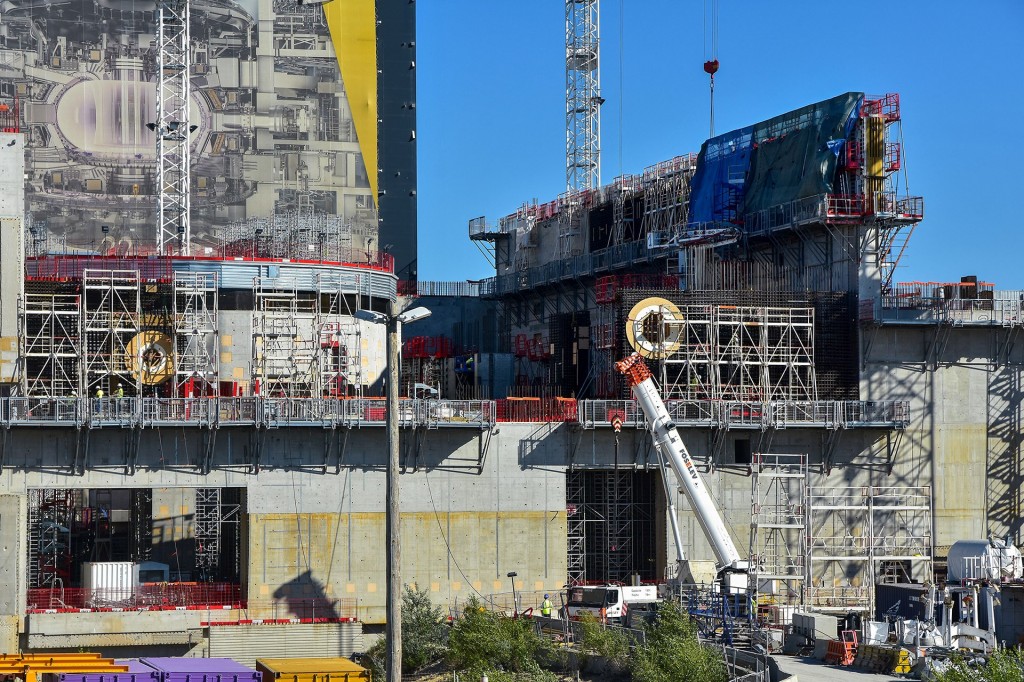
Bullseye?
2018-07-09 - Two perfectly circular structures, looking a lot like archery targets, have been installed on the west-facing wall of the Tokamak Complex. They mark the location of circular openings in the concrete for the passage of electrical cables.
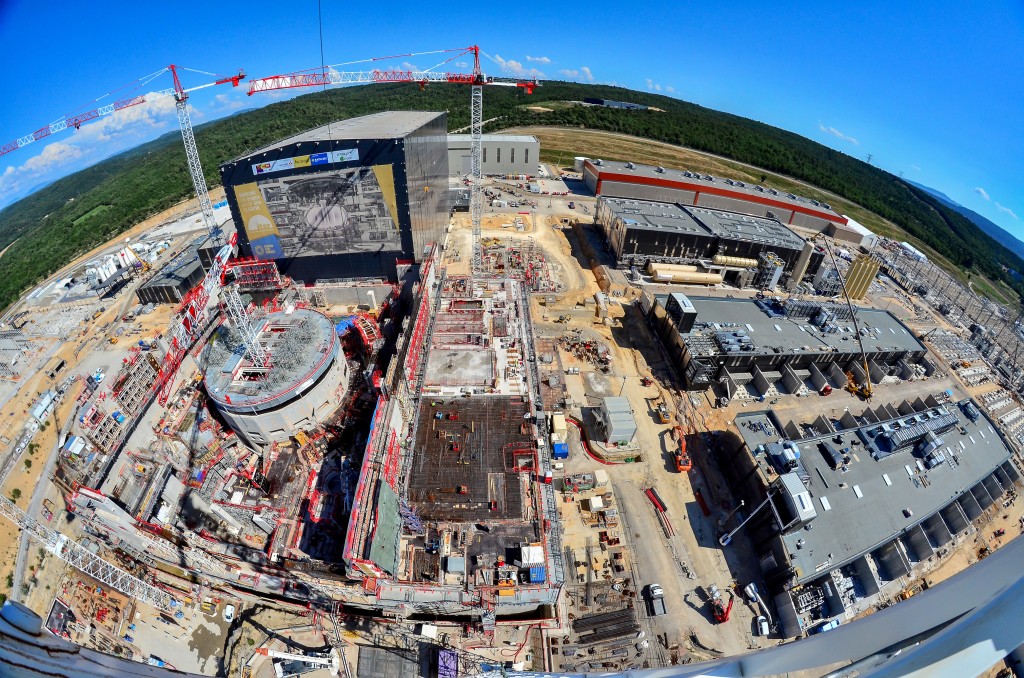
Levels 1, 2 and 3
2018-07-05 - The Tokamak Complex is evolving rapidly, as the Tritium, Tokamak and Diagnostic buildings have risen to L1, L2 and L3 levels respectively.
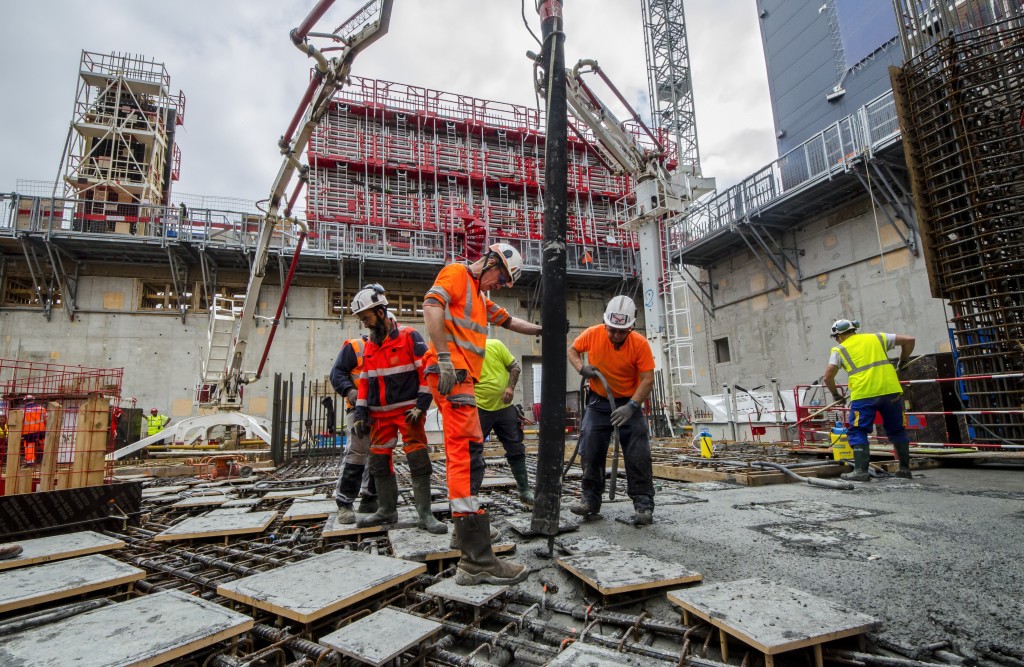
2,000 workers
2018-07-03 - There is activity on the worksite night and day, as nearly 2,000 workers participate in ITER construction in two shifts.
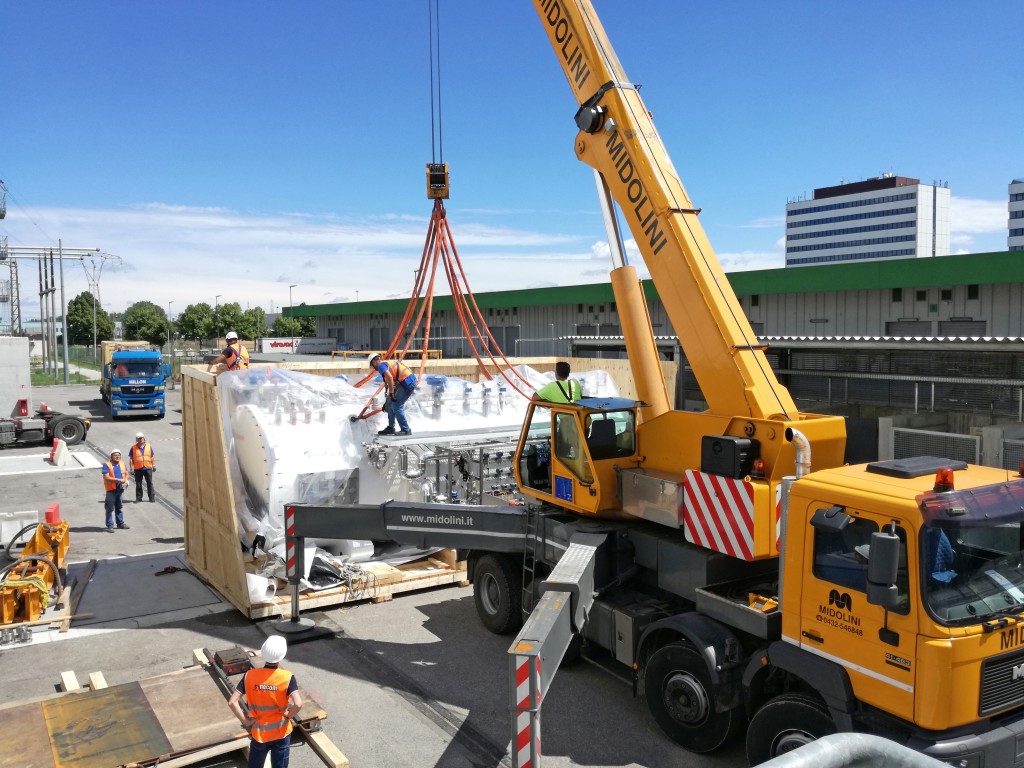
Cryogenic equipment for MITICA delivered
2018-06-25 - MITICA will require cryogenic pumps to maintain strong vacuum during operation. In June, Europe delivers the cryogenic equipment needed for cryopumping, including this auxiliary cold box. Photo: F4E

Running overhead
2018-06-25 - This "cabin" marks the starting point for a covered bridge that will shelter the electrical busbars running power from the Magnet Power Conversion buildings to the magnet coils in the Tokamak Building.

A last check
2018-06-12 - A test is underway to verify if the concrete that is about to be used to pour the radial walls and crown at the bottom of the machine well has the required fluidity characteristics.

First test bed enters operation
2018-06-11 - The negative ion source SPIDER is officially launched at the Consorzio RFX facility in Padua, Italy, in the early afternoon of 11 June 2018.
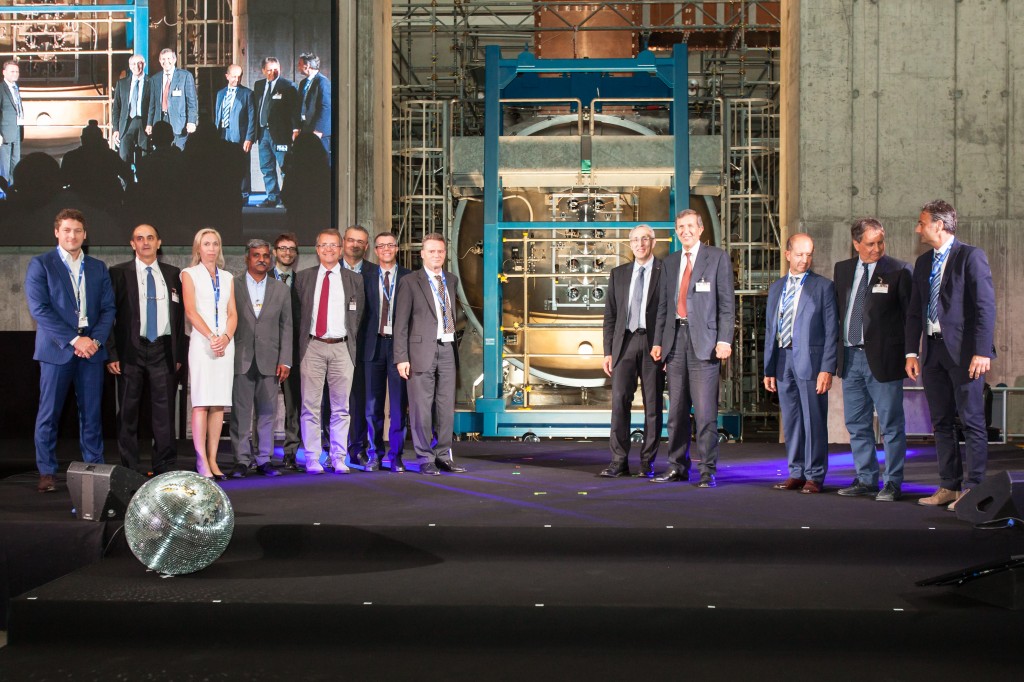
Inauguration and first plasma
2018-06-11 - Plasma is generated in the beam source for the first time during the ceremony in the presence of all stakeholders.
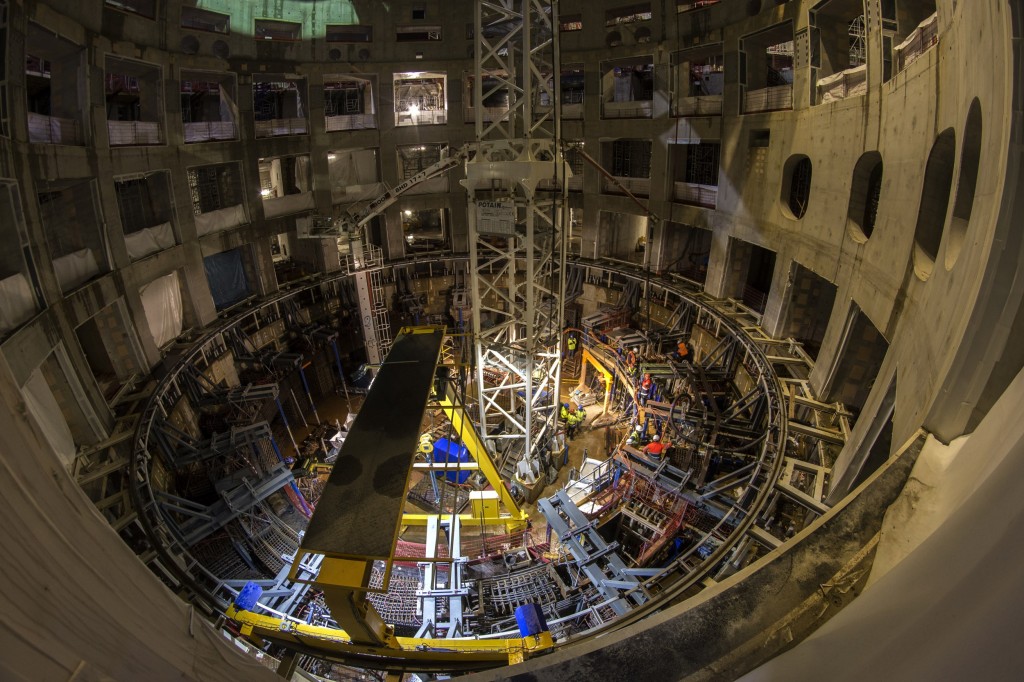
A midnight pour
2018-05-22 - The first plot of the Tokamak "crown" is poured on 22 May. The crown will support the combined mass of the Tokamak and its encasing cryostat (23,000 tonnes) while transferring the forces and stresses generated during plasma operation to the ground.

All columns in place
2018-05-18 - The first 22-metre-tall, 800-tonne SSAT tool is now in place. Precision hydraulic equipment will be installed next. (SSAT stands for vacuum vessel Sector Sub-Assembly Tool.)

90% completed
2018-05-18 - Imagine: two of these giant tools will be working side-by-side during the pre-assembly phase of the ITER vacuum vessel.

On-site storage
2018-05-17 - Z2—the largest on-site warehouse—provides a total of 15,000 m² of storage (9,000 m² internal, 6,000 m² external).
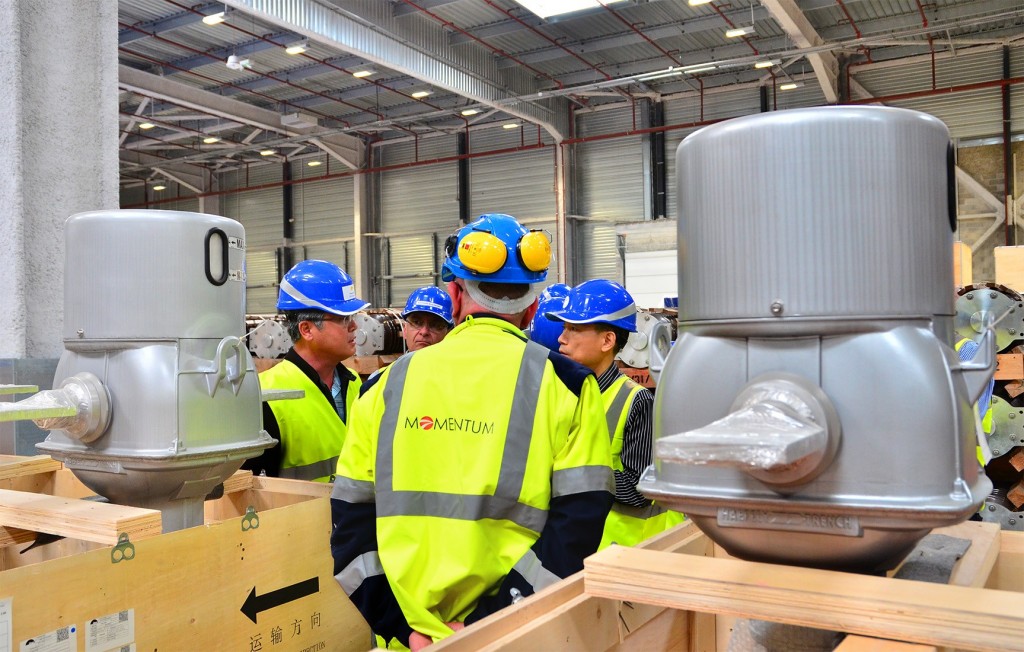
Managing the pieces
2018-05-17 - Logistics management is a critical activity for ITER. But the complexity of the machine and plant, the sheer amount of components to assemble, and the multiplicity of providers on three continents all make for a particularly daunting task at ITER.

Successful testing on site
2018-05-17 - The conversion system for MITICA's acceleration grid power supply completed site acceptance testing this year with excellent results. The equipment, manufactured by the Italian firm Nidec ASI, will convert AC power from the grid to the DC power required for the acceleration of the ion beam.

A touch of colour
2018-05-04 - The ITER construction site on a stormy day, with a bit of added colour.
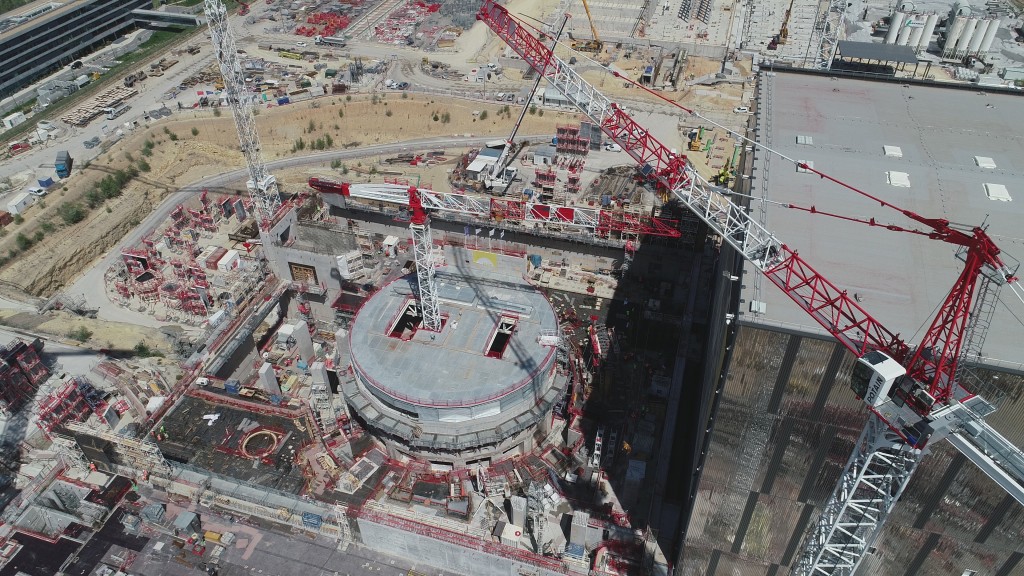
Under the lid
2018-04-25 - Under the lid of the ITER bioshield, teams are preparing to pour the first segment of the cryostat crown. The crown is a concrete wall that will support the base of the cryostat. © Les Nouveaux Médias/SNC ENGAGE
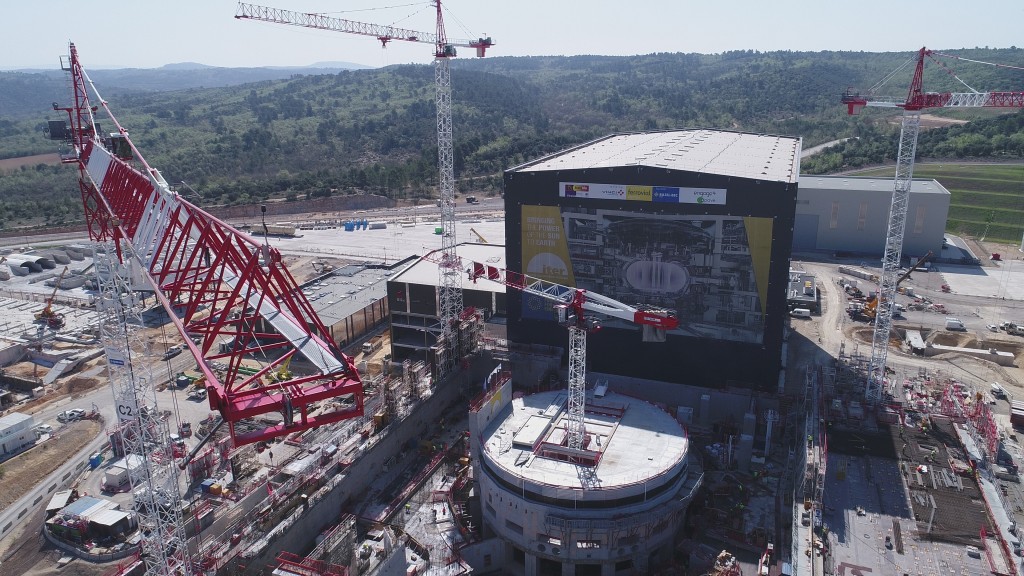
By drone
2018-04-25 - A drone snapped this shot as it flew over the tallest cranes on site. © Les Nouveaux Médias/SNC ENGAGE
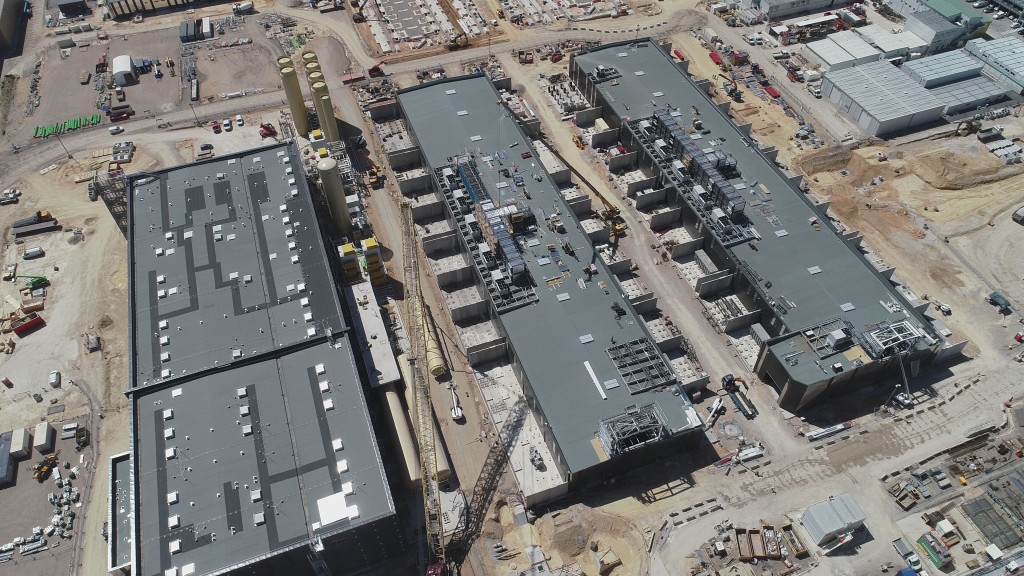
Finished in 2017
2018-04-25 - Three of the structures that were completed in 2017 and made ready for equipment: (from left to right) the cryoplant and two buildings dedicated to magnet power conversion. © Les Nouveaux Médias/SNC ENGAGE
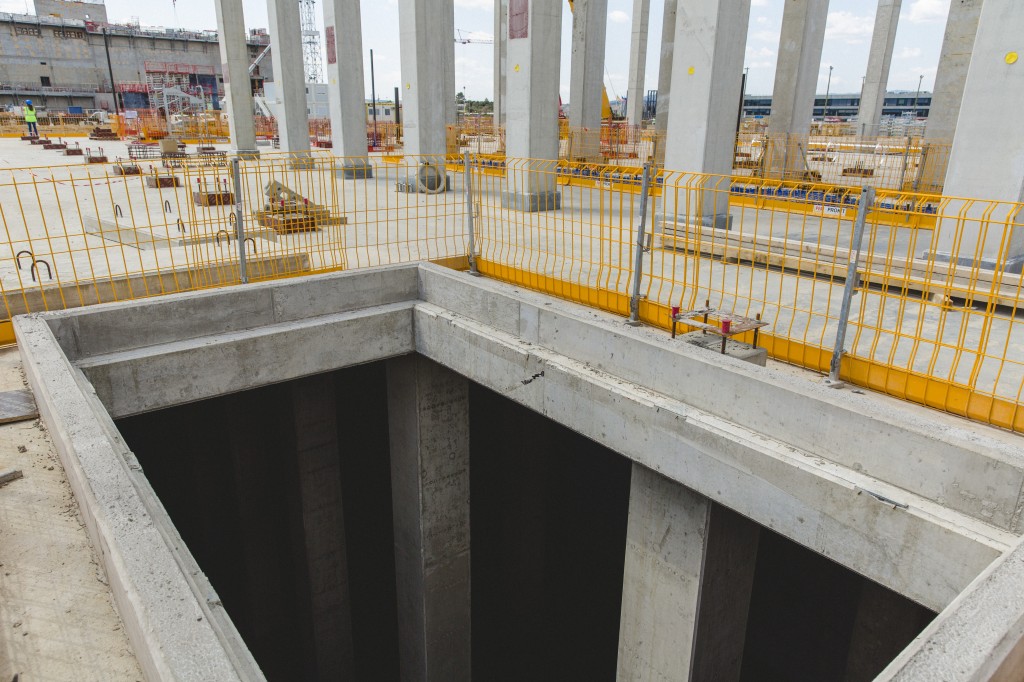
Down below
2018-04-25 - The hot basin has been covered over, but its depths are still visible through this opening. © Les Nouveaux Médias/SNC ENGAGE

Last job
2018-04-25 - The tall crawler crane (on site since February) has finished its last task—the installation of two quench tanks near the north end of the building. © Les Nouveaux Médias/SNC ENGAGE
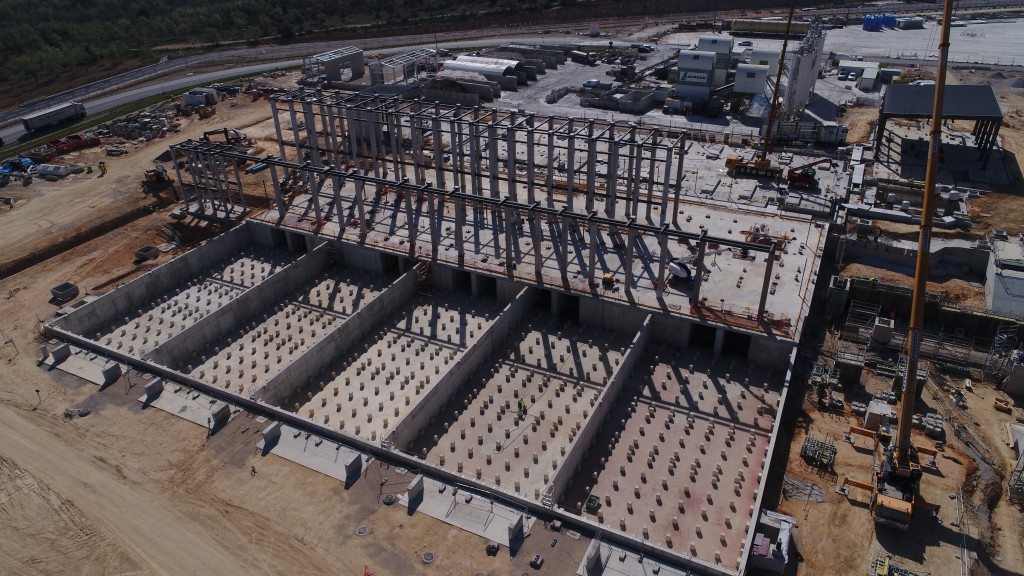
The cooling tower zone
2018-04-25 - The heat rejection infrastructure is concentrated in a 6,000-square-metre area that comprises hot and cold cooling water basins, powerful pumps, heat exchangers, and an induced-draft cooling tower with ten individual cells. © Les Nouveaux Médias/SNC ENGAGE
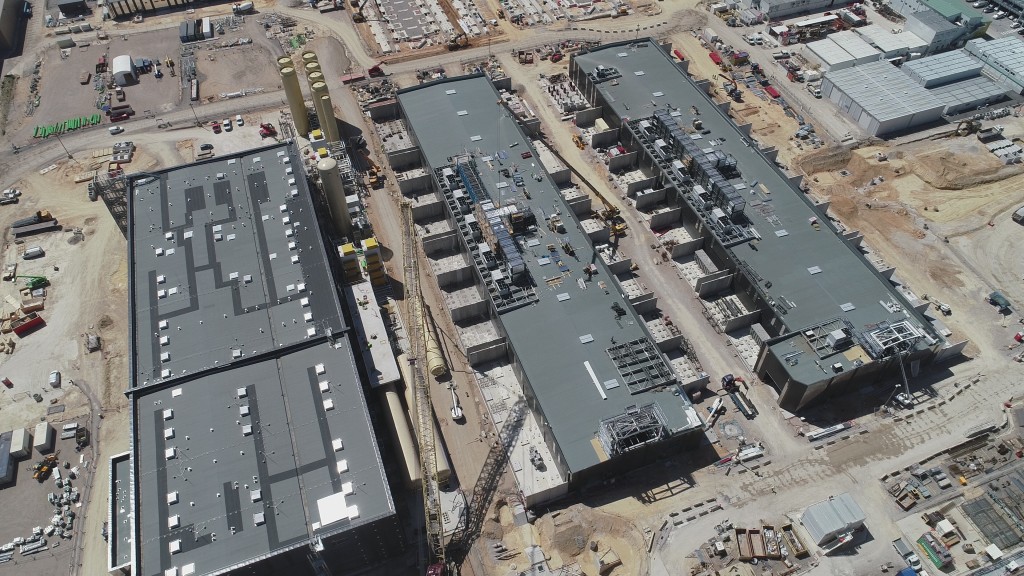
Finished in 2017
2018-04-25 - Three of the structures that were completed in 2017 and made ready for equipment: (from left to right) the cryoplant and two buildings dedicated to magnet power conversion. © Les Nouveaux Médias/SNC ENGAGE

Gates to be installed
2018-04-25 - Each cold basin can be closed off individually for maintenance, thanks to giant stop log gates that will be installed over the openings on the far side. © Les Nouveaux Médias/SNC ENGAGE
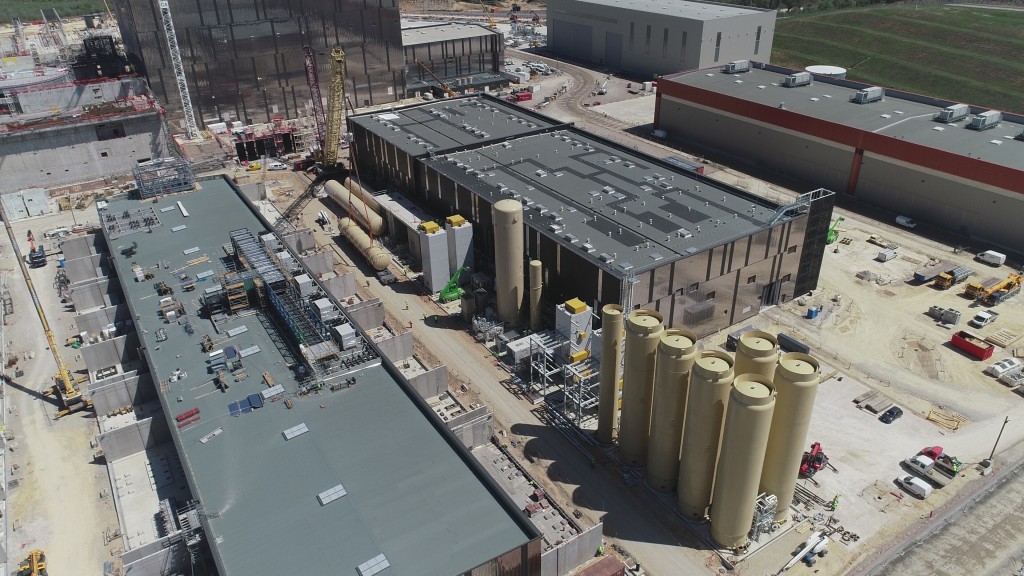
From the air
2018-04-25 - The ITER cryoplant: 5,400 m² of covered space and 2,600 m² of exterior storage. © Les Nouveaux Médias/SNC ENGAGE

All in a row
2018-04-25 - Seven tall storage tanks have now been installed outside of the cryoplant. © Les Nouveaux Médias/SNC ENGAGE

On its way
2018-04-23 - This quench tank travels from its storage area to the cryoplant on a self-propelled modular transporter with 18 independently manoeuvrable axles.
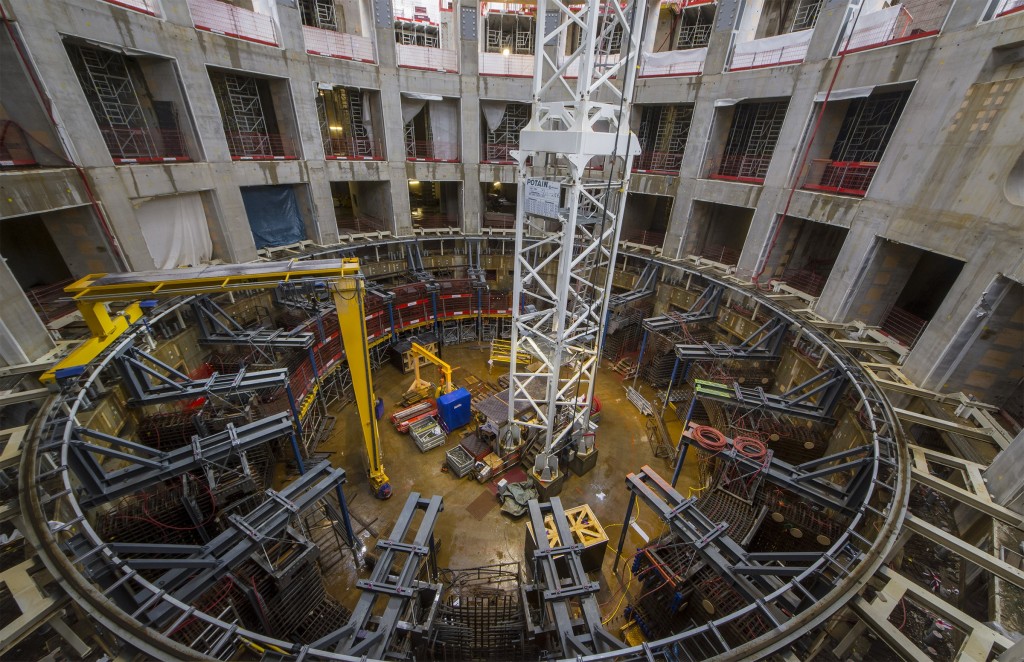
18 "spokes"
2018-04-23 - 18 radial walls will transfer loads from the cryostat crown to the bioshield.
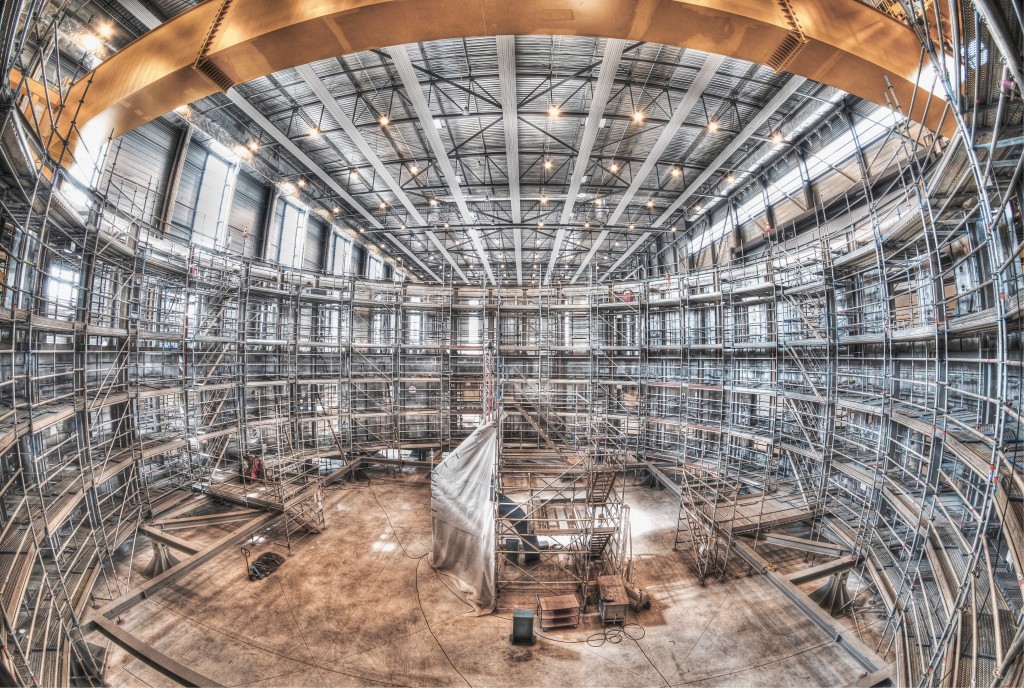
ITER—a challenge for science photography
2018-04-23 - During his most recent visit to ITER, German photographer Christian Luenig covered the ongoing work on the cryostat. He captured the lower cylinder and base section with their enormous dimensions using a technique called tone mapping which combines multiple exposures with particular contrast and colour adjustments. "Like every visit to the ITER construction site, it was a real challenge," says Luenig. To see his work on ITER and fusion go to: www.arbeitsblende.de/ ©ITER Organization/Christian Luenig
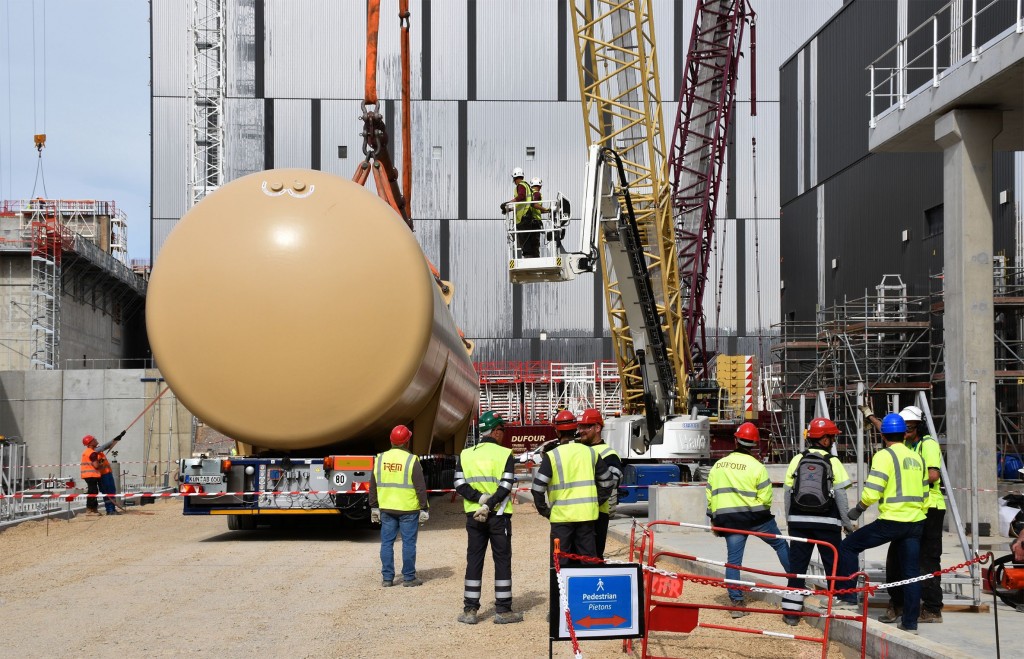
Two horizontal tanks installed
2018-04-23 - Two 35-metre quench tanks have been removed from temporary storage and transferred to their exterior bays near the cryoplant. They are designed to hold helium from the magnet system in the case of sudden loss of superconductivity (quench).

Pouring to start on cryostat crown in May
2018-04-23 - Down on the floor of the Tokamak Pit the steel reinforcement for about one-fourth of the crown has been set into place. Pouring will start in May.

Fire mesh
2018-04-22 - A "fire mesh" is being welded to the outer rebar of each radial wall. The mesh will sit just under the "skin" (15 to 20 millimetres) of the concrete surface and prevent spalling (splintering) in the case of fire.

Openings for deliveries
2018-04-22 - Two rectangular openings in the lid allow the equipment needed for the construction of the radial walls (formwork, rebar, etc.) to be delivered to the floor of the amphitheatre and dispatched by the circular crane visible on the right of this image.
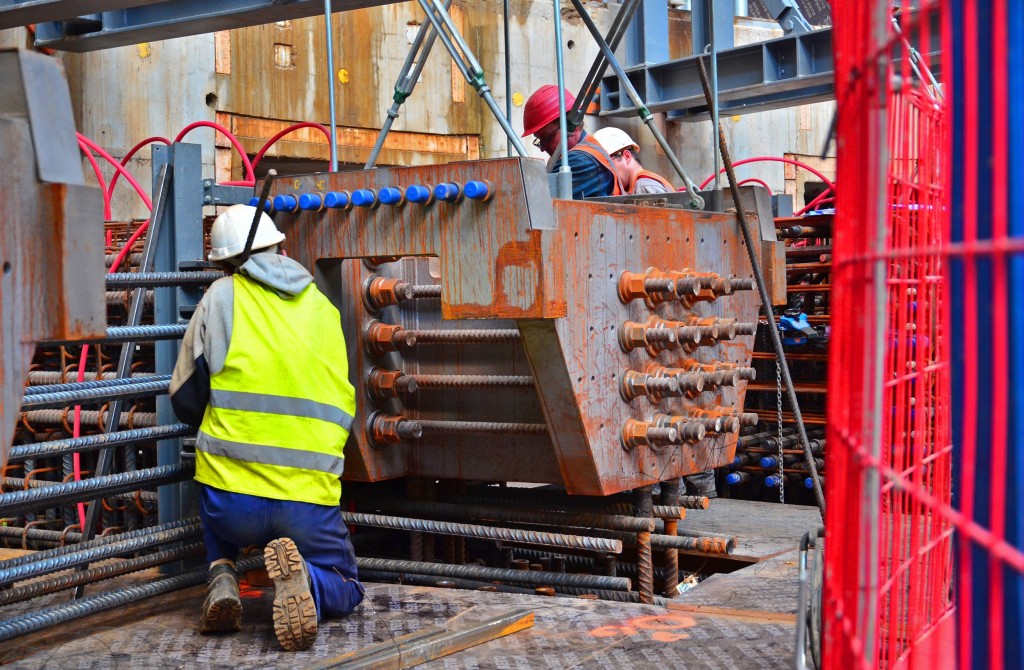
A path for the loads
2018-04-22 - Connected to the dense rebar of the radial wall, this 3.5-tonne "steel transition piece" provides a pathway for the transfer and distribution of the loads to the surrounding concrete structure.
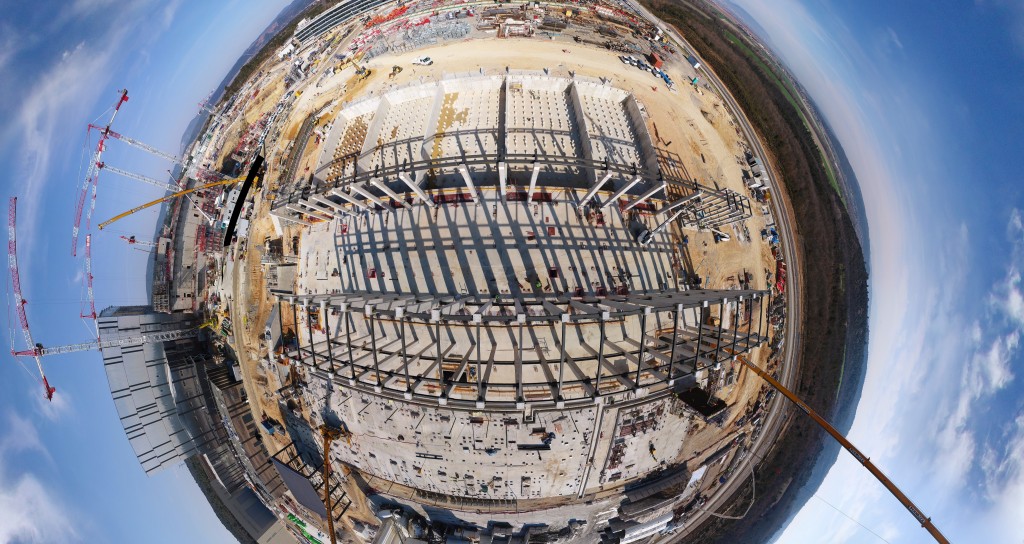
The cooling tower area, as the centre of the ITER planet
2018-04-20 - An original view of the cooling tower area, extracted from a series of drone videos taken in April. Photo: ITER Organization/EJF Riche
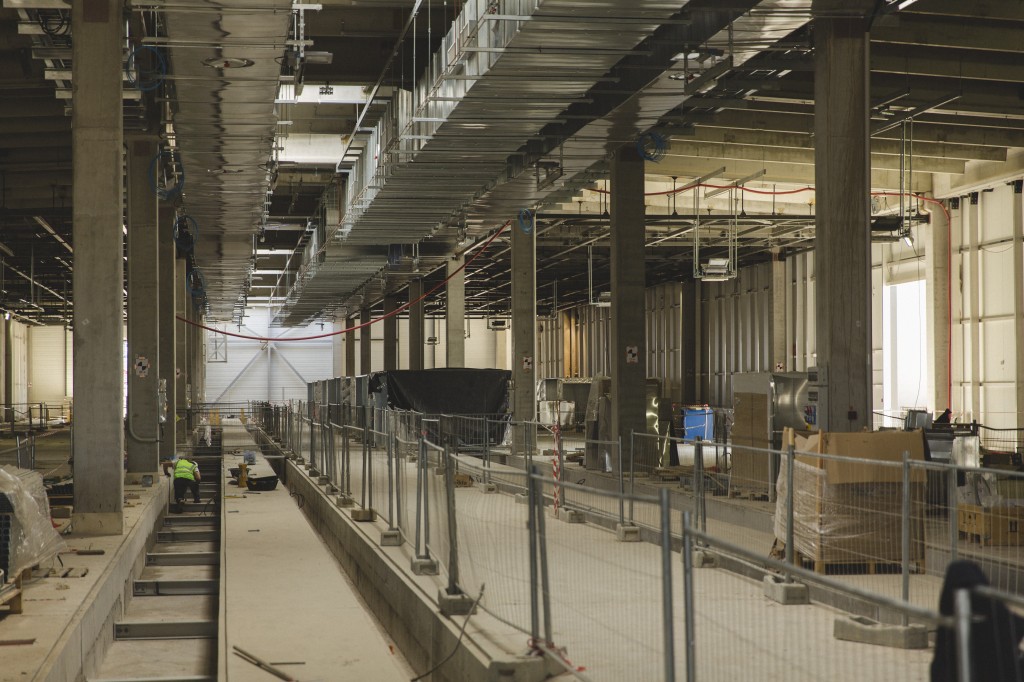
Work inside
2018-04-18 - Finishing work is underway on the inside of the buildings. © Les Nouveaux Médias/SNC ENGAGE
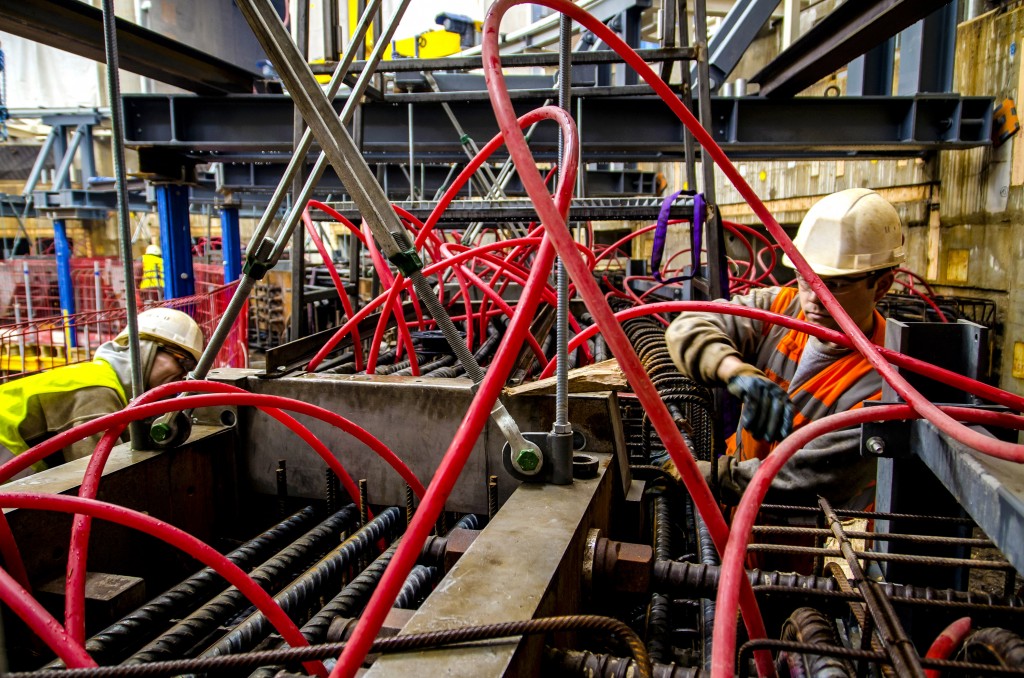
Red tubes?
2018-04-10 - To prepare for the first pour of the cryostat crown, teams are integrating 500 metres of cooling tubes. The temperature of the concrete during the hardening process will be regulated and homogenized by cooling water circulating inside these tubes and monitored by sensors distributed throughout the structure.
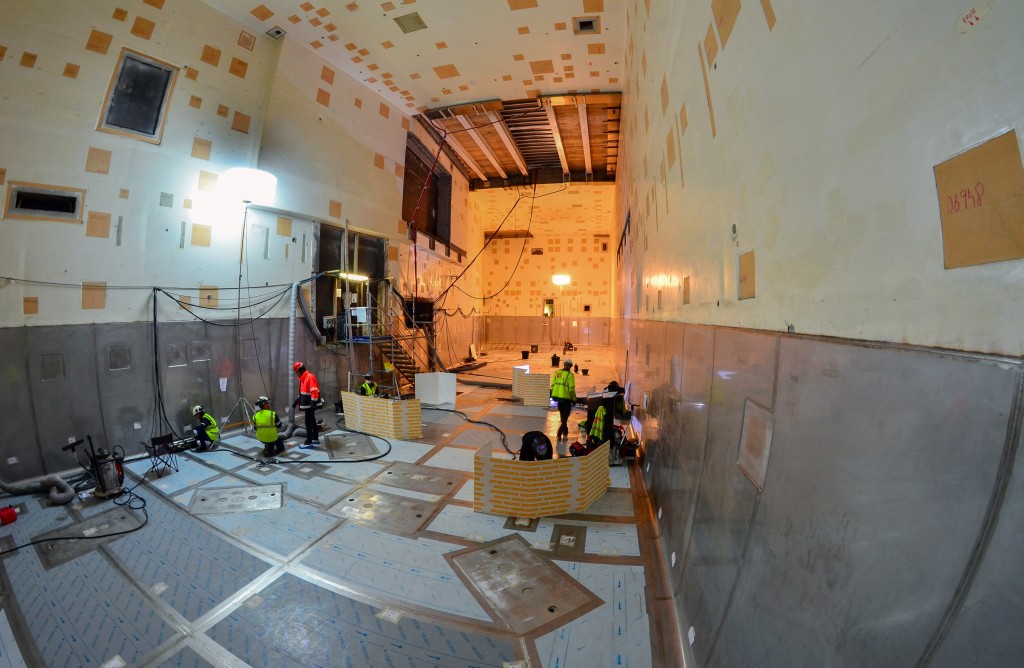
Drain tank room
2018-04-10 - A steel-lined drain tank room in the bowels of the Tokamak Complex. Seven steel tanks will be introduced through the roof of the room for the storage of Tokamak cooling water.
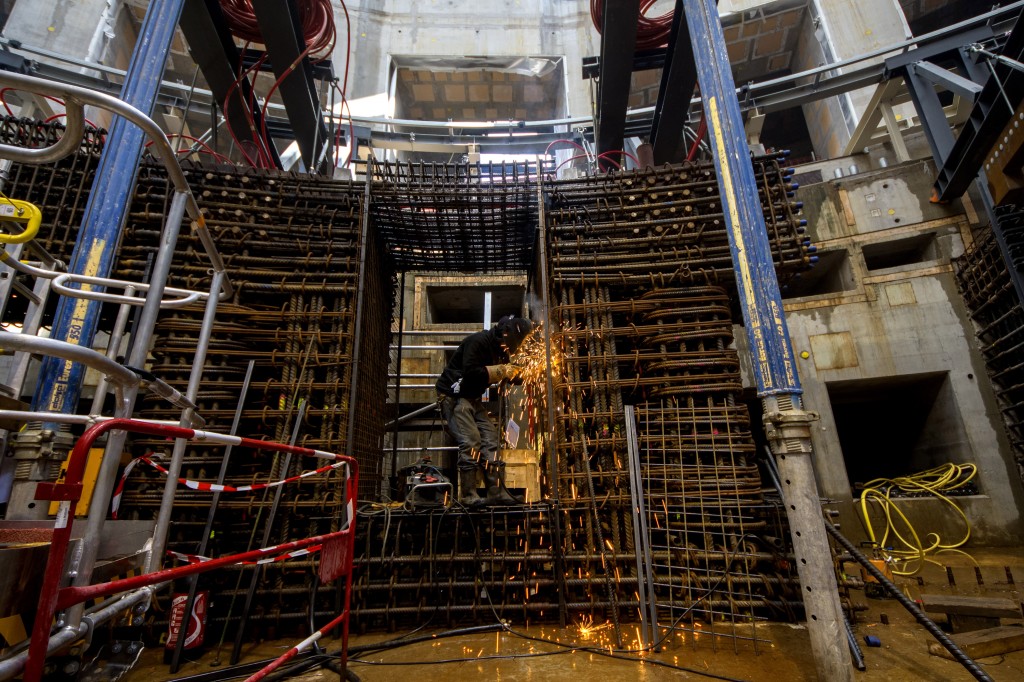
Crown rebar, shaping up
2018-04-10 - The first pour for the concrete crown that will be situated under the cryostat base is scheduled for early May. The rebar in this part of the Tokamak Complex is particularly dense.

Wings open
2018-04-09 - With its wings open, the tool is impressive indeed. Each wing will slowly rotate in to align 310-tonne toroidal field coils to each side of a vacuum vessel sector.

Next step: hot resin
2018-04-09 - Attached to the circular spreader beam, one of three finalized double pancakes (out of eight needed to complete the winding pack for PF5) is prepared for impregnation operations.
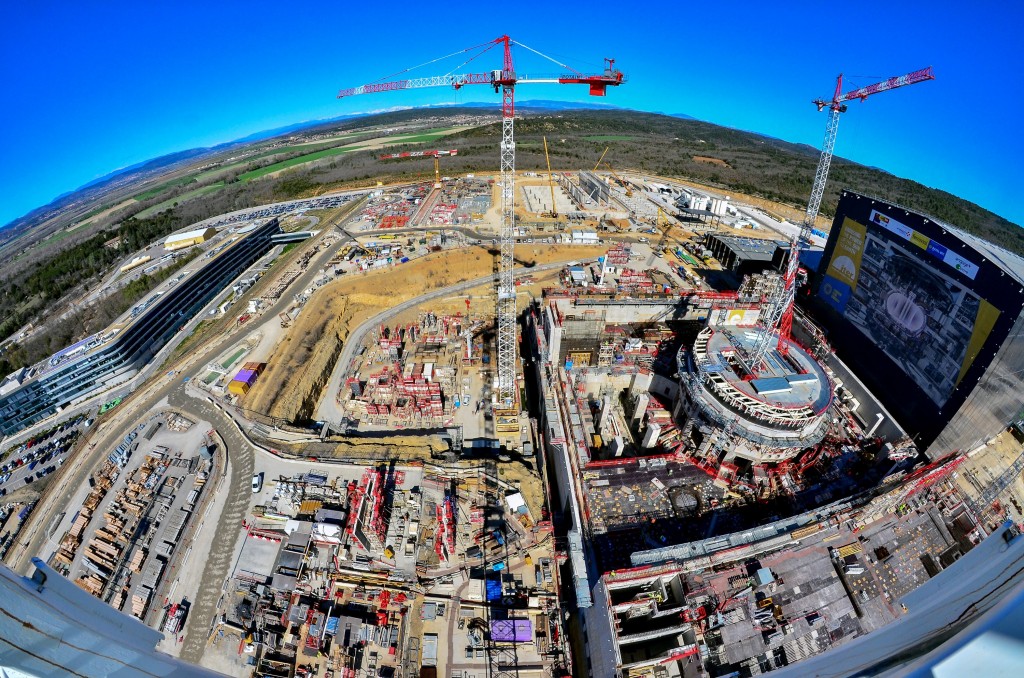
Looking north
2018-04-09 - From 70 metres above the worksite, the "box" of the Tokamak Building stands out clearly, with the machine well at its centre. The Diagnostics Building (at the bottom of the frame) and the Tritium Building (beyond the bioshied) complete the Tokamak Complex, which will be fully closed over in 2020.

Components through the top
2018-04-09 - Two rectangular openings in the bioshield lid will allow rebar and formwork to be delivered to the lower region, where work is underway on the "crown" that will support the cryostat. The first machine component will be introduced through these openings in the autumn.

Impregnation table
2018-04-09 - Technicians are busy assembling the vacuum containment vessel—the ''mould''—that will enclose the double pancakes throughout the lengthy and delicate resin impregnation process.
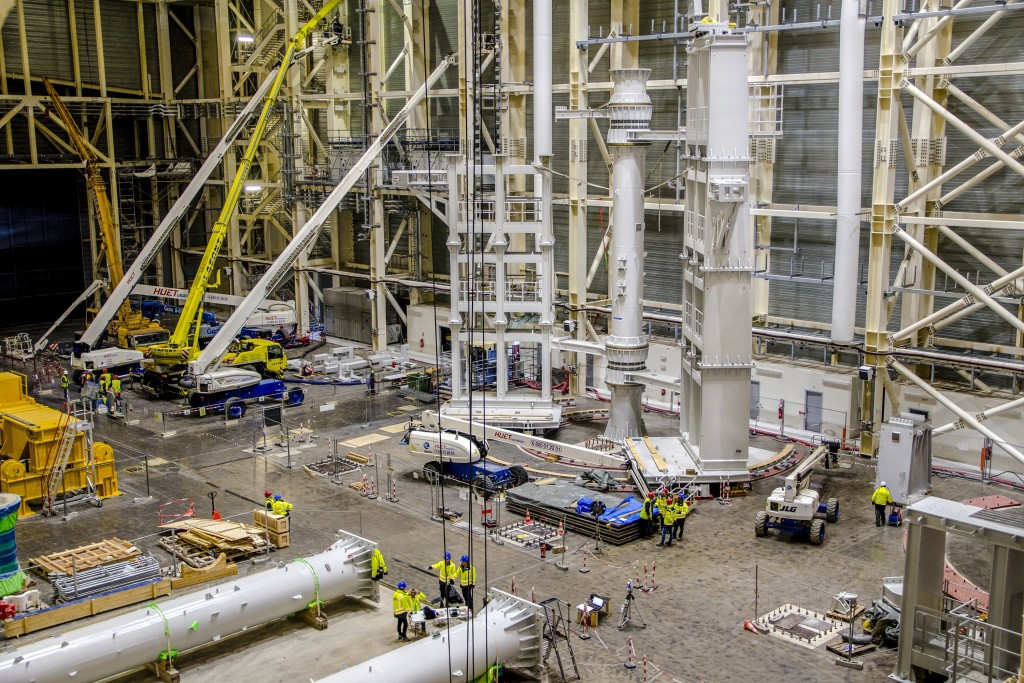
Two other columns
2018-04-09 - The two outboard columns, which have been assembled horizontally, will be standing by end-April.
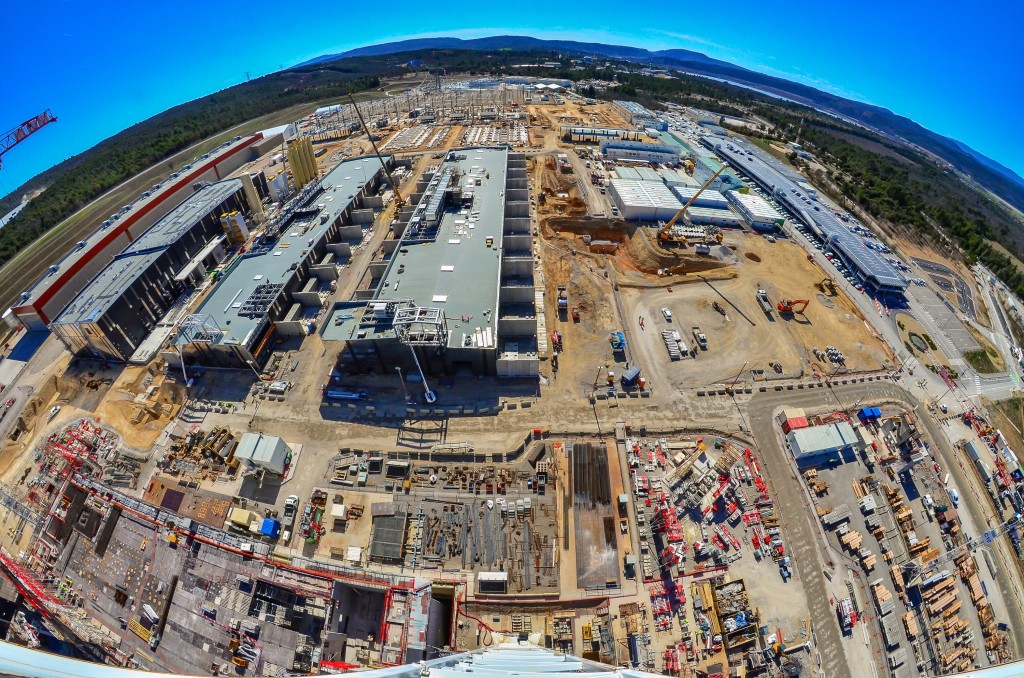
Vertical tanks visible
2018-04-09 - Looking south across the ITER platform a new feature has emerged: the vertical storage tanks that have been installed along the cryoplant at left.
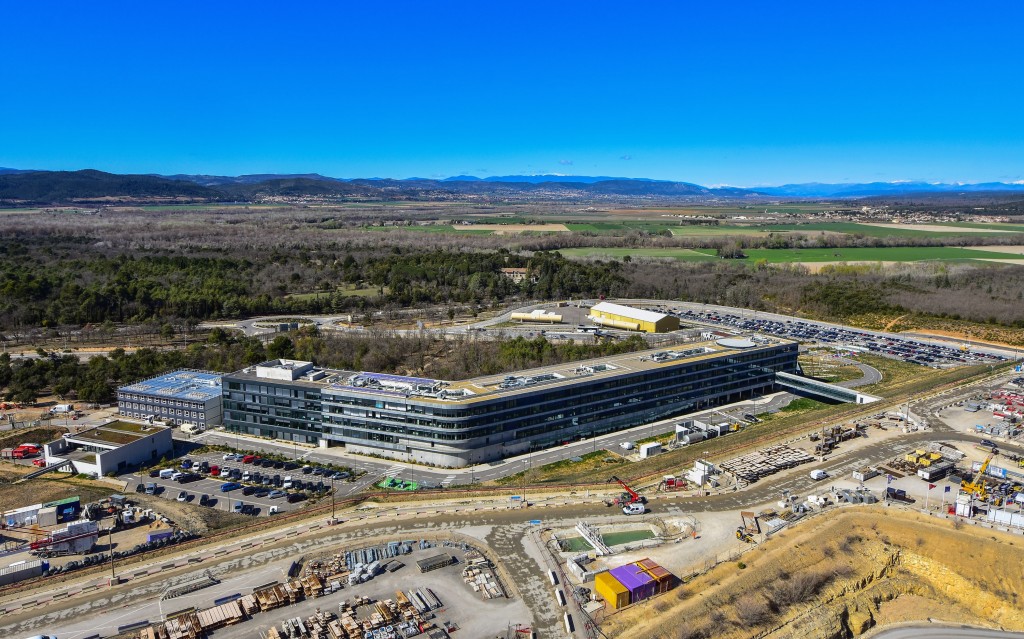
Additional space
2018-04-09 - To the left of the ITER Headquarters building, additional office space will soon be made available to ITER Organization staff and direct contractors, bringing the total capacity of this main office area to approximately 1,250 people.
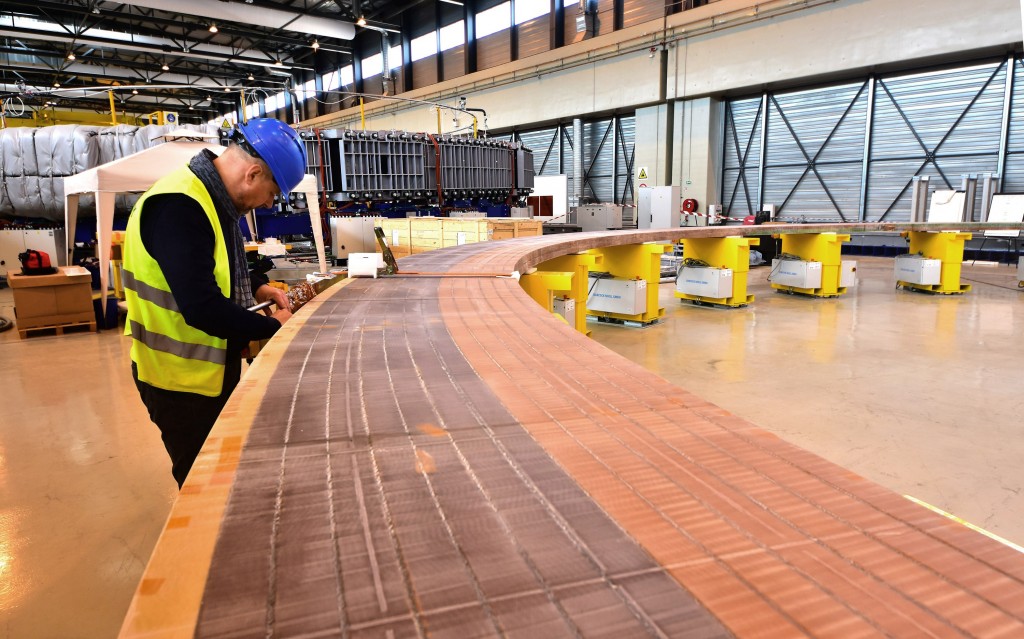
Qualifying the impregnation step
2018-04-09 - Resin-impregnation procedures were tested on this double pancake ''dummy''—a perfect replica of the conductor, only made of copper instead of the superconducting niobium-titanium alloy.
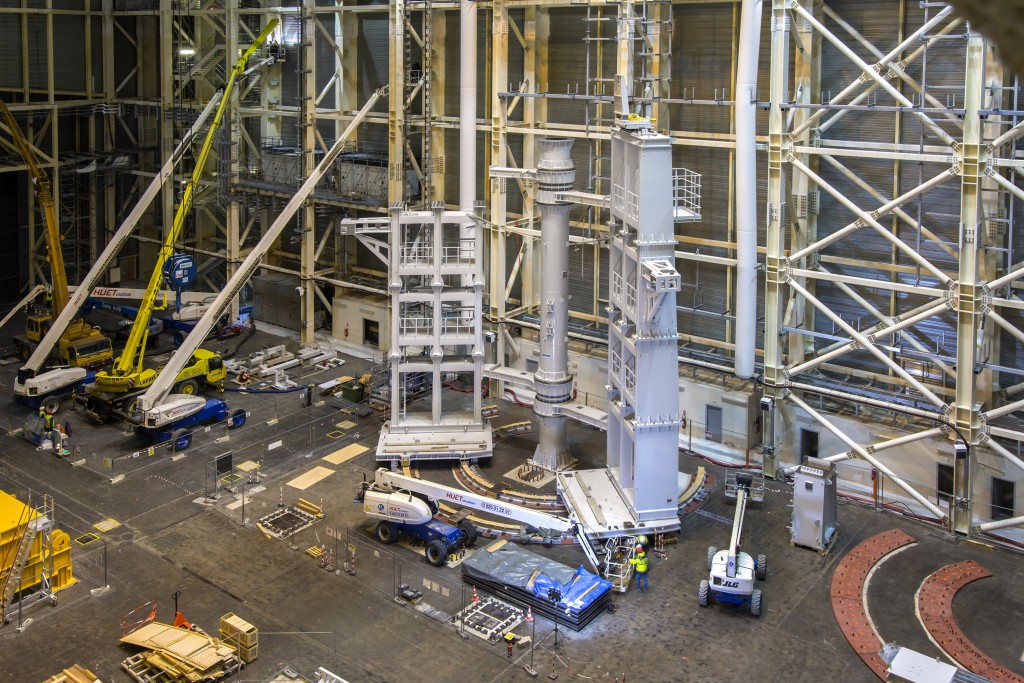
Two, for faster assembly
2018-04-05 - Next to the first tool, base rail plates have been installed for the twin tool that is undergoing factory acceptance tests now in Korea. Two tools will allow the vacuum vessel sector pre-assembly period to be divided by ... half.
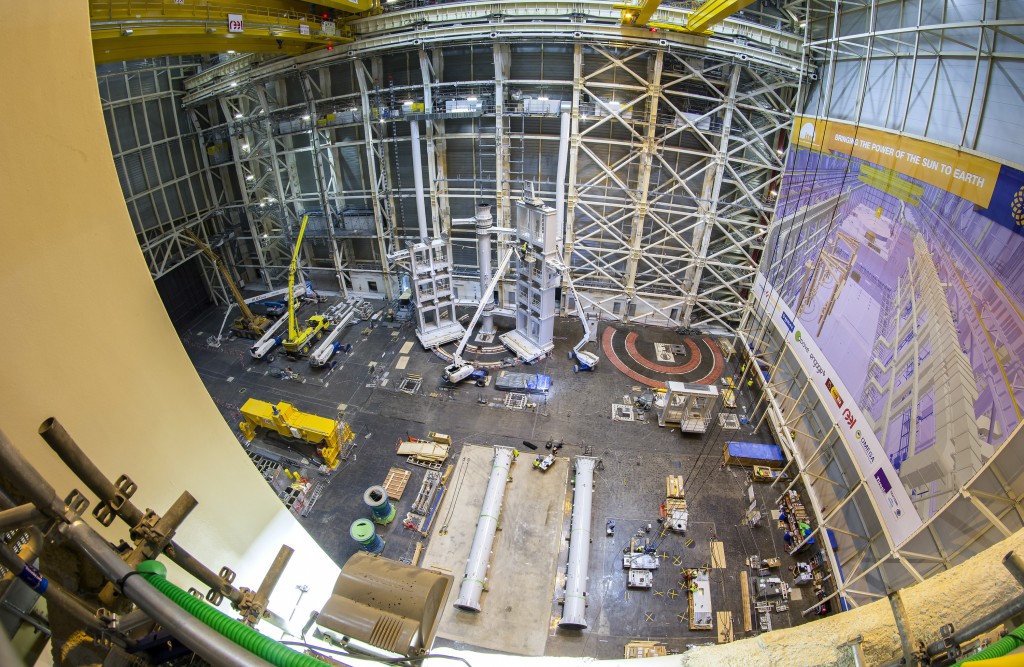
Behind the wall ...
2018-04-05 - When the Tokamak Building is completed, the temporary wall to the right will come down. The vacuum vessel sector sub-assemblies won't have far to travel to the Tokamak Pit.

Three strong legs
2018-04-05 - This tool has been designed for 1,200-tonne loads. Structural elements on the inside of the tool's three pillars contribute to stability.
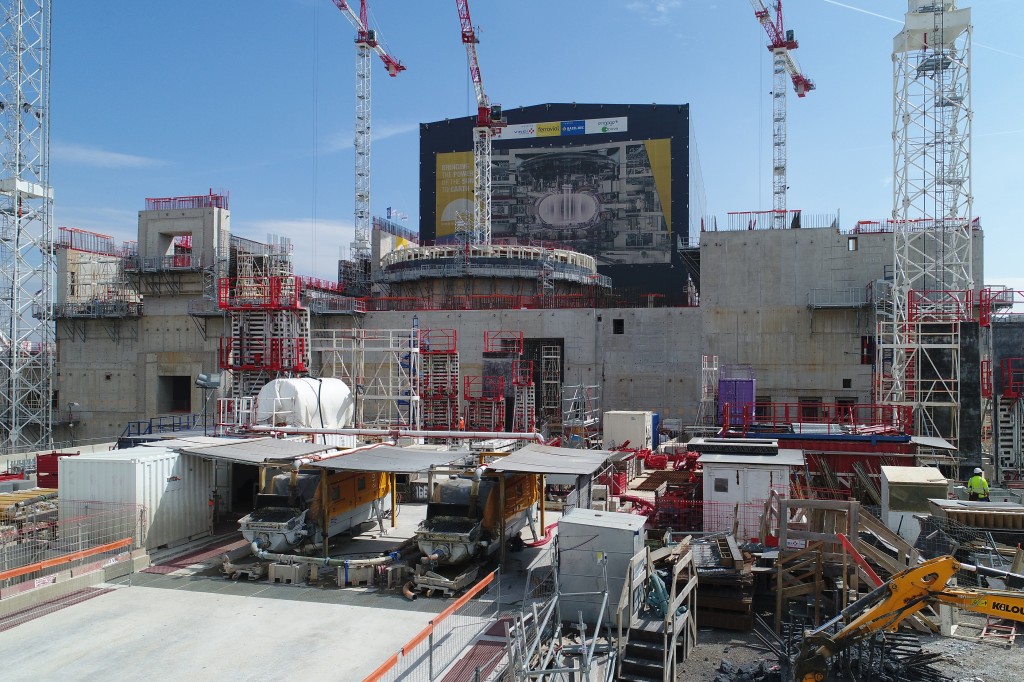
A concrete fortress
2018-03-27 - Here's one path to entering the Tokamak Complex by foot. Photo: ITER Organization/EJF Riche
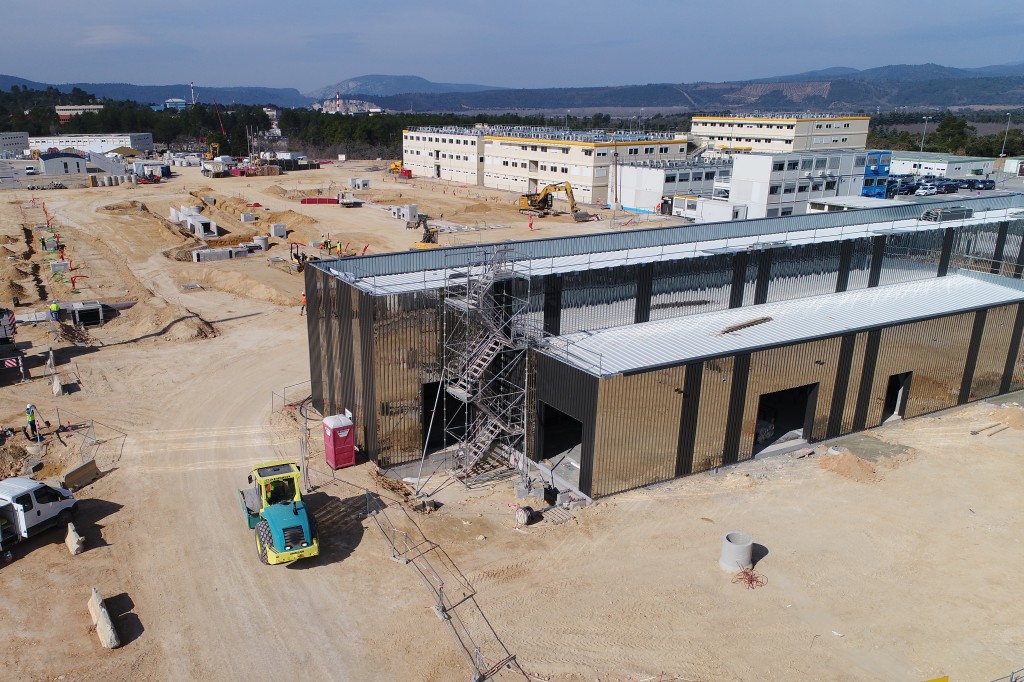
Reactive Power Compensation Building
2018-03-27 - This new building on the platform is part of the suite of buildings needed to house coil power systems. Photo: ITER Organization/EJF Riche
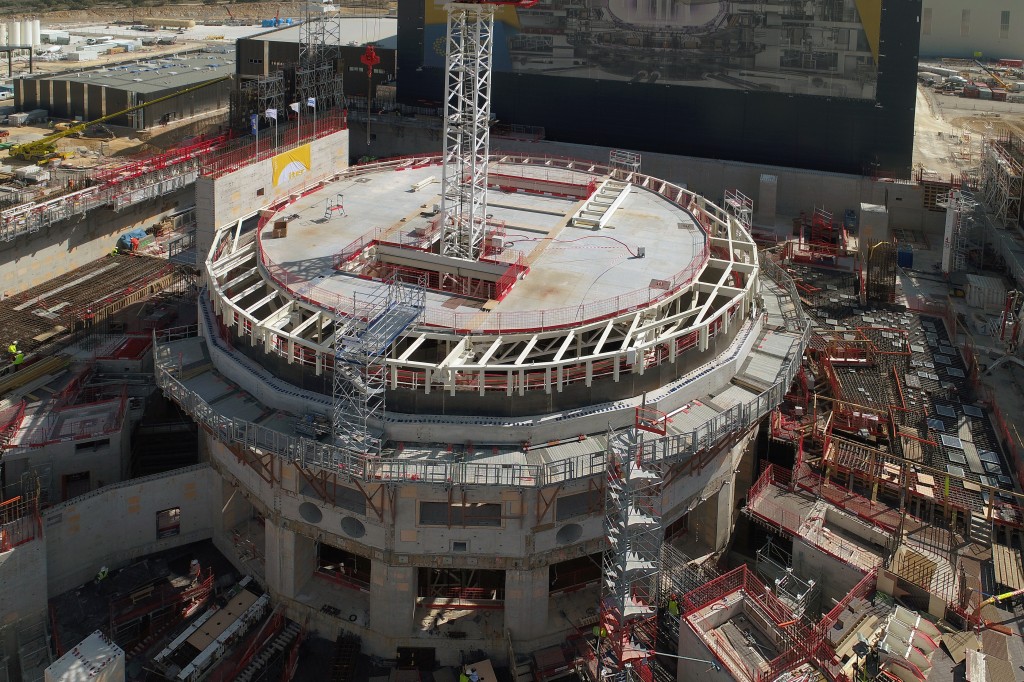
30-metre structure
2018-03-27 - The bioshield used to be visible from top to bottom; now, the building is catching up and we can only see the top third. Photo: ITER Organization/EJF Riche

Scaffolding
2018-03-27 - Scaffolding is set up on along the inner and outer walls of the lower cylinder, in order to weld from each side simultaneously. ©ITER Organization/Christian Luenig
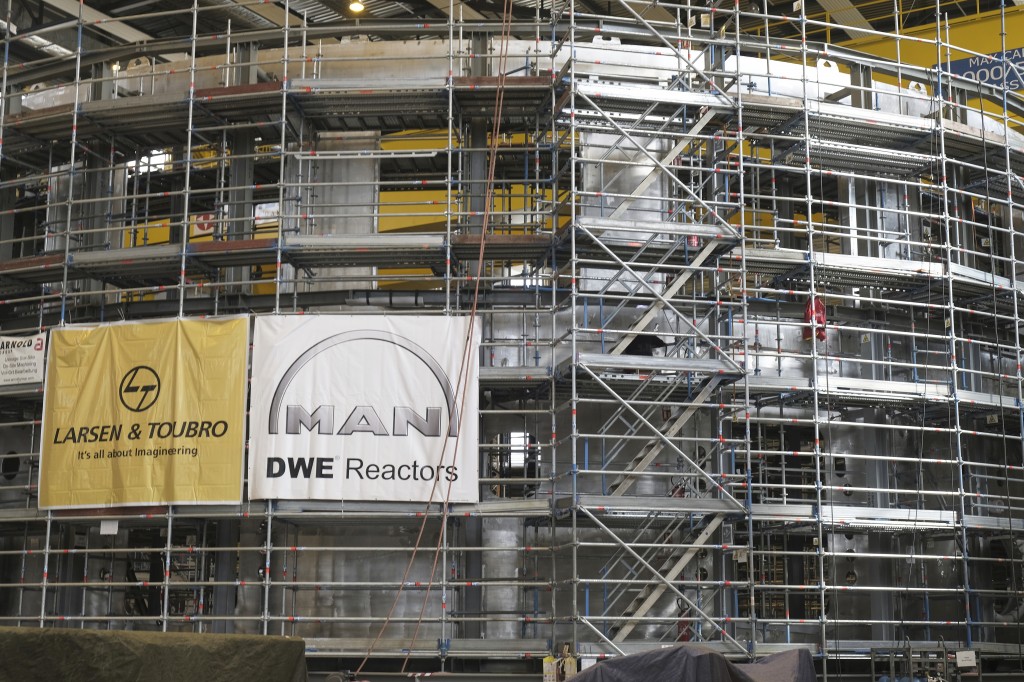
Who is responsible?
2018-03-27 - On the 10-metre-tall upper cylinder two banners are hung: Larsen & Toubro (ITER India contractor for manufacturing design, fabrication and assembly) and MAN Diesel & Turbo, Germany (Larsen & Toubro sub-contractor for on-site welding). ©ITER Organization/Christian Luenig
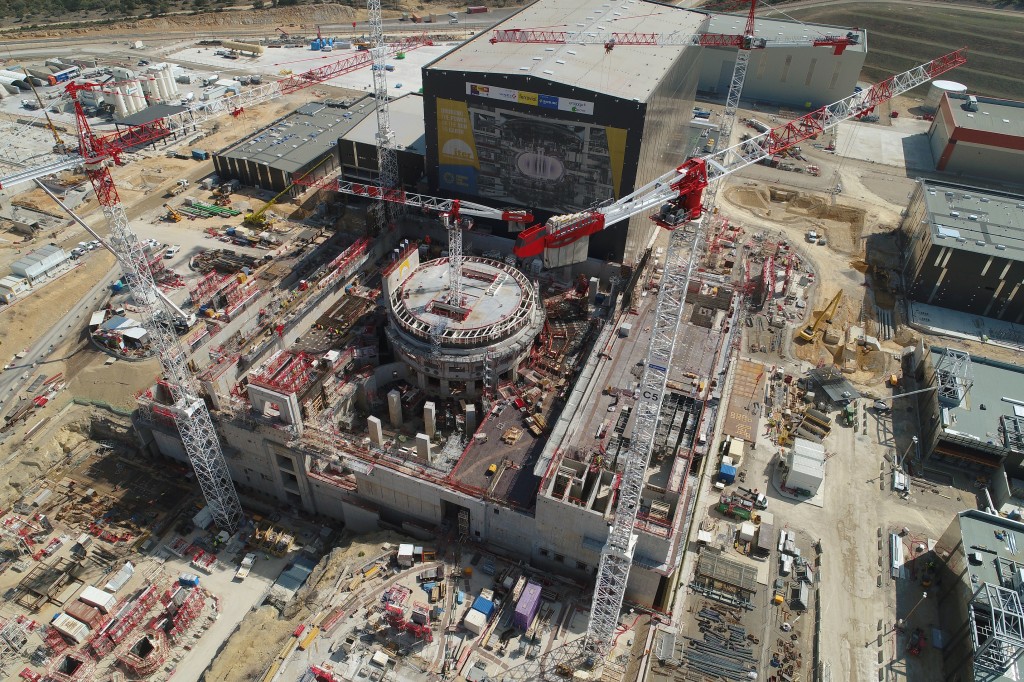
Bioshield completed
2018-03-27 - The concrete well for the Tokamak is now complete and the first installation activities can start on the inside. An inital group of "metrology nests" have been installed on the bioshield walls for alignment purposes. Photo: ITER Organization/EJF Riche
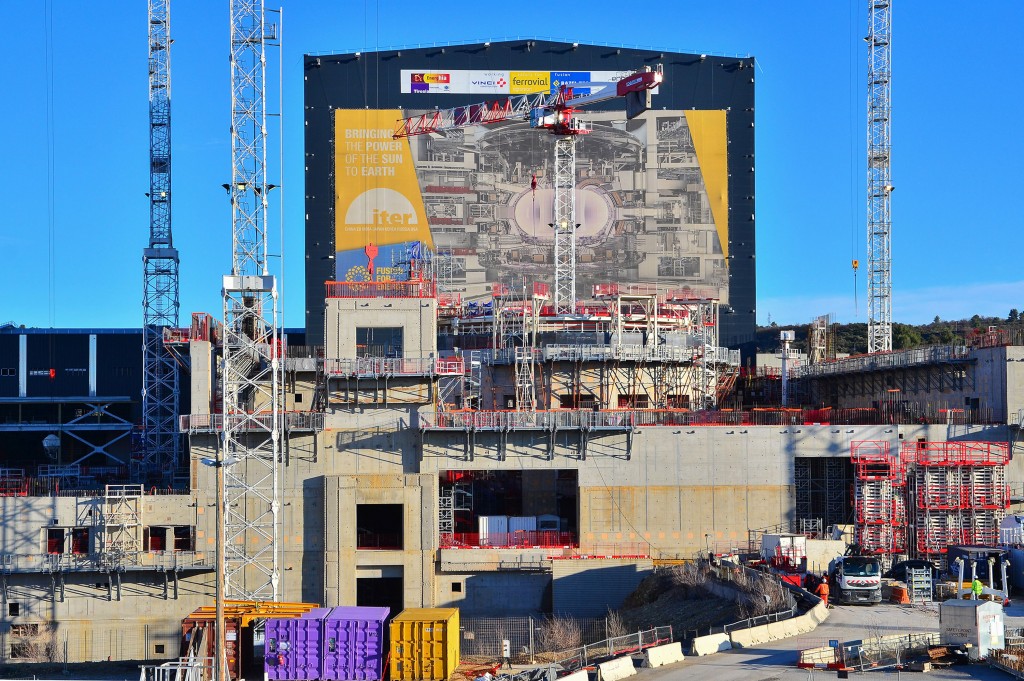
The House of the Tokamak is rising
2018-03-19 - The status of Tokamak Complex construction in mid-March. The elevator shaft for the "cask and plug" remote maintenance system stands out at left.
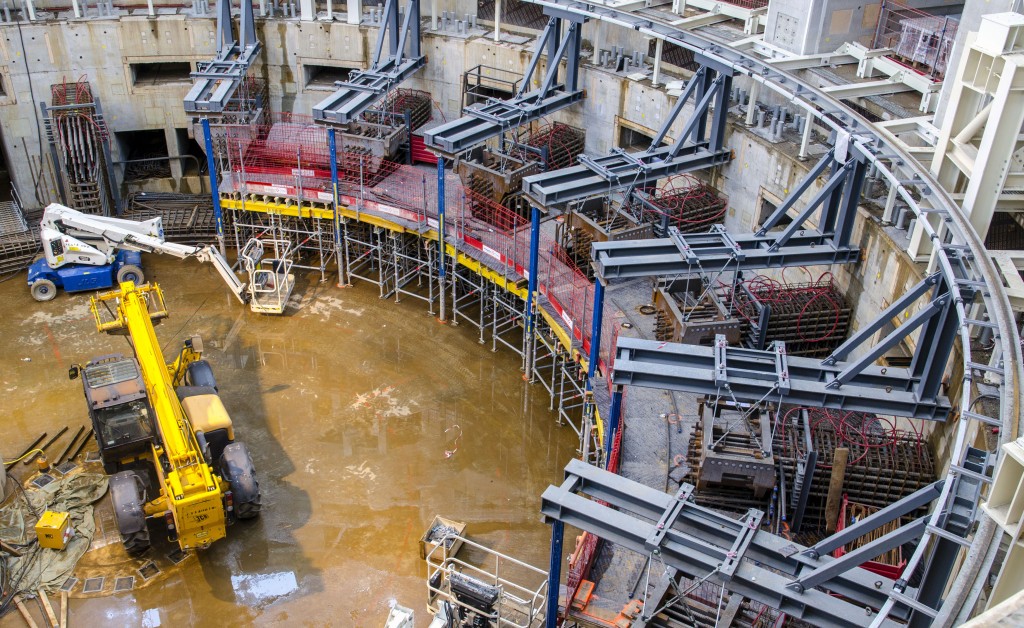
Important work
2018-03-13 - From both a structural and safety perspective, the crown and its radial walls are one of the most strategic parts of the ITER installation. They should be finalized by the end of the summer.

Approximately 200 tonnes
2018-03-13 - When a steel rim is added to fill in the gap around the lid, the structure will weigh approximately 200 tonnes.

Protection
2018-03-13 - From its position at the top of the bioshield, the lid creates a protected work space below.

30 metres down
2018-03-13 - At the bottom of the "pit" work is underway on the 18 radial walls that will transfer forces from the cryostat crown to the thick bioshield.
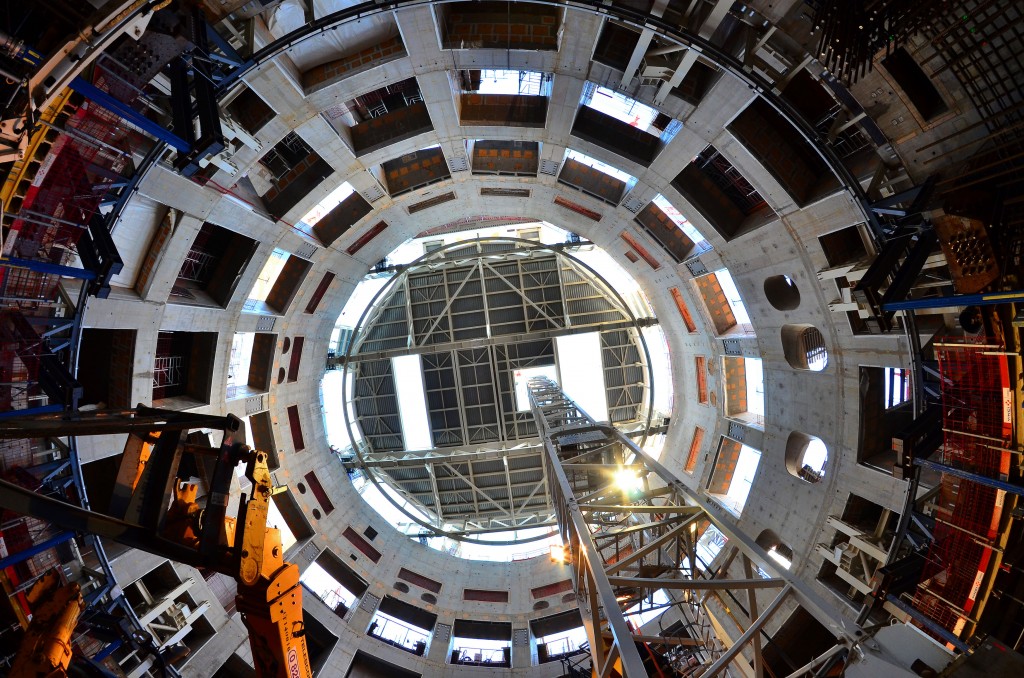
Reserved for the machine
2018-03-13 - The ITER machine will be assembled here, in this 30-metre-tall "Tokamak Pit."

A few hundred metres
2018-03-13 - This photo, taken from the top of the bioshield, shows the distance that cooling water leaving the Tokamak Building will travel to reach the heat rejection zone.

A pair of able hands
2018-03-13 - A gantry crane (in yellow) covers the complete circle of the "pit" to deliver the heavy steel transition pieces (3 tonnes) that are on top of each wall.

A forest of steel and concrete
2018-03-09 - The view of the French countryside is becoming spectacular, up at the top of the Tokamak Complex works.

8 hands
2018-03-09 - To lift the 150-tonne lid, eight hydraulic jacks were positioned on eight evenly spaced metallic structures.

Some trimming to do
2018-03-09 - As the cables are pulled up, technicians on each platform cut away the excess.

Lift operation underway
2018-03-09 - The black cables are slowly lifting the temporary lid—or floor, depending on your perspective. Until the Tokamak Complex is completed, the lid will remain at the top of the bioshield.
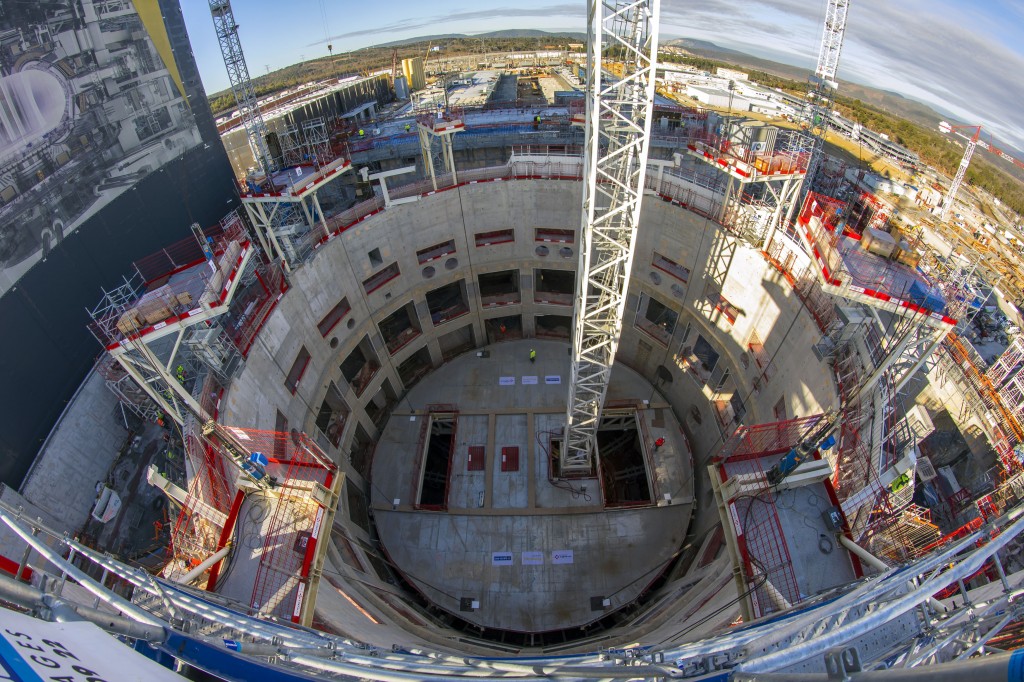
The scale
2018-03-09 - The worker in yellow standing on the lid gives a sense of perspective. The lid is 30 metres in diameter.

Blue and yellow
2018-03-09 - Participants to the lifting operation stand in front of the "Fusion for Energy" flag on the worksite. "Fusion for Energy" is another name for the European Domestic Agency for ITER, which has been charged with the construction of all site buildings and infrastructure.

Balancing job
2018-03-09 - Before allowing the eight hydraulic jacks to begin pulling, operators performed laser measurements to verify that the lid was in a perfectly horizontal position. If for any reason one jack failed, the lid would not tilt more than one millimetre.
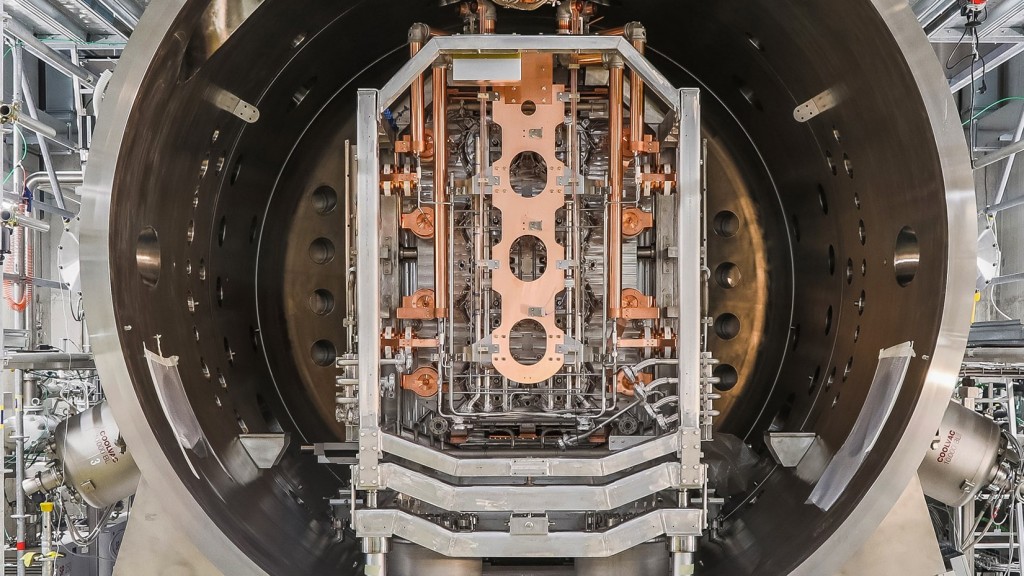
The world's most powerful negative ion source
2018-03-08 - The SPIDER beam source—a technological marvel and the world's most powerful negative ion source. A European consortium consisting of Thales (France), CECOM Srl (Italy), Galvano-T GmbH (Germany) and E.Zanon SpA (Italy) has been responsible for the manufacturing of the equipment for the European Domestic Agency.

Coordination group at Consorzio RFX
2018-03-01 - The Consorzio RFX leaders for diagnostics, interlock and control, thermo-mechanics, and power supplies stand with NBTF project leader Vanni Toigo (centre) in front of the sealed SPIDER vessel.
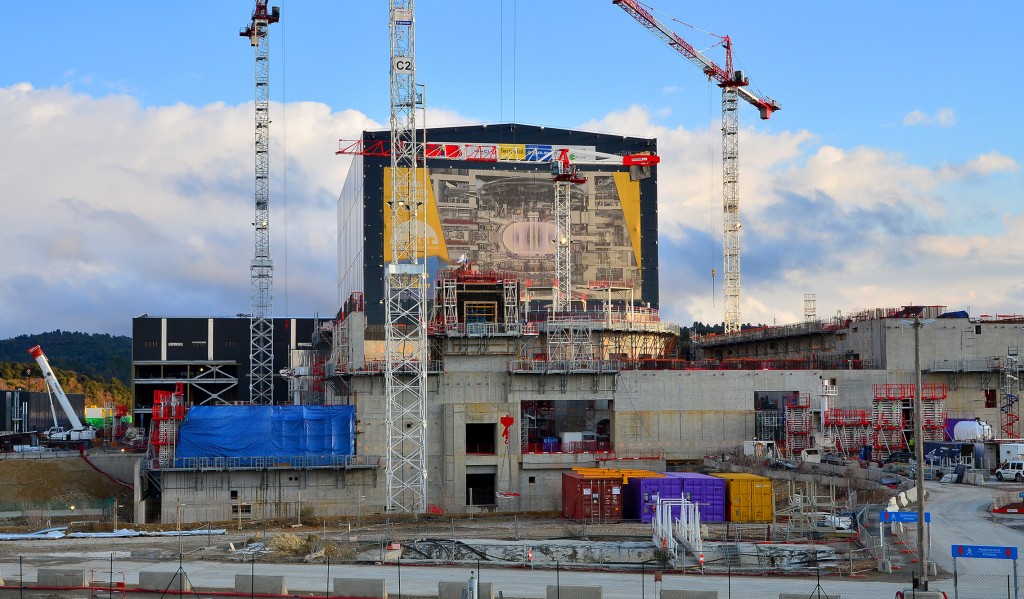
A special kind of elevator
2018-02-26 - The two gaping doors visible in the wall of the Tokamak Building are reserved for the cask and plug remote handling system. Bus-size containers will travel through these openings between the Tokamak and the Hot Cell, carrying components for refurbishment or replacement.

Load tests on new crane
2018-02-25 - The new gantry crane in the Poloidal Field Coils Winding Facility has a nominal lifting capacity of 400 tonnes. It was tested in February at 125% of nominal (static) and 110% of nominal (dynamic), with successful results.

Witnessing
2018-02-25 - The gantry crane is made up of a 30-metre-in-diameter steel structure supported by four hydraulic towers traveling on rails, capable of lifting the heaviest components of the ring-shaped coils throughout the last stages of fabrication.

First tool rising
2018-02-23 - After a long period during which the anchoring elements—including base plates and rails—were set into place and precise measurements taken, the installation of ITER's first giant assembly tool is underway.

Strong arms
2018-02-23 - The 800-tonne tool, once fully erected, will be capable of supporting loads of 1,200 tonnes.

One here, one there
2018-02-23 - About half of the major components for the first tool have been installed. In parallel, the second tool of the pair has been manufactured and assembled at Taekyung Heavy Industries (THI) in Korea, where testing is underway.

Number 4
2018-02-22 - A fourth tank is installed outside of the cryoplant. © Les Nouveaux Médias/SNC ENGAGE

Looking up
2018-02-21 - Standing in the centre of the cryostat lower cylinder, looking up toward the beams of the gantry crane.

Team work
2018-02-21 - Representatives of the ITER Organization, the European Domestic Agency and of all the contractors involved in the operation (Air Liquide, Dufour, Technilevage, Altead, SETIS and IREM) pose in front of the massive component, now bolted to its concrete platform.
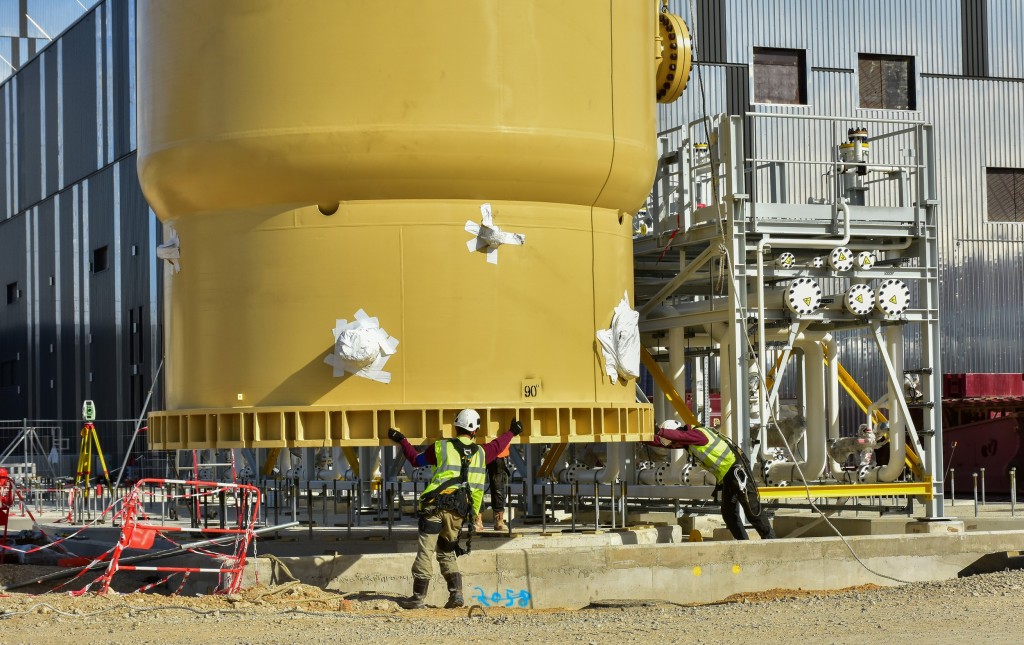
Pushing and pulling
2018-02-21 - It takes three men, weighing in with all their strength, to precisely align the openings in the tank's lower rim with the 36 rods anchored deep in the concrete.
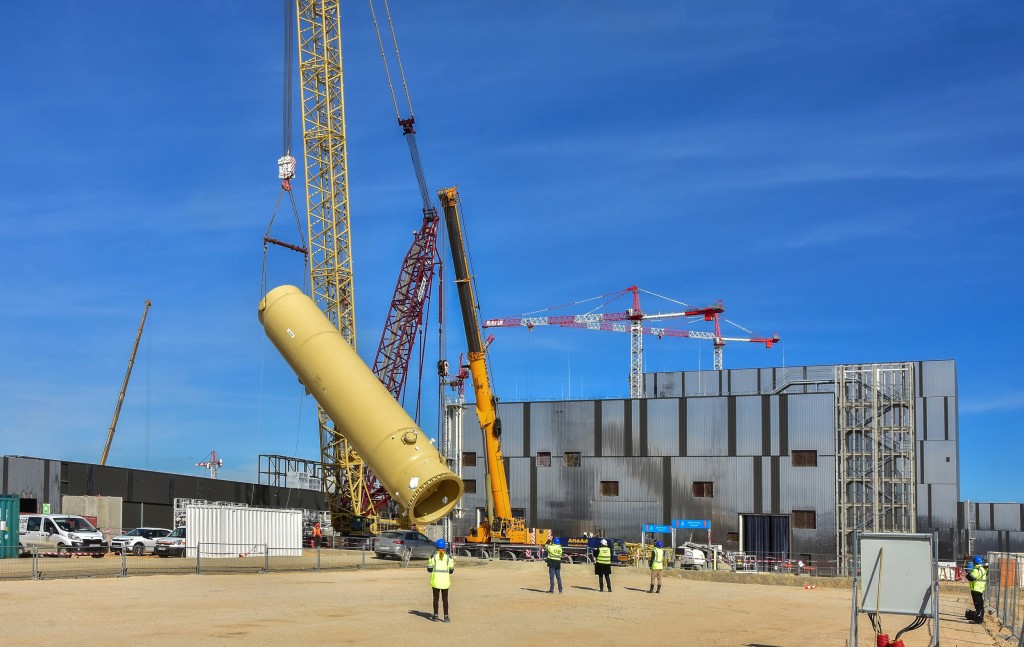
Verticality
2018-02-21 - Installed vertically because of space constraints, six identical tanks will store 380 cubic metres of gaseous helium each at a pressure of 22 bars.
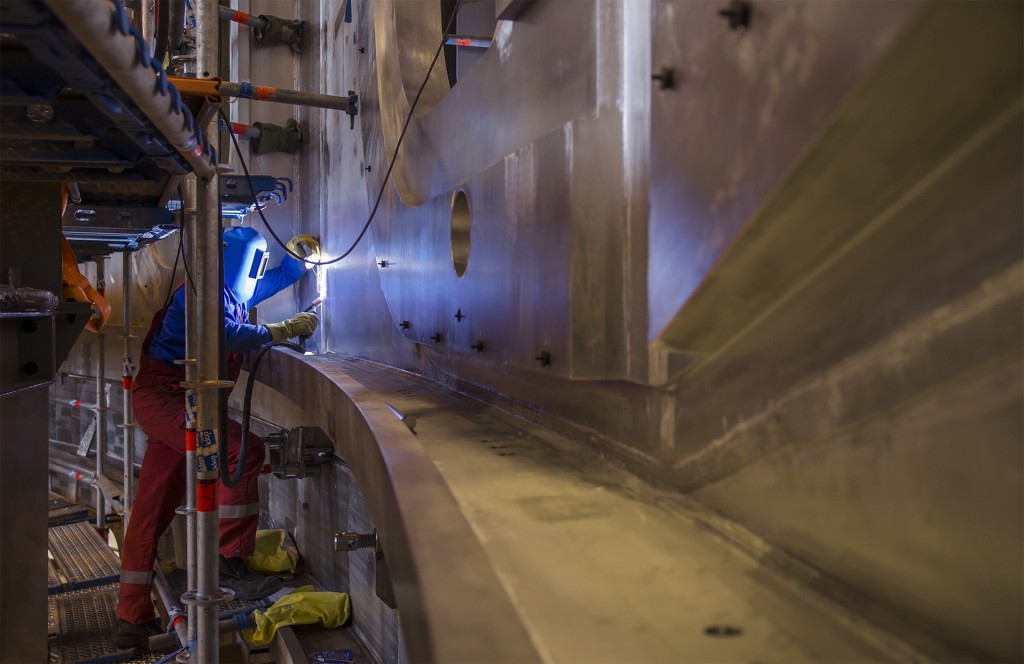
New phase for lower cylinder
2018-02-21 - Welding has started on tier two of the lower cylinder. The completed component will measure 10 metres in height and weigh 375 tonnes.
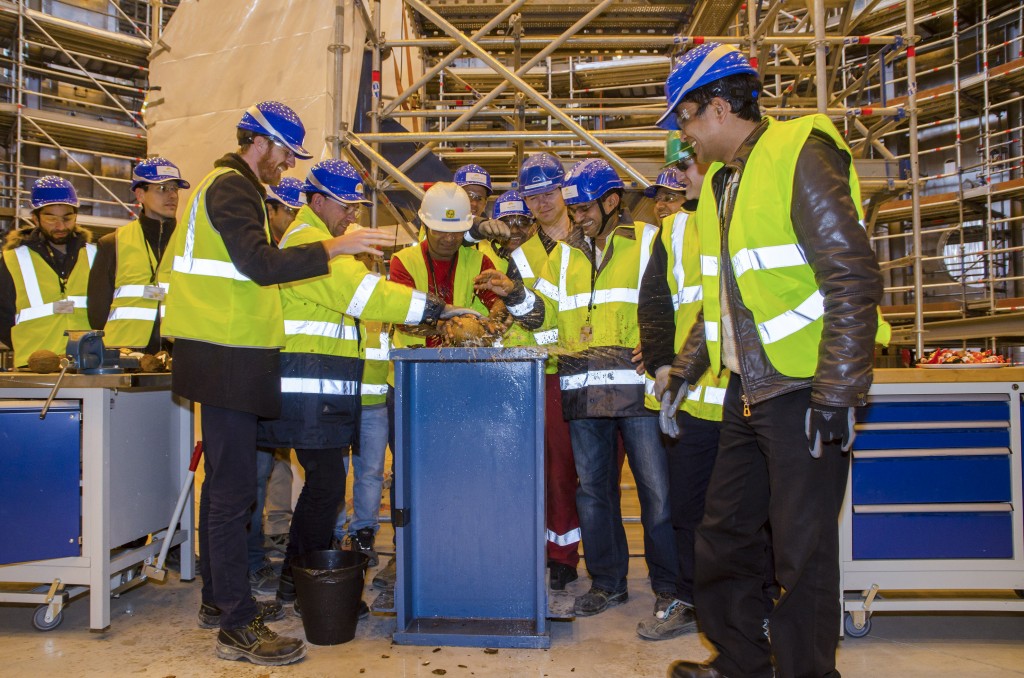
Good luck!
2018-02-21 - A ceremony is held in the Cryostat Workshop on 21 February to mark the start of welding on the second tier of the lower cylinder. The team is seen here inside the circle of the component breaking a coconut—an Indian tradition to bring good fortune to a new endeavour.
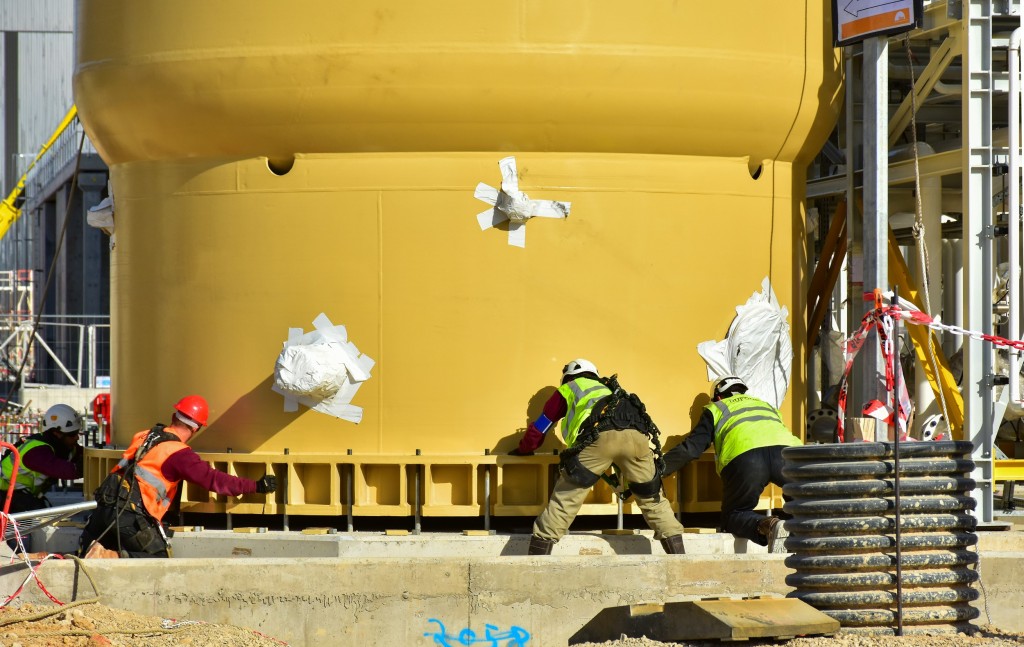
All rods in place
2018-02-21 - Less than one hour after the beginning of the lifting operation, the tank is in place. Each rod has passed through its corresponding hole in the lower rim and is ready to be bolted.
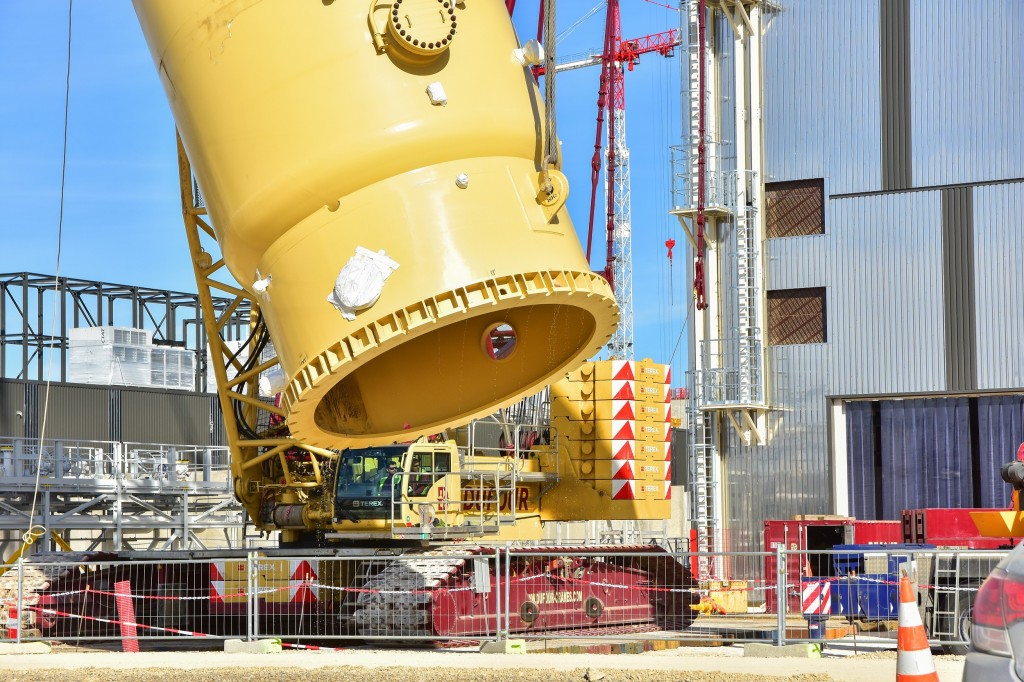
Up we go!
2018-02-21 - Seized at both ends by cranes working in tandem, the 20-metre high, 150-tonne steel tank is slowly transitioning to its final position.
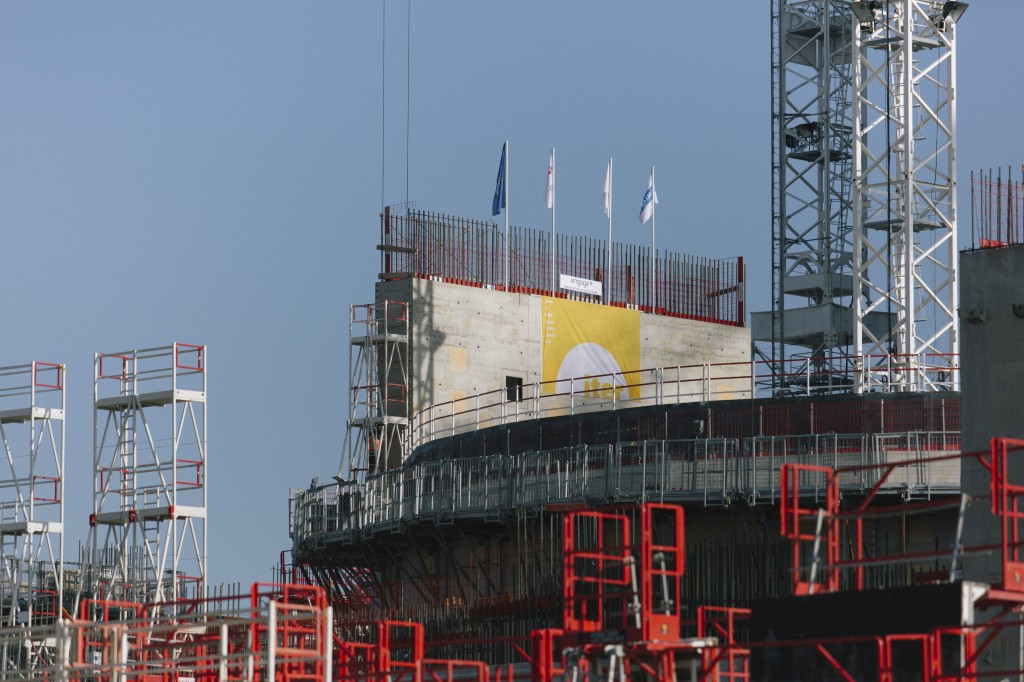
Higher still
2018-02-20 - This wall behind the bioshield is part of the last storey (L4/L5) of the Tritium Building. © Les Nouveaux Médias/SNC ENGAGE

Heavy machinery
2018-02-20 - Two pairs of hands will manoeuvre the ITER components from above in the Assembly Hall—the 1,500-tonne crane (on higher rails) and the 50-tonne crane, both visible in this photo. The cranes were supplied by the French firm REEL as part of European procurement contributions. © Les Nouveaux Médias/SNC ENGAGE

Tools to erect the tool
2018-02-20 - In the 100-metre Assembly Hall, telescopic cranes have moved in to assist with the assembly of the building's first tool. © Les Nouveaux Médias/SNC ENGAGE

Junior crane
2018-02-20 - This is the smaller of the two overhead crane pairs, which runs along rails underneath the larger crane. © Les Nouveaux Médias/SNC ENGAGE

Guide rails
2018-02-20 - Taken from behind the tool, this picture shows the floor rails that the wings travel along. © Les Nouveaux Médias/SNC ENGAGE

Power conversion halls
2018-02-20 - Deep electrical trenches have been prepared in the power conversion halls of the Magnet Power Conversion buildings. © Les Nouveaux Médias/SNC ENGAGE

Next door
2018-02-20 - Behind the white plaster board is the Radio Frequency Building. The waveguides for the ion and electron cyclotron resonance heating systems will be routed through the Assembly Hall to the Tokamak Building. © Les Nouveaux Médias/SNC ENGAGE
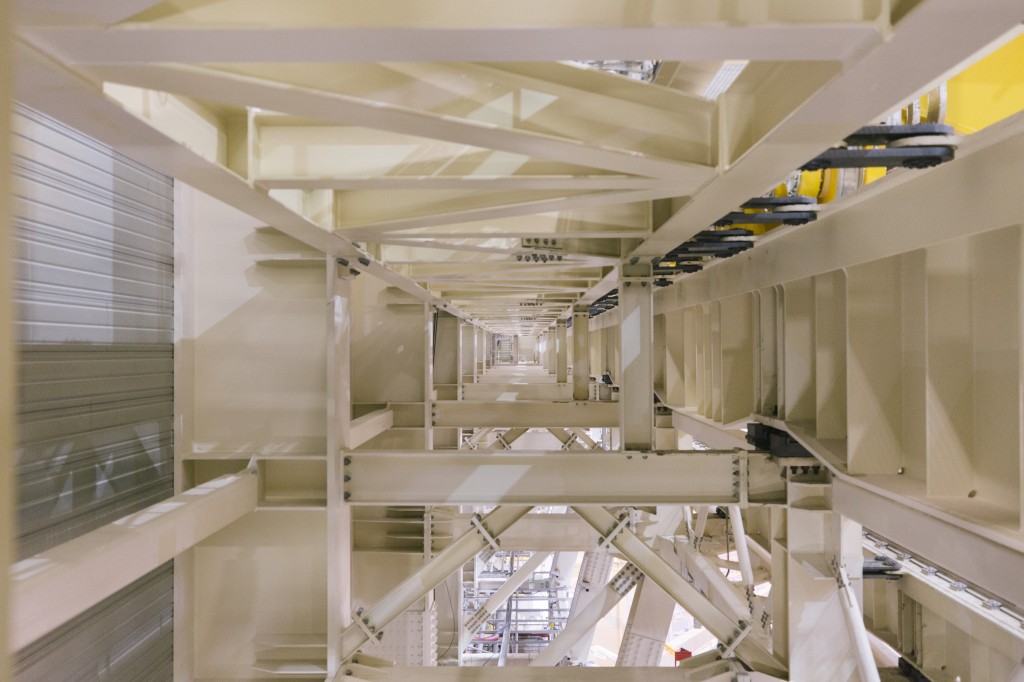
Unusual
2018-02-20 - This unusual photo was taken high up in the structure of the Assembly Hall. Double rows of columns—with bracing structures between them—will help to deflect the weight of the loads managed by the assembly cranes. © Les Nouveaux Médias/SNC ENGAGE
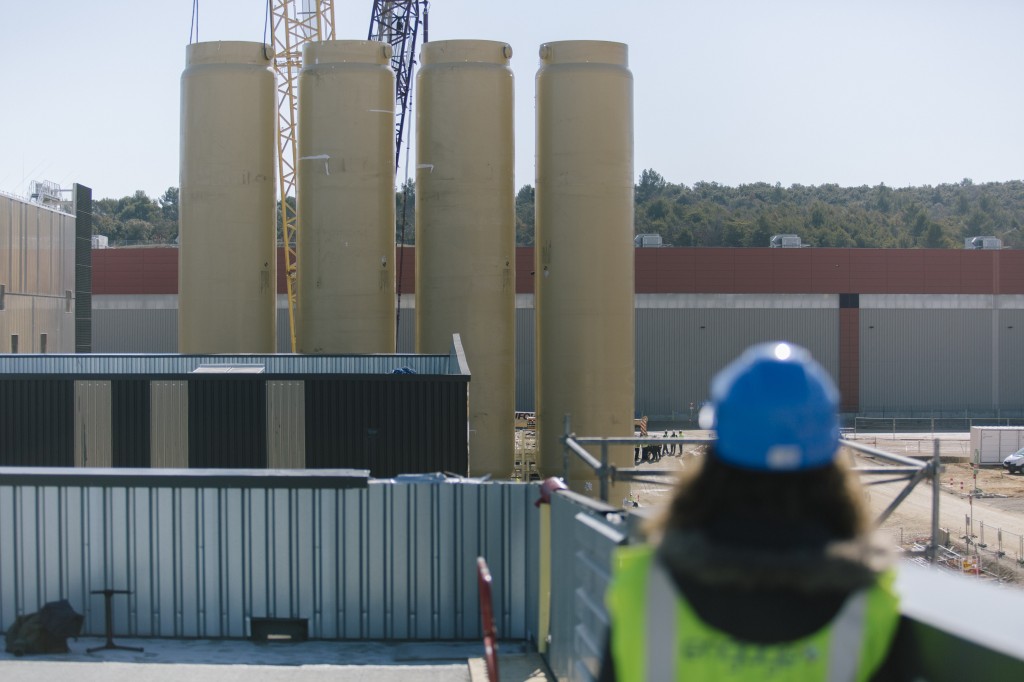
Changing platform
2018-02-20 - Four gaseous helium storage tanks procured by Europe have been installed near the cryoplant. © Les Nouveaux Médias/SNC ENGAGE

Heavy machinery
2018-02-20 - Two pairs of hands will manoeuvre the ITER components from above in the Assembly Hall—the 1,500-tonne crane (on higher rails) and the 50-tonne crane, both visible in this photo. The cranes were supplied by the French firm REEL as part of European procurement contributions. © Les Nouveaux Médias/SNC ENGAGE
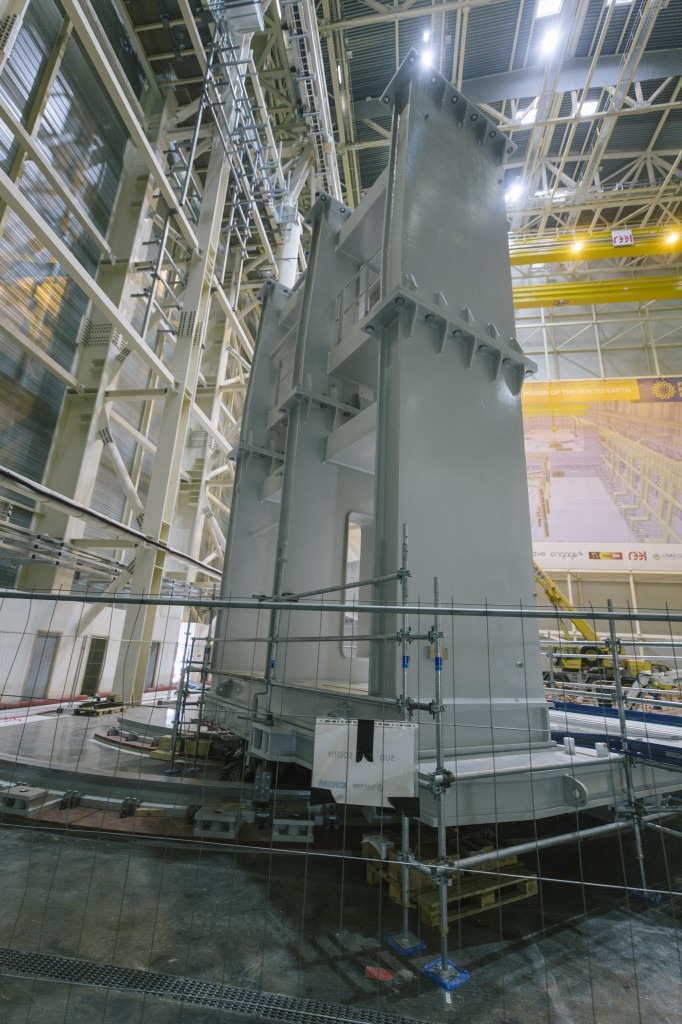
Sector sub assembly tool
2018-02-20 - The first lateral wing is going up. The wings will allow 310-tonne toroidal field coils to be rotated toward a suspended vacuum vessel sector for installation on either side. © Les Nouveaux Médias/SNC

Digging
2018-02-20 - Ground work is underway near the PPEN transformers (for Pulsed Power Electrical Network). © Les Nouveaux Médias/SNC ENGAGE
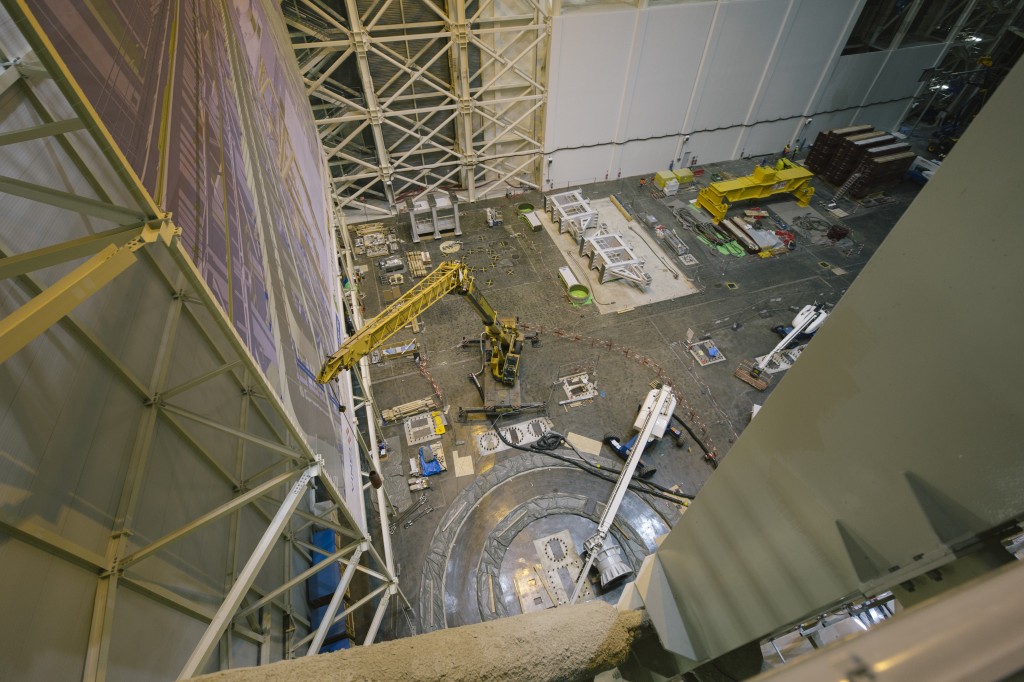
From the rafters
2018-02-20 - On the floor, are the rails for a second vacuum vessel sector sub-assembly tool (SSAT #2), which will be sent from Korea as soon as factory testing has concluded. © Les Nouveaux Médias/SNC ENGAGE

Three strong legs
2018-02-20 - The inboard column has just four metres to go to reach its final height. Two outboard columns will join the inboard column in anchoring the tool, which will support up to 1,200 tonnes. © Les Nouveaux Médias/SNC ENGAGE
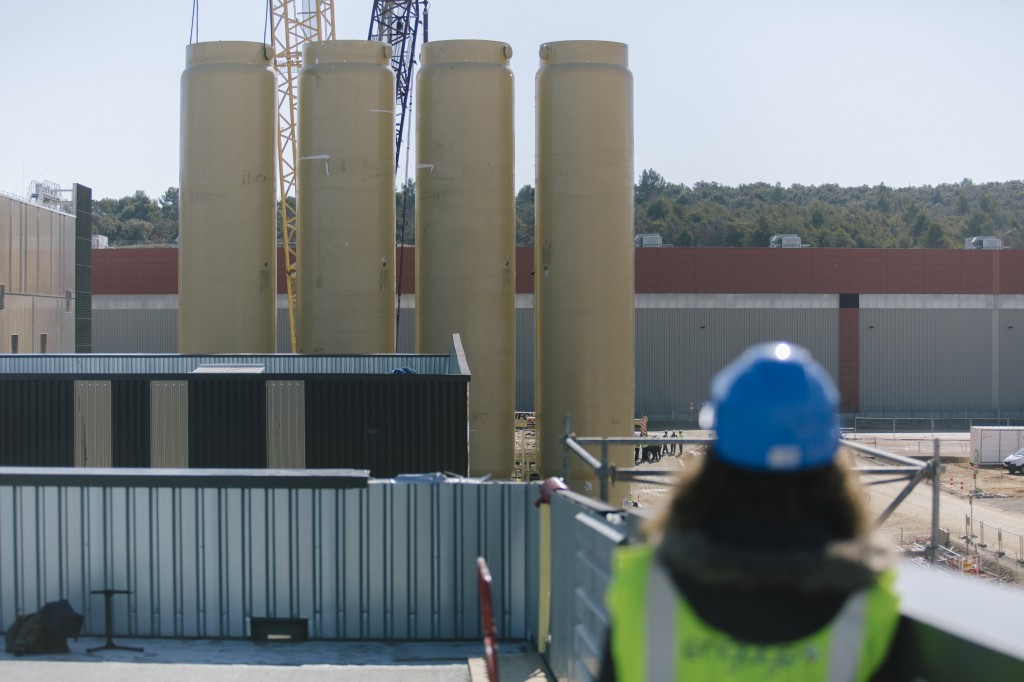
Changing platform
2018-02-20 - Four gaseous helium storage tanks procured by Europe have been installed near the cryoplant. © Les Nouveaux Médias/SNC ENGAGE
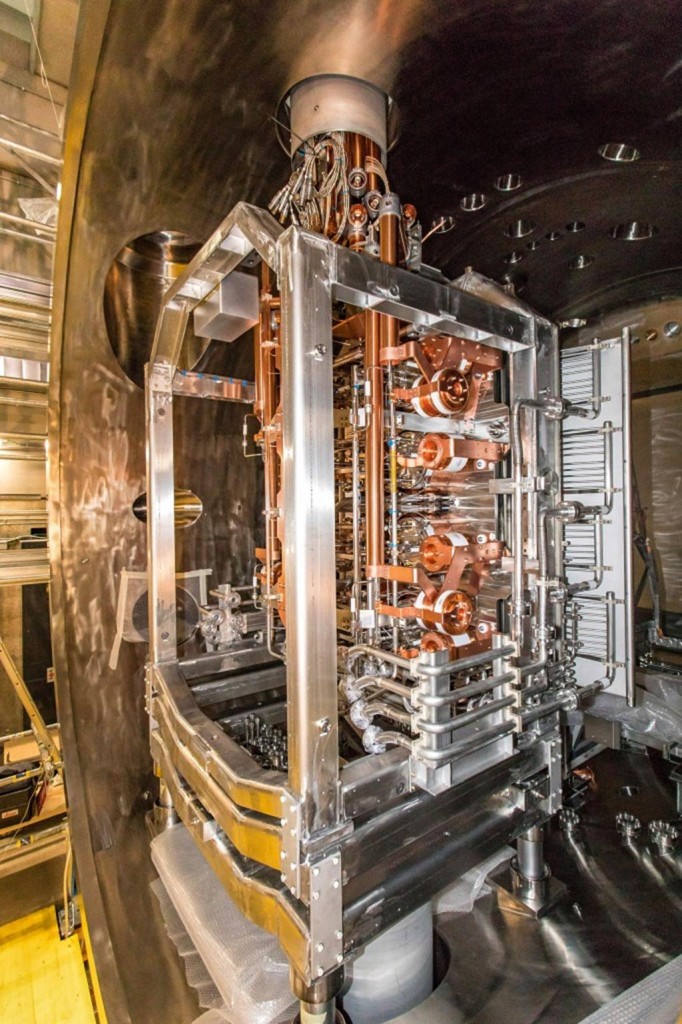
Integrated commissioning can start
2018-02-18 - Only auxiliary connections remain to be finalized. Once that is done the ITER Organization, the European Domestic Agency, and Consorzio RFX can begin integrated commissioning activities.
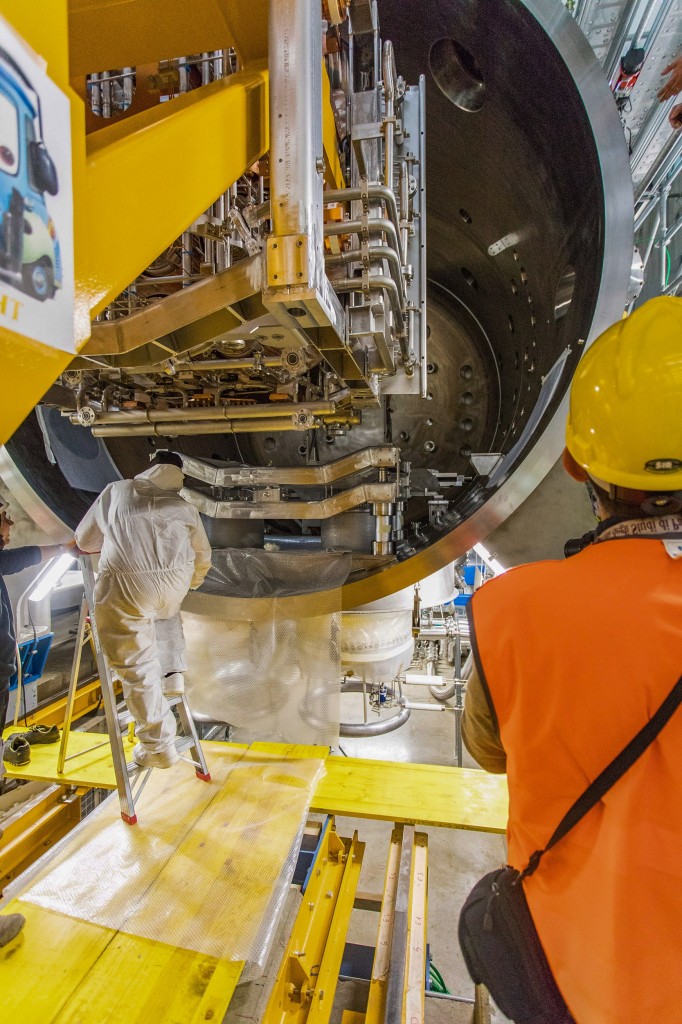
Into position
2018-02-17 - A dedicated handling tool is used to transfer the beam source onto its bed support structure in the vacuum chamber.
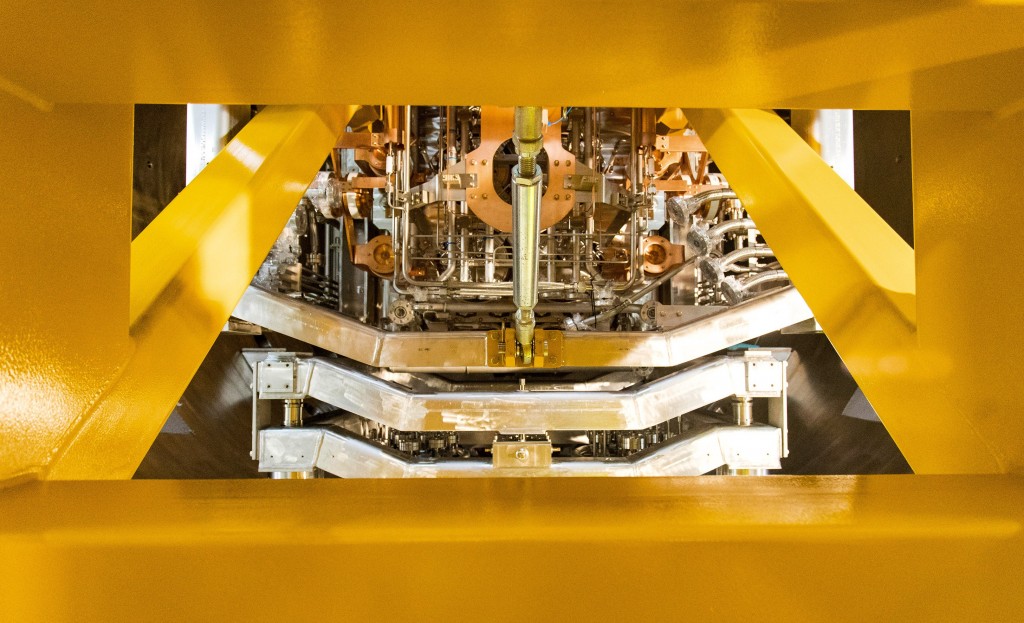
Four years to build, many more to design
2018-02-17 - The SPIDER beam source is an ITER-like full-size radio-frequency-driven plasma source capable of extracting a negative deuterium ion beam (D¯ beam) of 70A and then accelerating it to energies of 100 keV. Manufacturing required just over four years.

Tokamak Complex construction: a guide
2018-02-15 - A cutaway of the Tokamak Complex, seen from the perspective of someone standing in ITER Headquarters. Note the floating foundation contained within retaining walls and the central machine assembly well formed by the bioshield.
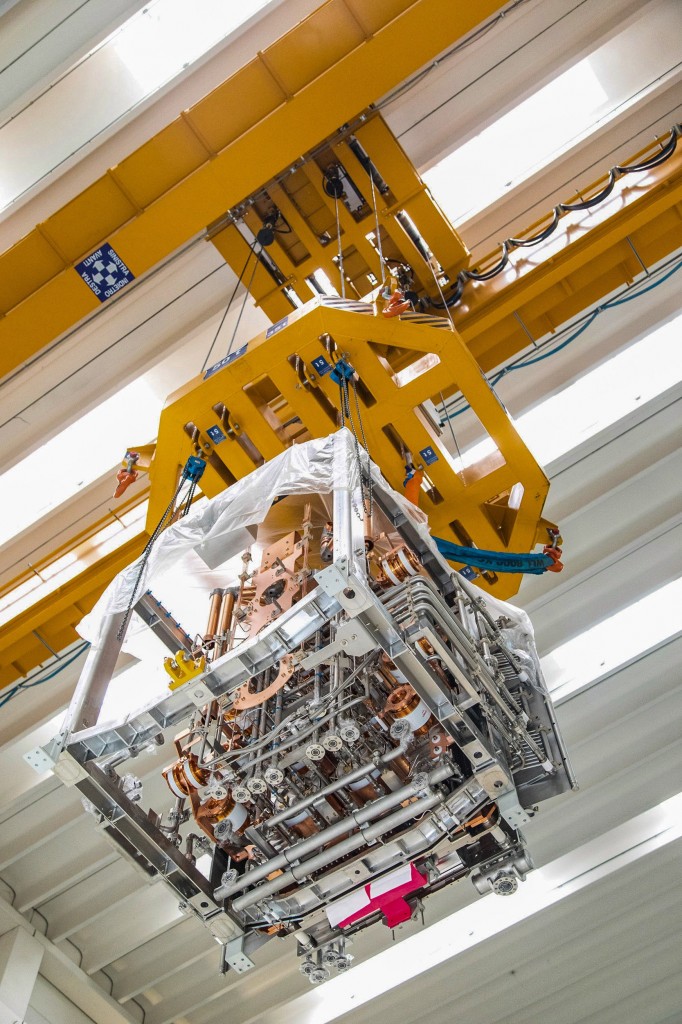
On its way
2018-02-15 - The five-tonne SPIDER beam source is transferred from the clean room—where it had been stored and tested—to its handling tool using the Neutral Beam Test Facility's 50-tonne crane.

Ready to lift
2018-02-12 - This large crawler crane was erected last week near the cryoplant. Beginning on 14 February, it will be used to lift vertical tanks for the storage of liquid and gaseous helium and nitrogen into position.
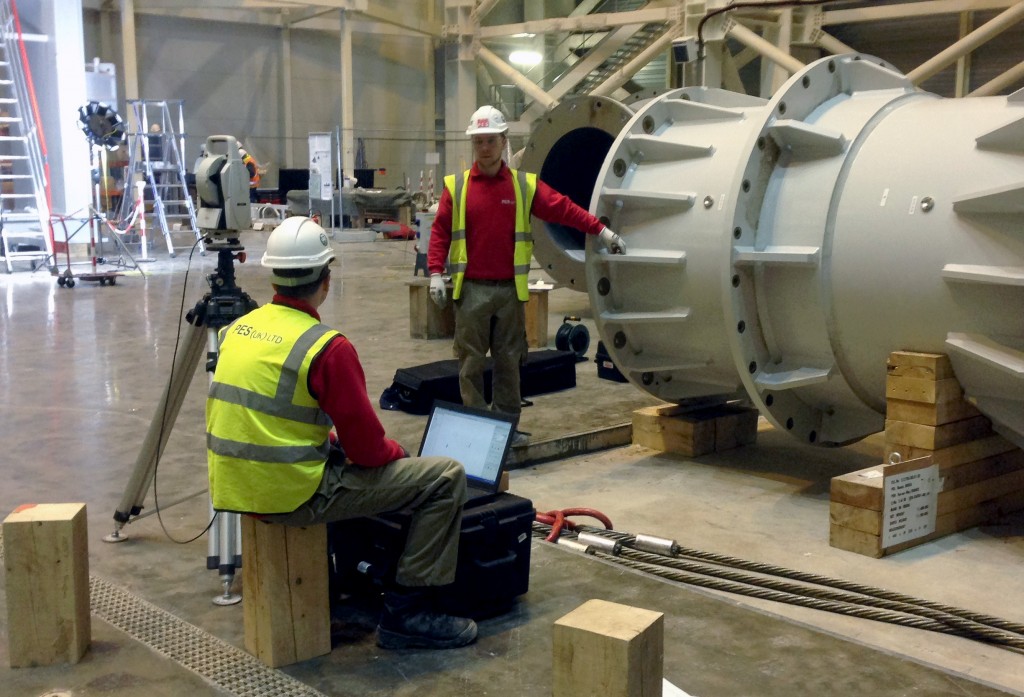
Helping to erect of the giant tools
2018-02-12 - Before and after each component of the sector sub-assembly tool (SSAT) is preassembled and put into place, metrology engineers carry out a variety of measurements and computational analysis to verify that every component is assembled and positioned in accordance with its design requirements.

The size of the pieces
2018-02-07 - Nothing gives a better sense of the size of the ITER machine than the ongoing works in the Cryostat Workshop, where the the lower cylinder and base section of the cryostat are being assembled and welded under the responsibility of Indian contractor Larsen & Toubro.
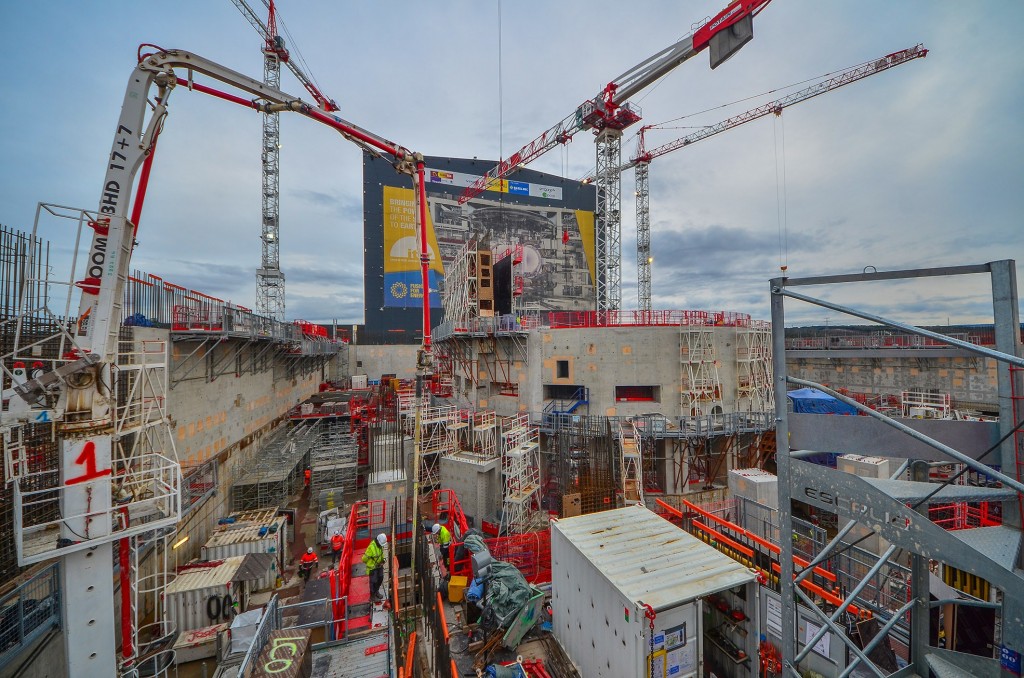
Standing room only
2018-02-07 - Each level of the Tokamak Building will be completely filled with plant equipment and systems supporting operation. Here, workers are walking at L2 level.

Make way for the neutral beam
2018-02-07 - More than 200 penetrations, some as large as four metres in width, pierce the ITER cryostat. The one pictured here is for the neutral beam injection system, one of the heating systems that will bring the plasma to the required fusion temperature.

Inside the soup plate
2018-02-07 - The base section of the ITER cryostat resembles a deep soup plate. For the moment however, only the base (where two workers are standing) and the rim are in place. The vertical "walls" to connect the two will be inserted at a later stage in order to provide more flexibility for adjustments.

A finished structure
2018-02-07 - Peeking through the columns at levels 1 (round penetrations), 2 (square penetrations) and 3/4 of the bioshield. Two basement levels are hidden from view. The worker in yellow gives a sense of scale.

The golden hour
2018-02-02 - The Tokamak Complex and Assembly Hall, framed by a half dozen tall cranes, are painted pink and gold in the late afternoon sun.
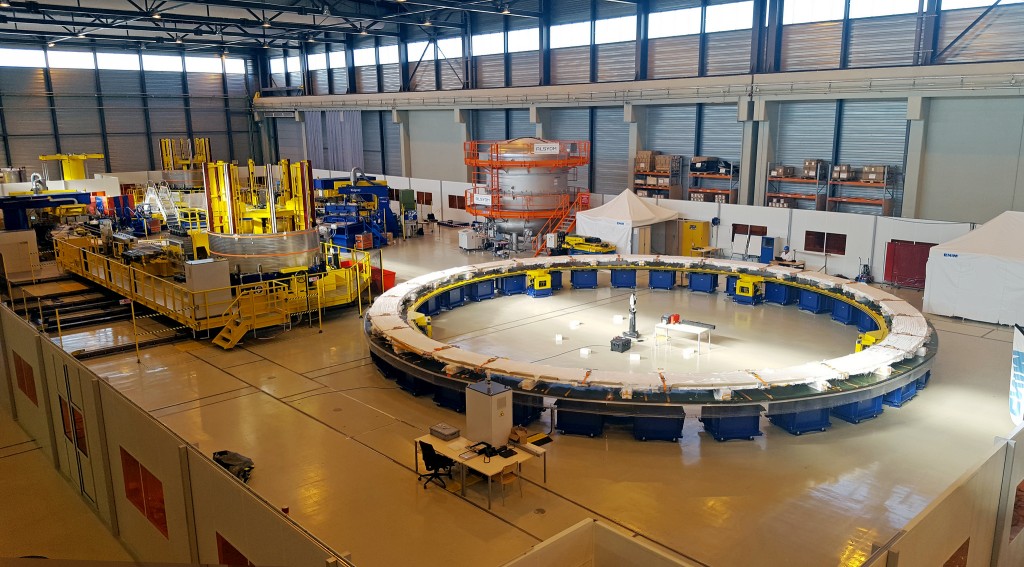
Work proceeding
2018-01-31 - Double pancake winding continues for poloidal field coil #5 (PF5). Eight pancakes will be stacked to form the final coil. Photo: F4E

Next: impregnation qualification
2018-01-31 - In January, teams are setting up for impregnation qualification activities. Photo: F4E

Pedestal welding
2018-01-30 - Twenty-five percent of the pedestal welding is complete. These technicians are watching the progression of the welding robot as it completes a run.

Alone in the arena
2018-01-30 - Stacked one upon the other, the two tiers of the cryostat's lower cylinder form a spectacular arena. Ten metres high and 30 metres in diameter, it dwarfs the lone Larsen & Toubro worker standing in the middle. Tier two segments are presently being aligned prior to welding operations. Work should be completed on this 375-tonne cryostat section this summer.
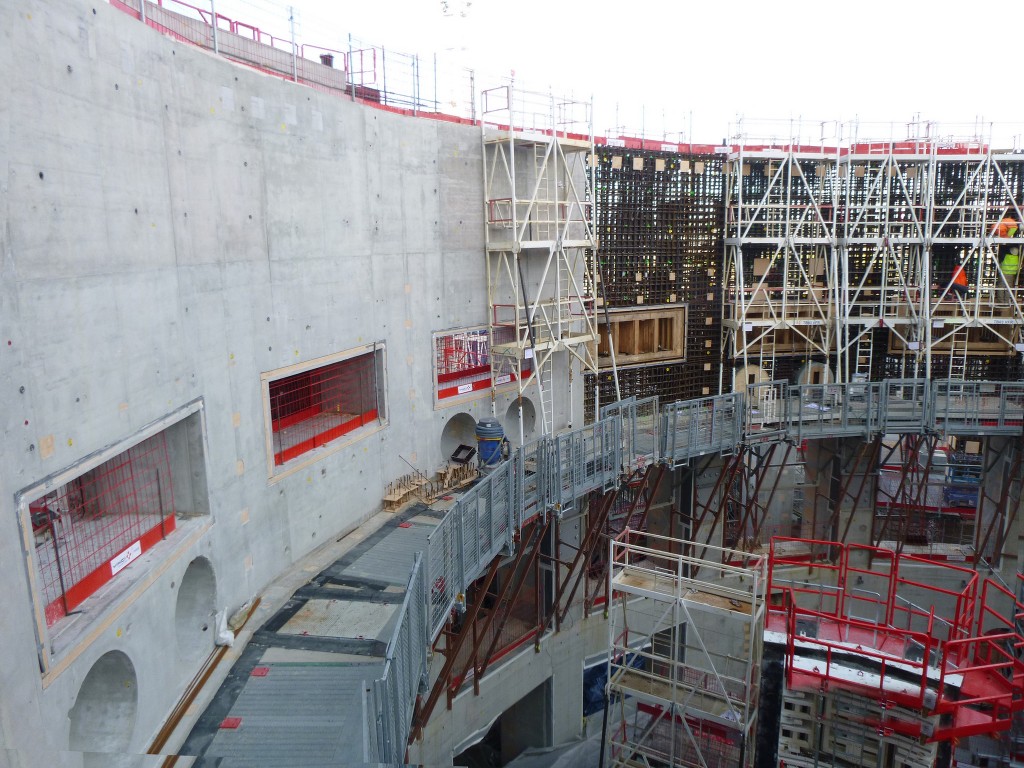
L4 exposed
2018-01-29 - The top level of the bioshield has been poured and the scaffolding is coming down. There are fewer penetrations at this level. Photo: ENGAGE
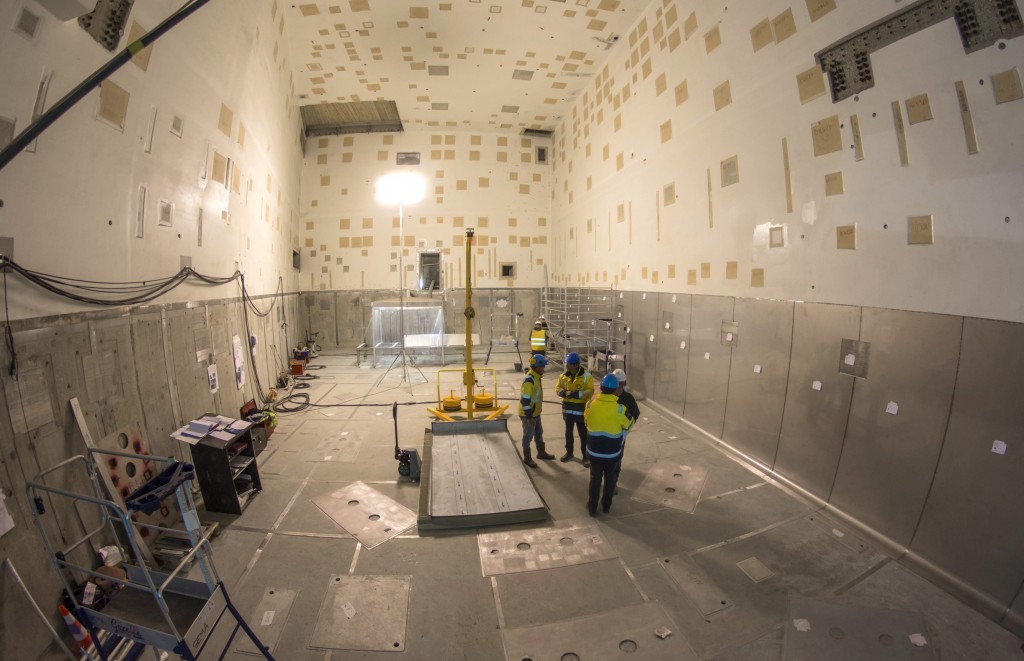
Tanks below
2018-01-27 - This steel-lined basement room will house water tanks for the Tokamak's cooling water and pressure suppression systems. The tanks will be introduced through the roof.

Down to the millimetre
2018-01-25 - Metrology teams are at work in the Assembly Hall to characterize segments of the SSAT tool before they are lifted into place.
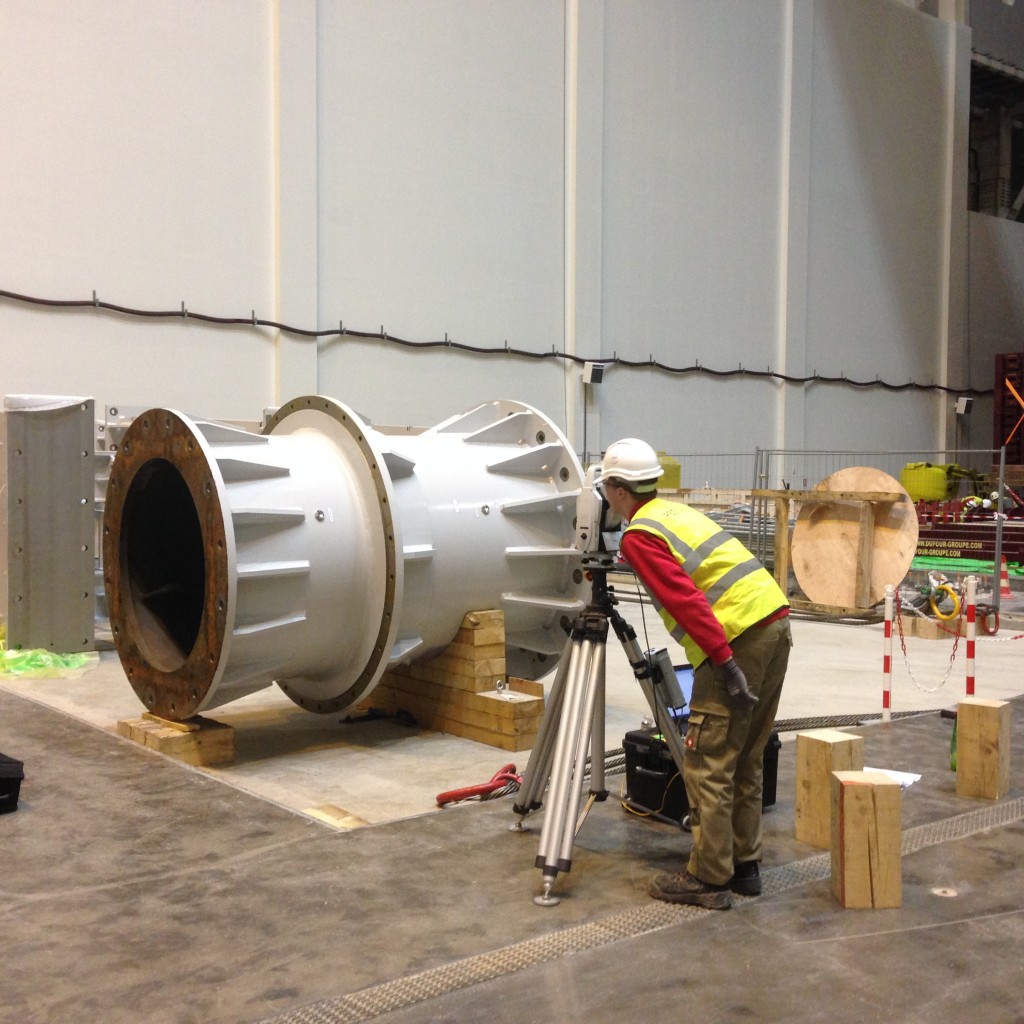
Several tools necessary
2018-01-25 - Due to the size of the vacuum vessel sector sub-assembly tool (SSAT), several metrology instrument positions are needed to achieve the best precision measurements. A network of target nests embedded in the ground of the Assembly Building helps position the instruments around the SSAT. Photo: PES Metrology

Several metrology tools necessary
2018-01-25 - Due to the size of the vacuum vessel sector sub-assembly tool (SSAT), several metrology instrument positions are needed to achieve the best precision measurements. A network of target nests embedded in the ground of the Assembly Building helps position the instruments around the SSAT. Photo: PES Metrology
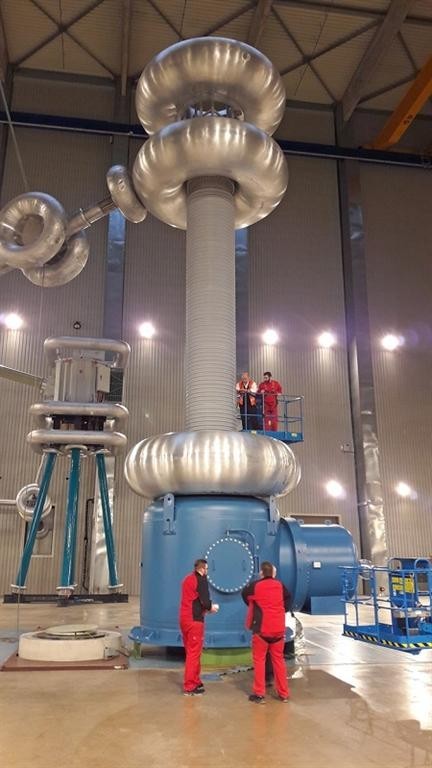
More first-of-a-kind equipment from Europe
2018-01-22 - The high-voltage bushing first passed electrical tests at HSP Gmbh, Germany, before being delivered to the NBTF facility in Italy. All required site tests have been completed. ©SIEMENS
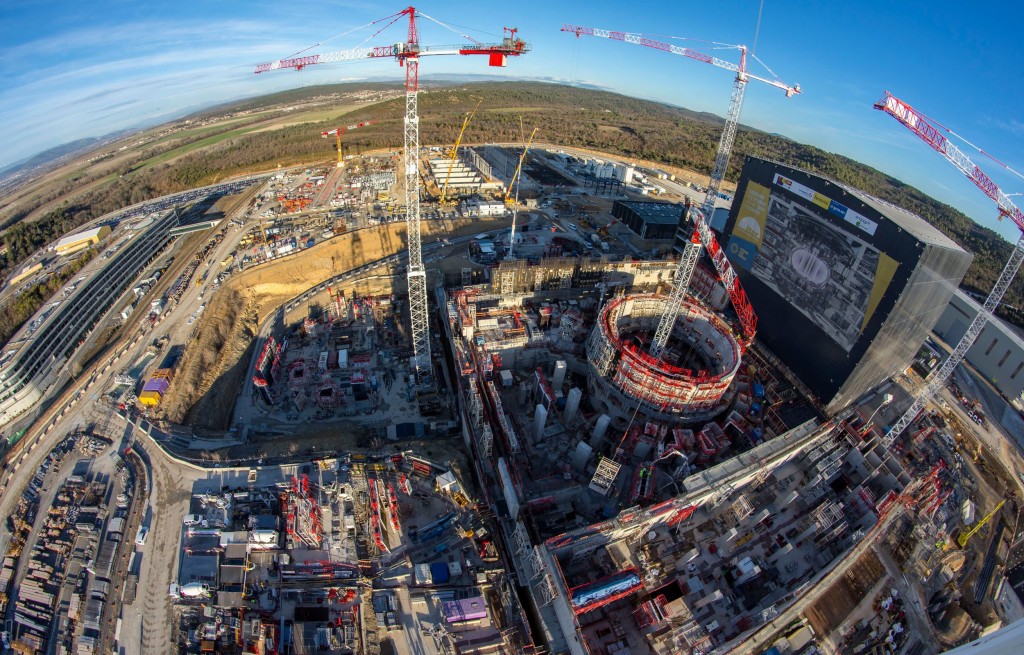
Soon to be capped
2018-01-19 - Once the bioshield has been capped with a temporary lid, work can proceed safely below. One of the upcoming tasks to be carried out is the positioning of "topographic benchmarks" to serve as guides in the installation of the cryostat sections.
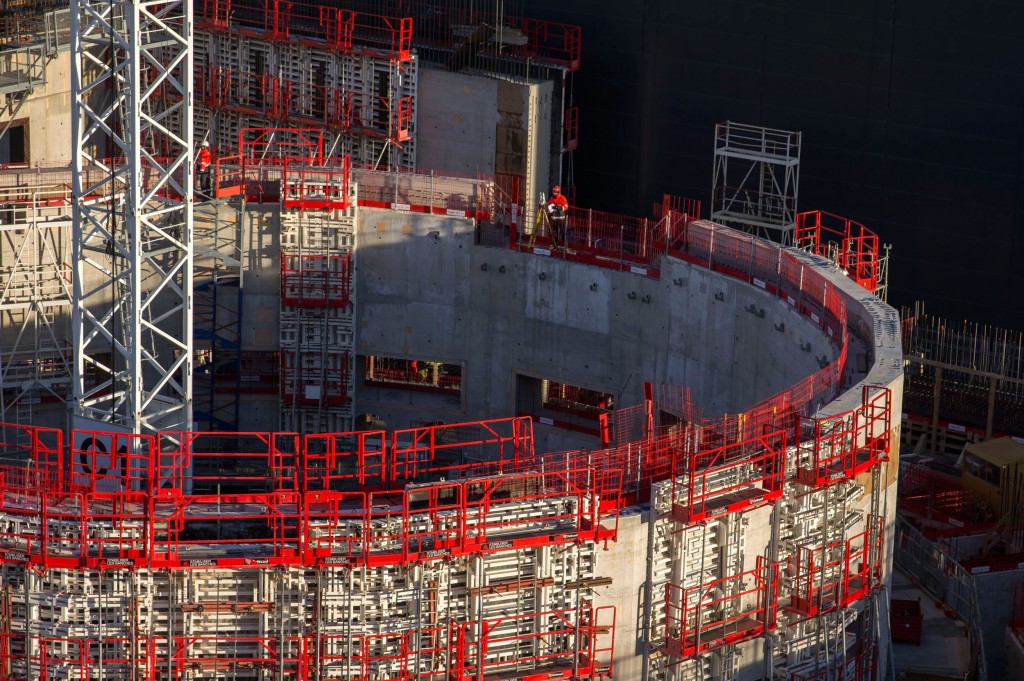
Lid to be moved
2018-01-19 - The temporary "lid" that is currently positioned at mid-height of the bioshield will be raised to the top to act as a roof. (A recess in the concrete shows where the lid will rest.)
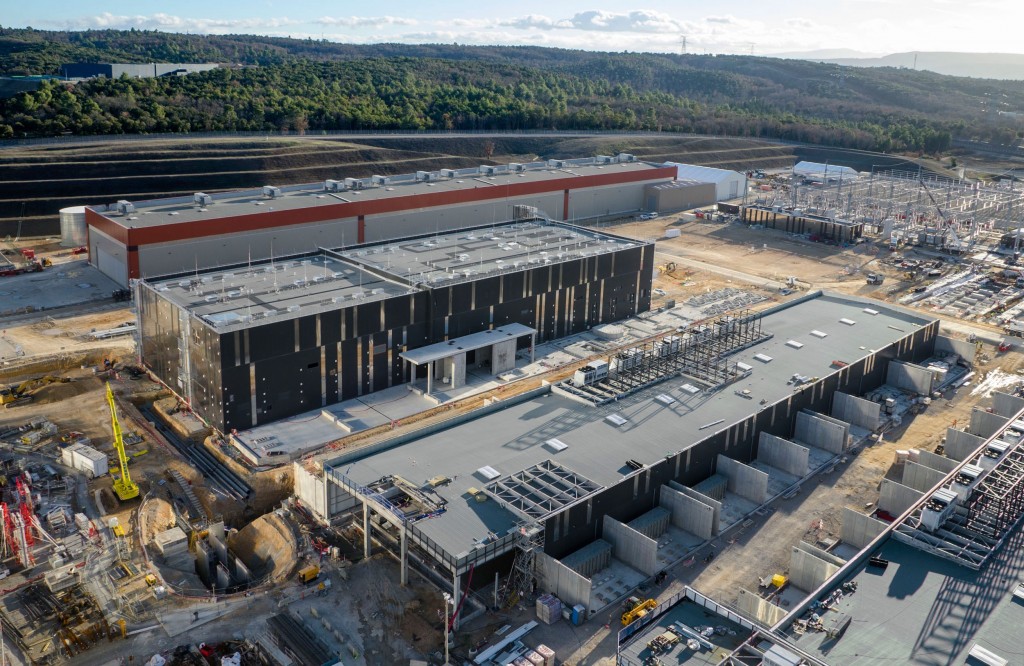
Limousine stop?
2018-01-19 - In front of the cryoplant (second building from the top) what looks like a theatre marquee, ready to shelter chauffeured limousines, is in fact a concrete platform that will support a 190,000-litre liquid helium tank—one of the 11 tanks that will be installed, either vertically or horizontally, along the building.

Interior partitions
2018-01-19 - Formwork is in place and pouring is underway for one of the inner walls at L1 level.
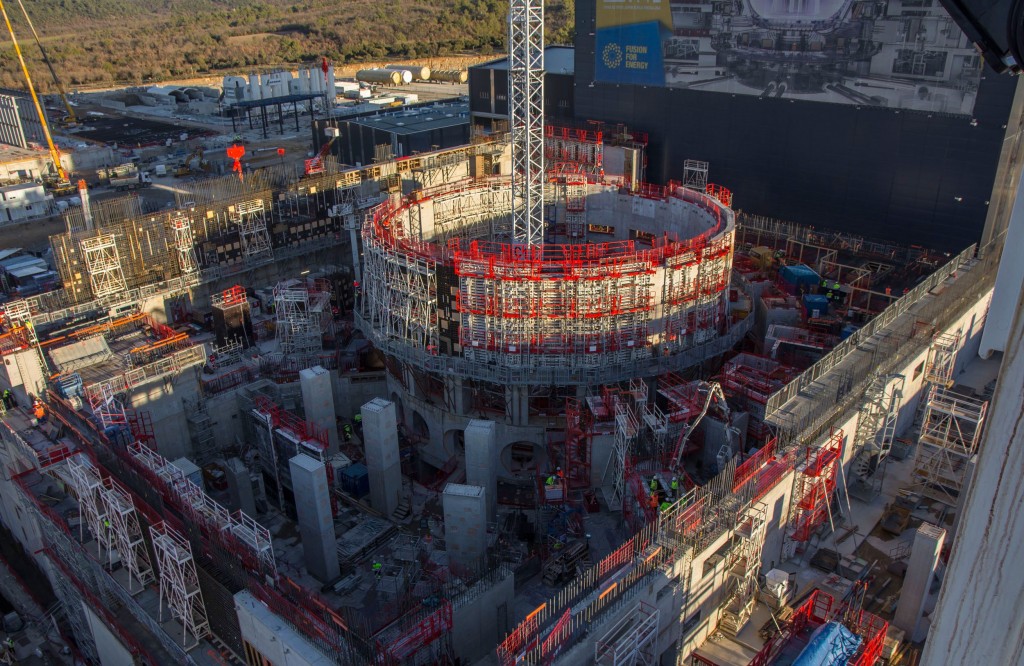
Neutral beam cell area
2018-01-19 - These columns going up in the foreground will support the roof of the neutral beam area. Large bus-sized injectors will be positioned in this space with access to the Tokamak through the round/oval windows visible in this photo.
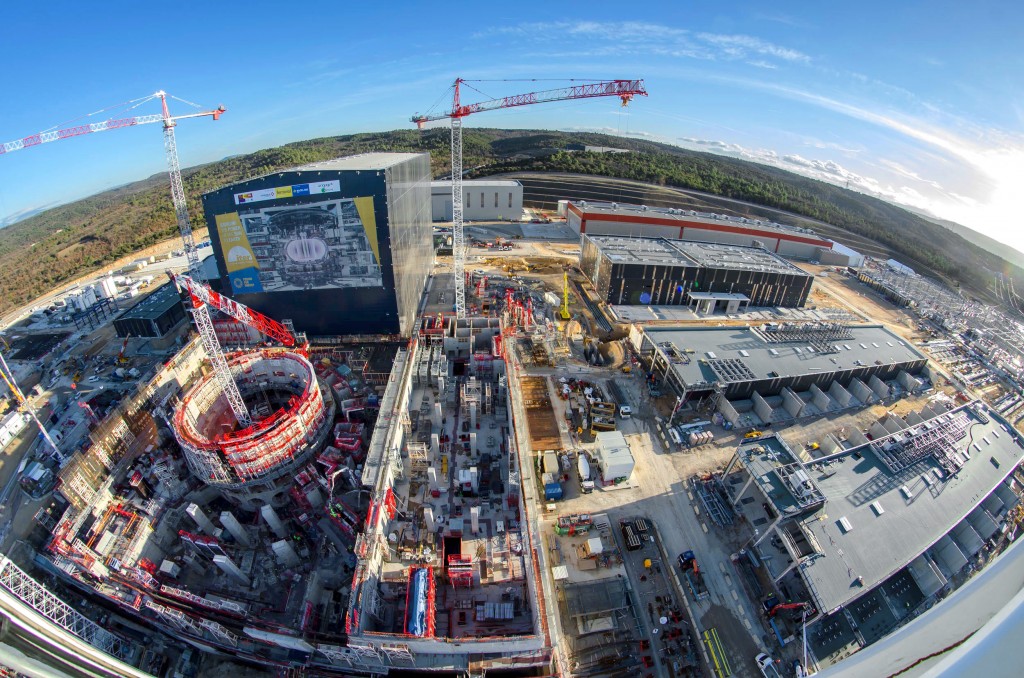
Last level of bioshield
2018-01-19 - In January, the last plot of the bioshield level 4 was poured. The structure rises 30 metres from the basement (B2) level to the top (L4).
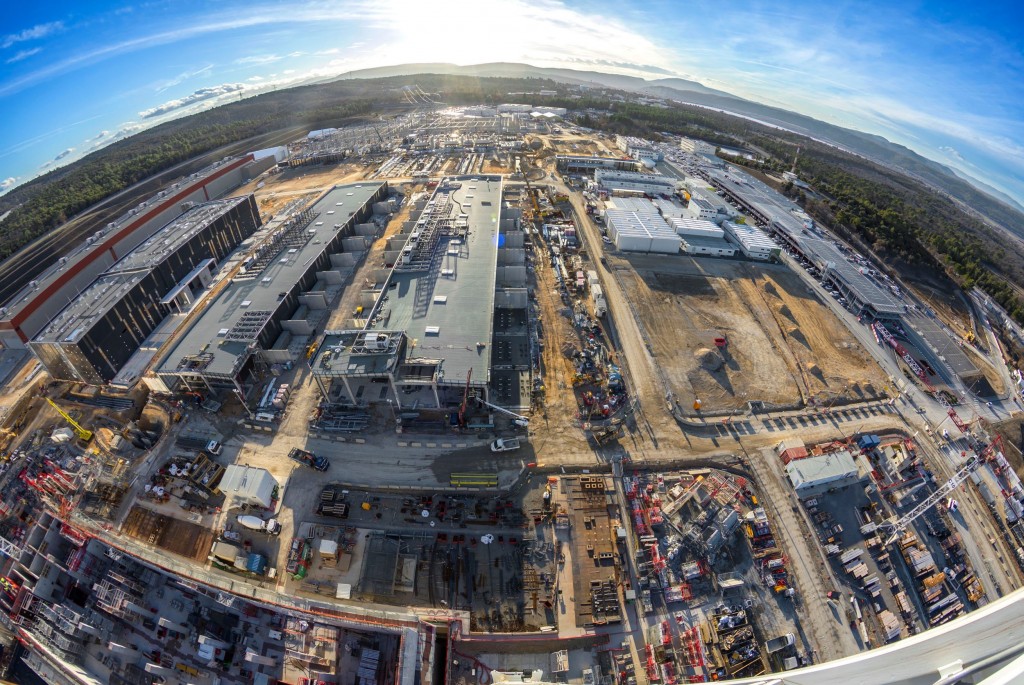
One kilometre of construction
2018-01-19 - All of the ITER plant buildings are located on the level 42-hectare construction platform, which is one kilometre in length. In the early years of the construction project, deep galleries were created under the surface of the platform for storm water, run-off water, and technical services like electricity and water. Most of these galleries have now disappeared from view, but their role will be critical during ITER operation.

A good place for photos
2018-01-18 - As the Tokamak Complex rises there is less to see at ground level. One possible viewpoint for the visitor is the roof of the contractor parking garage, where this photo was taken.
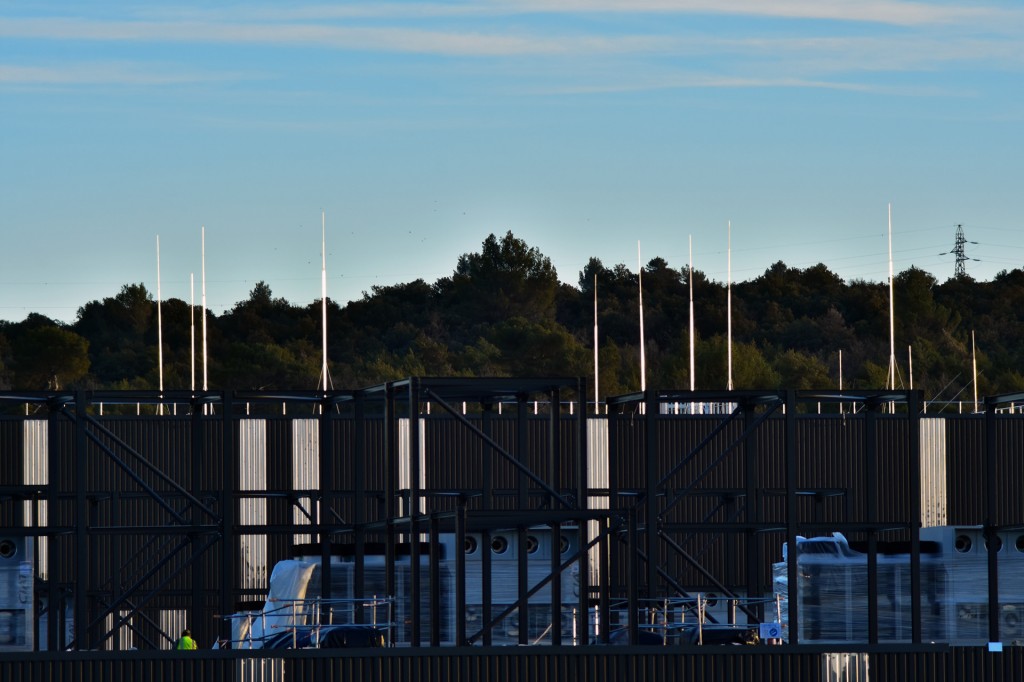
No sparks
2018-01-18 - A large number of lightening rods have been installed on the roof of the cryoplant.

New feature
2018-01-16 - A new feature on the cooling tower area: the tall columns of the Heat Exchanger Building. © Les Nouveaux Médias/SNC ENGAGE

Through to the basement
2018-01-16 - Looking down through a temporary lid to the basement levels of the bioshield. This lid will soon be moved to the top of the structure. © Les Nouveaux Médias/SNC ENGAGE

Moving up
2018-01-16 - From platform level, it's getting harder to see into the Tokamak Complex. In the foreground, the ITER Diagnostics Building. © Les Nouveaux Médias/SNC ENGAGE
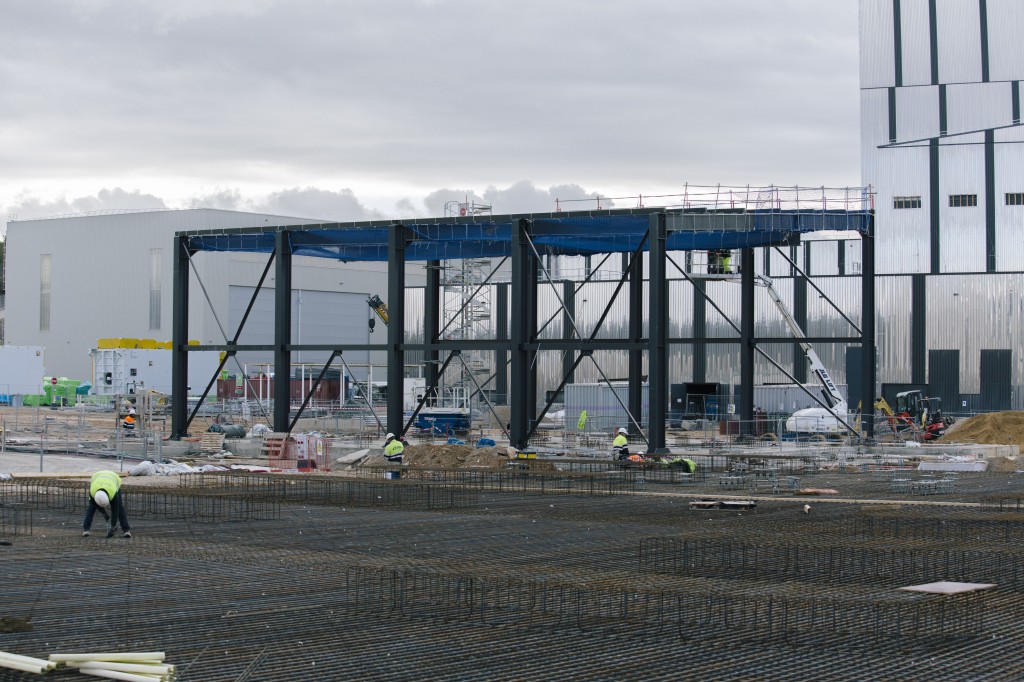
Pump house
2018-01-16 - This small structure frames out the future pump house of the heat rejection system. © Les Nouveaux Médias/SNC ENGAGE
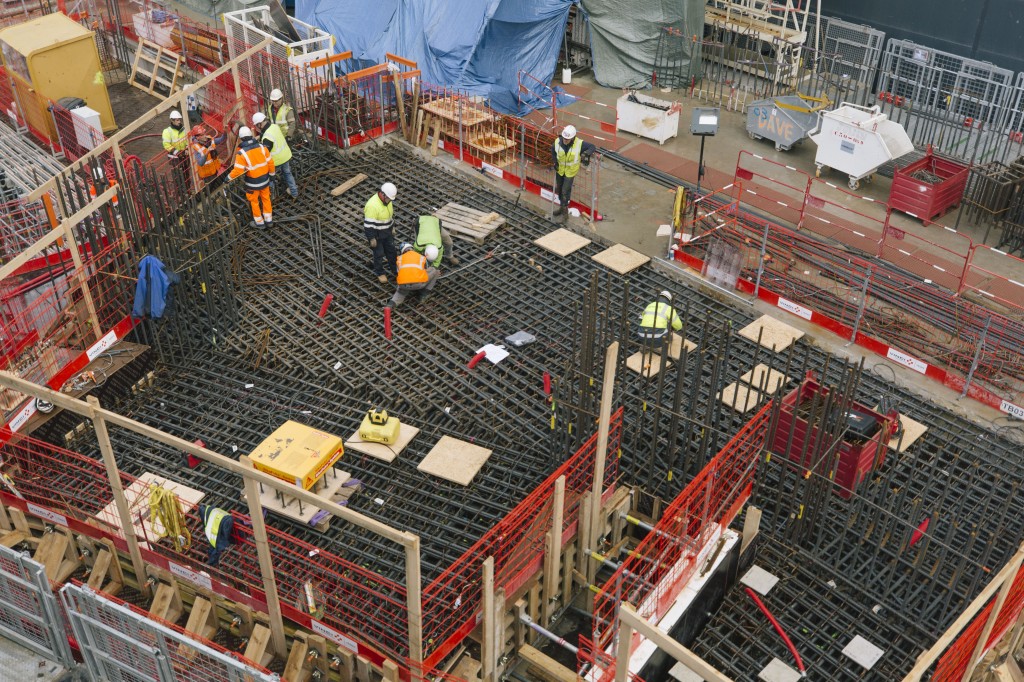
Worker numbers in January
2018-01-16 - Over 1,800 workers in two shifts are active on the ITER worksite. © Les Nouveaux Médias/SNC ENGAGE
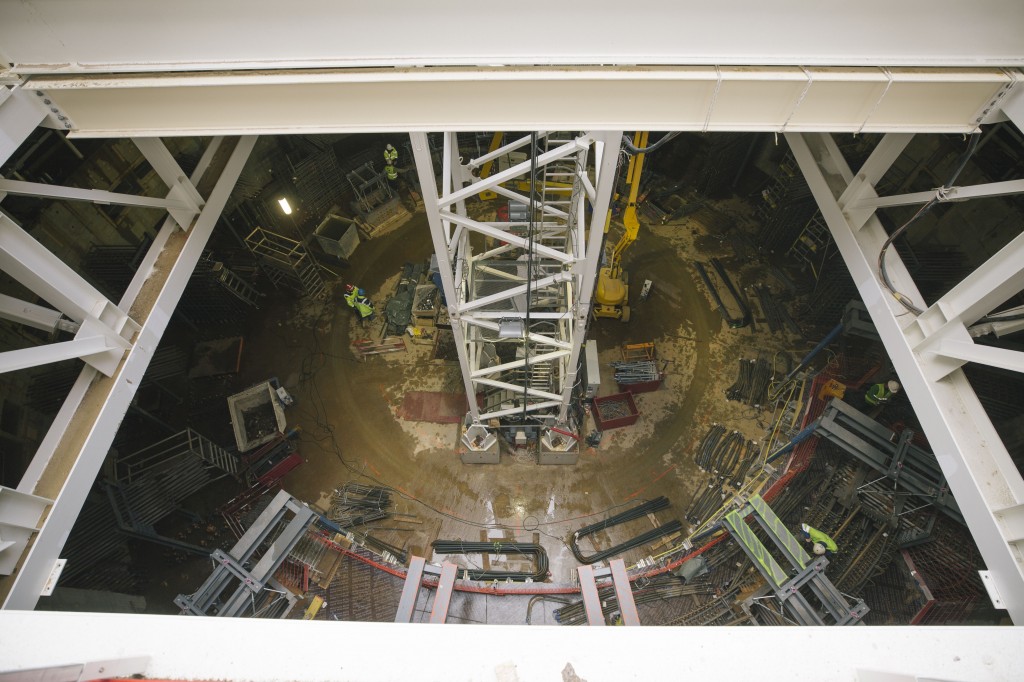
Down under
2018-01-16 - Space has been cleared below for work on the cryostat crown and radial walls. © Les Nouveaux Médias/SNC ENGAGE

Tank area ready
2018-01-16 - Beginning in February, teams will begin installing the exterior storage tanks for helium and nitrogen. In the zone pictured, the tanks will be installed vertically.

Crane on its way
2018-01-16 - To install the tanks, a tall crane will be needed. Early February, 40 trucks will deliver the crane components.

Final check
2018-01-16 - Before the final pour, this engineer is verifying that the penetrations have been marked out as planned. © Les Nouveaux Médias/SNC ENGAGE

Vast zone
2018-01-16 - The cooling tower area will occupy a zone of approximately 13,000 m³ on the northern corner of the platform. The tower and basin area represents about half of that; the rest is dedicated to housing pumps, heat exchangers, and other equipment. © Les Nouveaux Médias/SNC ENGAGE
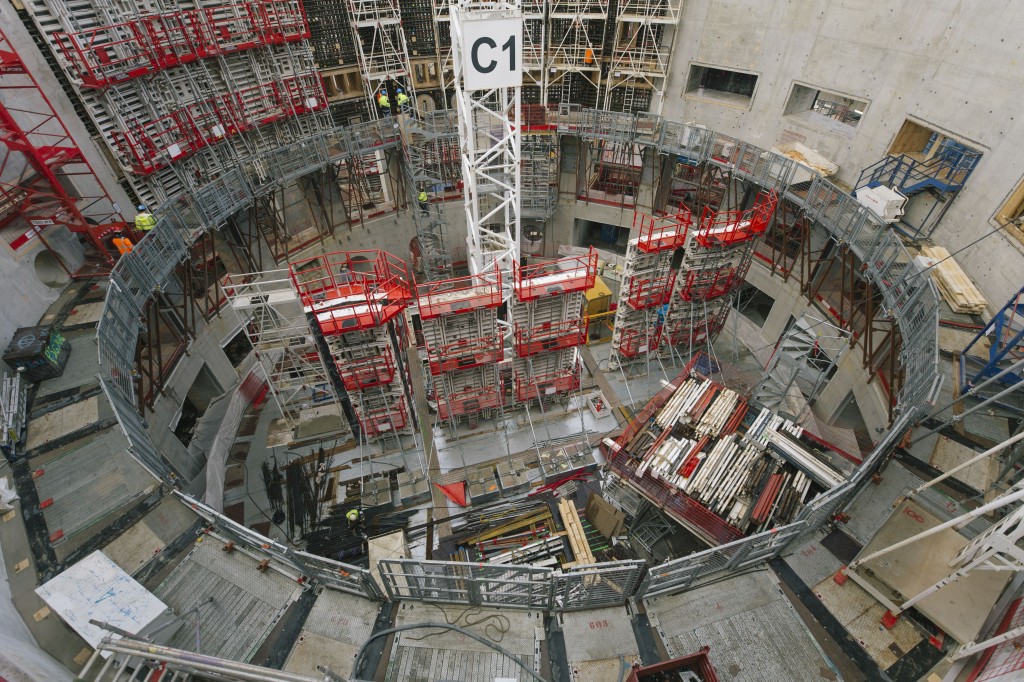
Formwork comes off
2018-01-16 - The concrete has dried and the formwork panels can be removed one by one. © Les Nouveaux Médias/SNC ENGAGE
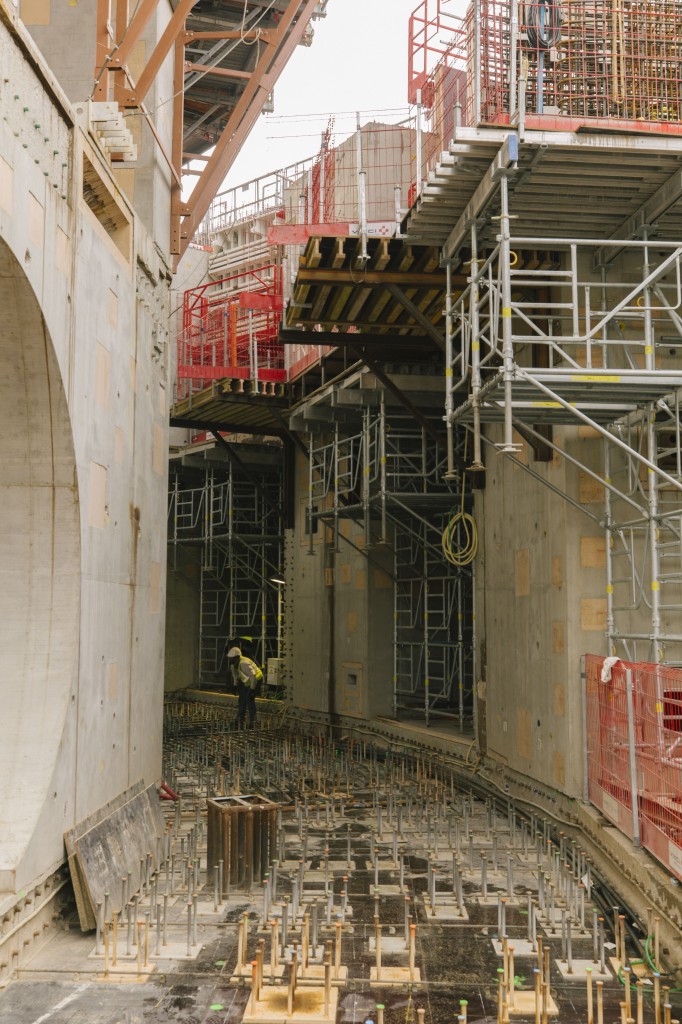
A river of anchor plates
2018-01-16 - In this area just outside of the bioshield, embedded plates are planned where equipment needs to be attached; that is, everywhere. © Les Nouveaux Médias/SNC ENGAGE
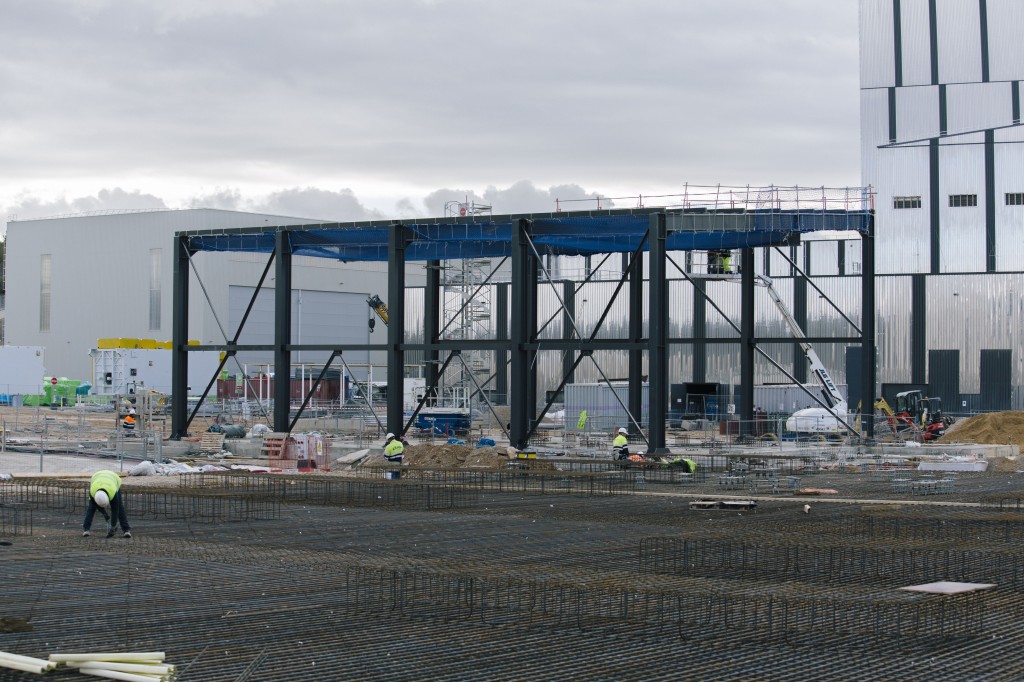
New building
2018-01-16 - This small structure frames out the future pump house of the heat rejection system. © Les Nouveaux Médias/SNC ENGAGE

Which way?
2018-01-16 - A sign on the worksite indicates the two closest villages to ITER--Saint Paul-lez-Durance and Vinon-sur-Verdon. © Les Nouveaux Médias/SNC ENGAGE

At the very top
2018-01-16 - Setting up the last pour of the bioshield, level 3/4. © Les Nouveaux Médias/SNC ENGAGE

In a cavern
2018-01-12 - For the moment the two lower levels of the bioshield are closed off. Soon, the lid will be repositioned at the top of the structure and workers will have unrestricted access to the entire volume of the Tokamak Pit.
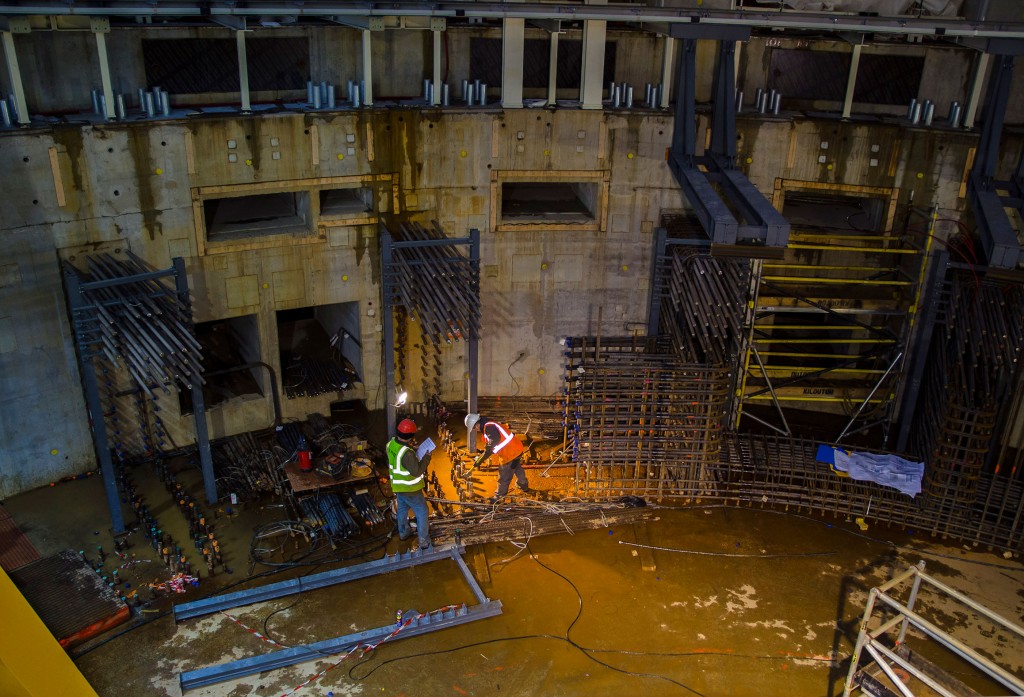
Crown and radial walls underway
2018-01-12 - One of the most strategic parts of ITER construction, the crown and radial walls necessitate the densest, thickest and most intricate rebar arrangements of the entire installation. This machine support structure should be finalized by the end of the summer.

The flying buttresses of ITER
2018-01-12 - Radial walls will permit the machine's support structure to transfer some of the "force" experienced during machine operation to the bioshield wall and Tokamak Building basemat.
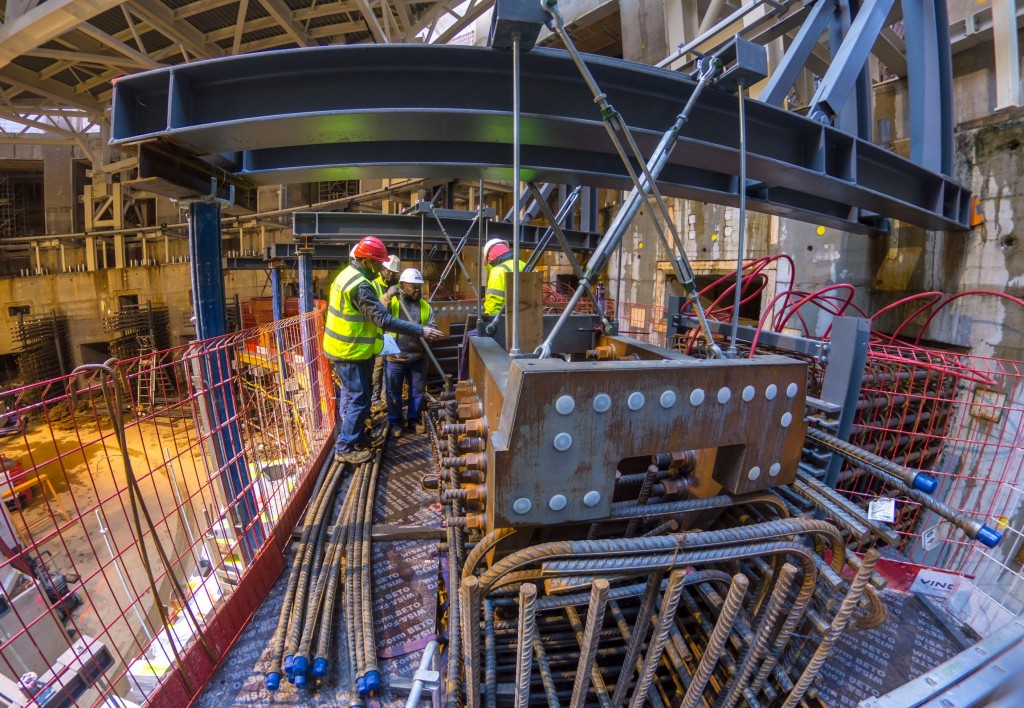
Helping to distribute the loads
2018-01-12 - Workers are busy installing the steel reinforcement for each radial wall: thick rebar (up to 50 millimetres in diameter) arranged in a complex geometry, and massive steel transition pieces (3 tonnes each) that will transfer and distribute the loads to the concrete civil work.

Starting on the crown
2018-01-12 - In the bottom of the Tokamak Pit, a concrete crown will support the base of the cryostat. After realizing a full-size mockup to validate constructability, workers are now carrying out the first steps.
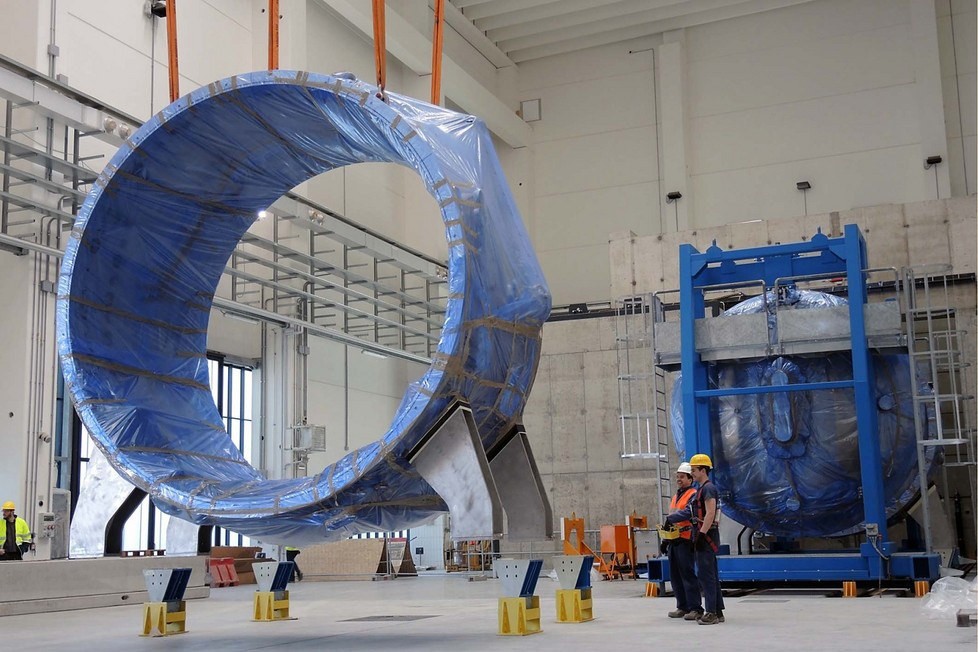
Large vessel, in segments
2017-12-21 - A section of the SPIDER beam source vacuum vessel arriving at the ITER Neutral Beam Test Facility.

Ready for installation
2017-12-20 - The concrete bays between the buildings are ready for the transformers arriving from Korea and China. © Les Nouveaux Médias/SNC ENGAGE

Explaining the space
2017-12-20 - Around the "box" of the Tokamak Complex, there is a two-metre gap. This allows the Complex to move as a monolithic structure in the case of an earthquake. © Les Nouveaux Médias/SNC ENGAGE

From the sky
2017-12-20 - The hot basin is now out of view, covered over by a concrete basemat and rows of columns. © Les Nouveaux Médias/SNC ENGAGE
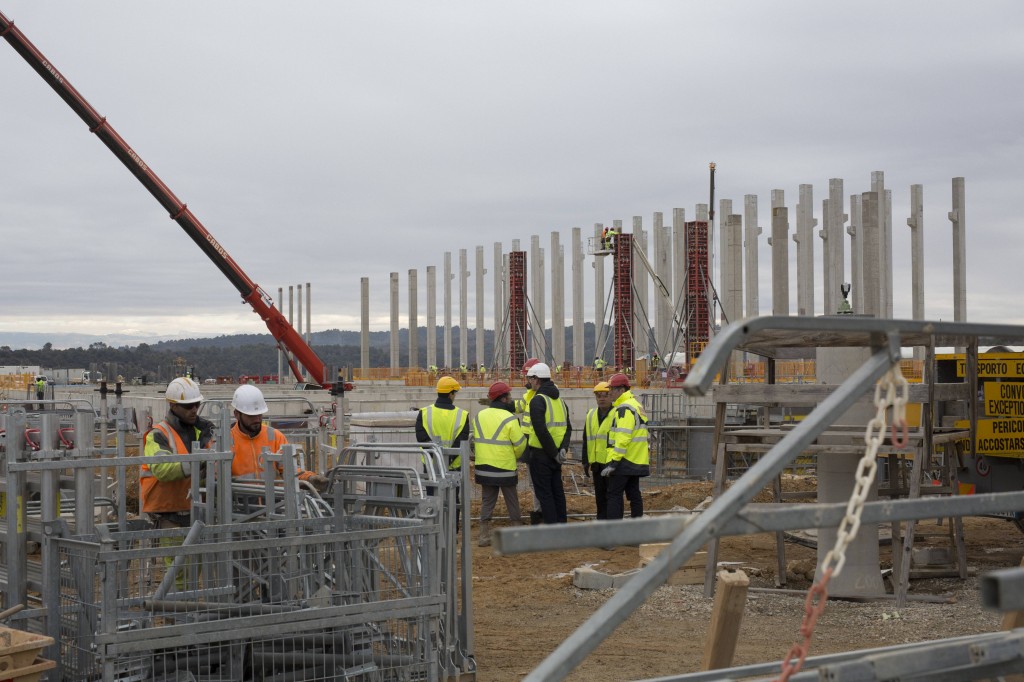
Mapping the route
2017-12-20 - Workers cluster around plans at the end of a long workday. © Les Nouveaux Médias/SNC ENGAGE

High storage
2017-12-20 - The concrete platform going up at right will support one of the horizontal storage tanks of the cryoplant. © Les Nouveaux Médias/SNC ENGAGE

Electrifying
2017-12-20 - Four transformers have been installed. ITER will need 32 for First Plasma and another 12 for full power operation. © Les Nouveaux Médias/SNC ENGAGE

Pump house
2017-12-20 - This smaller structure will house the cooling water pump station. © Les Nouveaux Médias/SNC ENGAGE

Bioshield: last steps
2017-12-20 - Teams are pouring the last segments of the circular bioshield, which now stands 30 metres tall. © Les Nouveaux Médias/SNC ENGAGE

Pipes: 5 km
2017-12-20 - Five kilometres of piping will be installed in the underground galleries of the cooling tower area. © Les Nouveaux Médias/SNC ENGAGE
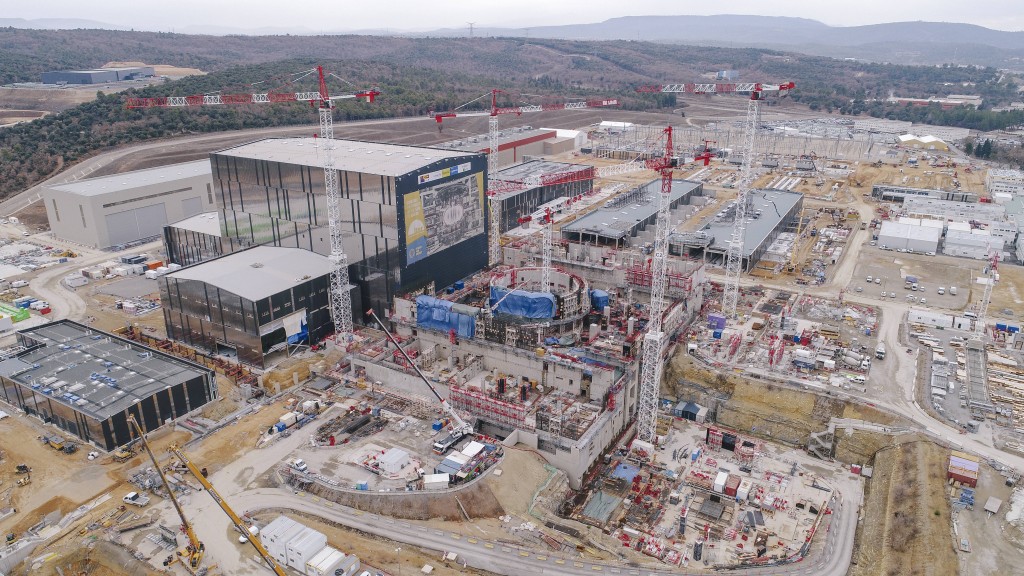
Late 2017
2017-12-20 - The ITER worksite, seen by drone in late 2017. © Les Nouveaux Médias/SNC ENGAGE

X marks the spot
2017-12-20 - Tank installation begins on 8 February.© Les Nouveaux Médias/SNC ENGAGE
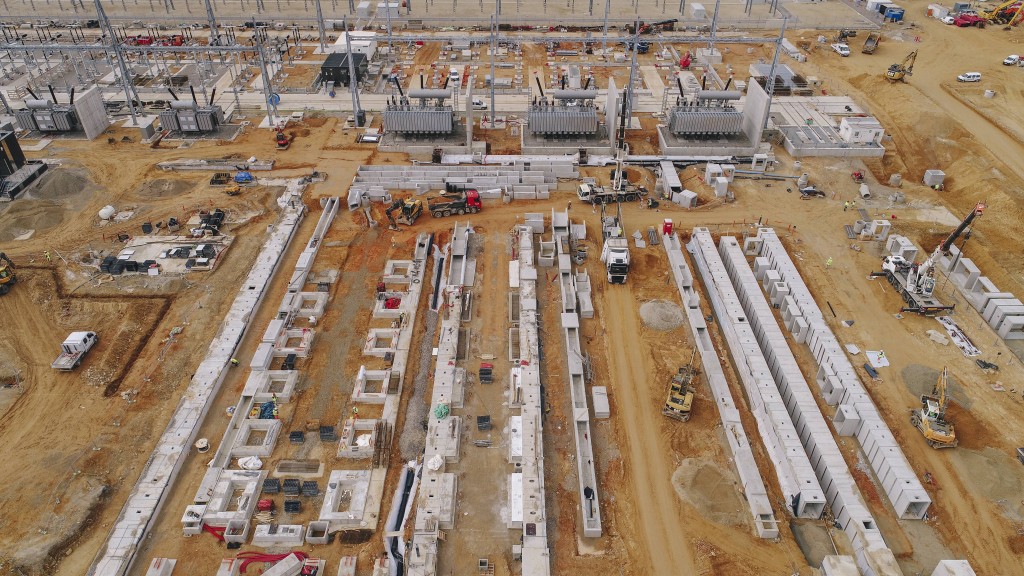
Electrical autoroute
2017-12-20 - Straight galleries run from the pulsed power electrical network transformers to the Magnet Power Conversion buildings. © Les Nouveaux Médias/SNC ENGAGE

In December
2017-12-20 - High columns are going up over the hot basin area. © Les Nouveaux Médias/SNC ENGAGE

Space reserved for Hot Cell
2017-12-20 - Standing where the Hot Cell Facility will one day be erected, looking toward the openings of the cask and plug transporter. © Les Nouveaux Médias/SNC ENGAGE

Equipment arriving
2017-12-20 - Large stop log gates to close off each of the cooling basin compartments for maintenance, as well as screens to keep debris from reaching the pumps, were delivered by the Indian Domestic Agency at the end of 2017. © Les Nouveaux Médias/SNC ENGAGE
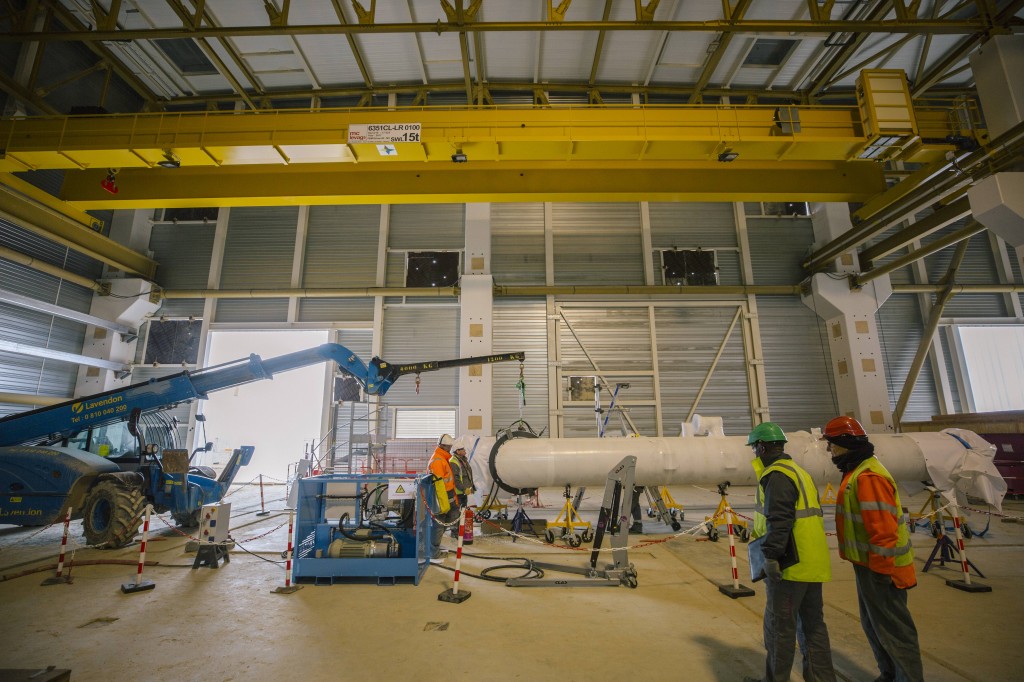
Deliveries
2017-12-20 - Equipment is delivered to the Compressor Building in December. © Les Nouveaux Médias/SNC ENGAGE
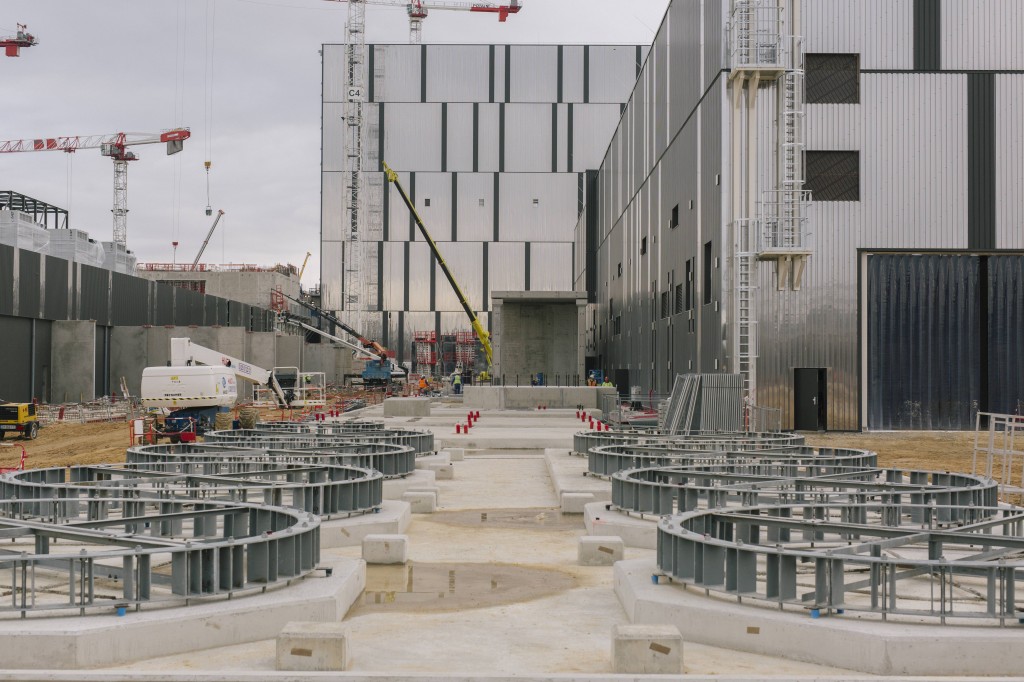
11 containers
2017-12-20 - The cryoplant will require 11 tanks for the storage of liquid and gaseous helium and nitrogen. © Les Nouveaux Médias/SNC ENGAGE

Installation activities
2017-12-20 - The focus is turning to equipment installation for these three long buildings, as the structures themselves have reached an advanced level of maturity. © Les Nouveaux Médias/SNC ENGAGE
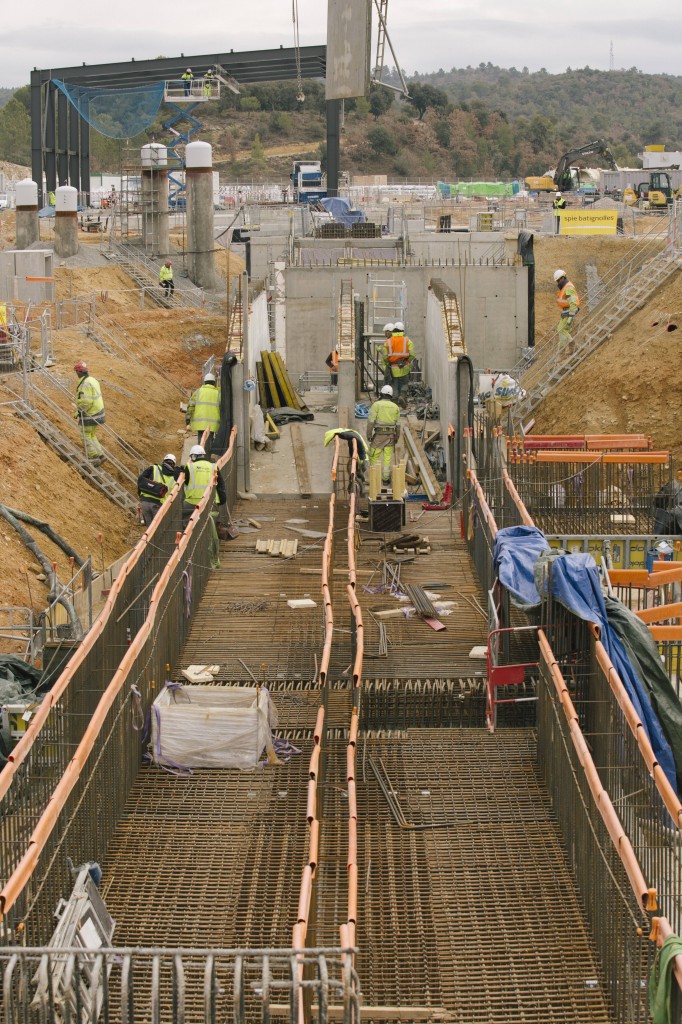
A consequential flow rate
2017-12-20 - Here is an especially large technical gallery heading out toward the heat rejection zone. The maximum total flow rate during operation toward this zone is 14 m³/s. © Les Nouveaux Médias/SNC ENGAGE

A small city?
2017-12-20 - This busy image, captured in December, makes the ITER construction site look like a small, bustling city. © Les Nouveaux Médias/SNC ENGAGE

Several entities are participating
2017-12-20 - The design and fabrication of the heat rejection system is part of India's procurement contributions to the ITER Project. Europe has excavated the site and created the concrete basins and structures; the equipment will be installed by the ITER Organization. © Les Nouveaux Médias/SNC ENGAGE
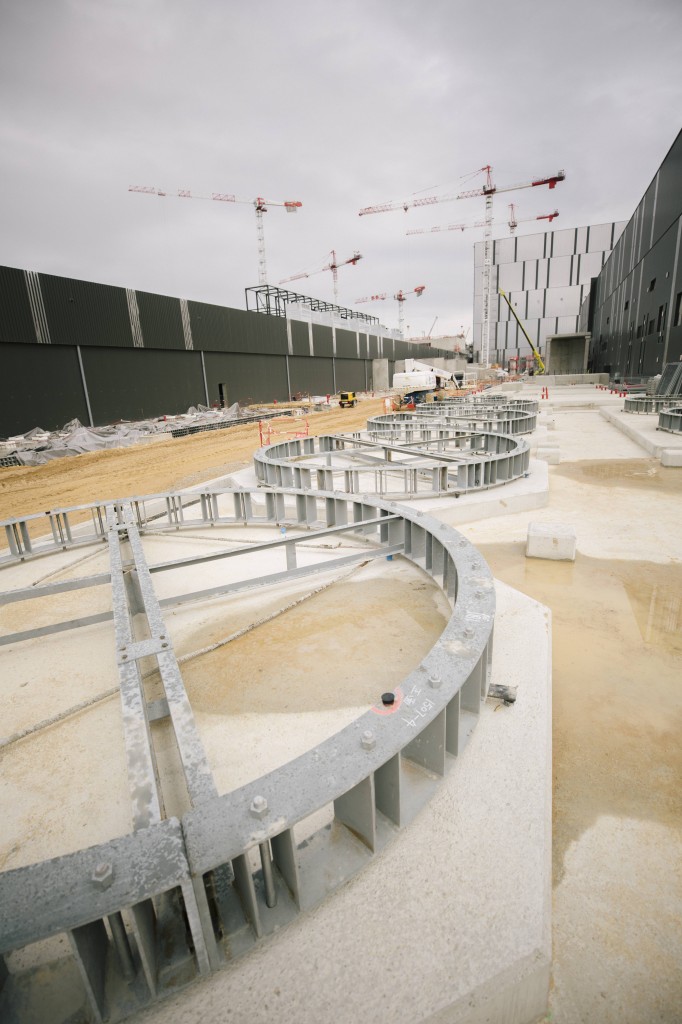
Basemat completed
2017-12-20 - The concrete finishing work for the exterior zone has been completed. © Les Nouveaux Médias/SNC ENGAGE

Two buildings, one roof
2017-12-20 - The 120-metre-long cryoplant is actually two buildings separated by a firewall—the Compressor Building (foreground) and the Cold Box Building. © Les Nouveaux Médias/SNC ENGAGE
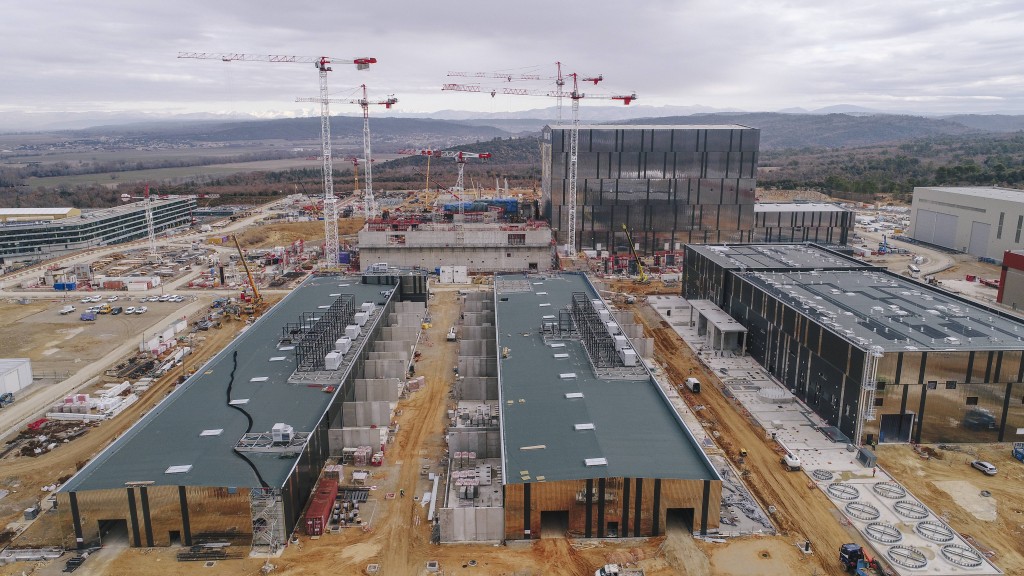
Installation activities
2017-12-20 - The focus is turning to equipment installation for these three long buildings, as the structures themselves have reached an advanced level of maturity. © Les Nouveaux Médias/SNC ENGAGE
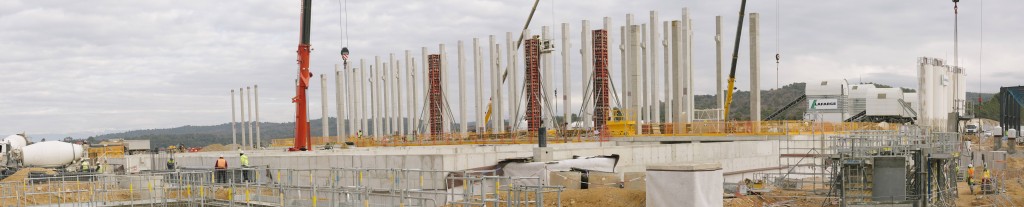
A widening area
2017-12-20 - The heat rejection zone is expanding under our eyes. Later, some of the equipment will be located where the concrete plant is today. © Les Nouveaux Médias/SNC ENGAGE

Tokamak Complex advances
2017-12-20 - Outside of the bioshield, workers are creating the walls and columns of the Tritium, Tokamak, and Diagnostics buildings. © Les Nouveaux Médias/SNC ENGAGE
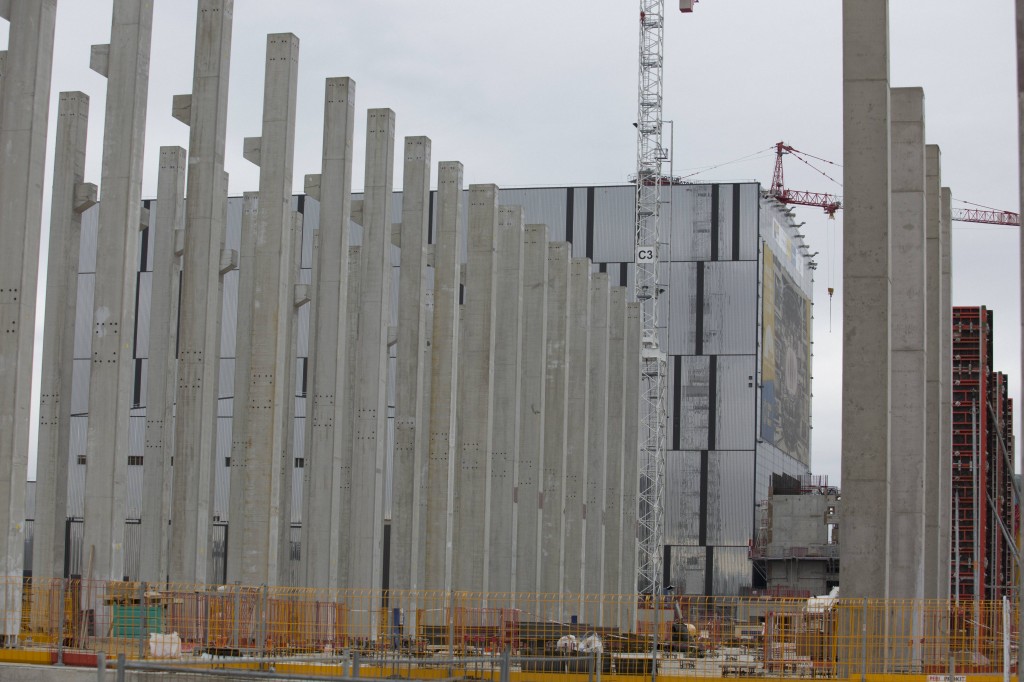
Not far from the fusion reactions
2017-12-20 - The heat rejection zone is just a few hundred metres from the Tokamak Complex, under construction in the background. © Les Nouveaux Médias/SNC ENGAGE

Deliveries
2017-12-20 - Equipment is delivered to the Compressor Building in December. © Les Nouveaux Médias/SNC ENGAGE
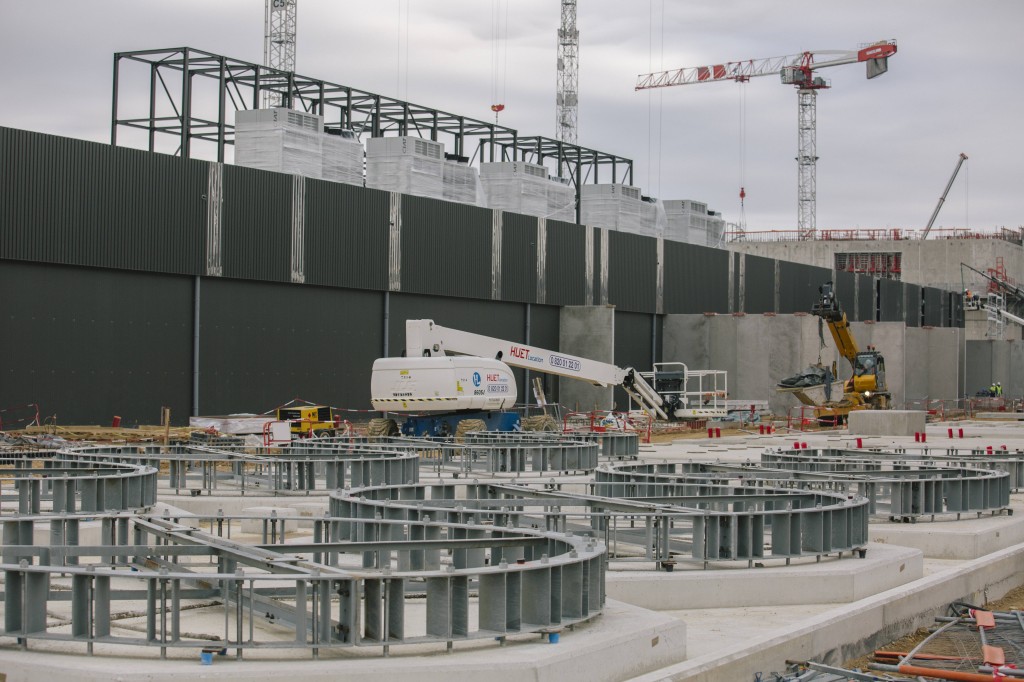
Tanks coming
2017-12-20 - Tank installation will begin in early February in this exterior storage area. © Les Nouveaux Médias/SNC ENGAGE
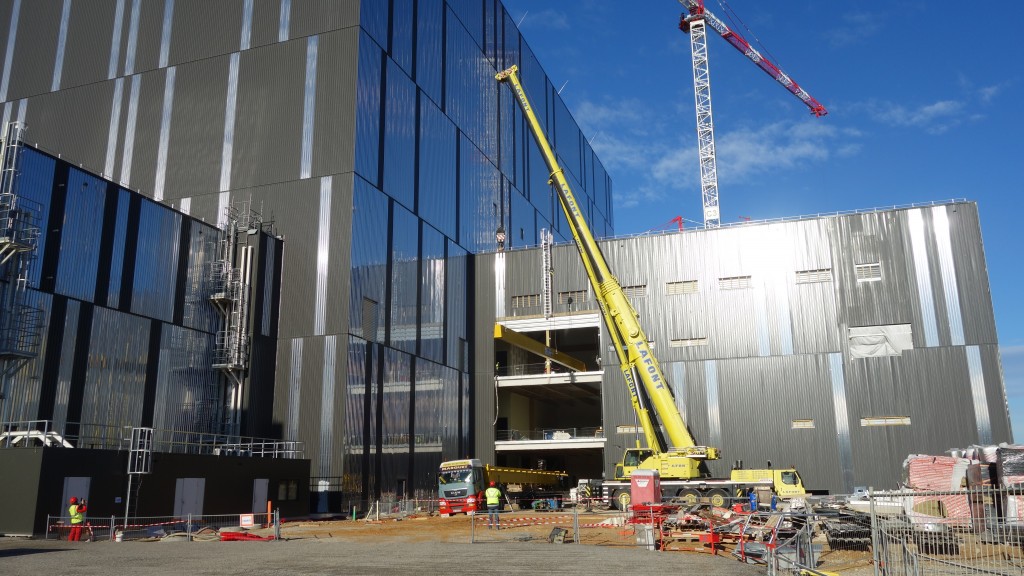
Up we go
2017-12-19 - The beams are lifted to the third floor of the building, where the wave generators will be housed.

Crane installed in Radio Frequency Building
2017-12-19 - This girder is one of two that will be lifted to level 3 of the Radio Frequency Building and installed with a trolley to be used in the installation of radio frequency and microwave heating components.
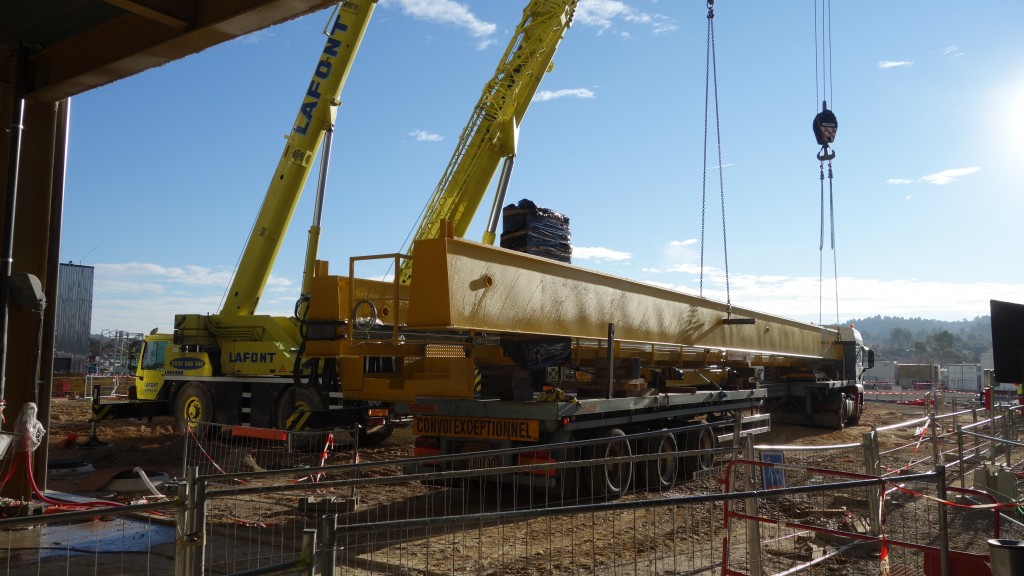
Platform delivery
2017-12-19 - Two crane girders are delivered to the Radio Frequency Heating Building.
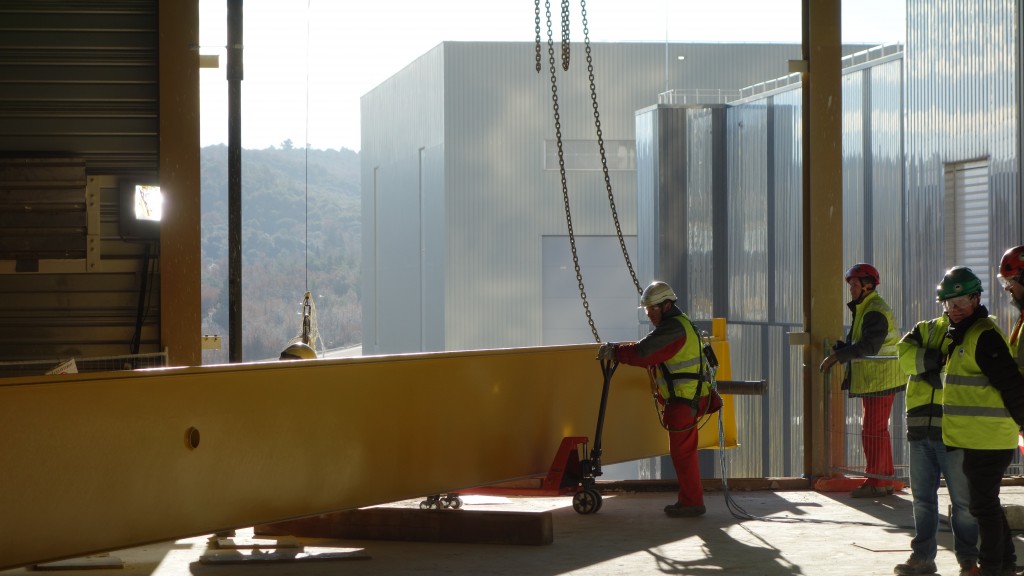
We have arrival
2017-12-19 - The first beam is detached from the crane and moved inside the building to make room for the delivery of the second.
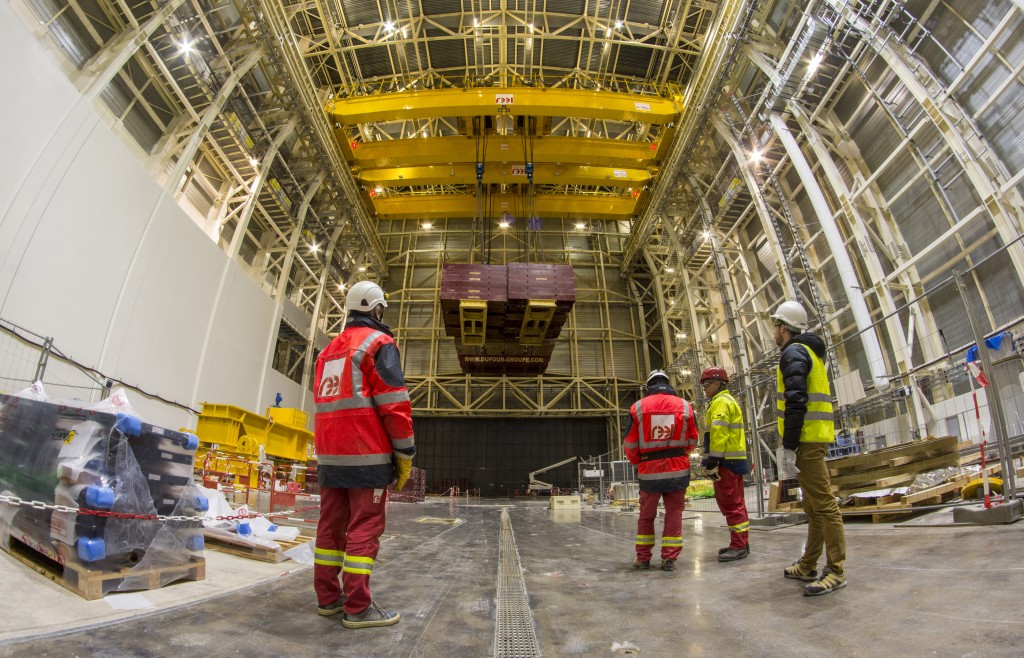
It's midnight, but these teams are at work
2017-12-18 - Observers during the load tests include representatives of the crane manufacturer Reel, the ITER Organization, the architect-engineer Engage, and the safety controller Bureau Veritas.

After-hours load tests for the crane
2017-12-18 - Late at night in December the principal crane of the Assembly Building was subjected to loads that were +10%/+25% of nominal—all part of commissioning tests for the important equipment.
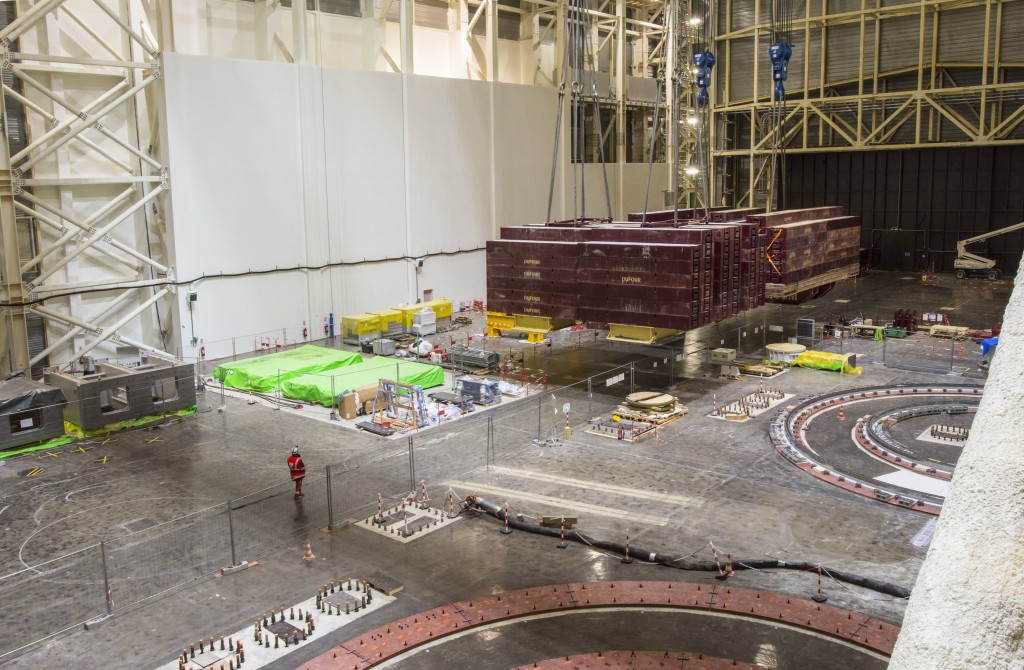
Standing ready
2017-12-18 - These heavy metal blocks—stacked seven tall—will be lifted some 50 metres overhead during testing.
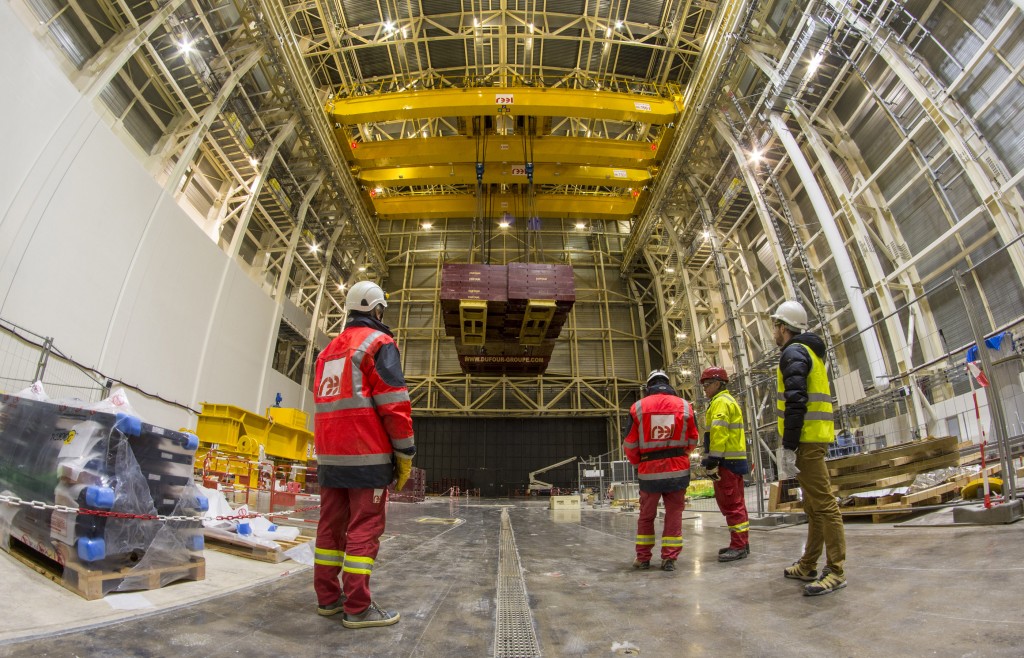
It's midnight, but these teams are at work
2017-12-18 - Observers during the load tests include representatives of the crane manufacturer Reel, the ITER Organization, the architect-engineer Engage, and the safety controller Bureau Veritas.
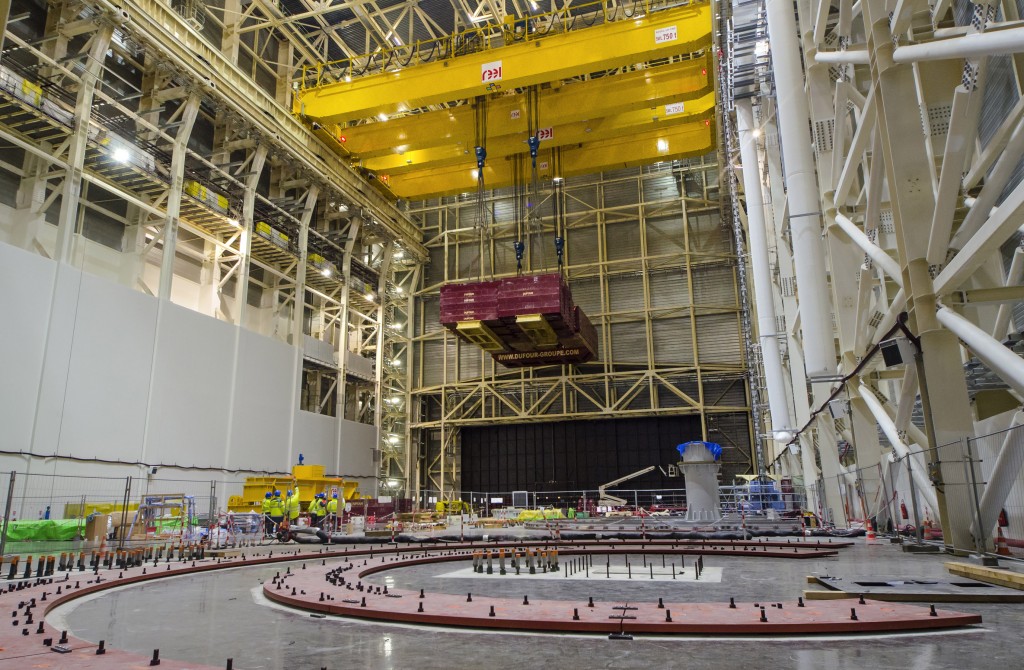
After-hours load tests for the crane
2017-12-18 - Late at night in December the principal crane of the Assembly Building was subjected to loads that were +10%/+25% of nominal—all part of commissioning tests for the important equipment.

Behemoth crane
2017-12-11 - Four hydraulic towers and circular beam in a square frame form the 30-metre-in-diameter gantry crane, capable of lifting 400 tonnes.

Crane enters building
2017-12-11 - In December, the new gantry crane was delivered to its installation location on the north end of the building, where it will be installed on its four "legs."
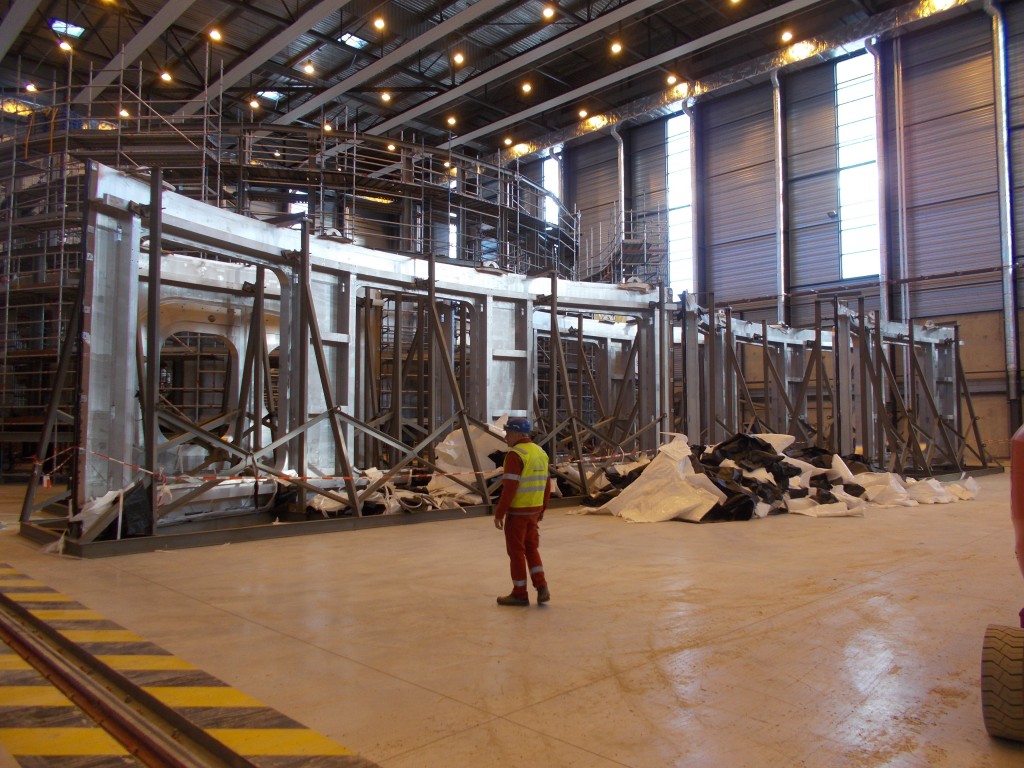
Unpacked in the workshop
2017-12-06 - The first tier-two segments of the lower cylinder have been unpacked in the Cryostat Workshop. These 5-metre-tall segments will be installed on top of the tier-one segments, making a 10-metre-tall component.
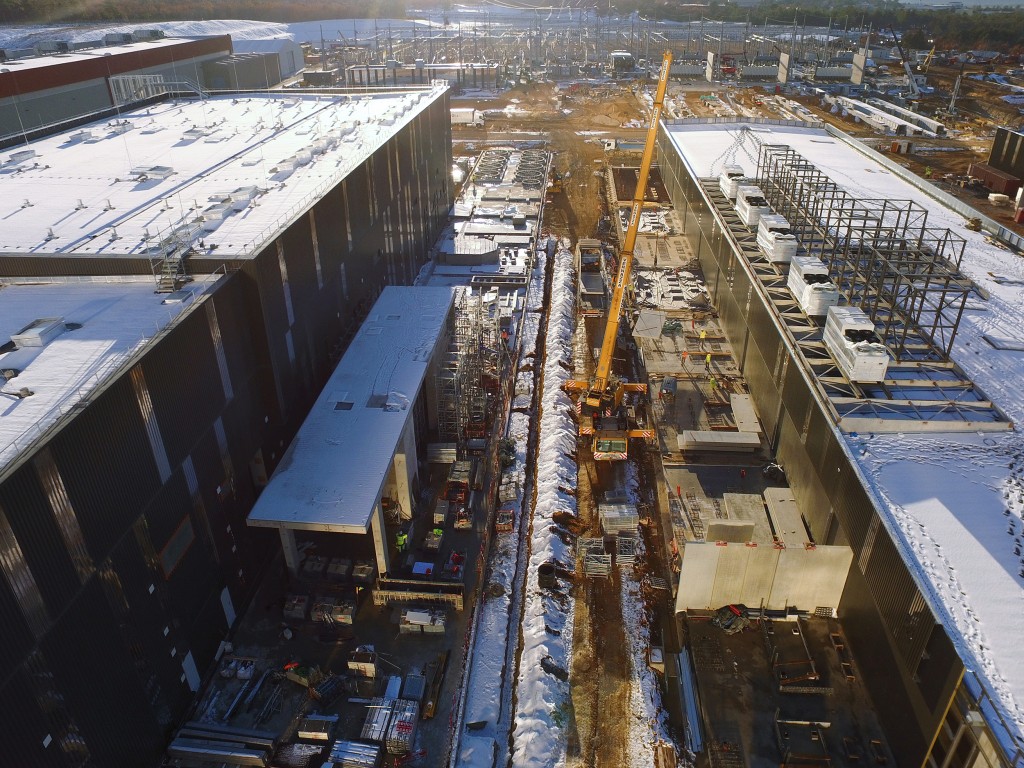
Snow on the rooftops
2017-12-05 - In December a light dusting of snow covered the rooftops of the cryoplant (left) and the Magnet Power Conversion building (right) for 24 hours. Photo: ITER Organization/EJF Riche

Snow on the rooftops
2017-12-05 - In December a light dusting of snow covered the rooftops of the cryoplant (left) and the Magnet Power Conversion building (right) for 24 hours. Photo: ITER Organization/EJF Riche
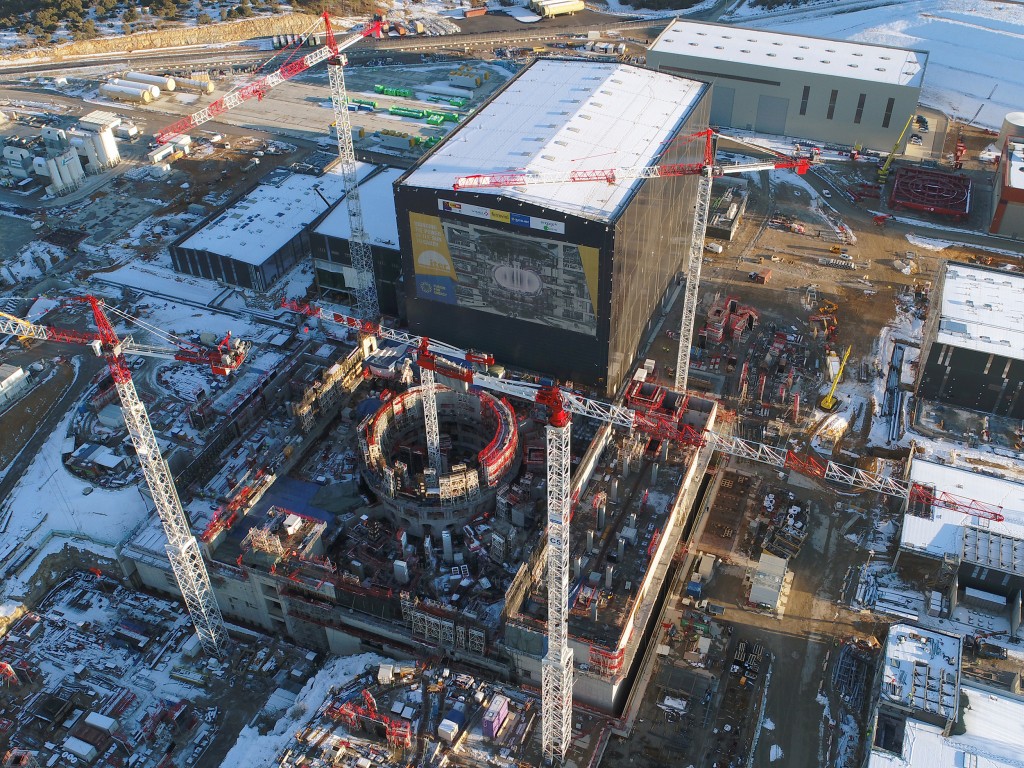
A wintery scene
2017-12-04 - A light dusting of snow graces the ITER worksite in December 2017. Photo: ITER Organization/EJF Riche
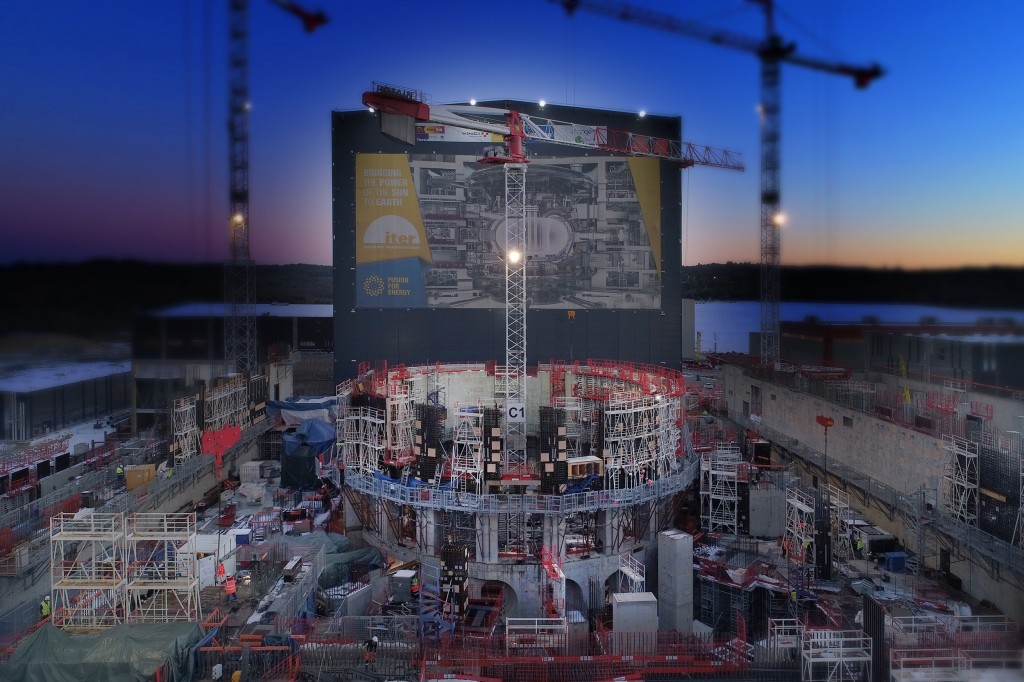
A model?
2017-12-04 - A few special effects and the vast ITER construction project seems to be transformed into a tiny model ... Photo: ITER Organization/EJF Riche

Overview
2017-12-04 - Looking west over the ITER construction site, with a component storage area front left, and buildings from left to right: the Poloidal Field Coils Winding Facility (red trim), the Cleaning Facility, the cryoplant, the Assembly Hall, the Radio Frequency Heating Building, and the Site Services Building (long and low). Photo: ITER Organization/EJF Riche
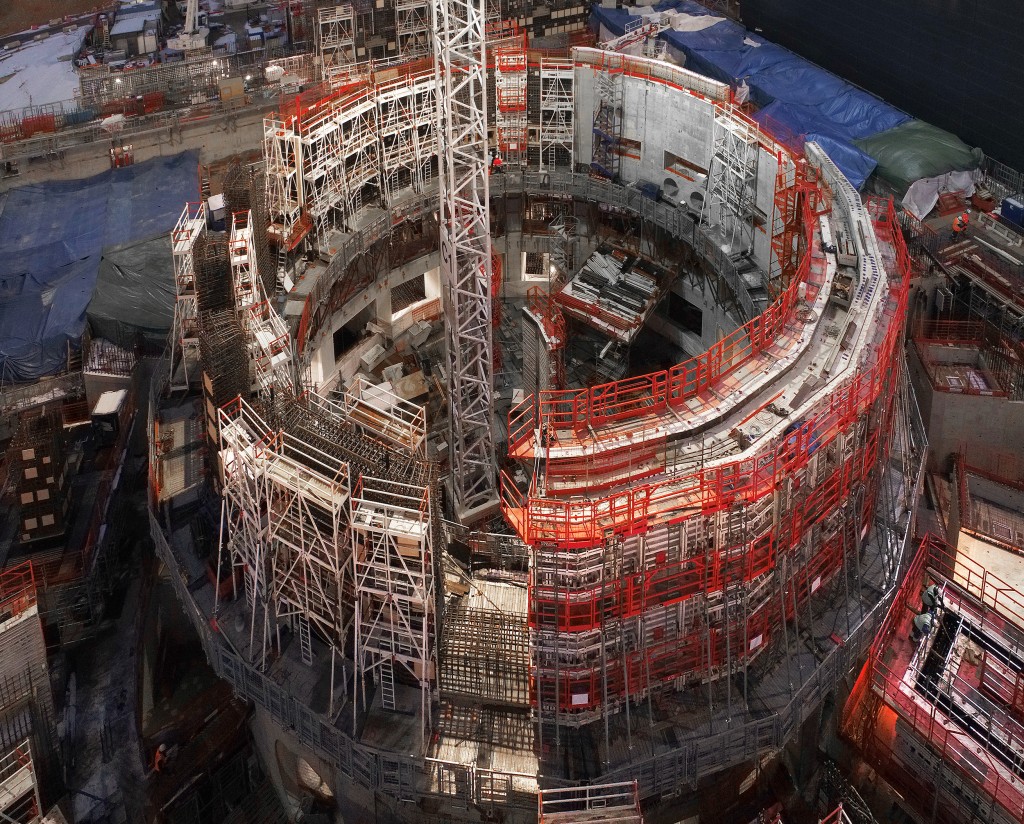
The bioshield
2017-12-04 - In the space of one year, the Tokamak bioshield has risen 20 metres. The circular structure, as thick as 3.2 metres in some areas, is designed to protect workers and the environment from radiation generated by the fusion reaction. Photo: ITER Organization/EJF Riche

Future assembly arena
2017-12-04 - Machine components will be lowered into the circular bioshield during the assembly phase. The beams of a massive assembly tool will be supported on its thick walls as the 440-tonne vacuum vessel sectors are aligned and welded "in pit." Photo: ITER Organization/EJF Riche

Last 2017 photo
2017-12-04 - At the close of 2017, the last levels of the bioshield (L3 and L4) have been framed out and concrete pouring is underway. Work is also proceeding at level 3 (L3) of the Diagnostics Building (foreground).
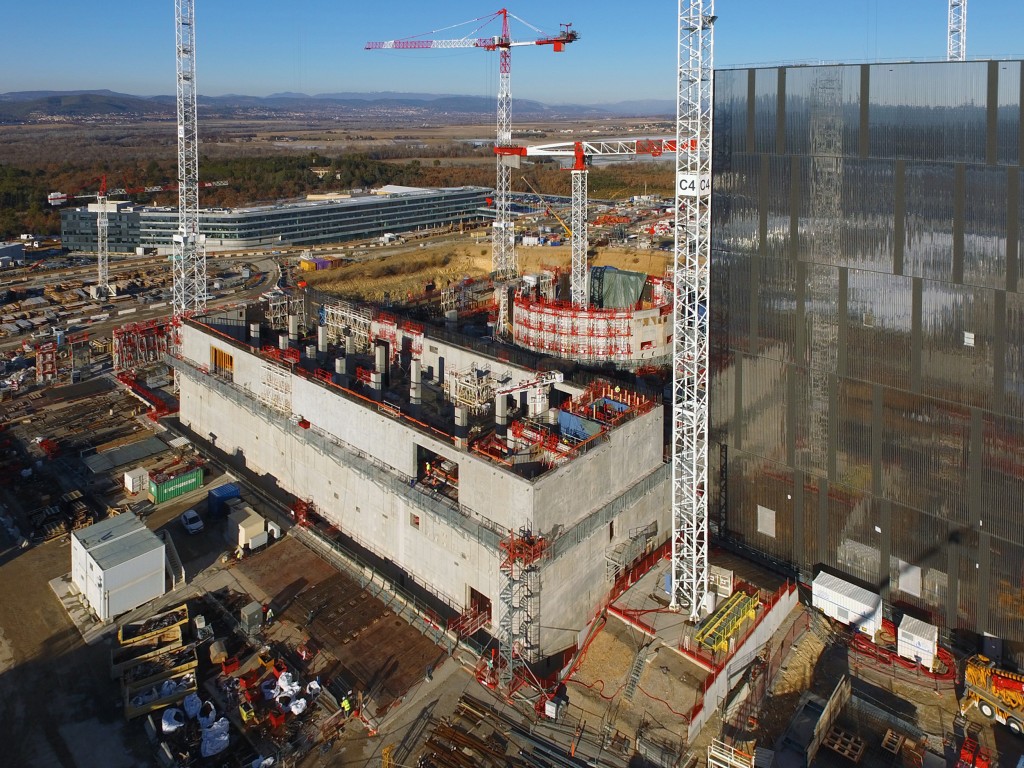
For diagnostic systems
2017-12-04 - The Diagnostics Building is actually five floors (two basement and three above-ground levels). It has reached its maximum height. Photo: ITER Organization/EJF Riche

Tokamak Complex under construction
2017-12-03 - On the left—the Diagnostics Building; in the centre—the Tokamak Building; on the right—the Tritium Building. Photo: ITER Organization/EJF Riche
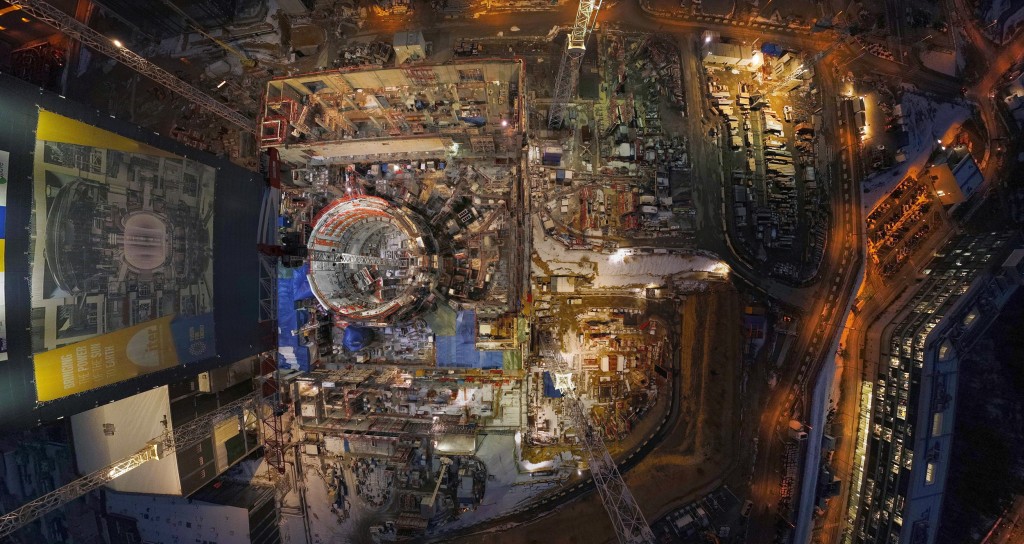
A commanding view
2017-12-03 - Looking deep inside the Tokamak Pit, where machine assembly activities will kick off in 2018. Photo: ITER Organization/EJF Riche

Ten metres tall
2017-11-27 - Second-tier elements have been installed and the lower cylinder now measures 10 metres in height. In the foreground are elements stored for the base of the cryostat.

All the stations
2017-11-27 - While double pancake winding is underway in the foreground, European contractors are preparing the second station—impregnation—for qualification tests.
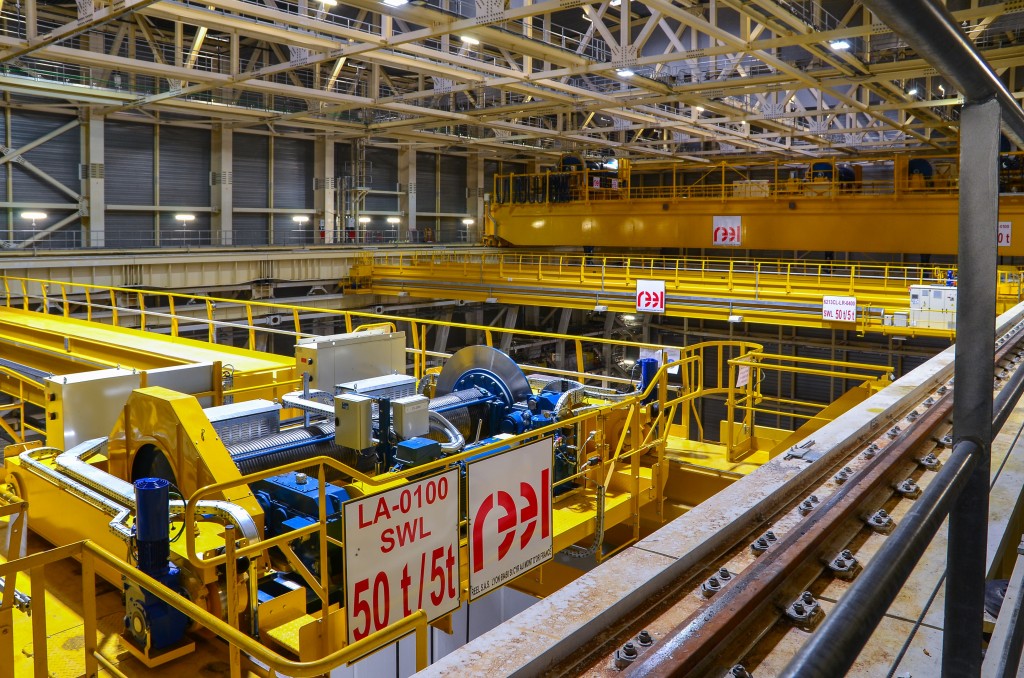
Complex machinery
2017-11-22 - Trolleys and cranes of various capacities fill most of the space in the Assembly Hall rafters. Like a catwalk in a theatre, they host the invisible machinery that makes the production possible.

Cranes galore
2017-11-22 - Cranes galore This striking view takes in the whole lifting system installed in the Assembly Hall: the massive double overhead bridge crane, with a lifting capacity of 1,500 tonnes (top), and its much smaller sibling the 50-tonne auxiliary crane sitting on rails three metres below.

Imagining the future
2017-11-22 - When construction of the Tokamak Building ends, the crane rails will be extended over the machine assembly area, as shown in the poster.

Hooked!
2017-11-22 - This massive hook is one of four, each with a lifting capacity of 375 tonnes, that belong to the double overhead bridge crane installed 43 metres above the floor in the Assembly Hall.
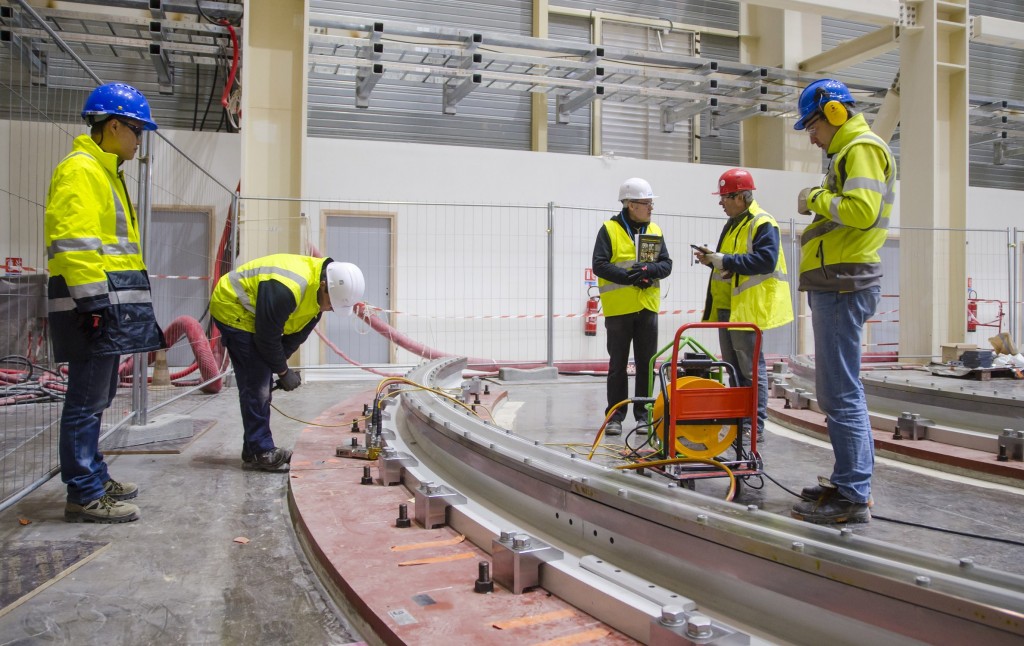
Laying rails, adjusting torque
2017-11-22 - Plates and rails for the first of the twin Titans, SSAT-1, are temporarily in place. Once the torque has been hydraulically adjusted on every bolt and the positioning laser-aligned, the assembly of the 20-metre-high handling tool will begin.

Lifting 1,500 tonnes ... and more
2017-11-22 - Load tests are scheduled to begin in the first week of December. A final test at 25 percent over-capacity (1,875 tonnes) will verify that the flexion of the 43-metre-long bridge crane girders remains within specifications.
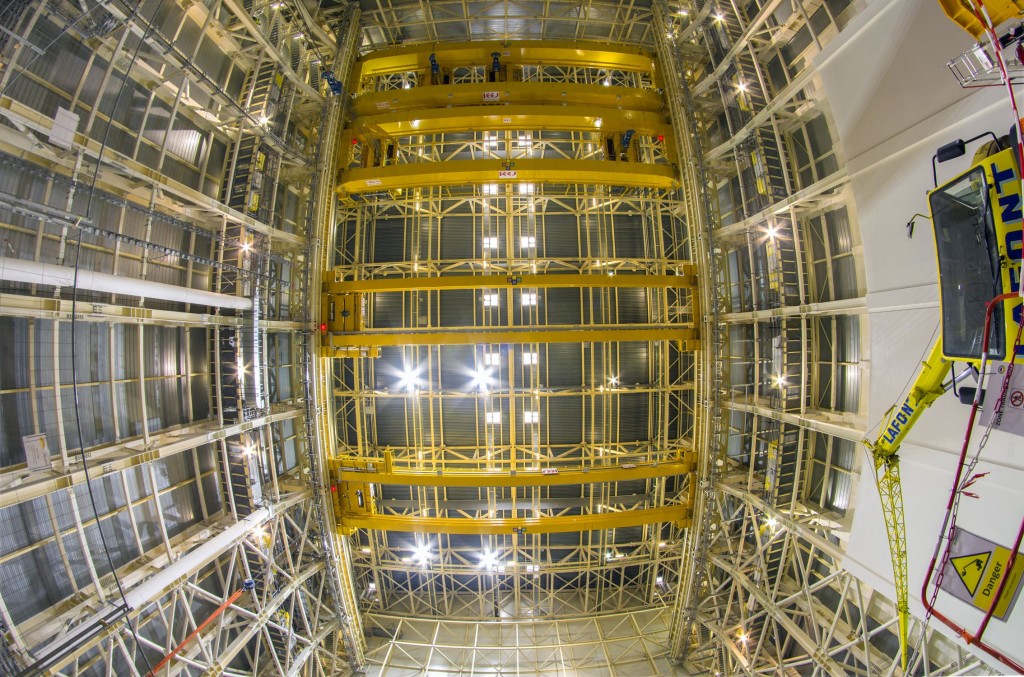
Cranes galore
2017-11-22 - This striking view takes in the whole lifting system installed in the Assembly Hall: the massive double overhead bridge crane, with a lifting capacity of 1,500 tonnes (top), and its much smaller sibling the 50-tonne auxiliary crane sitting on rails three metres below.

Lifting 1,500 tonnes ... and more
2017-11-22 - Load tests are scheduled to begin in the first week of December. A final test at 25 percent over-capacity (1,875 tonnes) will verify that the flexion of the 43-metre-long bridge crane girders remains within specifications.

Vertical assembly begins
2017-11-22 - Questions about grouting raised during the installation of the rails have been resolved, and the first tool segment can be moved into place.

A truly international operation
2017-11-22 - Procured by Korea, the twin SSATs are being assembled by technicians from the French company CNIM. The operation is being closely monitored by quality insurance specialists from the ITER Organization, by ITER's Construction Management-as-Agent contractor MOMENTUM, and by a representative of the manufacturer Taekyung Heavy Industries (THI).

Complex machinery
2017-11-22 - Trolleys and cranes of various capacities fill most of the space in the Assembly Hall rafters. Like a catwalk in a theatre, they host the invisible machinery that makes the production possible.
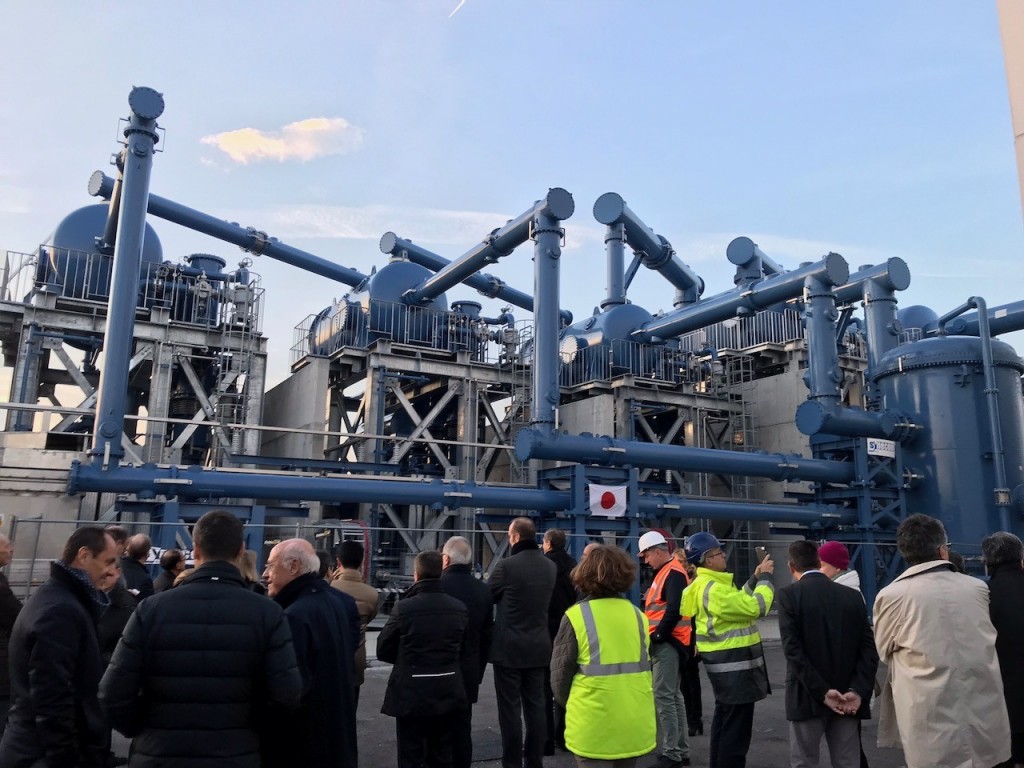
Power supply components
2017-11-20 - The acceleration grid power supply for MITICA is composed of a conversion system that feeds step-up transformers and diode rectifiers. A 1 MV transmission line then connects the power supplies to the injector.
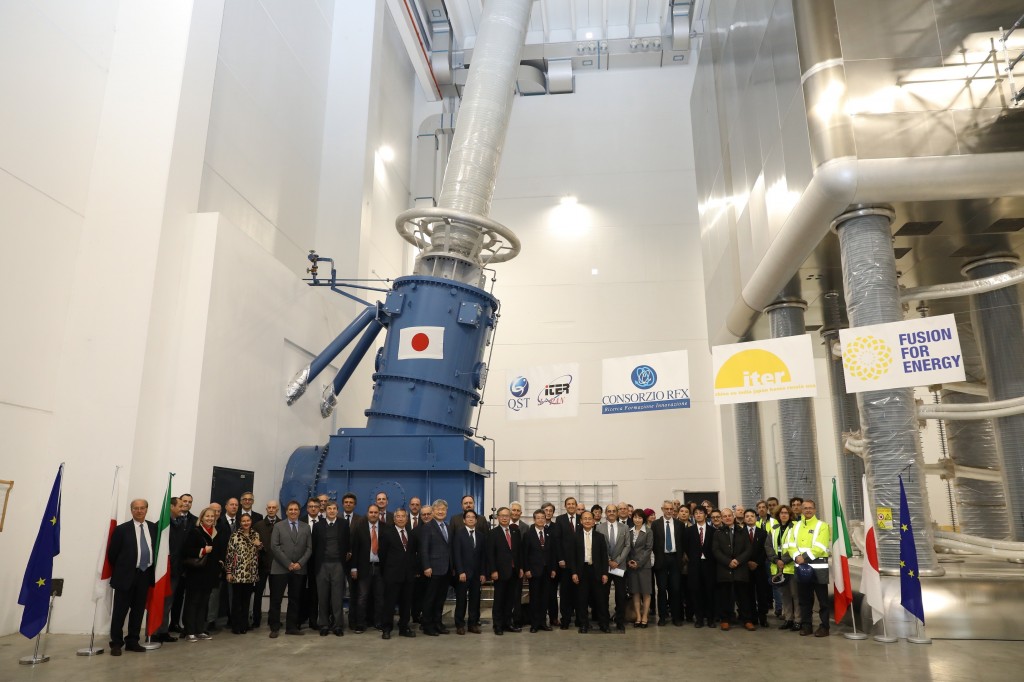
Japan completes deliveries
2017-11-20 - The Japanese Domestic Agency delivers its final contribution to the Neutral Beam Test Facility in November 2017. Over two years, Japan has delivered high-voltage components for the 1 MV power supply system of MITICA, including the megavolt bushing (pictured), the megavolt transmission line and the high voltage part of the megavolt power supply.

Blossoms for the start of the facility
2017-11-20 - A cherry tree gifted by Japan is planted at the test facility site in Padua. It will blossom about the time of facility start-up in spring 2018.

Skids positionned
2017-11-17 - All 18 helium compressor skids have been positioned on their concrete platforms in the cryoplant's Compressor Building.
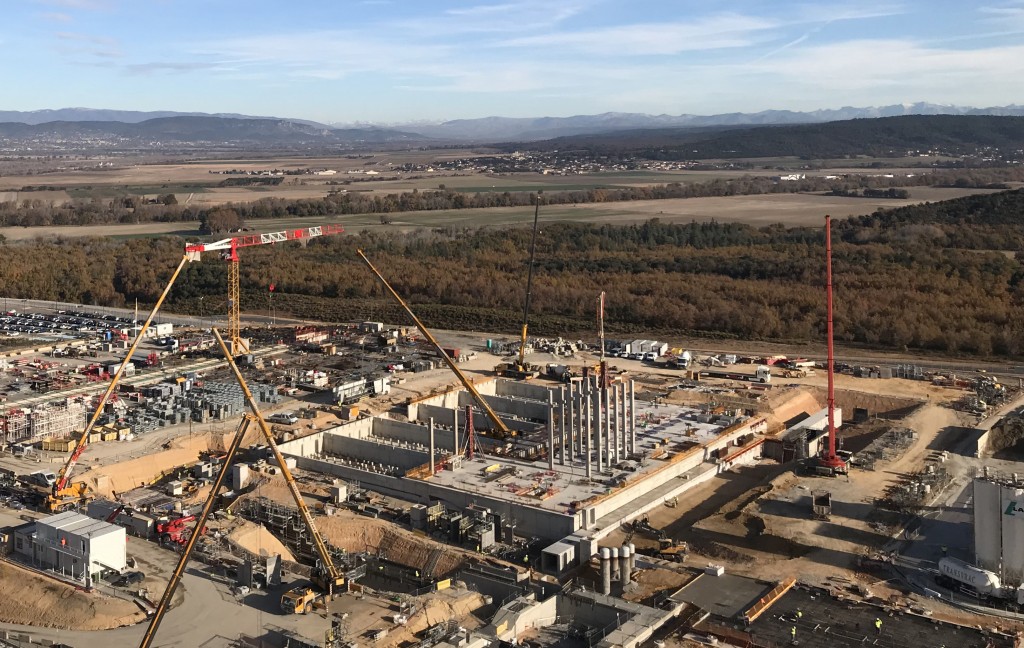
Equipment arriving
2017-11-17 - In addition to batches of piping that have been shipped regularly since 2015, the first equipment is starting to arrive for the heat rejection system. In November, large stop gates were delivered for each of the cold basin compartments, as well as debris screens.

Skids positionned
2017-11-17 - All 18 helium compressor skids have been positioned on their concrete platforms in the cryoplant's Compressor Building.
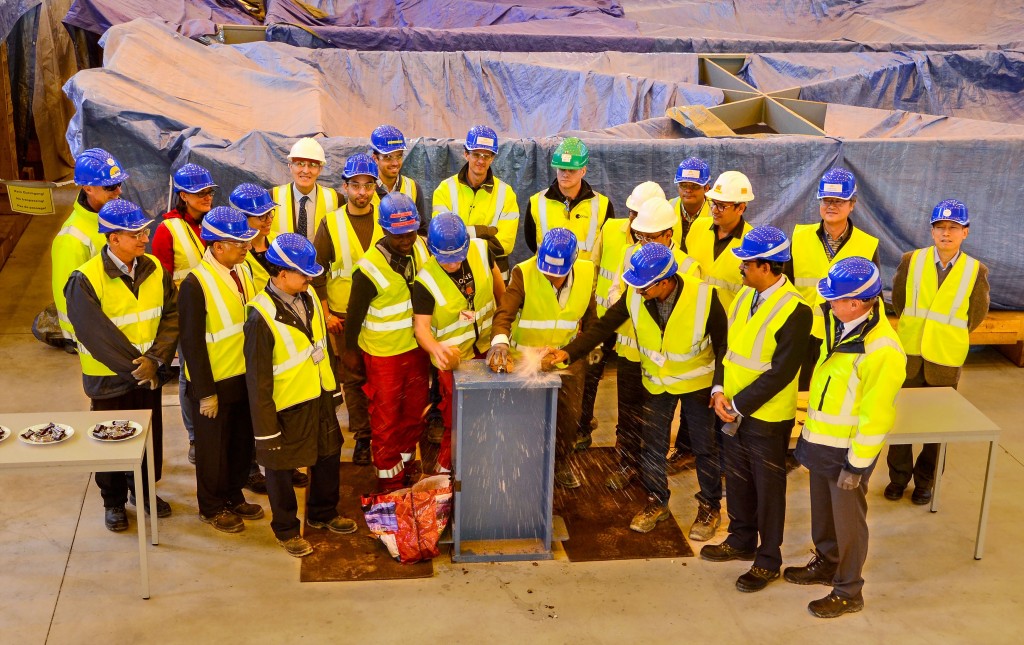
Work begins on the upper part of the base
2017-11-16 - In November, a traditional "coconut ceremony" heralds the start of welding operations on the base section tier two—a 750-tonne sub-component whose pedestal will support the combined mass of the Tokamak and cryostat (23,000 tonnes).
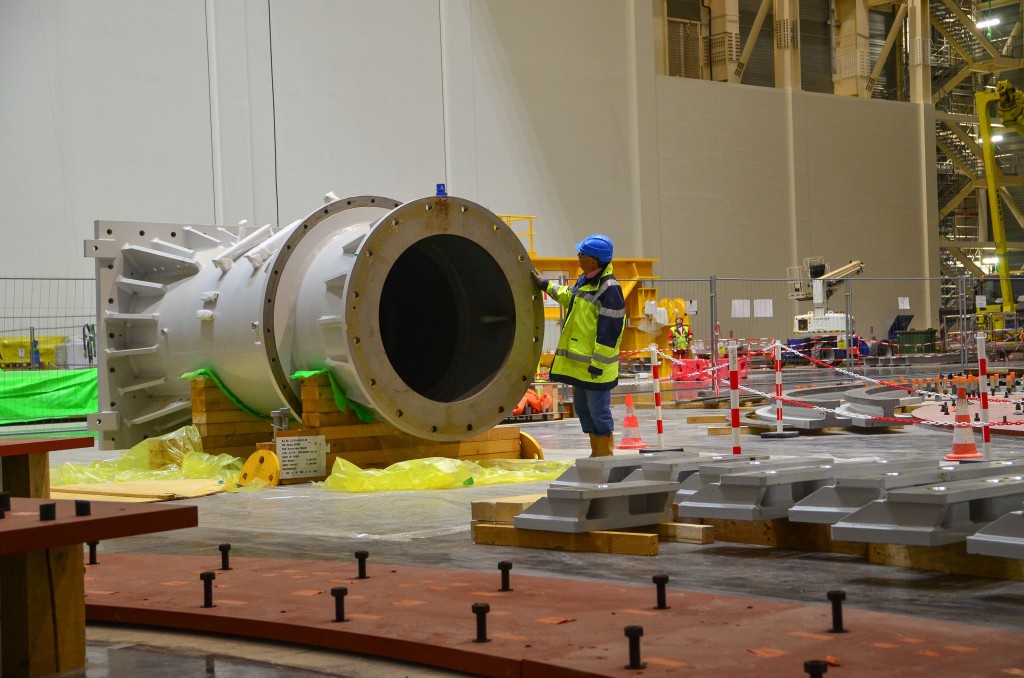
First foot
2017-11-10 - This large element will be the base segment of one of the tool's three huge columns. Three other segments of varying sizes will be stacked on top of it.

Looking beyond the wall
2017-11-10 - A new poster in the Assembly Hall shows how—once the temporary wall is removed—the cranes will travel into the Tokamak Building to deposit their loads.
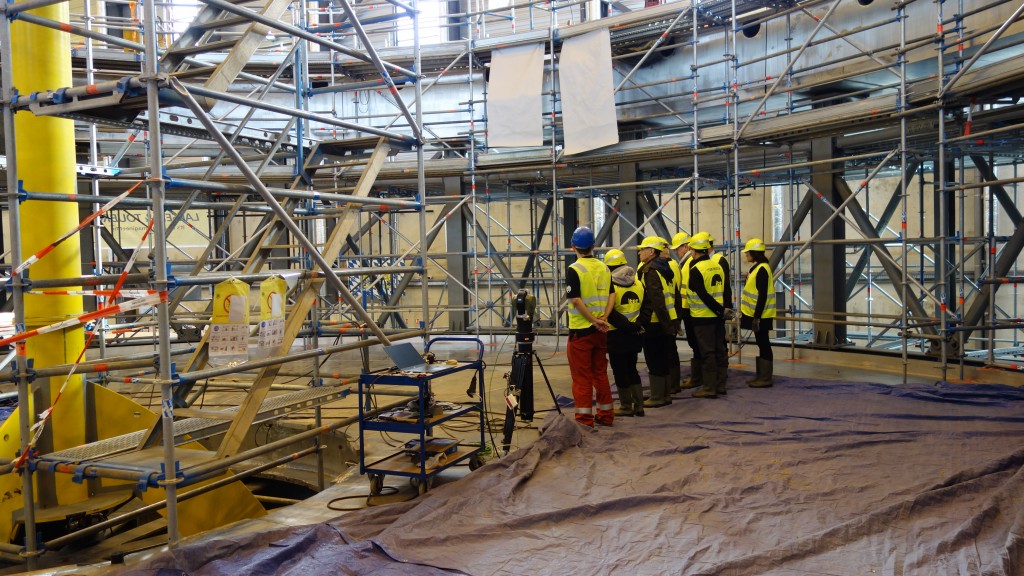
Impressive work, frequent visitors
2017-11-10 - Small groups of visitors to the Cryostat Workshop can be taken out onto tier one of the cryostat base (covered in purple). From there they have a good view on the work to come: welding the tier-two segments, including the heavy rim (shown above their heads here).
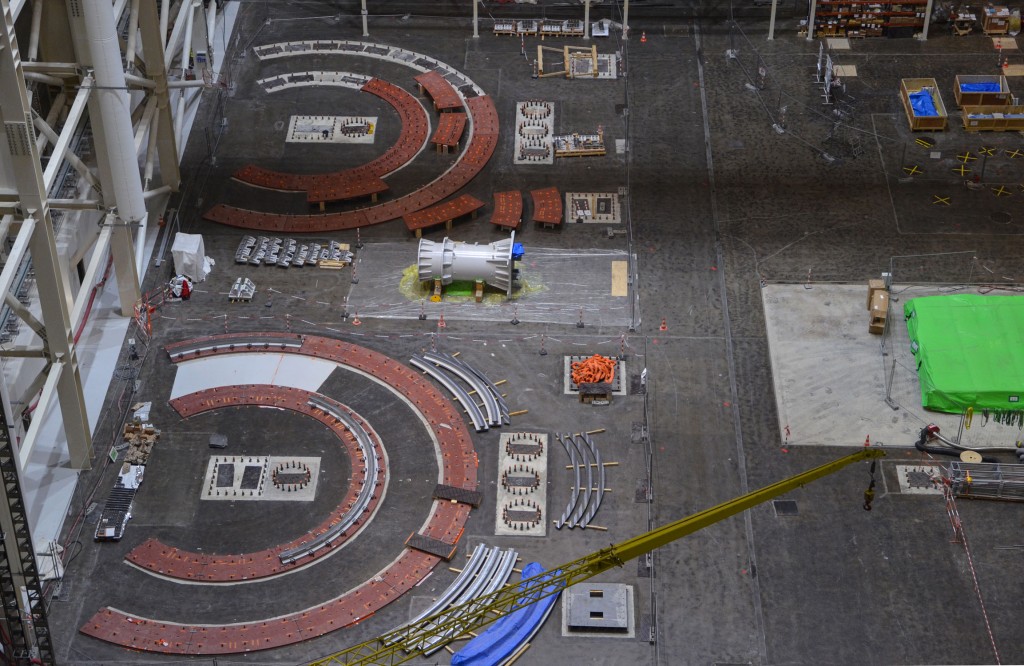
Like an Erector set
2017-11-08 - Everything is laid out for the first stages of assembly of the SSAT tools (for vacuum vessel Sector Sub-Assembly Tool), including the first "foot" of one of the massive columns.

A full view
2017-11-08 - Looking down across the full 97-metre length of the Assembly Hall. The travelling cranes are approximately 45 metres above floor level.
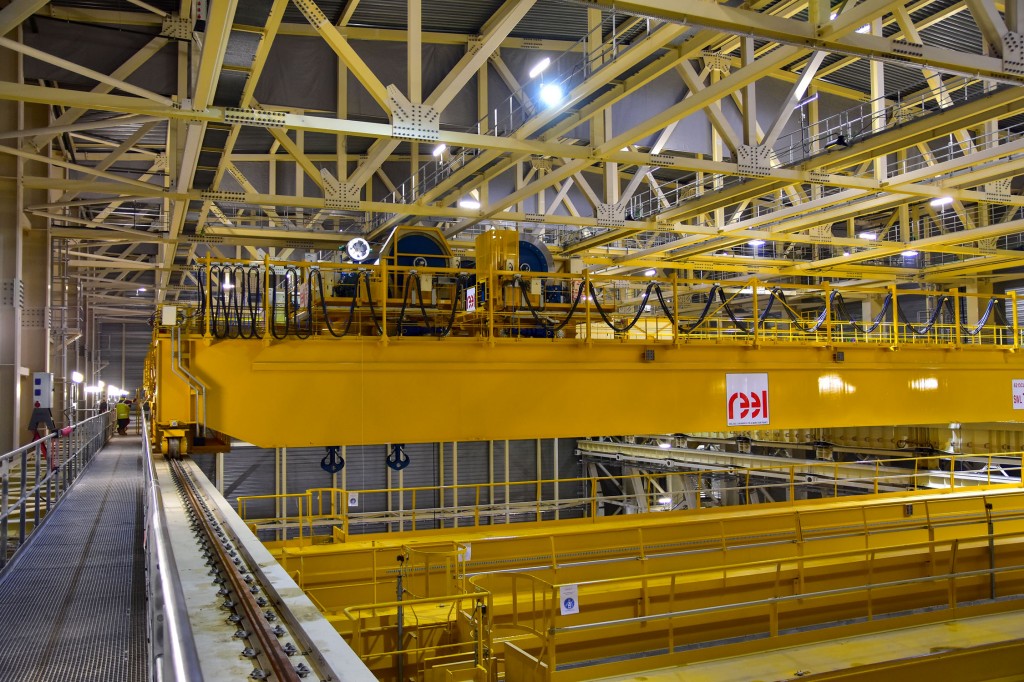
Working as partners
2017-11-08 - Just below the heavy lift cranes are two smaller, more agile cranes capable of lifting 50 tonnes.
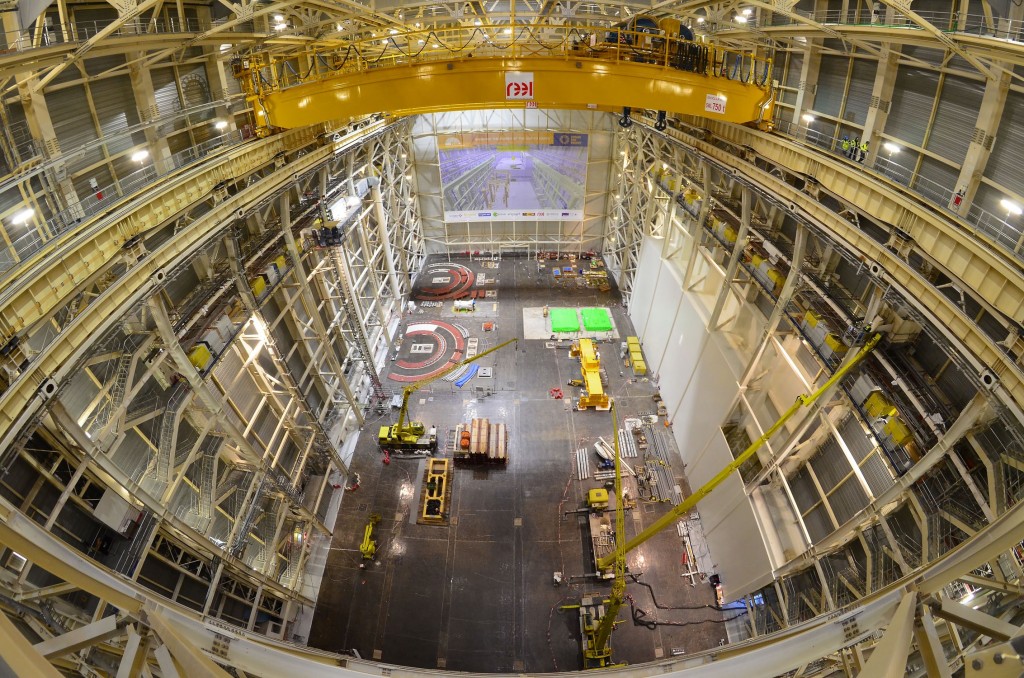
A full view
2017-11-08 - Looking down across the full 97-metre length of the Assembly Hall. The travelling cranes are approximately 45 metres above floor level.

In detail
2017-11-08 - A close-up of one of the 750-tonne cranes, with hooks that are ready to lift 375 tonnes each. Load tests will be run soon as part of the crane's commissioning activities.

High Voltage Hall
2017-11-07 - For MITICA to function, high voltages must be maintained over pulses of 3600 seconds. Pictured: the High Voltage Hall at the ITER Neutral Beam Test Facility.
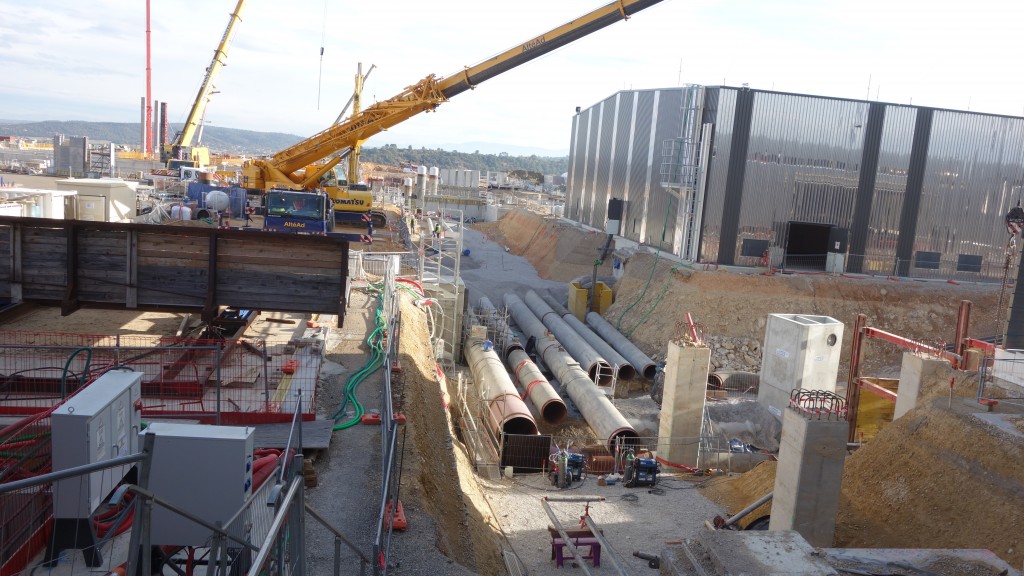
A thruway for pipes
2017-11-07 - These pipes are leading away from the Tokamak Complex to the heat rejection system on the northern corner of the platform. The nominal diameter of largest piping is 2 metres.

News from the Radio Frequency Building
2017-11-07 - Work is underway on the interior partitions and floors of the Radio Frequency Heating Building.
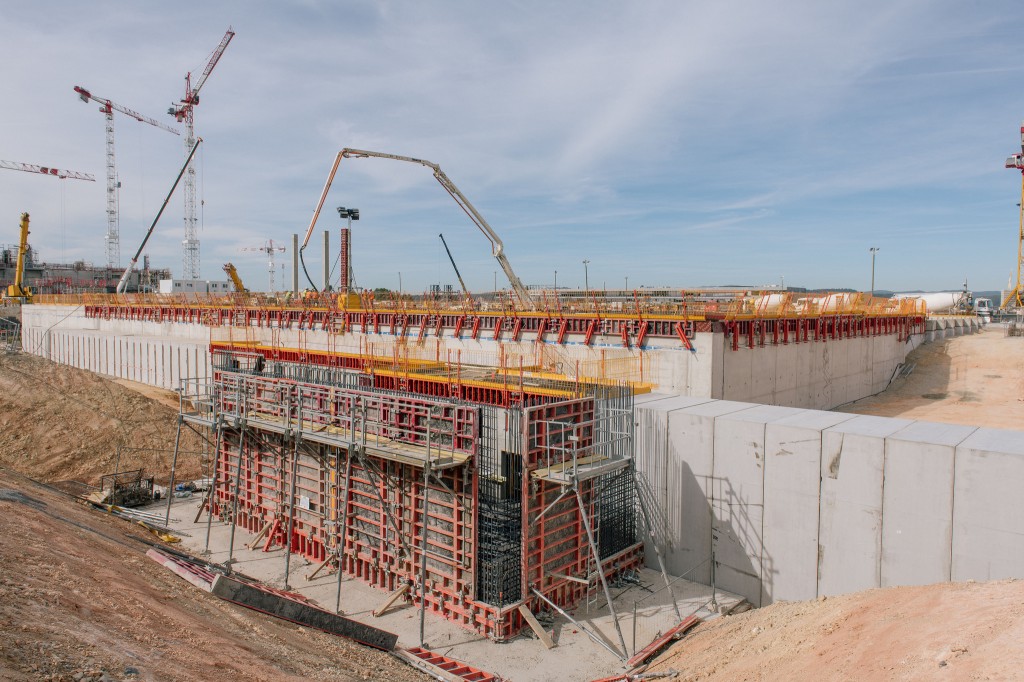
Heat rejection zone
2017-10-26 - On site, the hot and cold basins have been created below platform level and the cold basin area has been turned over to the ITER Organization for installation activities. One of the first activities will be to install metal footings in the cold basin to prepare for the installation of the cooling tower structural members. © Les Nouveaux Médias/SNC ENGAGE
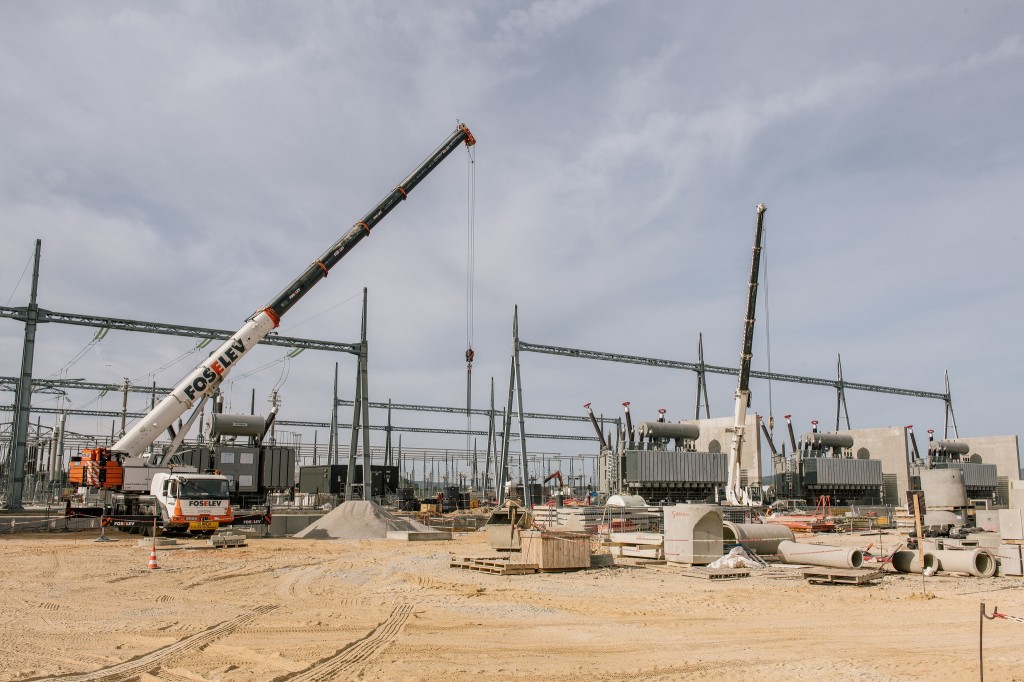
Distributing the power
2017-10-26 - A lot of work is underway on the technical galleries connecting the electrical switchyard to the Magnet Power Conversion buildings and others. © Les Nouveaux Médias/SNC ENGAGE
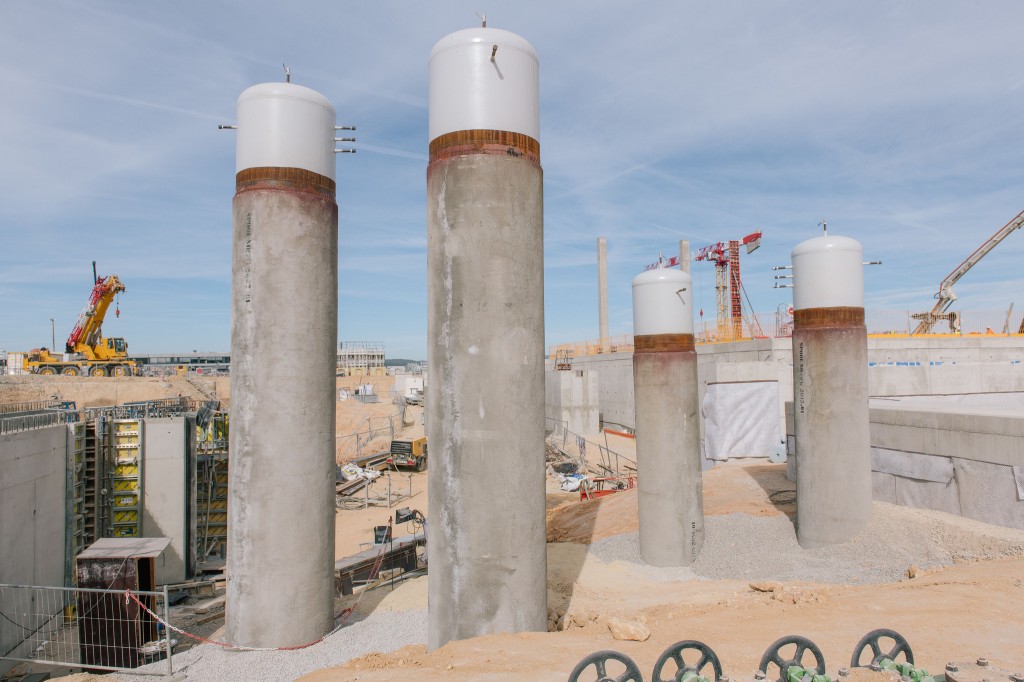
Pipes on hold
2017-10-26 - These pipes supplied by India will distribute cooling water for the heat rejection and component cooling water systems across the site. They are waiting to be connected to the above-ground piping network. © Les Nouveaux Médias/SNC ENGAGE
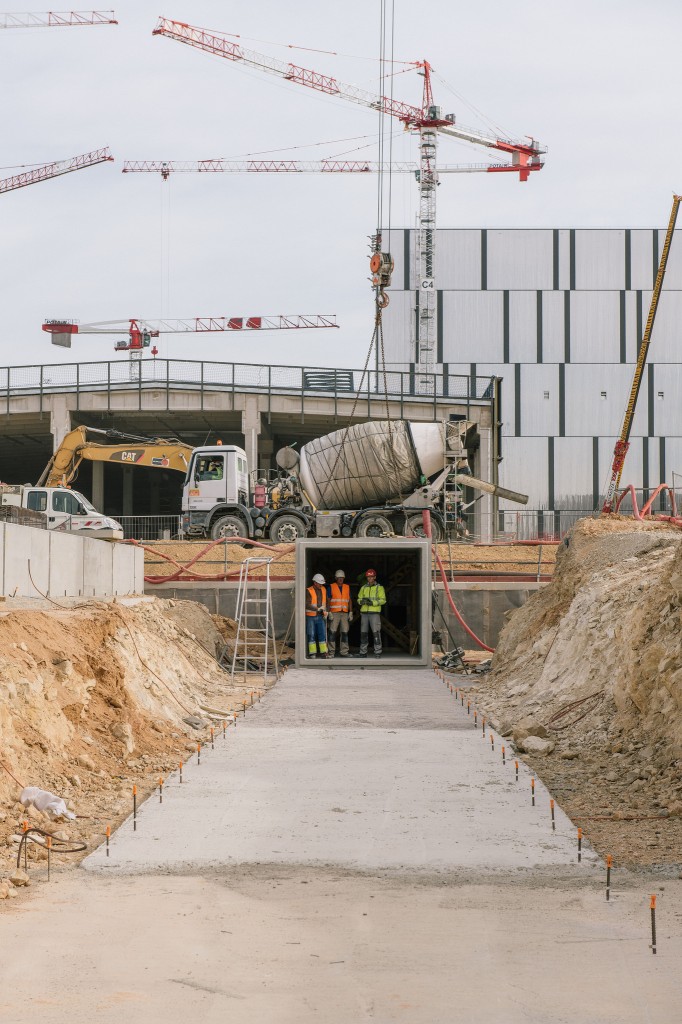
Technical galleries underway
2017-10-26 - Work is underway on—but also underneath—the ITER platform. © Les Nouveaux Médias/SNC ENGAGE

An evaporative process
2017-10-26 - Cooling water from the ITER facility will be pumped to the top of the cooling tower where it will slowly fall through layers of corrugated plastic fill and be subjected to a strong updraft of air. What doesn't evaporate will be collected in the cold basin, pictured. © Les Nouveaux Médias/SNC ENGAGE

Progress in the conversion buildings
2017-10-26 - Cable trenches have been created in the 150-metre-long Magnet Power Conversion buildings. © Les Nouveaux Médias/SNC ENGAGE

Cold basin work underway
2017-10-26 - Looking over the cold basin and its five compartments. The 20-metre-tall cooling tower will be installed over this basin. © Les Nouveaux Médias/SNC ENGAGE
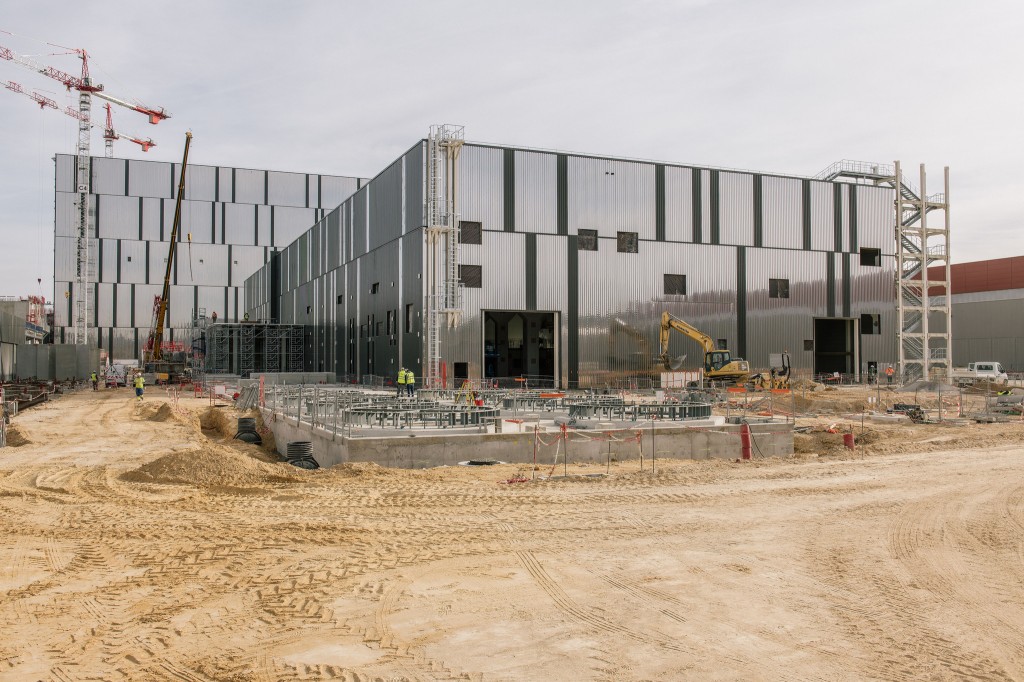
Tank storage area
2017-10-26 - A level area and footings have been created for the helium and nitrogen storage tanks outside of the cryoplant. © Les Nouveaux Médias/SNC ENGAGE
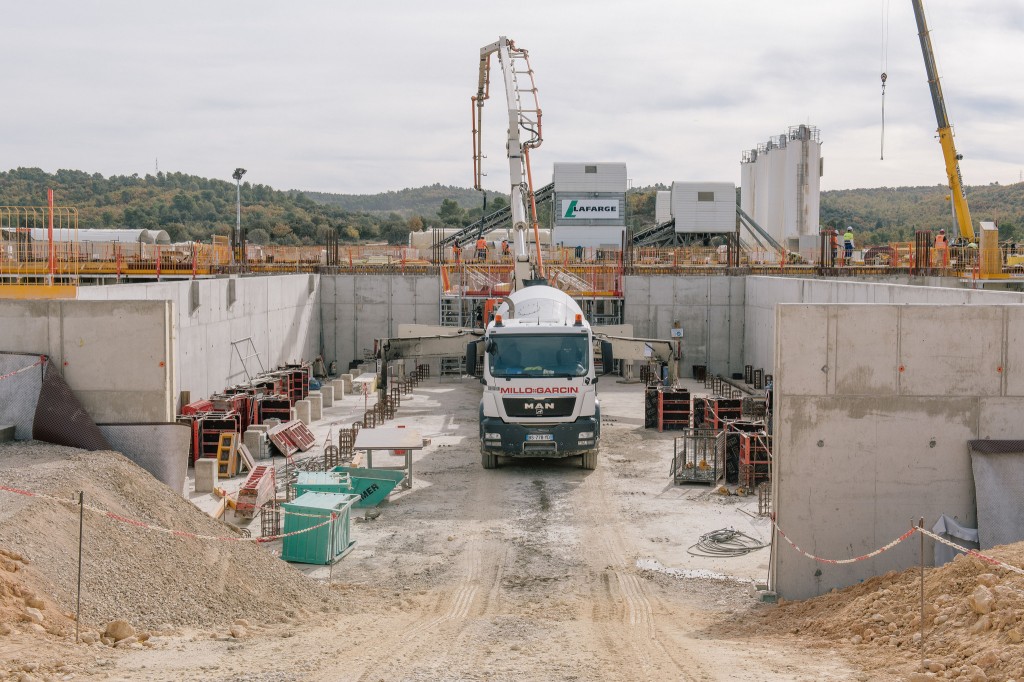
Under the cooling towers
2017-10-26 - The cooling tower cold basin has five compartments. Pictured: concrete pouring underway in the middle compartment in October. © Les Nouveaux Médias/SNC ENGAGE

Distributing the power
2017-10-26 - A lot of work is underway on the technical galleries connecting the electrical switchyard to the Magnet Power Conversion buildings and others. © Les Nouveaux Médias/SNC ENGAGE
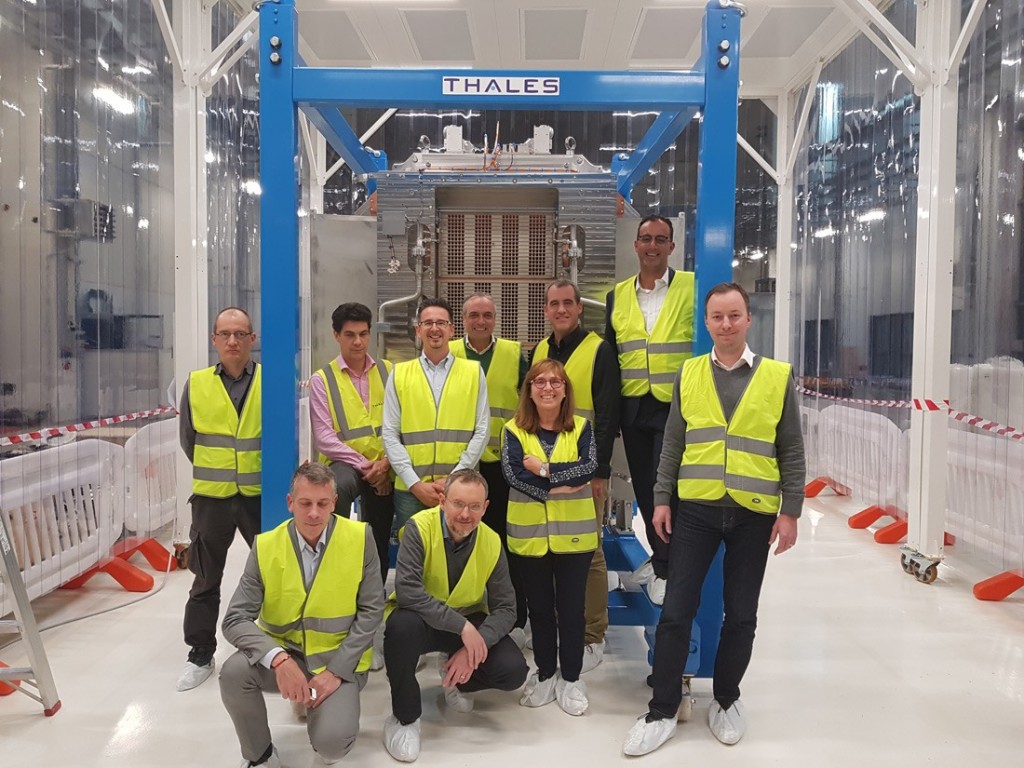
Test period begins
2017-10-22 - The SPIDER beam source has been placed temporarily in a clean room for a series of site acceptance tests. SPIDER is scheduled to begin operating in April 2018. ©Thales
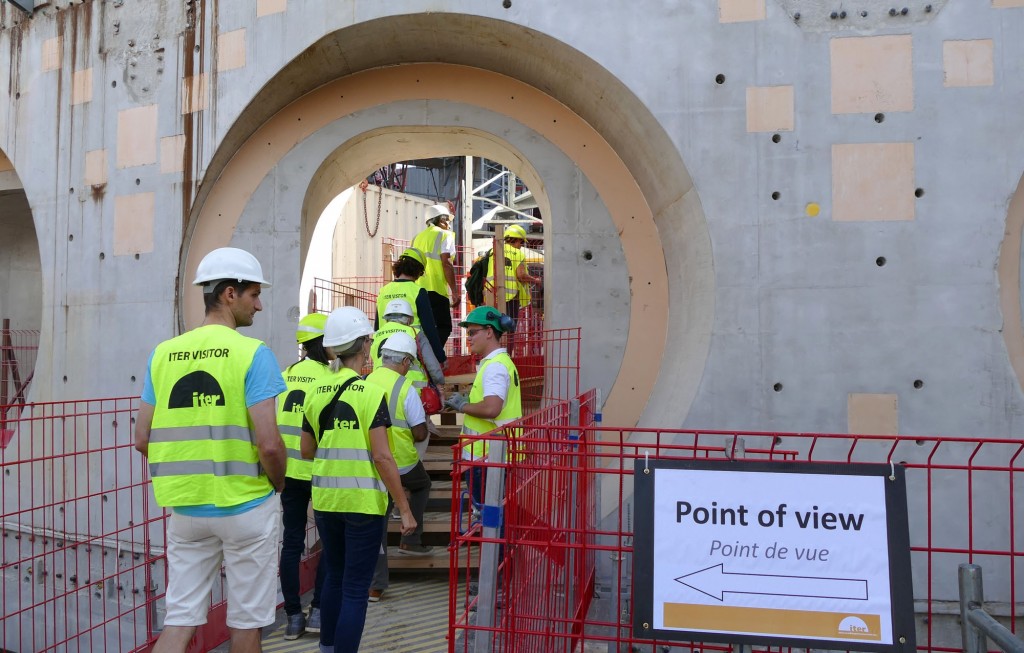
Through the magic door
2017-10-21 - Visitors entered the bioshield through an opening that will accommodate one of the neutral beam injectors, used to heat the plasma.
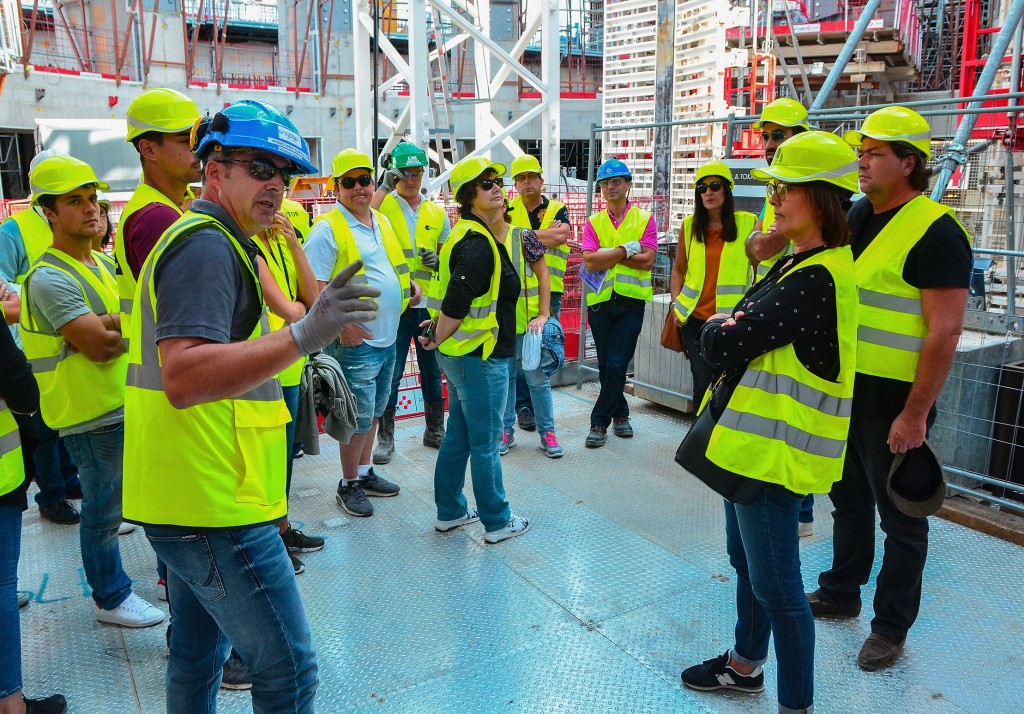
Visitors on a Saturday
2017-10-21 - During the ITER Open Doors Day on 21 October visitors were invited to walk out into the centre of the bioshield, where European Domestic Agency contractors were on hand to give explanations.
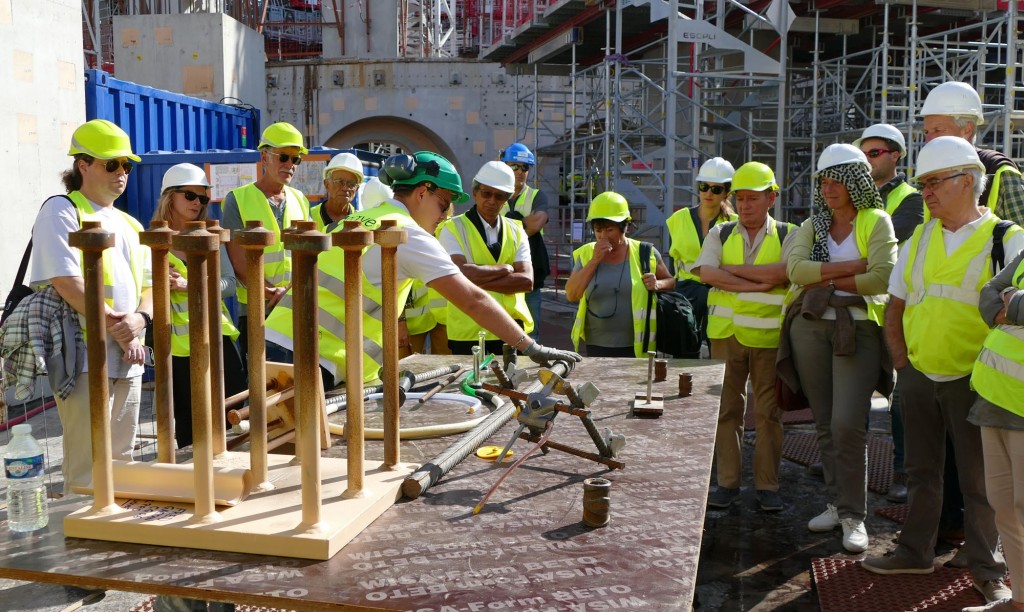
A table full of building materials
2017-10-21 - As part of explanations, visitors were shown the different elements used in Tokamak Complex construction ... including some of the thickest rebar on the market.

That ... is a large hook
2017-10-17 - Four giant hooks like this one will hang from the double overhead cranes in the Assembly Hall, each one with a lift capacity of 375 tonnes.
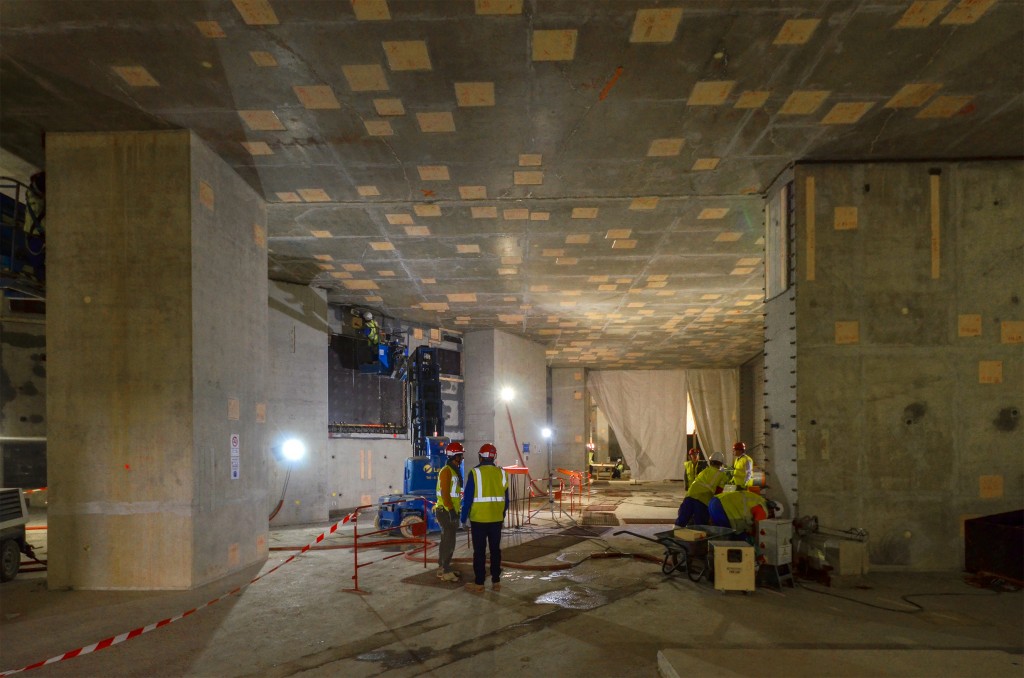
Non-random constellations
2017-10-17 - Each one of the embedded plates in the basement of the Diagnostics Building has been placed with care and its final position measured through laser techniques. Position will be important when it comes to attaching the systems and components planned for this level.

A peculiar opening
2017-10-17 - Most openings in the bioshield are perfect squares (4 m x 4 m). This one and three others, however, stand out due to their peculiar oval or round shapes—a distinctive sign that signals them out as the openings for the ITER neutral beam injectors.

The heaviest component
2017-10-12 - The six segments of the cryostat base, tier two, have been removed from storage and positioned on pillars above tier one for alignment and welding. The completed cryostat base will create the heaviest single component of the ITER machine ... and one that the Assembly Hall cranes have been sized for.

Act II for the cryostat base
2017-10-12 - Welding on the first part of the cryostat base (seen here wrapped in purple) has been successfully completed. Seen directly above, from the inside, is the rim of the six tier two segments that have been carefully aligned.
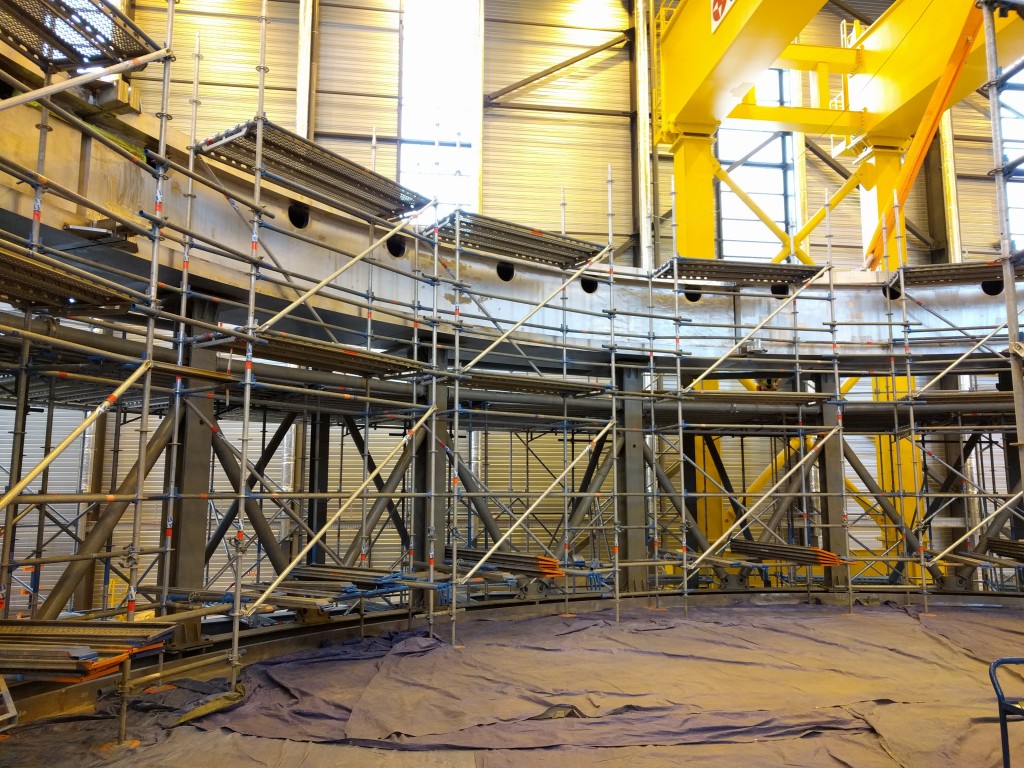
Upper rim of the base
2017-10-12 - The upper rim of the cryostat base has been installed over the completed lower disk. Work is underway to carefully align the segments.

A pedestal for the machine
2017-10-12 - When machine assembly is completed, it won't be a worker sitting here, but the Tokamak itself. These pedestal rings (part of tier two of the cryostat base) will support over 20,000 tonnes of dead weight, including the other cryostat sections, the vacuum vessel and magnets. Pictured here, a technician from Larsen & Toubro contractor MAN is taking precise measurements to align the segments of the base section (tier two).

A giant ring
2017-10-12 - In the Cryostat Workshop on site, two sections of the cryostat are now under assembly. Here, the team stands inside the ring of the lower cylinder, tier one (30 metres in diameter). An initial pass of the welding tools has all segments now joined; the second tier segments—en route now from India—will top the first, creating a 10-metre-high structure.

Lower cylinder: waiting for tier two
2017-10-12 - The lower cylinder will weigh 375 tonnes and measure 10 metres in height when tier two is added to tier one. Indian contractor Larsen & Toubro is responsible for the manufacturing design, fabrication and assembly of the ITER cryostat.

Seen in profile
2017-10-11 - The upper part of the cryostat base is seen here in profile, with its wide rim and its interior curved structure.

Transformers/converters
2017-10-11 - Between the two buildings, transformers will be installed for the transformation/conversion of the power supply destined for the superconducting magnets. The transformer bays are already in place.
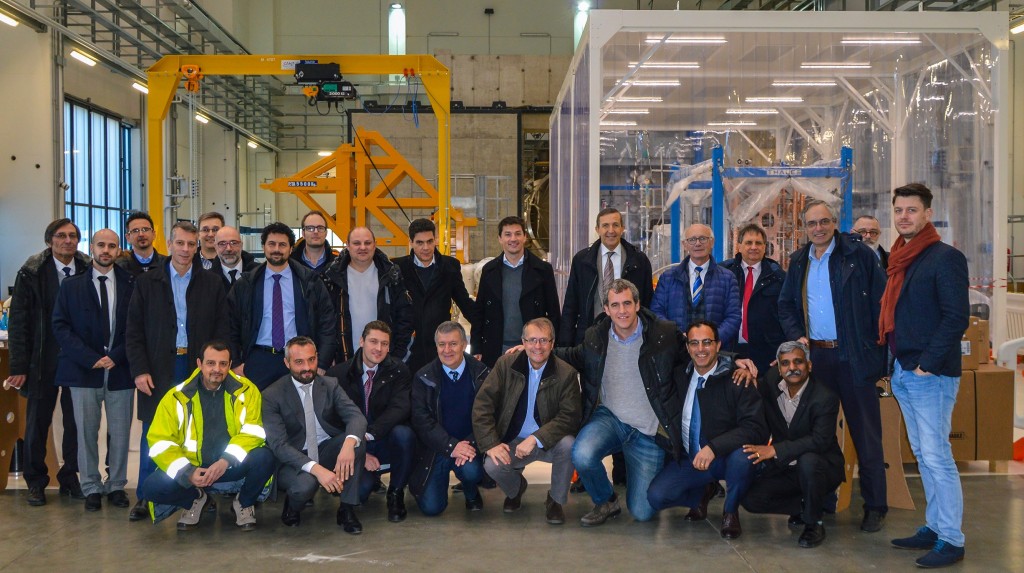
SPIDER: beam source delivered
2017-10-09 - A ceremony was held in October 2017 for the delivery of the beam source at Consorzio RFX. Present were representatives of the ITER Neutral Beam Section, the European Domestic Agency (responsible for the beam source procurement), facility host Consorzio RFX, and manufacturer Thales.

Like a giant bird's nest
2017-10-08 - Concrete pouring is about to begin on the third above-ground level of the ITER bioshield (L3).
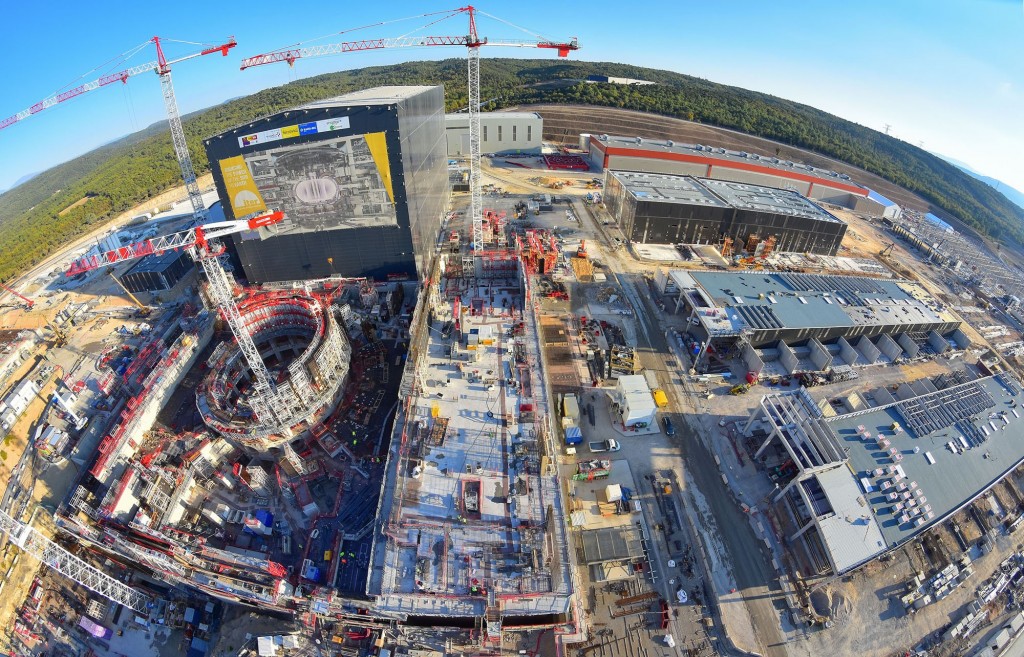
Early October on site
2017-10-08 - The ITER platform in early October, with work advancing on the Tokamak Complex, the twin Magnet Power Conversion buildings, and the cryoplant (counter clockwise).

Pouring the "mega" columns
2017-10-08 - Eighteen massive columns will provide structural support to the different levels of the Tokamak Complex; six among them will have the additional role of supporting the assembly crane rails. At the L2 level of the Tokamak Building, concrete is being poured into one of these "mega columns."

Cryoplant project
2017-10-08 - The cryoplant (adjacent to the red-topped building) is all closed up. An interior fire wall separates the building into two spaces. Work is underway on the exterior area for gas storage.

In the heart of Haute-Provence
2017-10-08 - Scrubland and forest, rounded hills and perched villages, the Alps half-masked by a blue haze ... the landscape that extends beyond the ITER site is typical of Haute-Provence. Looking north on a clear day the view extends all the way to the Massif des Écrins, a mountain range 200 kilometres distant with summits at more than 4,000 metres.

Looking through
2017-09-30 - The Tokamak Complex basement is visible through an opening in the bioshield lid. © Les Nouveaux Médias/SNC ENGAGE

The C1 crane
2017-09-30 - In the centre of it all: the C1 crane, which stands where the Tokamak will one day stand. © Les Nouveaux Médias/SNC ENGAGE

Parallel projects
2017-09-30 - The walls of the Tokamak Building are higher now by one level than those of the Tritium Building (foreground). © Les Nouveaux Médias/SNC ENGAGE

T alley
2017-09-30 - The first four transformers arrived from China in October and will be installed in these bays. © Les Nouveaux Médias/SNC ENGAGE

Northern portion
2017-09-30 - The heat rejection zone is situated on the northern portion of the platform between the concrete batching plant (far end) and the future ITER Control Building (area currently used for storage, foreground). © Les Nouveaux Médias/SNC ENGAGE
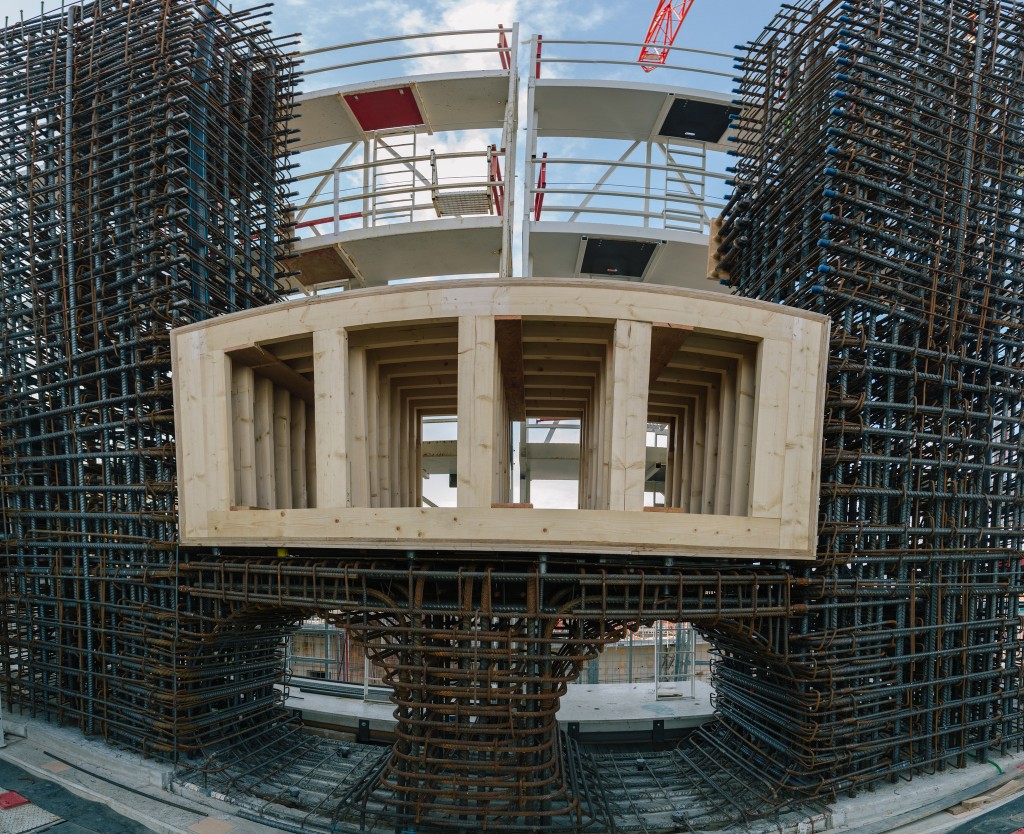
Interesting shapes
2017-09-30 - In the upper levels of the bioshield, openings are reserved for the passage of equipment. © Les Nouveaux Médias/SNC ENGAGE
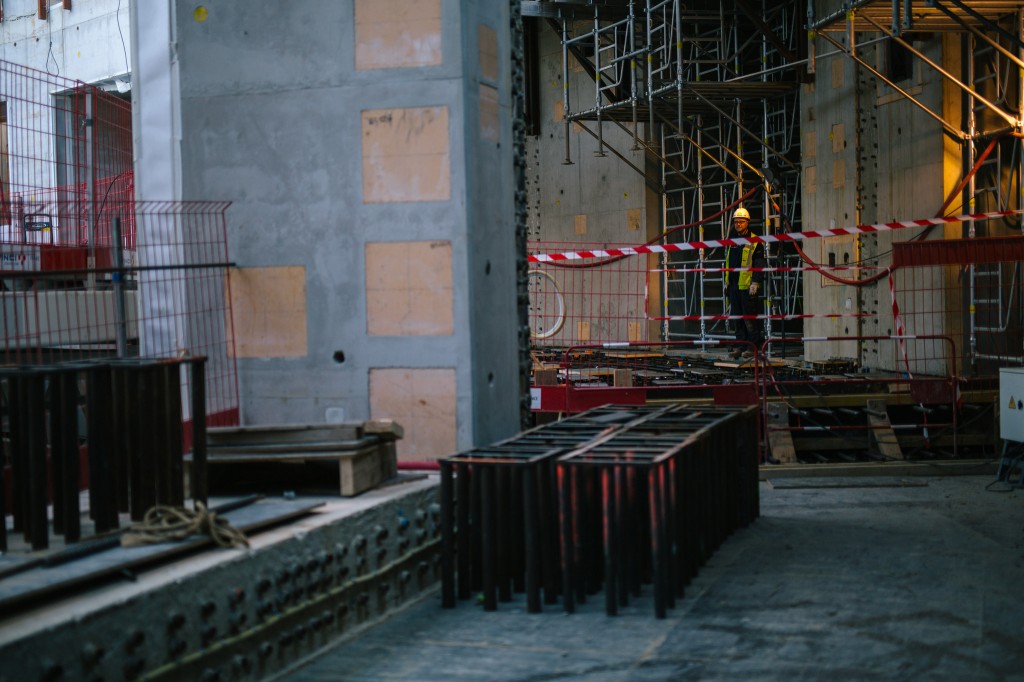
Plates galore
2017-09-30 - Embedded plates stud the floors, walls, columns and ceilings of the Tokamak Complex—more than 100,000 in all. © Les Nouveaux Médias/SNC ENGAGE
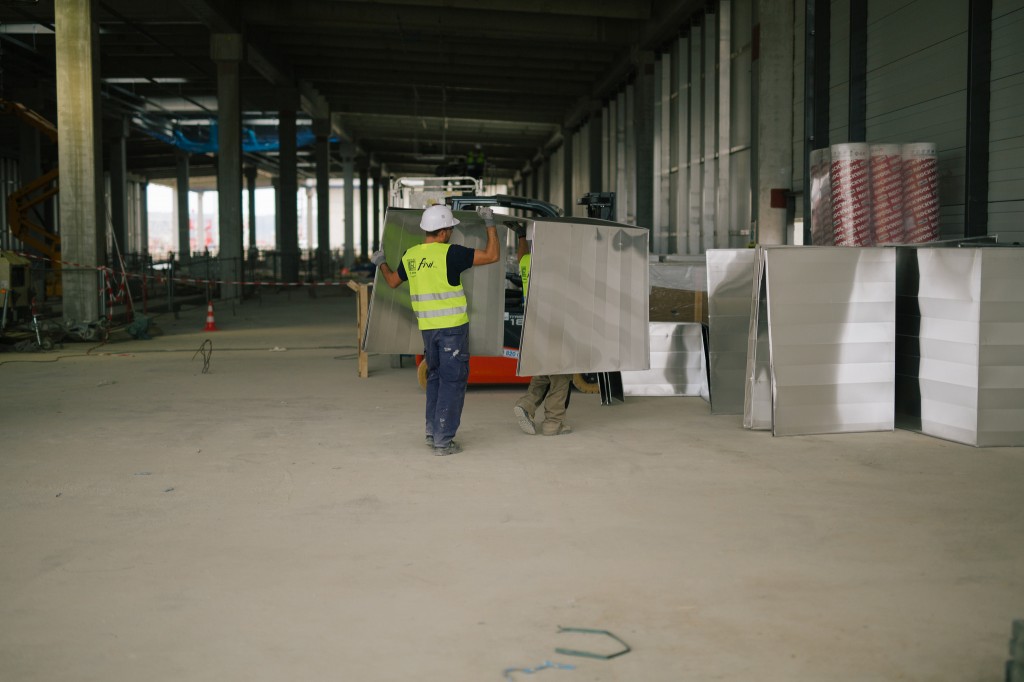
Lifting and storing
2017-09-30 - Materials storage in one of the Magnet Power Conversion buildings. © Les Nouveaux Médias/SNC ENGAGE

ITER artwork
2017-09-30 - Embedded plates are positioned ... very precisely ... before the concrete pouring team can move in. © Les Nouveaux Médias/SNC ENGAGE
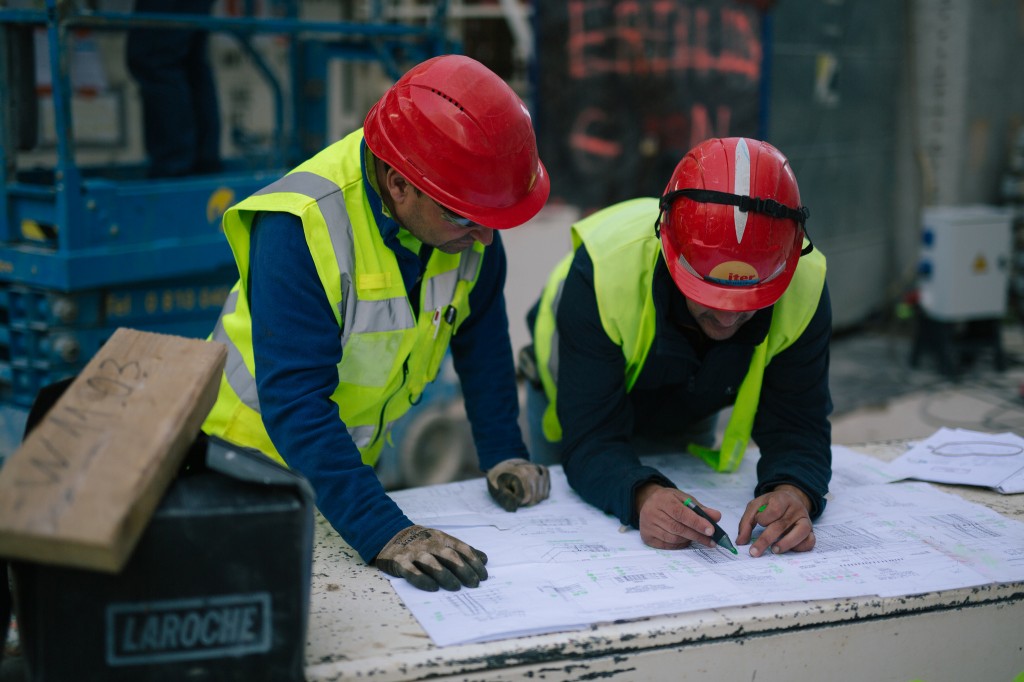
The red hats
2017-09-30 - Site foremen and women can be identified by their red hardhats. © Les Nouveaux Médias/SNC ENGAGE
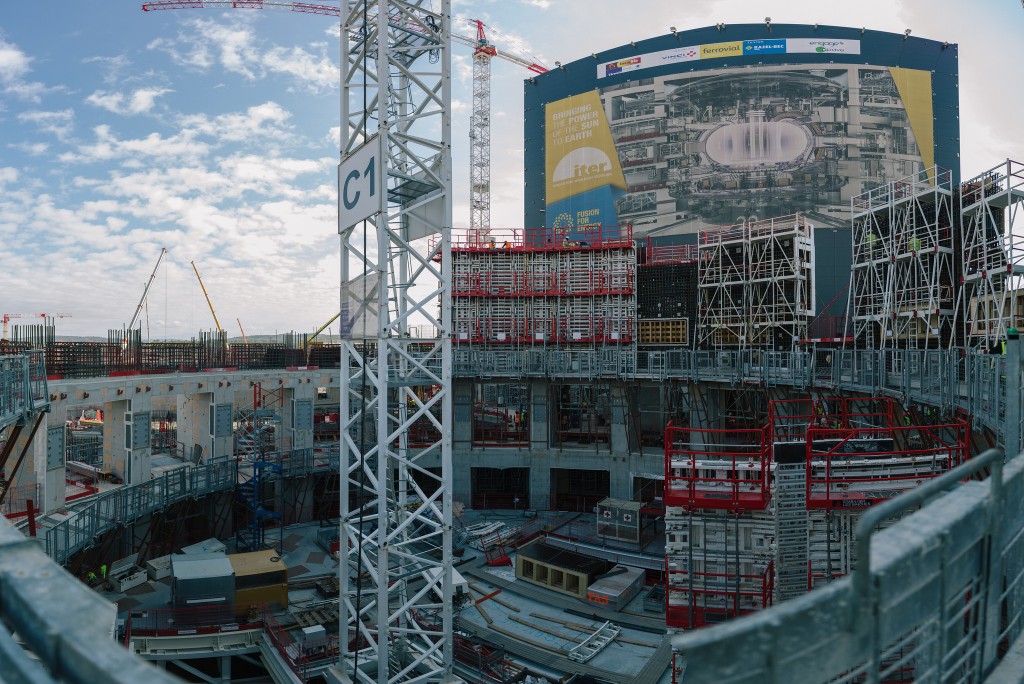
Climbing
2017-09-30 - On the perfect circle of the bioshield (stretched out here by the camera's lens) two new levels are under construction: L3 and L4. © Les Nouveaux Médias/SNC ENGAGE
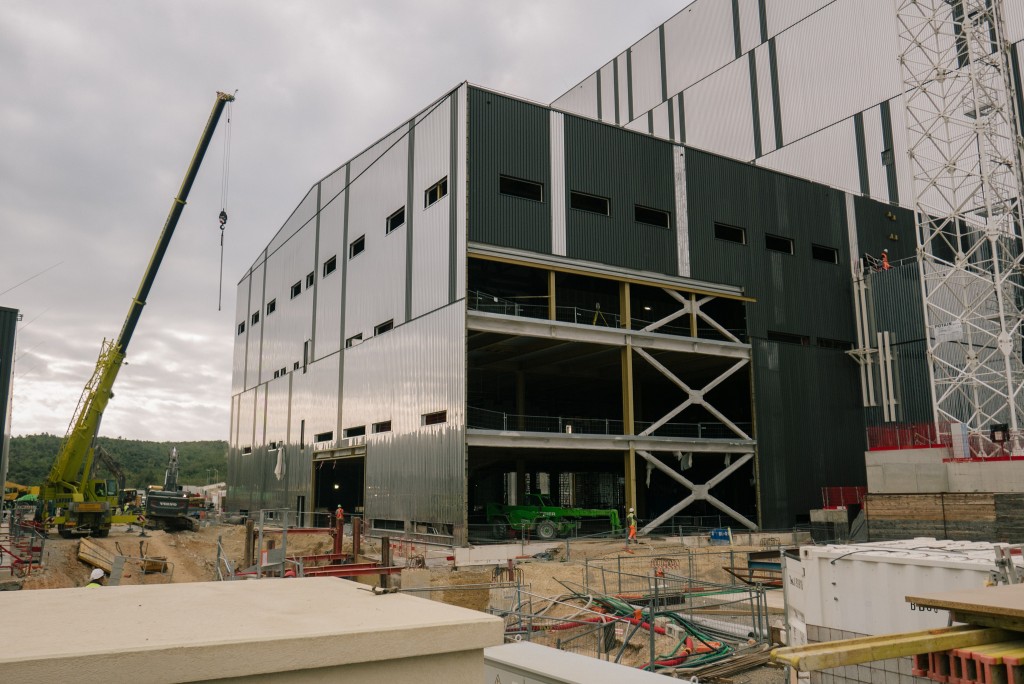
Waves generated here
2017-09-30 - Microwaves and radiofrequency waves generated in this building by the electron cyclotron and the ion cyclotron heating systems will travel along waveguides to the Tokamak. © Les Nouveaux Médias/SNC ENGAGE
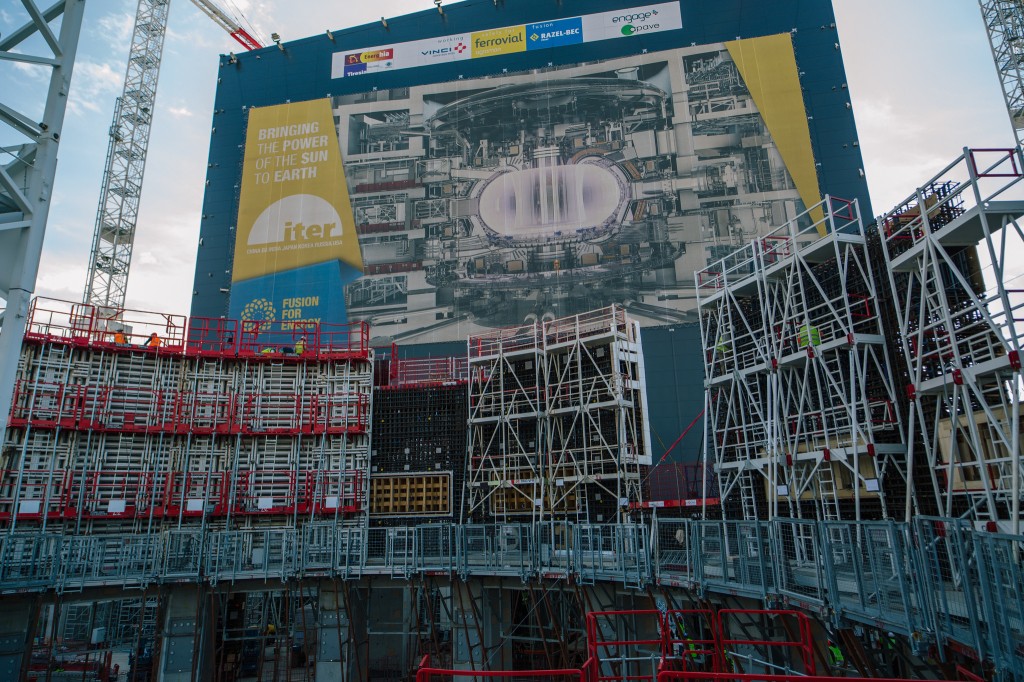
Bioshield: work proceeds on level 4
2017-09-30 - Formwork is in place for Level 4 (L4) concrete pouring. © Les Nouveaux Médias/SNC ENGAGE
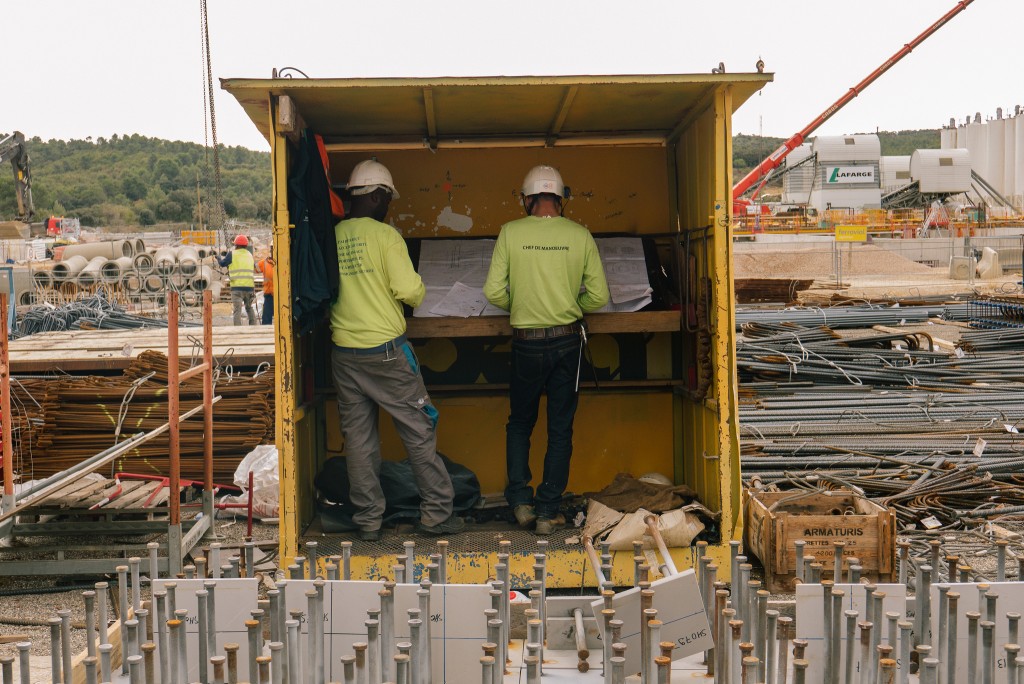
Under cover
2017-09-30 - The day's blueprints are kept out of the rain and wind ... © Les Nouveaux Médias/SNC ENGAGE

Everything ready
2017-09-30 - The transformer bays are ready to receive equipment. © Les Nouveaux Médias/SNC ENGAGE
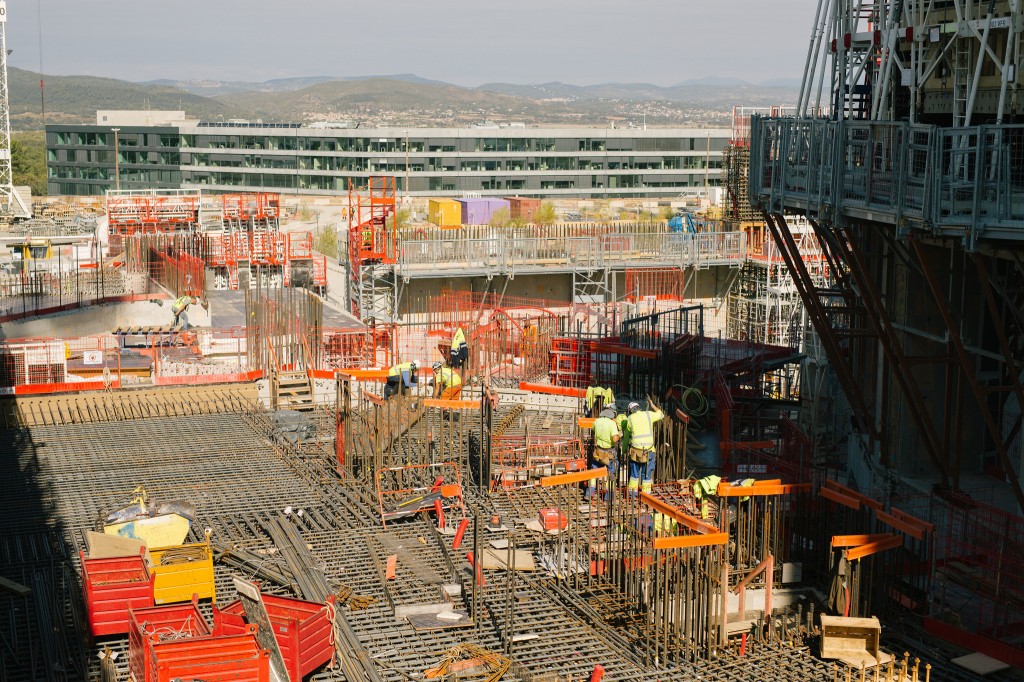
In late September
2017-09-30 - Looking from the Diagnostics Building towards ITER Headquarters. © Les Nouveaux Médias/SNC ENGAGE
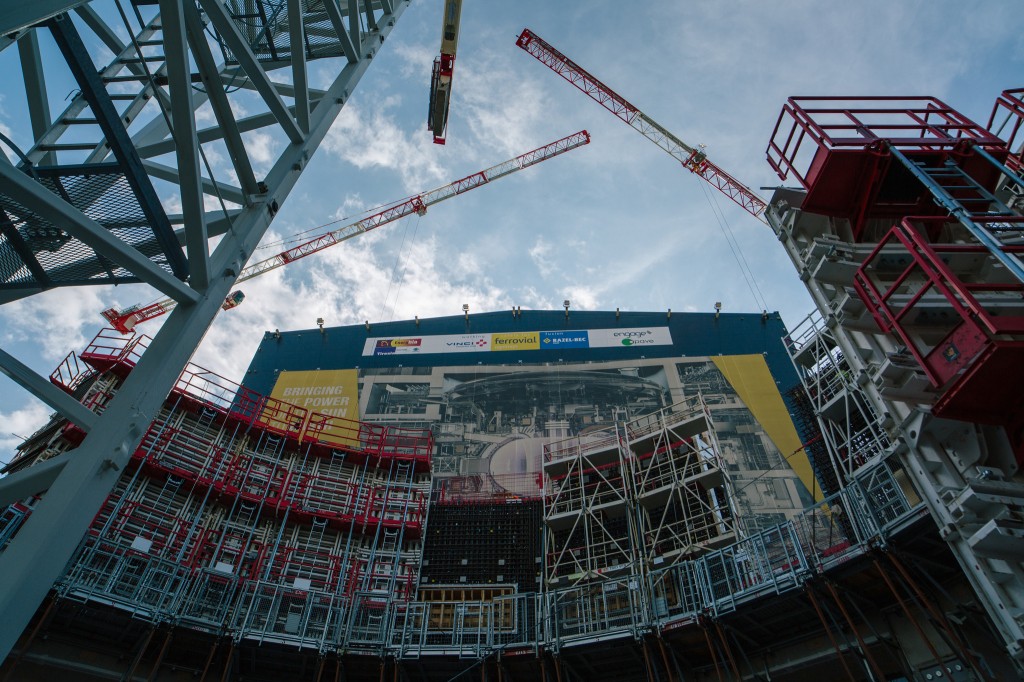
Last bioshield levels
2017-09-30 - Formwork advances for the L4 and L5 levels of the bioshield in September. When they are in place, the bioshield will be complete. © Les Nouveaux Médias/SNC ENGAGE
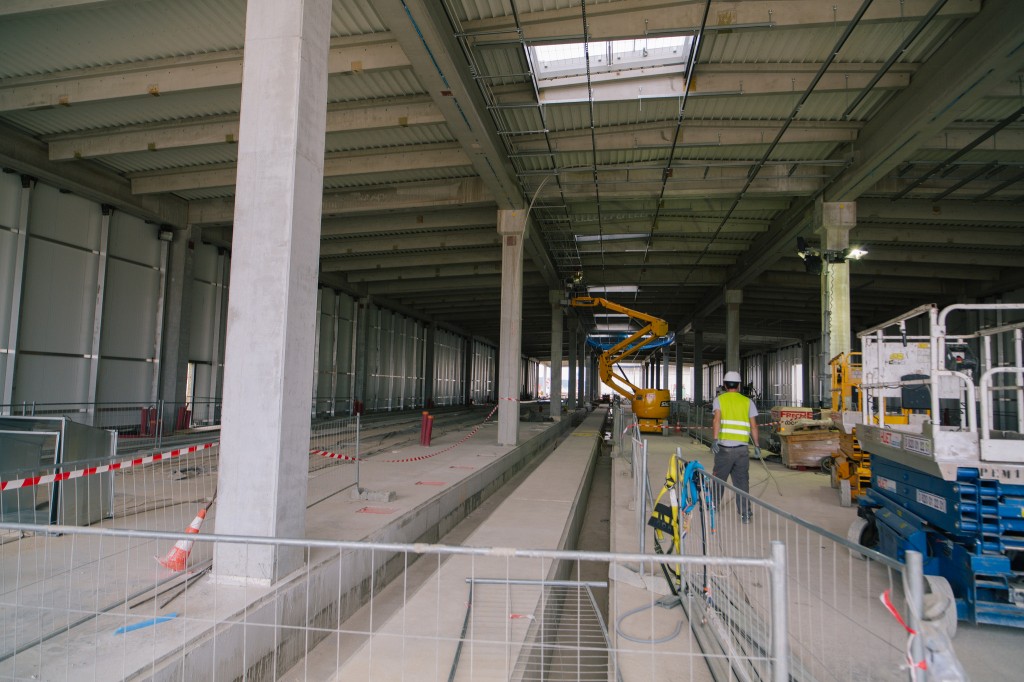
On the inside
2017-09-30 - The first of the 150-metre-long Magnet Power Conversion buildings. © Les Nouveaux Médias/SNC ENGAGE

One level to go on this side
2017-09-26 - The Diagnostics Building (in grey) now stands two stories above platform level. One more to go and the building is completed.
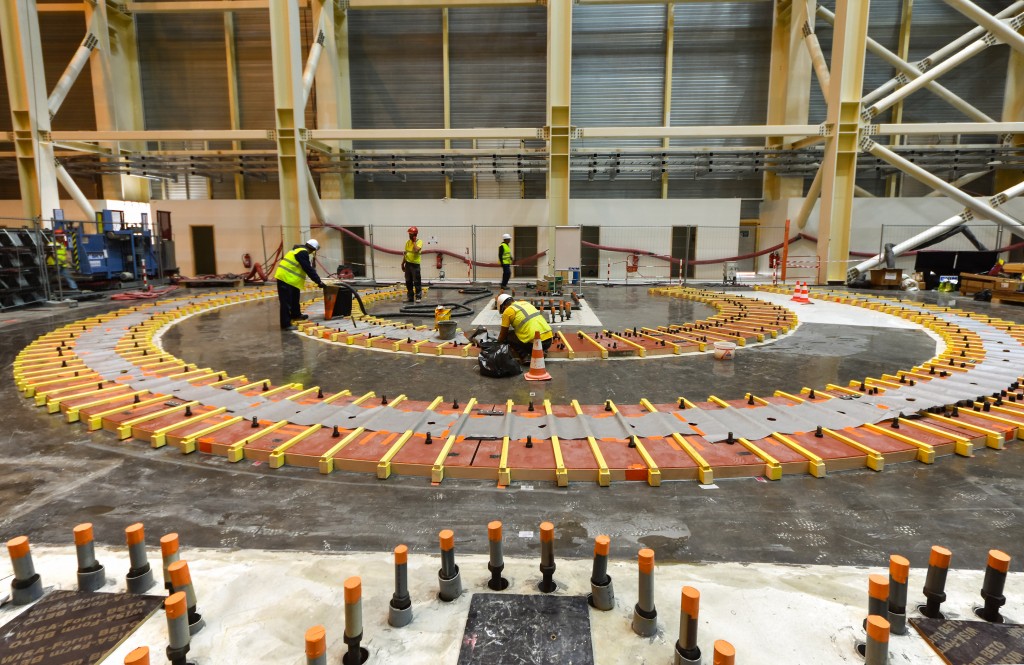
A careful first step
2017-09-26 - Before the mammoth tool can be erected in the Assembly Hall, the anchoring technology must be carefully installed.
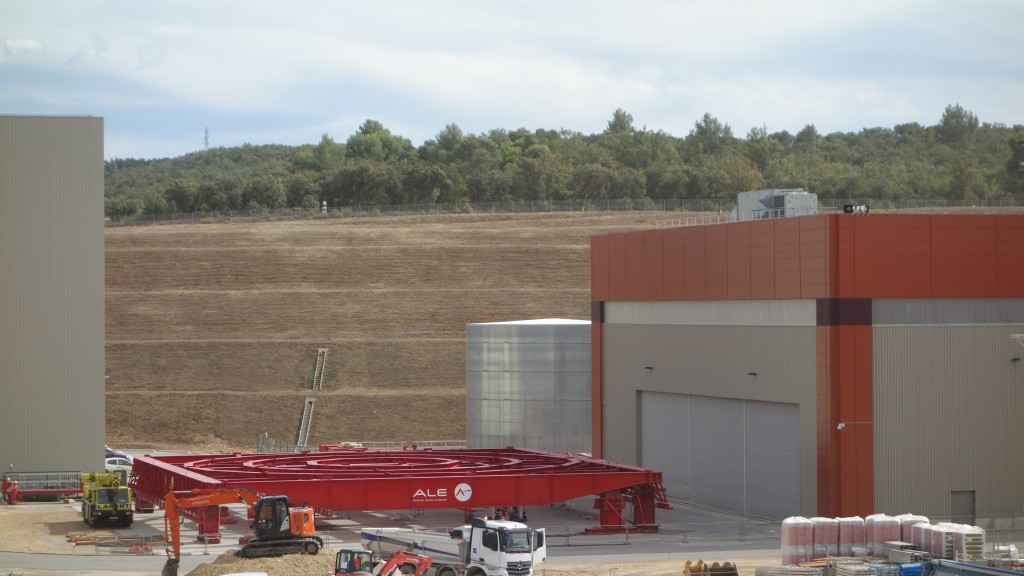
New gantry crane
2017-09-19 - The main structure of the new gantry crane has been assembled outside of the building and is now positioned outside of the north door.
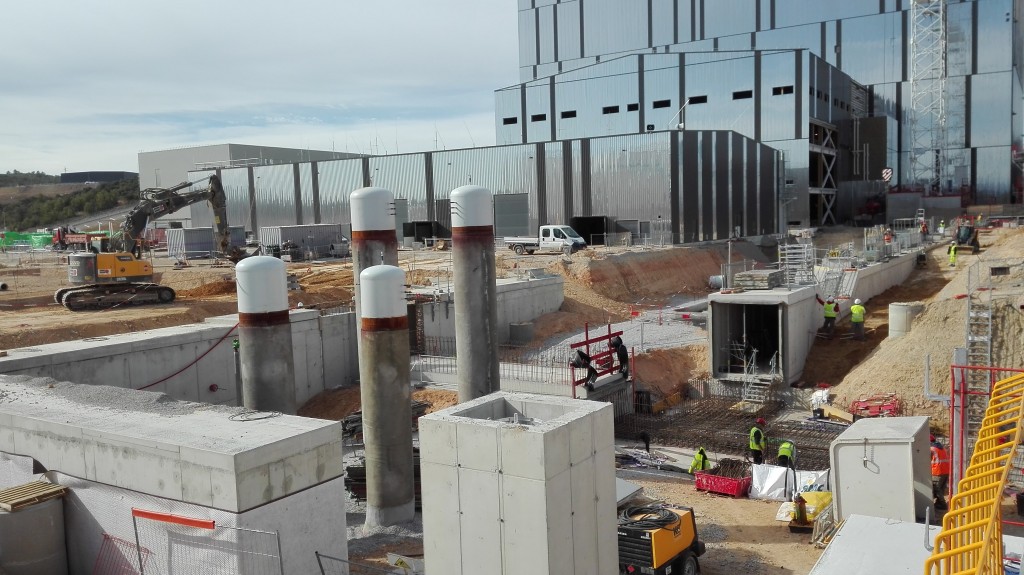
Underground work
2017-09-19 - Cooling water piping is stored vertically while it awaits installation. In the background work continues on the technical galleries that connect the cooling tower area to the Tokamak Complex.
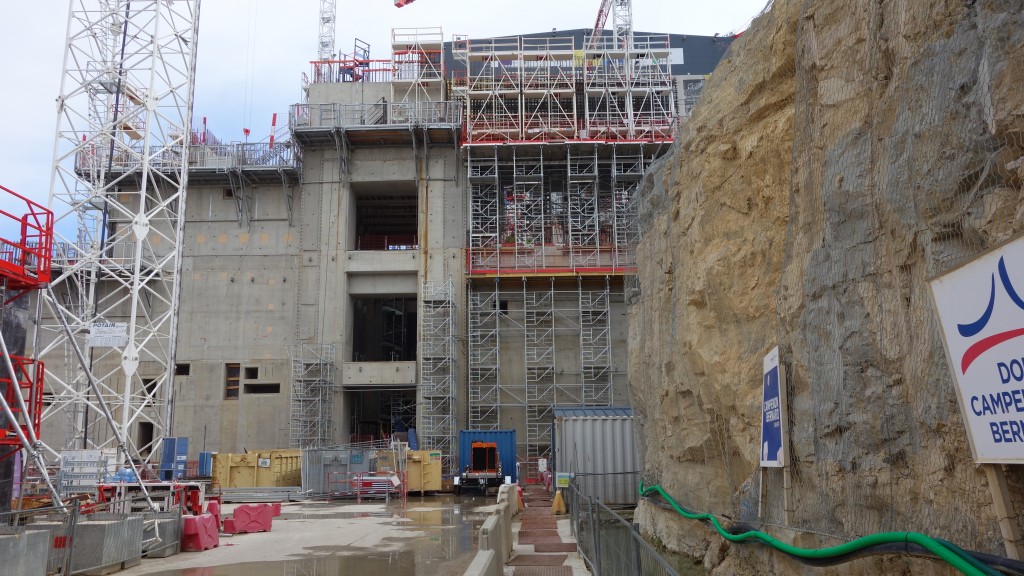
An elevator for bus-sized components
2017-09-19 - Between the Tokamak Building (under construction in the background) and the Hot Cell (excavated but not yet built) there will be a robotic system ensuring the remote transfer of in-vessel components between the vacuum vessel and refurbishment/disposal facilities. The three large openings in this photo are for bus-size casks that will be capable of servicing vacuum vessel ports on three levels.
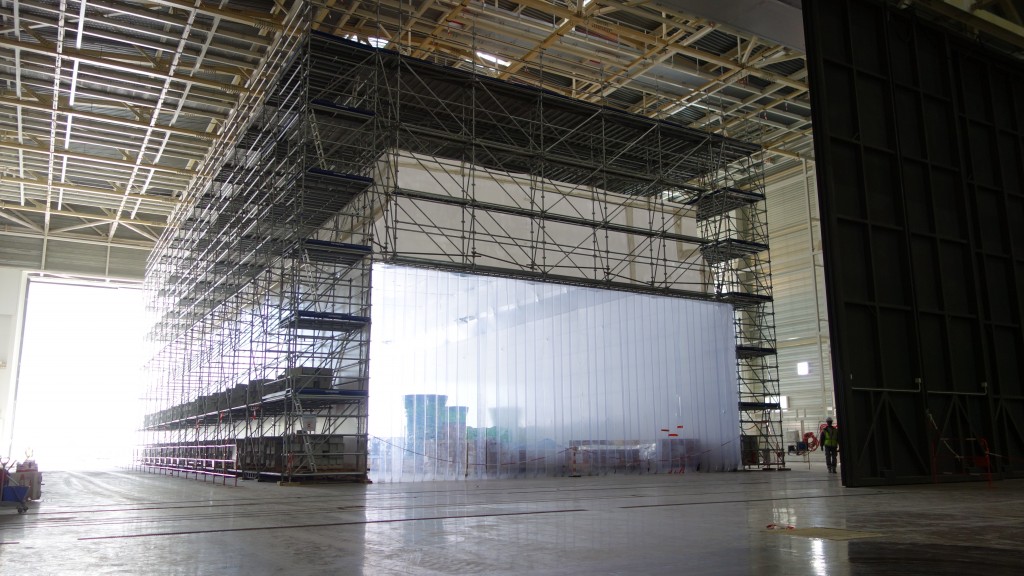
Cleaning facility
2017-09-19 - In the future, this vestibule will be dedicated to the cleaning of ITER components before they are delivered into the Assembly Hall. For now, though, part of it is reserved for storage.
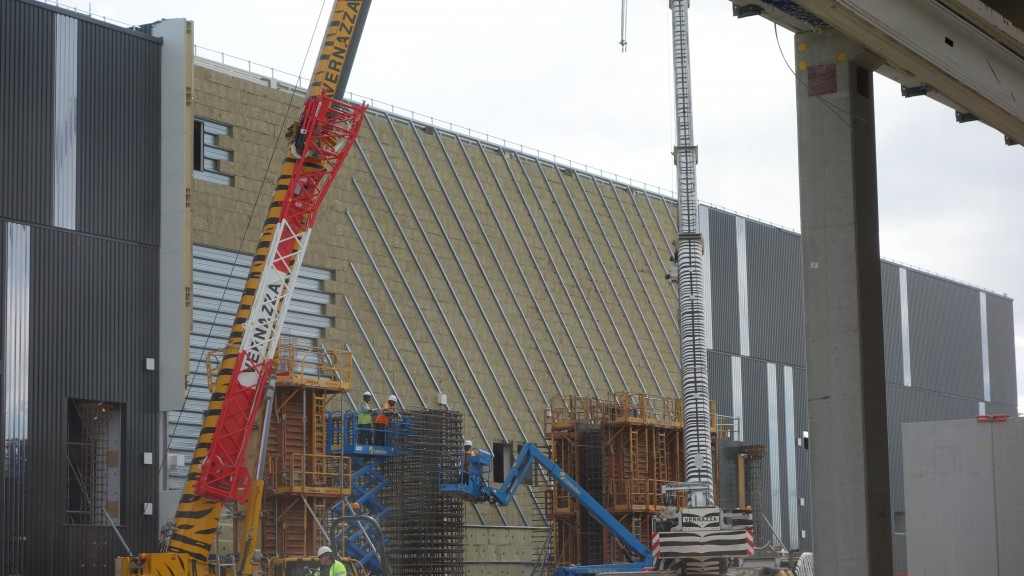
Cladding ending
2017-09-19 - Multiple layers of exterior cladding ensure the cleanest possible interior environment for the cryoplant. The last layer ties the cryoplant into the "look and feel" of the main ITER buildings.

Hot basin covered
2017-09-19 - This intermediate basin runs between the cold (left) and hot (right) basins. The hot basin is now completely covered over.
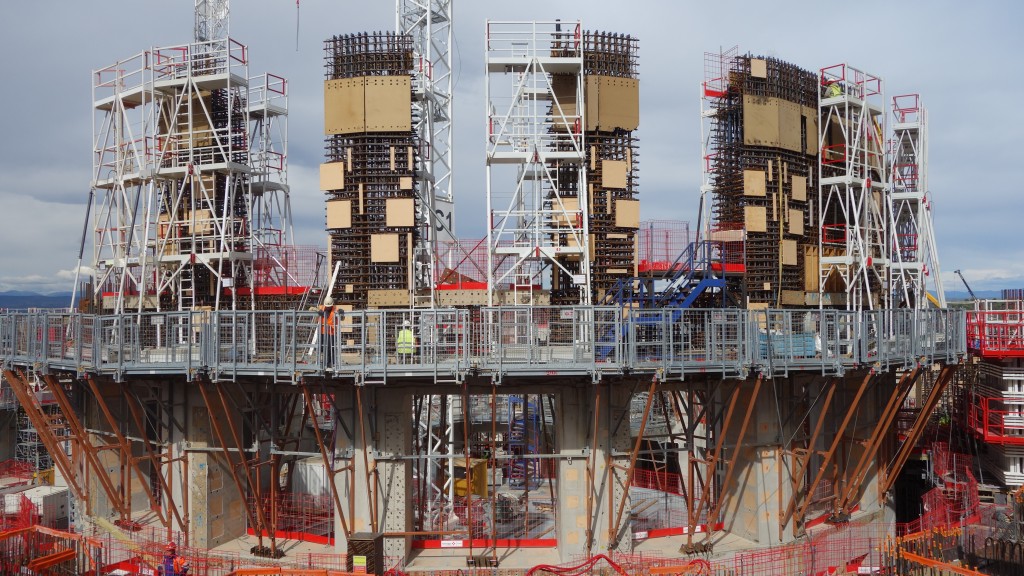
Level 3
2017-09-19 - Teams are currently working at L3 level, installing the iron rebar and positioning the embedded plates before the walls get poured.

First pancake wound
2017-09-19 - The first production double pancake has been placed in a staging area so that additional activities can be carried out (the addition of terminations, the brasing of the intra-pancake joint, and additional insulation).
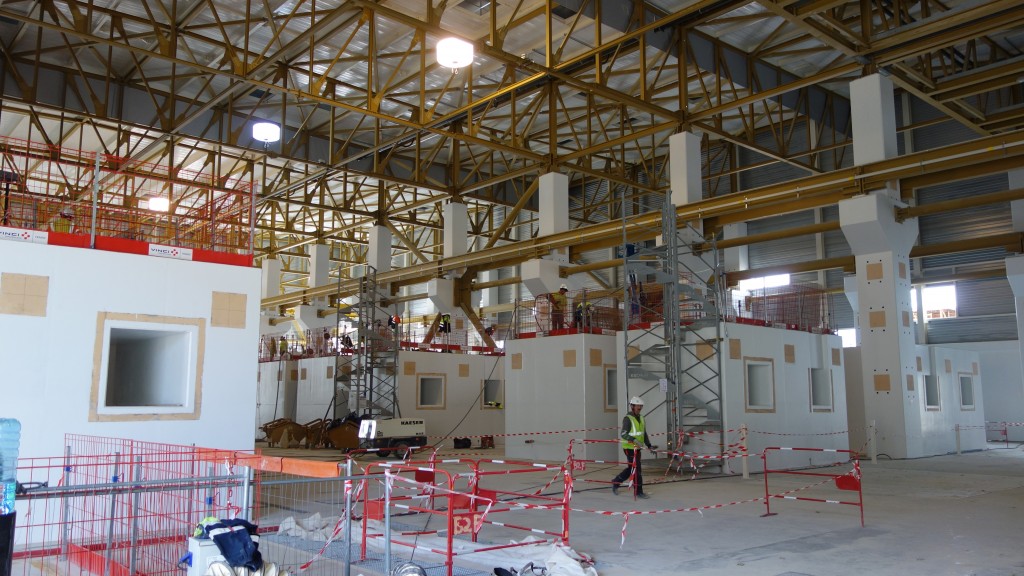
18 all in a row
2017-09-19 - Work is underway in September on the helium screw compressor skids platforms.
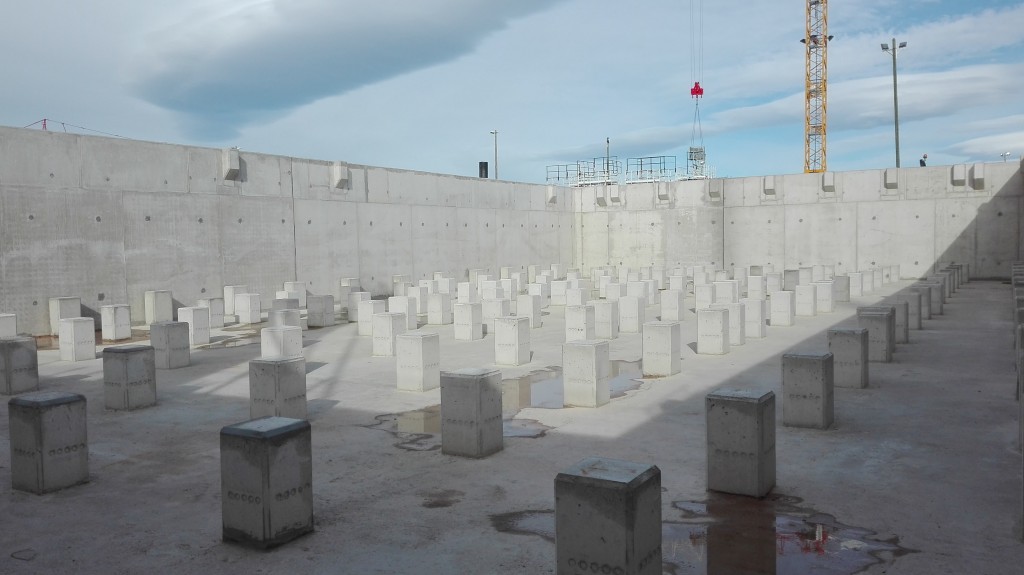
So many feet
2017-09-19 - Small columns in the cold basin will support the structural members of the cooling tower cells.
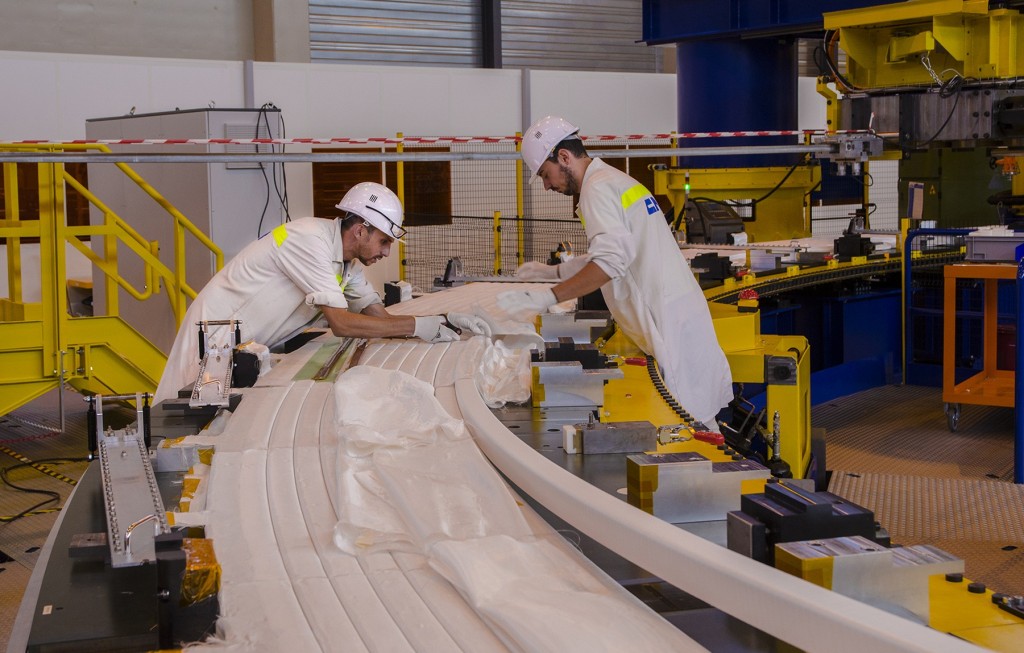
A tailor's workshop?
2017-09-18 - Immaculate fabric, precise measurements and a large pair of scissors: the winding table in the Poloidal Field Coils Winding Facility could be mistaken these days for a high-tech tailor's workshop. Here, technicians are manually inserting fiberglass material between the turns of conductor.
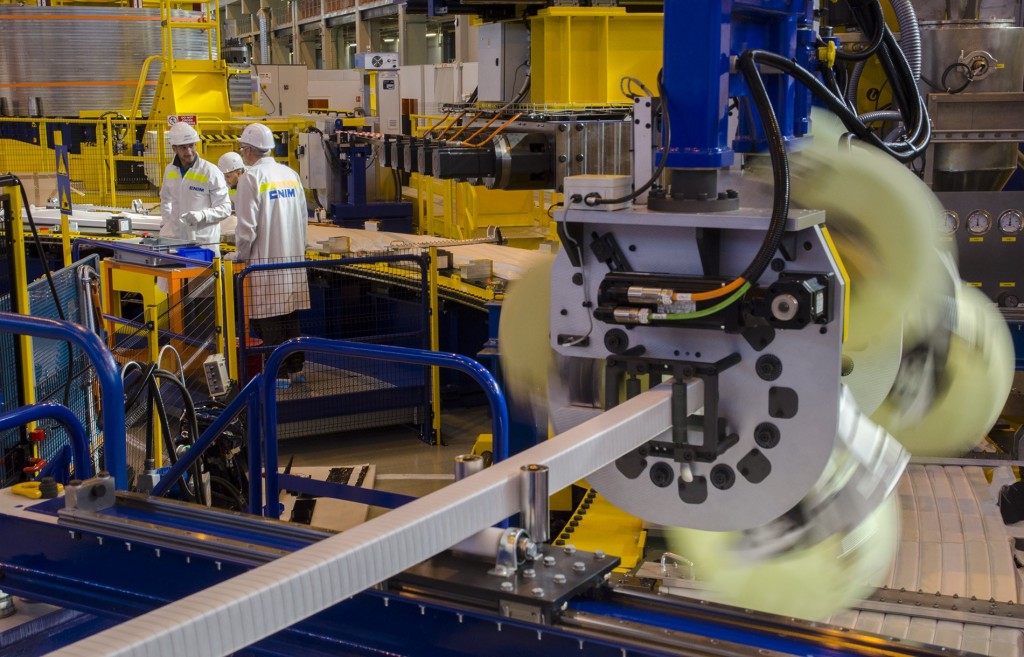
An automatic operation
2017-09-18 - The tape dispenser is in motion, automatically wrapping the conductor with five layers of insulating material.
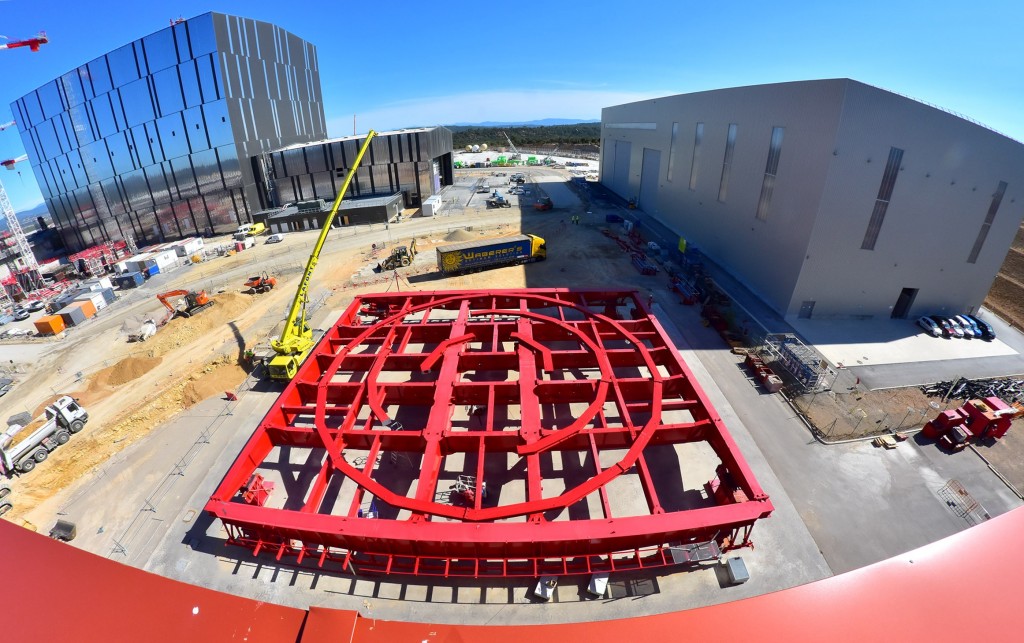
Extra handling
2017-09-17 - A large gantry crane is being assembled outside the north entrance to the Poloidal Field Winding Facility, which will soon be moved inside.

Practising on the crown
2017-09-12 - A 1:1 mockup is under construction on the ITER site that represents a 20-degree section of the cryostat crown and two radial walls. The concrete crown will support the weight of the full ITER machine—vacuum vessel, cryostat, thermal shield and superconducting magnets (23,000 tonnes).
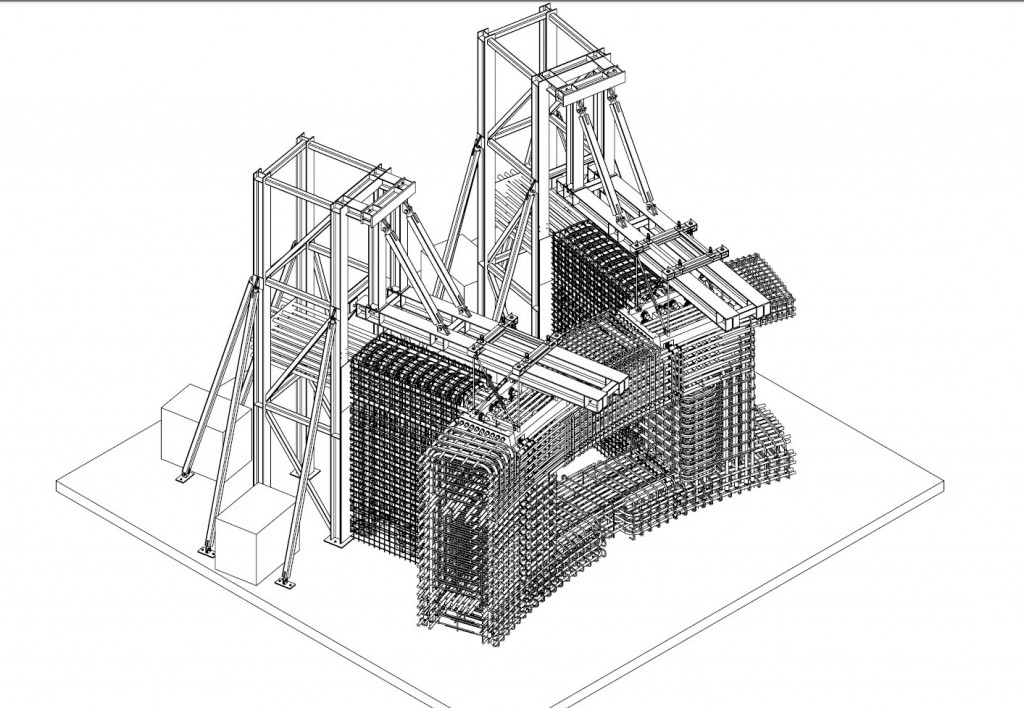
Underway now
2017-09-12 - In order to demonstrate the full constructability of the massive crown structure that will support the machine, a 1:1 mockup is being erected on the ITER platform.
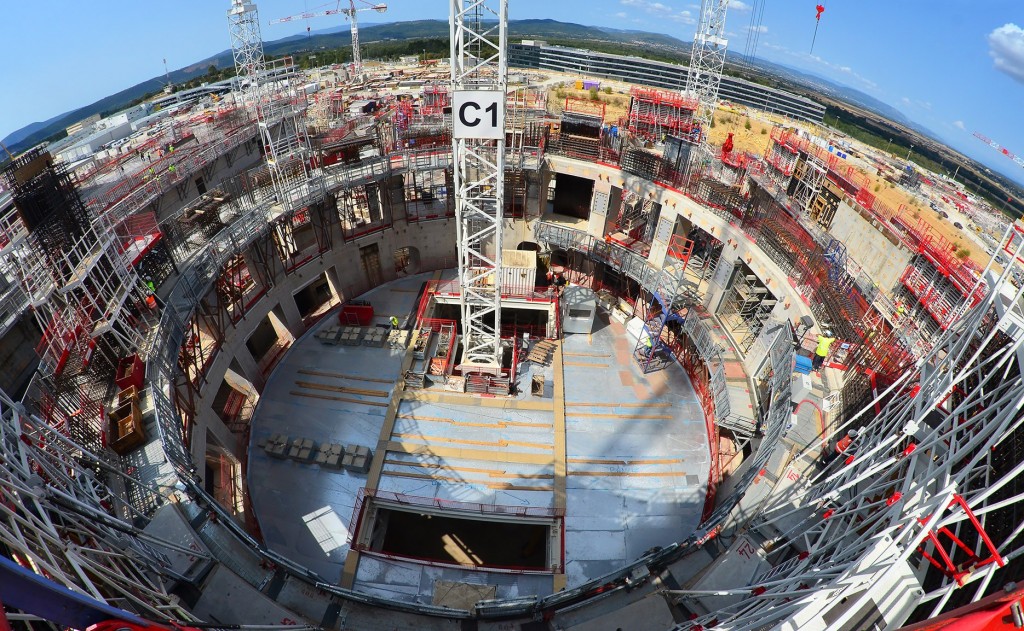
Lid in place
2017-09-12 - View from above: the ''lid'' is now in place. Two openings will allow material and equipment for the crown's construction to be delivered to the ground floor.
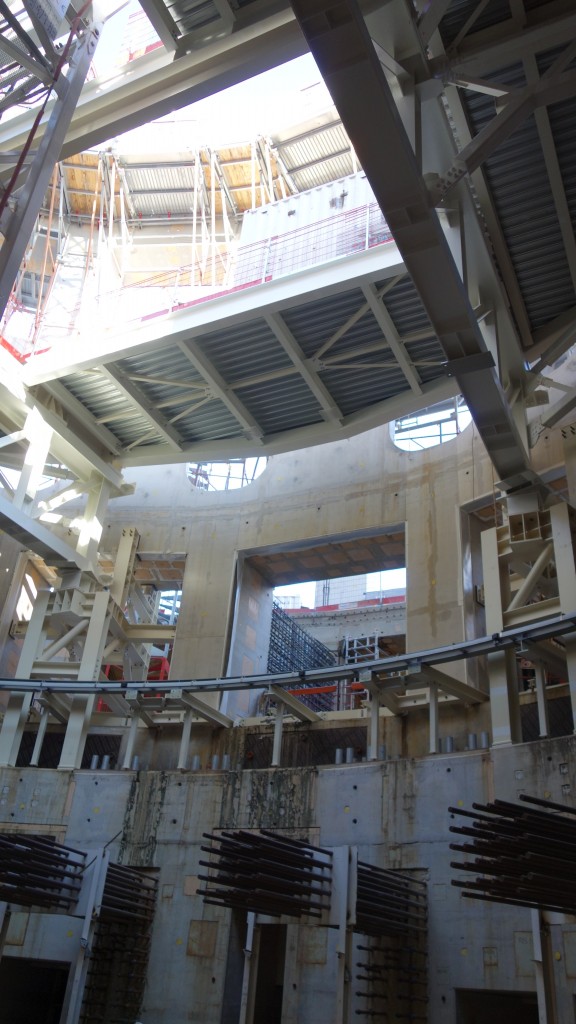
Under the lid
2017-09-12 - A peek into the basement levels of the bioshield, where work is scheduled to start this autumn on the heavily reinforced concrete crown that will support the weight of the machine.

From below
2017-09-12 - View from below: the steel structure will protect workers on the the lower-level of the machine ''well'' and will also be used as a storage platform.
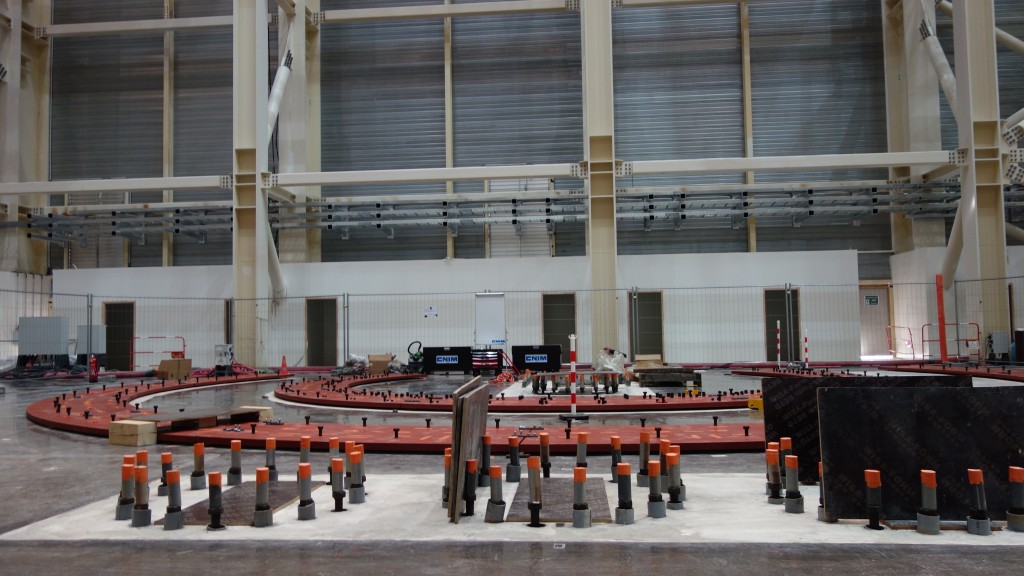
Assembly of first tool underway
2017-09-06 - The French company CNIM has been charged by the Korean manufacture of the SSAT (sector sub-assembly tool) with the responsibility of mounting the tool in the Assembly Hall. Work is underway now.

Rising in sync
2017-09-04 - The Diagnostics Building and the bioshield have both been built up to level 3 (L3). (The photo is taken from the L3 basement of the Diagnostics Building.)
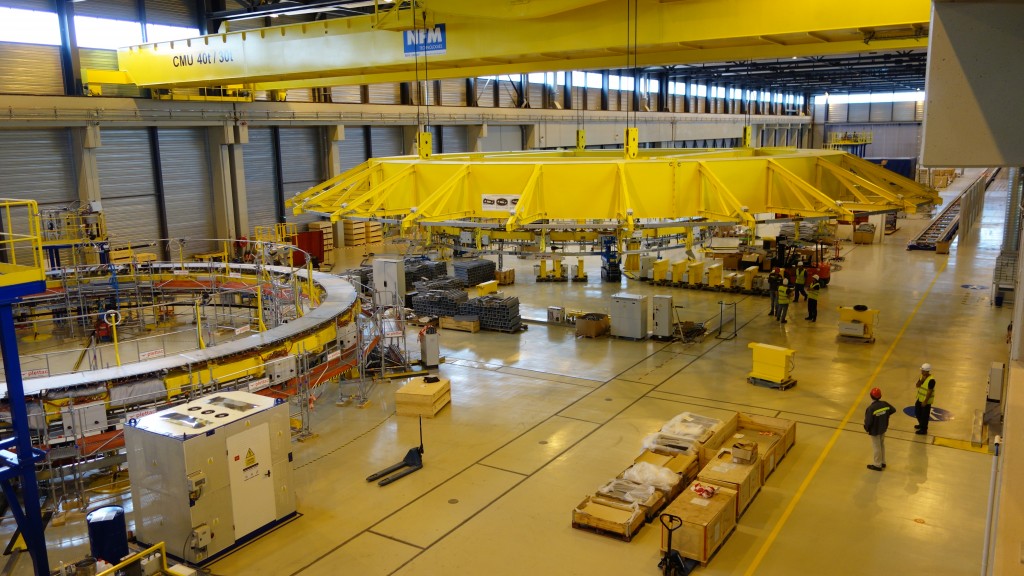
The spreader beam enters action
2017-08-31 - Here's how the double pancakes are transported from one station to another: the 40-tonne circular spreader beam.
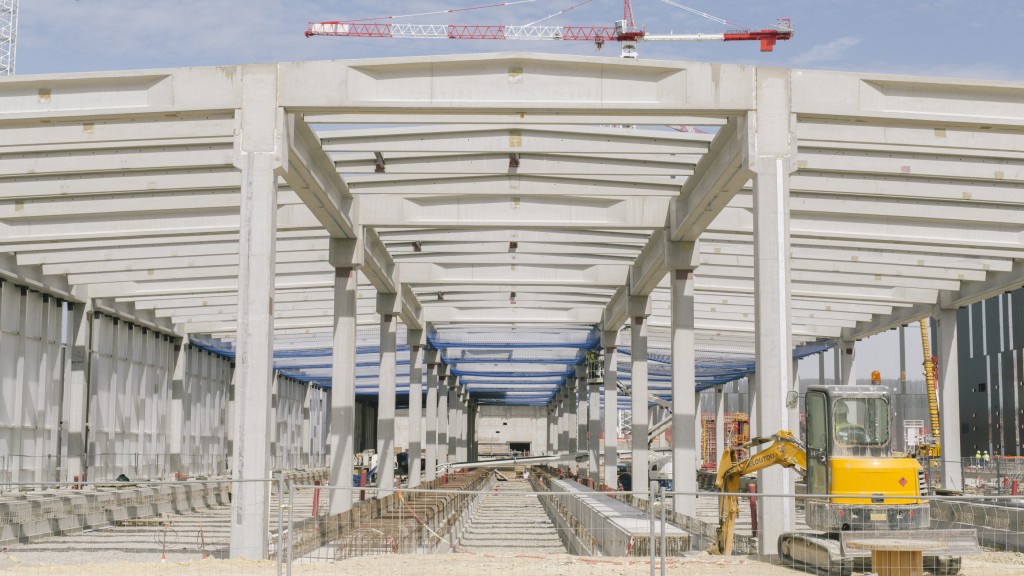
Power conversion components arriving
2017-08-29 - As the structures of the buildings progress, components are arriving from abroad. The first transformers will arrive for the exterior bays in September. © Les Nouveaux Médias/SNC ENGAGE
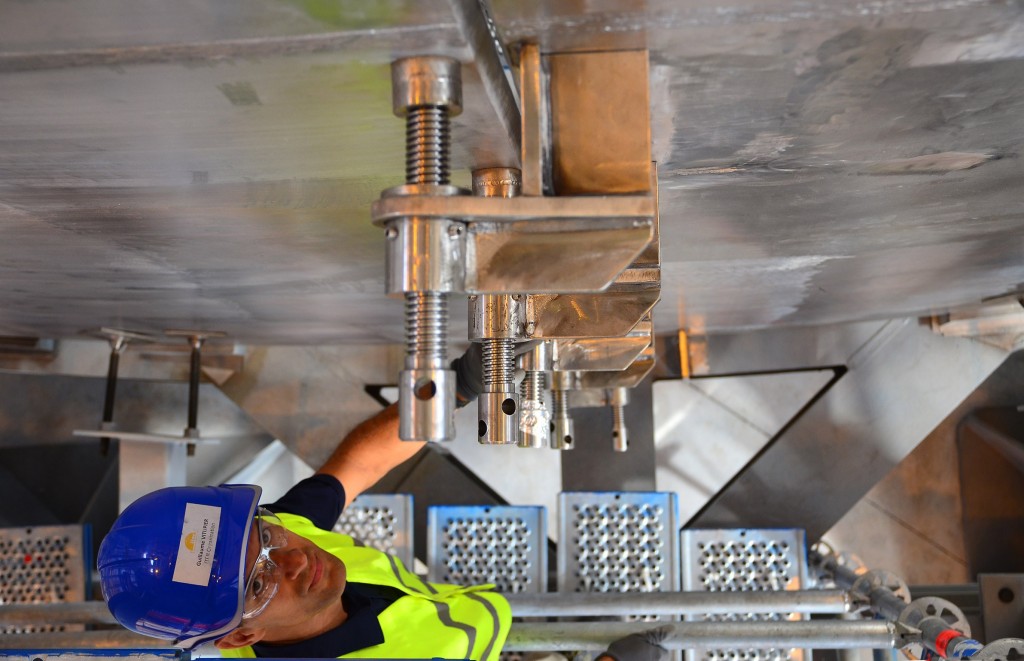
Being exact
2017-08-29 - In order to reach the required precision in positioning the segments, the most sophisticated technologies alternate with the most basic tools. ITER cryostat engineer Guillaume Vitupier is seen here next to the manual screw jacks used to fine-tune the segments' alignment.

The Main AC Current Building
2017-08-29 - A new building has gone up on site, alongside the row of SSEN transformers (for steady state electrical network). Here's a peek inside. © Les Nouveaux Médias/SNC ENGAGE
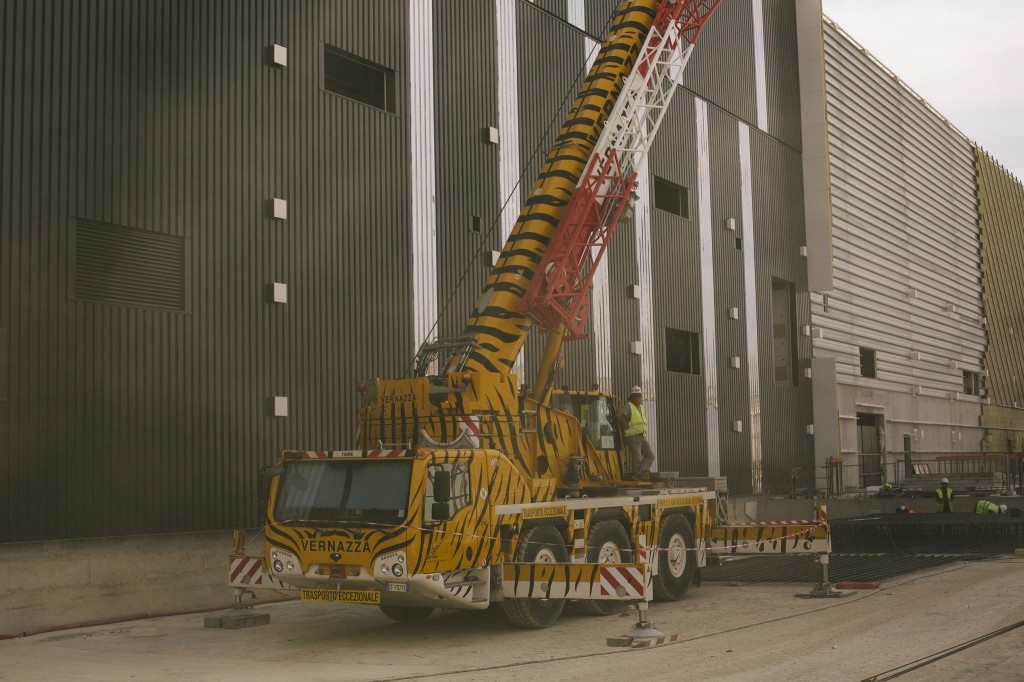
Exterior treatment: nearly completed
2017-08-29 - Workers are completing the cladding on the last corner of the cryoplant. Les Nouveaux Médias/SNC ENGAGE

Cladding advances in August
2017-08-29 - The cladding on the Radio Frequency Heating building (right) is filling in. Soon we'll have a trio of matching structures.
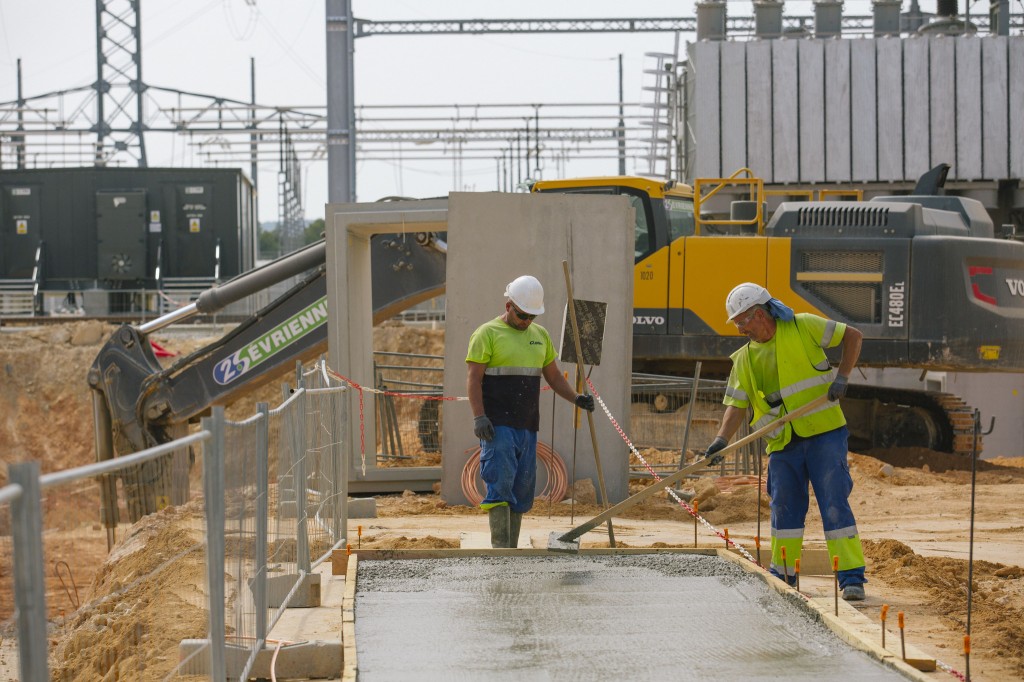
The e-zone
2017-08-29 - Between the electrical switchyard and the ITER buildings is a large zone dedicated to electricity, with transformers, substations, e-houses and technical galleries. Teams are hard at work in that area now. © Les Nouveaux Médias/SNC ENGAGE
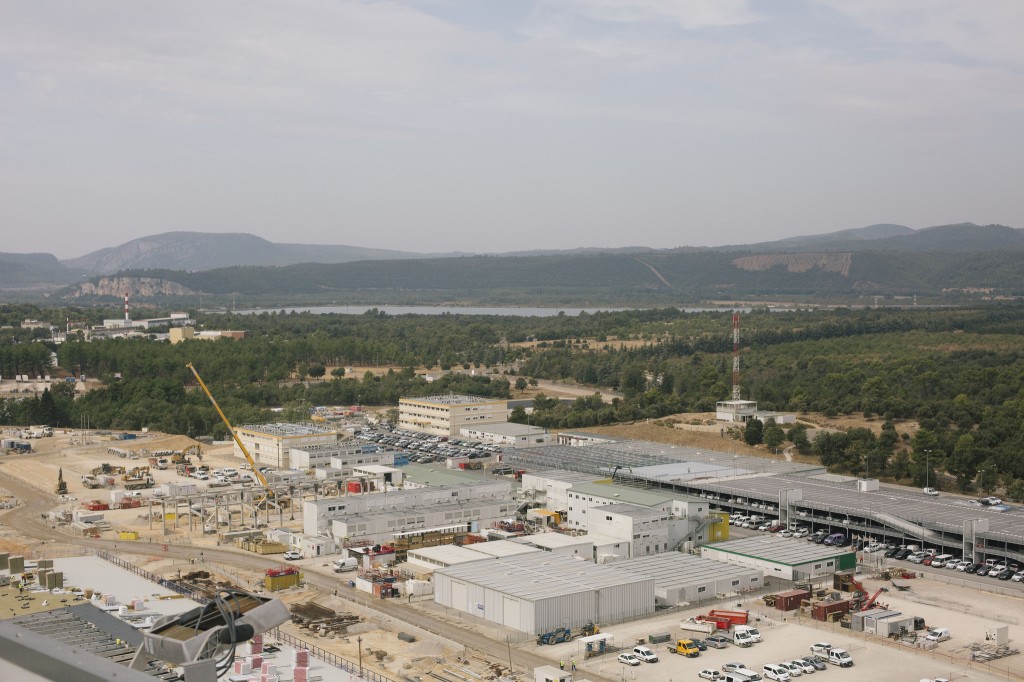
Contractors area
2017-08-29 - On this corner of the platform, companies or consortiums that have been awarded construction contracts by the European Domestic Agency have a small parcel of land for offices, comfort facilities and storage. © Les Nouveaux Médias/SNC ENGAGE.

Transformer row
2017-08-29 - In this picture, four transformers for the steady state electrical network are followed by three larger transformers for the pulsed power electrical network. The first group was procured by the United States; the second group was procured by China. © Les Nouveaux Médias/SNC ENGAGE
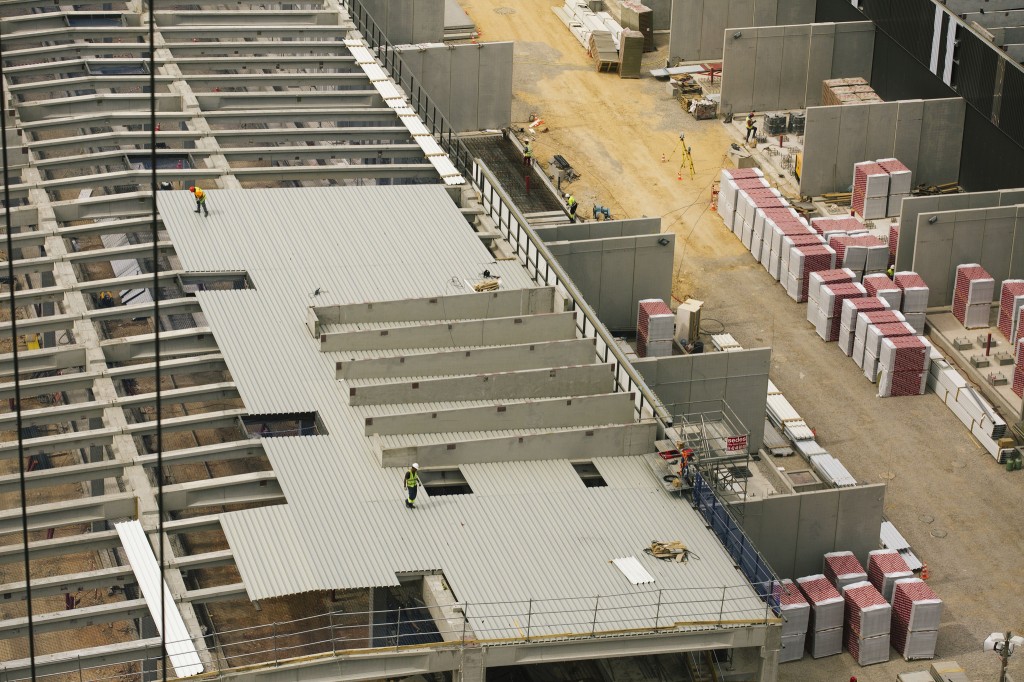
Power conversion building #2
2017-08-29 - The roof panels for the second Magnet Power Conversion building have arrived and installation is underway. © Les Nouveaux Médias/SNC ENGAGE
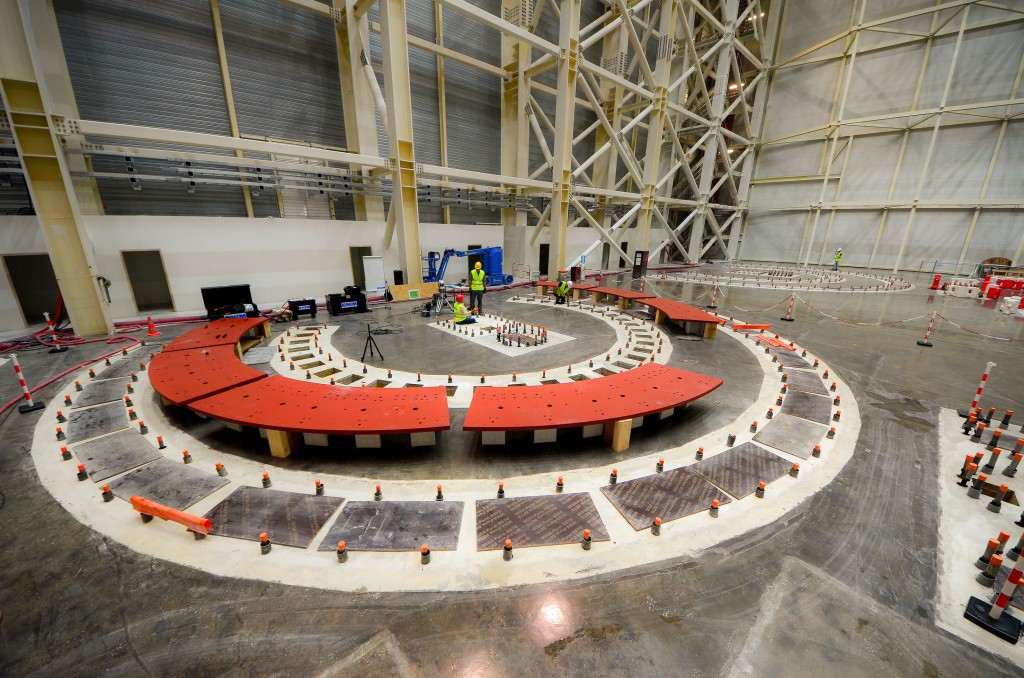
Preparing for giants
2017-08-29 - In one corner of the Assembly Hall, workers are installing the base plates that will support the rails of ITER's largest assembly tools—the twin sector sub-assembly tools (SSAT). The red panels will be moved forward to mesh with the pre-built apertures, before the operation is repeated for the second row.
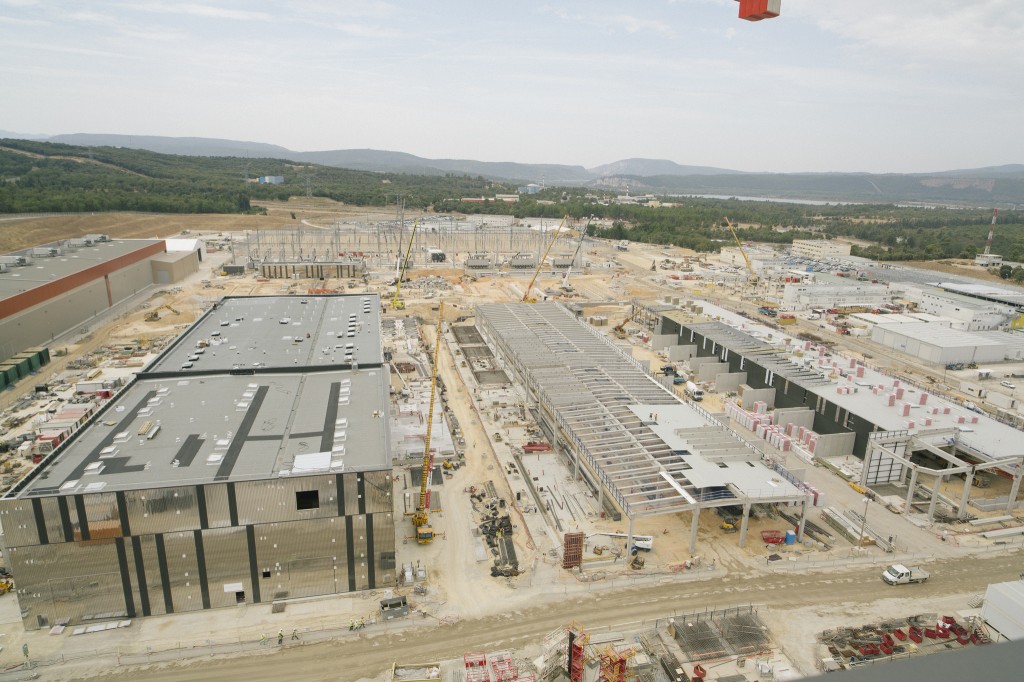
Cryo and conversion
2017-08-29 - On the left the cryoplant building is now fully framed out; on the right, the first bays have been created for transformers outside of Magnet Power Conversion building #1. © Les Nouveaux Médias/SNC ENGAGE
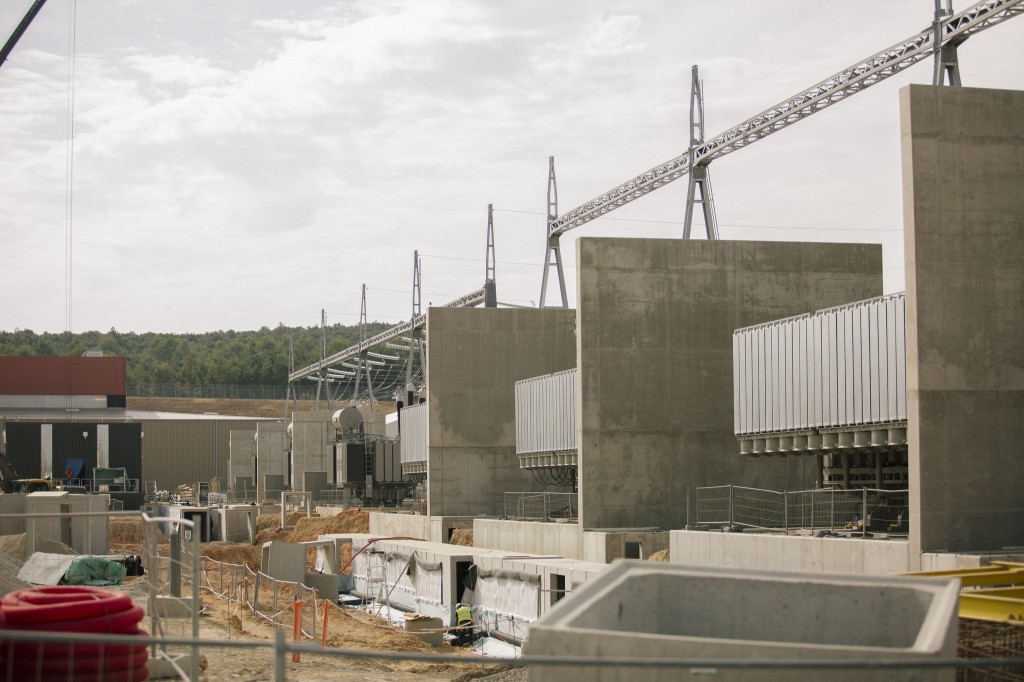
Transformer row
2017-08-29 - In this picture, four transformers for the steady state electrical network are followed by three larger transformers for the pulsed power electrical network. The first group was procured by the United States; the second group was procured by China. © Les Nouveaux Médias/SNC ENGAGE

Status late August
2017-08-29 - The hot basin of the heat rejection system is progressively covered over. © Les Nouveaux Médias/SNC ENGAGE

Measuring the size of the beast
2017-08-29 - The SSAT tools for the pre-assembly of vacuum vessel sectors are monsters, weighing 800 tonnes and standing 22 metres tall. Seeing the size of the footprint helps us to measure just how massive they are.

A mega component
2017-08-29 - Tier one of the cryostat lower cylinder is now assembled and readied for welding. Standing on the scaffolding of the sub-component, which is 30 metres in diameter, workers appear tiny. (Look closely!)
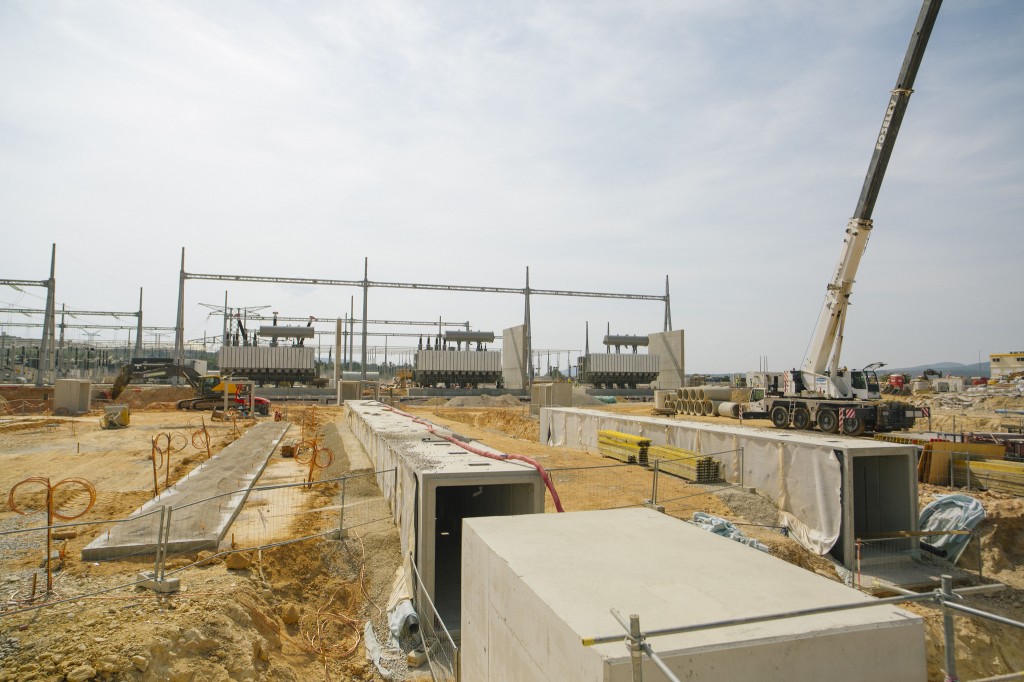
Late August
2017-08-29 - In the background are the three huge PPEN transformers (for pulsed power electrical network--needed to power the plasma pulses of the machine). Technical galleries are underway in the foreground. © Les Nouveaux Médias/SNC ENGAGE
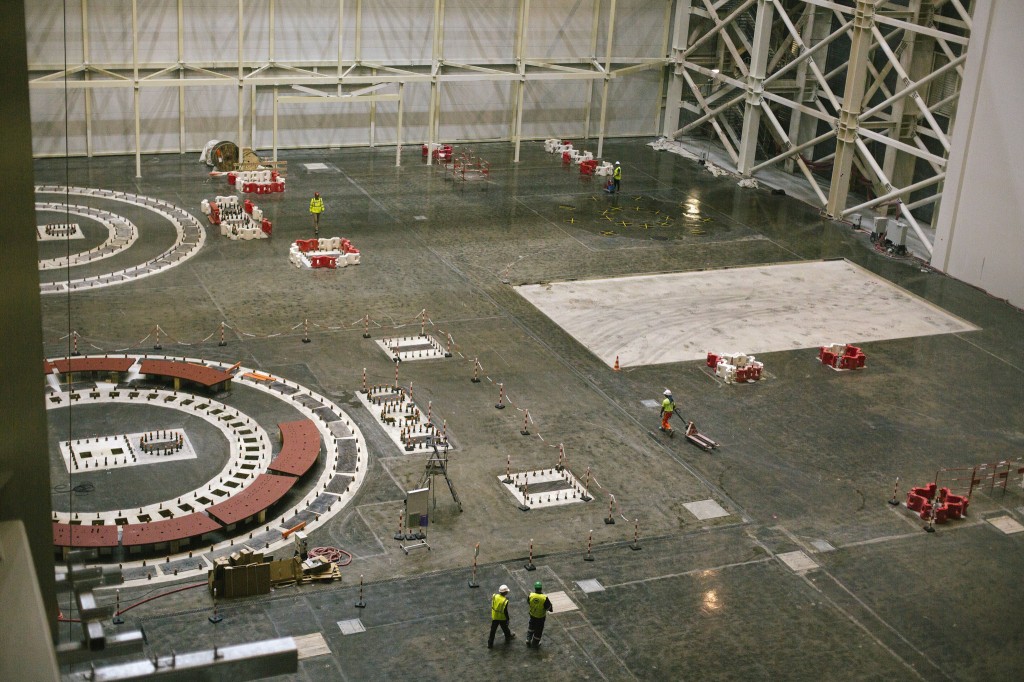
Anchoring the first tools
2017-08-29 - The red plates will anchor the rails of the Assembly Hall's largest tools: the vacuum vessel sub-sector assembly tools (SSAT). The first tool should be standing by the end of the year. © Les Nouveaux Médias/SNC ENGAGE

Progress on second conversion building
2017-08-29 - The first already has its walls and roof; the second is underway. The equipment in these buildings will deliver AC power at the required voltage to ITER's superconducting magnets. © Les Nouveaux Médias/SNC ENGAGE

A lot of weld material
2017-08-29 - A close-up of the weld gap between two lower cylinder segments. If the camera were to zoom out, we'd see that this V-shape gap is 5 metres high and that there are six welds to realize in total.

Tanks soon
2017-08-29 - Running along the length of the cryoplant, on the outside, is an exterior area dedicated to the storage of gases and liquids. Work is underway to prepare the foundations and the footholds now. © Les Nouveaux Médias/SNC ENGAGE
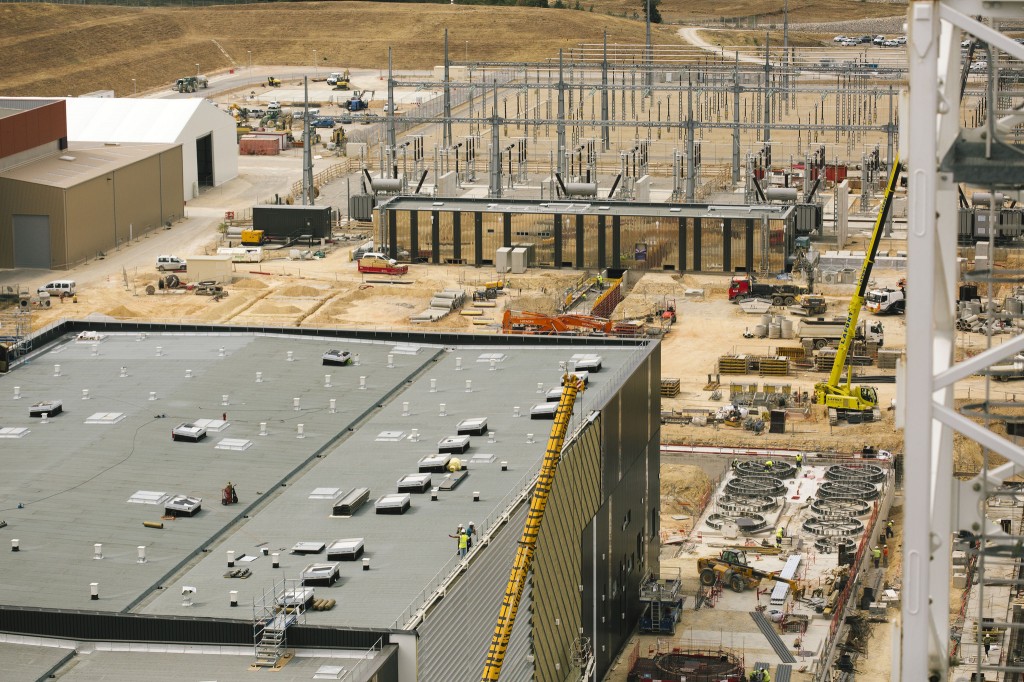
Small addition, southside
2017-08-29 - The small Main AC Current Building has received the same exterior treatment (alternating panels of stainless steel and grey lacquered metal) as the larger buildings of the facility. © Les Nouveaux Médias/SNC ENGAGE
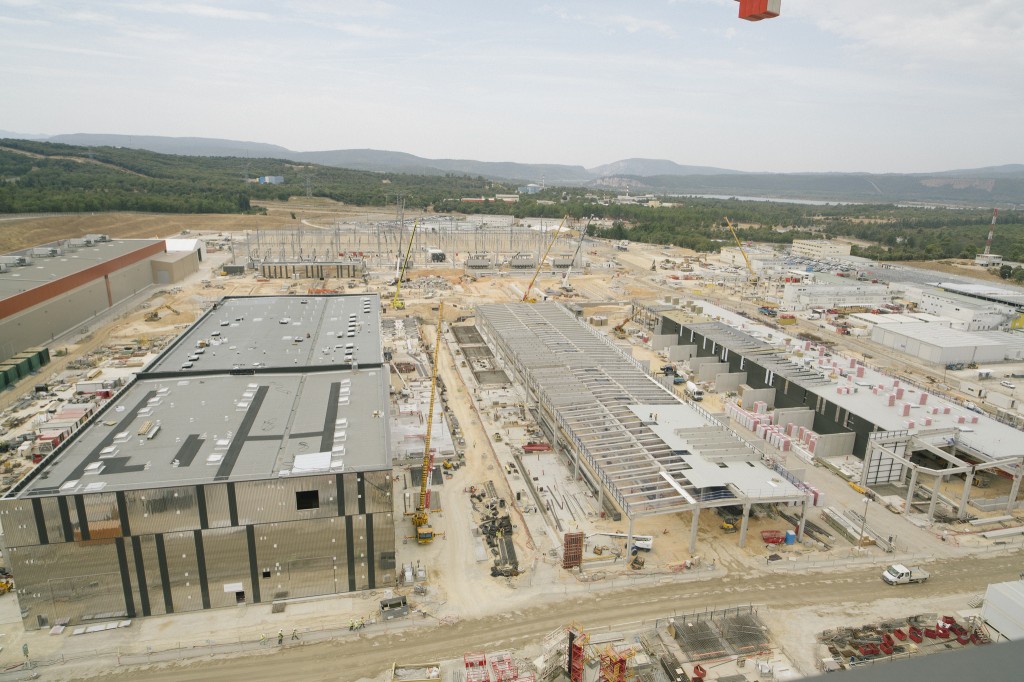
Cryo and conversion
2017-08-29 - On the left the cryoplant building is now fully framed out; on the right, the first bays have been created for transformers outside of Magnet Power Conversion building #1. © Les Nouveaux Médias/SNC ENGAGE

Hard to see
2017-08-23 - Hidden behind all of the scaffolding is the lower cylinder of the cryostat, tier one. A second tier will bring the lower cylinder's height to 10 metres. Photo: ITER Organization/EJF Riche

Starting on a second pancake
2017-08-22 - The first few metres of superconductor for the second double pancake winding are visible on the table. Photo: ITER Organization/EJF Riche
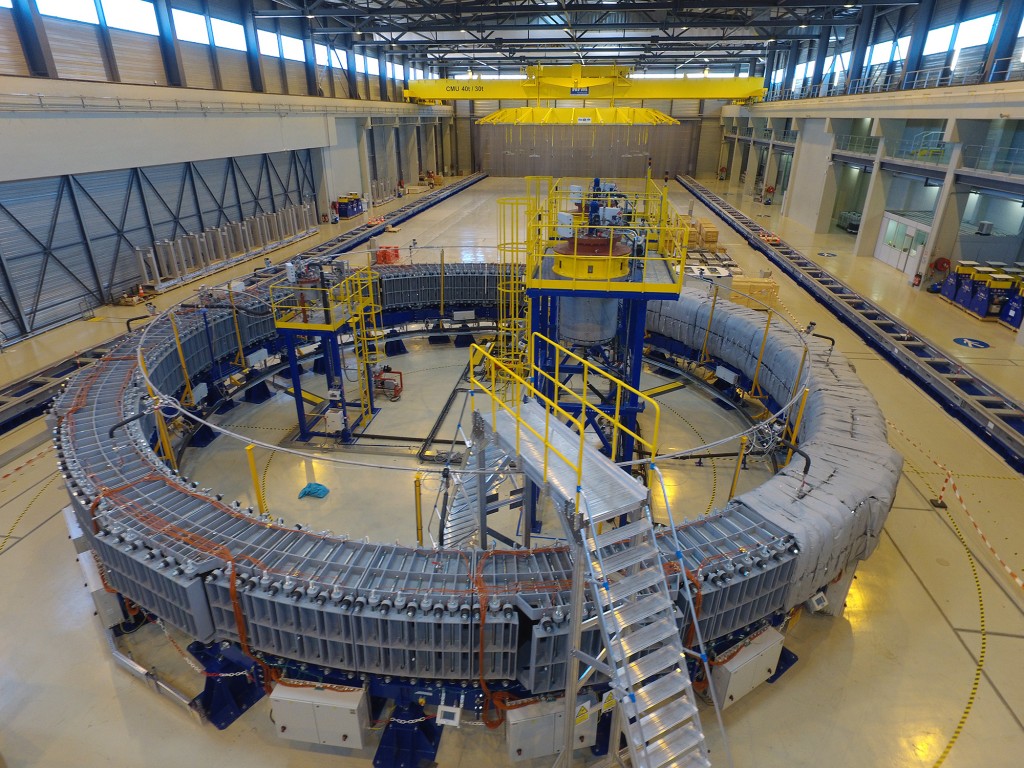
Floor rails installed
2017-08-22 - In the last third of the building, rails have now been installed on the floor to accommodate the new gantry crane. Photo: ITER Organization/EJF Riche
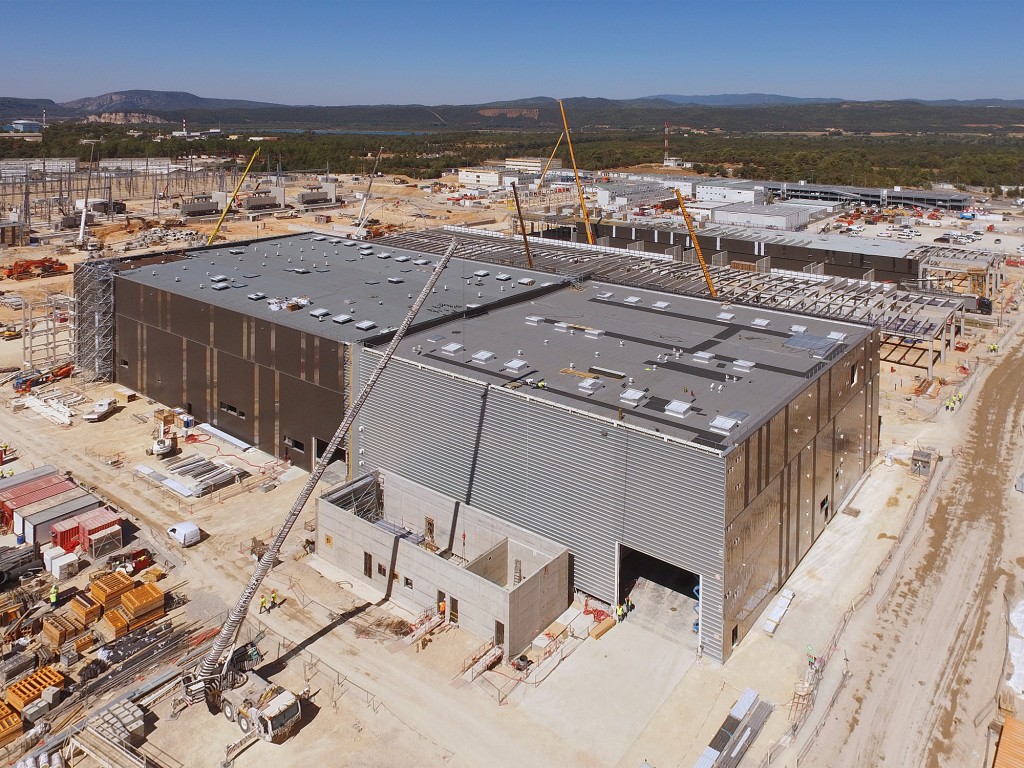
Good progress
2017-08-22 - The 5,400 m² cryoplant is now fully framed out, and the first components have been installed. Photo: ITER Organization/EJF Riche

Progress on the twin buildings
2017-08-21 - Late August, workers begin on the roof panels. Photo: ITER Organization/EJF Riche
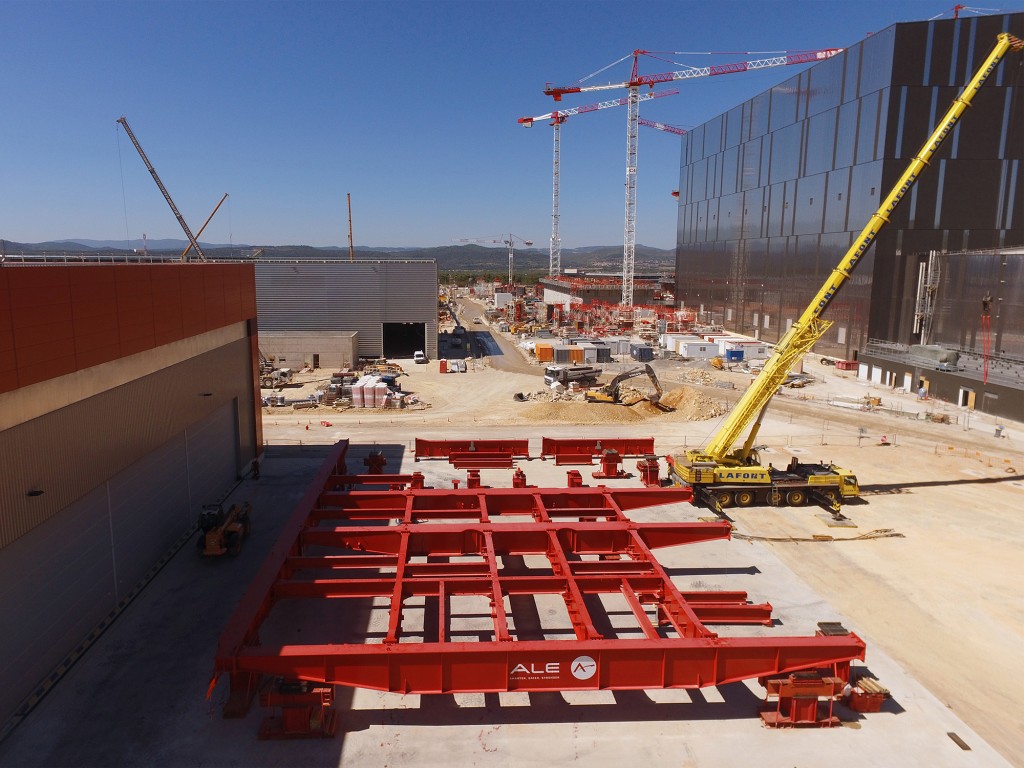
Assembly of gantry crane
2017-08-21 - Just outside of the Poloidal Field Coils Winding Facility teams are assembling a gantry crane, which will be installed at the end of the manufacturing line. Photo: ITER Organization/EJF Riche

An important role
2017-08-21 - Located between the 400 kV electrical switchyard and the Tokamak Complex, the buildings will furnish DC current to 10,000 tonnes of superconducting magnets. Photo: ITER Organization/EJF Riche

Last round
2017-08-21 - On this side of the building, workers are installing the last layer of cladding. Its shiny surface is the architect's "signature" on all the permanent buildings of the scientific facility. Photo: ITER Organization/EJF Riche

Exterior storage
2017-08-21 - A few tanks await transport to the cryoplant in this triangular storage zone on the northeast side of the platform. Photo: ITER Organization/EJF Riche
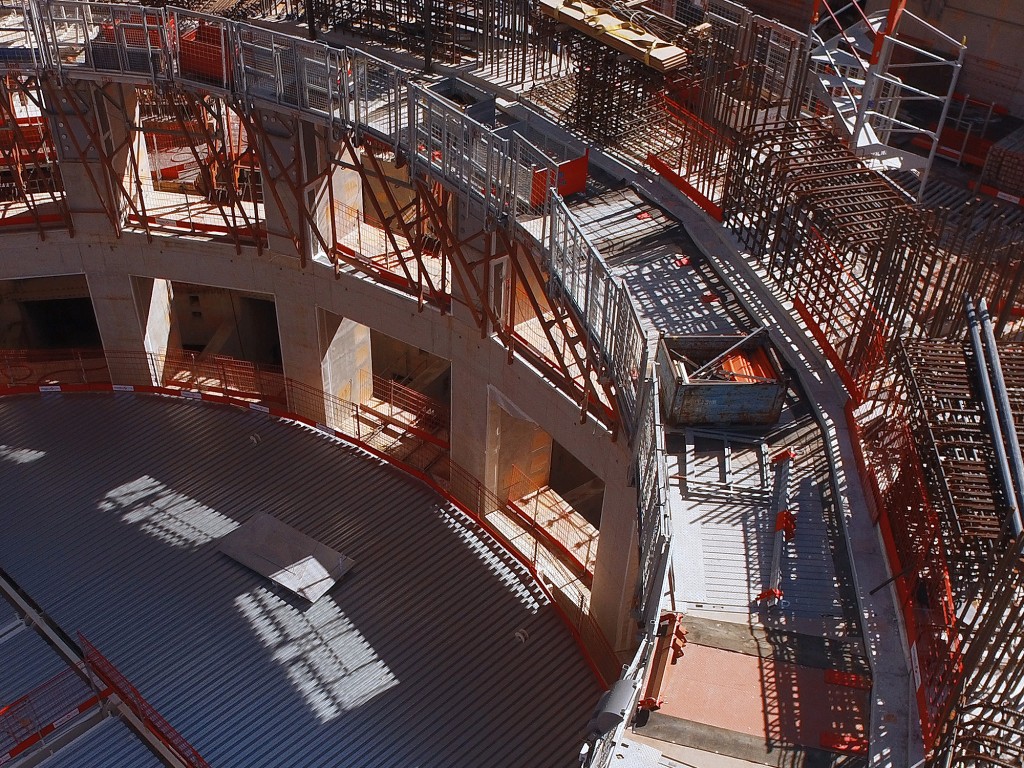
A temporary divider
2017-08-21 - A metal lid has been installed at L1 level, effectively dividing the basement levels from the rest. Photo: ITER Organization/EJF Riche
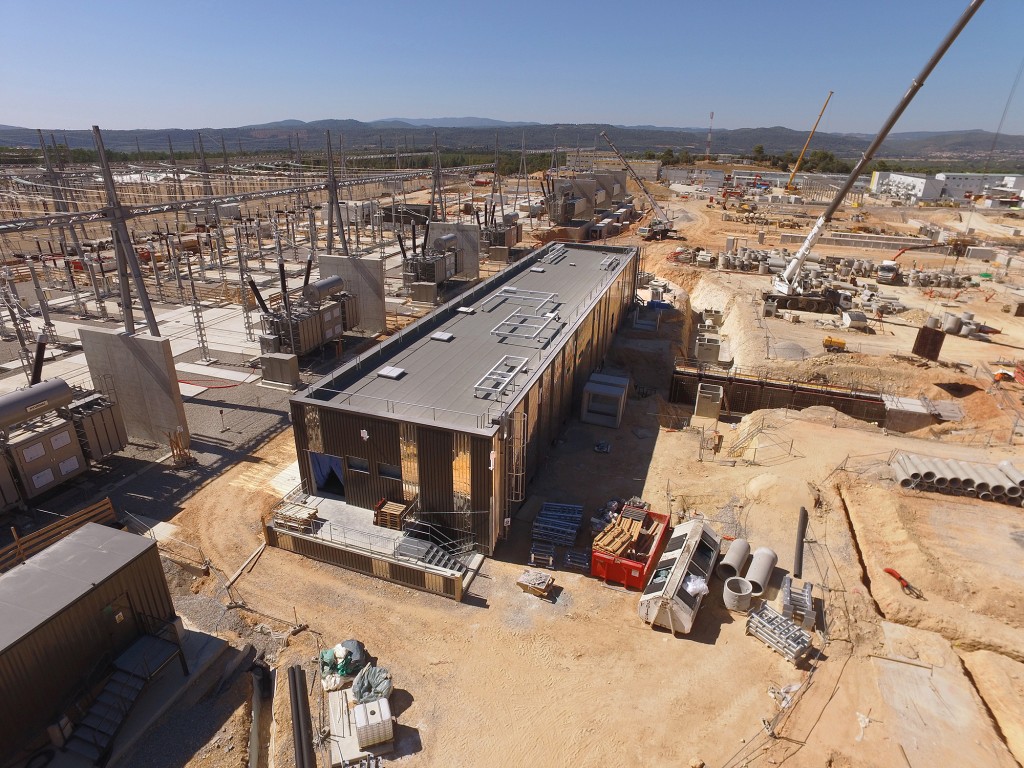
Something new on this side of the platform
2017-08-21 - A small building has gone up next to the electrical switchyard : the Main Alternating Current Distribution building. Photo: ITER Organization/EJF Riche

Layout
2017-08-21 - For the moment, all work is taking place at an underground level. However much of the equipment of the heat rejection system will be installed at platform level, including the 20-metre-high cooling tower. Photo: ITER Organization/EJF Riche

Long and low
2017-08-21 - The two 150-metre buildings will be densely packed with electrical converters, switches and fast discharge units. Photo: ITER Organization/EJF Riche
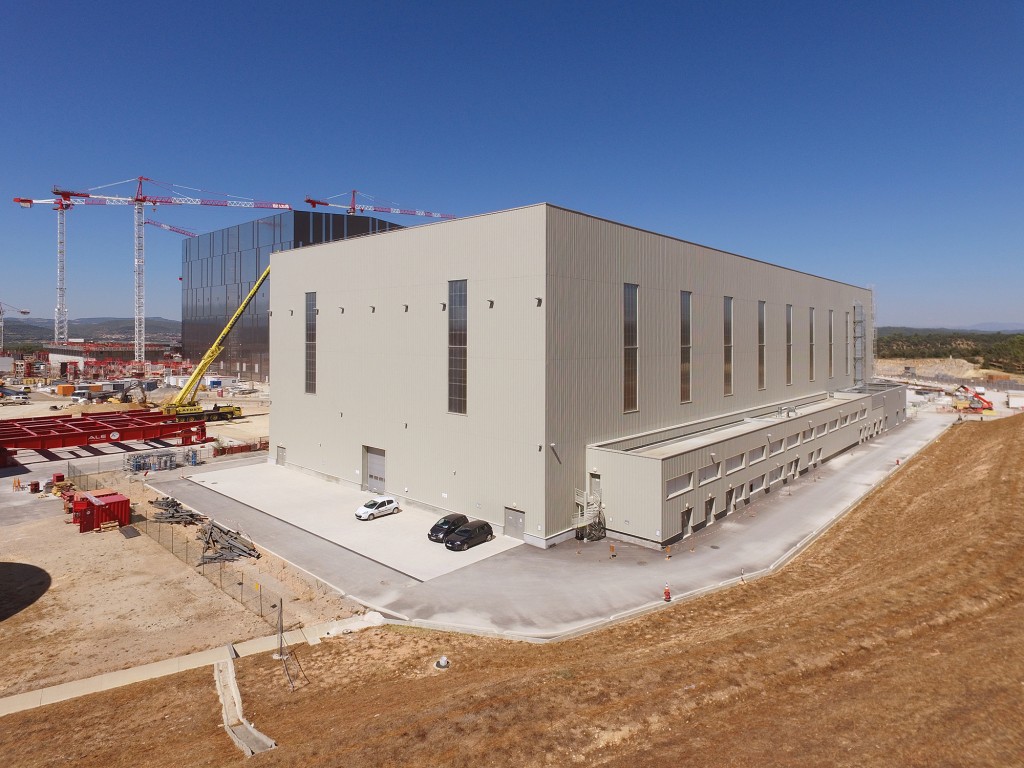
Seen from the outside
2017-08-21 - In this 6,000-square-metre building, Larsen & Toubro (contractor to the Indian Domestic Agency) is charged with the fabrication of the ITER cryostat. Work is underway now on the first two segments, the base and the lower cylinder. Photo: ITER Organization/EJF Riche

Wow!
2017-08-21 - This group of visitors throws the size of the cryostat lower cylinder into perspective ...

Still underway
2017-08-21 - The metal sheets still have to be laid on this side of the bioshield well. The opening will allow materials to be delivered to the lower levels. Photo: ITER Organization/EJF Riche
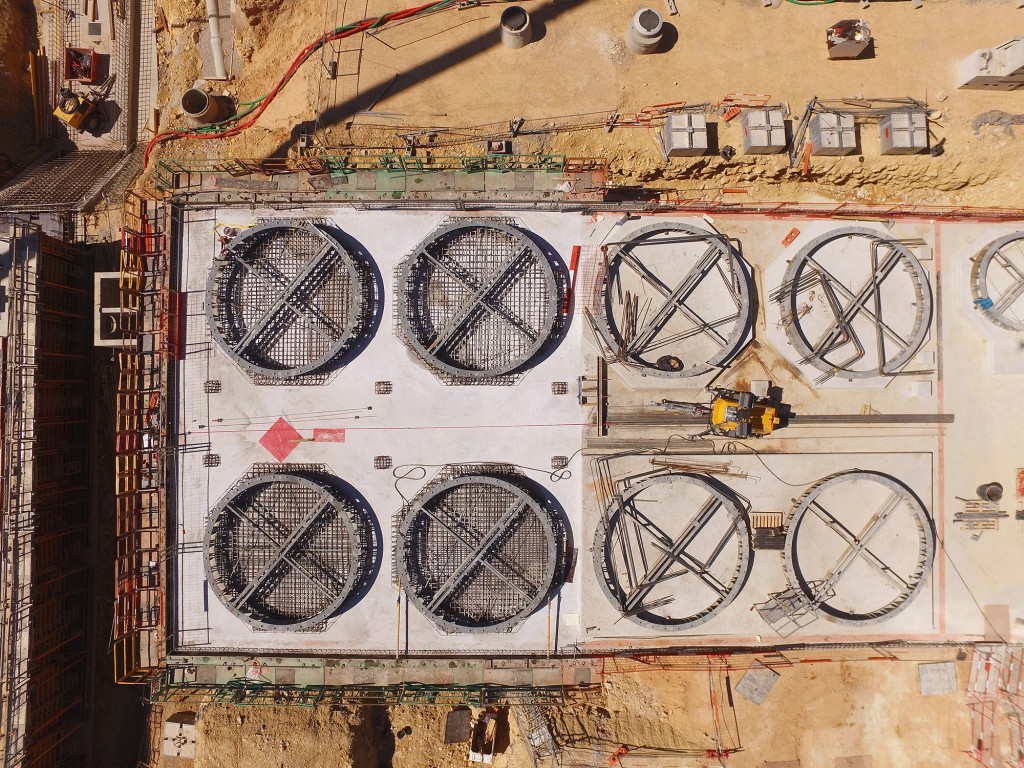
Footprints in the sand
2017-08-21 - These circular structures are in place to receive the standing tanks for gaseous and liquid helium and nitrogen. Photo: ITER Organization/EJF Riche
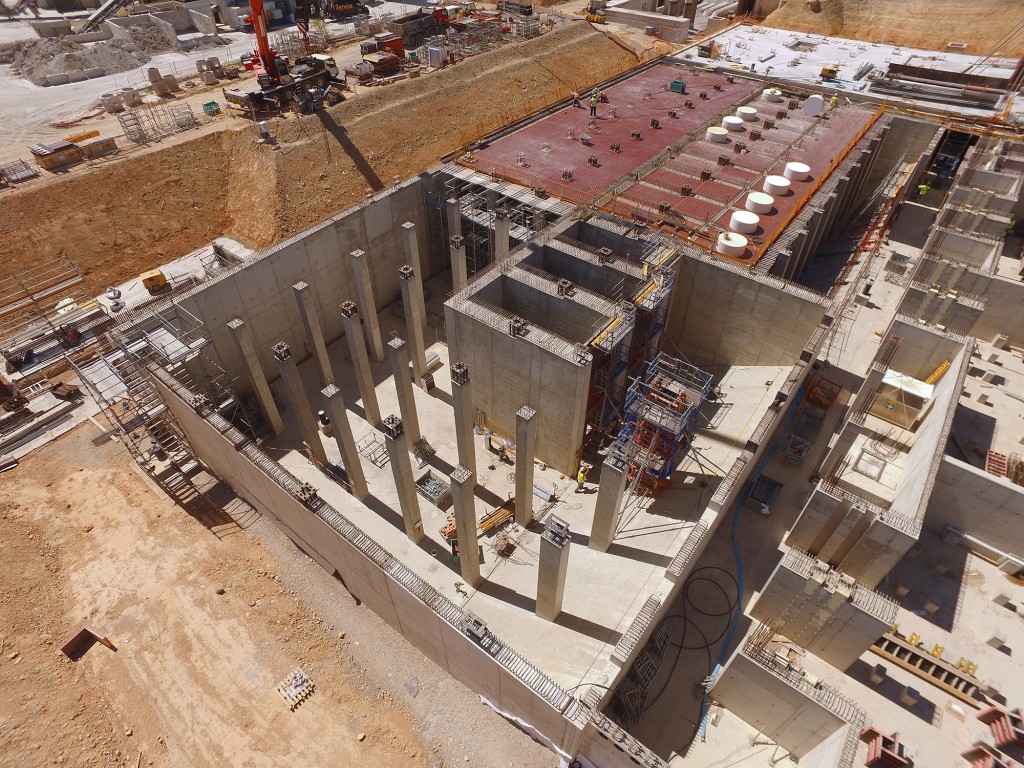
Update on the cooling tower zone
2017-08-21 - The hot basin is disappearing from view. Photo: ITER Organization/EJF Riche

Before the concrete
2017-08-17 - Anchor structures for the vertical storage tanks are set in place before concrete pouring begins.

Small crane
2017-08-17 - A small crane has been installed for the manipulation of building material under the temporary lid.
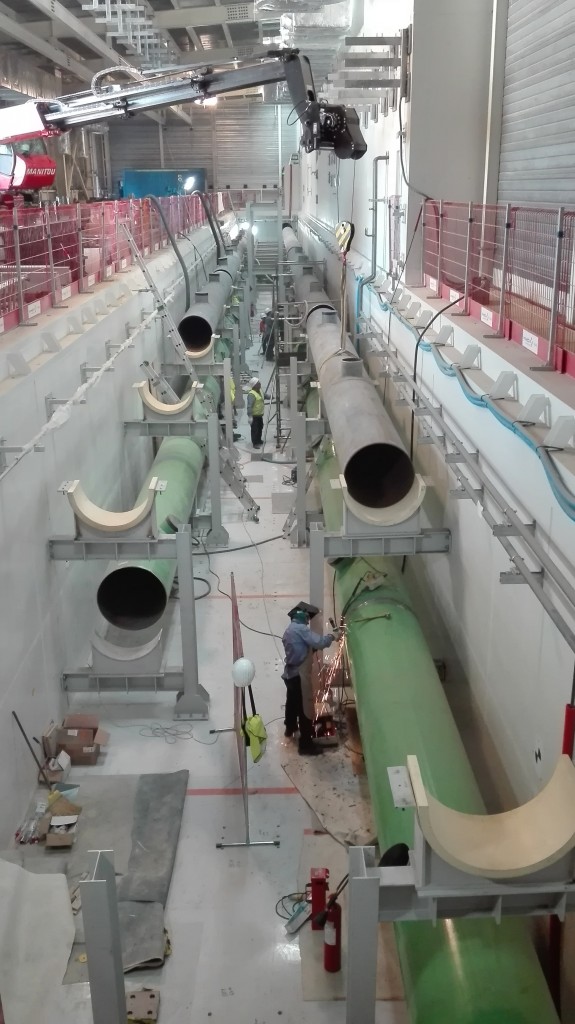
Services on site
2017-08-17 - The Site Services Building will accommodate a large chiller plant, a demineralized water plant and other industrial services. These pipes will help carry the chilled or demineralized water where it's needed.

Open sesame!
2017-08-17 - The 30-metre doors to the Workshop are open, giving us an original angle on work underway on the lower cylinder (tier one). The finish component will exit these doors.
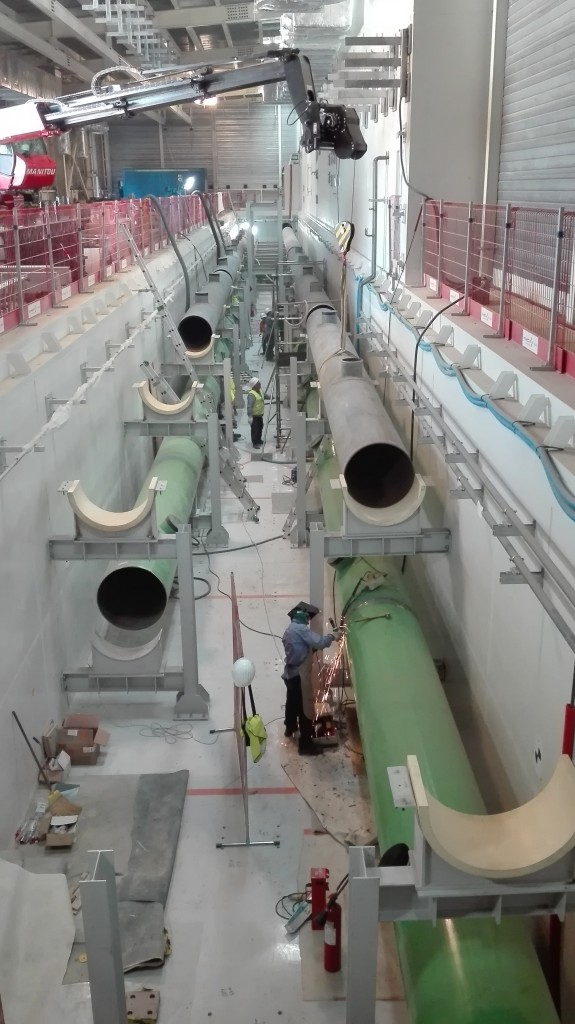
Services on site
2017-08-17 - The Site Services Building will accommodate a large chiller plant, a demineralized water plant and other industrial services. These pipes will help carry the chilled or demineralized water where it's needed.

More equipment
2017-08-17 - The "pieces" of the gantry crane are starting to arrive. The circular station in the background is where the entire coil assembly (eight stacked double pancakes in the case of PF5) will undergo impregnation—a process that "hardens" the assembly and insulates it electrically.
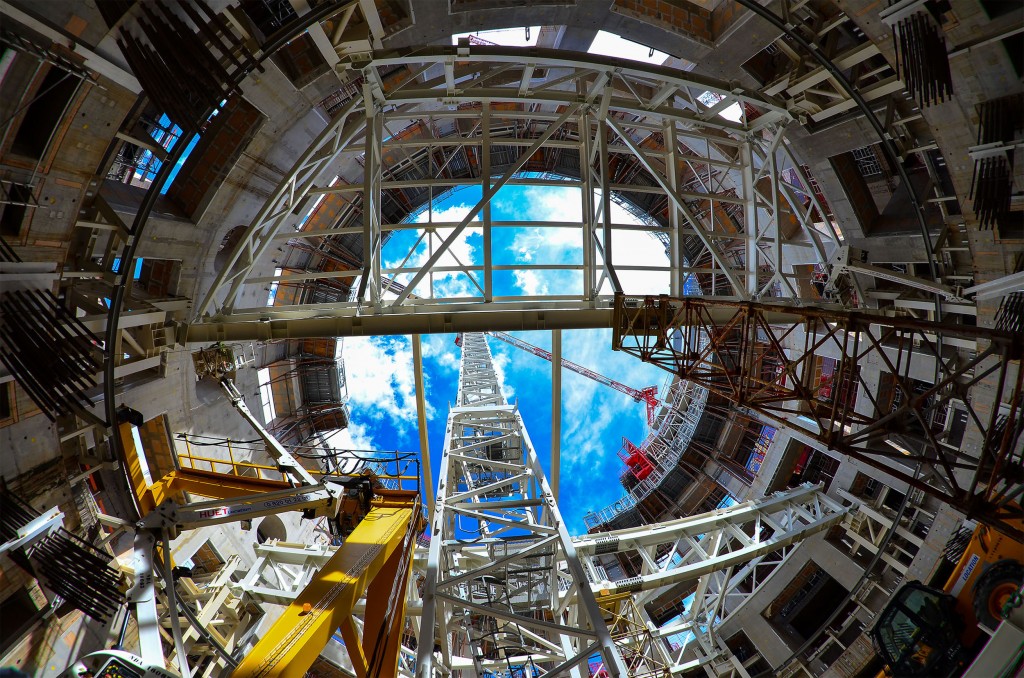
First beams
2017-08-11 - The first beams are installed at level B1 for the temporary lid. The lid is designed to be strong enough to act as a temporary storage platform for materials.
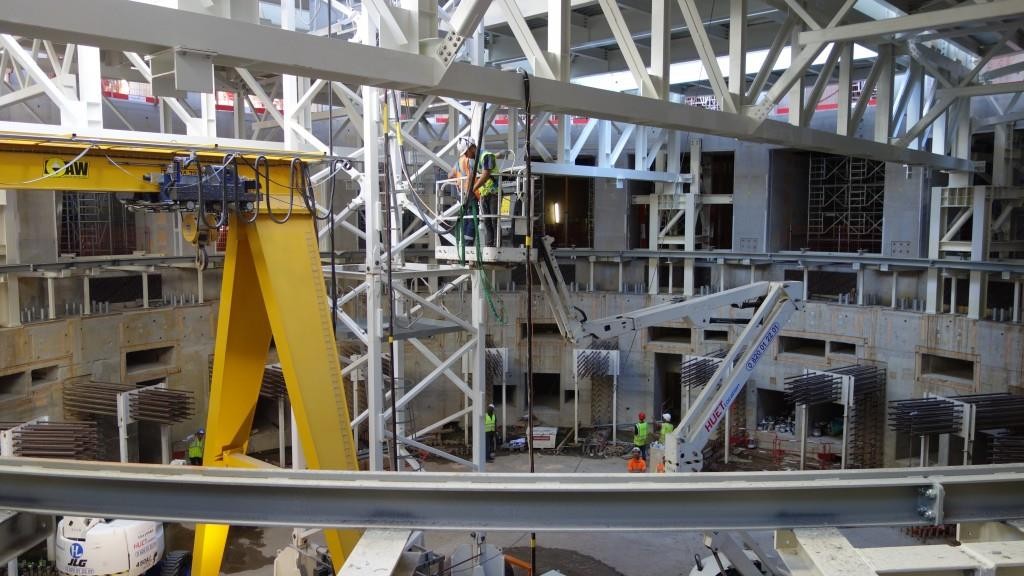
A temporary lid
2017-08-06 - The basement levels of the Tokamak assembly area will soon be covered over by a temporary lid, installed to protect the workers involved in the construction of the cryostat support crown and radial walls.
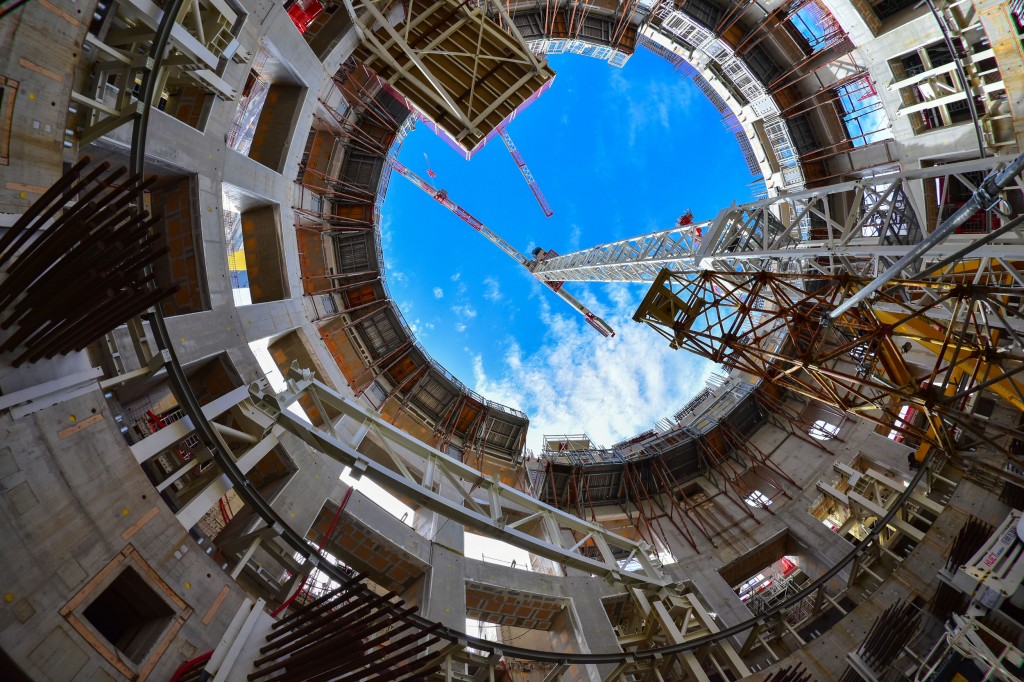
The towering bioshield
2017-08-02 - Looking up through the ITER bioshield in early August. Teams are currently working on the L3 (or second-to-last) level.
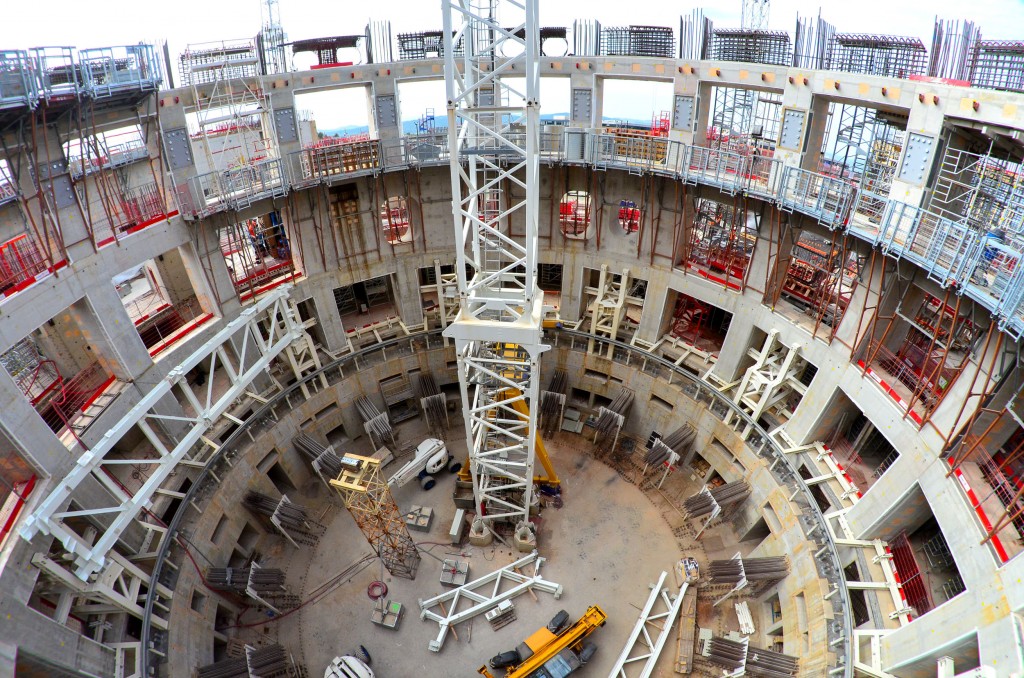
Last picture of full assembly arena
2017-08-02 - An incredible level of detail is discernible in this picture of the first four levels of the ITER bioshield. Soon, though, the basement levels will be hidden from view by a steel cap installed mid-way down.
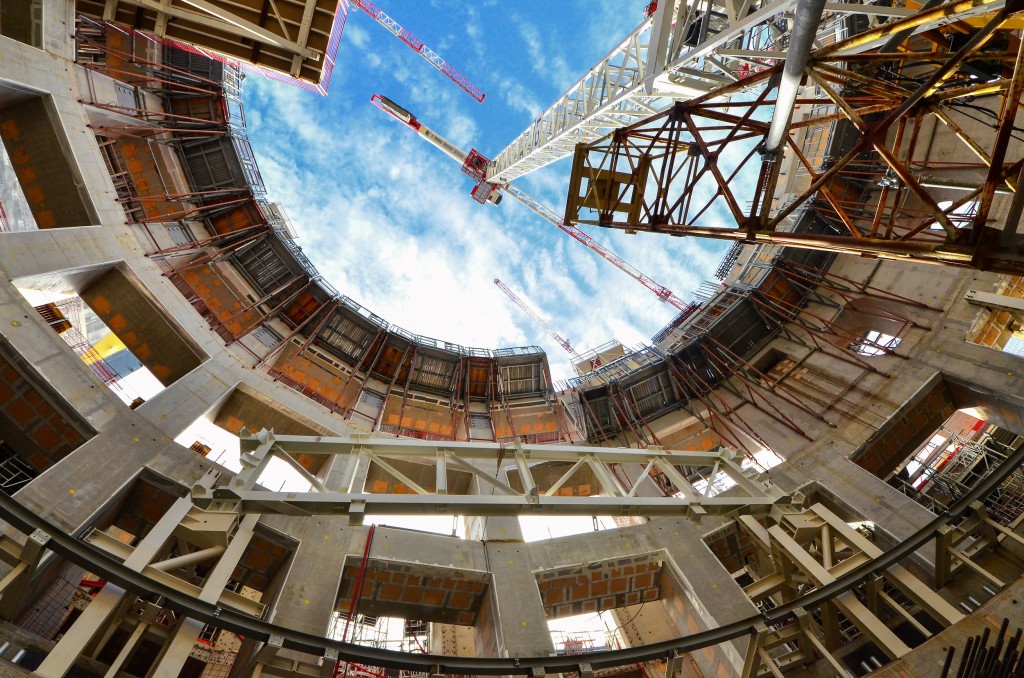
Preparing to "cap" the basement
2017-08-02 - White beams are being set into place at the level of the L1 basemat. Once these beams have been installed all the way across, a steel "cap" will be installed. The cap will protect workers below and serve as a storage platform above.
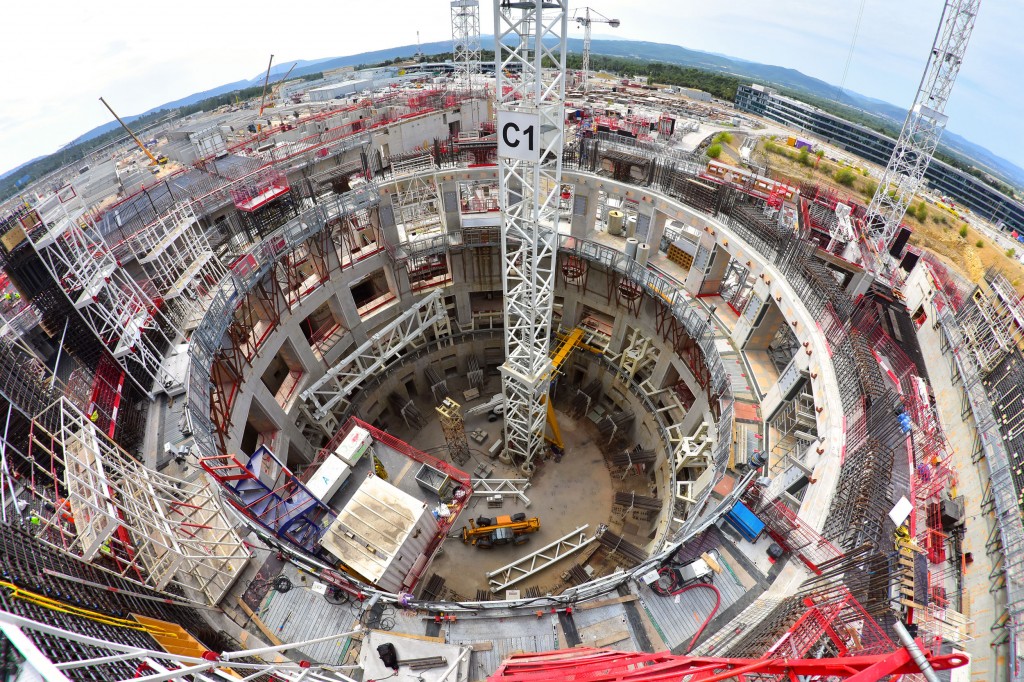
Wide-angle view
2017-08-02 - Taken from the first scaffolding elements at L4 level, this view takes in much of the south-southwest view, from the Magnet Power Conversion buildings under construction at left to ITER Headquarters at right.

From the rim
2017-07-13 - Four completed levels of the ITER bioshield are visible in this wide-angle photo, from the lowest basement level B2 through B1, L1 and finally L2. The single heaviest machine component—the 1,250-tonne cryostat base that is being assembled now in an on-site workshop—will sit at the bottom of this assembly pit on a concrete crown that has yet to be realized.

A crane for a crown
2017-07-13 - This crane has been specially designed to travel in a perfect circle at the bottom of the machine assembly well (B2 level). Its mission: to lift and deliver the loads for the construction of the concrete crown that will support the combined mass of the cryostat and Tokamak (23,000 tonnes).

Pipes and elbows
2017-07-13 - These supersize pipes (one metre and more in diameter) for the heat rejection system are designed for a flow rate of two cubic metres per second.

A star will be born
2017-07-13 - The early morning sun shines through one of the penetrations of the ITER bioshield, symbolizing the "star" that will be born when deuterium-tritium operations begin in 2035.

Pipes and elbows
2017-07-13 - These supersize pipes (one metre and more in diameter) for the heat rejection system are designed for a flow rate of two cubic metres per second.

Moving up from L2
2017-07-13 - Two columns of rebar have been implemented at the L3 level and pouring is set to start on plot 13.

Cooling off
2017-07-13 - Work is ongoing on one of the ''final links'' of the cooling water system: a vast zone (6,000 m²) that accommodates two large basins and a cooling tower installation made of 10 independent cells. Fabrication of the cooling tower elements has begun in India.
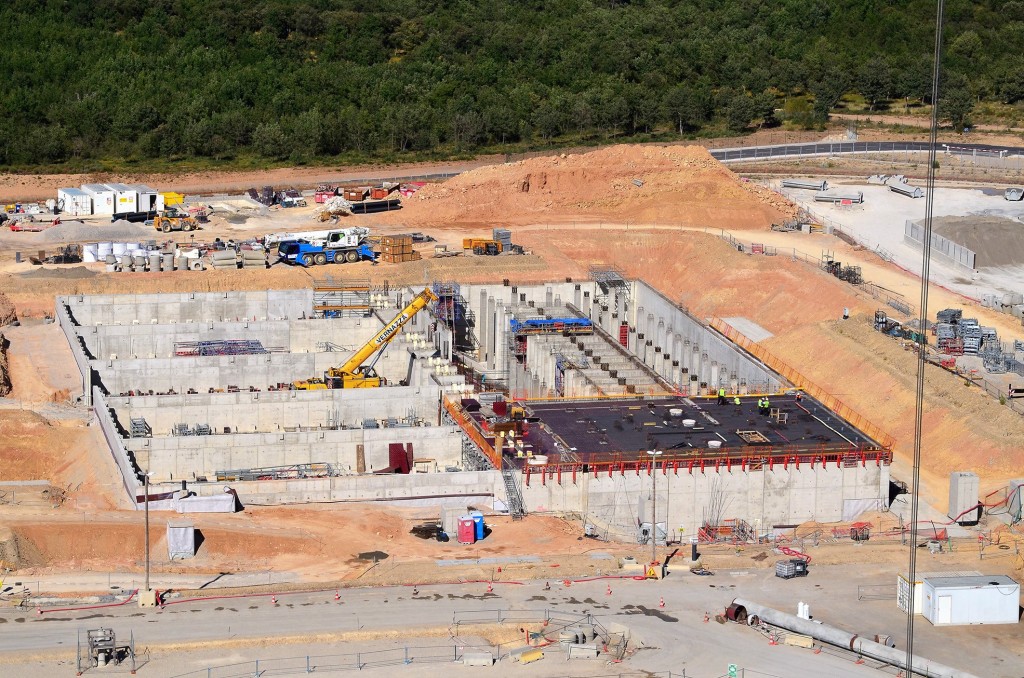
A deep box
2017-07-13 - Seen from above, the cooling water zone at the northeast end of the ITER site.
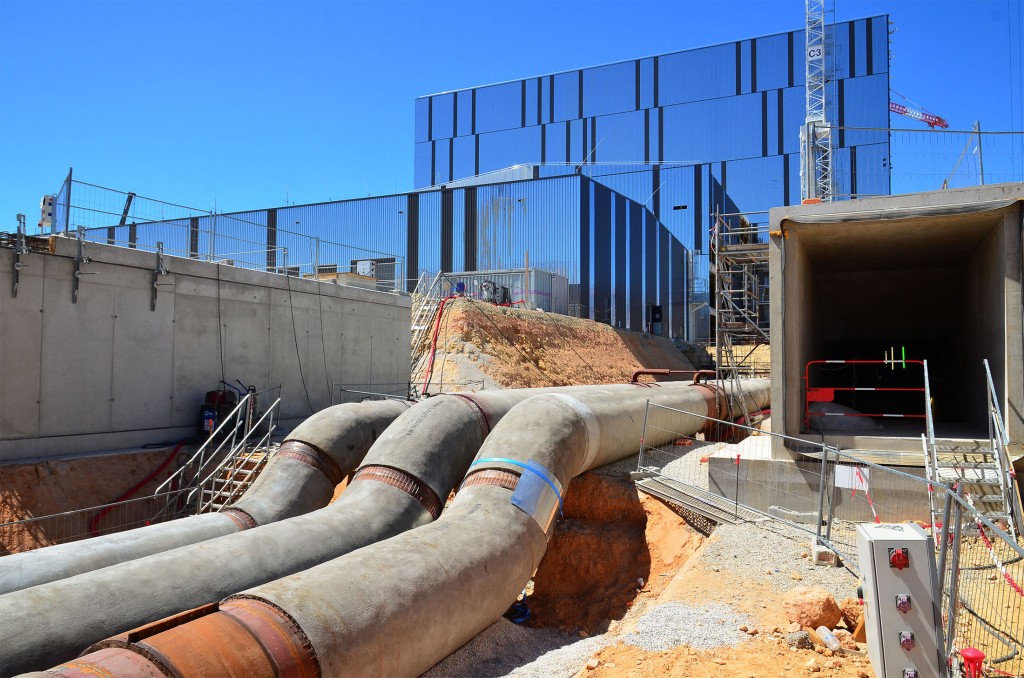
Pipes and elbows
2017-07-13 - These supersize pipes (one metre and more in diameter) for the heat rejection system are designed for a flow rate of two cubic metres per second.

From the northeast
2017-07-12 - The Assembly Hall is joined to two smaller buildings: the Cleaning Facility (left) and the Radio Frequency Heating Building (right).

Looking up
2017-07-12 - The two large overhead cranes of the Assembly Hall are currently undergoing functional tests.

July status
2017-07-12 - The ITER bioshield, centre, and the Diagnostics Building, right, have both reached L2 level and work is underway on L3. Approximately 400 workers in two shifts are in involved in Tokamak Complex construction.
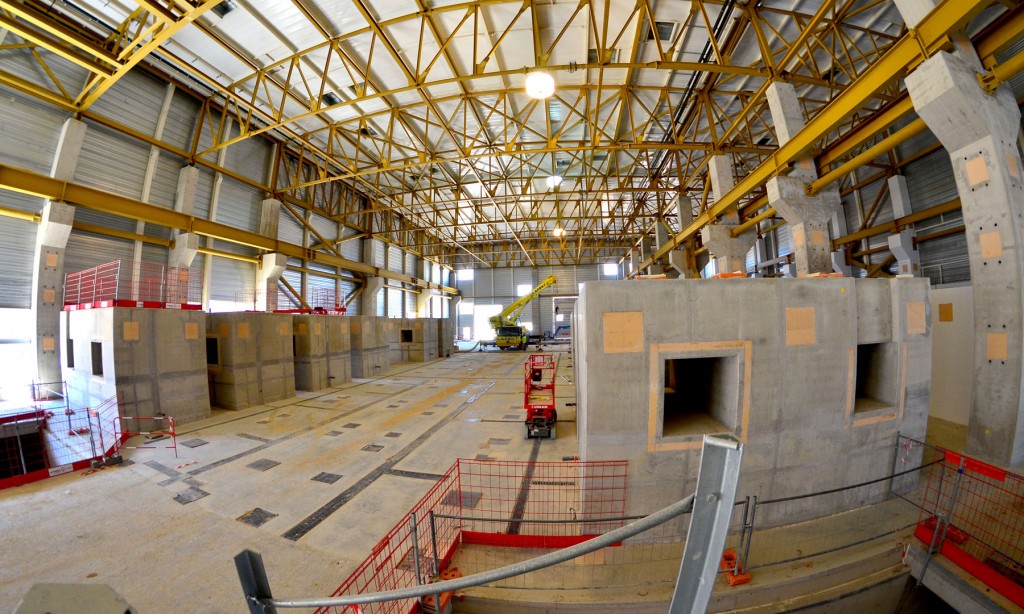
Row after row
2017-07-12 - The 18 concrete structures in the ITER Compressor Building are massive pads that will each support one 25-tonne helium compressor skid. What appears as "windows" in the concrete blocks are in fact passages for the dense interconnecting piping.

A place for storage
2017-07-12 - The storage "box" in the Cleaning Facility, seen from above. © Les Nouveaux Médias/SNC ENGAGE

Finishing the cladding
2017-07-12 - Workers have started to install the final reflective layer of cladding on the eastern face of the cryoplant.
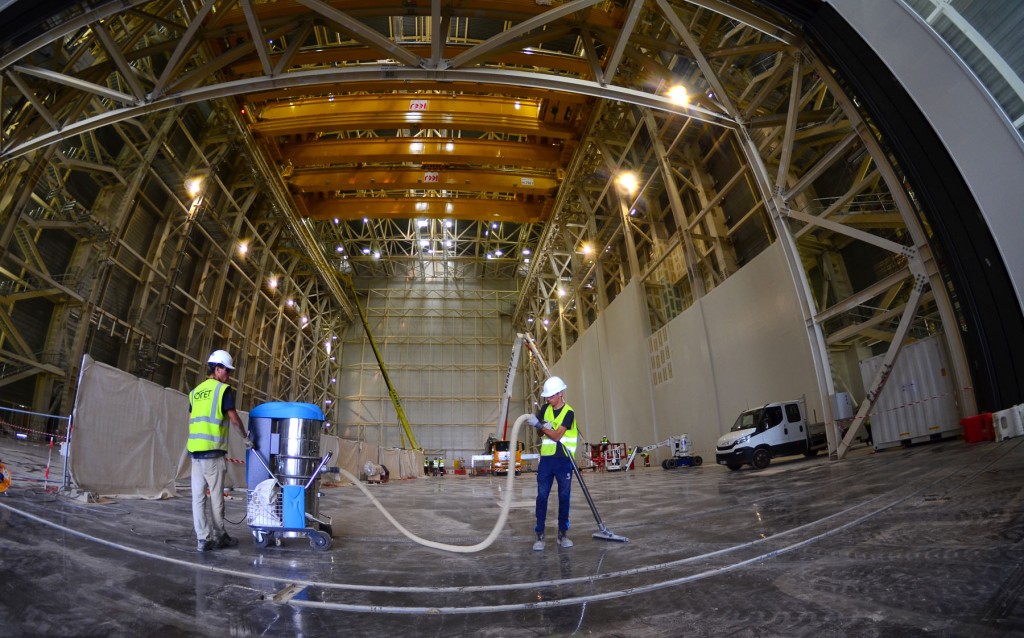
A vast volume to clean ...
2017-07-12 - In the 60-metre-tall building for pre-assembly activities, workers go over the painted surface of the basemat. Not a small task!

Looking up
2017-07-12 - The two large overhead cranes of the Assembly Hall are currently undergoing functional tests.

The mother of all embedded plates
2017-07-12 - Of the 115,000 embedded plates to be installed in the floors, walls and ceilings in the Tokamak Complex, this set of five (in beige, including one large circular plate) is unique. Located in the very centre of the machine assembly pit, with 48-millimetre-thick studs reaching more than one metre deep into the basemat slab, the set will anchor the main tool of Tokamak Pit assembly.
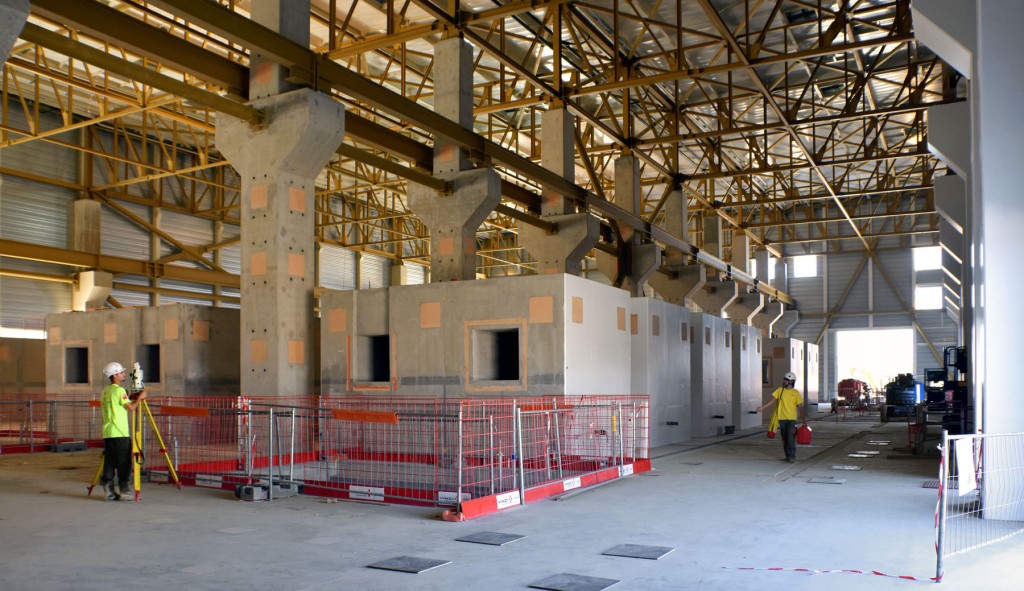
Concrete support
2017-07-12 - Work underway in the cryoplant to prepare for the arrival of 18 helium screw compressor skids. Each one of the 25-tonne units will be installed on top of its own four-metre-high concrete pad, allowing oil from the compressor to regain the oil separation system through gravity.
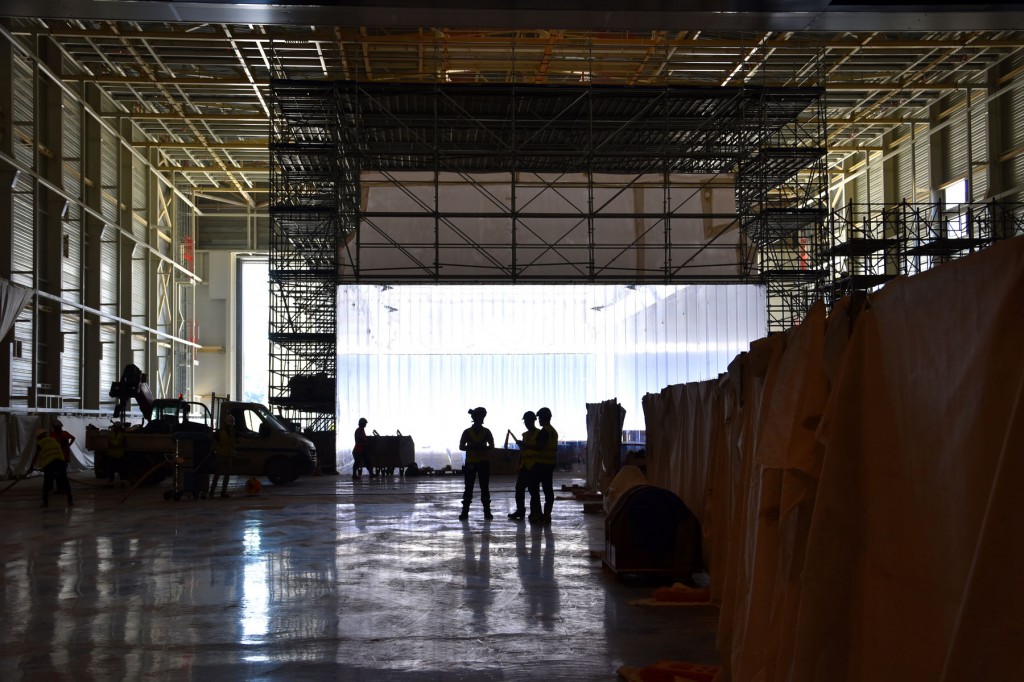
The box within the box
2017-07-12 - A "box within a box" space has been installed in the Cleaning Facility to store deliveries to the Assembly Hall.
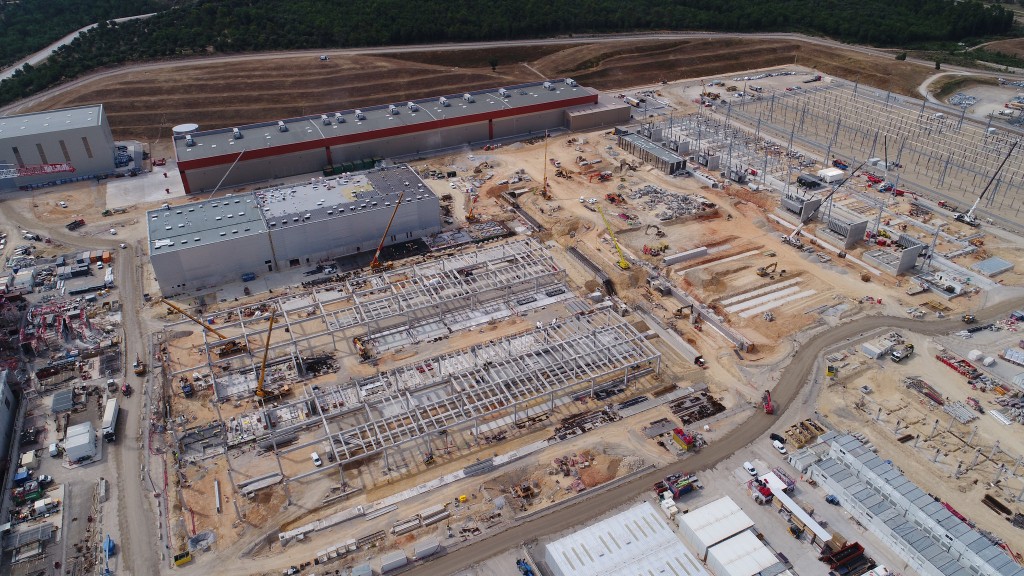
Midsection
2017-07-11 - To the south of the Tokamak Complex is the area reserved for: (top to bottom) the winding of poloidal field magnets (red-topped roof); the ITER cryoplant (in grey); and magnet power conversion (two buildings under construction). © Les Nouveaux Médias/SNC ENGAGE
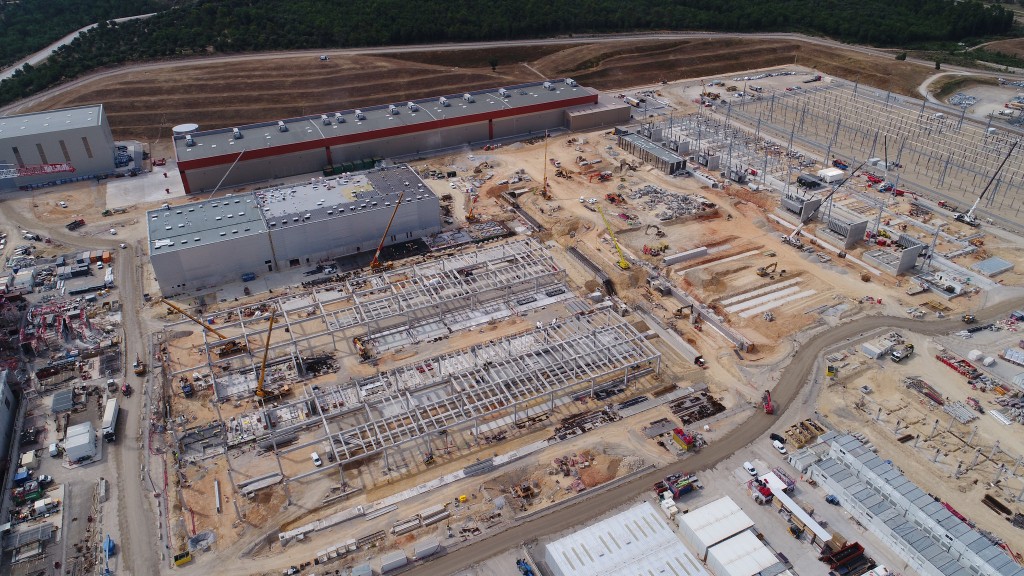
Midsection
2017-07-11 - To the south of the Tokamak Complex is the area reserved for: (top to bottom) the winding of poloidal field magnets (red-topped roof); the ITER cryoplant (in grey); and magnet power conversion (two buildings under construction). © Les Nouveaux Médias/SNC ENGAGE

Diagnostics Building
2017-07-11 - The Diagnostics Building has reached L2 level (second above-ground floor) and work is beginning to frame out the L3-level floor slab. © Les Nouveaux Médias/SNC ENGAGE

A row of transformers
2017-07-11 - Separated by concrete walls are seven large transformers that will convert power from the high voltage line down to voltages that can be used by the installation. In the foreground, the last of three PPEN transformers delivered by China for the pulsed power electrical network is about to be installed in its bay. © Les Nouveaux Médias/SNC ENGAGE
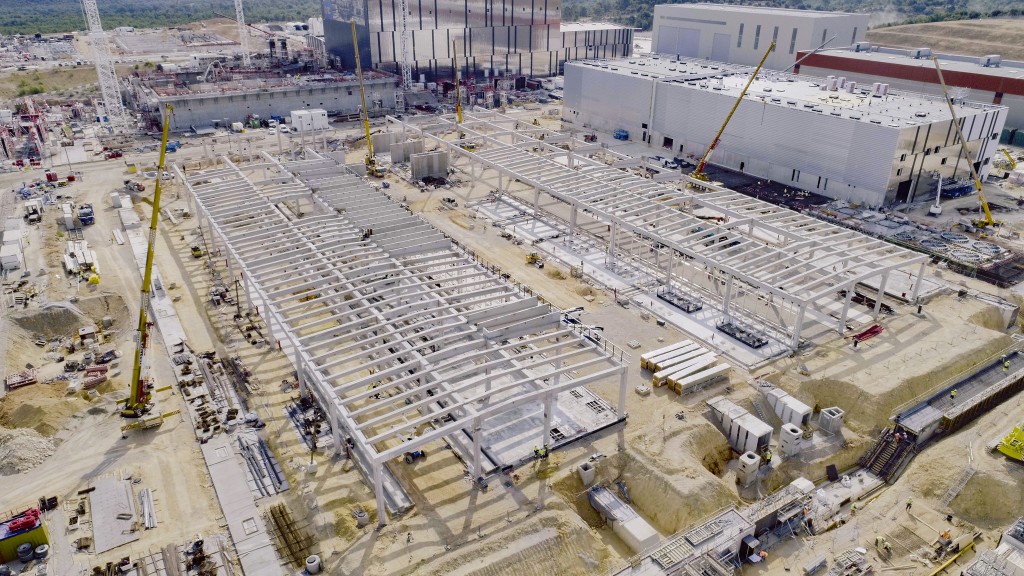
Frames visible
2017-07-11 - Over the summer, visible progress is accomplished on the structures of the twin buildings. © Les Nouveaux Médias/SNC ENGAGE
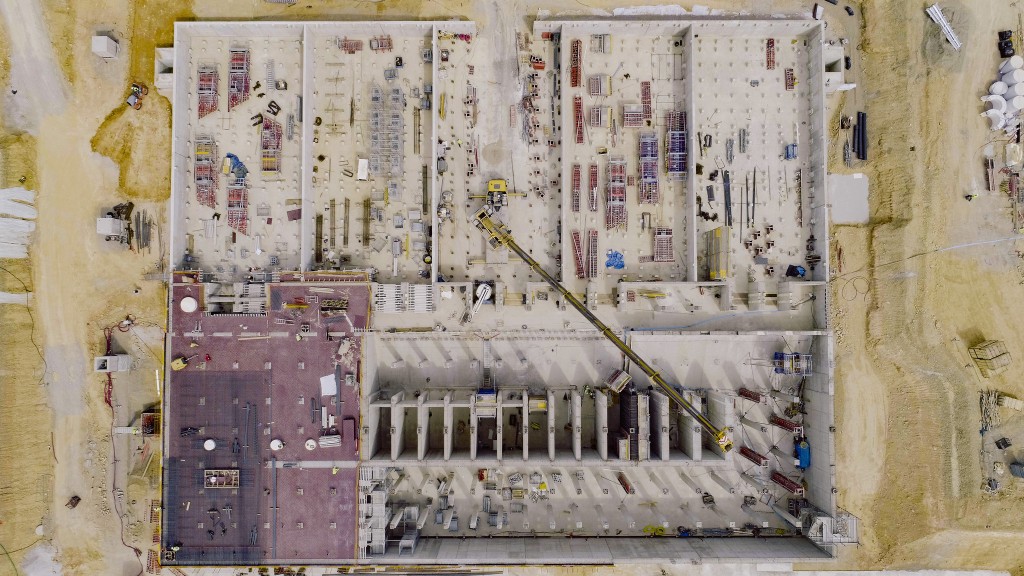
Heat rejection zone framed out
2017-07-11 - From the air we can see where the ten induced-draft cooling tower will be located (in five large bays, top) above the cold basin and, at bottom, the hot basin. © Les Nouveaux Médias/SNC ENGAGE
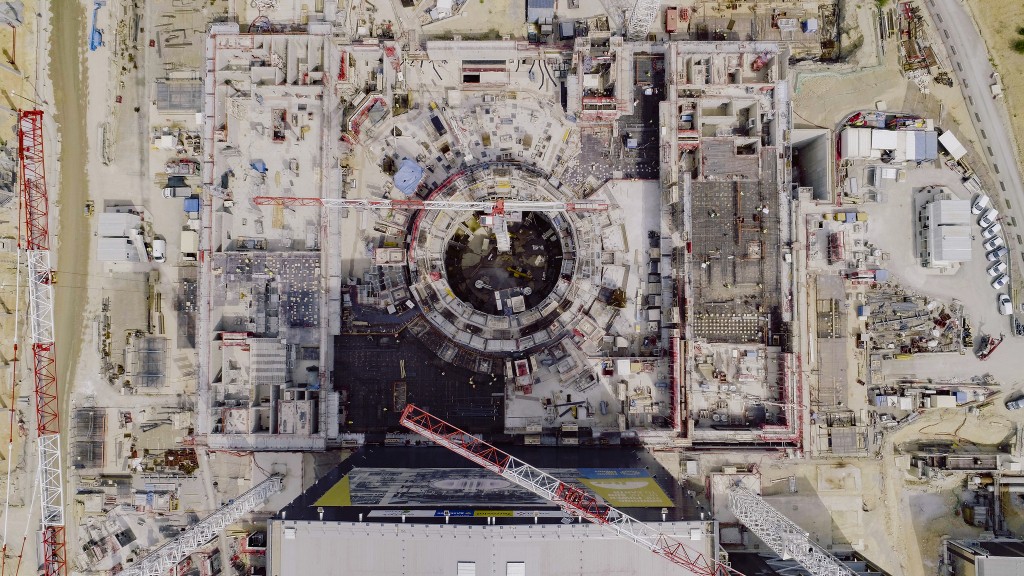
Eye from the sky
2017-07-11 - The Tokamak Complex "box" as seen by drone on a dry summer day in July. One quarter of the L1 Tokamak Building slab remains to be poured. © Les Nouveaux Médias/SNC ENGAGE

Dedicated handling tools
2017-07-07 - For Larsen & Toubro, the Indian contractor responsible for the fabrication of the ITER cryostat, carrying out its contract means not only machining the pieces in India, but also creating a dedicated assembly facility on the ITER site and equipping it with specialized handling tools and assembly platforms. Pictured: the lift beam and clamps for positioning the thin-walled segments of the lower cylinder.

Laser and level
2017-07-07 - Tolerance control in the assembly of the 60-tonne segments is achieved using sophisticated laser alignment and metrology equipment ... and also a standard spirit level.
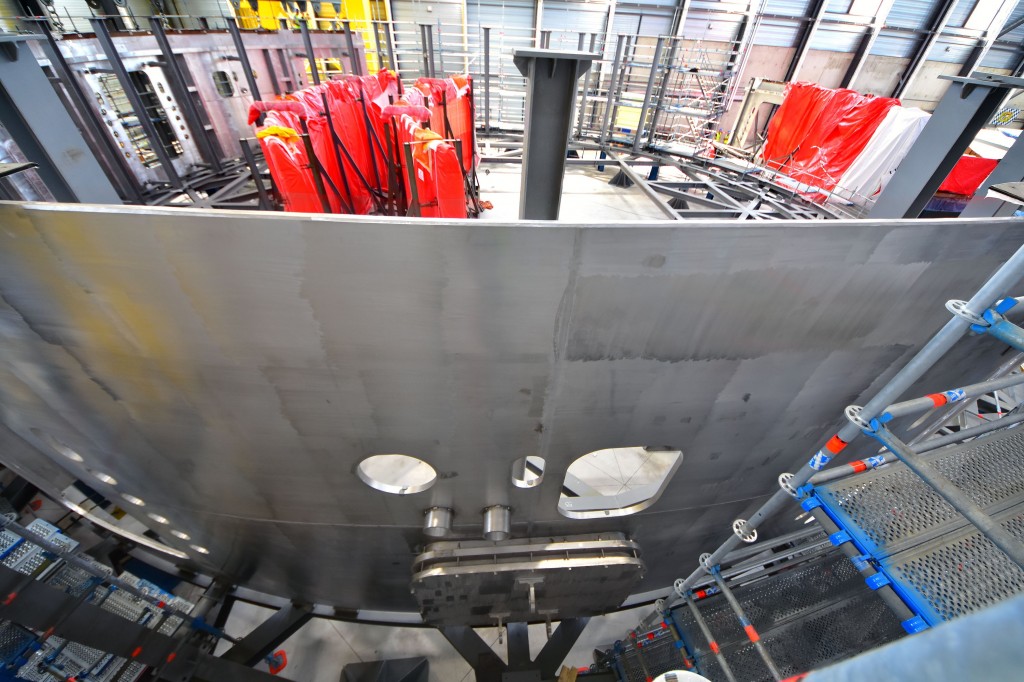
A manhole in a thin wall
2017-07-07 - Relative to the size of the segment, the 50-millimetre thick stainless steel plate appears rather thin. Under the openings in this photo is a an access door that will be used for inspection and maintenance inside the cryostat before the beginning of nuclear operations.

A steel ring pierced with openings
2017-07-07 - A tall steel ring pierced with dozens of openings—some perfectly circular, some rectangular with rounded angles, a few as high and wide as a cathedral door. This is tier one of the cryostat lower cylinder.

A crowded place
2017-07-07 - Cryostat base section at one end, lower cylinder at the other, and storage in between. The 110-metre-long Cryostat Workshop is a crowded and busy place with work progressing in parallel on two main cryostat sections.

Big Foot
2017-07-07 - The assembly platforms are raised so that welders can have access to the underside of the components.

Carefully now ...
2017-07-07 - Workers from MAN Diesel and Turbo, the German contractor responsible for assembly and welding, carefully manoeuvre one of the six 60-tonne lower cylinder segments into position on the assembly frame. The second-tier segments will come later, creating a 10-metre-tall component.

Getting a real idea of fabrication
2017-07-04 - On display for visitors in the European winding facility are some of the critical elements of the fabrication process: superconducting strand, cable, conductor, and helium inlet joints.

A sea of iron
2017-07-04 - Rebar reinforcement is in place for the platform level slab (L1) of the Tokamak Building.
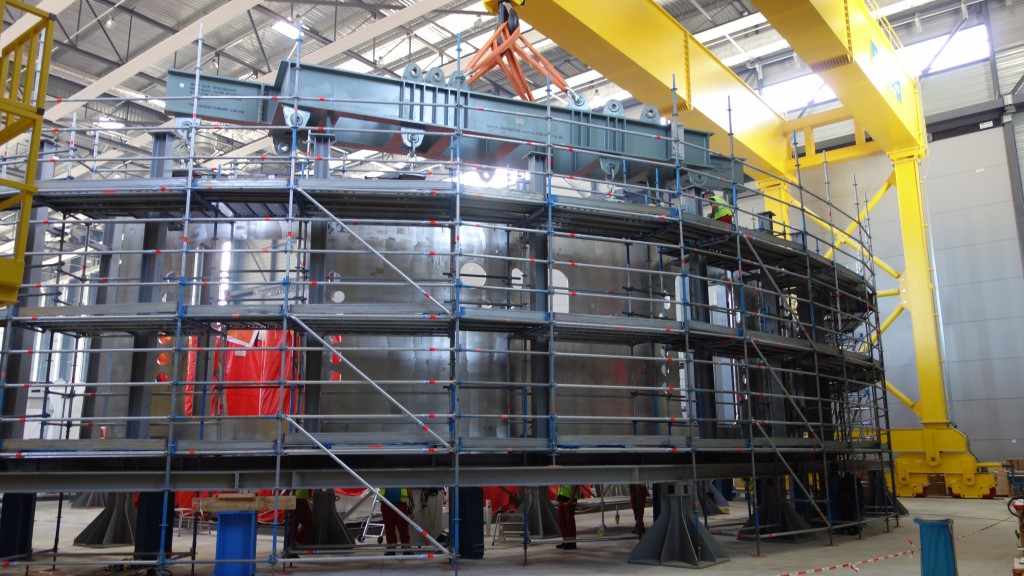
A perfect fit
2017-07-04 - The 60-degree segments of the lower cylinder (tier one) are installed on a tall assembly frame.
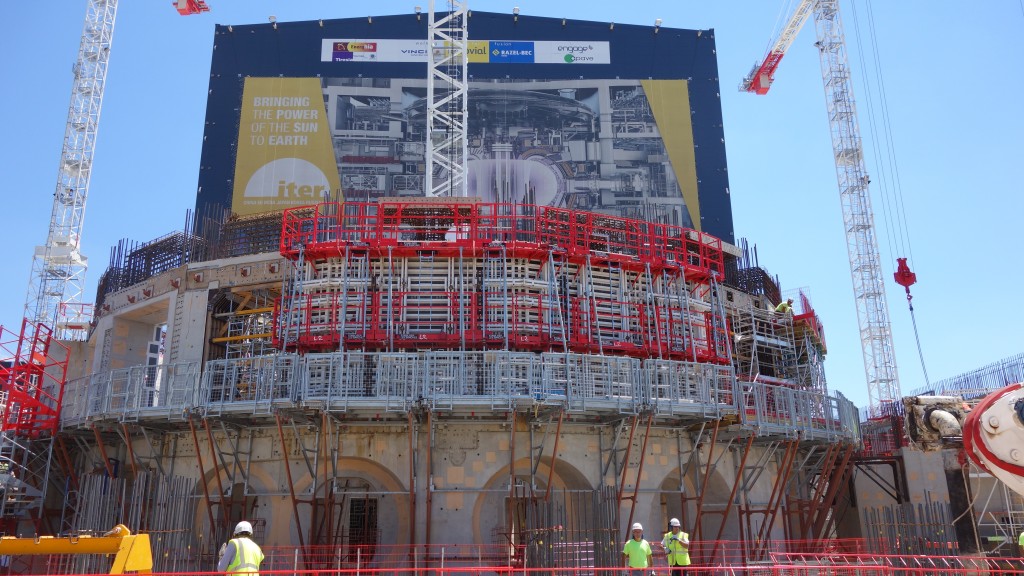
L2 emerging
2017-07-03 - The second above-ground level of the bioshield is emerging from its formwork.

Delivering millions of watts of heating power
2017-07-03 - An exploded isometric view of the ITER/MITICA beam source, composed of a radio frequency ion source and a seven-grid extractor and accelerator.

Making things just right
2017-07-03 - An optical metrology device is used to verify the alignment of the 60-degree tier 1 segments.
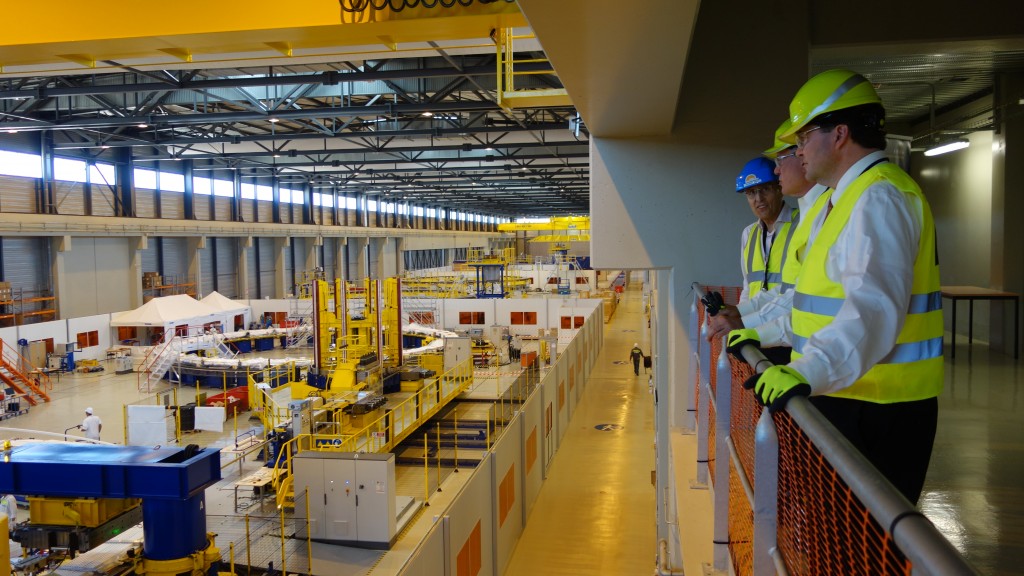
Several projects at once
2017-07-03 - While the first double pancake for poloidal field coil #5 is in the last stages of winding (out of frame, far left), the copper dummy winding on the staging table (centre) is being prepped for impregnation.

Compressor Building, when it's chock full
2017-07-01 - In the 3,400 m² available in the Compressor Building, contractors will install 18 oil-flooded screw compressors for the helium plant as well as other helium compressors and compressors for the liquid nitrogen plant.
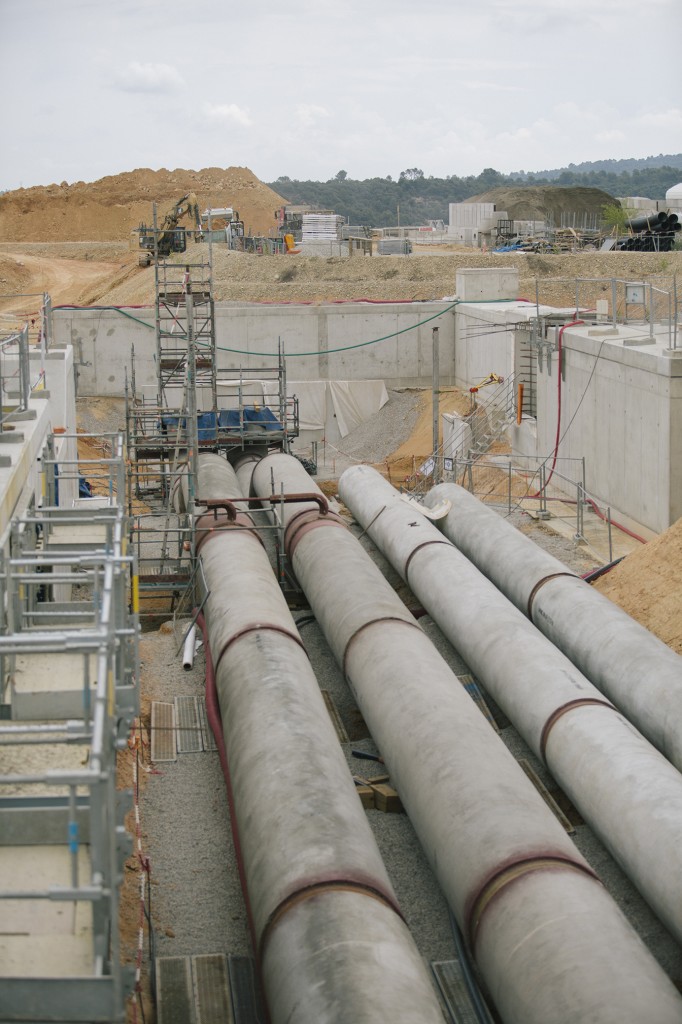
Buried piping
2017-06-28 - Water will travel out of the cooling water loops of the Tokamak and its systems, through these 1.6-metre-in-diameter pipes, and on to the heat rejection system. © Les Nouveaux Médias/SNC ENGAGE
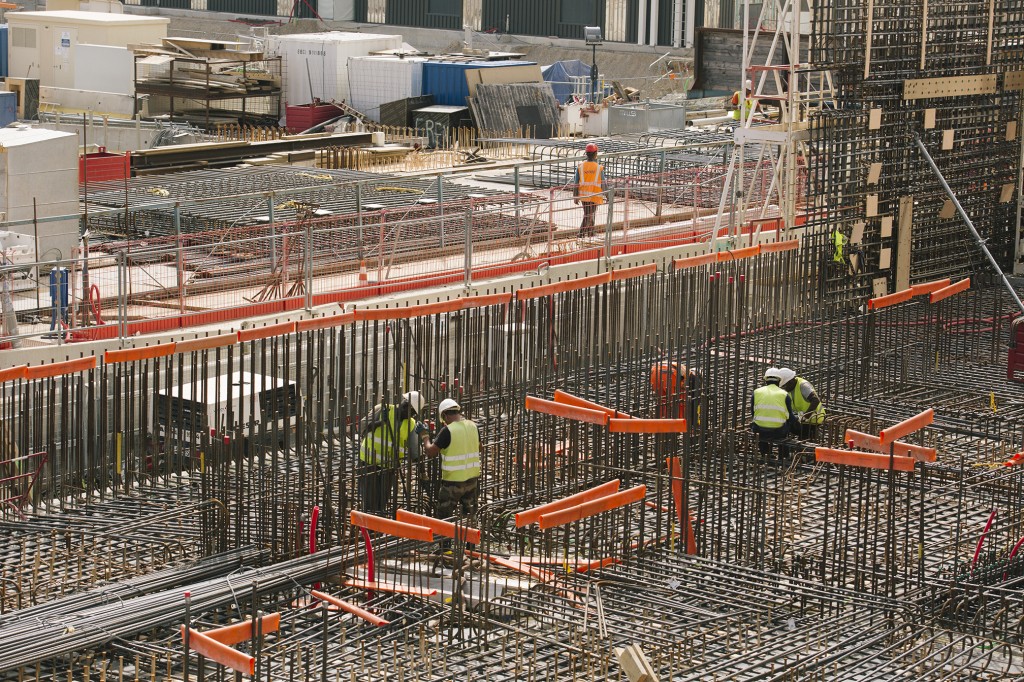
That's a lot of steel
2017-06-28 - Some 30,000 tonnes of steel reinforcement will be integrated into the walls, ceilings and floors of the Tokamak Complex. © Les Nouveaux Médias/SNC ENGAGE

Tokamak Complex, Level 1
2017-06-28 - This photo shows an area just outside of the bioshield that will be packed with systems and components. © Les Nouveaux Médias/SNC ENGAGE

Buried piping
2017-06-28 - Water will travel out of the cooling water loops of the Tokamak and its systems, through these 1.6-metre-in-diameter pipes, and on to the heat rejection system. © Les Nouveaux Médias/SNC ENGAGE
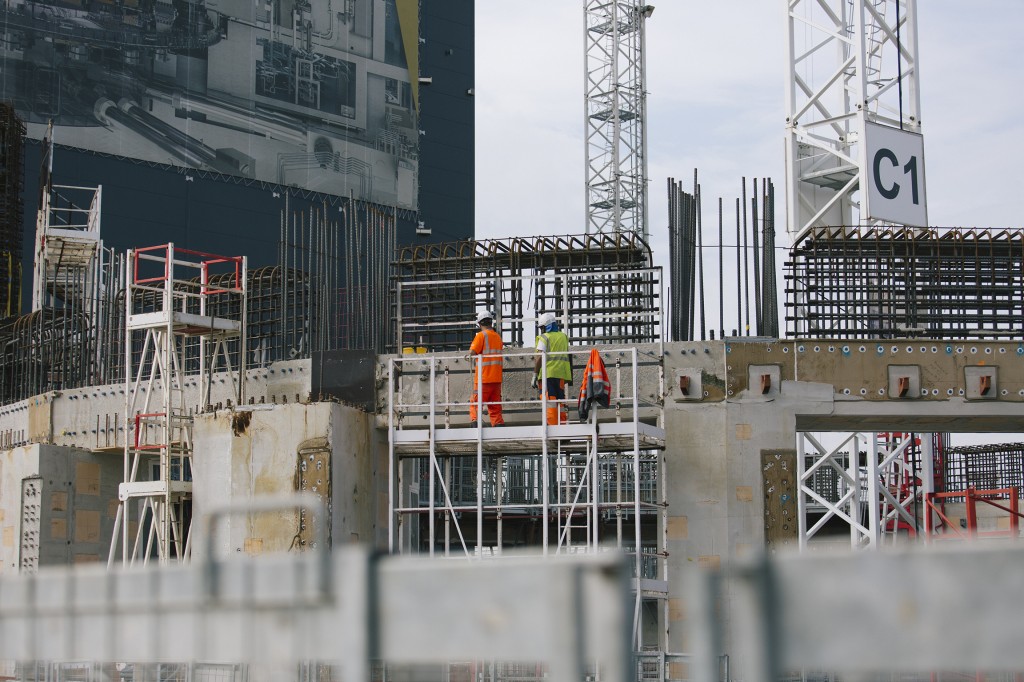
In late June
2017-06-28 - When completed, the top of the bioshield will be aligned (approximately) with the base of the poster. © Les Nouveaux Médias/SNC ENGAGE

Buried piping
2017-06-28 - Water will travel out of the cooling water loops of the Tokamak and its systems, through these 1.6-metre-in-diameter pipes, and on to the heat rejection system. © Les Nouveaux Médias/SNC ENGAGE
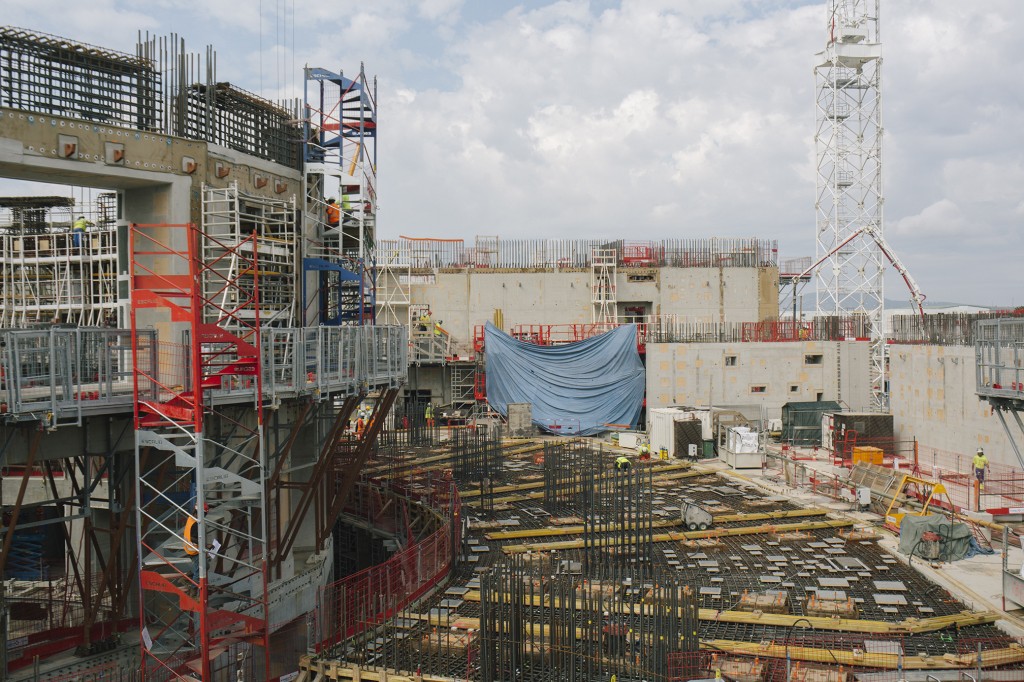
Rounding the corner
2017-06-28 - One of the last areas around the bioshield that has not yet been poured. Preparations are underway. © Les Nouveaux Médias/SNC ENGAGE
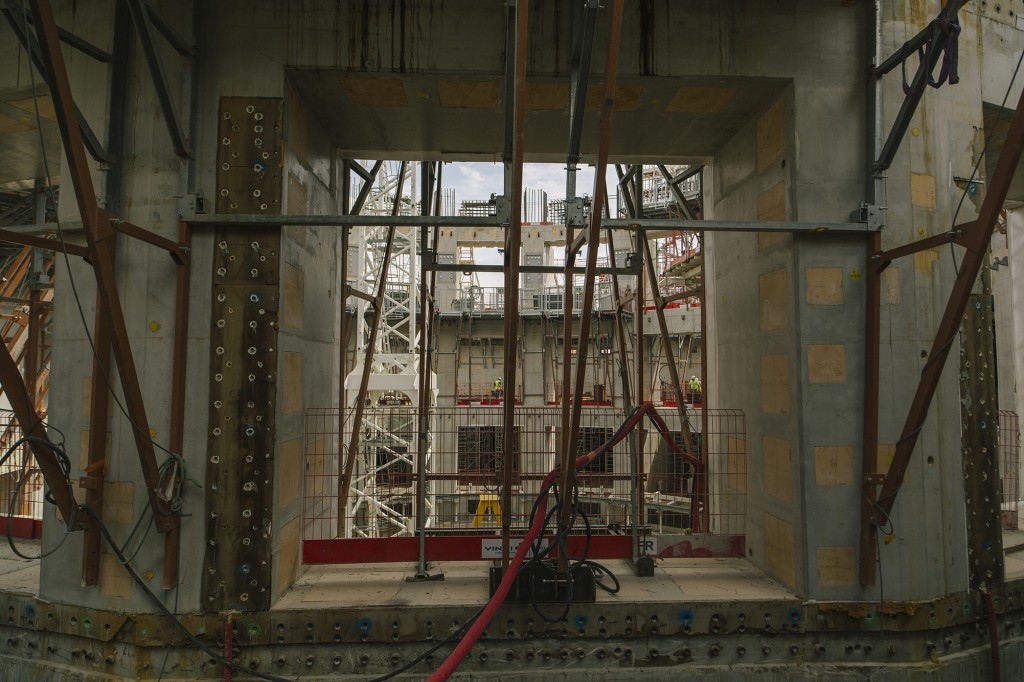
A window to the Tokamak
2017-06-28 - The largest openings in the bioshield are approximately 5 x 5 metres. (For a sense of the opening's true size, see the worker in yellow on the other side.) © Les Nouveaux Médias/SNC ENGAGE
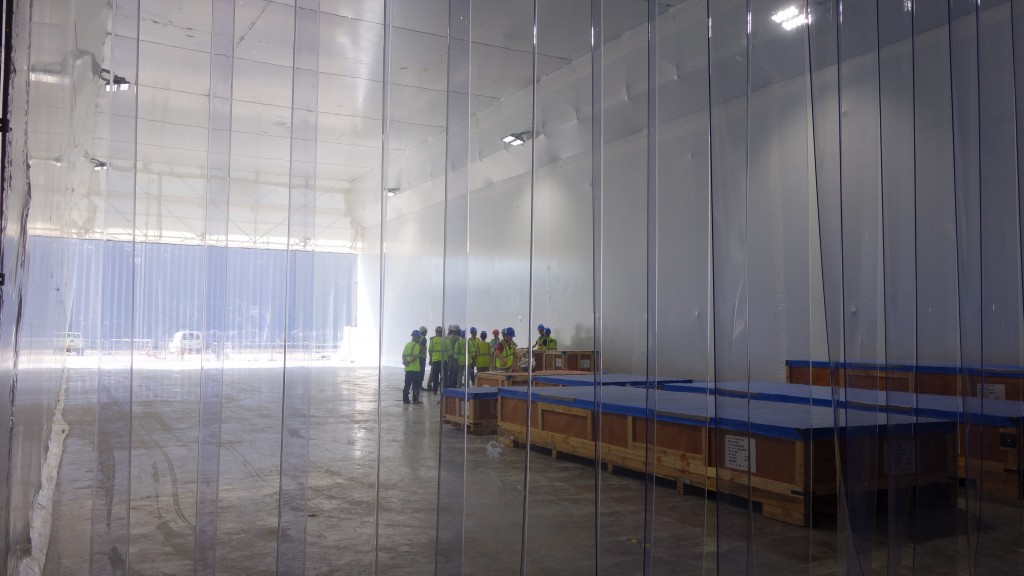
A clean space in the Cleaning Facility
2017-06-27 - In the adjacent Cleaning Facility, a storage structure has been erected to keep the elements of the sector sub-assembly tools out of the dust during assembly. The first crates reached ITER in June from Korea.
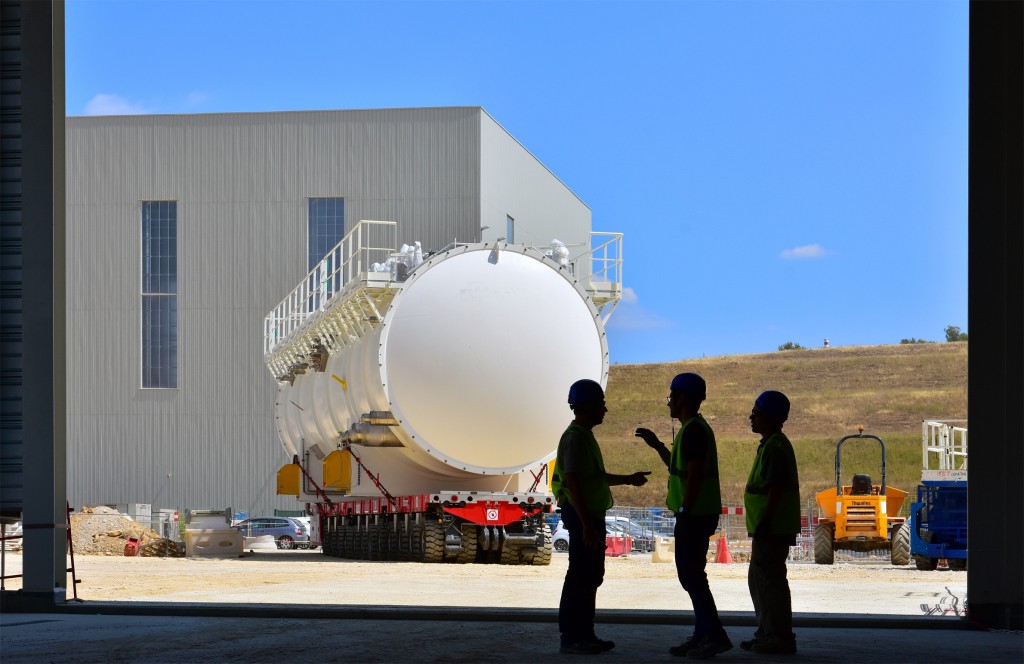
Cold boxes take their place
2017-06-23 - One of the three helium cold boxes is transported through the open door of the on-site cryoplant.
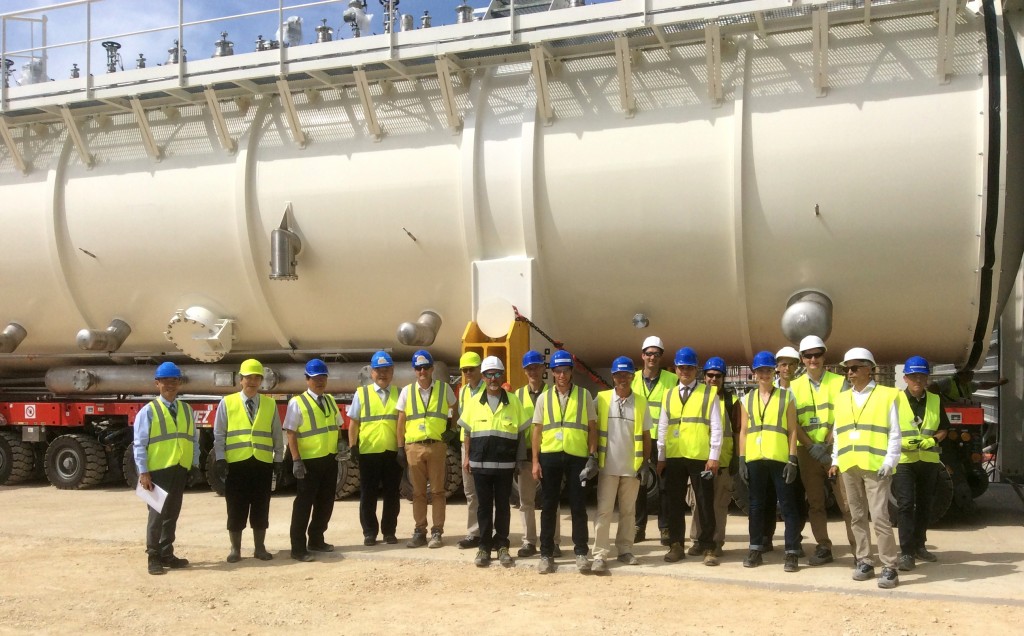
Celebrating a Council milestone
2017-06-22 - In the presence of ITER Director-General Bernard Bigot and his two deputies, Chief Operating Officer Gyung-Su Lee and Relations Coordinating Officer Eisuke Tada, the team responsible for cold box installation celebrates the respect of an ITER Council milestone that scheduled the "Start of work in the cryoplant" for June 2017.

Celebrating a Council milestone
2017-06-22 - Celebrating a Council milestone In the presence of ITER Director-General Bernard Bigot and his two deputies, Chief Operating Officer Gyung-Su Lee and Relations Coordinating Officer Eisuke Tada, the team responsible for cold box installation celebrates the respect of an ITER Council milestone that scheduled the "Start of installation work in the cryoplant" for June 2017.

The doors are open today
2017-06-22 - Around the back of the Assembly Hall, we can see through the open doors of the Cleaning Facility. A temporary structure has been erected there for the storage of assembly tool components that are arriving from Korea. In the meantime, a helium cold box is transported along the road to the cryoplant.
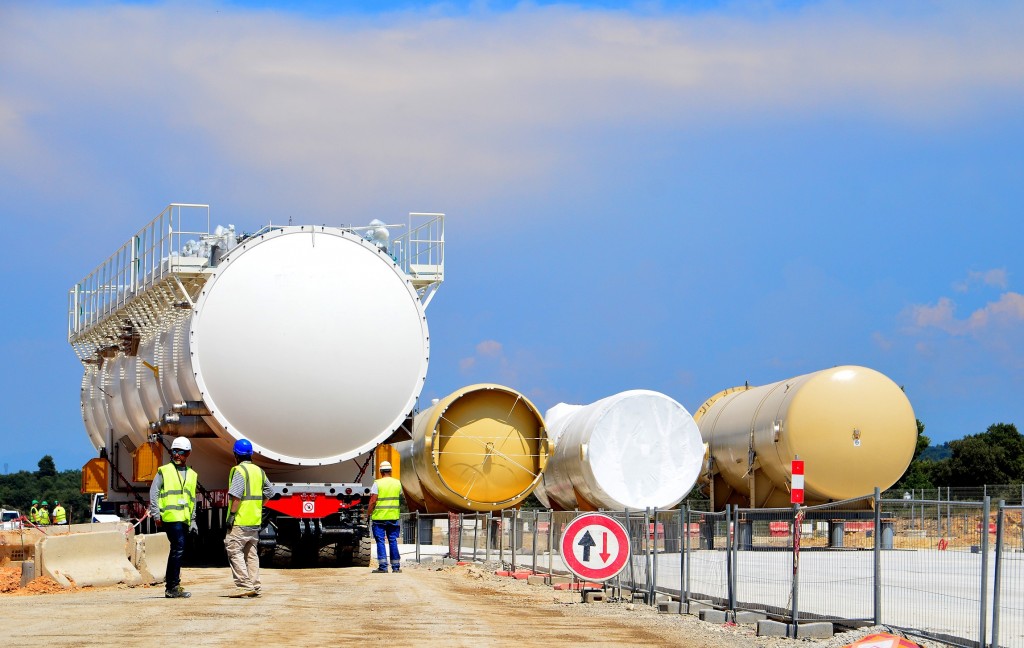
Temporary tank storage
2017-06-22 - On its way to the cryoplant, the second cold box on its transport trailer passes three tanks (two for gaseous helium and a third, at right, for liquid nitrogen). They too will be transported to the cryoplant for installation in the exterior storage area.
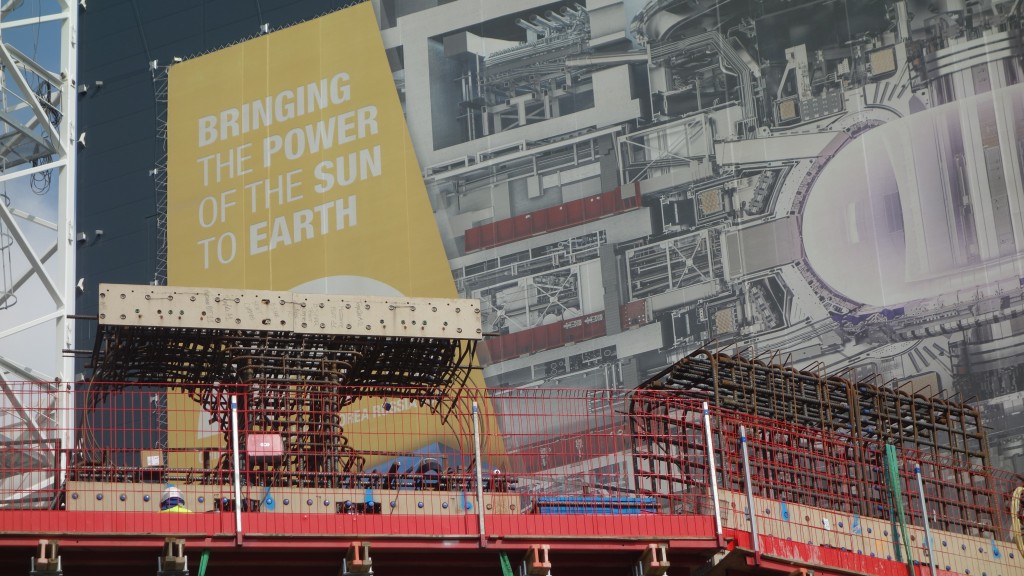
Bringing the power of the Sun to Earth
2017-06-22 - A large poster adorns the temporary wall of the Assembly Hall. Against this spectacular backdrop, workers are advancing the L3 level of the bioshield.

Exceptional transport
2017-06-22 - Snaking around the back of the platform, between the Cleaning Facility at left and the Cryostat Workshop plus Poloidal Field Coils Winding Facility at right, is the transport convoy for an element of the cryoplant.

Careful manoevring
2017-06-22 - The multi-wheeled transporter positions the second cold box next to the first. The equipment will now be propped up and the trailer removed.
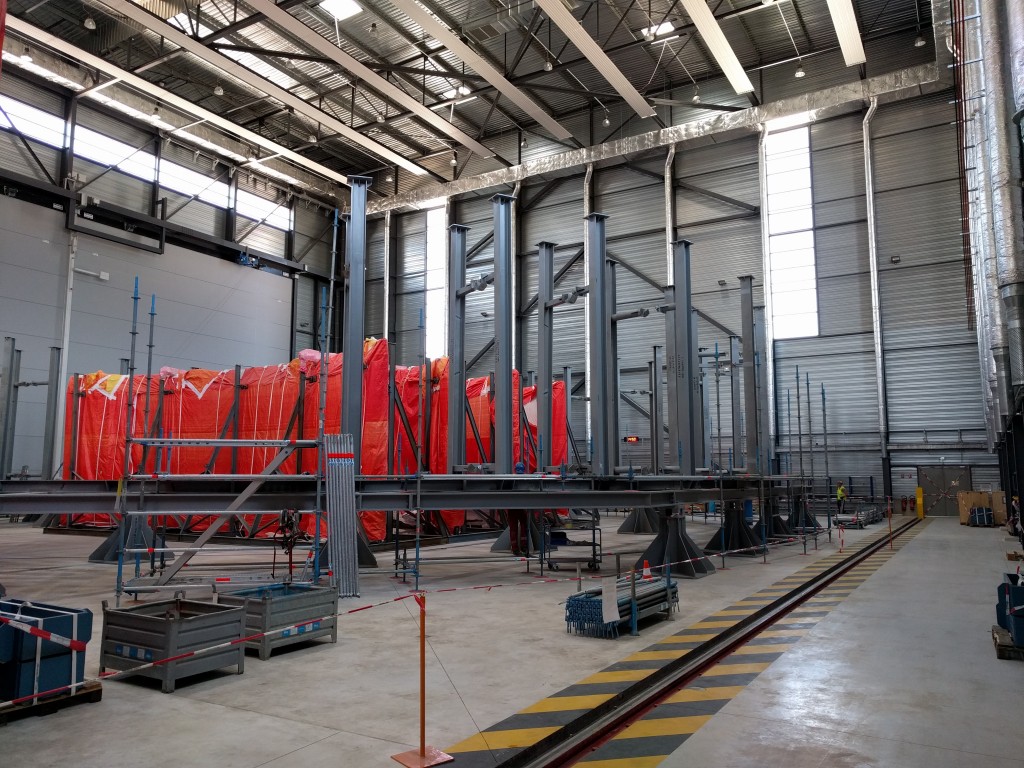
Second assembly frame going up
2017-06-20 - In the Cryostat Workshop, a 10-metre-tall assembly platform is being installed to receive the segments of the lower cylinder.
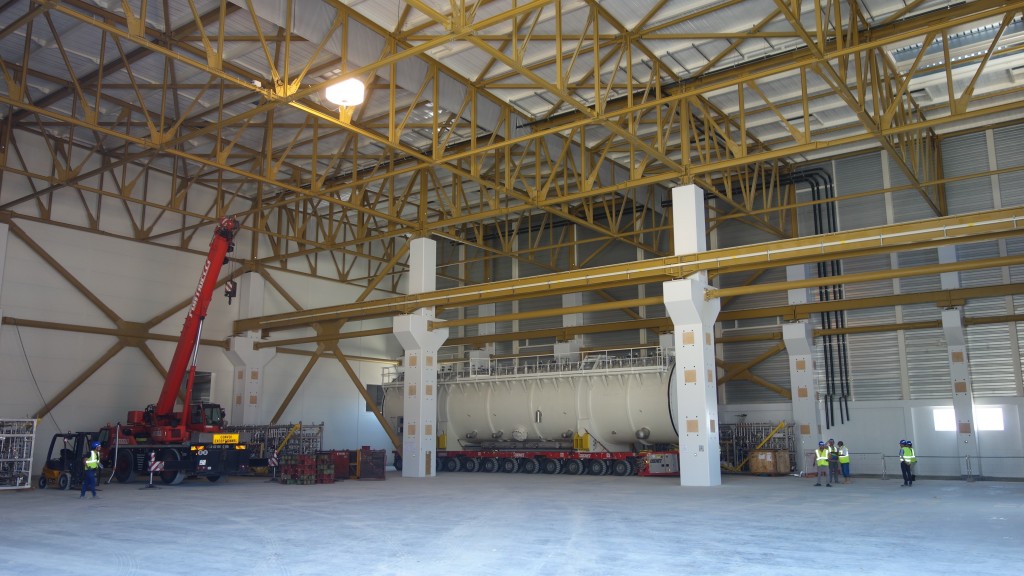
First components!
2017-06-20 - On 20 June three helium coldboxes were moved from storage at the entrance of the ÏTER site to the Cold Box Building of the ITER cryoplant. This is the first equipment to be installed ... but certainly not the last!
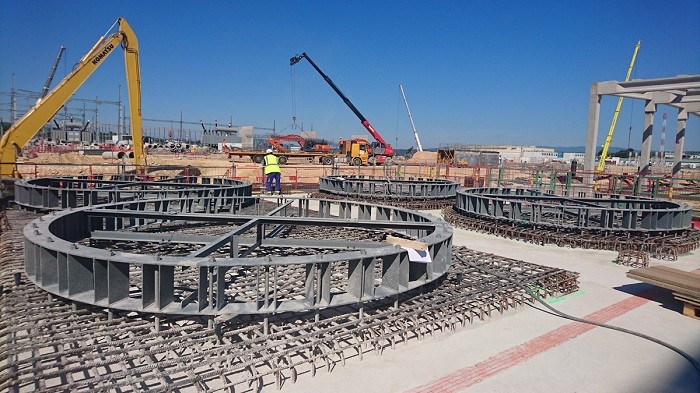
Special anchors
2017-06-20 - On the exterior storage area of the cryoplant, embedded anchors are in place for the helium and nitrogen storage tanks that will be installed vertically. Photo: F4E
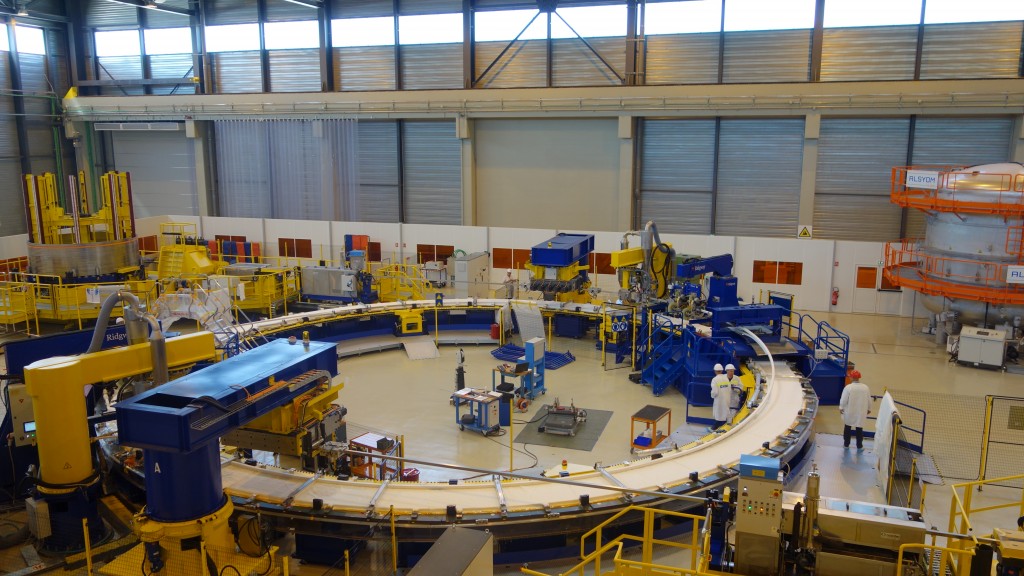
A meticulous process
2017-06-20 - In a vast manufacturing facility on the ITER site, the poloidal field coil team is starting on the second layer of production double pancake number one.
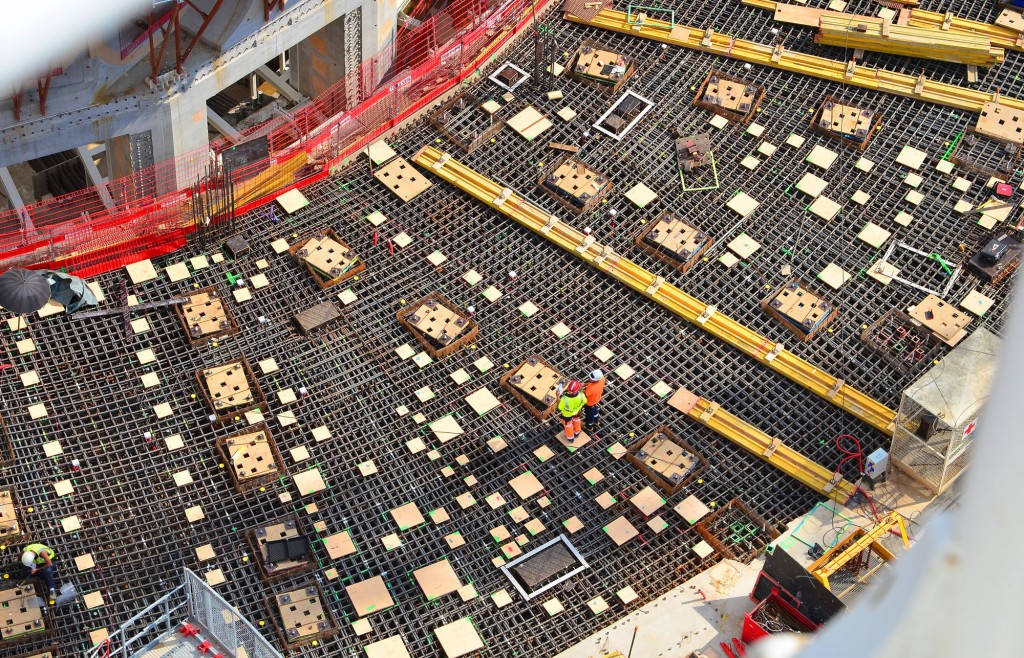
Embedded plates galore
2017-06-19 - An estimated 110,000 steel plates will be embedded in the Tokamak Complex floors, walls and ceilings to anchor equipment.
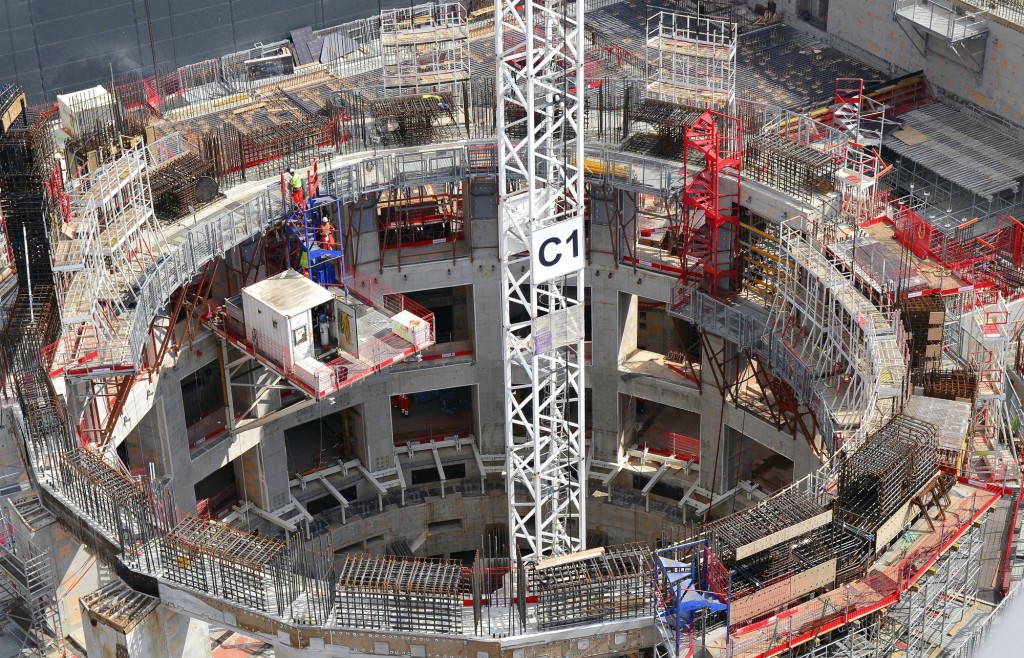
Up close
2017-06-19 - Close to five levels high (B2, B1, L1, L2 and L3 underway), the ITER bioshield forms the "pit" for Tokamak assembly activities.

Central arena
2017-06-19 - Looking more and more like a coliseum, the ITER bioshield rises from the centre of the Tokamak Building.
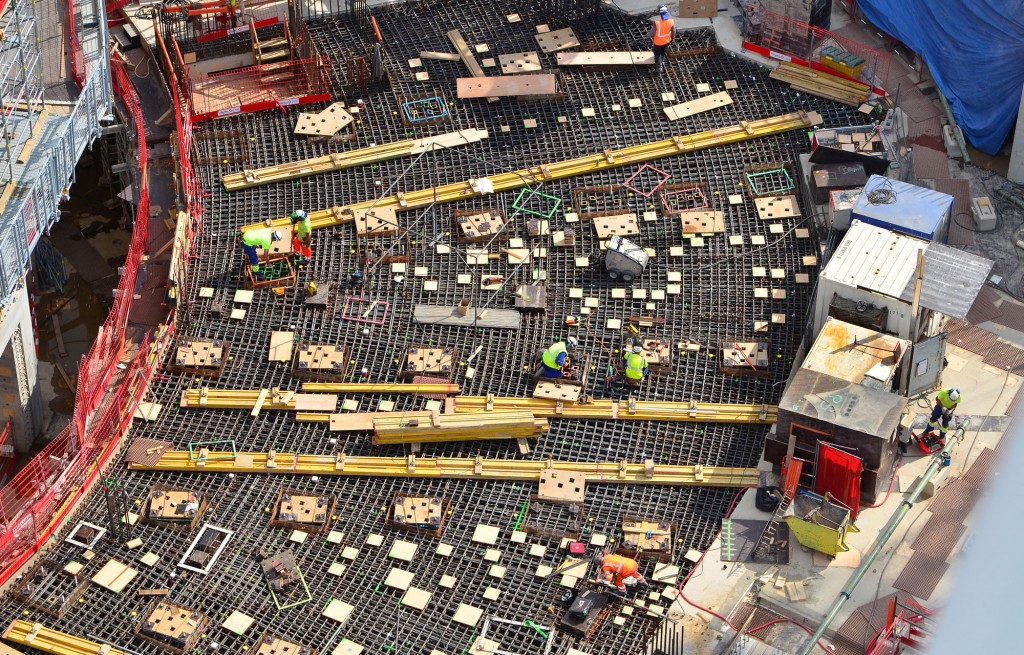
Completing the L1 floor slab
2017-06-19 - Workers are finalizing the installation of embedded plates on this part of the L1 Tokamak Building slab. Note the gap that exists for the moment between the L1 floor and the bioshield (at left).
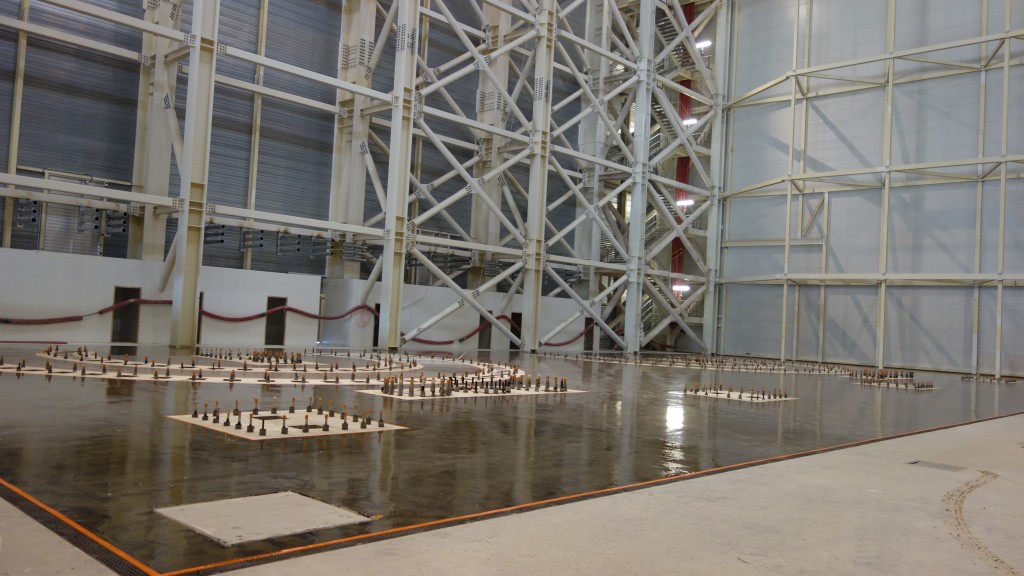
Where the giants will stand
2017-06-14 - As the elements of the first giant sector sub-assembly tool begin arriving on site from Korea, workers are readying the corner of the Assembly Hall where they will stand.

From the centre
2017-06-14 - Inside of the Tokamak Pit, looking up. Unlike the lower levels, the top level of the bioshield (L4) will be an unbroken wall (with zero openings).
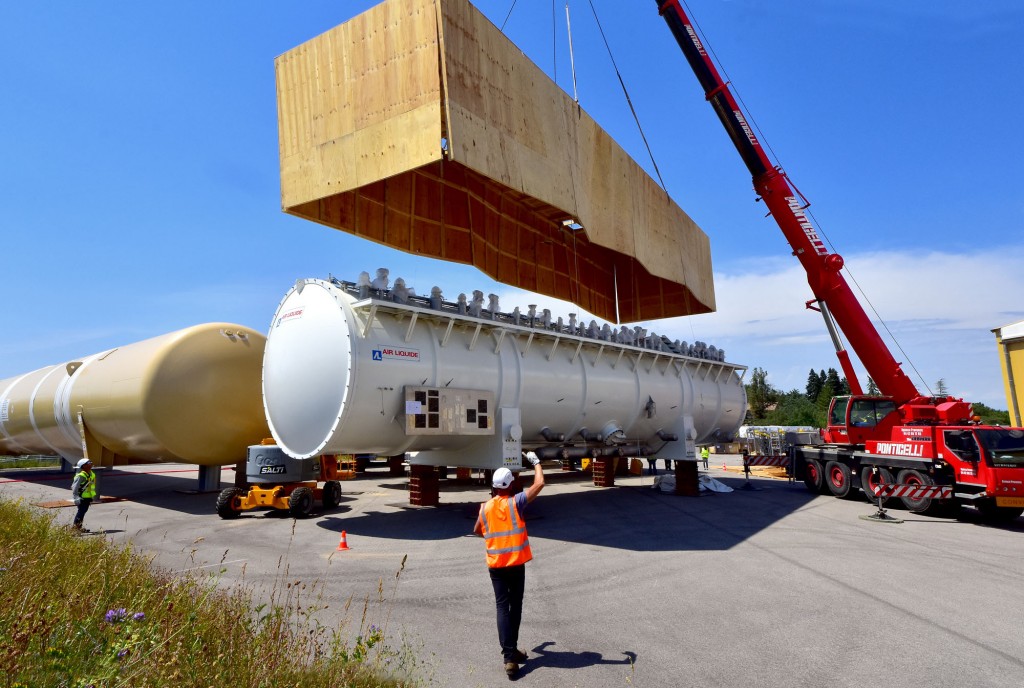
Ready to go!
2017-06-14 - Mid-June, the three helium cold boxes in storage were uncovered and prepared for transport to the cryoplant, where they will be installed.
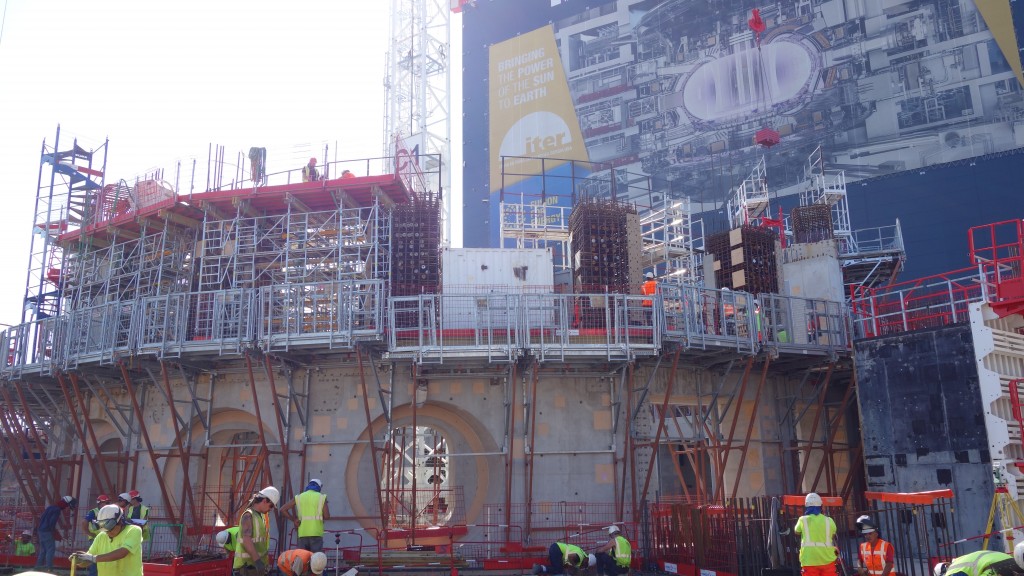
Closing up the L2 bioshield
2017-06-14 - The circle of concrete is closing in at L2 level and work is already underway on the next. The ITER bioshield wall is 3.2 metres at its thickest.
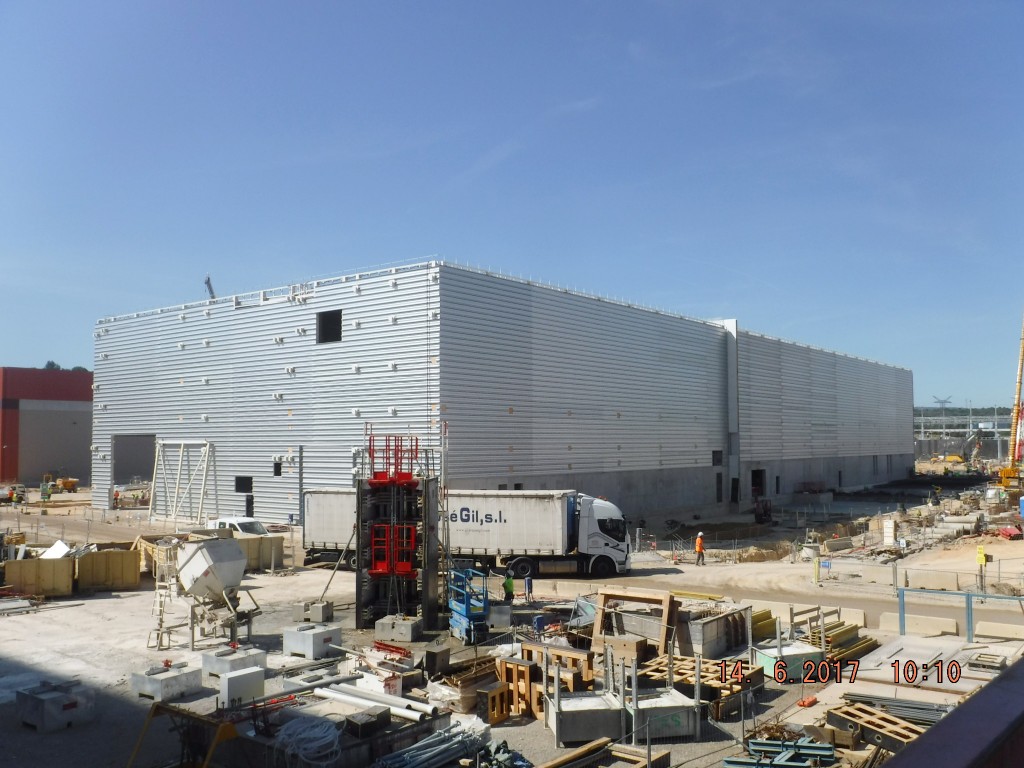
A 5 400 m² factory
2017-06-14 - The ITER cryoplant has been fully framed out by European contractors. Work is starting now to equip the building. © Engage
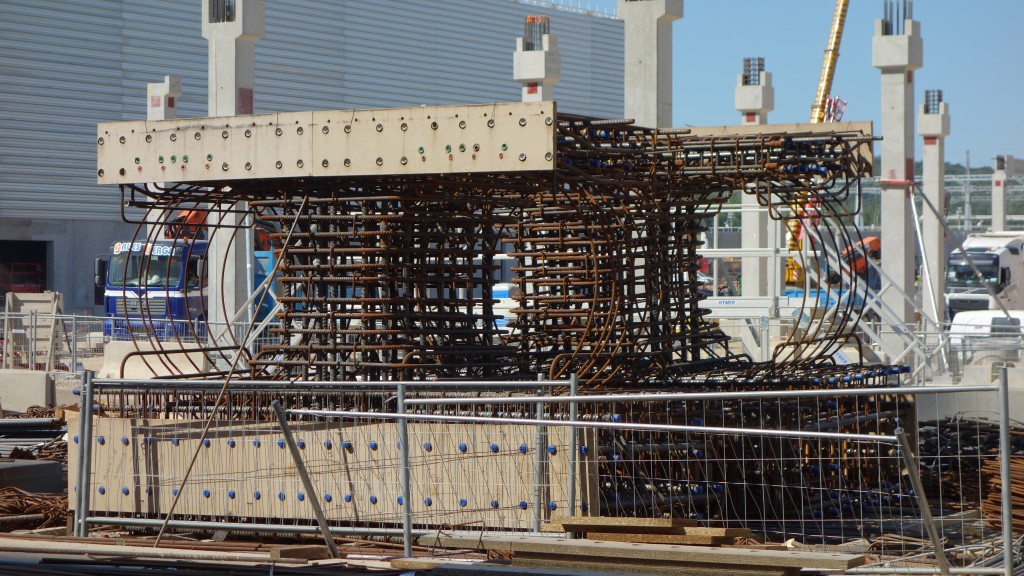
Waiting to be installed
2017-06-14 - The preformed element will be installed in one of the upper levels of the ITER bioshield.
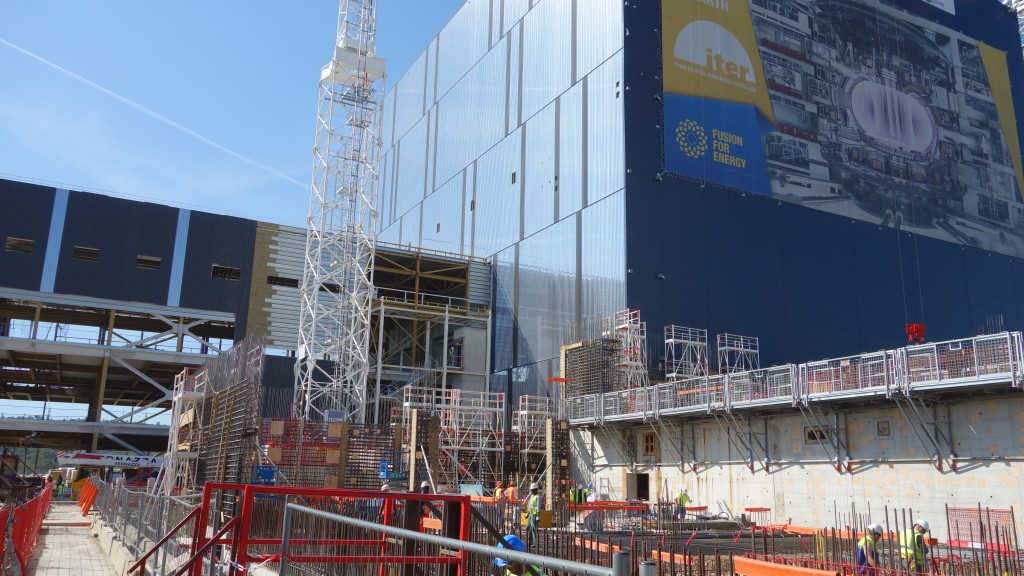
Working on site in two shifts
2017-06-14 - Construction of the Tritium Building (foreground) progresses at ground level. In the background, multiple levels of cladding are installed on the Radio Frequency Heating Building.

Activity is heating up
2017-06-14 - Workers install multiple layers of cladding to the metal structure of the Radio Frequency Heating Building.
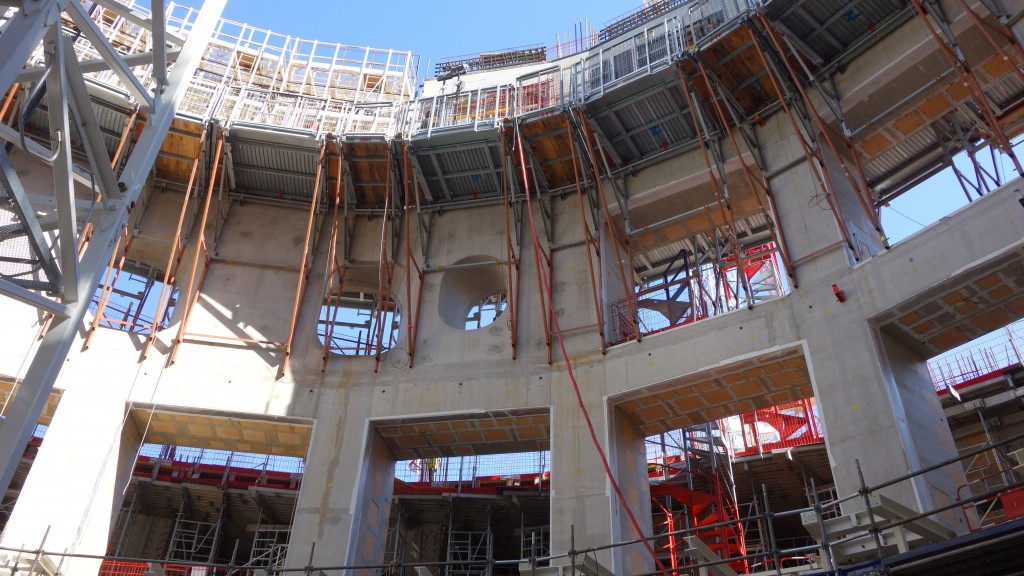
Specially designed openings
2017-06-14 - Each bioshield opening is scaled for the systems that will pass through. Some openings are square, some circular, some oval ...

Equipment delivered
2017-06-14 - Part of the equipment delivered for the ITER cryoplant, these "warm panels" will be connected to the helium cold boxes

Converting the voltage
2017-06-14 - The two long, low buildings are going up between the 400 kV switchyard and the Tokamak Complex.

Taking it in steps
2017-06-14 - The qualification winding, made of copper conductor, rests on a staging table while preparations are made for impregnation.
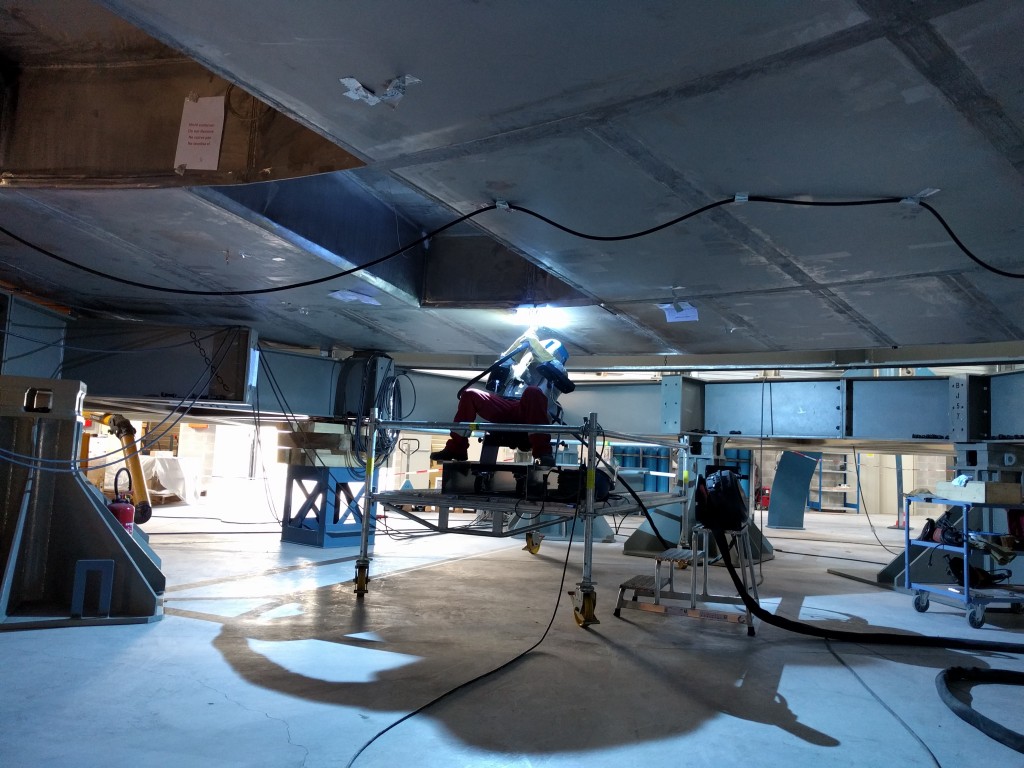
Working from below
2017-06-13 - A welder from MAN Diesel & Turbo, Germany, works on the underside of the cryostat base.
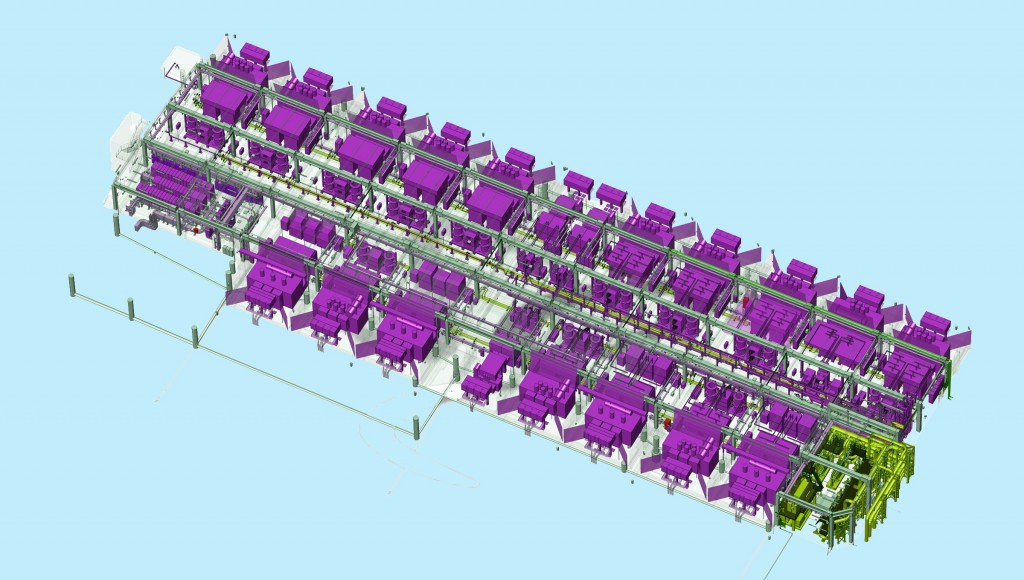
Inside the Magnet Power Conversion buildings
2017-06-10 - Densely packed with electrical converters, switches and fast discharge units, the twin, 150-metre-long Magnet Power Conversion buildings act as an AC/DC converter for the ITER magnetic system. (The interior layout of one building is shown here.)

Resting horizontally, for now
2017-06-09 - Seen resting horizontally, one of the segments of the lower cylinder (tier two) in the Indian factory. Each large opening corresponds to an equivalent opening in the vacuum vessel.

Successive pours at level 2
2017-06-09 - Scaffolding surrounds the ITER bioshield as workers advance on the L2 level (note the concrete pump at left).
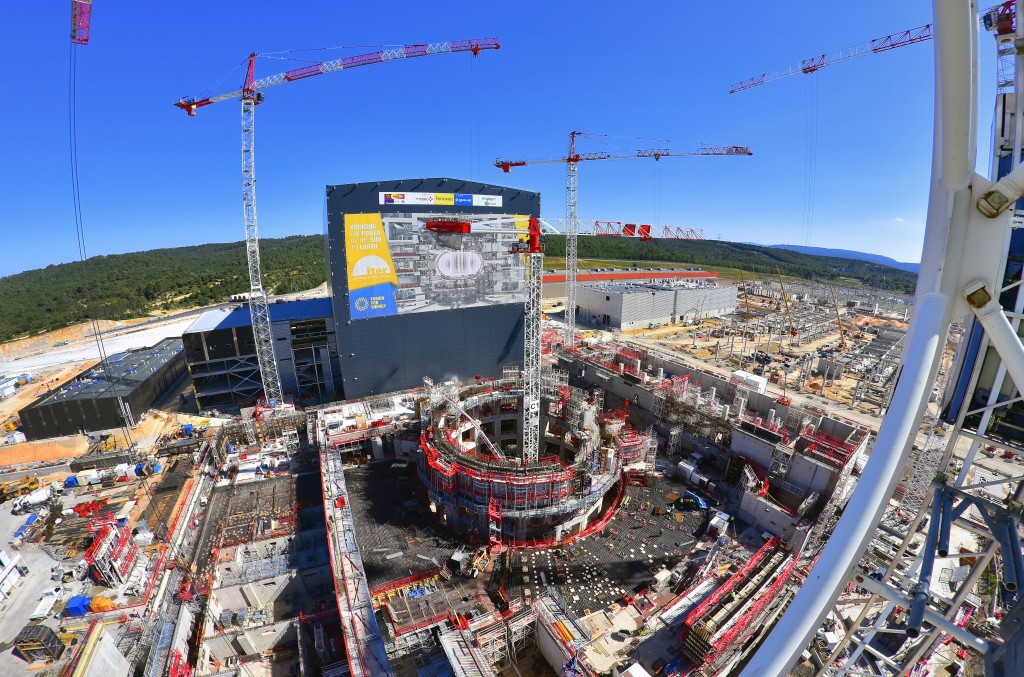
View from above
2017-06-08 - The Tokamak Complex worksite, seen from the C2 crane on the northern corner.
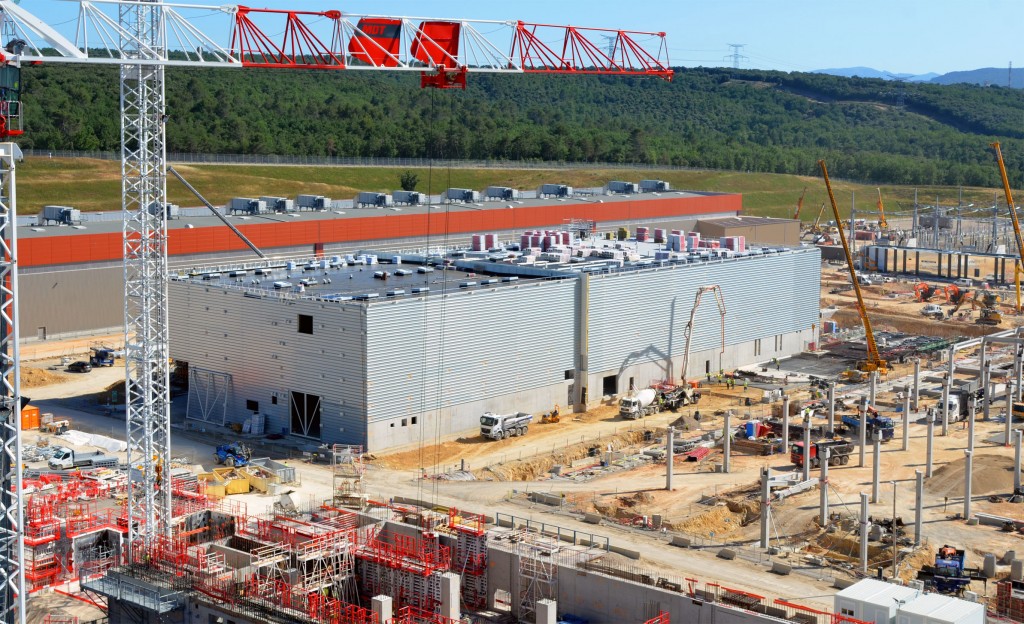
Nearly ready for access
2017-06-08 - The building's cladding is nearly finalized and work is underway to pour the ground slab for the exterior storage area (foreground). Later this month, the three helium cold boxes will be transferred from storage for installation inside of the building.
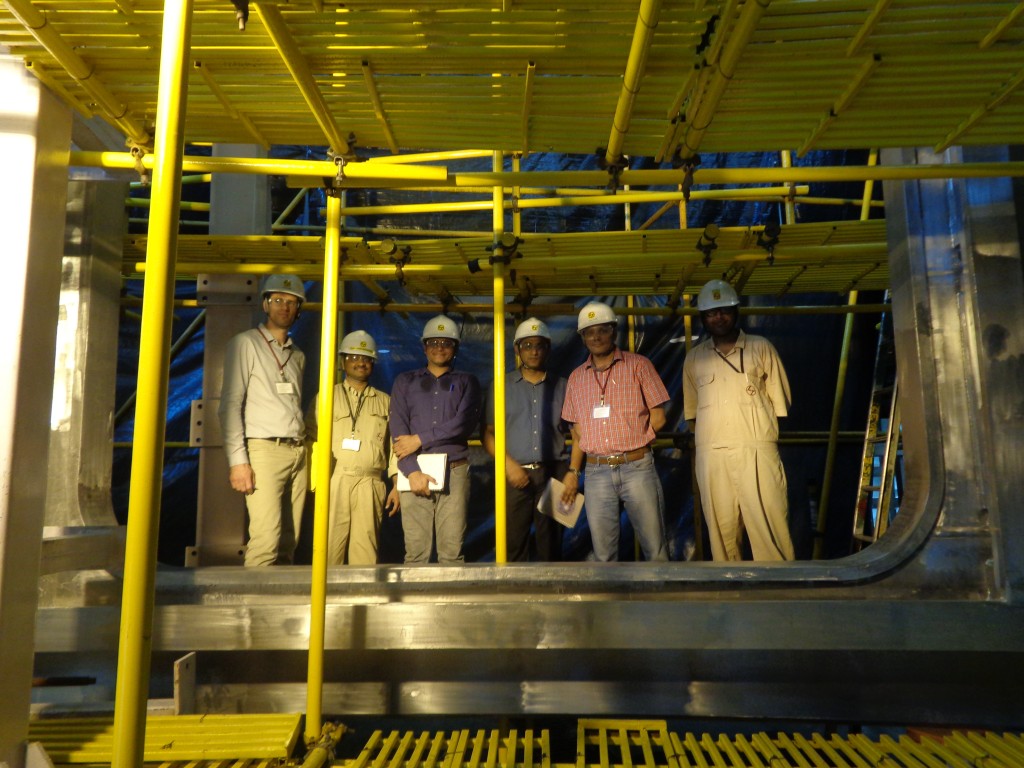
Preparing other segments
2017-06-08 - Back in India, in the Hazira factory of Larsen & Toubro, work is underway on the tier-two segments of the lower cylinder.

Buildings mushrooming
2017-06-08 - This June photo documents how far the ITER cryoplant (at right, fully clad) and the Radio Frequency Building (at left, partially clad) have come.
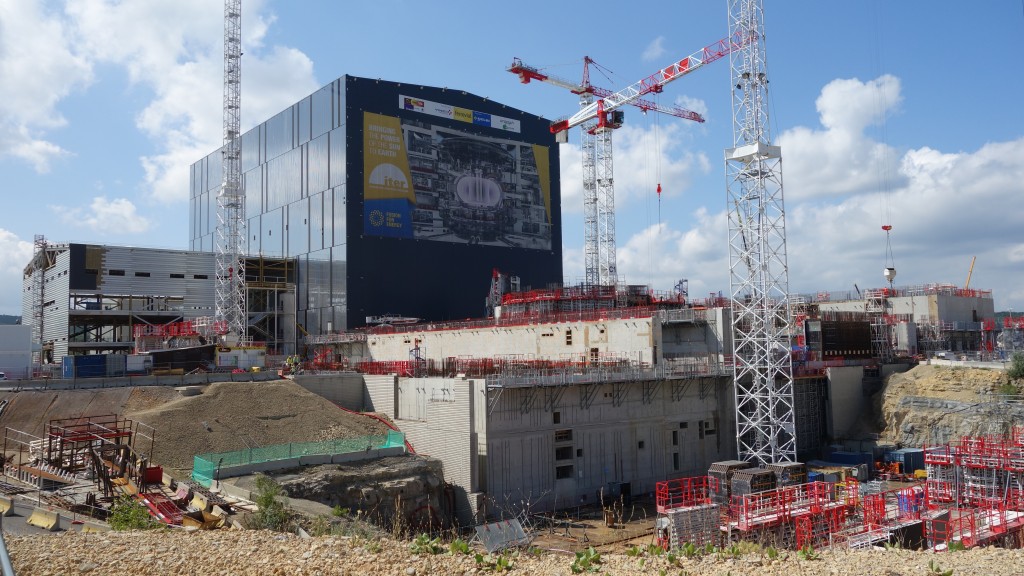
Tokamak Complex rising
2017-06-02 - The basement levels of the Tokamak Complex are framed out; work is under way on the first ground floor (L1) of the Tokamak Building at centre and L2 of the Diagnostics Building at right.

Putting heads together
2017-06-01 - Regular technical collaboration meetings are held at Consorzio RFX on design, manufacturing, and installation issues, with representatives from the ITER Organization, the participating Domestic Agencies, and the host lab taking part. All of the critical heating neutral beam components will be tested at NBTF.

Off with the covers
2017-06-01 - For the first time, we see one of the lower cylinder segments without its cover.

Preparing to assemble the next cryostat section
2017-06-01 - In one half of the workshop welding and testing is underway on the base of the cryostat. Now, in the other half, technicians are constructing the assembly platform that will be used for the next segment—the lower cylinder.
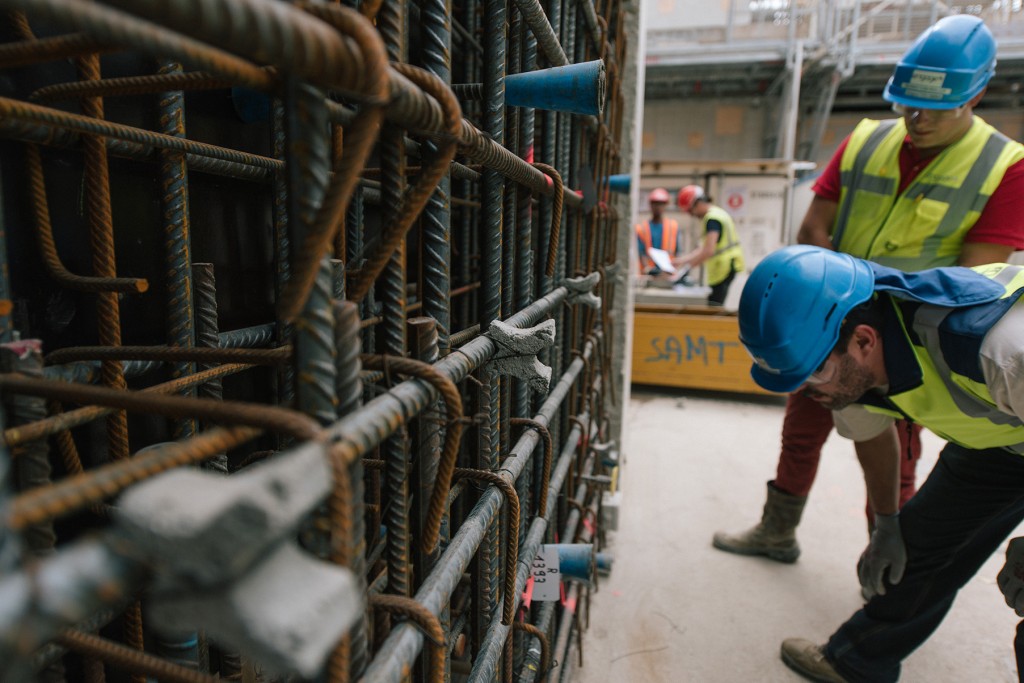
Inspecting the works
2017-05-31 - Work on the construction site is like a well-tuned orchestra, with each party playing an important role. Here representatives of the architect/engineer ENGAGE inspect the works. © Les Nouveaux Médias/SNC ENGAGE

Two buildings under one roof
2017-05-31 - The gap in the cladding permits us to distinguish the Cold Box Building, at left, from the Compressor Building, at right. © Les Nouveaux Médias/SNC ENGAGE

Proud to be part of it
2017-05-31 - Approximately 400 workers are currently working in two shifts on the Tokamak Complex. © Les Nouveaux Médias/SNC ENGAGE
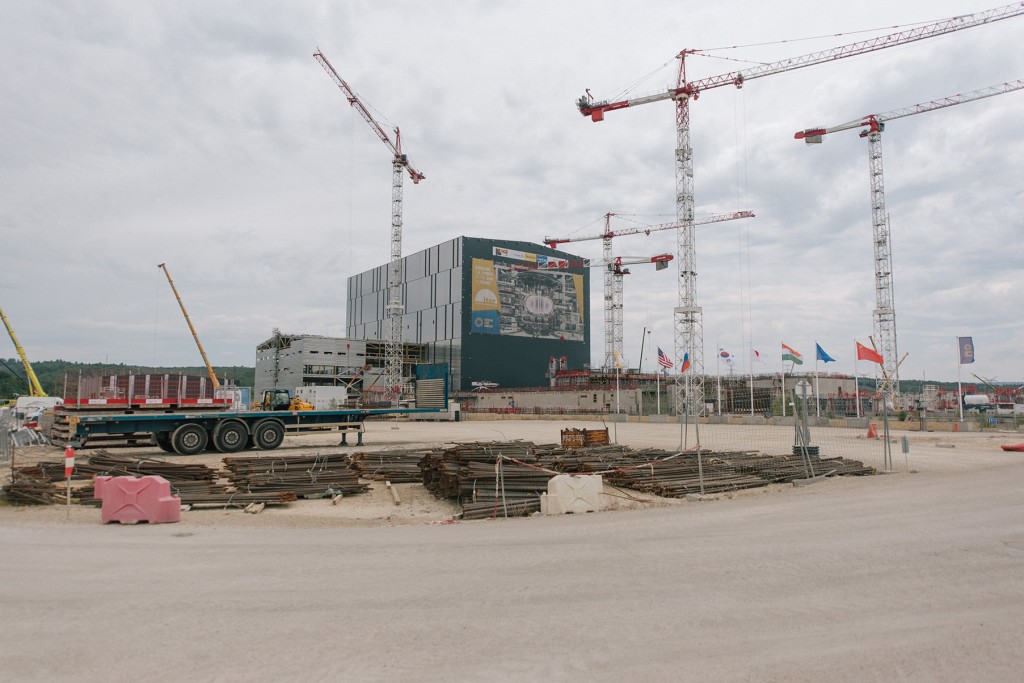
Standing tall
2017-05-31 - The Assembly Hall remains the tallest structure on the ITER platform. © Les Nouveaux Médias/SNC ENGAGE

Checking the plans
2017-05-31 - Representatives of ENGAGE (architect engineer for the European Domestic Agency) and Ferrovial (part of the VFR consortium chosen to build the Tokamak Complex and eight other buildings) review plans. © Les Nouveaux Médias/SNC ENGAGE

Dark clouds for a change
2017-05-31 - On a cloudy day in late May, the photographer captured this shot. © Les Nouveaux Médias/SNC ENGAGE
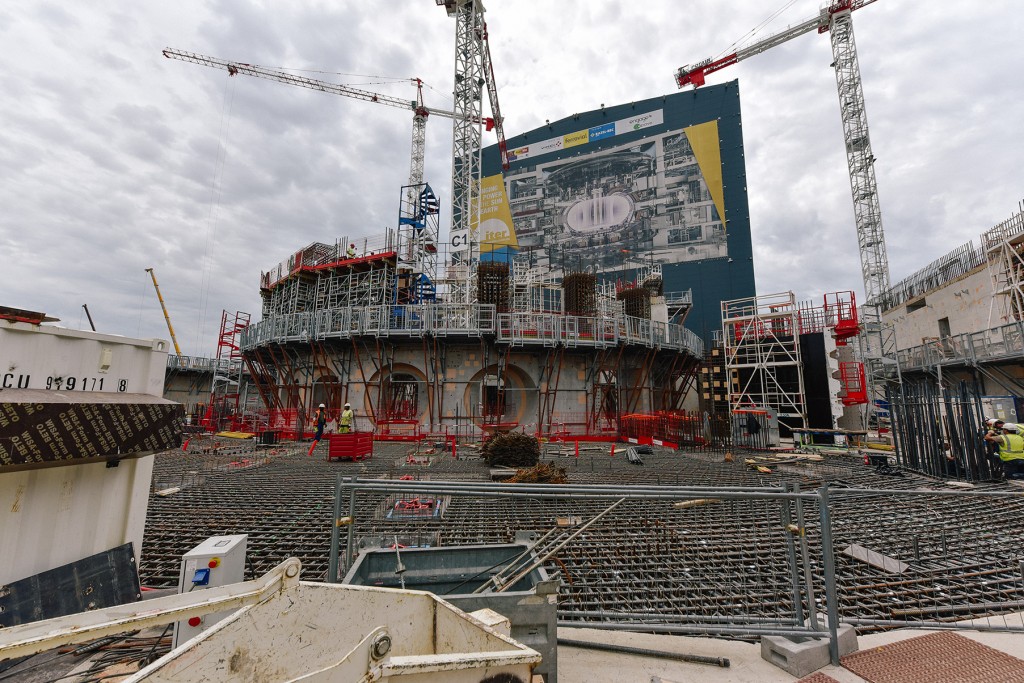
Two more levels
2017-05-31 - Pouring is underway on the L2 level of the Tokamak bioshield. There are two more levels to come (L3 and L4). © Les Nouveaux Médias/SNC ENGAGE

Looking south
2017-05-31 - From low in the cooling tower zone we can see the Assembly Hall to the south. © Les Nouveaux Médias/SNC ENGAGE
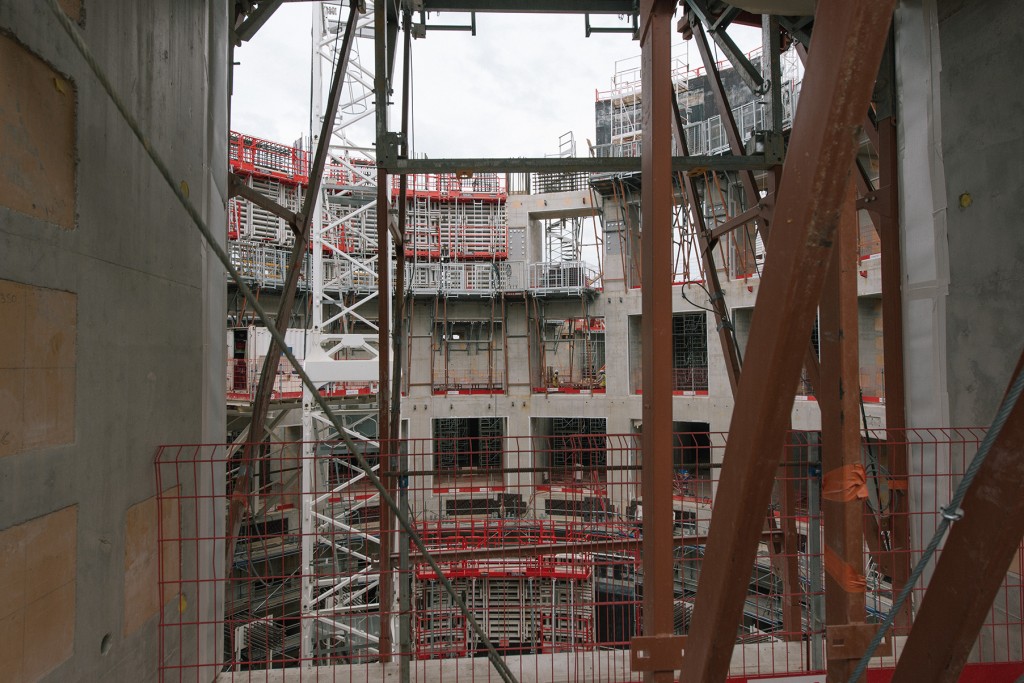
Peeking through
2017-05-31 - The Tokamak assembly pit is already nearly 30 metres deep when you count the basement levels. © Les Nouveaux Médias/SNC ENGAGE
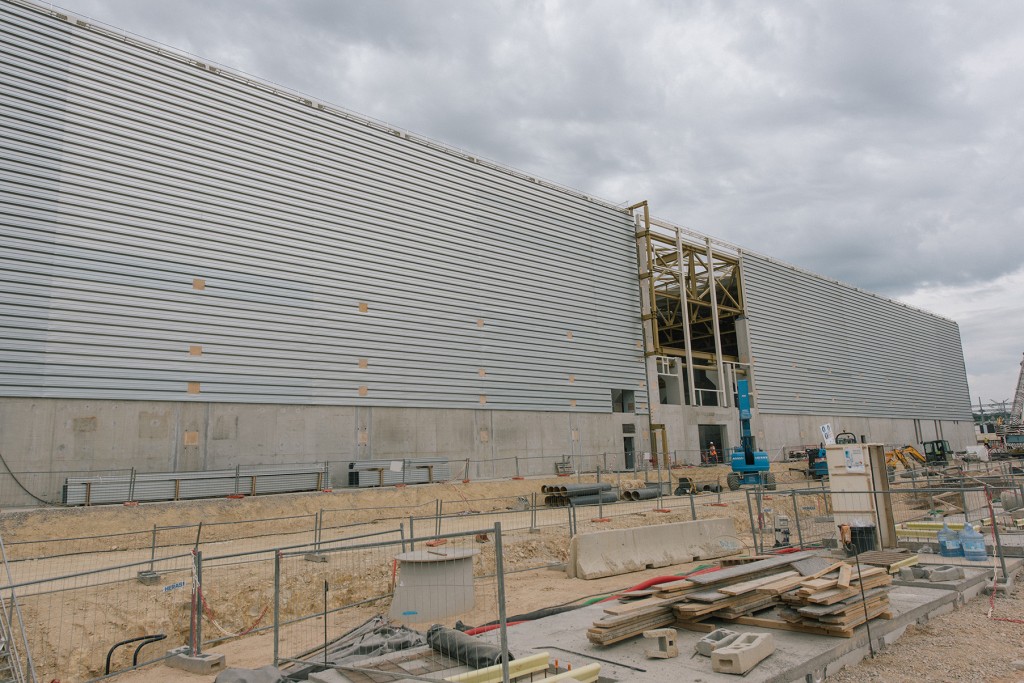
First phase of cladding
2017-05-31 - Late May, the first phase of cladding is nearly complete. © Les Nouveaux Médias/SNC ENGAGE
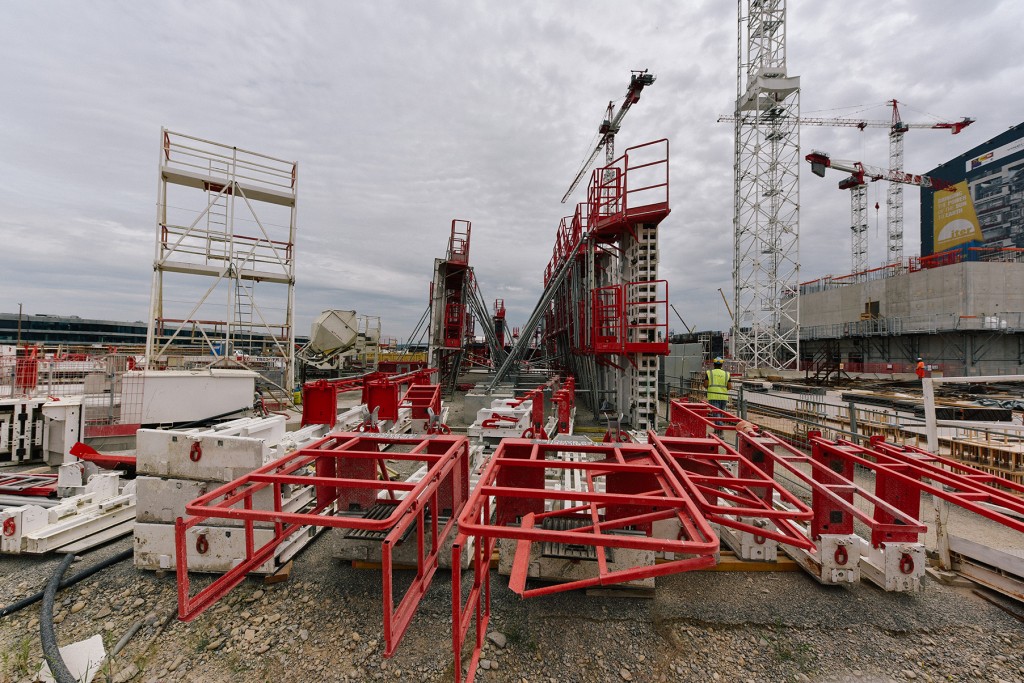
Staging ground
2017-05-31 - All around the Tokamak Complex available space is used for the storage of materials such as embedded plates, formwork and scaffolding. © Les Nouveaux Médias/SNC ENGAGE
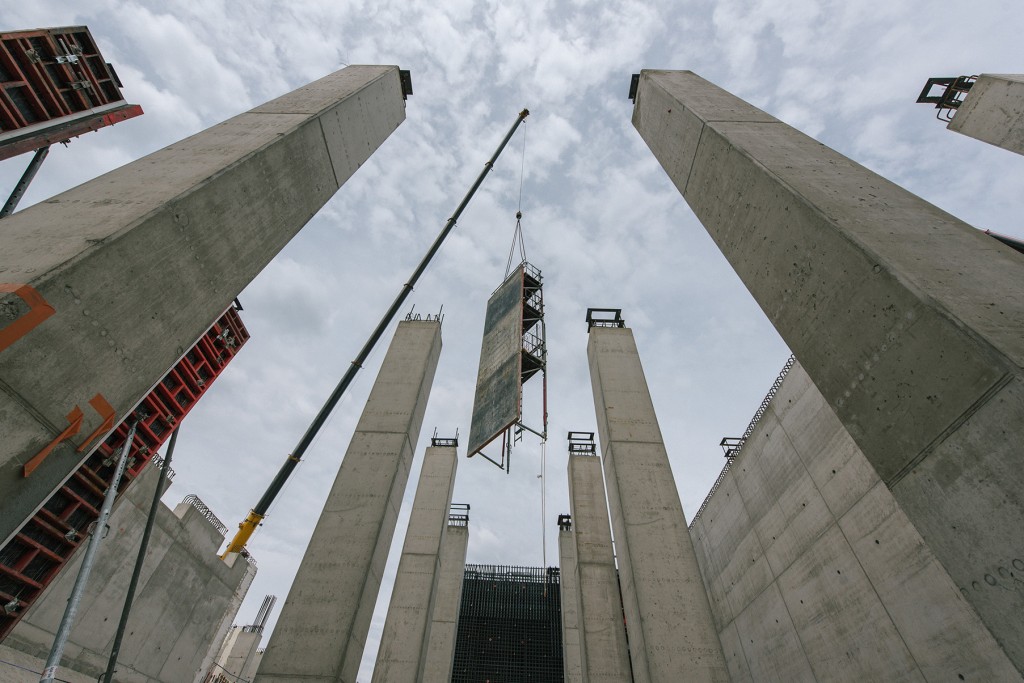
Columns in the cooling basins
2017-05-31 - The heat rejection system provides the final heat sink and rejects all heat loads in the ITER machine and plant. Its main clients are the secondary cooling circuits, the cryogenic system and the steady state electrical power network. © Les Nouveaux Médias/SNC ENGAGE
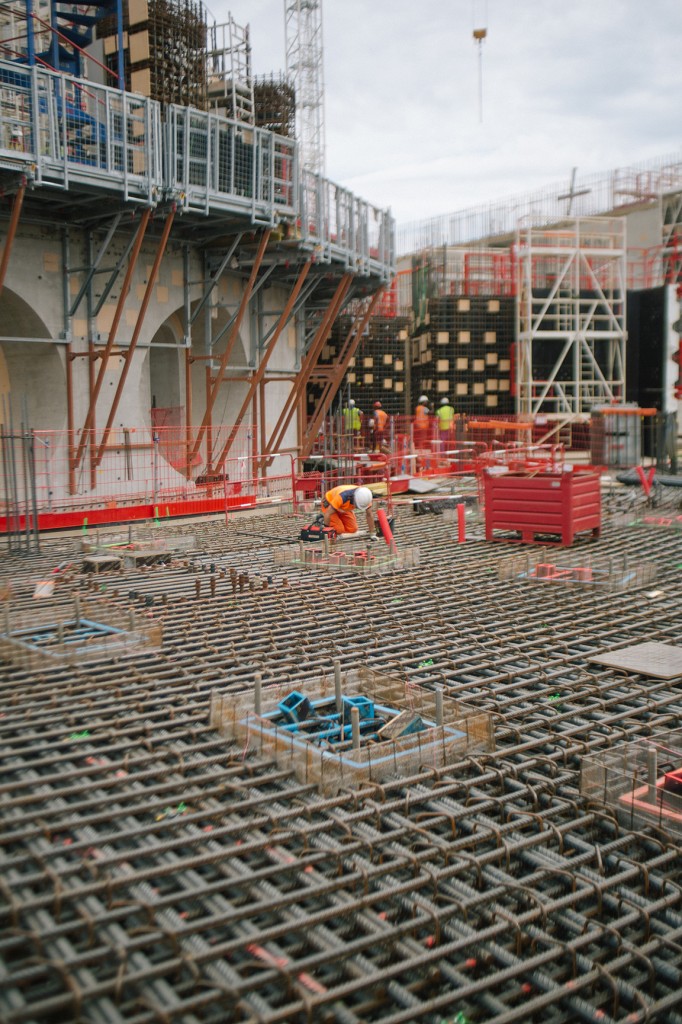
Dense rebar
2017-05-31 - The last part of the L1-level basemat in the Tokamak Building is readied for concrete pouring. © Les Nouveaux Médias/SNC ENGAGE

Quick work
2017-05-31 - The relatively "simple" building frames are going up quickly. © Les Nouveaux Médias/SNC ENGAGE
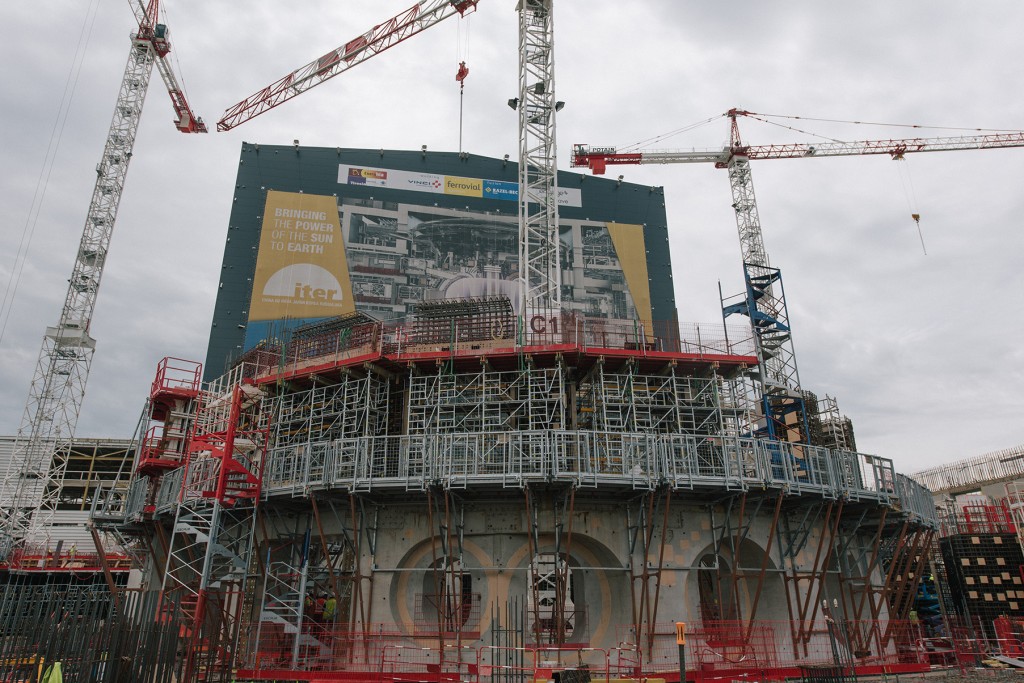
Medieval castle?
2017-05-31 - Under a grey sky, the bioshield and its scaffolding looks something like a medieval castle ...© Les Nouveaux Médias/SNC ENGAGE
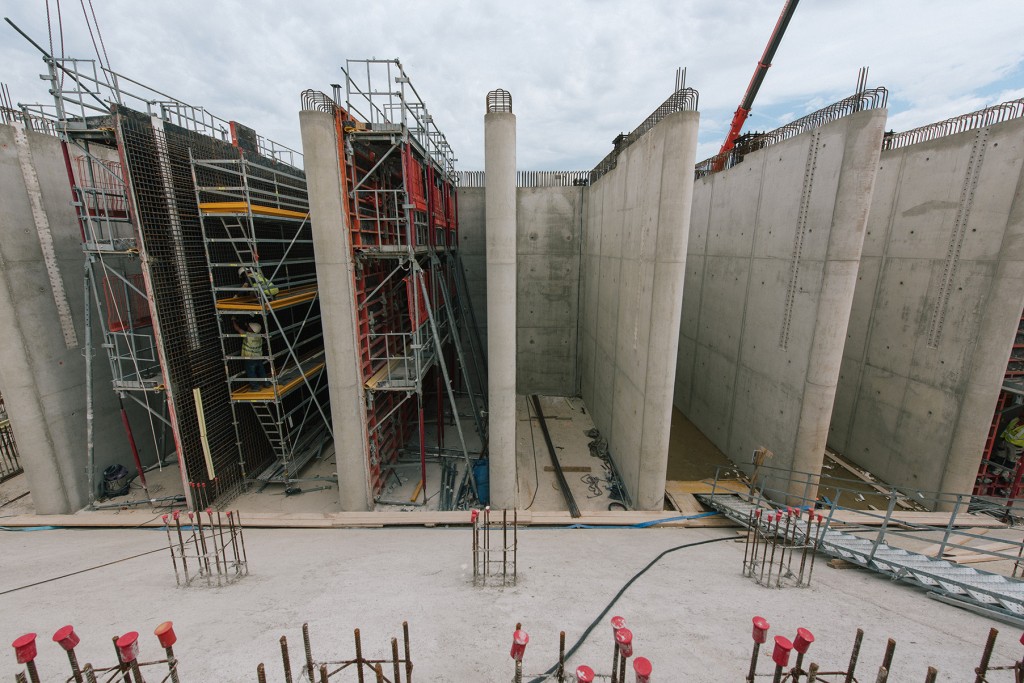
In the northern zone of the construction platform
2017-05-31 - The cold basin is compartmentalized for maintenance with each compartment collecting water from one of the cooling tower cells. © Les Nouveaux Médias/SNC ENGAGE
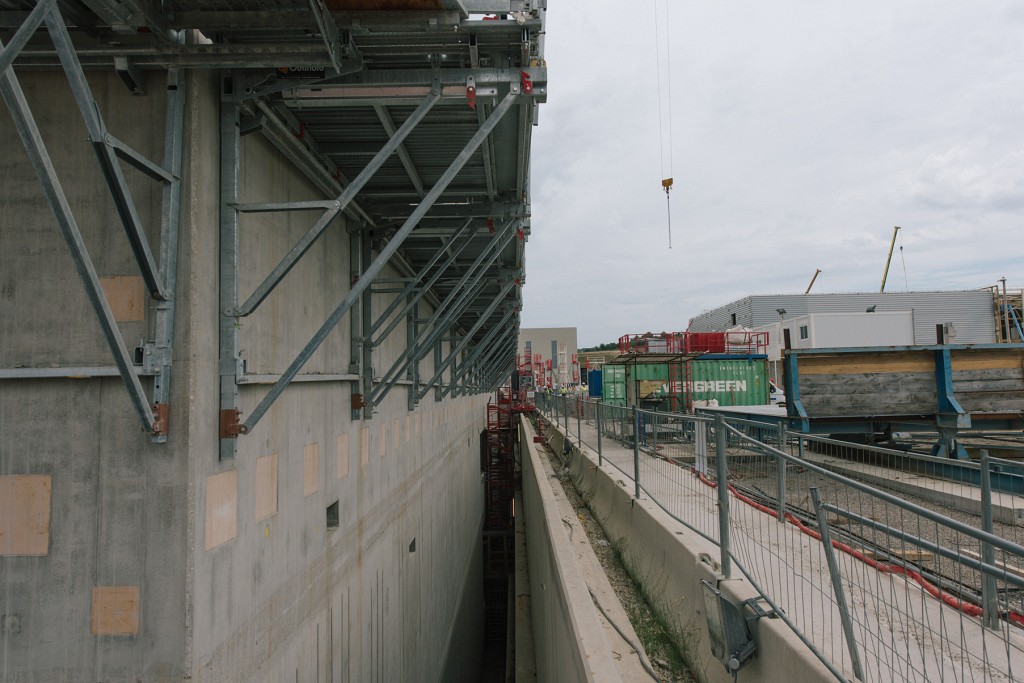
Floating foundation
2017-05-31 - All around the Tokamak Complex a gap of approximately two metres allows the three-building complex on a single foundation to "move" on its seismic pads and absorb—in case of need—the accelerations linked to earthquake-induced ground motion. © Les Nouveaux Médias/SNC ENGAGE.

Diagnostics box
2017-05-31 - The Diagnostics Building is framed out at platform level (L1). © Les Nouveaux Médias/SNC ENGAGE

The design of the heat rejection system
2017-05-31 - The heat rejection system of ITER is made up of cooling tower cells, hot and cold basins, vertical turbine pumps, a chemical dosing system, ozonator, strainers, valves and piping. © Les Nouveaux Médias/SNC ENGAGE

Showing off progress
2017-05-20 - Work was halted on the Tokamak Building worksite on Saturday 20 May, in order to allow ITER Open Doors day participants to get as close as possible to the bioshield.
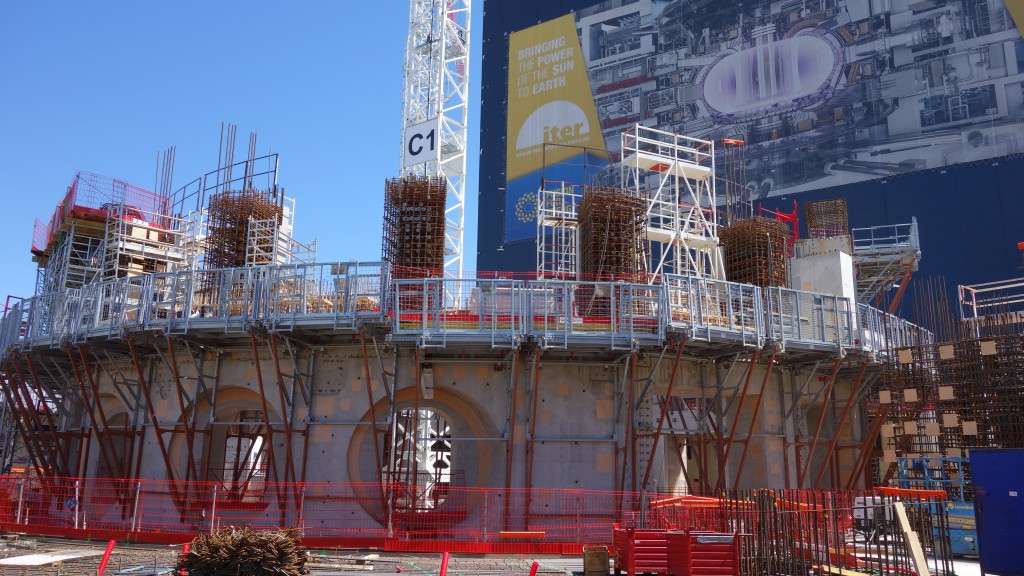
Building up around the centre
2017-05-20 - The C1 crane marks the centre, where Tokamak assembly will begin next year.

View of the basins
2017-05-15 - In May, the cooling water basins are completely framed out. © Les Nouveaux Médias/SNC ENGAGE

170-metre crane bay
2017-05-15 - During the assembly of the ITER machine, components will be transported from Assembly Hall (foreground) to the Tokamak Pit (background) by overhead crane.
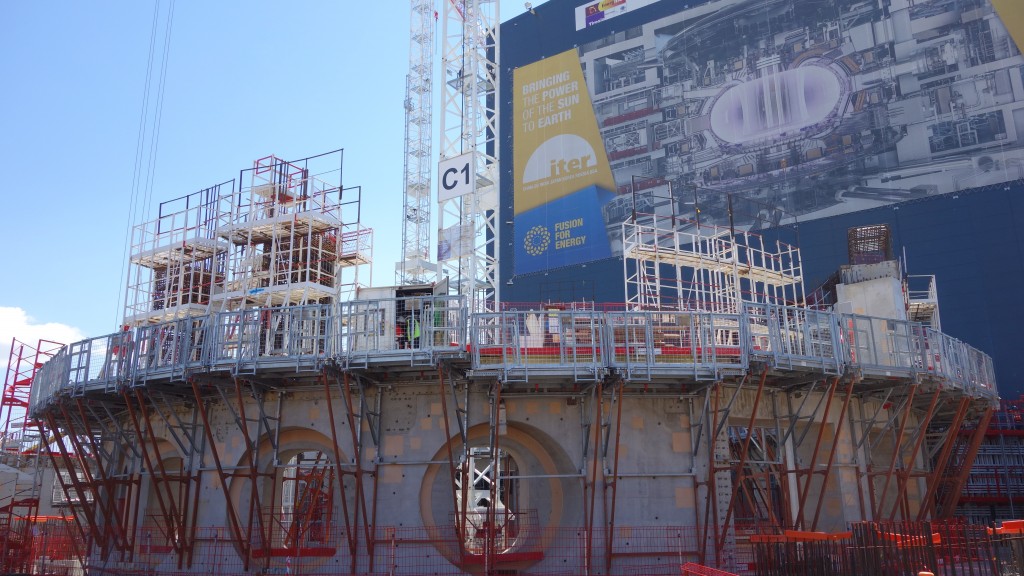
Hobbit haven
2017-04-28 - Level L1 of the bioshield seems to be more hole than wall. Some of the openings would please a Hobbit ...
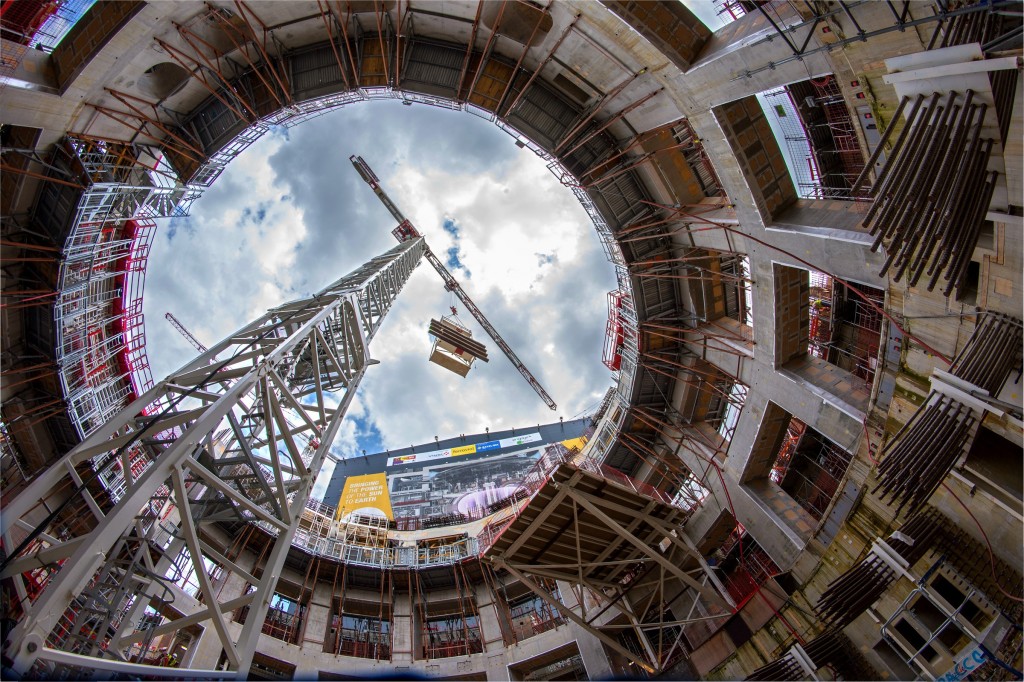
Like a rocket aiming for the stars
2017-04-28 - From inside the Tokamak Pit, looking out past the successive levels of the ITER bioshield.

Door panels
2017-04-27 - The Cleaning Facility at the entrance of the Assembly Hall is being equipped with sliding doors. © Les Nouveaux Médias/SNC ENGAGE
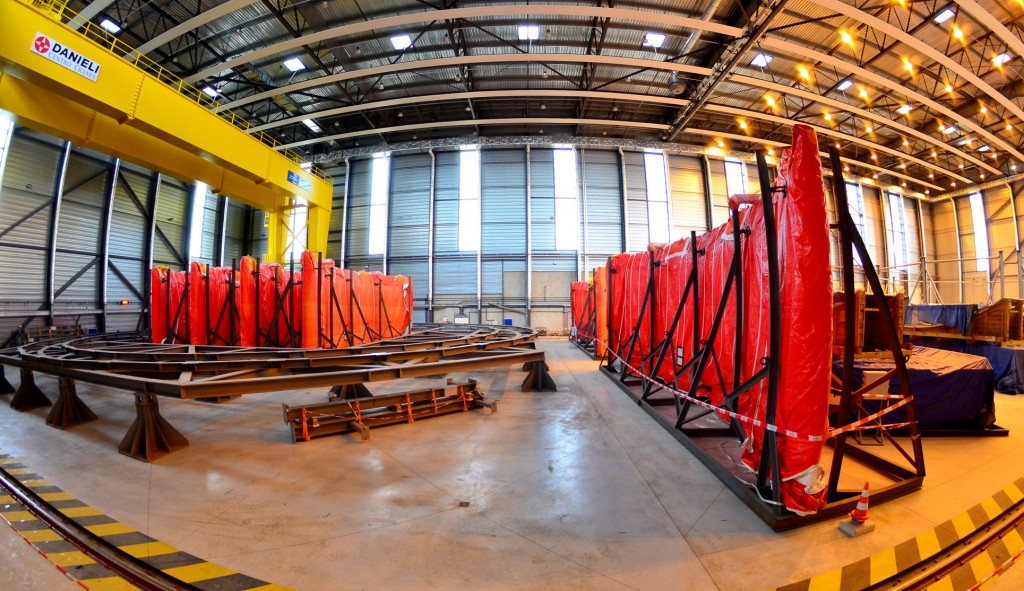
Standing in wait
2017-04-27 - The elements of lower cylinder tier 1 are stored on, or next to, a second assembly platform. Fabrication is underway in India on the second tier segments..
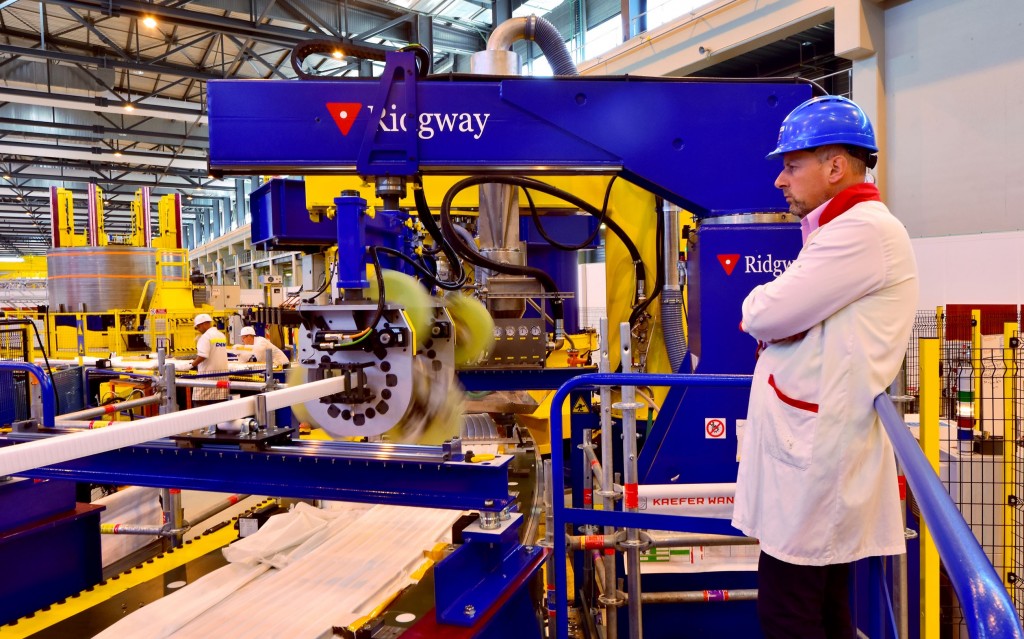
Under watchful eyes
2017-04-27 - Winding activities are closely monitored by the European Domestic Agency and specialists from the engineering integrator ASG Superconductors. Note the tape dispenser spinning in the background.

Standing taller and taller
2017-04-27 - Looking in toward the bioshield. Each of the openings corresponds to an opening in the cryostat © Les Nouveaux Médias/SNC ENGAGE
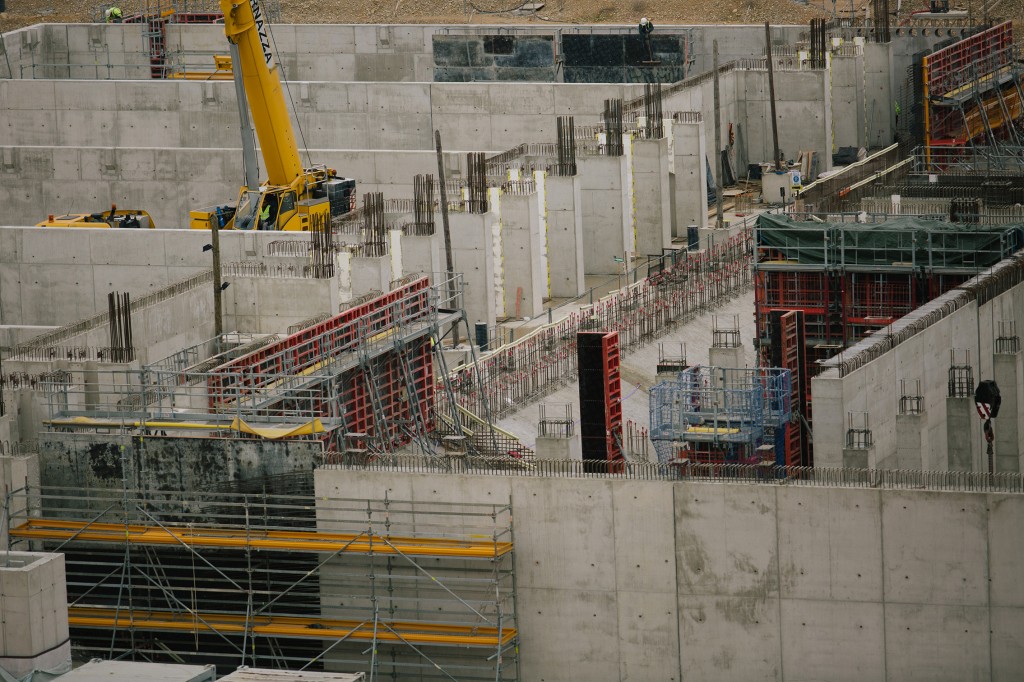
Cooling tower cells
2017-04-27 - Above-ground work on the ITER cooling towers. © Les Nouveaux Médias/SNC ENGAGE

Finishing works underway
2017-04-27 - Interior clapboard and painting works are underway in the Assembly Hall, which will receive its first large assembly tool this summer. © Les Nouveaux Médias/SNC ENGAGE

Power conversion
2017-04-27 - Two identical buildings are going up side by side on the worksite. © Les Nouveaux Médias/SNC ENGAGE

The good old calliper
2017-04-27 - Creating the first double-layer winding pack for poloidal field coil #5 is a highly sophisticated technological operation. But when it comes to measurements, nothing beats the good old calliper.

It takes two ... or three
2017-04-27 - Pre-welding operations on cooling water piping in April. © Les Nouveaux Médias/SNC ENGAGE

Starry ceilings
2017-04-27 - It's harder to see by drone, but work is still being carried out in the lower levels of the Tokamak Complex. Here, workers smooth the edges around each of the embedded plates that has been planned for the anchoring of equipment. © Les Nouveaux Médias/SNC ENGAGE
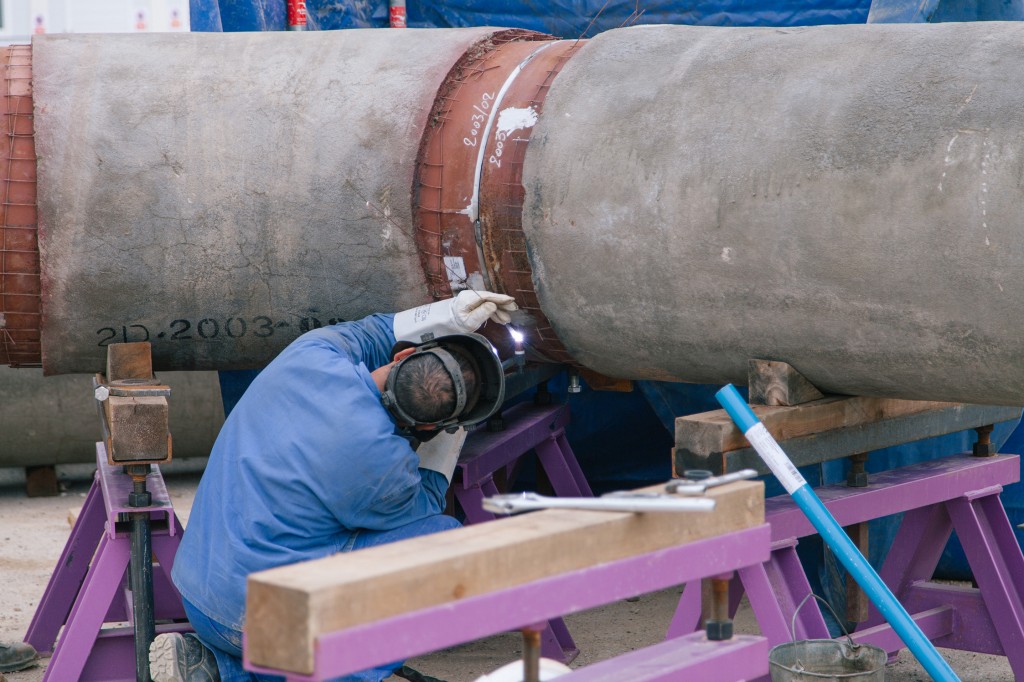
Welding elbows
2017-04-27 - Segments of cooling water piping shipped from India are welded on site.© Les Nouveaux Médias/SNC ENGAGE

It takes two ... or three
2017-04-27 - Pre-welding operations on cooling water piping in April. © Les Nouveaux Médias/SNC ENGAGE

Only one more to go for the Diagnostics Building
2017-04-27 - The building that will house the back systems of the ITER diagnostics is composed of two basement levels and three above-ground levels. Work is underway now on L2. © Les Nouveaux Médias/SNC ENGAGE

Welding the pie
2017-04-27 - Welding is underway on bottom plates that will "close" the base section, tier one. Each of the six ''pie-shaped'' segments of the base has three bottom plates.

Fabrication begins!
2017-04-27 - After the validation of qualification activities, Europe begins the winding of coil #5 in April in the on-site Poloidal Field Coils Winding Facility.
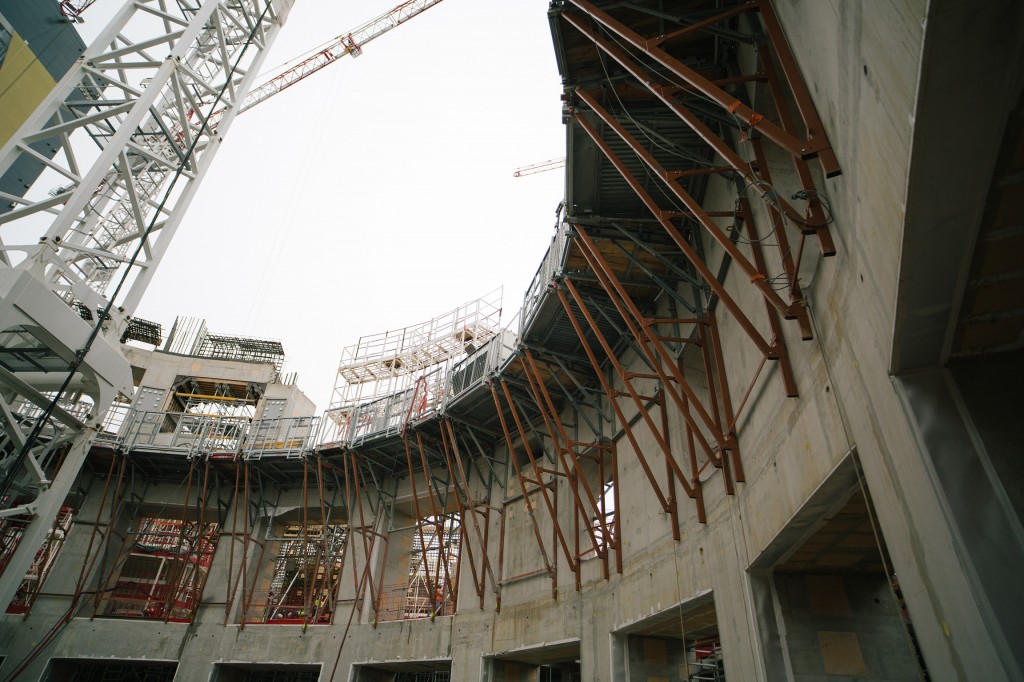
From the inner circle
2017-04-27 - At the L2 level of the bioshield, heavy metal plates are embedded into each column. These plates will support the Tokamak in-pit assembly tool. © Les Nouveaux Médias/SNC ENGAGE

Building up from the basin
2017-04-27 - The deep cooling water basin, on the right, can no longer be seen. © Les Nouveaux Médias/SNC ENGAGE

Heading up!
2017-04-27 - To access the overhead cranes, please take the stairs! Commissioning tests are planned soon on the two 750-tonne cranes that are installed 45 metres overhead. © Les Nouveaux Médias/SNC ENGAGE
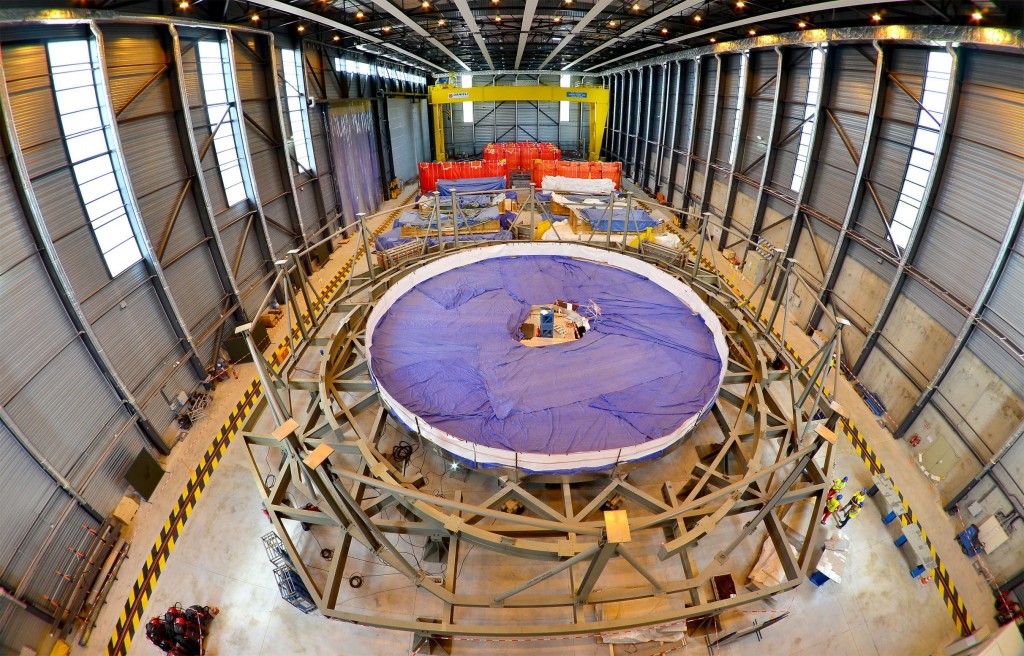
Completed disk
2017-04-27 - Seen from above, the completed tier one base section (20 metres in diameter) on its assembly/transport frame.
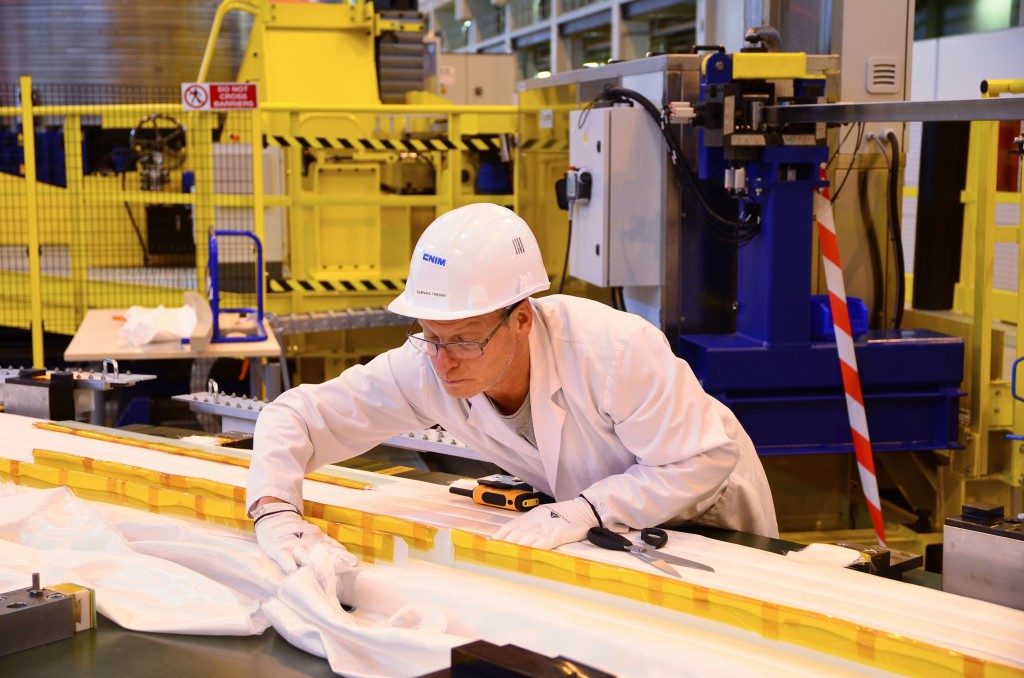
Like an Egyptian mummy
2017-04-27 - The steel-jacketed conductor is wrapped with several layers of tight-fitting insulating tape, and then enveloped in a special fabric. This technician from the European firm CNIM (contractor to the European Domestic Agency) carefully checks the conformity of the tight gaps between conductor turns.
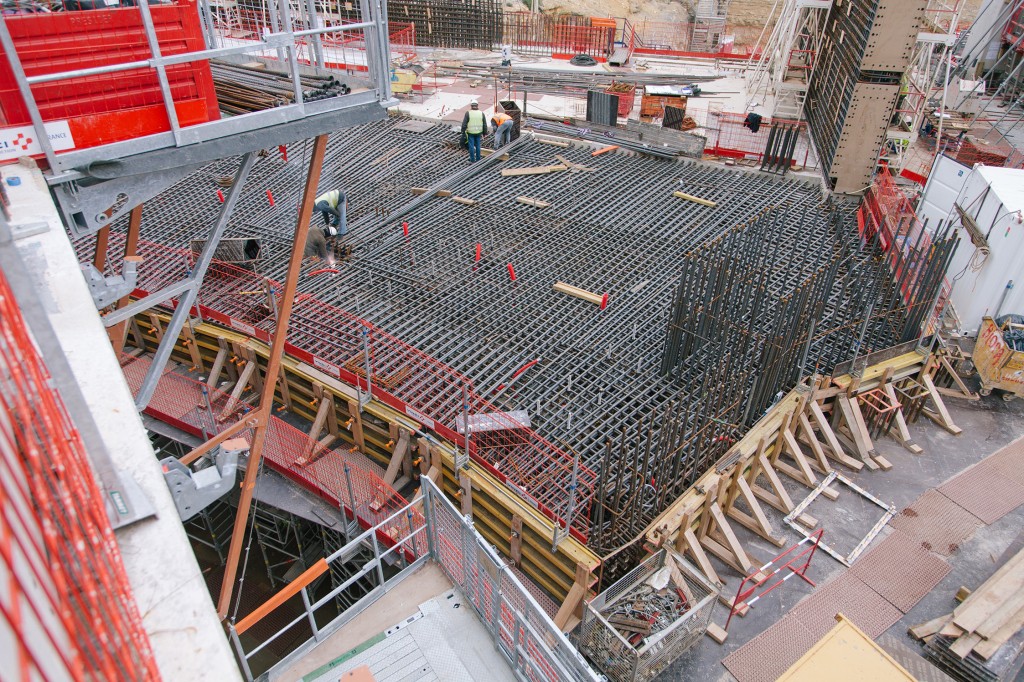
Ground level, Tokamak Building
2017-04-27 - Pouring continues on the basemat slab of the Tokamak Building, ground level (L1). © Les Nouveaux Médias/SNC ENGAGE
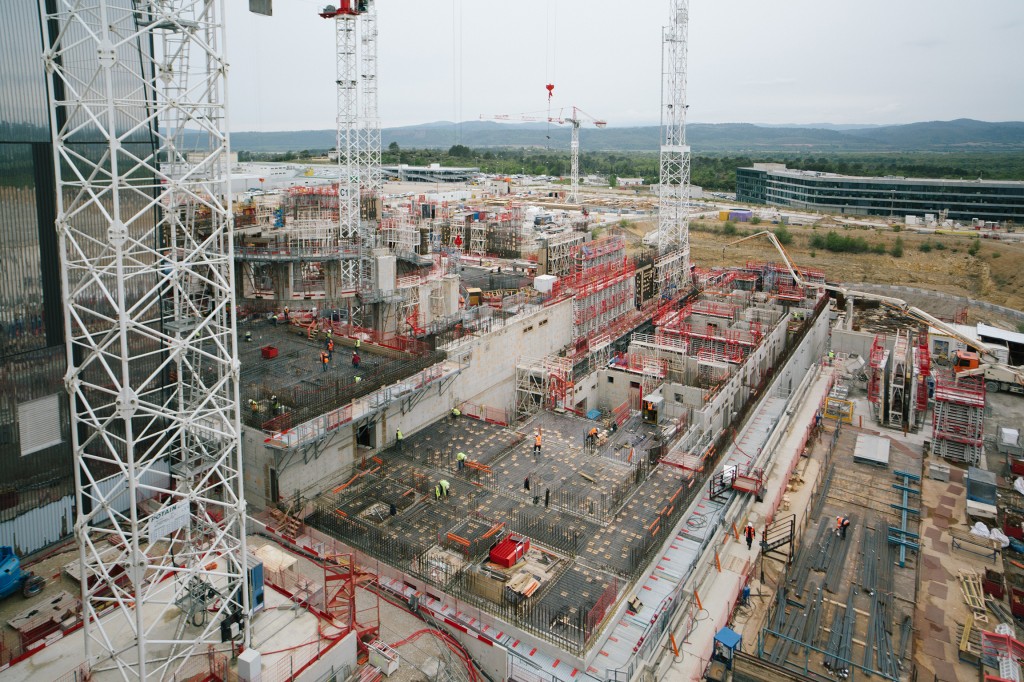
Seen from the northeast corner
2017-04-27 - The basement of the Tokamak Complex has disappeared. On the right: the Tritium Building; on the left: the Tokamak Building and bioshield. © Les Nouveaux Médias/SNC ENGAGE
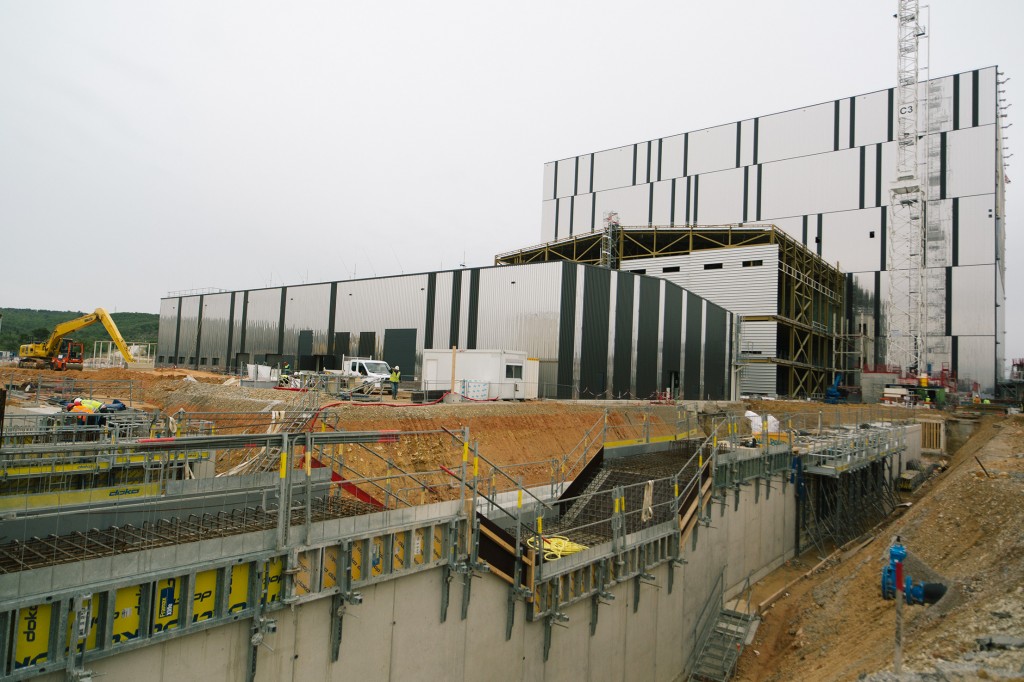
No longer stands alone
2017-04-27 - With the completion of the Site Services Building (foreground) and the strong progress on the Radio Frequency Heating Building (adjoining) the Assembly Hall no longer stands alone in the middle of the platform. © Les Nouveaux Médias/SNC ENGAGE
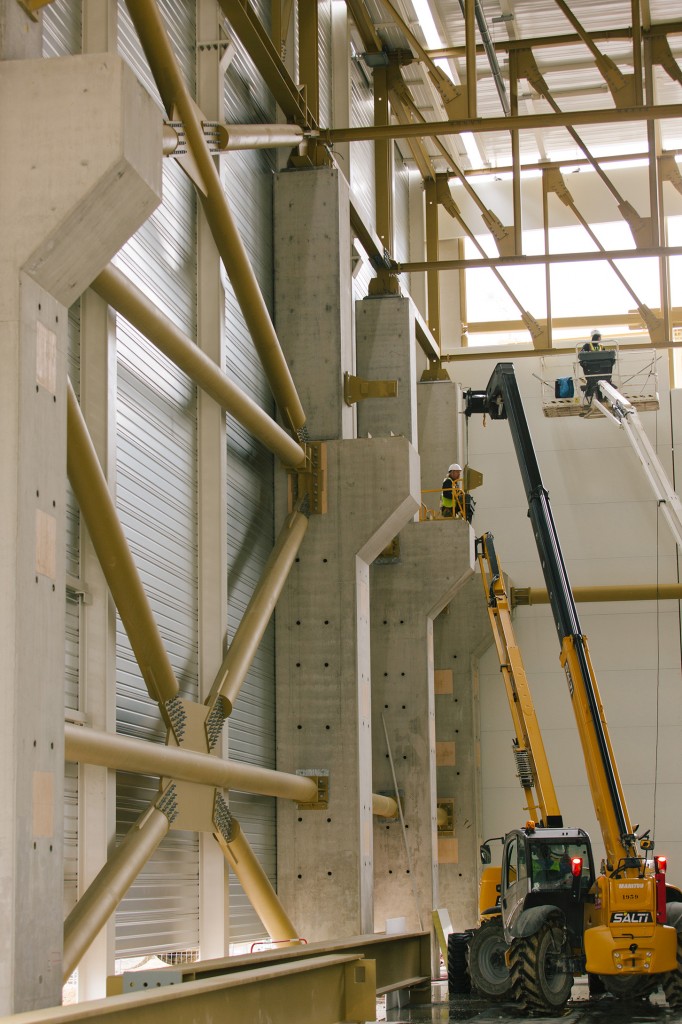
Closing in
2017-04-27 - The cladding of the cryoplant is going up. In this photo, the work is seen from the inside. © Les Nouveaux Médias/SNC ENGAGE

Refilling the tape dispenser
2017-04-27 - Operators can wind approximately 20 metres of conductor before it's time to renew the taping heads and replenish the sandblasting cleaning equipment with fresh sand.
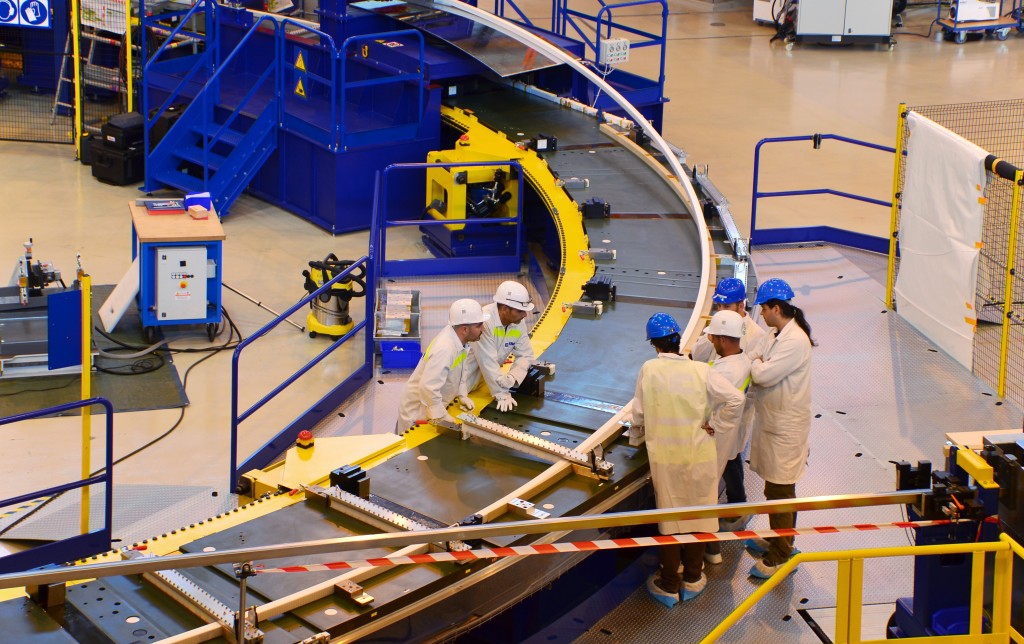
Get equipped
2017-04-27 - Lab coats and overshoes are mandatory in the "clean room" where operators have started on the first conductor turn for poloidal field coil #5 (PF5).

It takes two ... or three
2017-04-27 - Pre-welding operations on cooling water piping in April. © Les Nouveaux Médias/SNC ENGAGE
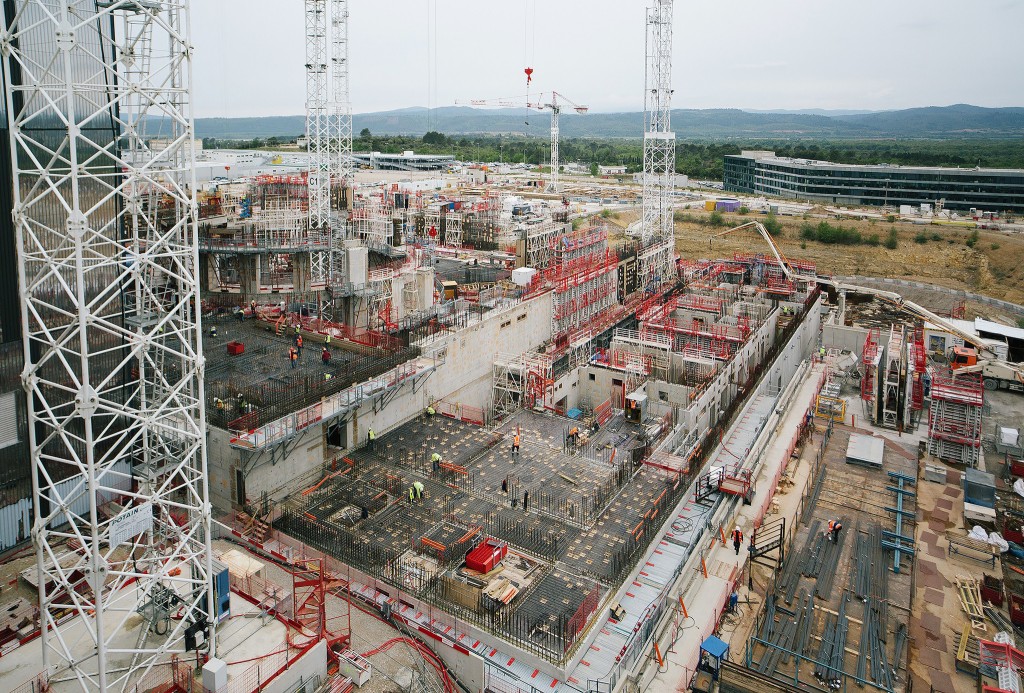
Tritium Building reaches B1 level
2017-04-20 - The progress of the B1 slab basemat and walls of the Tritium Building. ©LNM

Circle rising
2017-04-19 - One of the most spectacular features of the ITER site is the perfectly circular bioshield, which will rise up to the L4 level and then be capped. The bioshield will surround the cryostat, which in turn surrounds the steel vacuum vessel.
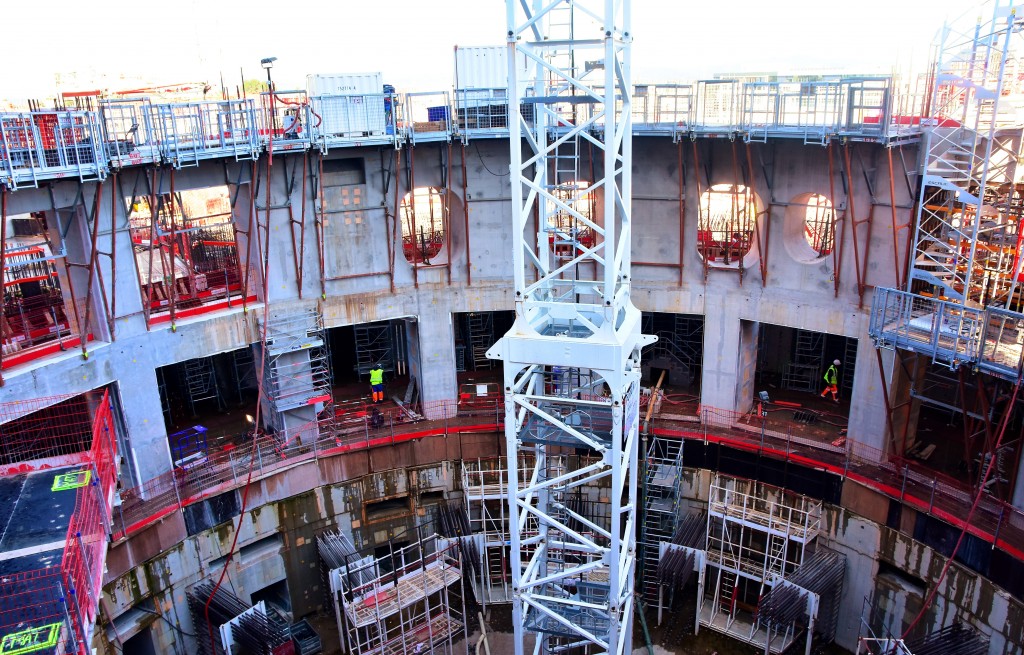
Soon to be two zones
2017-04-19 - A temporary cap will soon be installed at B1 level, where you see the red line in this picture. The cap will allow workers to work safely below, while work on the bioshield continues above up to the final level: L4.

Inside the arena
2017-04-19 - A peek into the deep "well" where the ITER Tokamak assembly will begin next year.
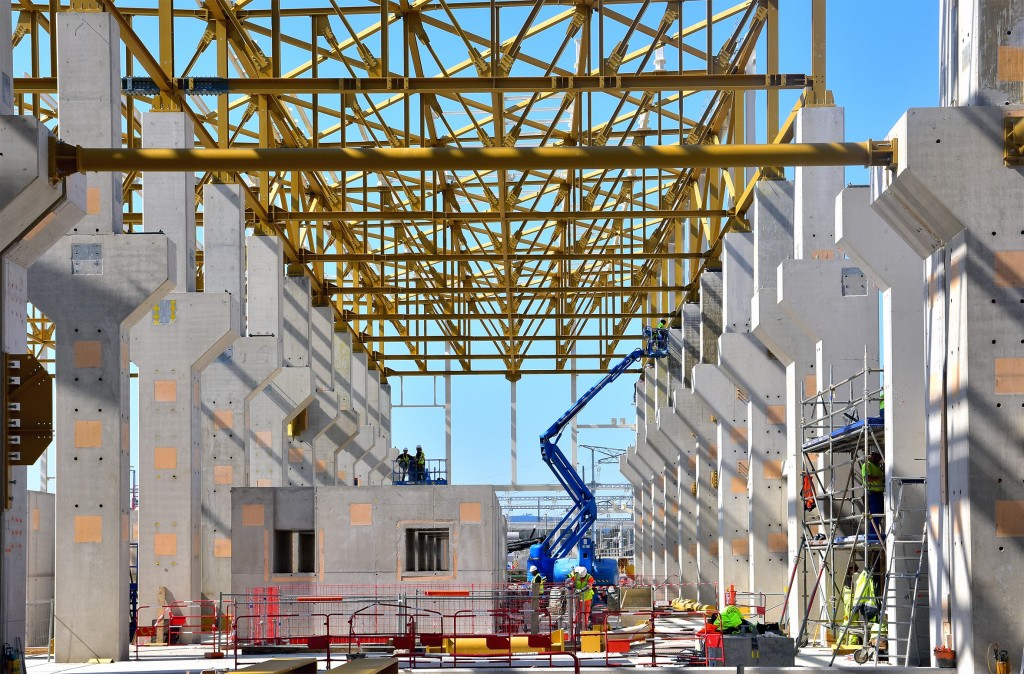
Early installation activities will start in June
2017-04-19 - Work is progressing on the ITER cryoplant building. Early access for the first component installation activities is expected in June, with the full building completed in September.
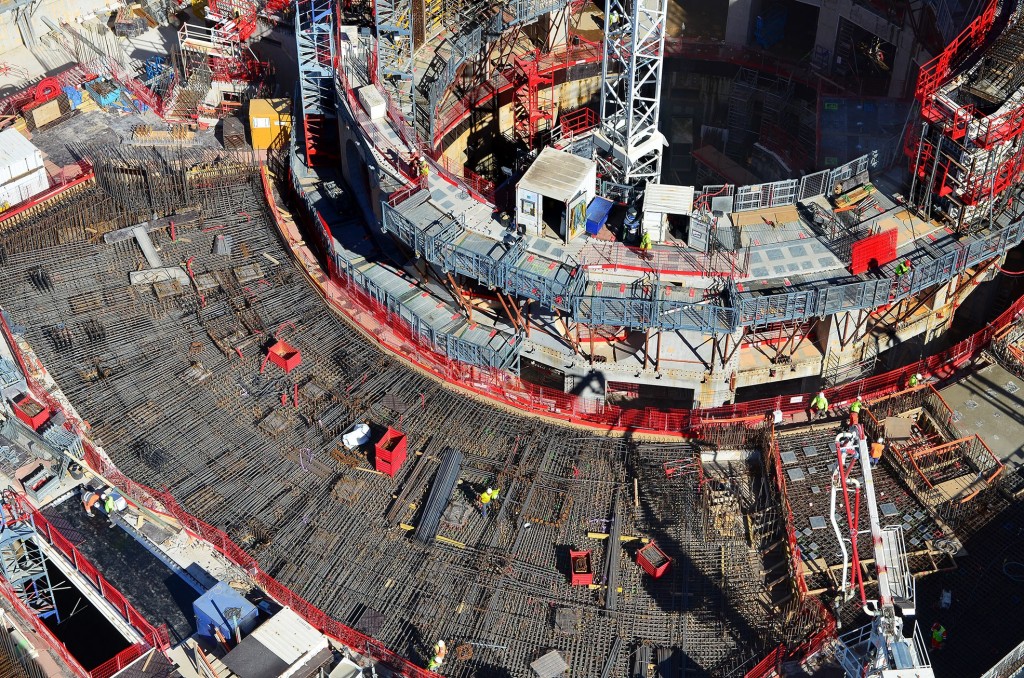
Seen from above
2017-04-19 - Workers are preparing to pour the last segments of the Tokamak Building L1 slab ... laying rebar, positioning anchor plates, setting up scaffolding. Visitors to ITER's Open Doors Day in May will be able to walk out over the finished concrete (L1 is the equivalent of ground level).
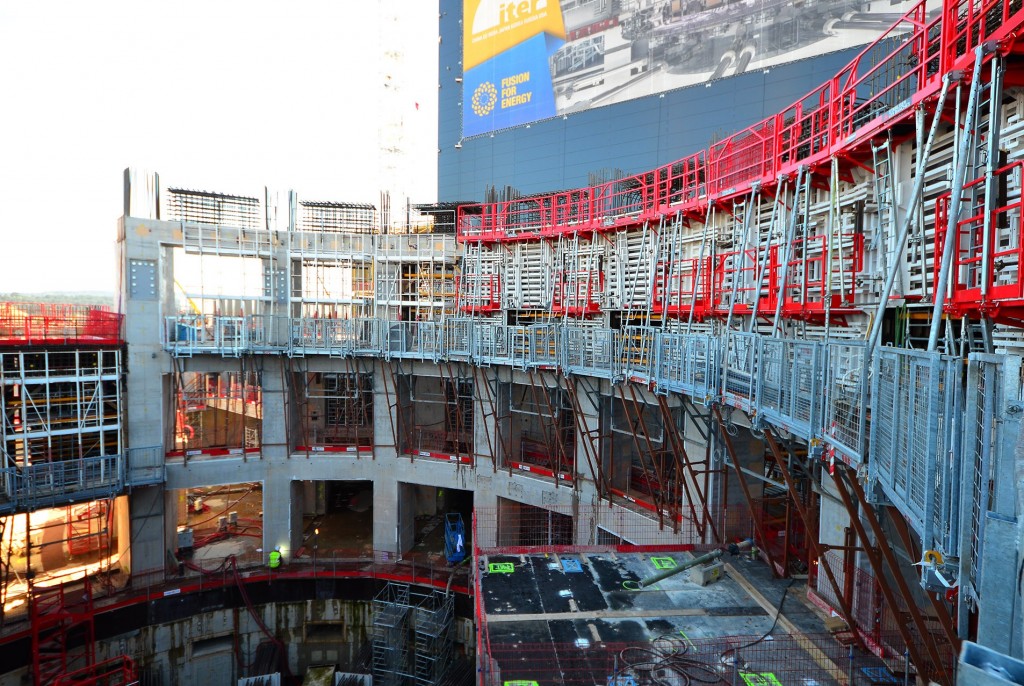
Looks like an apartment complex, is not
2017-04-19 - Inside the huge well of the ITER bioshield, teams are working on different levels simultaneously. The worker in yellow stands at B1 level, where the base of the cryostat will one day be supported on a concrete crown. At L1 level a temporary structure has been erected to support some of the tools and equipment needed for concrete pouring and, just above, work continues to finalize the L2 level which hosts the multi-tonne steel plates that will anchor the main assembly tool in the Tokamak Pit.

Compressor and cold box rooms
2017-04-19 - From the exterior it will look like one building, but in fact a thick firewall will separate the Cold Box Building (helium plant) from the Compressor Building (helium and nitrogen compressors). A break in the roof structure marks where the firewall will be erected.

The three buildings of the Tokamak Complex
2017-04-19 - The Tritium, Tokamak and Diagnostic buildings, seen from the top of a crane. A maze of concrete and rebar.
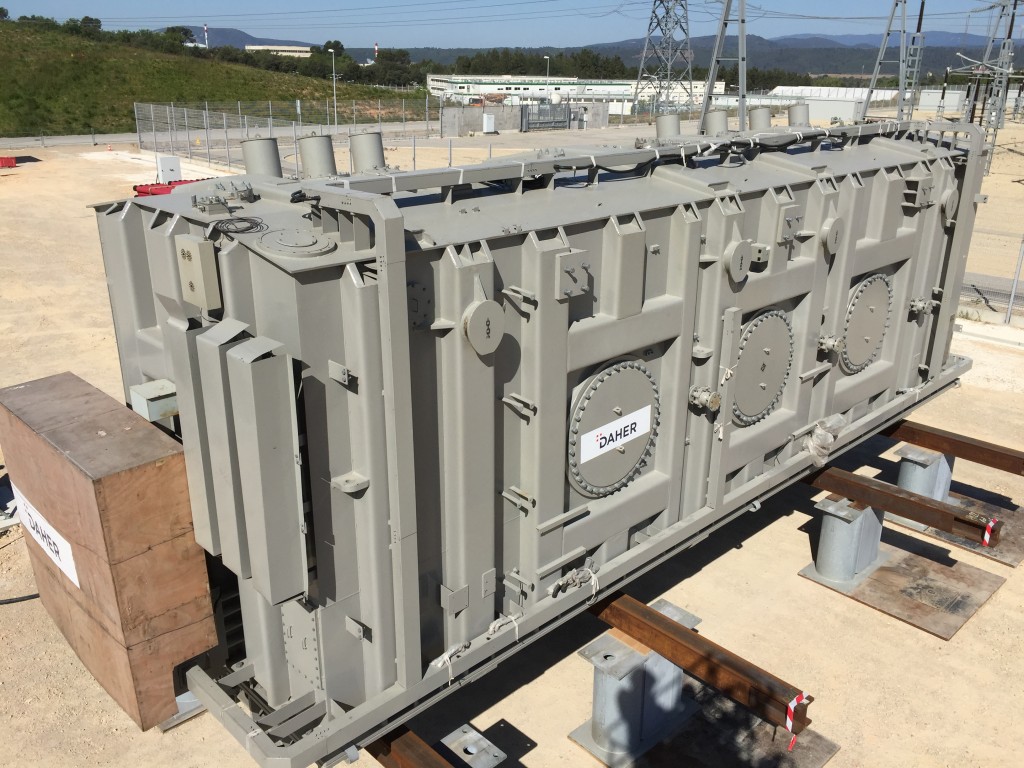
Temporary docking
2017-04-18 - This large transformer and its sister, delivered this week from China, are temporarily stored on the platform until permanent installation is possible.

Component installation to begin soon
2017-04-13 - Seen from one of the worksite cranes, the cryoplant is taking shape. In late June, the first components will be installed.

Off and running
2017-04-12 - Technicians from the European contractor CNIM supervise the first stage of operations: the uncoiling and straightening of the spooled niobium-titanium conductor.

It starts here
2017-04-12 - The first conductor length enters the straightening equipment at the start of the winding table. Conductor is fed in from two points at once in a process known as "double-hand winding."
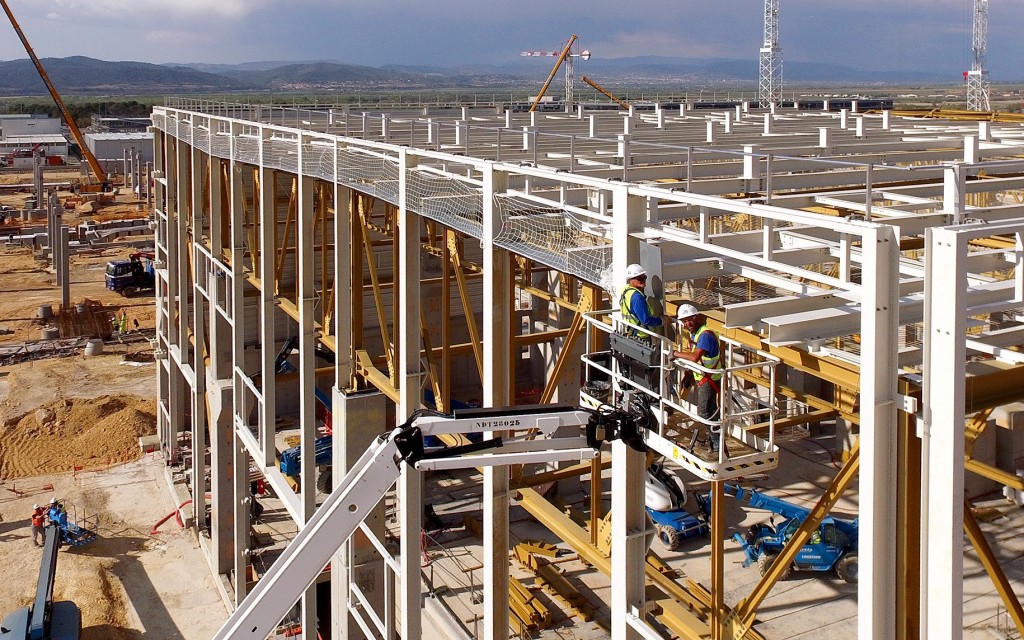
Closing the building in
2017-04-11 - On this side of the 20-metre-tall building, work to install the first layer of aluminium cladding has just begun. Workers are momentarily distracted, though, by the sound of the camera drone ... Photo: ITER Organization/EJF Riche
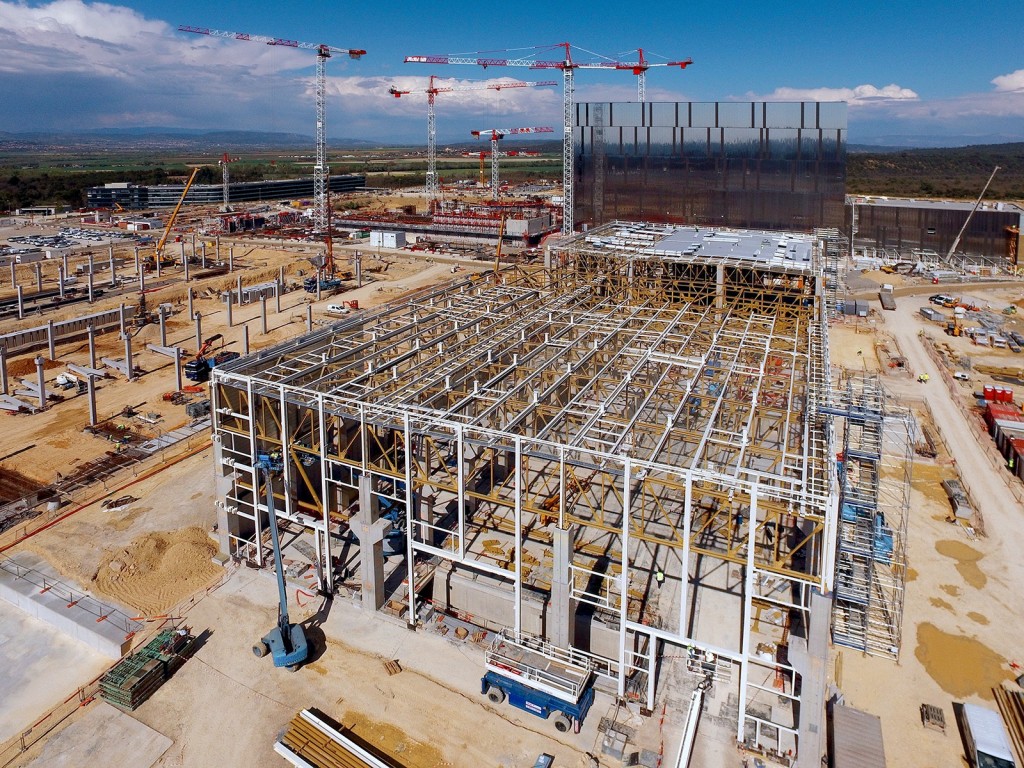
Demanding clients
2017-04-11 - Cooling fluids generated in the 45 x 120-metre Cryoplant Building will travel along process lines to the Tokamak Building, where it will be distributed to the different "clients" through a three-kilometre network of cryolines. The ITER magnets will consume 45 percent of cryogenic power followed by the thermal shield (40 percent) and the cryopumps (15 percent). Photo: ITER Organization/EJF Riche
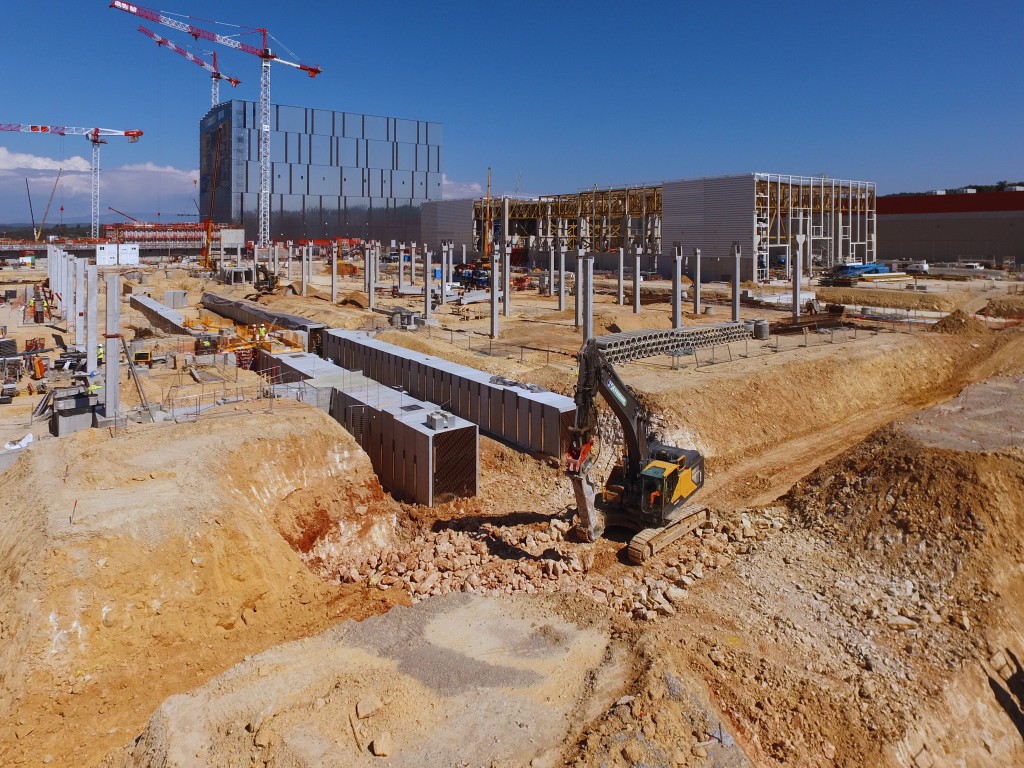
Below and above
2017-04-10 - Work on underground technical galleries is underway between the worksites for the two buildings. Photo: ITER Organization/EJF Riche

Highest yet
2017-04-10 - The Diagnostics Building is the Complex building that has advanced the fastest. Workers are currently pouring the L2 (second storey) slab. Photo: ITER Organization/EJF Riche
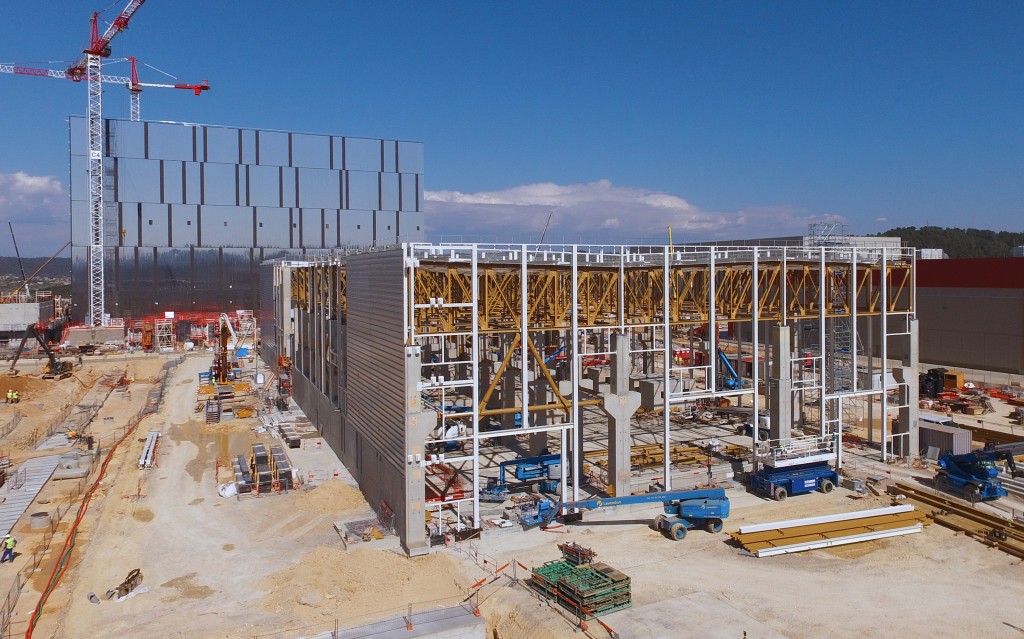
Exterior storage
2017-04-10 - Work is underway to the left of the cryoplant on a 2,600 m² exterior storage area for the tanks that will house gaseous and liquid helium and nitrogen. Photo: ITER Organization/EJF Riche

Beginning to look like the Colosseum
2017-04-10 - With its regularly spaced openings over several levels, ITER bioshield could almost look like ... the Colosseum in Rome. Photo: ITER Organization/EJF Riche
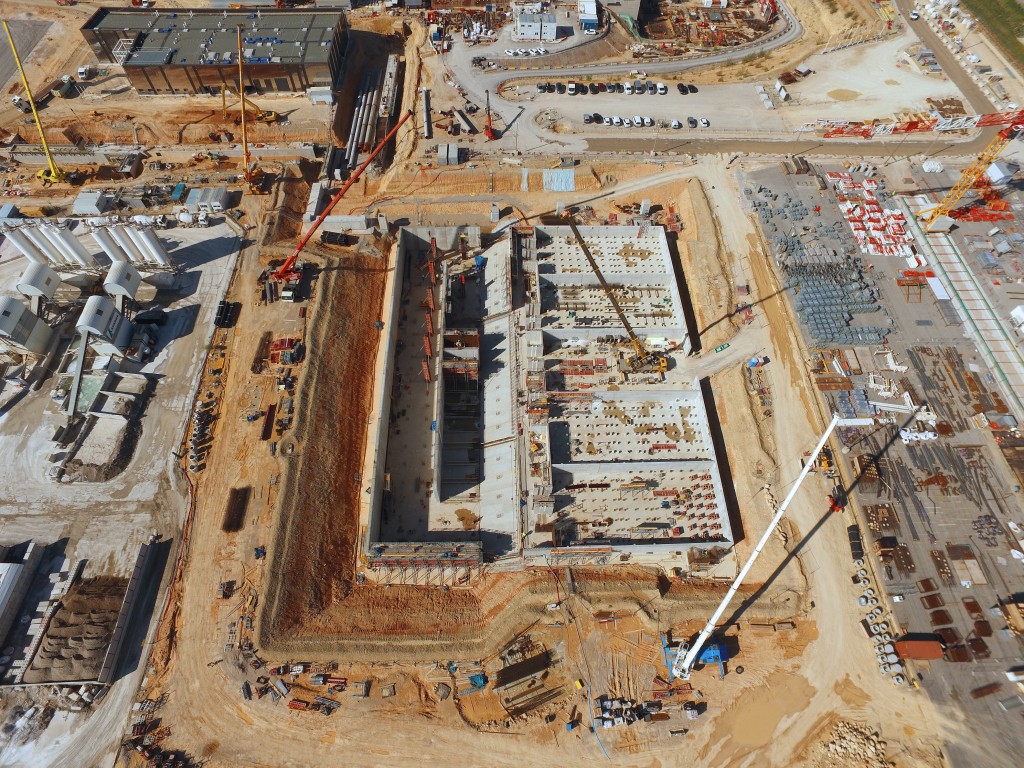
Cooling tower area progresses
2017-04-10 - In April, the concrete frame of the cooling tower zone is visible from above. Besides the hot and cold basins that we see framed out, there will be quite a bit of equipment installed at platform level (the heat exchangers, for example). Photo: ITER Organization/EJF Riche
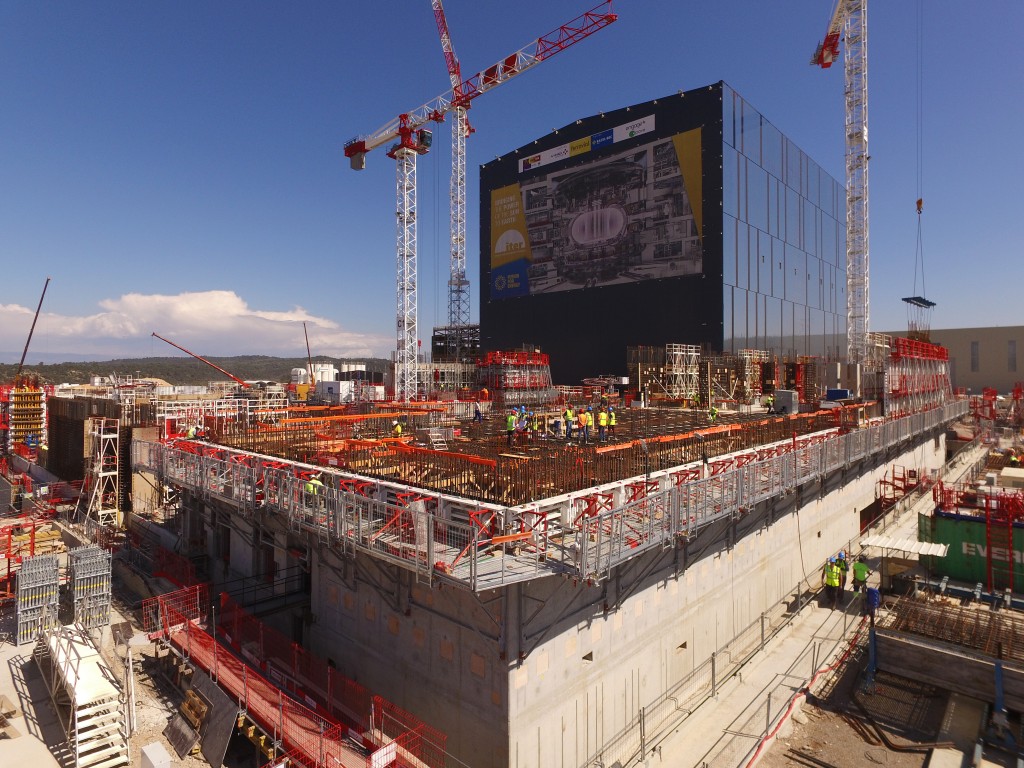
Second storey work
2017-04-10 - It's easy to see that the first storey of the Diagnostics Building is in place and that work is underway on the second. Photo: ITER Organization/EJF Riche
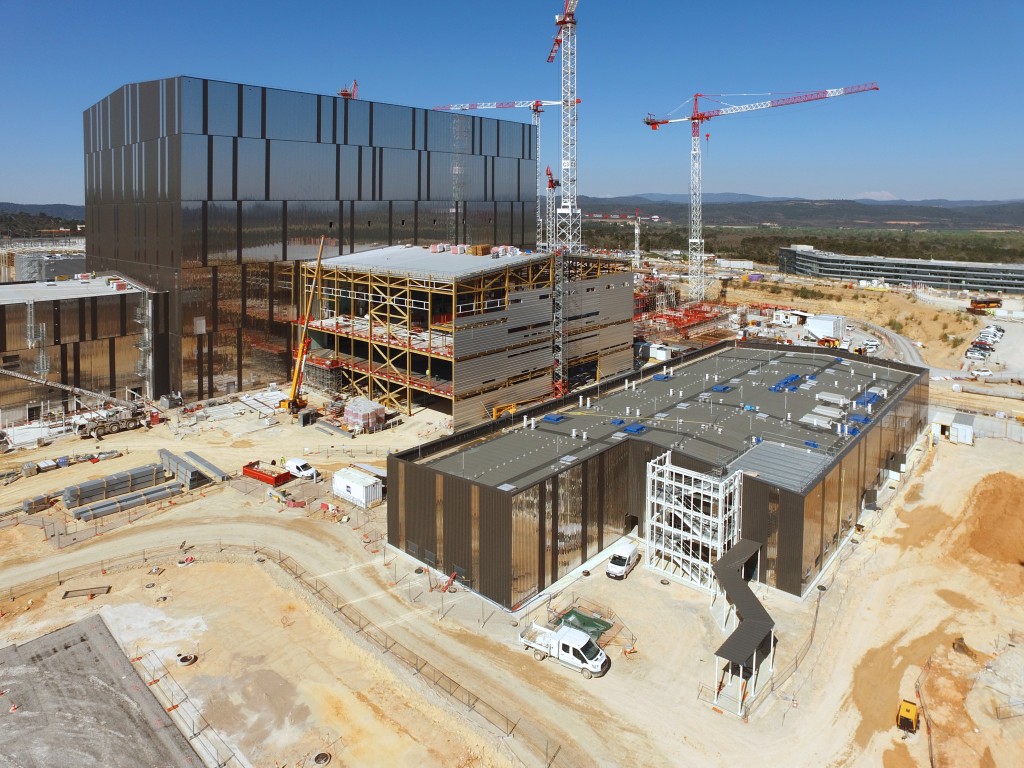
Radio Frequency Building: starting to fit in
2017-04-10 - As the first layer of cladding is filled in, the RF Building is beginning to look at home with its neighbours (from left to right the Cleaning Facility, the Assembly Hall and the Site Services Building). Photo: ITER Organization/EJF Riche
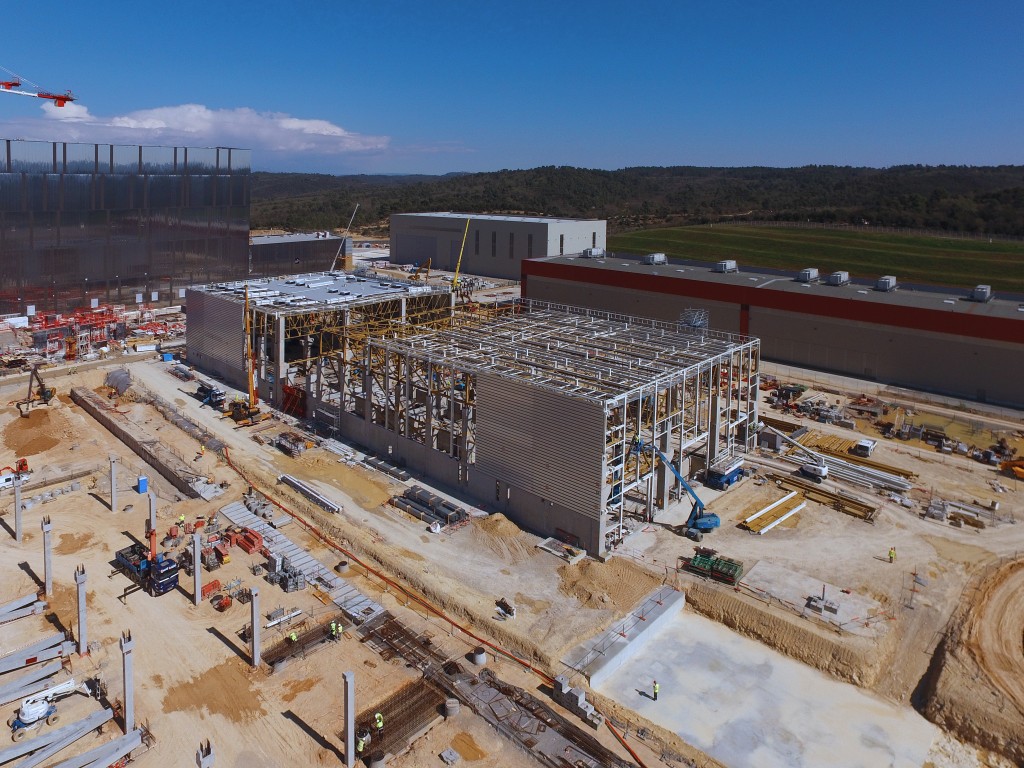
From the sky
2017-04-10 - The two buildings of the cryoplant—the Cold Box Building (left) and the Compressor Building (right)—are separated by a gap in the frame that won't be visible once the building is finished. Photo: ITER Organization/EJF Riche

A sea of iron
2017-04-10 - The density of rebar in this critical area of the Tokamak Complex is high, both for the bioshield and the surrounding slab. Photo: ITER Organization/EJF Riche
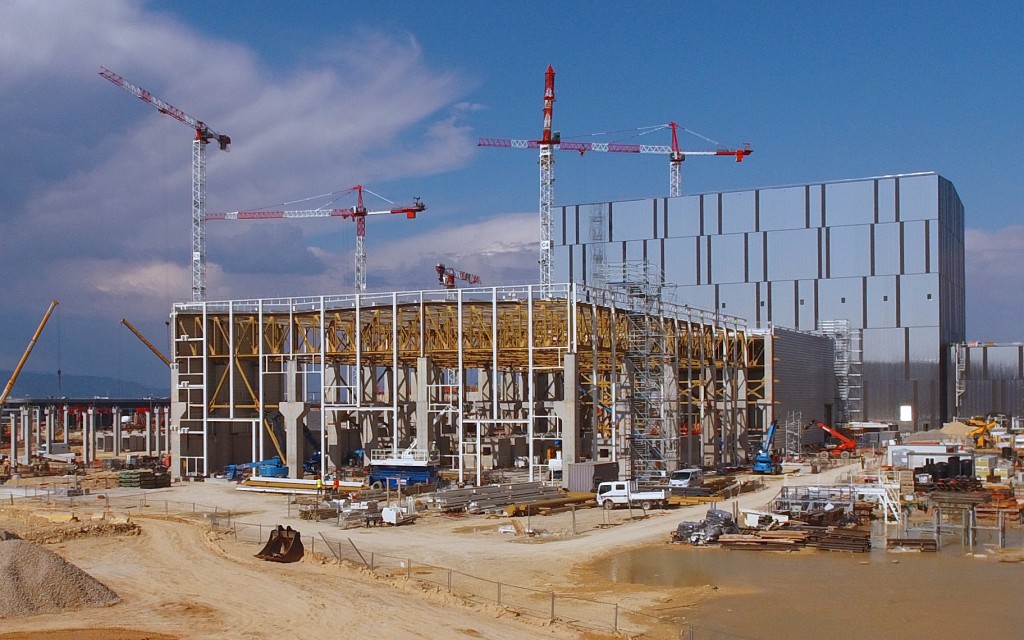
Cryoplant taking shape
2017-04-10 - Construction of the world's largest concentrated cryoplant is progressing; the installation of the first components is scheduled for June. Photo: ITER Organization/EJF Riche

Nice and regular
2017-04-10 - Anchor plates for attaching equipment are spaced regularly on this part of the Tokamak Building slab. Photo: ITER Organization/EJF Riche
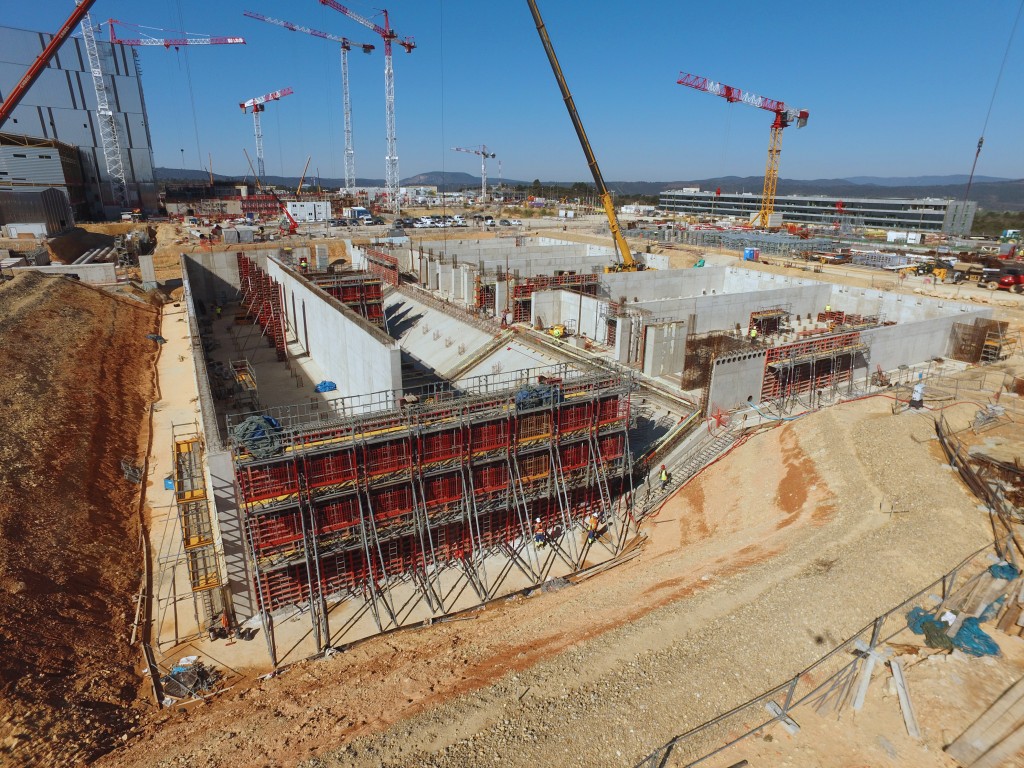
Water evaporation zone
2017-04-10 - To the right, the concrete bays reserved for 10 water tower cells and cold basin; to the left, the hot basin. Photo: ITER Organization/EJF Riche

Gouging the giant's eye
2017-04-06 - On 6 April, the massive formwork is removed— or rather ''gouged out''—from openings in the bioshield wall.

Arrival in workshop
2017-04-05 - All six segments of the cryostat lower cylinder (tier 1) are now stored in the Cryostat Workshop.
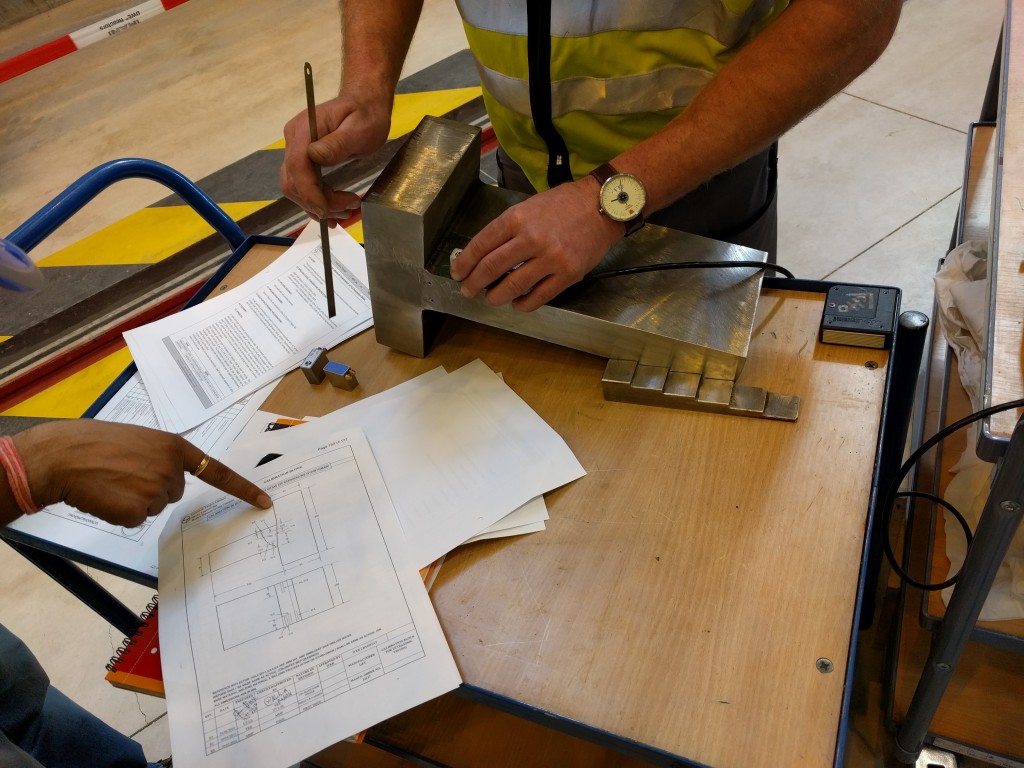
Checking each step in the process
2017-04-04 - The elements of the cryostat machined in India—large and small—are assembled in the on-site workshop by Indian Domestic Agency contractors.

Inside the workshop
2017-04-04 - Behind the technicians a few of the lower cylinder elements are visible, covered in red tarp.
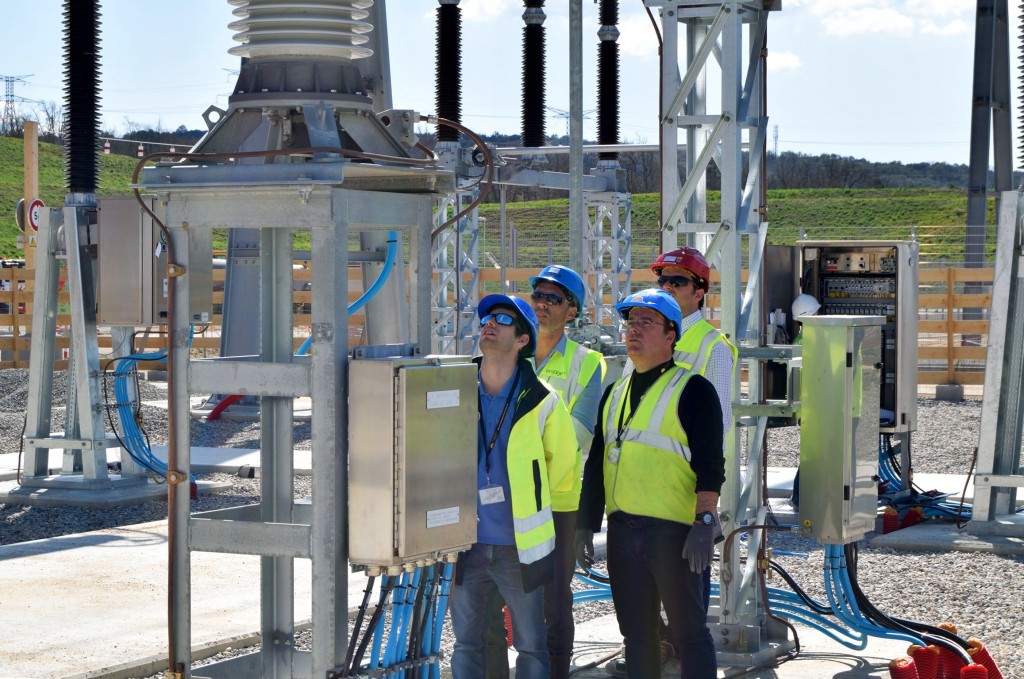
When a transformer purrs
2017-03-30 - A test energization procedure is carried out on the first of four 22 kV steady state electrical network (SSEN) transformers, which have not managed power since factory acceptance tests in 2014. By "revving them up," the team is verifying that all is well.
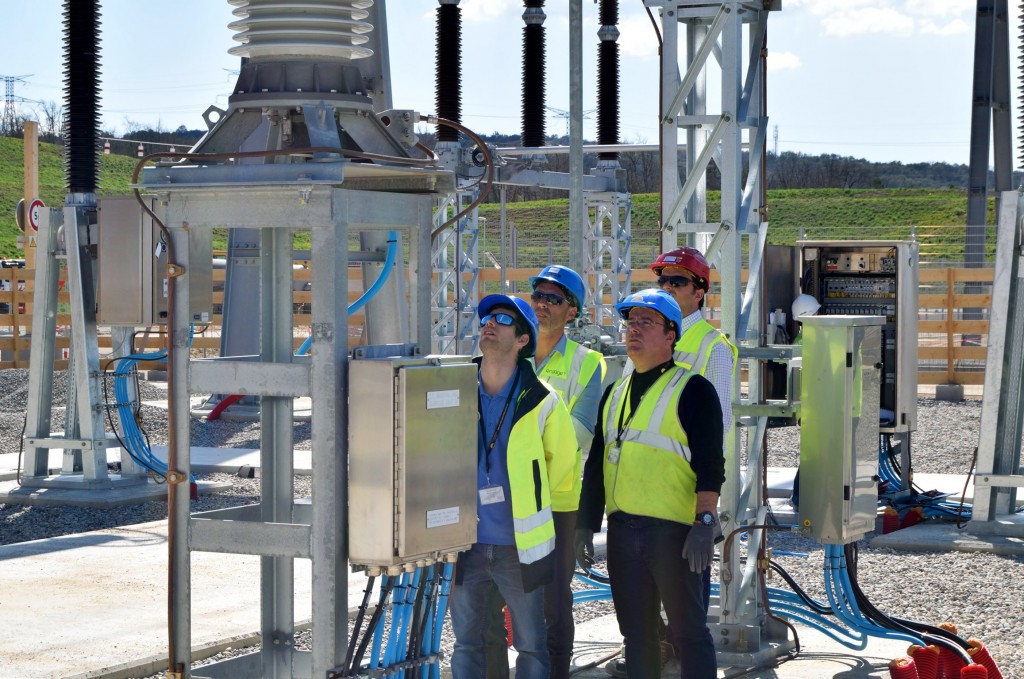
When a transformer purrs
2017-03-30 - On 30 March, electricity flows without a hitch from the grid substation to the 400 kV ITER switchyard, and from there into one of the four 22 kV worksite transformers. This "energization" will be repeated now for each of the three remaining 22 kV transformers of the steady state electrical network (SSEN).
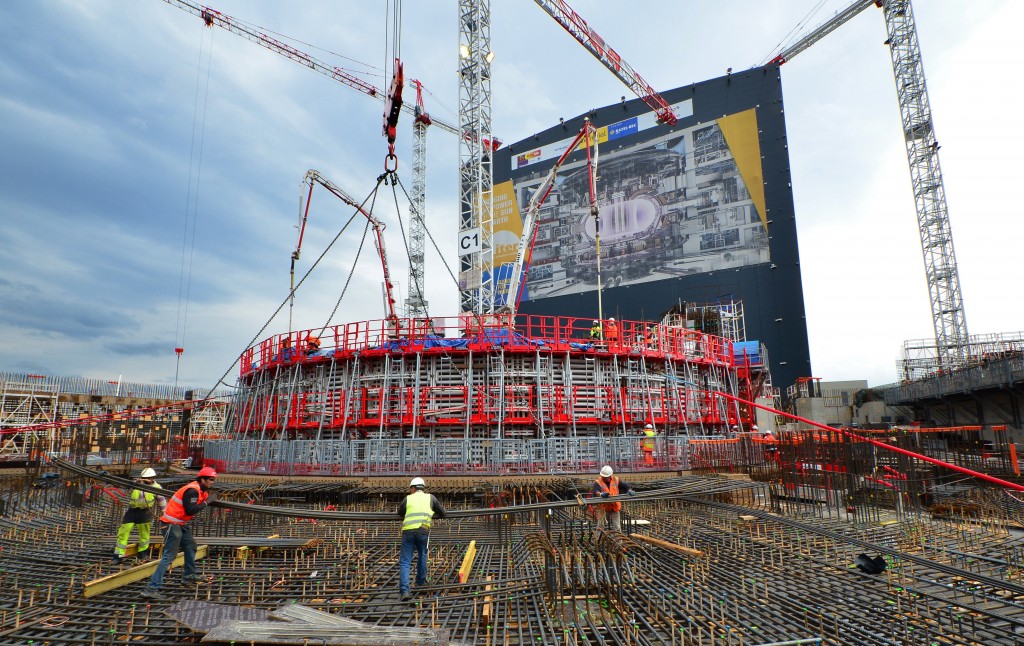
Different teams, different projects
2017-03-24 - As concrete pouring proceeds in the background, workers on the L1 level of the building are busy handling a bundle of 12-metre-long bars for the steel reinforcement of the neutral beam cell slab.

Top of the bioshield
2017-03-24 - At the top of the ring, work starts on the L3-level bioshield. L4 will be the last level of this huge concrete structure that is designed to completely enclose the machine. Photo: ENGAGE
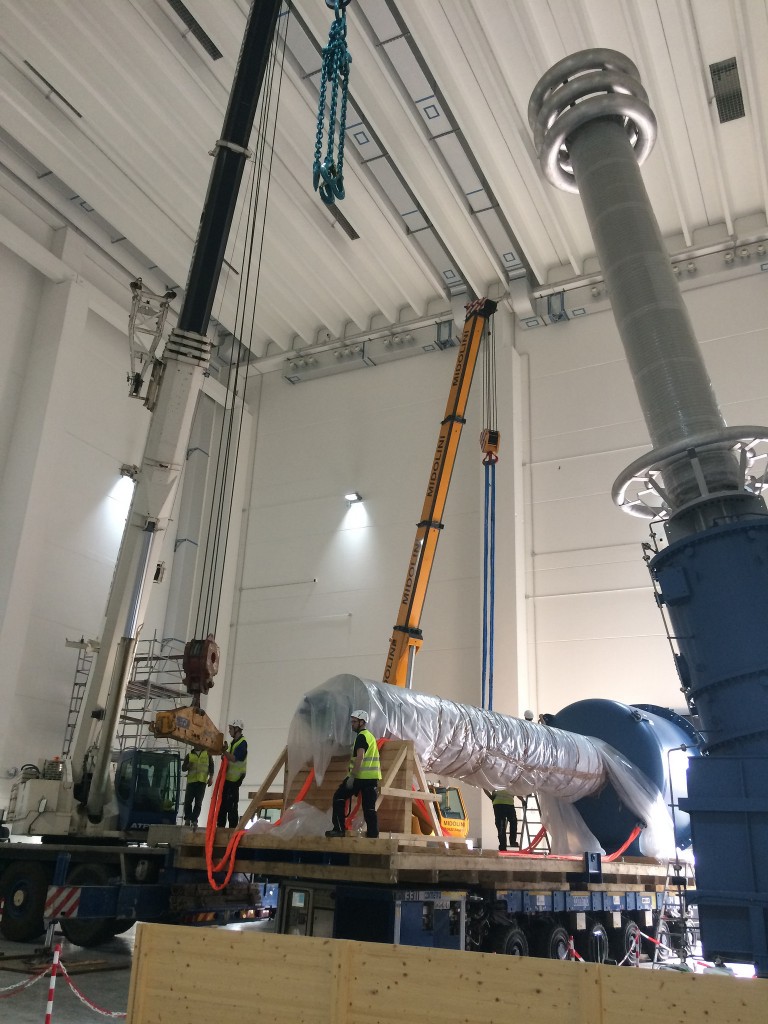
Arrivals from Europe and Japan
2017-03-24 - Europe and Japan deliver several large components to the NBTF high voltage hall in March. Photo: F4E
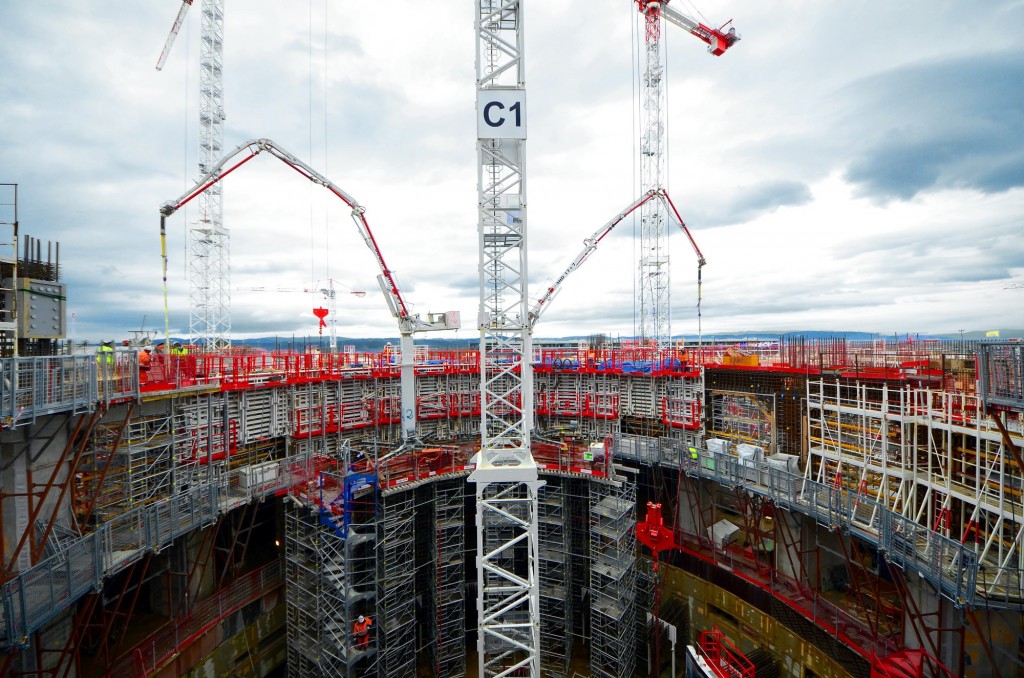
Successive pours for the bioshield
2017-03-24 - Connected to mixer trucks by pipes running through the basement of the Tokamak Complex, the two pumps can deliver some 30 cubic metres of concrete per hour.
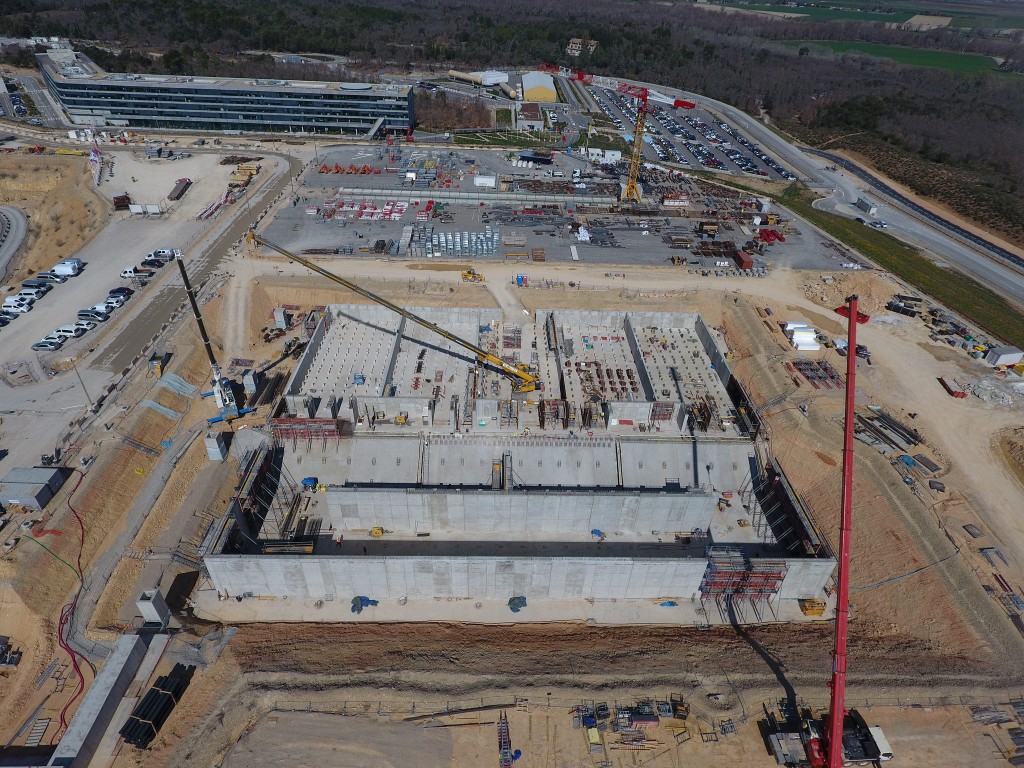
Hot basin, seen by drone
2017-03-22 - In the photo, the lower level construction and sloped area is part of the hot basin. Vertical pumps will be installed to draw from the basin and discharge to the top of the cooling tower. © Les Nouveaux Médias/SNC ENGAGE

First cladding
2017-03-22 - The first cladding appears on the cryoplant building structure in March. © Les Nouveaux Médias/SNC ENGAGE
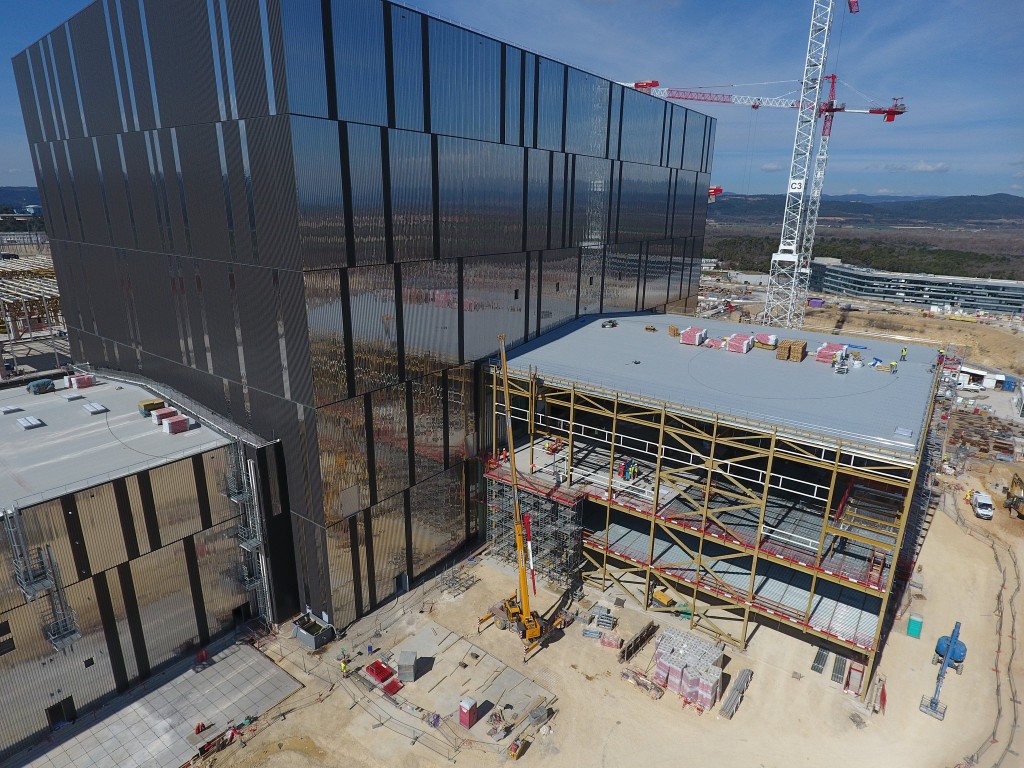
Cladding activities to start soon
2017-03-22 - Scaffolding is in place for the start of Radio Frequency Building cladding activities. © Les Nouveaux Médias/SNC ENGAGE
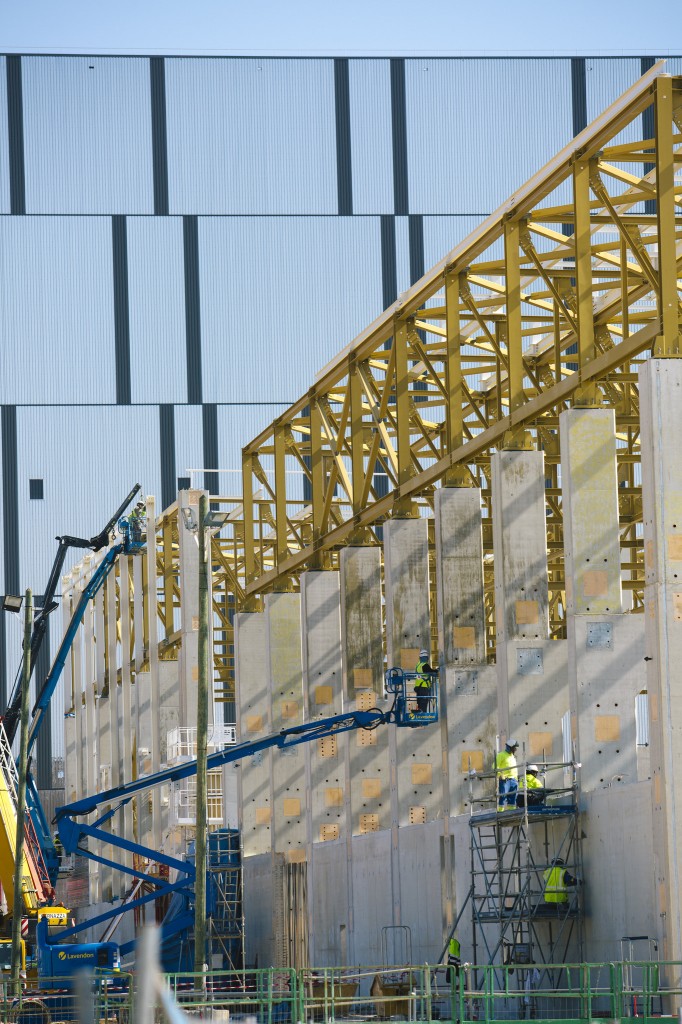
Working toward the start of component installation
2017-03-22 - The western facade of the Cryoplant Building, late March. © Les Nouveaux Médias/SNC ENGAGE

Work in every zone
2017-03-22 - In front of the partially constructed cryoplant, material is stored for the underground networks which are being installed between the buildings. © Les Nouveaux Médias/SNC ENGAGE
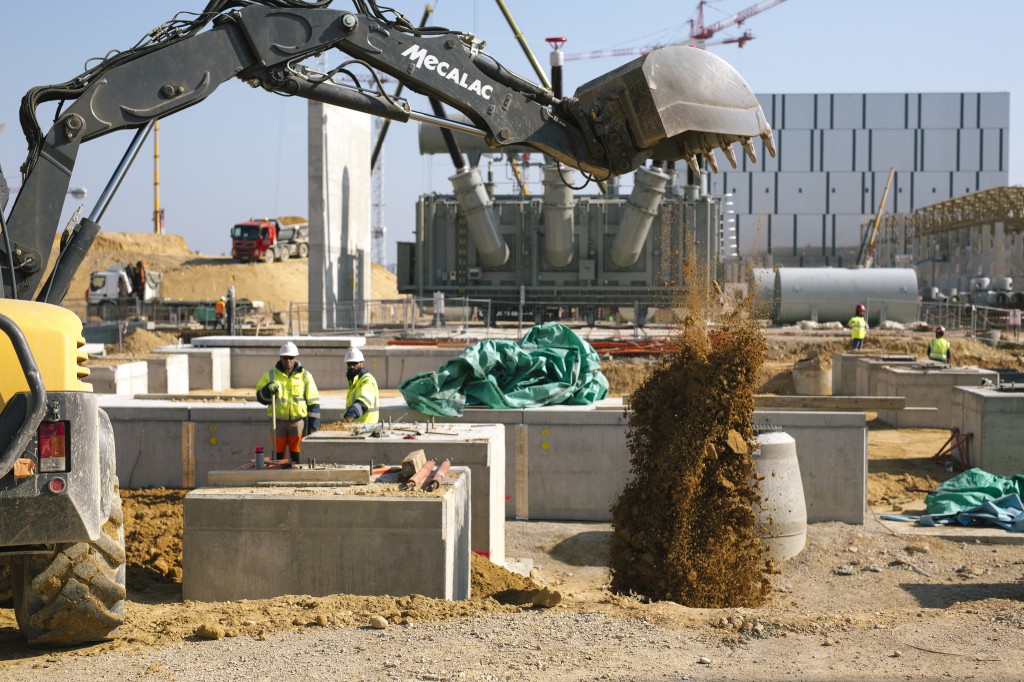
Electrical works
2017-03-22 - Works continue to prepare the on-site electrical switchyard, including the "first energizing" procedure for the first of seven bays. © Les Nouveaux Médias/SNC ENGAGE
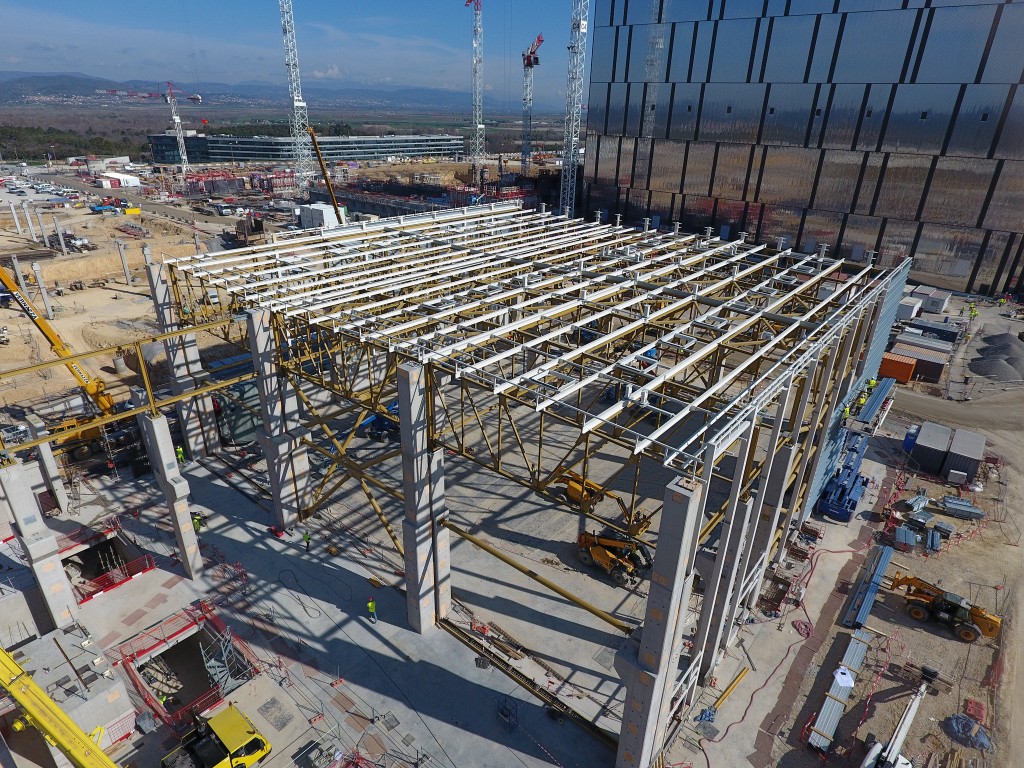
Cold Box Building
2017-03-22 - Process lines carrying cryogens will travel from the Cold Box Building (pictured) to the Tokamak Building over a bridge installed 13 metres above platform level. © Les Nouveaux Médias/SNC ENGAGE
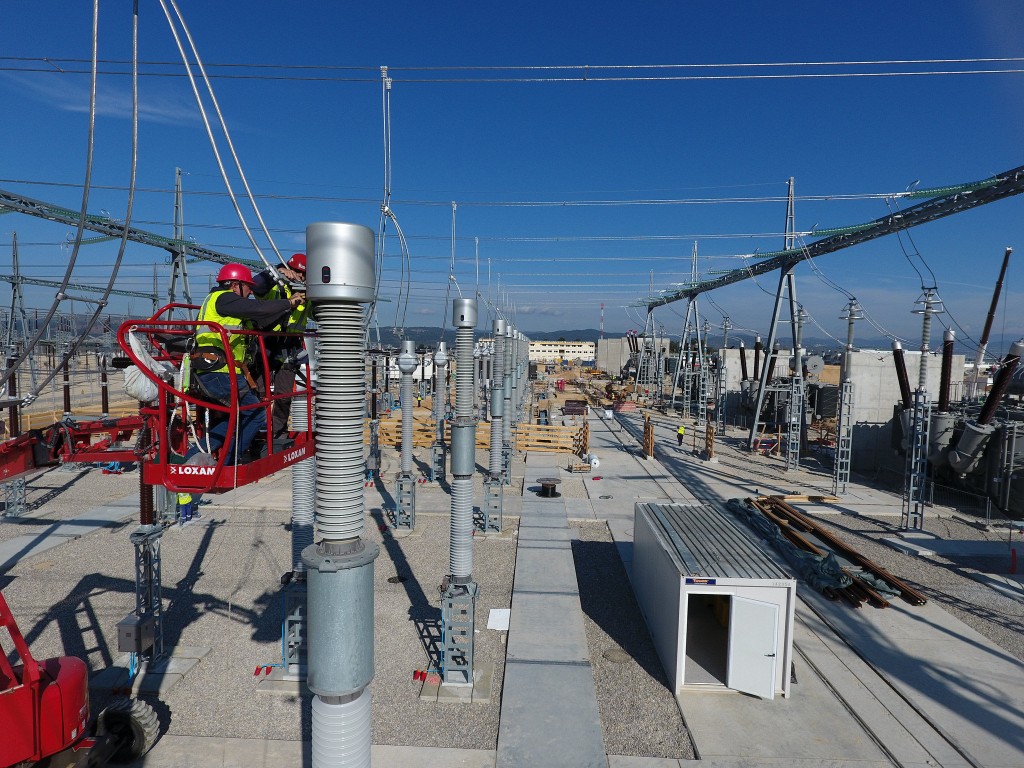
Hundreds of separate components
2017-03-22 - Bringing down the voltage from the 400 kV power line to a level useable by the ITER facilities takes a huge switchyard and hundreds of components. © Les Nouveaux Médias/SNC ENGAGE
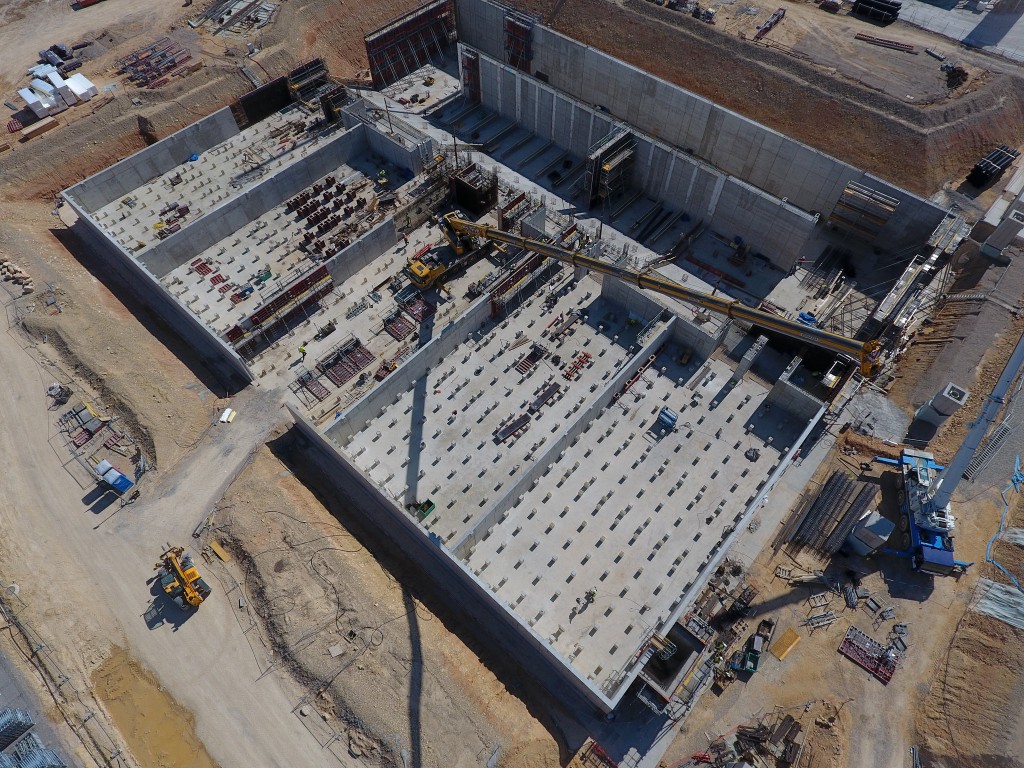
10 independent cooling cells
2017-03-22 - ITER's induced-draft cooling tower, under construction now, is made of 10 independent cells located above the cold basin. Each of the five bays in the photo will contain two cells. © Les Nouveaux Médias/SNC ENGAGE
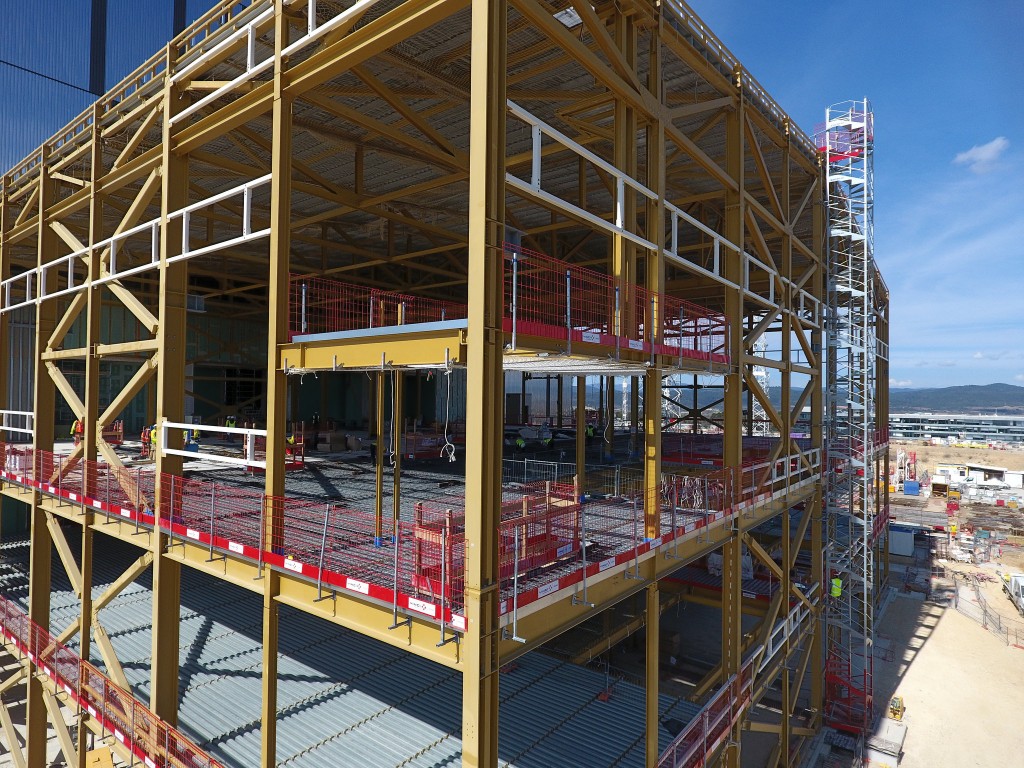
Peeking inside
2017-03-22 - Close up to the three-storey Radio Frequency Building on the northern side of the Assembly Hall. © Les Nouveaux Médias/SNC ENGAGE
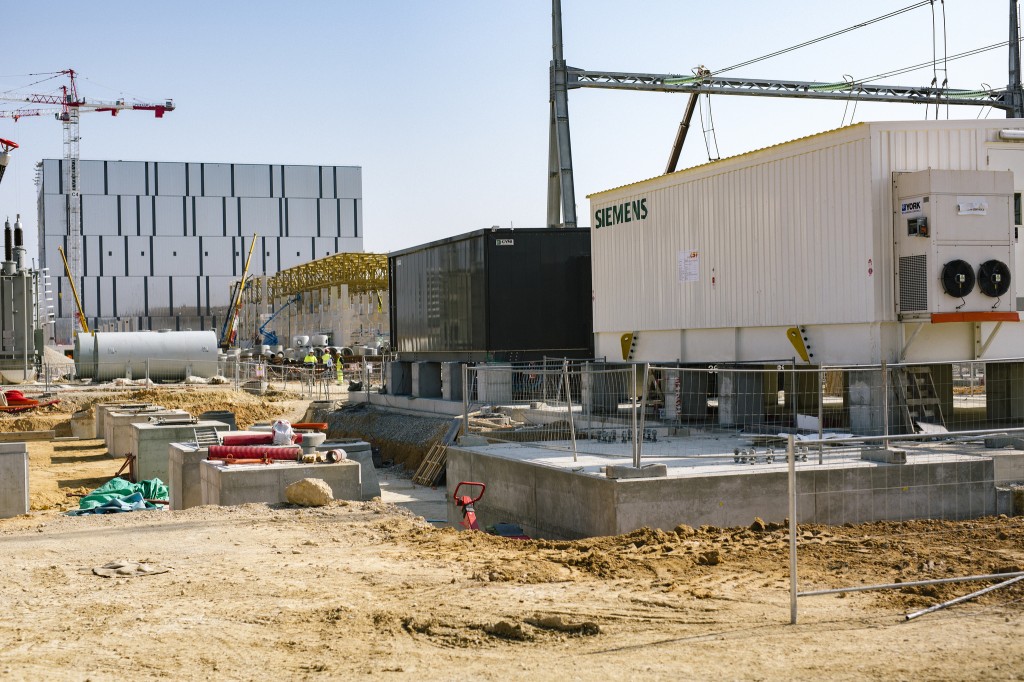
E-houses installed
2017-03-22 - Two E-houses for the pulsed power electrical network are now installed on site. © Les Nouveaux Médias/SNC ENGAGE

E-houses installed
2017-03-22 - Two E-houses for the pulsed power electrical network are now installed on site. © Les Nouveaux Médias/SNC ENGAGE
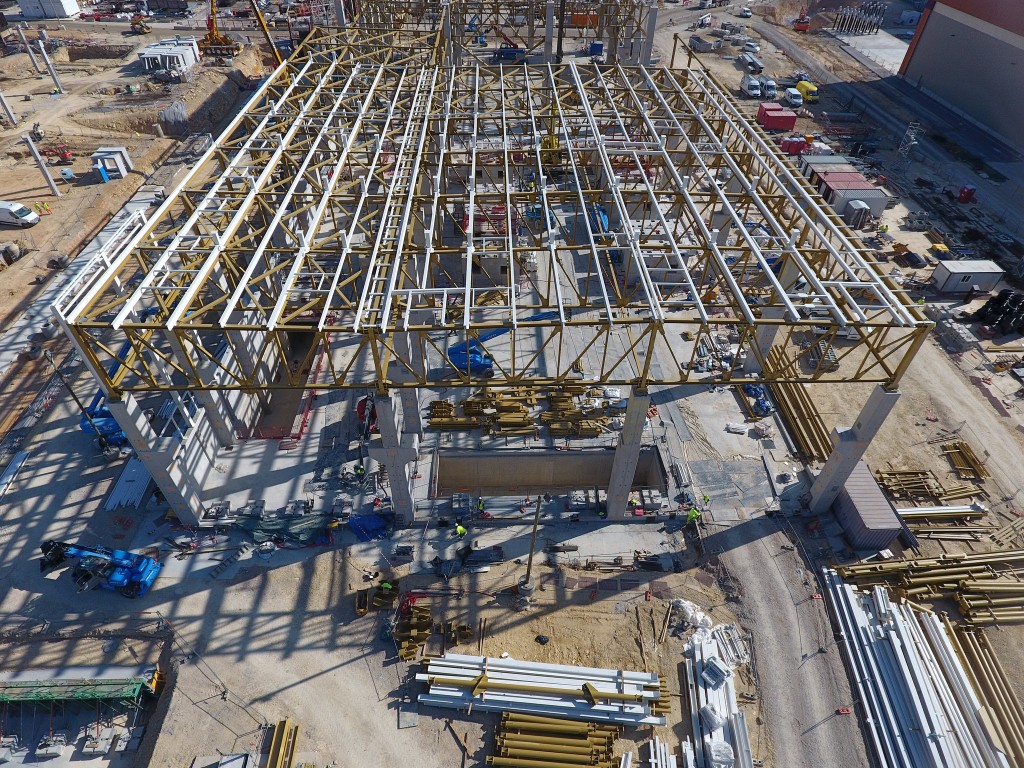
Cryoplant roof frame
2017-03-22 - The southern portion of the cryoplant, seen from above. A large exterior area for the storage of helium and nitrogen in liquid and gaseous forms will be created to the left. © Les Nouveaux Médias/SNC ENGAGE
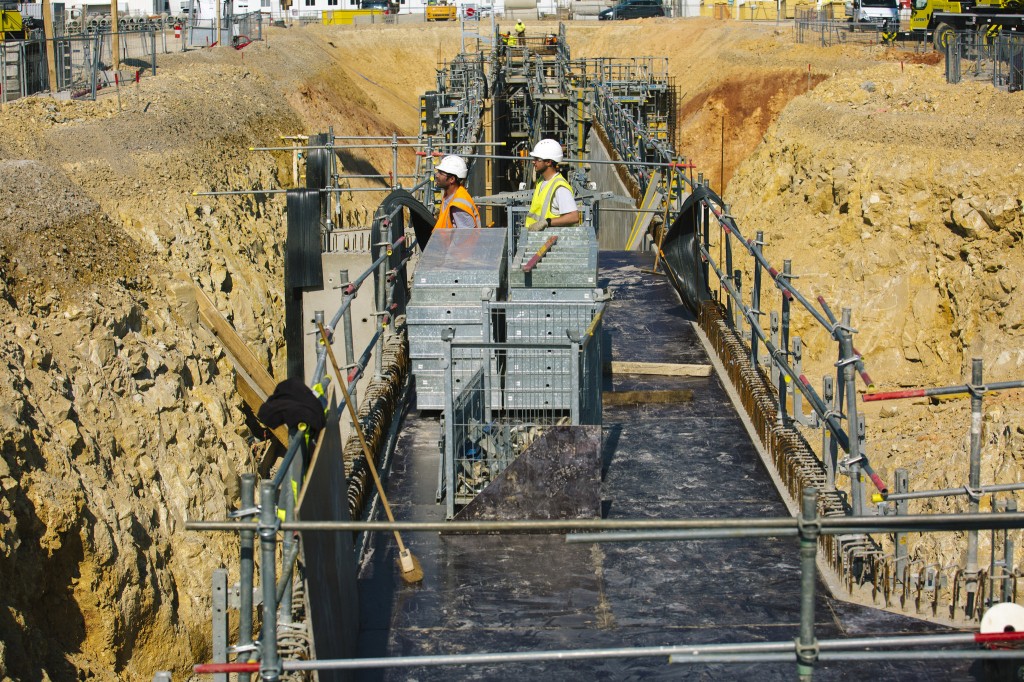
(More) underground networks
2017-03-22 - Since 2012, teams have been working on the different underground networks of the platform. Four kilometres of networks are planned in all. © Les Nouveaux Médias/SNC ENGAGE

Concentrating the resources on the centre
2017-03-18 - Work is underway on three levels of the bioshield at the same time (L1, L2, L3). Three hundred workers, in two shifts, are participating.
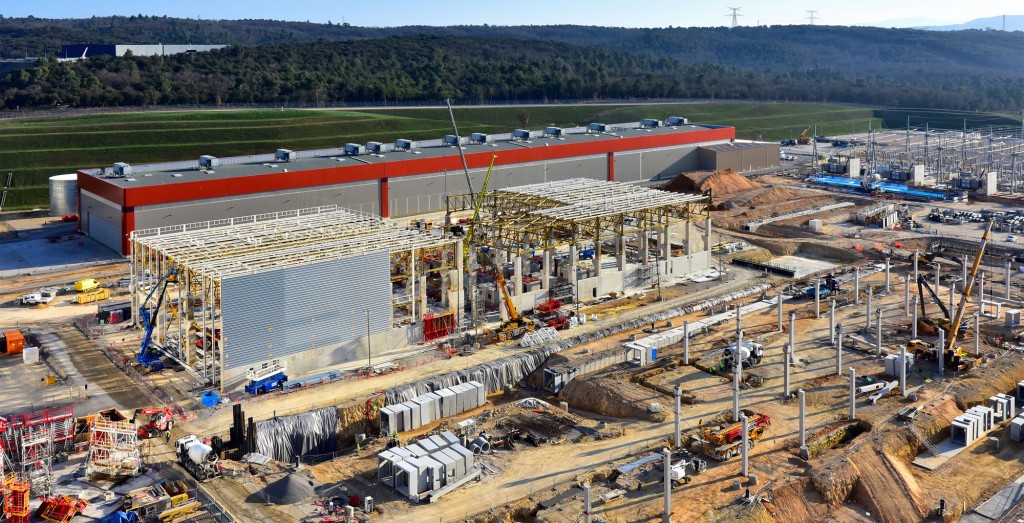
Cladding!
2017-03-16 - The cryoplant structure is beginning to look like a building as the first level of metal cladding is set into place ...

Four more to come
2017-03-13 - Four other lower cylinder segments await transport in Fos-sur-Mer, after arriving from India.

Next steps for the cryostat
2017-03-10 - Segments of the cryostat lower cylinder are stored in the Cryostat Workshop.
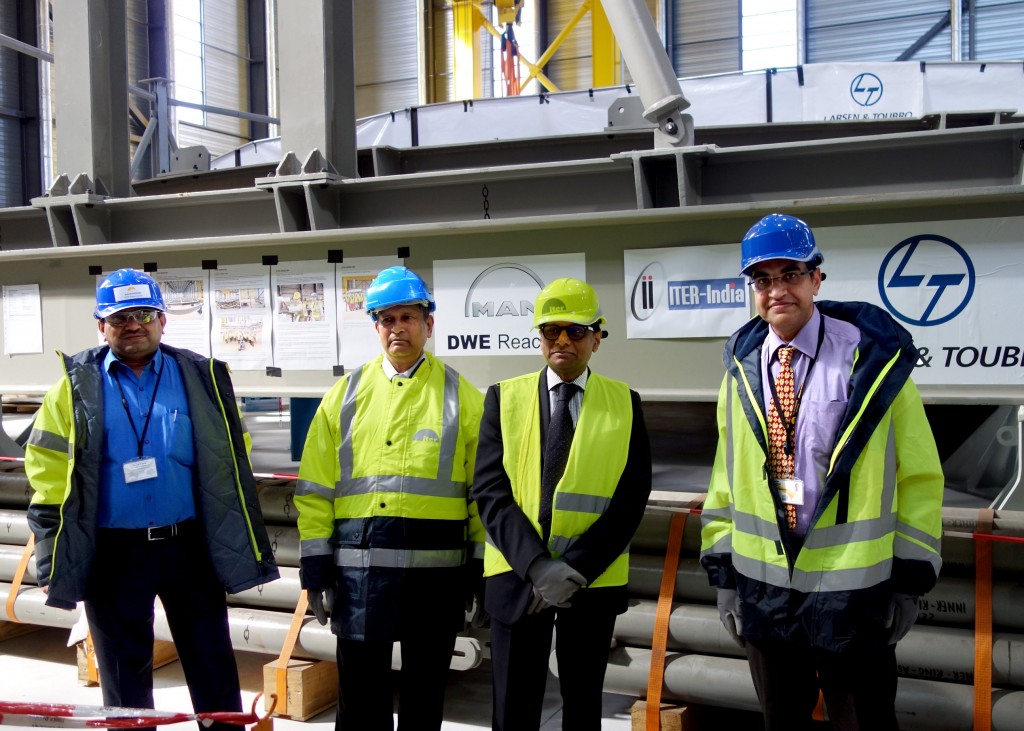
Indian ambassador visits Cryostat Workshop
2017-03-10 - His Excellency Mohan Kumar (second from right), India's Ambassador to France and the Principality of Monaco, makes a stop in the Cryostat Workshop during a visit to ITER on 10 March.
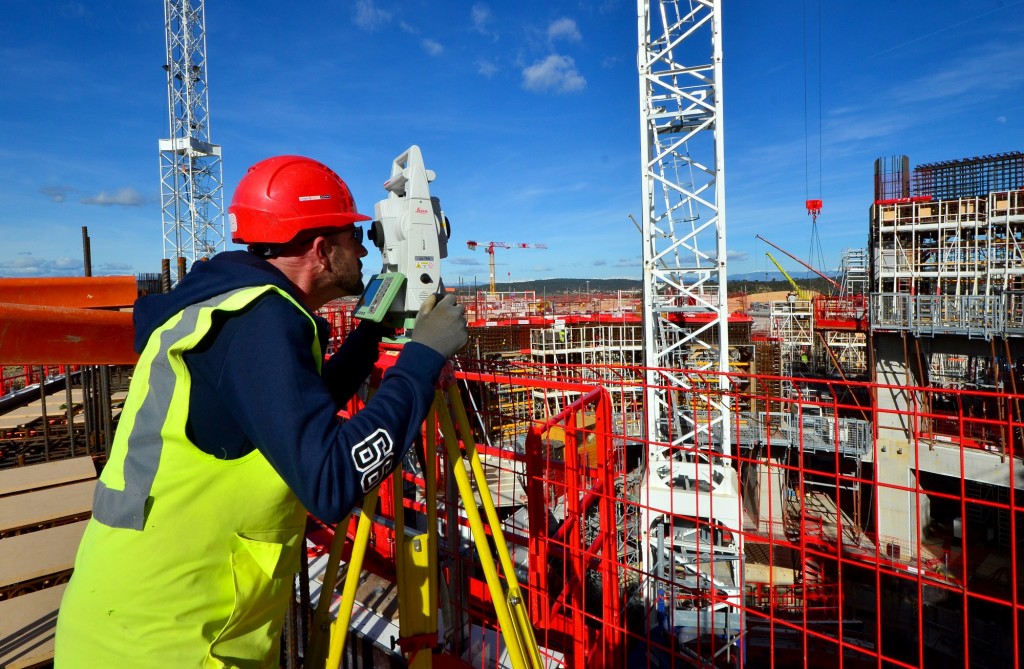
Measuring the as-built result
2017-03-08 - As the ITER bioshield rises, metrologists are on site to measure the as-built construction ... including the precise position of openings and embedded plates.

The pre-Alpes in the background
2017-03-08 - Snow-peaked mountains provide a spectacular backdrop to this worker preparing for a lift operation.

The most unmovable surface around
2017-03-08 - Exploiting the most reliable (i.e., unmovable) surface available—the concrete bioshield—the metrology team at ITER will establish a matrix of reference "targets," or fixed points, for use in measuring and aligning tokamak components during the assembly phase.

Tower rising
2017-03-08 - Having completed the bioshield basement levels B2 and B1, workers are now advancing on the "L" levels above-ground. L1 has been poured and is seen still surrounded by scaffolding in this picture; L2 is half framed out; and the first reinforcement bars are visible at the L3 level.
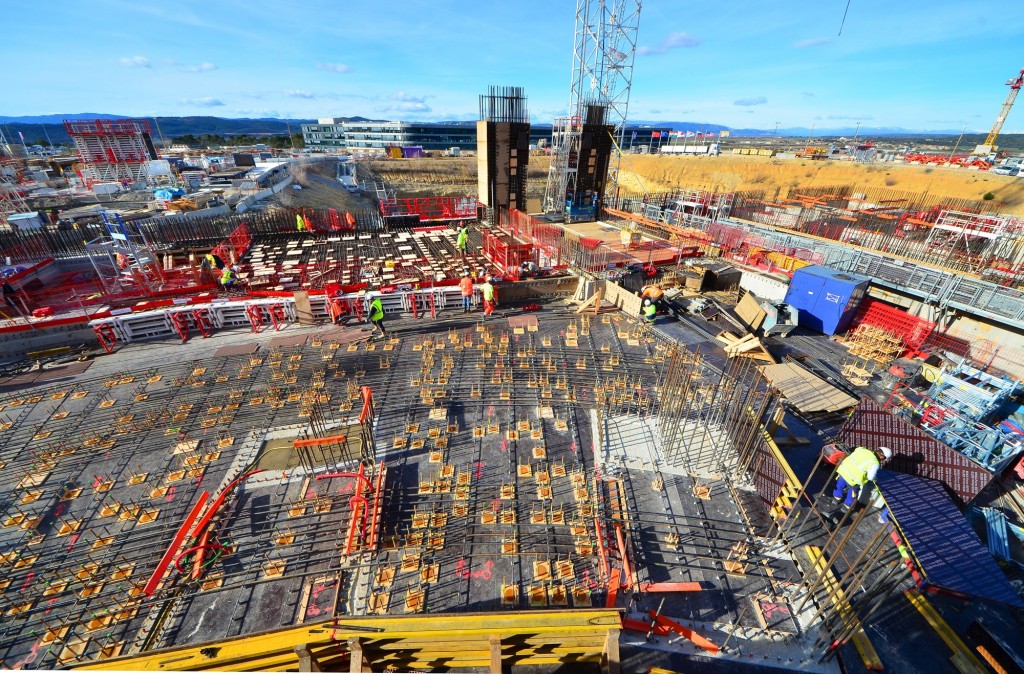
A sea of plates
2017-03-08 - These embedded plates will one day support equipment for the neutral beam injection system. In the distance, the towers are part of the cargo lift system that will transfer components between the Tokamak Building and the Hot Cell Facility.

Working on the bioshield, L2 level
2017-03-08 - Scaffolding is transported by crane to the L2 level of the bioshield, where concrete pouring continues.

The Tokamak Pit
2017-03-08 - Looking down from the L2 level of the bioshield into the Tokamak Pit ... where the ITER machine will be assembled from bottom up beginning in 2018.

Preparing for circular openings
2017-03-08 - Circular areas are reserved in the rebar at the L3 level of the ITER bioshield for future magnet feeders.
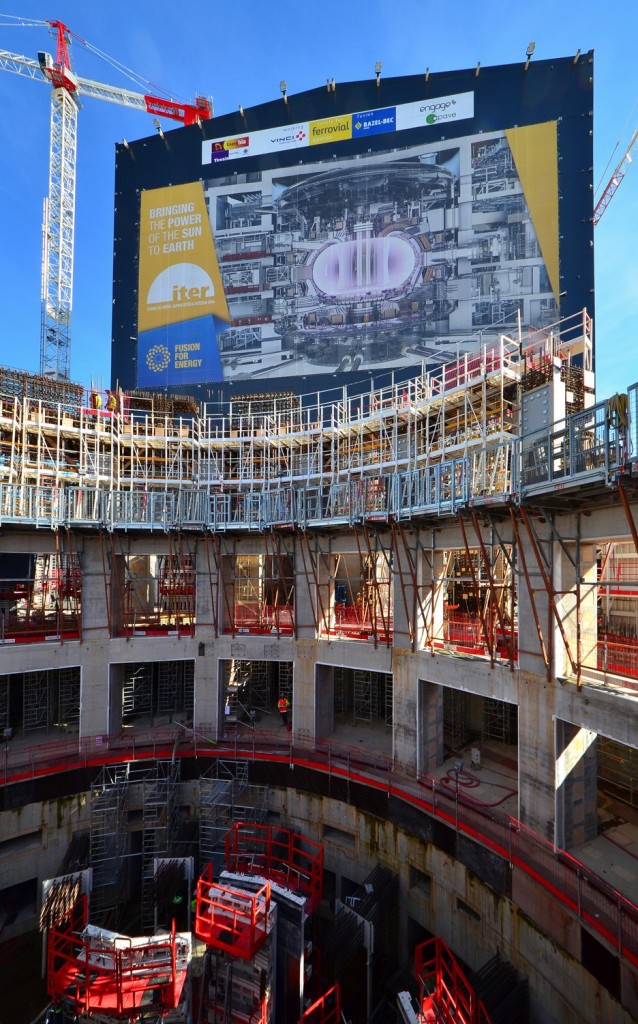
Looks small ... is not
2017-03-08 - Look closely at the worker in orange to get a real idea of the size of the ITER bioshield.

Coming full circle
2017-03-02 - Looking into the circle of the ITER bioshield, where the first ground level L1 (seen as the top level in this photo) is framed out for final concrete pouring.
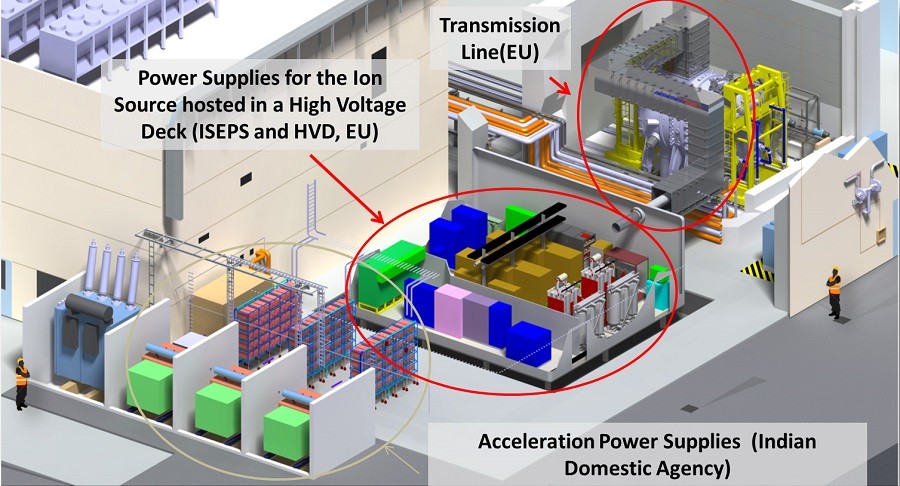
Ion source power supply, exploded view
2017-03-01 - The power supplies and transmission line for SPIDER. © F4E
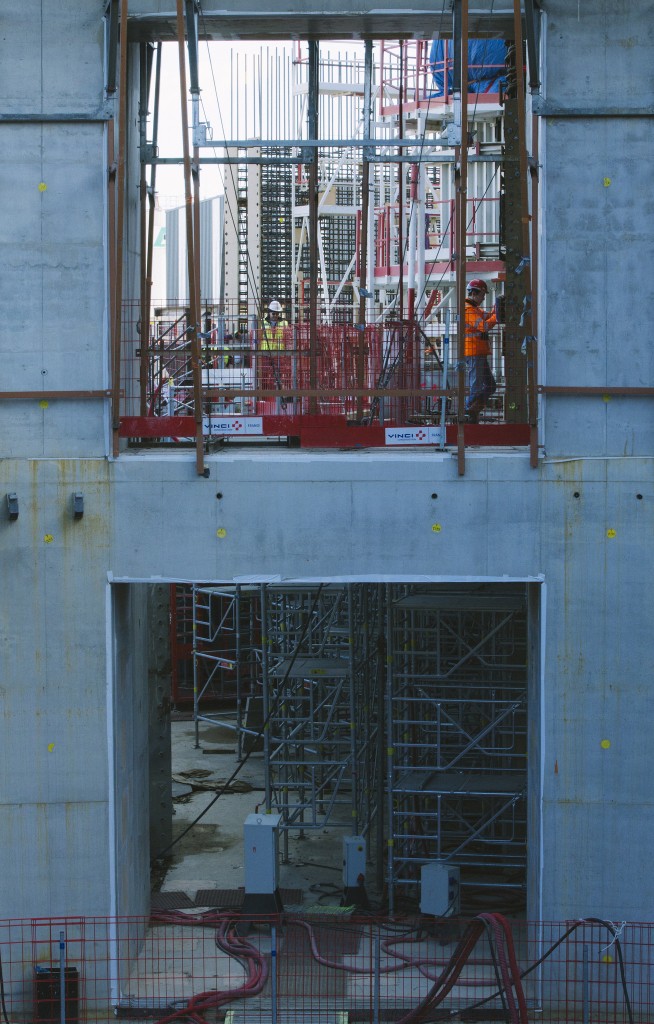
Perfect squares
2017-02-28 - Openings in the bioshield, perfectly aligned, evoke a city-like structure ... © Les Nouveaux Médias/SNC ENGAGE

Ten large cells
2017-02-28 - In the area at left, ten individual cooling cells (16 m x 16 m each, and 20 m tall) will be installed in the five large bays of the cooling tower. © Les Nouveaux Médias/SNC ENGAGE
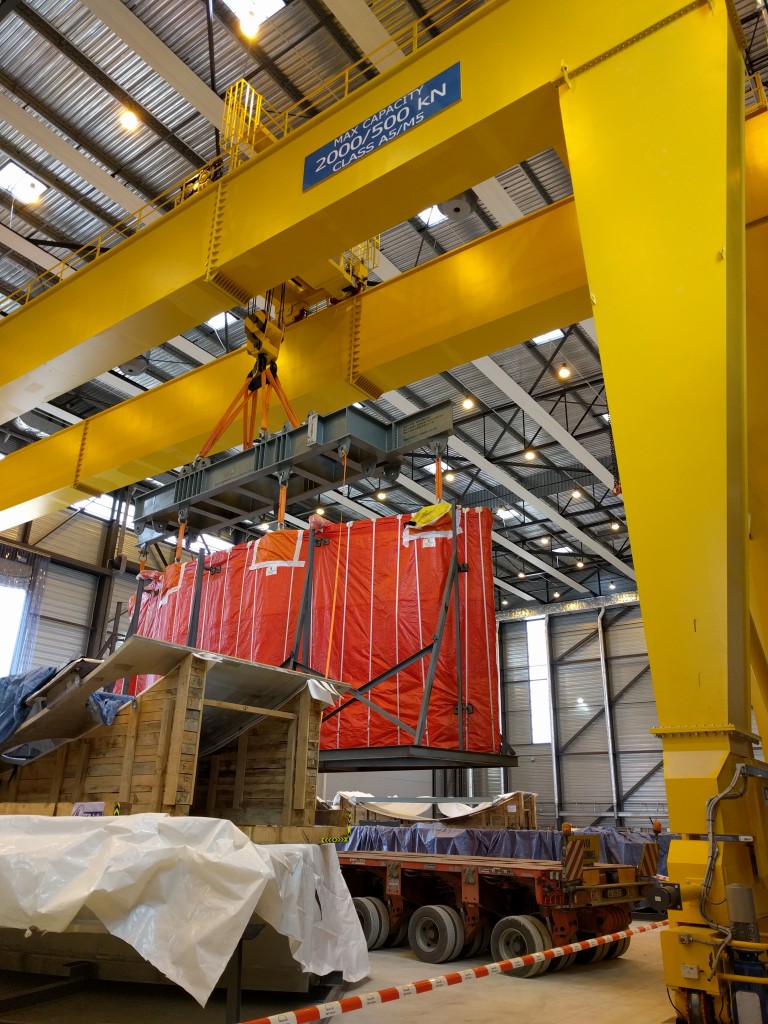
First lower cylinder segments
2017-02-28 - On 28 February, the first element of the lower cylinder arrived on site in the Cryostat Workshop. Five others are stored at the French port of Fos-sur-Mer and will arrive in the weeks to come.
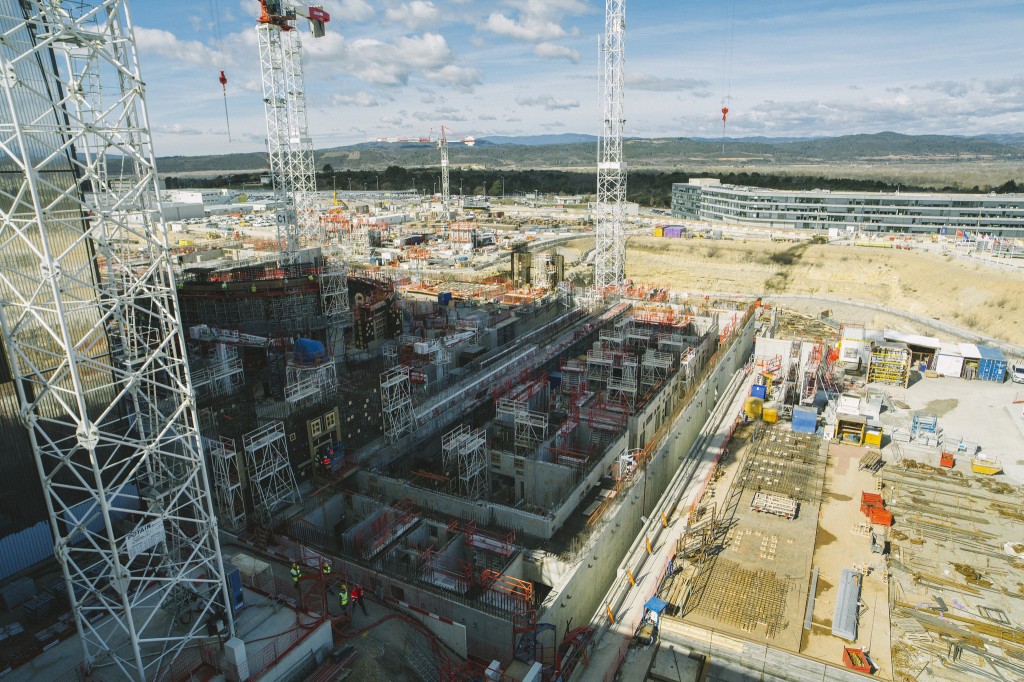
Three buildings on a "floating" foundation
2017-02-28 - Looking down at the Tritium Building. Note the two-metre gap between the Tokamak Complex buildings and the retaining wall, which allow the buildings to move as one (on a single foundation) in the case of a seismic event. © Les Nouveaux Médias/SNC ENGAGE

Heavy metal
2017-02-28 - The reinforcement of the bioshield is practically the densest on site: 300 kg/m³. © Les Nouveaux Médias/SNC ENGAGE
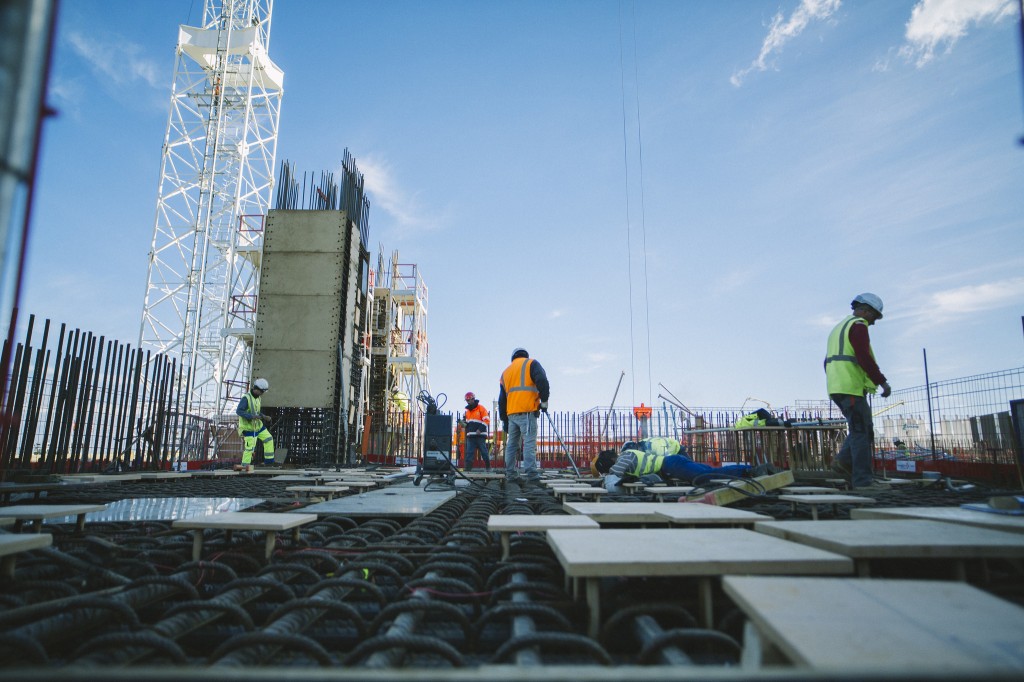
It takes precision
2017-02-28 - Each embedded plate is carefully aligned and secured. There will be over 80,000 of these on the walls, floors and ceilings of the Tokamak Complex. © Les Nouveaux Médias/SNC ENGAGE

State of cryoplant: February
2017-02-28 - A 5,400 m² building, divided into two sections, will house all of the equipment necessary to deliver the cryogenic power needed at ITER. © Les Nouveaux Médias/SNC ENGAGE

Amazing
2017-02-28 - The concrete bioshield rises like an arena in the middle of the Tokamak Complex. © Les Nouveaux Médias/SNC ENGAGE
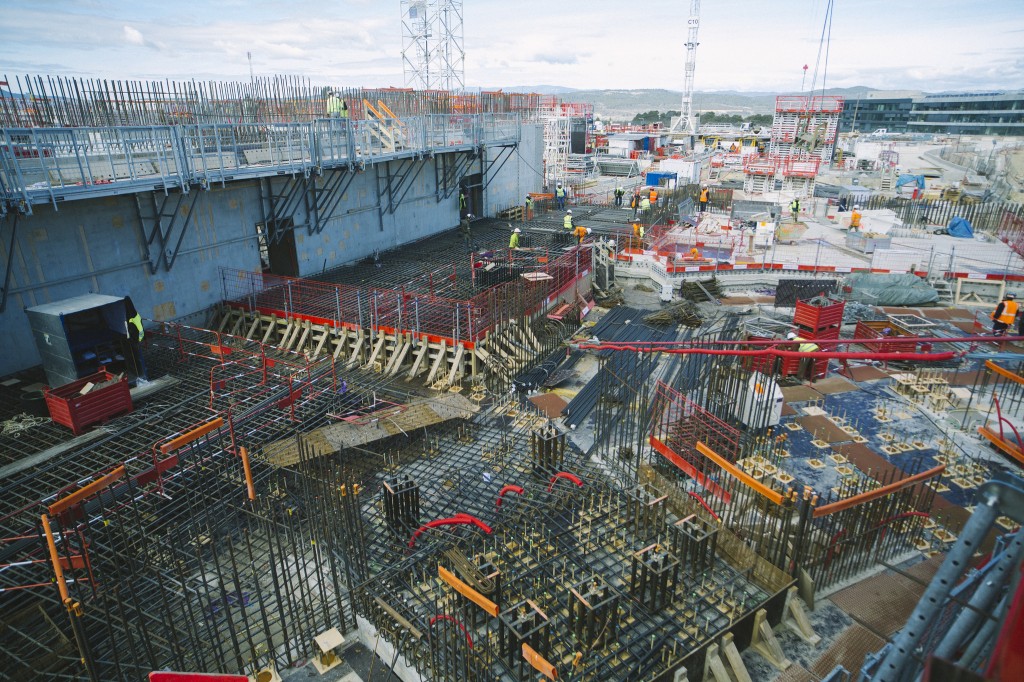
Bewildering complexity
2017-02-28 - In this area of the Tokamak Complex, where the circular meets the linear, the construction plans are bewildering complex. © Les Nouveaux Médias/SNC ENGAGE

Small jacket, tall wall
2017-02-28 - The yellow jacket at right helps us to judge the scale of the concrete partitions of the hot basin. © Les Nouveaux Médias/SNC ENGAGE
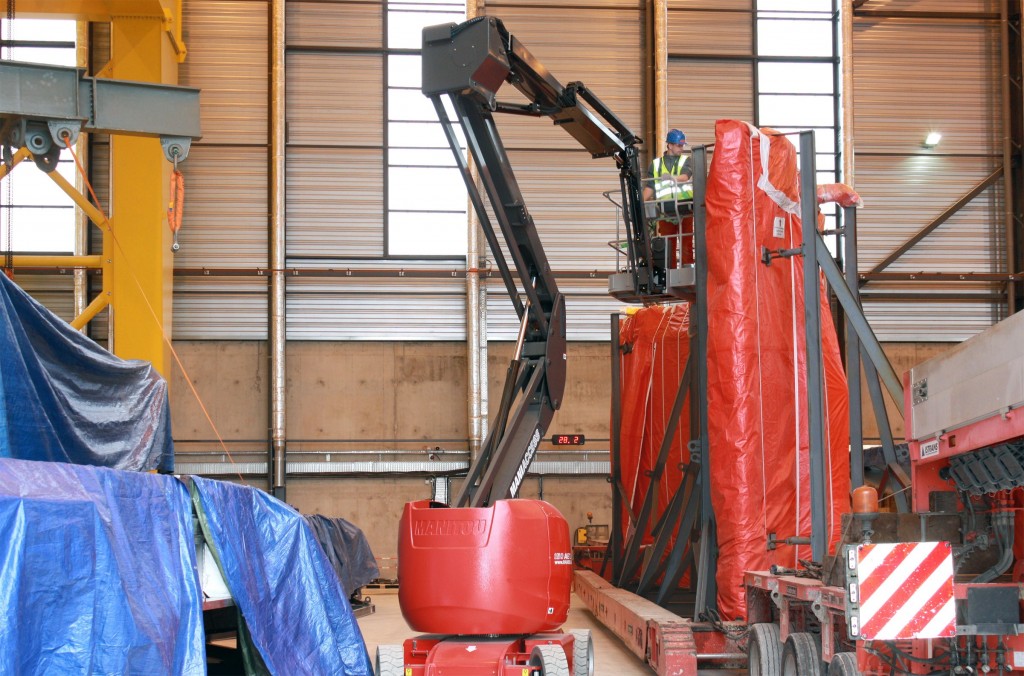
Another assembly platform to be installed in Workshop
2017-02-28 - Once all six segments of the lower cylinder have arrived and passed inspection, they will be installed on the lower cylinder fabrication frame—the second in the Workshop—to be assembled and welded.
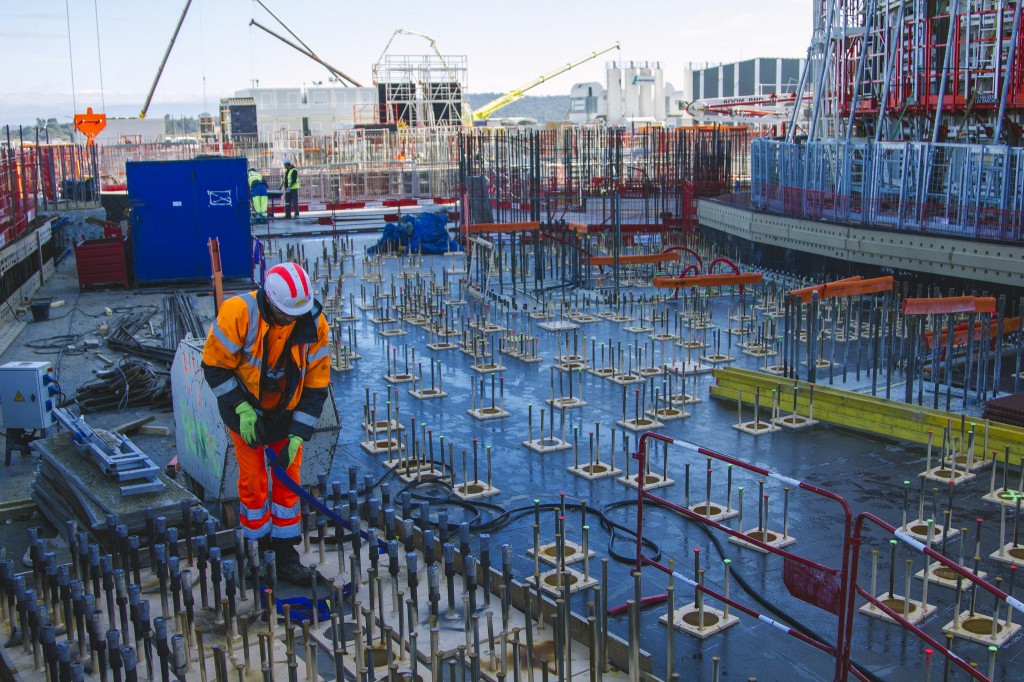
Call in the pumps!
2017-02-28 - Everything is nearly in place for the start of concrete pouring in this section of the Tokamak Building. © Les Nouveaux Médias/SNC ENGAGE
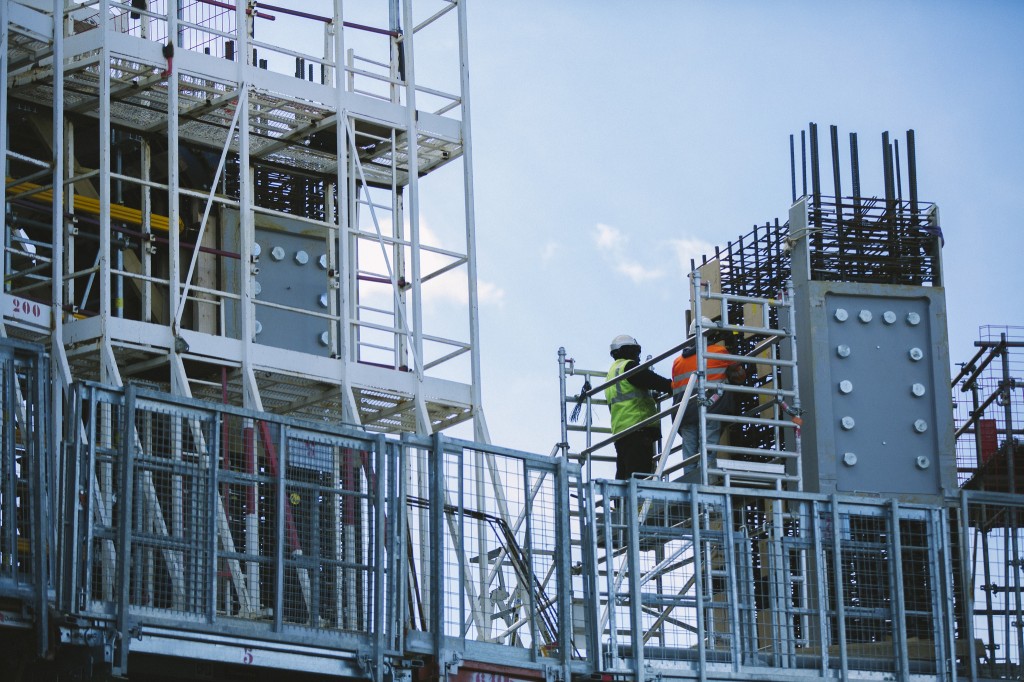
18 embedded plates at L3 level
2017-02-28 - These heavy steel plates will support the weight of the in-pit assembly tool—a tree-like structure that will support the weight of the vacuum vessel sectors during welding. © Les Nouveaux Médias/SNC ENGAGE
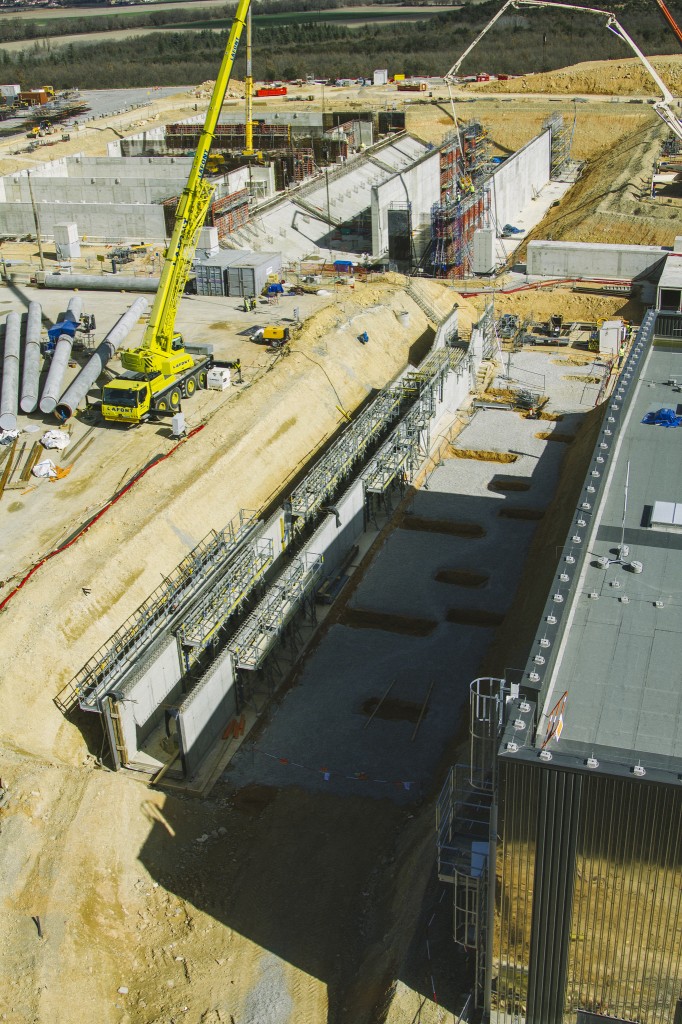
Partitions installed
2017-02-28 - In the foreground: technical galleries; in the background: concrete partitioning at the worksite for the cooling towers and basins. © Les Nouveaux Médias/SNC ENGAGE
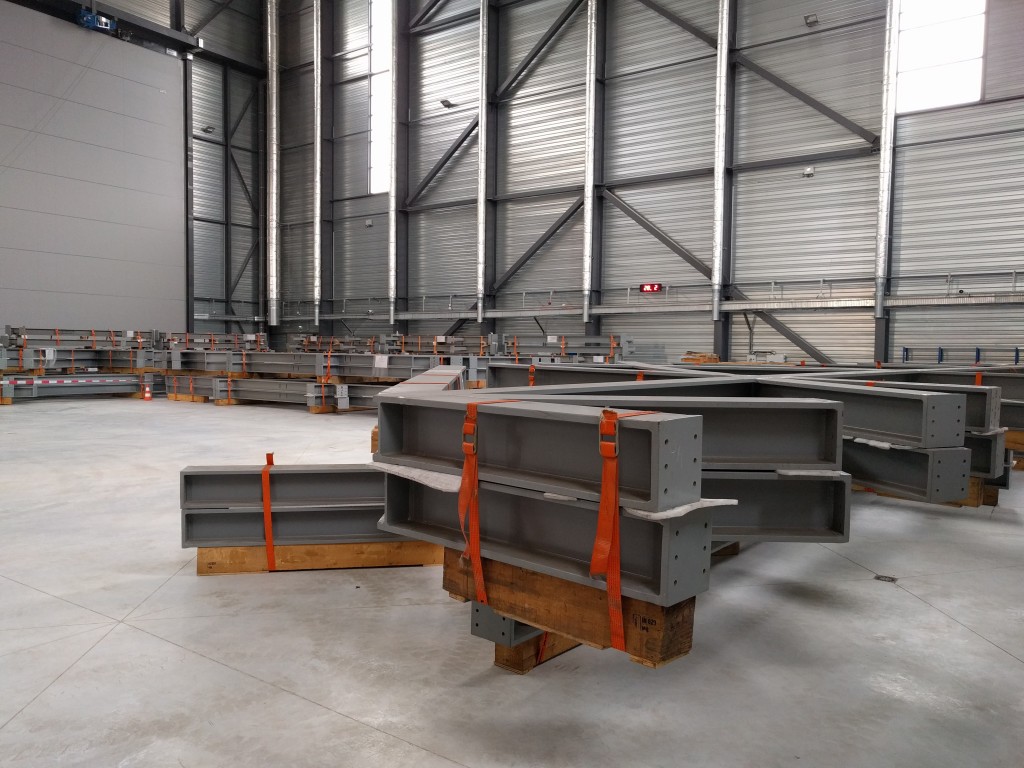
Second assembly frame
2017-02-28 - While welding and testing activities continue on the base of the cryostat, a second assembly platform has been shipped to the Cryostat Workshop for the start of activities on the lower cylinder.
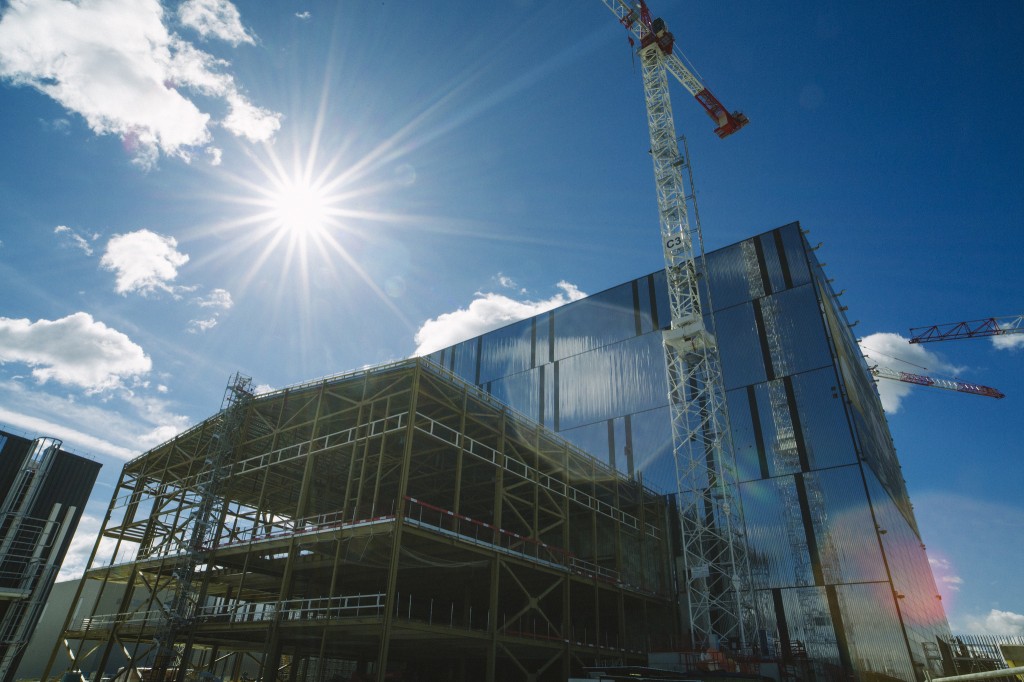
Creating floors and inner partitions
2017-02-28 - The three-storey Radio Frequency Building is going up against the northern face of the Assembly Hall. © Les Nouveaux Médias/SNC ENGAGE
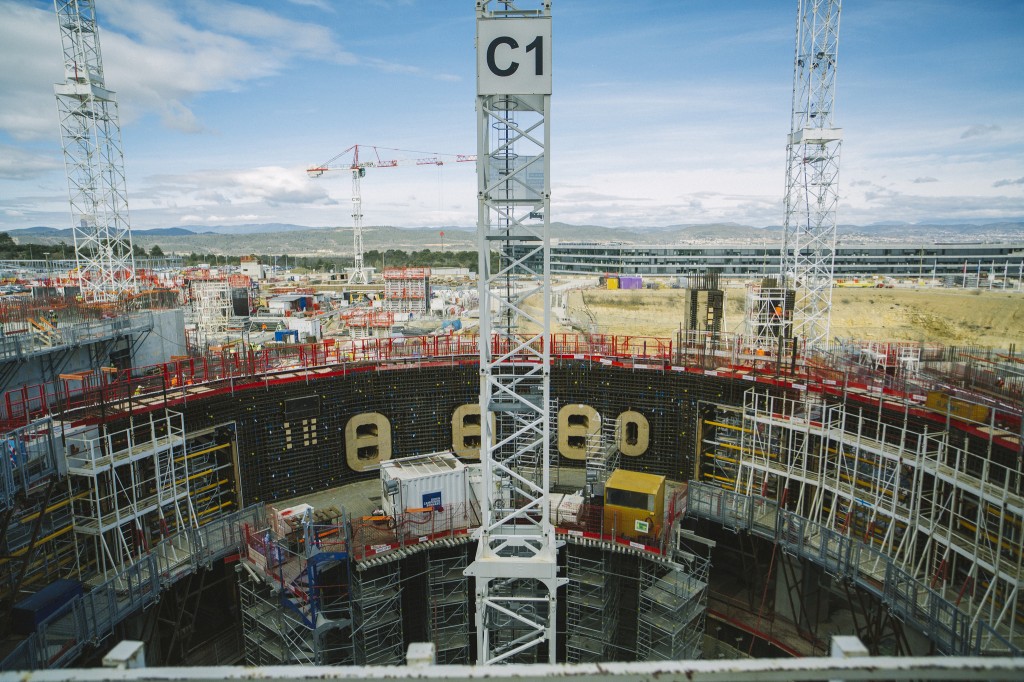
Looking over the bioshield toward Headquarters
2017-02-28 - A special area of the ITER bioshield, with four ovoid openings reserved for the heating and diagnostic neutral beam injectors. © Les Nouveaux Médias/SNC ENGAGE
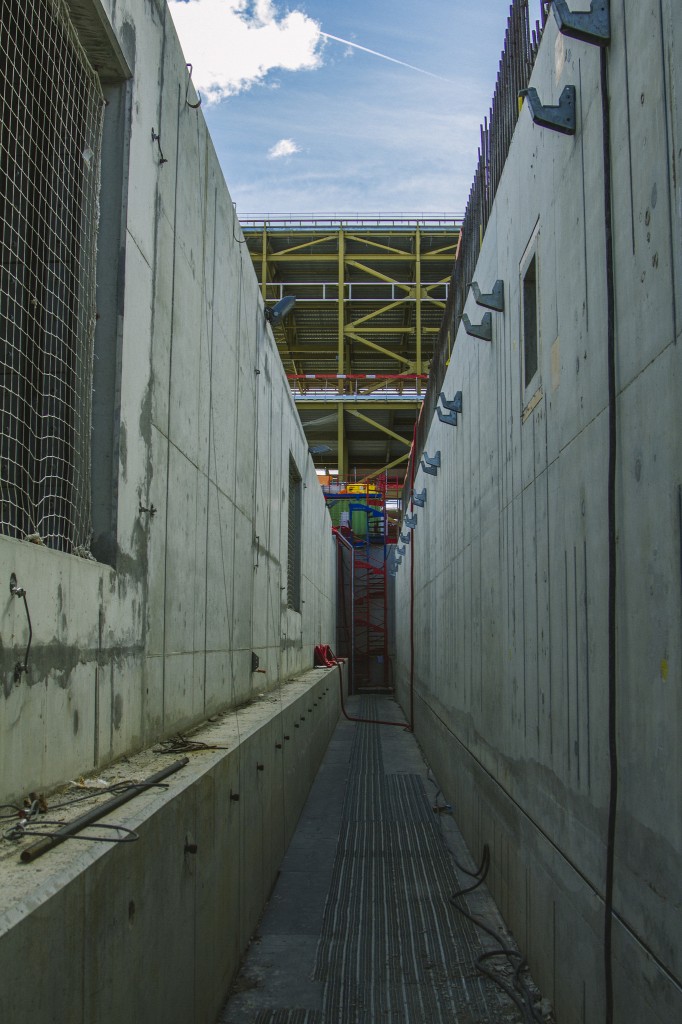
Secret passageway
2017-02-28 - A two-metre-wide alley between the retaining walls (left) and the start of the Tokamak Complex (right). © Les Nouveaux Médias/SNC ENGAGE

Power conversion buildings: what purpose?
2017-02-28 - Two buildings will house rectifier and power smoothing equipment to convert AC power from the pulsed power switchyard to the DC power needed by the superconducting magnet system. © Les Nouveaux Médias/SNC ENGAGE
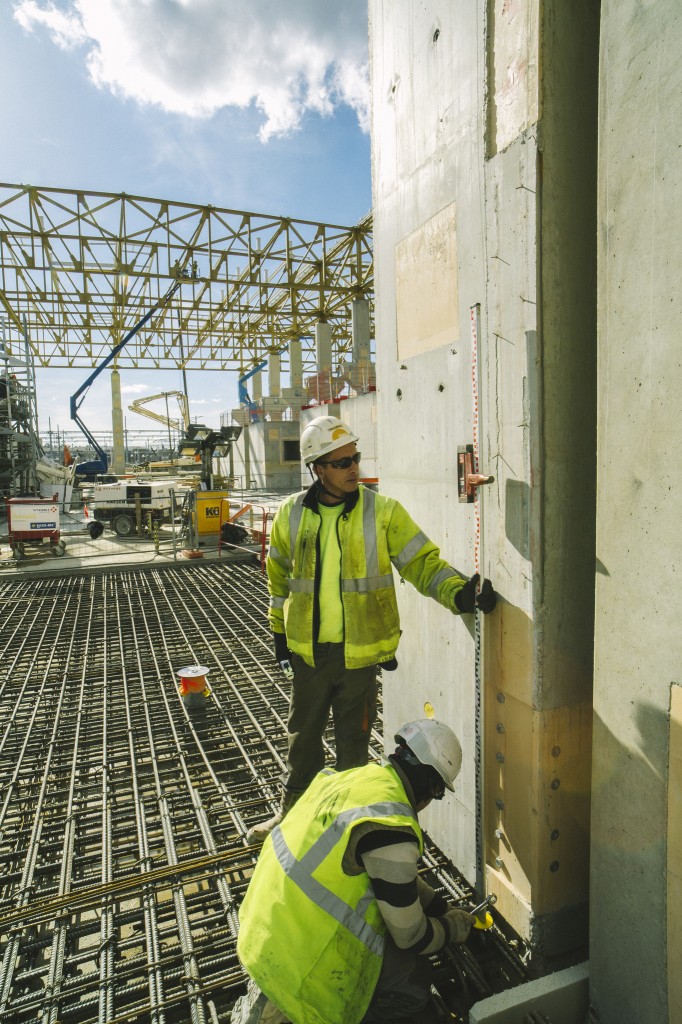
Cryoplant: progress on the Compressor Building
2017-02-28 - Work advances in February on the basemat, columns and steel structure of the cryoplant Compressor Building. © Les Nouveaux Médias/SNC ENGAGE

Looking up
2017-02-28 - Down in the bowels of the Tritium Building, looking up toward the Assembly Hall. © Les Nouveaux Médias/SNC ENGAGE
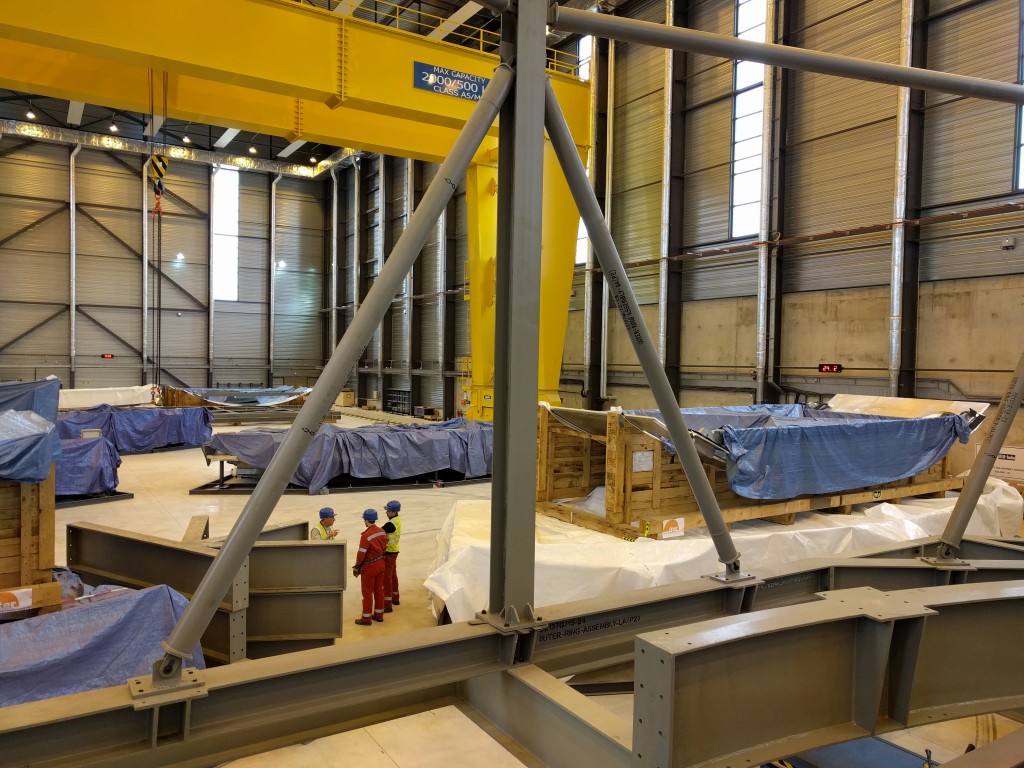
Giant Erector set
2017-02-24 - Cryostat base segments (tier 2) are stored in the Cryostat Workshop until needed for assembly.
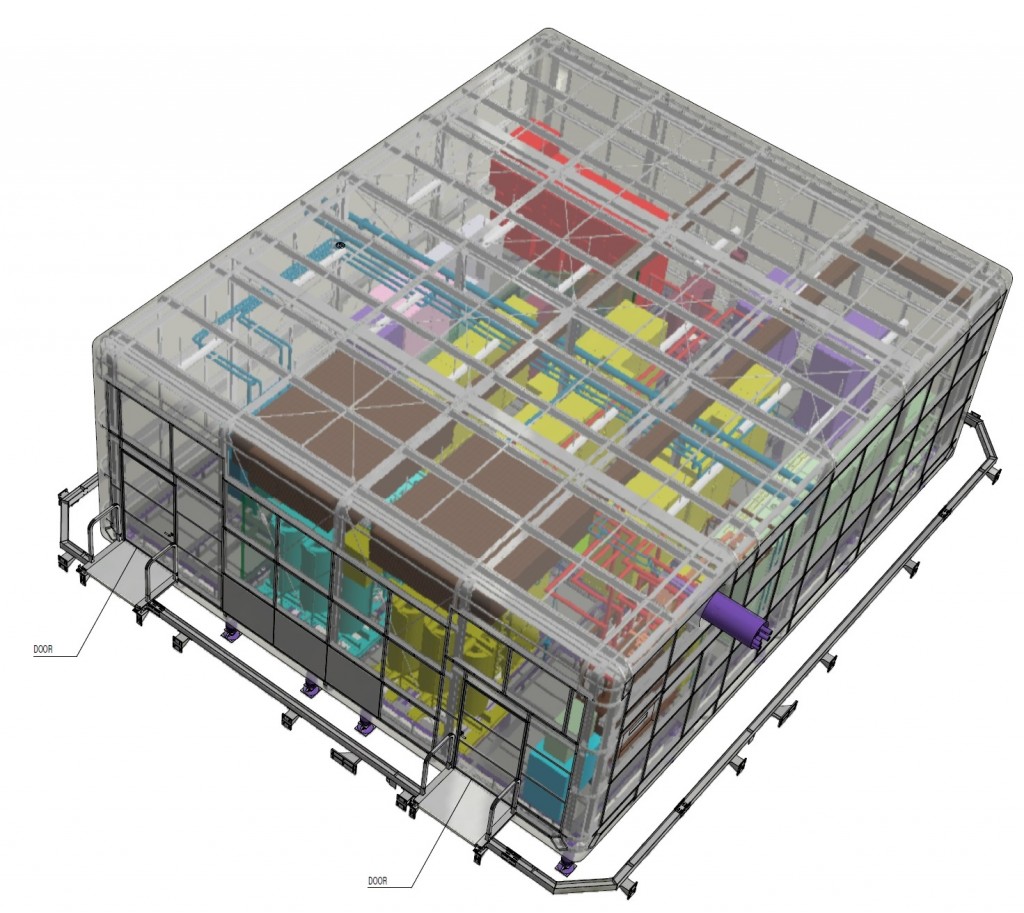
Ion source power supply
2017-02-13 - The power required for the operation of SPIDER will be provided in part by this room-size ion source extraction grid power supply provided by Europe.
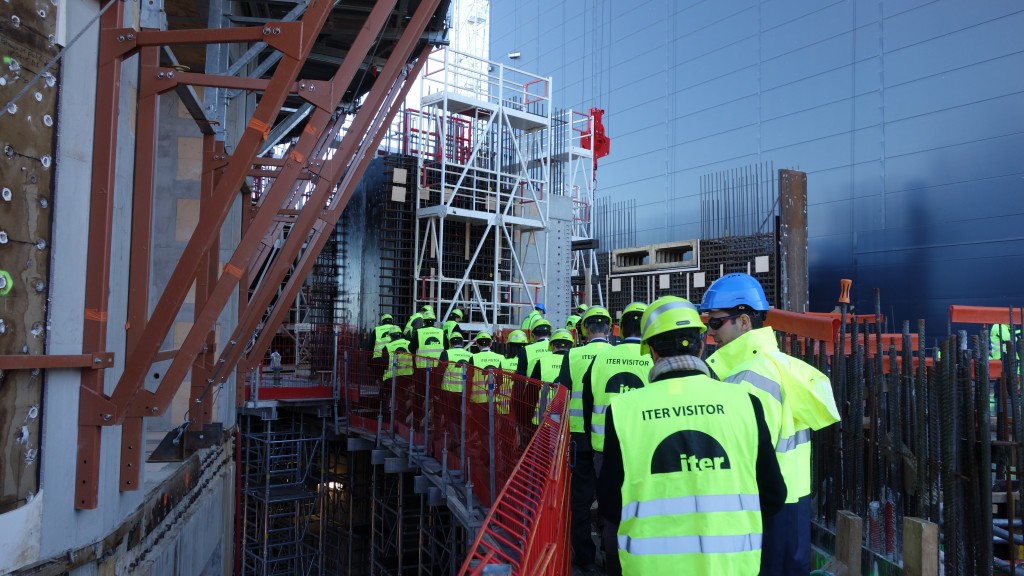
Yellow vests and hats
2017-02-06 - Visitors are a daily feature on the ITER worksite. In 2016 the project welcomed nearly 15,000 people and organized 600 visits.
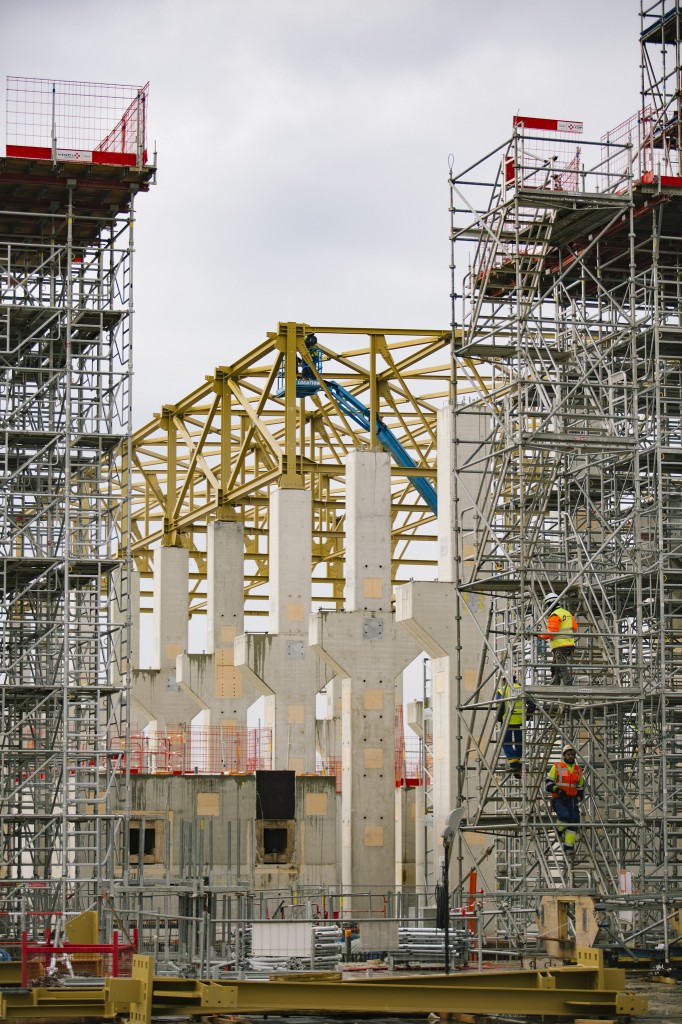
One building, two areas
2017-01-25 - The cryoplant building will be divided by a fire wall into two separate spaces. Giant columns for the fire wall are going up now. © Les Nouveaux Médias/SNC ENGAGE
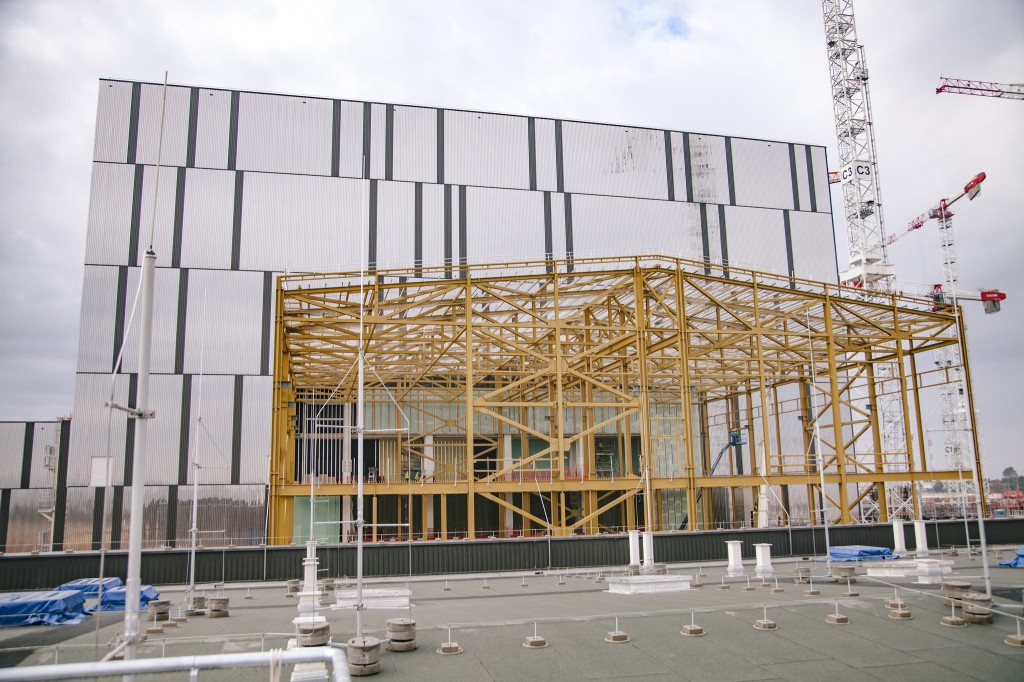
From a nearby roof
2017-01-25 - This photo was taken from the roof of the Site Services Building, located just a few metres away. © Les Nouveaux Médias/SNC ENGAGE

Mirror mirror on the wall
2017-01-25 - All of the principal buildings of the ITER installation will be covered in mirror cladding, as seen here on the Cleaning Facility, Assembly Hall and Site Services Building. © Les Nouveaux Médias/SNC ENGAGE

Looking north
2017-01-25 - Standing near the Tokamak Complex, looking north over the site of the cooling towers and basins. © Les Nouveaux Médias/SNC ENGAGE
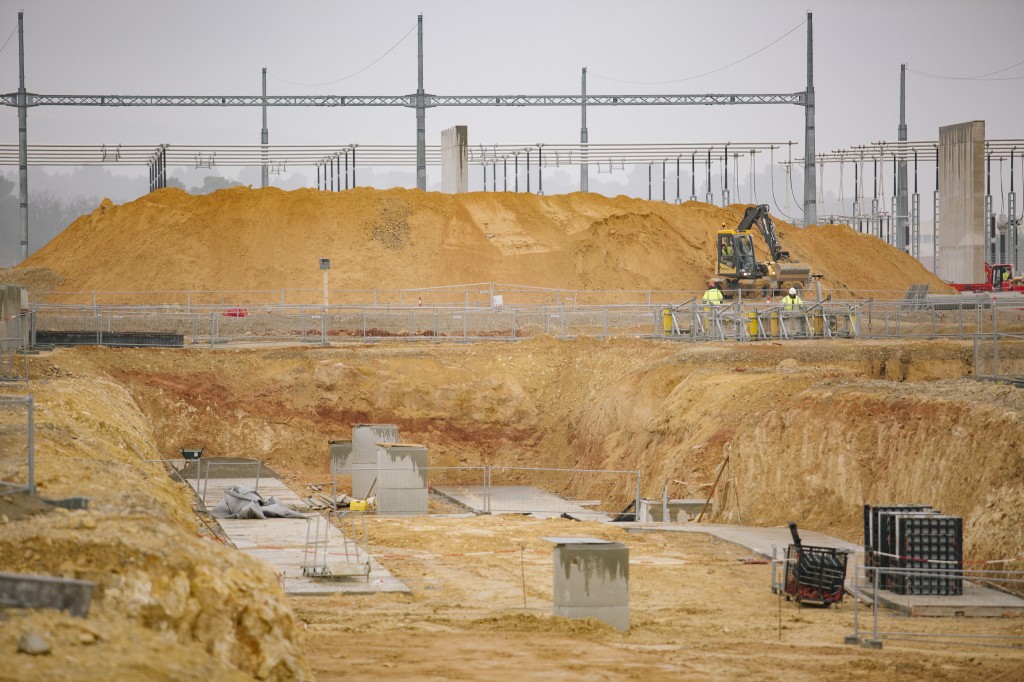
New project on the worksite
2017-01-25 - Work underway on the site of one of the Magnet Power Conversion buildings. © Les Nouveaux Médias/SNC ENGAGE
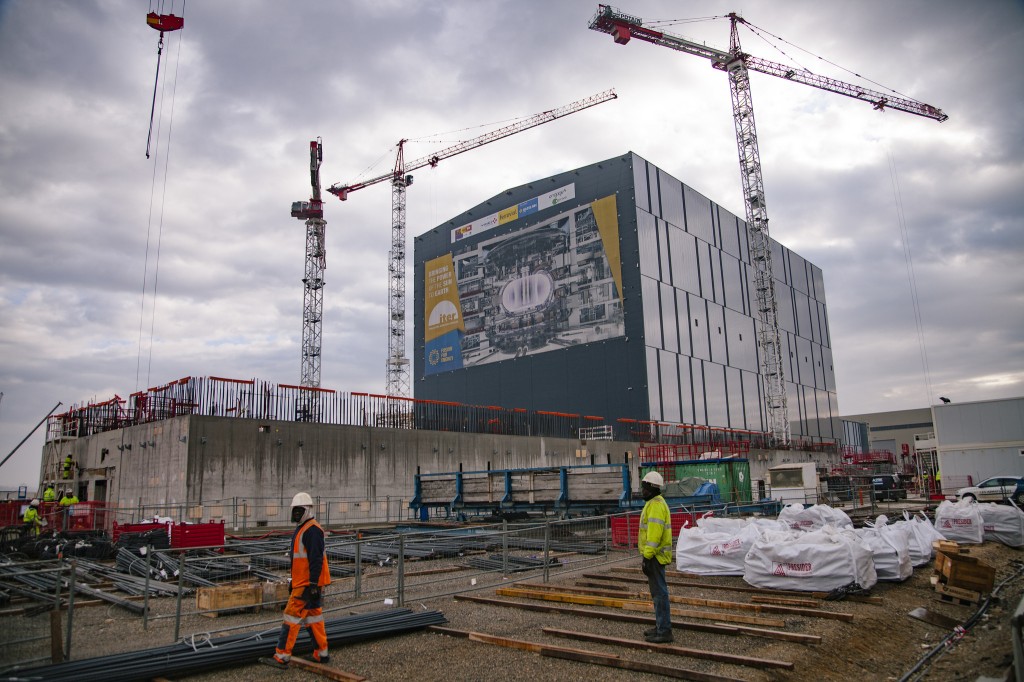
Diagnostic Building rises
2017-01-25 - The 40 x 80 metre Diagnostic Building has reached L1 level. Each diagnostic system will be assigned a room on one of the three central floors of the building, to house the electronic and information systems that will receive, record and interpret signals from the operational arena. © Les Nouveaux Médias/SNC ENGAGE
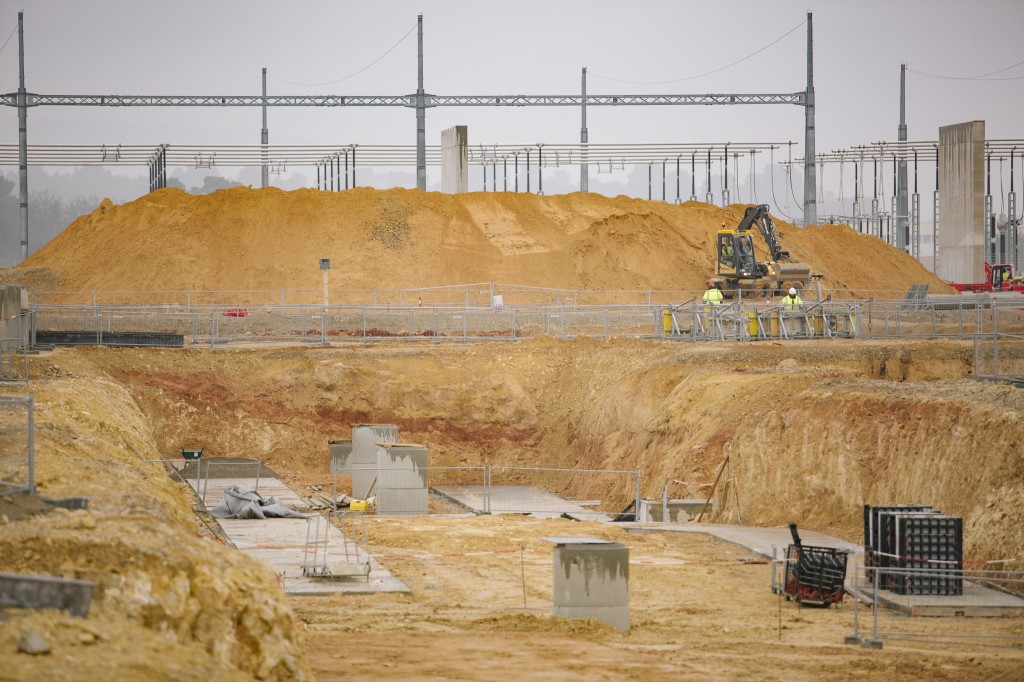
New project on the worksite
2017-01-25 - On the site of one of the buildings. © Les Nouveaux Médias/SNC ENGAGE
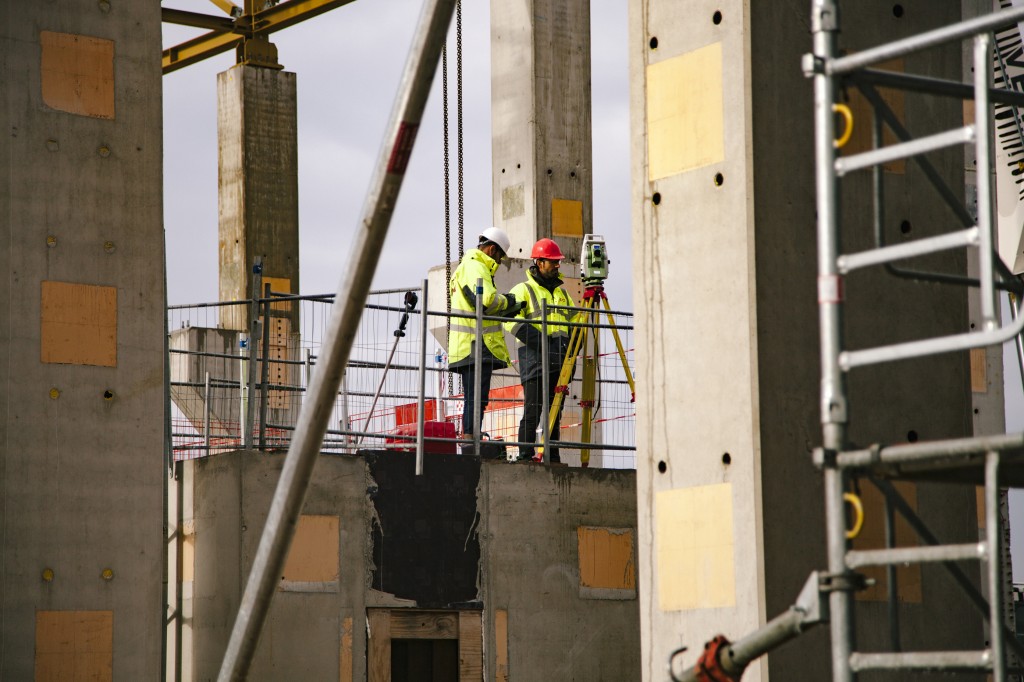
Measurements underway
2017-01-25 - A common sight on the ITER platform: metrologists. © Les Nouveaux Médias/SNC ENGAGE

Factory dimensions
2017-01-25 - The ITER cryoplant will be 20 metres high, 120 metres long and 45 metres in width. © Les Nouveaux Médias/SNC ENGAGE
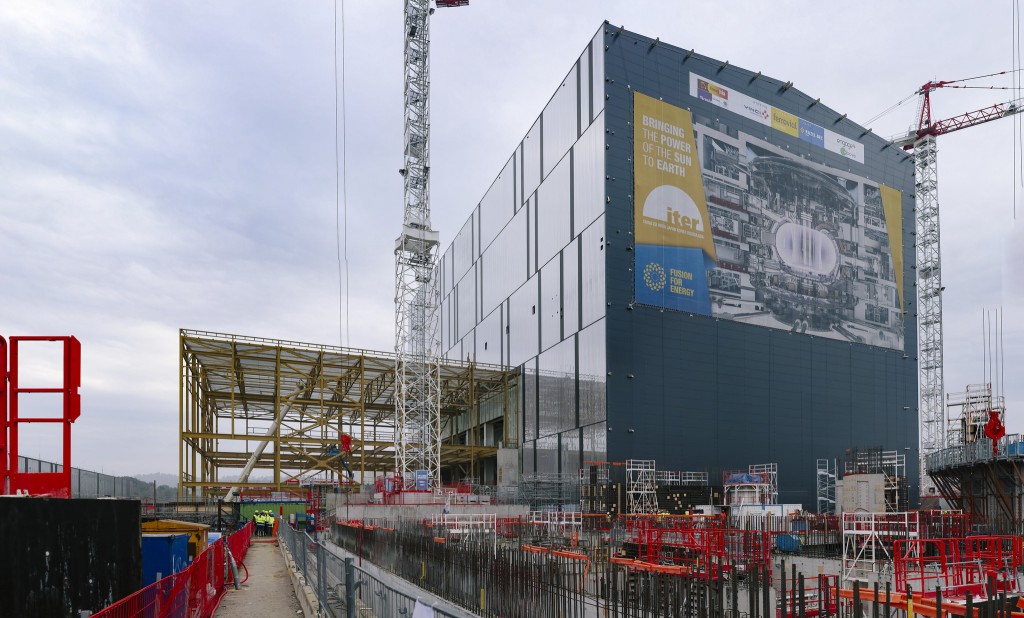
Ground level
2017-01-25 - Walking along scaffolding at the ground level (L1) of the Tritium Building. © Les Nouveaux Médias/SNC ENGAGE
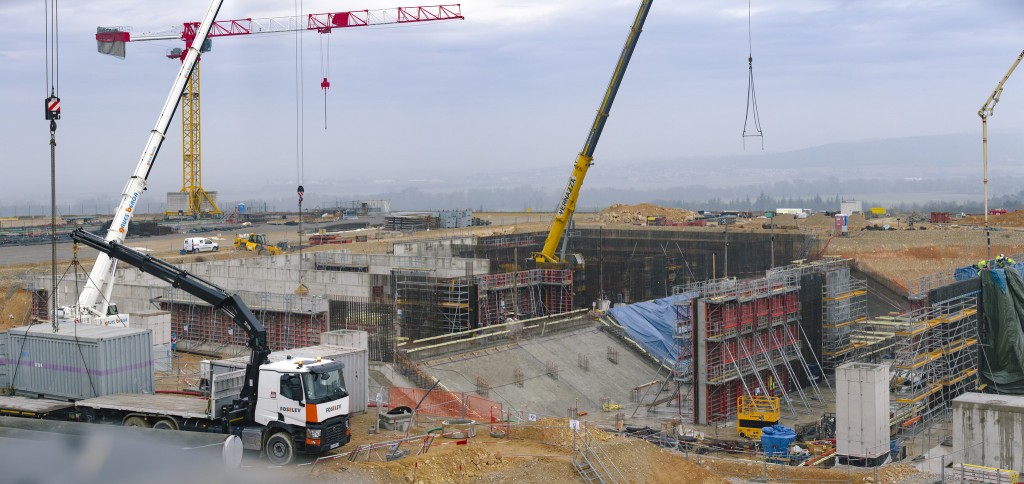
Heat rejection zone
2017-01-25 - Vertical pumps will draw from the hot basin (lower level) and discharge to the top of the cooling tower. © Les Nouveaux Médias/SNC ENGAGE
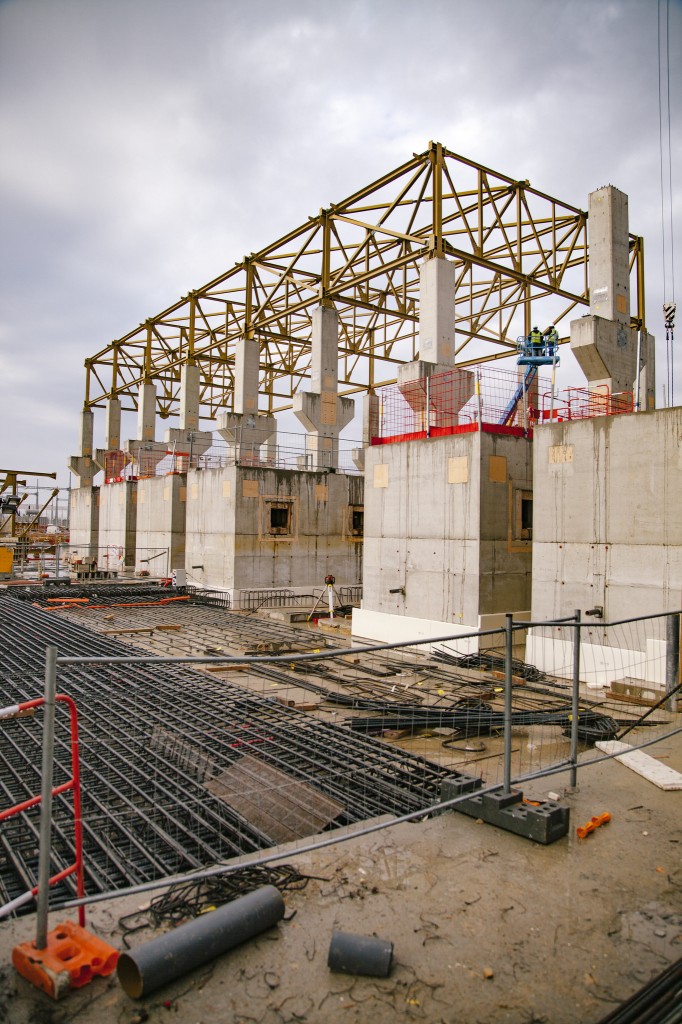
First and secondary structures
2017-01-25 - After the main steel structure of the cryoplant is erected, workers will install a secondary structure to support the building's cladding. © Les Nouveaux Médias/SNC ENGAGE
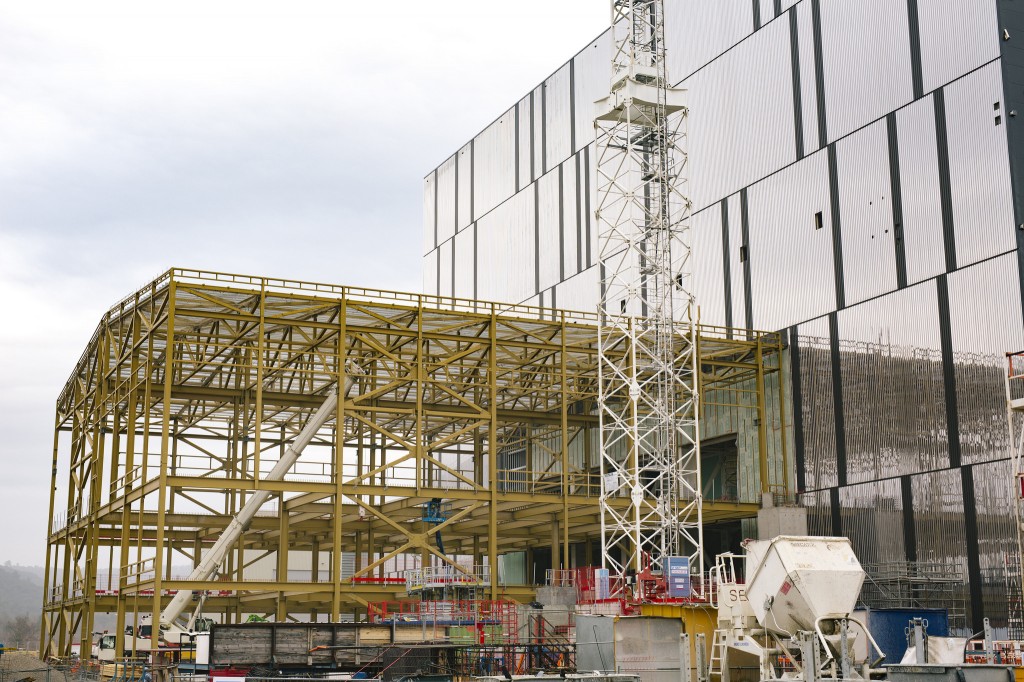
Good progress on the RF heating building
2017-01-25 - A view of the Radio Frequency Building, in late January. © Les Nouveaux Médias/SNC ENGAGE
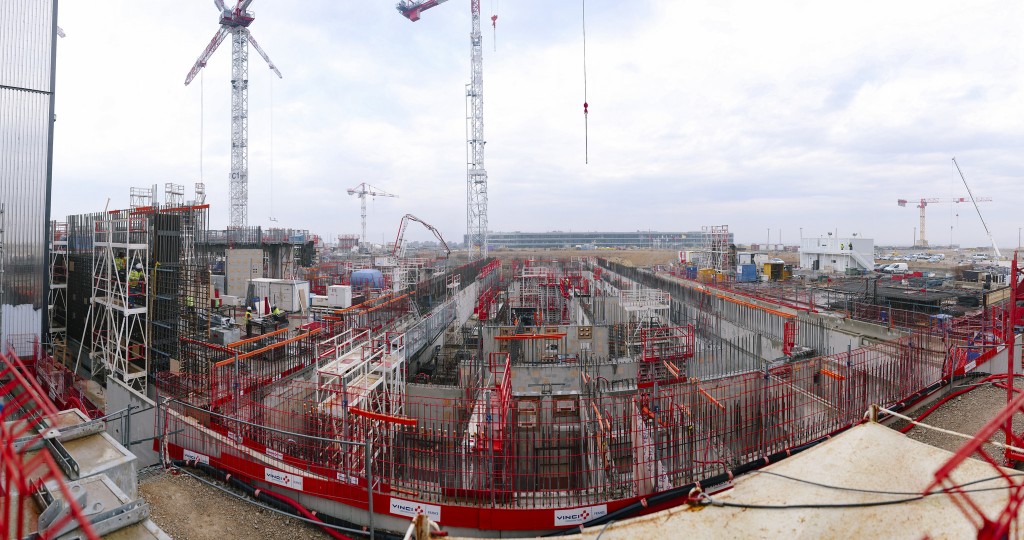
Tritium Building
2017-01-25 - Interior partioning is underway at the B1 (upper basement) level of the Tritium Building. © Les Nouveaux Médias/SNC ENGAGE
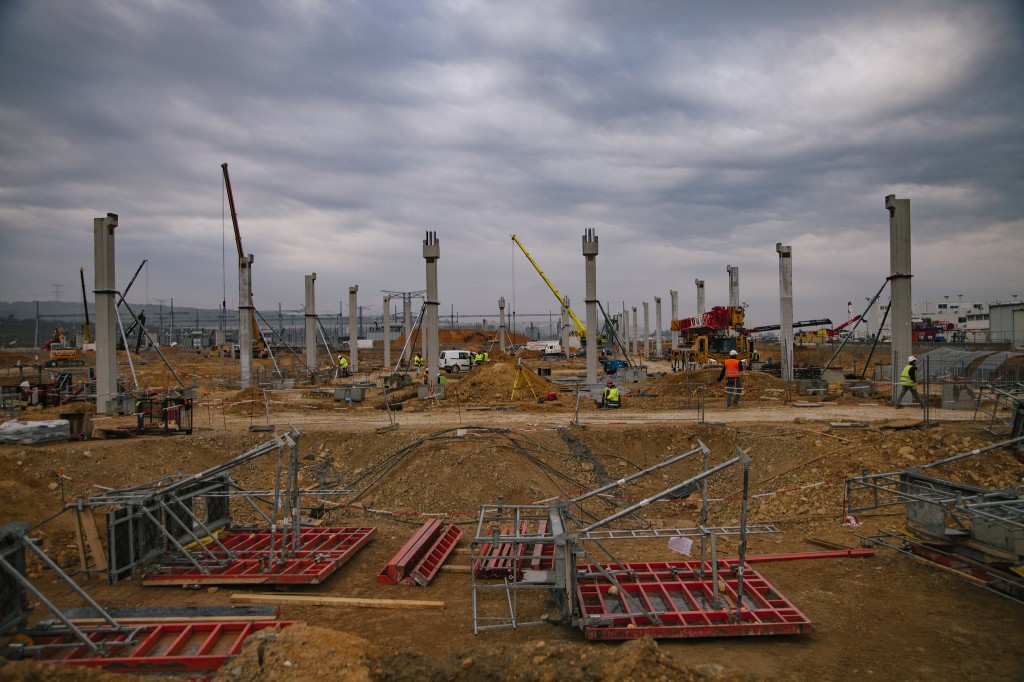
Magnet power conversion will take place here
2017-01-25 - The columns of the—rather light—conversion buildings are being installed in advance of the foundation slabs. © Les Nouveaux Médias/SNC ENGAGE
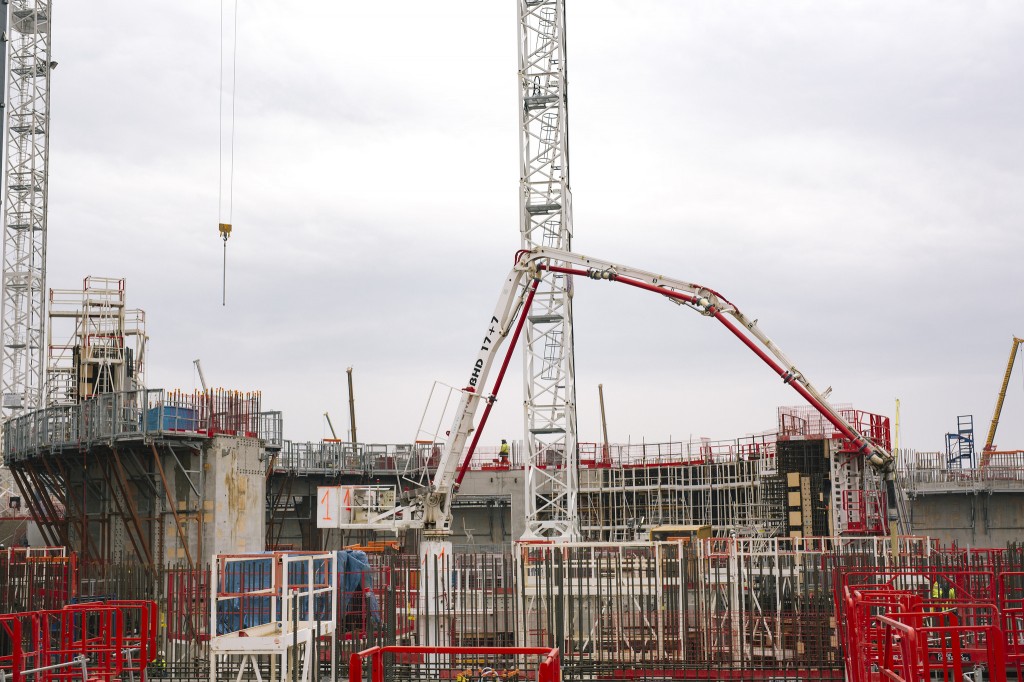
20 metres high already
2017-01-25 - The three-metre-thick ITER bioshield now rises 20 metres, including five metres above the level of the construction platform. Out of sight are the two basement levels B2 and B1. © Les Nouveaux Médias/SNC ENGAGE
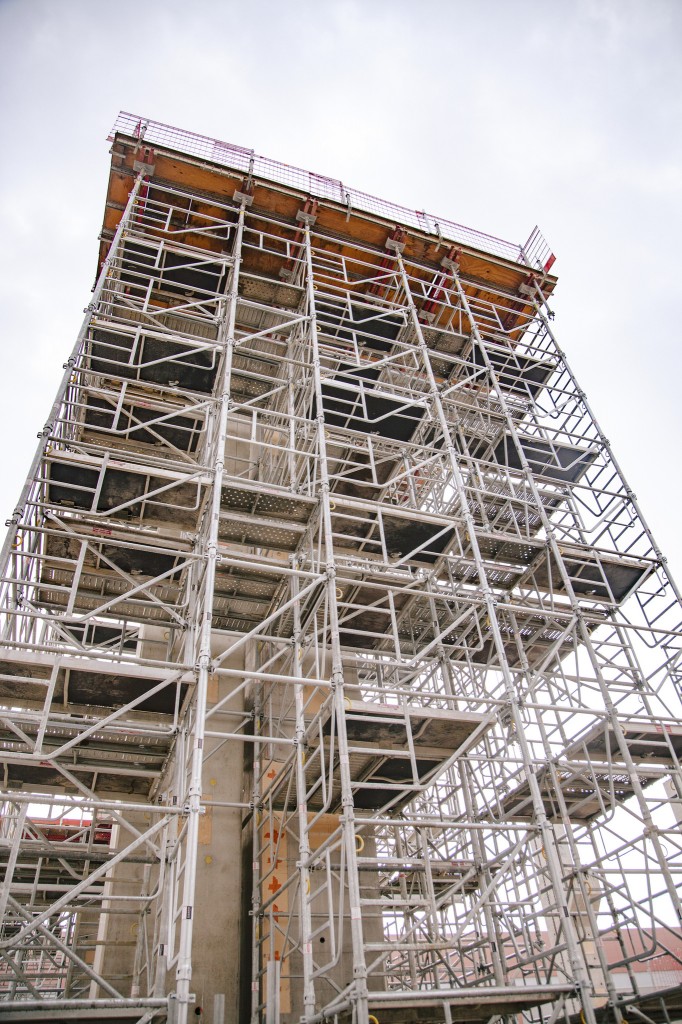
Massive columns
2017-01-25 - One of the massive columns that will support the firewall between the two covered areas of the cryoplant. © Les Nouveaux Médias/SNC ENGAGE
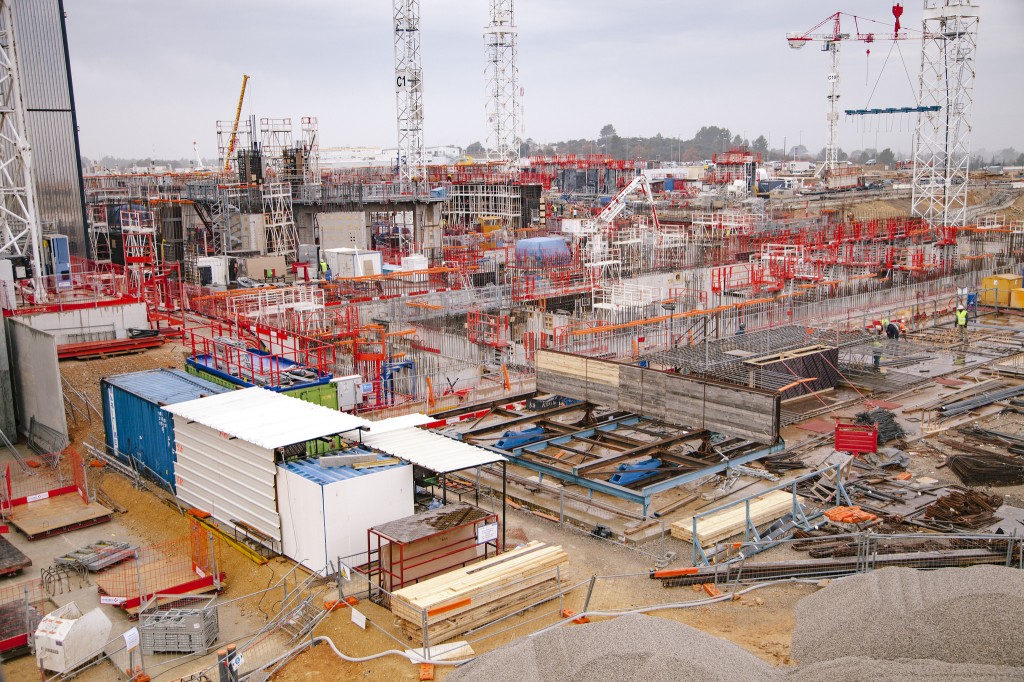
Dizzying
2017-01-25 - The complex worksite of the Tokamak Complex, with the Tritium Building in the foreground. © Les Nouveaux Médias/SNC ENGAGE
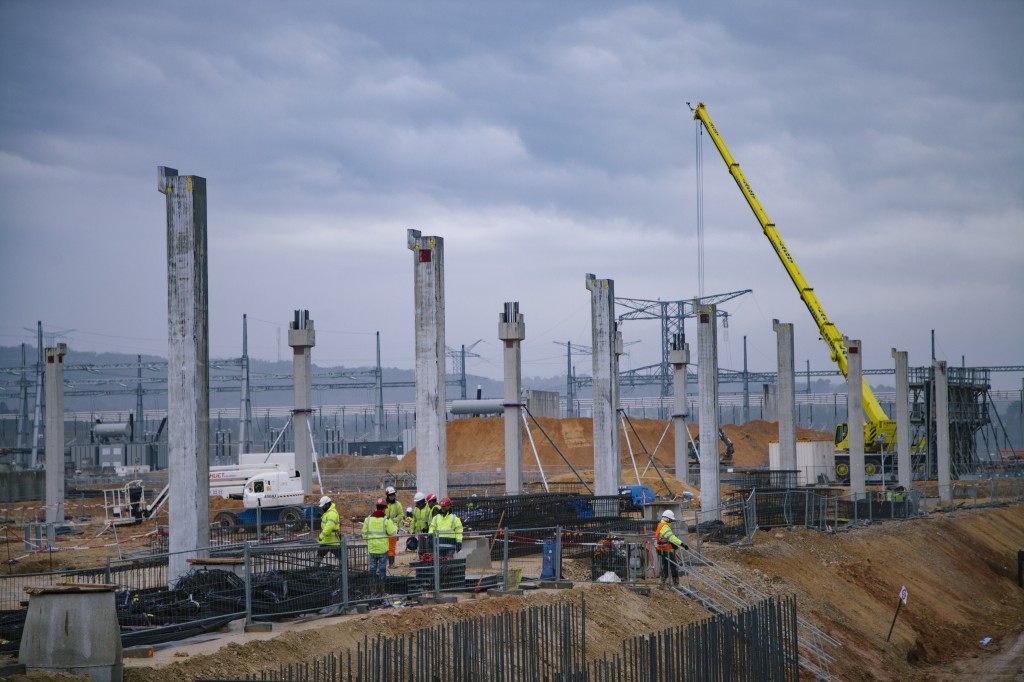
Going up fast
2017-01-25 - These columns, erected in January, will support the roof structures. © Les Nouveaux Médias/SNC ENGAGE

Working toward energizing the switchyard
2017-01-20 - In close coordination with the French transmission system operator RTE the ITER Organization is now embarked on the step-by-step process that will lead to the "energization" of the ITER switchyard. Tests started in January on the first of the switchyard's seven bays.
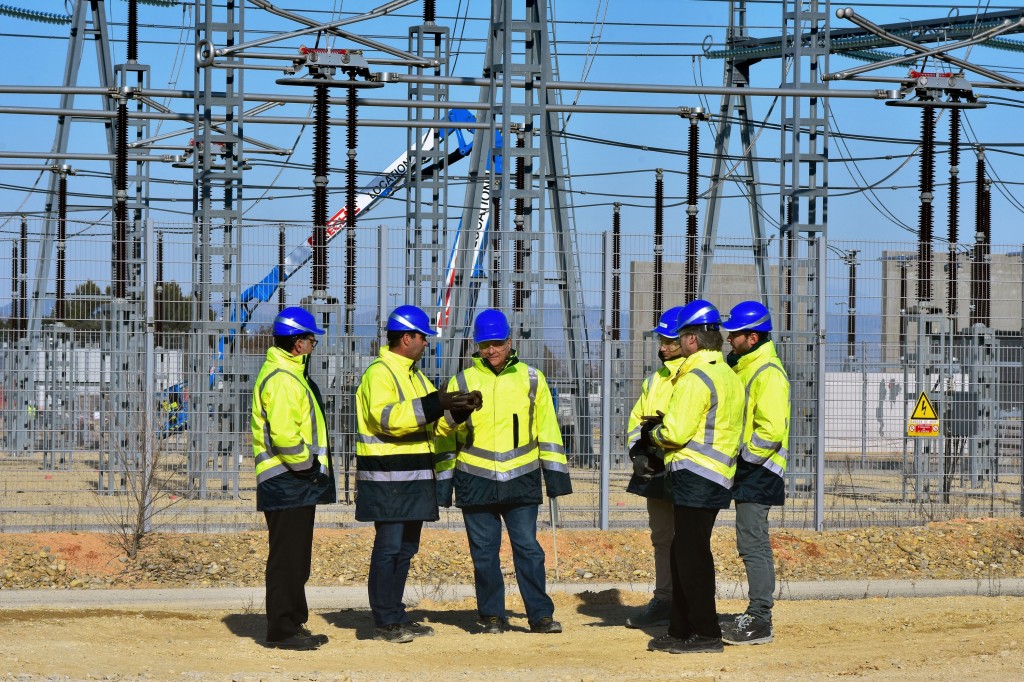
Working toward energizing the switchyard
2017-01-20 - In close coordination with the French transmission system operator RTE the ITER Organization is now embarked on the step-by-step process that will lead to the "energization" of the ITER switchyard. Tests started in January 2017 on the first of the switchyard's seven bays.
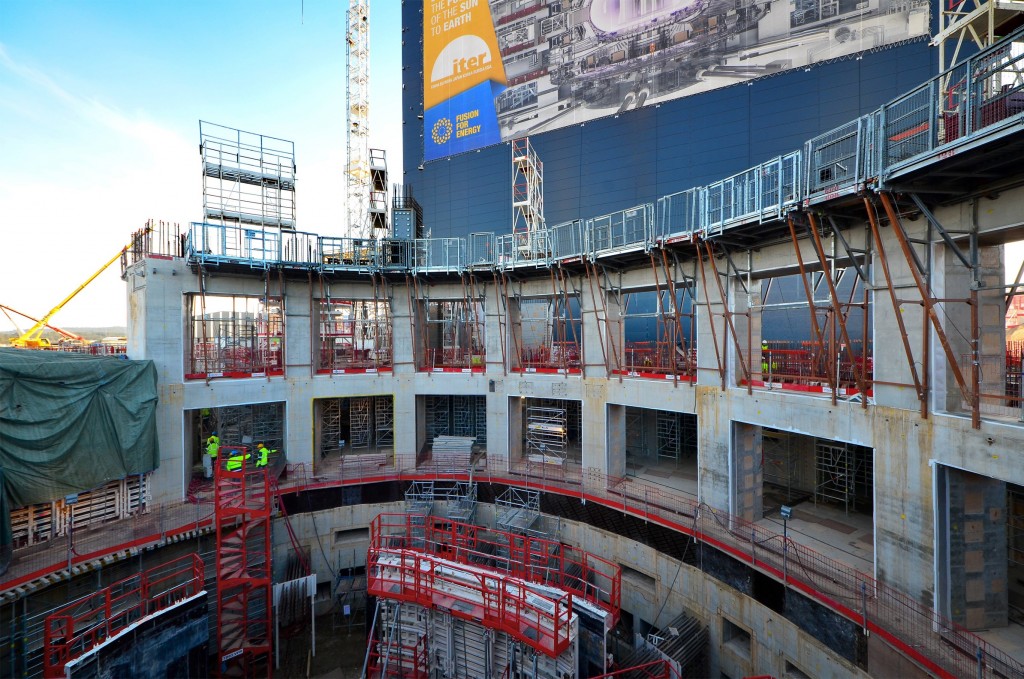
The bioshield rises
2017-01-19 - The bioshield structure is rising at the heart of the Tokamak Building. The last plot of the B1 level was poured last week (the workers in yellow are at B1 level); about half of the first ground level (L1) is now complete (level above the workers); and the first elements of L2 are in place (see scaffolding).
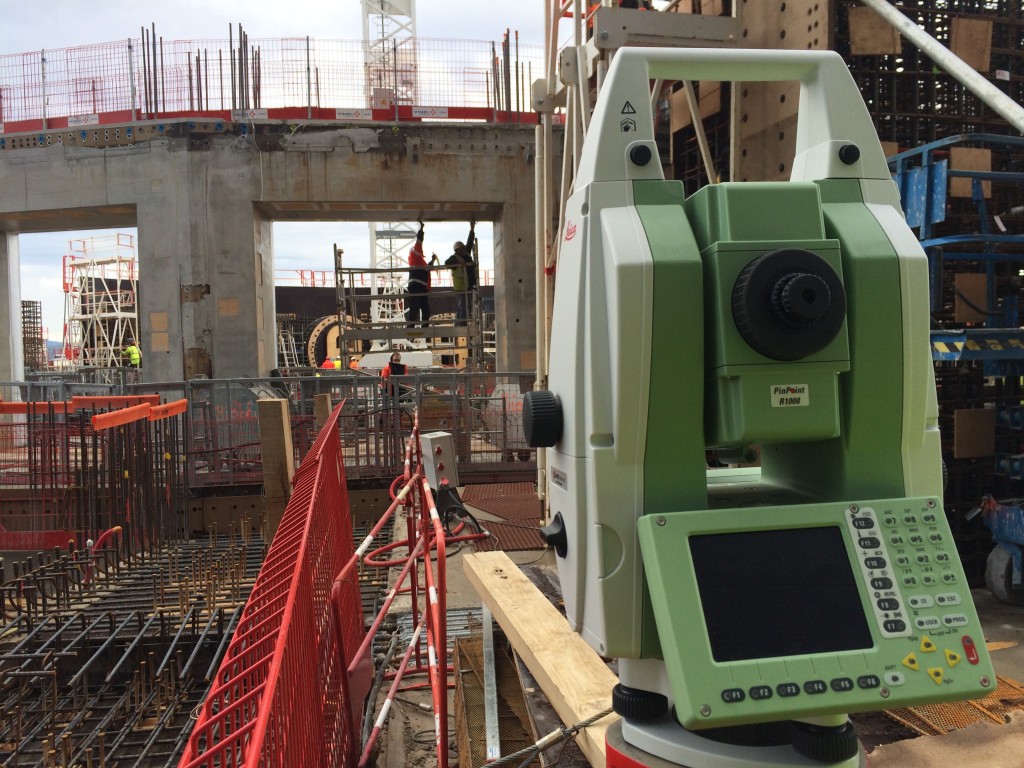
Providing the "as-built" data
2017-01-16 - One of the optical metrology tools used to take measurements on the ITER site. As the buildings rise, metrology teams carry out the measurements that provide the "as built" footprint to ITER teams.

Underground labyrinth
2017-01-12 - Digging continues on the underground technical galleries of the buildings. Photo: ITER Organization/EJF Riche
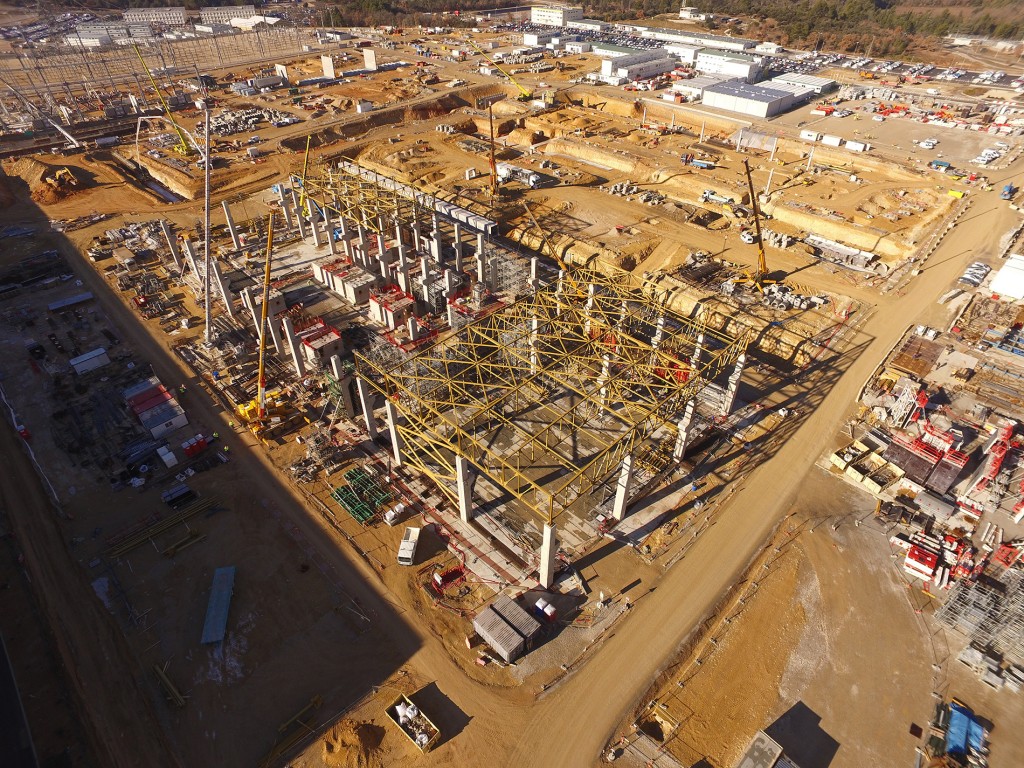
Three zones for the cryoplant
2017-01-12 - The soccer field-size installation comprises 5,400 m² of covered buildings plus a large exterior area (far side) for the storage of helium and nitrogen in liquid and gaseous forms. Photo: ITER Organization/EJF Riche

Workshop tooling progressing
2017-01-12 - The Poloidal Field Winding Facility as photographed in January 2017. Tooling stations are now framed out from one end of the building to the other.
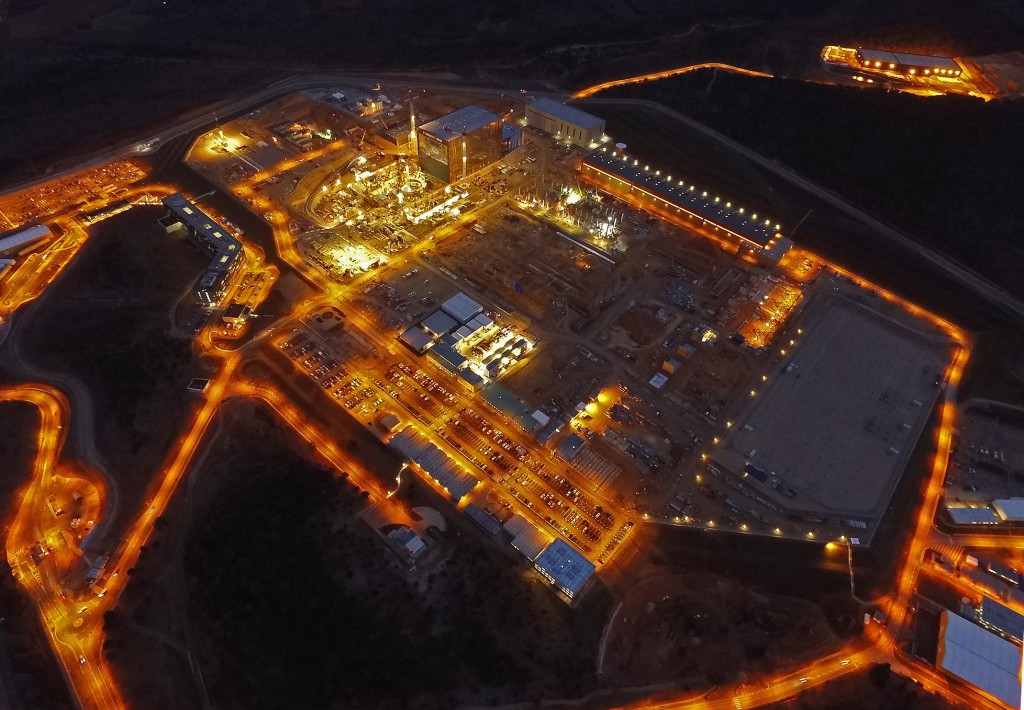
Landing pad for ITER
2017-01-12 - The worksite's sodium lights grow yellow at night, creating this futuristic image that brings to mind an intergalactic spaceport. Photo: ITER Organization/EJF Riche

From the sky
2017-01-12 - The technical areas of the ITER construction platform from bottom left to middle right: the transformers of the electrical switchyard; work underway on the technical galleries of the Magnet Power Conversion buildings; and the columns of the ITER cryoplant. Photo: ITER Organization/EJF Riche
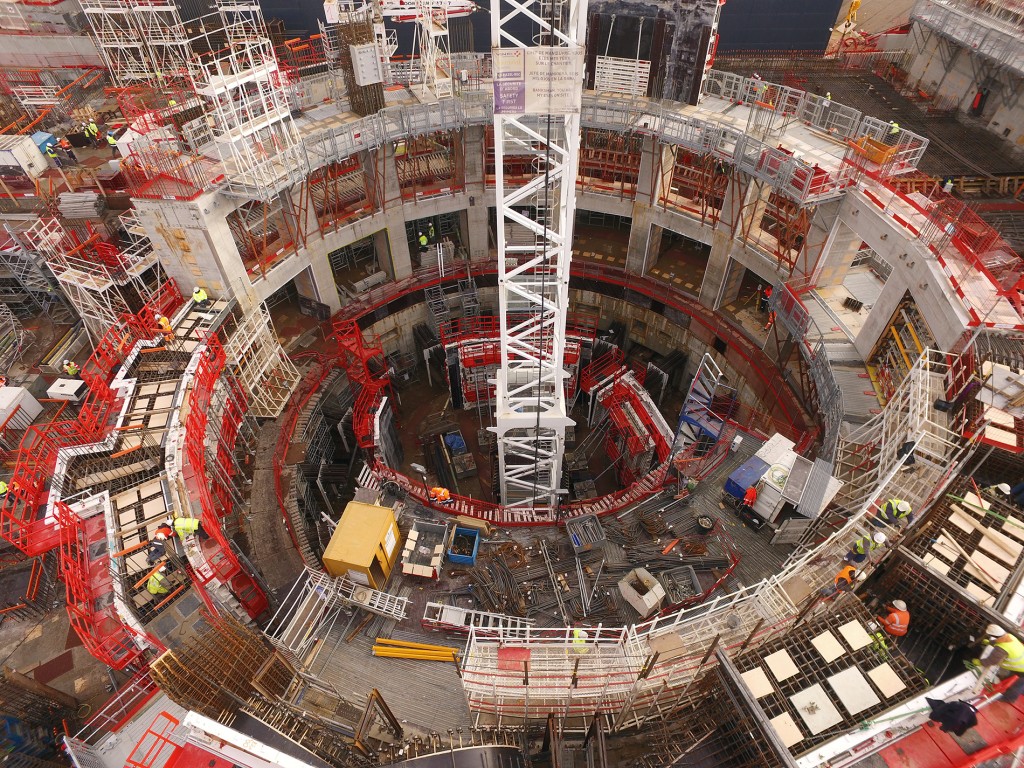
Peeking in
2017-01-12 - A temporary platform is in place as workers frame out level L1 of the bioshield. Also visible in the photo, the first activities on level L2. Photo: ITER Organization/EJF Riche
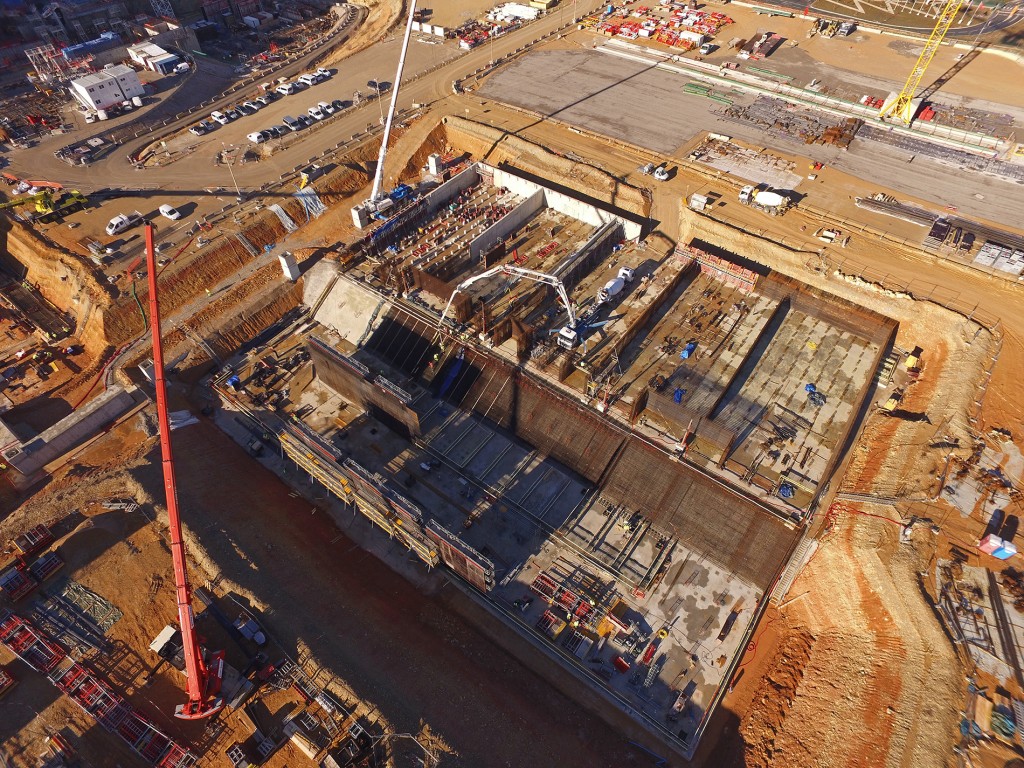
Cooling tower zone
2017-01-12 - Seen by drone, the infrastructure of the heat rejection system on the northern side of the platform. Photo: ITER Organization/EJF Riche
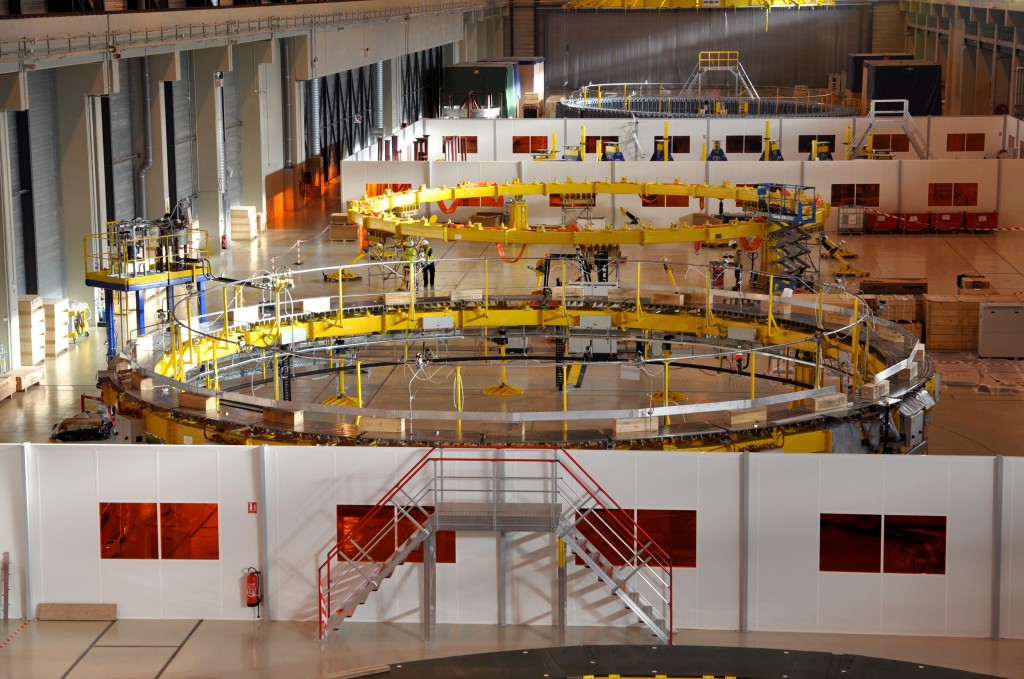
Impregnating and bonding
2017-01-12 - Before they are stacked to form a coil, each double pancake must be impregnated with epoxy resin under vacuum pressure to electrically insulate and bond each double pancake into a rigid assembly. Two impregnation stations are under construction now.
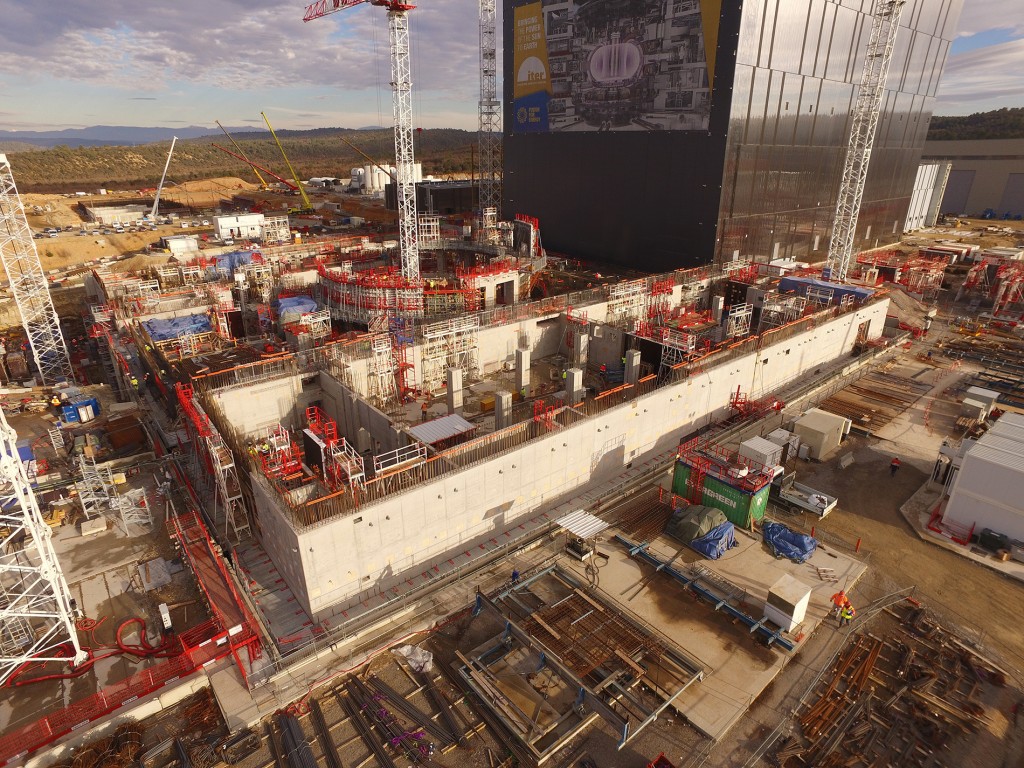
Diagnostics Building rises
2017-01-12 - Level L1 (platform level) of the Diagnostics Building is now clearly frame out. The building will comprise five stories in all—two underground and three above. Photo: ITER Organization/EJF Riche

Cryoplant roof frame
2017-01-12 - A photo of progress on the ITER cryoplant, taken in January 2017. Photo: ITER Organization/EJF Riche

First station
2017-01-12 - The 20-tonne conductor spools delivered by China are installed by overhead crane (with the assistance of the star-shaped tool at right) on the tower situated at left. From there, the conductor is straightened, cleaned and then bent again on the winding table to match the geometry of the future coil.
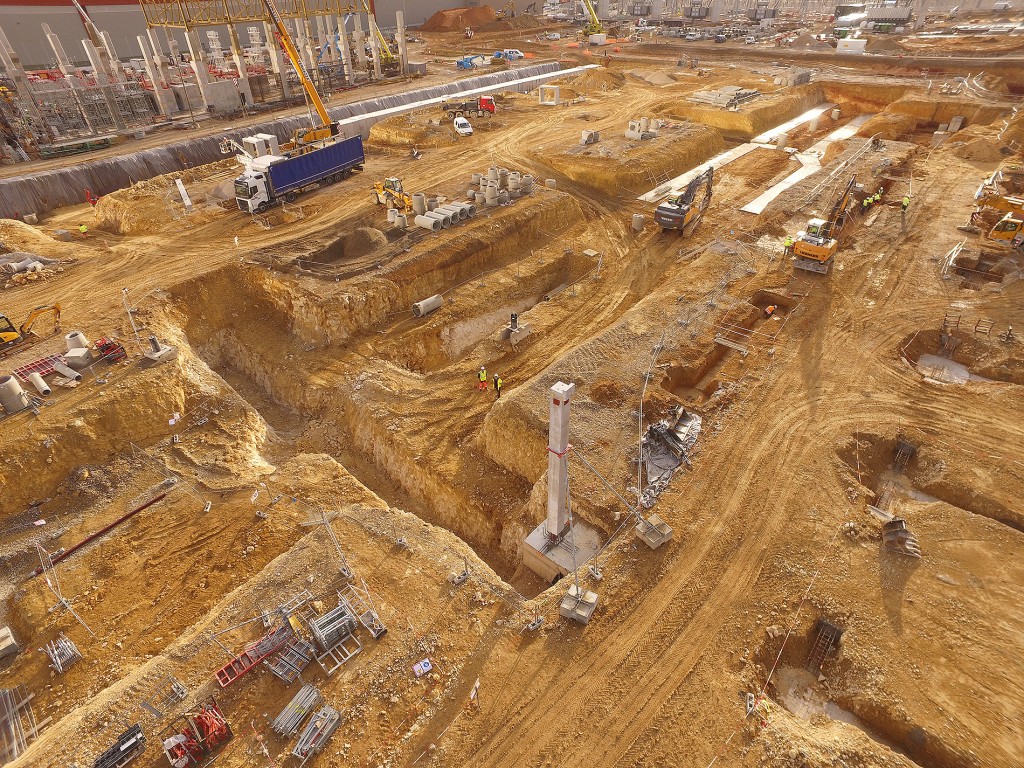
Underground labyrinth
2017-01-12 - Digging continues on the underground technical galleries of the Magnet Power Conversion buildings. Photo: ITER Organization/EJF Riche

Ground-level bioshield
2017-01-12 - The ITER bioshield now rises 5 metres above ground level. Photo: ITER Organization/EJF Riche
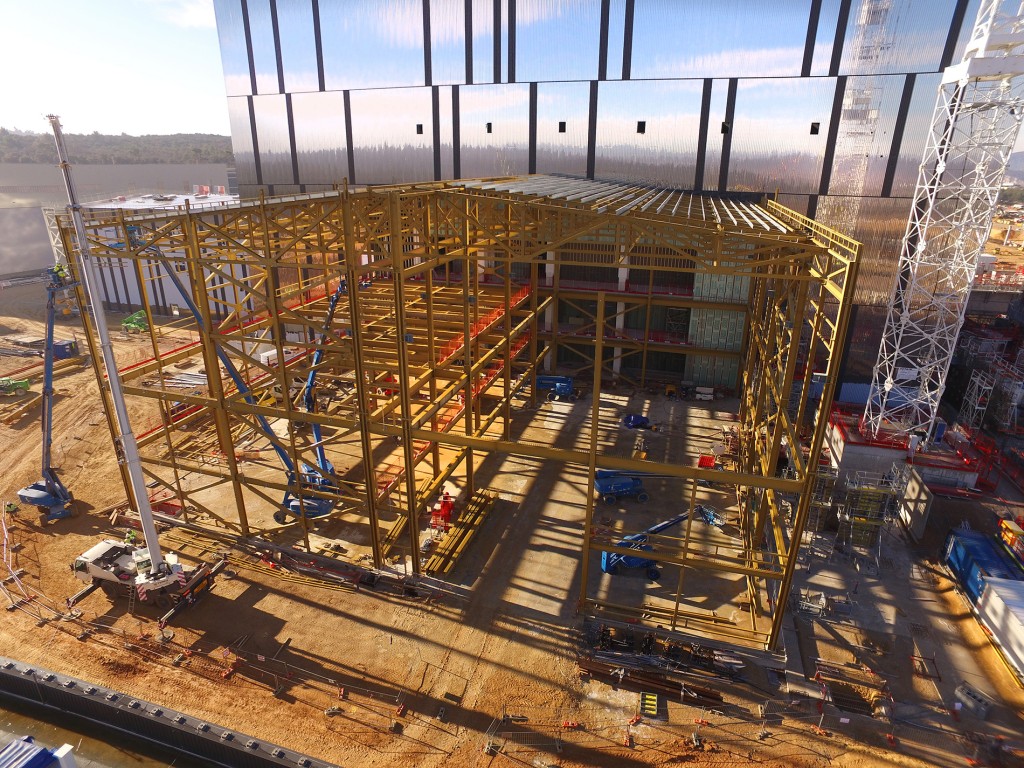
Dedicated to external heating sources
2017-01-12 - Powerful radio frequency waves will travel along waveguides through the Assembly Building in order to reach the tokamak. Photo: ITER Organization/EJF Riche

Last impregnation
2017-01-12 - In the last production phase, double pancakes are stacked and connected electrically. The several-hundred-tonne winding pack is transferred to the final station for resin impregnation of the whole assembly.
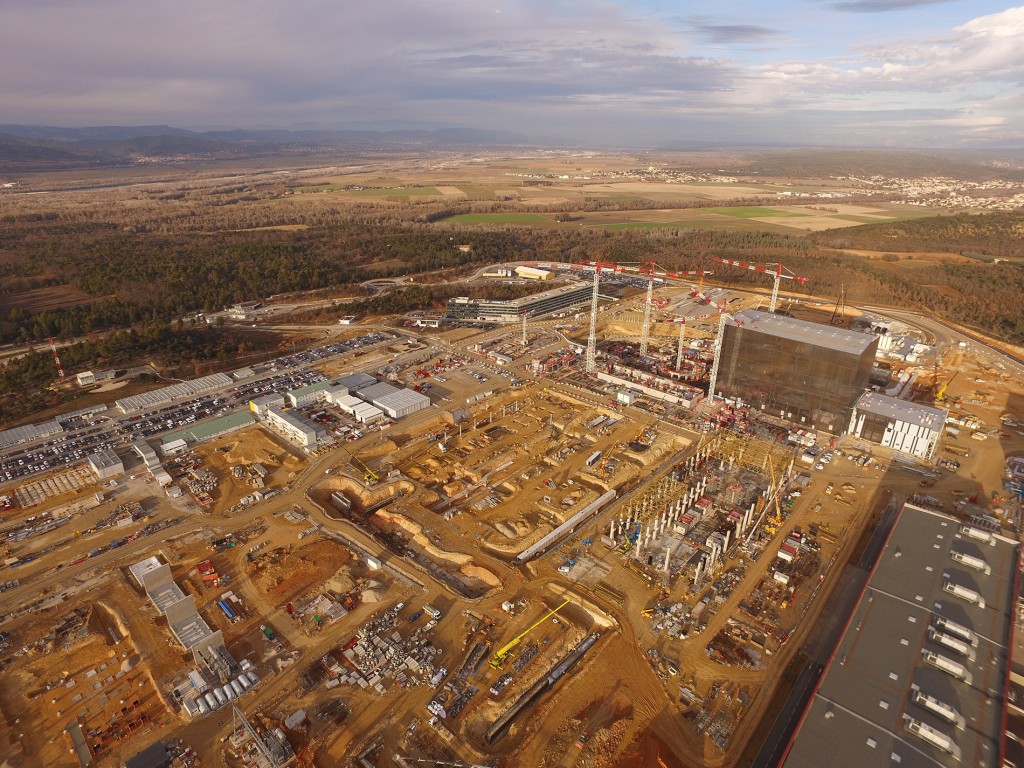
From the sky
2017-01-12 - The technical areas of the ITER construction platform from bottom left to middle right: the transformers of the electrical switchyard; work underway on the technical galleries of the Magnet Power Conversion buildings; and the columns of the ITER cryoplant. Photo: ITER Organization/EJF Riche
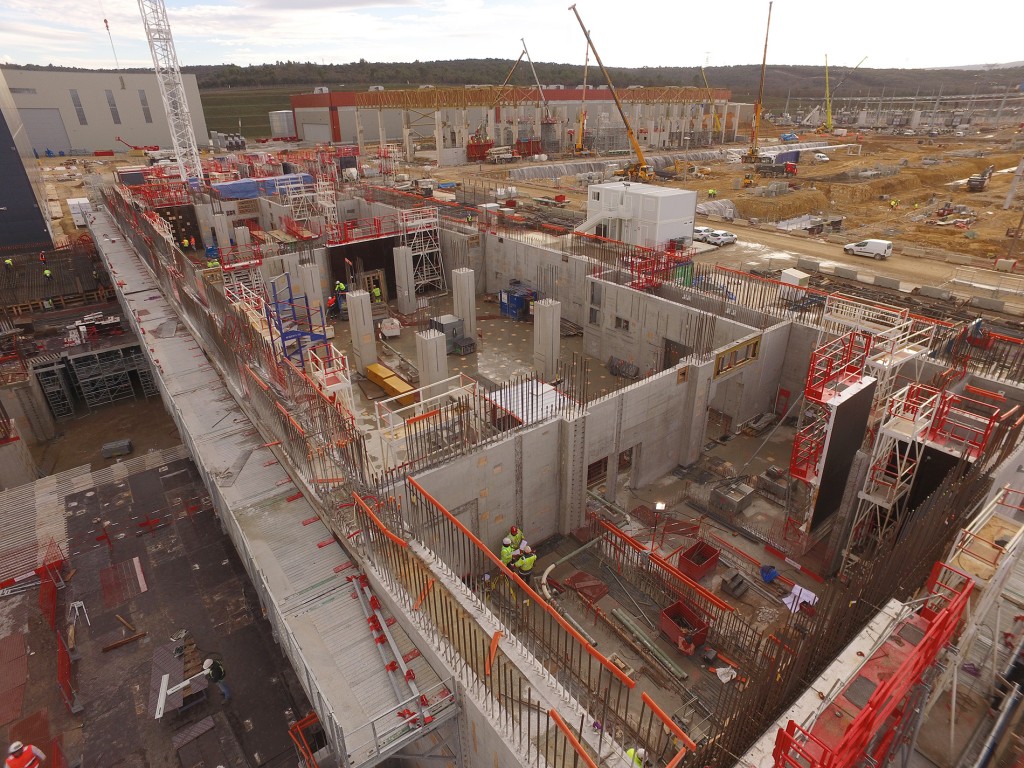
Five-storey "Diagnostic Hotel"
2017-01-12 - Diagnostics signals will leave the tokamak arena along waveguides, cables or fibre optics and travel as much as 40 metres to the back-end electronic and information systems housed in the Diagnostics Building. Photo: ITER Organization/EJF Riche
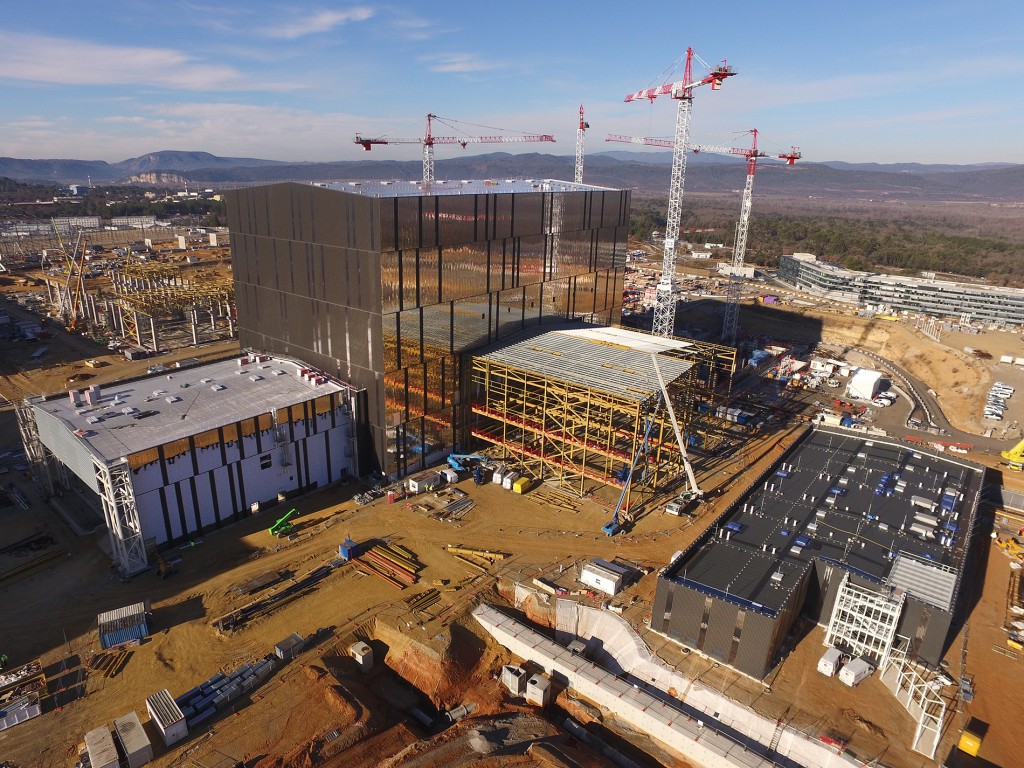
Looking west
2017-01-12 - From left to right: the Cleaning Facility, the Assembly Hall, the Radio Frequency Building; the Site Services Building. Photo: ITER Organization/EJF Riche

Winding and wrapping
2017-01-12 - As the conductor enters the winding table, a device comparable to a complex, high-tech scotch tape dispenser tightly wraps it in layers of insulating fiberglass tape. The carefully synchronized winding and wrapping operations result in a "double pancake" made of several "turns" of insulated coil.

Four circular openings
2017-01-11 - Four circular openings, in all, are reserved in the bioshield for ITER's neutral beam injectors: three for the heating neutral beams (first three in the photo, from left) and one for the diagnostic neutral beam (foreground, smaller).

Long seams
2017-01-11 - Submerged arc welding is used to close a seven-metre seam on the top plate of the cryostat base. Six of these welds have been completed.
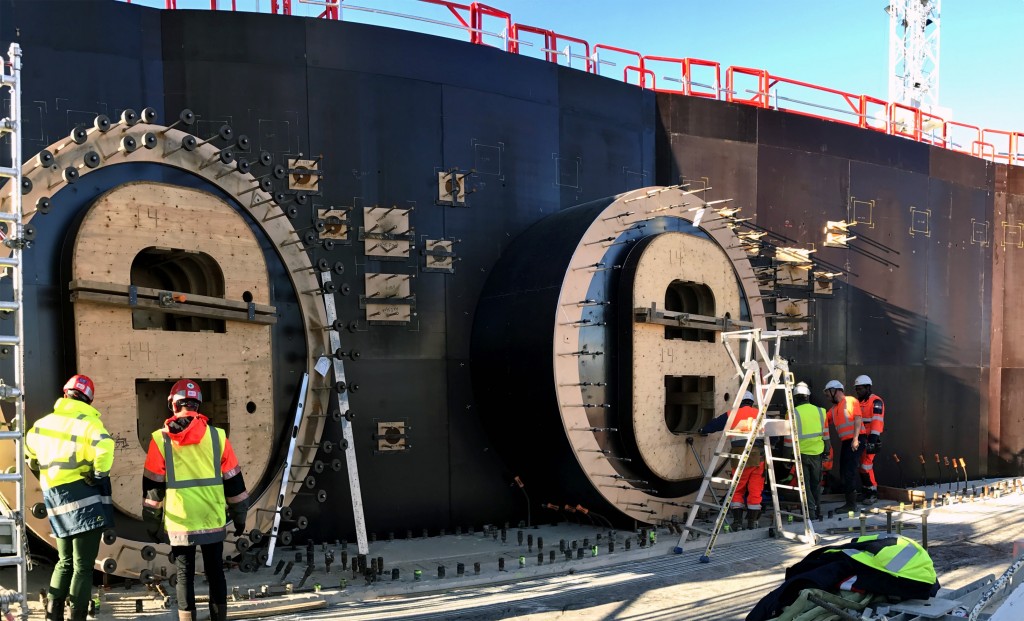
Hobbit holes?
2017-01-09 - These large circular openings in the bioshield are reserved for the neutral beam injection system that will feed some 30 MW of heating power into the plasma.
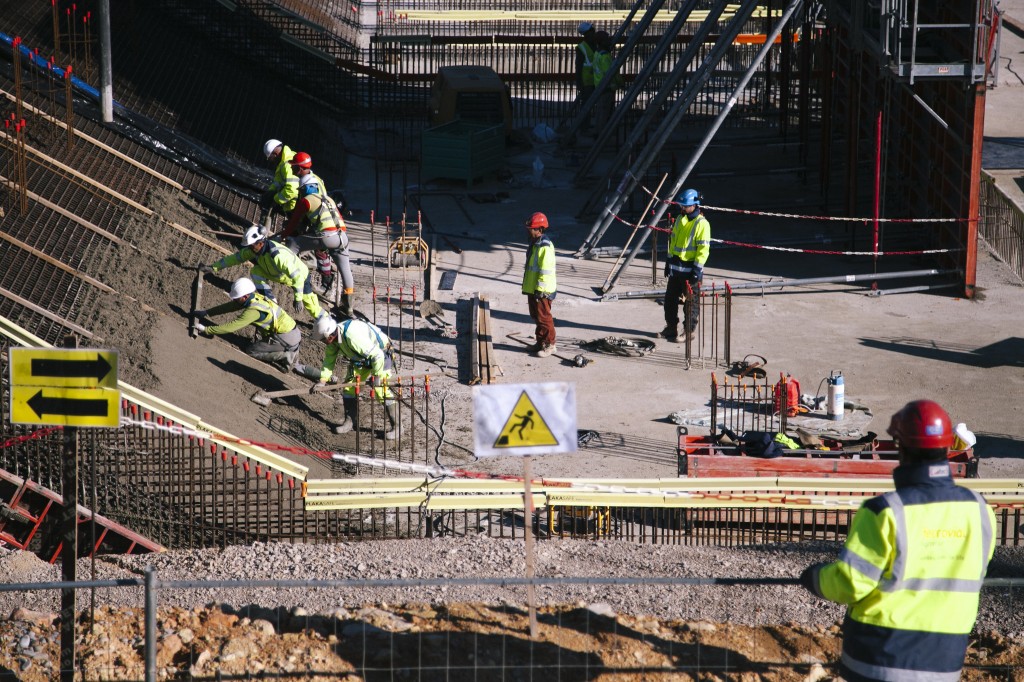
Concrete pouring in December
2016-12-20 - Concrete pouring is underway on the site of the cooling towers and basins.
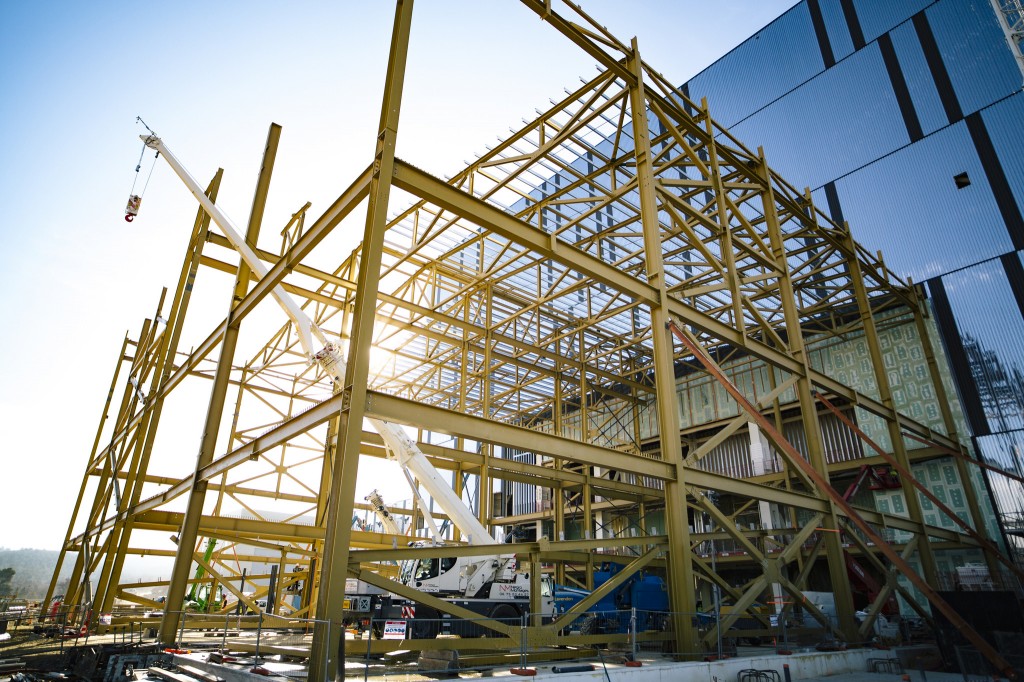
An important neighbor
2016-12-19 - The Radio Frequency Building, now nearly framed out, will be 50 metres long, 43 metres wide and 25 metres tall. © Les Nouveaux Médias/SNC ENGAGE

ITER bioshield: poured segment by segment
2016-12-19 - At the foot of the Assembly Building, the concrete structure of the ITER bioshield emerges from its formwork. © Les Nouveaux Médias/SNC ENGAGE
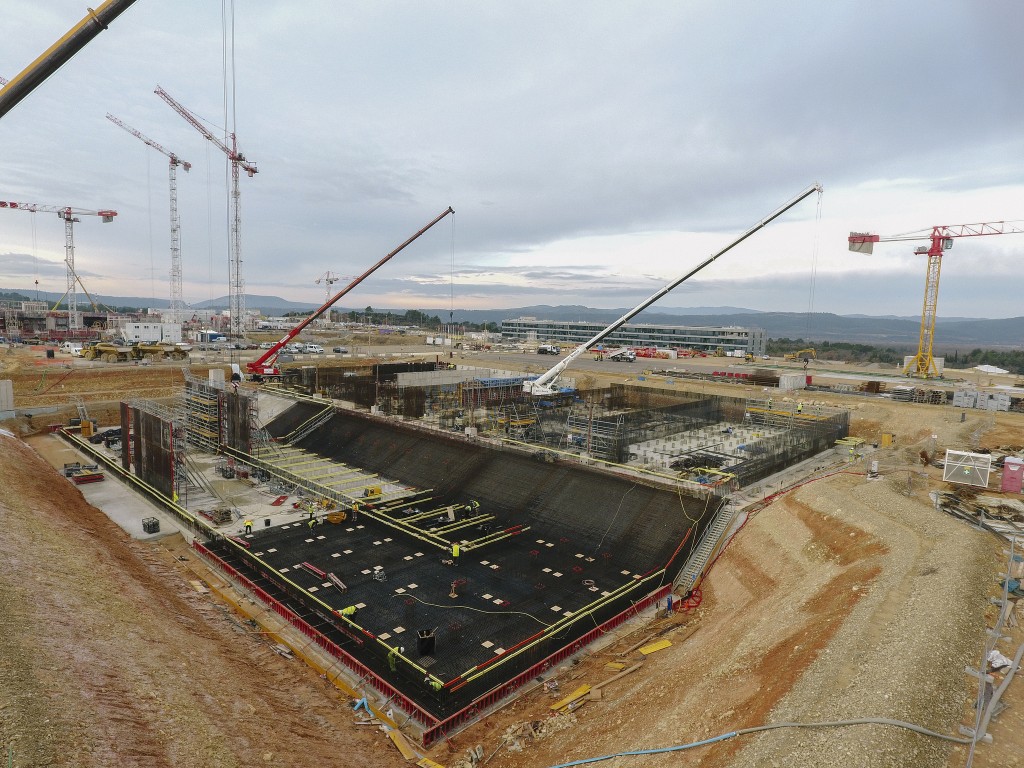
Pouring on the northern corner of the platform
2016-12-19 - Now that the rebar is in place, pouring has started on the site of the cooling basins. © Les Nouveaux Médias/SNC ENGAGE
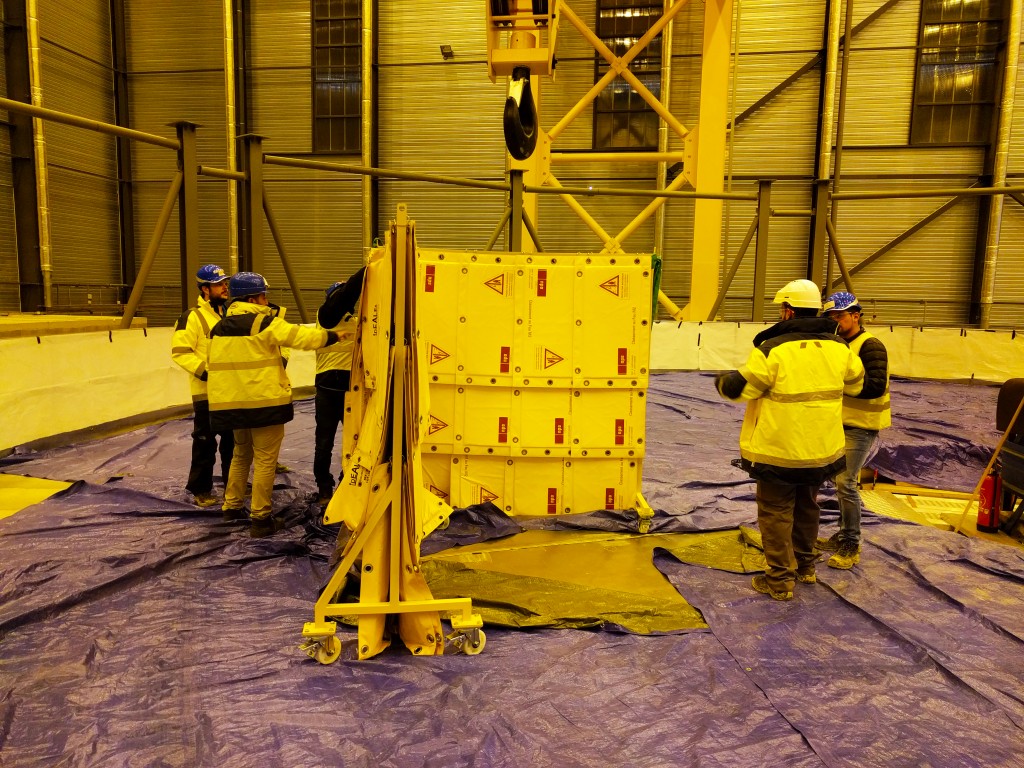
Radiographic testing underway
2016-12-19 - Radiographic testing is underway in the Cryostat Workshop on the first cryostat welds. Here, workers implement lead shielding panels before a testing series begins.

Technical galleries
2016-12-19 - Contractors are creating technical galleries between the future Magnet Power Conversion Buildings (left) and the ITER cryoplant (right, with columns). Four kilometres of technical galleries will crisscross the ITER platform in all, just under the surface. © Les Nouveaux Médias/SNC ENGAGE
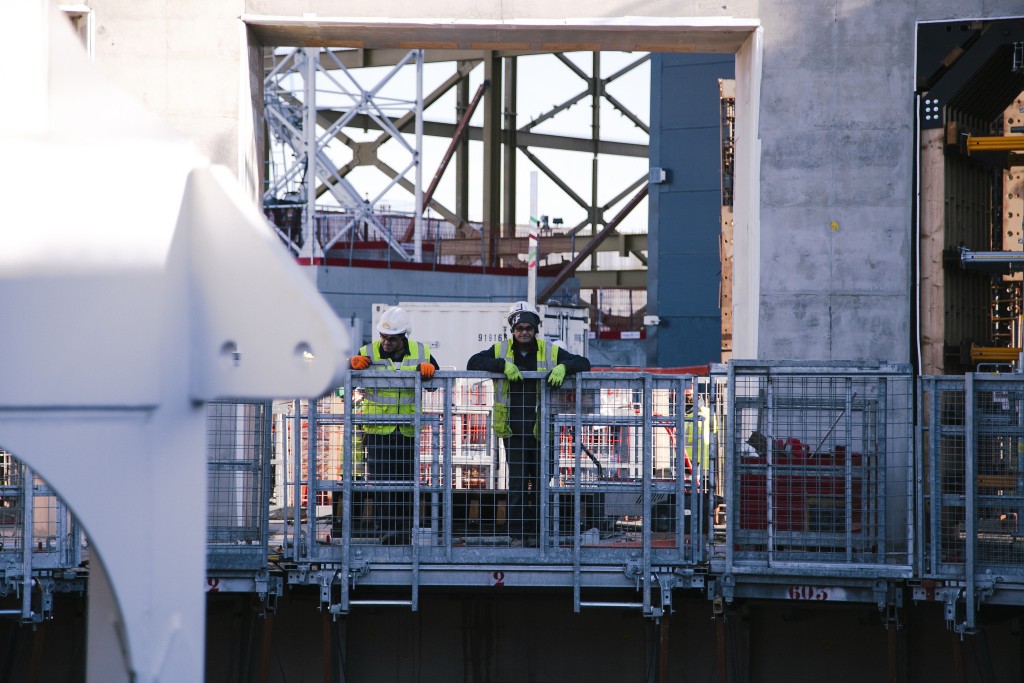
Two of many!
2016-12-19 - Some 1,200 people are currently active on the worksite in two shifts and another 800 people in the offices. The European Domestic Agency is charged with the construction of the ITER installation, in close collaboration with the ITER Organization. © Les Nouveaux Médias/SNC ENGAGE
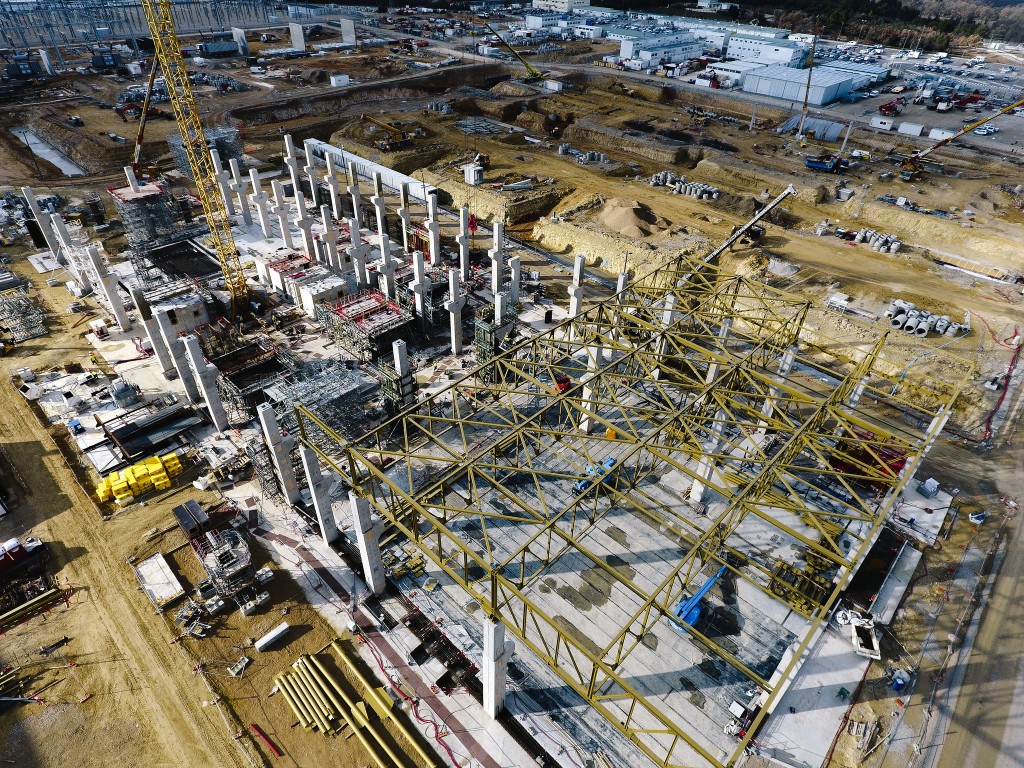
Roof structure for the cryoplant
2016-12-19 - The cryoplant worksite, seen from above. In December, work progresses on the roof structure. © Les Nouveaux Médias/SNC ENGAGE
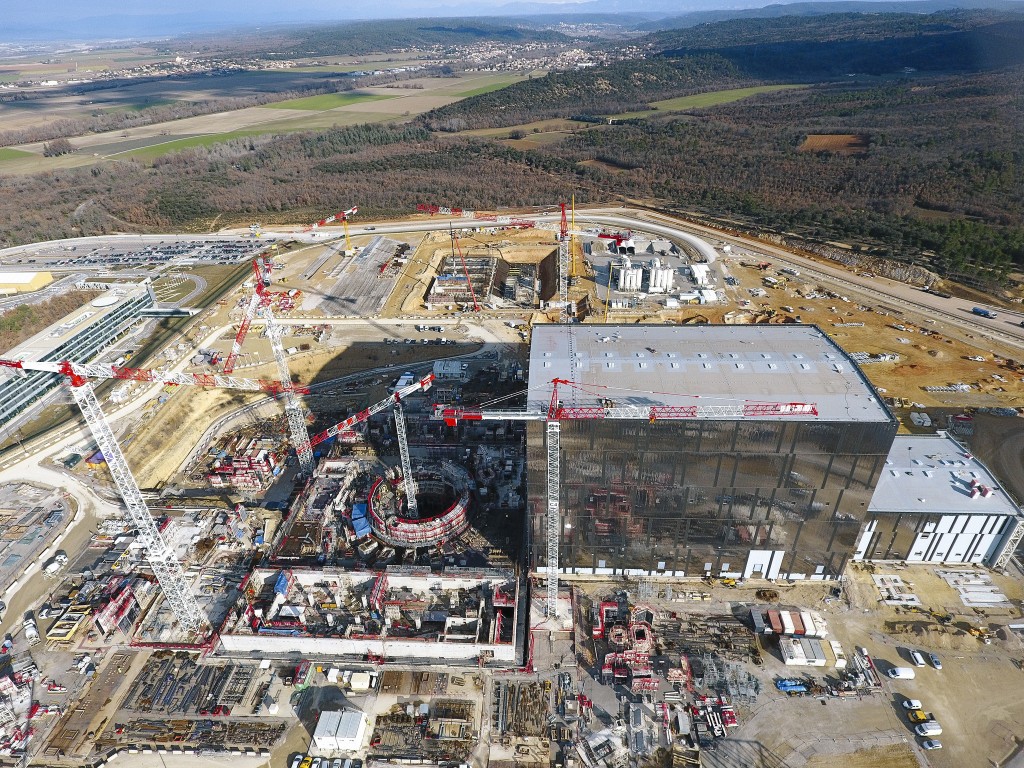
The northern side of the construction platform
2016-12-19 - Looking northeast over the ITER site. From left to right: the Tokamak Complex (under construction), the Assembly Hall and its antechamber—the Cleaning Facility. © Les Nouveaux Médias/SNC ENGAGE

Full of power supplies and generators
2016-12-19 - Originally planned for installation in the Assembly Hall, radio wave equipment for the electron and ion resonance heating systems will now have a building of its own: the Radio Frequency Building that is going up now against the north side of the Assembly Hall. © Les Nouveaux Médias/SNC ENGAGE
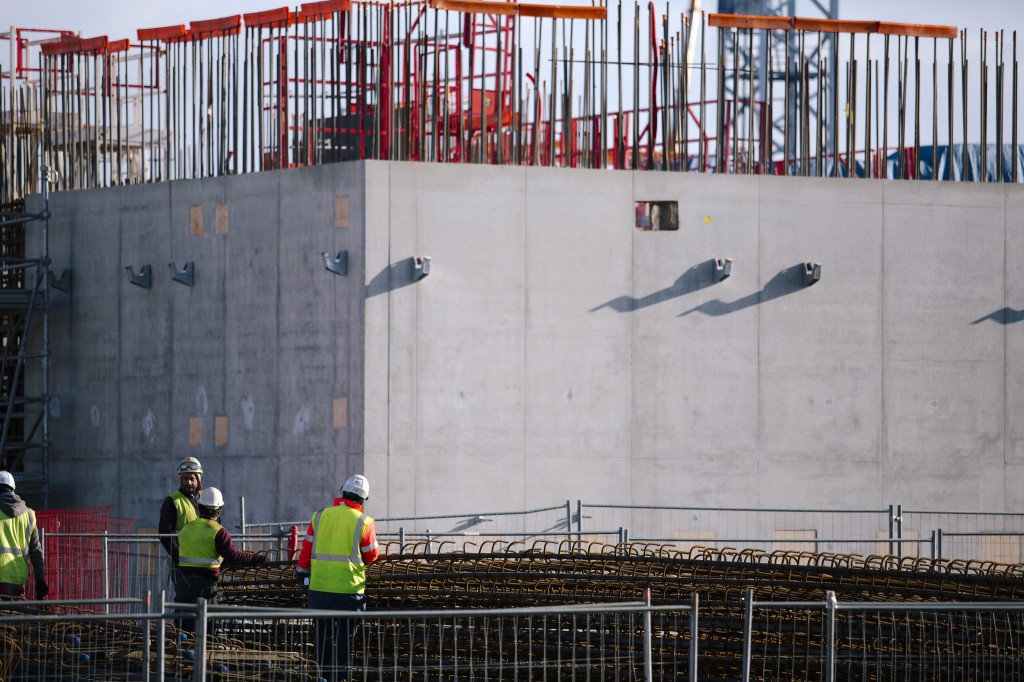
Going up
2016-12-19 - The first ground level of the Diagnostics Building (L1). © Les Nouveaux Médias/SNC ENGAGE

The two-level cooling tower worksite
2016-12-19 - The cold basin, taking shape at right, will sit under the ten cooling tower cells. © Les Nouveaux Médias/SNC ENGAGE

Slowly but surely
2016-12-19 - In front of the Assembly Hall, work is progressing on level L1 of the Tokamak Complex (ground level). When the Tokamak Building is completed in 2018, it will stand as tall as the Assembly Hall.

L1 bioshield
2016-12-19 - The L1 level of the ITER bioshield (ground level 1) is progressing well and formwork is arriving for the L2 level. © Les Nouveaux Médias/SNC ENGAGE
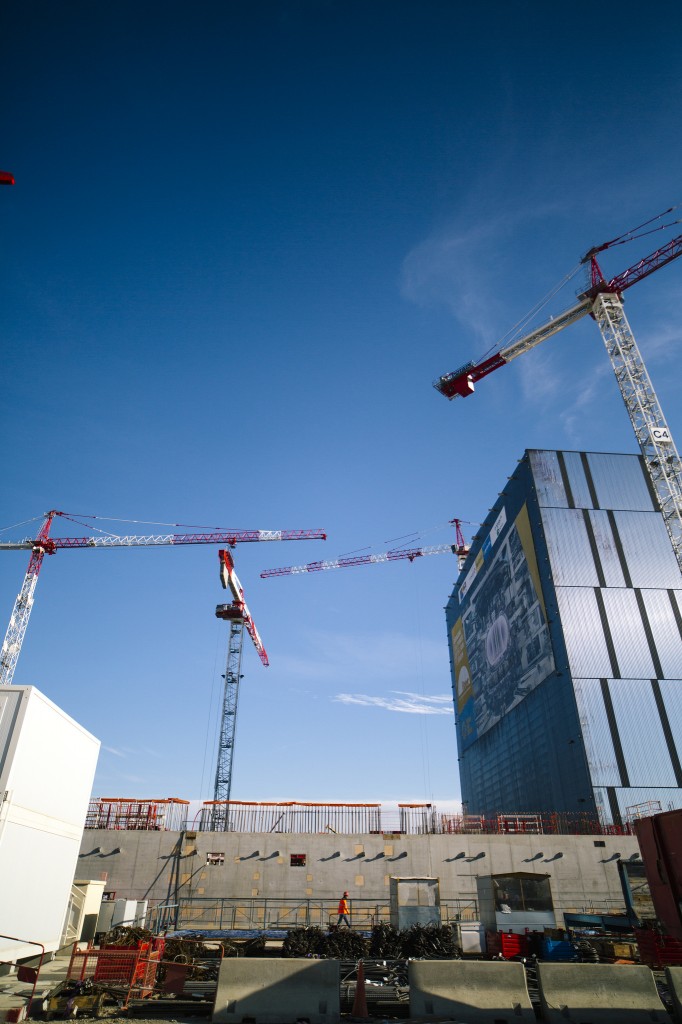
Tokamak Complex now higher than platform
2016-12-19 - The Diagnostics Building is the first to rise above the platform (pictured, the L1 level wall). © Les Nouveaux Médias/SNC ENGAGE
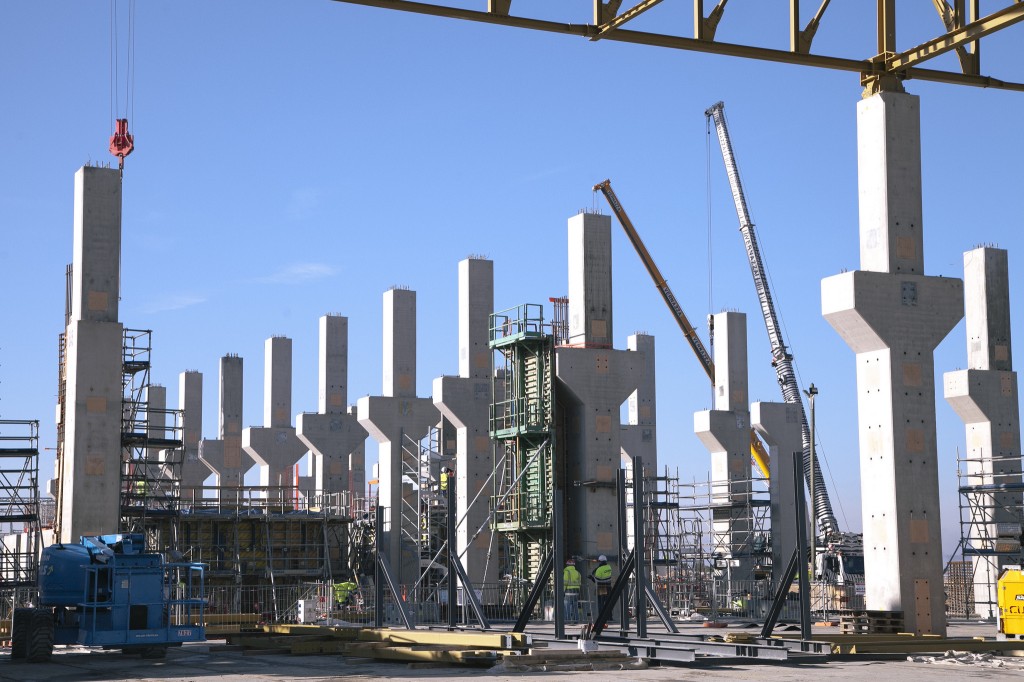
8,000 square metres for cryogenics
2016-12-19 - The ITER cryoplant will occupy an 8,000-square-metre area on the ITER platform. Gases and liquids will be stored on the outside, while the building will be divided between the compressor room and the helium plant zone. © Les Nouveaux Médias/SNC ENGAGE
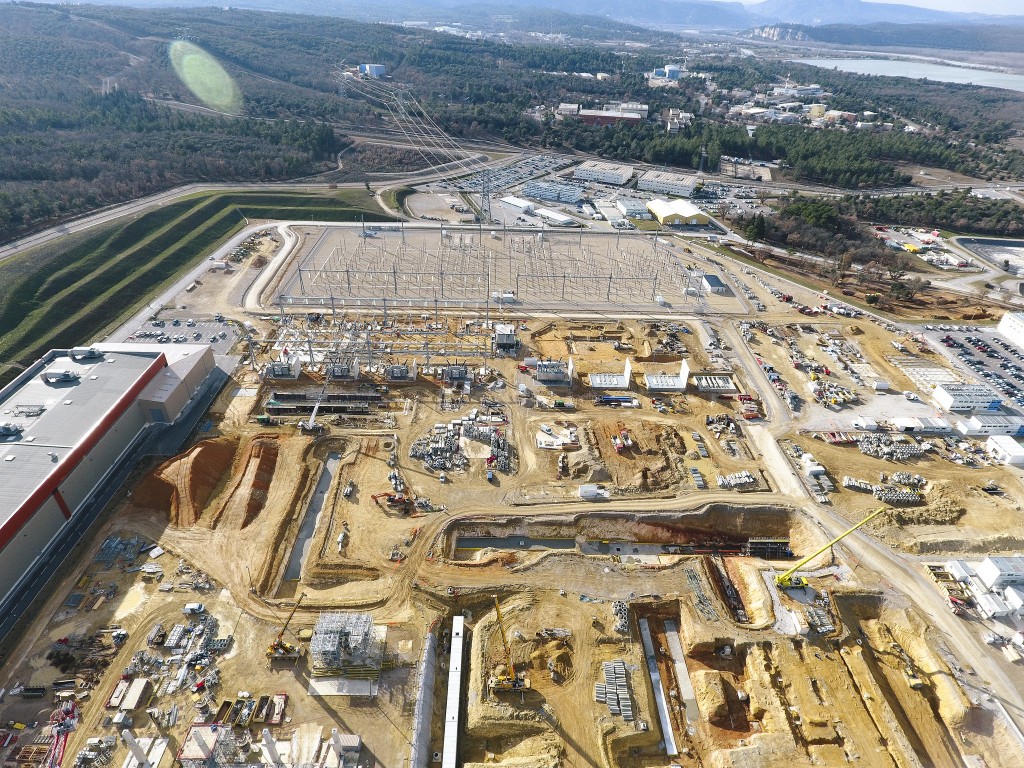
The southern side of the platform
2016-12-19 - New projects are underway on the southern side of the platform. © Les Nouveaux Médias/SNC ENGAGE
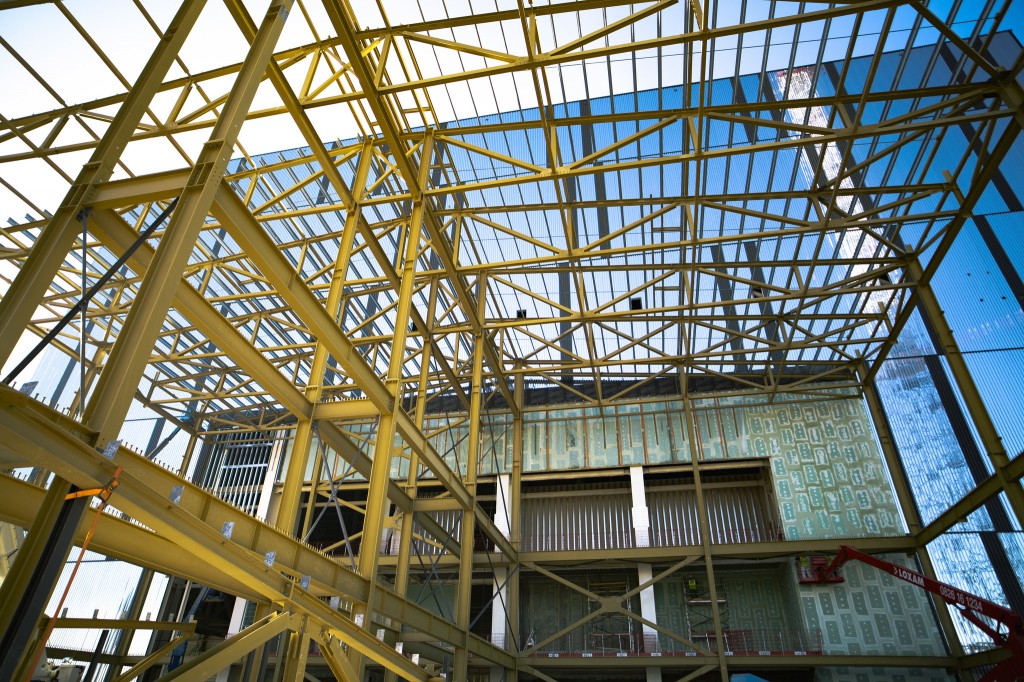
Three floors planned
2016-12-19 - The first two floors of the building will be occupied by power supplies (a total input of 100 MW). The top floor will host the wave generators (gyrotrons and tetrodes). © Les Nouveaux Médias/SNC ENGAGE

Structure advances
2016-12-19 - The roof frame is going up for the ITER cryoplant. © Les Nouveaux Médias/SNC ENGAGE

The southern side of the platform
2016-12-19 - New projects are underway on the southern side of the platform. © Les Nouveaux Médias/SNC ENGAGE
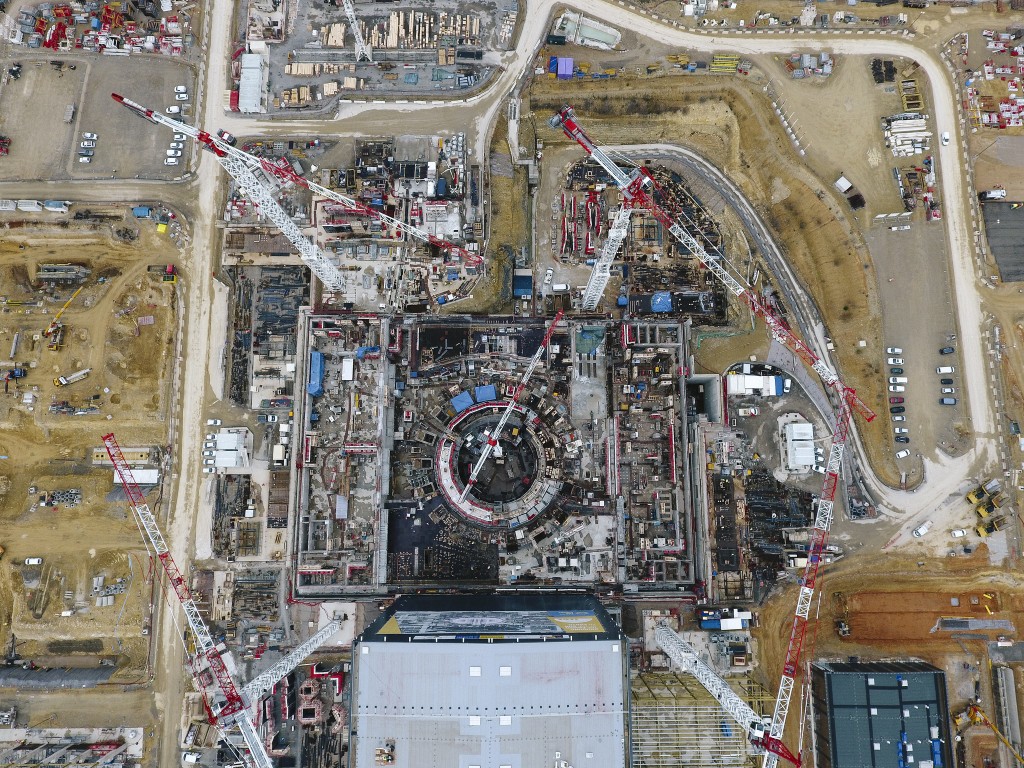
Basement levels filling in
2016-12-19 - The emerging Tokamak Complex is clearly distinguishable from a height of 100 metres. The 80 x 120 metre "box" will contain the three principal buildings of the ITER installation: the Tokamak, Diagnostic and Tritium buildings. © Les Nouveaux Médias/SNC ENGAGE
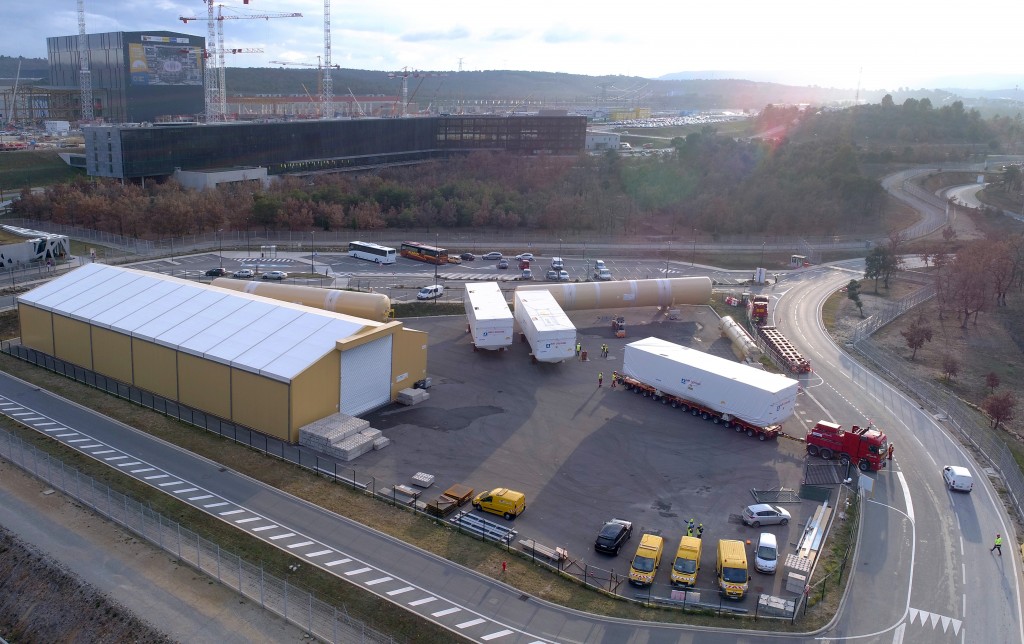
Cryoplant components "en attente"
2016-12-15 - At the entrance to the ITER site, five large elements of the cryoplant are temporarily stored—three coldboxes for the liquid helium plant (in white, procured by the ITER Organization) and two large quench tanks procured by Europe that will store helium in the event of a magnet quench.
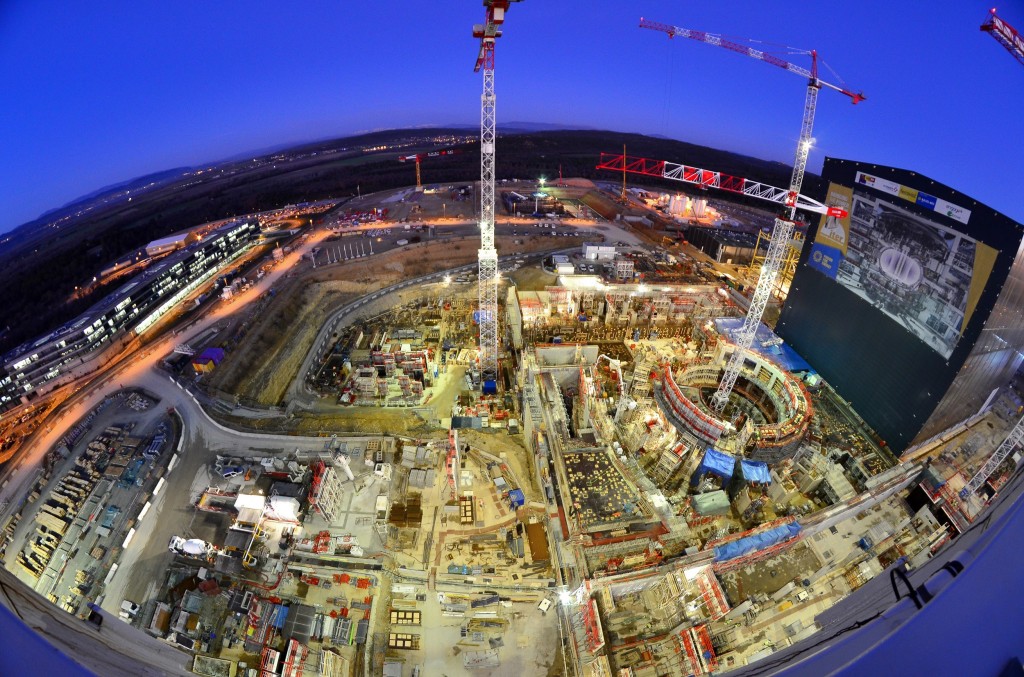
From one crane
2016-12-13 - The Tokamak Complex worksite is photographed one evening in December from one of the tallest cranes.

One winter evening
2016-12-13 - A fish-eye lens helps our photographer to capture the construction site across its entire breadth in December 2016.

Transformer bays
2016-12-12 - Four transformers procured by the US are now installed on the ITER platform. To the left, bays are ready to receive three larger transformers procured by China.
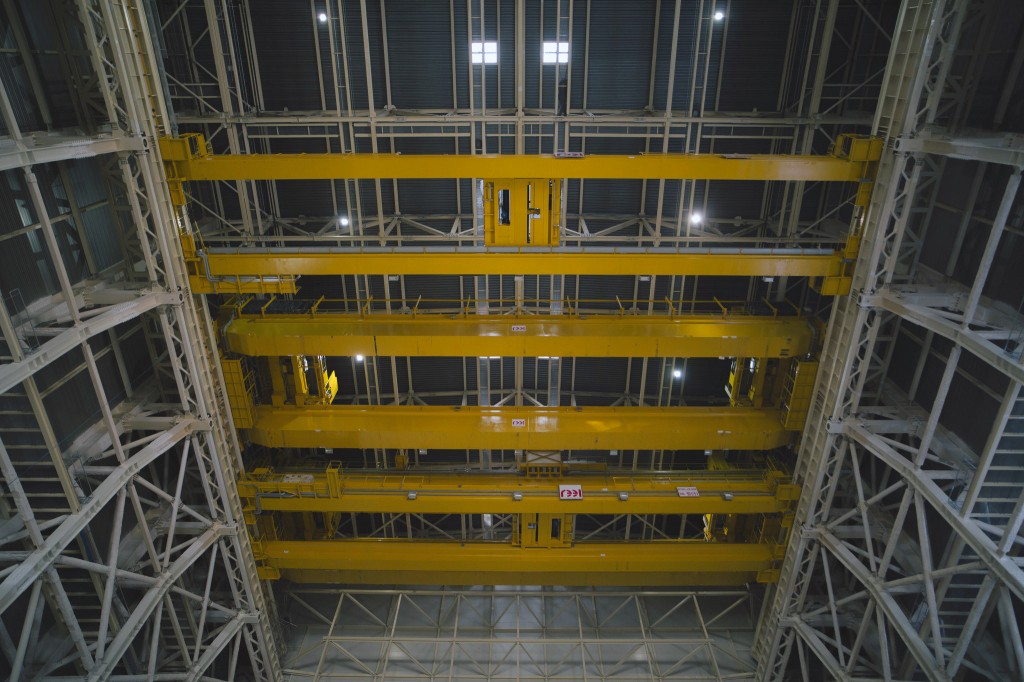
Sister cranes
2016-12-12 - Two overhead cranes with a capacity to lift 50 tonnes each are shown installed a few metres below the one of the two 750-tonne cranes (the second is not pictured). © Les Nouveaux Médias/SNC ENGAGE
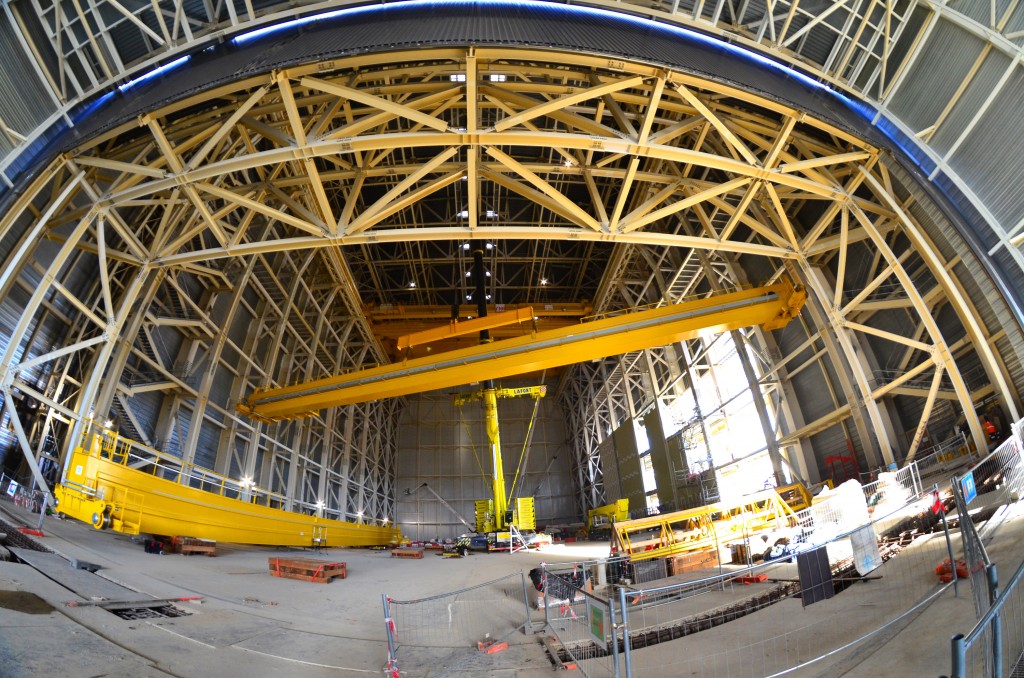
To come next: tooling
2016-12-08 - After the installation this week of the facility's second overhead crane, the next milestone will be the delivery of the first bespoke tool for ITER assembly—one of the two giant sub-sector assembly tools.
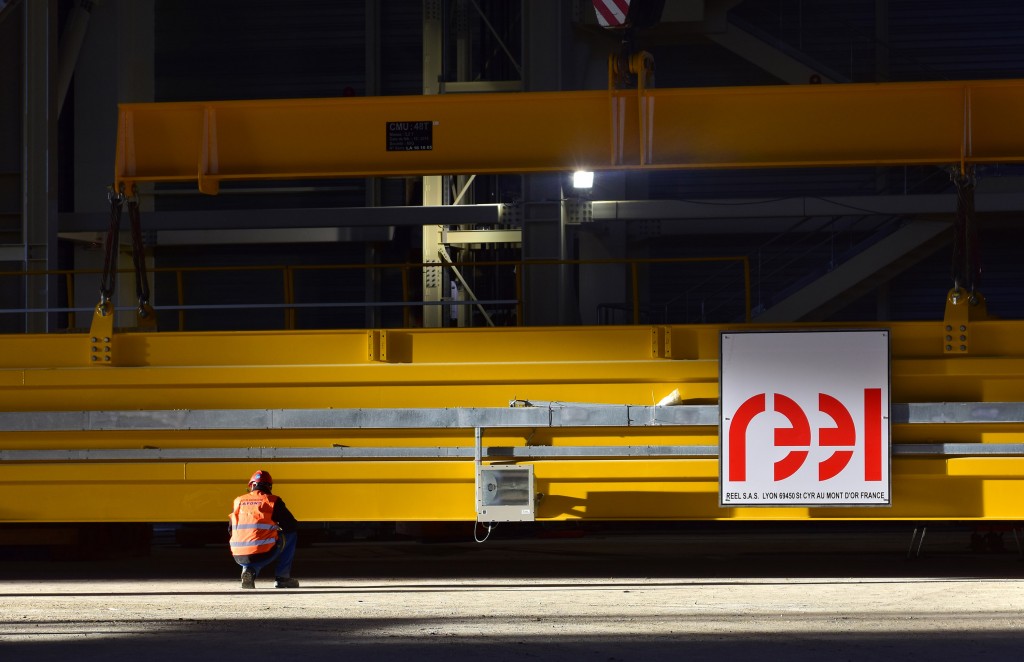
A second pair of hands
2016-12-08 - The NKMNOELL-REEL consortium (formed by NKMNoell Special Cranes, Germany and REEL SAS, France) has manufactured two pairs of cranes for the Assembly Hall: the 750-tonne cranes installed in June 2016 and the 50-tonne auxiliary cranes, pictured.
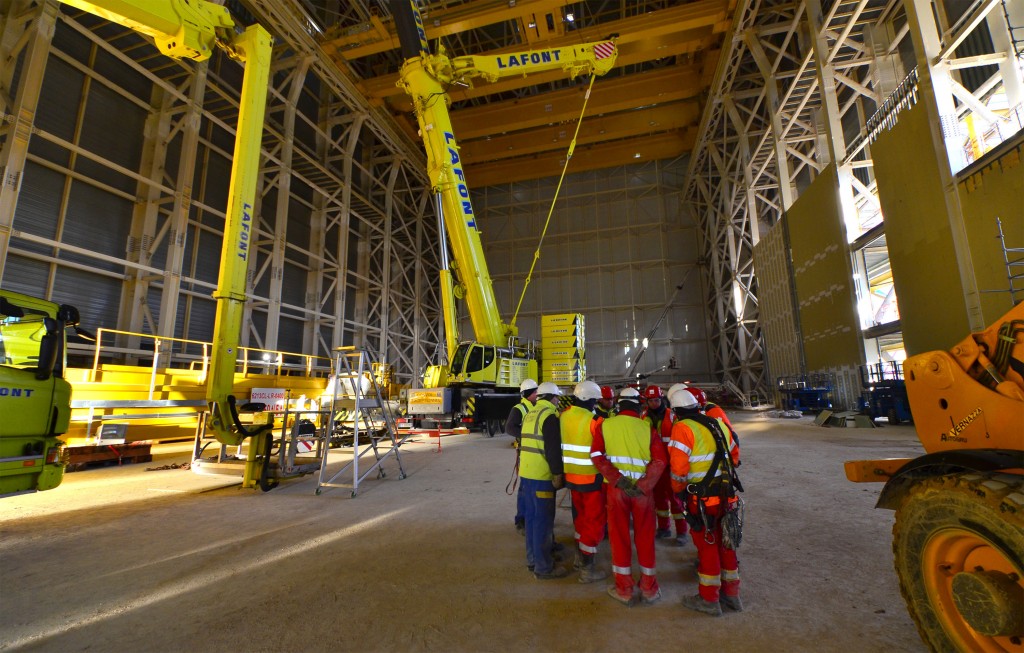
Cranes installed in December
2016-12-08 - Cranes are used inside the building to lift the girders of the 50-tonne crane into place. This auxiliary crane will be installed on rails that are a few metres below the heavy-lift crane.
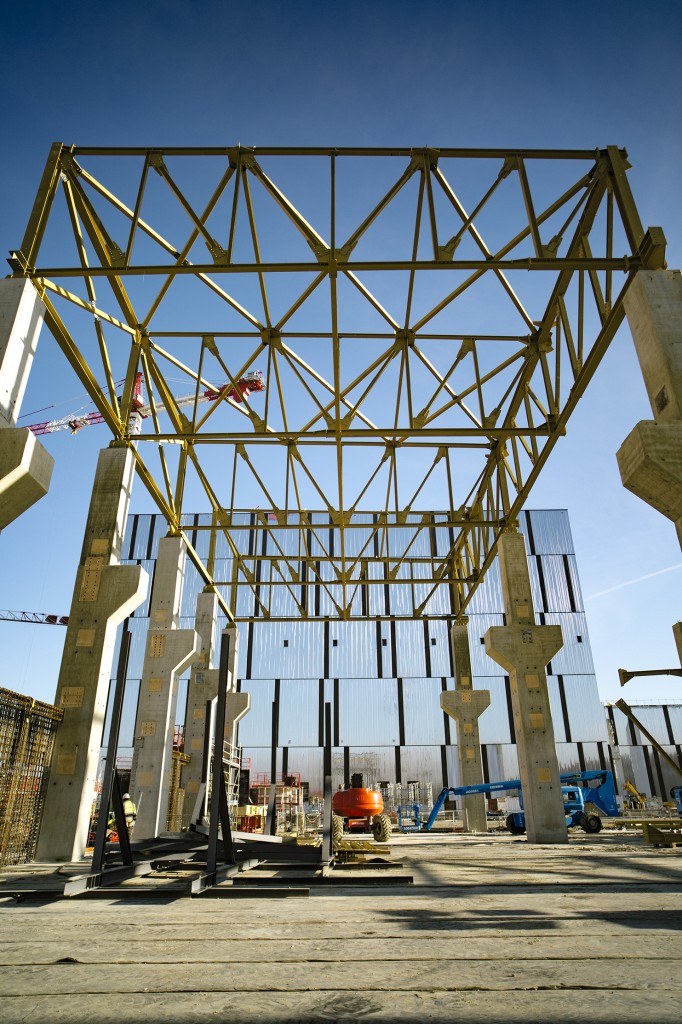
Significant space for ITER's single-platform cryoplant
2016-12-02 - The cryoplant takes up a 8,000-square-metre zone on the ITER platform. © Les Nouveaux Médias/SNC ENGAGE
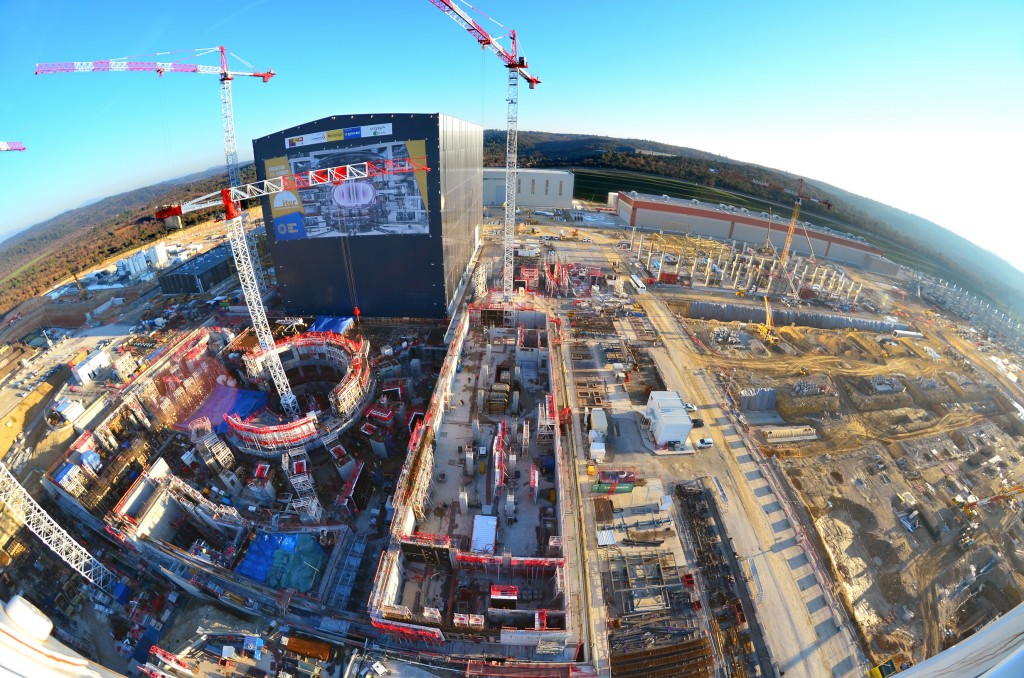
Worksite filling in
2016-12-02 - Separate construction projects are distinguishable from the air: the Tokamak Complex (lower left), the cryoplant (upper right), groundwork for the Magnet Power Conversion buildings (lower right).
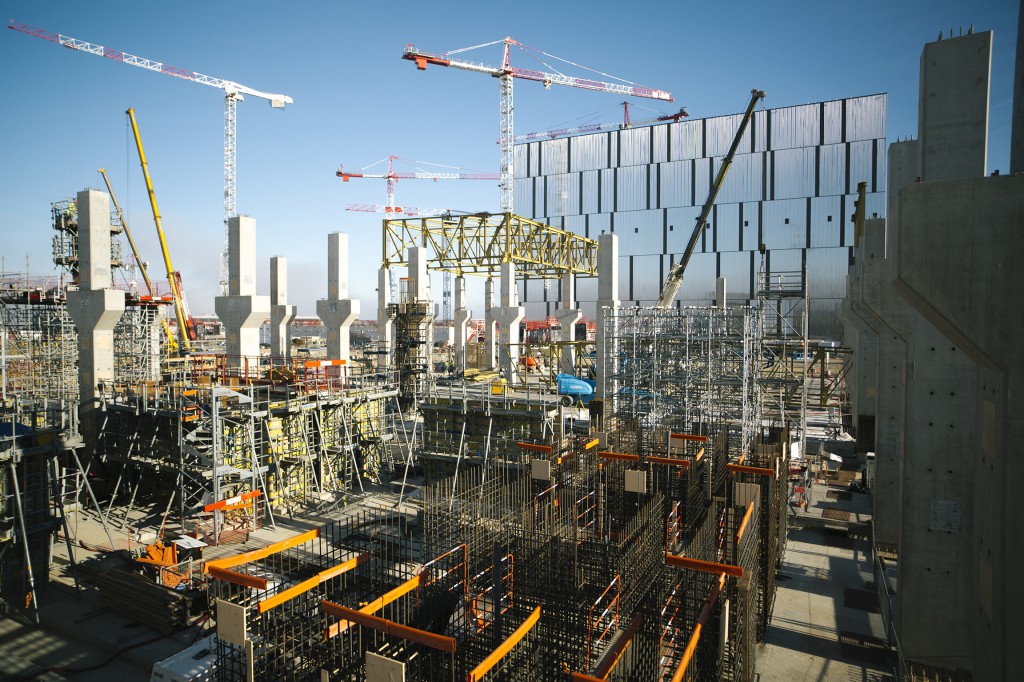
Building: the rhythm accelerates
2016-12-02 - The concrete basemat of the cryoplant is disappearing under the first columns and partitions. © Les Nouveaux Médias/SNC ENGAGE
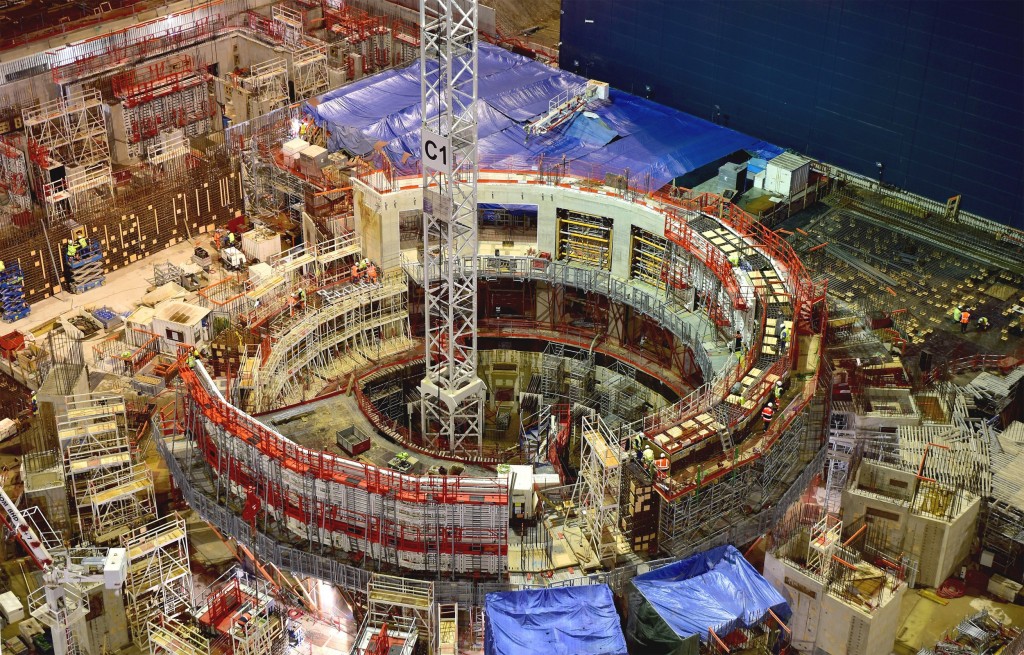
44 openings
2016-12-02 - Forty-four openings, or ports, in the vacuum vessel will allow access for remote handling, diagnostic, heating, fuelling and vacuum systems. These openings are reflected in the bioshield (photo) that is under construction now.
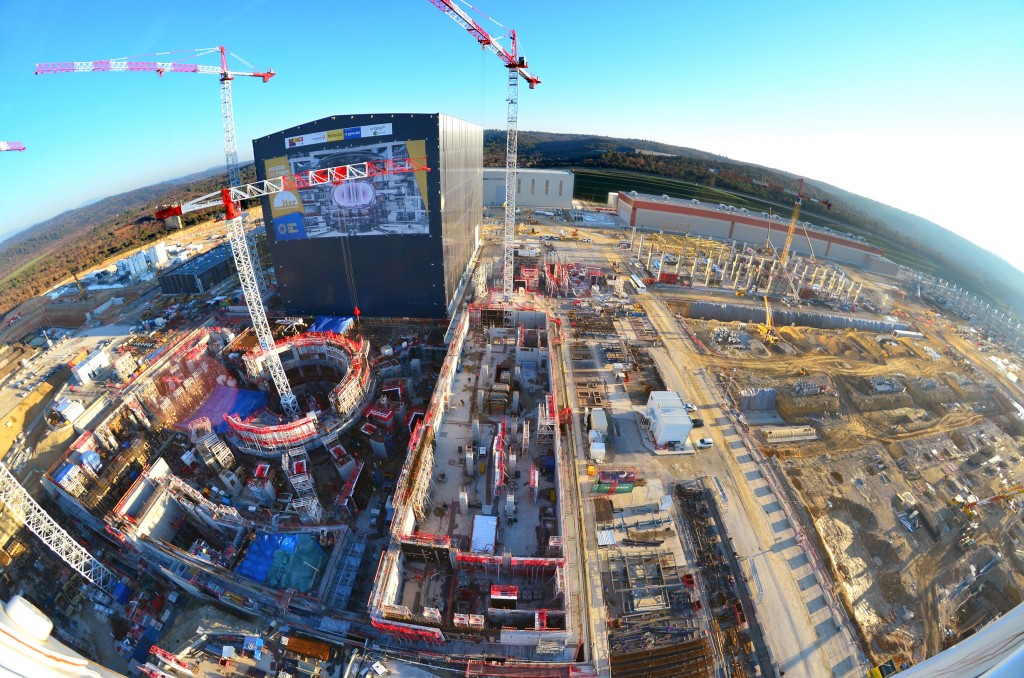
Worksite filling in
2016-12-02 - Separate construction projects are distinguishable from the air: the Tokamak Complex (lower left), the cryoplant (upper right), groundwork for the Magnet Power Conversion buildings (lower right).

Ten to do the job
2016-12-02 - The structures of the ten cooling cells will sit on these concrete pedestals in the cold basin. © Les Nouveaux Médias/SNC ENGAGE
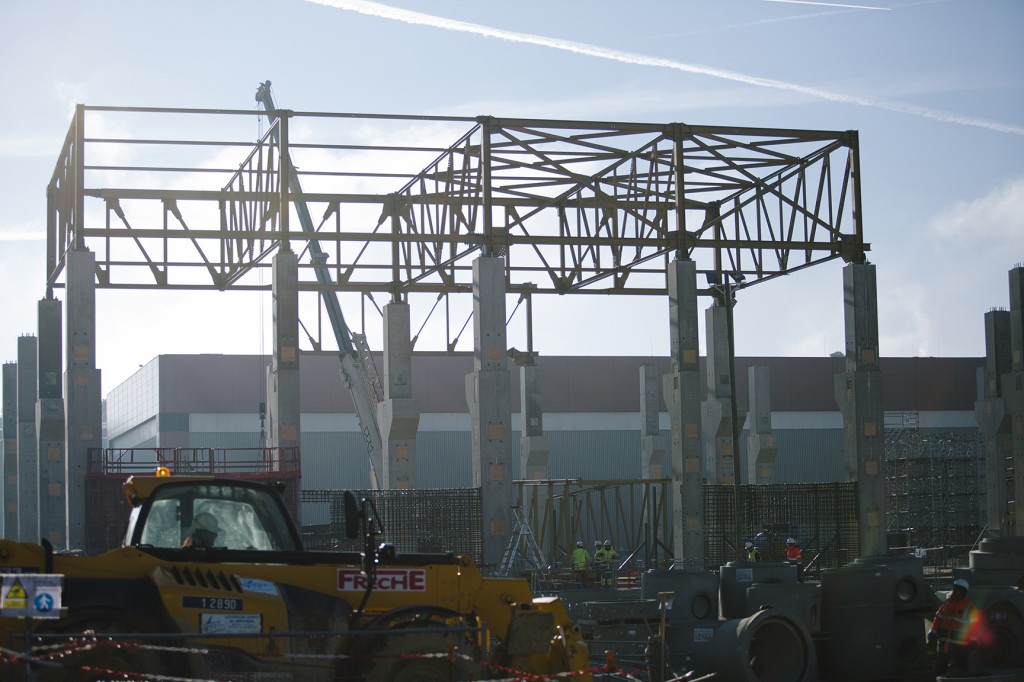
Building delivered in 2017
2016-12-02 - Workers have begun installing the roof structure for the ITER cryoplant. © Les Nouveaux Médias/SNC ENGAGE
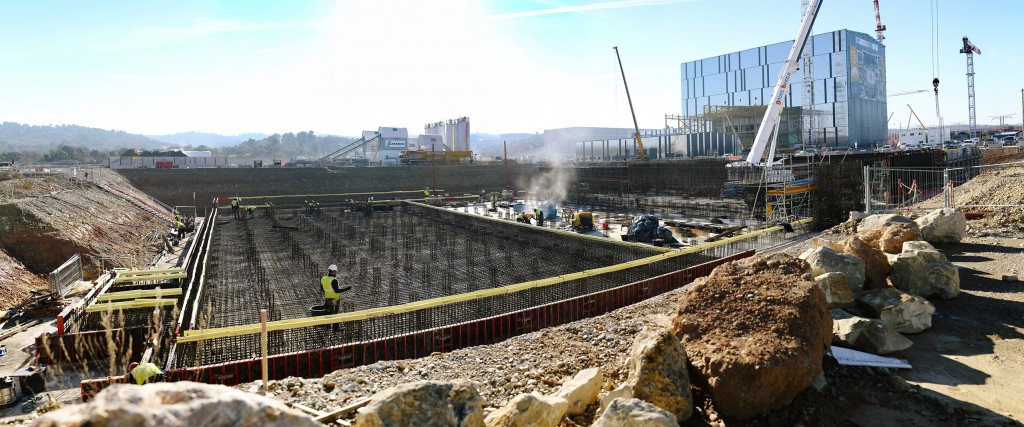
In charge of dissipating heat
2016-12-02 - Water will be used in ITER to remove heat from the vacuum vessel and its components, and to cool auxiliary systems such as radio frequency heating and magnet power supply. © Les Nouveaux Médias/SNC ENGAGE
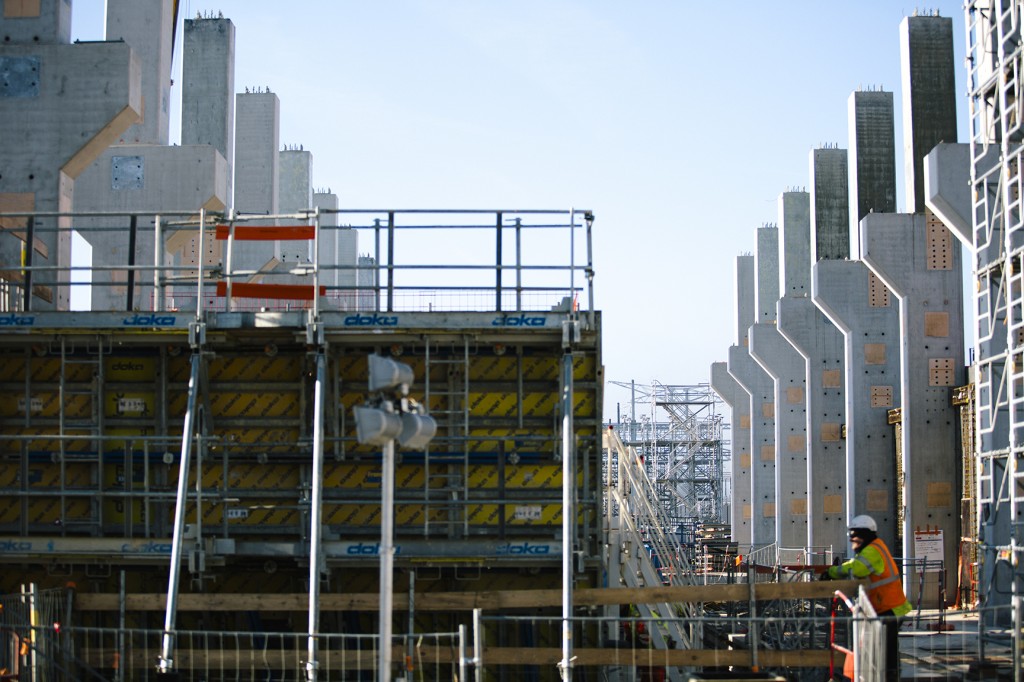
Cranes planned for cryoplant facility maintenance
2016-12-02 - These tall columns are sized to support the weight of the installation's maintenance cranes. © Les Nouveaux Médias/SNC ENGAGE

ITER bioshield rises
2016-12-02 - The perfectly circular ITER bioshield is rising in the centre of the Tokamak Complex. In this photo, we see progress advancing on Level L1 (the first "aboveground" level).
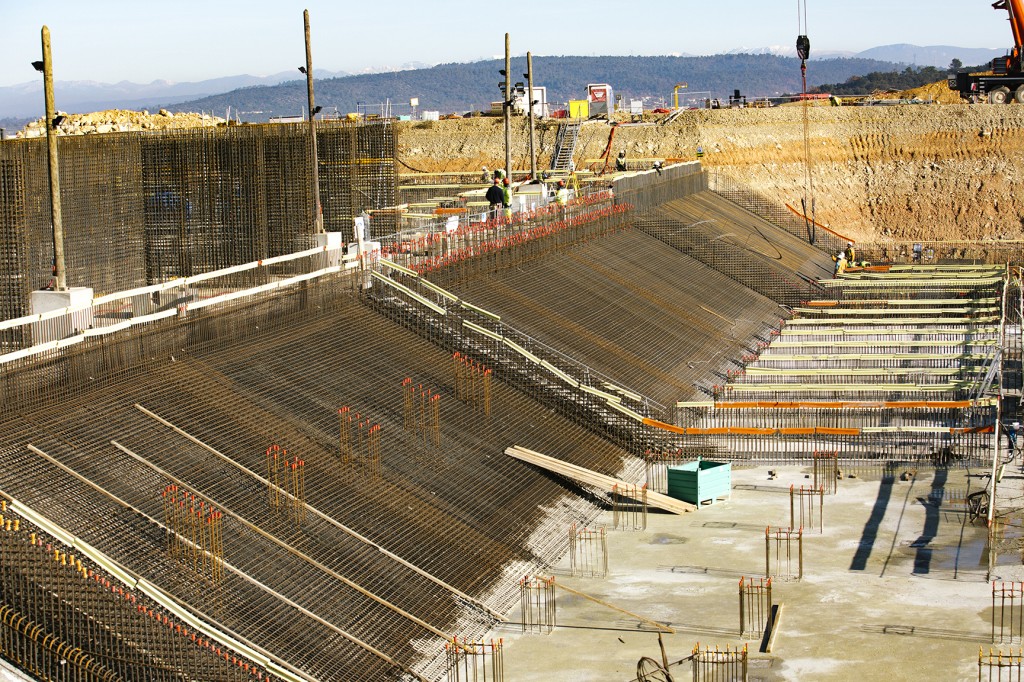
From machine to hot basin
2016-12-02 - The hot water basin is a C-shaped structure in the lowest part of the installation. Water will arrive in the hot basin during the plasma pulses, and then be released to the cooling tower and cold basin during dwells. © Les Nouveaux Médias/SNC ENGAGE
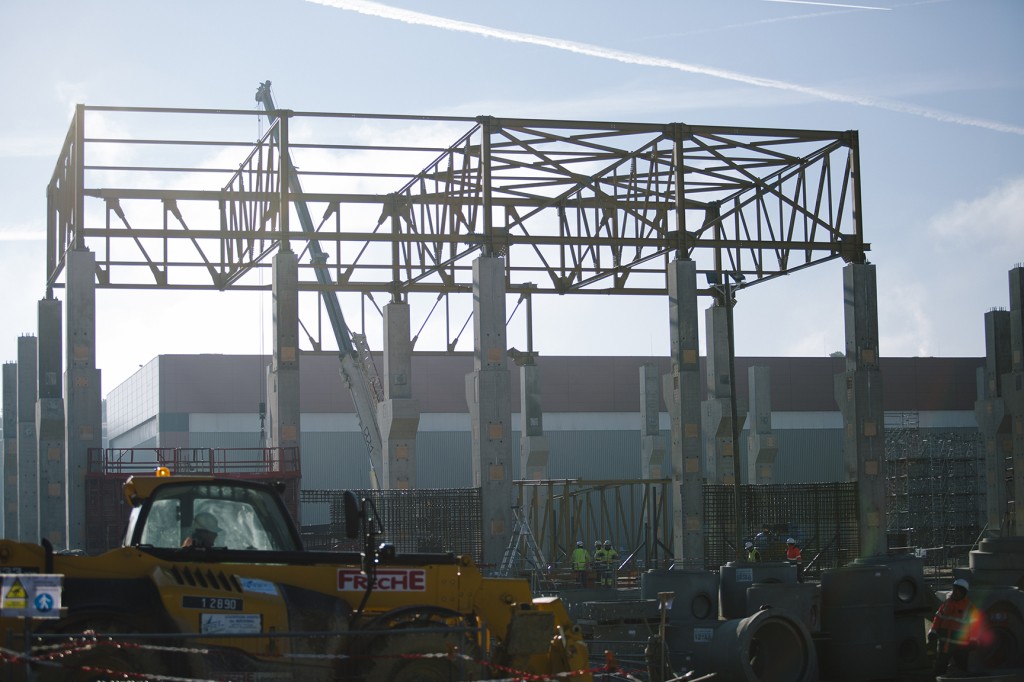
Building delivered in 2017
2016-12-02 - Workers have begun installing the roof structure for the ITER cryoplant. © Les Nouveaux Médias/SNC ENGAGE
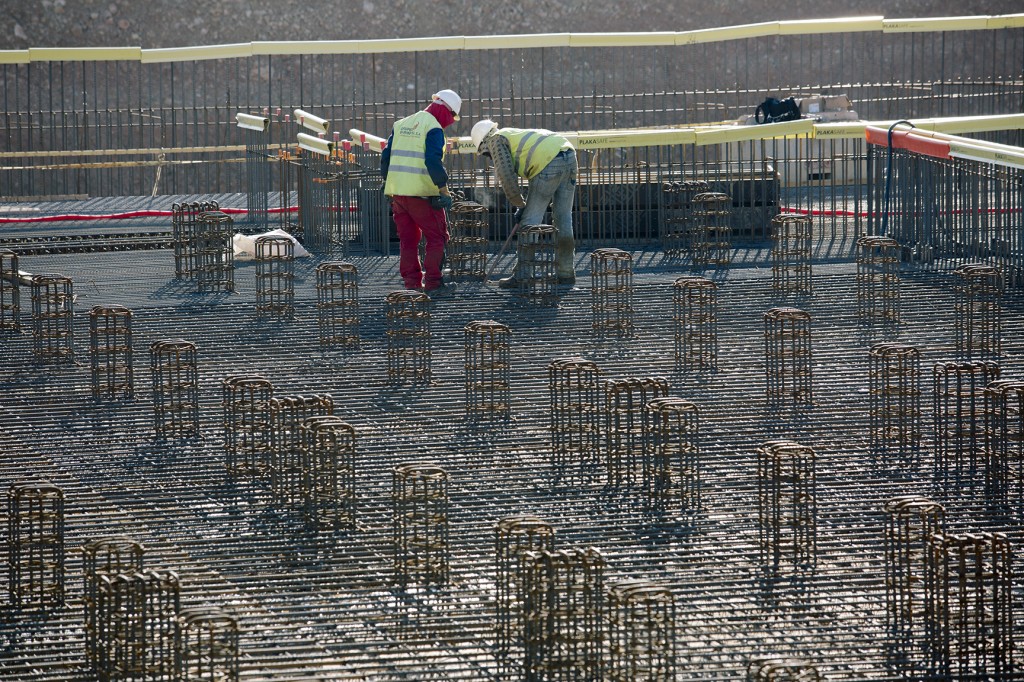
Precision work
2016-12-02 - Rebar is set into place for the numerous concrete columns to be poured on the site of the cold basin. © Les Nouveaux Médias/SNC ENGAGE
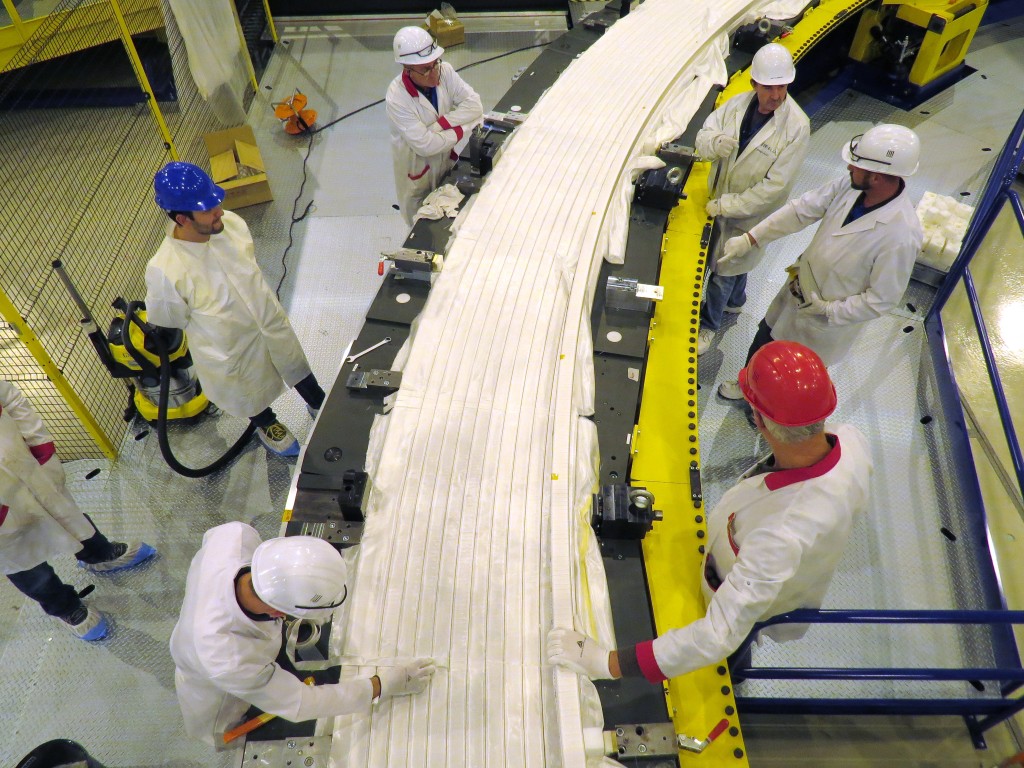
Production in stages
2016-11-24 - Following the winding stage, technicians verify the glass-fibre tape that is used to electrically insulate the turns of conductor. Photo: F4E
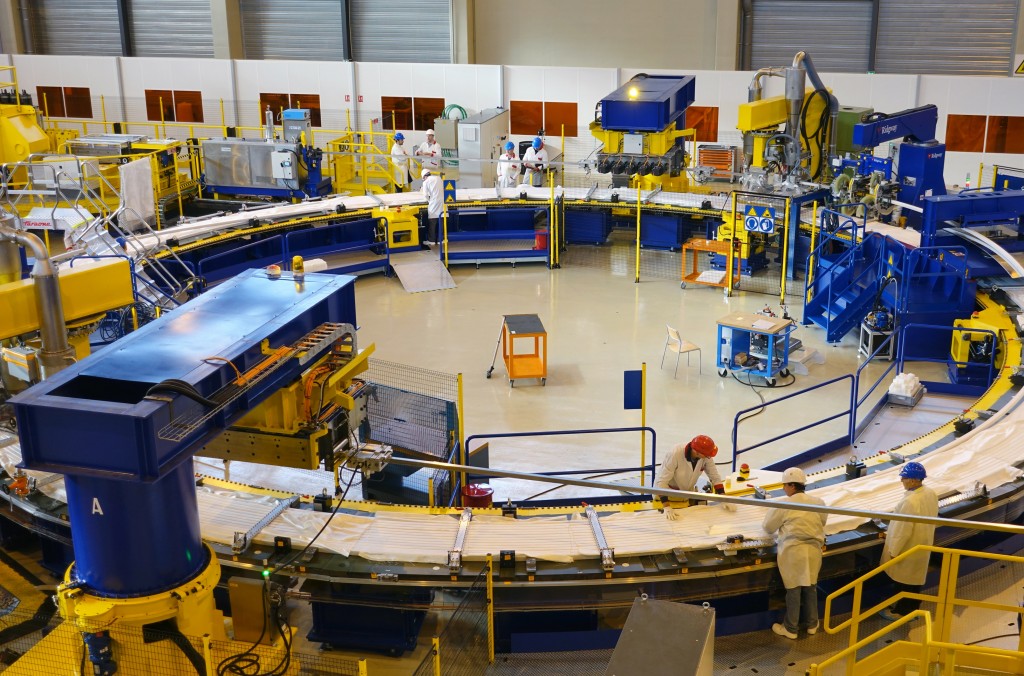
"Dummy" winding takes shape
2016-11-23 - The first complete double pancake layer, made from "dummy" conductor in copper, reflects the dimensions of ITER's fifth poloidal field coil (PF5).
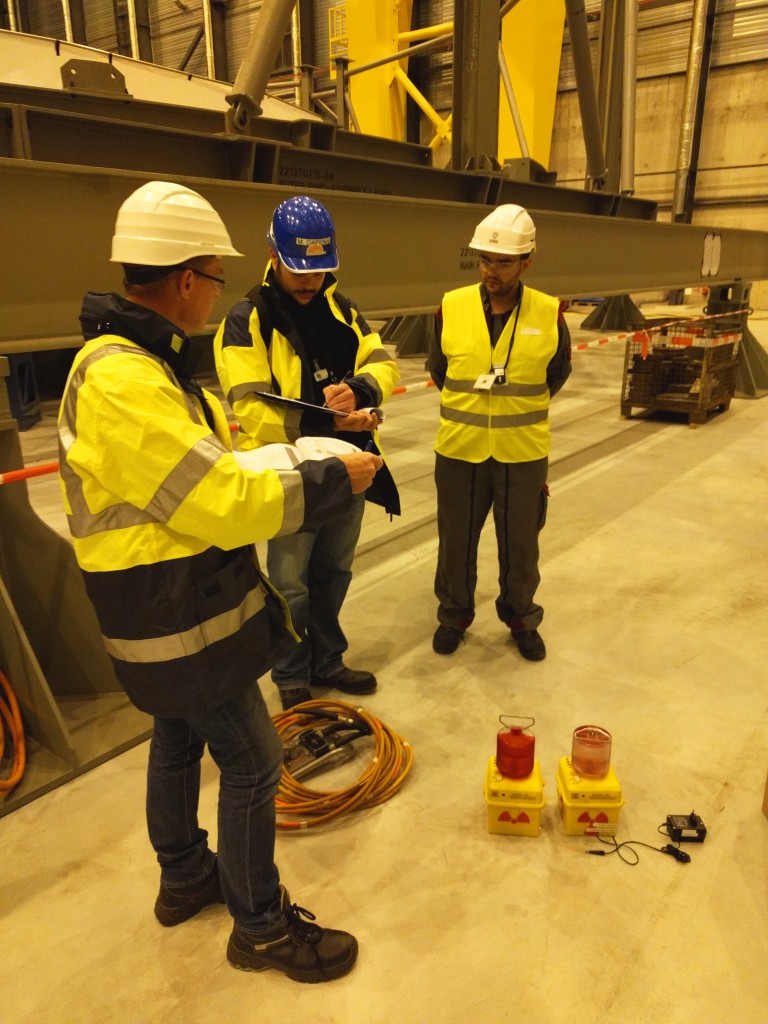
Test equipment verified
2016-11-22 - Some of the radiographic test equipment is verified before work gets underway. Radiographic testing detects the presence of flaws that could challenge the structural integrity of the welds.
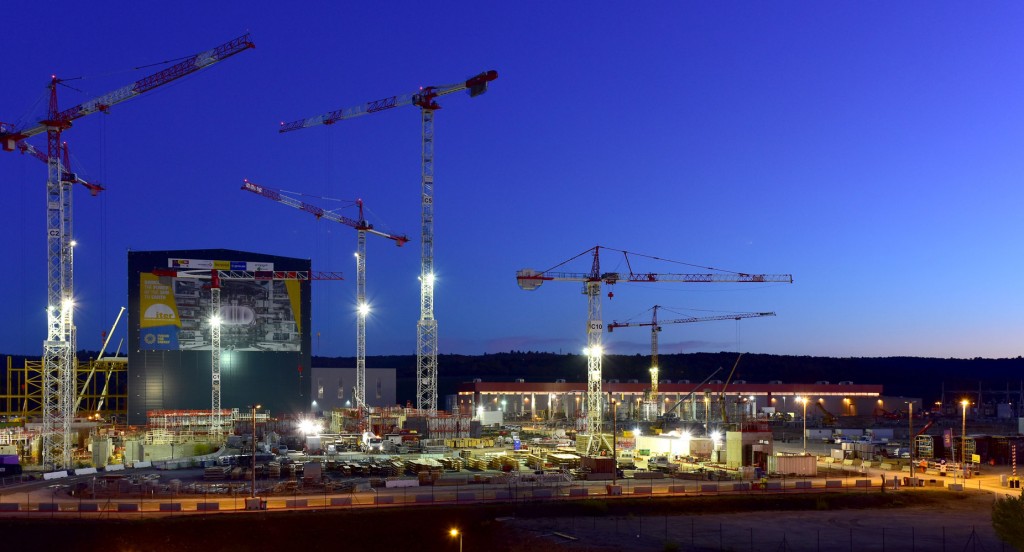
As the lights come on
2016-11-14 - The ITER construction site in November, photographed from the roof of the Headquarters building.
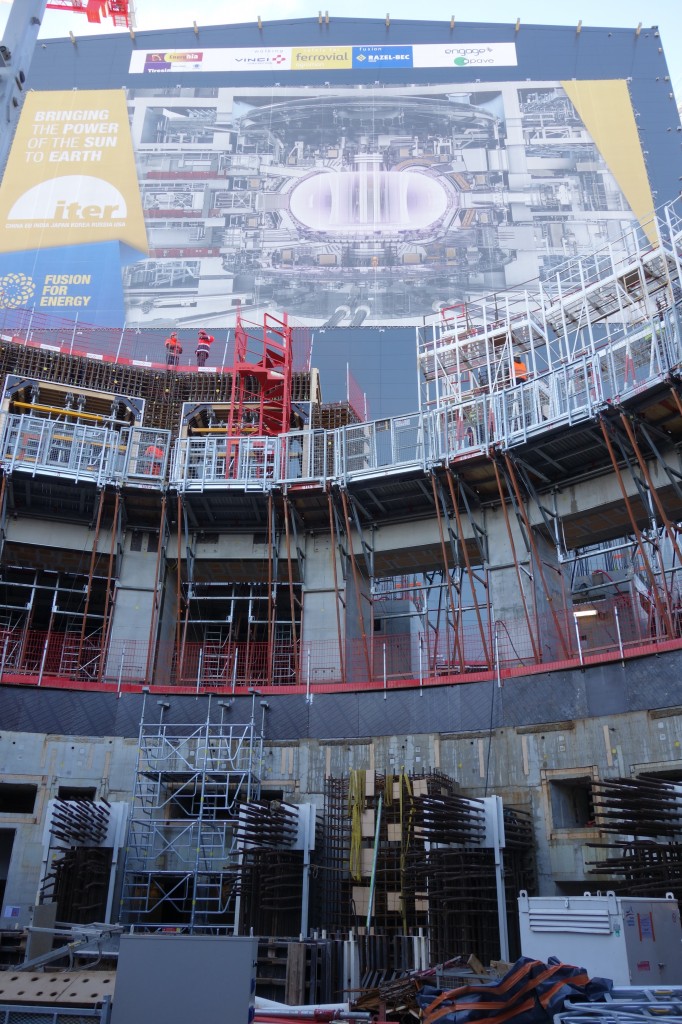
The Tokamak Assembly arena
2016-11-10 - The building is rising all around, but the central well for the Tokamak remains. Tokamak assembly can start here as soon as the building is ready for occupation.
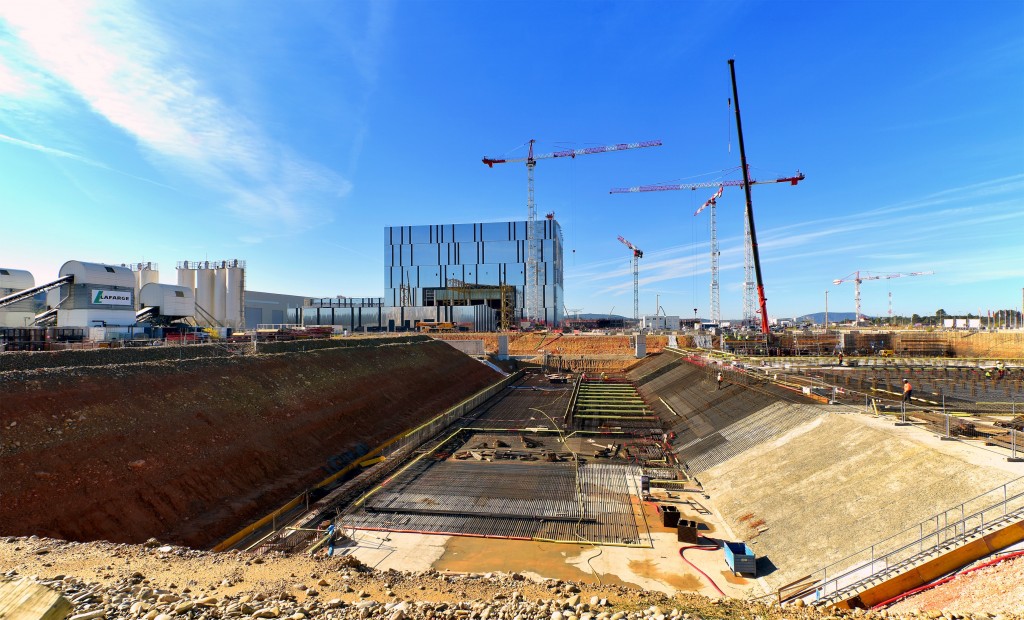
Letting off operational heat
2016-11-10 - This 6,000 m² area on the northeast side of the construction platform will accommodate two basins with a total volume of 20,000 m³ as well as an induced-draft cooling tower made of 10 independent cells.
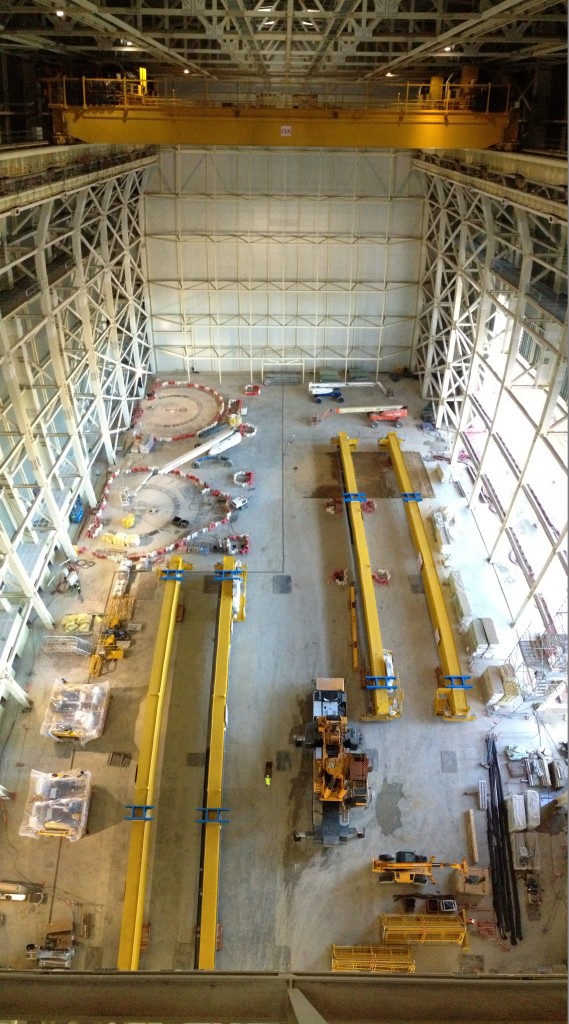
To be installed
2016-11-10 - The girders for the 50-tonne crane will be installed just below the principal crane assembly seen at the top of the image. Photo: ENGAGE

Four new crane girders arrive
2016-11-10 - In addition to two overhead cranes with a lift capacity of 750-tonnes each, the Assembly Hall will be equipped with a set of 50-tonne cranes. In November, four girders for this smaller set were delivered to the shop floor.
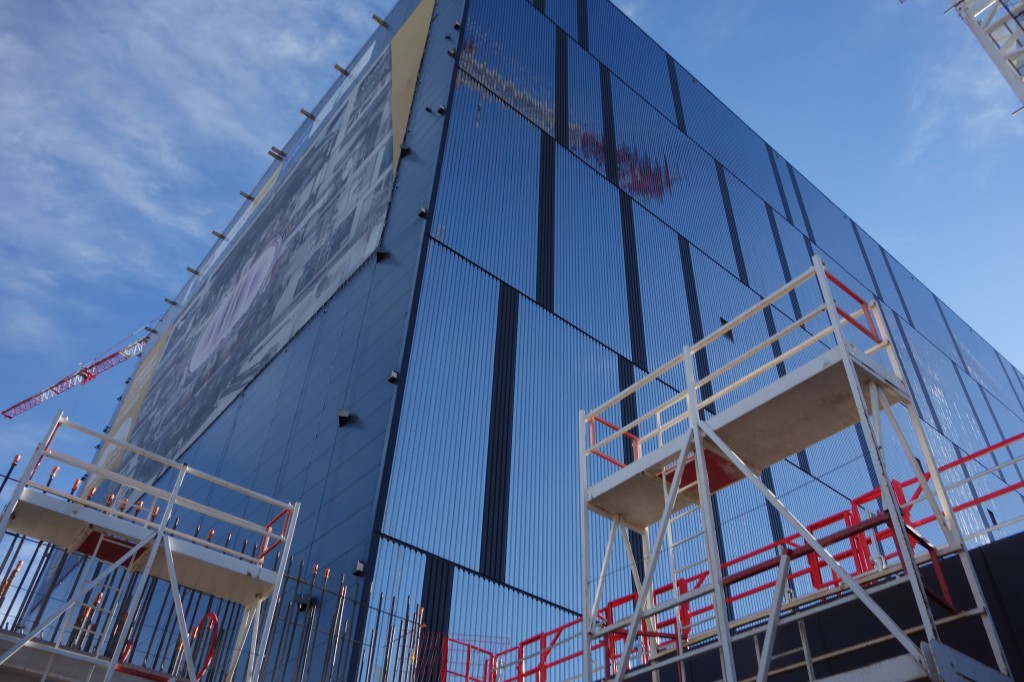
Could cause crick in the neck
2016-11-10 - Looking up towards the top of the 60-metre-tall Assembly Building, from the Tokamak Complex worksite.
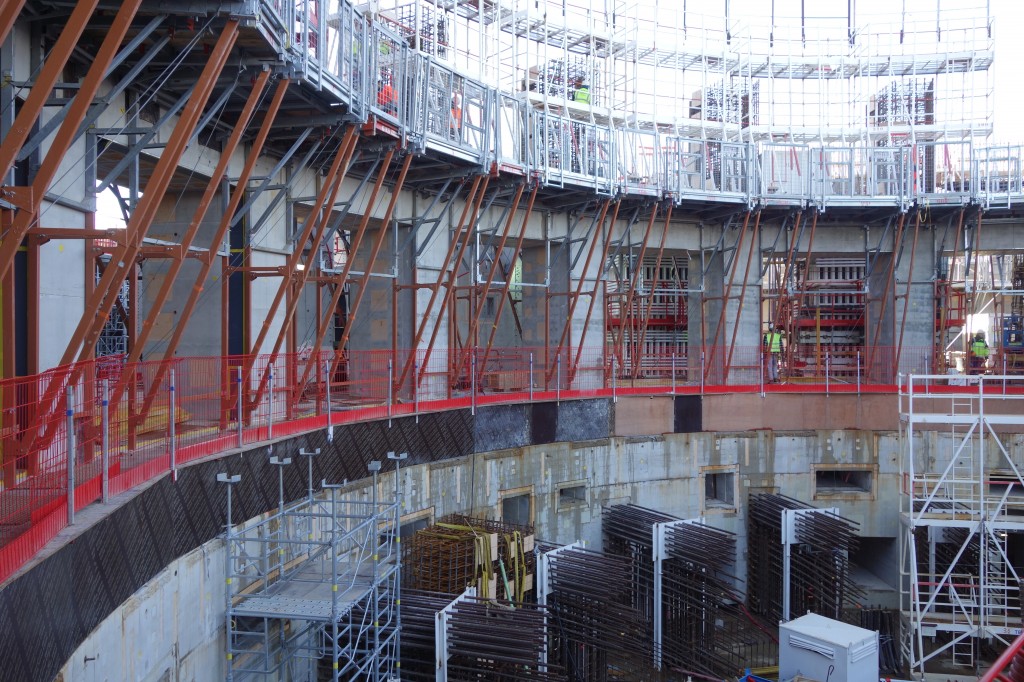
Regular access
2016-11-10 - The B1 level (first basement level) of the concrete bioshield is pierced by regular openings for the access of plant systems to the cryostat and tokamak.
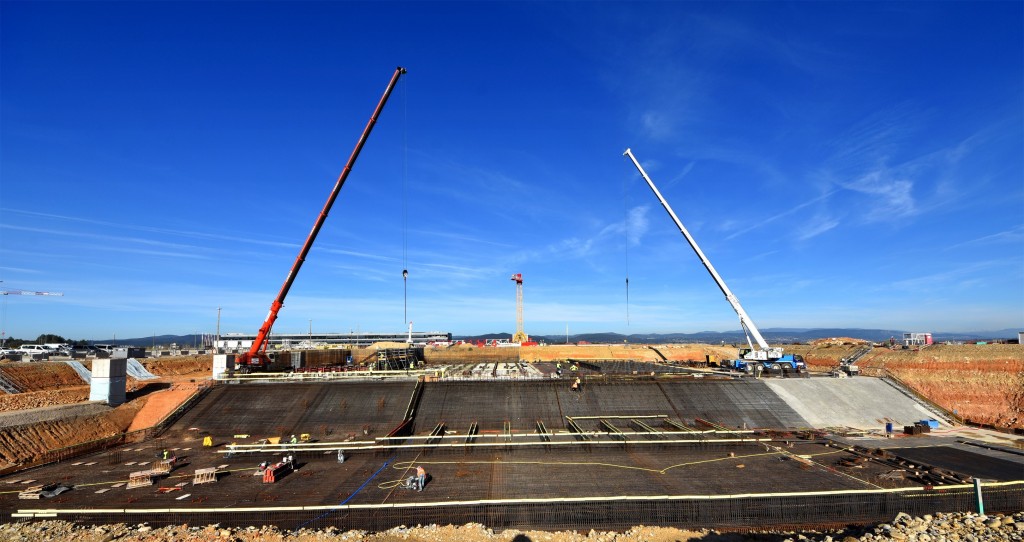
Team work
2016-11-10 - The design and fabrication of the heat rejection system is part of India's procurement contributions to the ITER Project. Europe is excavating the site and creating the infrastructure; the equipment will be installed by the ITER Organization.
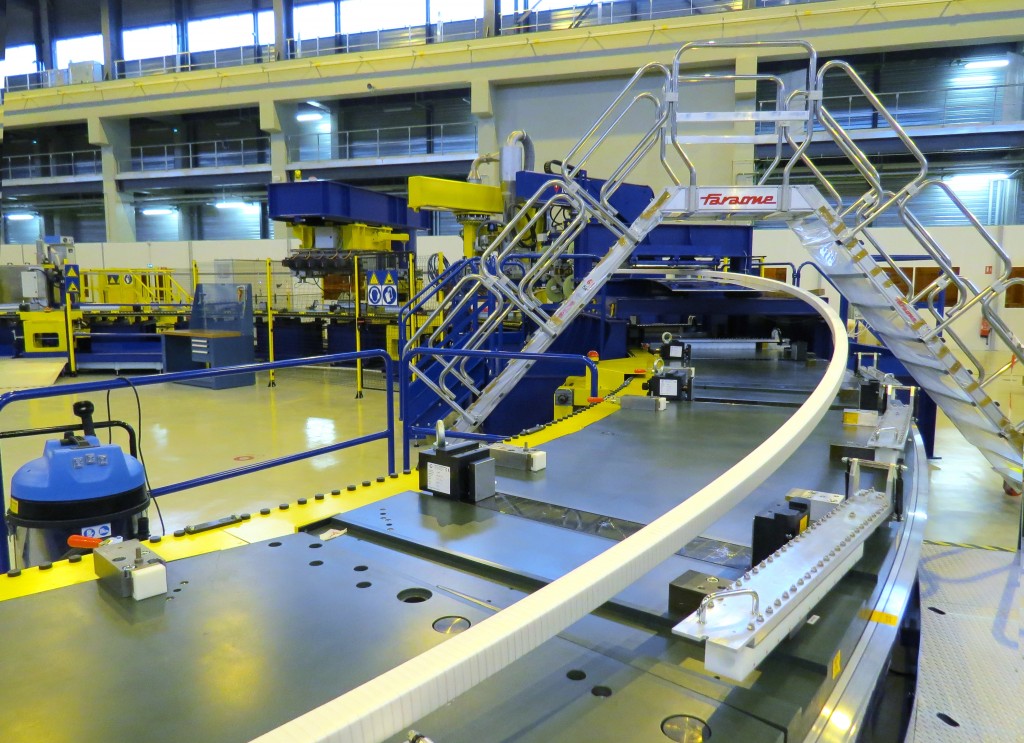
Precision tools
2016-11-09 - Rotating tape heads enter into action as the conductor joins the tooling table to be "turned" into the precise dimensions required for each coil. Photo: F4E
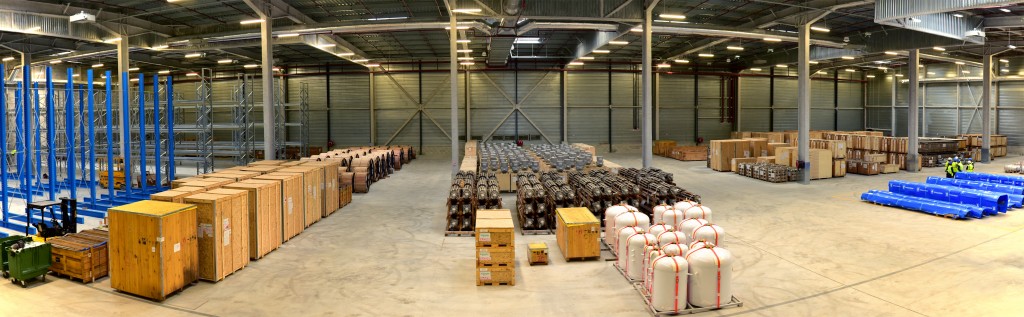
Waiting for assembly to begin
2016-11-08 - Inside of the largest on-site storage facility, components shipped by the ITER Members are tagged and stored.

A welding robot
2016-11-07 - Eyes riveted to their control screen, welders from the German firm MAN Diesel & Turbo, contractor to Larsen & Toubro, closely monitor the quality of the welds as a welding robot progresses along the gap between two pedestal plates. The gap is approximately 20 millimetres wide and 200 millimetres deep and requires dozens of "passes" to be filled.

Helium leak testing
2016-11-07 - Specialists in leak detection test the first welds of the cryostat base (tier 1). Metre by metre, each weld will be verified.
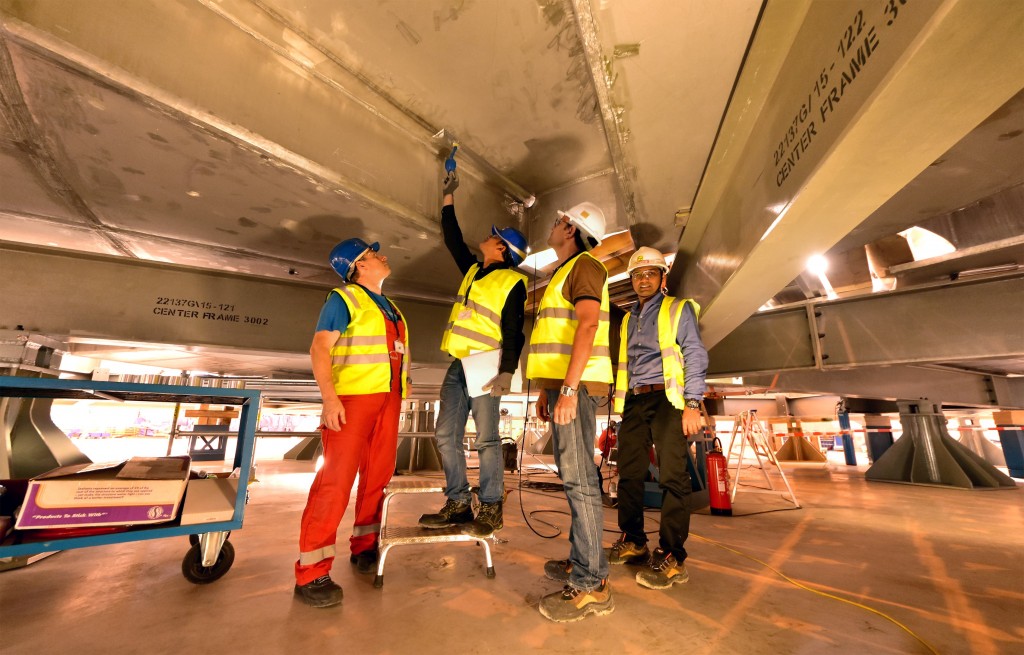
Checking for defects
2016-11-07 - In helium leak testing, helium injected into the leak tight box below one metre of weld will be detectable on the other side by mass spectrometer—if a crack exists.
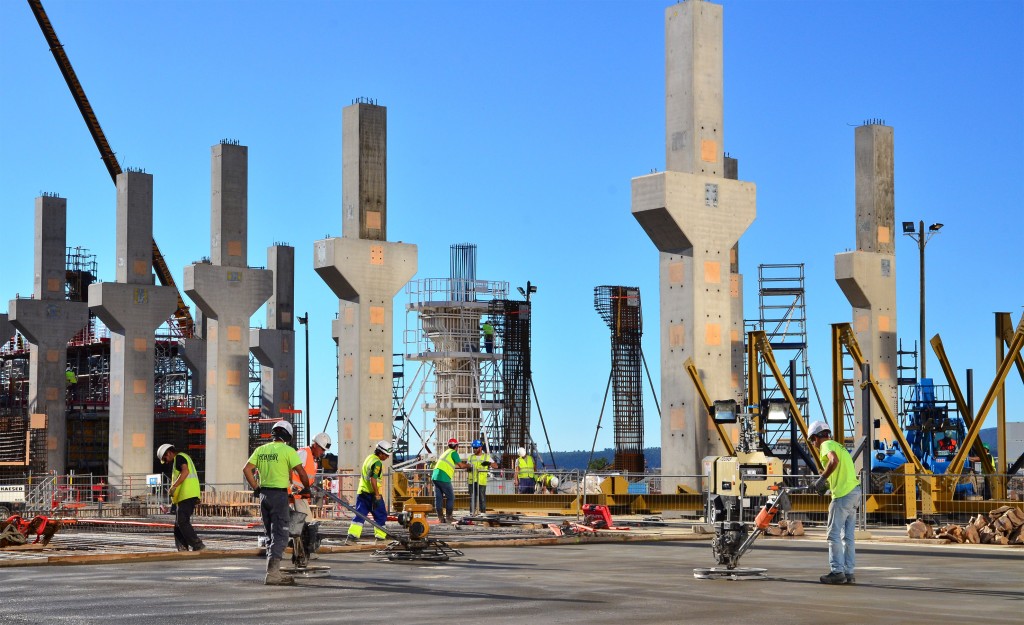
End-of-day light
2016-10-27 - End-of-day light on the cryoplant worksite, where teams are working overtime to ready at least part of the facility for component installation activities to begin in the second quarter of 2017.
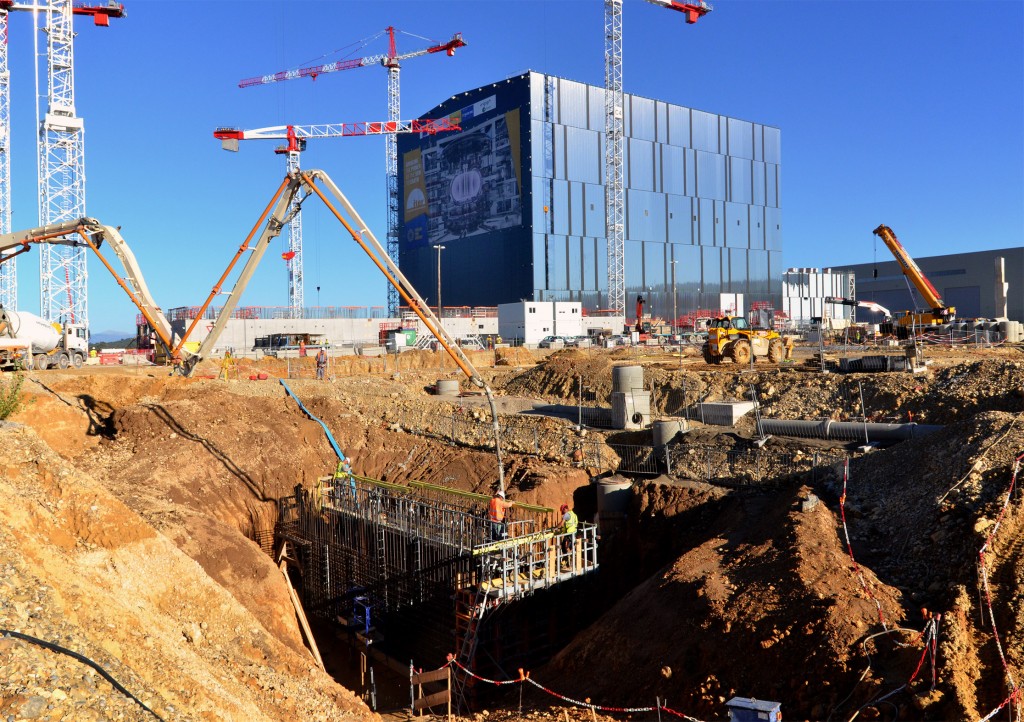
Planning for power conversion
2016-10-27 - On the worksite of the Magnet Power Conversion buildings, digging is underway for the electrical galleries.
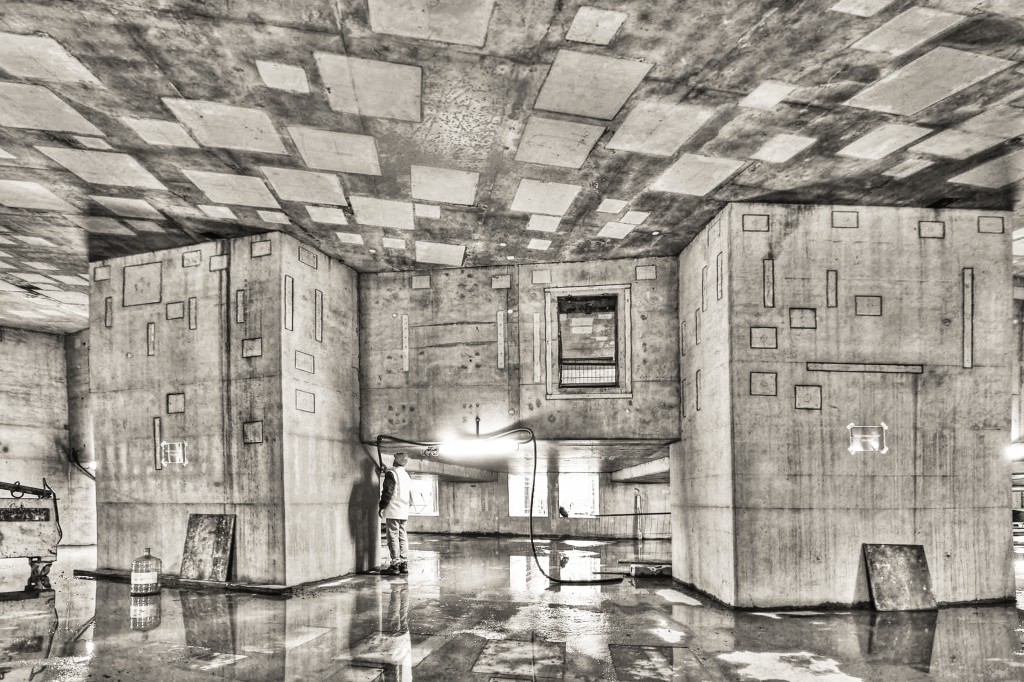
In the Tokamak's subterranean world
2016-10-25 - A cathedral-like space, massive columns, a "sky" speckled with "stars" ... here is the fascinating atmosphere of the basement of the Tokamak Complex, captured by ITER's photographer and interpreted by Christian Lünig (Christian Lünig/VG Bild und Kunst).

Down under
2016-10-24 - In the belly of the Tokamak Building, between the B2 and B1 levels. During the lead-up to Tokamak operation, the space will be completed filled with pipes, cables, feeders and busbars, all secured to the embedded plates visible in the floors, walls and ceilings.

9,000 km later
2016-10-21 - Loaded at the port of Hazira, on the west coast of India, the last cryostat segments travelled 9,000 km to reach ITER.

All base pieces have reached the Cryostat Workshop
2016-10-21 - The last segments of the cryostat base—three 120-tonne components for tier-2—were delivered in October.
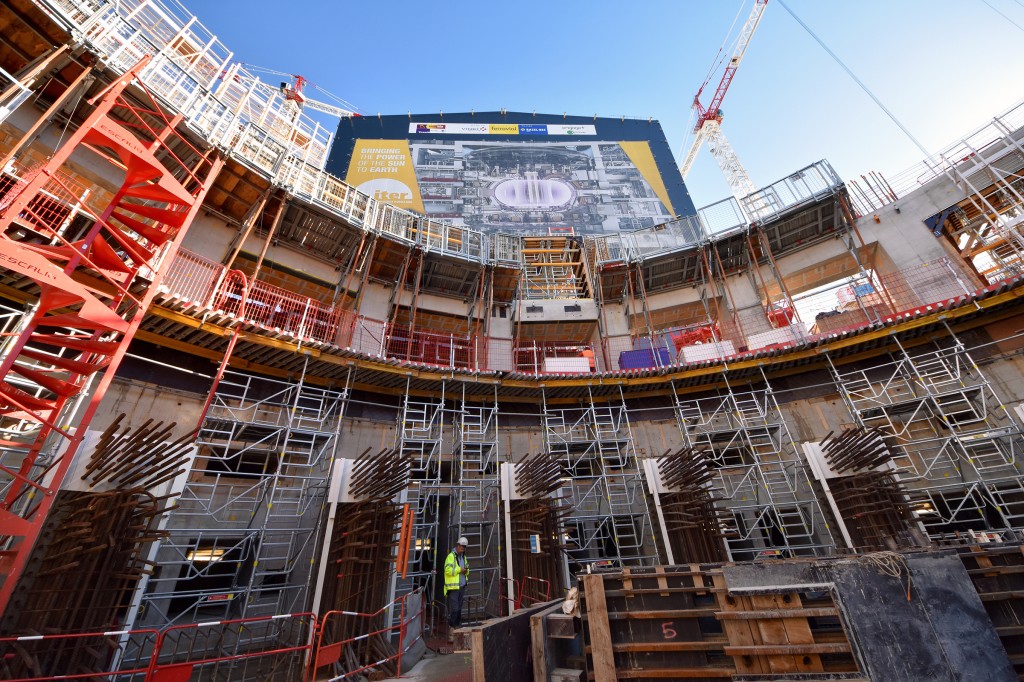
In the "pit"
2016-10-19 - As the Tokamak Building rises, the Tokamak "pit" in the centre becomes more distinct. Here, over one million components will be assembled into the ITER machine.
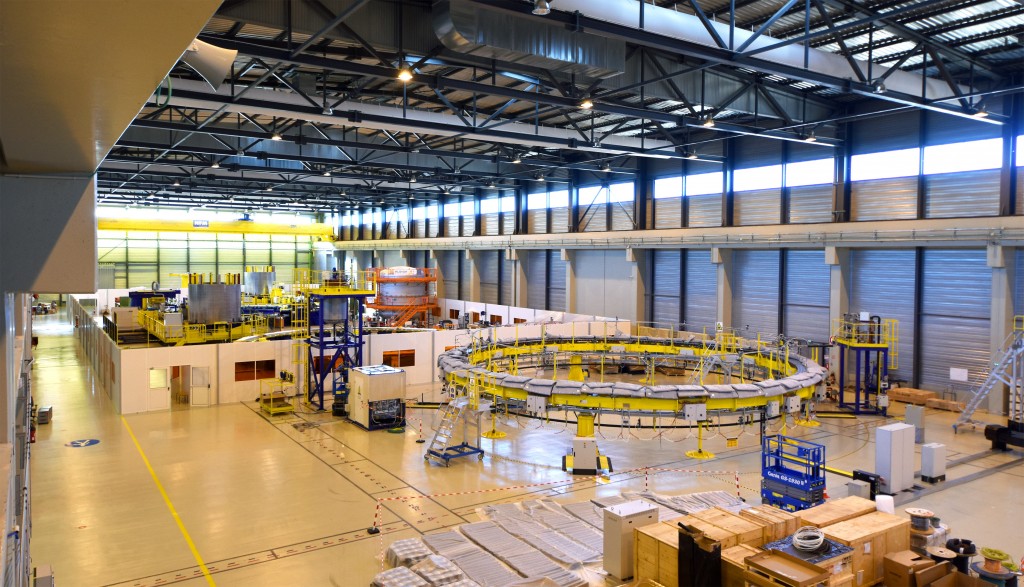
During a visit
2016-10-19 - From a visitor gallery in the middle of the 257-metre-long building, we look south toward the impregnation and winding stations.

Cryoplant Building under construction
2016-10-08 - Cold components are arriving now for the ITER cryoplant. The 5,400 m² building that will house them is under construction on the southeast portion of the platform.
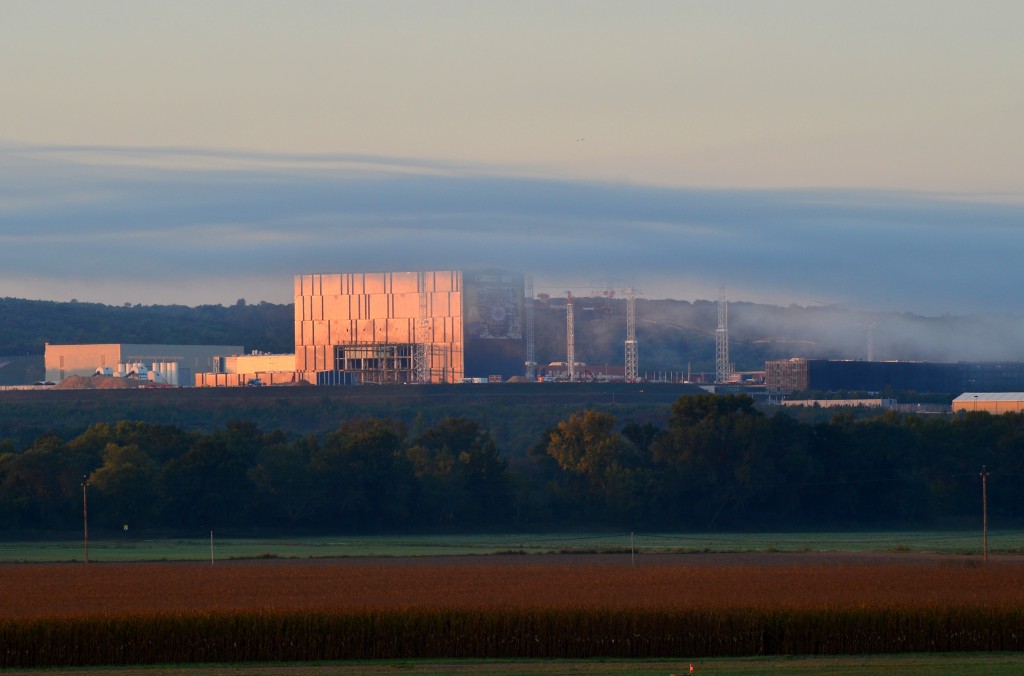
ITER from afar
2016-10-08 - The Assembly Hall, with its giant poster of the ITER machine, is the most visible feature of the ITER site from a distance. In 2018, the adjacent Tokamak Building will match it in height.
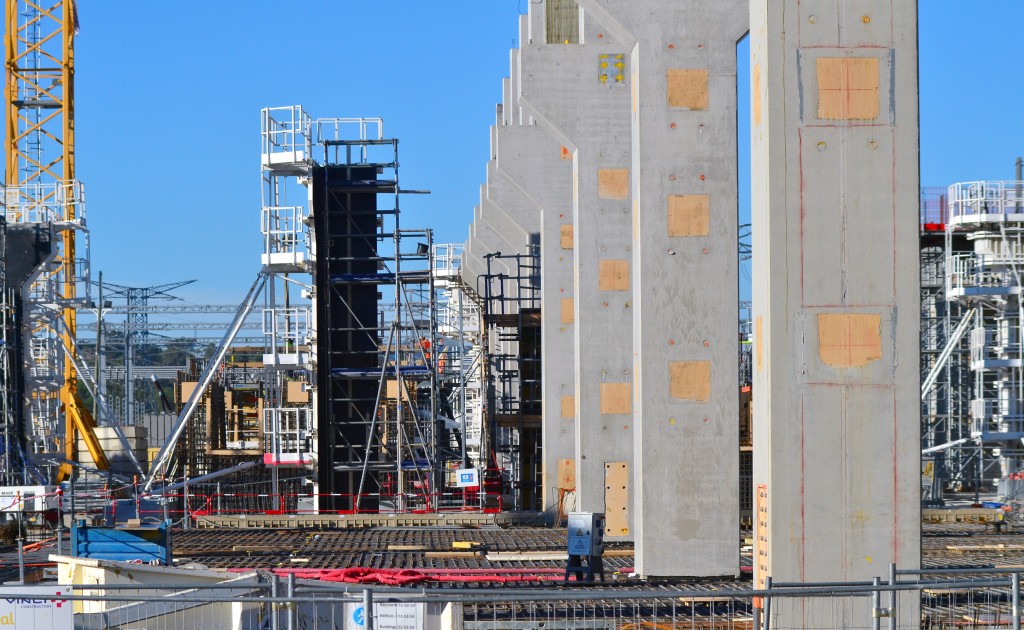
Giant columns for the Cryoplant Building
2016-10-08 - These massive columns will support the structure of the Cryoplant Building. The worker in orange (on the scaffolding) gives an idea of their size.
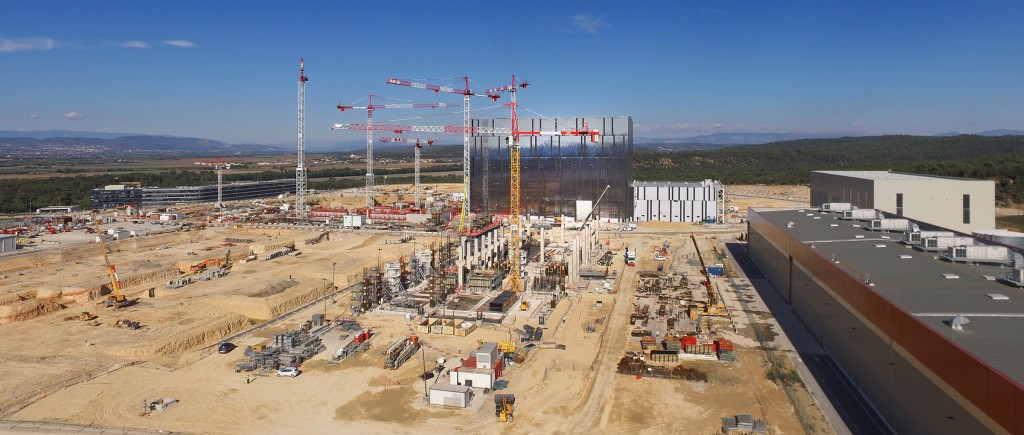
The ITER construction platform
2016-10-07 - The ITER scientific facility is under construction on a 42-hectare platform in Provence, France, at 315 metres above sea level. Photo: ITER Organization/EJF Riche
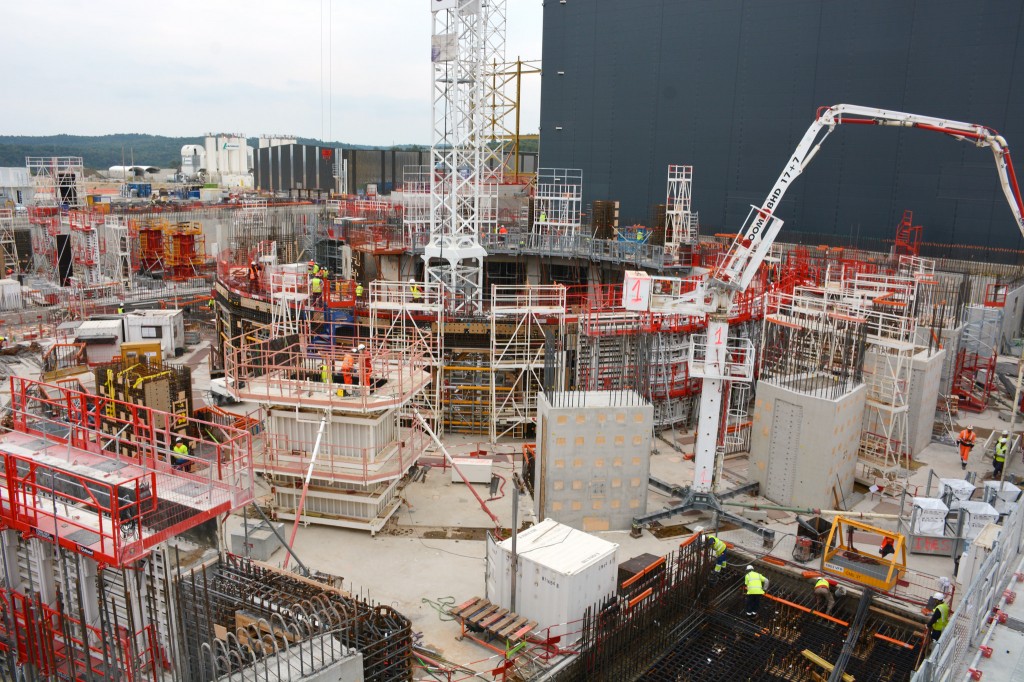
2,000 hands
2016-10-06 - About 200 workers are involved in Tokamak Complex construction at this stage, and another 800 elsewhere on the platform. Photo: F4E
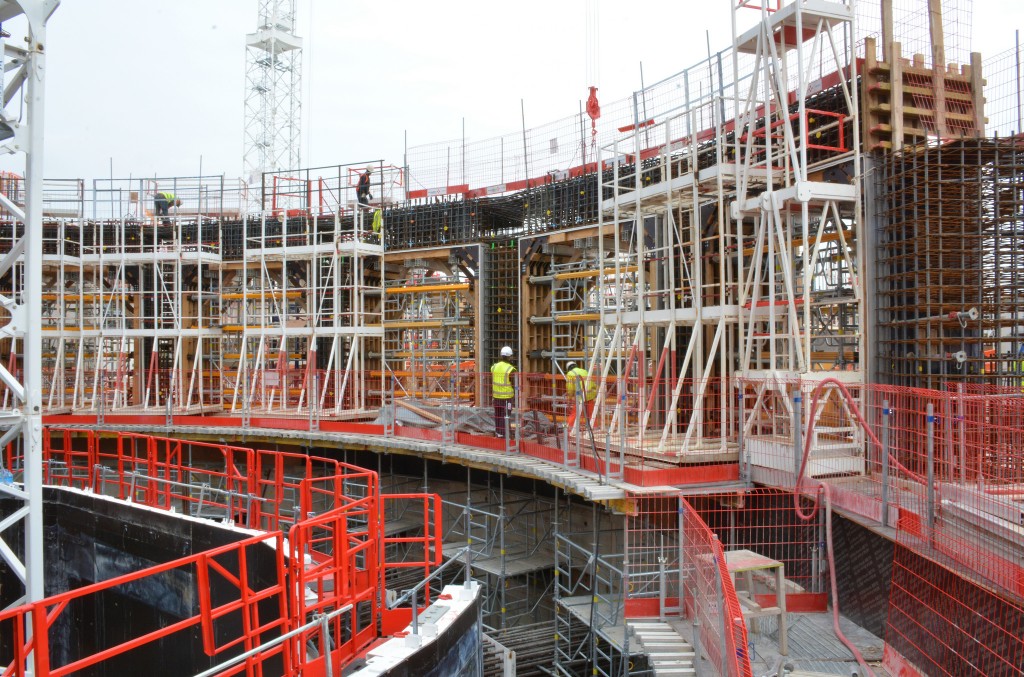
Bioshield reinforcement now visible at platform level
2016-10-06 - Work advances on the L1 level of the ITER bioshield—the thick concrete wall that will completely surround the machine. L1 corresponds to the first "above-ground" level. Photo: F4E

First PPEN transformer installed
2016-10-06 - The first 280-tonne transformer for ITER's pulsed power network (PPEN) has been installed on site. Once equipped with additional components and filled with oil, this Chinese-procured component will weigh 460 tonnes. Two others like it will arrive at ITER in early 2017.
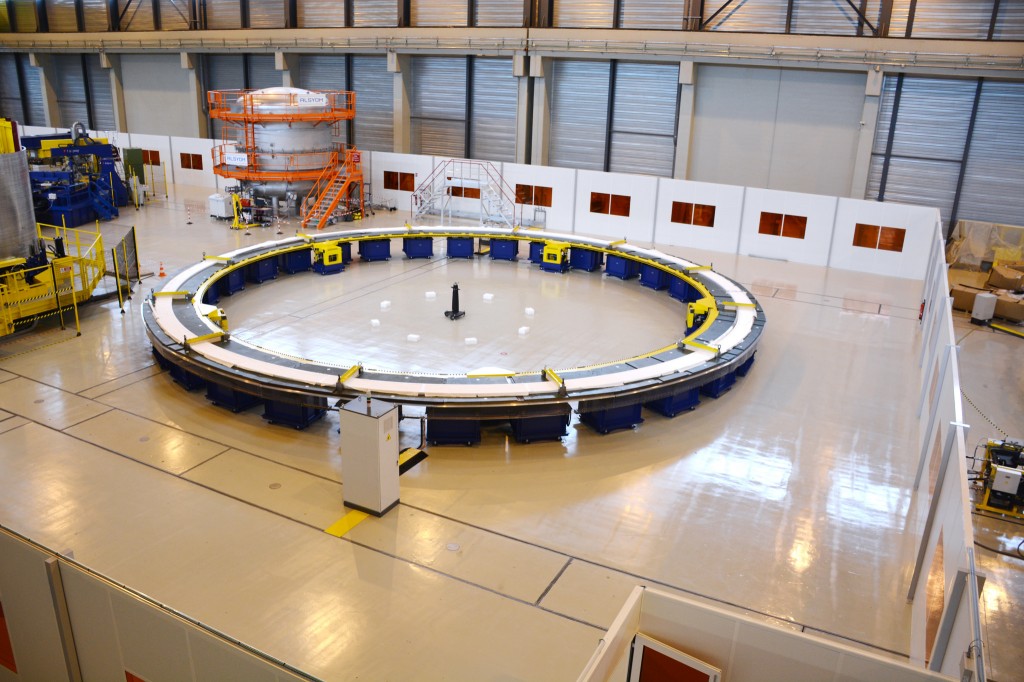
First pre-dummy qualification winding
2016-10-06 - As a qualification activity for tooling and processes, European contractors have produced a pre-dummy winding of eight turns of conductor (pictured, in white). Photo: F4E
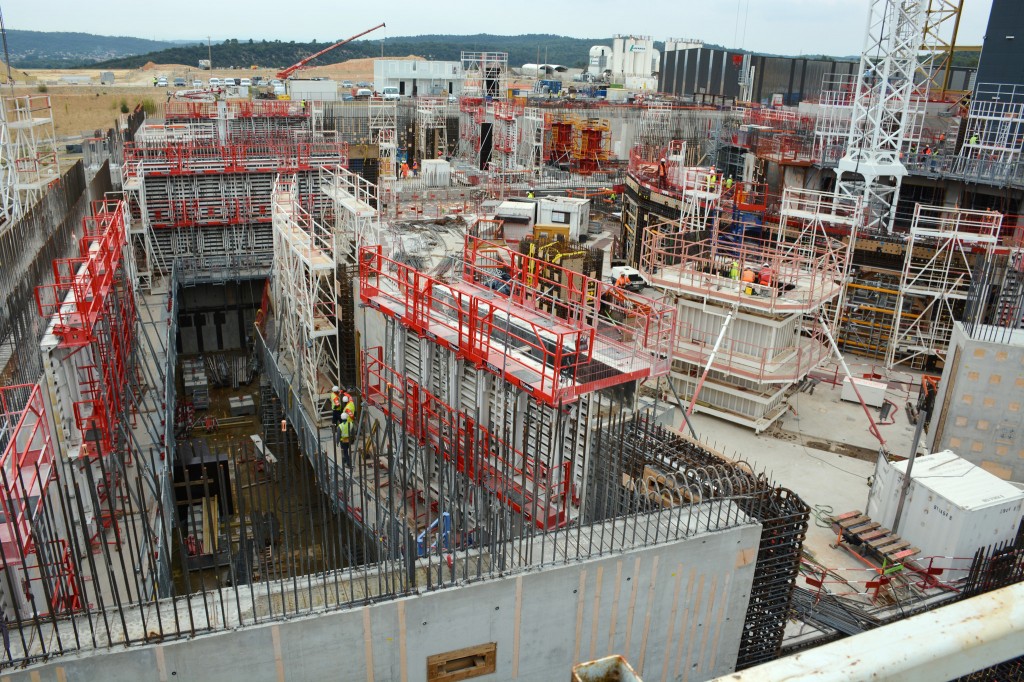
A door for drain tanks
2016-10-06 - This "opening" has been reserved in order to allow the five drain tanks of the tokamak cooling water system to be installed. Photo: F4E

Close up of works
2016-10-06 - In the foreground, the Tokamak Complex is rising to meet the level of the platform. Towering above the workers is the ITER Assembly Hall. Photo: F4E
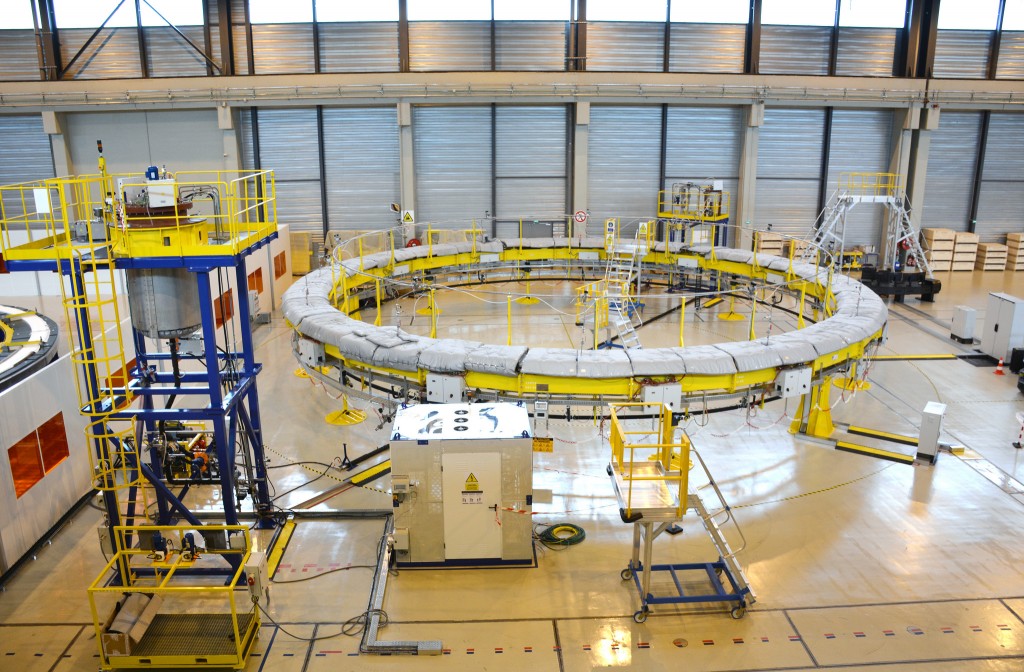
Resin station
2016-10-06 - Completed double pancakes will be transferred by overhead crane to this impregnation station, where the components will be "hardened" with epoxy resin. In the blue stand at left is the resin tank. Photo: F4E
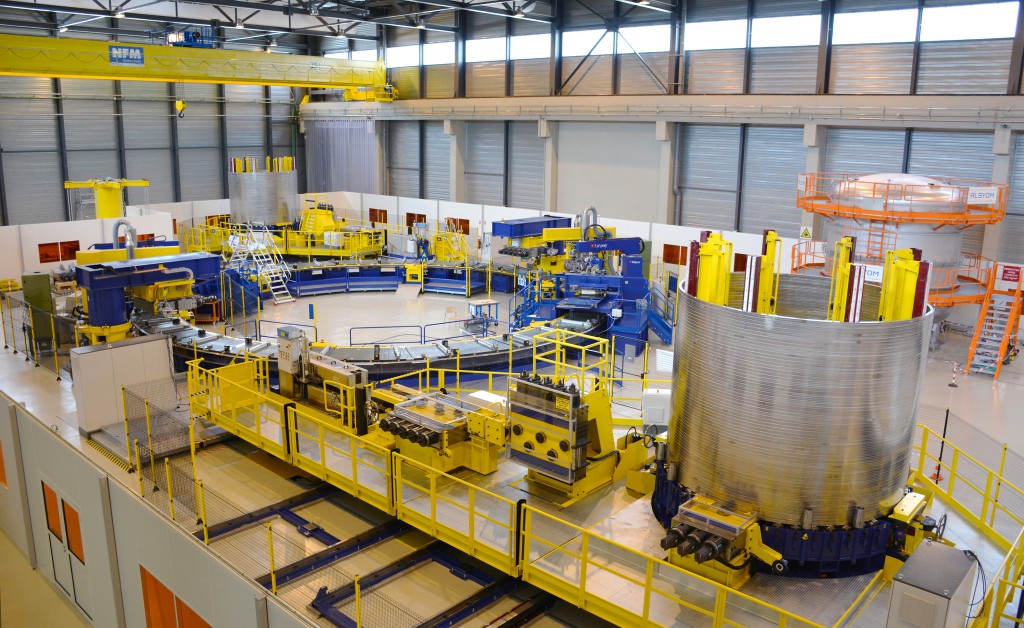
Two hands simultaneously
2016-10-06 - The blue winding station is served by two ("double hand") spools of conductor. Operators will produce 30 double pancakes to constitute the building blocks for the four poloidal field coils produced on site (PF2, PF3, PF4, PF5). Photo: F4E
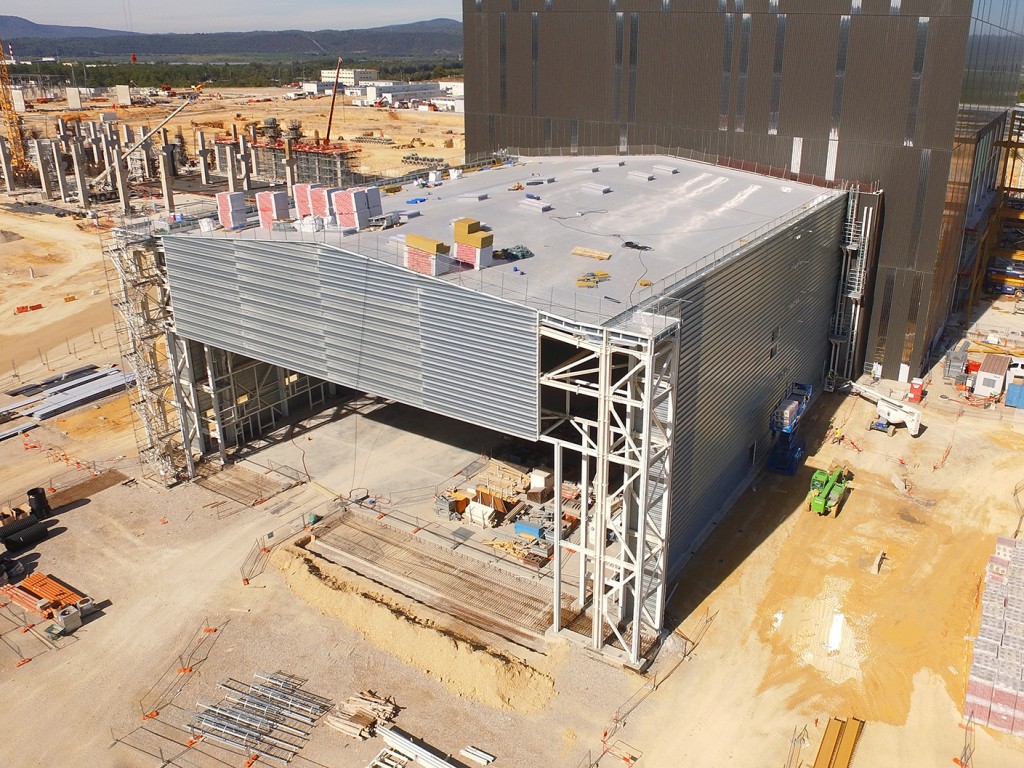
Components enter here
2016-10-05 - On the south side of the Assembly Hall, the Cleaning Facility will be the entry point for components. The building will function as an airlock to minimize the amount of dust from the platform that gets into the clean environment inside. Photo: ITER Organization/EJF Riche
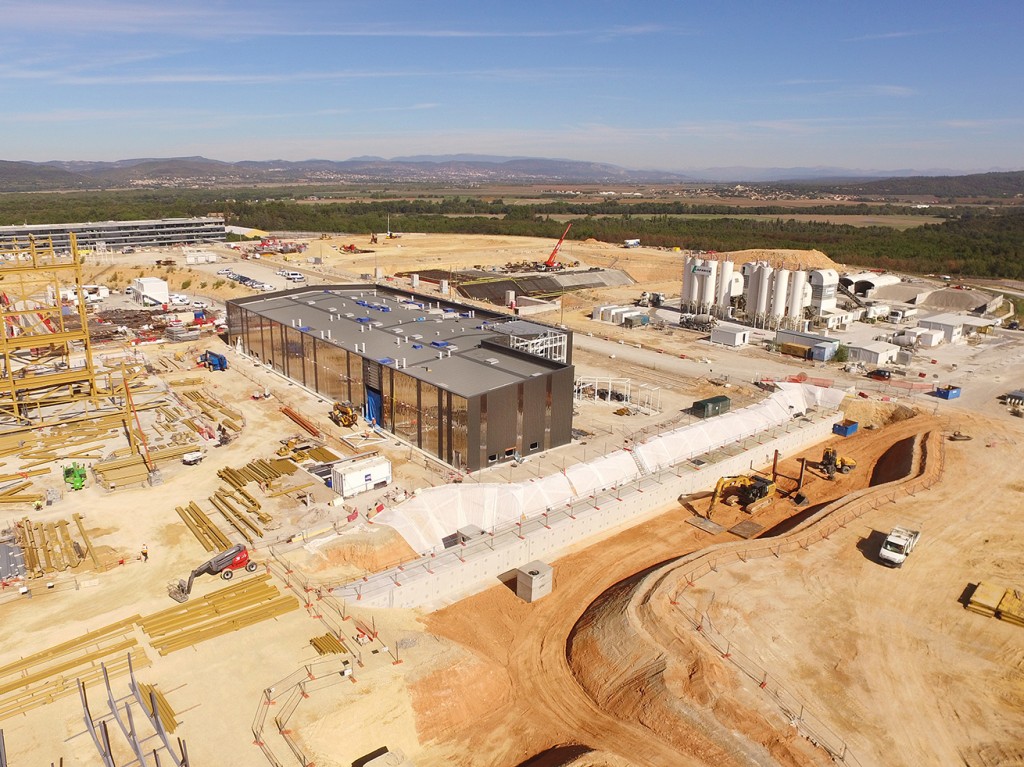
Serving the whole installation
2016-10-05 - The Site Services Building will host a chiller plant for cooling water as well as a demineralized water plant, air compressors and a maintenance and instrumentation workshop. Photo: ITER Organization/EJF Riche
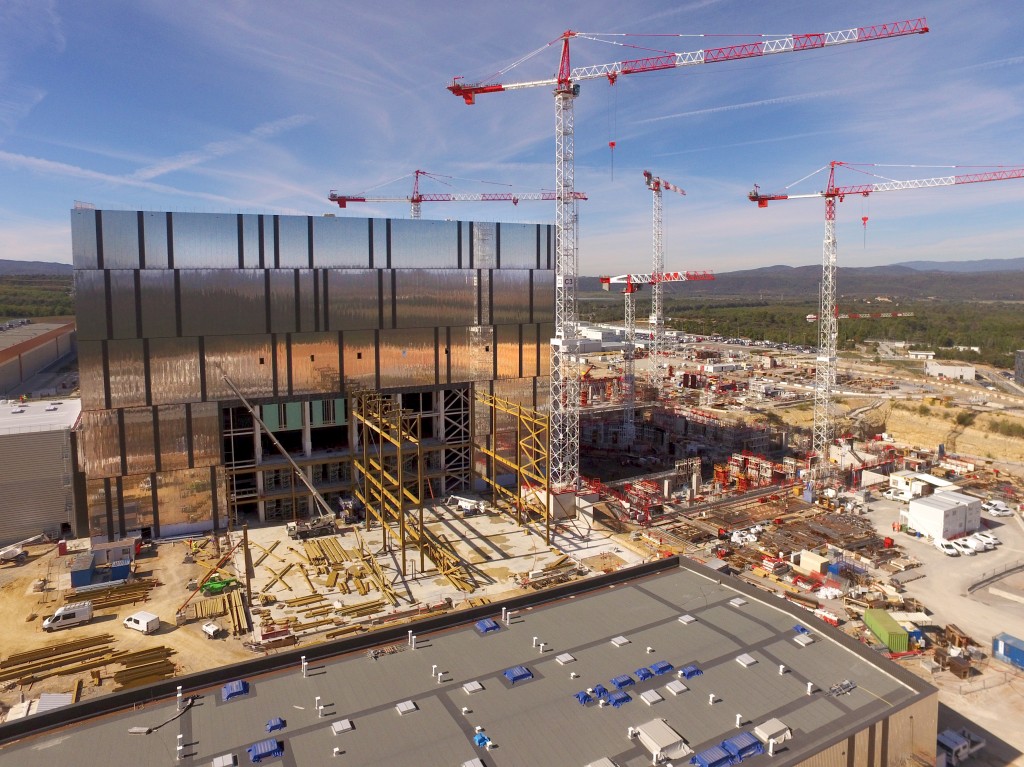
External heating to be housed here
2016-10-05 - The large opening in the reflective surface of the Assembly Hall is reserved for the Radio Frequency Heating Building, under construction now. Photo: ITER Organization/EJF Riche
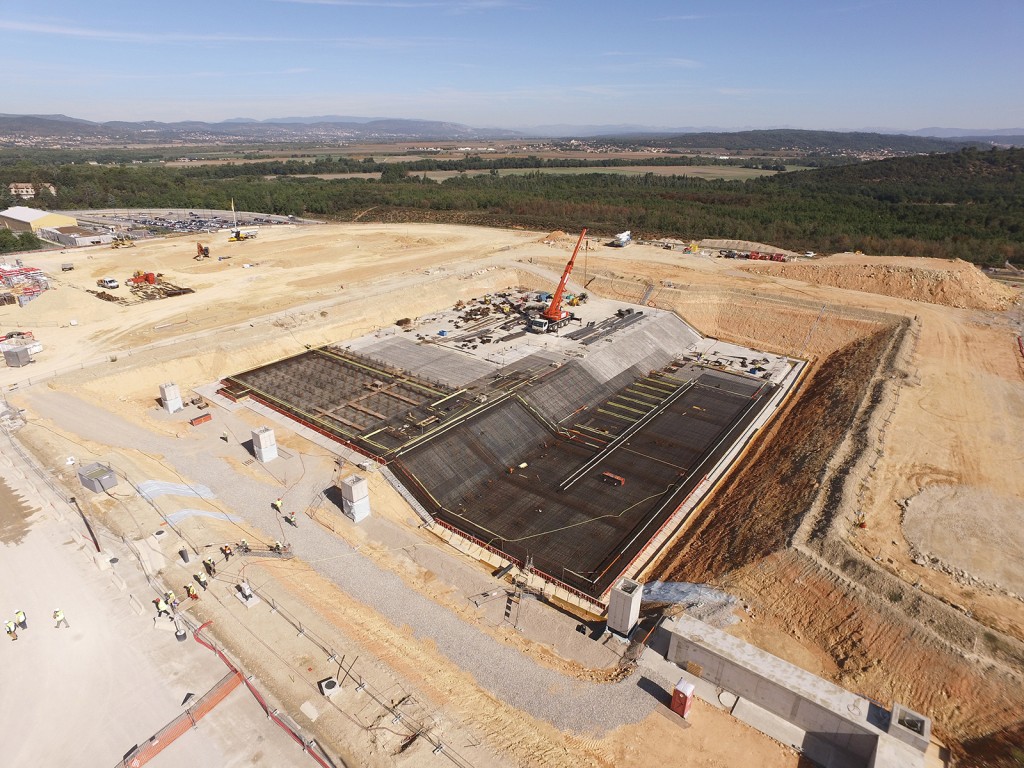
Large basins
2016-10-05 - Up to 20,000 m³ of water will be stored in the hot and cold basins of the heat rejection system. Photo: ITER Organization/EJF Riche
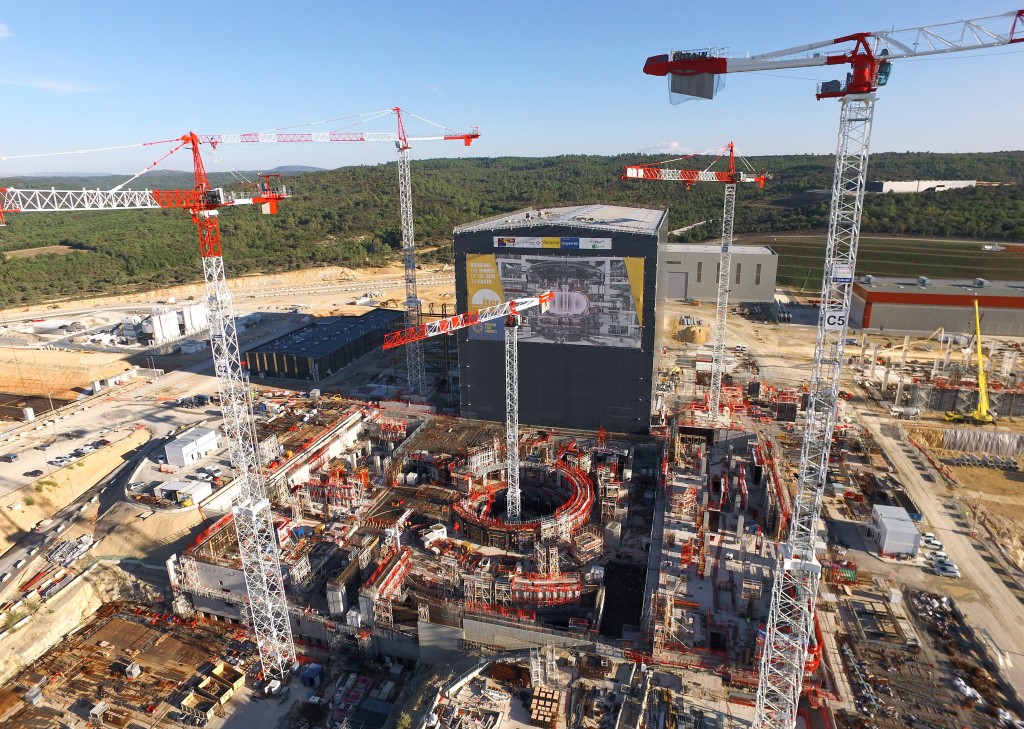
The complexity of the Tokamak Complex
2016-10-04 - Within the concrete "box" of the Tokamak Complex, three buildings are going up on a single foundation: the Tritium Building, the Tokamak Building and the Diagnostics Building. Fully equipped, they will weigh 400,000 tonnes. Photo: ITER Organization/EJF Riche
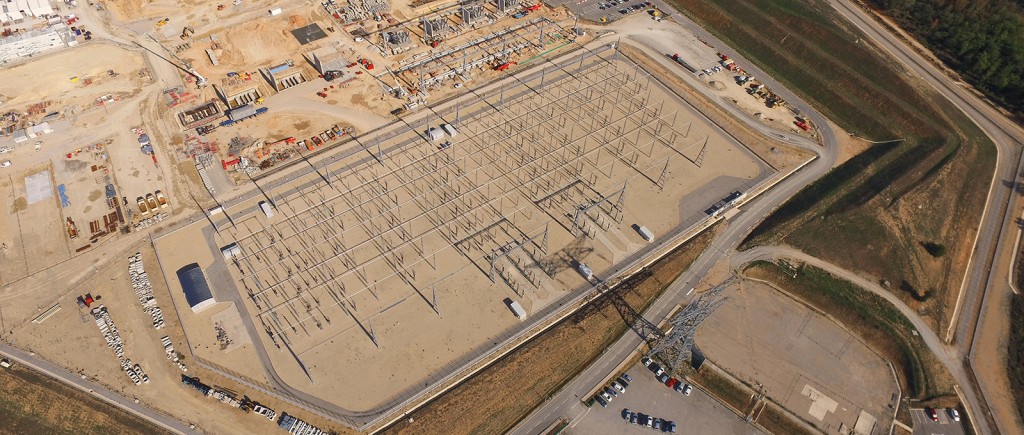
Electrifying
2016-10-04 - The very high voltage electrical substation on the south side of the platform was realized as part of France's commitment to ITER. Photo: ITER Organization/EJF Riche
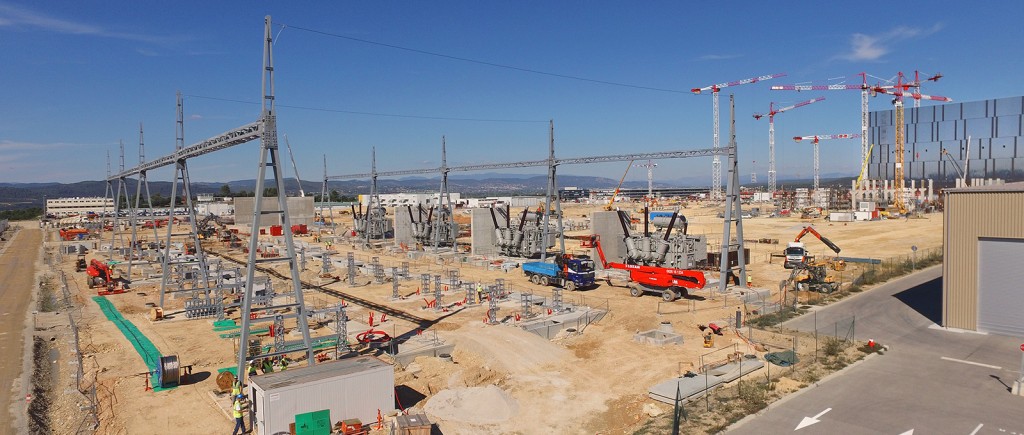
Come on down
2016-10-04 - Located next to the high voltage switchyard, these components will "bring down" the voltage to useable levels. Photo: ITER Organization/EJF Riche

Cryoplant construction: seen from above
2016-10-04 - The building that will house the ITER cryoplant is under construction on the southeast portion of the platform. Its basemat and columns are visible from the air. Photo: ITER Organization/EJF Riche

Transformer town
2016-10-04 - On the south end of the platform, five of seven transformers are in place for ITER's electrical networks (pictured: a US-procured transformer for the steady state electrical network). Photo: ITER Organization/EJF Riche

Nearly level with the platform
2016-10-04 - Work progresses in October on level B1 (the first basement level). The Diagnostics Building is already flush with the platform (right side of the Complex); the central Tokamak Building and the Tritium Building (left) won't be long in following. Photo: ITER Organization/EJF Riche
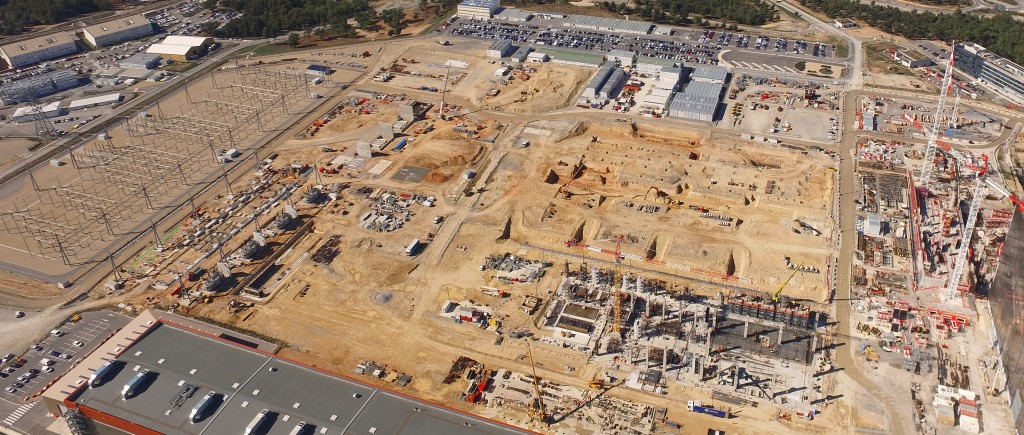
Site work begins for Magnet Power Conversion buildings
2016-10-04 - In this vast area between the electrical switchyard and the Tokamak Pit, digging has started on the site of two Magnet Power Conversion buildings, which will house equipment for converting AC power to DC power for the superconducting magnet system. Photo: ITER Organization/EJF Riche
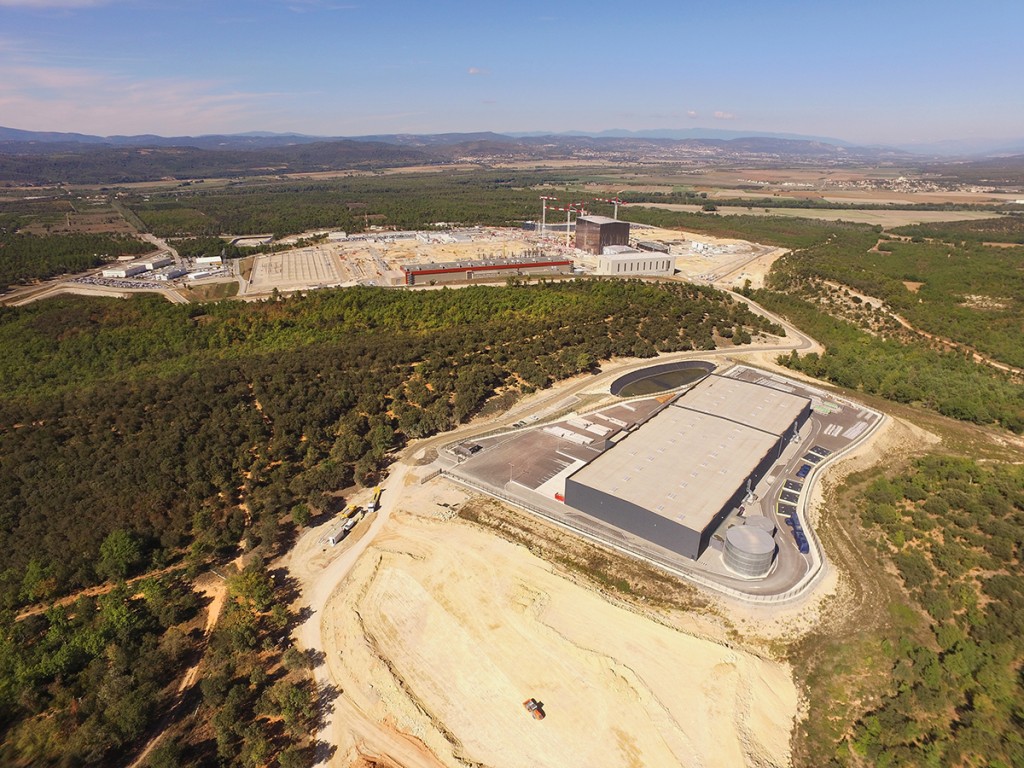
Storage warehouse in service
2016-10-04 - On the hill behind ITER, a large warehouse has been constructed for the storage of components delivered by the ITER Members. Photo: ITER Organization/EJF Riche
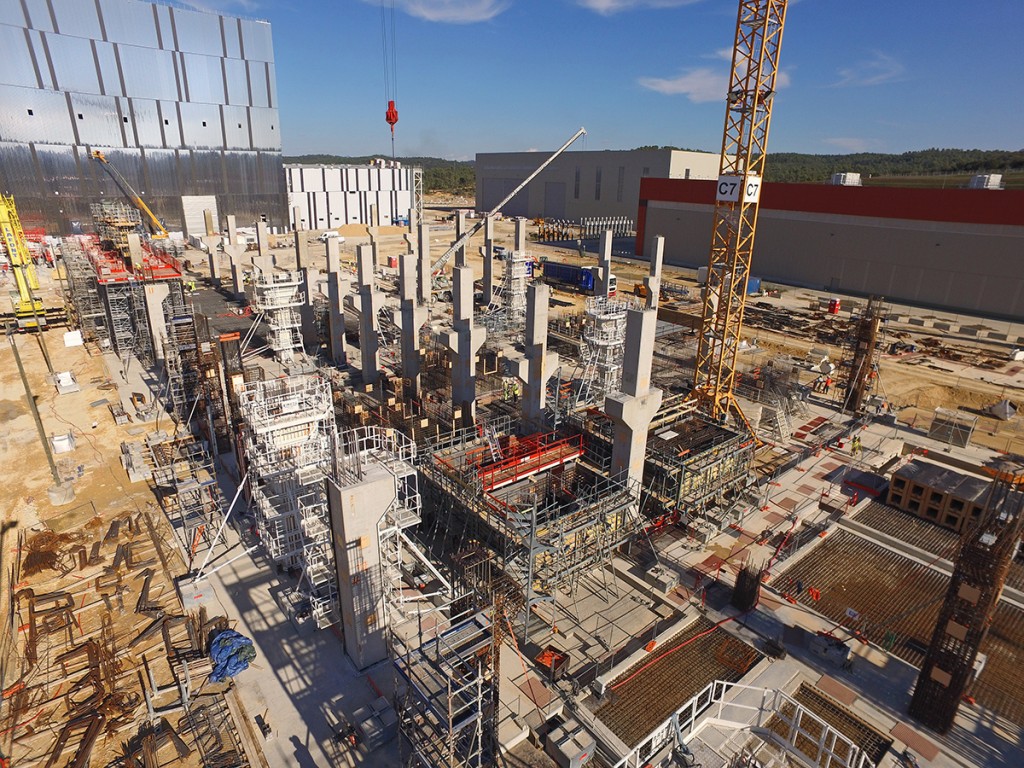
5,400 m² to house cold boxes, compressors and tanks
2016-10-04 - Columns are going up on the site of the ITER cryoplant. The building will be ready to receive components in 2017. Photo: ITER Organization/EJF Riche
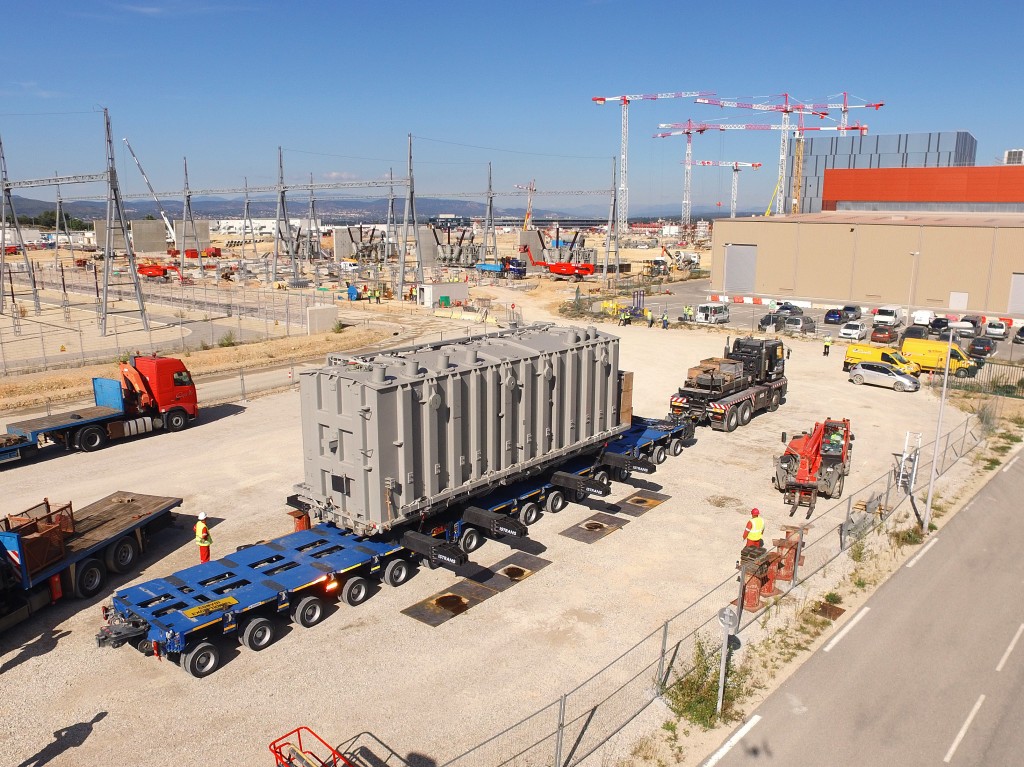
Large transformer moved to permanent home
2016-10-04 - Three large transformers like this one will be part of the network that distributes pulsed power to the installation. The 280-tonne component was installed in its permanent "pit" on site. Photo: ITER Organization/EJF Riche

Reserved for the machine!
2016-10-04 - A perfect circle is preserved as the Tokamak Complex rises all around. This is the machine assembly area, where the first assembly activities will begin in 2018. Photo: ITER Organization/EJF Riche

Site work begins for Magnet Power Conversion buildings
2016-10-04 - In this vast area between the electrical switchyard and the Tokamak Pit, preparatory works have started on the site of two power conversion buildings. Photo: ITER Organization/EJF Riche

High voltage park
2016-09-28 - The very high tension arriving along the 400 kV line will be converted in this area of the platform before being distributed to the ITER systems. ©F4E/LNM
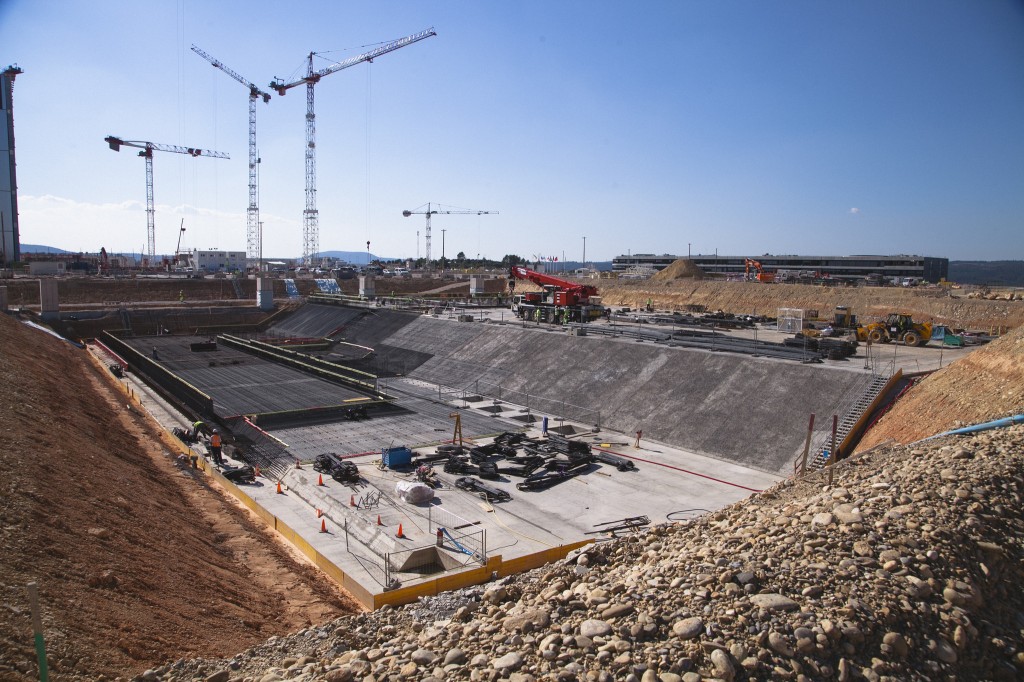
Starting with the foundations
2016-09-28 - A ten-unit cooling tower unit will be built here, on the northern corner of the platform. Connected to the heat removal system, it is designed to encourage a maximum amount of dissipation through evaporation. Photo: F4E
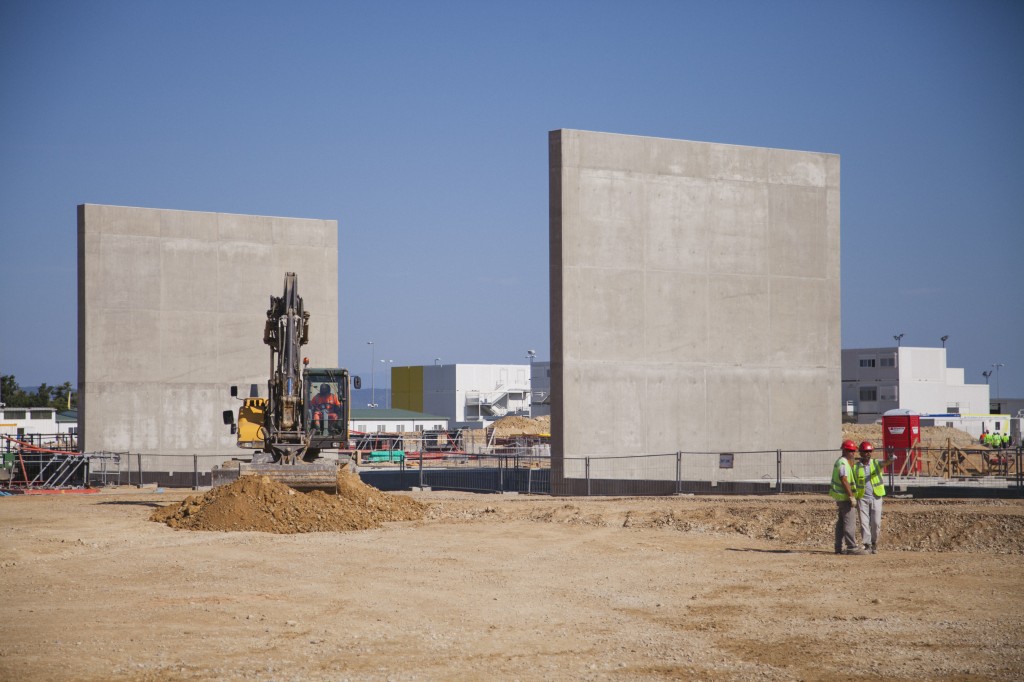
Reserved for Chinese transformers
2016-09-28 - Two other large transformers have been fabricated in China for ITER. As we wait for their arrival, workers are preparing their on-site beds. © Les Nouveaux Médias/ENGAGE
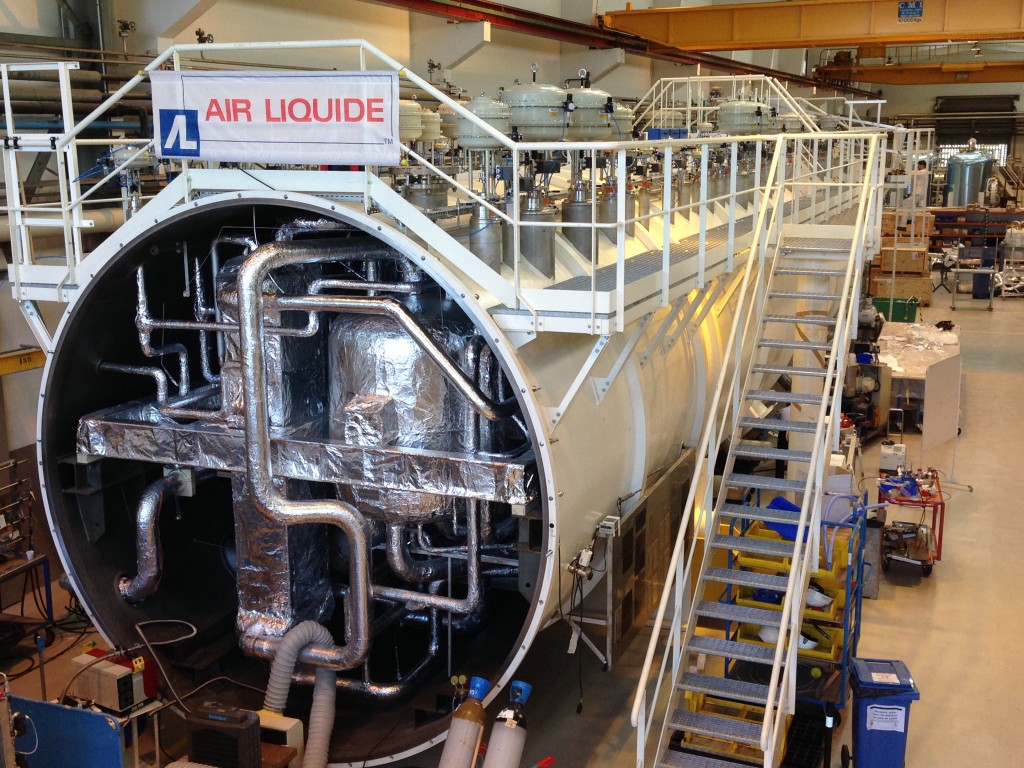
Cold boxes: providing insulation for key components
2016-09-26 - Each 4.2 x 21 metre cold box will weigh about 137 tonnes once all internal components are integrated. Three identical helium plants will store and circulate liquid helium (at a temperature of 4 K or minus 269 °C) throughout the installation.
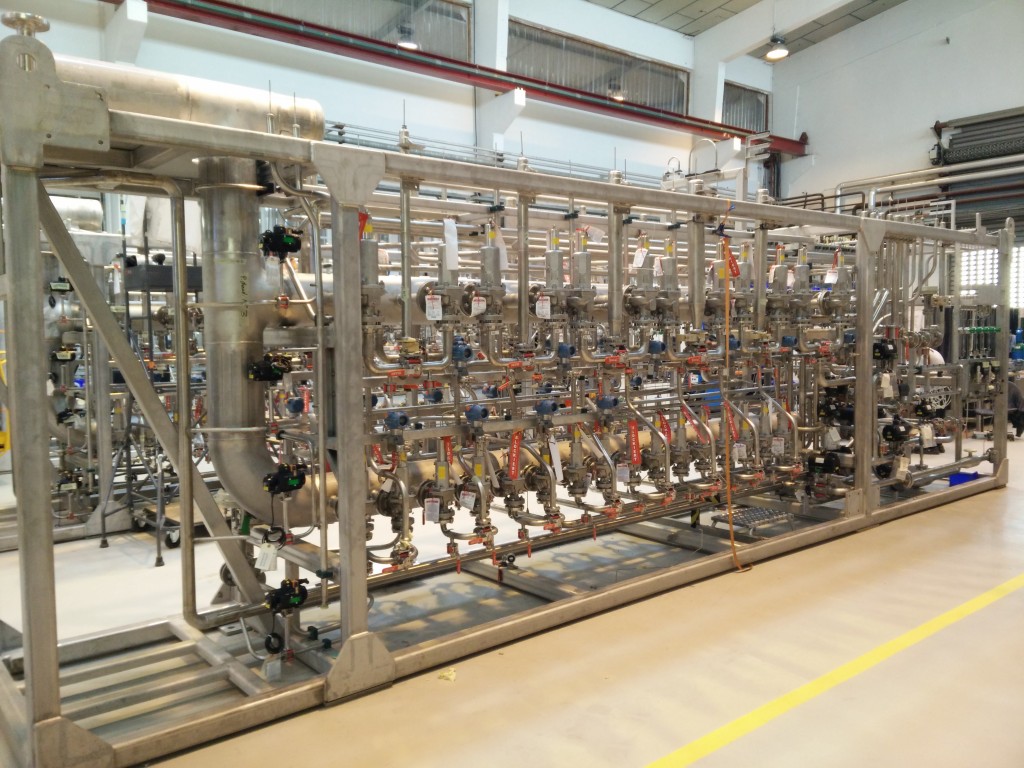
Hundreds of components
2016-09-26 - The different components of the ITER cryoplant are expected to arrive at ITER in 450 shipments. Pictured: the warm panels of the liquid helium cold boxes.
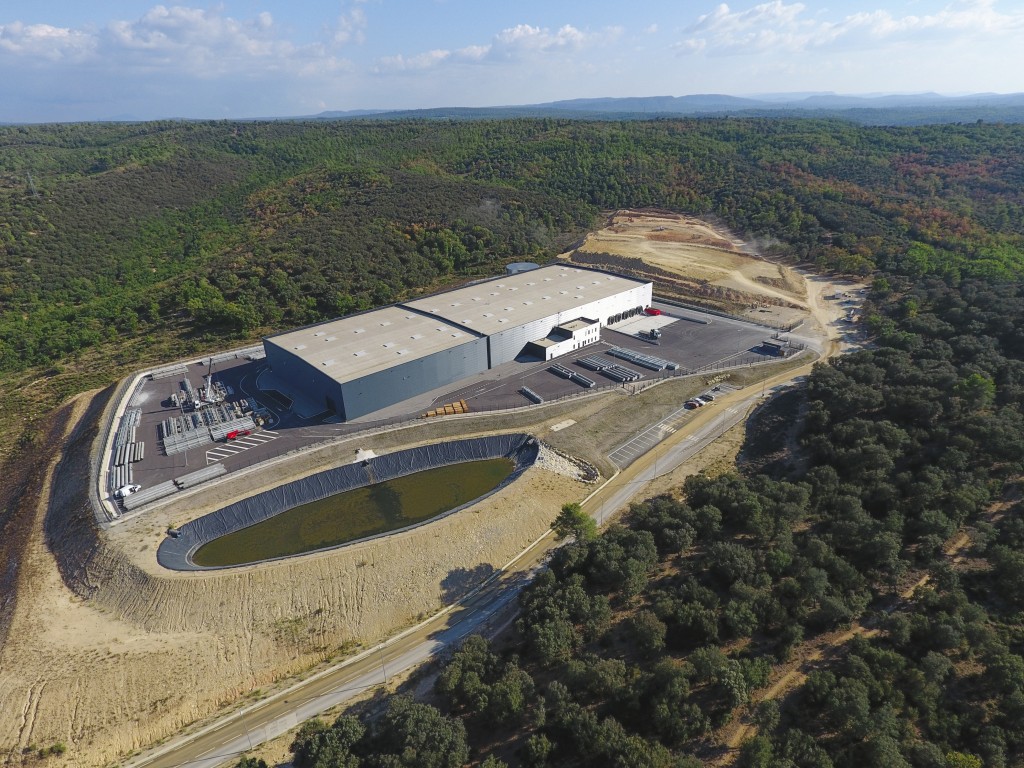
Largest storage facility
2016-09-21 - The 9,000 m² warehouse, built behind the construction platform, is already storing ITER components. © Les Nouveaux Médias/ENGAGE

Three zones in a row
2016-09-21 - On either side of the cooling water tower/basin worksite is the concrete plant (background) and the site of the future Control Room (foreground). © Les Nouveaux Médias/ENGAGE
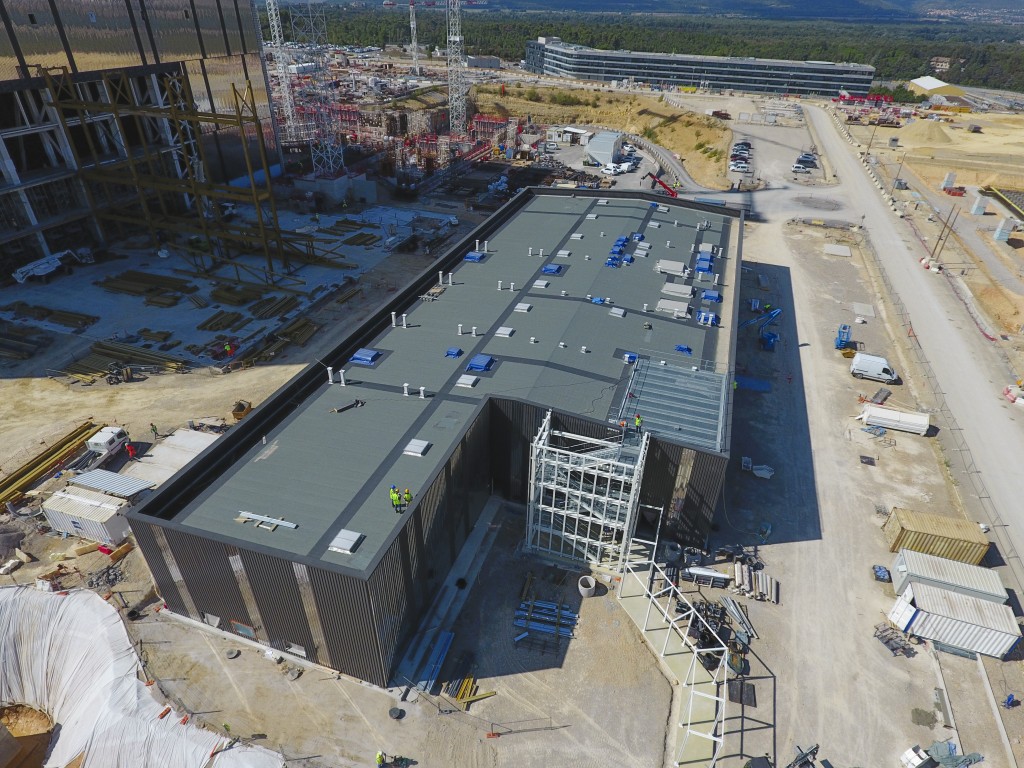
Servicing the site
2016-09-21 - Work continues on the inside of the Site Services Building, where the chiller room is now fully equipped. © Les Nouveaux Médias/ENGAGE
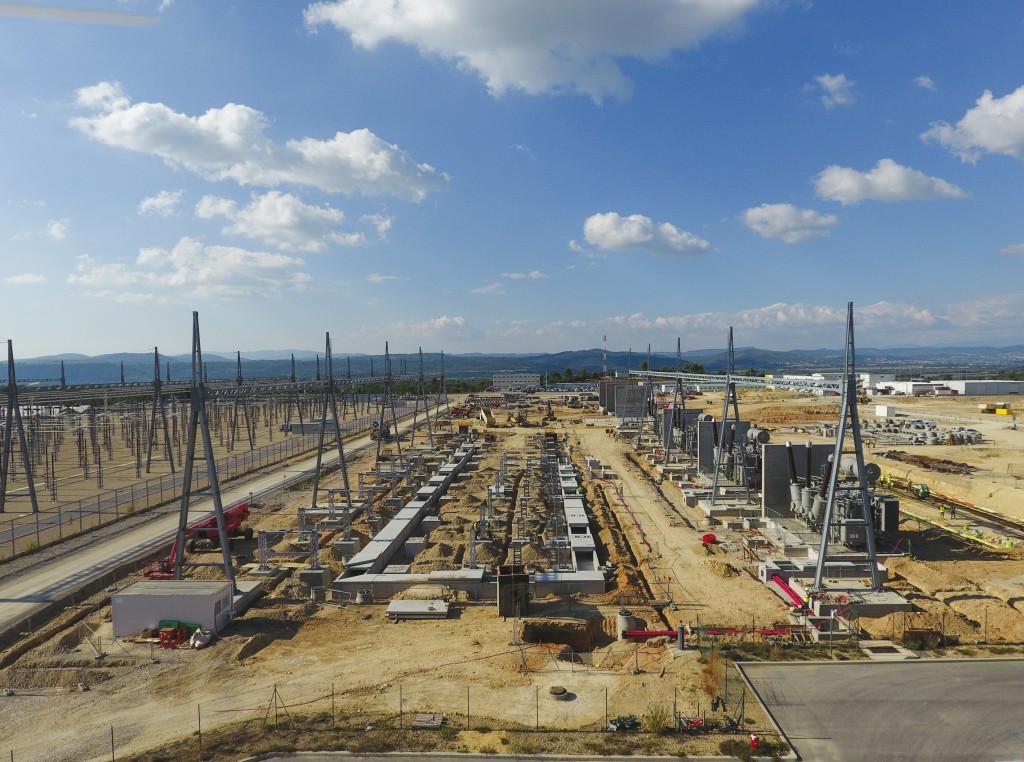
Work in the 400kV switchyard
2016-09-21 - As the needs of the construction site ramp up, the project will require more electricity than the neighbouring CEA network can supply. The 400kV switchyard will be powered up by Europe during the first quarter of 2017 to supply the 22kV network on site. © Les Nouveaux Médias/ENGAGE

Cooling zone
2016-09-21 - After removing the heat load from the machine and its components during operation, cooling water will be transferred through a cascade of cooling loops to the heat rejection zone located on the northern edge of the platform, where it will be cooled using an evaporative process. © Les Nouveaux Médias for ENGAGE

Three zones in a row
2016-09-21 - On either side of the cooling water tower/basin worksite is the concrete plant (background) and the site of the future Control Room (foreground). © Les Nouveaux Médias/ENGAGE

A perfect circle
2016-09-21 - The two-level Tokamak Complex basement is in place with, at its centre, the assembly arena for the ITER machine. © Les Nouveaux Médias/ENGAGE

Latest good news on liquid nitrogen plant
2016-09-16 - In a recent milestone, two nitrogen compressors for ITER's liquid nitrogen plant successfully complete factory testing in Europe. Photo: F4E

One small step practiced
2016-09-16 - A European contractor practices one important stage of the manufacturing process: creating the inlets in the conductors for helium. An average of eight helium inlets will be needed per coil.
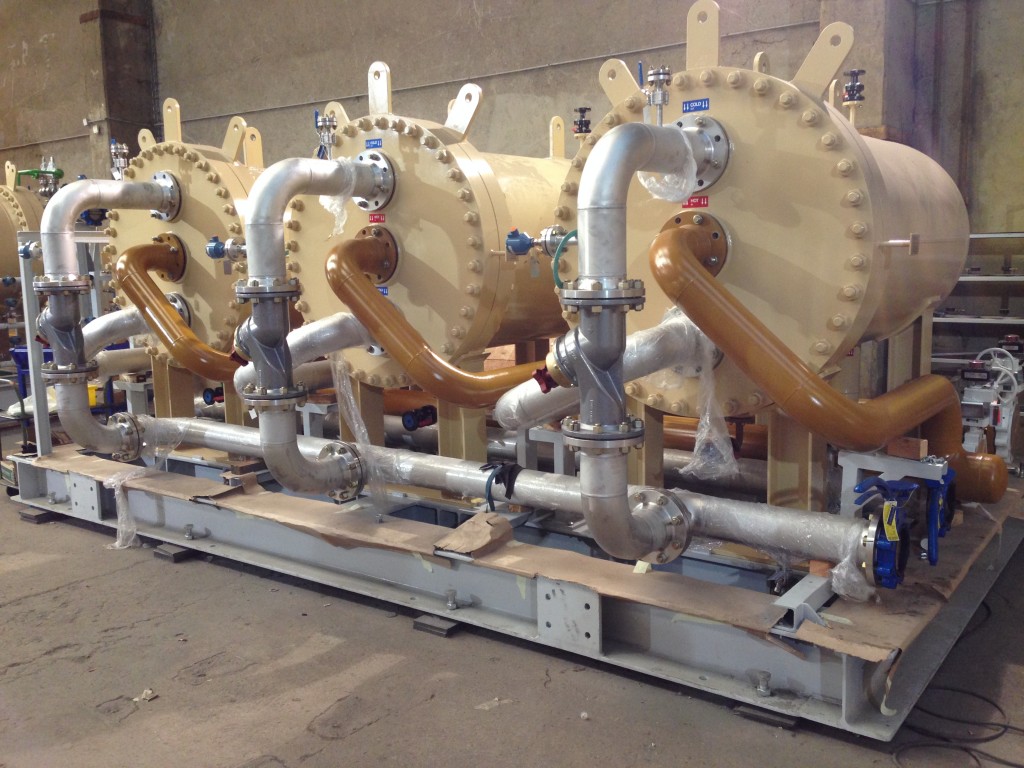
4,500 individual components
2016-09-13 - The ITER cryogenic system: 50 cold boxes, 3 kilometres of cryolines, and 4,500 components. Ninety percent of components were delivered in 2016 (pictured: heat recovery skids for the liquid helium plant).
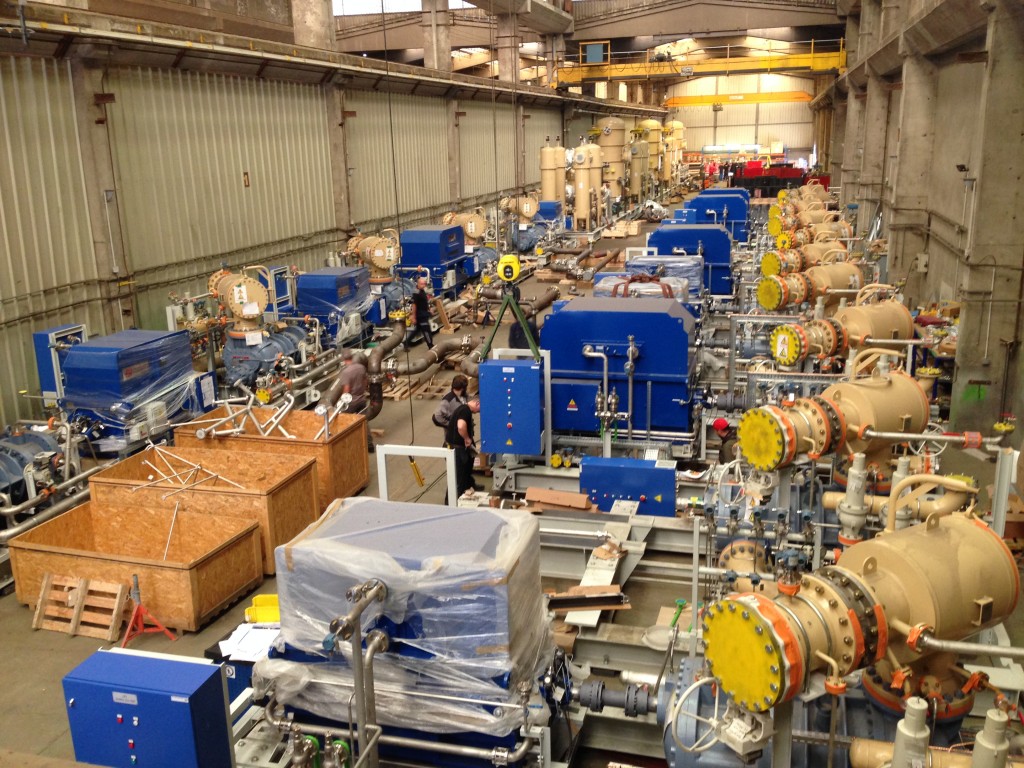
Compressor fabrication
2016-09-13 - 18 compressors will be required for the operation of the helium refrigerators. In a factory in the northeast of France, near Metz, compressor parts are being assembled on the shop floor.

Welding begins!
2016-09-08 - A ceremony on 8 September marks the beginning of cryostat welding activities. Behind the crowd, a welder awaits on the first tier of the cryostat base.

A ceremony to perform first
2016-09-08 - Cryostat welding gets off to an auspicious start as ITER Director-General Bernard Bigot performs the coconut ceremony that calls on the protection of Ganesh, "Remover of Obstacles."

A multifunctional platform
2016-09-08 - Welding activities kicked off once the different cryostat segments were positioned and aligned on this giant platform. Once the cryostat base is completely assembled, the platform will serve as a transporter.

One you see one you don't
2016-09-08 - Welders work in pairs. For every welder above the 50 millimetre gap that has to be filled by welding there is another one below.

See one, but there may be two!
2016-09-08 - Often the gap between two segments is filled simultaneously by welders working above and below. The minimum weld thickness for the base section is 25 mm.

A small vacuum chamber
2016-08-30 - The spools of conductor undergo helium tests before the material is introduced on the winding lines. Here, we see the top part of the vacuum chamber that is used for the testing.
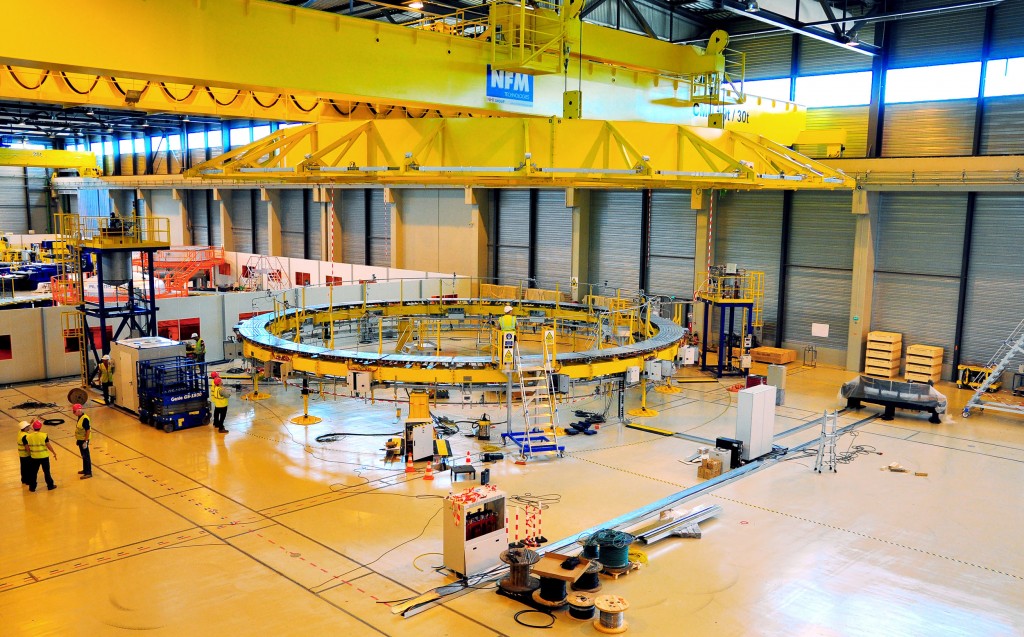
Ready for the handling operations
2016-08-30 - The overhead crane and its spreader beam will be capable of lifting the individual windings and transporting them from one station to the next with a minimum of tilt. For the handling of the final assemblies, however, a gantry crane will be necessary.
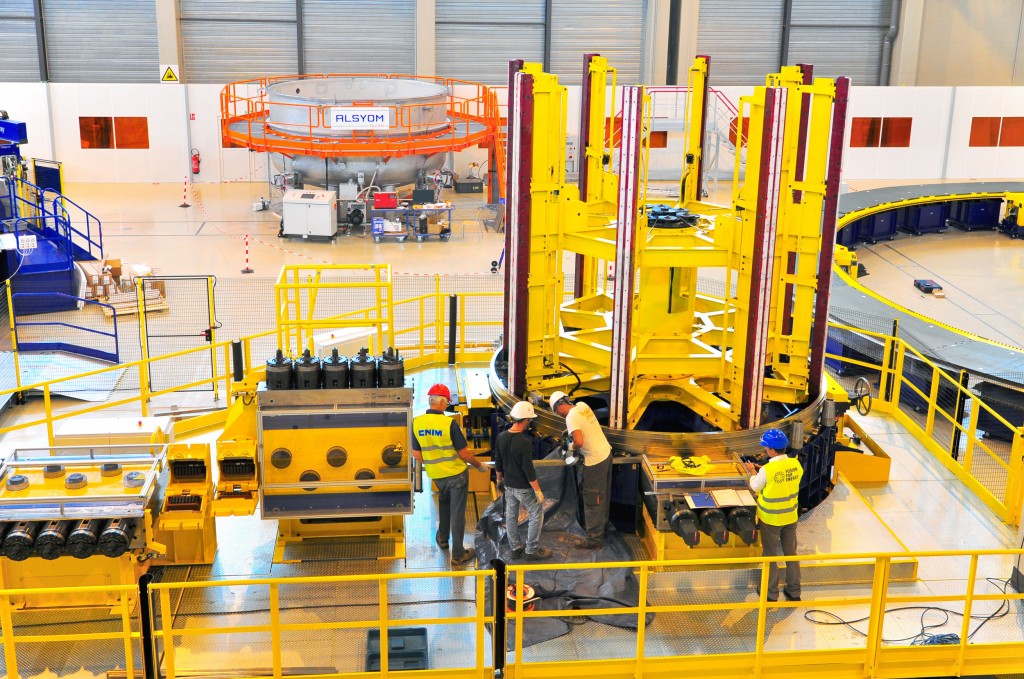
Despooling
2016-08-30 - In the winding stage of fabrication, the conductor is uncoiled from the spools and straightened before passing through cleaning and sandblasting machines that prepare its surface to receive several layers of glass-fibre insulating tape.

Work station 2
2016-08-30 - Late August, contractors install the impregnation table in the Poloidal Field Coils Winding Facility.
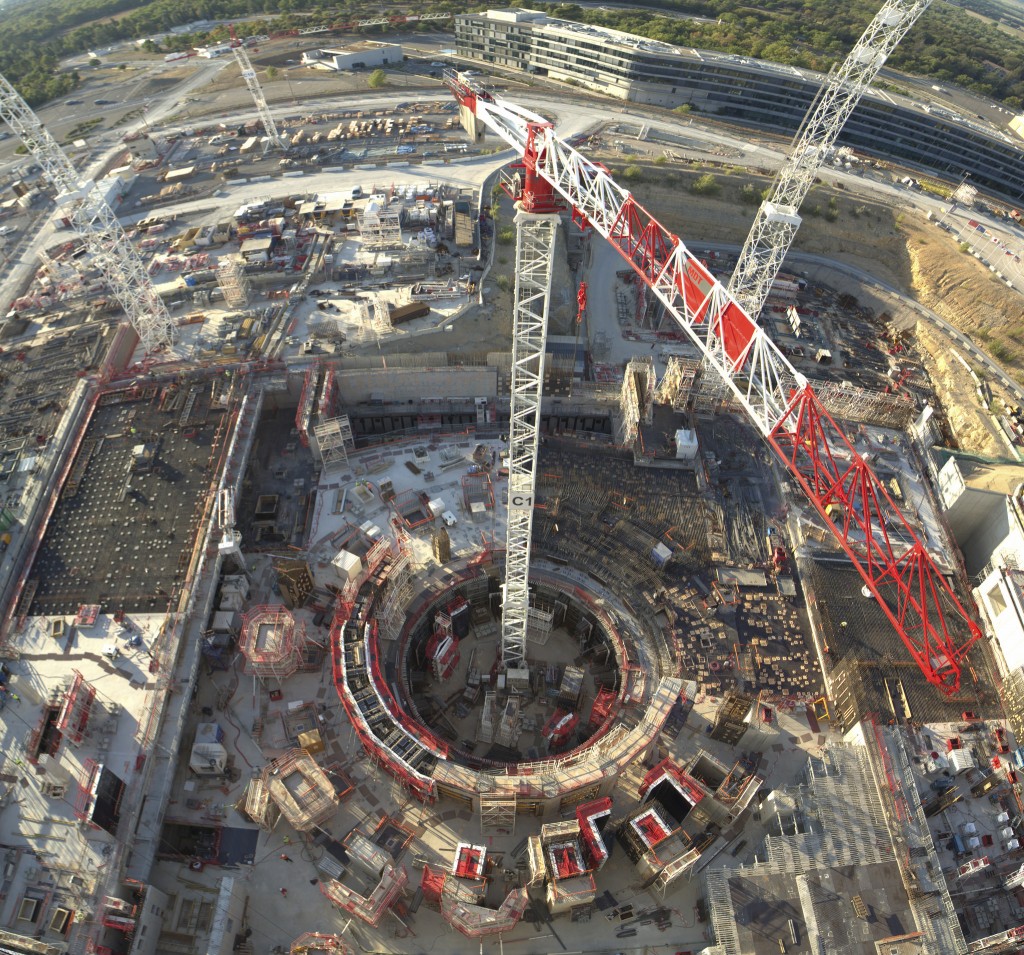
In the late August light
2016-08-25 - The Diagnostic and Tritium buildings (left and right) frame the central Tokamak area. The lowest-level basemat has completely disappeared. ©LNM/F4E
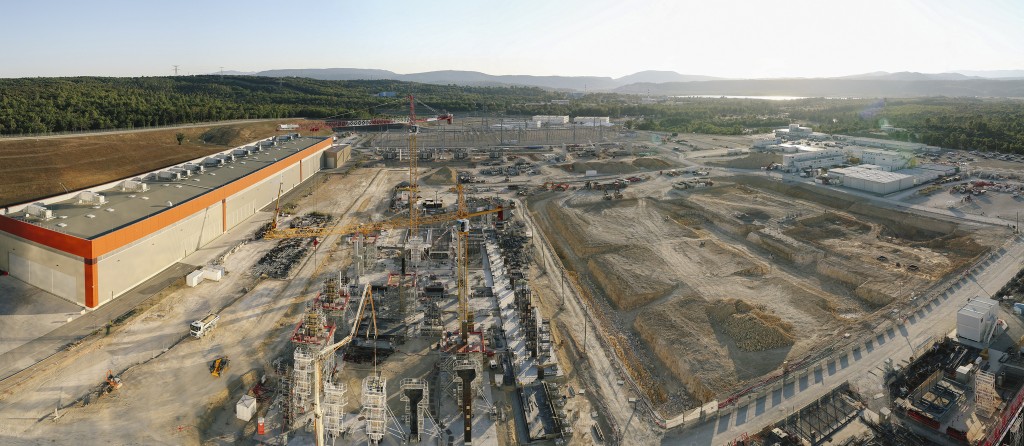
An indoor-outdoor facility to house the cryoplant
2016-08-25 - The site of the ITER cryoplant, under construction in August 2016. Two connected buildings will be complemented by an external storage area. Photo: © LNM/F4E
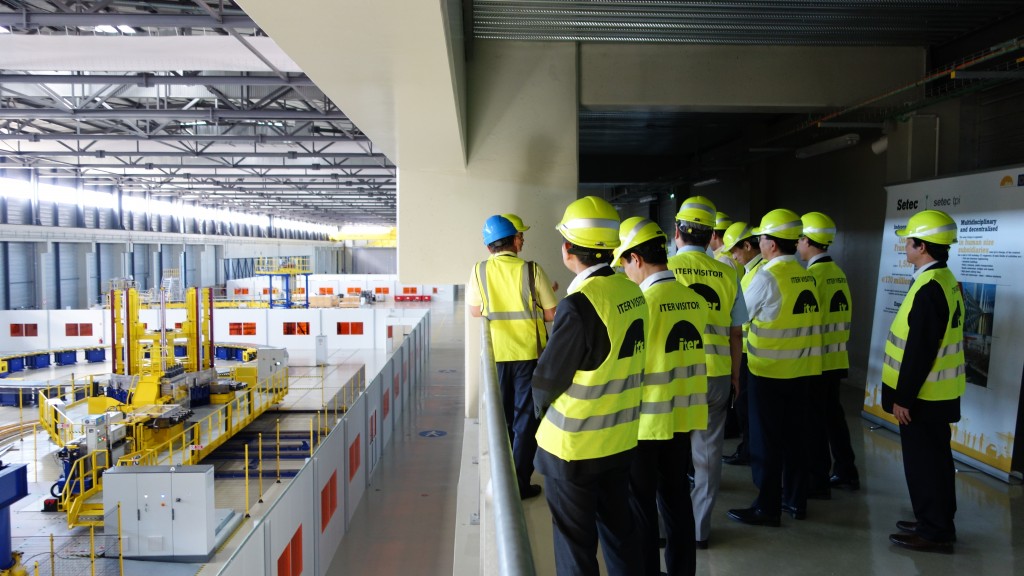
Visiting the first on-site manufacturing activities
2016-08-12 - In July, a delegation from Japan looks out over the first on-site manufacturing activities for the ITER poloidal field magnet coils.
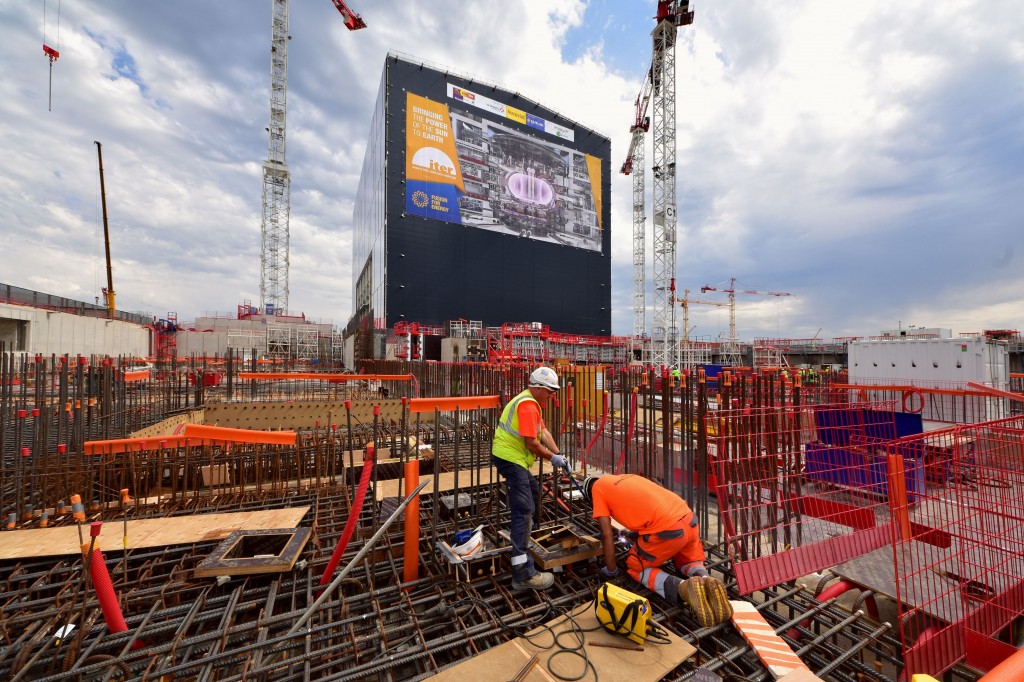
A poster ... for now
2016-08-01 - The Assembly Building, now adorned with a giant poster of the ITER machine, dominates the ITER landscape. Eventually, as the Tokamak Building rises, the temporary cladding on the northwest facade will be removed and the two buildings will be joined into one.
Second storey of the Tritium Building
2016-08-01 - In early August, work progresses on the B1 level (upper basement level) floor slab of the Tritium Building.

The lower basement level has disappeared from sight
2016-08-01 - Half of the B1 basemat (the upper basement level slab) has now been poured for the Tokamak Building, in the centre of the image.
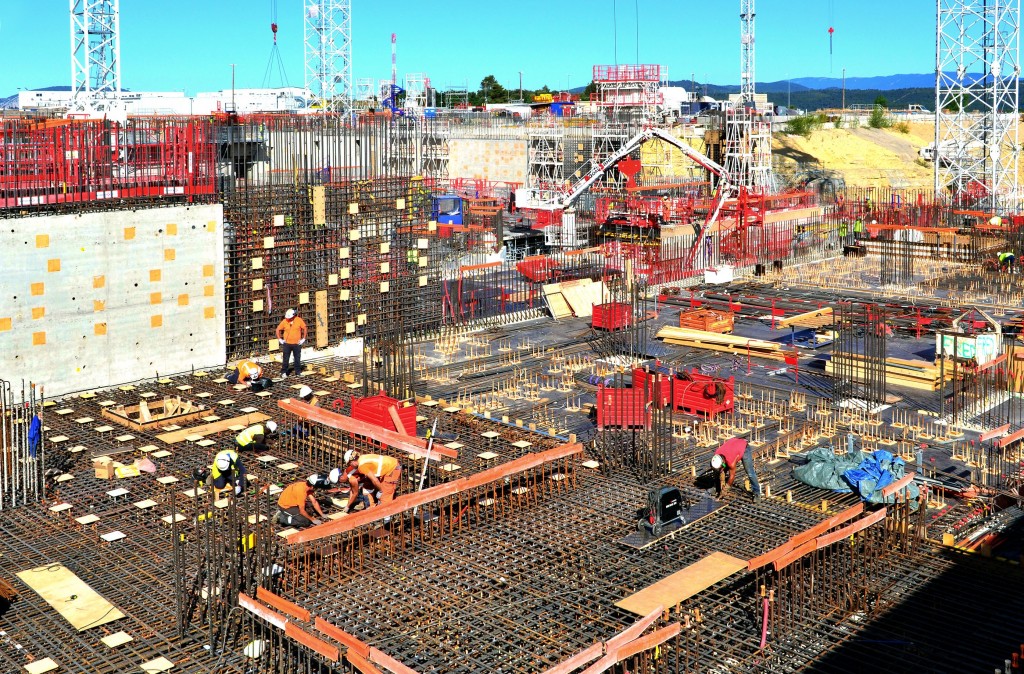
For strong anchorage
2016-08-01 - Workers are carefully positioning hundreds of embedded plates in the dense rebar lattice before pouring the concrete for the B1 basement of the Tritium Building.
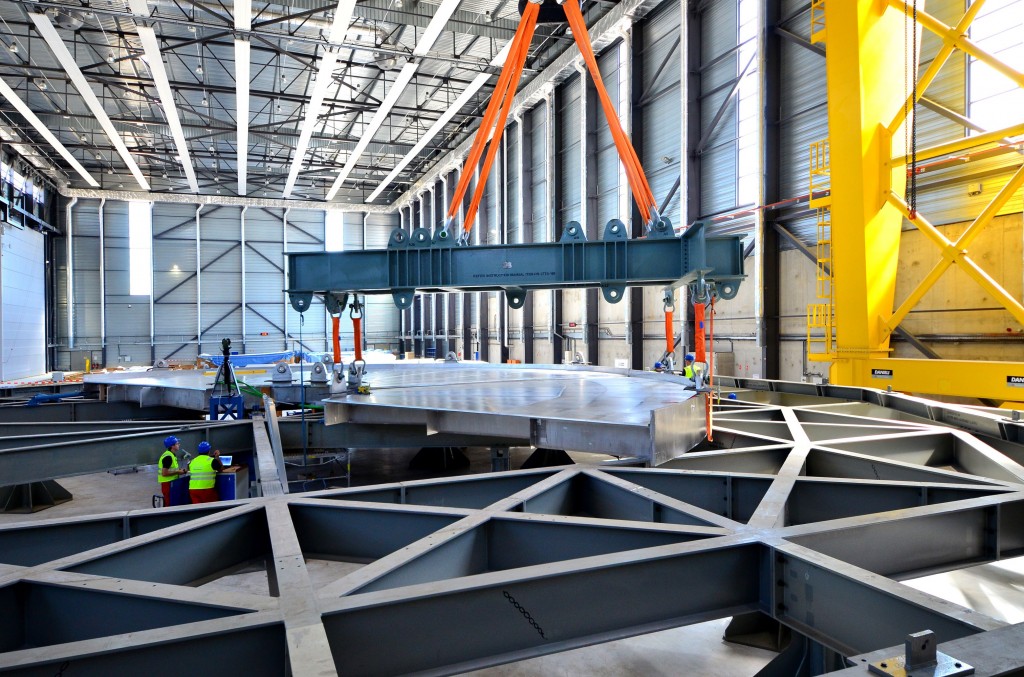
Aligning the pieces
2016-07-27 - Six 50-tonne triangular segments form tier 1 of the cryostat base. They are positioned on the assembly frame in the Cryostat Workshop in preparation for welding activities.

Preparing for assembly
2016-07-27 - Dimensional checks are carried out on the three cryostat segments already installed on the assembly platform.

Spools awaiting
2016-07-27 - These spools of conductor delivered by China will be installed on the tower-like "de-spooler" (in yellow) to be straightened before winding. Photo: F4E

Step-by-step process
2016-07-27 - Coil manufacturing is carried out in a series of steps. The double pancakes are first wound and then prepared for treatment with epoxy resin in the first clean area (foreground) and then transported to the impregnation station that is just visible on the far right of the photo. Photo: F4E

On the inside of the Site Services Building
2016-07-26 - Work is underway on the interior fittings of the Site Services Building.

Framed by rebar
2016-07-26 - The 60-metre-tall Assembly Building seen from the B1 level of the Tokamak Complex. Work is currently underway on level two of the seven-storey building.
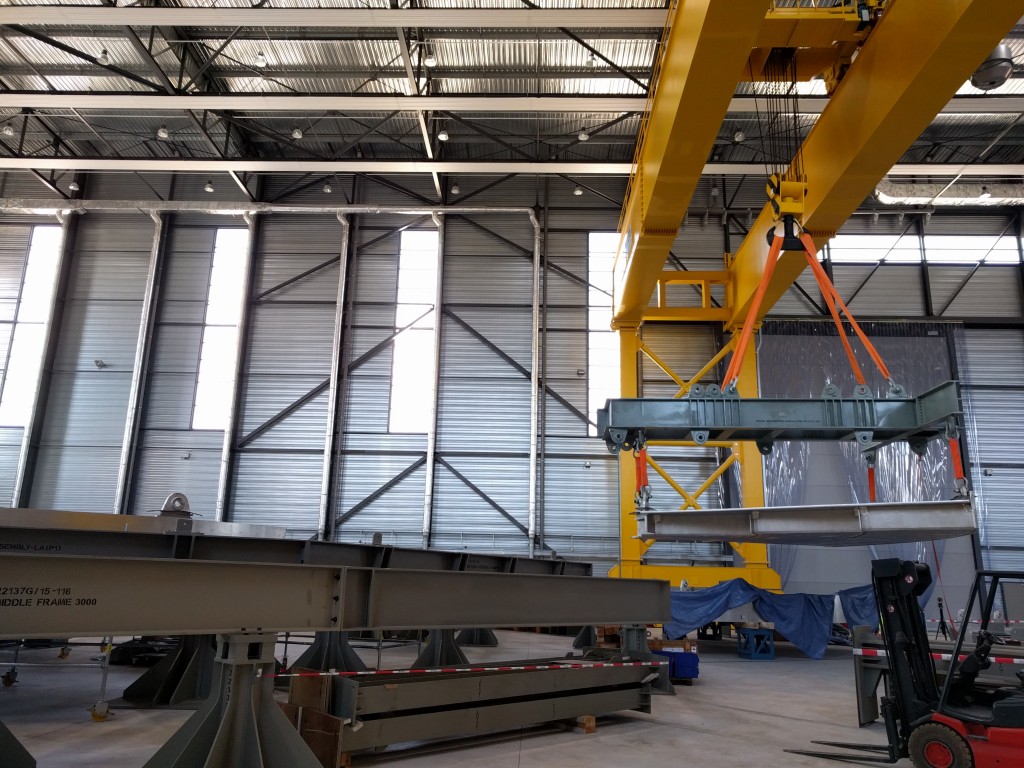
First lifts
2016-07-25 - The first elements of the cryostat base are transported by gantry crane on to the assembly platform. Welding activities are scheduled to start in September.
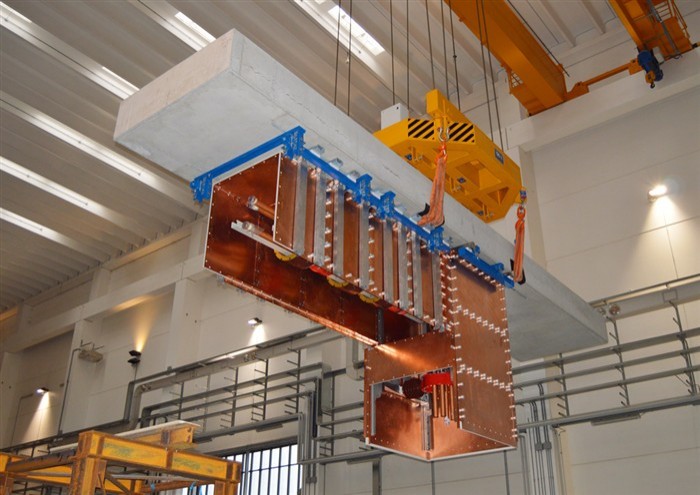
Transmission line connected
2016-07-25 - Part of the 35-metre-long, winding transmission line that will be connected to the SPIDER vessel. Photo: F4E
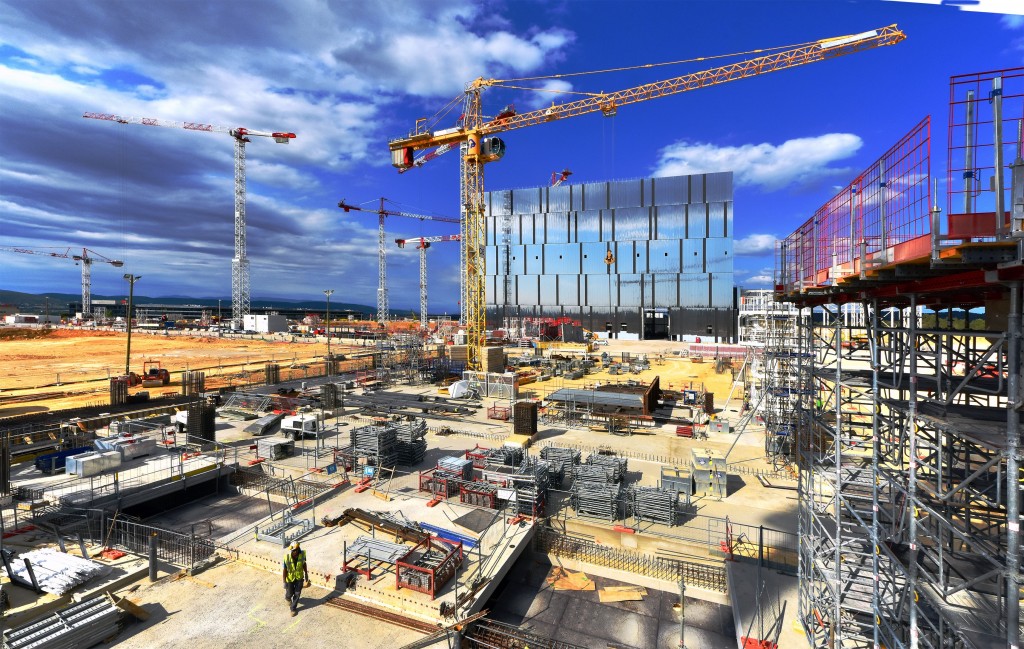
The cold house
2016-07-20 - The ITER cryoplant will deliver 75 kW of combined cooling power to the ITER installation. Work is underway now on the building, and before the end of the year most of the equipment will have been delivered to the site.

Assembly Building ... extended
2016-07-20 - The frame of the Cleaning Facility is up on the eastern side of the Assembly Building.
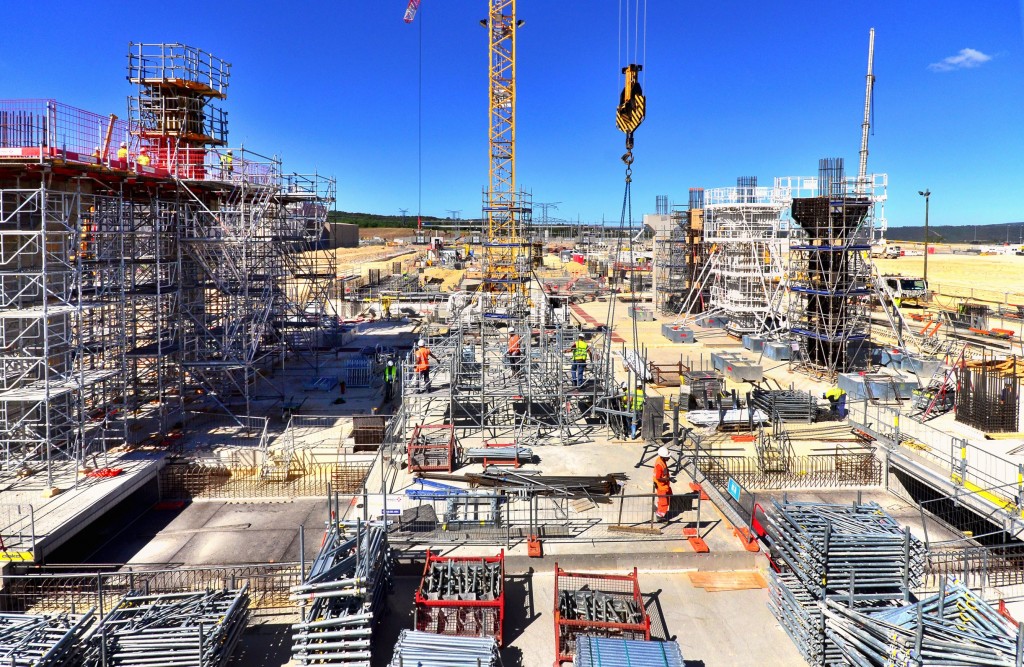
Cryoplant rises
2016-07-20 - Columns are rising for the ITER cryoplant, now that the underground galleries and the foundations are finished.

Tooling progresses
2016-07-19 - The winding zone (near) and impregnation zone (far) are both visible in this photo of the Poloidal Field Coils Winding Facility.

Foundations underway
2016-07-19 - Work is underway on the foundations of the Radiofrequency Heating Building.

Impregnation tooling installed
2016-07-19 - In the second clean zone of the facility, an impregnation table has been installed. Here, the coiled "double pancakes" produced during the winding stage are impregnated with epoxy resin in order to provide rigidity and electrical insulation.
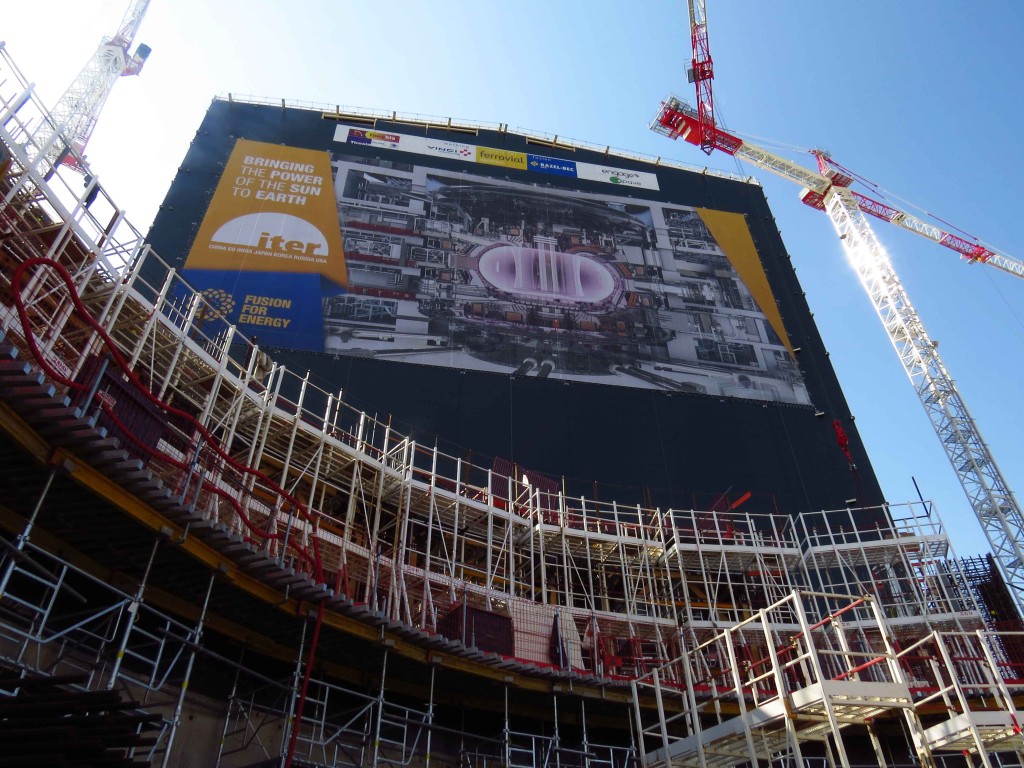
Inside of the "Pit," looking up toward the ITER Assembly Building
2016-07-15 - When the seven stories of the Tokamak Building are completed, the two buildings will match in height (60 m above platform level).
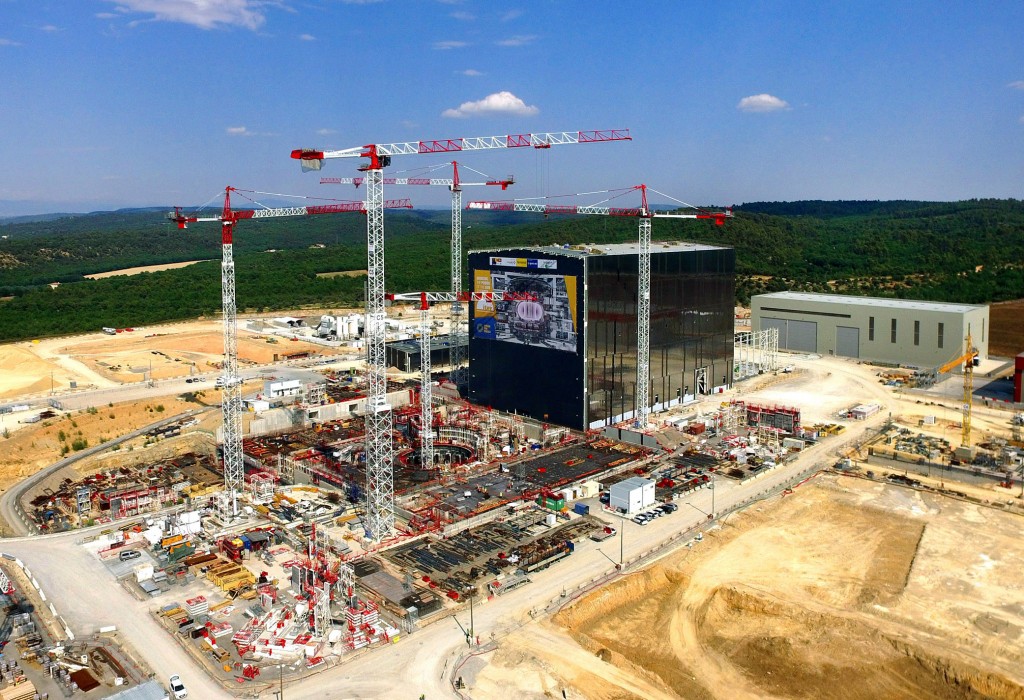
The largest structure on the platform
2016-07-11 - In some light, the silver cladding on the sides of the Assembly Building appears black. © EJF Riche
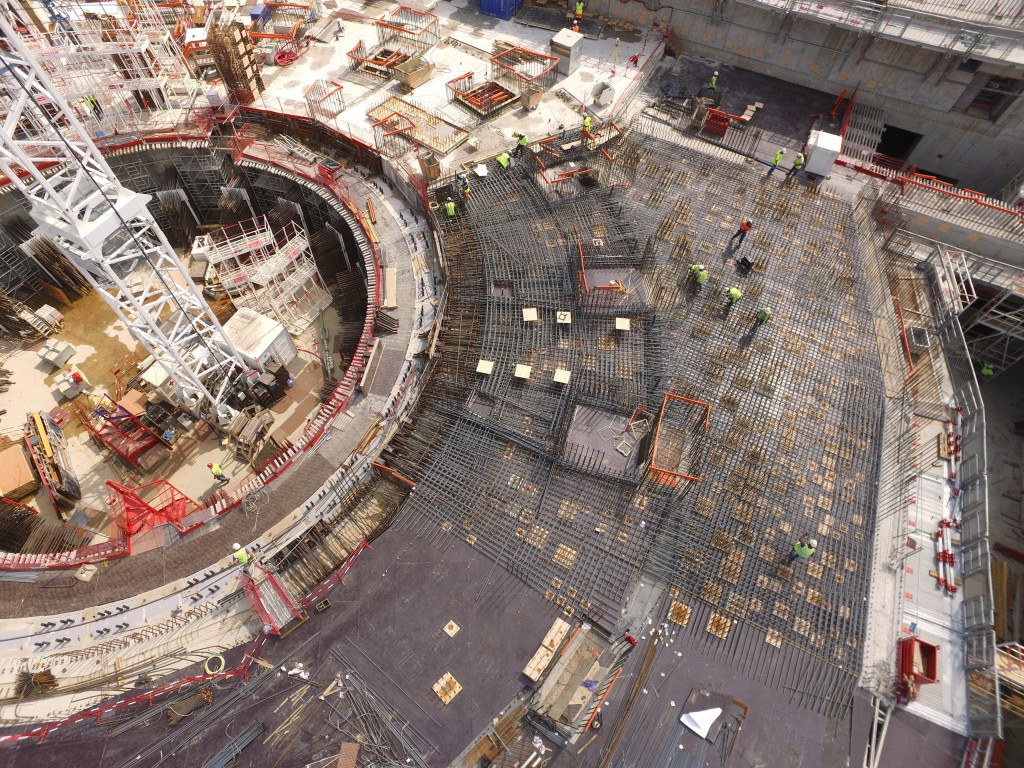
Plates galore
2016-07-11 - On the subject of embedded plates, this photo allows us to see the plates that have been positioned on the underside of the basemat (the ceiling of one level), as well the ones on the floor of another.
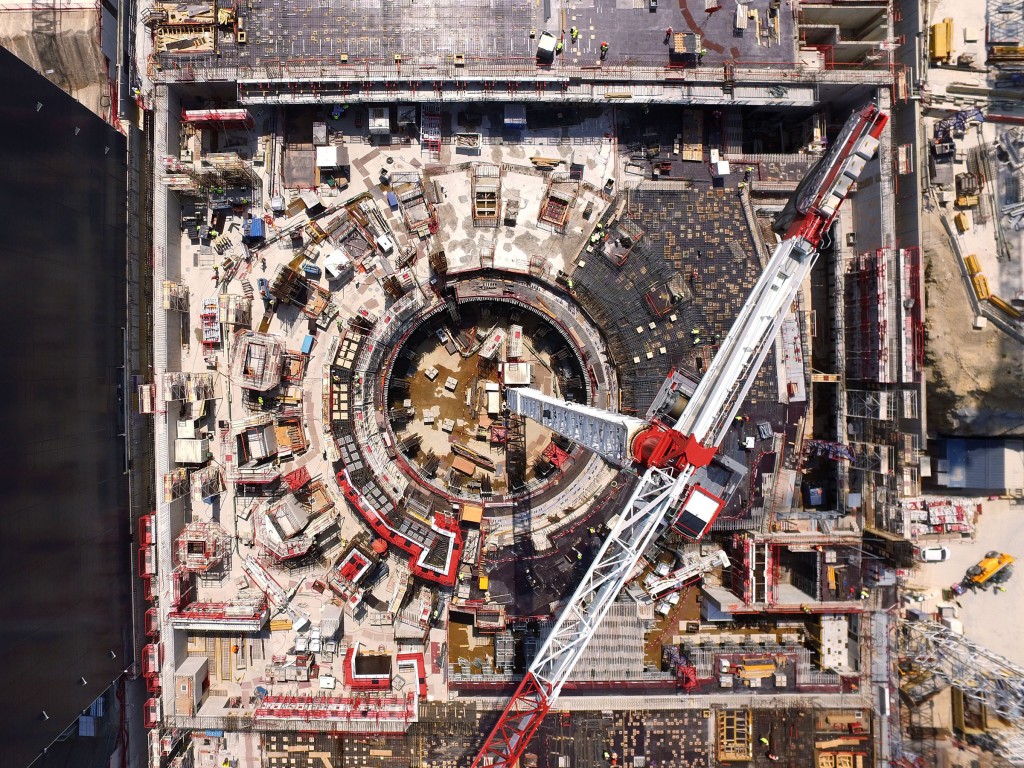
Dizzying
2016-07-11 - The progression of the Tokamak Building, captured by drone in July 2016. © EJF Riche
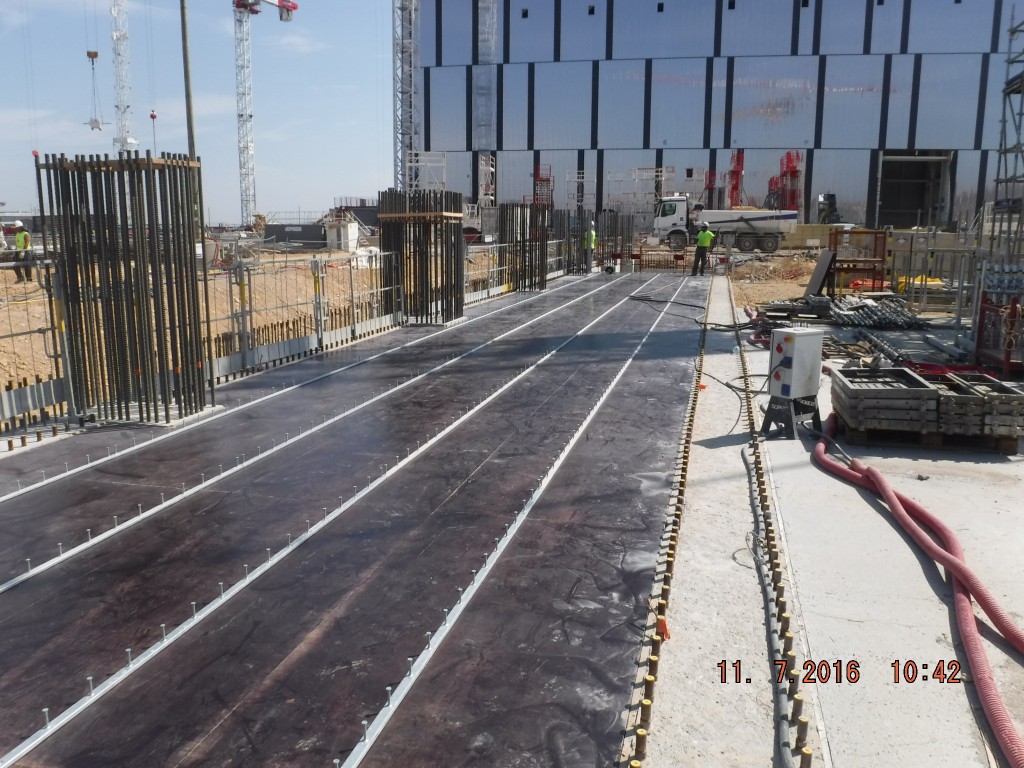
Tanks will go here
2016-07-11 - Infrastructure works are underway on the westernmost portion of the cryoplant worksite to support the warm and cold storage tanks that will be capable of storing the entire inventory of helium and liquid nitrogen during maintenance periods.
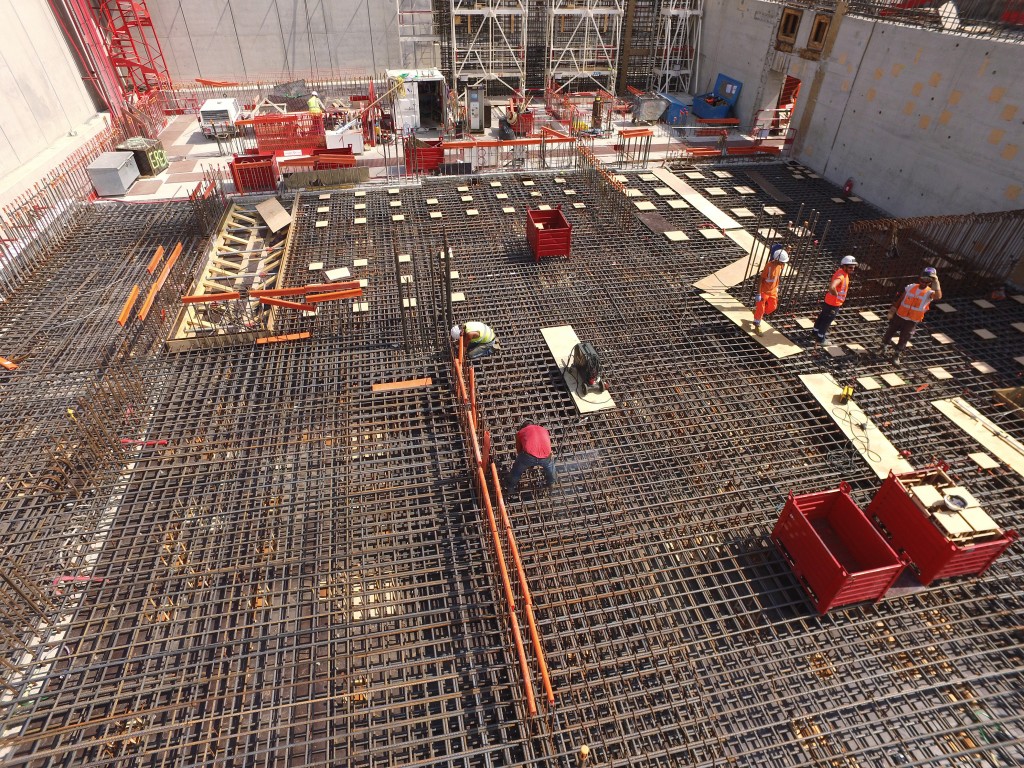
Precision demanded
2016-07-11 - Tens of thousands of embedded plates will be installed throughout the seven levels of the Tokamak Complex to provide anchorage for equipment such as cable trays, cooling water system tanks and diagnostics. These plates must be inserted into the rebar lattice prior to concrete pouring.
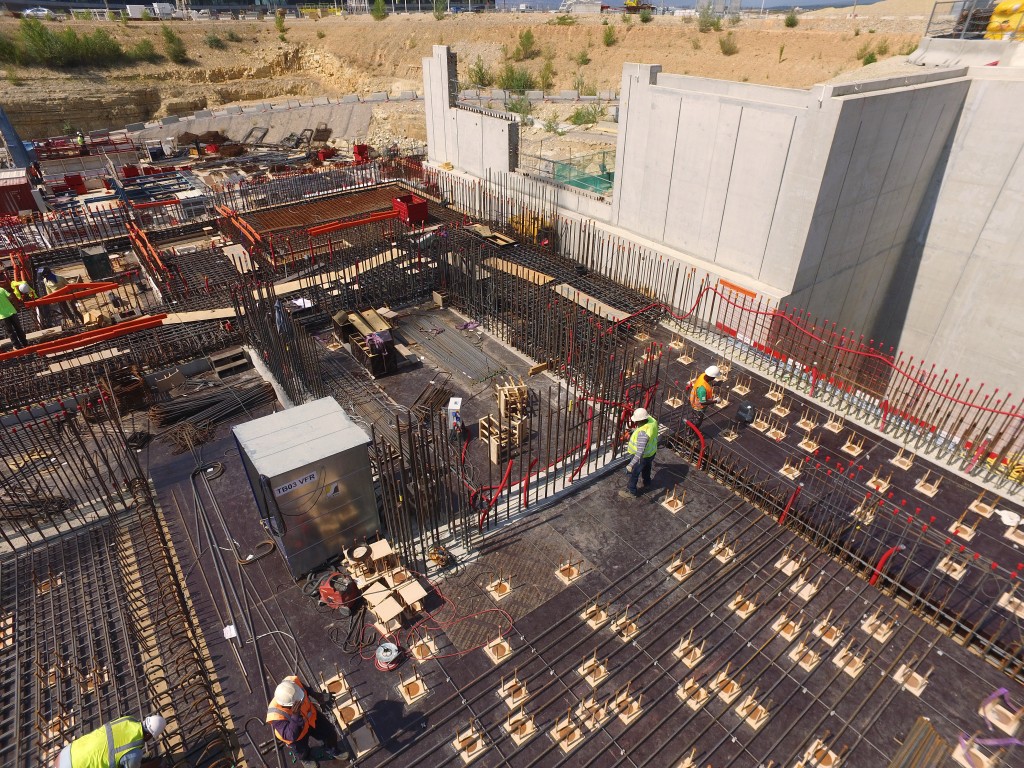
Tritium Building, level B1
2016-07-11 - After the installation of six captive components (water detritiation tanks), work is now progressing to frame out the B1-level basemat. © EJF Riche

A suite of three
2016-07-11 - The three buildings of the Tokamak Complex—Tritium, Tokamak and Diagnostics—are clearly visible in this photo taken by drone. © EJF Riche

All in a line
2016-07-11 - At the top right of the photo, we can see how the cryostat segments will leave the Cryostat Workshop through the large doors and travel in a straight line to the Cleaning Facility/Assembly Hall, before being delivered by overhead crane to the Tokamak Pit. © EJF Riche

A perfect circle
2016-07-11 - Here's where the ITER Tokamak will be assembled. The first major component to be installed will be the 1,250-tonne cryostat base. © EJF Riche
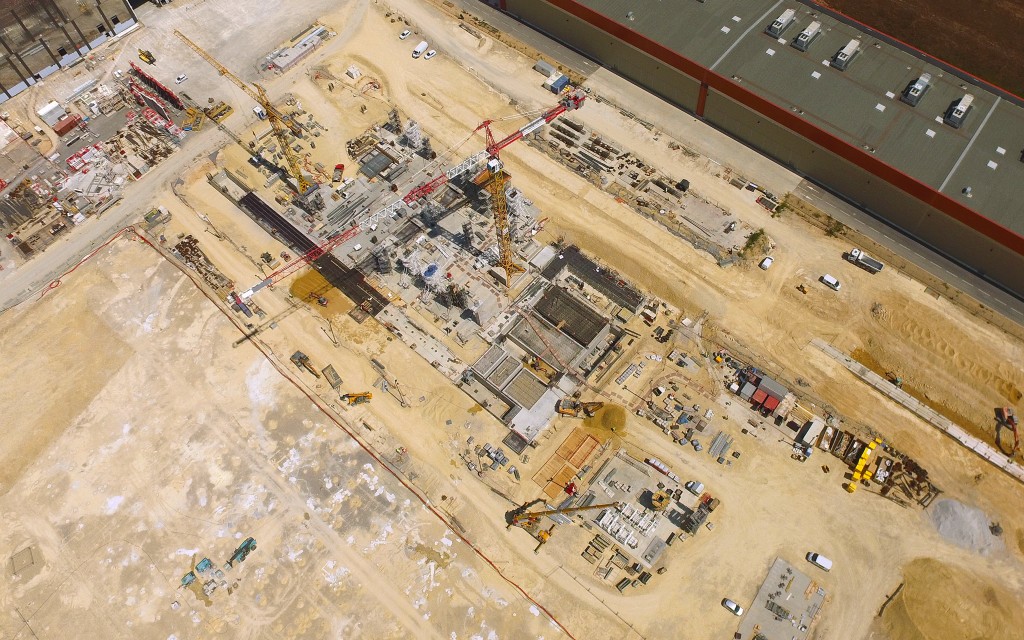
From above
2016-07-11 - Parallel to the winding facility for poloidal field coils (at right) the construction of the ITER cryoplant is underway. Photo: ITER Organization/EJF Riche

Progress on the ITER cryoplant
2016-07-11 - On the completed foundations, pillar frames are starting to rise.

Like so many spokes
2016-07-11 - The centre of it all: the Tokamak installation arena, with spokes (reinforcement for radial walls) all around. © EJF Riche

Filling in
2016-07-11 - In the central Tokamak Building area, the B1-level floor is progressively cast in concrete. © EJF Riche
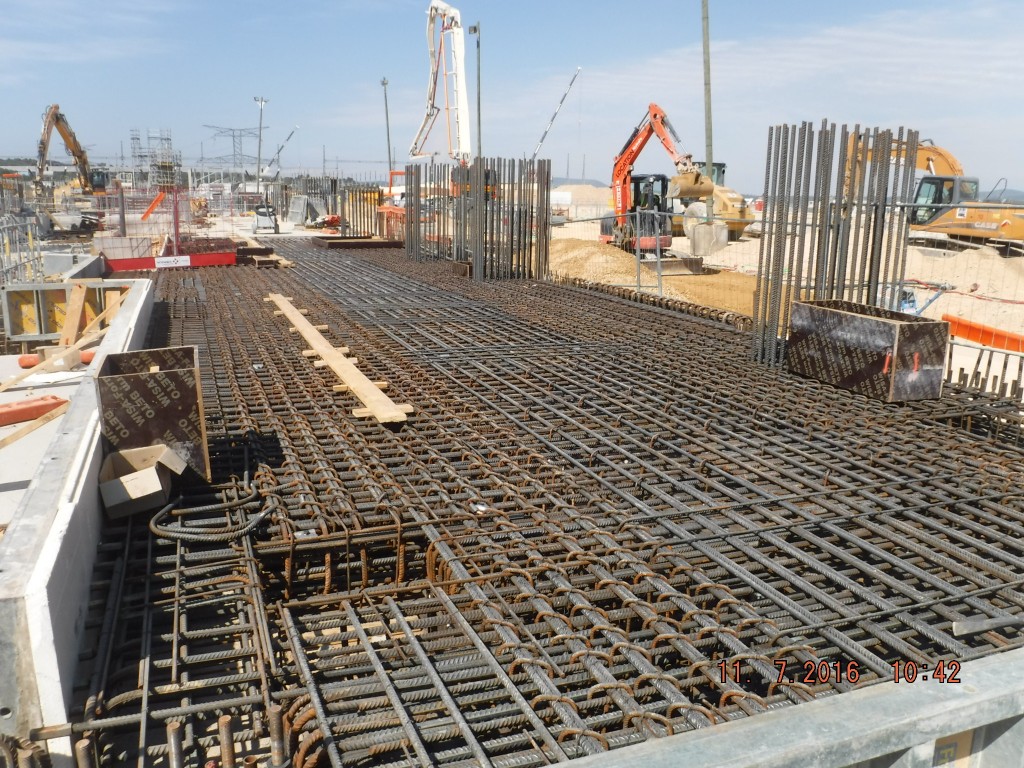
Cryoplant, in June 2016
2016-07-11 - Adjacent to the Assembly Building, work is underway on the ITER cryoplant building.
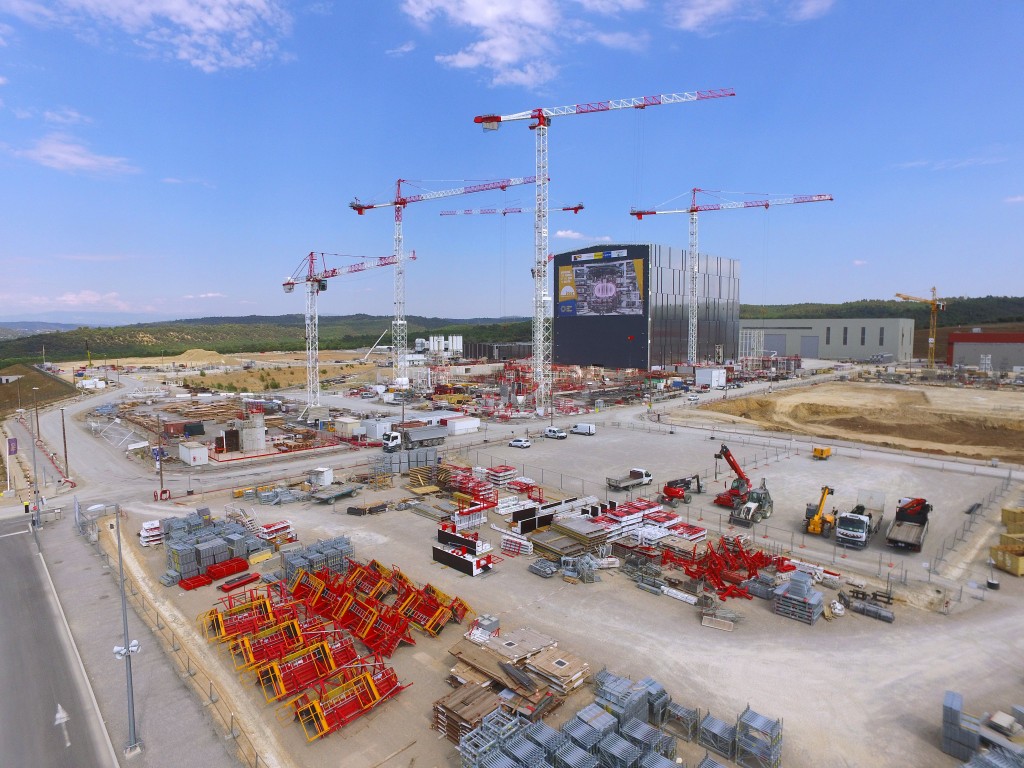
Looking northeast
2016-07-11 - The northern end of the ITER platform, with material storage areas in the foreground. Photo: ITER Organization/EJF Riche
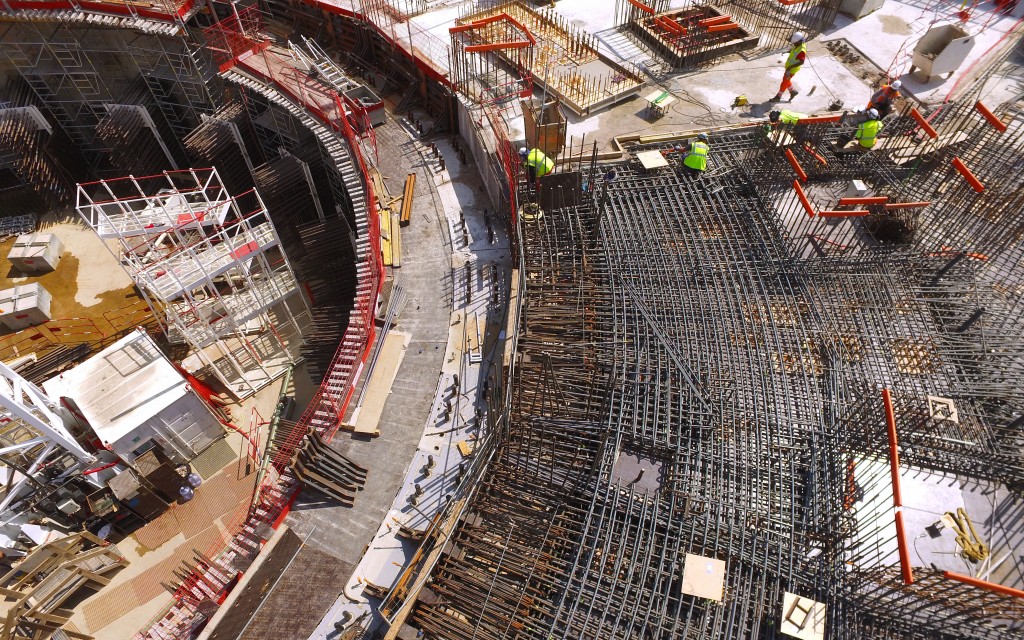
Concrete, and more concrete
2016-07-11 - Outside of the circular bioshield, workers are pouring the B1 basemat in sections. © EJF Riche
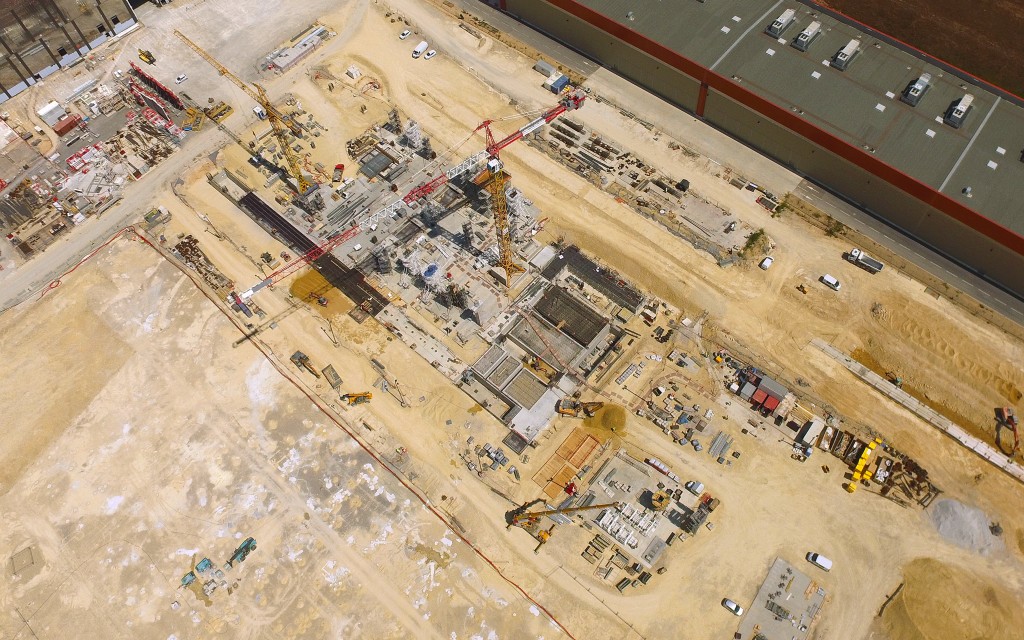
From above
2016-07-11 - Parallel to the winding facility for poloidal field coils (at right) the construction of the ITER cryoplant is underway. Photo: ITER Organization/EJF Riche
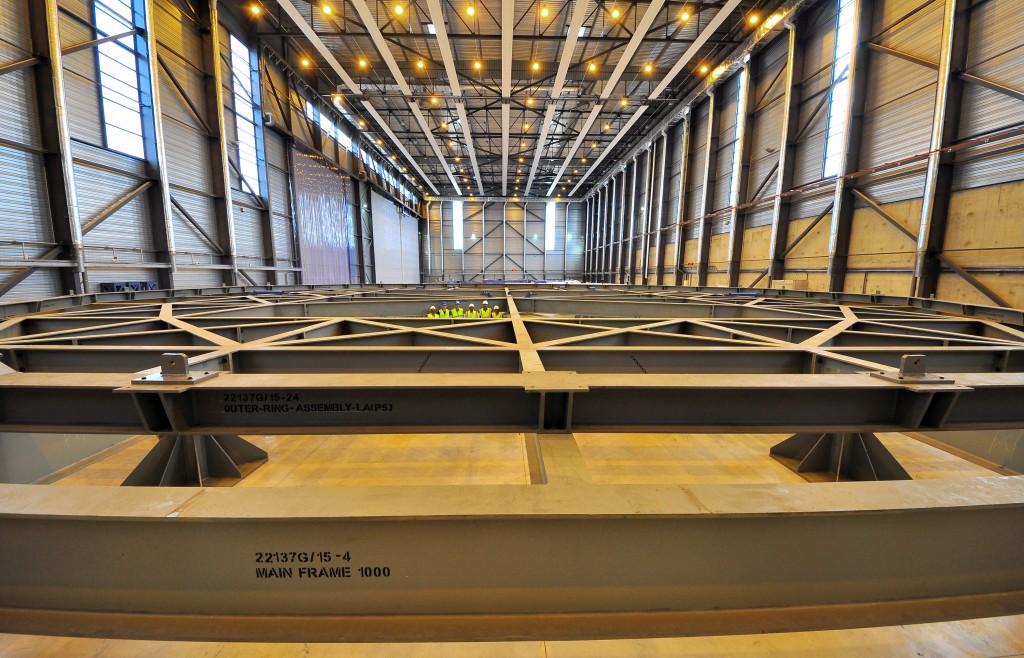
The frame is ready, welding can begin
2016-07-08 - This 34-metre-wide frame will serve as a support platform while the cryostat base segments are welded together. It will also serve as a transport platform when the completed base section travels out of the workshop.
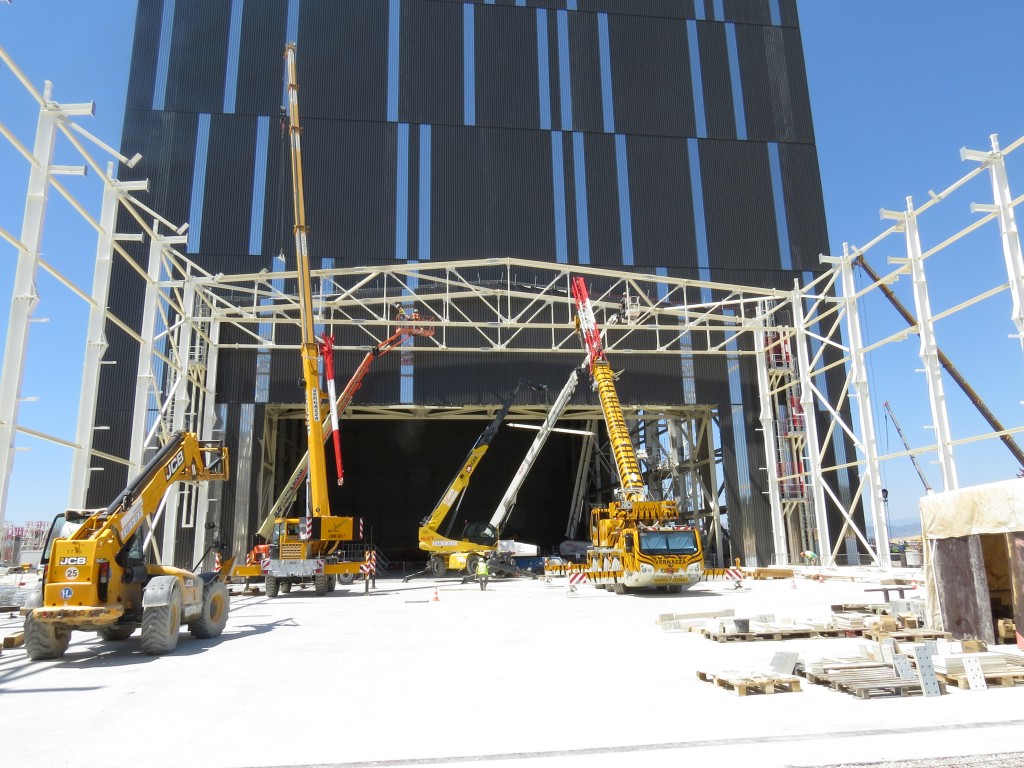
Clean and white
2016-07-07 - Elements of the Cleaning Facility's structure permit to visualize the dimensions of the future building.
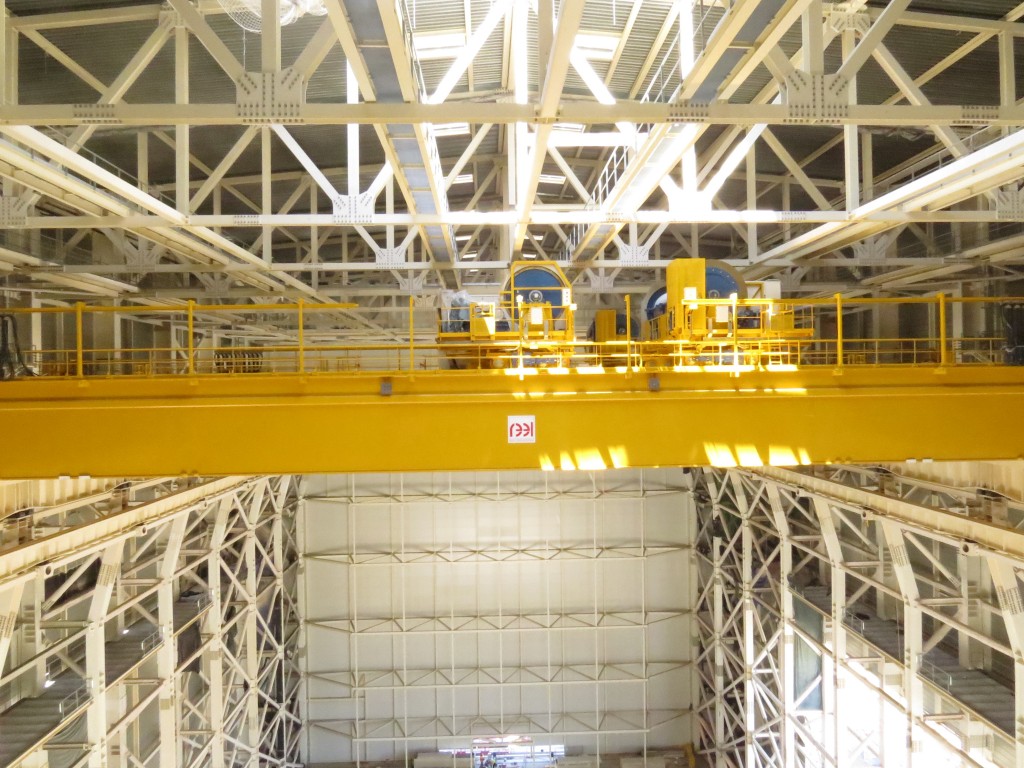
Mission completed
2016-07-07 - The assembly cranes are in place, and a project milestone for 2016 has been achieved.
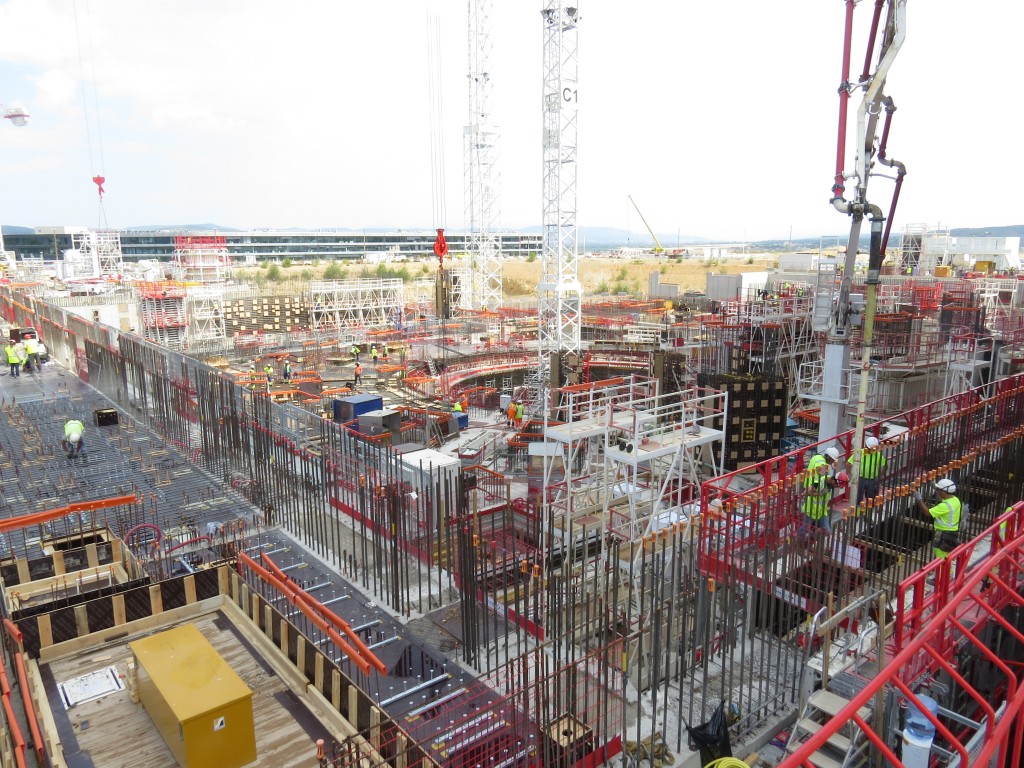
A busy scene
2016-06-30 - From the Diagnostics Building, where formwork is underway for the Level L1 basemat (which will bring the building flush with the platform), we look across the complex scape of the Tokamak Building, with its multitude of steel bars, embedded plates, and equipment.
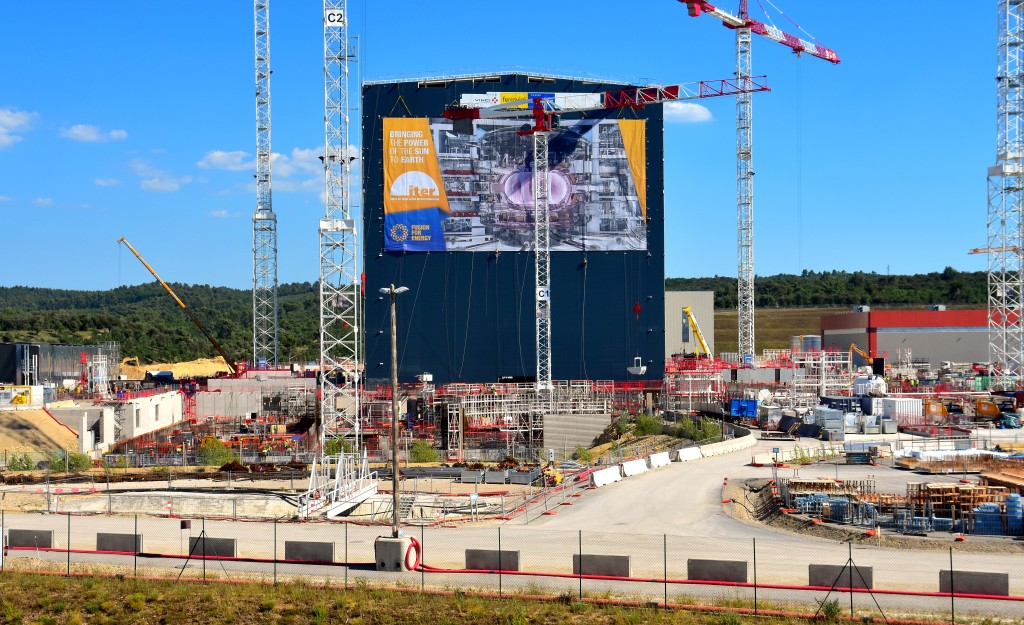
Tall building ... giant tokamak
2016-06-28 - A giant poster (25 x 50 m) of the Tokamak ensconced in its concrete building has been installed on the temporary wall of the Assembly Building. The poster image is 70 percent of the machine's actual size.

Installation of main cranes advances well
2016-06-27 - In late June, two trolleys remain to be lifted and installed for the main Assembly Hall cranes. Two smaller cranes, each with a lifting capacity of 50 tonnes, will be installed in September/October.

Makes you feel small ...
2016-06-27 - The person standing on the support rails looks positively tiny next to the mammoth 47-metre-long steel girder ...
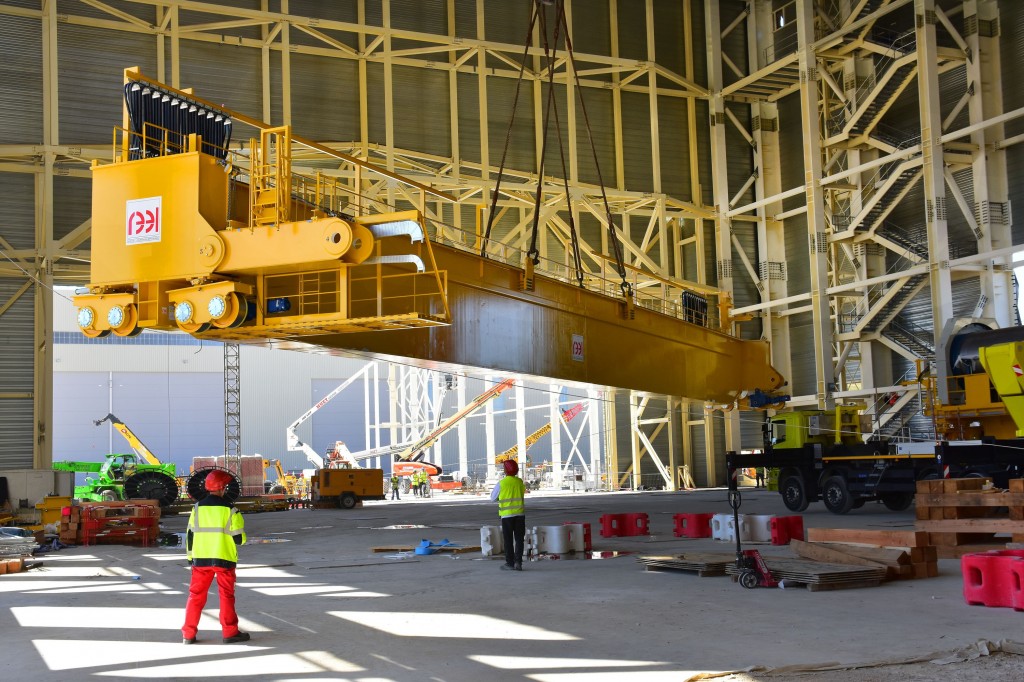
A balancing act
2016-06-26 - Before the lift, the load must be carefully balanced on the hook. This operation takes much longer than the actual lifting.
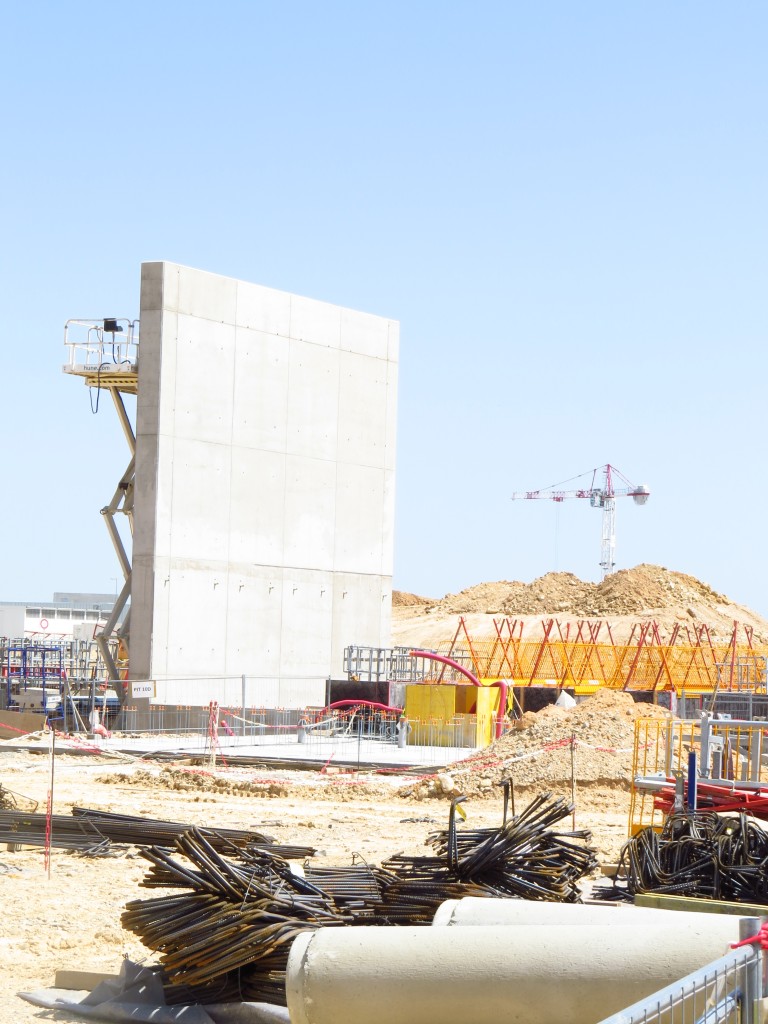
Preparing for the first Chinese transformer
2016-06-24 - Work is underway on the platform to prepare for the installation of the first PPEN transformer (for the pulsed power electrical network) delivered by China.
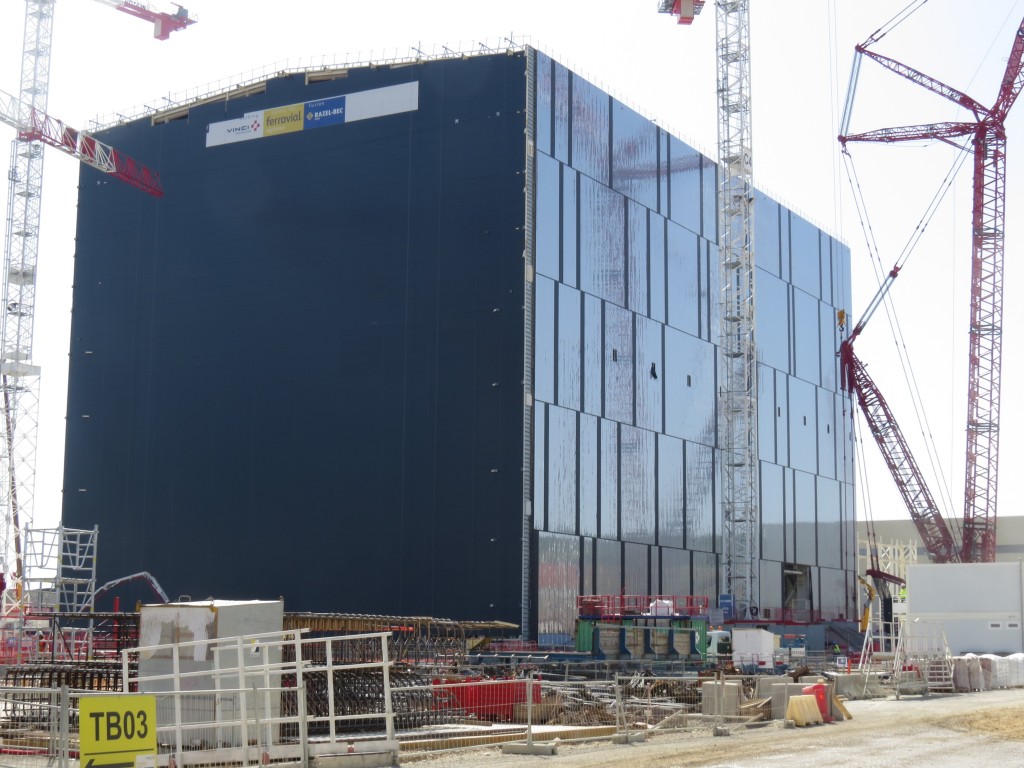
Like a giant blackboard
2016-06-24 - Cladding is now completed. In a few days, a giant poster of the ITER Tokamak will be installed.
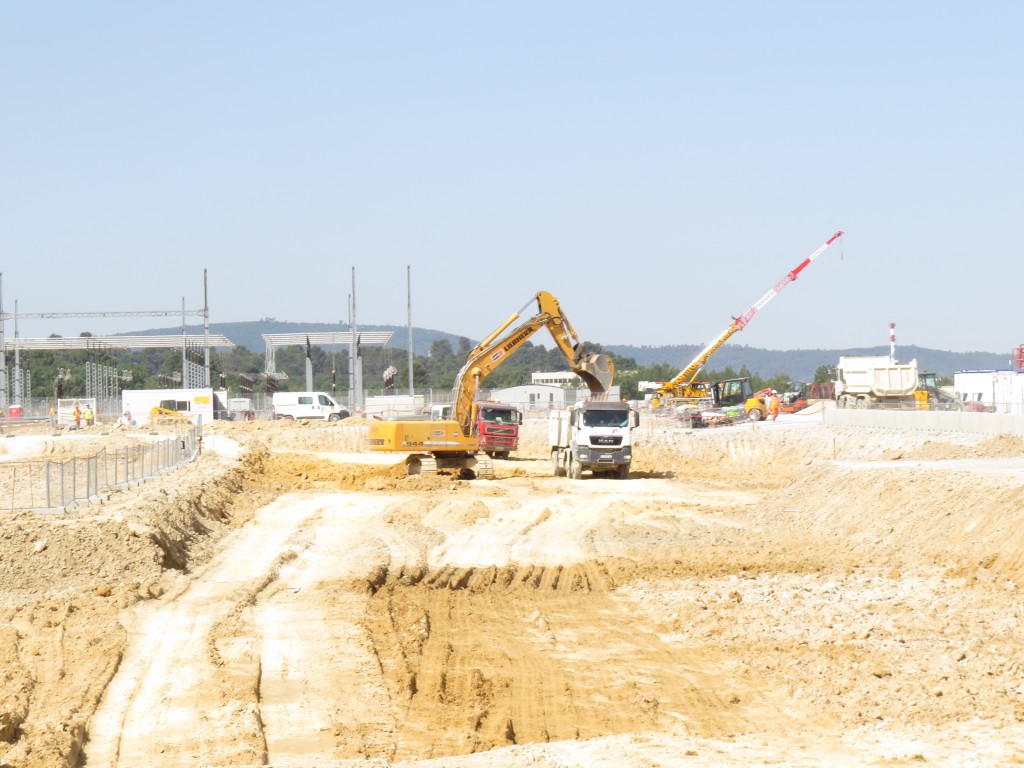
Excavation works
2016-06-24 - Digging continues on the site of the Magnet Power Conversion buildings in June.
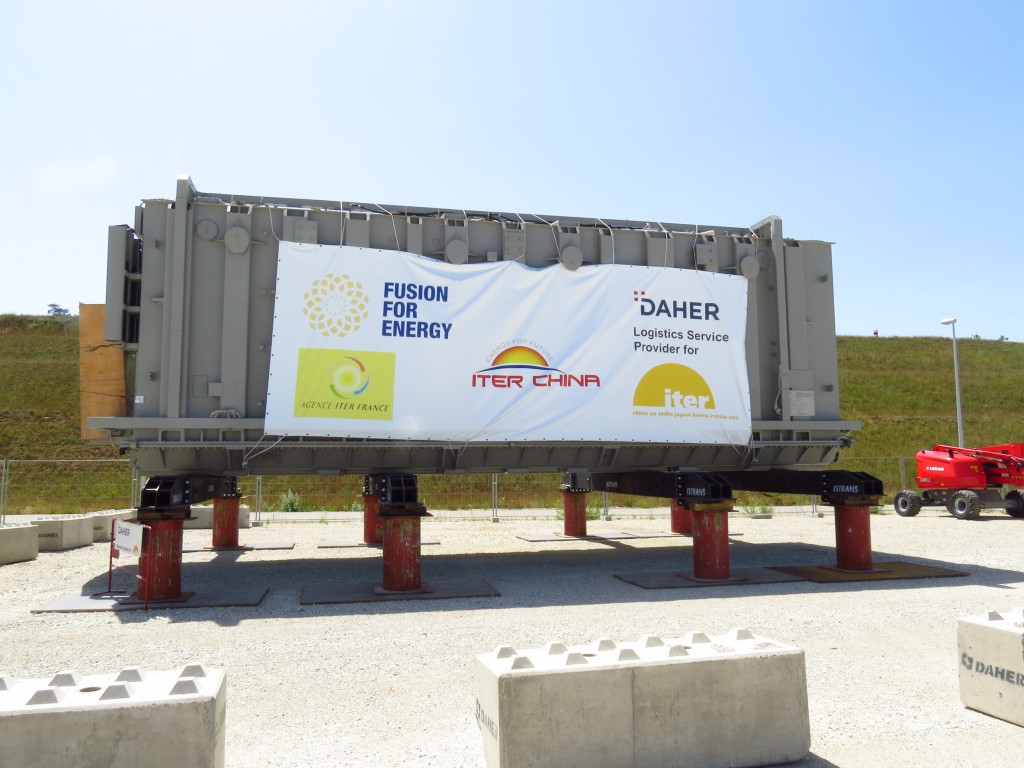
Standing in wait
2016-06-24 - This is the first of three transformers delivered by China for ITER's pulsed power electrical network (PPEN). It is in temporary storage on the ITER platform while the transformer "pit" is readied.

More in June
2016-06-24 - Three more base section segments have arrived on site. The 60-degree, 120-tonne sections form half of Tier 2 of the cryostat base.

Segments arriving
2016-06-24 - Three large 60° segments of the ITER cryostat base (tier 2) arrive on site for delivery to the Cryostat Workshop.
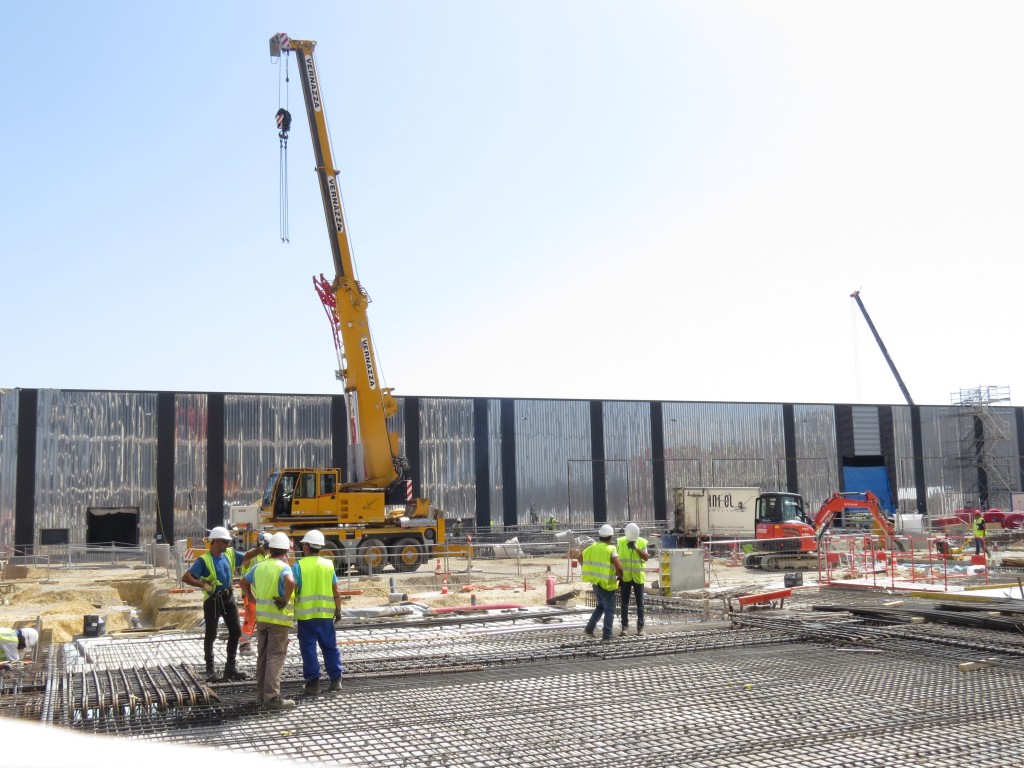
Activity all over the platform
2016-06-24 - Adjacent to the Site Services Building (completed, in background) work is underway on the foundations of the Radio Frequency Heating Building.

Trolley rides to the top
2016-06-17 - On Friday 17 June, a trolley is lifted to join the two girders already in place. Operators moved the girders to the end of the building to free the opening in the roof.
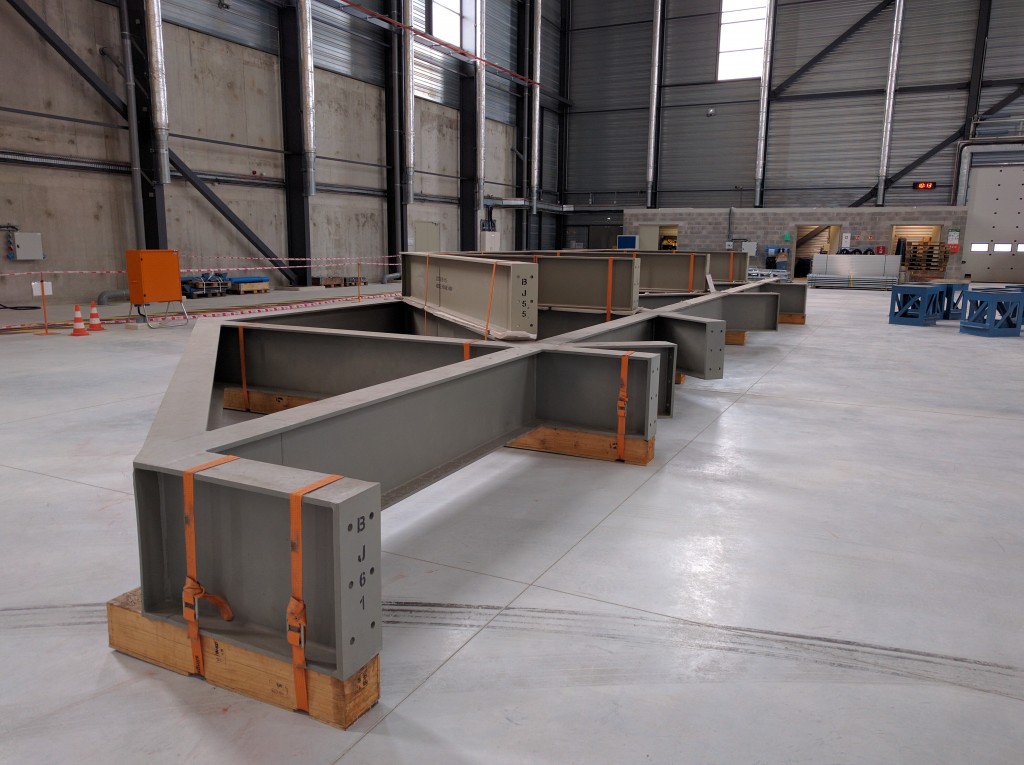
Frame to be assembled
2016-06-16 - 30 x 30 metre steel frames will be used as assembly platforms and transporters for the completed cryostat sections. They first frame segments arrived in June.

Assembly frame arrives in batches
2016-06-16 - Welding activities will take place on large steel frames that act first as assembly platforms and later as support fixtures that interface with the transport vehicles. The frames are arriving in pieces from India for assembly in the Cryostat Workshop.

Tokamak Building, June 2016
2016-06-15 - As the building rises on all sides, the circular Tokamak assembly area—called the "pit"—becomes more and more pronounced.

Through a hole in the roof
2016-06-14 - A man-sized hook is passed through an opening in the roof by the beam of the crawler crane. The crane operator, with no direct line of sight to the lifting operations, receives radio instructions from the "rigger," who oversees the whole operation.
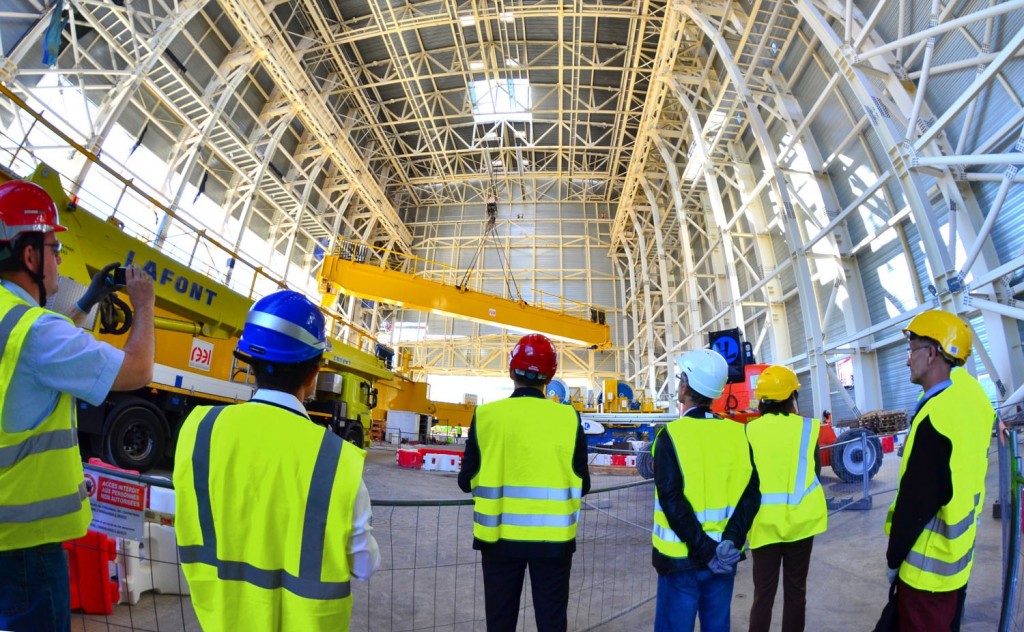
June lift
2016-06-14 - Four girders and four trolleys will be lifted into place over a period of 10 days. The first girders were installed on 14 and 16 June, followed by first of the four 100-tonne trolleys.
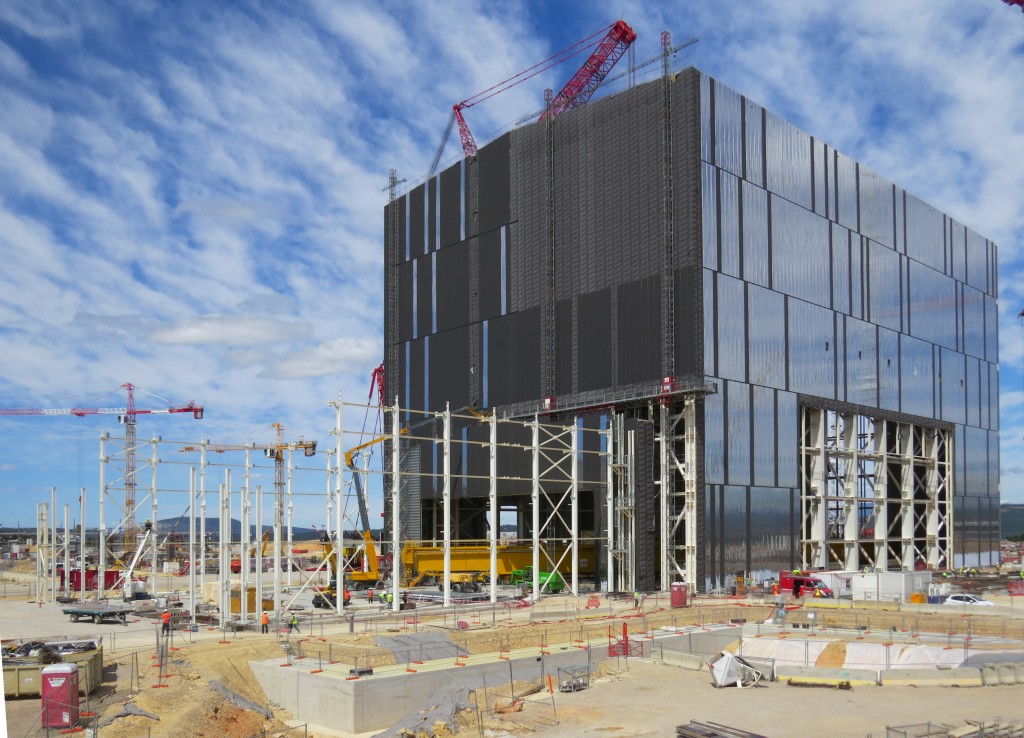
Cleaning Facility
2016-06-14 - The frame is up for the Cleaning Facility, through which all components will pass before entering the Assembly Hall. The other opening in the Assembly Hall, at right, is reserved for the access of the radio frequency heating systems.
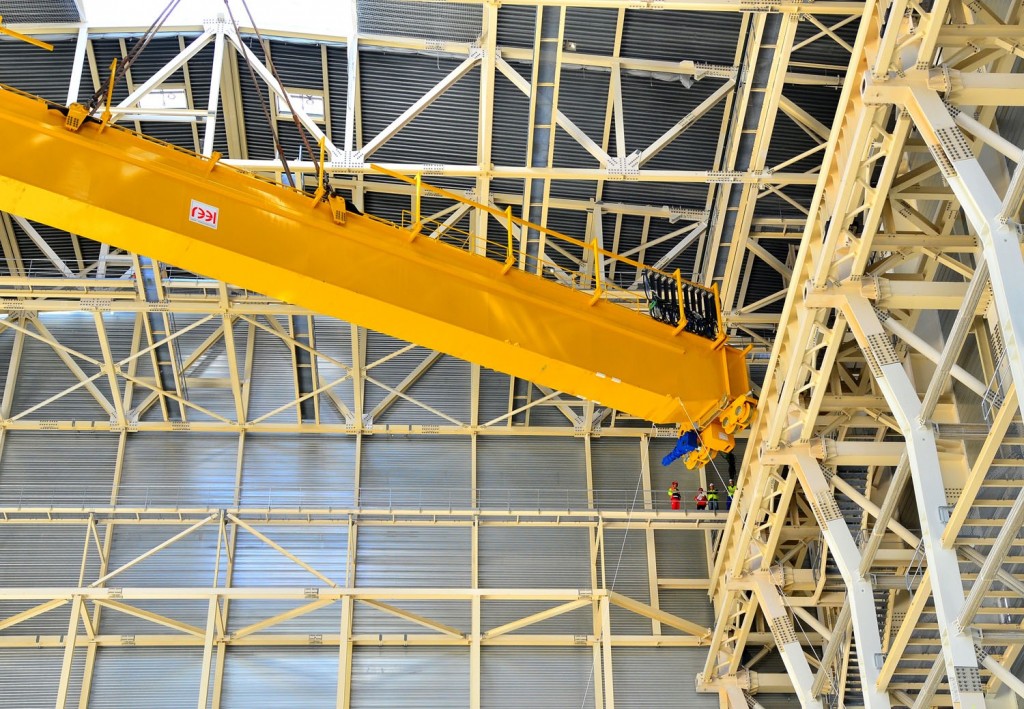
Push, pull and tilt
2016-06-14 - As the girder is lifted toward the overhead rails, 43 metres above the basemat of the Assembly Hall, a bit of pushing and pulling tilts it in the right direction.
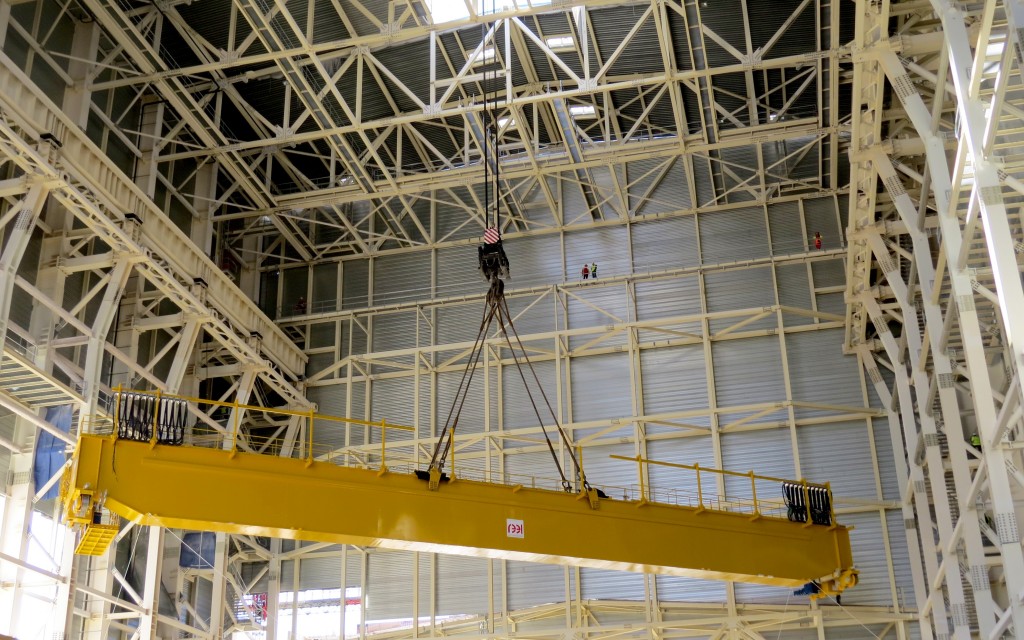
Gaining weight
2016-06-14 - Gear motors, wheels, braces, and electrical equipment ... the fitting out of the girders has added some 30 tonnes. Each girder now weighs 186 tonnes.
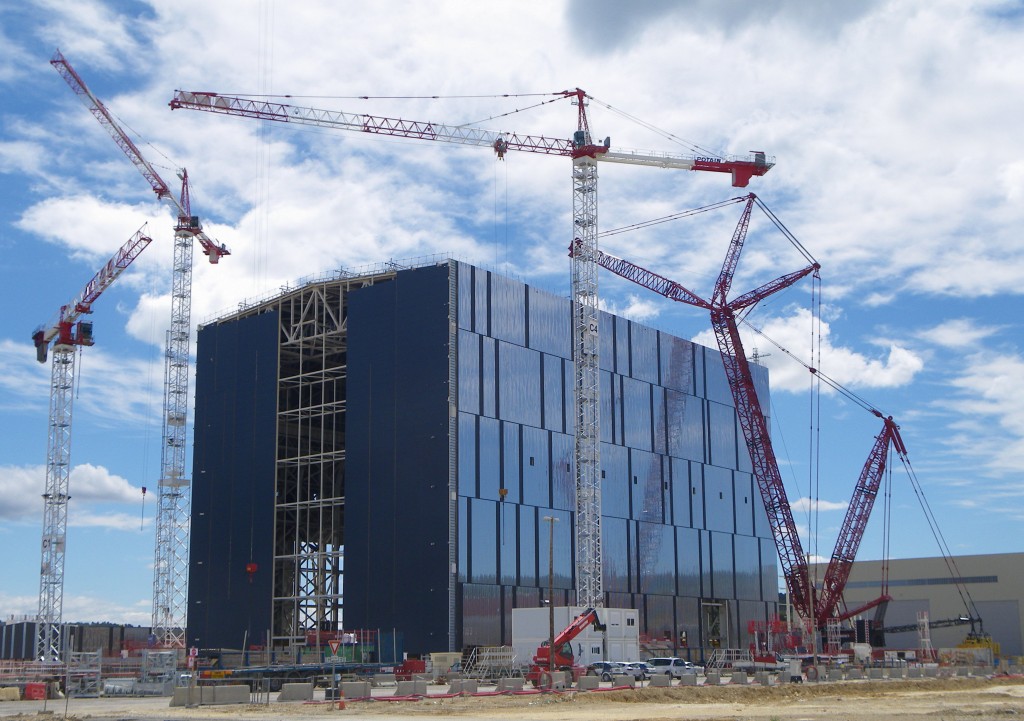
Assembly Building in June
2016-06-14 - The cladding on the northwest facade of the building is nearly completed, and the crawler crane is in place for crane assembly.

Often seen on site
2016-06-07 - From left to right: Laurent Schmieder, head of ITER Site, Buildings and Power Supplies for the European Domestic Agency; and Georges Romero, construction works expert.

First mechanical equipement for Tokamak Building
2016-06-07 - Part of the nuclear effluent drainage system, this 18 m³ tank is the first mechanical equipment to be lowered into the Tokamak Building.
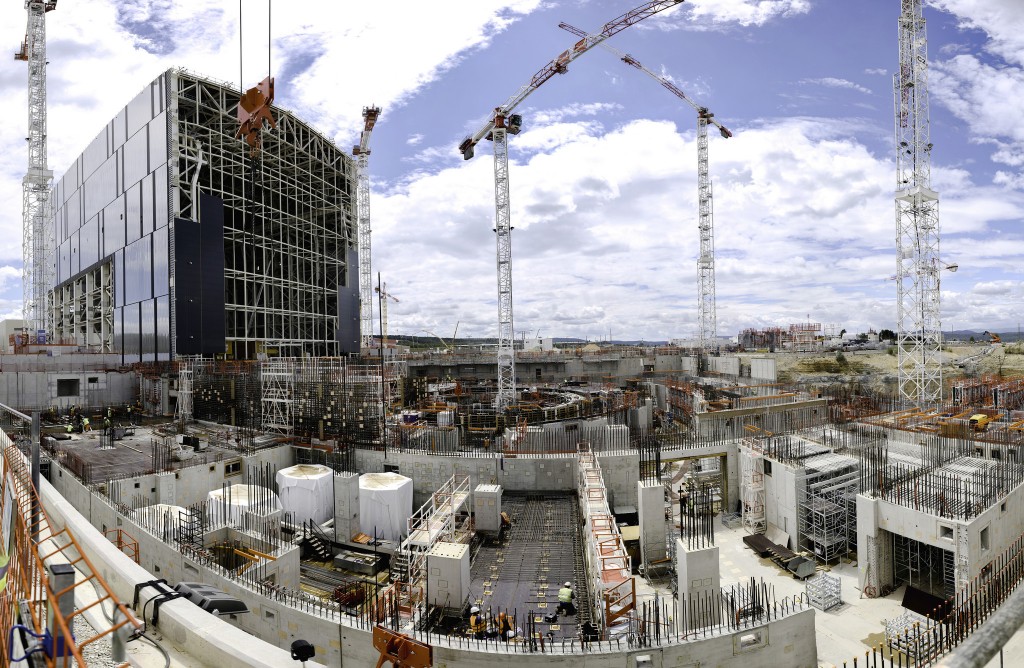
Looking into the Tokamak Complex
2016-06-04 - Looking from the Tritium Building (level B2) towards the central Tokamak area. To the left, the face of the Assembly Building will soon be covered in cladding. Photo: F4E

Magnet power conversion
2016-06-02 - Work will be starting soon in this area of the platform, reserved for the two Magnet Power Conversion buildings.

Spectacular operation to come
2016-06-02 - The girders and trolleys of the overhead cranes are delivered to the Assembly Hall in early June. They will be lifted into position by a huge crawler crane operating from outside the building and passing its hook through an opening in the roof.
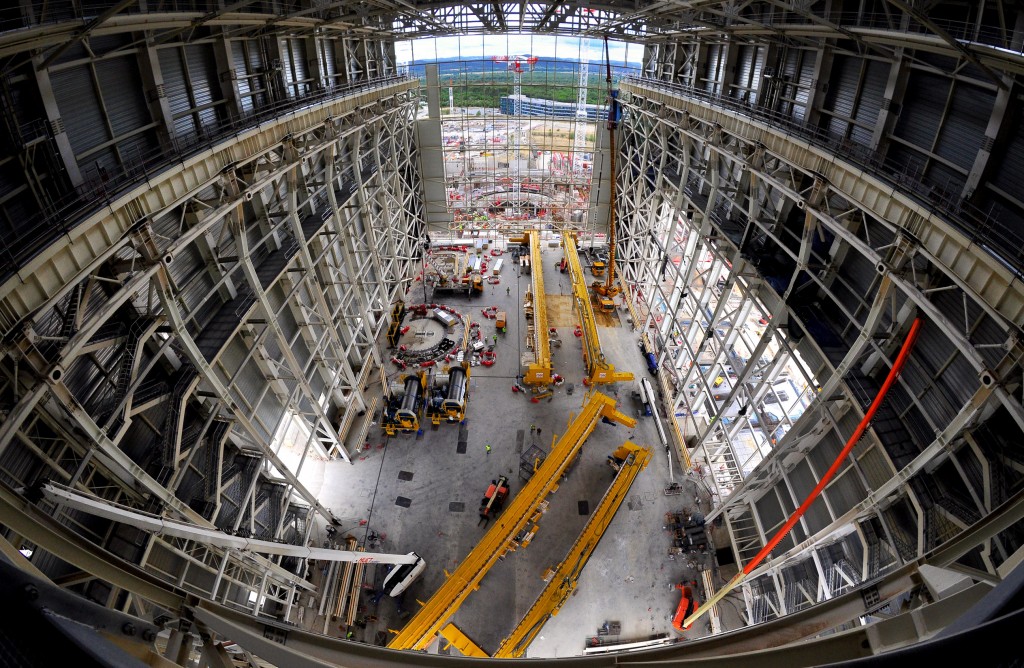
At the level of the overhead cranes
2016-06-02 - After the lifting operation, the cranes will be able to move along the rails of the Assembly Building (visible here). Later, when the Tokamak Building is completed, the rails will be extended over the Tokamak Pit installation area.

Filling in
2016-06-02 - The B1-level walls of the Diagnostic Building reach the level of the platform. Visible to the right, the gap of approximately two metres that completely surrounds the buildings—a space that allows the buildings, on their basemat, to absorb ground motion in the case of an earthquake.

Working on the B1 level
2016-06-02 - On the left, the B1 level basemat for the Diagnostics Building is in place and work has started on the inner partitions. The part of the Tokamak Building B1 basemat that was realized on 26 April can be seen in the lower right of the frame.

Magnet power conversion
2016-06-02 - Work will be starting soon in this area of the platform, reserved for the two Magnet Power Conversion buildings.

A view that won't be around forever
2016-06-02 - This spectacular angle for photography is about to be closed off as a temporary wall is progressively built between the Assembly Building and the Tokamak Pit.

An unusual view
2016-06-02 - The Tokamak Pit and ITER Headquarters, as seen from the rear of the Assembly Building.
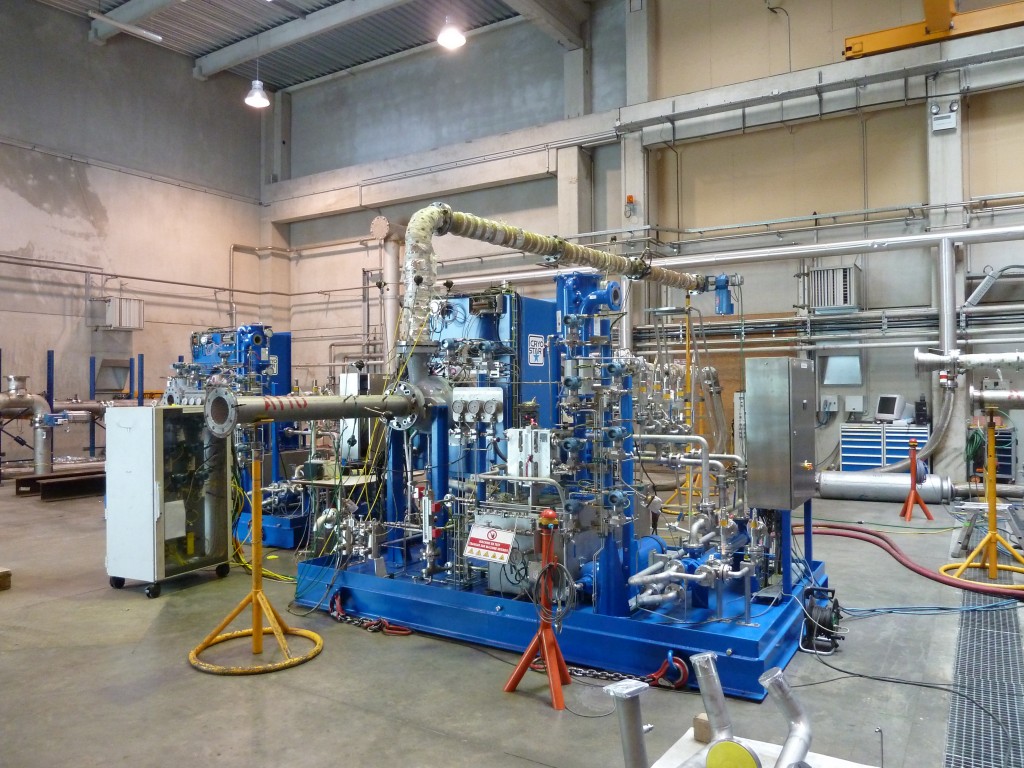
Liquid nitrogen plant components pass tests
2016-05-24 - Four turbines produced for ITER's liquid nitrogen (LN2) cryogenic plant have successfully passed factory acceptance testing. Photo: F4E

Four girders await
2016-05-18 - The four overhead crane girders have been stored in the Poloidal Field Coil Winding Facility until they can be assembled with gear motors, braces, electrical equipment and the like. In June, they will be moved to the Assembly Hall for installation.
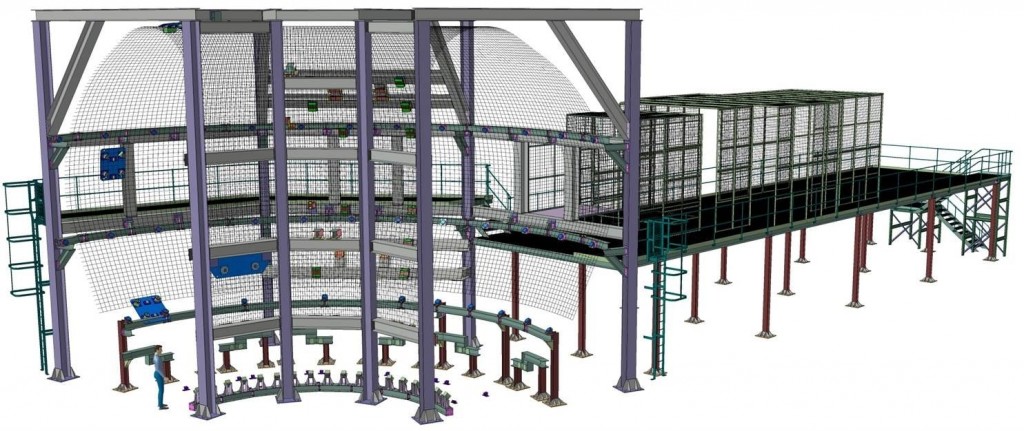
Modular tools for in-vessel assembly
2016-05-15 - In order to carry out the installation of the ITER in-vessel components—such as the diagnostic looms, in-vessel coils, blanket shield blocks and first-wall panels—the ITER Organization will require a set of specifically engineered tools. The ITER Organization is working with CNIM (Toulon, France) for a trial, test and training facility that demonstrates that the tooling can achieve the required in-vessel assembly tasks.
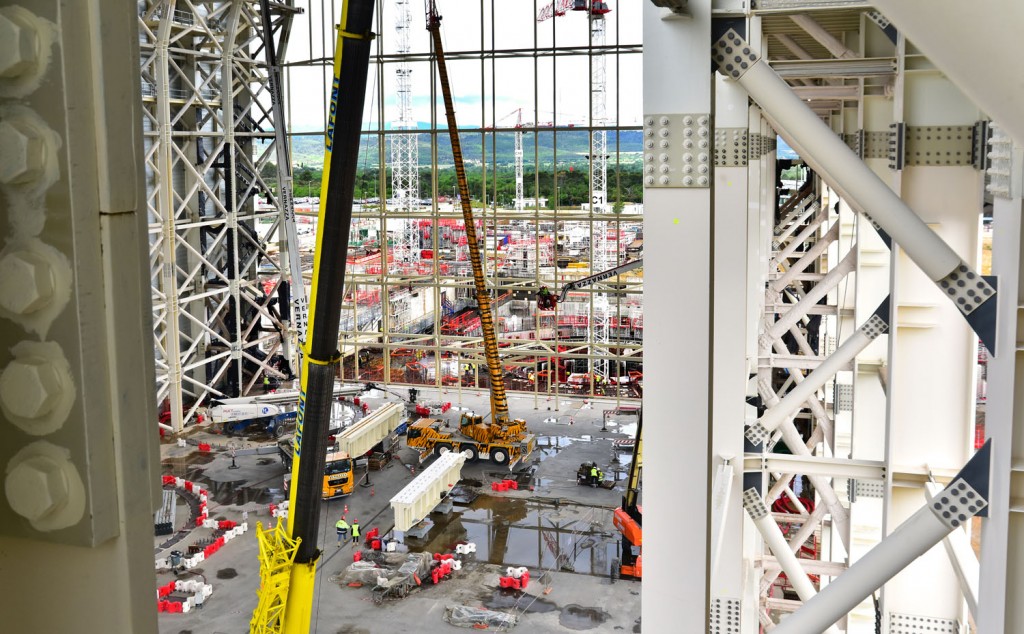
Climbing 45 metres toward the roof
2016-05-12 - Heading up to the level of the overhead crane rails (15 stories), our photographer shot this picture through the pillars of the Assembly Hall.
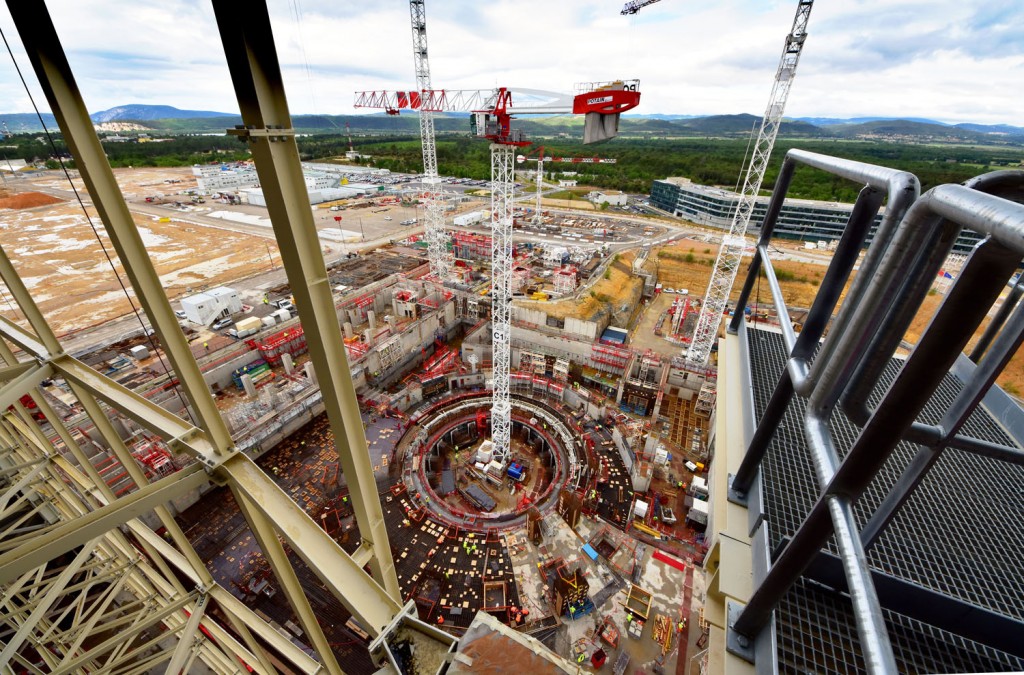
Eagle-eye view
2016-05-12 - From the Assembly Hall, the view of the Tokamak Pit is exceptional. Workers are advancing on the B1 level (basement 1) of the Tokamak Complex.
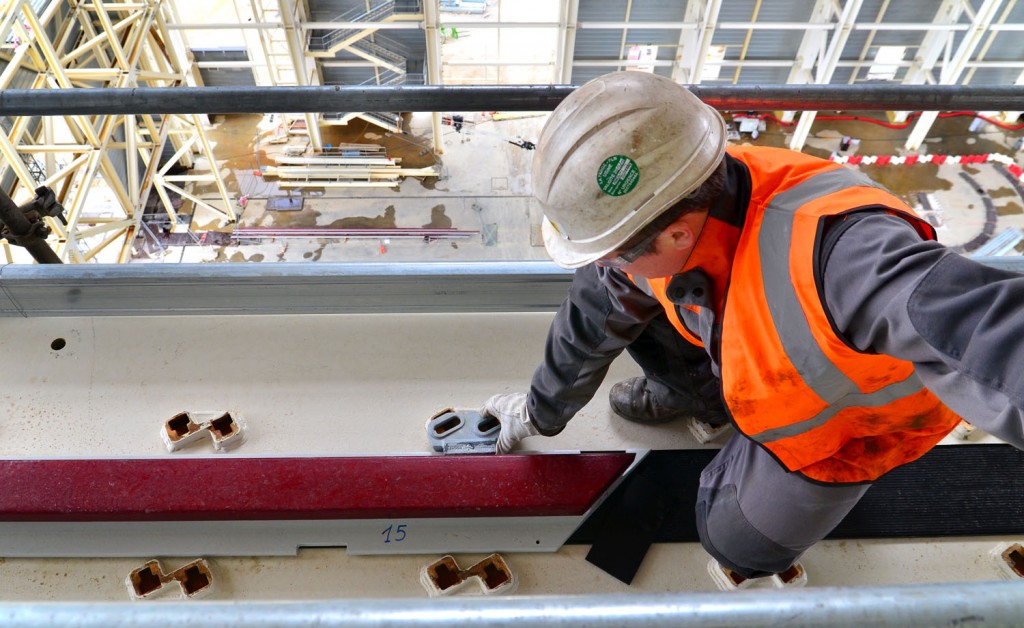
Careful assembly process
2016-05-12 - It will take a few weeks to install the rails and fine tune their alignment.
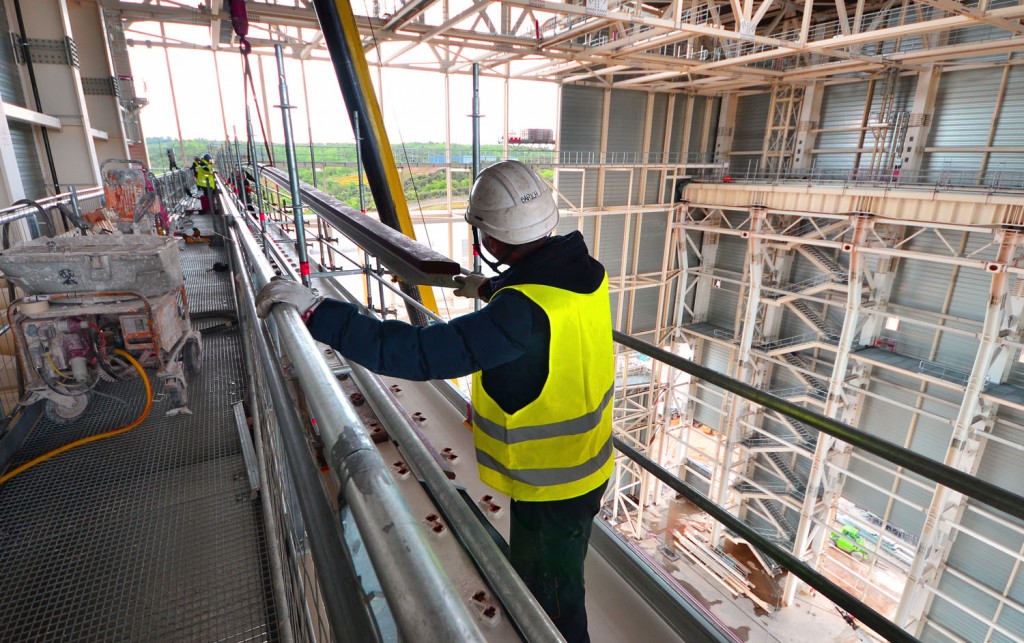
Another rail is positioned
2016-05-12 - Each rail is fastened with heavy clips to the ledge formed by the railway beams.
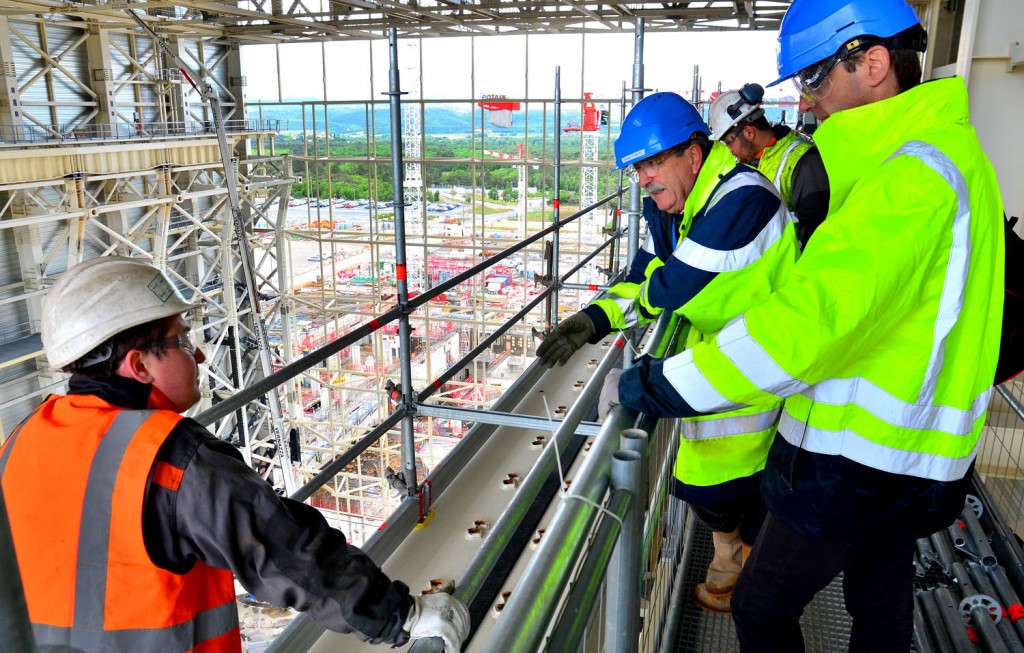
Adding the rails
2016-05-12 - 43 metres above the basemat of the Assembly Hall, workers are laying the rails for the lifting system that will handle components weighing up to 1,500 tonnes.

Piece by piece
2016-05-12 - Each rail segment is between 10 and 18 metres long and will rest on beams that run the entire length of the Assembly Building (and, one day, the Tokamak Building).
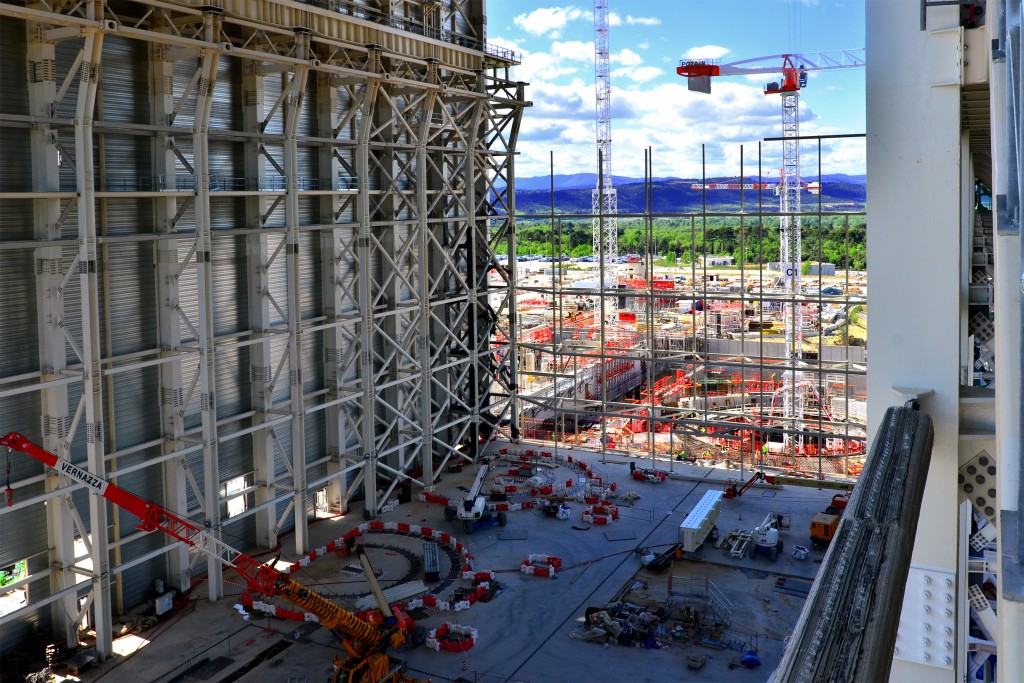
Cranes coming soon
2016-04-26 - Rails will be set in place for the components of the massive overhead cranes. The rails will be 45 metres above the basemat.

The Assembly Hall ... from the inside
2016-04-26 - To capture this original view of the 60-metre-tall ITER Assembly Hall, our photographer stretched out flat on his back.

A temporary wall
2016-04-26 - The frame is up for the temporary wall that will be erected between the Assembly Hall and the Tokamak Complex, until construction of the Tokamak Complex is complete.
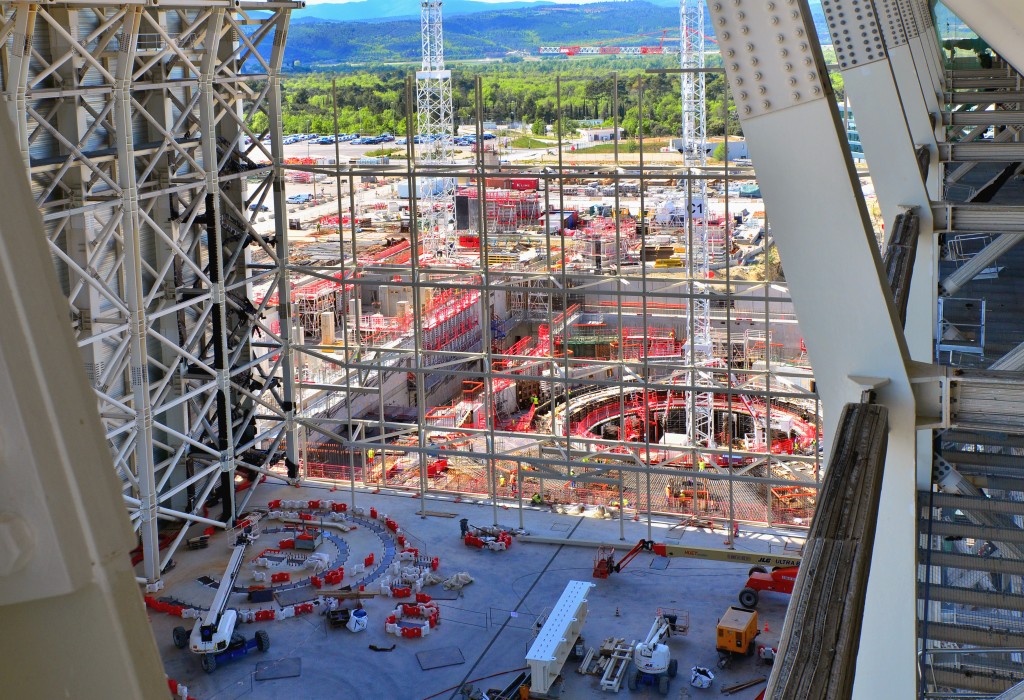
The Tokamak "Pit"
2016-04-26 - As the B2 basement level of the Tokamak Complex disappears under the reinforcement of the B1-level basemat, the central assembly area for the ITER machine (called the "Pit") becomes more and more visible—especially from a certain height.
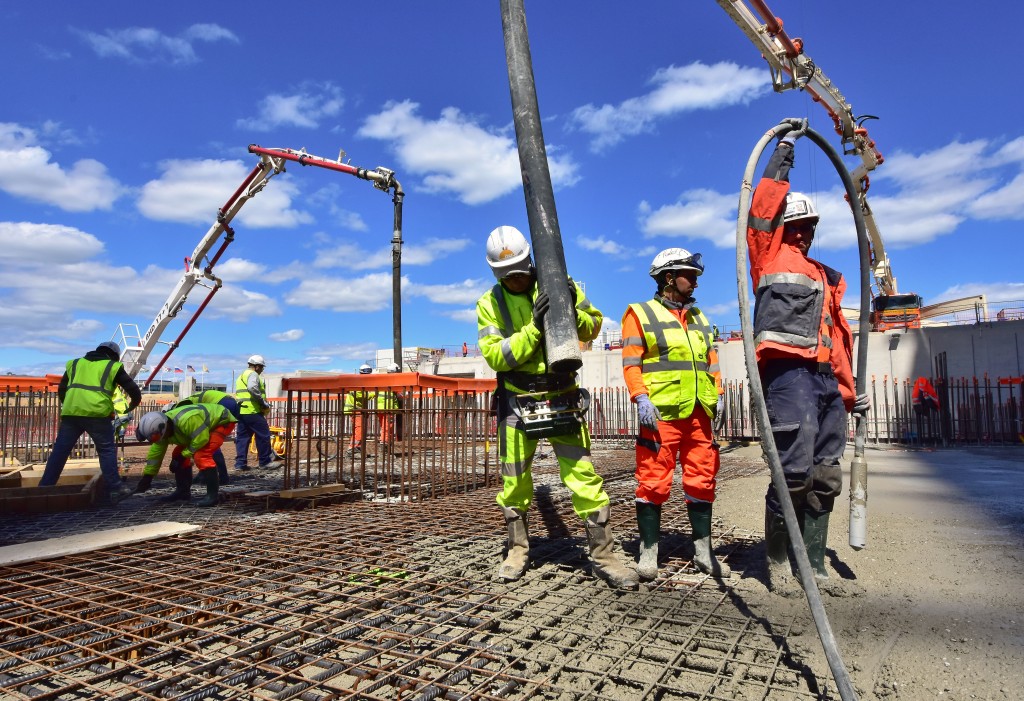
A full day of pouring
2016-04-26 - Some 540 cubic meters of concrete are employed in filling a 750 square-metre area (plots 4 and 5) for the B1 basemat of the Tokamak Building.
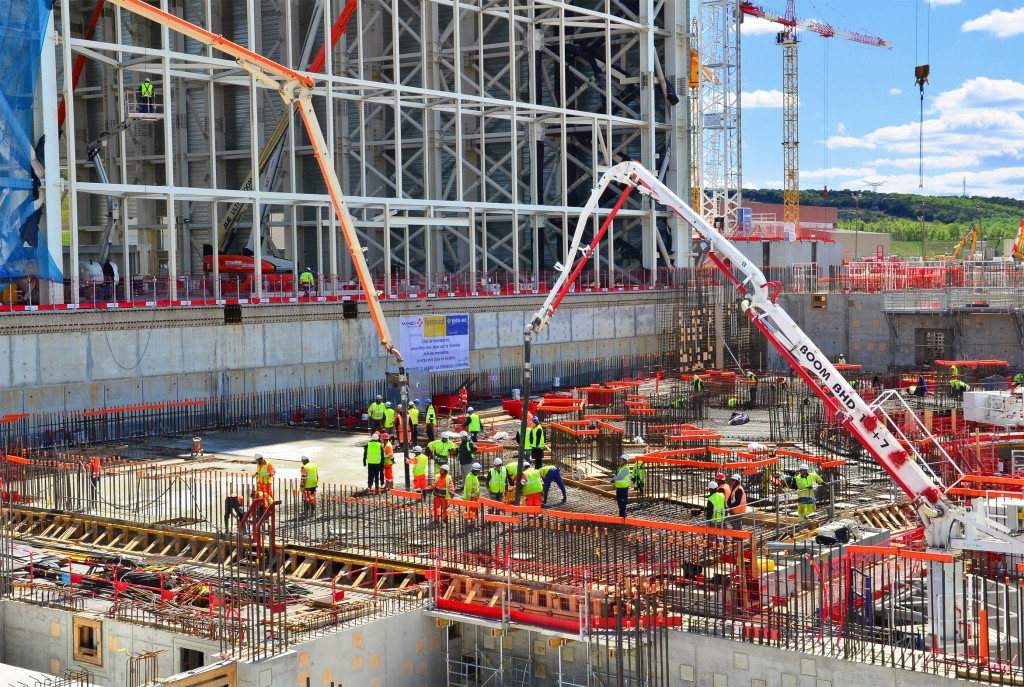
Milestone for the Tokamak Building
2016-04-26 - Concrete pouring for the B1 basement level of the Tokamak Building begins on Tuesday 26 April. When the B1 floor (basemat) is in place, the construction of B1 walls will bring the Tokamak Complex flush with the level of the platform.
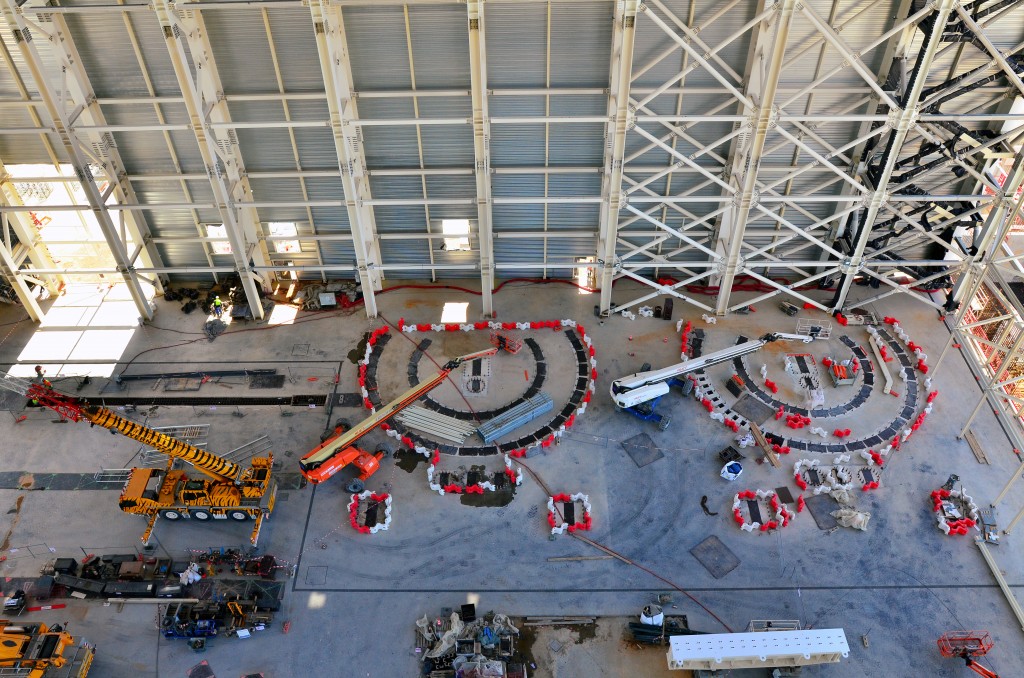
From a high perch
2016-04-26 - What looks like small Lego bricks are actually barriers protecting the anchor plates for ITER's largest assembly tools—the 800-tonne sub-sector assembly tools.
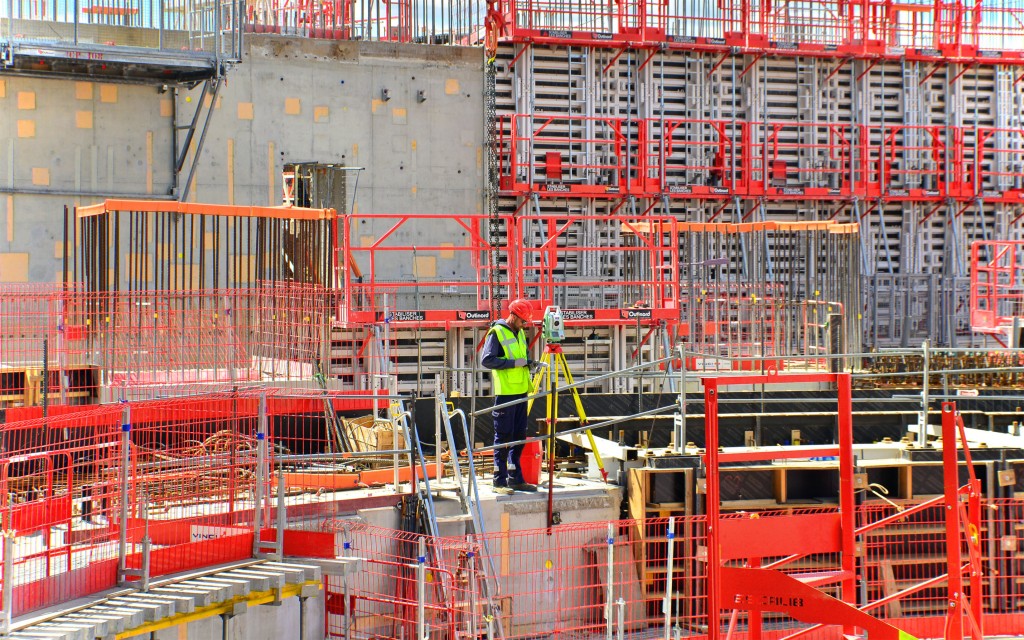
Optical metrology
2016-04-26 - Metrology activities are contributing significantly to the success of Tokamak Complex construction operations.
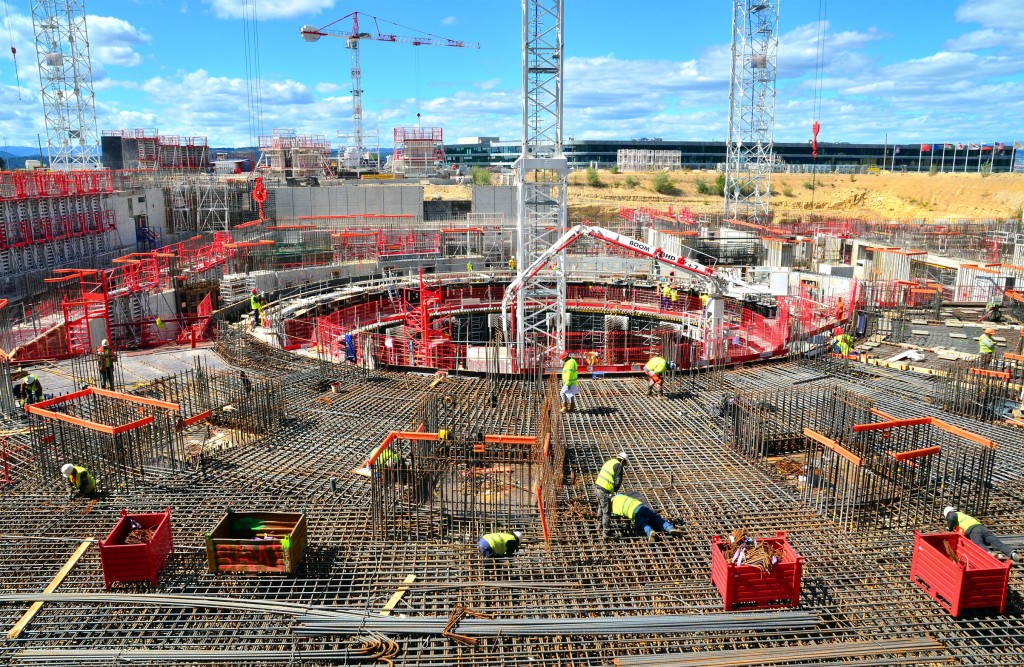
Last touches to the rebar
2016-04-25 - While just outside the frame to the right workers are starting on the first concrete pour of the Tokamak Building, another team puts the finishing touches on the rebar of the central segments. Pouring will resume in May.
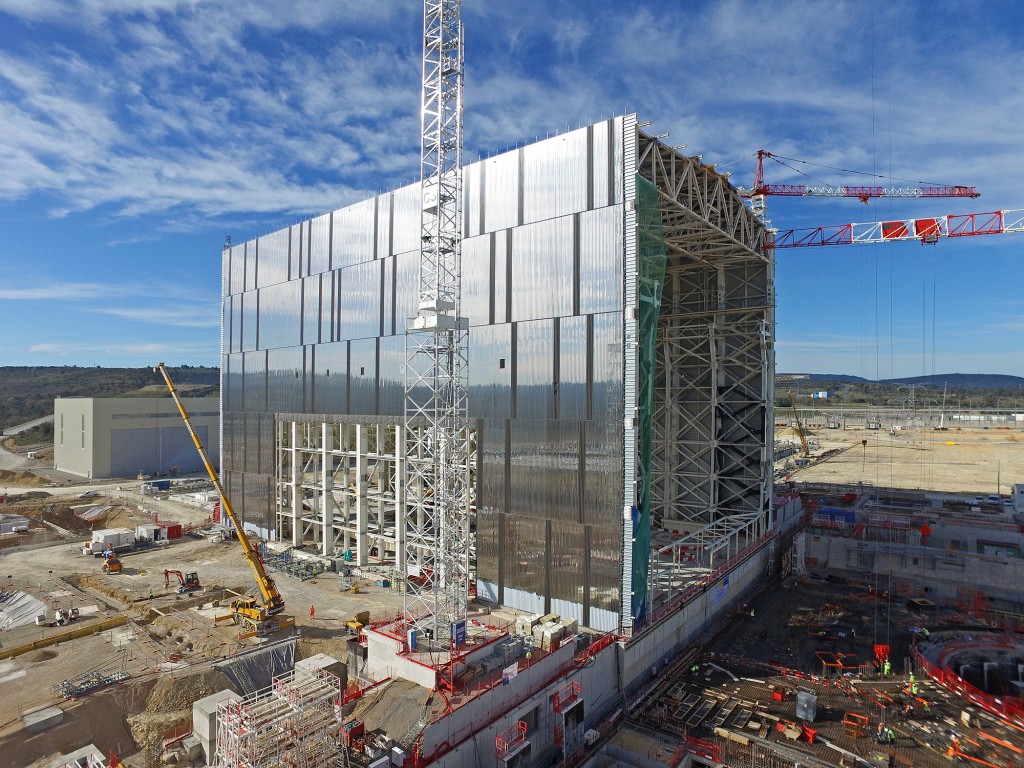
Polished!
2016-04-22 - Cladding work has ended on the north face. The cut-out section is reserved for the Radio Frequency Heating Building, which will be built up against the Assembly Hall. © EJF Riche
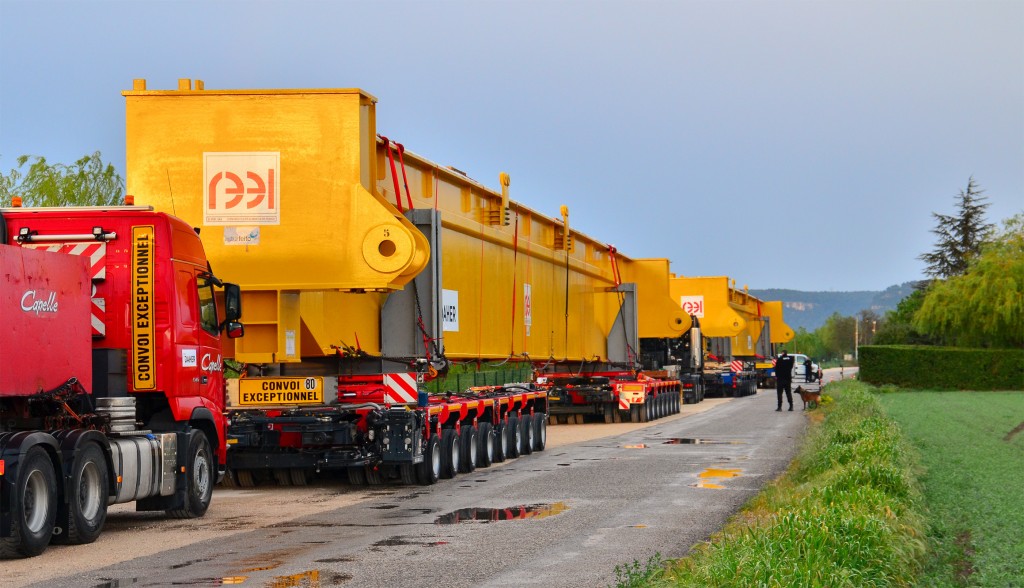
A second pair of girders
2016-04-21 - The logistics of bringing two 47-tonne girders along the roads from the Mediterranean Sea to the ITER site takes careful planning. Here, the double convoy is parked near Peyrolles-en-Provence while operators wait for nightfall to conduct the components at 5 km/hour along the last leg of the ITER Itinerary.

Site acceptance tests for the ion source power supply
2016-04-13 - The multi-year development of the ion source extraction grid power supply came to an end in 2016, with successful site acceptance tests at the NBTF facility. Representatives of the European contractor OCEM ET (Italy) and principal subcontractor Himmelwerk GmbH (Germany) were present. Photo: F4E
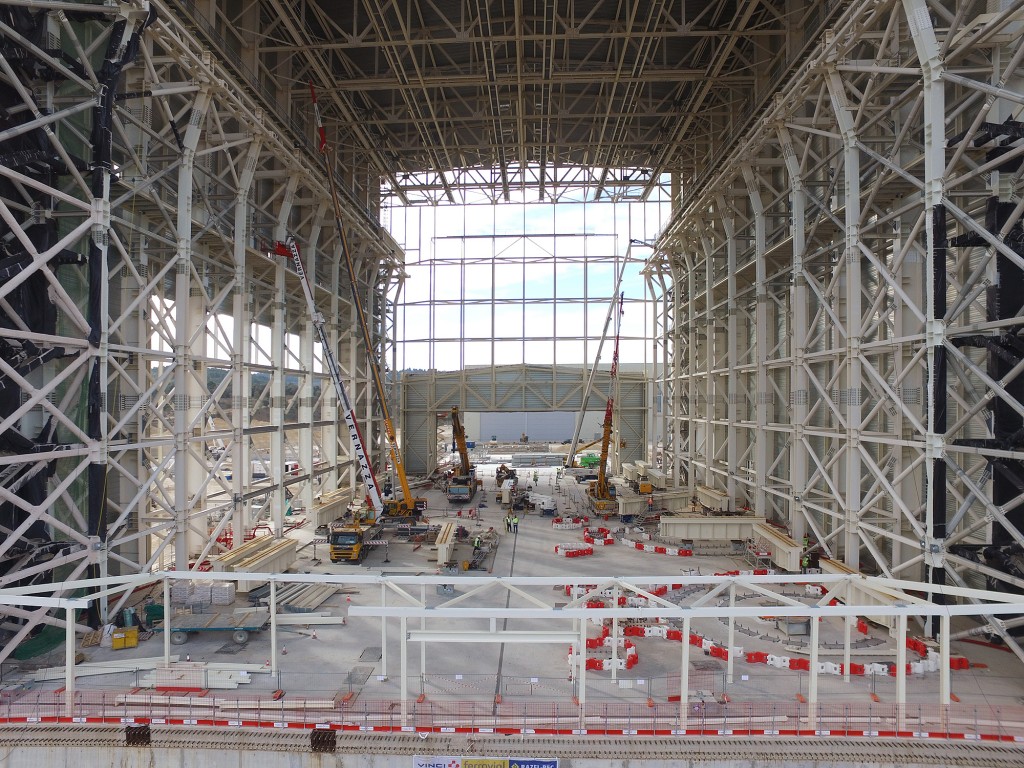
Flying past
2016-04-12 - Taken by drone, this photo captures the interior of the 97-metre-long Assembly Building, where the largest tokamak components will be pre-assembled before their installation. © EJF Riche
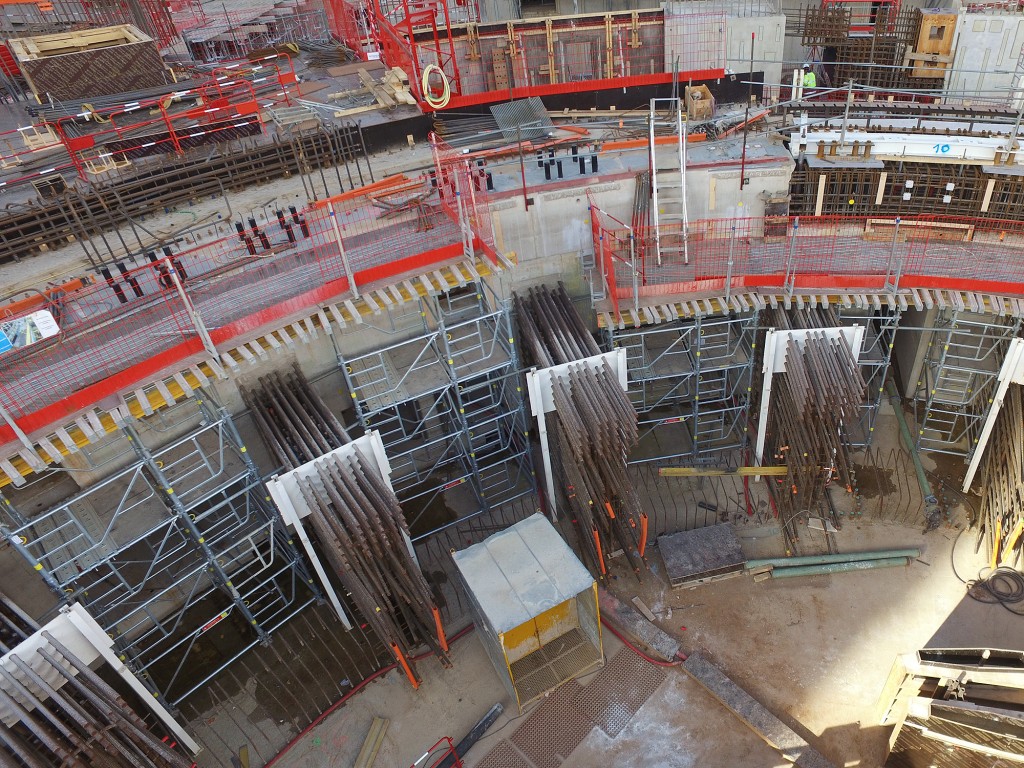
Connecting to the crown
2016-04-12 - One-metre thick radial walls (pictured here as spokes) will connect the massive ITER bioshield to the concrete Tokamak crown, which will support the combined mass of the cryostat, the vacuum vessel, the magnet system and the thermal shield. © EJF Riche

Cryoplant: underground structure completed
2016-04-07 - Work on the foundations and underground structures of the ITER cryoplant is coming to an end. Soon, approximately four dozen 16-metre-high pillars will be erected to support the building's steel structure.

Carefully now!
2016-04-07 - The worksite team slowly lowers one of the tanks into its bed. The water detritiation system is part of Europe's contribution to the ITER Project. Photo: F4E
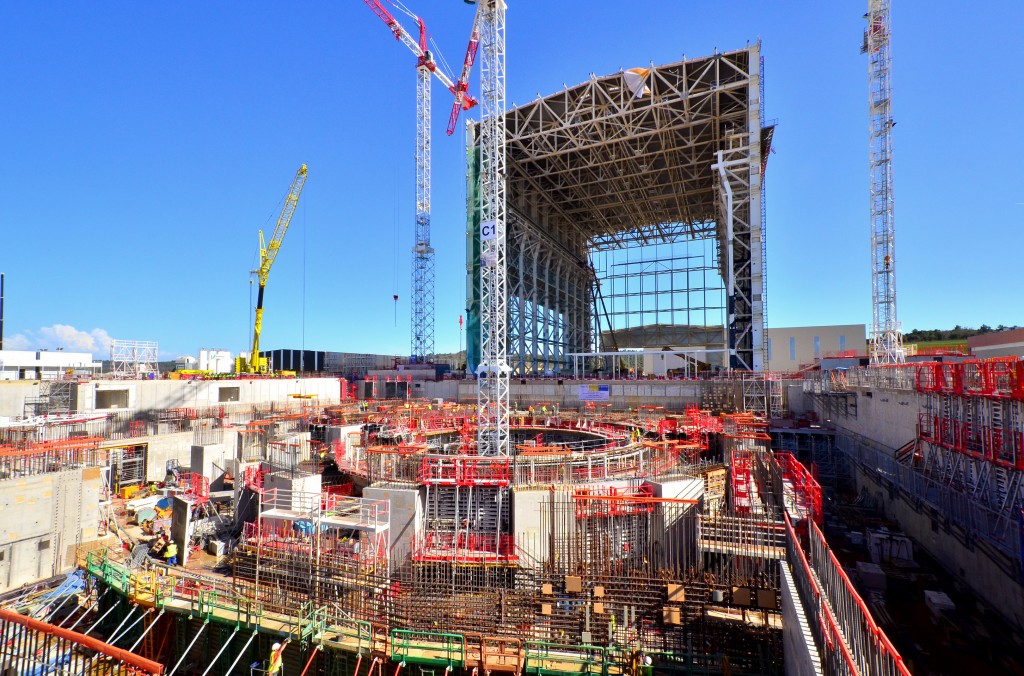
Ever-wider circles
2016-04-07 - Concentric circles of metal and cement surround the space reserved for the ITER Tokamak where, for now, only the central crane stands.

Up another level
2016-04-07 - The installation of rebar installation is progressing on plot #2 of the Tokamak Complex (B1 level) at the right side of the photo. The completion of this second basement level will bring the Tokamak Complex flush with the ITER platform.
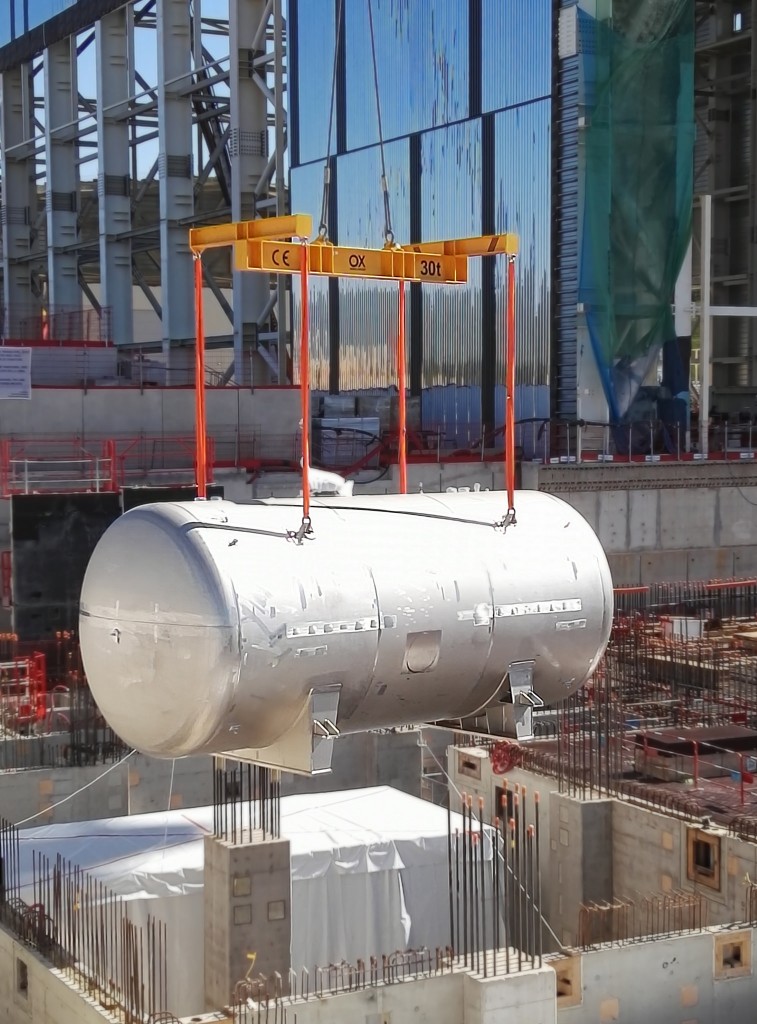
Settled into the basement of the Tokamak Complex
2016-04-07 - Six water detritiation tanks are now in place in the B2 basement level of the Tritium Building—the first plant components to be installed inside the reactor building (the Tokamak Complex). Photo: F4E

Impressive logistics
2016-04-07 - Progress on the ITER site relies on finely tuned logistics. As concrete mixer trucks rush to the cryoplant worksite, every inch of ground surrounding the Tokamak Pit seems to be occupied by stacks of embedded plates, formwork equipment and steel rebar.
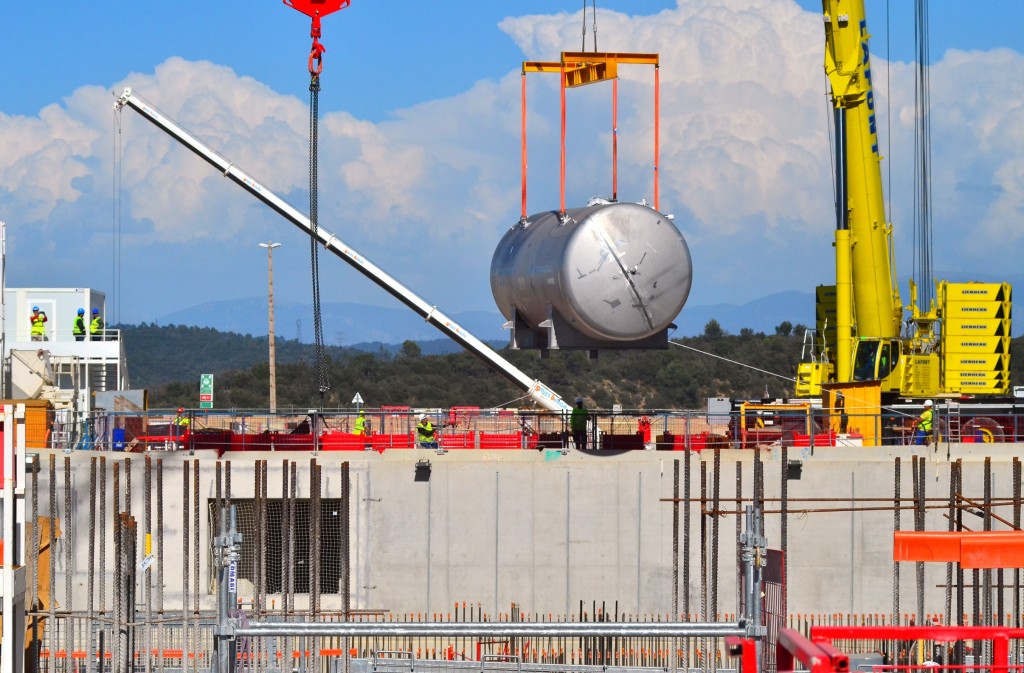
Second drain tank
2016-04-07 - Two of these 100-cubic-metre tanks will join four smaller (20-cubic-metre) tanks in the basement of the Tritium Building before work can start on the next building level. Photo: F4E

(More) men at work
2016-04-07 - The workforce involved with Tokamak Complex construction is set to increase significantly in the next three months. Some 40 formworkers and close to 100 rebar specialists will be added to the teams presently working on the bioshield and the B1 level.

First component placed in Tritium Building
2016-03-29 - The first of six water detritiation tanks was installed on 29 March in the lowest basement level (B2) of the Tritium Building. This is the very first component to be installed in the Tokamak Complex.
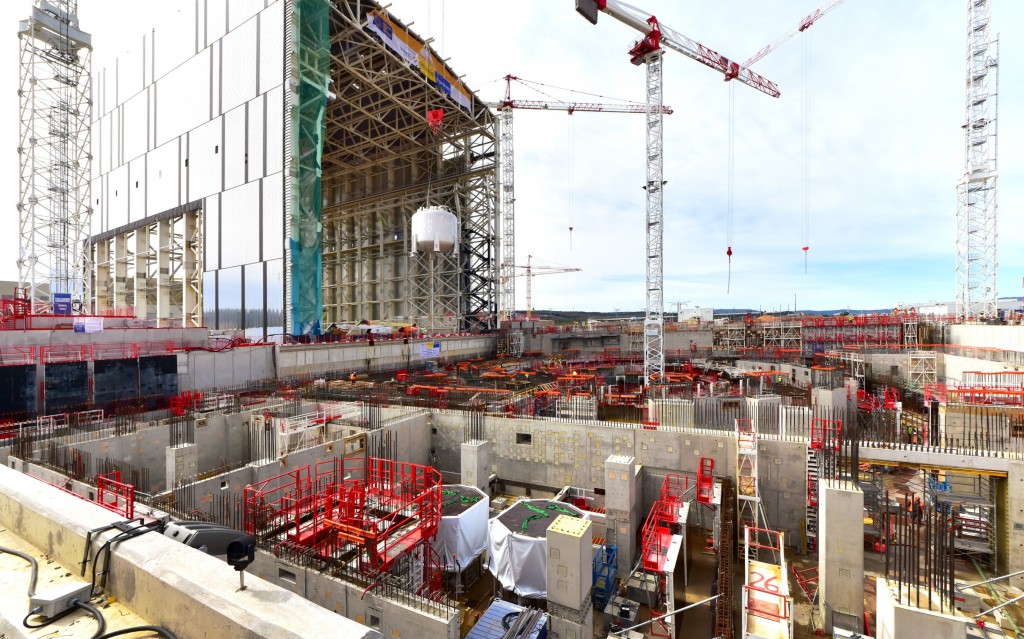
Six in all
2016-03-29 - Six metal tanks supplied by Europe will be installed in the Tritium Building for ITER's water detritiation system.

Temporary shelter
2016-03-25 - The mammoth assembly crane beams will be stored in the Poloidal Field Coils Winding Facility until their installation in the Assembly Building in June.
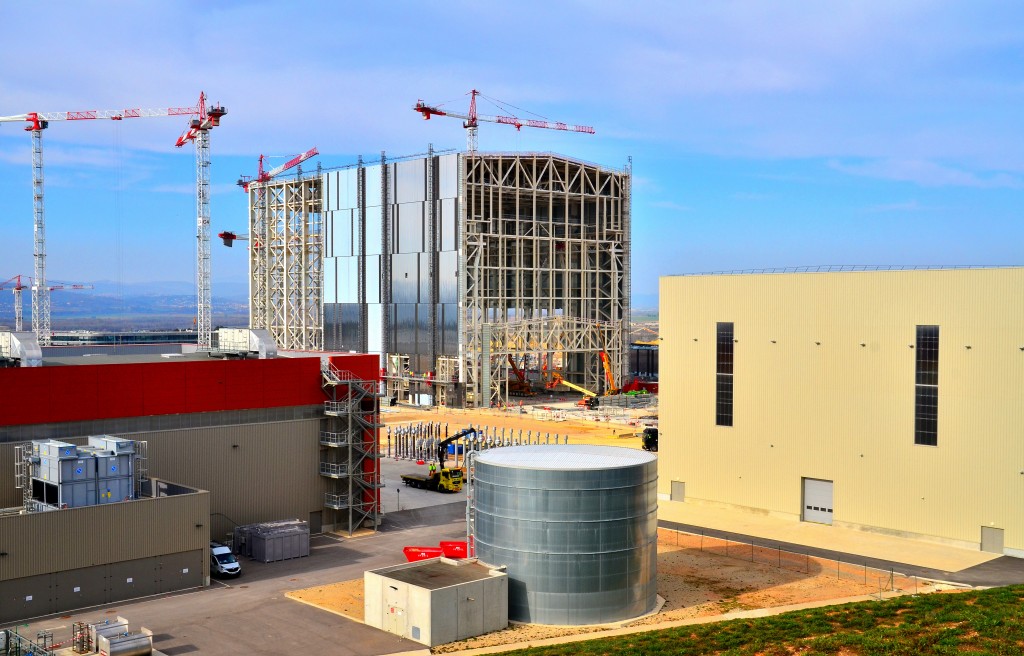
The intended effect
2016-03-22 - As the reflective cladding advances along the metal structure of the Assembly Building, the colours of a March day in Provence appear.
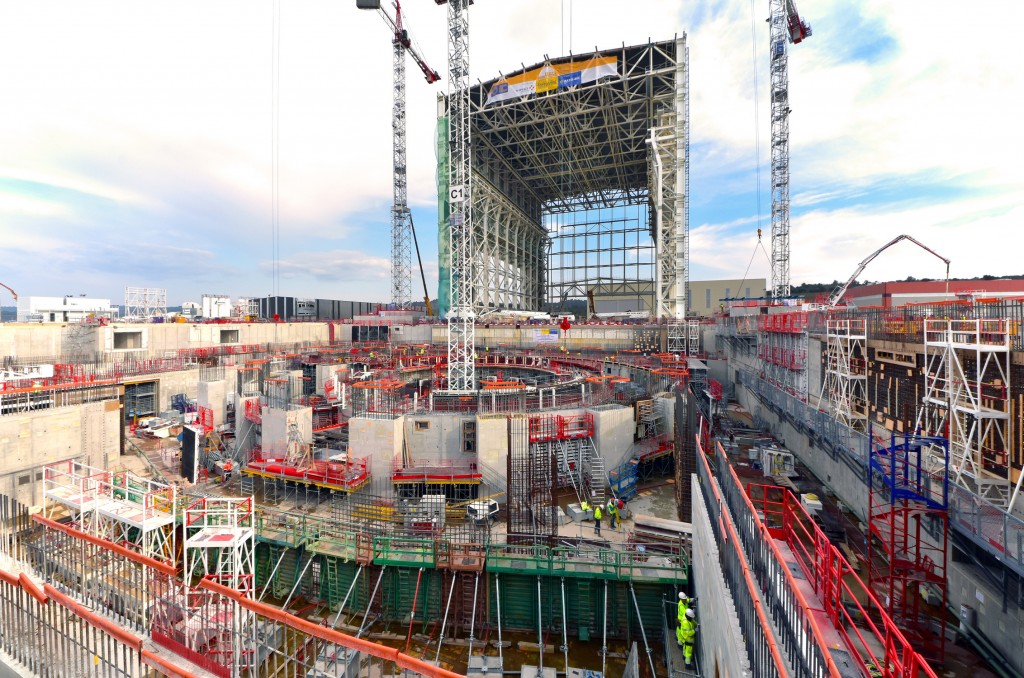
Basement fills in
2016-03-22 - To the right of the photo, work on the B1 basement level of the Diagnostics Building advances, bringing the structure flush with the ITER platform.
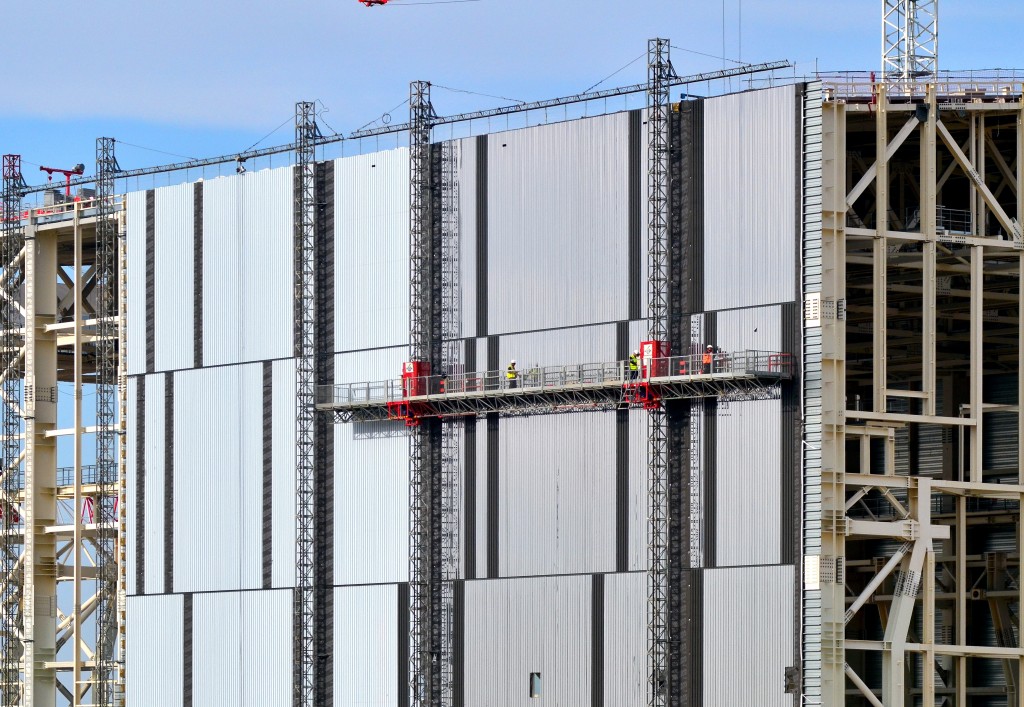
Working at heights
2016-03-22 - The installation of cladding on the 60-metre-tall ITER Assembly Hall requires specific techniques and safety measures.
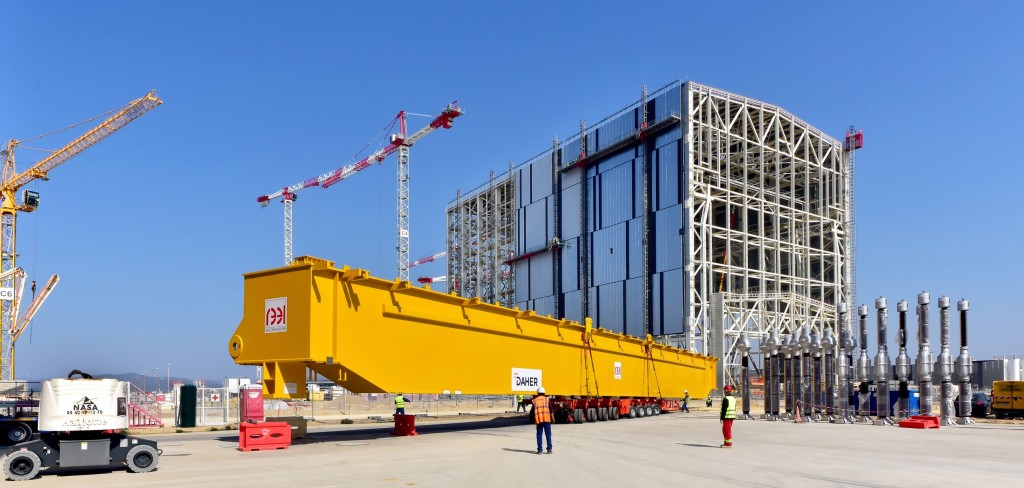
First girder
2016-03-18 - In June this girder, and three others, will be installed on rails inside of the Assembly Building—some 45 metres overhead.
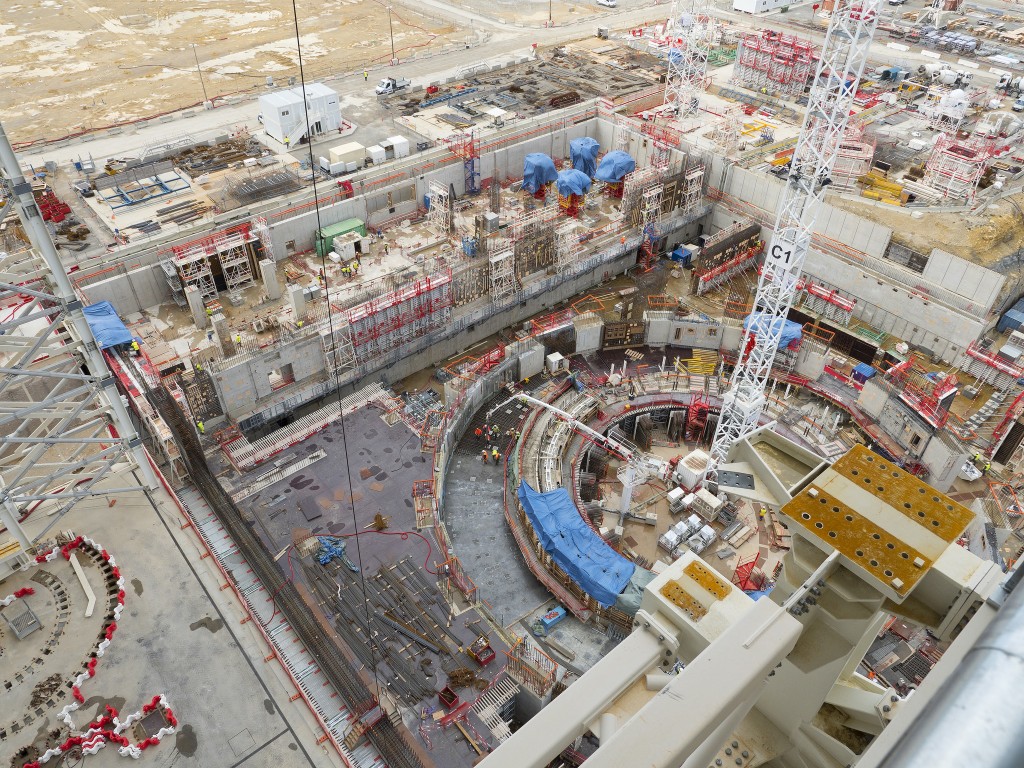
The "Pit"
2016-03-03 - From the top of the Assembly Hall, it's easy to see why we call the tokamak assembly area the "Tokamak Pit." Photo: F4E

Giant footprints
2016-03-03 - The concrete basemat of the hall is ready to receive the twin Sector Sub-Assembly tools, 800 tonnes each, that will pre-assemble the vacuum vessel sectors with the toroidal field magnets and thermal shielding before installation in the pit. Photo: F4E
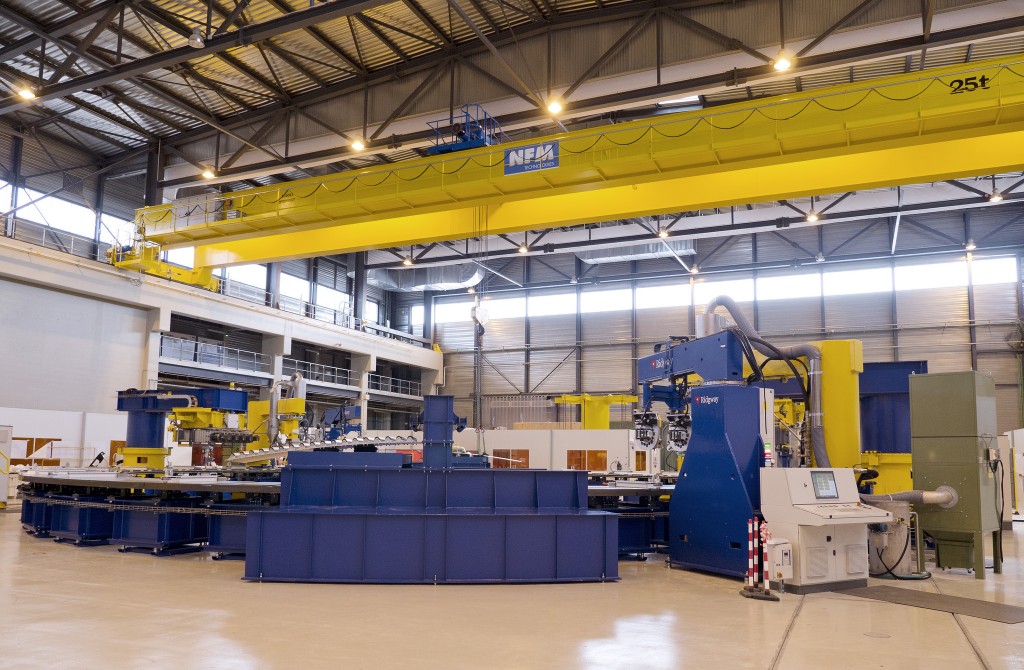
Crane overhead
2016-03-03 - Once wound, the double pancakes will be transported by overhead crane to the next station for impregnation with epoxy resin. Photo: F4E
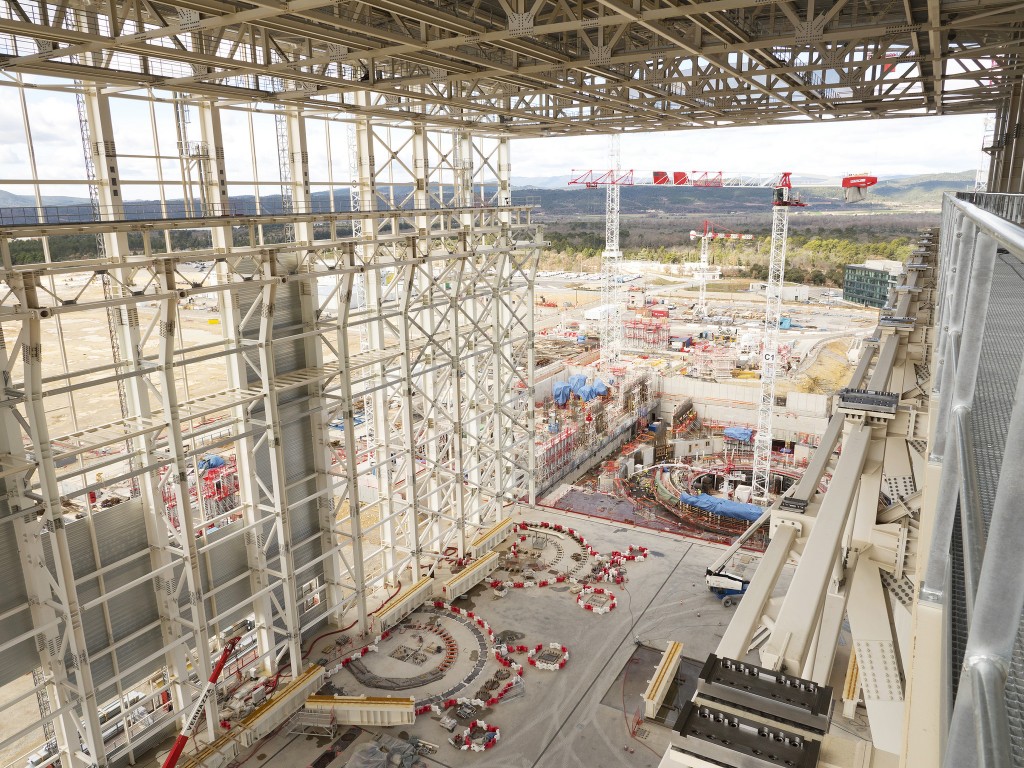
Running 175 m
2016-03-03 - Crane rails will run the entire length of the Assembly Building, and later the Tokamak Building, to form a continuous, 175-metre-long crane bay. Photo: F4E
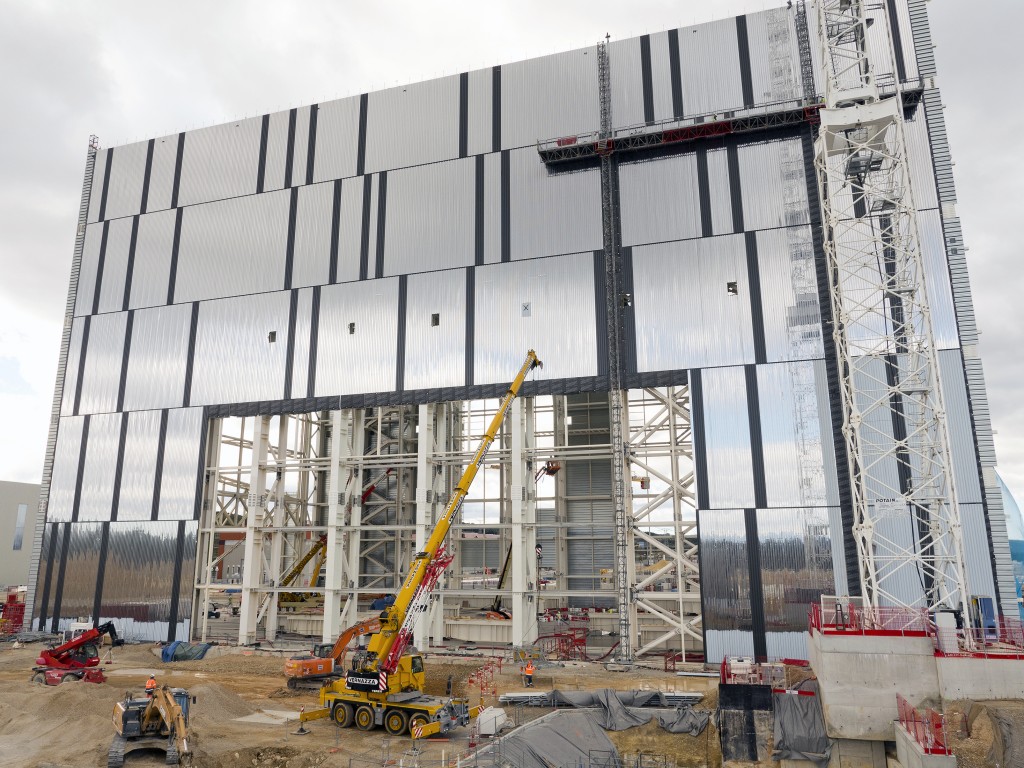
A steel exterior
2016-03-03 - The steel exterior of the Assembly Hall reflects the technological nature of the assembly operations that will take place inside. Photo: F4E

Sophisticated tooling
2016-03-03 - A detail of some of the winding tooling now installed in the building. Photo: F4E

Bioshield mezzanine
2016-03-03 - Just outside the 3-metre-thick ITER bioshield (partially covered in blue), workers are pouring the south side of the bioshield mezzanine. Photo: F4E
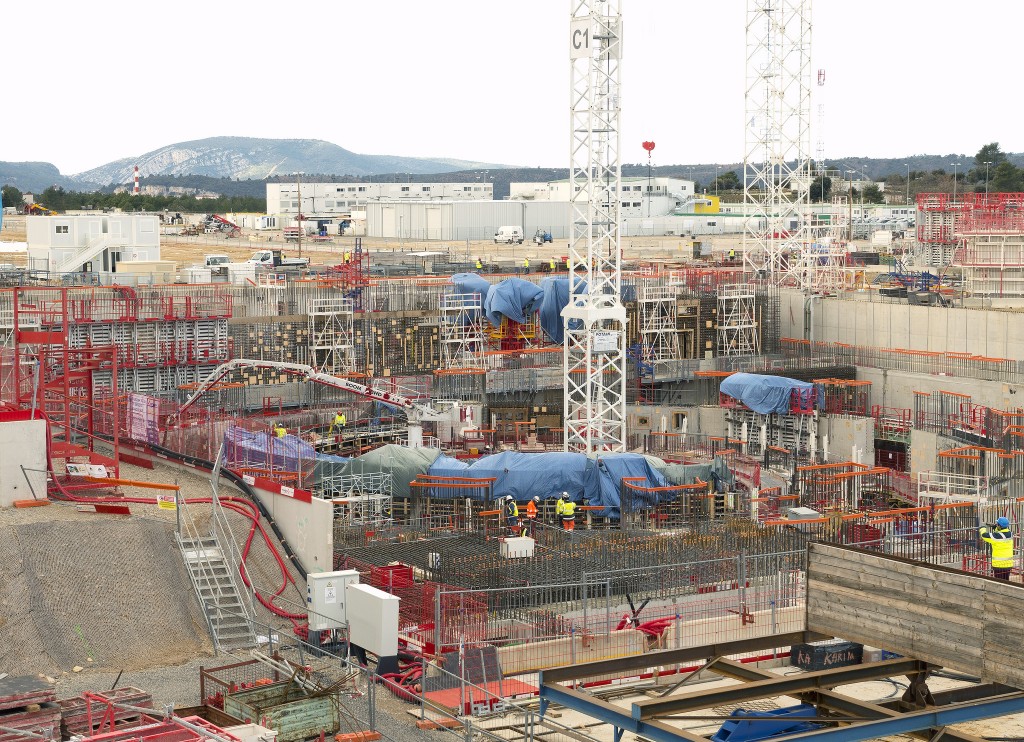
Managing work on site
2016-03-03 - Behind the main construction area, prefabricated buildings house the on-site teams of the consortia charged with carrying out work by the European Domestic agency. Photo: F4E
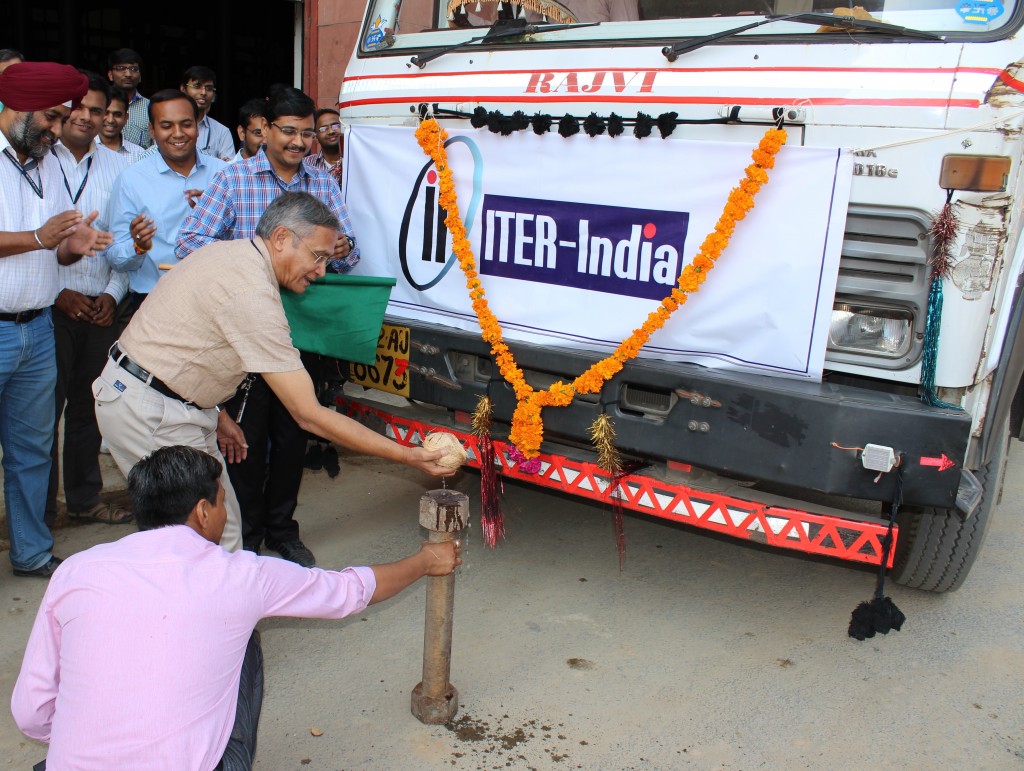
Power supply components en route from India
2016-03-01 - Nine trucks containing components for SPIDER's 100 kV power supply—transformers, switching modules, controllers, high-voltage racks, cables disconnector switches—are now en route to the port of Mundra, on India's west coast, for shipment to Italy.
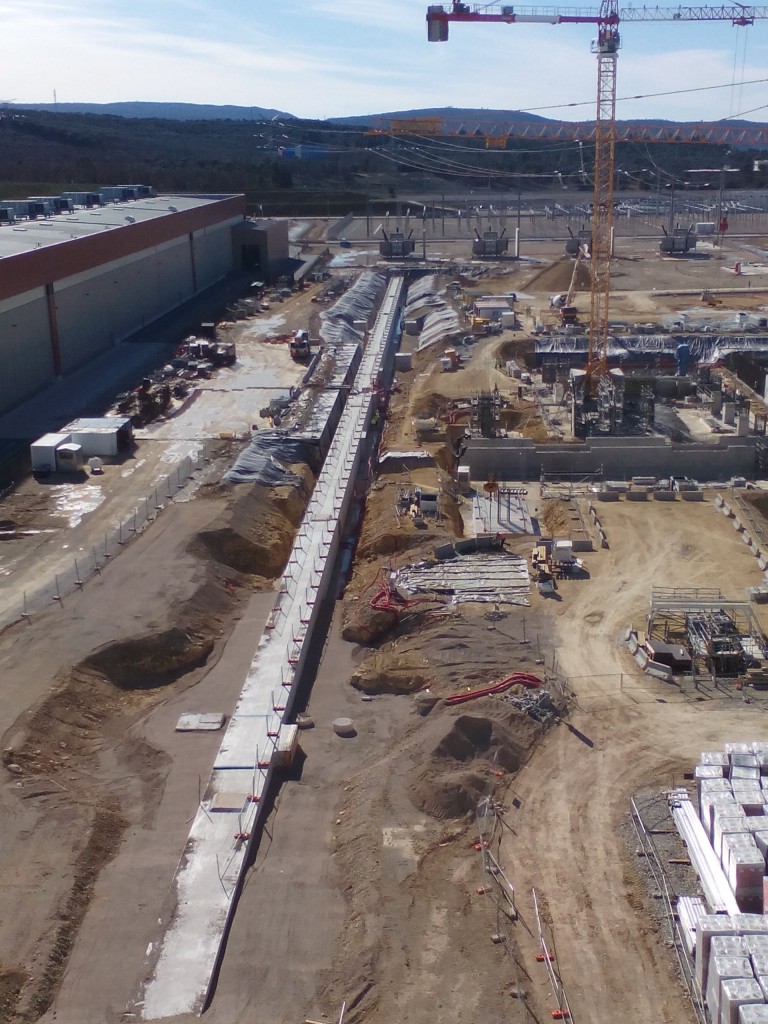
Backfilling underway
2016-02-24 - More than 4 km of technical galleries will run under the surface of the platform by the end of ITER construction. Backfilling is underway for the section of gallery that runs alongside the Poloidal Field Coils Winding Facility. Photo: ENGAGE
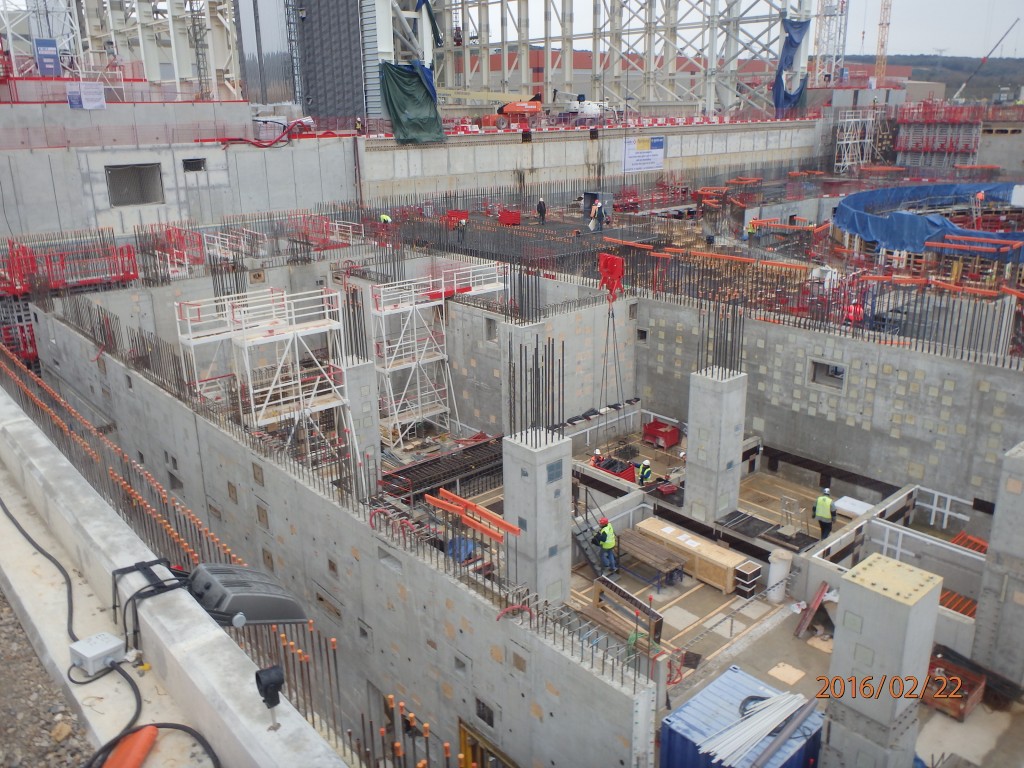
Partitions galore
2016-02-22 - The partitions of the B2 (lower basement) level of the Tritium Building are nearly completed. Photo: ENGAGE
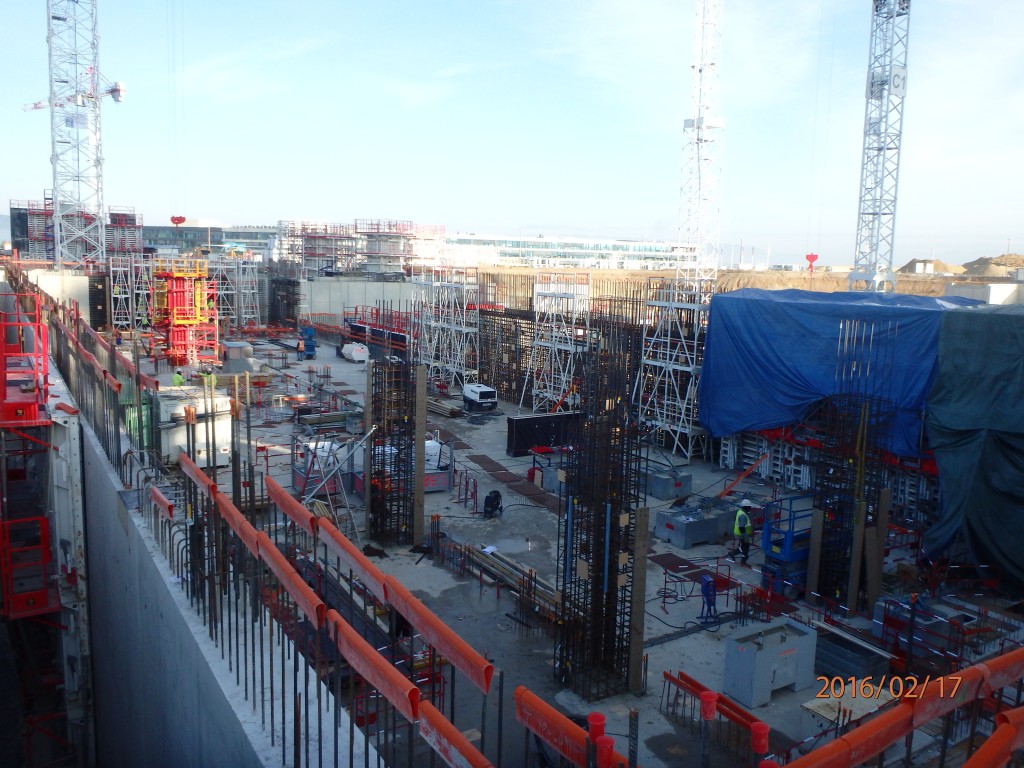
Diagnostics Building - reaching ground level
2016-02-17 - Work advances well on both the interior and exterior walls of the Diagnostics Building at level B1. In April, propping work will begin at ground level (L1). Photo: ENGAGE

Strong legs
2016-02-16 - A double-column structure is in place to support the incredible weight of the cranes themselves (700 tonnes each) and their heaviest loads (1,250 tonnes). Photo: ENGAGE
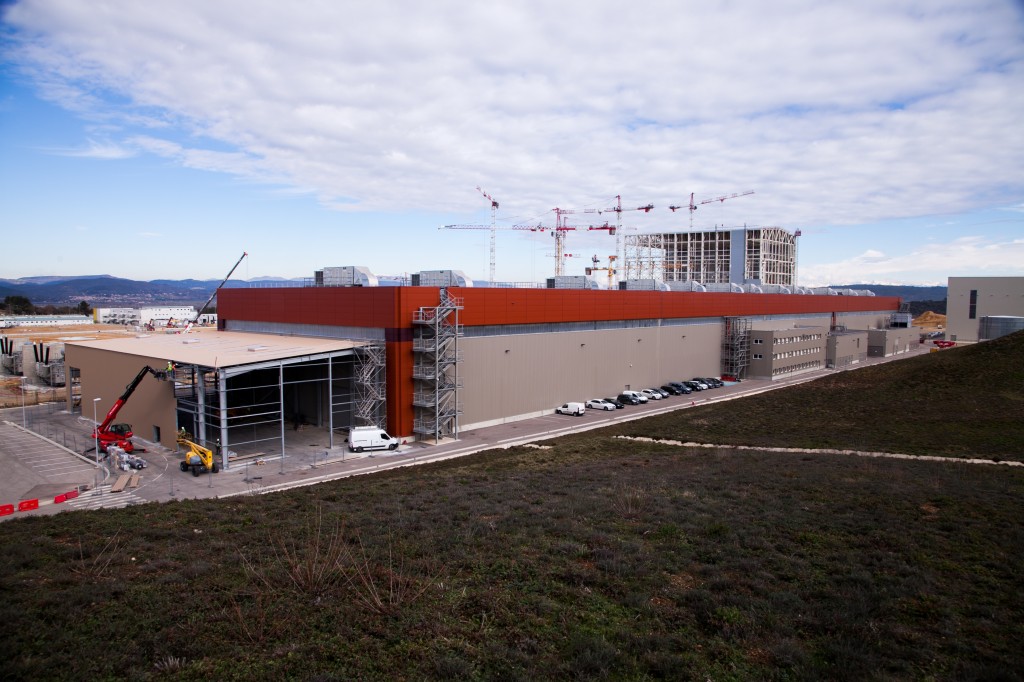
Storage facility advances
2016-02-16 - Part of the parking lot on the south side of the facility has now been given over to storage. Photo: ENGAGE

On the site of the future cooling towers
2016-02-16 - On the north side of the platform, work has just begun on the site of the future cooling water basin and towers. Photo: ENGAGE
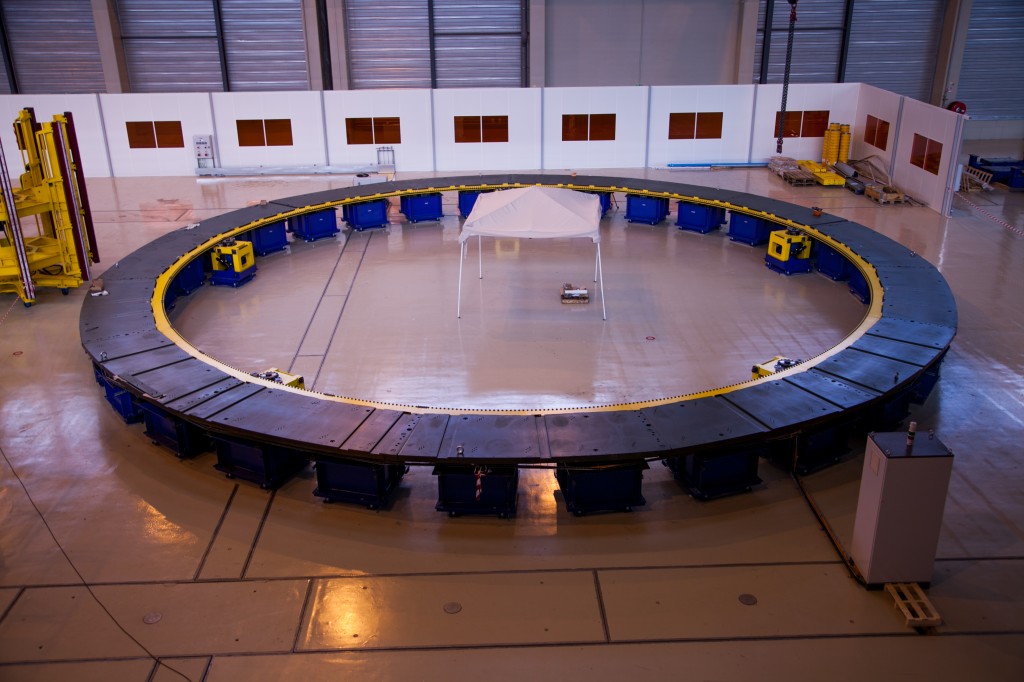
17 m in diametre
2016-02-16 - This support structure will be used after the winding operations, as the completed double pancakes are prepared for the impregnation phase. It allows us to visualize the size of the first two coils to be wound (PF#2 and PF#5)—approximately 17 m in diameter. Photo: ENGAGE
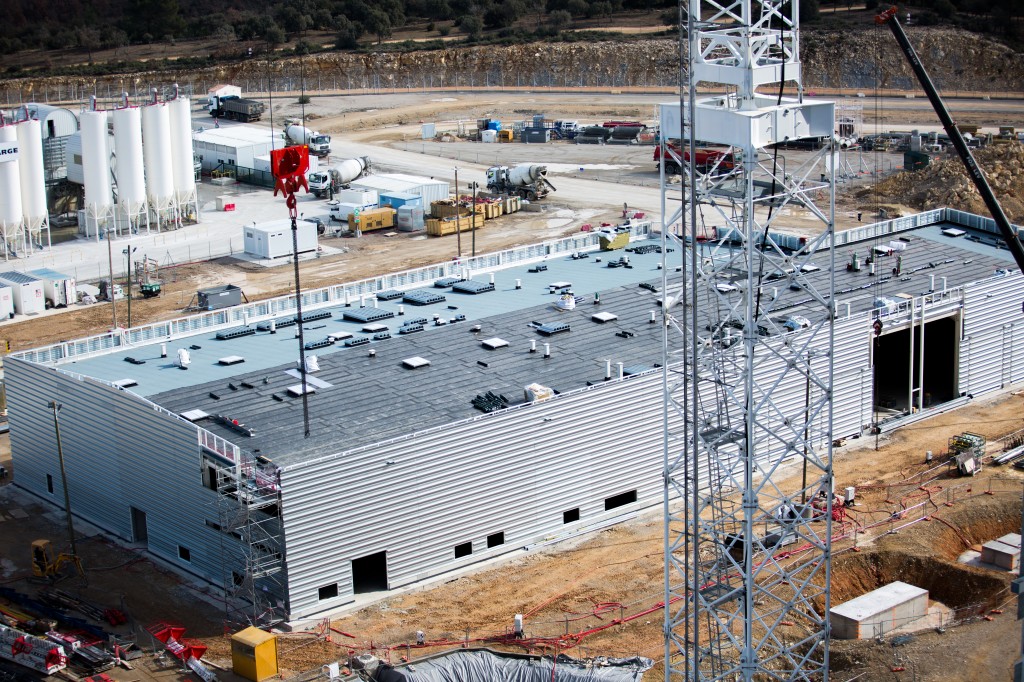
Site Services Building - quickly framed out
2016-02-16 - Cladding works on the Site Services Building are well underway. In June, contractors will begin installing electrical and mechanical service equipment. Photo: ENGAGE
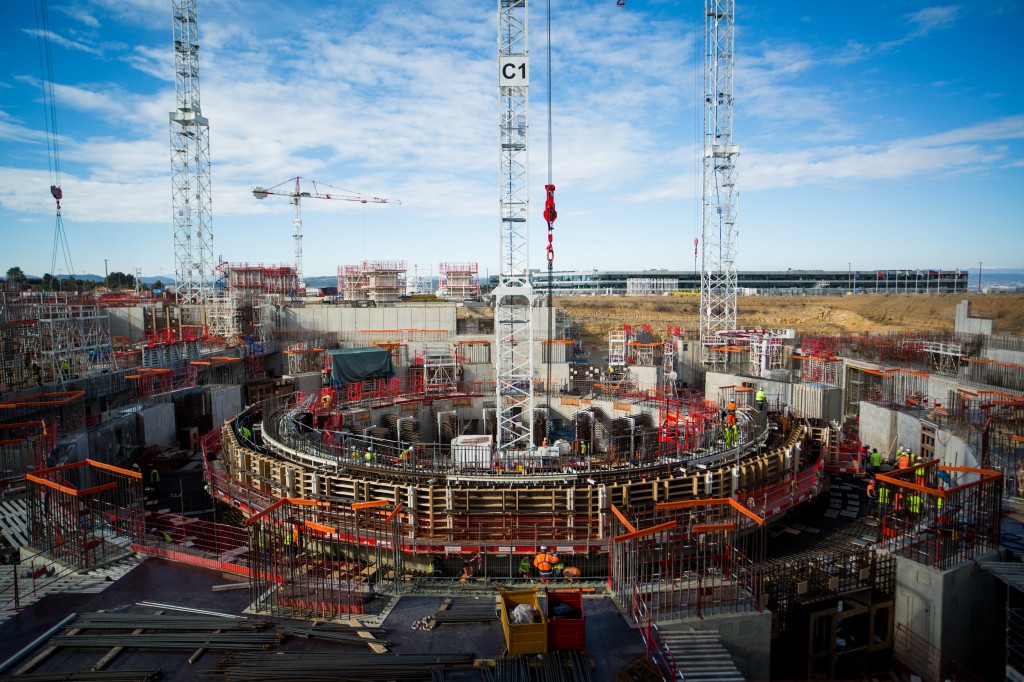
Bullseye
2016-02-16 - The C1 crane is anchored exactly where Tokamak assembly will begin. Photo: ENGAGE
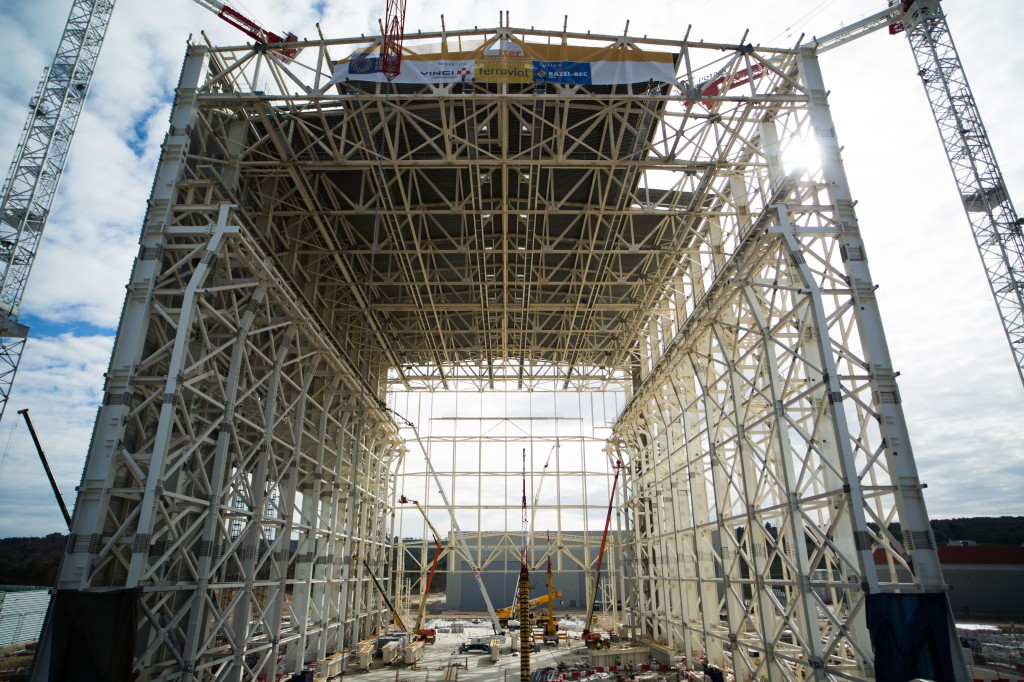
Giant beams, coming soon
2016-02-16 - Four large girder beams (45 metres in length) will cross the breadth of the Assembly Hall to support the overhead cranes. The support beams, visible in this photo, run the full 97 metres of the facility. Photo: ENGAGE
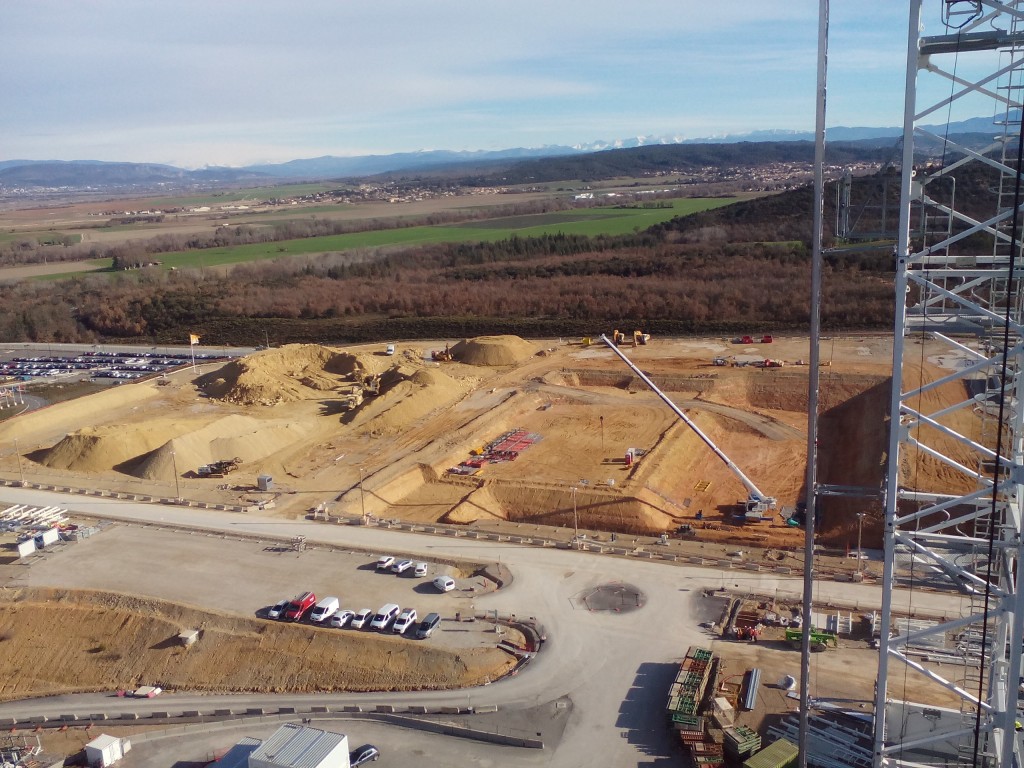
On the site of the future cooling towers
2016-02-16 - On the north side of the platform, work has just begun on the site of the future cooling water basin and towers. Photo: ENGAGE
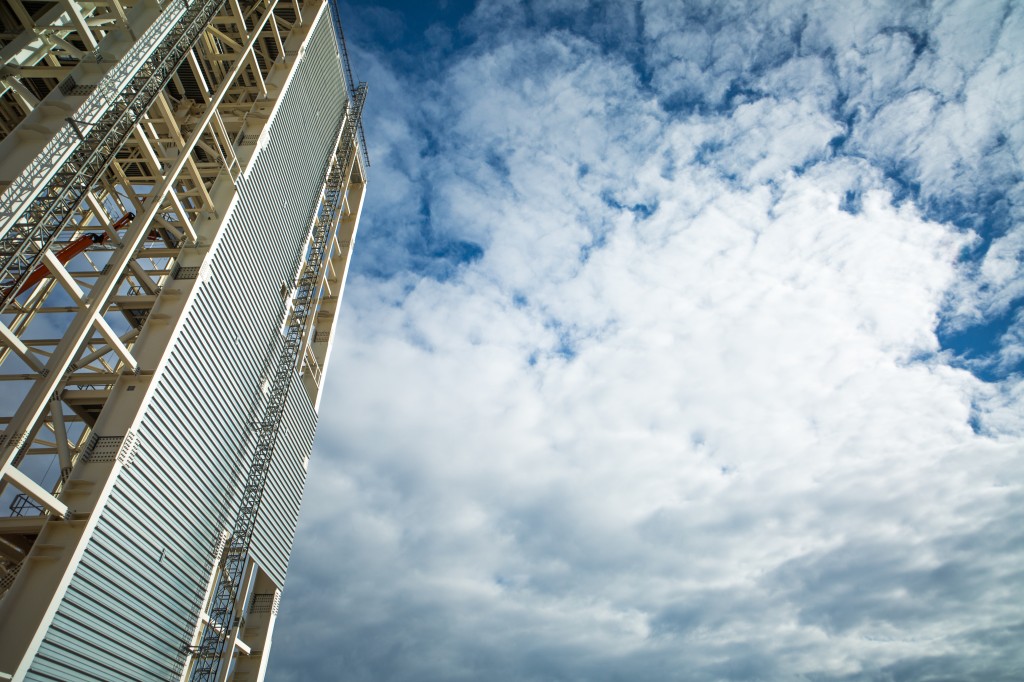
Cladding advances
2016-02-16 - The first panels are in place on the south side. The building should be entirely covered in cladding in June. Photo: ENGAGE
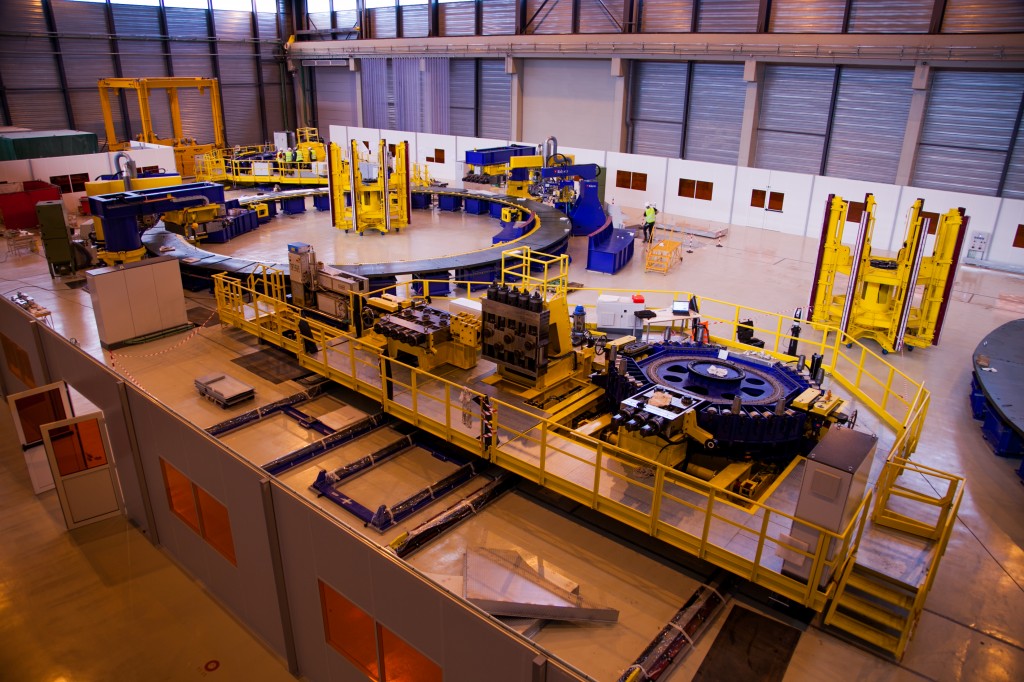
The winding area
2016-02-16 - The winding tooling is colour-coded: yellow for the moving parts and blue for the static ones. Photo: ENGAGE

From above
2016-02-16 - Work on the ITER cryoplant is captured from a crane in February 2016. Photo: ENGAGE
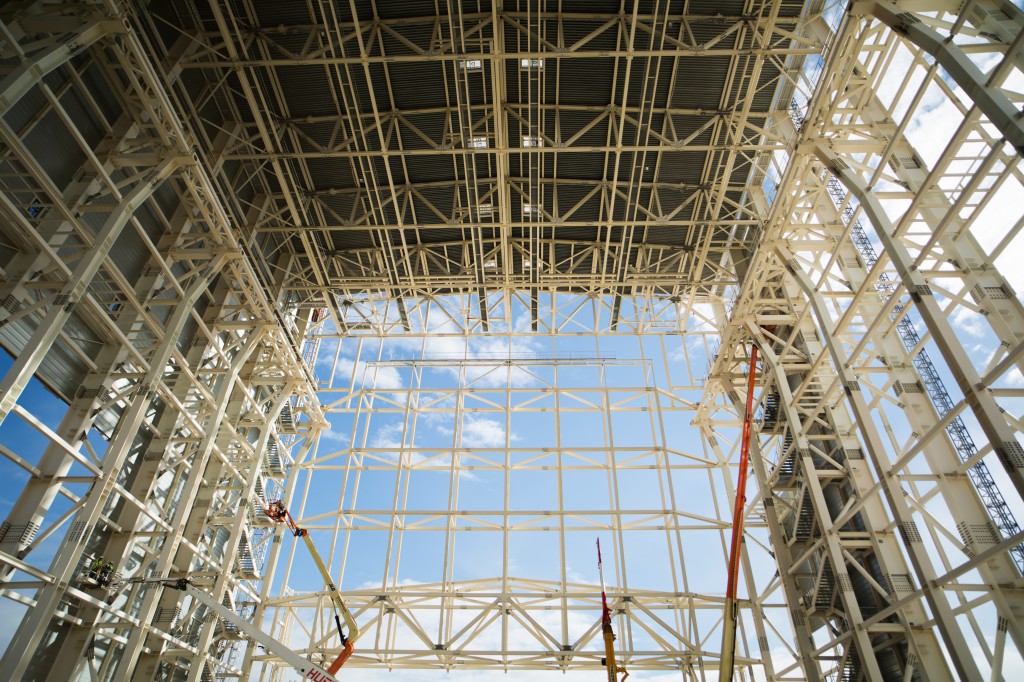
Starting on the other side
2016-02-16 - Northern-facing cladding has now been connected to the roof and the first panels are in place on the south side (at right, behind the stairs). Photo: ENGAGE

Well-laid plans
2016-02-16 - Early one morning in February, in the centre of the Tokamak Pit, the field team examines a diagram of the day's work. Photo: ENGAGE
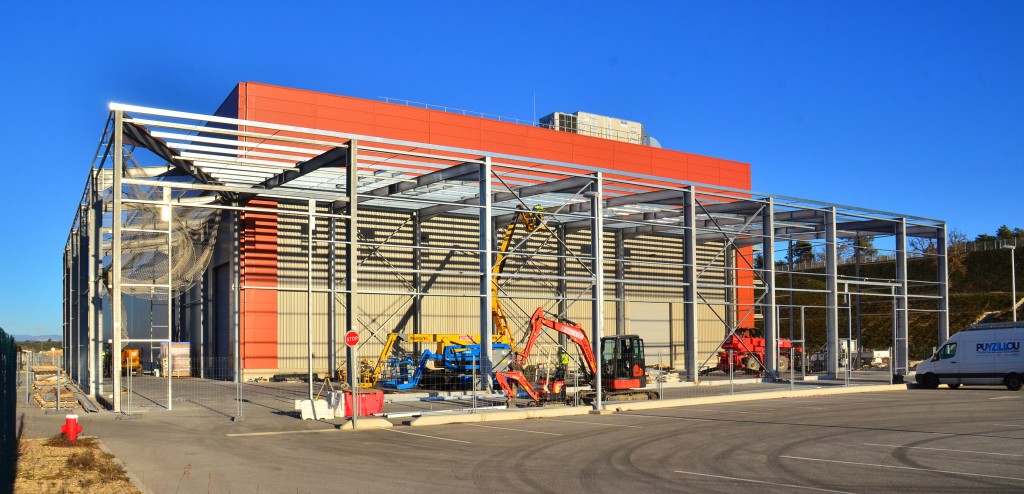
Extra space
2016-02-04 - A small extension is going up on the south side of the Poloidal Field Coils Winding Facility. It will be used for storage.
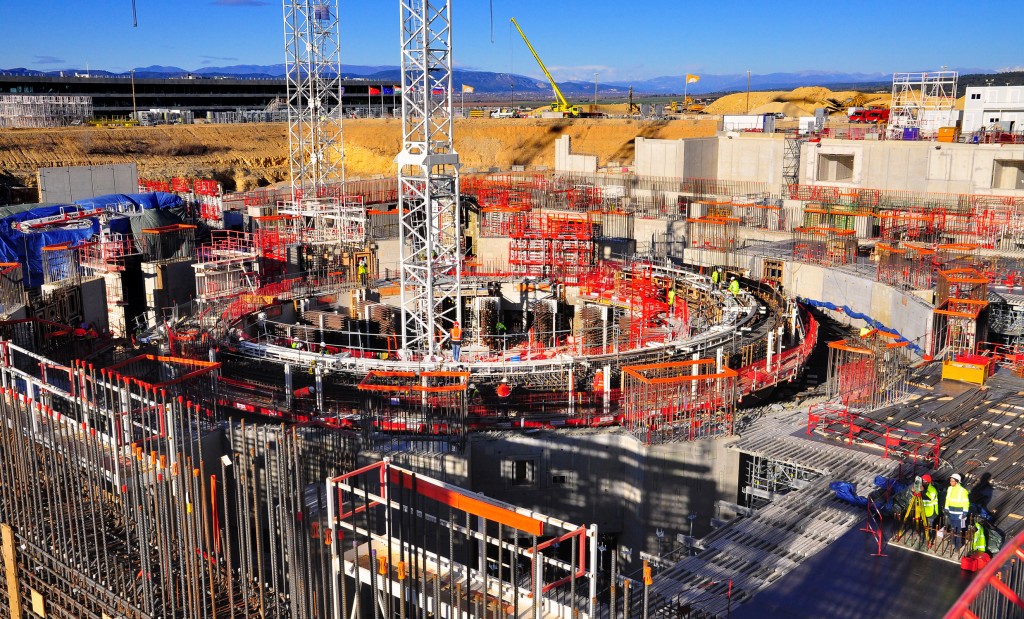
Bioshield, rising
2016-02-04 - On top of the first circle of bioshield, work is now underway on the skirts and plates of the next level. A mockup has been created on site to validate the procedures of this second-step pour.
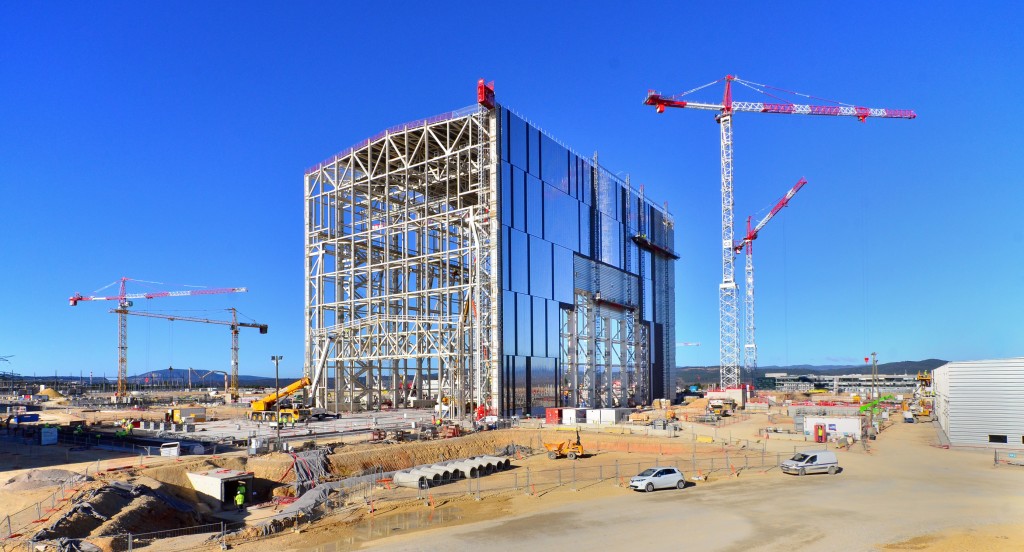
Reflecting the blue sky
2016-02-04 - On the northern face of the Assembly Building, work progresses on four layers of cladding. The last layer, in polished steel, will reflect the colour of the sky.
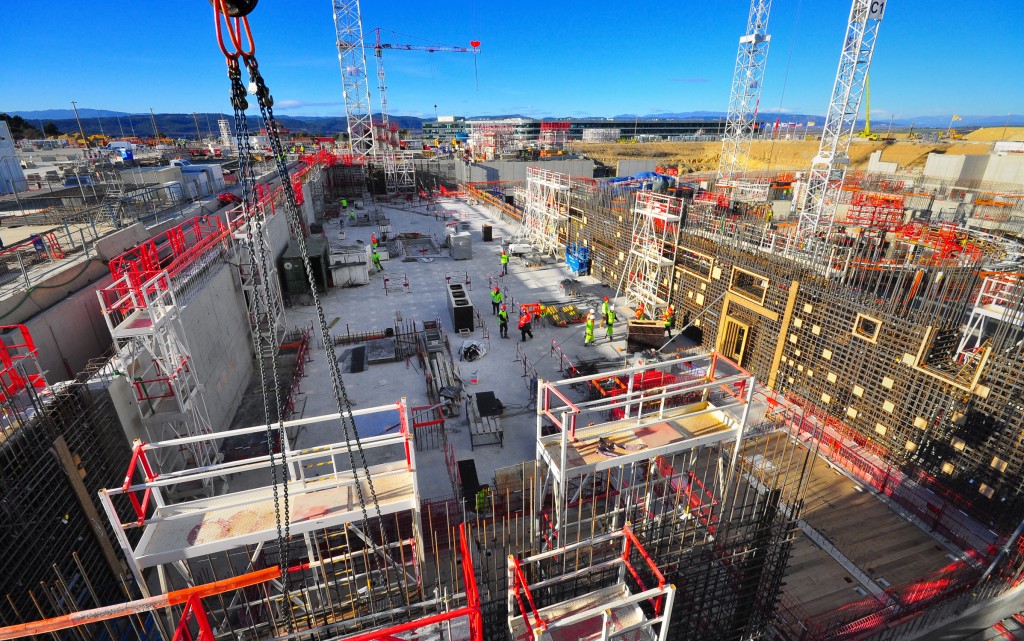
Many a plate ...
2016-02-04 - The pre-installed squares that are noticeable on the vertical reinforcement are embedded plates, designed to provide robust anchorage for Diagnostic Building equipment.

Cryoplant technical galleries
2016-02-04 - Work on the technical galleries of the cryoplant is almost completed. The floor slab and steel frame will follow ... in time to deliver the building in 2017.

Tooling progresses
2016-02-04 - Tooling progresses in the on-site winding facility for poloidal field coils. Work will begin this summer on the first "pre-dummy" winding that kick off the qualification phase for tools and procedures.

360° bioshield
2016-02-04 - The second pour for the ITER bioshield took place on 20 January—now the full ring is in place at the lower level.
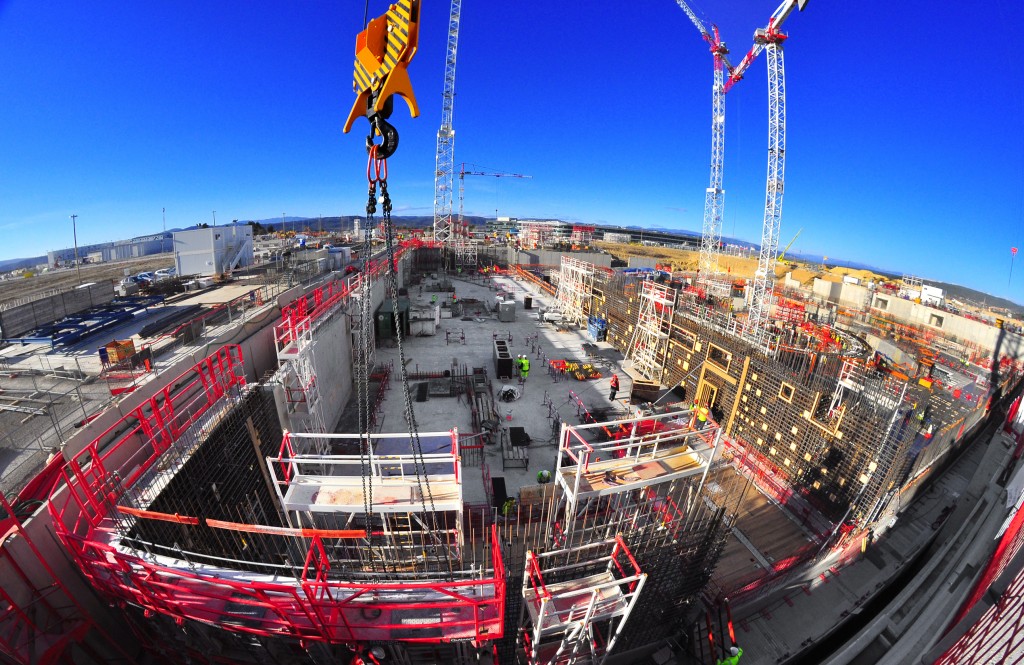
Level B1
2016-02-04 - In the Diagnostics Building, basement level one (B1) now has a floor and work is underway on the propping for the walls.
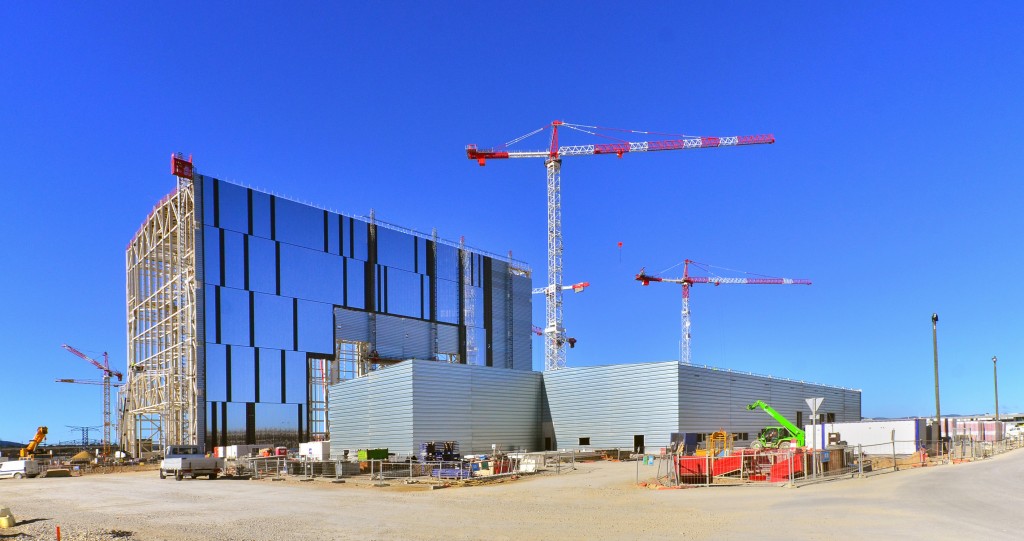
Site Services Building framed out
2016-02-04 - Work is ending on the cladding/roof of the Site Services Building (foreground). In May, contractors will begin installing HVAC and piping.
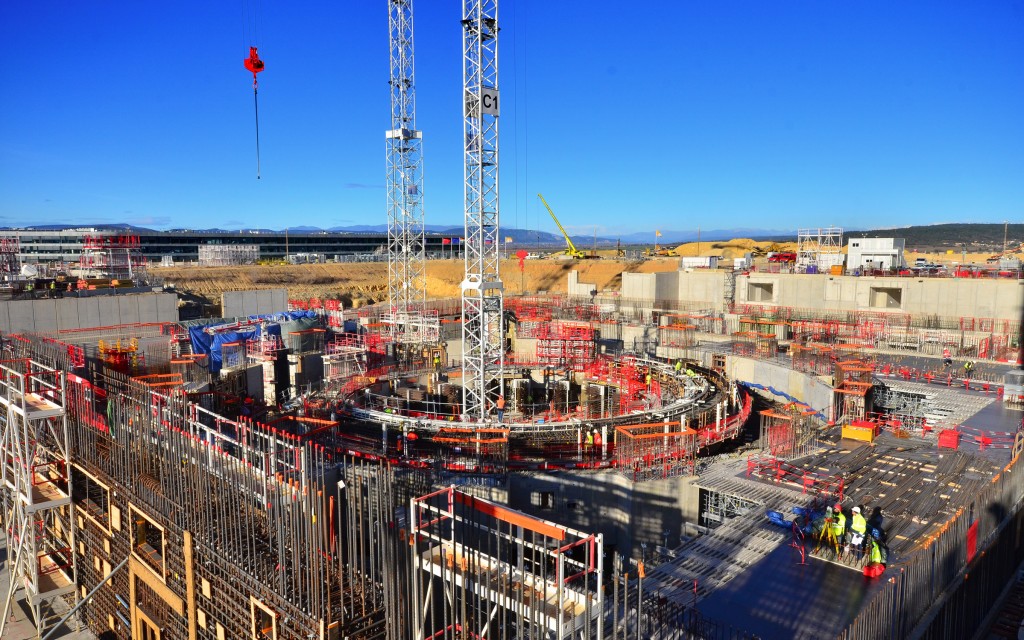
Moving in toward the centre
2016-02-04 - When all Tokamak Complex civil work is done, only the centre of the area will remain accessible for the assembly and installation operations of the ITER Tokamak.
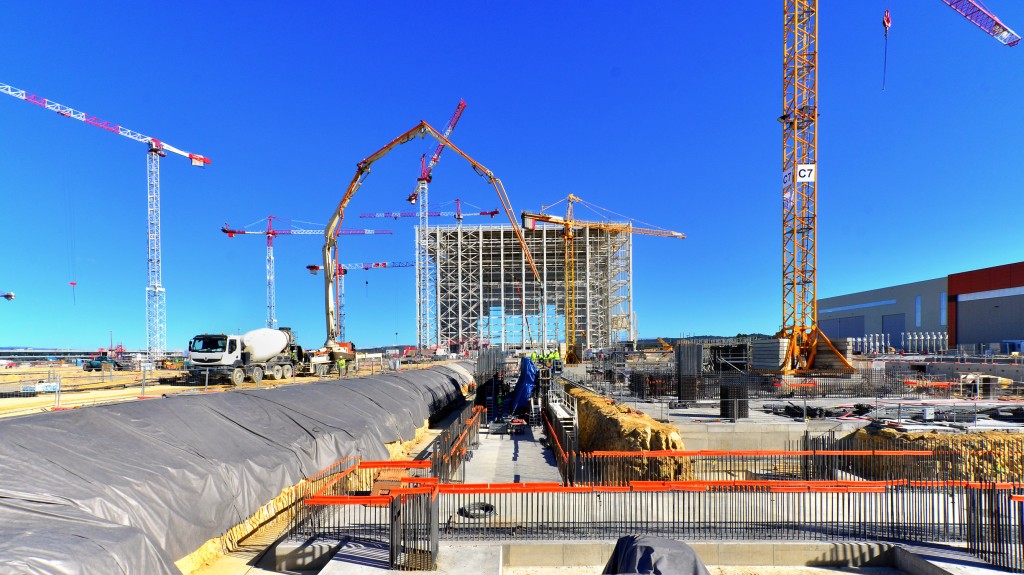
The largest concentrated cryogenic system in the world
2016-02-04 - The ITER cryoplant will be capable of providing cooling power at three different temperature levels: 4 K, 50K and 80K. Currently, work is underway on the building's foundations.

Full cladding by May
2016-01-31 - If all goes according to schedule, work on the cladding will end in April.
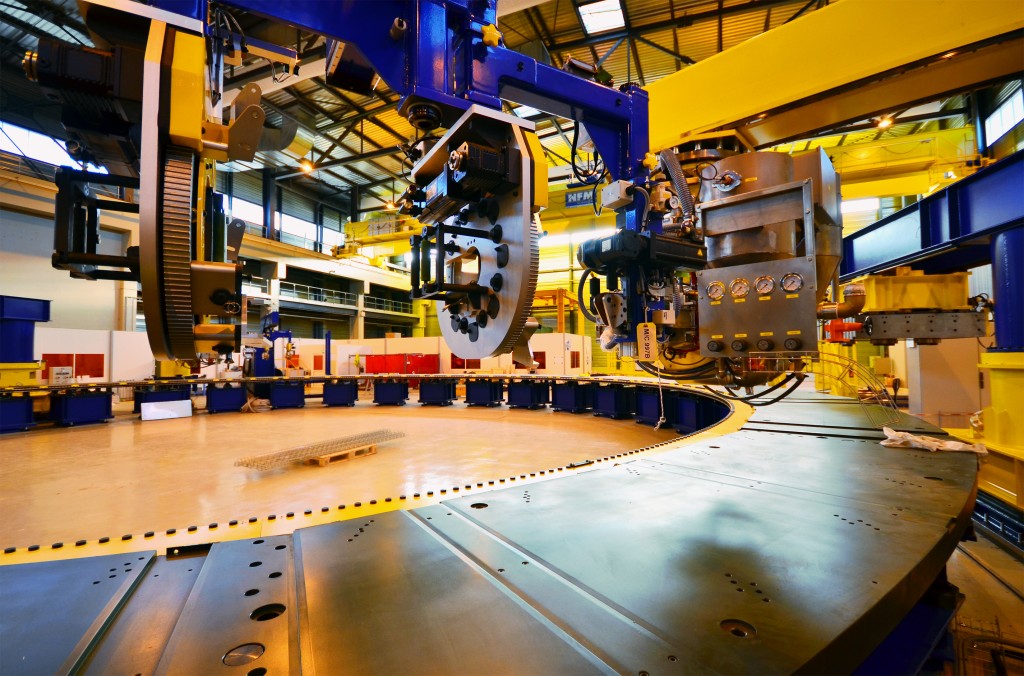
Tooling for poloidal magnets 2 and 5
2016-01-13 - Four poloidal field coils will be manufactured in the on-site winding facility (coils 2, 3, 4, and 5). Operations will begin at the double winding station on the south side of the building. Here, spools of niobium-titanium (NbTi) superconductor will be wound into flat, spiralled coils called "double pancakes." Up to eight double pancakes will be assembled into each magnet coil.
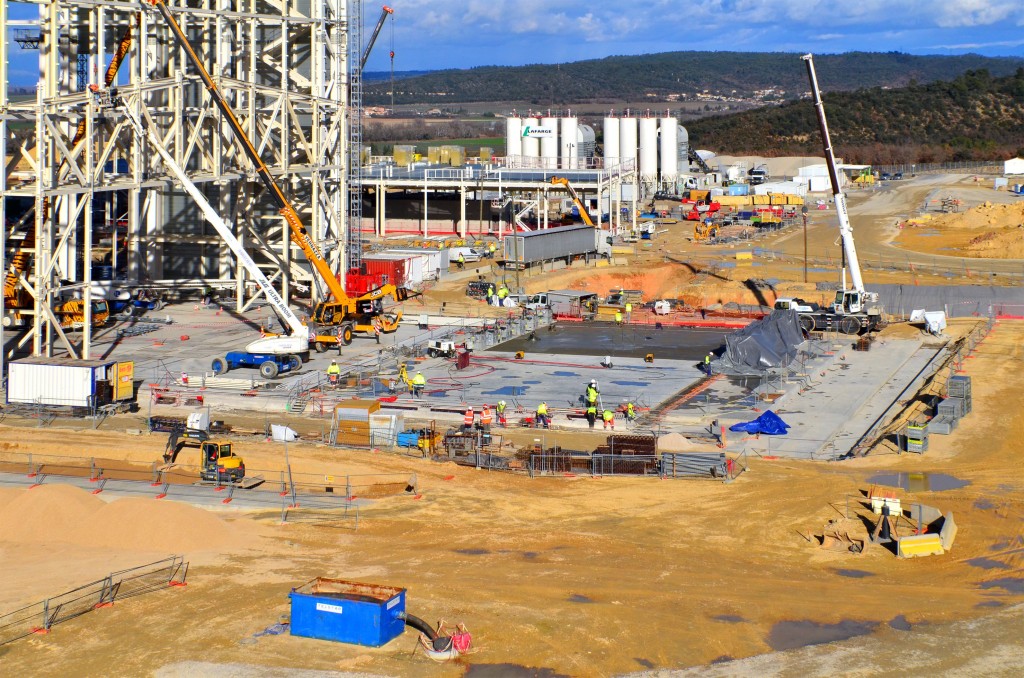
The entry point to the Assembly Hall
2016-01-12 - Before they enter into the Assembly Hall ITER components will need to be cleaned using a number of different techniques such as compressed clean air, pressurized demineralized water, and special detergents. Construction of the Cleaning Facility is underway on the south side of the building.
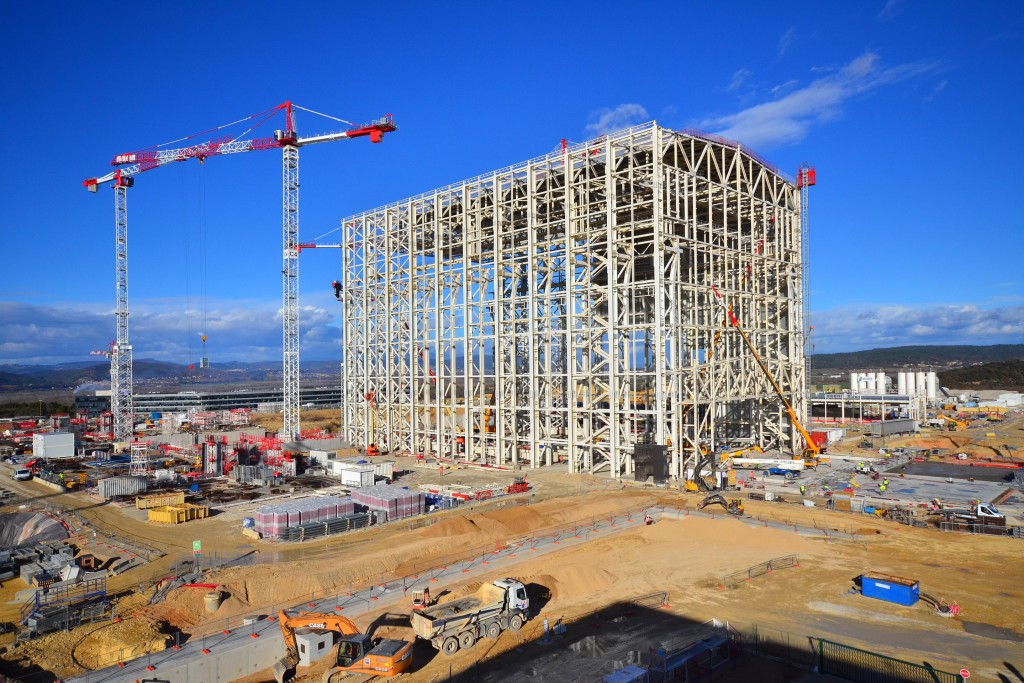
Installing crane beams
2016-01-12 - During ITER assembly, a pair of independent bridge cranes will run the entire length of the Tokamak and Assembly buildings, manoeuvring and transporting components. The first beams for the crane bay were lifted into place in January to trial the bolting operations. After all the beams are in place, workers will install the rails in time for the arrival of the first bridge crane late in June.
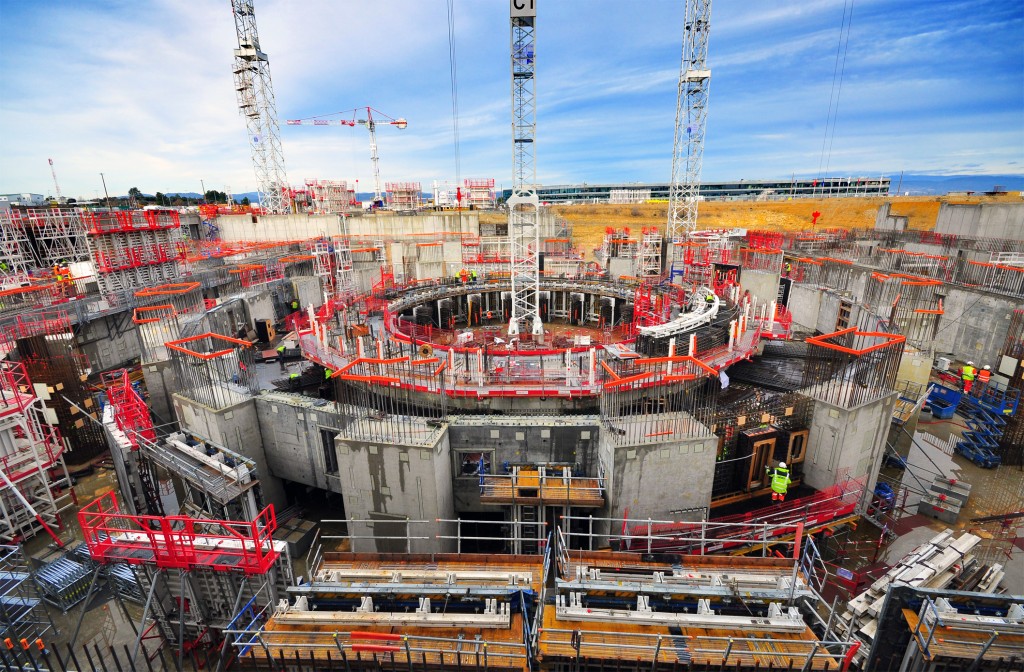
Completing the lowest level
2016-01-12 - In the centre of the Tokamak Pit, the walls of the Tokamak Building are rising—the east, west and south sides have been poured at the B2 (lower basement) level and 70 percent of columns are in place. B1-level civil works will start in the Tokamak Building during the first quarter of 2016.
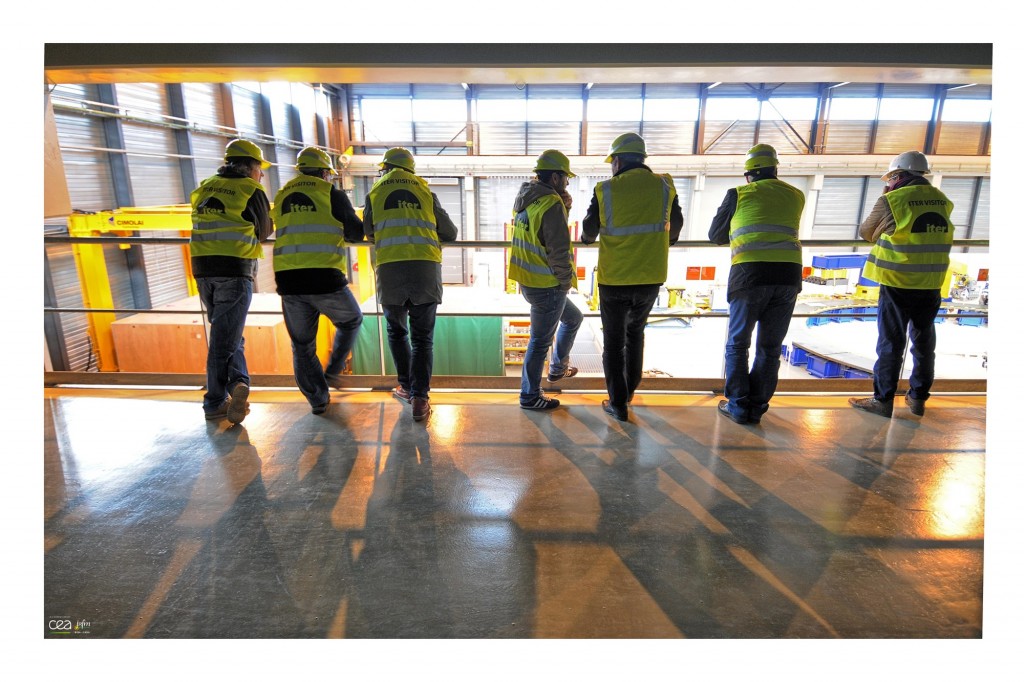
From the visitor gallery
2016-01-08 - Tooling installation is progressing in the Poloidal Field Coils Winding Facility. Visitors have a great view of work underway from the second-floor gallery that has been created on the southern side of the building. Photo: Christophe Roux, IRFM
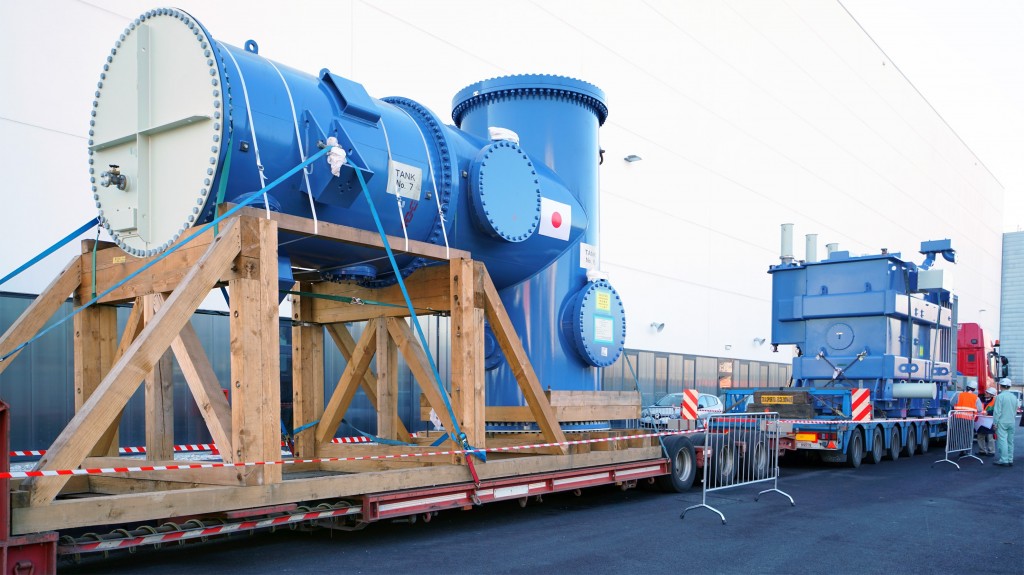
First components from Japan
2015-12-22 - Japan delivers elements of the power supply system of the MITICA test bed: a transmission line that will be filled with SF6 at 0.6 MPa and the first three 200 kV step-up transformers that are part of the DC generator. (Pictured: the outer tank pressure vessel, part of the 100-metre transmission line.)
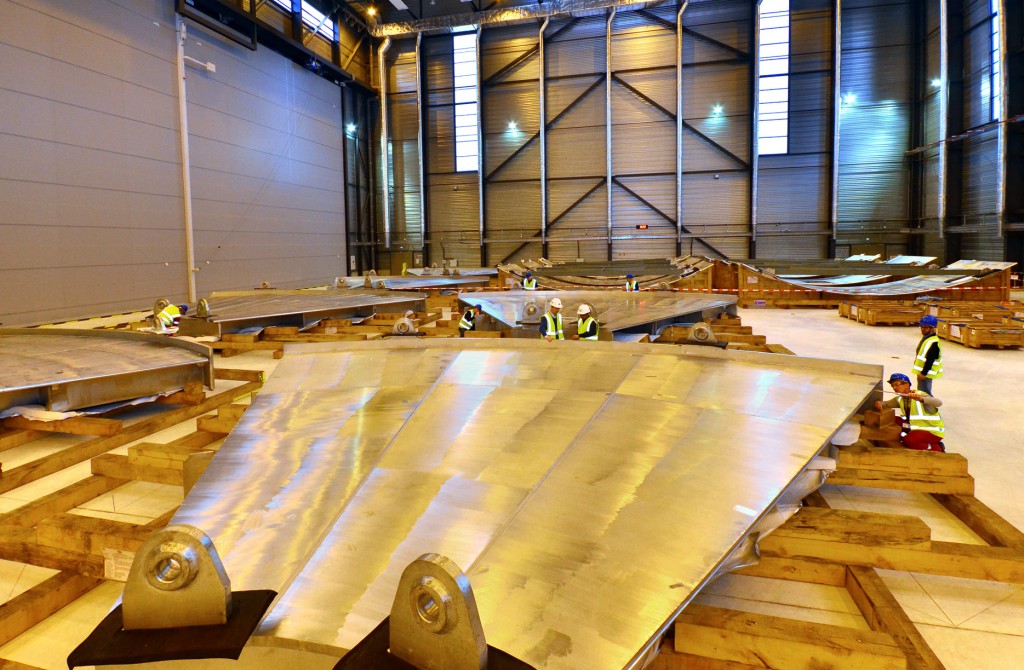
Full shipment received
2015-12-18 - Some 460 tonnes of components are now stored in the Cryostat Workshop: six 19-tonne shells and six 60° base sections.
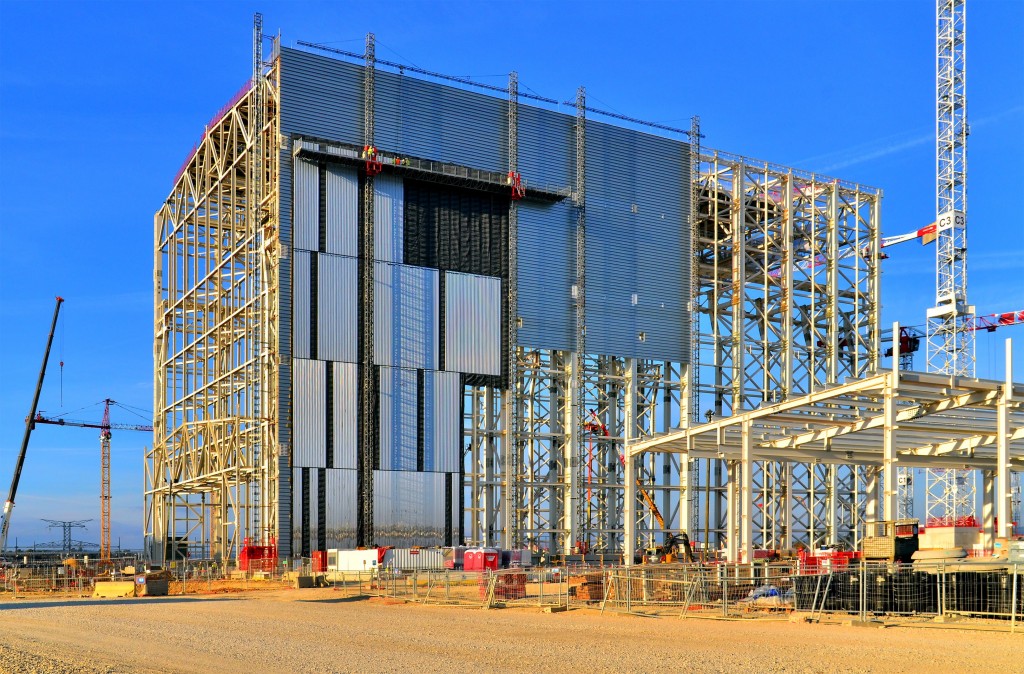
Dressing the steel skeleton
2015-12-17 - Four layers of the cladding will eventually cover the Assembly Hall, including an insulating layer. The outermost panes will be mirror-like, to reflect the sky and surroundings.

Unloaded, delivered, unwrapped...
2015-12-11 - Shaped like so many slices of pie, these three 60° segments are the first pieces of the cryostat to arrive on site.

14,000 m² to be covered
2015-12-10 - 60 metres tall, 97 metres long, 60 metres wide. There are 14,000 square metres of surface to cover with cladding.
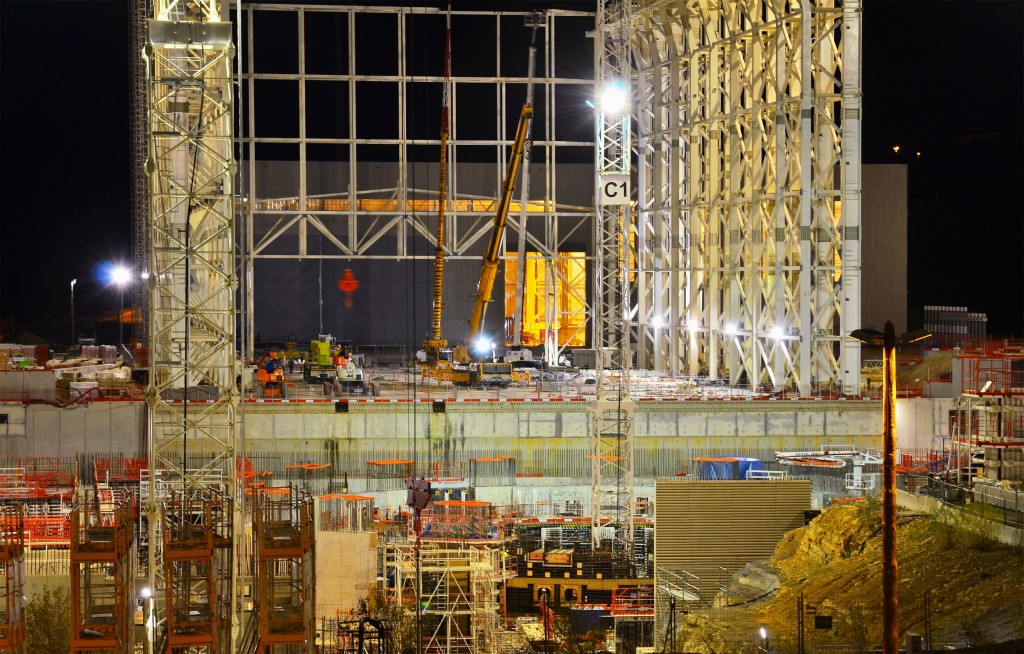
All lit up
2015-12-10 - In December lights stay on late in the Tokamak Pit, where the last shift leaves off at 10:00 p.m. Concrete pouring on the second level of the Tokamak Complex will begin in early 2016.

Plenty of storage space
2015-12-10 - The segments will be stored in the Cryostat Workshop until welding operations begin in the summer of 2016.

Part of the cryostat base
2015-12-10 - Procured by India and manufactured at Larsen & Toubro Ltd's Hazira plant, the six 60-degree segments will form Tier 1 (460 tonnes) of the cryostat base (1,250 tonnes).
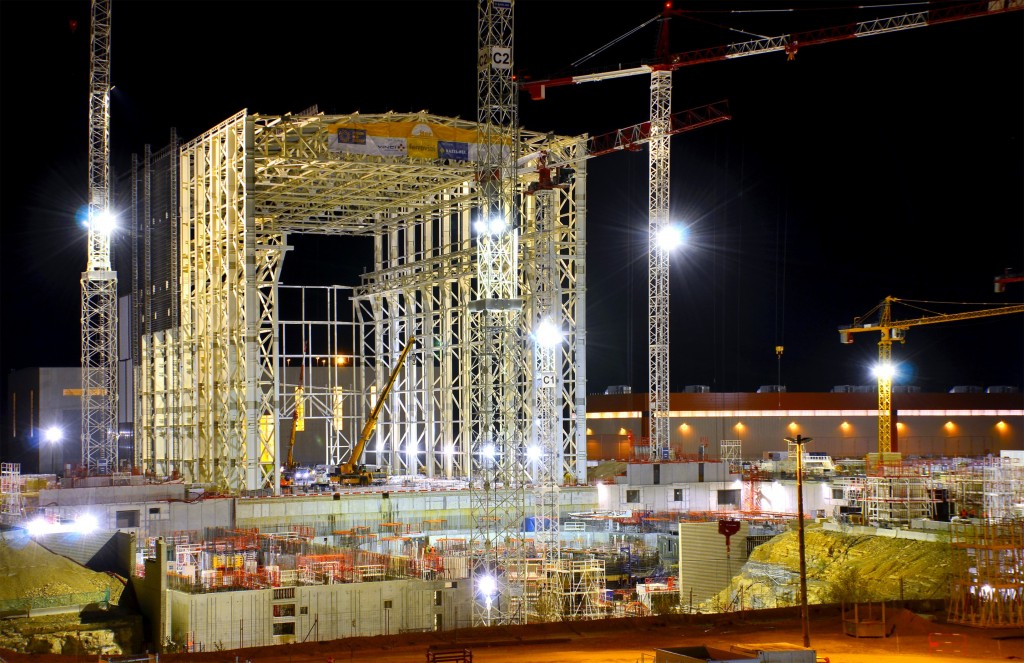
Cladding operations underway
2015-12-10 - The 6:00 p.m. to 5:00 a.m. night shift is at work on the far side of the Assembly Hall, bolting together the steel lattice that will support the metal cladding.

With the help of the gantry crane
2015-12-10 - On 10 December 2015, the first cryostat segments were unloaded in the Cryostat Workshop. Each segment weighs close to 50 tonnes.

Underground galleries
2015-12-01 - Before work begins on the cryoplant itself, workers are creating underground galleries for the transport of electricity/fluids. Photo: F4E

Reinforcement and concrete pouring progress for the Diagnostics Building
2015-12-01 - The workers in the foreground are standing on the first basement level (B1) of the Diagnostics Building. Photo: F4E
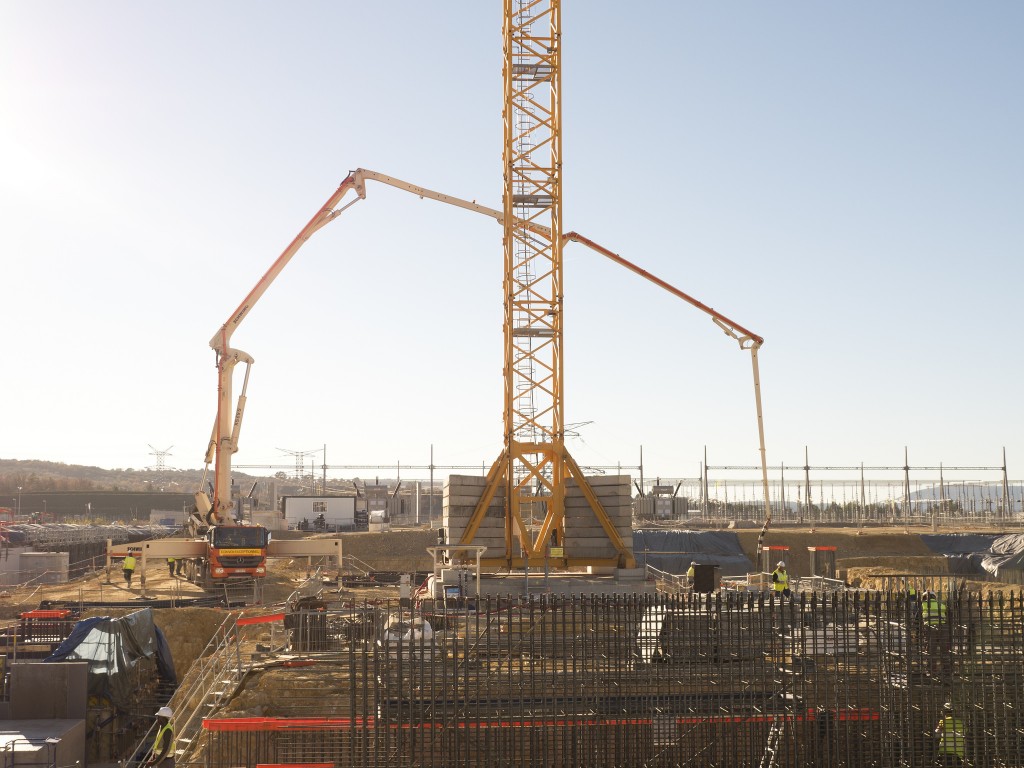
Cryoplant foundations underway
2015-12-01 - Extensive cryogenic technology will create and maintain low-temperature conditions for the magnet and vacuum pumping systems as well as some diagnostics. On site, work has started on the foundations of the ITER cryoplant. Photo: F4E

A new project on the platform
2015-12-01 - In December, excavation begins for one of the auxiliary buildings of the scientific facility—the Radio Frequency Heating Building (in the background: the frame of the Site Services Building). Photo: F4E
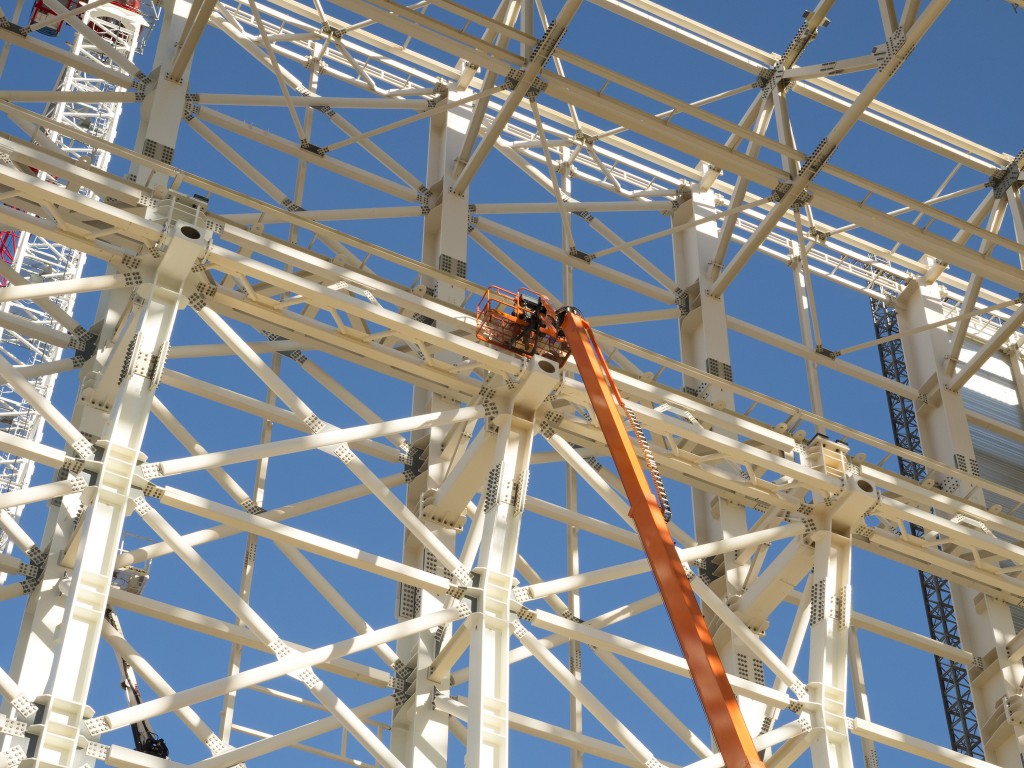
45 metres above ground
2015-11-30 - In November, an operator works on the Assembly Building, where the crane rails will be installed. Photo: F4E
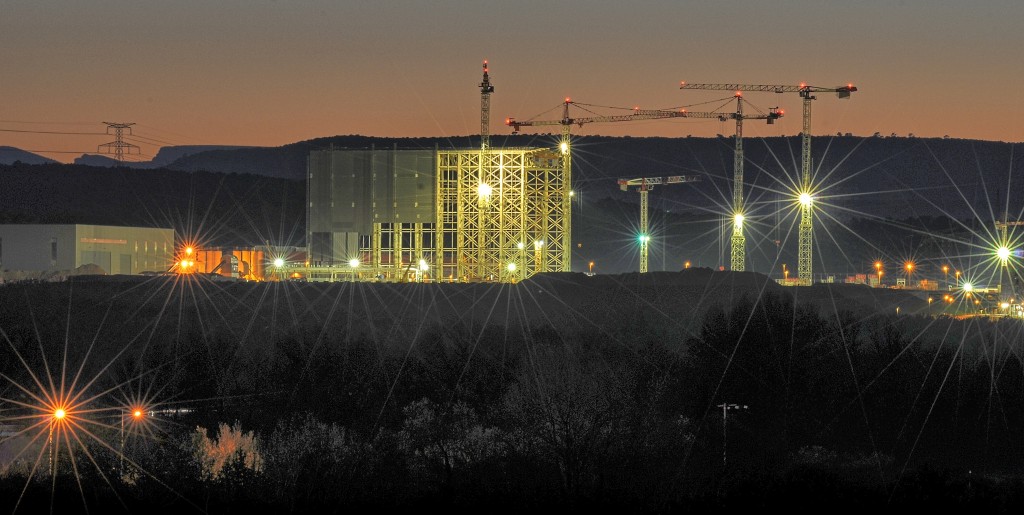
ITER at night
2015-11-27 - The ITER Assembly Hall stands out on the construction platform on a clear and cold November evening. ©Christophe Roux - CEA/IRFM
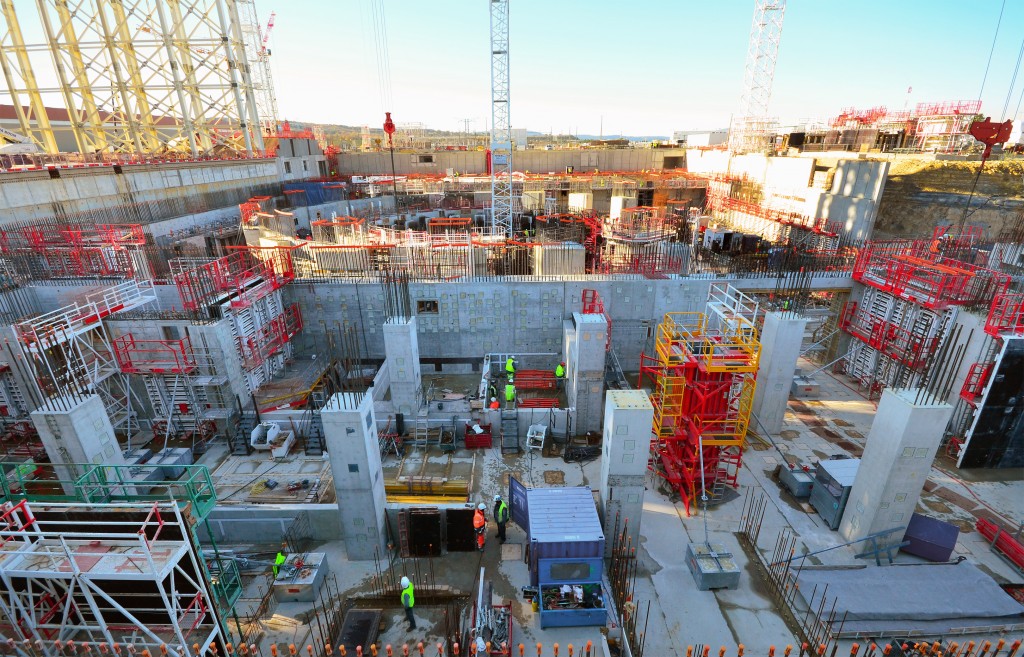
Tritium Building - level B2 nearly completed
2015-11-24 - On the northernmost end of the Tokamak Pit, the final walls and pillars are being poured for the Tritium Building.
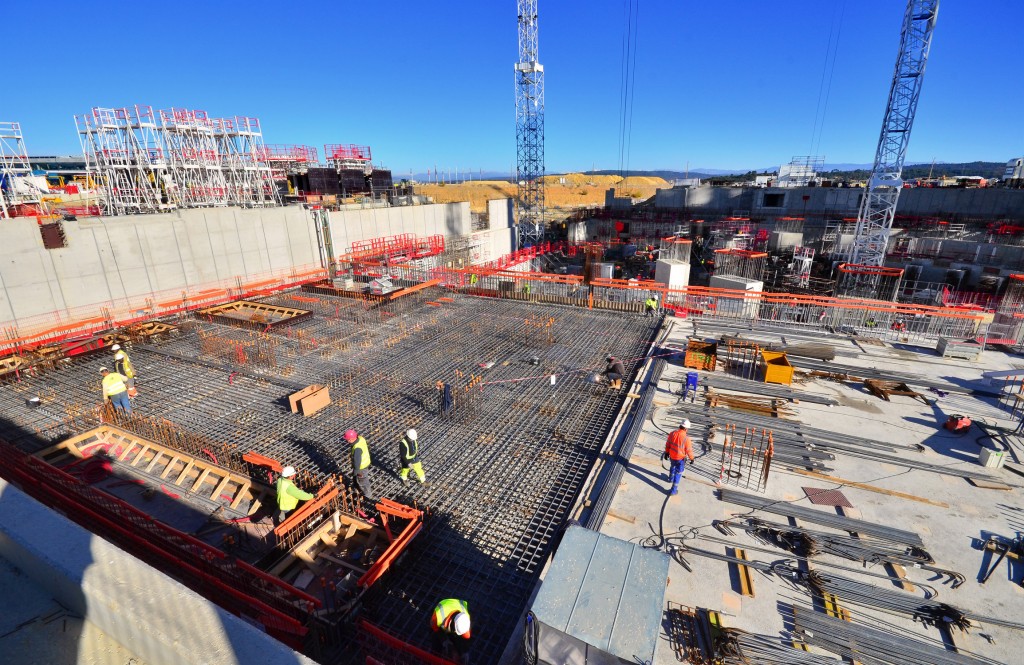
First B1 reinforcement in place
2015-11-24 - Reinforcement activities on basement level 1 (B1) of the Tokamak Complex get underway in November.

Lower level hidden from view
2015-11-24 - Wooden formwork and rebar lattices now completely cover the lower level of the Diagnostic Building. The first concrete slab for the B1 level of the Diagnostics Building has been poured.
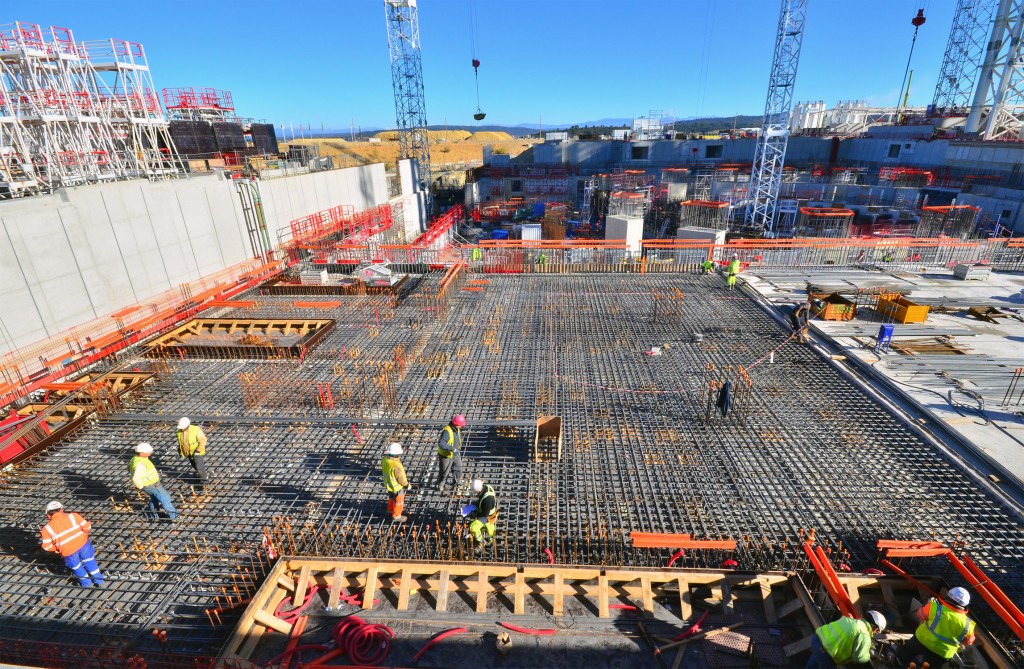
Progress on the Tokamak Complex
2015-11-24 - Work is advancing on the Tokamak Complex in two 8-hour shifts.

High voltage hall emerging
2015-11-17 - The MITICA high voltage hall is under construction. Photo: F4E
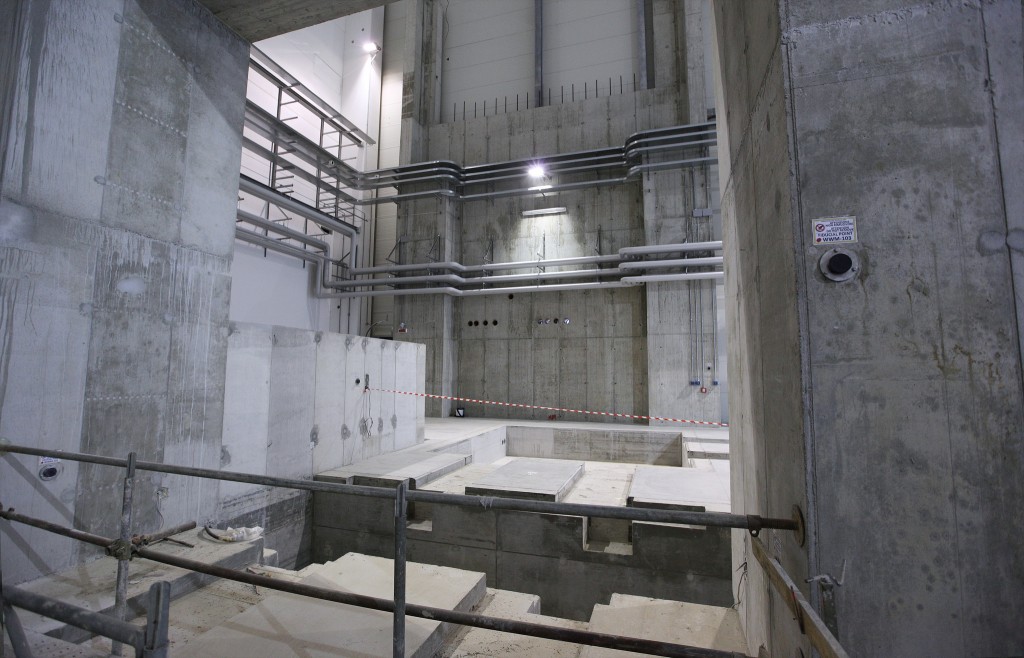
Preparing for MITICA
2015-11-17 - Looking out from the MITICA test bed, through the bioshield door. Photo: F4E
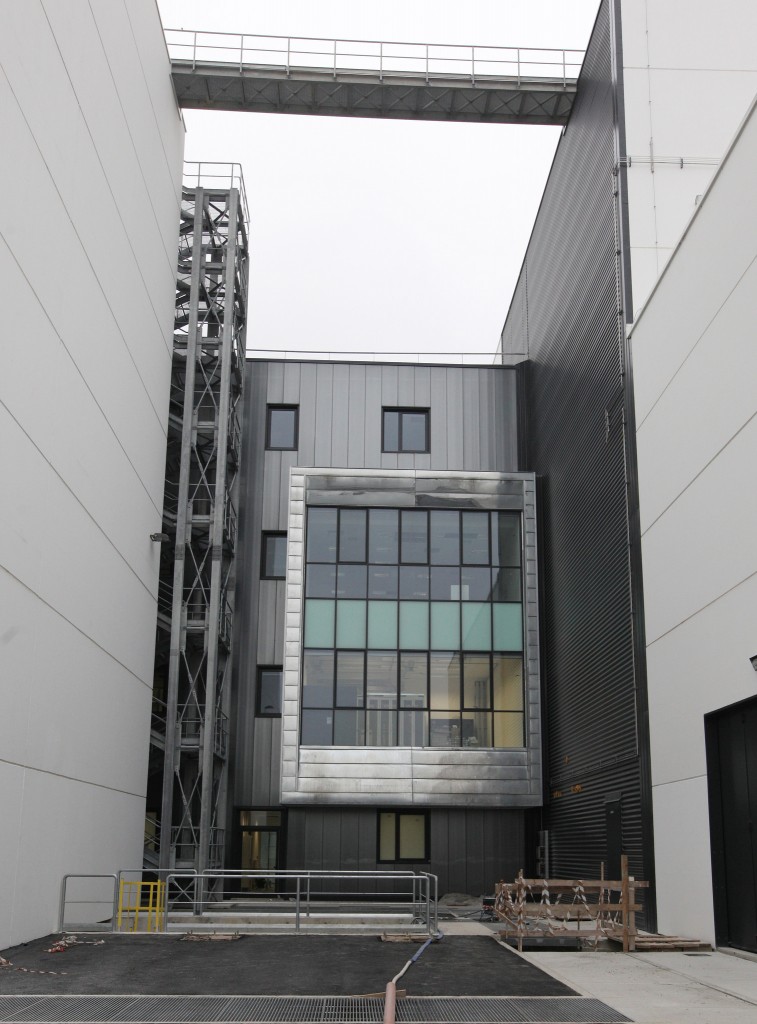
Office space
2015-11-17 - The control rooms of the Neutral Beam Test Facility in Padua, Italy. Photo: F4E

A dedicated enclosure
2015-11-17 - Workers are installing the bioshield to the SPIDER test bed. Photo: F4E
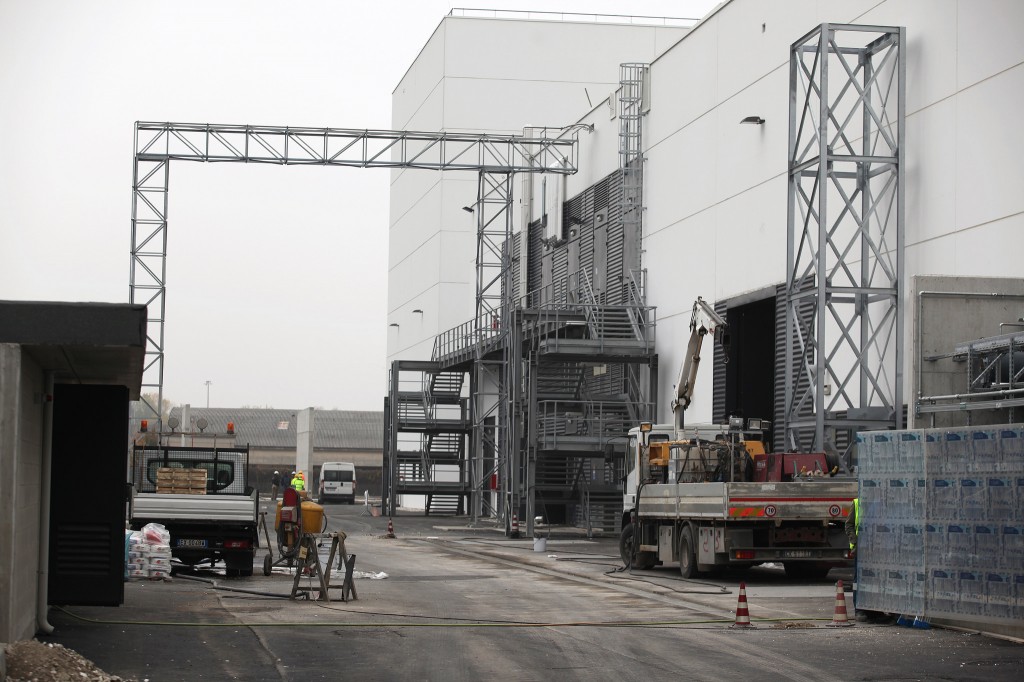
Exterior area
2015-11-17 - Work underway at Consorzio RFX to prepare the exterior areas for transformers and other electrical equipment.

First tooling equipment
2015-11-13 - Workers from the European contractor SEA ALP (Turin, Italy) are currently installing the first poloidal field coil winding tooling table in the on-site Poloidal Field Coils Winding Facility.
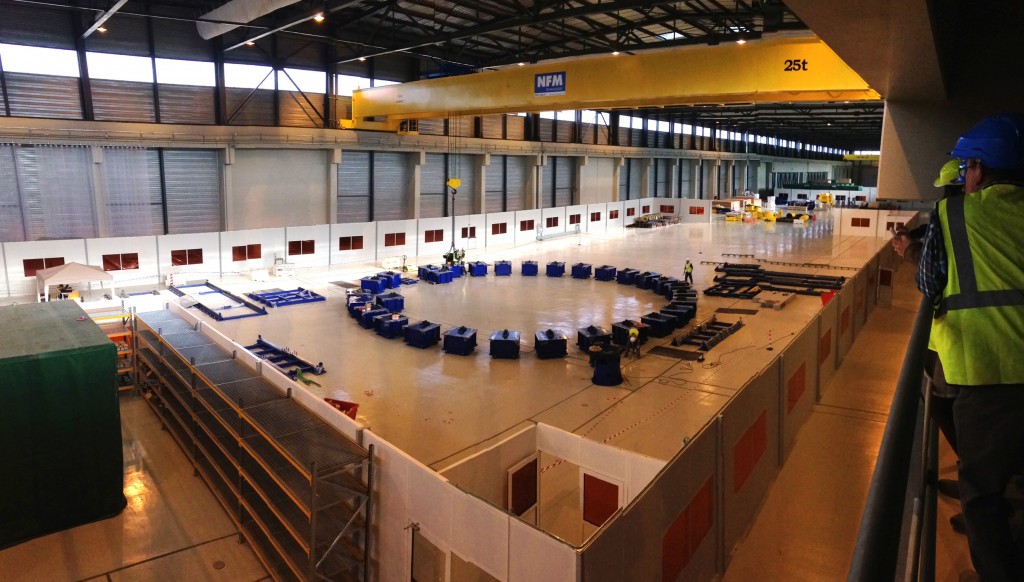
Room for two tables
2015-11-13 - Two winding tables will operate side by side to produce flat, spiralled coils called "double pancakes." In this building, up to eight double pancakes will be stacked to form the final coils.

A sense of scale
2015-10-24 - Under the vast structure of the Assembly Building the visitors seem ... very small. They stand on the edge of the Tokamak Pit, where pouring activities are underway on the lowest basement level of the Tokamak Complex.

Three-fifths of a circle
2015-10-24 - In light grey, we can see the poured bioshield concrete—a segment of 200 degrees. It will take 28 days to dry completely.

Work on the next basement level underway
2015-10-24 - Work is underway on the second basement level of the Tokamak Complex (B1). Pictured, the installation of propping and formwork for the Diagnostics Building.

First pour for the bioshield
2015-10-21 - In the early hours of Wednesday, 21 October, workers poured the first 200° segment of the bioshield, in an all-day operation that took some 15 hours to complete.
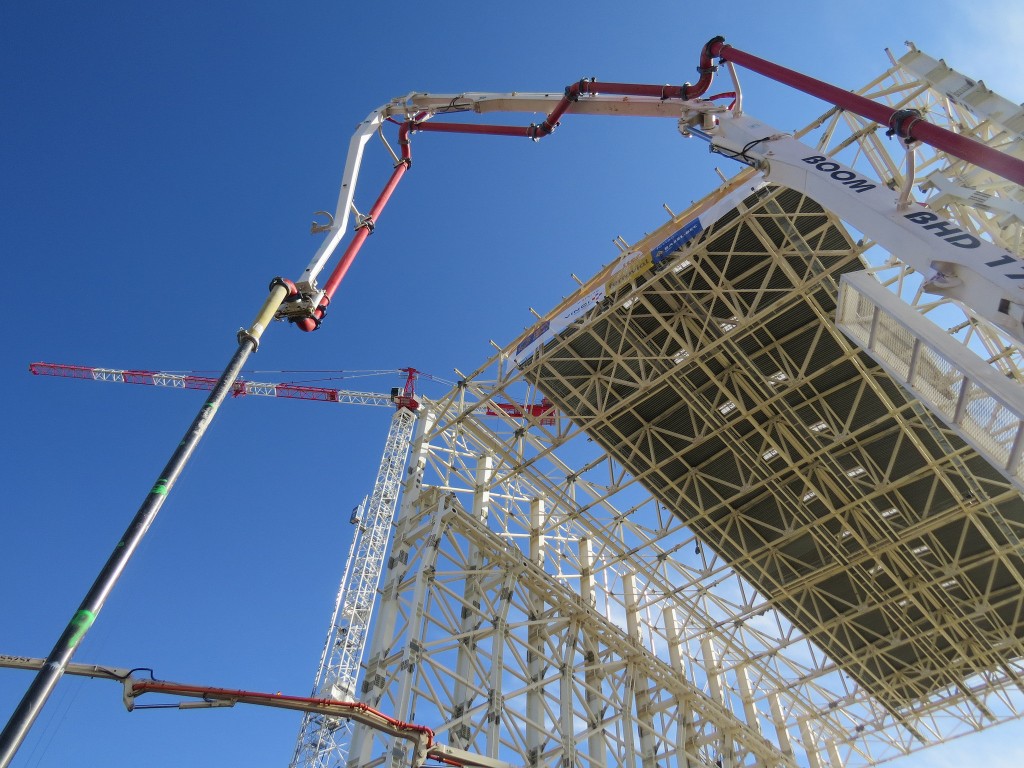
Bioshield takes shape
2015-10-21 - Concrete pouring begins on the ITER bioshield (21 October 2015). Photo: F4E

First walls for Site Services
2015-10-20 - The walls are rising for the 80-metre-long Site Services Building, which will furnish industrial services (chilled or demineralized water, compressed air) to the rest of the installation. Photo: F4E
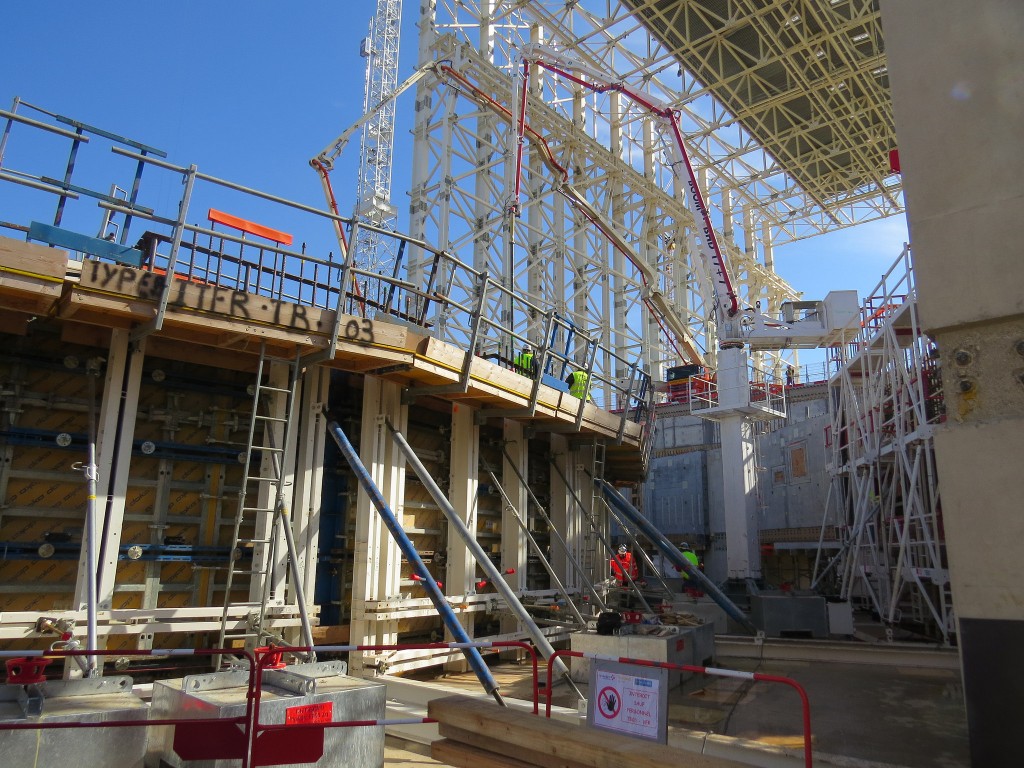
Preparing for the bioshield concrete
2015-10-20 - Formwork marks out the shape of the ITER bioshield on the B2 (second basement) level of the Tokamak Complex. Photo: F4E
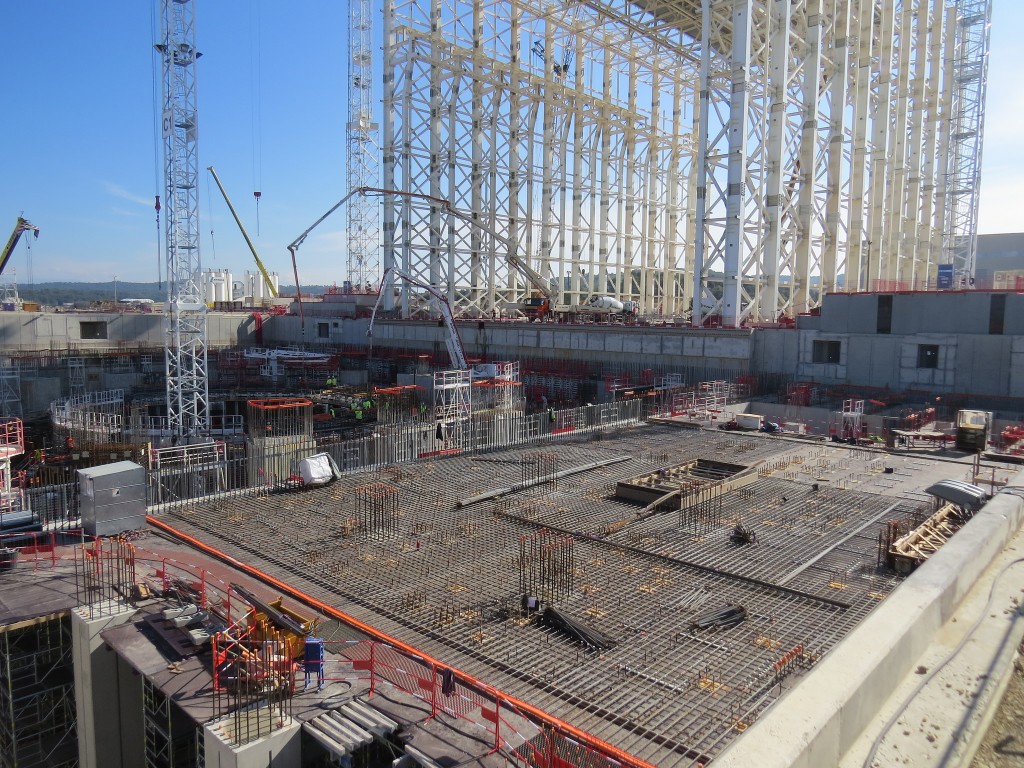
Next level pouring to start for the Diagnostics Building
2015-10-20 - Workers are positioning the formwork for the next level (B1) of the Diagnostics Building. Photo: F4E
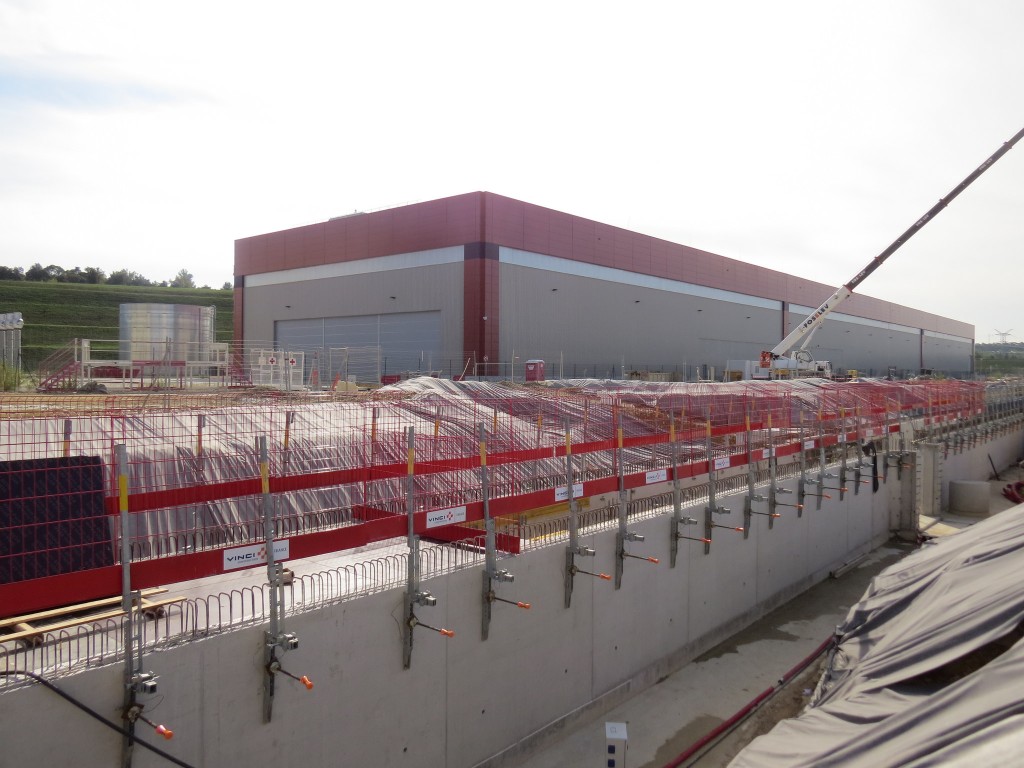
Closing up the galleries
2015-10-20 - The last operation for these technical galleries running alongside the Poloidal Field Coils building will be to "close up the box." Photo: F4E

Foundations for the Cryoplant Building
2015-10-20 - In October, site teams began work on the reinforced foundations of the Cryoplant Building. Photo: F4E
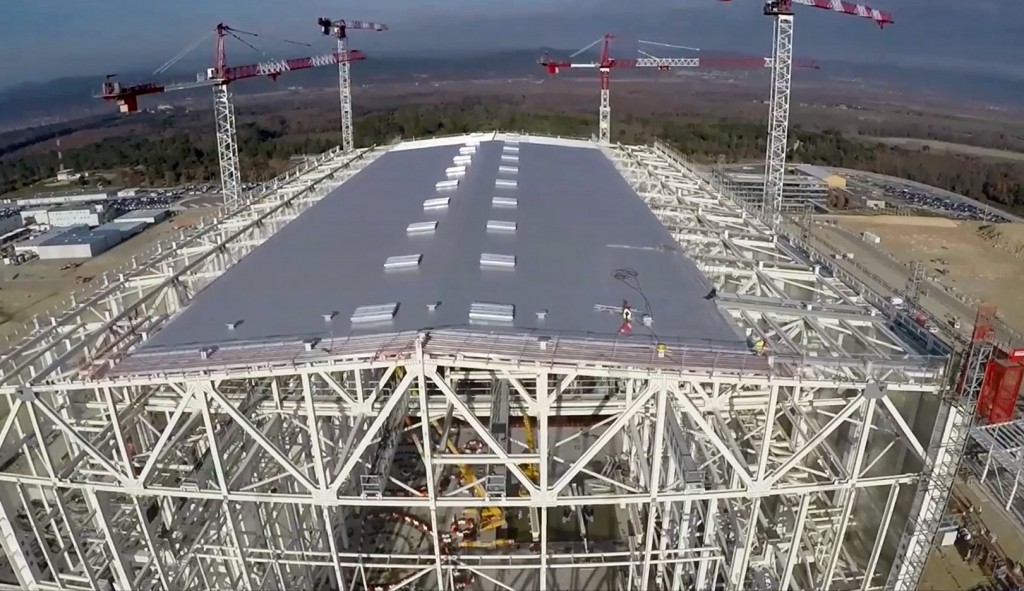
Seen from above
2015-10-15 - A drone shot of the Assembly Building roof structure. In order to install the heavy-lift cranes inside the building, part of the roof will be opened to allow a lift cable—from a tall crane outside of the building—to be lowered within.
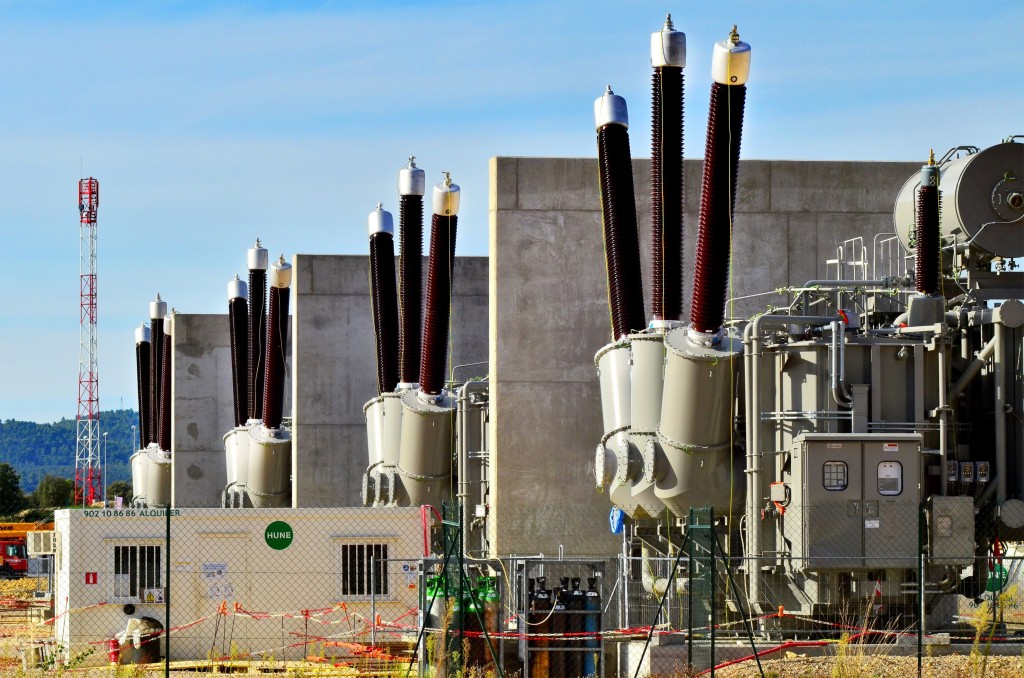
Four transformers installed
2015-10-14 - Transformers are made of hundreds of parts that can only be assembled once the main body is in its final position. After a few months of intensive work, the four SSEN 400kV transformers, part of the US procurement to ITER, are now fully assembled and filled with 60,000 litres of insulating oil each.

Projects mushrooming
2015-10-14 - Preparatory works have begun for the buildings that will house the giant magnets power conversion units. As for all other buildings, the process kicks off with "soil investigation," where long drill bits are pushed as much as 15 metres below the surface in order to identify possible discontinuities or cavities created by water erosion (karsts). Holes are bored approximately every five metres.

Structural concrete
2015-10-14 - Between the 18 massive columns that provide structural support to the different levels of the Tokamak Complex, walls will be made of a special, high-density concrete (3.9 tonnes per cubic metre as compared to 2.5 tonnes for regular concrete).

Galleries galore
2015-10-14 - Work on the platform technical galleries is not quite completed (here, "area 5" along the Poloidal Field Coils facility). In all, four kilometres of underground galleries will service the ITER scientific installation.

At your service
2015-10-14 - The Site Services Building will accommodate and distribute a large number of industrial support services that are indispensable for operating ITER. Among these, a chiller plant will feed cooling water to buildings through a four-kilometre network of piping. Concrete pouring for the 80-metre-long facility has started.
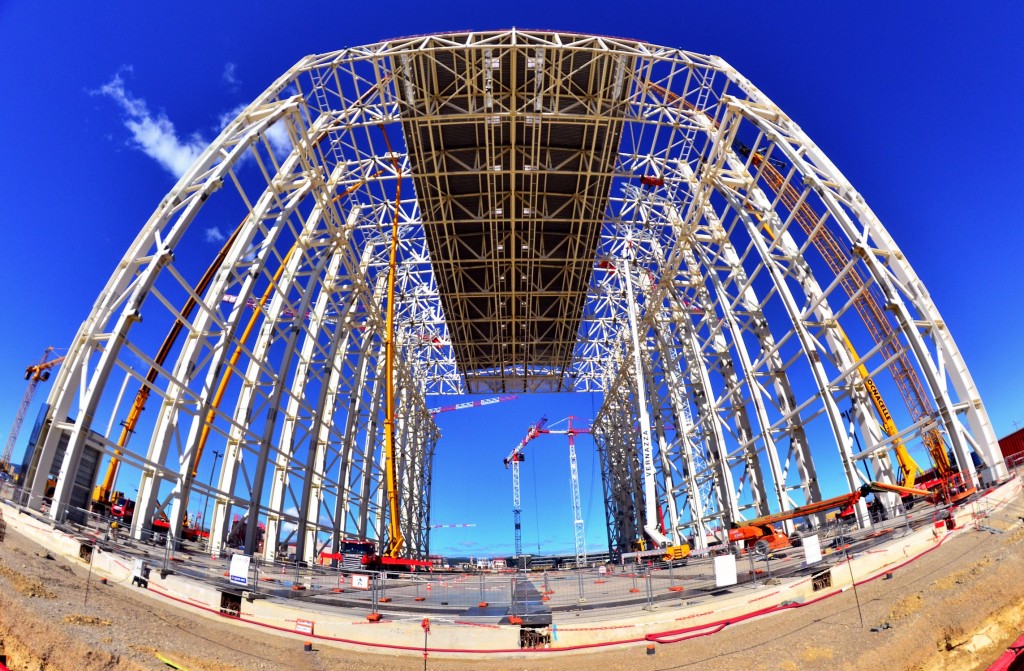
Spider Hall
2015-10-14 - A giant, 22-legged arachnid seems to have taken up residence on the ITER site ... Following the roof lifting operation on 11 September, the temporary structures that held the hydraulic jacks have been removed and workers have nearly finished tightening 3,000 connexion bolts.
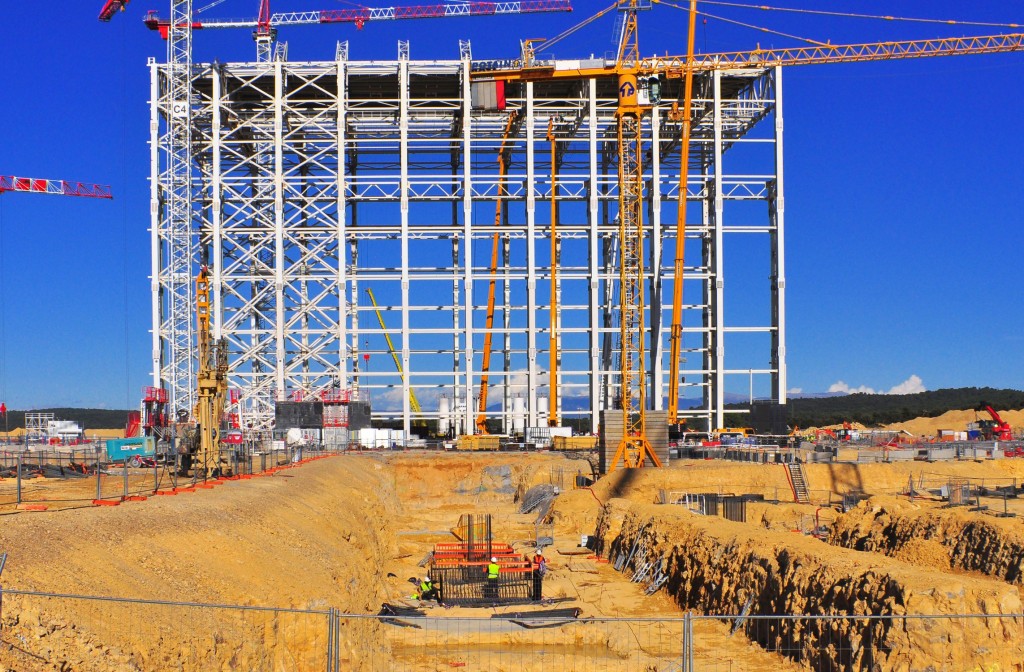
First works on Cryoplant Building
2015-10-14 - Excavation has started for the ITER Cryoplant Building near the Assembly Hall. The 121-metre-long, 47-metre-wide and 19-metre-high Cryoplant Building will host one of the world's largest clusters of cryogenic equipment.

Rebar forest
2015-10-14 - Plastic caps of many colours protect the couplers that ensure the vertical continuity of the bioshield's steel reinforcement. Pouring will take place in two phases: first a lower segement, then an upper segment (propping is visible between the two).
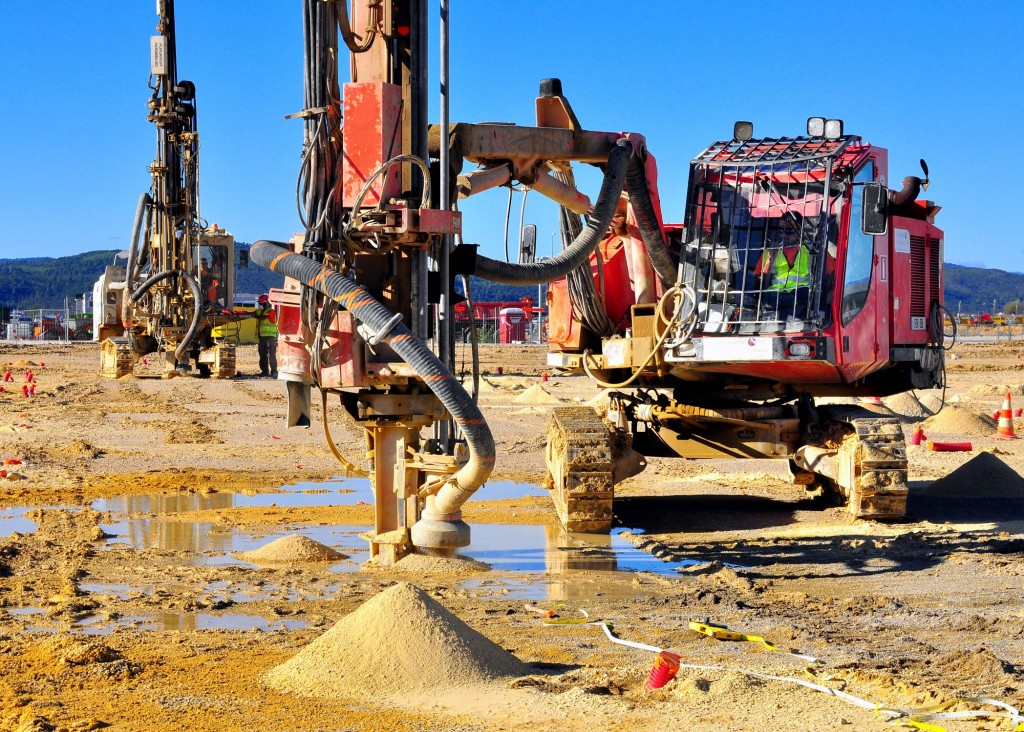
Projects mushrooming
2015-10-14 - Preparatory works have begun for the buildings that will house the giant magnets power conversion units. As for all other buildings, the process kicks off with "soil investigation," where long drill bits are pushed as much as 15 metres below the surface in order to identify possible discontinuities or cavities created by water erosion (karsts). Holes are bored approximately every five metres.

The ITER bioshield
2015-10-12 - Work to install the rebar of the 3.2-metre-thick bioshield was carried out from April to September 2015. Pouring activities are about to begin.
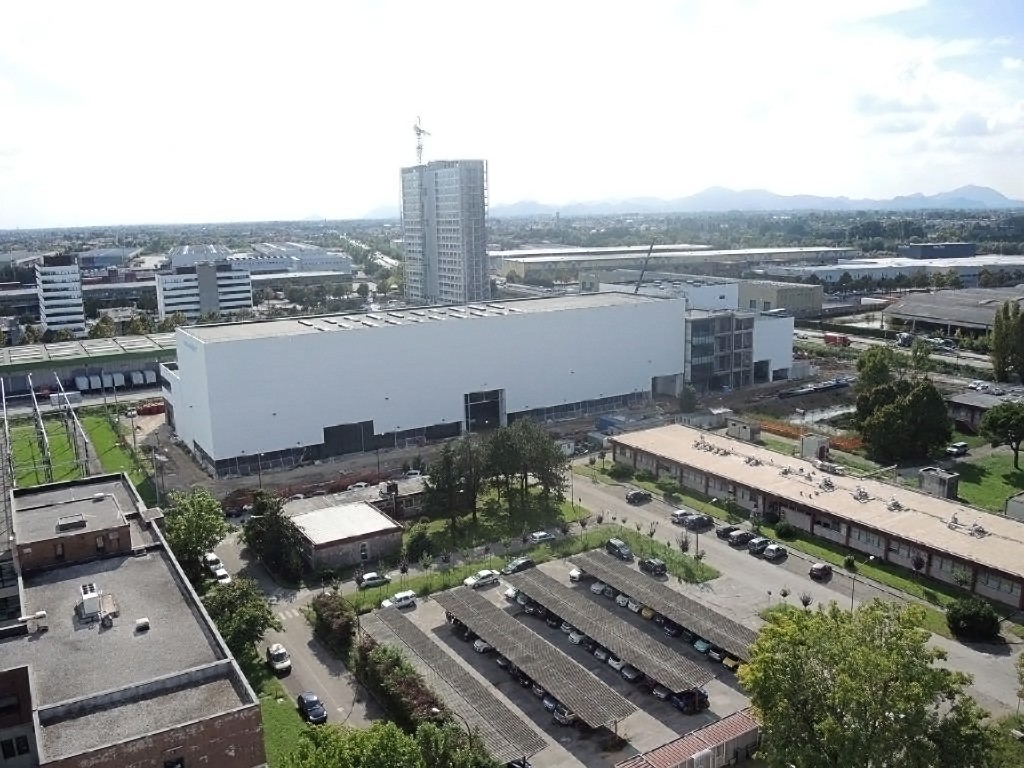
Finished
2015-10-06 - The main building of the NBTF facility is completed and ready for its first components.
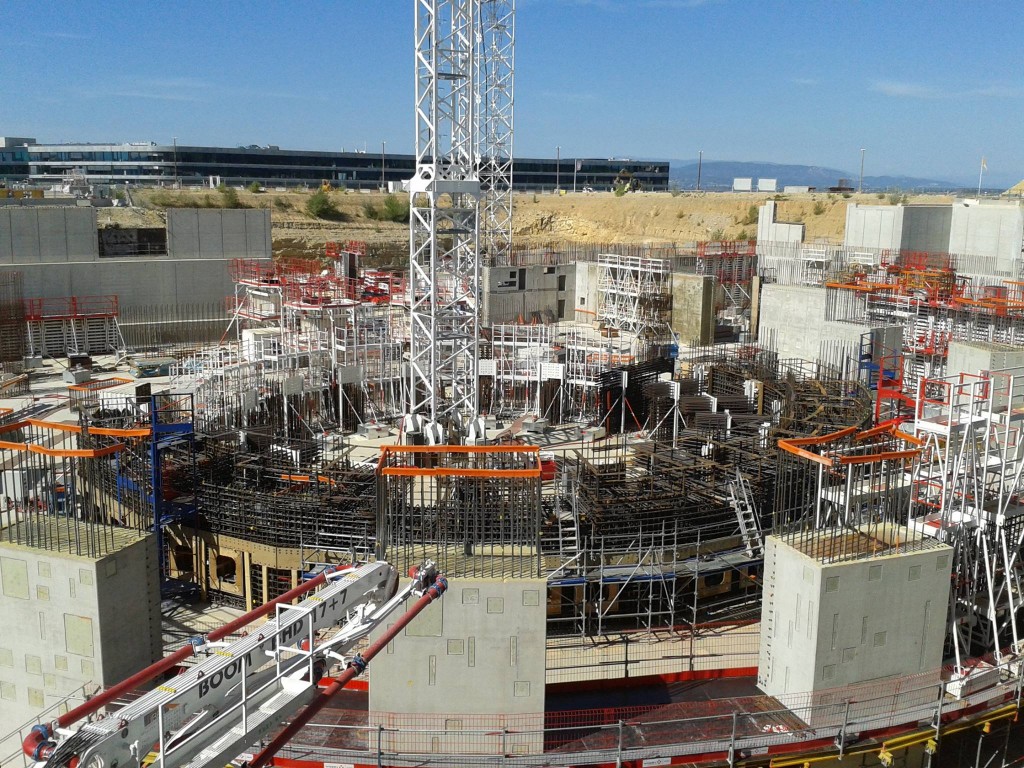
The Tokamak Building
2015-09-29 - In the centre of the Tokamak Pit, concrete pouring for the columns has ended. Work to pour the ITER bioshield begins in October.
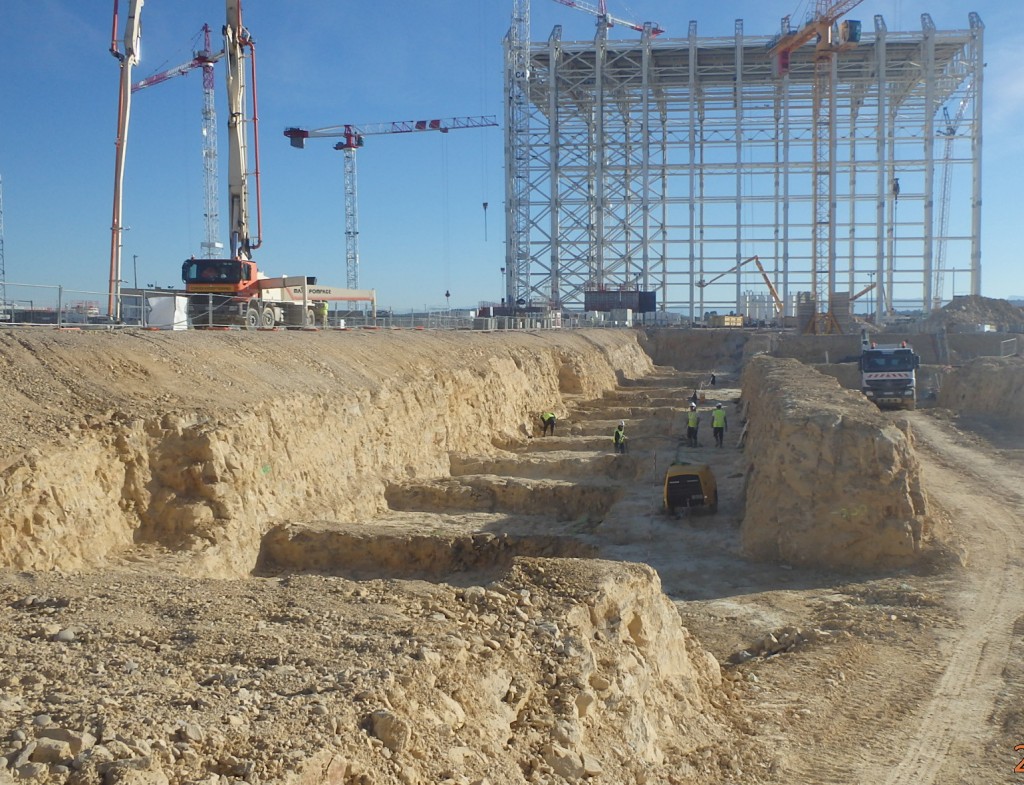
Cryoplant preparatory works
2015-09-28 - Excavation works for the ITER cryoplant have ended. The cryoplant will produce the cooling power required for operation and distribute it through a complex system of cryolines and cold boxes. Photo: ENGAGE

Big yellow hands
2015-09-25 - Overhead cranes will travel the length of the 257-metre Poloidal Field Coils facility to transport the double pancake windings from station to station. The complete process, from winding to finished coil, will take approximately two years.
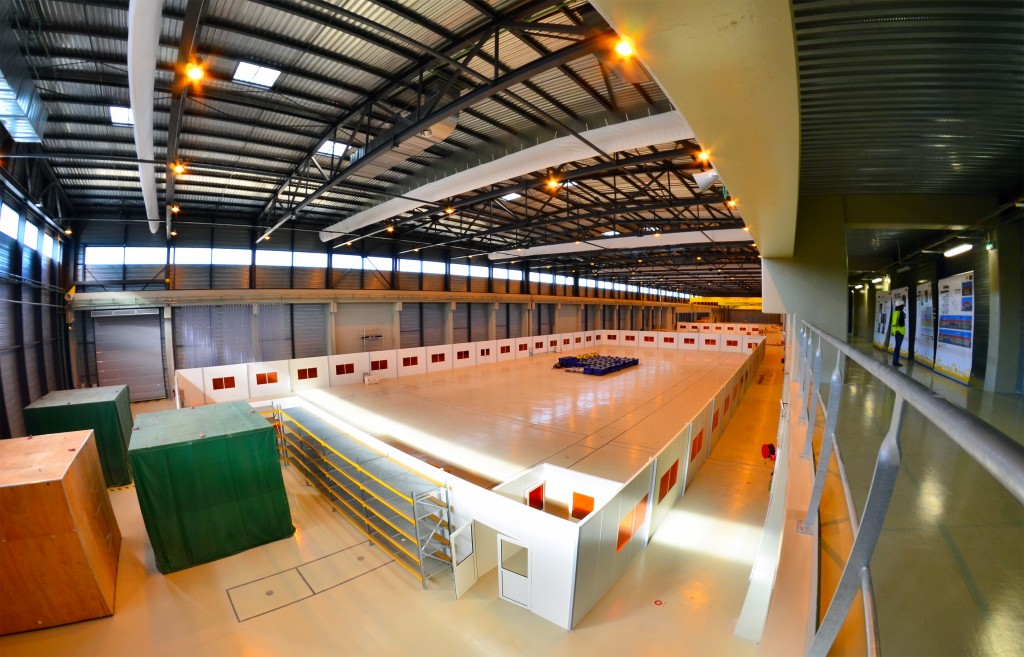
Two clean areas
2015-09-25 - The clean area on the south side of the building will host two winding tables, where lengths of niobium-titanium conductor will be fed from two spools simultaneously ("two-in-hand" winding), insulated, and wound into double pancakes. Dummy conductor for tooling qualification is stored in the crates, at left.

And the tallest is ...
2015-09-21 - The ITER Assembly Building is now the tallest structure on site. © MatthieuCOLIN.com
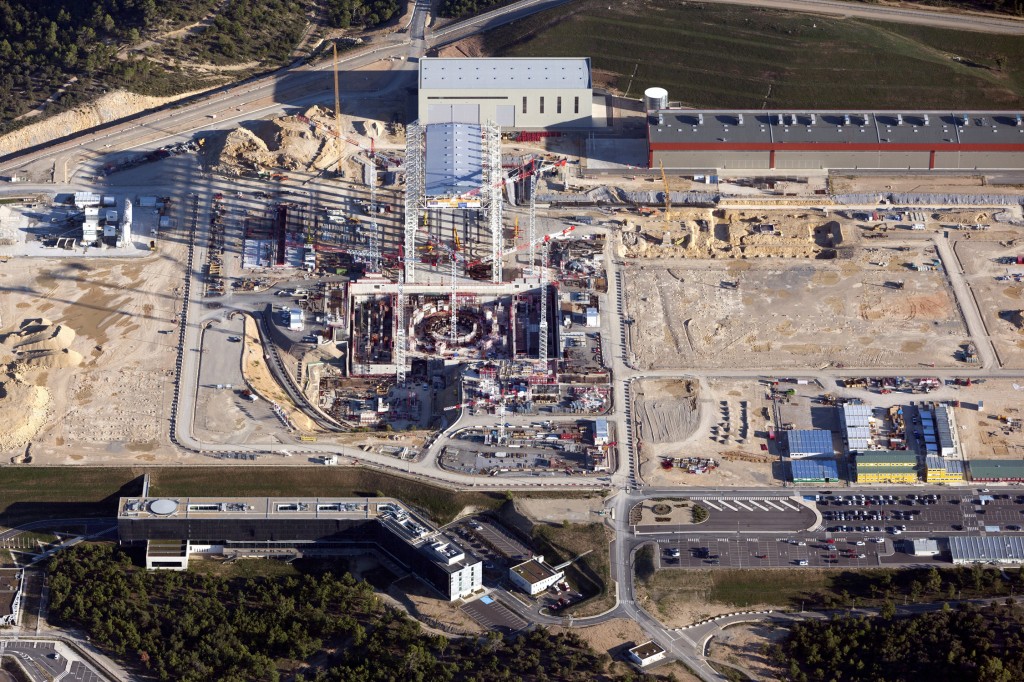
Perfect alignment
2015-09-21 - From the sky, it's easy to see how the assembly cranes will deliver their loads from the Assembly Hall (grey roof) along a 175-metre crane bay into the Tokamak Pit. © MatthieuCOLIN.com

Inside
2015-09-16 - Inside of the storage facility, the first crates have been temporarily stored in one corner. The space will soon be fitted out with storage shelves and pallet racks.
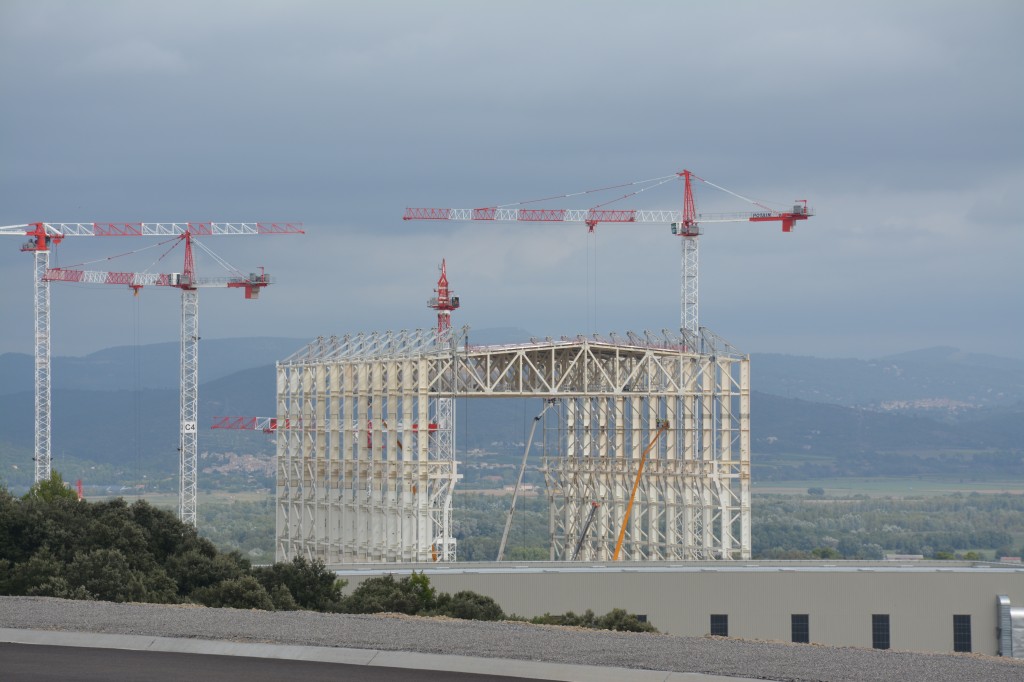
From behind the hill
2015-09-16 - The steel structure of the Assembly Building, seen from the logistics platform located behind the platform. (In the foreground, the Cryostat Workshop is visible.)
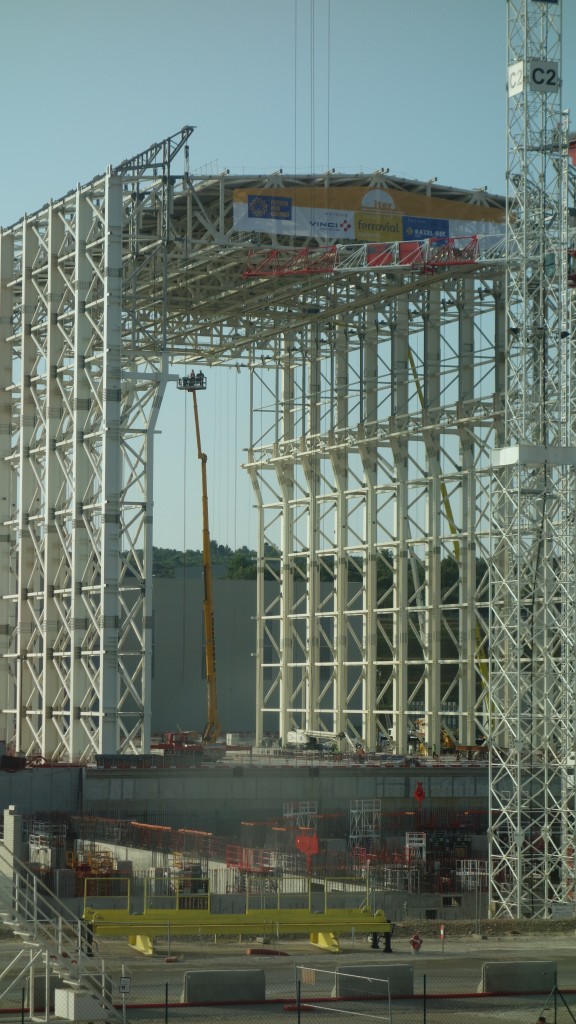
A few weeks to secure the structure
2015-09-11 - When the roof structure is fully secured to the side columns, the temporary structures put in place for the lift cables (top) will be dismantled.

The symbolic ribbon cutting
2015-09-11 - On 11 September 2015, Director-General Bernard Bigot underlines the importance of the latest milestone achieved on the worksite: "Here, in this antechamber to the Tokamak Complex, the principal elements of the machine with be fitted out and preassembled. Without this building, there would be no assembly, and without assembly there would be no machine and no project."

In a few years ...
2015-09-11 - One day, the Tokamak Building (under construction, foreground) will be as high as the just-topped Assembly Building.
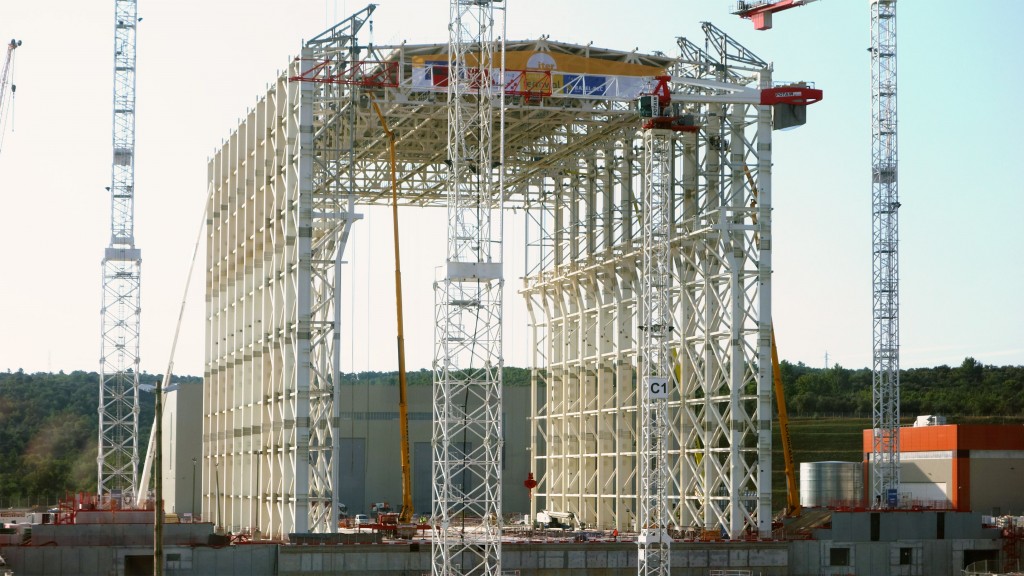
Successful lift operation
2015-09-11 - The roof segment of the ITER Assembly Building is successfully raised to its final position in September. Held in place by temporary jacks following a 14-hour lift operation, the 730-tonne metal structure will be secured to the side pillars in the weeks to come.

They've done it!
2015-09-11 - Posing for a group picture under the Assembly Hall roof are staff members from the Buildings, Infrastructure and Power Supplies (BIPS) Project Team, architect-engineer Engage, APAVE (safety specialists), Martifer (steel structure assembly), and VSL (heavy lifting).

Lifted at 5 km/hour
2015-09-10 - The structure is first lifted 20 cm and left to hang in order to measure the deflection of the steel and check the hydraulic pressure of the jacks. Then, the structure is lifted at approximately 5 km/hour.

Centimetre by centimetre
2015-09-10 - Over the course of 14 hours, 22 hydraulic jacks hoisted the huge structure along thick steel cables that hung from support structures that had been temporarily fixed to the top of the pillars.
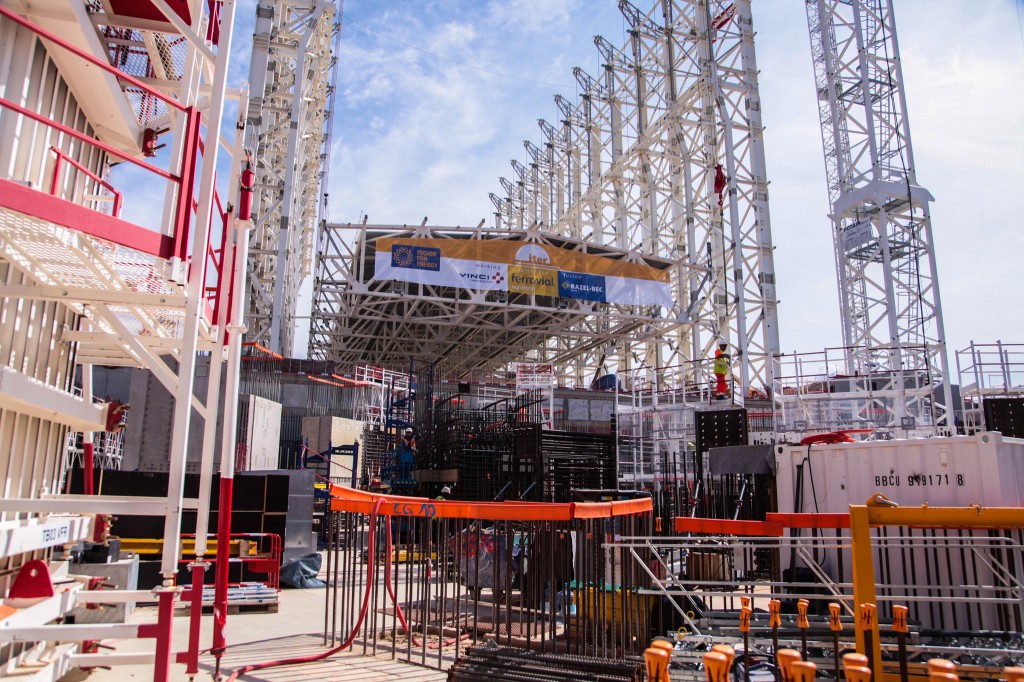
Roof lift, seen from the pit
2015-09-10 - And the roof structure rises, inch by inch. © Les Nouveaux Médias/SNC ENGAGE

And off it goes
2015-09-10 - Laser metrology is used to verify the position of the structure as it is lifted. Tolerances of only 35 mm from highest to lowest point are permitted.

800-tonne roof structure lifted 10-11 September 2015
2015-08-31 - In a 15-hour operation that began on 10 September, the 800-tonne roof structure for the Assembly Building is being slowly lifted to its final position at 50 metres above the basemat. A ceremony is planned to mark the end of the construction milestone on 11 September.
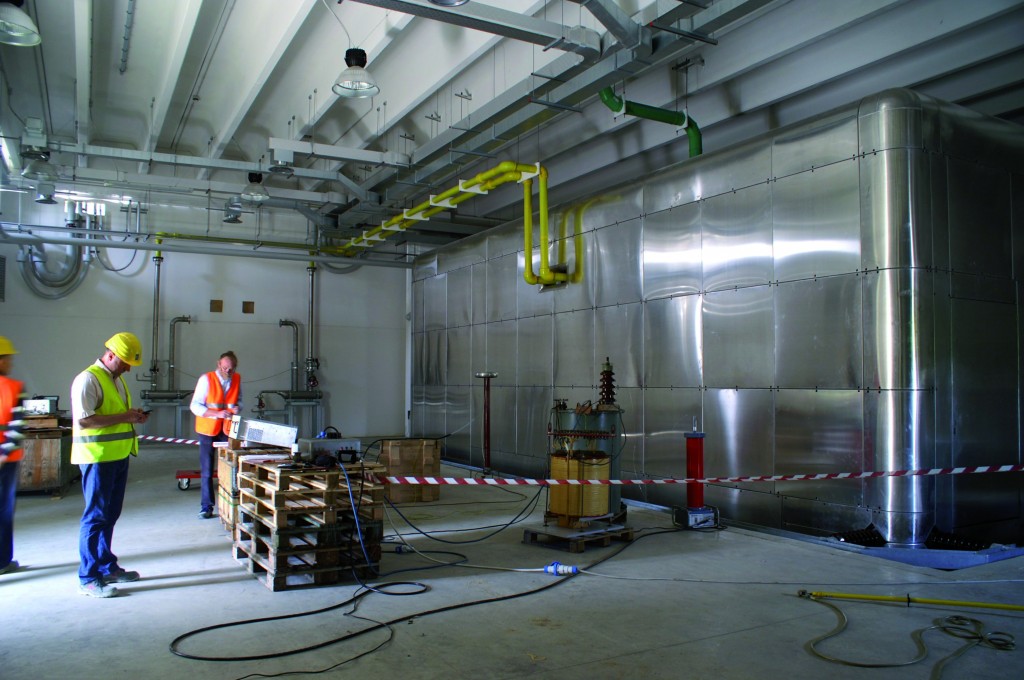
First European equipment installed
2015-08-31 - The first European component installed at the Padua facility is the high voltage deck for SPIDER. The European agency collaborated with the Italian company COELME for the design, manufacture and installation of the high voltage deck, a mechanical structure that will hold power supply equipment weighing around 40 tonnes. Photo: F4E

Manufacturing preparations begin
2015-07-21 - In July, a clean area is established around the area of the Poloidal Field Coils Winding Facility that will host the winding tooling. The first tooling elements also arrived by truck this month.

Side pillars near completion
2015-07-17 - The southern side of the structure will soon be completed. When that happens, the roof beams will be lifted into place.

Sturdy as they come
2015-07-10 - These massive columns will support the B1 (basement 1) level of the Diagnostic Building.

Unloading docks and a mega door
2015-07-10 - On the north side of the warehouse, there are five unloading docks and one mega door (6m x 6m). Due to the slope of the access road (max 8%), the warehouse isn't designed for ITER's largest and heaviest components.

According to plan
2015-07-10 - A milestone was met in July when propping and formwork operations got underway for the next basement level of the Tokamak Complex.

In July 2015
2015-07-10 - On the Tritium Building site of the worksite, workers have completed the concrete pouring for the external wall. Work continues on interior walls and columns.

Largest warehouse nearly completed
2015-07-10 - Construction activities are nearly over on the largest ITER warehouse—a 10,000 m² facility behind the ITER platform (160 metres long, 60 metres wide, 12 metres high).
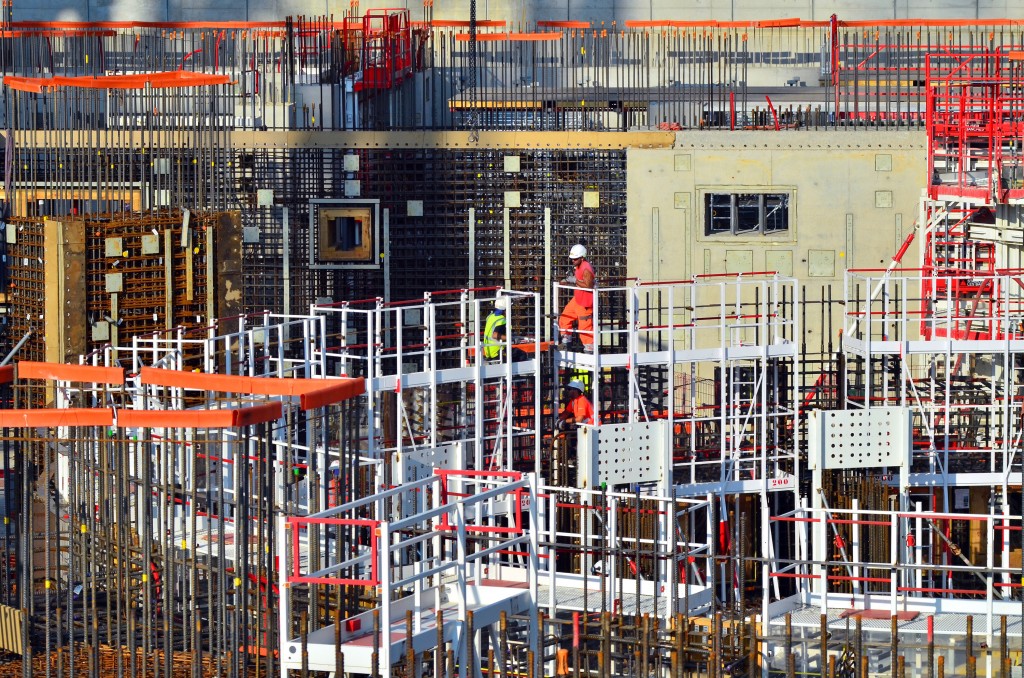
A circle in white
2015-07-10 - The white scaffolding marks out the ITER bioshield, a three-metre-thick concrete wall that will surround the tokamak and cryostat.

Summer 2015
2015-07-07 - The ITER office buildings will be closed for one week in August, but there will be no pause in the activity on the work site ...

First B1 formwork
2015-07-07 - In the Diagnostic Building area, workers have started to install formwork for the next-level floor.

A white circle is apparent
2015-07-07 - Looking into the Tokamak Pit from the south rim. It's easy to see where Tokamak assembly will take place in a few years.

An assembly of steel beams
2015-07-07 - Over 200 individual beams—and 85,000 bolts—make up the metal structure of the Assembly Building.
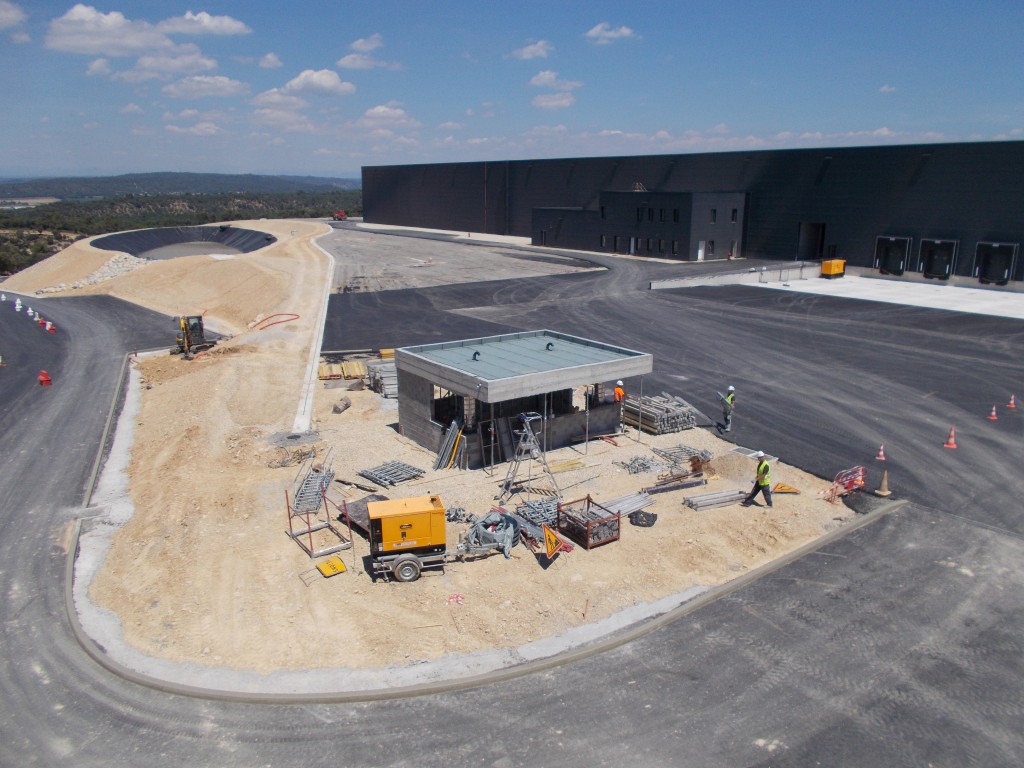
Activity to commence in early 2016
2015-06-26 - The building will be ready to store its first components early next year. The zone is also equipped with a guardhouse (foreground), a parking lot, a storm basin sized for centennial rains (+20%) and a garage for six fork lifts.
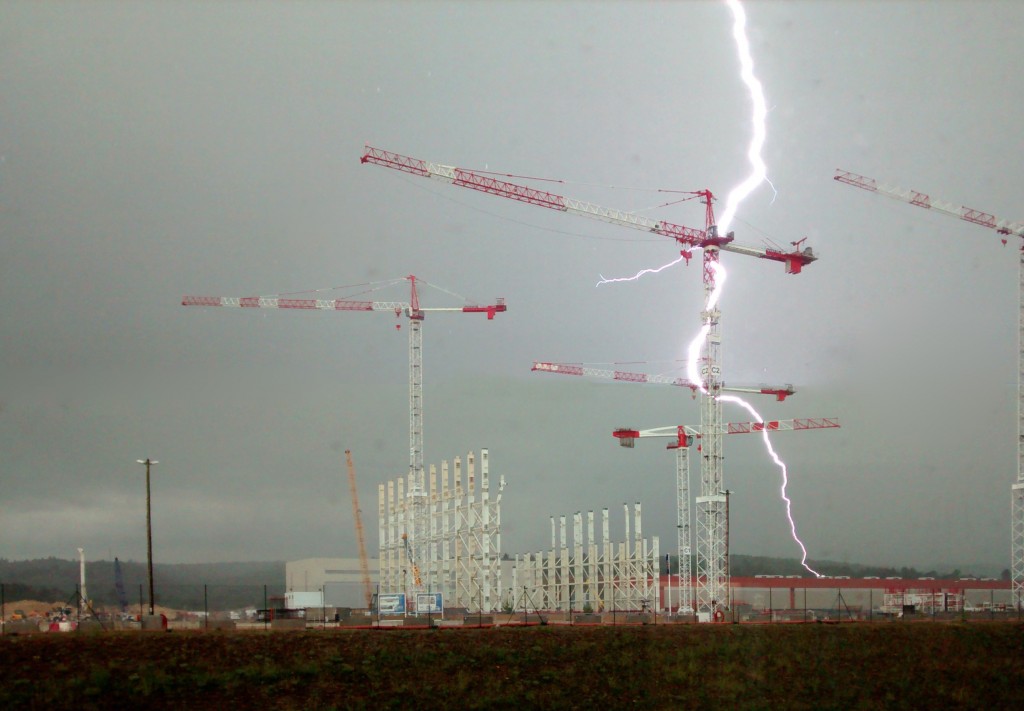
Mega jolt
2015-06-09 - At 3:37 p.m. on Tuesday 9 June 2015, a monster bolt of lightning was captured on film as it zigzagged into - and out of - crane #2.

Transformer is equipped
2015-06-08 - The first transformer to be installed on the platform has been equipped with ancillary components (oil radiators, an oil conservator, and long ceramic insulators called "bushings"). In a final installation step, the transformer will be filled with the transformer will be filled with 60,000 litres of oil.

Peeking in
2015-06-03 - Looking down into the Tokamak Pit where the B2-level walls and columns are progressively taking shape. Each level of the Tokamak Complex civil structure should take about six months.

First basement level advances well
2015-06-03 - A fisheye lens allows the full breadth of the future Tritium Building (foreground) to be captured in a photo. The construction of pillars and walls for the B2 basement level is advancing.
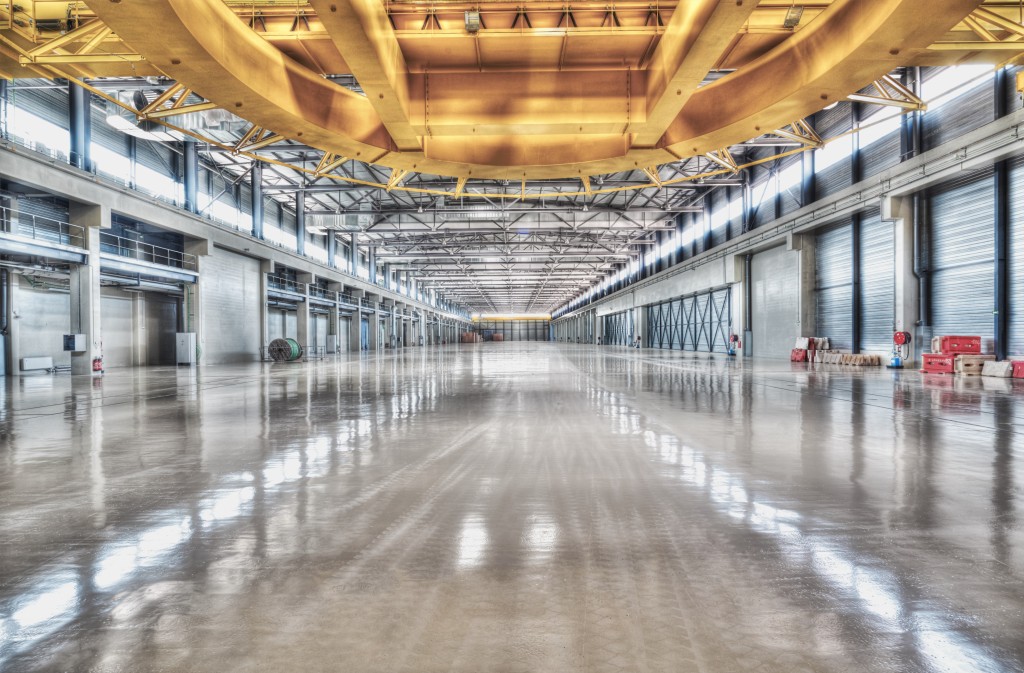
Last photos before activity
2015-05-30 - Professional photographer Christian Luenig took a series of interior shots of the Poloidal Field Coils Winding Facility in May 2015. Photo: Christian Lünig/ VG Bild und Kunst (Follow all manufacturing news at https://www.iter.org/construction/SiteFabricationPFcoils

Double pillars for strong support
2015-05-30 - Within the Assembly Building, two 750-tonne cranes working in tandem will lift loads up to 1,500 tonnes during assembly, assisted by two 50-tonne auxiliary cranes. Photo: Christian Lünig/ VG Bild und Kunst

Framing out the bioshield
2015-05-30 - The ITER bioshield is a 3.2-metre-thick circular structure surrounding the Tokamak, whose role is to protect workers and the environment from radiation generated by the fusion reactions. The bioshield is under construction now. Photo: Christian Lünig/ VG Bild und Kunst¶
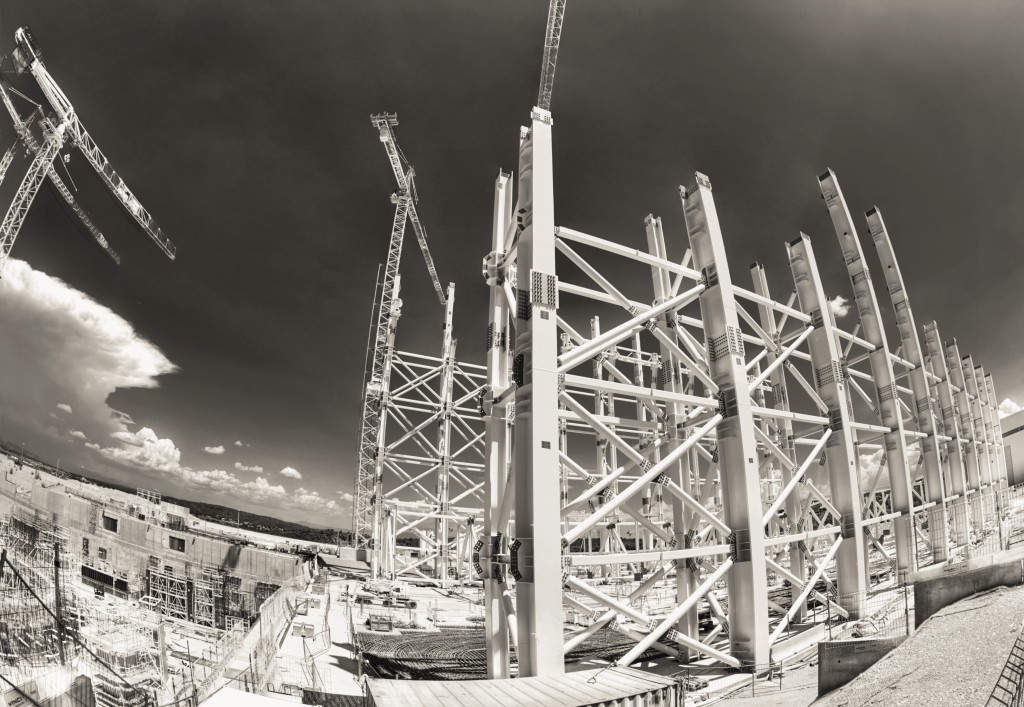
In black and white
2015-05-30 - Soon to reach 60 metres, the pillars of the Assembly Building loom over the Tokamak Seismic Pit below. Photo: Christian Lünig/ VG Bild und Kunst

All eyes look up
2015-05-30 - The structure of the Assembly Building, seen from the Tokamak Pit, is truly impressive.
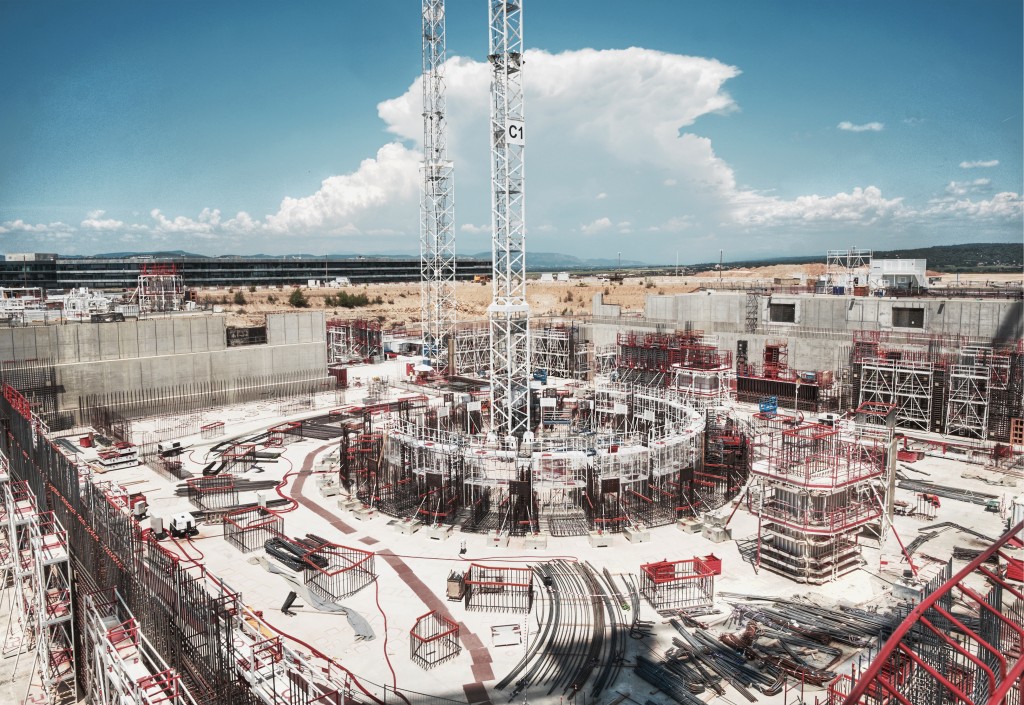
Looking north
2015-05-30 - The Tokamak Complex worksite, late May 2015. Photo: Christian Lünig/ VG Bild und Kunst
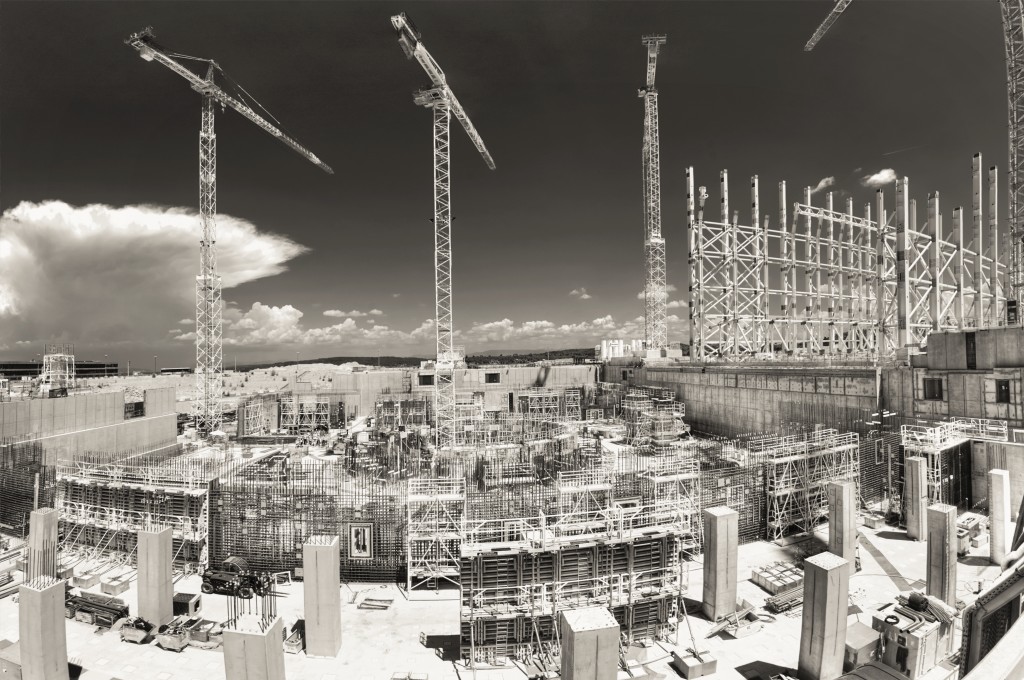
A black and white perspective
2015-05-30 - In the foreground: Diagnostic Building pillars. In the background: framing the walls of the Tokamak Building. Photo: Christian Lünig/ VG Bild und Kunst
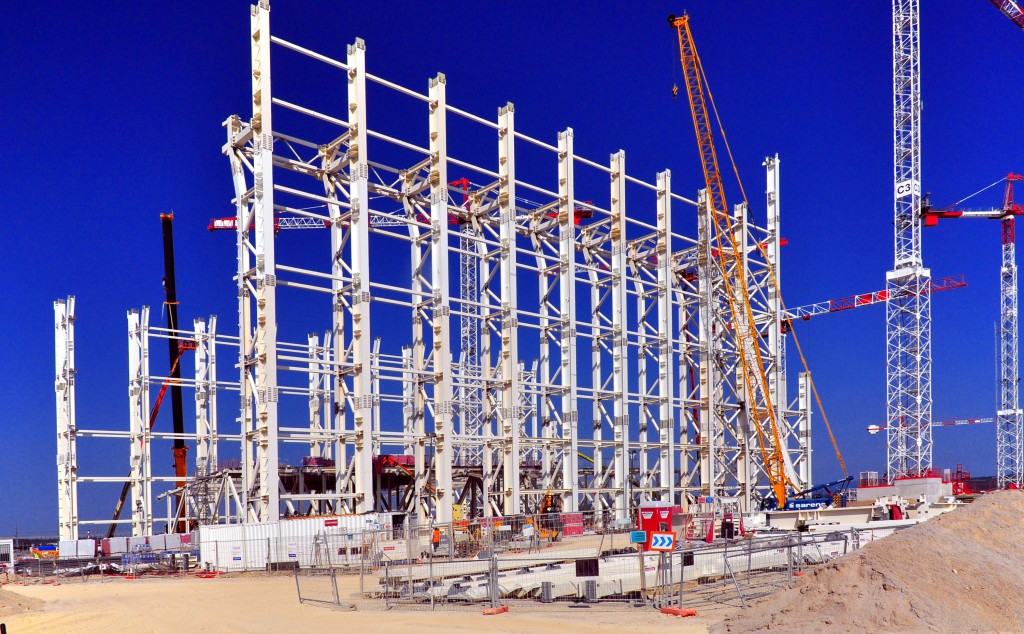
Soon to be the tallest structure
2015-05-27 - When completed, the Assembly Building will stand 60 metres tall (nearly 200 feet).
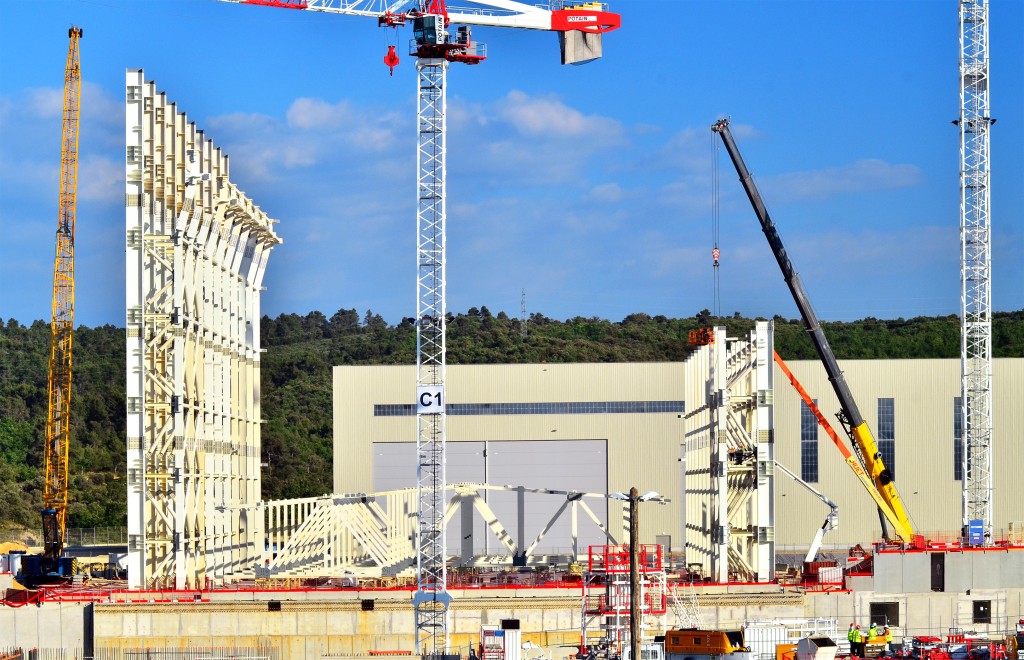
Assembly of roof structure underway
2015-05-27 - As the pillars of the Assembly Building rise, work is underway in parallel to assemble the roof structure. In August, the roof assembly will be lifted in one piece by way of hydraulic jacks and cables.

One more level to go
2015-05-27 - On the north side of the Assembly Building basemat, four vertical pillar segments out of five are in place (appr. 48 m). Visible in the picture: the metal balcony that will support rails for the overhead assembly cranes.
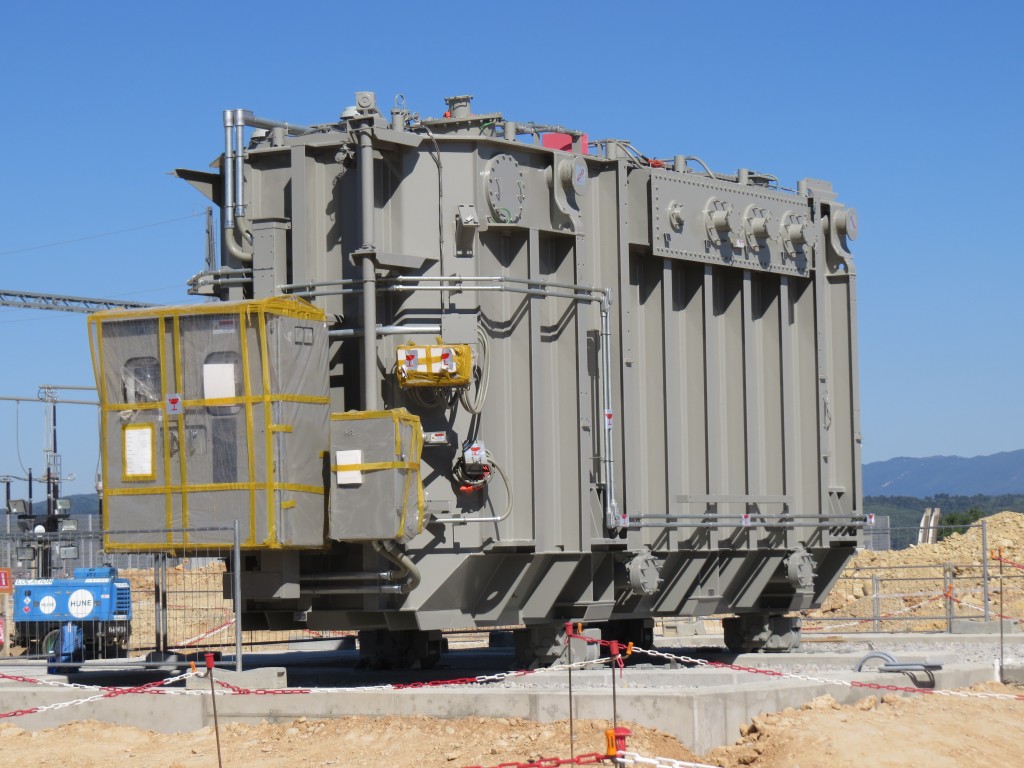
In place
2015-05-21 - The 87-tonne transformer sits over a 1.5-metre-deep, gravel-covered pit that has been dimensioned to receive the 44 cubic metres of oil the component contains (oil is used as an insulator) in case of a leak. Photo: F4E

First installed component of the ITER plant!
2015-05-21 - The first of four transformers for ITER's steady state electrical network is installed in its permanent location on 21 May 2015—the first installed component of the ITER plant.

For the feet of giants
2015-05-05 - On the Assembly Building basemat, workers pour concrete into the areas reserved for the largest assembly tools. The tools themselves will be fixed to the floor by steel plates and rails. Photo: F4E
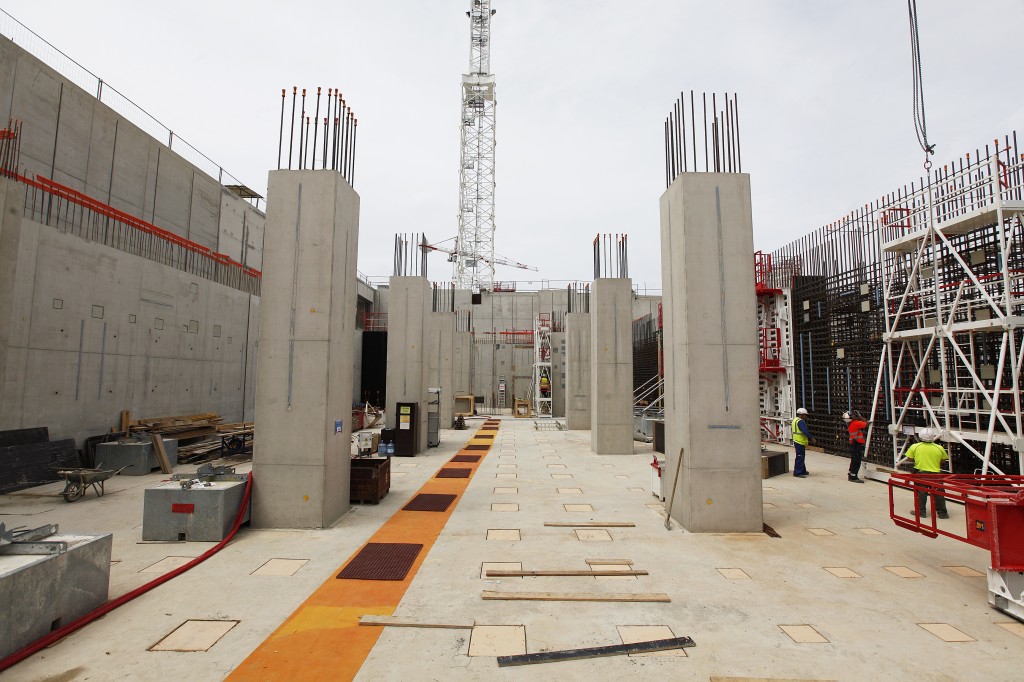
Future "Diagnostic Hotel"
2015-05-05 - Walking through the hallways of the future Diagnostic Building will feel a little like walking along the corridors of a hotel, with doors on every side opening to the back-end systems for specific diagnostics. Photo: F4E
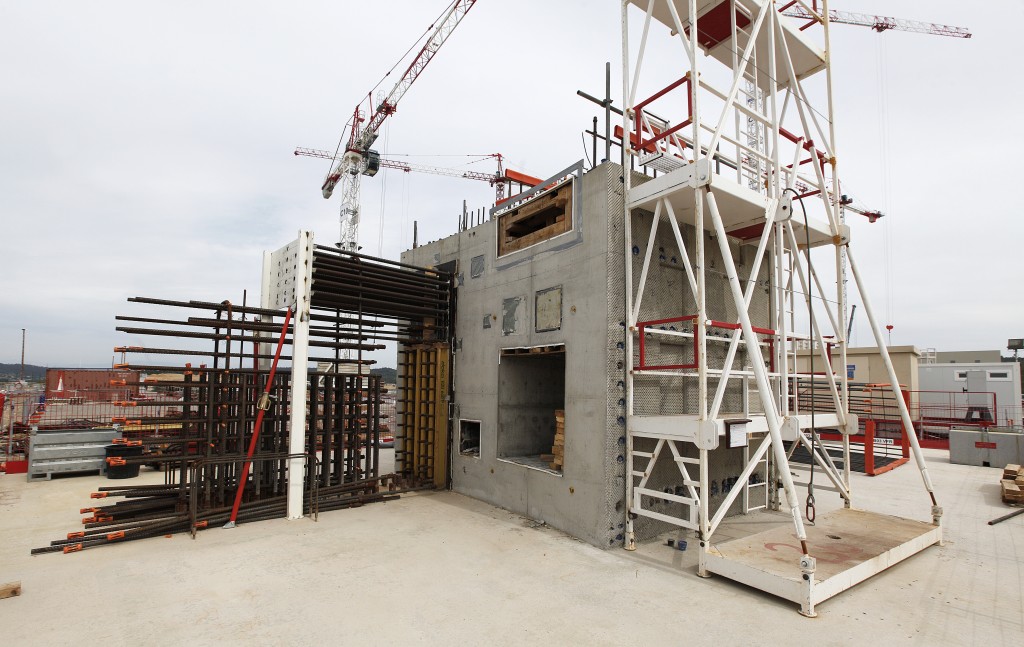
1/18th of the cryostat crown and bioshield
2015-05-05 - This construction mockup reproduces 1/18th of the crown that will support the cryostat and surrounding bioshield. Photo: F4E
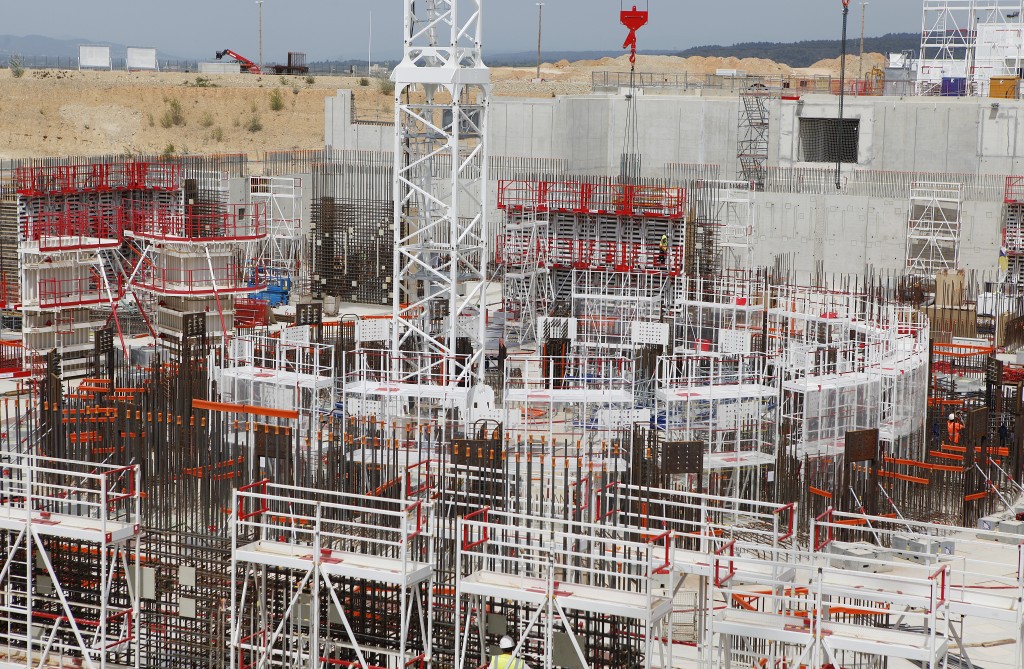
Central ring
2015-05-05 - When closed up, at the end of ITER assembly, the bioshield will completely surround the machine. Here, the white formwork marks out the very lowest level of the protective wall. Photo: F4E

The largest assembly tool
2015-05-05 - The steel "footprint" (at right) gives an idea of the largest tool for ITER assembly - the 22-metre-tall, 800-tonne Sector Sub-Assembly tool. Two of these giants, operating side by side in the Assembly Building, will equip the sectors of the vacuum vessel before their installation in the machine. Photo: F4E

Hot Cell storage area
2015-05-05 - In the foreground, the area excavated for the future ITER Hot Cell is used to store, and pre-assemble, the materials used for wall construction.
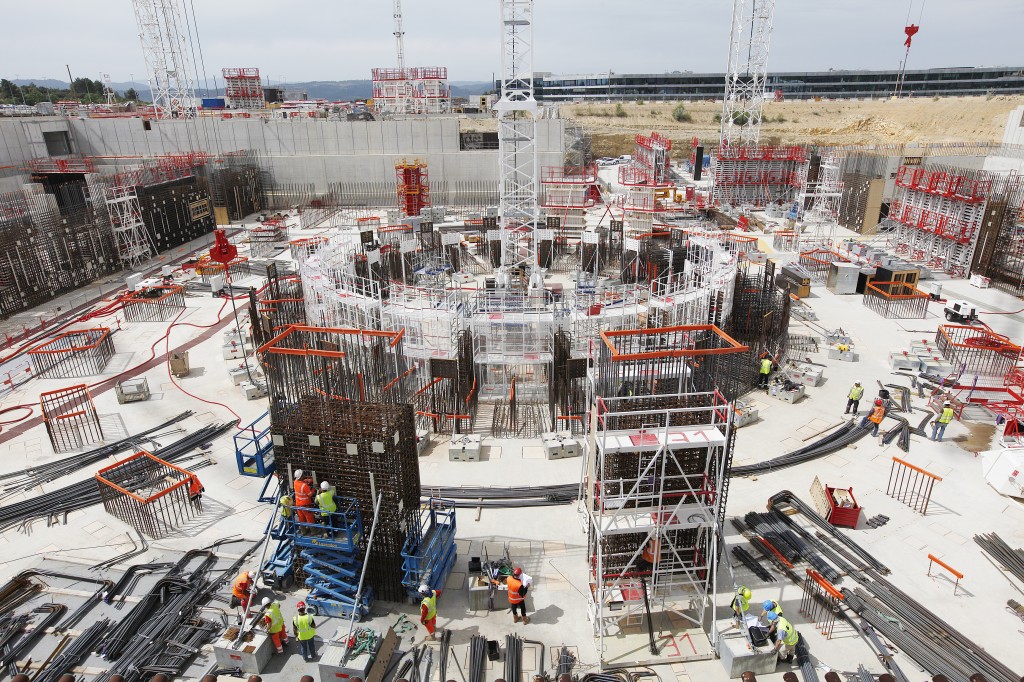
The heart of construction
2015-05-05 - In May, reinforcement operations are underway in the Tokamak Building, which will house the machine and a wide number of systems. Photo: F4E
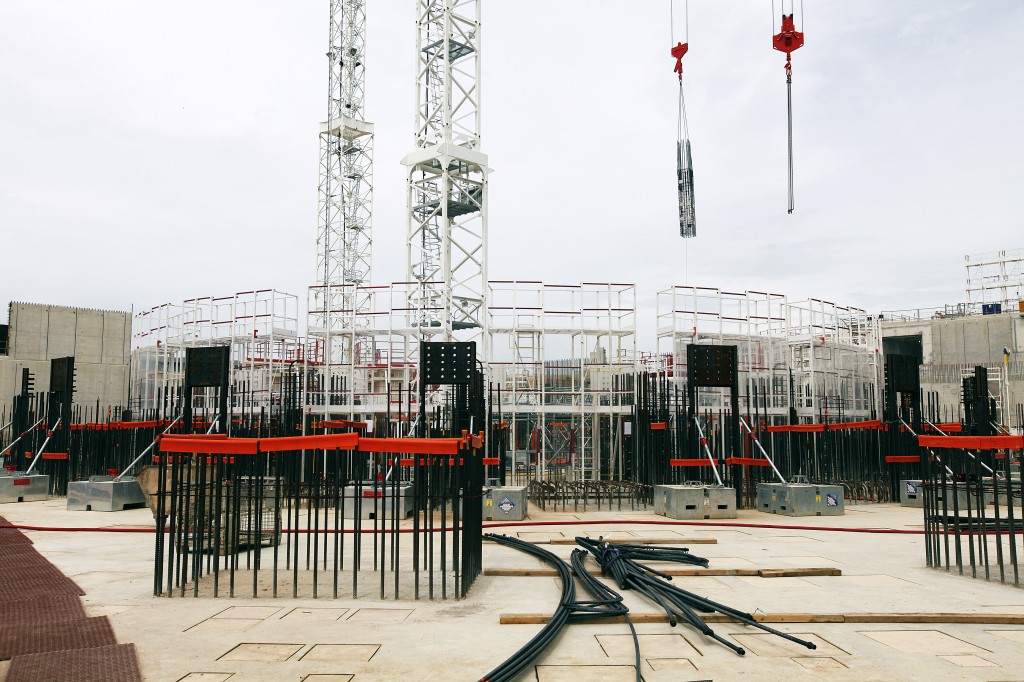
A perfect circle
2015-05-05 - Formwork, in Plexiglas, shapes out the lower part of the bioshield—the three-metre-thick structure that will surround the cryostat. Photo: F4E
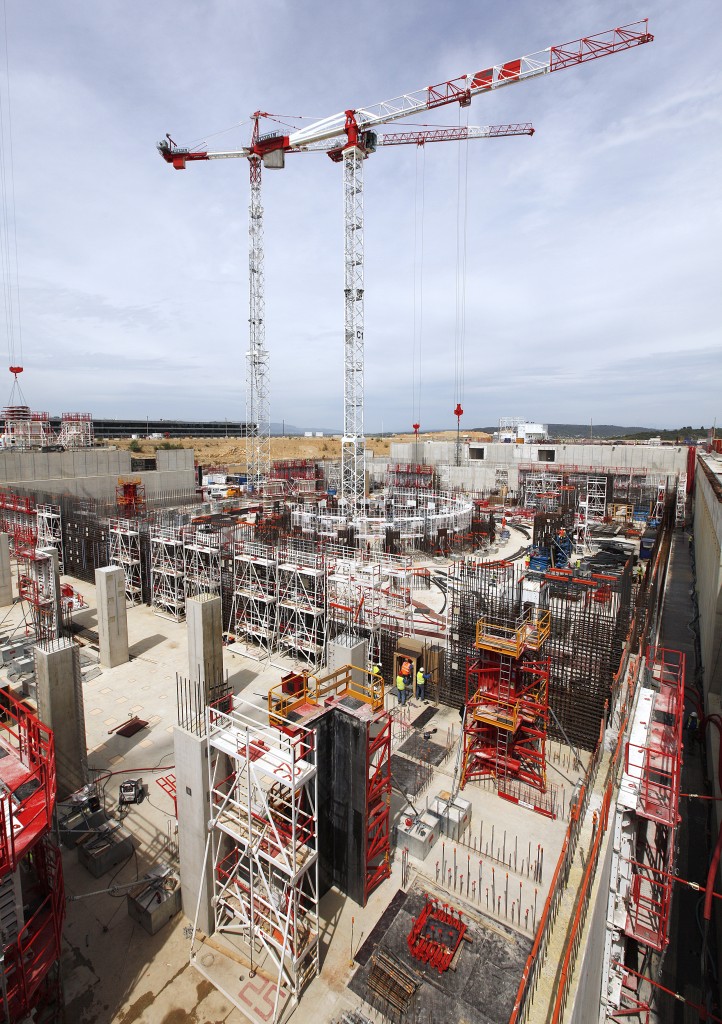
Looking north
2015-05-05 - From this angle, several features of the Tokamak Complex worksite are visible: the cubicles of the Diagnostic Building in the foreground, the round circle of the bioshield in the centre and, on the far side, the walls of the Tritium Building. Photo: F4E
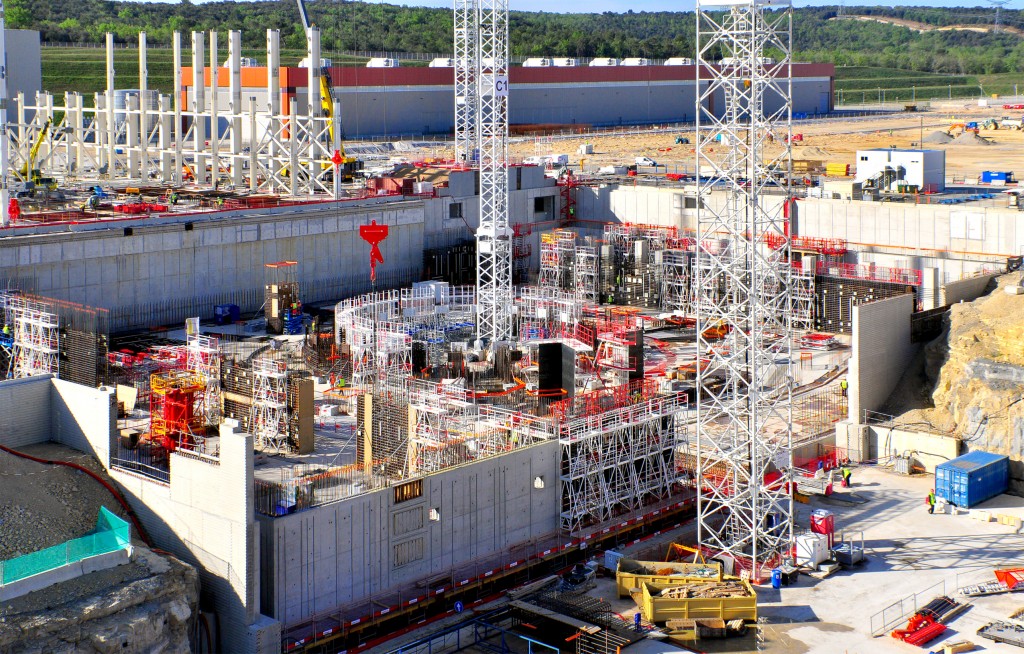
Progress on the B2 level
2015-04-29 - In the Tokamak Complex Seismic Pit, work on the lowest basement level (B2) progresses well. The pillars have all been poured for the Diagnostics Building (far end) and the external walls of the Tritium Building are in place (left). In the centre, preparatory work is underway in advance of concrete pouring for the bioshield.

Fourth-level colums and work on the roof
2015-04-28 - As the fourth level columns are installed (bringing the structure to 48 metres), work has started on the ground to assemble the structure of the roof, which will be lifted and set into place in one piece.

Pillars in place
2015-04-21 - The last pillars of the Diagnostics Building were poured late April. Beginning mid-2015, work will begin on the second Tokamak Complex level (B1).
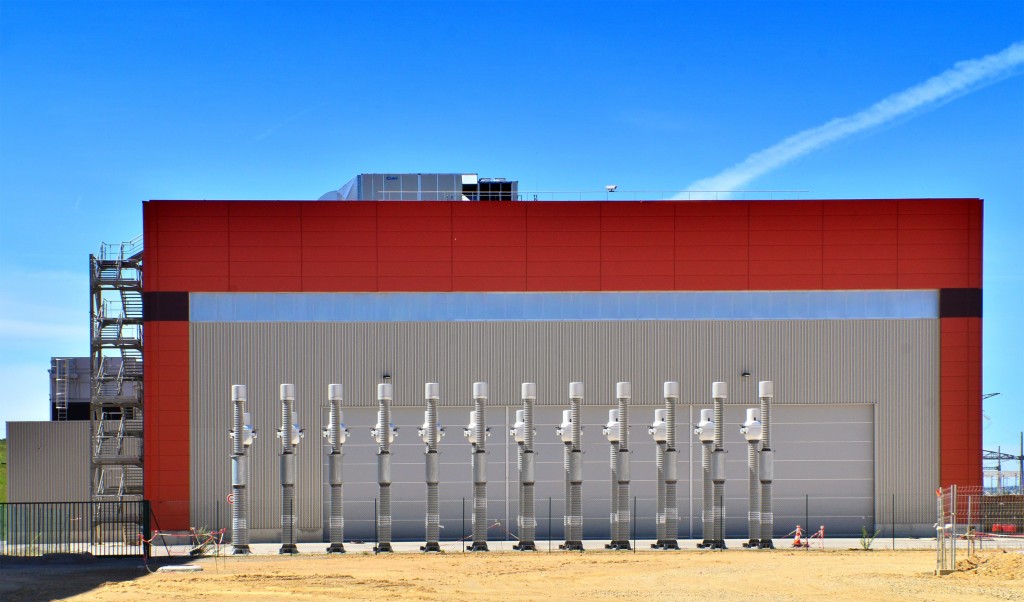
Standing at attention
2015-04-21 - A dozen 400 kV electrical components for current and tension measurements are momentarily "stored" near the Poloidal Field Coils Winding Facility. Solidly bolted into concrete and installed vertically to preserve their oil-filled insulation system, they will be installed in their final location on the platform later in the year.
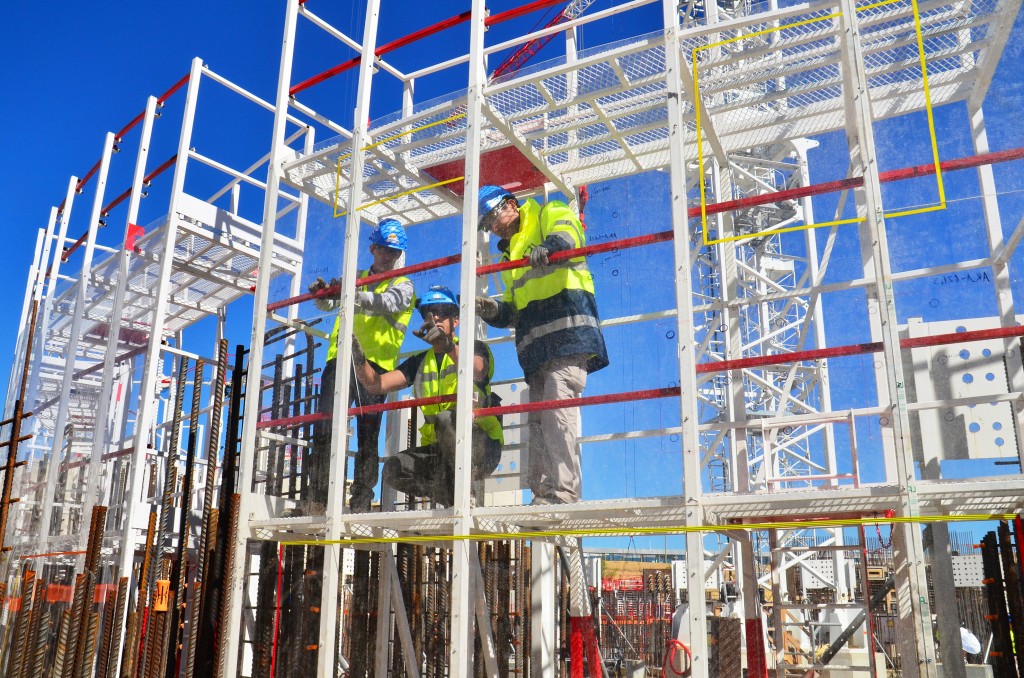
See-through formwork
2015-04-21 - In April, Plexiglas formwork is installed along the circle of rebar that marks out the ITER bioshield. The transparent material allows workers to verify the position of the bioshield's future embedded plates and studs (drawn onto the formwork) during the installation of the reinforcement rods.
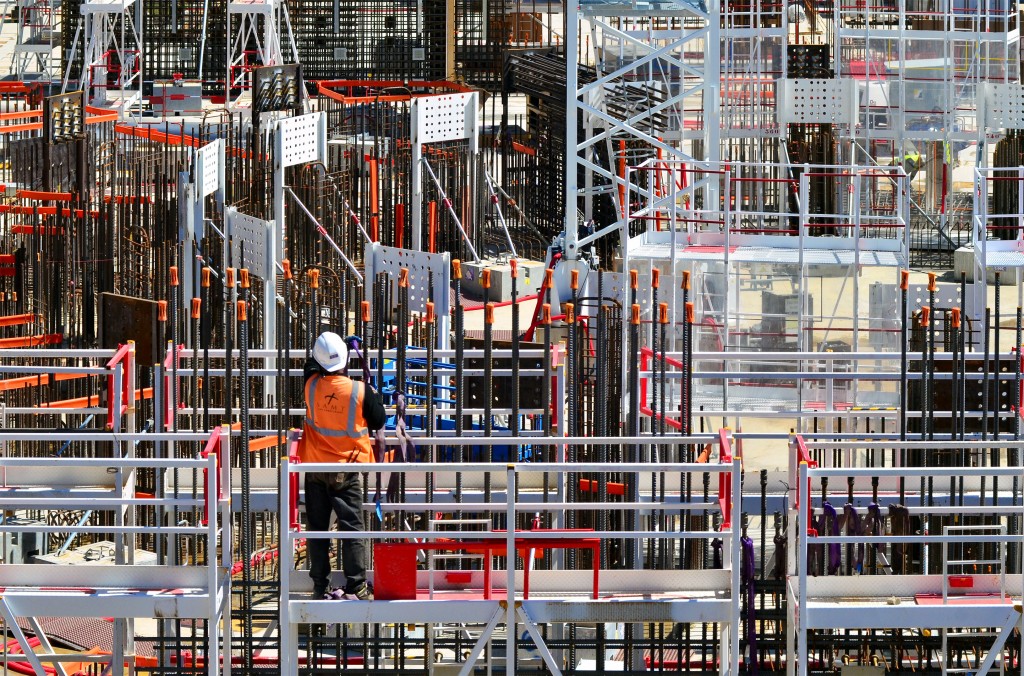
A rebar forest
2015-04-21 - Vertical rebar marks out the internal walls of the Diagnostics Building and—in the centre—the bioshield.

Graphic shapes
2015-04-21 - These graphic shapes mark the spots reserved for embedded plates in this section of Tokamak Complex wall.

Site service building galleries: weathertight
2015-04-13 - The backfilling has been completed around the deep technical galleries of the Site Services Building and the last wall will be poured this month. Photo: Engage Consortium
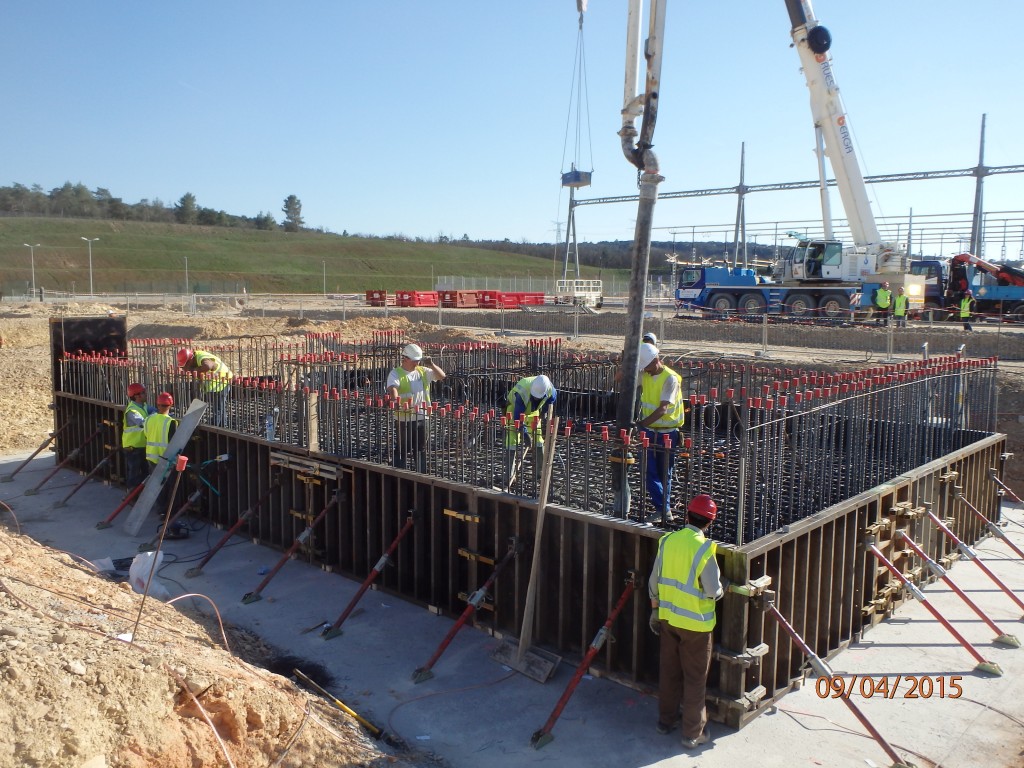
87-tonne transformer
2015-04-09 - The 87-tonne transformer that will take its place here was procured by the US, manufactured in Korea, and delivered to the ITER site in January. Concrete pouring is nearly completed on the reinforcement wall and supports. Photo: Engage Consortium

Up to the third level
2015-04-08 - The Assembly Building construction project, on a clear day in April.
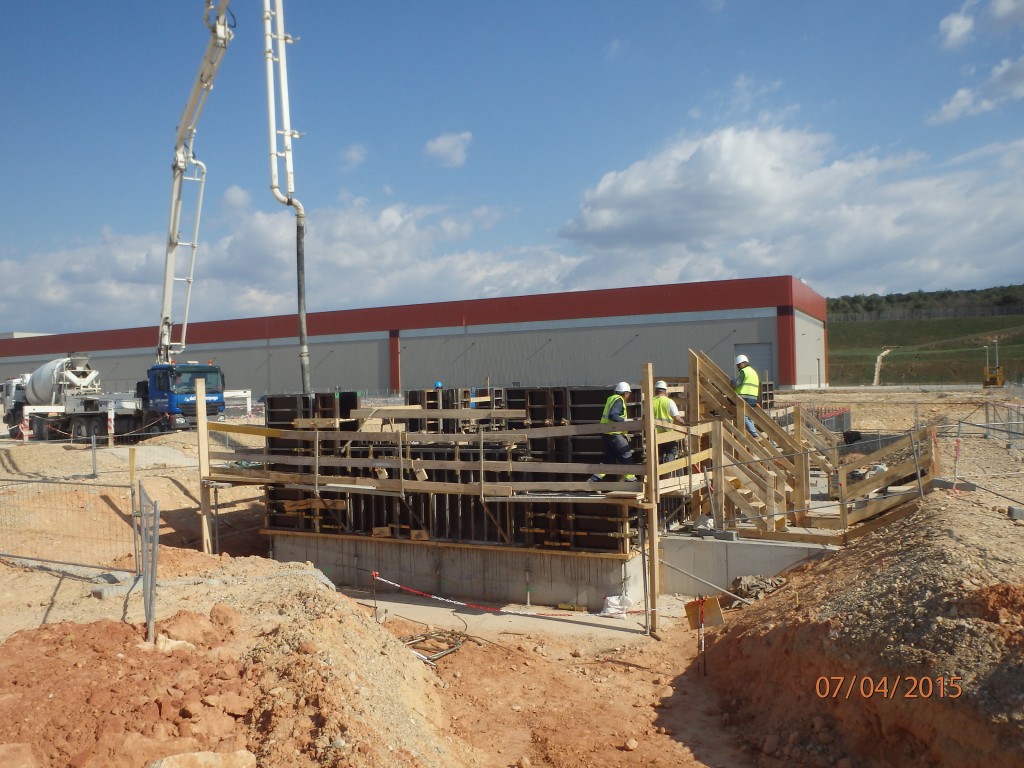
First transformer pit
2015-04-07 - Near the 400 kV switchyard, a reinforced pit has been created for the first of four electrical transformers that will connect the switchyard to ITER's AC electrical distribution system. Photo: Engage Consortium

The practical side of building ITER
2015-03-26 - In the contractors zone on the ITER platform, temporary offices have been erected by the construction consortiums (yellow and red buildings) and a full-service canteen (foreground) serves up to 1,000 meals per day.
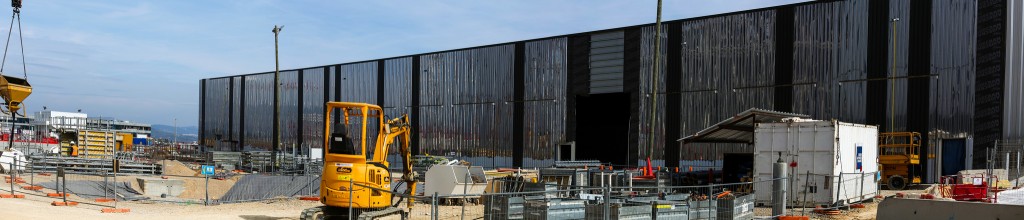
Service building
2015-03-26 - The Site Service Building is entirely framed out and clad. © Les Nouveaux Médias/SNC ENGAGE

900 workers on site
2015-03-04 - In March, 900 workers are engaged in construction activities on the ITER worksite and 300 more are expected in the weeks to come. Photo: Engage
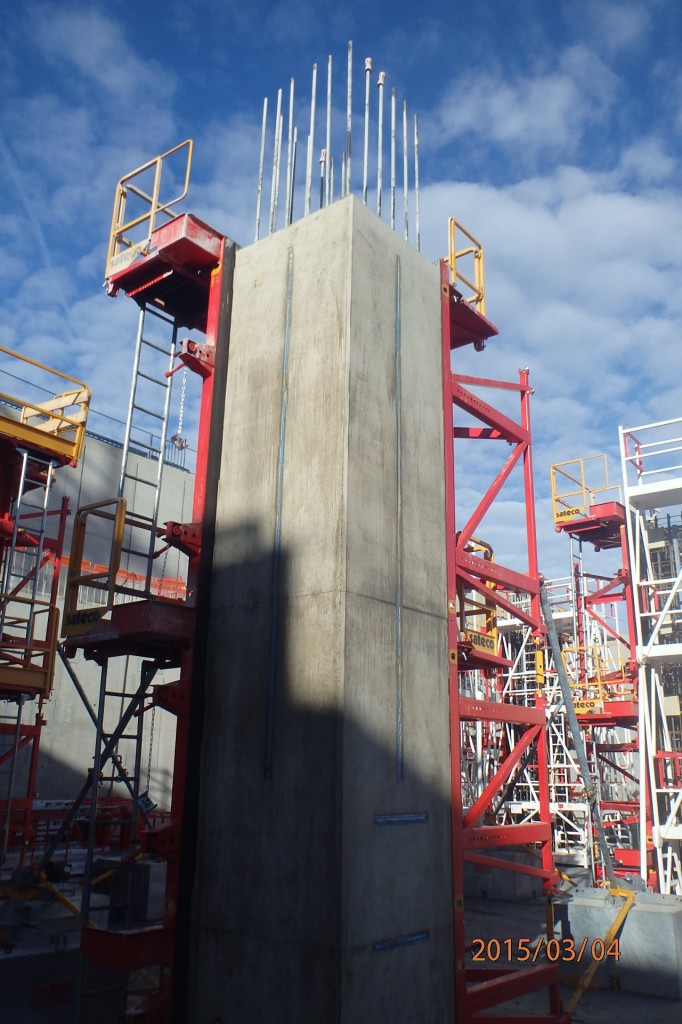
In the basement of the Tokamak Complex
2015-03-04 - This concrete pillar, and others like it, will support the B1 level of the Diagnostics Building basement. Photo: Engage
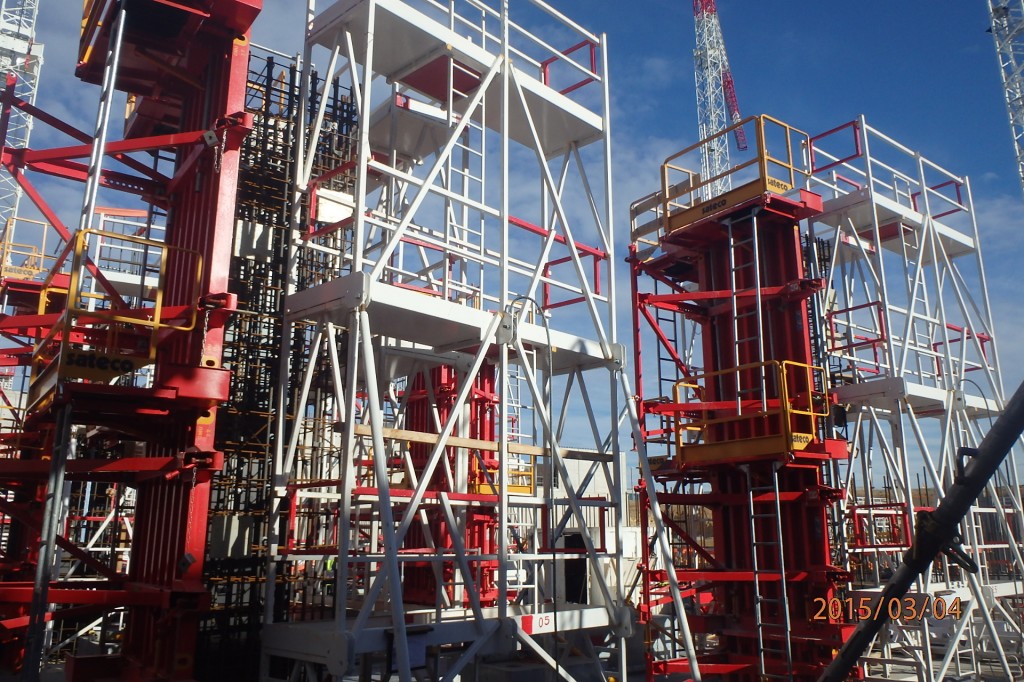
Shaping the pillars and more
2015-03-04 - On the B2 level of the Tokamak Complex basemat, there are 250 independent "pours" to be carried out, including the pillars (pictured). The work should be completed by May. Photo: Engage
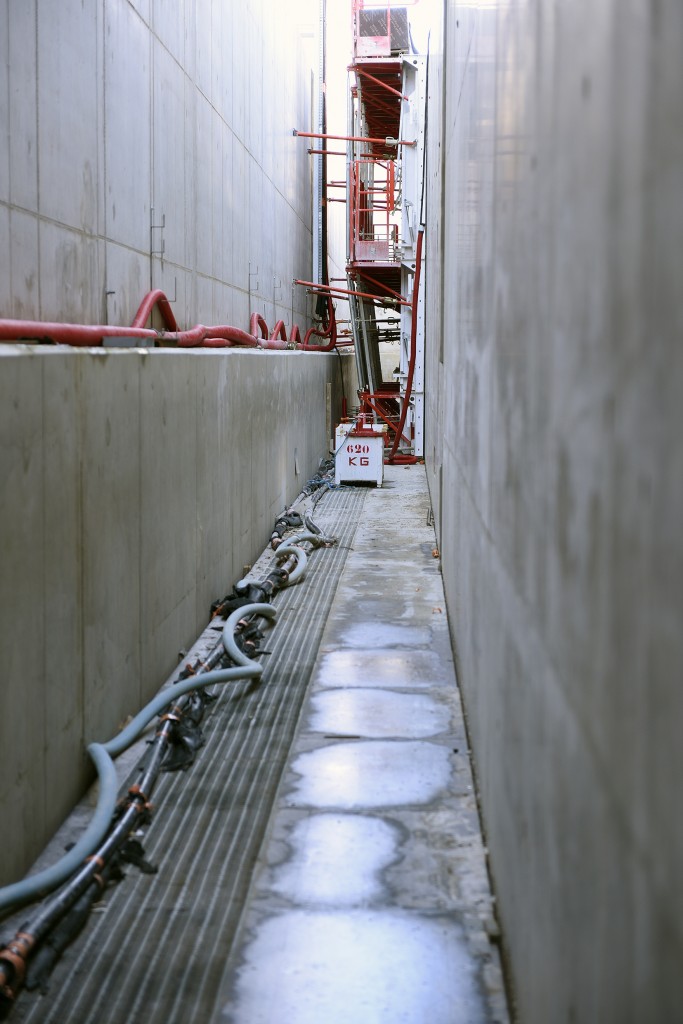
In the basement of the Tokamak Complex
2015-02-16 - Approximately 12 metres below the level of the platform, the basement level walls (level B2) of the Tokamak Complex are under construction. Photo: F4E
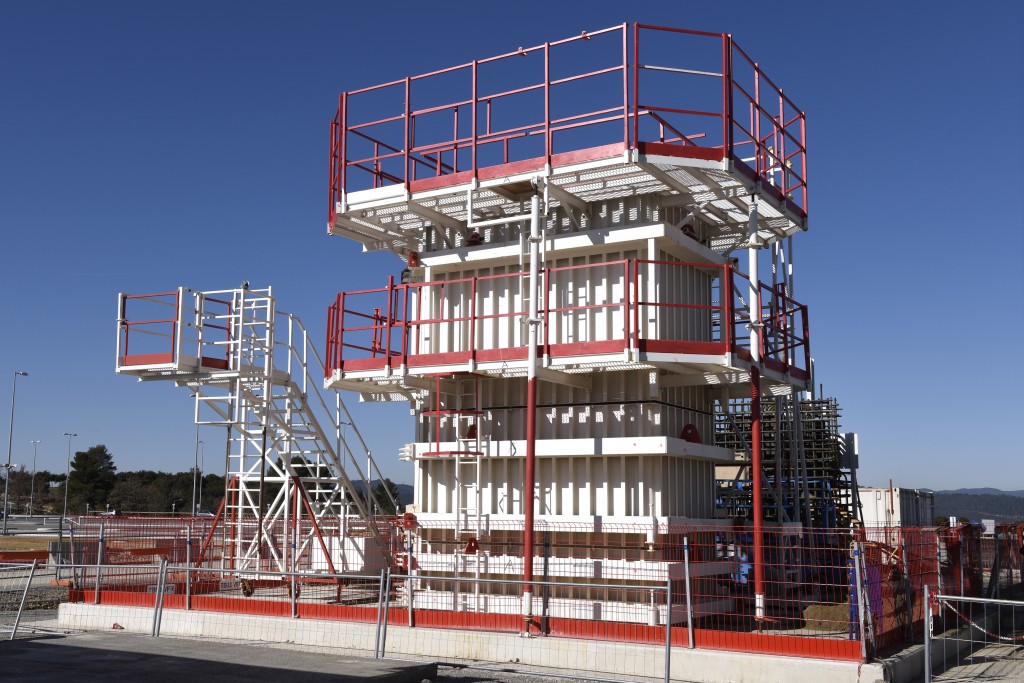
Standing tall
2015-02-15 - This real-scale mockup of the Tokamak support system (cryostat crown and bioshield) has been under construction on the ITER site since late 2014. The mockup reproduces 1/18th of the support system. Photo: F4E
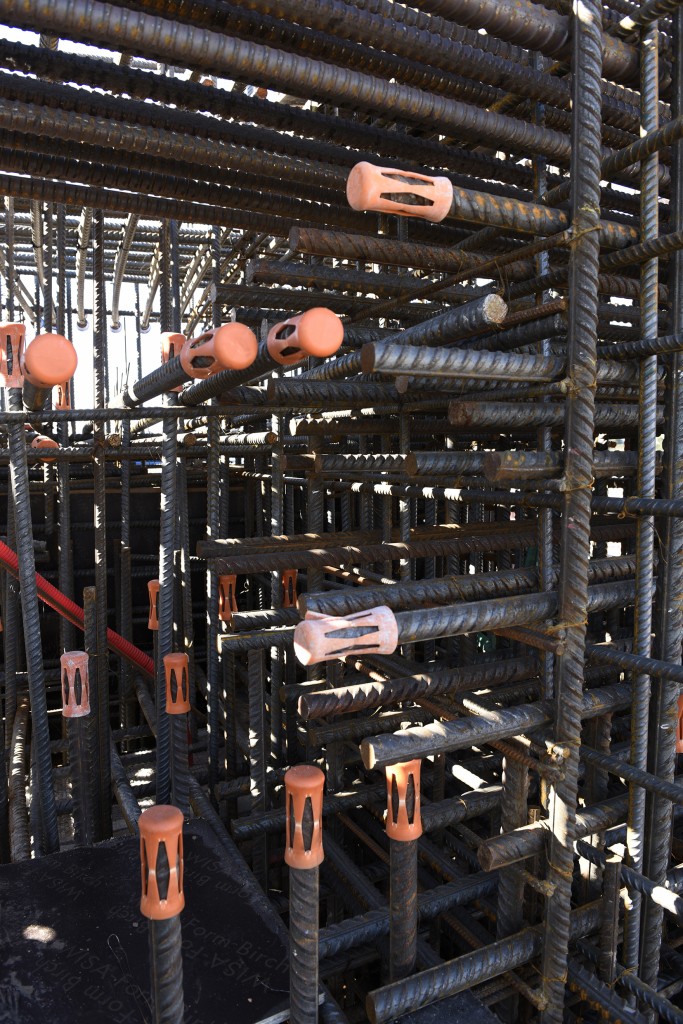
That's crowded!
2015-02-15 - The dense reinforcement of the ITER crown (a thick, circular concrete structure connected to the three-metre-thick bioshield by radial concrete walls) is illustrated in the real-size mockup currently under construction on the platform. Photo : F4E
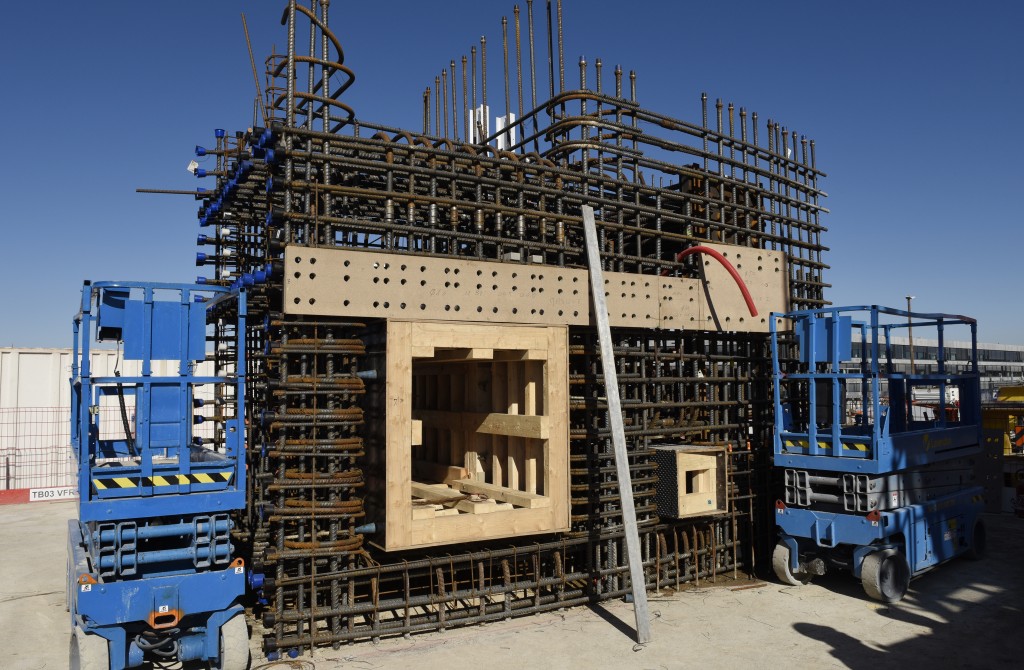
Part of the cryostat crown, in full scale
2015-02-15 - Part of the cryostat crown and the ITER bioshield are being reproduced in this on-site mockup. For a structural element as complex and as strategic as the crown, which will support the weight of the machine and cryostat, this intermediate step is necessary to demonstrate constructability. Photo: F4E
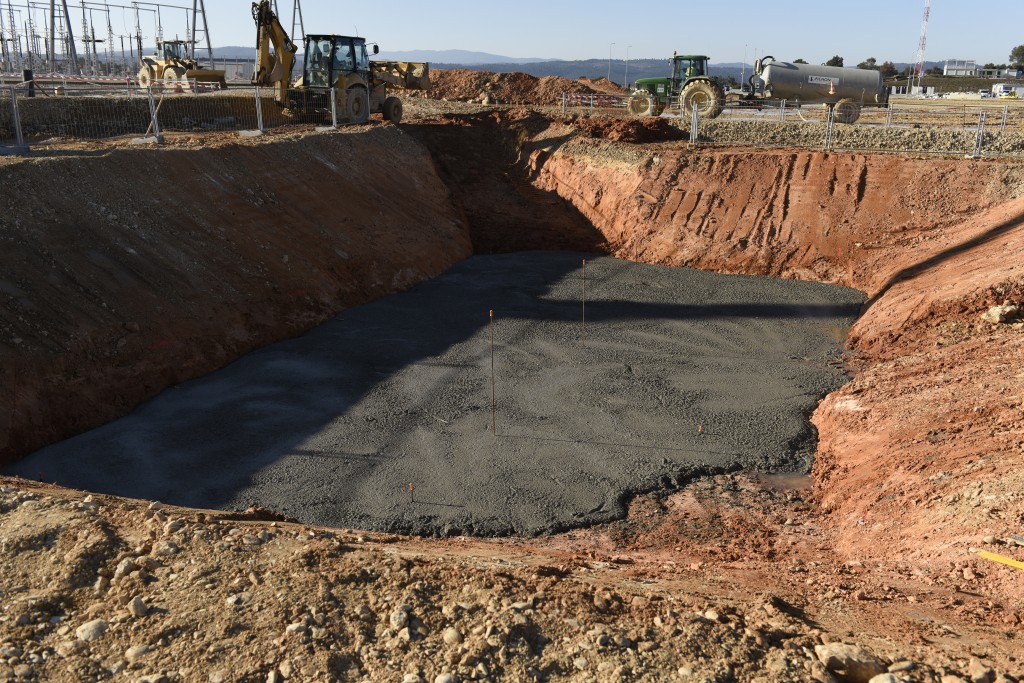
A parking spot for a large electrical transformer
2015-02-13 - This concrete has been set into place to support the first of four electrical transformers that will connect the 400kV switchyard to the AC electrical distribution system. The 87-tonne transformer will be positioned shortly. Photo: F4E
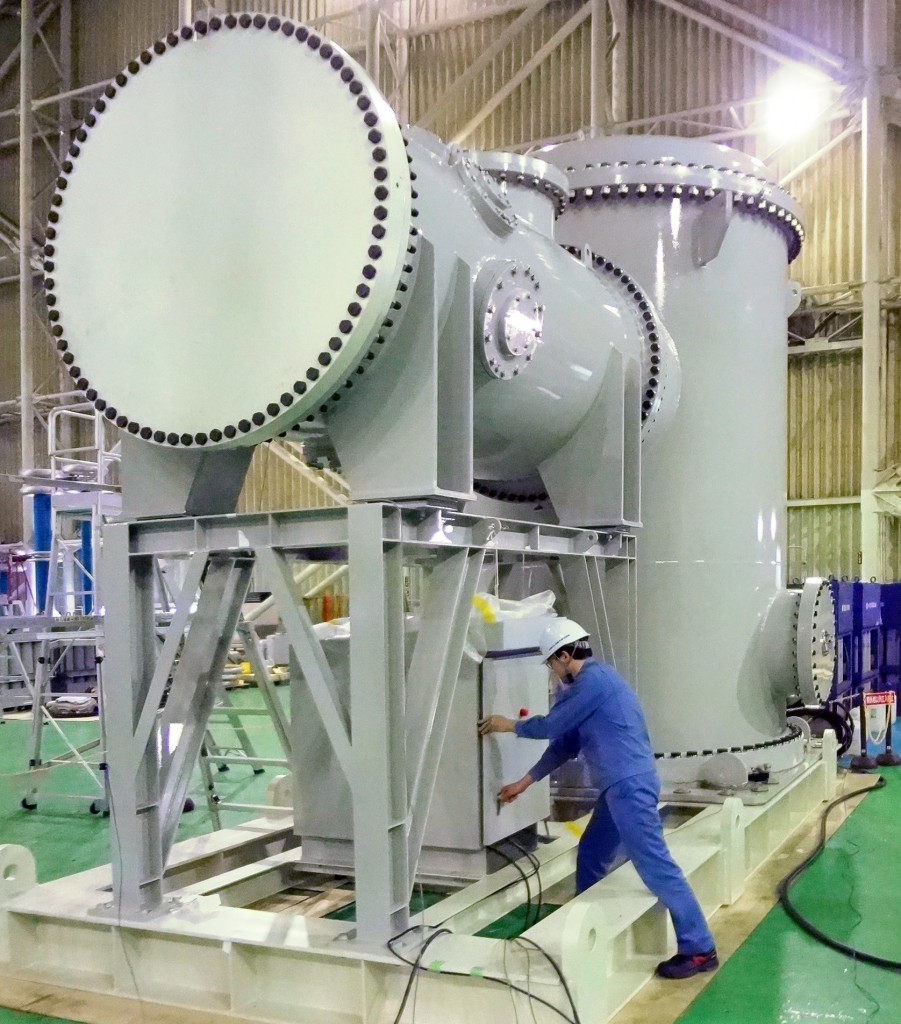
Ultra-compact, but just right for the job
2015-02-13 - The Japanese Domestic Agency and its supplier have been able to design and fabricate an ultra-compact testing power supply, which will be used to test the neutral beam injection power supplies at NBTF, then at ITER.
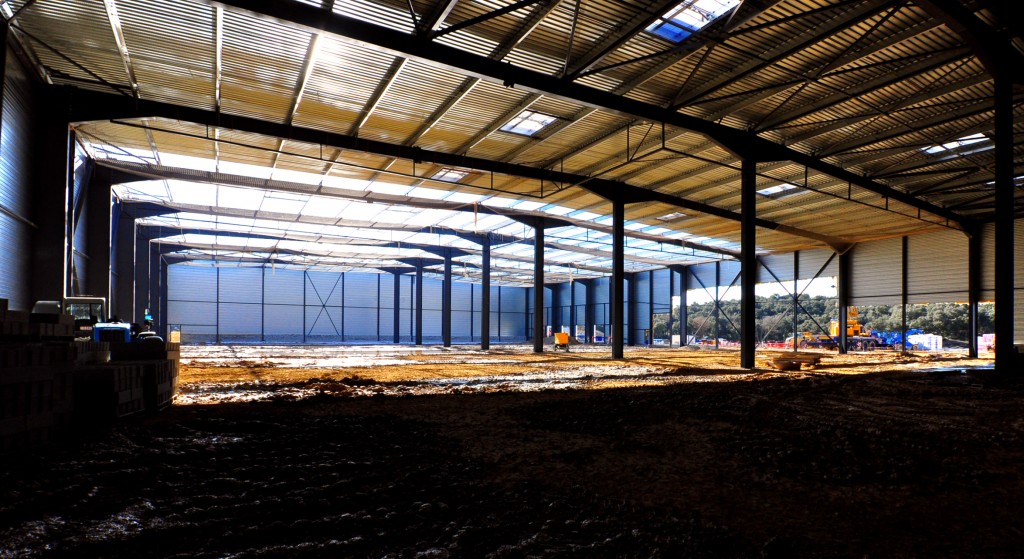
Good progress this month
2015-02-12 - Work on the largest of four planned storage facilities is proceeding rapidly.
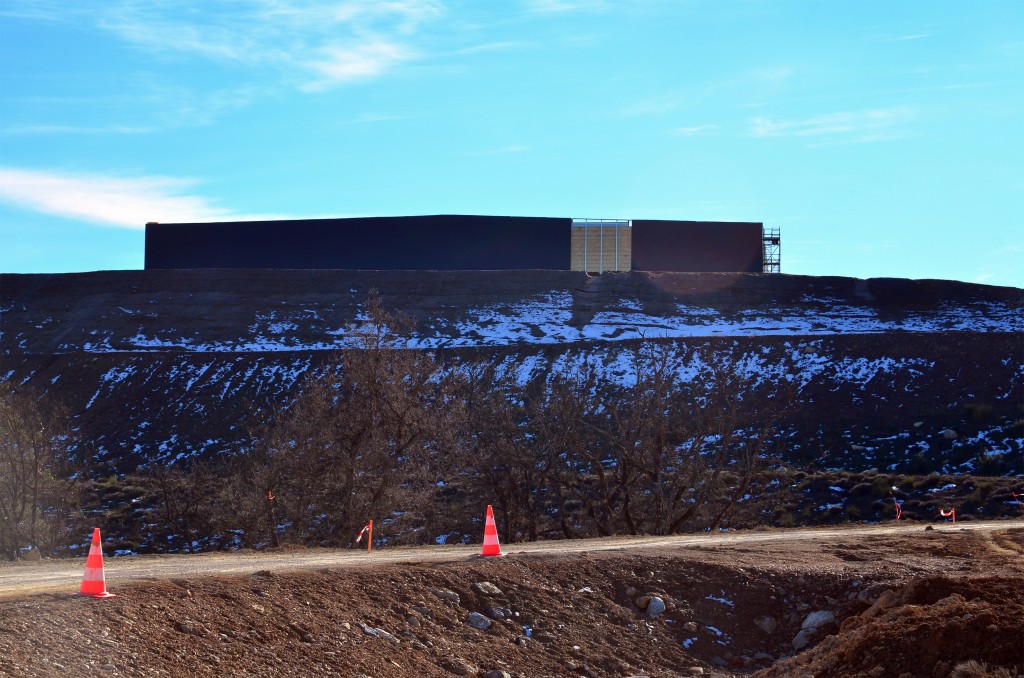
Up on the hill
2015-02-12 - Designed for the storage of medium-sized ITER components, the warehouse on the hill can be reached by a road through the forest.

Flurries in February
2015-02-12 - In the 80 x 120 metre Tokamak Pit, where scaffolding is up for the first basement-level walls, a few flurries in February complicated works.
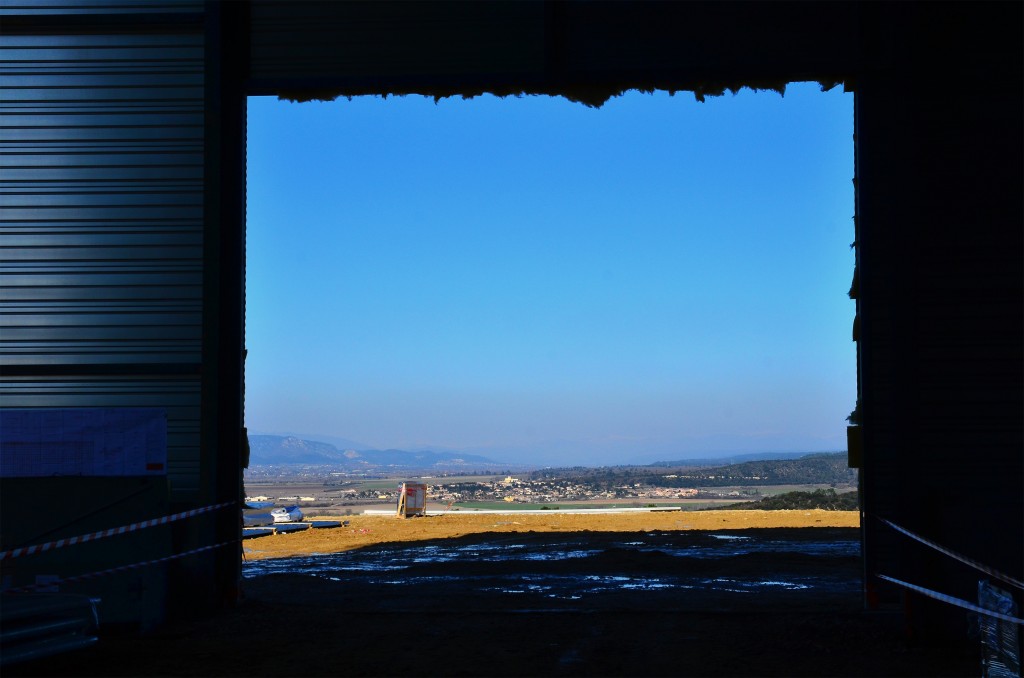
A warehouse with a view
2015-02-12 - Looking out of the largest of four storage facilities that are under construction for the storage of ITER components.
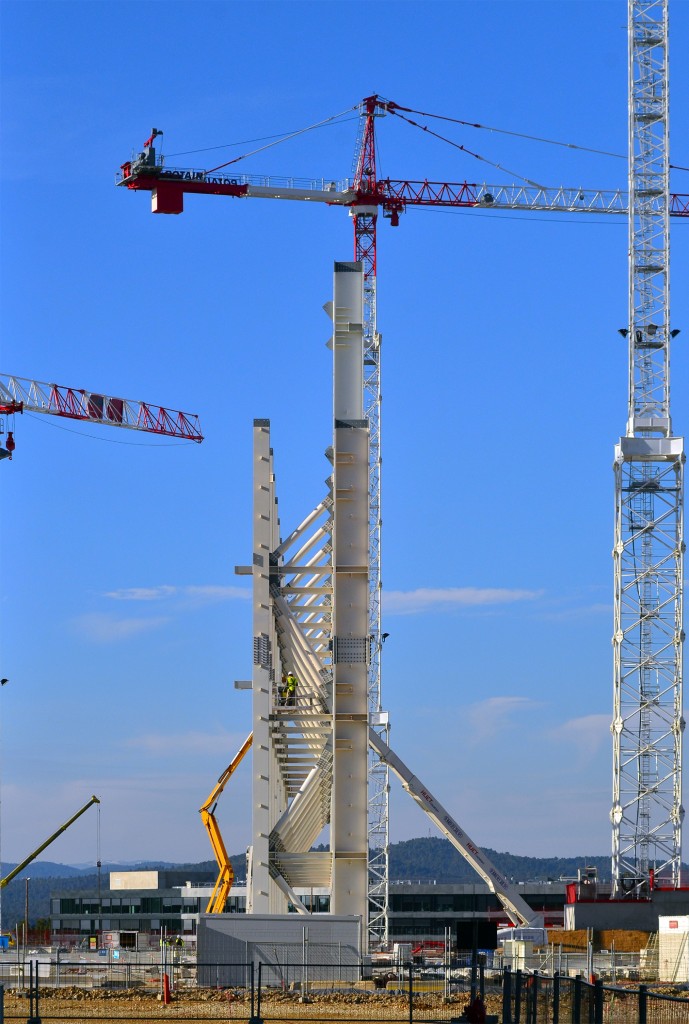
12 ... 24 ... 36
2015-02-12 - The first third-level pillar is up, and the metal structure of the building is now 36 metres tall.
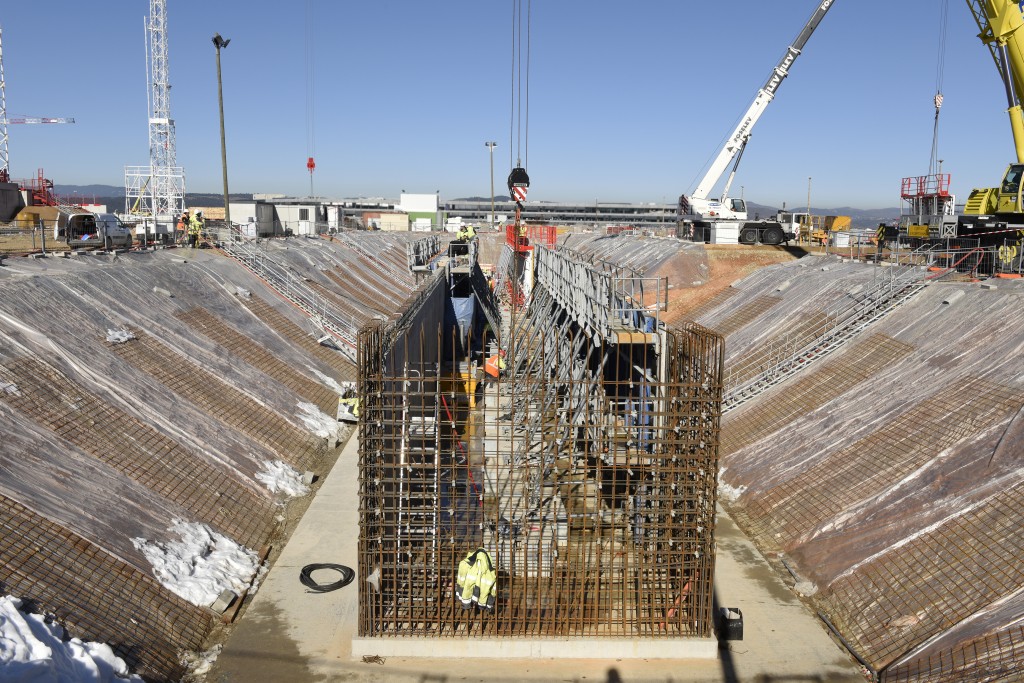
Site Services building
2015-02-11 - In what will be the basement of the Site Services building, work is under way on technical galleries. Photo: F4E
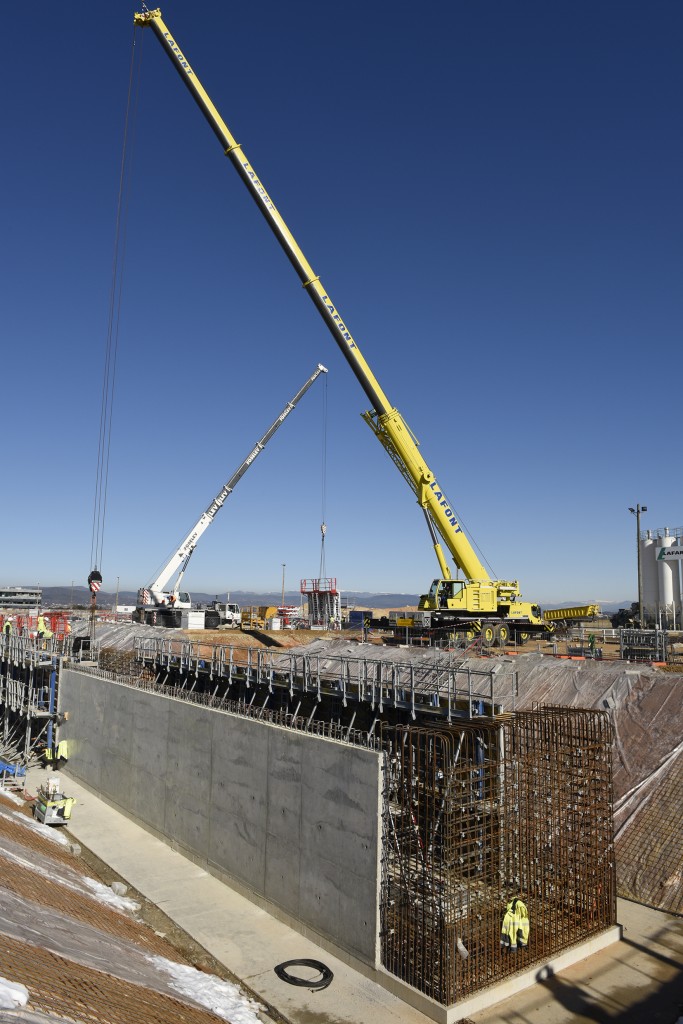
Preparing the galleries
2015-02-11 - From these galleries, which run the length of the Site Services building, important industrial support services will be distributed to the ITER plant. Photo: F4E
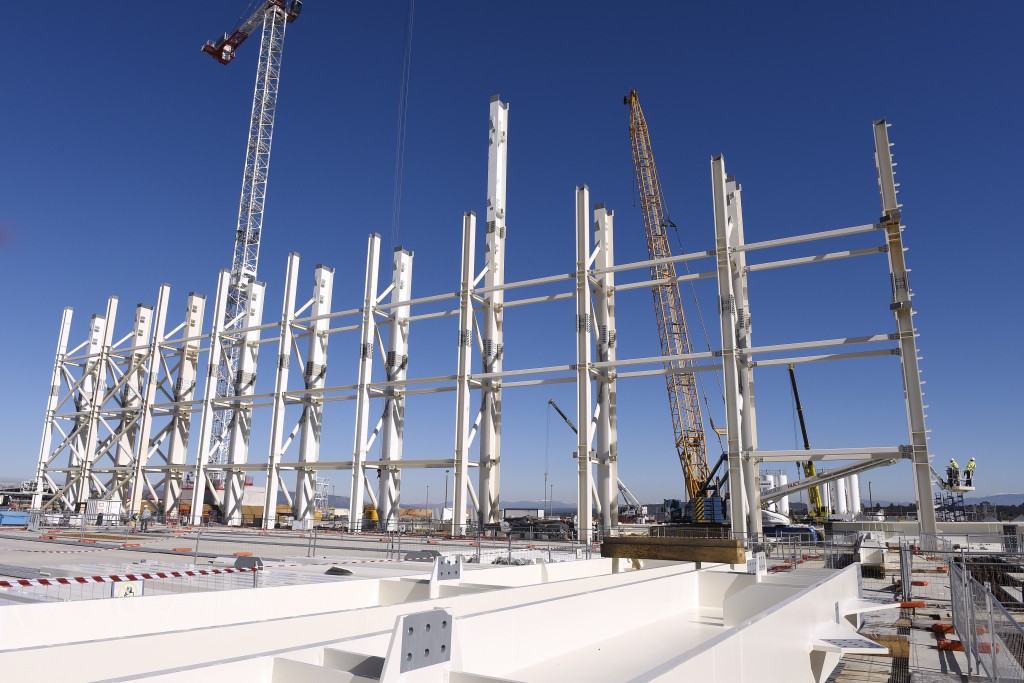
Ten in a row
2015-02-11 - Double pillars stand aligned on the Assembly Building basemat. An eleventh pillar will take its place (at left) when the Tokamak Complex walls reach the same level. Photo: F4E
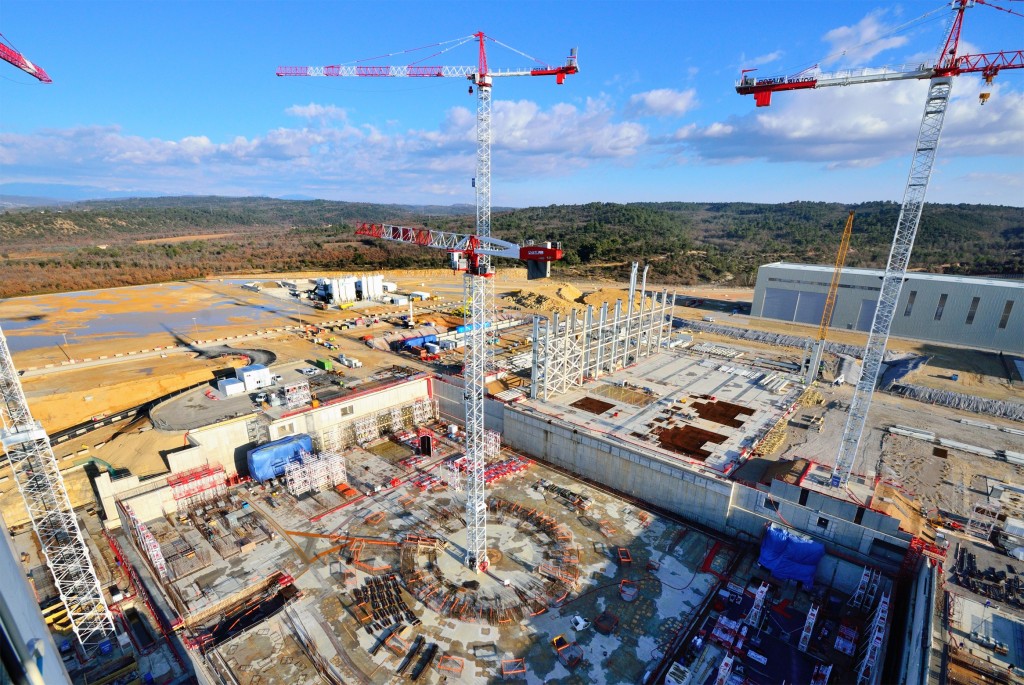
See the building from above!
2015-02-03 - Progress on the Assembly Building pillars is easily measured from above.
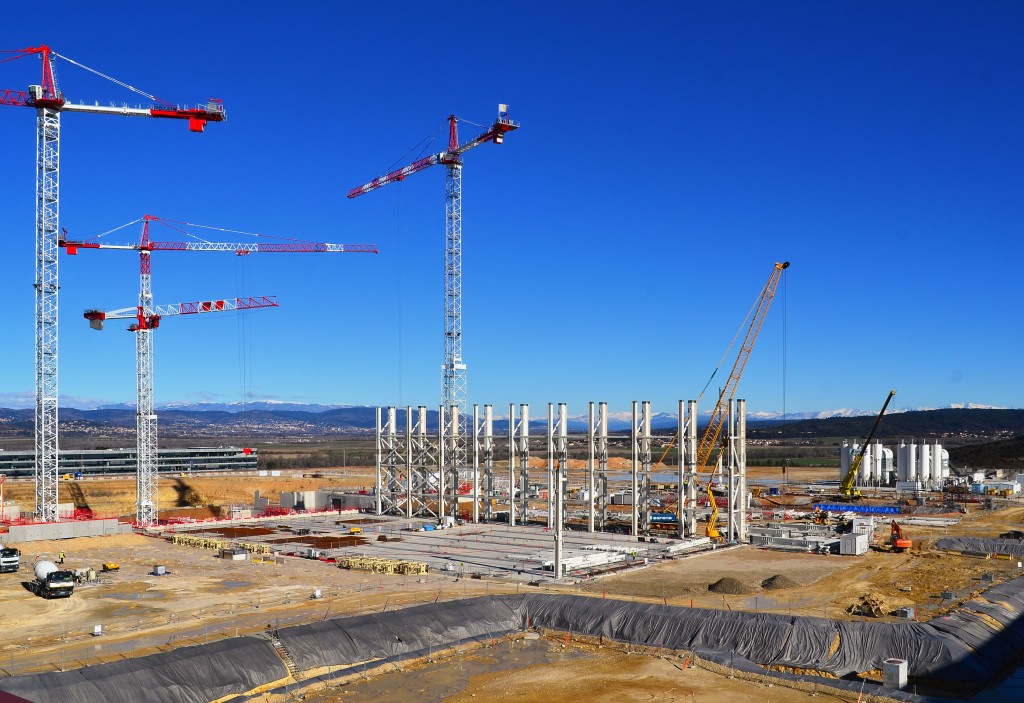
Beginning on the other side
2015-02-02 - The first pillar is in place on the opposite of the Assembly Building basemat.
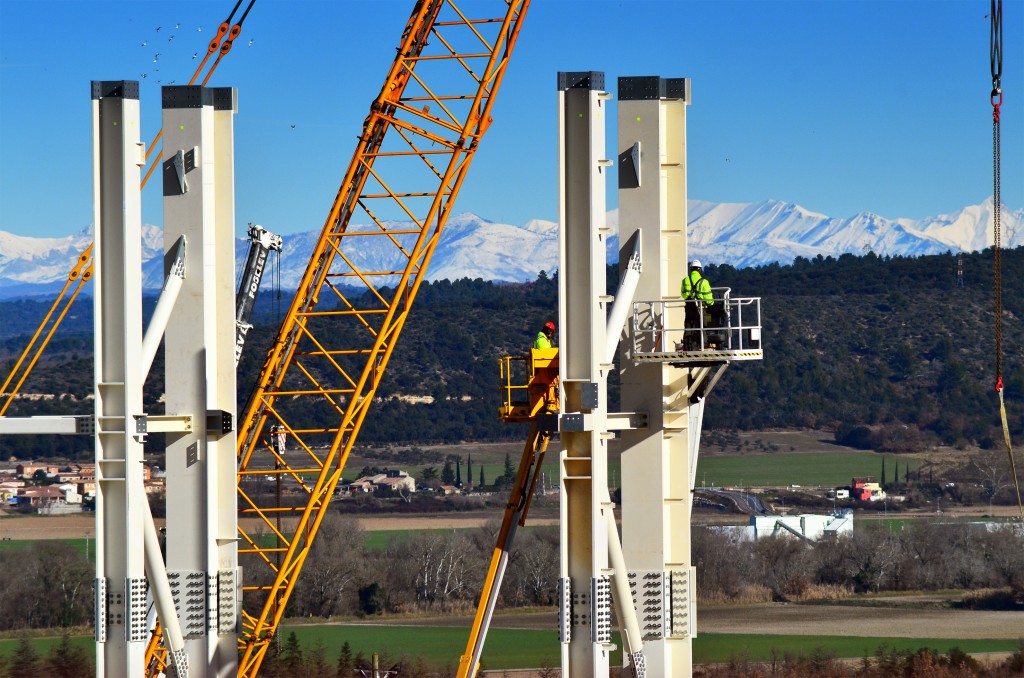
Tightening the bolts
2015-02-02 - For each pillar assembly, a two-person team manually tightens the bolts on columns weighing 23 tonnes (exterior) or 11 tonnes (interior).
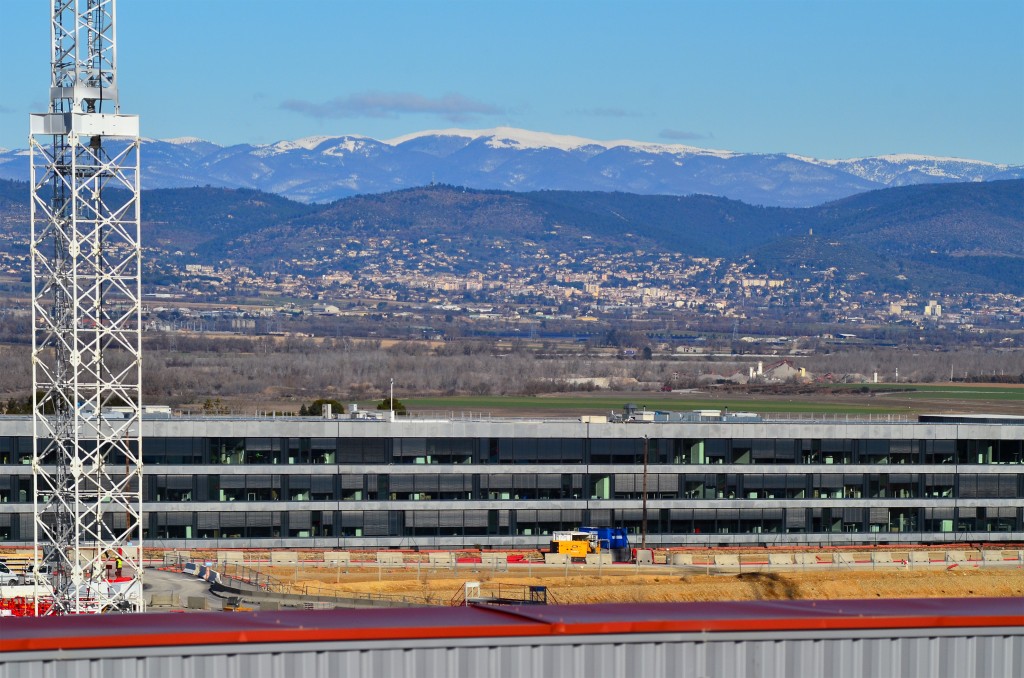
A winter scene over Headquarters
2015-02-02 - The ITER Headquarters seen from the construction platform with, as a backdrop, the town of Manosque and the Alps.
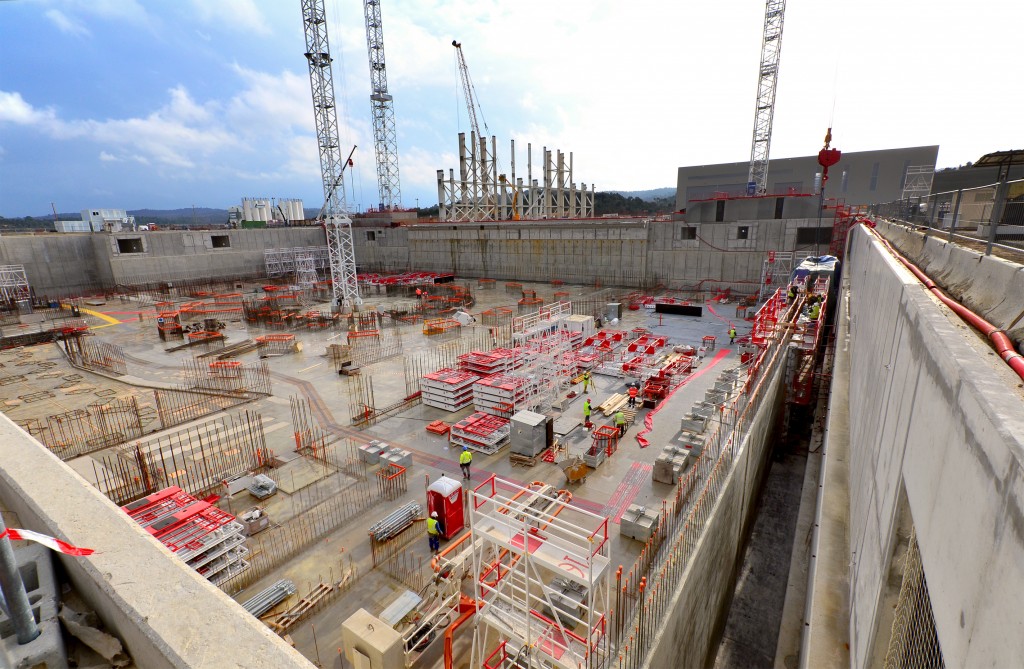
Basement-level walls
2015-01-16 - The first B2-level wall is now in place on the Diagnostic Building side of the basemat. A gap of approximately 2 metres will separate the Tokamak Complex from the retaining walls; this gap will permit the Complex to move on its seismic pads as one block in the case of earthquake.

The first wall of the Tokamak Complex
2015-01-16 - In January, workers complete the first wall of the Diagnostics Building, on the south side of the Tokamak Complex.
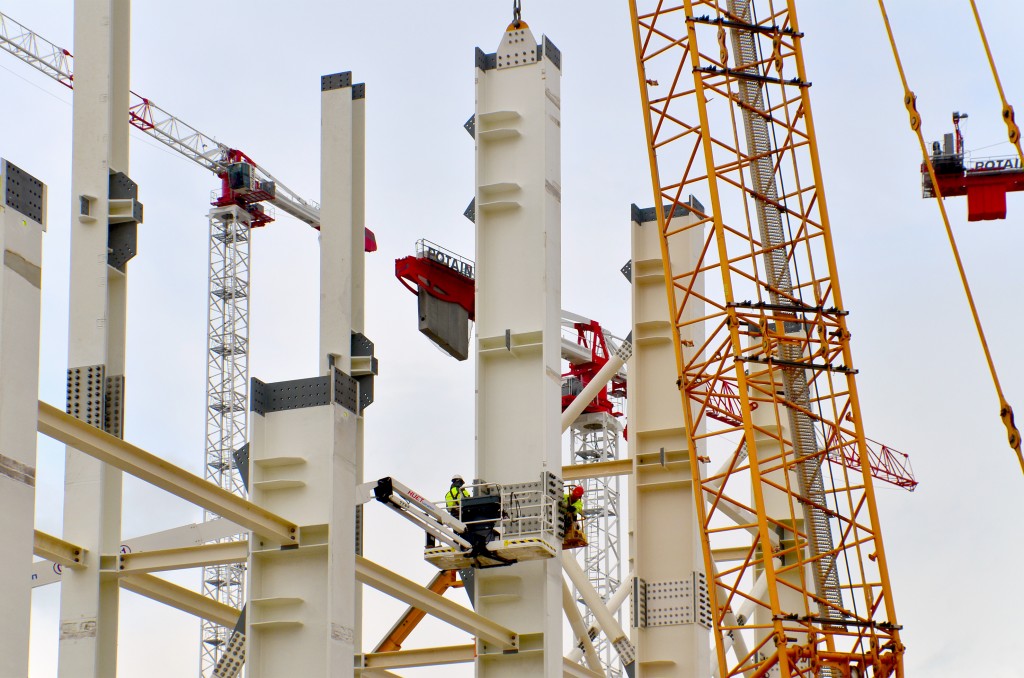
The Assembly Building worksite in January
2015-01-16 - As the Assembly Building's steel skeleton is progressively bolted into place, the massive size of the construction becomes more and more evident.
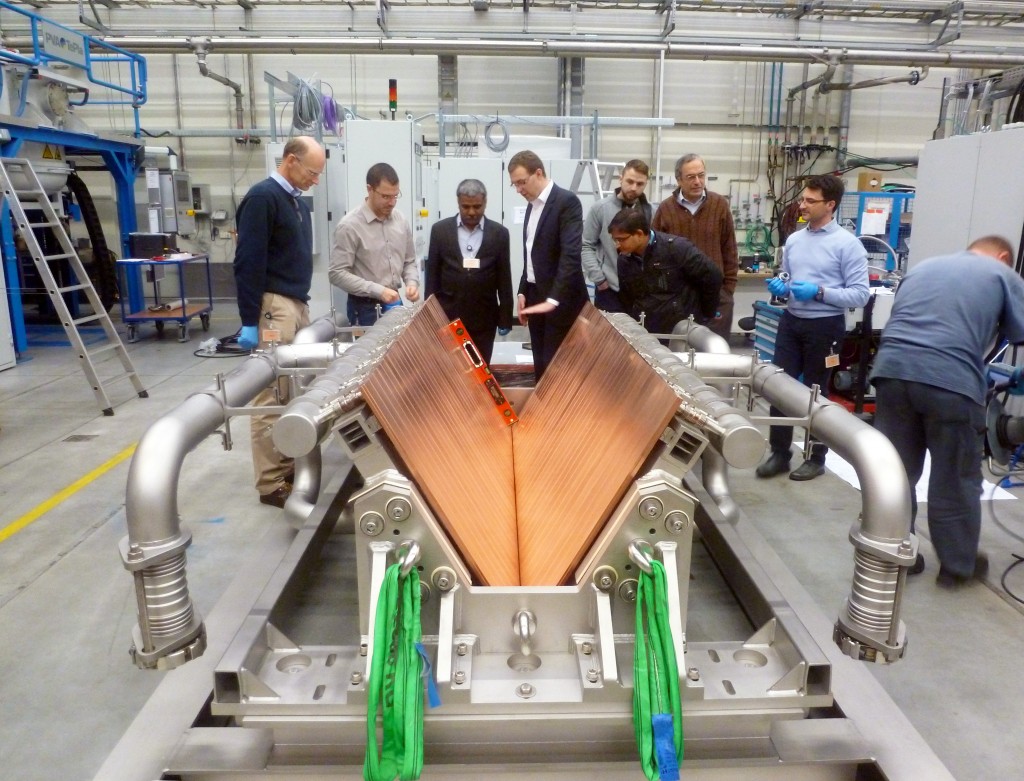
Indian "beam dump" arrives
2014-12-22 - The SPIDER beam dump—designed to absorb the ion beam power up to 6.1 MW extracted from the SPIDER beam source—is the first component delivered by the Indian Domestic Agency.
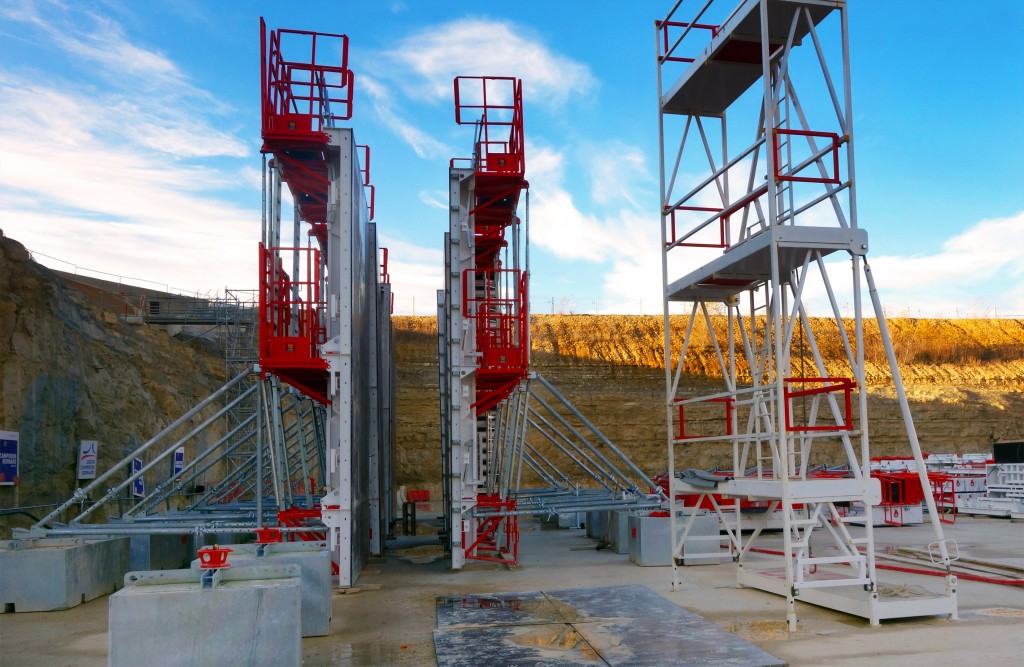
Wall pouring continues
2014-12-19 - Three wall sections have been poured for the basement level walls of the Tokamak Complex. The formwork panels used to frame out the sections are assembled by fours before being transported by crane to the work area.
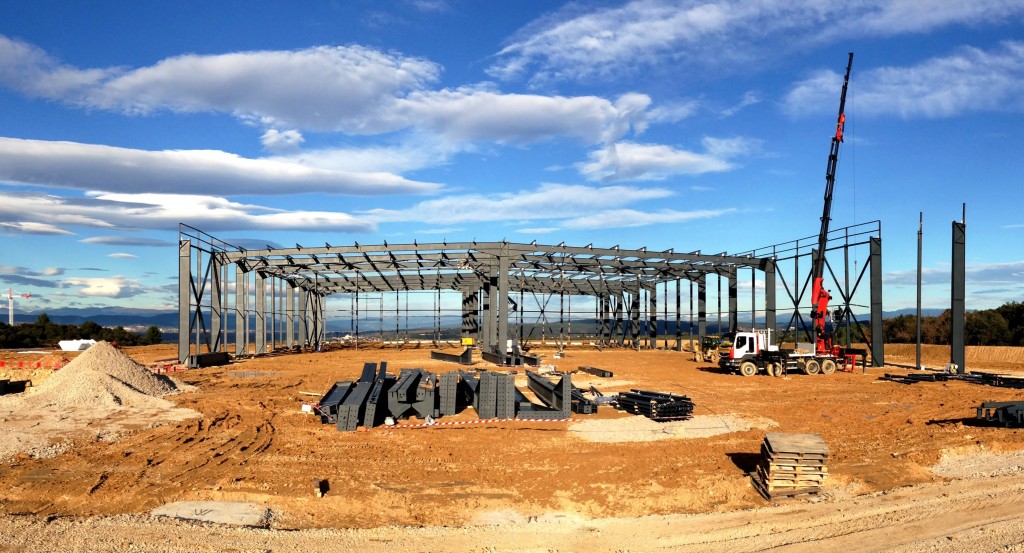
Logistics centre
2014-12-19 - A new 150-metre long, 60-metre wide, 12-metre high storage facility is rising quickly on the back portion of ITER land.
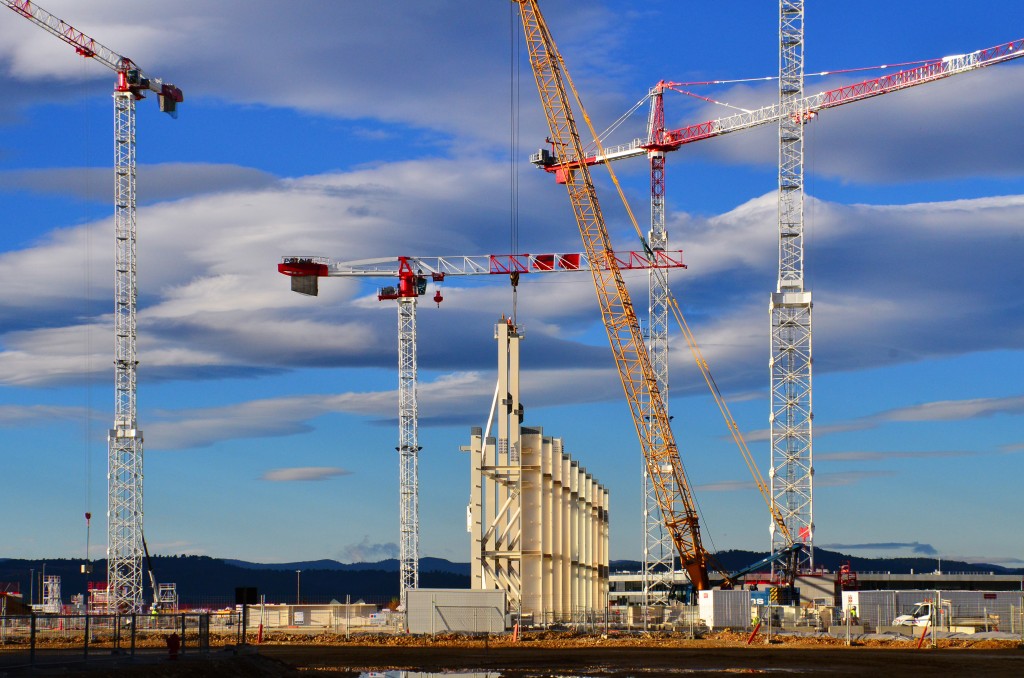
Reaching the sky
2014-12-18 - When finished, the Assembly Building will reach the height of the tallest crane.
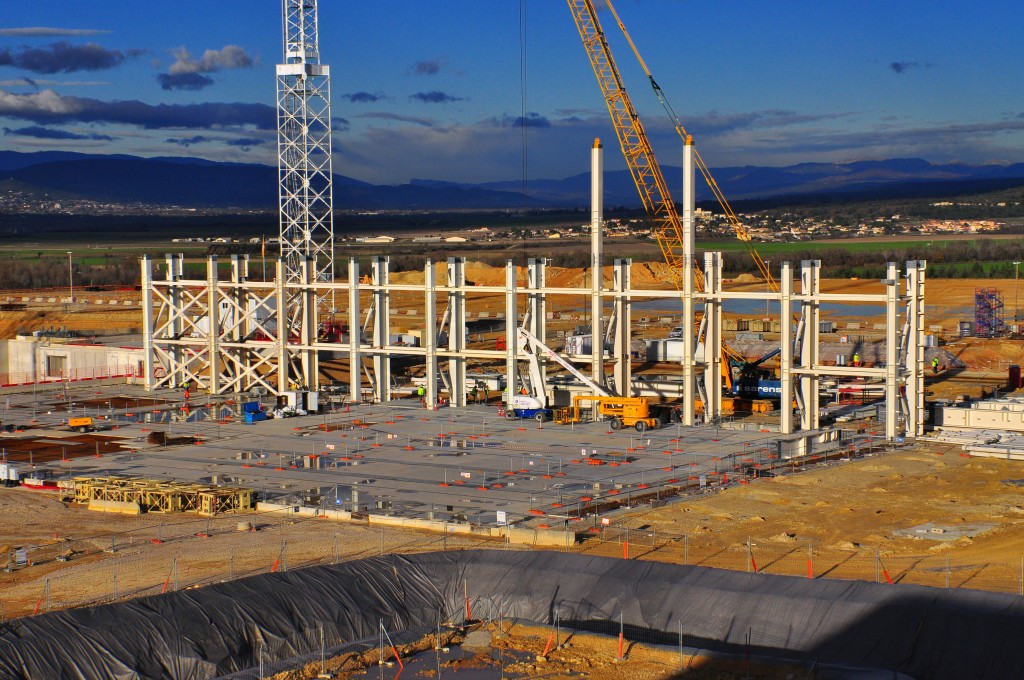
Starting on the second level
2014-12-18 - On one side of the Assembly Building basemat in December, work begins on the second level of pillars.
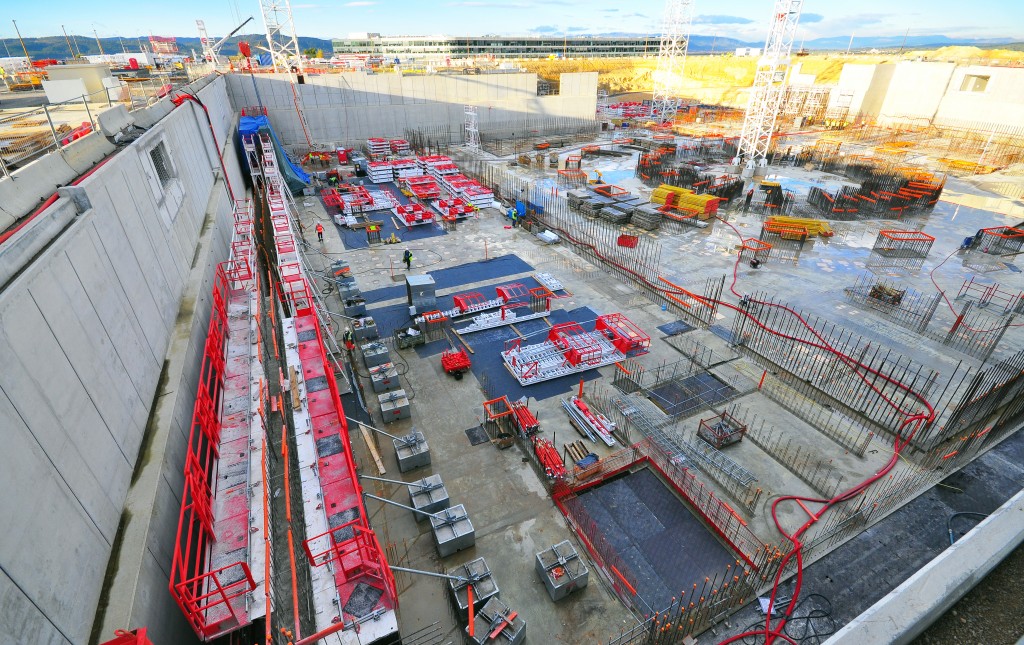
Ready, set ...
2014-12-18 - Everything's ready for tomorrow's first pour in one corner of the Tokamak Complex Seismic Pit. Photo: F4E
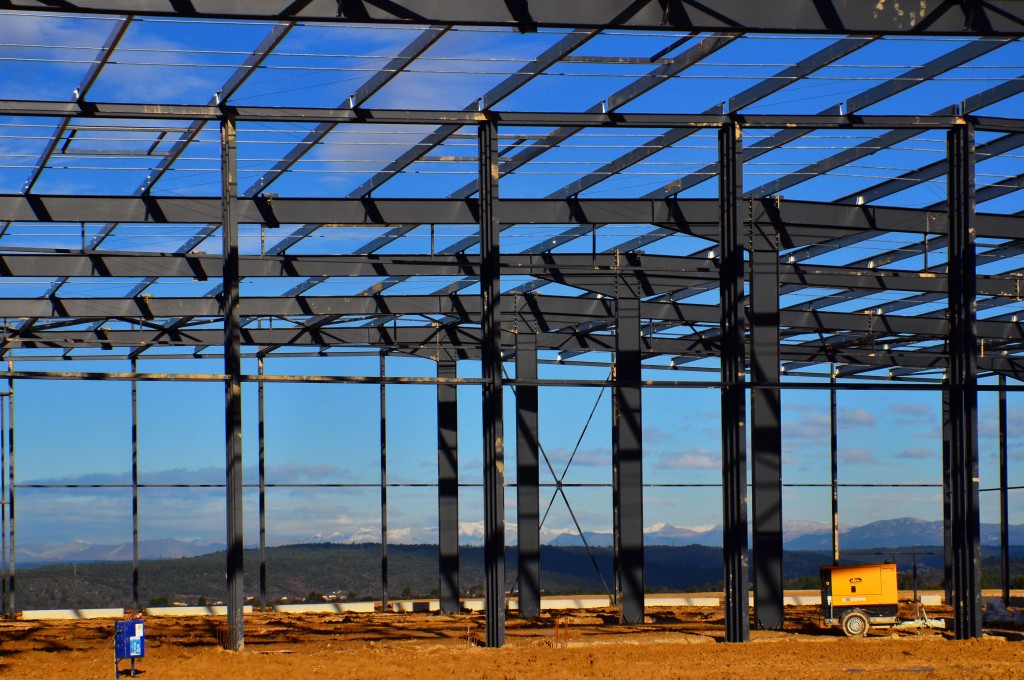
Behind the hill
2014-12-18 - The two-hectare logistics platform will host the 9,000 m2 warehouse and an outdoor storage area. It is located on a stretch of land that was transferred from CEA to the ITER Organization in 2014.
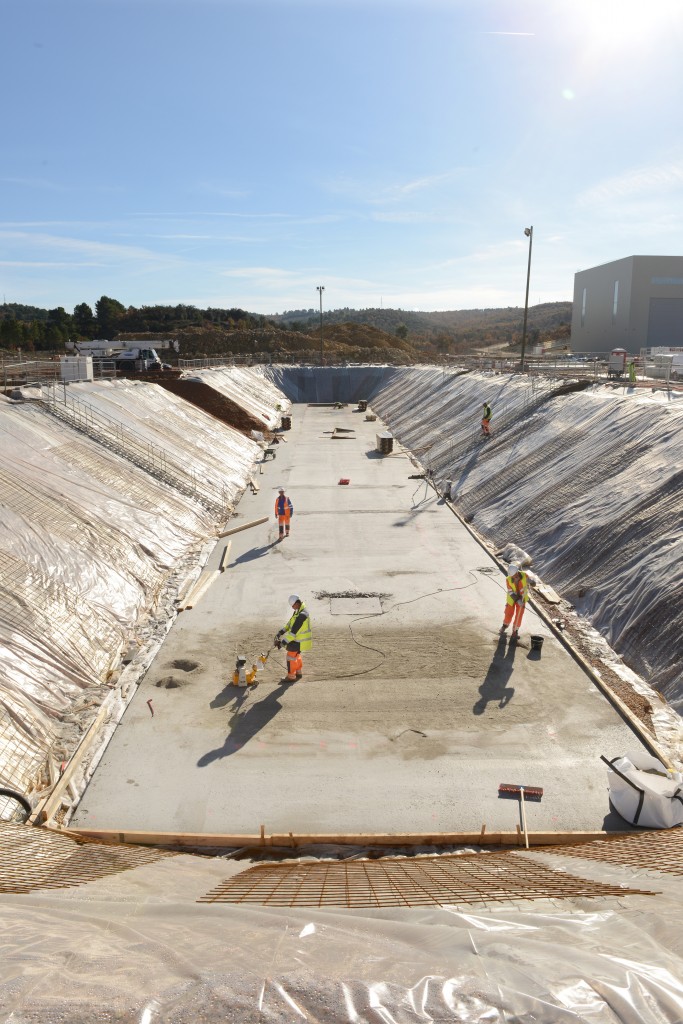
Preparatory work for the Site Services Building
2014-12-03 - Under the future Site Services Building (utilities, fluid management), galleries have been dug, and reinforced, for the passage of piping. Photo: F4E
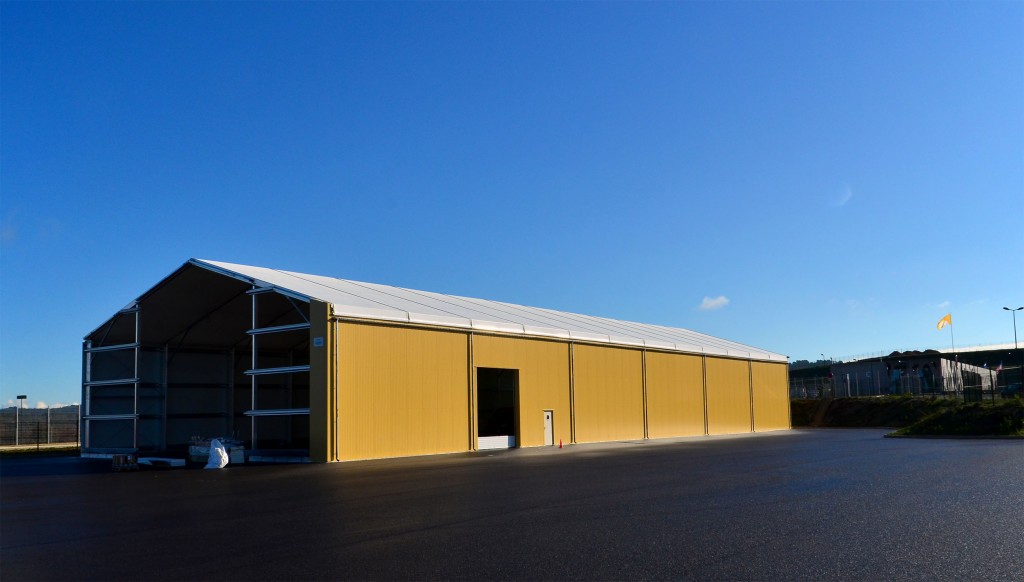
Temporary storage facility rising
2014-12-02 - Near the entrance to the ITER site, a new storage facility will soon be ready to receive components shipped from manufacturing sites in China, Europe, India, Japan, Korea, Russia and the United States.
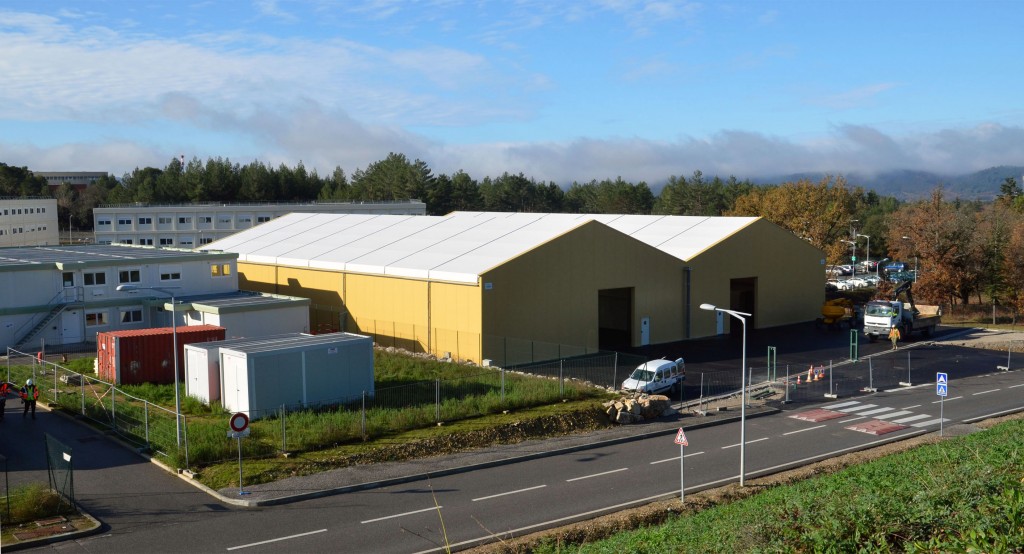
More storage
2014-12-02 - Two other storage facilities are rising near the original ITER Headquarters building, to the south of the ITER platform.
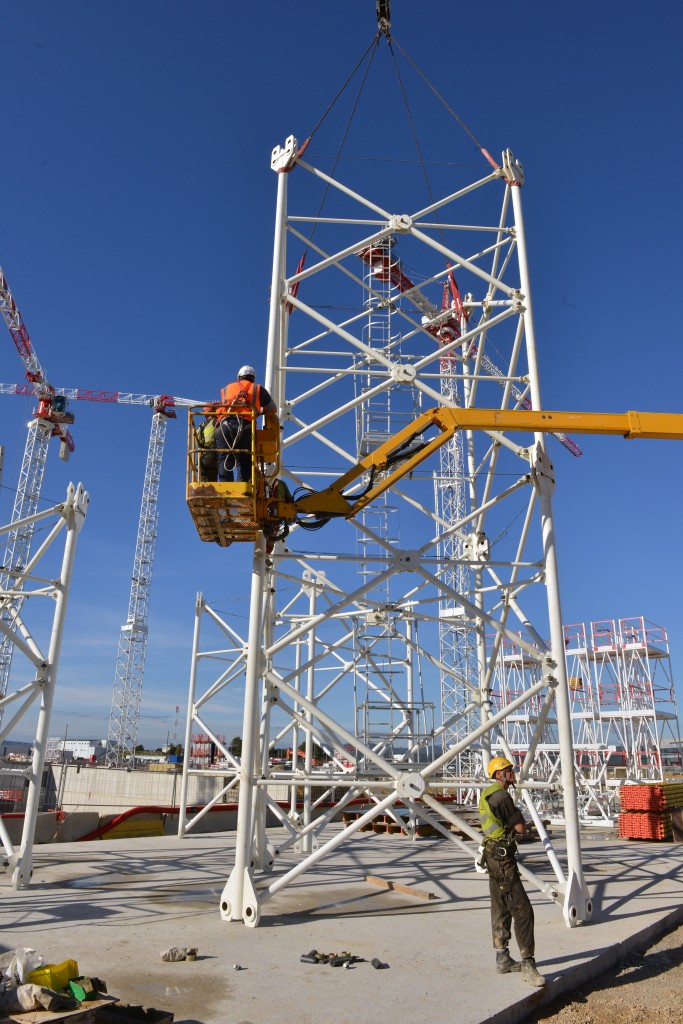
Five building cranes now in place
2014-12-01 - Tokamak Complex construction will require at least four years. Five tall cranes are now in place around the Seismic Pit ... ready to deliver the materials to the wall construction site 12 metres below the level of the platform. Photo: F4E
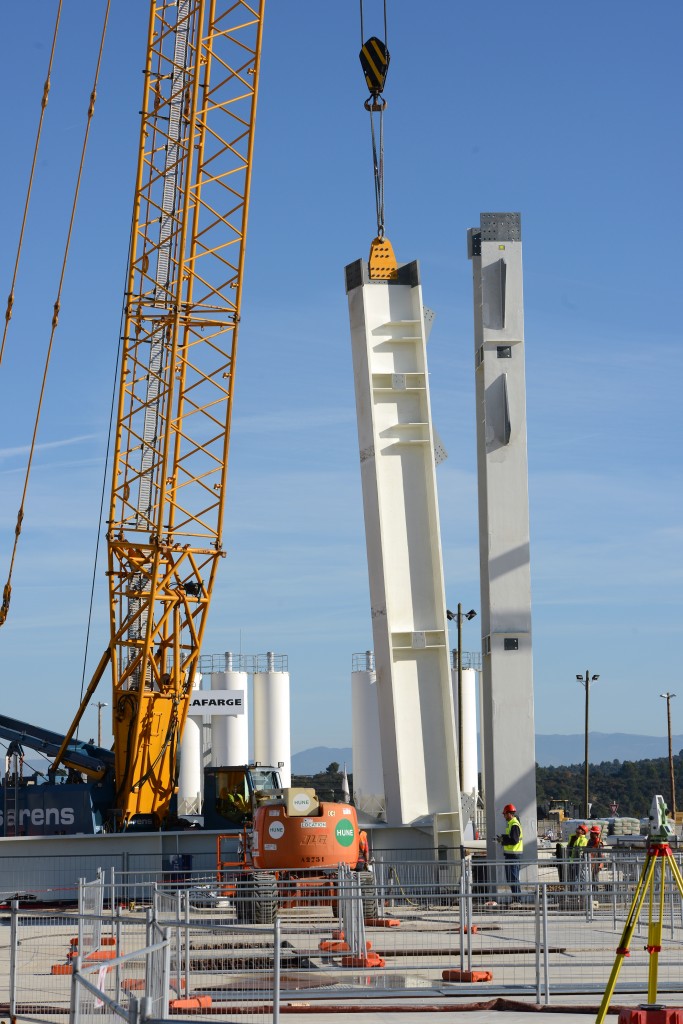
First level finished on one side
2014-12-01 - In December, the first level of steel pillars is completed along one side of the Assembly Building basemat; work begins on level two before the end of the month. Six thousand tons of steel will be needed for the building's structure. Photo: F4E

First two walls
2014-11-29 - The first walls of the Tokamak Complex are going up in the southern corners of the Seismic Pit, at left (completed) and at right (underway). Photo: F4E
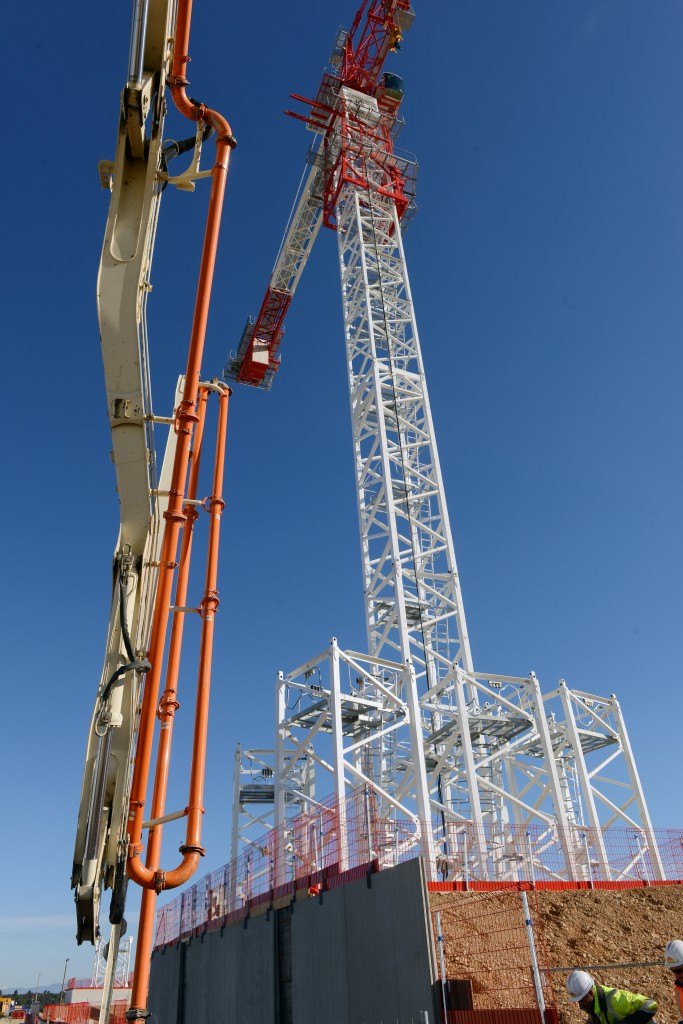
Long arms needed
2014-11-29 - Pouring activities for the first basement-level walls of the Tokamak Complex are taking place approximately 12 metres below the level of the platform. Photo: F4E
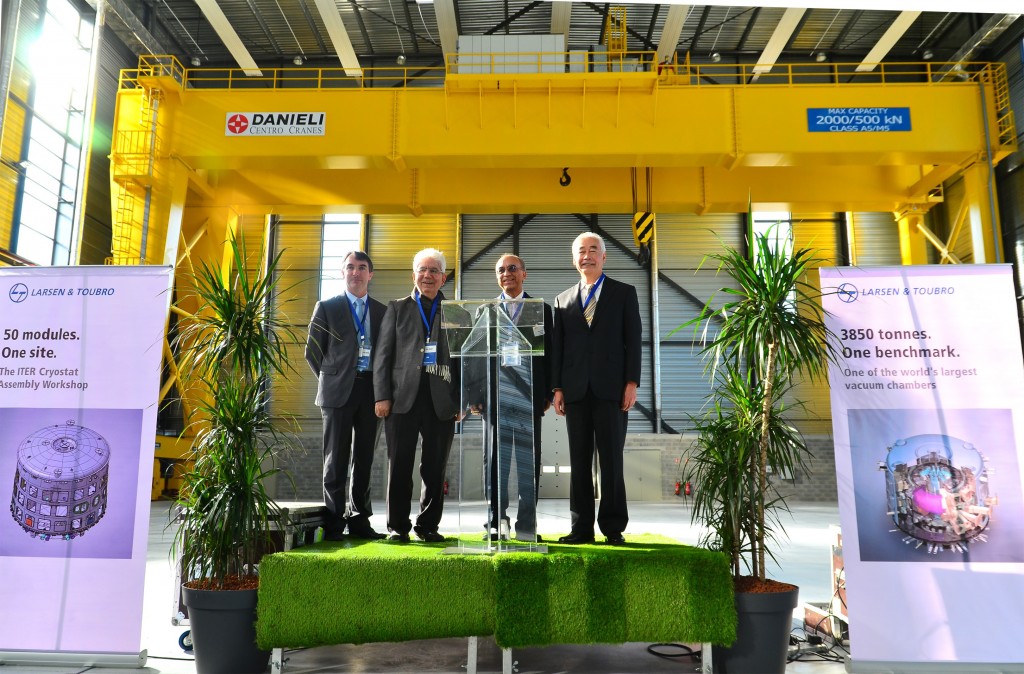
Cryostat Workshop inauguration
2014-11-21 - On Friday 21 November 2014, the on-site Cryostat Workshop is inaugurated in the presence of members of the press. Left to right: Benoît Moncade, director-general of building contractor Spie-Batignolles; Predhiman Krishan Kaw, member of the Indian delegation to the ITER Council; M.V. Kotwal, the president of Larsen & Toubro's Heavy Engineering Division (responsible for the fabrication of the ITER cryostat); and ITER Director-General Osamu Motojima. Follow all fabrication news at: https://www.iter.org/construction/sitefabricationcryostat

In the basement of the Tokamak Complex
2014-11-20 - The Tokamak Complex will be a seven-storey structure: two basement levels and five storeys. On 20 November 2014, pouring began for basement level B2.
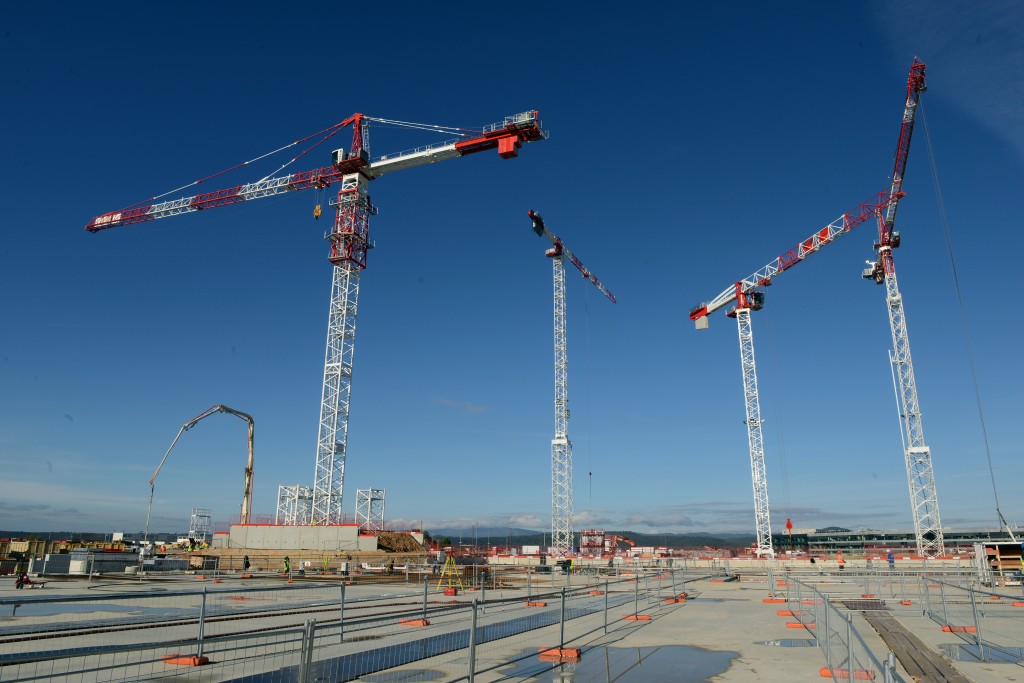
Four out of five
2014-11-20 - Looking across the Assembly Building basemat toward Headquarters, we see that four of the five cranes for Tokamak Complex construction are in place. Photo: F4E

Another 48 metres to go
2014-11-20 - The first level pillars for the Assembly Building measure 12 metres in height. Four more 12-metres sections will be installed on this base to complete the 60-metre structure. Photo: F4E
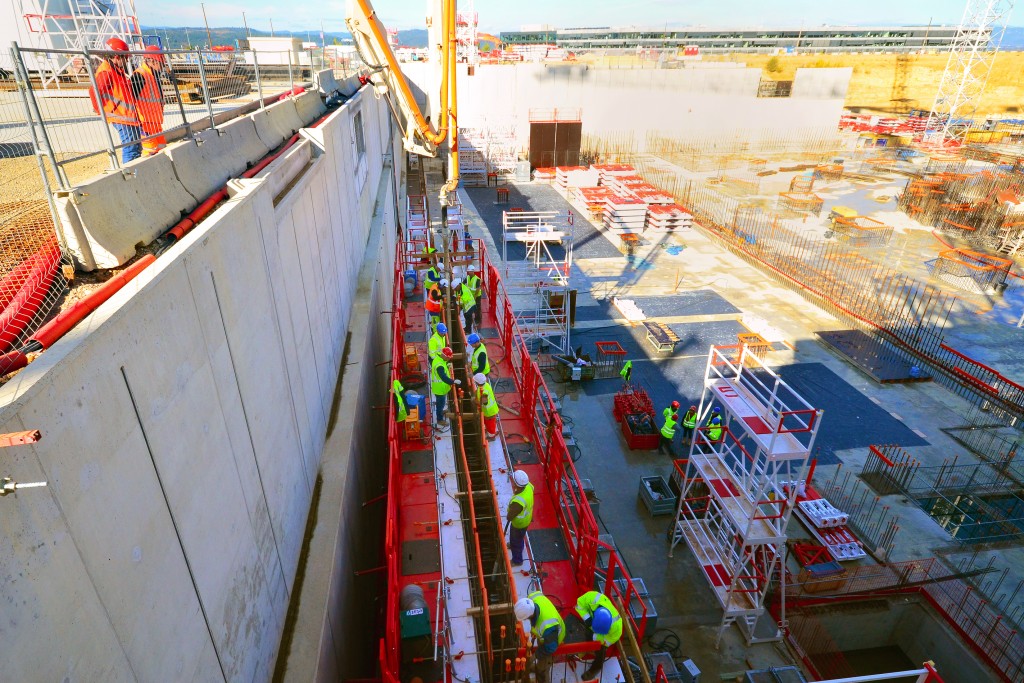
Level B2
2014-11-20 - Work on the first level walls of the Tokamak Complex (basement level B2) is expected to last until mid-2015.

Beams going up
2014-11-20 - The erection of 12-metre beams continues along the northern side of the Assembly Building basemat. Photo: F4E
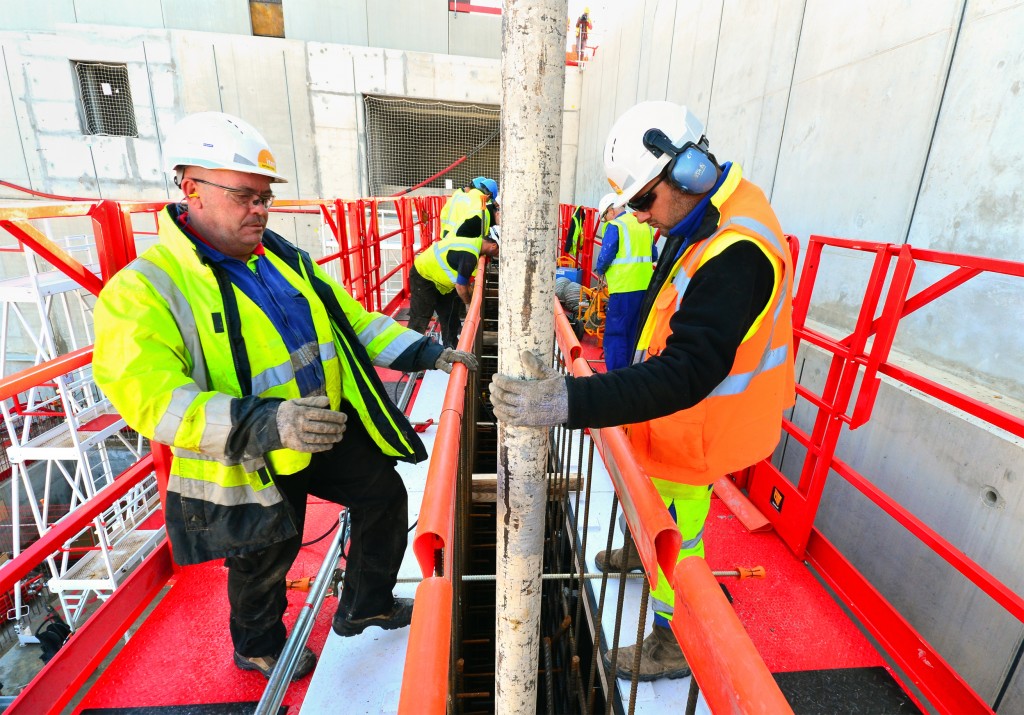
Walls: the first pour
2014-11-20 - Concrete pouring for the first wall of the Diagnostics Building takes place on 20 November.

A peek inside
2014-11-18 - The interior of the completed Cryostat Workshop photographed in November 2014.
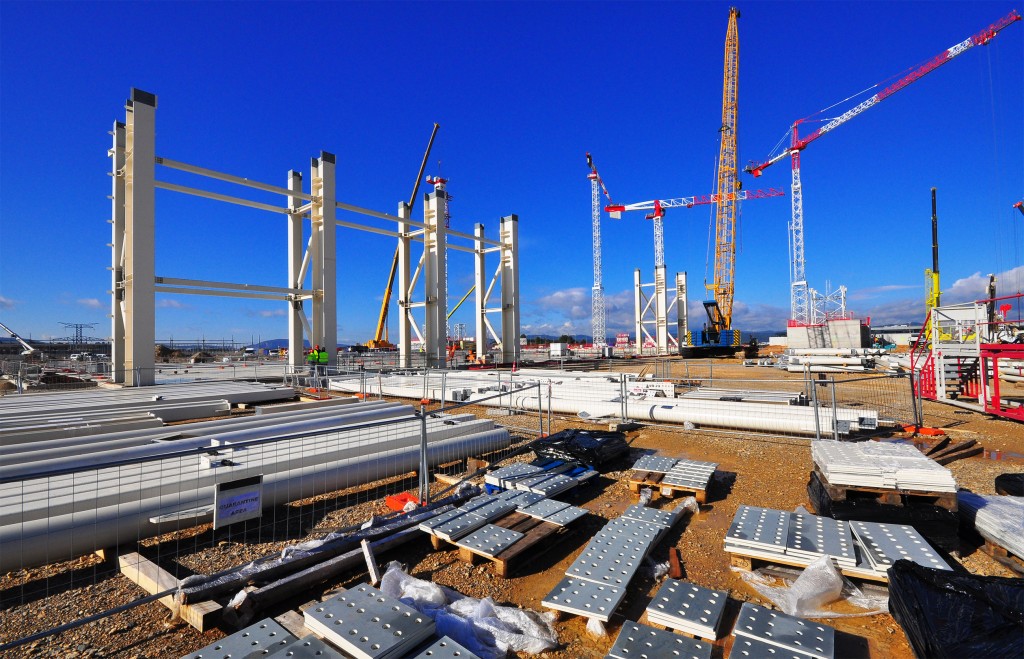
Pillar parts
2014-11-18 - Stored near the worksite where the pillars are being assembled are the plates, bolts and bars of the pillar assemblies.
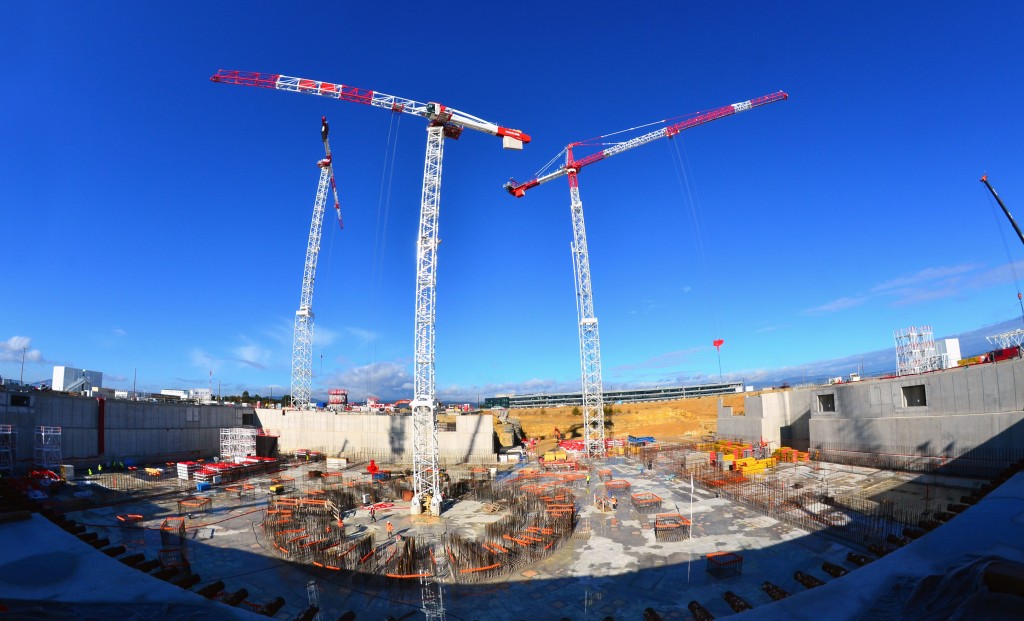
Where the work is starting
2014-11-18 - The ITER Tokamak Complex Seismic Pit: 120 metres long, 80 metres wide.

On-site assembly of four large cryostat sections
2014-11-18 - Within the on-site workshop, cryostat assembly activities will take place on two huge steel platforms built to support the weight of the components, jigs and fixtures.

The footprint of a large tool
2014-11-18 - In this area of the Assembly Building basemat, large custom-built tools will be anchored.
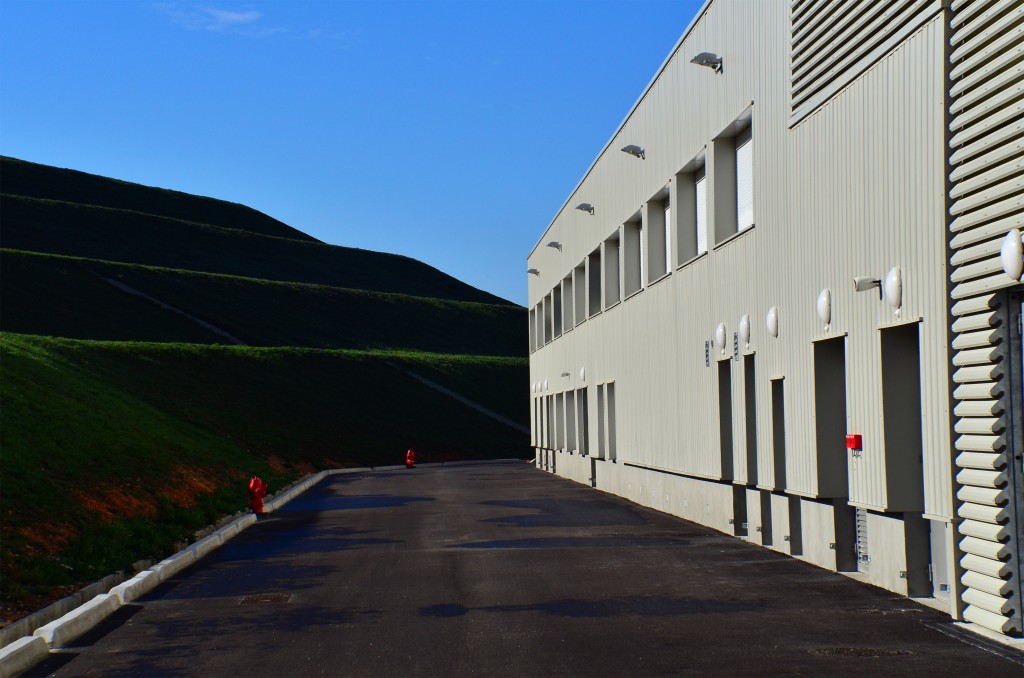
On the other side
2014-11-18 - It's not often that we get to see around the back of the building ...
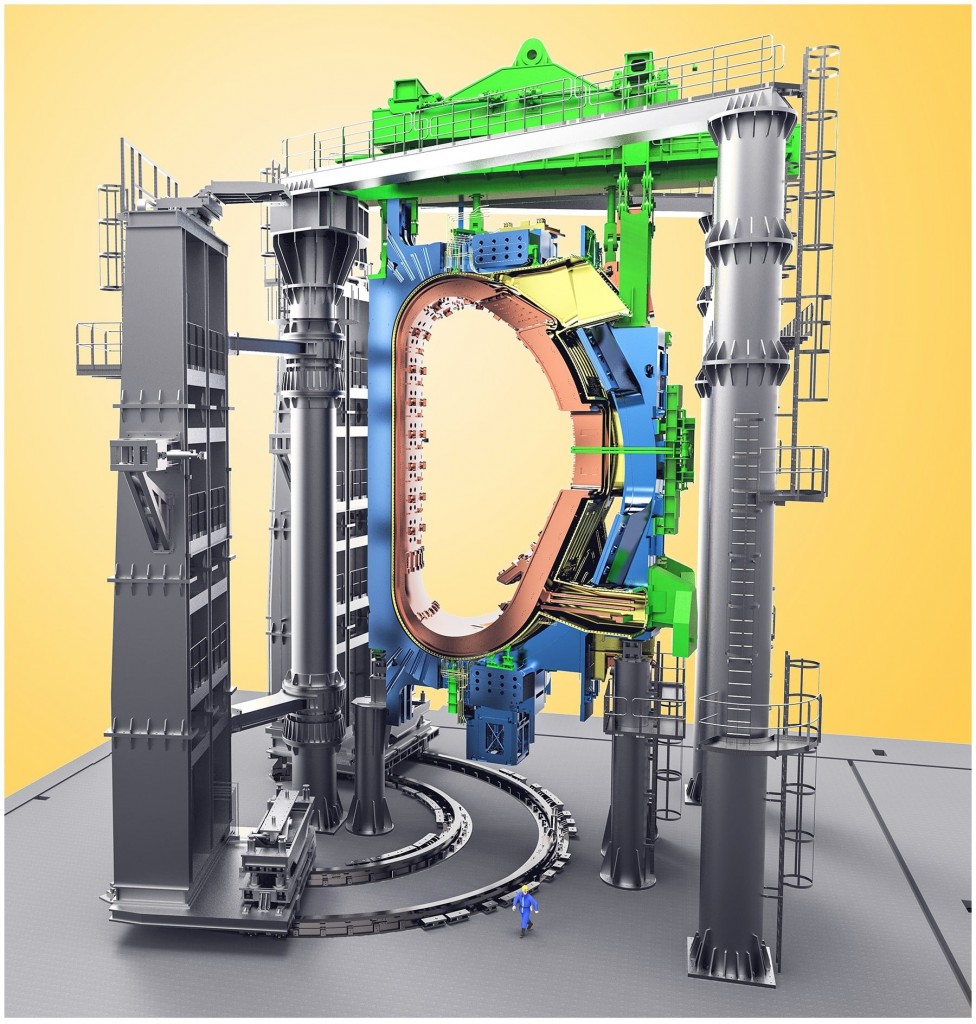
Extremely specialized sub-assembly equipment
2014-11-14 - This 22-metre-high sector sub-assembly tool will assemble components weighing a combined mass of 1,250 tonnes: one 40° vacuum vessel sector; two toroidal field coils; and thermal shields. Most of specialized purpose-built tooling for ITER assembly will be supplied by Korea, as part of its procurement commitments to ITER.
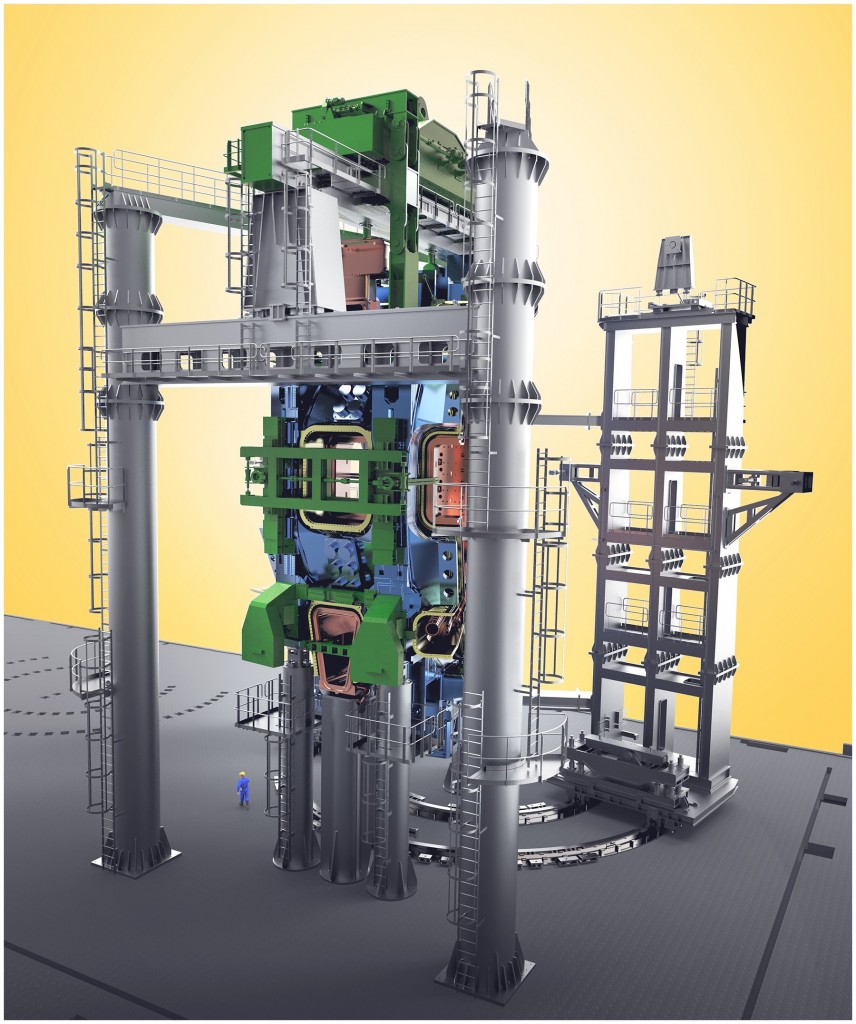
The vacuum vessel Sector Sub-Assembly tool
2014-11-13 - Standing shoulder to shoulder, two Sector Sub-Assembly tools will suspend the vacuum vessel sectors from the top while carefully positioning and installing—via the rotary motion of the "wings"—the vacuum vessel thermal shielding and two toroidal field coils.

The "basement" of the Tokamak Complex
2014-10-28 - Underneath the B2 basemat slab are the 493 pillars and anti-seismic bearings that will support the weight of the Tokamak Complex. With 1.9 metres between the lower concrete slab and the upper slab, there's plenty of room to move around.
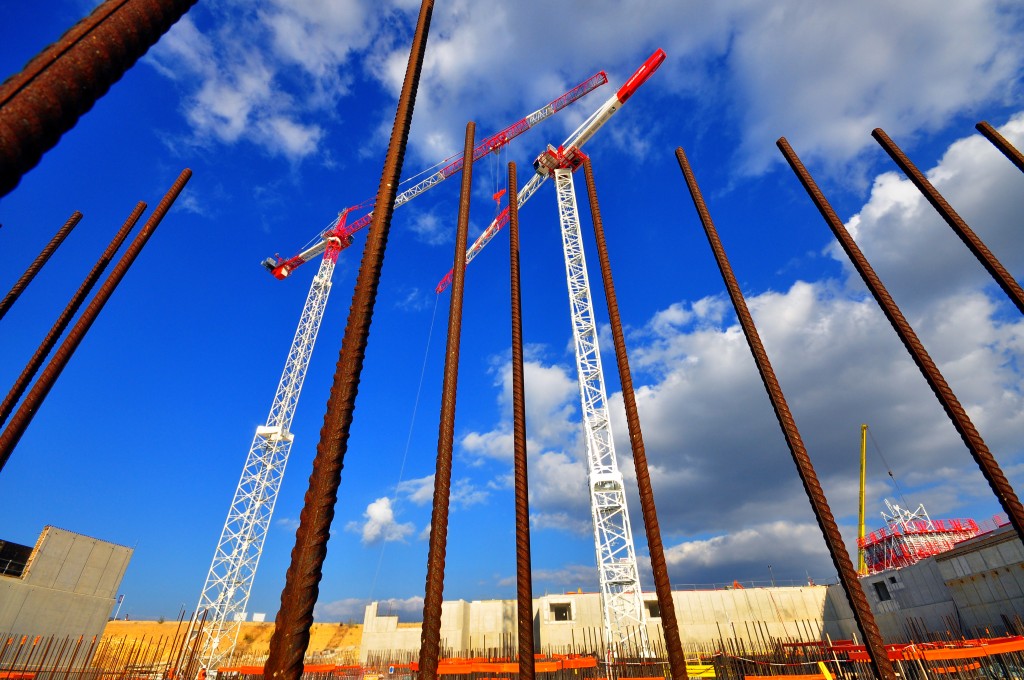
Looking up
2014-10-28 - At its final height, the Tokamak Complex will be nearly as tall as the crane at left—60 metres above platform level.

Piece by piece
2014-10-28 - An inspection of one of the 12-metre column sections that will be assembled as part of the steel "skeleton" of the Assembly Building.

Two of the tools will be twice this height
2014-10-28 - These 12-metre columns are tall, but let's put them in perspective. The two tools that will manage vacuum vector sector sub-assembly will stand 22 metres tall in the Assembly Building—or nearly twice the columns pictured.
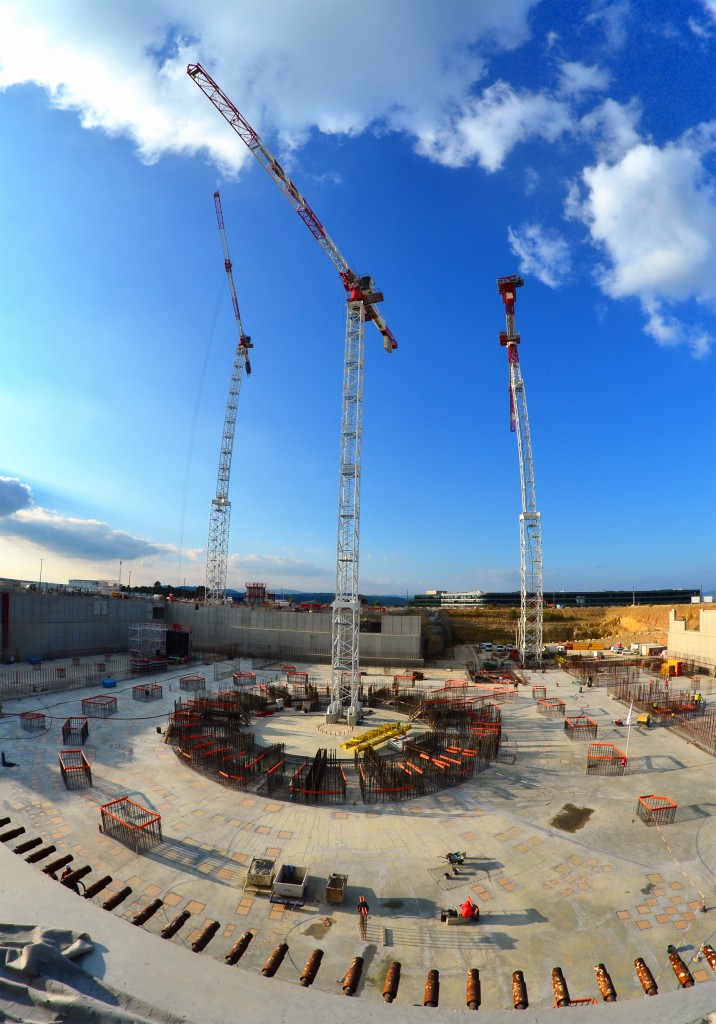
Prepared for heavy loads
2014-10-28 - A third crane is now in place in the centre of the basemat. Five tall cranes—one on every corner and one in the centre—will soon be in place for the construction of the Tokamak Complex.
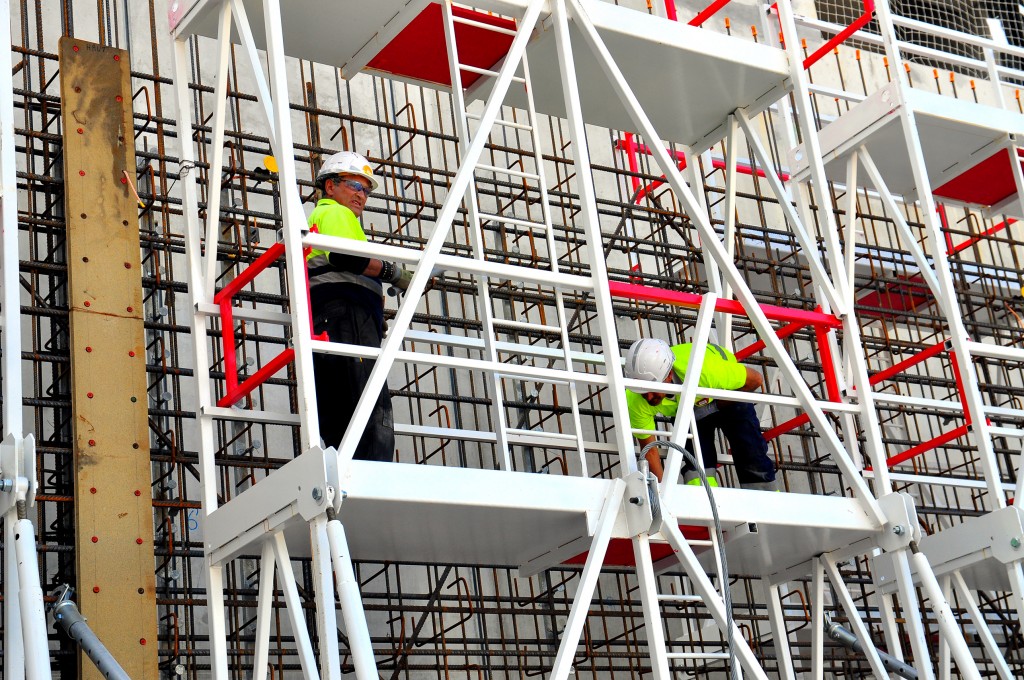
First walls in November
2014-10-28 - Scaffolding, reinforcement bars - everything is ready for the first Tokamak Complex walls to be poured in November.

Heavy bolts
2014-10-28 - A parallel row of columns will support the Assembly Building roof from each side of the basemat. Pictured, the support braces that tie the rows together.

Giants
2014-10-27 - Three of the five cranes planned for Tokamak Complex construction activities will rise over 75 metres (76 m, 80 m and 82 m) and have lifting capacities of 6-8 tons at the tip of their 55- to 65-metre-long booms.

A new phase for ITER
2014-10-20 - Formwork is positioned for the first walls of the Diagnostics Building. The beginning of wall construction marks a new phase in ITER construction: the four-year drive to build the Tokamak Complex and eight other buildings. Photo: Engage
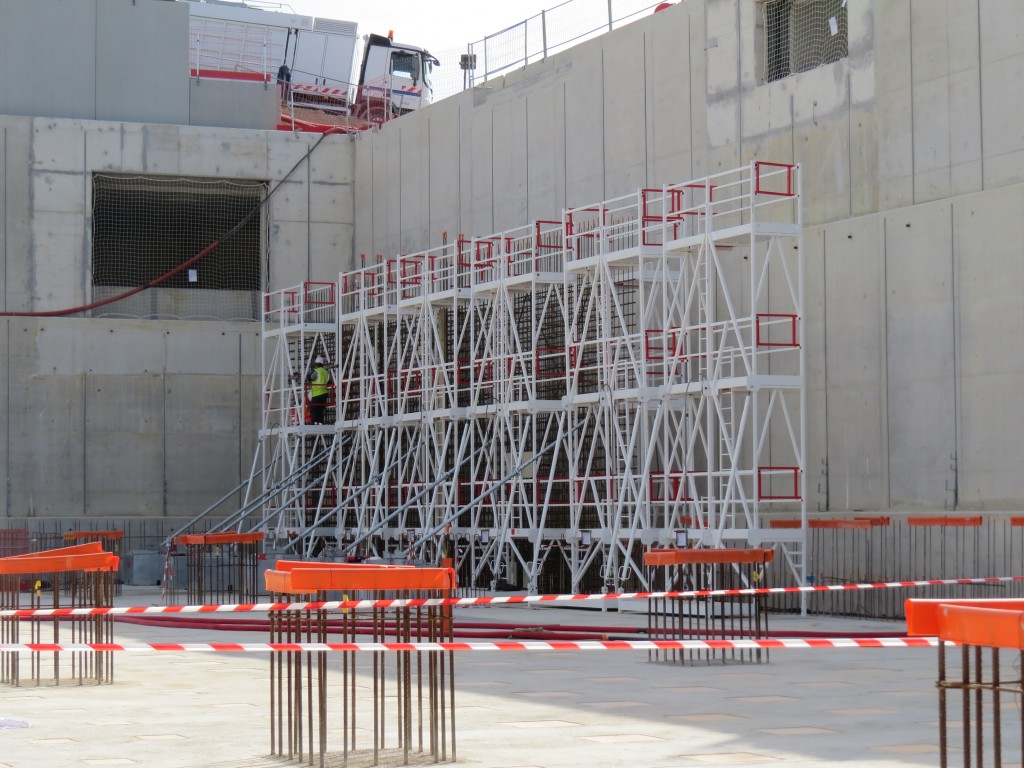
Propping and formwork in October
2014-10-20 - Propping work has begun on the south end of the Seismic Pit. In November, the first walls will be poured for the Diagnostics Building. Photo: Engage
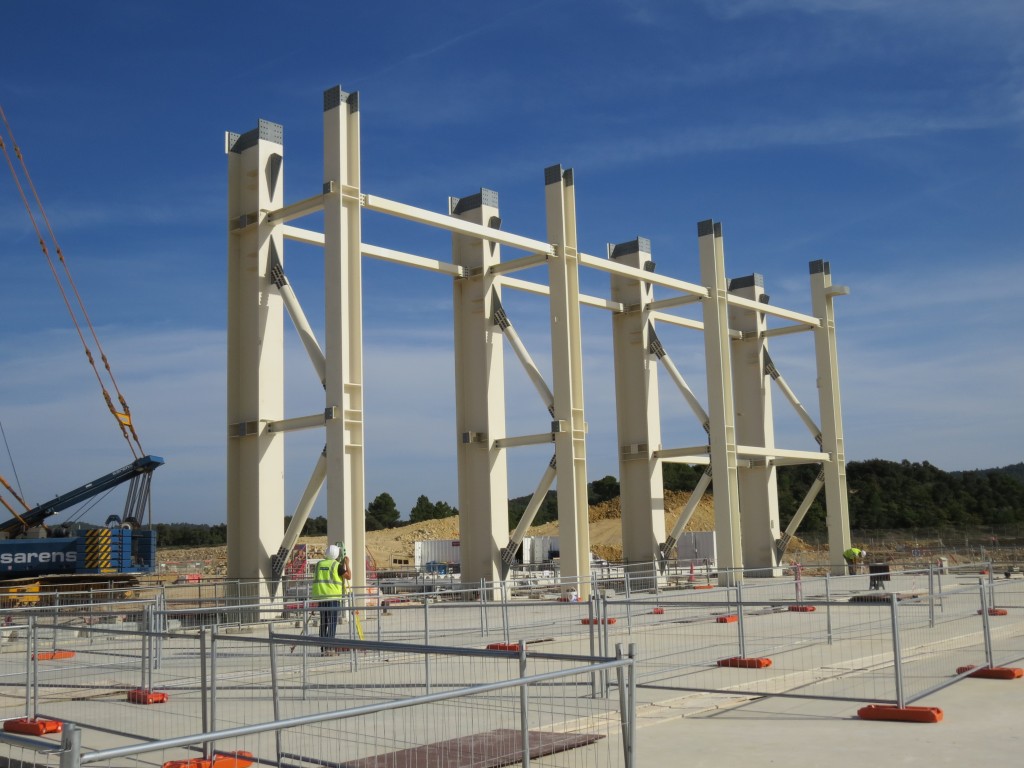
Work begins on the Assembly Building
2014-10-20 - Another seven double pillar assemblies like those pictured here will complete one side of the supporting structure for the Assembly Building, before workers begin erecting pillars on the opposite side. The 12-metre columns are one-fifth of their final height. One year of construction will be necessary to complete the Assembly Building. Photo: Engage
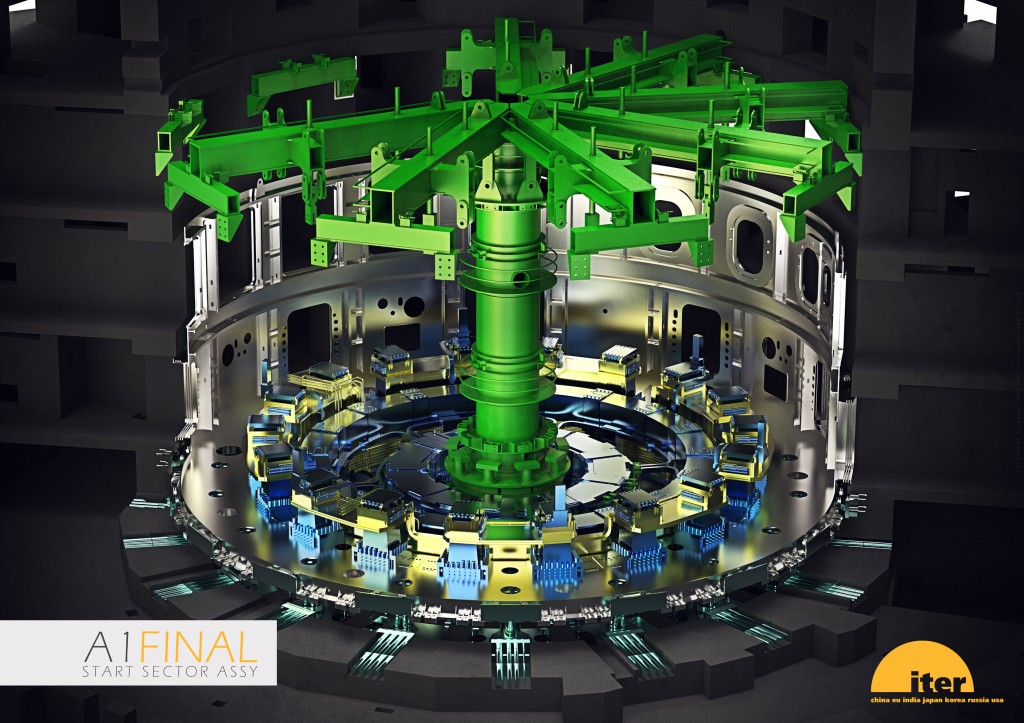
Assembling the vacuum vessel
2014-10-06 - The in-pit assembly tool is made up of a central tower and a series of beams. This tool will support the vacuum vessel sub-assemblies and align them while the vacuum vessel is assembled.
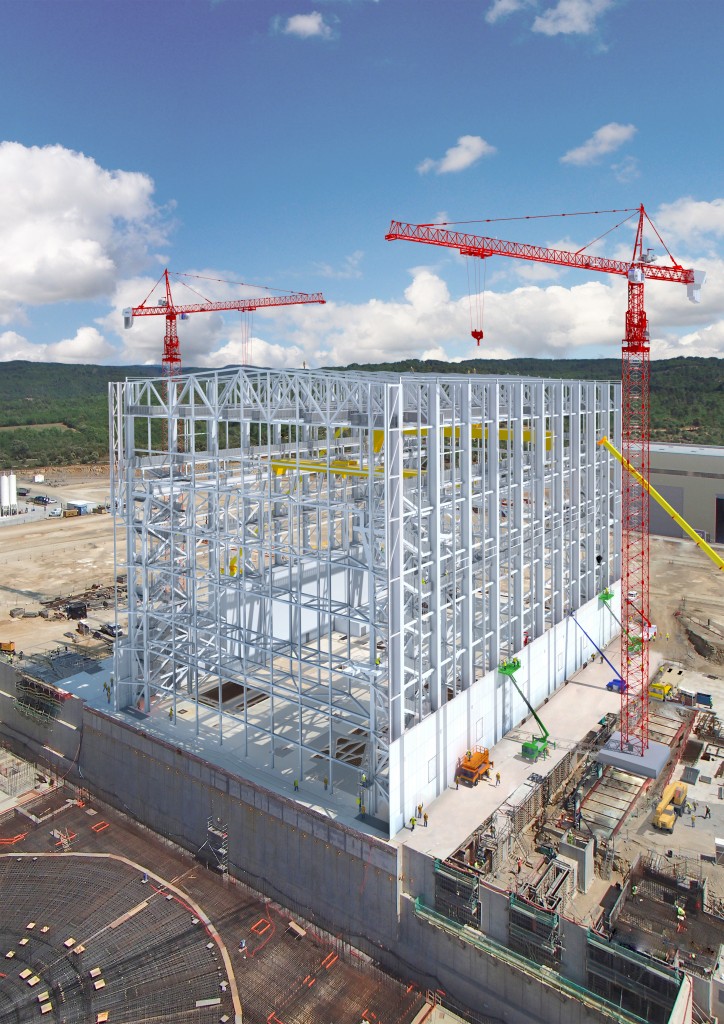
How it will look
2014-10-01 - The 60-metre tall Assembly Building is the antechamber to the Tokamak Building. Its overhead cranes (in yellow) will run the full length of both buildings to deliver pre-assembled components for in-pit assembly. Image courtesy of Groupement VFR (Vinci - Ferrovial - Razel)
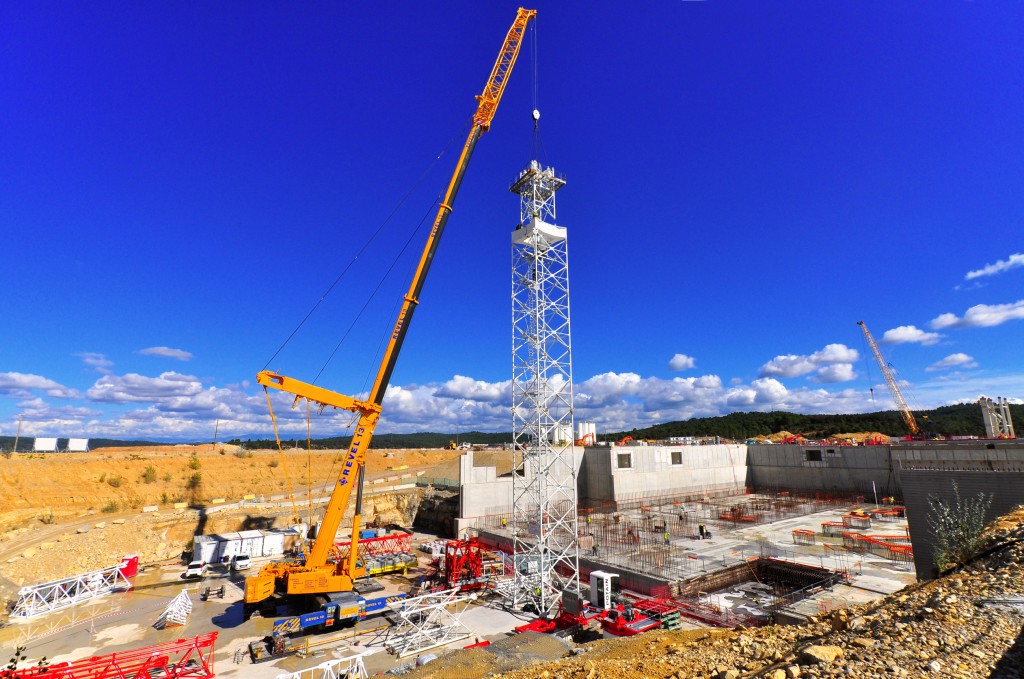
The workhorse of the worksite
2014-10-01 - Of the five cranes that are being installed for the construction of the Tokamak Complex, this will be the largest (85 metres) with a lifting capacity of 18 tonnes.

Twice as high as the Cryostat Workshop
2014-10-01 - The Assembly Building will rise 60 metres, or more than twice as high as the Cryostat Workshop seen in the background.

Tall cranes going up
2014-10-01 - In one corner of the Seismic Pit, a tower crane is going up to prepare for the next phase of work: the pouring of the B2 slab that will act as a floor to the three buildings of the Tokamak Complex.
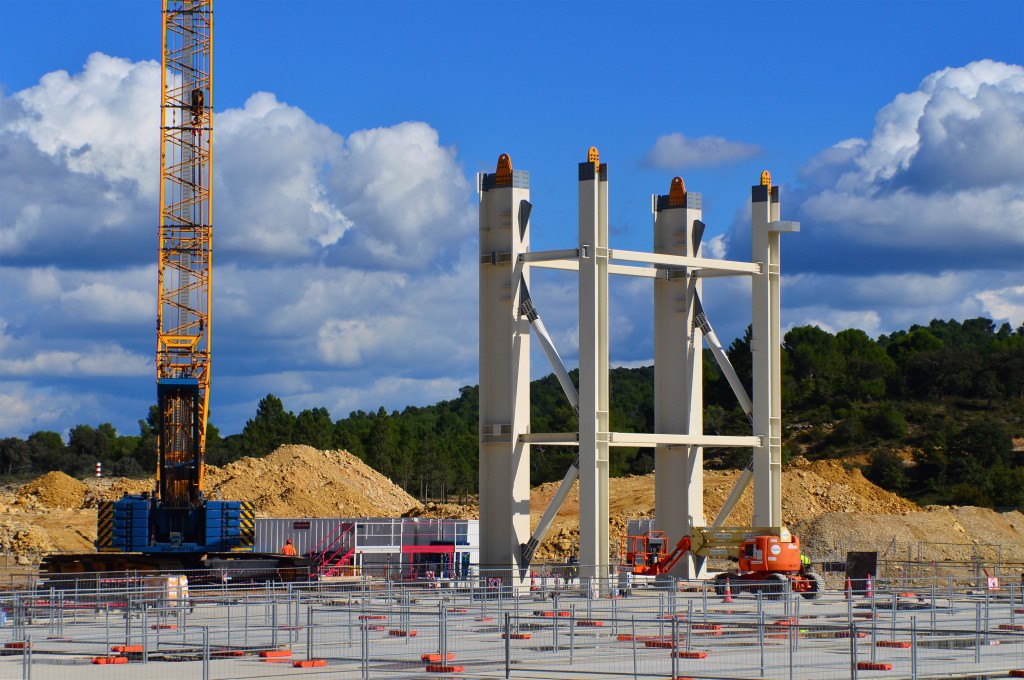
The first pillars
2014-10-01 - Late September, the first pillars of the Assembly Building were installed. Eleven main pillars, and 11 supporting pillars, will be erected along each side of the basemat.
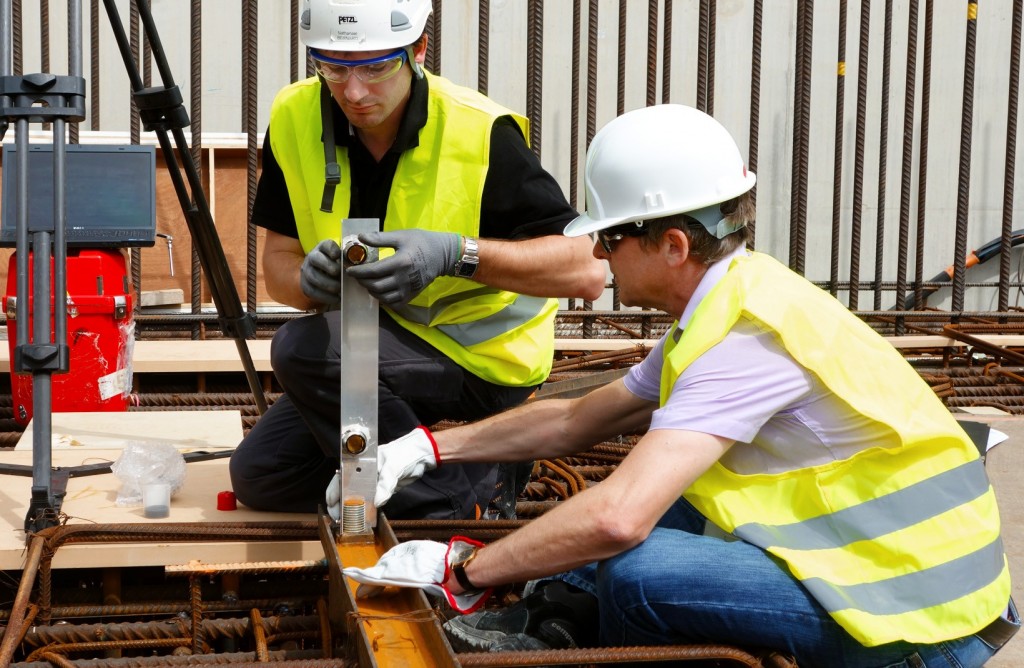
Metrology on the construction site
2014-09-29 - Surveyors from the metrology consortium G2Métric & Arkadia use laser measurement equipment to verify the position and elevation of the 80 embedded steel plates used to anchor the drain tanks.

Facility will be in place end 2015
2014-09-26 - By the end of 2015, a climate controlled, steel-structure warehouse will be in place on a parcel of land behind the ITER platform. Half of its surface will be used for mass storage; the other half will be equipped with racks up to eight metres high for pallet storage.
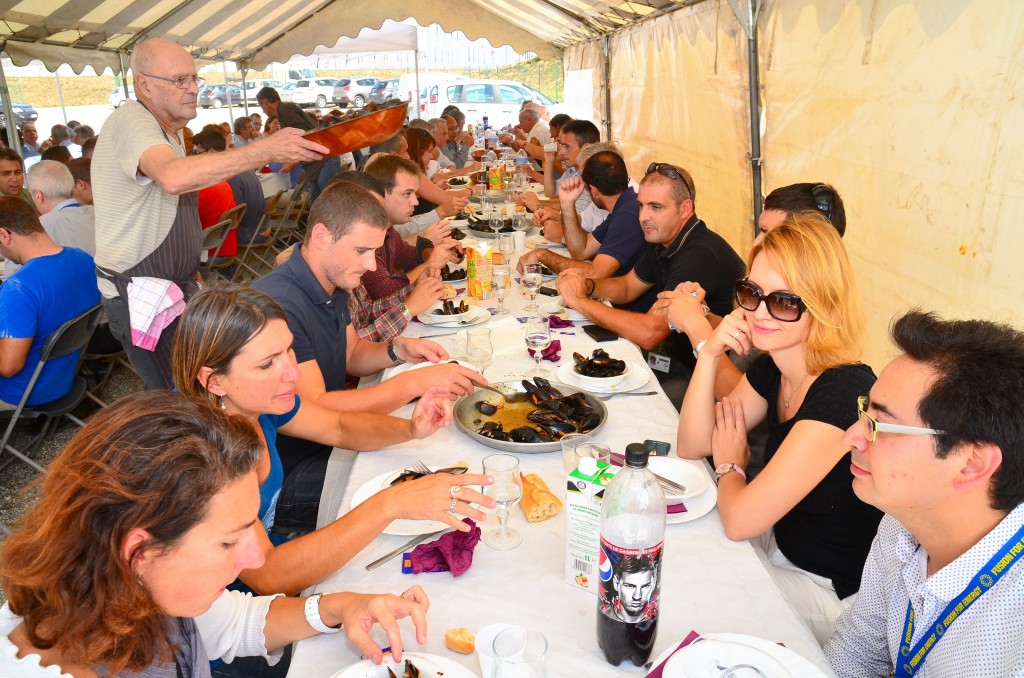
Mission accomplished
2014-09-18 - The end of B2 slab works is celebrated with a traditional méchoui (roast lamb on a spit) on 18 September.

Extension completed
2014-09-17 - The 35-metre extension to the Headquarters building is completed in September 2014. Following its official handover to the ITER Organization (on 30 September) work can now begin to carry out the necessary arrangements for move-in (furnishings, IT connections).
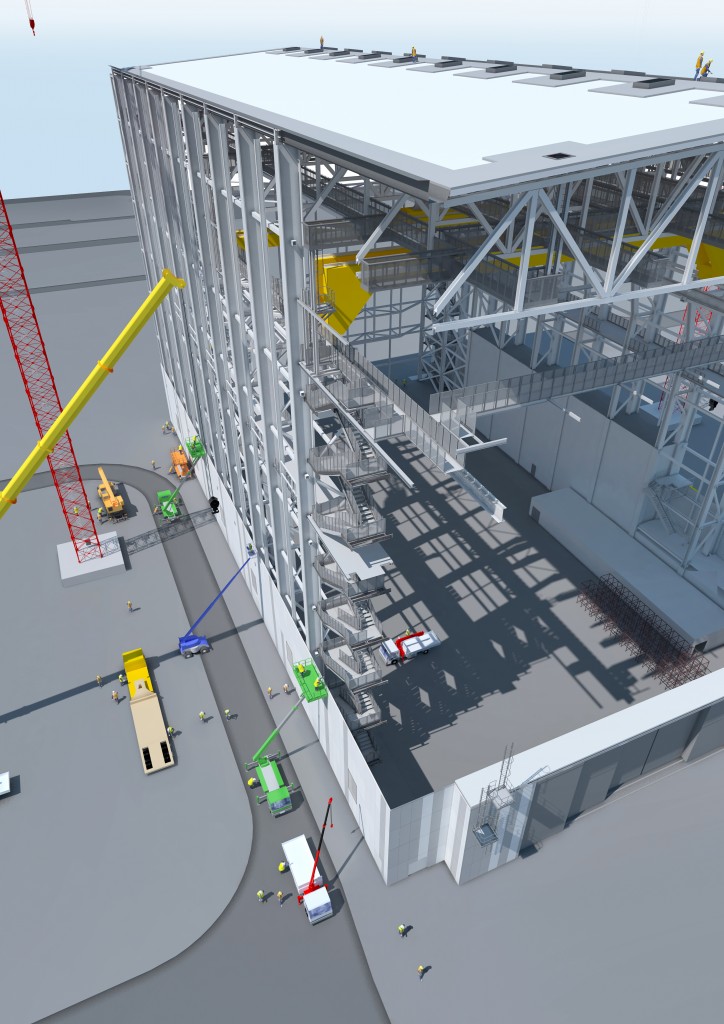
A busy workshop
2014-09-08 - This vast workshop will host custom-made tools as well as two 750-tonne cranes that will travel the length of the building to pre-assemble components for the ITER Tokamak. Image courtesy of Groupement VFR (Vinci - Ferrovial - Razel)

Enter through this door!
2014-09-08 - The Assembly Building and the Tokamak Building (in solid white) will stand 60 metres tall on the ITER platform. Image courtesy of Groupement VFR (Vinci - Ferrovial - Razel)
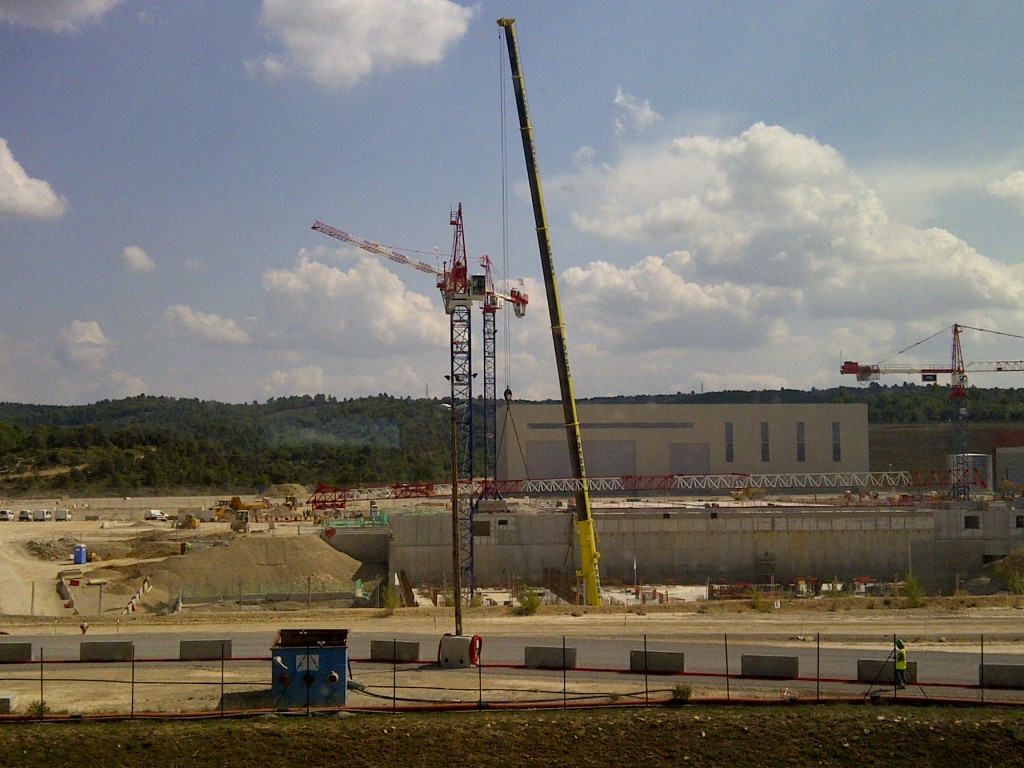
Lowering the cranes
2014-09-08 - Now that the Tokamak Complex foundations are in place, the four corner cranes used by the GTM consortium are coming down. They will be replaced by five taller cranes (including one that will work from the centre of the basemat) for wall construction.

The completed slab
2014-09-02 - The B2 slab—14,000 m³ of concrete, 3,600 tonnes of reinforcement and 2,500 embedded plates—stands ready to receive the first walls of the Tokamak Complex.

The B2 slab is "topped out"
2014-09-02 - An olive branch is left by workers in the centre of the completed Tokamak Complex basemat slab (B2 slab). Originating in Eastern Europe, this construction tradition called "topping out" symbolizes the end of works.

The floor is finished
2014-08-27 - 493 anti-seismic columns and pads are sandwiched between the B2 slab, completed today, and the lower basemat installed on the floor of the Tokamak Pit. The B2 slab will be the first basement level of the Diagnostic, Tokamak and Tritium buildings.

A landmark day for ITER
2014-08-27 - The completion of the 9,300 m² B2 slab on 27 August concludes four years of work (2010-2014) to create a ground support structure for the Tokamak Complex.
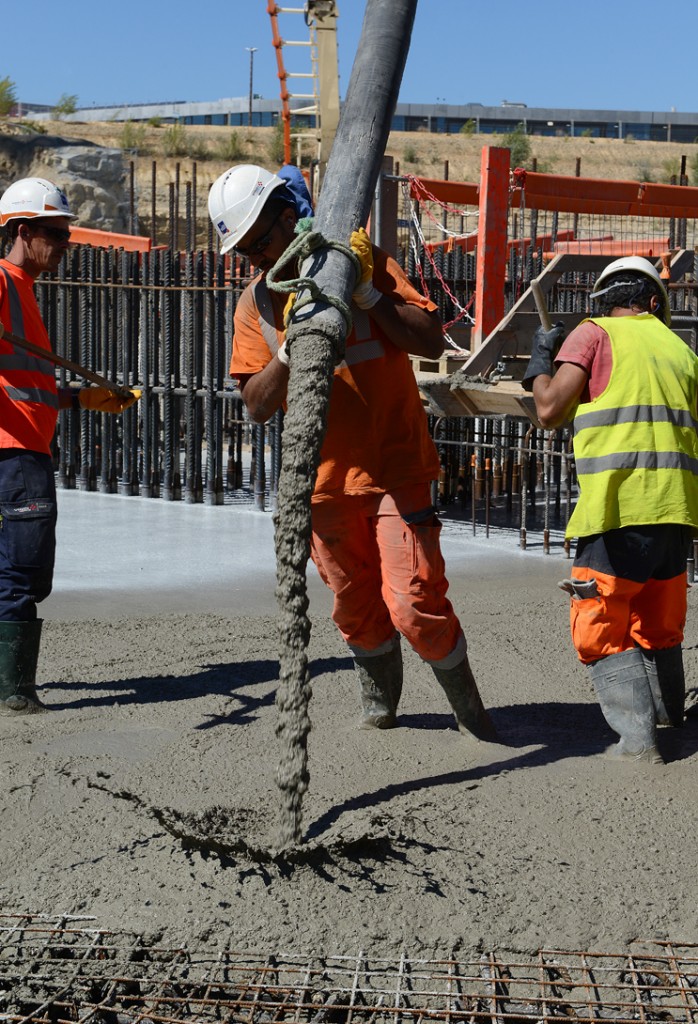
Just the right formulation
2014-08-27 - Consistency and spreadability are important to ensuring the homogenous distribution of the concrete. These parameters are tested as the concrete leaves the on-site batching plant, before it gets loaded into the mixer trucks. Photo: F4E

Standing on the slab
2014-08-27 - Works were carried out by the F4E construction consortium led by GTM Sud from France. GTM was also in charge of the excavation of the Tokamak Complex Seismic Pit (August 2010-April 2011) and the construction of the lower level basemat and retaining walls (April 2011-April 2012).

A lot of material
2014-08-27 - The last pour—for the circular central segment of the basemat—required 865 m³ of concrete. In total, the 1.5-metre-thick B2 slab contains 3,600 tonnes of rebar and 14,000 m³ of concrete.
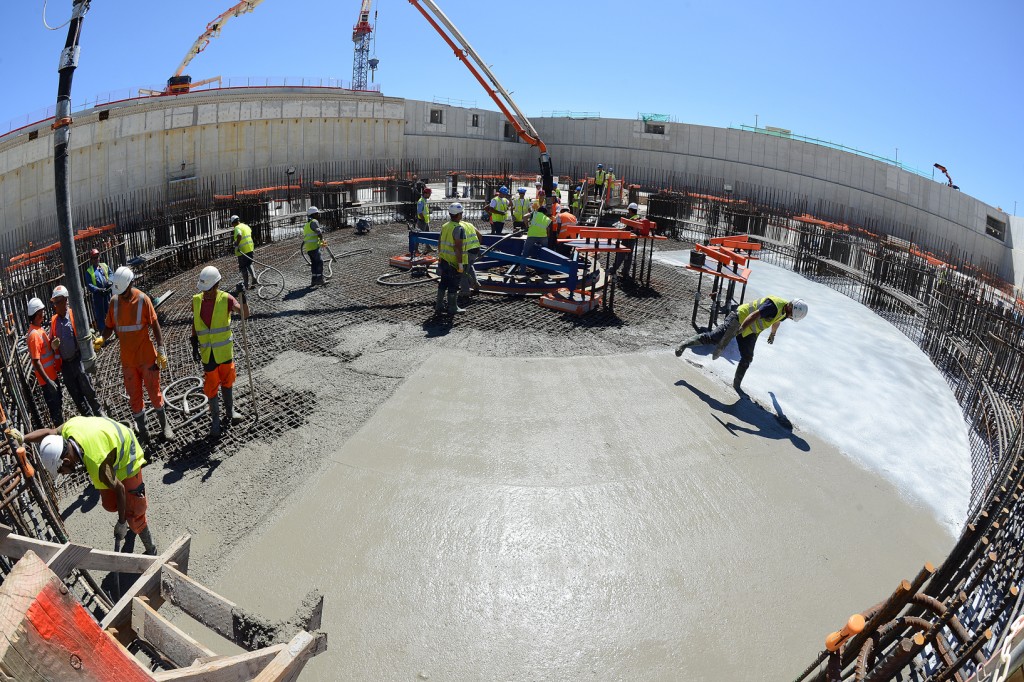
A series of important operations
2014-08-27 - The concrete is poured (far left), vibrated to eliminate air pockets (middle left) and smoothed for a perfect finish (far right). Photo: F4E

It's done!
2014-08-27 - The B2 slab, which will support some 400,000 tonnes of building and equipment (including the 23,000-tonne ITER Tokamak), is now in place.
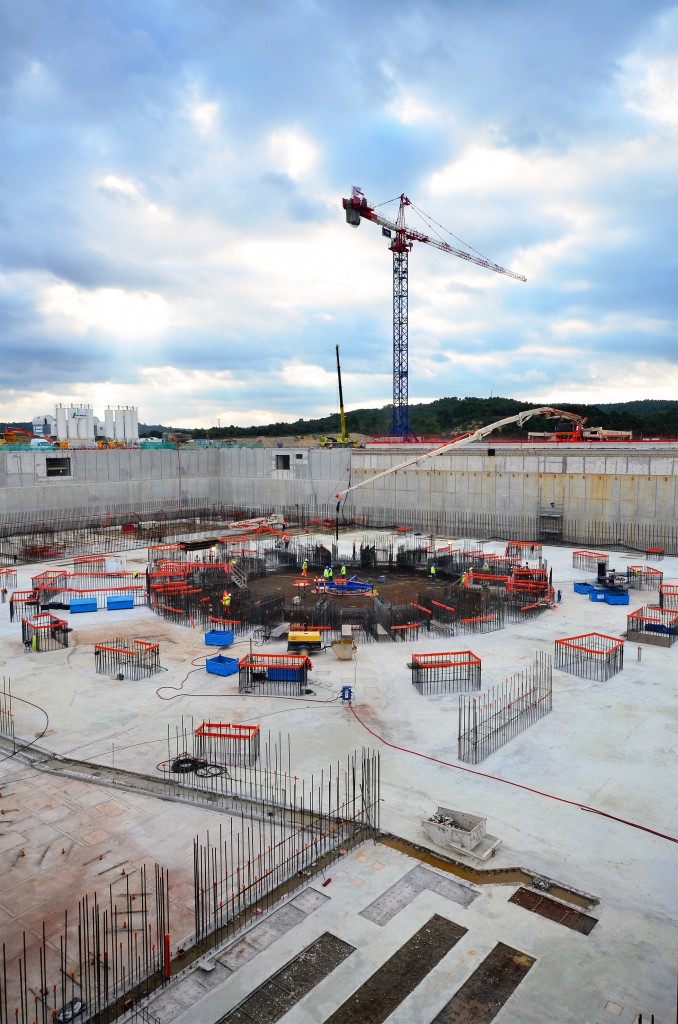
Any day now
2014-08-26 - On 26 August, workers carry out the final activities on the central segment to prepare for concrete pouring, which is imminent.
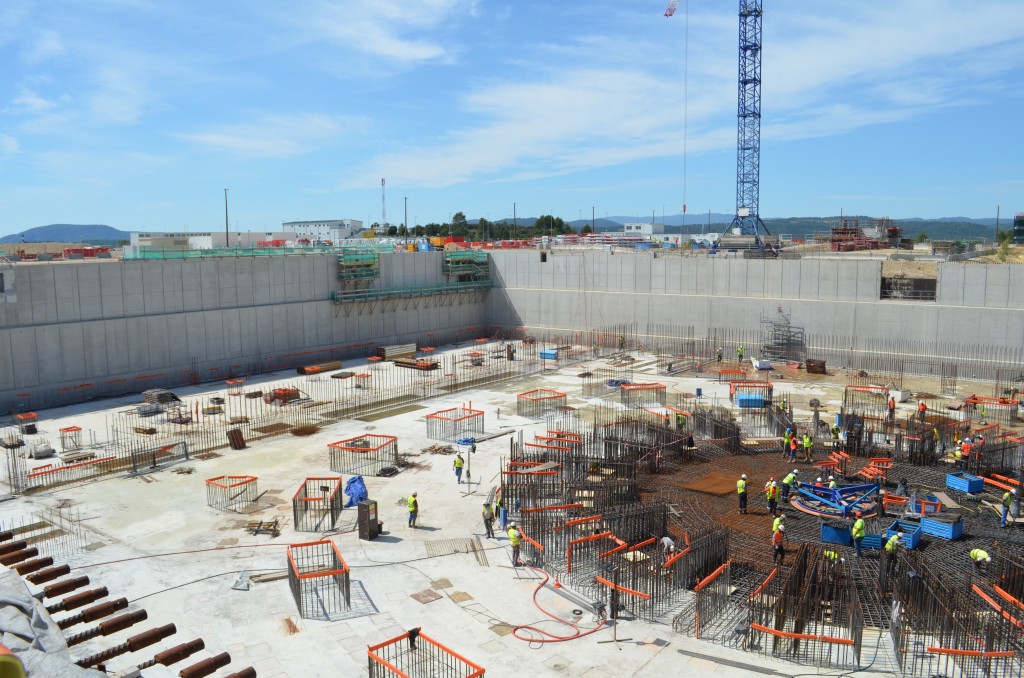
Southern segments completed
2014-08-21 - A smooth concrete surface is now in place in the southern part of the Tokamak Pit, where the foundations of the Diagnostic Building abut those of the Tokamak Building.
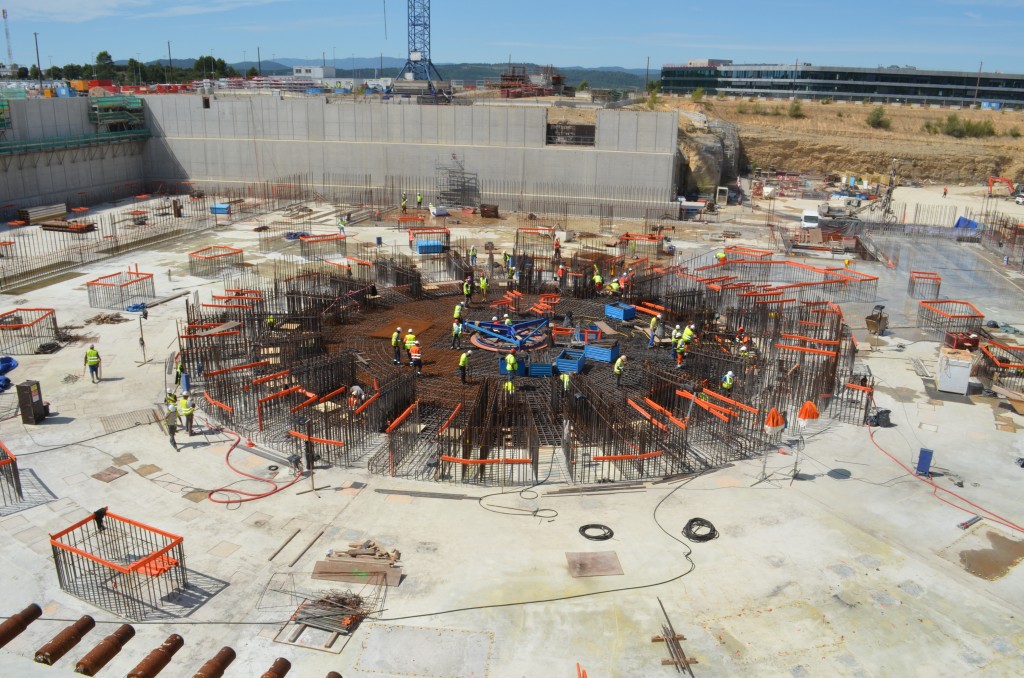
The last pour will be circular
2014-08-21 - In terms of volume, it's slightly less than the surrounding segments. The last pour of the B2 basemat slab will require 865 m³ of concrete.

Preparing for the last pour
2014-08-21 - Workers are busy preparing the last pour of the Tokamak Complex B2 slab.
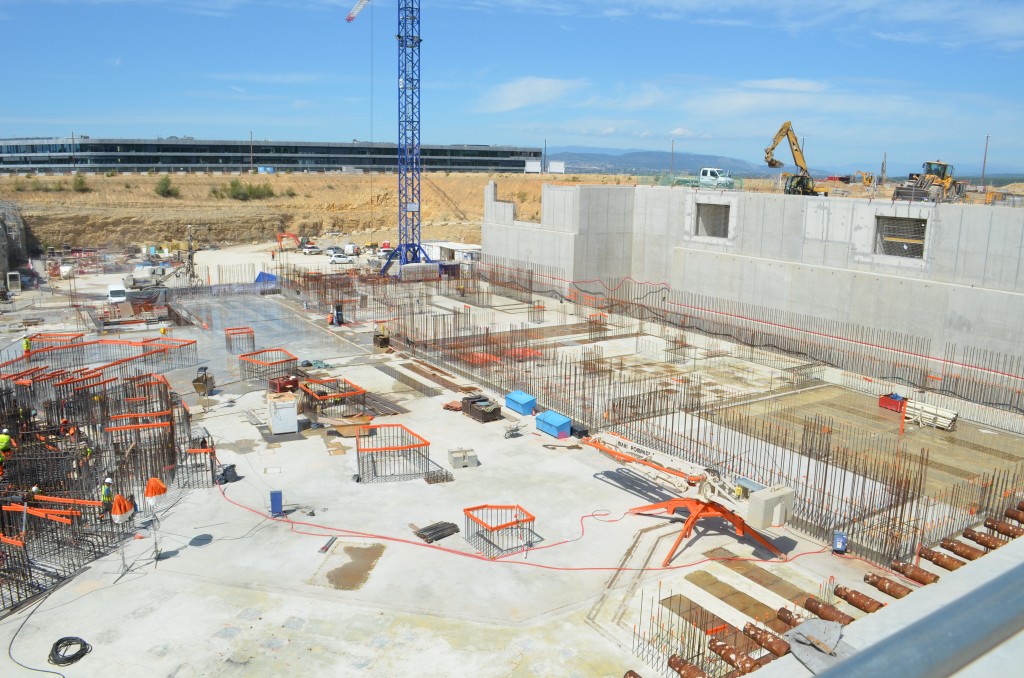
Northern segments completed
2014-08-21 - Looking toward the excavated area for the future Hot Cell, and also towards ITER Headquarters, the concrete foundation of the Tritium Building is now flush with that of its neighbour, the Tokamak Building.
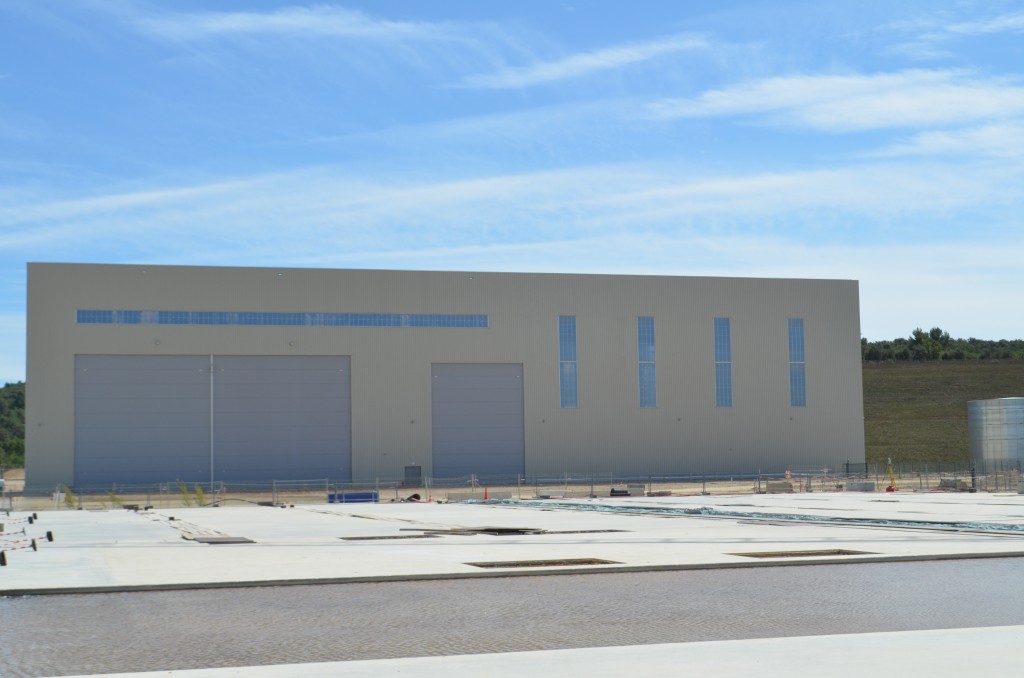
Signed, sealed, delivered
2014-08-21 - The complete Cryostat Workshop, seen from the foundations of the Assembly Building.
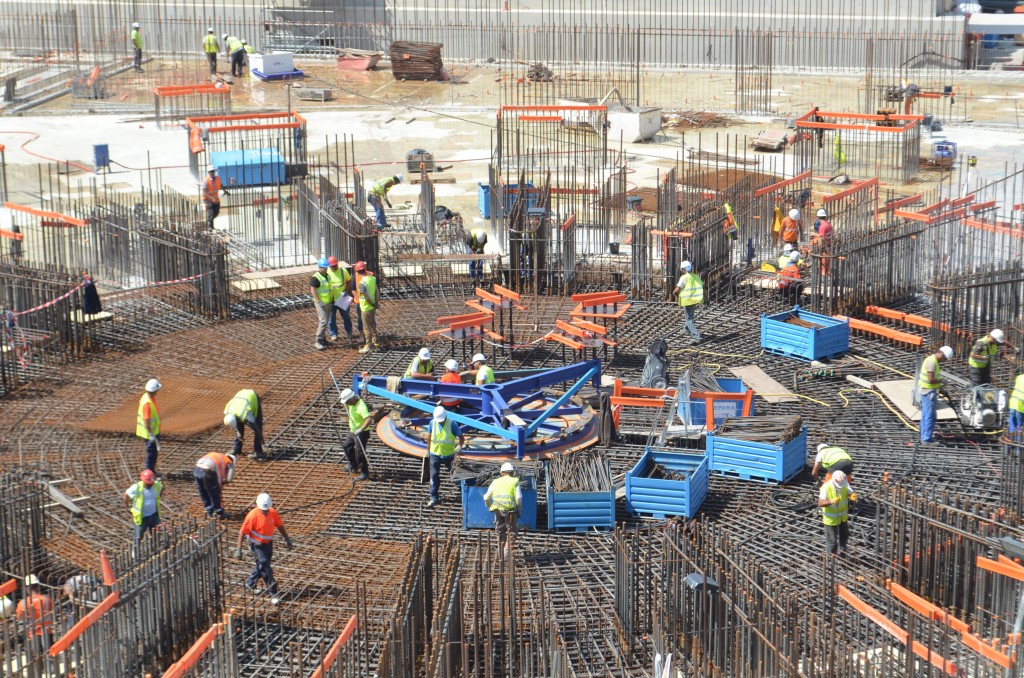
Bull's eye
2014-08-21 - In the very centre, is a large circular embedded plate that will be used as a base for securing machinery or equipment.
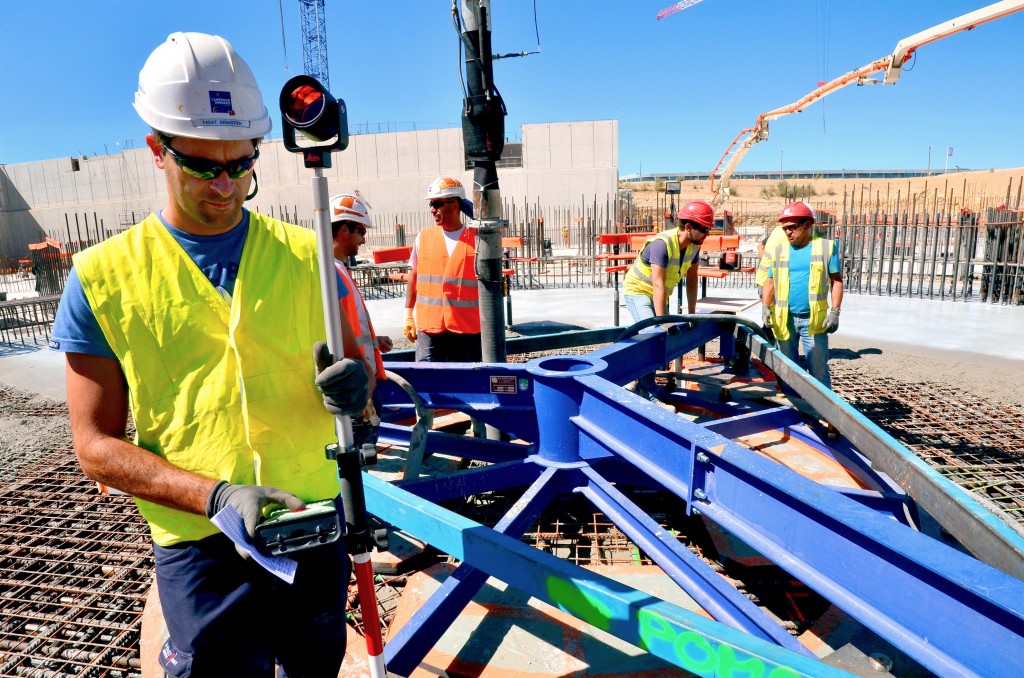
Last measurements before pouring
2014-08-09 - In the centre of the basemat, a large steel ring (topped with a blue steel structure designed to prevent deformation) will be deeply anchored in the concrete. Its purpose? To provide a base for the huge inner support column that will stabilize the vacuum vessel sectors during the first stages of machine assembly.

Rapid progress on the B2 slab
2014-08-05 - The thirteenth B2 slab segment out of fifteen) is poured on 5 August. Photo: F4E
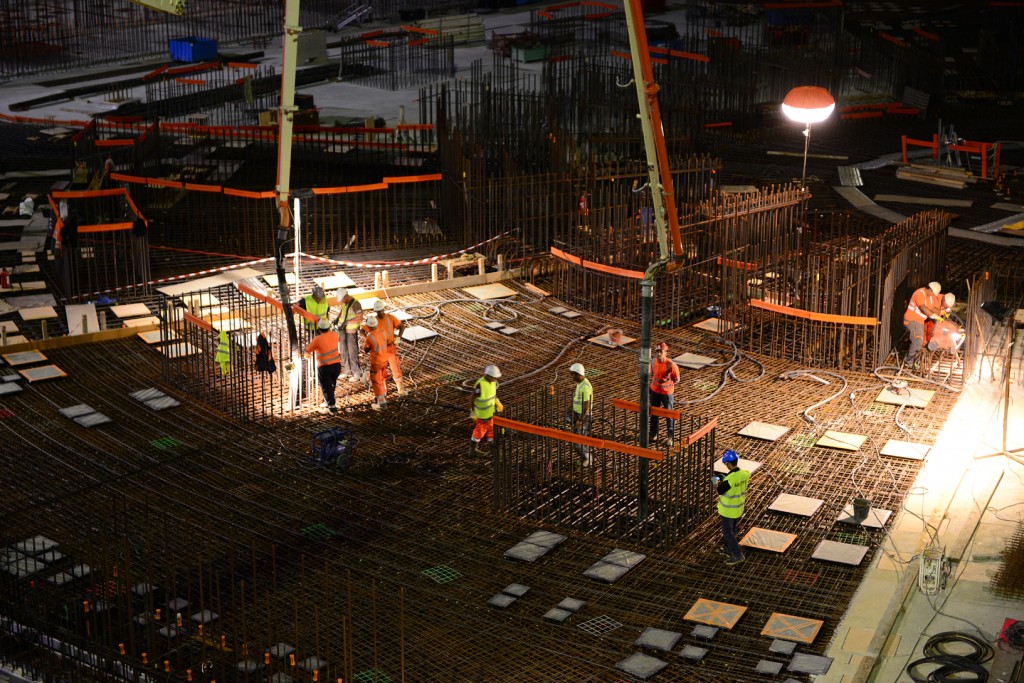
All through the night
2014-08-05 - For three weeks this summer, contractors had the authorization to carry out night pours. On a summer night, the temperature is ideal for concrete pouring ... Photo: F4E

Taking advantage of a clear night
2014-08-05 - On three occasions in July and in August, the pouring operations took place at night from 10:30 p.m. to noon the next day. Photo: F4E

Closing in on the centre
2014-07-29 - On 29 July, the fourth of nine central segments is poured. To create the 9,600 square-metre Tokamak Complex basemat slab, workers will have used 14,000 cubic metres of concrete and 3,600 tonnes of rebar.

A fish-eye view of the Tokamak Pit
2014-07-29 - Pouring continues for the central segments of the Tokamak Complex basemat on 29 July.
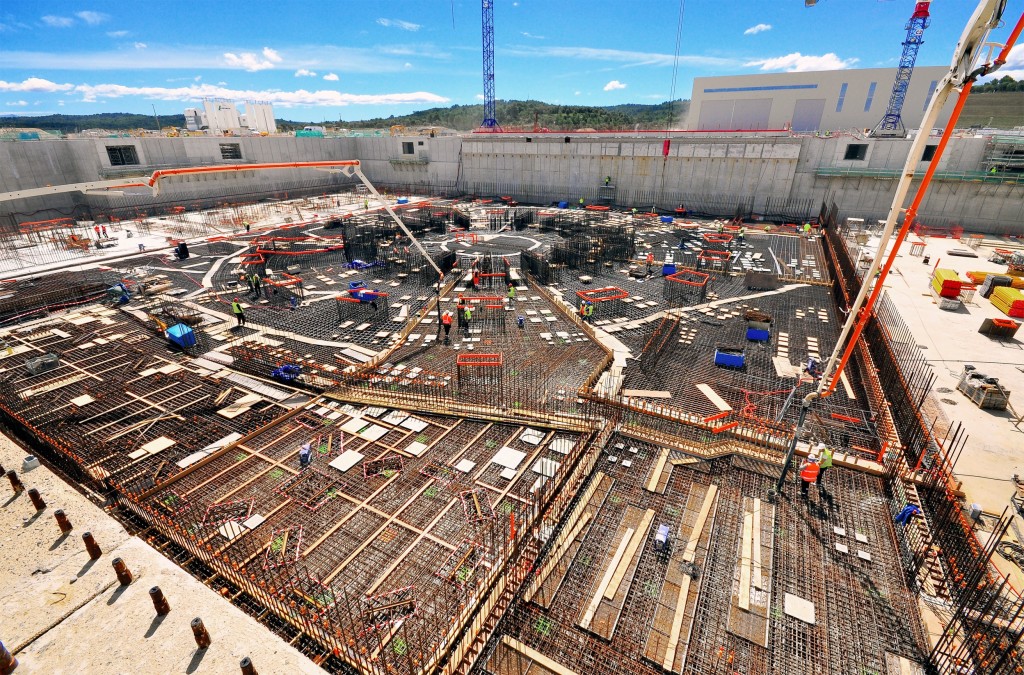
Work begins on the central area
2014-07-10 - Pouring begins on 10 July 2014 on the central area of the B2 slab--which will support the machine--following the green light from the French Nuclear Safety Authority (ASN). Nine segments make up the central part of the slab.
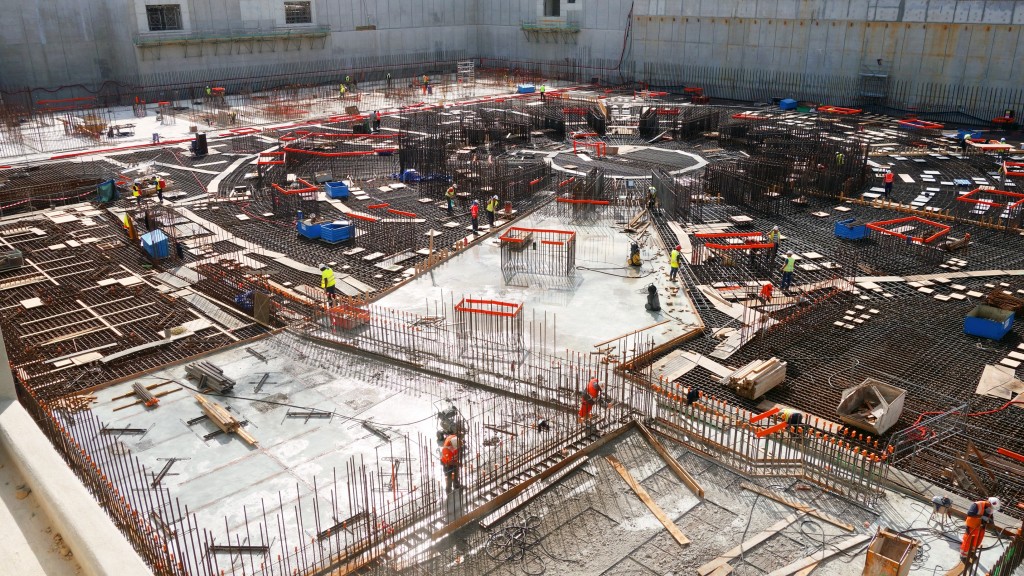
Starting in one corner
2014-07-10 - A 627-square-metre segment, adjacent to the Diagnostics Building slab on the north side of Seismic Pit, was the first of nine plots to be poured on 10 July.
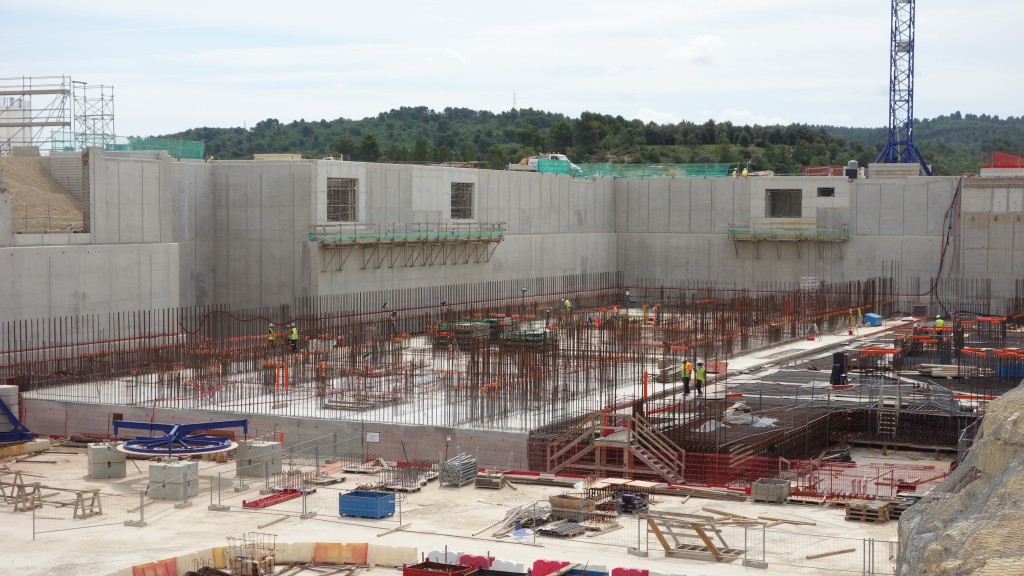
1.5 metres thick
2014-07-07 - From this angle the thickness of the B2 basemat slab (1.5 metres) is clearly visible.

A solid foundation for the Tokamak Complex
2014-07-01 - When completed, the 9,600 m² Tokamak Complex basemat will have incorporated some 14,000 tonnes of concrete and 3,600 tonnes of steel.

Nine segments to go
2014-07-01 - Concrete pouring in the central area will be carried out from July to September 2014.
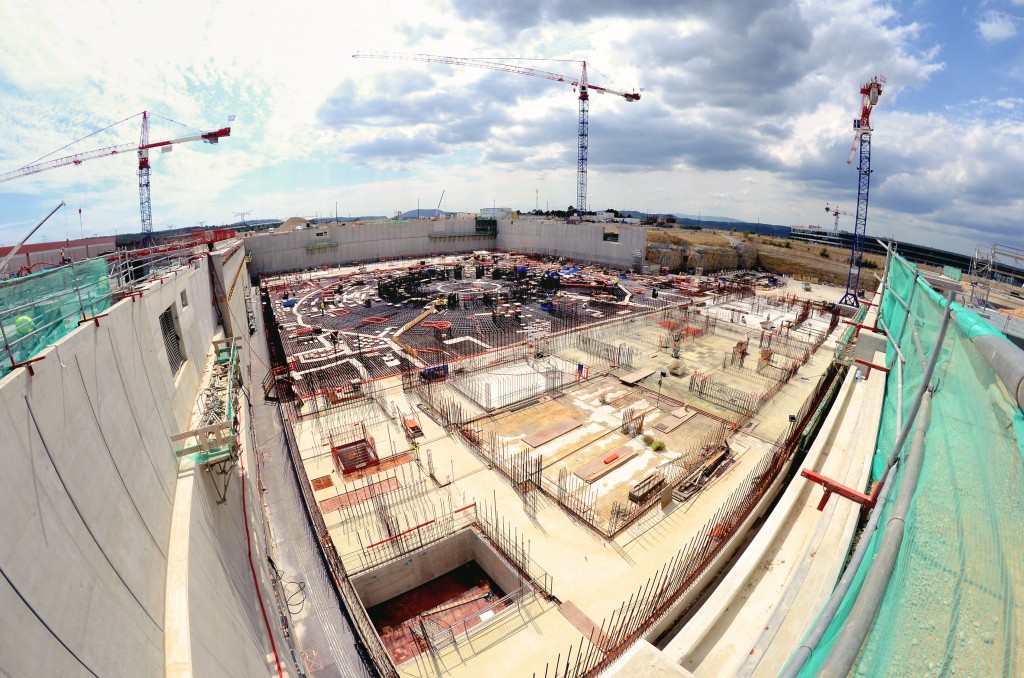
Tritium slab completed
2014-07-01 - The third and final pour for the Tritium Building basemat was carried out on 26 June. Now only the nine central segments remain to complete the Tokamak Complex basemat.

Next, the walls will rise
2014-07-01 - Rebar is already in place for certain of the Tokamak Complex's walls. Building construction begins in 2014.

Pouring on a sunny day
2014-06-19 - 1,155 cubic metres of specially formulated concrete went into the second segment of the Tritium Building basemat slab. Pouring conditions on 19 June were ideal.

Segment #5 is poured in June
2014-06-19 - On 19 June, workers pour the second Tritium Building basemat segment. There are ten segments to go to complete the Tokamak Complex slab
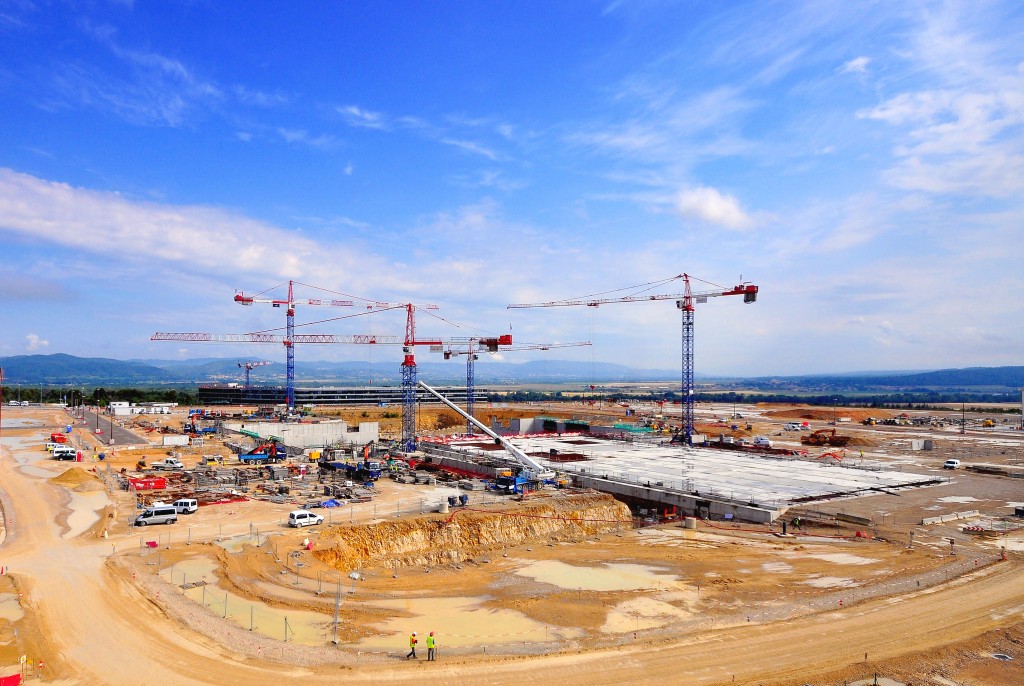
Pre-assembly operations will happen here
2014-06-17 - The Assembly Building—a vast antechamber to the Tokamak Complex—will house the specialized assembly tooling required for pre-assembly operations. The 6,000 m² basemat of the Assembly Building won't be visible for long: construction begins this year on the walls of the facility, which will rise 60 metres above the platform.

Continuity
2014-06-02 - As contruction progress has now reached level 5, the ITER Headquarters extension now stands in perfect continuity with the main building.

Strong progress in the Seismic Pit
2014-05-27 - Approximately 100 people are currently working in the Seismic Pit, laying rebar, securing embedded plates, and preparing for the next two segment pours for the Tritium Building.

4,000 tons of iron and a mockup
2014-05-21 - Iron elements for the B2 foundation slab are stored near a full-scale mockup on the platform that reproduces the most complex areas of reinforced concrete. Once poured, the concrete will be closely examined to make sure that it is uniformly distributed throughout the mockup's dense metal skeleton.
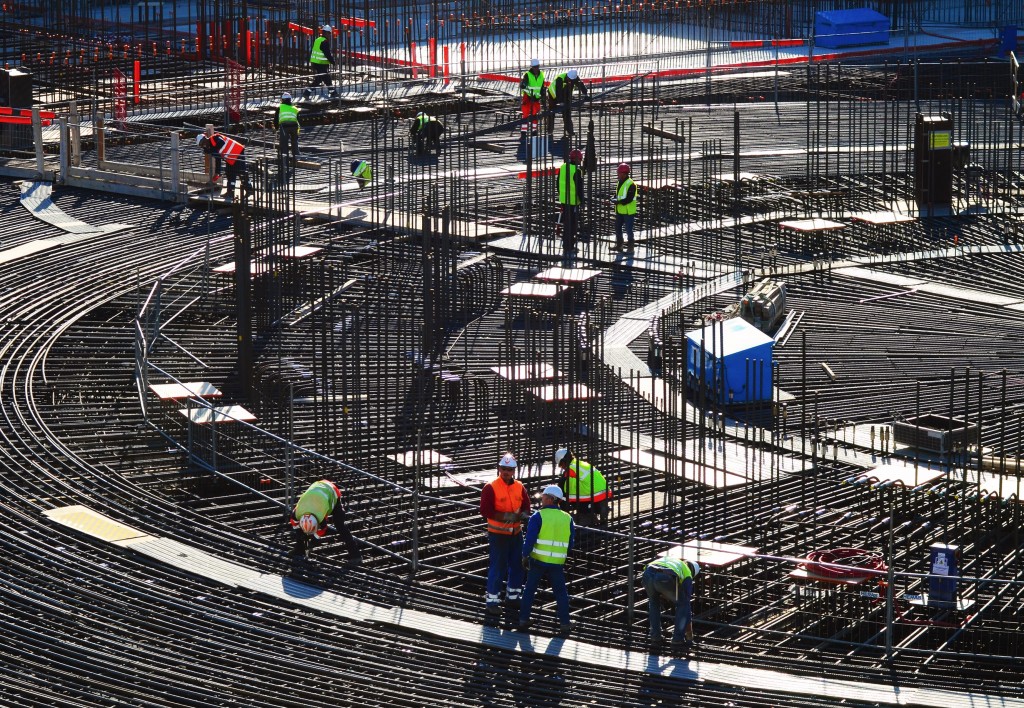
Under the future machine
2014-05-21 - The ITER machine (vacuum vessel, magnets plus cryostat) will measure 30 metres in width and as many in height. It will weigh an estimated 23,000 tonnes.
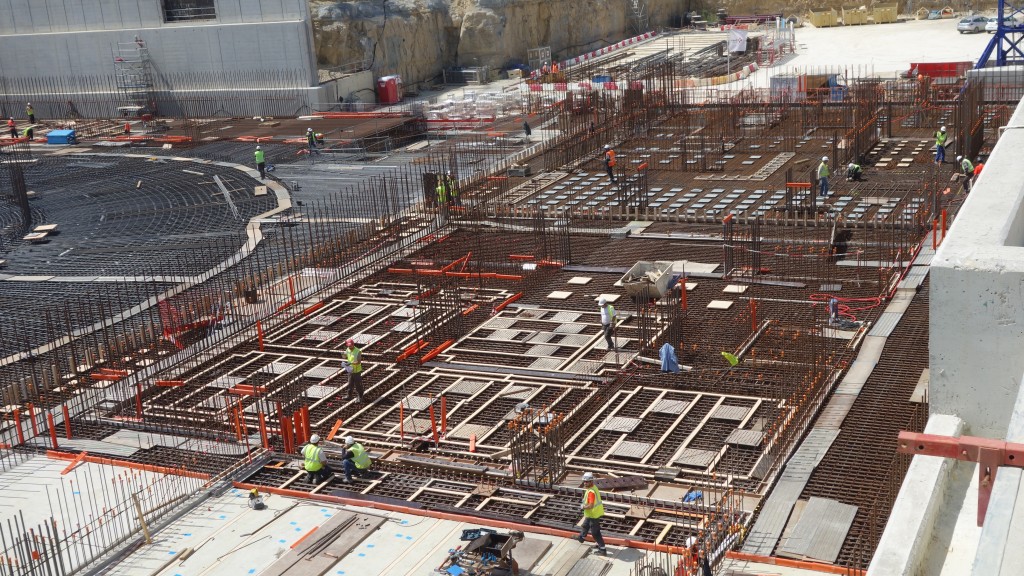
Thousands of embedded plates
2014-05-20 - Embedded plates are set into position before any concrete pouring activity can be carried out; once the buildings are in place, equipment and machinery will be welded to these plates.
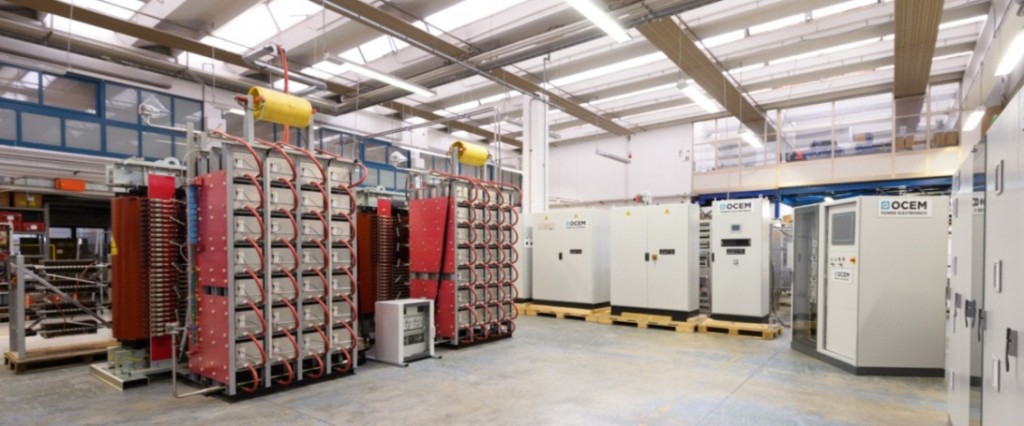
Success in factory tests
2014-05-14 - The last components of the ion source and extraction grid power supply (ISEPS) successfully pass factory acceptance tests at the supplier facility in San Giorgio di Piano, Italy (OCEM Energy Technology). The radio frequency power supplies and the DC power supply (provided by OCEM) and the radio frequency generator (provided by sub-contractor Himmelwerk from Germany) were tested on dummy load. Photo: F4E

SPIDER power supply
2014-05-14 - A schematic of the SPIDER power supply, describing the contributions of Europe (blue) and India (yellow).

All in one frame
2014-04-29 - In this shot of the ITER platform, the progress that's been made on the installation is easy to measure. In the background: the cryostat and poloidal field magnets assembly facilities; in the centre: the Tokamak Complex Seismic Pit and adjacent Assembly Building; and in the foreground: ITER Headquarters.

Playing heavy metal
2014-04-29 - Some say it looks like the largest record player in the world! Some 400,000 tonnes of building, machinery and equipment will be contained in this large concrete box called the Tokamak Complex Seismic Pit.

Construction is over
2014-04-29 - From above, the completed Cryostat Workshop (in grey) stands alongside the manufacturing facility for the poloidal field coils (in red). Work ended on the facility in April 2014 after approximately 18 months of construction. Photo: © LESENECHAL/PPV-AIX.COM
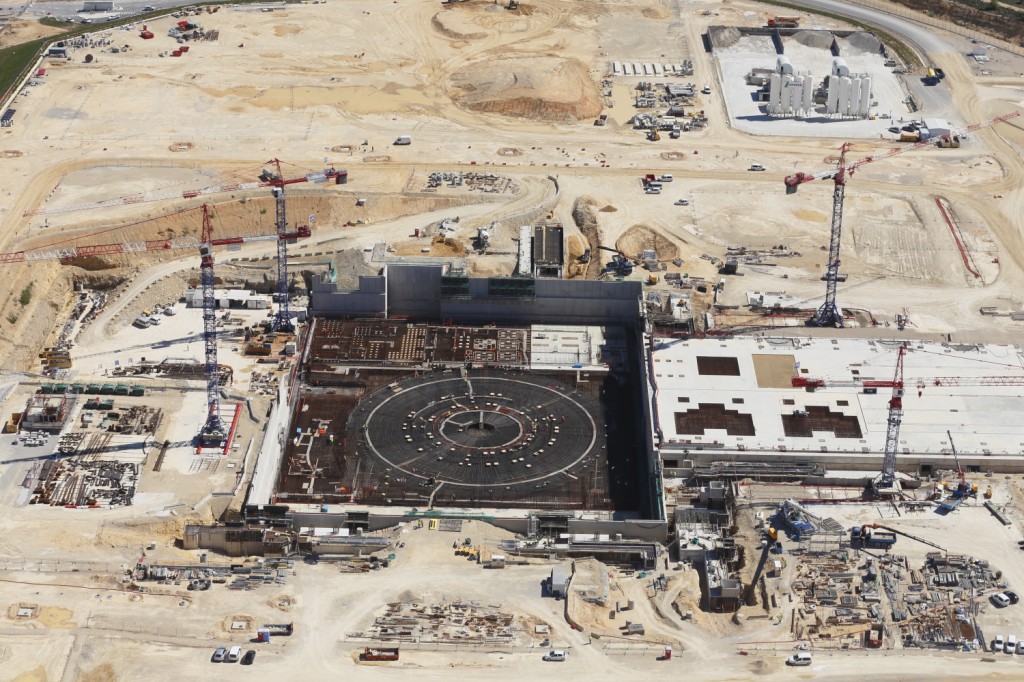
From the air in April
2014-04-29 - A late April view of work on the platform. In the projection of the Tokamak Complex Seismic Pit, the long concrete slab of the Assembly Building stands waiting (with three cut-outs for specialized assembly tooling).

Having a look at progress
2014-04-25 - The metallic super-structure is finished; the gantry crane is in place. A small delegation from the ITER Organization and the Indian Domestic Agency (which is responsible for cryostat fabrication and assembly) notes the progress accomplished on the Cryostat Workshop since building works began in June 2013.
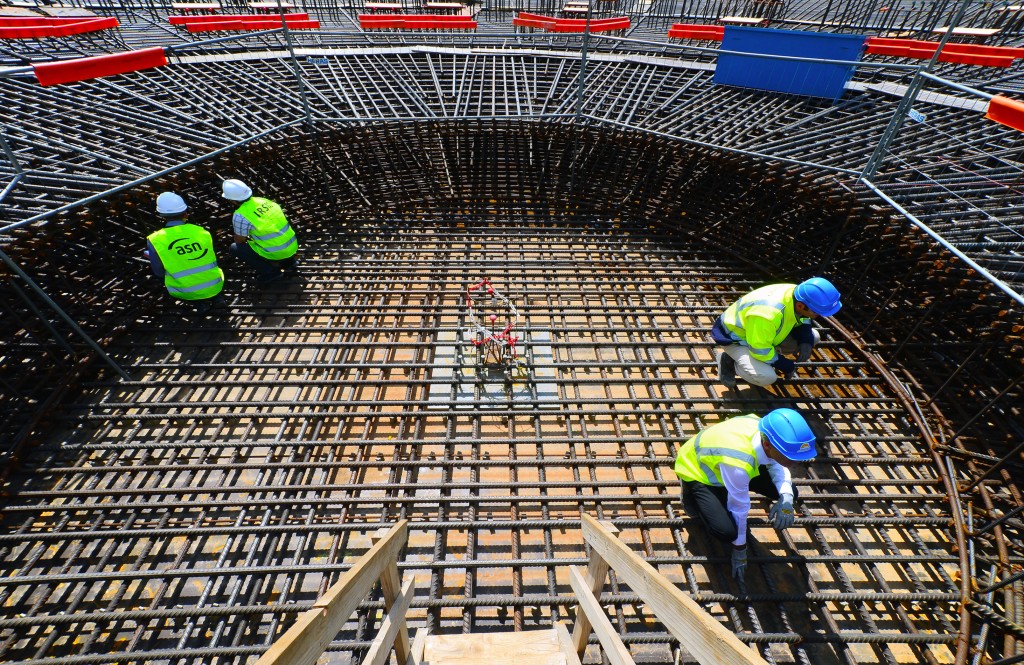
Inspectors in the heart of the web
2014-04-24 - On Thursday, 24 April, inspectors from the French Nuclear Safety Authority (ASN) carry out an inspection of ongoing reinforcement work on the Tokamak Complex basemat slab. They are pictured inspecting the very centre of the rebar web that will support the future Tokamak Building.

The most complex part of the puzzle
2014-04-21 - Some 4,000 metric tons of steel rebar will reinforce the Tokamak Complex basemat. The central part of the basemat will be poured in nine segments. Photo: F4E

Planning for pouring
2014-04-21 - In the dense rebar under the Tokamak Building, space is left every few metres for the vibrating tools that will ensure that the wet concrete reaches every nook and cranny. Photo: F4E
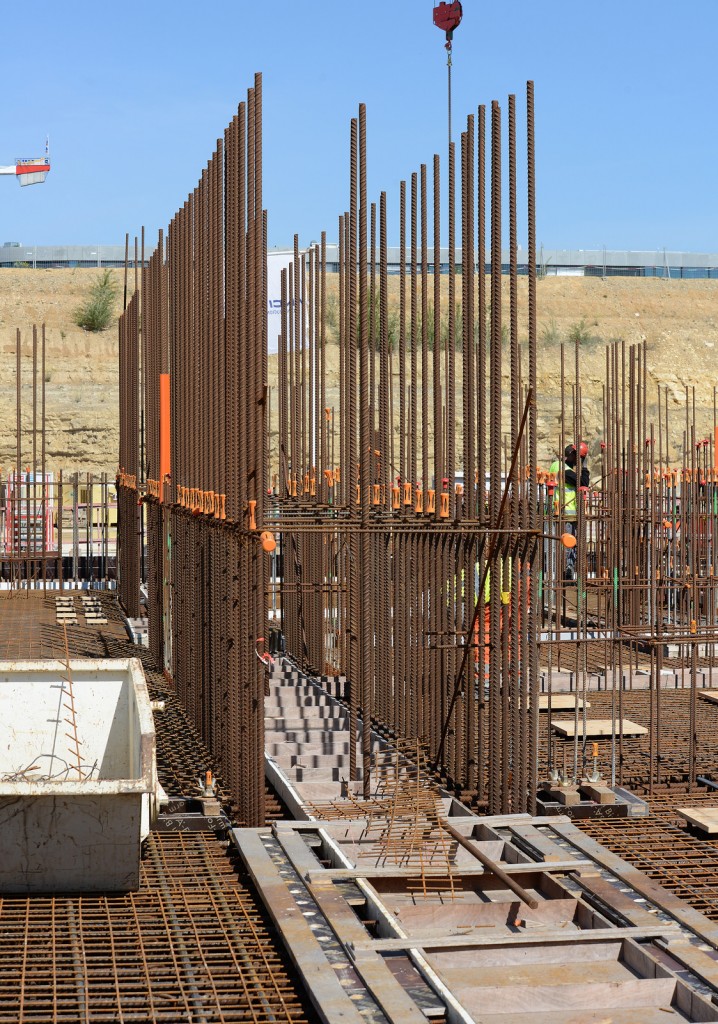
Going up!
2014-04-21 - This vertical rebar is the first set into place for the future walls of the Tokamak Complex. Photo: F4E
Inside the facility
2014-04-18 - Workers installed the main door of the SPIDER bioshield in April 2014. Photo: F4E

Final design review in India
2014-04-16 - In August, the Indian Domestic Agency hosts the final design review for the acceleration grid power supplies for SPIDER. Pictured: a 3D view of the acceleration grid power supply hall at NBTF.

Consorzio RFX hosts
2014-04-15 - The NBTF facility is going up on the premises of Consorzio RFX, an Italian research laboratory for plasma physics and controlled nuclear fusion in Padua, Italy, about 40 km west of Venice.

State of play on the worksite
2014-04-12 - Looking northwest across the site in April: in the foreground, on-site assembly facilities for the poloidal field coils (left) and the cryostat (right); in the distance, ITER Headquarters is growing by 35 metres to the left; and in the centre, three cranes indicate the location where work is advancing on the foundations for the Tokamak Complex.
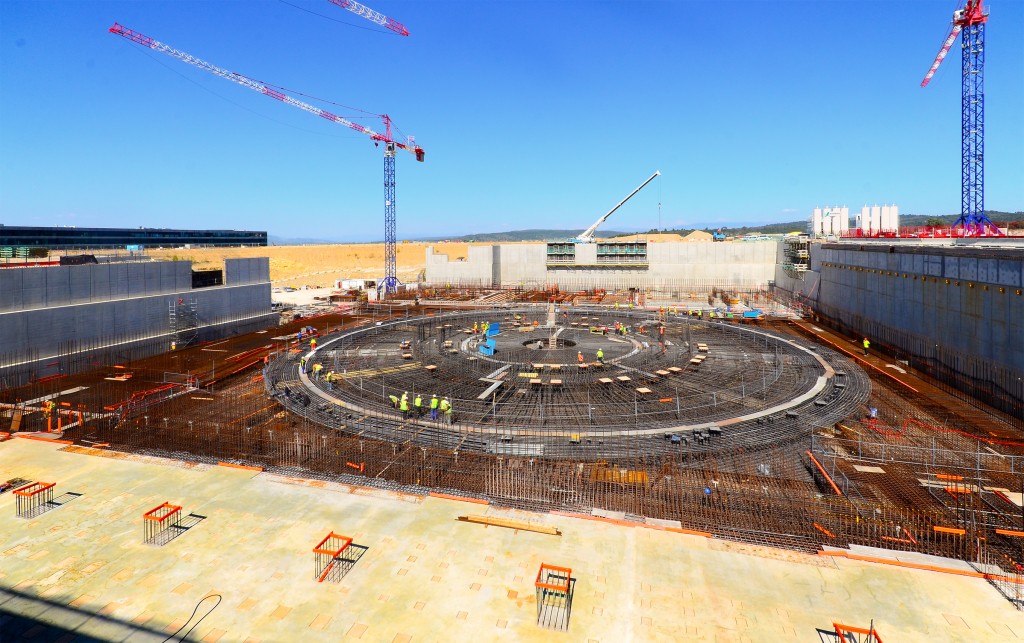
Eleven segments to a completed basemat
2014-04-10 - The Tokamak Complex basemat will be poured in fifteen segments. Pour days are scheduled this month and next to complete the Tritium Building basemat (at the far end of the Seismic Pit); rebar work in the centre should be finished in July.

Headquarters extension rises
2014-04-10 - Workers progress in April on the fourth storey of the ITER Headquarters extension. When completed this summer, an extra 350 desks will be available to staff or contractors.

Early morning Cryostat Workshop
2014-04-08 - Taken before 7:00 a.m., the completed Cryostat Workshop glows silver as the day rises. The 18-metre-tall gantry crane is now in place on the inside.

Assembly Building: heavy tools to come
2014-03-21 - The Assembly Building basemat will support the load of the heavy custom-built tools that will pre-assemble vacuum vessel components. The openings in the concrete, visible in the image, are reserved for the embedded plates that will fix the tools to the basemat.
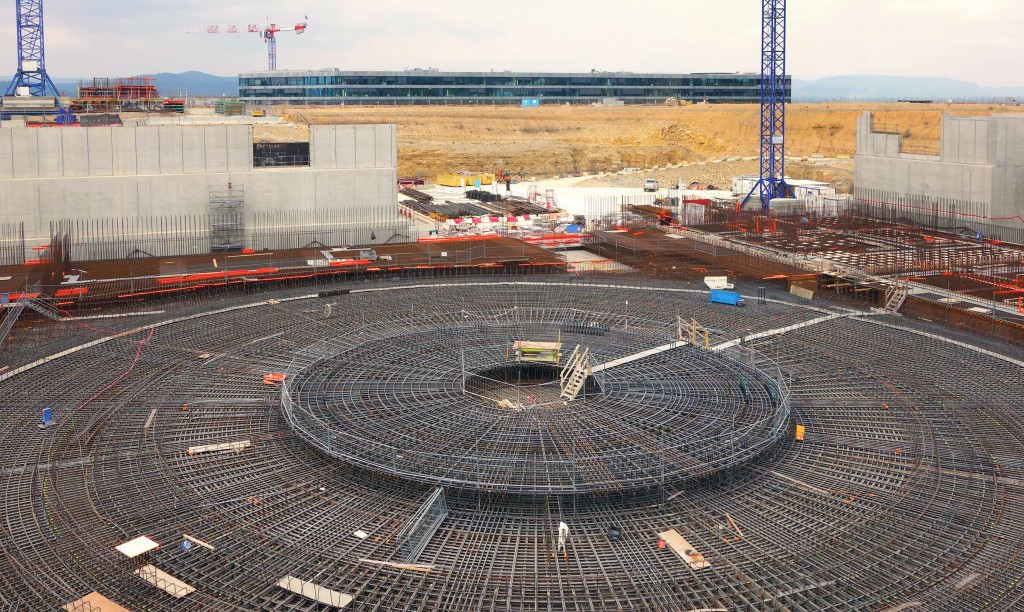
The eye of the torus
2014-03-21 - In the central area of the Tokamak Pit, a combination of orthogonal and orthodradial rebar create a particularly tight and complex pattern. As work advances, metal "chairs" are installed to separate the first layers of rebar from the top layers.
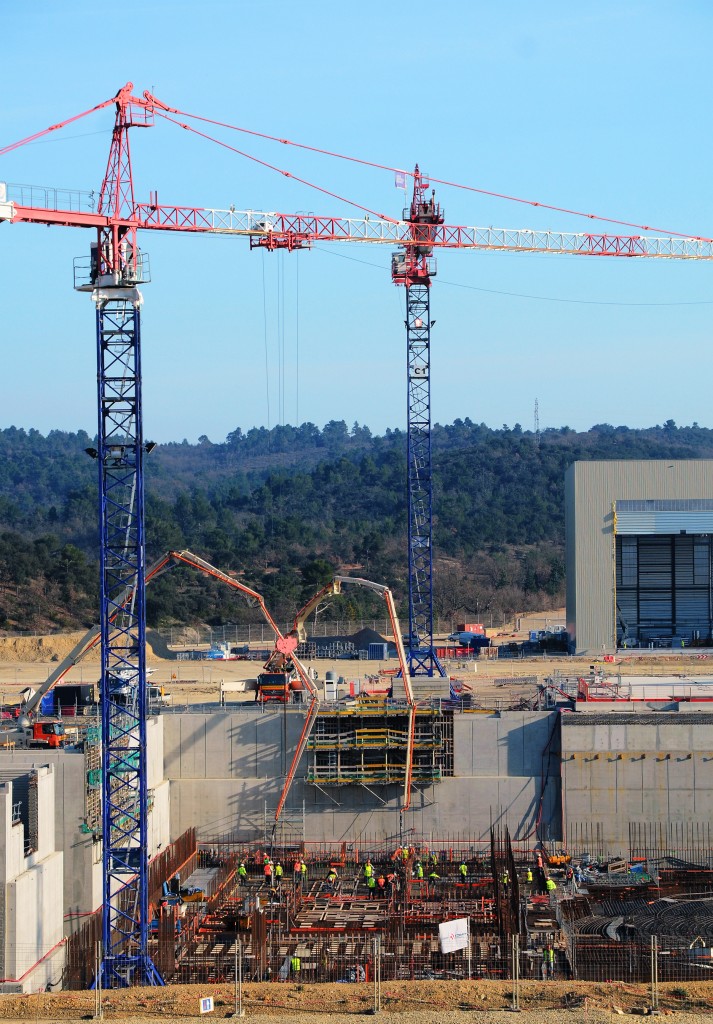
Let's switch sides!
2014-03-19 - Concrete is poured on 19 March in the northeast corner of the Tokamak Pit. This fourth segment (638 square metres, 957 cubic metres of concrete) is the first part of the Tritium Building basemat to be poured.

The exit doors
2014-03-19 - After assembly, the large sections of the cryostat will leave the Workshop through the large door on the west facade for transportation to the Tokamak Pit.
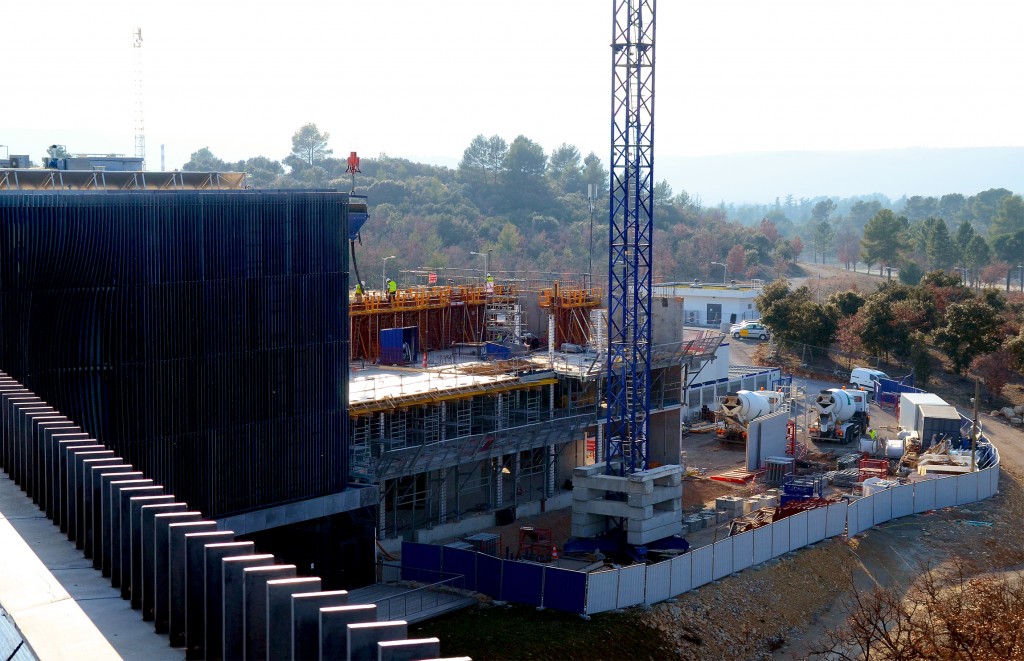
Going up!
2014-03-19 - From the roof of the main building, it's easy to follow the progress of the Headquarters extension in March.
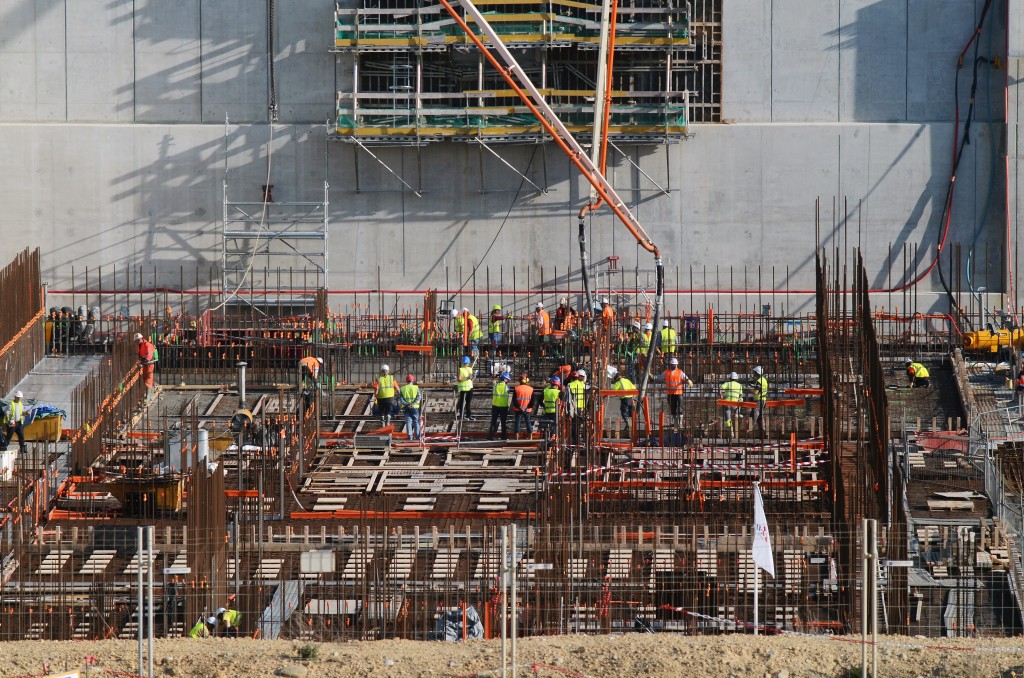
Progress on the basemat
2014-03-19 - The fourth pour day for the Tokamak Complex basemat was carried out on 19 March. Pouring has begun for the Tritium Building basemat on the north end of the Pit.

Where orthoradial and orthogonal meet
2014-03-04 - Under the future Tokamak, crisscrossed layers of orthoradial (circular) and orthogonal (right-angled) rebar form a pleasing geometric pattern.

Maintaining a clean surface
2014-03-04 - On the completed Diagnostics Building basemat, pressurized air is used to keep the surface clean. The cages in the picture mark out the pillars that will be poured to support the second floor of the building.
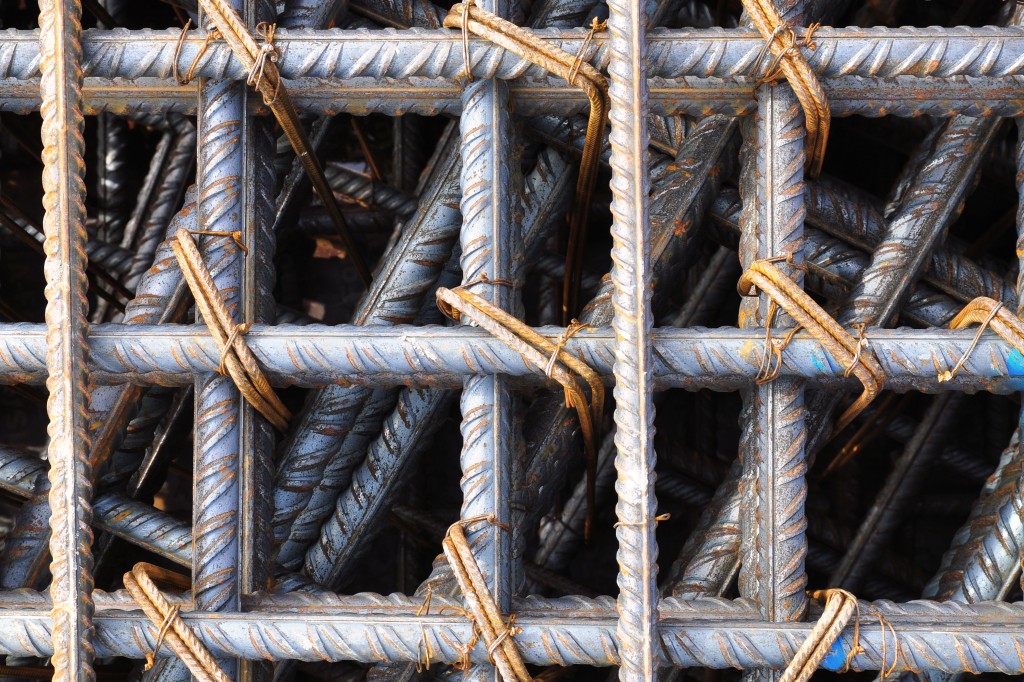
Rebar grid
2014-03-04 - A close-up view of the dense rebar that is being laid for the Tokamak Complex basemat.
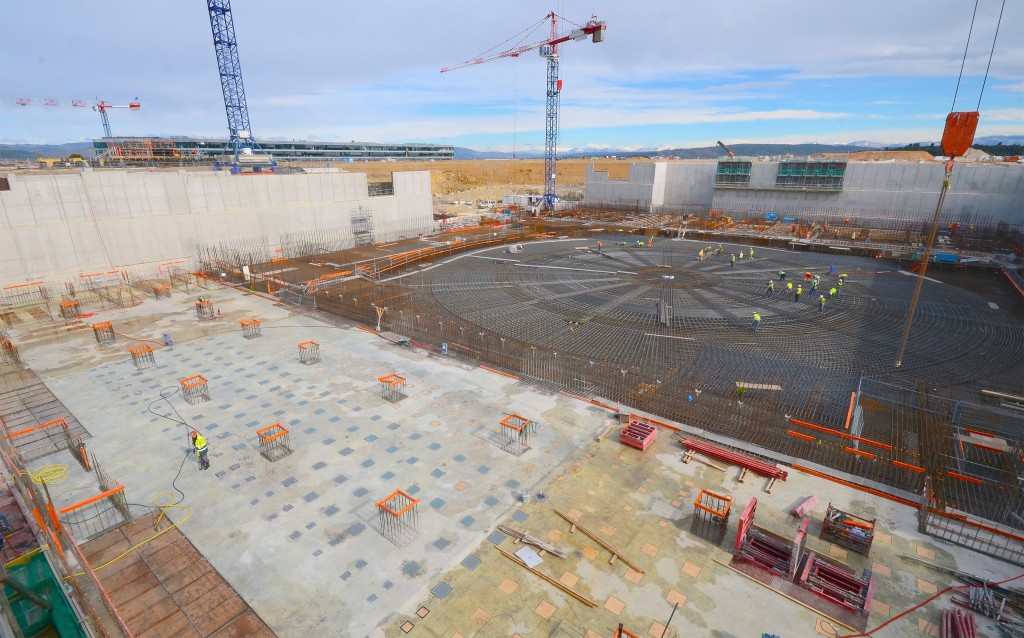
Diagnostics Building basemat
2014-03-04 - The completed basemat for the Diagnostics Building now stands 1.5 metres over the rebar of the central section. By next autumn, the floor of the Tokamak Complex will be in place.
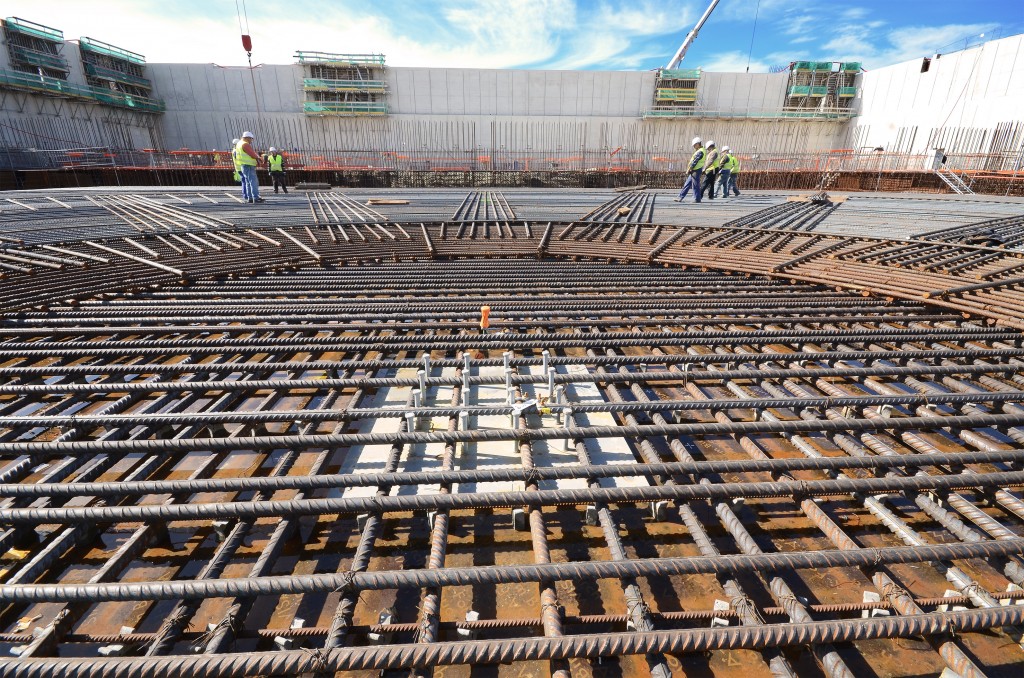
Spot in the middle
2014-03-04 - In the very centre of the Seismic Pit stands the last viewable seismic pad. The Tokamak Complex will rest on 493 such pads, part of the measures that will protect the scientific infrastructure in the case of ground motion.

A 1:1-scale mockup for Tokamak basemat reinforcement
2014-03-04 - This mockup of Tokamak basemat reinforcement is being prepared for concrete. Because of the complexity and density of rebar in the region under the Tokamak, concrete pouring is a complex operation that will be tested first here.
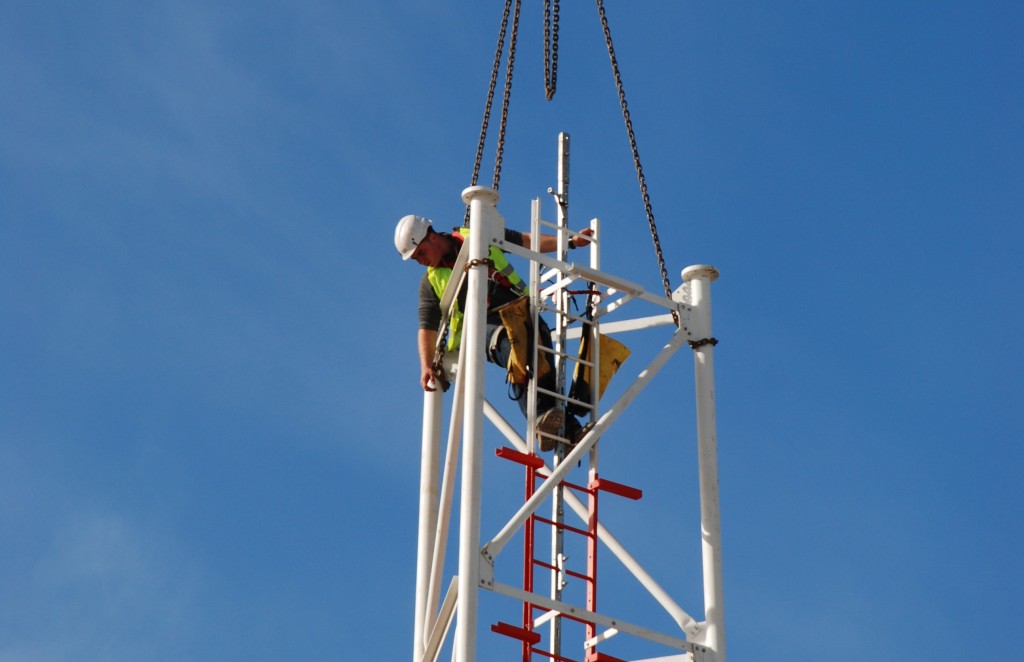
Acrobatic work
2014-03-01 - Early in 2014 a telecommunications tower was installed on the ITER site, equipped with 2G and 3G technologies.
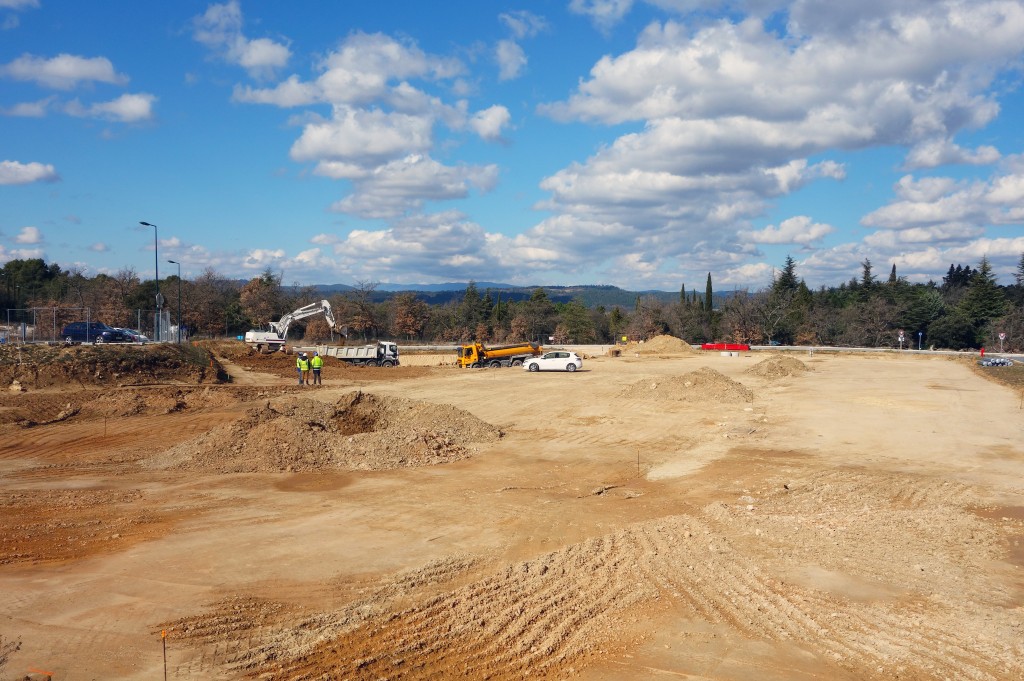
Storage facility at ITER entrance
2014-03-01 - Work is currently underway to level a vacant lot at the entrance of Headquarters in order to build a 6,000 m² storage area.
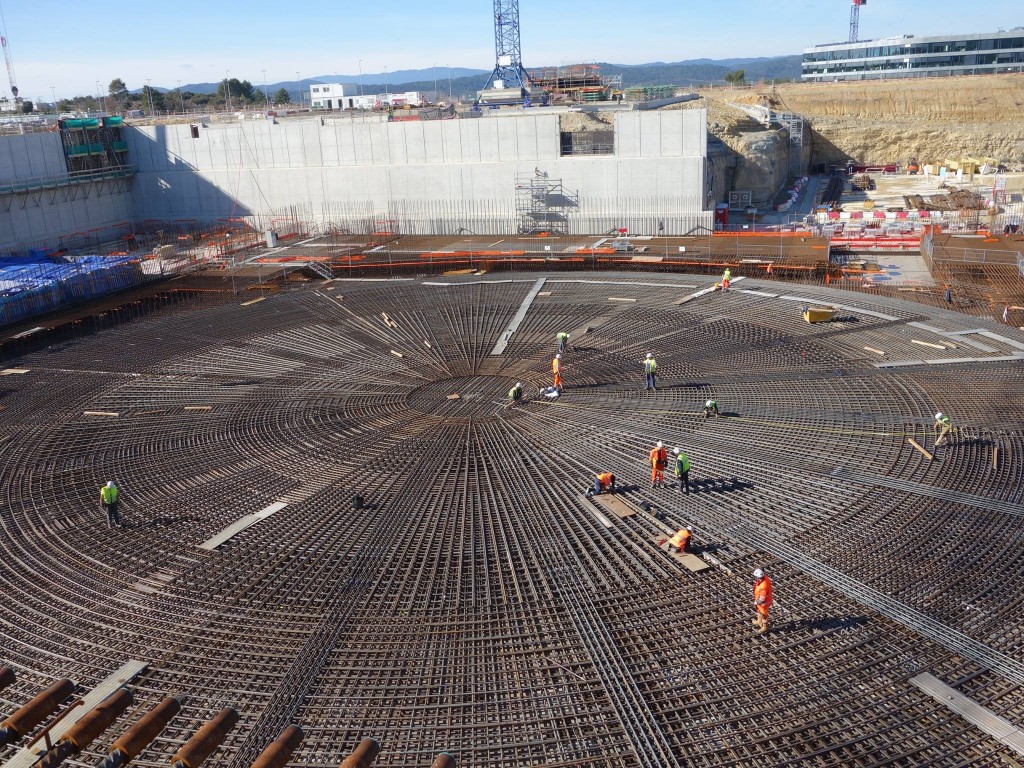
The Pit in February
2014-02-27 - In February, work on the rebar arrangement in the centre of the Tokamak Pit--that will support the machine--resumes. Sixteen layers of orthoradial (circular) and orthogonal (right-angled) rebar will be integrated into the 1.5-metre-thick basemat.
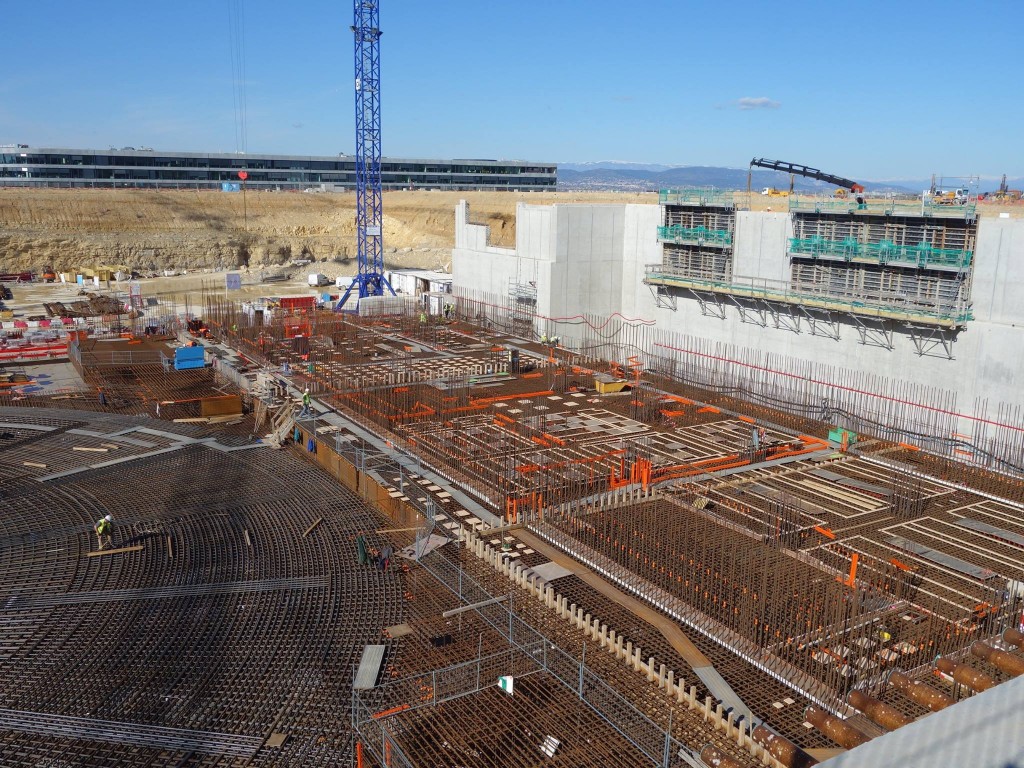
Getting ready to pour the foundations of the Tritium Building
2014-02-26 - The next area of the B2 slab to be poured is on the north side of the Seismic Pit under the Tritium Building. Just like for the Diagnostics Building, pouring will take place in three stages (beginning in March).
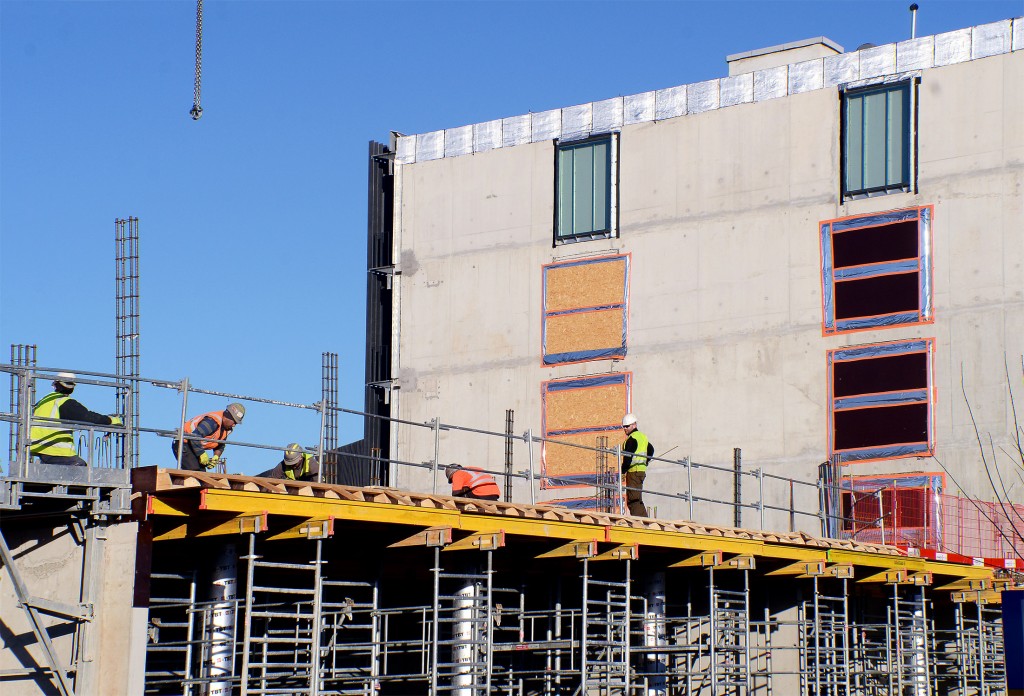
Structure begins to rise
2014-02-24 - Work is underway on the first floor of the extension to Headquarters. At a rate of approximately one storey every three weeks, the five-storey structure will be framed out by late May.

A sea of iron
2014-02-19 - Reinforcement works should continue in the Tokamak Pit through July. Some 4,000 tonnes of iron rebar will be part of the Tokamak Complex slab. Photo: F4E
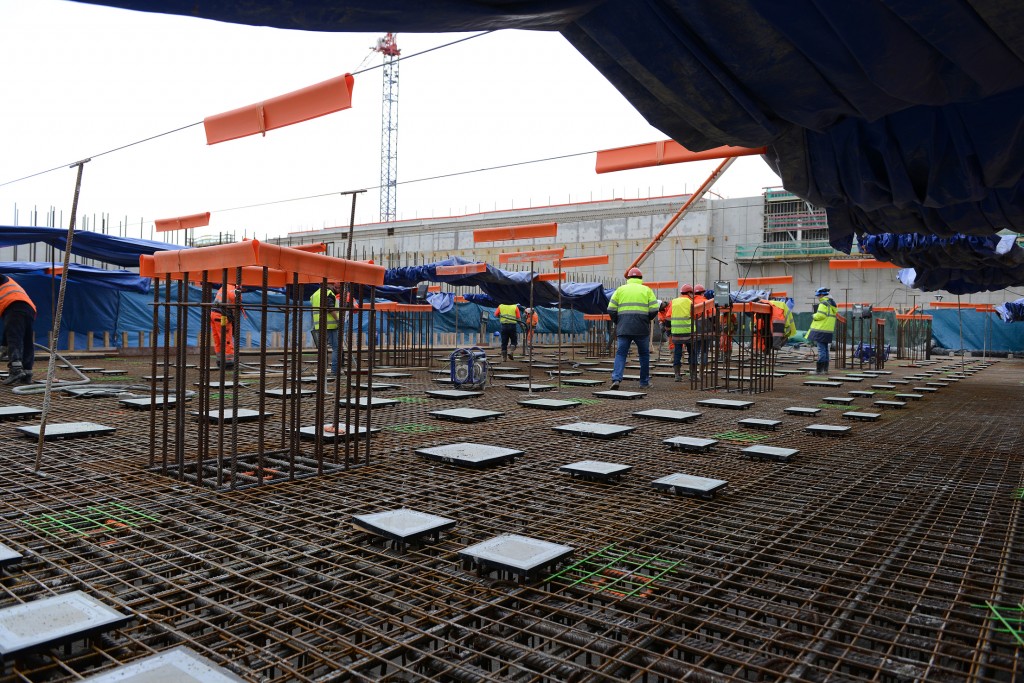
Standing on the rebar
2014-02-15 - On the Diagnostic Building side of the Tokamak Pit, work to prepare for a concrete pour is underway. The squares at ground level are the embedded plates that will be used to fix equipment and machinery in the completed structure. Photo: F4E
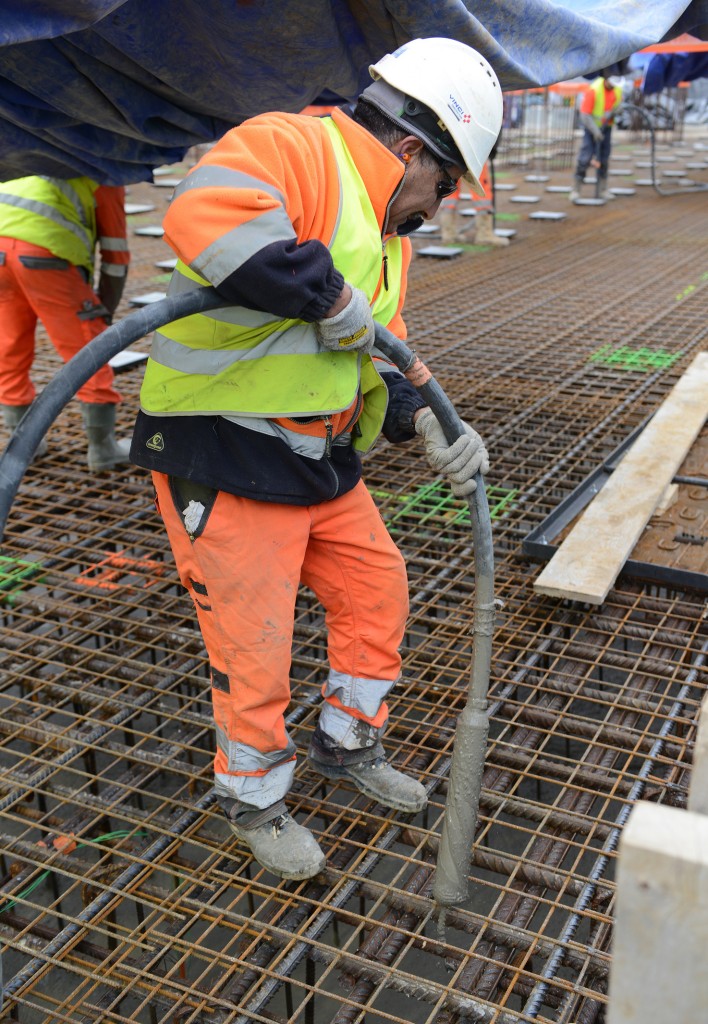
A full day of work
2014-02-15 - As concrete is poured in February for the Diagnostics Building basemat, workers use equipment to ensure that the material settles uniformly, without air pockets. Photo: F4E

Looking west
2014-02-15 - The tall crane allows us to imagine the height of the future Tokamak Complex: 60 metres. Photo: F4E
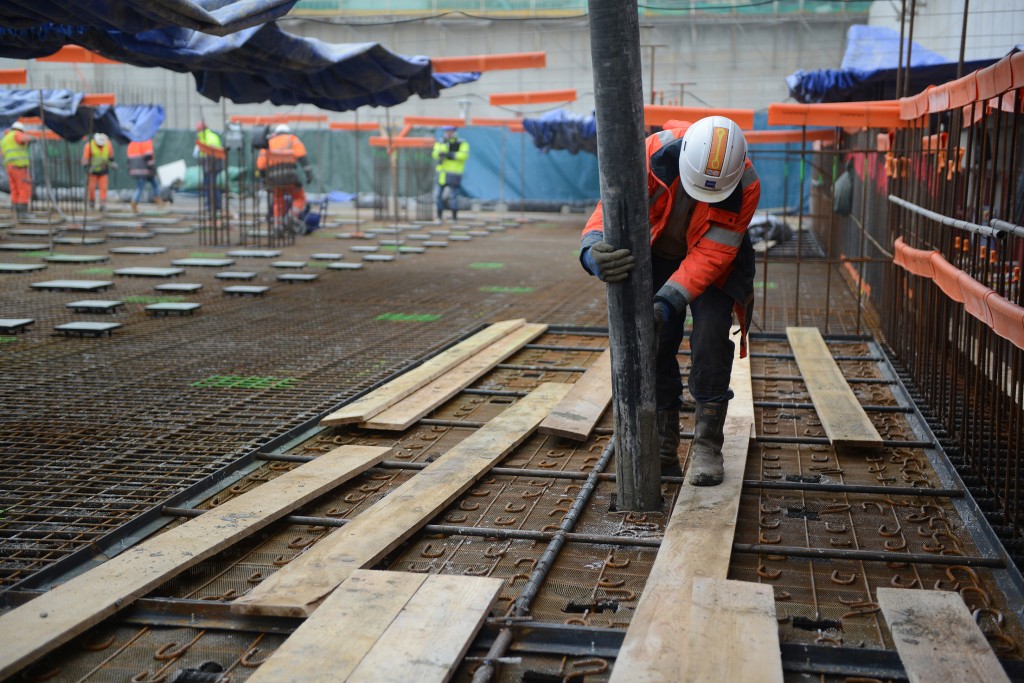
Last pour for the Diagnostics Building
2014-02-15 - The final segment poured on the south side of the Tokamak Pit measures 600 square metres (900 cubic metres of concrete). Photo: F4E
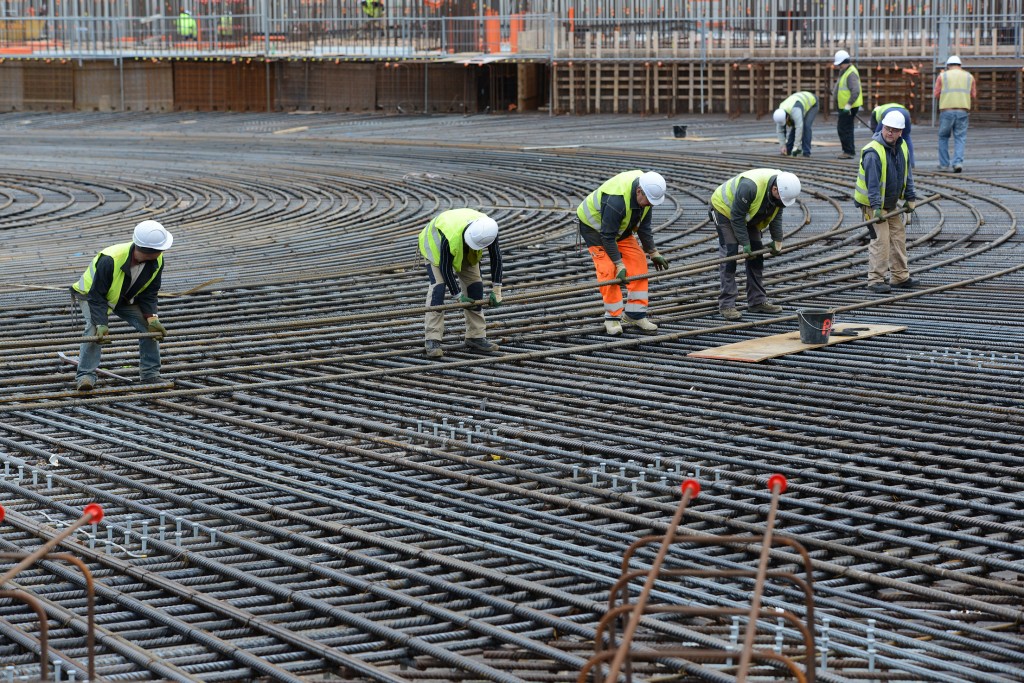
Heave ho!
2014-02-15 - Alternate layers of rebar—circular or radial—are set into place under the future ITER machine. Photo: F4E
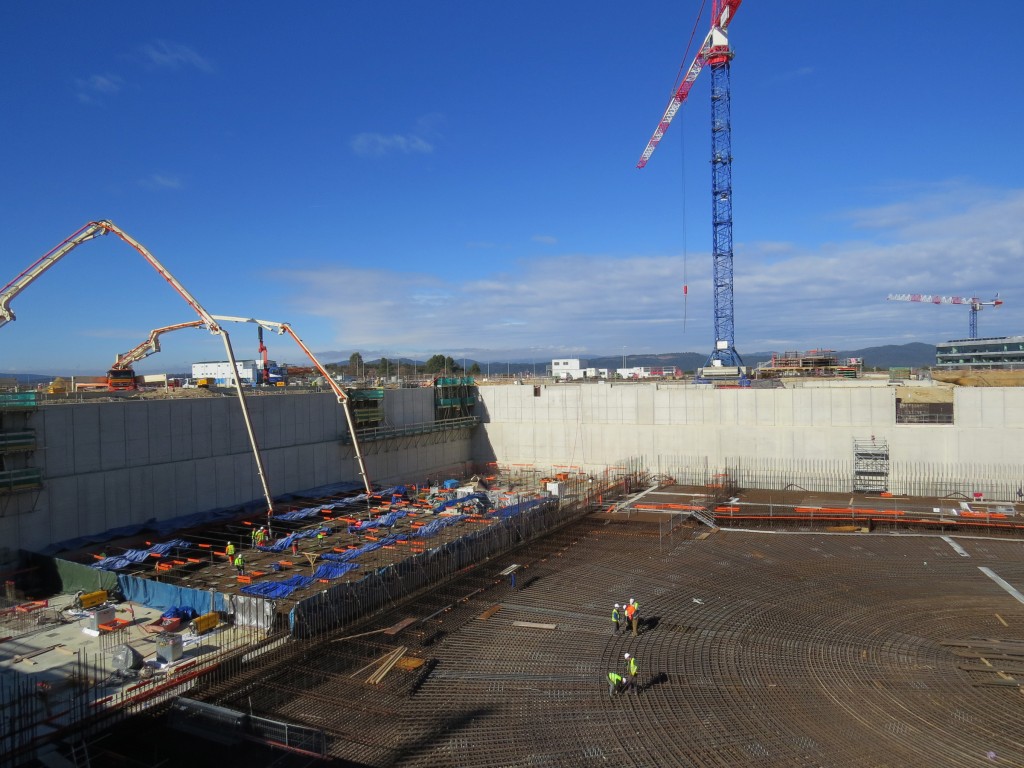
Pouring completed for Diagnostics Building basemat
2014-02-13 - On Thursday 13 February, the third and final segment of the Diagnostics Building basemat was successfully poured. Concrete pouring activities will continue in March on the opposite end of the Seismic Pit, under the future Tritium Building. Photo: ENGAGE
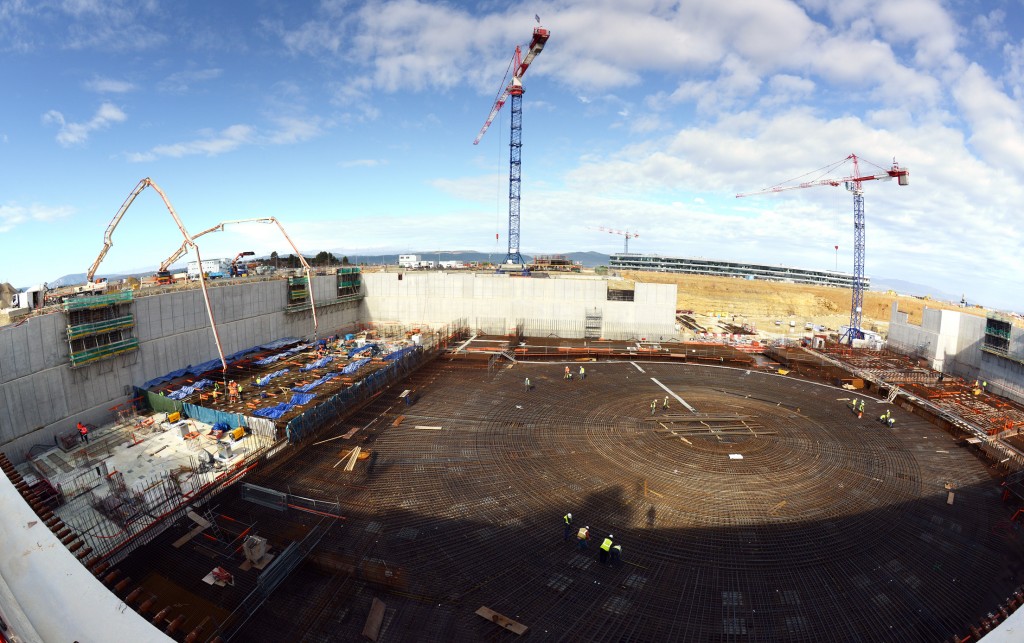
Where the action is happening
2014-02-13 - A wide angle lens captures nearly the entire Tokamak Pit. Photo: F4E
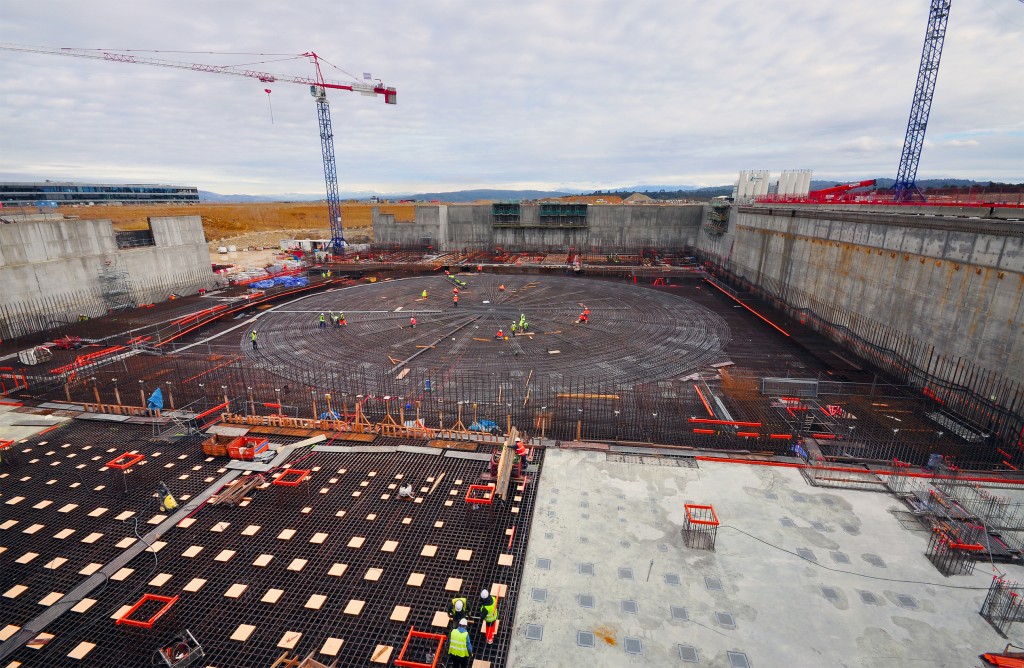
Looking north
2014-02-12 - Three distinct work areas are visible in February in the 90 x 130 metre Seismic Pit: in the foreground, the beginning of concrete works for the Diagnostic Building slab; at the far end, ongoing reinforcement works for the Tritium Building slab; and in the centre, the positioning of rebar layers (16 in all) under the future Tokamak Building.

Assembly Building: walls will rise in June
2014-02-12 - Work on the steel frame of the Assembly Building is scheduled to begin in early July.
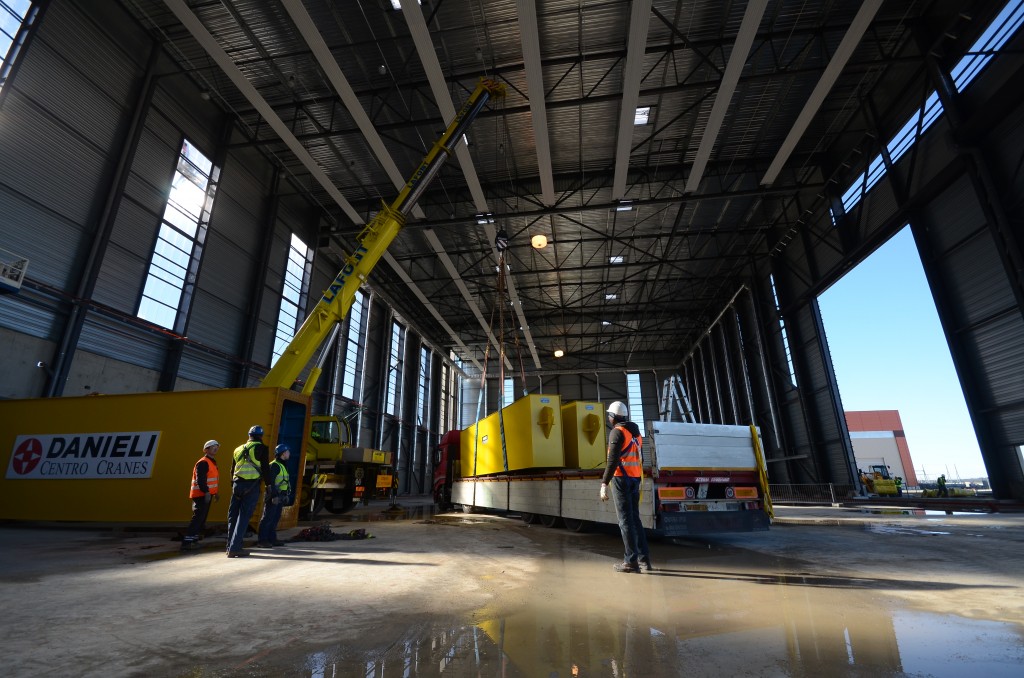
Equipping the interior
2014-02-12 - On 12 February 2014, nine months after construction began on ITER's on-site Cryostat Workshop, the first elements of the workshop's gantry crane were delivered to the ITER site.

Phase one of the Headquarters extension successfully completed
2014-02-12 - We can't see them yet, but soon the first-storey walls of the Headquarters extension will be visible from the platform. The concrete basemat for the 3,500 m² extension was poured on 30 January, marking the end of the foundation work phase. Work has begun on the walls; the complete exterior shell should be in place in June.
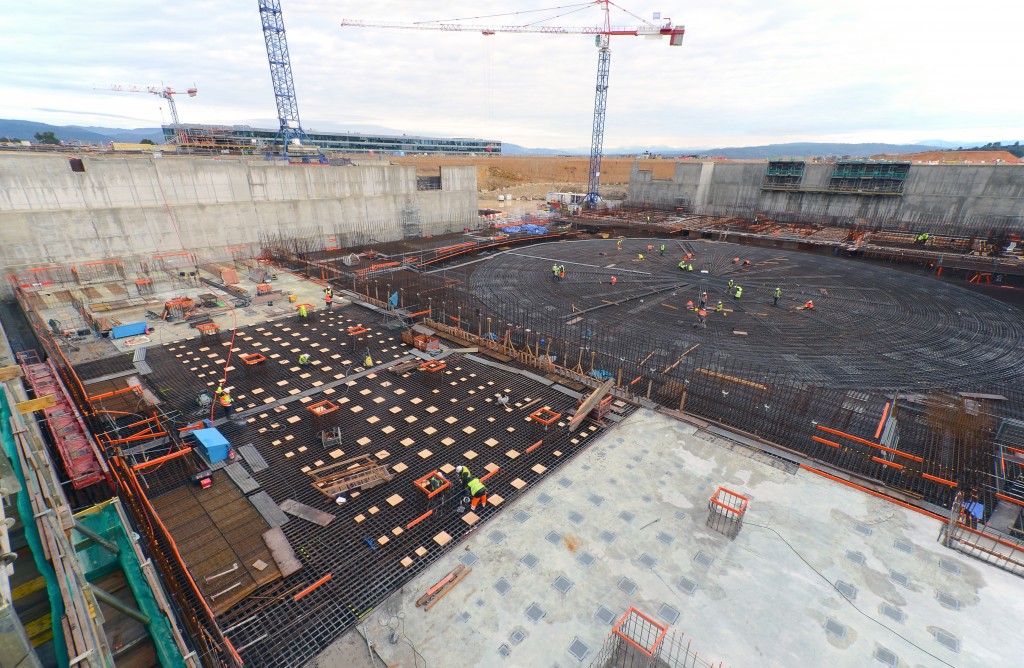
Progress on the basemat
2014-02-03 - On the southern end of the Seismic Pit, two of the three basemat segments are in place and the third will be filled in mid-February. Concrete pouring activity will then be transferred to the opposite side.
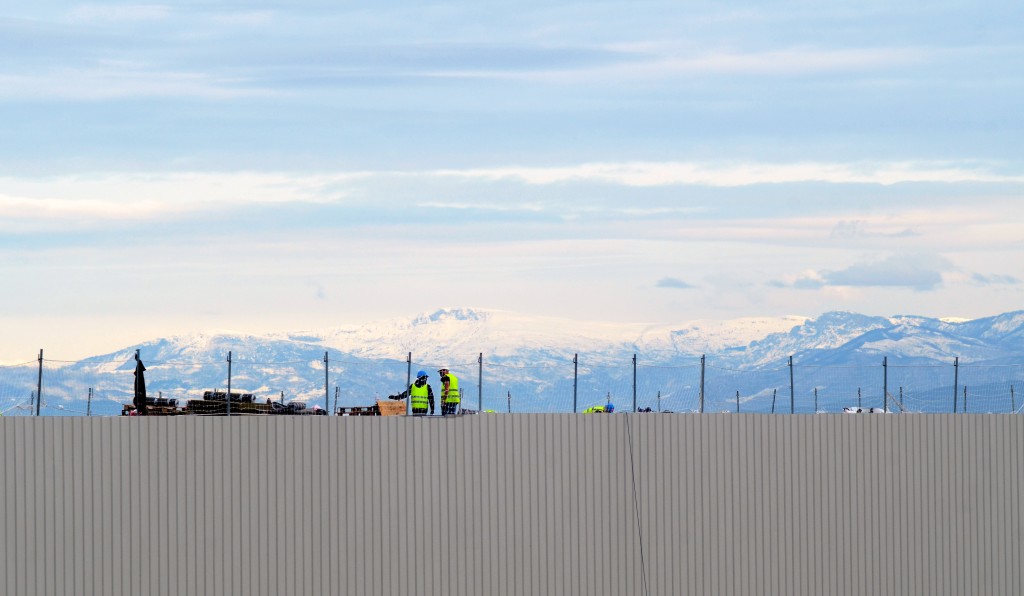
Completing the Cryostat Workshop cladding
2014-02-03 - Against the backdrop of the snowy pre-Alps, workers on the roof of the Cryostat Workshop in February position large pieces of aluminum cladding.

Careful calculations
2014-02-03 - Each iron bar, weighing nearly 100 kilos, is carefully laid and affixed.
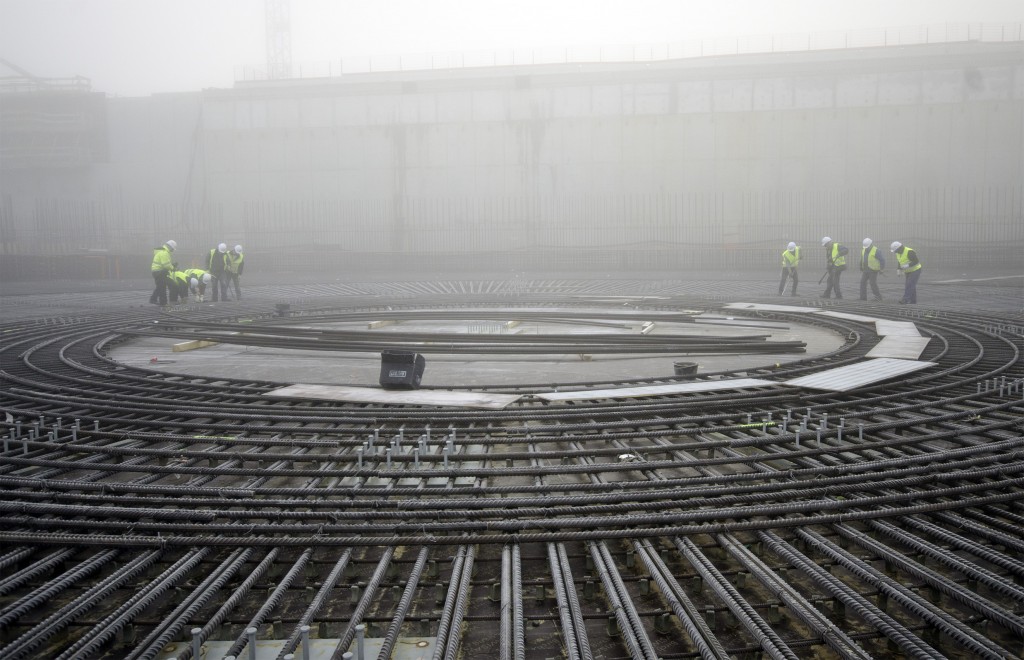
Reinforcement work resumes
2014-01-28 - In the centre of the Seismic Pit, under the future Tokamak, work resumed on the complex pattern of steel reinforcement bars.
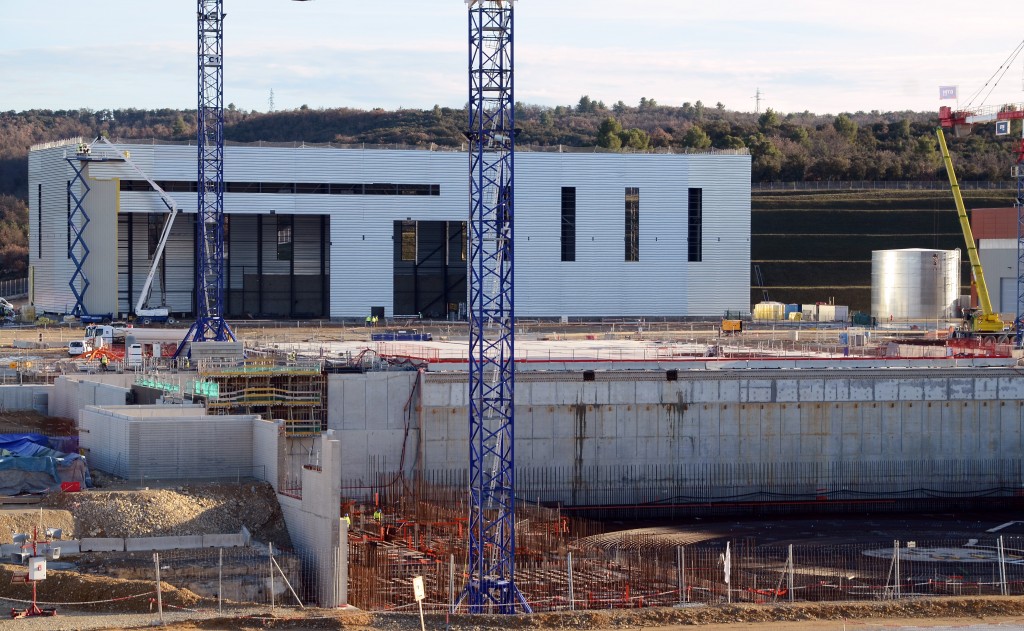
Four large segments
2014-01-28 - The four ITER cryostat segments—with a diameter of 30 metres each—will leave the facility by the great door on the left to be positioned in the Tokamak Building.
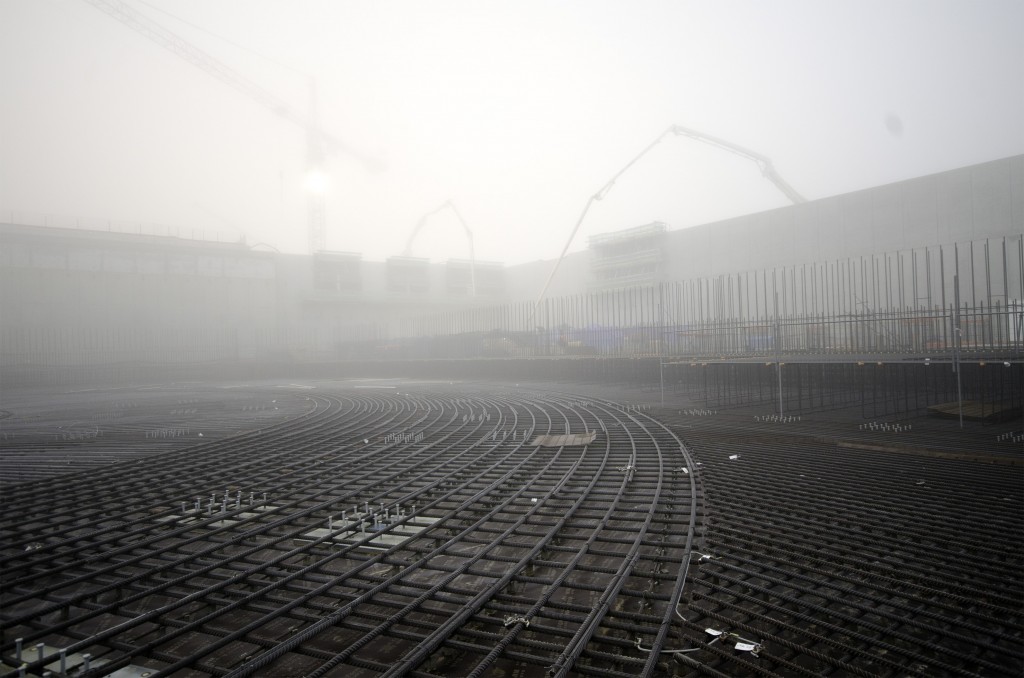
Early morning fog
2014-01-22 - The raised reinforcement along the Seismic Pit wall that we can just distinguish to the right will on day support the load of the Diagnostics Building. A third and final pour will complete this part of the basemat.
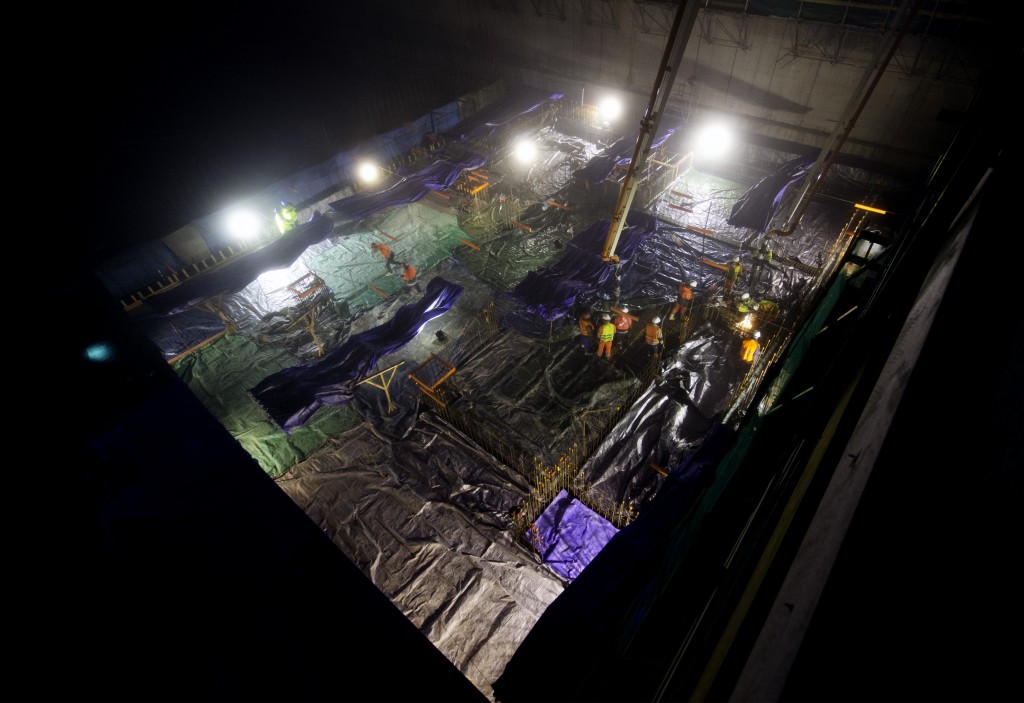
Second segment of basemat completed
2014-01-22 - On 22 January 2014, the second of fifteen Tokamak Complex basemat segments was poured over a ten-hour shift starting at 6:00 a.m. All work should be completed in July.
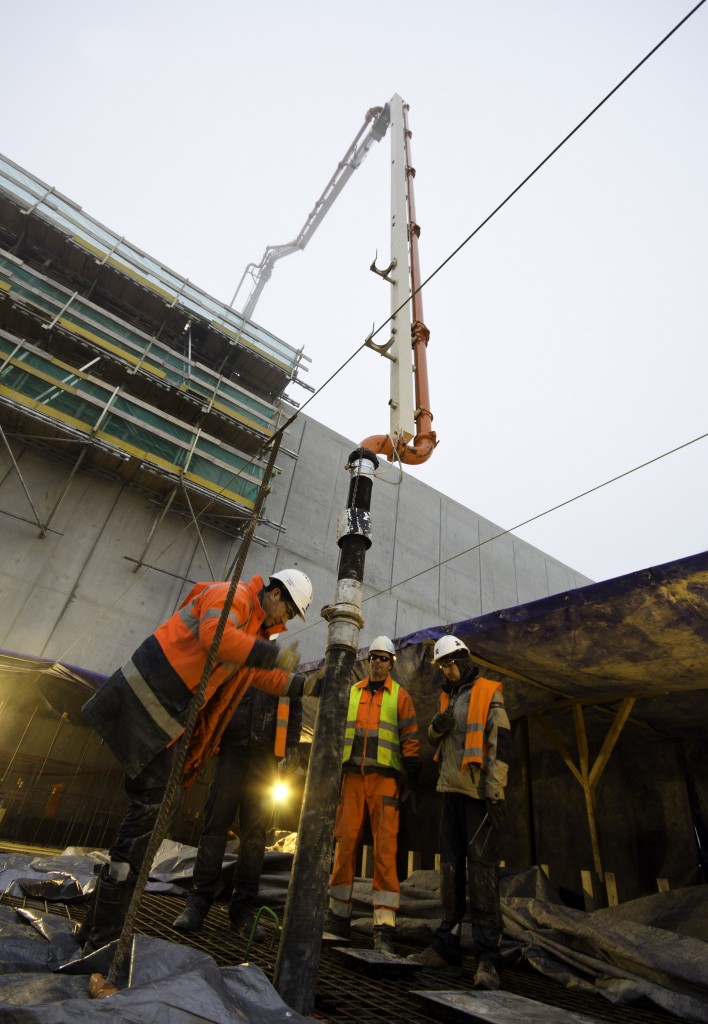
Pouring on a cold day
2014-01-22 - The concrete is still warm when it arrives at its destination, having lost only a couple of degrees Celsius during transport. The concrete is made with heated water and gravel in the on-site batching plant and leaves the facility at 14-17 °C.

Reaching over the galleries
2014-01-22 - In the shadow, an example of the galleries that surround the Tokamak Complex. Pipes, cable trays and ducts servicing the machine will be housed here.
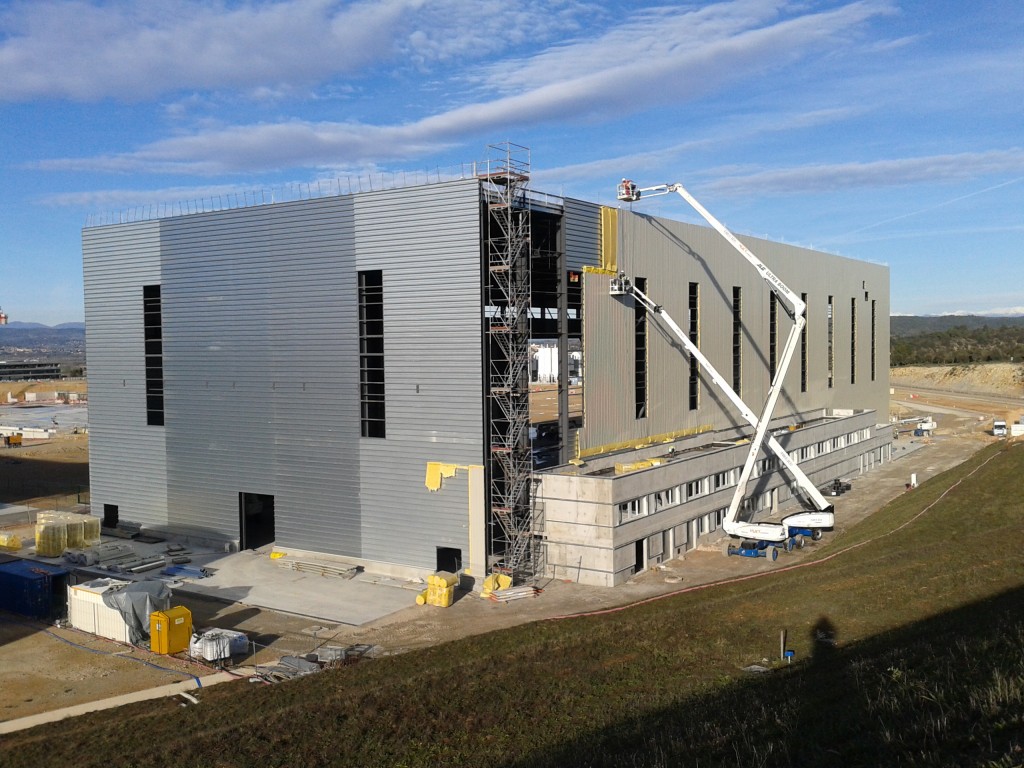
Assembling a giant component
2014-01-15 - The vacuum container that will surround the tokamak and the magnets (the ITER cryostat) will be approximately 30 metres tall and 30 metres wide. Four large segments will be assembled in this on-site workshop.
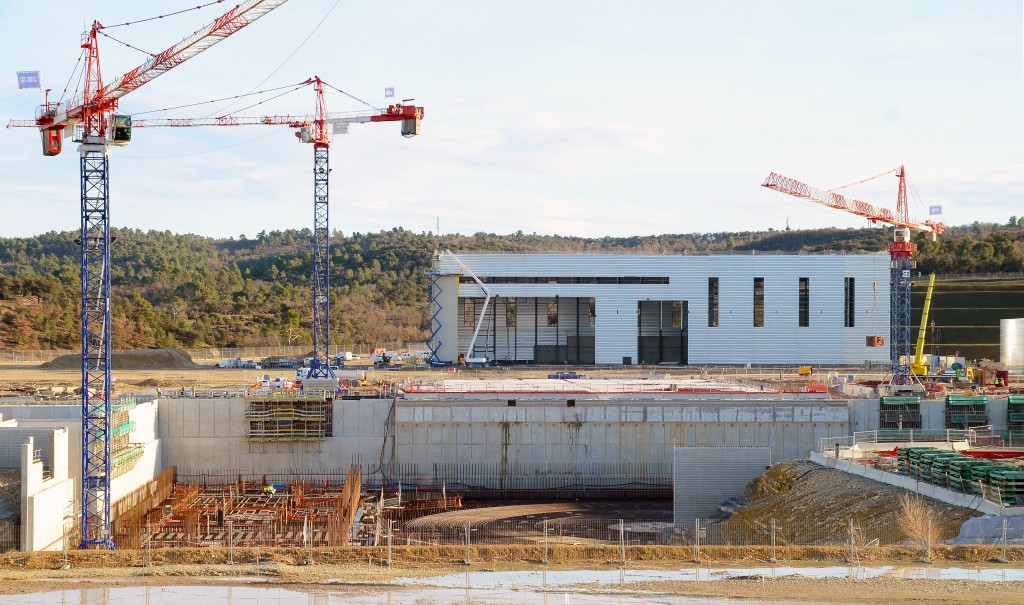
And on the left ...
2014-01-15 - It's easy to distinguish the reinforcement going on for the Tritium Building, which will occupy the left side of the Seismic Pit, from the reinforcement that will support the weight of the ITER Tokamak and Tokamak Building (centre).
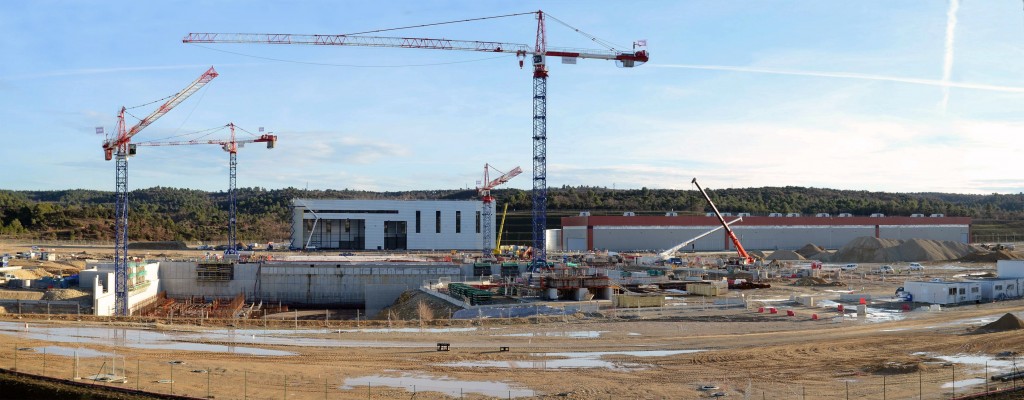
The tallest building on the platform ... for the moment
2014-01-15 - The Cryostat Workshop (left) takes its place next to the Poloidal Field Coils Winding Facility as the second structure on the ITER platform. A total of 39 buildings or technical areas are planned in all.
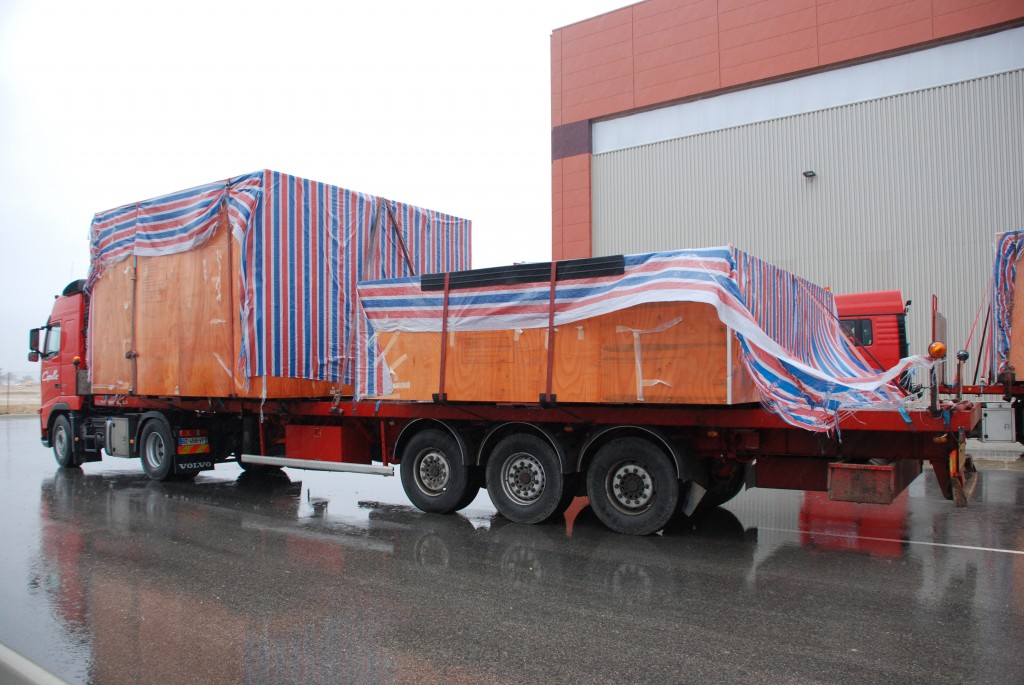
Delivery from China
2014-01-13 - Following a first convoy in June 2013, a second delivery of qualification conductors from China reached the Poloidal Field Coils Winding Facility on 17 January. This material will be used for cabling and coil manufacturing process qualification.
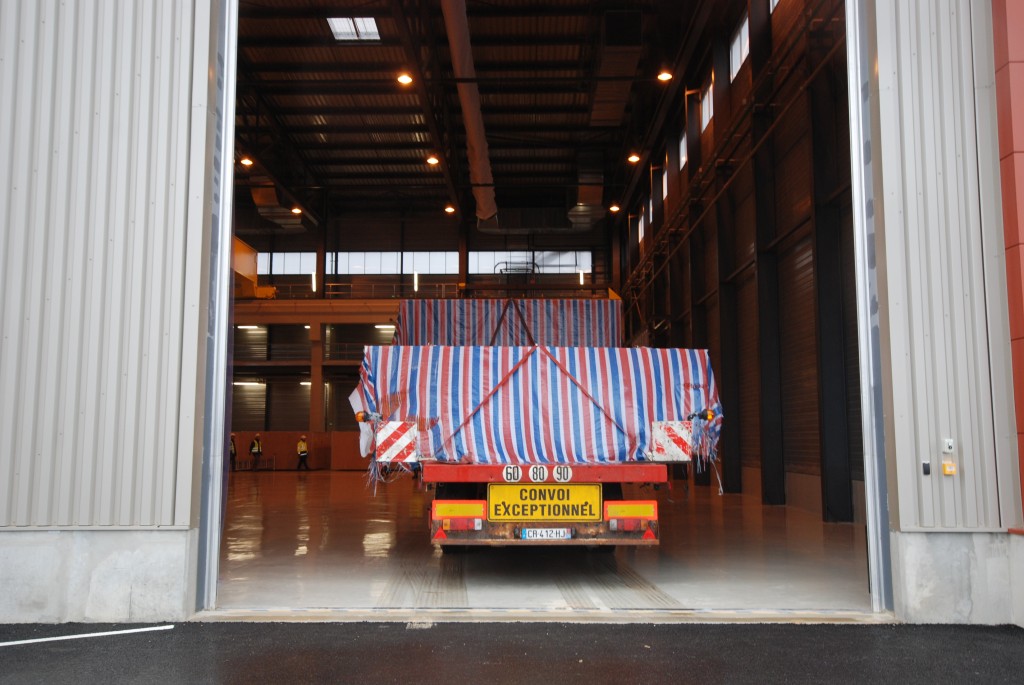
The doors open
2014-01-13 - Conductor for the commissioning of the Winding Facility enters through the north door. It will be stored until the manufacturing line for the poloidal field coils is in place.
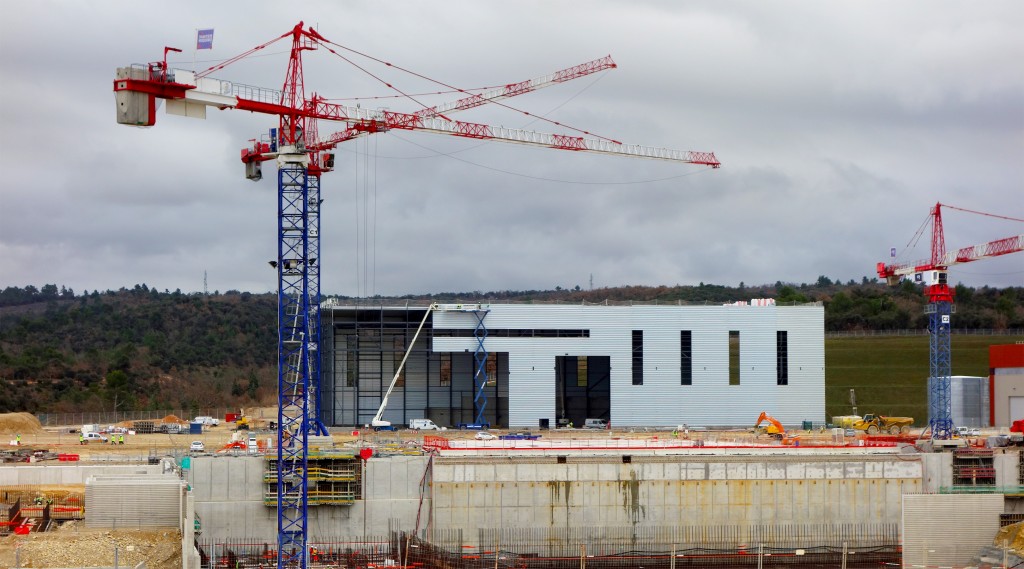
The platform is changing
2014-01-07 - As cladding progressively covers the metallic structure of the Cryostat Workshop, it becomes one of the most visible features of the ITER platform.
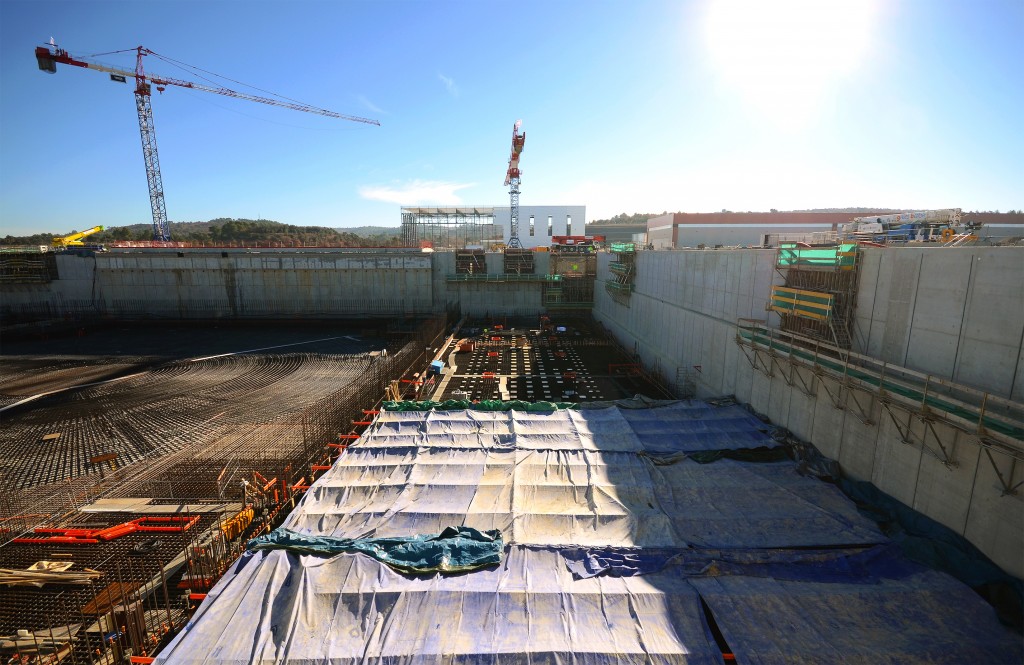
First B2 segment in place
2013-12-17 - Under the blue drying tents, the first 21 x 26 metre segment is in place for the Tokamak Complex basemat slab (the B2 slab). The next pour is scheduled for early 2014.
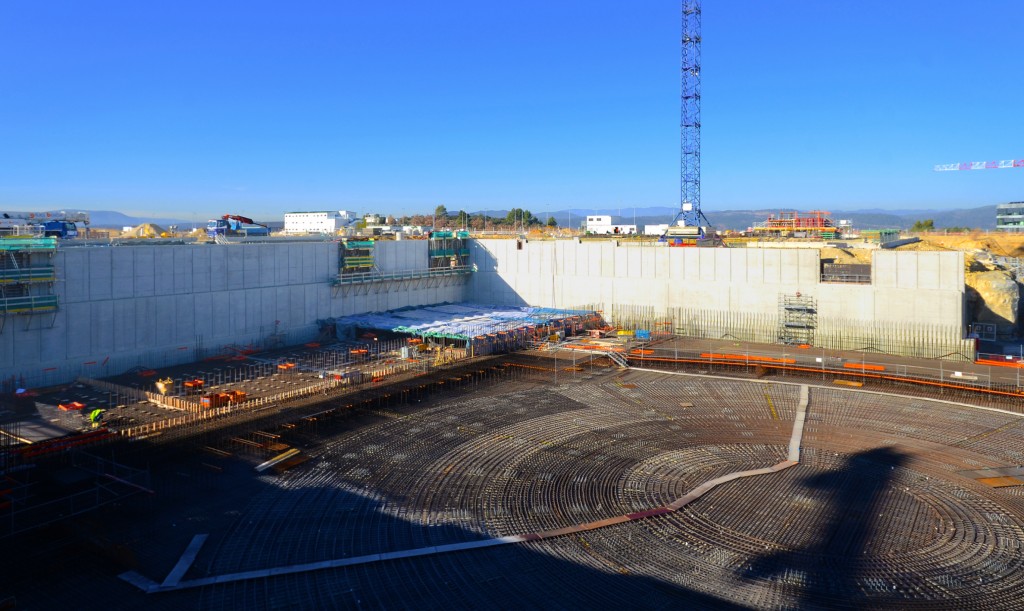
One down, fourteen to go
2013-12-17 - The first concrete pour took place under the future Diagnostics Building, part of the three-building Tokamak Complex. Fifteen pour days in all will be necessary to complete the B2 slab; then, the walls will begin to rise.
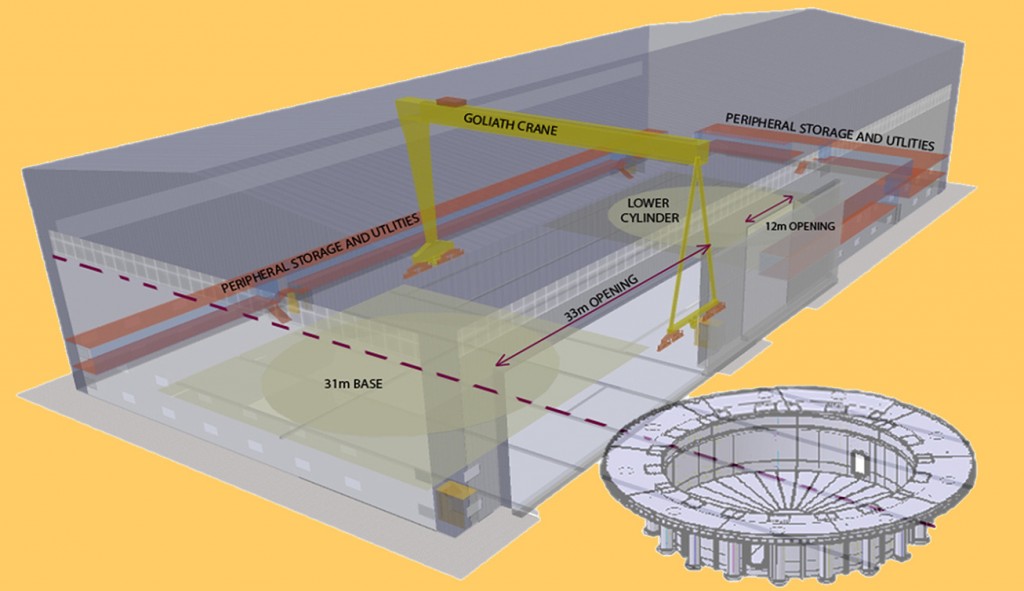
Inside of the Cryostat Workshop
2013-12-12 - In this schematic, we get a look inside the Cryostat Workshop where a goliath crane will run the length of the building between the two assembly areas. Four completed components, weighing from 600-1,250 tonnes, will leave the facility by the western door.

The best lookout point
2013-12-11 - As the ITER site becomes more and more congested, the best lookout point will soon be the top of the Cryostat Workshop!
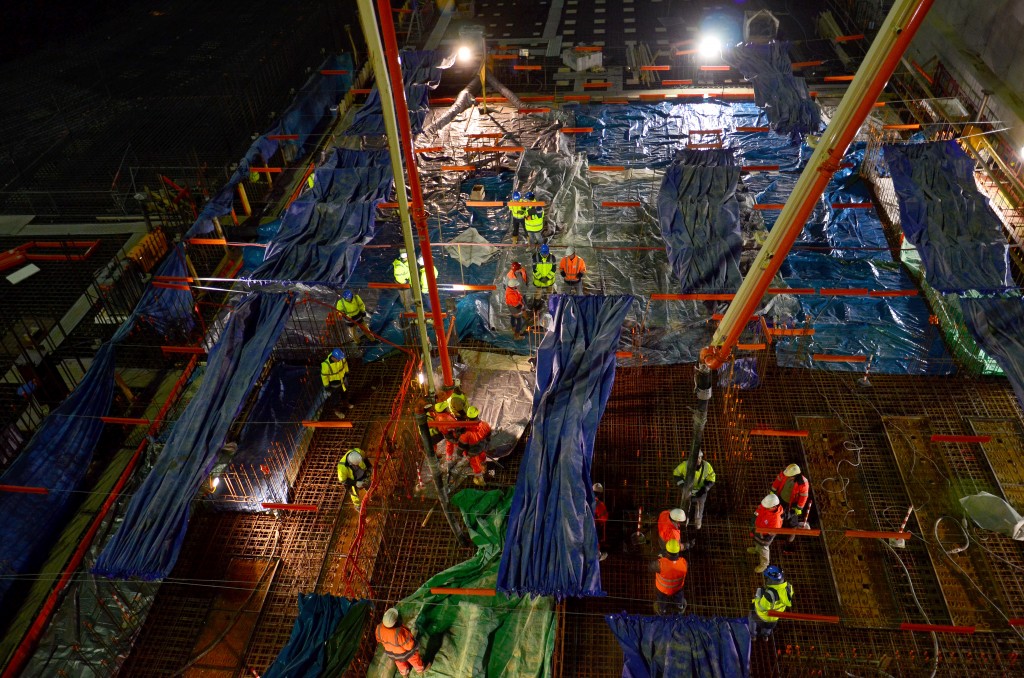
Keeping the concrete warm
2013-12-11 - Special measures were put into place to keep the concrete at its minimum required temperature, including protective covers and hot air blowers at the pouring site.
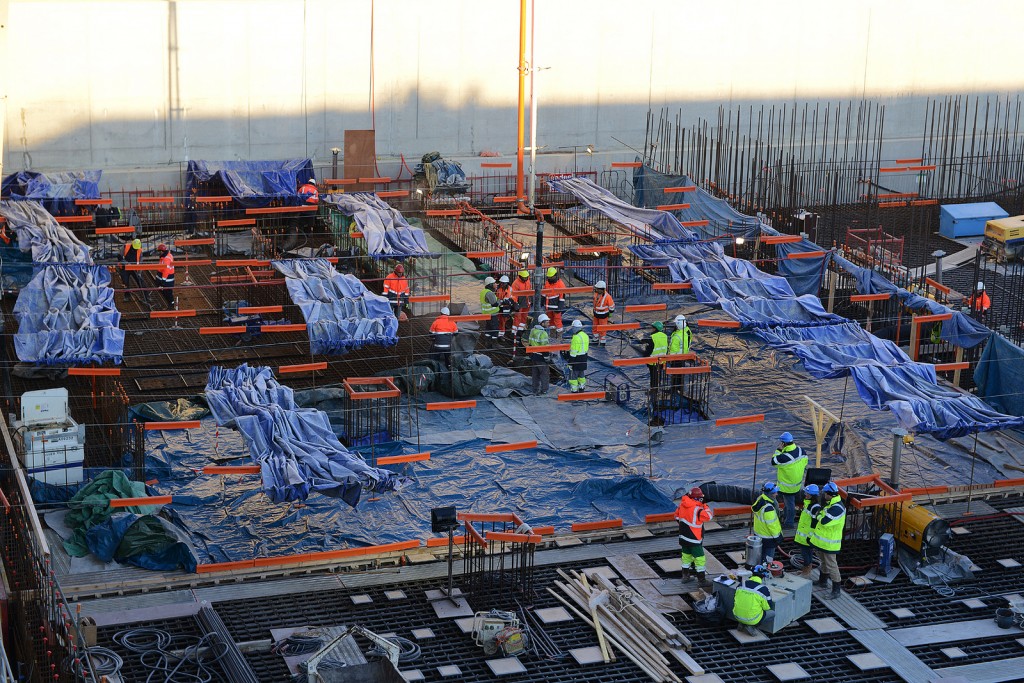
12-hour pour day
2013-12-11 - The first segment is a 21 x 26 m area under the future Diagnostics Building. Over the 12-hour day, a volume of 800 m3 of concrete is poured. Photo: F4E
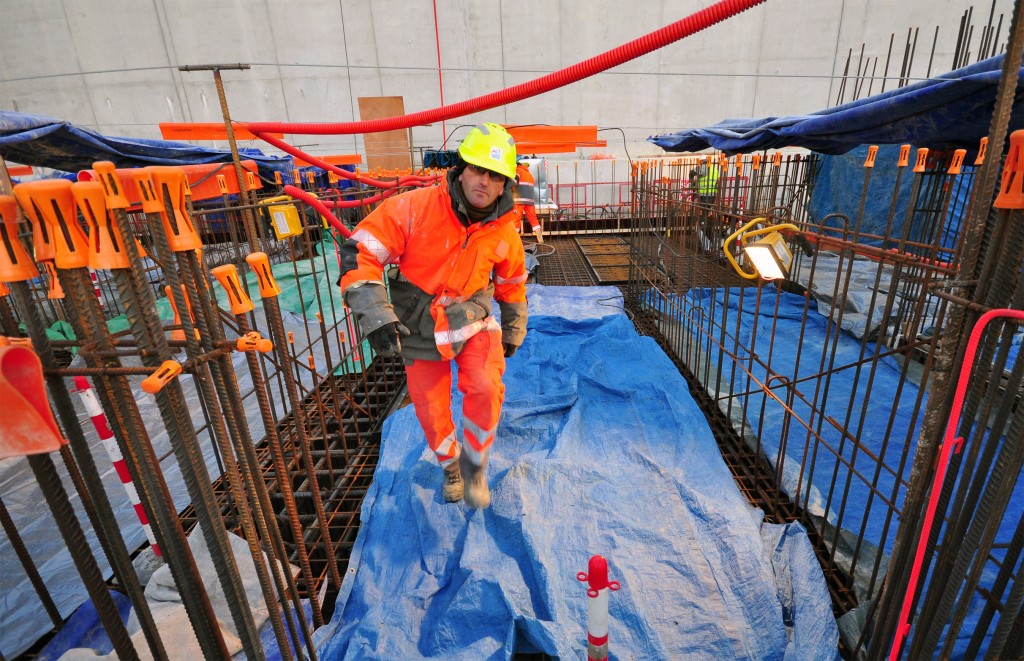
An early day for some
2013-12-11 - The first segment of the B2 basemat was poured in approximately 12 hours by two shifts of workers. The first team of 20 began the day at 4:00 a.m. to prepare the work site.

Cladding underway
2013-12-11 - Cladding works continue on the structure of the Cryostat Workshop as 2013 draws to a close.
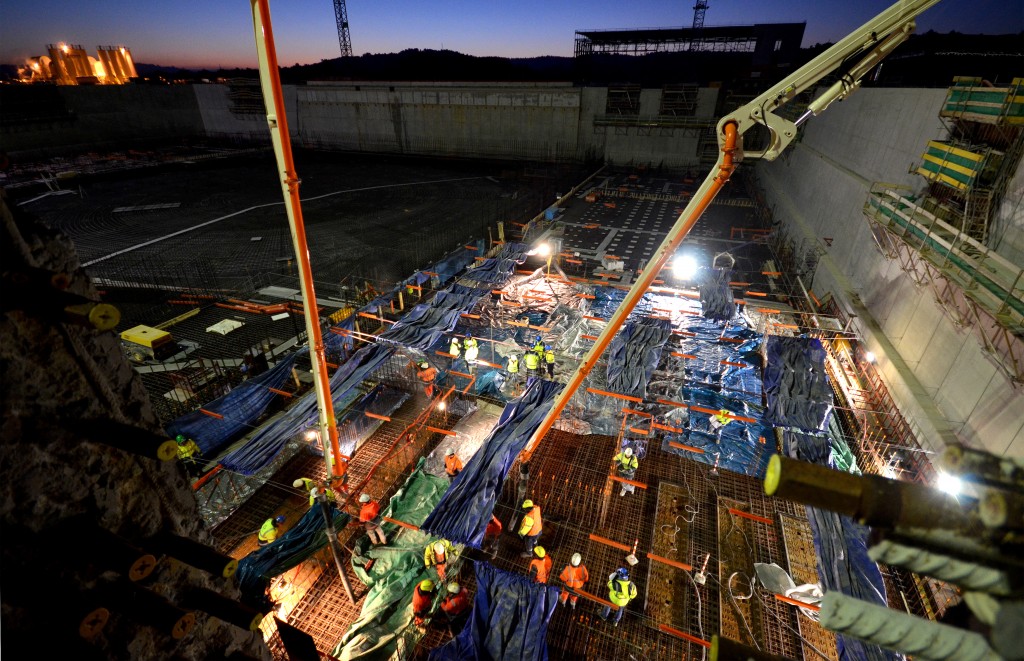
On-site production of concrete
2013-12-11 - Two pumps worked in unison to deliver the special-grade concrete, qualified for the specificities of the ITER facility through extensive testing and produced in an on-site batching plant.
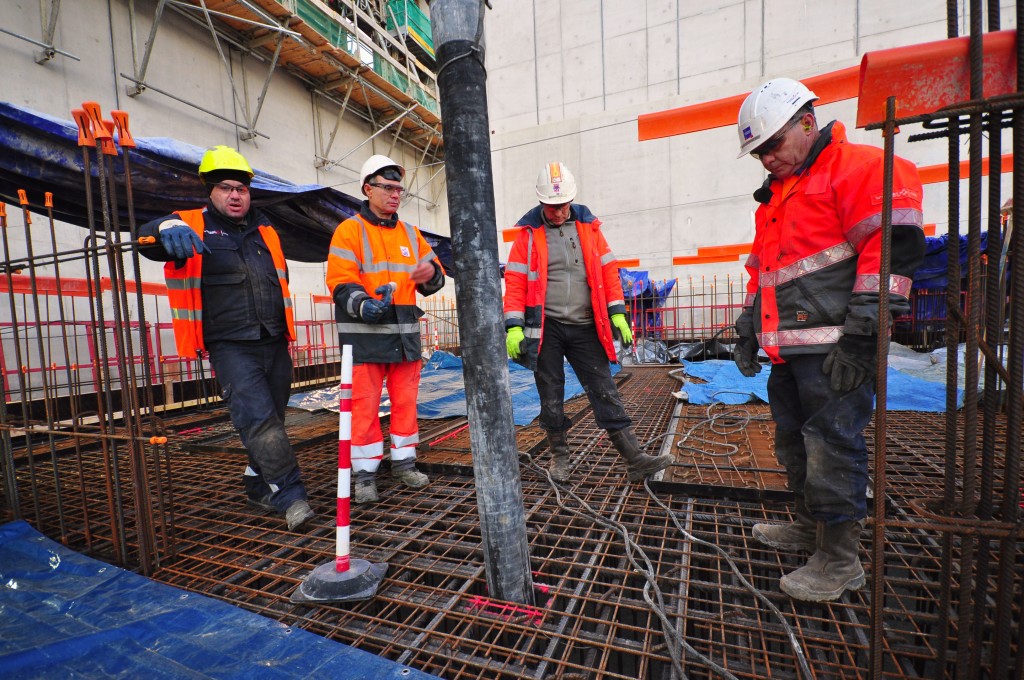
ITER-grade concrete
2013-12-11 - The concrete formulation is the same as that used for the seismic columns of the Seismic Pit, tested over twenty times for its properties of stability, water permeability and gas confinement.
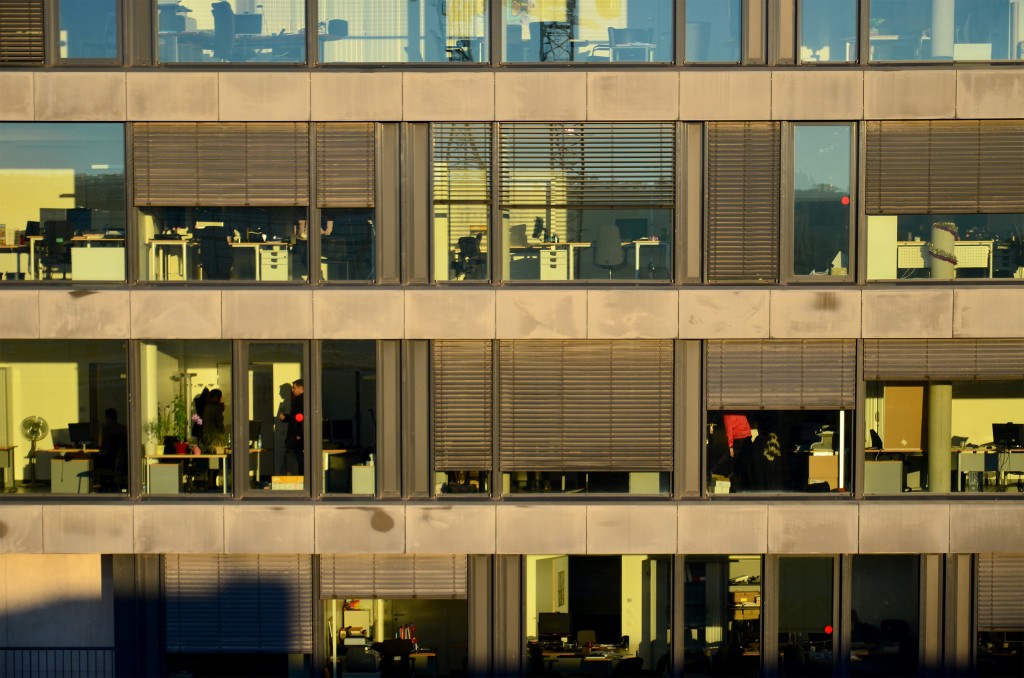
Coffee anyone?
2013-12-11 - As the sun rises over the ITER site, the first employees arrive at their offices.
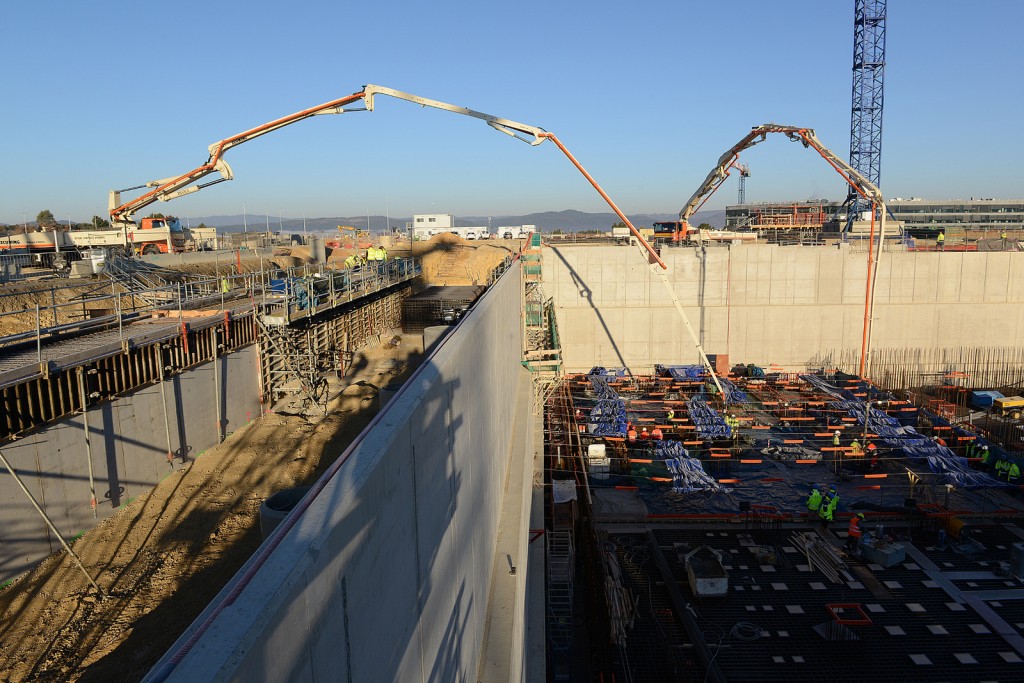
Continuous flow
2013-12-11 - The pumps are fed in a continuous flow by concrete trucks that drive back and forth from the on-site batching plant. Photo: F4E
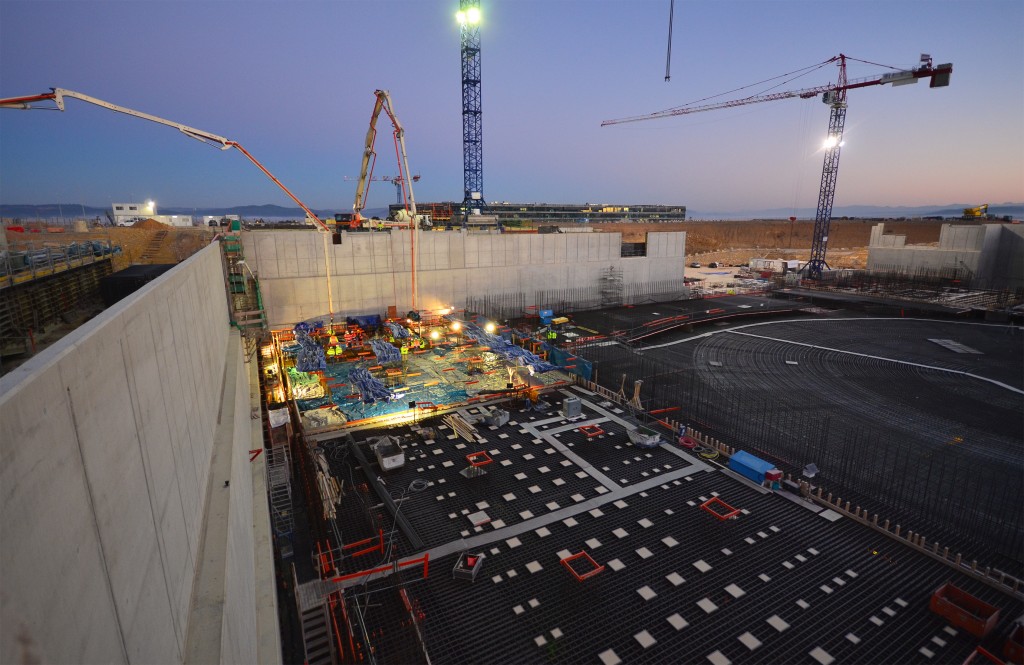
Pouring begins
2013-12-11 - In the northwest corner of the Seismic Pit, under the future Diagnostics Building, the first concrete pouring for the B2 slab got under way at 6:24 a.m. on 11 December 2013.
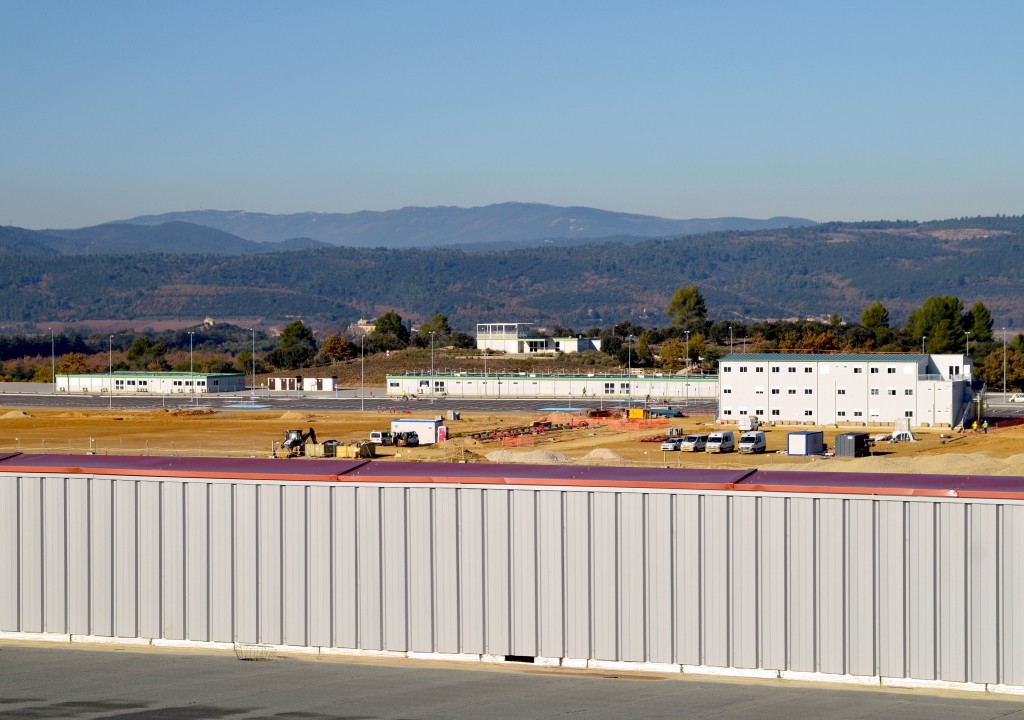
On-site contractors area
2013-11-29 - Below the ITER Visitors Centre are building consortium offices, and an infirmery and a canteen for the workers on the ITER site.

A home for the Tokamak
2013-11-29 - The 23,000-tonne ITER Tokamak will have a seven-storey home. Machine assembly will begin two levels underground.
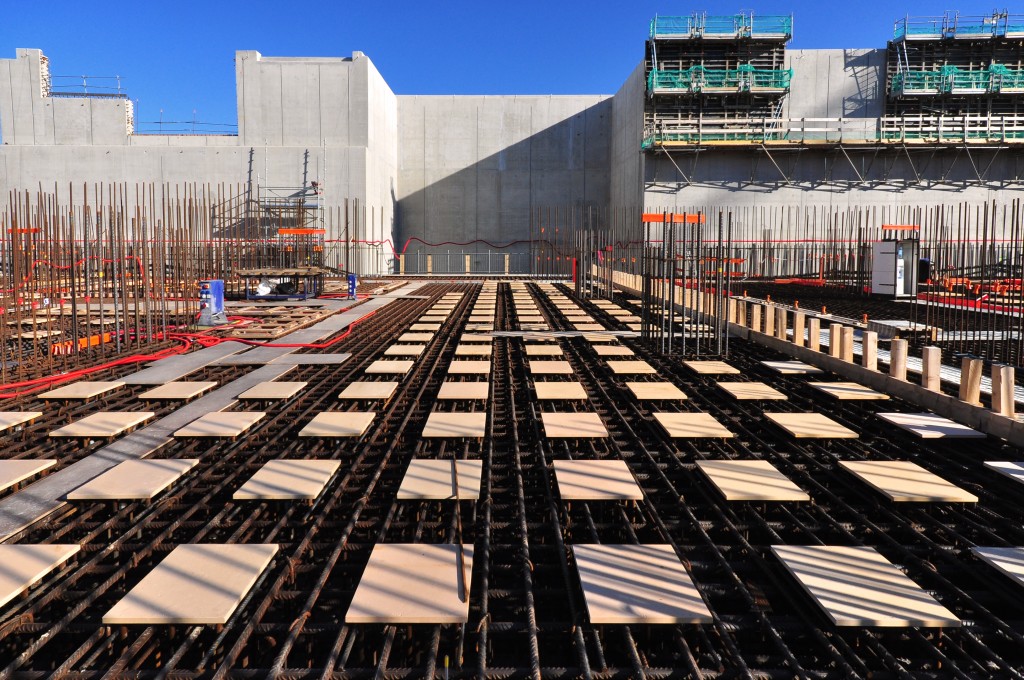
All in a row
2013-11-29 - Some 750 of the 2,600 planned embedded plates for the Tokamak Complex basemat have been installed. These plates provide robust anchorage for equipment and tooling.
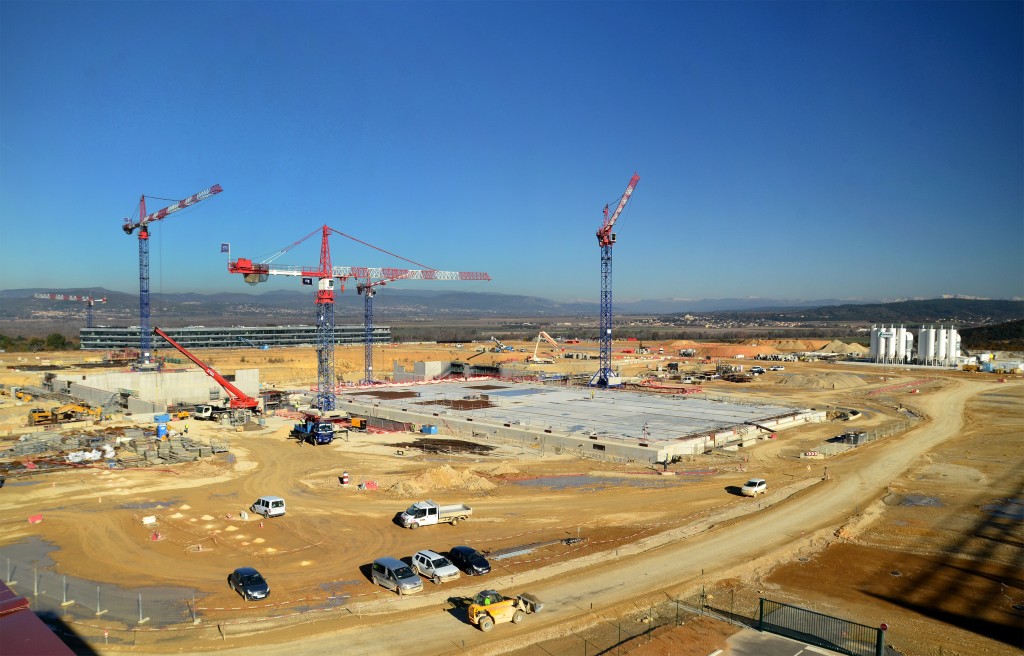
The platform at the of 2013
2013-11-29 - Technical galleries are underway all around the Assembly Building. The building should begin to take form at the same time as the adjacent Tokamak Complex.

In a straight line
2013-11-29 - Segments of the cryostat will leave the Workshop and be transported in a straight line directly into the Assembly Building, whose foundation slab is visible through the beams.

Parallel assembly activities
2013-11-29 - The cryostat segments will be needed in two waves—first the two lower segments, and then approximately two years later the two upper segments. Two assembly platforms will permit parallel assembly activities in the Cryostat Workshop.
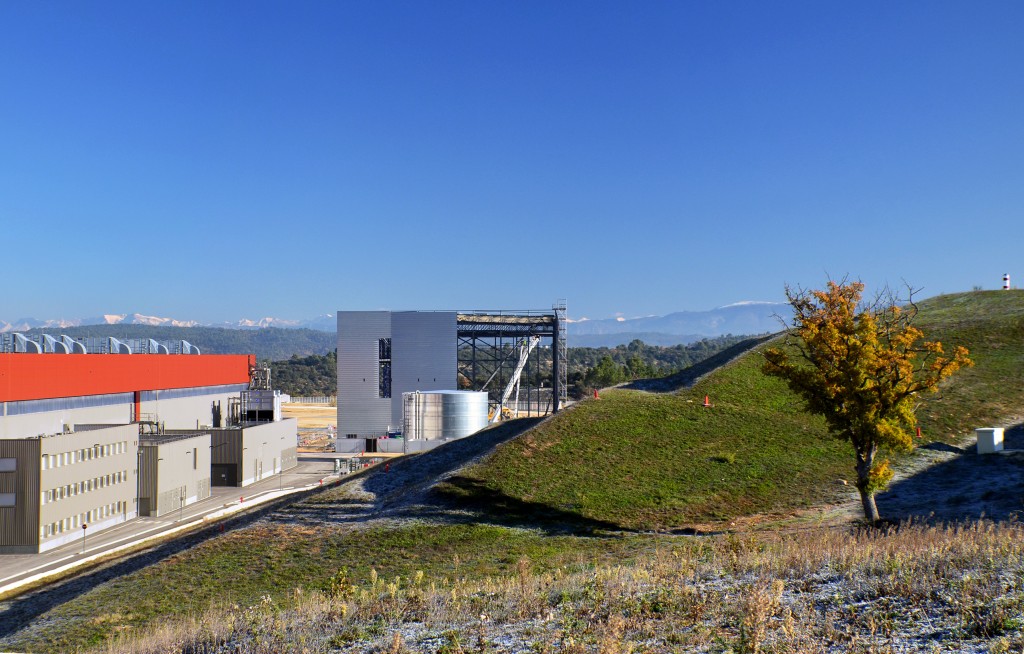
Tallest building yet
2013-11-29 - The Cryostat Workshop is nine metres taller than its closest neighbour—the Poloidal Field Coils Winding Facility.
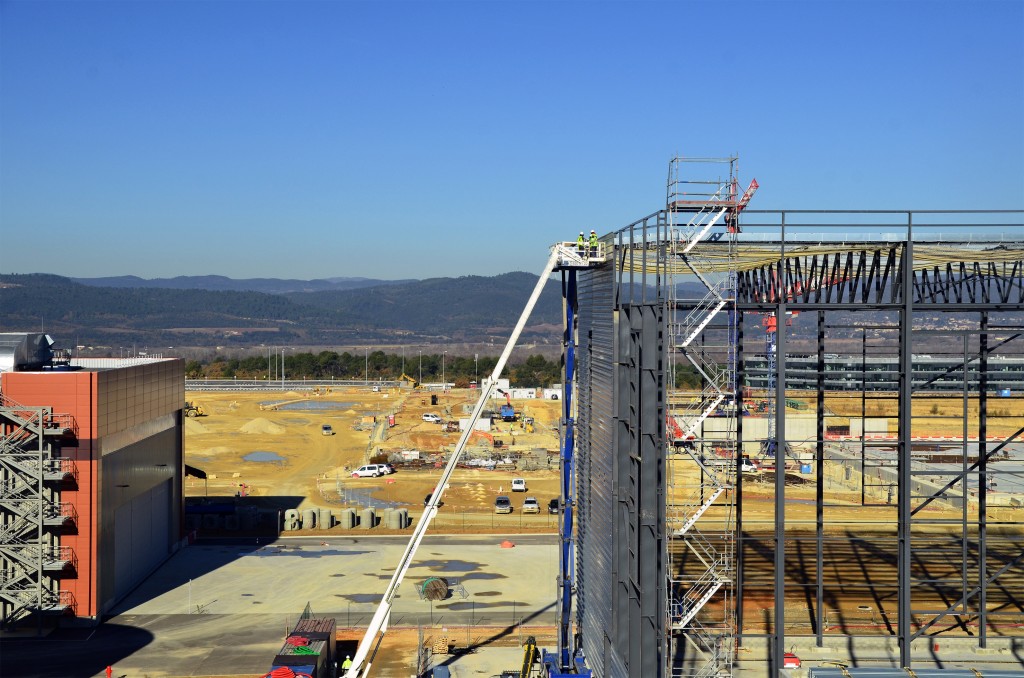
Work progressing well
2013-11-29 - Approximately 25 people are currently working on the site of the Cryostat Workshop and works are progressing as scheduled.
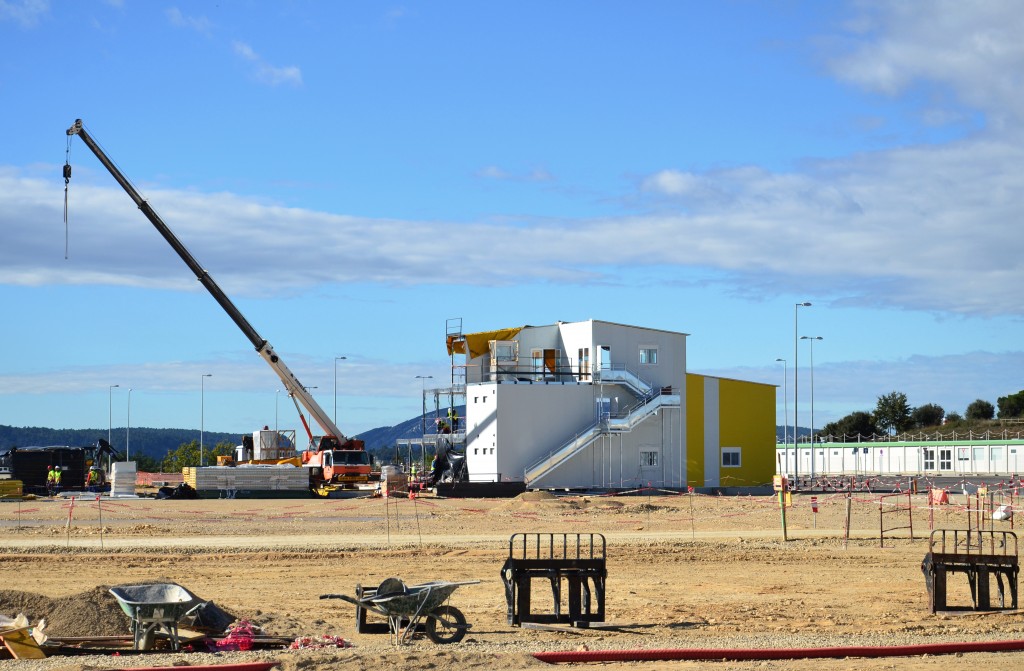
First contractor offices on the platform
2013-11-06 - In Contractors' zone on the southern end of the platform, the first modular building is going up. The main Tokamak Complex building contract will be piloted from here.
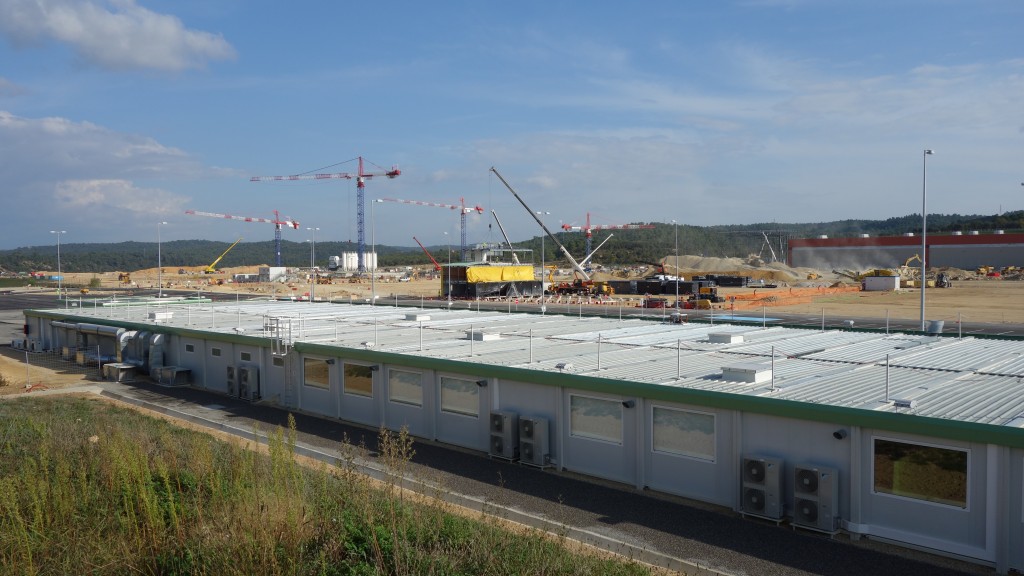
"À table"!
2013-10-31 - The worksite canteen is now open for business. At the peak of construction activities, 1,500 meals will be served here per day.
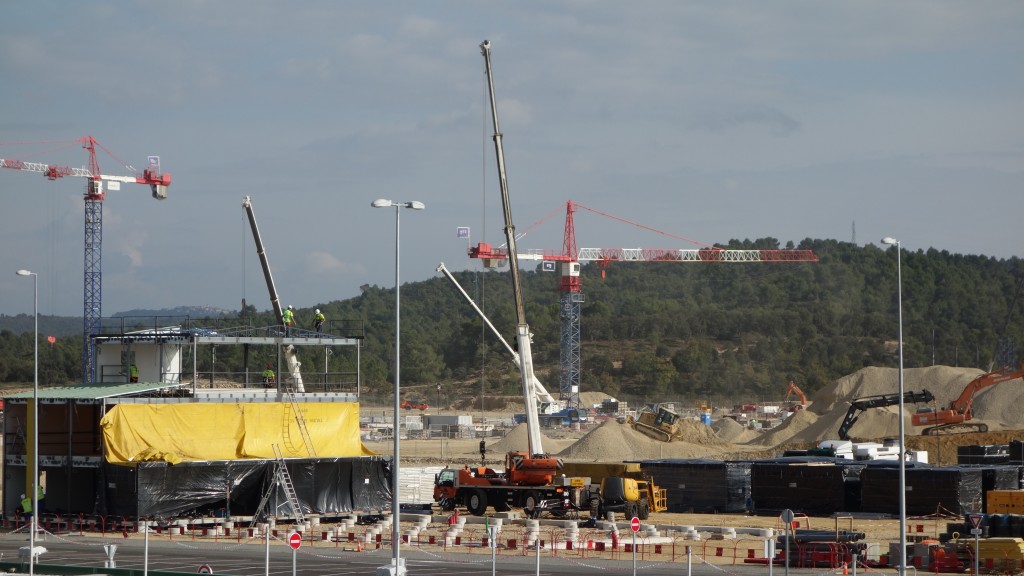
Settling in for a few years
2013-10-31 - All of the principle contracting companies will be issued an area on the platform where they can create their "home base" - an area for offices, storage shed, workshops and a few parking spaces.
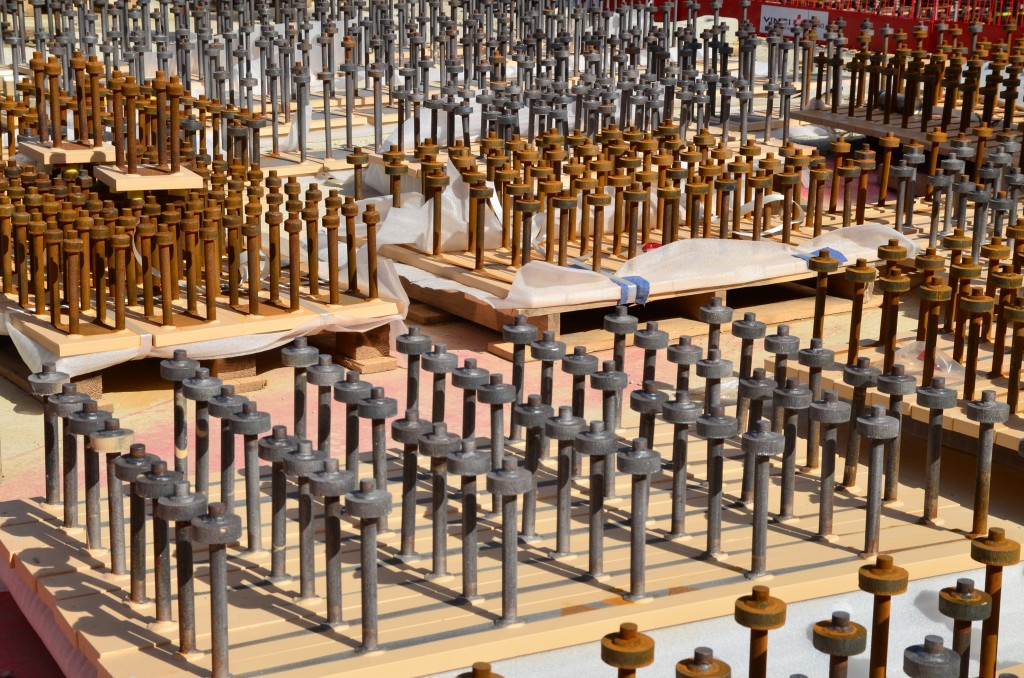
Small coffee tables with supernumerary legs?
2013-10-08 - No. Embedded plates waiting for installation. These plates will provide extremely robust anchorage for the devices that need to be attached to the walls (or floors, or ceilings) of the Tokamak Complex and that can weigh several tons.

Installation of embedded plates
2013-10-08 - Once the foundation is poured, these embedded plates will be solid support for the elements that will be welded to their surface.
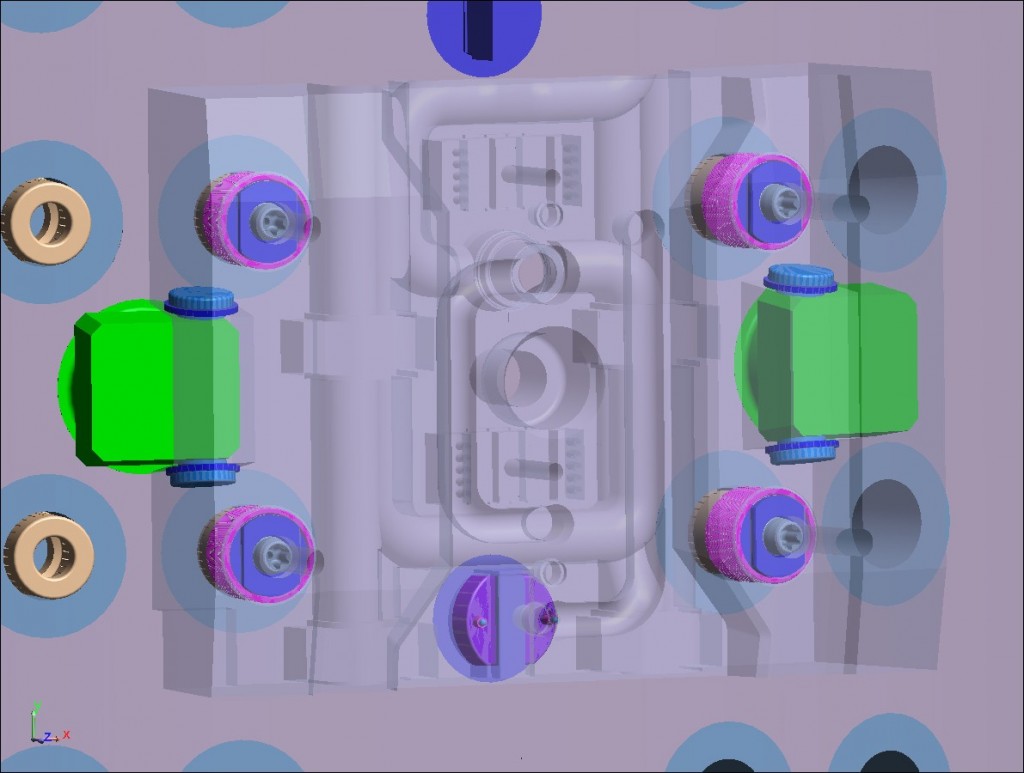
Aligning the blanket
2013-10-07 - Central to identifying the variances—and defining customization requirements—are sophisticated optical metrology techniques. Alignment of the ITER blanket will be achieved by customizing approximately 4,000 interfacing components.
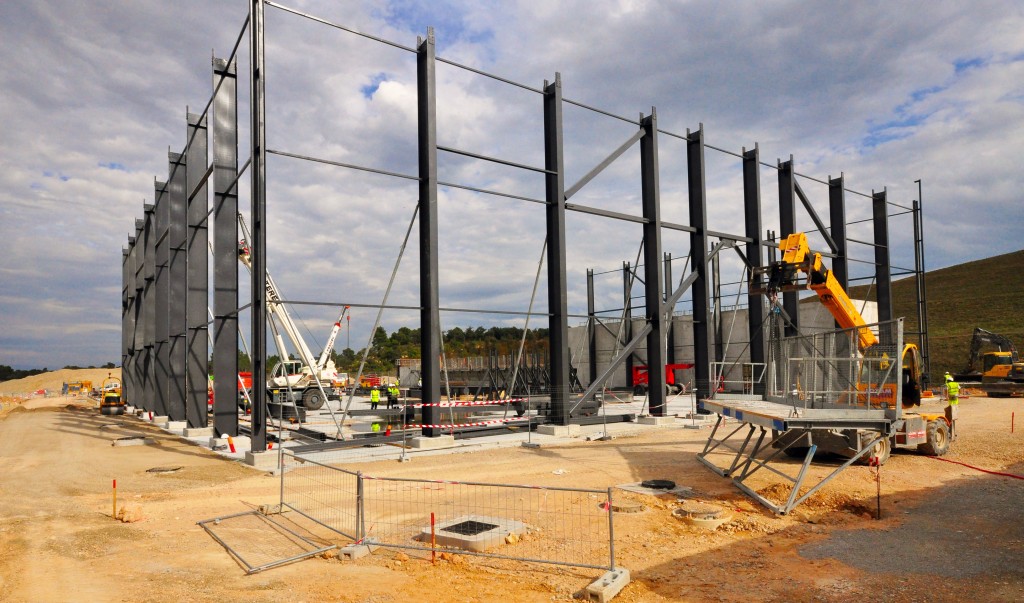
Grey livery for the Cryostat Workshop
2013-10-03 - The steel structure will be light, but sturdy for a building this size. Approximately 500 tonnes of steel will go into the trusses, beams and columns—enough to withstand the strong Mistral wind that regularly blows over Provence.
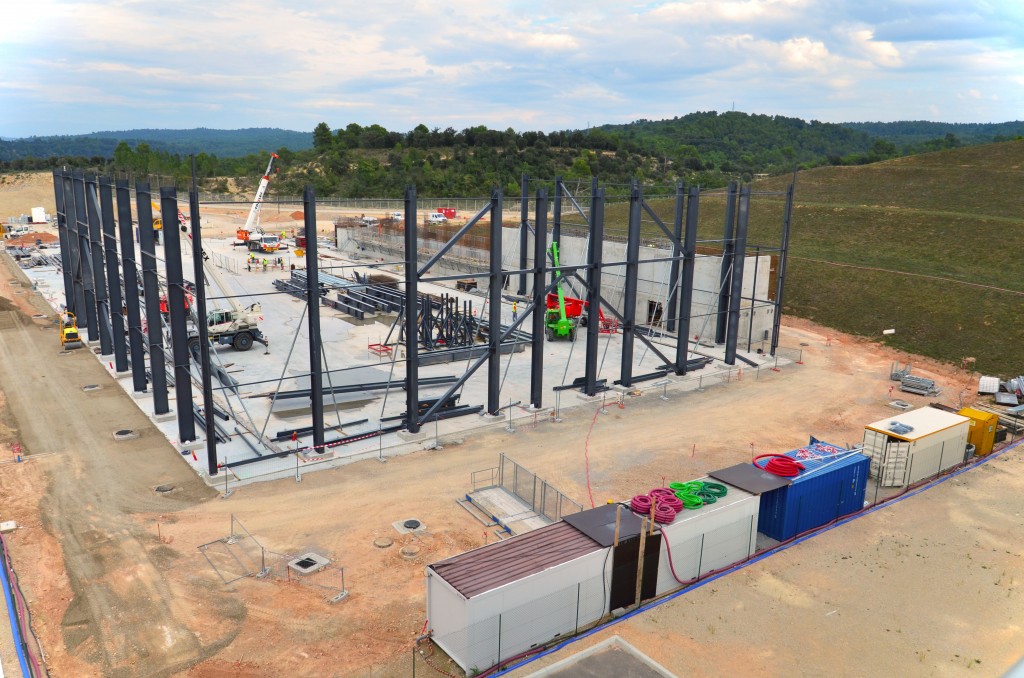
Another factory rises
2013-10-03 - At 110 metres long, 44 metres wide and 27 meters tall, the Cryostat Workshop will be more of a factory than a workshop. When it is completed in February 2014 it will be second industrial building on the ITER platform.
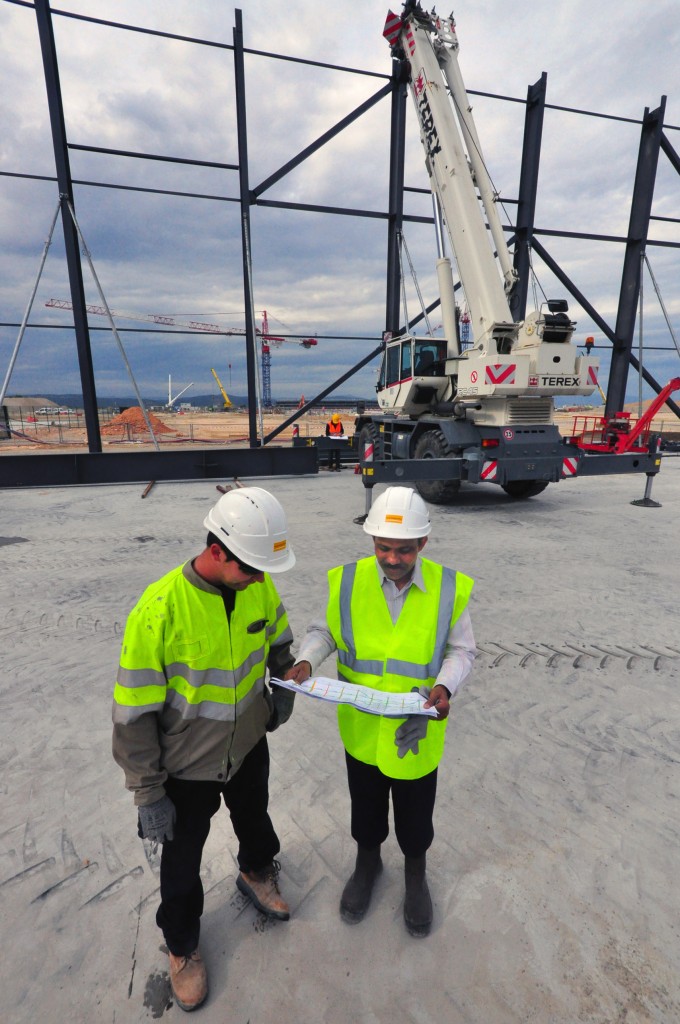
Trusses up
2013-10-03 - About half of 50 steel columns are already in place; in the coming weeks they will double in height to attain 27 metres.
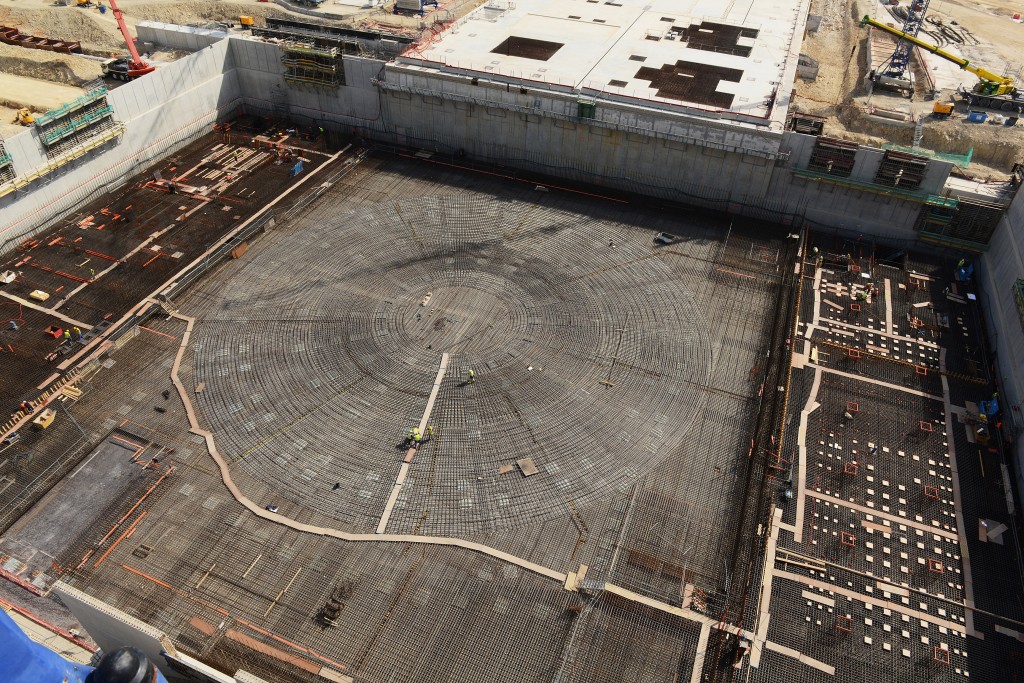
Seen from the crane
2013-10-02 - To the left of the future Tokamak Building: Tritium. To the right: Diagnostics. Concrete pouring for the B2 basemat slab will begin in these areas. Photo: F4E
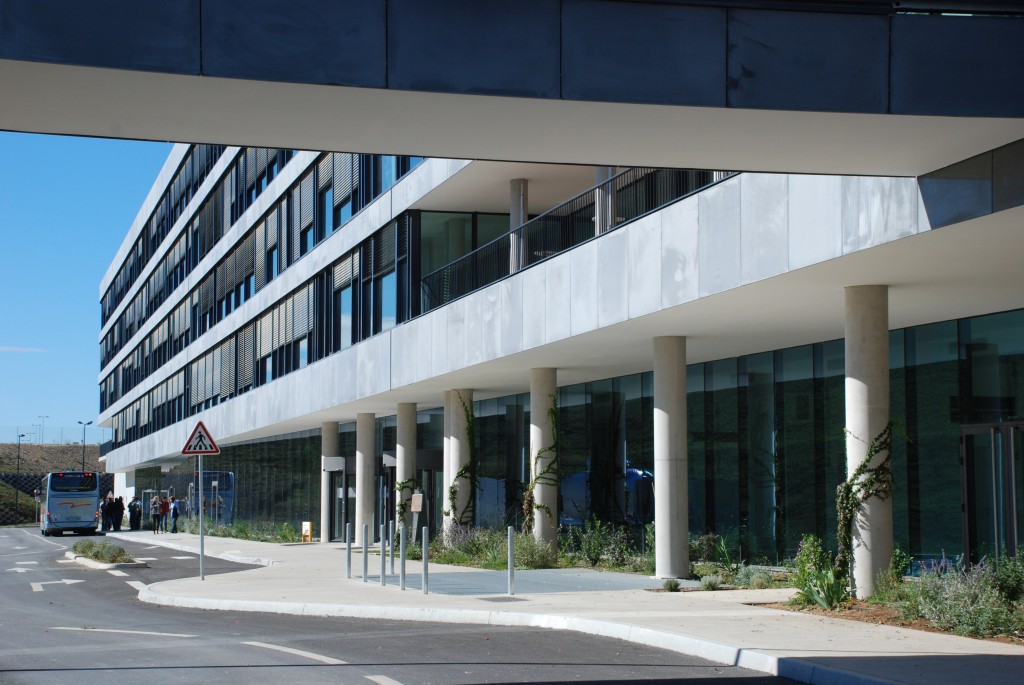
Regular buses
2013-10-02 - Regular shuttle buses run between ITER Headquarters and two other ITER office buildings ... with increased frequency at lunch time.

Positioned just so
2013-10-01 - The encounter of radial reinforcement and linear reinforcement creates a striking pattern on the floor of the Tokamak Complex.
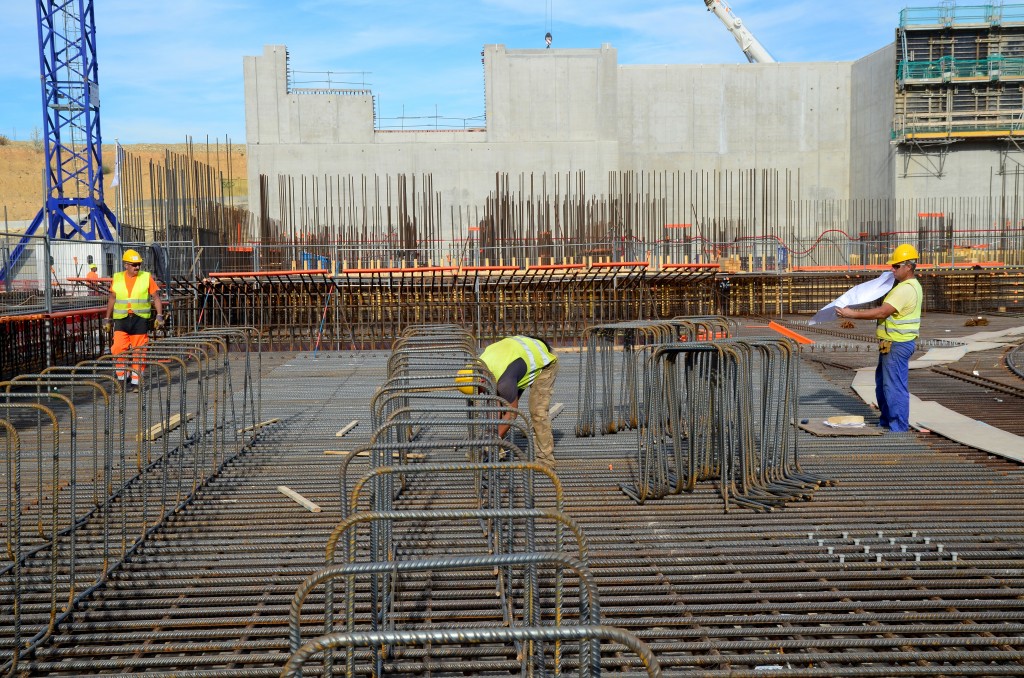
1.5 metres of reinforcement in the Tokamak Complex basemat
2013-10-01 - Metal "chairs" are positioned on the bottom layer of crisscrossed rebar. Steel reinforcement will be built up to 1.5 metres before foundation pouring begins.
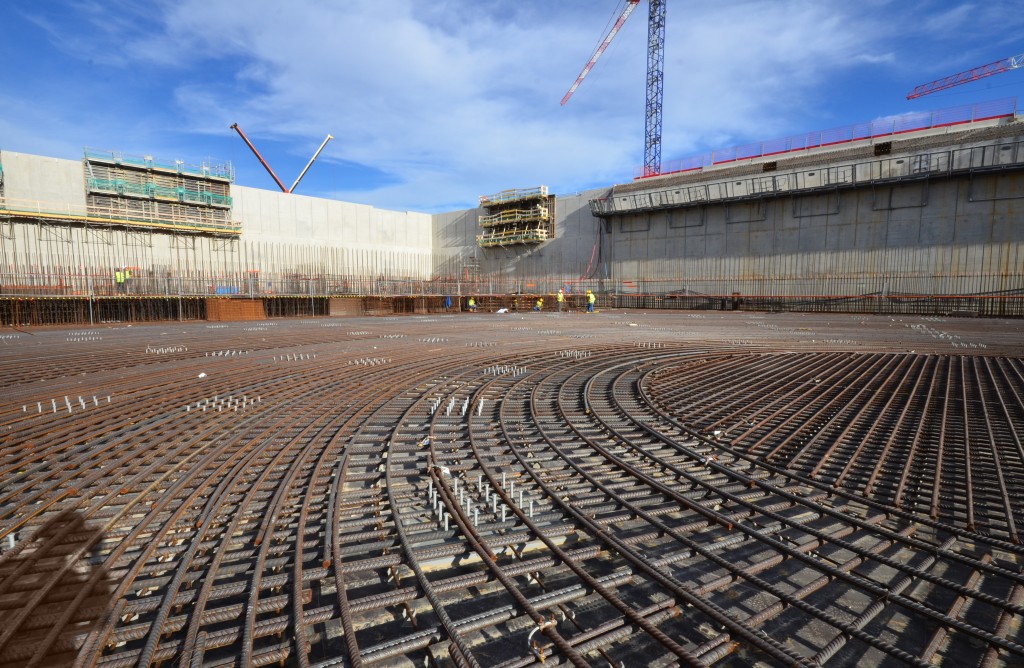
The complexity of the Tokamak Complex basemat
2013-10-01 - Finger-like, the tops of the seismic pads protrude through the pattern of rebar.

Space to walk all around
2013-10-01 - Between the Tokamak Complex and the retaining walls of the Seismic Pit there will be a gap of about 2 metres ... space for lateral movement in case of ground motion.
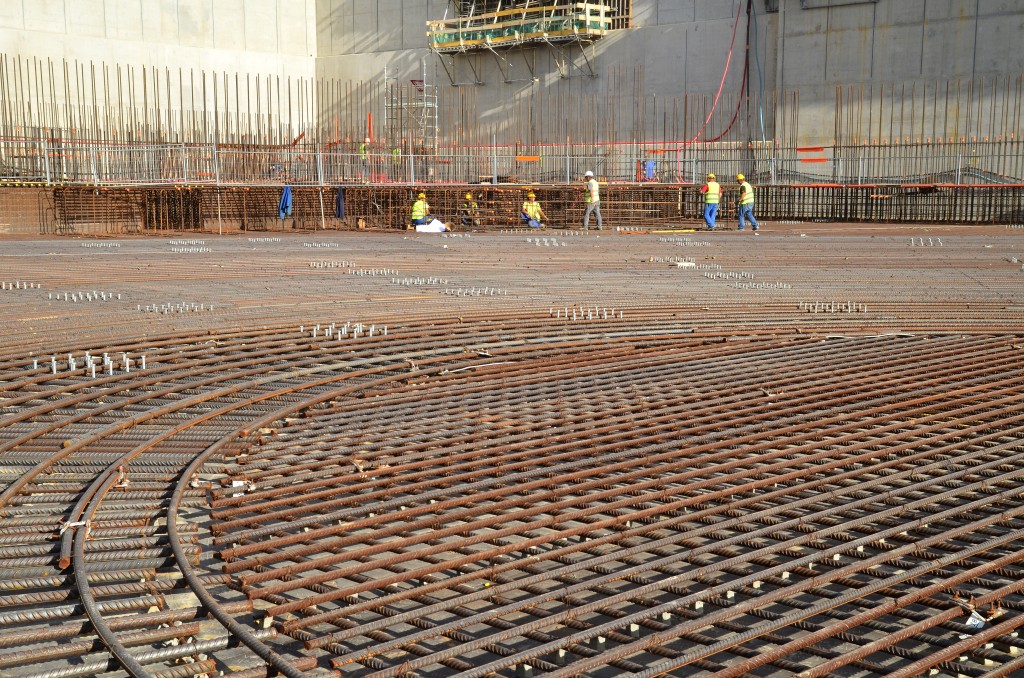
Reinforcement underway
2013-10-01 - When reinforcement work ends, 4,000 tonnes of steel rebar will be in place at the bottom of the Tokamak Seismic Pit—part of the B2 foundation slab that will support the Diagnostic, Tokamak and Tritium buildings.
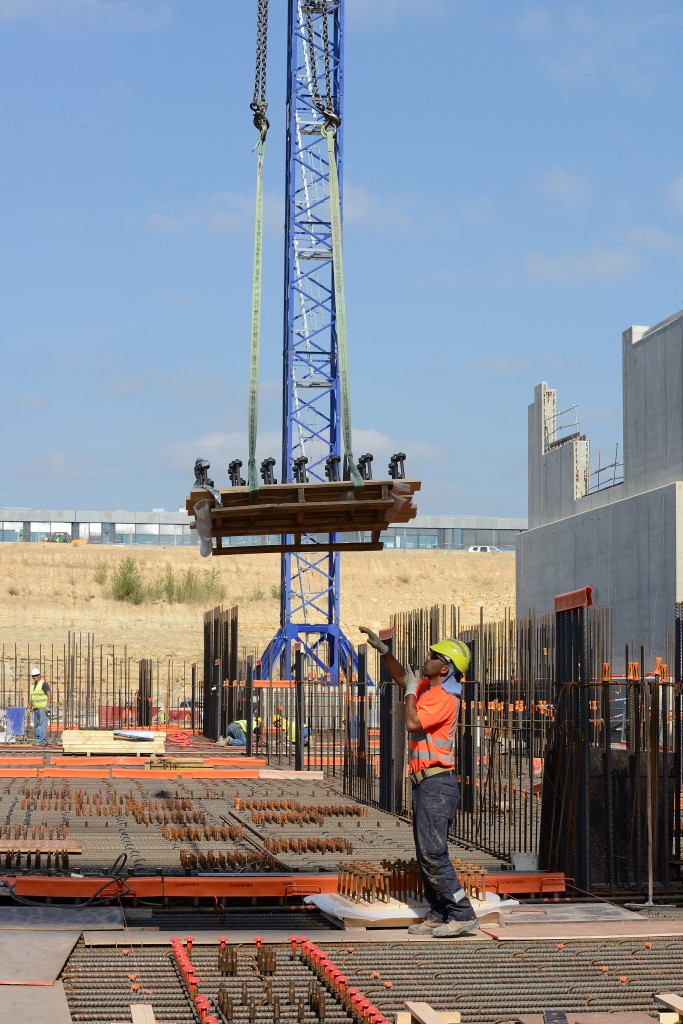
Heads up!
2013-09-26 - In the floors, walls and ceilings of the Tokamak Complex there will be roughly 60,000 embedded plates to provide extremely robust anchorage, capable of supporting loads of up to ~90 metric tons in pure traction. Photo: F4E

Filling in
2013-09-26 - Work on the critical networks—the deepest networks on the ITER platform—ends in October 2013. The deep trenches that were a permanent feature on the platform for more than a year have now been filled in. Photo: F4E
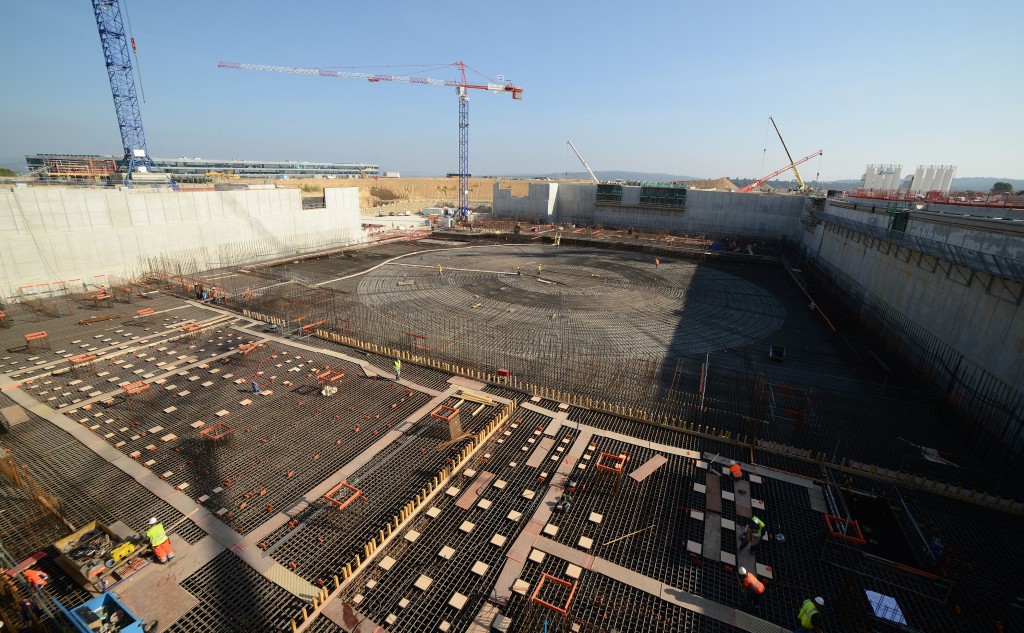
In so many rows
2013-09-26 - Sixteen of the sixty thousand embedded plates will be integrated into the Tokamak Complex basemat (see the squares being settled into place on the Diagnostics end of the Seismic Pit).
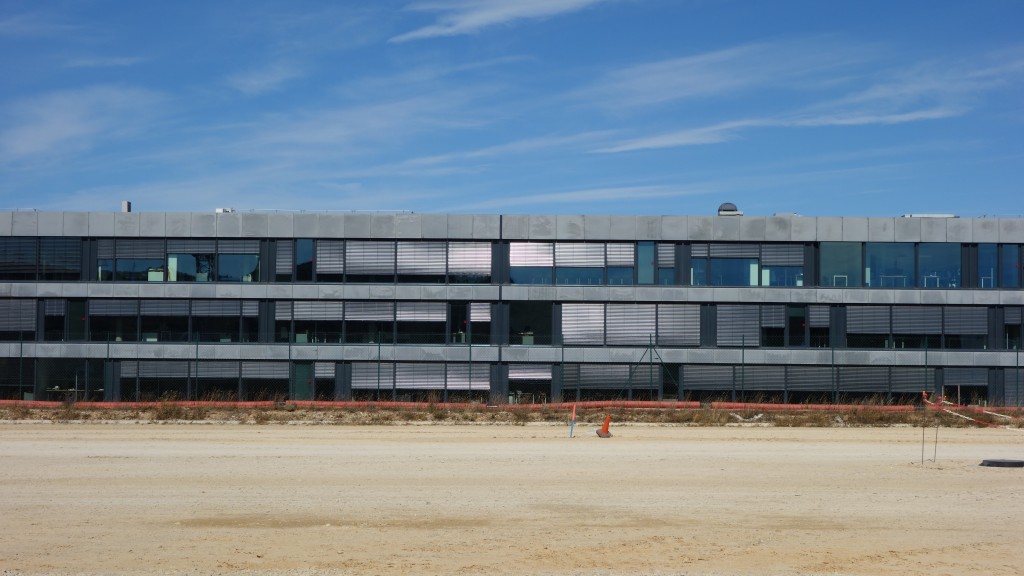
From the worksite
2013-09-19 - The top three storeys of ITER Headquarters have a view of construction works.
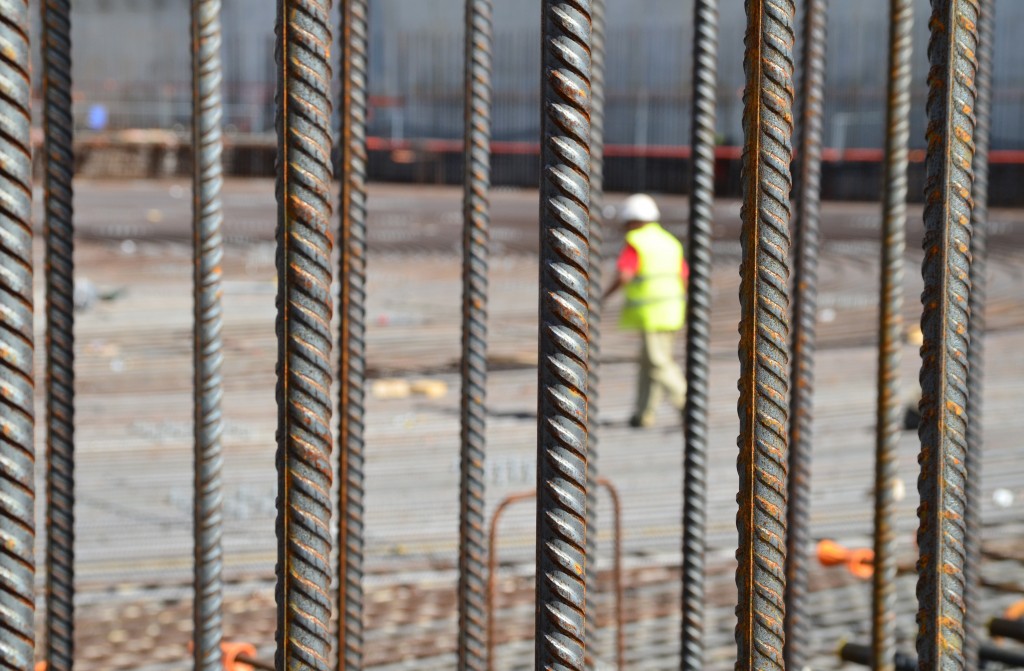
Progress is in the details
2013-09-18 - Concrete pouring will begin in October on the opposite ends of the Tokamak Pit, where workers have nearly completed the 1.5 metres of reinforcement.
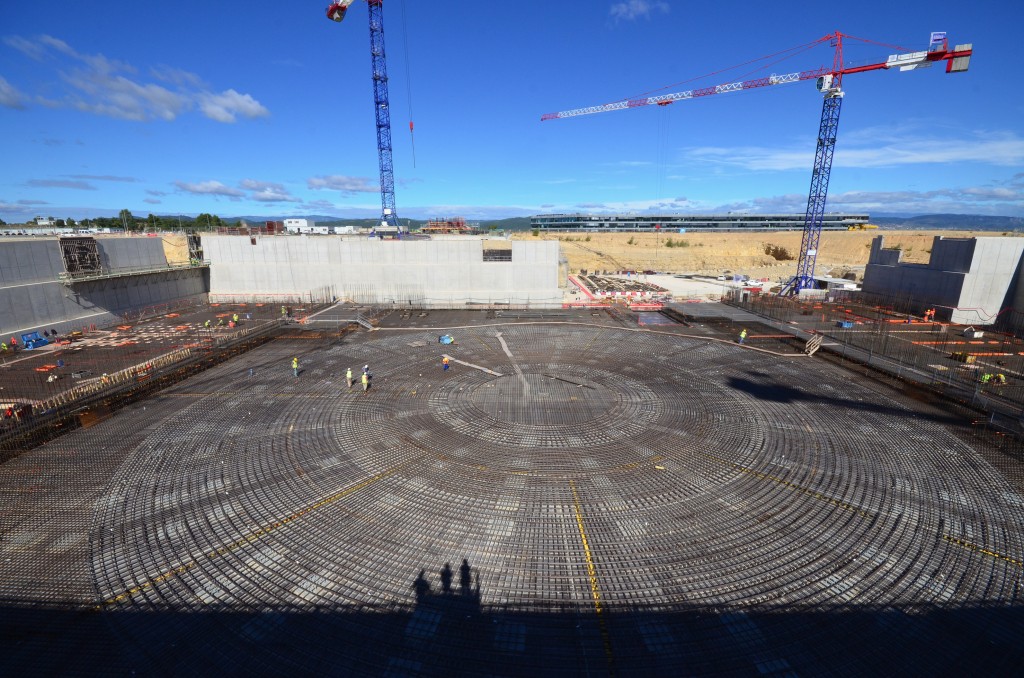
Machine + cryostat + bioshield
2013-09-18 - In the area occupied by circular rebar, the ITER Tokamak (23 metres in diameter) will be positioned in the centre, surrounded by its cryostat (30 metres in diameter) and concrete bioshield.

In September
2013-09-18 - Steel trusses are stocked on the basemat, while construction progresses on the offices and technical rooms of the Cryostat Workshop.
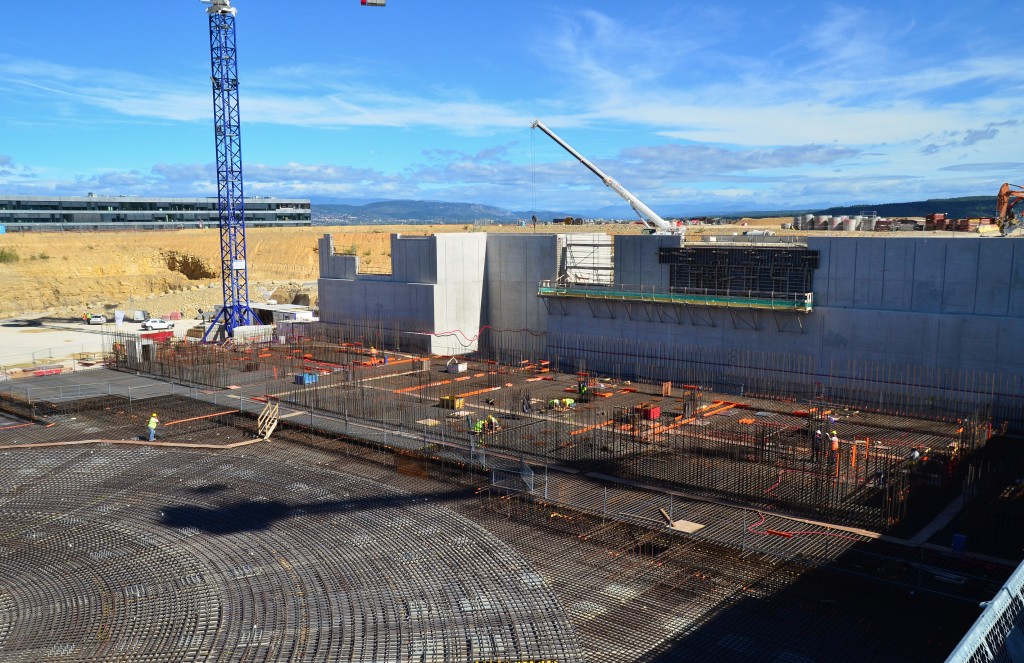
Two storeys below ground
2013-09-18 - When the B2 basemat slab is completed in 2014 the Tokamak Complex will begin to rise. The lower elements of the Tokamak machine will sit two levels below the surface of the platform.

Latest aerial photograph
2013-09-11 - A view from the sky of the Tokamak Complex worksite, where walls will begin to rise next year, and the completed basemat of the Assembly Building (foreground).
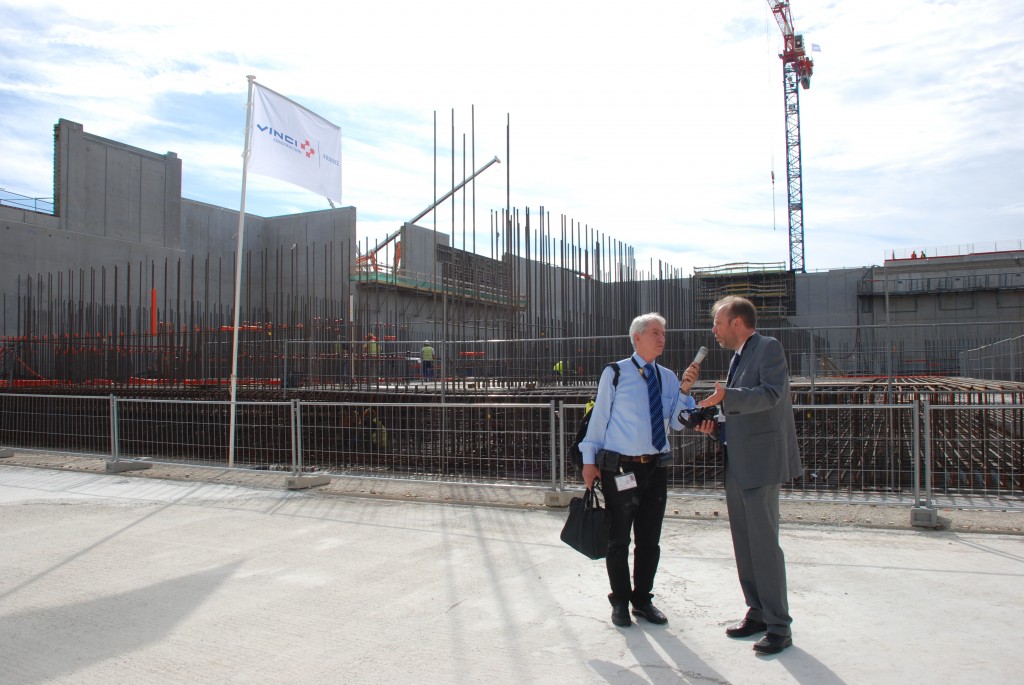
Rebar rises
2013-09-06 - A wall of rebar rises on the site of the future Tritium Building. Early in the morning on 6 September 2013—the day of the Ministerial-Level Meeting—a last interview takes place before the buses return to Headquarters.

Tokamak Pit covered
2013-09-03 - The last section of the Tokamak Pit to be covered by formwork is the lift shaft for the transfer of components between the Tokamak Building and the Hot Cell.

The ITER platform in late August 2013
2013-08-29 - As the last foundation segment is poured on the far side of the basemat, work begins in the foreground on the walls of the technical workshops and offices.
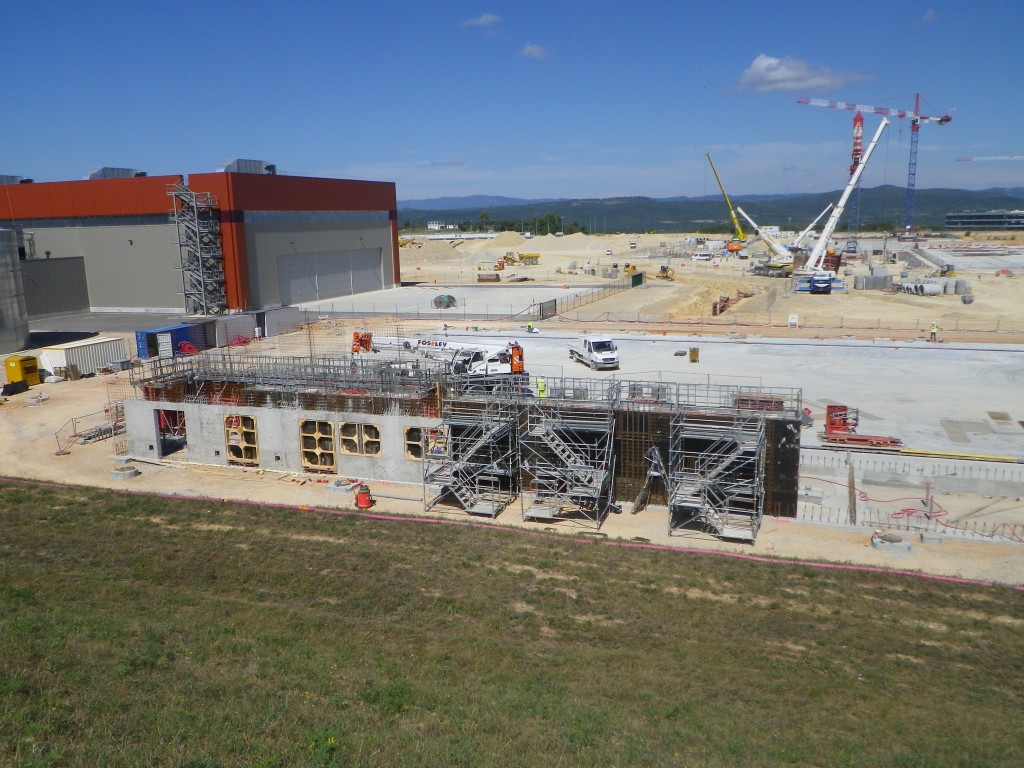
Small team moving quickly
2013-08-26 - Approximately 20 people are working currently on the site of the Cryostat Workshop, where the basemat is nearly completed and pouring is about to begin on the first floor of the office building.
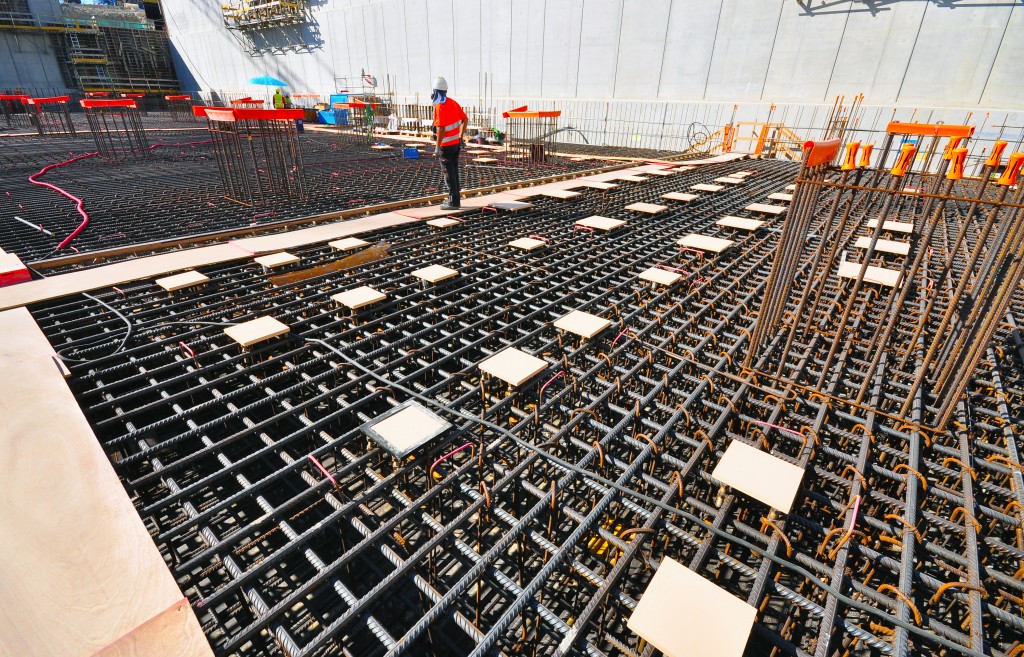
A lot to support
2013-08-22 - Before concrete pouring can begin, space must be set aside for embedded parts—some 60,000 anchor plates that will be embedded into the slab and walls of the Tokamak Complex to support equipment.
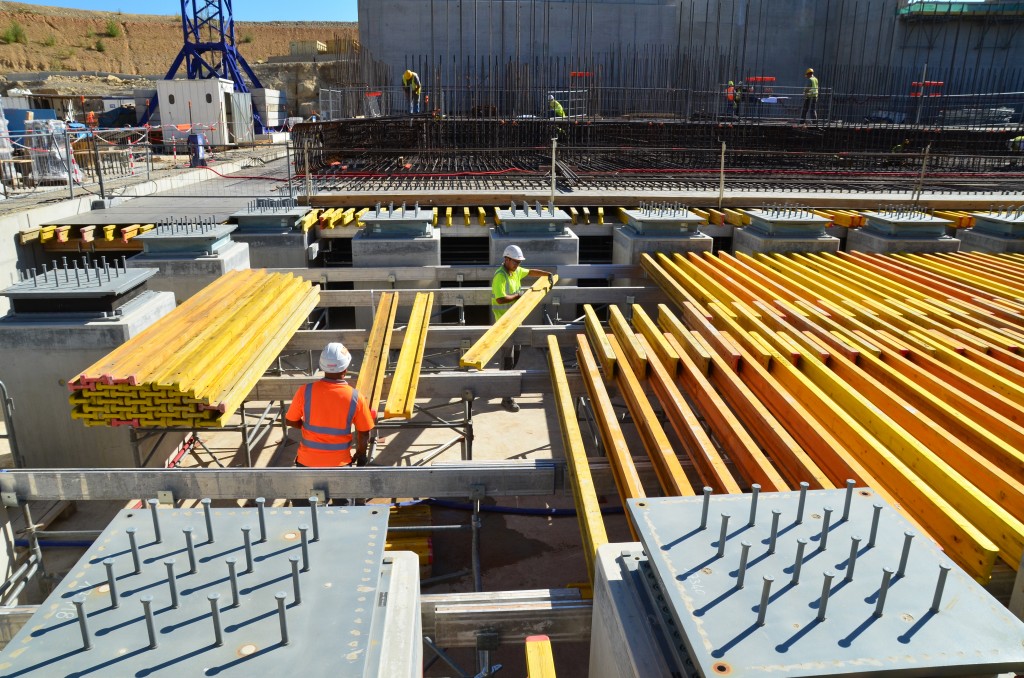
The basement of the Tokamak Complex
2013-08-22 - Underneath the 1.5-metre-thick concrete floor of the Tokamak Complex there will be room to move around—nearly 2 metres worth, enough for the regular inspection of the seismic pads.
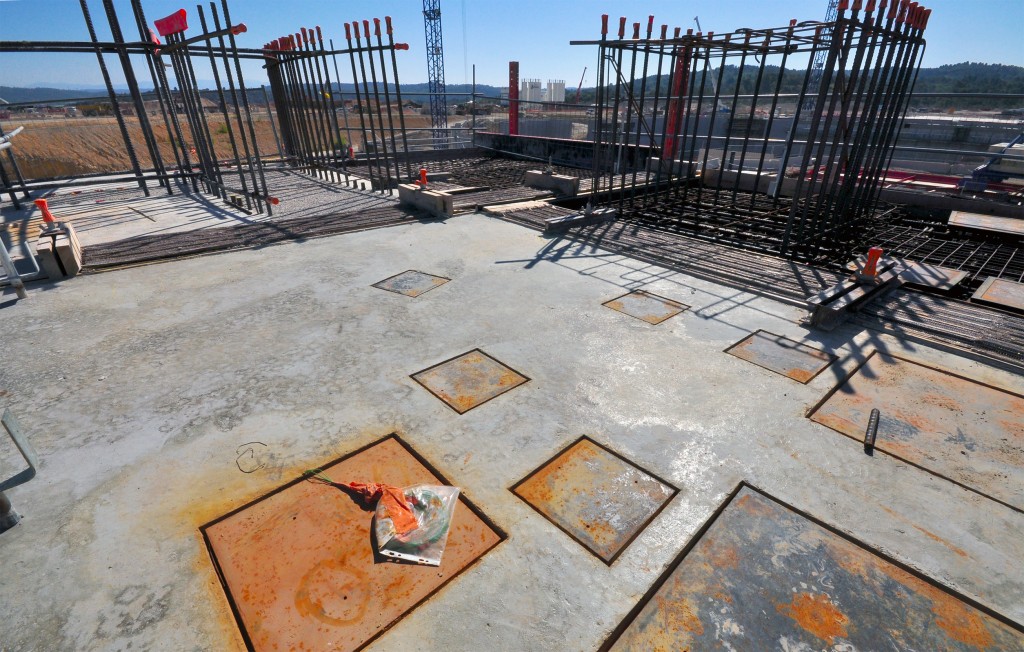
A small B2 slab
2013-08-22 - A smaller version of the next-phase Tokamak Complex basemat slab (B2) can already be found on site: the 150 m2 slab mockup even recreates the various-size anchor plates that will be embedded to support equipment.

Visible progress on the Cryostat Workshop site
2013-08-22 - Adjacent to the Cryostat Workshop, the ancillary building under constrution will house offices, machinery, power supplies and other utilities.
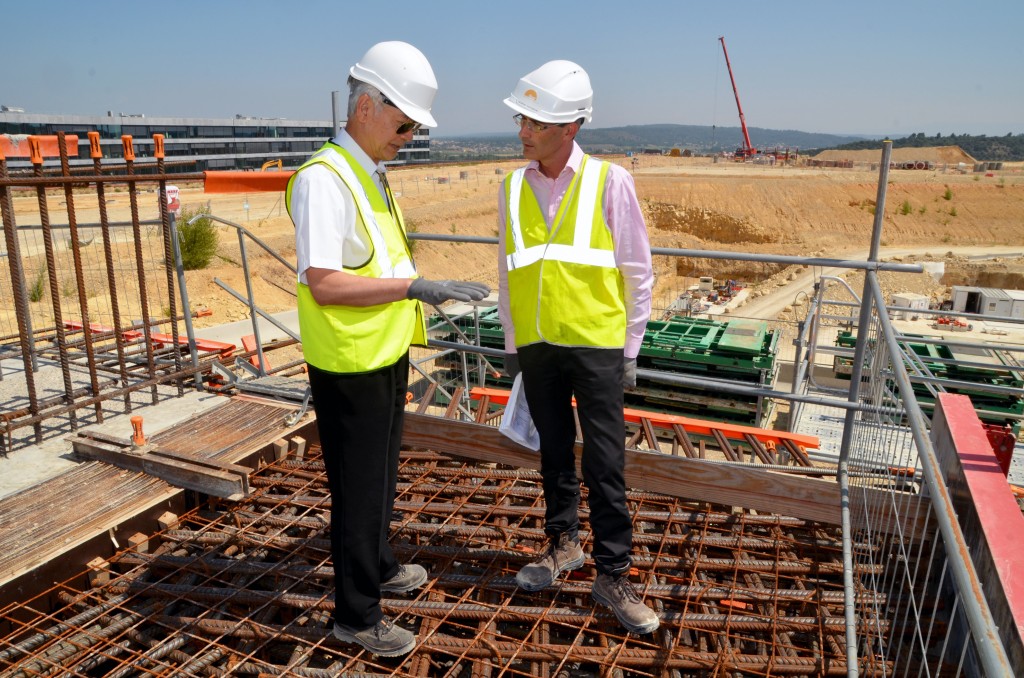
Scale mockup still in use
2013-07-24 - The Director-General of ITER, Osamu Motojima, stands with Nuclear Buildings Section Leader Laurent Patisson on top of the scale model of B2 reinforcement situtated to one side of the Seismic Pit. Here the complex pattern of steel reinforcement planned for the Tokamak Complex slab is studied.

Into the Pit
2013-07-23 - From above, the nine segments of the ITER vacuum vessel—plus their associated thermal shielding and a toroidal field coil on either side—will be lowered into the Tokamak Pit by overhead crane.
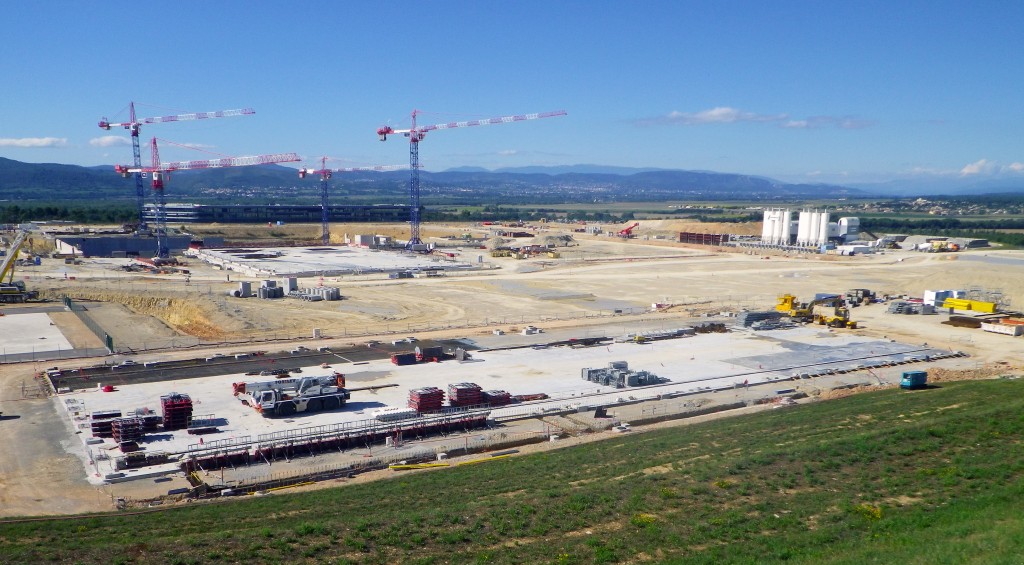
Assembling the four segments of the cryostat
2013-07-22 - Within the on-site Cryostat Workshop, assembly activities will take place on two huge steel platforms built to support the weight of the components, jigs and fixtures.
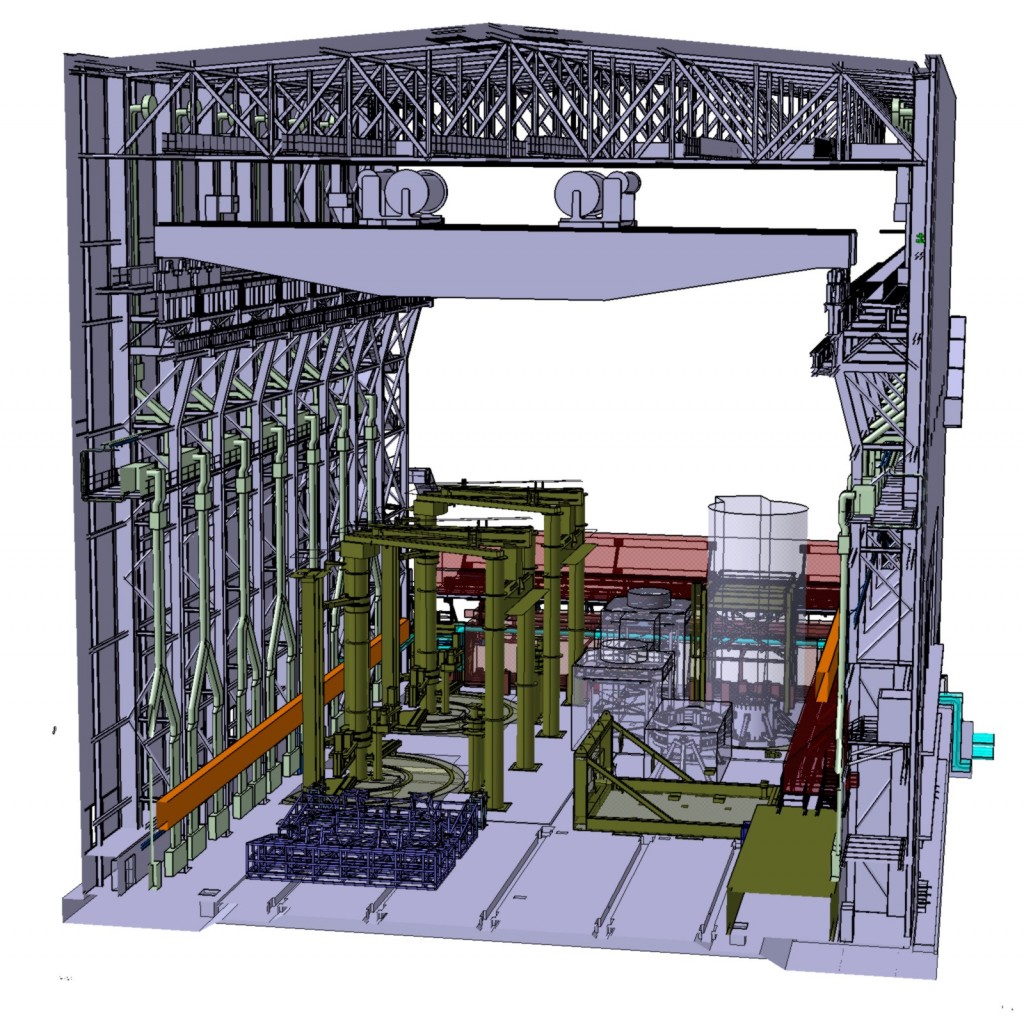
Housing the pre-assembly of components
2013-07-21 - Working together, the four 375-tonne main hoists in the Assembly Building will handle loads of up to 1,500 tonnes.

Building up the rebar to 1.5 metres
2013-07-20 - The second basemat in the Tokamak Pit—the 1.5-metre-thick B2 slab—will be the floor of the Tokamak Complex, supporting the Diagnostic, Tokamak and Tritium buildings. The basemat should be in place by the end of the year.
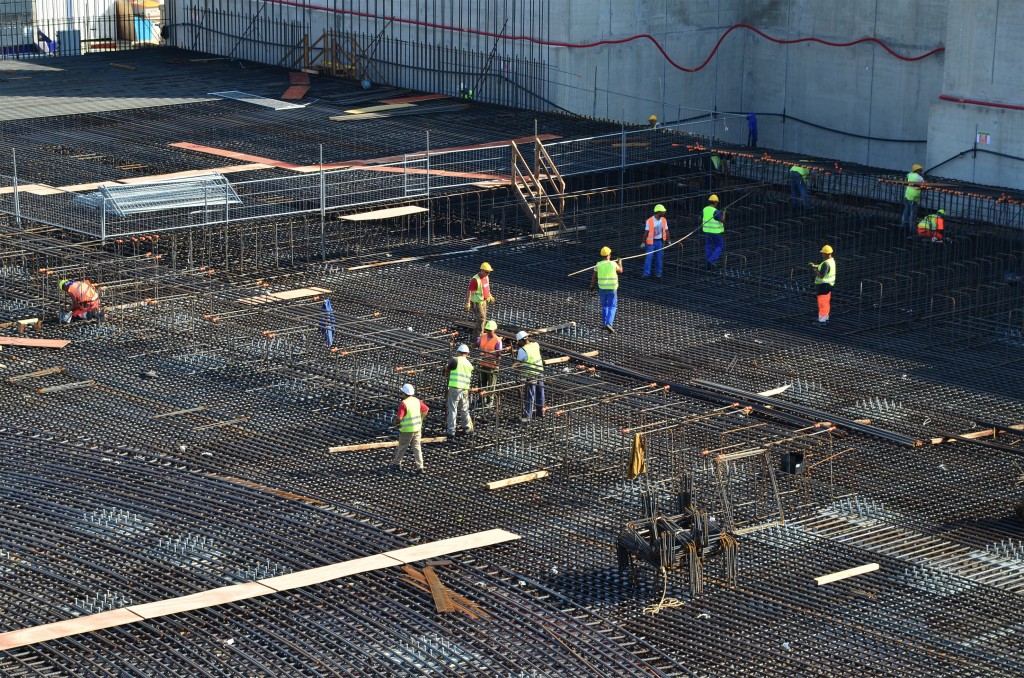
Reinforcement continues
2013-07-20 - Successive layers of metal reinforcement are positioned in the Tokamak Pit. Concrete pouring will be carried out throughout the autumn.

Finishing the basemats
2013-07-20 - Foreground: the basemat for the temporary Cryostat Workshop. Left: the exit platform for the completed poloidal field coils. Right centre: the Assembly Building basemat.
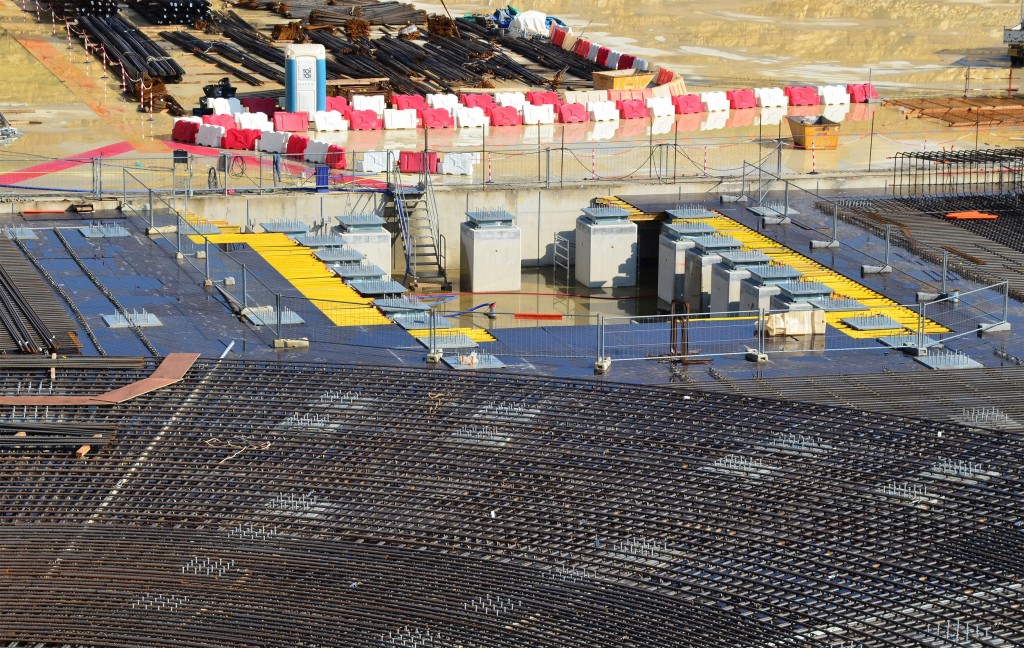
One last section
2013-07-20 - Of the 11,700 square metre surface of the Seismic Pit, this small area is the only one not yet covered by propping, formwork and rebar. Machinery for the cask transfer lift, which will transport components between the main building and the Hot Cell, must be installed first.

Last bits
2013-07-20 - Finishing, cleaning and testing works are carried out on the Assembly Building slab in July.

New roads for the construction consortiums
2013-07-16 - Asphalt is poured in and around the new Contractors Area (CA2) where teams will soon settle in to manage the large construction contracts that have been awarded in the last six months.

Another large steel structure
2013-07-15 - Workers complete rebar operations on the 5,500 square-metre slab of the Cryostat Workshop, adjacent to the Poloidal Field Coils Winding Facility.
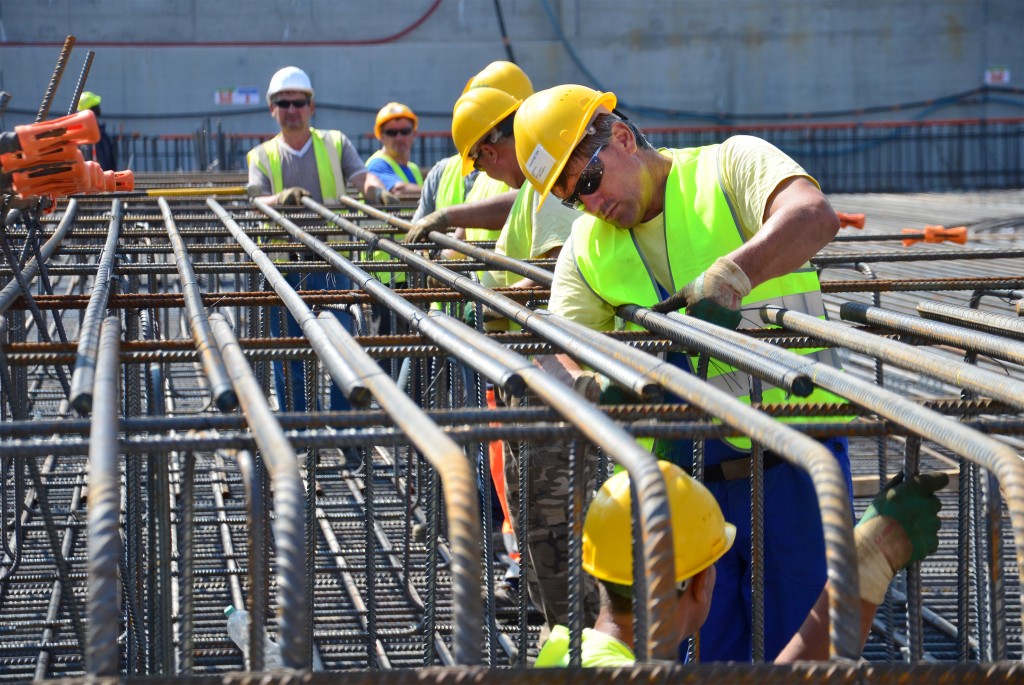
Assembling the rebar
2013-07-15 - On the site of the future Diagnostics Building, rebar structures take their place. If all goes according to schedule, concrete pouring will begin on this side of the Tokamak Pit in August.

Cryostat Workshop steams ahead
2013-07-15 - Concrete pouring is about to begin on the Cryostat Workshop in July 2013.
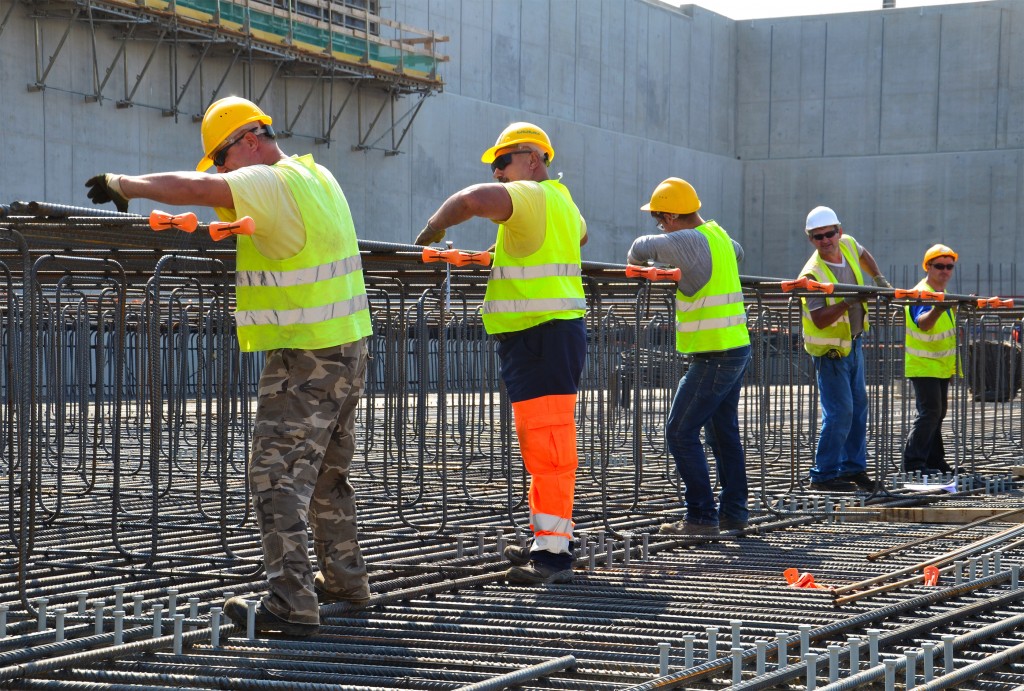
All together now
2013-07-15 - From approximately 200 people on site currently, worker numbers will rise to 1,000 at the end of the year, before climbing to 2,000, then 3,000 at the peak of construction activities.
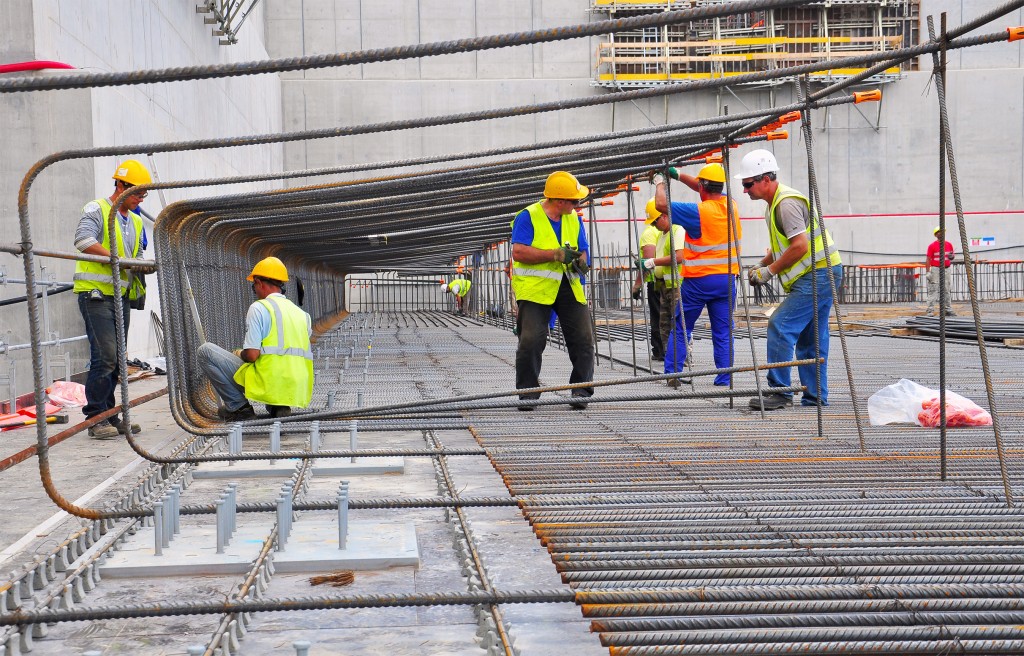
The thickness of the basemat
2013-07-10 - Looking at the rebar from the side, we get a sense of the thickness of the basemat that will support the weight of the Tokamak Complex.
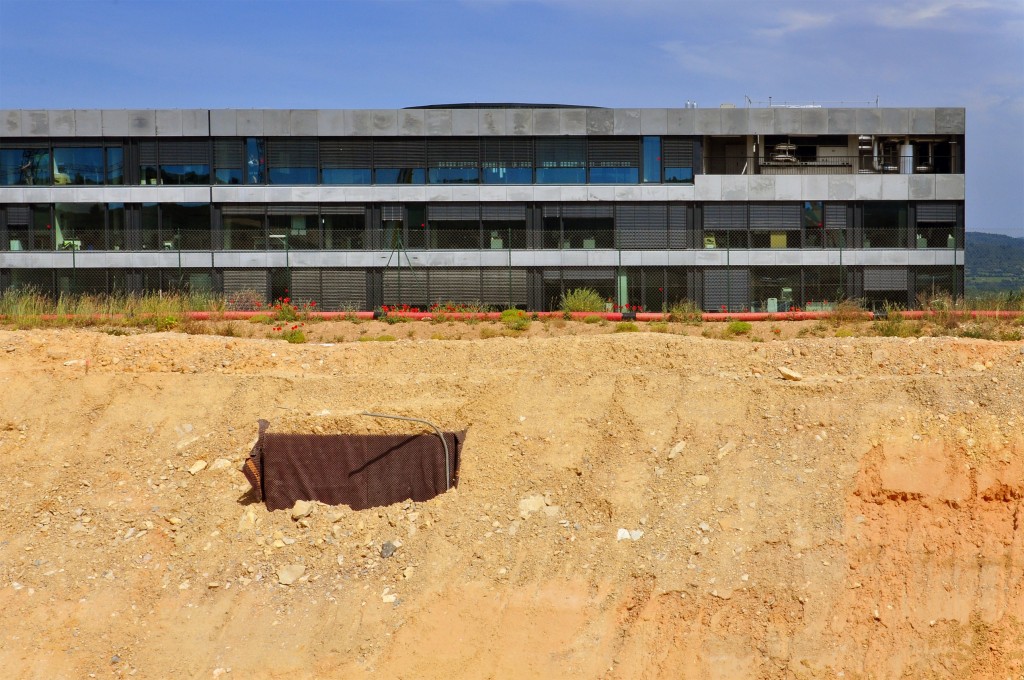
End of the tunnel?
2013-07-01 - This tunnel, leading from the second floor of ITER Headquarters, will give scientists and technicians access to the Control Building situated on the north corner of the platform. For the moment, though, it sits waiting ...
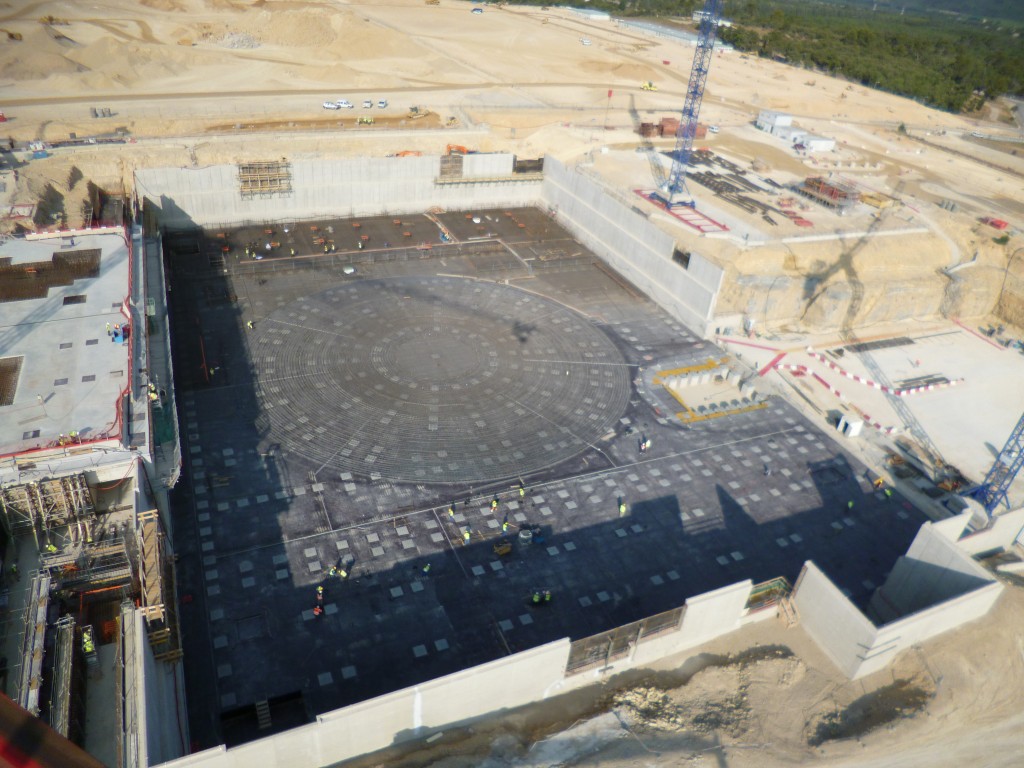
The Pit ... from above
2013-06-26 - The far end of the 90 x 130 metre Seismic Pit is reserved for the Diagnostic Building—as an experimental machine ITER will have some 45 diagnostic systems. The near end rectangle will house the Tritium Building. And in the centre ... well, you don't need us to tell you. Photo: GTM Bâtiment VINCI
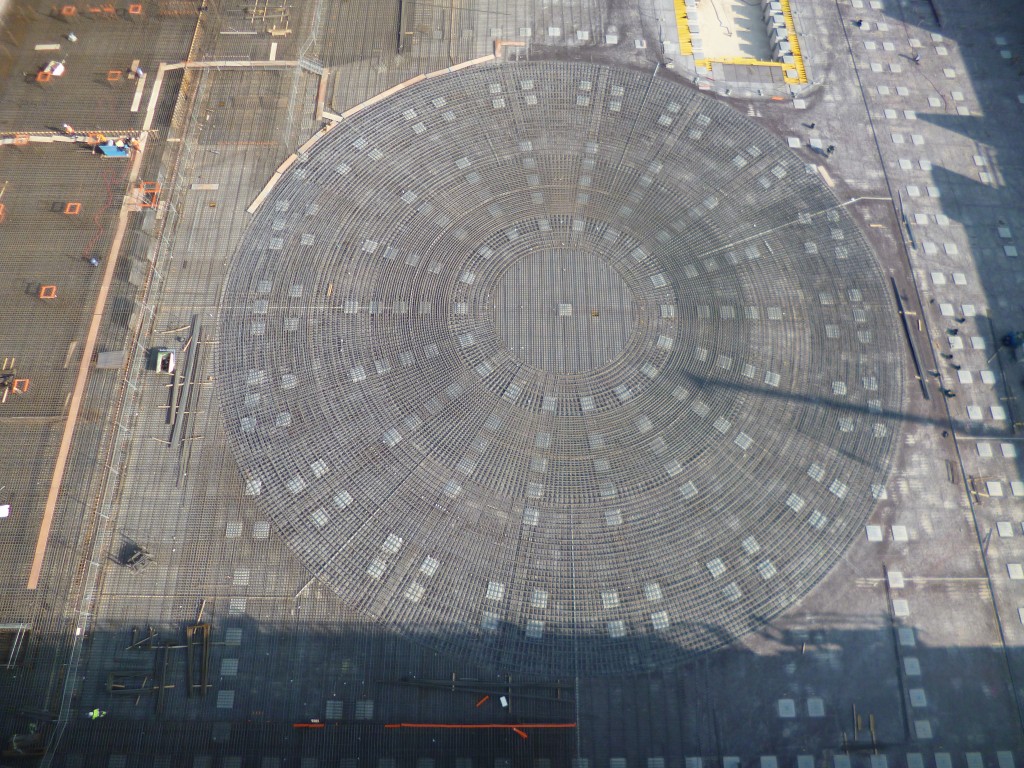
The heart of the matter
2013-06-26 - The ITER Tokamak will sit in the centre of the Tokamak Pit, surrounded by its cryostat and bioshield. The machine will weigh 23,000 tonnes—or three times the weight of the Eiffel Tower. Photo: GTM Bâtiment Vinci
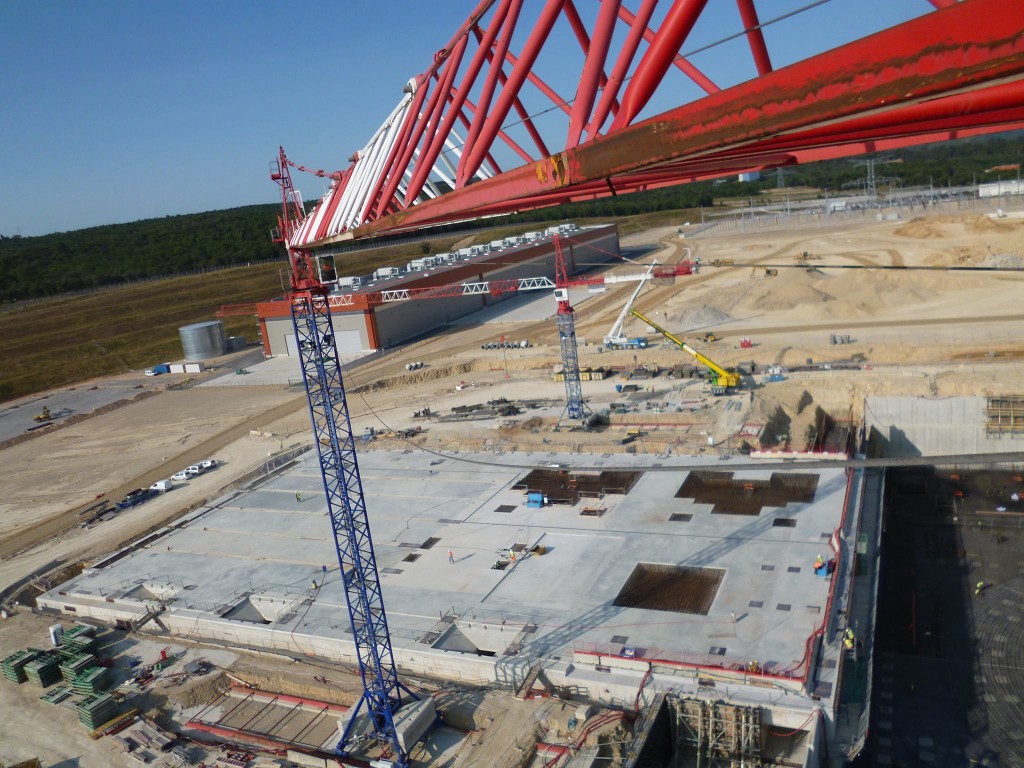
A platform for assembly
2013-06-20 - Overhead cranes running the length of the Assembly and Tokamak buildings will operate like a pair of safe hands to move the heavy components to the Tokamak Pit and position them during assembly. Photo: GTM Bâtiment VINCI
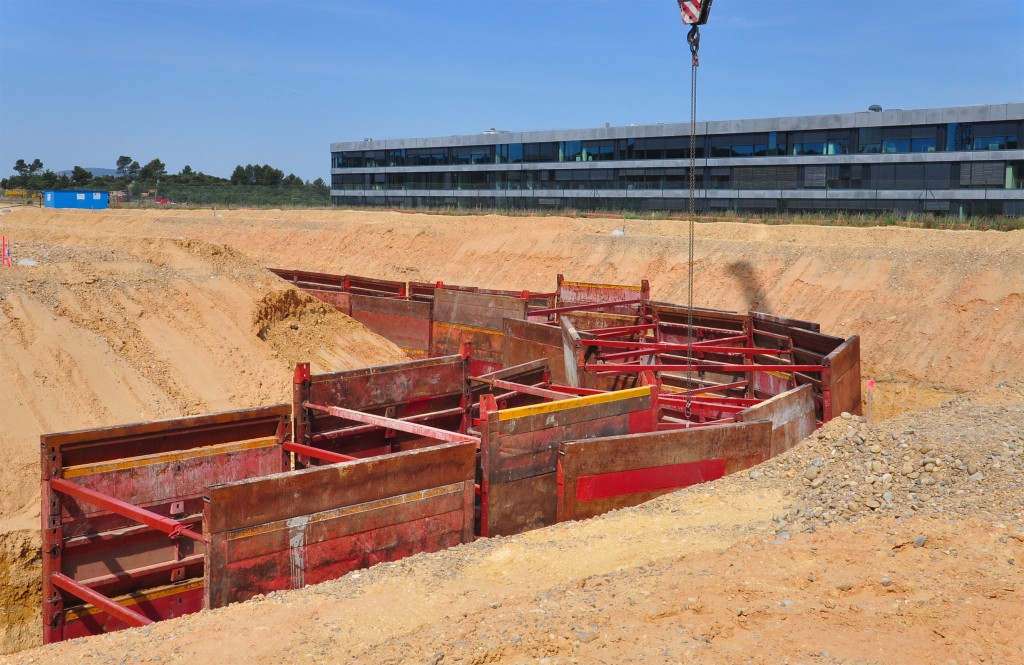
She'll be coming 'round the mountain ...
2013-06-18 - The pipes of the precipitation overflow network are protected by concrete, before backfilling and levelling operations can begin.
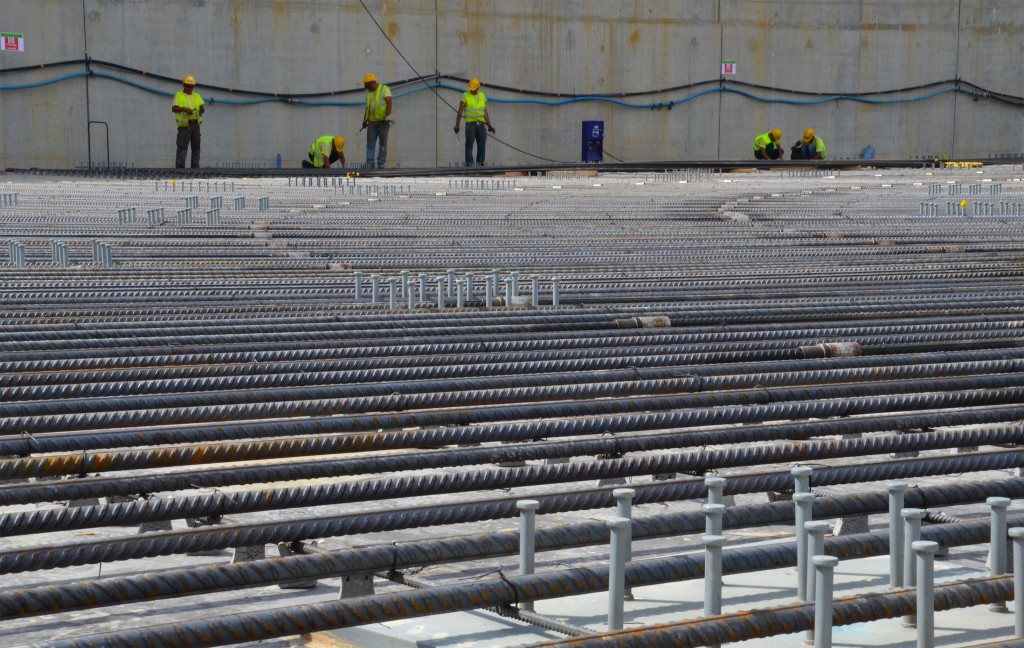
A bit of vertical in the horizontal
2013-06-18 - Poking up from the horizontal bed of rebar are the tops of each seismic pad.
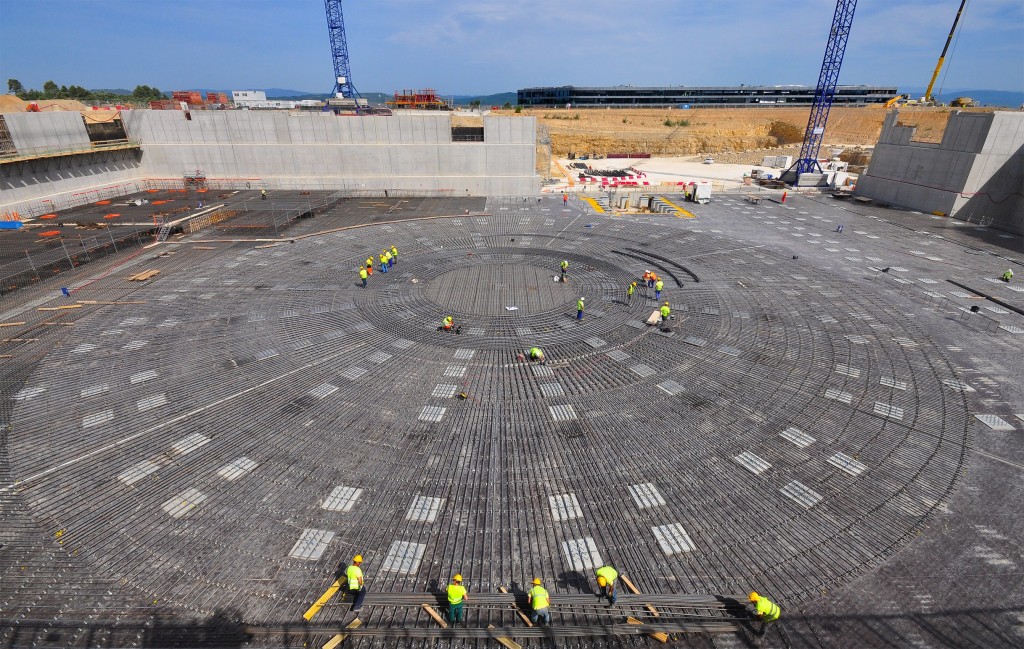
Reinforcement work underway
2013-06-18 - In mid-June, only a small section of the Tokamak Pit still requires propping and formwork. Work is underway to position 4,000 tonnes of steel rebar—in radial/circular patterns in some areas, linear in others.
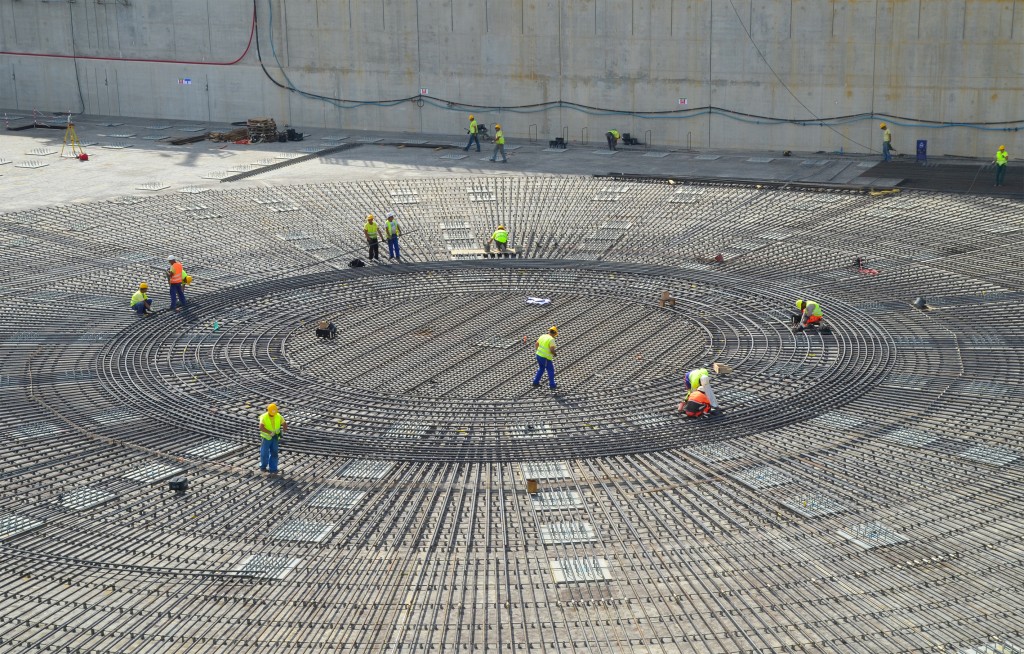
Metal sculpture
2013-06-18 - It's art that is appearing on the floor of the Tokamak Pit! Carefully placed, concentric circles of rebar at the exact spot where the Tokamak will be installed and assembled.
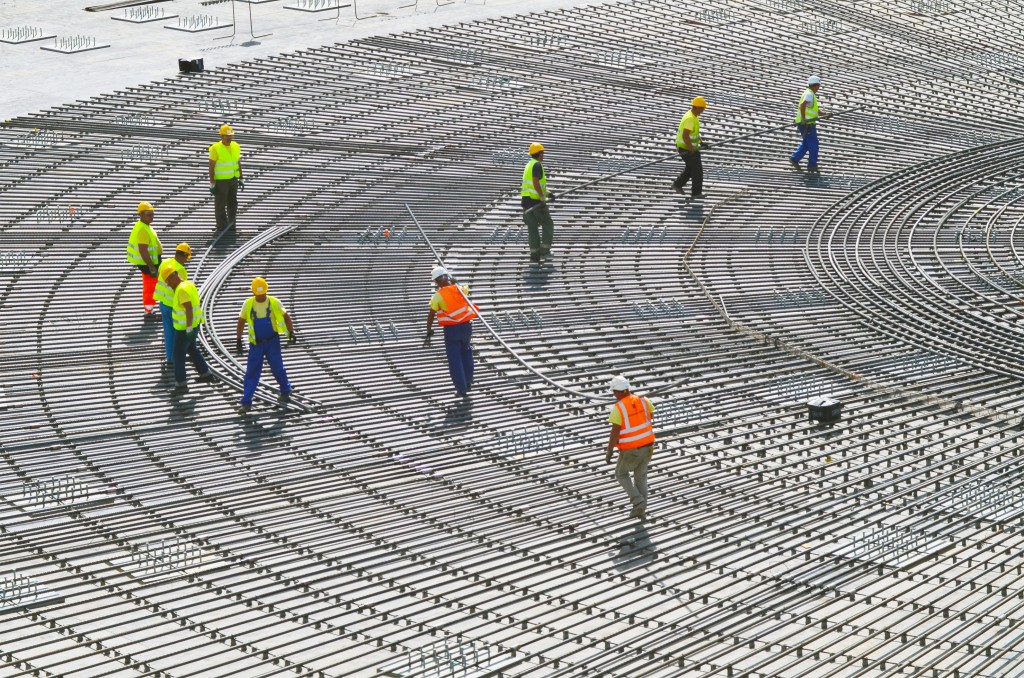
Layer two
2013-06-18 - After the first radial pattern of reinforcement, workers are now laying concentric circles of rebar around the central point.

Space left for tooling
2013-06-18 - On the completed Assembly Building basemat the footprints of three large assembly tools are visible. Here anchor plates will provide the interface between the tools and the concrete basemat.
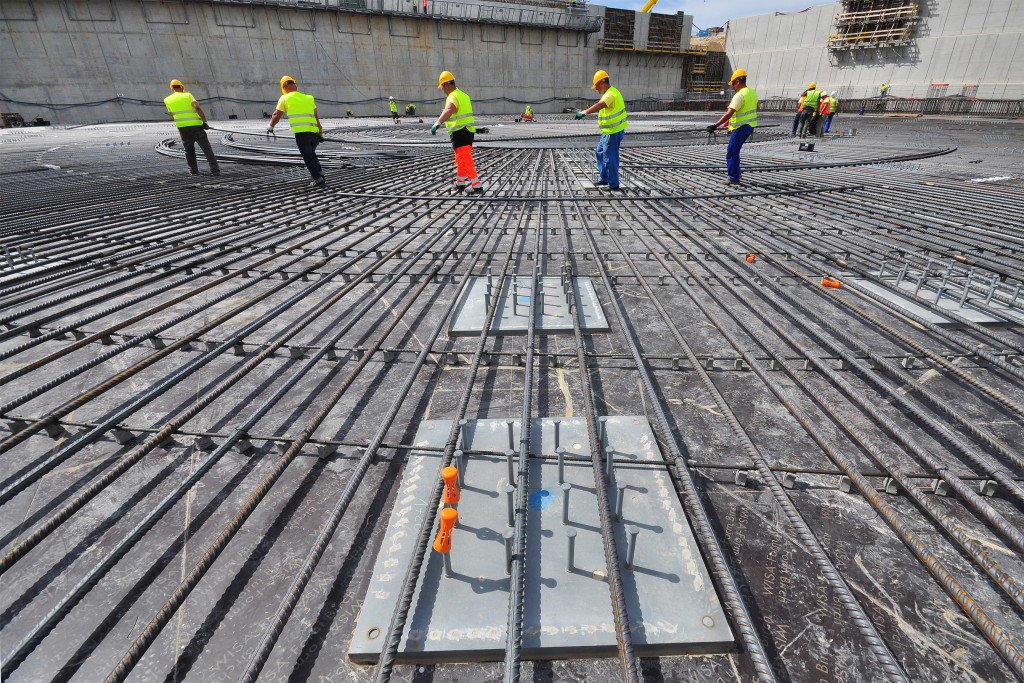
Careful calculations
2013-06-18 - Bar by bar, whether curved or straight, the reinforcement for the B2 slab is positionned and tied into place.
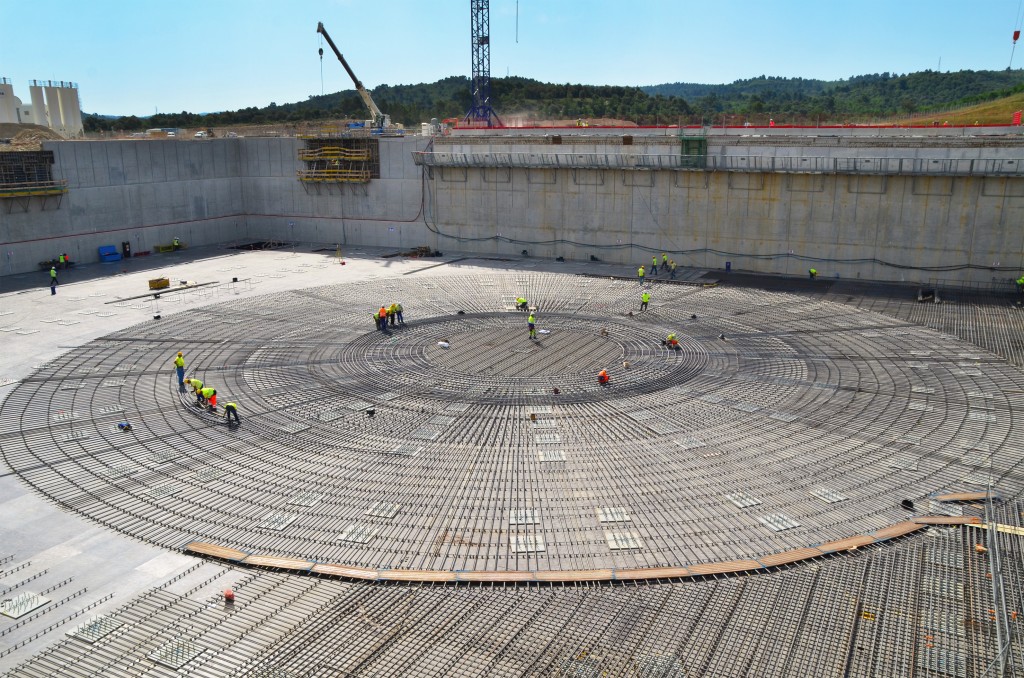
That's it, they're gone
2013-06-18 - The 493 seismic pads are now hidden from view and the Seismic Pit is no longer 17 metres deep ... With the completion of the ground support structure and the newest propping, it's more like 13 metres deep.
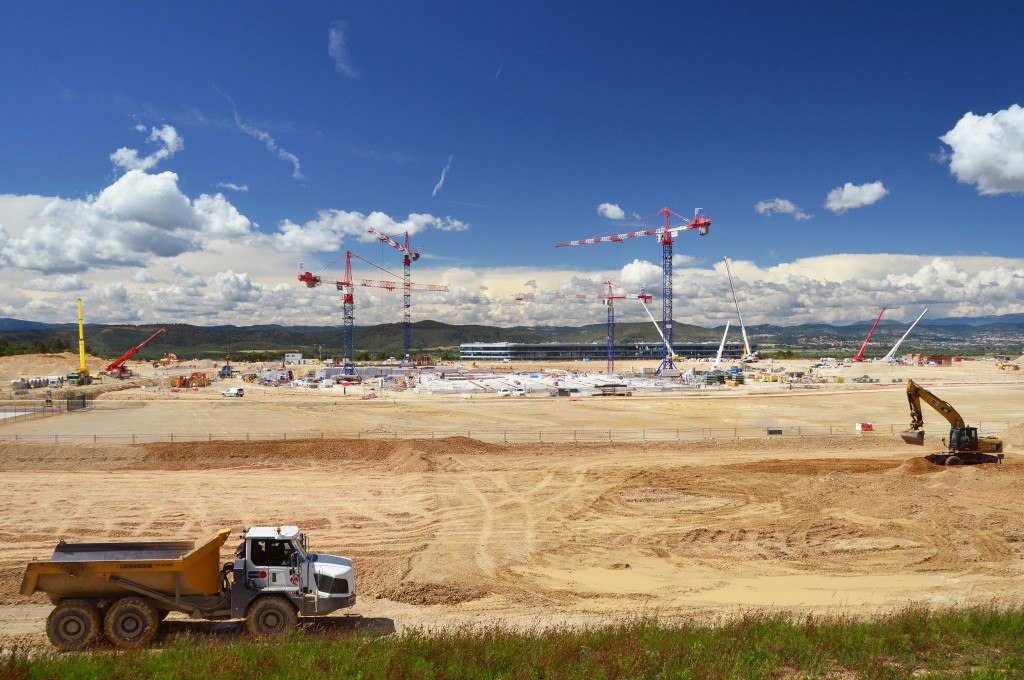
18 months of construction
2013-06-12 - The football field-size (50 x 100 m) Workshop will have equipment for machining, welding and testing, and a large "goliath" crane capable of travelling the facility's full length.
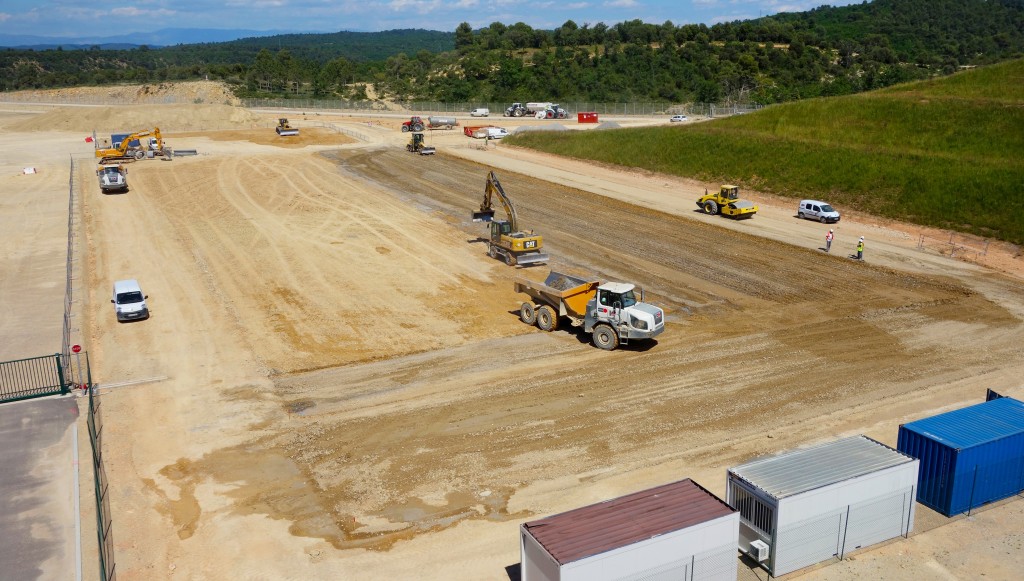
From the PF rooftop
2013-06-12 - The Poloidal Field Winding Facility and the Cryostat Workshop, side by side on the platform, are the two structures on site that will house the assembly of components that are too large to travel from the Domestic Agencies.

Short ride by rail
2013-06-12 - The Cryostat Workshop, which will occupy the parcel of land in the foreground, will be only a hundred metres or so from the entrance to the Assembly Hall.

Groundbreaking ceremony on 6 June
2013-06-06 - A large excavator symbolically scratches the earth on the site of the future Cryostat Workshop during a ground breaking ceremony in June. Since this small portion of the ITER platform has been made available to the Indian Domestic Agency, it was natural to place the parcel-sized piece of India under the protection of Ganesha, the "Remover of Obstacles."
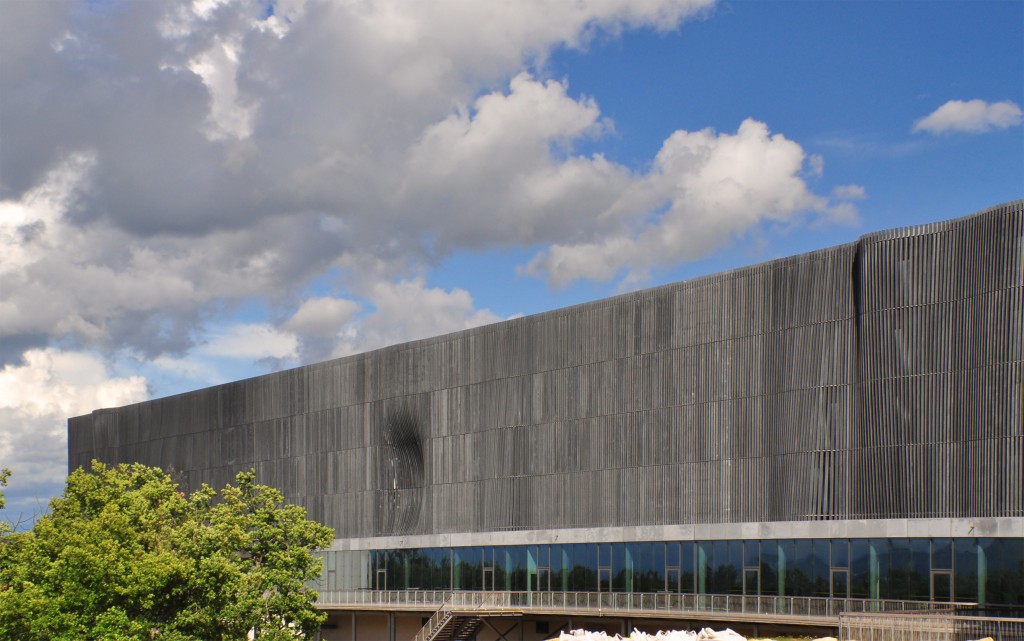
The ITER Organization's new Headquarters building
2013-05-29 - The ITER Headquarters, photographed in May between two storm clouds. The northwest-facing cafeteria occupies the lower level of the building.
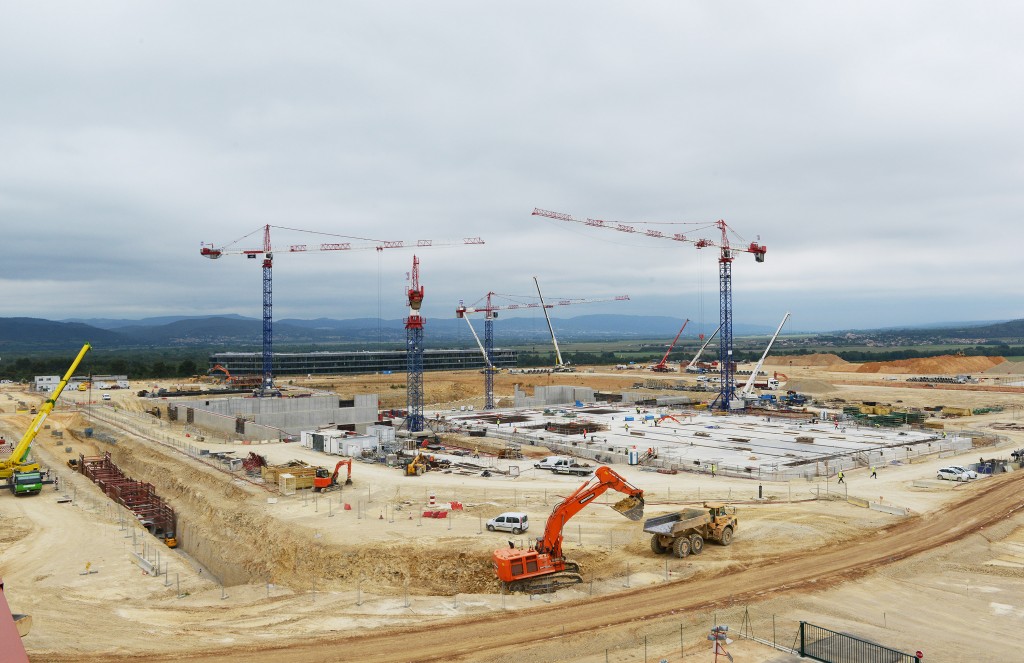
Basemat done, spaces remain for the anchoring of large tools
2013-05-28 - On the completed Assembly Building basemat, three segments (or box-outs) remain unpoured. The largest assembly tools will be anchored here; some interfaces between the anchor plates and the tooling remain to be defined. Photo: F4E
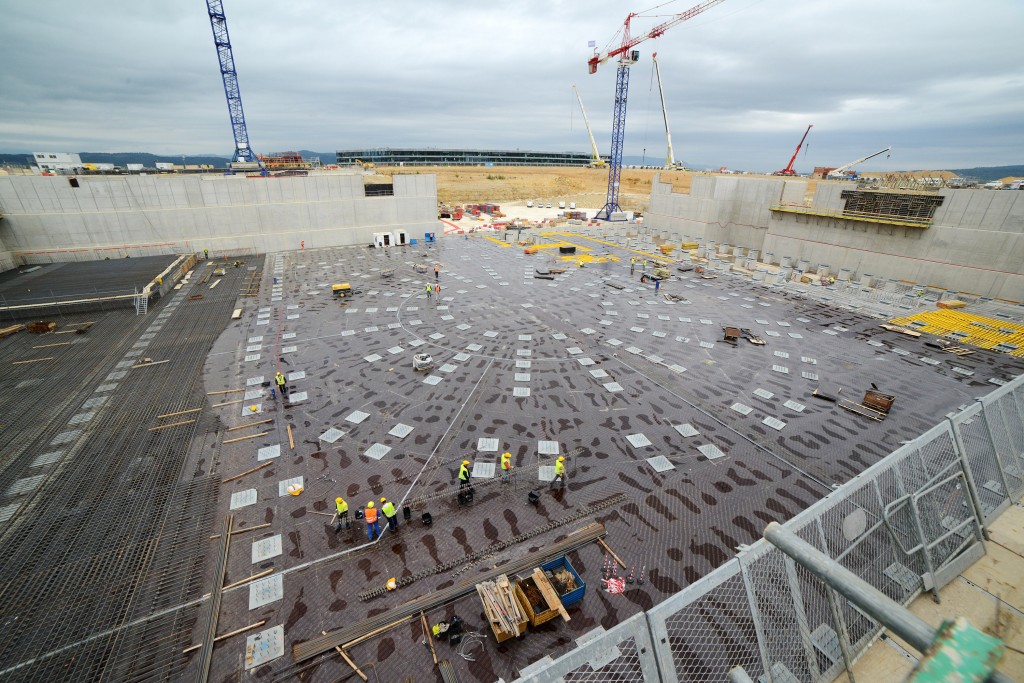
B2 basemat prep work progresses
2013-05-27 - This picture dates from late May. As of mid-June 2013, 85% of formwork has been completed and reinforcement activities are in full swing. Photo: F4E
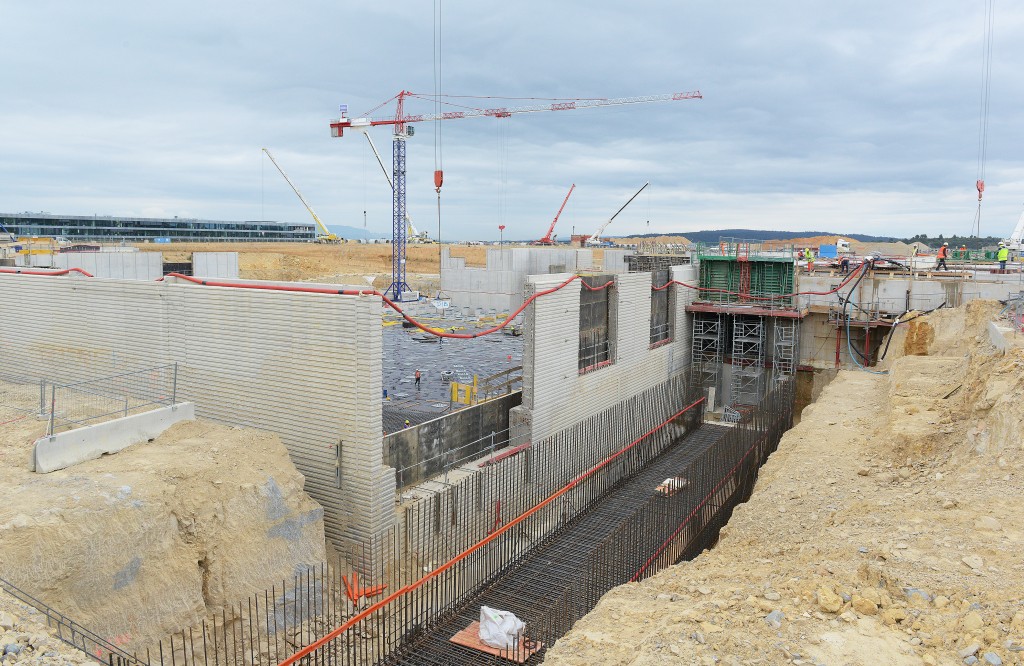
In between the behemoths
2013-05-27 - This gap between the Tokamak Complex and the Assembly Building will permit the installation of critical networks such as electricity, piping and cooling. Photo: F4E

Careful alignment
2013-05-27 - In one corner of the Tokamak Pit reinforcement begins; for this first level, the steel rebar is held in place by temporary props. Photo: F4E
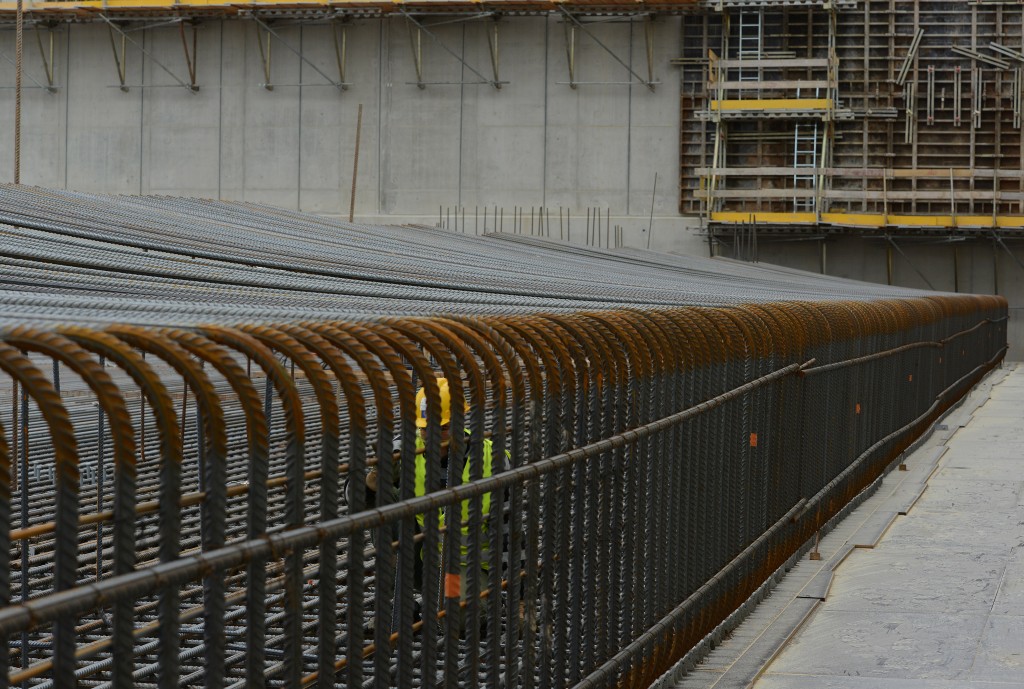
A wave of steel rebar
2013-05-27 - Rebar in installed in pre-decided patterns on the floor of the Tokamak Pit. Approximately two metres will subsist between the Tokamak Complex basemat and the surrounding walls, so that the entire Complex can move on its seismic pads in case of ground motion.
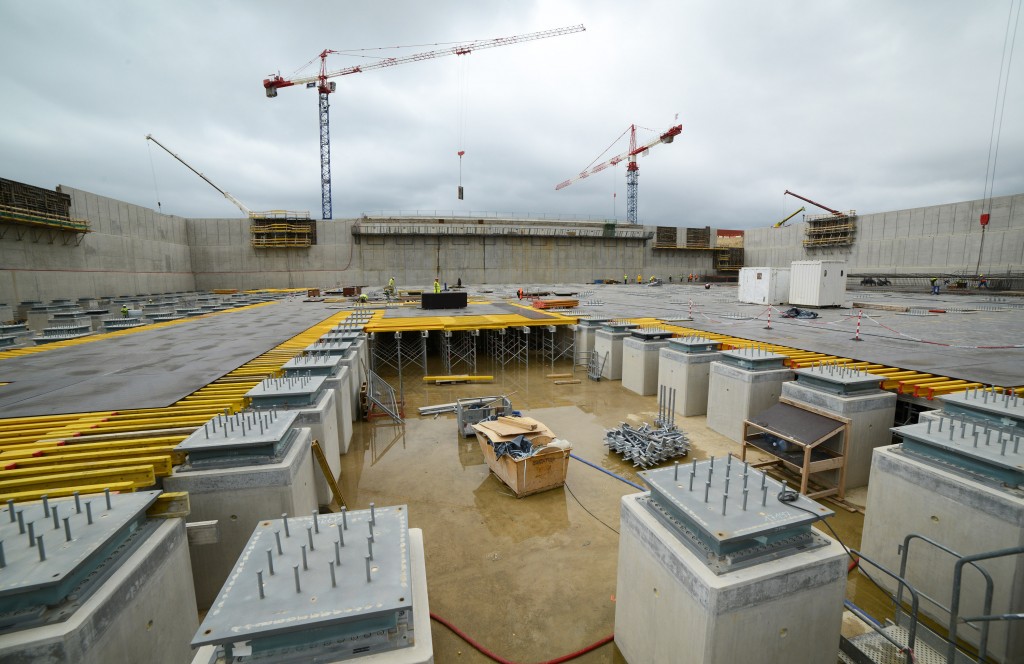
The shoring toolkit
2013-05-27 - Everything needed to shore up the yellow formwork is ready for the next shift: aluminum props, connectors, clasps ...
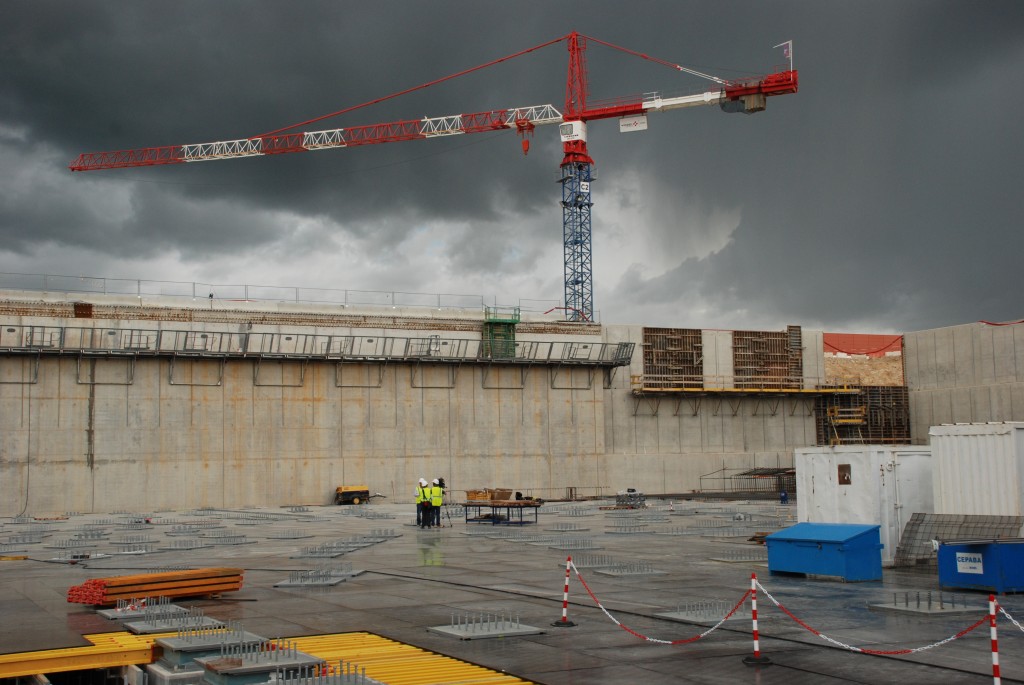
Storm's coming!
2013-05-26 - One afternoon in late May the storm clouds gather over the Tokamak Pit. Time to call it a day!

A long day's work
2013-05-26 - Fifteen metres below the surface of the platform men are at work to prepare for the B2 slab concrete pouring activities.
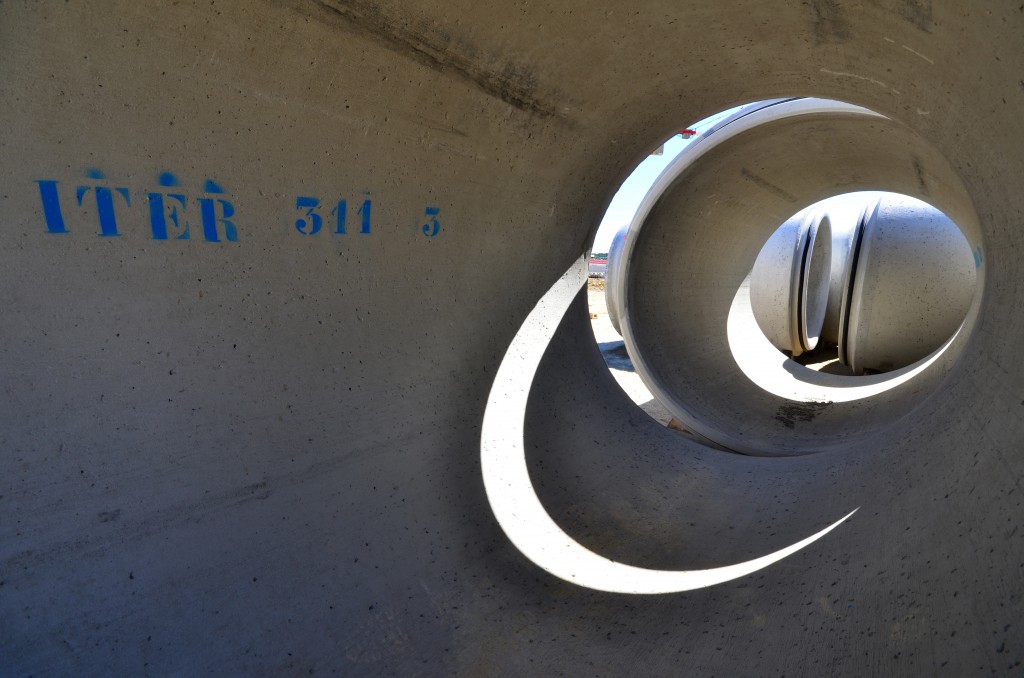
Platform networks
2013-05-21 - Hundreds of metres of concrete pipes (two-metres in diameter) have been installed for the platform's deep rainfall drainage network. The mountains of dirt will soon disappear: 80% of backfilling and levelling is now completed.
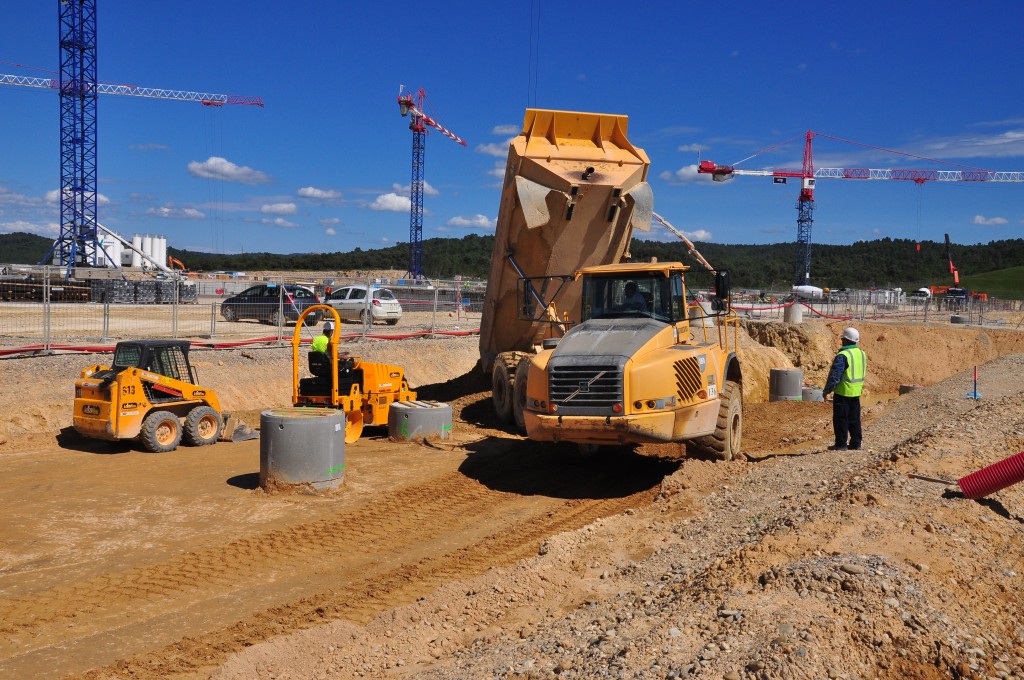
Backfilling is easier in clement weather
2013-05-21 - Backfilling operations continue after the heavy rainfall of mid-May. The deepest galleries will be filled over; at a later stage, digging will begin again for the cooling water pipes that will lead to and from the Tokamak Building.
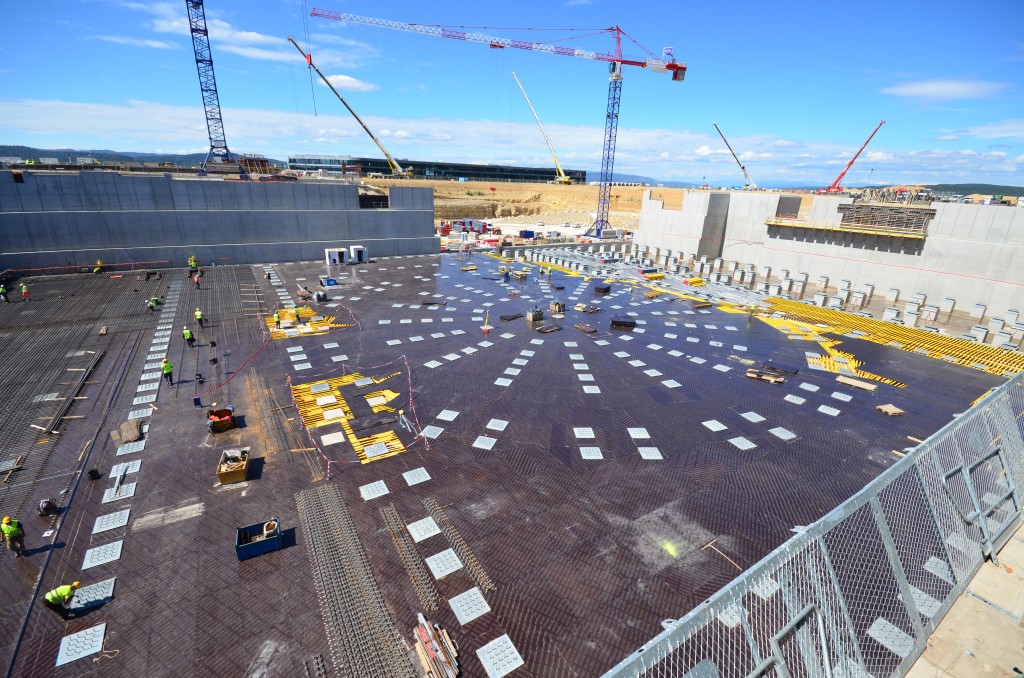
A strategic notch in the wall
2013-05-21 - The propping and formwork extends to the very walls of the Seismic Pit. And yet, all of these materials will have to be removed once the basemat is in place so that the seismic pads will remain accessible for inspection. How will it be done? A notch in the far wall will be the "exit door" through which the material will be removed.
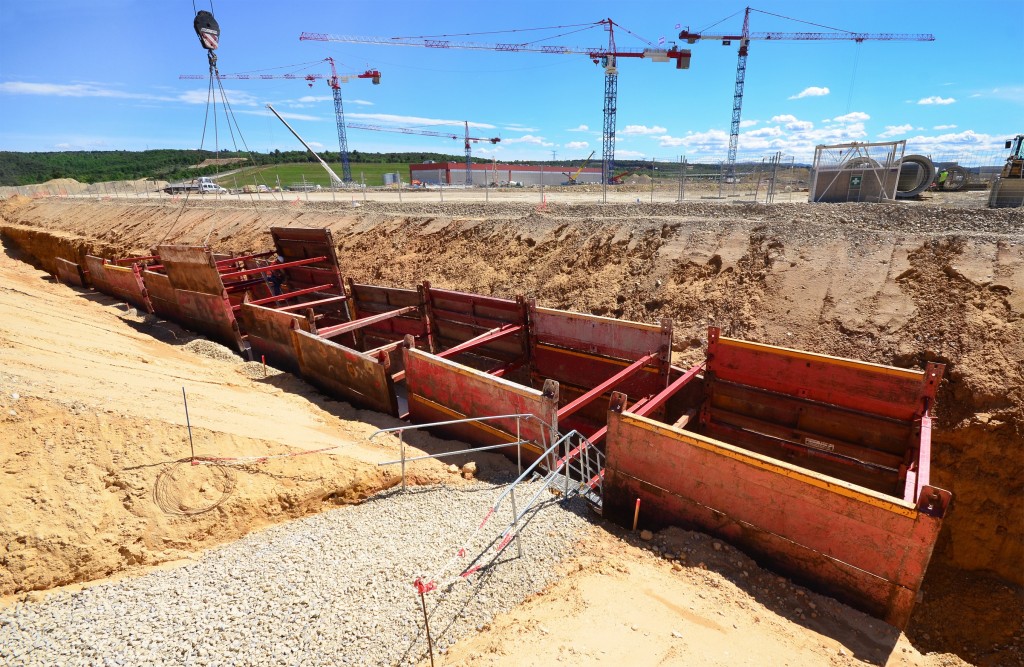
Galleries and pipes finished in July
2013-05-21 - As the bottom slab (B2) of the Tokamak Complex takes shape, the realization of technical galleries around the Tokamak Building continues.

A train station?
2013-05-21 - Spaces are maintained between the different segments of the basemat to accommodate the tracks of a small ITER "railroad." The four large cryostat segments--cylinders measuring 30 metres in diameter—will travel from the Cryostat Workshop to the Assembly Building by rail.
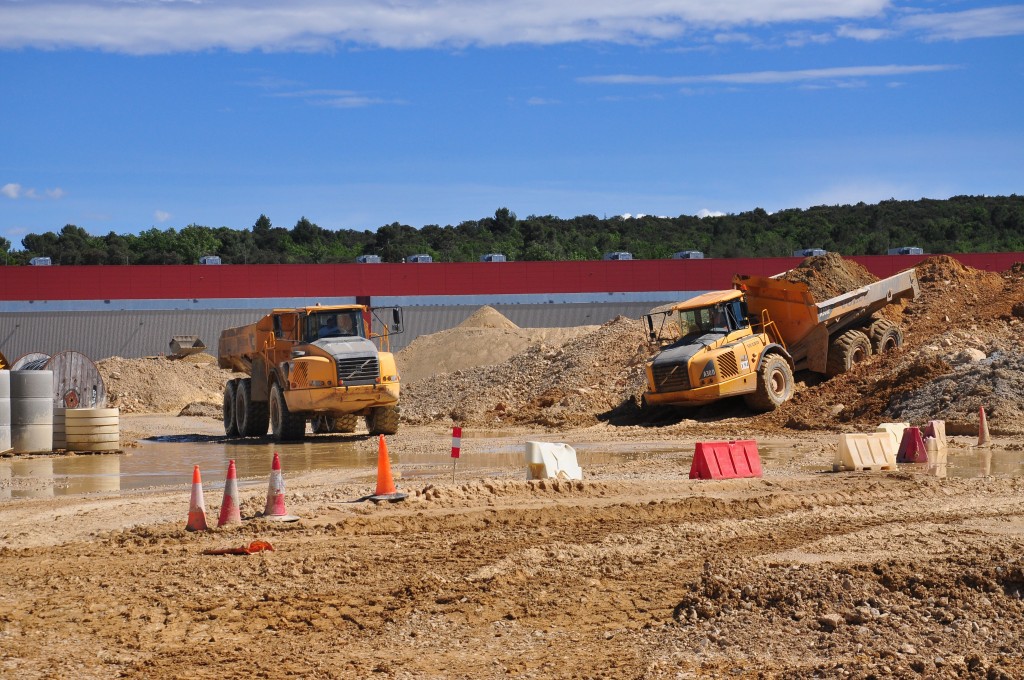
Upheaval on the platform
2013-05-21 - All around the Tokamak Pit galleries are being dug for critical networks (heating, cooling, electricity). The excavated material is then used for backfill.
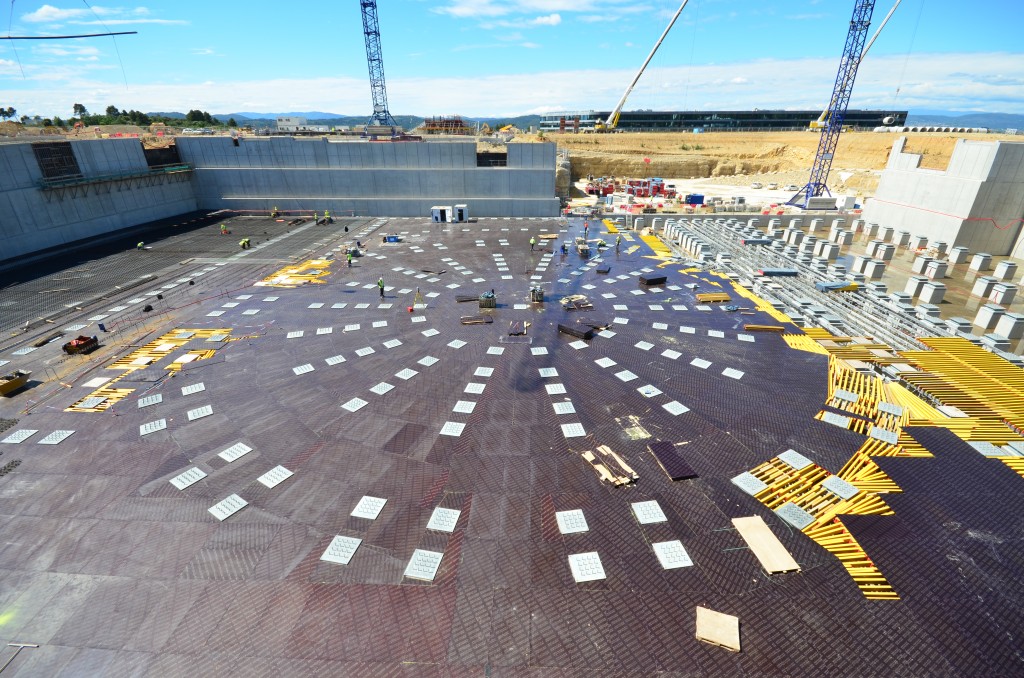
Looking towards Headquarters
2013-05-21 - In just three months, the seismic columns have nearly disappeared from view. Work will begin late in May on reinforcement work in the area of the Tokamak.
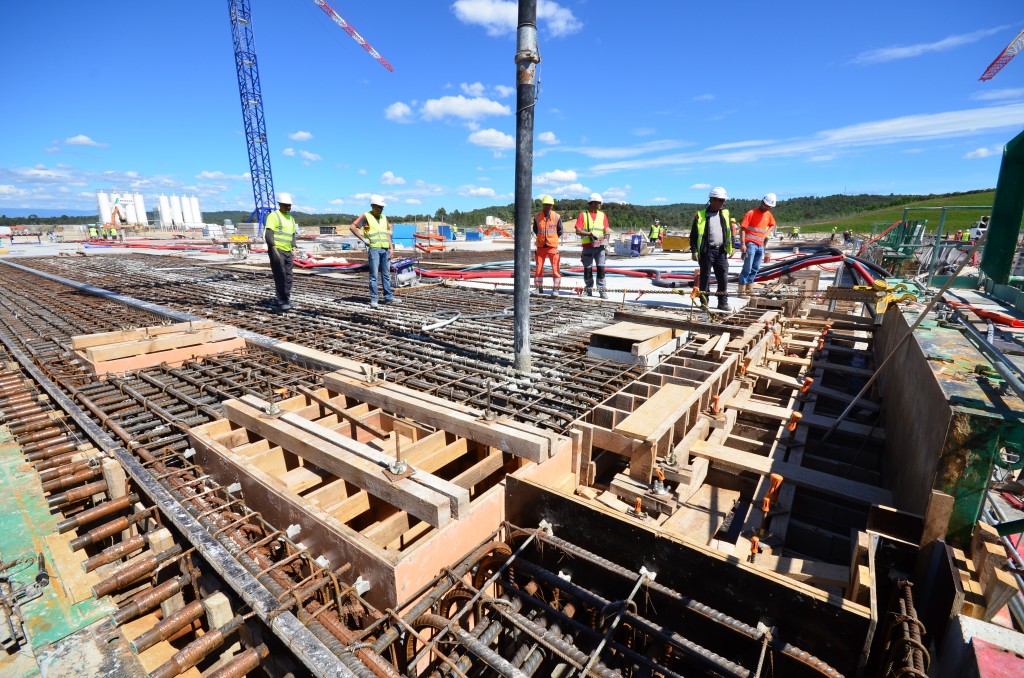
Last pouring day
2013-05-21 - Work begun in November 2012 is concluded in May 2013 with the last pour for the Assembly Building basemat.

Propping and formwork are nearly done; reinforcement begins
2013-05-21 - Level with the top of the seismic pads, the crisscrossing of reinforcement bars gets underway in May. Four to five months will be necessary to lay 4,000 tonnes of rebar.
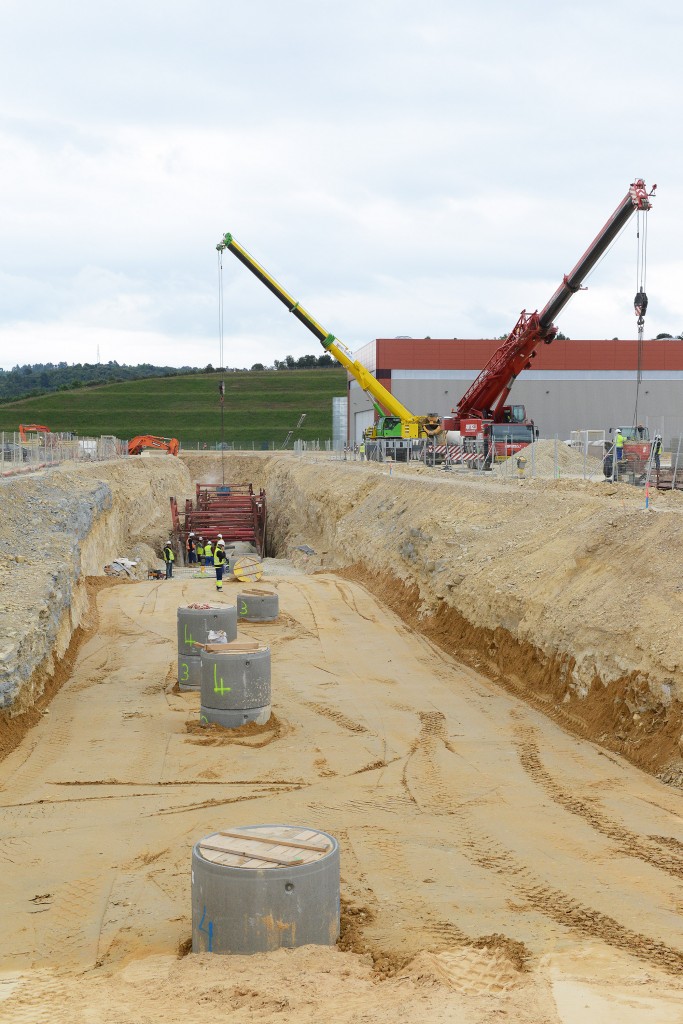
The deepest on-site networks
2013-05-20 - Crossing the platform between the Headquarters building and the Poloidal Field Coils manufacturing facility is part of the platform's deep precipitation network. Photo: F4E
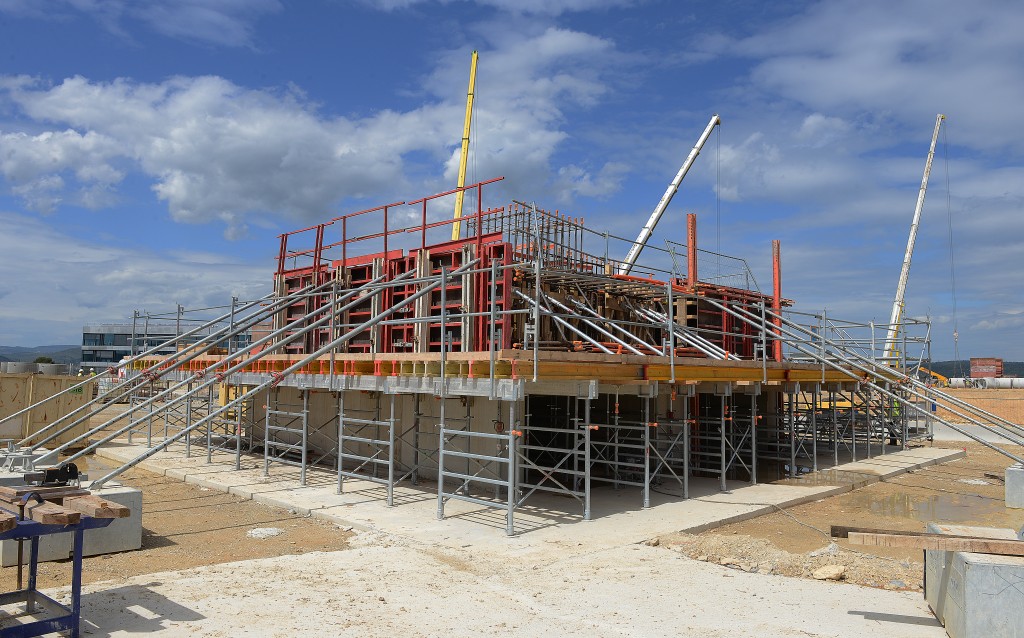
Concrete pouring tests on mockup
2013-05-07 - The 1:1 scale mockup of B2 foundation slab reinforcement is now ready for concrete pouring tests. The challenge will be to ensure that the concrete is uniformly distributed throughout the mockup's dense metal skeleton. Photo: F4E
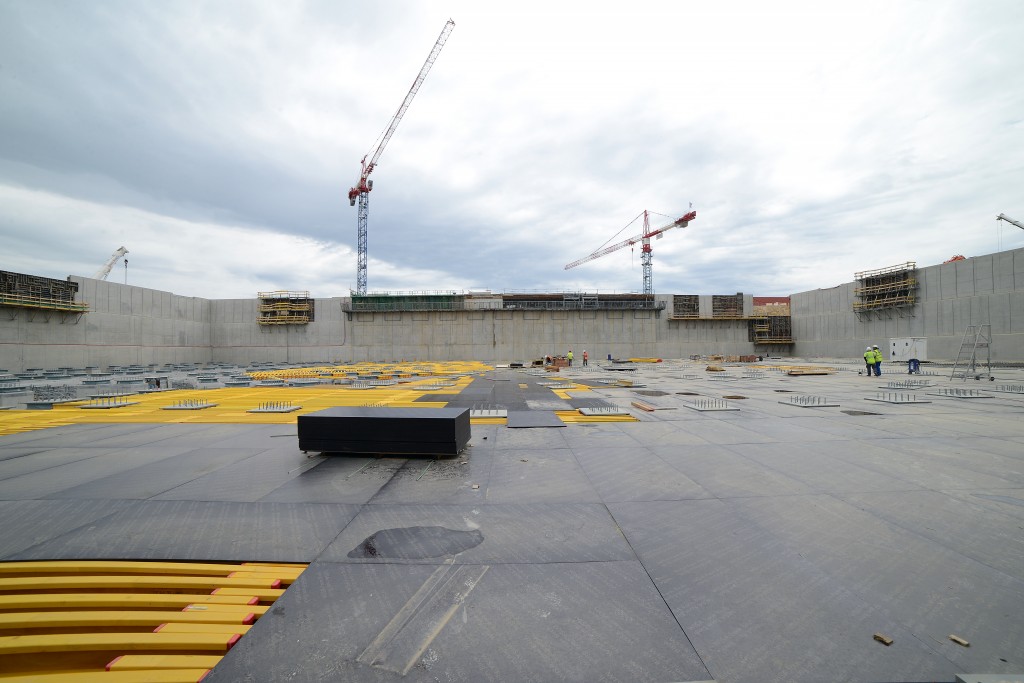
It used to be 17 metres deep
2013-05-07 - The Seismic Pit was 17 metres deep after its excavation. But after the first 1.5-metre-thick basemat was set into place, followed by two metres of seismic columns and pads ... workers are now standing approximately 13 metres below the platform. Photo: F4E
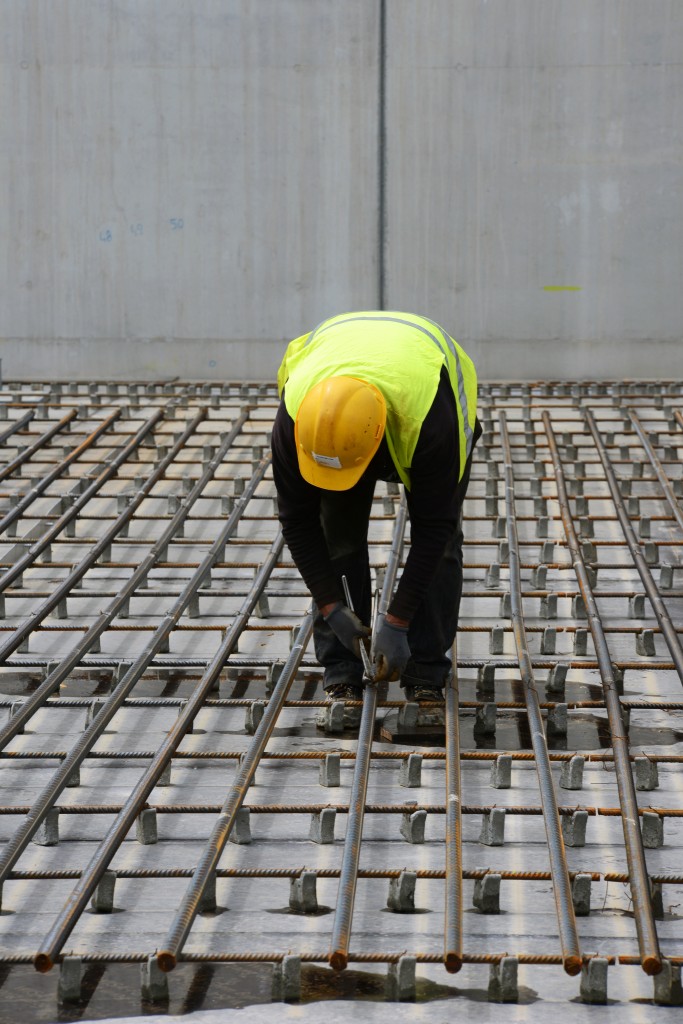
Precision work
2013-05-07 - Reinforcement work begins in the Tokamak Pit, approximately 13 metres below platform level. The second basemat, like the first, will be 1.5 metres thick. Photo: F4E
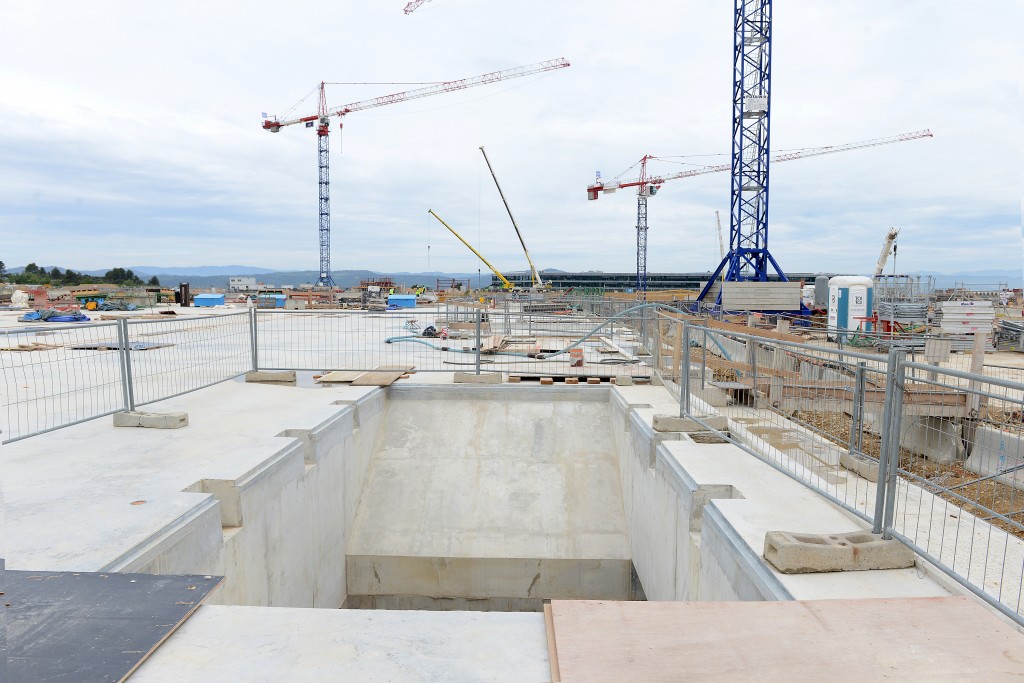
Basemat now finished
2013-05-07 - Space has been reserved within the basemat of the Assembly Building for the passage of electrical cables. Photo: F4E
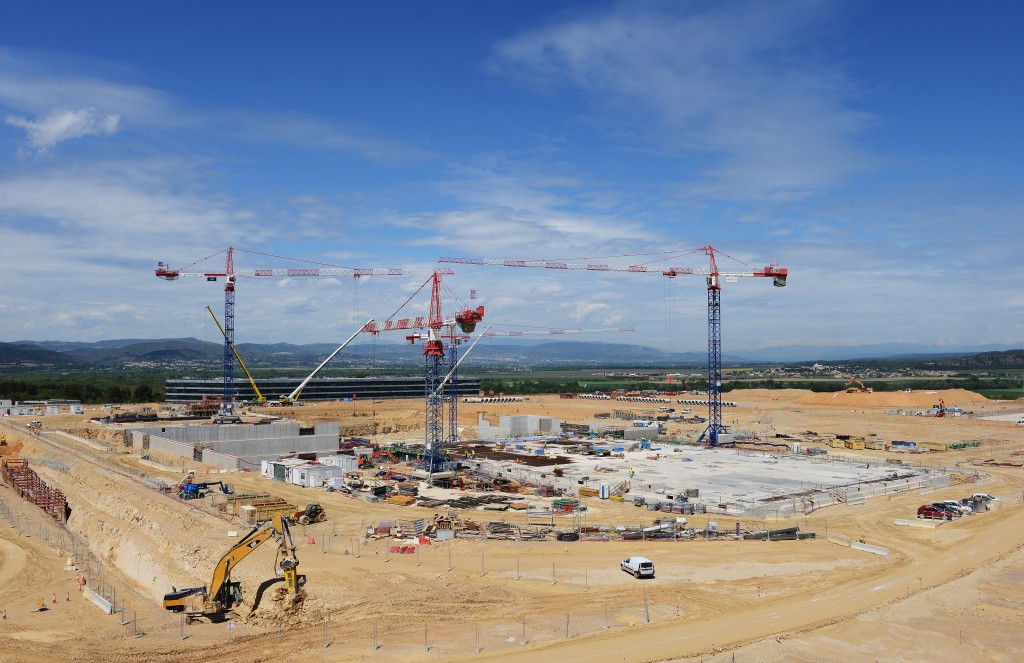
The centre of it all
2013-05-07 - The heart of construction activity will take place here in the next years: the Tokamak Complex and Assembly Building. Both structures will rise above the tallest cranes to reach 60 metres. Photo: F4E

Heave ho
2013-05-07 - This propping, like so many broad shoulders, will support the weight of the concrete basemat that will begin to take shape in August. Once the basemat is in place, these materials will be removed. Photo: F4E
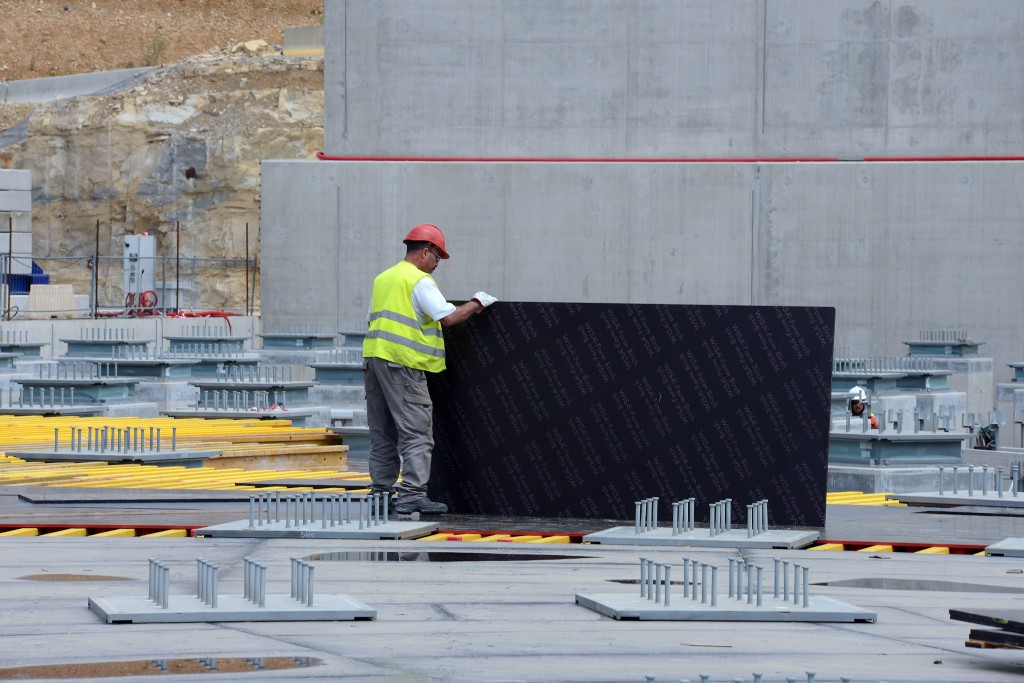
End of shoring/formwork activities in July
2013-05-07 - Workers prepare for the pouring of approximately 14,400 cubic metres of concrete for the basemat of the Tokamak Complex. Photo: F4E
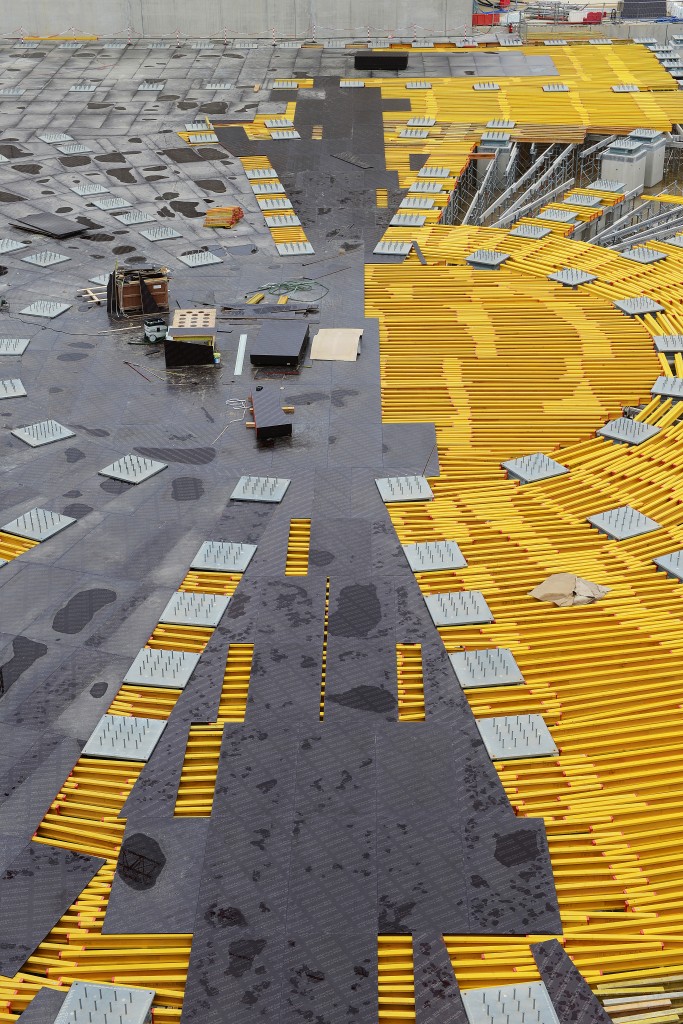
The ITER Tokamak
2013-05-07 - The ITER Tokamak, surrounded by its cryostat and bioshield, will sit in the centre of the Tokamak Pit. Twenty-three thousand tons, that's three times the weight of the Eiffel Tower. Photo: F4E
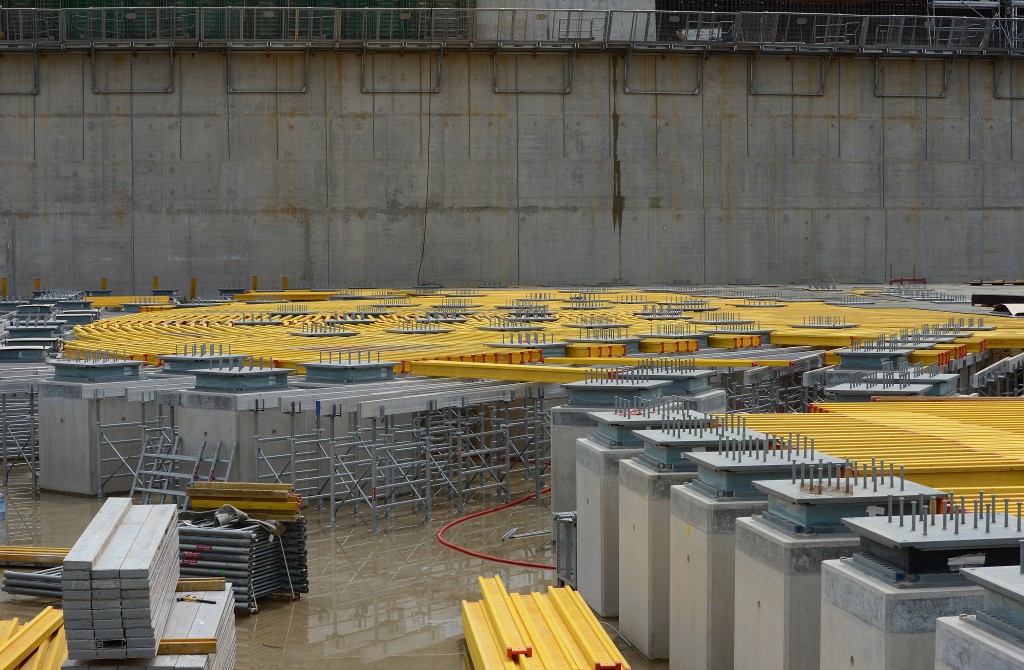
A rainy spring in Provence
2013-05-07 - Despite uncharacteristically poor weather, work to prepare for the Seismic Pit's second concrete basemat advances. Photo: F4E

Completing the technical galleries
2013-05-07 - Technical galleries are finalized all around the Tokamak Complex in May.
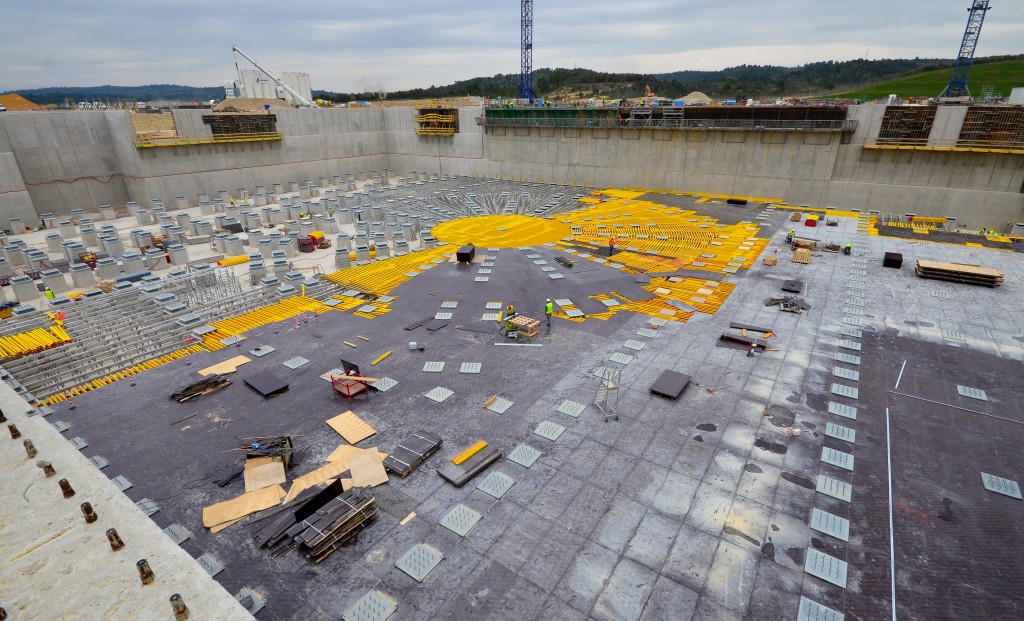
A yellow sun
2013-04-25 - It's easy to see where the ITER Tokamak will sit inside of the Seismic Pit
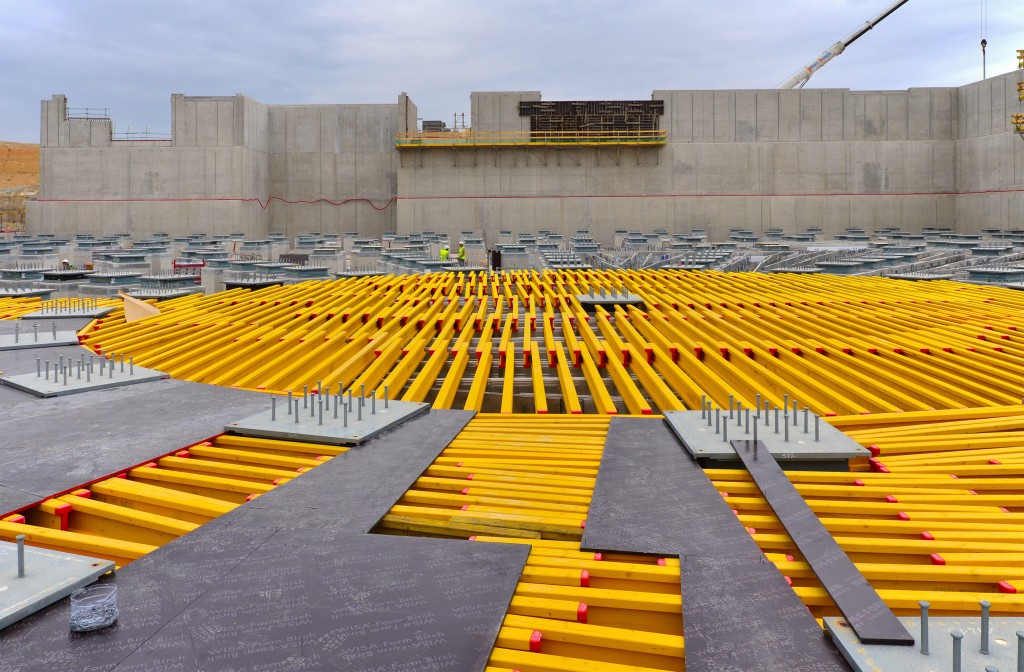
Careful cutting
2013-04-25 - Despite the complexity of the different angles, the formwork arrives—perfectly aligned—at the level of each seismic pad.
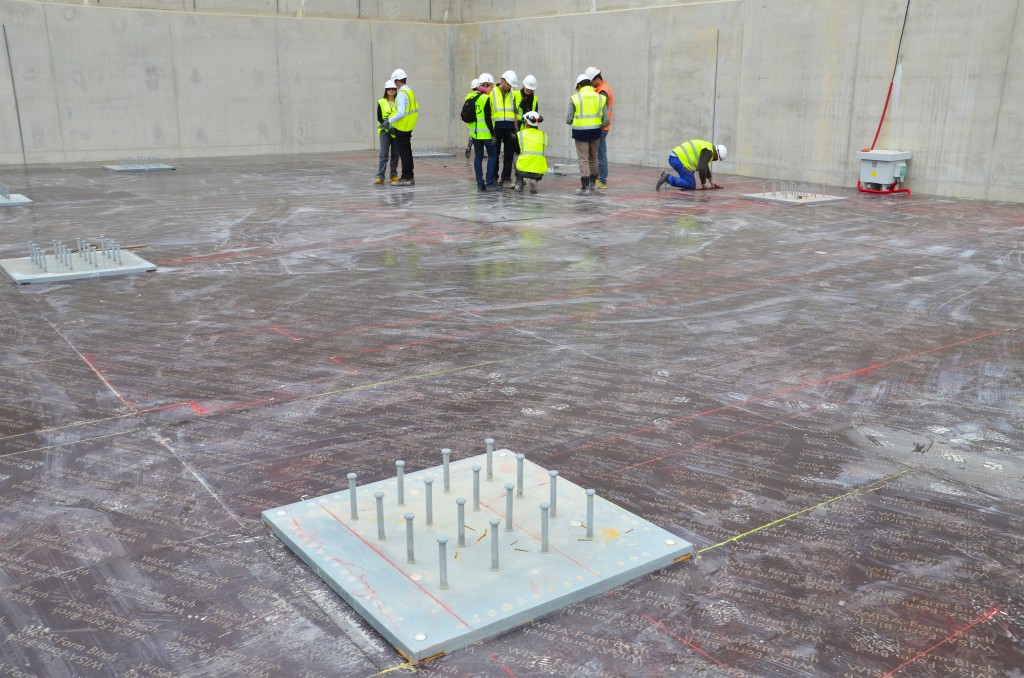
Sixth inspection since July 2011
2013-04-25 - On 25 April, the French nuclear regulatory inspectors (ASN), accompanied by one expert from the French Radioprotection and Nuclear Safety Institute (IRSN), scrutinized the ongoing works in the Seismic Pit.
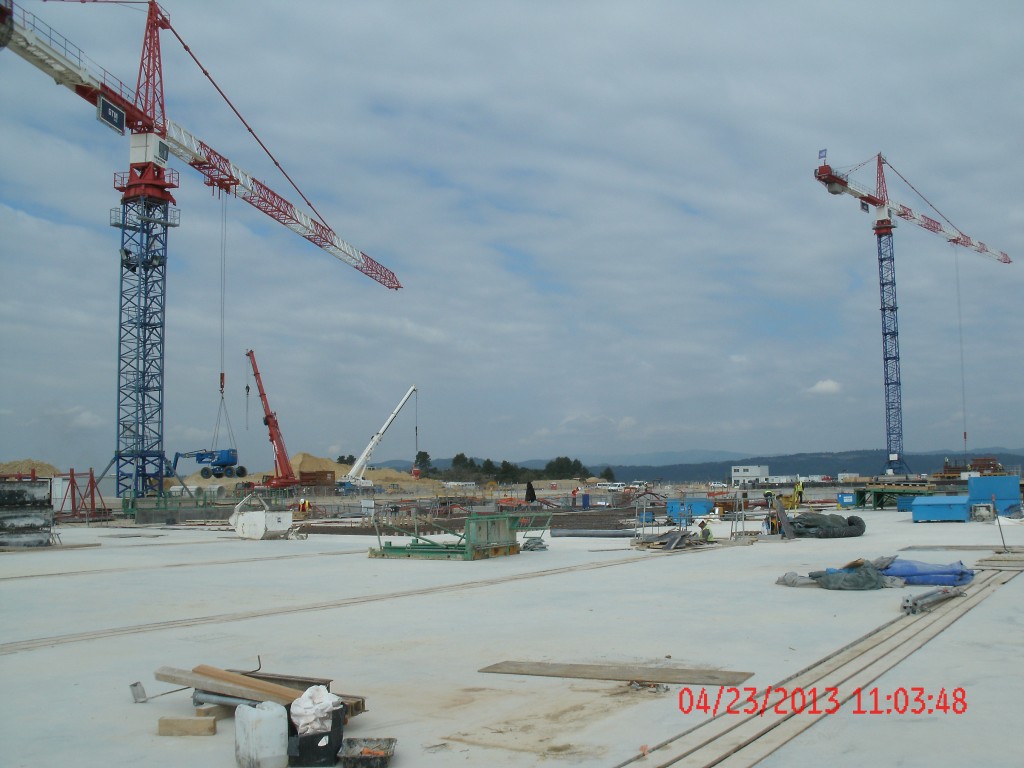
Basemat 85% completed
2013-04-23 - The basemat of the Assembly Building is nearly finished. Beginning next year, work will begin on the metal frame of the 60-metre-tall building, which will house two overhead cranes capable, together, of manipulating loads up to 1,500 tonnes. Photo: F4E/Engage
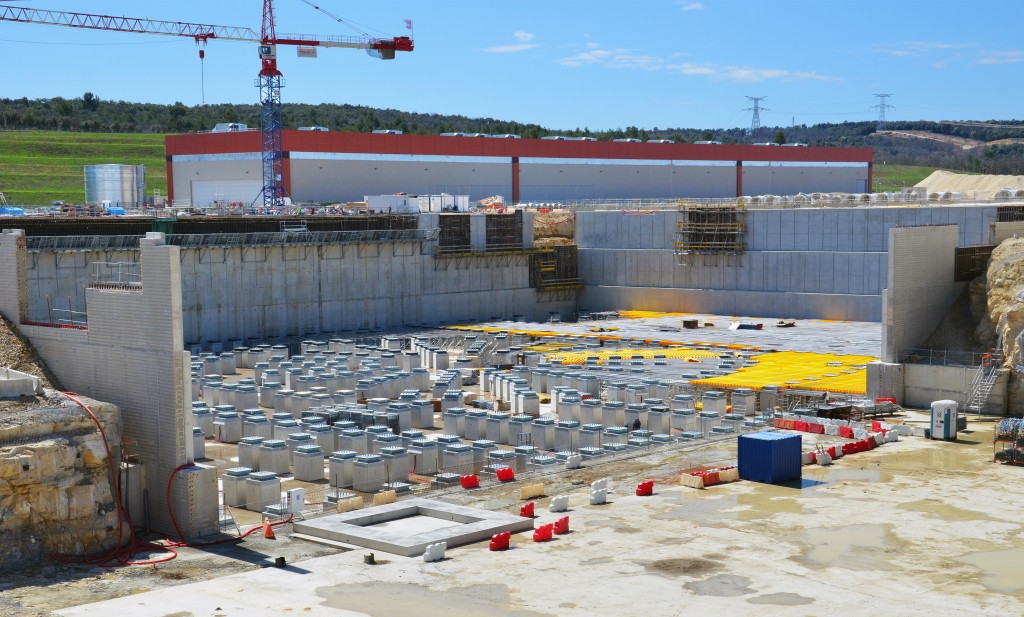
Seismic pads, au revoir!
2013-04-12 - Mid-April, the formwork is gaining on the seismic pads. Soon, we will see only concrete.
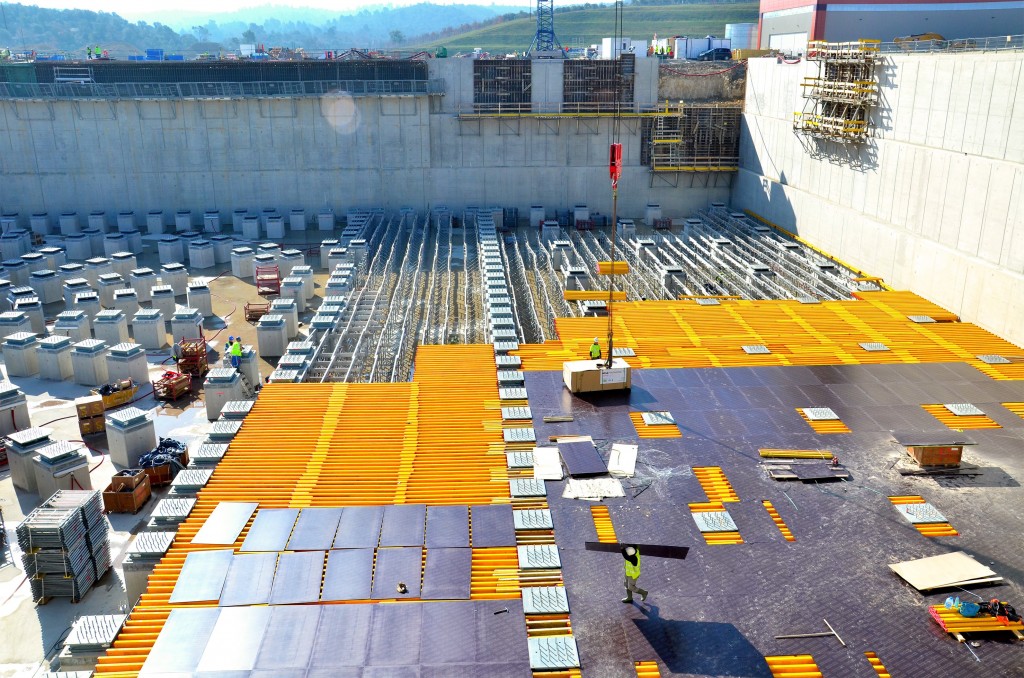
Under the future Diagnostics Building
2013-04-08 - Built upon the same foundation, the Diagnostics and Tritium buildings will stand to one side and another of the Tokamak Building. Under the future Diagnostics Building, it's easy to see the linear pattern of the anti-seismic pads and columns, compared to the Tokamak "star pattern" at left.
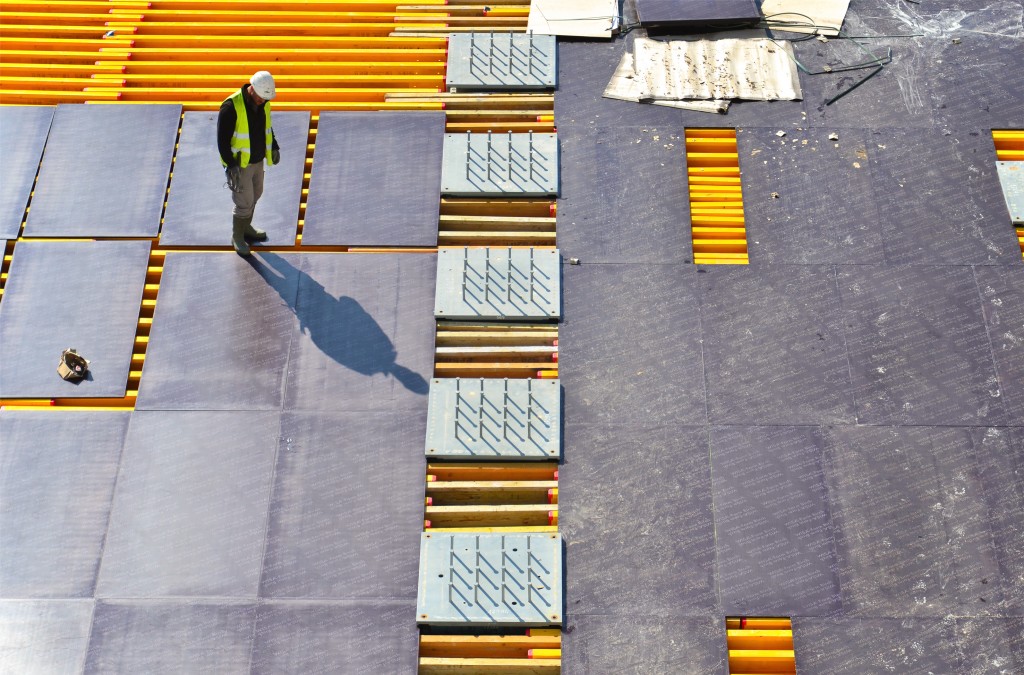
Stage by stage
2013-04-03 - The B2 slab will progress in stages: propping and formwork will take place February through June, followed by reinforcement work (April through August) and concrete pouring (June through December).
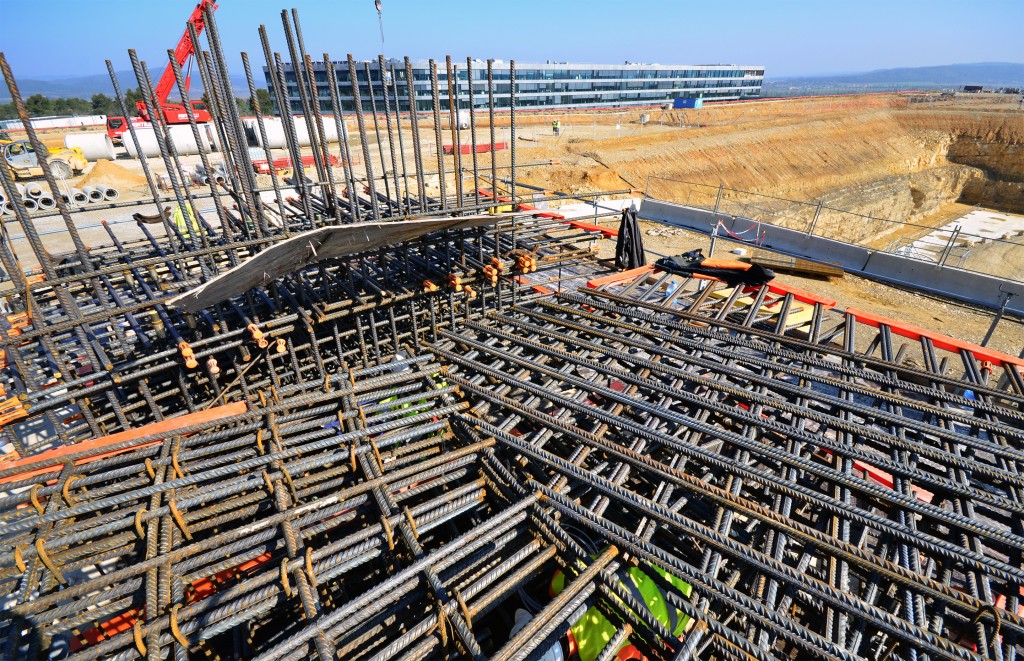
Scale model of B2 reinforcement
2013-04-03 - Adjacent to the Tokamak Pit, a 150 m2 mockup has been set up to demonstrate the complex pattern of the steel reinforcement bars planned for the B2 foundation slab. Four different areas of rebar presenting specific challenges (density, complexity) will be reproduced at 1:1 scale in the mockup.
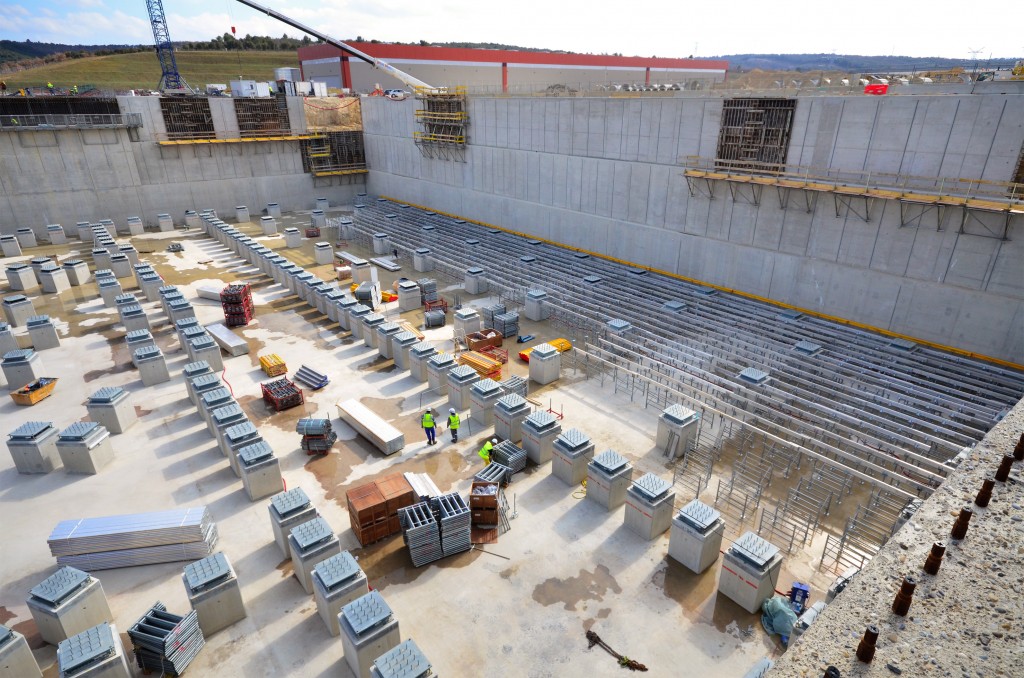
Preparatory works for the B2 slab
2013-03-22 - First silver, then yellow, then brown: on top of these aluminium props, workers will install yellow formwork, which in turn will be covered by wooden structures.
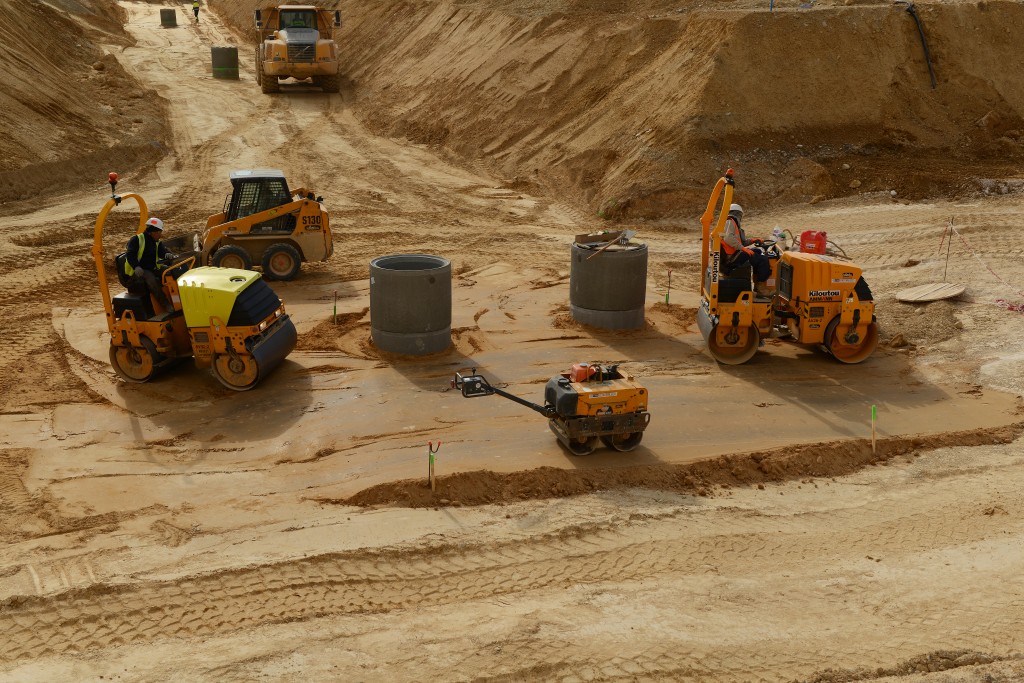
A chimney here, a chimney there
2013-03-14 - Workers fill in the trenches for the overflow drainage network progressively, as sections of the network are completed. Regular chimneys (pictured) will provide access to the pipes for inspection. Photo: F4E
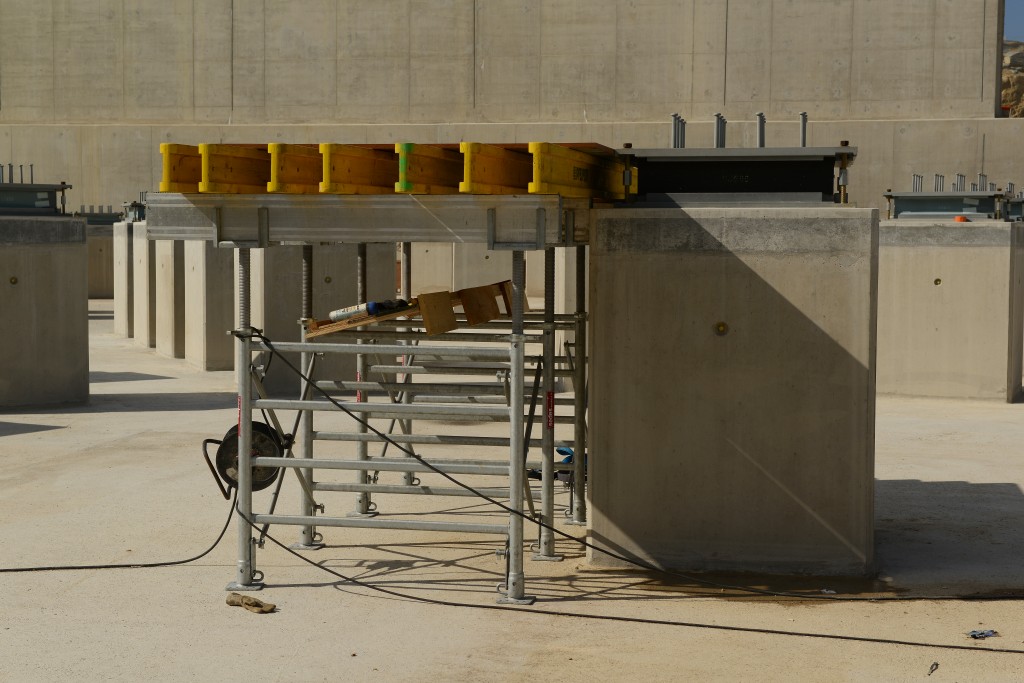
Around every column
2013-03-14 - Four sides ... 493 columns. In order to pour a single foundation slab for the Tokamak Complex, a lot of precise formwork must be done in advance. Photo: F4E
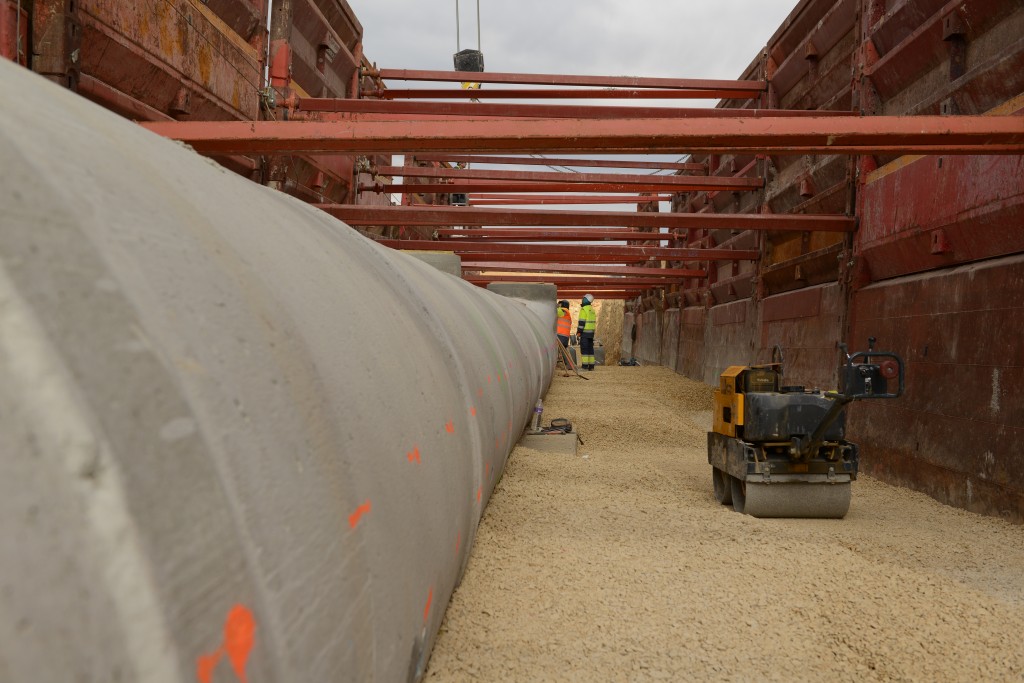
Compaction
2013-03-14 - The backfill around the drain pipes is filled in progressively and compacted in stages. Photo: F4E
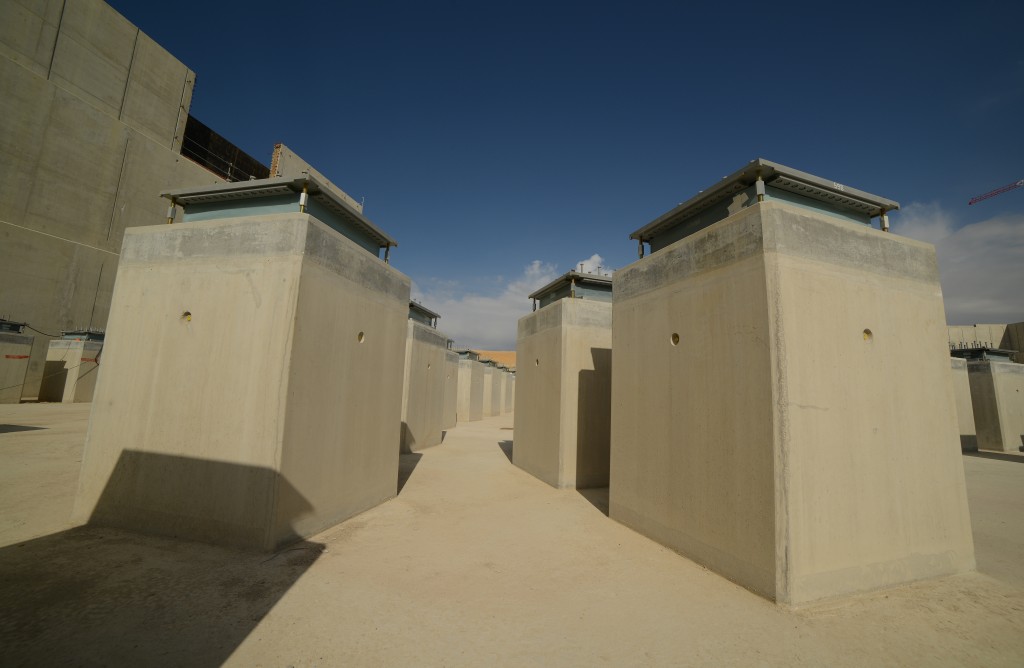
One day
2013-03-14 - In the next years, the Tokamak Building will rise 73 metres above these columns (60 metres above platform level). Photo: F4E
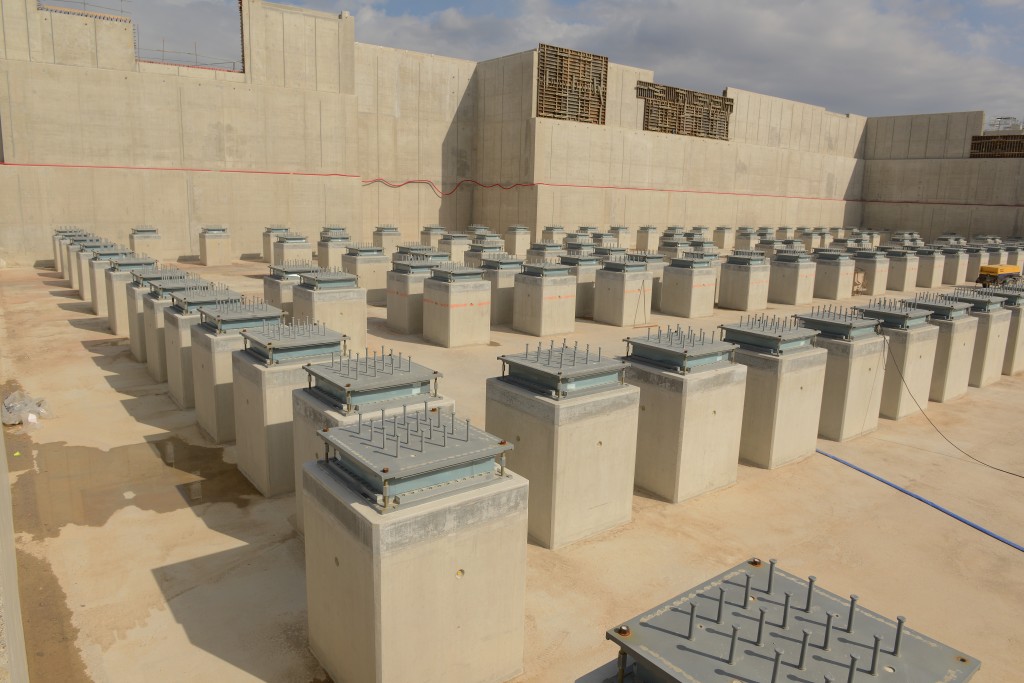
Protecting the openings
2013-03-14 - In preparation for the buzz of activity planned in the Seismic Pit during the construction of the B2 slab, wooden props are going up in the penetrations of the retaining wall. These both protect workers below and protect the openings. Photo: F4E
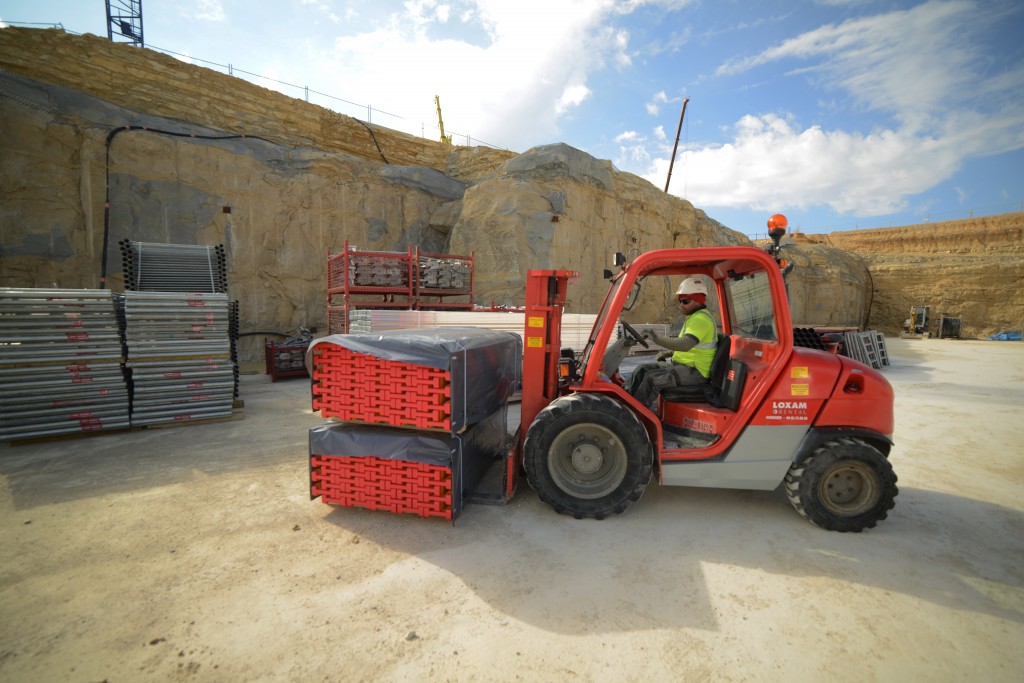
Storage nearby
2013-03-14 - In the Hot Cell area, material is stored for the B2 prep work. Propping and formwork activities are underway and will continue through June 2013. Photo: F4E
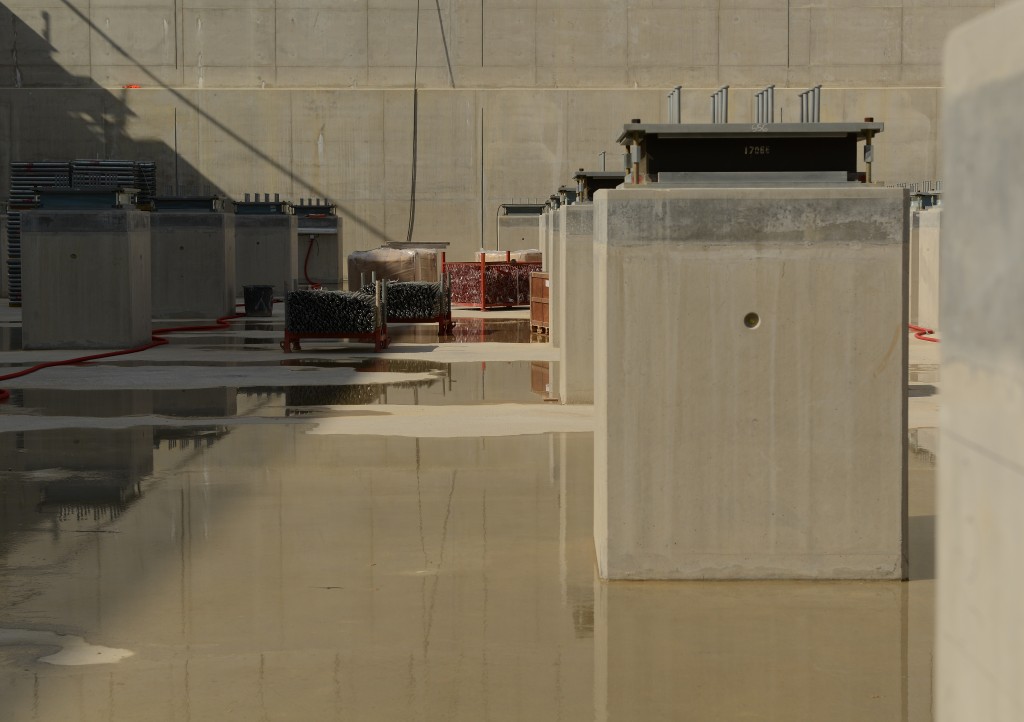
Pointing up
2013-03-14 - The metal fingers (studs) on the top of the seismic pads will be crisscrossed with metal rebar and become part of the B2 slab. Space will remain between the two slabs for regular inspections. Photo: F4E
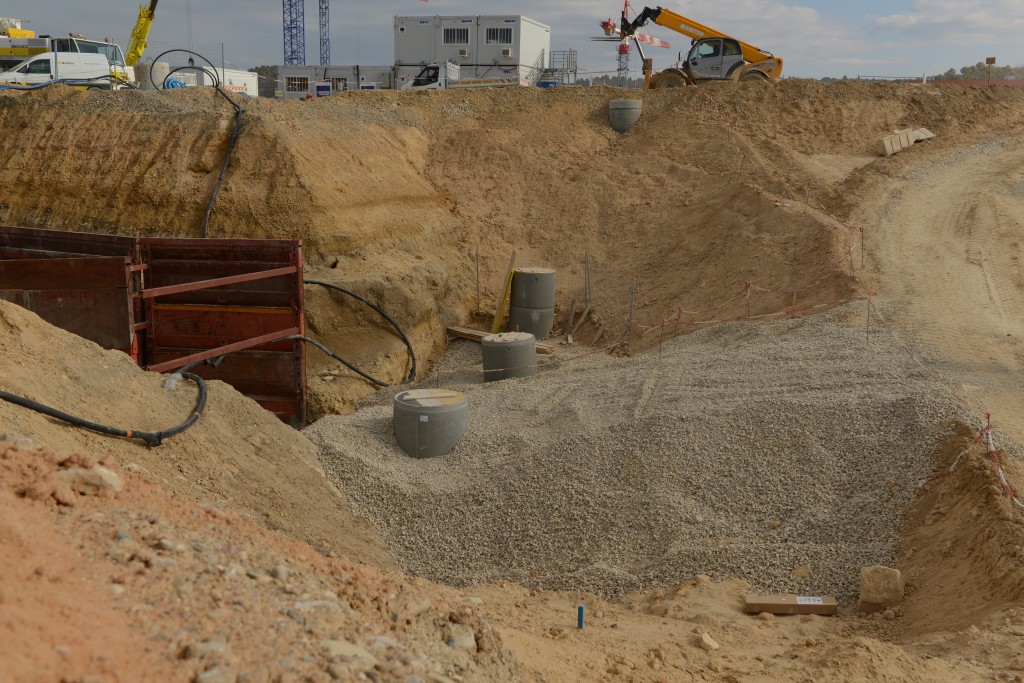
At the crossroads
2013-03-14 - The different stages of pipework are visible in this photo: galleries not yet filled in to the left, chimneys poking up from completed networks to the right. Photo: F4E
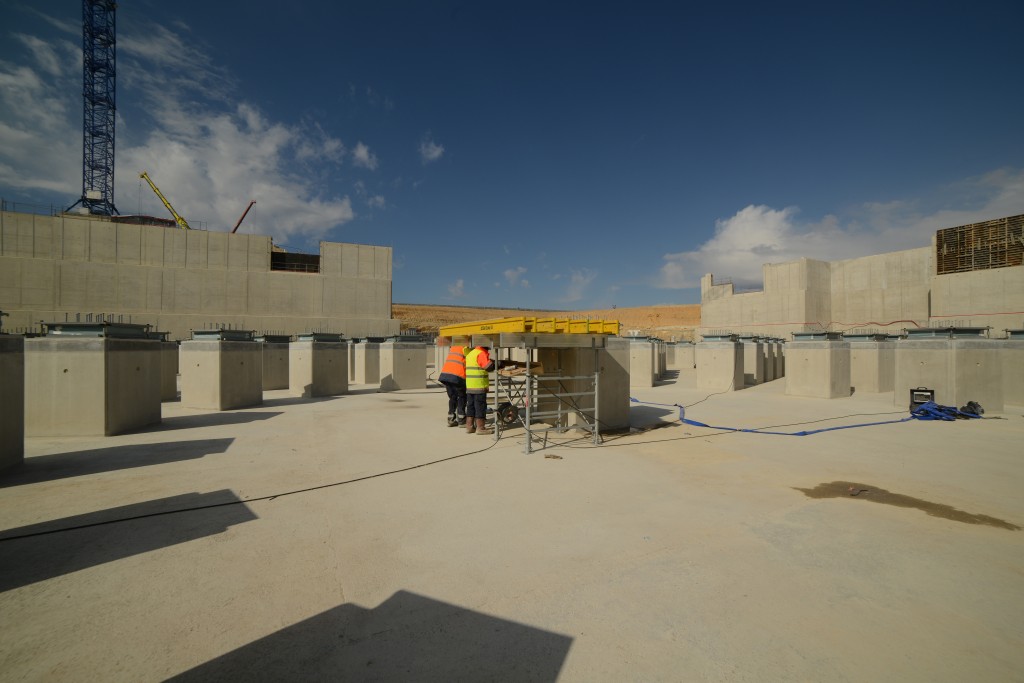
Just over their heads
2013-03-14 - Wooden formwork will be installed on top of these yellow panels. The seismic pads will be protected throughout the duration of foundation work. Photo: F4E
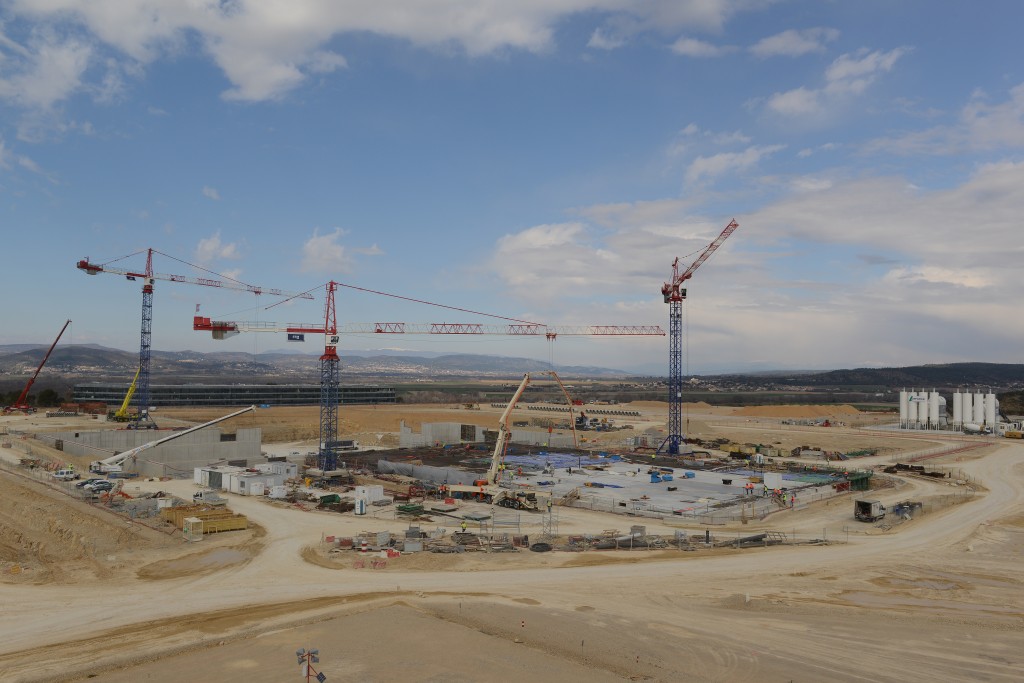
The cranes are back
2013-03-14 - From the top of the Poloidal Field Coils Winding Facility, the progression of the Assembly Building slab is evident: the last segment will be poured in May 2013. On the left, the first crane is positioned for foundation work in the Seismic Pit. Photo: F4E
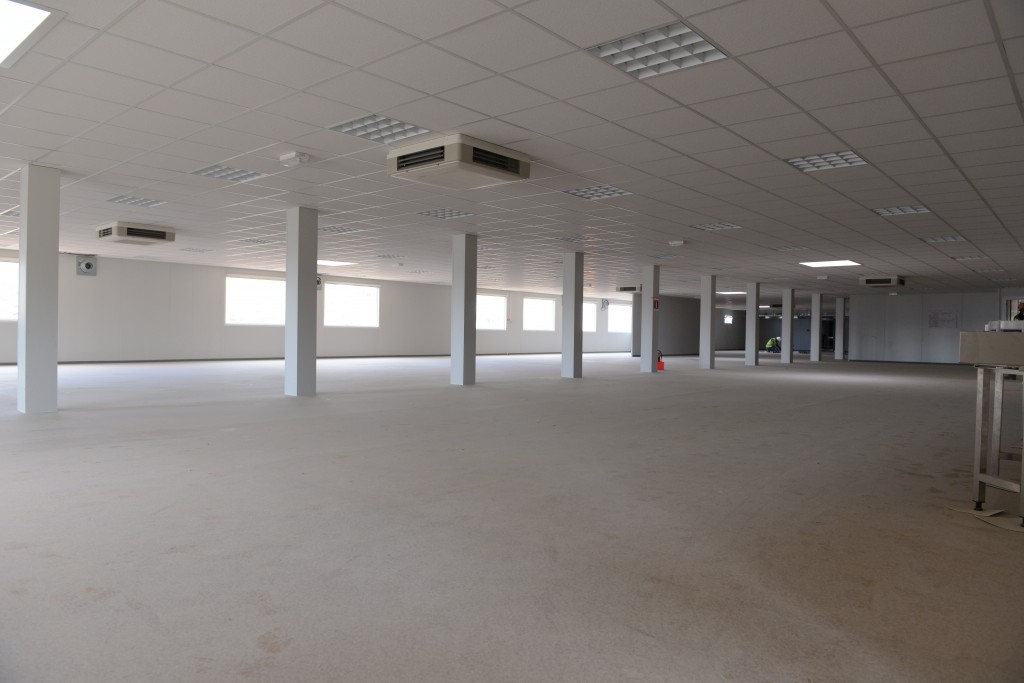
Almost ready
2013-03-14 - The worksite canteen will be ready to serve its first hungry clients in September 2013. In the swing of construction works, evening meals will be served as well as noon meals. Photo: F4E
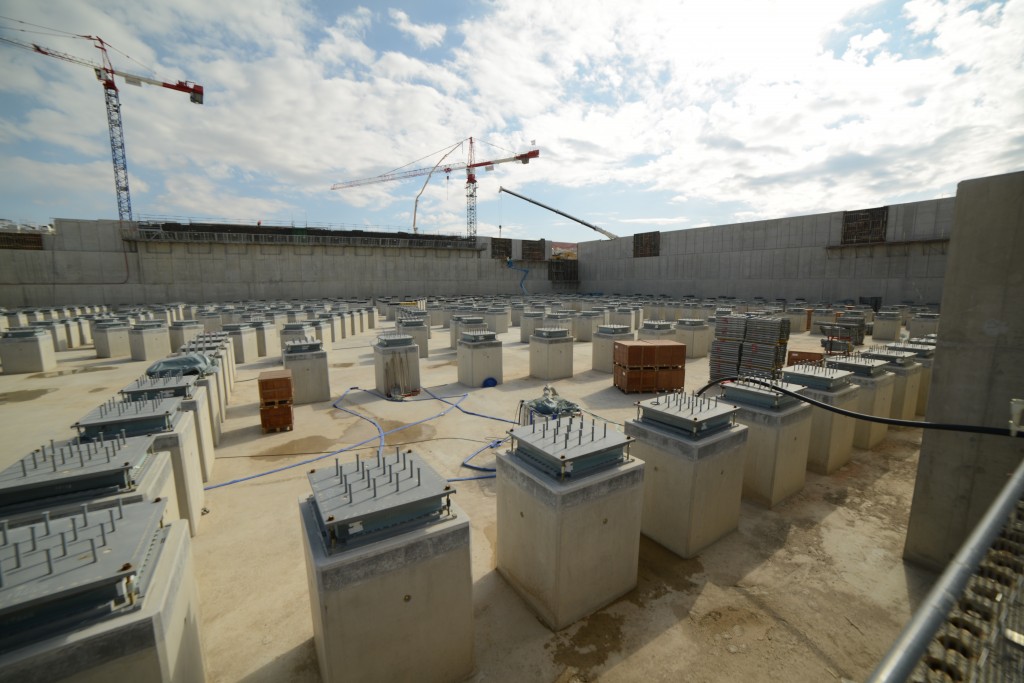
Looking south
2013-03-14 - Looking toward the Assembly Building worksite, where work on the foundation slab will be completed in May 2013. Photo: F4E
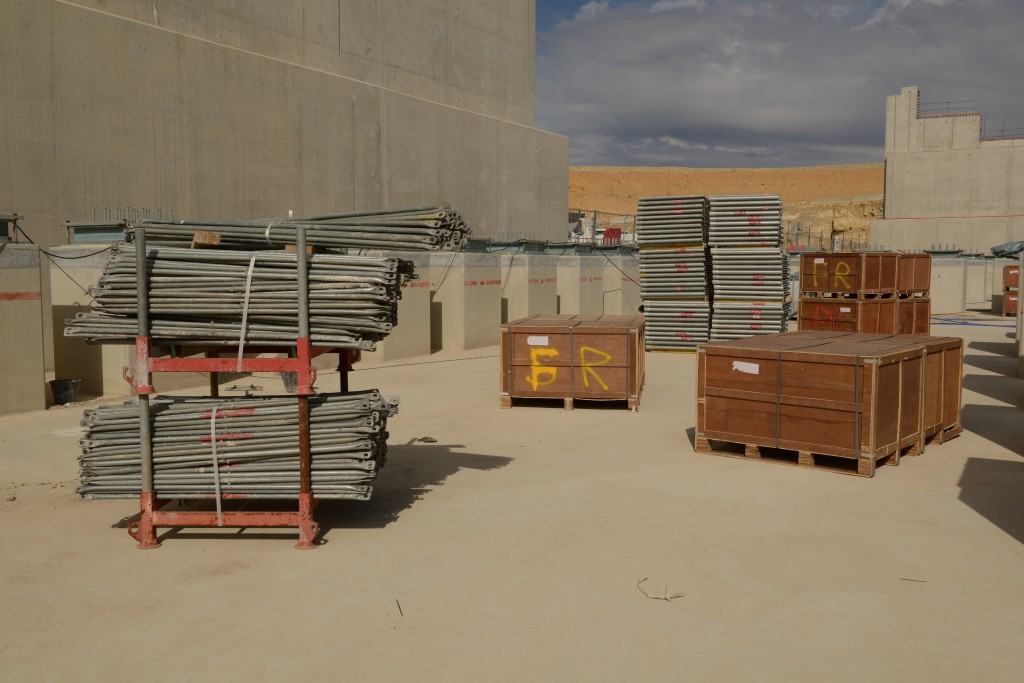
Moving in
2013-03-14 - Material is being moved into the Seismic Pit for propping and formwork activities: at precisely 2 metres above the first slab, the floor of the Tokamak Complex will be in place by year's end. Photo: F4E
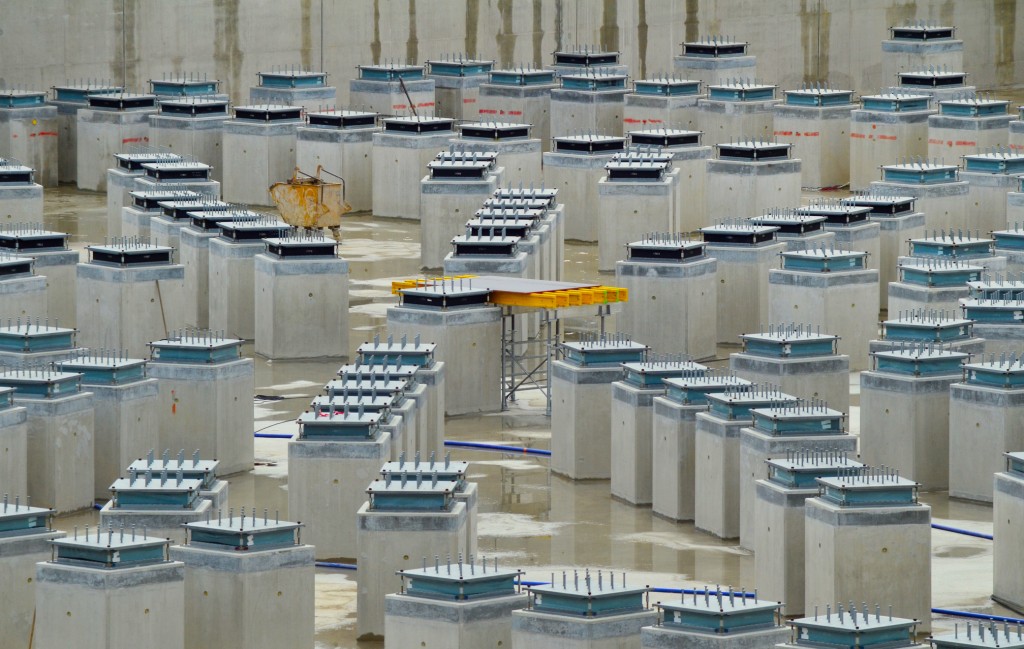
B2 prep work begins
2013-02-27 - The basemat for the Tokamak Complex—the 1.5 metre-thick B2 slab—will sit directly on top of the Seismic Pit's 493 columns and pads. On 27 February 2013, the Central Integration & Engineering Directorate completed the challenging mission of closing B2 slab design and obtaining model approval in a meeting held with the European Domestic Agency and the Architect Engineer ENGAGE. Work began immediately on B2 propping and formwork activities in the Seismic Pit.
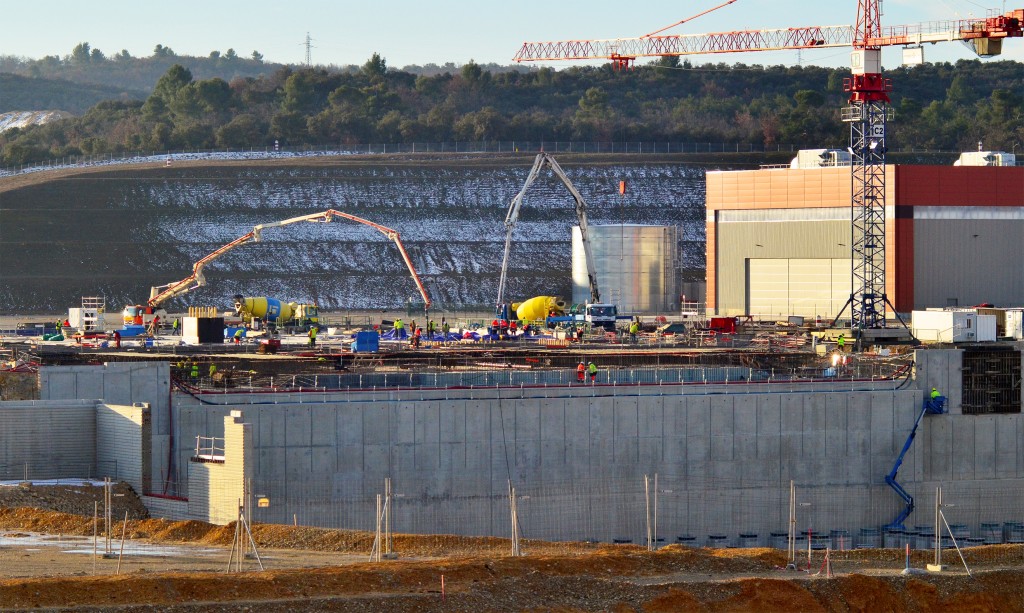
Pouring continues
2013-02-14 - Work begins at sunrise on another slab of the Assembly Building basemat. Currently 70 workers are active in this area of the platform.
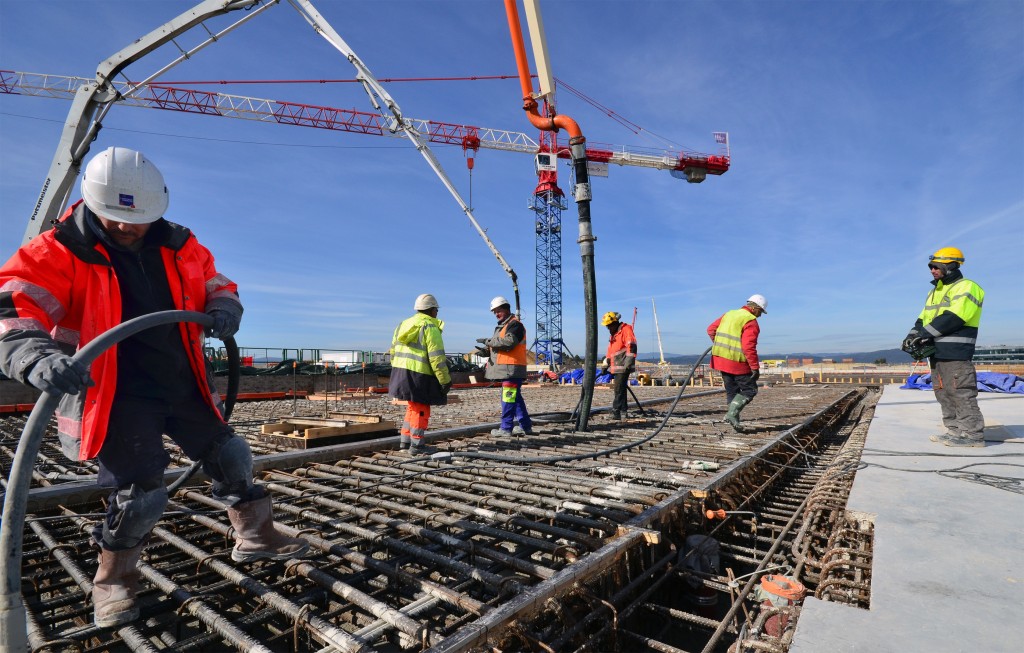
Two pieces
2013-02-14 - Each concrete plot is poured in two segments with a joint between them that will be filled in once the concrete is dry. This technique avoids cracking.
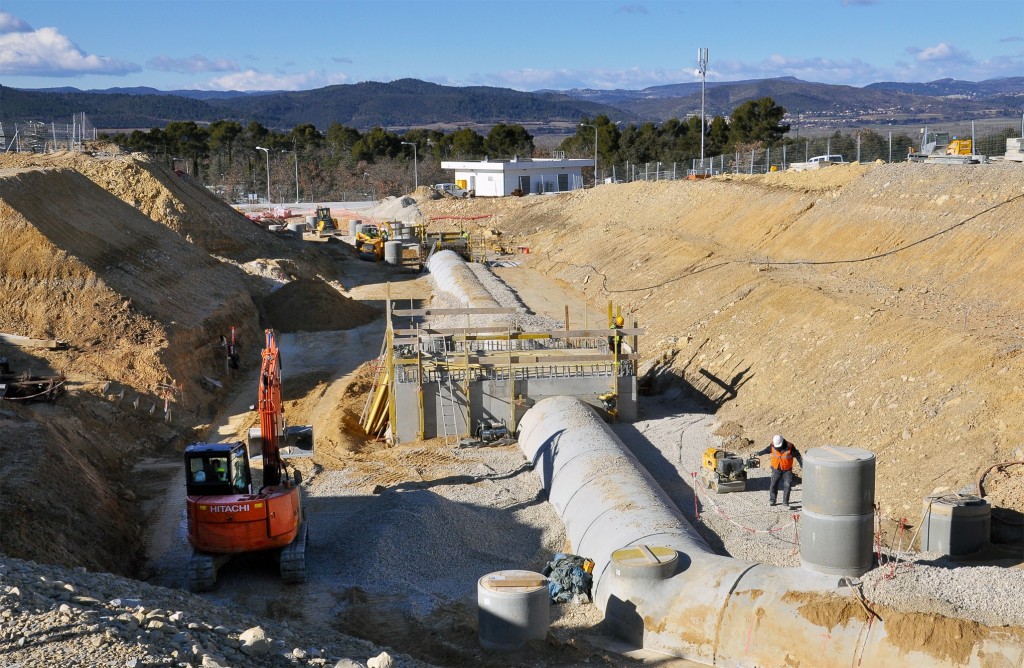
Networks that are critical
2013-02-11 - Critical network piping will crisscross the ITER site for precipitation drainage and cooling water release. In this section of the network, the pipes have been installed and backfilling is underway.
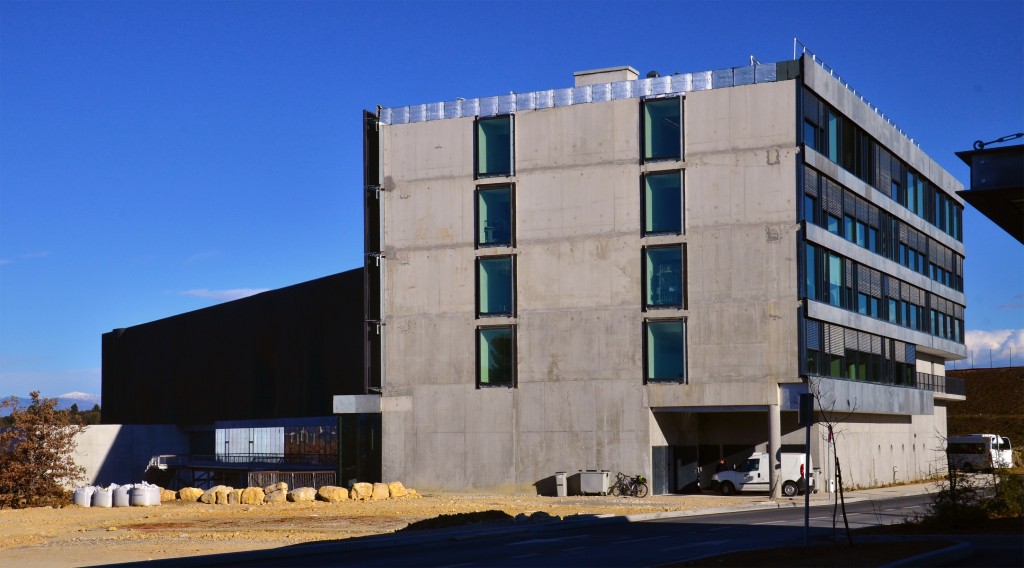
The unfinished side
2013-02-07 - Contrary to the other side of the building, this end was left unfinished. In 2013, work will begin to extend the building by 35 metres for an additional 350 desk spaces.
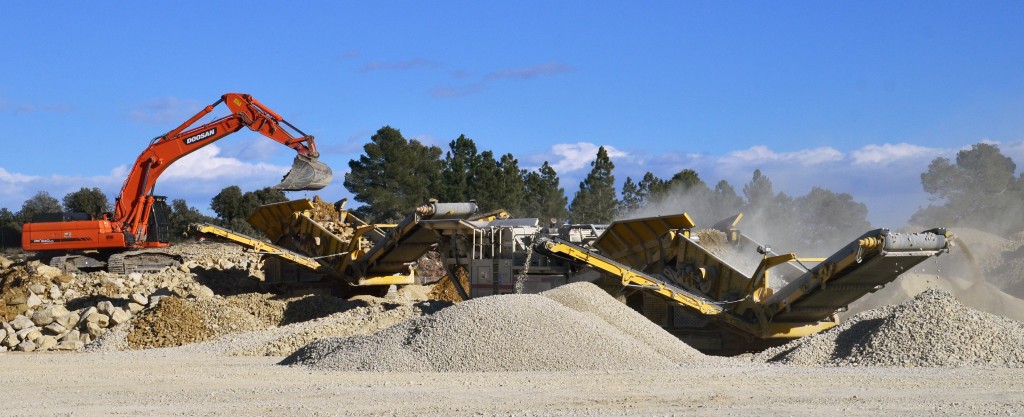
Recycling materials
2013-02-07 - Material dug up from the drainage trenches on site is reused—once crushed into a finer ground—for backfill.
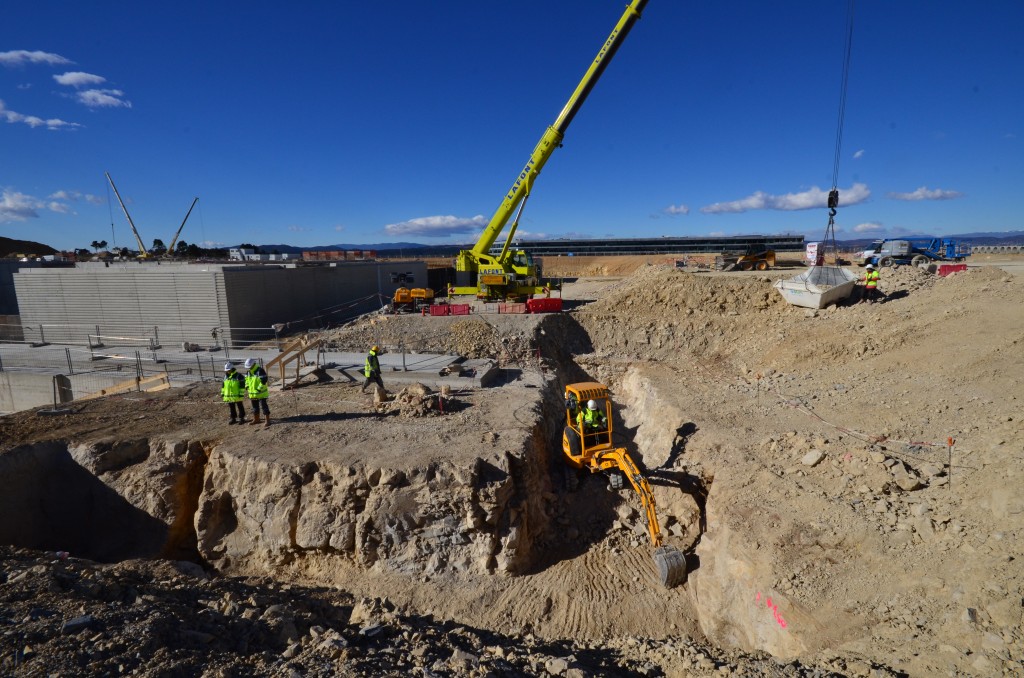
North of the Tokamak Complex
2013-02-07 - Galleries dug in February will service the Tokamak Complex in essentials like power and water.
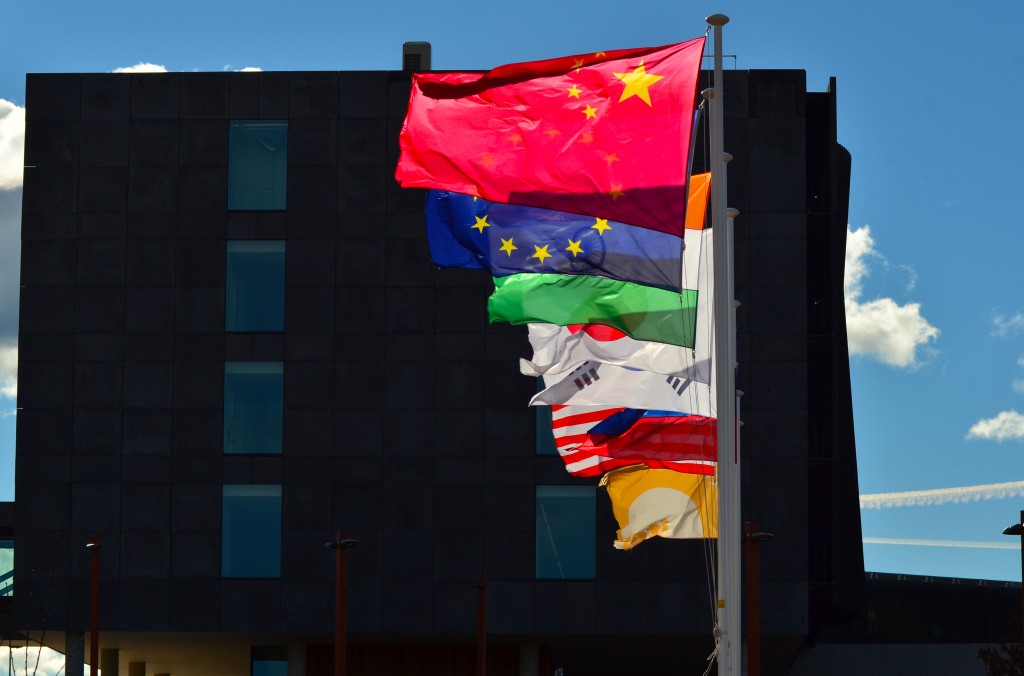
Welcome!
2013-02-04 - At the entrance of the new ITER Headquarters building, flags from the seven ITER Members and the yellow flag of the ITER Organization unfurl in the early February wind.
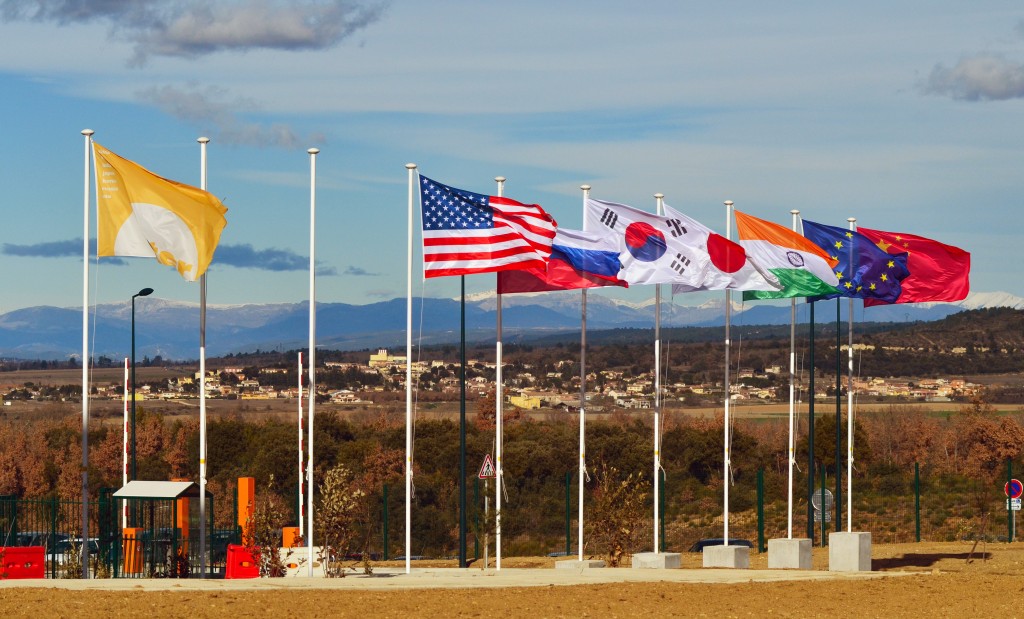
United colours of ITER
2013-02-04 - On a brisk day in February, the ITER Member flags stand proudly against a backdrop of snow-covered mountains.
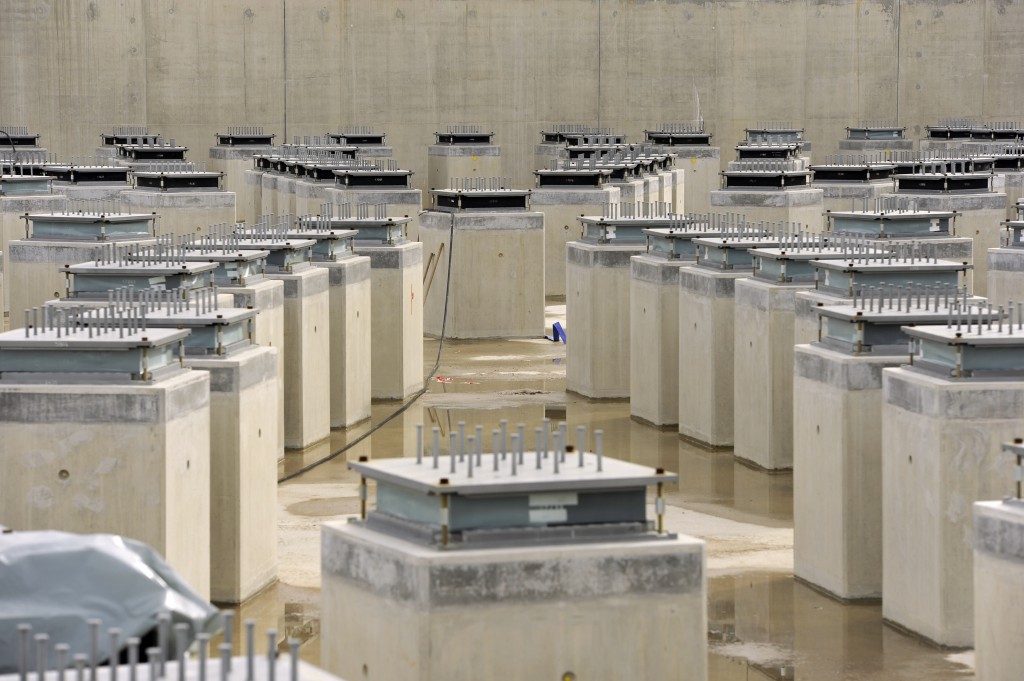
The 1.8 metre column plus pad
2013-02-01 - Between the bottom slab (which the seismic pads rest on) and the upper slab there will be a gap of two metres. All of the formwork supporting the second slab will have to be removed through this gap. Photo: F4E
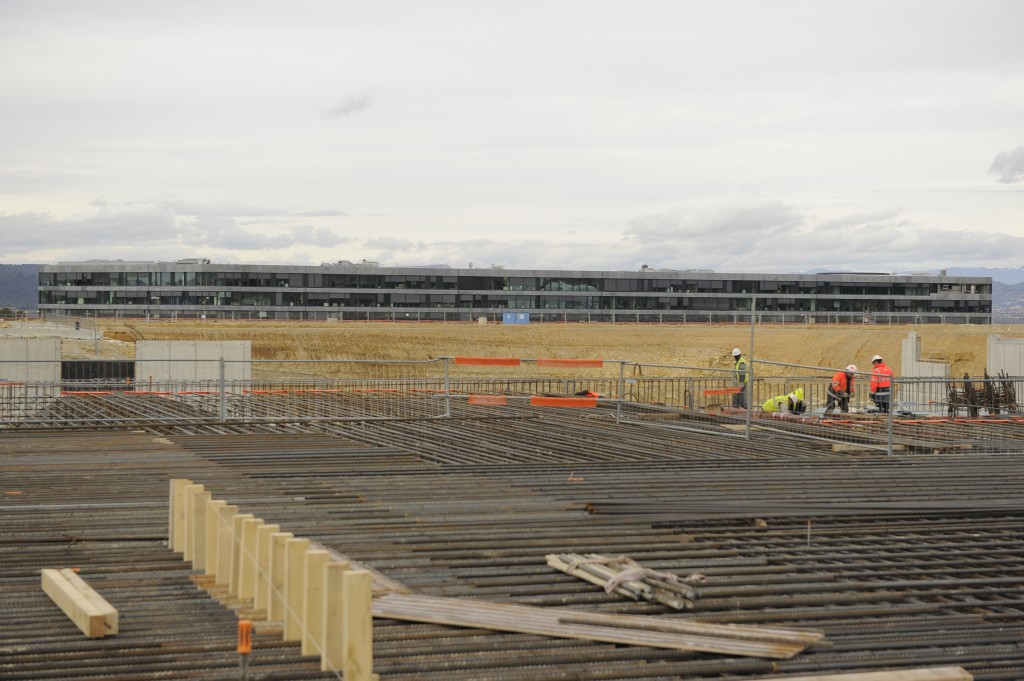
Offices with a view
2013-02-01 - Across from the Assembly Building worksite, where reinforcement and concrete pouring continues, the top three stories of the new ITER Headquarters building rise over the platform. Photo: F4E
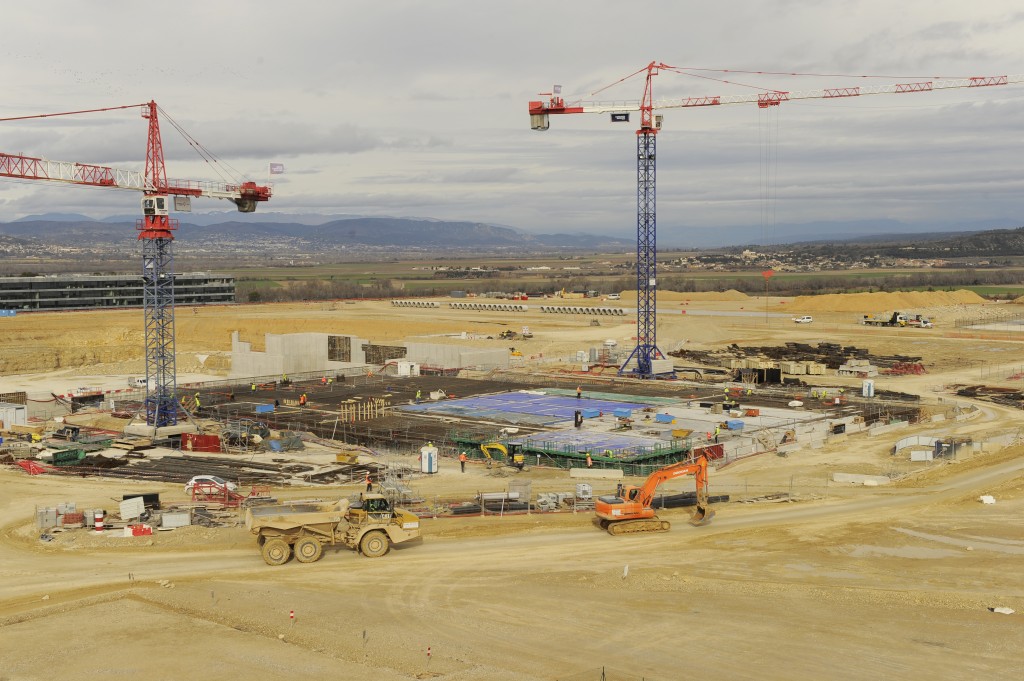
An antechamber to the Tokamak Complex
2013-02-01 - On the 6,000 m² footprint of the Assembly Hall, it's easy to see the portions of the foundation that are completed. Photo: F4E
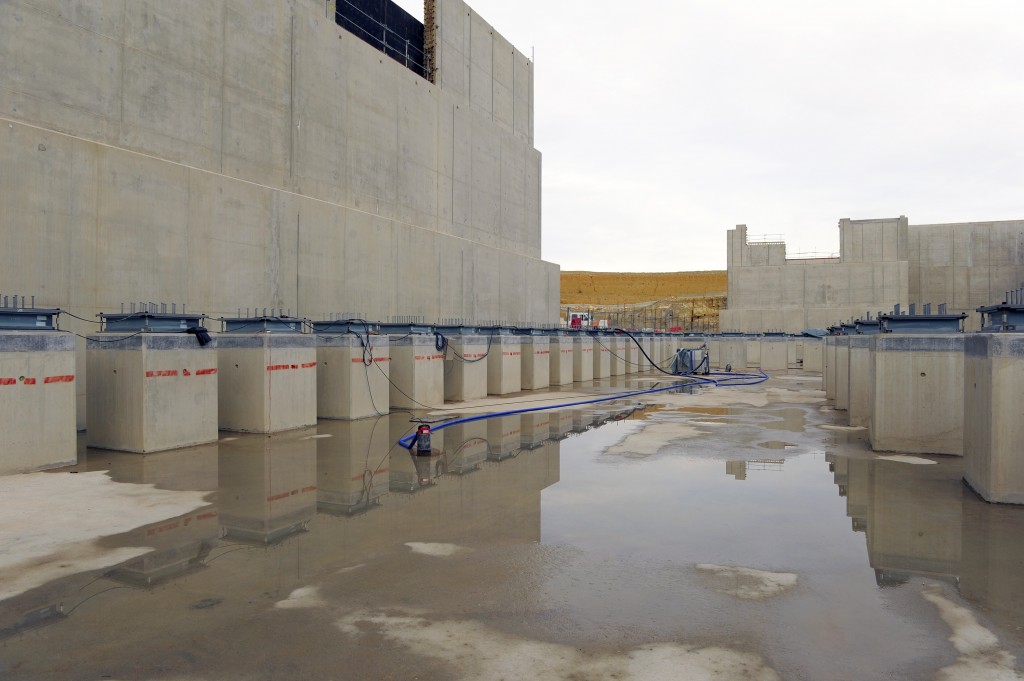
Six months to pour the concrete
2013-02-01 - By December 2013, the B2 slab—or Tokamak Complex basemat—will be in place. Photo: F4E
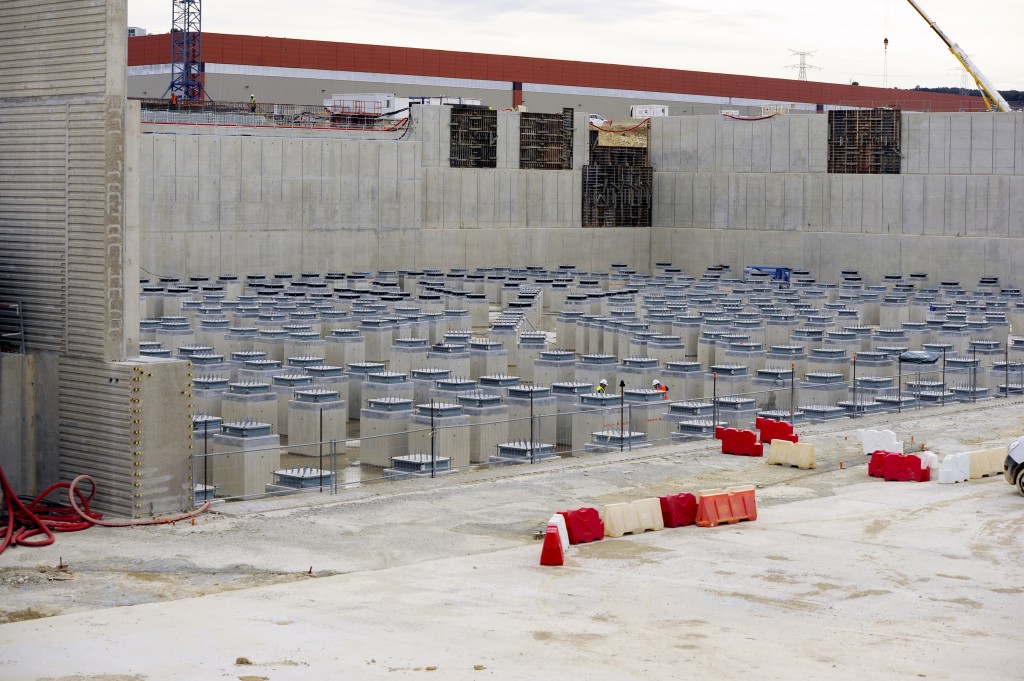
The Tokamak Complex will rise here
2013-02-01 - The construction consortium chosen in December to build the 360,000-tonne Tokamak Complex is establishing offices on site and working on the detailed design of the structure. As the formwork is removed from the drying basemat in November, work will begin on the civil works. Photo: F4E
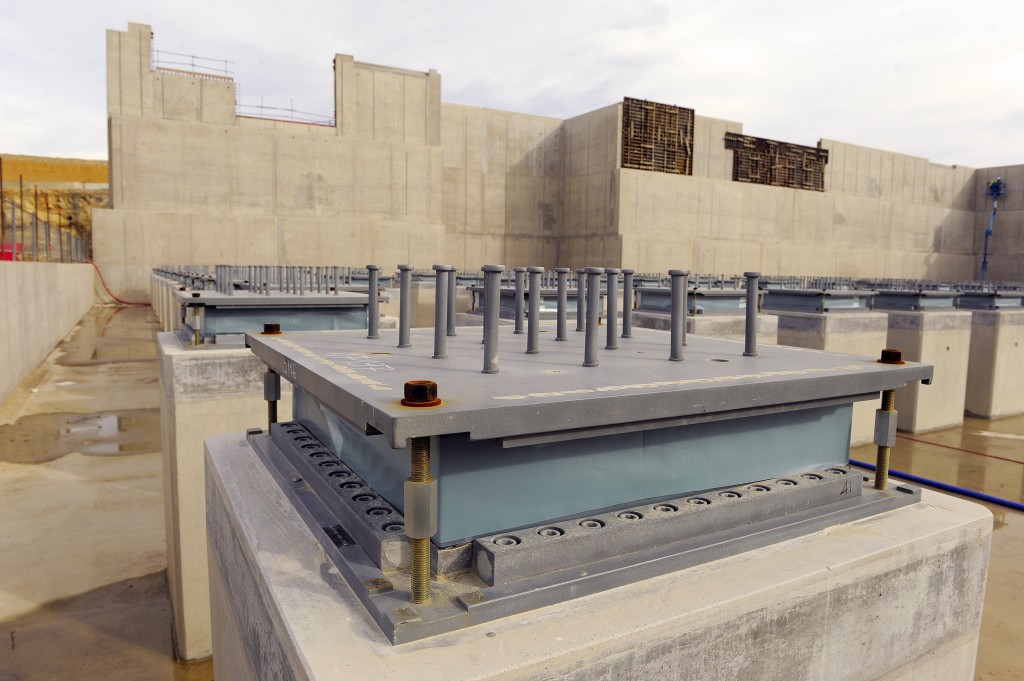
The last pictures of the seismic pads
2013-02-01 - These are the last pictures of the complete seismic protection system that will soon be hidden from view: formwork and propping will begin end February. Photo: F4E
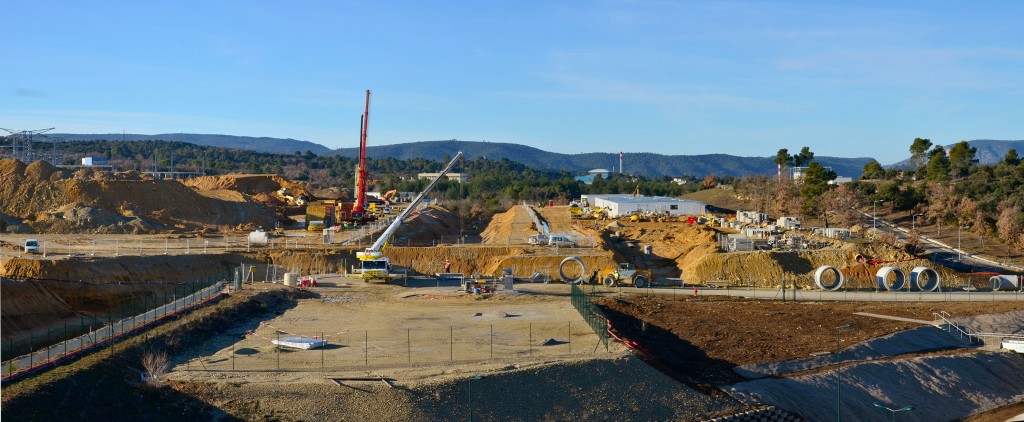
The southeast corner of the platform
2013-01-22 - Work progresses on Contractors Area 2 in January 2013. The area will be operational in March 2013.
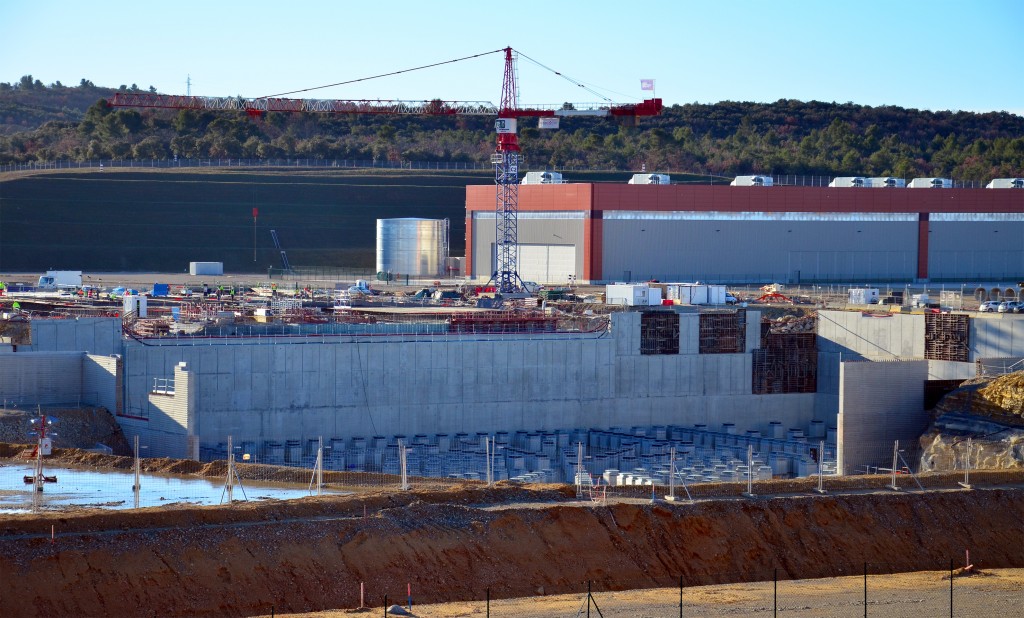
Winter colours
2013-01-22 - The Seismic Pit is wearing its cloak of winter blue for this late-day photo taken mid-January. Building begins here in 2013 on the Tokamak, Diagnostic and Tritium buildings.
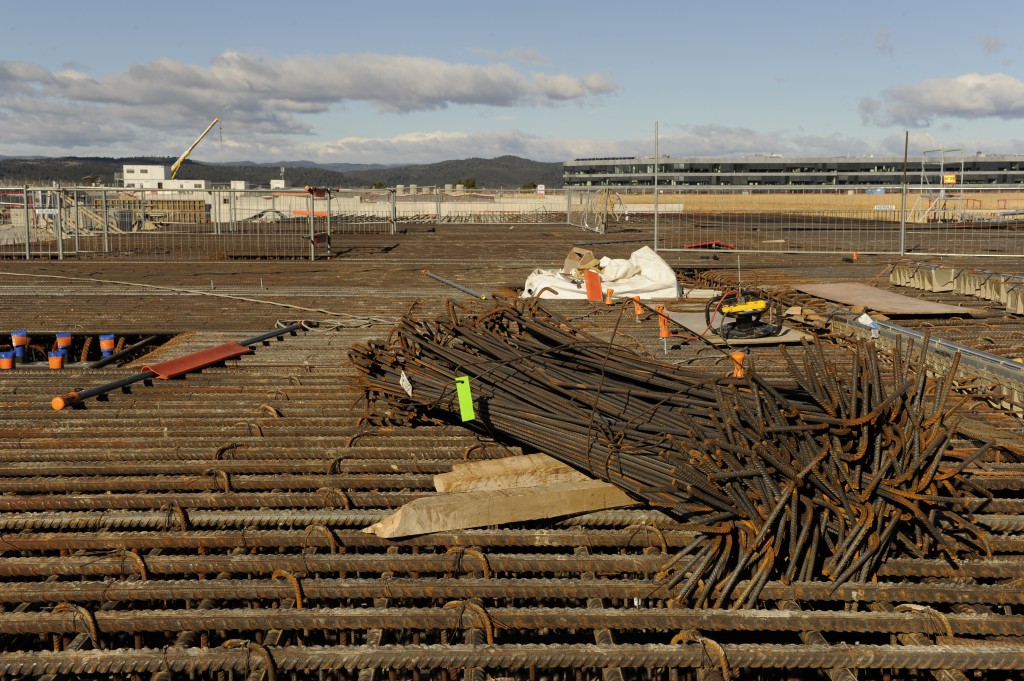
Rebar stirrups
2013-01-11 - Part of the 1,400 tonnes of steel planned for the Assembly Building basemat, these rebar stirrups will link the upper and lower rebar layers. Photo: F4E
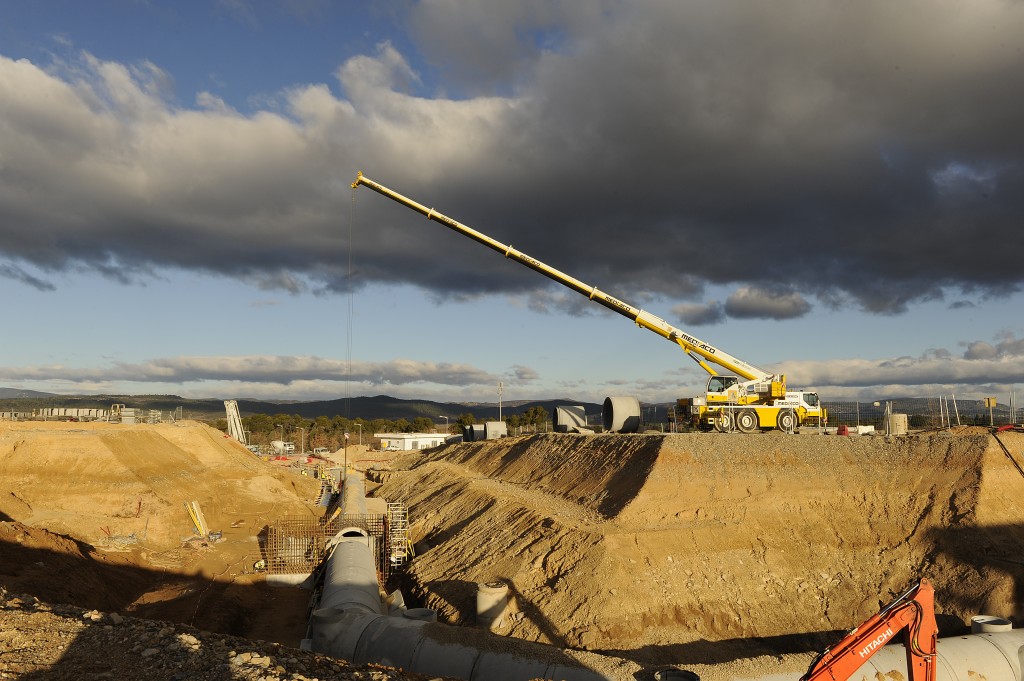
These important networks will soon be covered over
2013-01-11 - With the piping in place, work continues now on cement casing and backfilling. Photo: F4E

New contractor office building
2013-01-11 - By June, this office building for 50 and the surrounding parking areas must be completed for staff that will arrive to manage the construction of the Tokamak Complex. Photo: F4E
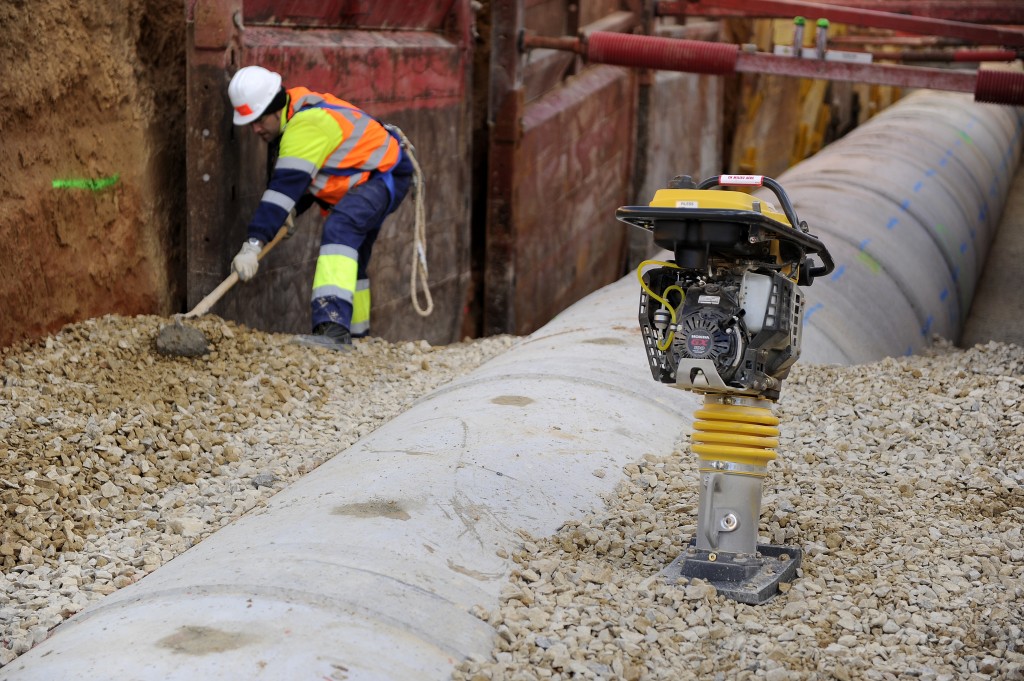
Backfill operations
2013-01-11 - As the props are removed one by one, the excavated area around the precipitation drainage pipes is filled with backfill. Photo: F4E
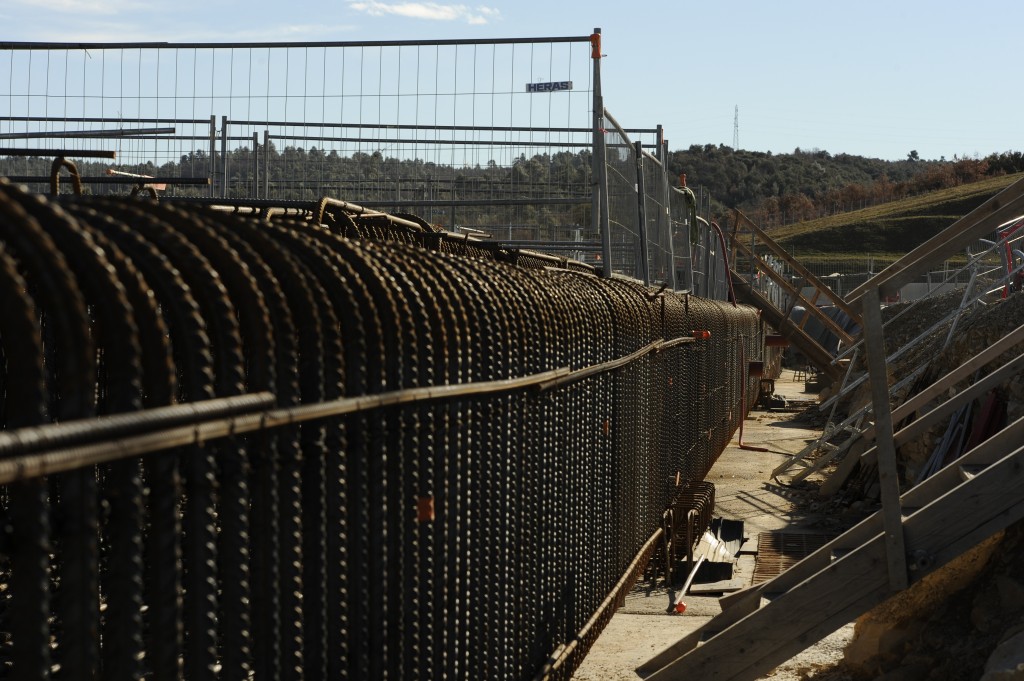
The pedestal for a tall building
2013-01-11 - A building 60 metres high will rest on these foundations which, in some areas, attain 2.2 metres in thickness. Photo: F4E
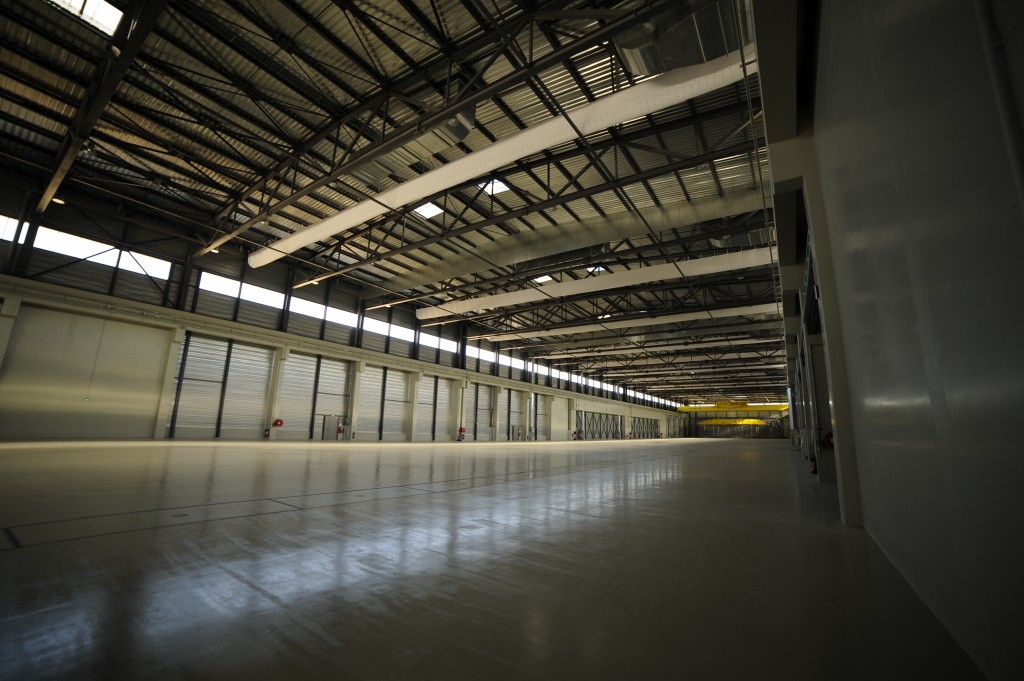
Future factory
2013-01-11 - 49 metres wide, 257 metres long: the Winding Facility will house the different assembly stations for ITER's large poloidal field coils. Photo: F4E
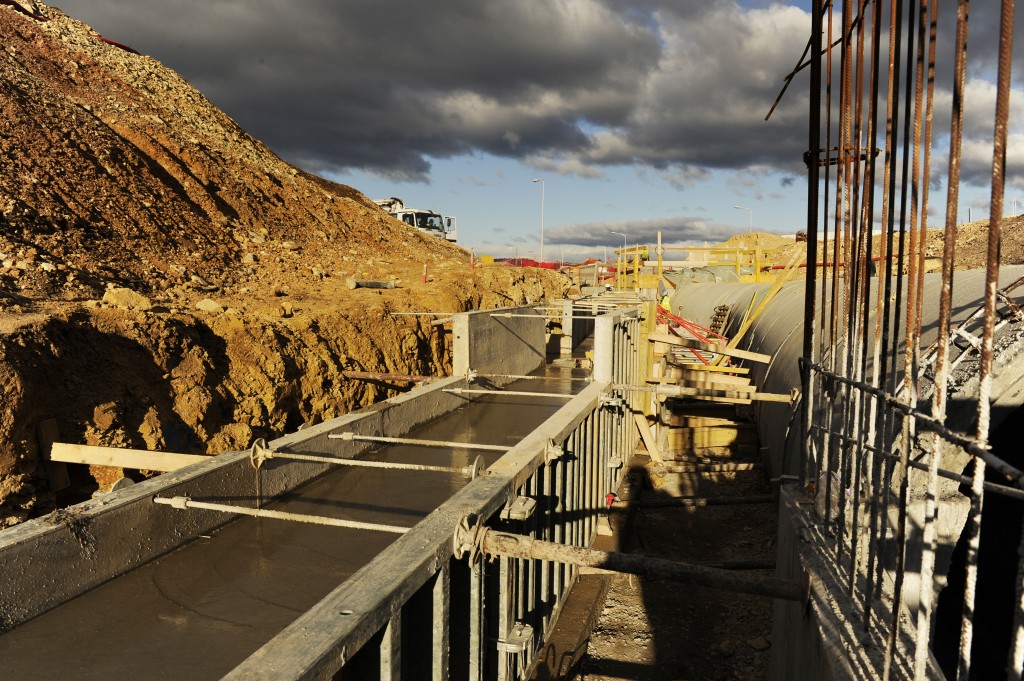
Site works in January
2013-01-11 - Next to the large drainage network, concrete is drying around a smaller network of pipes. Photo: F4E
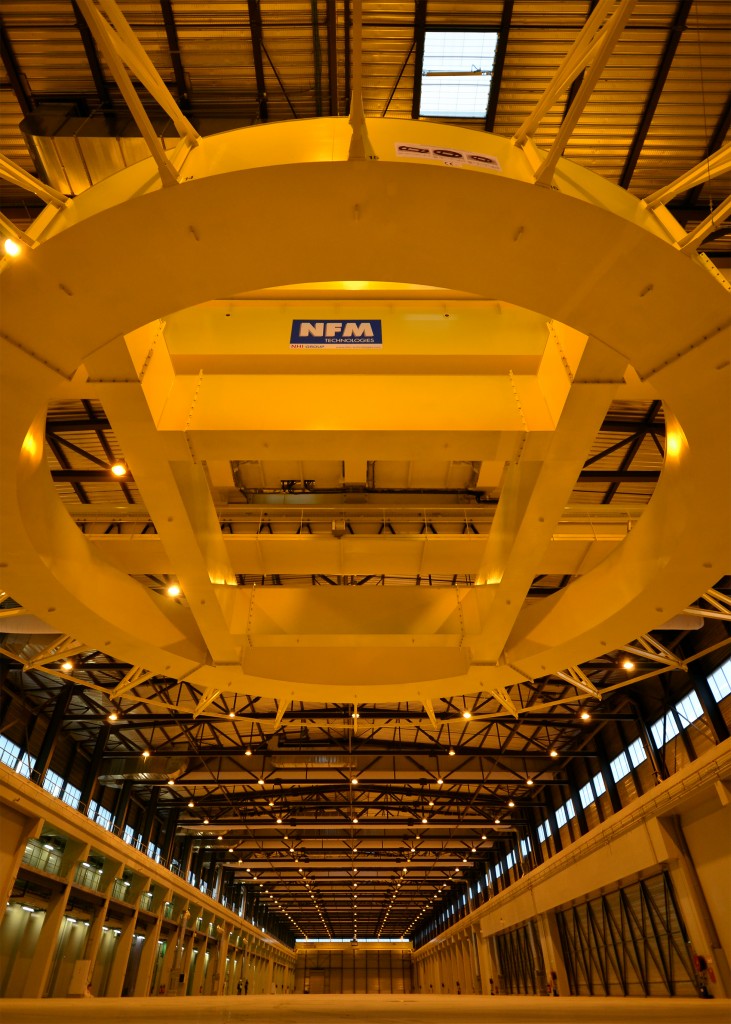
Heavy lift equipment for large components
2012-12-20 - The 40-tonne circular spreader beam can travel the length of the building to move the poloidal field conductor assemblies from the winding station, on to impregnation with epoxy resin, and finally stacking and joining.
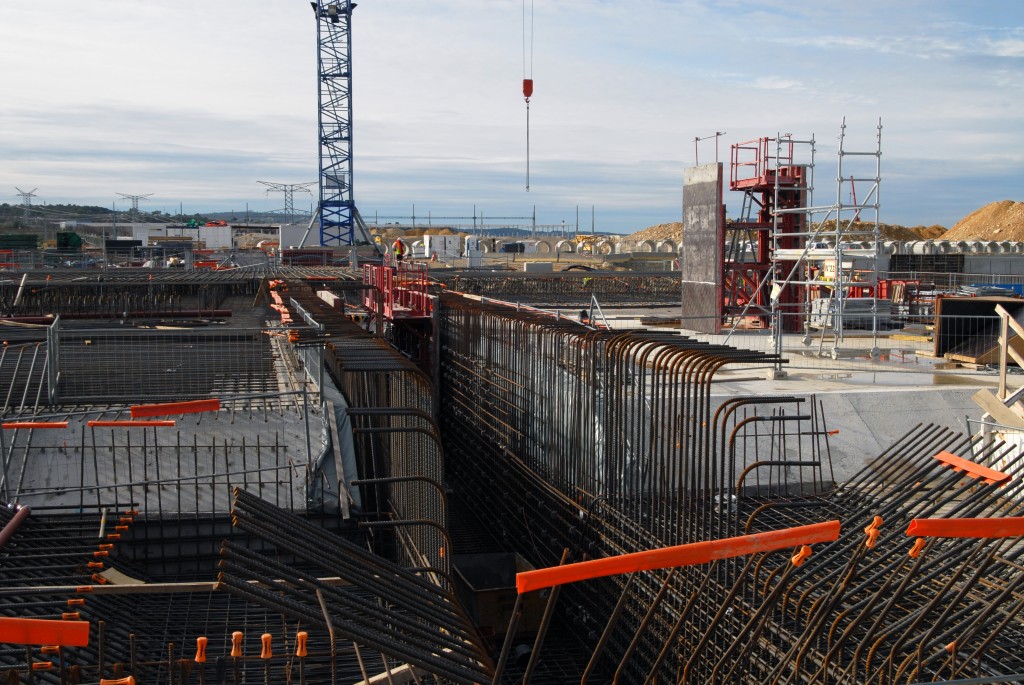
Tailored reinforcement
2012-12-19 - Concrete pouring for the Assembly Building will be completed by the time pouring begins for the adjacent Tokamak Complex in spring 2013. The rebar has been tailored to meet the building's complex system of galleries and penetrations. Photo: F4E
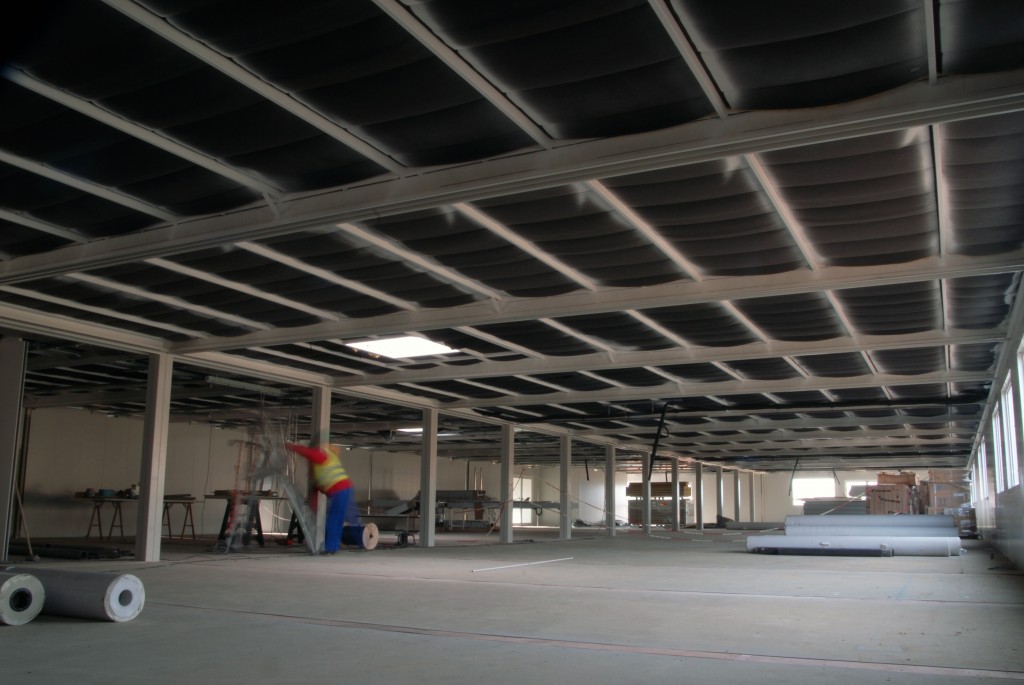
Inside the canteen
2012-12-19 - The worksite canteen is scaled for 1,500 people. During the peak of construction activities, when over 3,000 workers are expected on site, certain construction companies will plan their own dining halls. Photo: F4E
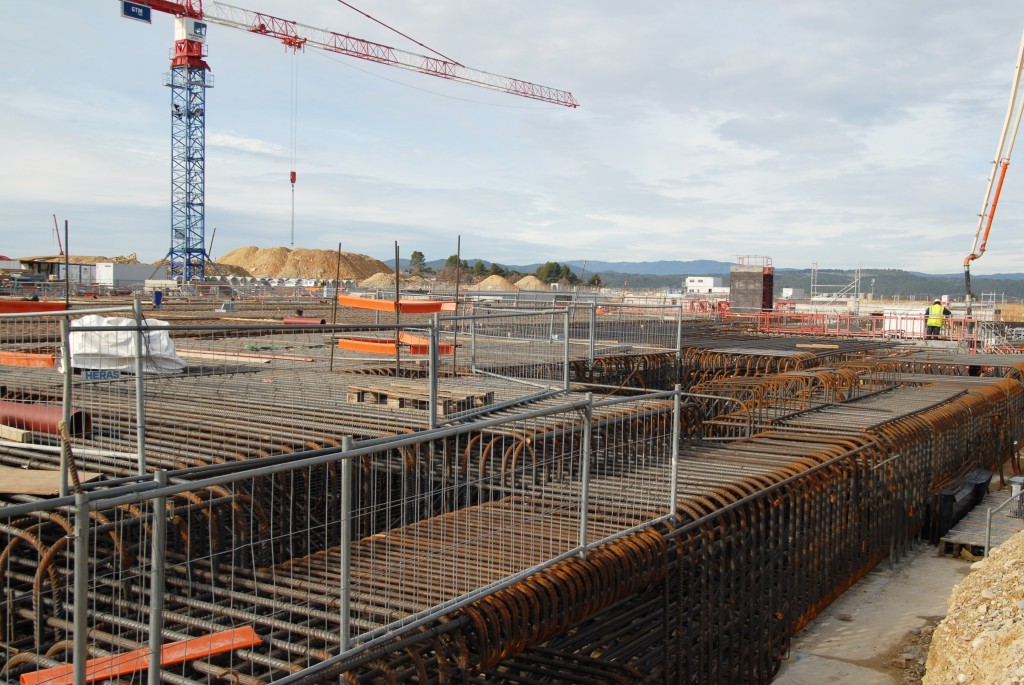
A sea of iron
2012-12-19 - Fourteen hundred tons of steel are now distributed in an area measuring 60 x 100 metres. The building's foundation will have a thickness of 1.2‒2.2 metres. Photo: F4E
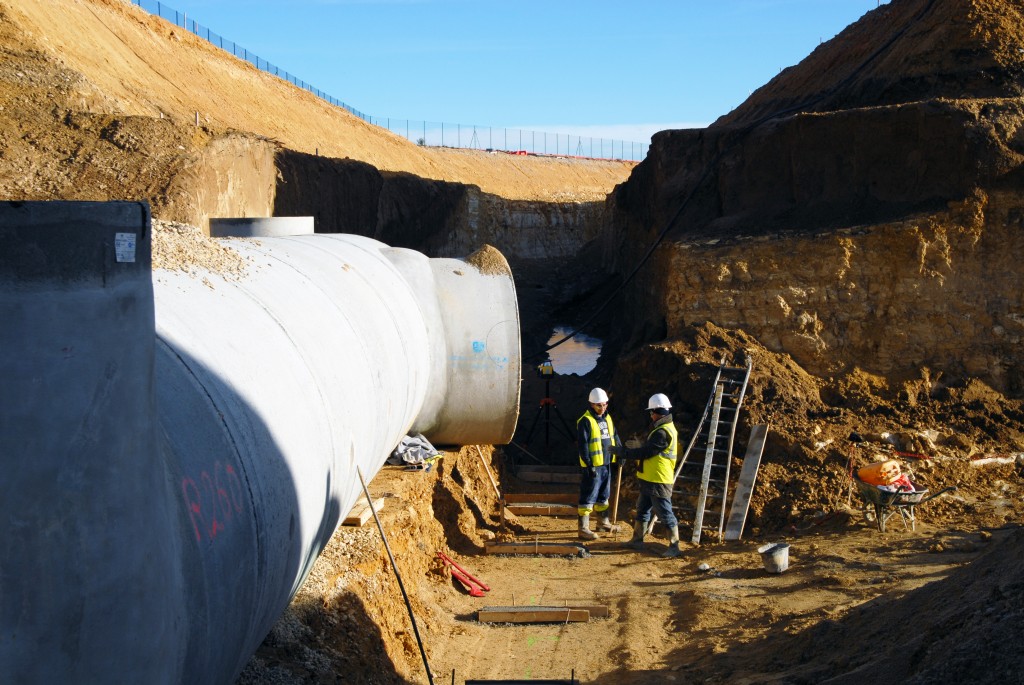
Ten metres underground
2012-12-19 - Section by section, piping is installed for the platform's precipitation overflow area. Photo: F4E
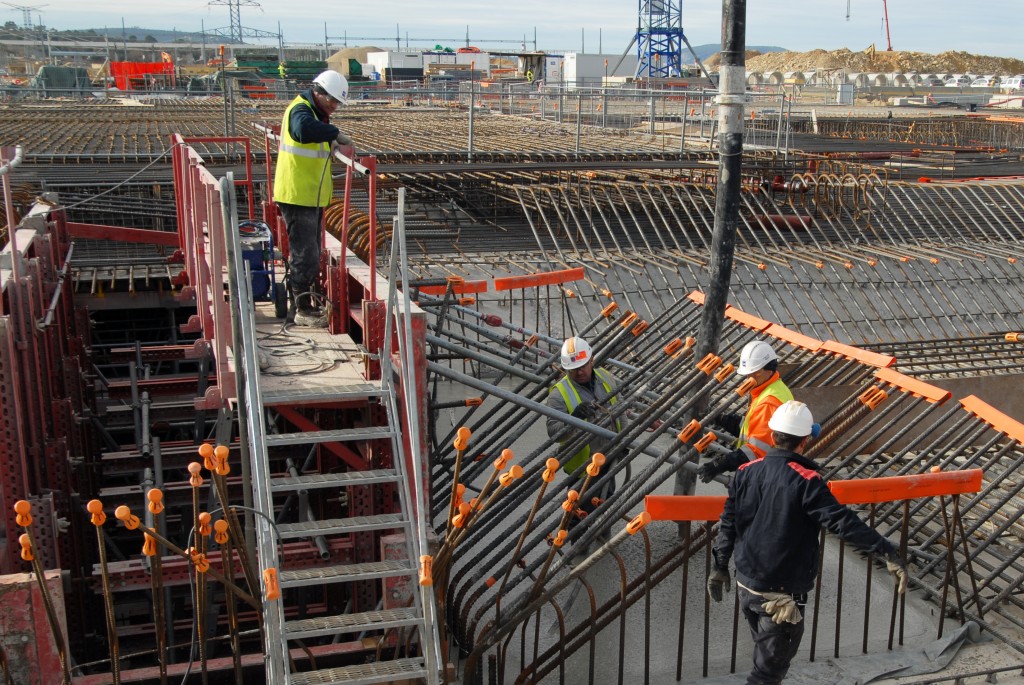
Ankle-deep in fresh concrete
2012-12-19 - Another "plot," or section, of the Assembly Building basemat is poured. Photo: F4E
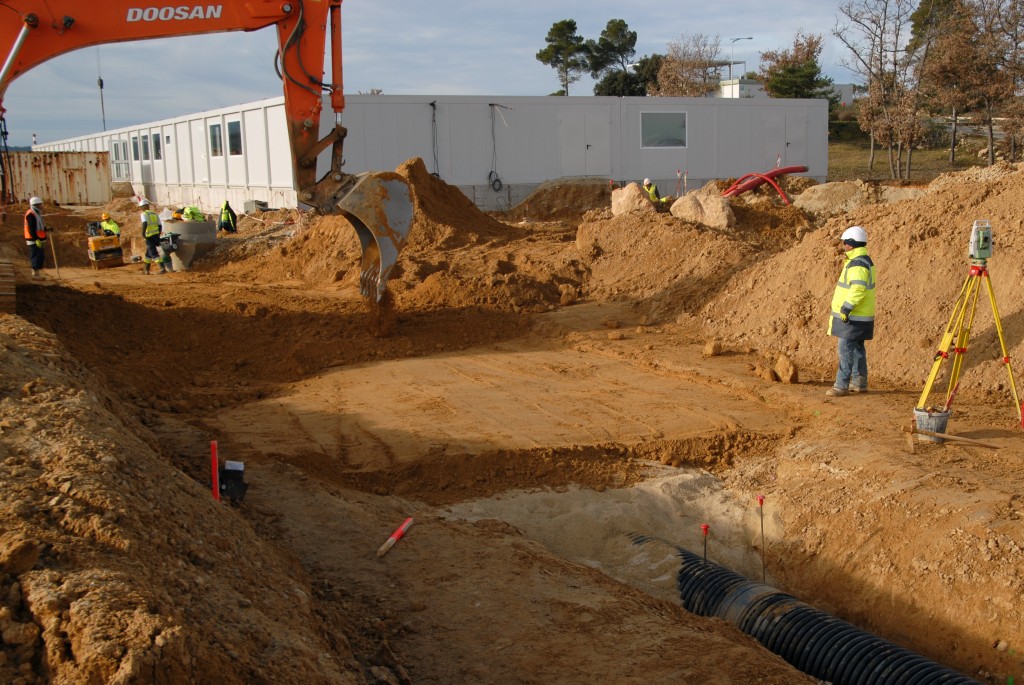
Critical services
2012-12-19 - Critical networks for Contractors Area #2 (sanitary, electrical, drinking water) are installed in December 2012. Photo: F4E

Temporary office structures
2012-12-19 - Modular offices for 50 people are positioned in the Contractors Area. Occupancy is expected in March 2013. Photo: F4E
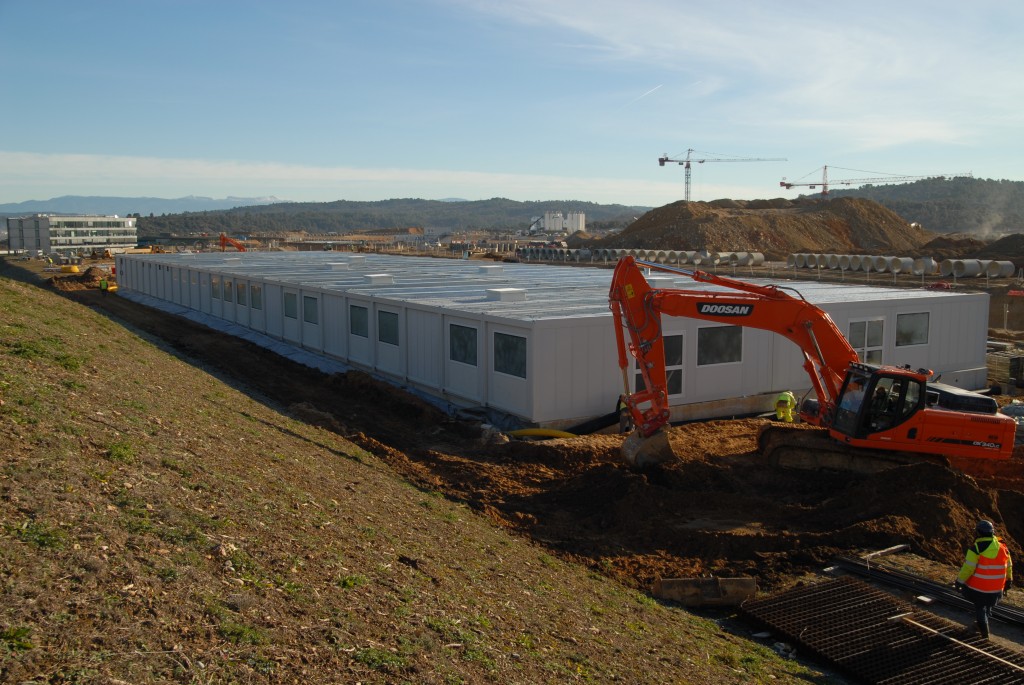
Worksite canteen
2012-12-19 - Seventy modular buildings make up the worksite canteen, with a capacity to serve 1,500 meals per day. The canteen will be operational in September. Photo: F4E
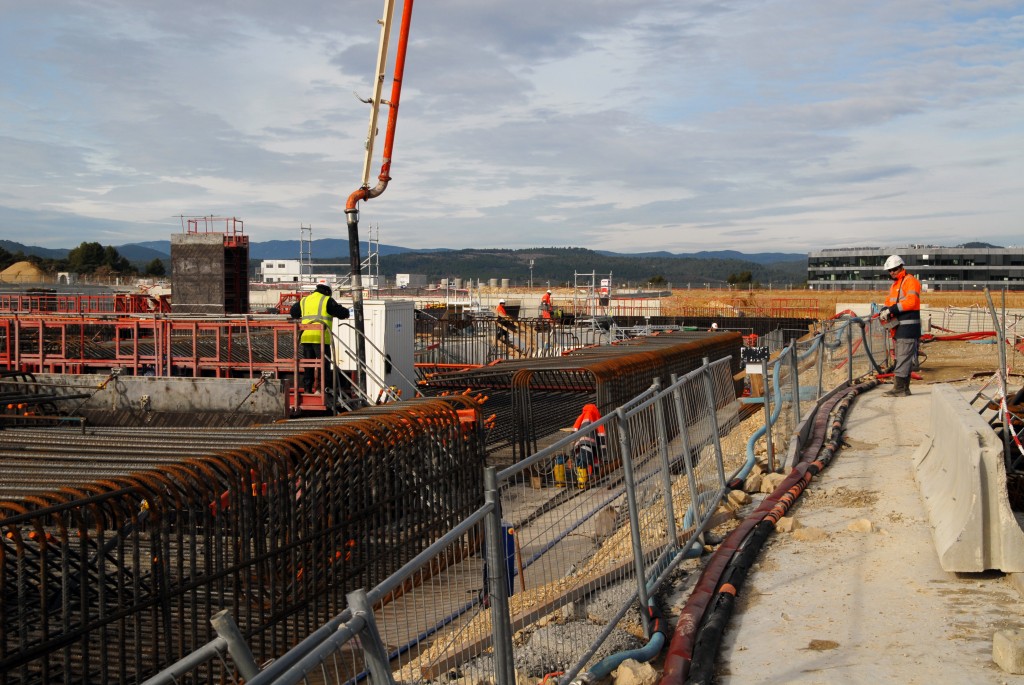
The smooth floor of the Assembly Building
2012-12-19 - Concrete pouring for the Assembly Building floor continues, section by section. The total surface area to treat is 6,000 square metres. Photo: F4E
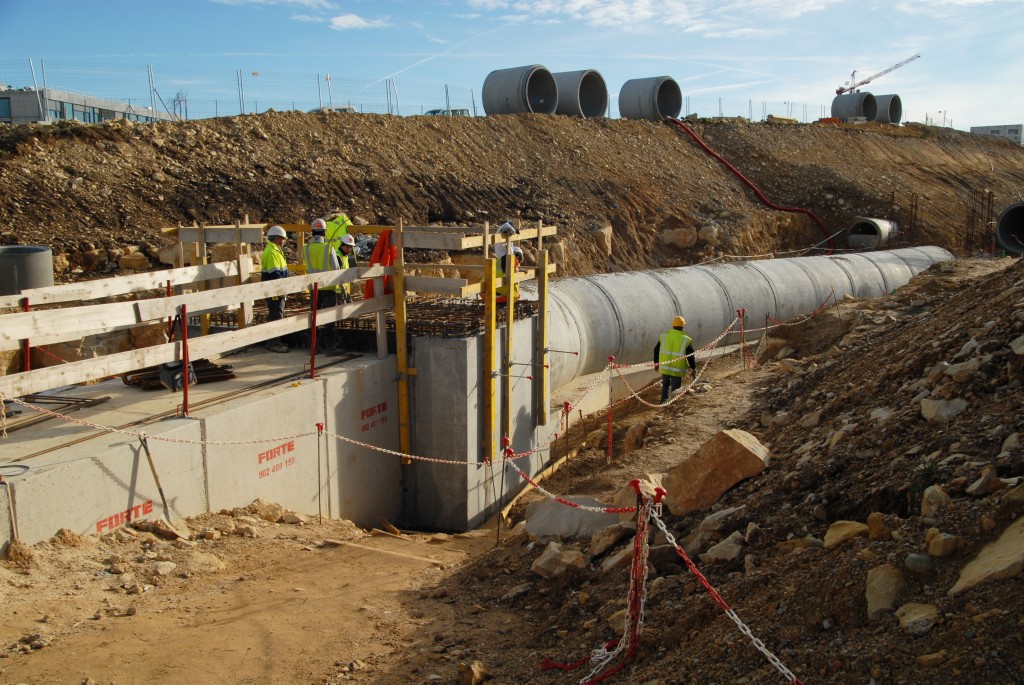
Boxing in the pipes
2012-12-19 - Reinforcement and concrete pouring around the drainage network pipes is carried out in December 2012. Photo: F4E
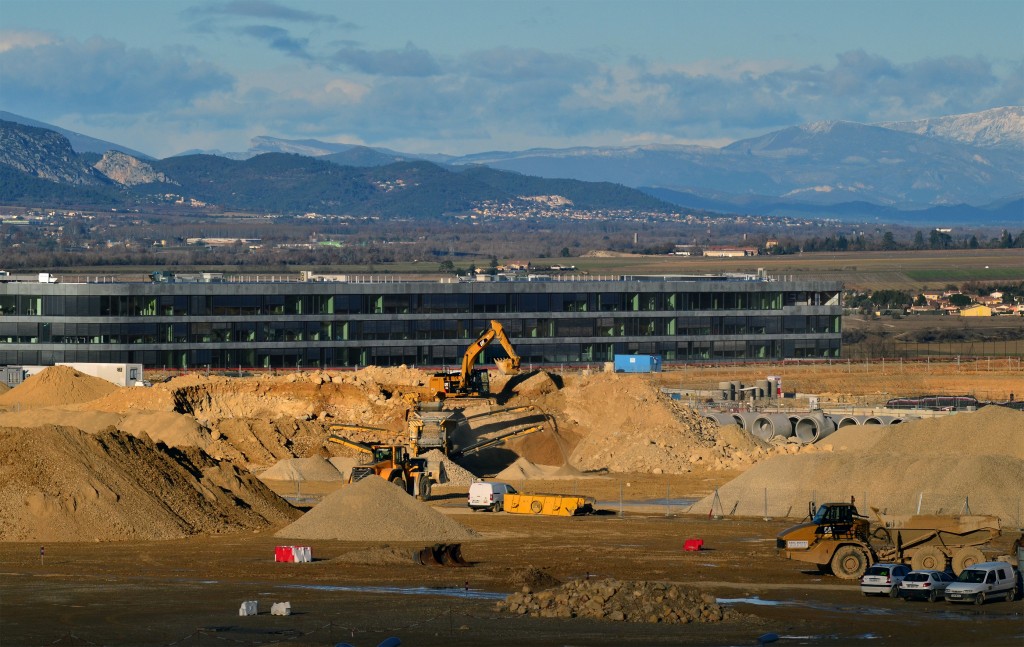
A building and its surroundings
2012-12-18 - The ITER Headquarters building was conceived as a kind of 'visual pedestal' for the Tokamak Building. Seen from this angle, it is also a 'visual pedestal' for the distant mountains ...
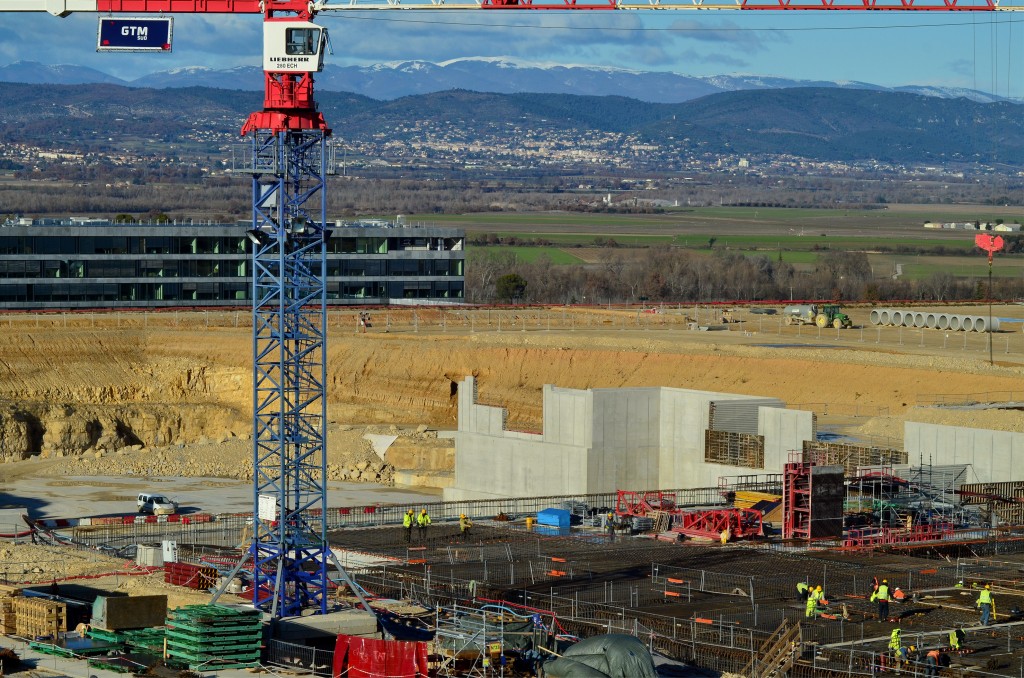
Looking north
2012-12-18 - In the distance, the snowcapped Montagne de Lure (alt. 1,600 m) and its small family ski resort.

Progress on the Assembly Building basemat at year-end
2012-12-18 - Seventy people are involved in reinforcement and concrete pouring works for the Assembly Building basemat in December.

Back to the usual weather
2012-12-10 - Snow never lasts for long in Provence - five days after this winter's first episode, nothing remains. ¶In the foreground, deep precipitation networks are put into place more than 10 metres below the surface of the platform.
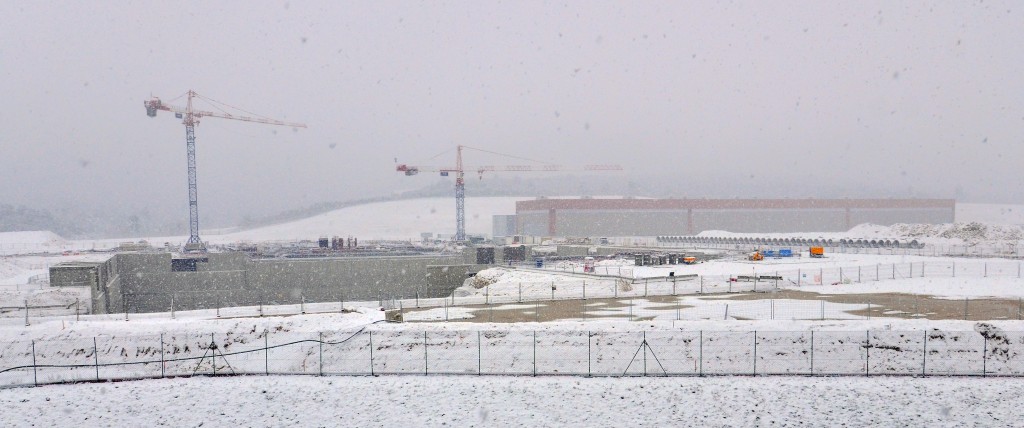
La neige?!
2012-12-07 - For the 70 people working on the foundations of the Assembly Building (see cranes in photo), work ends early on Friday, 7 December.
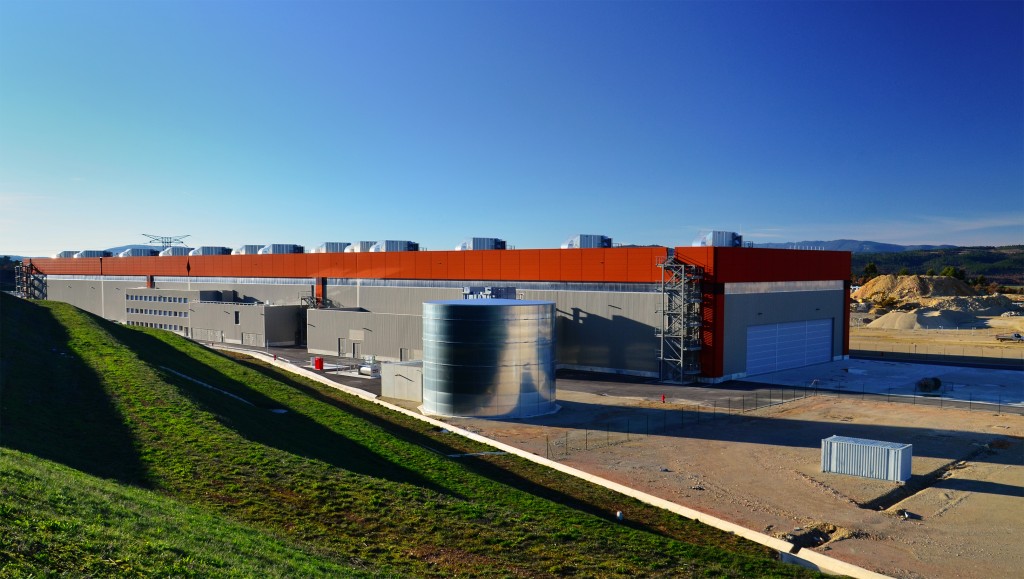
December 2012
2012-12-06 - The sharp light of December illuminates the Poloidal Field Coils building and casts long shadows ...
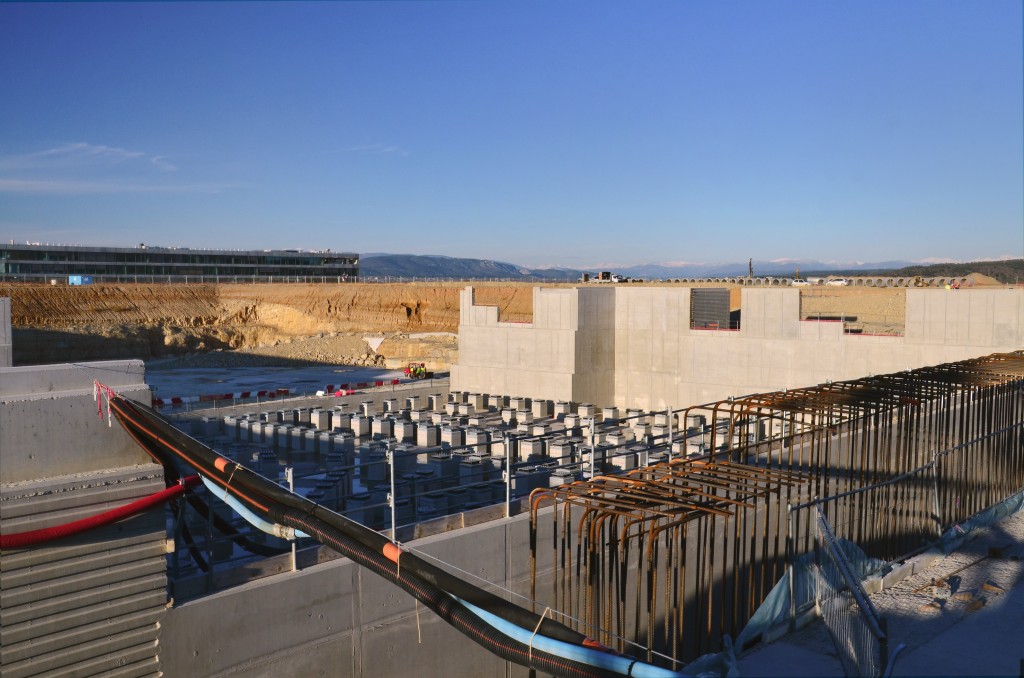
The pieces will be assembled here
2012-12-06 - The Assembly Building is a close neighbour to the Tokamak Building. Large, overhead cranes mounted on rails will run the entire length of the two buildings during assembly, along a continuous, 175 metre-long crane bay.
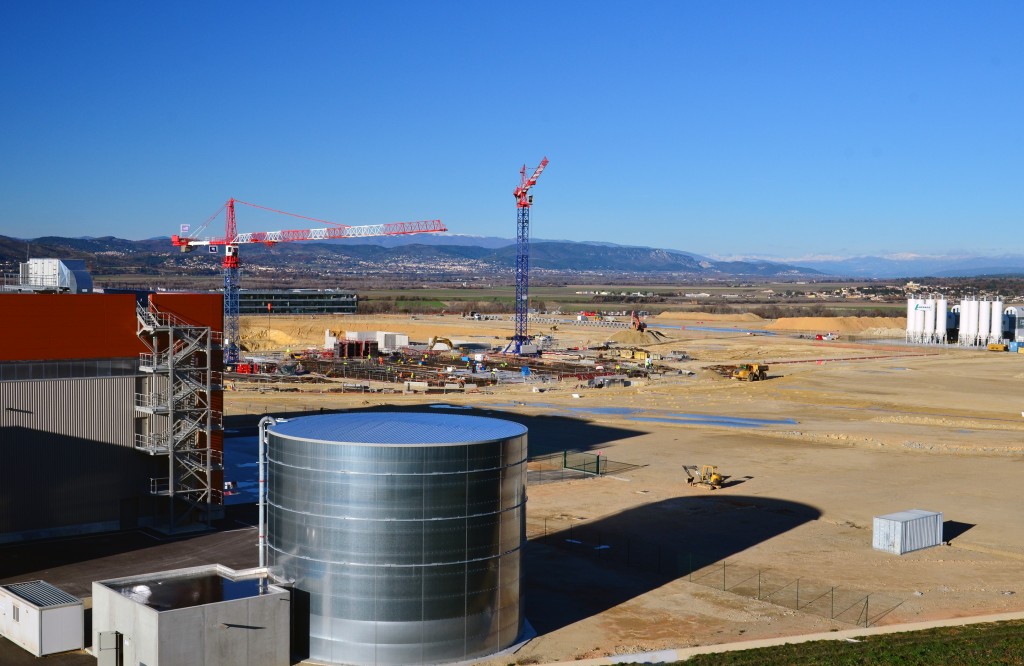
Smack in the middle
2012-12-06 - In the very centre of the ITER platform: the Assembly Building worksite.
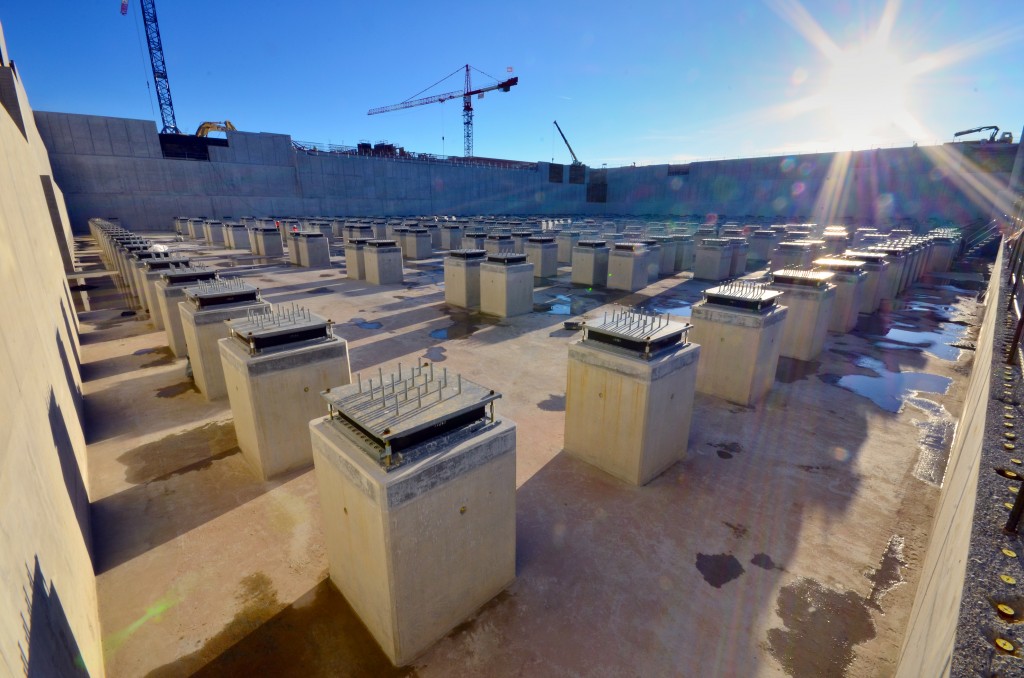
Early one December morning
2012-12-06 - The sun rises over the Seismic Isolation Pit. In 2013, work will begin on the foundations that will hide these columns and seismic bearings from view.
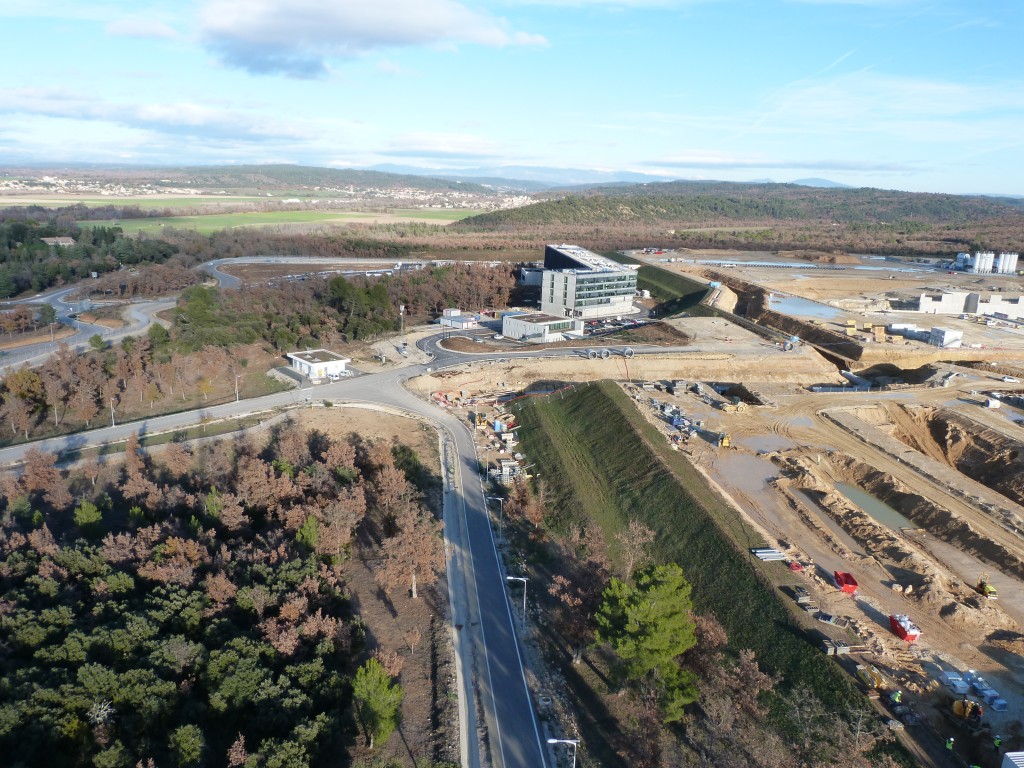
Looking toward the village of Vinon-sur-Verdon
2012-12-03 - The northern corner of the ITER site. The seat of the ITER Organization—the Headquarters building—sits below the elevated, 42-hectare platform where the scientific facilities will be installed. © Sylvain Couturier
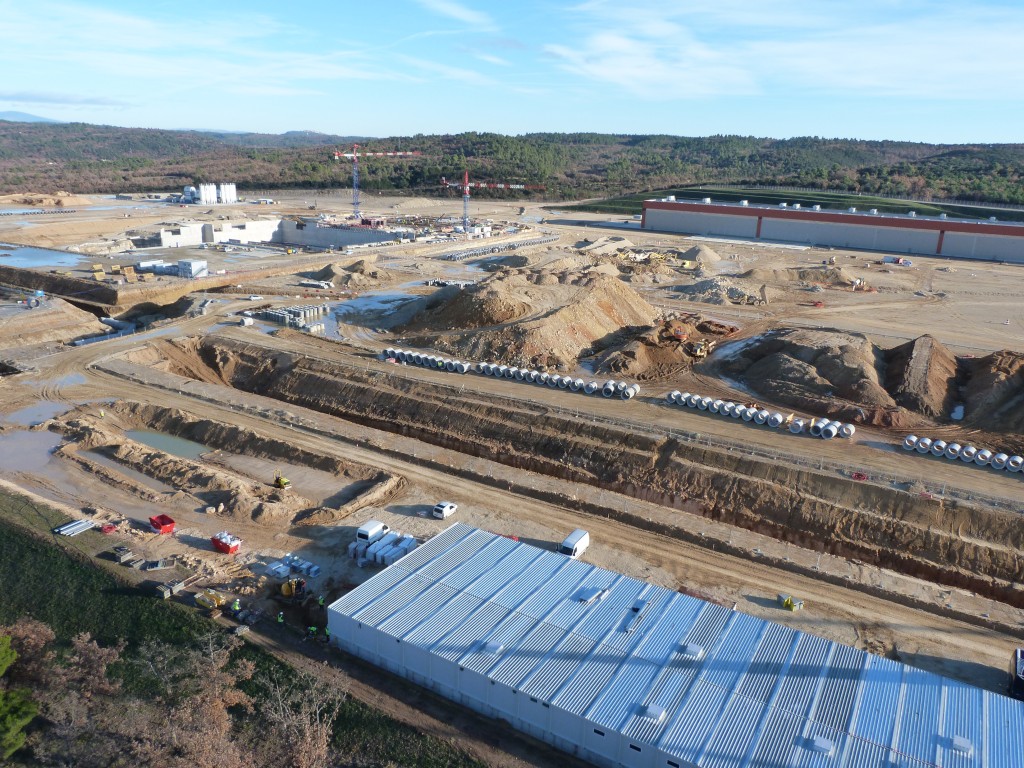
Seen from 40 metres
2012-12-03 - The winding facility for the poloidal field coils is the first completed building on the ITER platform. Opposite the facility is a 3,500 m² area under development for the contractors that will be responsible for the next major project: the civil engineering works on the Tokamak Complex. © Sylvain Couturier
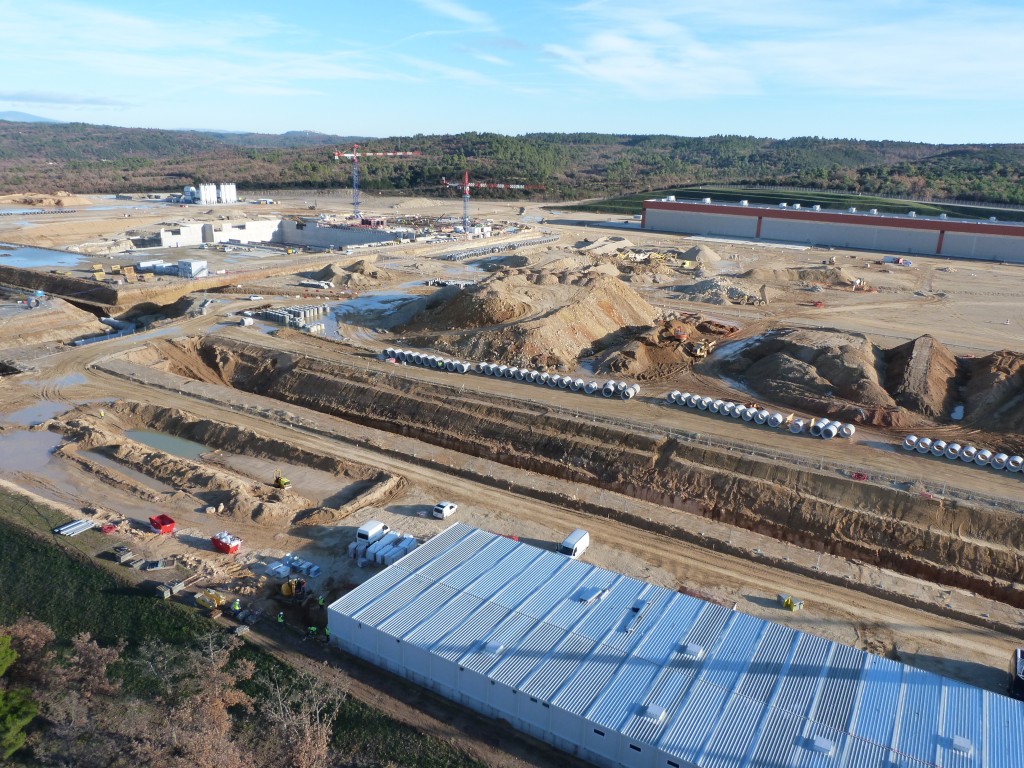
The ITER platform seen from 40 metres above
2012-12-03 - On the left, the Seismic Pit (with the cement batching plant in the background); on the right, the Poloidal Field Coils Winding Facility. In the foreground, CA2—the contractors area under preparation for the peak in construction activity planned in 2014-2015. © Sylvain Couturier
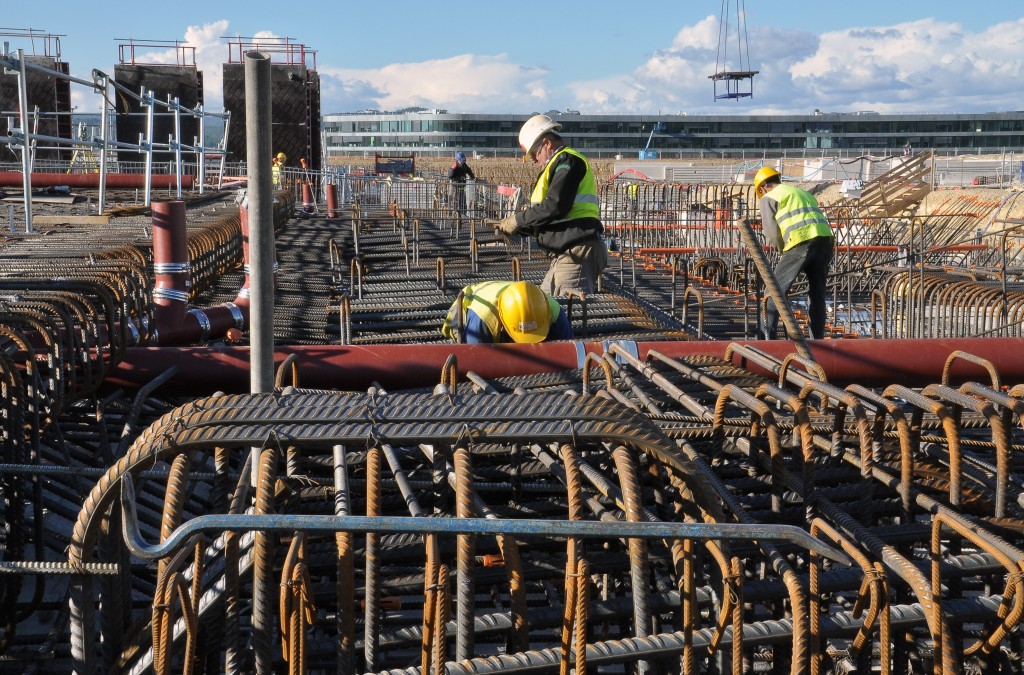
Hills and vales of steel
2012-11-28 - On the 6,000 square-metre site of the future Assembly Building, a complex grid of rebar is taking shape.
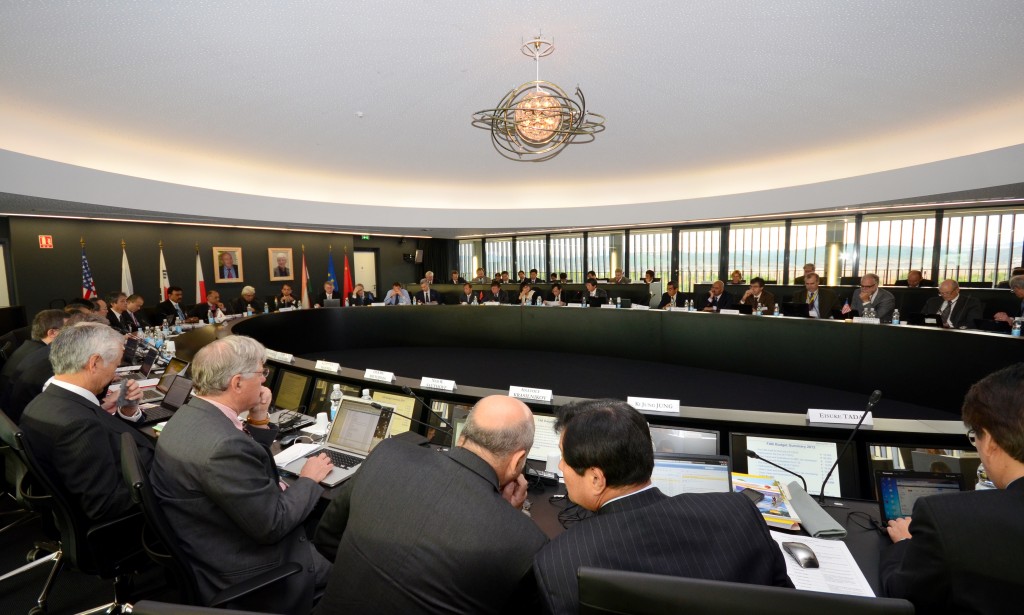
The Council Chamber
2012-11-28 - In the completed Headquarters building, the ITER Council meets for the first time in the fifth-floor Council Chamber.
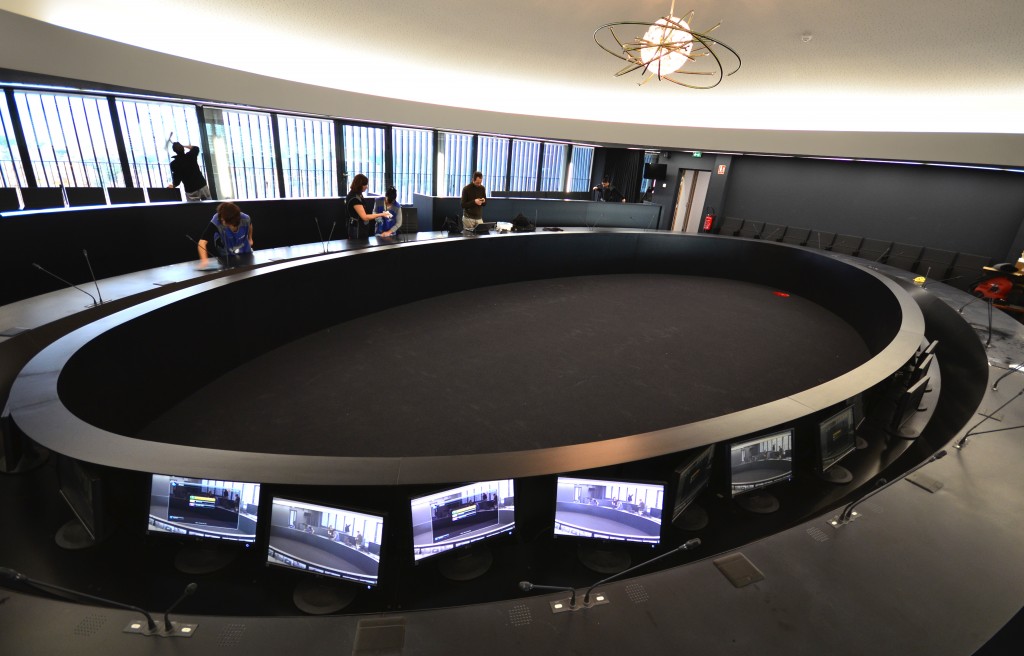
Last touches to the Council Chamber
2012-11-26 - Before the Eleventh ITER Council convenes from 28-29 November 2012, the Council Chamber undergoes a last round of waxing, window washing and equipment testing.
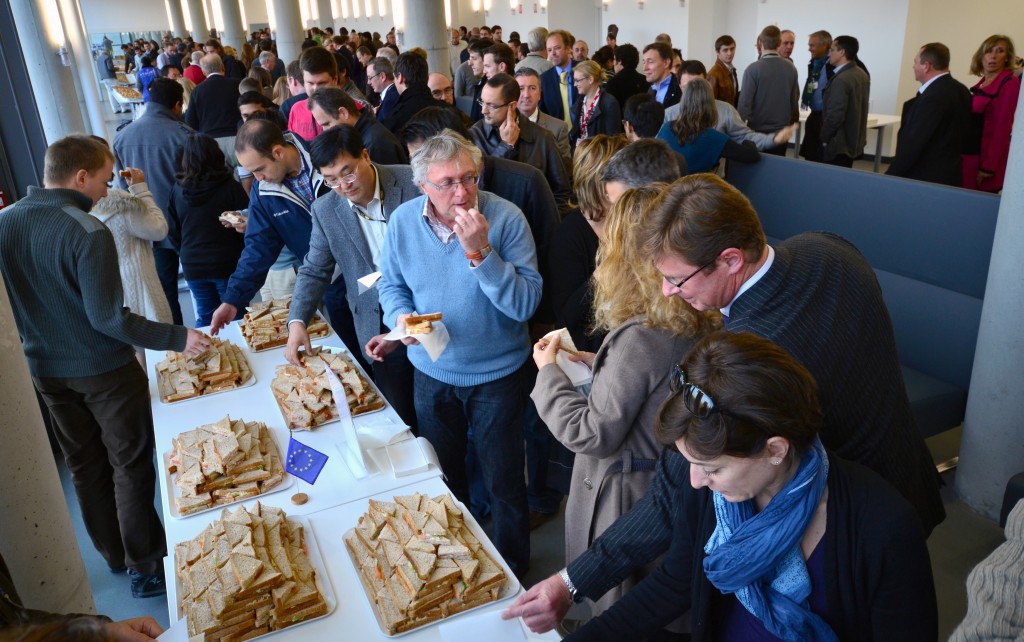
Filled to capacity
2012-11-23 - On 23 November the ITER community gathers to celebrate cuisine from Europe on the occasion of the third ITER Member Day. For the first time, it's standing room only in the ITER cafeteria ...
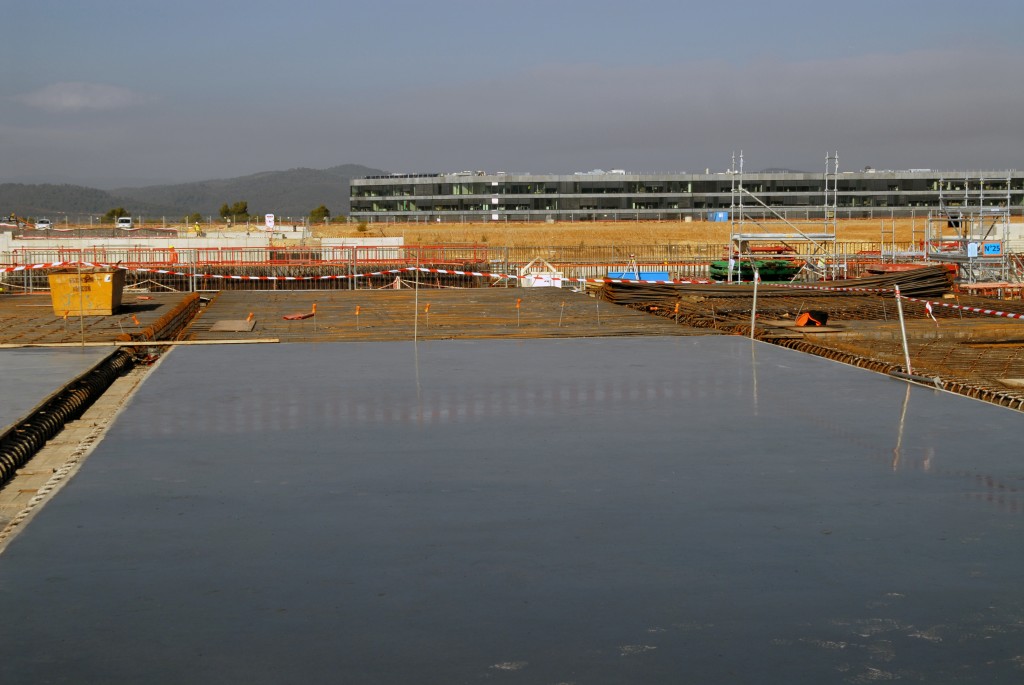
As smooth as glass
2012-11-16 - The concrete poured for the Assembly Building is of the finished variety: the finished product will be the actual floor of the tall workshop. Photo: F4E

Mountains of dirt
2012-11-16 - With work on the deep drainage networks and on Contractor Area 2, it's not as easy as it once was to see across the ITER platform. In the foreground, foundations are installed for the worksite canteen. Photo: F4E
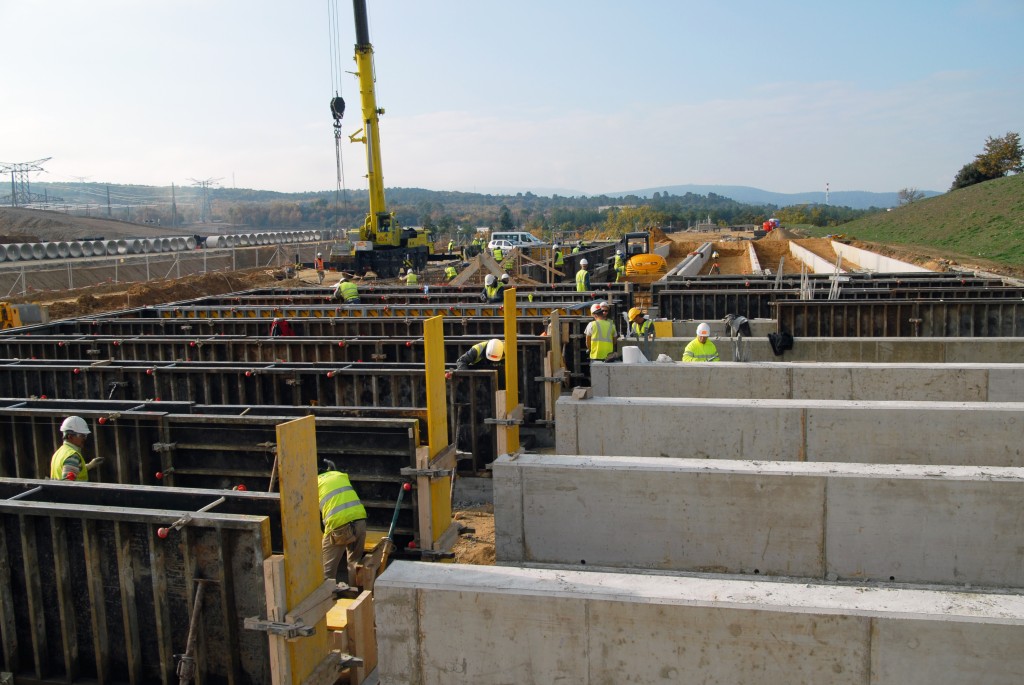
Peak of construction activities beginning 2014
2012-11-16 - Each contractor will have a modular office and storage area on the ITER platform. Photo: F4E
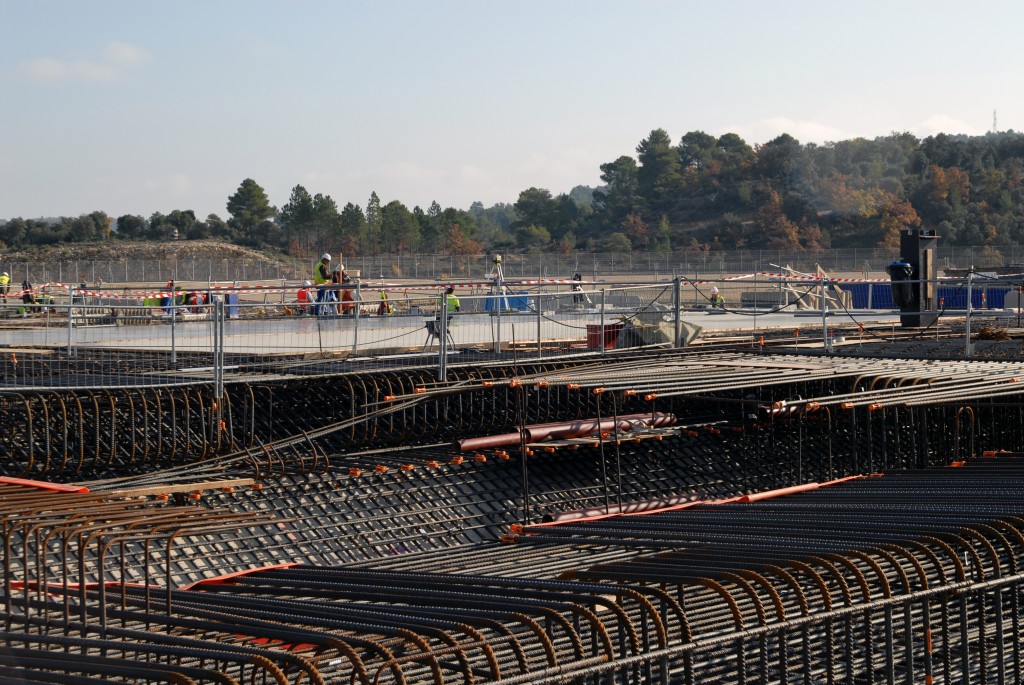
Complex rebar shapes
2012-11-16 - The foundation for the 60 metre-tall building ranges in thickness from 1.2‒2.2 metres. In between the metal rebar cages, space has been reserved for the electrical galleries, drainage, piping and tunnels that will service the neighbouring Tokamak Complex. Photo: F4E
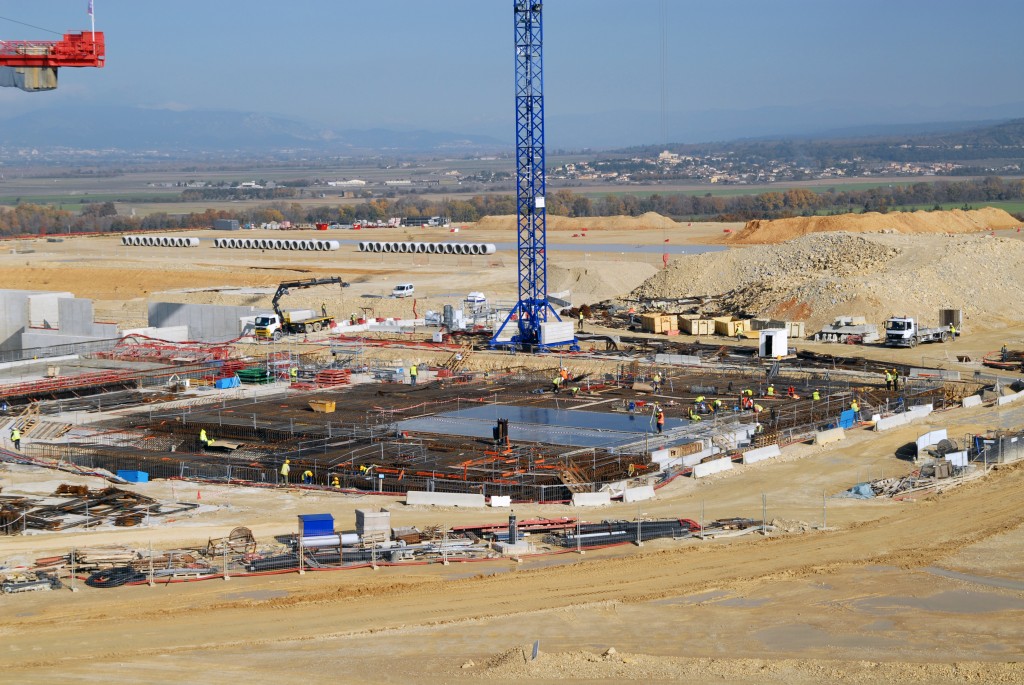
Here will stand the tooling
2012-11-16 - The basemat for the Assembly Building will be finished in March. The anchor plates for 4 large assembly tools will be cemented into the concrete. Photo: F4E
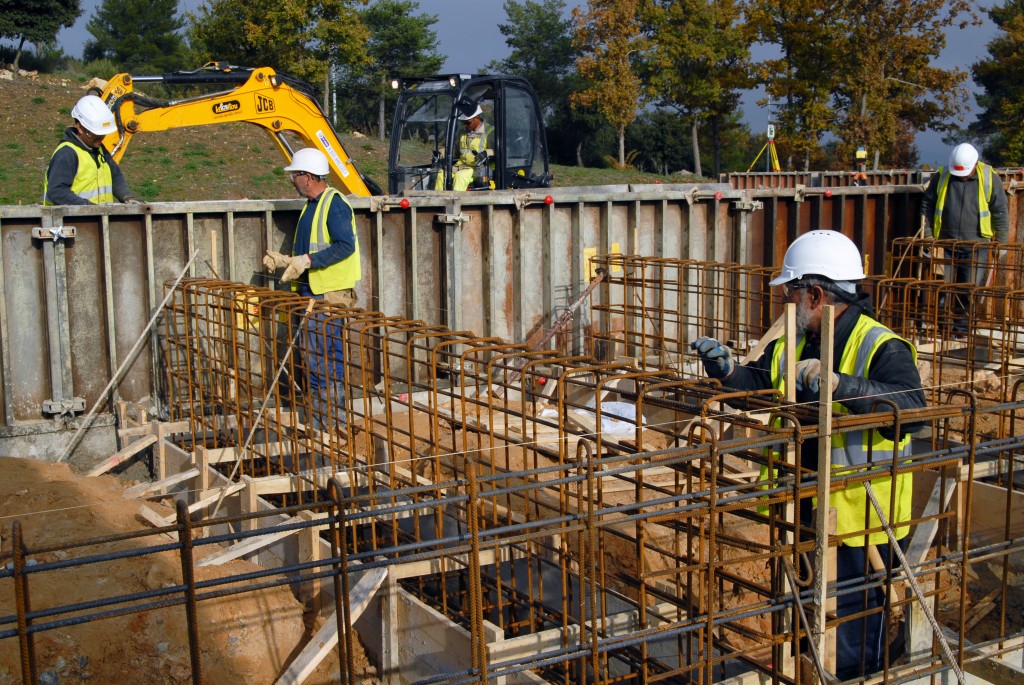
Canteen to serve 1,500 meals
2012-11-16 - It will take 70 modular "cubes" to make up the contractors canteen (1,500 meals/day). The canteen will be up and ready for September 2013. Photo: F4E
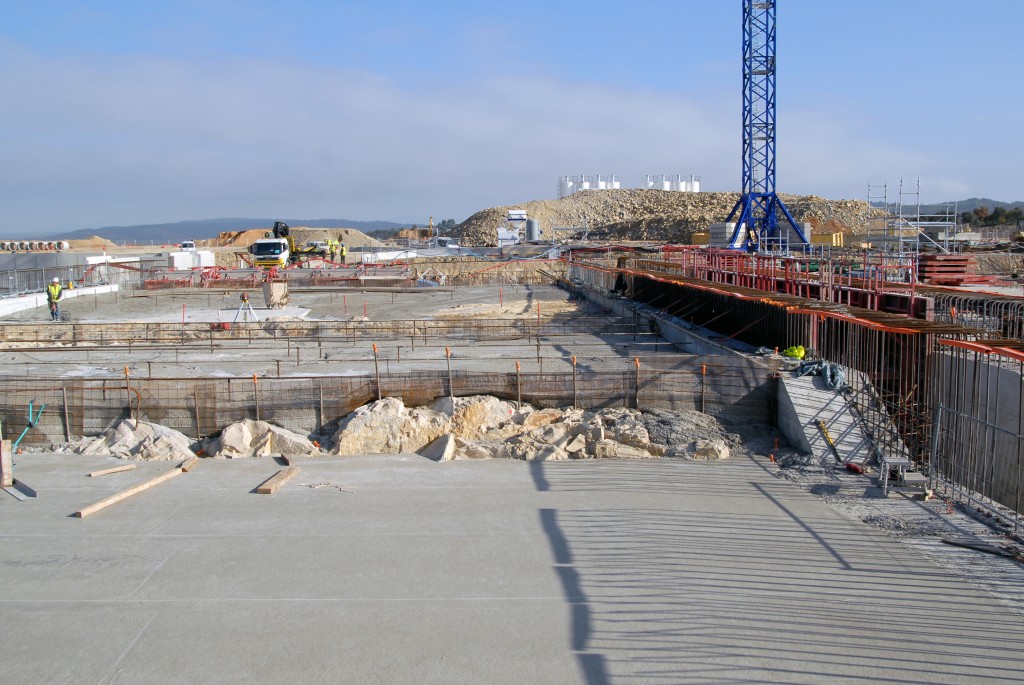
Surface area: 5,400 square metres
2012-11-16 - Concrete pouring for the Assembly Building slab has been progressing segment by segment since November. Photo: F4E
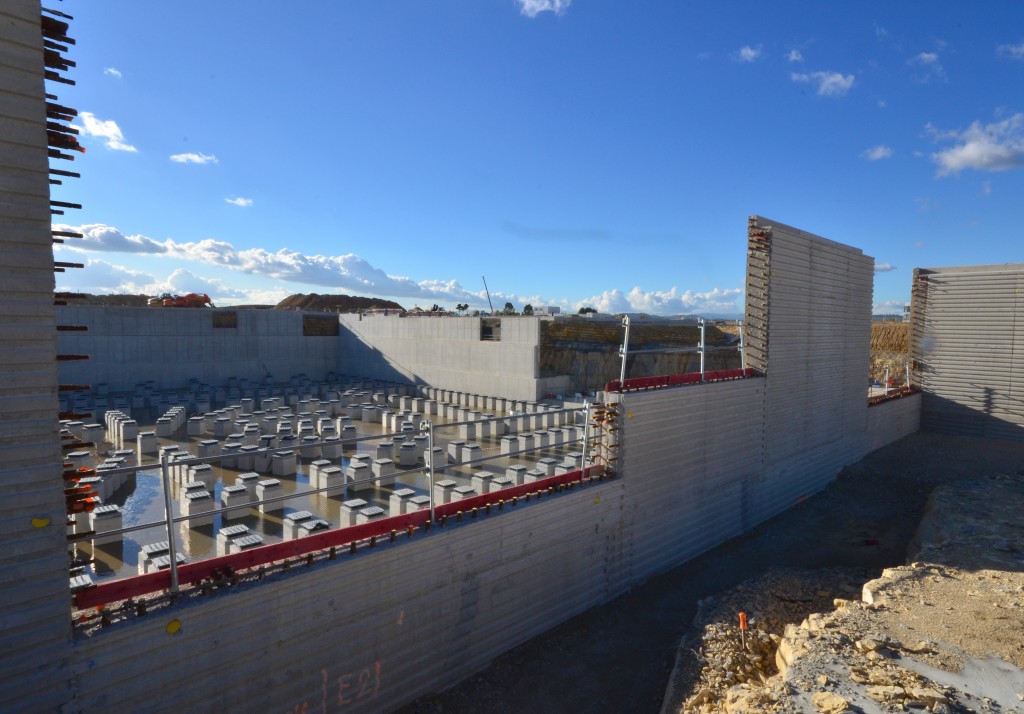
Pumps are working in November
2012-11-06 - The waterproof Seismic Isolation Pit is designed to keep water OUT of the foundations of the Tokamak Complex ... but as long as it's open to the sky, water also stays IN.
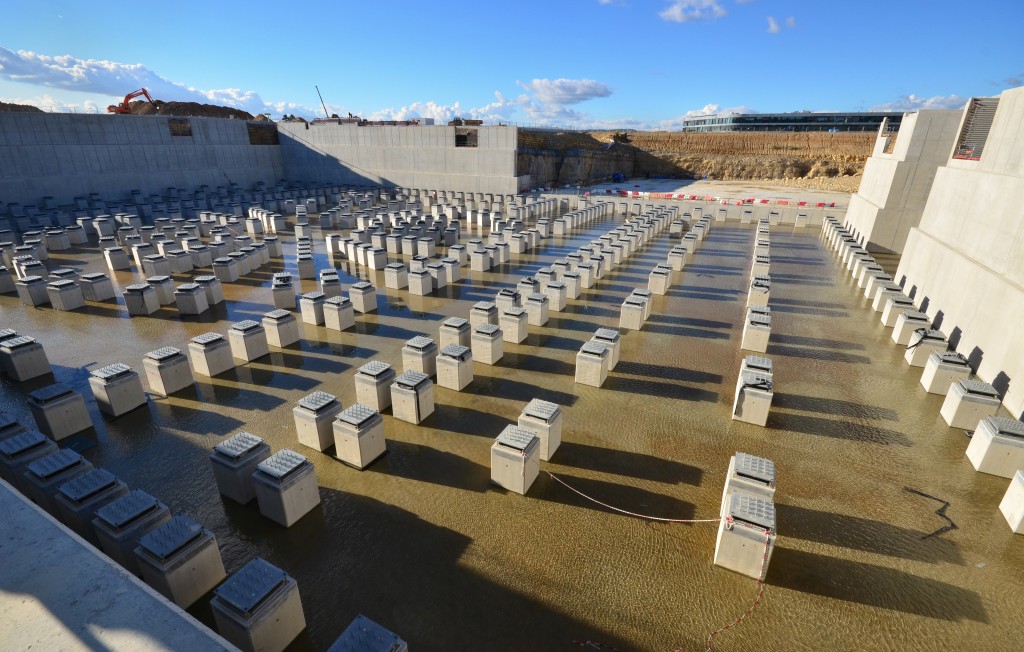
Ripples in the Tokamak Pit
2012-11-06 - Ten centimetres of water in the Seismic Pit attest to the heavy rainstorms that passed over Provence in early November.
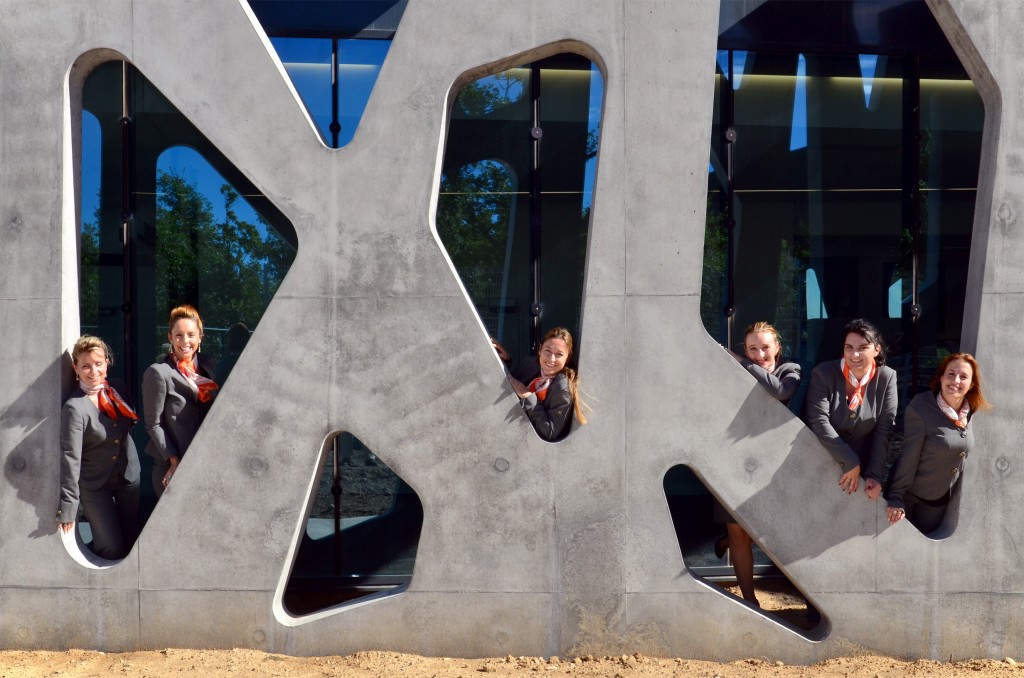
They are ready to welcome you!
2012-10-15 - An average of 90 people visit the ITER Headquarters every day. First stop: the Access Control building, pictured.
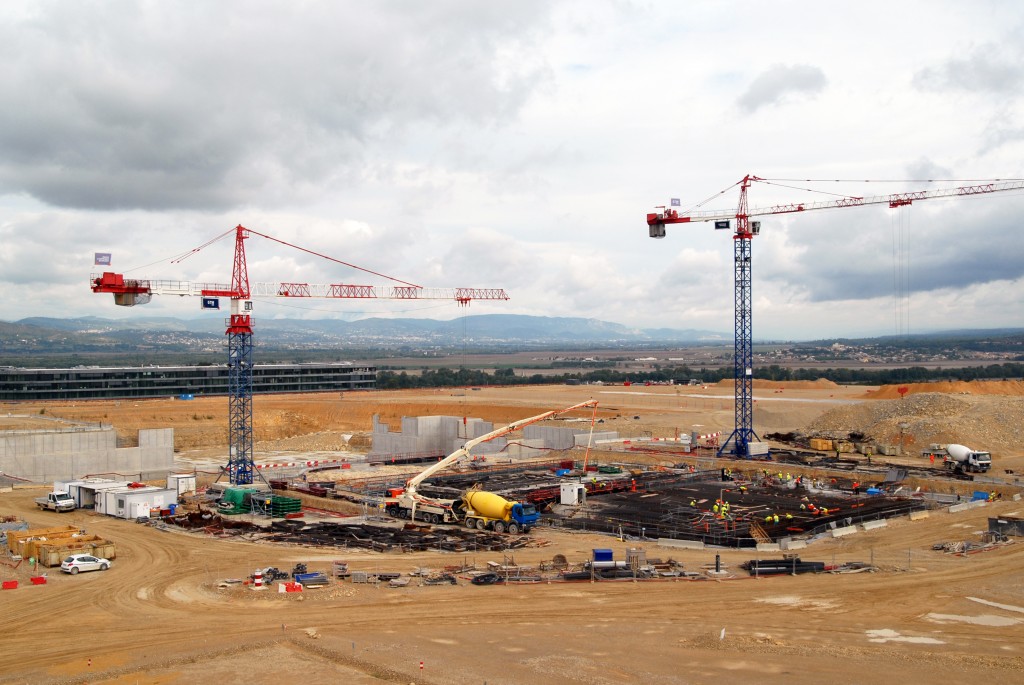
A tall hall for pre-assembly activities
2012-10-12 - Heavy works are underway for the future antechamber to the Tokamak Building: the Assembly Building, which will house two 750-tonne cranes and pre-assembly activities.
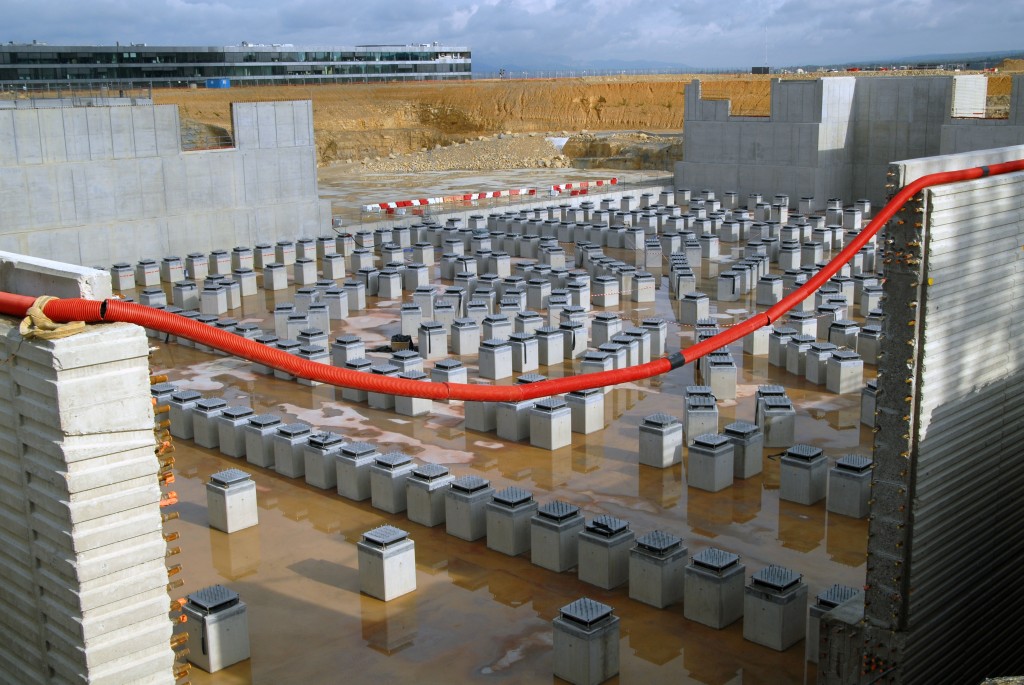
The "box"
2012-10-12 - Standing above the 90 x 130 Seismic Pit, future home to the Tokamak, Diagnostic and Tritium buildings. Photo: F4E
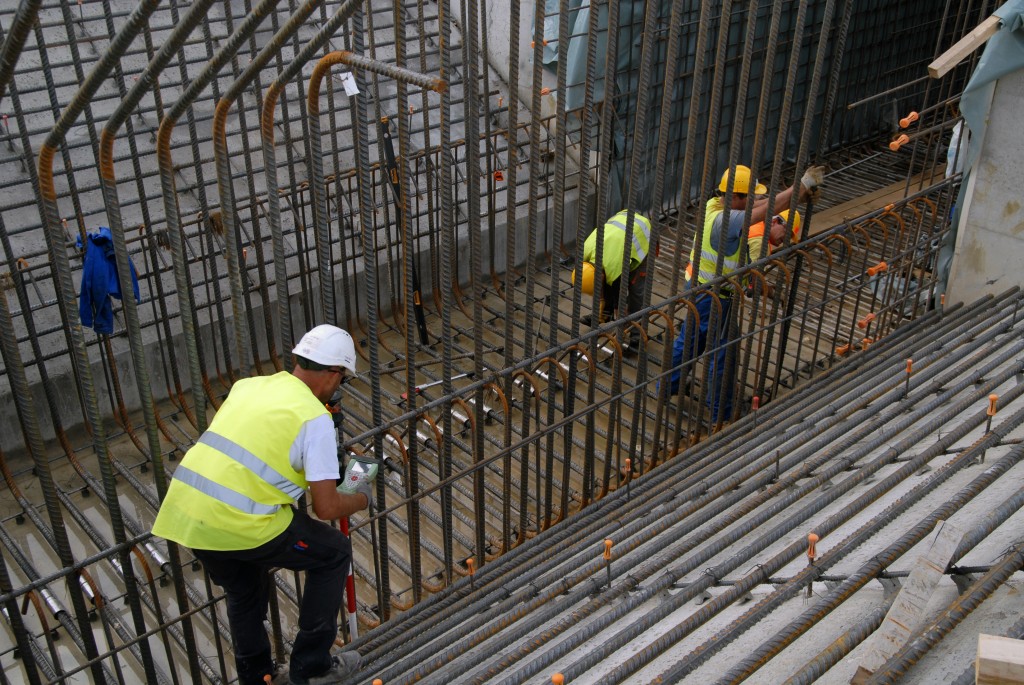
A complicated geometry
2012-10-12 - Space has been reserved in the foundations for tunnels to house electrical galleries, drainage and piping. Photo: F4E
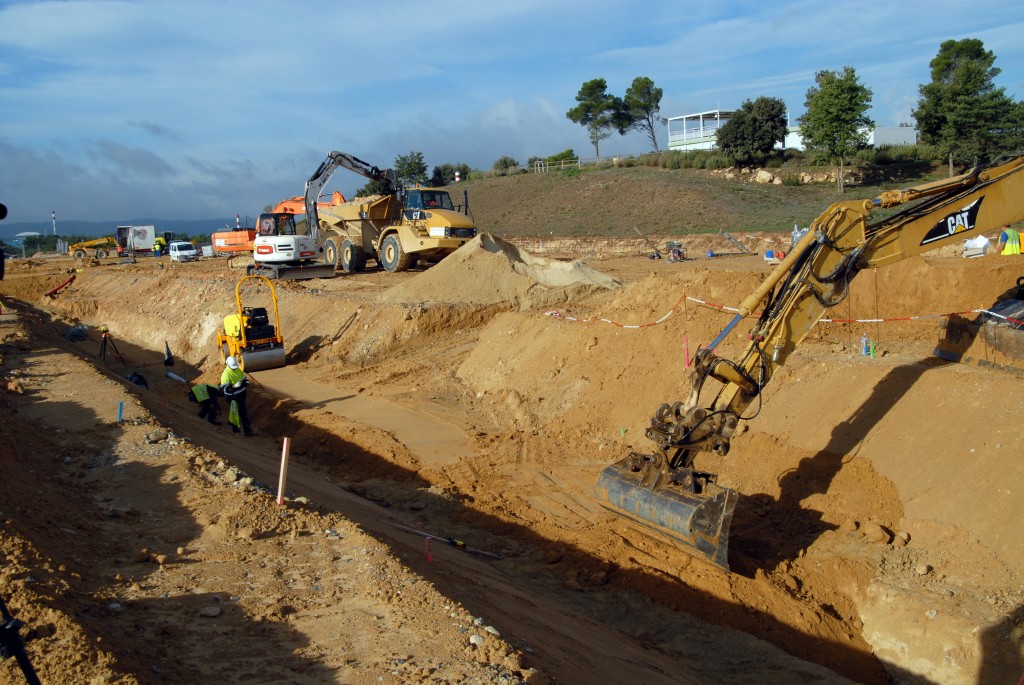
13,000 visitors
2012-10-12 - The ITER Visitors Centre stands on the hill overlooking the site (top right). Nearly 13,000 people came through this building in 2012. Photo: F4E
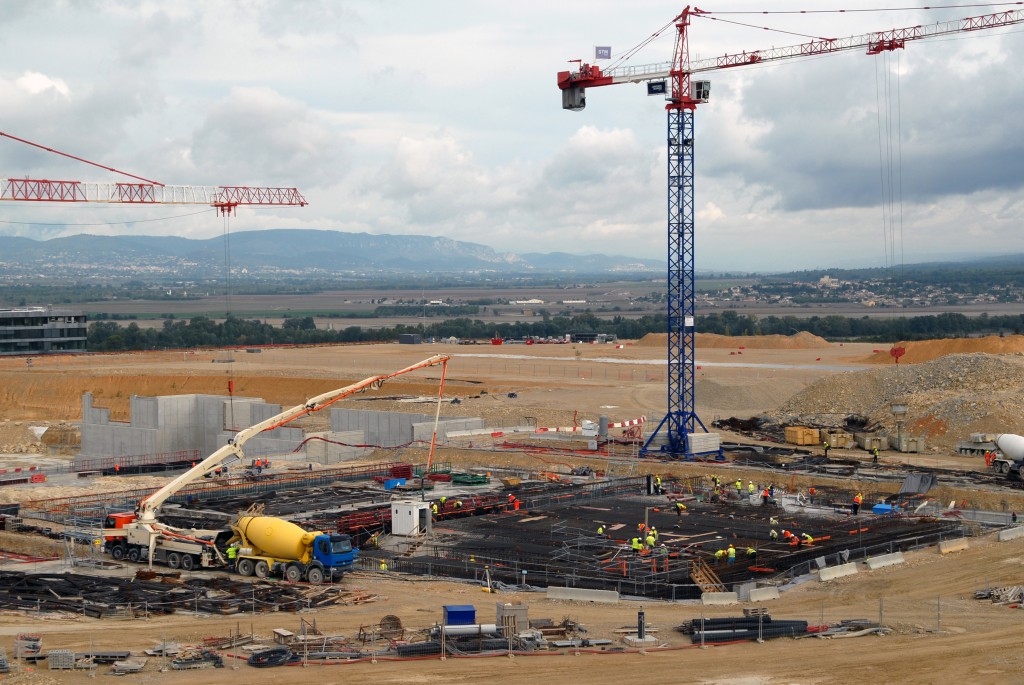
The centre of it all
2012-10-12 - The Tokamak Complex and the Assembly Building will form a "T" in the middle of the platform (with the Assembly Building in the supporting role). Photo: F4E
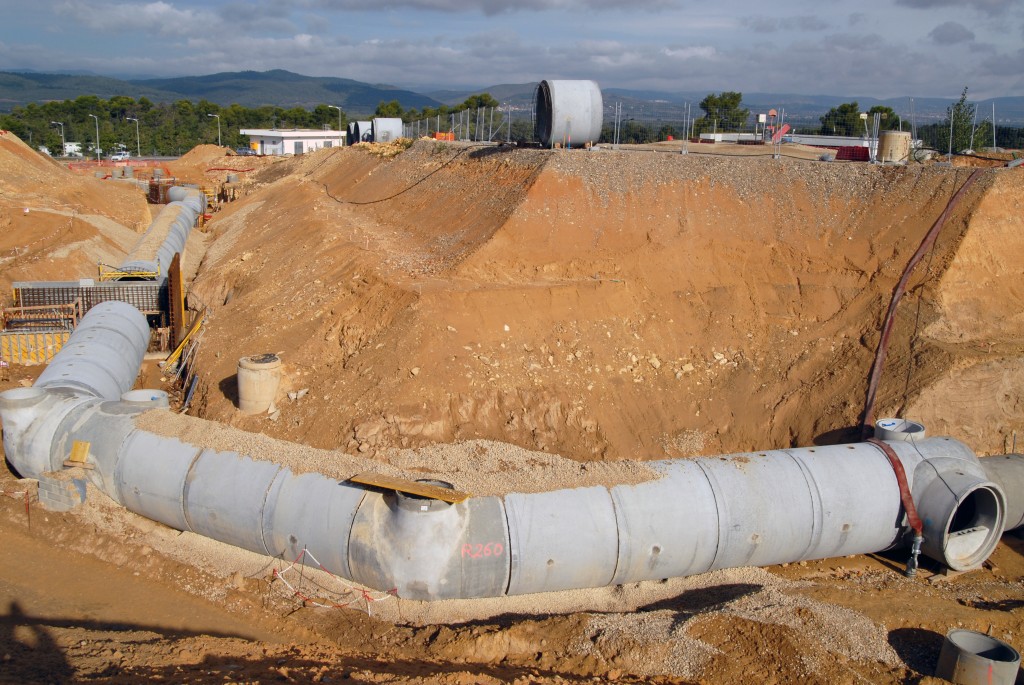
Evacuating rainfall
2012-10-12 - Pipes are installed for ITER's deep precipitation network. Photo: F4E

Contractors area must be ready for March 2013
2012-10-12 - The corner of the platform reserved for contractor parking lots, modular buildings and storage areas. Photo: F4E
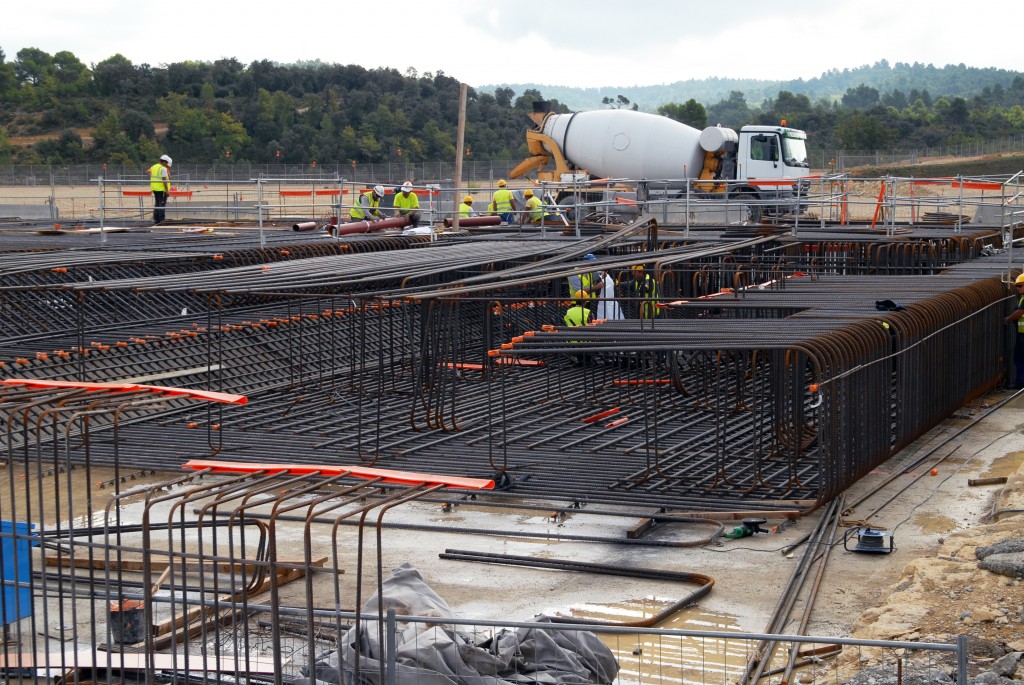
Supporting the load ...
2012-10-12 - The foundation slab will vary in thickness from 1.2-2.2 metres. Parts of the foundation will support the embedded anchor plates of the building's large and heavy custom assembly tools. Photo: F4E
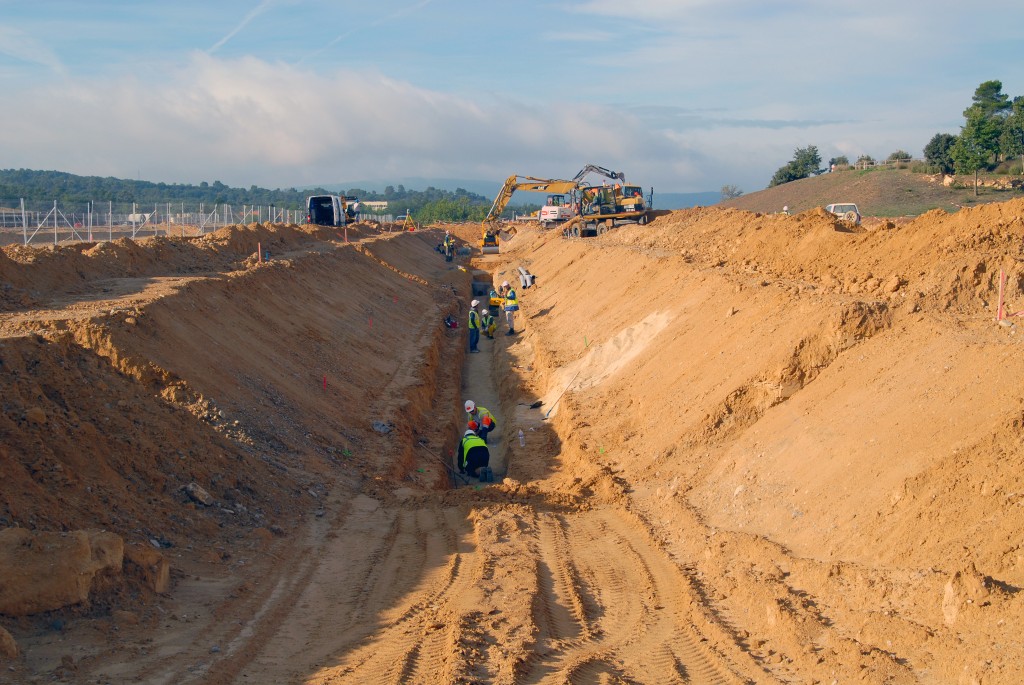
Trenches crisscross the platform
2012-10-12 - Deep underground networks are under preparation for the evacuation of run-off water. Photo: F4E
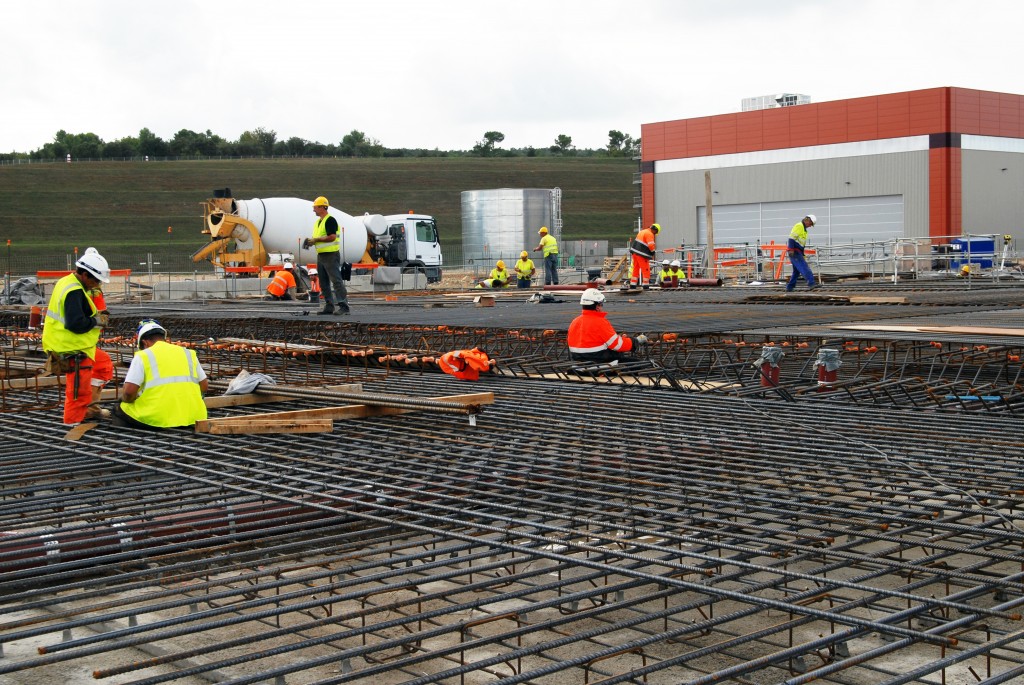
A few metres away
2012-10-12 - The five poloidal field magnets that will be fabricated in the on-site Winding Facility (in red) won't have far to travel to the Assembly and Tokamak buildings. Photo: F4E
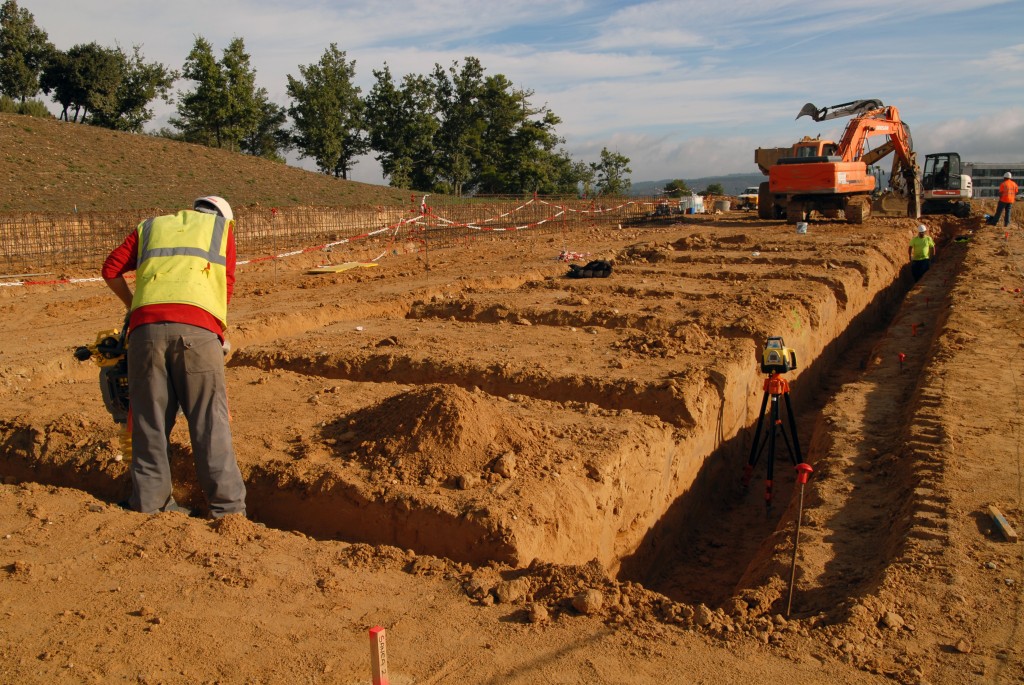
Foundation work for modular buildings
2012-10-12 - Work progresses on Contractors Area 2—a 3,500 square-metre area that will be reserved for the companies participating in the peak construction activities of the next few years. Photo: F4E
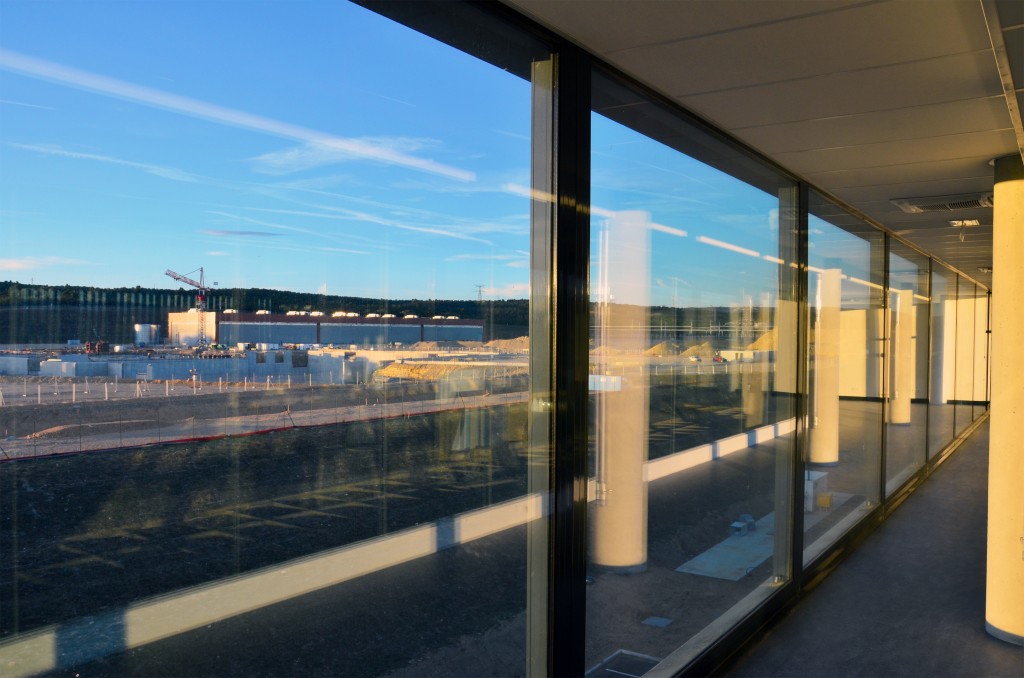
Sunrise on the platform
2012-10-08 - From the fifth floor of the building, it's possible to take in the entire 42-hectare construction site.
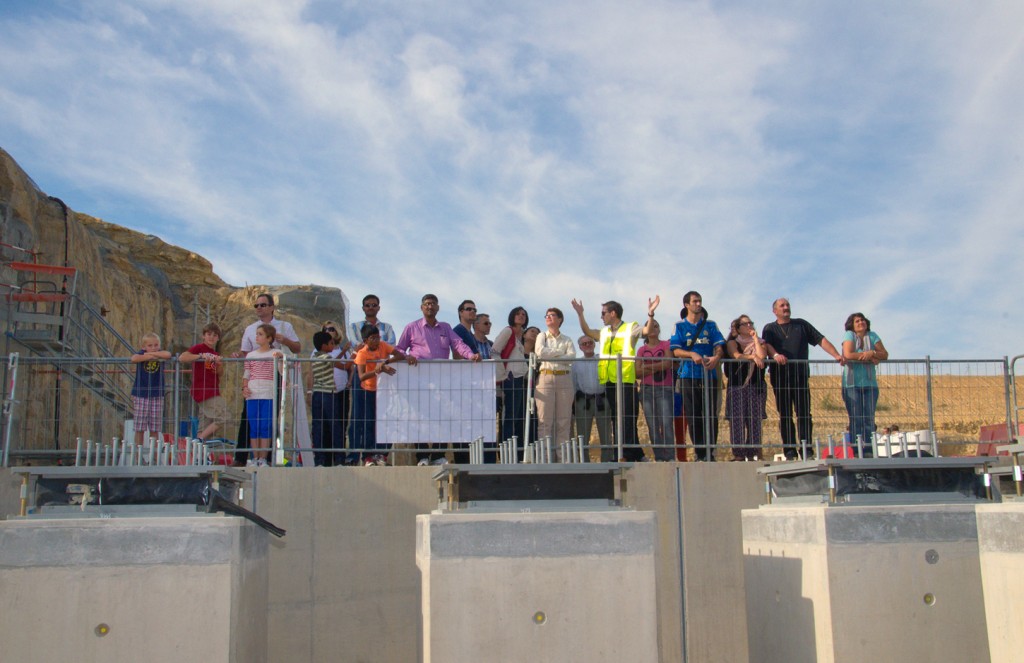
A unique opportunity
2012-10-07 - On 6 October 2012, ITER hosts 1,300 visitors for its second annual Open Doors Day. Guests are treated to a historic walk through the foundations of the Tokamak Complex, soon to be covered over by the next-level basemat.
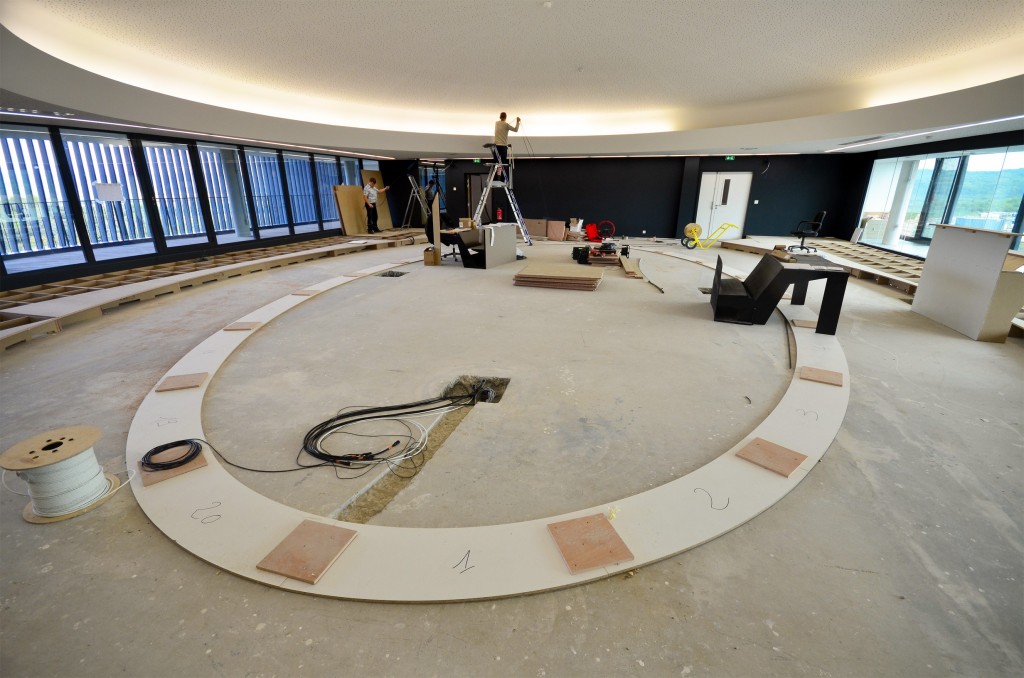
Hurry!
2012-10-05 - There's just about one month left to complete the Council Room, before the ITER Council invests the space to convene its eleventh meeting on 28-29 November 2012.
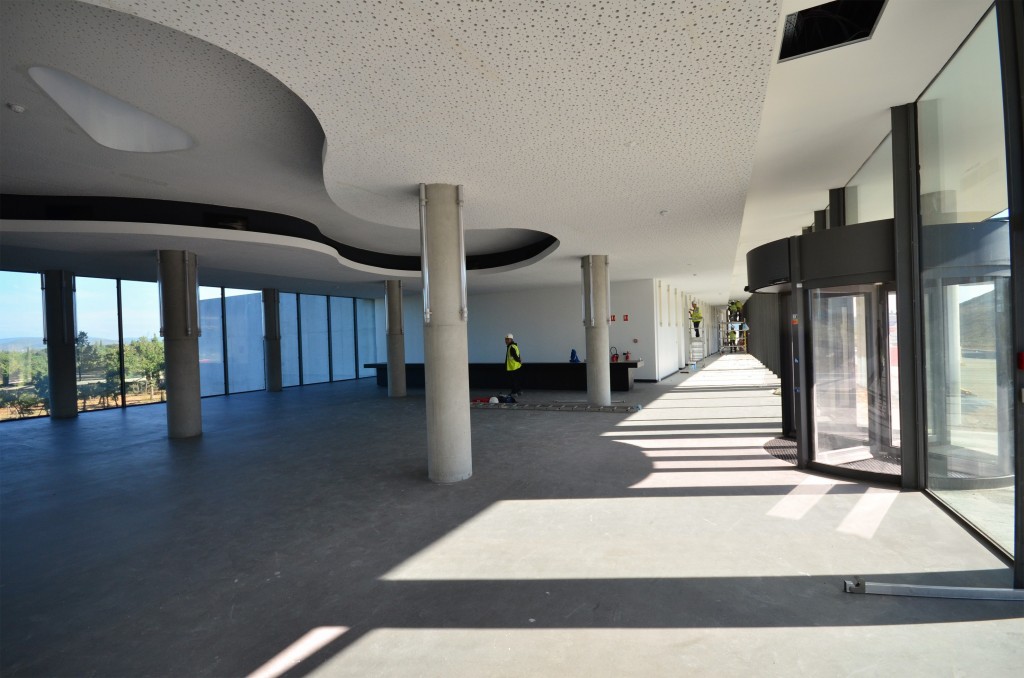
Through the revolving doors
2012-10-03 - Sun pours into the lobby of the Headquarters building on Moving Day in October.
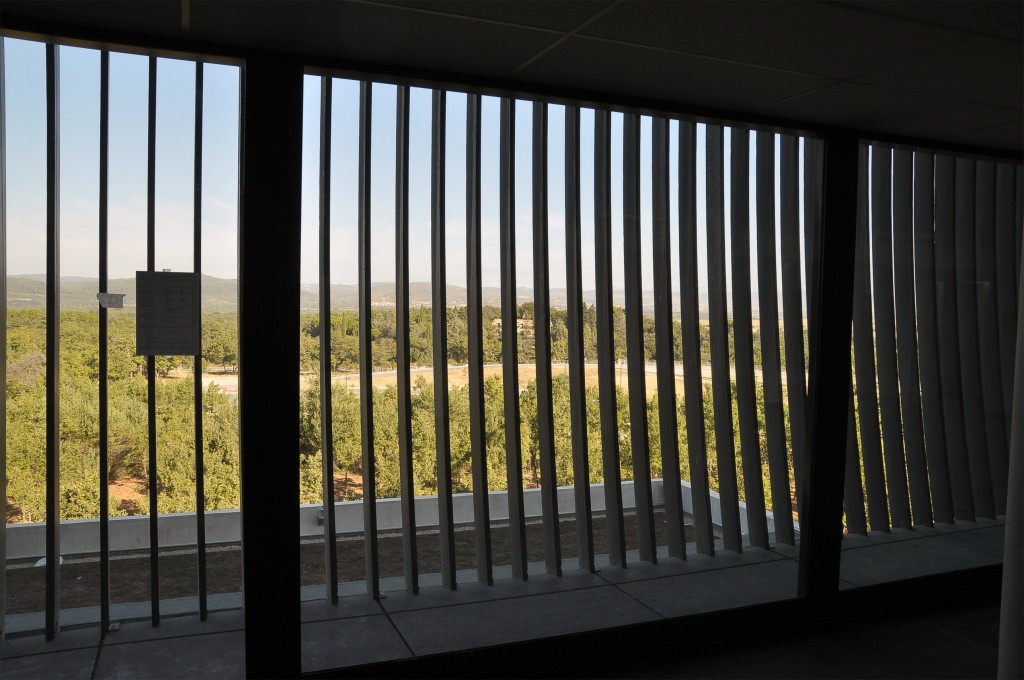
"A view needs to be framed"
2012-10-03 - Looking out of one of the north-facing offices. According to architect Laurent Bonhomme, who paired with colleague Rudy Ricciotti from Marseille to design the office building, as with a painting or a photograph, "a view needs to be framed"—especially in an office setting where concentration is important.
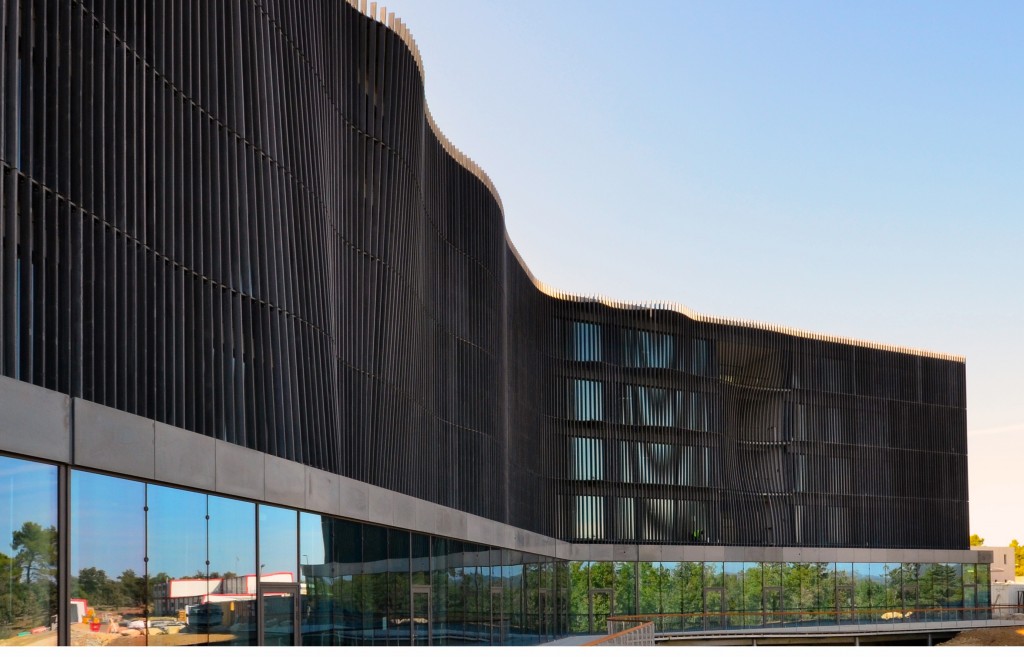
Headquarters: completed
2012-10-01 - The undulating northwestern facade of the ITER Headquarters building faces the road.

One day, these patios will have trees
2012-09-21 - Glass predominates throughout the structure, on both the interior and exterior walls.
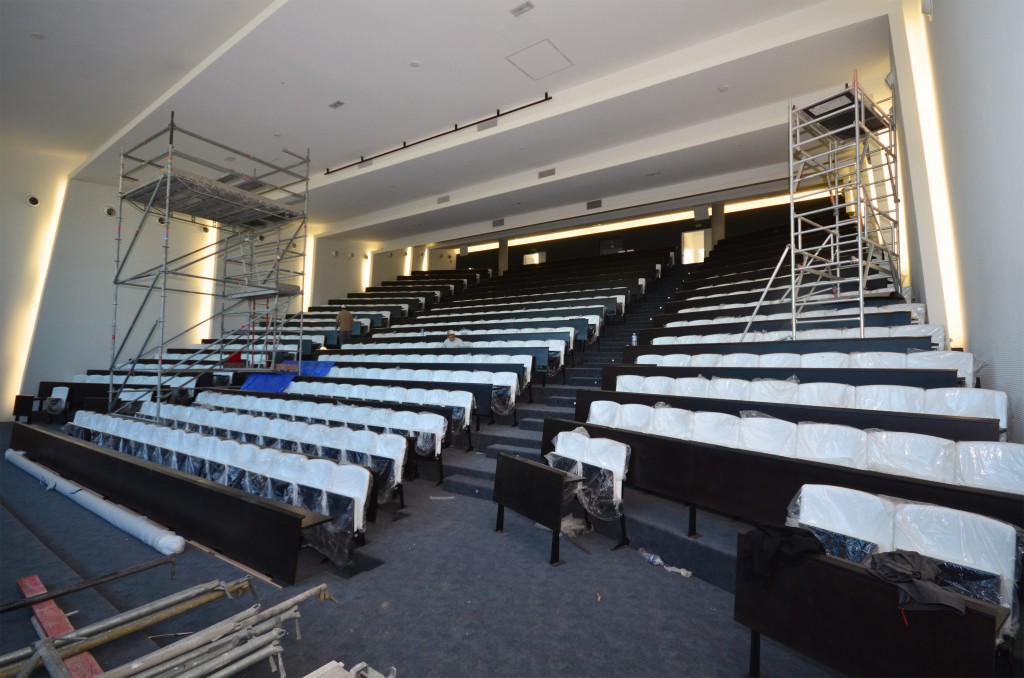
Please, take a seat
2012-09-21 - Furniture, carpeting and audiovisual equipment complete the 500-seat amphitheatre in September.
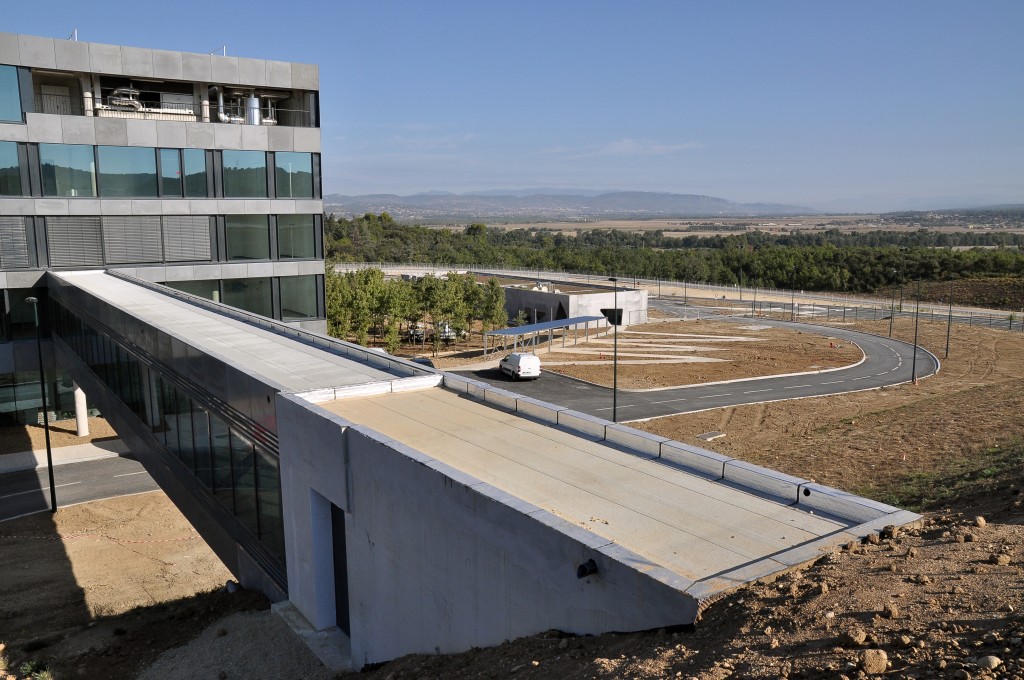
Take a tunnel to work?
2012-09-21 - From the second floor of the completed Headquarters building, scientists will have access to the Control Room of the ITER Tokamak.
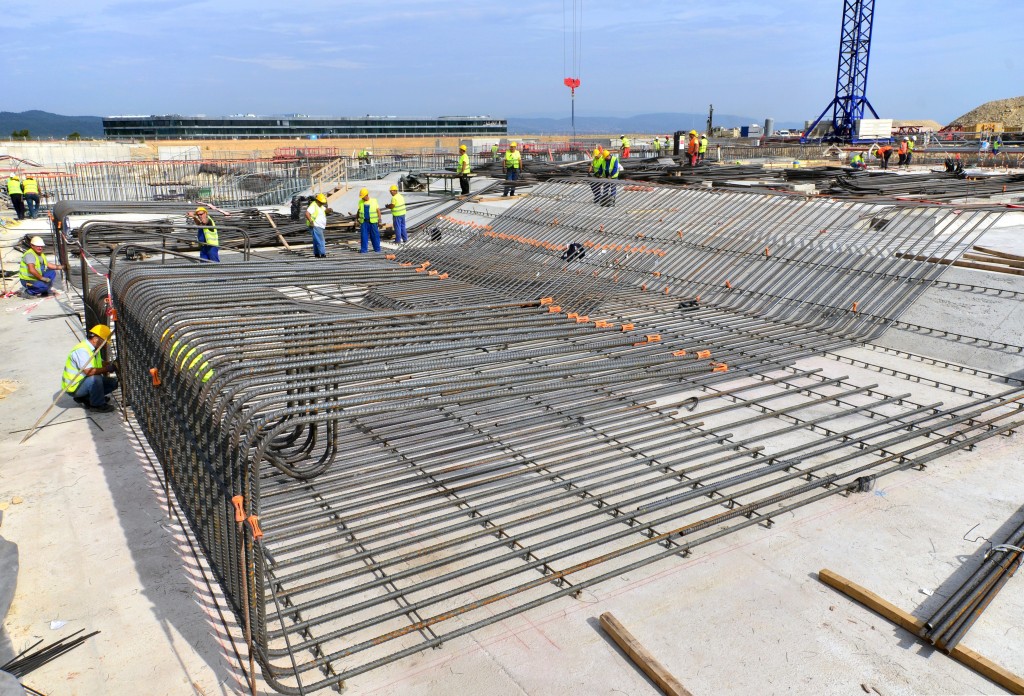
Mapping out the steel
2012-09-15 - On top of the blinding layer of concrete, 1,400 tonnes of steel rebar will be placed according to a very specific diagram. Photo: F4E
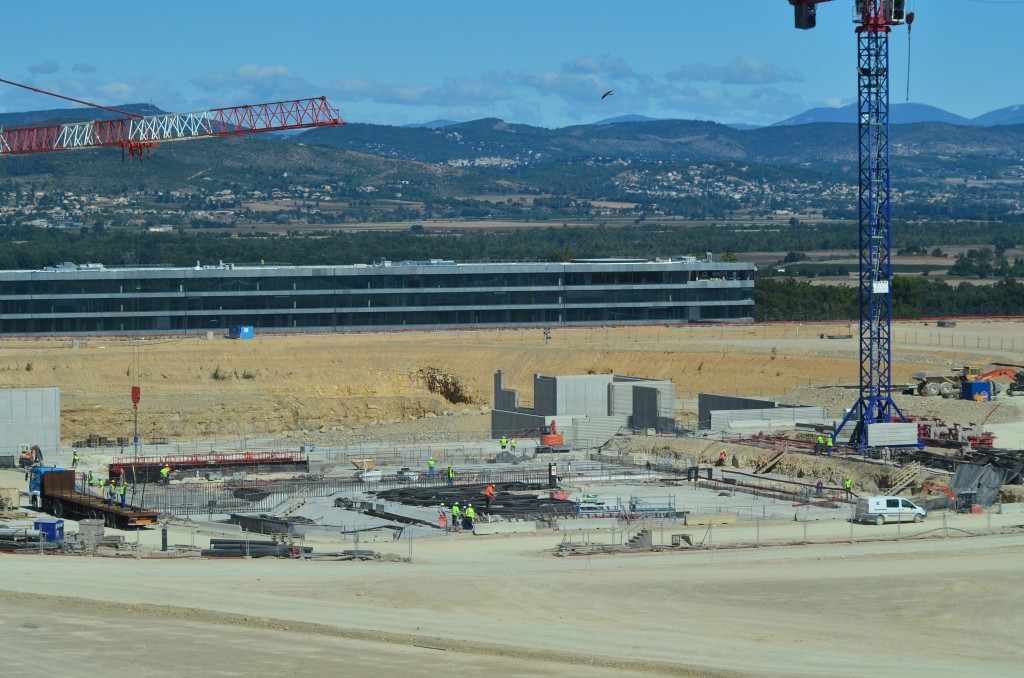
Rebar activities begin
2012-09-13 - The 5,400 square-metre area of the Assembly Building is covered with a layer of blinding concrete, to prepare for the reinforcement activities to come.
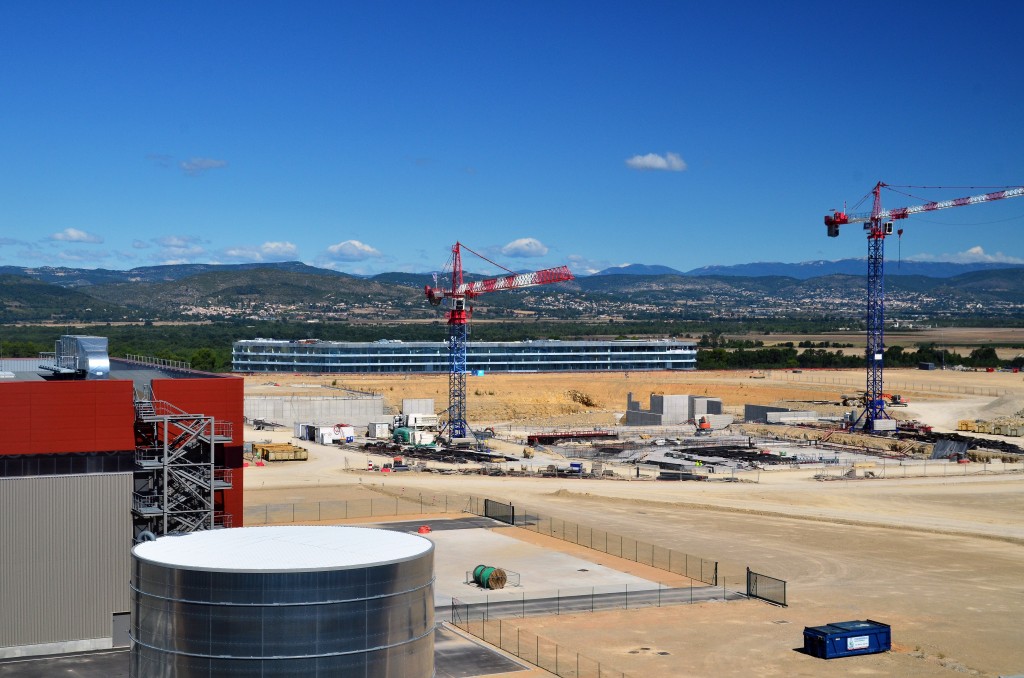
Site in September 2012
2012-09-13 - Looking across the platform from the completed winding facility at the Assembly Hall worksite (mid-platform) and the new ITER Headquarters (background).
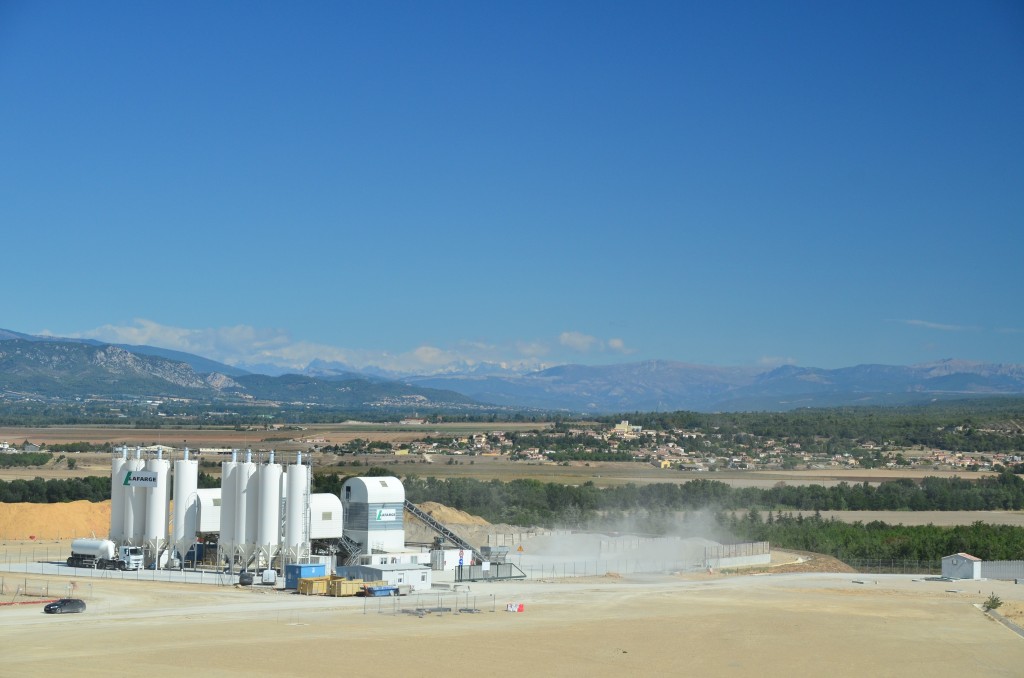
Latest cement production is for the Assembly Building worksite
2012-09-13 - ITER's cement batching plant is back in action in September 2012.
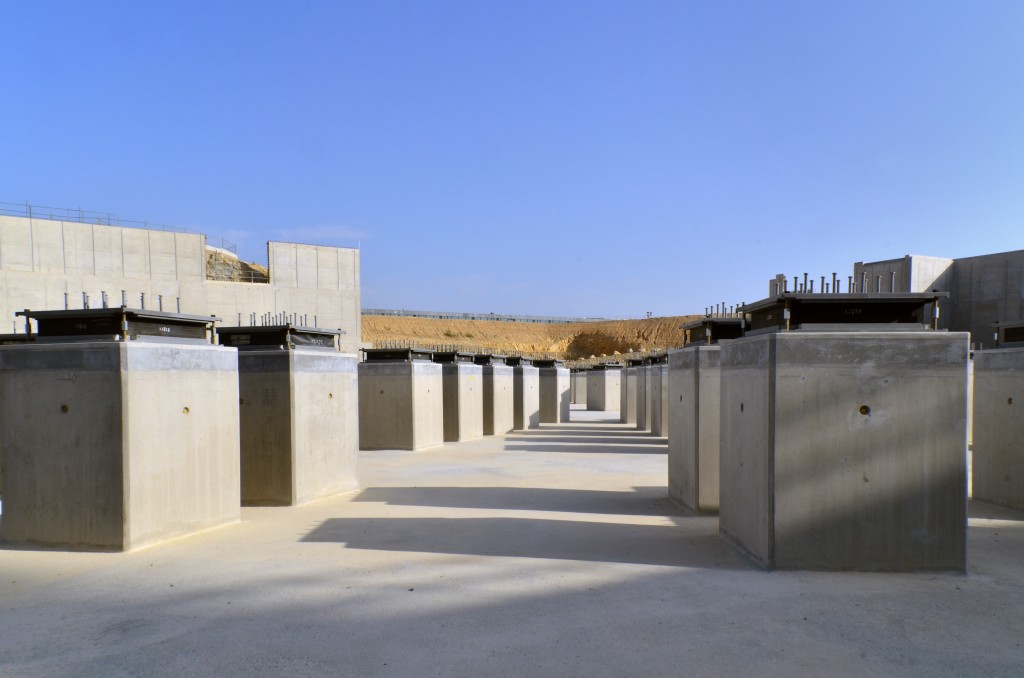
The hot sun of August
2012-08-22 - The Seismic Pit stands ready for the next phase of work, which should begin in 2013: the formwork, reinforcement and concrete pouring for the next-level basemat that will hide the anti-seismic bearings from view.
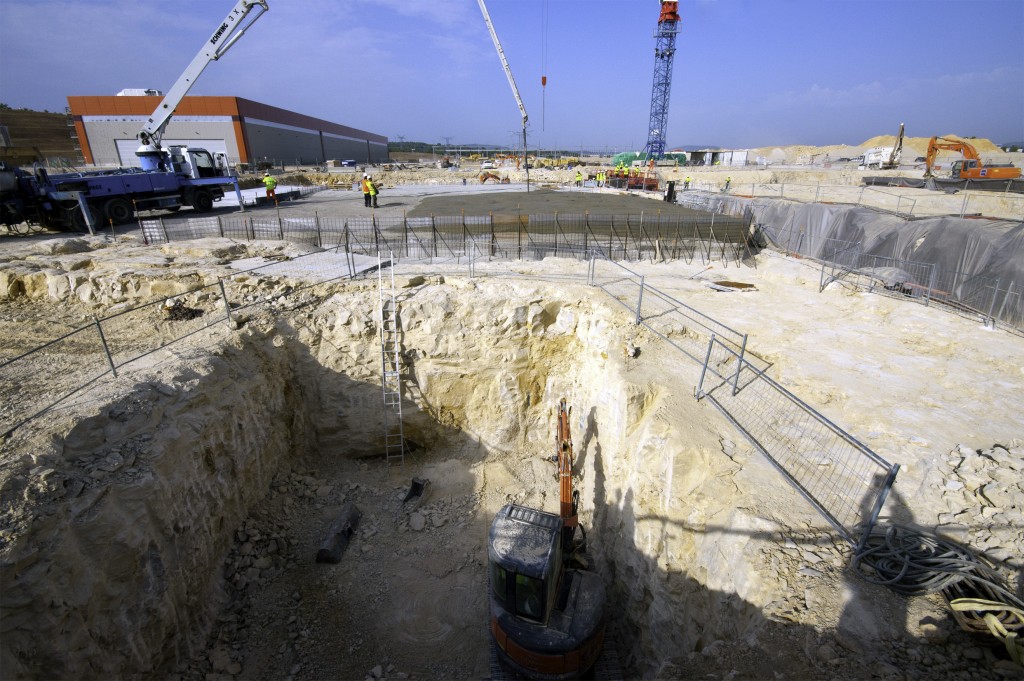
Tooling power supplies will run through here
2012-08-22 - An excavator is at work on an 7x8 metre gallery that will serve as an entry point for most of the electrical cables for the assembly tools and devices.
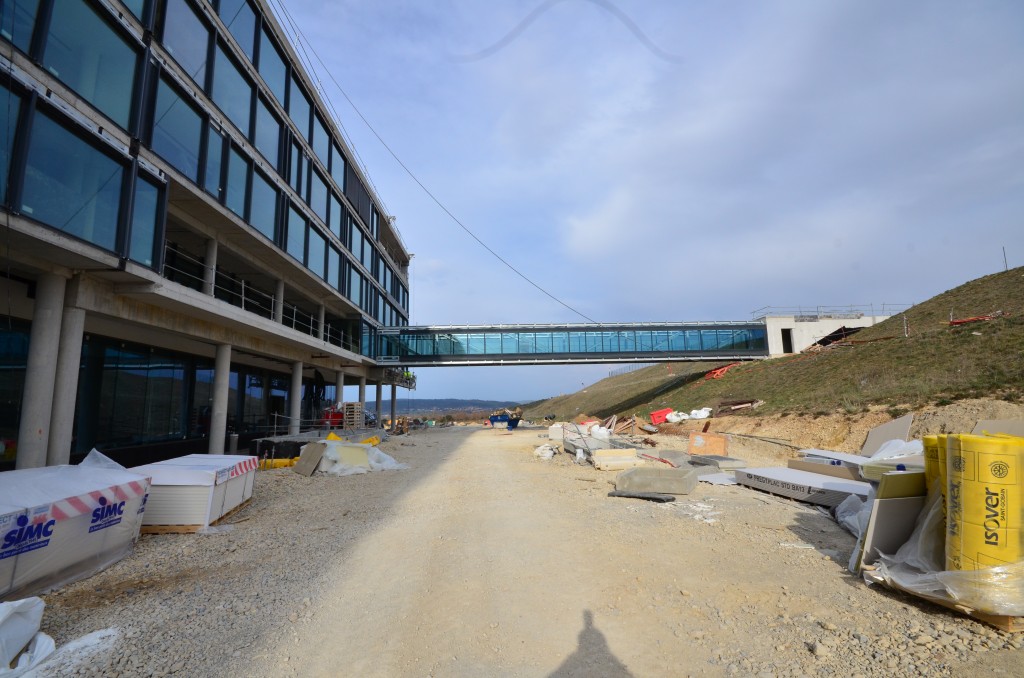
Framing out the last office spaces
2012-08-20 - As the dog days of summer come to an end, the ITER Headquarters building prepares for Moving Day, scheduled in October.
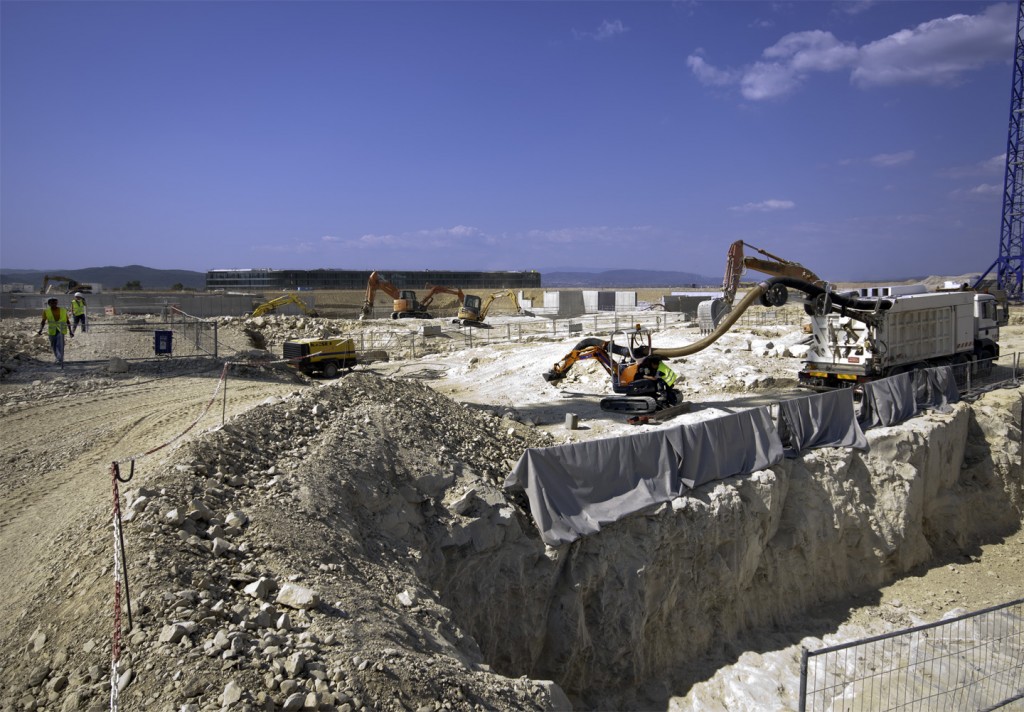
That's a lot of digging
2012-07-24 - With all of the digging operations for the Assembly Building foundations, the deep underground drainage networks and the establishment of Contractors' Area #2, the tour buses on the site these days are limited to the periphery.
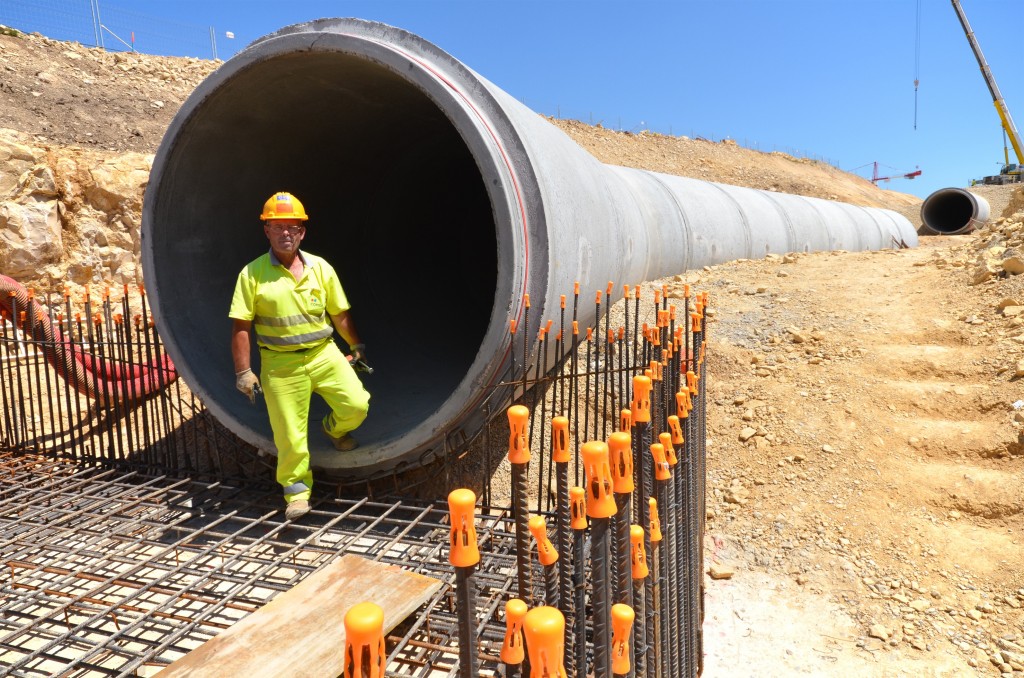
Evacuating the rainwater
2012-07-13 - Large concrete pipes, measuring up to 2.2 metres in diameter, will collect rainwater from the platform buildings, roads and trenches. The deep underground network is configured to handle the water flow coming from a "centennial rain"- extreme rainfall that statistically occurs only once every century.
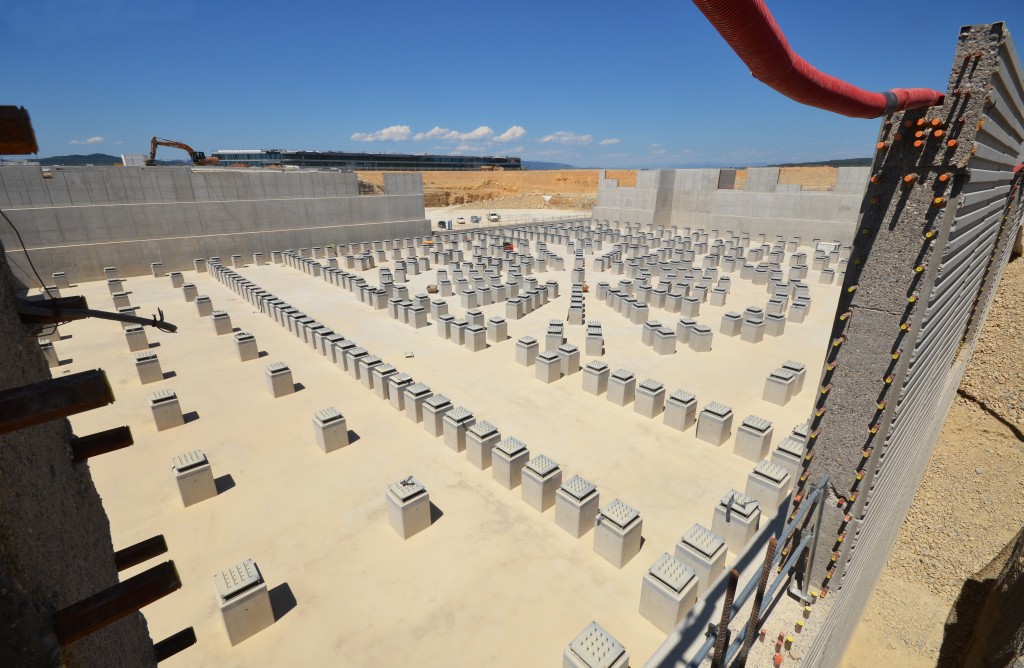
360,000 tonnes of building and equipment
2012-07-09 - This 90x130 Seismic Pit will support the weight of the Tokamak Complex. Made up of the Tokamak, Tritium and Diagnostic buildings, the total weight of the Tokamak Complex is estimated at 360,000 tonnes.
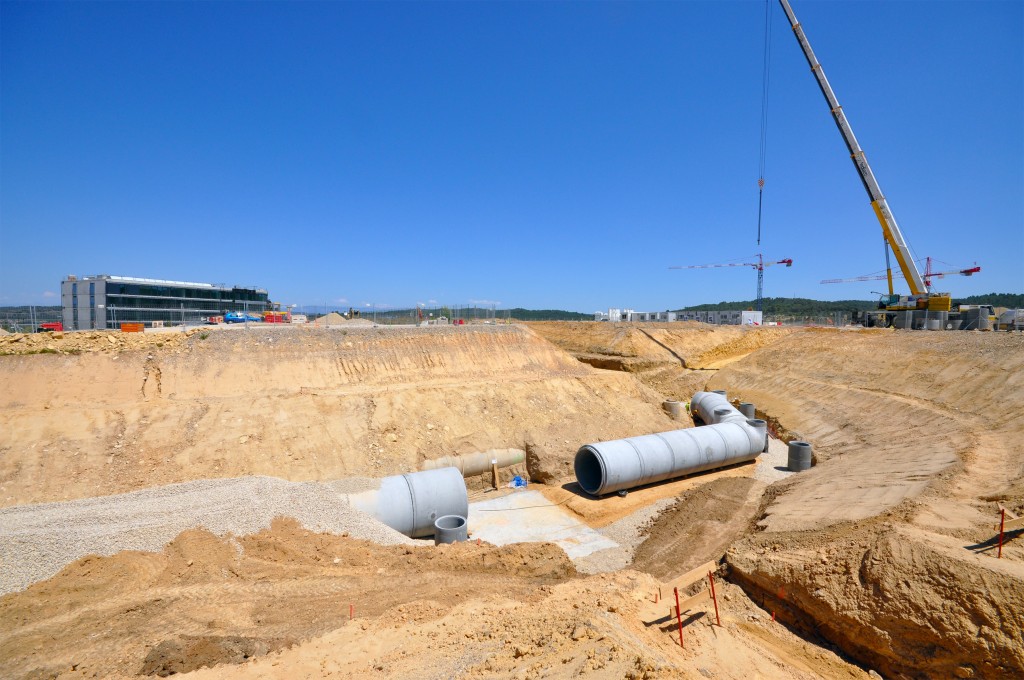
1.6 kilometres of underground pipes
2012-07-09 - The rainwater captured on the platform will be carried by underground networks to the storm basins located at the southwest corner of the site. Work on this drainage network begin in March 2012 and will be completed in November.
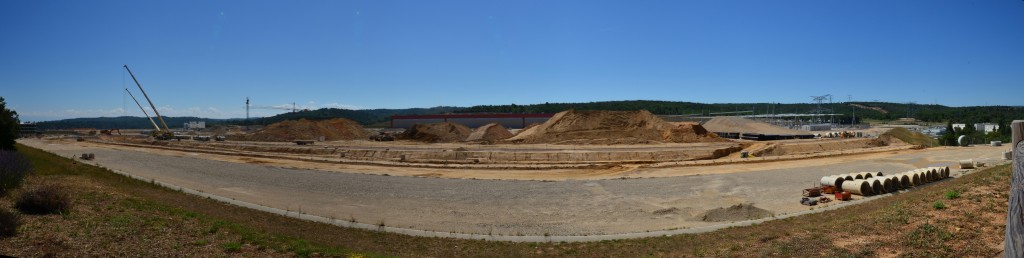
42 hectares in a glance
2012-07-03 - A panoramic view of the ITER worksite taken from the southwest corner of the platform.
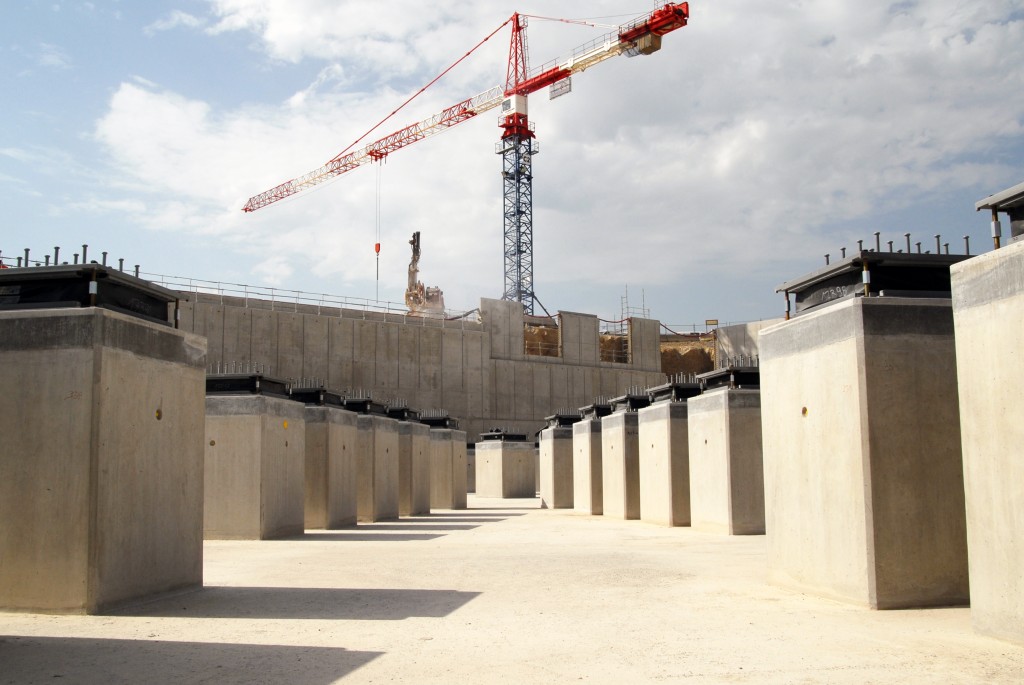
Assembly will take place next door
2012-06-28 - Seventeen metres above the basemat, excavation work progresses on the site of the future Assembly Hall. Photo: F4E
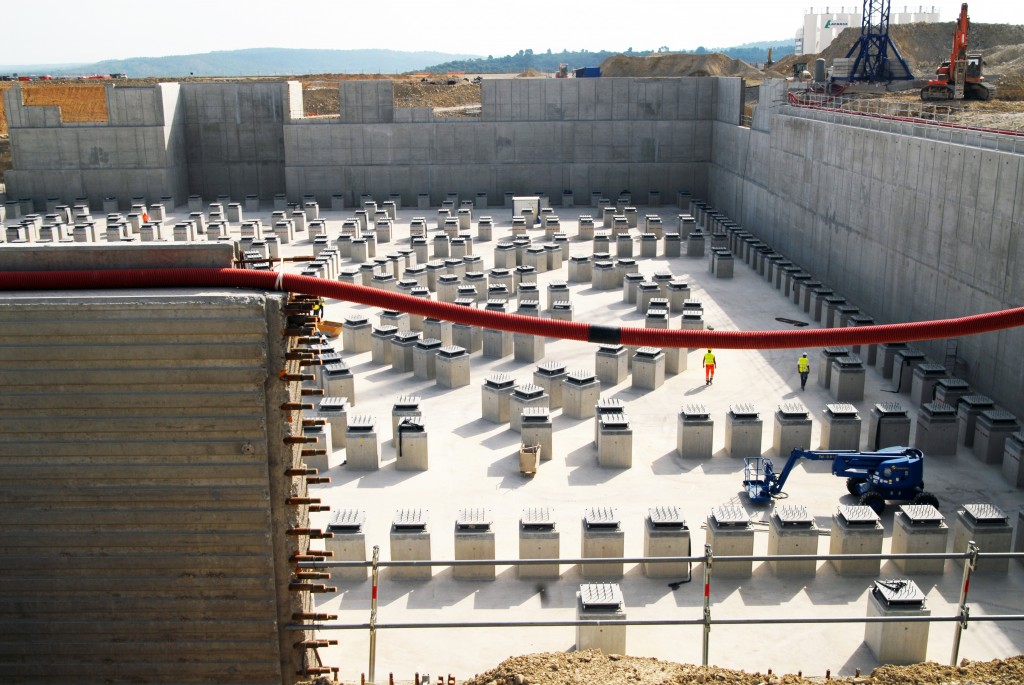
Please stand back!
2012-06-28 - In 2013, the seismic protection system that is now visible will be entirely covered by the floor of the Tokamak Complex. The view is impressive, but don't get too close to the edge!
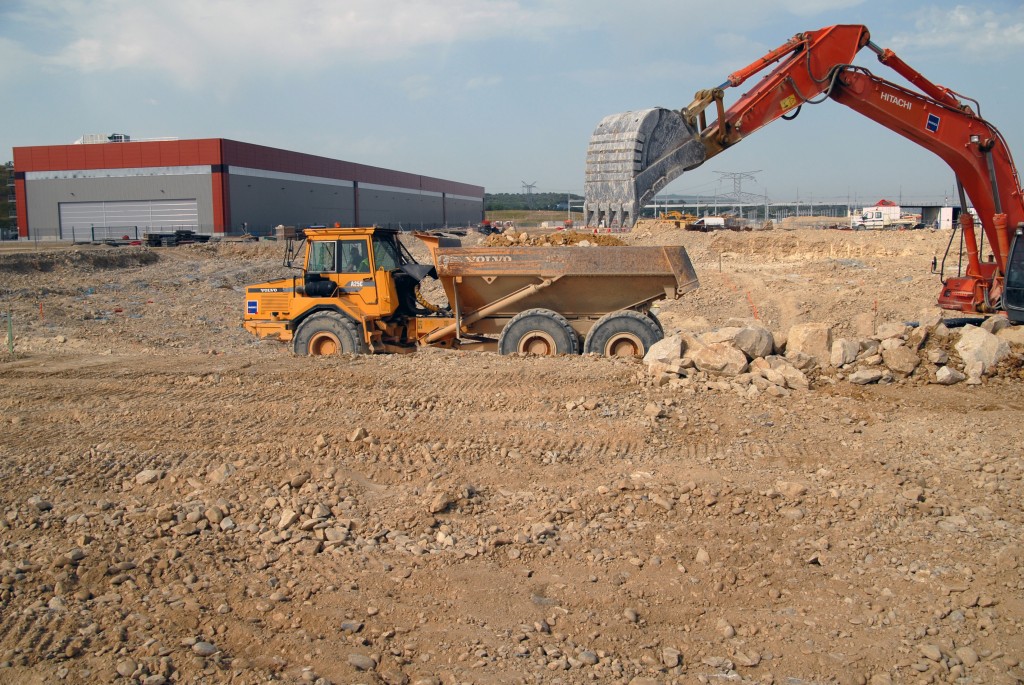
Back to the bulldozers
2012-06-28 - Excavation works for the Assembly Hall aren't as spectacular as those for the Seismic Isolation Pit: only 10,000 m³ needs to be removed.
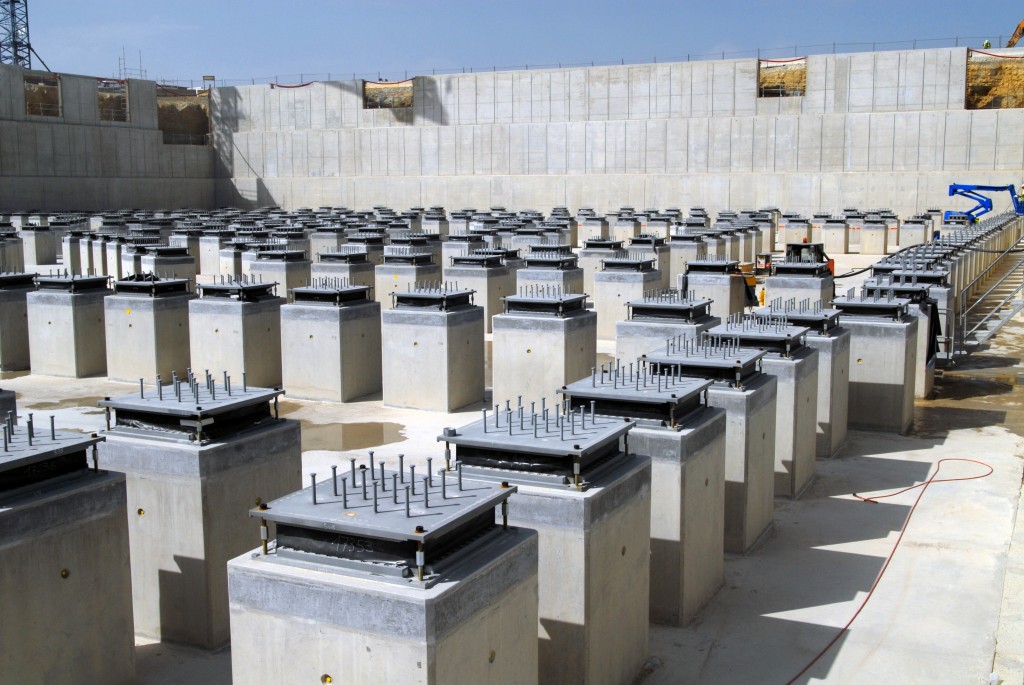
The columns are actually taller than you!
2012-06-28 - It may not look like it, but each concrete column is taller than most people standing: 1.9 metres (approximately 6"3). Photo: F4E
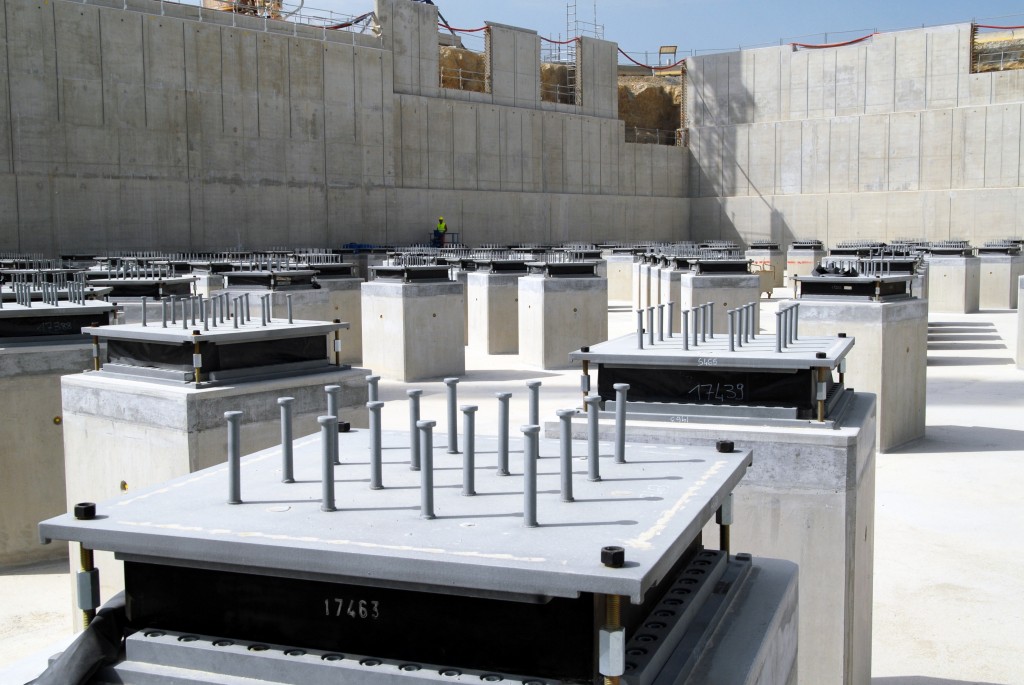
Some serious support
2012-06-28 - Each plinth and seismic bearing assembly measures precisely 1.9 metres in height. Numbering 493 in all, they will bear the weight of the massive Tokamak Complex, estimated at 360,000 tonnes. Photo: F4E
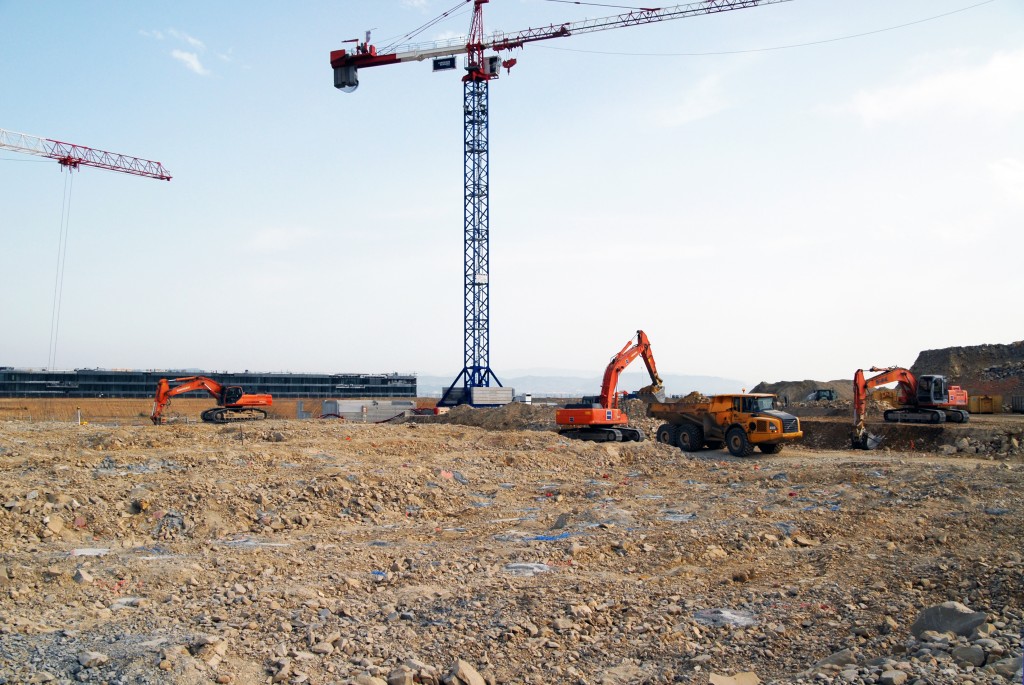
Vast antechamber to the Tokamak Building
2012-06-28 - The Assembly Building will occupy an area of 6,000 m² to the south of the Tokamak Complex. The vast hall will house the specialized tooling that will accomplish pre-assembly activities for the Tokamak components.
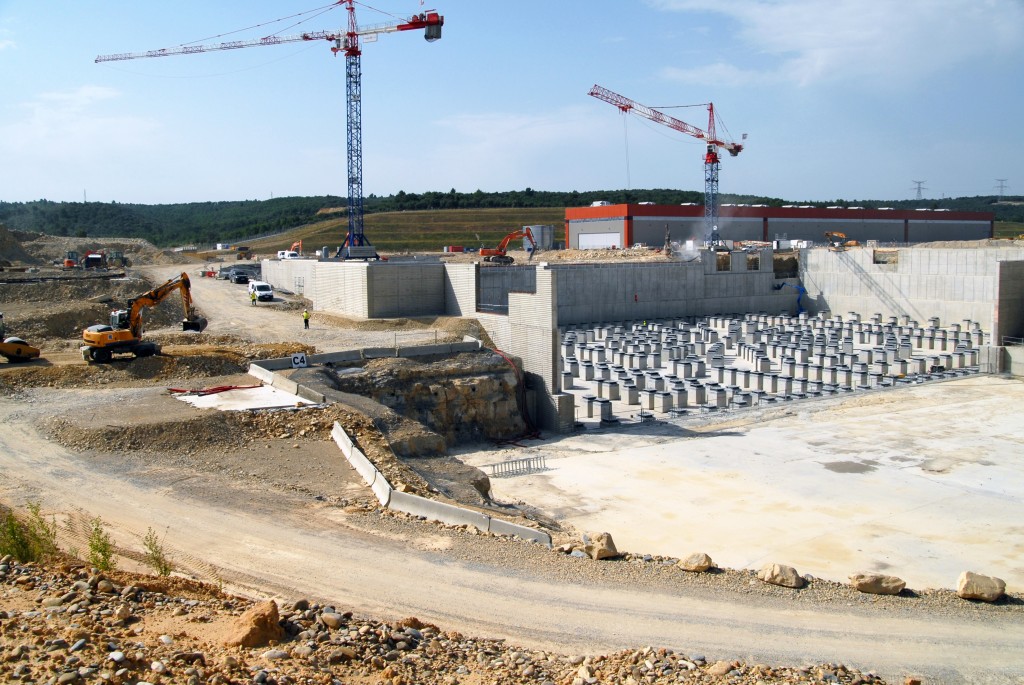
Assembly Hall on one side, Hot Cell on the other
2012-06-28 - In the foreground, space has been cleared and foundations set for the ITER Hot Cell building. On the other side of the Tokamak Pit: the worksite for the future Assembly Building. Photo: F4E
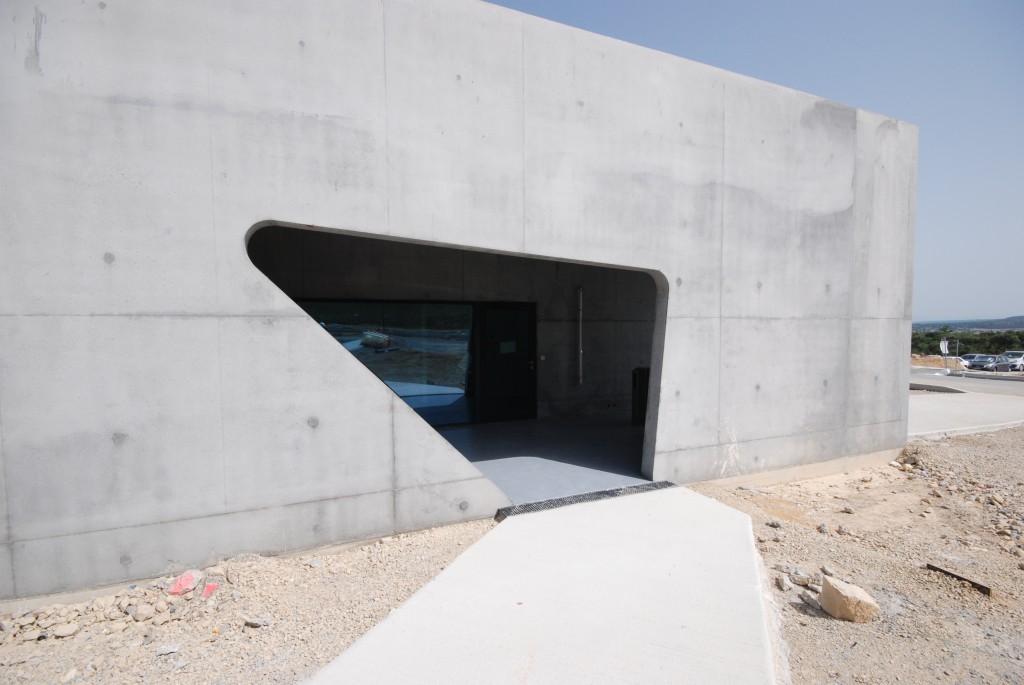
Site Access
2012-06-26 - Staff will badge in here, at the Site Access Control Building, before following the path to ITER Headquarters.
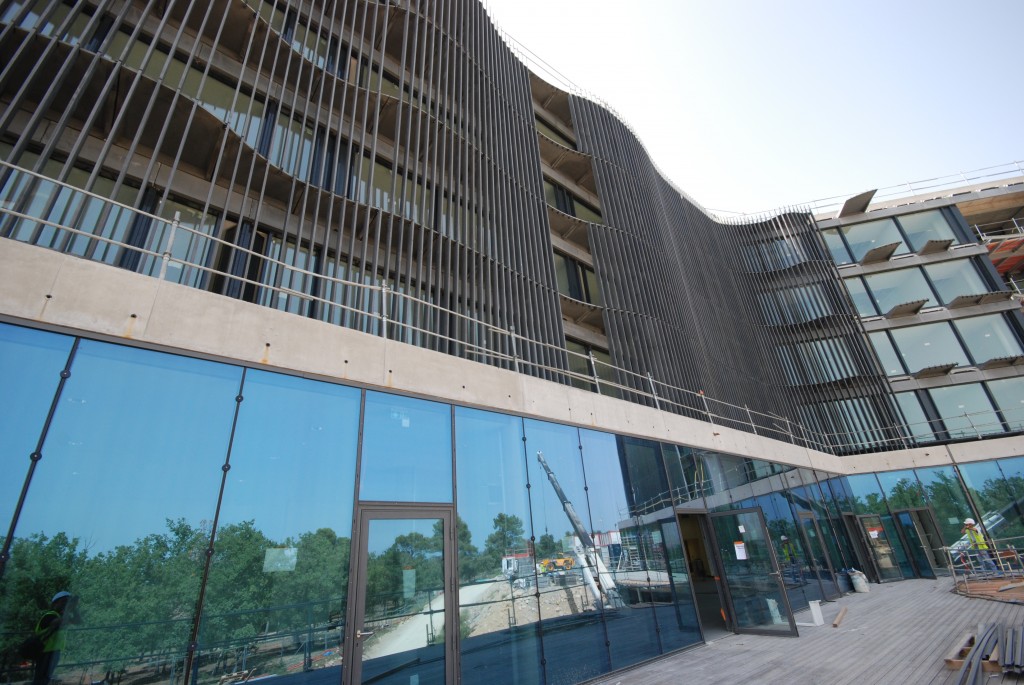
An undulating veil
2012-06-26 - Above the ITER cafeteria, workers install the last vertical slats on the top four storeys of the building.
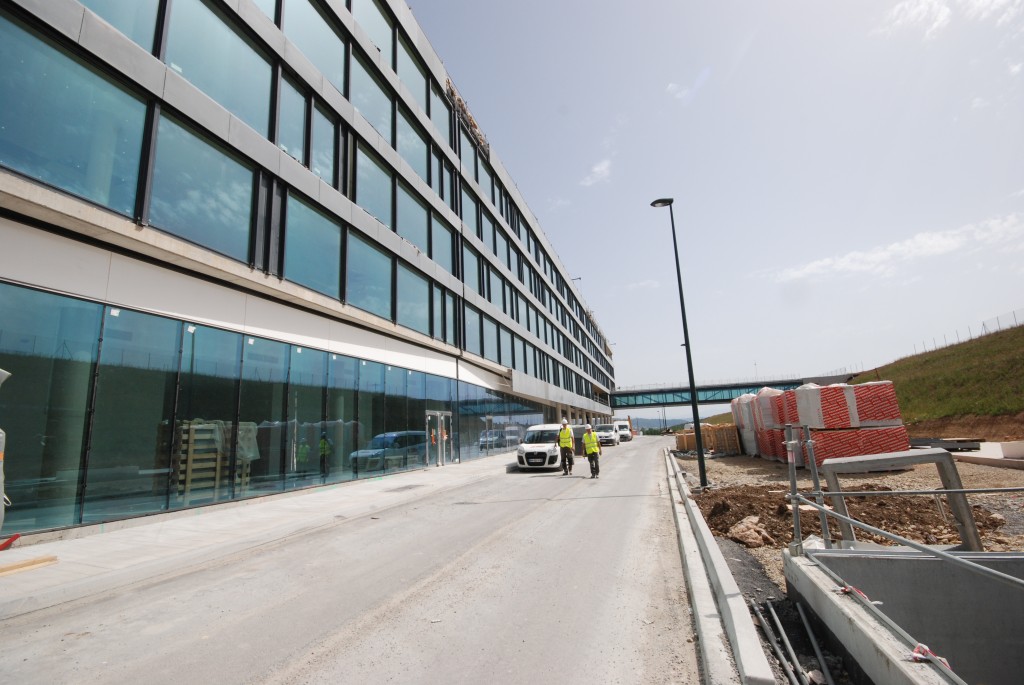
Northwest corner
2012-06-26 - One hundred and eighty metres long, the Headquarters building is situated on the northwest corner of the platform. The building will be ready for delivery in two months.
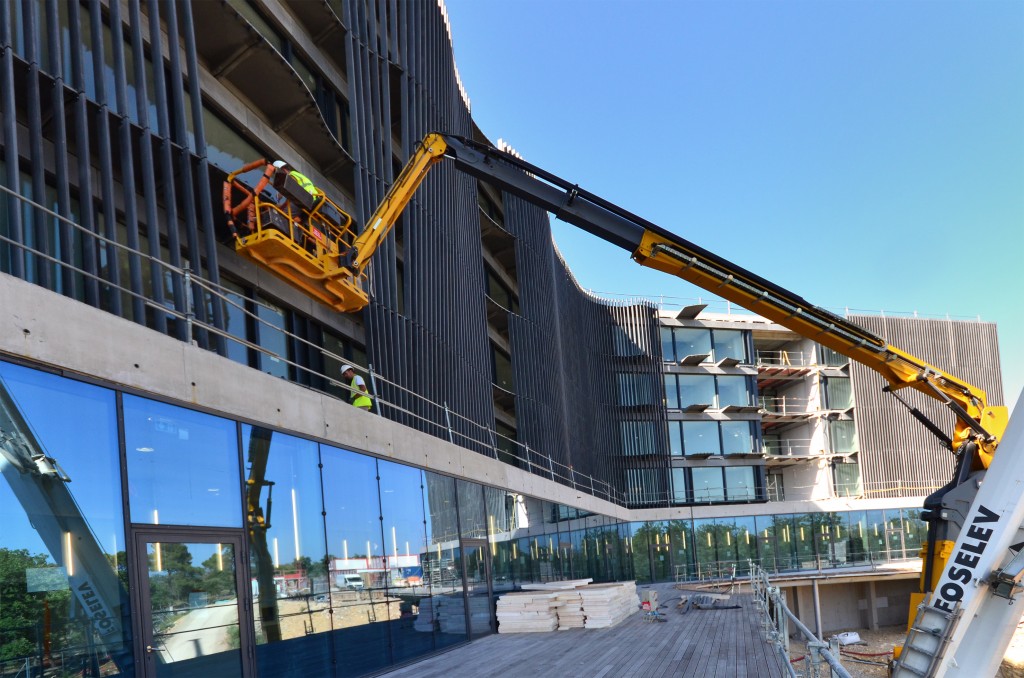
slideshow_homepage
2012-06-21 - Following the installation of the last glass windows in November, the stage is set for the immense vertical slats that will adorn the northern facade of ITER Headquarters. Over 3,000 of these slats will create an external veil 14 m high and 180 m long.
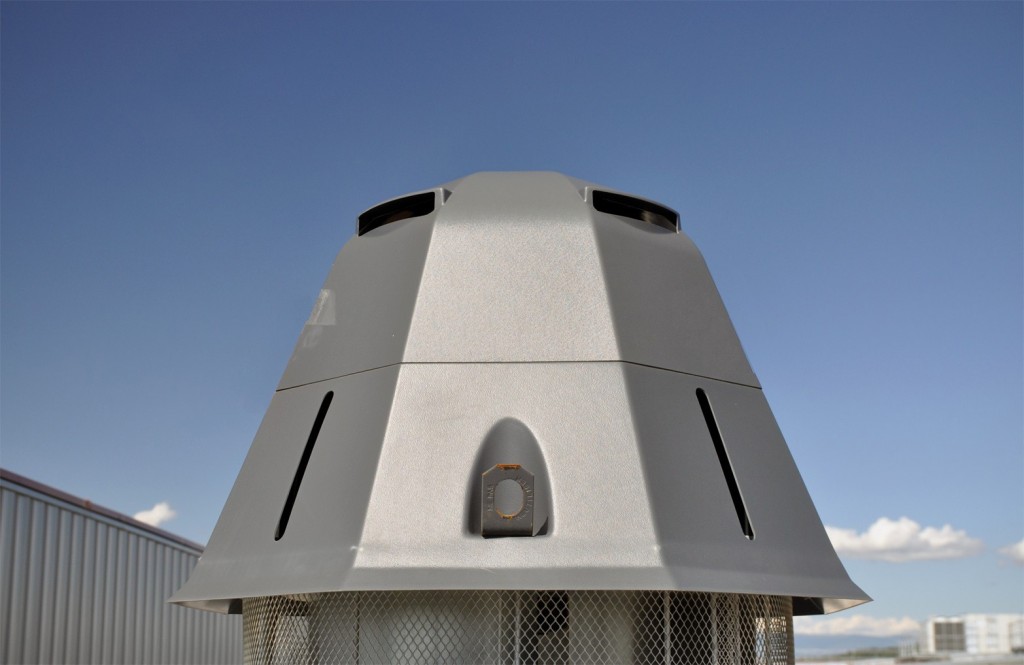
Strange exhaust unit
2012-06-21 - This Darth Vader-like structure sitting on the roof of the Poloidal Field Coils Winding Building is one of several exhaust fans that will suck air out of the vast building.
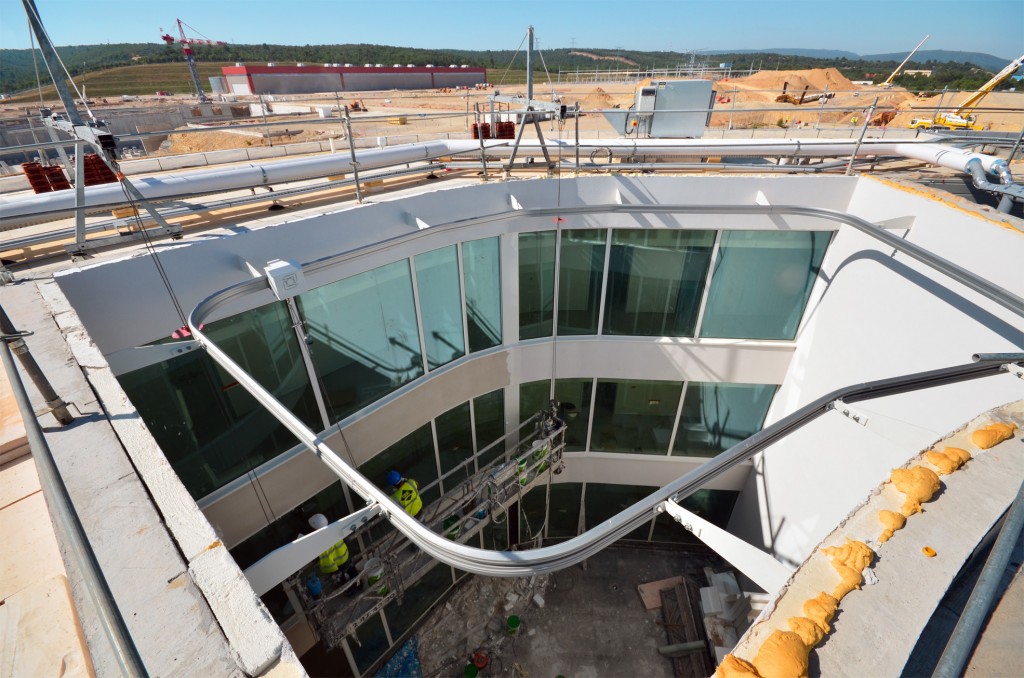
Natural light for the inner corridors
2012-06-21 - Light shafts are foreseen all along the 180 metres of the new ITER office building—some 3-storey (pictured), some 5-storey.
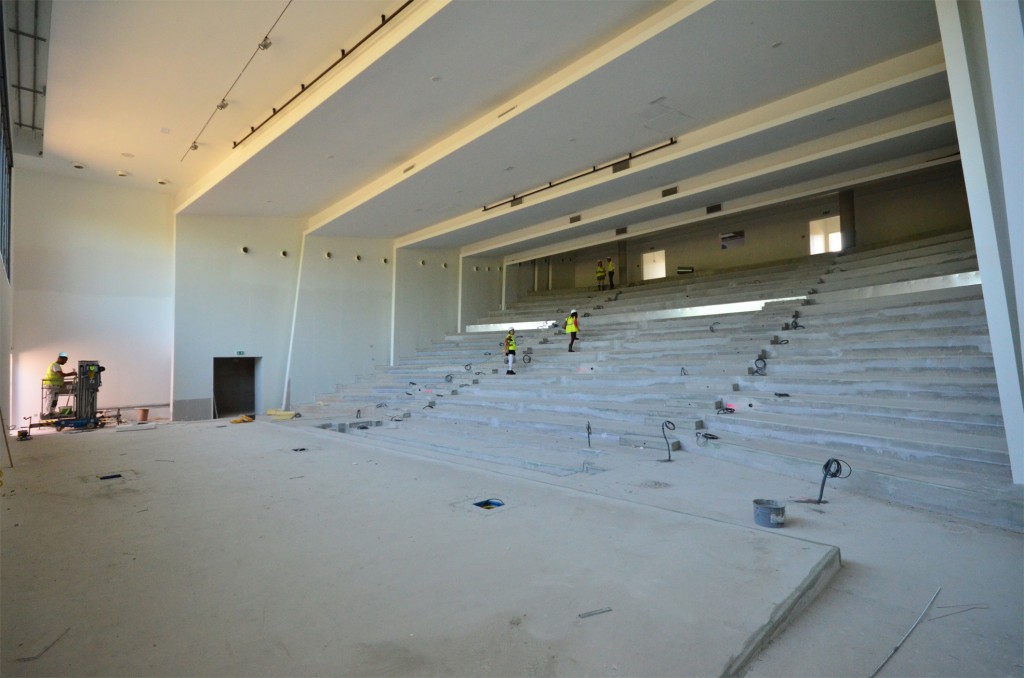
The 500-seat amphitheatre
2012-06-21 - Only the furniture is missing in the 500-seat ITER amphitheatre. Staff will enter on the ground floor, through doors (upper right) situated just a step away from the lobby entrance.
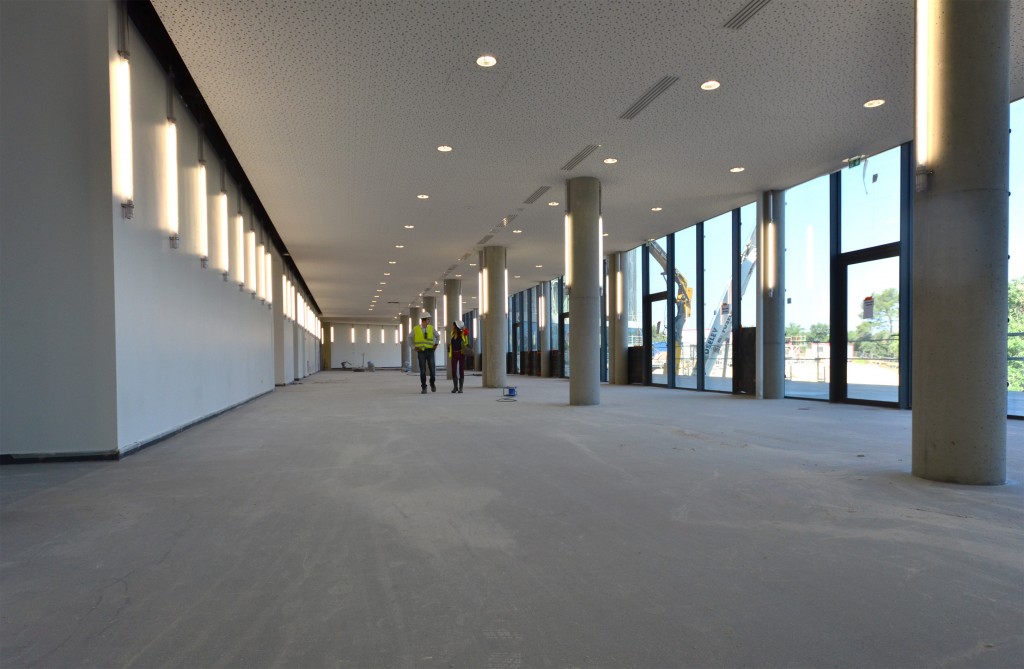
Cafeteria nearly finished
2012-06-21 - The Headquarters cafeteria is situated at the back of the building, with a terrace overlooking a wooded parcel.
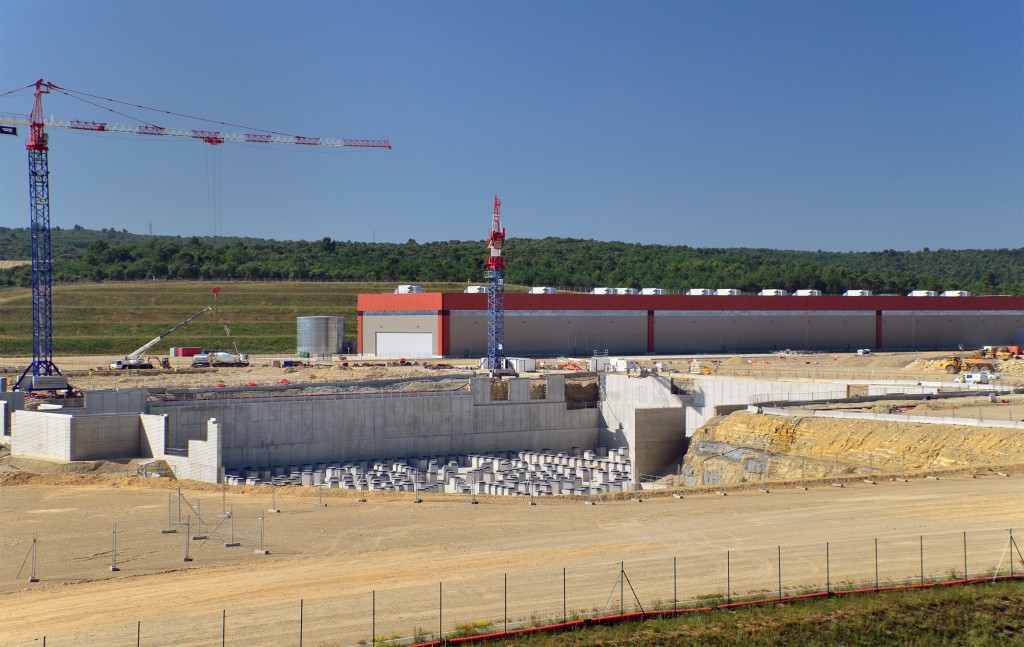
Doors are closed for now
2012-06-21 - The building that will house the on-site assembly line for five of ITER's six poloidal field coils stands ready on the southeast edge of the platform for activity to begin at the end of the year.
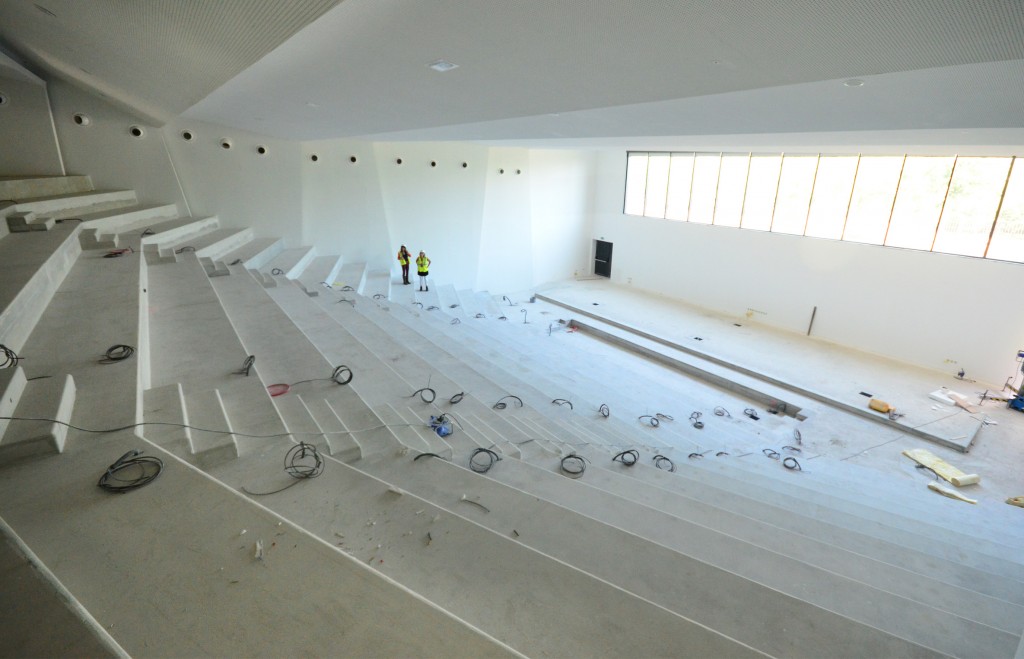
Meetings galore
2012-06-21 - The amphitheatre in the new building will provide ITER staff with the opportunity to assemble in one room—something that had been impossible in the temporary offices the team has occupied since 2006.
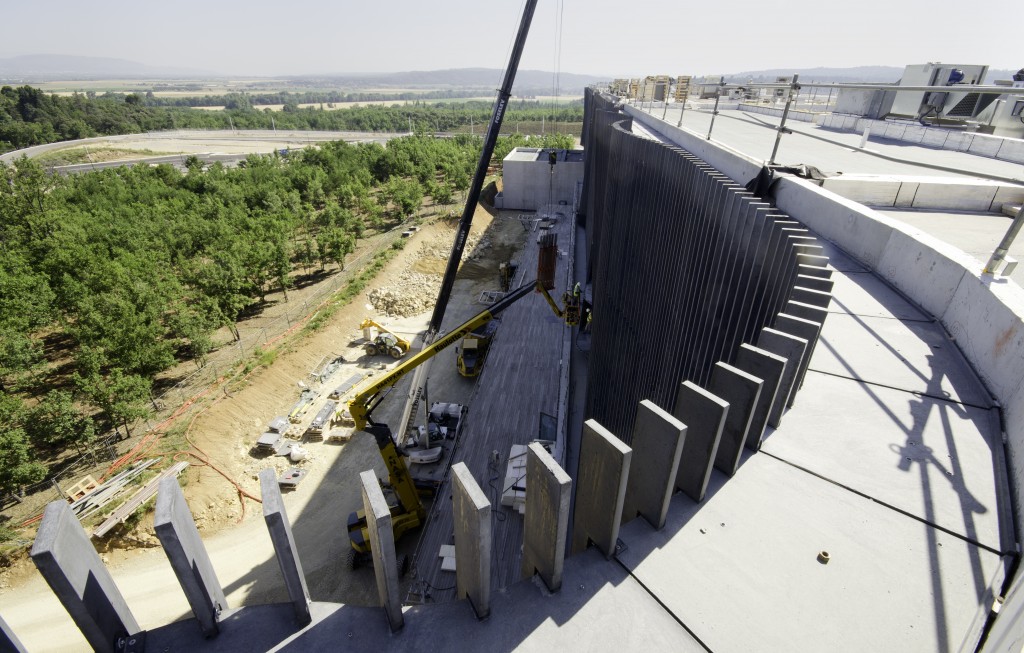
Curves seen from above
2012-06-21 - From the roof, looking down toward the cafeteria terrace, it's easy to see how the architectural slats are mounted all along the building's northwest face.
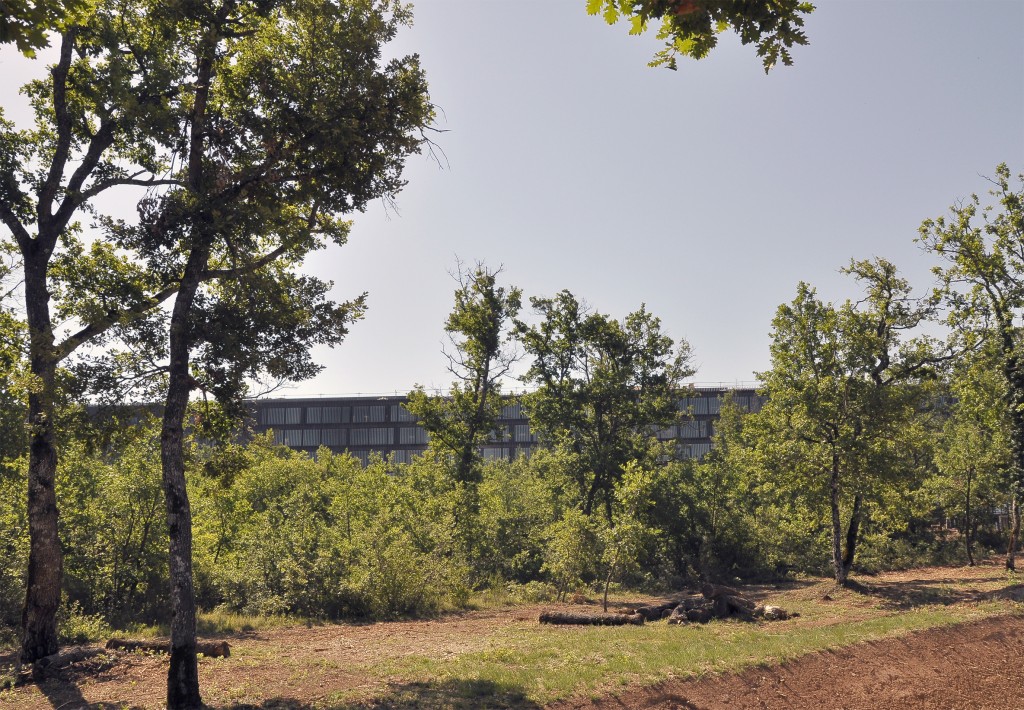
5 floors, 180 m long
2012-06-21 - The near-completed ITER Headquarters building is visible from the road between St-Paul-lez-Durance and Vinon-sur-Verson.
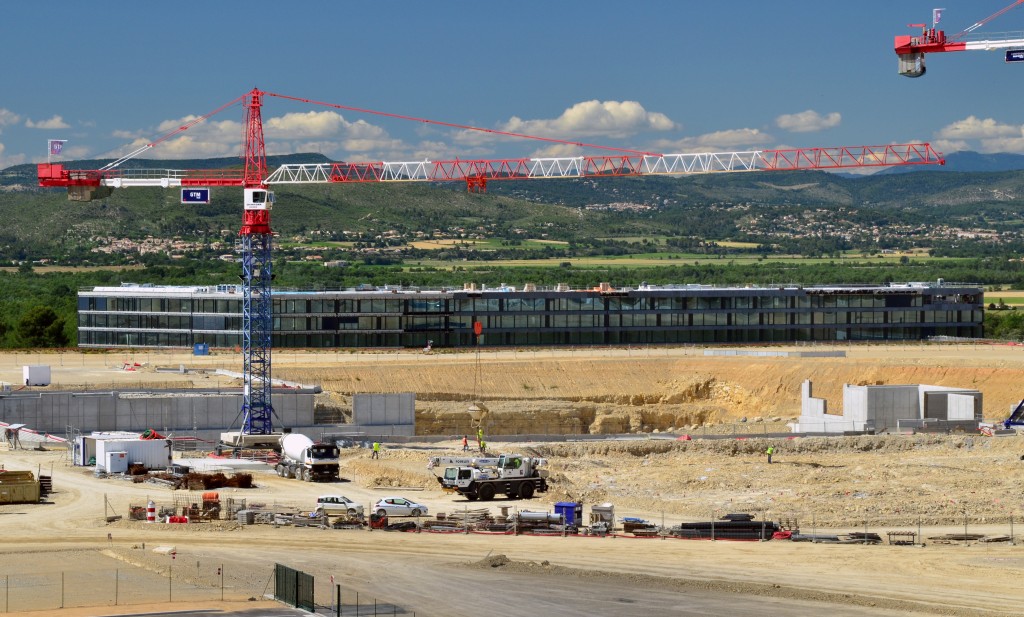
The ITER platform in June
2012-06-13 - Work proceeds in the vicinity of the completed Seismic Isolation Pit on underground networks and on ground preparation works for the Assembly Hall.
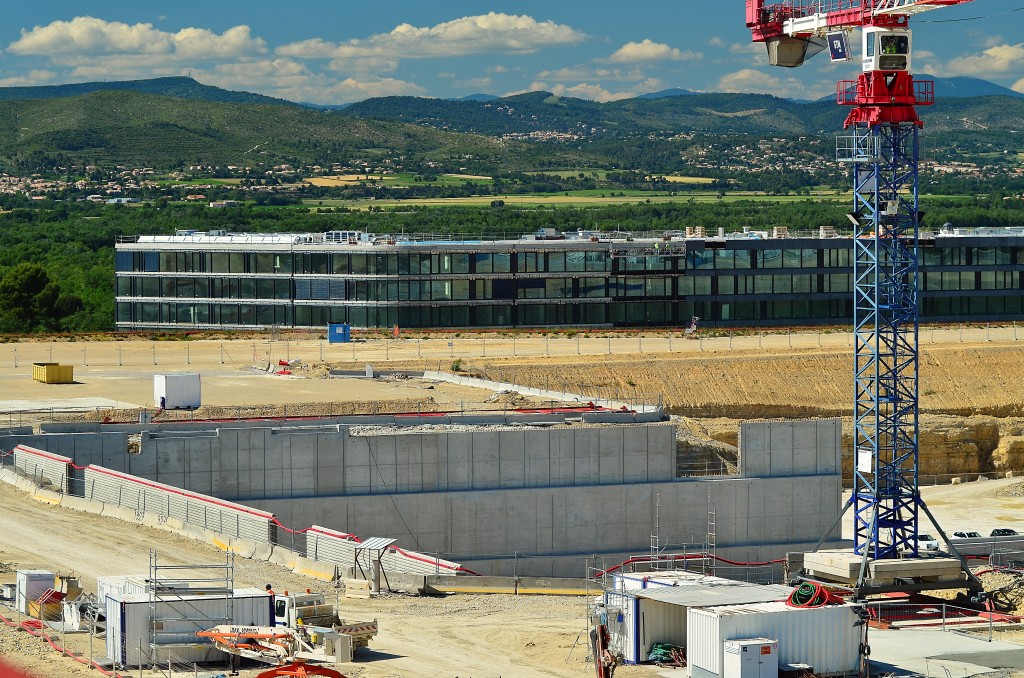
A waterproof box
2012-06-13 - In one corner of the Seismic Pit, the three-tiered retaining walls maintain and stabilize the surrounding rock, and keep water out.
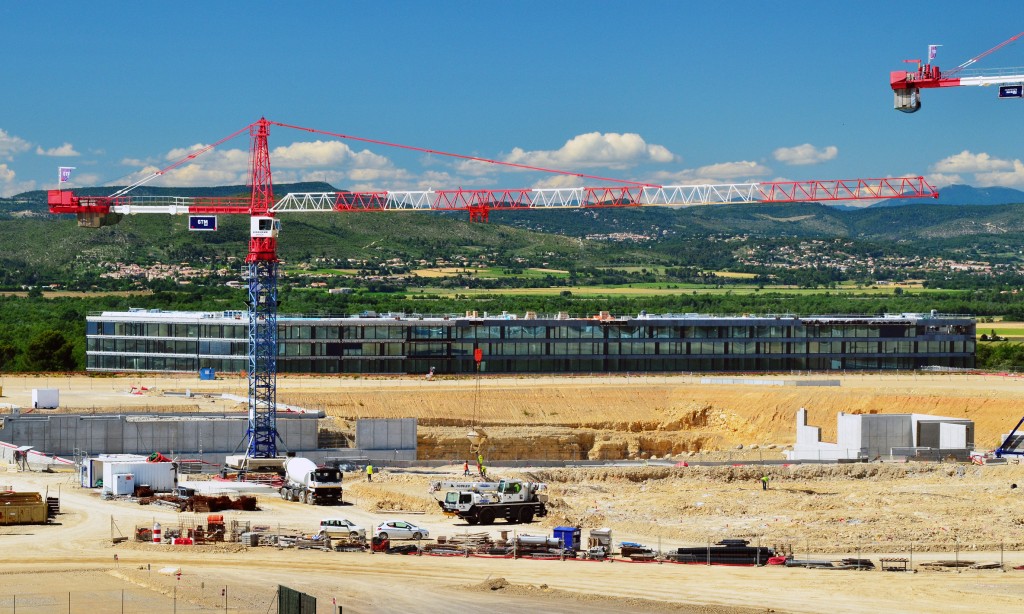
Nestled up against the platform
2012-06-13 - The ITER Headquarters building sits below the platform; some of the upper offices will look out directly onto the ITER laboratory.
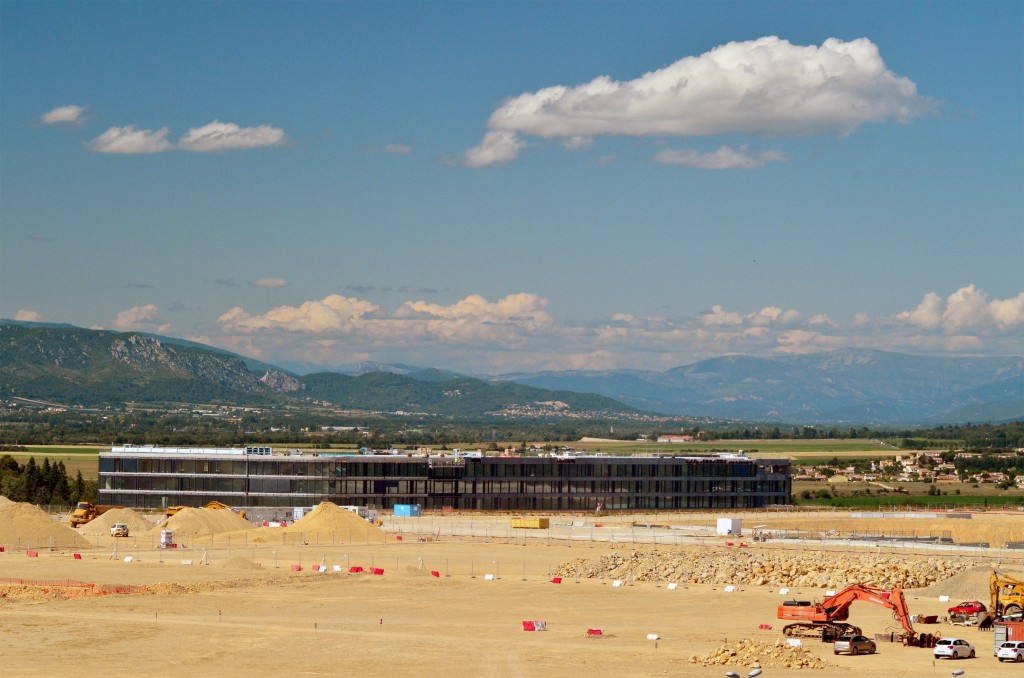
On a clear day, we see the mountains
2012-06-13 - Looking over the near-completed Headquarters building toward the pre-Alps.
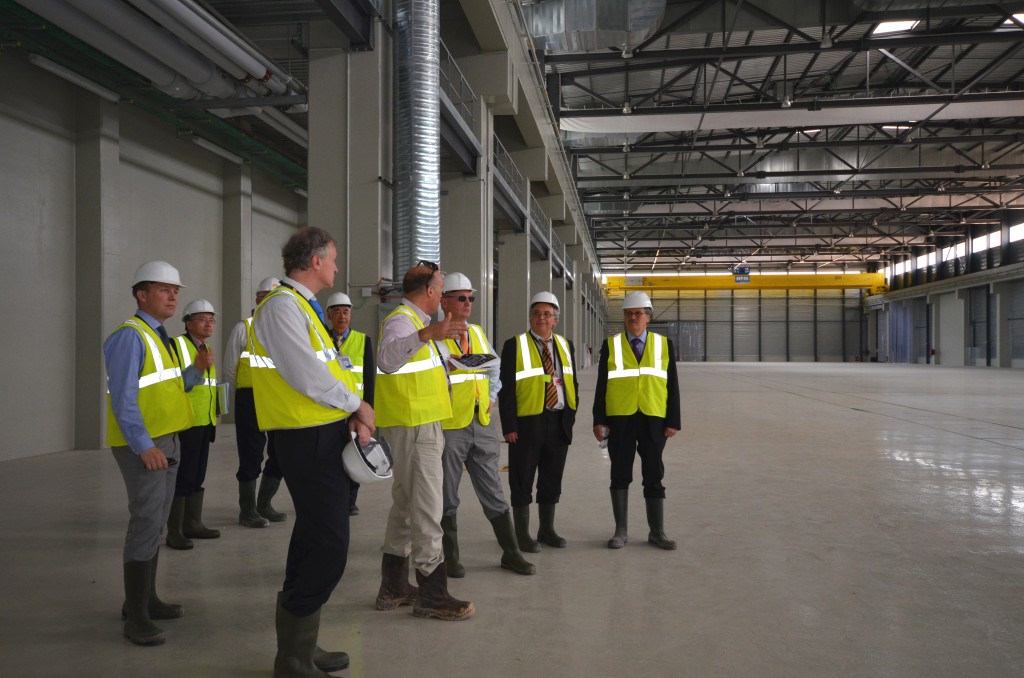
Before the equipment moves in
2012-06-08 - In June, a group of visitors from Sweden is treated to a tour of the PF Winding Facility.
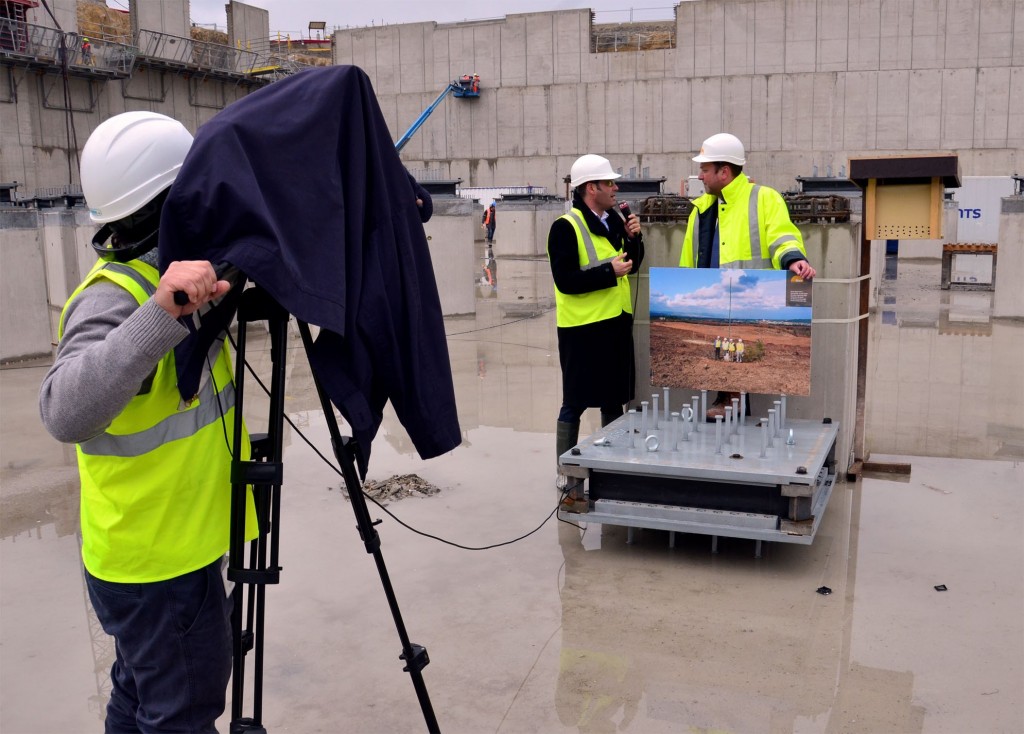
Then ... and now!
2012-06-08 - For a TV program on ITER (local French channel TLP), an interview is conducted on the precise spot where—five years earlier—a flag flew to mark the location of the future ITER Tokamak.
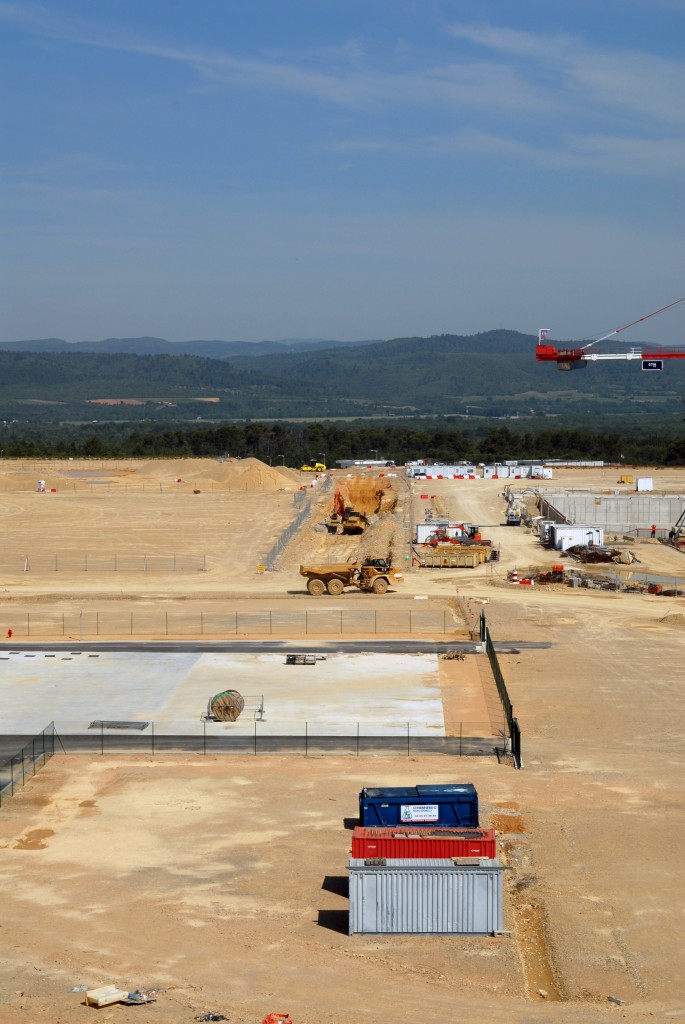
An on-site facility for gigantic components
2012-05-31 - From the north end of the facility, the gigantic coils won't have far to go to enter the Assembly Hall, which will be built on the near side of the Tokamak Seismic Pit. Photo: F4E
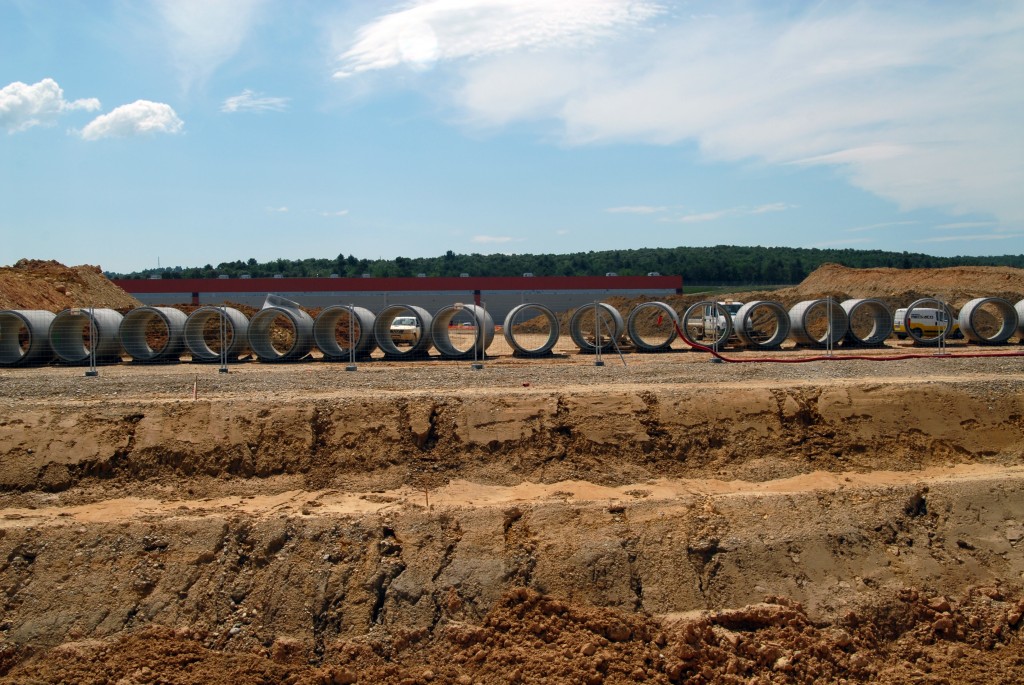
Drainage water
2012-05-31 - Rows of drainage water pipes await assembly 8 metres below the level of the platform. Photo: F4E
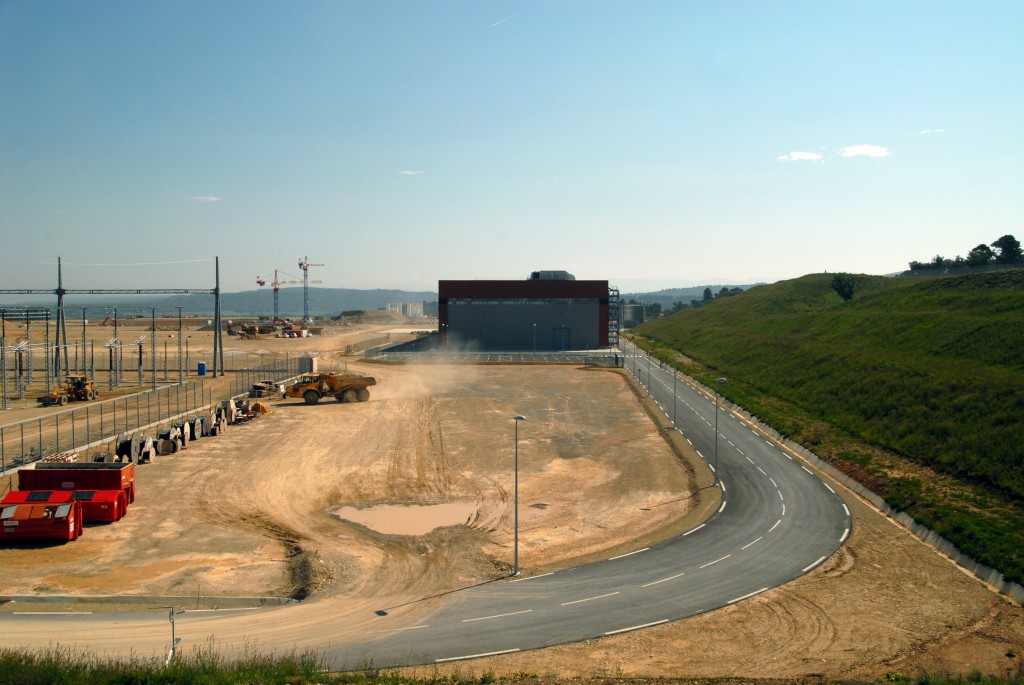
Ready for the delivery trucks
2012-05-31 - The area around the PF Winding Facility is now paved. In 2013, trucks carrying the first conductor spools from China, Europe and Russia will enter this end of the building to deliver their loads. Photo: F4E
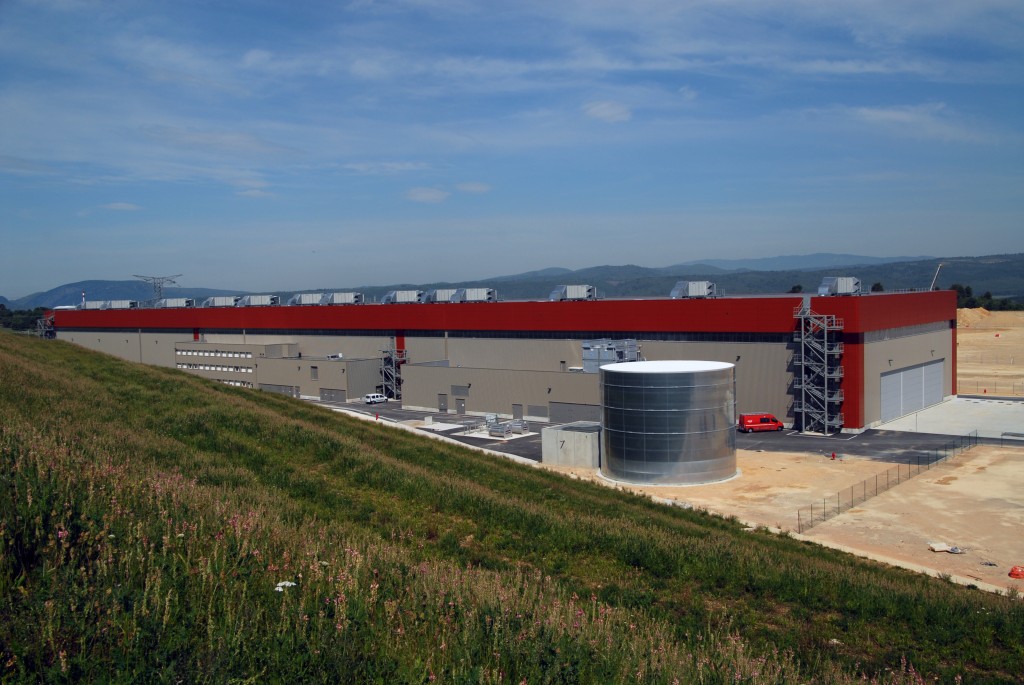
Water storage ... in case
2012-05-31 - Water for the Winding Facility's firefighting system is stored in this cylindrical tank. Photo: F4E
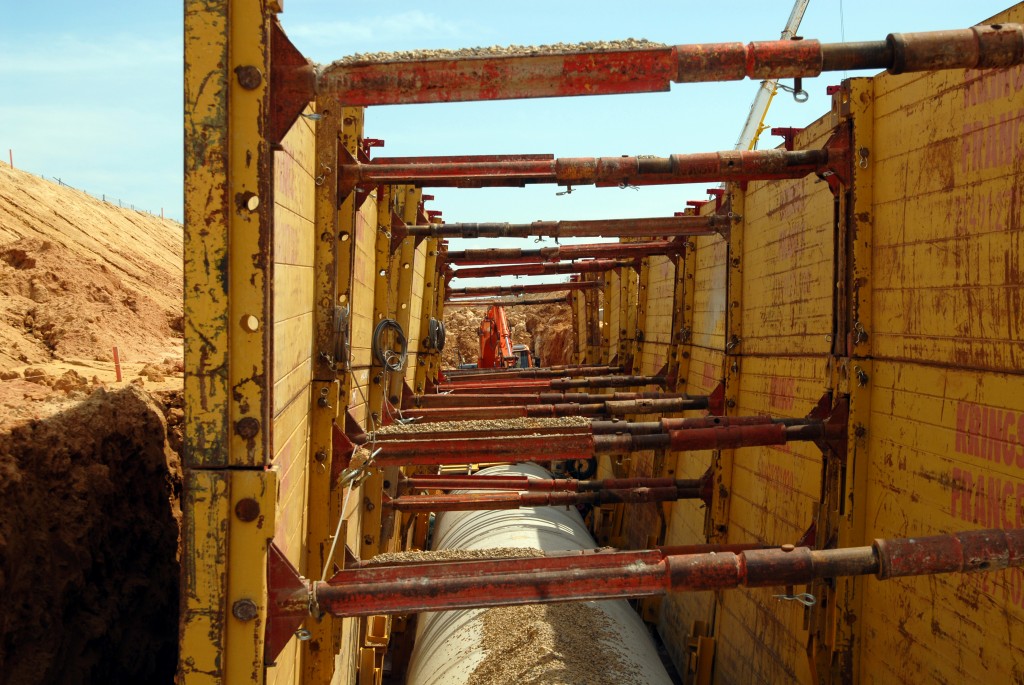
Work begins on drainage
2012-05-31 - Work begins on the critical networks: the installation of 2.2-metre-diameter concrete pipes 10 metres below the surface of the platform. Photo: F4E
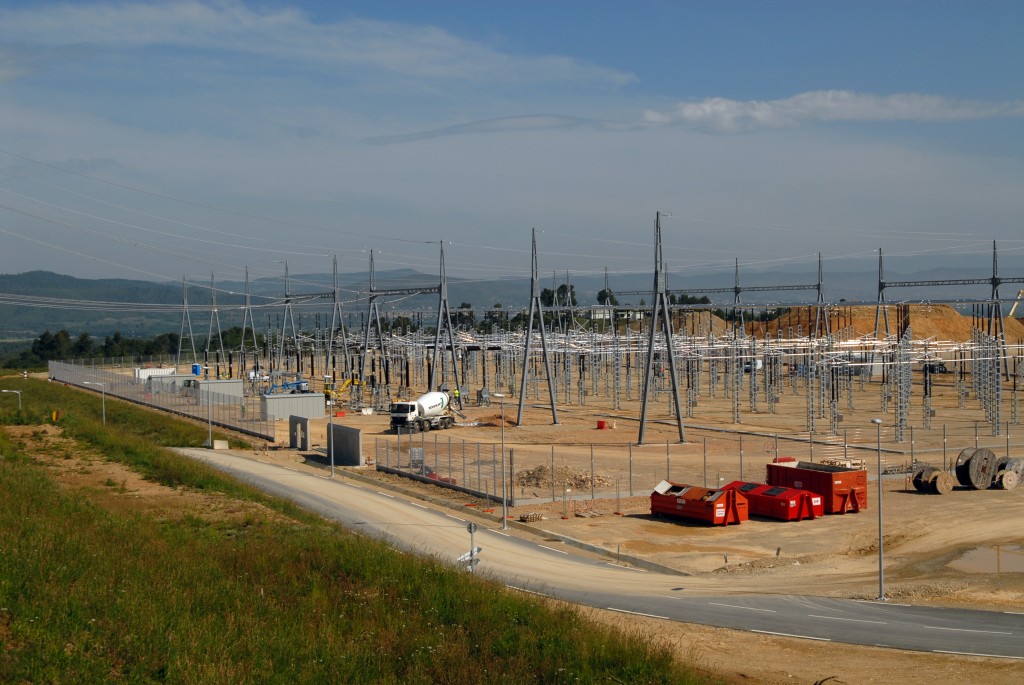
Energizing ITER
2012-05-31 - Four years are necessary to bring the ITER switchyard to fruition. Beginning with technical and environmental studies and ending with 12 months of construction works, the realization of the RTE switchyard is part of France's commitment to the ITER project. Photo: F4E
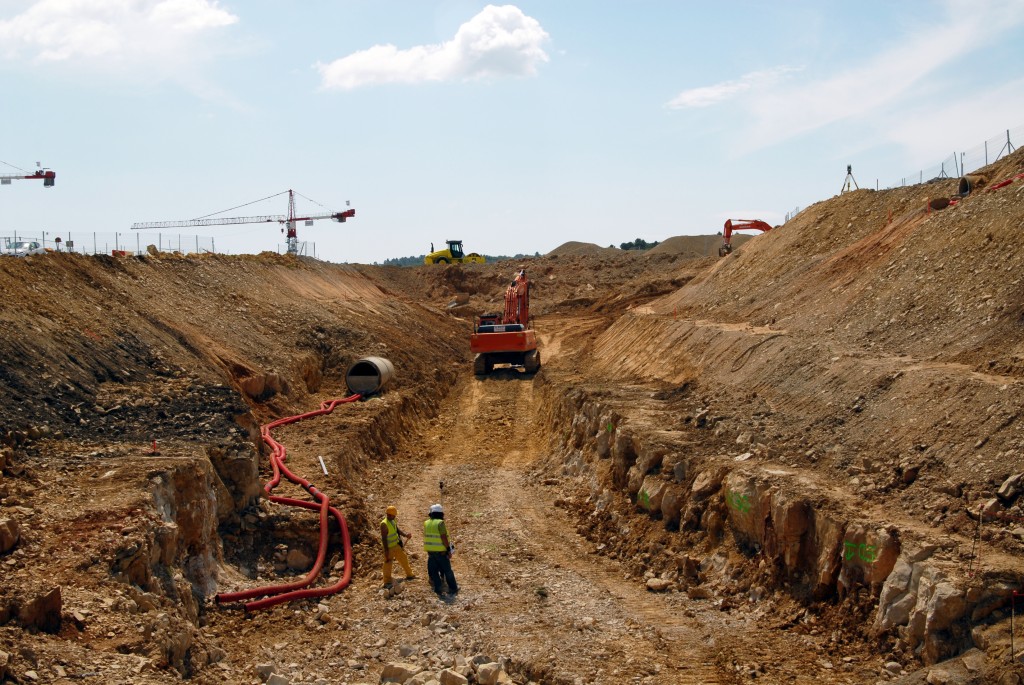
Trenches crisscross the site
2012-05-31 - Digging for the underground networks begins in March. The trenches are from 8-11 metres deep. Photo: F4E
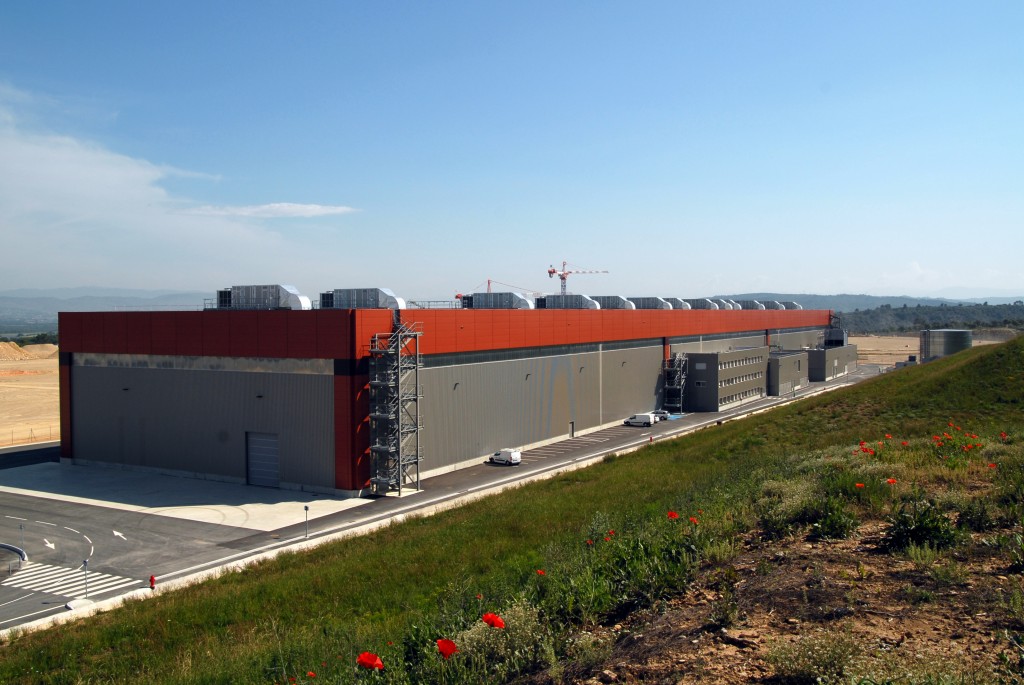
The only manufacturing building
2012-05-31 - This 257-metre-long building will be equipped with three manufacturing stations. The sequential operations necessary for completing one poloidal field coil will take at least 24 months. Photo: F4E
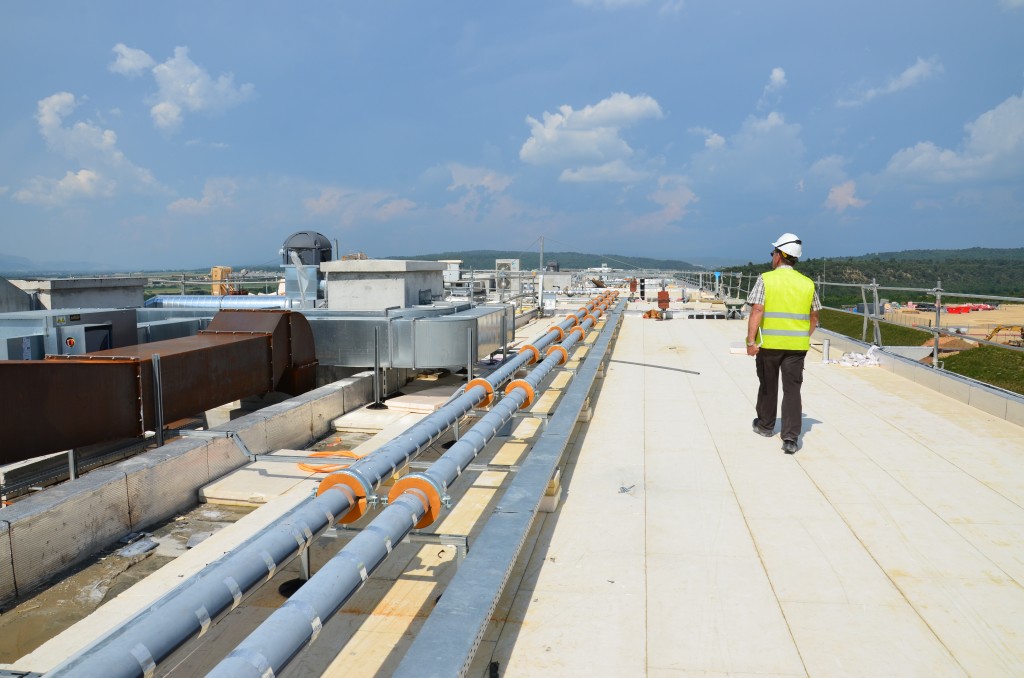
Ventilation now installed
2012-05-30 - On the roof of the Headquarters building, rooftop ventilation and air conditioning units have been installed. Photo: AIF AM
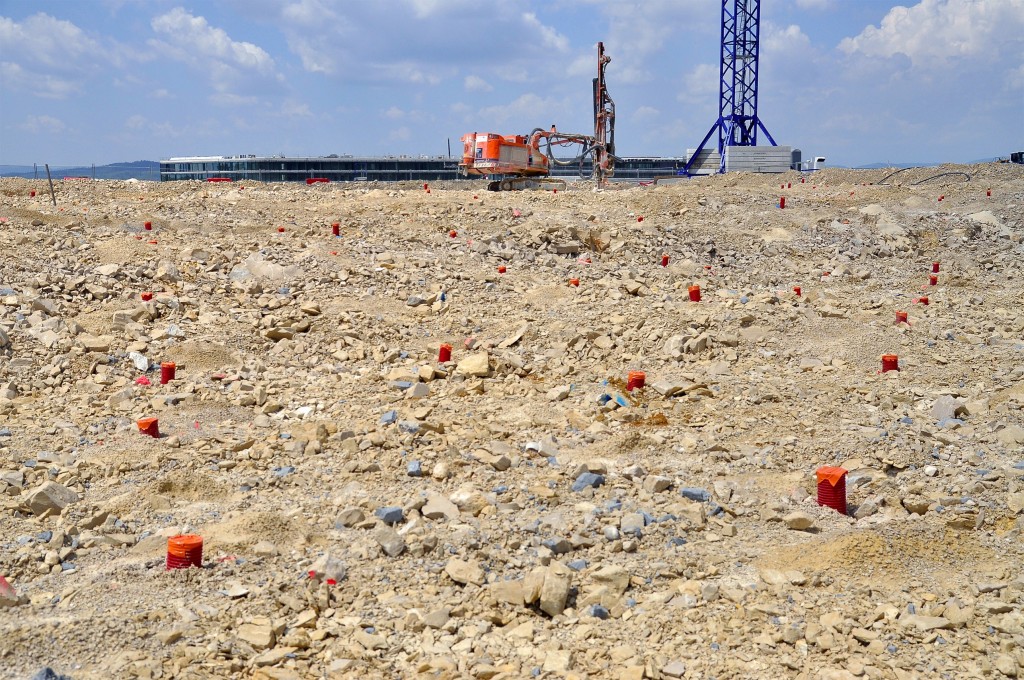
500 holes
2012-05-30 - As part of excavation work for the future Assembly Hall, 500 holes have been drilled down to 7 metres to profile the rock substrata.
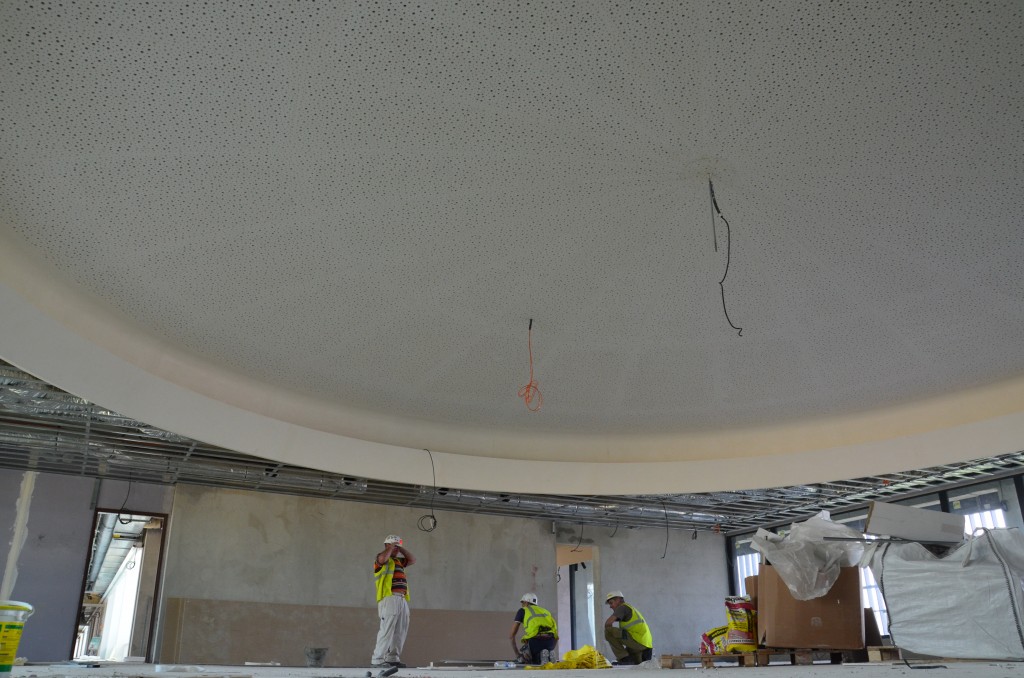
A space for discussion and decision-making
2012-05-30 - On the fifth floor of building, workers install an acoustic ceiling over the oval ITER Council boardroom. Photo: AIF AM
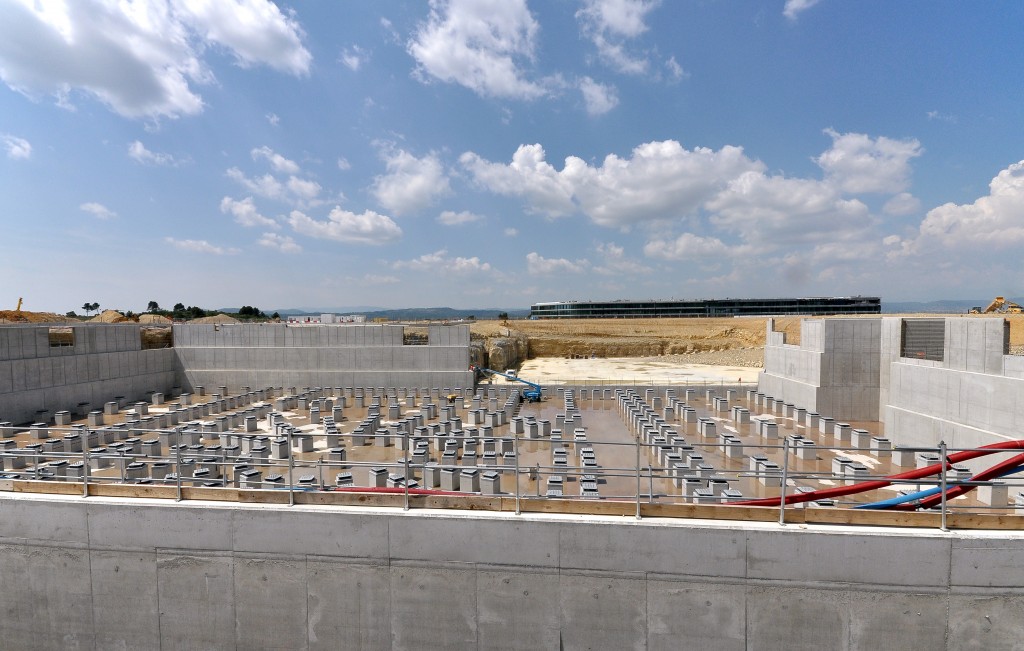
Pipes and cables through here please
2012-05-30 - In the completed Seismic Isolation Pit, the largest opening in the retaining walls looks onto the site of the future Hot Cell Facility. Smaller openings in the walls have been created to permit underground pipes and cables to reach the Tokamak Complex buildings.
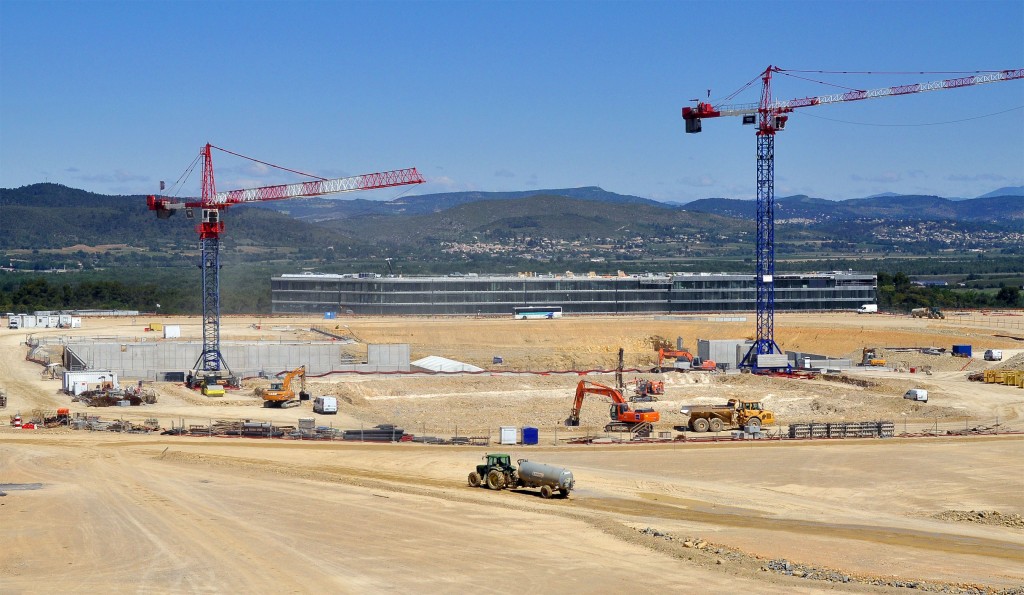
Future Assembly Hall
2012-05-16 - Excavation work has begun in a large square area next to the Tokamak Pit, where an Assembly Hall will be constructed to house pre-assembly activities for Tokamak components.
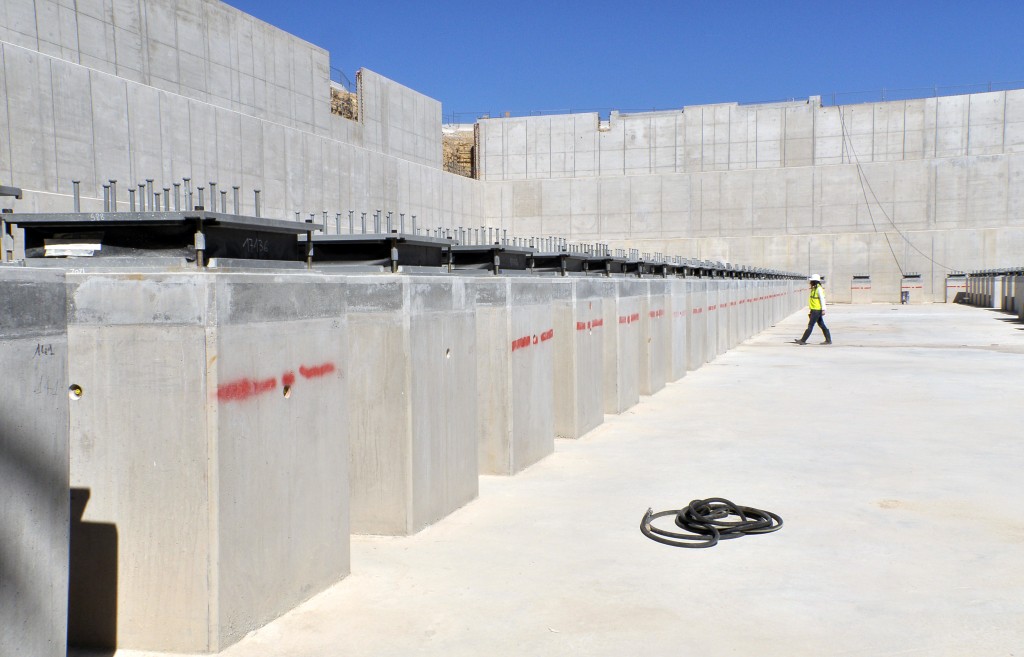
The workers have left the Seismic Pit
2012-05-16 - After 18 months of presence, the workers have temporarily quitted the Seismic Pit for other areas of the platform: site trench work and excavation for the Assembly Hall.
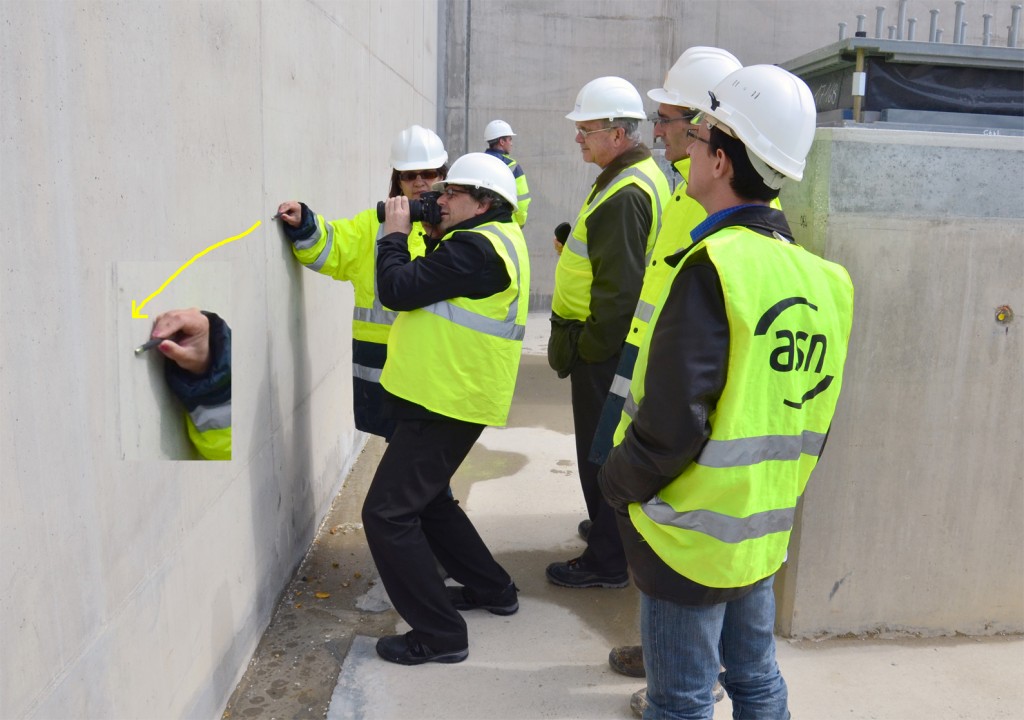
Leaving no crack unchecked
2012-04-24 - The French Nuclear Safety Authority (ASN) inspects the ITER retaining walls in April 2012, verifying each crack (most of them a fraction of a millimetre deep), scratch, chipped concrete edge, and other slight departures from perfection.
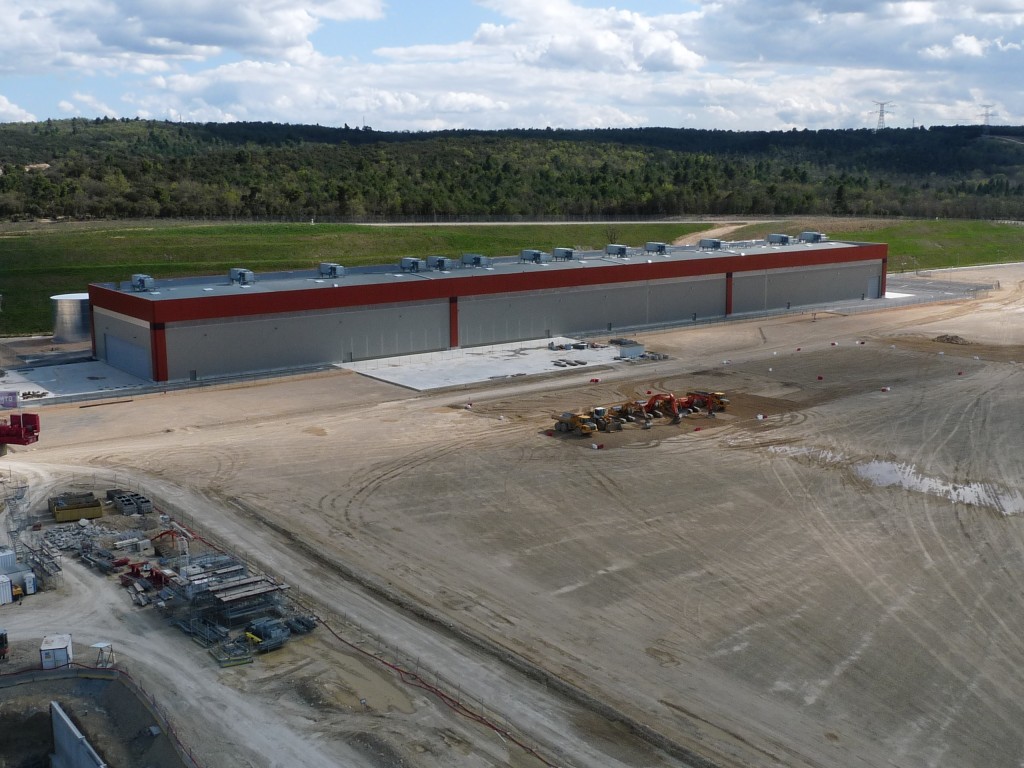
Not for long
2012-04-20 - The Poloidal Field Coils Winding Facility will not be the only building on the platform for long: the contract for the three-building Tokamak Complex (Diagnostic, Tritium and Tokamak buildings) will be signed later this year. Photo: Engage-AP
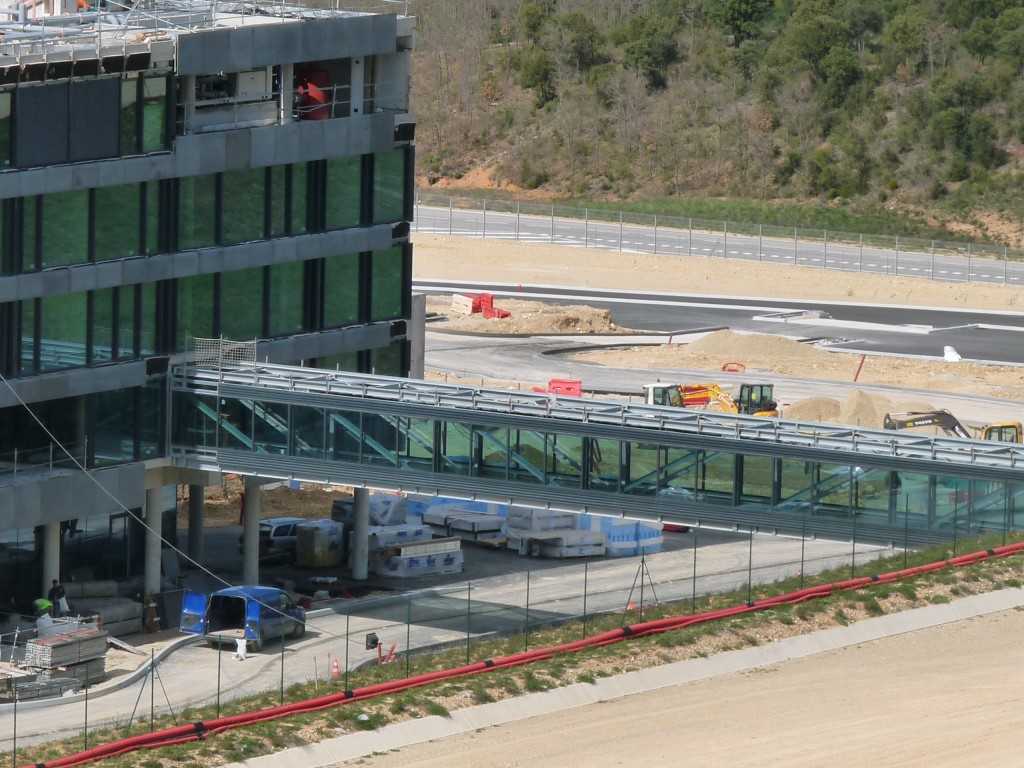
Heigh ho, heigh ho ...
2012-04-20 - Thirty-three metres in length, this glass-walled walkway gives access to subterranean technical rooms and the ITER Tokamak control centre. Photo: Engage-AP
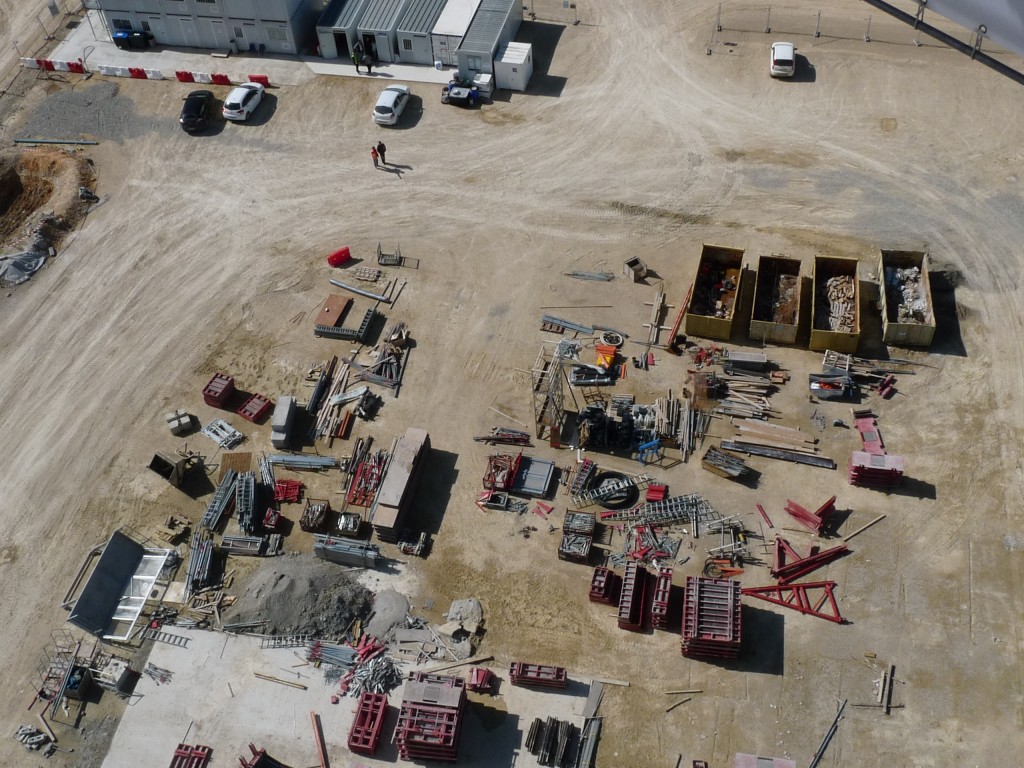
That's a tall ladder
2012-04-20 - For some on the ITER worksite. a day's work is accomplished 65 metres above ground level. Photo: Engage-AP
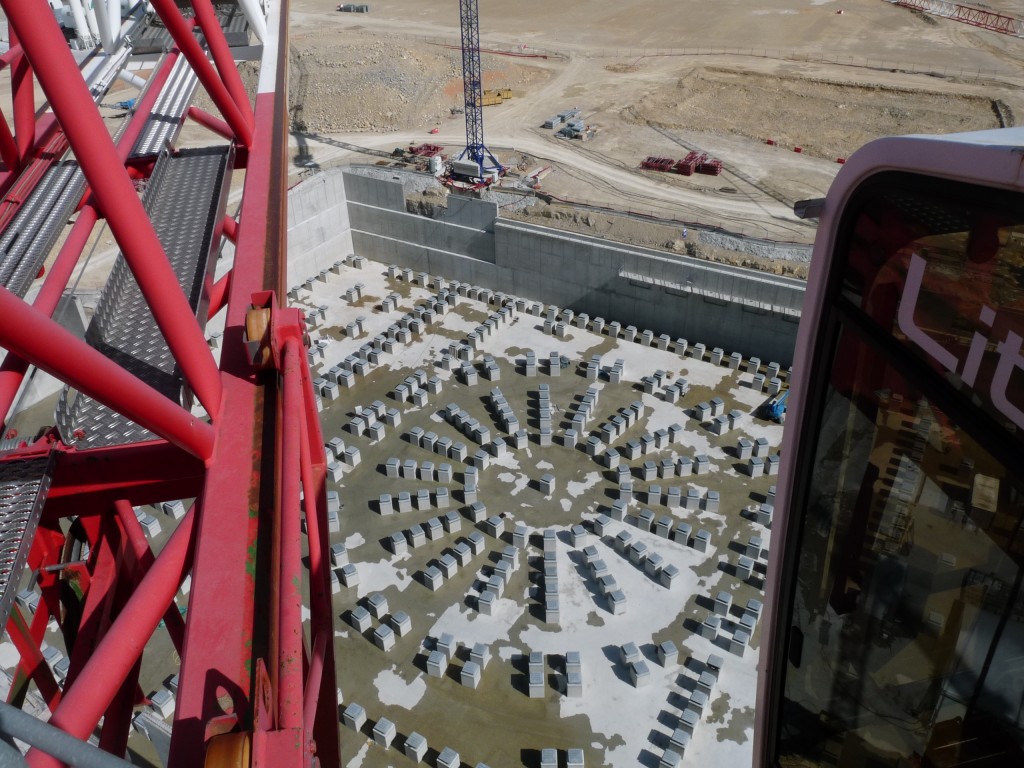
Seen from the crane
2012-04-20 - Late April, the completed Seismic Pit is photographed from one of the corner cranes. Photo: Engage-AP
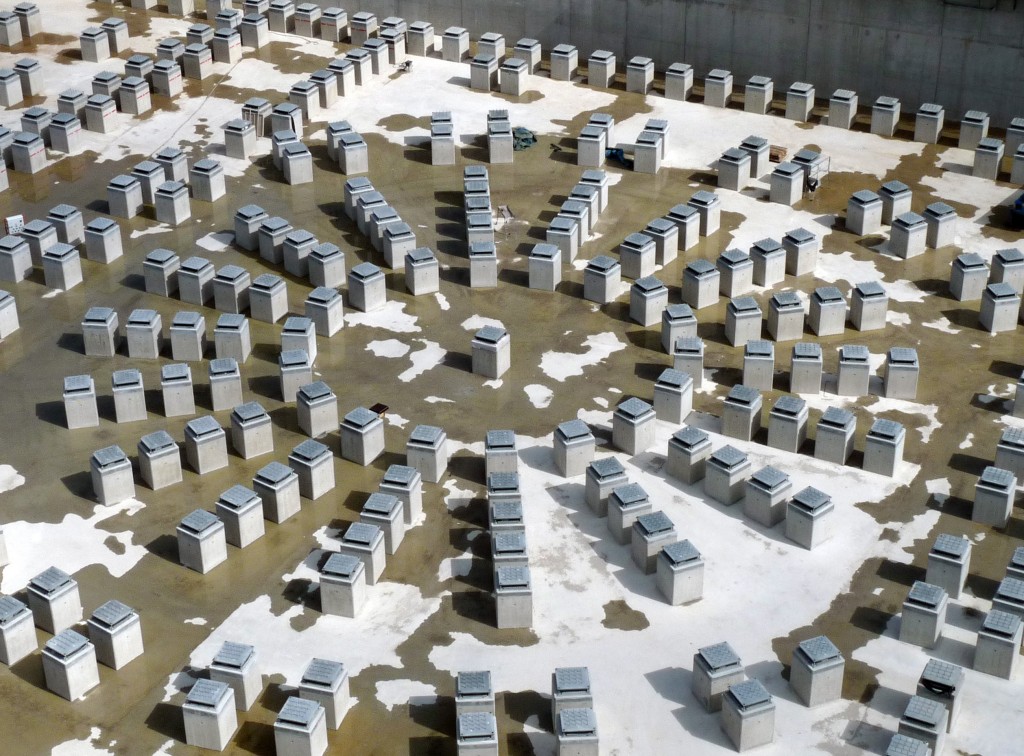
Just waiting for the Tokamak
2012-04-20 - Support in the shape of a star for the ITER experimental device: the very device that aims to bring the energy of the stars down to Earth. Photo: Engage-AP

Precise alignment made to look easy
2012-04-20 - A perfectly aligned row of seismic columns and pads. Photo: Engage-AP
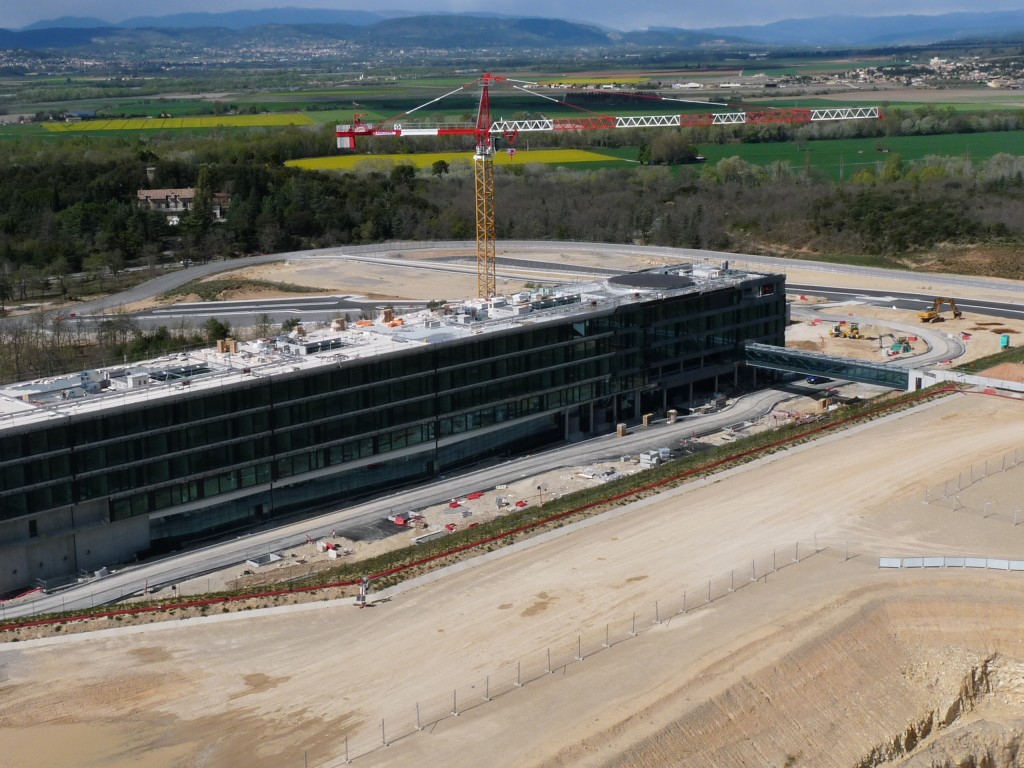
May in Provence
2012-04-20 - Spring blossoms in Provence and work on access roads continues in the vicinity of the Headquarters building. Photo: Engage-AP
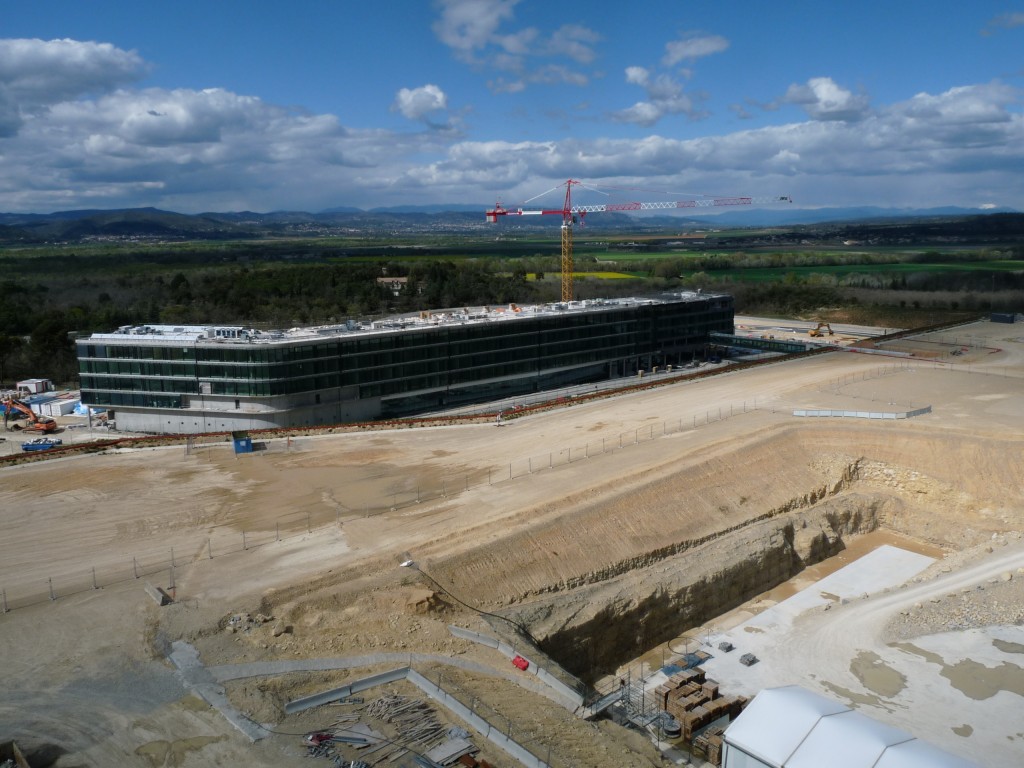
Looking north
2012-04-20 - ITER Headquarters seen from the top of a worksite crane on a sunny day in April. Photo: Engage-AP
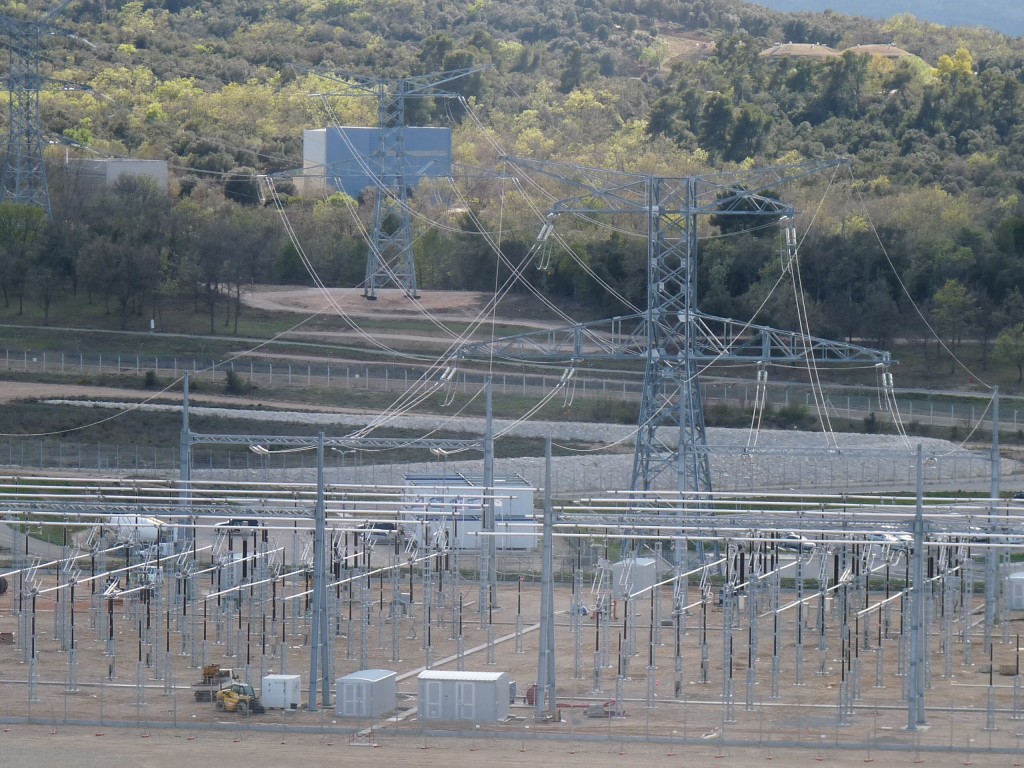
Soon to be "powered up"
2012-04-20 - Installing and financing the ITER switchyard and power-line extension was part of France's commitment to ITER. The switchyard will be "powered on" in June. Photo: Engage-AP
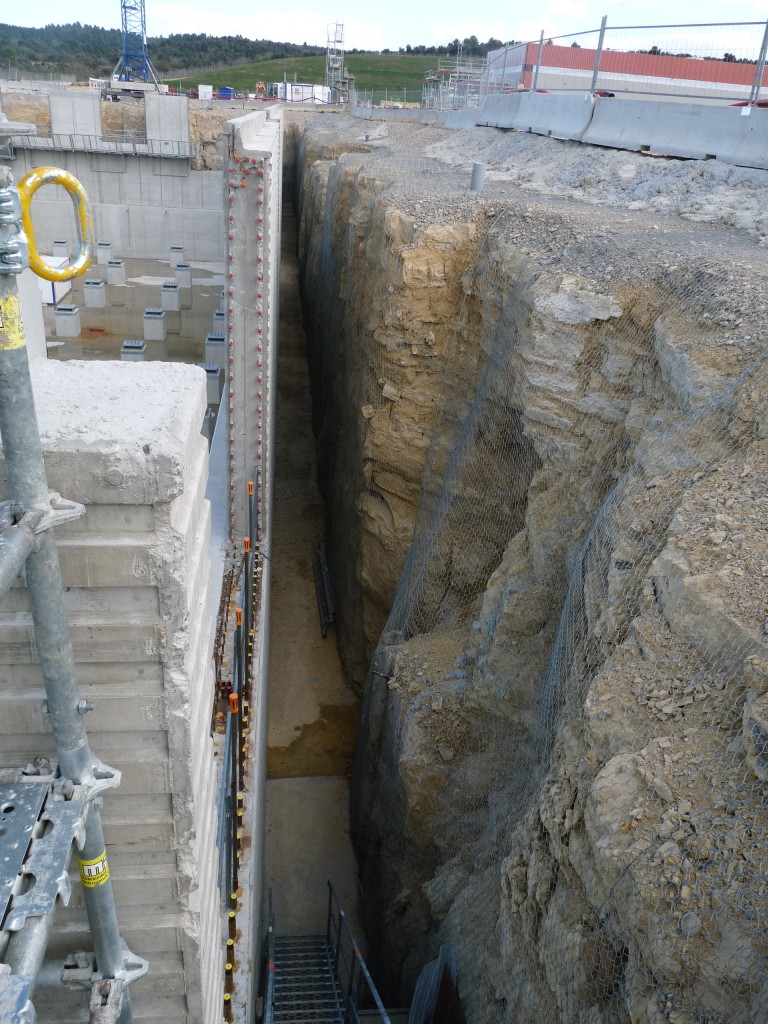
A peek behind the walls
2012-04-20 - Between the rough face of the rock and the 15-metre-tall retaining walls, a space persists. At a later stage in the contruction works the space will be filled with sand and gravel and compacted. Photo: Engage-AP
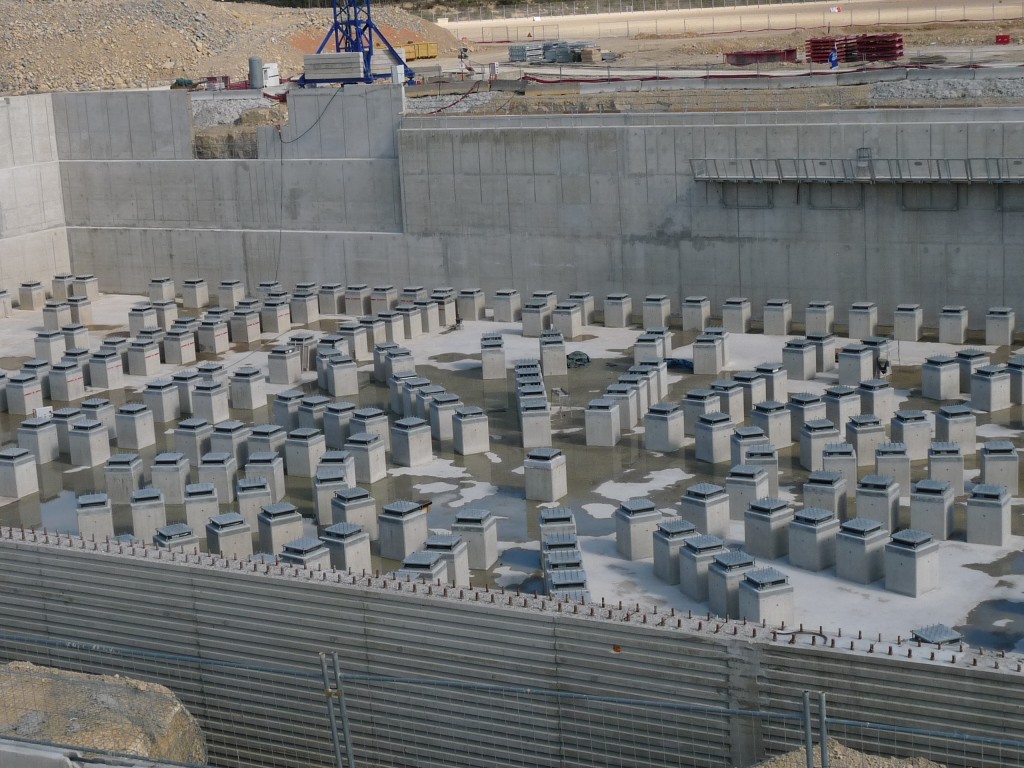
Here it is: the completed ground support structure
2012-04-20 - The first-phase works in the Tokamak Pit are over. The next stage: the civil works on the Tokamak Complex, beginning with the creation of a reinforced basemat on top of the seismic pads. Photo: Engage-AP
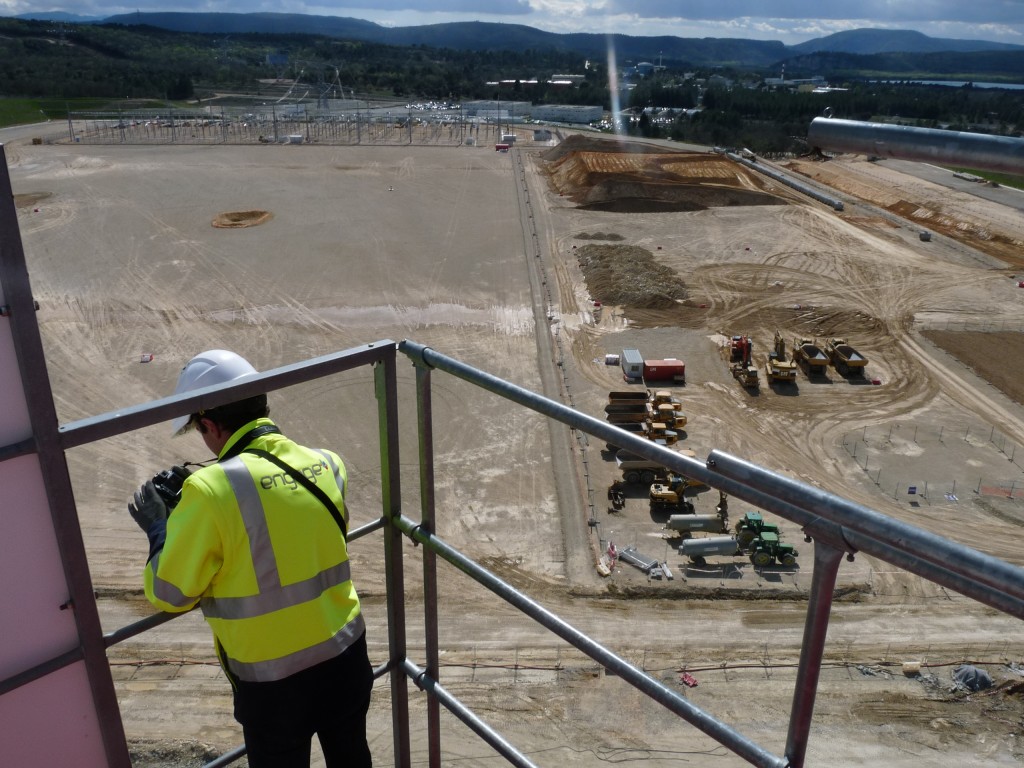
Bird's-eye view
2012-04-20 - An image taken from a crane at the corner of the Tokamak Pit shows the RTE electrical switchyard (left) and the beginning of construction works (right) for a new contractor area (offices, parking lot, facilities). Photo: Engage-AP
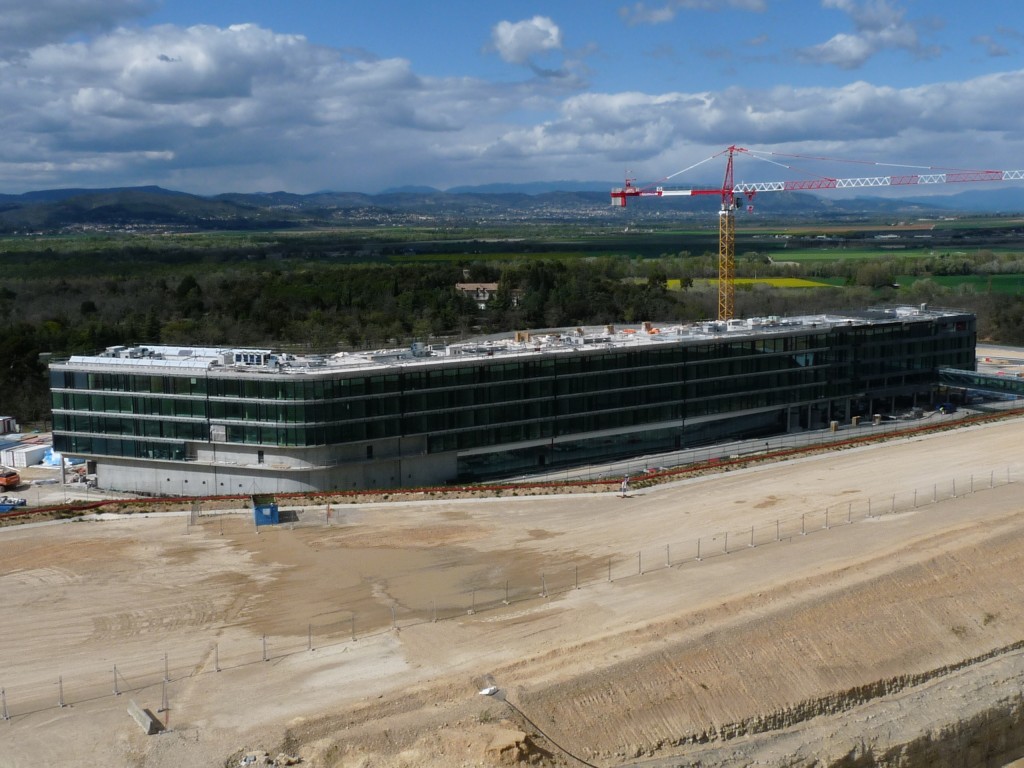
Just a few months from completion
2012-04-20 - Late April: most of the work is happening on the inside now. Photo: Engage-AP
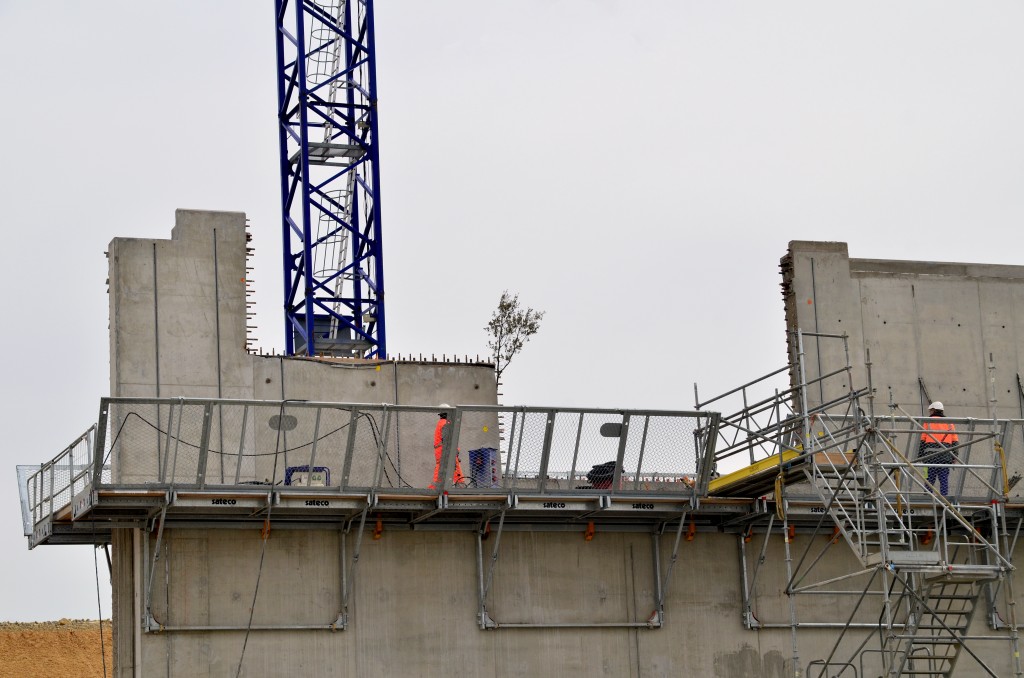
A symbolic branch
2012-04-18 - Construction on the retaining walls of the Tokamak Complex Seismic Pit ends in April. A branch is hung from one of the tallest points to symbolize the end of works—a construction tradition originating in Eastern Europe called "topping out."

Thick, thicker, thickest
2012-04-18 - From the side, it's easy to see that the retaining walls measure 1.5 metres at their base, 1.0 metres in the middle, and 0.5 metres at the top.
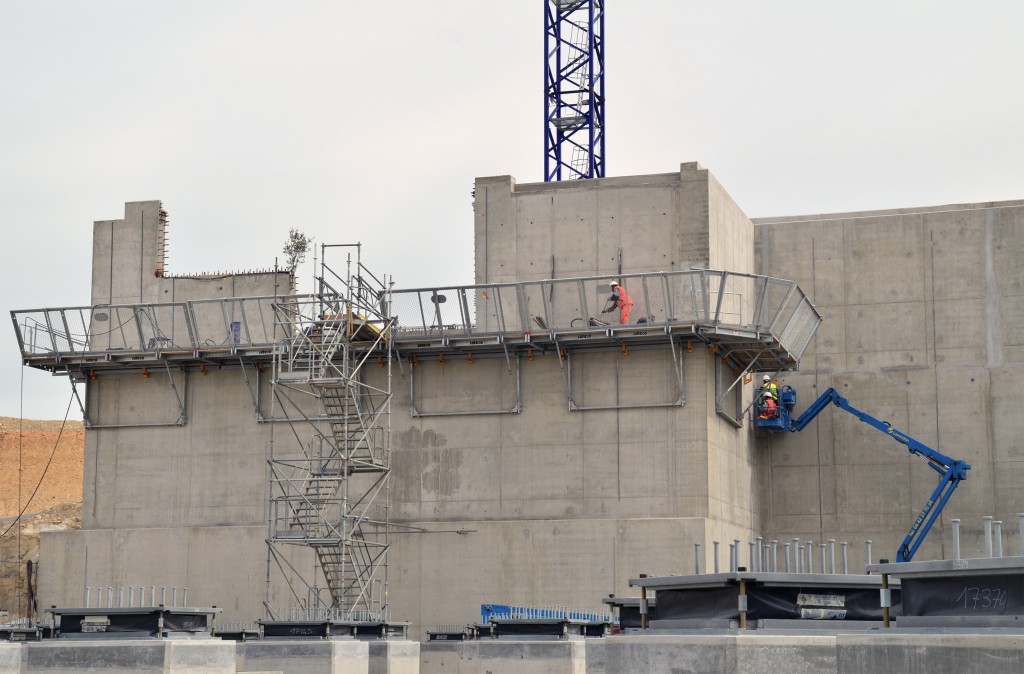
The walls are done!
2012-04-18 - The ground support structure for the Tokamak Complex—basemat and walls—is now complete. The retaining walls maintain and stabilize the surrounding rock and "waterproof" the Seismic Pit.
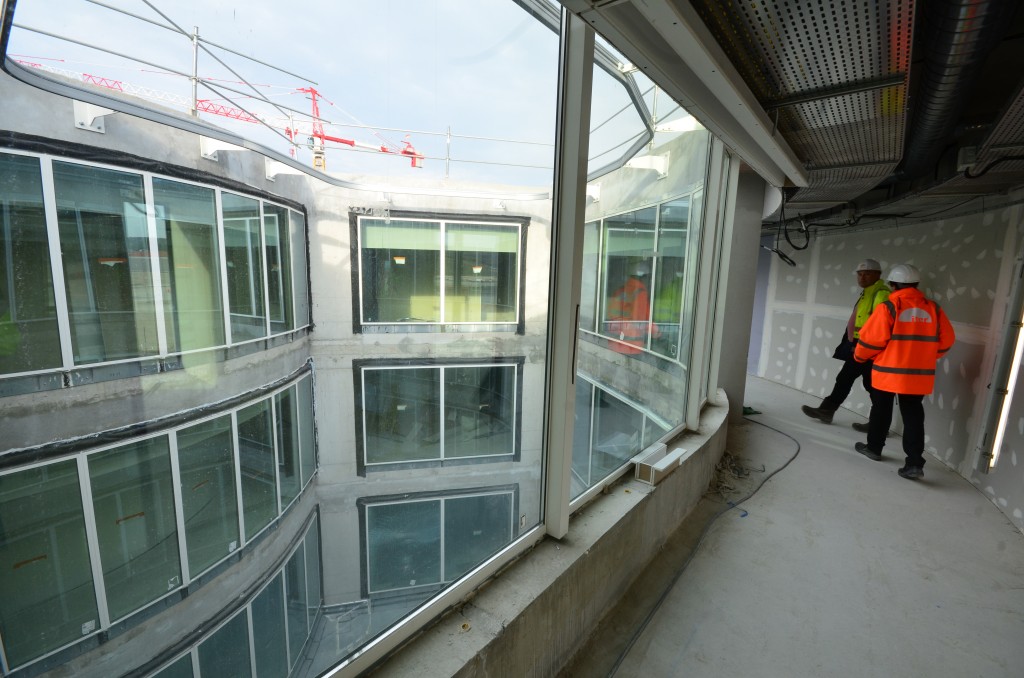
On the inside
2012-04-10 - The superstructure of the Headquarters building was finished in September 2011. Since this date, workers have been equipping the interior of the building.
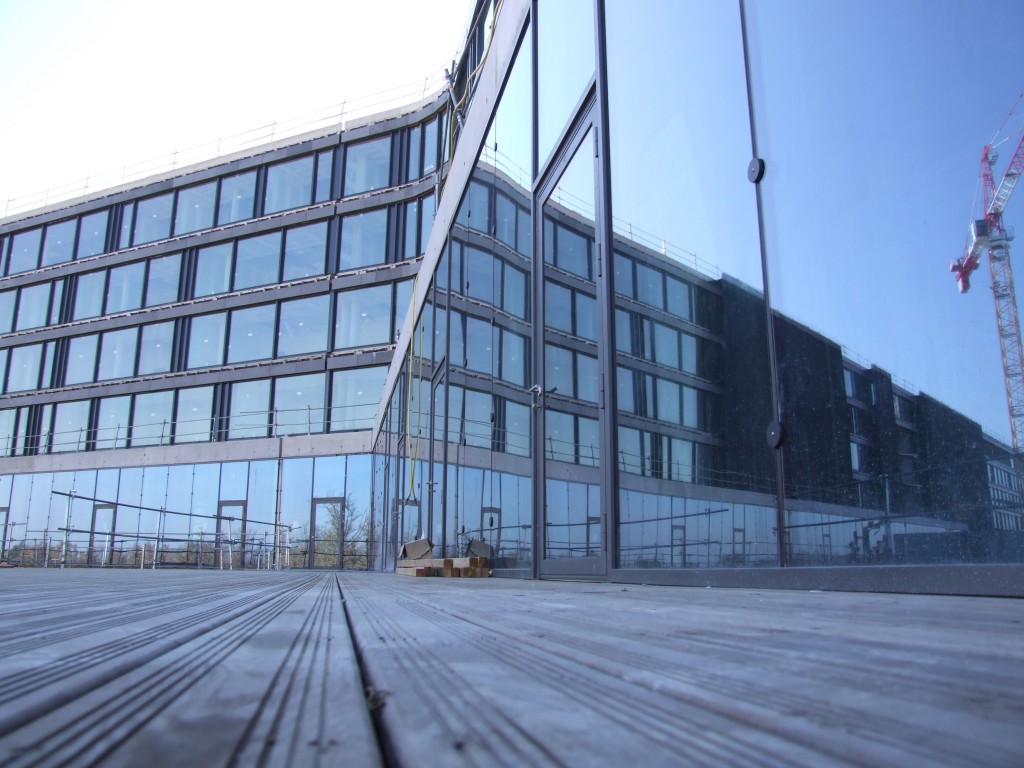
Installation of vertical sunshades
2012-03-24 - Vertical sunshades are positioned by crane and bolted into place along the northwest façade of the ITER Headquarters building. When the work is finished, the shades will create 14-metre-tall vertical lines. Photo: AIF.AM
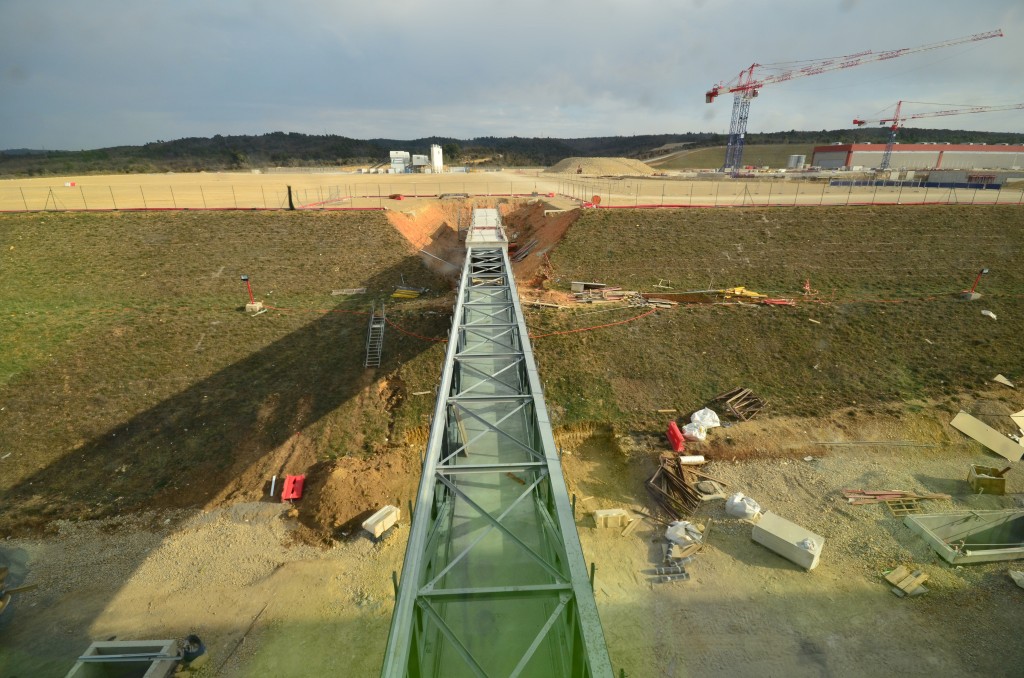
A tunnel to the control tower
2012-03-24 - Looking down onto the walkway, then tunnel, that leads to the area on the ITER platform where the Control Room will be located in a few years.
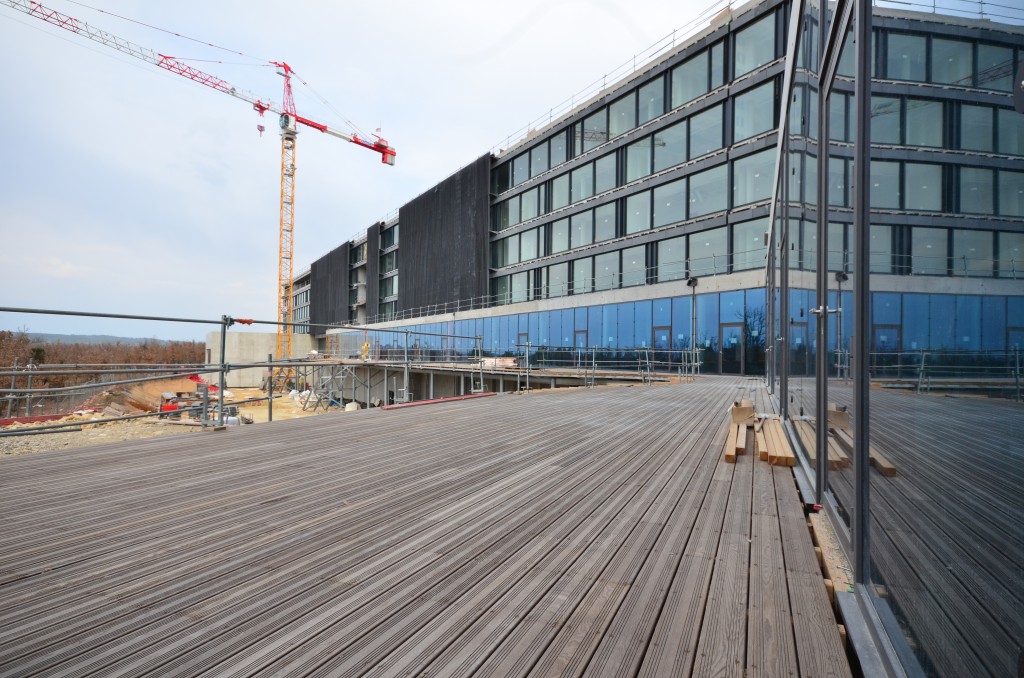
Eating out on a sunny day
2012-03-24 - The ITER canteen on the ground floor will have its own outside terrace.
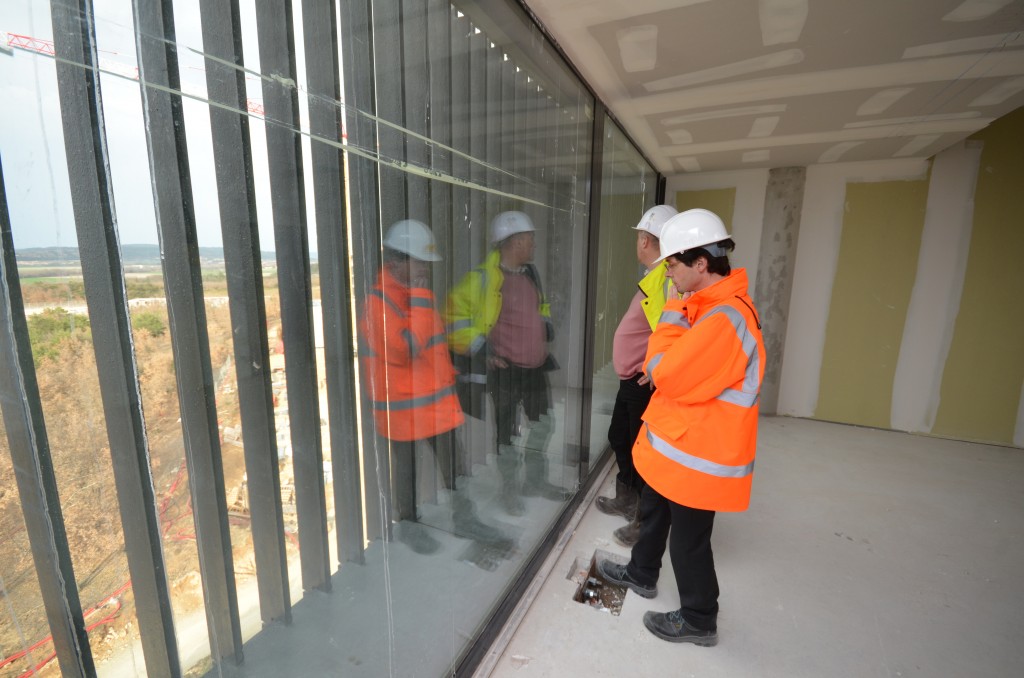
What will it be like cohabitating with the architectural slats?
2012-03-23 - The vertical slats seen from the inside ...
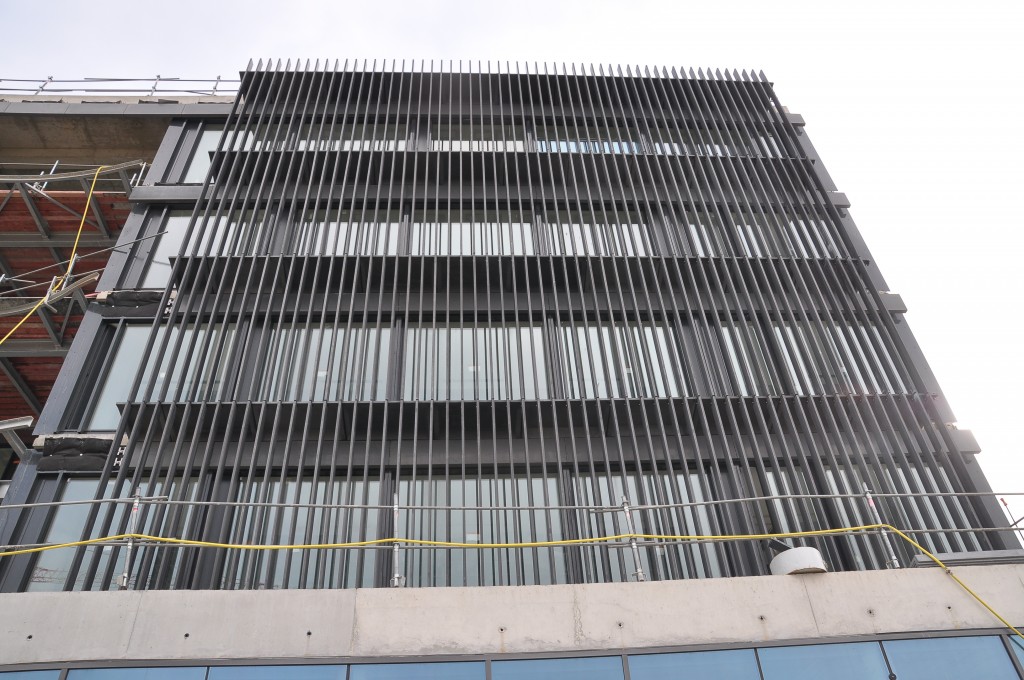
Filtering the Provençal sun, without blocking the view
2012-03-23 - The vertical slats seen from the outside ...
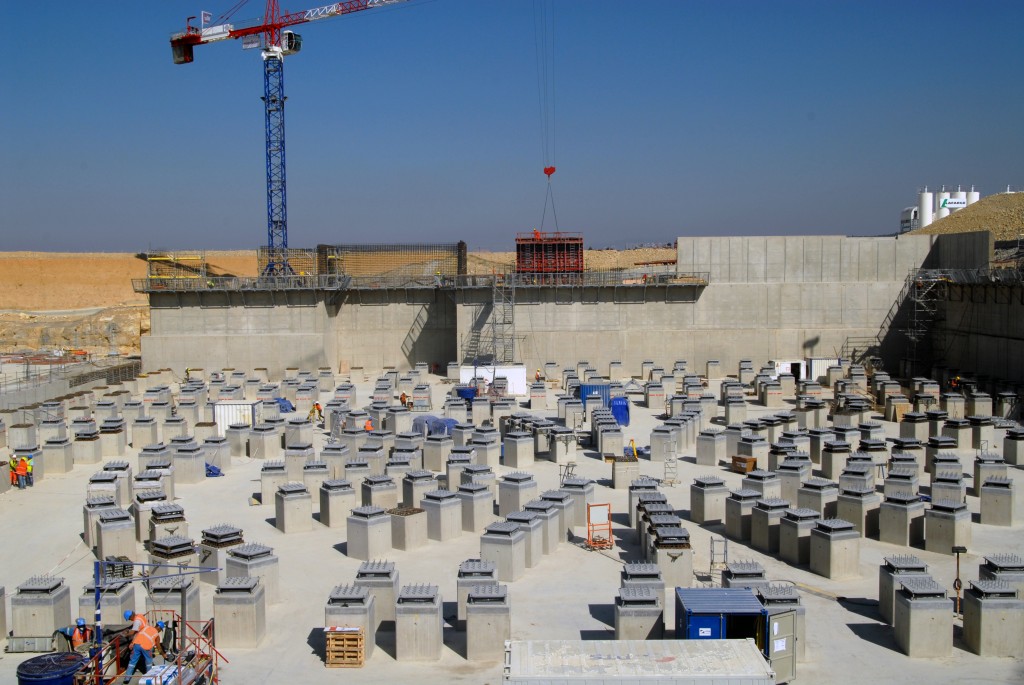
An opening on one side
2012-03-15 - The Seismic Isolation Pit looking north. The break in the retaining wall to the left opens onto the future Hot Cell Facility. Photo: F4E
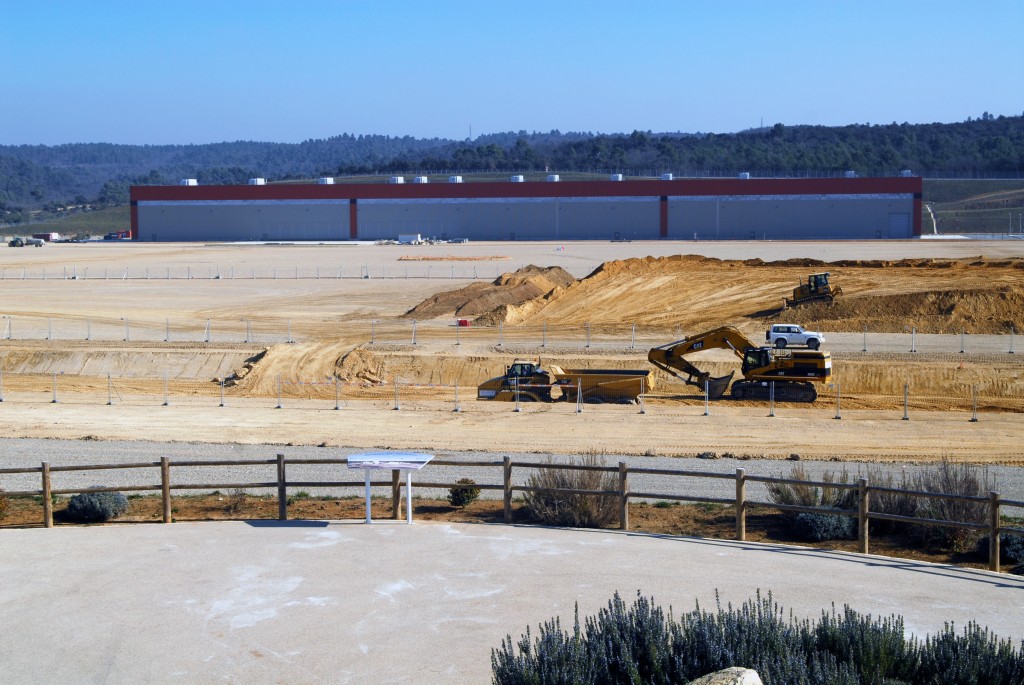
All is quiet
2012-03-15 - The completed Poloidal Field Coils Winding Facility awaits busier days. Later this year, the selected coil manufacturer will move in to equip the building. Photo: F4E
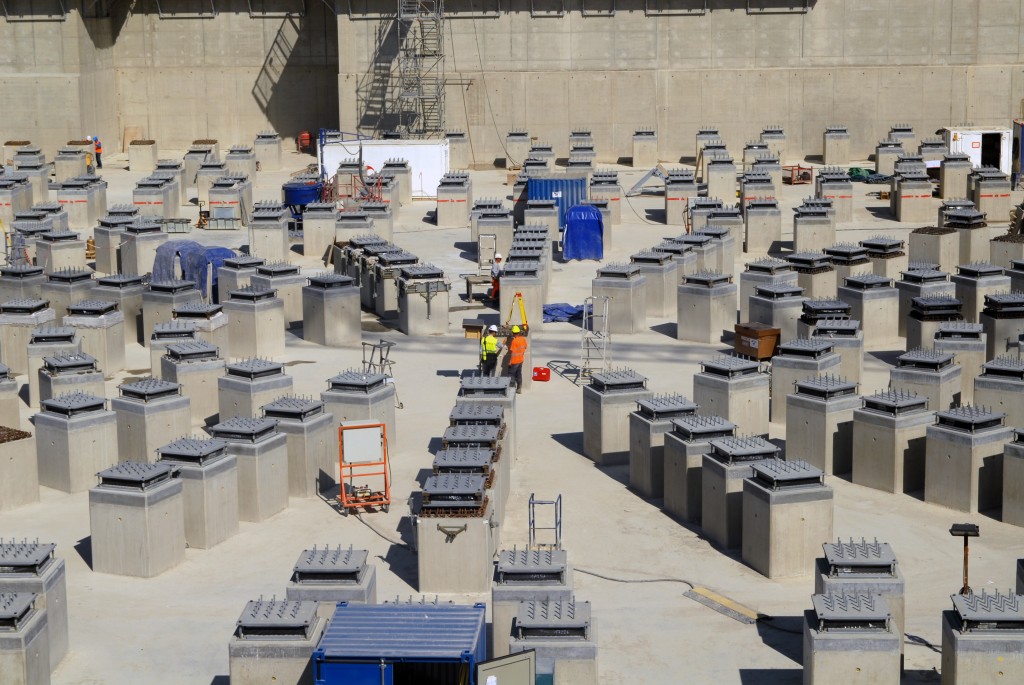
The centre of ITER
2012-03-15 - These workers are standing on the precise spot where the Tokamak will be assembled in a few years, several metres over their heads. Photo: F4E
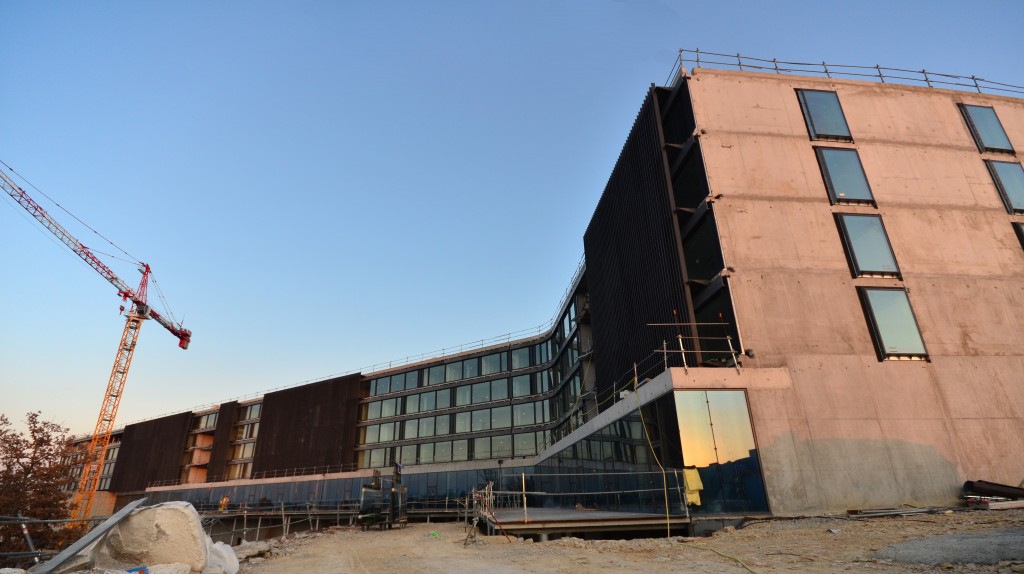
Late in the day
2012-03-14 - The late-day sun illuminates the western facade of the ITER Headquarters.
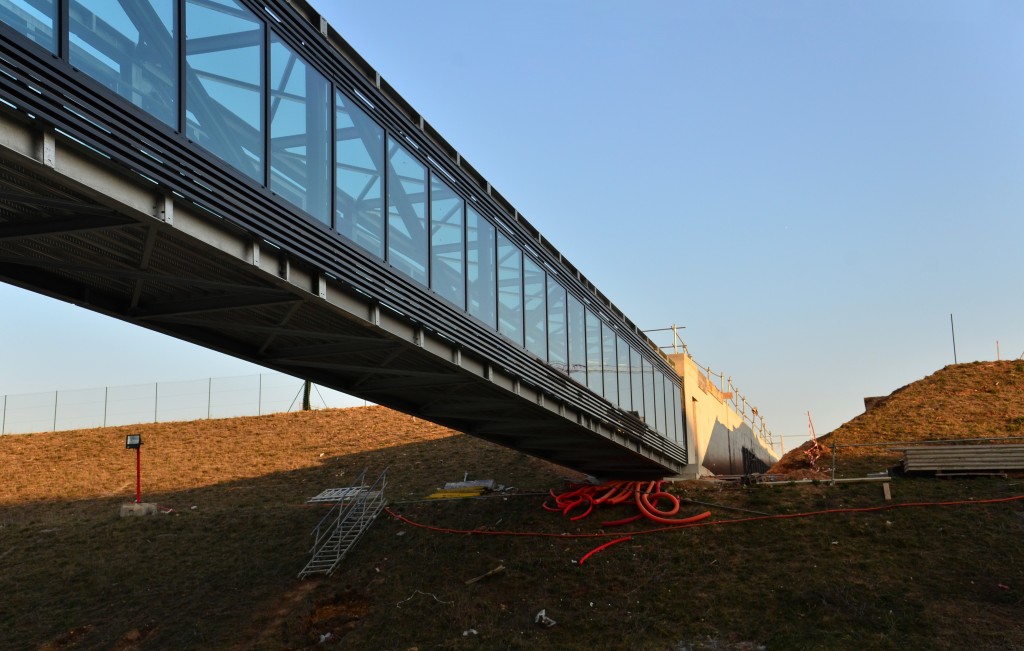
Rain or shine
2012-03-14 - Windows and a glass ceiling have been installed on the footbridge that links the ITER offices to the Control Room on the platform.
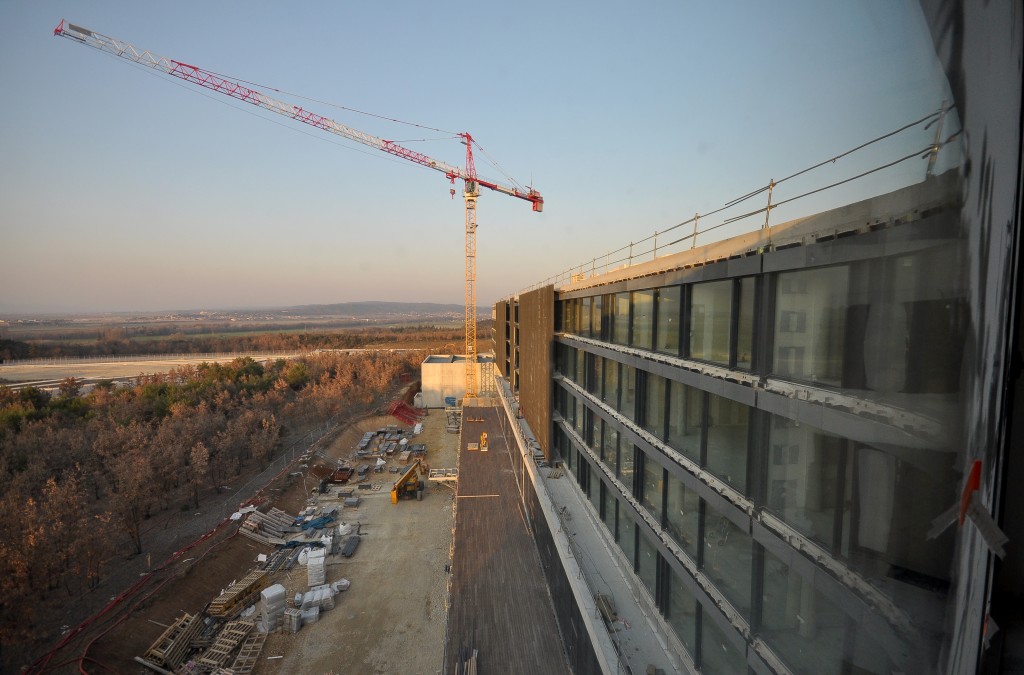
Inside and out
2012-03-14 - On the inside, workers are installing some 12,000 square metres of dividing walls to shape out the offices. On the outside, work continues on the "exterior veil."
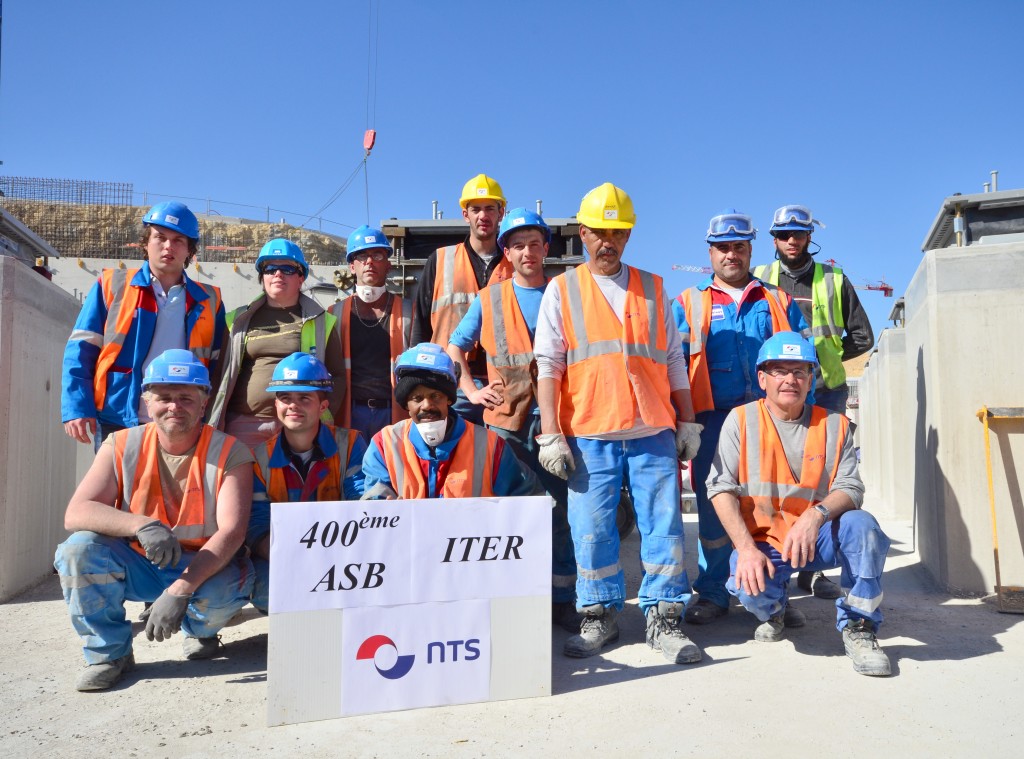
400th seismic bearing in the Tokamak Pit
2012-03-14 - The team from Nuvia Travaux Spéciaux (NTS) celebrates the installation of the 400th seismic bearing on 14 March.
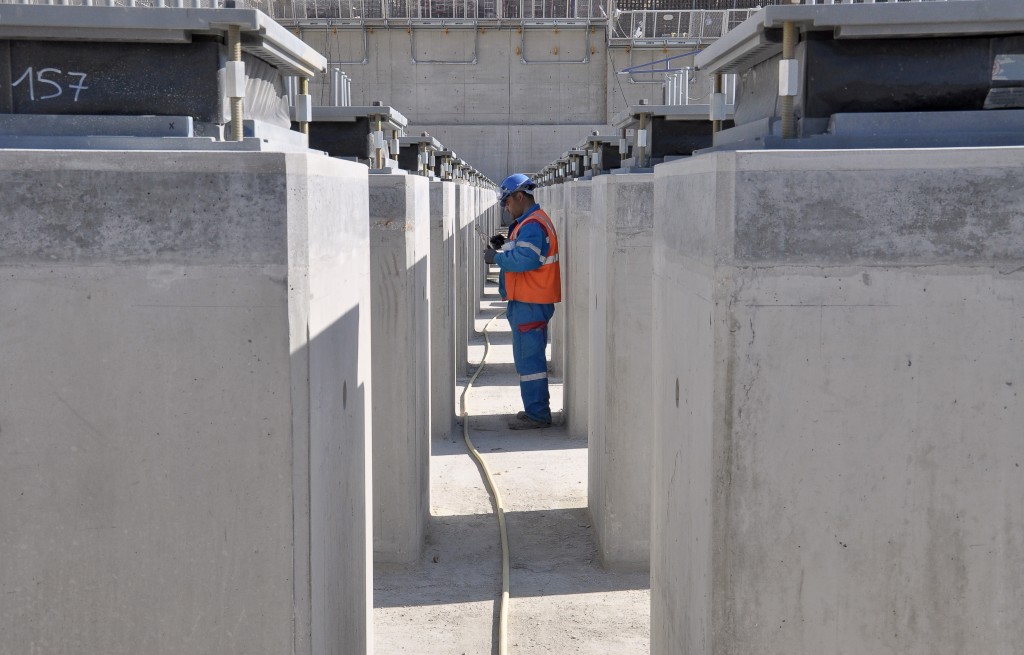
An army of standing columns
2012-03-13 - The concrete pillars (1.7 metres tall) and their seismic pads form an army of standing columns upon which the Tokamak Complex will be built. The area between the two concrete basemats will remain accessible for regular inspection of the seismic pads.

Northwest facade
2012-03-08 - Looking up from the basement level of the Headquarters building toward the ITER canteen and four storeys of office space. Photo: AIF.AM
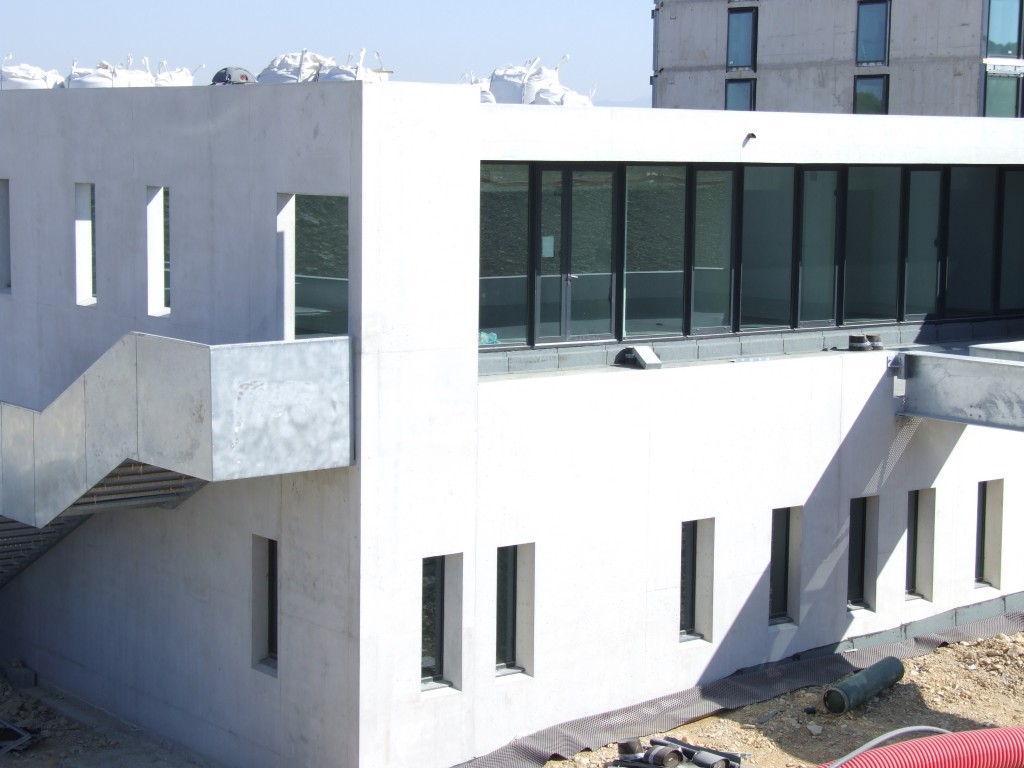
Work is completed on annex building
2012-03-08 - Located next to the ITER Headquarters, this building will house the ITER Medical Centre and research facility access checkpoint. Photo: AIF.AM
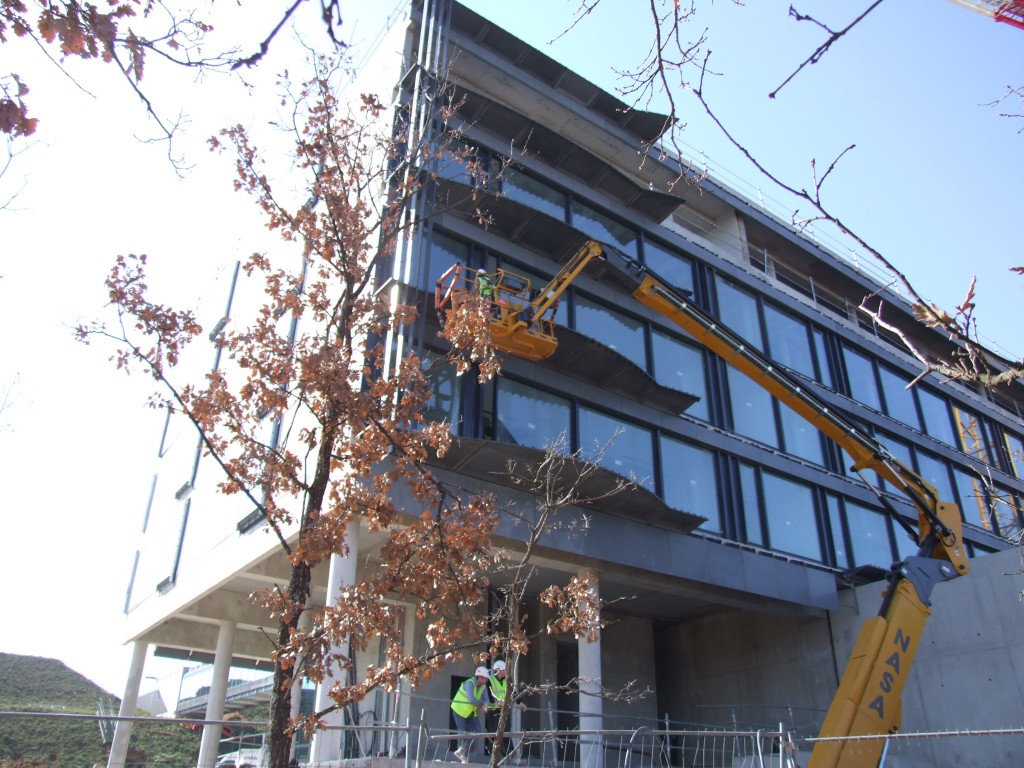
Piece by piece
2012-03-06 - On the northern corner of the Headquarters building, these "balconies" have been installed to receive 14-metre-tall vertical slats. Photo: AIF
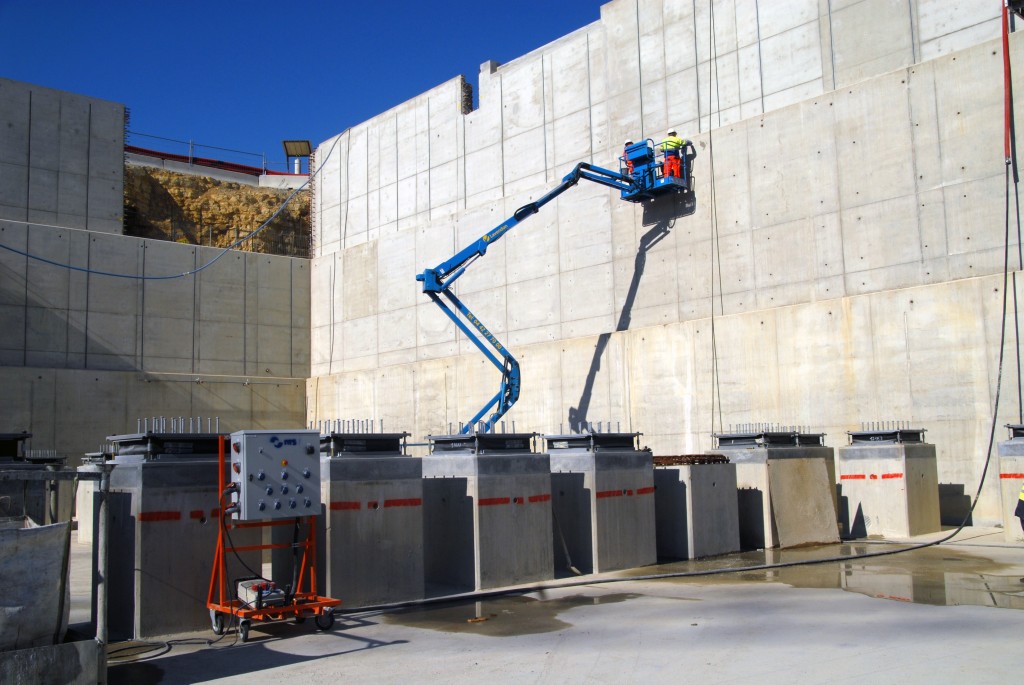
From bottom to top
2012-03-02 - Work on the third five-metre segment of retaining wall is nearly finished. Photo: F4E
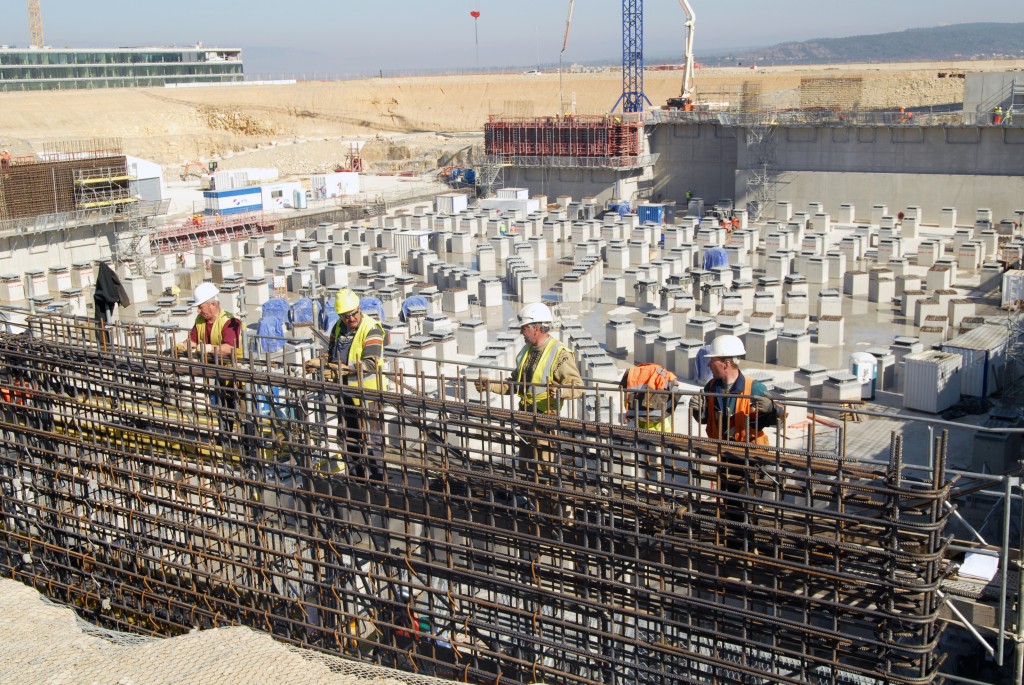
Heave ho!
2012-03-02 - Workers arrive at the final phase of retaining wall reinforcement. Photo: F4E
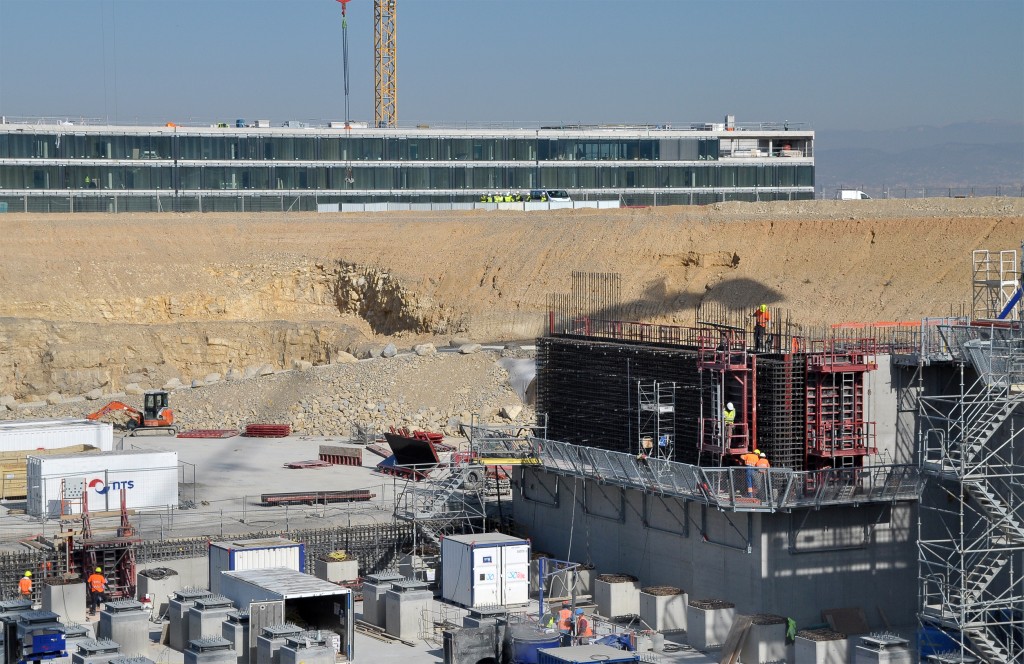
Spectacular progress
2012-02-29 - The top three levels of ITER Headquarters have front-row seats to the work on the platform. Beginning next fall, the building will be occupied.
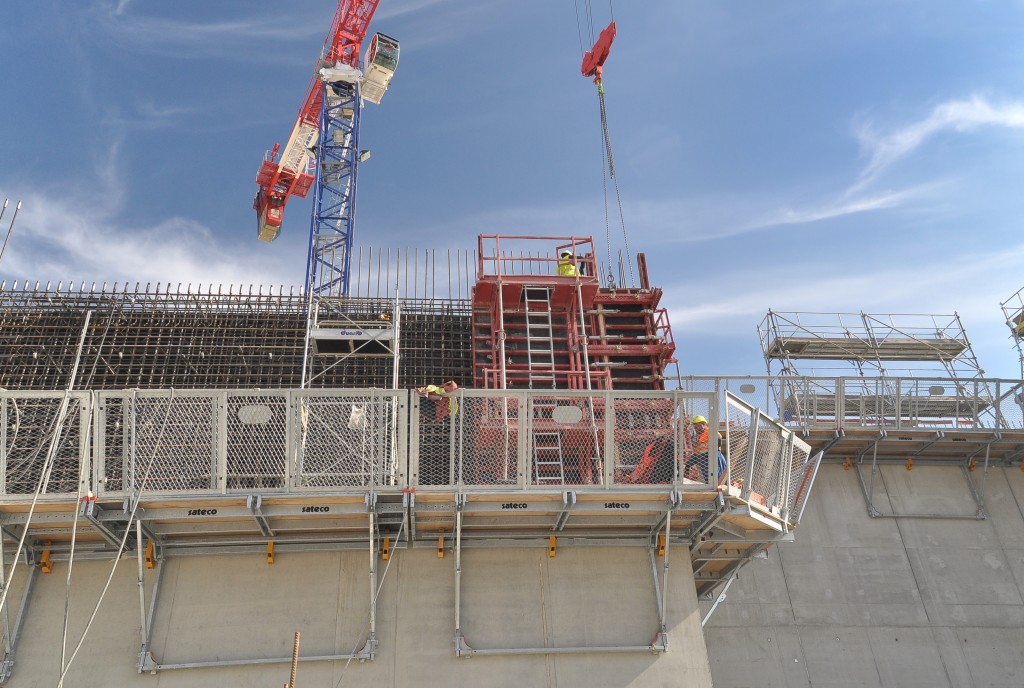
Up to the top
2012-02-29 - Workers make progress on the top third of the Seismic Pit retaining walls.
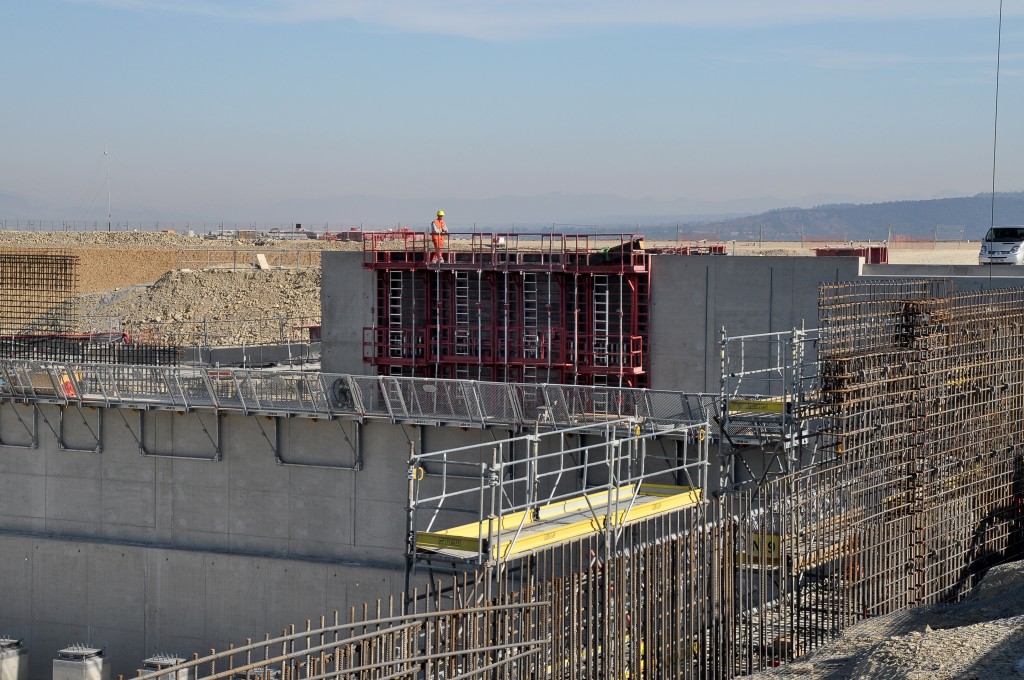
Now 15 metres tall
2012-02-29 - Section by section, the top, 0.5-metre-thick segment of retaining wall is set into place. Work on the walls will finish in March.
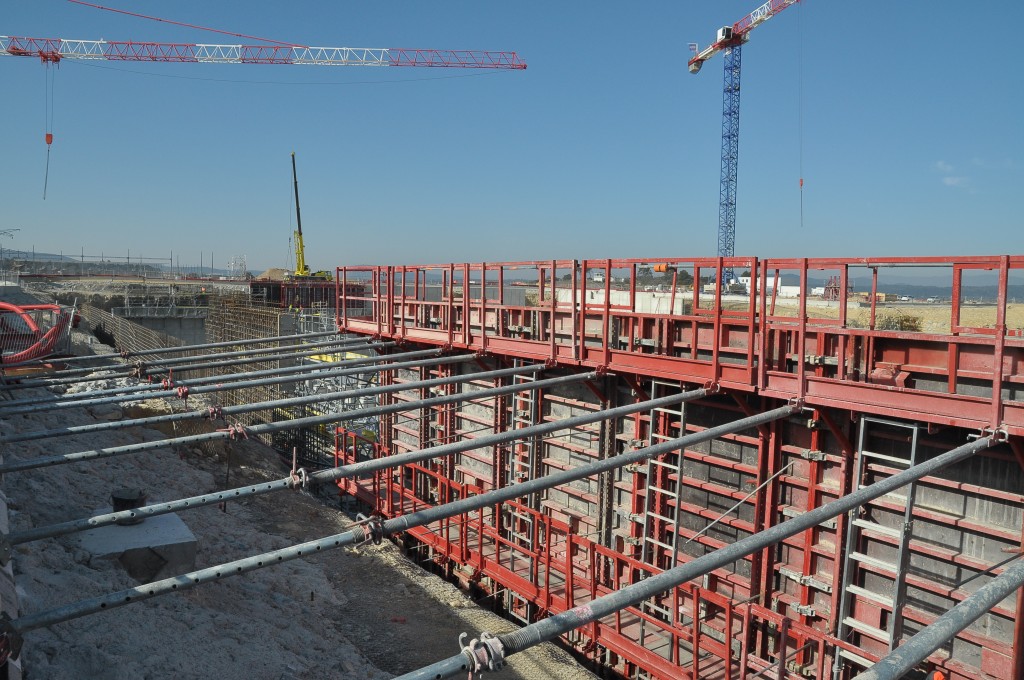
While the concrete sets
2012-02-29 - Formwork used to shape the retaining walls is supported during drying time. The space between the walls and the rock face will be filled with a mix of gravel and sand and compacted.
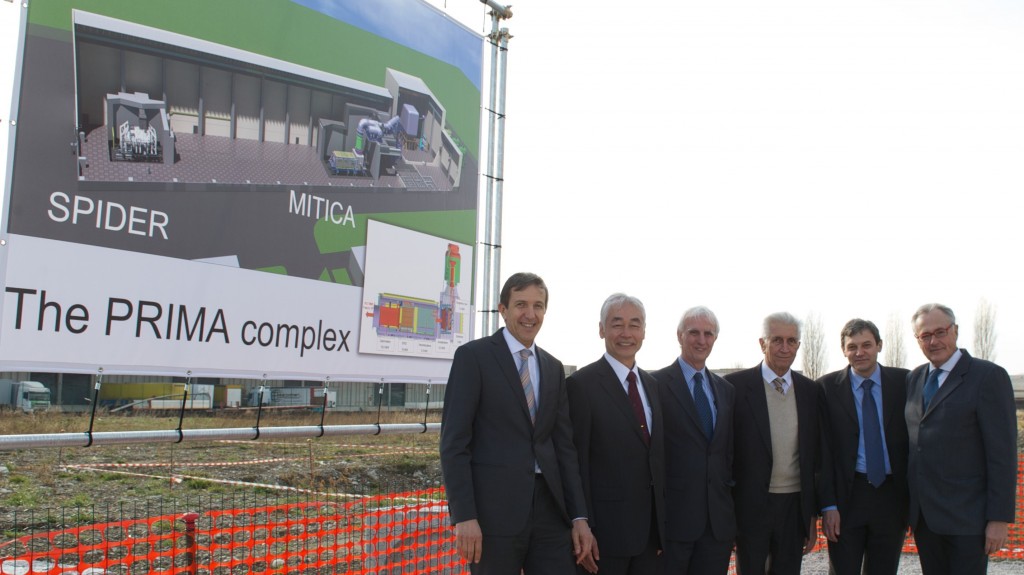
Groundbreaking
2012-02-27 - Ceremony participants stand on the site of the future 17,500 m² building, whose construction will be financed by the Italian government as a voluntary contribution to the neutral beam test facility.
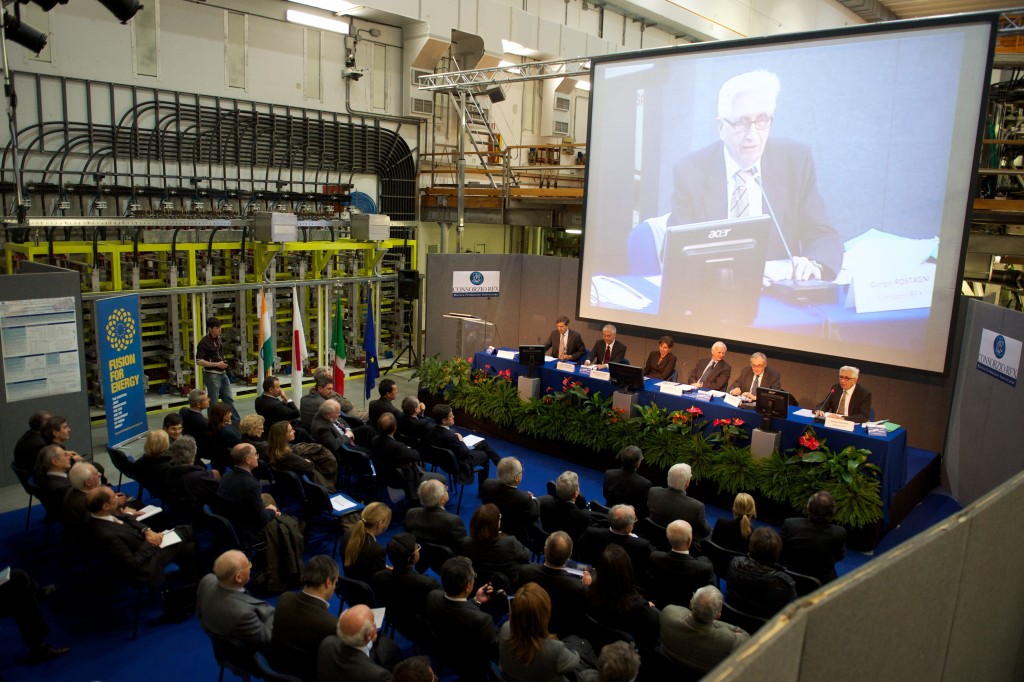
Construction project launched in Italy
2012-02-27 - A ceremony was held in Padua, Italy, on 27 February 2012 for the launch of the ITER Neutral Beam Test Facility.
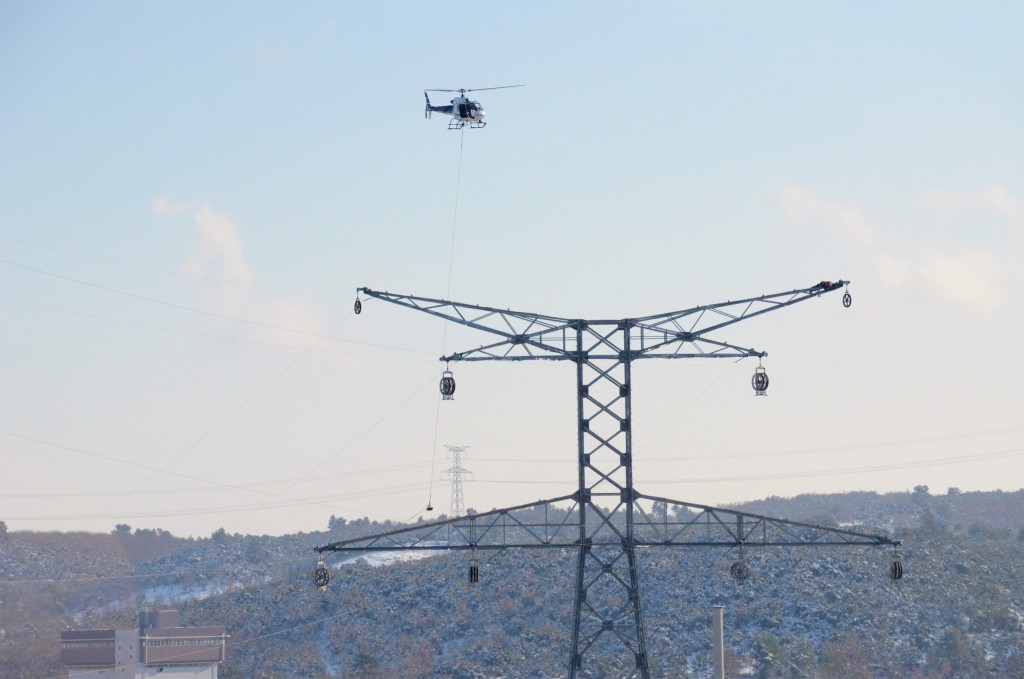
Help from the sky
2012-02-08 - In difficult areas, helicopters are used to position temporary "pulling cables" that will later be attached to the actual power cables and pulled by a ground-based winch. Photo: © CEA/Corinne Guis
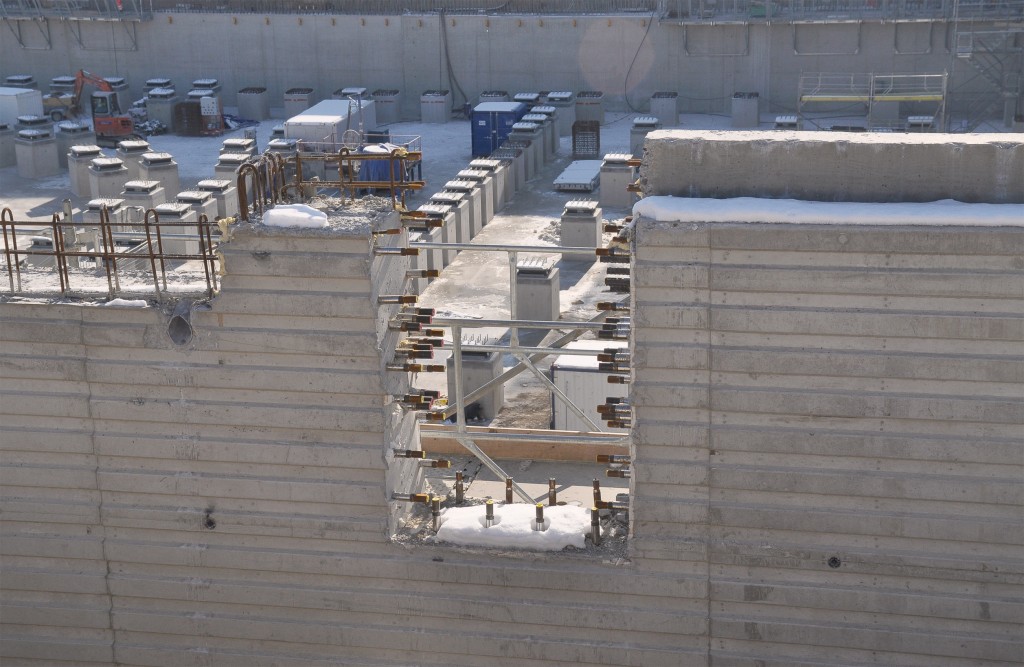
Space reserved
2012-02-07 - This opening in the retaining wall will allow underground pipes and cables to reach the Tokamak Complex buildings.

A sea of cables and wires
2012-02-07 - On the left, the "pantograph" has been deployed; on the right its articulated arms sit waiting. The 400kV pantographs connect the RTE busbars, source of high voltage current, to the ITER transformers.
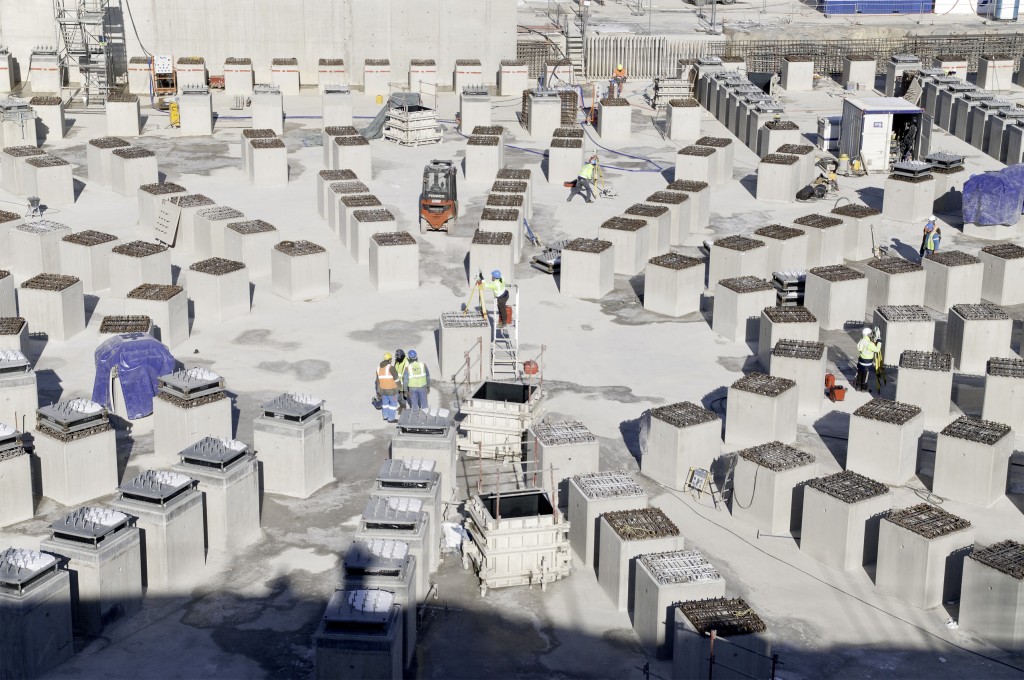
Nearly there
2012-02-07 - As of early February 2012, 481 out of 493 concrete plinths had been cast (the formwork used for these 90 x 90 cm pillars can be seen in white and black in the photo). Three hundred and four plinths have now been topped with seismic bearings.
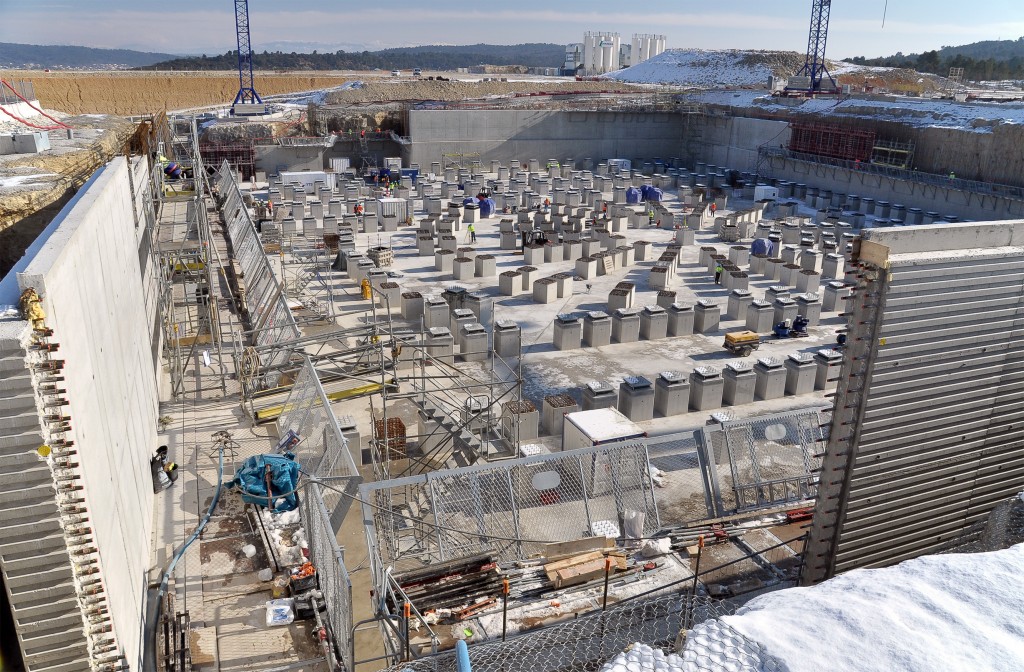
One year later
2012-02-07 - The excavation of the Tokamak Complex Seismic Pit, which required the displacement of 210,000 cubic metres of earth and rock, was completed in February 2011. One year later, progress made on construction is spectacular. Photo: F4E
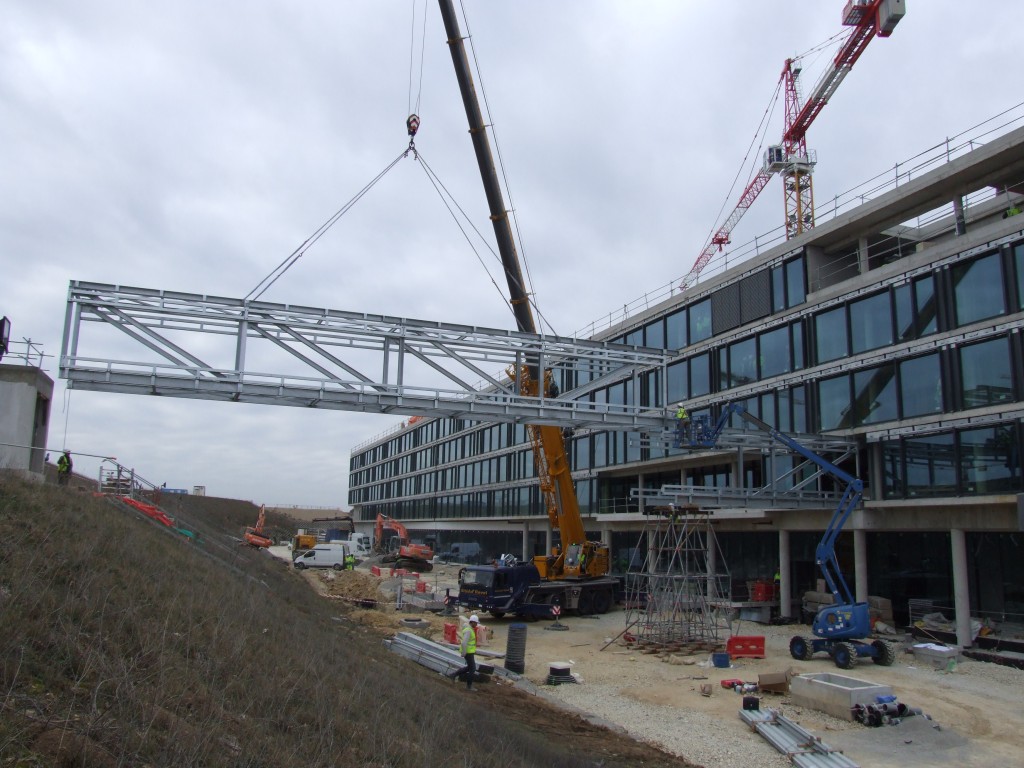
Footbridge to the experiments
2012-02-03 - This 33-metre metal footbridge will link ITER Headquarters to the scientific facilities on the platform, by way of an underground tunnel. Photo: AIF.AM

Restaurant inside, deck outside
2012-02-03 - The terrace adjoining the ITER canteen is equipped with a wooden deck. Photo: AIF.AM

By "rack" of six
2012-02-03 - One 3.2-metre "rack" of 6 sunshades is readied for installation. Four racks like these complete one vertical assembly. Photo: AIF.AM
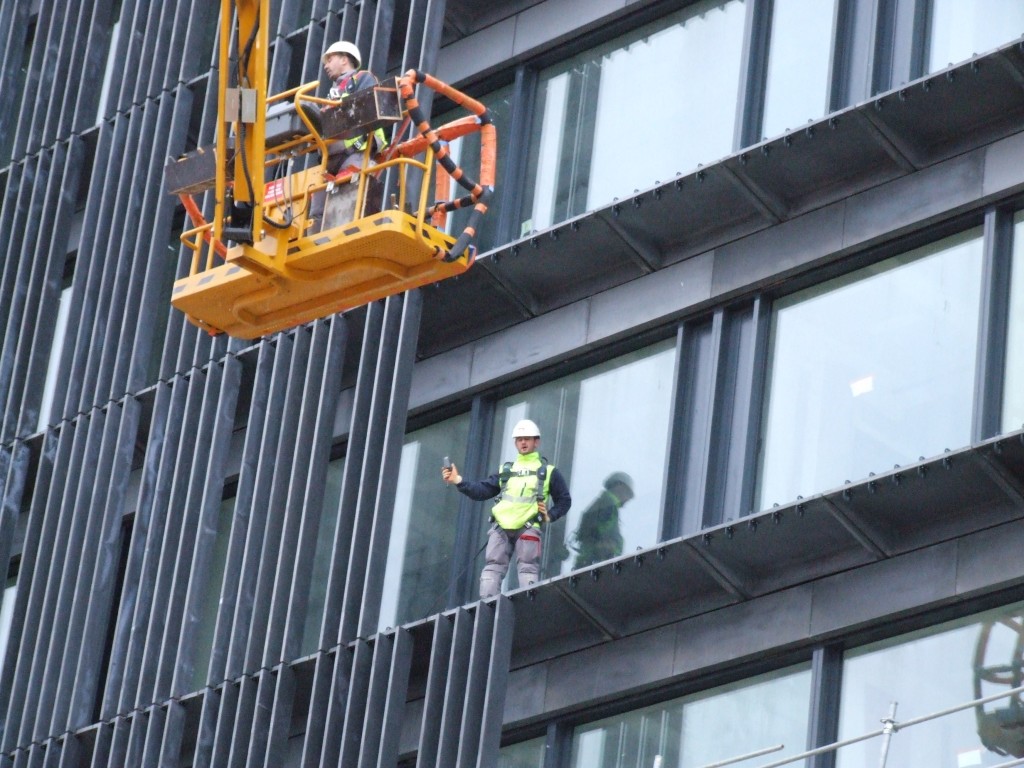
Installation of vertical sunshades
2012-02-03 - Vertical sunshades are positioned by crane and bolted into place along the northwest façade of the ITER Headquarters building. When the work is finished, the shades will create 14-metre-tall vertical lines. Photo: AIF.AM
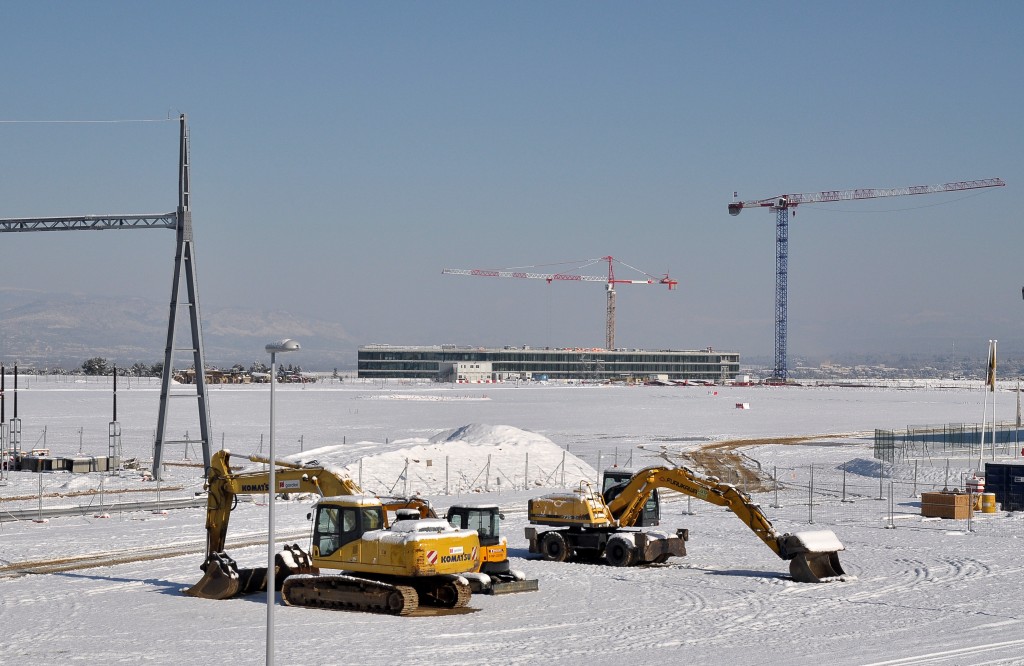
The permanent ITER Headquarters building
2012-02-01 - Across a quiet platform, work continues on the inside of the future ITER Headquarters.
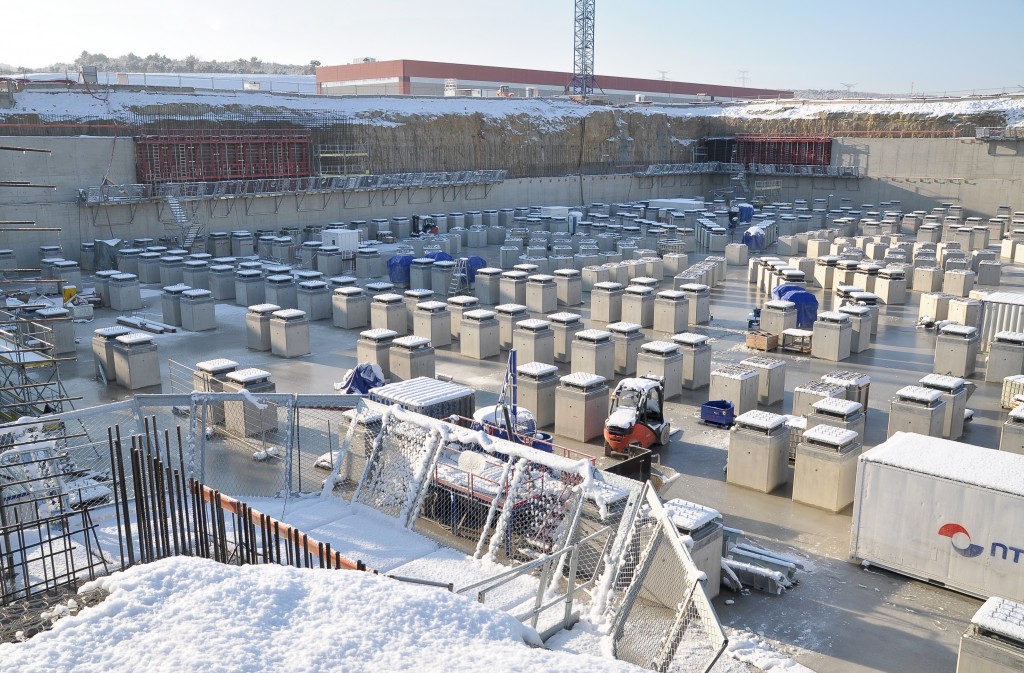
Instead of a flurry of activity ... flurries of snow
2012-02-01 - Activity in the Tokamak Pit is briefly halted as construction teams await better conditions for concrete pouring.
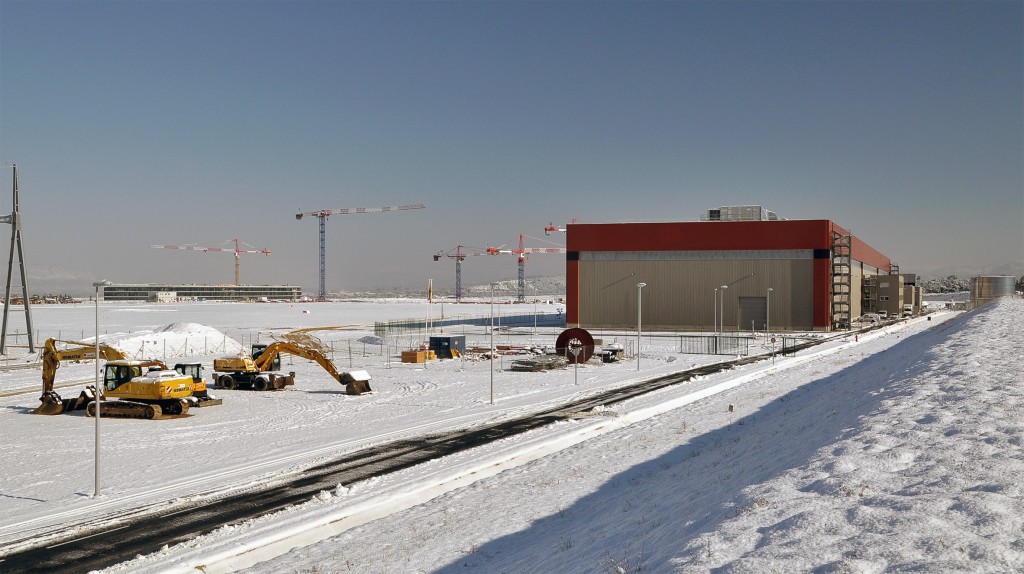
It's done
2012-02-01 - Snow hasn't hampered the works on the Poloidal Field Coils Winding Facility: the building is now completed and awaits handover from the building contractors (the French consortium Spie Batignolles, Omega Concept and Setec) to the European Domestic Agency for ITER, Fusion for Energy.

Looking towards the Hot Cell Facility
2012-01-19 - In this second excavated area—adjacent to the Tokamak Pit—the ITER Hot Cell Facility will be erected. Photo: F4E

Tokamak star
2012-01-12 - Among the "standing soldiers" at the bottom of the Tokamak Pit, it's easy to distinguish the future location of the machine by the spokes that branch out from a central plinth.
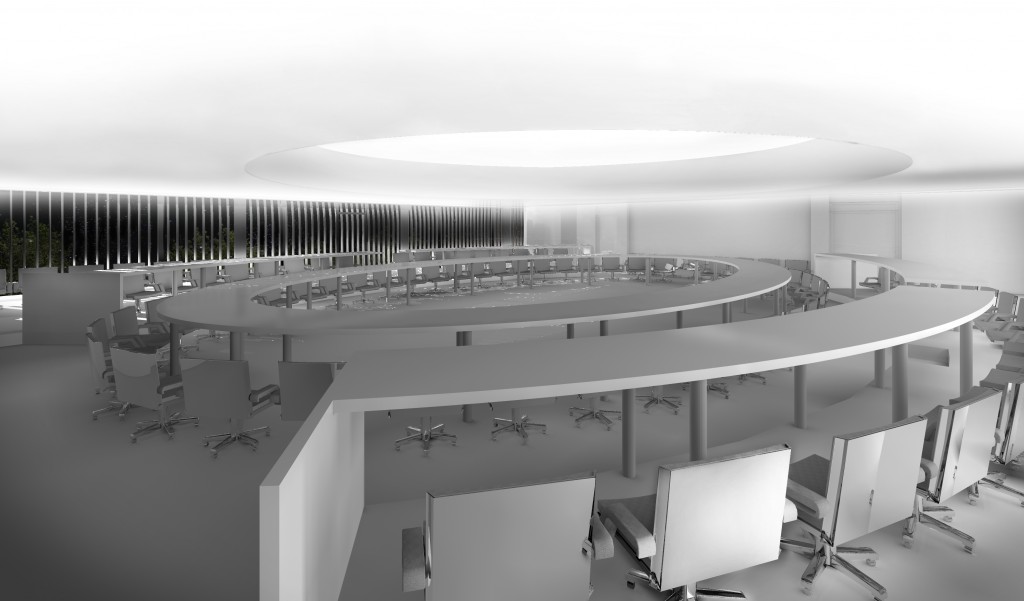
The eleventh ITER Council will be held here in November 2012
2012-01-12 - The architect's vision of the future Council Room located on the top floor of ITER Headquarters. ©Ricciotti
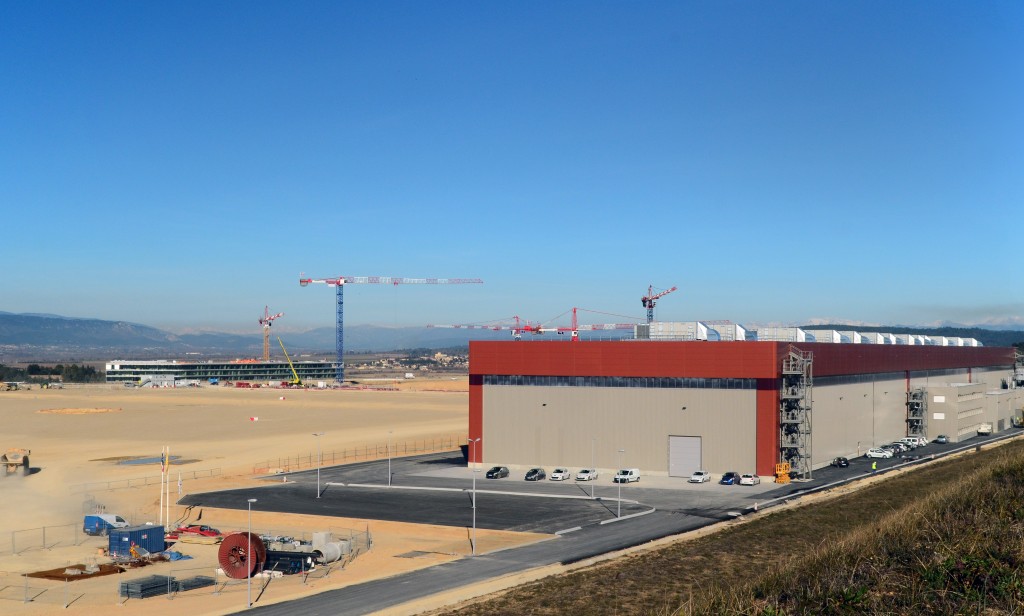
Exterior work completed
2012-01-12 - Roadwork has now been completed around the Poloidal Field Coils Winding Facility.
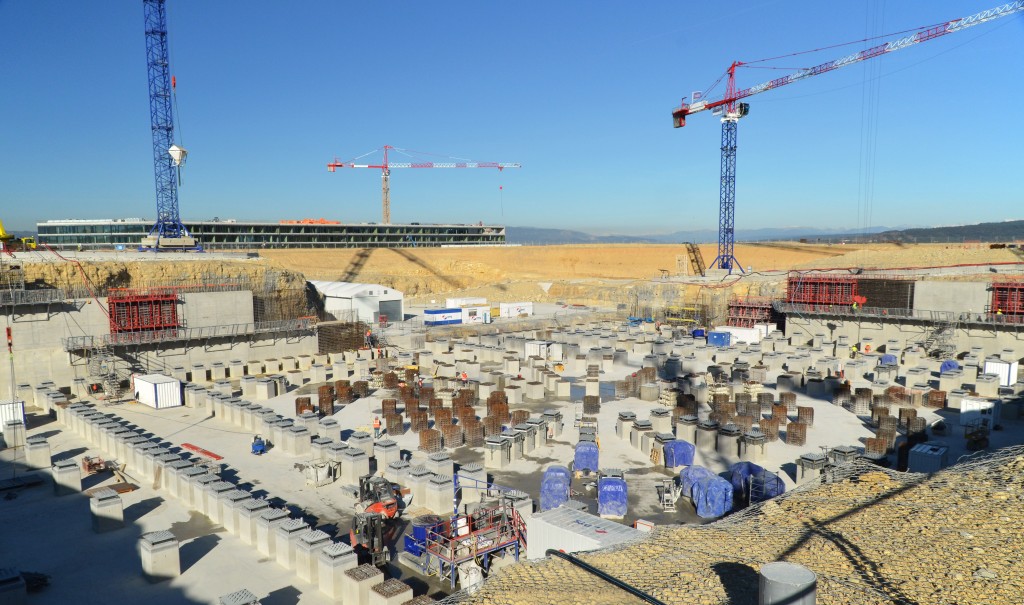
Progress in the Tokamak Pit
2012-01-12 - The 1.5-metre-thick Seismic Pit basemat is now completed, work on the retaining walls advances, and 385 out of 493 concrete plinths have been cast.

Second-stage pouring
2012-01-12 - The second five metres of retaining wall seamlessly join the first in one corner of the Seismic Pit.
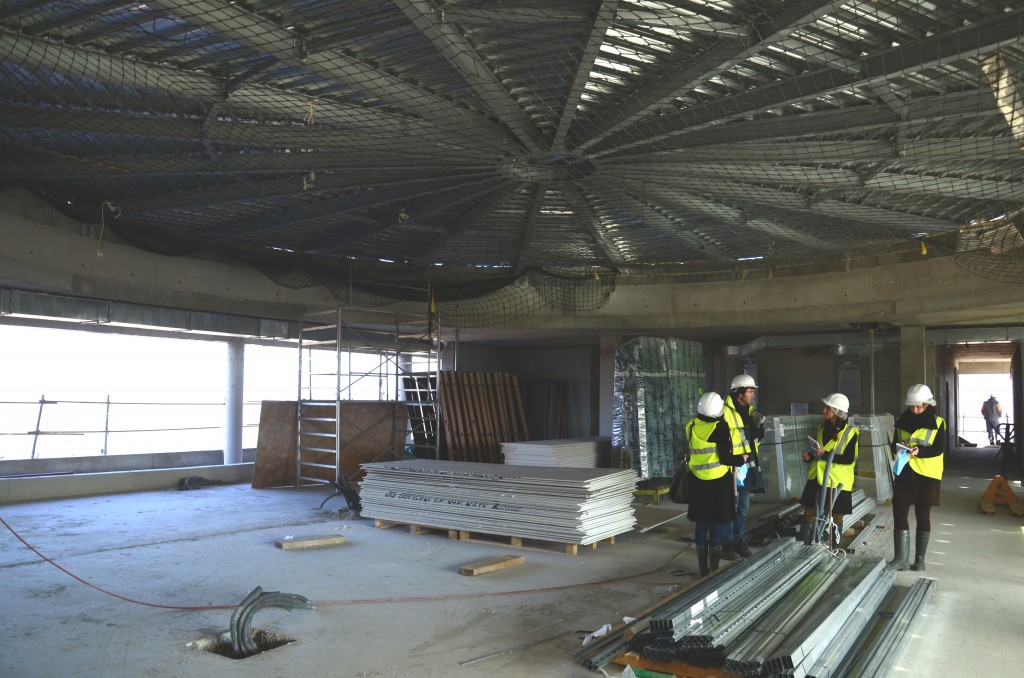
Under the round ceiling of the Council Room
2012-01-12 - On the top floor of the building, a circular Council Room for 80 is under construction.
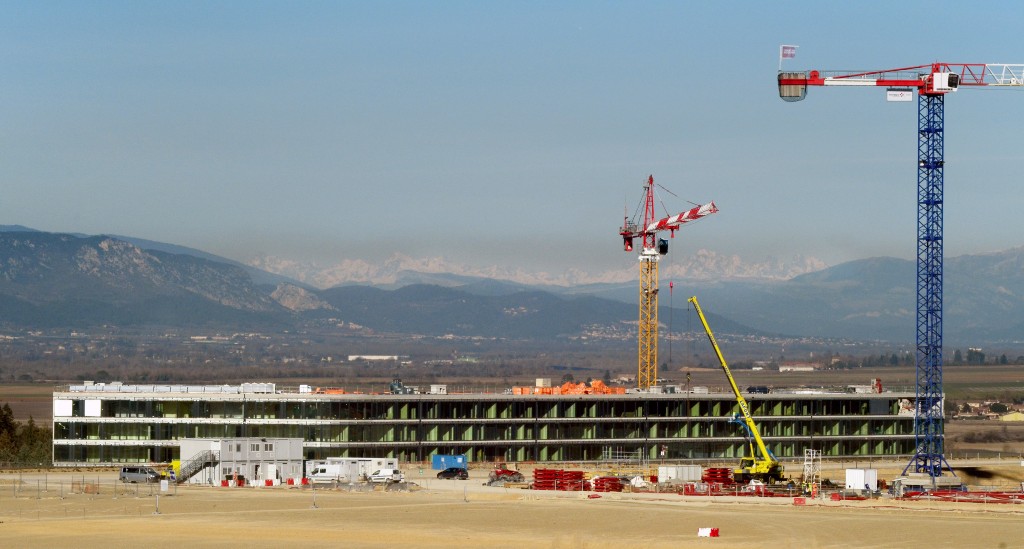
Seen from across the platform
2012-01-12 - On the top left of the building, work begins to install the exterior venetian blinds that will protect the offices from Provence's 300 days of strong sunlight per year.
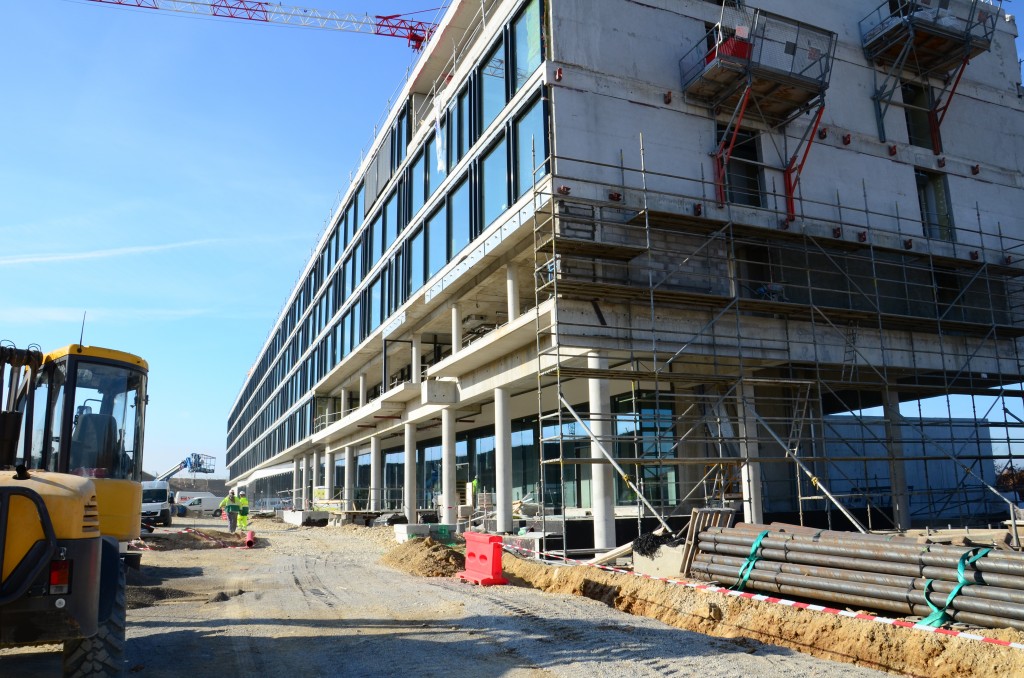
Enter from this side
2012-01-12 - The future entrance to the ITER Headquarters on the northeast corner of the building.
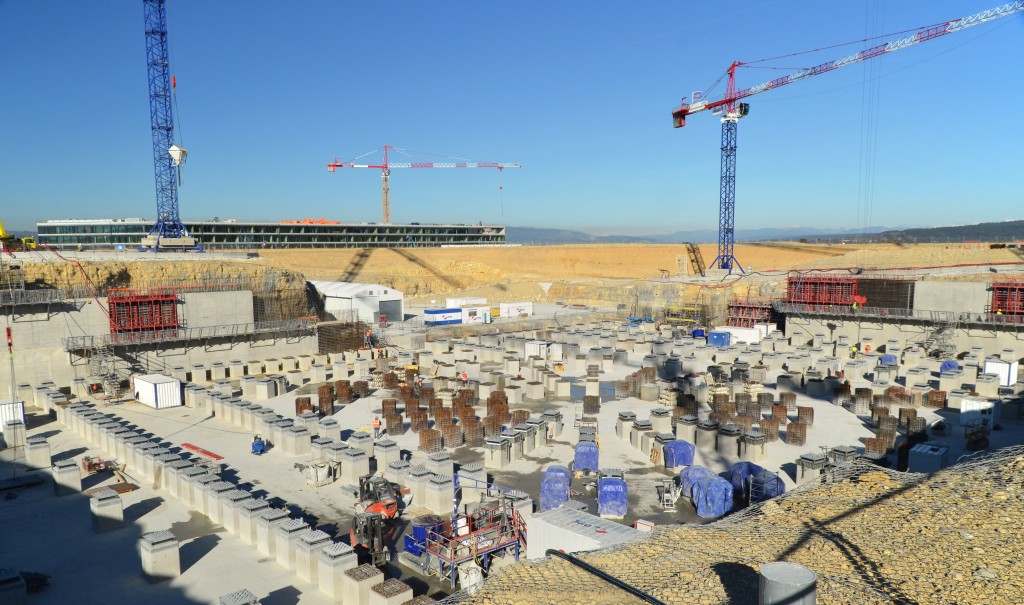
Rooms with a view
2012-01-12 - The top floors of the Headquarters building will have an unparalleled view of the 39 buildings and facilities that make up the ITER fusion laboratory.
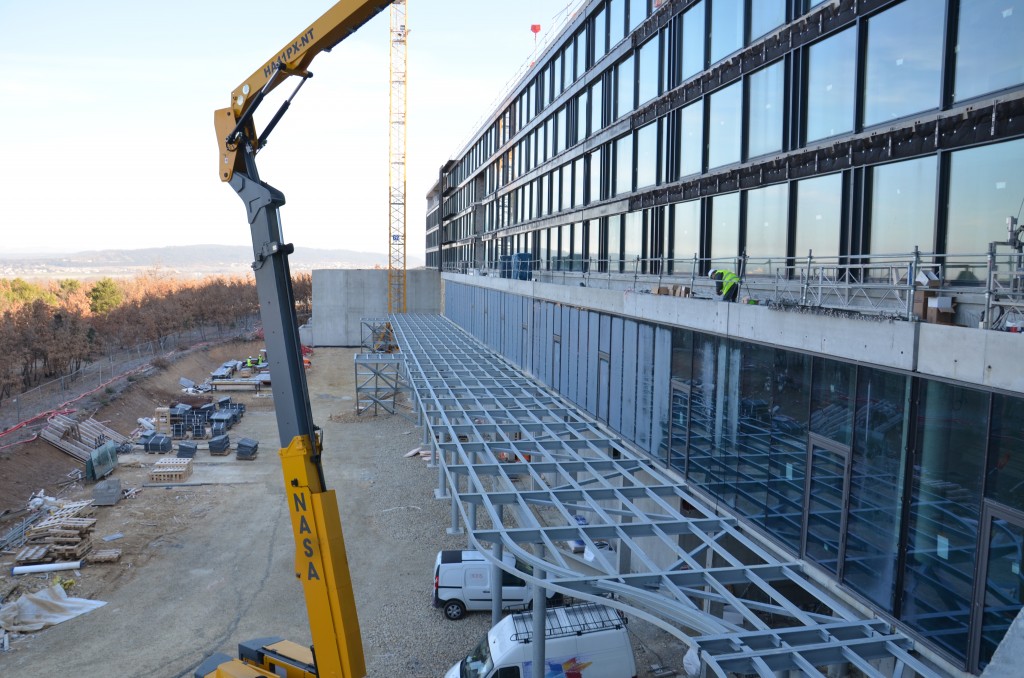
The ITER canteen
2012-01-12 - Workers install the metal structure that will support a terrace accessible from the canteen.

End of March
2012-01-04 - Work on the retaining walls of the Seismic Pit should be completed by March. Photo: F4E
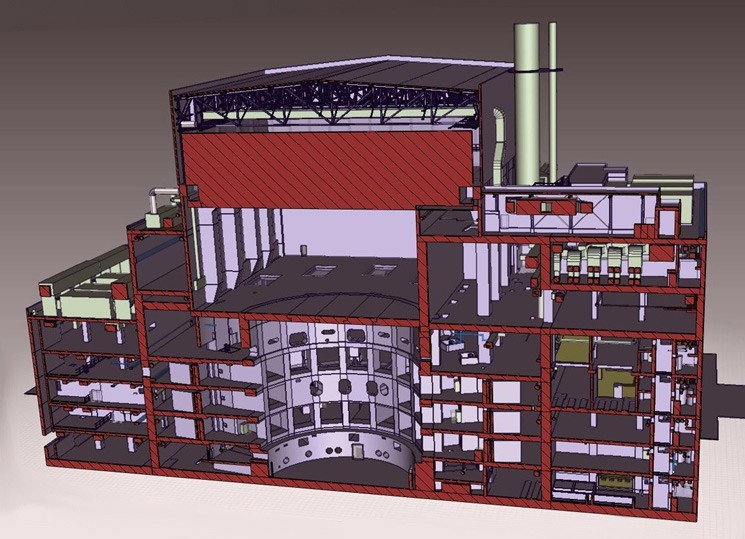
The ITER Tokamak Complex
2012-01-01 - Seven storeys tall—including two basement levels—the ITER Tokamak Complex is in fact three buildings: the Tokamak Building (centre), the Tritium Building (left) and the Diagnostics Building (right).
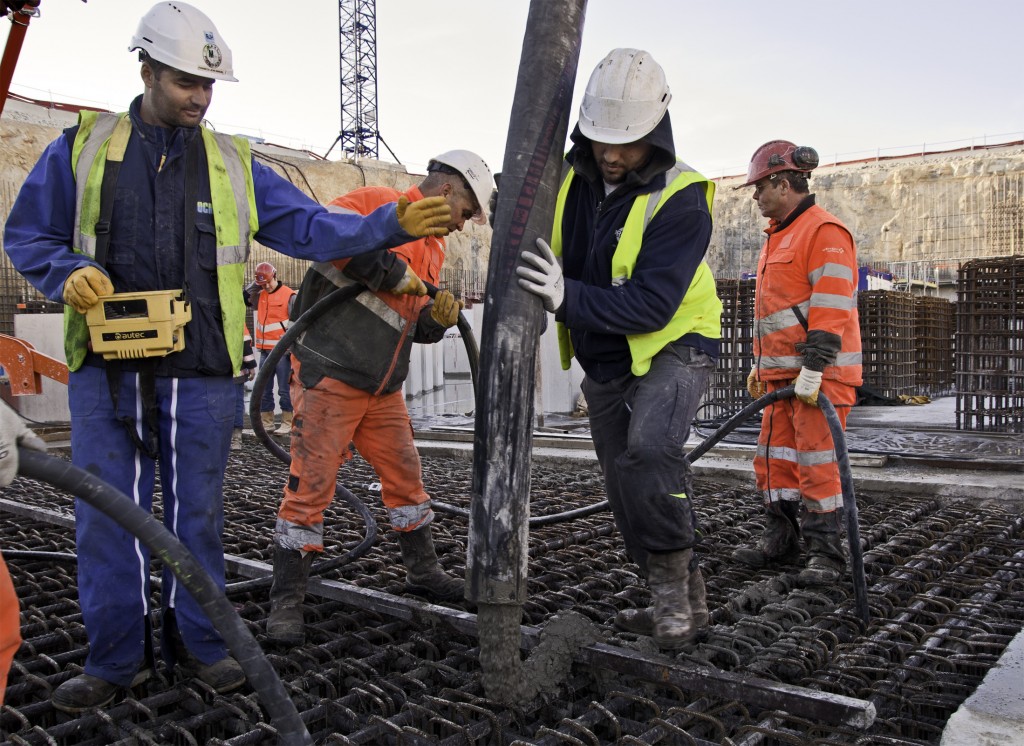
The final pour
2011-12-22 - Three-and-a-half months were necessary to complete the 1.5 metre-thick Seismic Pit basemat. The works underwent regular inspection: both internal audits and those conducted by the French nuclear safety regulators (ASN) have confirmed the good quality of the works.
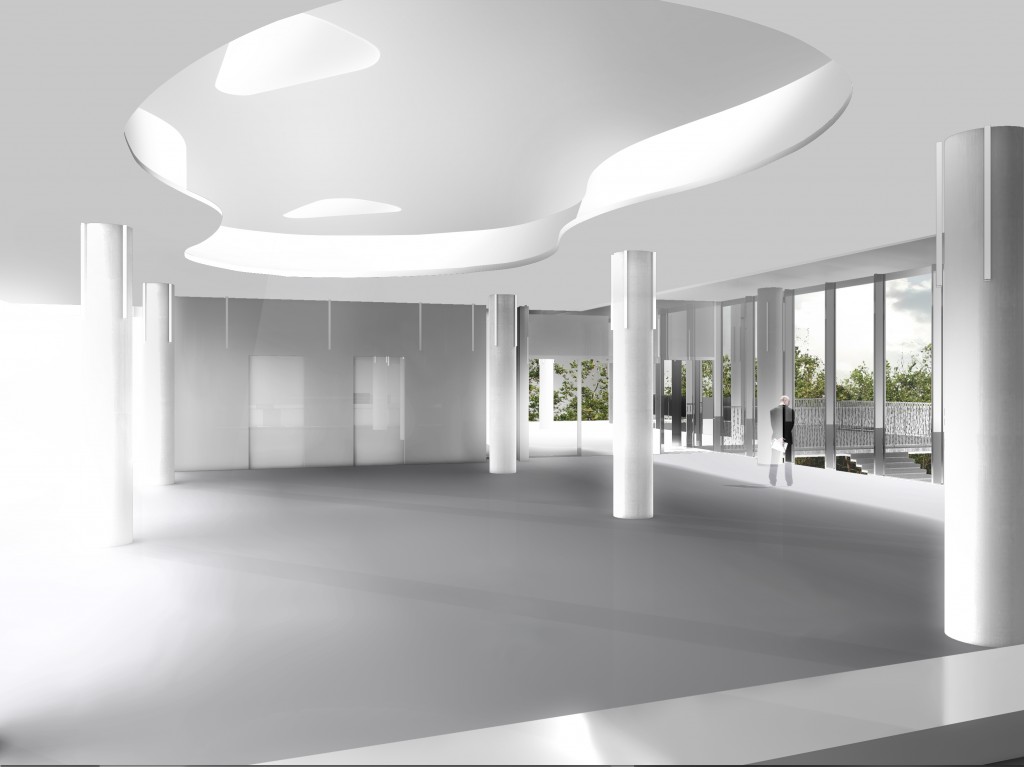
In a few months
2011-12-22 - The architect's drawing of the ITER Headquarters entrance hall. ©Ricciotti
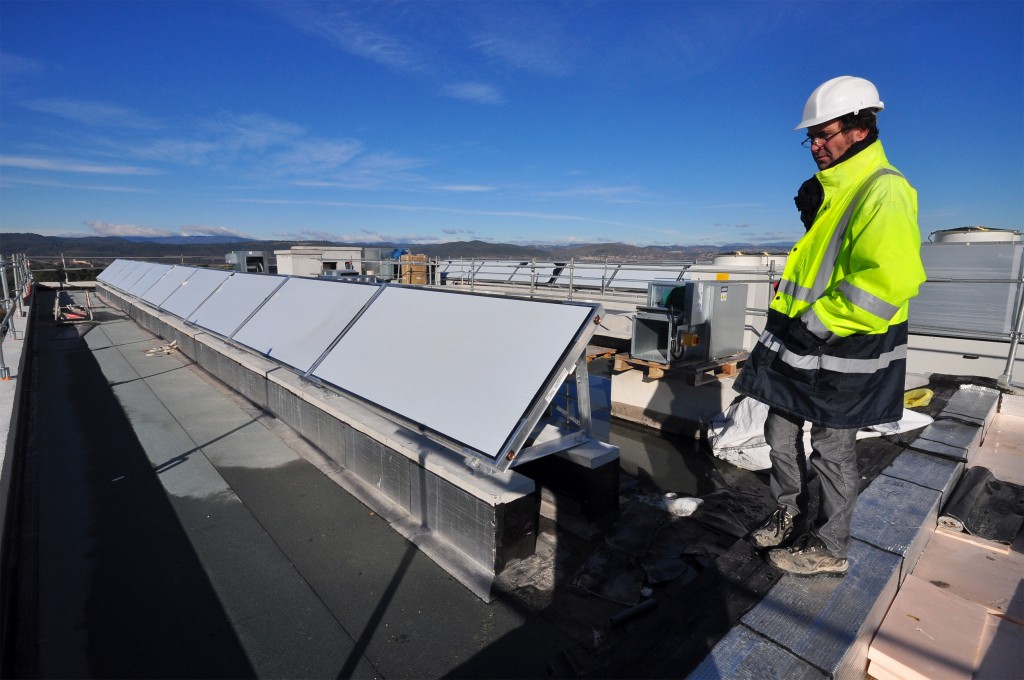
Hot water, anyone?
2011-12-22 - Seventy-five metres of solar panels installed on the roof will furnish the cafeteria's needs in hot water.
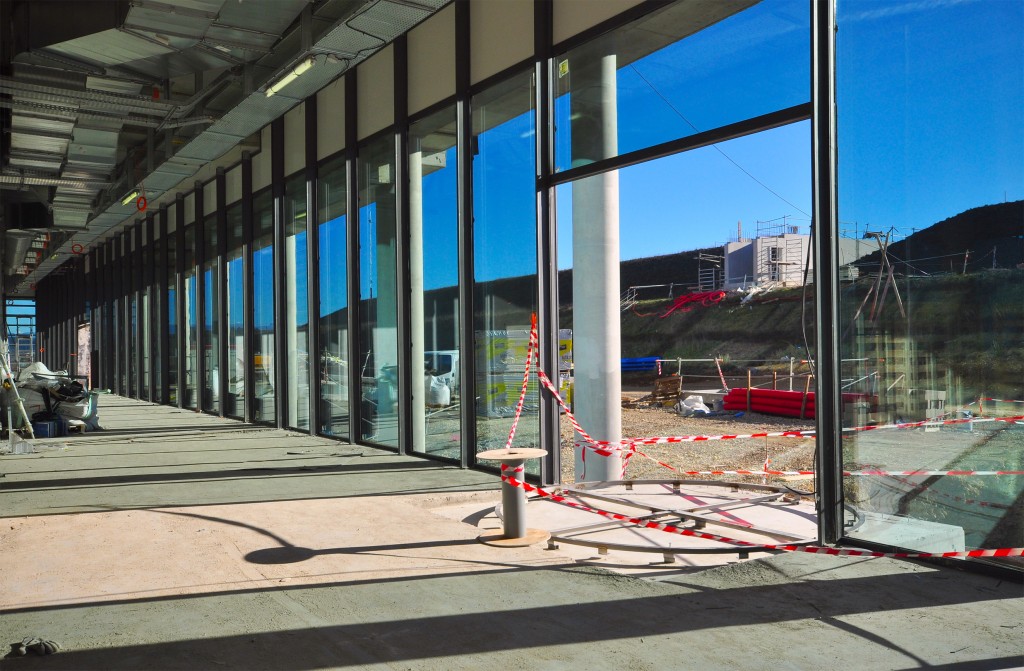
Ground floor entry hall
2011-12-22 - The bright and spacious entry hall of the ITER Headquarters building faces the platform. Elevators heading from this area to the upper floors have already been installed.
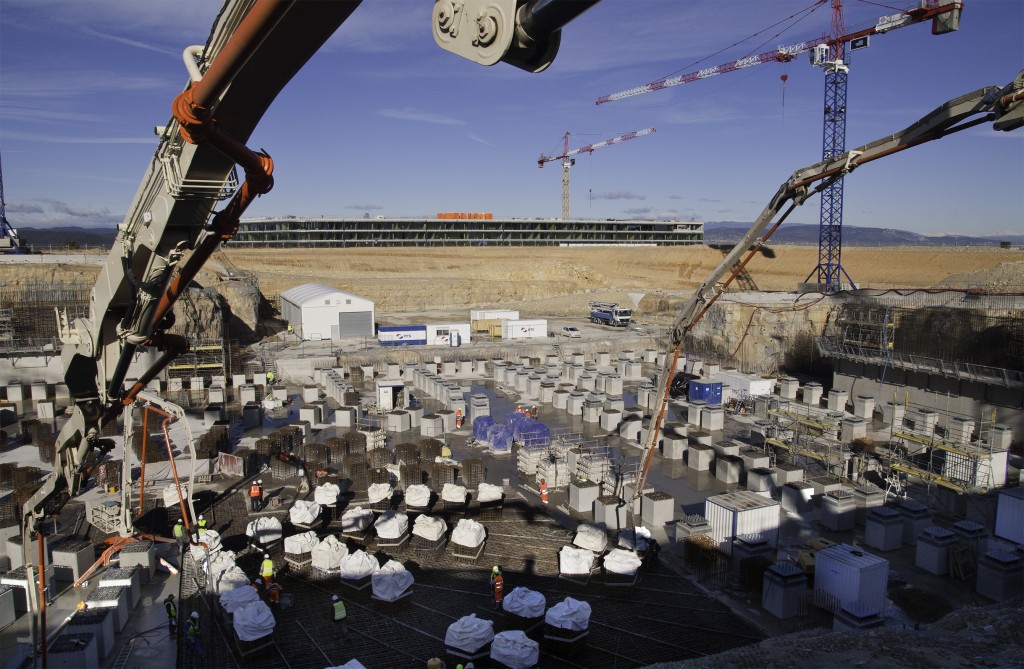
The last segment is poured in December
2011-12-22 - The lower basemat of the Seismic Pit was completed on 22 December, as workers pour the twenty-first and final segment.
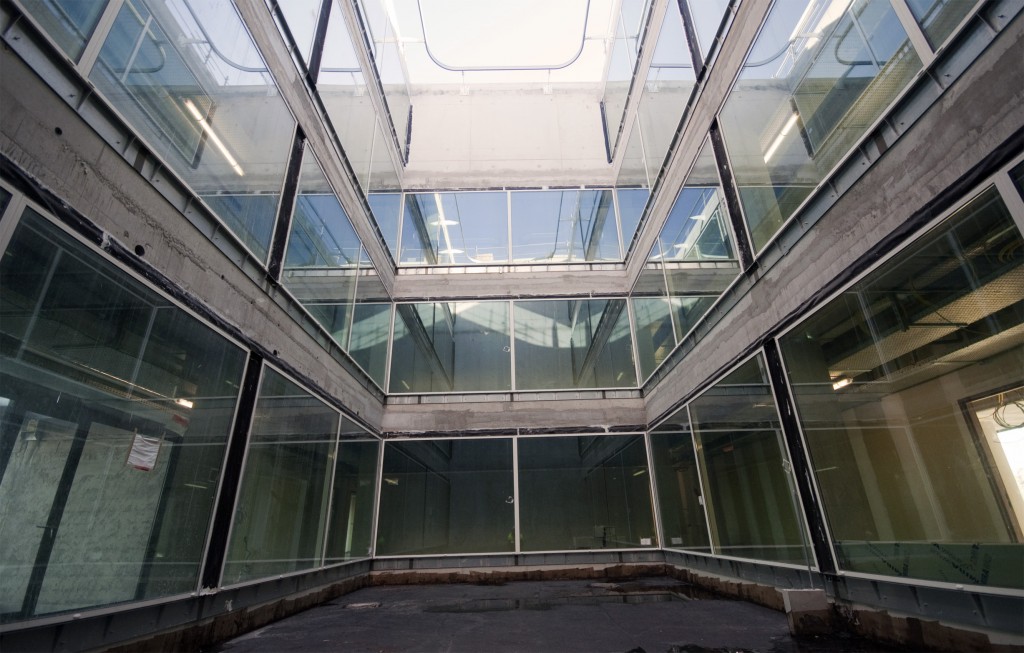
Light for the interior of the building
2011-12-22 - The installation of bay windows in the six interior patios was completed in December.
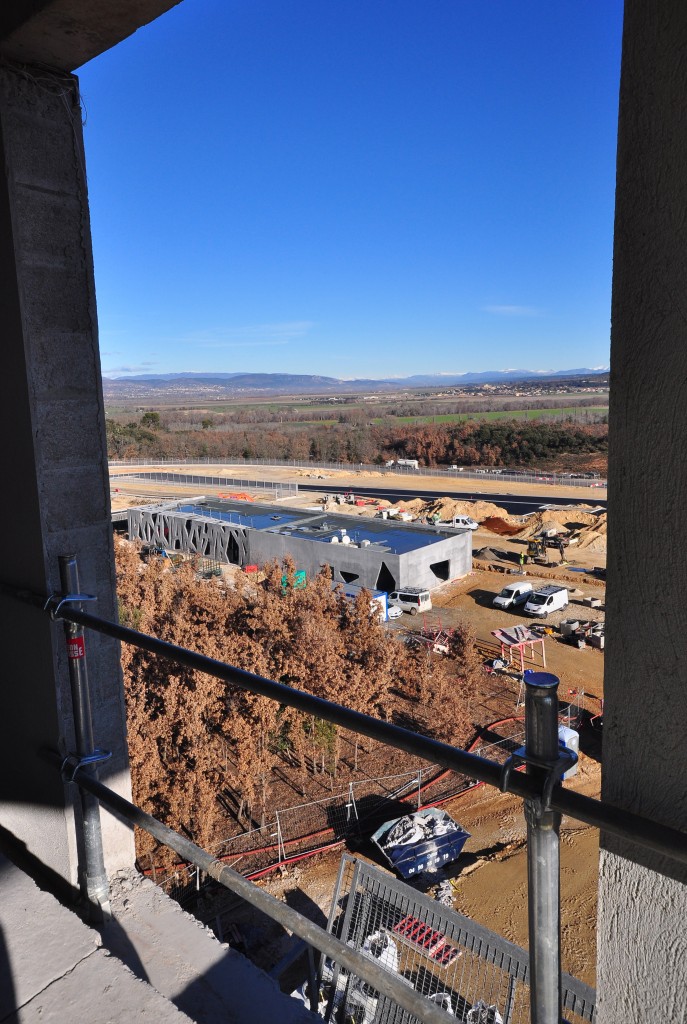
From the top floor looking down
2011-12-22 - Far below, the Site Access Control Building (not yet equipped with its "green" roof).
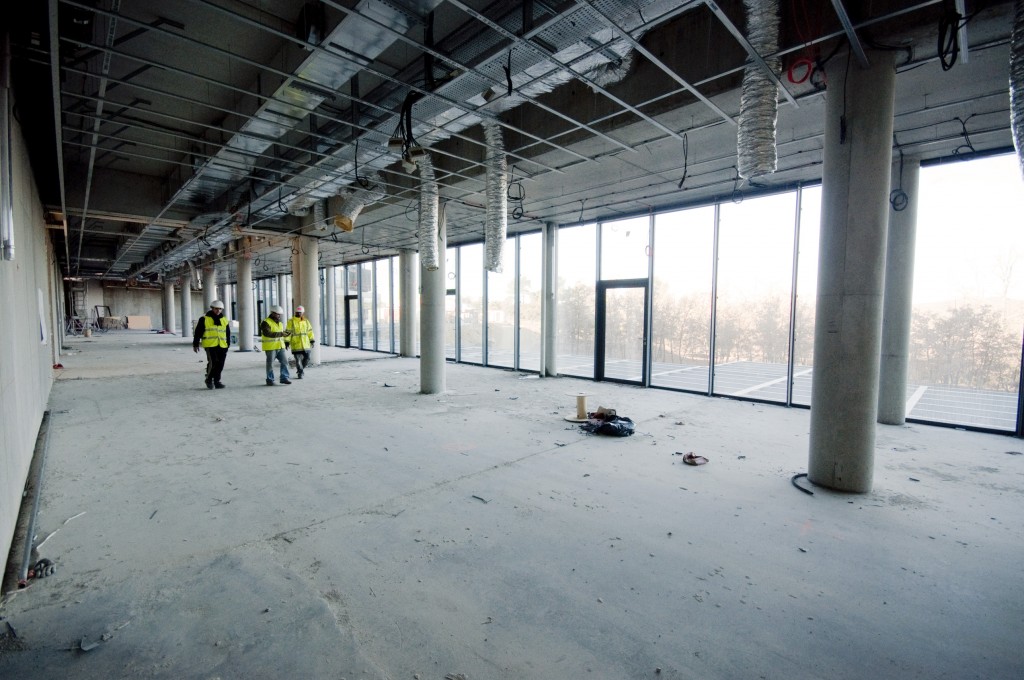
A cafeteria catering to 1,000
2011-12-22 - Occupying the first floor of the building, the cafeteria spans its entire width from east to west. The doors visible in this photograph exit to an outside terrace and stairs down to a grassy area.
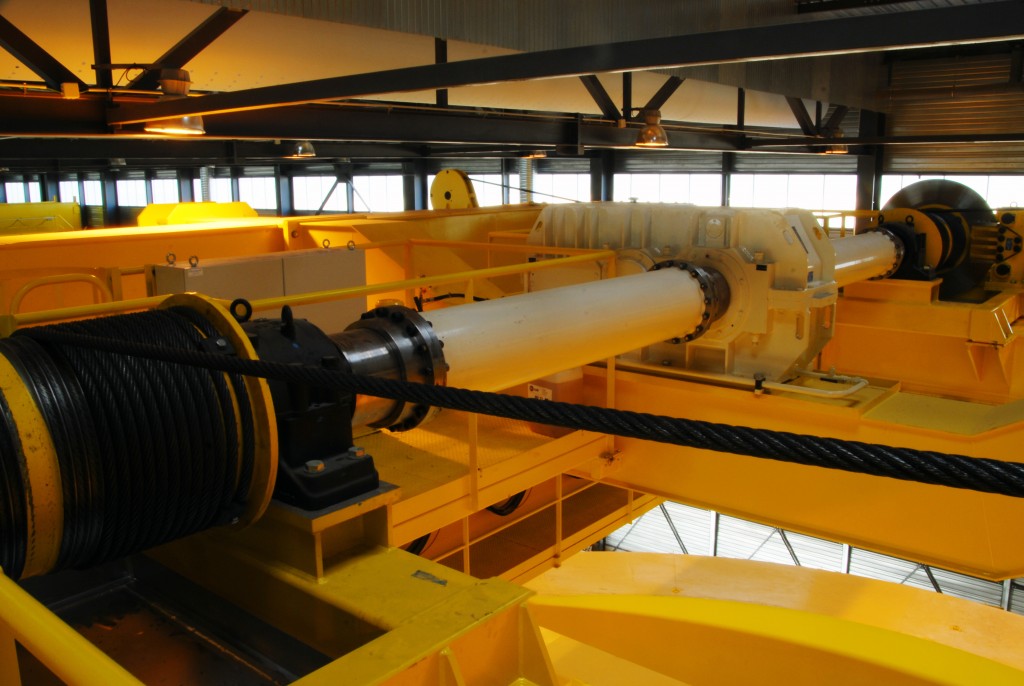
Bring out the heavyweights
2011-12-21 - Heavy winches and cables support the weight of the 40-ton spreader beam, which will be used during the assembly stage of coil manufacture. Photo: F4E
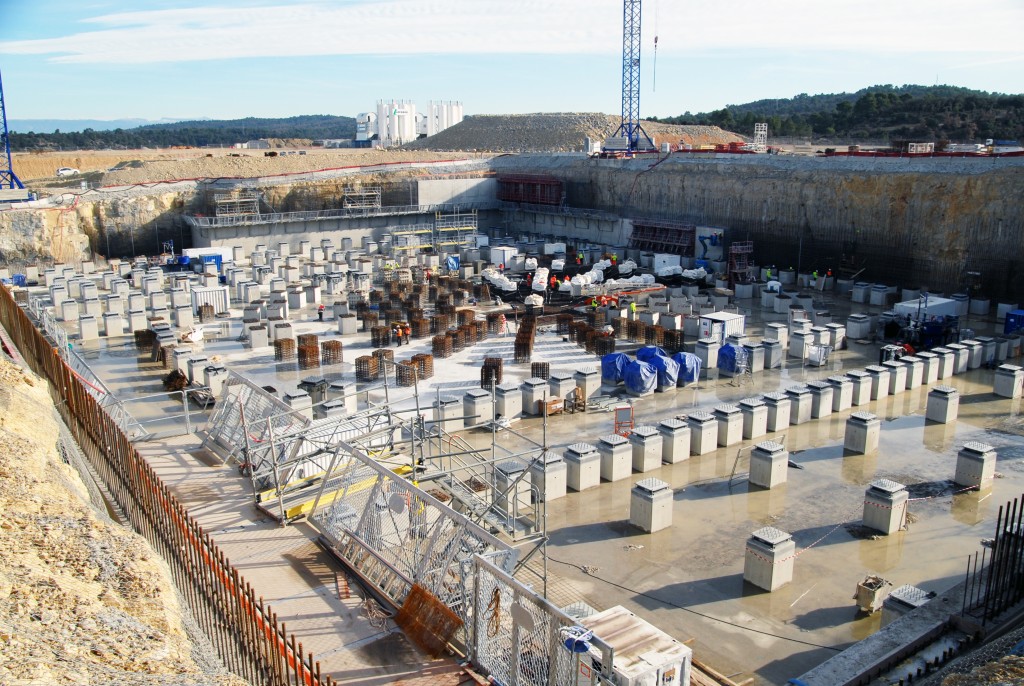
Under the ITER Tokamak
2011-12-21 - The 140 "oriented plinths" in the centre of the basemat are the last to be poured: these plinths will directly support the 23,000-ton ITER Tokamak. Photo: F4E

Operations to begin this year
2011-12-21 - The completed interior of the Winding Facility. In this 257-metre-long building work will begin in late 2012 on the winding and assembly of five poloidal field coils (PF2, 3, 4, 5 and 6). Photo: F4E
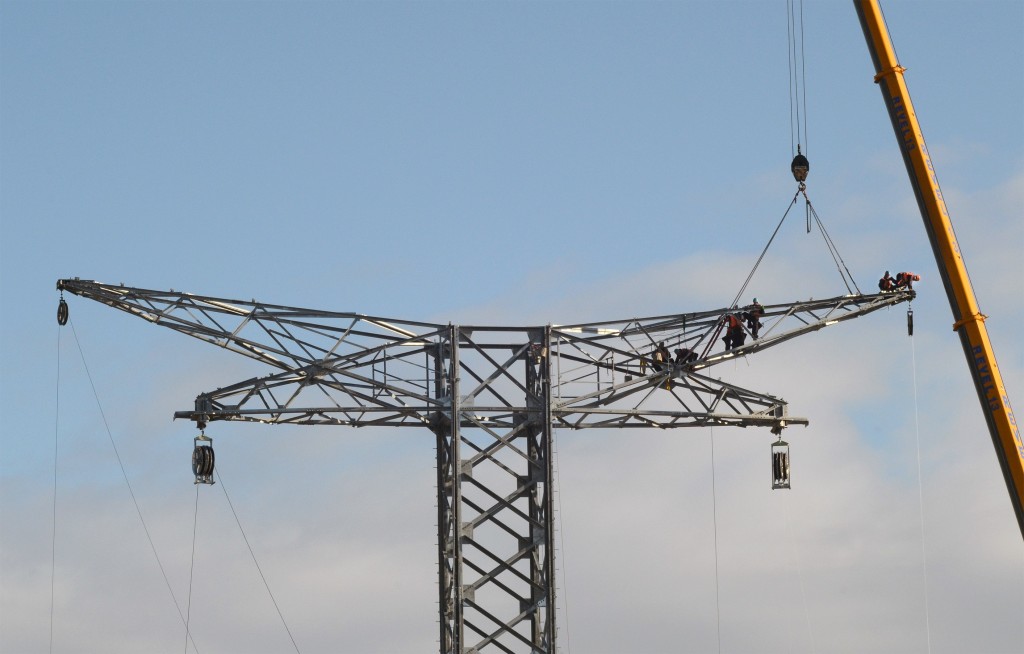
120-tonne giant
2011-12-15 - The first 120-tonne pylon is erected in December 2011 by aerial acrobats; twelve more like this are necessary to link the ITER facilities to the 400 kV power line six kilometres distant.

Drive on in!
2011-12-12 - Trucks delivering the raw material for coil manufacture—niobium-titanium conductor—will enter the facility through this door and unload in a dust-free environment. Photo: F4E
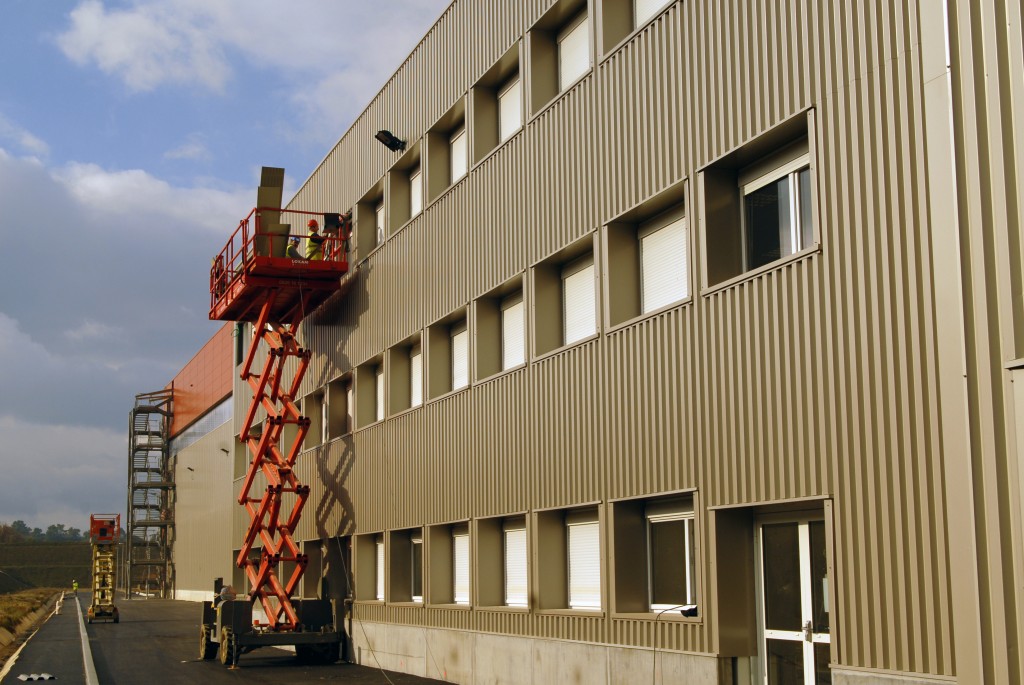
Offices ready
2011-12-12 - Office space for 100 people is located along the south-eastern wall of the building. Photo: F4E

Last completed edge
2011-12-12 - Exterior stairwell, paved roads ... the last touches to the Poloidal Field Coils Winding Facility are carried out before handover on 14 February. Photo: F4E
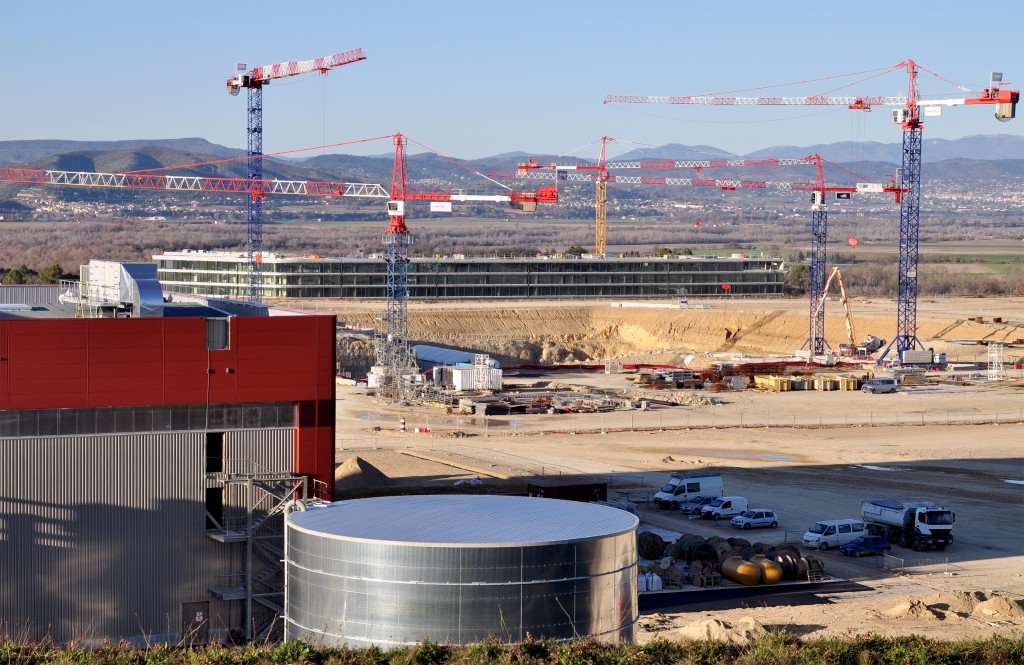
One year of progress in a picture
2011-12-08 - The three projects that transformed the ITER platform in 2011: the PF Coils Winding Facility (foreground); the Tokamak Pit excavation and foundation work (centre); and—in the distance—the ITER Headquarters.
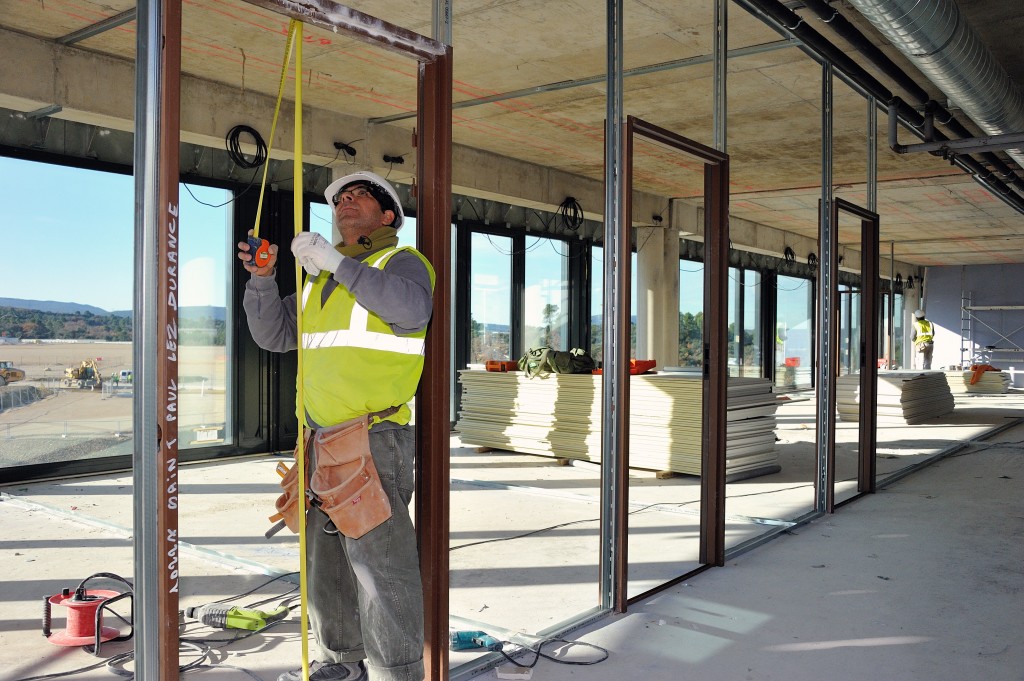
Door frames and interior fittings
2011-12-06 - Door frames are installed for the platform-facing offices. Next step: interior walls. ©VPaul
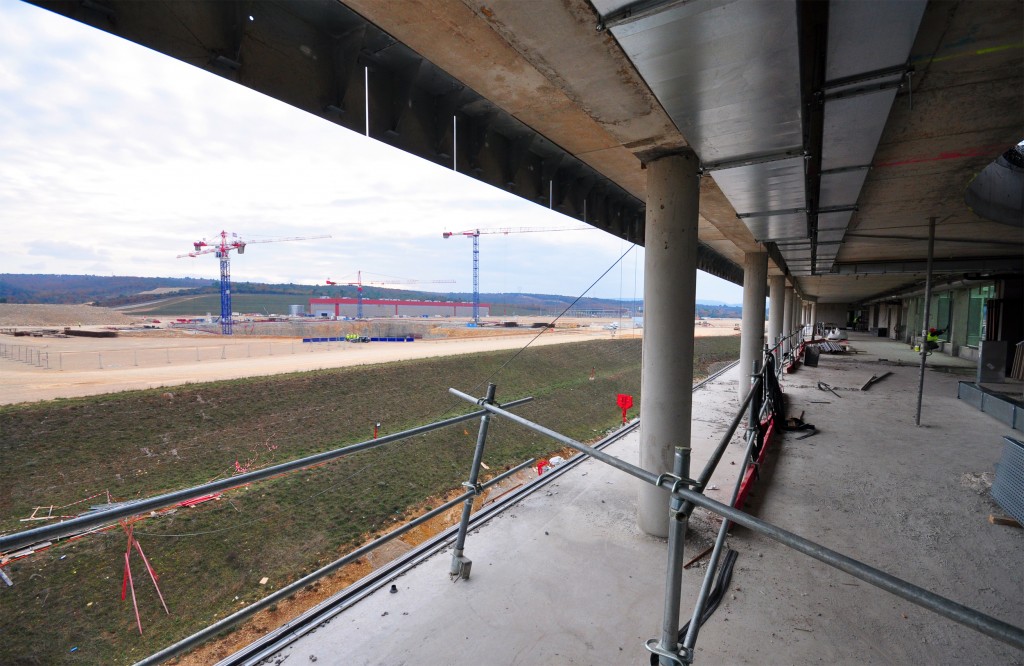
An eagle-eye view
2011-12-01 - From the upper floors of the ITER Headquarters, the view over the platform is spectacular.
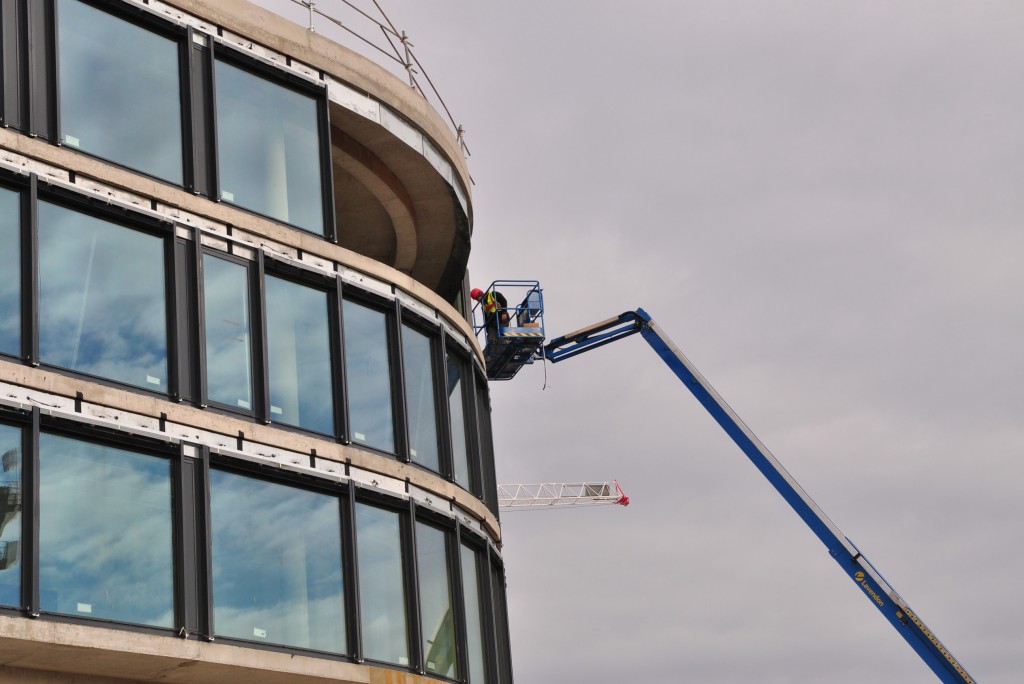
Work completed on the windows
2011-11-29 - The last windows are installed along the curved south-eastern face of the building in December 2011.
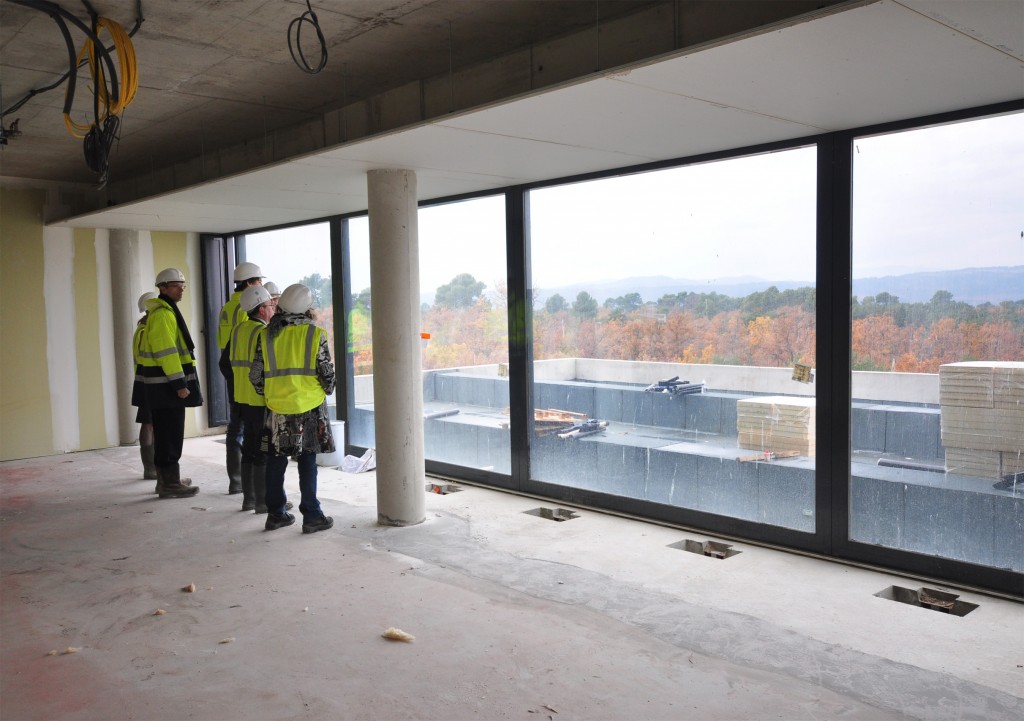
Interior fittings underway
2011-11-29 - Looking out from one of the large, open-plan offices on the west side of the building.
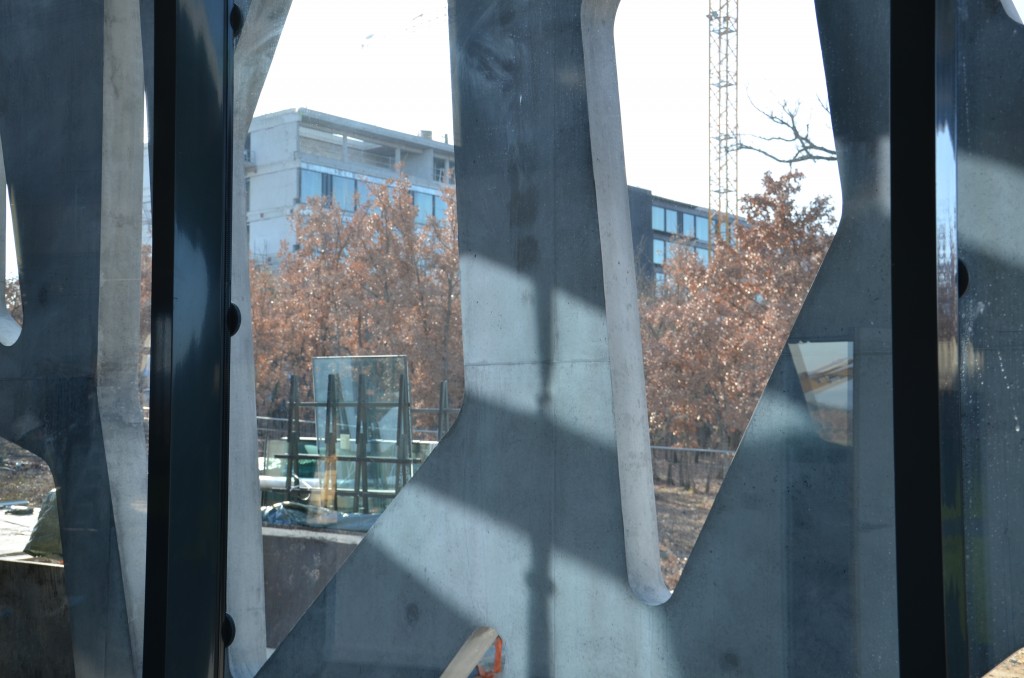
The seat of the ITER project
2011-11-29 - ITER Headquarters, seen through the atypical openings of the Site Access Control Building.
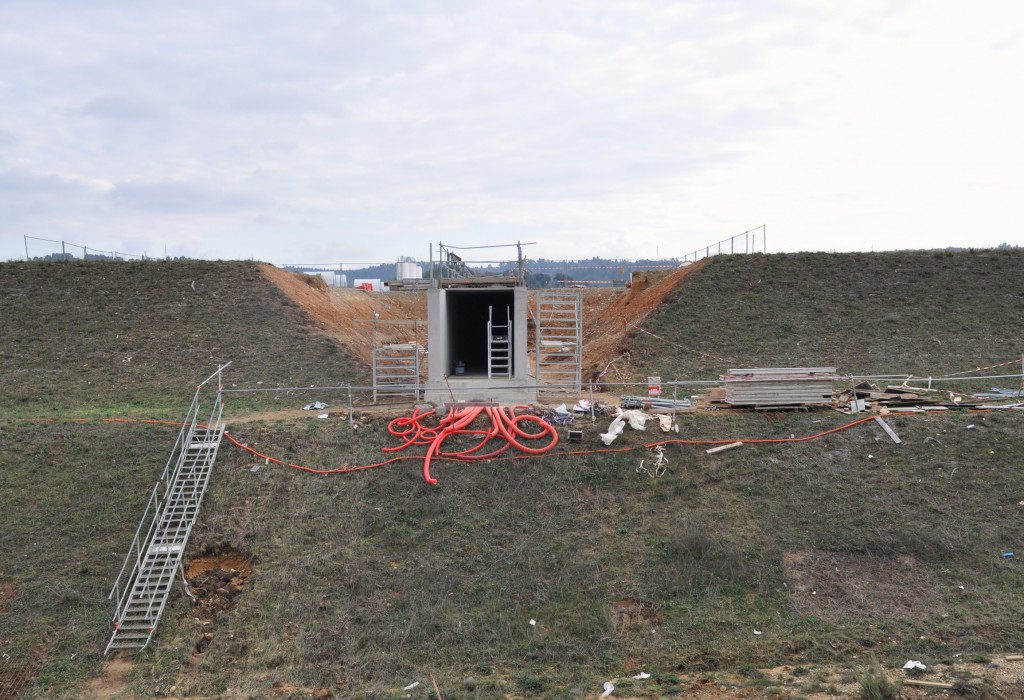
Through the tunnel
2011-11-29 - A 33-metre-long metal footbridge will connect Headquarters to this tunnel in the platform, which will lead to the ITER Control Room.
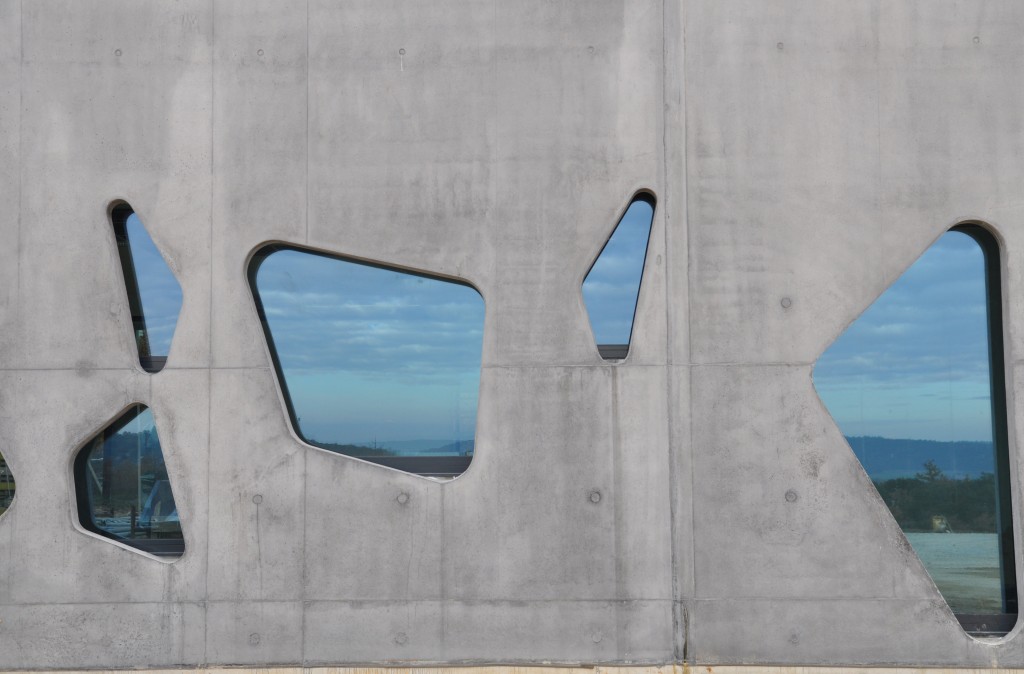
You'll make your first stop at ITER here
2011-11-29 - The 550m² Site Access Control Building will be equipped with a "green" roof to improve climate control.
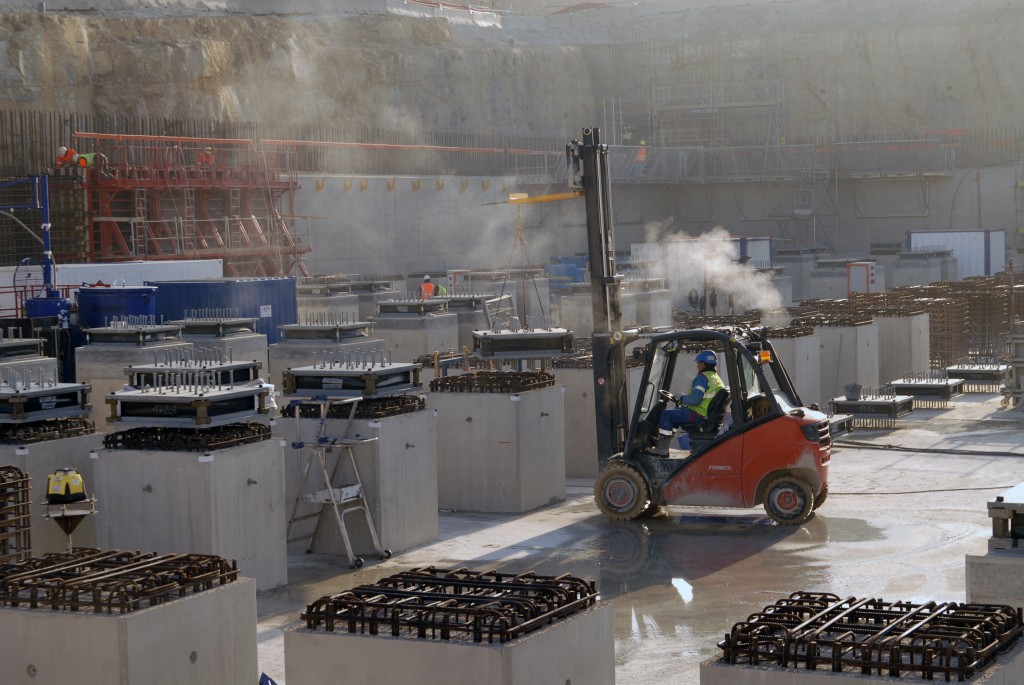
Careful measurements
2011-11-28 - The surface elevation, roughness (guaranteeing that the second-phase concrete will adhere perfectly) and height of the reinforcement at the top of the plinth are verified before each bearing is installed. Tolerance for these measurements is in the range of one millimetre. Photo: F4E
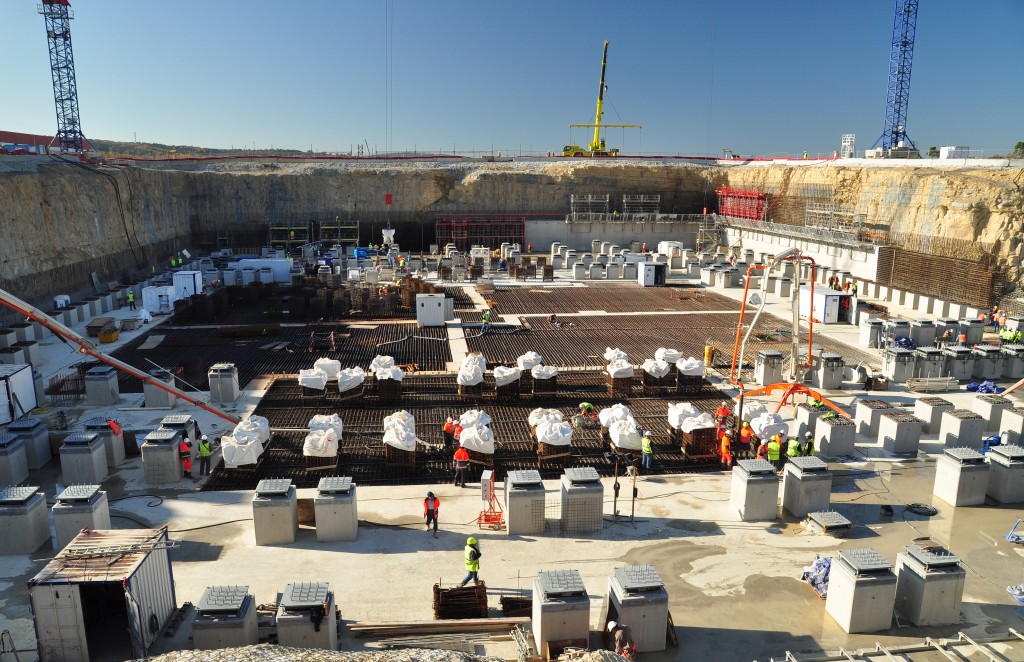
80% there
2011-11-23 - Late November 2011, the concrete slab at the bottom of the Tokamak Pit is 80 percent complete: 14,000 out of 17,000 cubic metres of concrete have been poured since August.
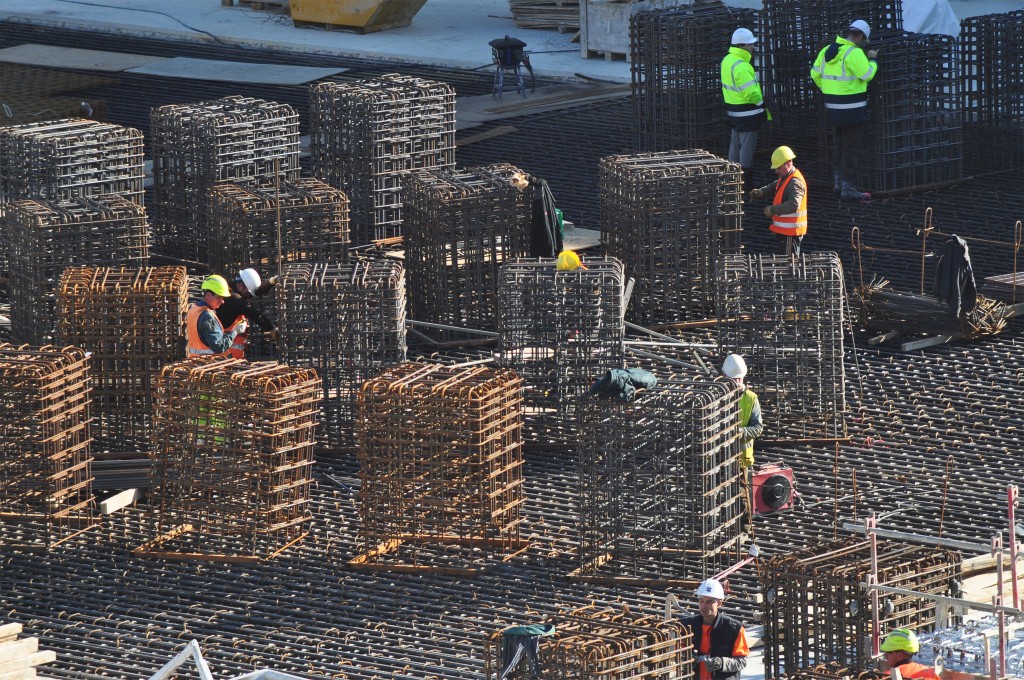
The shape of the Tokamak is distinguishable
2011-11-23 - In the centre of the Tokamak Pit, it's easy to distinguish the "spokes" of seismic reinforcement that will bear the weight of the ITER device.
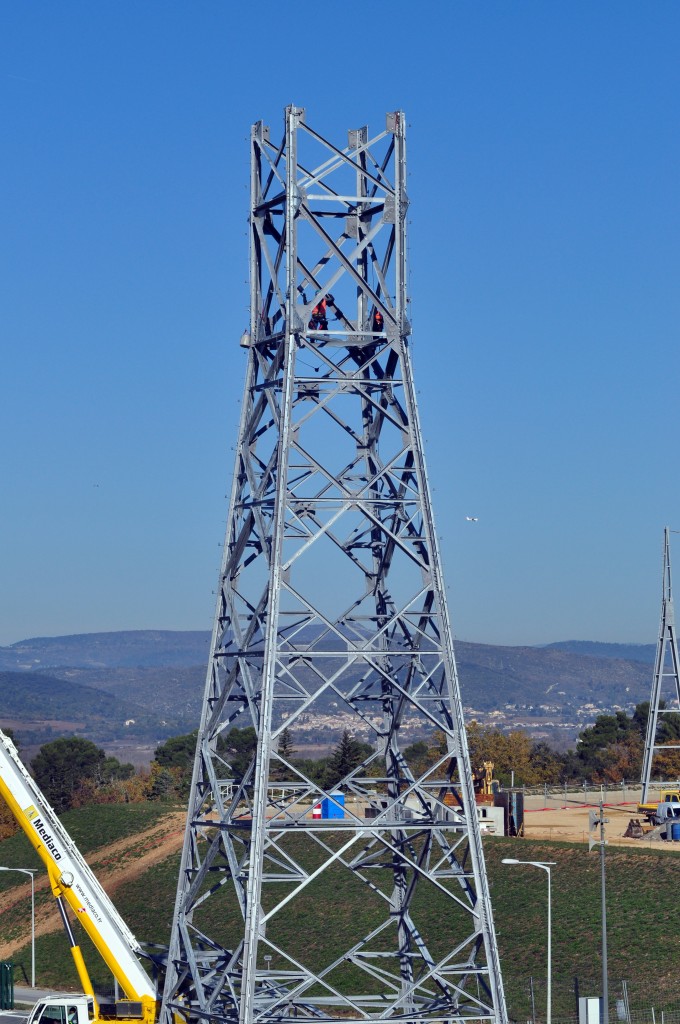
43 metres tall
2011-11-23 - Electrical supply to the ITER site will be assured by an existing network that feeds the Tore Supra Tokamak; a one-kilometre extension will be enough to link the ITER machine into the network. Operating the ITER Tokamak will require from 120 MW to up to 620 MW of electricity for peak periods of 30 seconds.
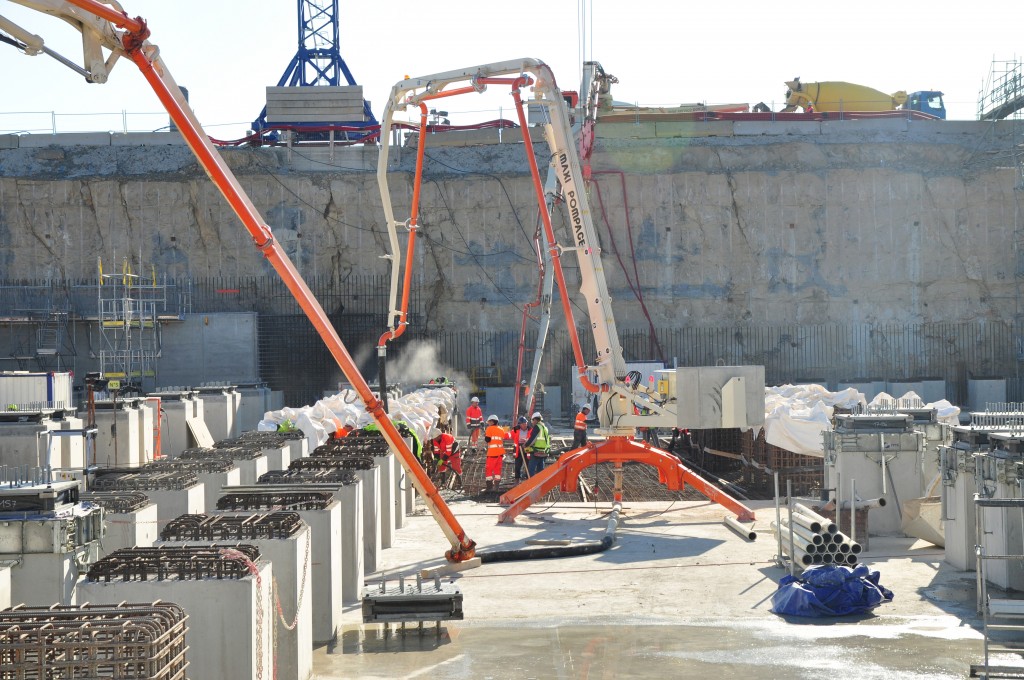
Double pumping
2011-11-23 - Concrete pouring for the Seismic Pit basemat progresses at a rhythm of one slab per week. The twenty-one slabs, once completed, will form a single, smooth surface.
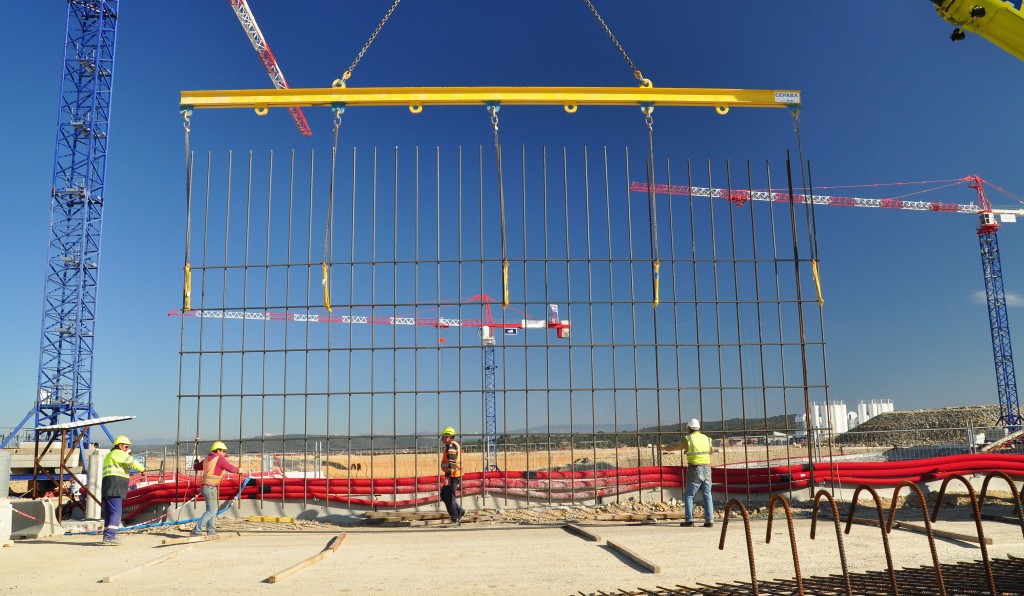
Reinforcing the walls
2011-11-23 - Cranes lower metal reinforcement for the retaining walls of the Seismic Pit.
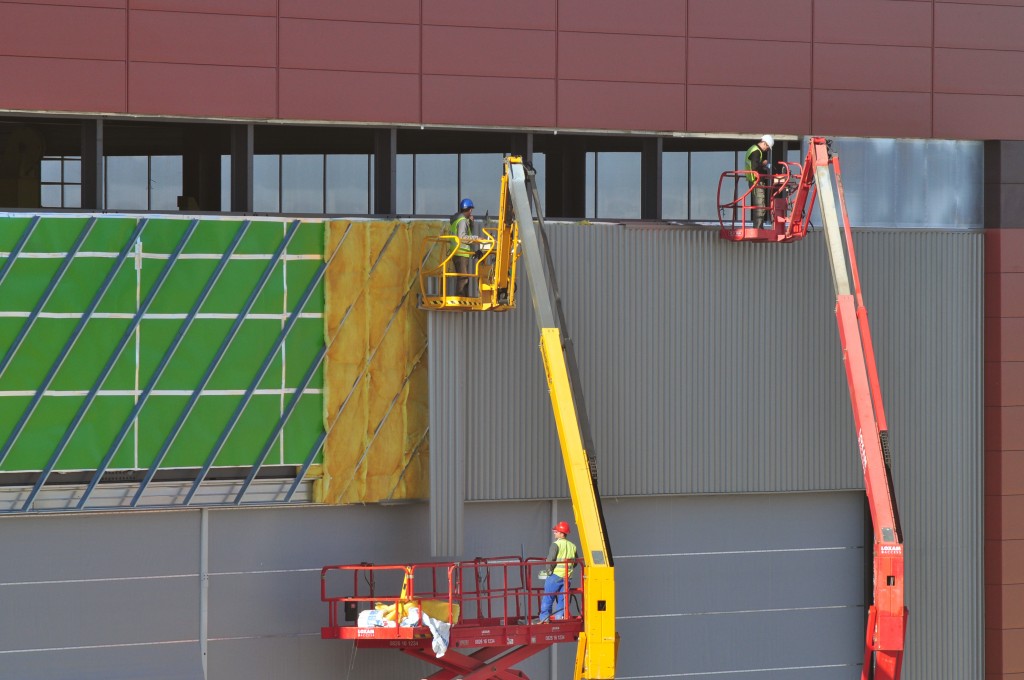
Cladding operations end
2011-11-23 - The bright colours of the Winding Facility disappear as the last layer of cladding is put into place.
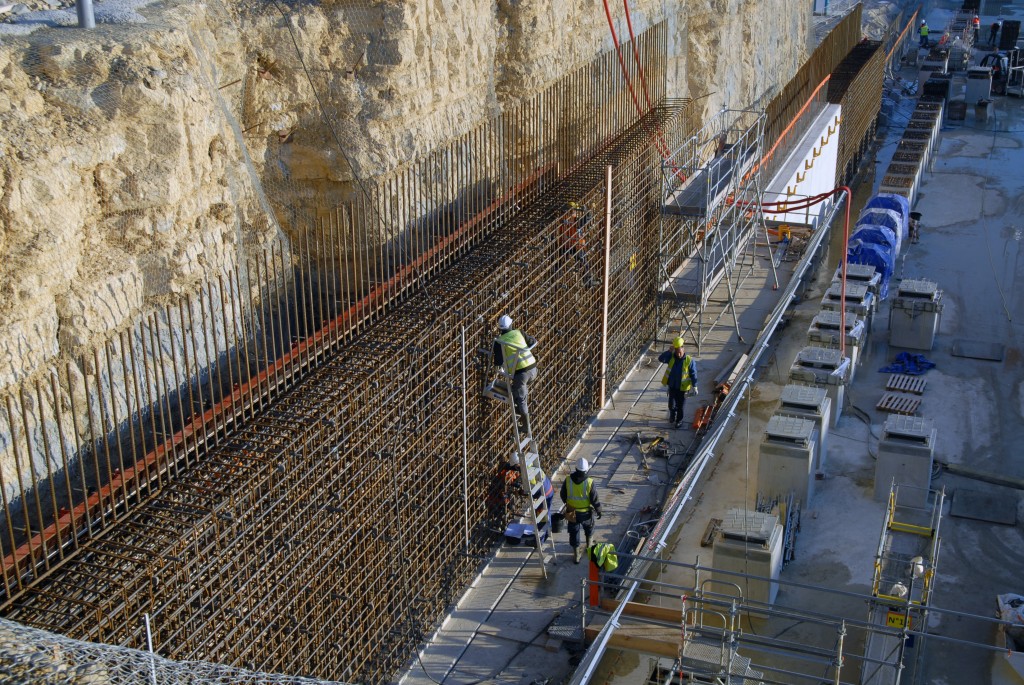
A concrete box
2011-11-18 - One and a half metres thick at their base, the retaining walls will form a box around the foundation slab of the Tokamak Pit and the anti-seismic pillars and bearings. Photo: F4E
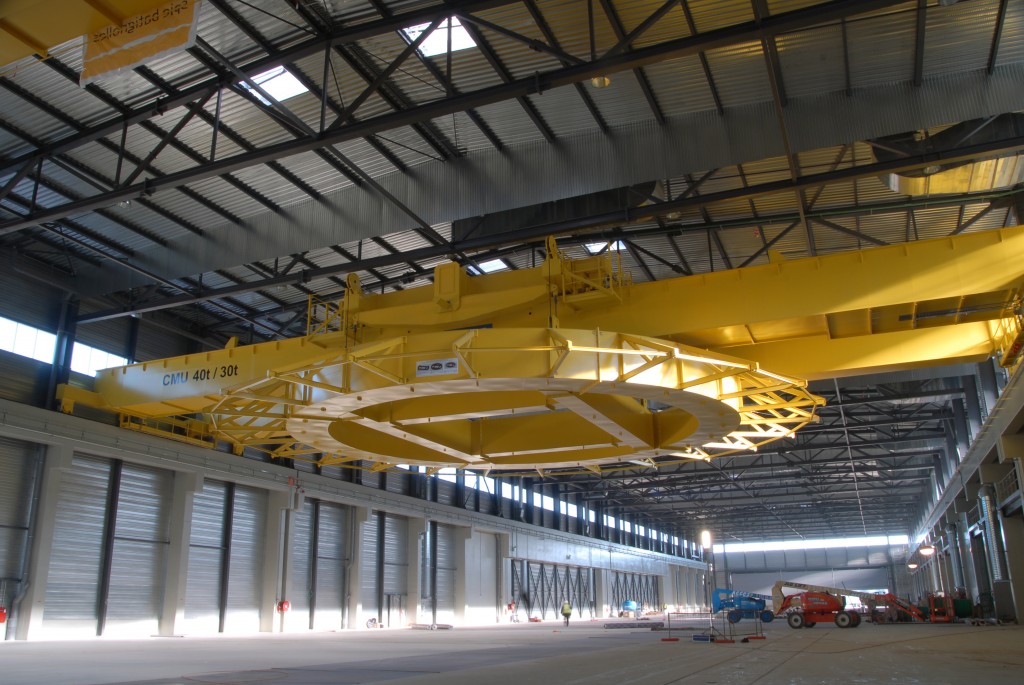
Nearly 200 tonnes
2011-11-18 - The spreader beam (40 tonnes) is supported by a trolley (48 tonnes) that runs between two steel beams (43 and 48 tonnes). The entire assembly weighs close to 200 tonnes. Photo: F4E
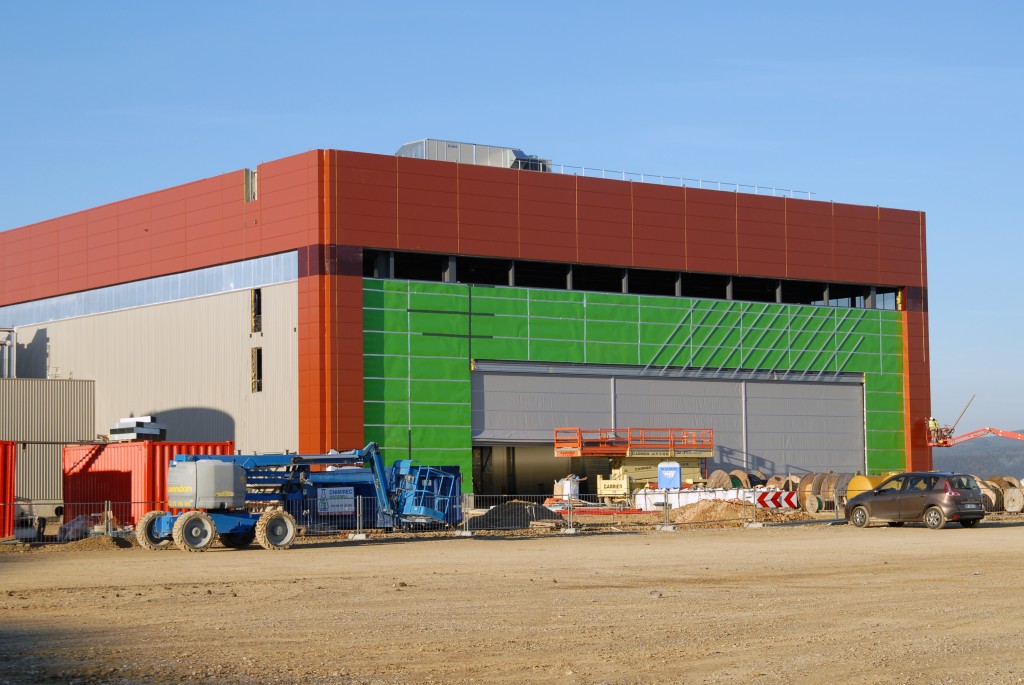
257 m x 49 m x 18 m
2011-11-18 - Cladding operations are completed on the north end of the Winding Facility. The 257 m x 49 m x 18 metre facility required 9,500 square metres of steel cladding and 11,000 square metres of roofing. Photo: F4E
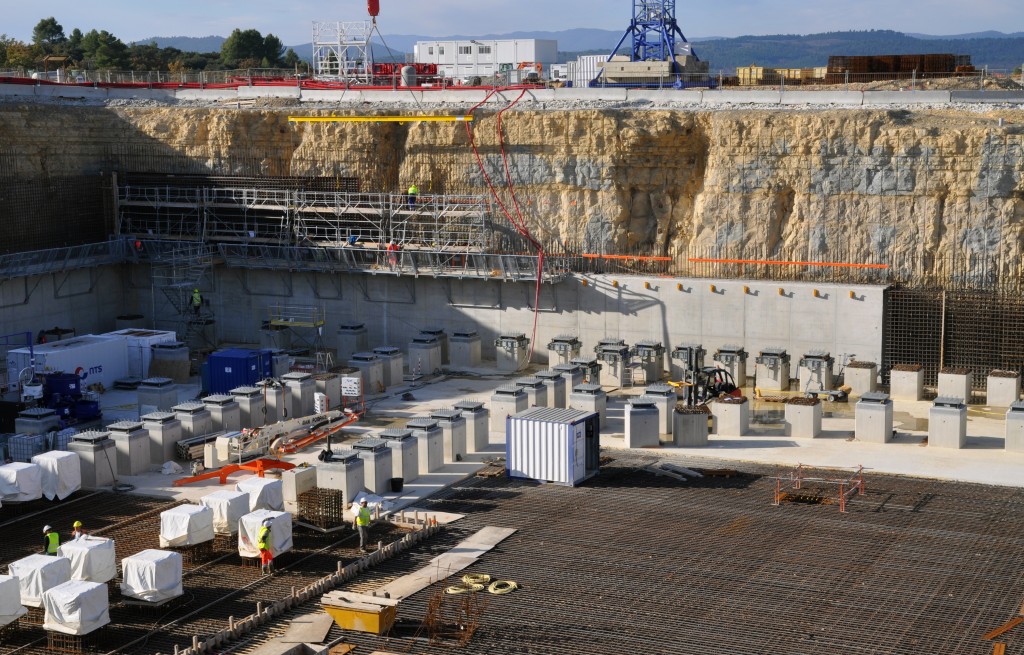
The lower retaining wall
2011-11-15 - Nearly 6,000 cubic metres of concrete will be necessary for the retaining walls of the Seismic Pit. Work began mid-October and will continue through February 2012.
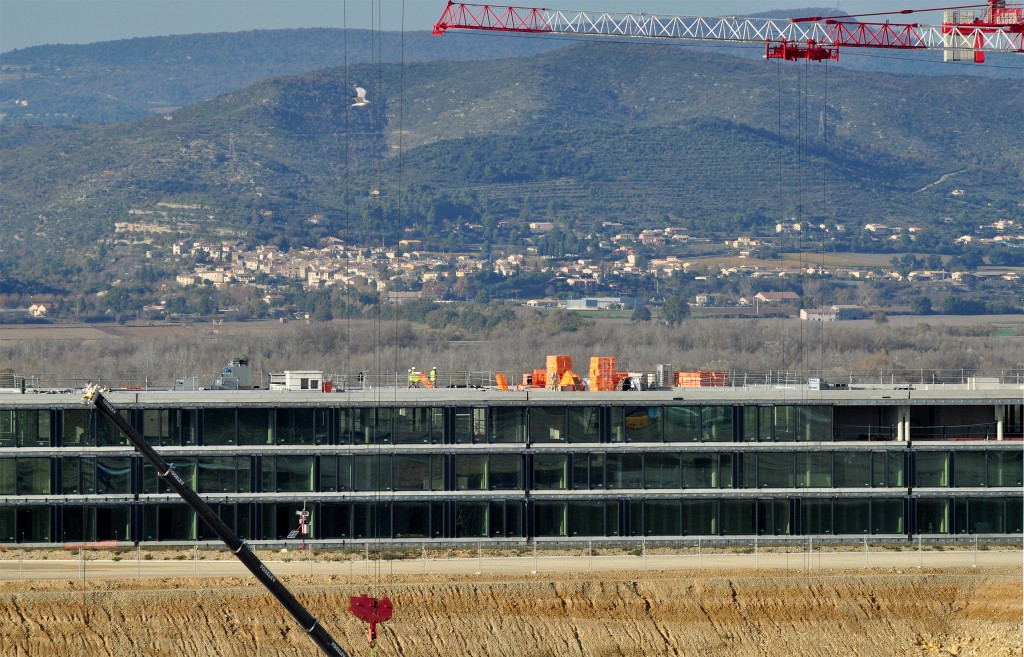
As the crow flies
2011-11-15 - The Provençal village of Corbières (approximately 10 kilometres distant) seen from over the top of the Headquarters building.
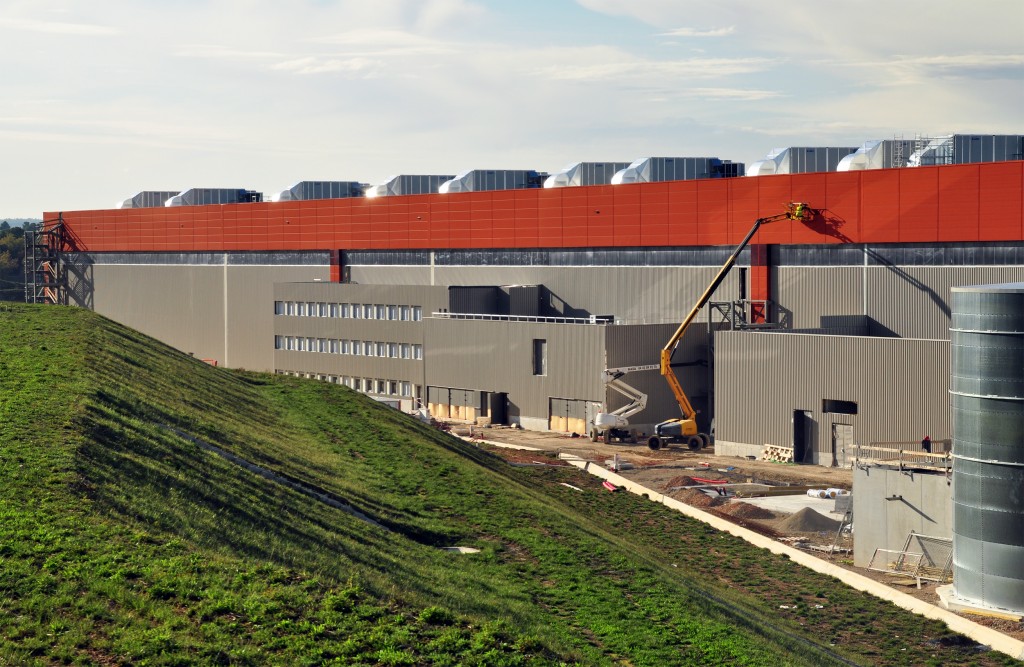
Metal-frame building
2011-11-15 - The weight of the Winding Facility's metal structure is 1,000 tonnes. Each of the rooftop heating and ventilation units weighs a further 9 tonnes.
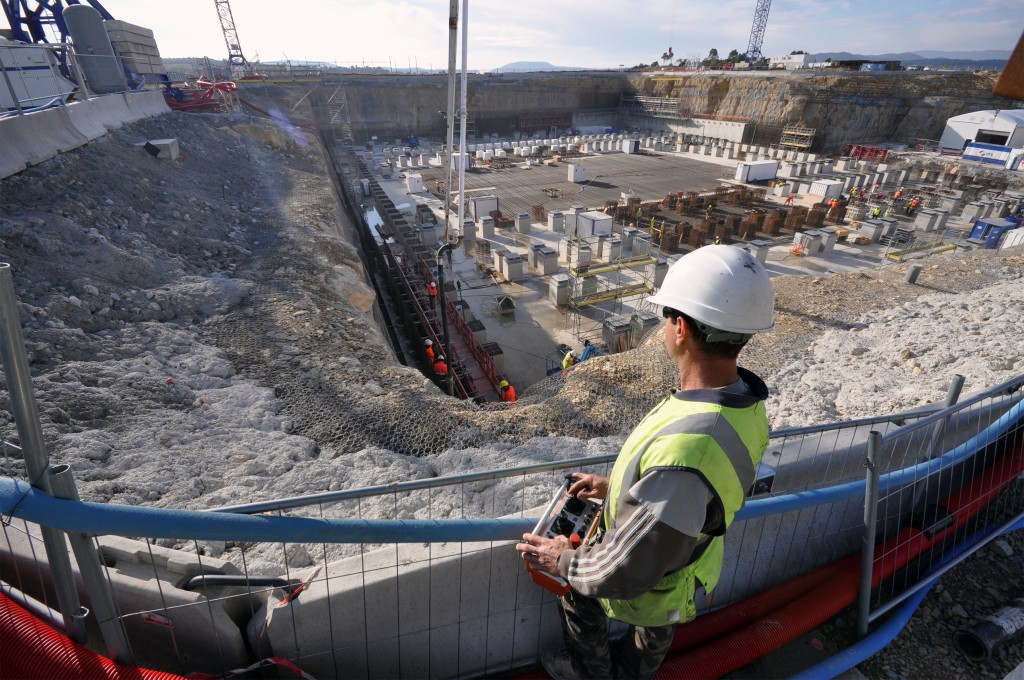
Directing the operations from above
2011-11-15 - After a prolonged rainy period, foundation work has picked up again in the Tokamak Pit.
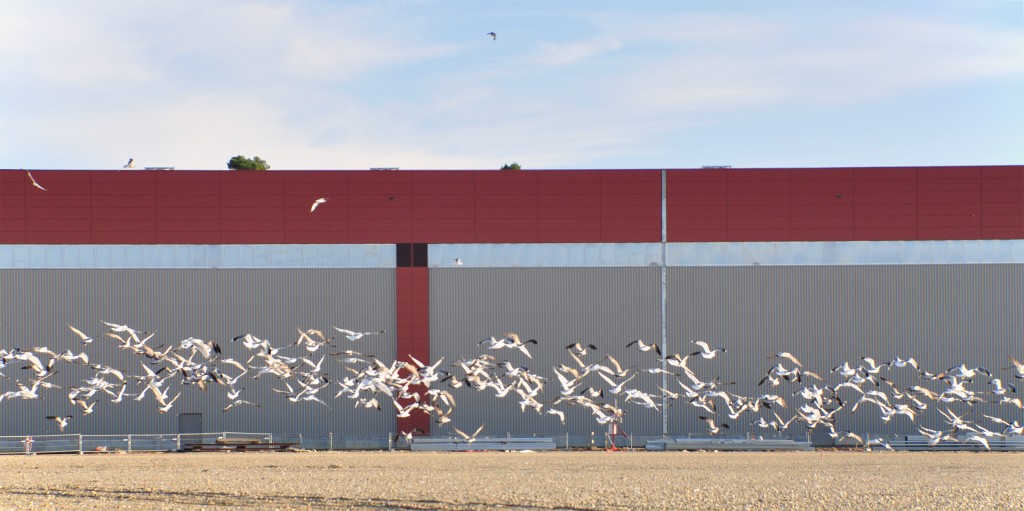
Across the platform ...
2011-11-15 - The Winding Facility is situated on the far end of the 400 metre-wide ITER platform. In seven years, what is now empty space will be entirely filled in with the infrastructure and installations in support of the ITER Tokamak.
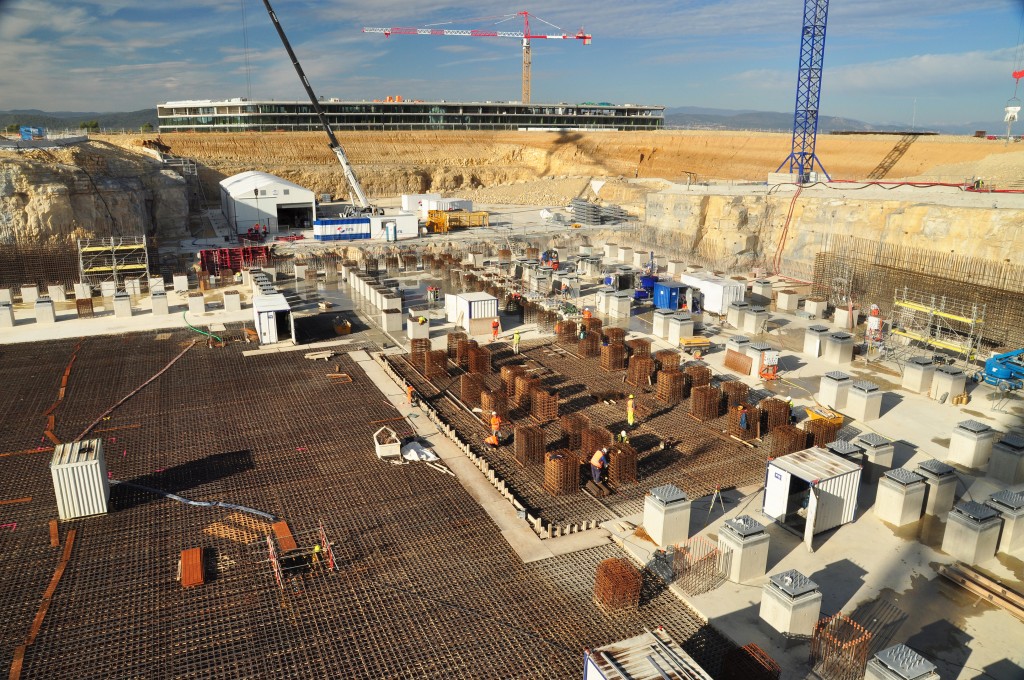
100 bearings and counting
2011-11-15 - The installation of seismic bearing pads has passed the 100 mark and foundation pouring continues—at least on a sunny day.
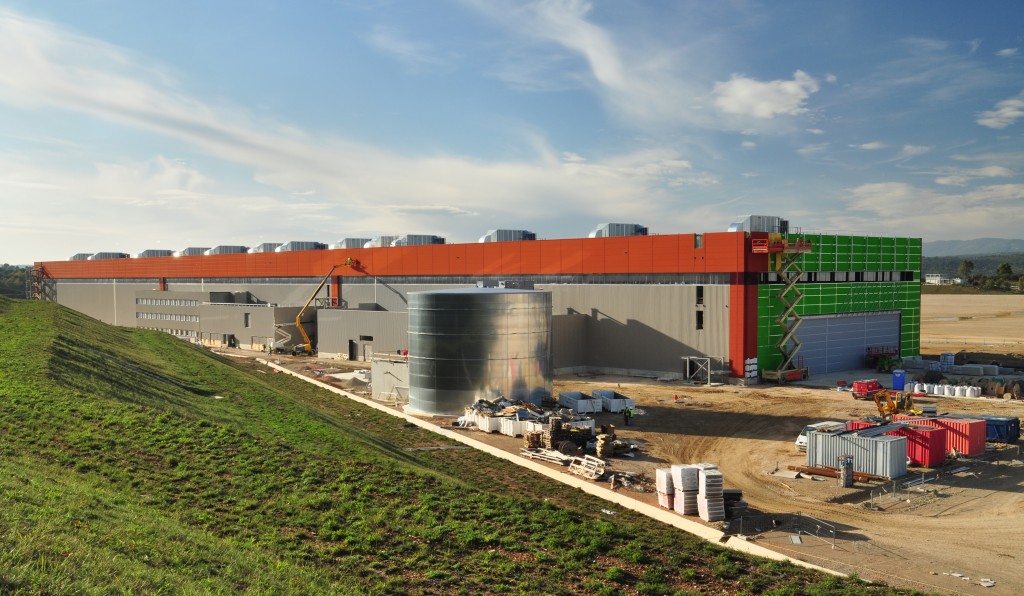
Final stages
2011-11-15 - With one month to go before work on the Poloidal Field Coils Winding Facility ends, workers carry out the last cladding operations on the north face of the building. In the foreground, a cylindrical tank that will store water for the Facility's independent fire fighting system.
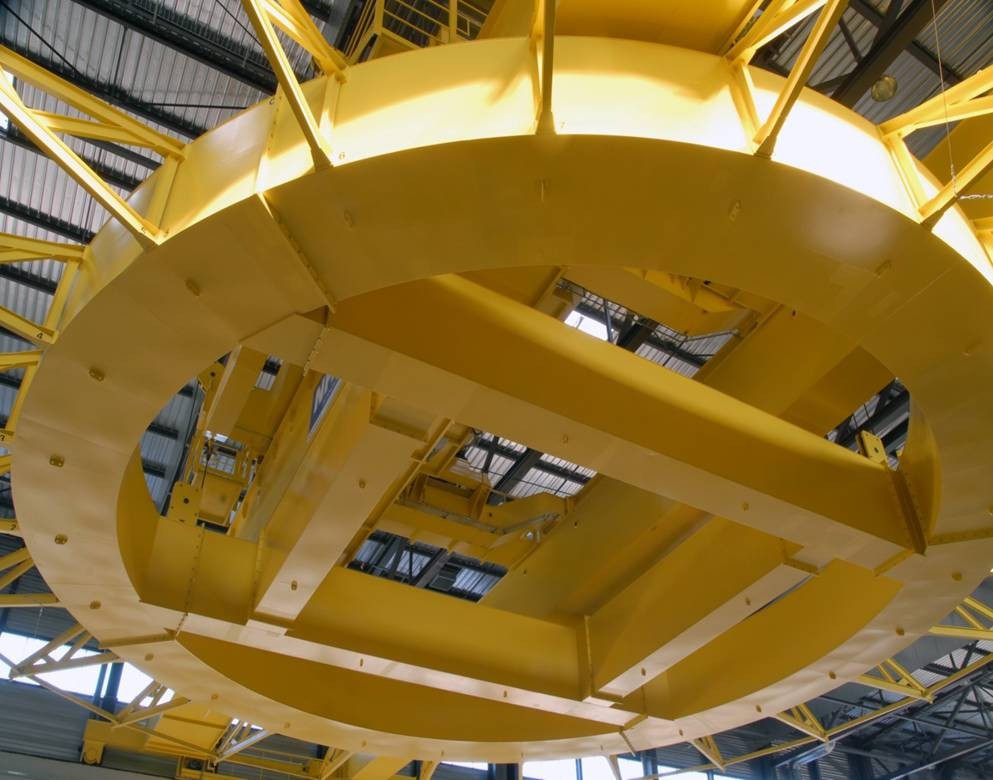
A spreader beam to carry the completed coils
2011-11-15 - This 25 metre-wide spreader beam has 24 brackets that will bear the weight of the poloidal field coils as smoothly and evenly as possible, and avoid tilt. Photo: F4E
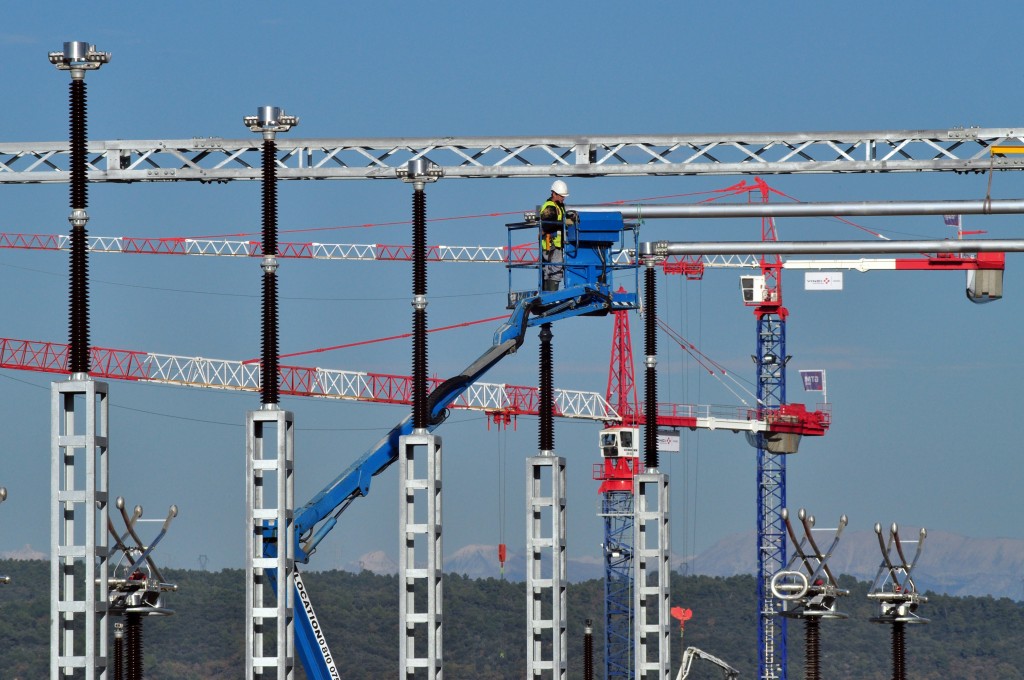
Sky high
2011-11-15 - Work continues on the very high voltage electrical substation on the south side of the ITER platform.
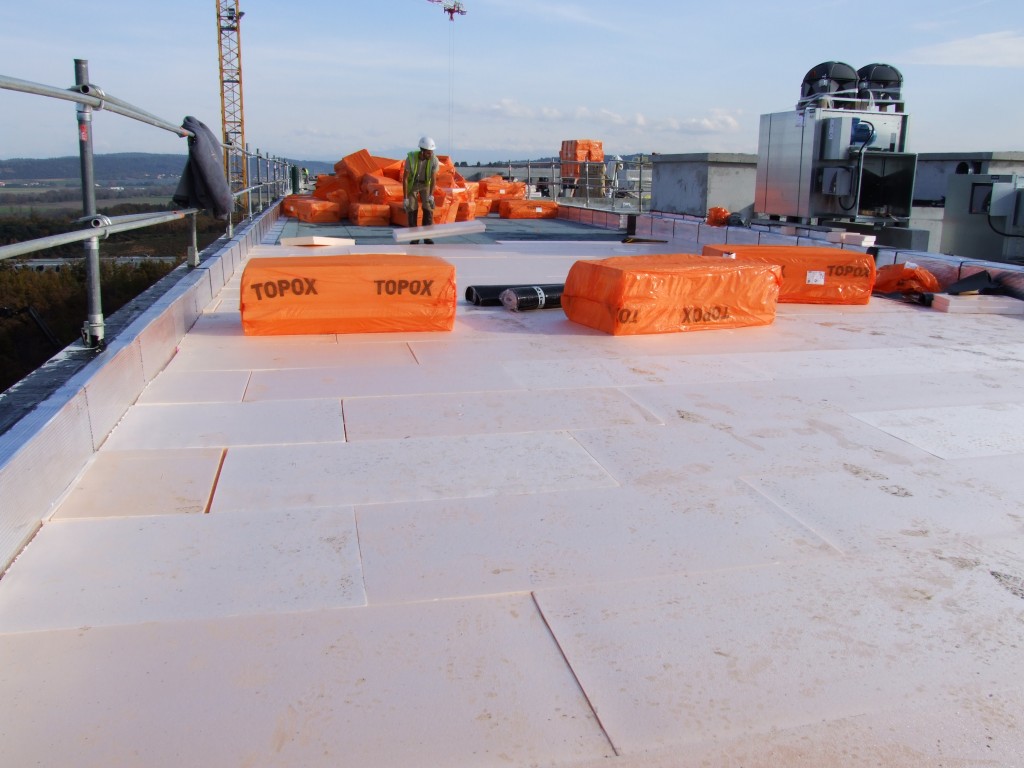
Work on the roof
2011-11-14 - Blocs of insulation are installed on the roof of the ITER Headquarters building, some 20 metres above ground level. Photo: AIF
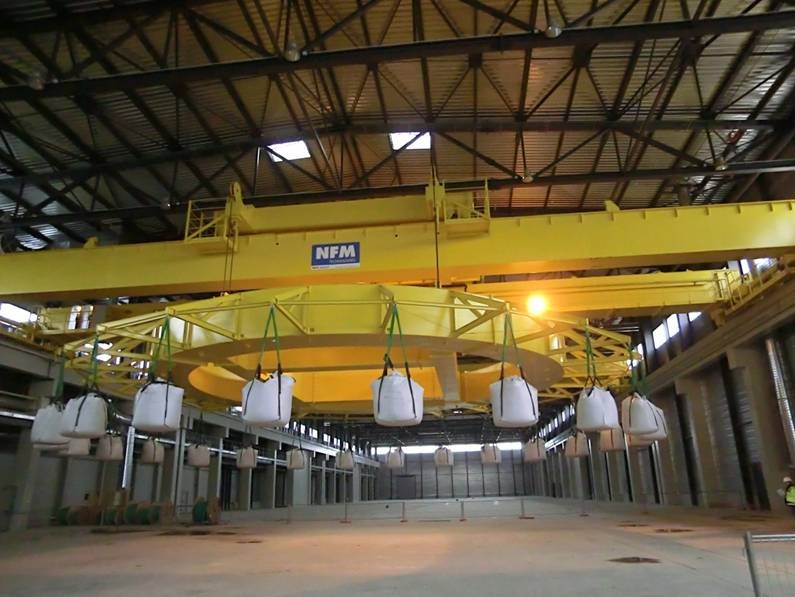
Slowly but surely
2011-11-10 - In November 2011, static load and dynamic movement tests were carried out on the 40-tonne spreader beam, which must be capable of transporting loads as smoothly and evenly as possible, with a maximum authorized tilt of 10 mm. Photo: F4E
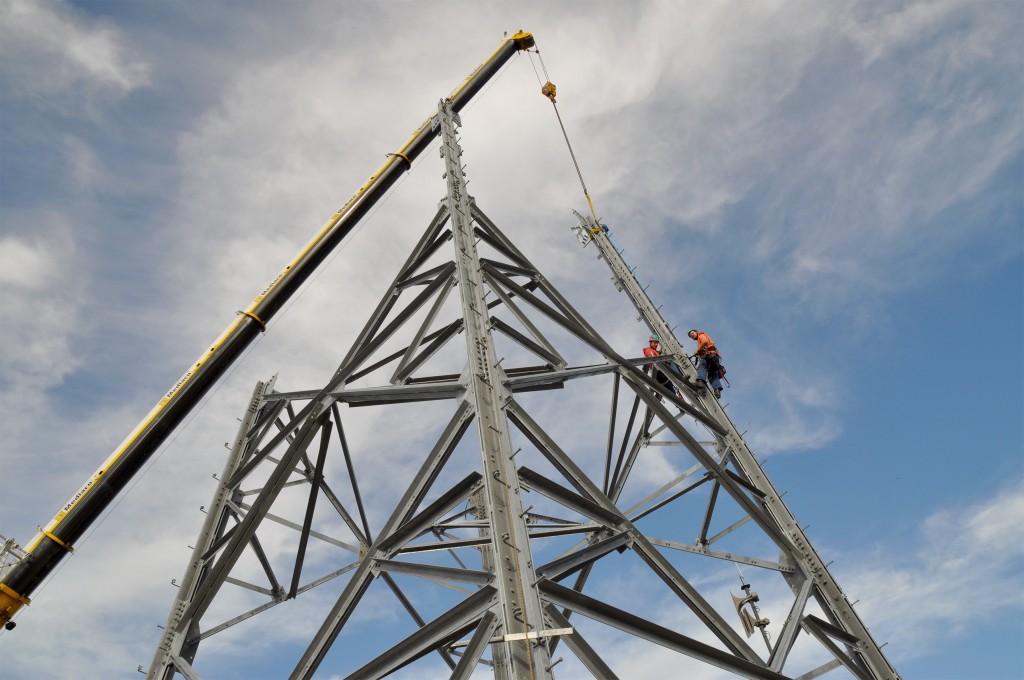
Giant Erector Set
2011-11-10 - It will take 22 pylons to connect the ITER platform switchyard to the existing 400kV power line feeding the neighbouring Tore Supra installation at the CEA. Each 43-metre steel pylon weighs 100 tonnes.
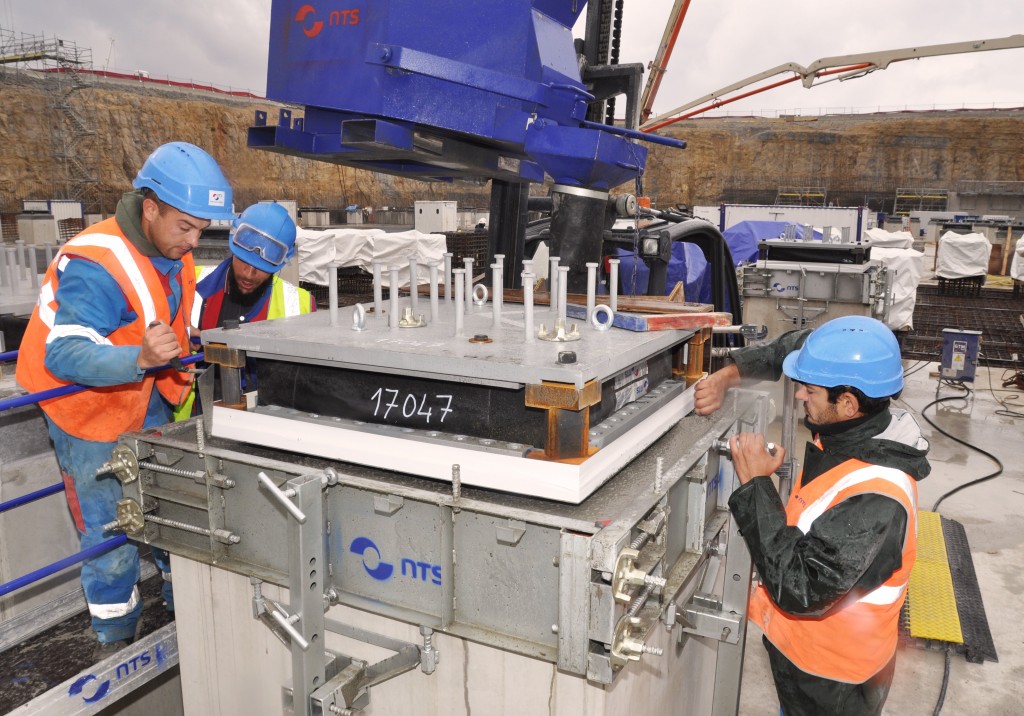
Precise and careful alignment for Seismic Pad #100
2011-11-06 - Early November, workers completed the installation of seismic pad number 100.
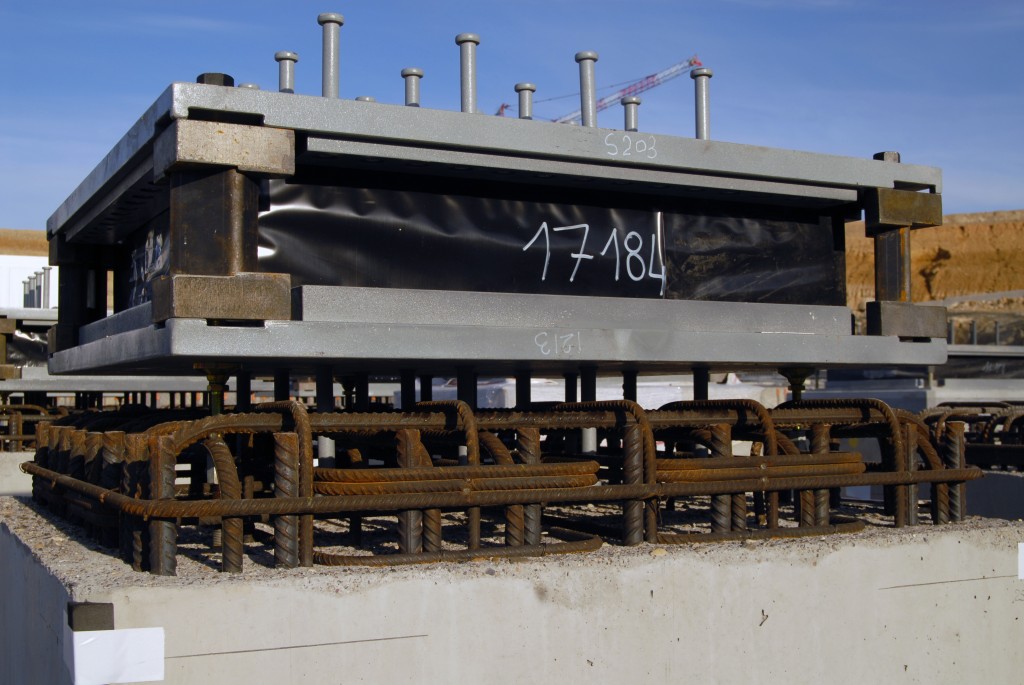
Solidifying the two pieces
2011-11-05 - The bearing is placed on top of a height adjustment system that enables the position, level and inclination of the bearing to be fine tuned. Topographical checks are performed before plinth and bearing are ready to receive the second-phase concrete. Photo: F4E
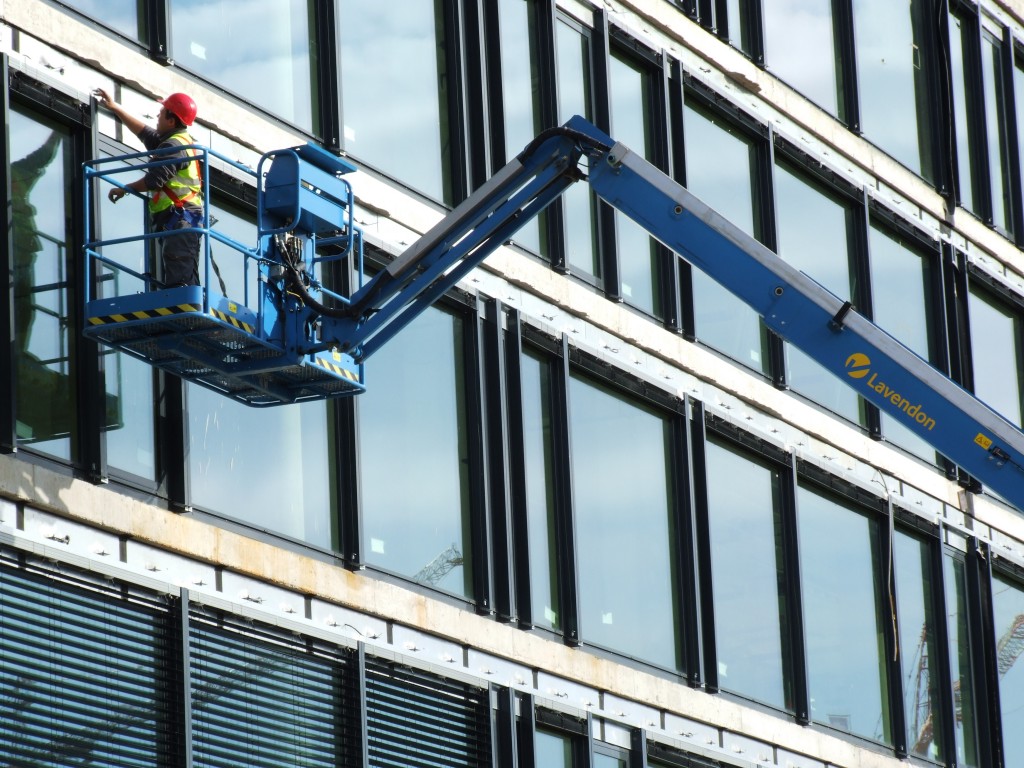
Exterior blinds
2011-11-05 - Along the eastern face of the building, the offices will be protected from the sun by exterior venetian blinds. Photo: AIF
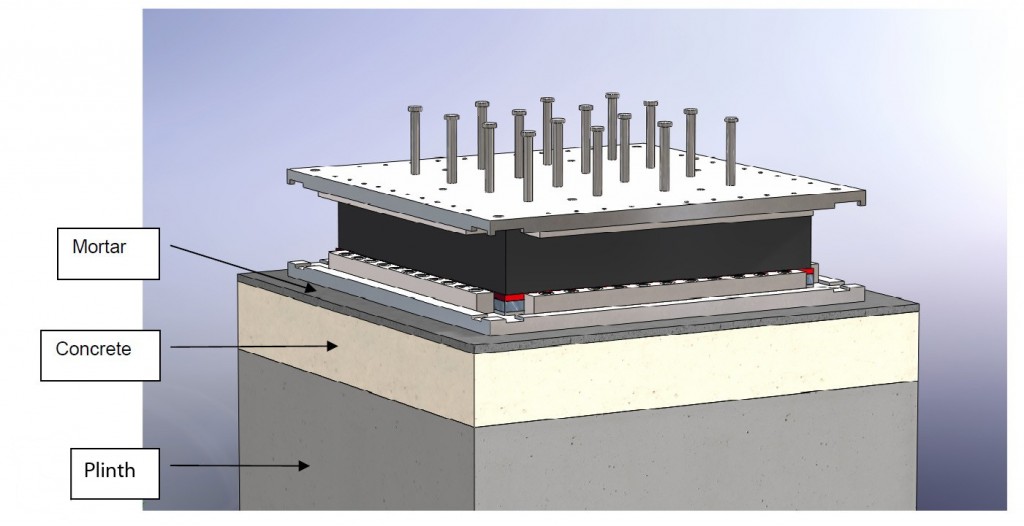
Cementing the seismic pads
2011-11-05 - Cohesion between the plinth, second-phase concrete and mortar is essential to achieve the monolithic behaviour of the structure. Image credit: ITER Organization
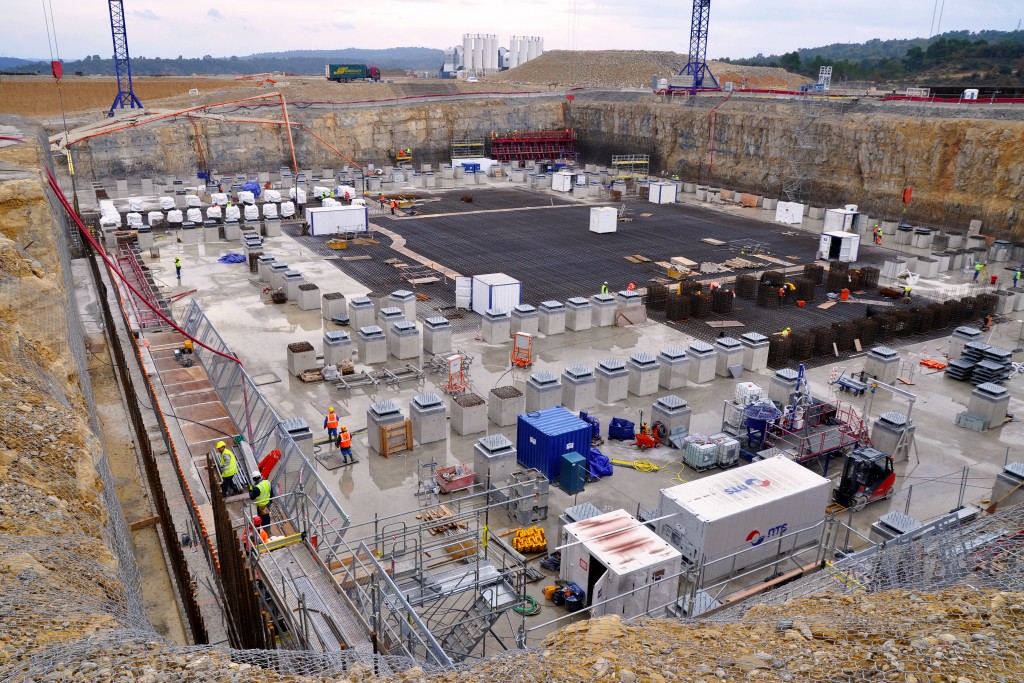
Seismic pads, all in a row
2011-11-03 - Early November, seismic pads are installed on top of their concrete columns at a rhythm of five per day.
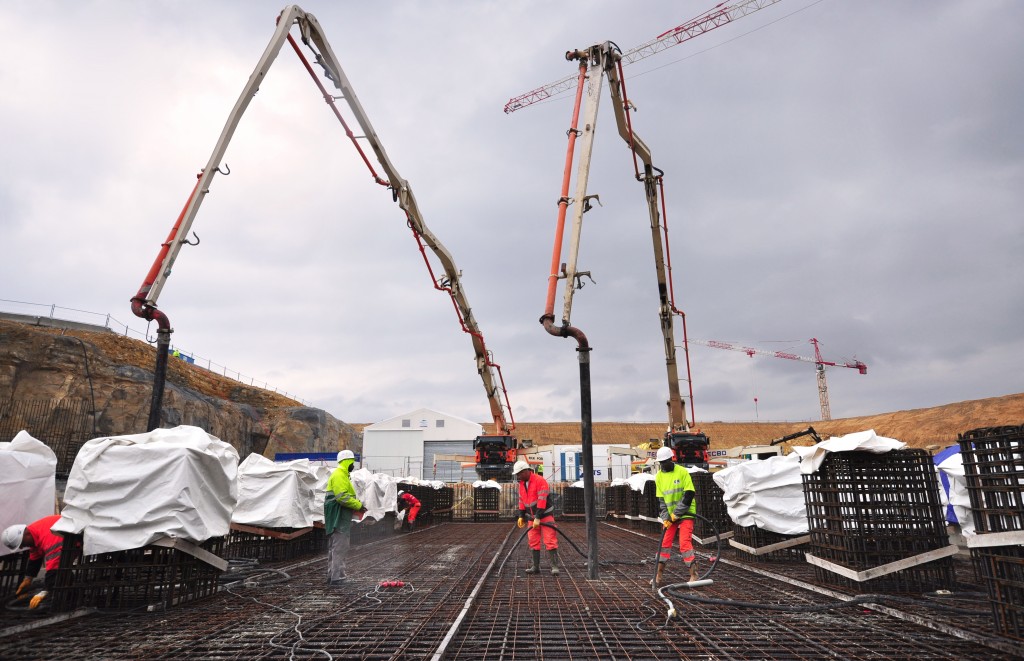
No air pockets allowed
2011-11-03 - Workers use vibration to render the freshly poured concrete in the Seismic Pit homogeneous and to break any air pockets.
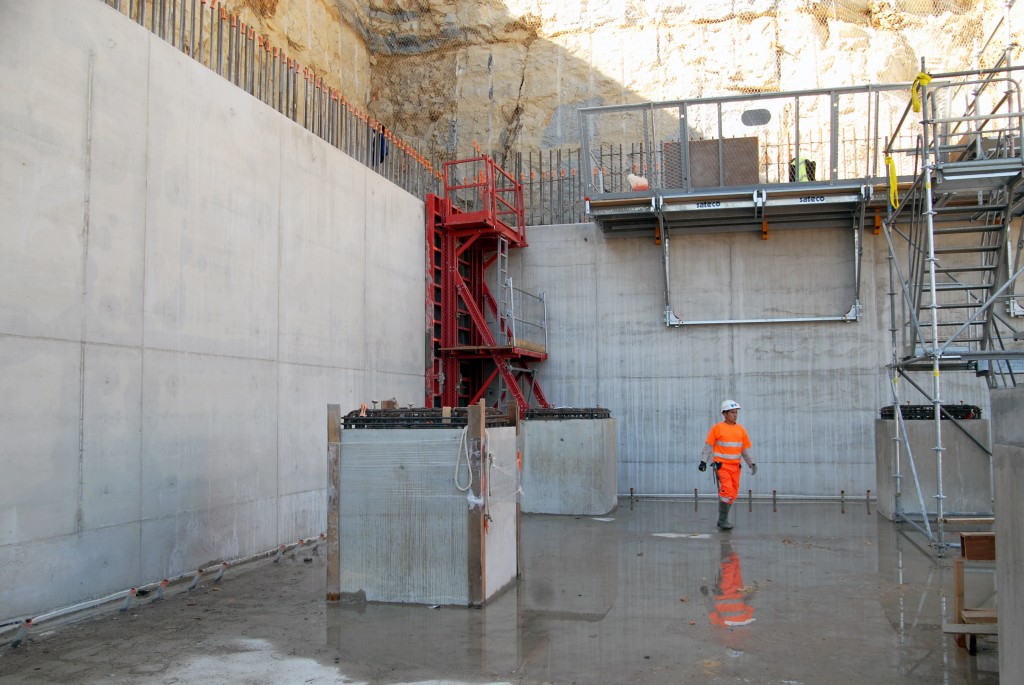
Wall pouring progresses
2011-10-26 - The first five-metre vertical segment of retaining wall has been poured in this corner of the Seismic Pit. At this level, the retaining walls are 1.5 metres thick. Photo: F4E
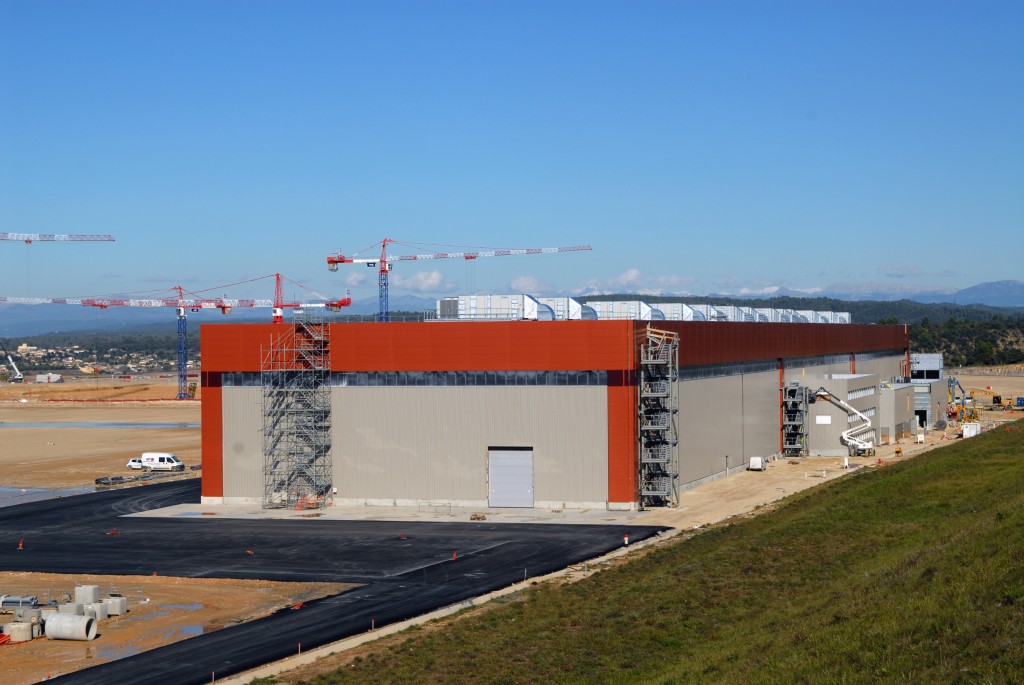
This is the "delivery" end of the Winding Facility
2011-10-26 - Spools of niobium-titanium conductor will be delivered here at the south end of the facility. Winding operations will happen in a sequential manner until the finished coils leave the opposite end of the building on a self-propelled transporter. Photo: F4E
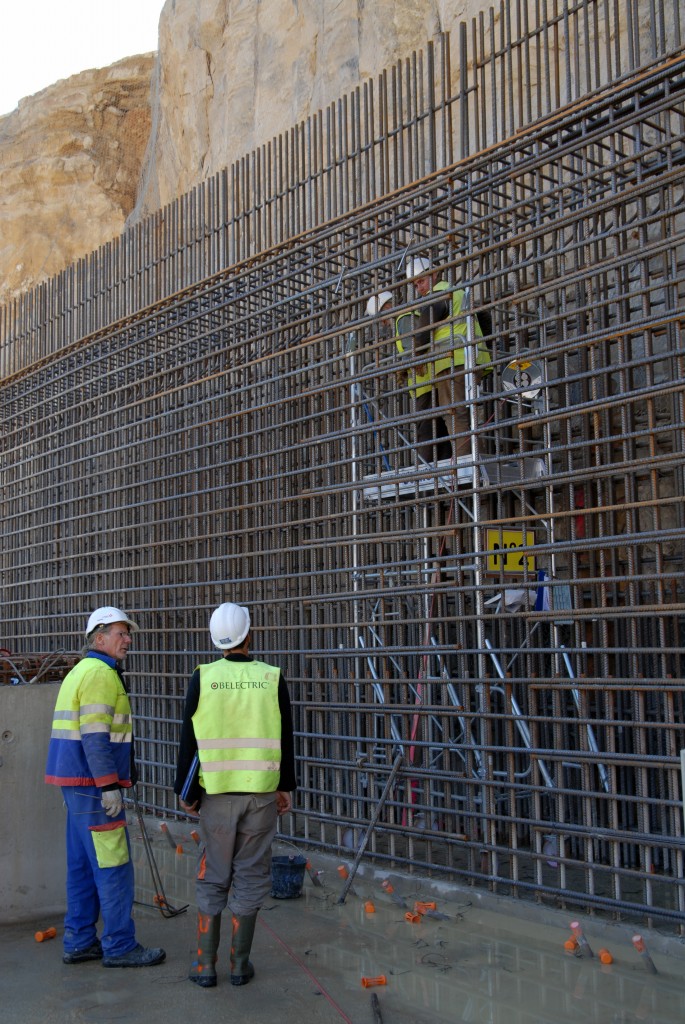
Steel cage
2011-10-26 - Workers finish the steel reinforcement for the retaining walls of the Tokamak Pit. Photo: F4E
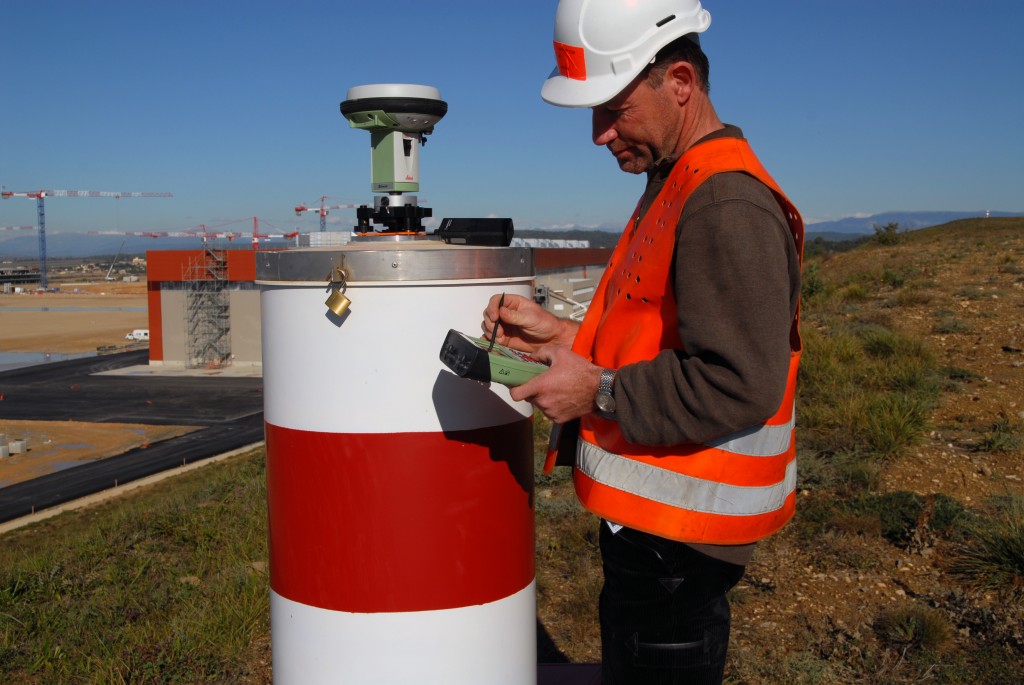
Metrology measurements in October 2011
2011-10-26 - Metrology contractors (GDV) take GPS measurements as part of the primary survey network qualification survey. Photo: F4E
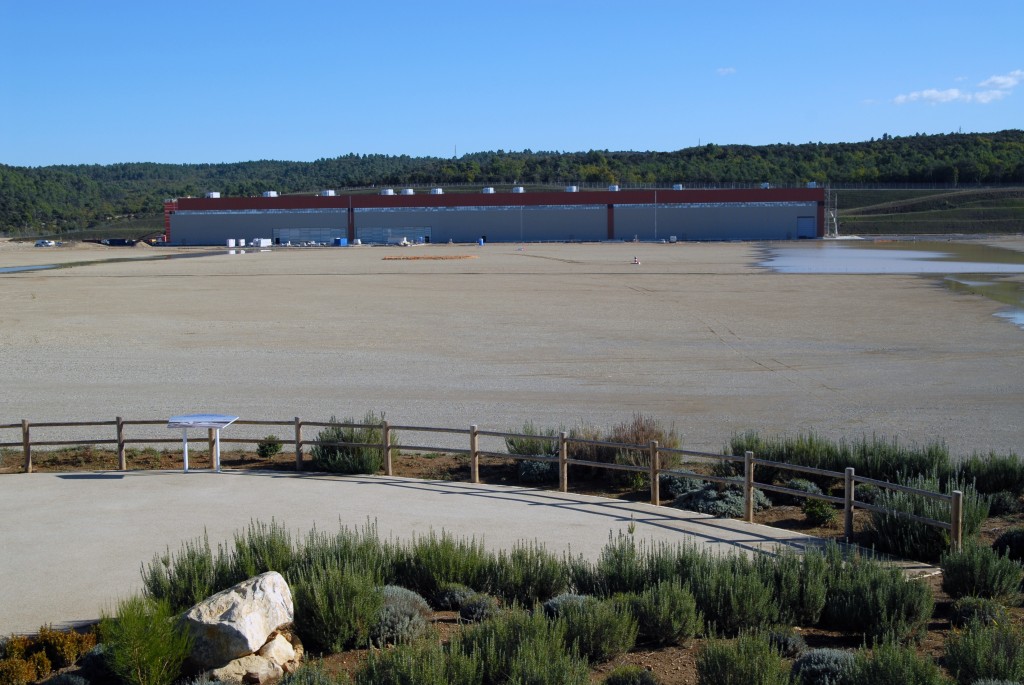
Seen from the ITER Visitor Centre
2011-10-26 - Four hundred metres across the platform, the first completed building. Work will begin here in 2012 to wind ITER's largest magnets: the poloidal field coils. Photo: F4E
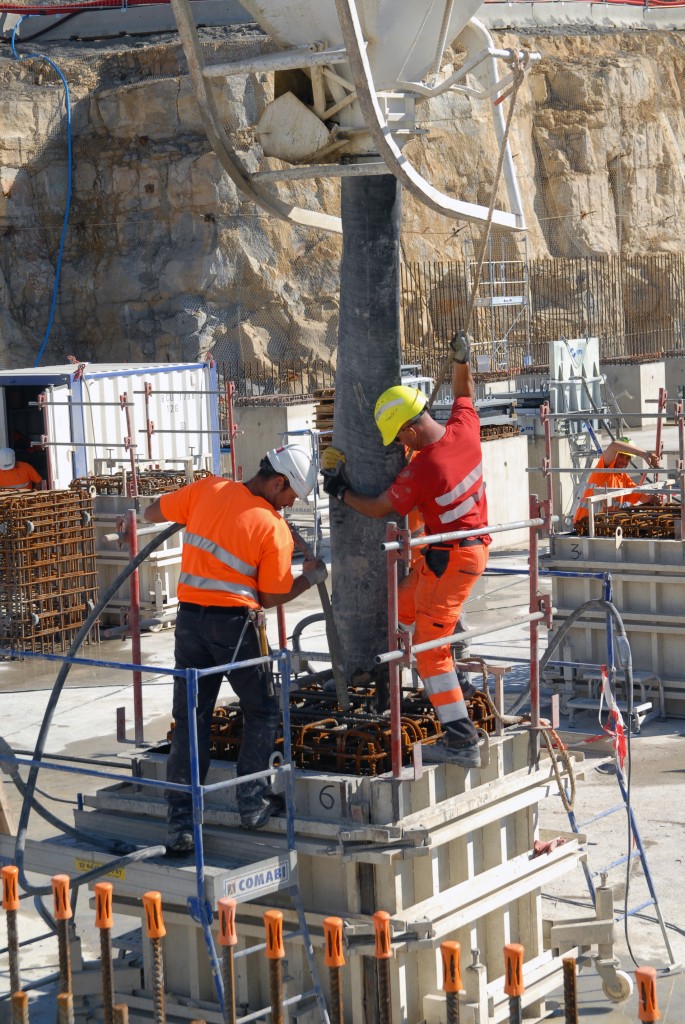
Second-phase concrete
2011-10-26 - Workers guide just the right dose of concrete onto the top of each seismic pillar; this "second-phase" concrete will join the pillar to the seismic bearing. All over the Seismic Pit, this operation is being repeated 493 times. Photo: F4E
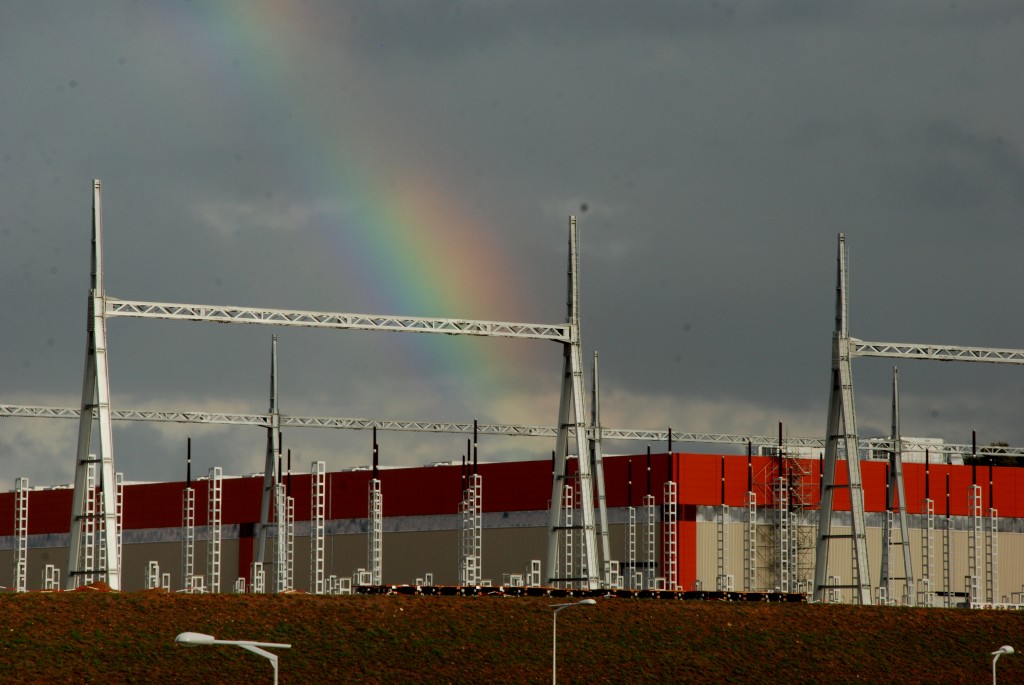
Rainbow in October
2011-10-25 - An October rainbow briefly illuminates the ITER platform and the near-completed Poloidal Field Coils Winding Facility.
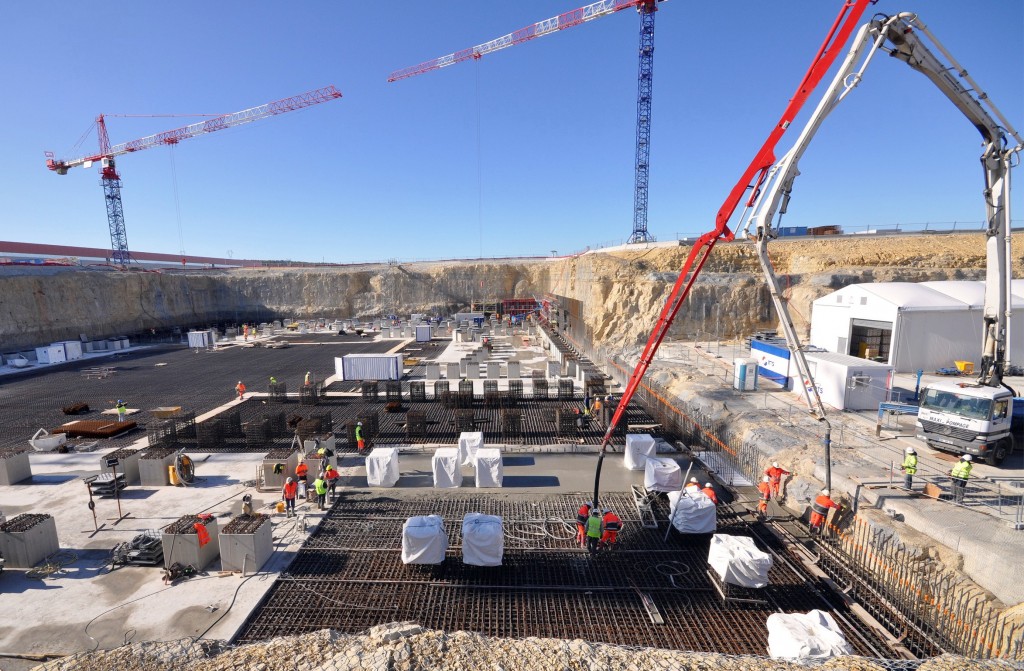
As large as a football field
2011-10-20 - Looking south over the football-pitch-sized Seismic Pit. To the right: the cleared area for the Hot Cell Facility. To the left: the long red line of the Poloidal Field Coils Winding Facility.
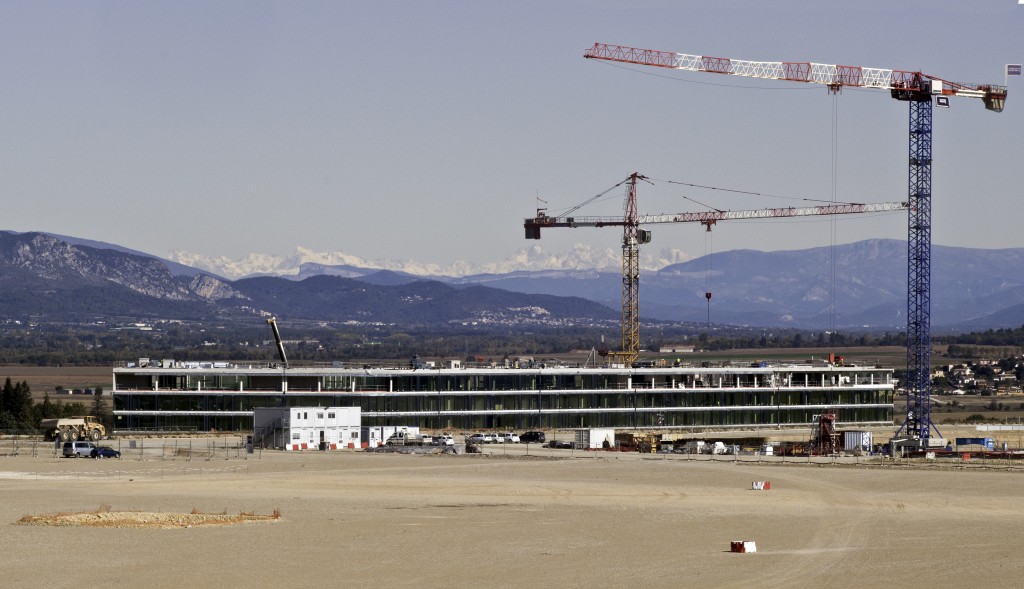
Snow visible from the platform
2011-10-20 - Fresh October snow in the pre-Alps is visible from the ITER platform on a clear day. Approximately 250 km beyond the ITER Headquarters are the Mont Pelvoux (far left, 3,946 m) and the Barre des Écrins (left, 4,102 m).
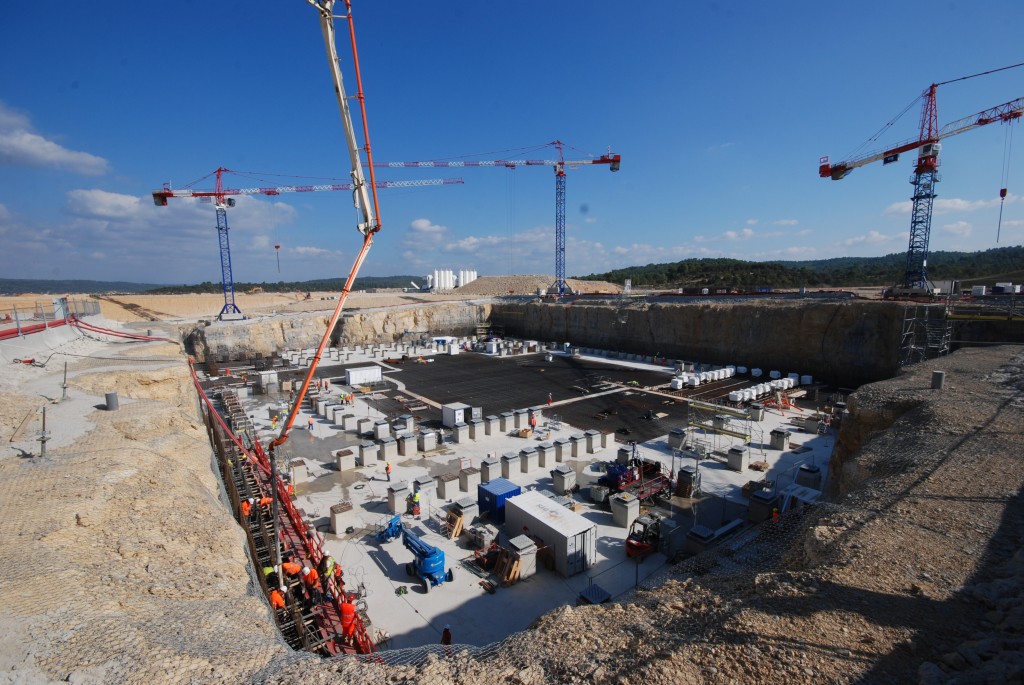
The Tokamak Pit in October
2011-10-19 - The seismic basemat—the white "floor" of the Tokamak Pit—is filled in progressively. Along the western wall, work has begun on the retaining walls (lower left).
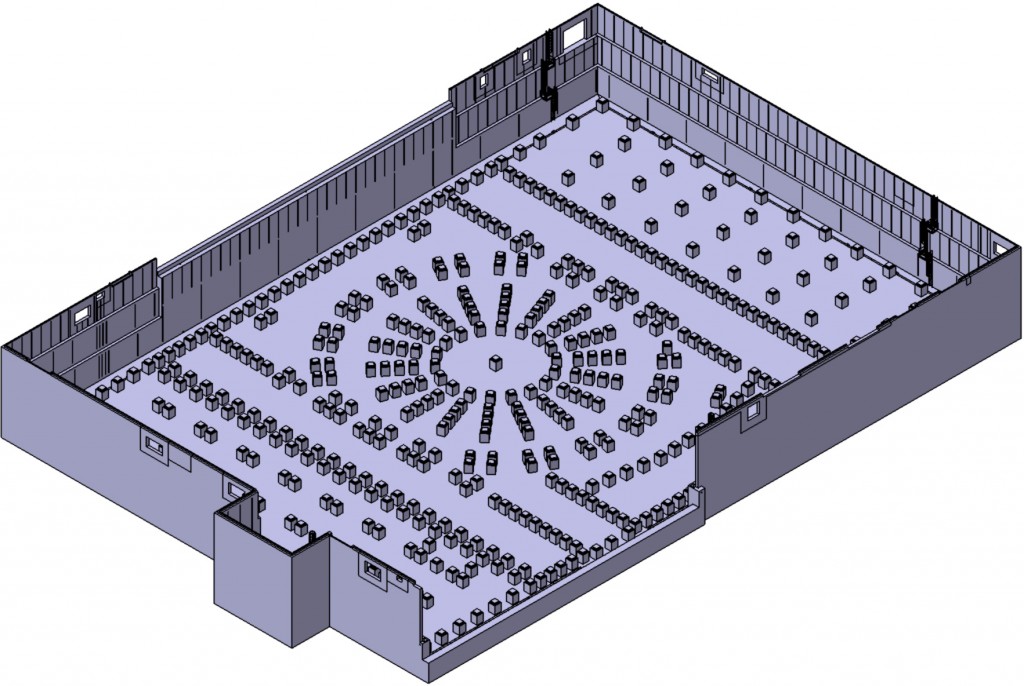
Seismic pad layout
2011-10-18 - 493 seismic pads will protect the ITER machine and the Tokamak Complex (Tokamak, Diagnostic and Tritium Buildings). This CAD-generated image shows the exact configuration of the pads on the 1.5-metre-thick Seismic basemat. Image credit: ITER Organization
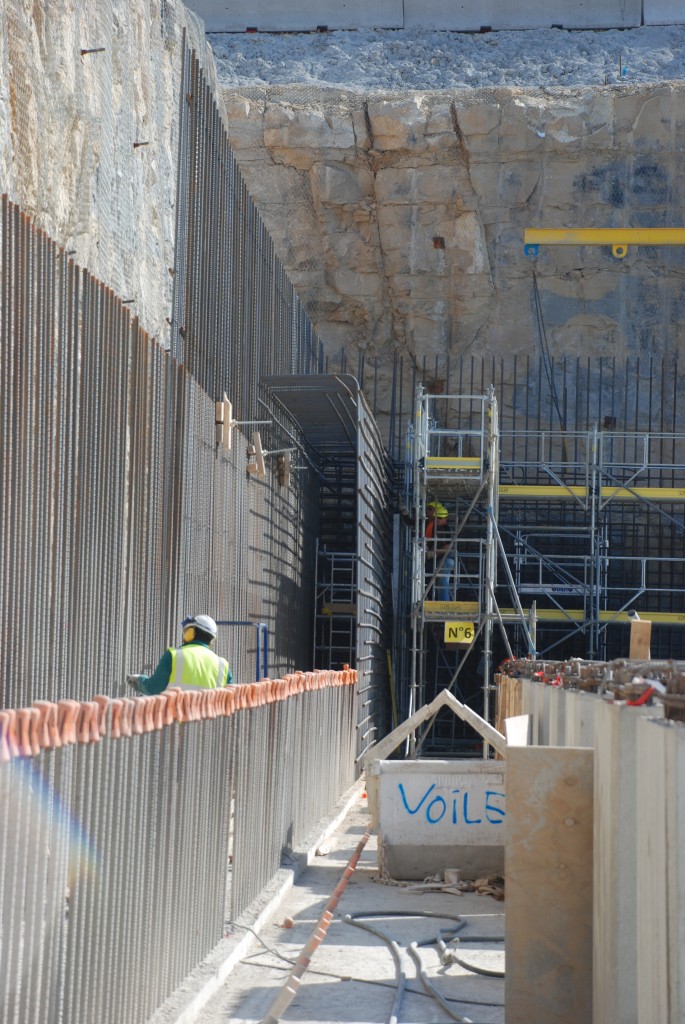
The lowest segment is thickest
2011-10-17 - The lower five metres of retaining wall will be the thickest. From one and a half metres at its base, the wall will taper to 0.5 metres at its highest point.
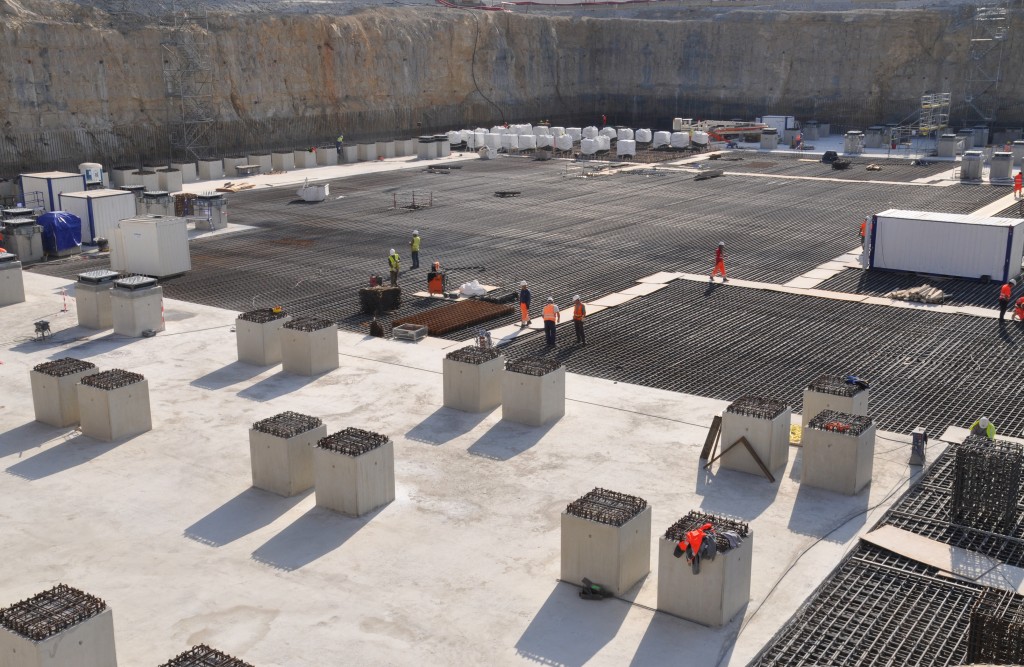
Filling in the Seismic Pit basemat
2011-10-17 - Now that the perimeter of the Seismic Pit has been filled in, work advances towards the zones in the centre.
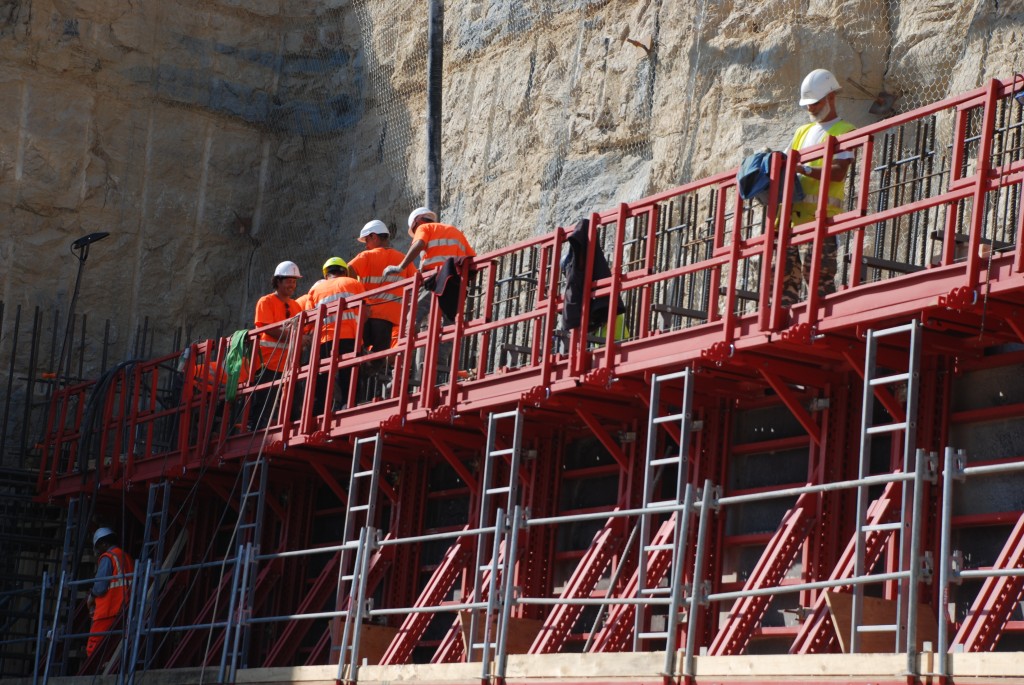
Work on the retaining walls
2011-10-17 - Scaffolding is set into place along the rock face for work on the retaining walls of the Seismic Pit.
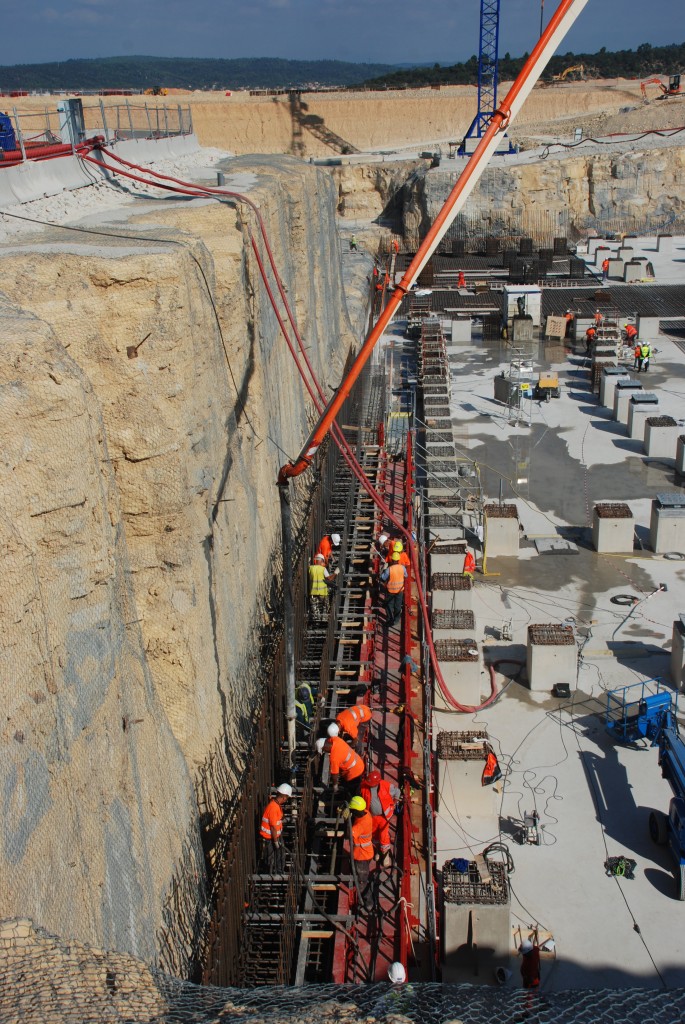
Looking down into the Pit
2011-10-17 - Seen from above: the construction of the Seismic Pit retaining wall.
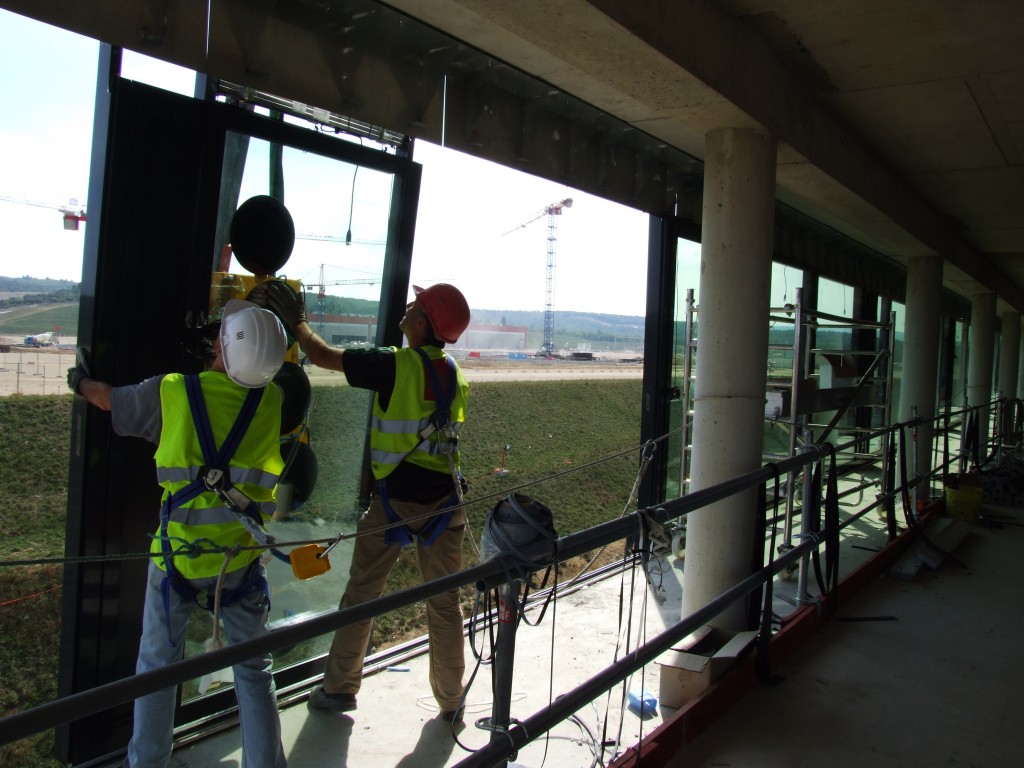
Sliding 500 kilos 'effortlessly' into place
2011-10-12 - The 500-kilo glass window blocks are slid into position one after another following a patented installation system developed for the ITER Headquarters project. Up to 50 frames can be slid into place per day. Photo: AIF
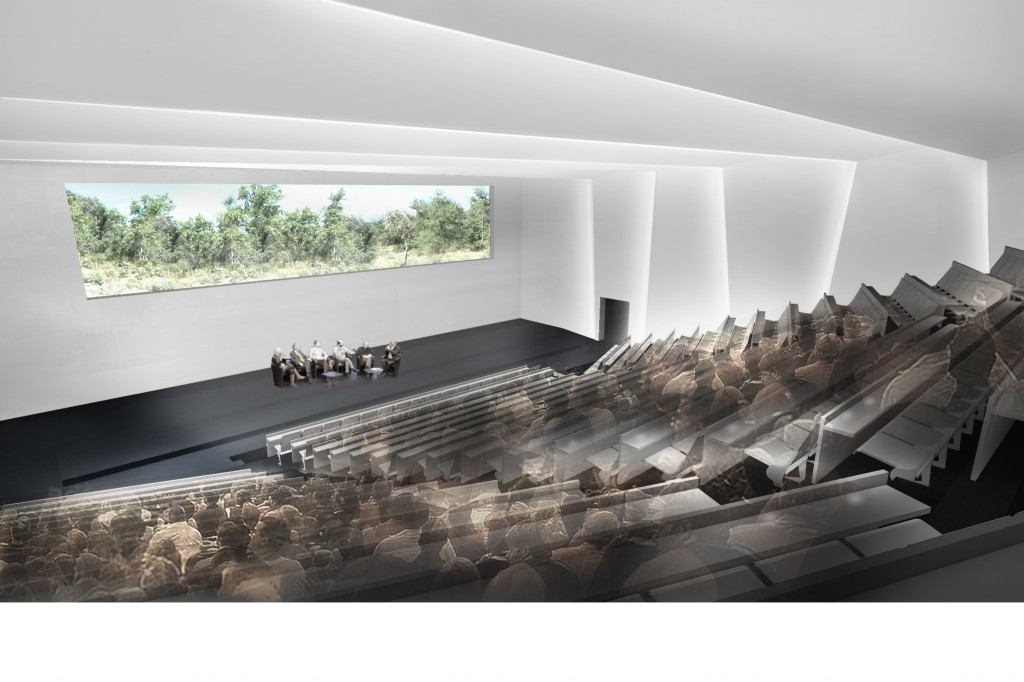
Spacious
2011-10-11 - The architect's drawing helps us to imagine the Headquarters amphitheatre in one year's time. ©Ricciotti

Meetings galore
2011-10-11 - The amphitheatre, with its large bay window, will hold up to 500 people. Photo: AIF
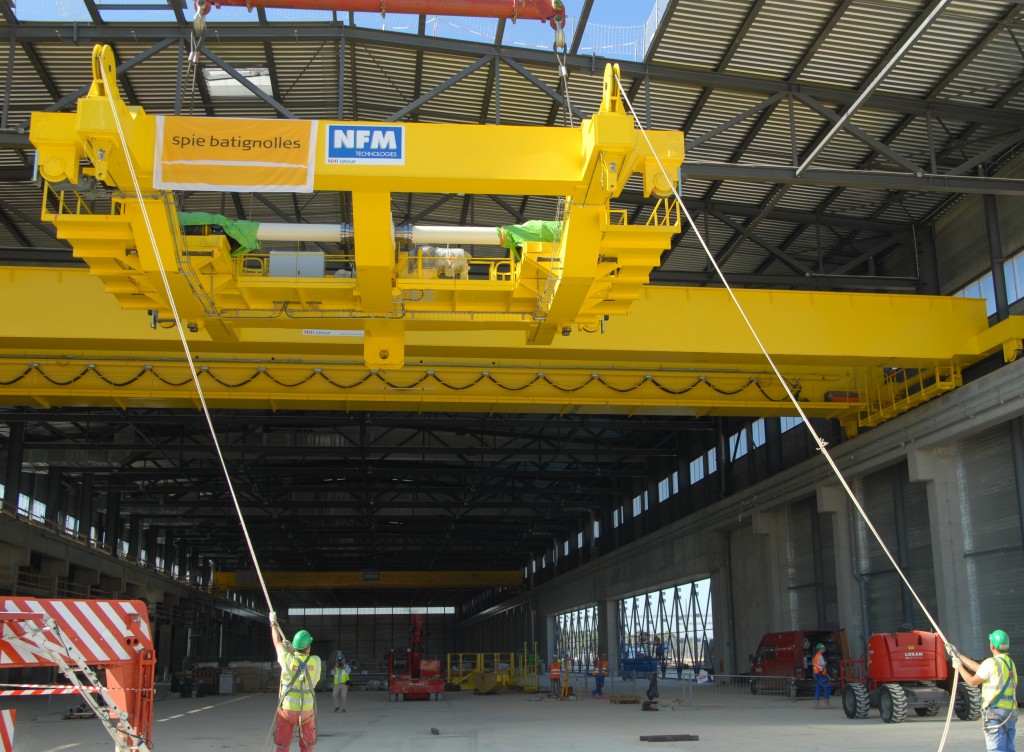
Installation takes two days
2011-10-06 - Following delivery from the factory in San-Sebastian, Spain, the second travelling crane of the Poloidal Field Facility is installed in two days. Photo: F4E
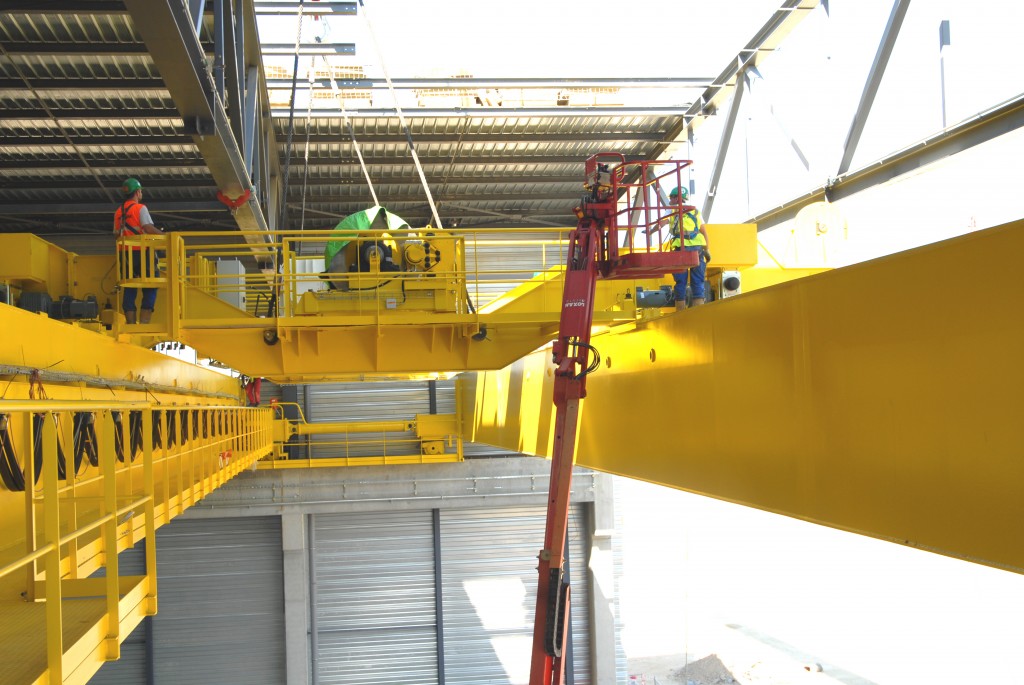
The "heavyweight" travelling crane for finished components
2011-10-06 - The first beam (43 t) is joined by the second (48 t) and between the two a hoisting trolley is installed. Photo: F4E
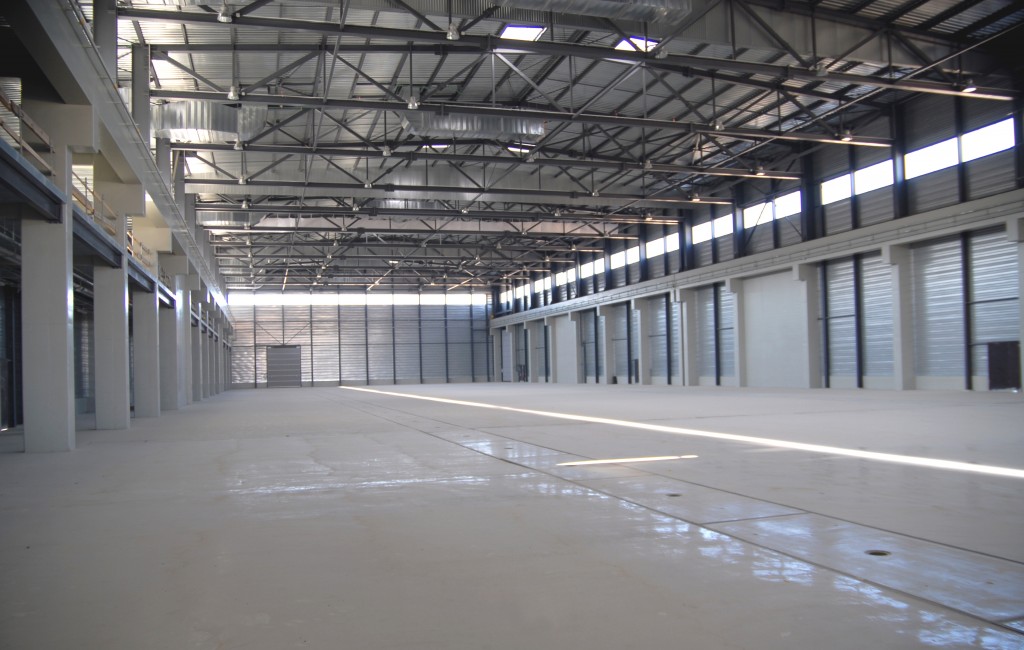
Completed interior
2011-10-06 - Interior painting is finished; in 2012 this building will be fitted out with equipment for the winding of ITER's poloidal field magnets. Photo: F4E
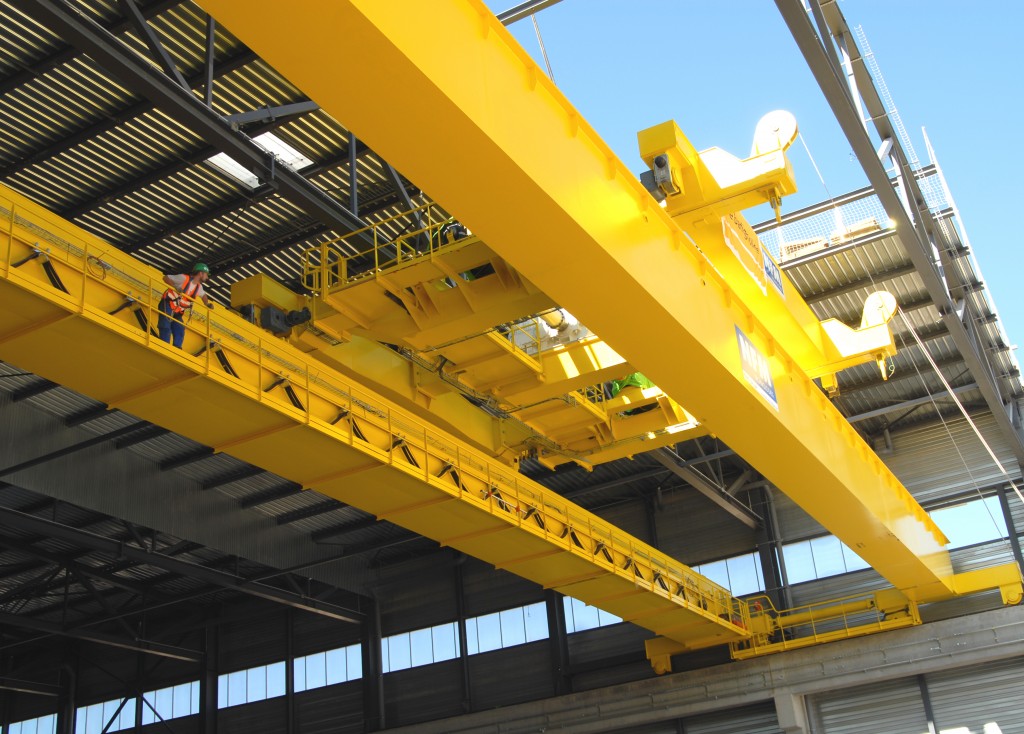
The central trolley
2011-10-06 - The central trolley (48 tonnes) will support the weight of the 40-tonne spreader beam and allow it to transfer loads across the width of the Winding Facility. Photo: F4E
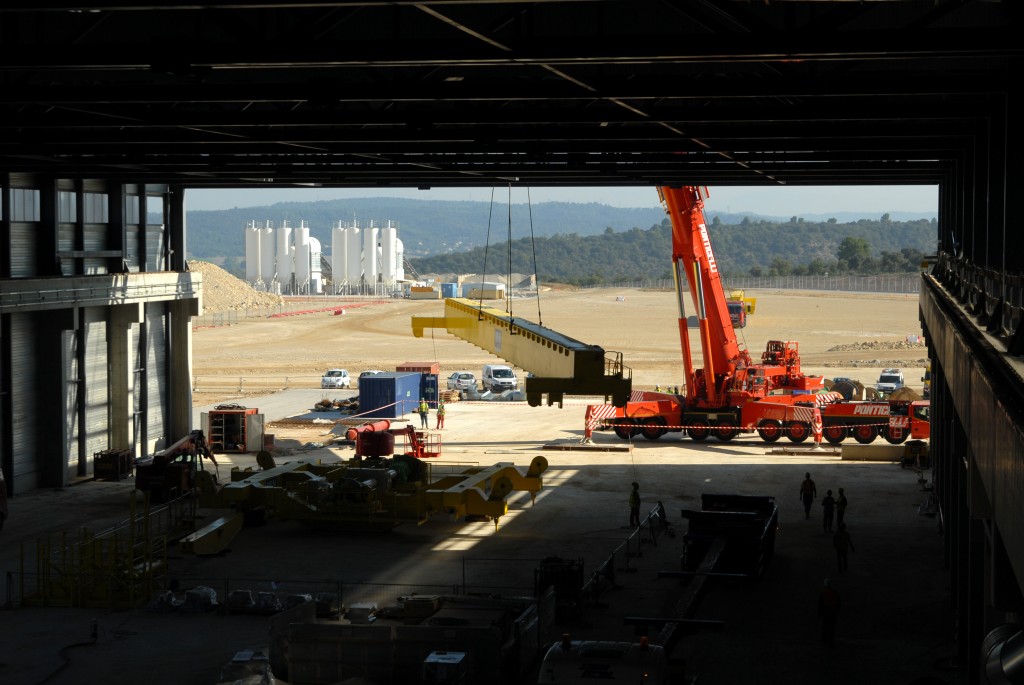
Assembling the second crane
2011-10-04 - Components for the second bridge crane—two 40-tonne beams and a hoisting trolley (seen on the floor)—are delivered to the ITER site in October. Photo: F4E
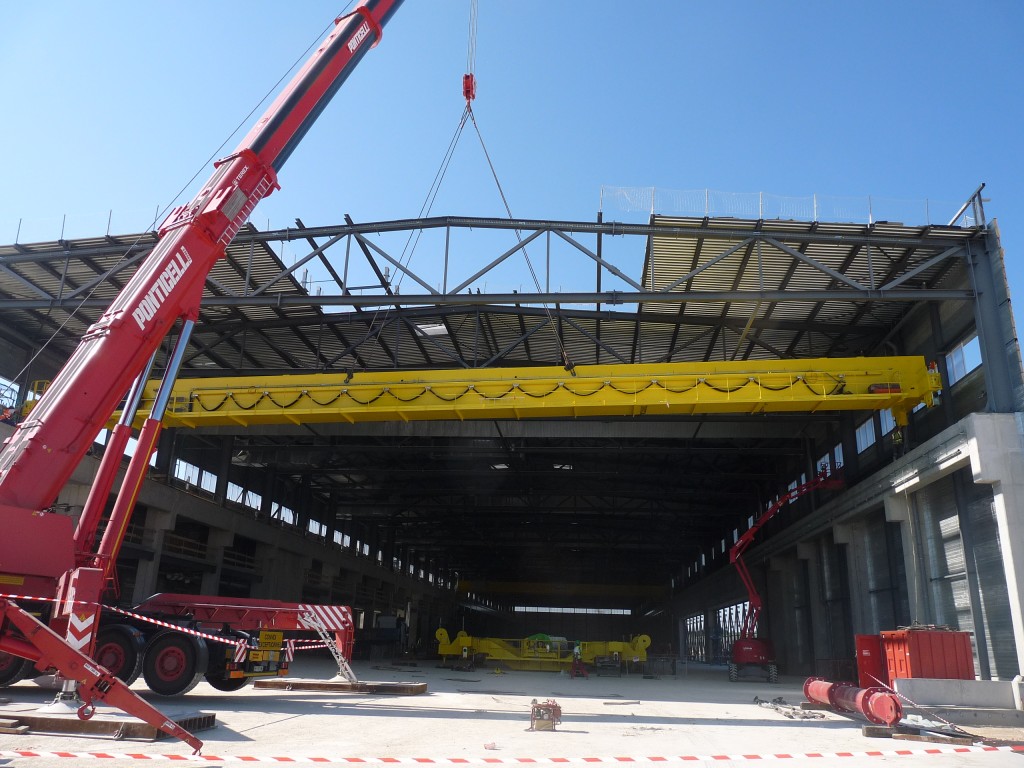
Here's the second crane
2011-10-04 - The first 40-metre steel beam—part of the Winding Facility's second travelling crane—is lifted onto the waiting rails. Photo: ENGAGE.AP

15 metres tall
2011-09-30 - In six months' time, the retaining walls for the Tokamak Complex will completely cover the rock face of the Seismic Pit. Photo: F4E
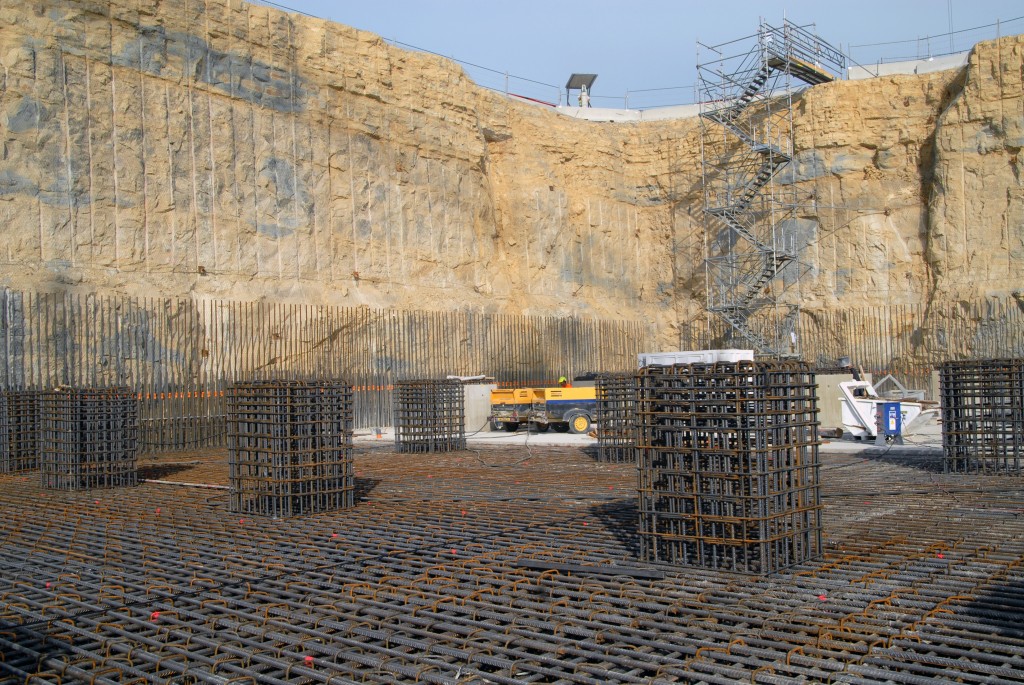
A crawl space between two basemats
2011-09-30 - The "crawl space" between the Seismic Pit basemat and the Tokamak Complex basemat will permit regular inspection of the seismic pads, which are designed to last well beyond the lifetime of ITER. Photo: F4E
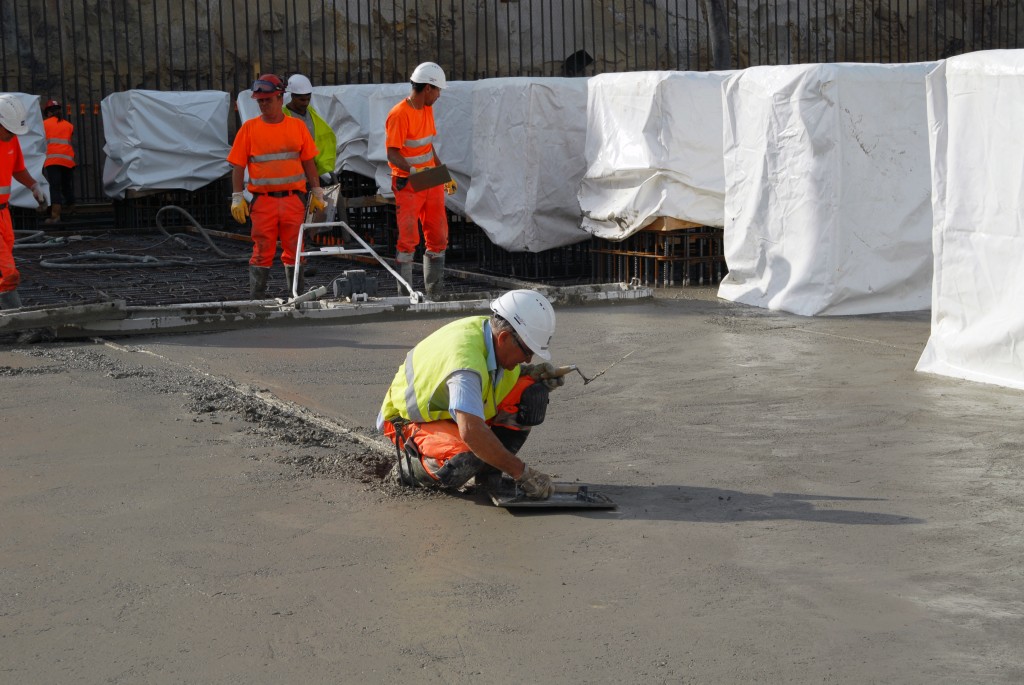
One month to dry fully
2011-09-30 - The concrete begins to harden in 48 hours and is completely dry in 28 days. Photo: F4E
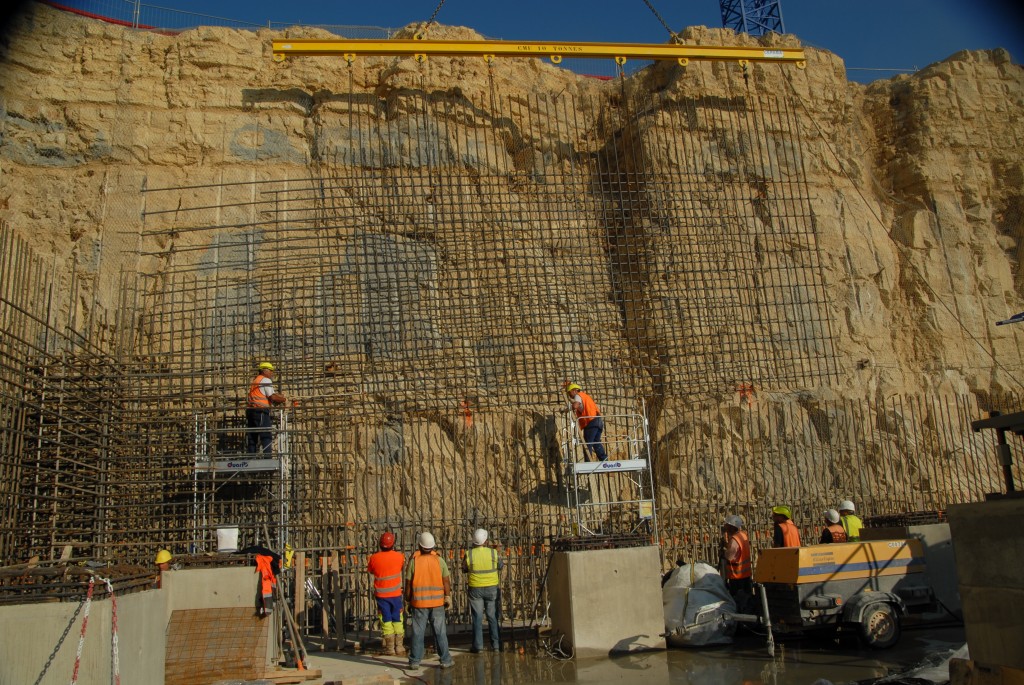
Rebar for the side walls
2011-09-30 - Iron rebar is set into place in September for the vertical retaining walls of the Seismic Pit. Photo: F4E

Lower segment framed out
2011-09-30 - The 15-metre-tall retaining walls will be poured in three 5-metre stages; the lowest five-metre segment, seen framed out here, is 1.5 metres in width. Space between the upper segments of the concrete retaining wall and the rock face will be filled in with gravel and sand and compacted. Photo: F4E
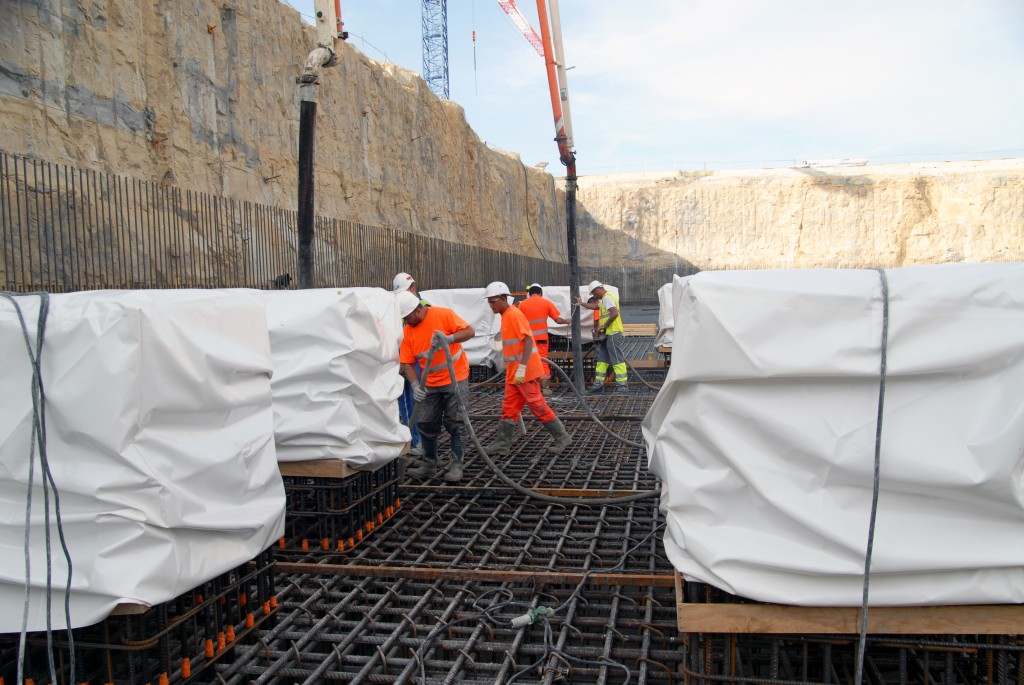
Rubber boots and long pouring arms
2011-09-30 - Concrete pouring is carried out around metal cages that frame out a half dozen of the future seismic pillars. Photo: F4E
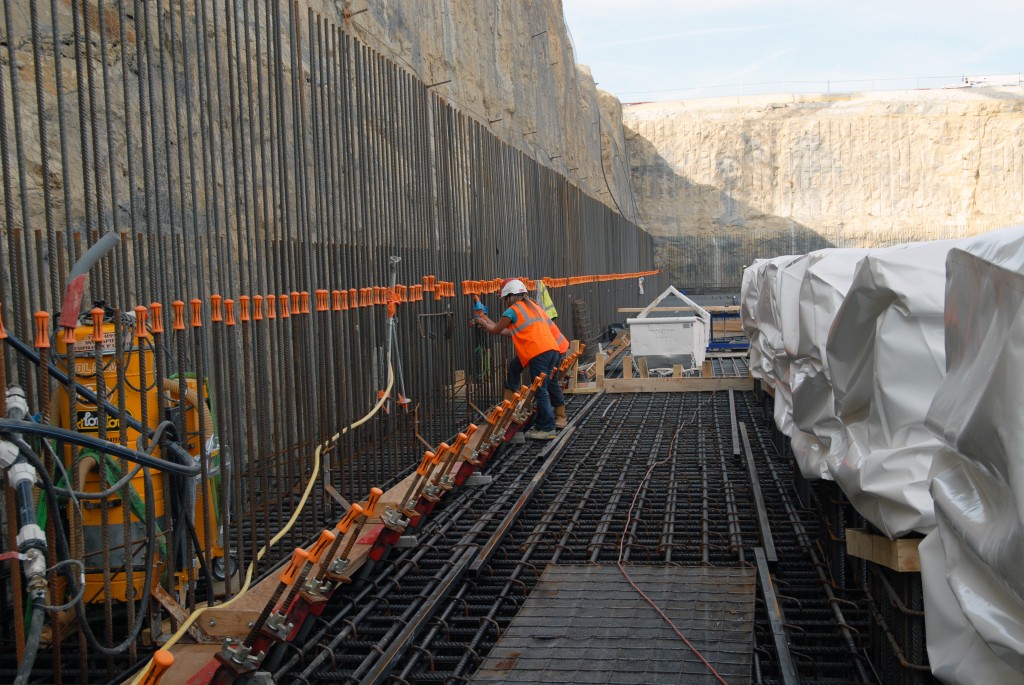
Work to pour the side walls will begin soon
2011-09-30 - Concrete pouring for the retaining walls of the Seismic Pit will be carried out between October 2011 and March 2012. Photo: F4E
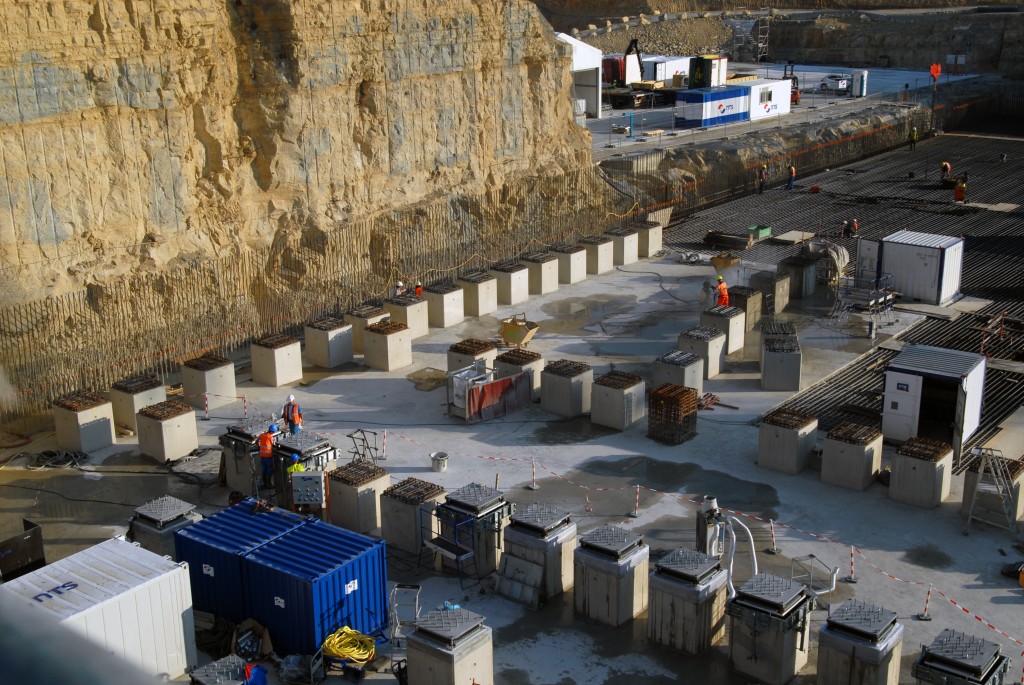
Work on the seismic pads progresses
2011-09-27 - On the floor of the Seismic Pit, work progresses on the Seismic Isolation system for the ITER Tokamak Complex. Photo: F4E
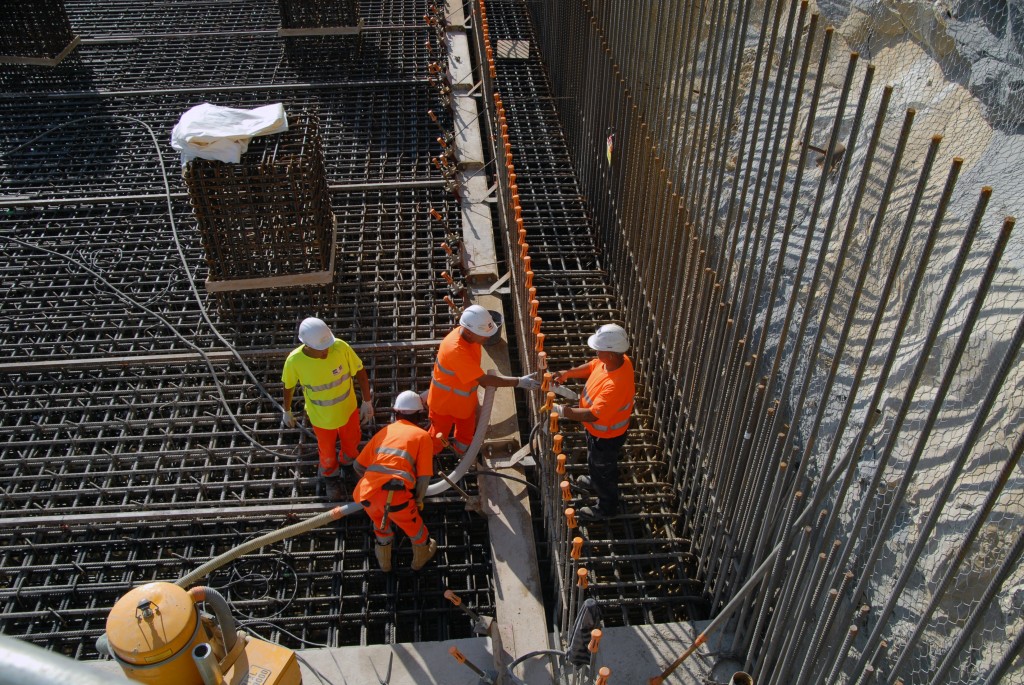
1.5 metre-thick retaining walls
2011-09-27 - Workers set the rebar structure into place for the retaining walls of the Seismic Pit. Photo: F4E
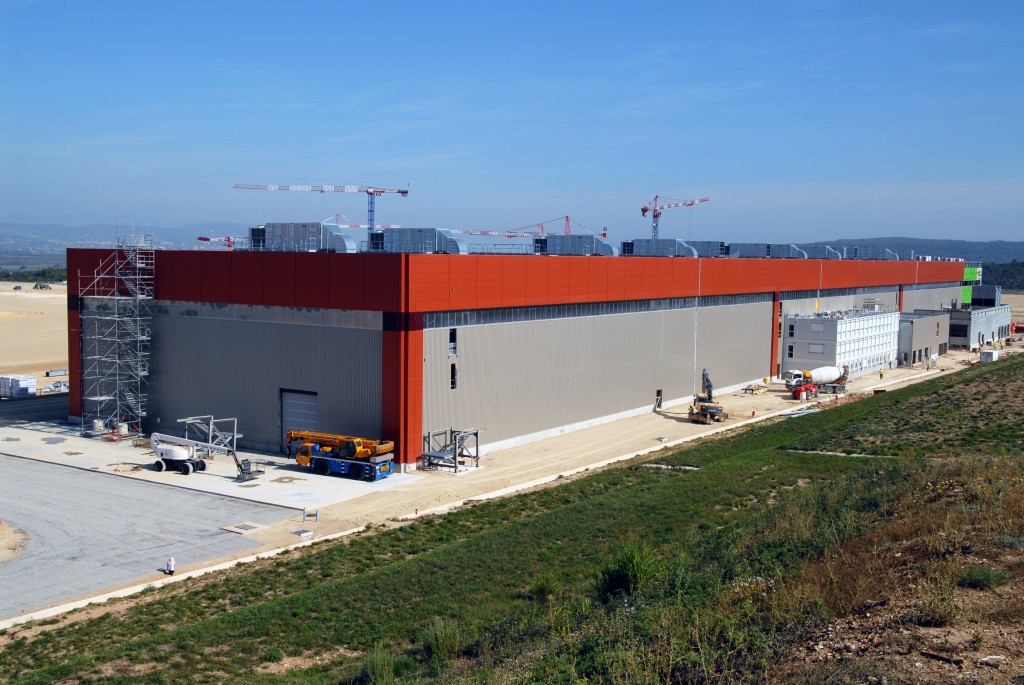
Work on the exterior areas
2011-09-27 - Finishing touches are made to the south end of the Poloidal Field Coils Winding Facility and work begins to pave roads. Photo: F4E
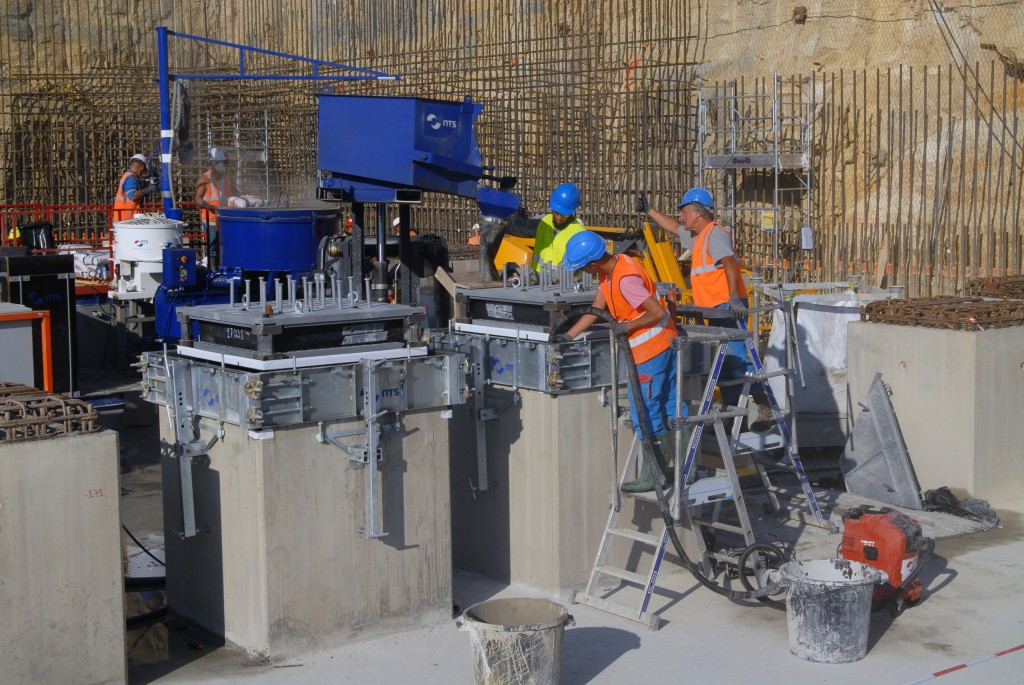
Phase 2 concrete
2011-09-27 - Metal formwork surrounds the fresh concrete poured between each supporting pillar and seismic pad. Photo: F4E
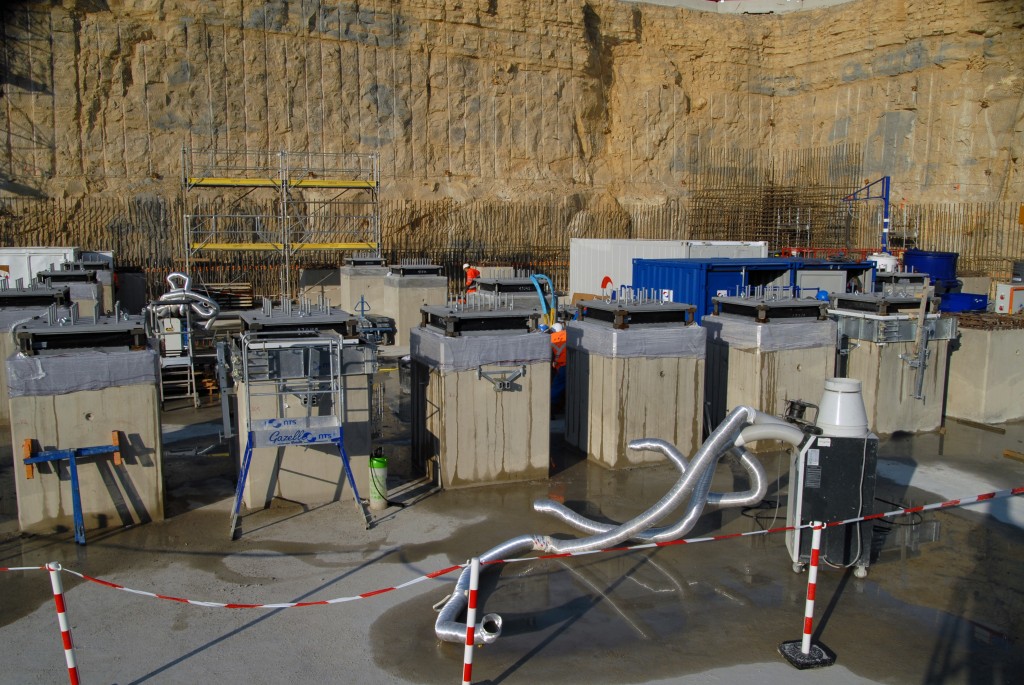
Temperature-controlled concrete
2011-09-27 - In order to cure the "second-phase" concrete below each seismic bearing, workers use a local heating unit to maintain the concrete temperature around 30 degrees centigrade. Photo: F4E
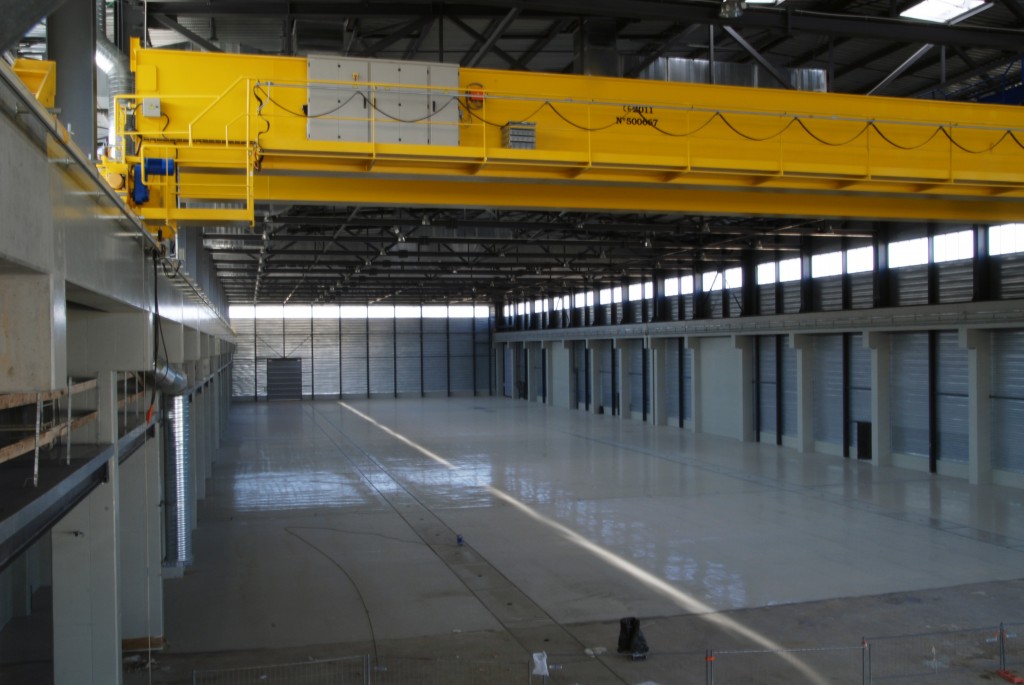
A fresh coat of paint
2011-09-27 - Floor surface treatment is completed on one-half of the Winding Facility. The travelling crane, in yellow, will have the capacity to travel the entire length of the building. Photo: F4E
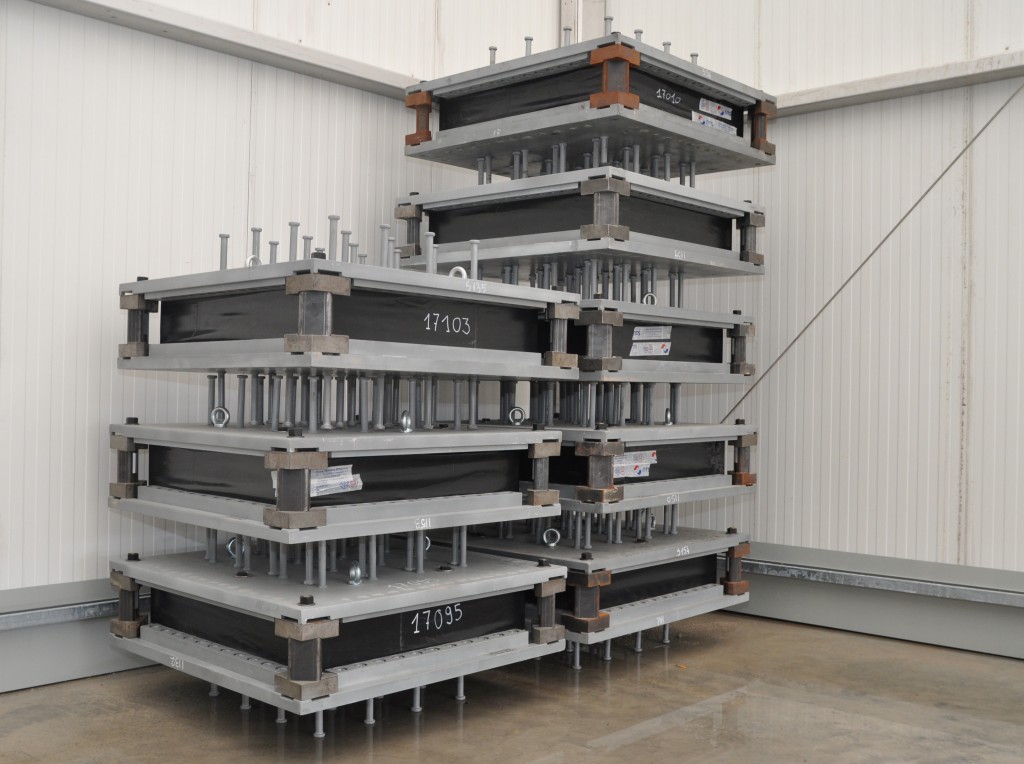
Ten per week
2011-09-19 - On the ITER site, seismic isolation pads await installation. In the months to come, the pads will be installed at a rhythm of approximately ten per week.
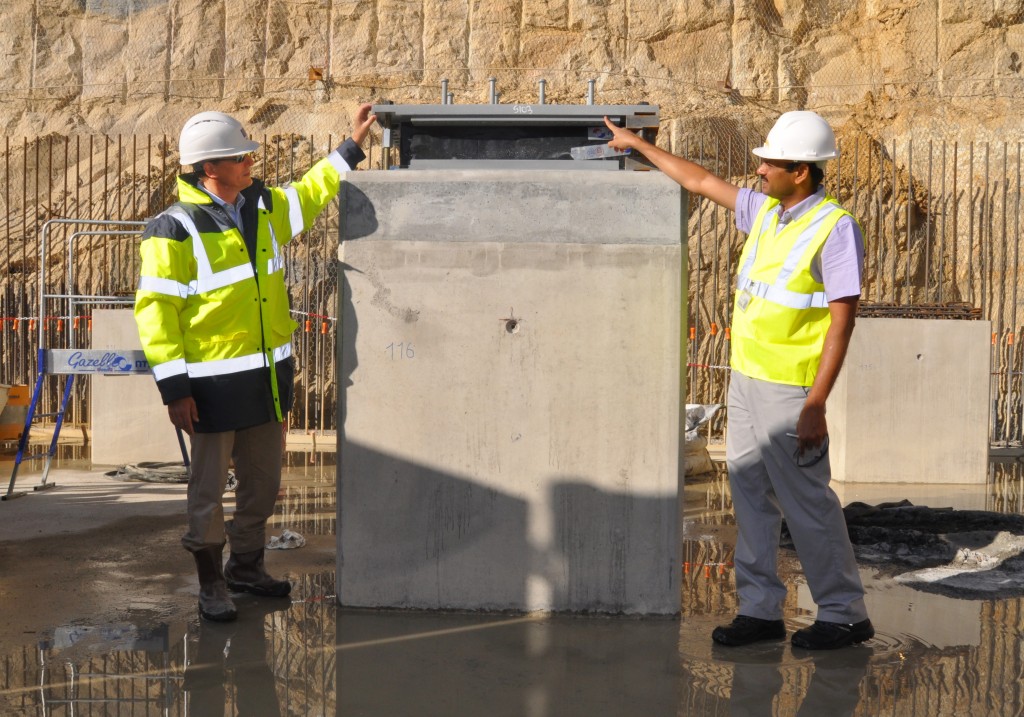
The final result
2011-09-19 - Atop the concrete plinth, the seismic pad has been positioned and cemented into place. When completely dry, the newer concrete will take on the exact colour of the older concrete.
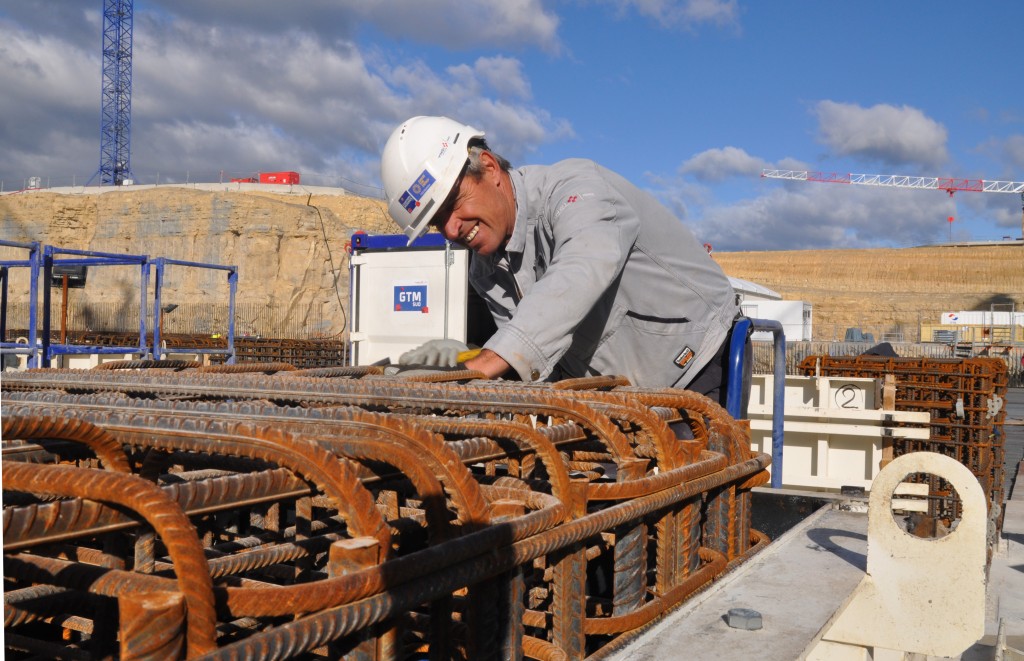
The seismic pads will sit on top
2011-09-19 - A 90 x 90 cm seismic isolation pad will take its place on top of this rebar structure and be cemented into place.
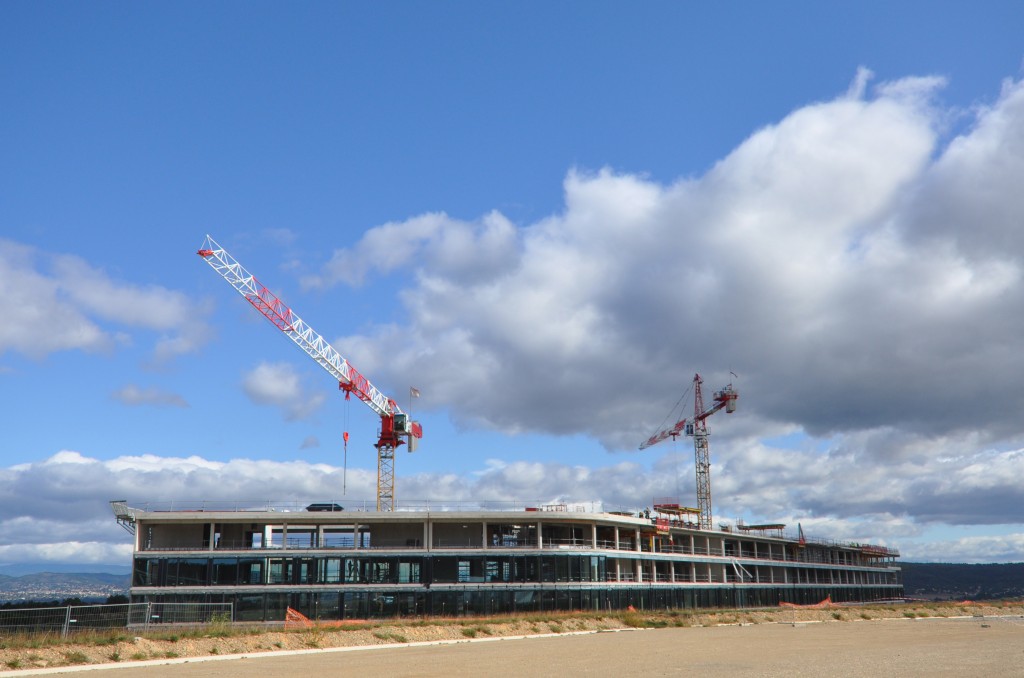
Frame completed
2011-09-19 - Work on the top floor of the ITER Headquarters nears completion in September 2011. The building will have a ground level plus five floors—a total of six levels in all.
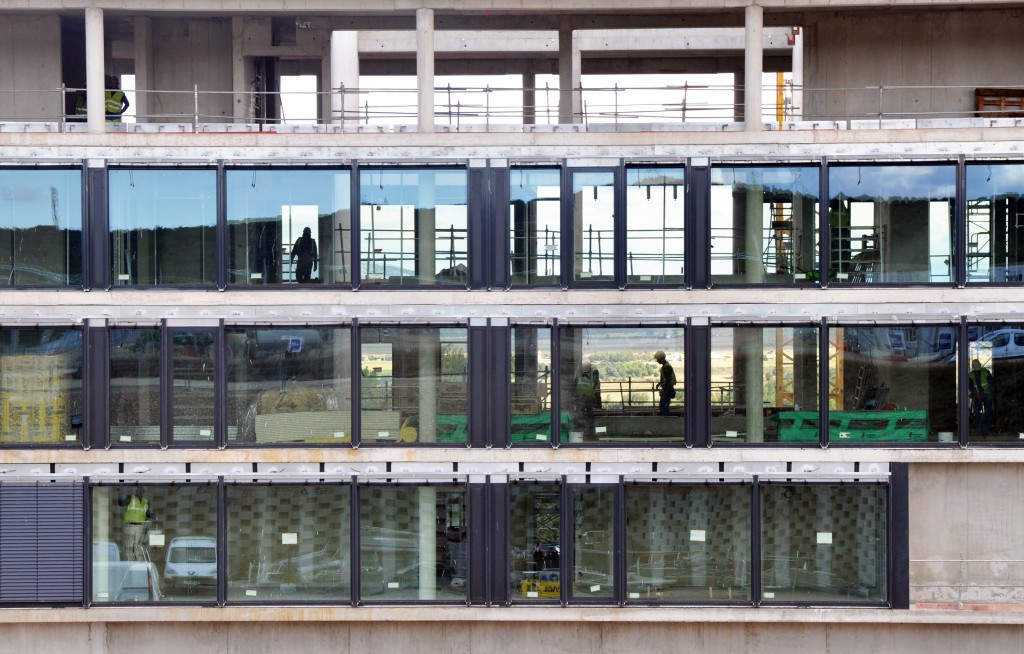
Looking through the glass
2011-09-19 - Natural light predominates on the upper floors of the ITER Headquarters.

Around the edges
2011-09-19 - Seismic Pit basemat pouring continues in September 2011. The areas framed out by wooden walkways are next in line to be poured.
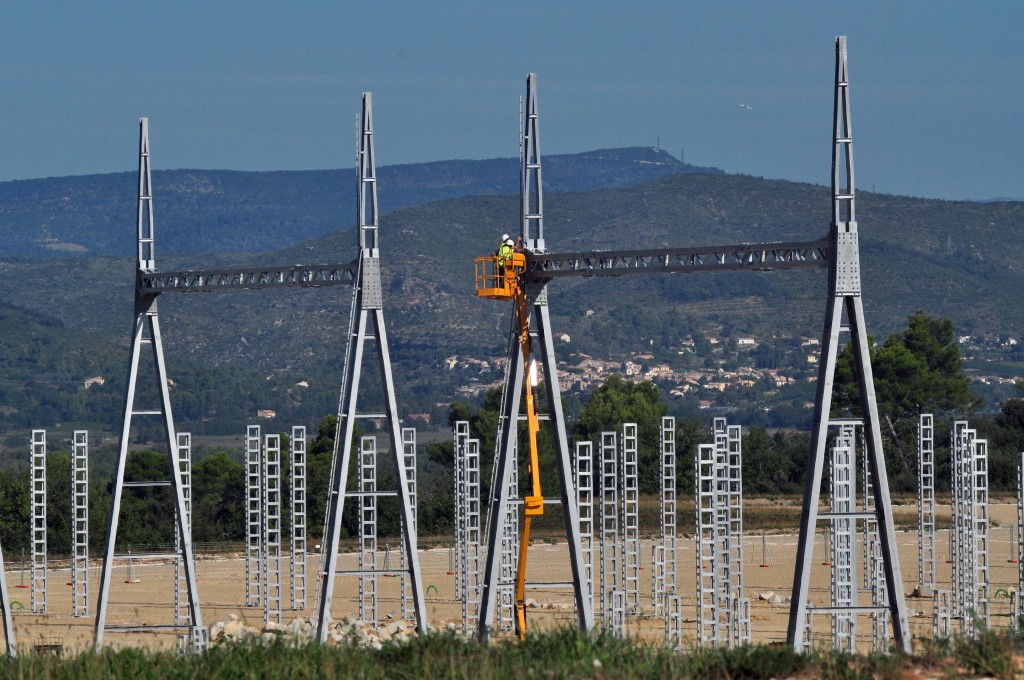
Four hectares for the ITER transformers
2011-09-15 - The 22-metre pylons in the foreground support five-ton crossbars; from here, electricity will be directed toward seven 400 kV transformers. ITER's very high voltage electrical substation will be remotely controlled by RTE (Réseau de Transport d'Electricité).
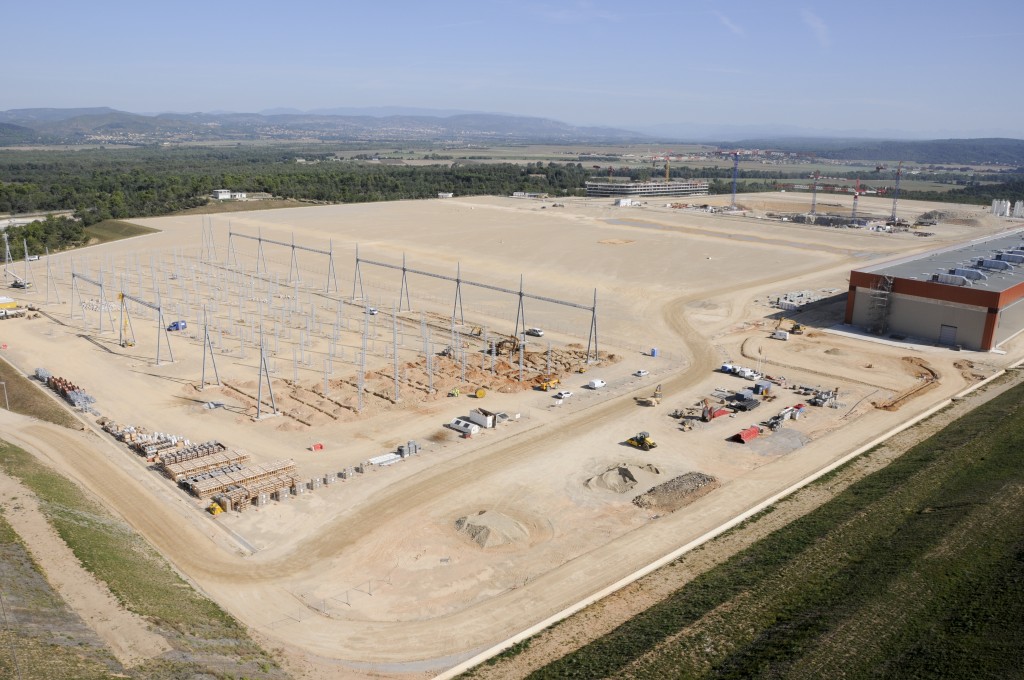
42 hectares
2011-09-14 - The 42-hectare ITER platform, seen from the southern corner in September 2011. Counterclockwise from left: the RTE switchyard, the Poloidal Field Coils Winding Facility, the Seismic Pit—home to the future ITER Tokamak—and, in the distance, the ITER Headquarters, forecast for completion in July 2012. Photo: Altivue/ITER Organization
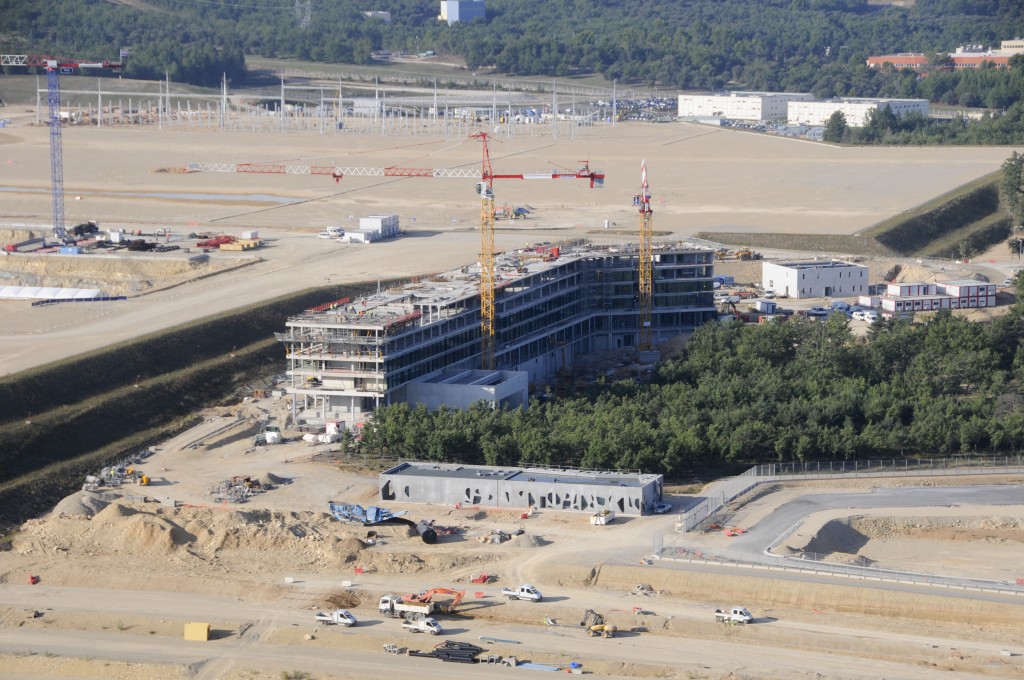
Seen from the north
2011-09-14 - The future ITER Headquarters, the Site Access Control Building (in the foreground) and the Medical Centre and research facility access building (behind the Headquarters) are seen from the north. Photo: Altivue/ITER Organization
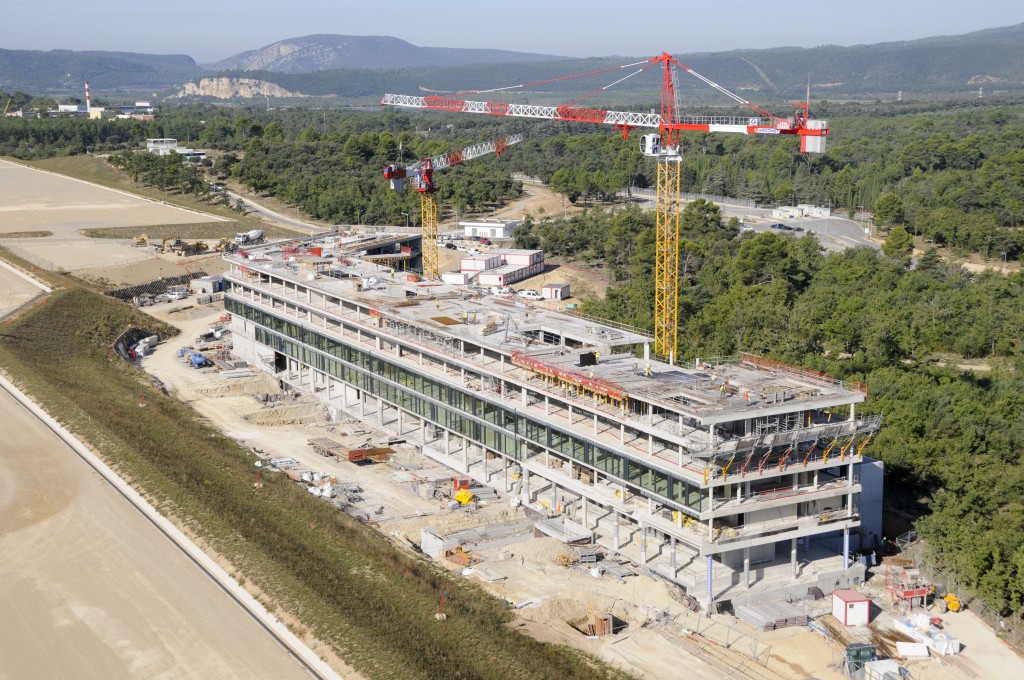
Designed by local architects
2011-09-14 - The ITER Headquarters was designed by local architects Rudy Ricciotti and Laurent Bonhomme, in association with SNC-Lavalin and Cap-Ingelec. Construction began one year ago in October 2010. Photo: Altivue/ITER Organization
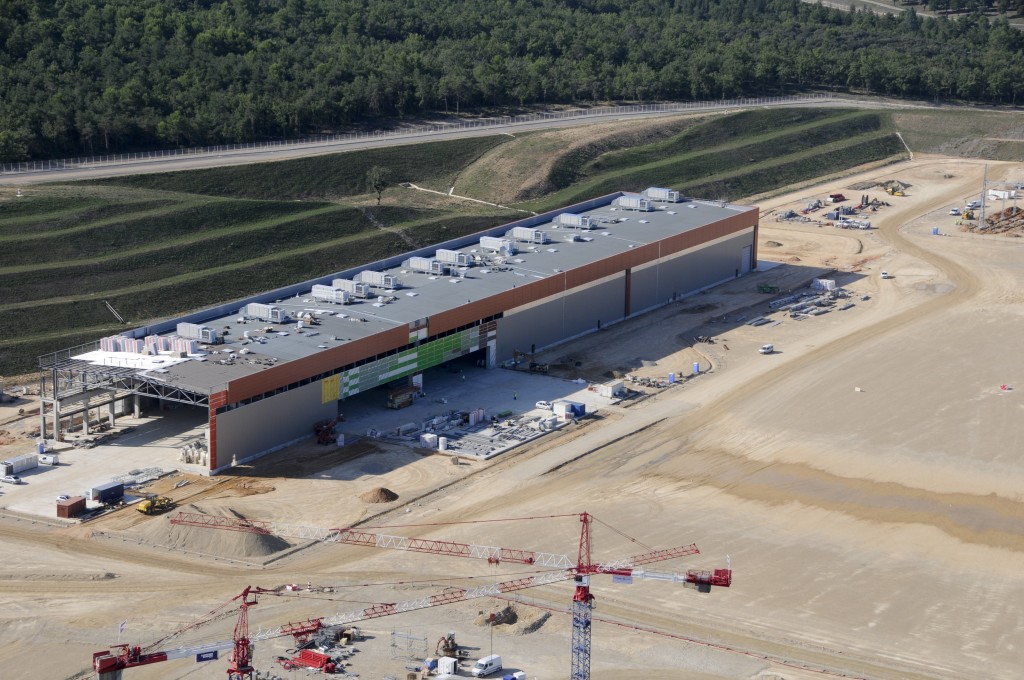
Test power and HVAC in October
2011-09-14 - The Winding Facility is just a few months from completion. Scheduled for October: power, HVAC (heating and air conditioning) and fluid tests; the delivery of the second bridge crane, and painting inside the building. Photo: Altivue/ITER Organization
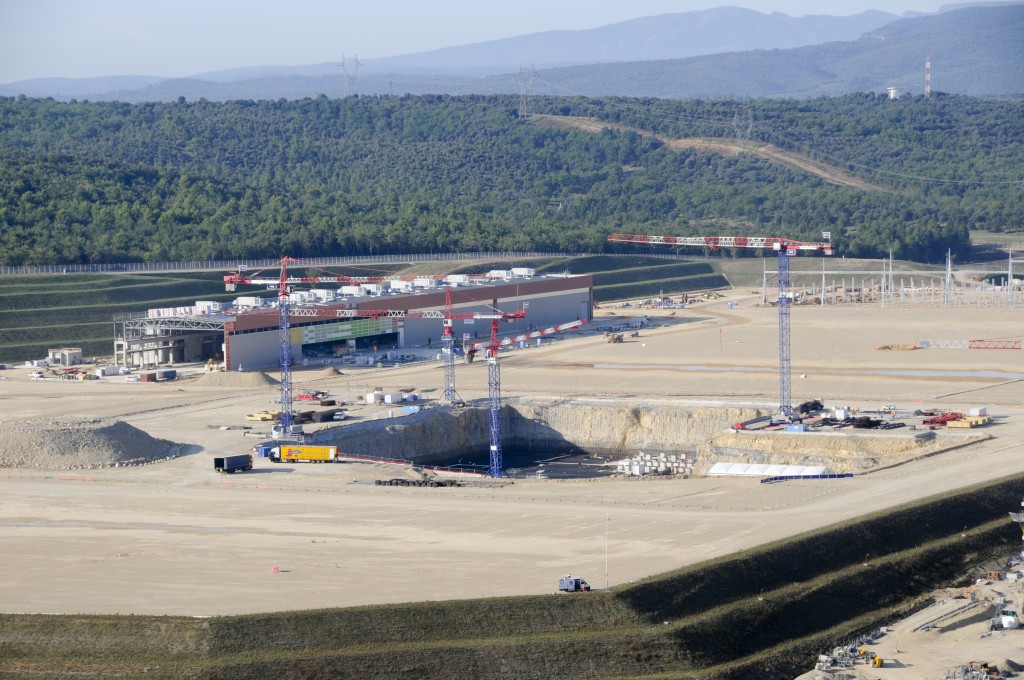
Completed in December
2011-09-14 - The north face of the Poloidal Field Coils Winding Facility will remain open until the final bridge crane is delivered in October and installed directly on the rails. Photo: Altivue/ITER Organization
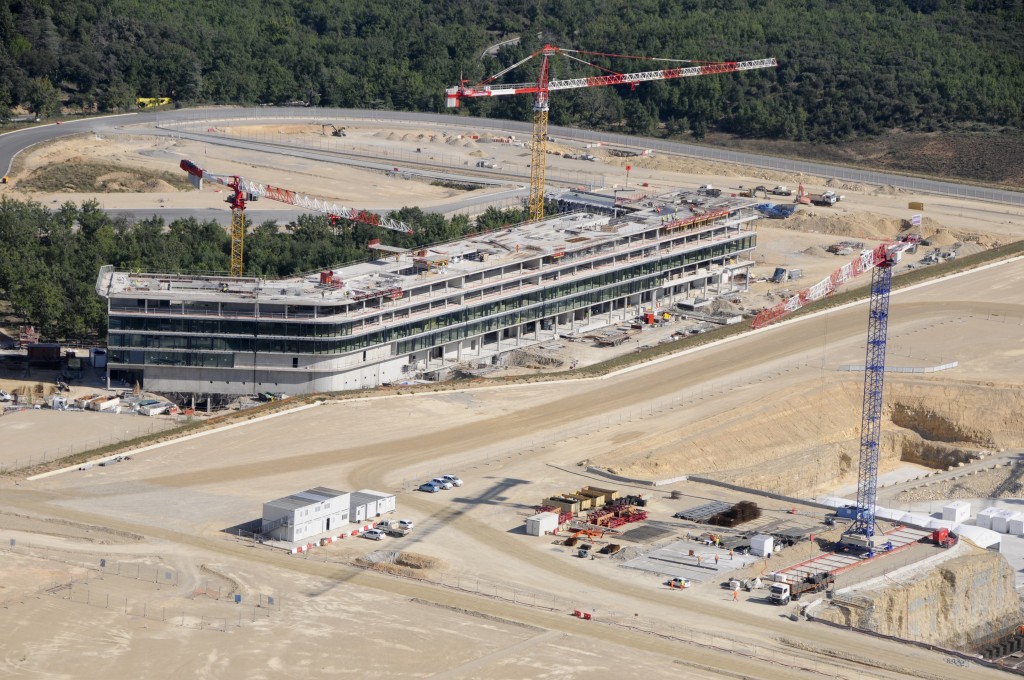
Facing the platform
2011-09-14 - Seen from the sky, the offices on the southeast side of the ITER Headquarters building look toward the platform. Photo: Altivue/ITER Organization
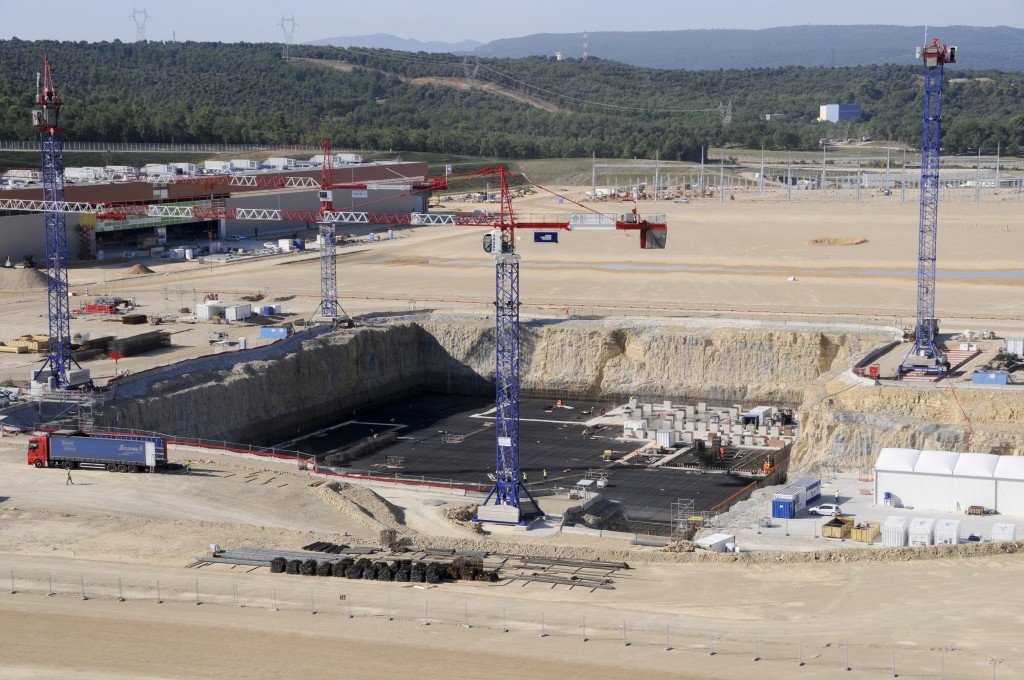
Aerial view in September 2011
2011-09-14 - Looking south over the Tokamak Complex Seismic Isolation Pit in September 2011. Photo: Altivue/ITER Organization
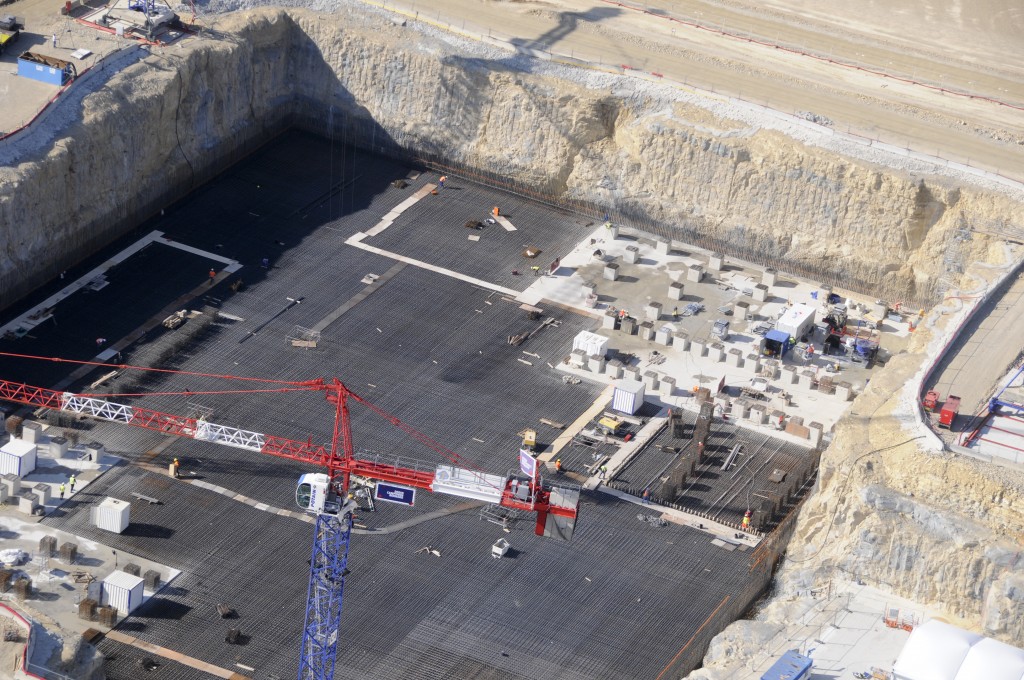
Foundation work seen from the sky
2011-09-14 - Seismic pads fabricated in Romania and assembled in France are installed on supporting plinths in September 2011. Photo: Altivue/ITER Organization
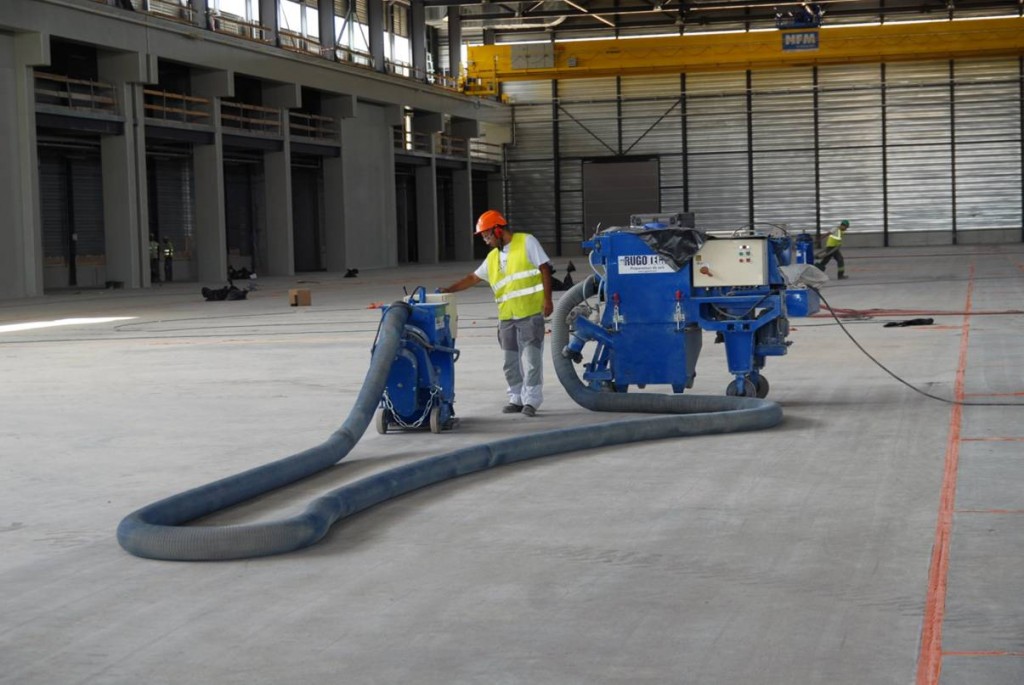
Floor preparation
2011-09-12 - Workers "shotblast" the floor to prepare for painting operations in September 2011. Photo: F4E
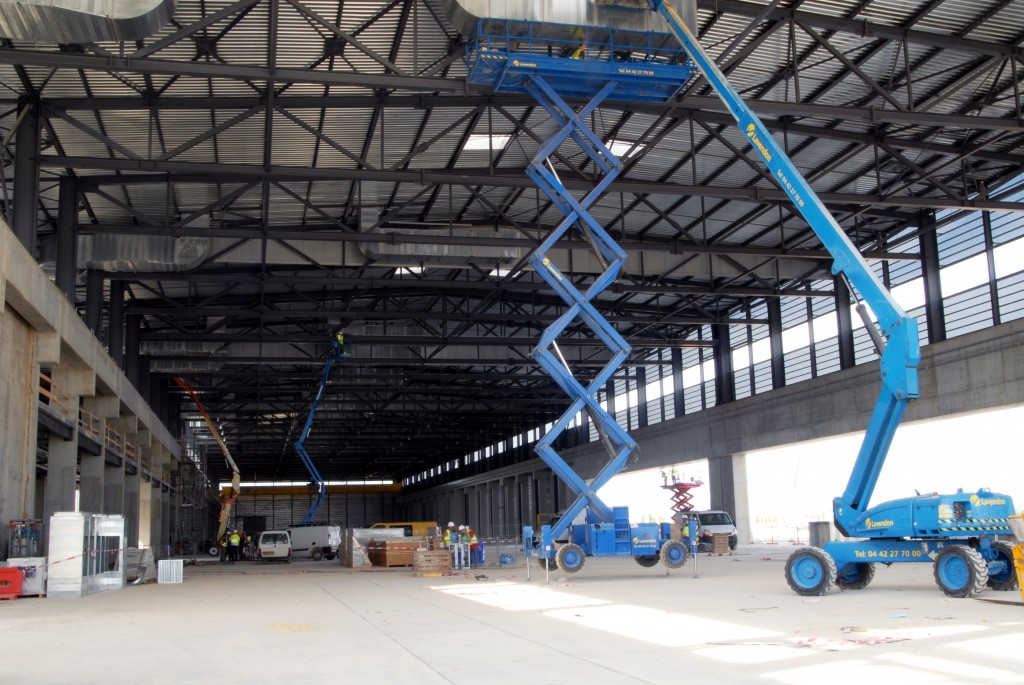
The inside of the winding facility
2011-09-01 - The Poloidal Field Coils Winding Facility is 257 metres long, 49 metres long and 18 metres high. Photo: F4E
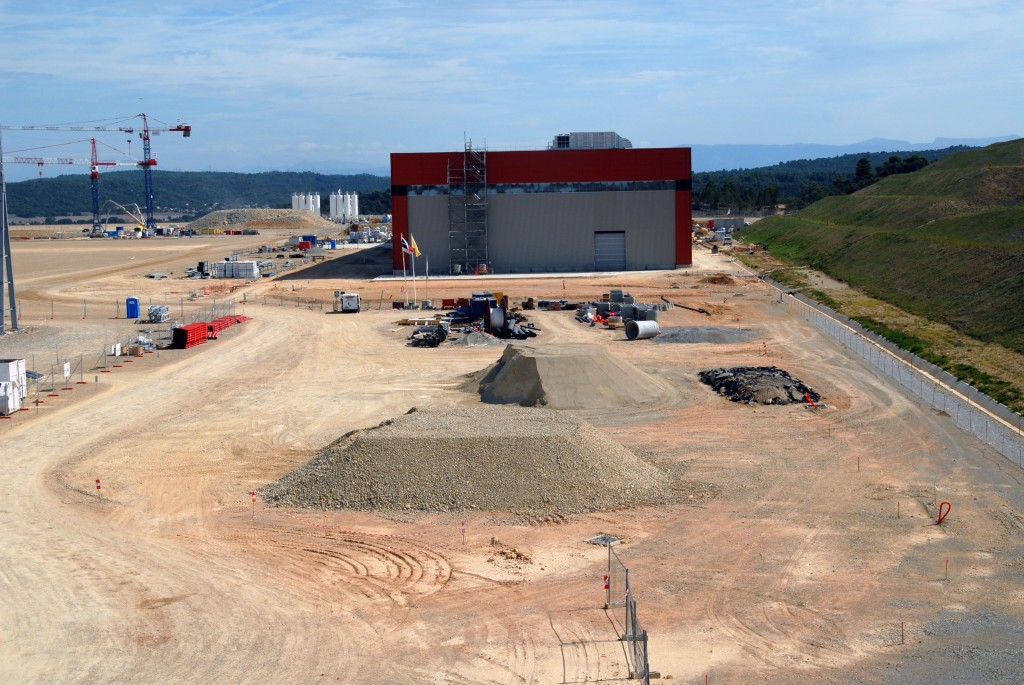
On schedule
2011-09-01 - Work to finish the Winding Facility progresses as scheduled; delivery is on time for December 2011. Photo: F4E
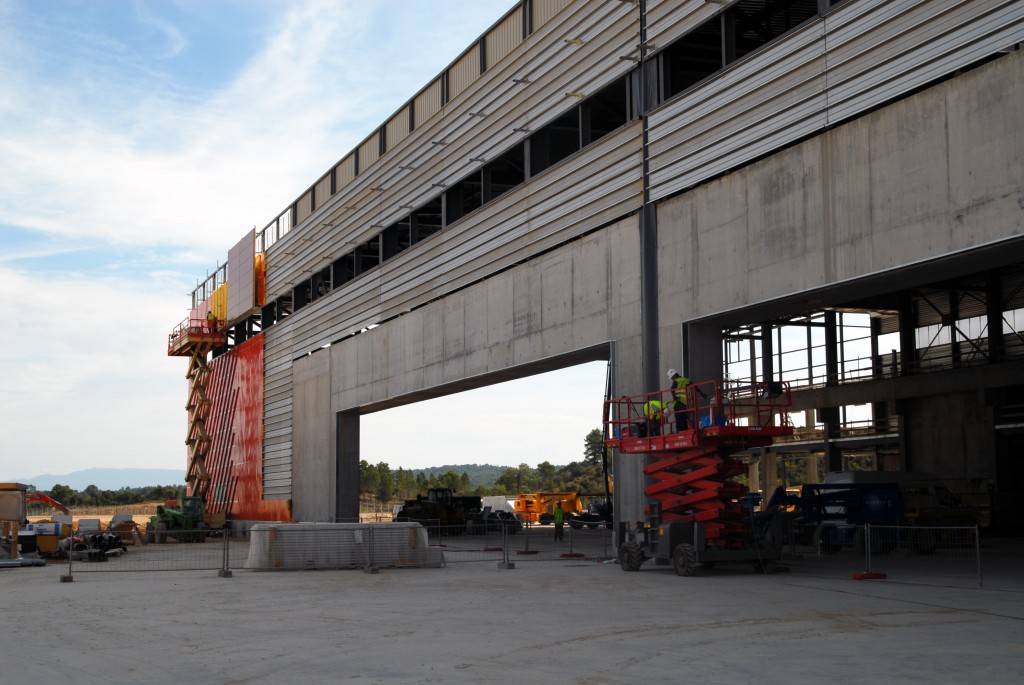
Once finished ...
2011-09-01 - Integrated into the west face of the Winding Facility: two large exit doors for the completed coils. Photo: F4E
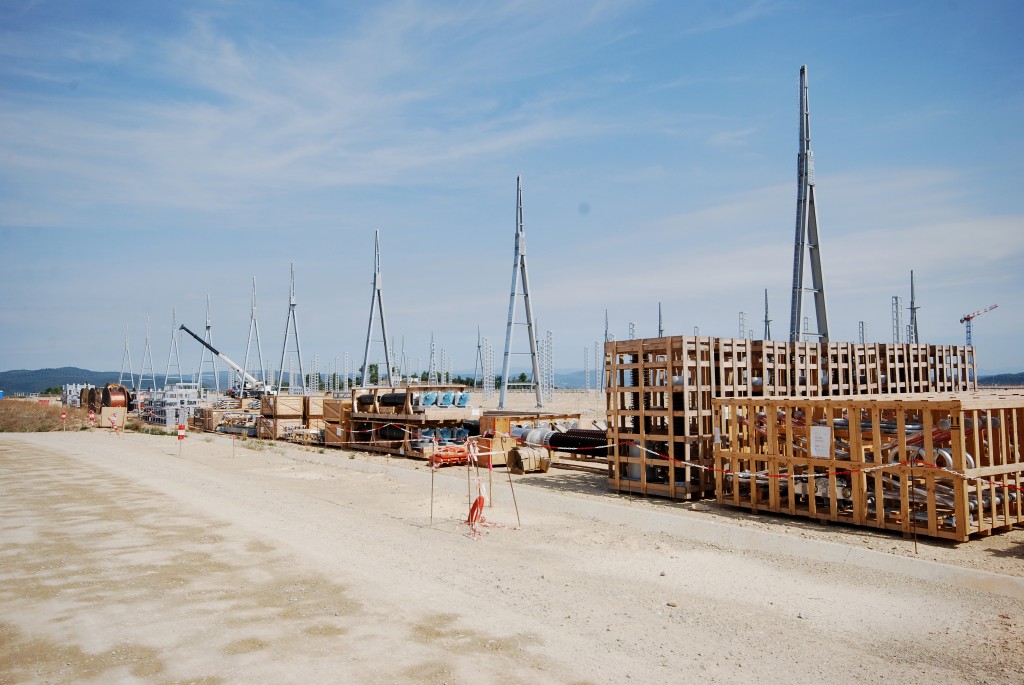
Switchyard emerges
2011-08-31 - In a four-hectare area on the southwest portion of the platform, pylons are installed for the RTE (Réseau de Transport d'Electricité) switchyard that will deliver power from the French grid to the ITER facilities.
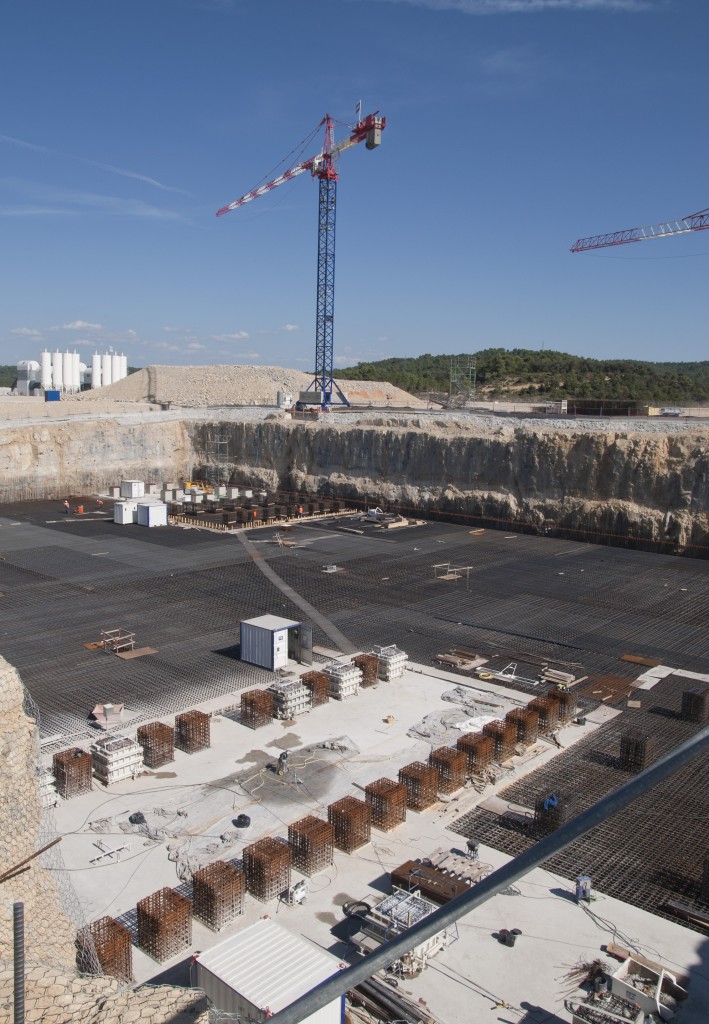
Sandwiched between the Seismic basemat and the Tokamak Complex basemat
2011-08-30 - Each 90 x 90 cm pillar (1.7 metres tall) will support a seismic isolation pad made of alternate layers of metal and rubber. The floor of the Tokamak Complex will rest on a total of 493 pillars.
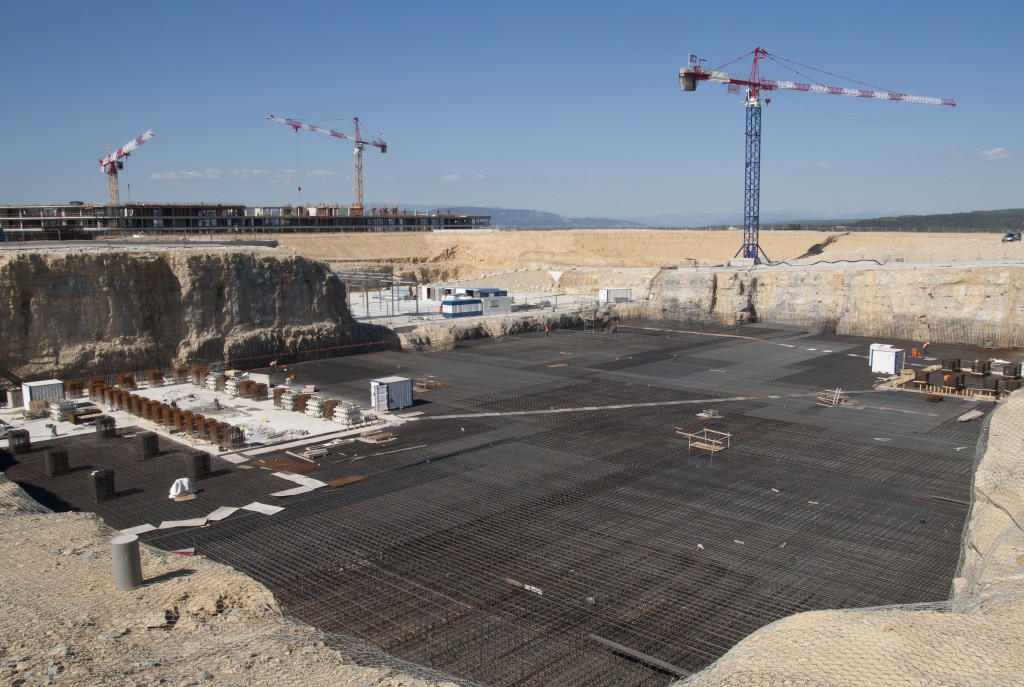
Rows of pillars
2011-08-30 - On one completed corner of the Seismic Pit basemat, the concrete pillars, or plinths, of the seismic isolation system take shape.
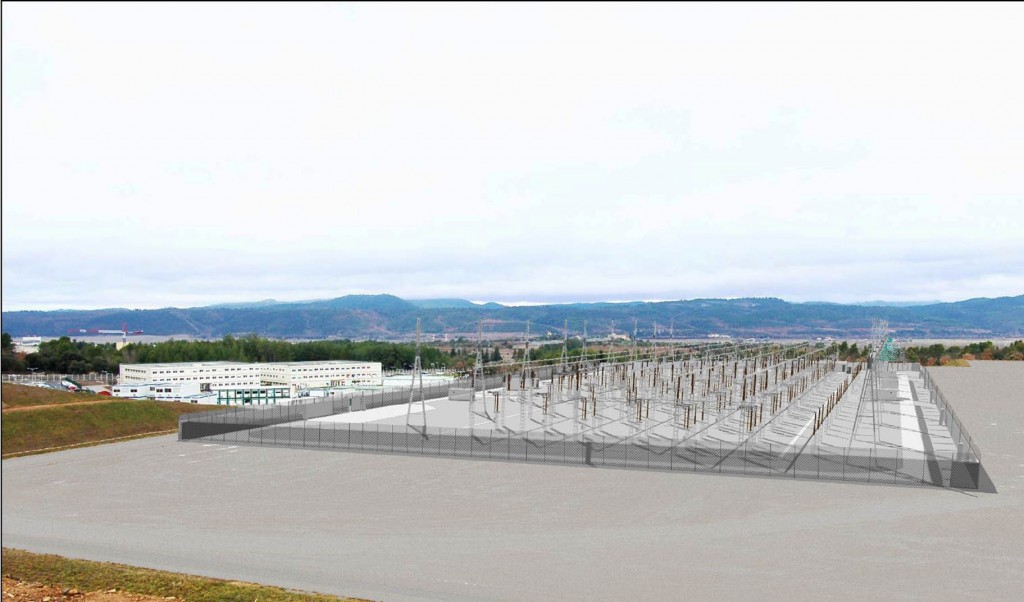
Bringing electricity to the ITER site
2011-08-30 - An artist's view of the 4,000 square metre "switchyard" through which power will be fed to ITER. Image credit: AIF
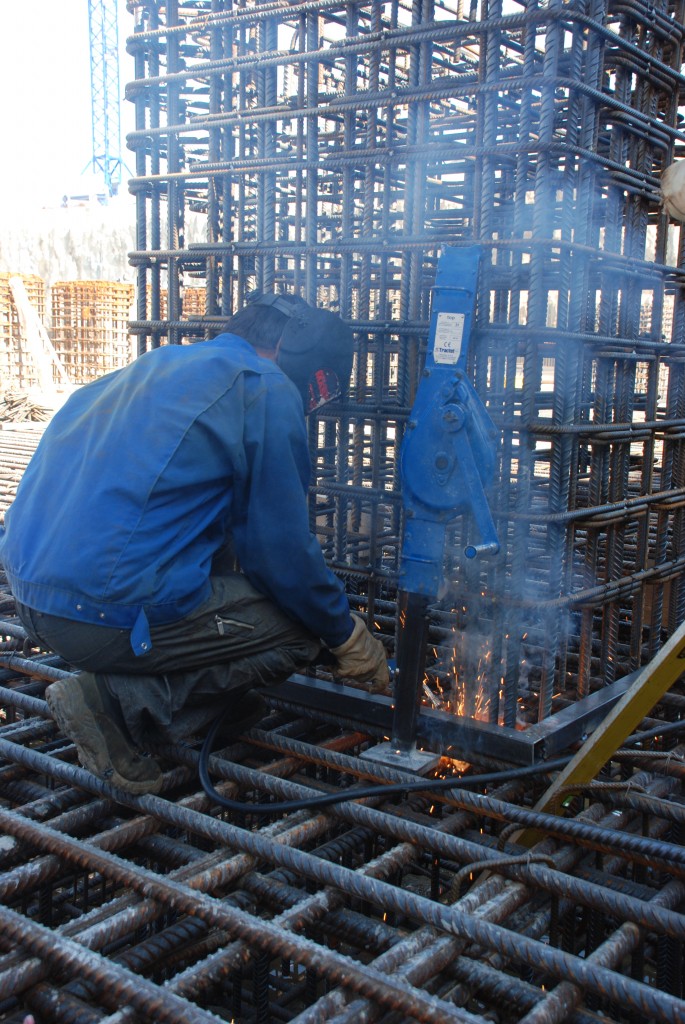
Welding the rebar cages
2011-08-29 - The rebar cages for the 90 x 90 cm concrete plinths are secured into place before each pouring.
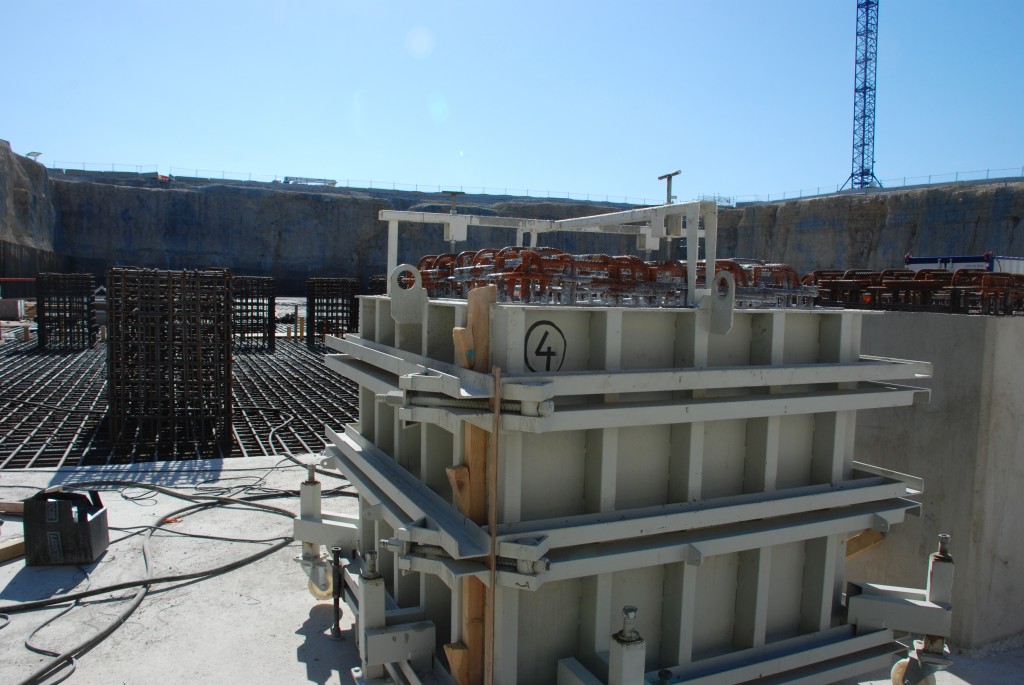
493 concrete plinths
2011-08-29 - This portion of the Seismic Pit basemat has dried, and second phase work begins: the pouring of the 493 concrete plinths that will support the anti-seismic bearings of the Tokamak Complex.
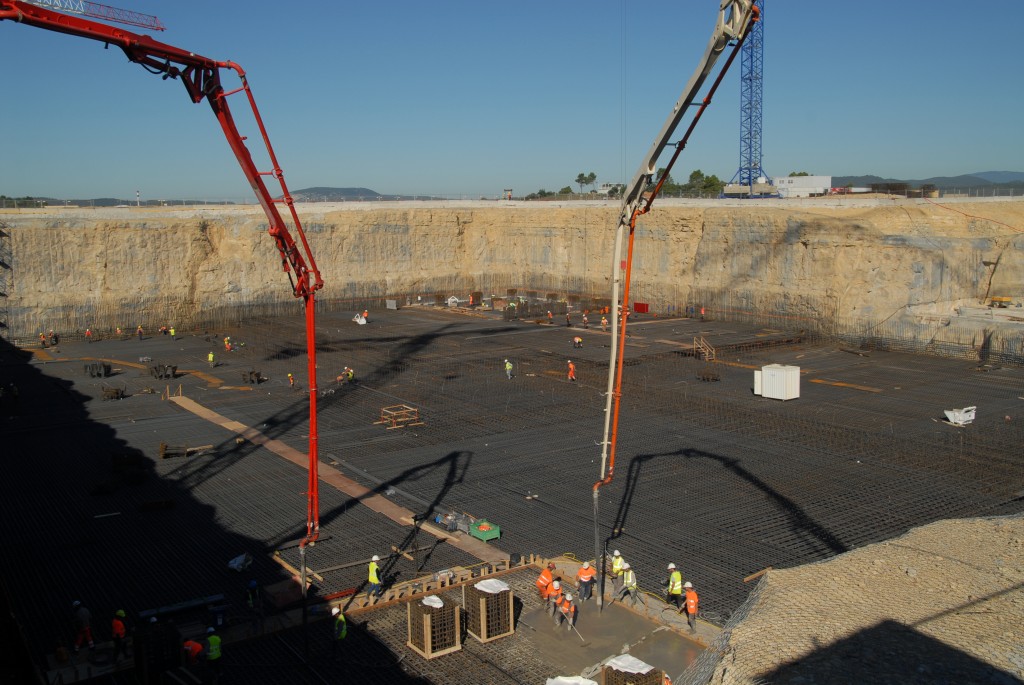
One "pour" follows another
2011-08-11 - Pouring activities begin in the north-west corner of the Seismic Pit; in the opposite corner, preparations are underway for the second day's pour planned for the following week. Work will continue—first one side, then the other—in a counter-clockwise direction until the edges of the basemat are filled in. Photo: F4E
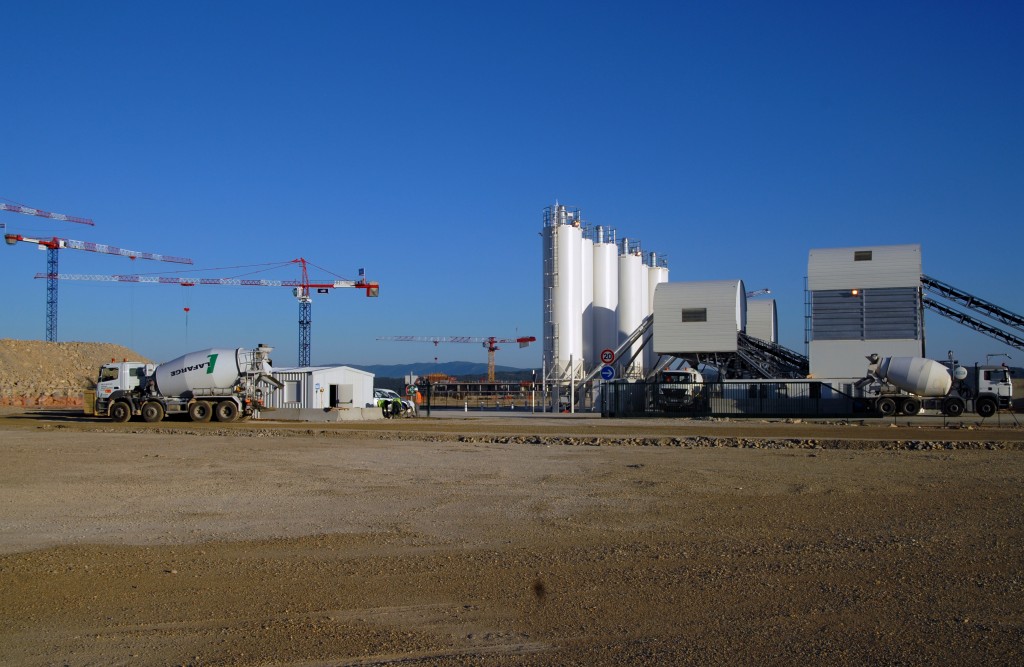
Queueing up for cement
2011-08-11 - The two concrete batching plants on site are each capable of providing a flow of 100 m³ per hour. One plant serves as a backup to the other, ensuring that no disruption occurs in supply during the 12-hour pouring days. Photo: F4E
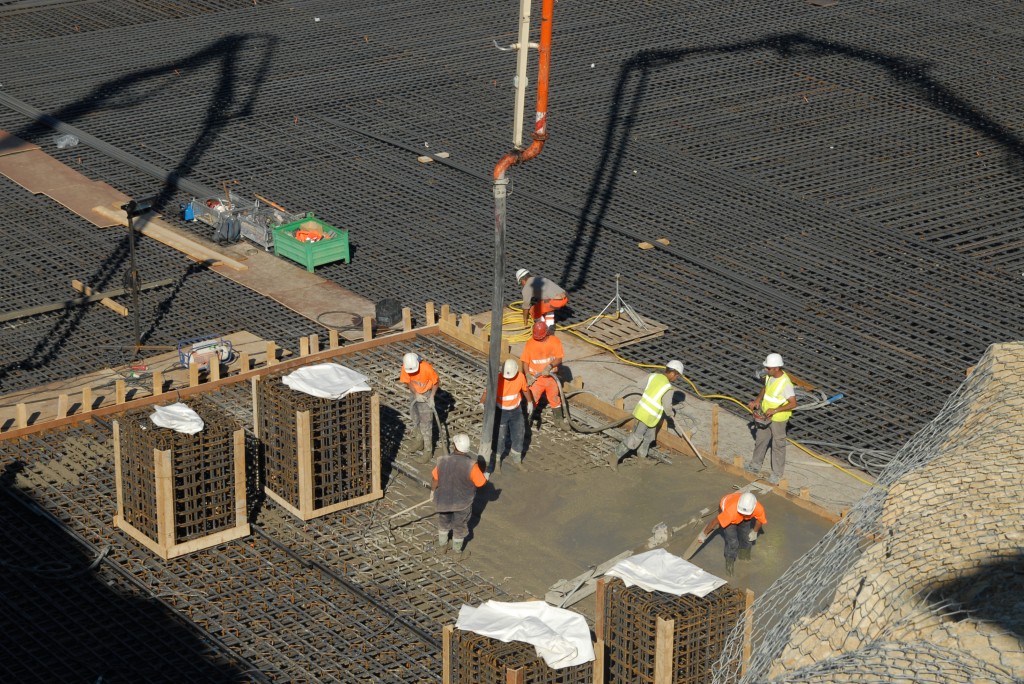
The lower basemat
2011-08-11 - Approximately 18,000 m³ of concrete will be necessary for the 1.5-metre lower basemat of the Seismic Pit. Photo: F4E
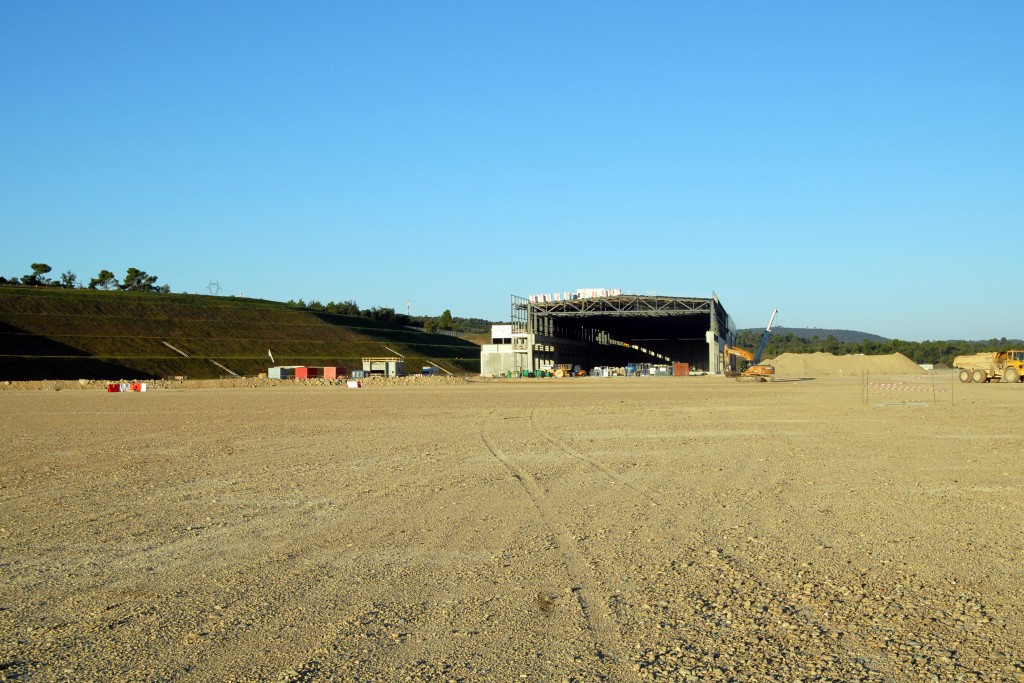
Waiting for the second bridge crane to arrive
2011-08-11 - The far end of the Winding Facility will be closed up after the delivery of the second bridge crane in October. Photo: F4E
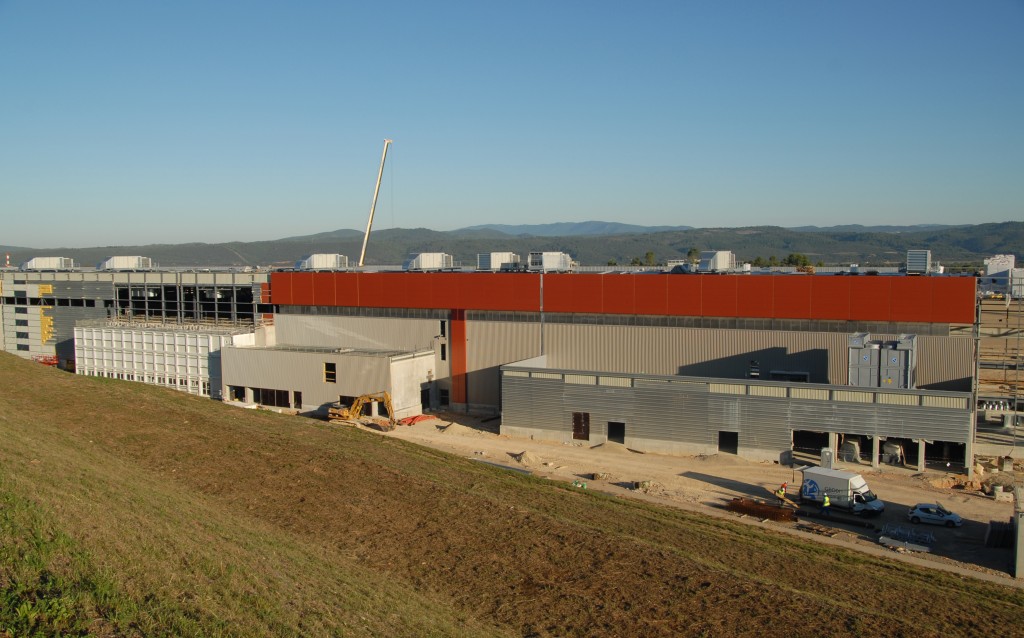
And now, the windows
2011-08-11 - Windows are installed along the top of the Winding Facility in August 2011. Photo: F4E
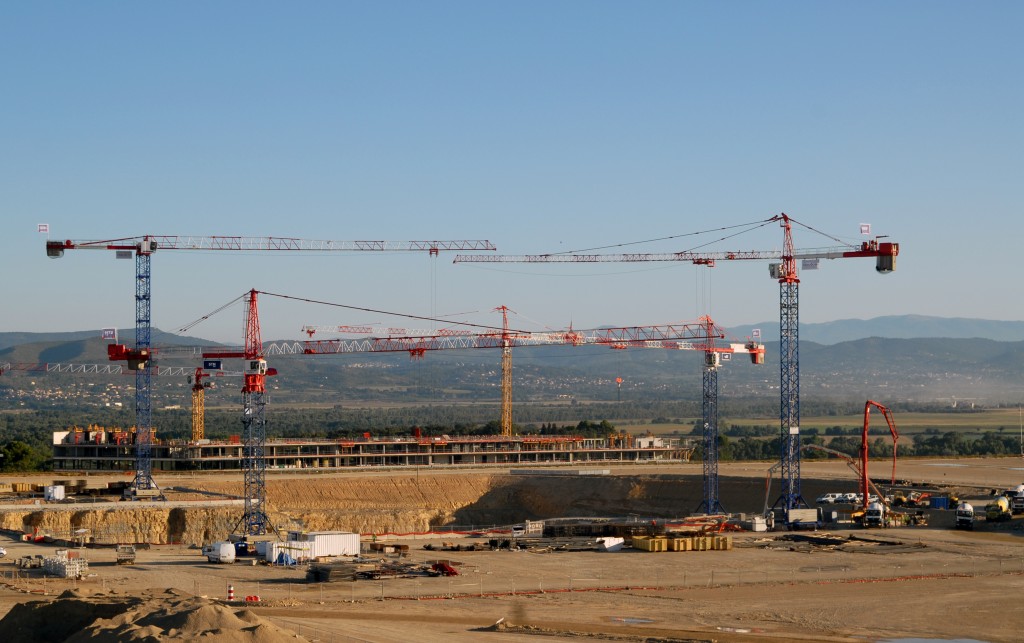
Headquarters now visible from the platform
2011-08-11 - ITER Headquarters emerges from behind the Tokamak Pit, as work begins on the last storey of the building. Photo: F4E
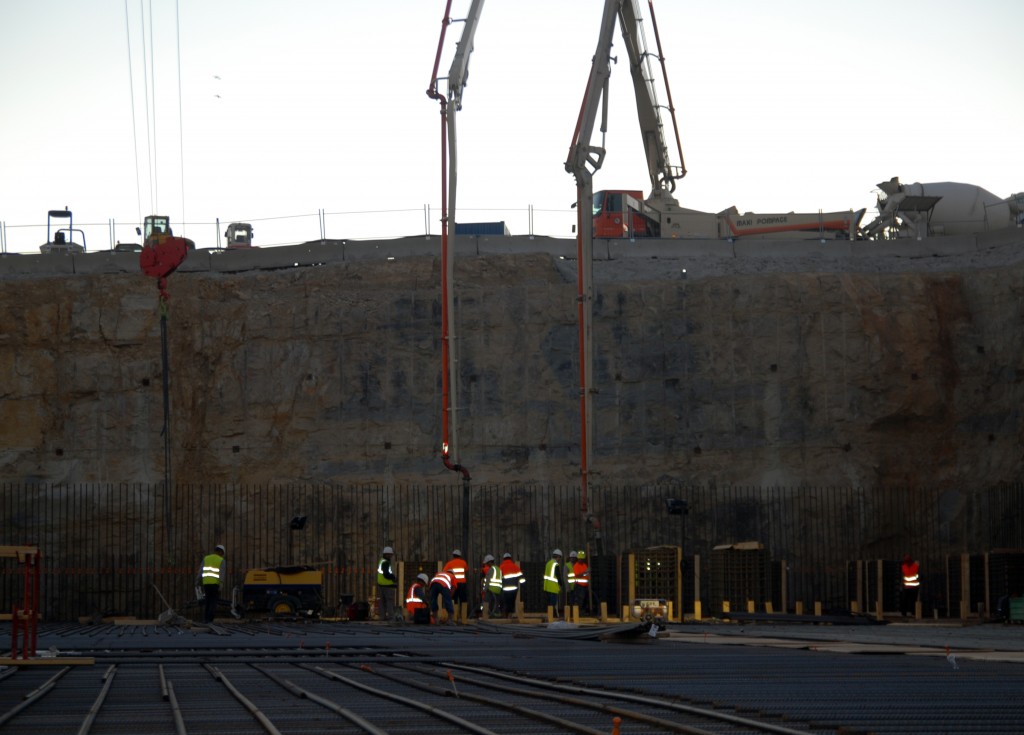
Completing the first "lot" takes 12 hours
2011-08-11 - Some 800 m³ of concrete are poured on the first day. This 12-hour operation will have to be repeated 21 times over the next 3 months to complete the basemat of the Seismic Pit. Photo: F4E
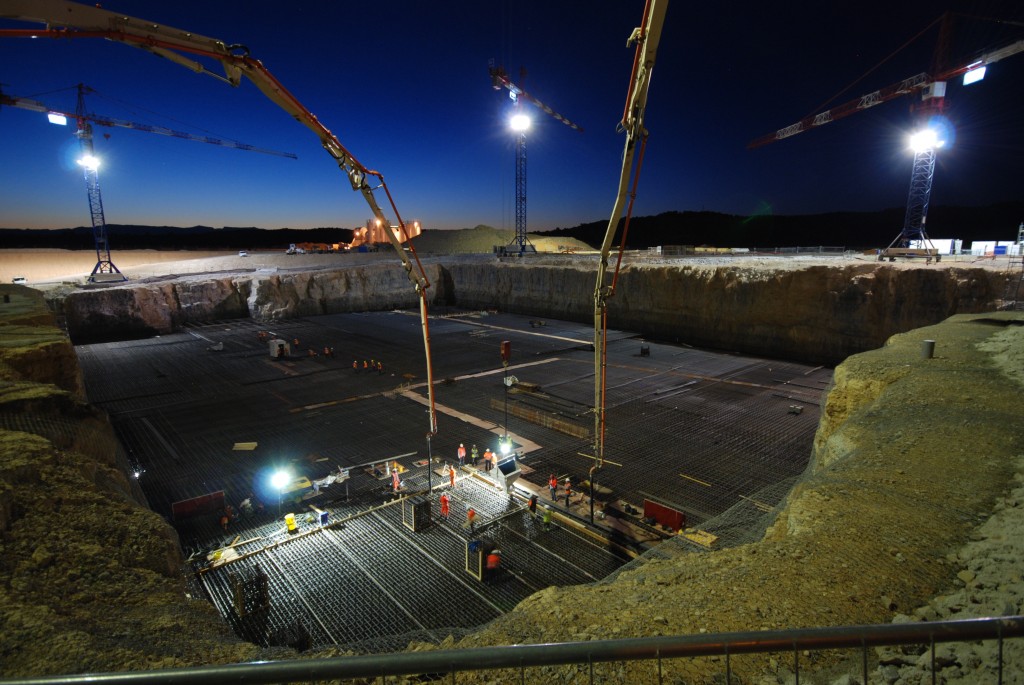
Foundation work begins
2011-08-09 - At 5:00 a.m. on Tuesday, 9 August, foundation pouring begins to create the basemat of the Seismic Pit.
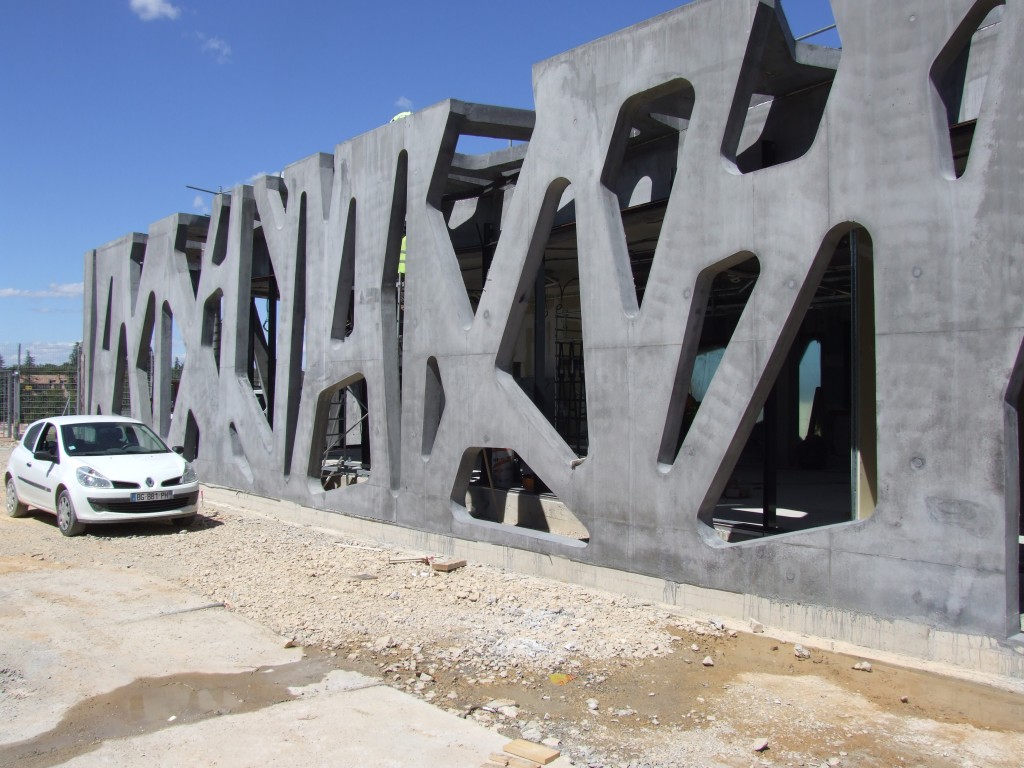
The ITER Site Access Control Building
2011-08-08 - The interesting shapes of the ITER Site Access Control Building seen from the south side. The architectural motifs resemble those of the Provence-Alpes-Côte d'Azur International School situated in Manosque, conceived by the same architect. Photo: AIF
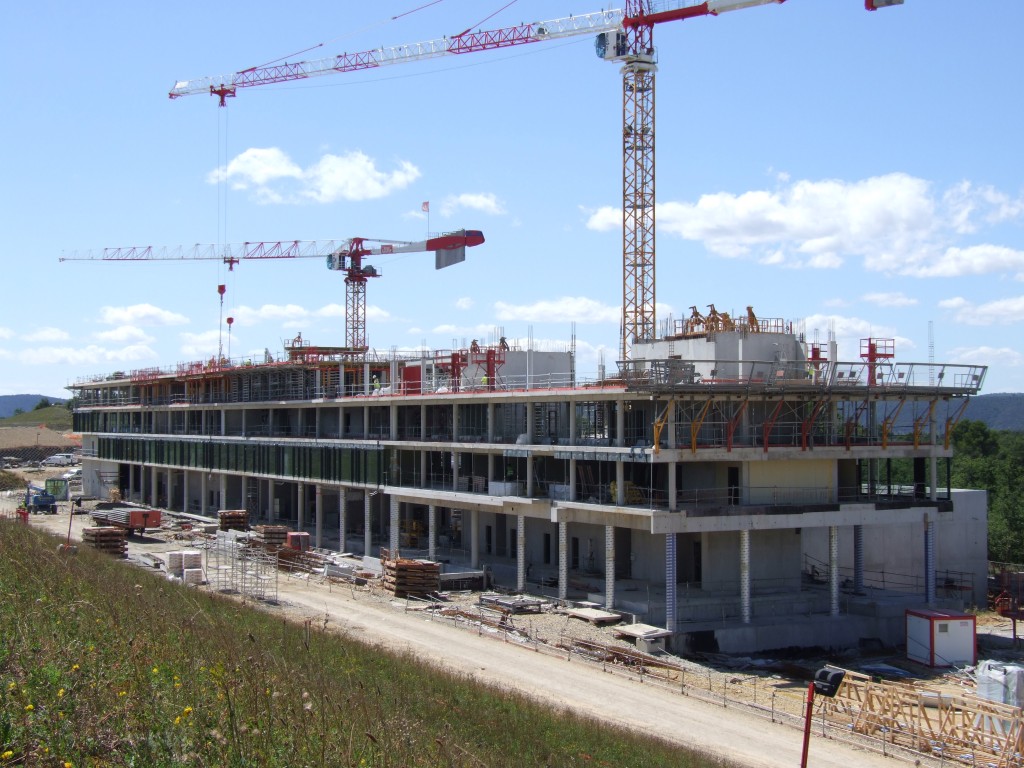
A large boat?
2011-08-08 - The ITER Headquarters, seen from the northeast, could almost look like a large boat. Photo: AIF
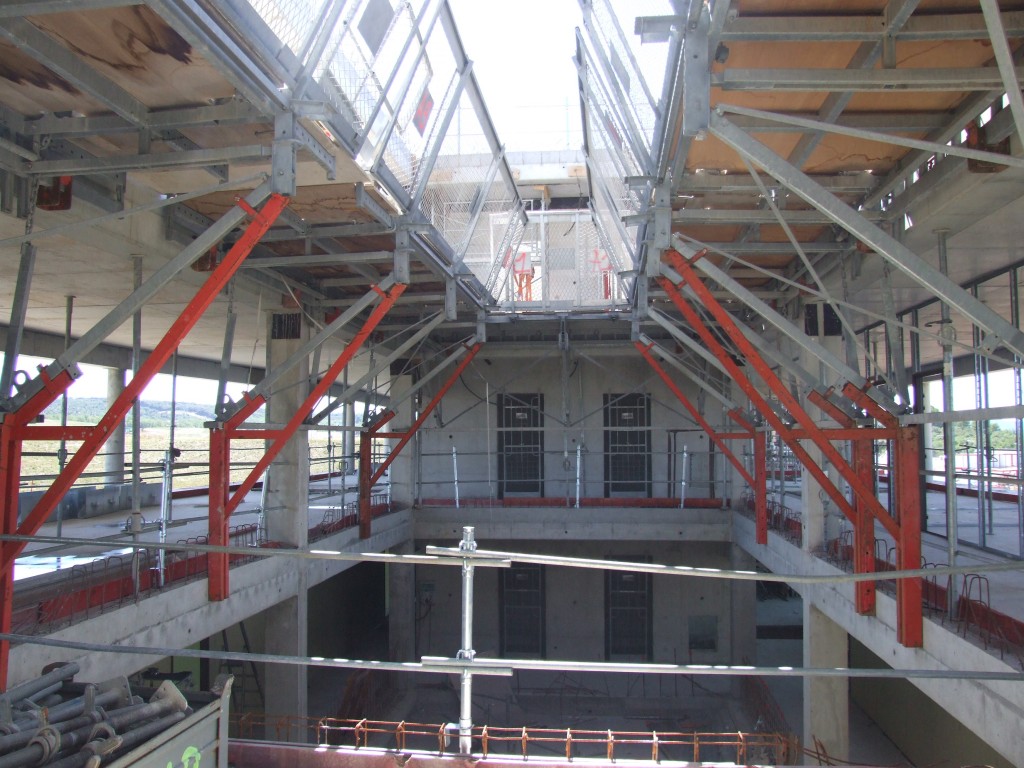
Atriums for the future Headquarters building
2011-08-08 - Two- to three-storey interior patios, planted with vegetation, will generate ventilation and let natural light into the ITER Headquarters. Photo: AIF
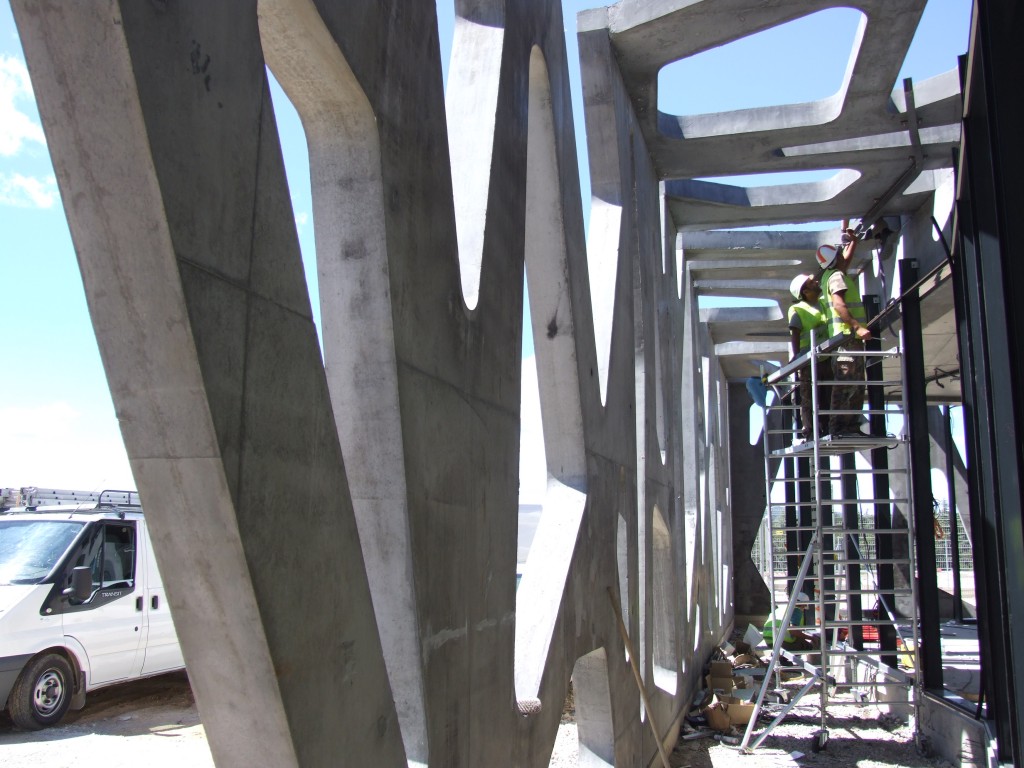
Light and shapes and shadow
2011-08-08 - The ITER Site Access Control Building from within. Photo: AIF
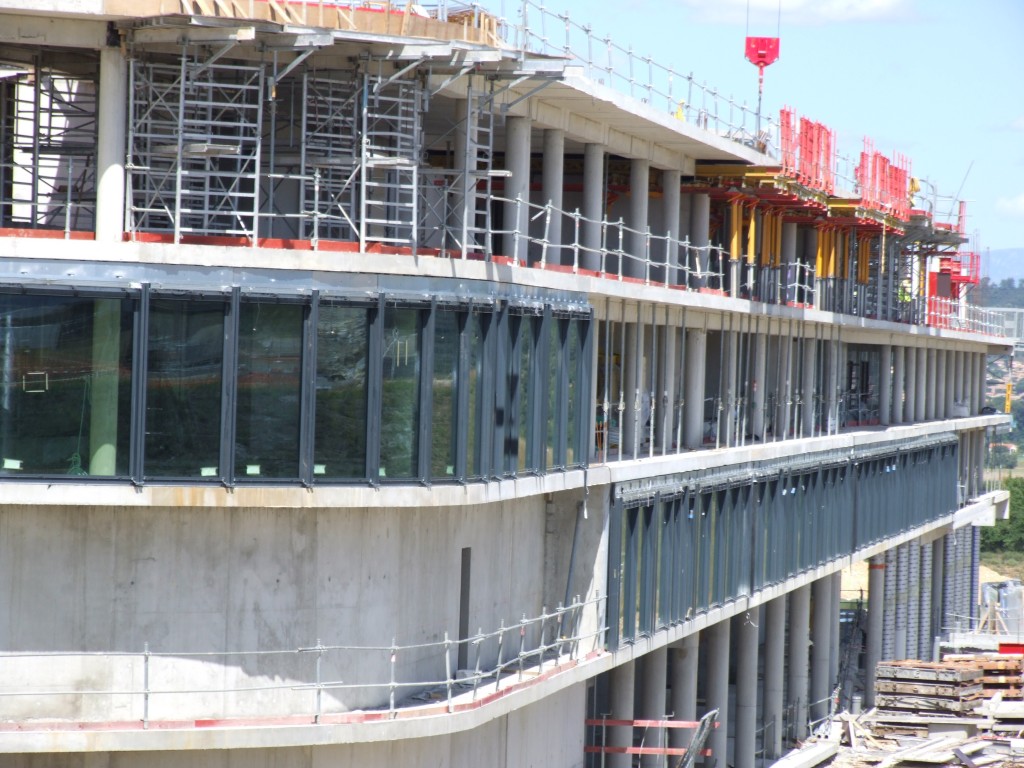
Progress!
2011-08-08 - Four storeys are now framed out and work begins on the fifth and last. Photo: AIF
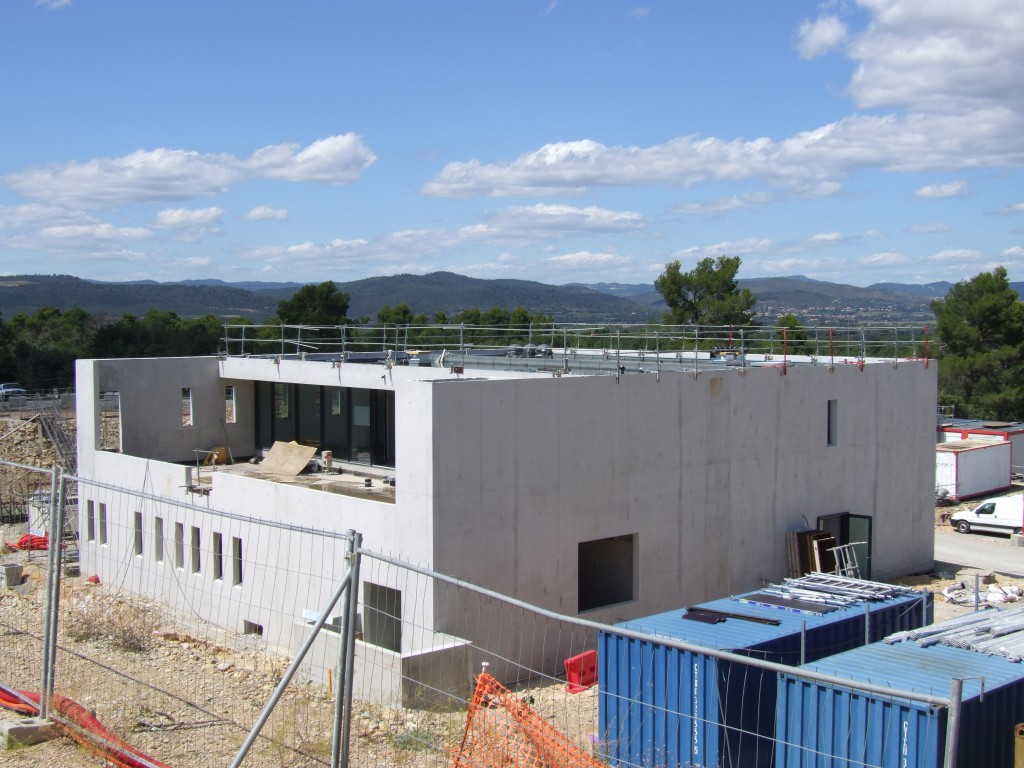
The ITER Medical Centre
2011-08-08 - Close to the ITER Headquarters, this building will house the ITER Medical Centre and research facility access checkpoint. Photo: AIF July 2011
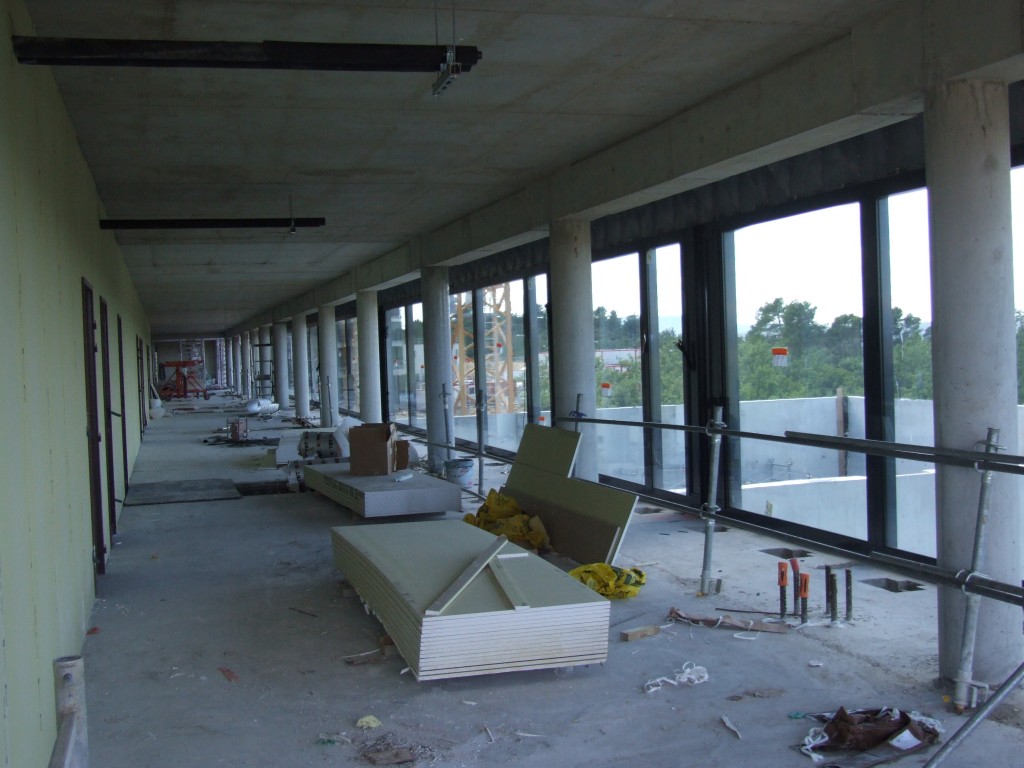
Large bay windows
2011-08-08 - The wide corridors and large bay windows of the second storey of ITER Headquarters, looking toward the parking lot. Photo: AIF
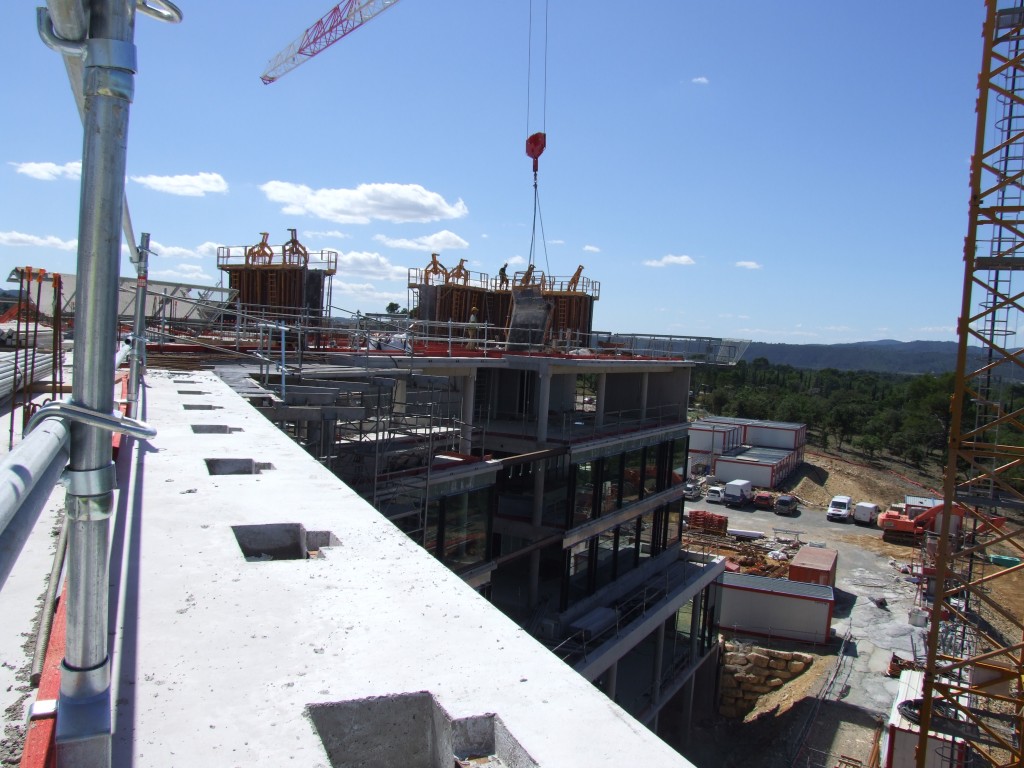
One floor to go
2011-08-08 - Standing on the fourth storey rooftop where work is about to begin on the last level of the ITER Headquarters. Photo: AIF
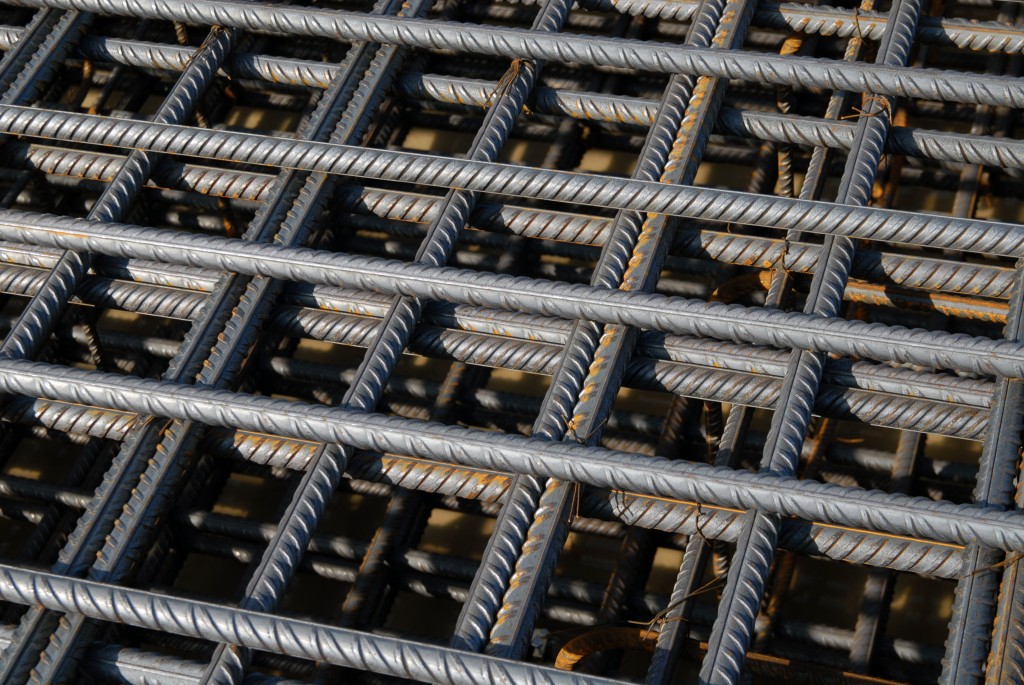
3,400 tons of metal
2011-07-28 - Thousands of metal bars like these will reinforce the foundations of the Tokamak Complex. Photo: F4E
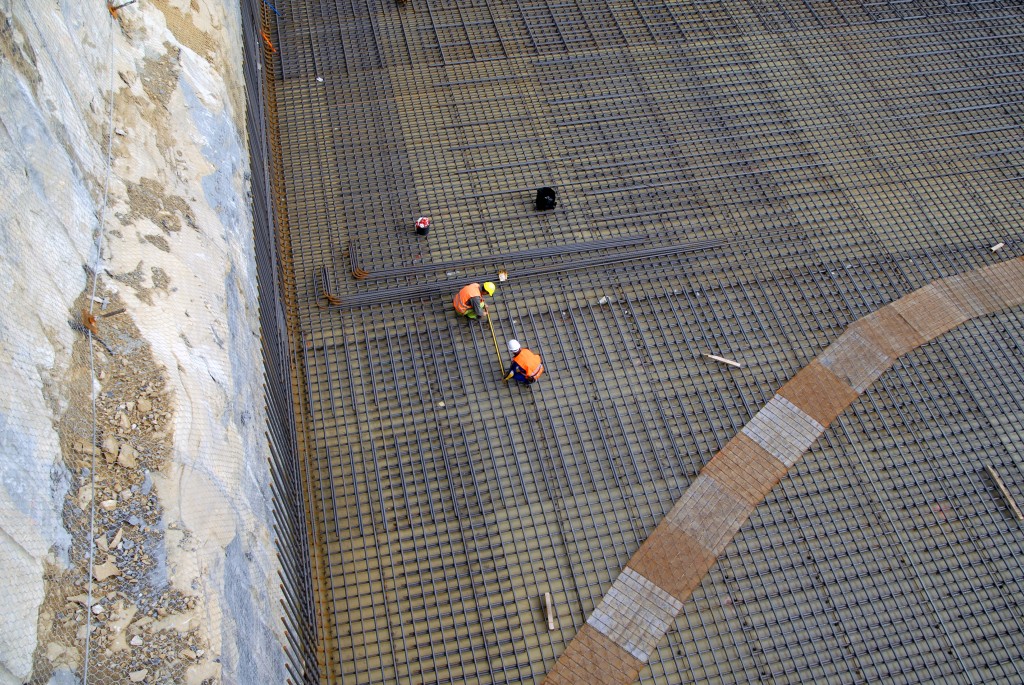
Measuring makes it perfect
2011-07-28 - Workers measure the exact spacing of the rebar used on the floor of the Seismic Pit. Regular spacing and tying off the bars so that they remain in position are important to achieving the desired strength of the completed concrete. Photo: F4E
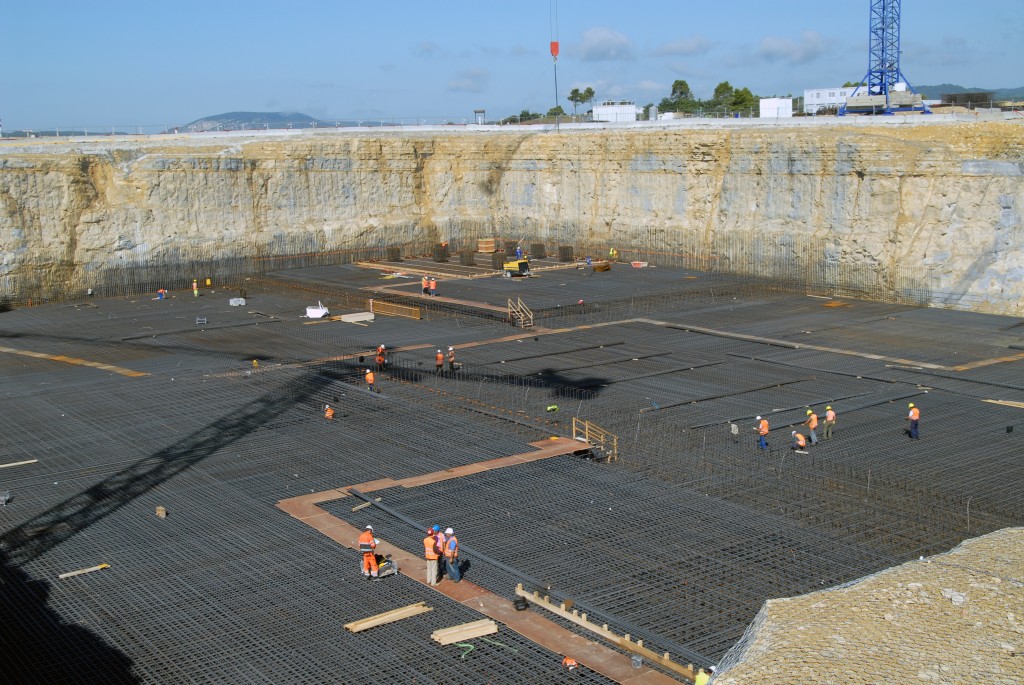
A single foundation for the Tokamak Complex
2011-07-28 - The three buildings of the Tokamak Complex will share a single foundation: having a monolithic structure avoids the relative displacement of process pipes crossing the buildings. Photo: F4E
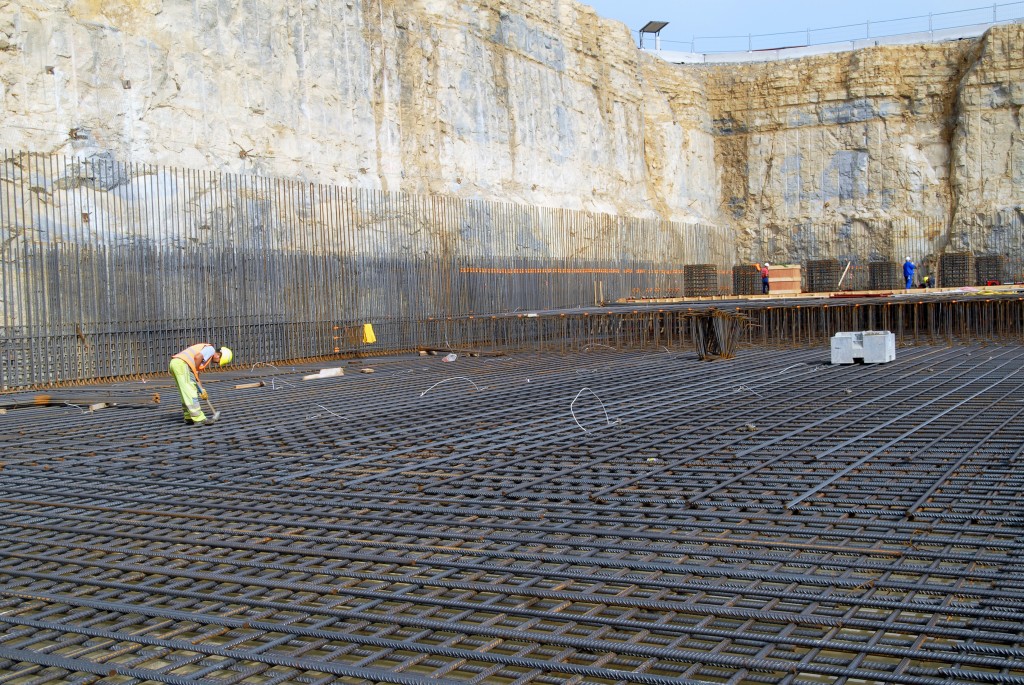
Vertical bars
2011-07-28 - The vertical reinforcement bars standing five metres high against the rock face will be part of the lower retaining wall of the Seismic Pit. Photo: F4E
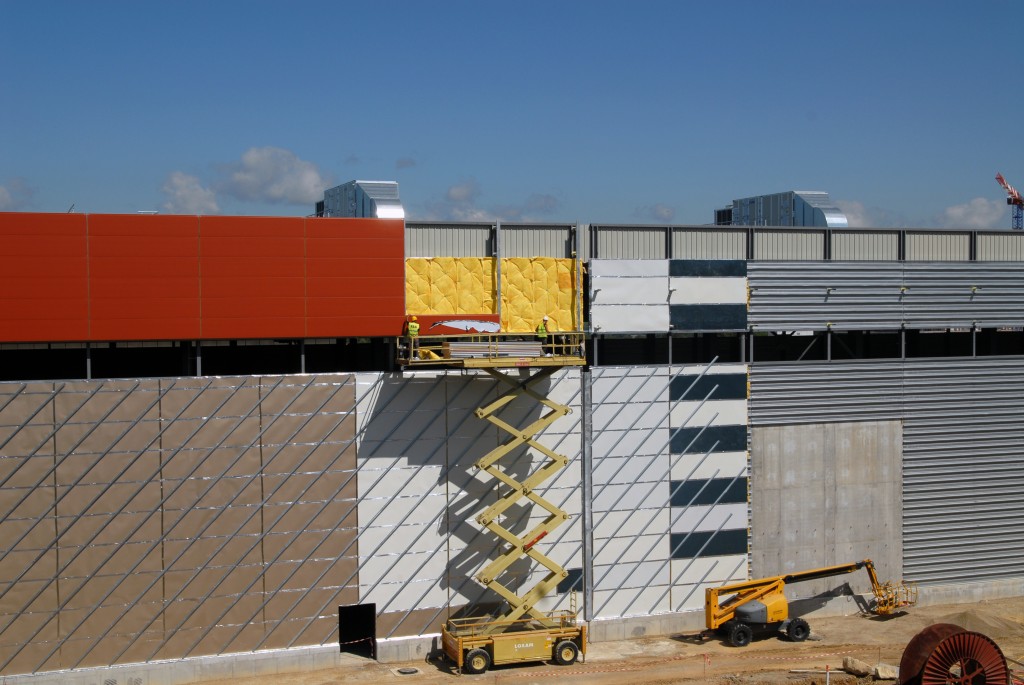
Cladding activities on the south-east side
2011-07-28 - Corrugated metal on the inside, plus two layers of glass wool insulation and two layers of metal sheeting sealed with tape—these five layers make up the walls of the Poloidal Field Coils Winding Facility. Photo: F4E
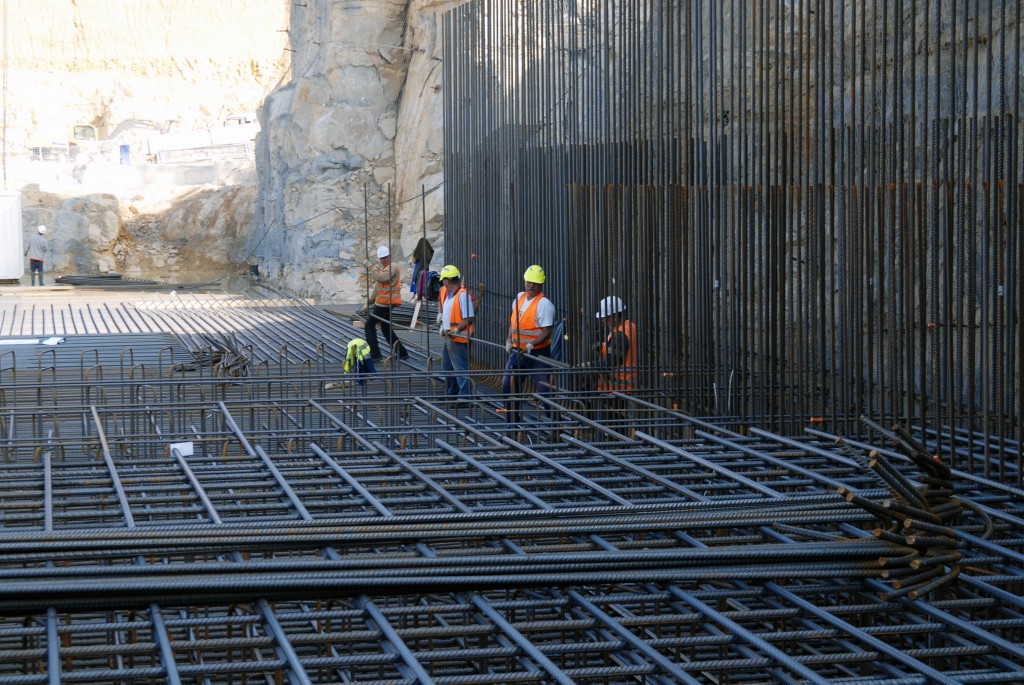
The work advances
2011-07-28 - Workers tie rebar into place to form the reinforced structure of the Seismic Pit basemat. Photo: F4E
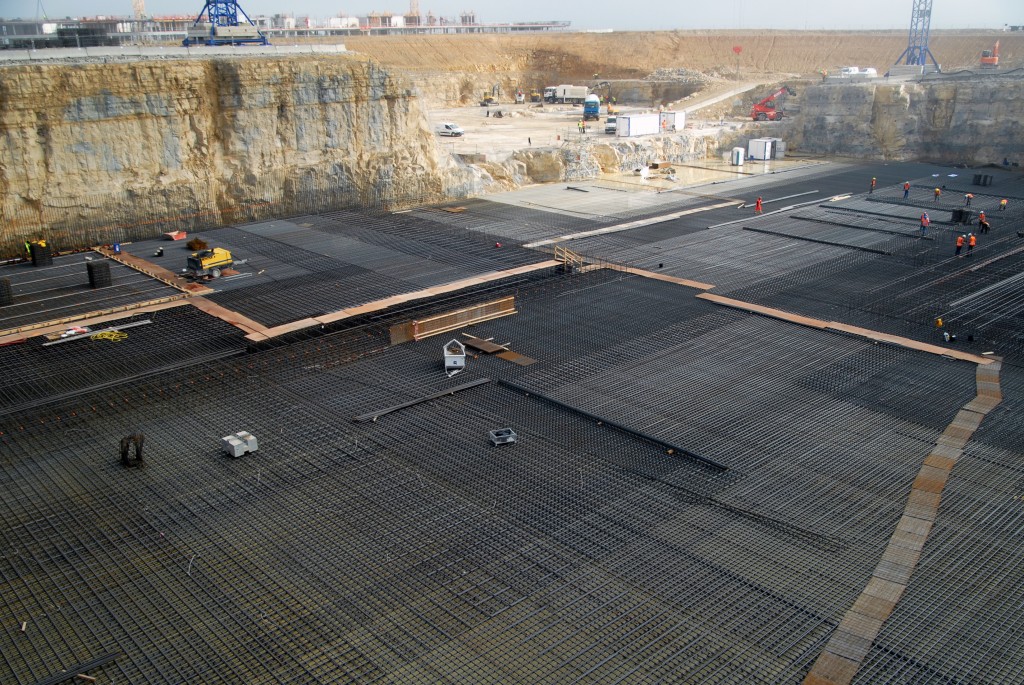
1.5 metres of reinforcement in the lower basemat
2011-07-28 - Metal "chairs" are positioned on the bottom layer of crisscrossed rebar. Steel reinforcement will be built up to 1.5 metres before foundation pouring begins. Photo: F4E
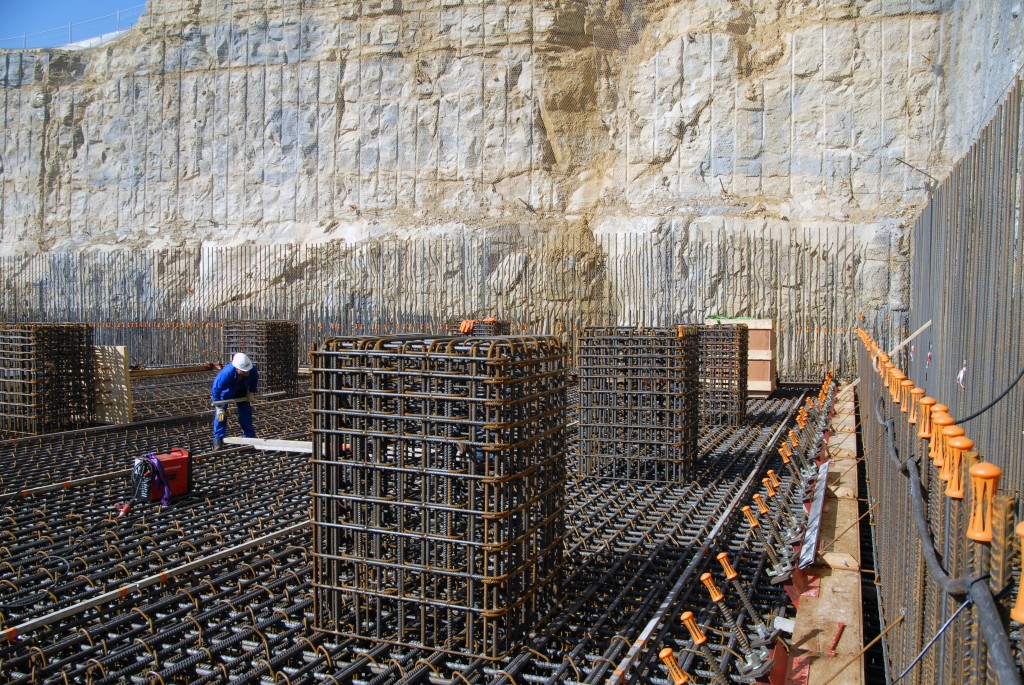
Preparing the concrete plinths
2011-07-28 - Sitting atop the Seismic Pit basemat, 493 of these 1.7 metre concrete columns, or "plinths," will support the seismic pads. These, in turn, will support the basemat of the Tokamak Complex—the actual "floor" of the installation. Photo: F4E
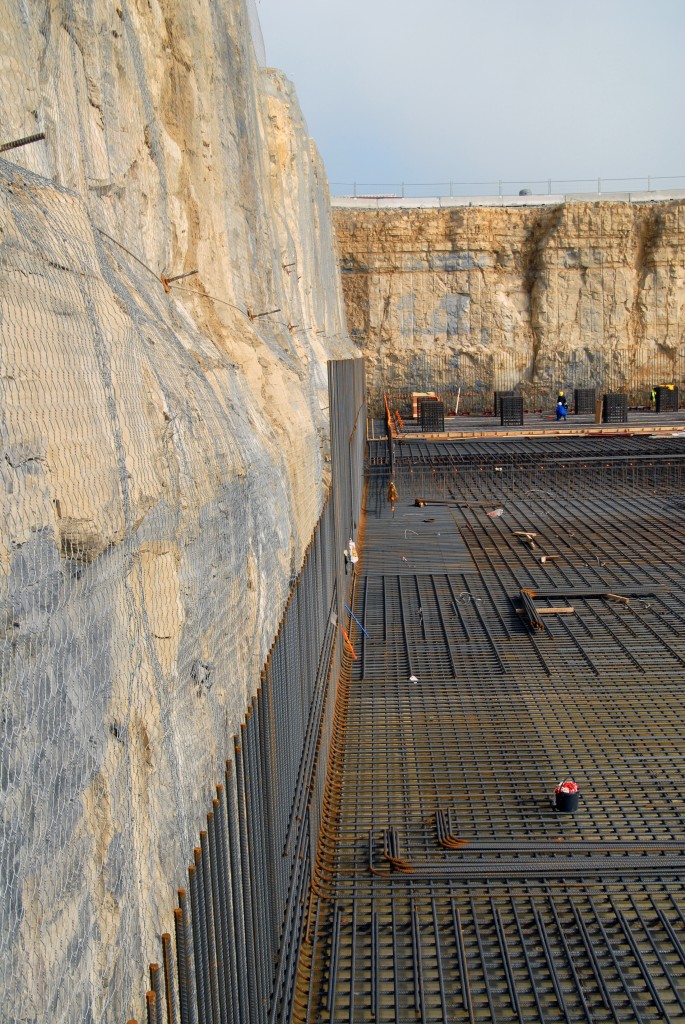
Retaining walls
2011-07-28 - The Seismic Isolation Pit for the ITER Tokamak Complex will be composed of a basemat (1.5 metres of concrete) and thick retaining walls. Photo: F4E
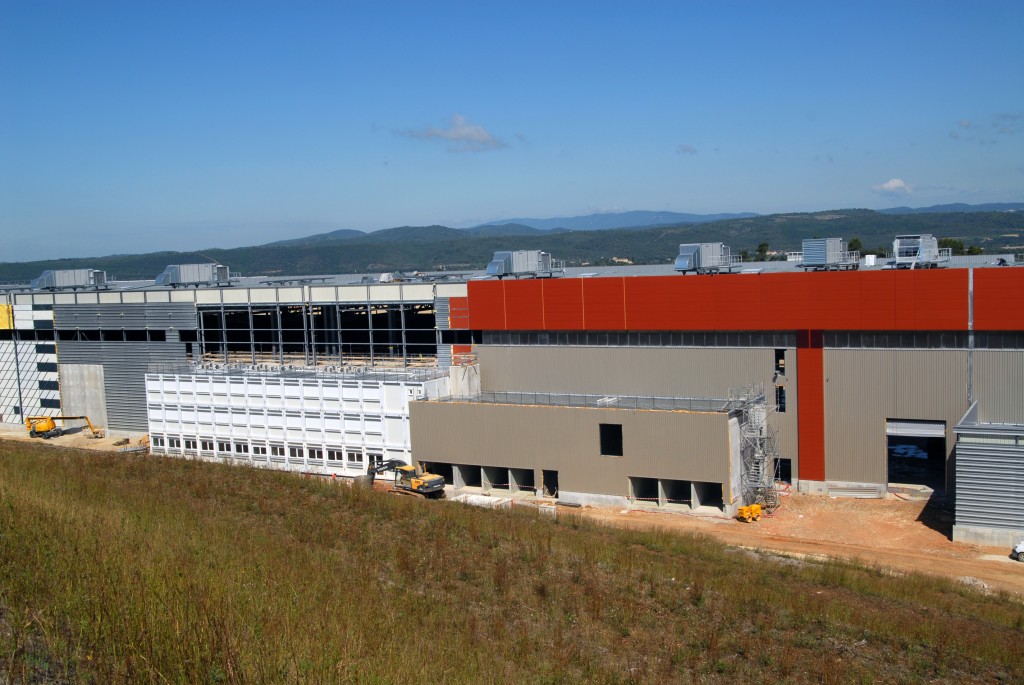
Offices are in
2011-07-28 - Three storeys of office space, in white, have been installed along the Winding Facility's east face. Photo: F4E
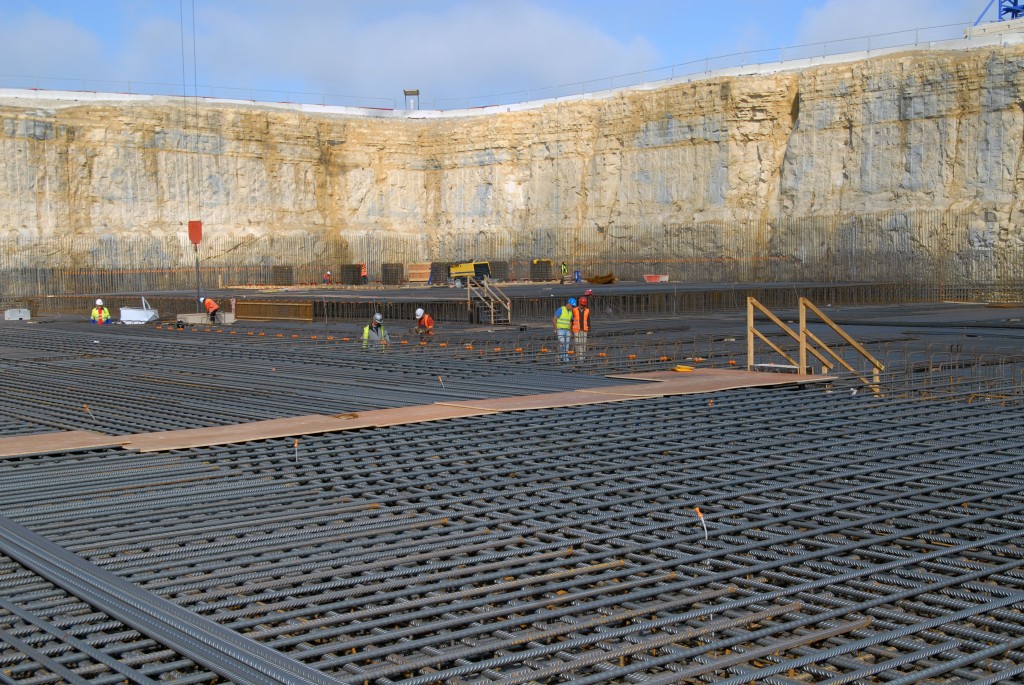
Metal "chairs" are part of the reinforcement
2011-07-28 - Workers install metal "chairs" for structural stability between the lower and higher levels of crisscrossed reinforcement. Foundation pouring will begin in August. Photo: F4E

Five months from finish
2011-07-28 - Work advances rapidly on the 257-metre-long Poloidal Field Coils Winding Facility in July 2011: the cladding is nearly finished, the three-floor office building is in place ... Photo: F4E

Stirrups are installed one by one
2011-07-20 - Rebar stirrups (seen in brown) linking the upper and lower rebar layers.
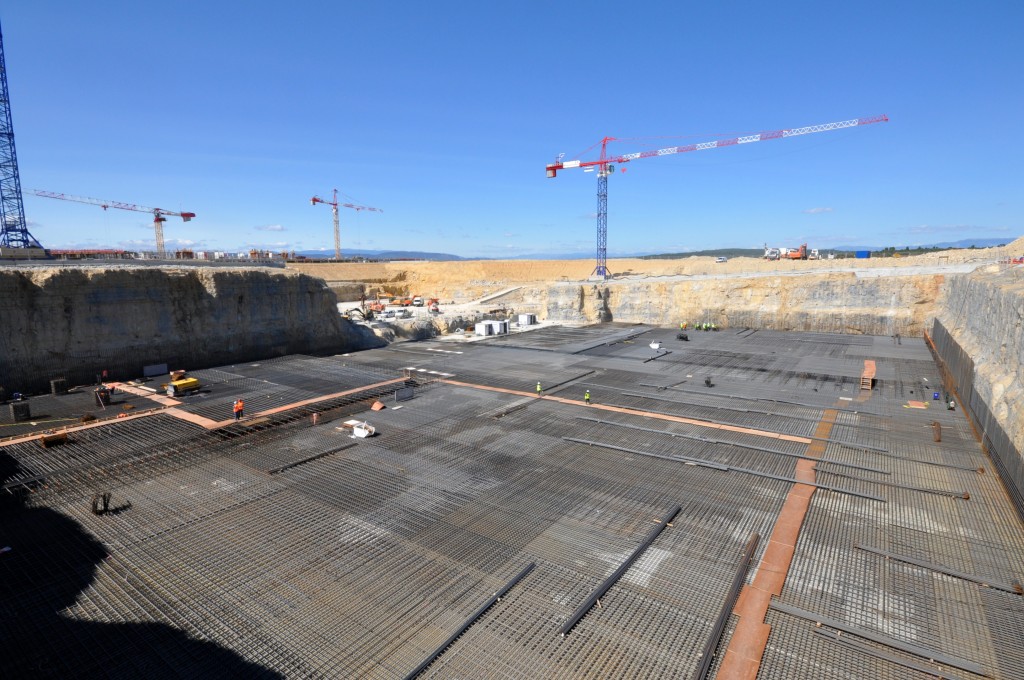
A rebar cage for the foundations of the Tokamak Complex
2011-07-20 - The rebar cage for the basemat of the Seismic Pit is under construction in July 2011.

Shaping the concrete floor
2011-06-27 - Portable framework tables are used to accelerate the pouring of concrete floor on the third level of the ITER Headquarters. Twenty-four of these wooden framework tables are placed side by side, allowing nearly 200 square metres of floor space to be poured every day. Photo: AIF
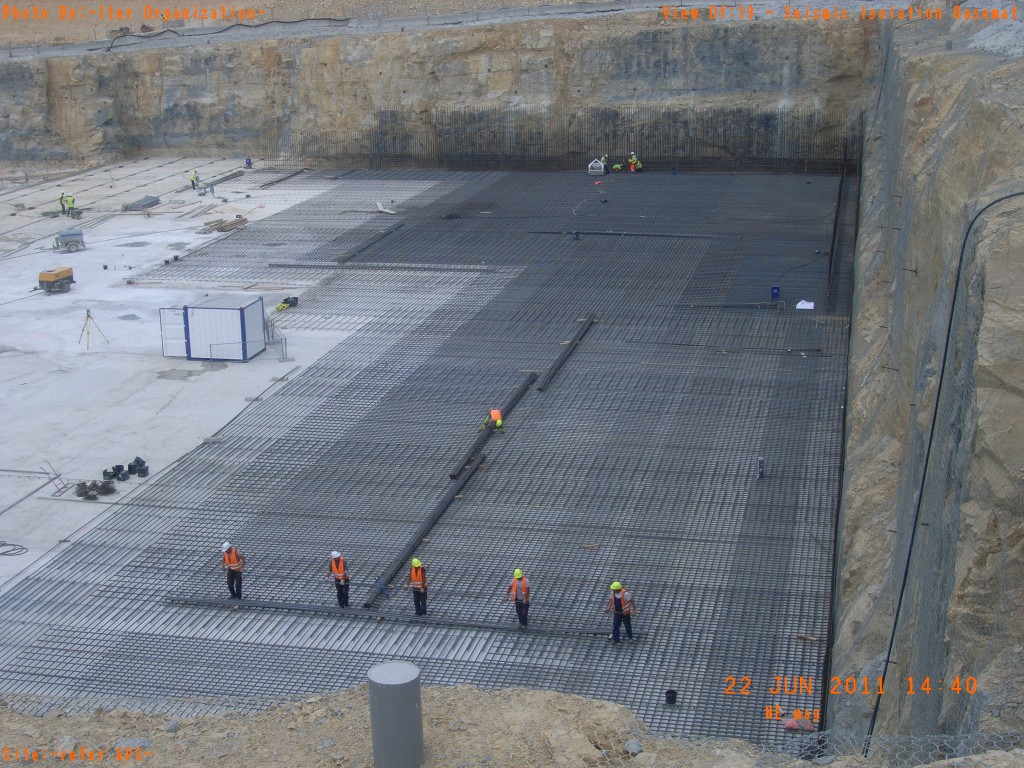
Blinding concrete nearly finished
2011-06-22 - In late June 2011, the blinding layer of concrete is 75% finished, and the reinforcement work progresses steadily.
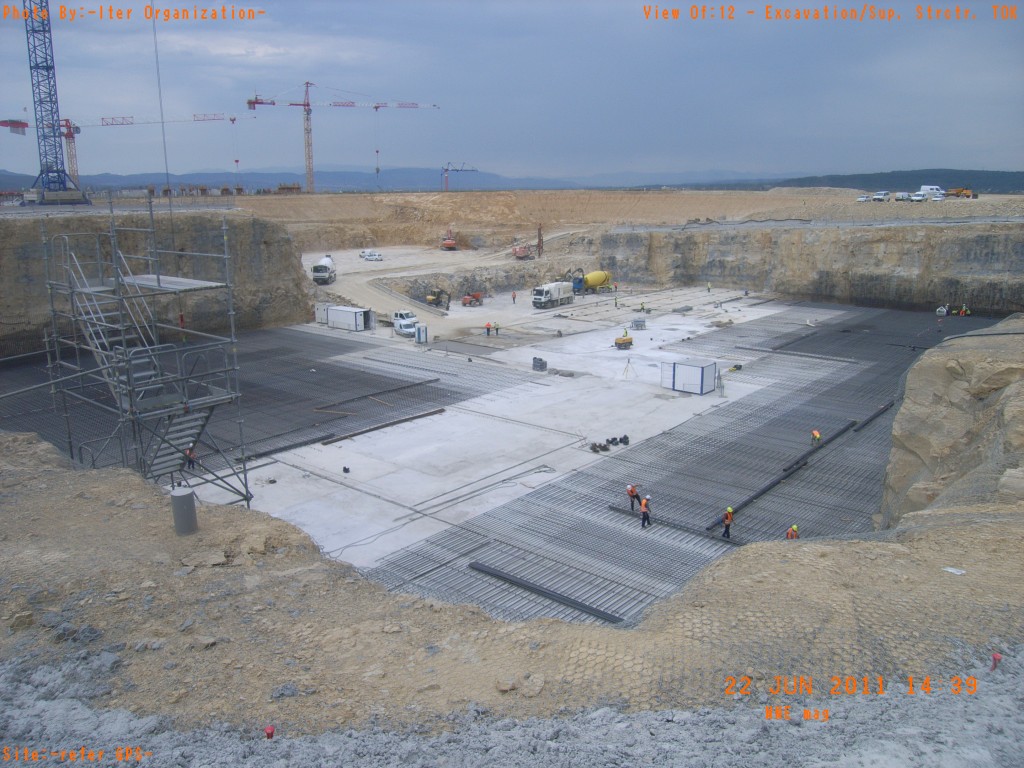
How many steps down?
2011-06-22 - One of four pedestrian access staircases into the Tokamak Complex Seismic Pit. Some seventy workers involved with foundation work go up and down these staircases daily.

"Blinding" concrete
2011-06-20 - On top of a five to ten centimetre layer of "blinding concrete," workers position steel rebar in June 2011. Some 3,400 tons of rebar is planned for the first level of foundations: the Tokamak Complex Seismic Pit basemat. Photo: F4E

Successive layering
2011-06-20 - Successive layers of cladding can be distinguished in this photo taken in June 2011. Photo: F4E
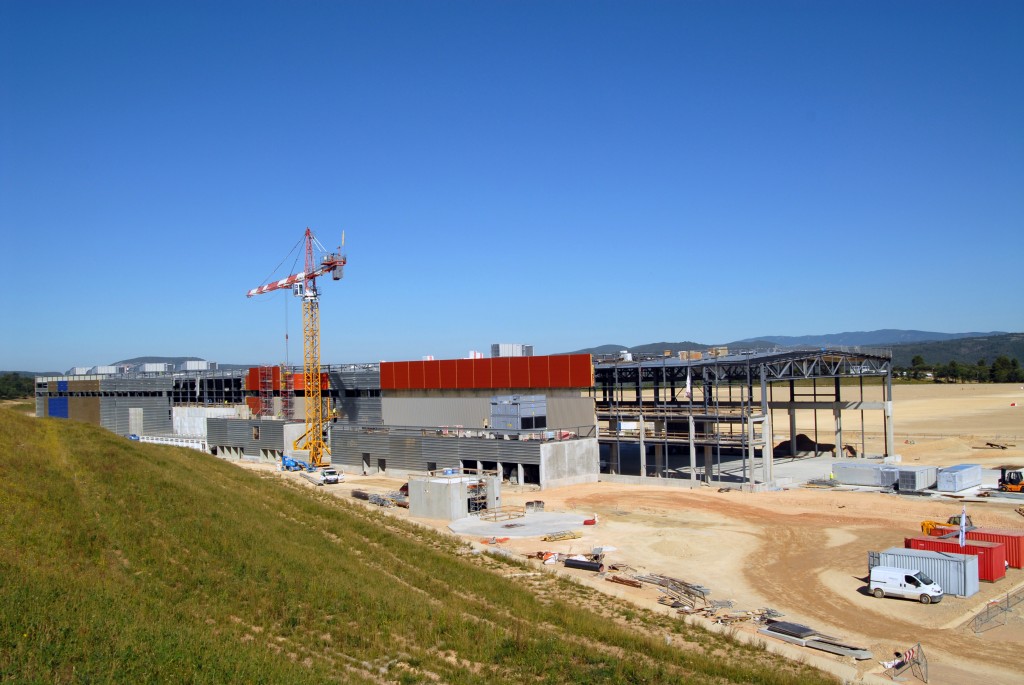
The Winding Facility in June 2011
2011-06-20 - Even the Technical and Production Buildings on the eastern side of the Winding Facility are covered with metal cladding. Photo: F4E
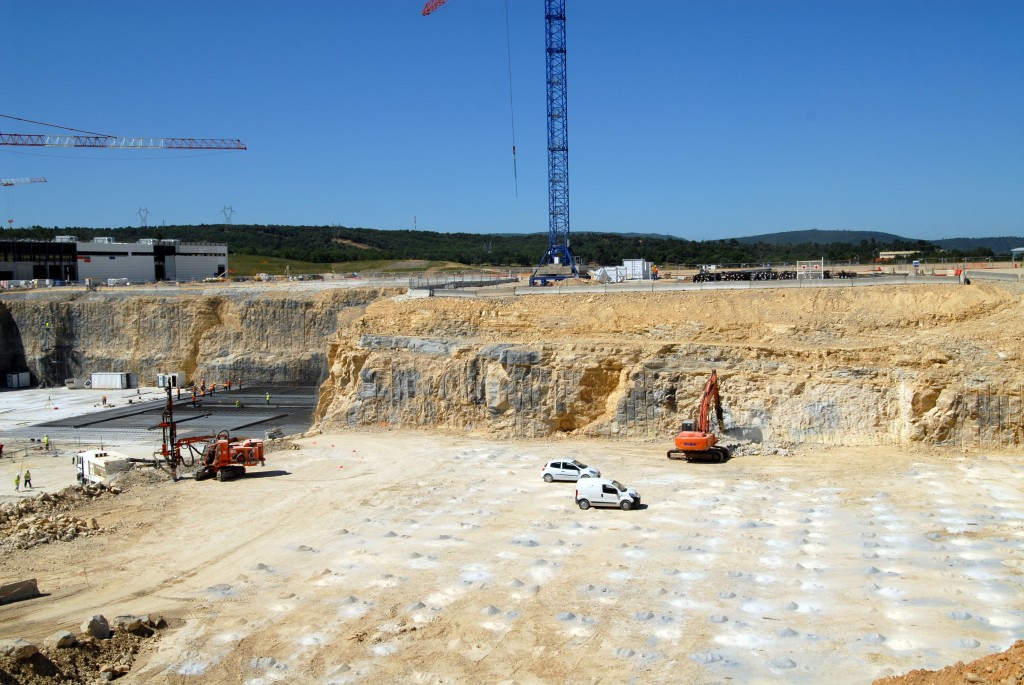
Work progresses in the neighbouring Hot Cell Facility area
2011-06-20 - Finishing touches to the Hot Cell Facility area before work begins on the blinding layer of concrete, reinforcement and foundation work, just like in the Tokamak Complex area seen beyond. Photo: F4E
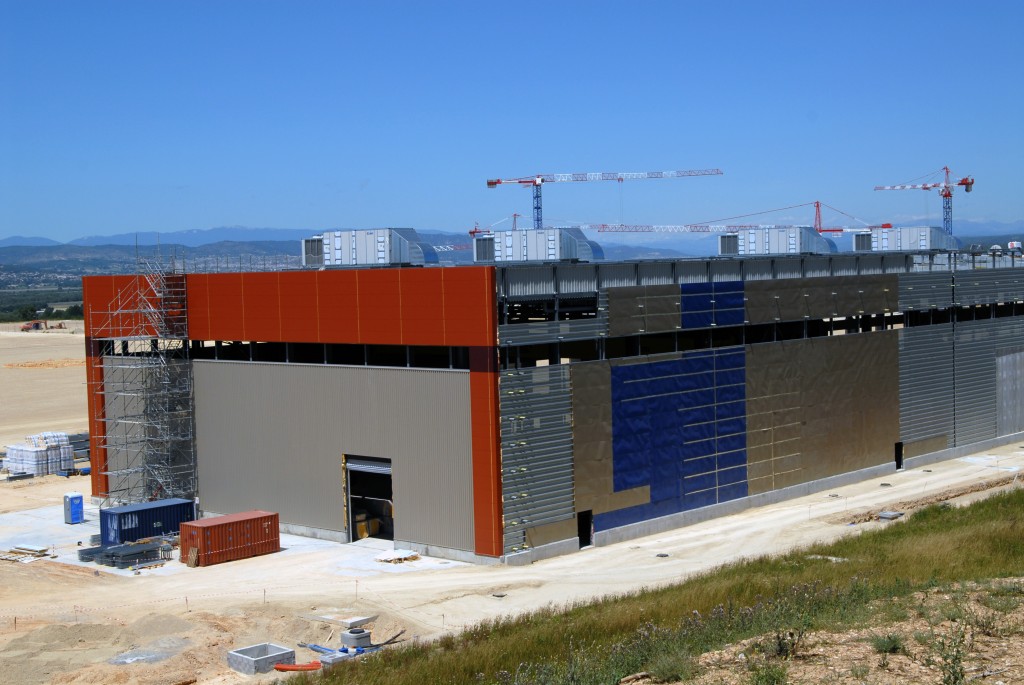
Final colours
2011-06-20 - On the south face of the Poloidal Field Coils Winding Facility, the last layer of cladding has been set into place. Photo: F4E
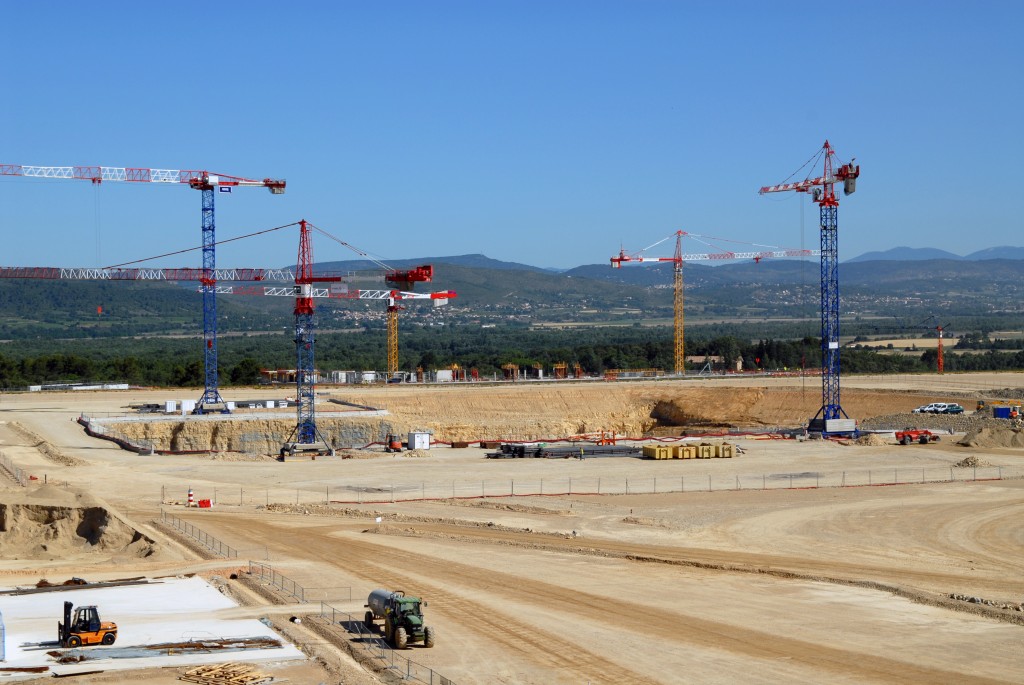
The worksite in June 2011
2011-06-20 - The worksite for the Tokamak Complex Seismic Isolation Pit in June 2011. Photo: F4E

Tower cranes in the distance
2011-06-20 - From the roof of the Winding Facility, the tower cranes working around the Seismic Isolation Pit (blue) and the ITER Headquarters (yellow) are visible in the distance. Photo: F4E
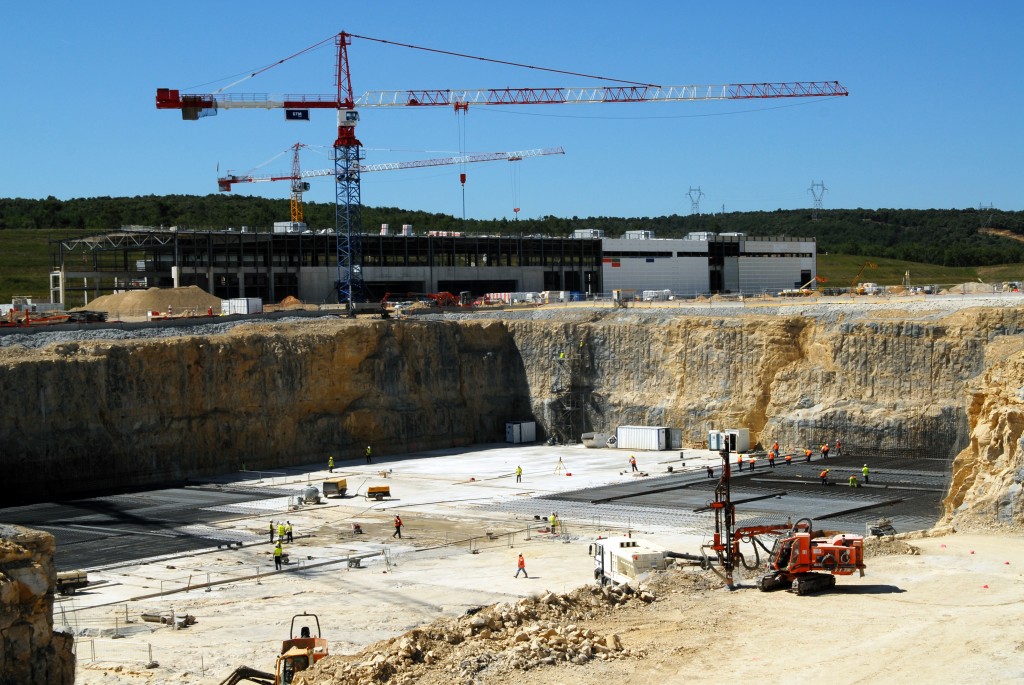
The ITER platform, nearly one year into construction activities
2011-06-20 - The Poloidal Field Coils Winding Facility is seen from the north-west rim of the Seismic Isolation Pit in June 2011. Photo: F4E
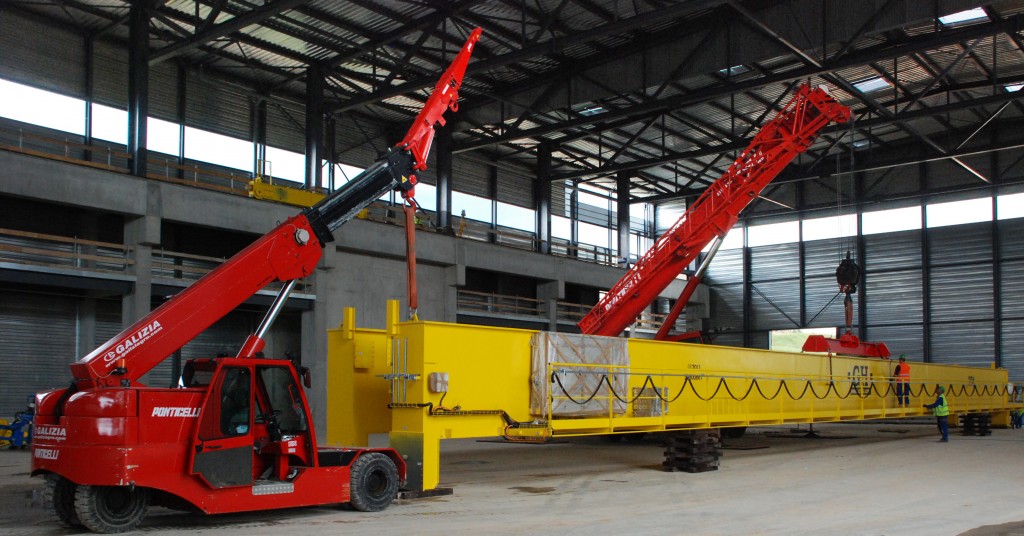
Placed overhead on the south end of the facility
2011-06-07 - Straddling the workspace across its width (approximately 40 metres) and installed at opposite ends of the Winding Facility, two overhead cranes will travel along metal rails that span the building's entire length, lifting loads up to 25 and 100 tonnes resepctively. Photo: AIF
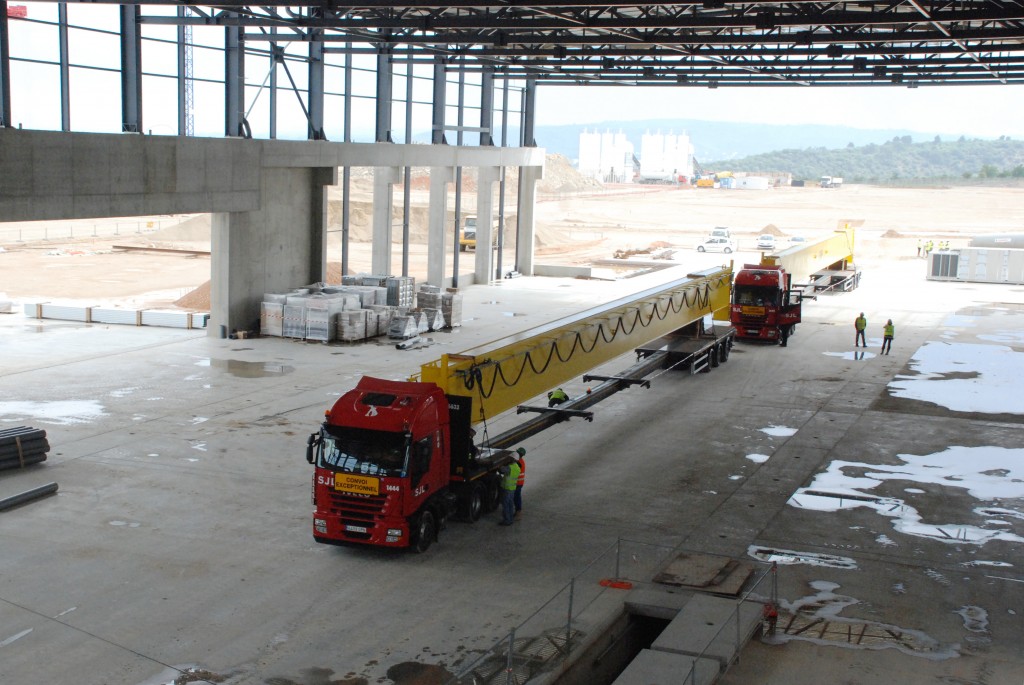
Heavy lifting
2011-06-07 - The heavy lifting required for poloidal field coil assembly will be done by the overhead bridge cranes. Beams for the first crane arrive on site in June 2011. Photo: AIF
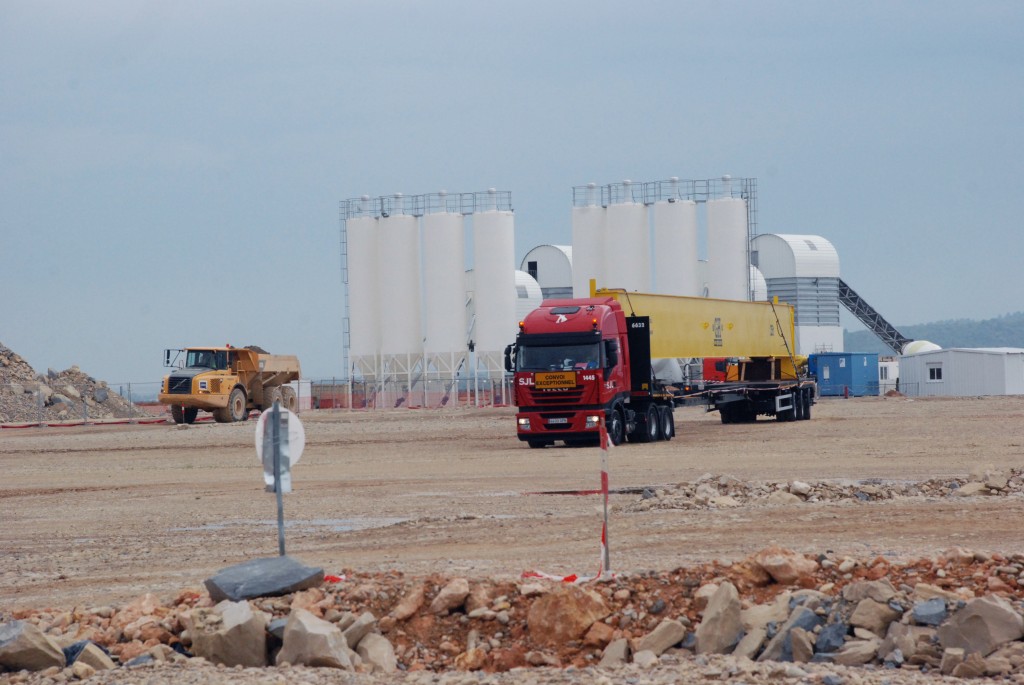
Special delivery for the Winding Facility
2011-06-07 - This 38.3 metre-long steel beam is one of two beams delivered in June 2011 for the Winding Facility's 25-tonne travelling crane. Photo: AIF
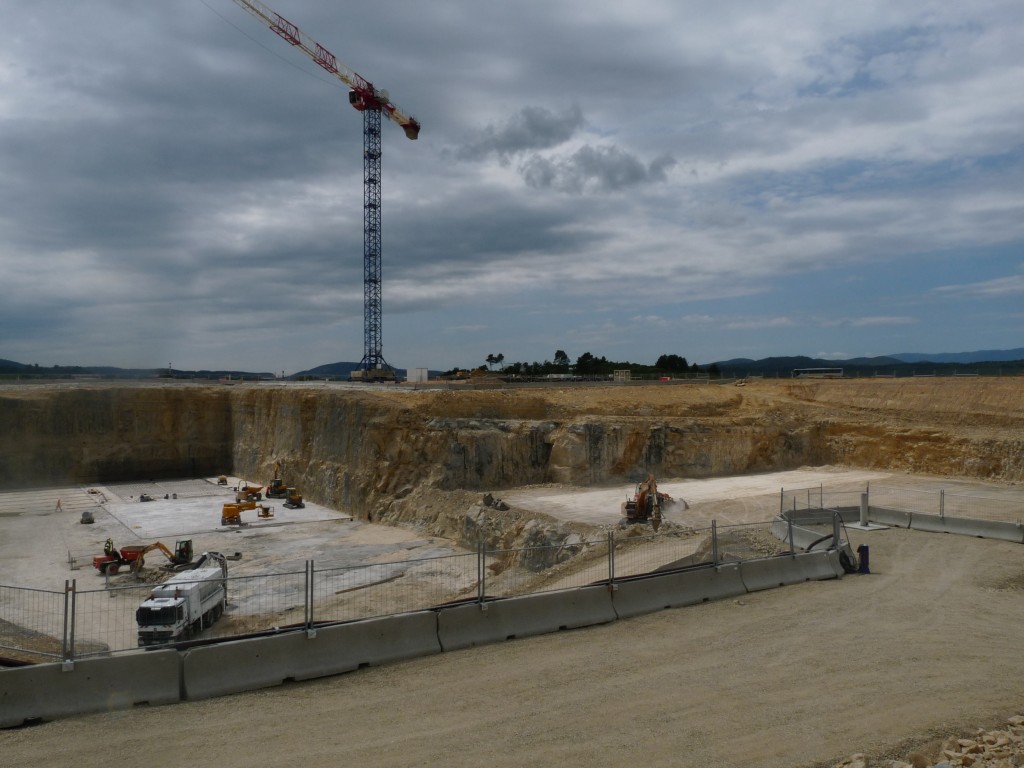
The Hot Cell Facility will be adjacent to the Tokamak Complex
2011-05-27 - The Tokamak Complex Seismic Pit to the left, 17 metres deep, and to the right, the smaller and more shallow area that will house the foundations of the Hot Cell Facility. Photo: AIF
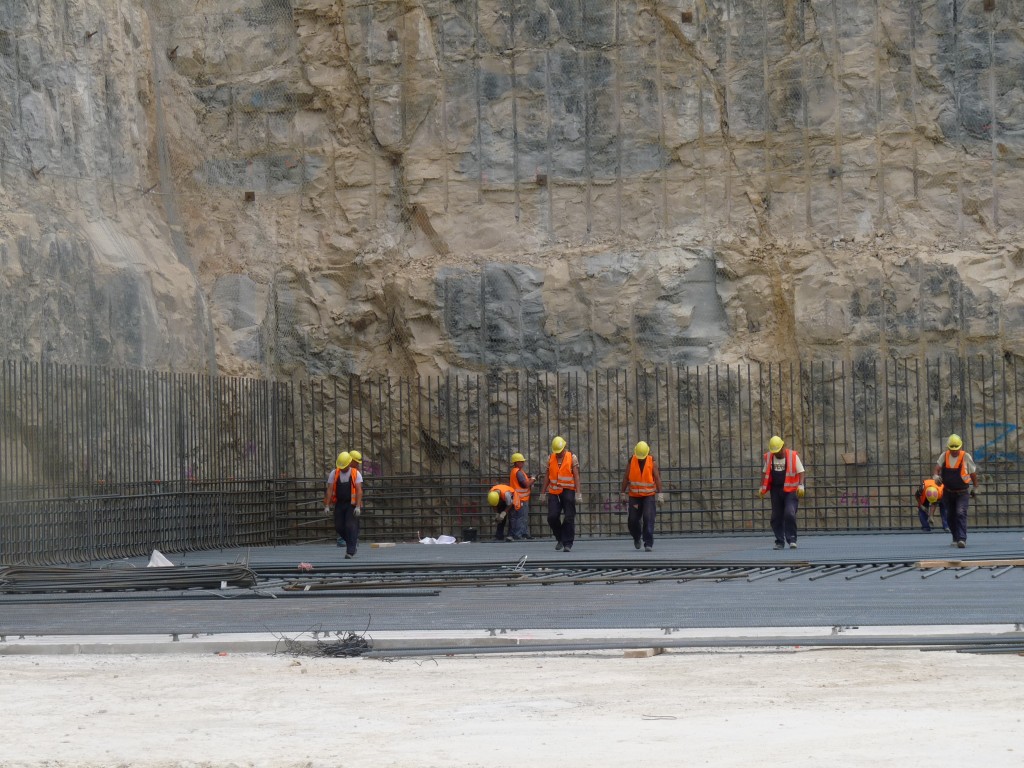
Reinforcement work begins in May
2011-05-27 - Seventeen metres below the surface of the ITER platform, reinforcement work begins for the basemat of the Tokamak Complex Seismic Pit. Photo: AIF

Three storeys of office space
2011-05-27 - A small pre-fabricated structure will installed along the back side of the building for offices and administrative services. Photo: AIF
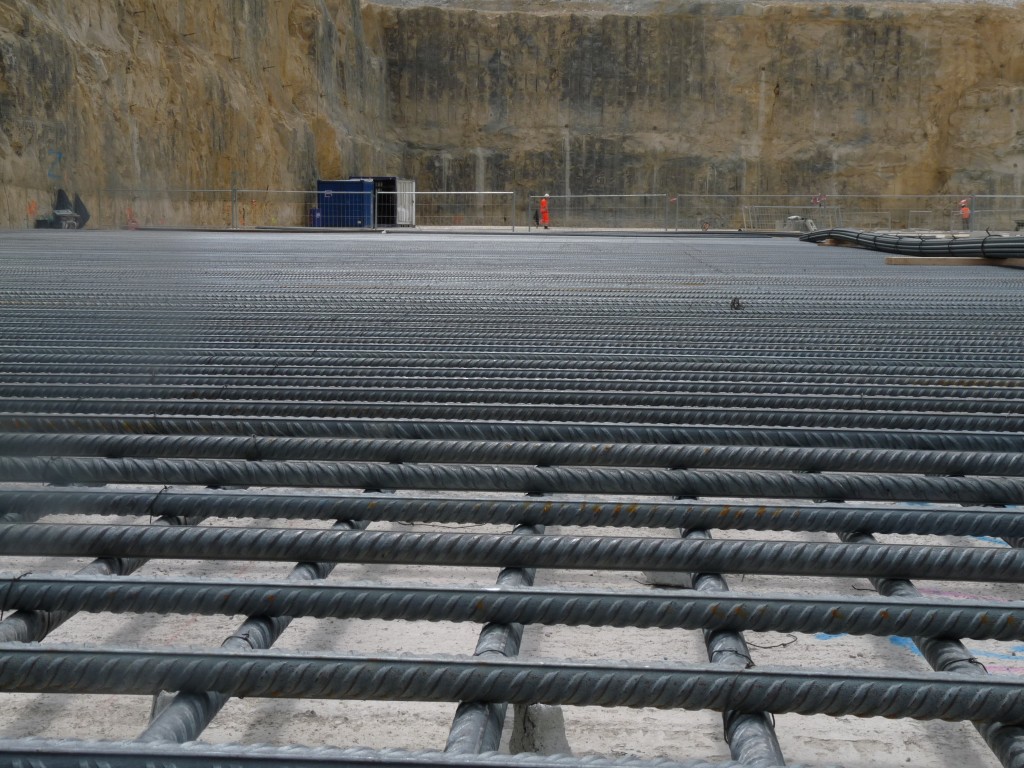
Criss-cross pattern
2011-05-27 - The first level of steel rebar is positioned on the floor of the Seismic Ísolation Pit. Reinforcement for the Seismic Pit basemat will be 1.5 metres high. Photo: AIF
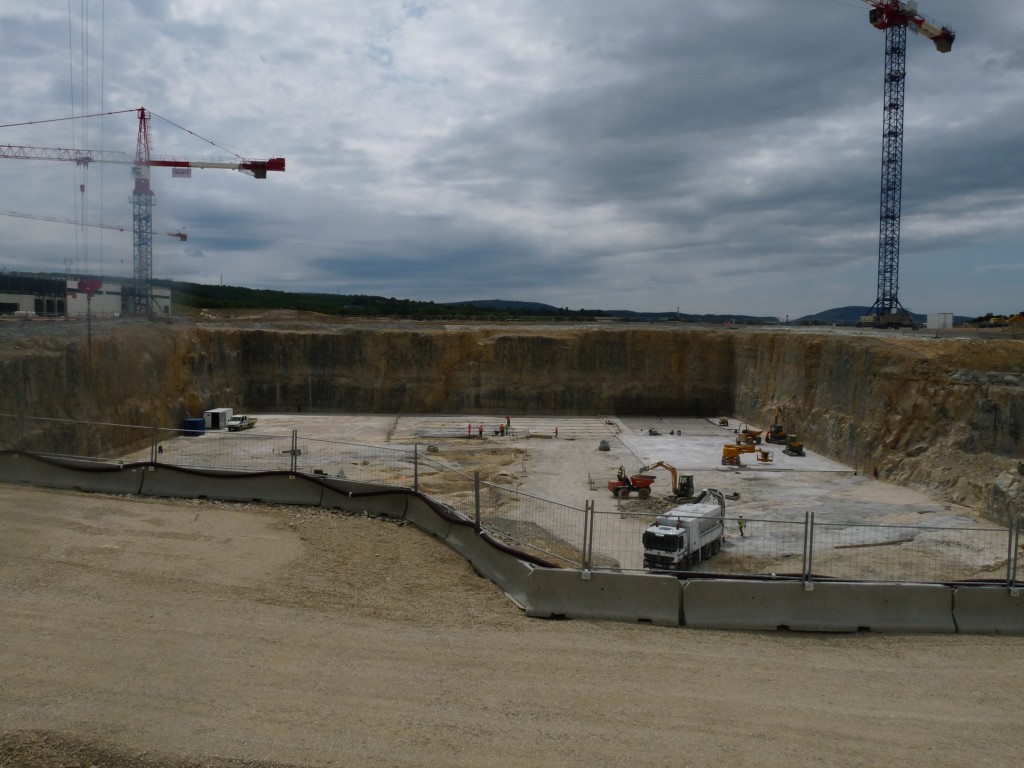
A thin layer of blinding concrete
2011-05-27 - A five-ten centimetre layer of "blinding concrete" will create a smooth and flat work surface. Photo: AIF
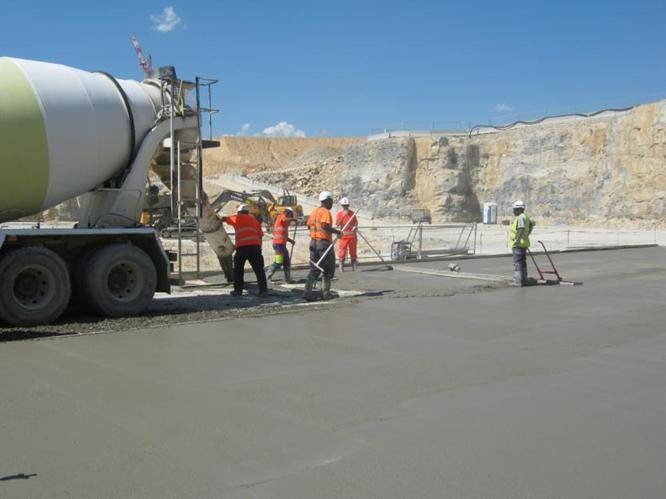
A thin layer of concrete
2011-05-27 - A thin layer of concrete is spread to create a clean and flat surface upon which to begin foundation operations. In the Seismic Pit, 550 m³ of concrete were necessary.
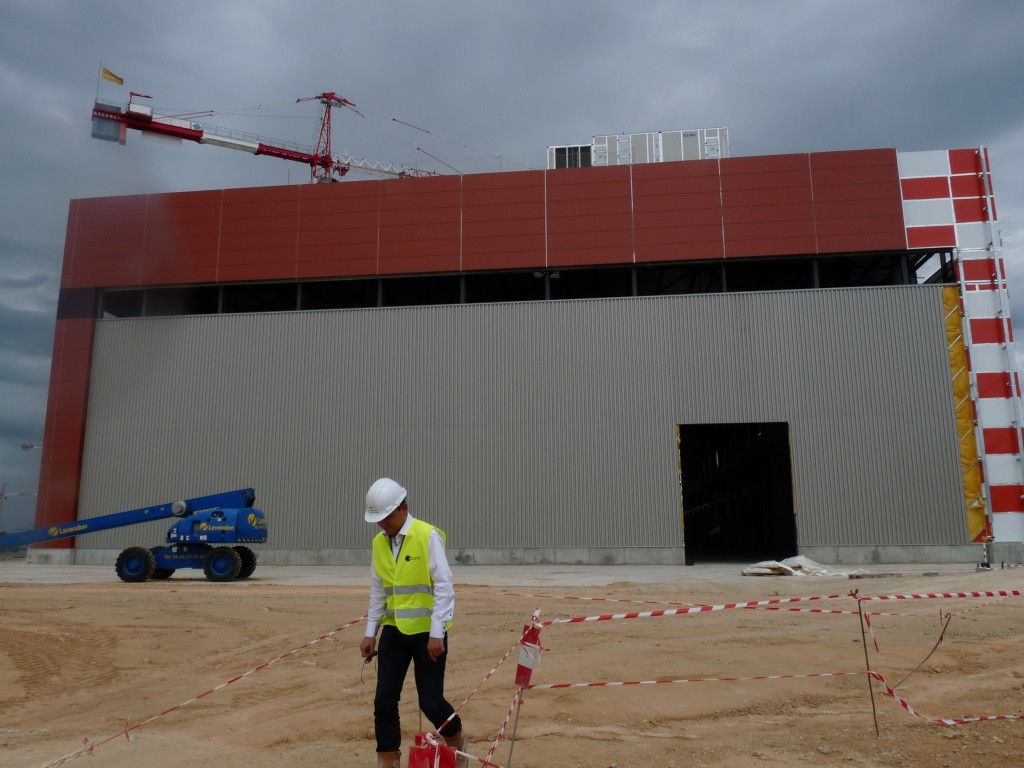
Taking on its final appearance
2011-05-27 - With the exception of the right edge, where yellow insulation and the first layers of cladding are still apparent, the Poloidal Field Coils Winding Facility takes on its final colours. Photo: AIF
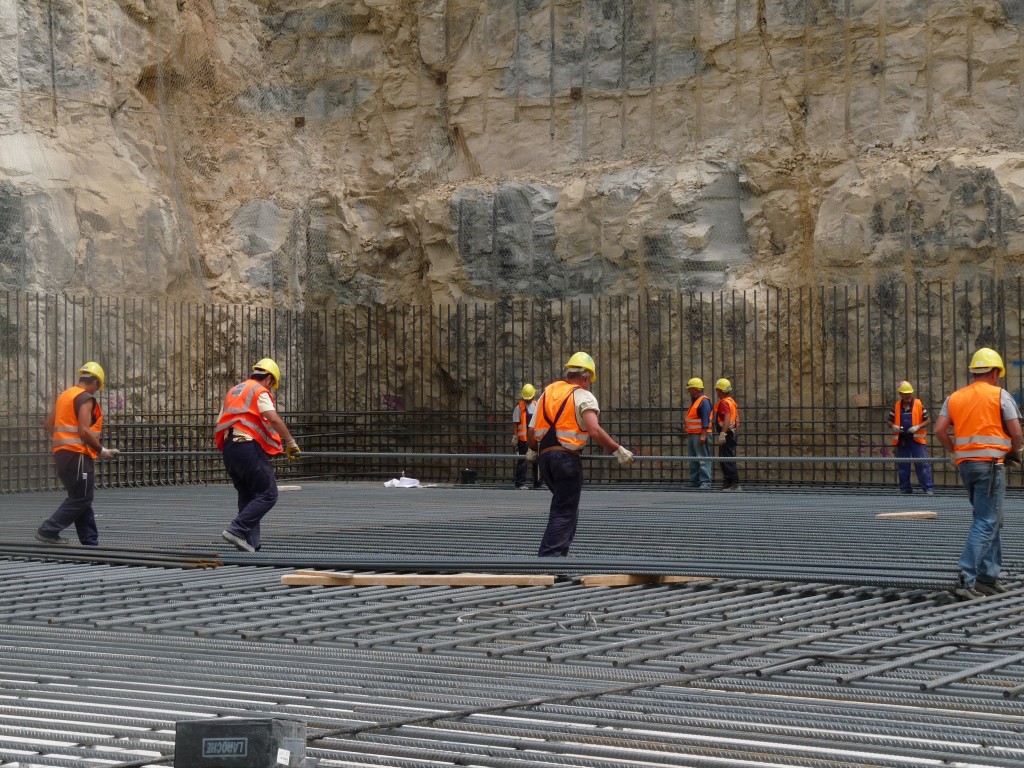
Nearly 100 kilos per bar
2011-05-27 - Four men share the weight of the 16-metre-long, nearly 100 kg steel rebar. Photo: AIF
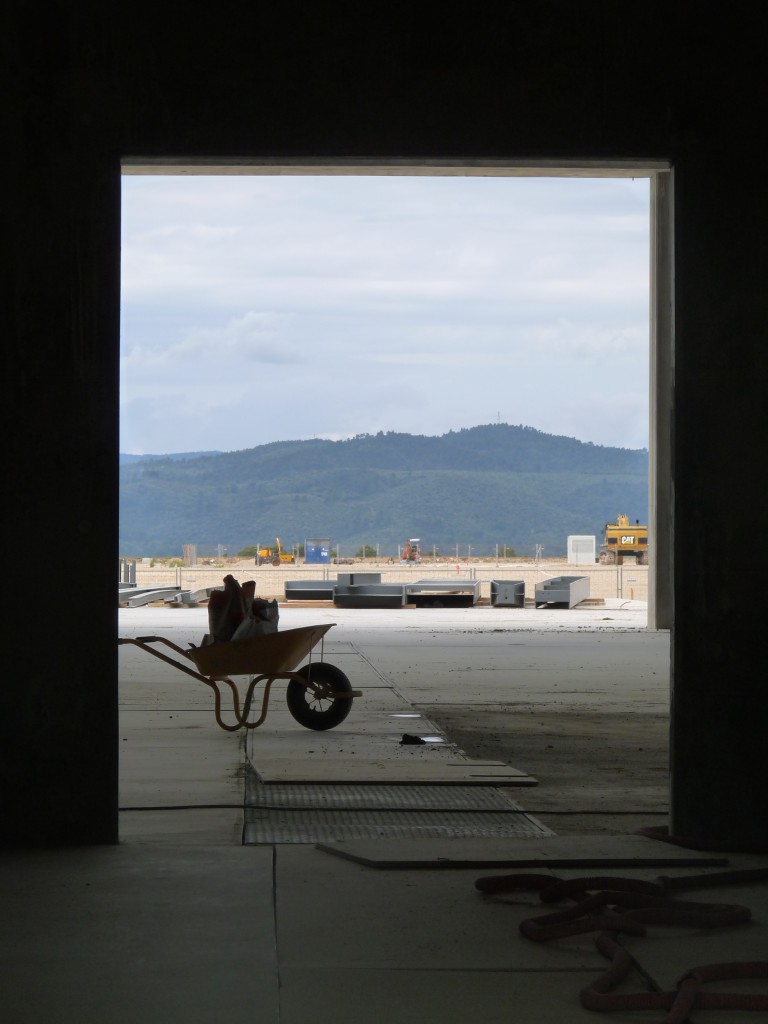
Approximately 6 months from completion
2011-05-27 - Looking out from the first structure to go up on the ITER platform. Photo: AIF
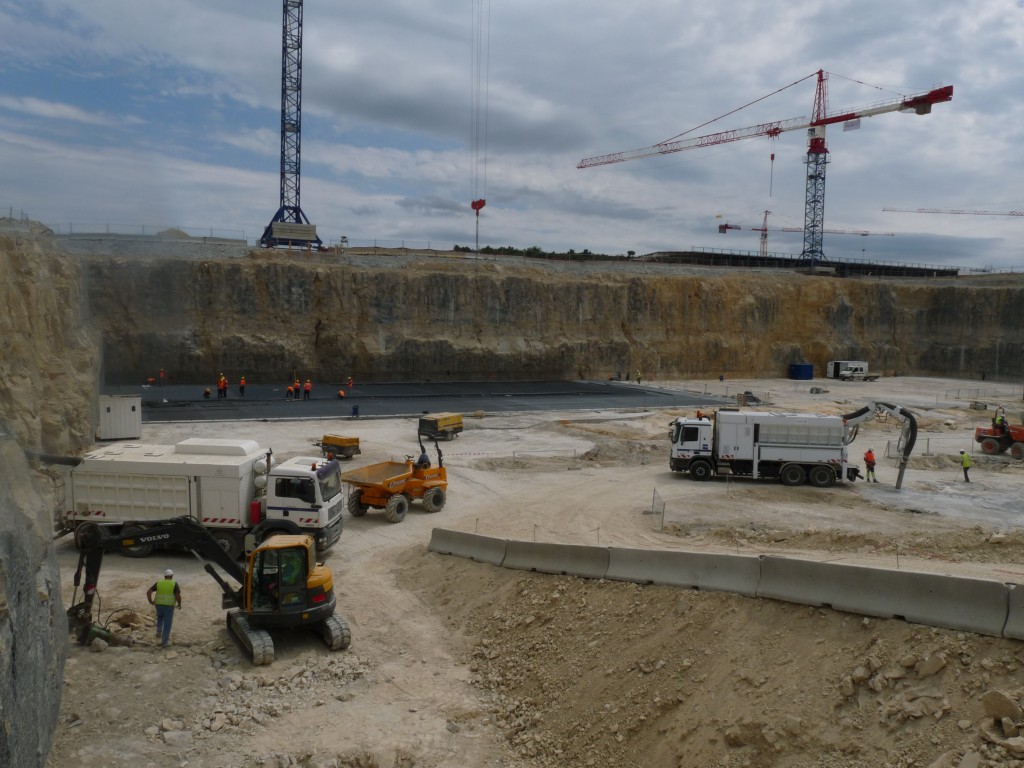
Profiling now finished
2011-05-27 - The final bottom and façade profile is completed in May, and work begins on the blinding layer of concrete. Photo: AIF
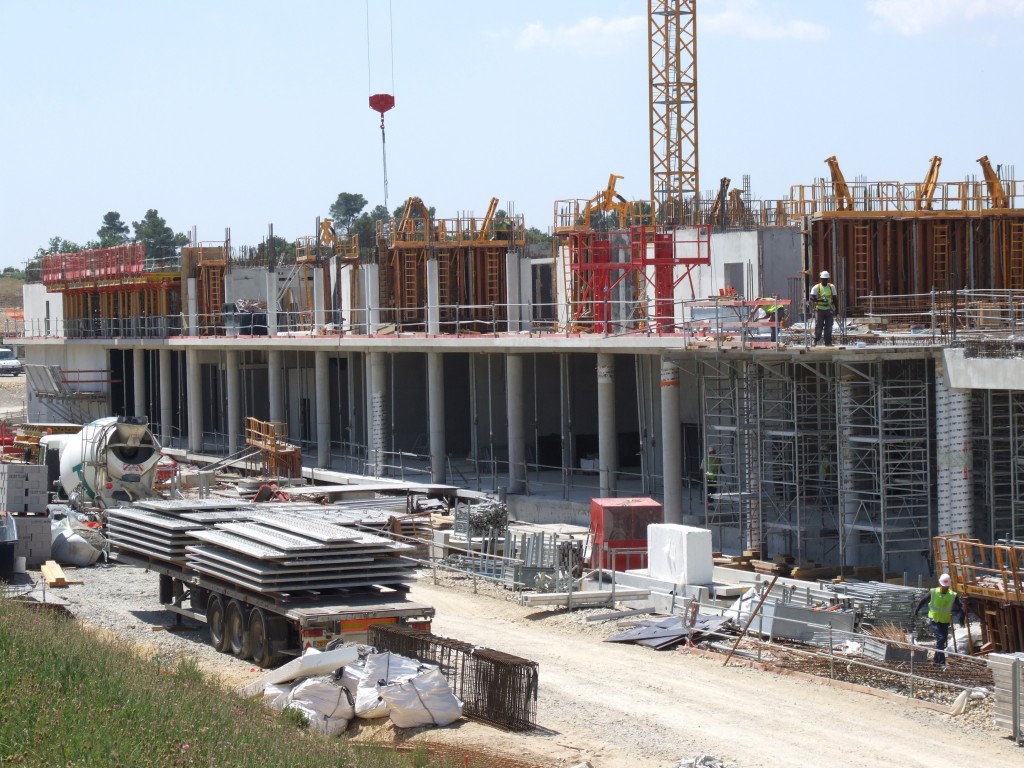
On its way
2011-05-24 - The shell of the ITER Headquarters—walls, floor, roof—is forecast to be completed in summer 2011. Photo: AIF
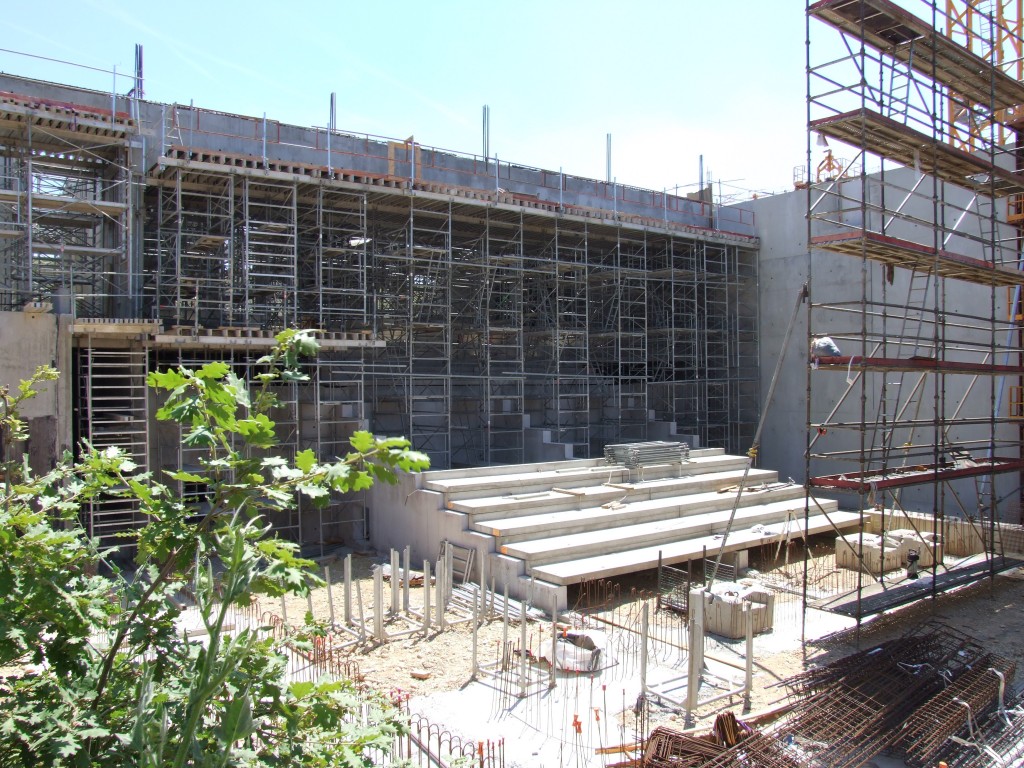
Future amphitheatre
2011-05-24 - The 500-person amphitheatre will be partly integrated under the building. Photo: AIF
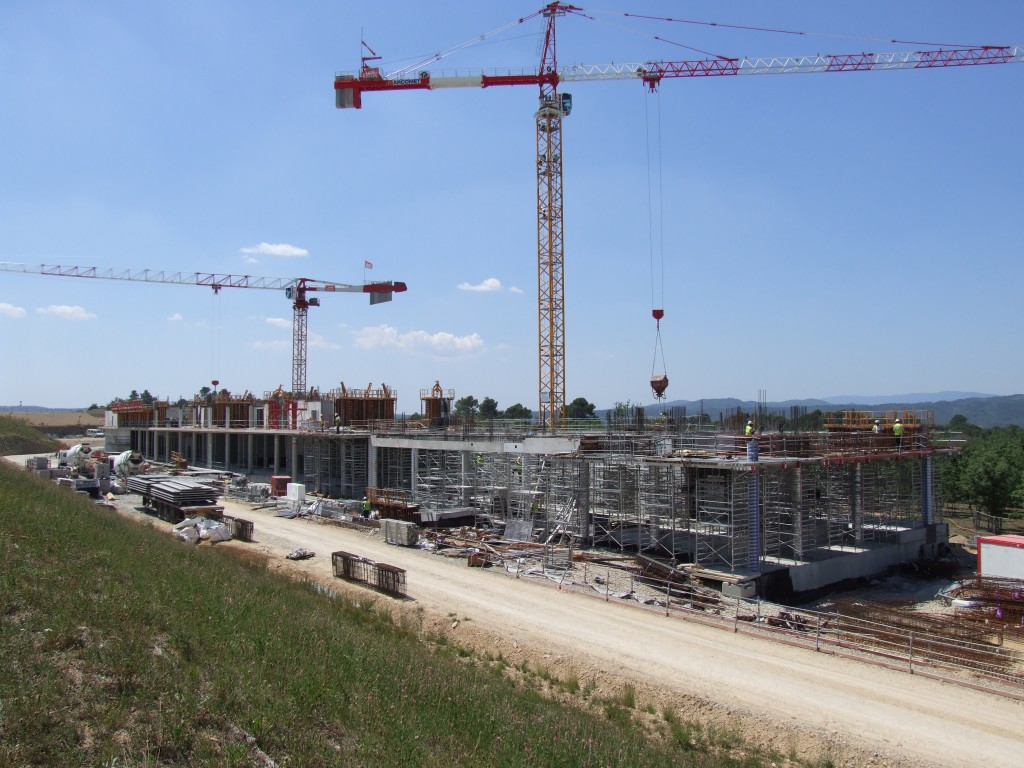
Occupying the smallest "footprint" in the landscape
2011-05-24 - The long, tall ITER Headquarters building was conceived by the architects to occupy a limited amount of ground space, leaving most of the wooded parcel ... wooded. Photo: AIF
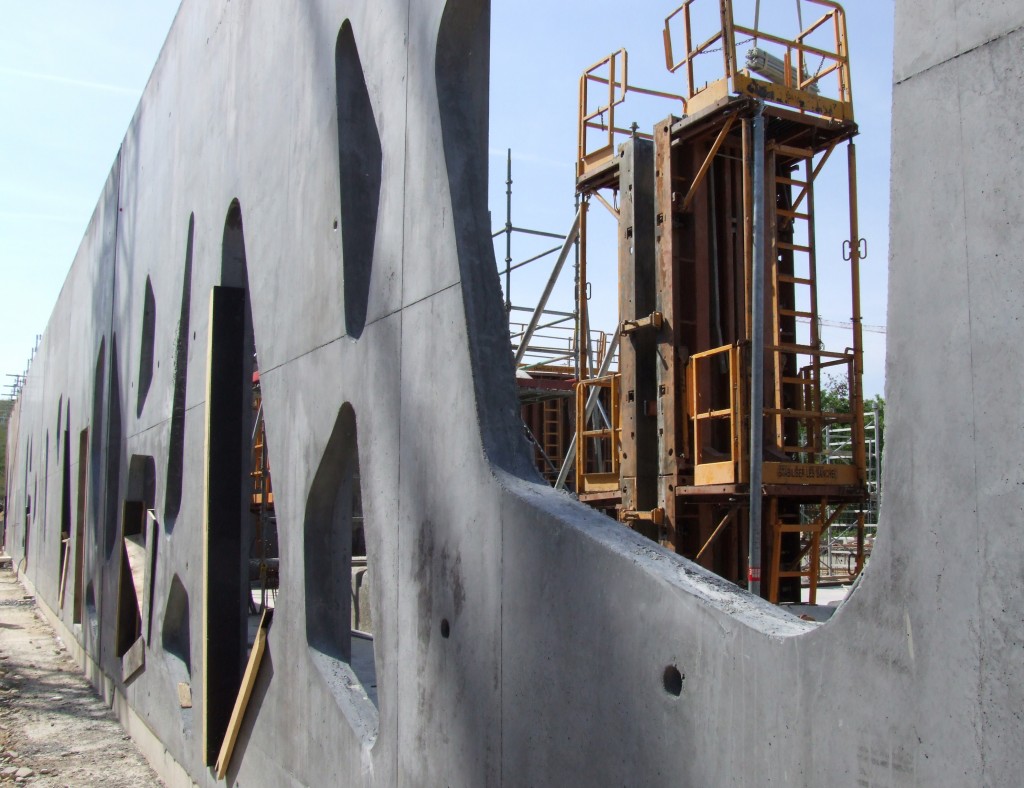
Peeping in
2011-05-17 - Peeping into the future Site Access Control Building in April 2011. Photo: AIF
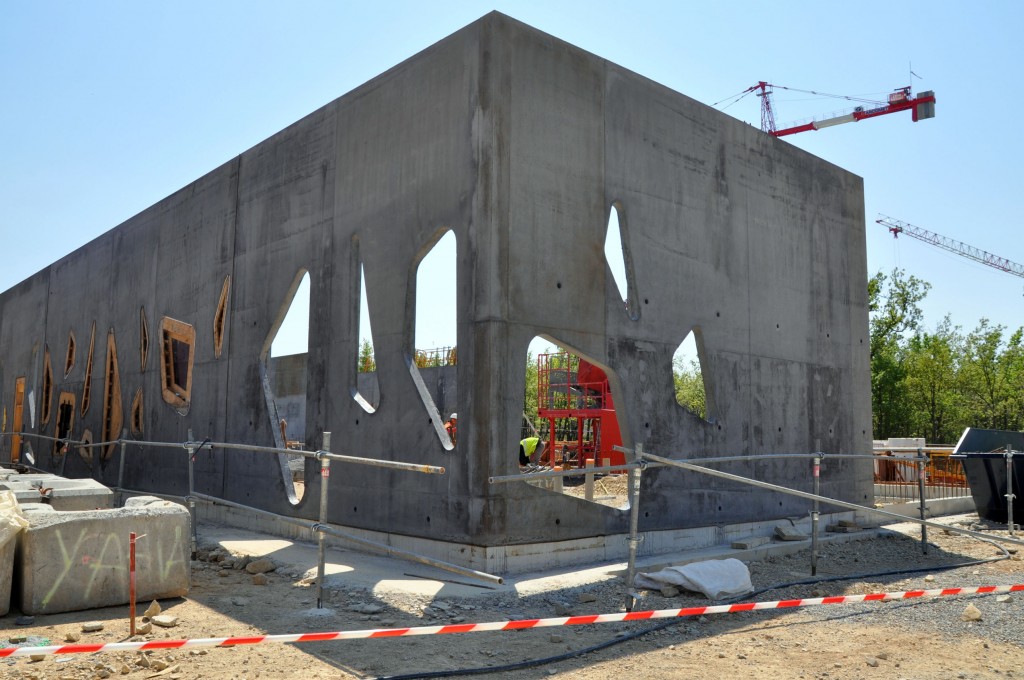
Asymmetric openings
2011-05-17 - The first walls and asymmetric openings of the Site Access Control Building.
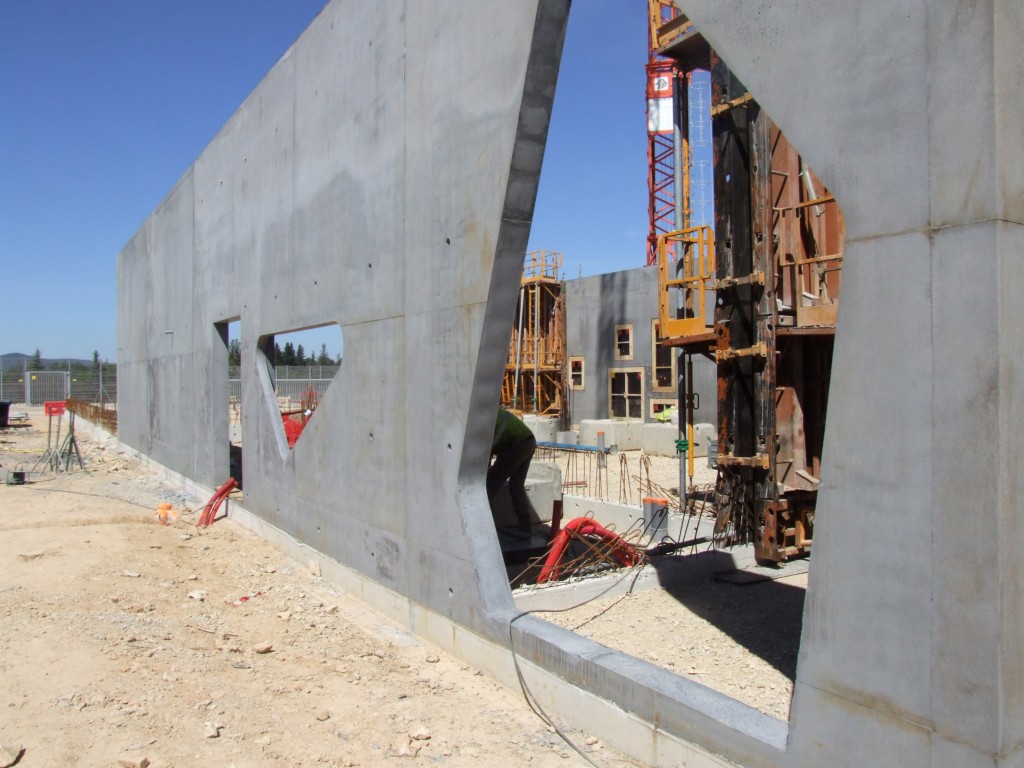
Free-form concrete
2011-05-16 - Architectonic concrete is used to give structural strength to the Site Access Control Building, whose creative geometric openings are airy and aesthetic. Photo: AIF
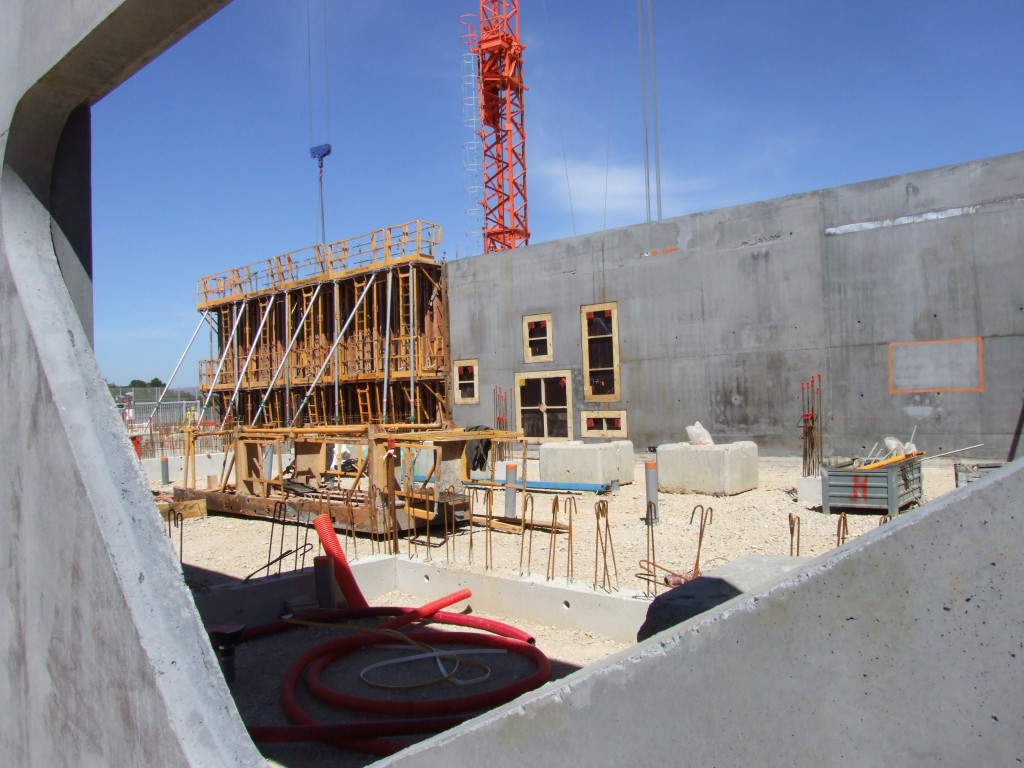
The Site Access Control Building
2011-05-15 - Located near the ITER Headquarters the Site Access Control Building, equipped with a 50-person conference room, will be accessible by the public. Photo: AIF
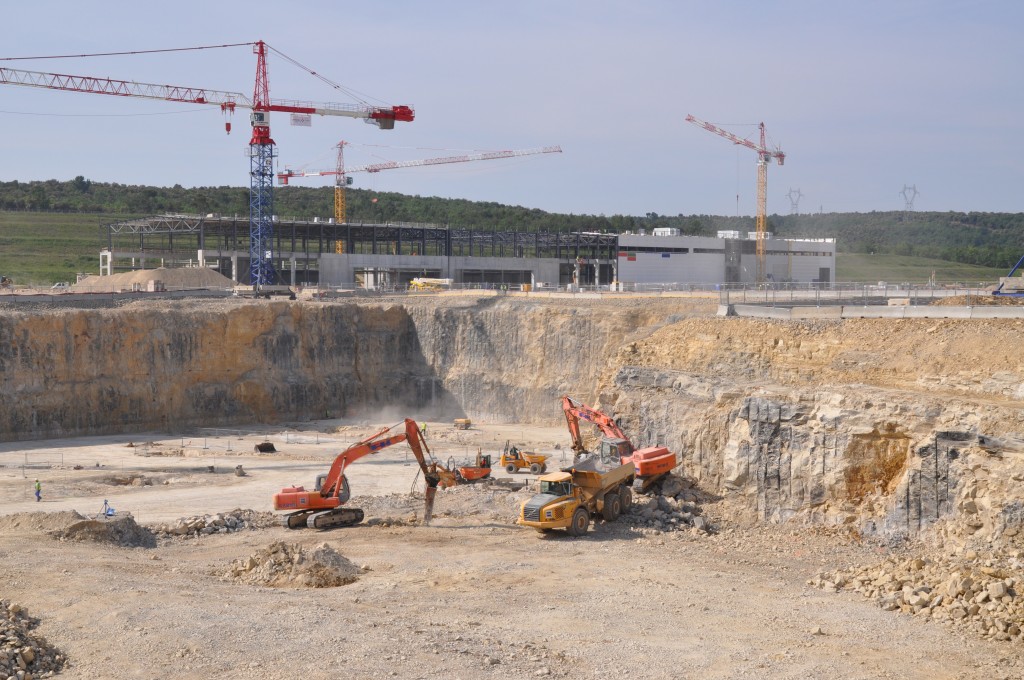
Drilling and clearing
2011-05-12 - Work continues to clear, clean, and fill the irregularities in the rock floor of the Seismic Pit. In the background—the first building on the ITER platform.
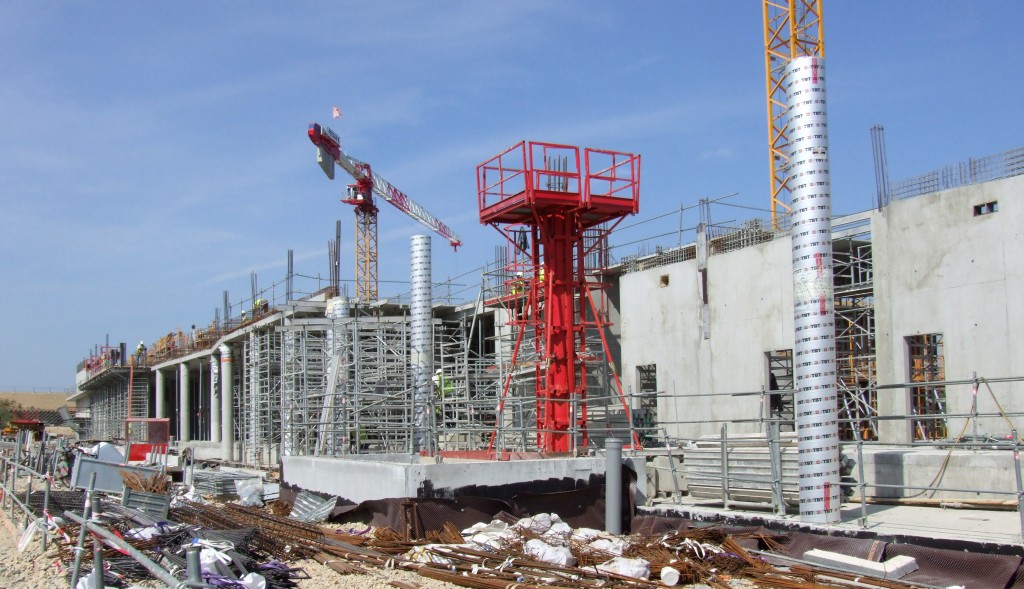
Ultra high performance fibrous concrete
2011-05-12 - The Headquarters worksite in May 2011. For thin constructions, ultra high performance fibrous concrete is used. Incorporating steel fibres, this self-compacting concrete has exceptional durability and extremely high compression resistance: between 130 and 250 MPa (Mega Pascal) in normal conditions. The high resistance is accompanied by a very high density and almost zero permeability of water, oxygen or chloride ion diffusion. Photo: AIF
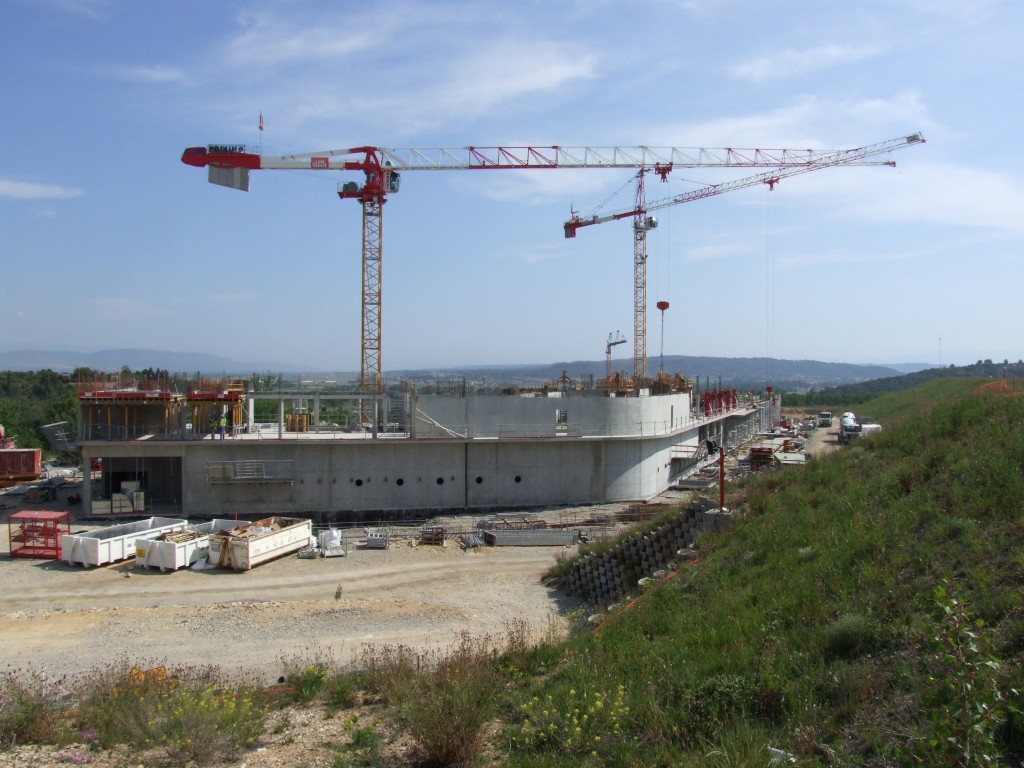
Tower cranes
2011-05-11 - A 60-metre crane and a 42-metre crane hard at work on the walls of the future ITER Headquarters in May 2011. Photo: AIF
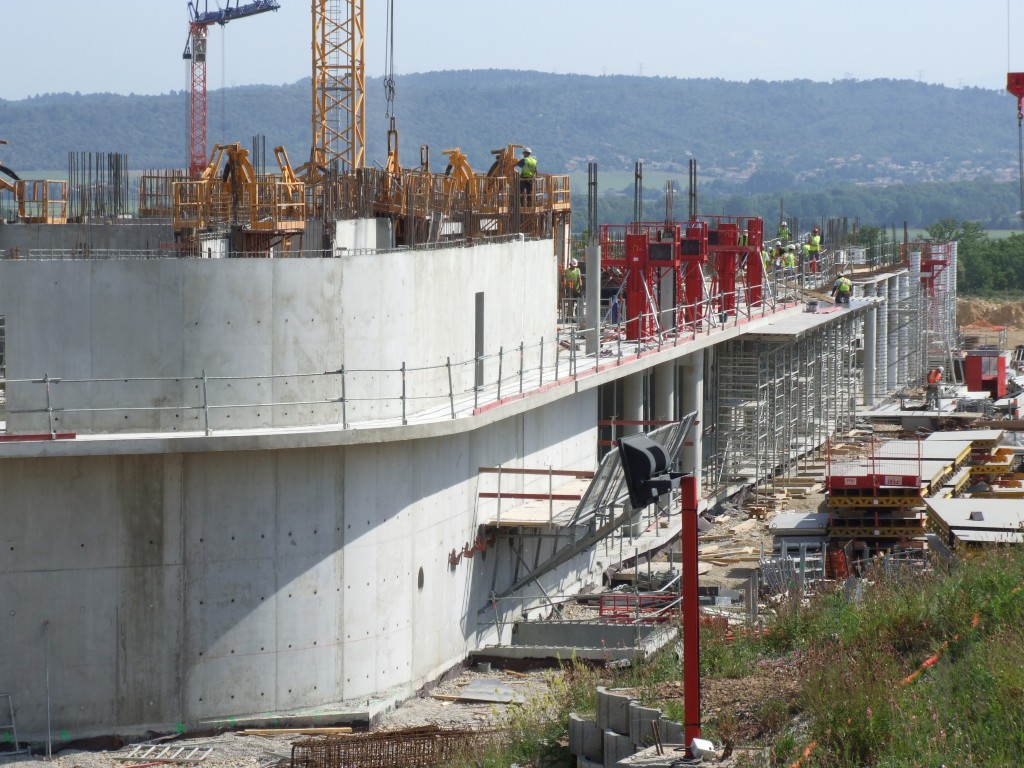
26 different "formulas"
2011-05-11 - Twenty-six different types of concrete will be used for the construction of the ITER Headquarters—26 different "formulas" depending final use (posts, beams, floors, external walls ...) and taking into account the different resistance levels, colours, plasticity, setting speeds, and aggregate size. Photo: AIF
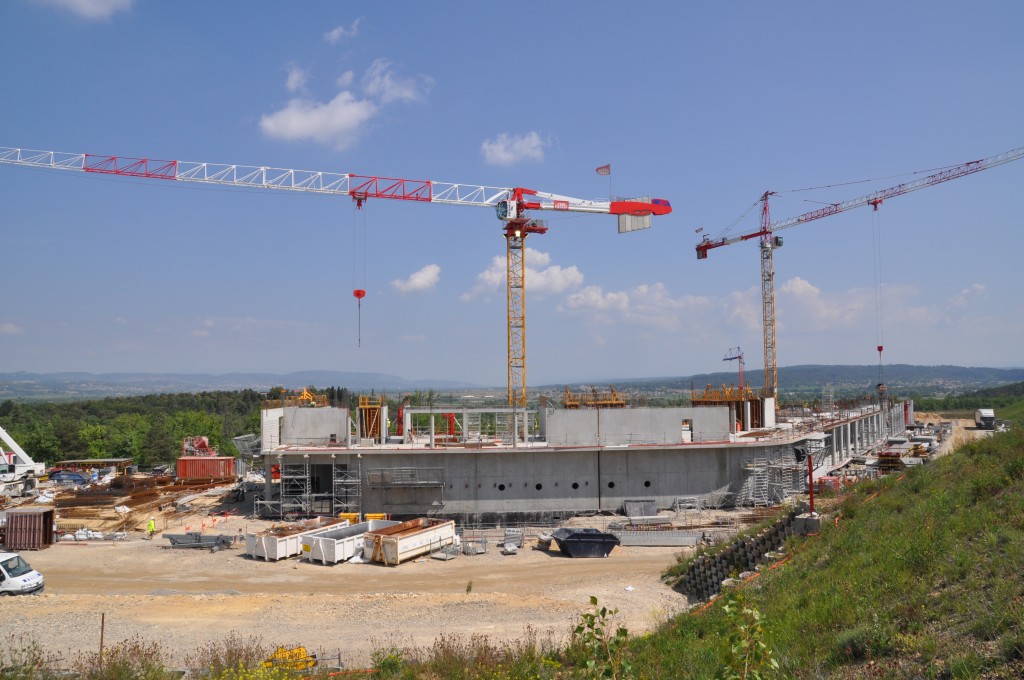
The southeast facade faces the platform
2011-05-05 - To help regulate the temperature inside the building, the southeast facade will be equipped with Venetian blinds to adjust the amount of incoming light room by room. Photo: AIF
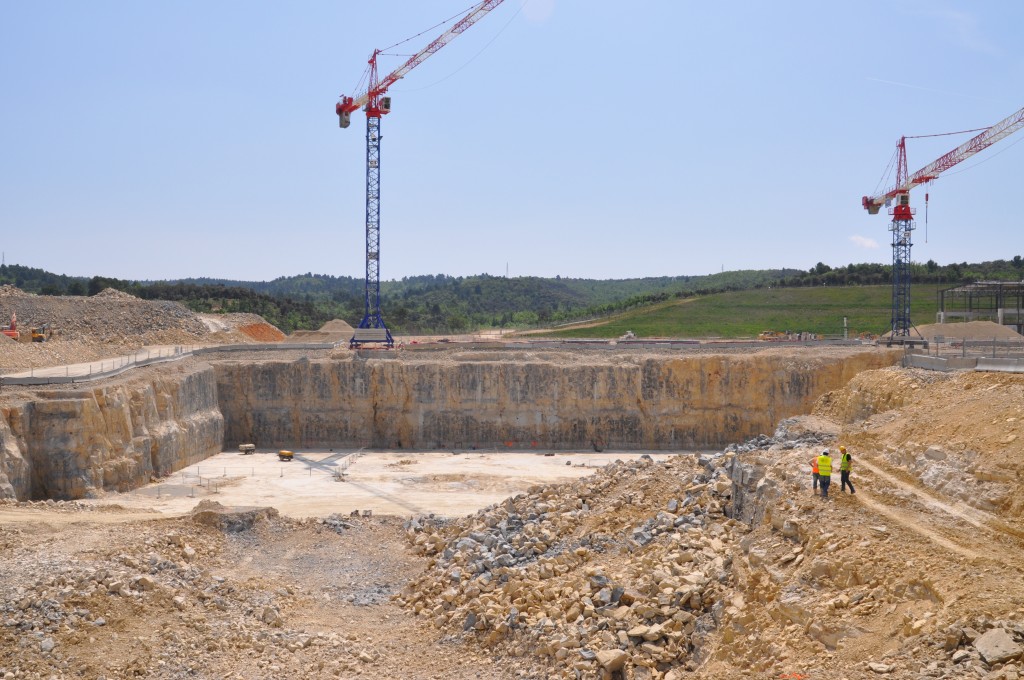
Tower cranes in place
2011-05-05 - Tower cranes at each of the four corners of the Seismic Isolation Pit will be used to lower the tons of steel rebar needed for the reinforced foundations of the Tokamak Complex.
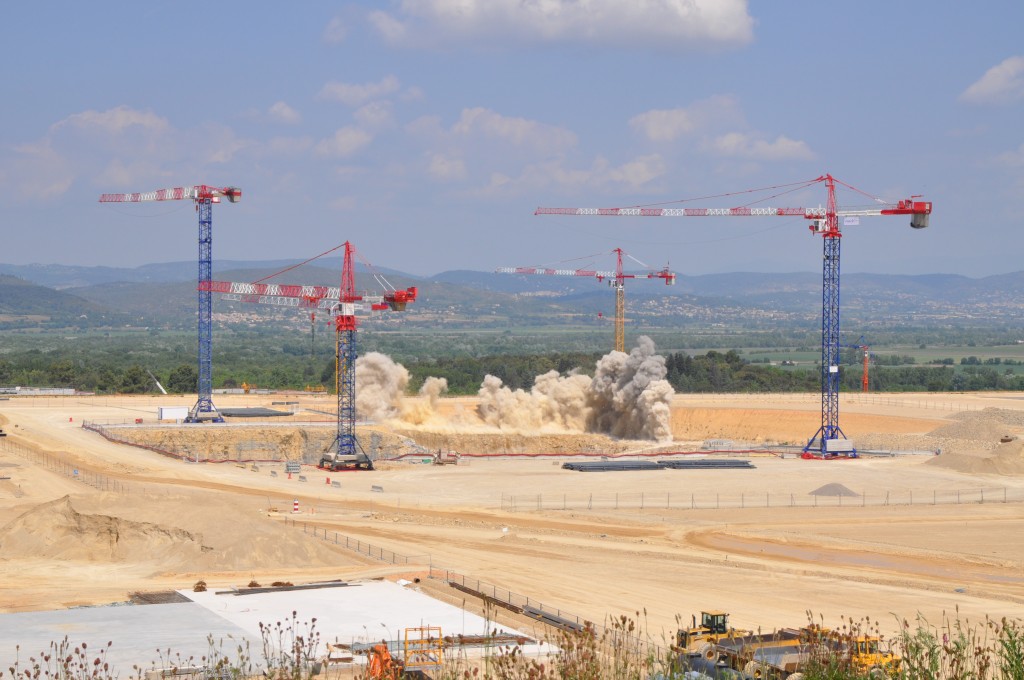
A last bit of blasting
2011-05-05 - Final "profile" blasting is carried out in May on the contours of the Tokamak Complex Seismic Isolation Pit.

Dealing with geological particularities
2011-04-29 - Karsts, or small cracks in the geological surface of the Seismic Pit, are cleaned, inspected, enlarged, and filled with concrete.

The Seismic Pit in April 2011
2011-04-29 - Work continues on the floor of the Seismic Pit to explore and widen karsts - or fissures - in the first five metres of rock.
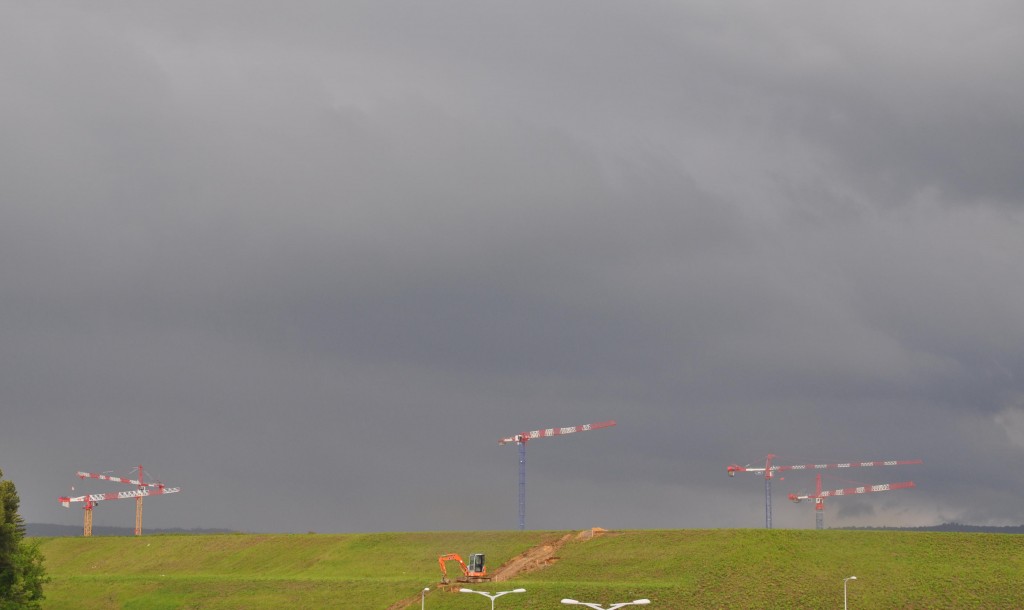
Green banks below
2011-04-28 - The green banks of the ITER platform, planted last year with over 3.5 tonnes of seeds, stand out against a grey April sky. A lone digger works to create a staircase to lead from the contractors' area below to the worksites on the platform.
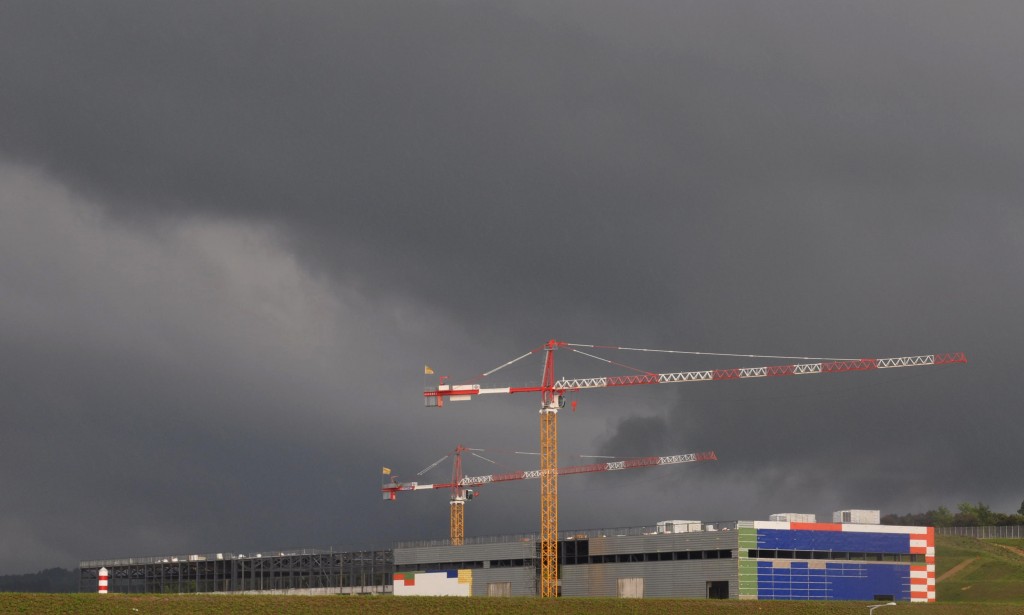
As the clouds roil ...
2011-04-28 - On a stormy day, the colourful layers of cladding of the Poloidal Field Coils Winding Facility.
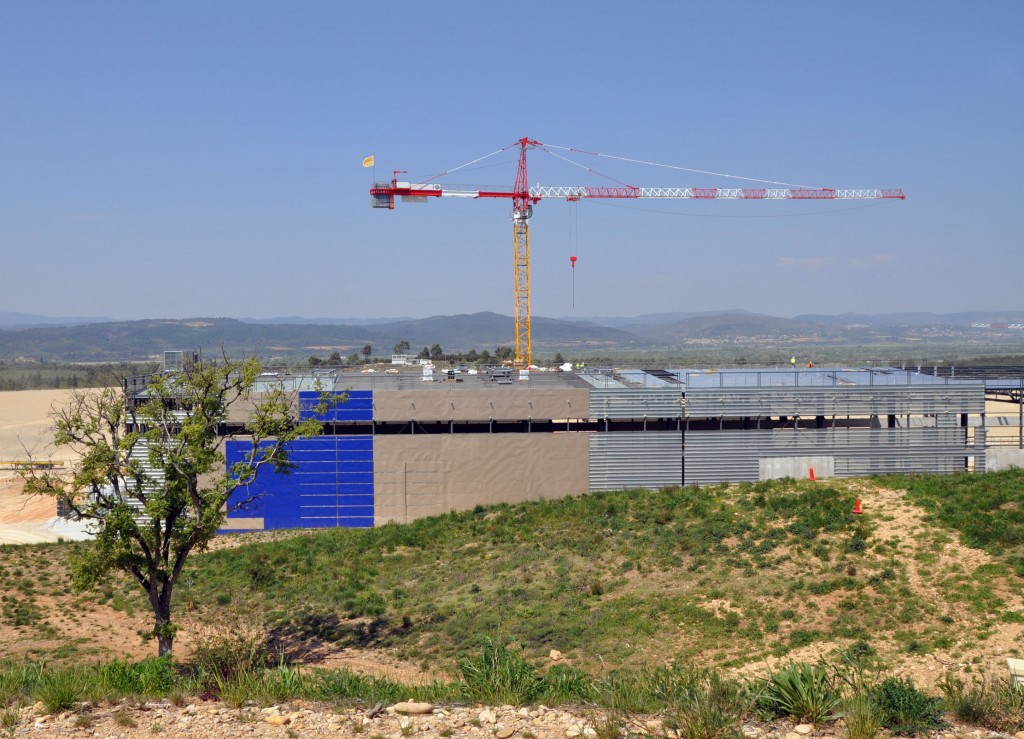
Building #1 of 39
2011-04-21 - The first of 39 buildings on the ITER platform: the Poloidal Field Coils Winding Facility.
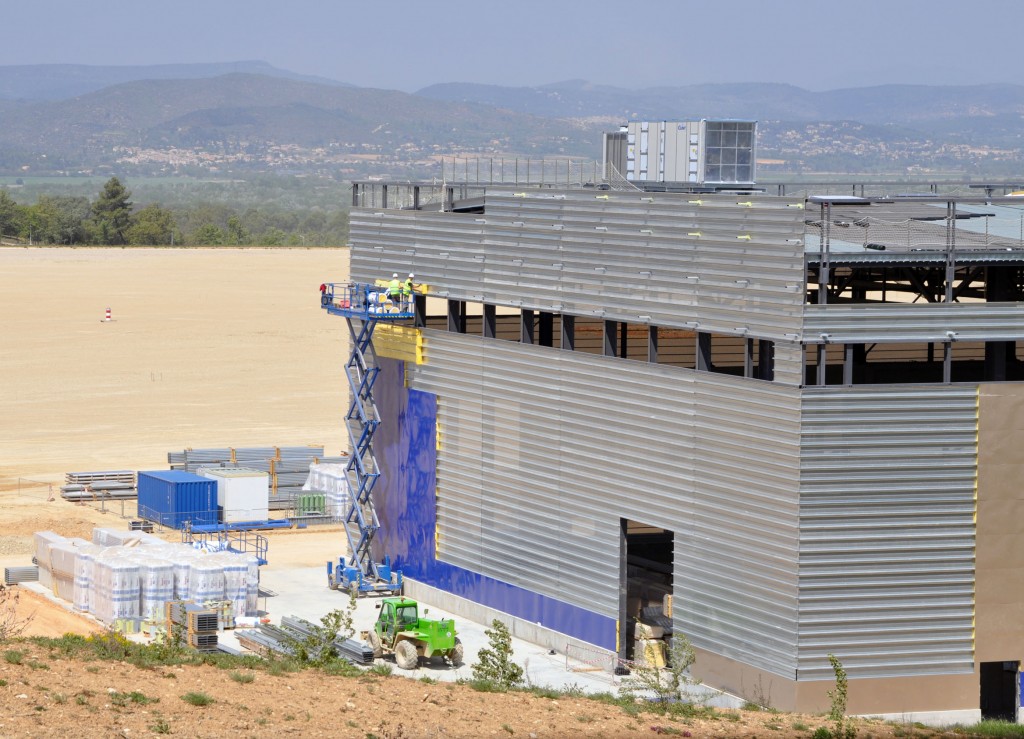
Cladding on the south face
2011-04-21 - Successive layers of cladding are applied to the exterior of the Winding Facility in April 2011. These include an inner layer of sheeting containing small holes to absorb work area noise; two layers of glass wool insulation; and finally two layers of metal sheeting sealed with tape against dust. The final colours will be grey and burnished red.
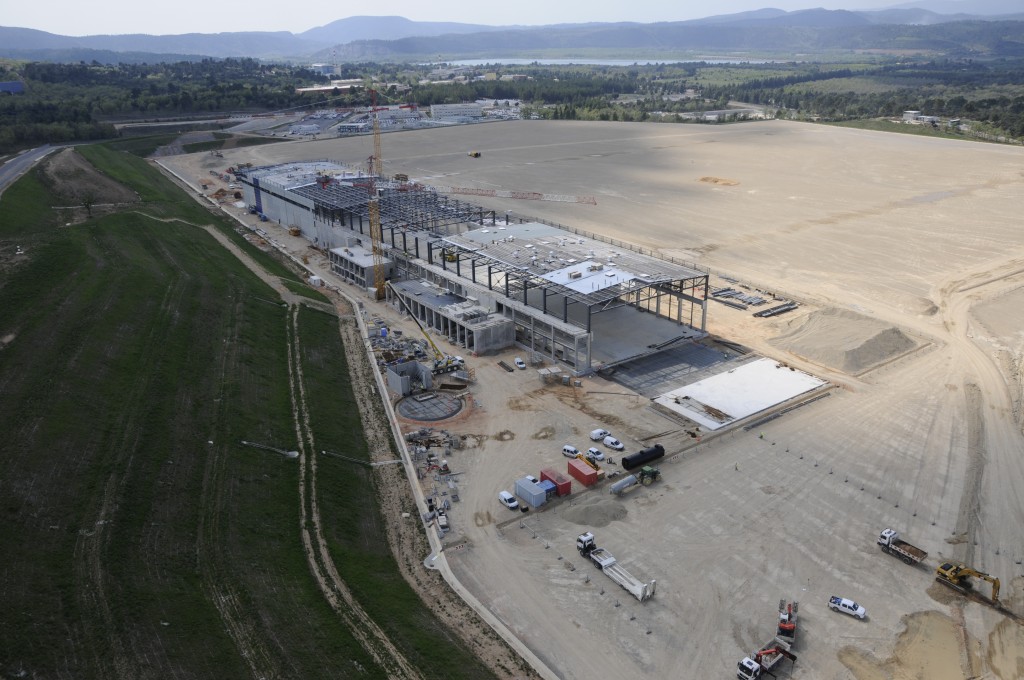
The Winding Facility in April
2011-04-17 - Seen from above: the Poloidal Field Coils Winding Facility. Photo: Altivue/Spie Batignolles
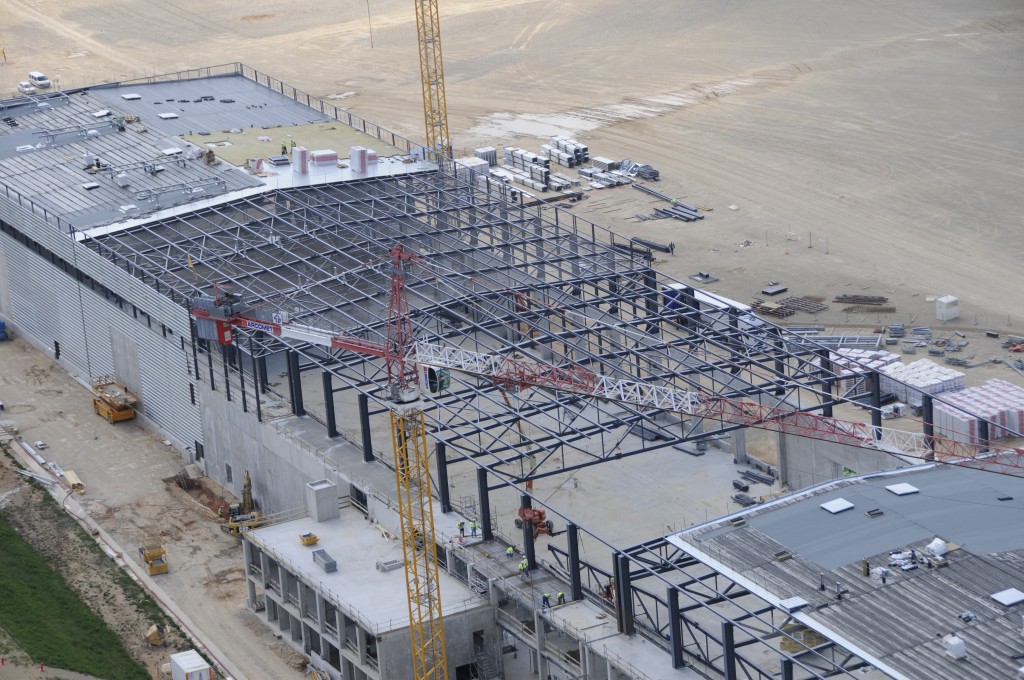
Seen from the sky
2011-04-17 - The poloidal field coil system consists of six horizontal coils placed outside the toroidal magnet structure. Due to their size, the actual winding of five of the six poloidal field coils will take place here, in this dedicated, 257-metre long facility on the ITER site in Cadarache. (The smallest of the coils will be manufactured offsite and delivered finished.) Photo: F4E
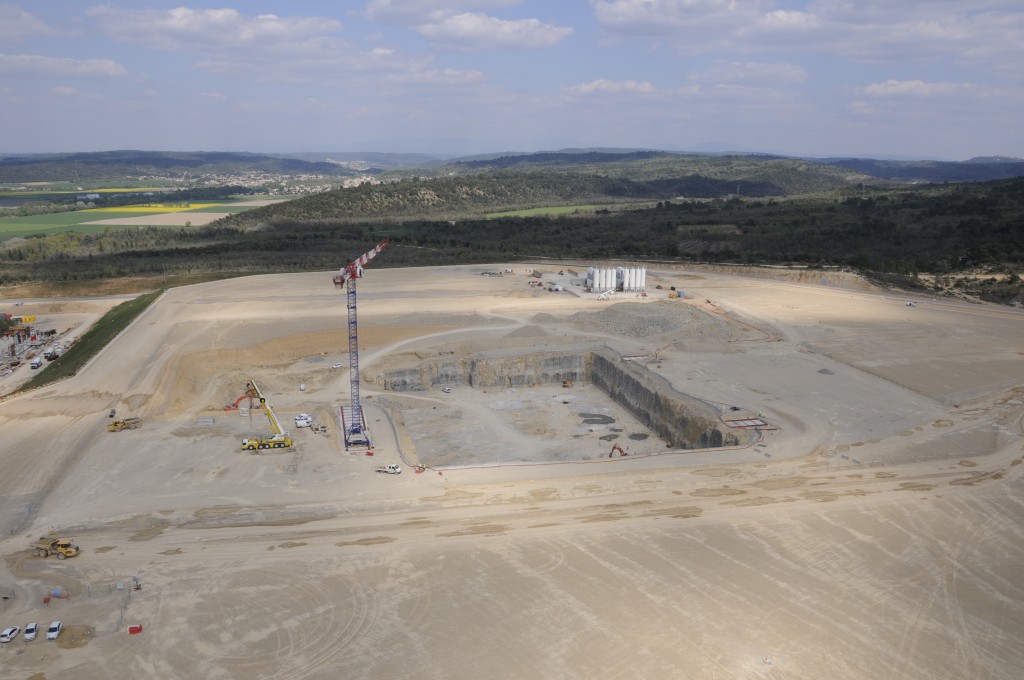
The ITER platform—looking northeast
2011-04-17 - Looking northeast over the Tokamak Complex Seismic Isolation Pit in April. Photo: Altivue/Spie Batignolles
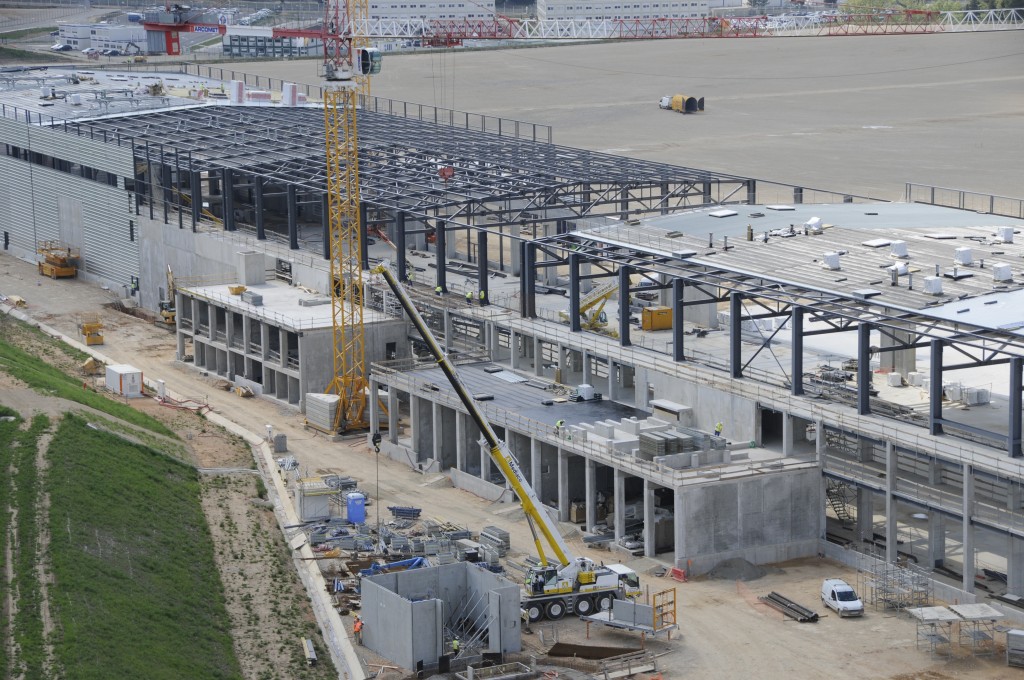
Successive production zones
2011-04-17 - The Winding Facility will accommodate docking stations for the unloading and temporary placement of the superconducting coils, production zones corresponding to the successive steps of the winding and assembly process, and offices. Photo: Altivue/Spie Batignolles

The double batching plant seen from above
2011-04-17 - The on-site concrete batching plant, seen from above. Photo: Altivue/Spie Batignolles
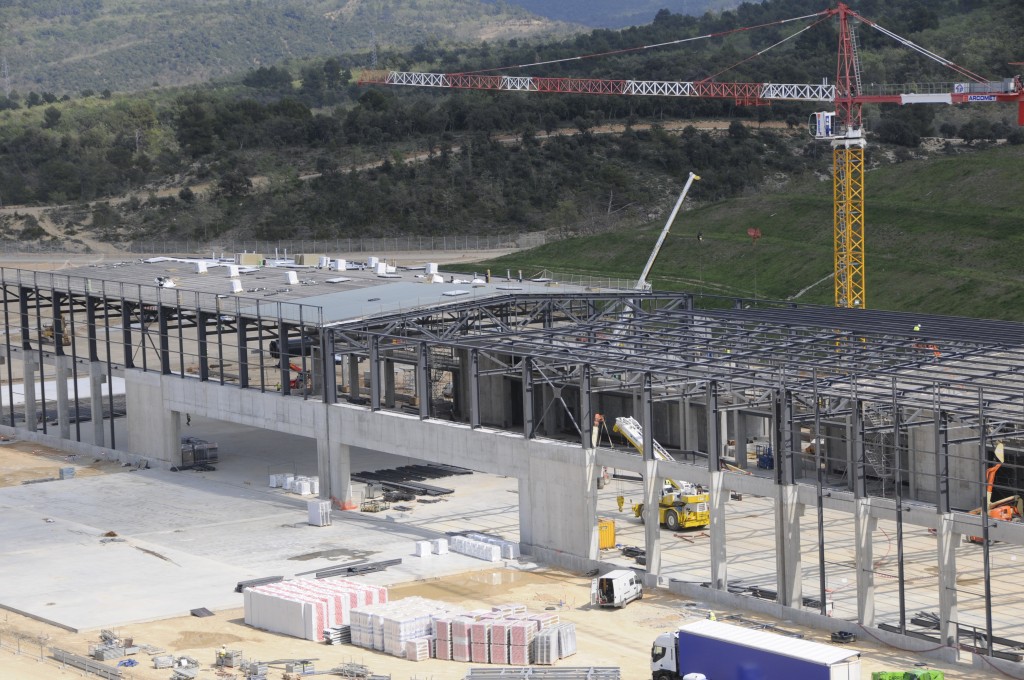
Four layers of rooftop insulation
2011-04-17 - The roof of the Winding Facility is covered with four layers of insulation: steel, rock wool, elastomer, and tar. Photo: Altivue/Spie Batignolles
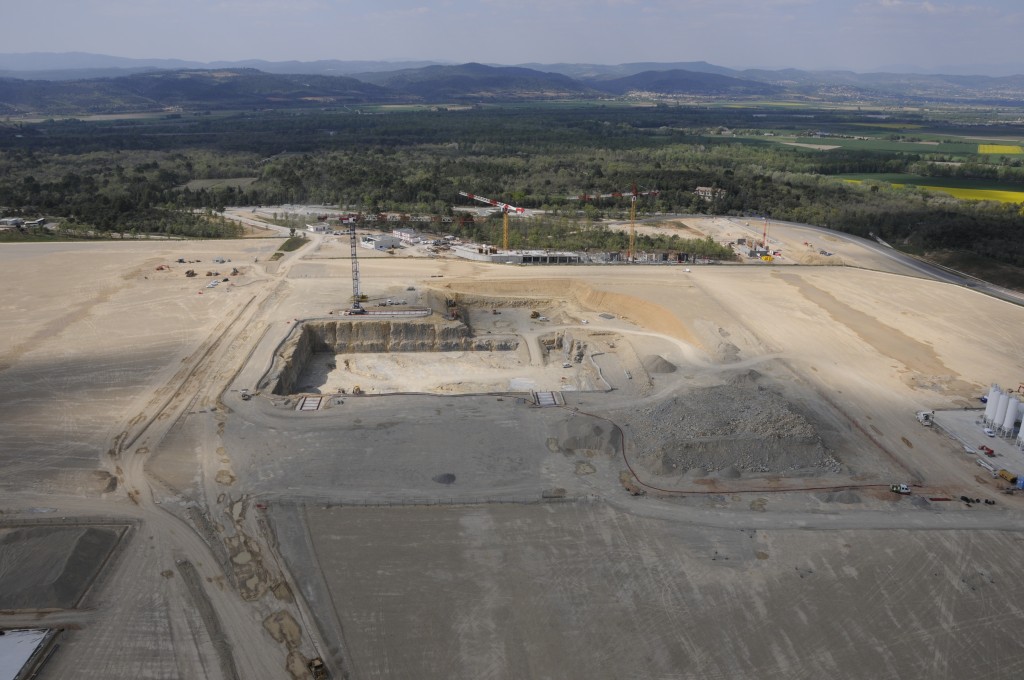
Blasting for the Hot Cell Facility
2011-04-17 - Less profound than the main work site, the square area that abuts the Tokamak Complex Seismic Isolation Pit to the north is reserved for the foundations of the ITER Hot Cell Facility. Final trim blasting will be carried out in May 2011 to finalize the perimeters of this area. Photo: Altivue/Spie Batignolles
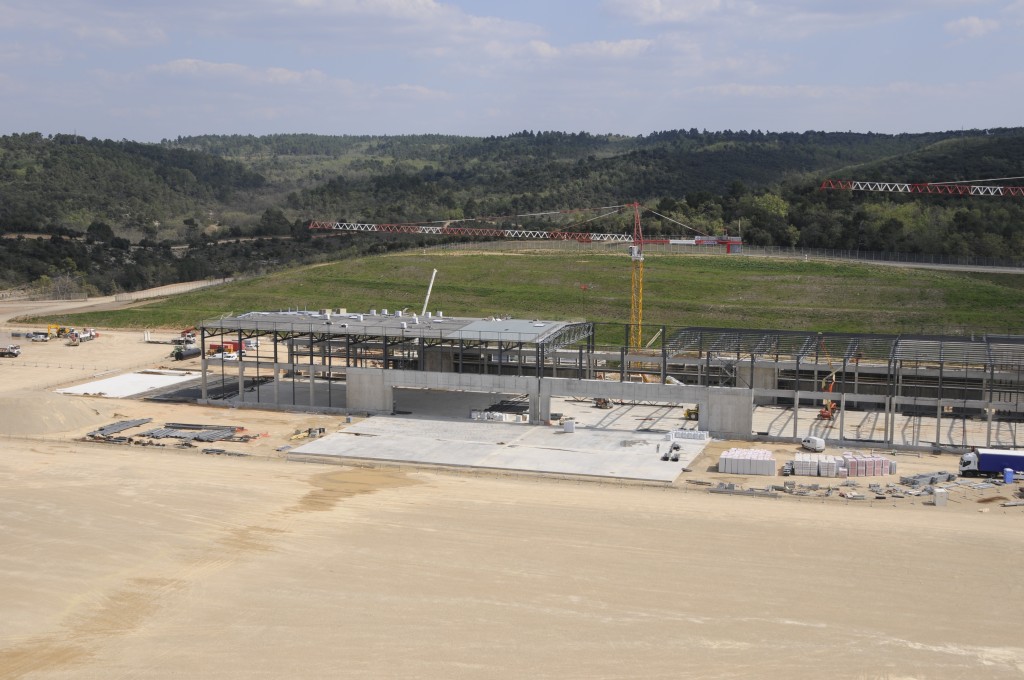
Where is the exit?
2011-04-17 - A smooth concrete platform is built outside of the exit doors of the Poloidal Field Coil Winding Facility for the safe transfer of the completed coils. Photo: Altivue/Spie Batignolles
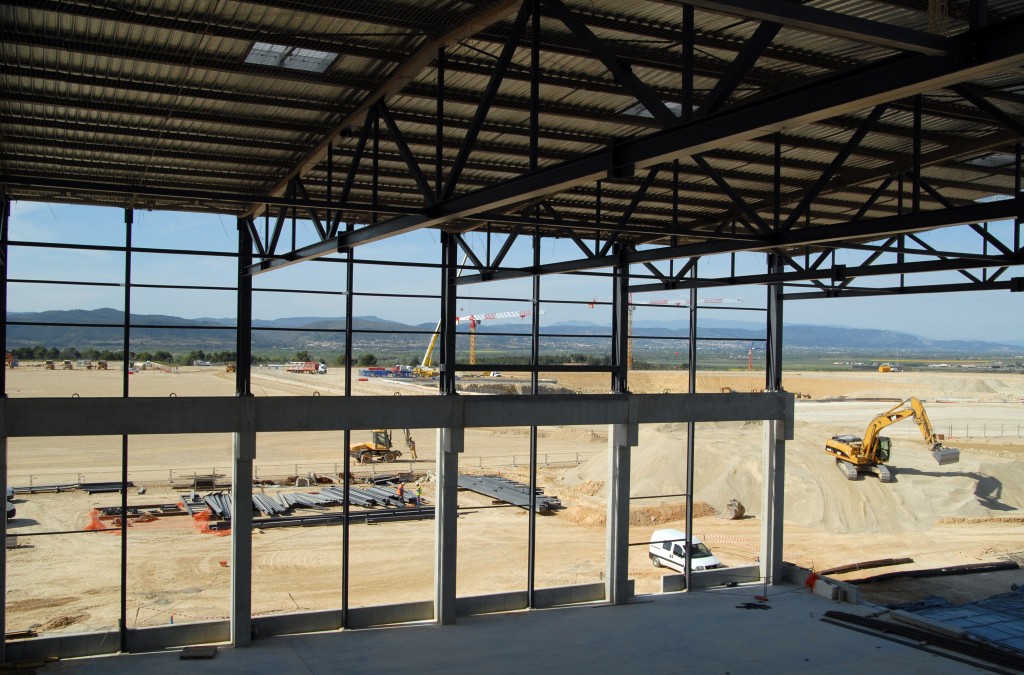
Concrete works end in April
2011-04-13 - All concrete for the Winding Facility is poured by April 2011. Photo: Altivue/Spie Batignolles
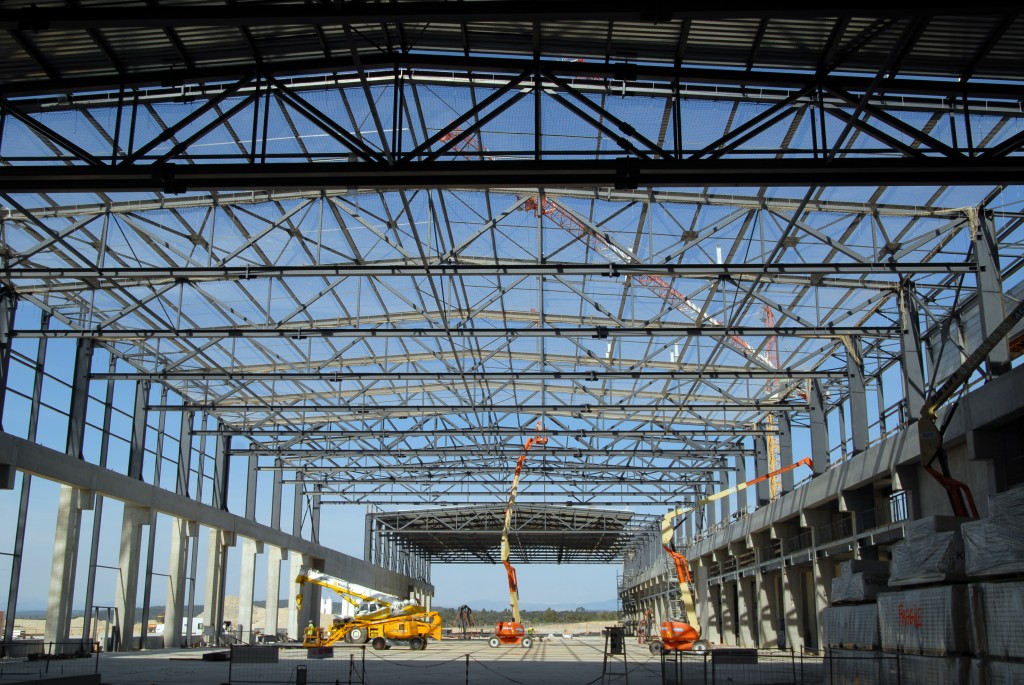
What role for the poloidal field magnets?
2011-04-13 - The poloidal field magnets pinch the plasma away from the walls and contribute in this way to maintaining the plasma's shape and stability. Photo: F4E
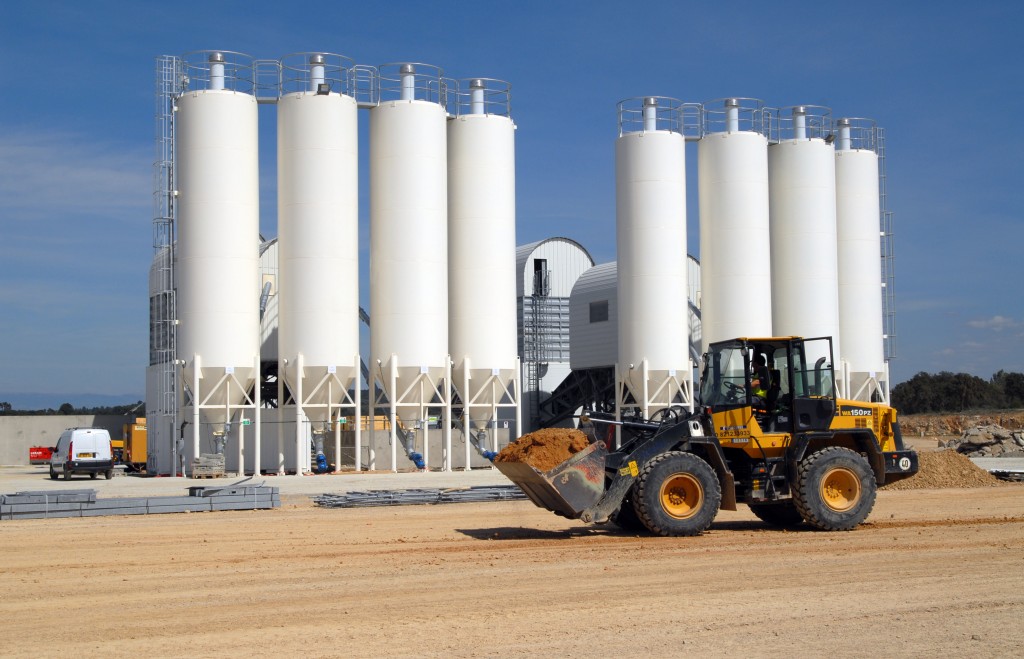
Concrete produced on site
2011-04-13 - To produce the estimated 250,000 m³ of concrete necessary for the construction of the ITER facilities, a specially dedicated concrete batching plant was built on site. Here: the two mixing machines, each with four tanks. Photo: AIF
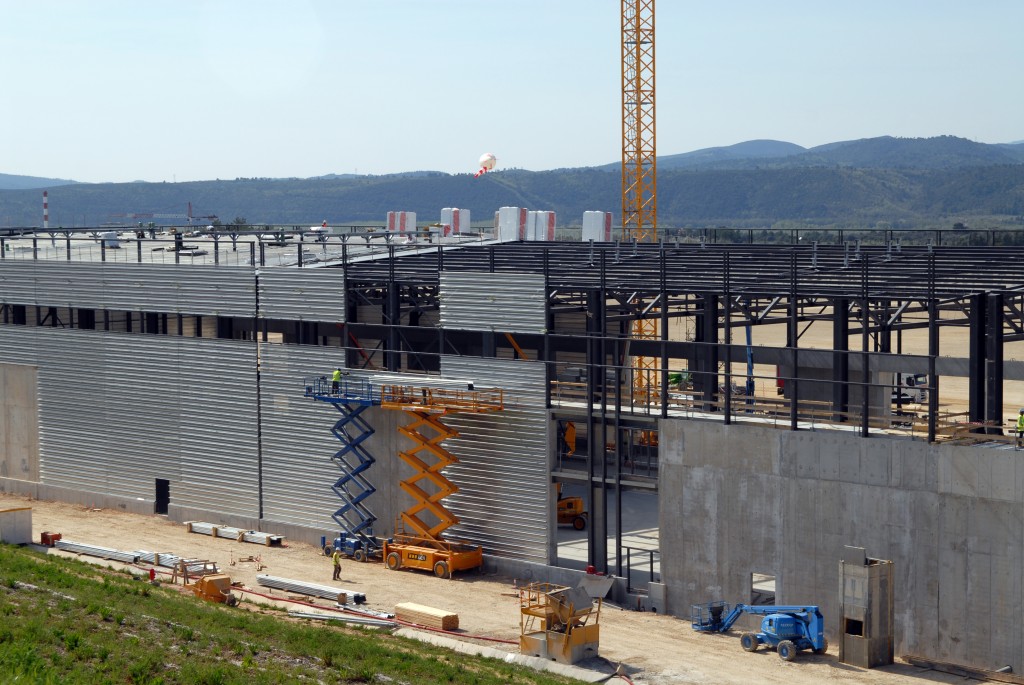
Cladding work begins
2011-04-13 - Work begins on the metal cladding of the Winding Facility. Five layers of metal cladding and insulation will protect the work space inside—where cleanliness is a priority—from the infiltration of dust. Photo: F4E
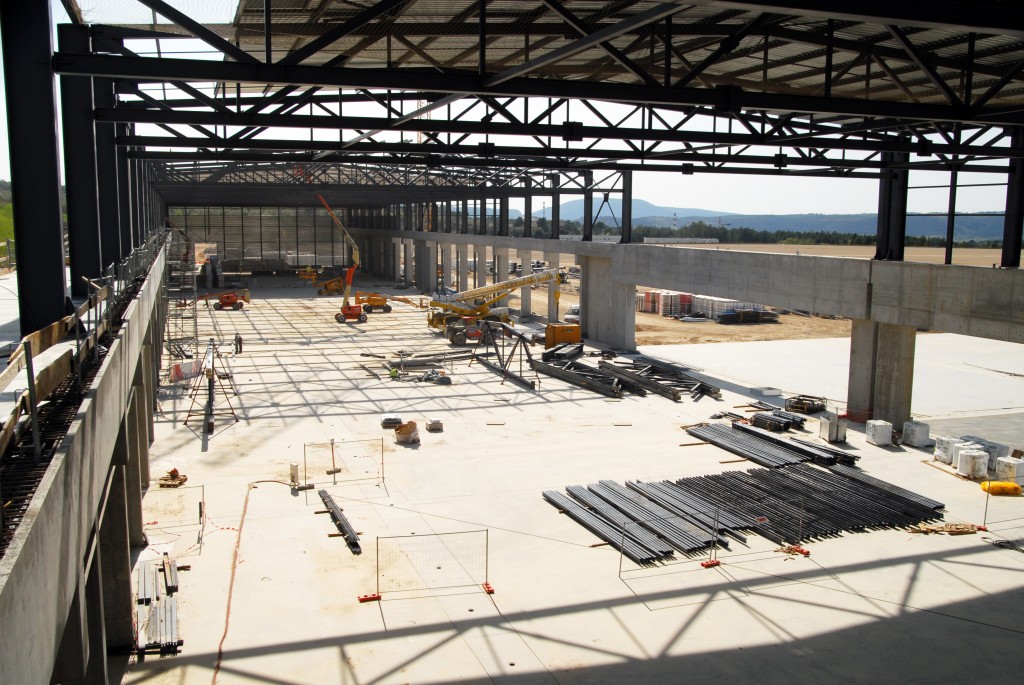
12,000 square metres
2011-04-13 - A surface area of 12,000 square metres dedicated to the winding and assembly operations of ITER's poloidal field coils. Photo: F4E
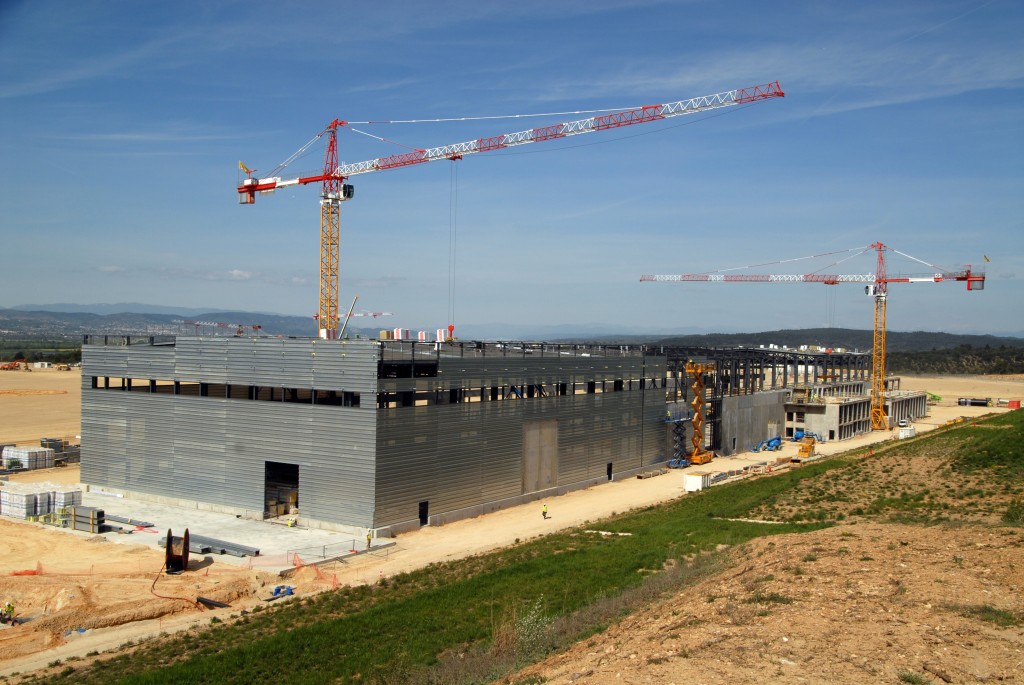
Construction in 18 months
2011-04-13 - Some 80 workers are involved in the construction of the Poloidal Field Coils Winding Facility, which will be completed in December 2011. Photo: F4E
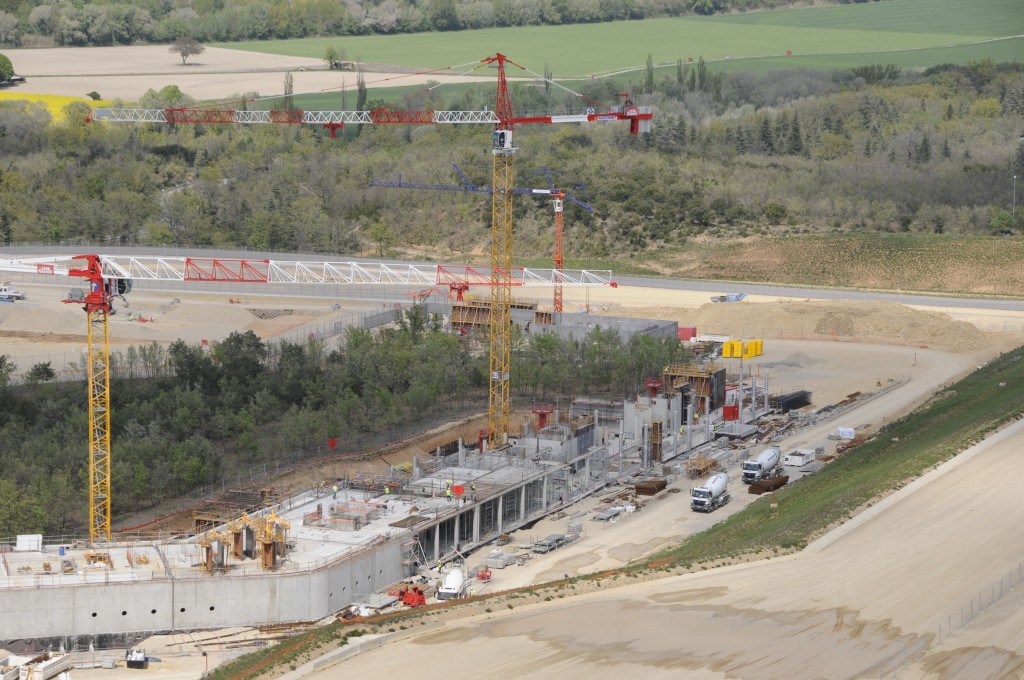
ITER's window to the project
2011-04-01 - Facing the main entrance to the ITER site, the ITER Headquarters building will be the window to the ITER project for the world. Photo: Altivue/AIF
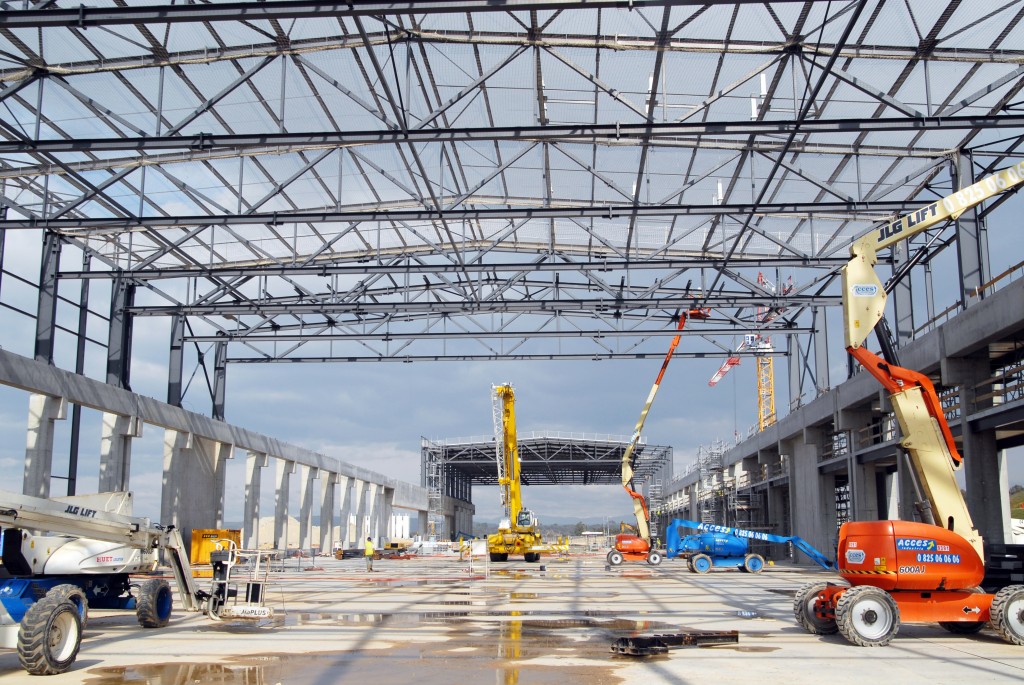
Preparing for the travelling cranes
2011-03-17 - Embedded plates will be installed along the horizontal beams on either side of the Poloidal Field Coils Winding Facility for the rails of the travelling cranes. Photo: F4E

As heavy as the Empire State Building
2011-03-10 - Some 360,000 tonnes of foundation and building will rest on the bottom of the Seismic Isolation Pit; 360,000 tonnes is the weight of New York's Empire State Building. Photo: F4E
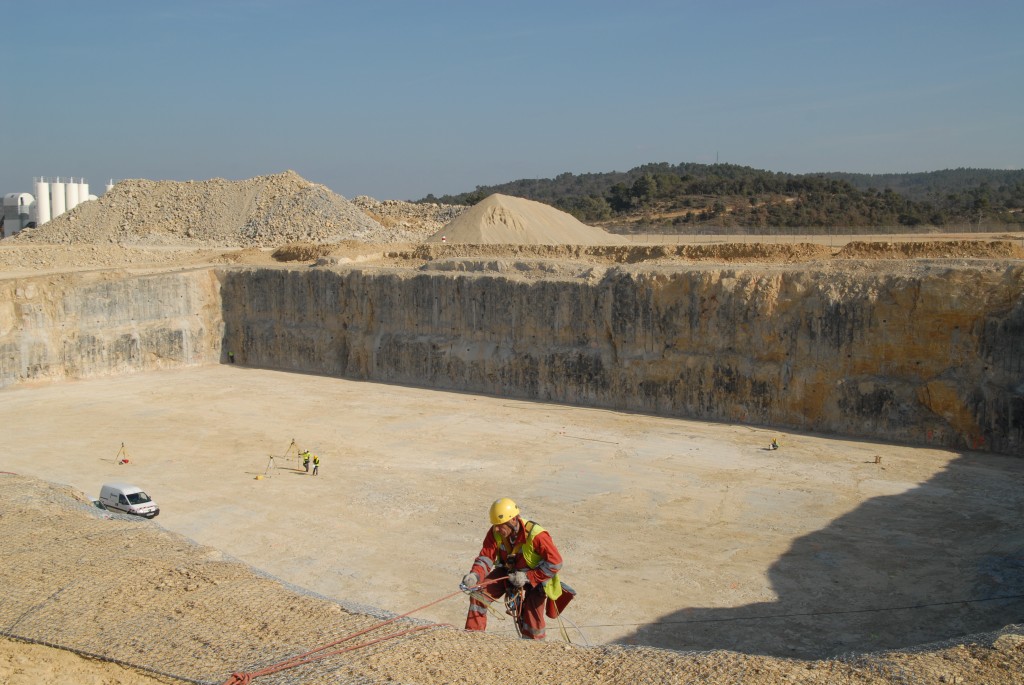
Safety mesh installed along the rock face
2011-03-10 - Workers rappel down the walls of the Seismic Isolation Pit to install wire mesh along the rock face as a protective measure for those working below. The horizontal rock surface of the 90 x 130 metre Tokamak Complex Seismic Isolation Pit is as smooth as a billiard table. Photo: F4E
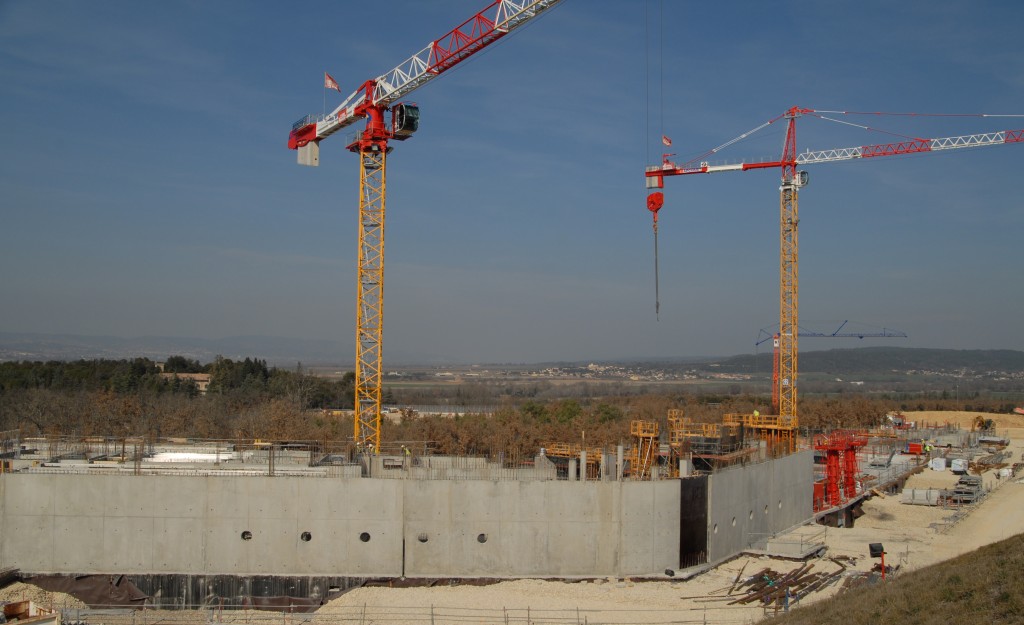
Shaped like the wings of a bird
2011-03-10 - The wing-shaped ITER Headquarters emerges against the backdrop of southern France. Photo: AIF
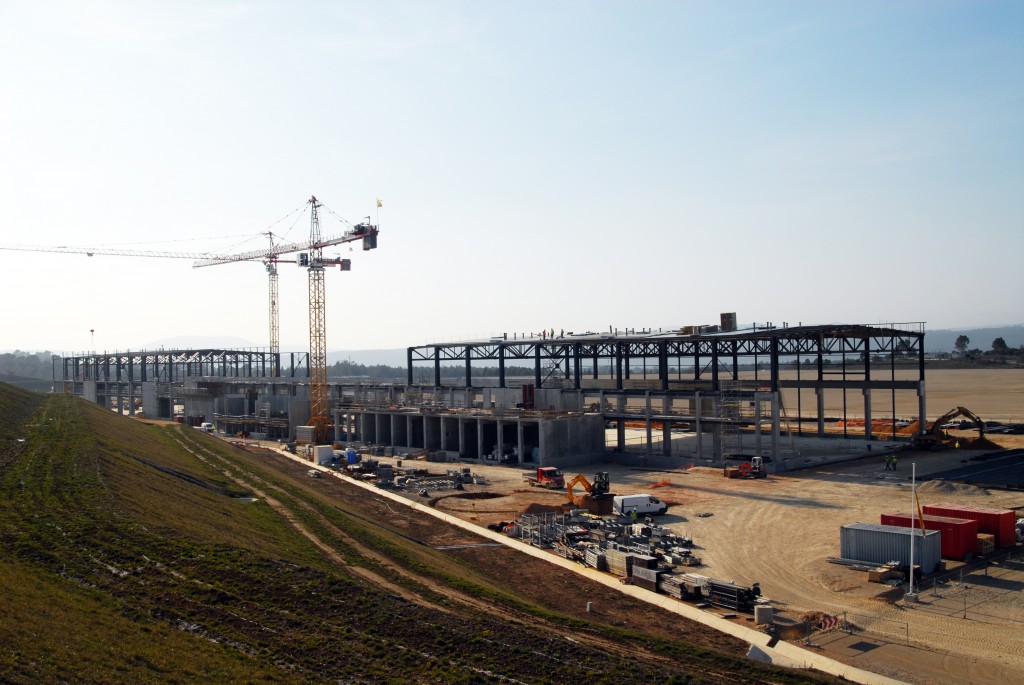
257 metres long
2011-03-10 - The 257-metre Poloidal Field Coils Winding Facility stretches off into the distance ... Photo: F4E
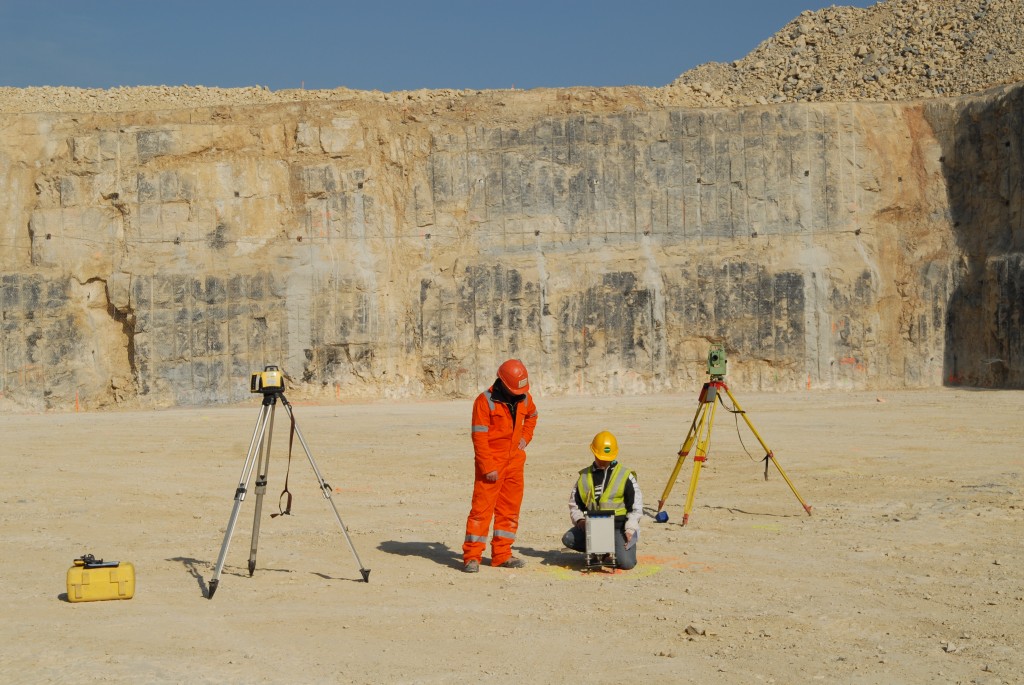
Checking the geometry of the excavation
2011-03-10 - Laser and land surveyor rods are used to measure the surface levelling before foundation work begins. The technique of microgravity is used to measure gravity variations in order to determine rock properties. Photo: F4E
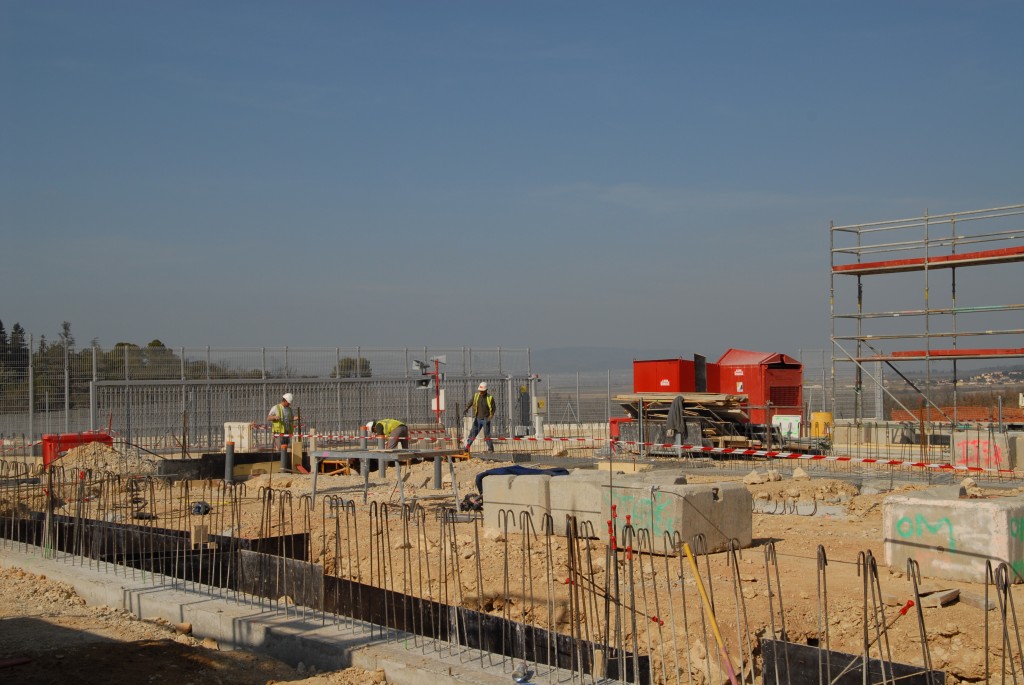
Workforce increasing
2011-03-10 - 40 people were involved in the construction of the first stage of the ITER Headquarters (shell). This number will progressively increase to 220 between April and September 2011. Photo: AIF
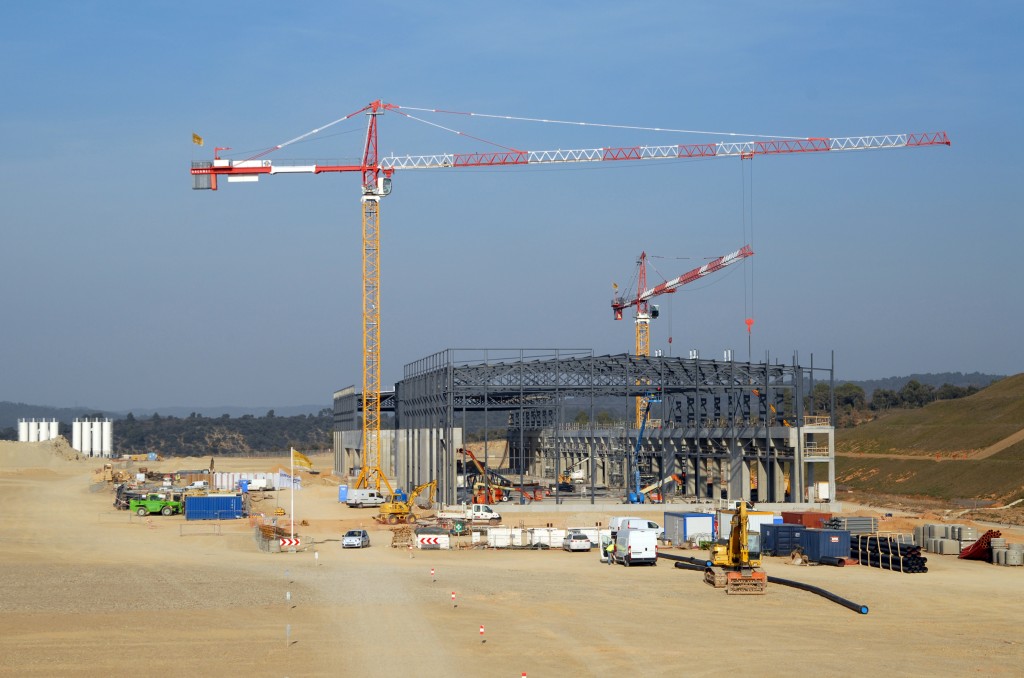
Looking north
2011-03-10 - Looking north past the Poloidal Field Coils Winding Facility on the eastern edge of the ITER platform. Photo: F4E
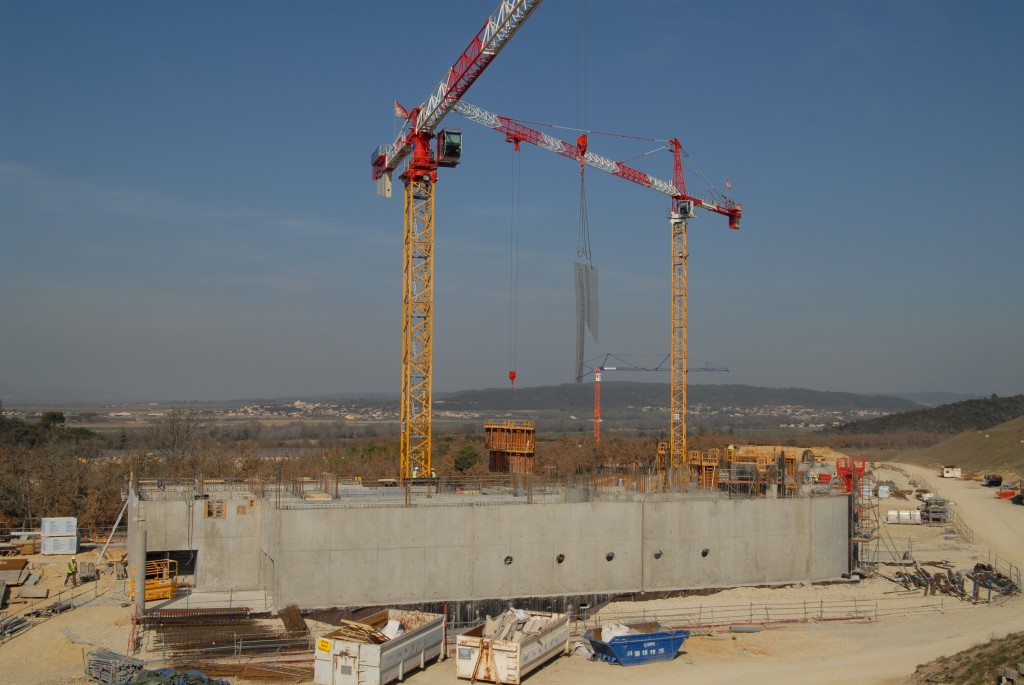
The walls of ITER Headquarters emerge
2011-03-10 - The shell of the ITER Headquarters will require 700 tons of steel and approximately 10 000 m3 of concrete. Photo: AIF
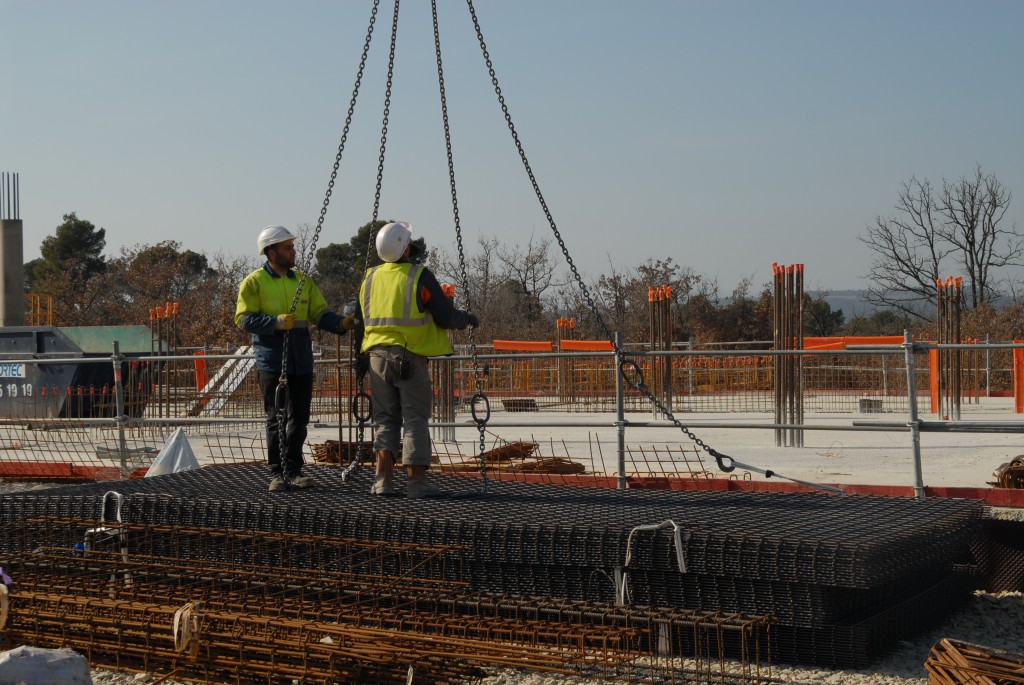
Steel reinforcement
2011-03-10 - Part of the 700 tons of steel required to reinforce the concrete poured for the ITER Headquarters. Photo: AIF
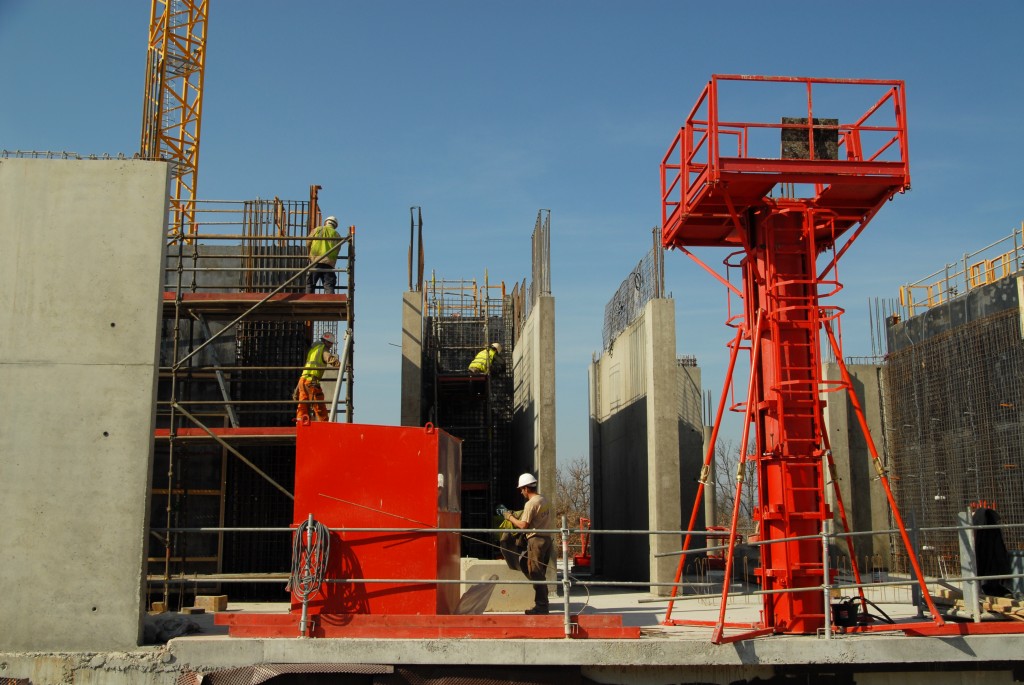
Taking shape
2011-03-10 - Workers position pre-formed walls on the second floor of the ITER Headquarters. Photo: AIF
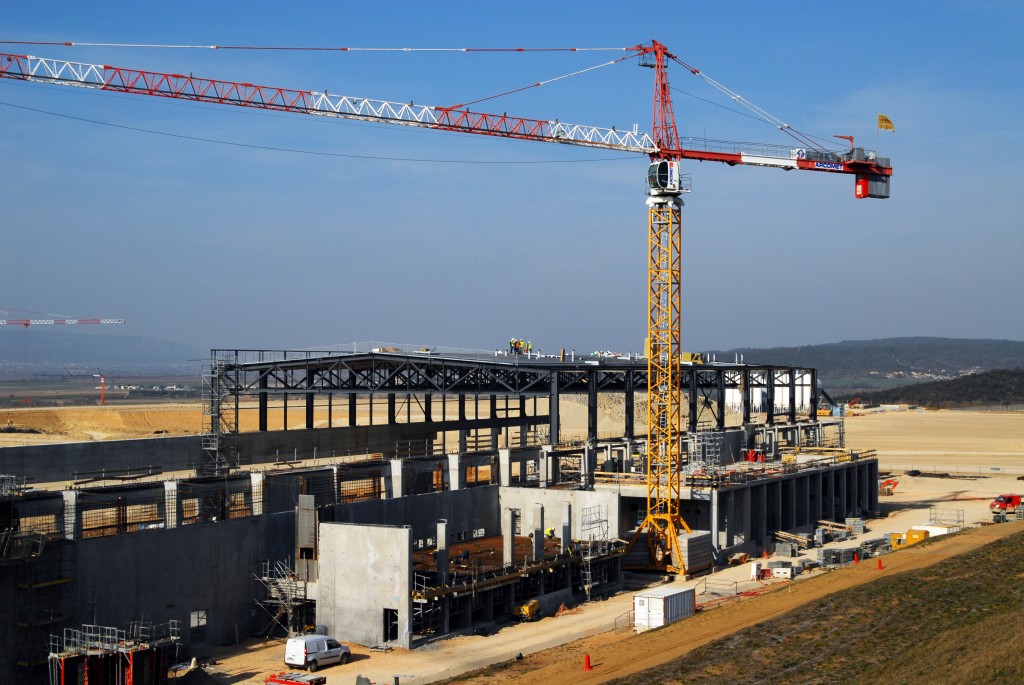
Technical areas for production
2011-03-10 - The Technical (electricity) and Production (cooling water, chiller, boiler) Buildings go up alongside the main Winding Facility. Photo: F4E
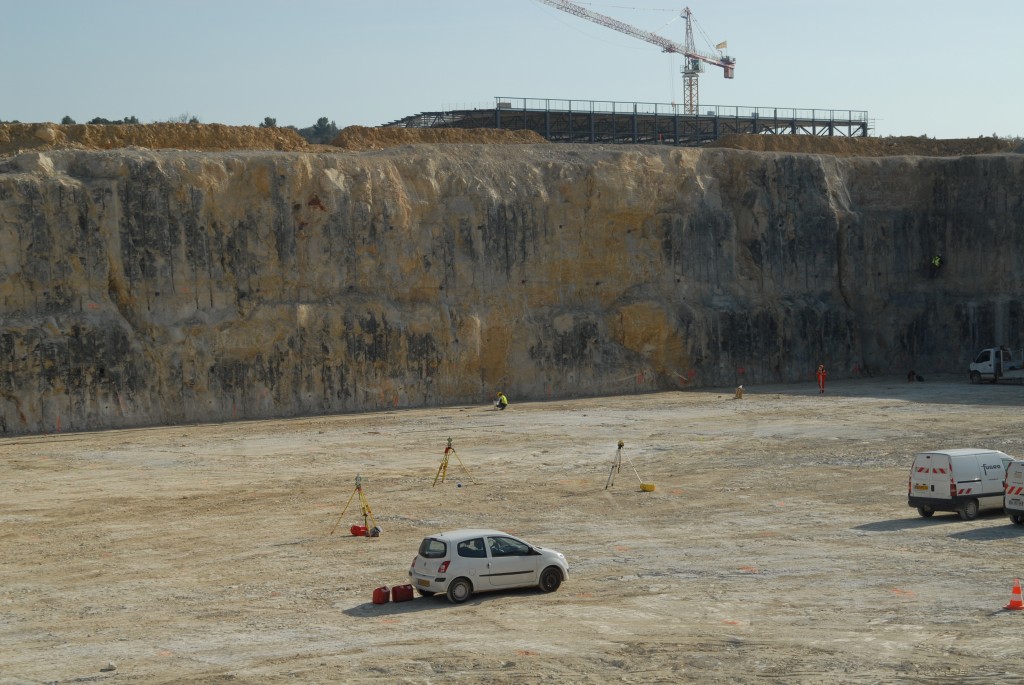
Making sure the level surface is perfect
2011-03-10 - On the clean-swept floor of the Seismic Pit, land surveyors' instruments are used to verify the exactness of the levelling operations. Photo: F4E
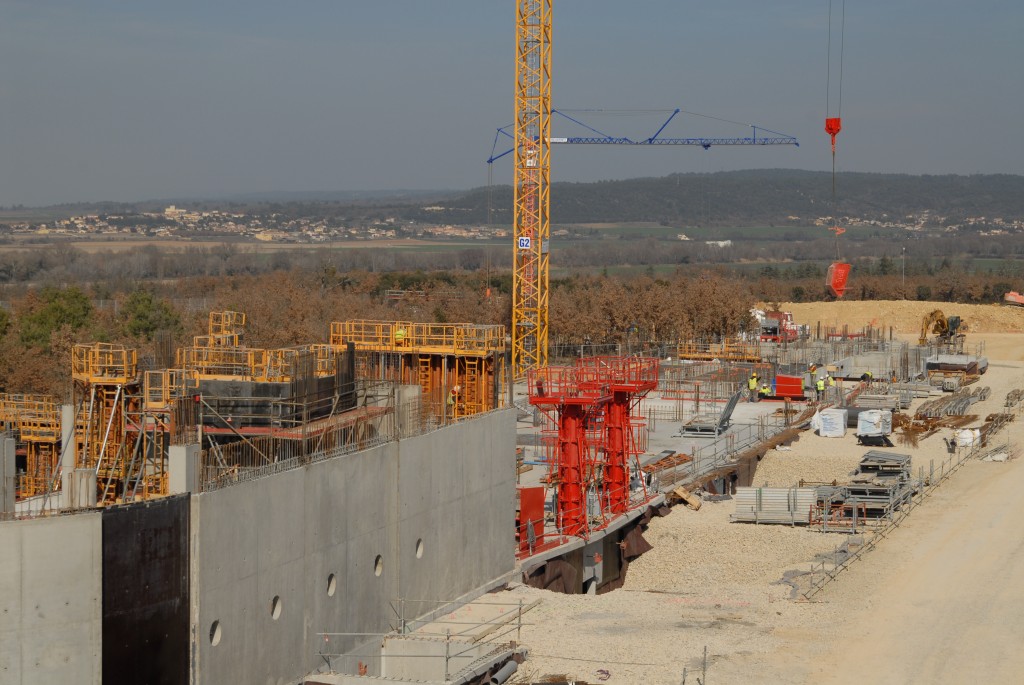
The weather helps!
2011-03-10 - Clement weather allows work on the ITER Headquarters to progress rapidly. Photo: AIF
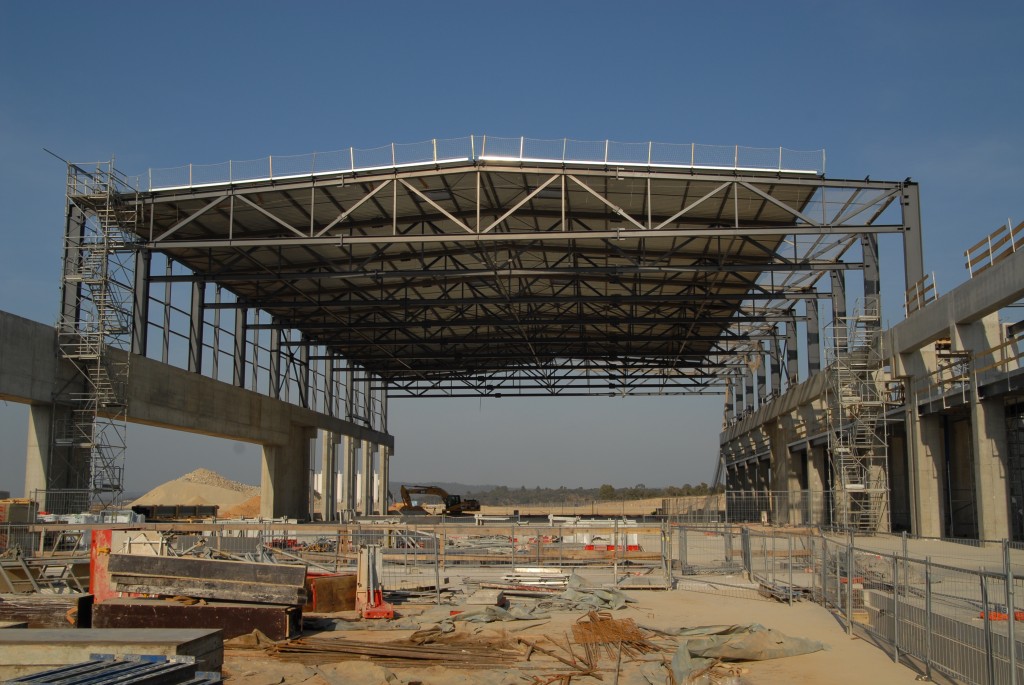
Floor slab nearly completed
2011-03-10 - Designed to carry loads of up to 42 tonnes per square metre, the floor slab for the Winding Facility is completed in March 2011. To ensure such high resistance, the subsoil was treated with a special hydraulic binder before reinforcement was laid and concrete poured. Photo: F4E
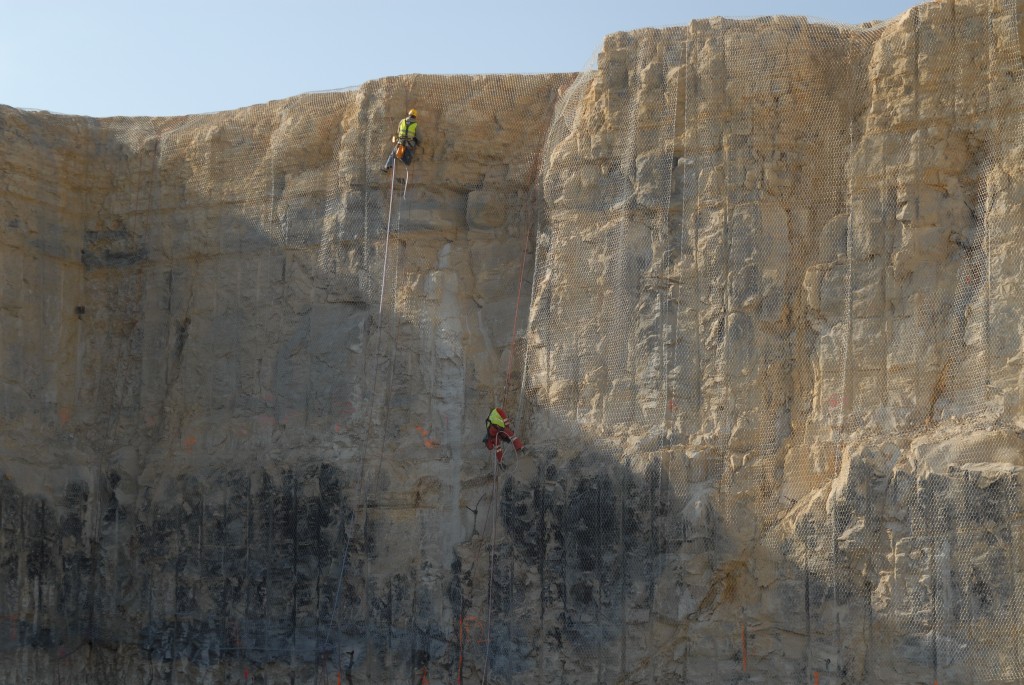
Steel mesh for safety
2011-03-10 - Workers secure steel mesh for the stabilization of rock faces. Photo: F4E
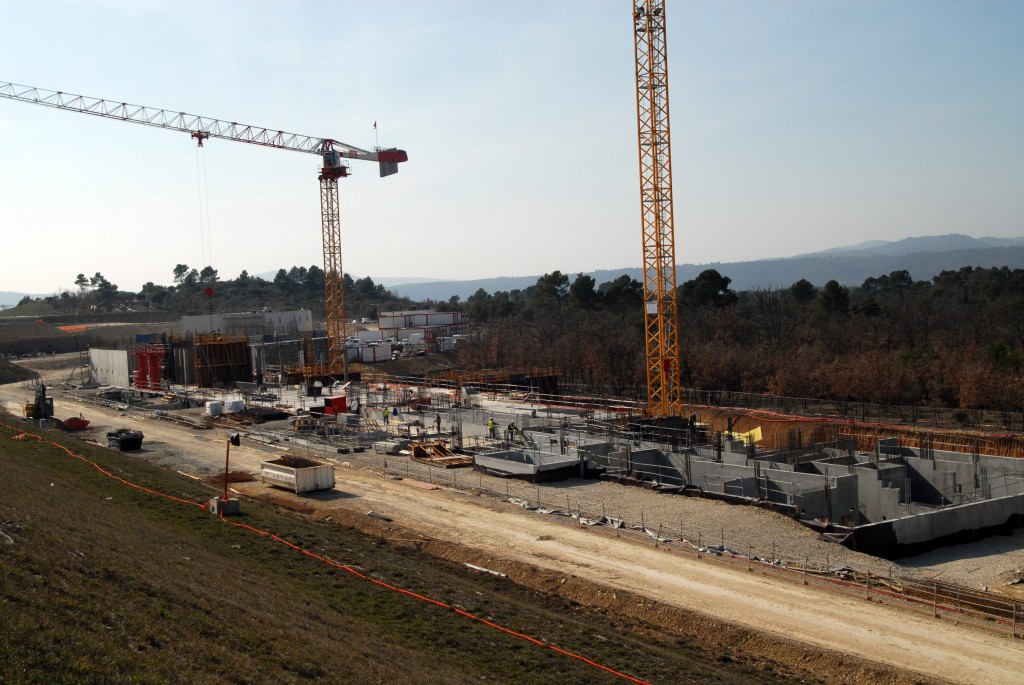
Six acres of wooded land
2011-03-10 - The Headquarters building is situated below the ITER platform on six acres of wooded land to the northeast. Photo: AIF
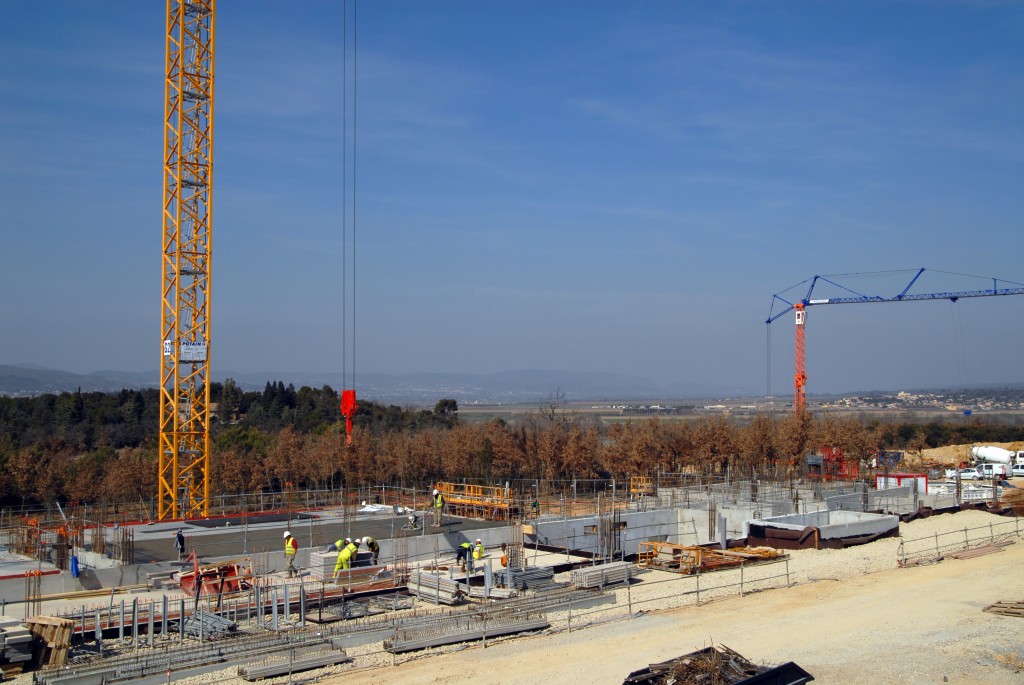
Moving up, floor by floor
2011-03-10 - Work advances in March 2011 on the future ITER Headquarters. Photo: AIF
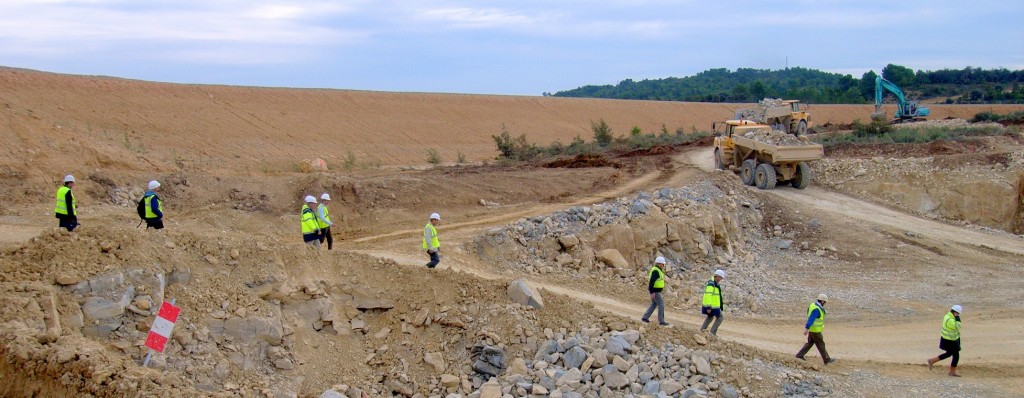
ITER will be a busy place
2011-03-03 - At the peak of ITER construction in 2014-2015, 5,000 people are expected on the ITER site, up from 1,400 in 2011. The projected rise is due to a sharp increase in the number of construction workers on the platform.
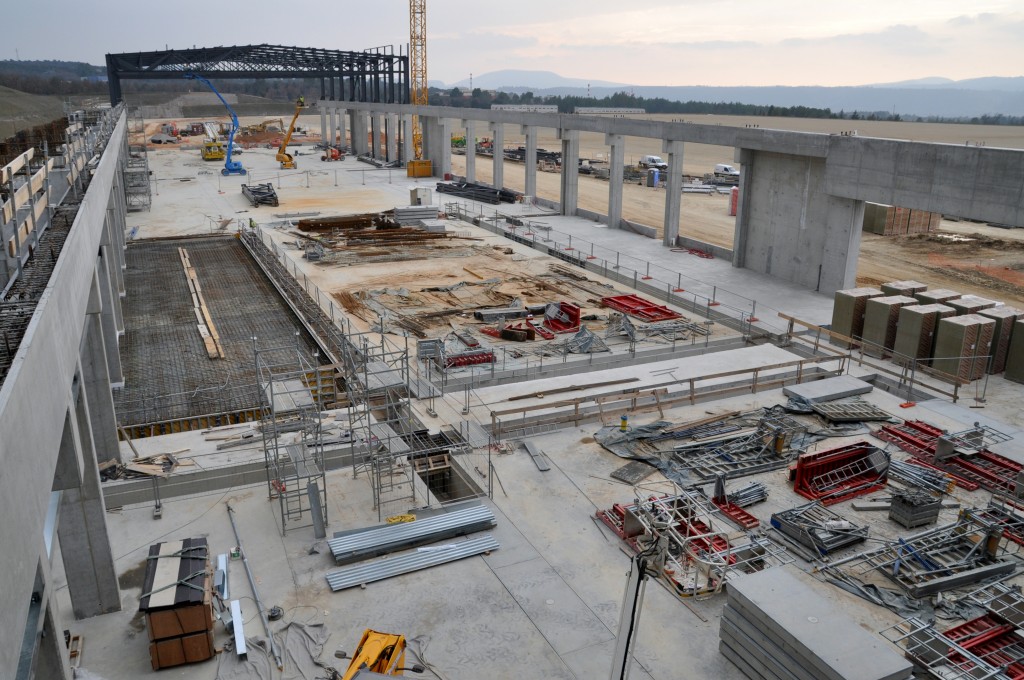
The last floor segment
2011-03-02 - Ready to cast the last of the concrete floor in the Poloidal Field Coils Winding Facility in March 2011.
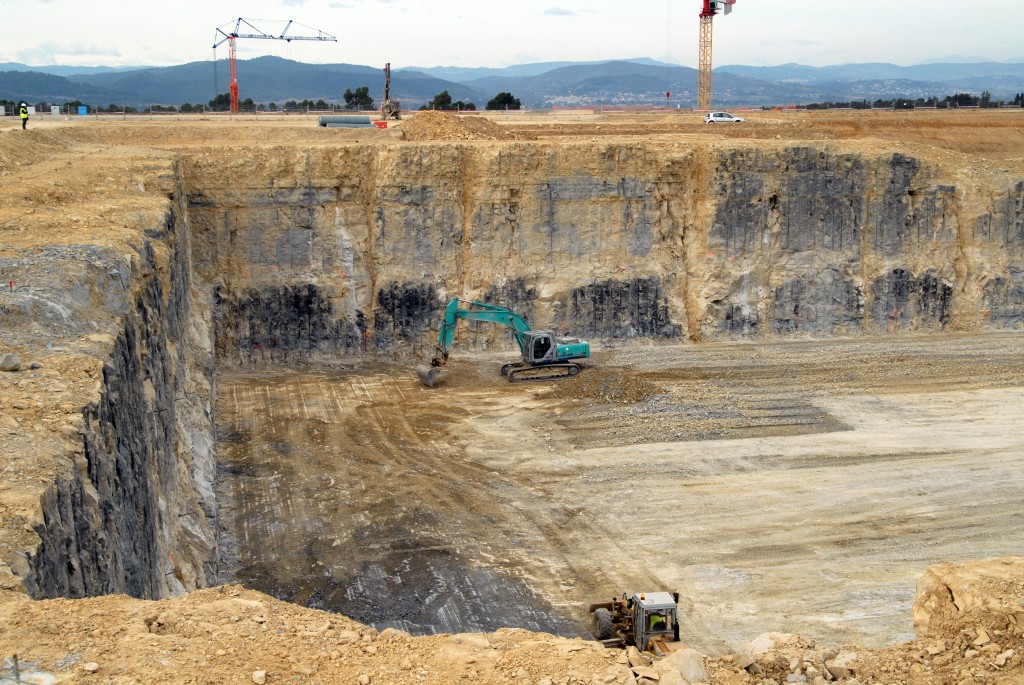
Next step: the blinding layer of concrete
2011-02-24 - Precise measuring instruments are used to create the level surface required for the anti-seismic installation of the Tokamak Complex. Next step: the pouring of a thin, "blinding" layer of concrete to have a perfectly smooth work surface. Photo: F4E

Seventeen metres below the surface of the platform
2011-02-24 - The final excavation phase now involves "milling" the rock in order to achieve a perfectly flat surface, on which to commence the construction of the lower basemat. Photo: F4E
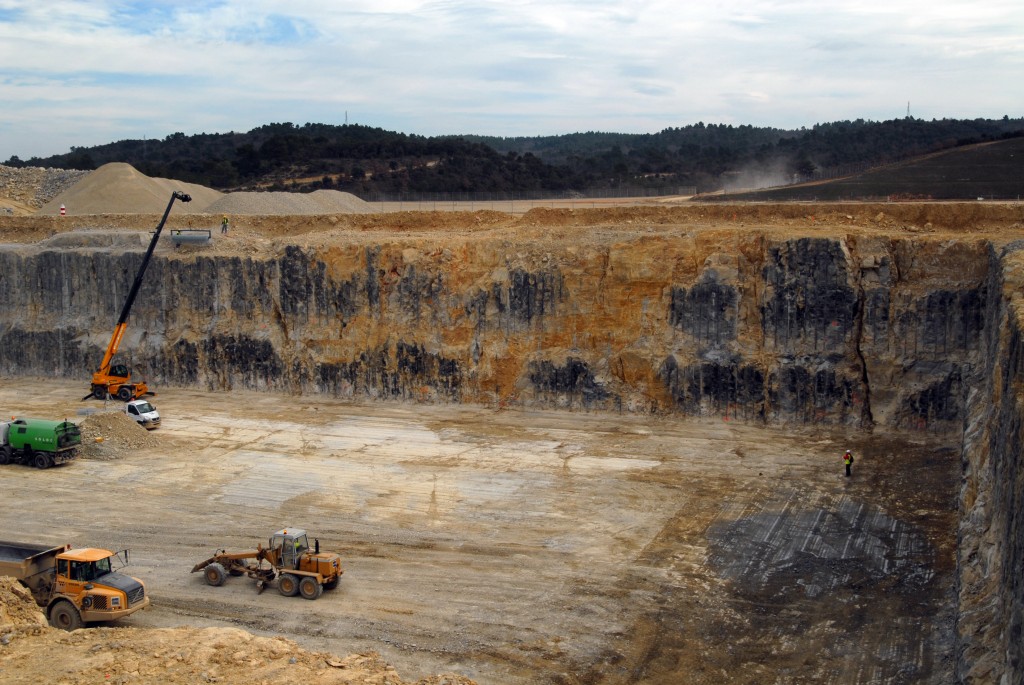
Next come the ground surveys
2011-02-24 - The floor of the Seismic Pit is 17 metres below the level of the platform. Ground surveys will provide information about the underlying bedrock in order to verify the assumptions used for the design of the Tokamak Complex. Photo: F4E
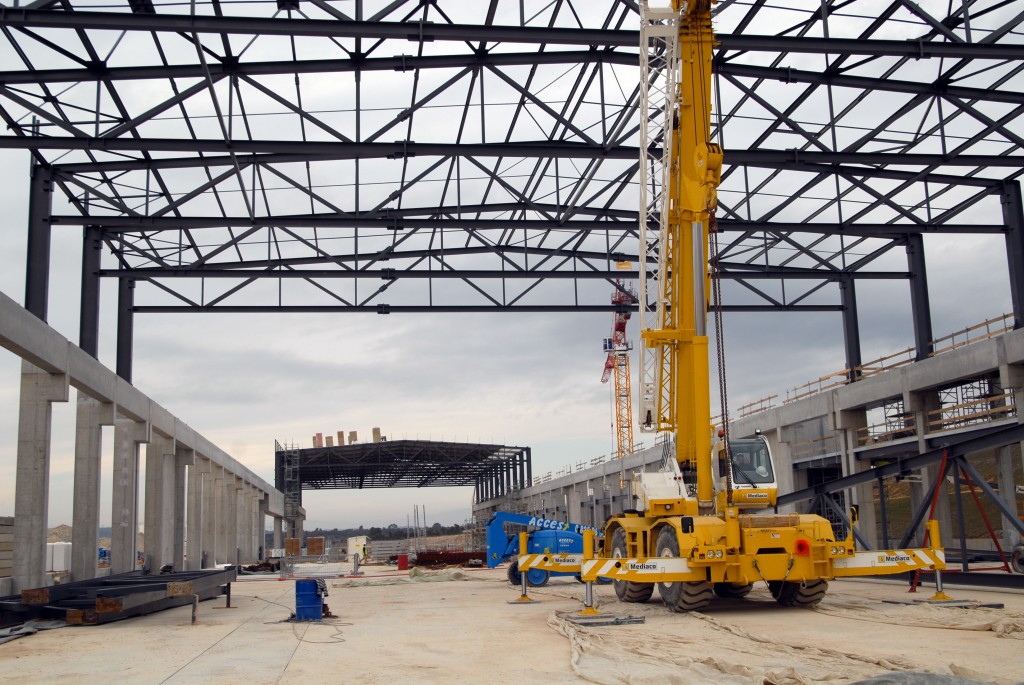
Roofing elements delivered
2011-02-24 - On the far end of the Winding Facility, cranes have delivered roofing materials ...to the roof. Photo: F4E
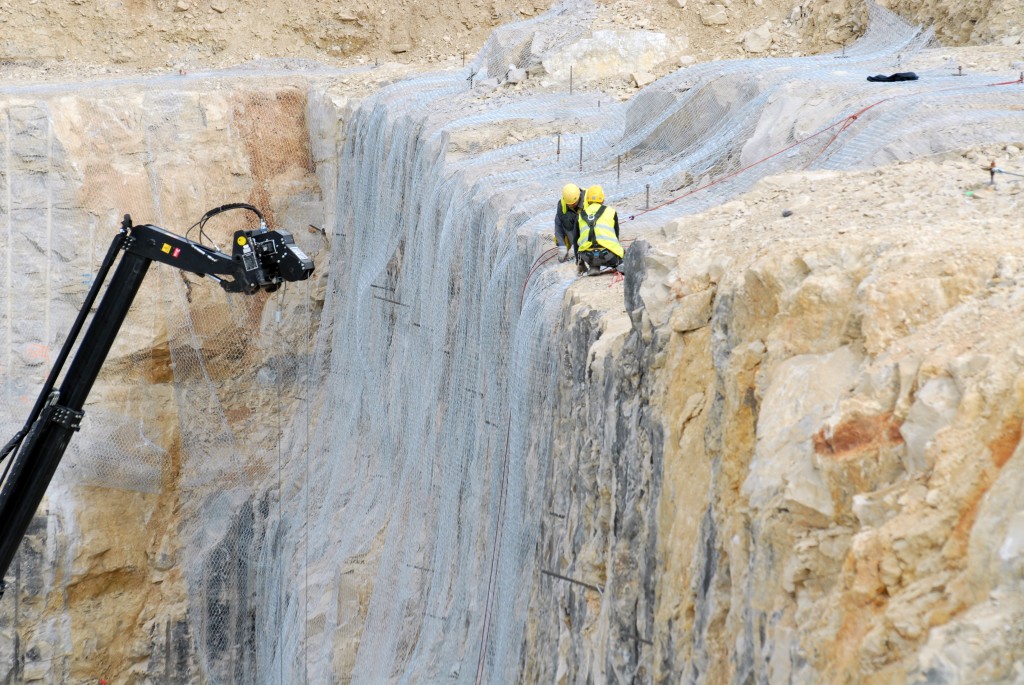
Mesh protection
2011-02-24 - The rock face is draped with protective steel mesh as the last diggers, scrapers and dumpers prepare the Seismic Pit for the concrete pourers to move in. Photo: F4E
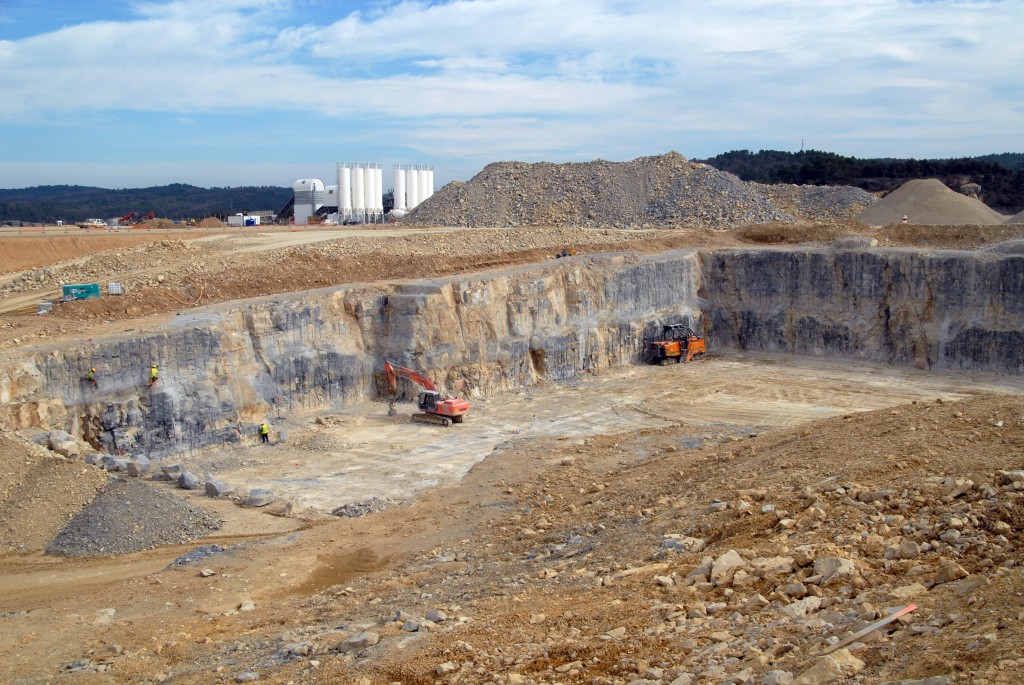
The southwest rim
2011-02-24 - Seen from the southwest rim: the 87 m x 123.6 m hollow in the ITER platform that will house the future ITER Tokamak. Photo: F4E
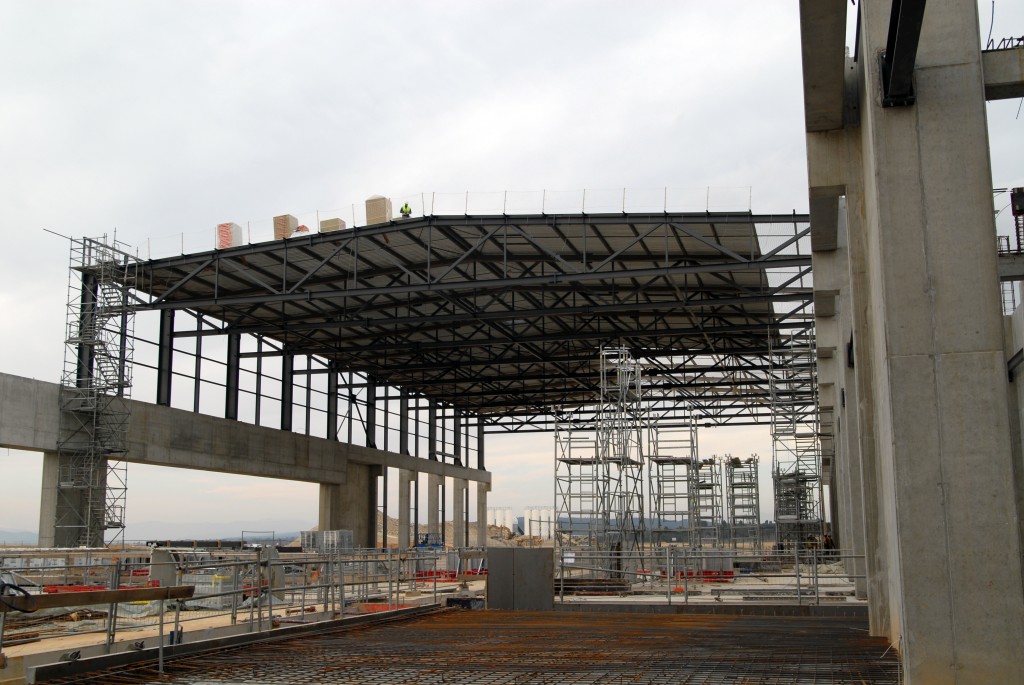
Giant exit doors
2011-02-24 - Five of ITER's six poloidal field coils are too large to be transported and will be wound on site in the Poloidal Field Coils Winding Facility. The finished coils, measuring up to 24 metres in diameter, will leave the building through one of two 30-metre exit doors (visible at left in the photo). Photo: F4E
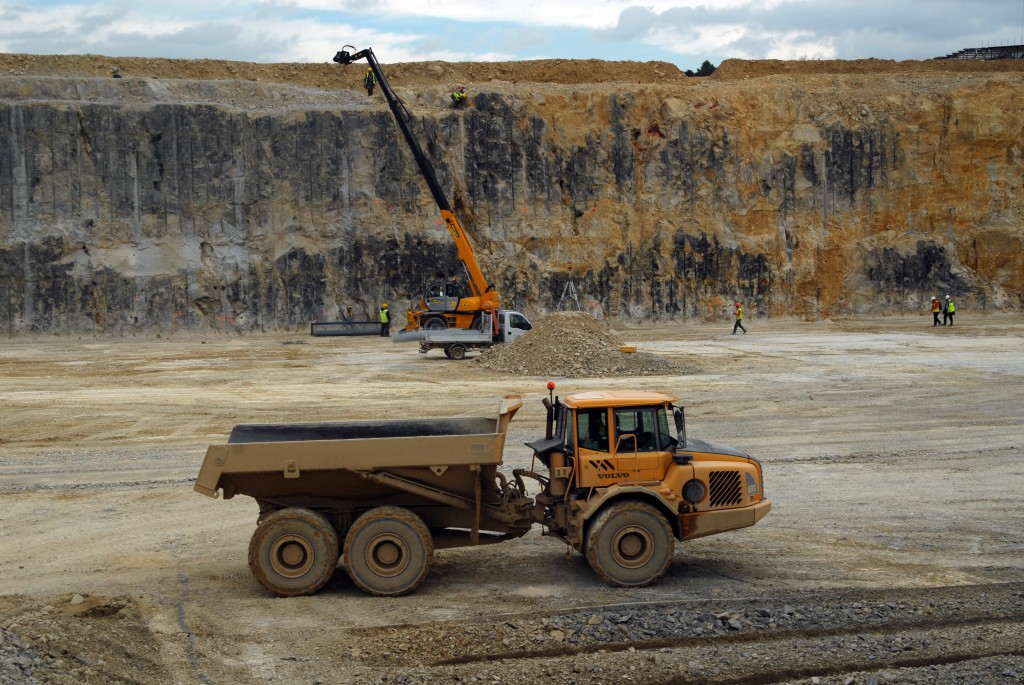
The last sweeping operations
2011-02-24 - Mesh is installed in the background as the last gravel is swept from the floor of the Tokamak Complex Seismic Isolation Pit. Photo: F4E
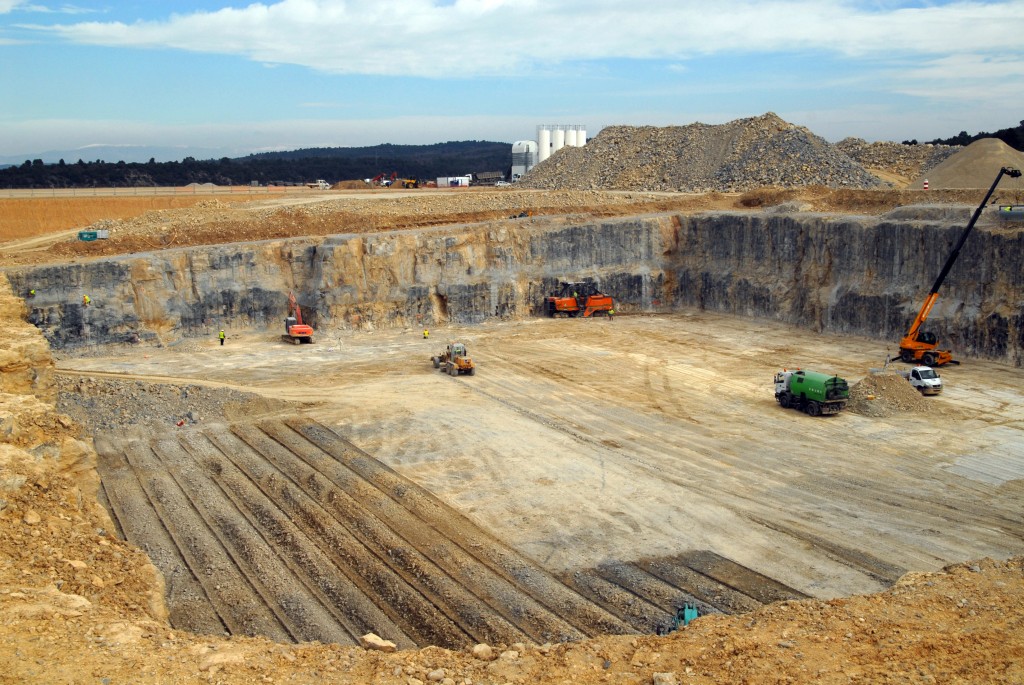
Milling the surface
2011-02-24 - The Tokamak Excavation area is readied for the pouring of a thin layer of "blinding concrete" that will create the clean and flat work surface upon which to create the 1.5 metre-thick basemat. Photo: F4E
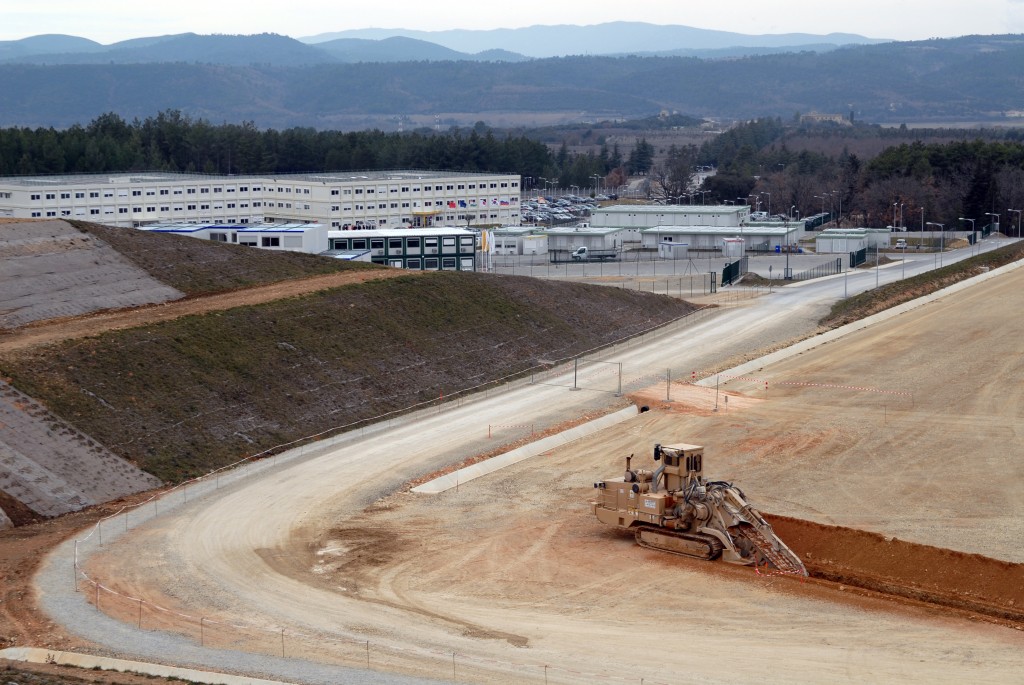
Underground networks
2011-02-24 - Trenches for the underground networks of the Poloidal Field Coils Winding Facility are dug in the foreground; in the background—the current office buildings of the ITER Organization. Photo: F4E
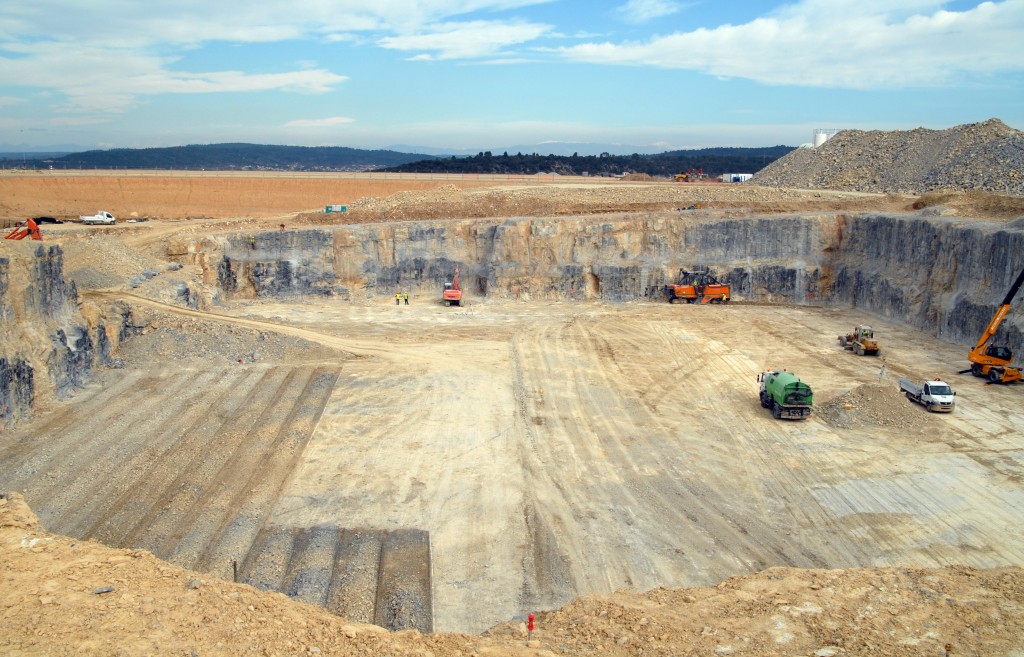
The future home of the ITER Tokamak
2011-02-24 - The heavy excavation works for the future Tokamak Complex were completed in four months. Photo: F4E
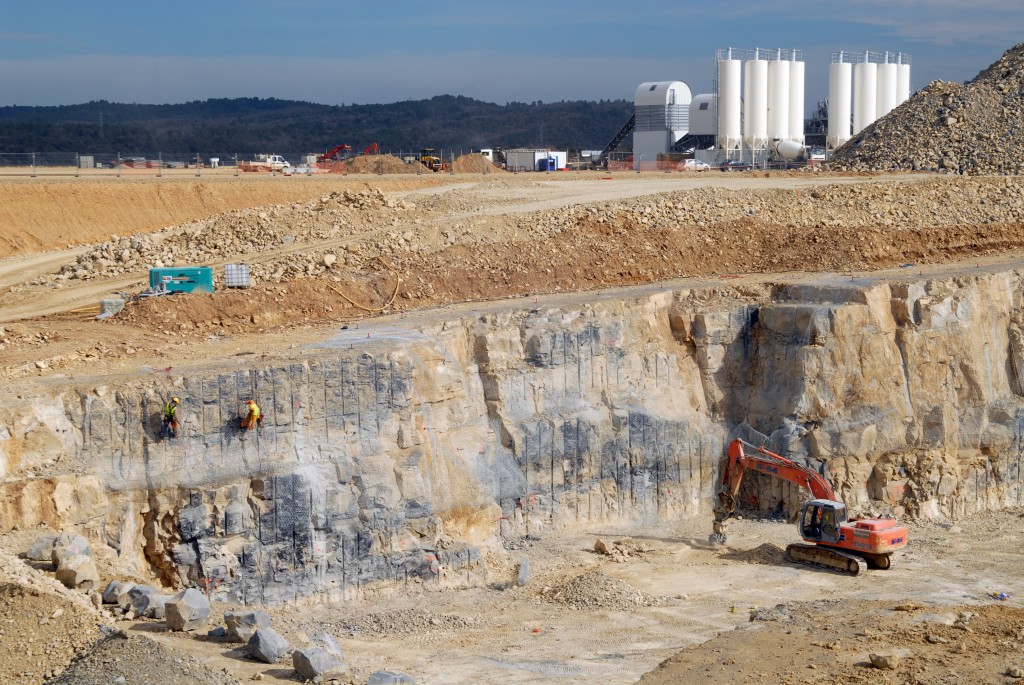
Investigating the rock substrata
2011-02-24 - By way of radar mapping and the boring of more than 500 holes, geological surveys provided a detailed map of the substratum. Some voids were detected, the largest being a few cubic meters in volume; these small voids, or "karsts" must now be filled with concrete. Photo: F4E
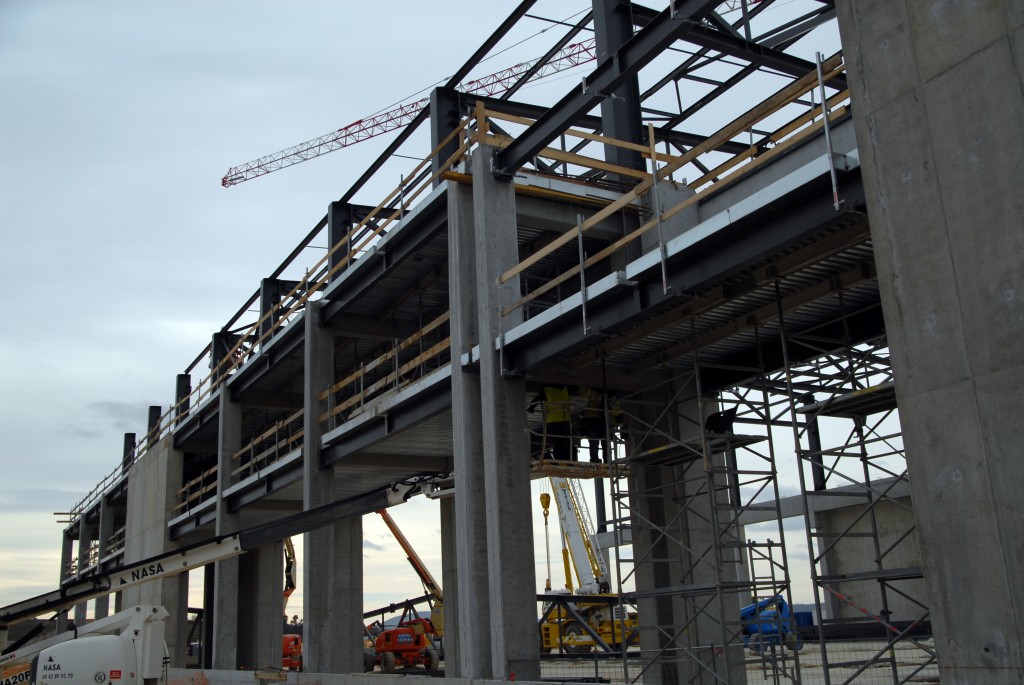
State-of-the-works in February 2011
2011-02-24 - Looking into the Poloidal Field Coils Winding Facility in February 2011. Photo: F4E
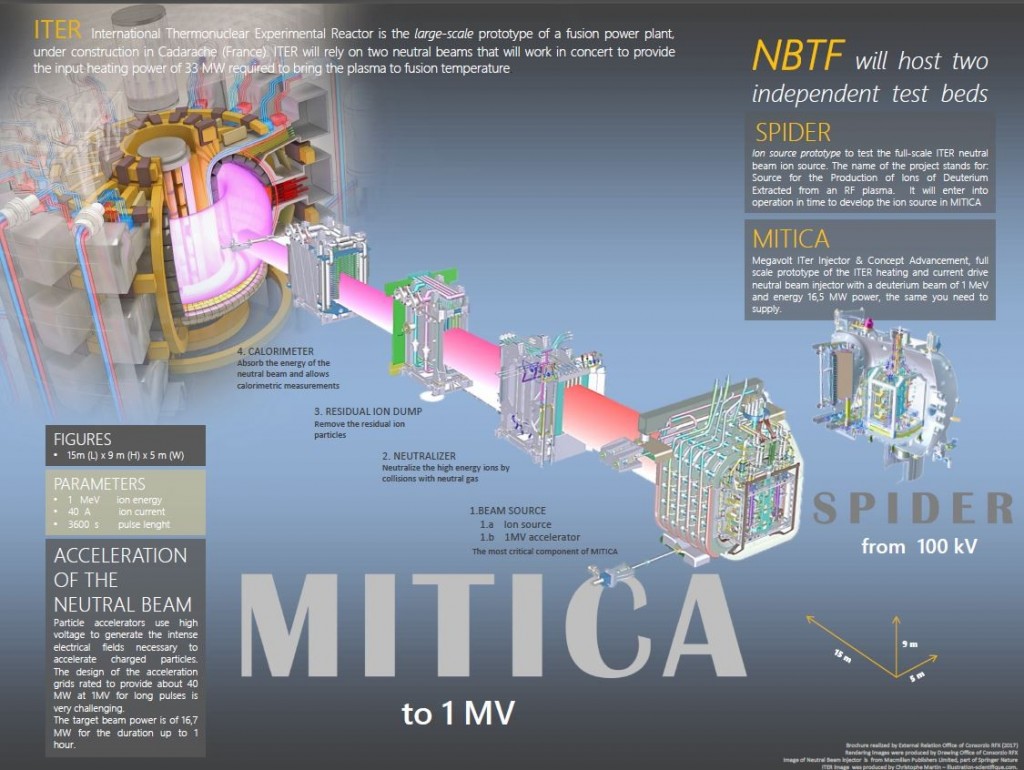
SPIDER and MITICA
2011-02-11 - SPIDER is the ITER-scale negative ion source. MITICA will test all of the integrated technologies of the injector (source, electrostatic accelerator, neutralizer, separator of residual ions, calorimeter, etc) with a 1 MeV line.
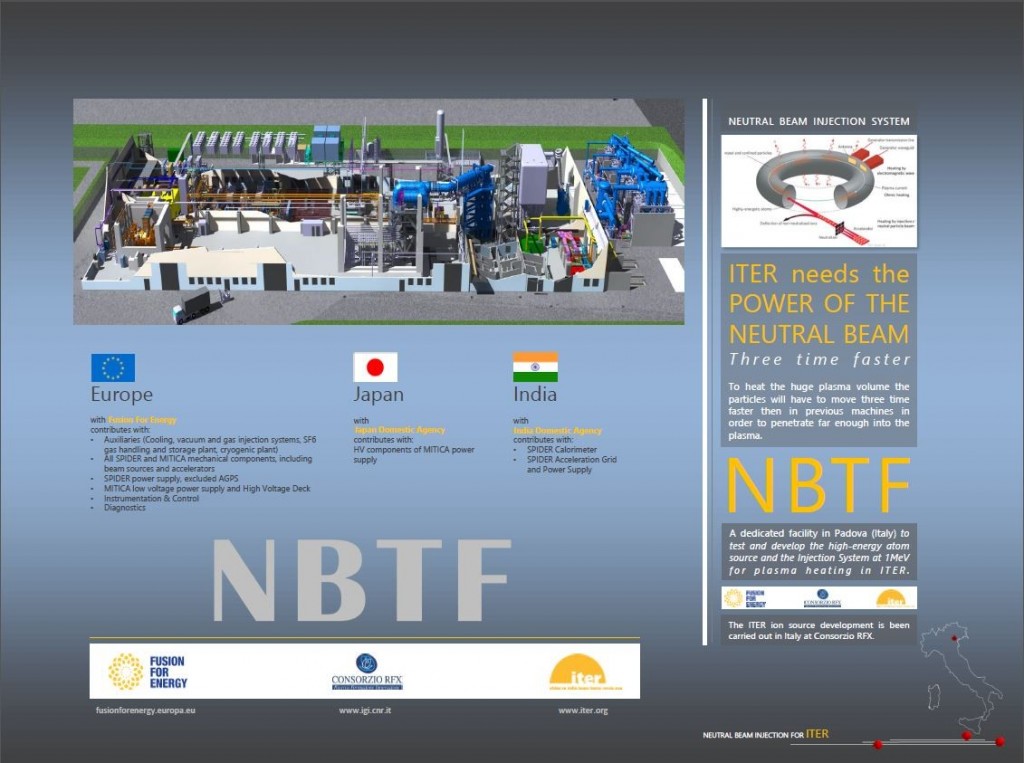
Testing ITER-scale neutral beam injection
2011-02-11 - To heat the huge plasma volume in ITER (830 m³), the injected heating particles will have to move three times faster than in previous machines in order to penetrate into the centre of the plasma. The technologies involved will be tested at NBTF in advance of ITER operation.

The rocky slope ...
2011-02-10 - The access road for construction vehicles into the Tokamak Complex Seismic Isolation Pit. Photo: F4E
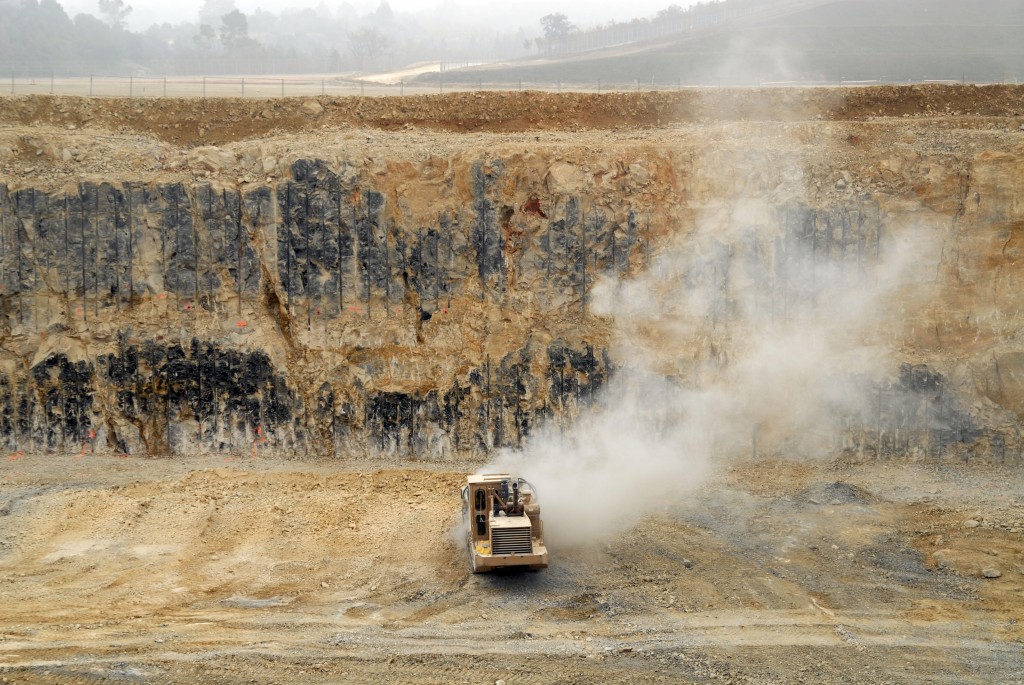
Planing machine in action
2011-02-10 - The planing machine in action on the floor of the Seismic Isolation Pit. Photo: F4E
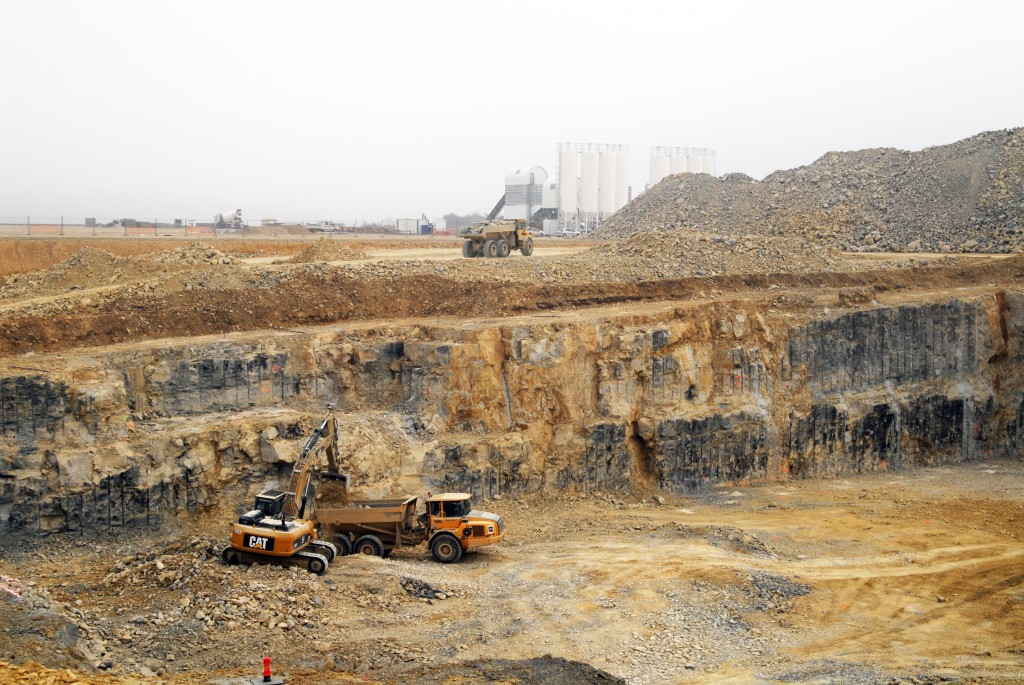
210,000 cubic metres of material
2011-02-10 - Trucks move back and forth continuously between the excavation site and a rubble storage area located to the east of the ITER platform. Storing the material on site limits the amount of construction traffic on the roads closest to ITER. Photo: F4E

PF Facility in the distance
2011-02-10 - The walls and roof trusses of the Poloidal Field Coils Winding Facility go up in the distance, blurred by the dust from the excavation site. Photo: F4E
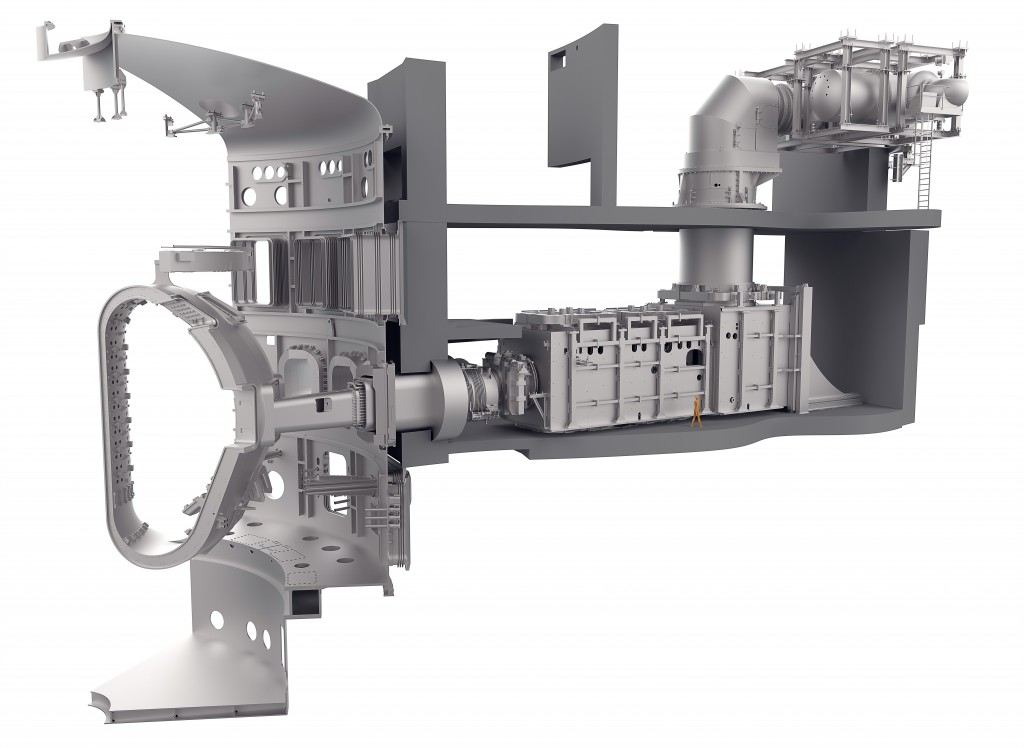
A first-of-a-kind injector
2011-02-09 - The neutral beam injectors shoot uncharged high-energy particles into the plasma where, by way of collision, they transfer their energy to the plasma particles ... much in the same way that a household cappuccino machine uses steam to heat milk. Left: the ITER machine. Right: a stick figure that gives a sense of scale.

Drilling holes every four to five metres
2011-02-07 - Boring holes up to five metres deep to develop a detailed "picture" of the rock substrata of Seismic Pit floor. Photo: F4E
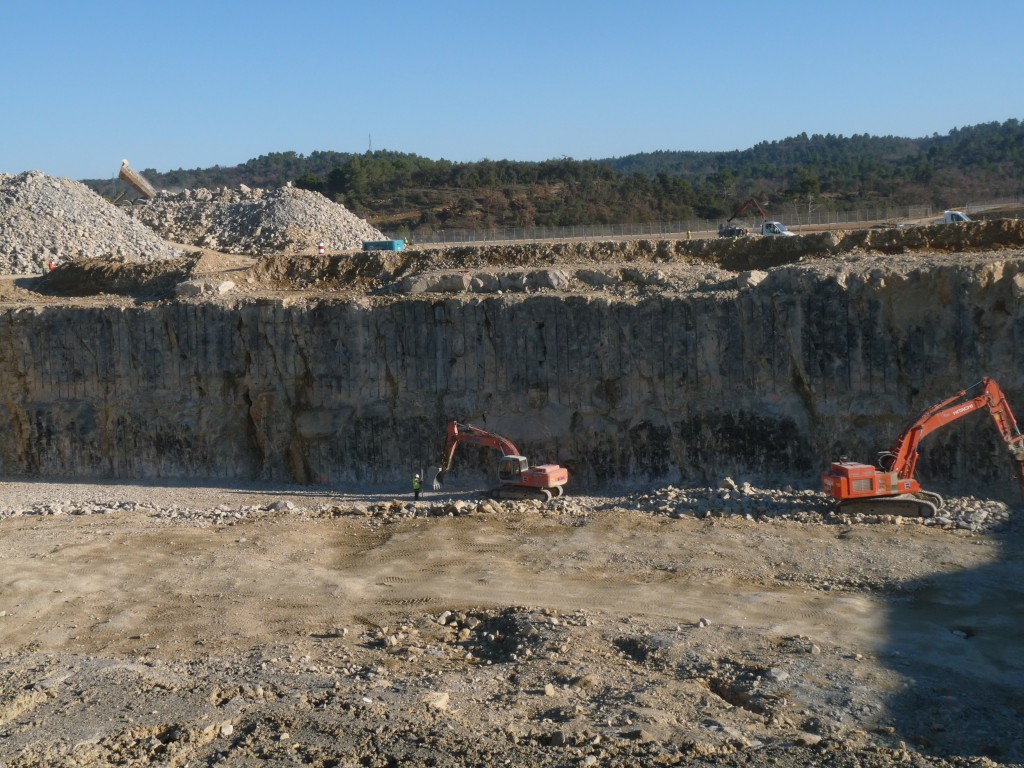
An Arc de Triomphe in Provence
2011-02-07 - The Tokamak Building will sit 13 metres below ground and 60 metres above ground. 60 metres is the approximate height of the Arc de Triomphe in Paris. Photo: F4E
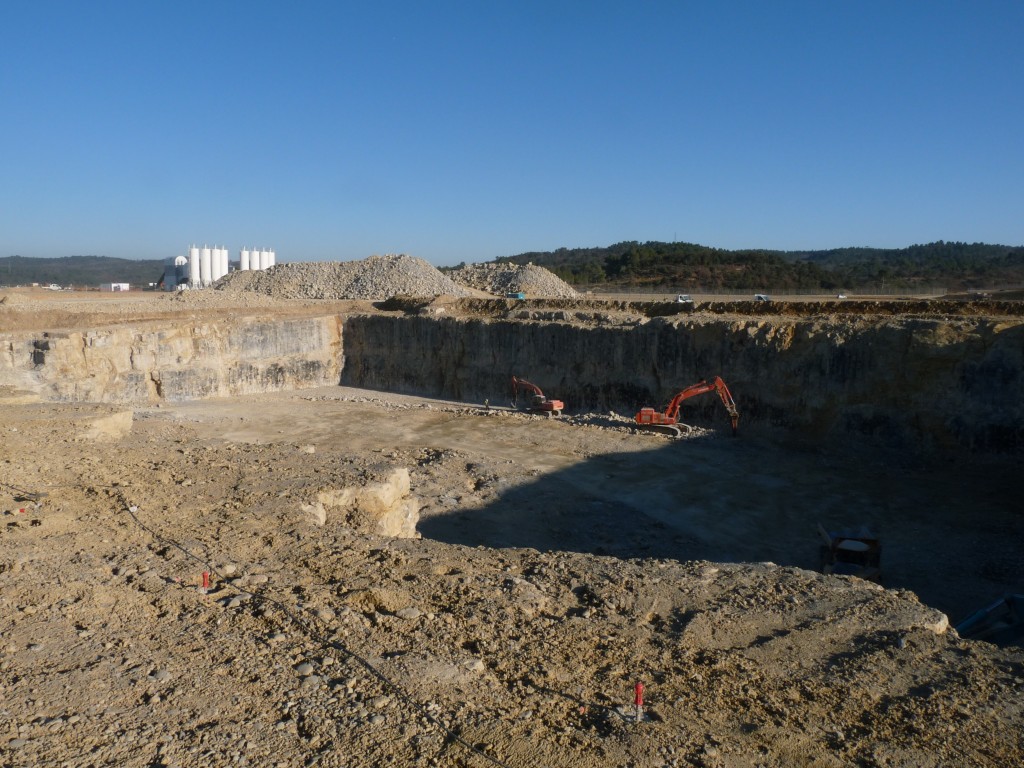
Boring and drilling activities continue
2011-02-07 - Drilling is carried out every 4 to 5 metres and up to 5 metres deep in order to explore the rock surface of the Seismic Pit. Photo: F4E

How many tons??!
2011-02-07 - The Tokamak Seismic Isolation Pit will house the anti-seismic foundations of the future Tokamak Complex. Some 360,000 tonnes will rest on the bottom of this Pit, including the foundations, the ITER Tokamak, and Complex edifice. Photo: F4E
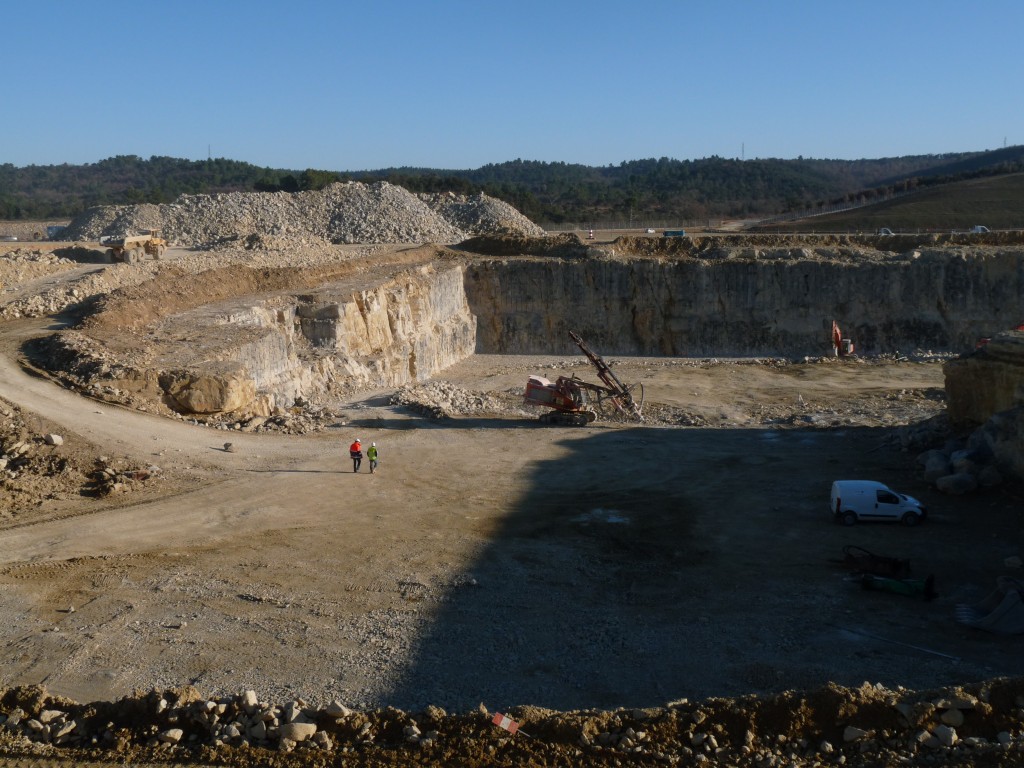
The Hot Cell Facility: The Tokamak Complex's closest neighbour
2011-02-07 - In the foreground: the location of the future Hot Cell Facility. Trim blasting for this area will be carried out in April 2011. Photo: F4E
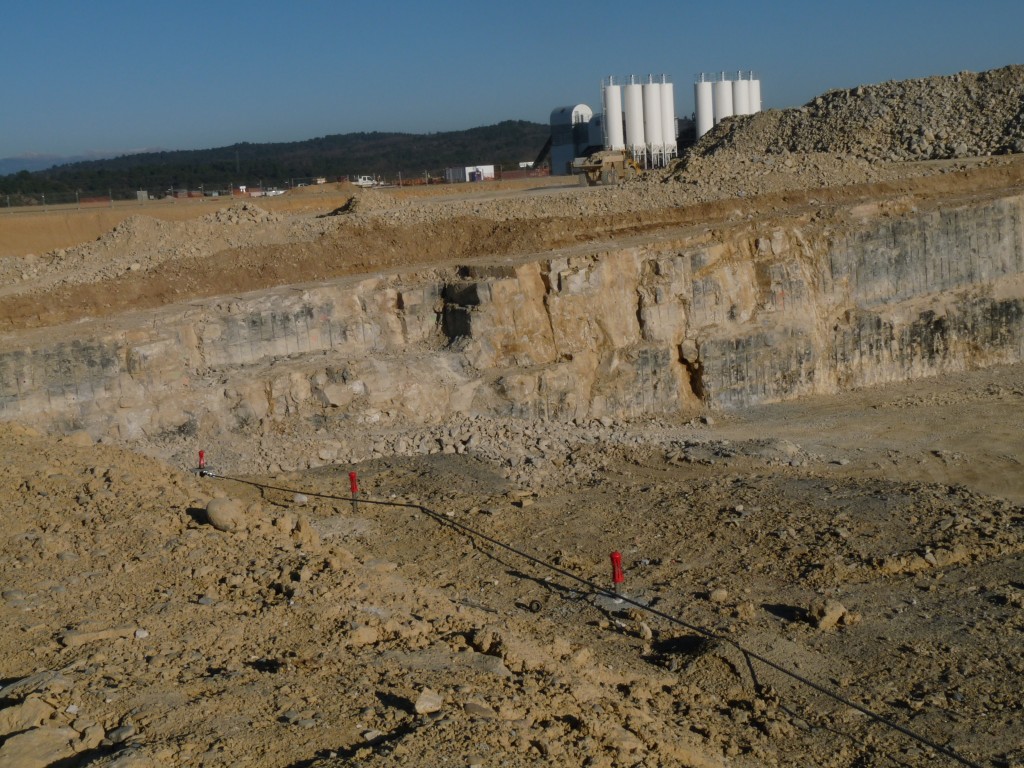
A steady supply of concrete
2011-02-07 - The concrete batching plant seen in the distance will supply the 150,000 tonnes of concrete necessary for the ground support structure of the Tokamak Complex (foundations and retaining wall). Photo: F4E
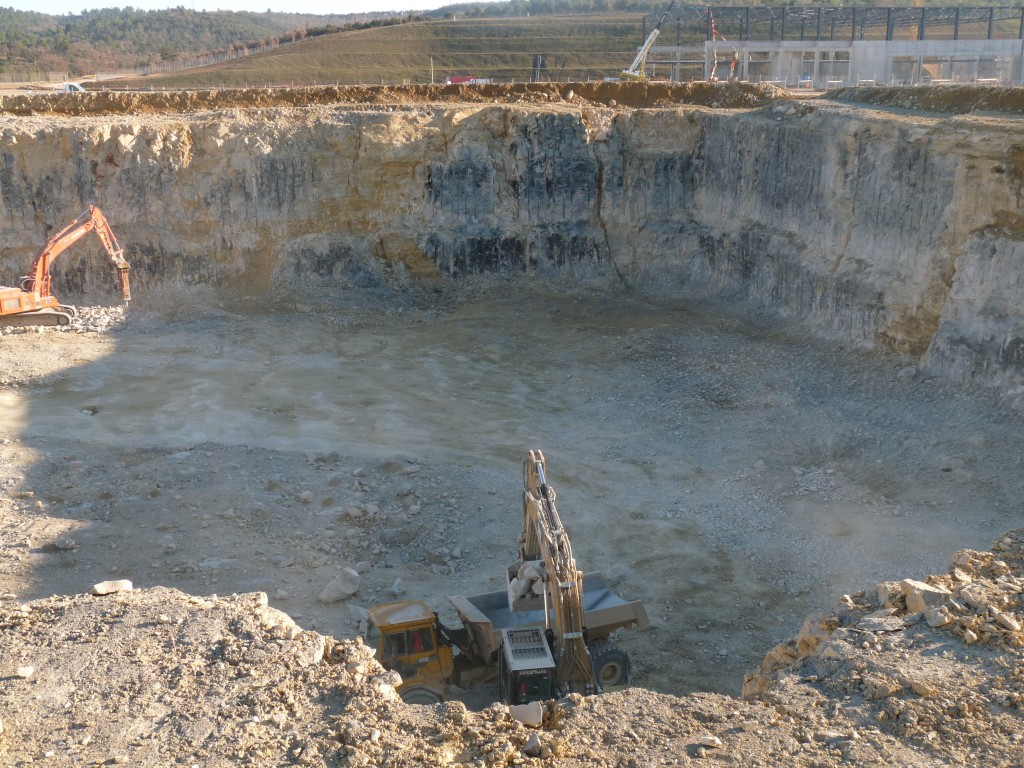
Exploring the rock surface
2011-02-07 - Rubble is removed and fissures, faults and karsts on the rock surface explored. With radar mapping and the boring of more than 500 holes, geological surveys provided a detailed map of the substratum. Photo: F4E
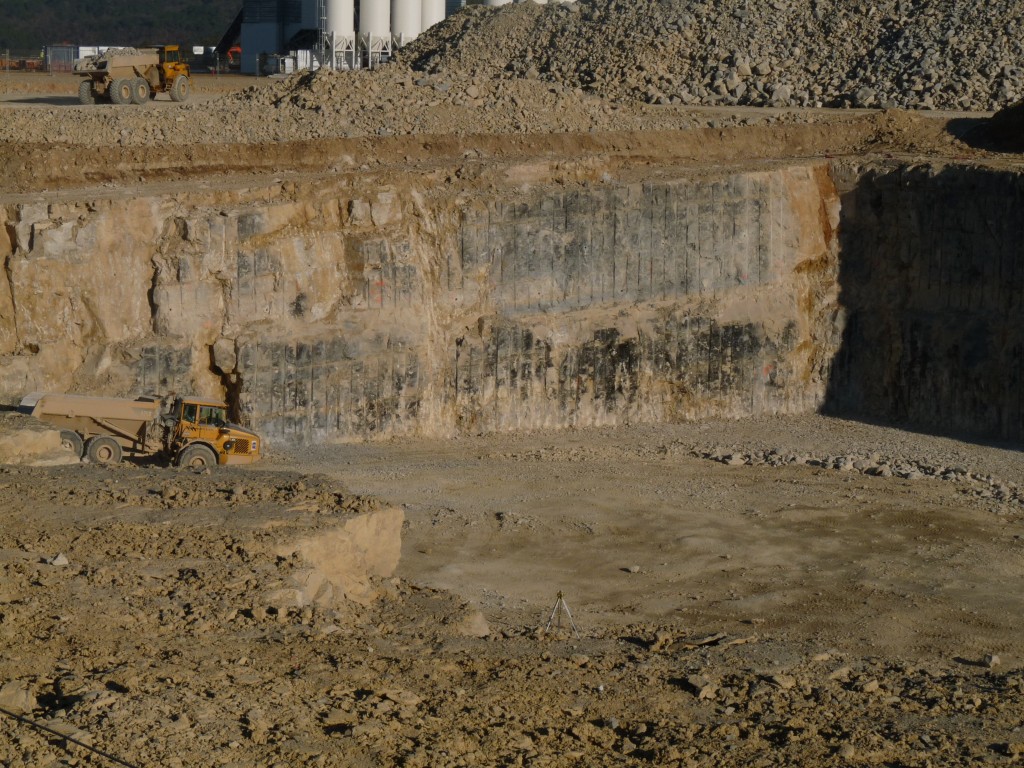
360,000 tonnes of building
2011-02-07 - The quality of the rock substrata on the 42-hectare ITER platform has determined the exact location of the 360,000-tonne Tokamak Complex. In the area of the Tokamak Building, the soil bearing capacity will be at least 100 tonnes per square metre. Photo: F4E
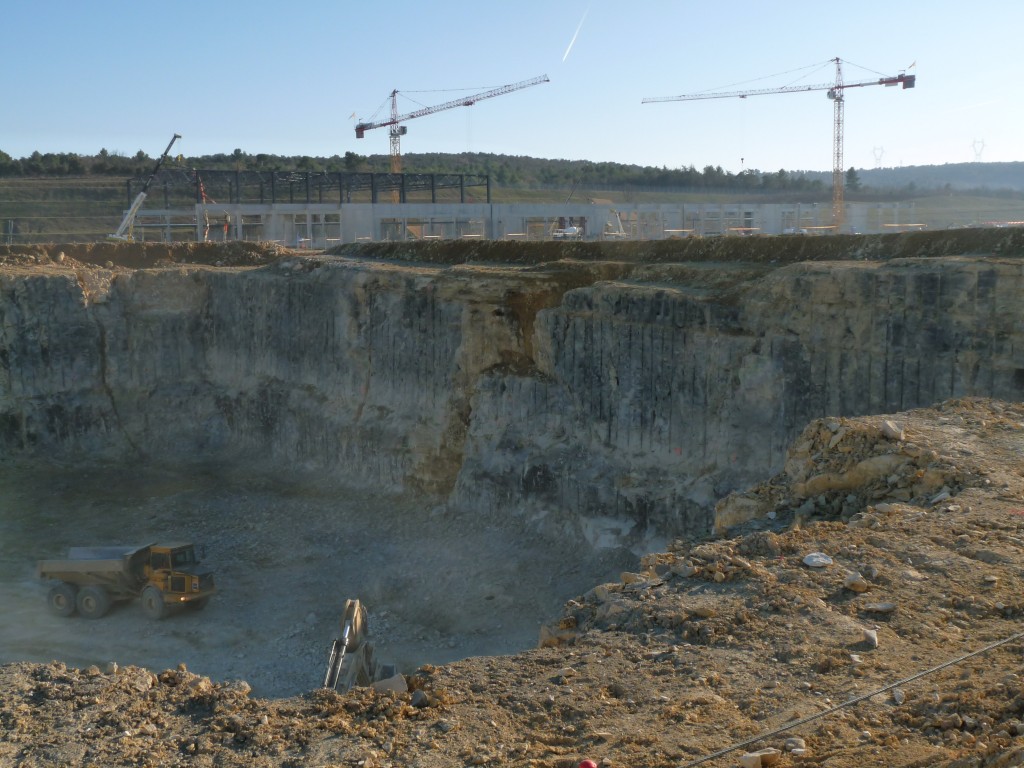
Officially 17 metres deep
2011-02-07 - Blasting operations are over: trucks work on the floor of the Tokamak Complex Seismic Isolation Pit to remove rubble from the area. Photo: F4E

A building for winding and assembling
2011-02-03 - In this vast building, the operations for the winding and assembly of the poloidal field magnets will be carried out in successive order. The finished coils will exit one of the large openings in the west wall, for transfer to the Assembly Hall of the Tokamak Building. Photo: F4E
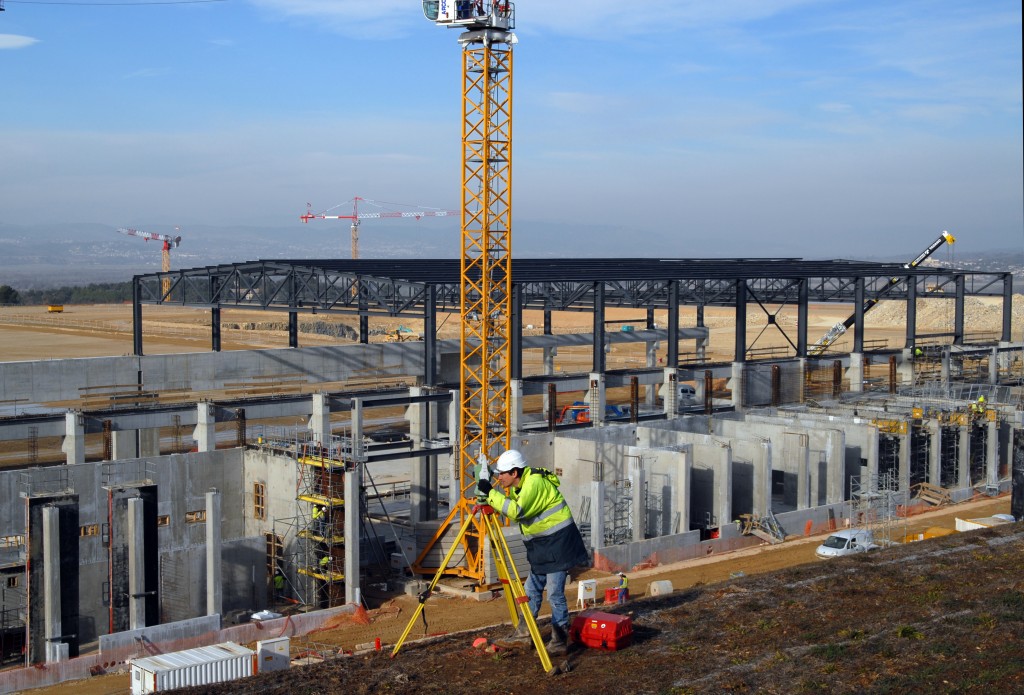
Roof trusses progress quickly
2011-02-03 - Construction of the metal framework has been underway for several weeks. It consists of a strong triangular shaped lattice with a 40-metre-long base. Photo: F4E
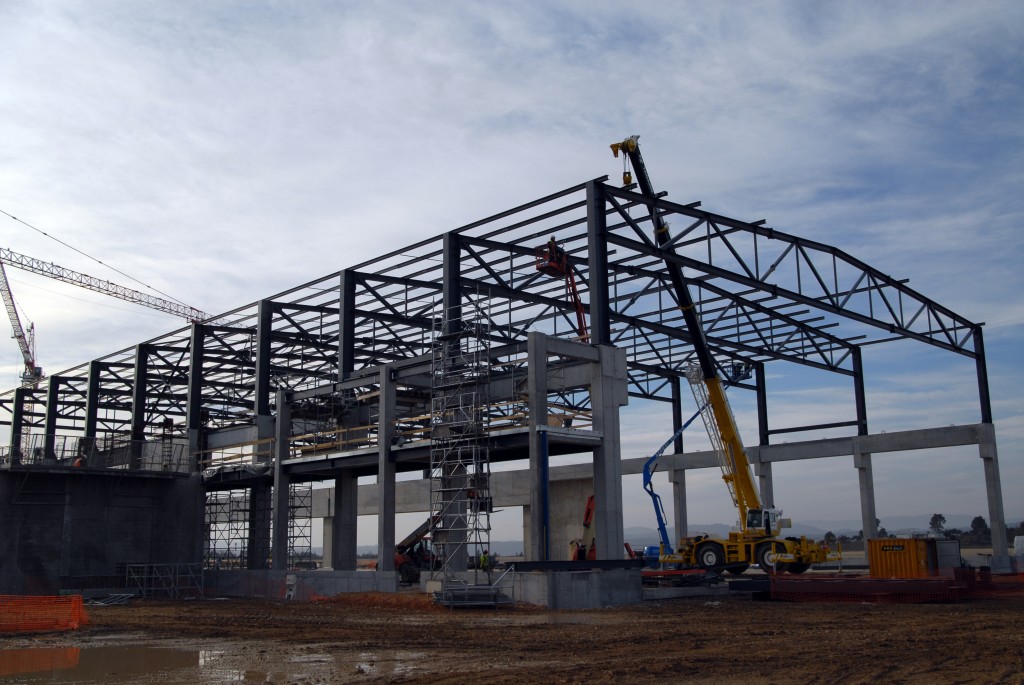
950 tonnes in the roof
2011-02-03 - Thirty-four steel trusses spanning the 40-metre width of the Poloidal Field Coils Winding Facility: 950 tonnes in all. Photo: F4E
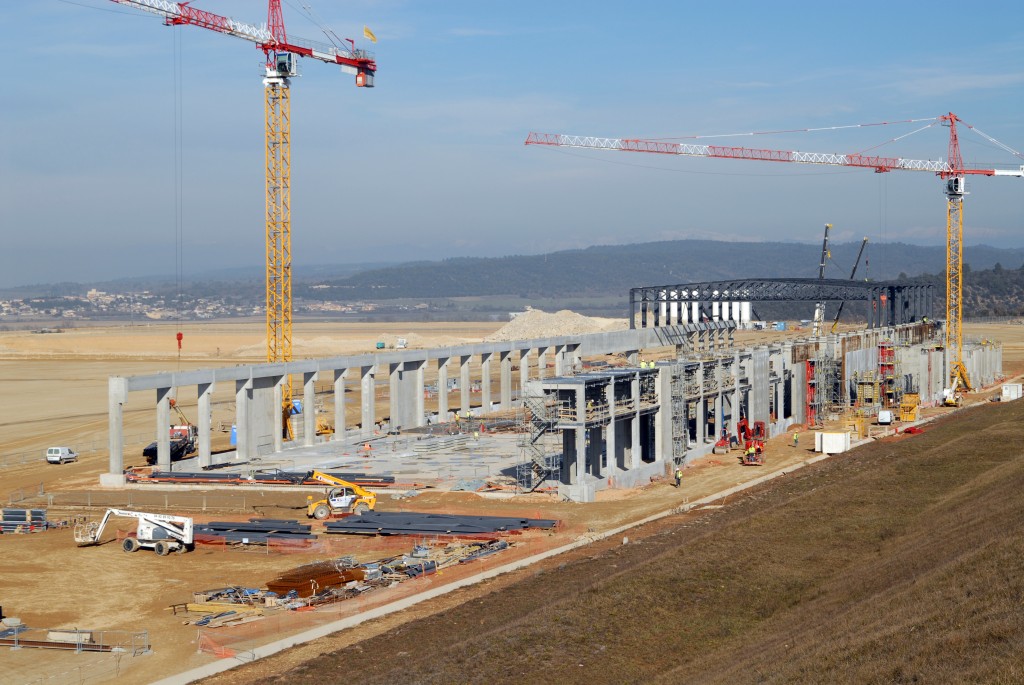
Part of Europe's commitment
2011-02-03 - The Poloidal Field Coils Winding Facility is financed by Europe, who will carry out the winding operations for the poloidal field coils in this building from superconductor delivered by China, Europe and Russia. Europe is responsible for the construction of all of the buildings on the ITER platform as part of its commitment to the ITER project. Photo: F4E
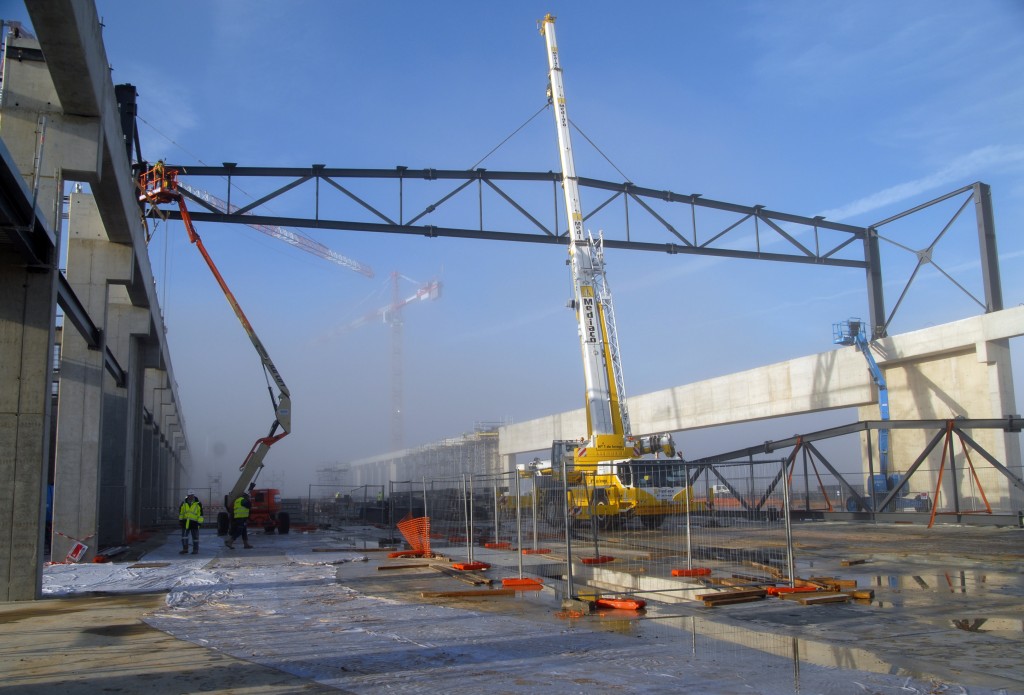
And now, on to the roof
2011-01-14 - The metal trusses for the roof of the Poloidal Field Coils Winding Facility weigh eight tons each. Due to their weight, the metal parts are first assembled on the building's reinforced concrete slab, then lifted by crane to a height of 19 metres. Photo: F4E
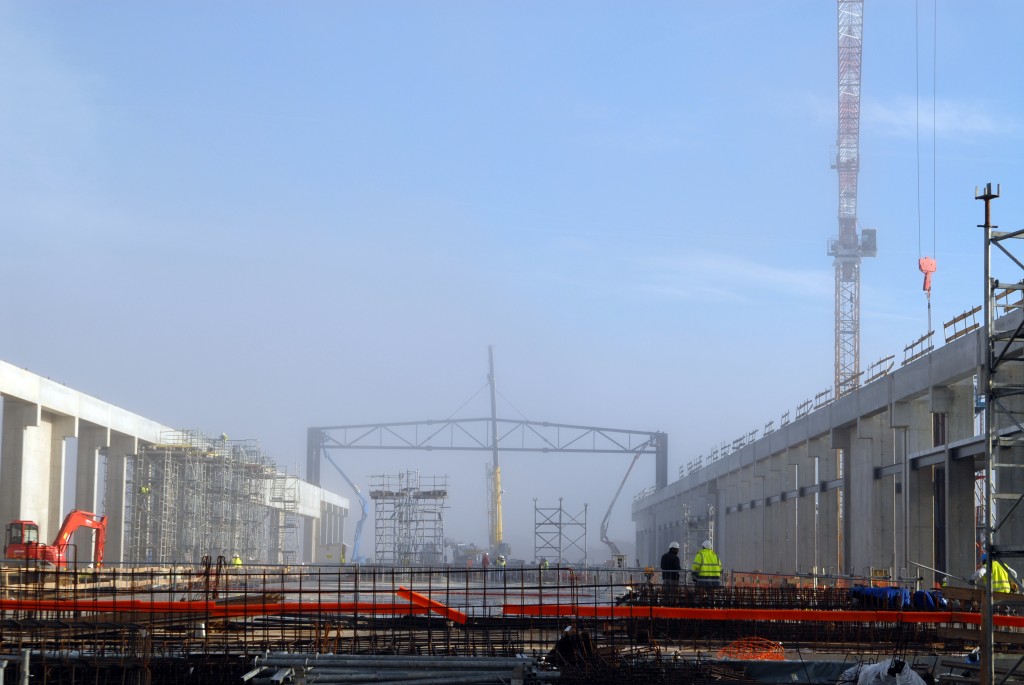
The Poloidal Field Coils Winding Facility in January 2011
2011-01-14 - The Poloidal Field Coils Winding Facility in January 2011, after five months of construction. Photo: F4E
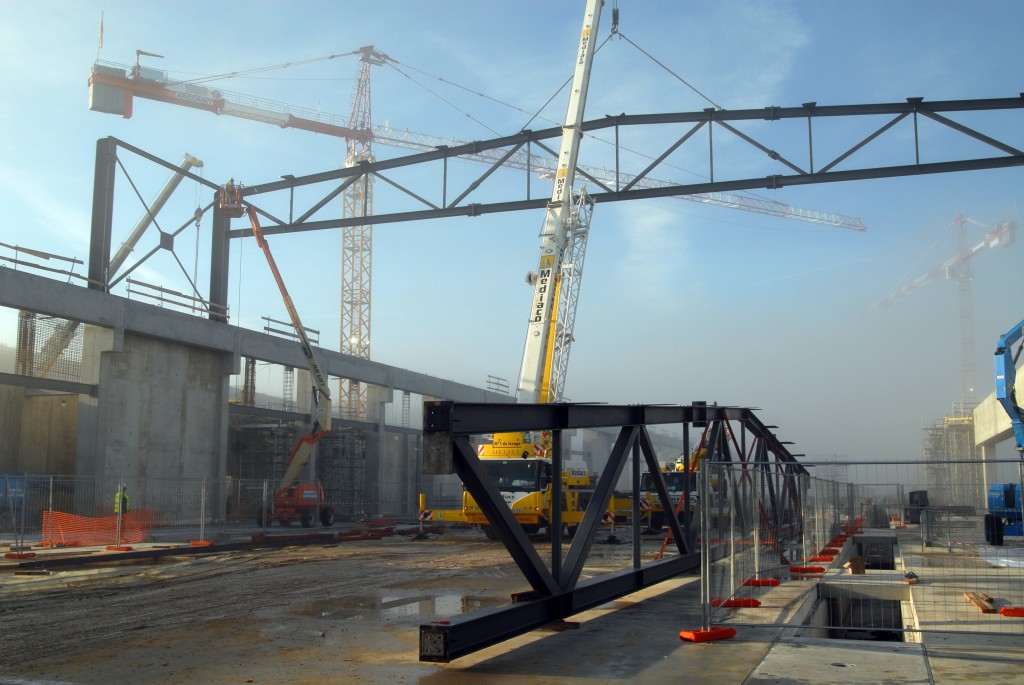
Thirty-four steel trusses
2011-01-14 - Each steel roofing truss is 4 metres high and 40 metres wide. Thirty-four trusses in all will support the roof of the 257-metre-long Poloidal Field Coils Winding Facility. Photo: F4E

Working from the ground up
2011-01-01 - In January 2011, concrete pouring for the floor slab continues on one end of the building, while the first metal roof truss is set into place on the other. Photo: F4E
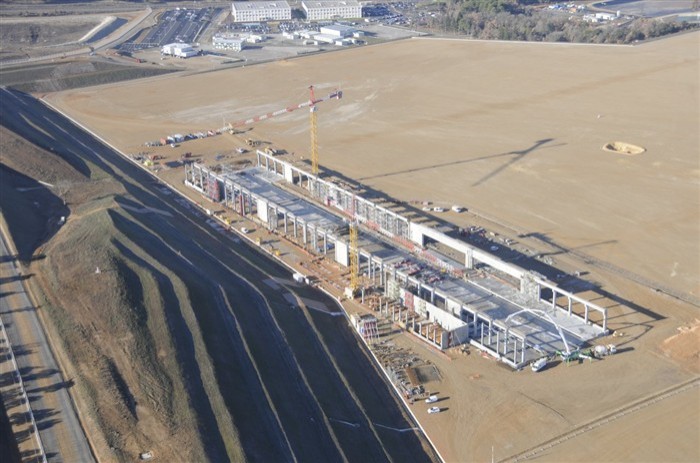
Posts and beams in place
2011-01-01 - The concrete pillars and beams of the Winding Facility are up and nearly all of the 12,000 m² floor slab has been set into place. The wide openings visible on the west face of the building are the exit doors for the completed coils; each door is 30 metres wide. Photo: Altivue/AIF
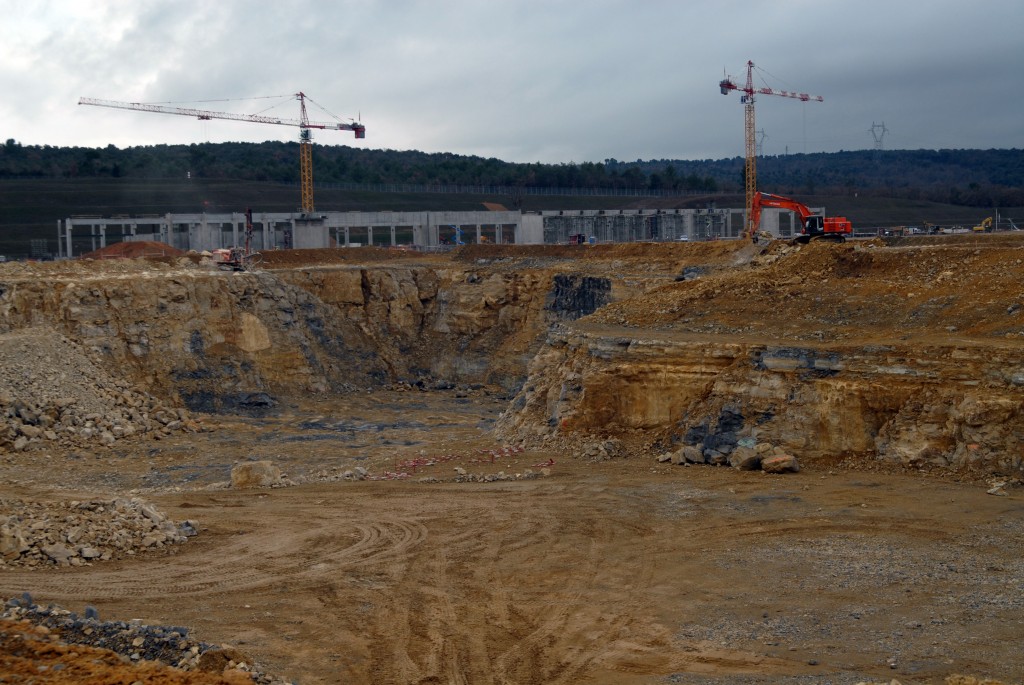
Two projects advancing
2010-12-21 - Across the excavation worksite, the first concrete pillars of the Poloidal Field Coils Winding Facility are seen in the distance. Photo: F4E
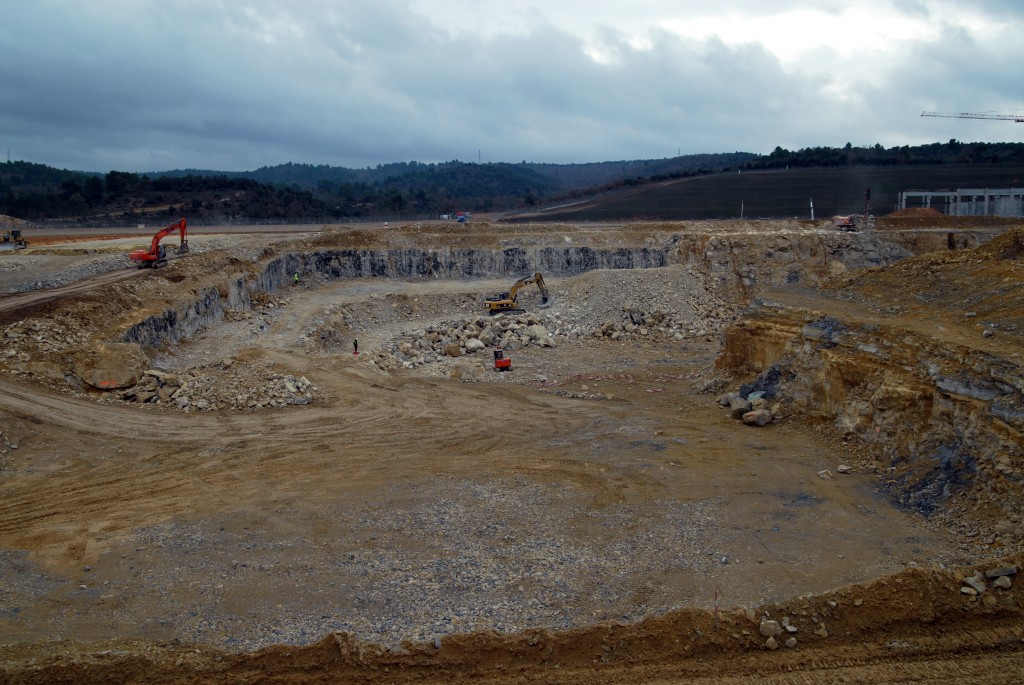
Tons and tons of rock
2010-12-21 - Excavating to 17 metres requires the removal of an estimated 210,000 cubic metres of rock and soil from the ITER platform—a feat that was accomplished in four months. Photo: F4E

Seen from above
2010-12-19 - The Tokamak Complex excavation worksite seen from the sky in December 2010. Photo: Altivue/AIF
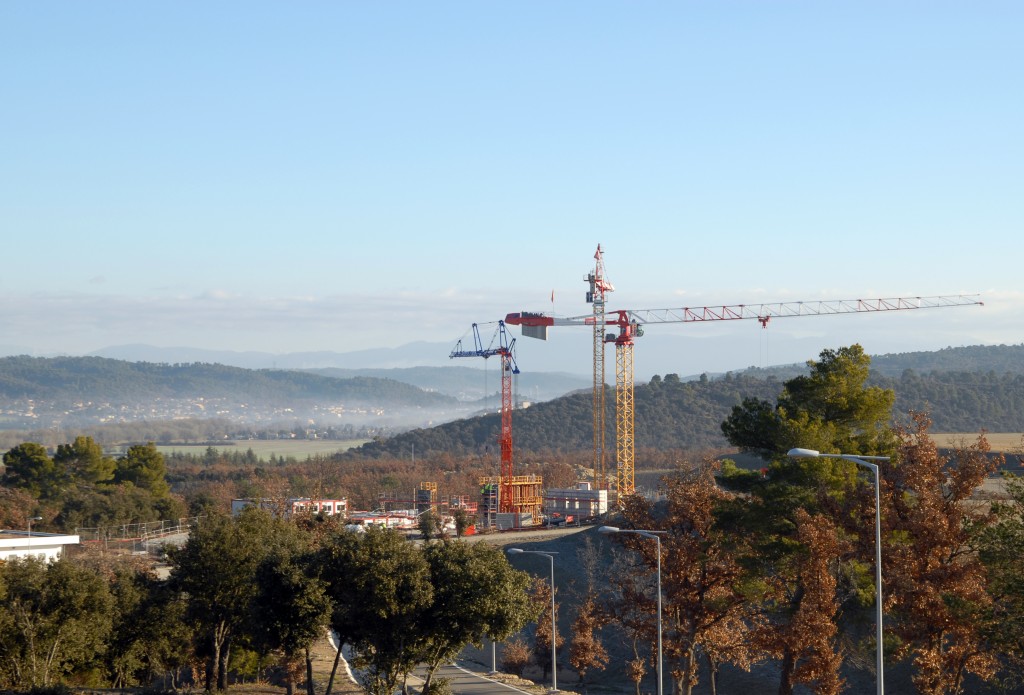
The future ITER Headquarters
2010-12-13 - In addition to the 20,500 square-metre ITER Headquarters, a small building is planned to welcome the public and a second to manage site access and house medical services. Photo: AIF

First phase of excavation is over
2010-12-10 - The 90 m x 130 m Seismic Pit is measured at 298.65 m above sea level; the ultimate excavation depth of 17 m is almost achieved.
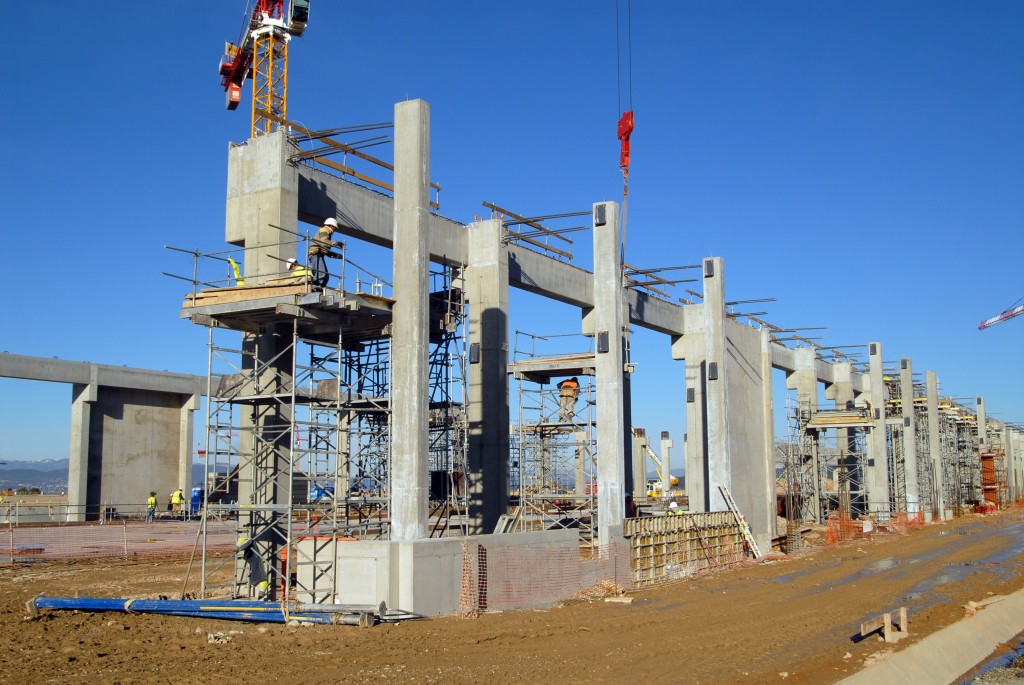
Nineteen metres high
2010-12-09 - Each of the Winding Facility's 62 concrete columns is 19 metres high. Photo: F4E
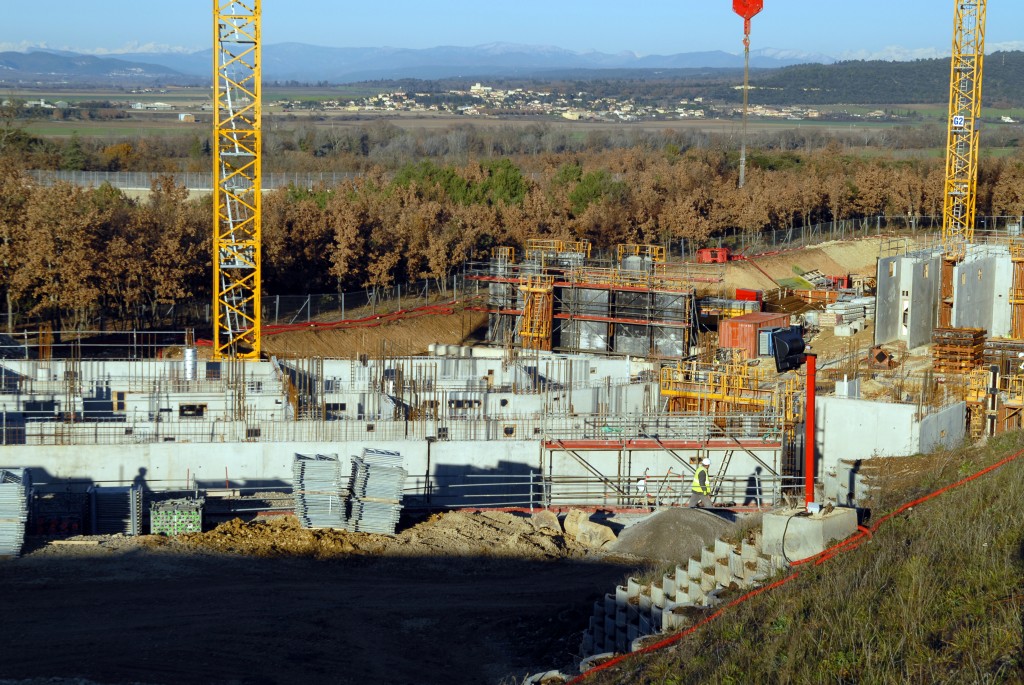
180 metres in length
2010-12-09 - The 180 metre-long, five-storey ITER Headquarters will provide office space for about 500 employees, a cafeteria, an amphitheatre with 500 seats, and a boardroom. Photo: AIF
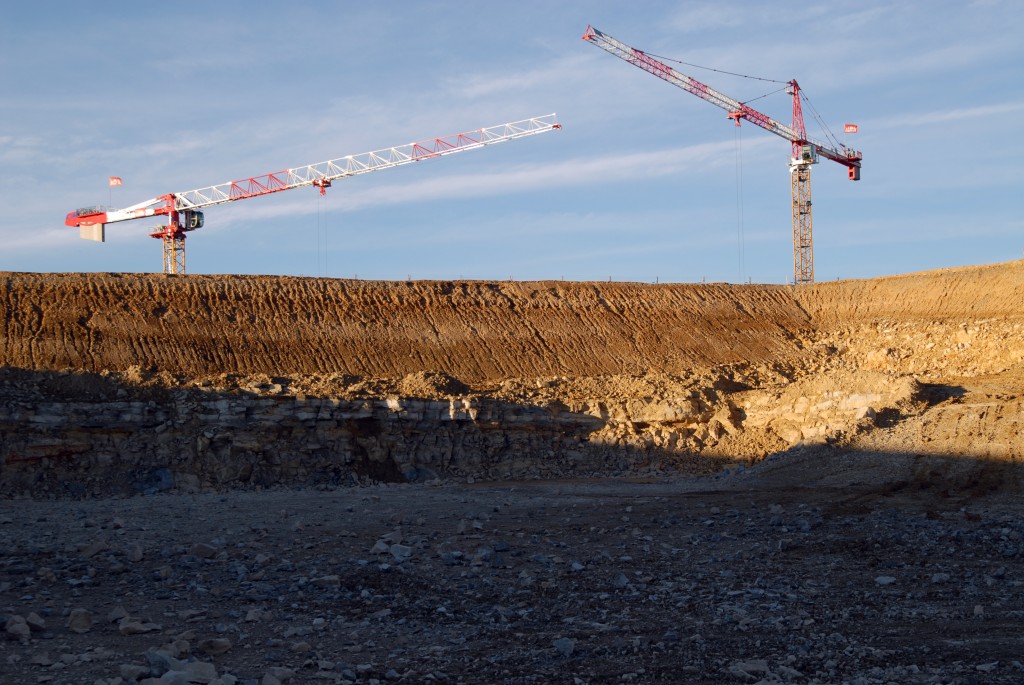
As the year ends ...
2010-12-09 - In the late afternoon sunshine in December, the blasting marks are clearly visible along the face of the Seismic Isolation Pit.
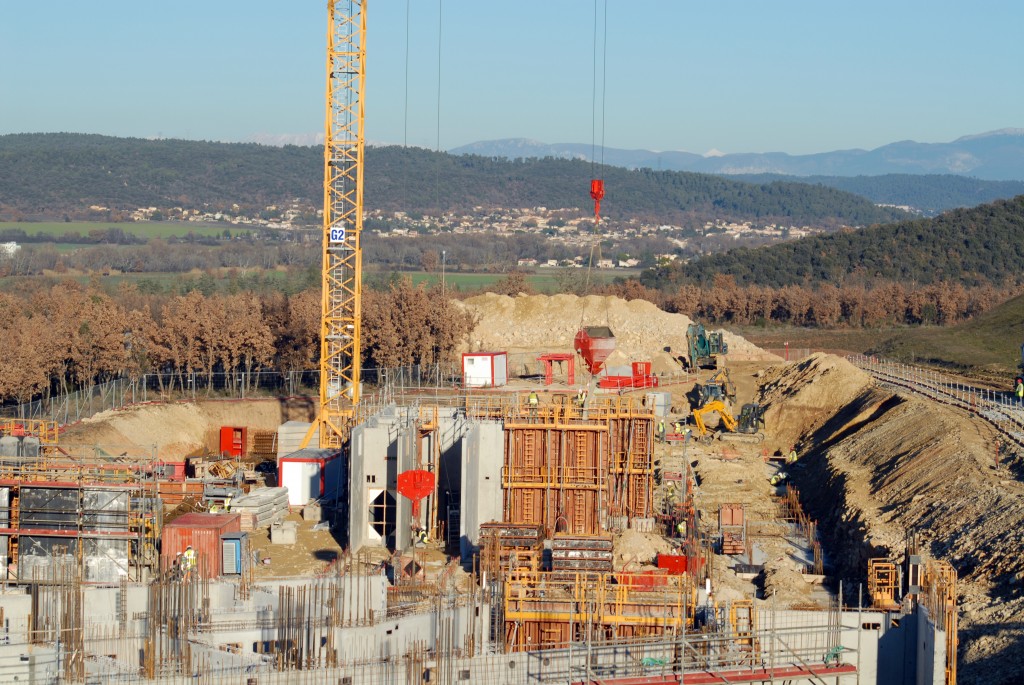
Heavy works
2010-12-05 - The construction of the ITER Headquarters is financed by the European Domestic Agency, F4E, and France as Host country. Photo: AIF
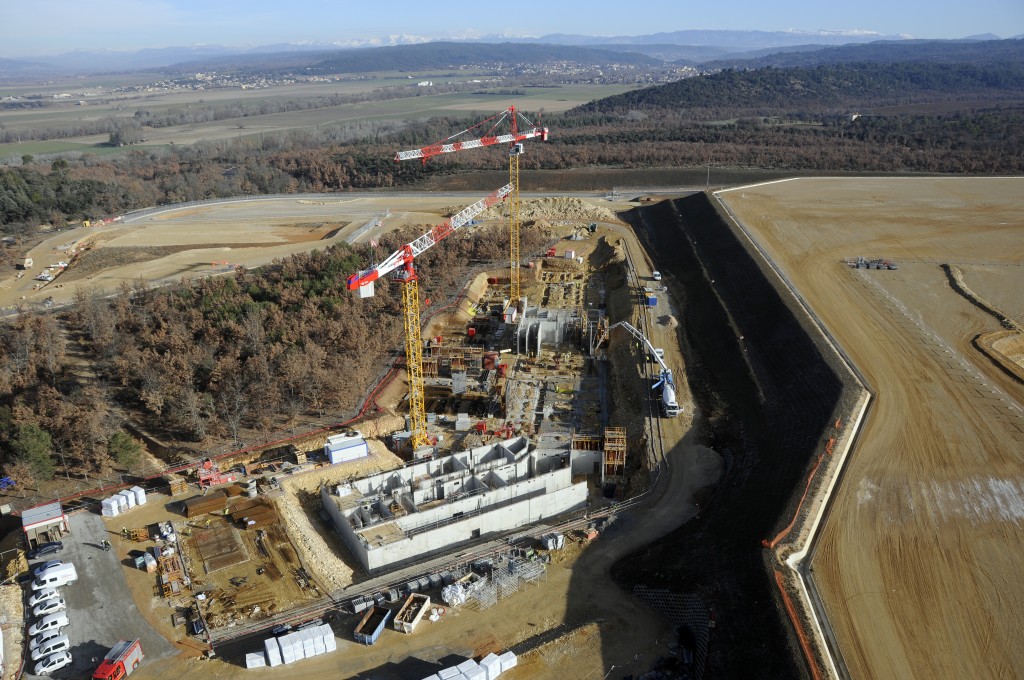
Footbridge to the Control Room
2010-12-01 - A footbridge will link the first floor of the Headquarters to the ITER Control Room which will be located one level below the project construction platform. The thirty-metre-long footbridge will become a tunnel when it reaches the platform, providing direct pedestrian access to the research facilities. Photo: Altivue/AIF
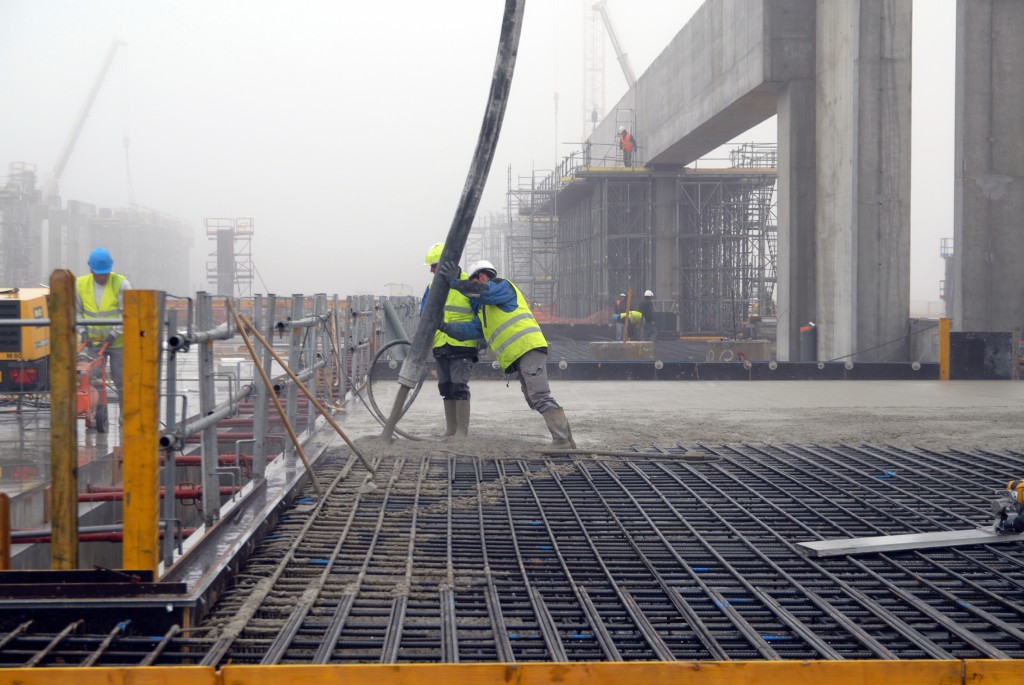
November fog
2010-12-01 - Concrete pouring activities continue despite the thick fog that covers the ITER platform. Photo: F4E
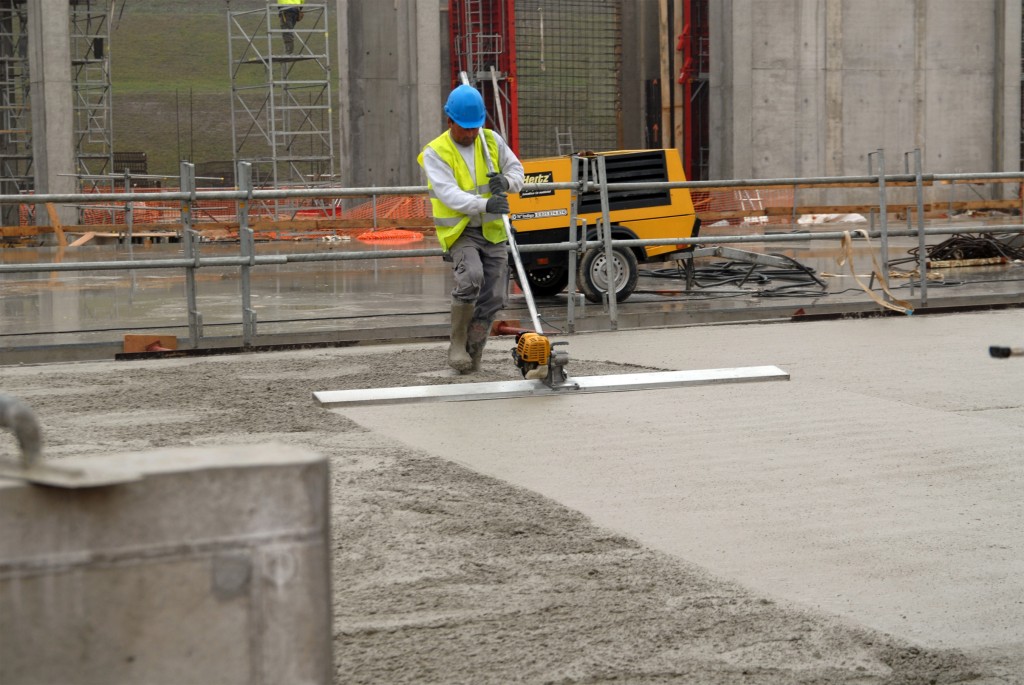
Finishing touches
2010-12-01 - Workers smooth the wet concrete that has been cast for the floor of the Winding Facility. Photo: F4E
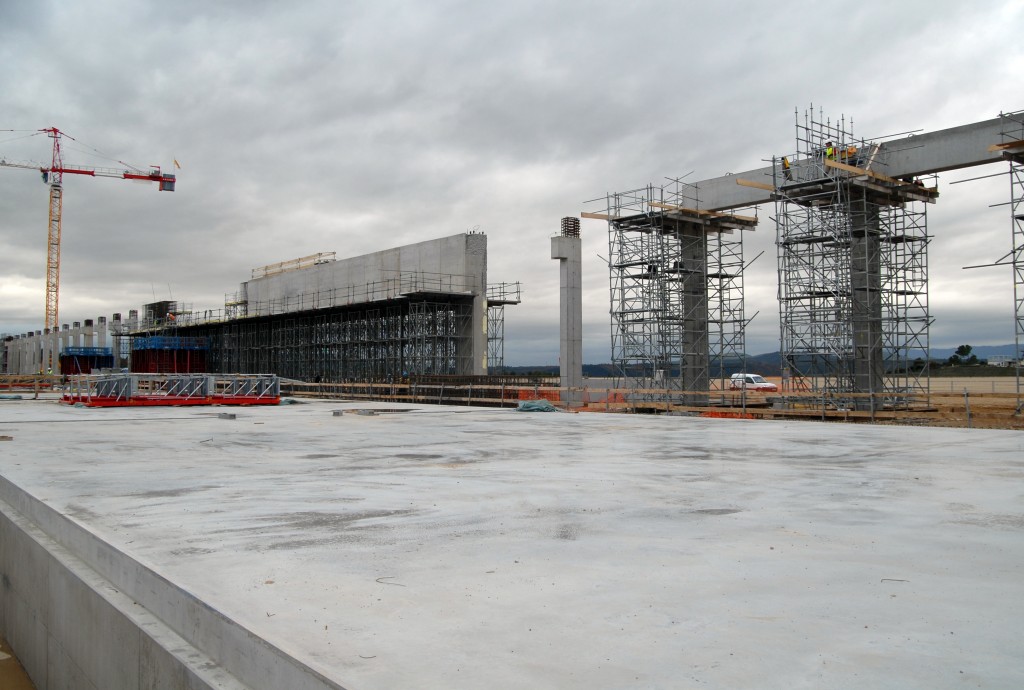
Every eight metres
2010-11-15 - Day by day, the 62 reinforced concrete columns are set into place, spaced every eight metres. Photo: F4E

Solidly anchored
2010-11-01 - The columns of the Winding Facility are solidly anchored four metres deep in the ground. These columns will support the structure of the building and bear the weight of two travelling bridge cranes that will have a lifting capacity, respectfully, of 25 and 100 tonnes. Photo: F4E
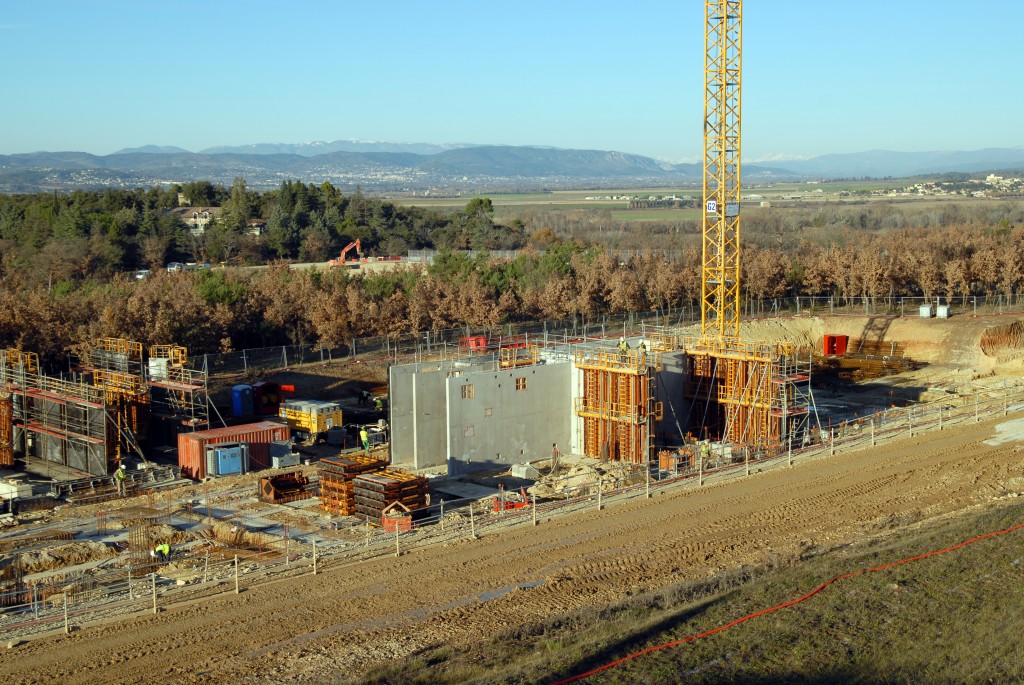
Work on the first floor begins
2010-10-15 - Work begins on the first floor of the ITER Headquarters building in October 2010 and progresses quickly at the rate of twelve linear metres per day. Photo: AIF
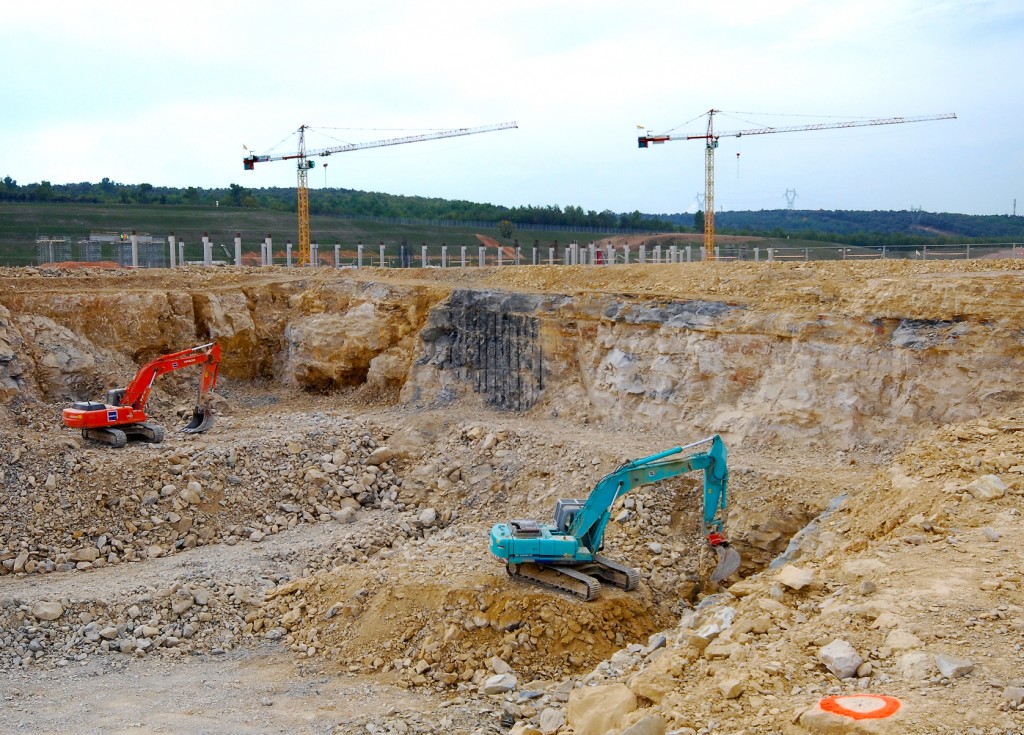
Digging and blasting down to 17 metres
2010-10-08 - Ongoing rock blasting and excavation activities on the ITER platform to create the Tokamak Complex Seismic Isolation Pit.
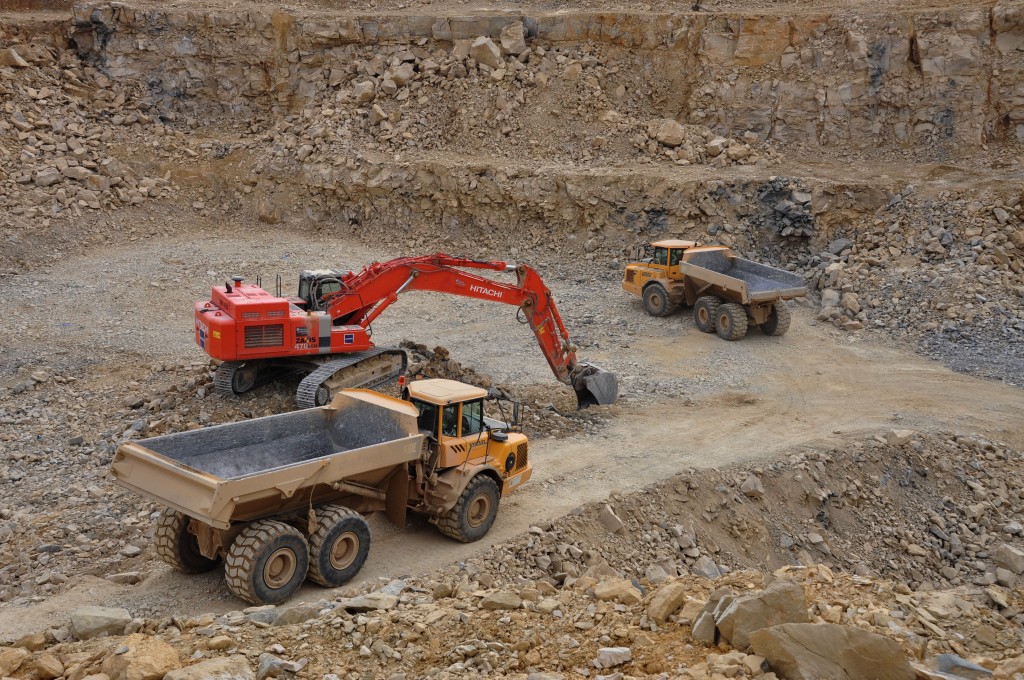
Soil and rock excavated
2010-10-08 - Over the course of four months, 210,000 cubic metres of soil and rock are excavated from the ITER platform to form the Tokamak Complex Seismic Isolation Pit.
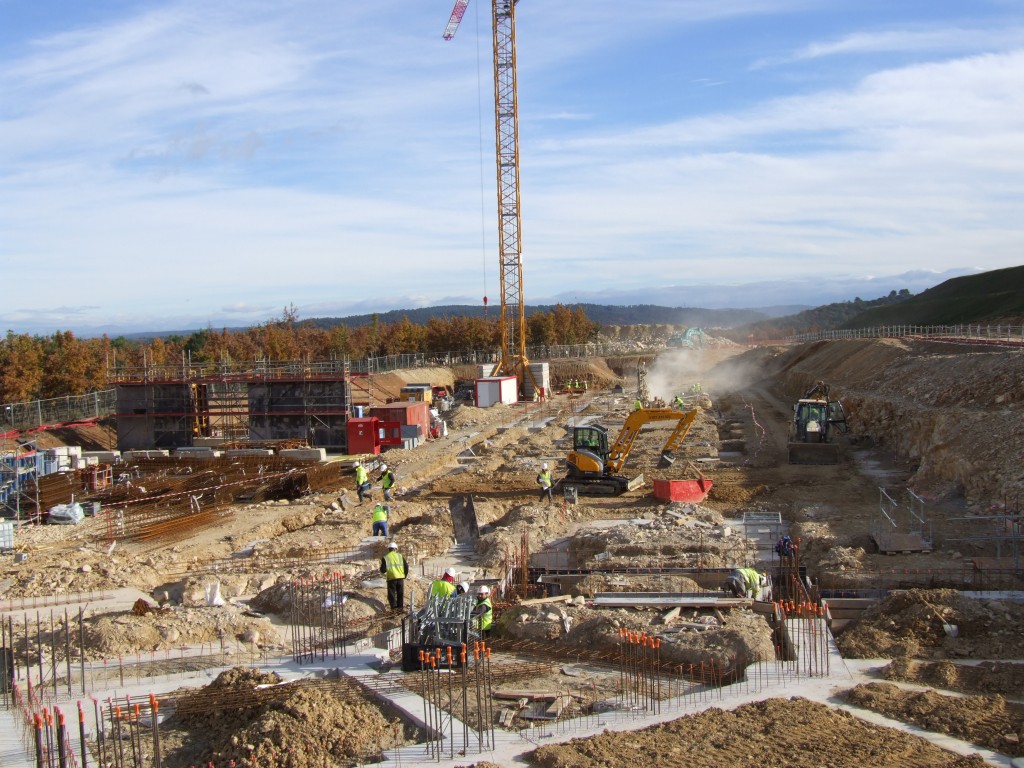
Foundation work for the ITER Headquarters
2010-10-02 - Work on the foundations of the ITER Headquarters building is launched in October 2010. The tall building will be solidly anchored five metres deep in the ground. Photo: AIF
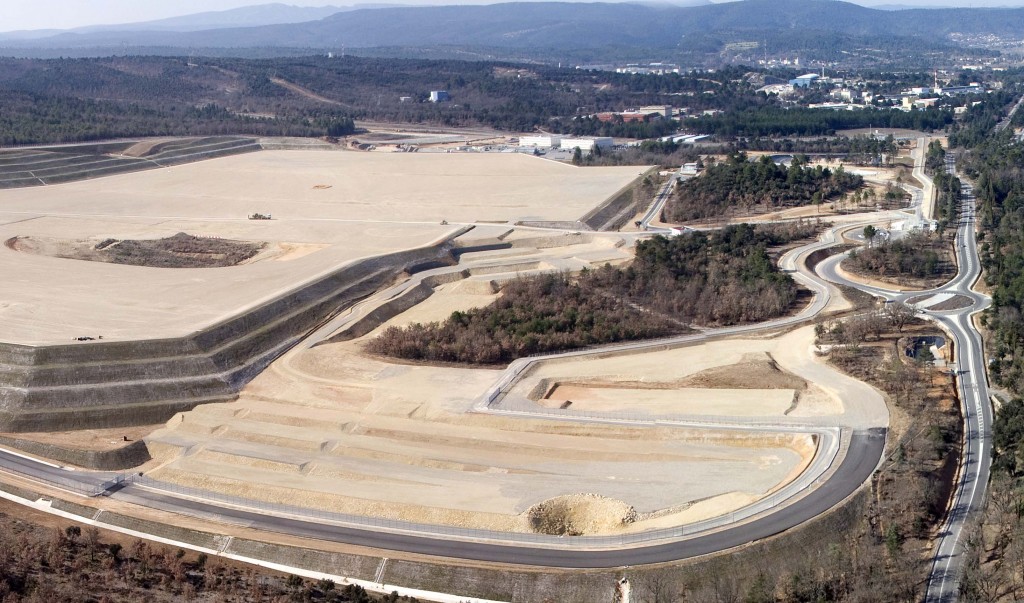
ITER Headquarters will be situated here, close to—but down from—the ITER platform
2010-09-15 - Just past the trees, nestled up against the bend in the ITER platform, a patch of land has been cleared for the construction of the permanent ITER Headquarters. Photo: Altivue/AIF
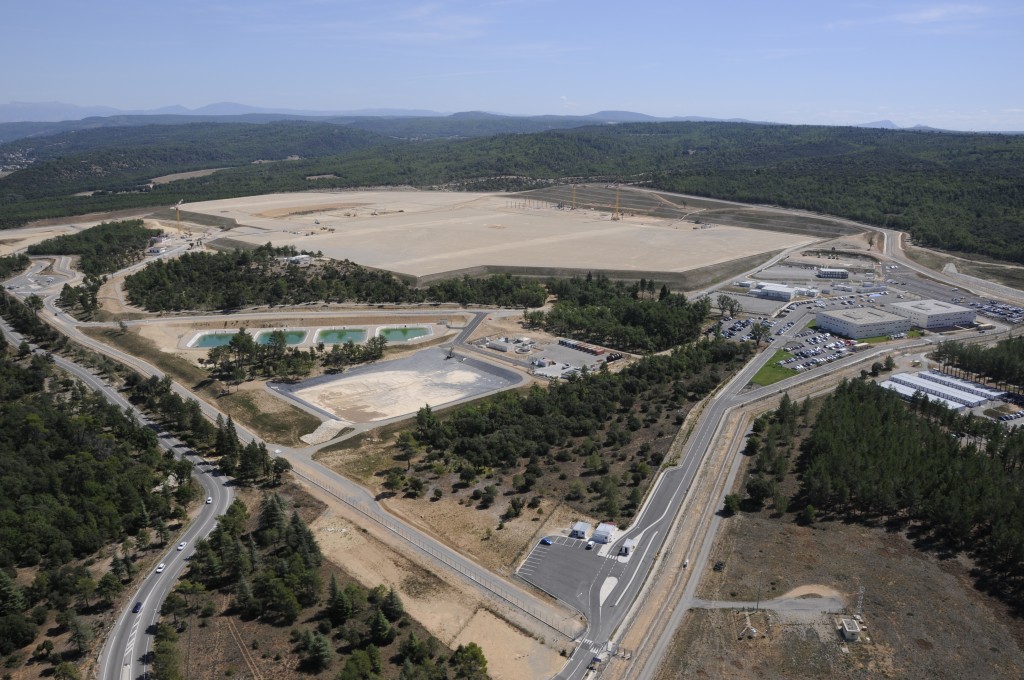
ITER seen from the sky as construction is launched
2010-09-15 - This aerial photo, taken in September 2010, shows the ITER site as the digging begins for the Tokamak Complex. Photo: Altivue/AIF
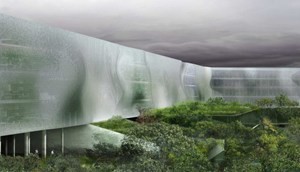
Architect's View #2
2010-09-01 - The underground auditorium of the ITER Headquarters will have a "green roof"—a natural way to regulate the temperature in the building. Photo: Ricciotti
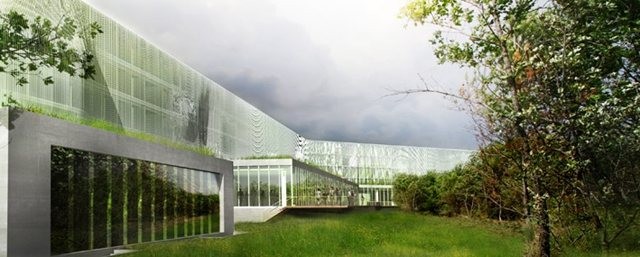
Architect's view #4
2010-09-01 - Work begins in September 2010 on the future ITER Headquarters, which will be situated on a six-hectare wooded parcel to the west of the ITER platform. Photo: Ricciotti
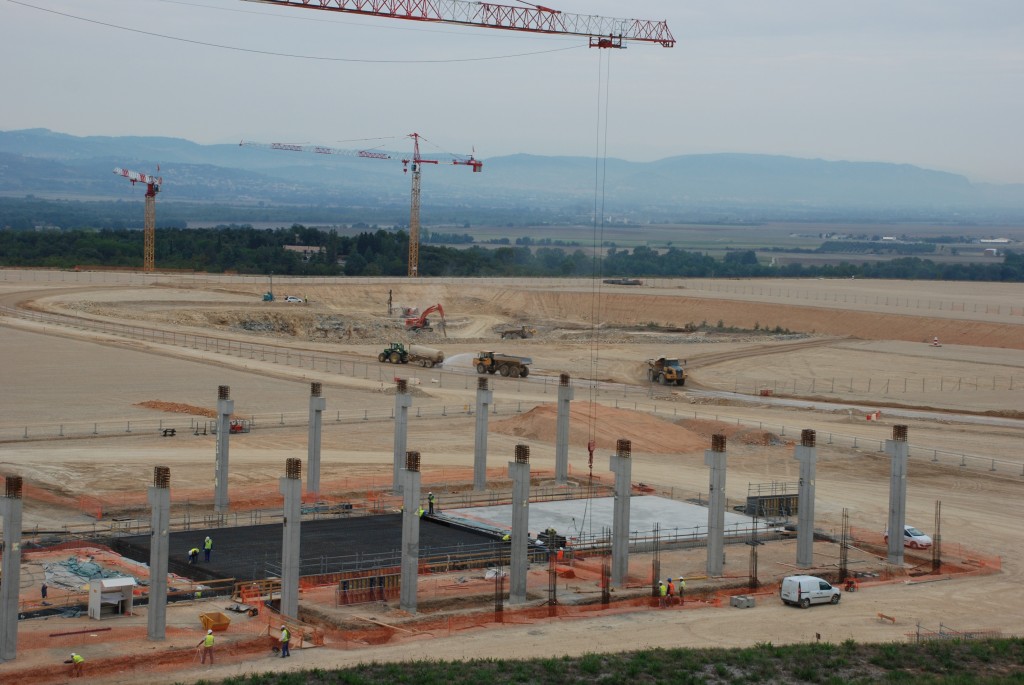
The first building on the ITER platform
2010-09-01 - Work begins on the first building on the ITER platform in August 2010: the Poloidal Field Coils Winding Facility. The French consortium Spie Batignolles, Omega Concept and Setec was chosen by the European Domestic Agency F4E to design and build the facility. Photo: Altivue/AIF
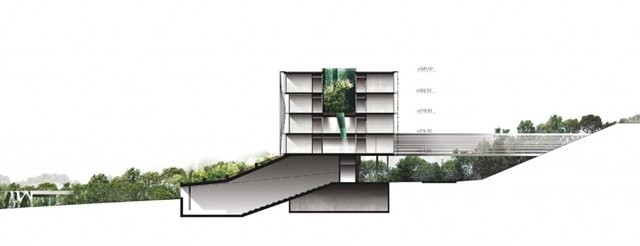
Architect's view #1
2010-09-01 - Two- to three-storey interior patios—spaced evenly along the central walkways of the building and planted with vegetation—will generate ventilation, let in natural light, and provide a convivial setting for common areas. Photo: Ricciotti
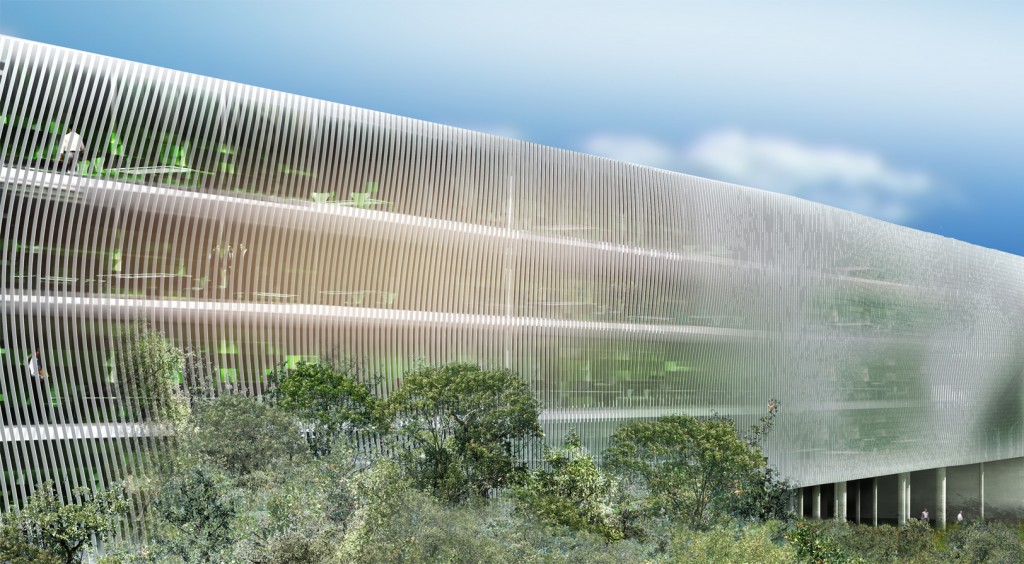
Architect's view #3
2010-09-01 - "Undulating vertical slats." This is the way the architect describes the most prominent visual feature of the Headquarters building. These sunshades will provide protection from the sun on the northwest facade of the building and reduce the need for cooling within. Made of highly resistant fibre concrete, the 3,104 sunshades will also provide structural strength. Photo: Ricciotti
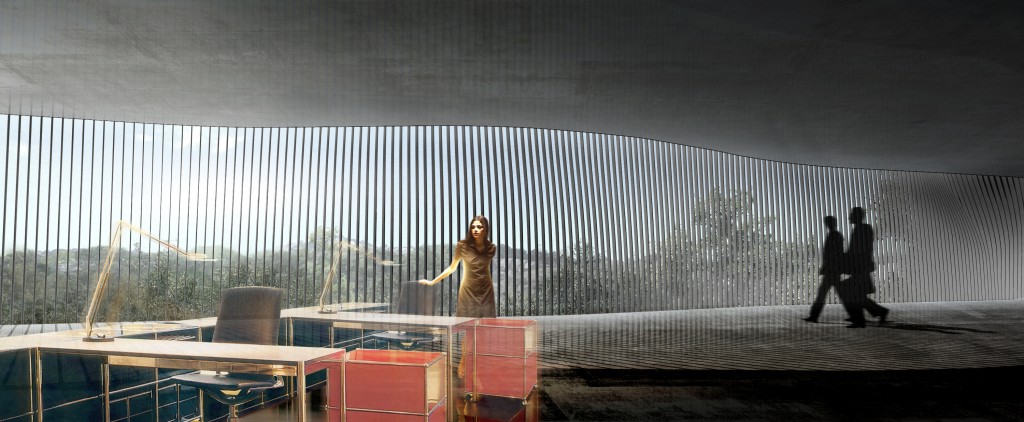
Architect's view #5
2010-09-01 - An artist's view of the future ITER Headquarters. Sanitary water for the building will be heated by approximately 80 square metres of solar panels. Photo: Ricciotti
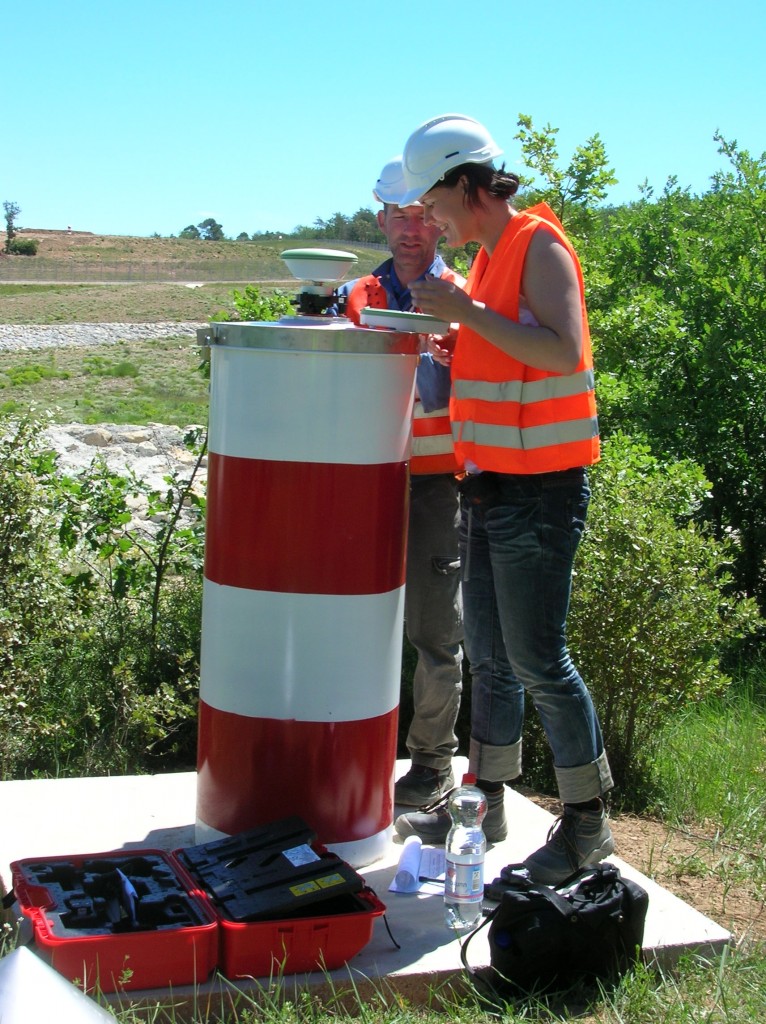
Eleven monuments in the ITER Primary Survey Network
2010-06-02 - Eleven survey monuments were positioned around the ITER site in 2010 as part of the ITER Primary Survey Network. Two additional temporary monuments were used during the surveys to shorten the measurement distance to improve the accuracy. On top of the monument is a Leica GPS Receiver. Photo: ITER Organization (Pictured: contractors from GDV Systems GmbH, Germany)
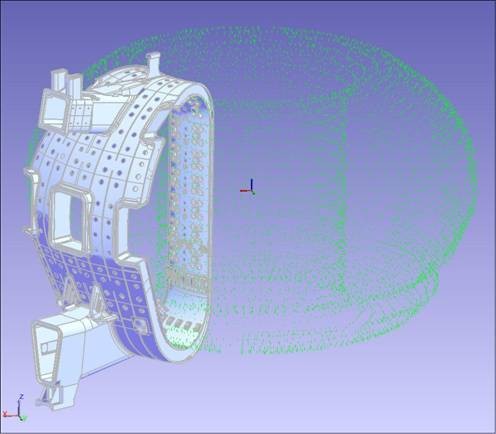
9000 measurement targets to simulate in-vessel survey
2010-06-01 - Once assembly is complete, a survey will be carried out to determine the as-built position of the interfaces for in-vessel components. Using software tools developed specifically for ITER, a survey simulation was carried out to determine achievable accuracy. 9,000 measurement targets were simulated using the CAD file as a template, to represent targeting the complete vacuum vessel.

In-vessel photogrammetry survey simulation
2010-06-01 - In this illustration, the field of view for each camera is modelled and used to identify measurable targets. This array of cameras is repeated 18 times toroidially around the ITER vacuum vessel.
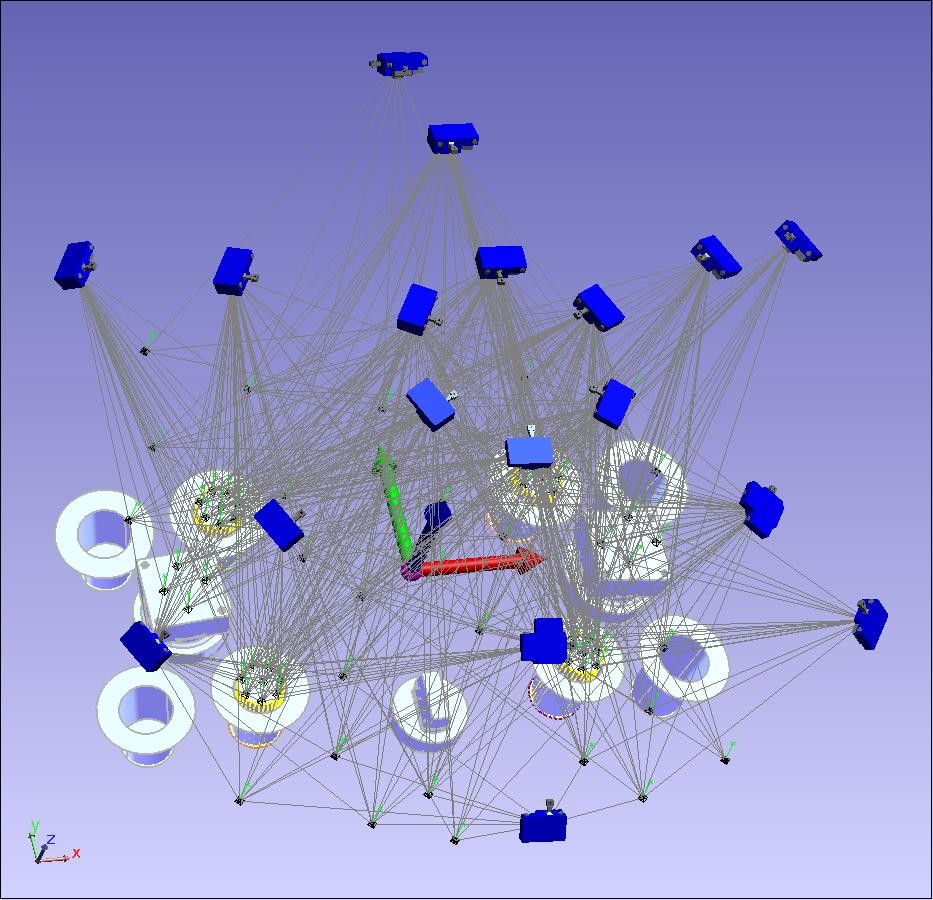
Photogrammetry simulation
2010-06-01 - Measurement geometry for the survey of the interface components of an inboard blanket shield module. Photogrammetry simulation is used to predict the measurement uncertainty.
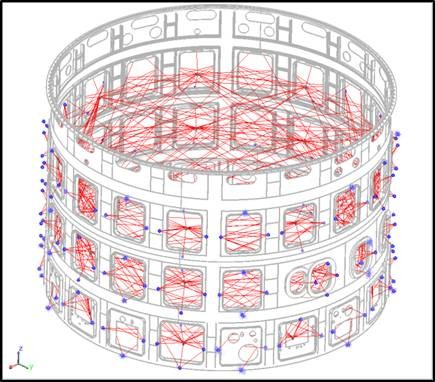
The ITER pit survey network
2010-06-01 - The ITER pit survey network will consist of approximately 220 target nests mounted to the bioshield wall at the port cell openings. Metrology instruments mounted on dedicated stands, within the port cells, will extend through the cryostat ports into the pit to measure and align tokamak components with respect to this network. Lines of sight have been carefully studied to ensure that the network remains available throughout construction of the principle tokamak components.
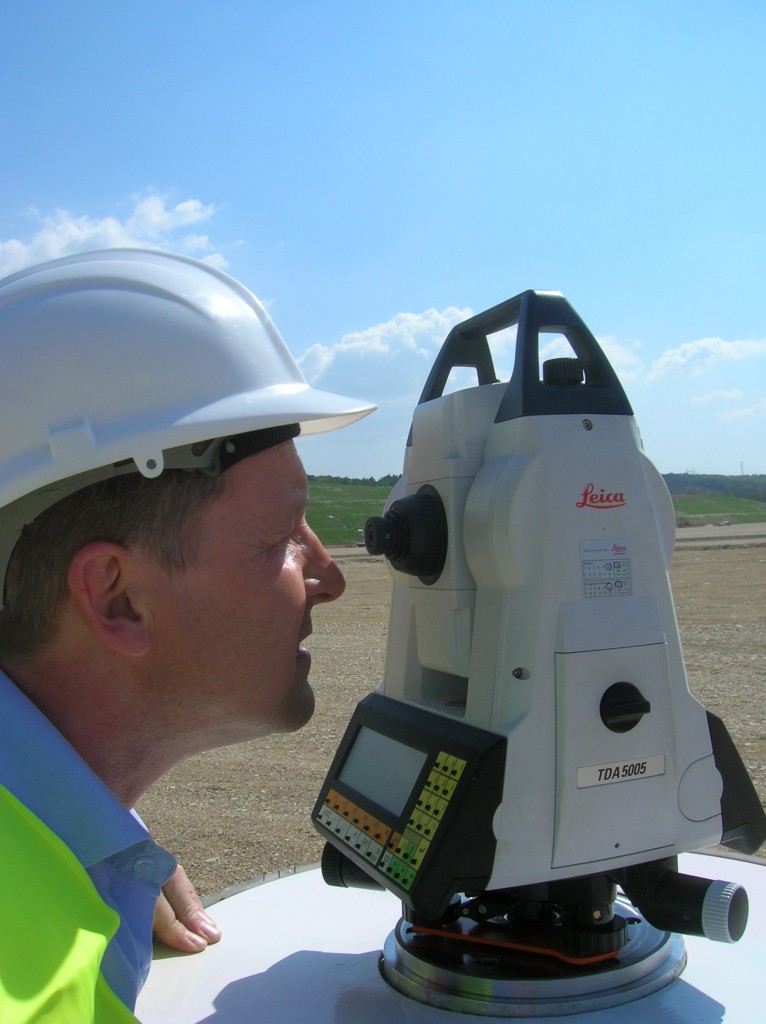
Accuracy of approximately 1 mm
2010-04-28 - The first survey of the ITER Primary Survey Network, as well as subsequent monitoring surveys, was carried out using a combination of terrestrial measurements (pictured here with a Leica Total station) combined with differential GPS and levelling measurements. An accuracy of approximately 1 mm was achieved for these surveys.
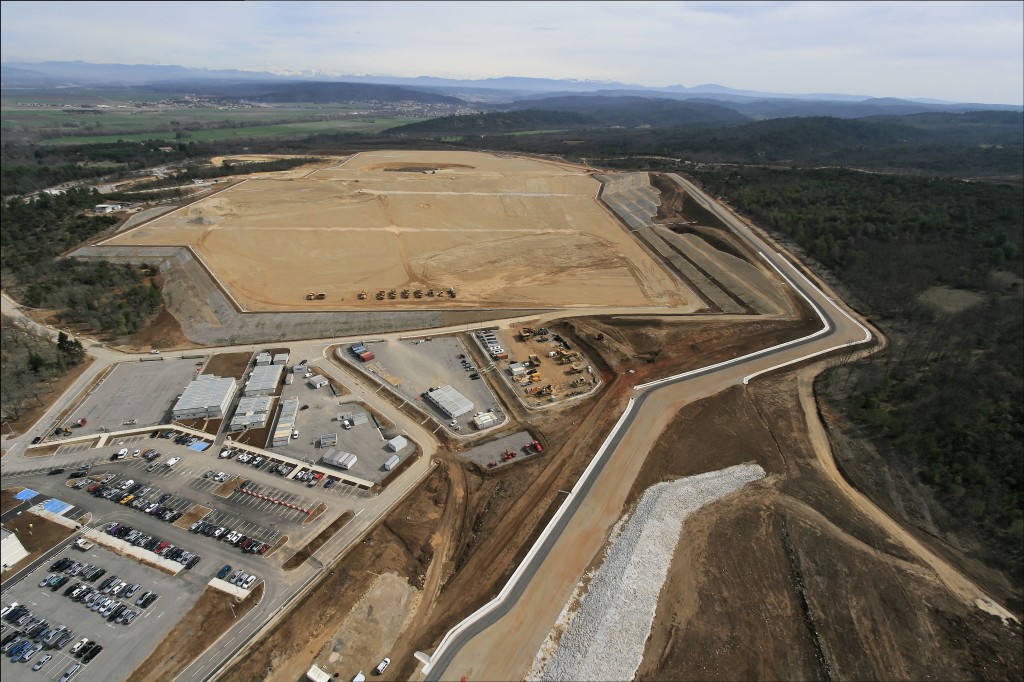
The ITER site
2009-03-31 - Water for the installation will be delivered by gravity through underground piping from the Canal de Provence. And as for electricity, the same 400 kV line that feeds the Tore Supra tokamak, next door, will deliver power to ITER. About half of the 180 hectares reserved for ITER have been exploited.
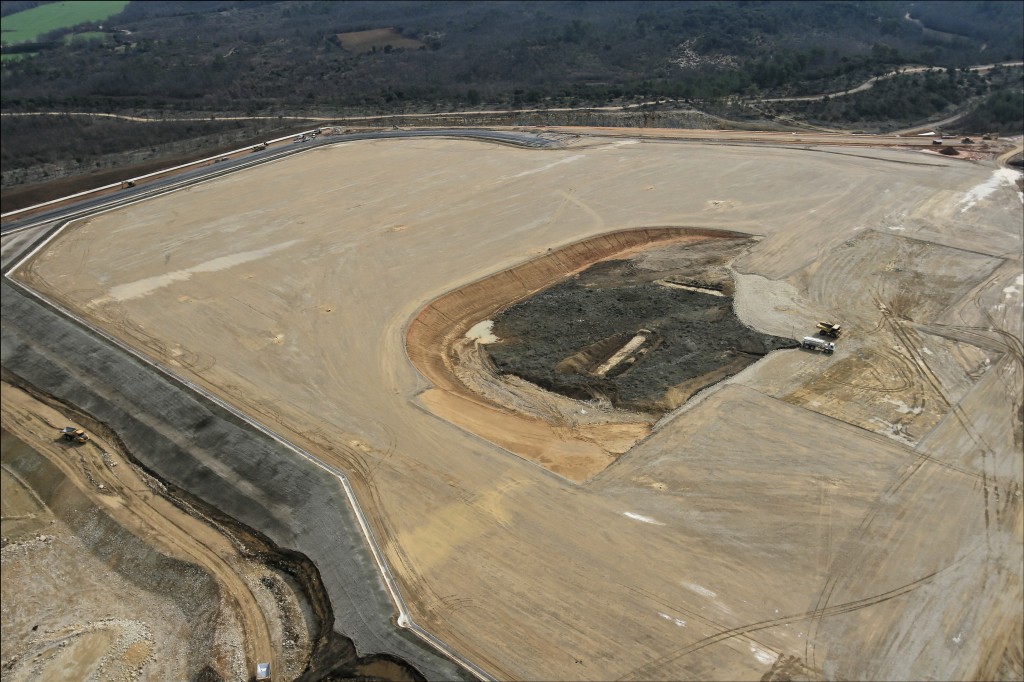
The Tokamak will stand here
2009-03-31 - On the level ITER platform, the quality of the rock substrata has determined the exact location of the future 360,000-tonne Tokamak Complex, where physics experiments will be conducted. Photo: Altivue/AIF

The Tokamak will be here
2009-03-31 - The depression in the surface of the platform indicates the exact spot where the future Tokamak will be installed.

The platform is ready
2009-01-29 - 1,000 metres long, 400 me wide: the platform that will house the ITER scientific buildings is ready for construction to begin.
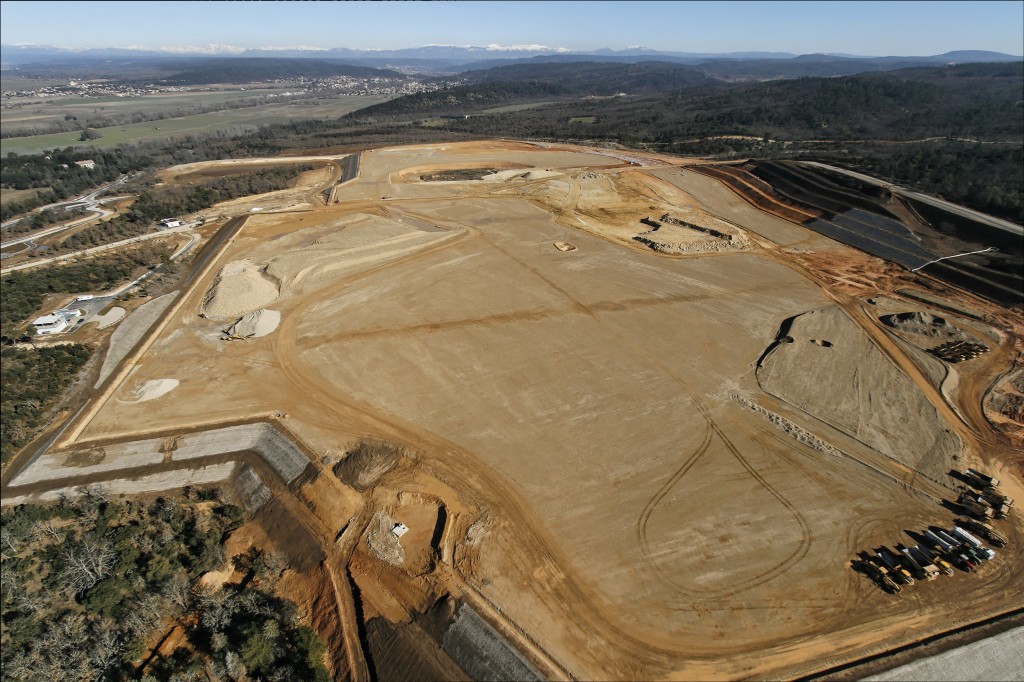
The 42-hectare ITER platform in Cadarache, France
2009-01-29 - From 2007-2009, work on the ITER site work was divided into two phases: the clearing of 90 hectares; and the levelling of a vast platform to house the buildings and facilites of the ITER scientific experiments. Photo: Altivue/AIF
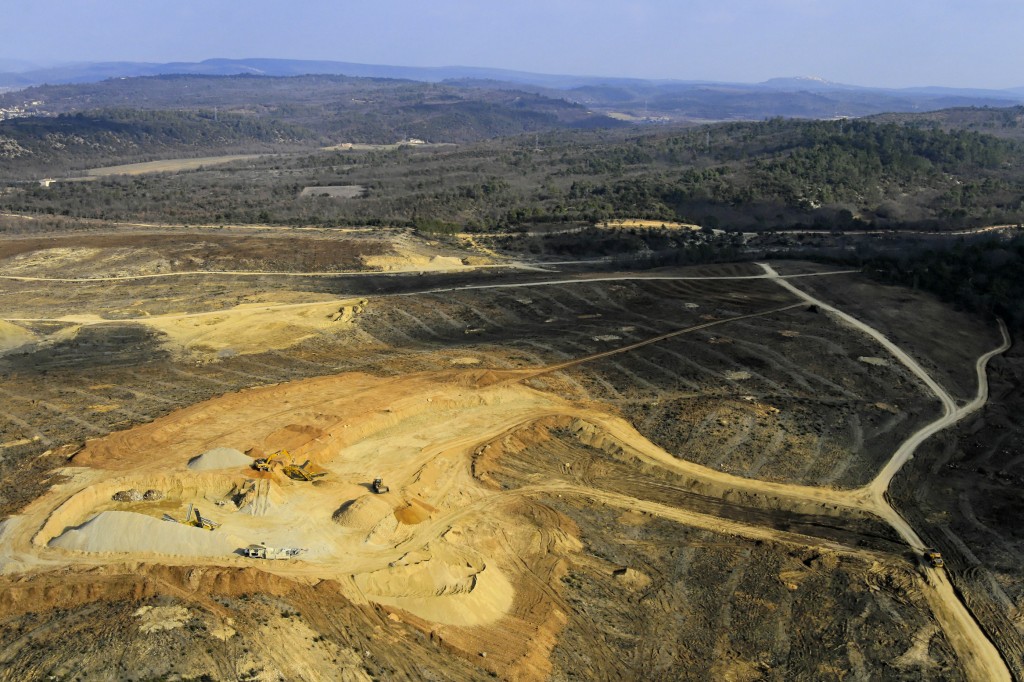
Clearing works are finished
2008-11-02 - The ITER site seen from above in February 2008. Photo: AIF VDC
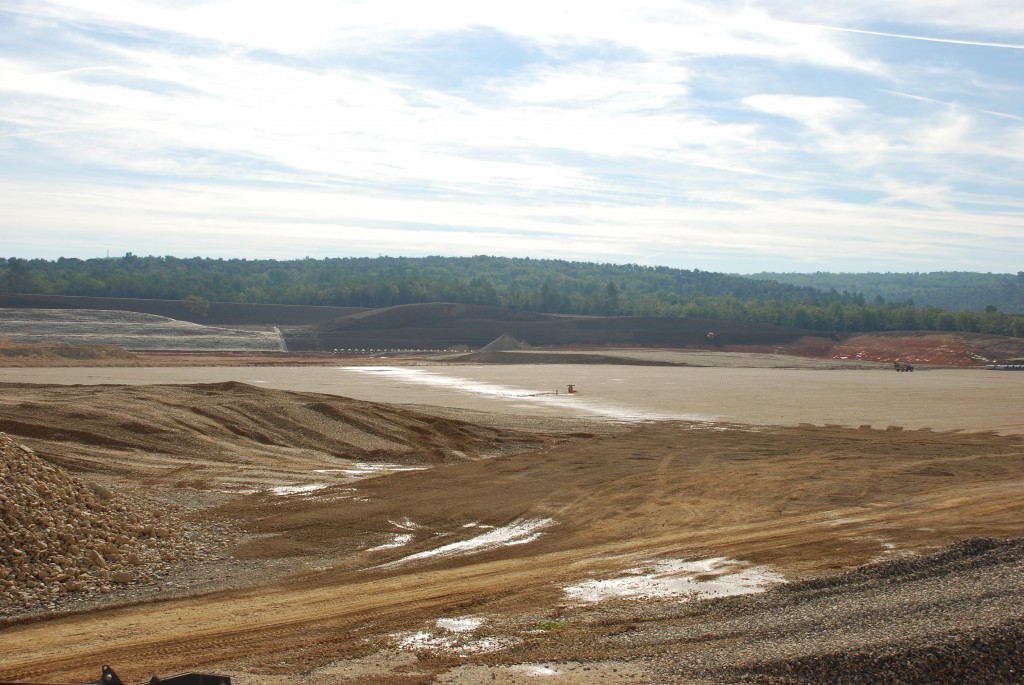
Two years of preparatory work
2008-10-27 - Over the course of two years (2007-2009), a large storm basin, 20 km of hydraulic networks (on and off site), and four cooling water basins were realized in addition to the 42-hectare ITER platform.

One year of levelling works
2008-09-22 - Site levelling works began in March 2008 and lasted one year.

Looking east over the platform
2008-09-22 - A Visitors Centre and viewpoint are created on a point overlooking the platform in 2008.

One day: the Tokamak Complex
2008-09-01 - The quality of the underlying rock and soil were tested in order to determine the best location for the tokamak on the ITER platform. The chosen area, a zone of limestone, will one day support the weight of the 400,000-tonne Tokamak Complex.

Levelling begins
2008-07-15 - The ITER platform in Saint-Paul-lez-Durance in July 2008 after the start of levelling works.

Moving earth
2008-06-15 - Preparatory site work took two years to complete, including clearing and levelling of 40 hectares for the ITER platform. Photo: AIF.

315 metres above sea level
2008-04-28 - Originally, differences of at least 40 metres separated the hills and vales of the ITER site. Engineering studies established the ideal altitude for the platform—315 metres above sea level—as the best technical, economic and environmental compromise.
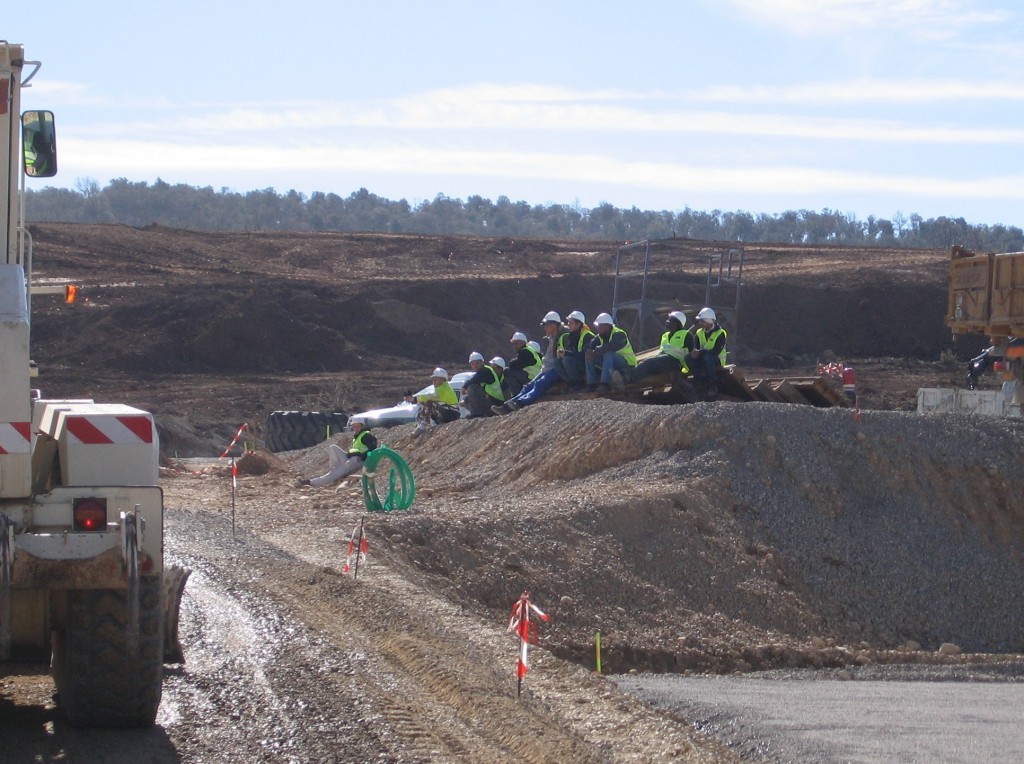
A break, from time to time
2008-04-15 - Site preparations are continuing full speed ahead but, from time to time, a break is welcome!

The ITER platform is taking shape
2008-04-10 - Approximately 25% of the ITER platform is in place. Thirty-nine buildings will be constructed on the platform, which measures 400 x 1,000 metres.

Replanting the slopes
2008-01-10 - The slopes of the ITER platform replanted with local seeds ... some 3.5 tonnes of seed in all. Photo: AIF AM

A lot of material
2008-01-01 - 2.3 million cubic metres of rock and soil are removed to create the ITER platform—that's nearly as much as the pyramid of Kheops! Photo: AIF
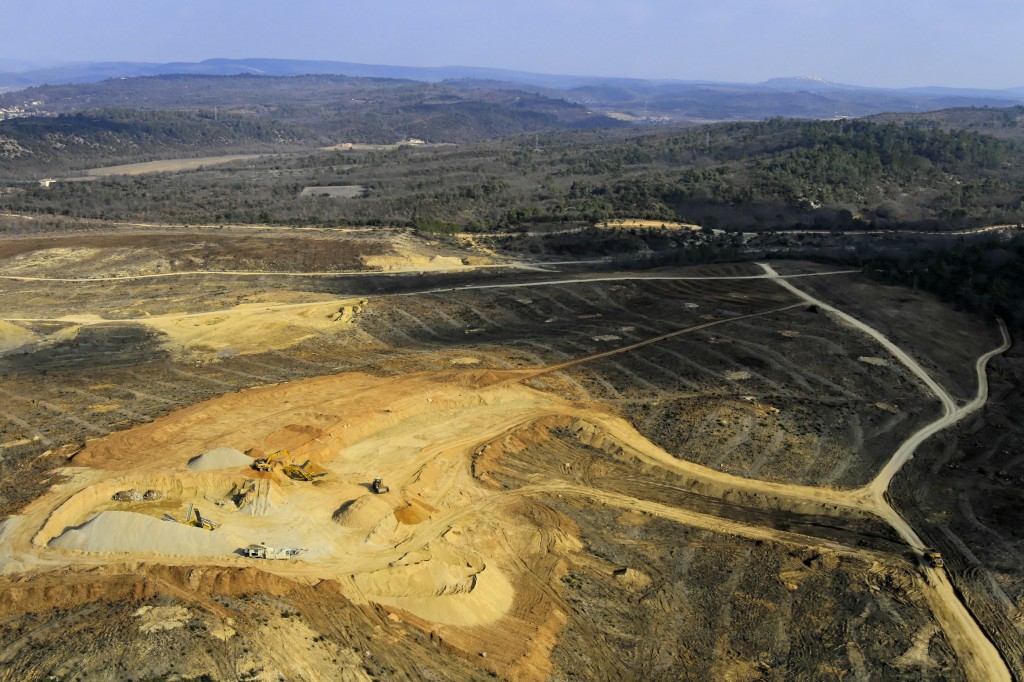
2007-2009
2007-12-10 - From 2007-2009, site preparatory works were undertaken by Agence Iter France (une agence du CEA). work was divided into two main phases: the clearing of 90 hectares and the levelling of a vast platform to house the buildings and facilities of the ITER scientific experiments.
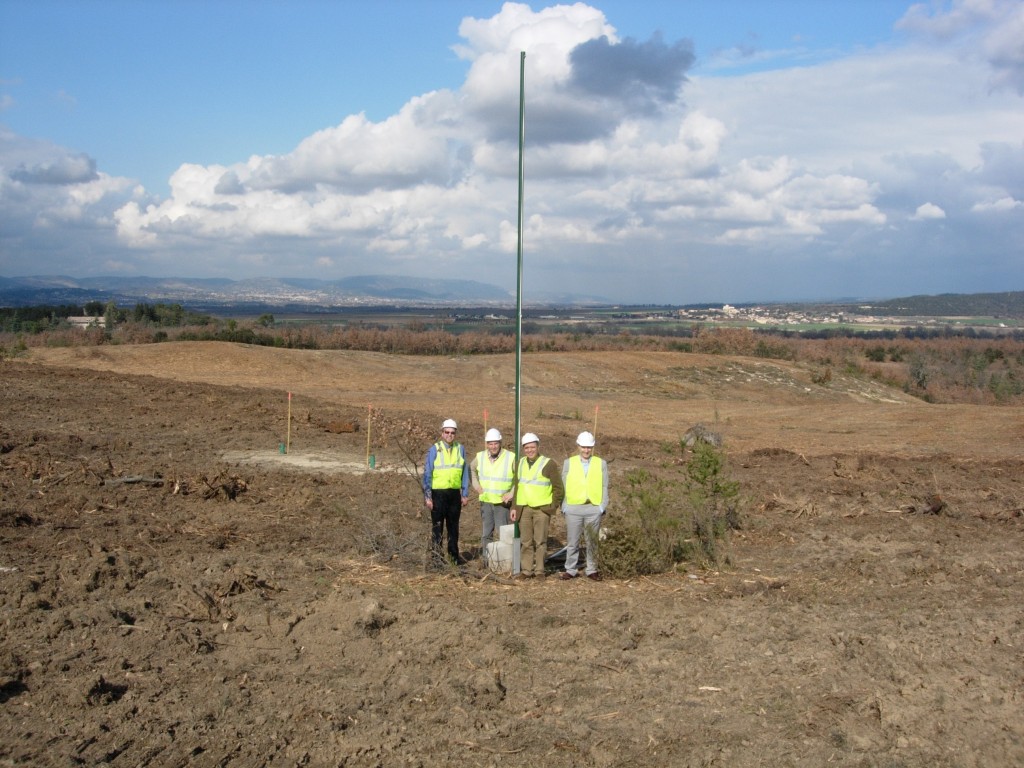
X marks the spot
2007-03-10 - Some of the first ITER employees stand where the ITER Tokamak will one day be assembled and installed.
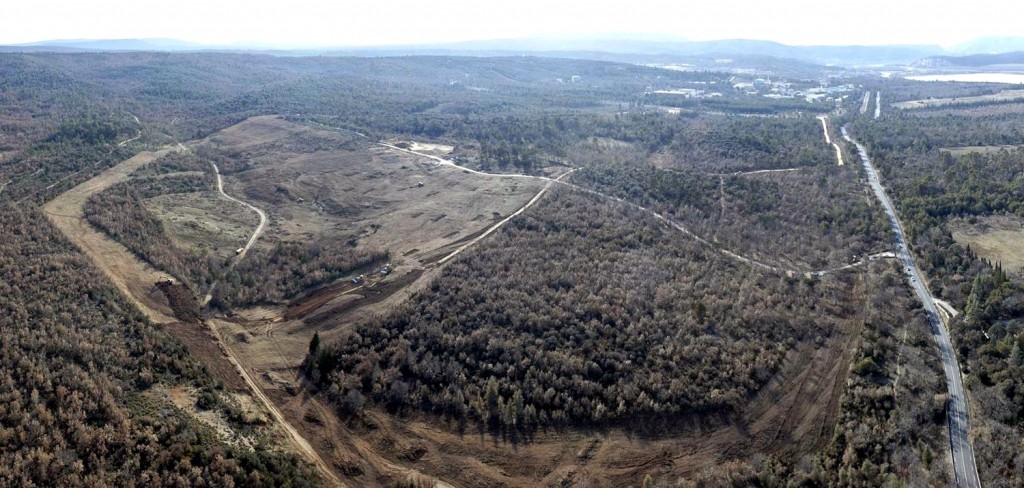
It starts with the purchase of land
2007-01-21 - The French Alternative Energies and Atomic Energy Commission (CEA) acquired approximately 180 hectares for the ITER Project in southern France, near the CEA Cadarache nuclear research centre.
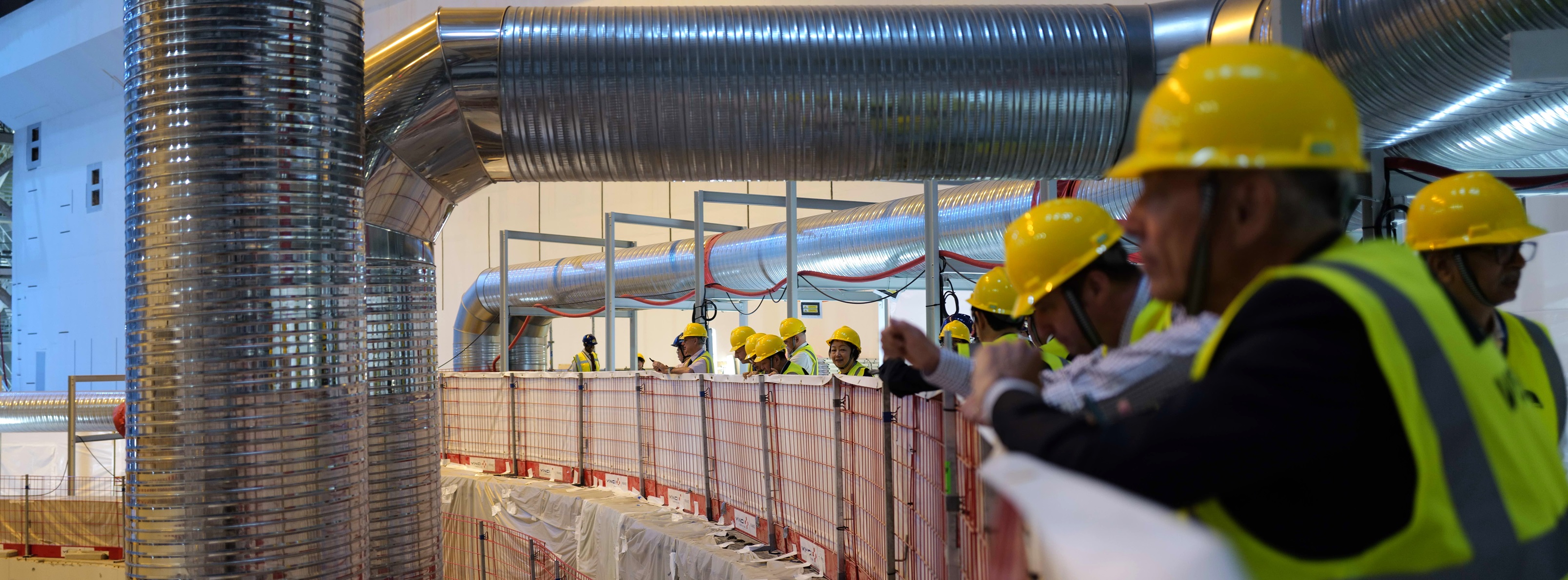
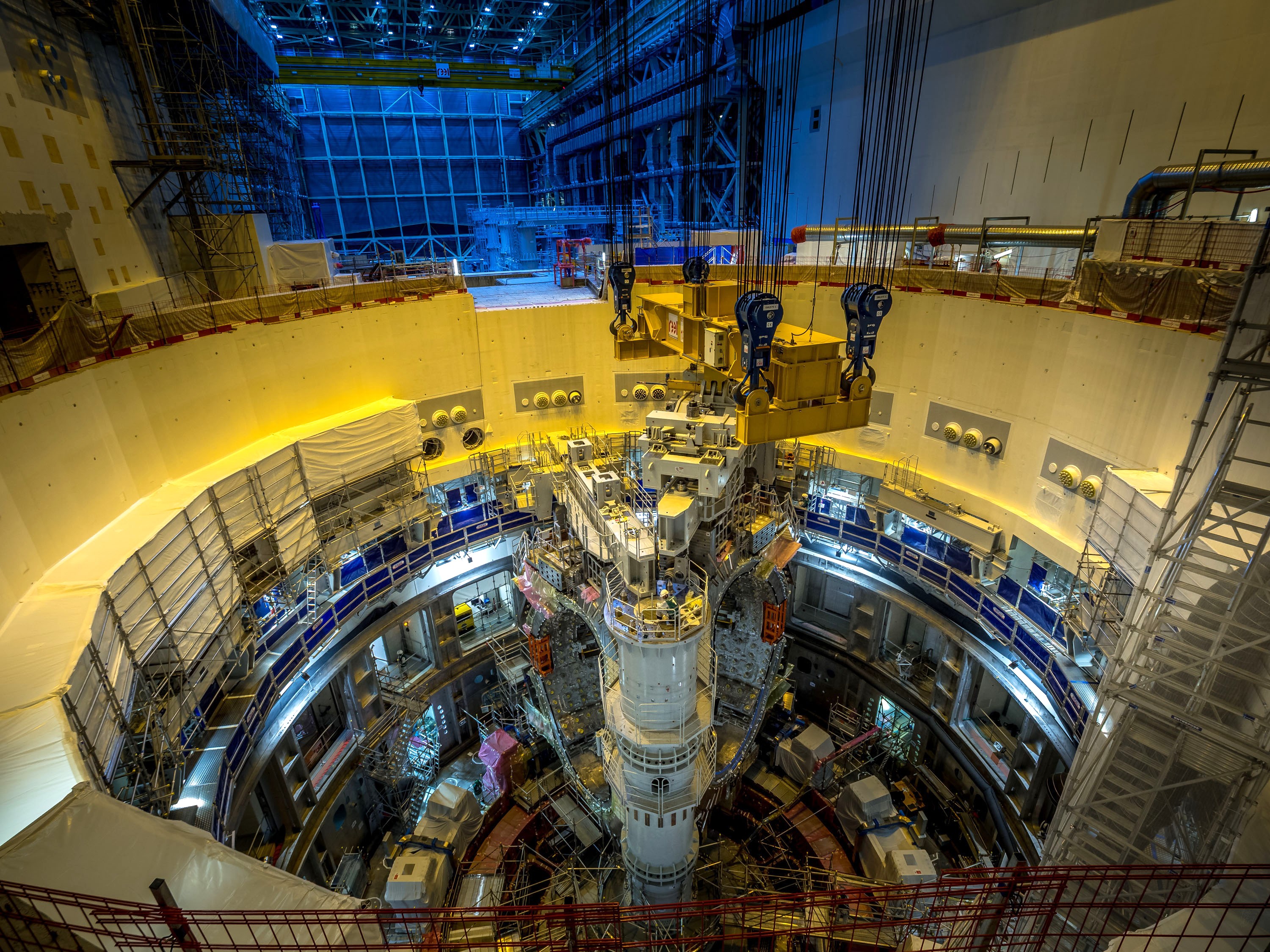
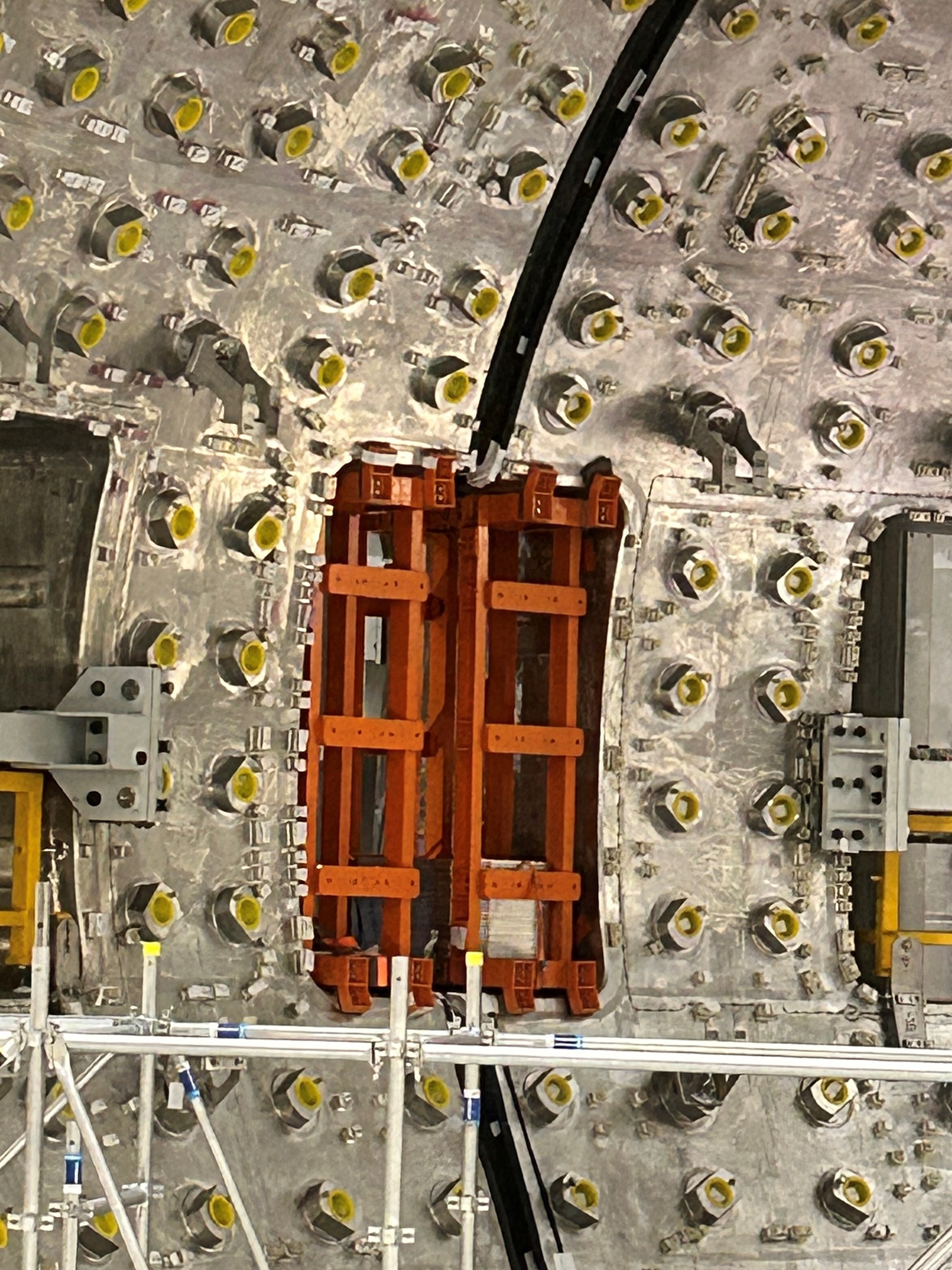
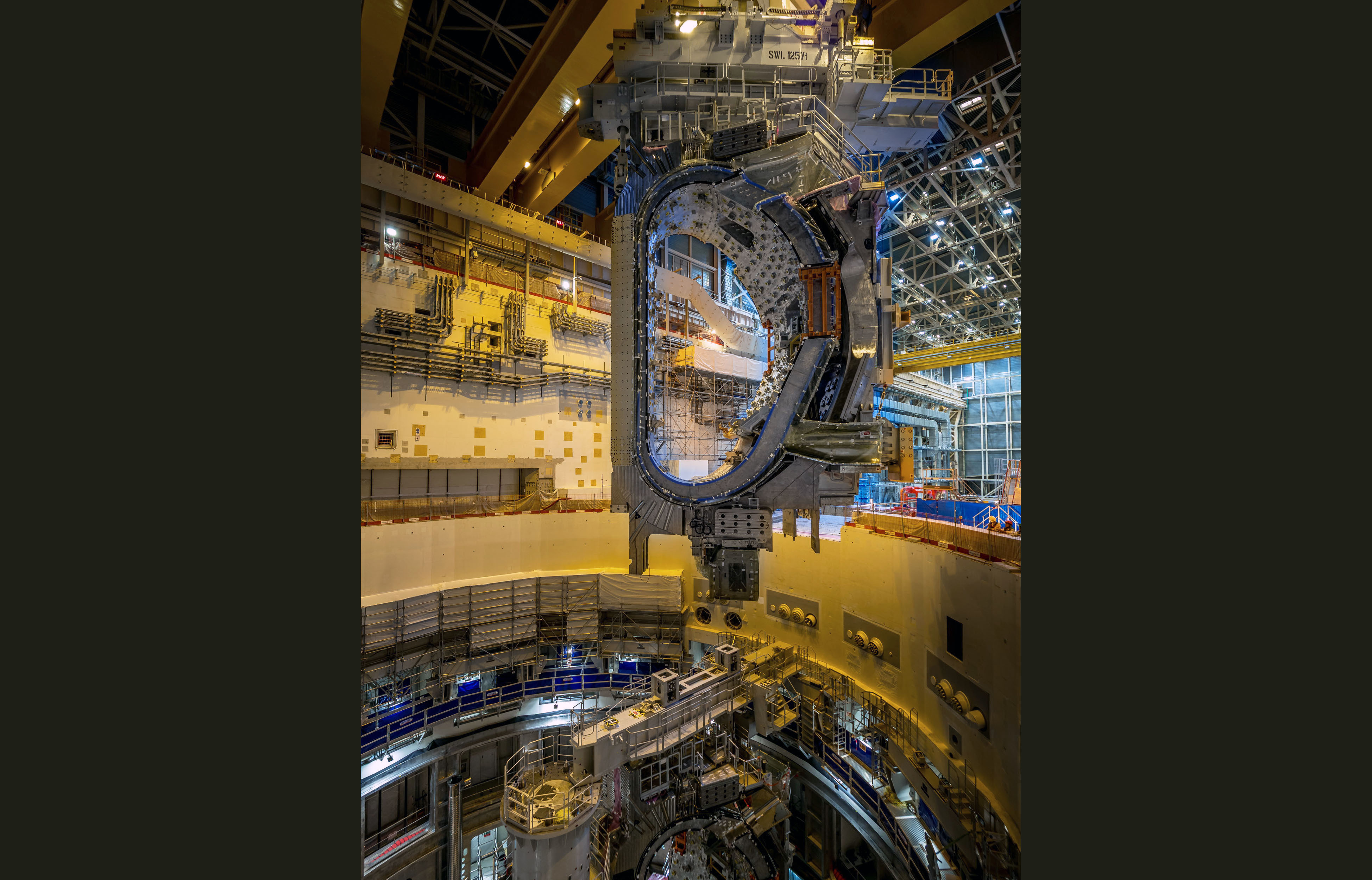
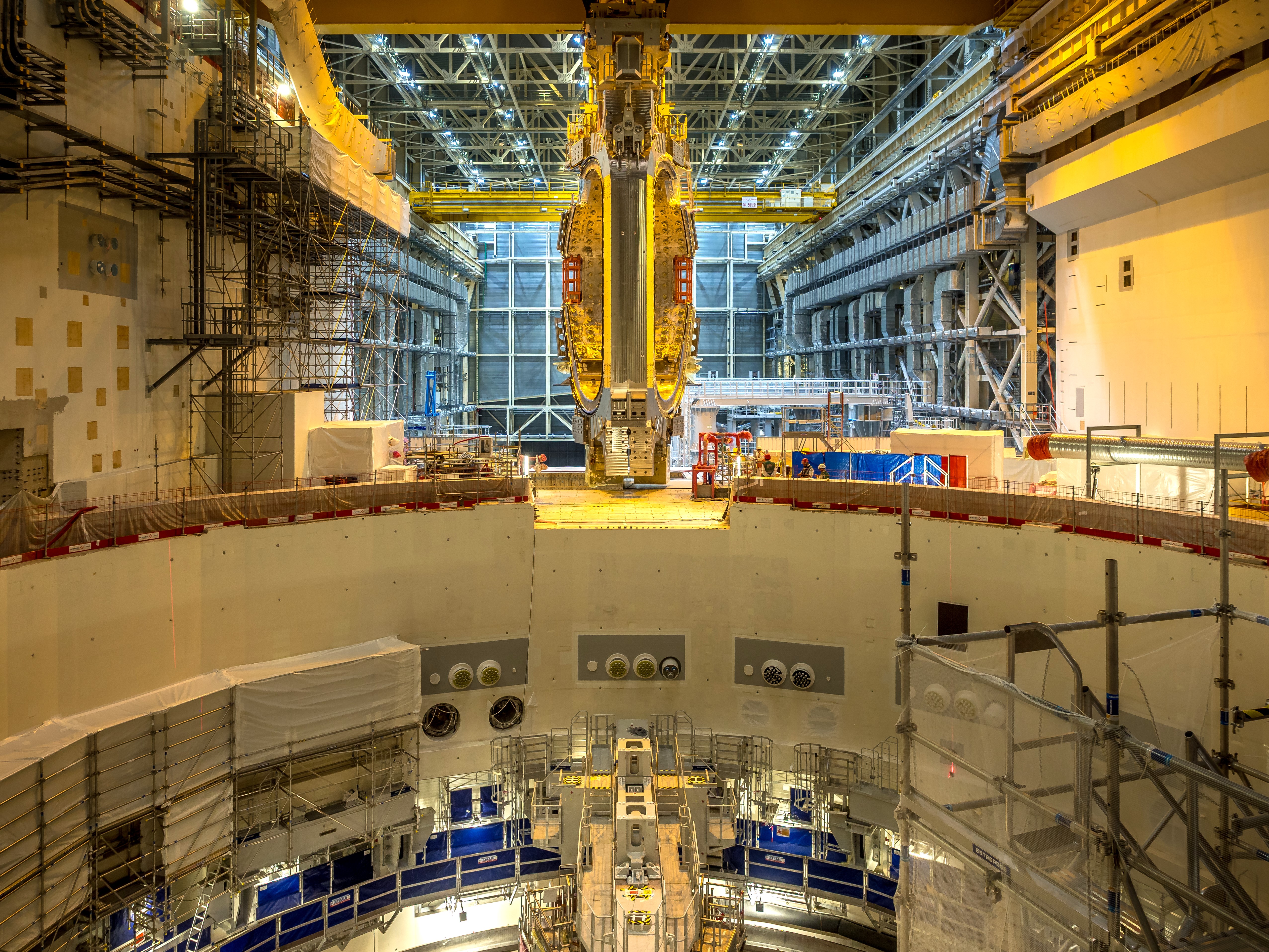
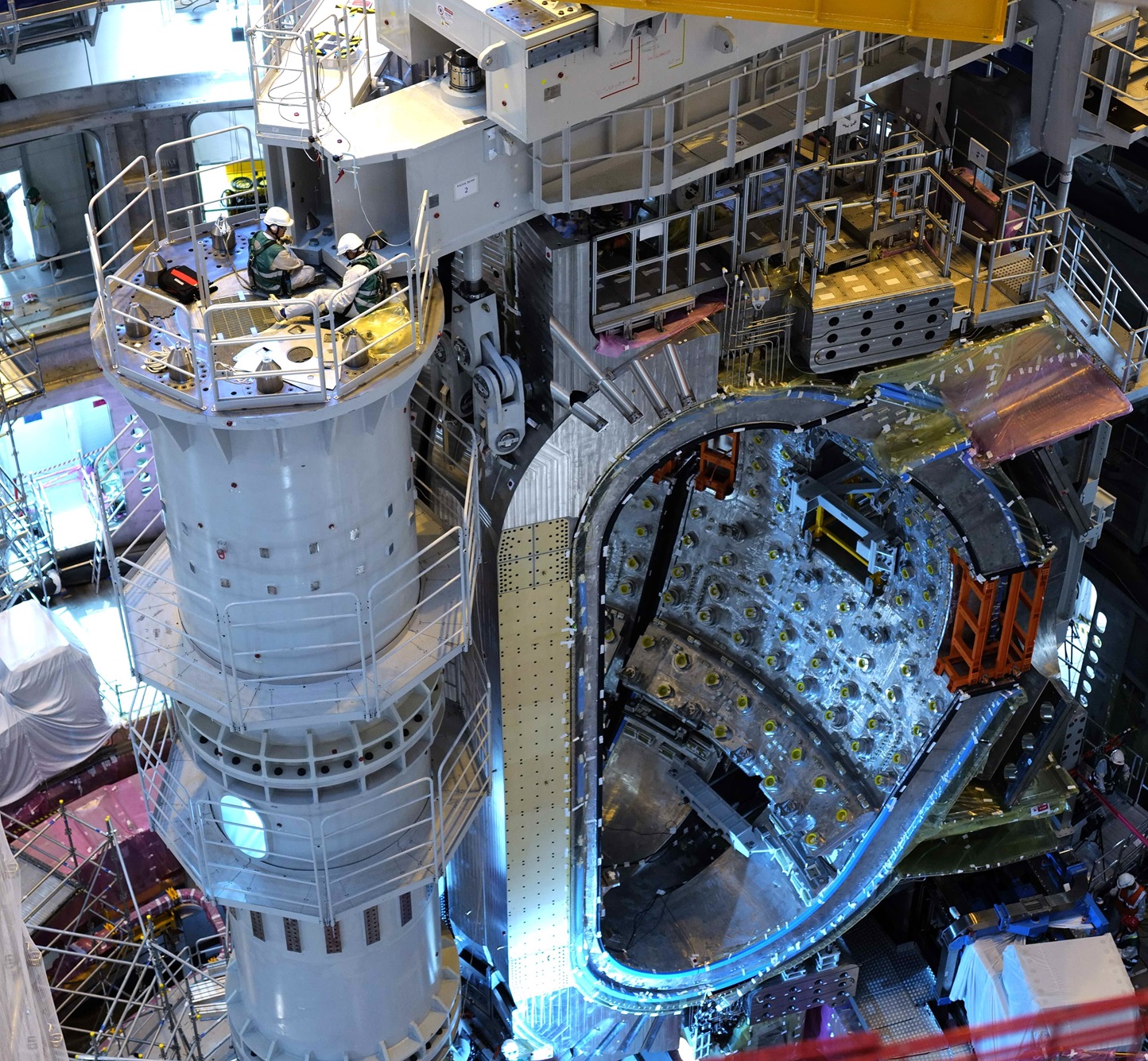
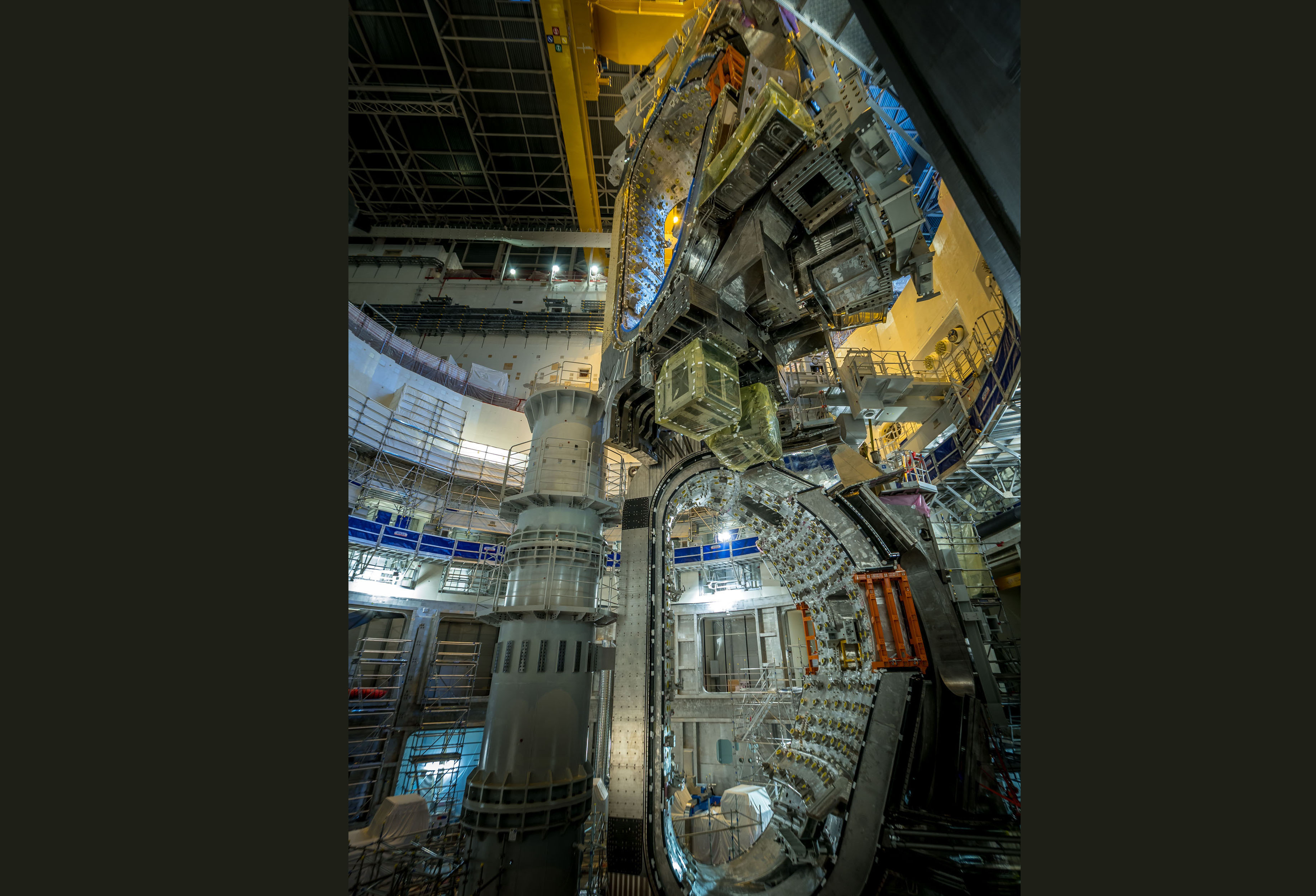
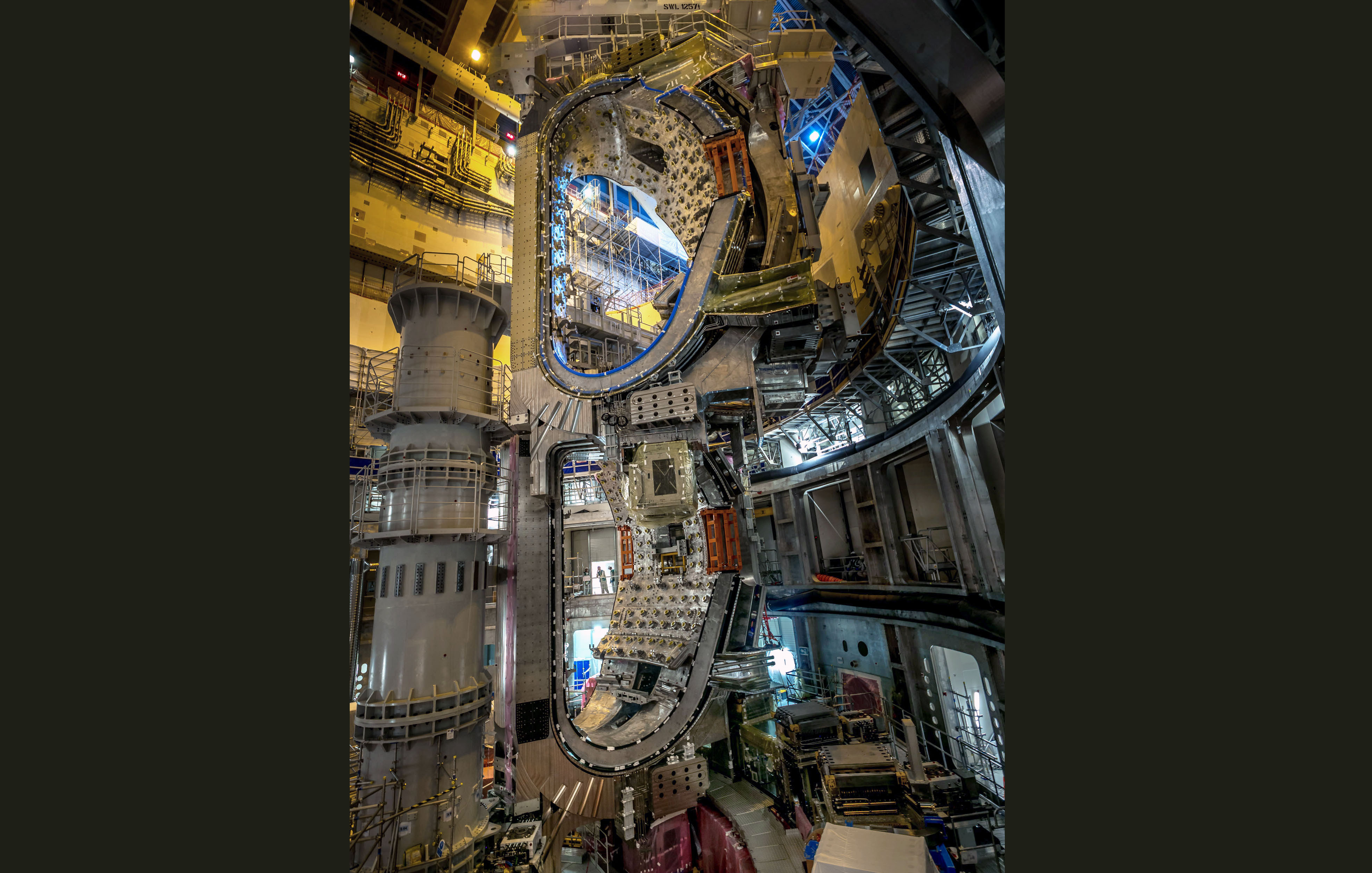
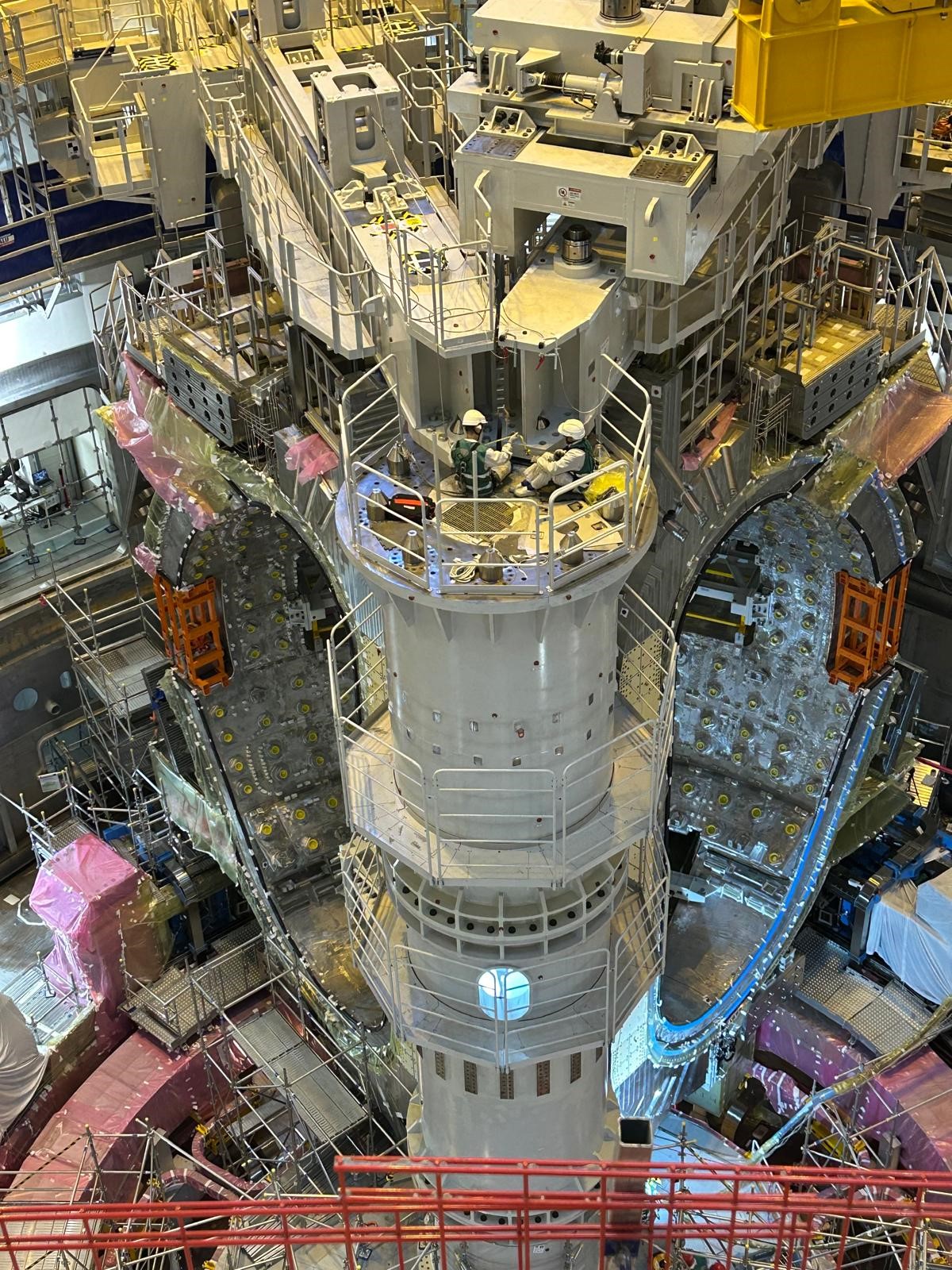
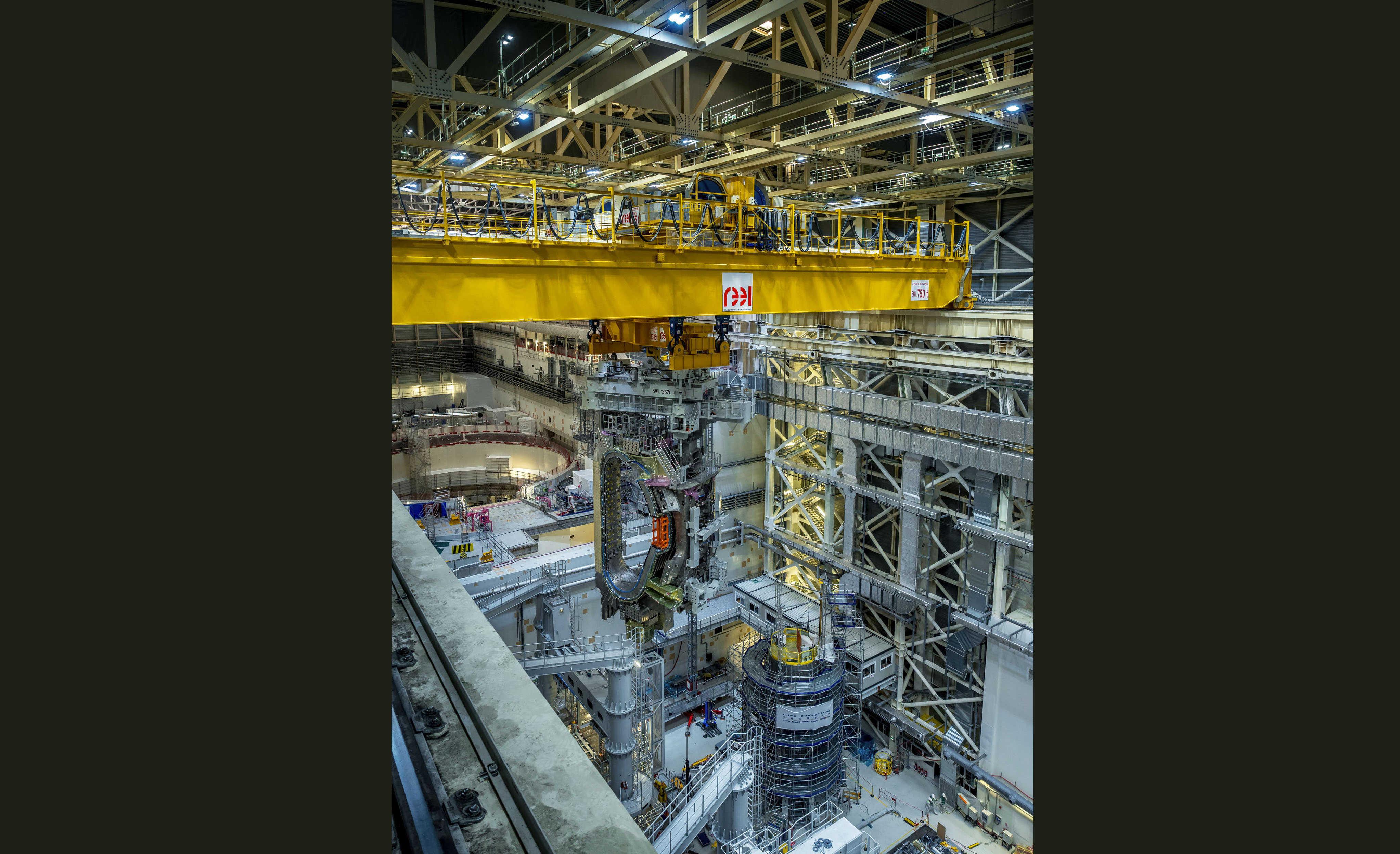
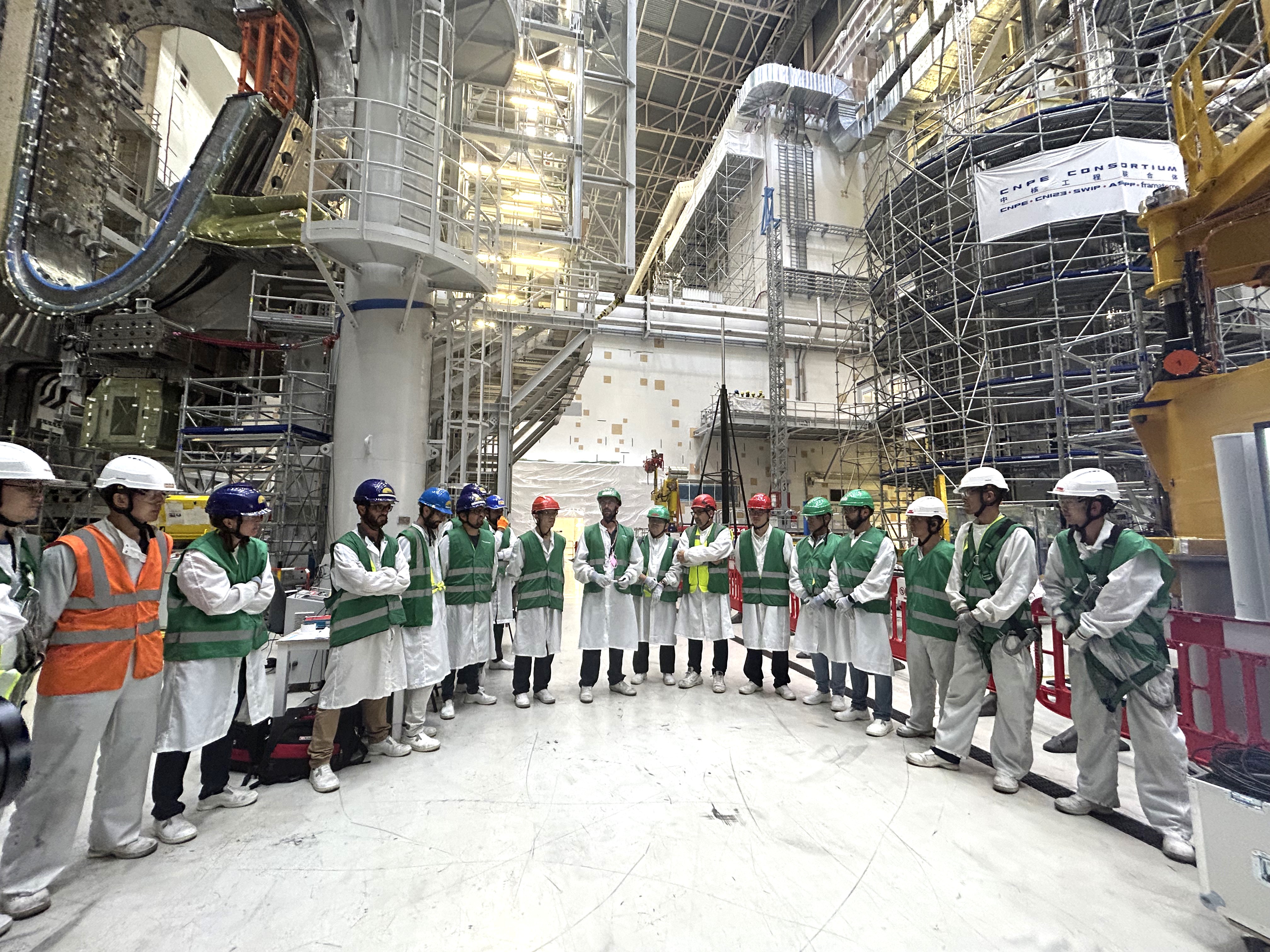
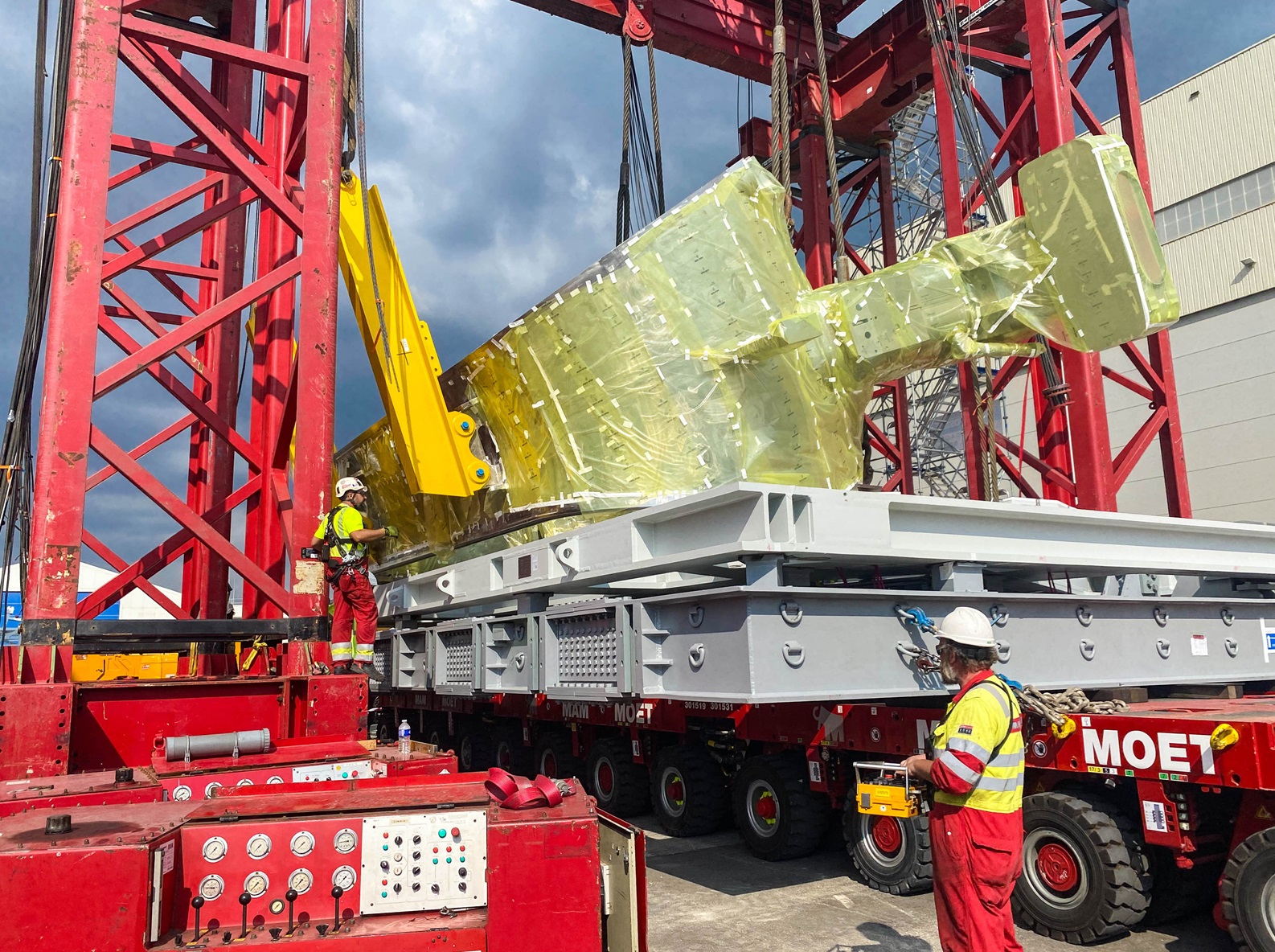
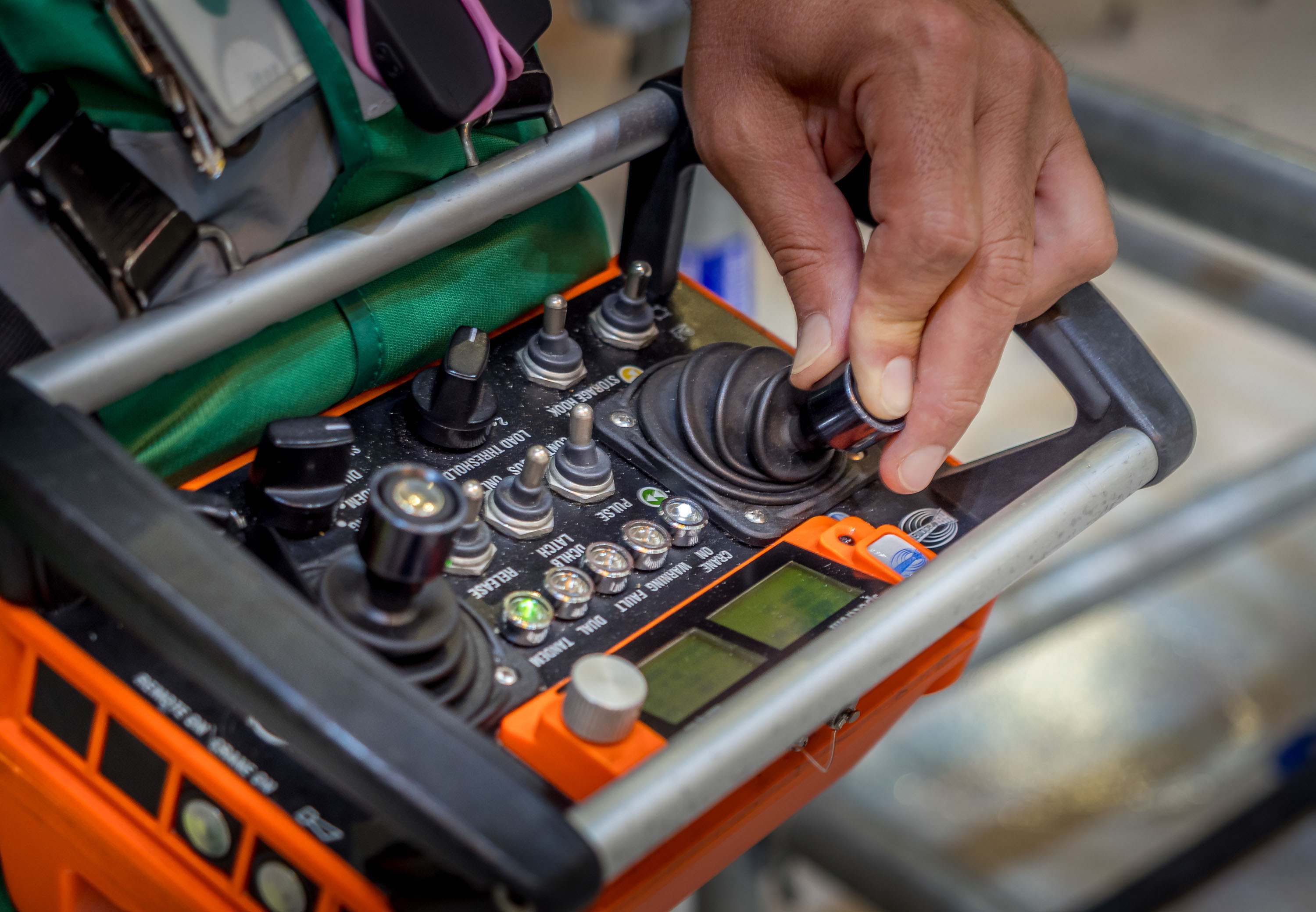
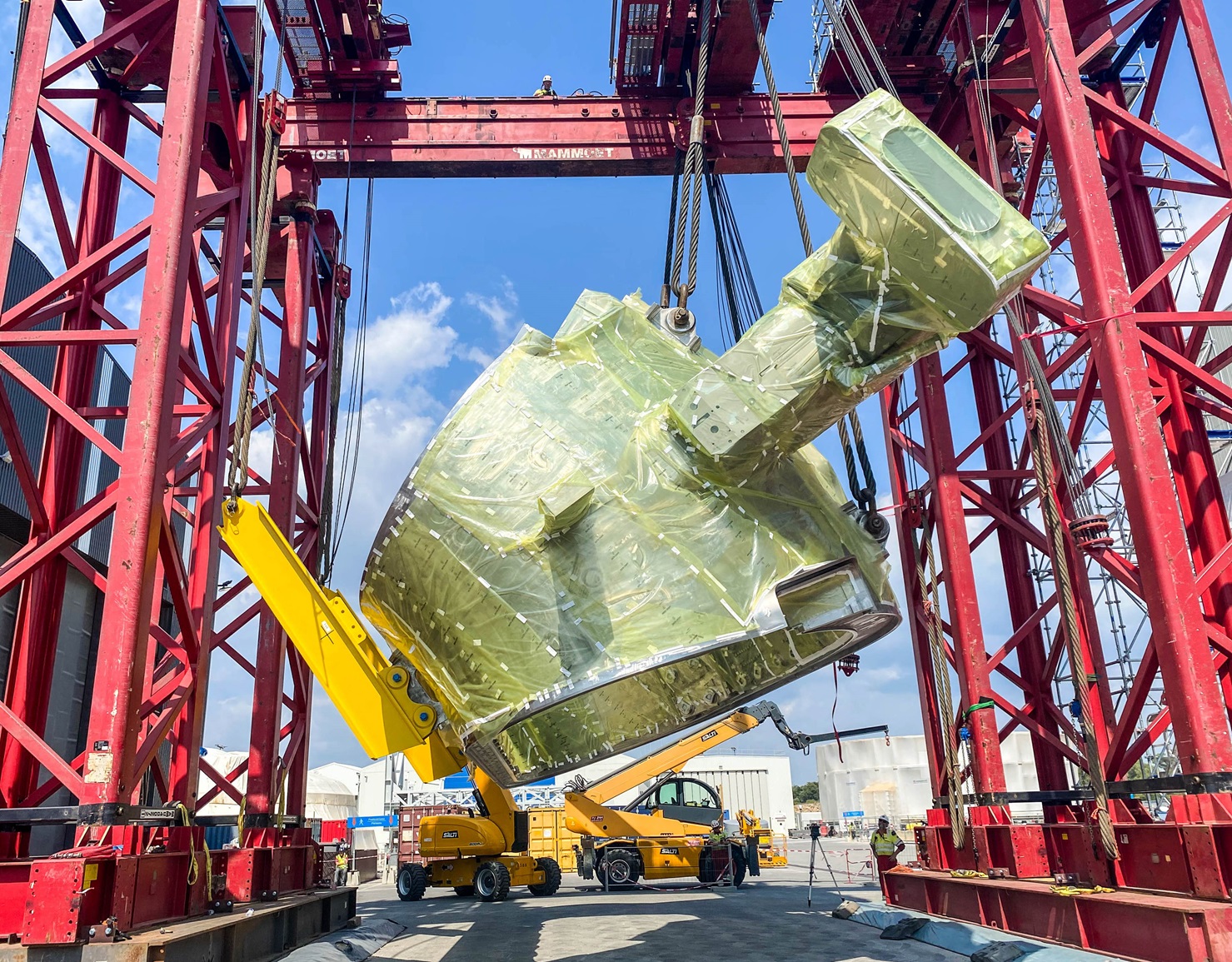
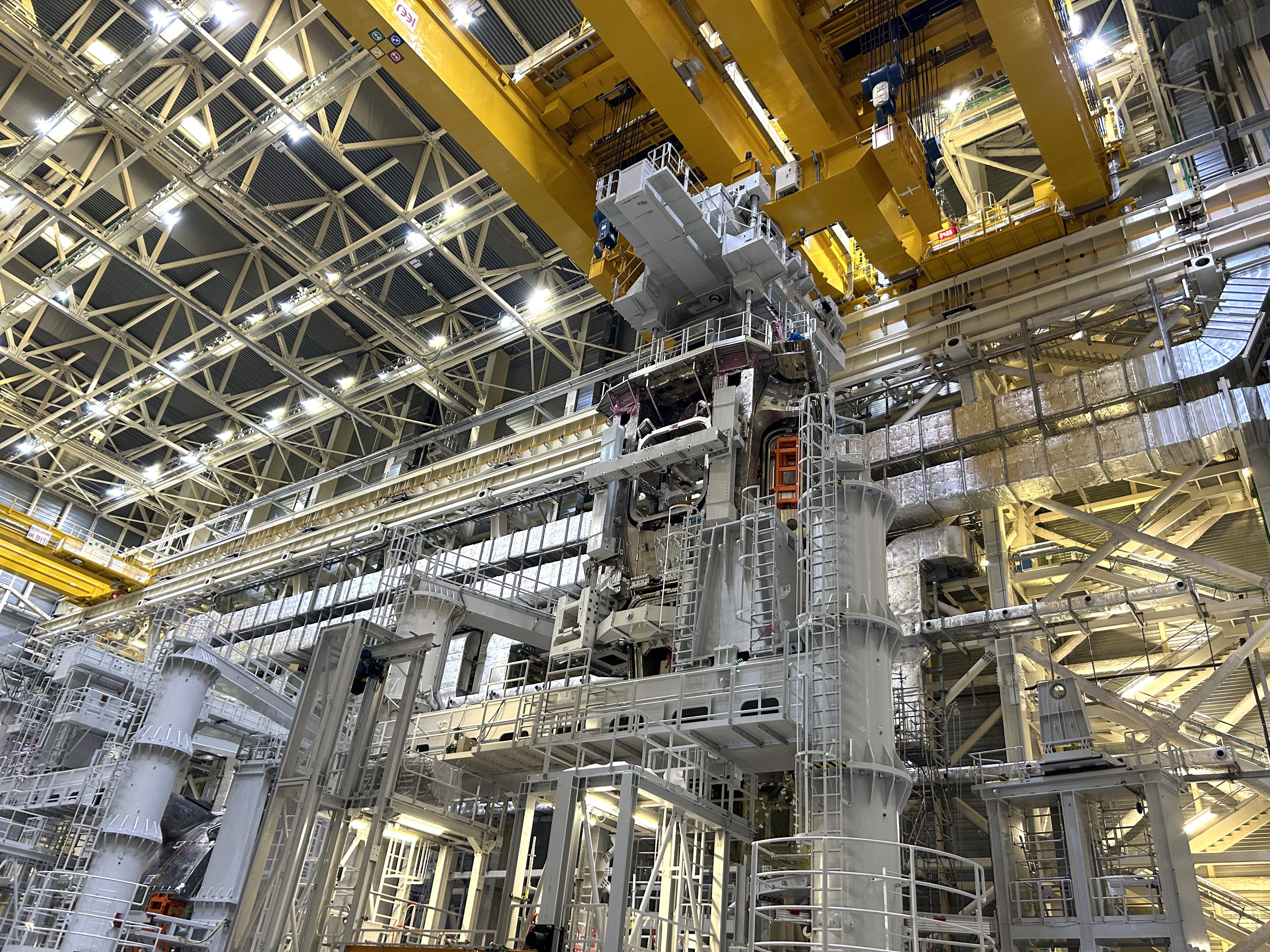
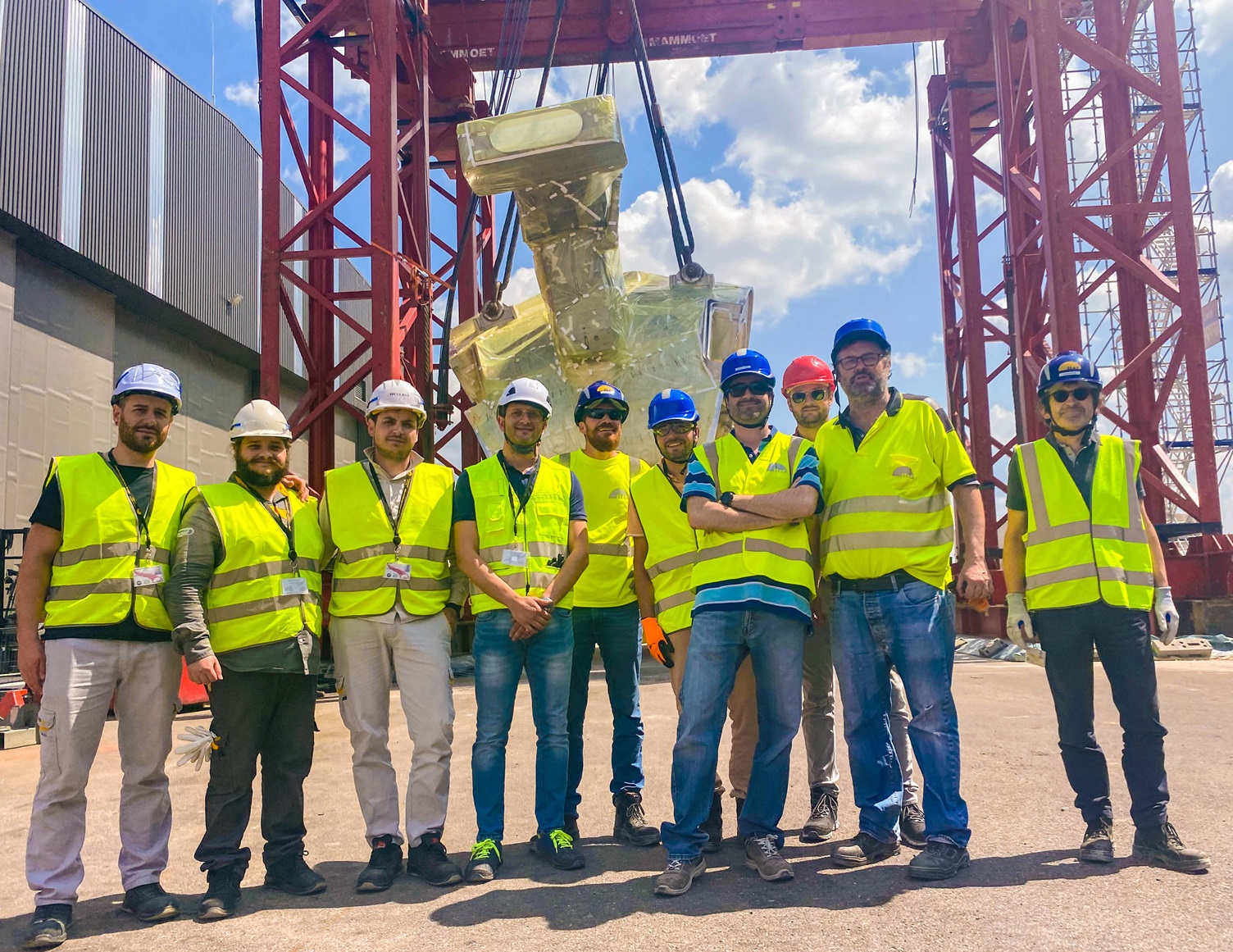
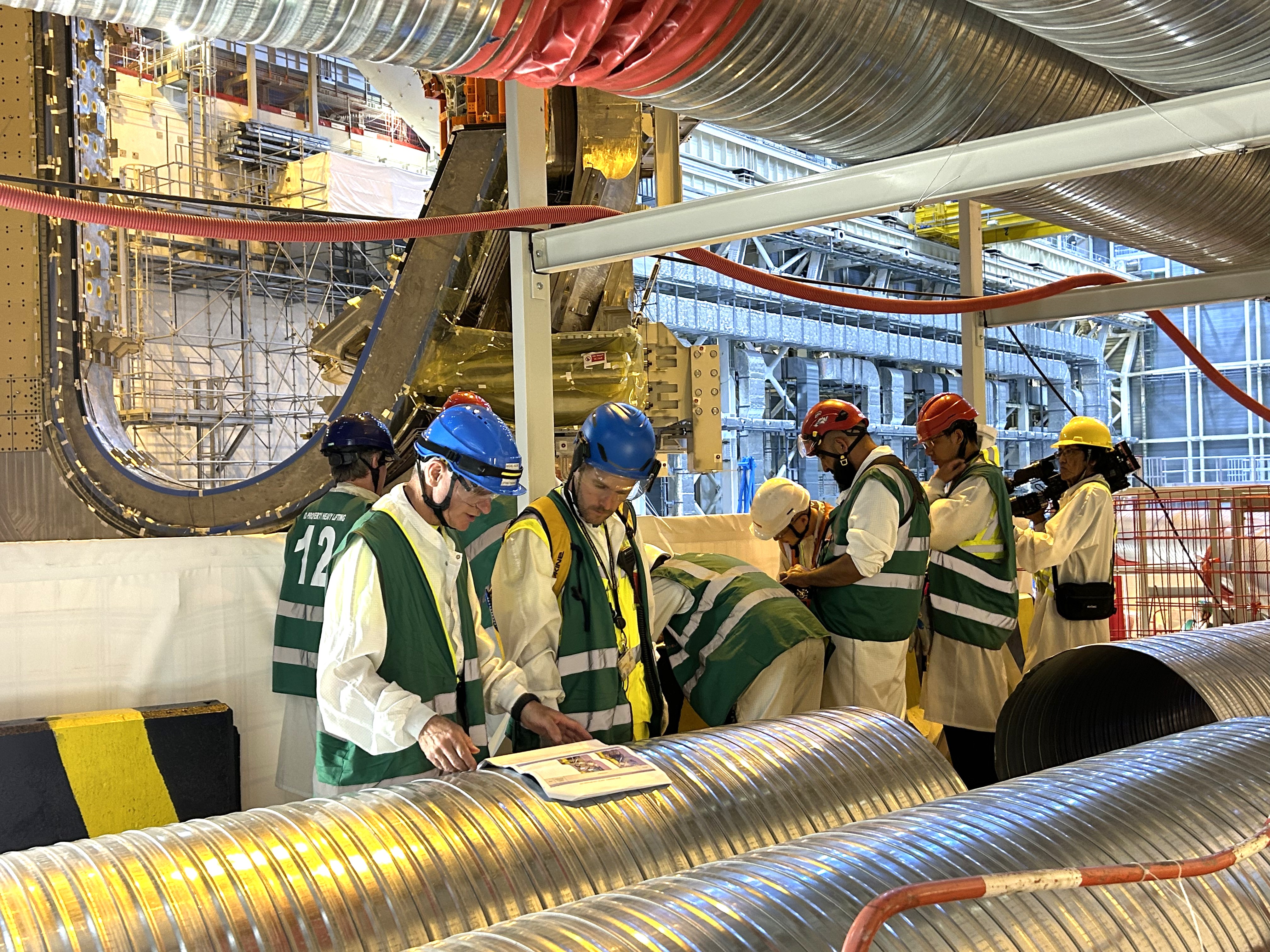
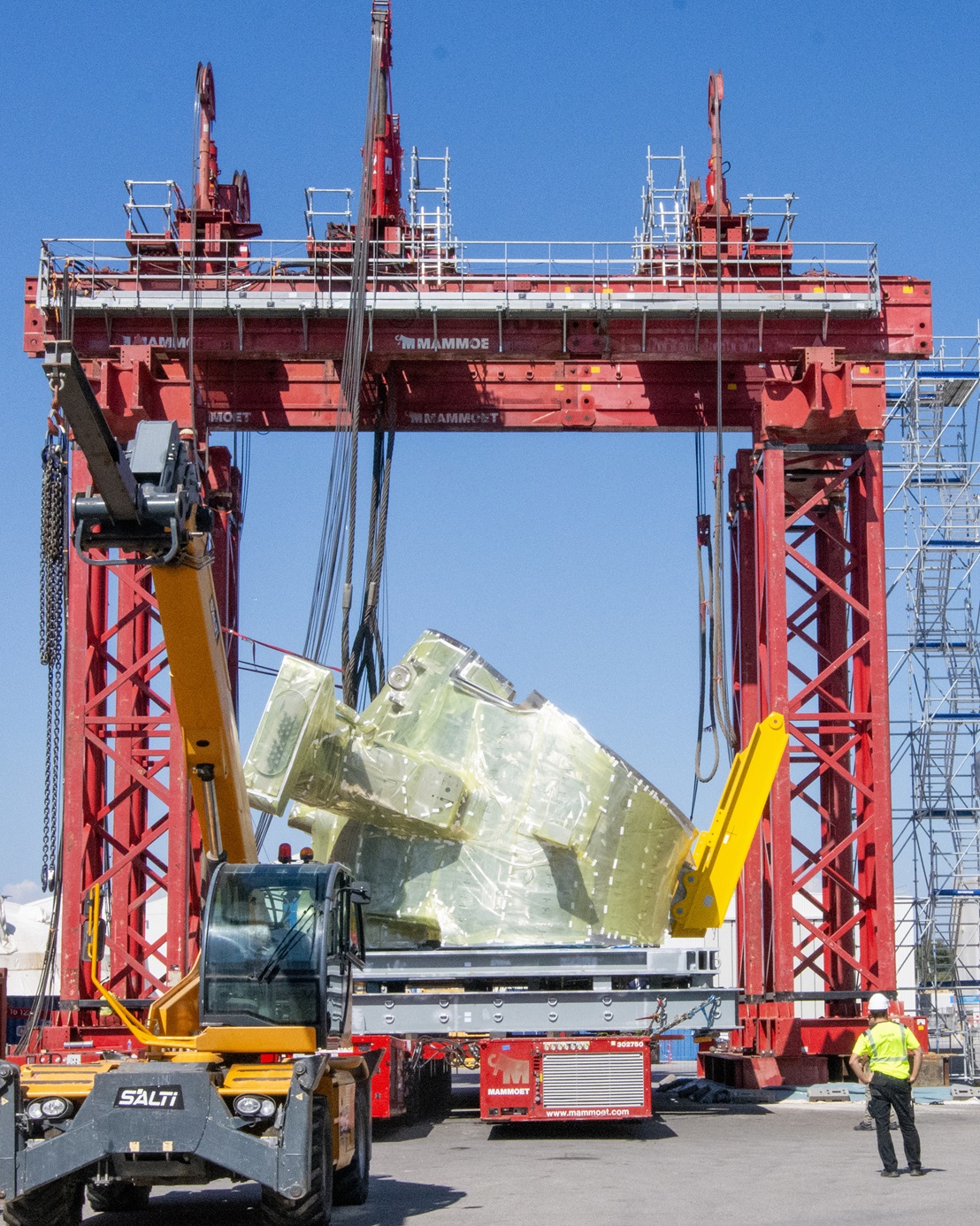
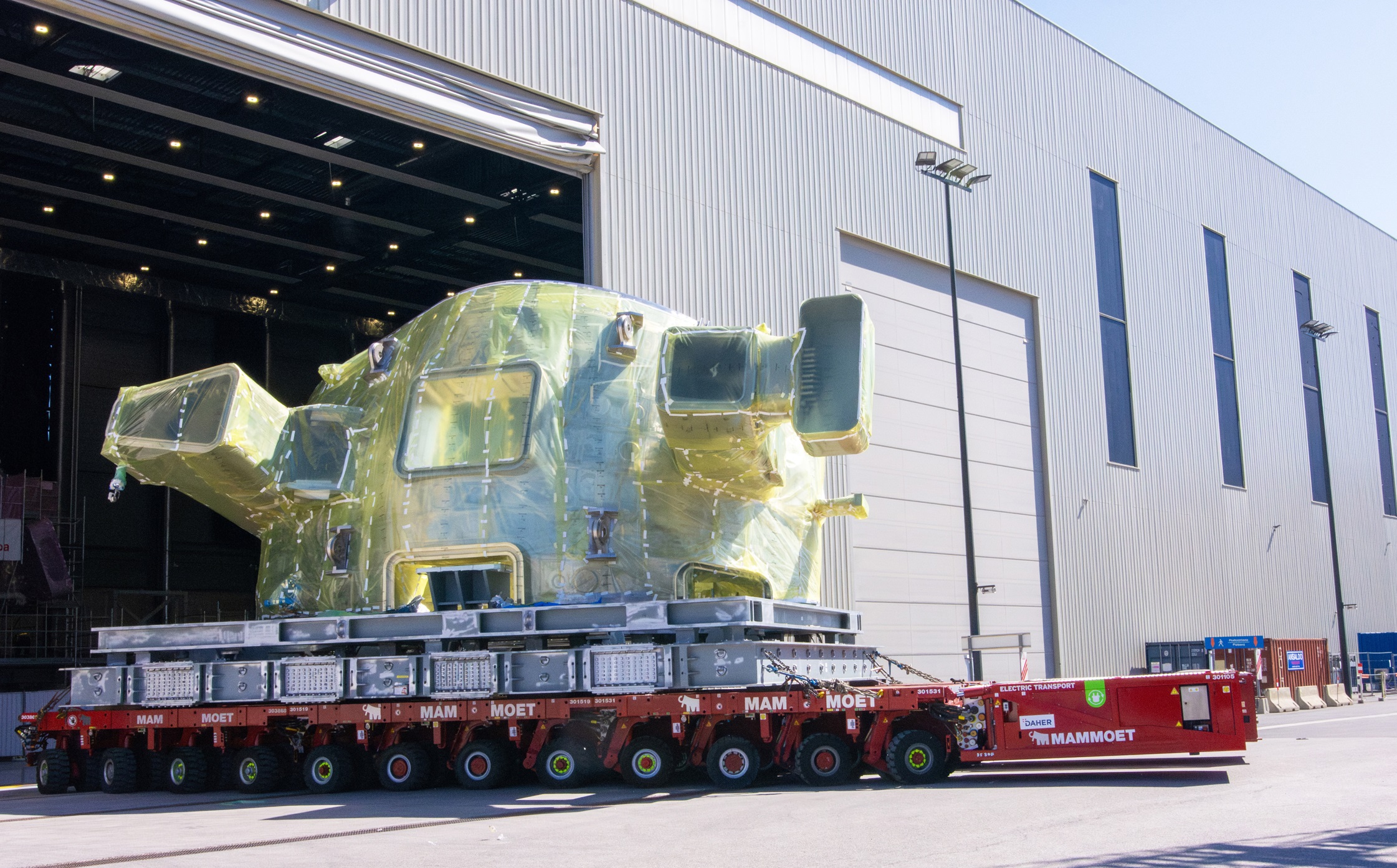
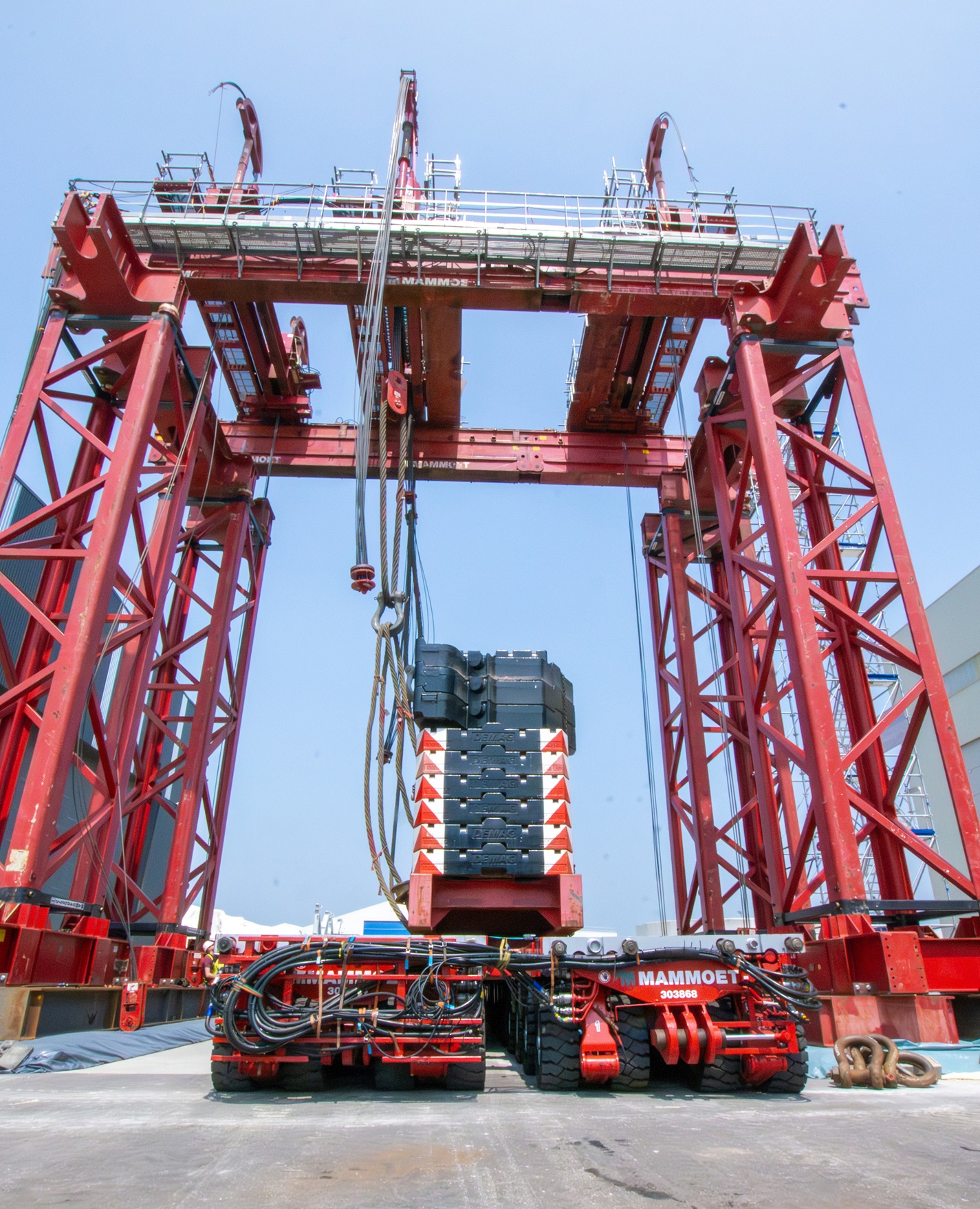
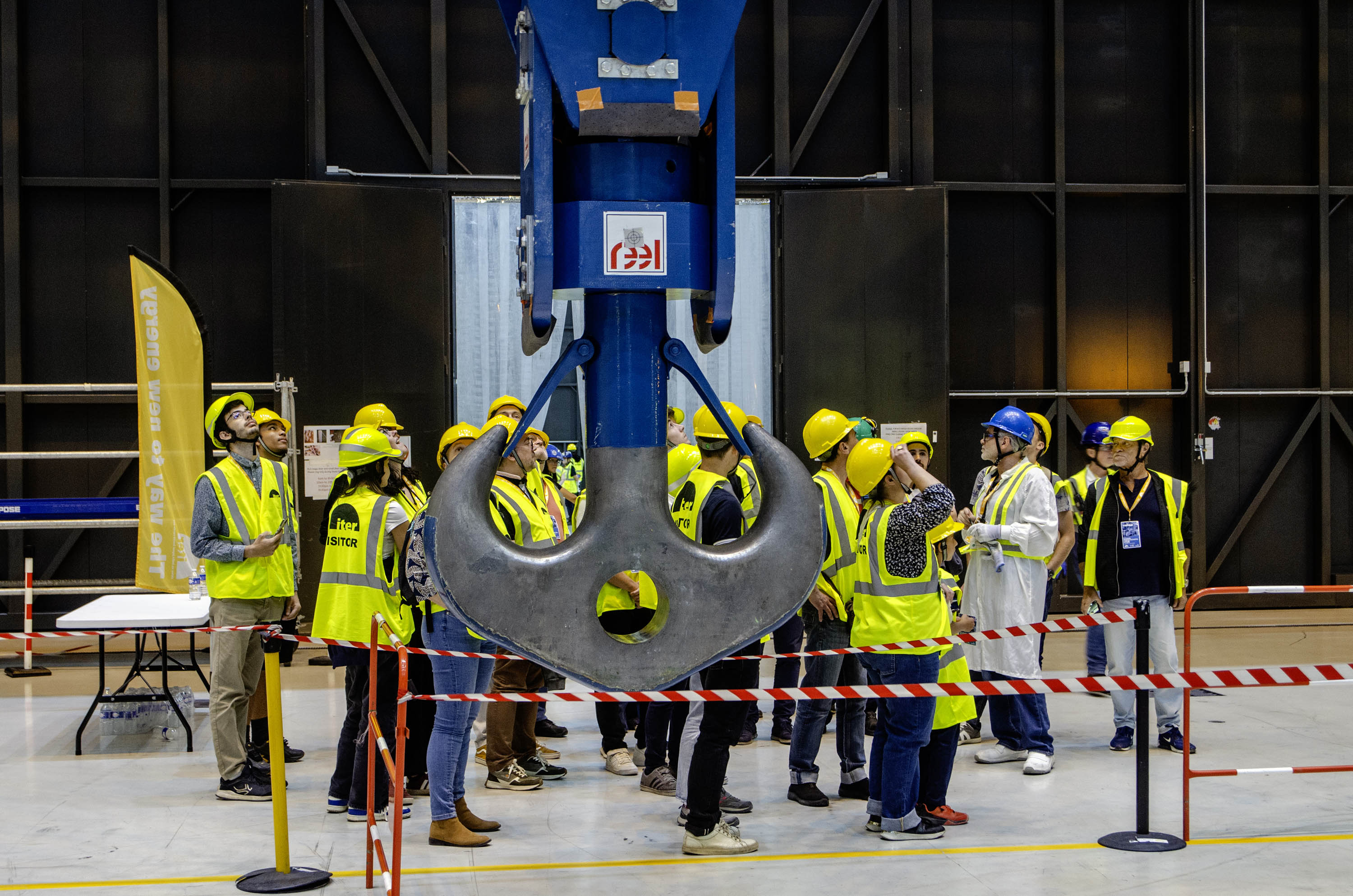
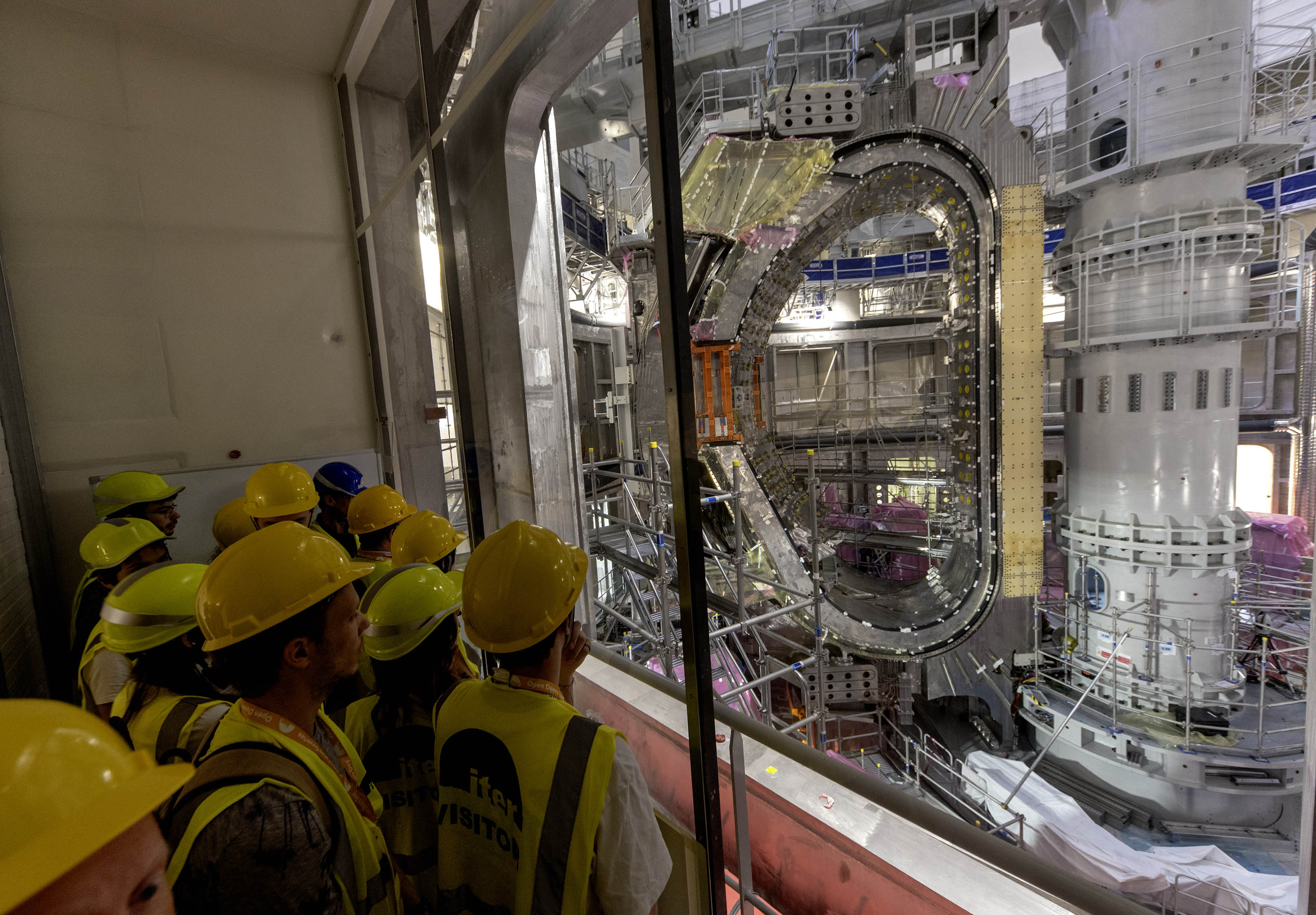
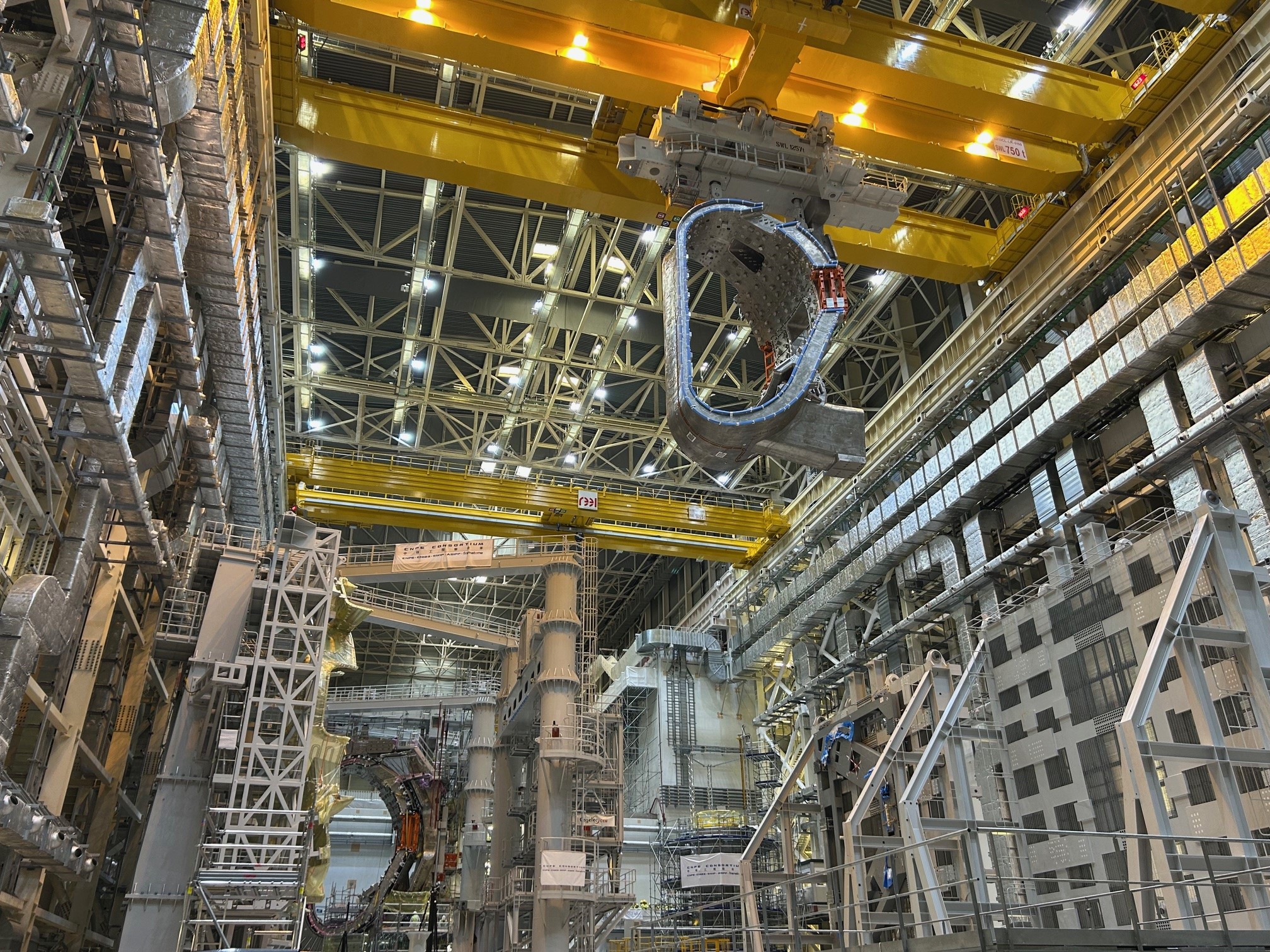

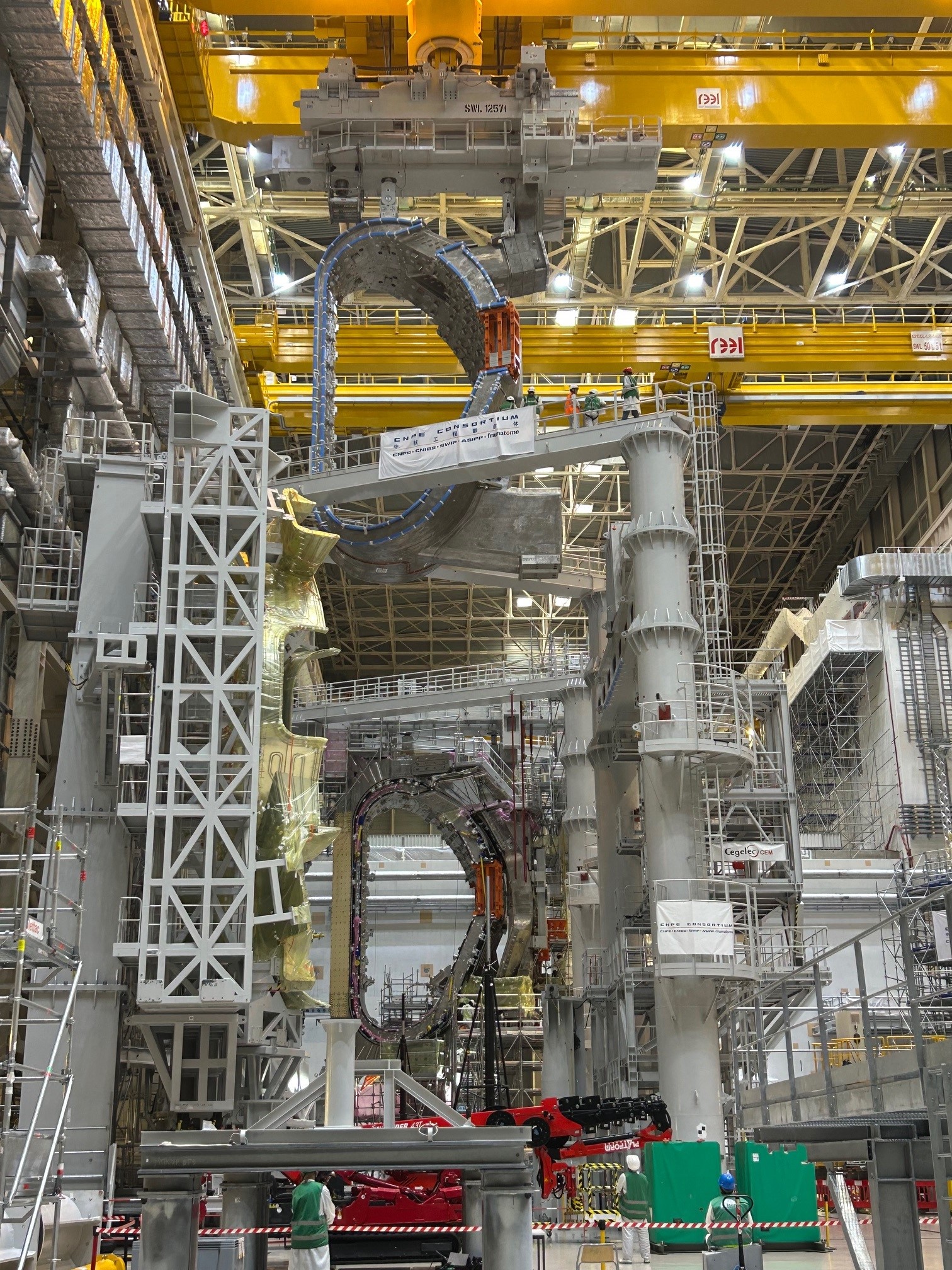
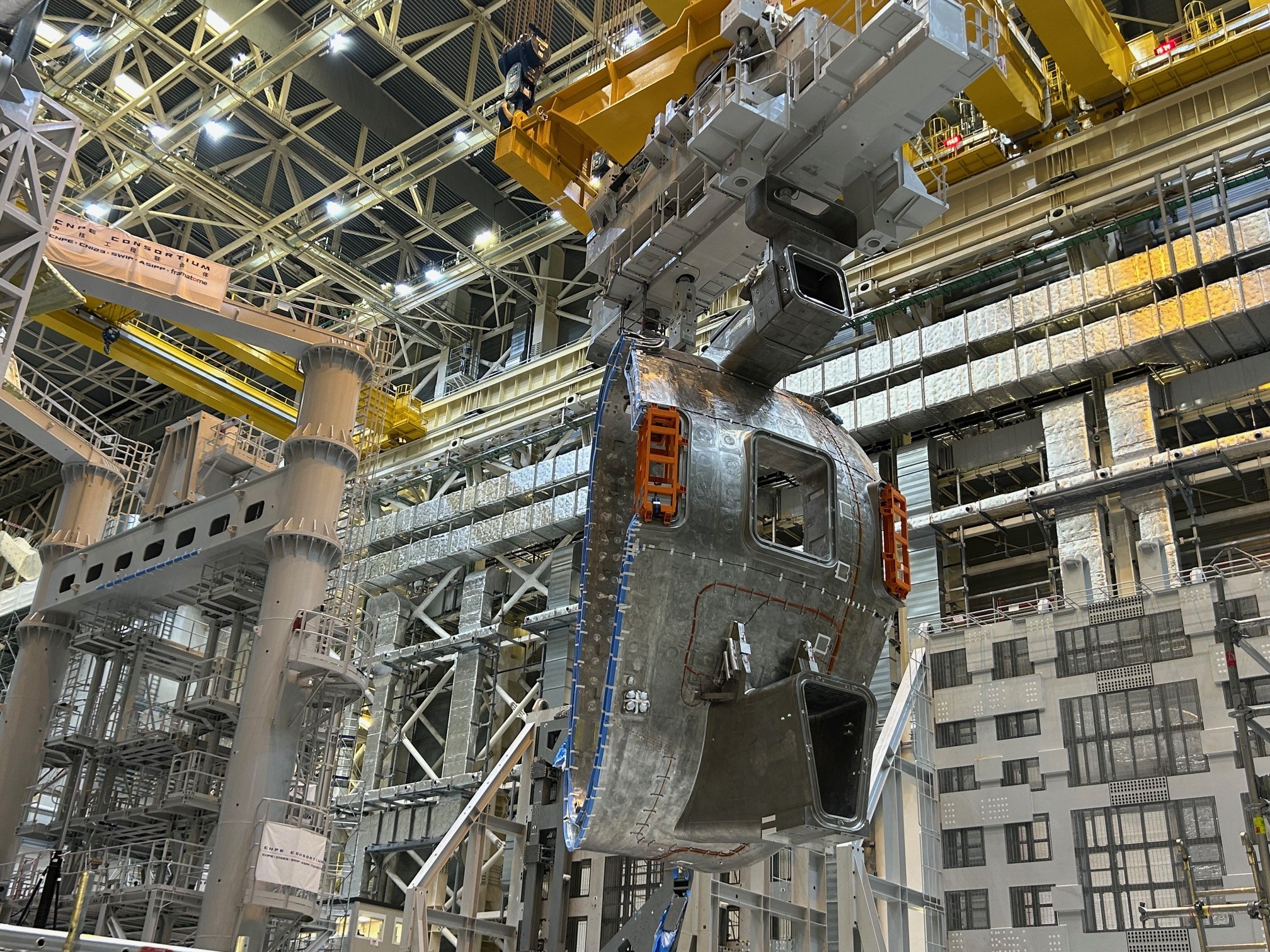
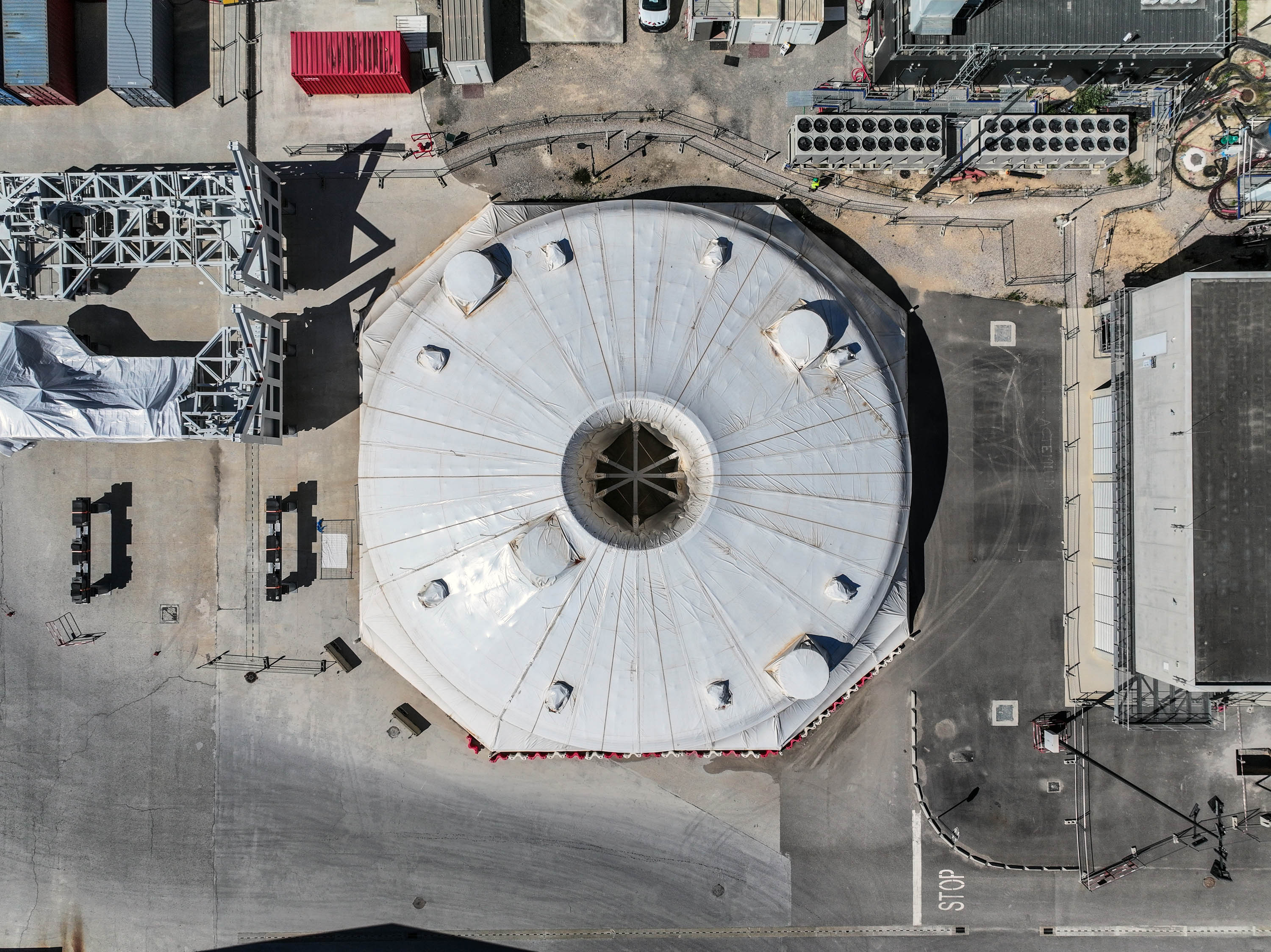
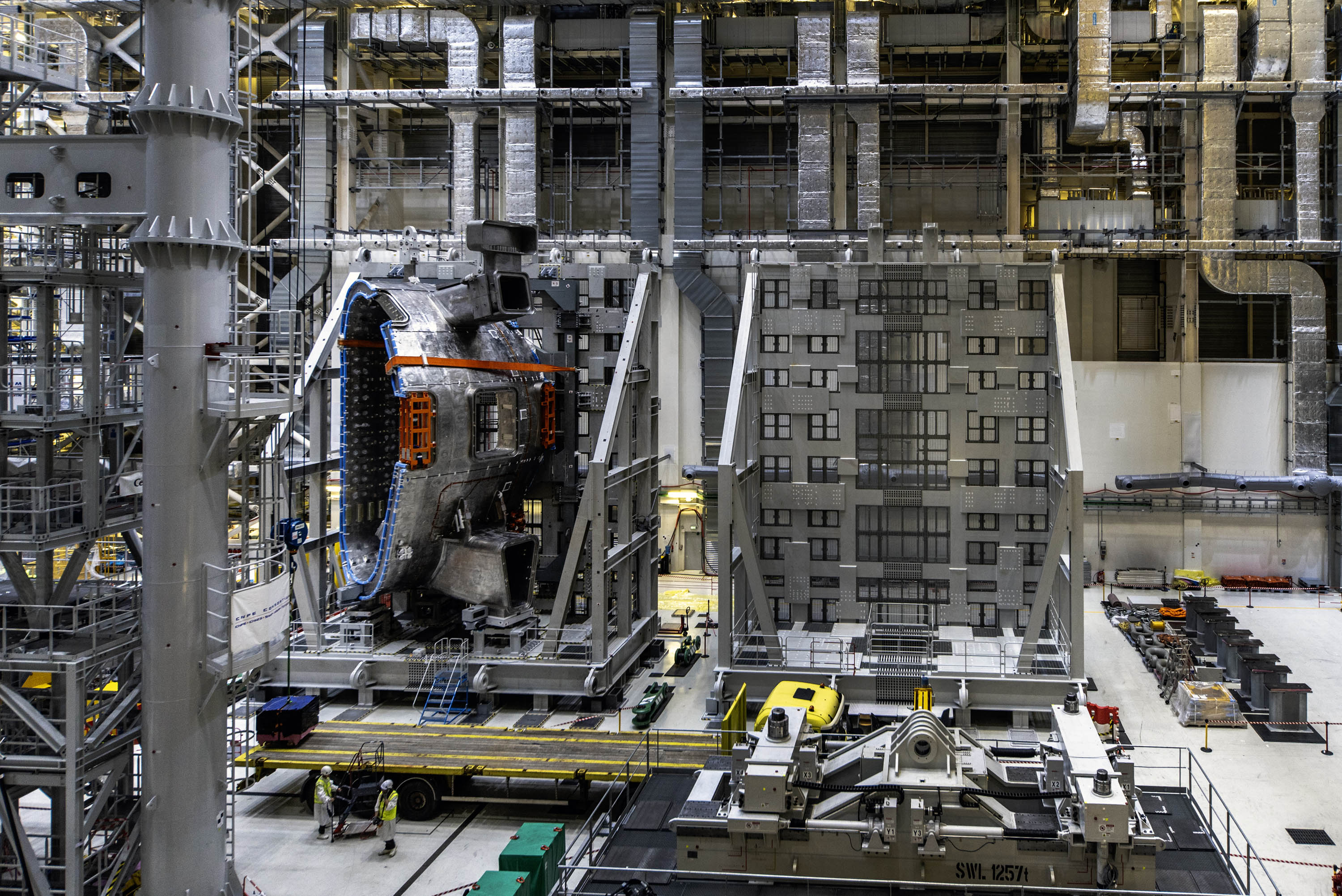
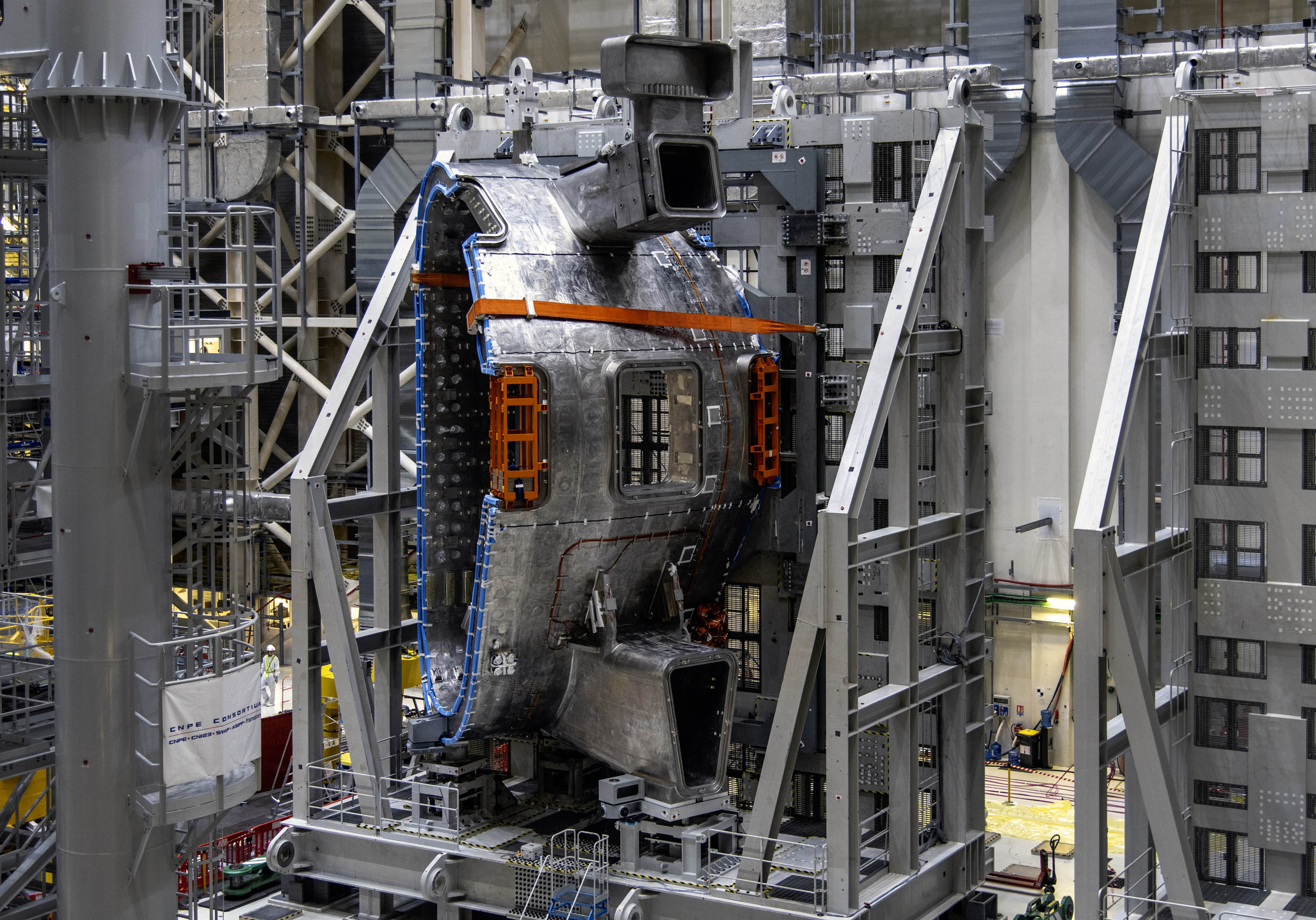
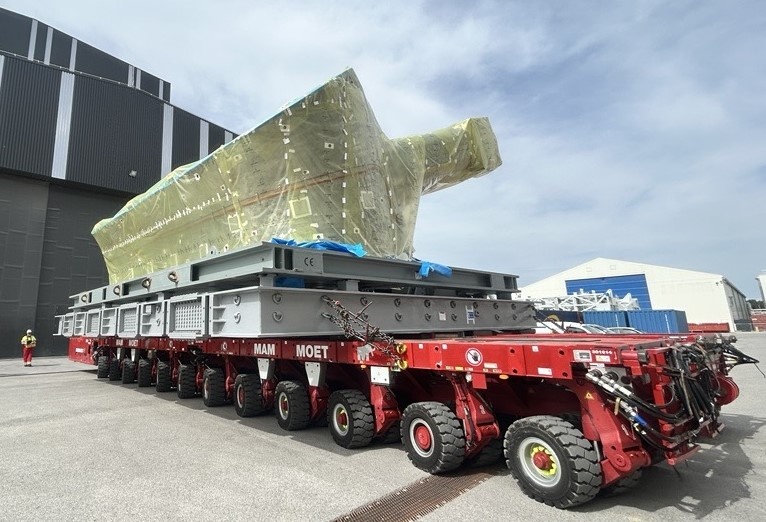
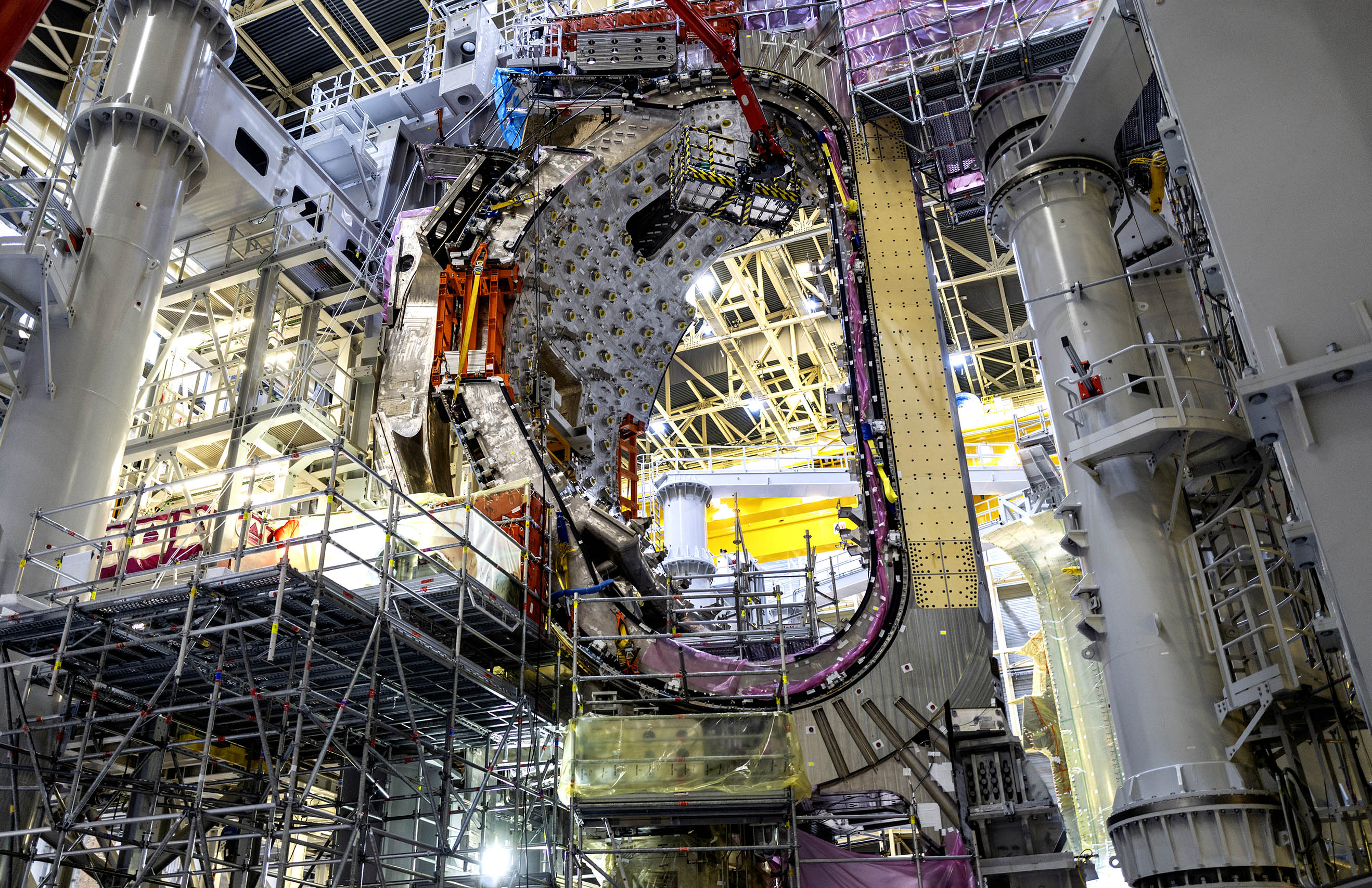
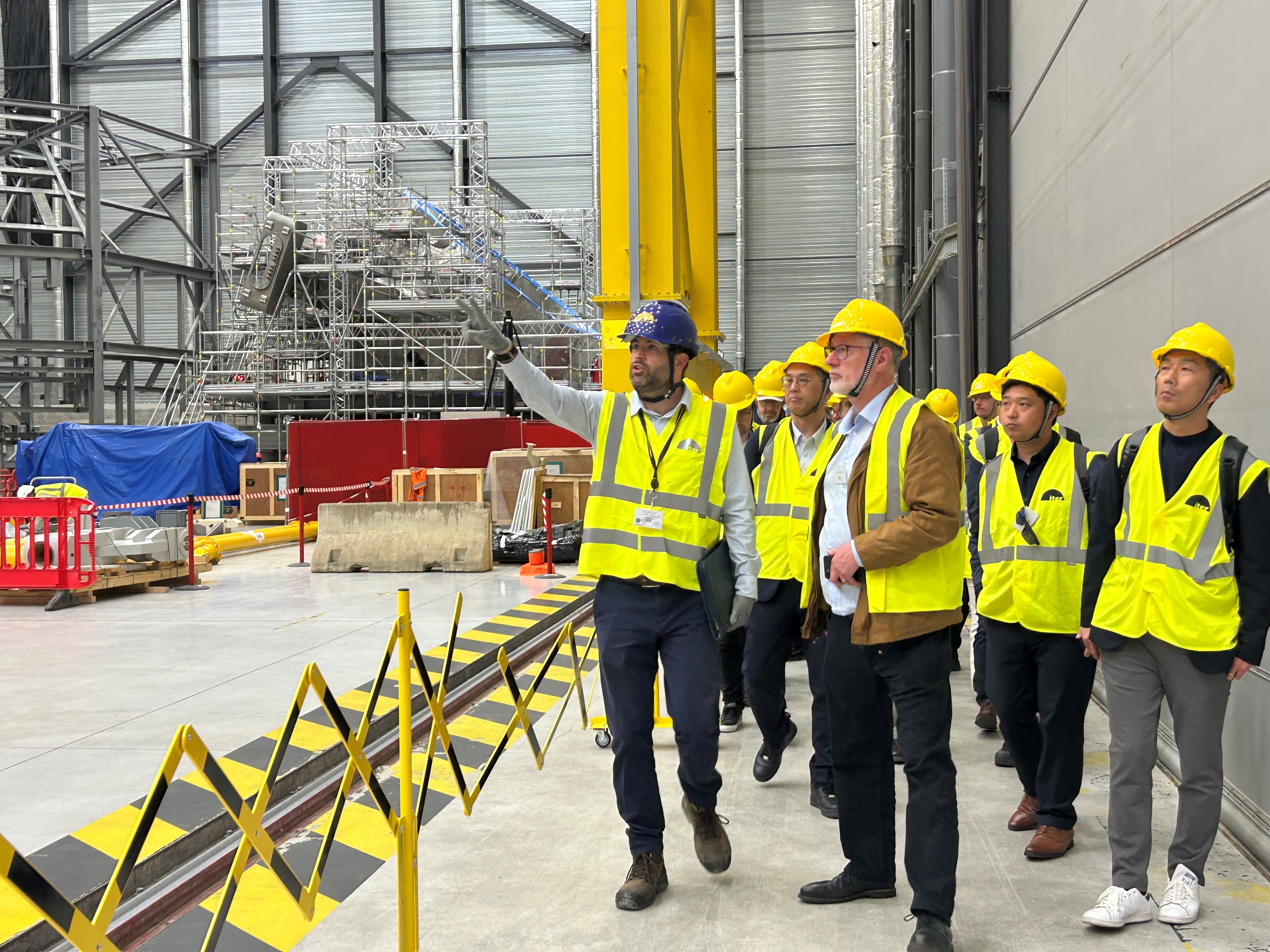
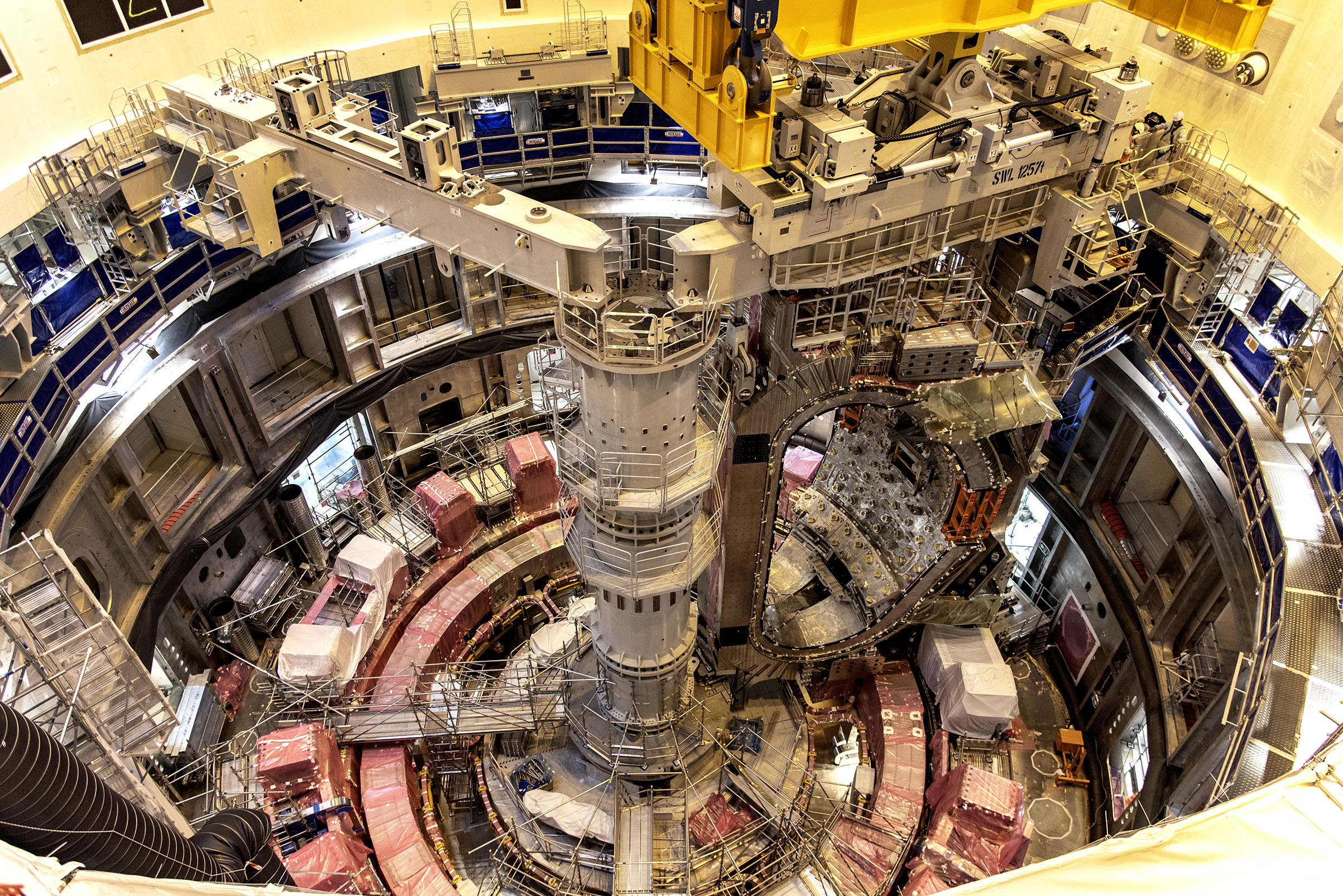
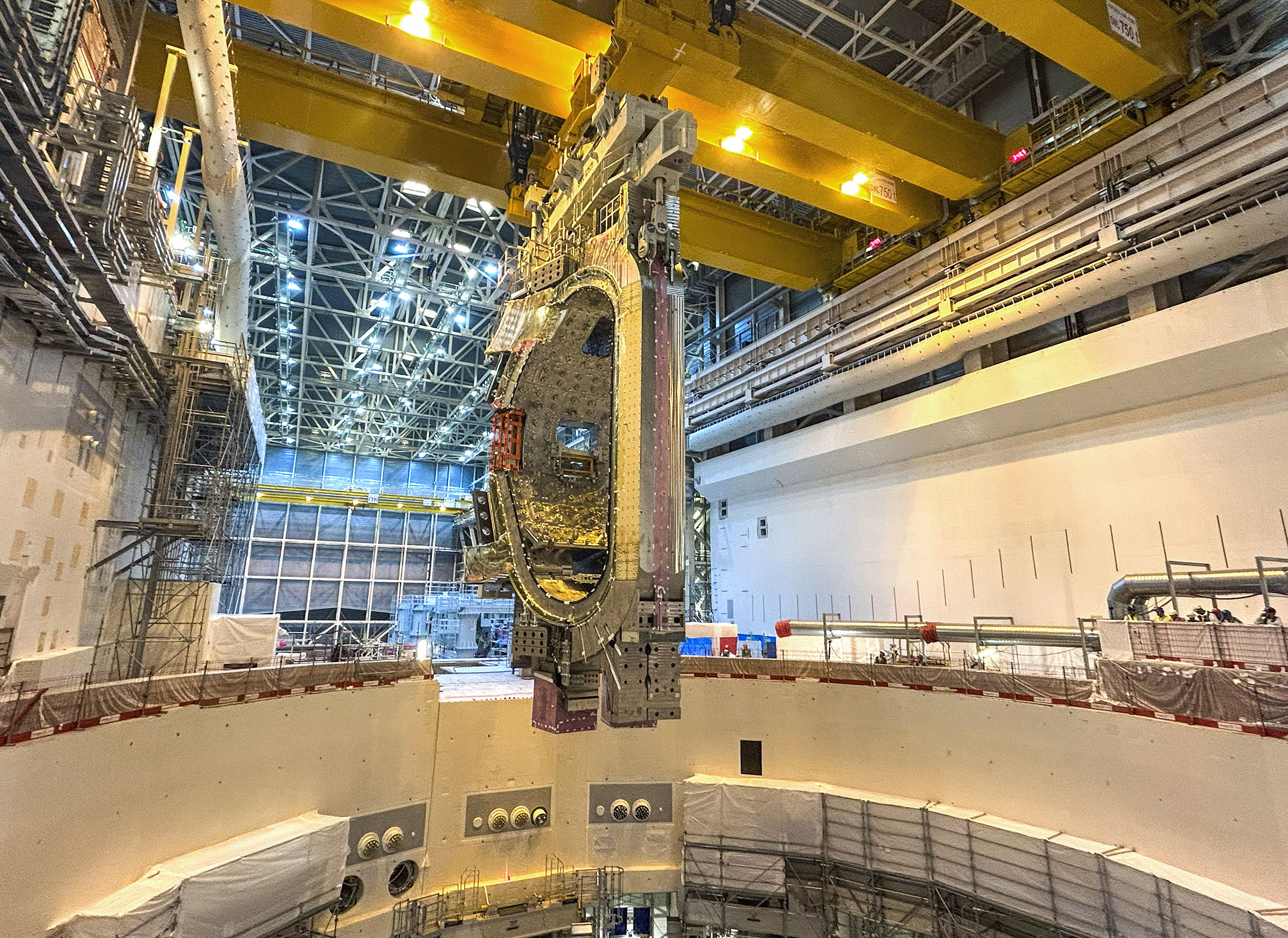
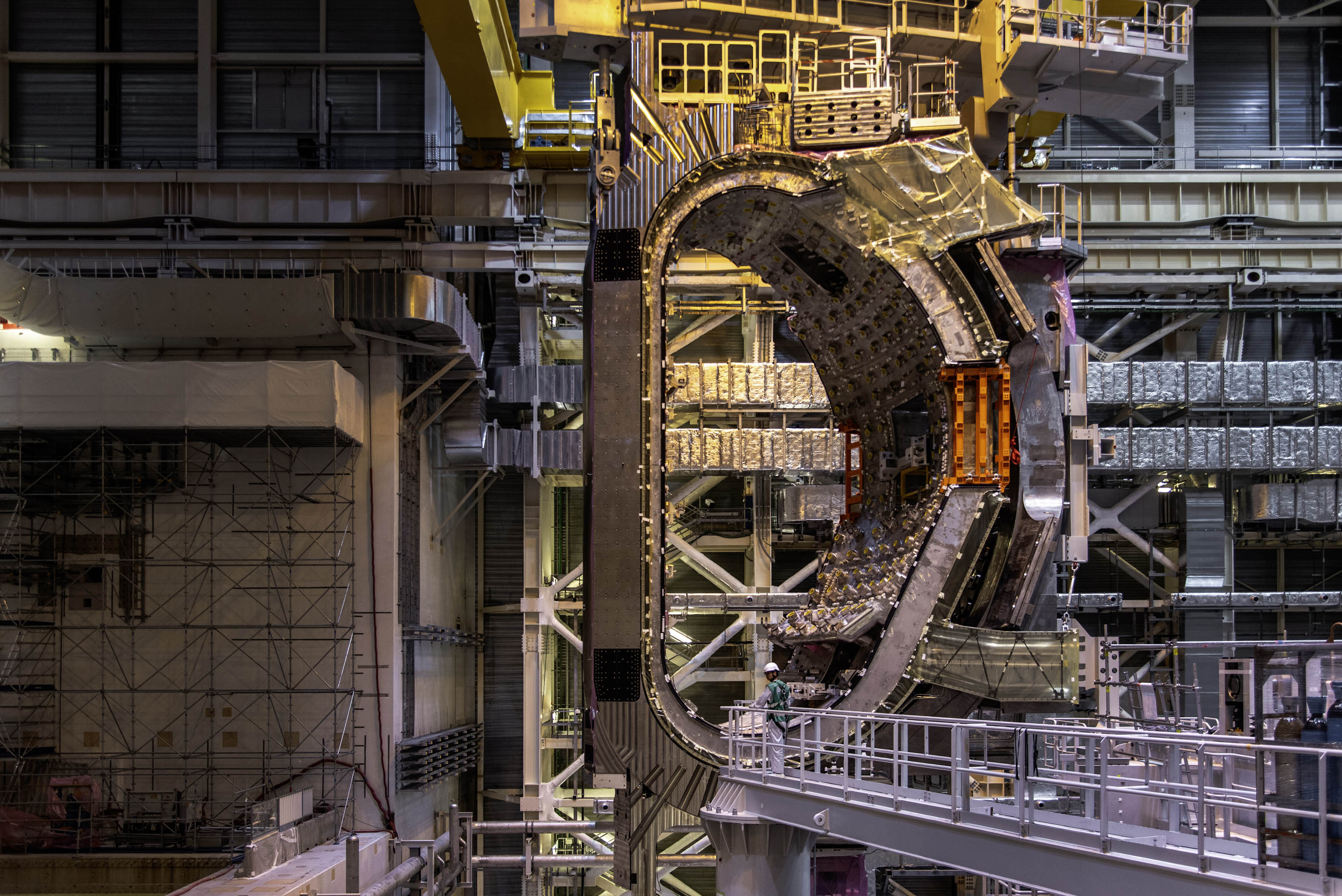
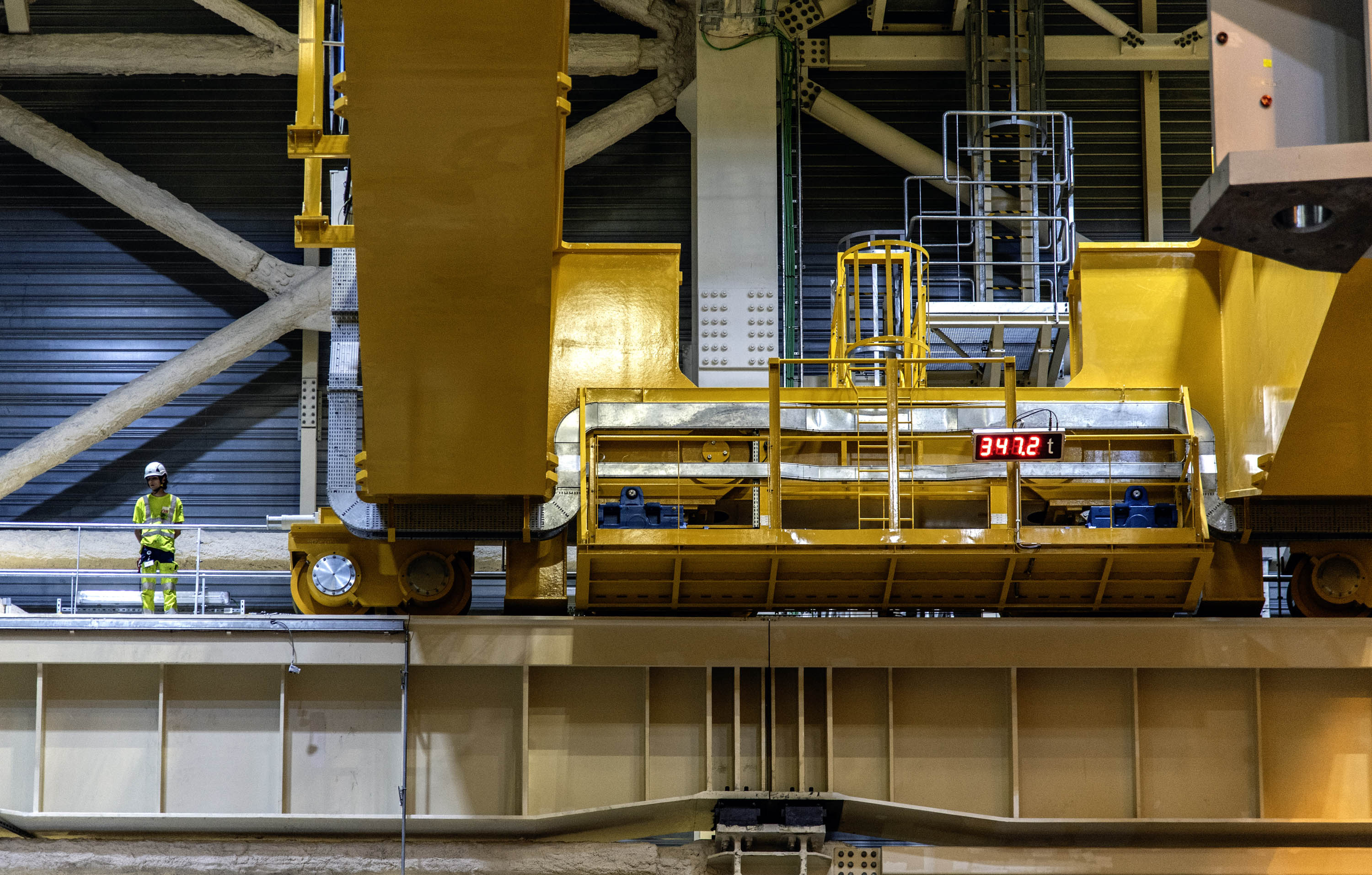
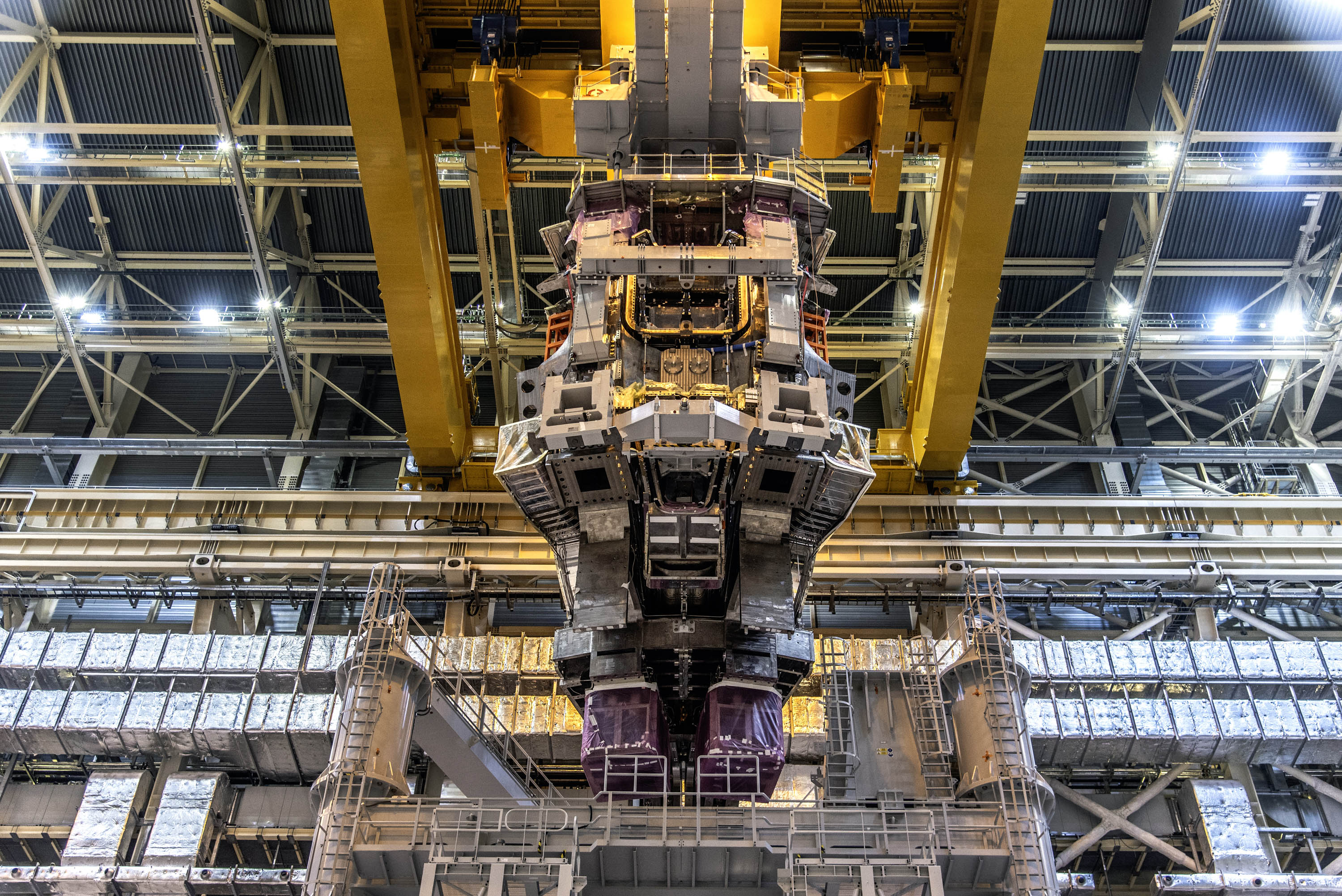

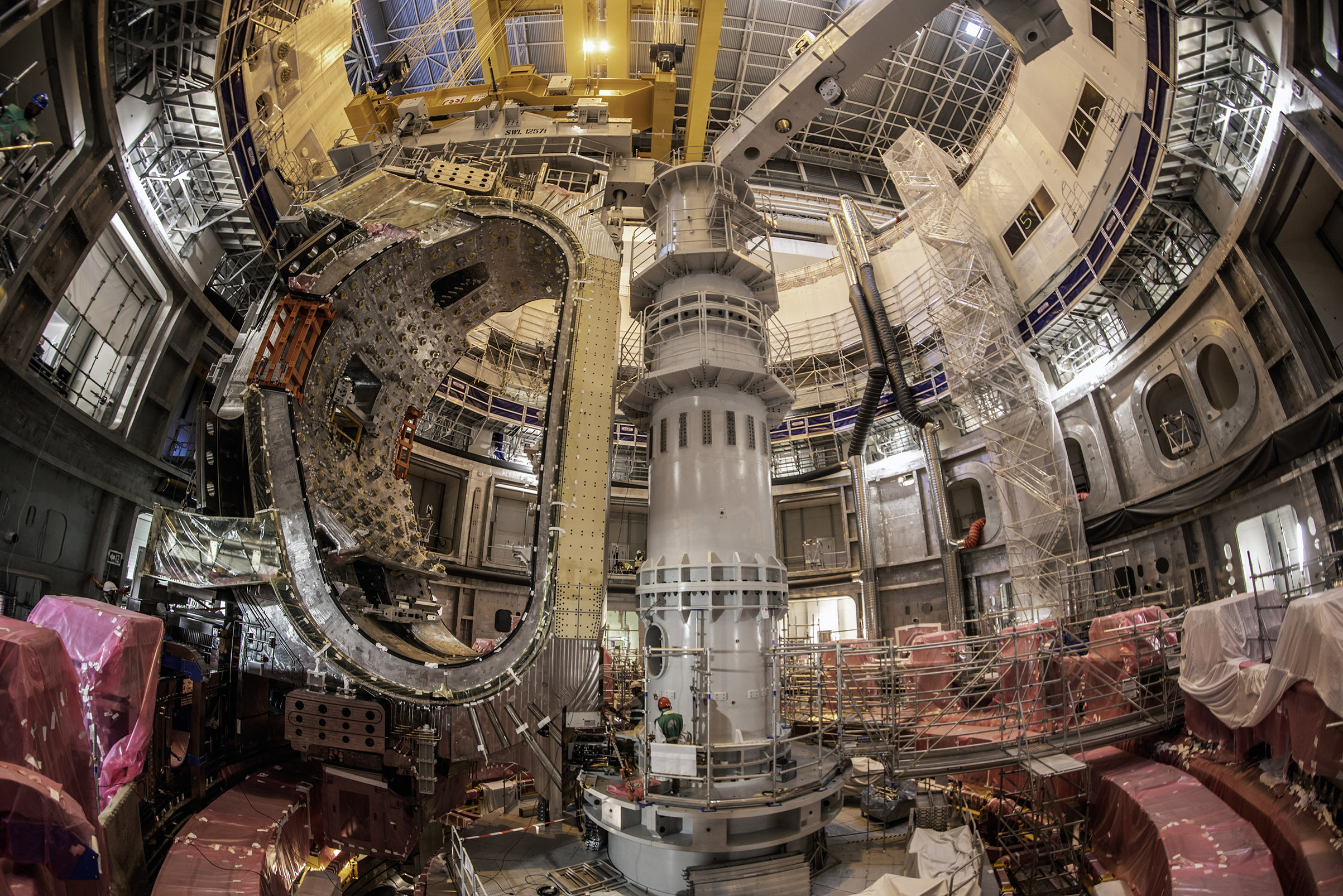
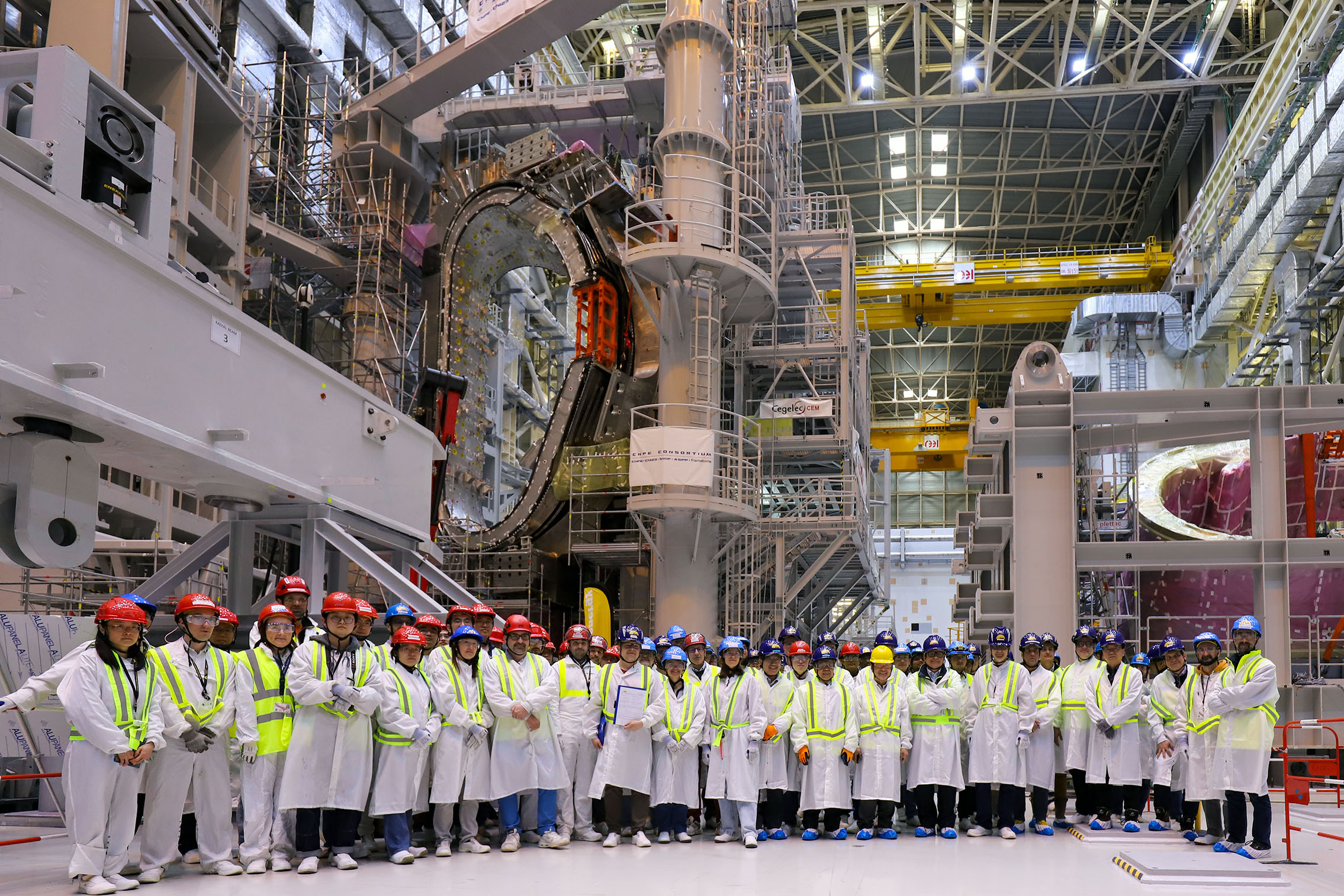
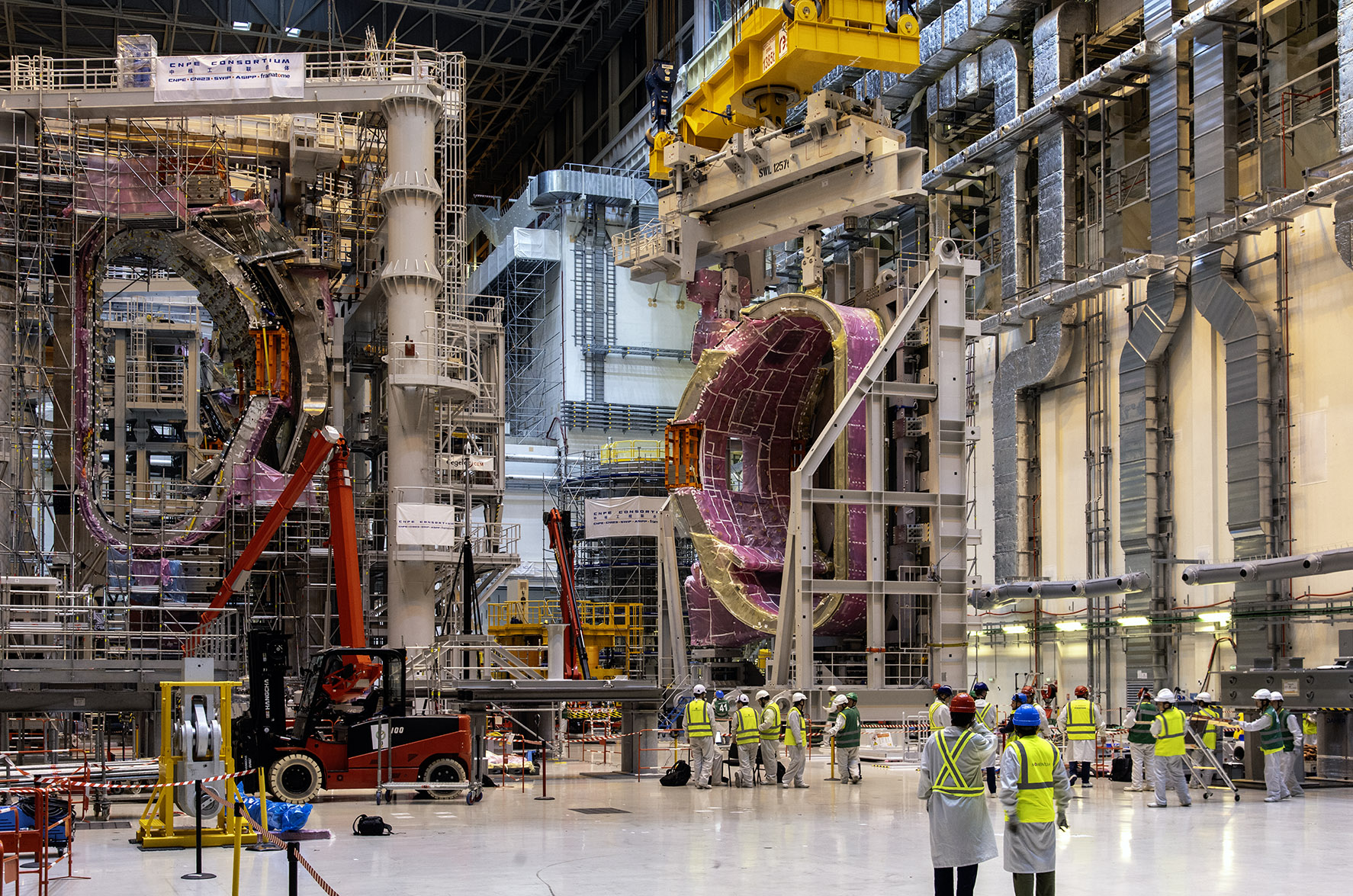
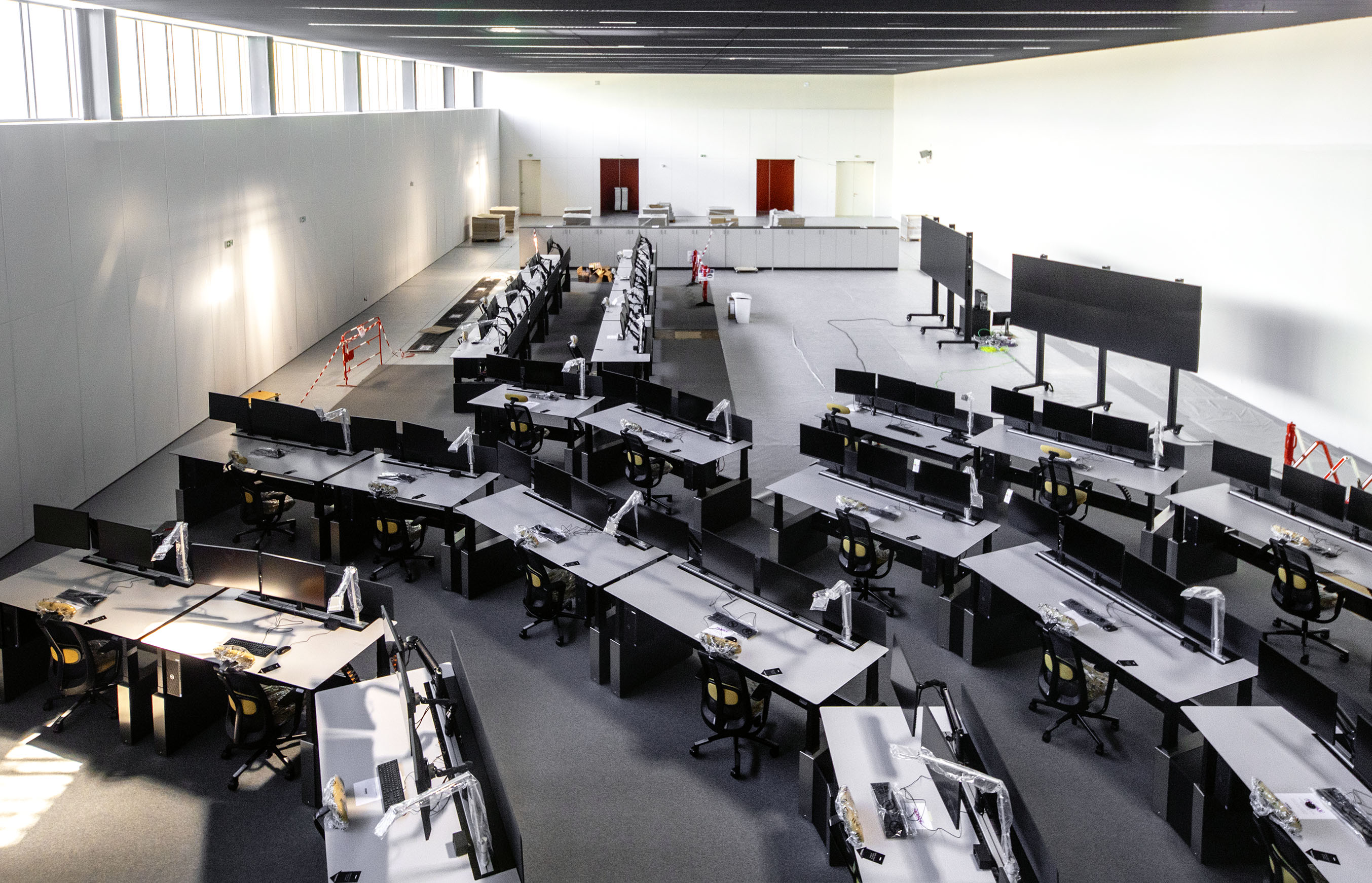
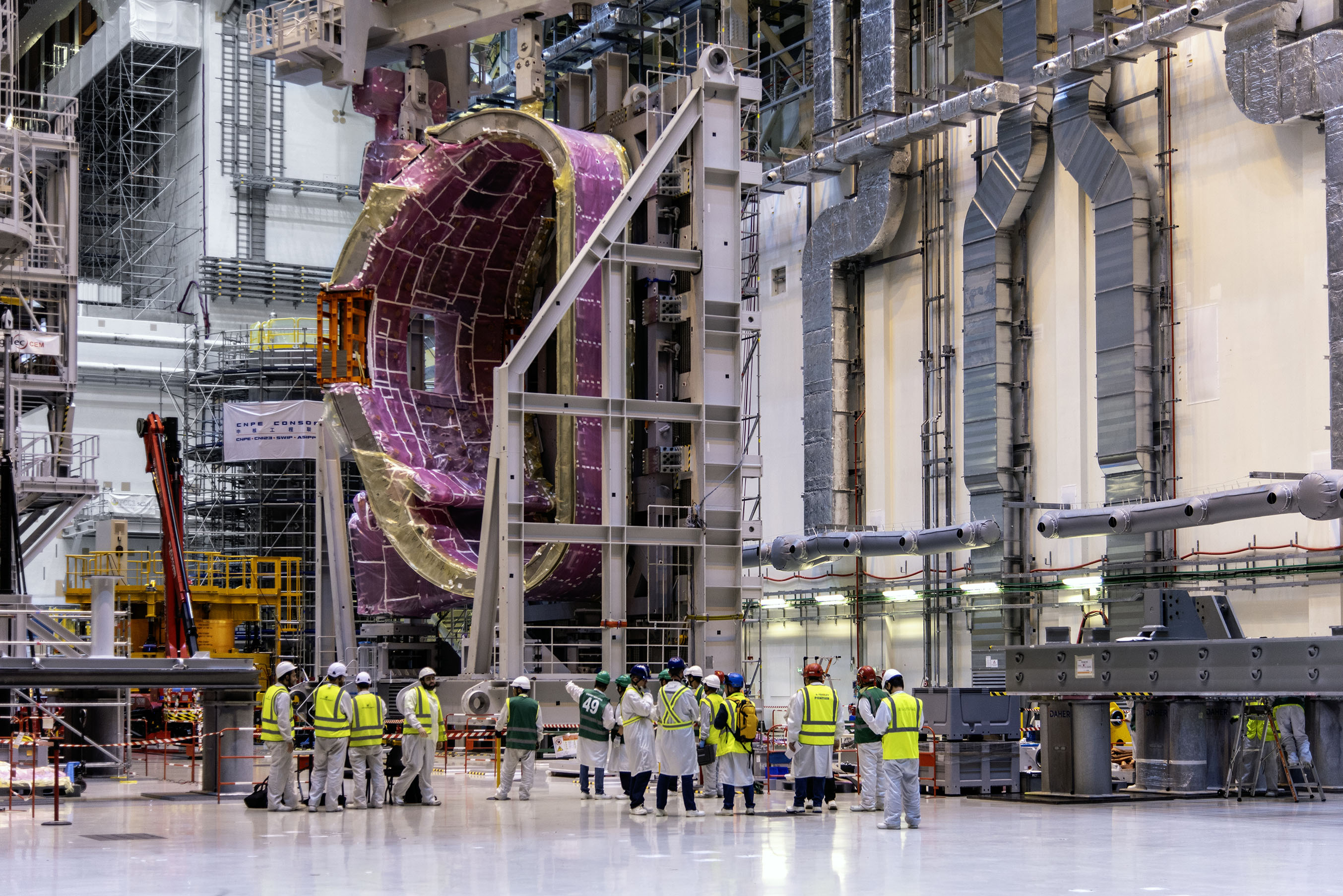
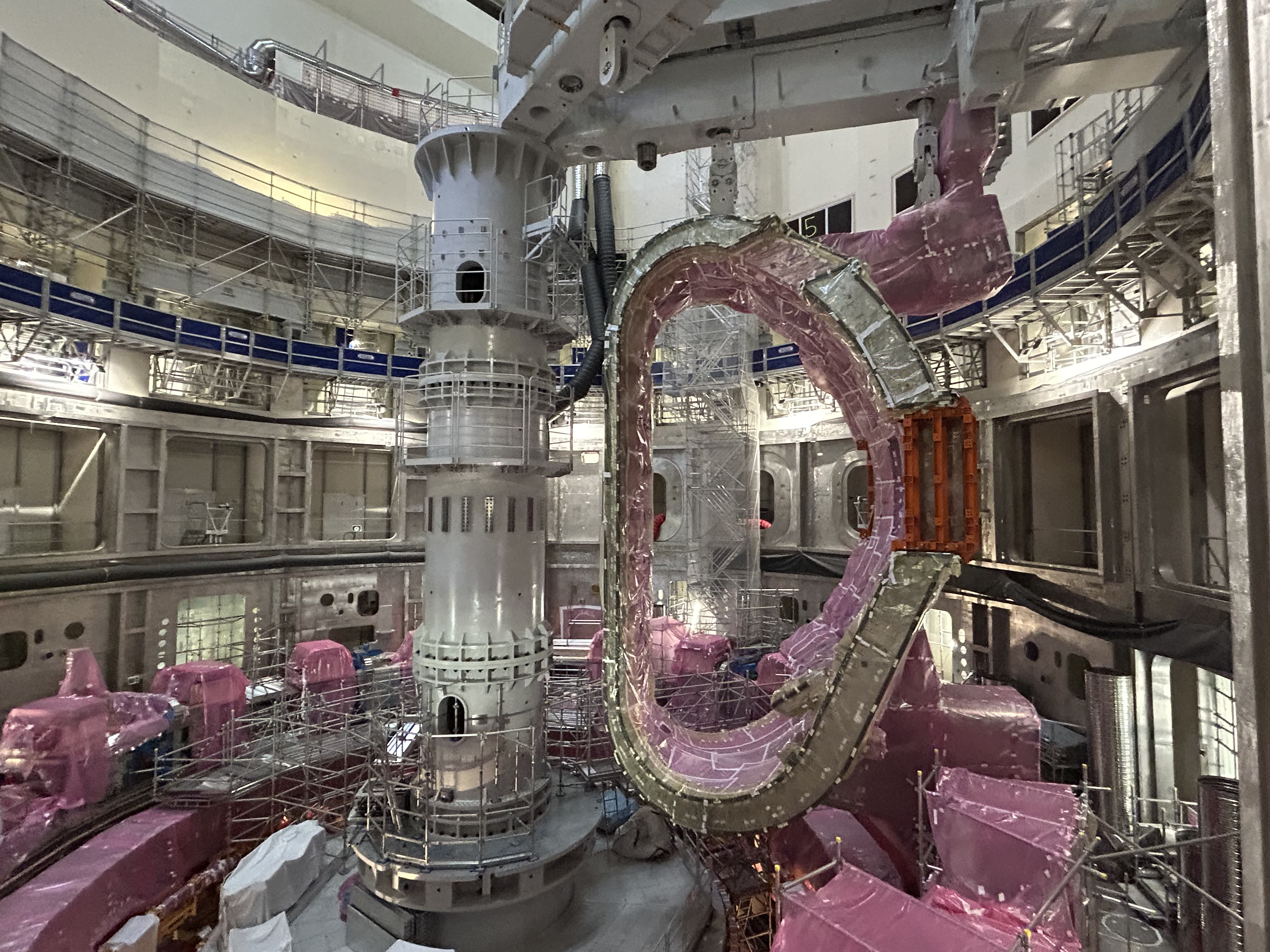
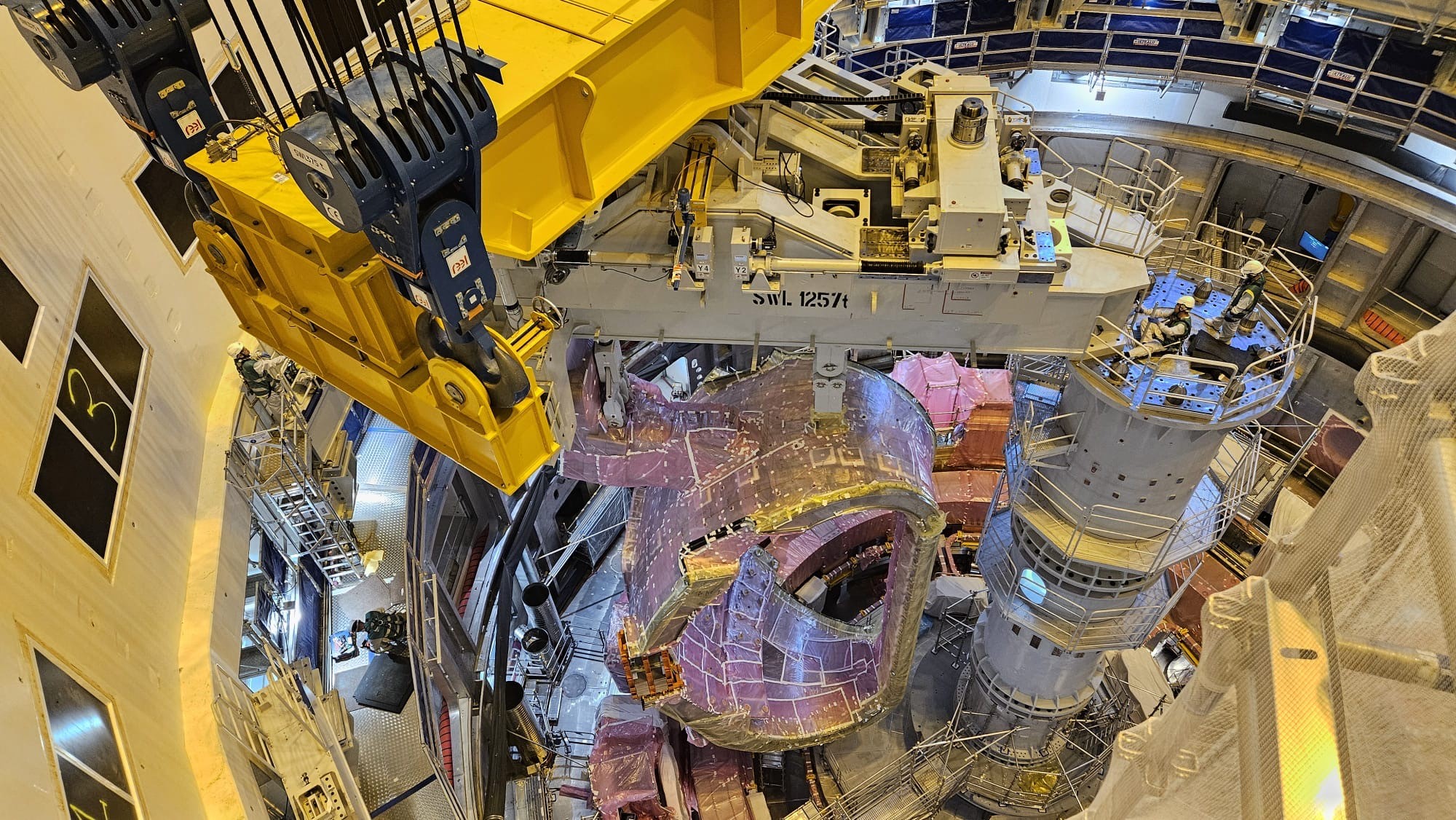
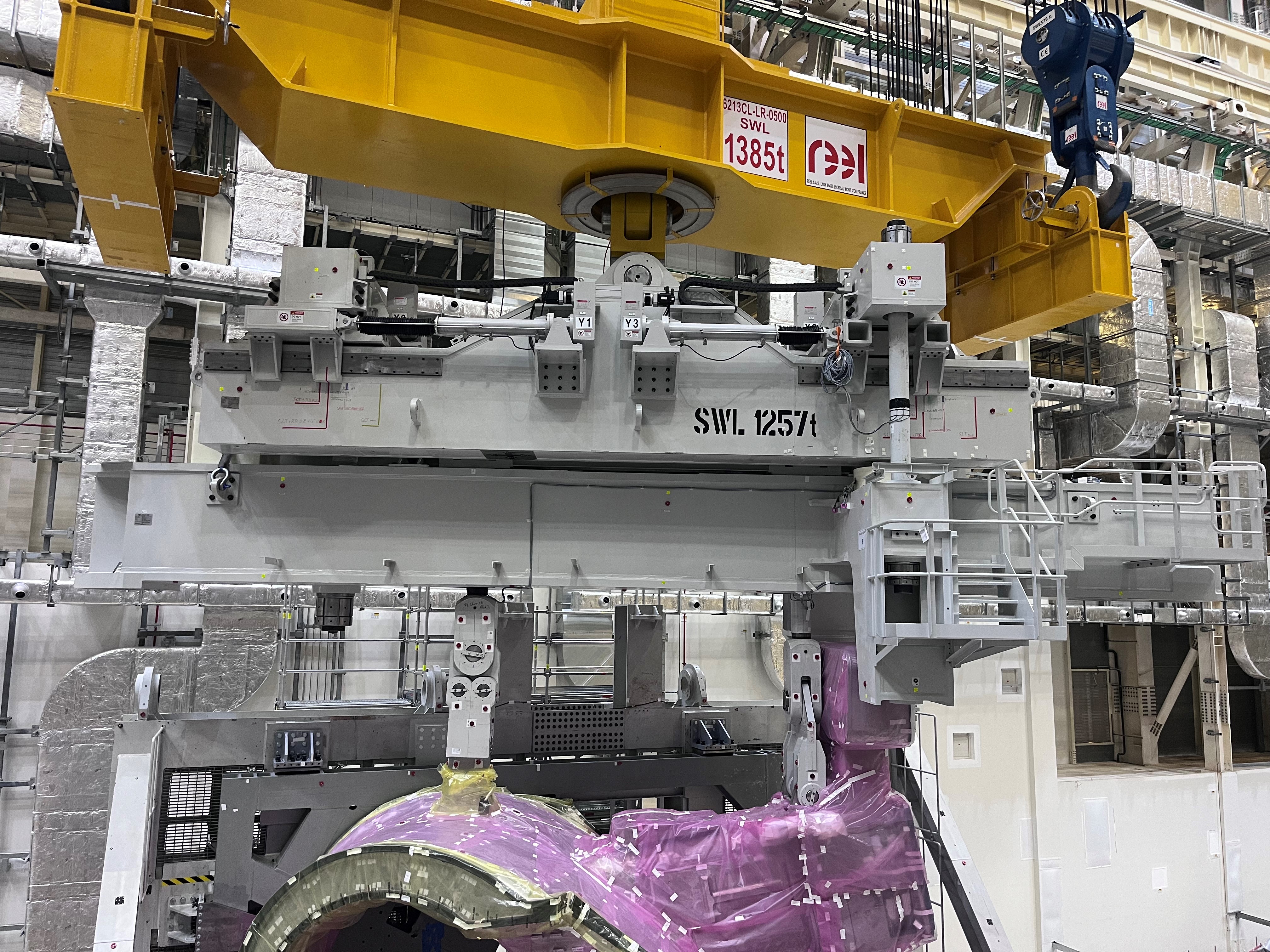
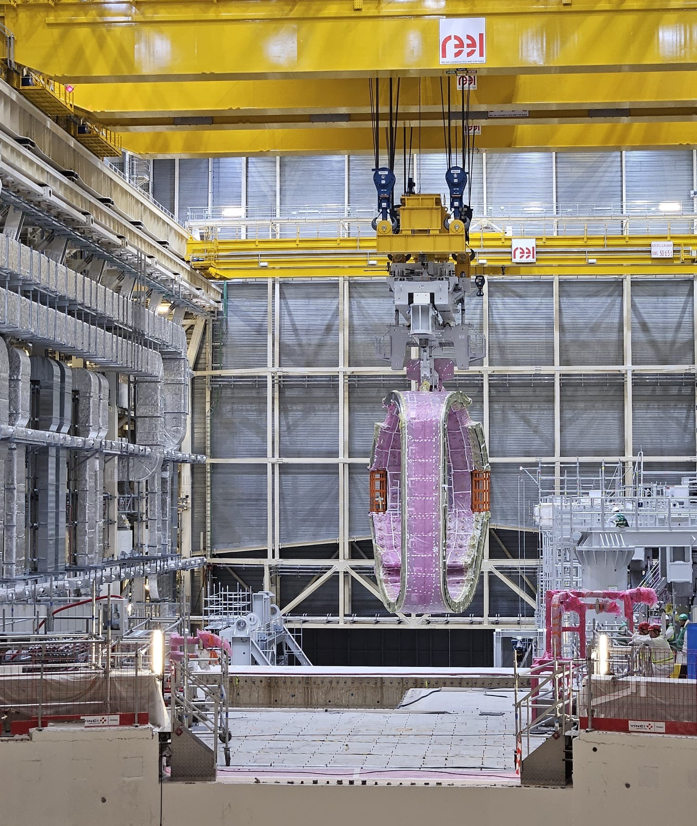
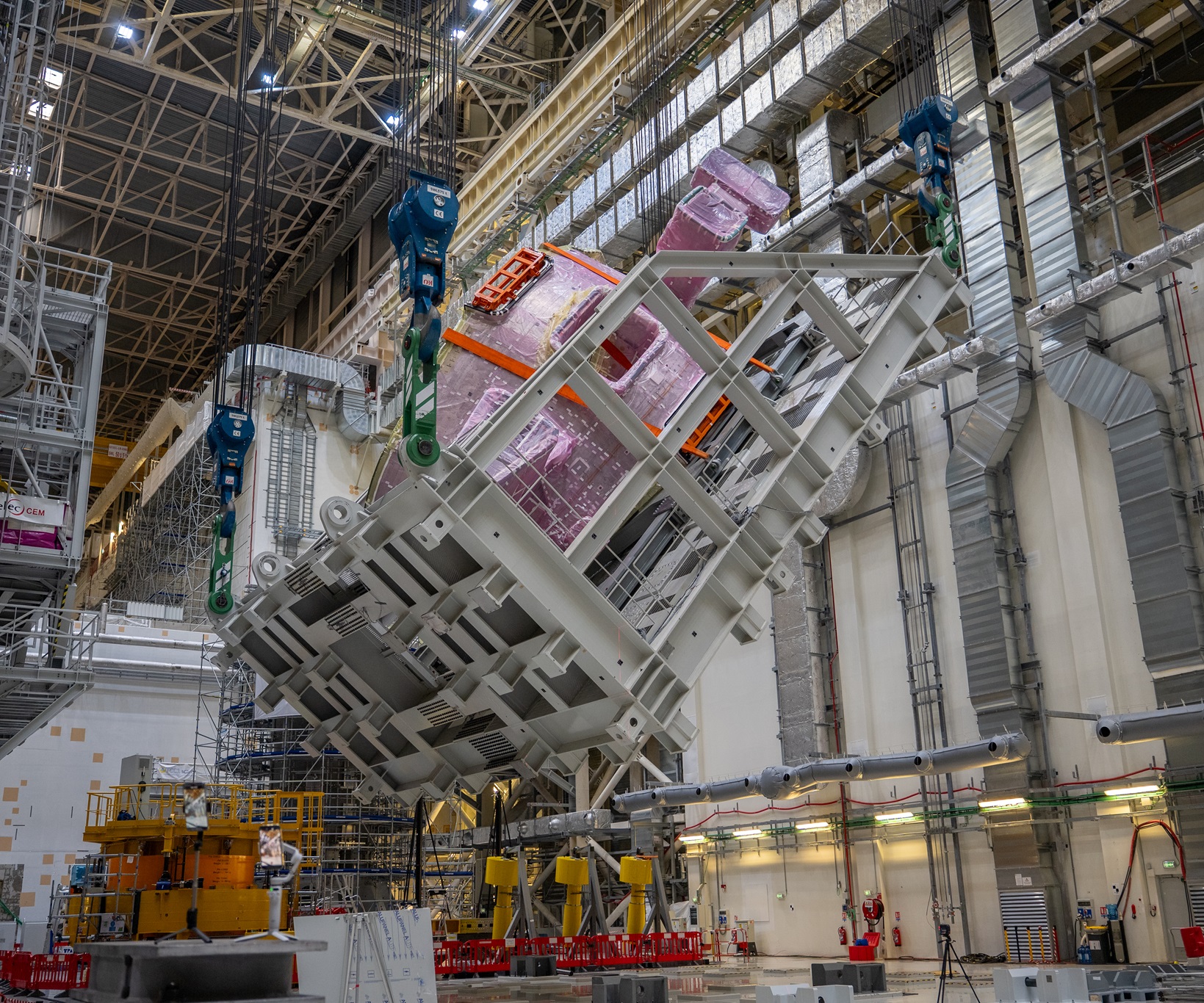

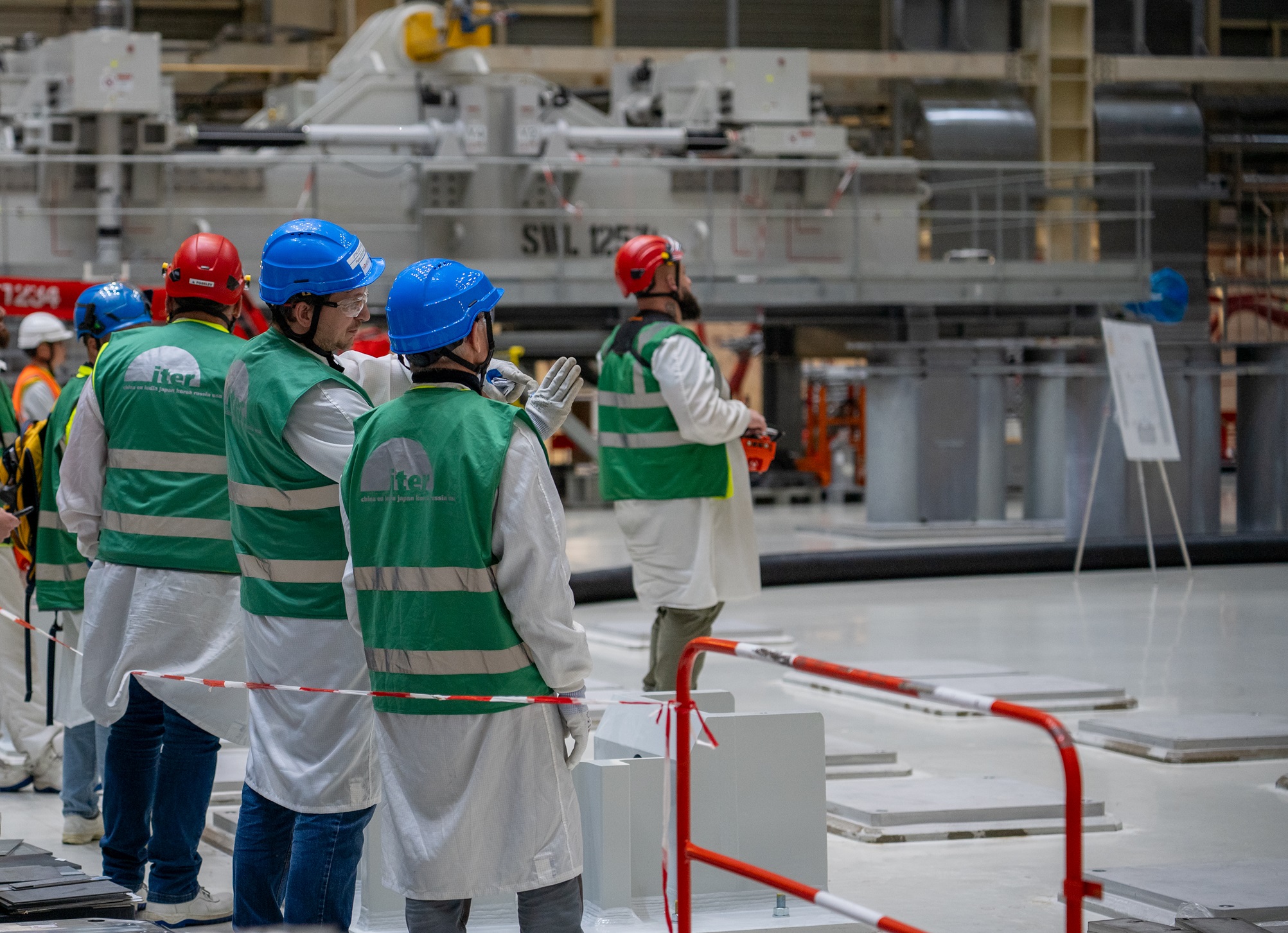
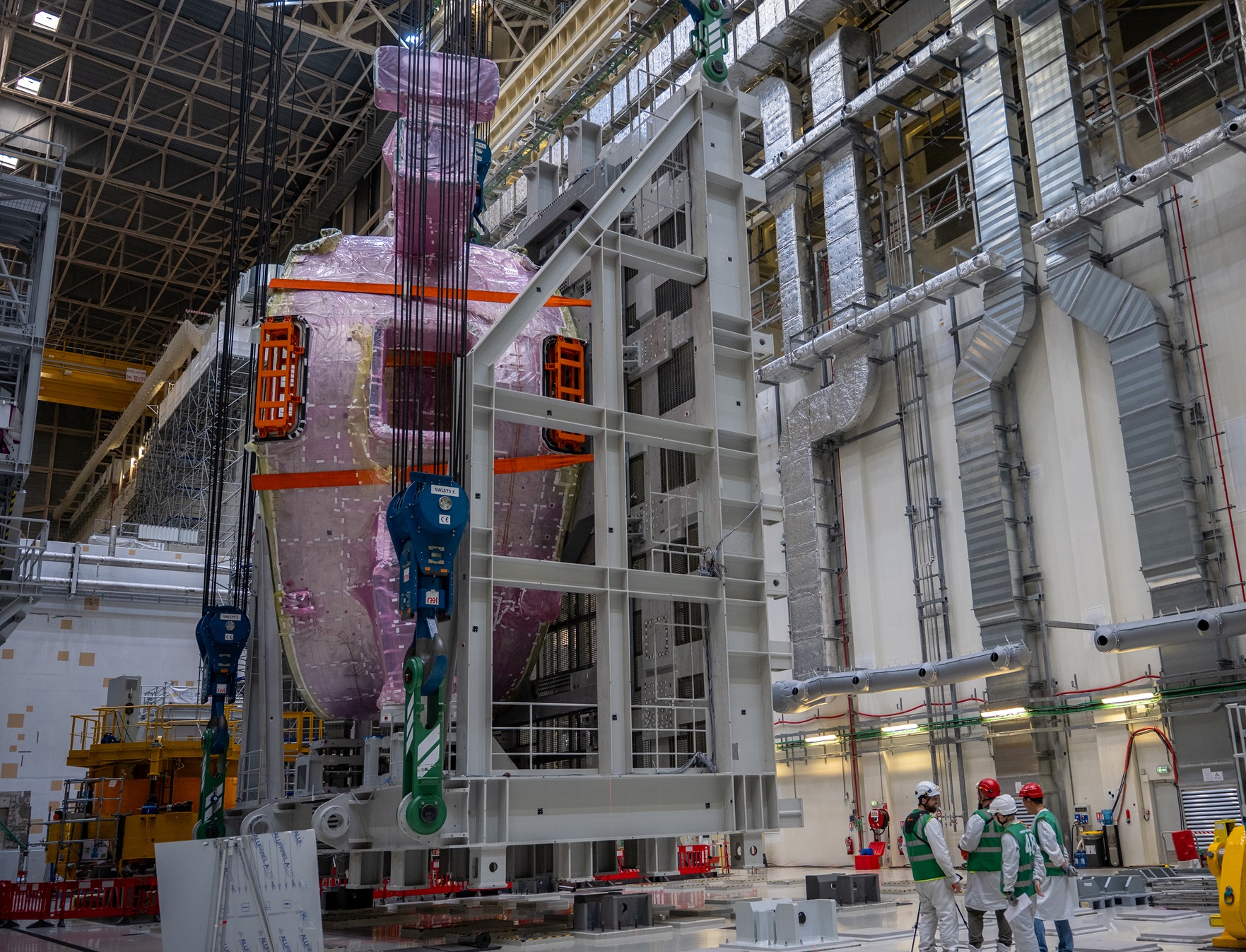
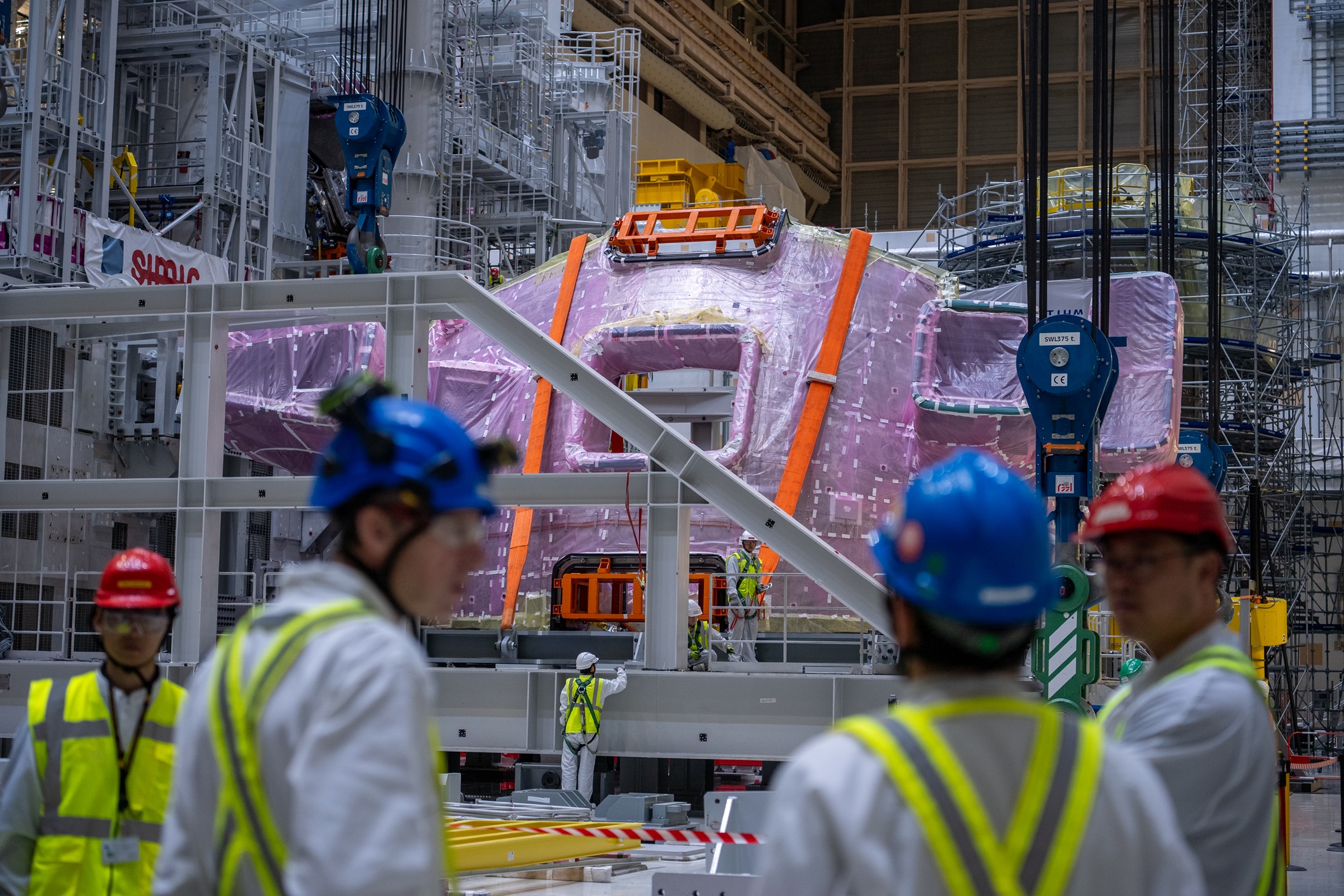
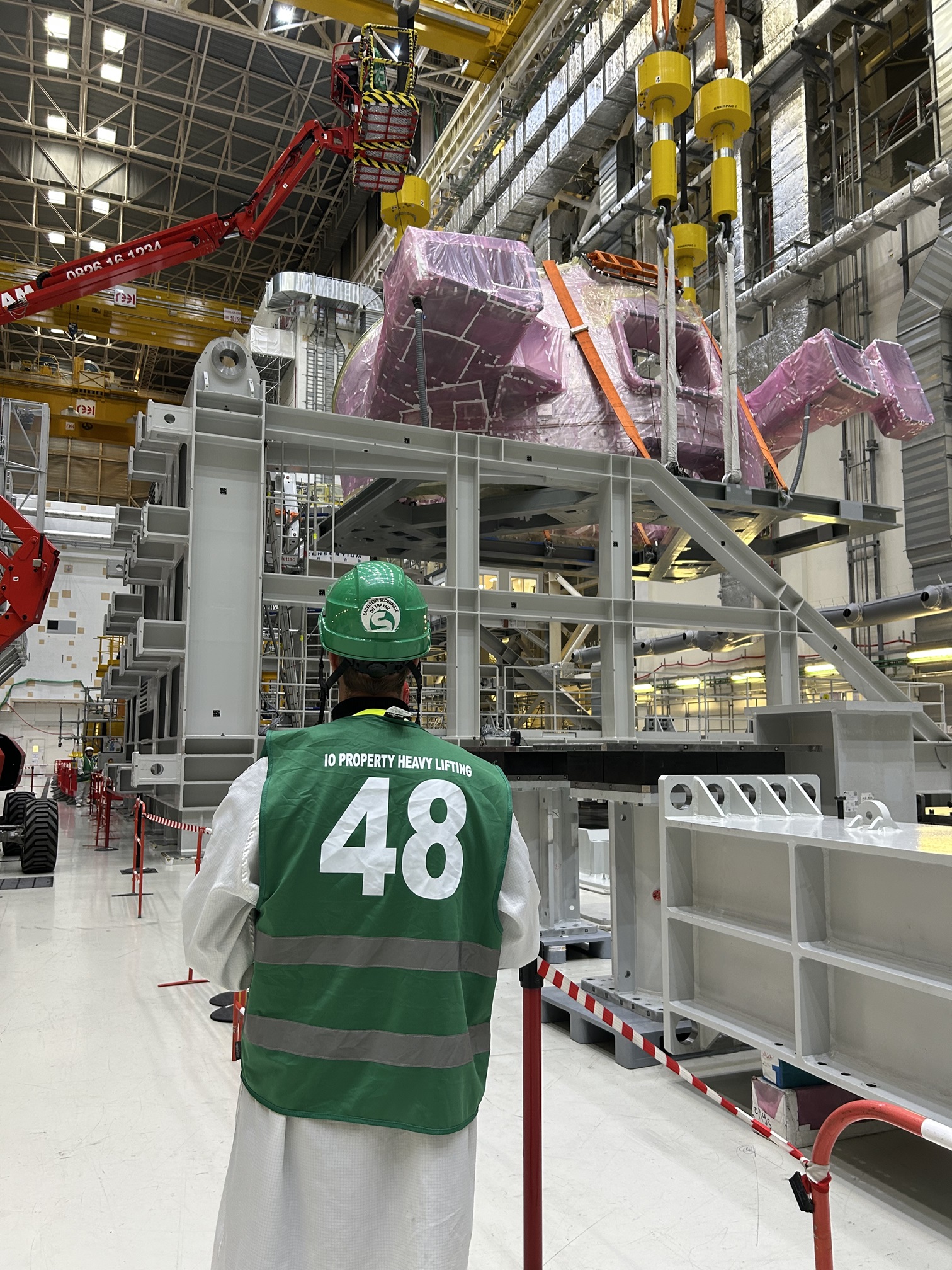
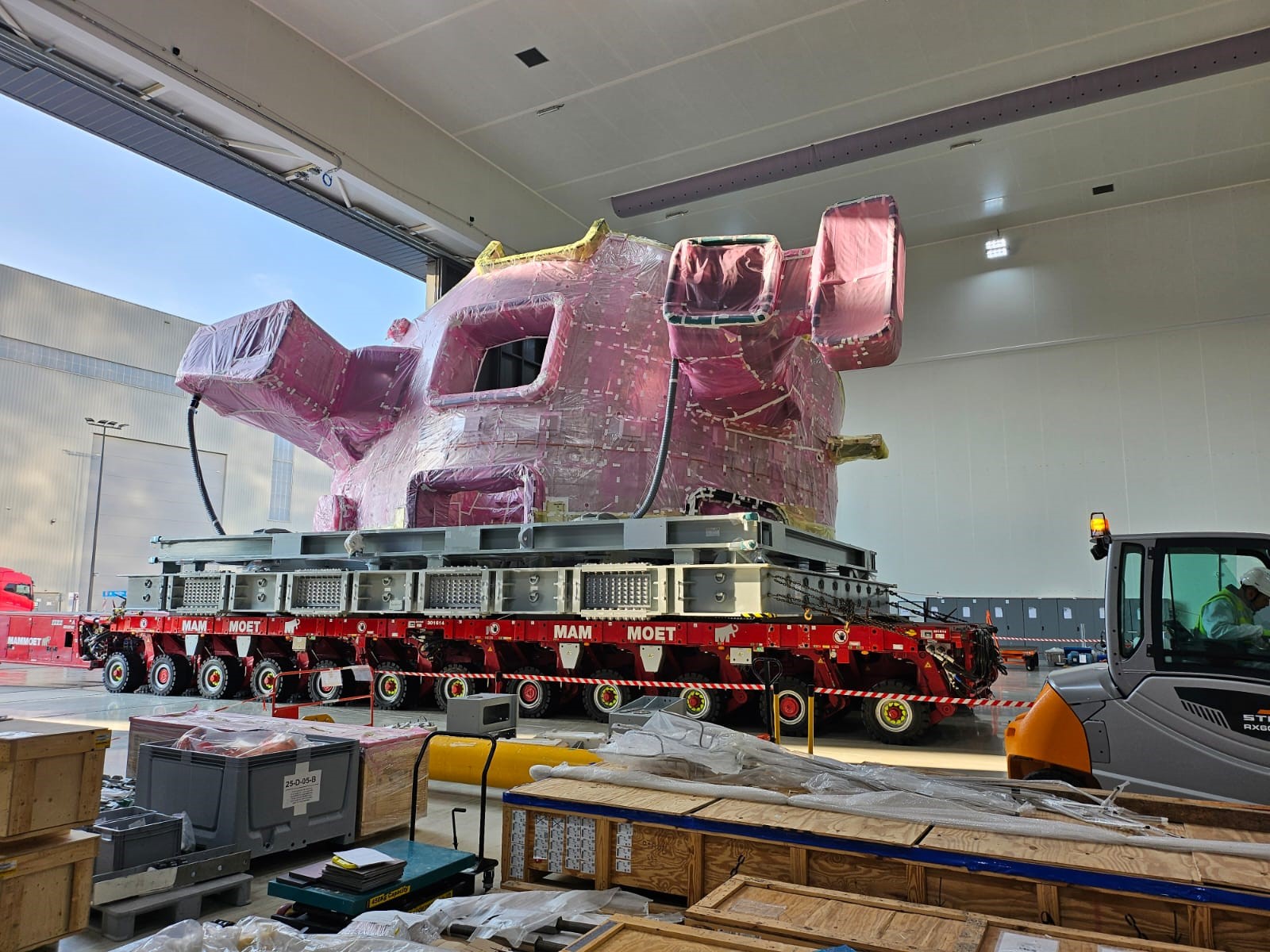
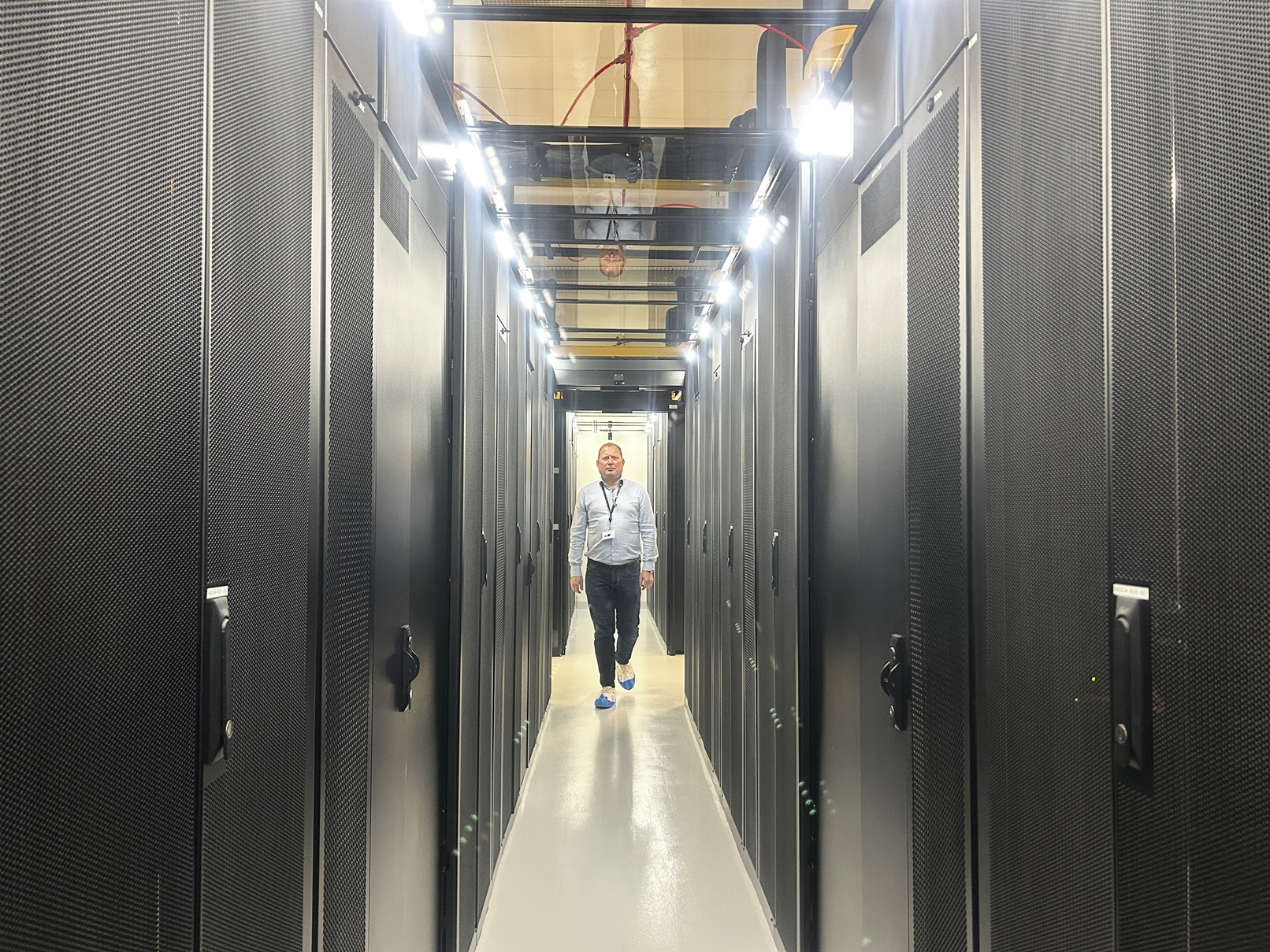
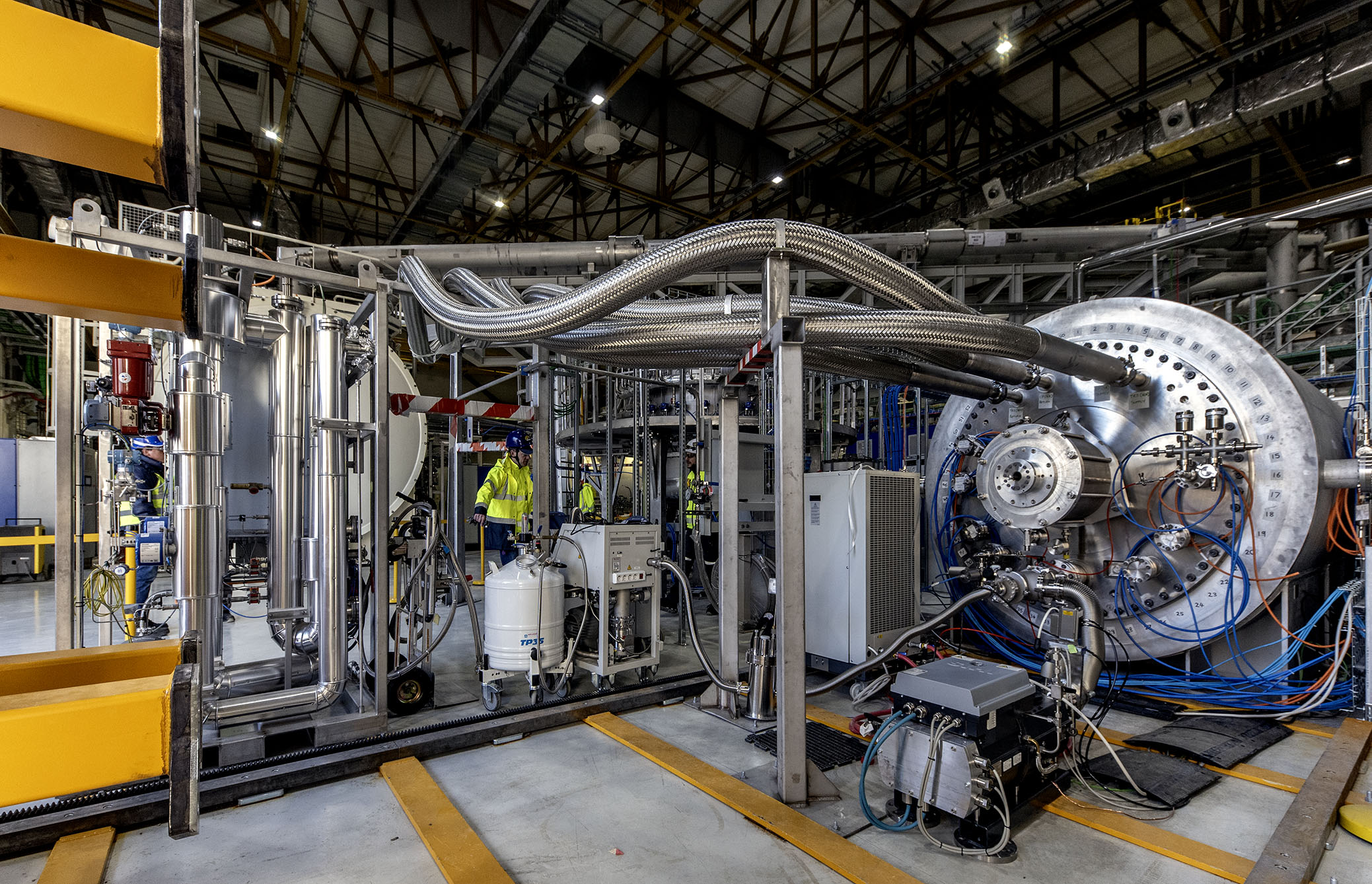
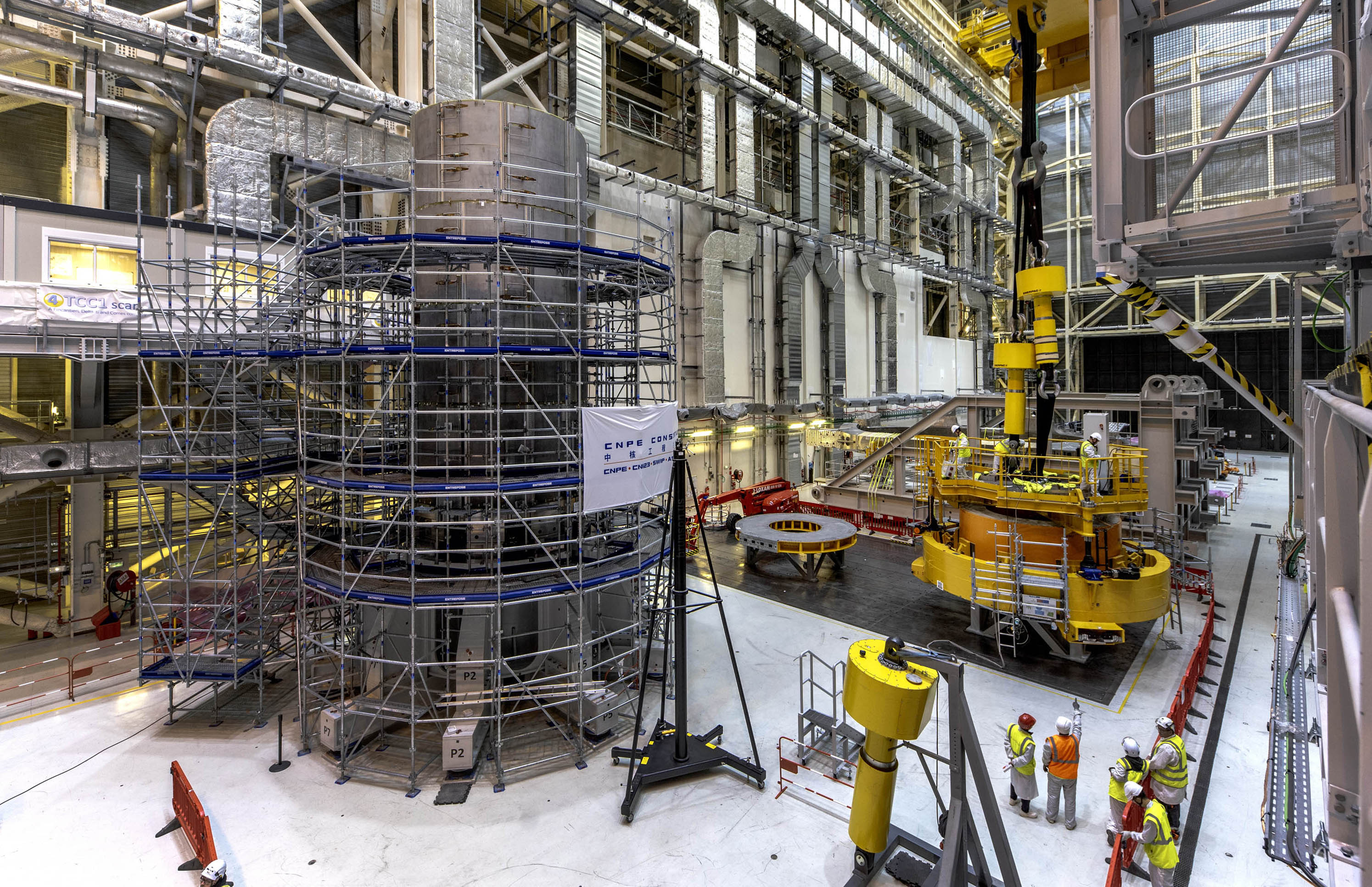
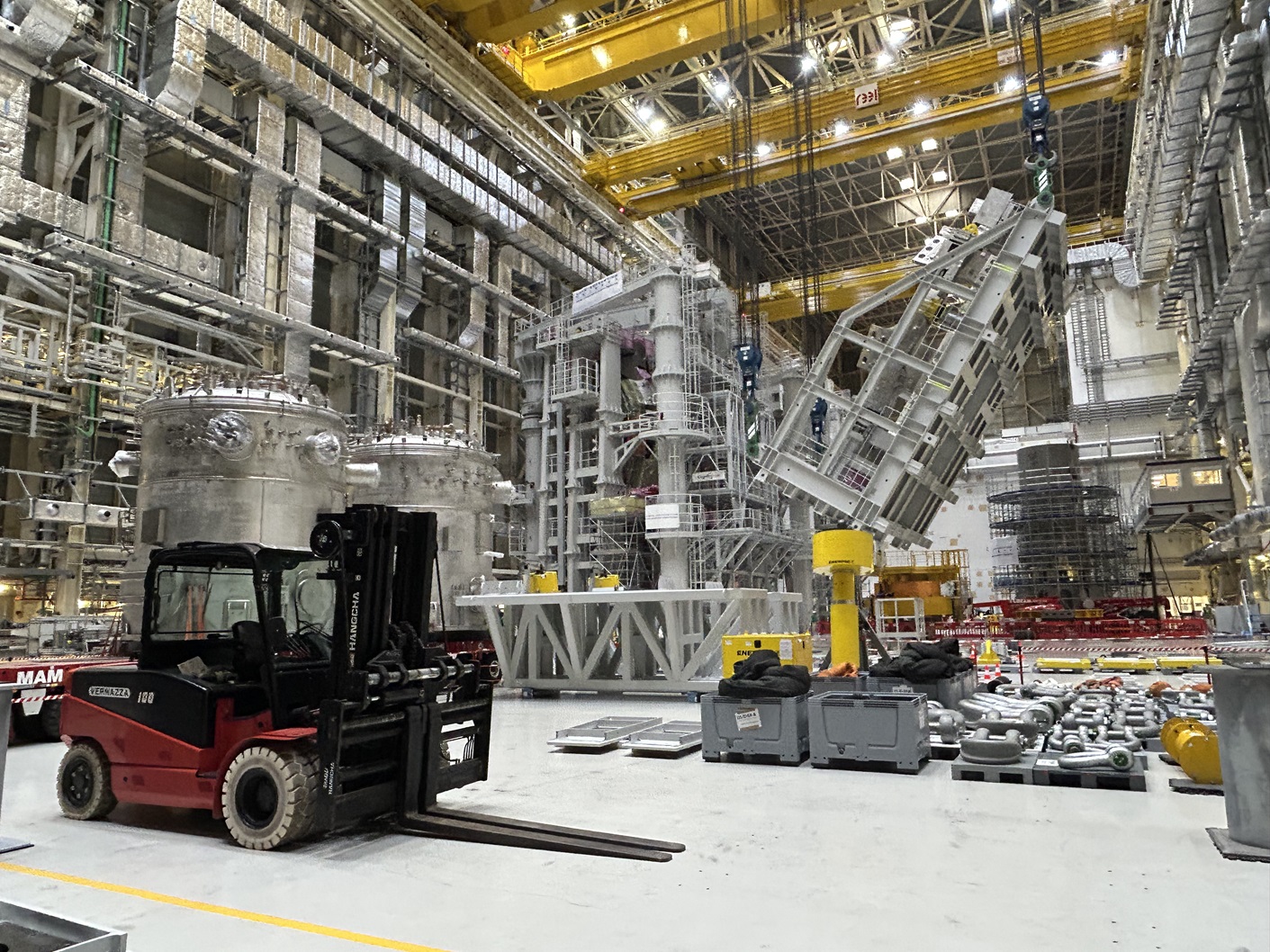
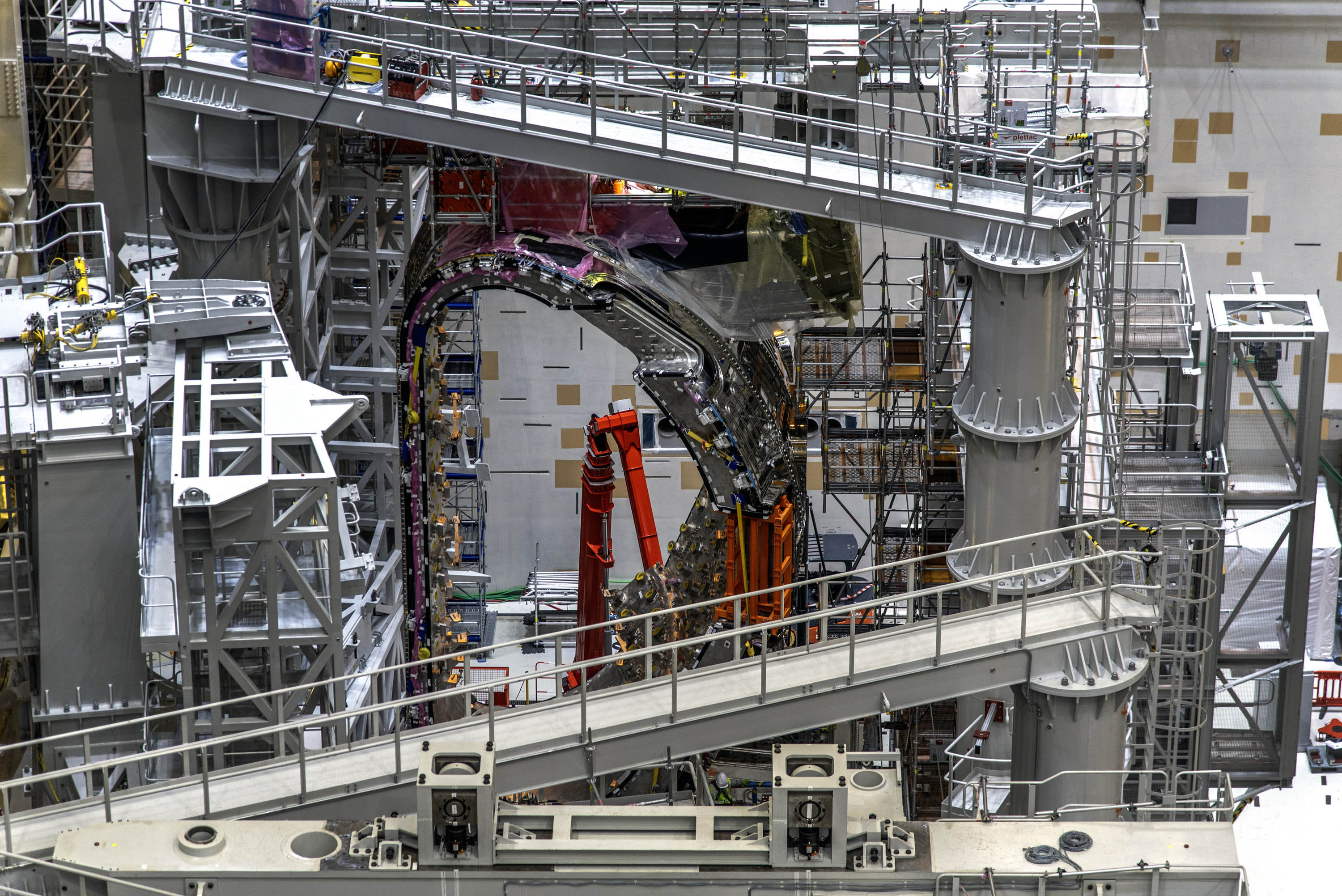
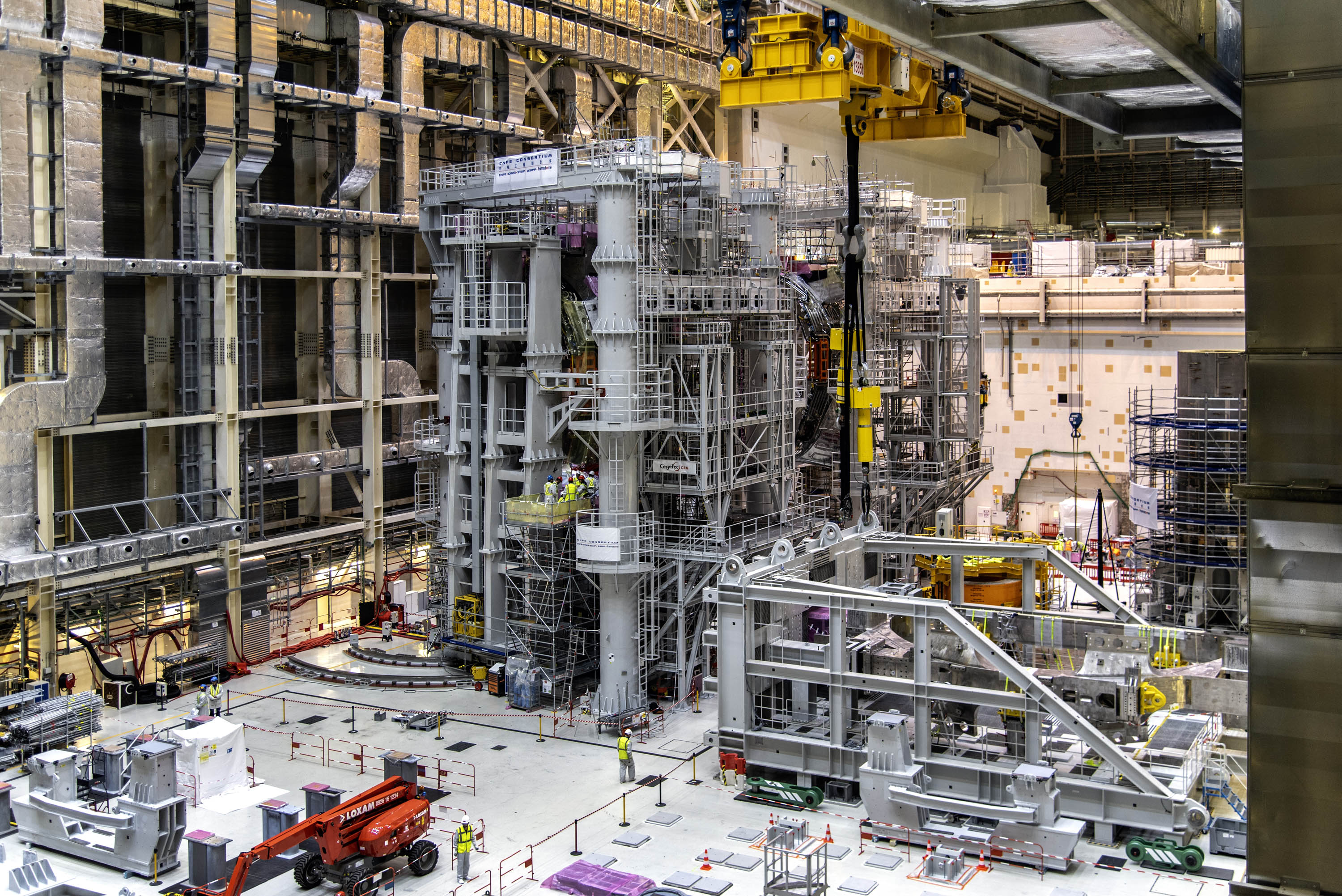
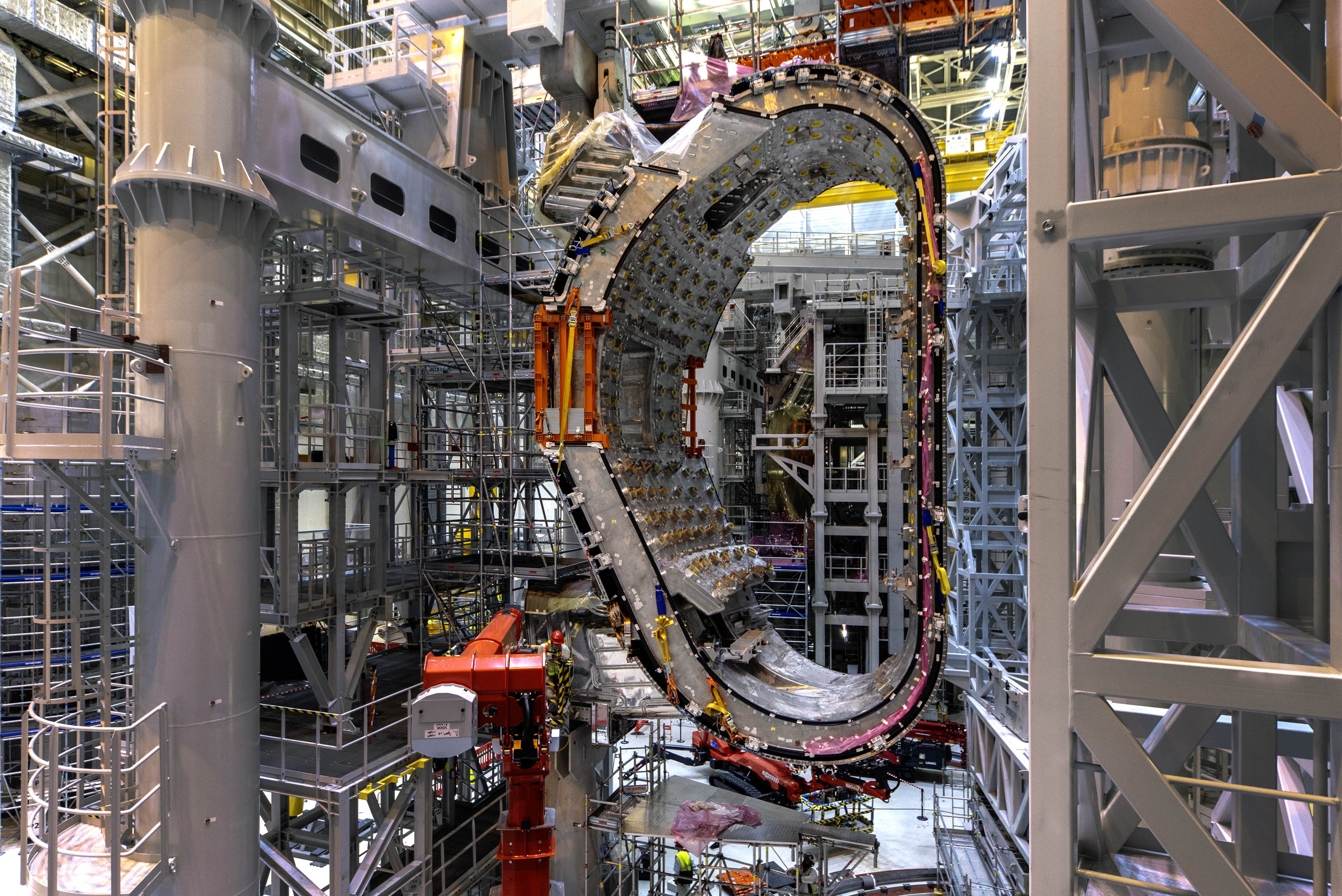
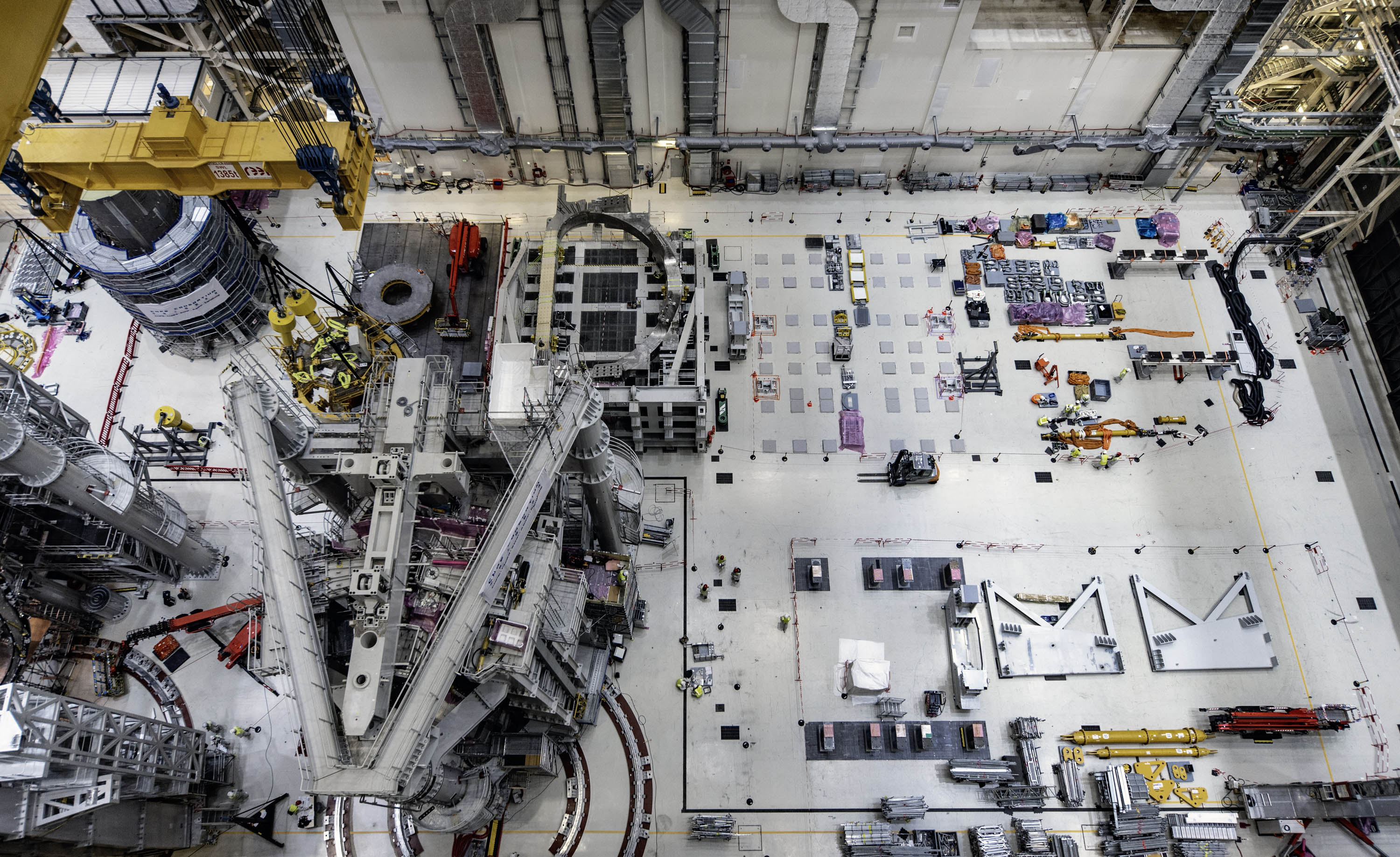
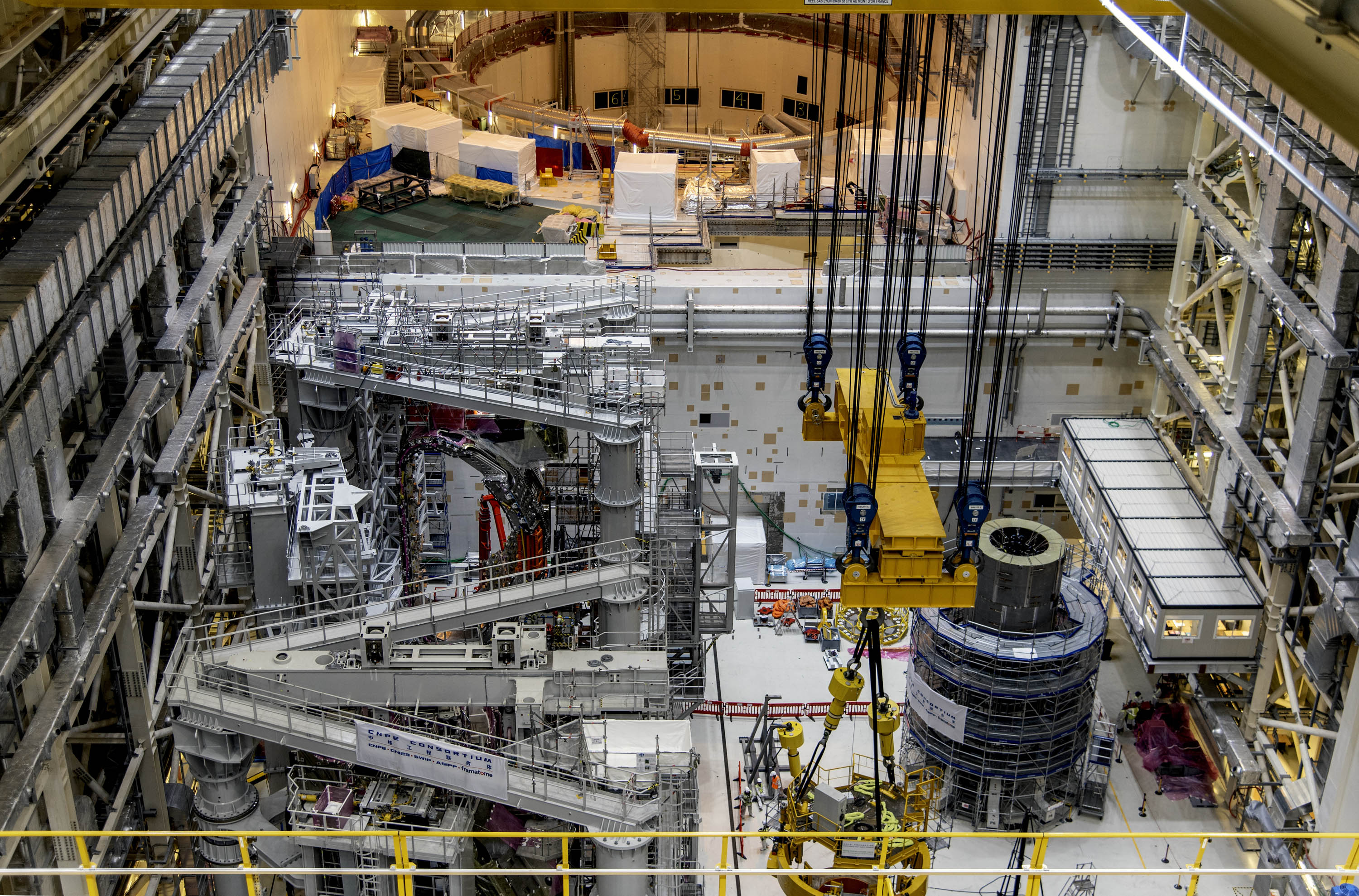
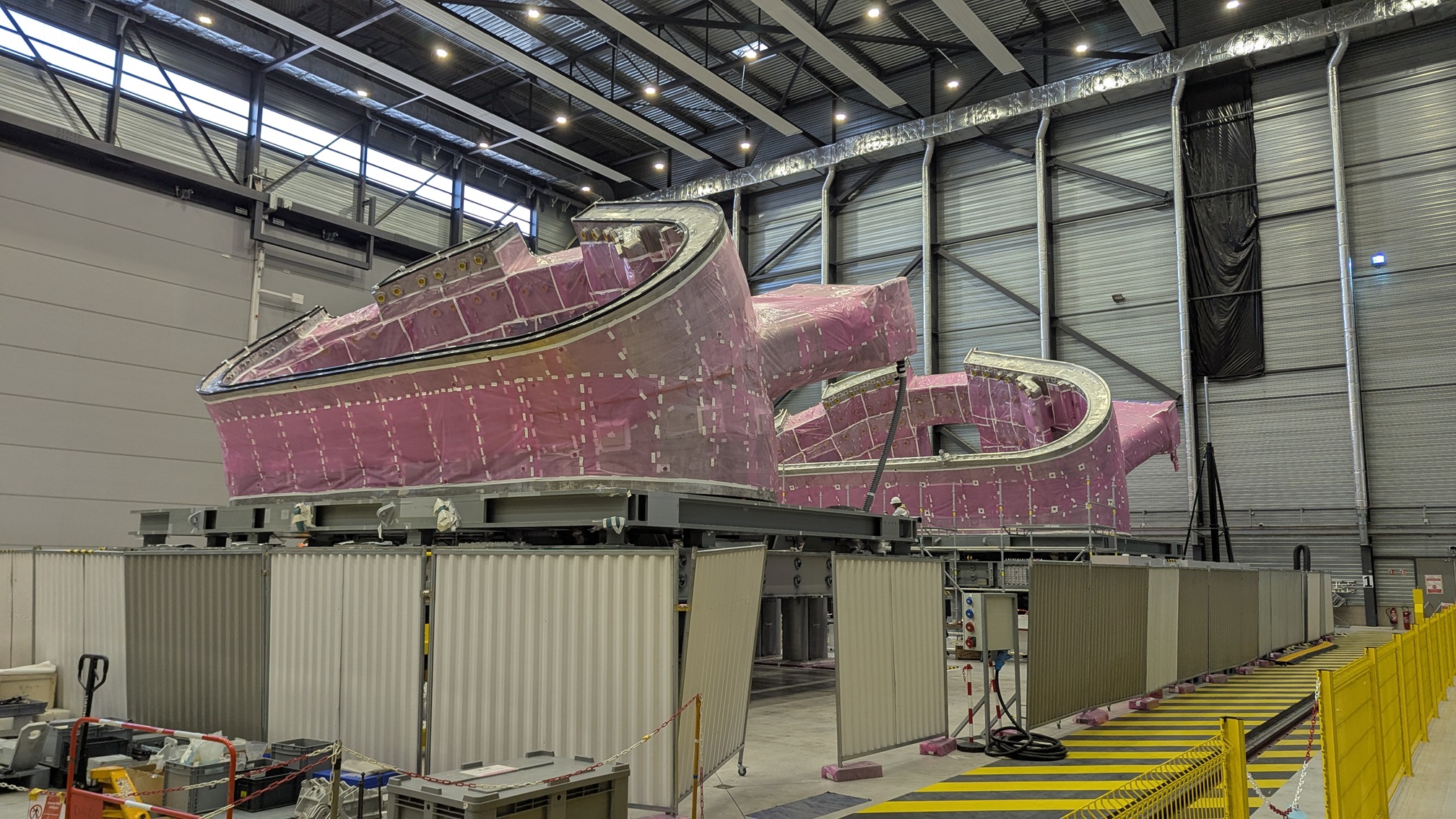
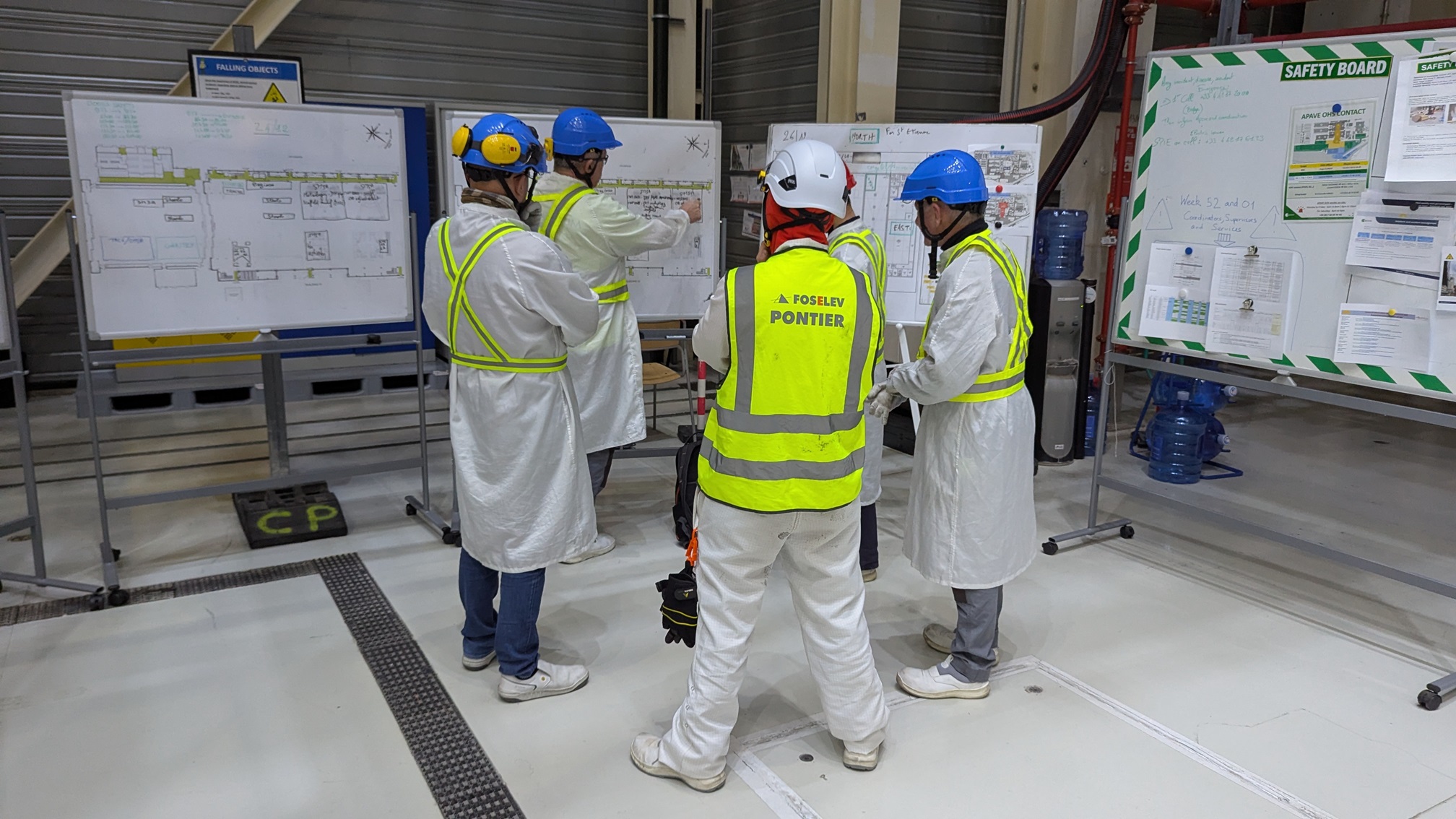

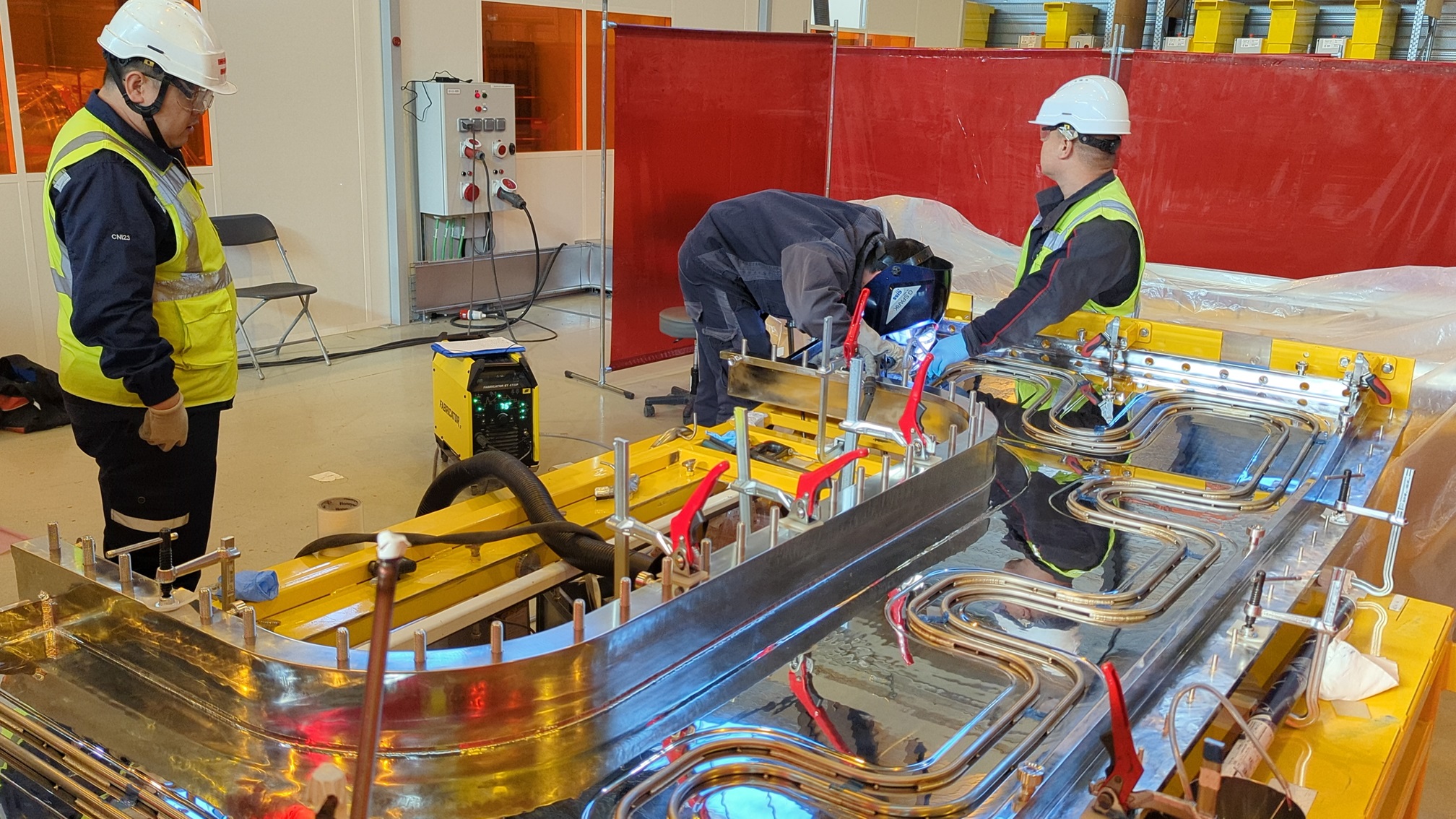
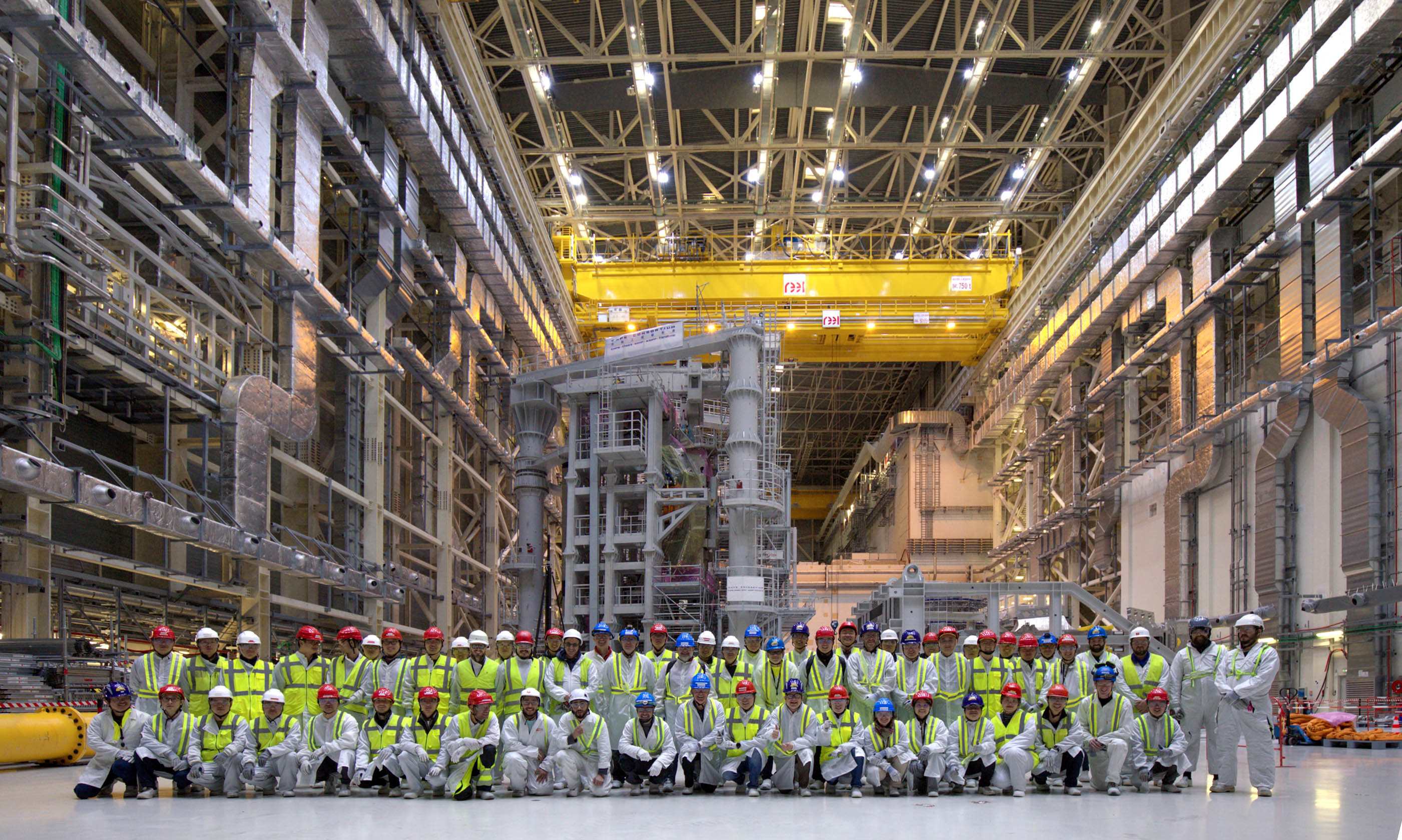
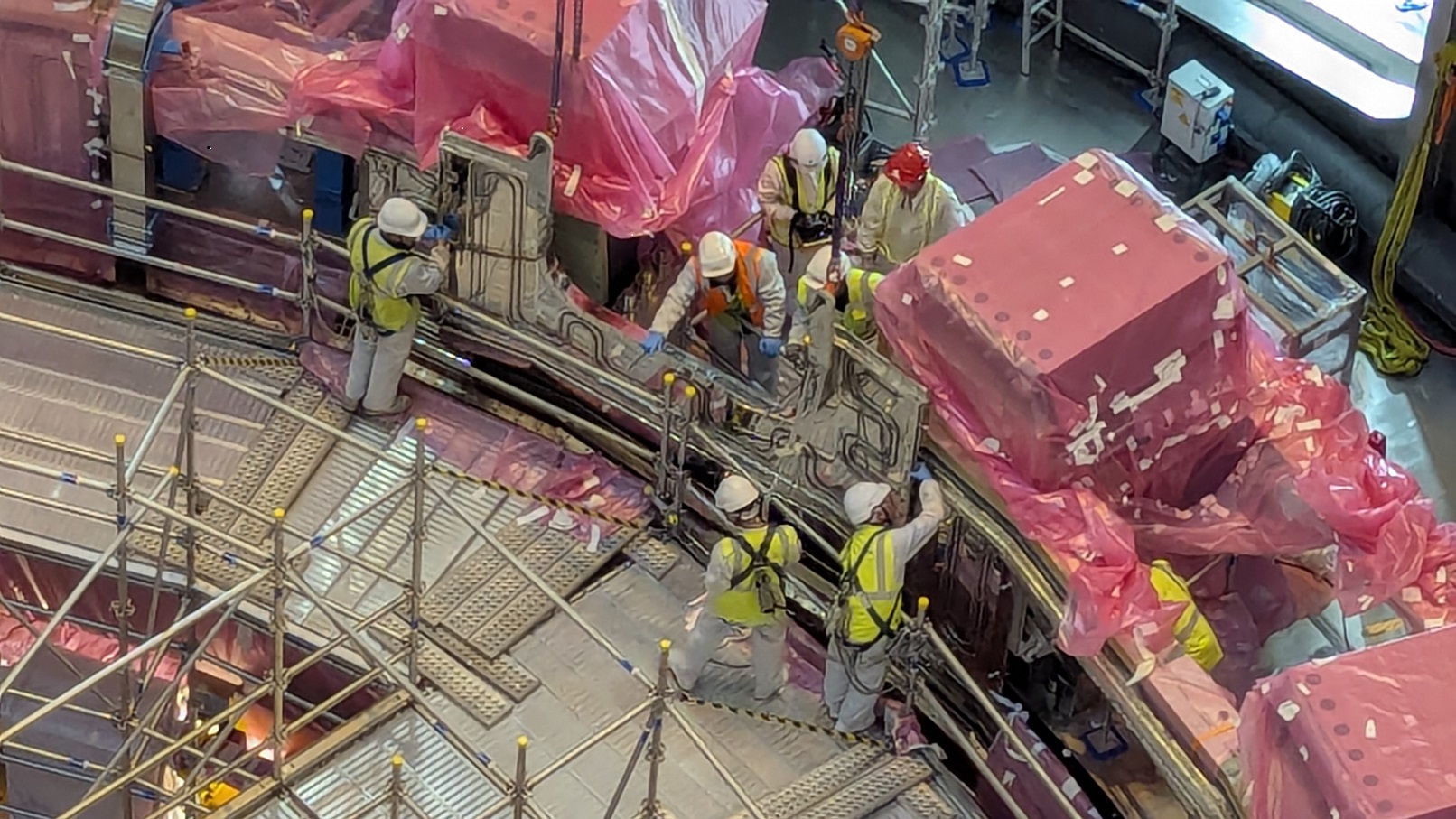
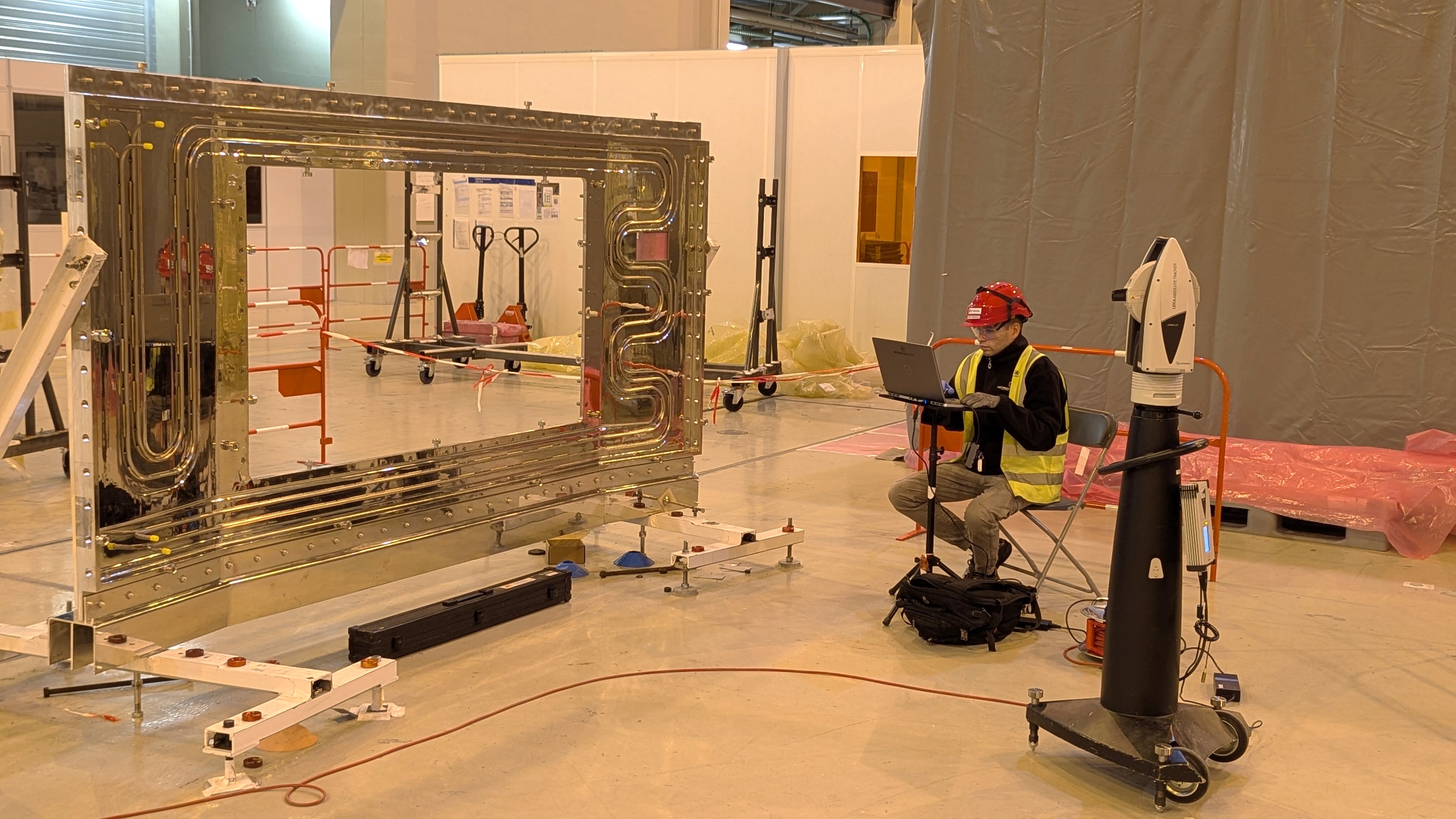

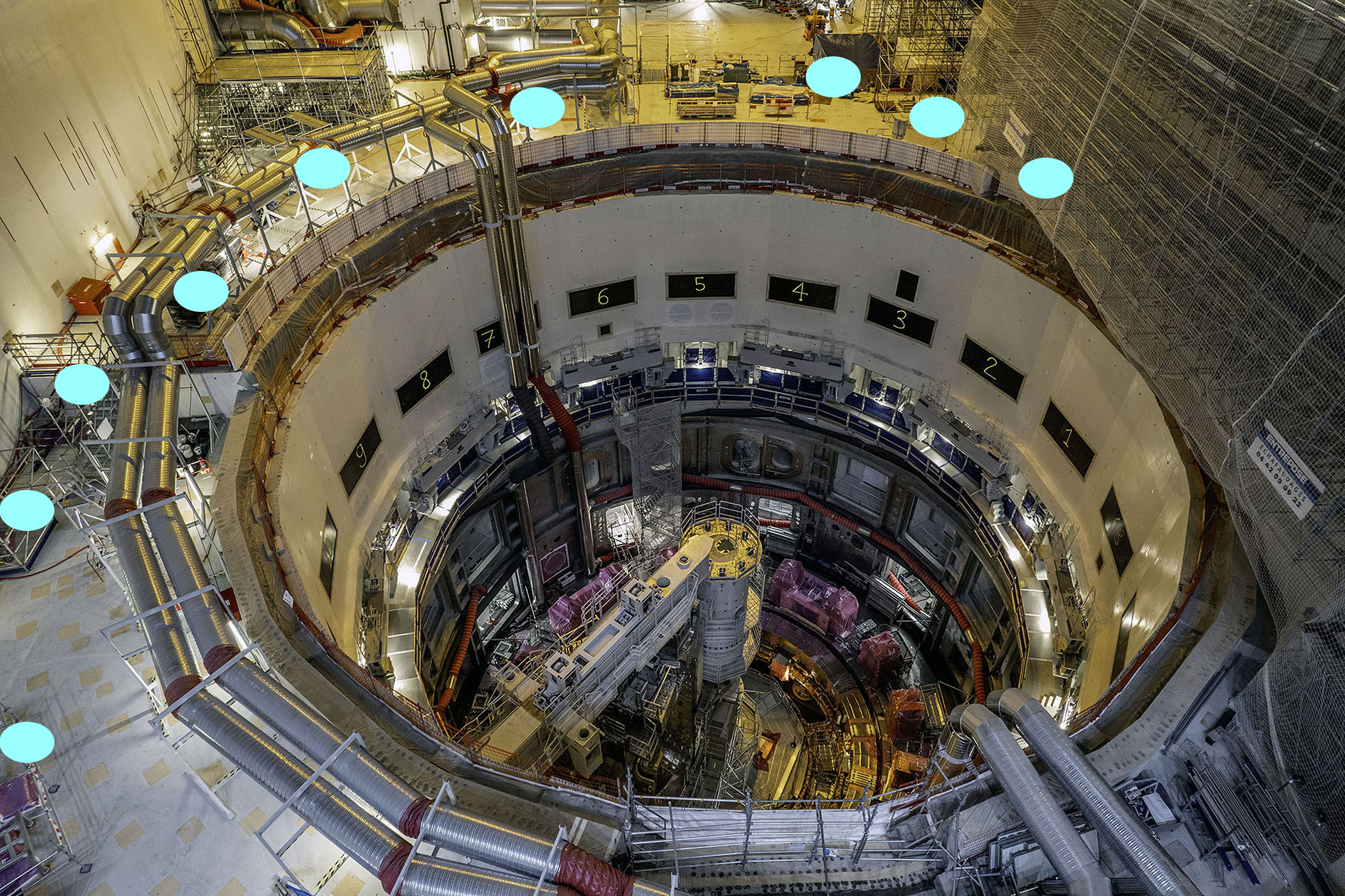
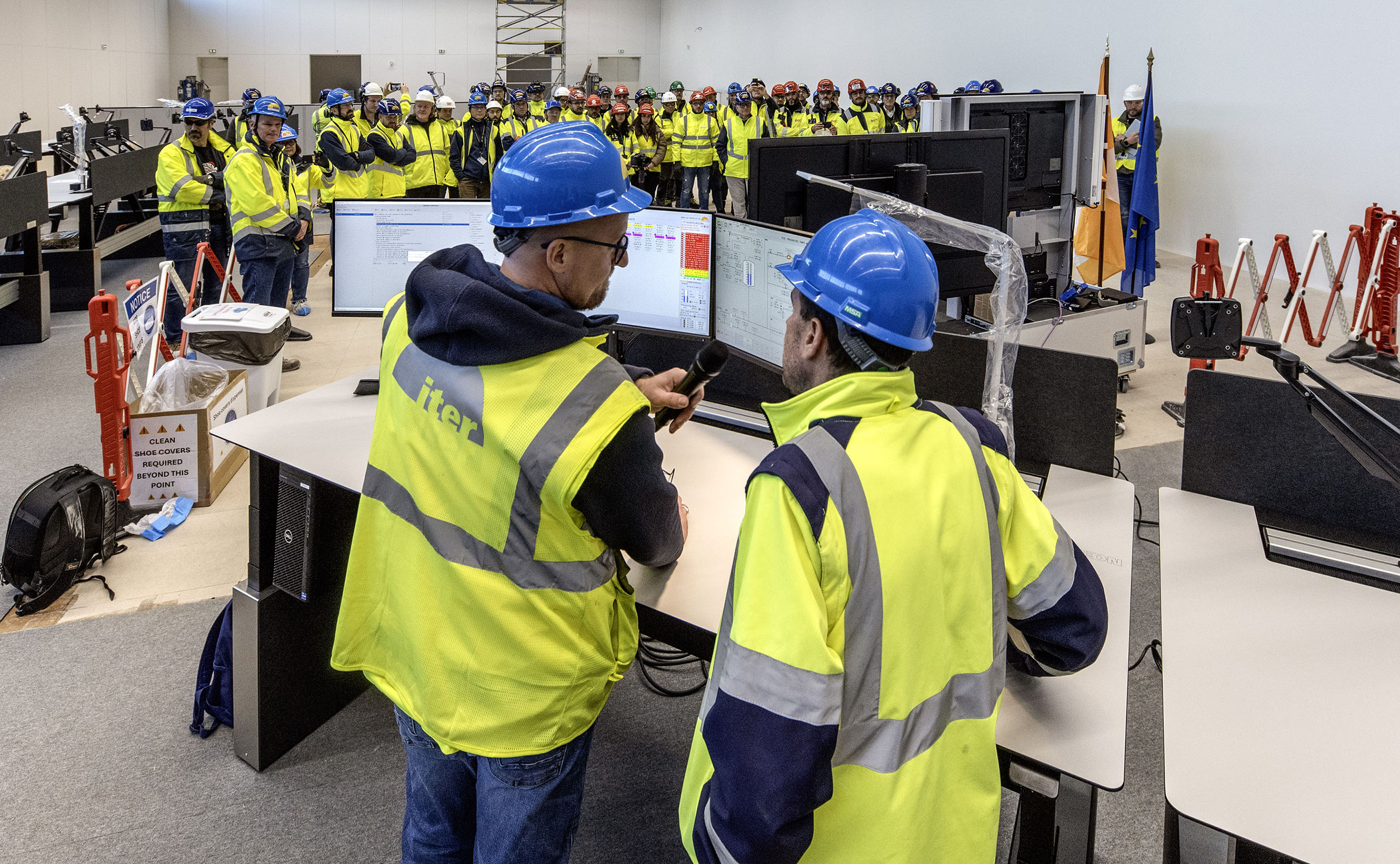
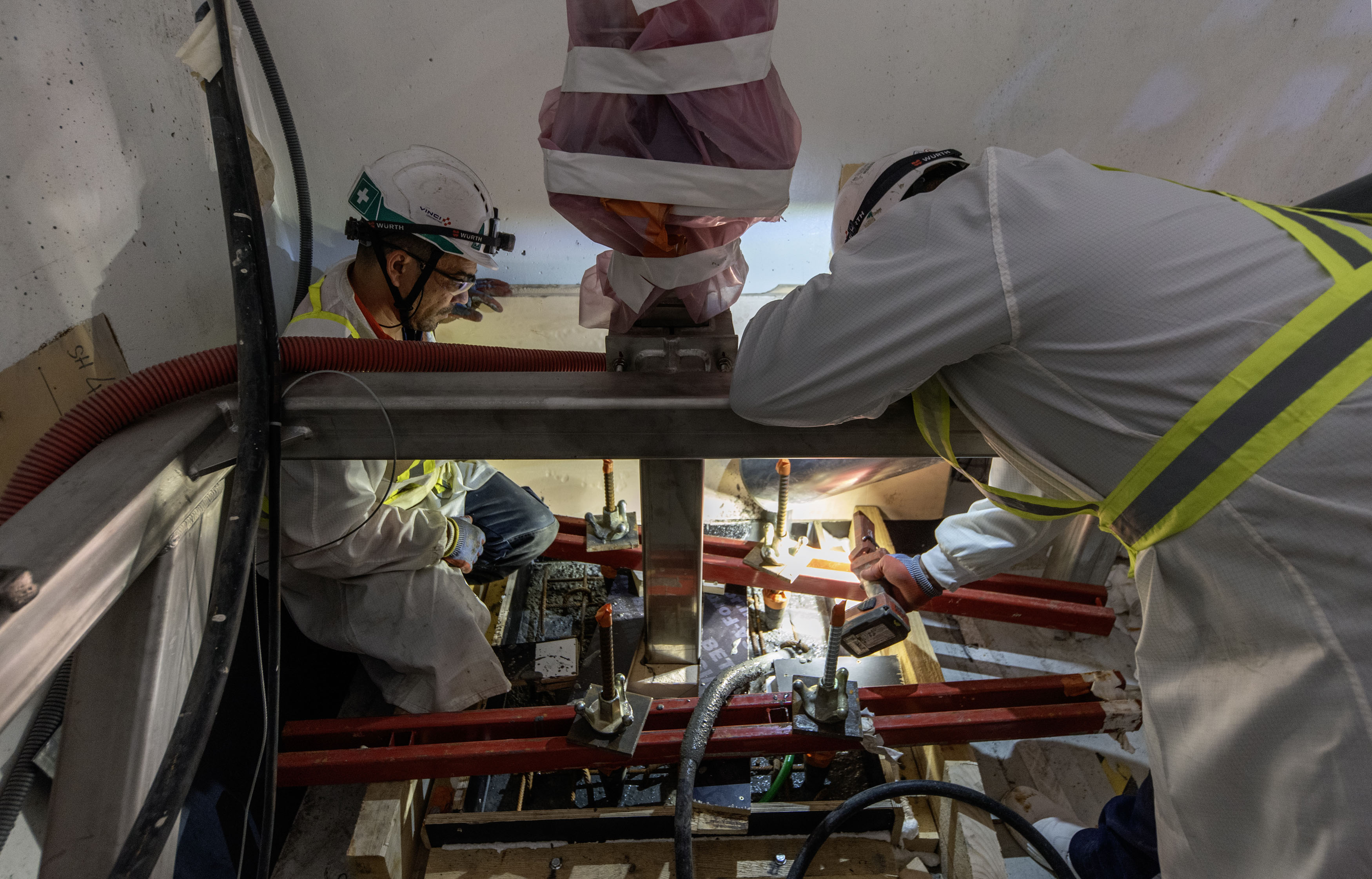


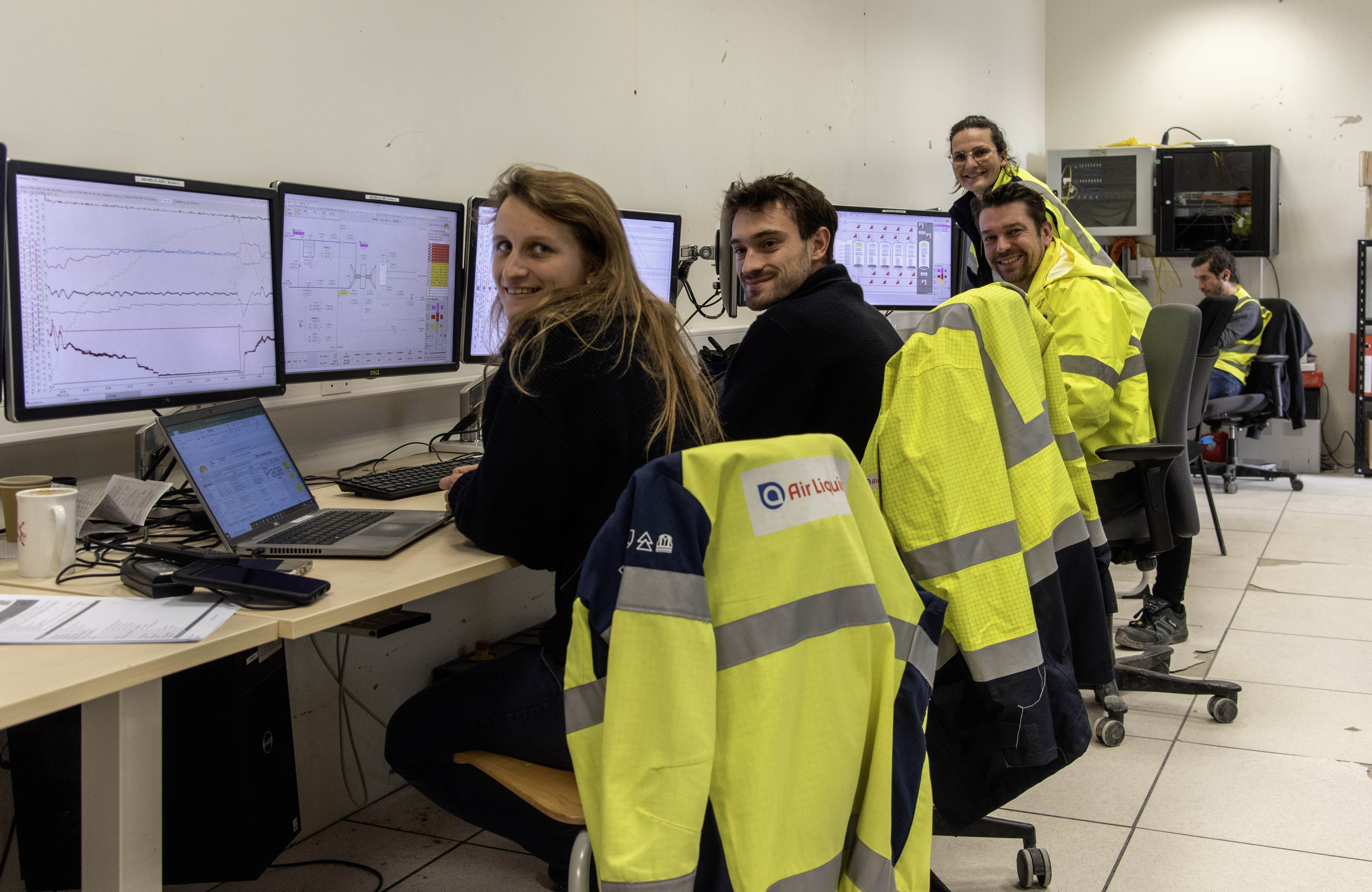
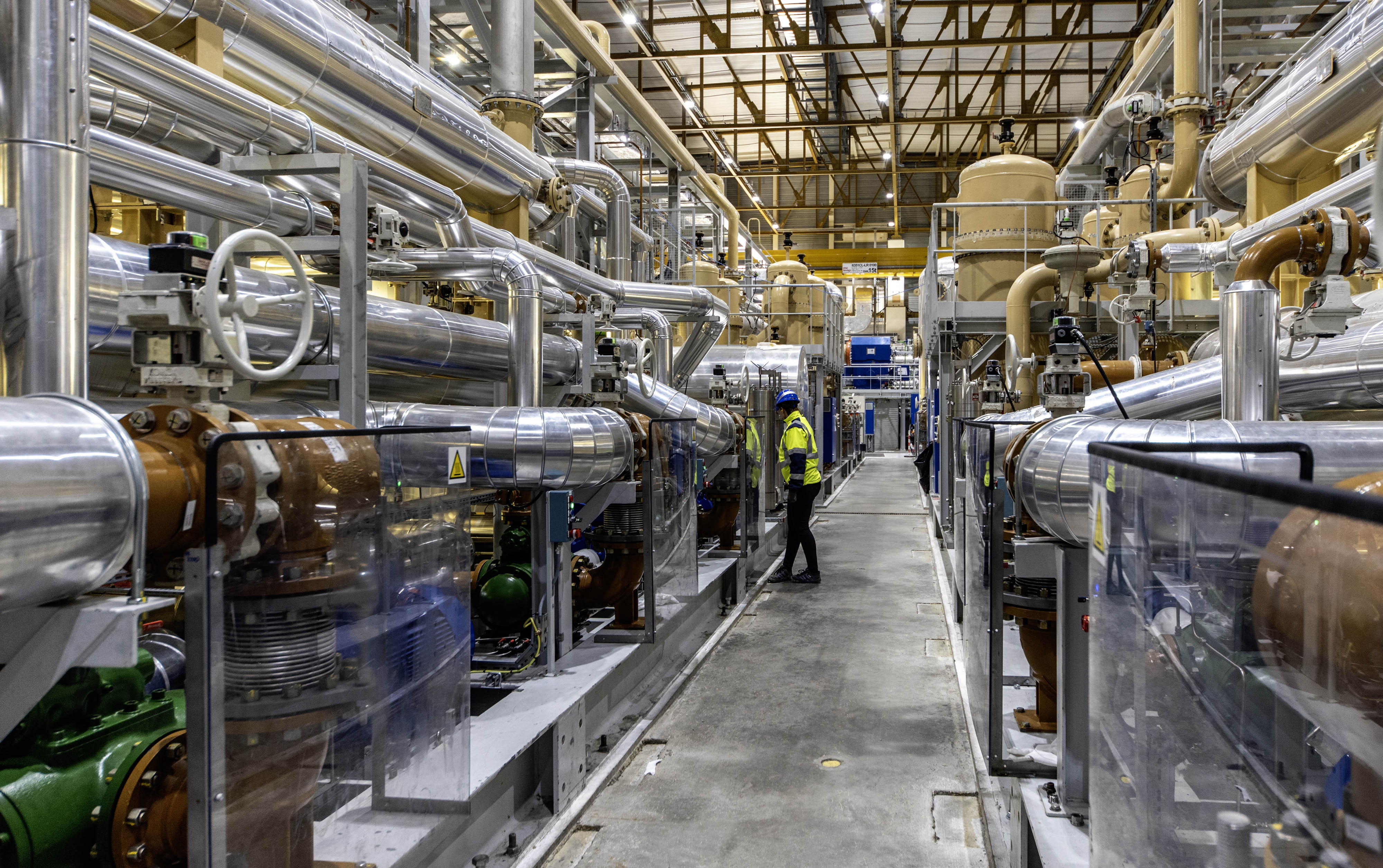
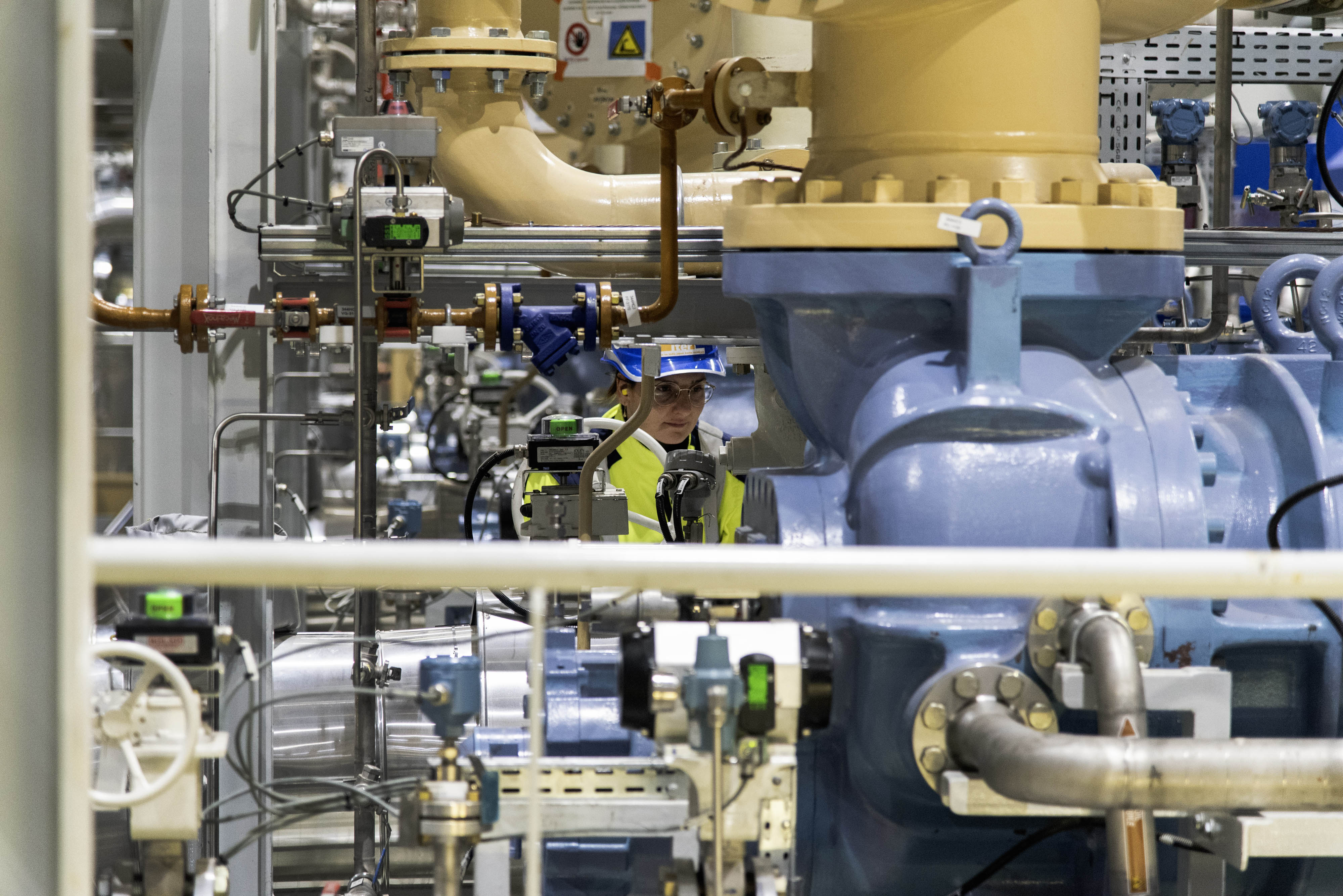
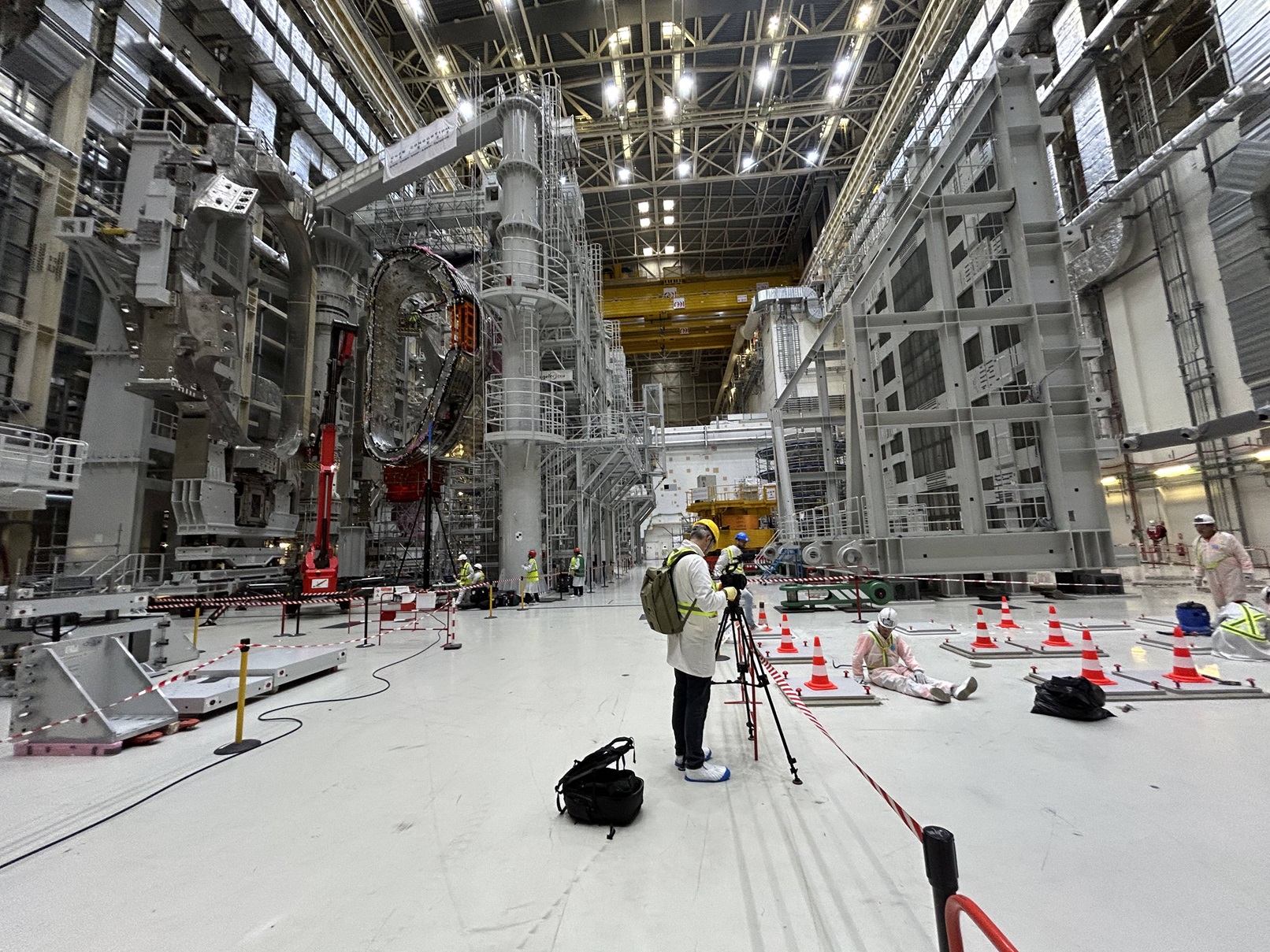
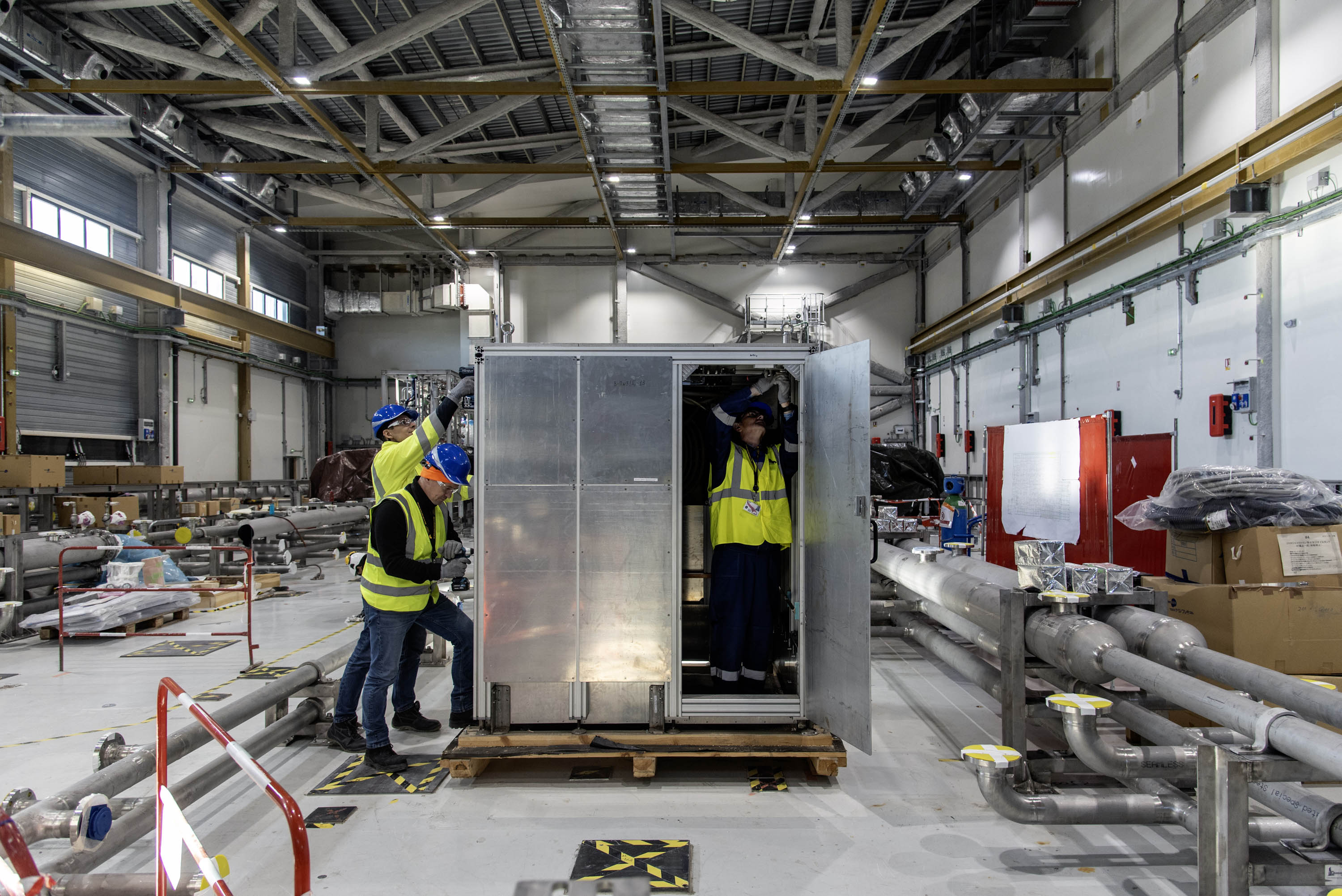
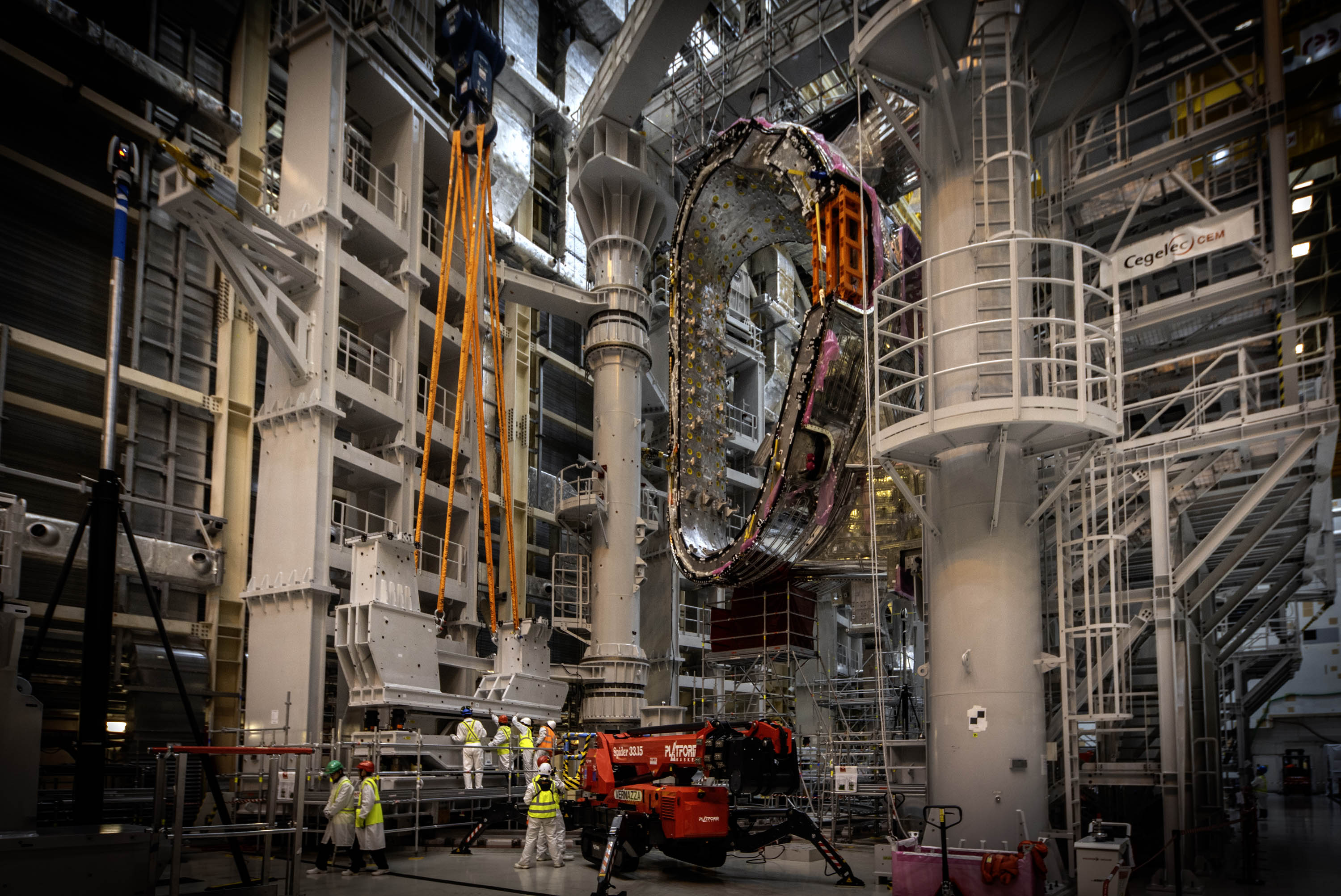
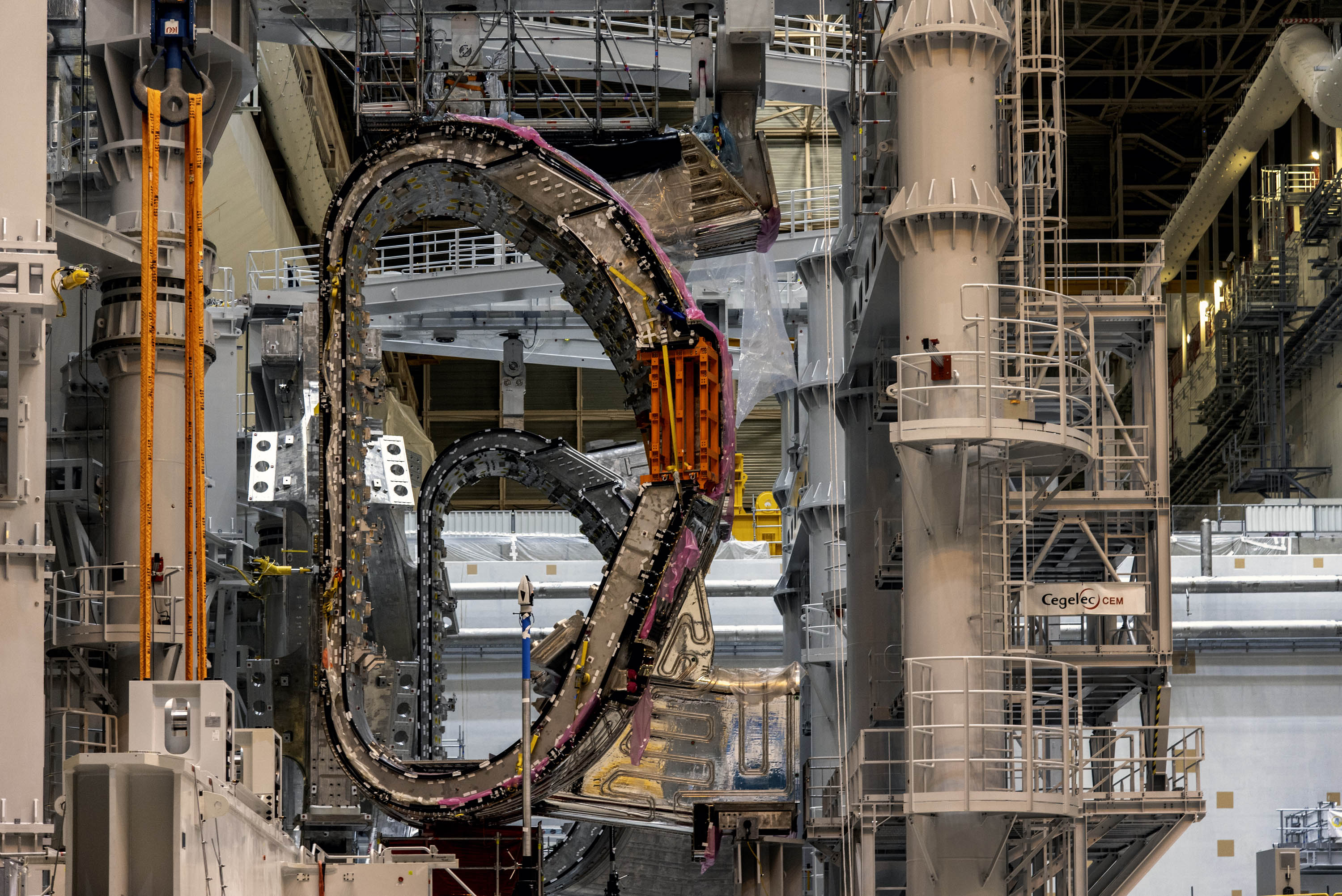
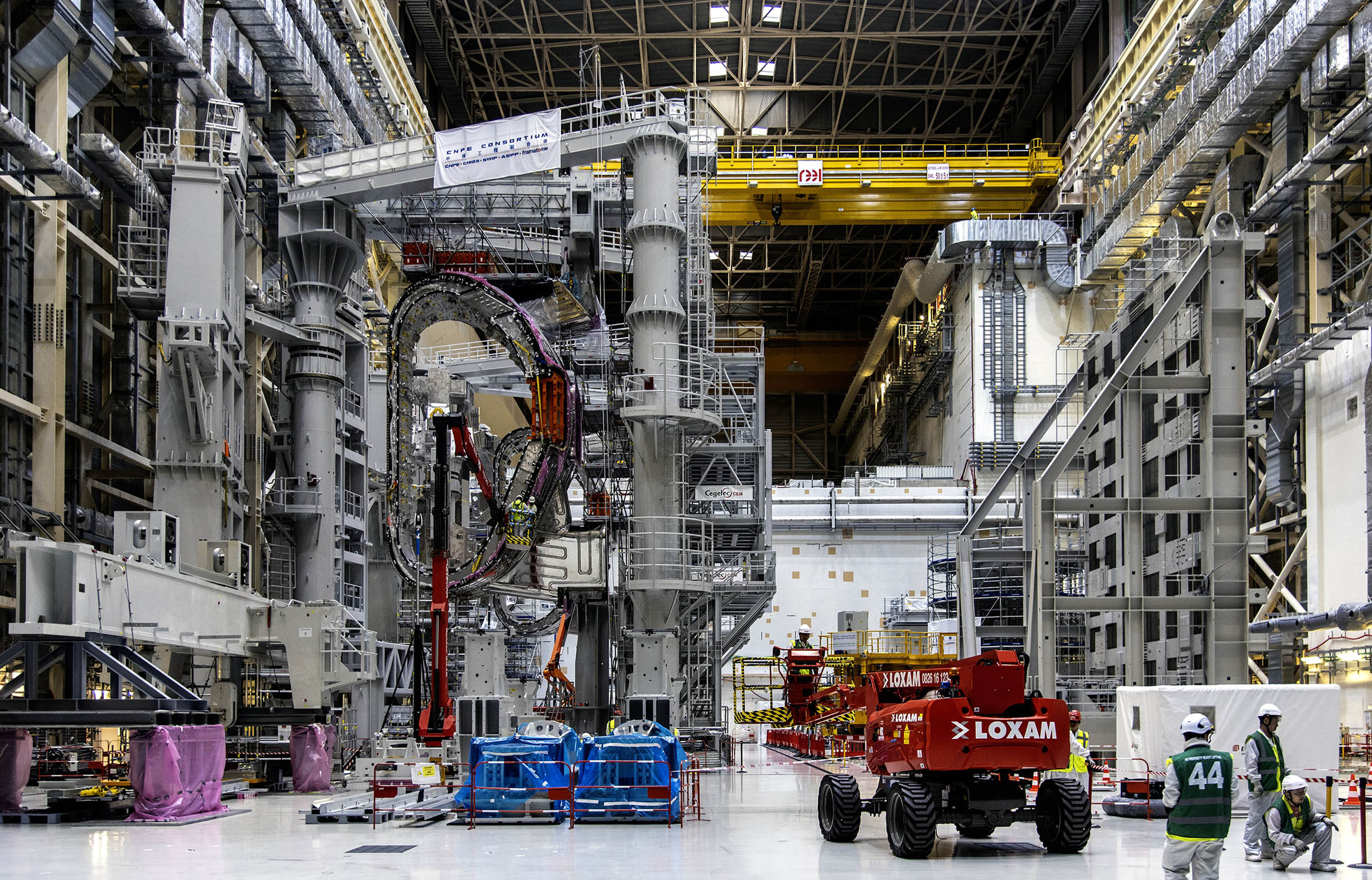

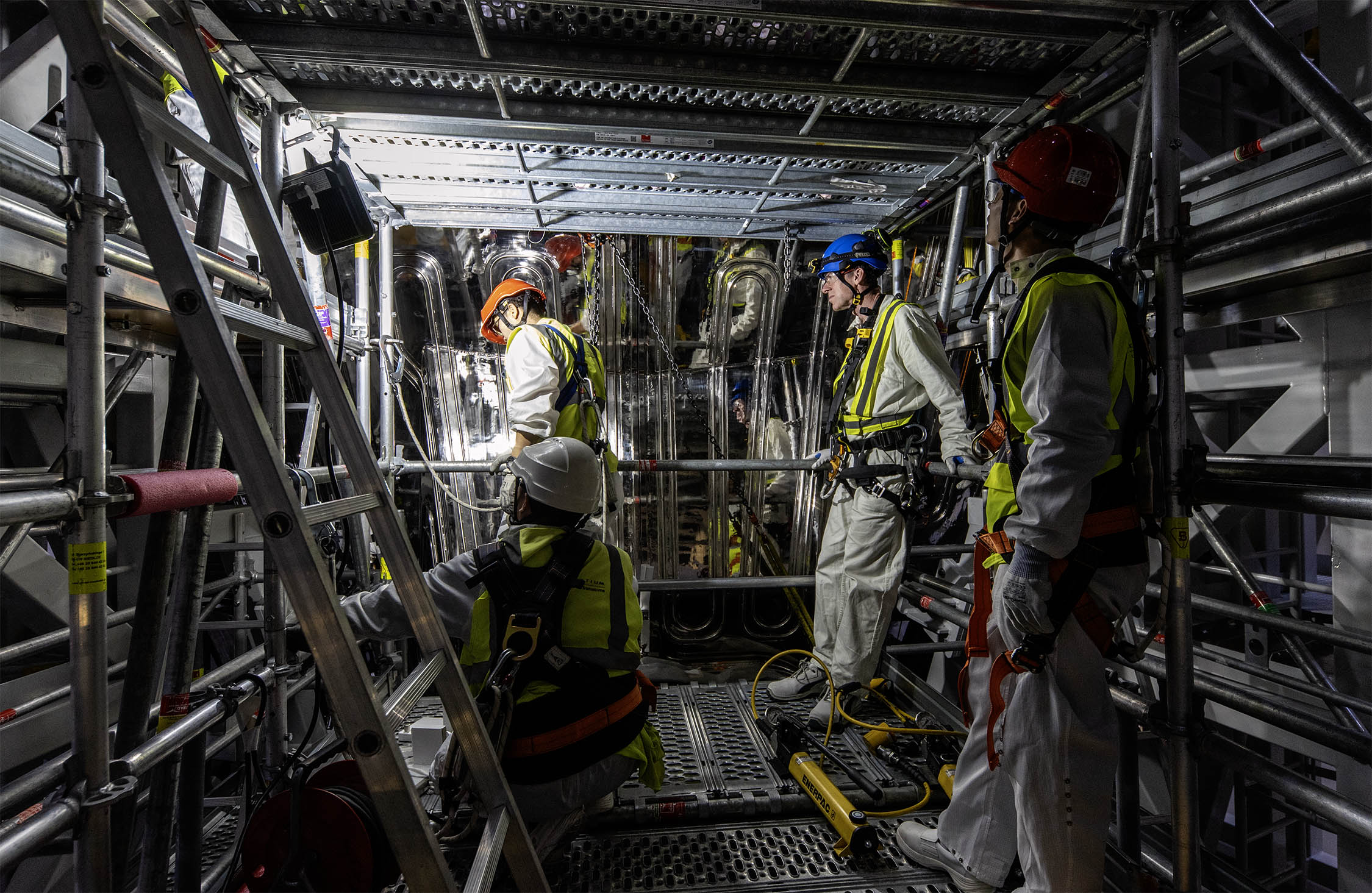
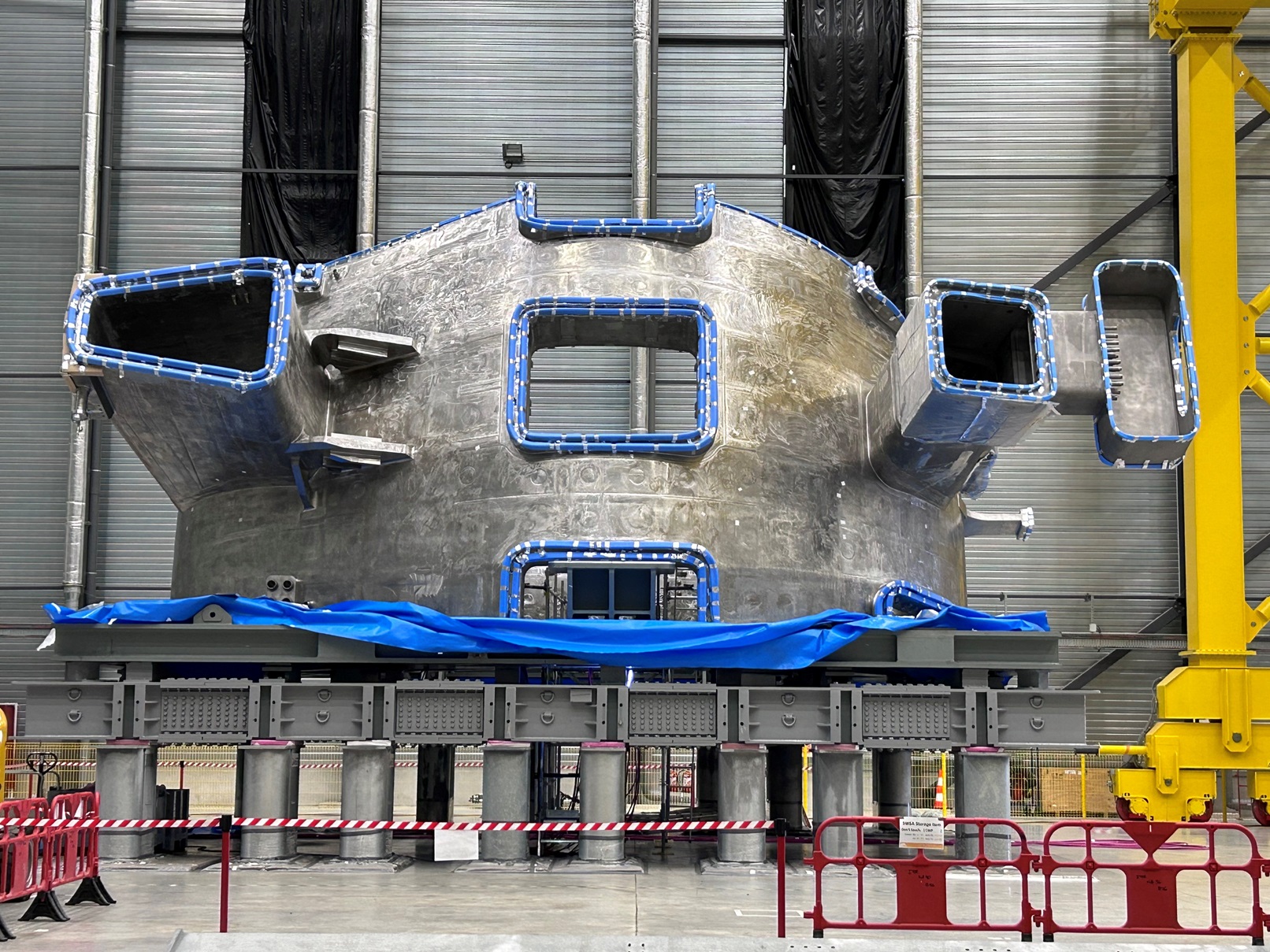
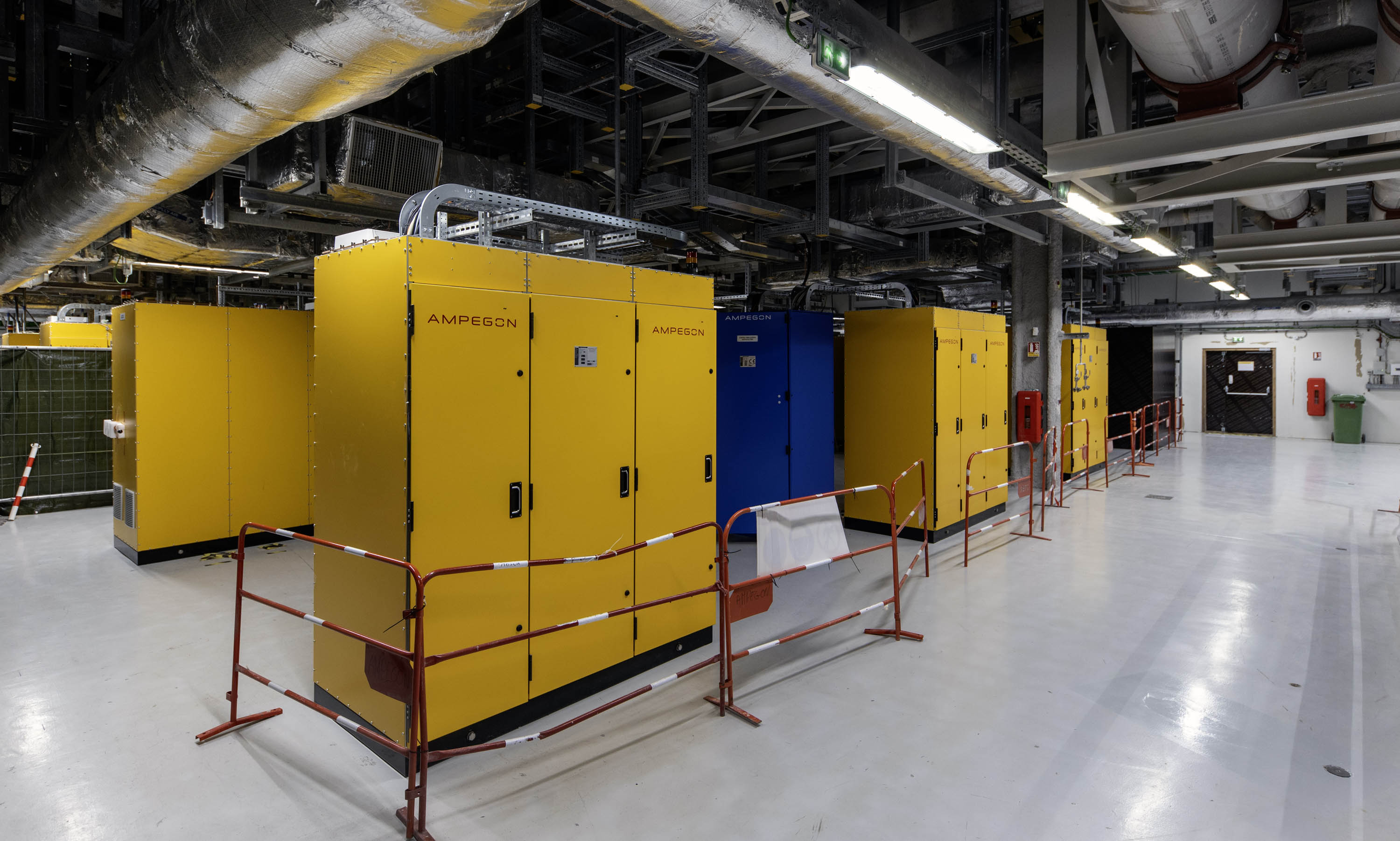
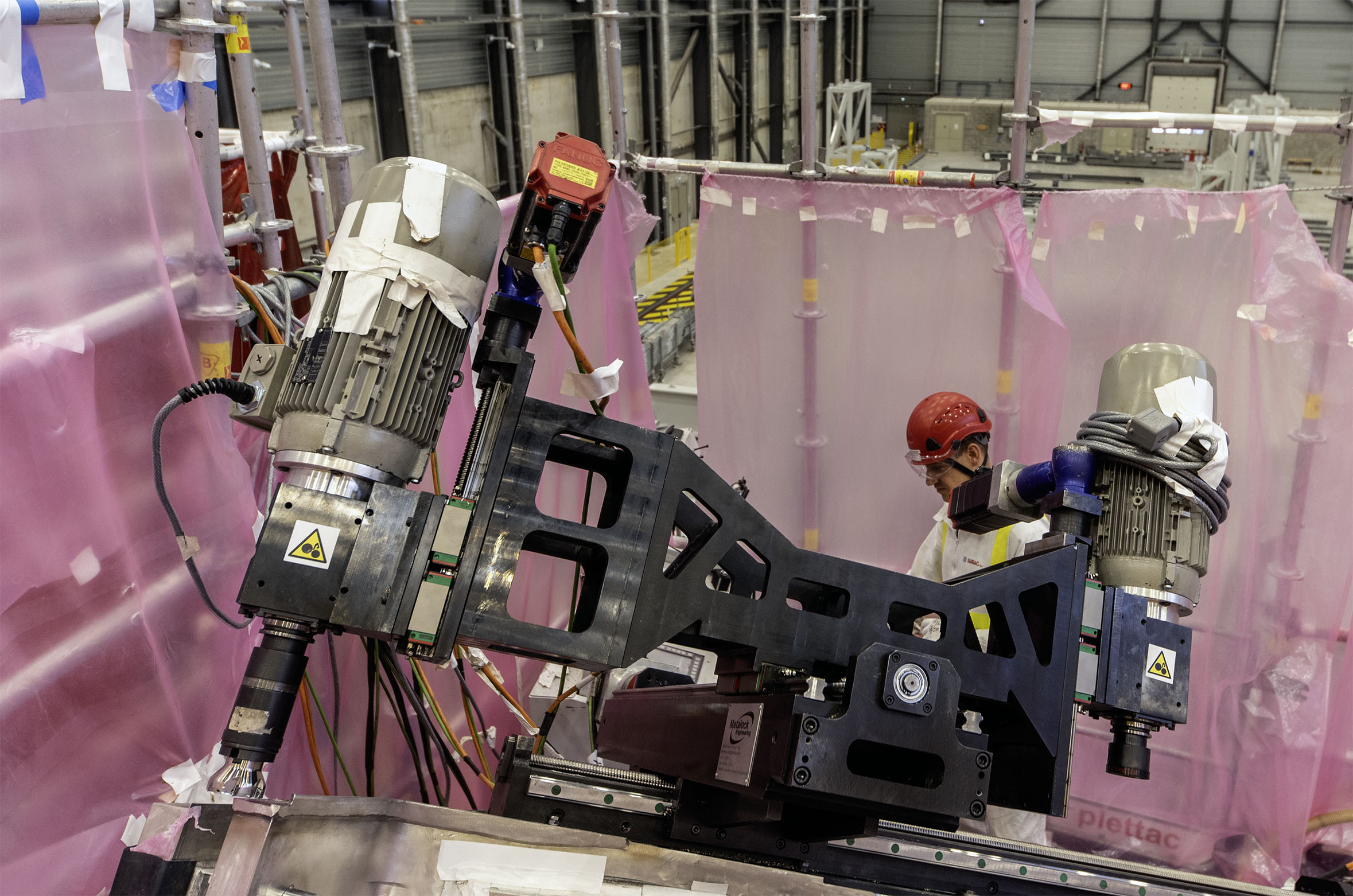
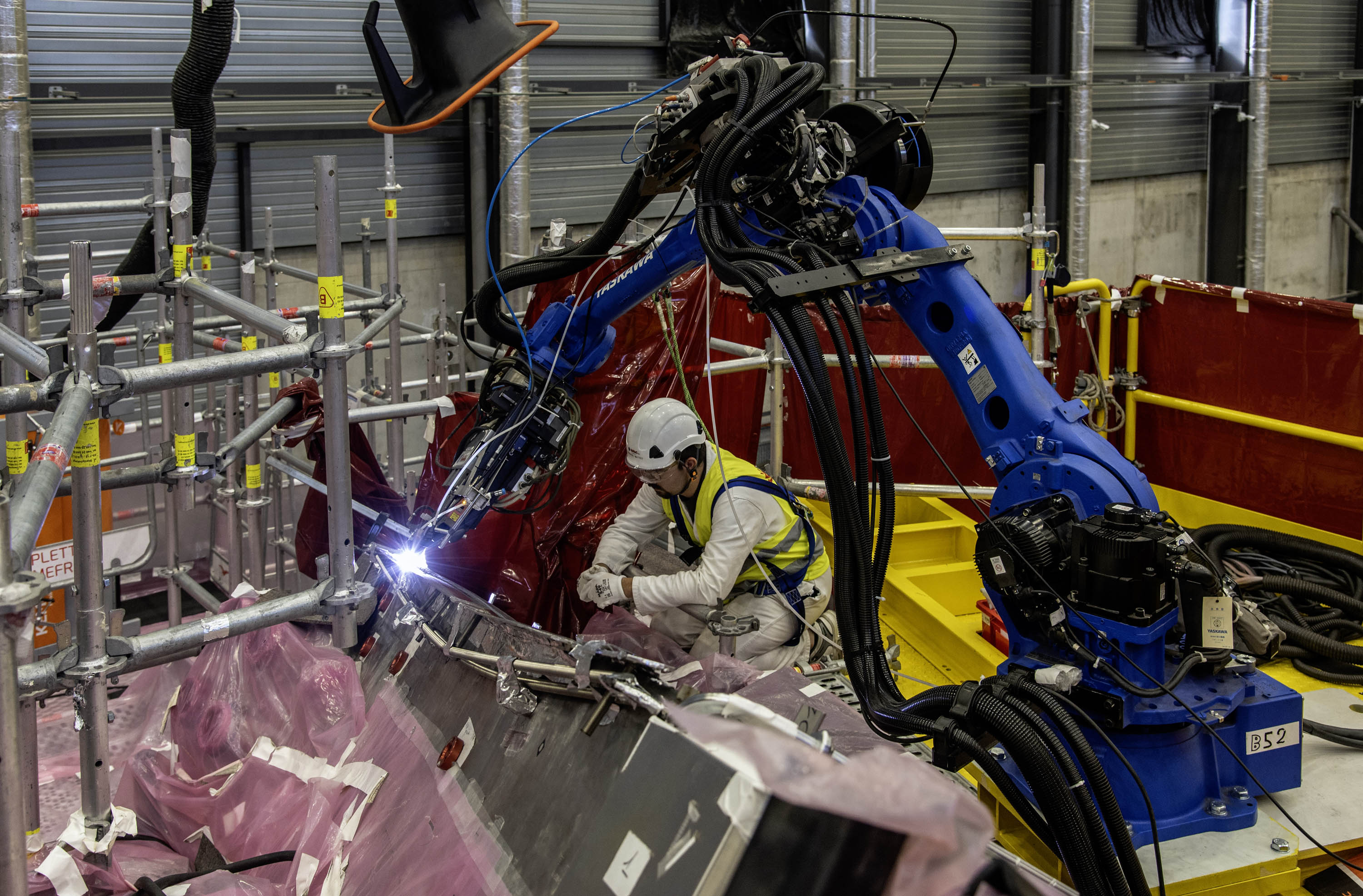
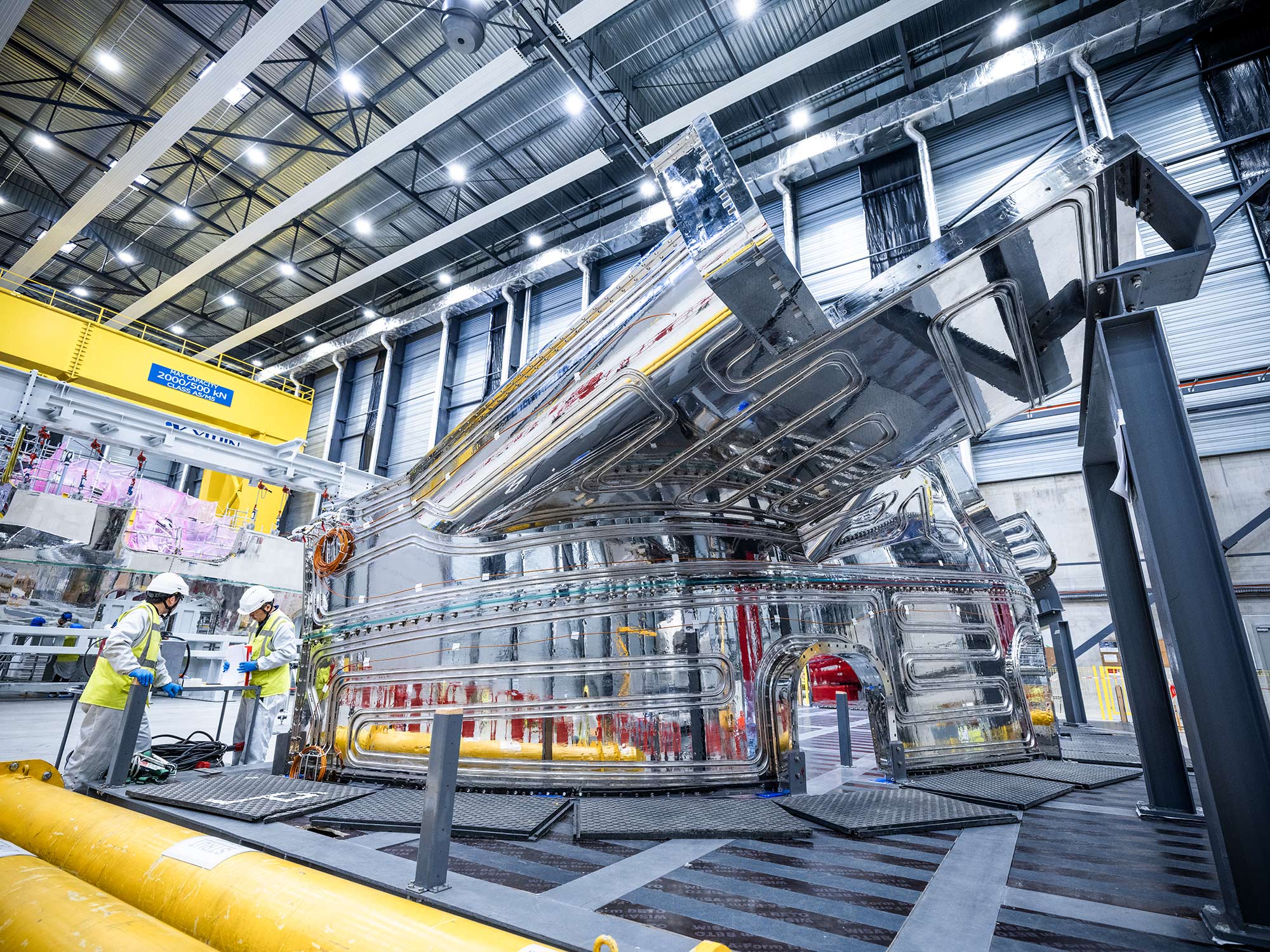
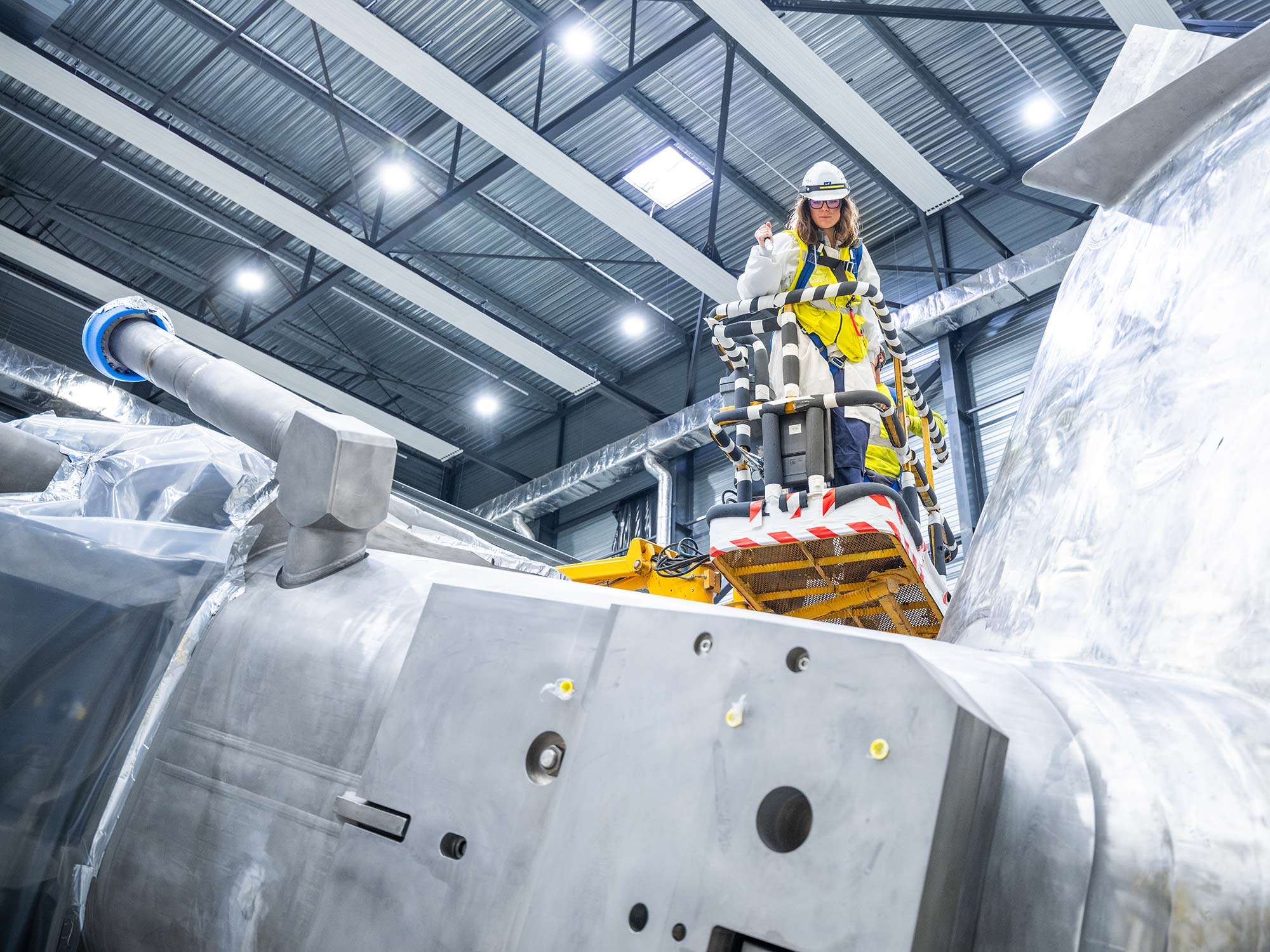
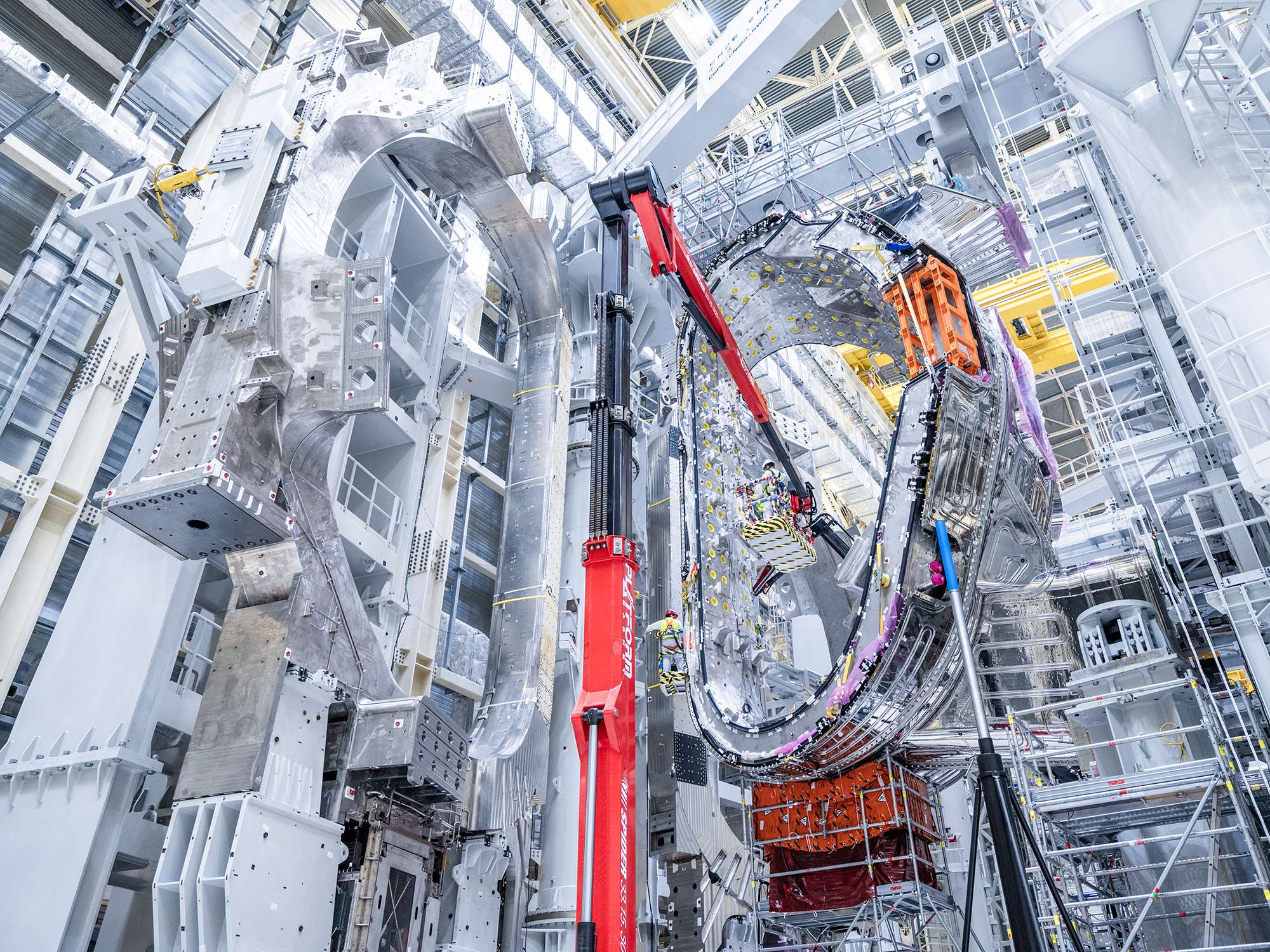
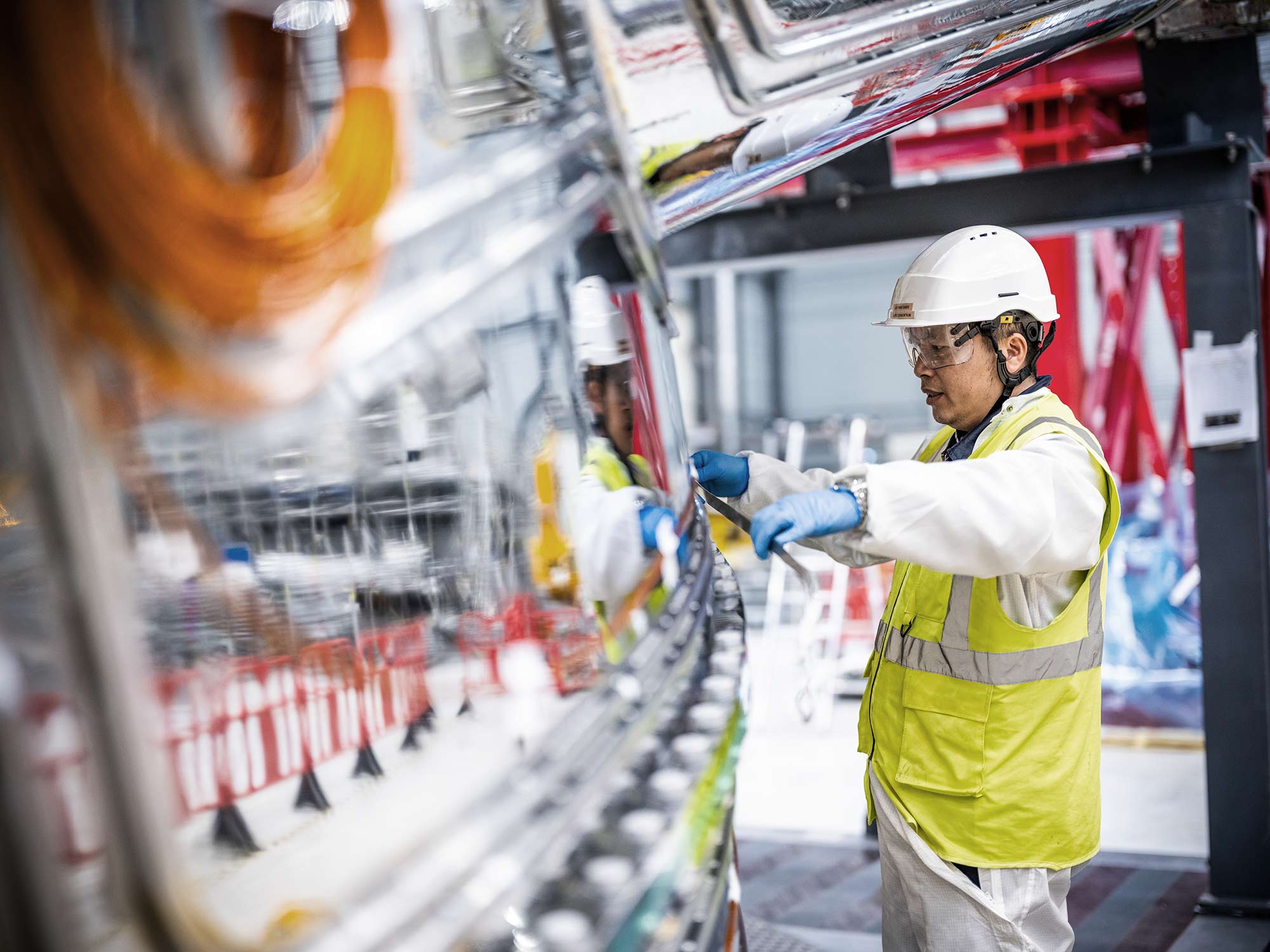
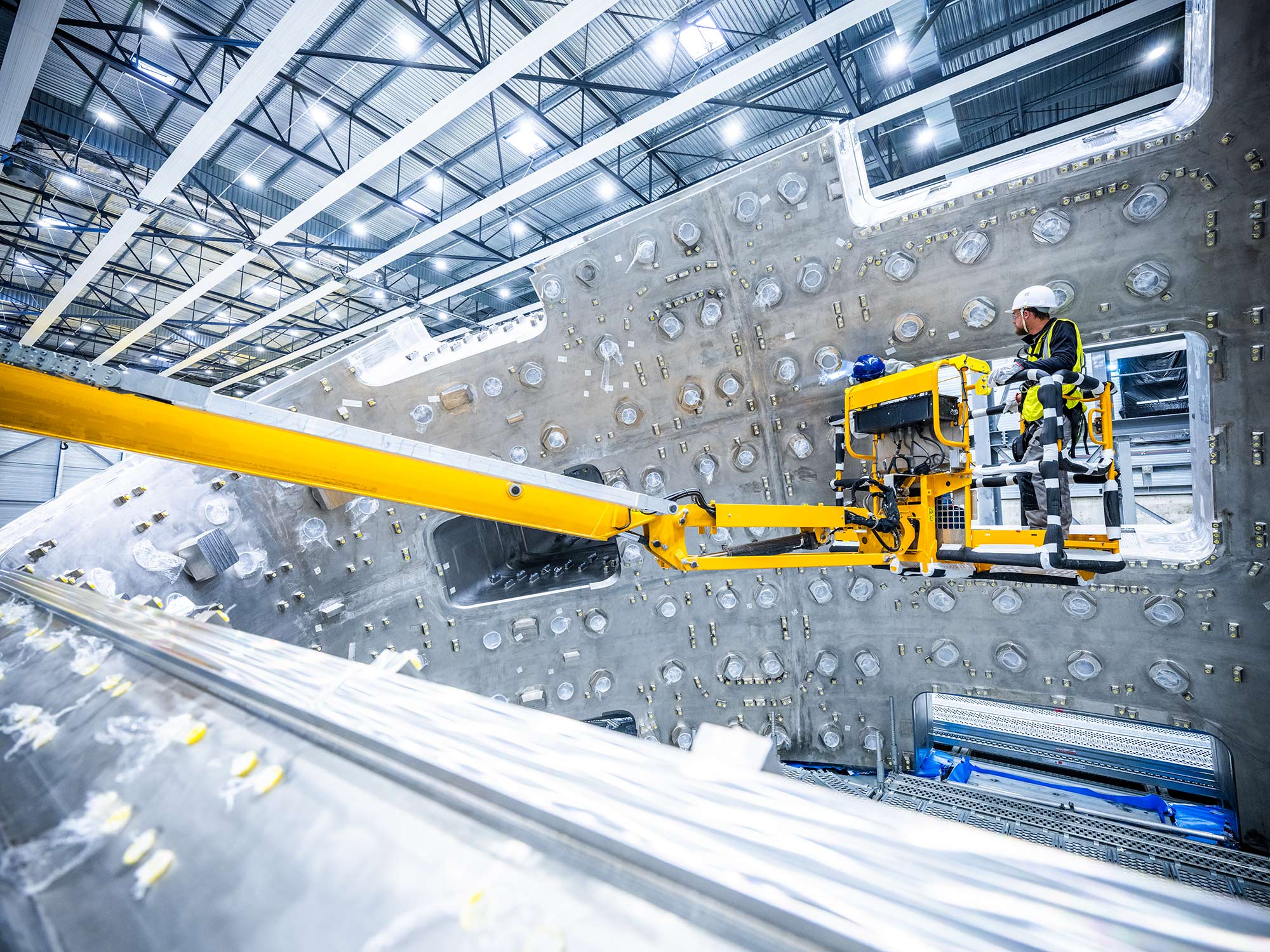
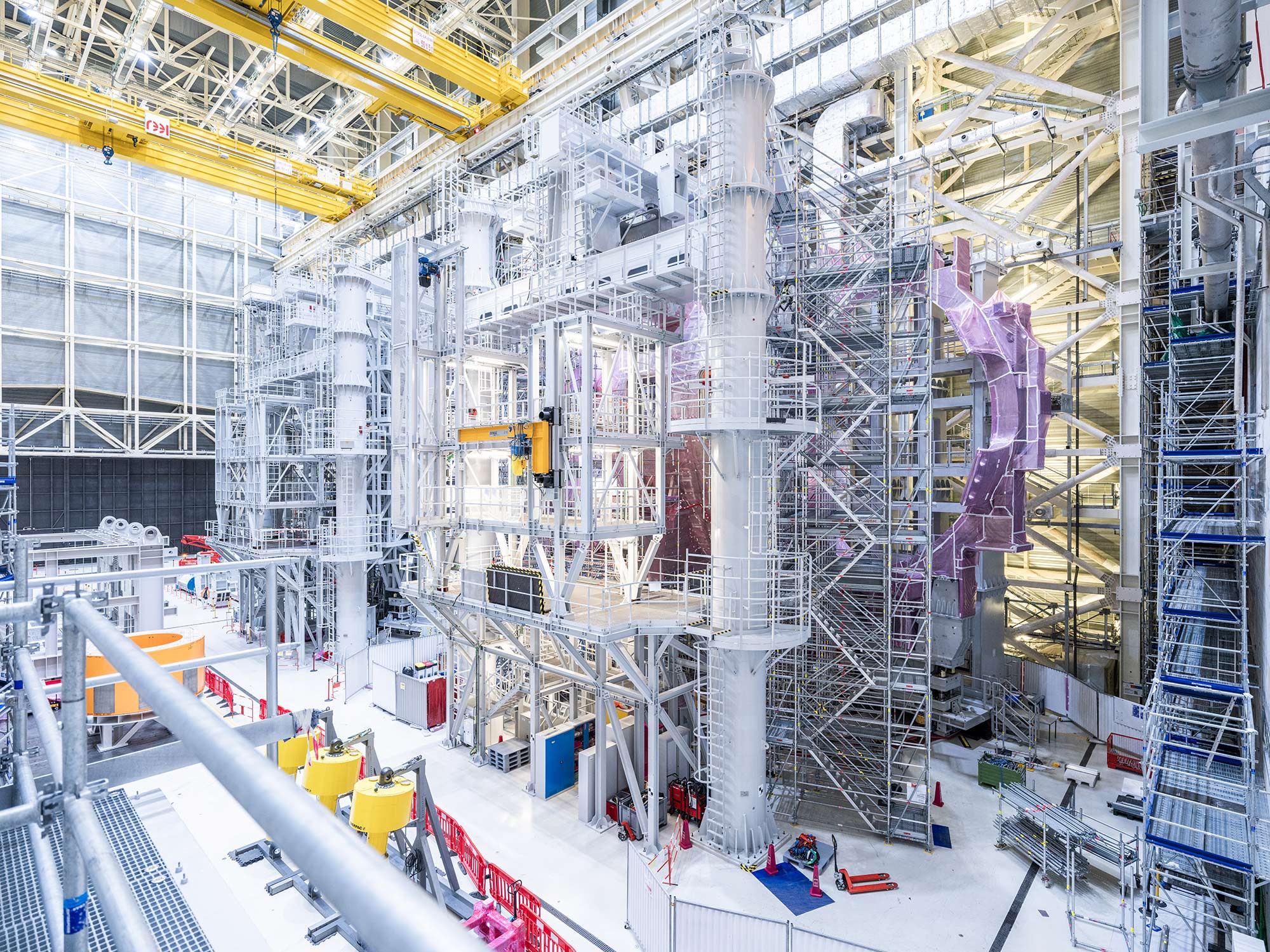
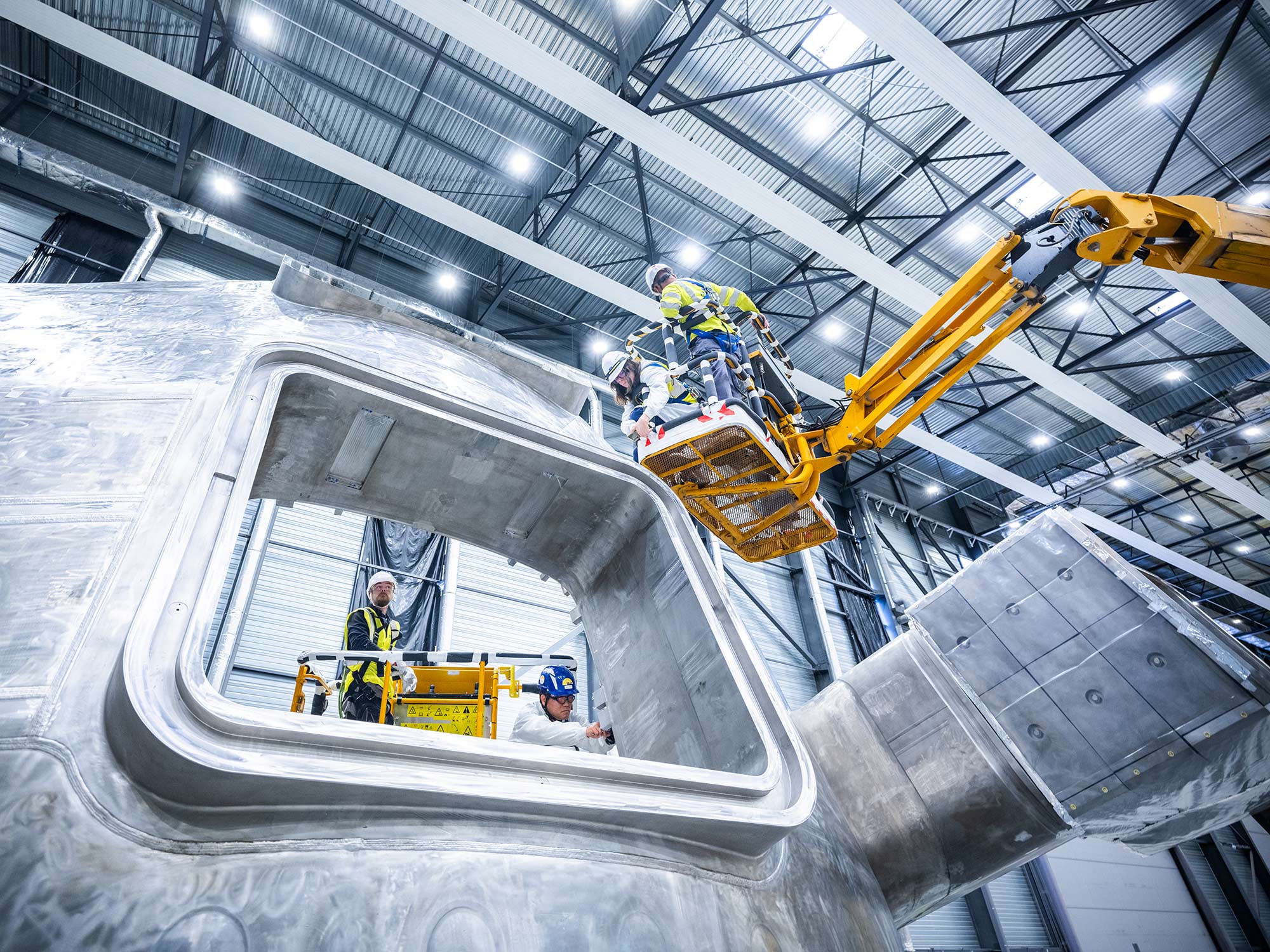
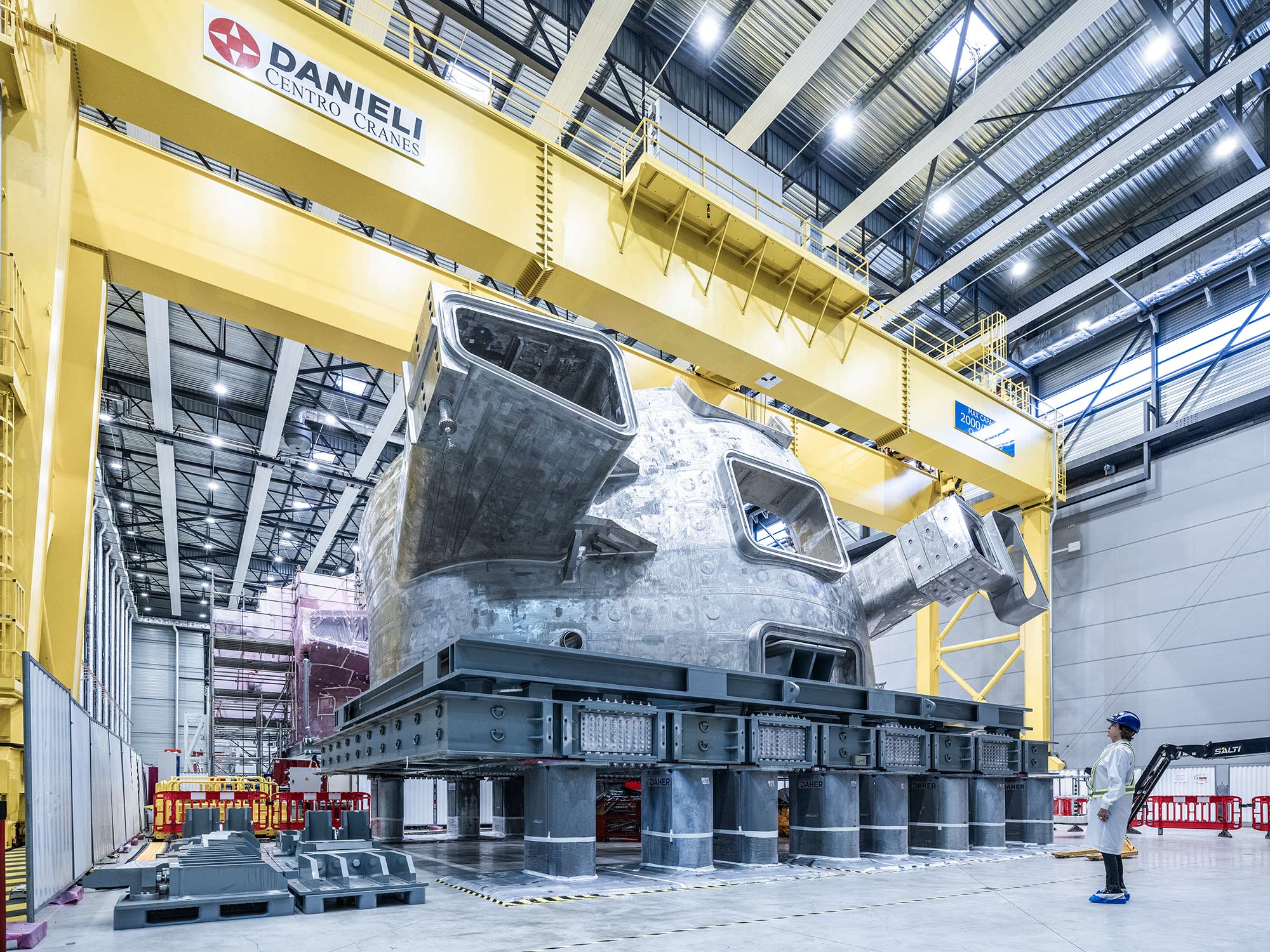
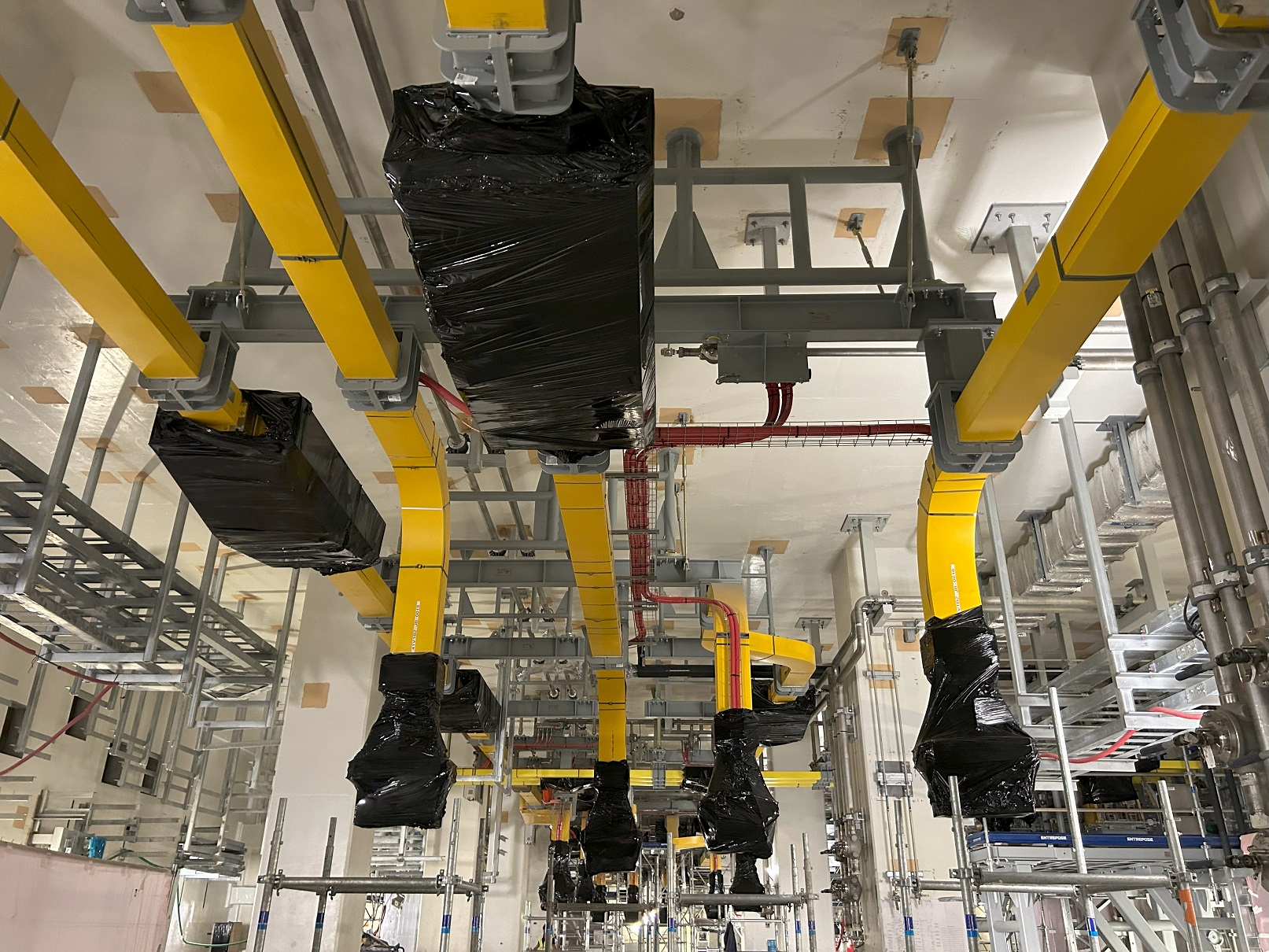



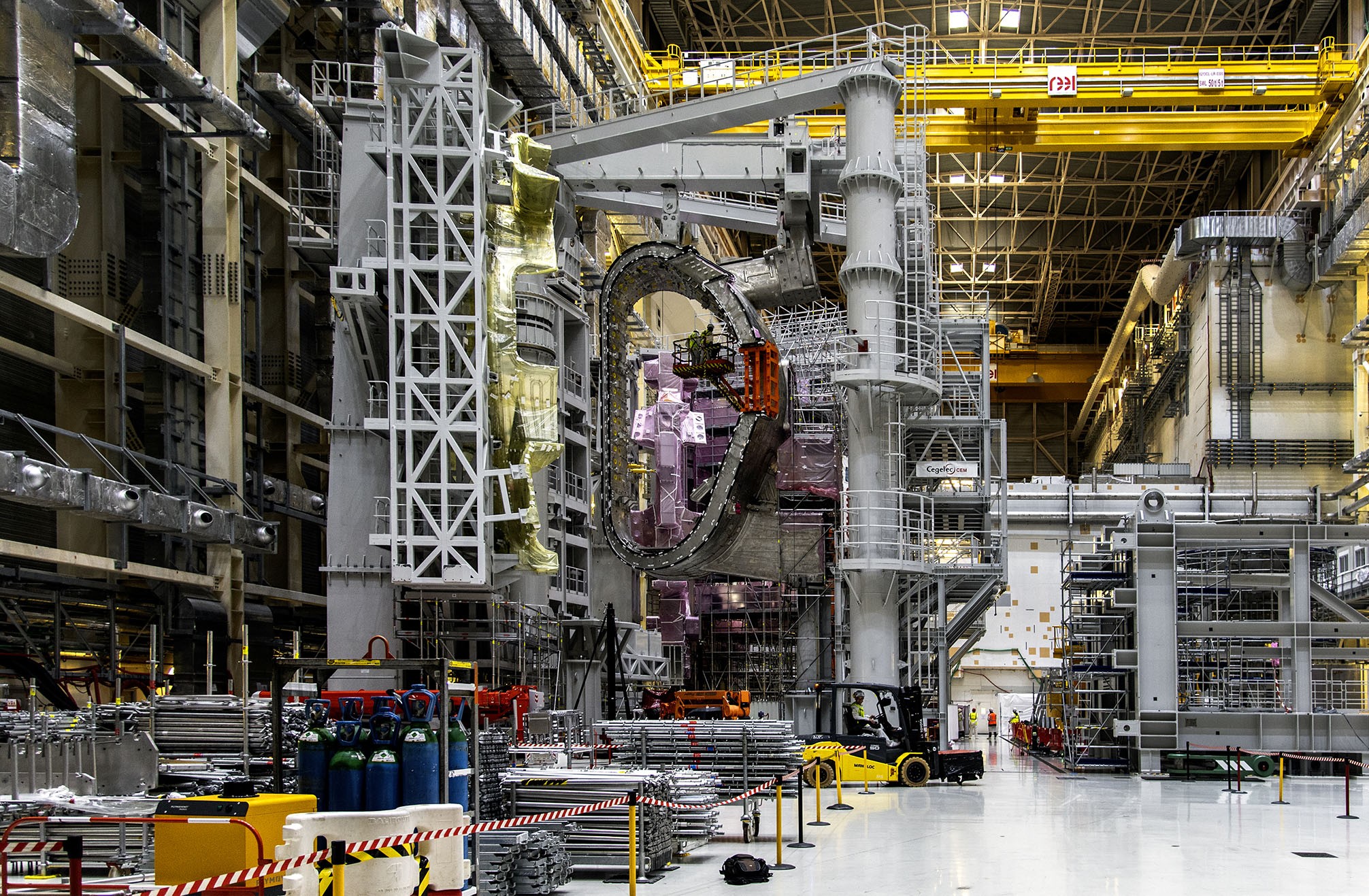
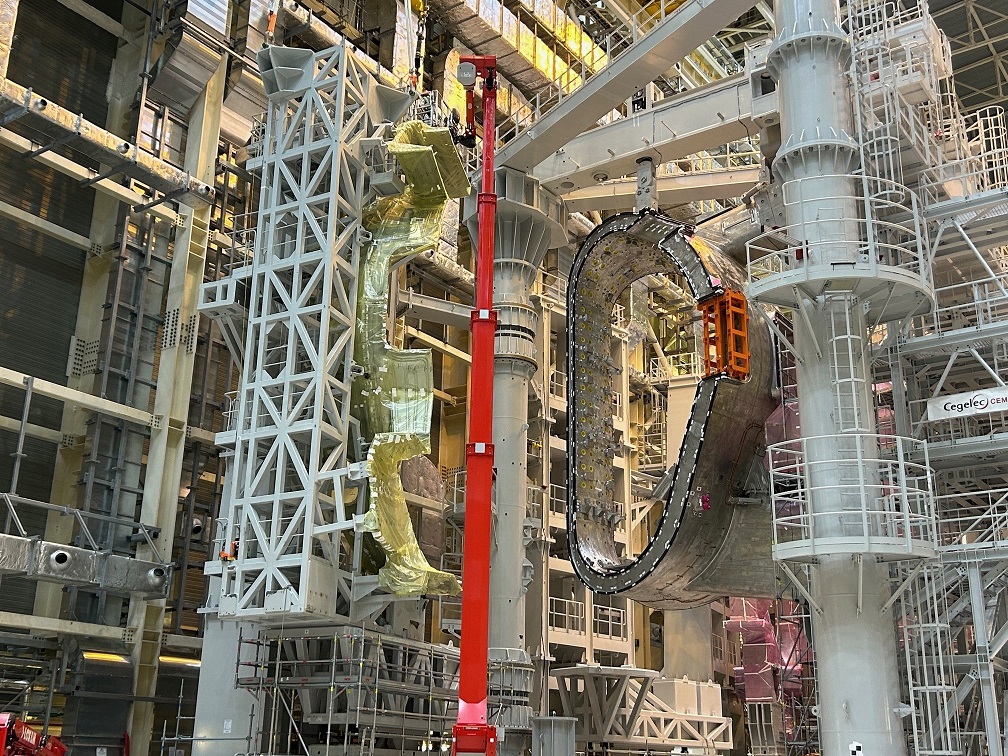

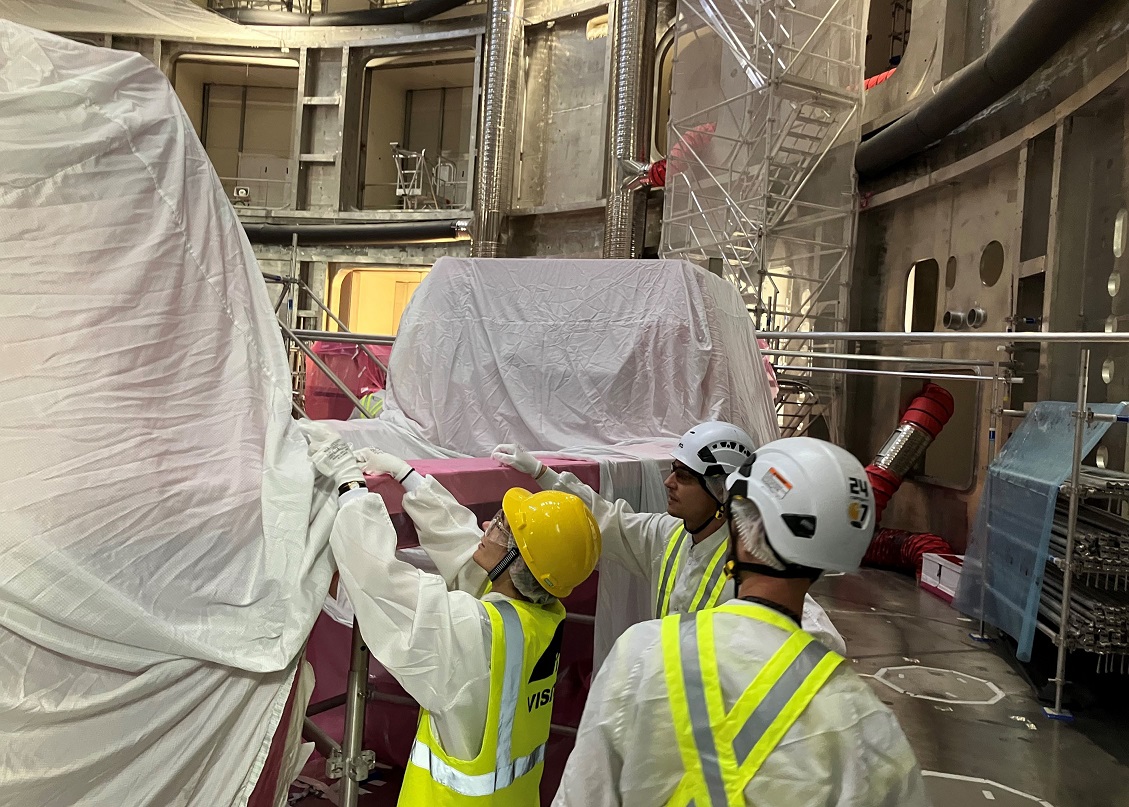





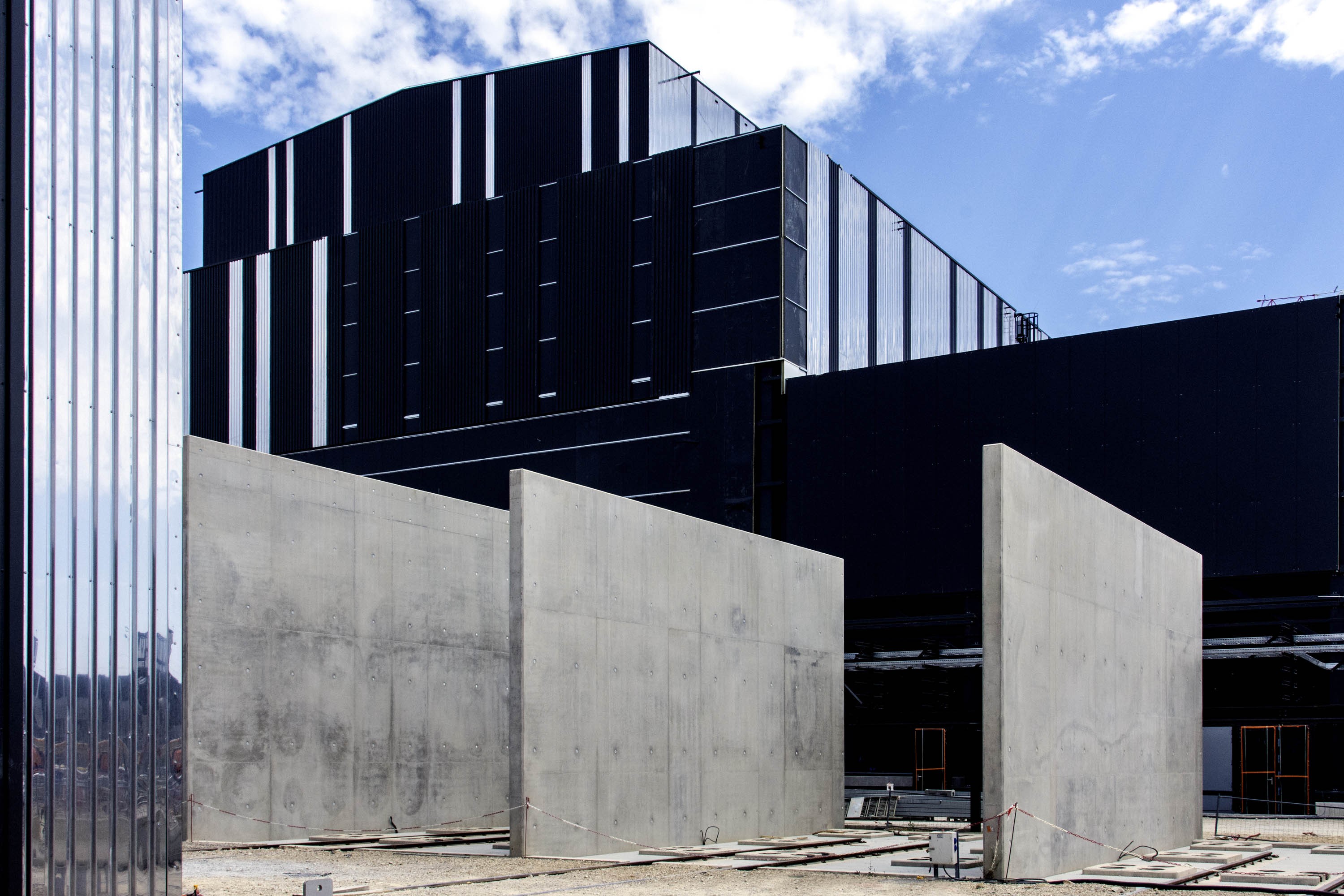
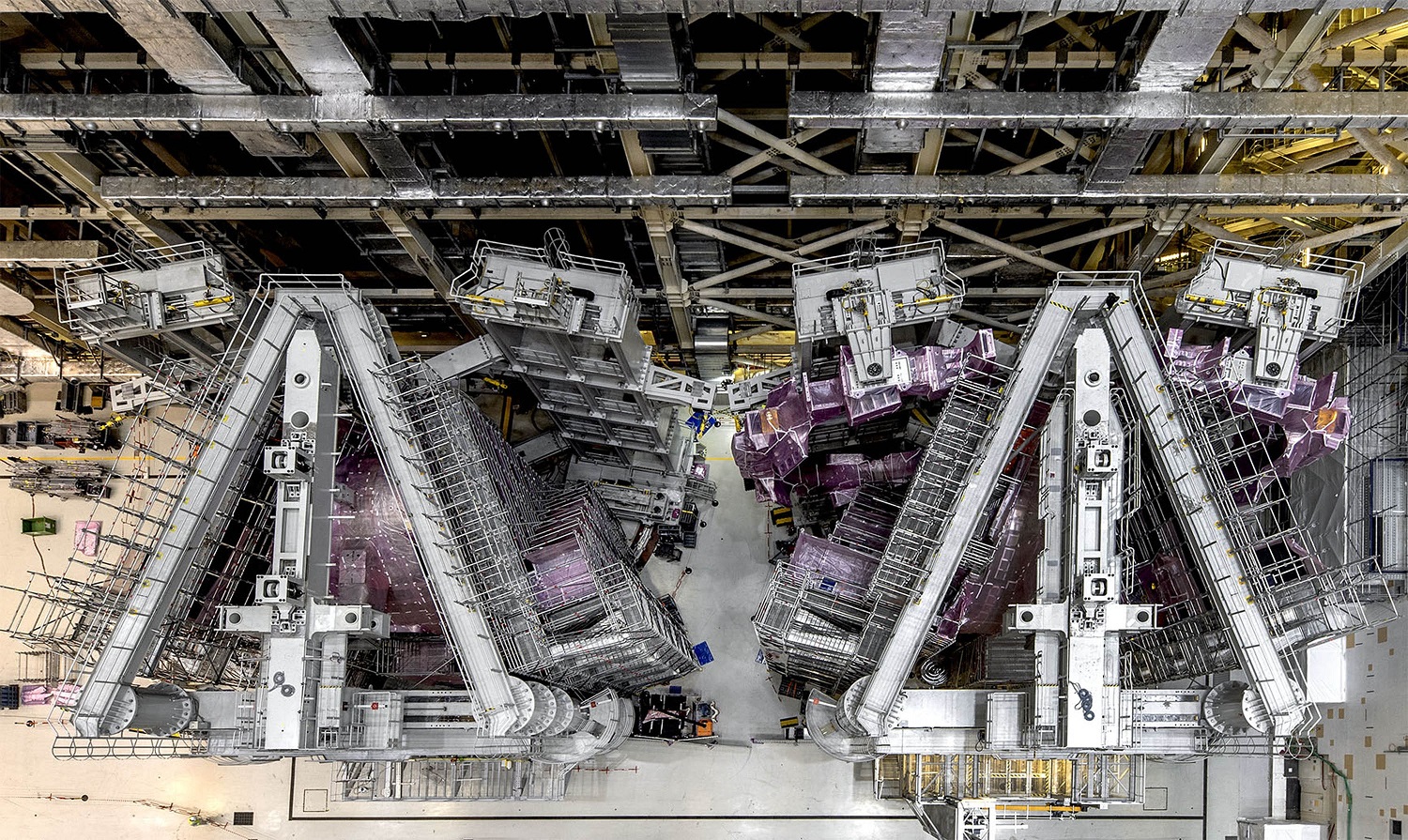
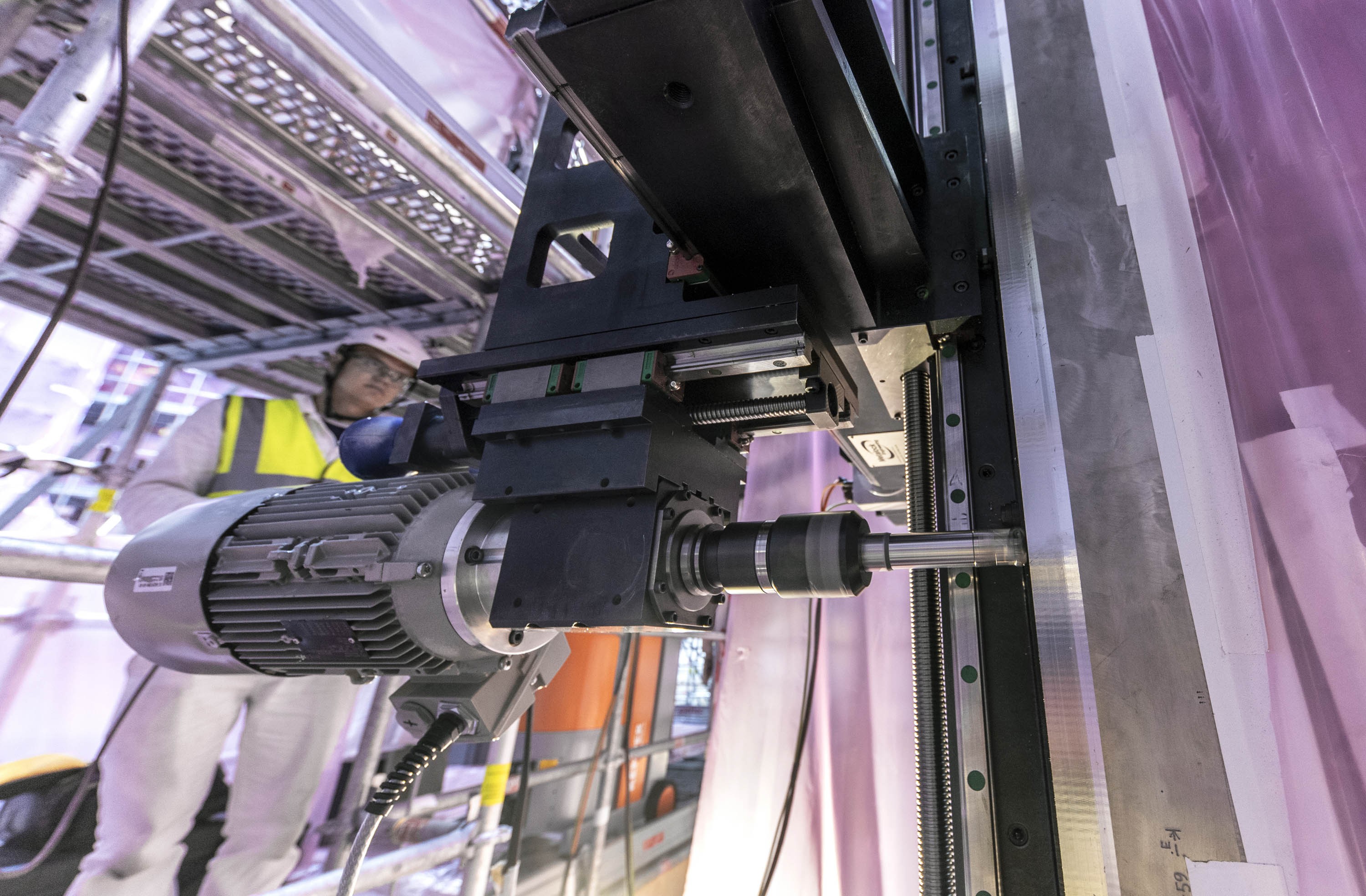

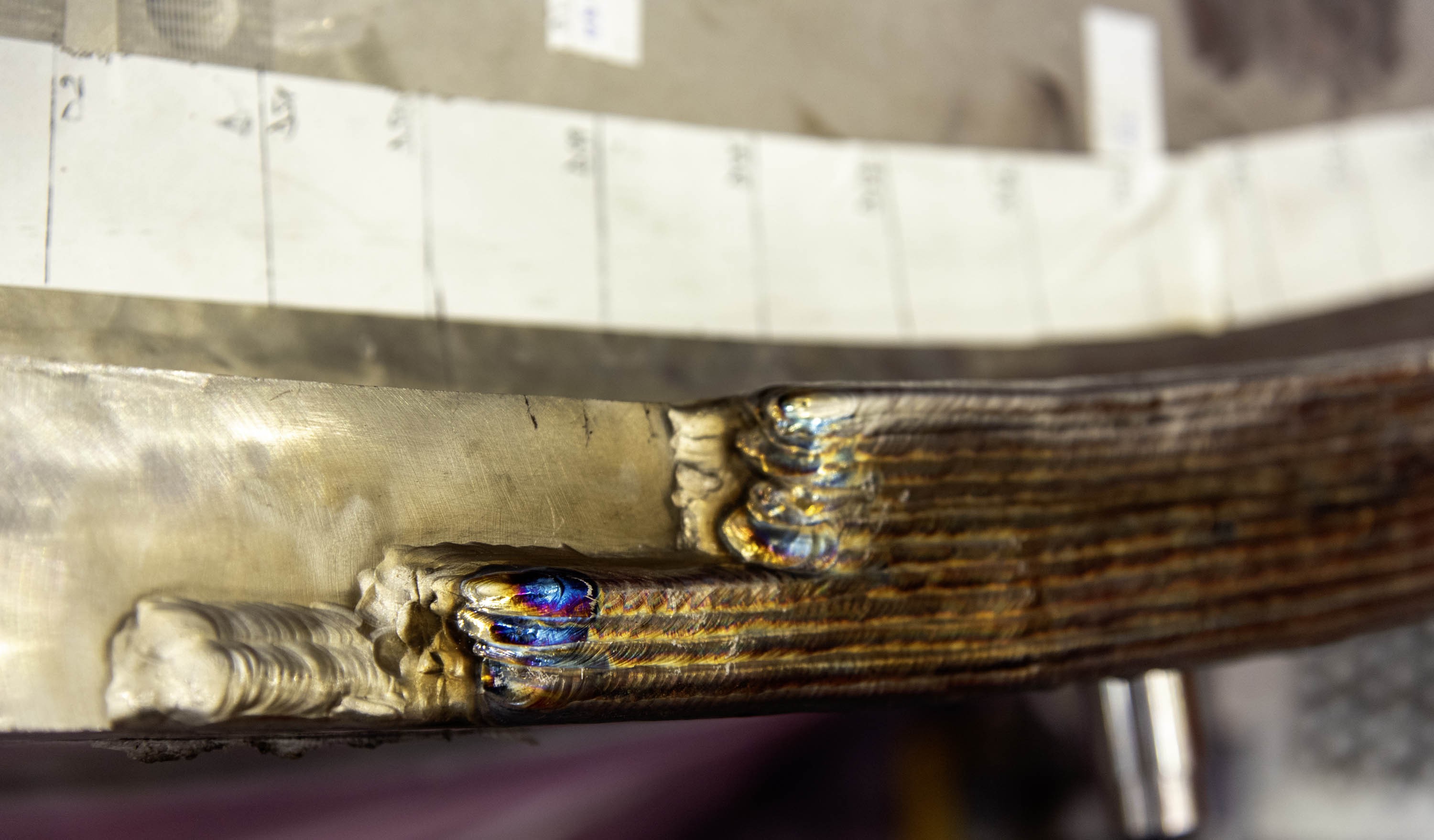
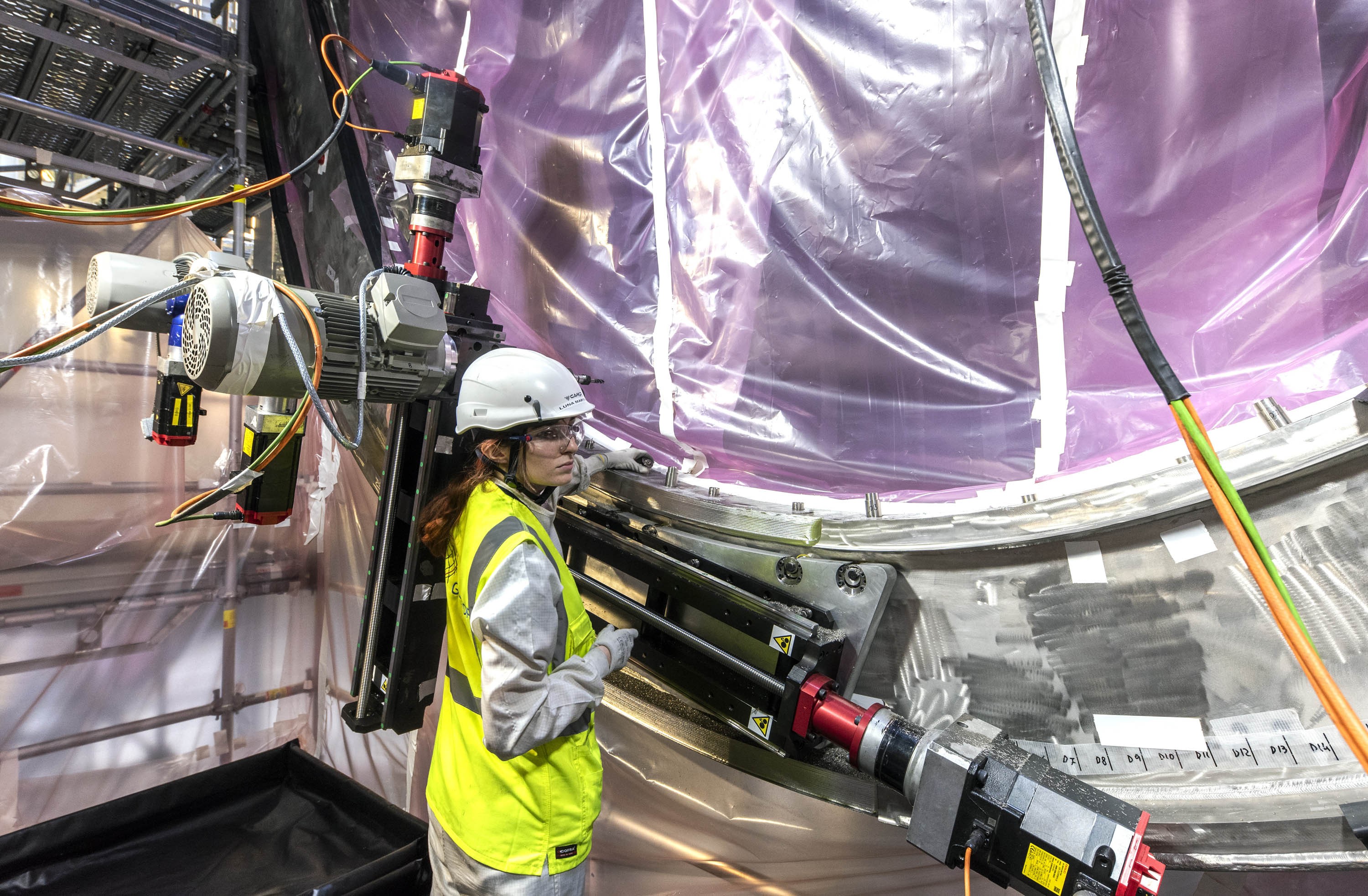


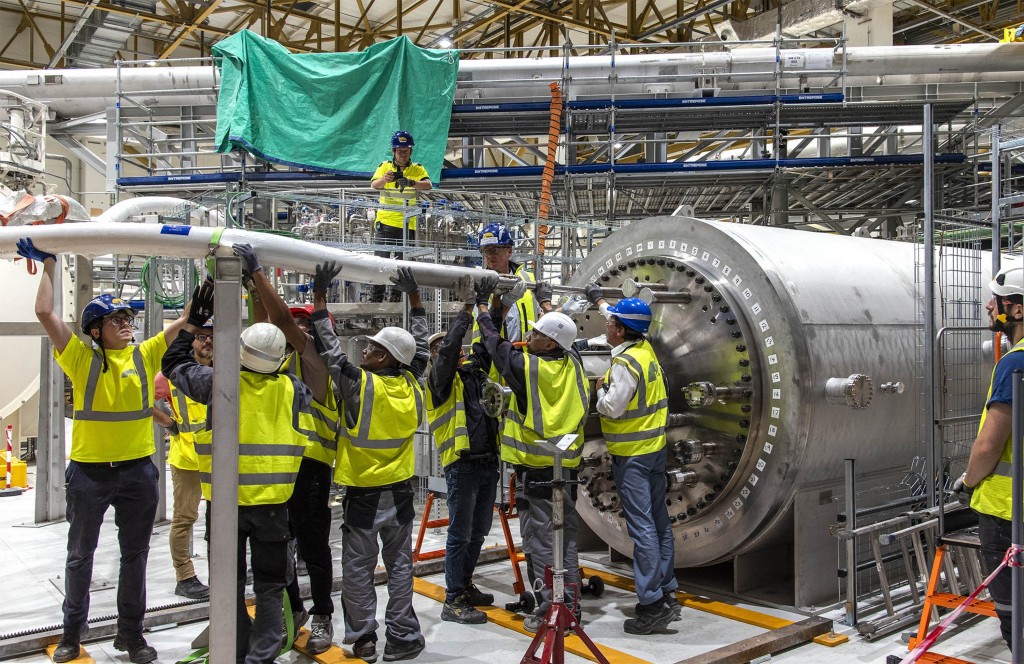
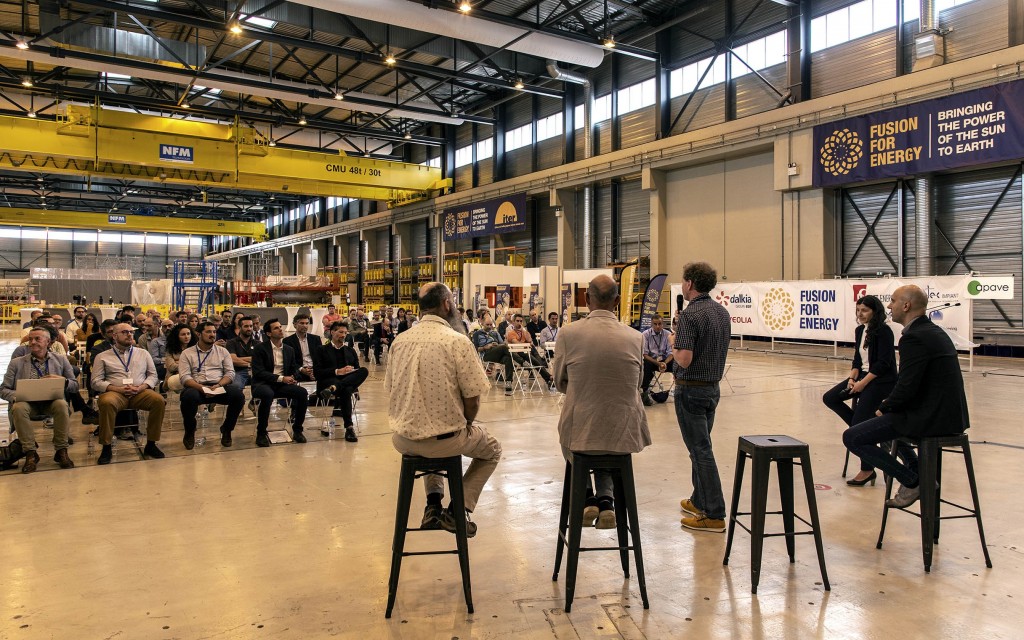
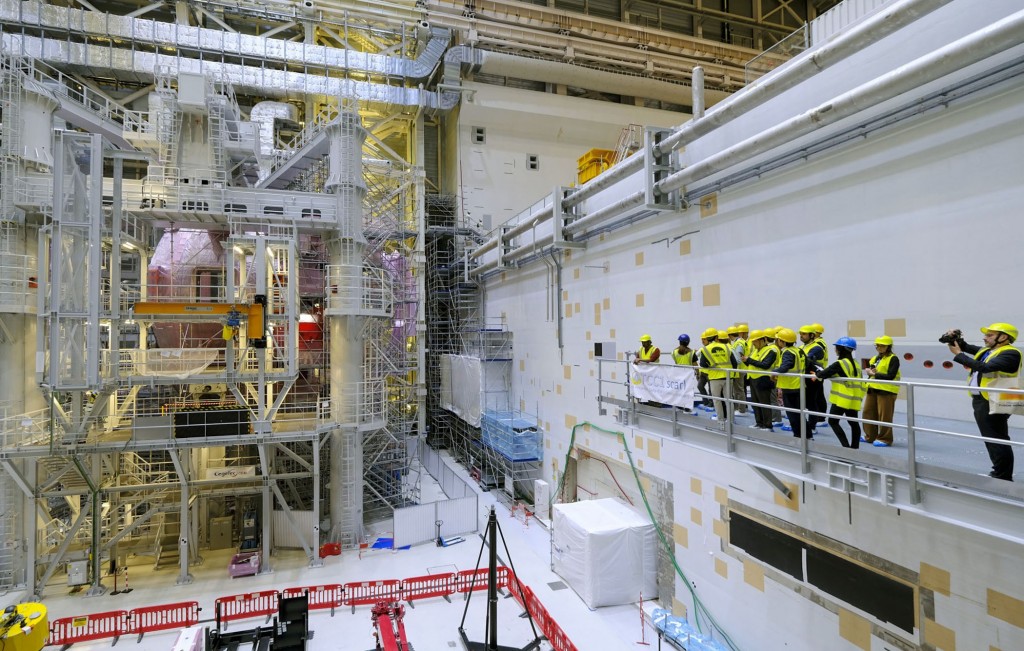
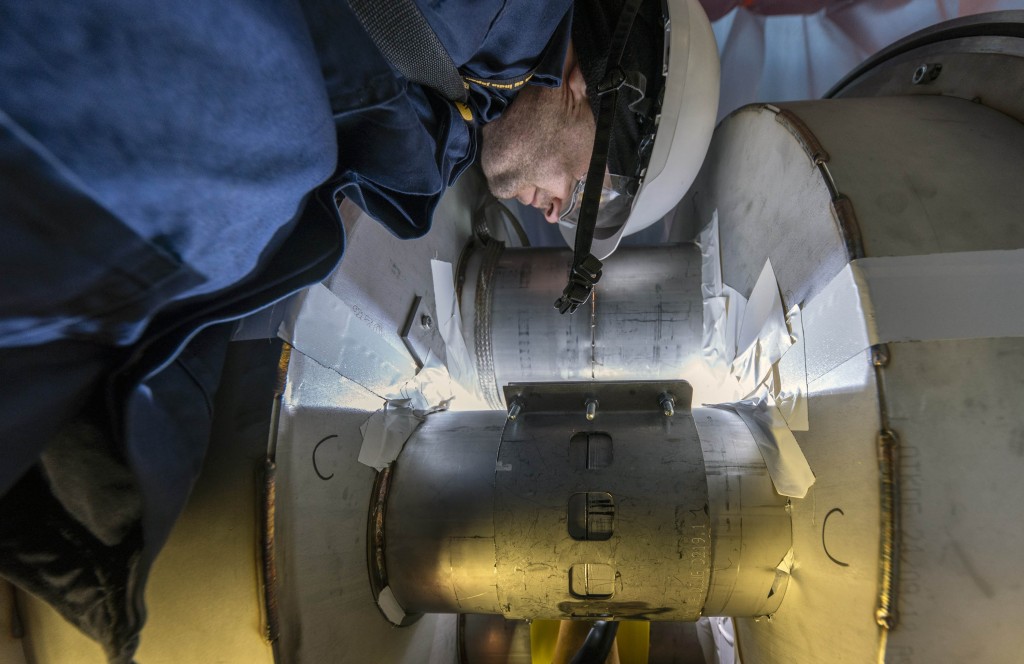
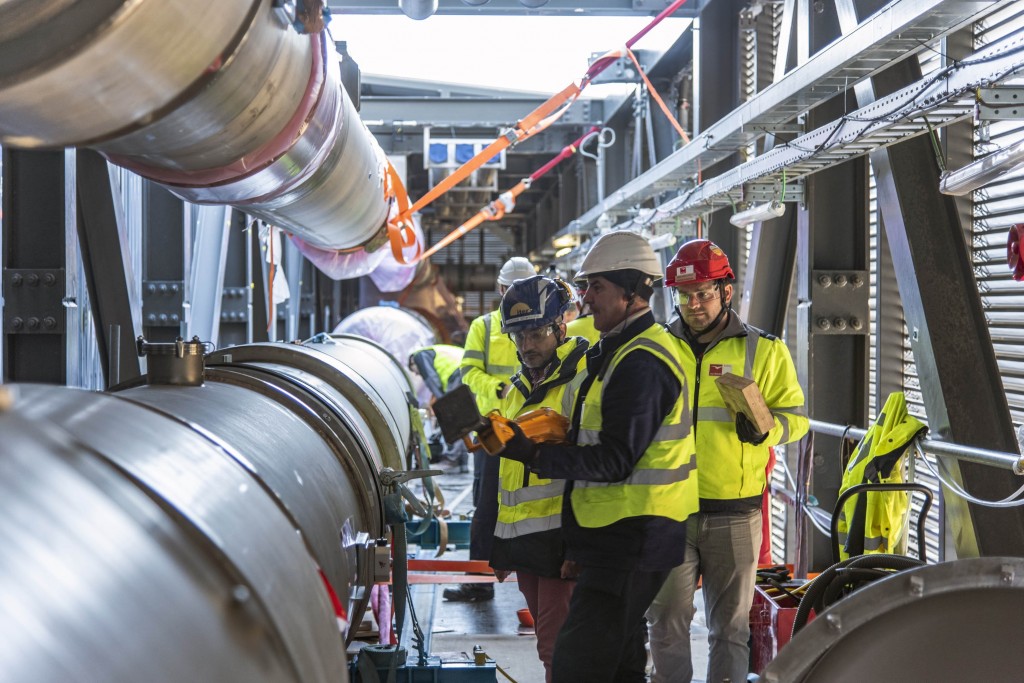
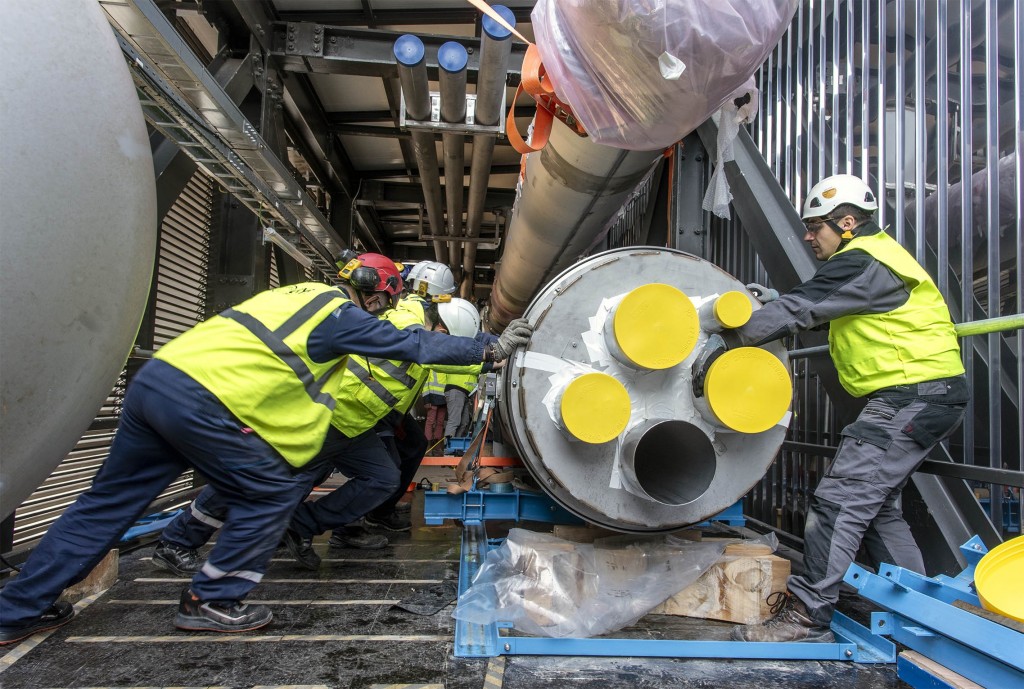


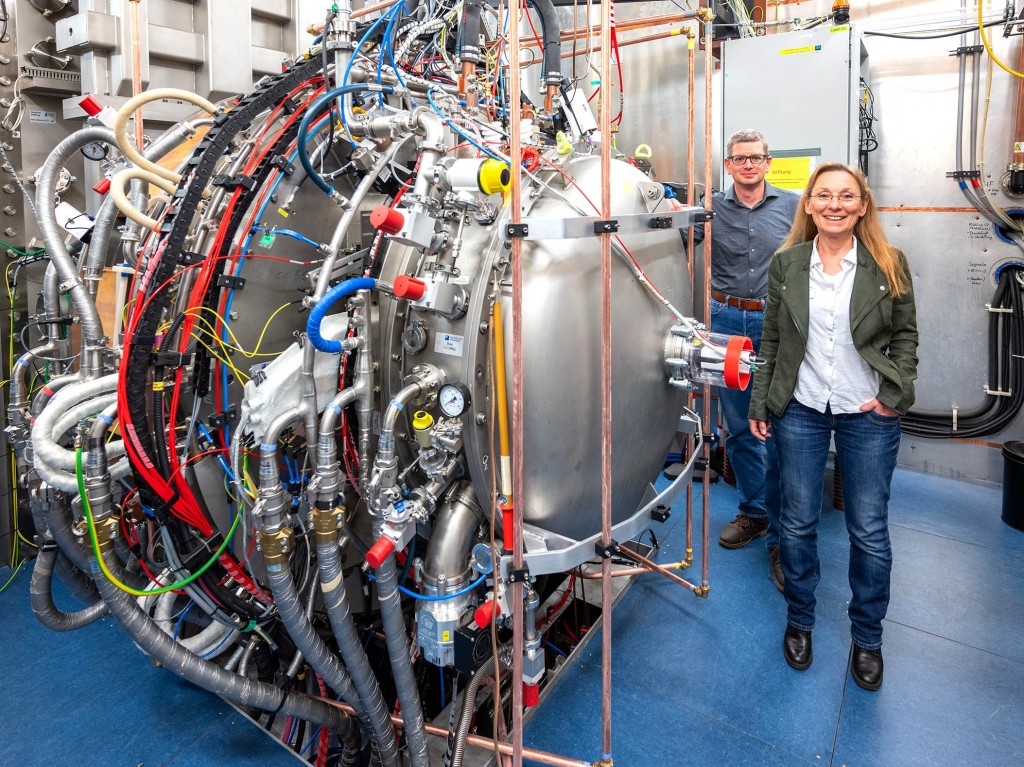
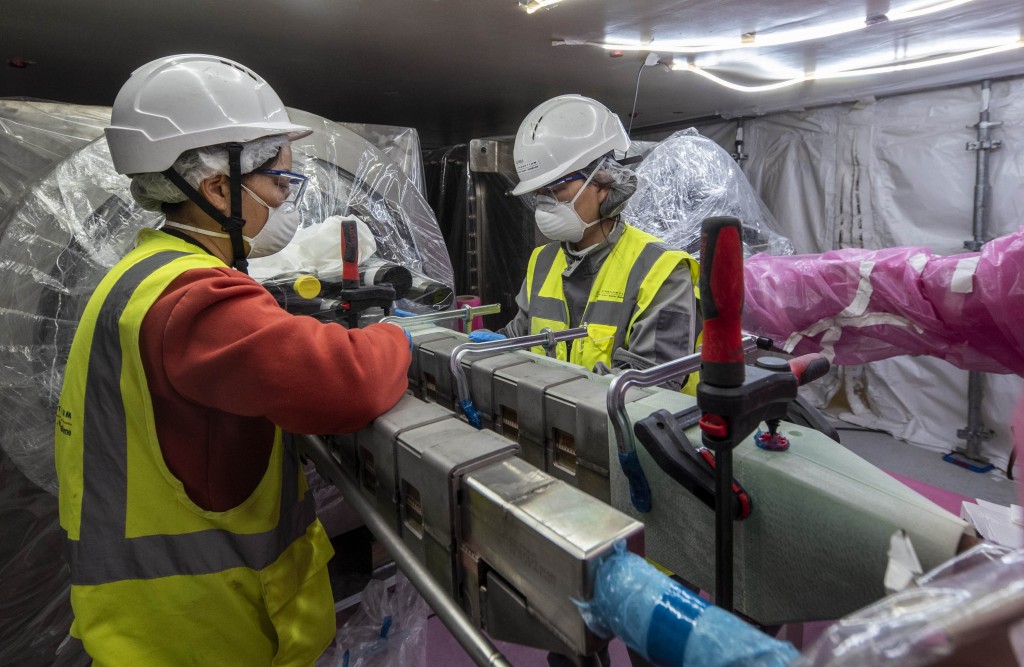
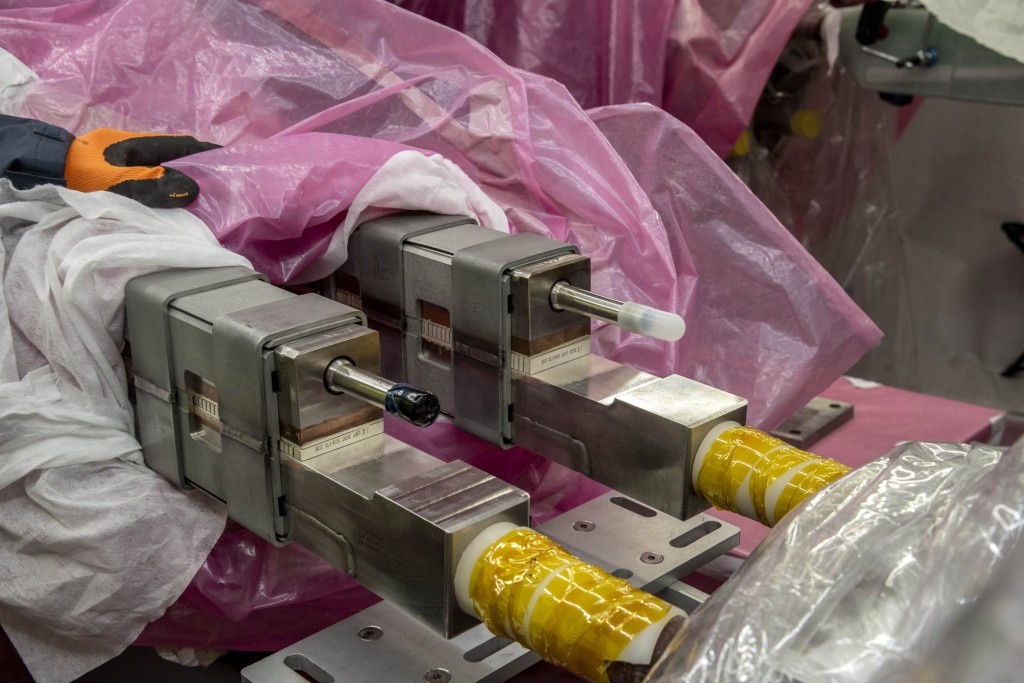

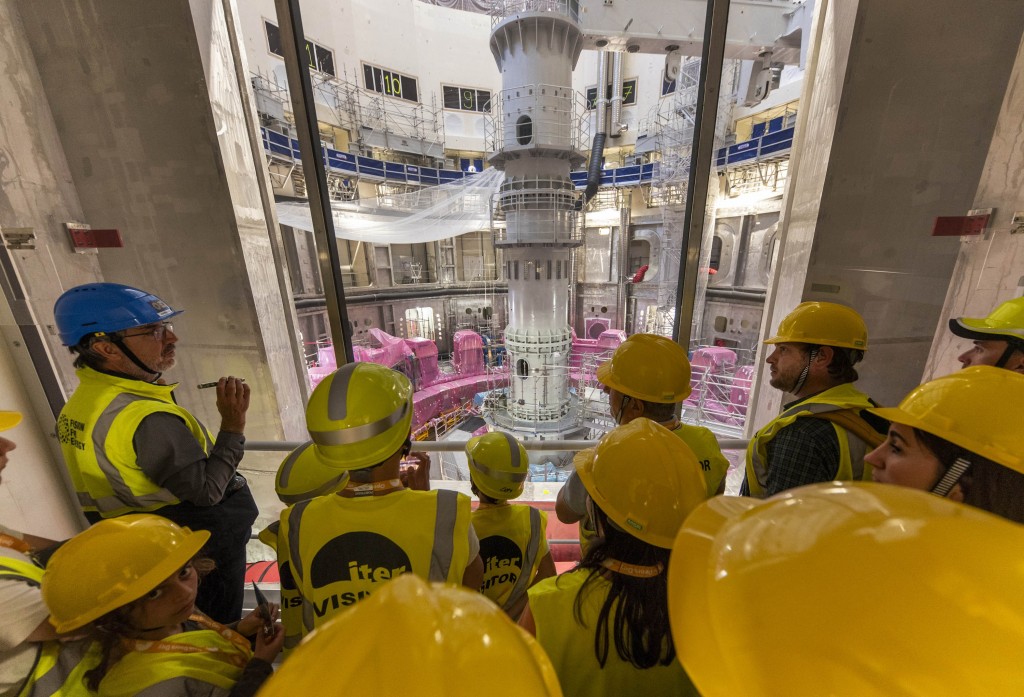

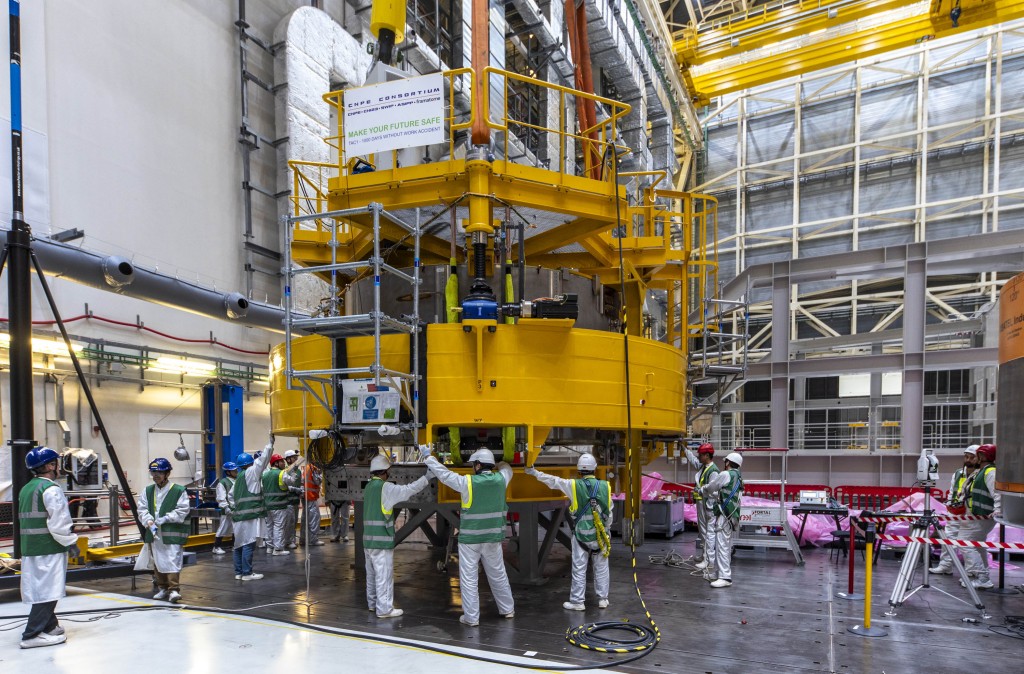

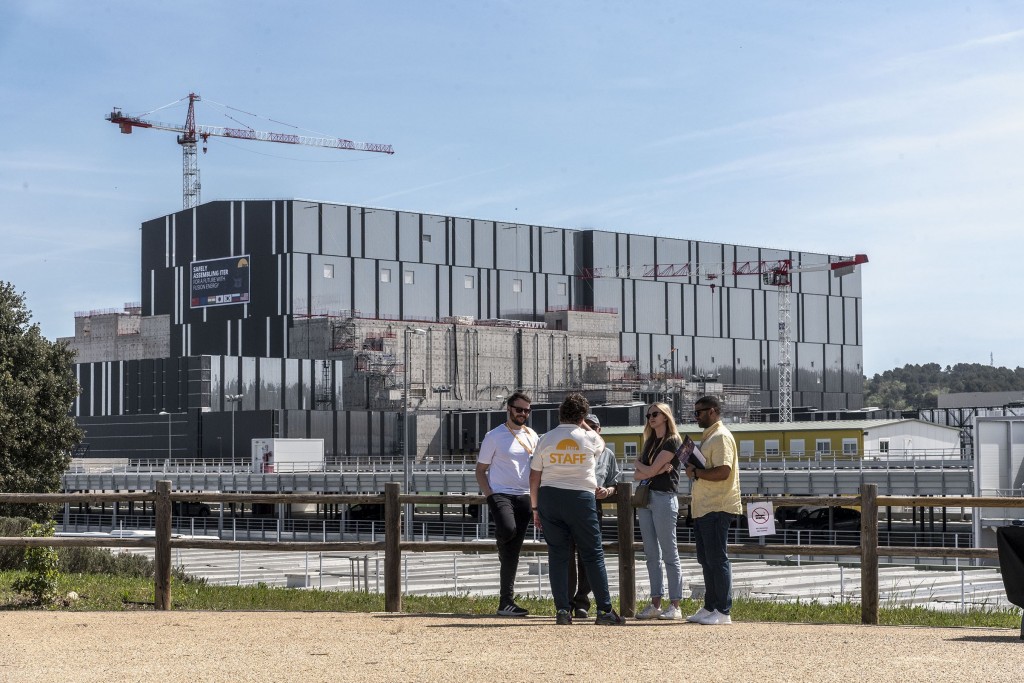

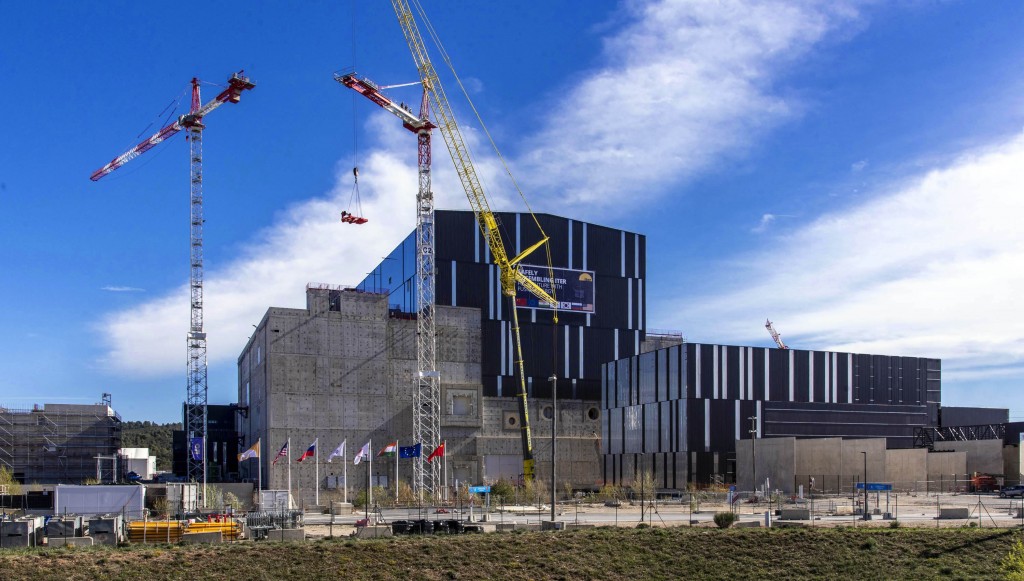
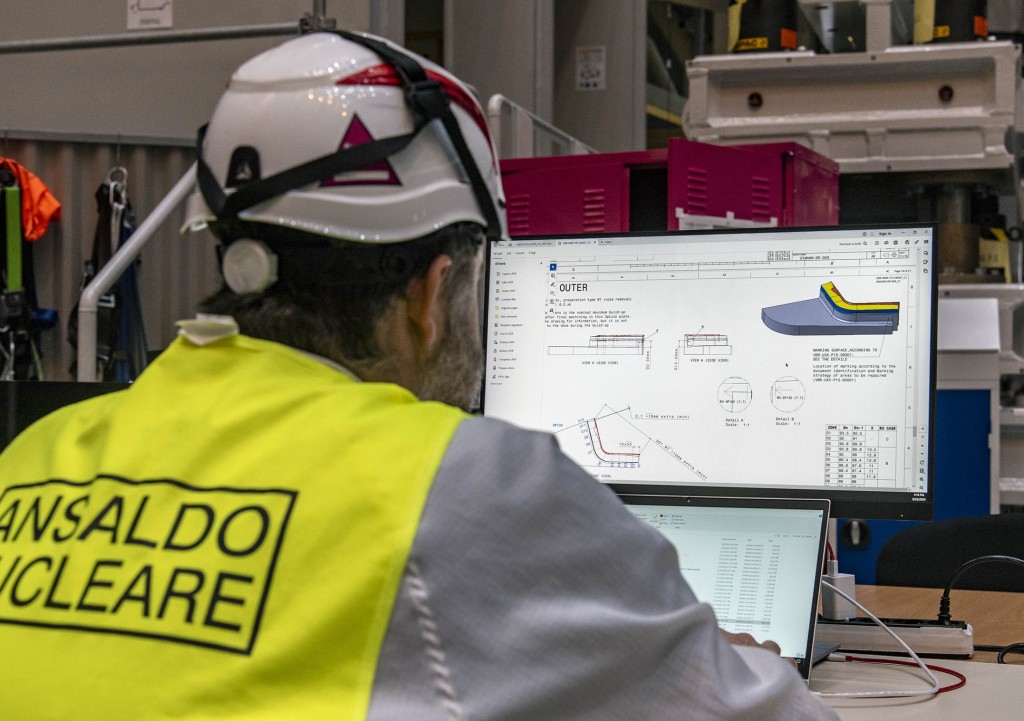

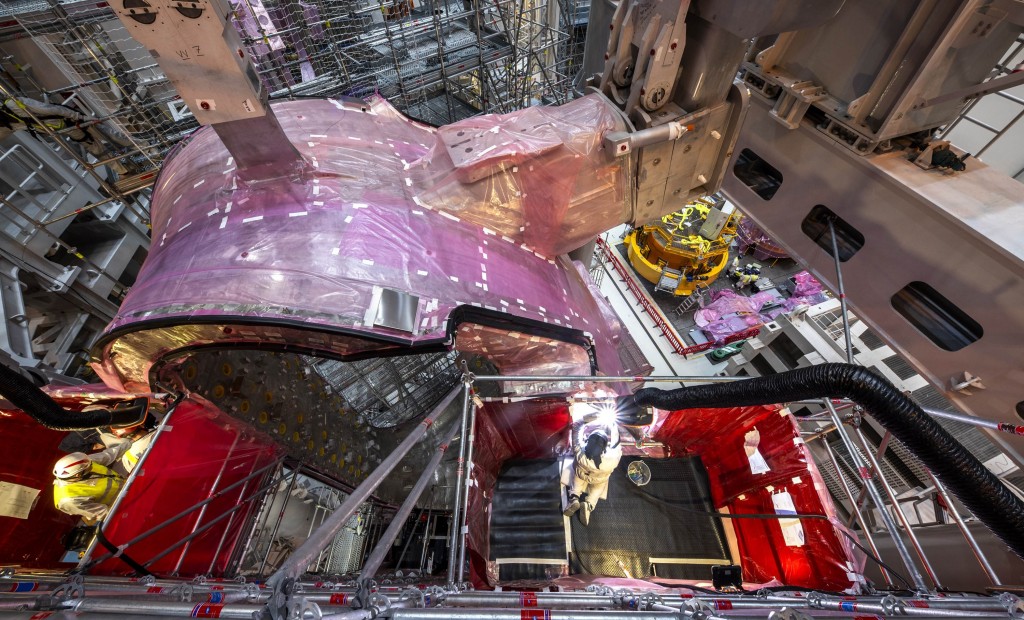
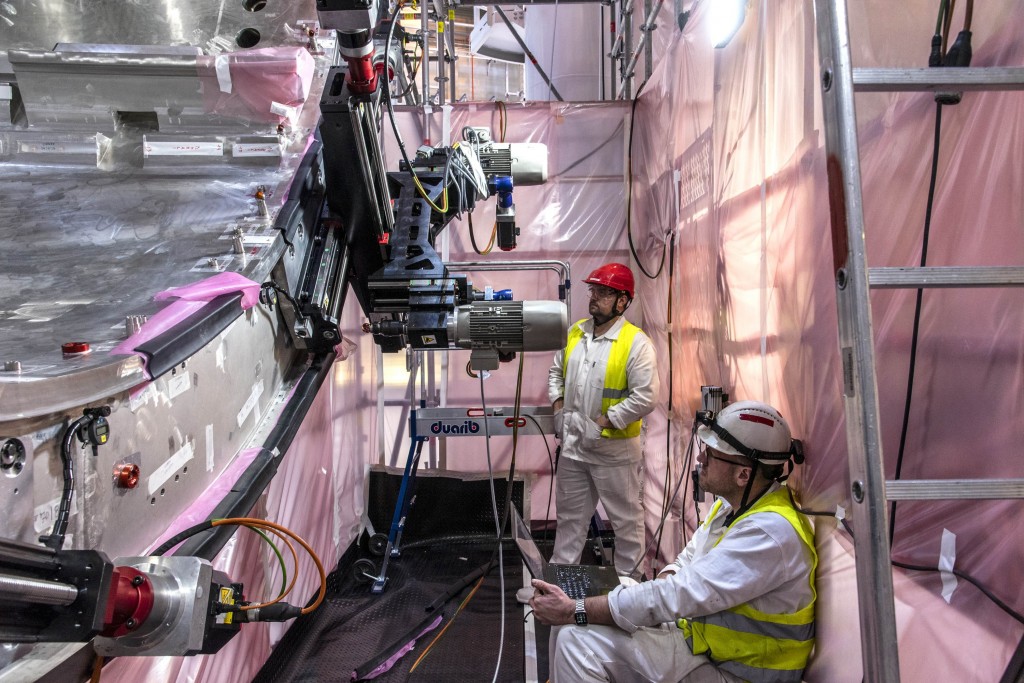
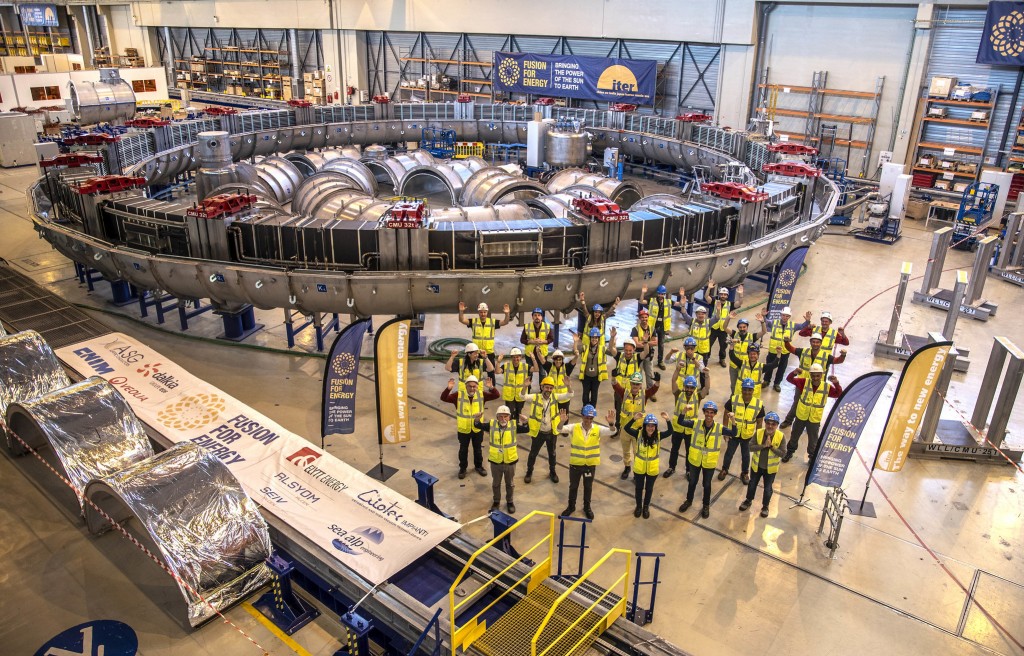

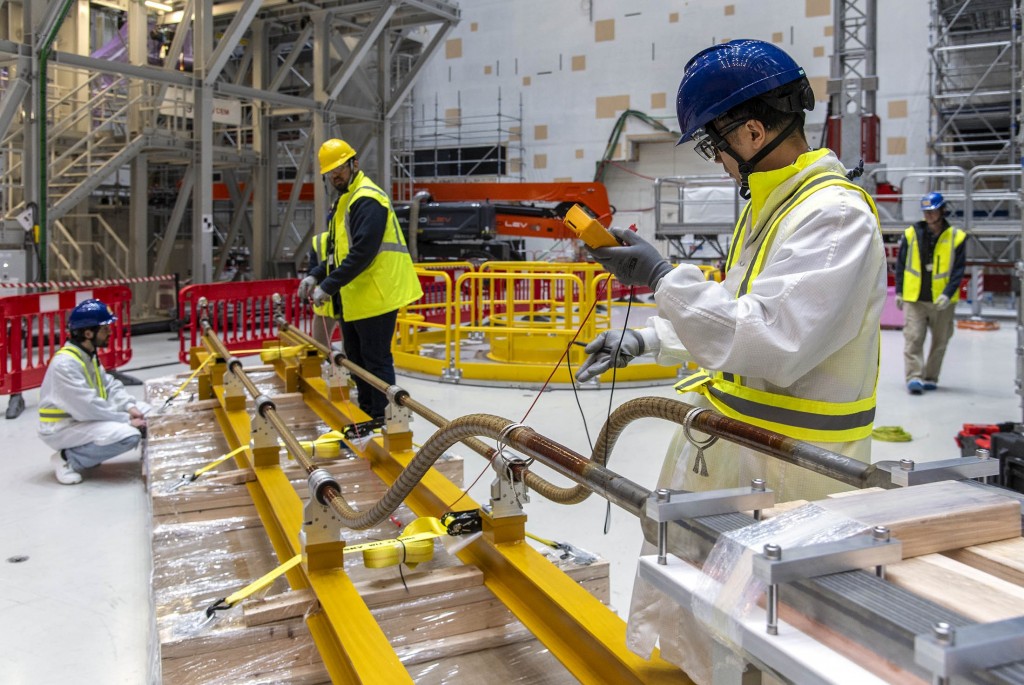





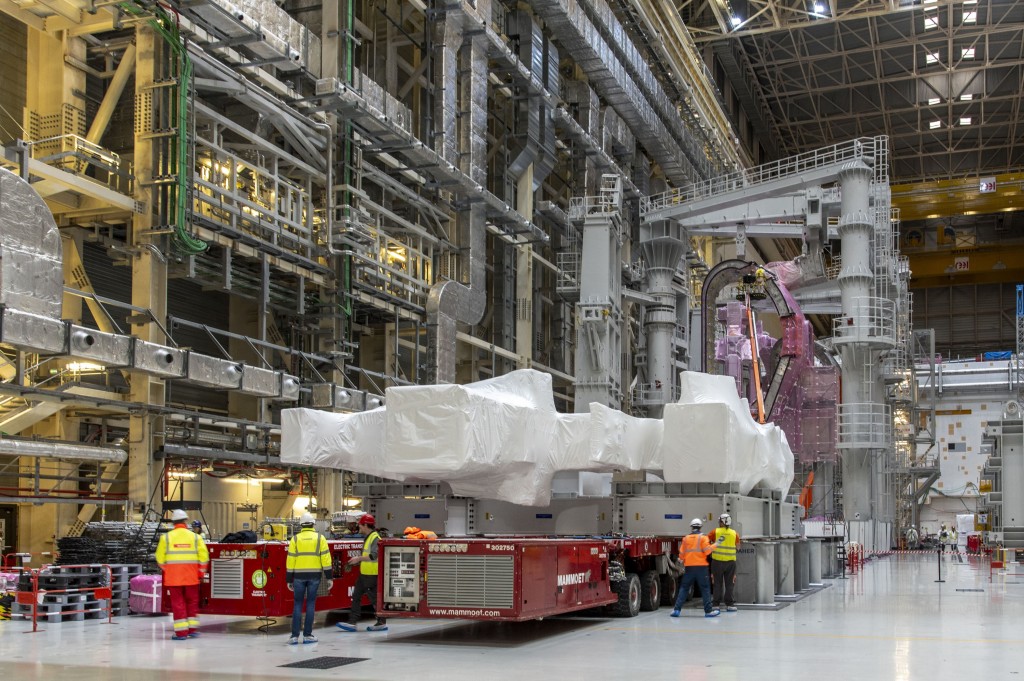

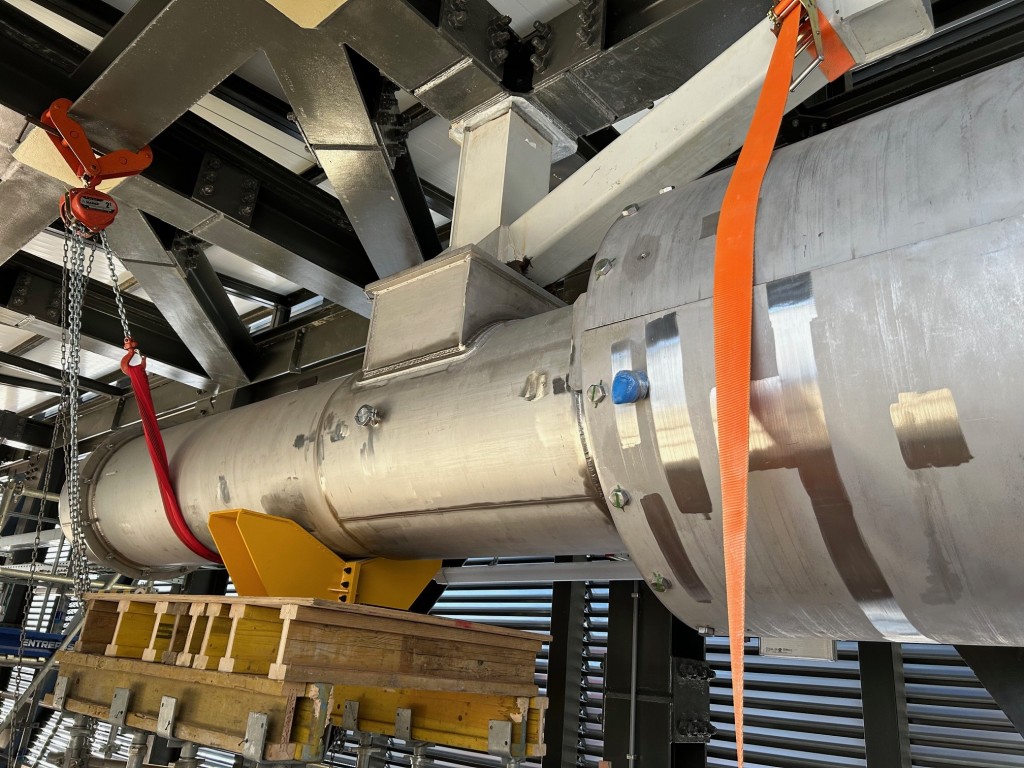

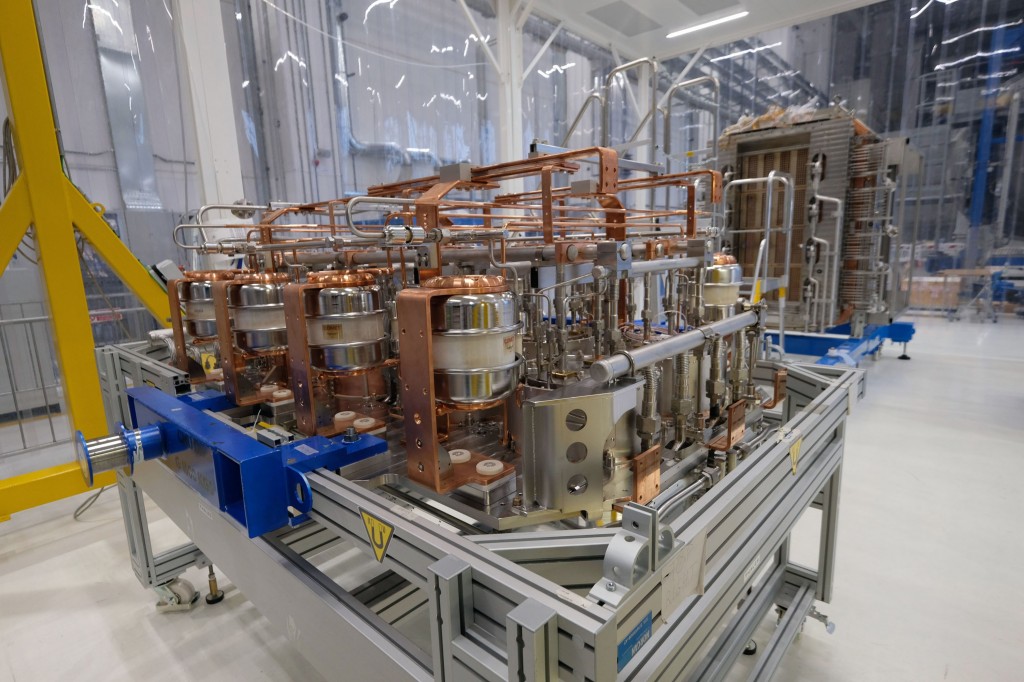
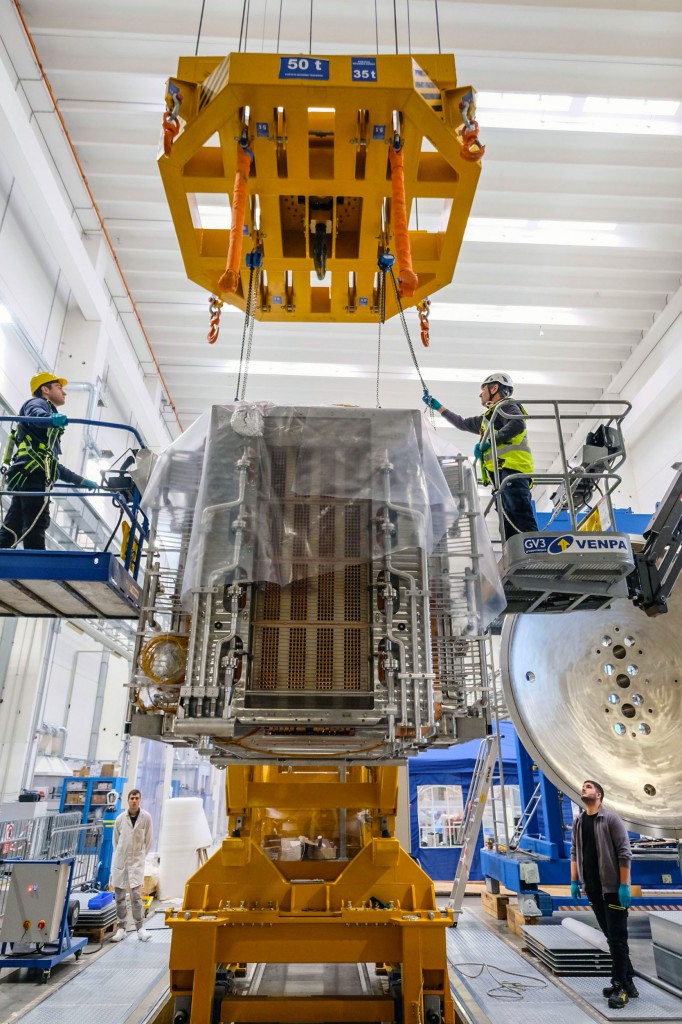
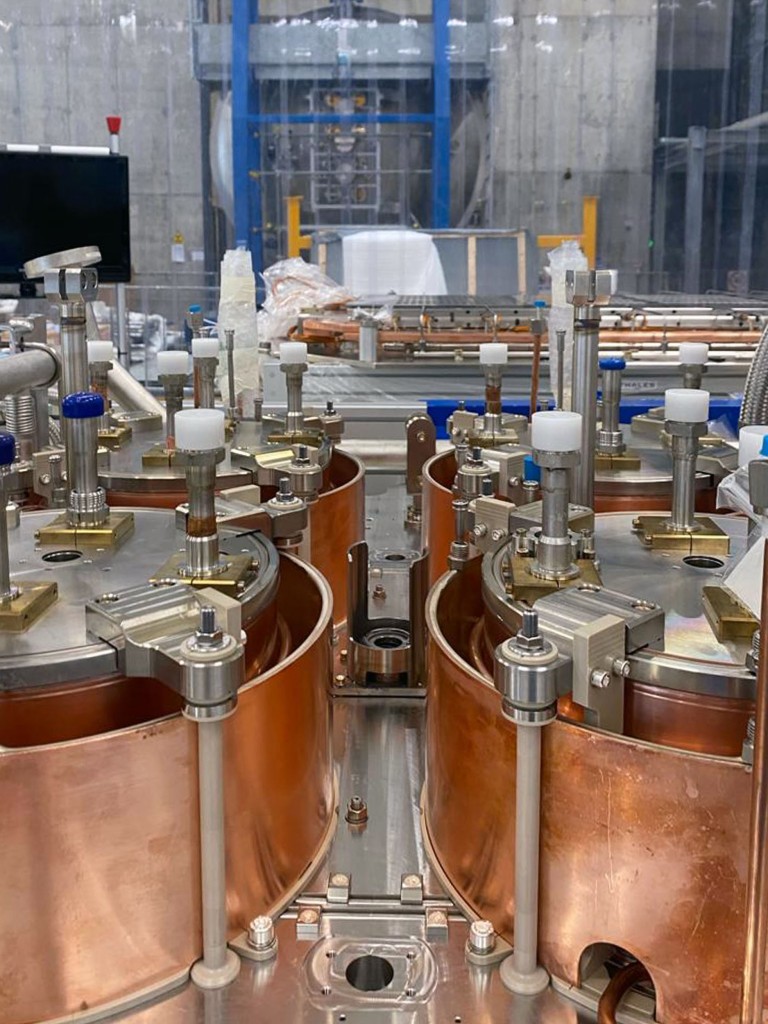
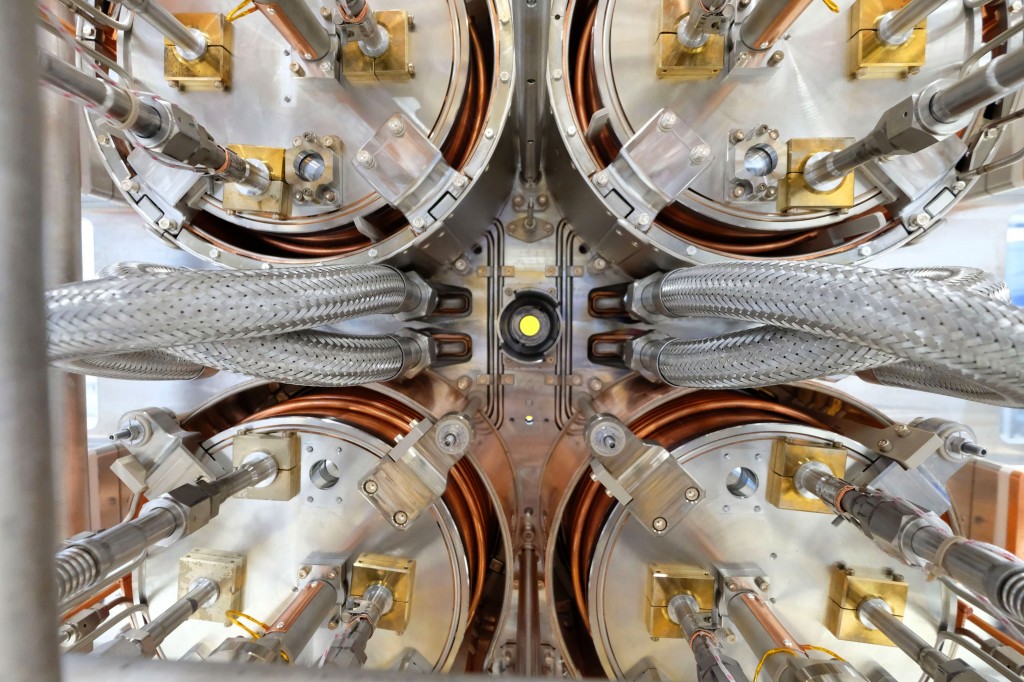

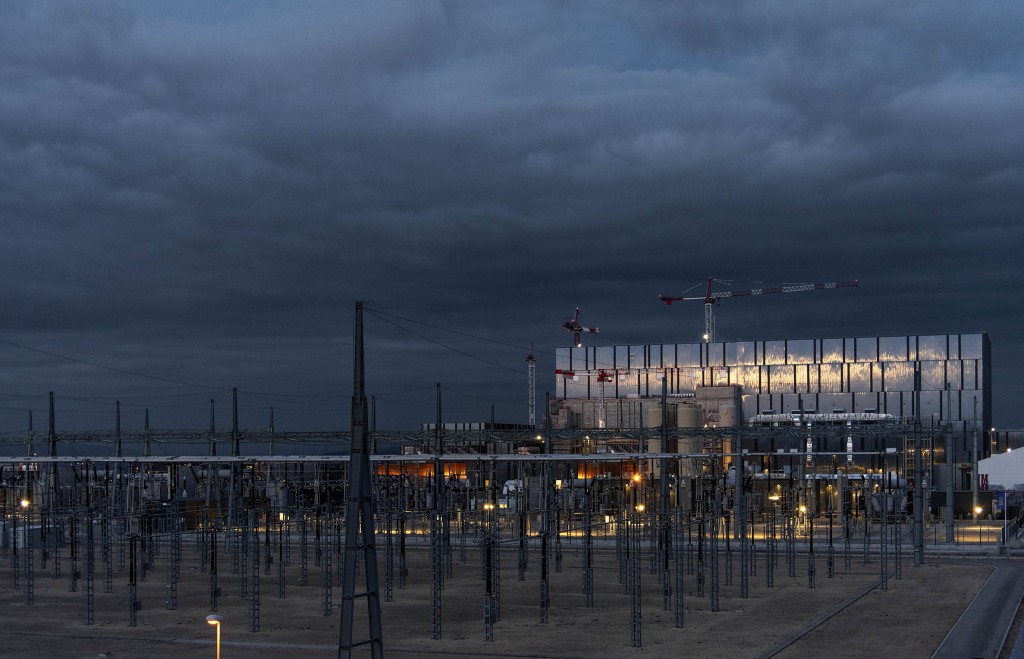

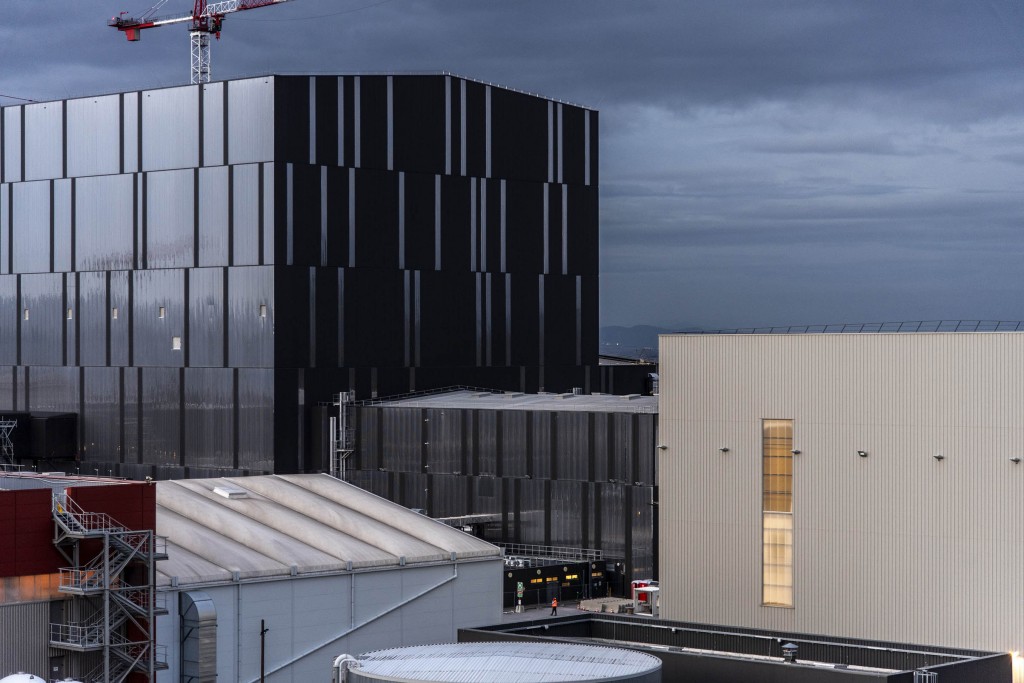

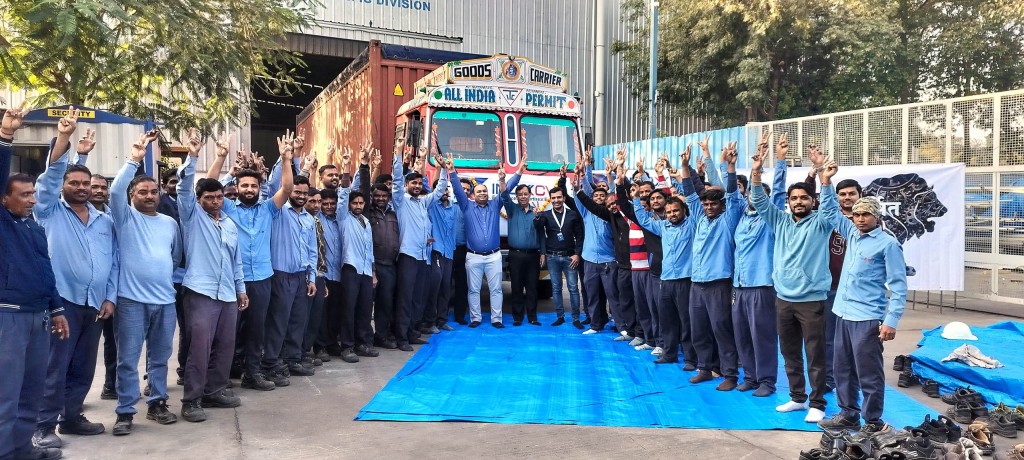

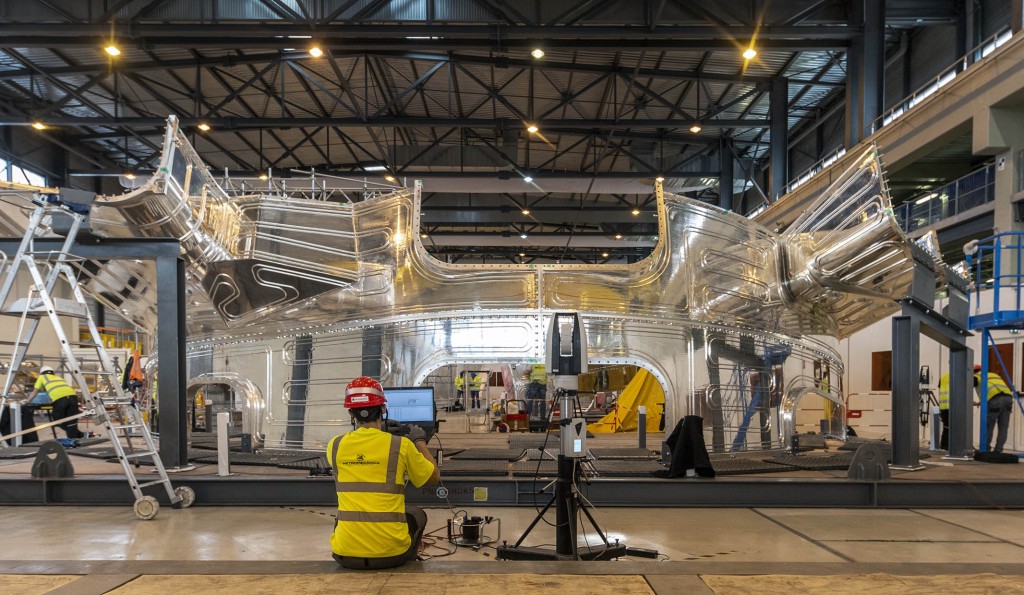

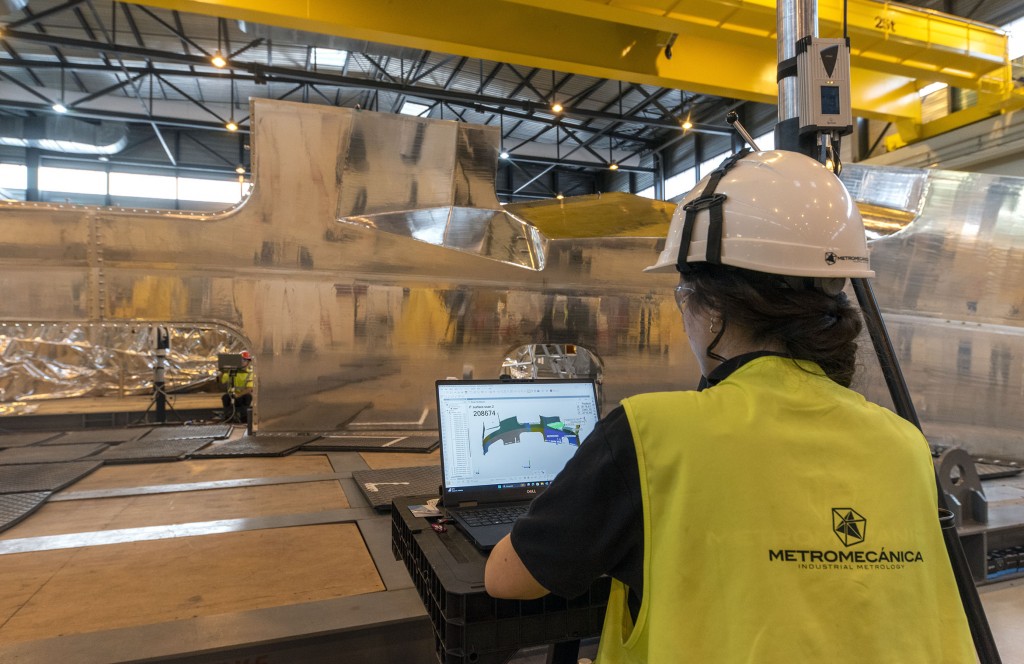


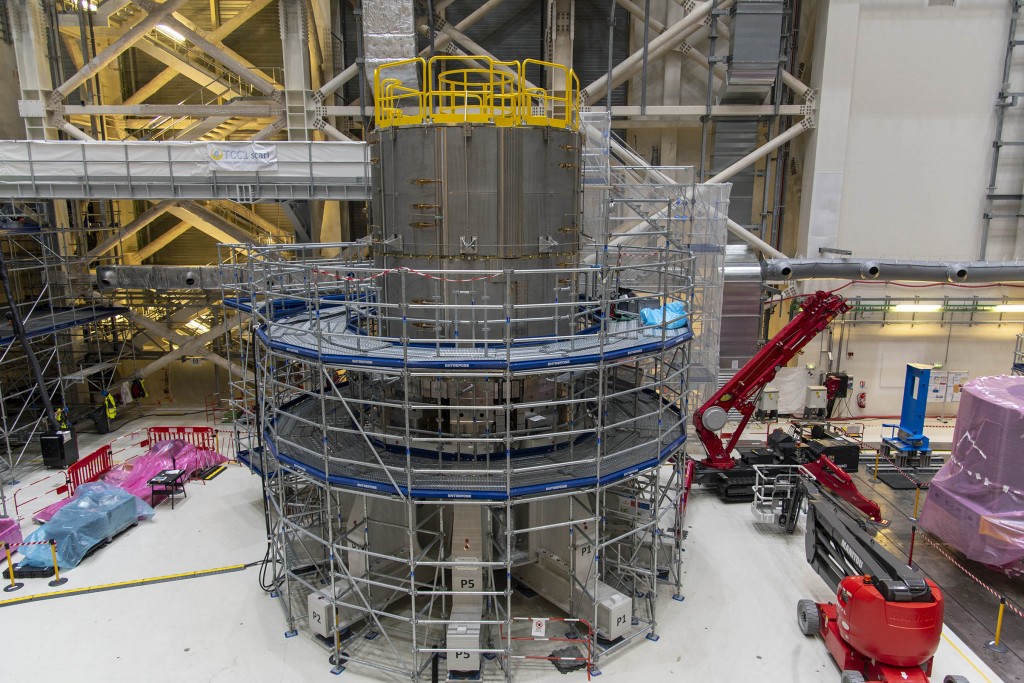
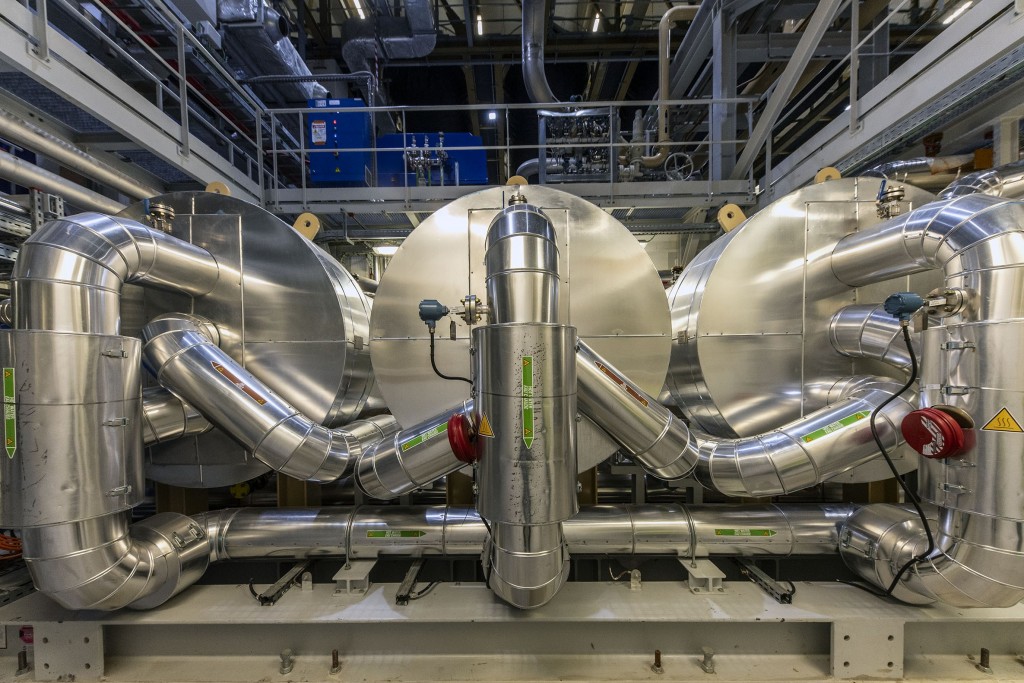

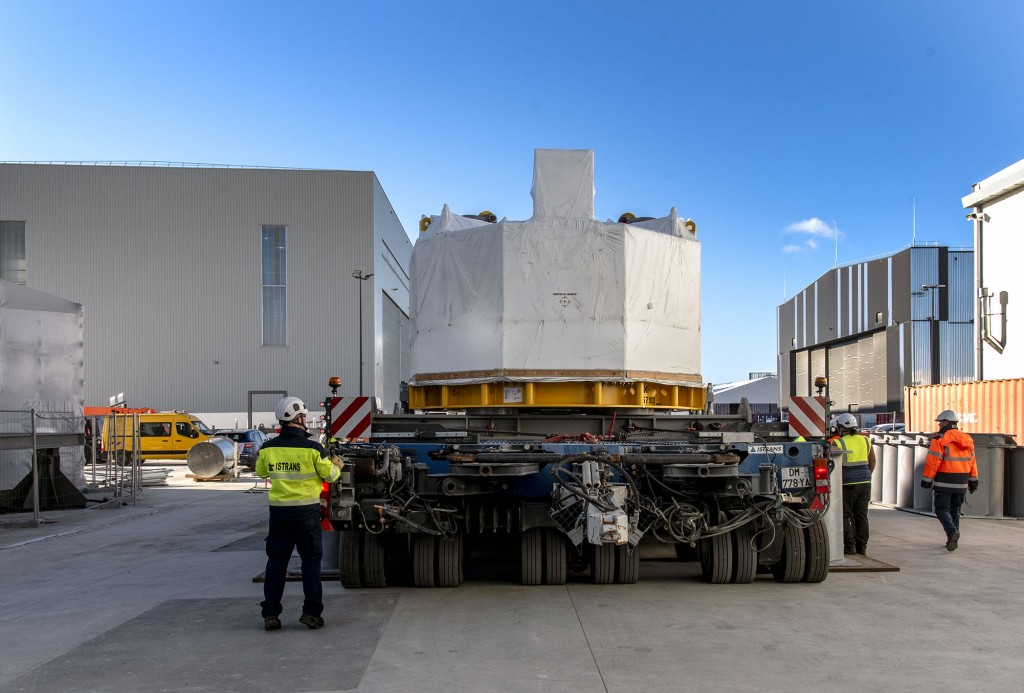




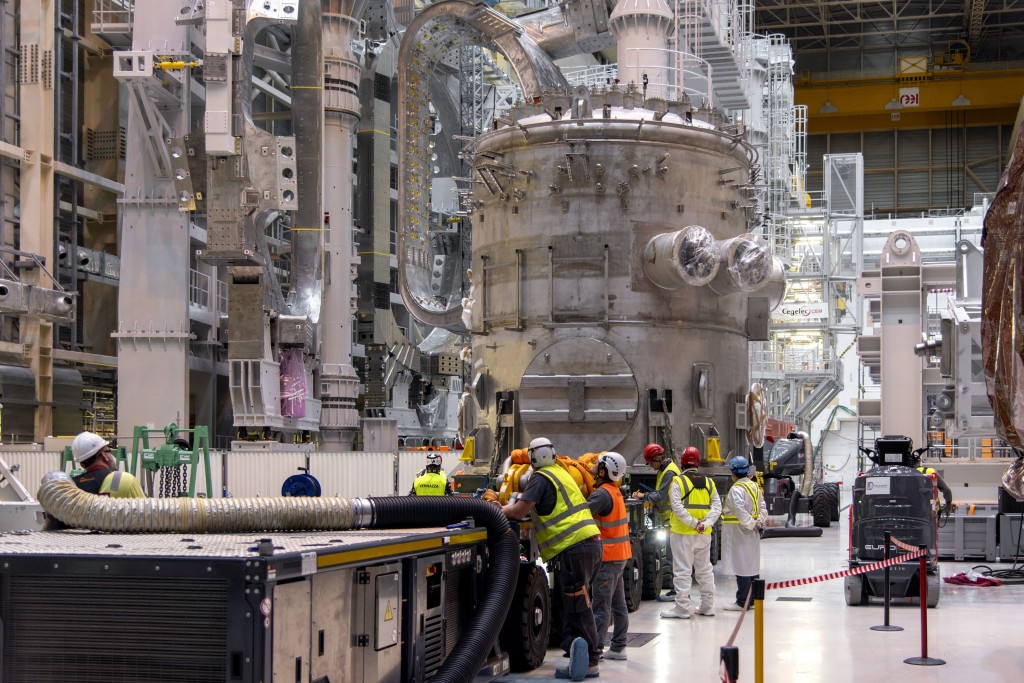
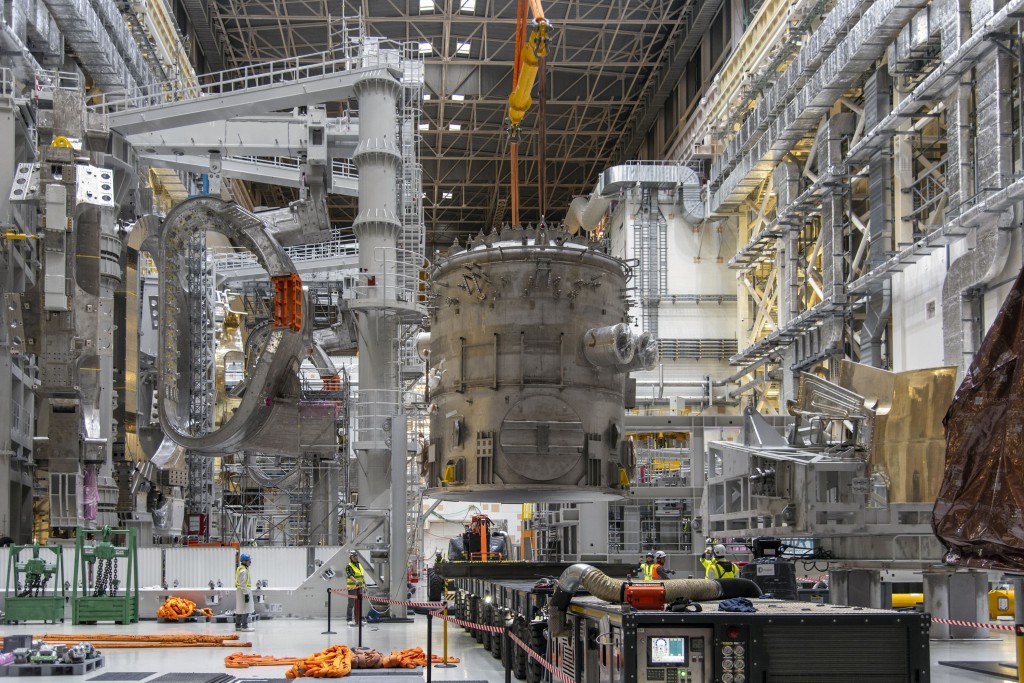



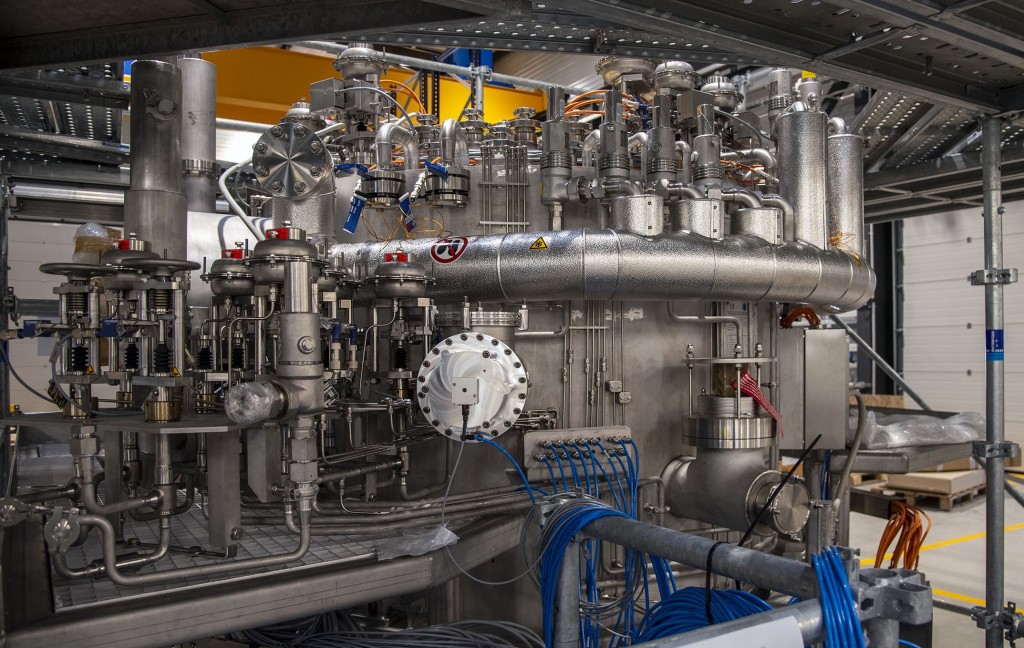

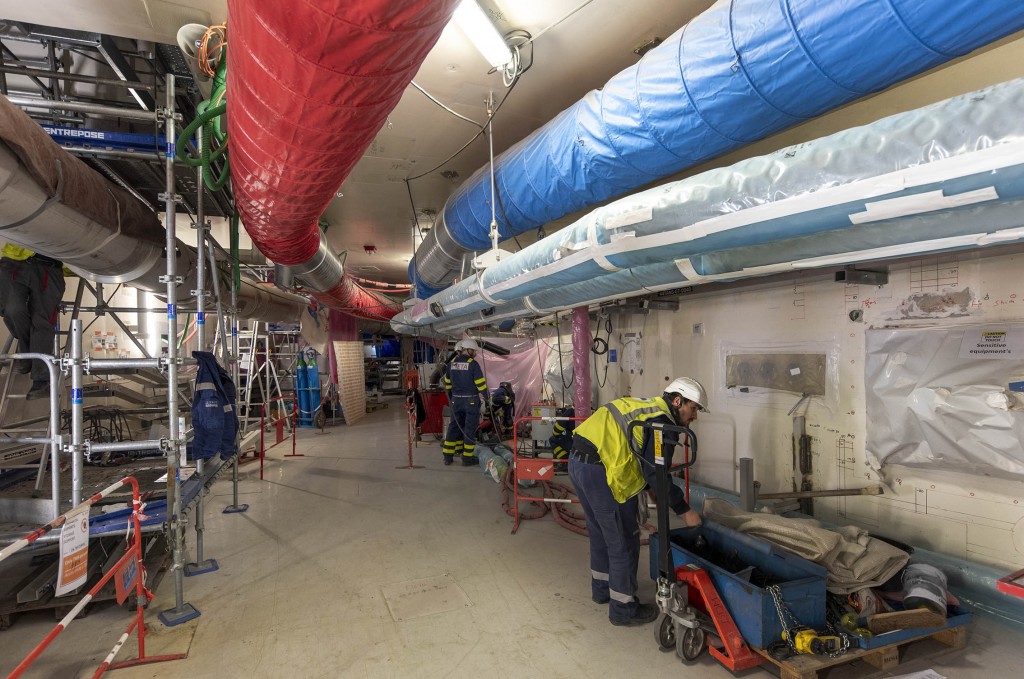

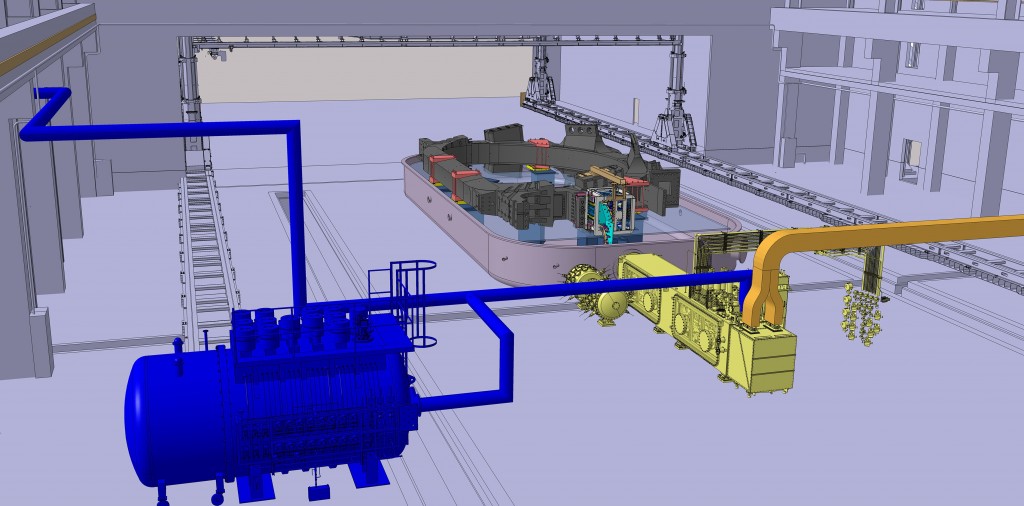


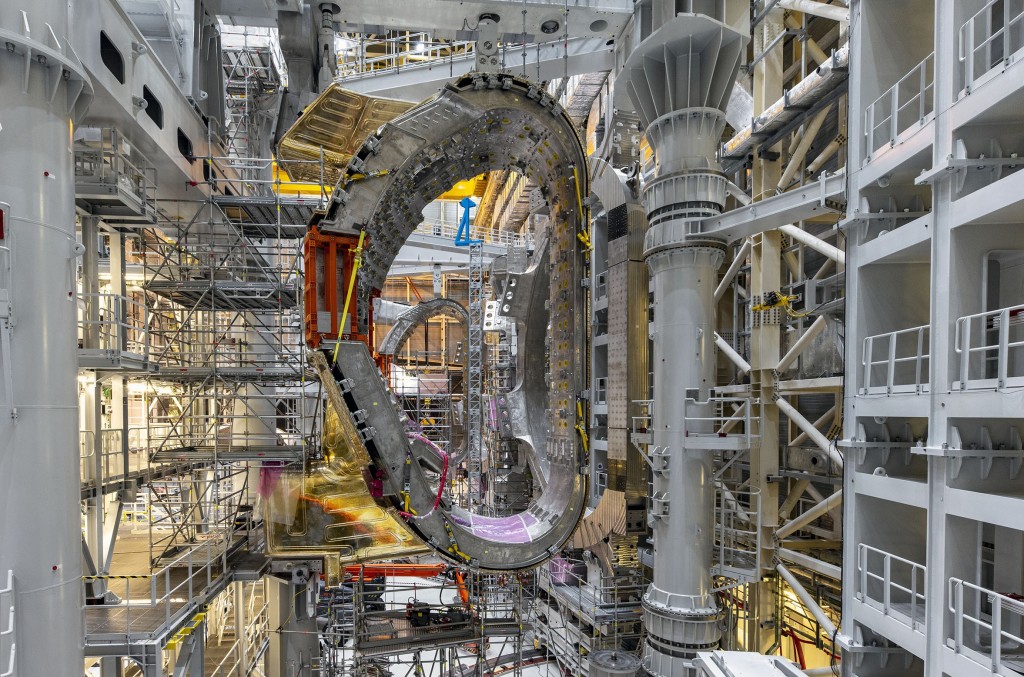





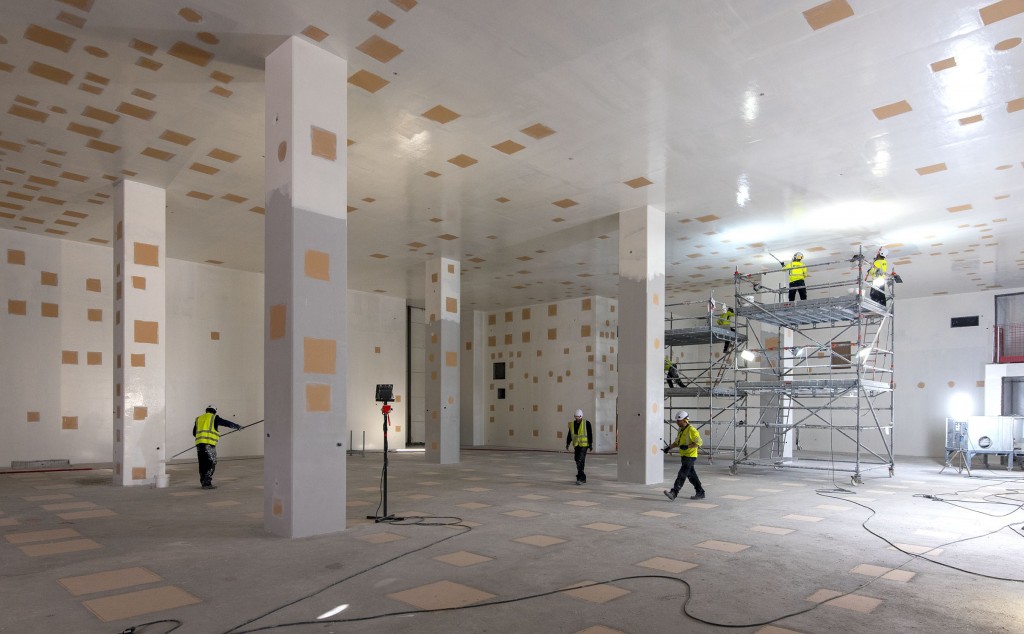

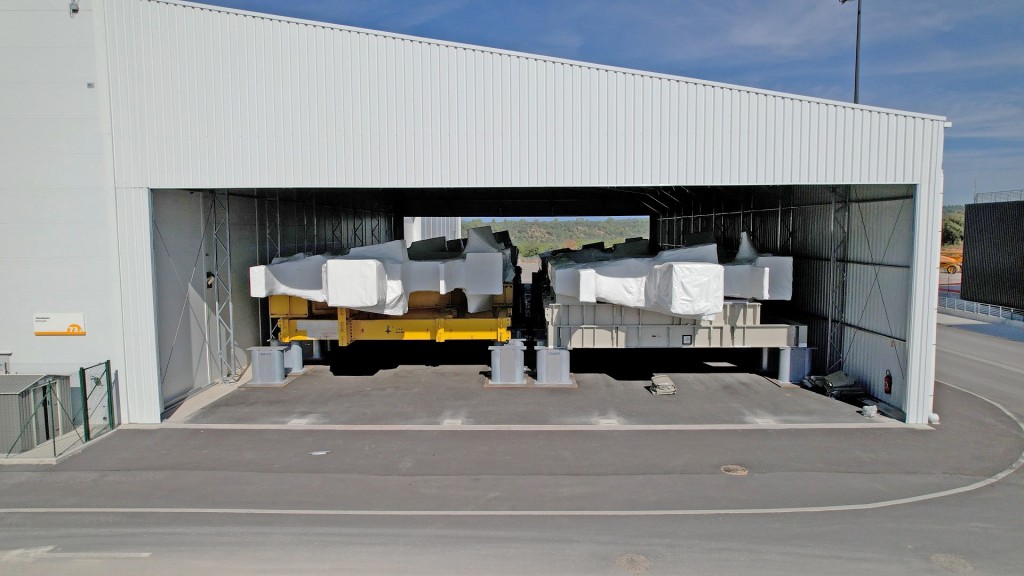


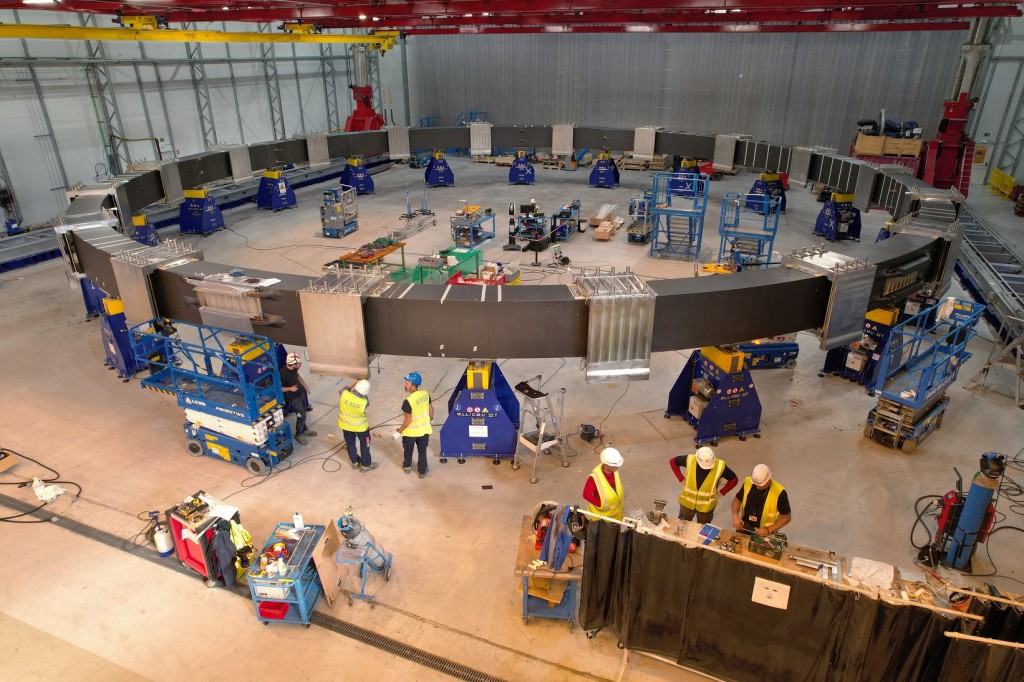
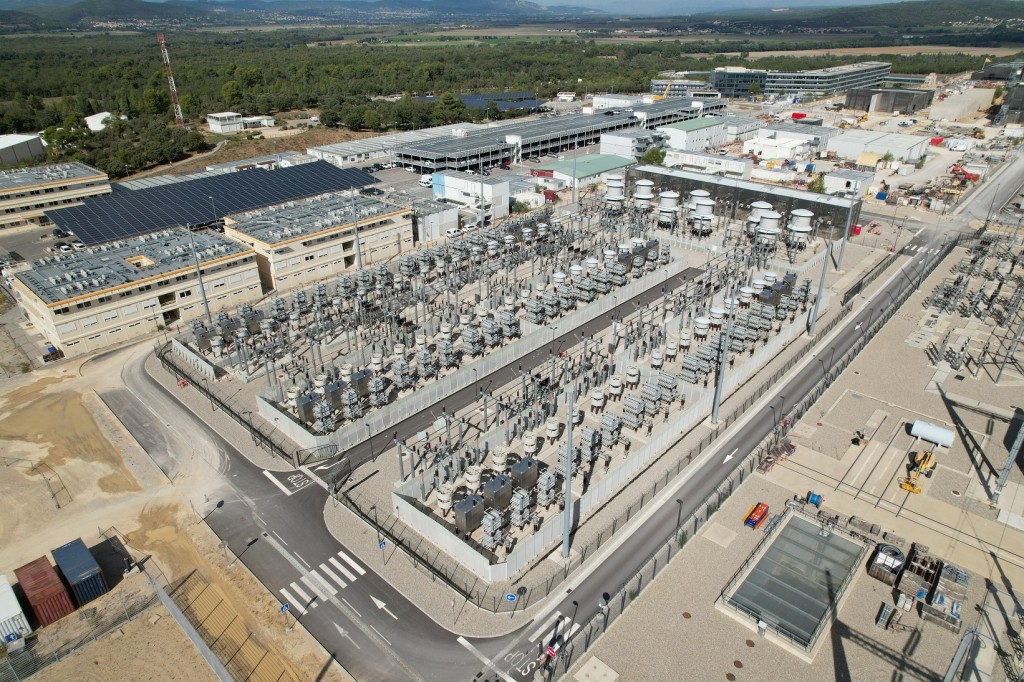
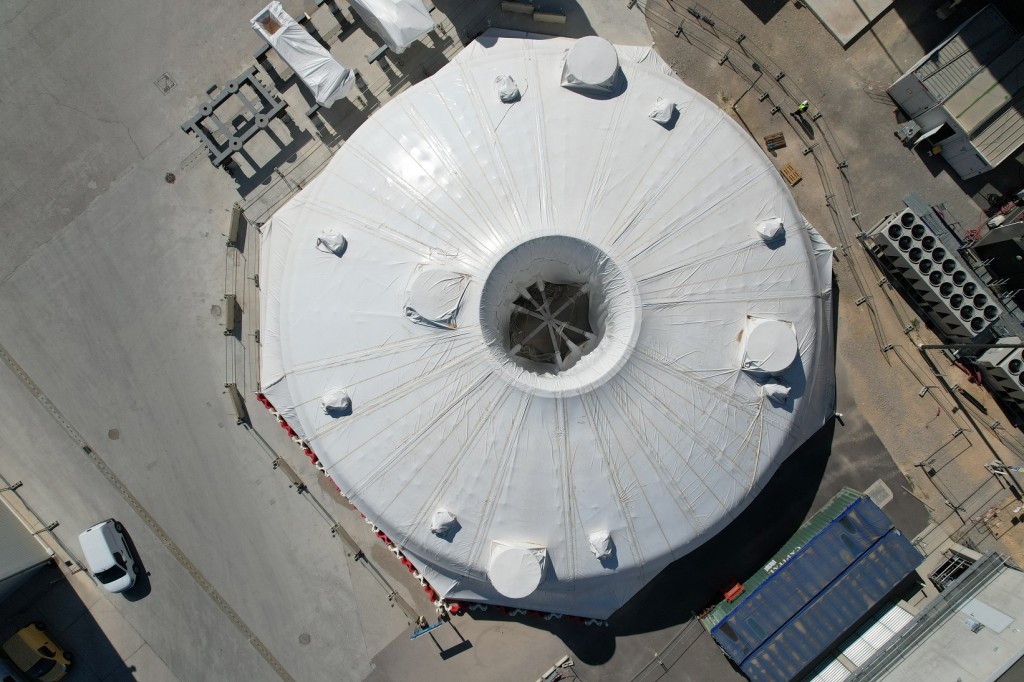
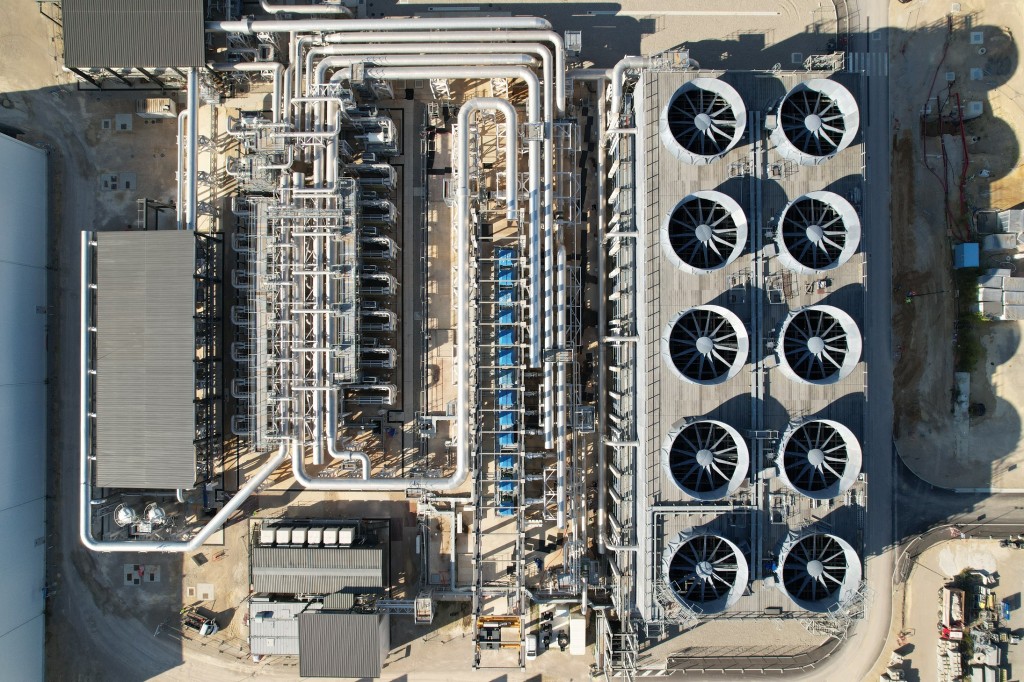
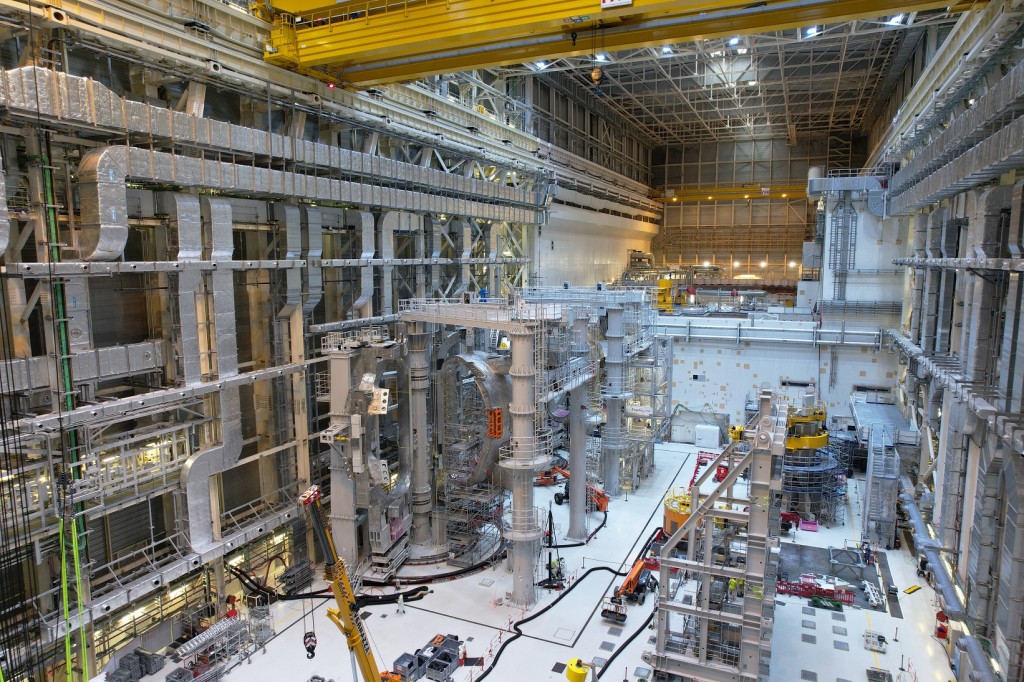
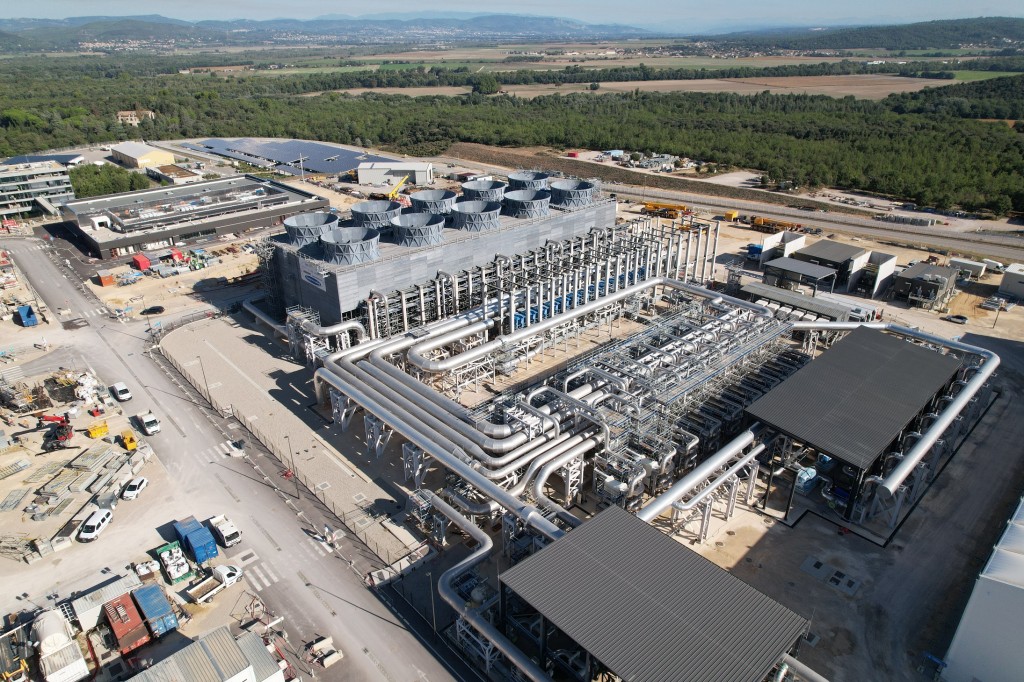
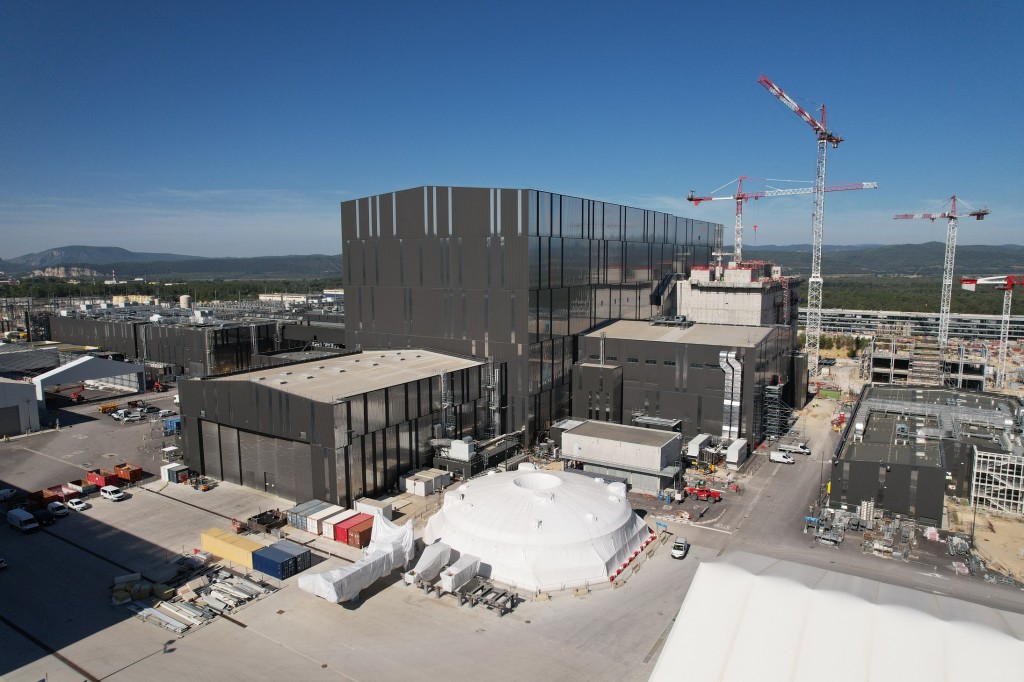
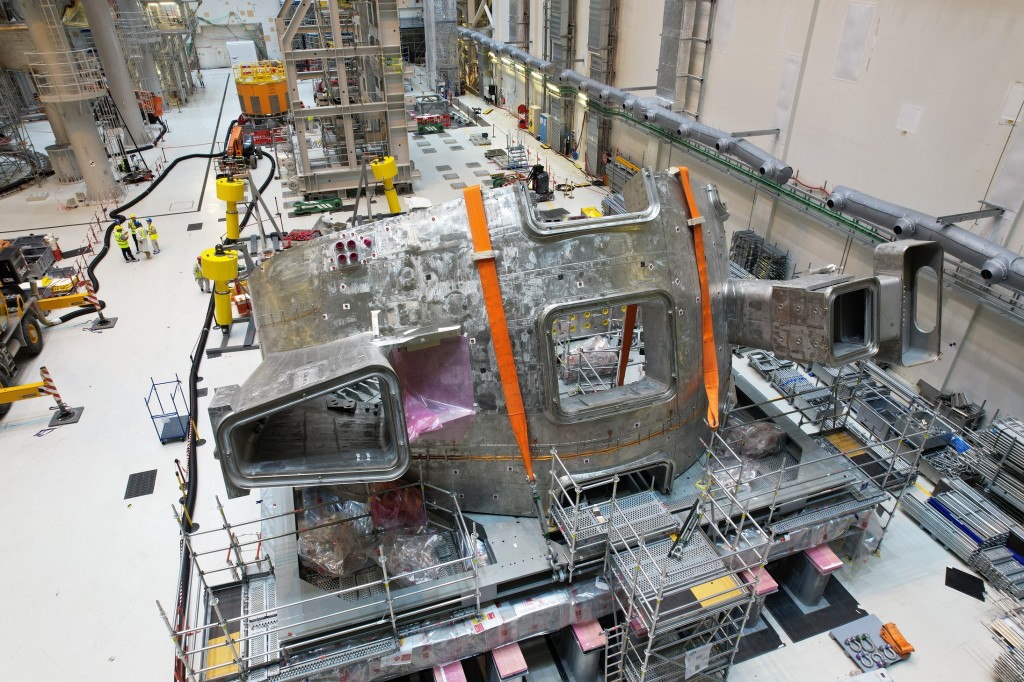

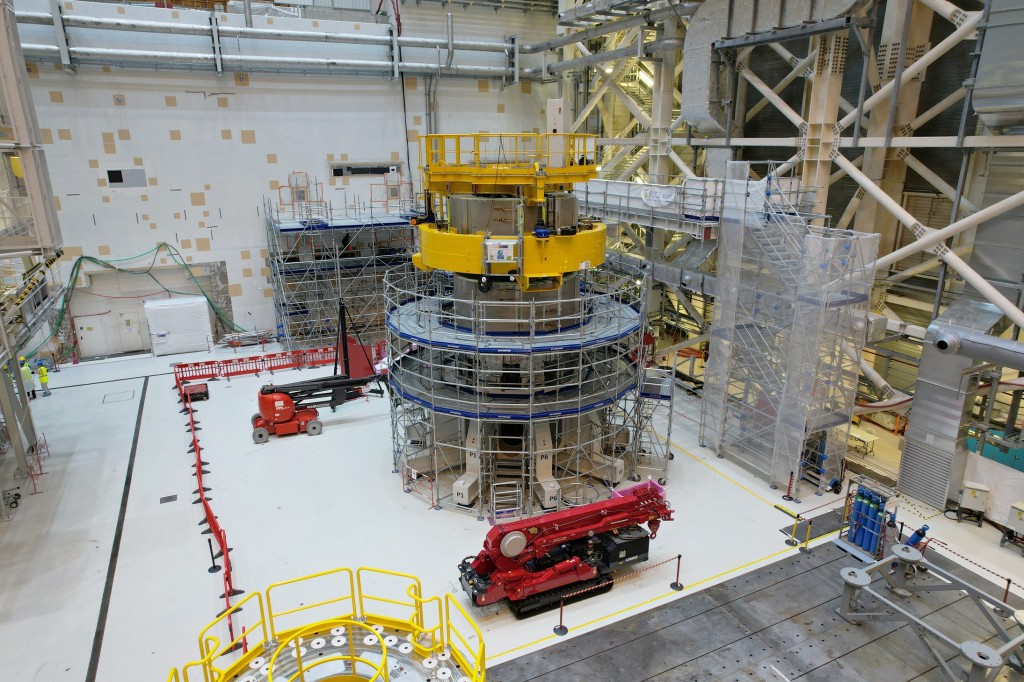



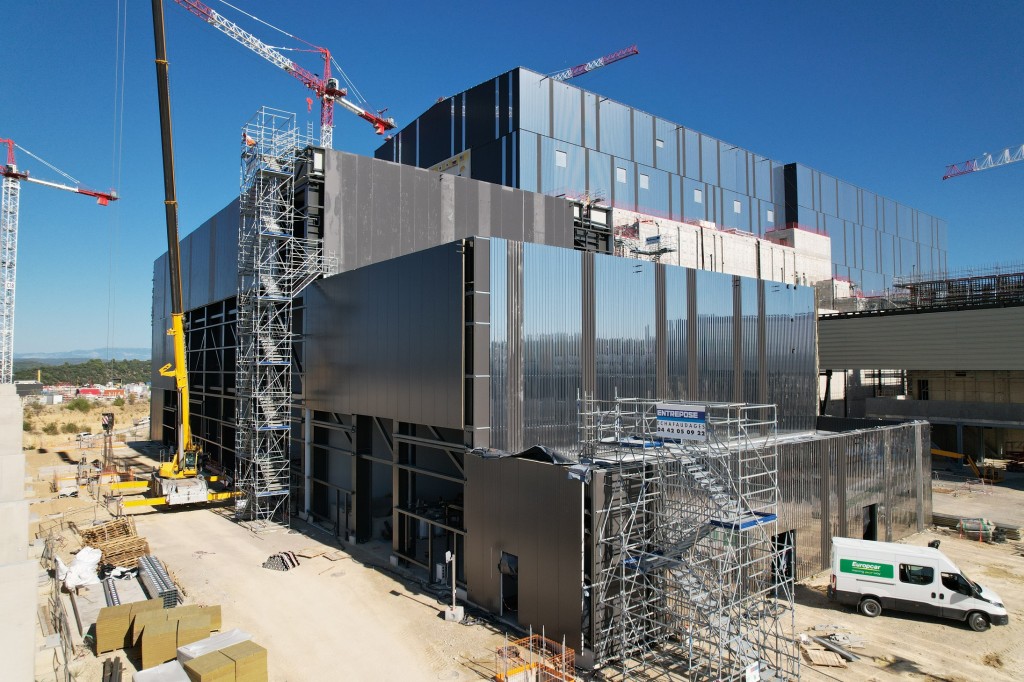
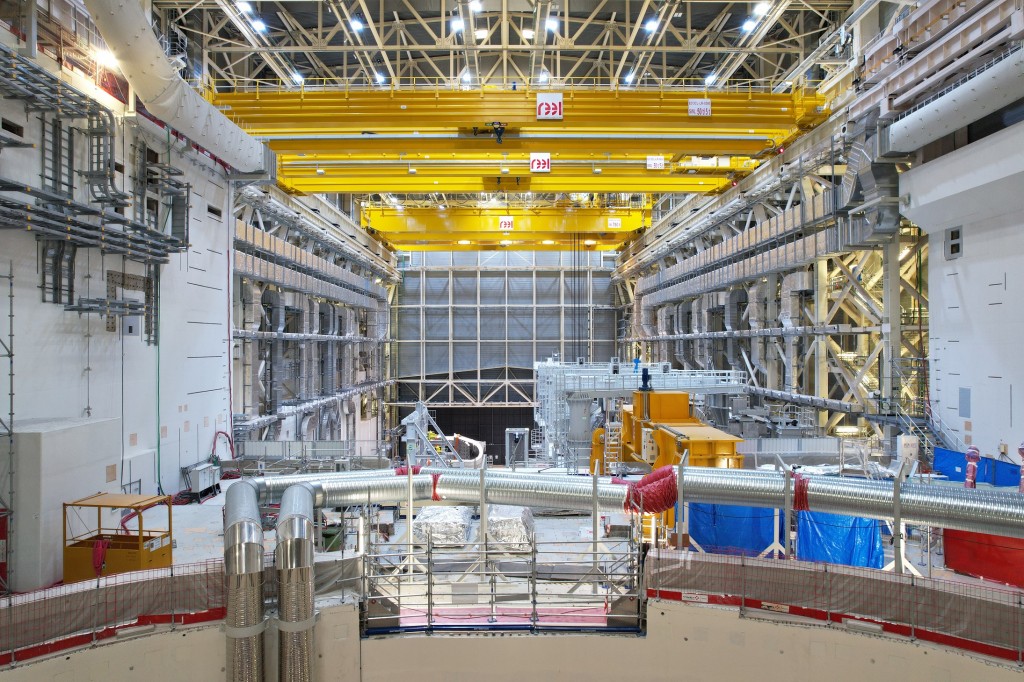
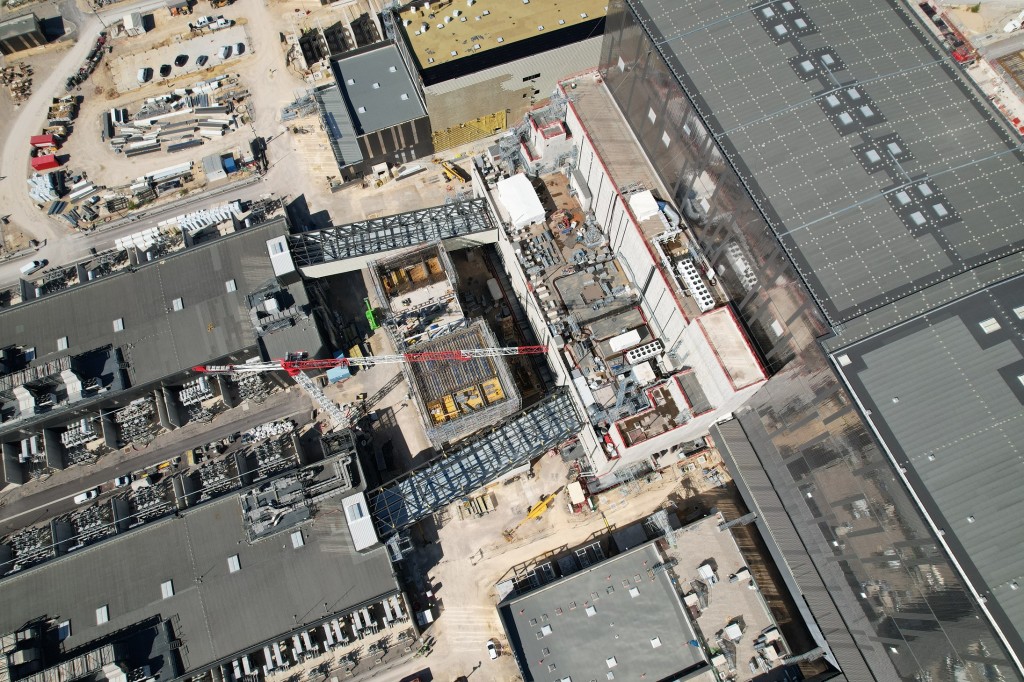
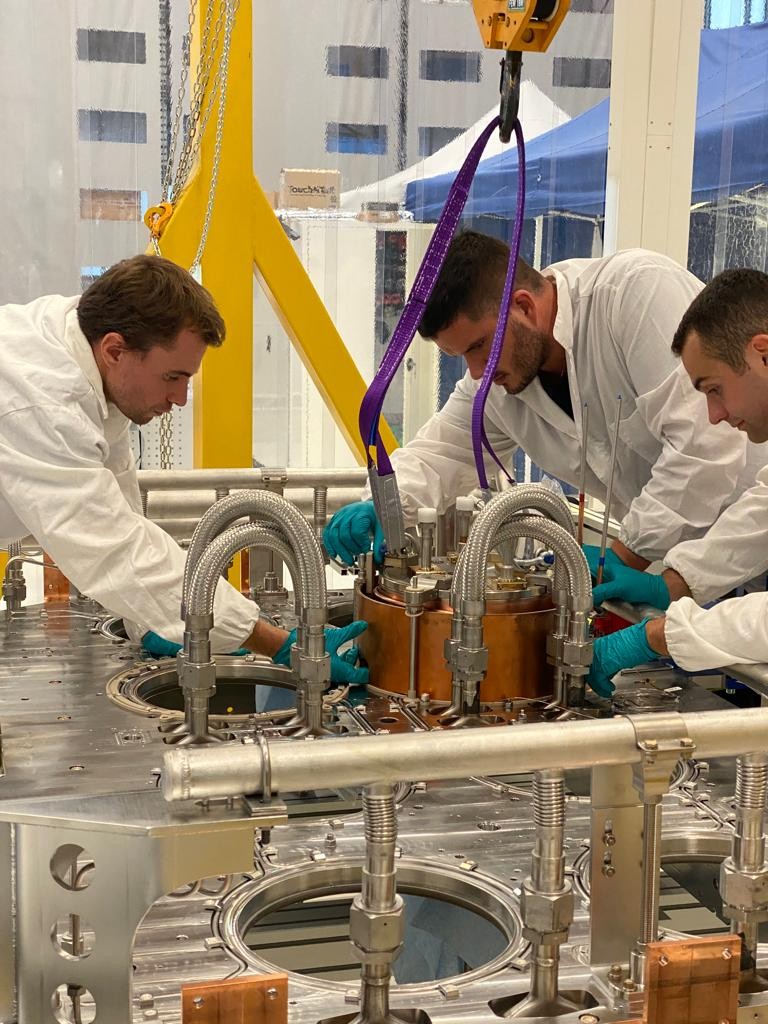
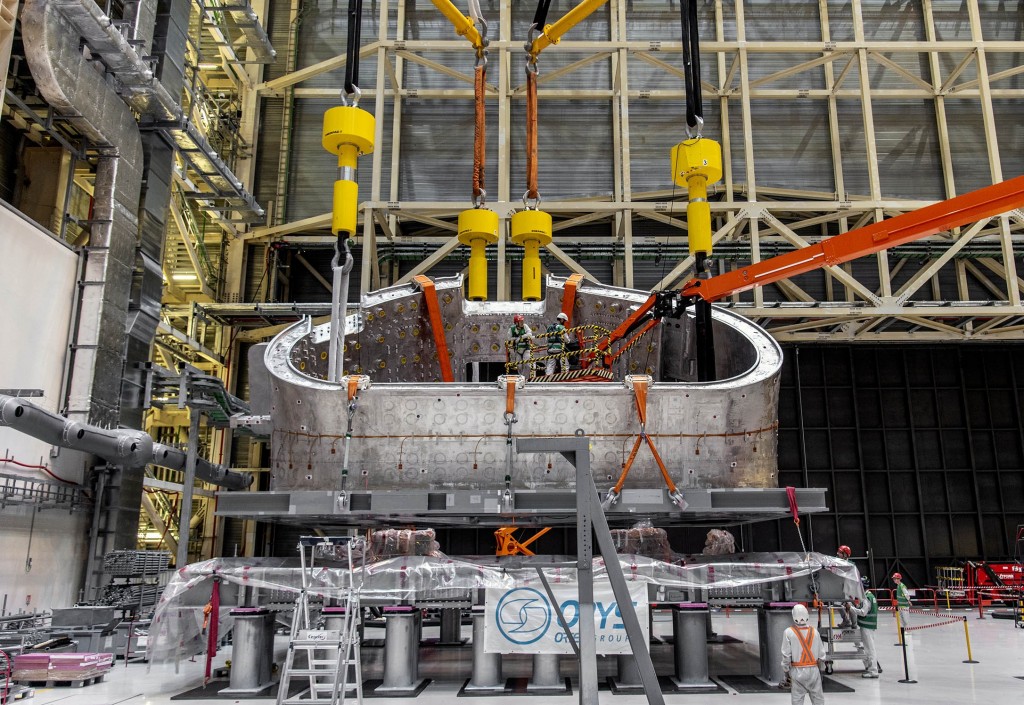


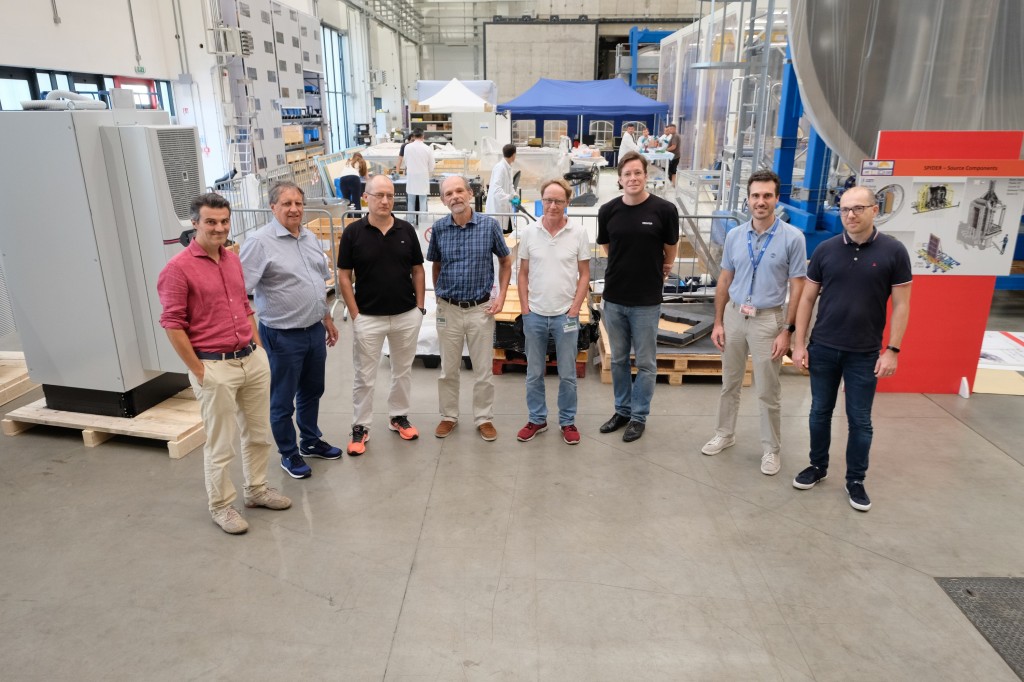
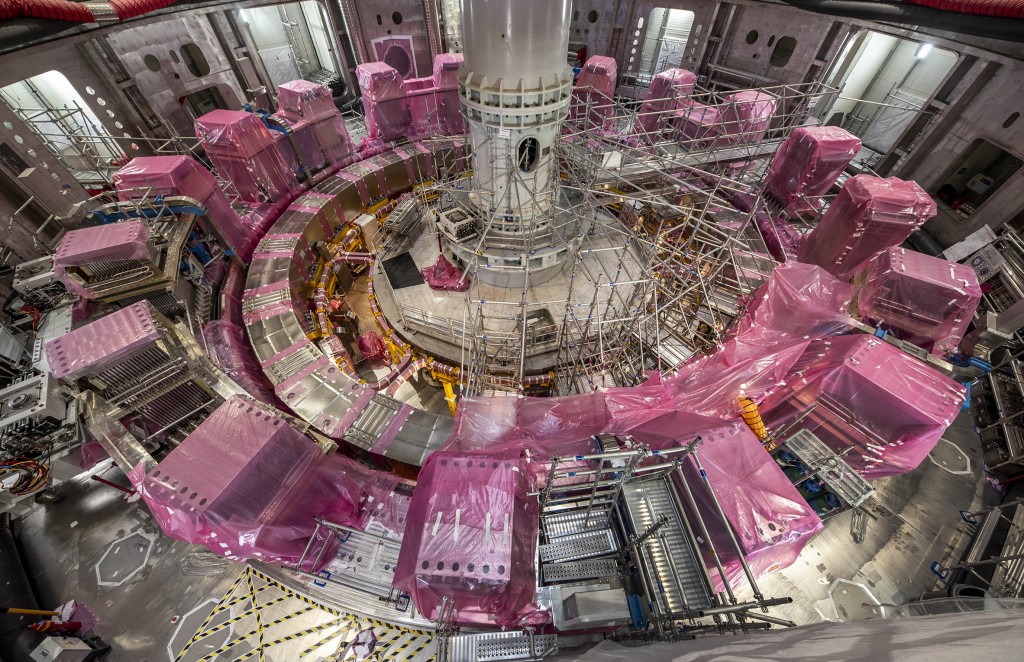

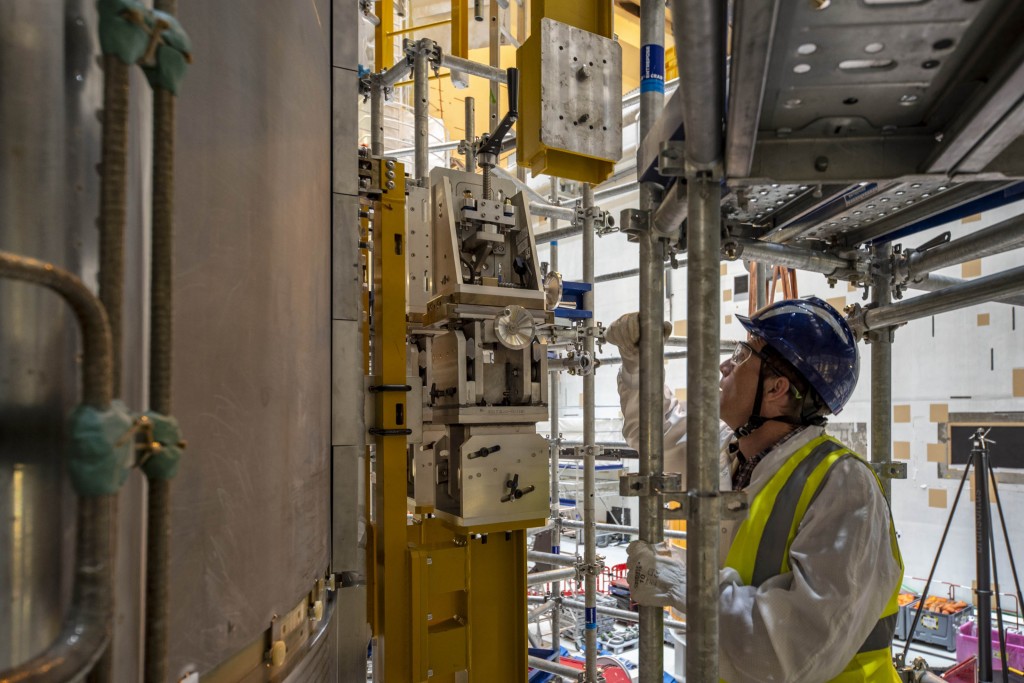
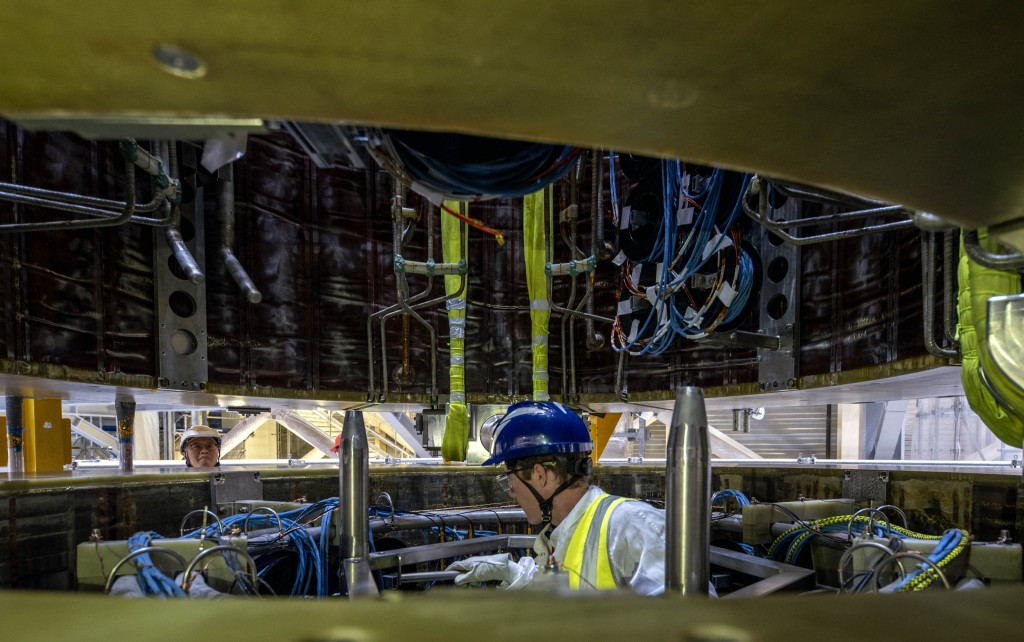
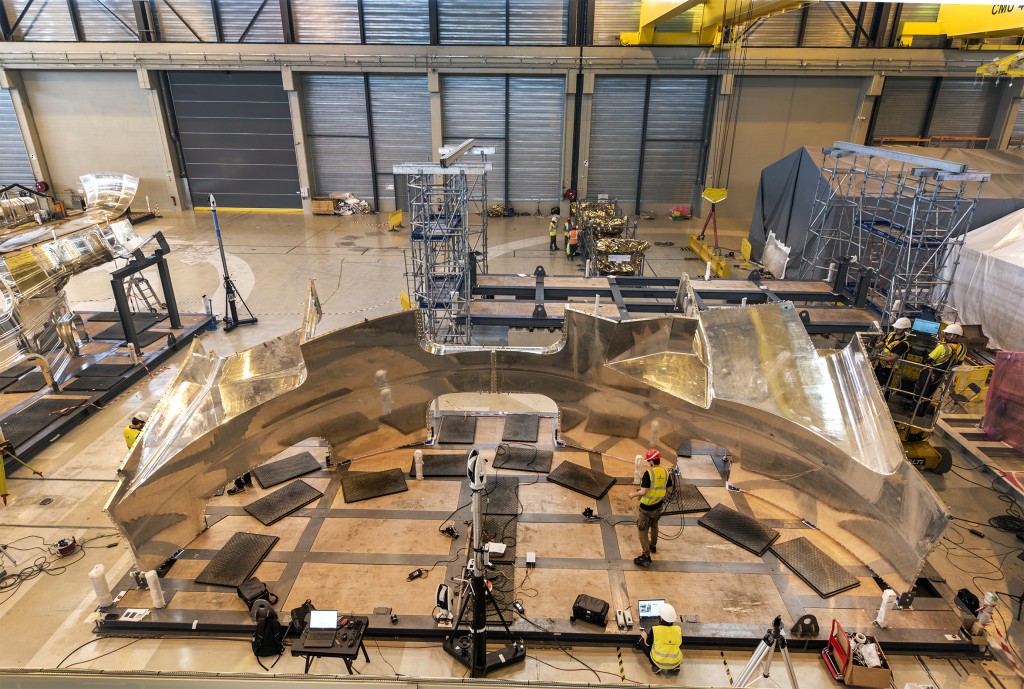
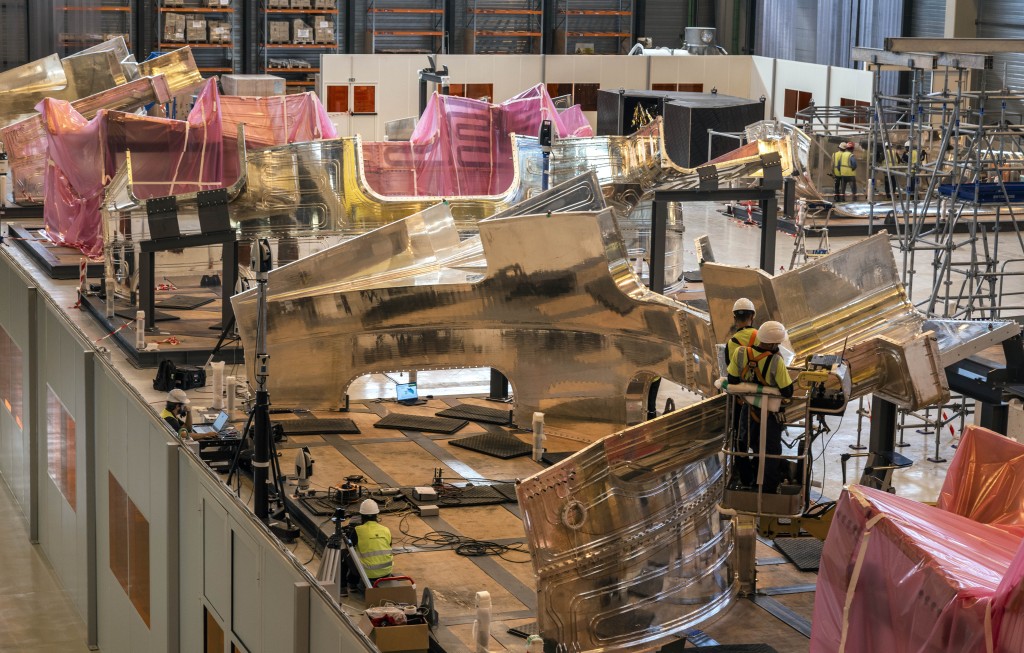

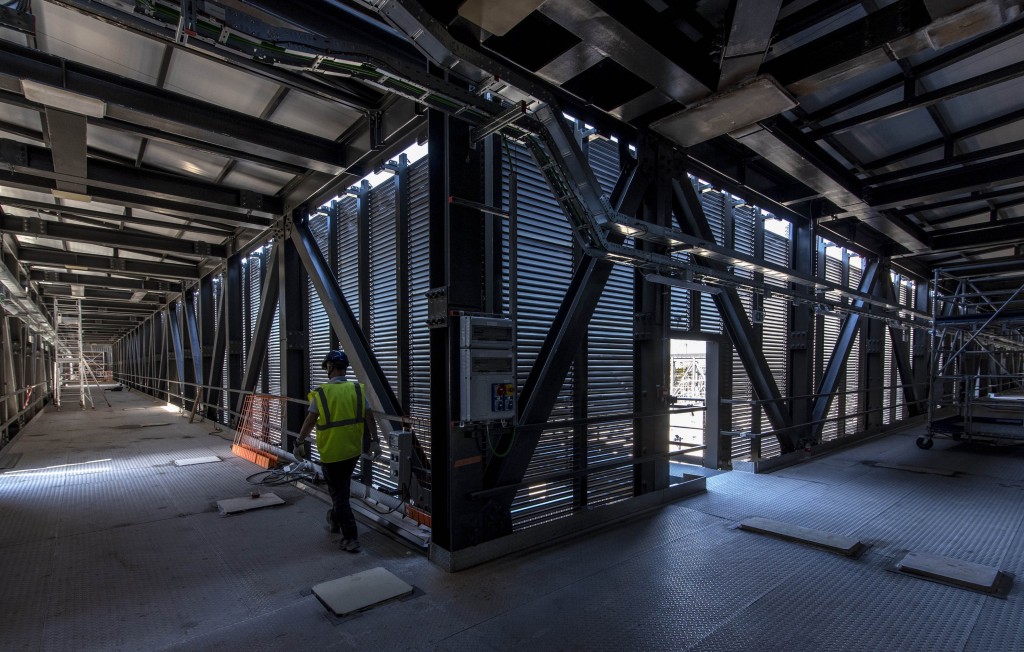
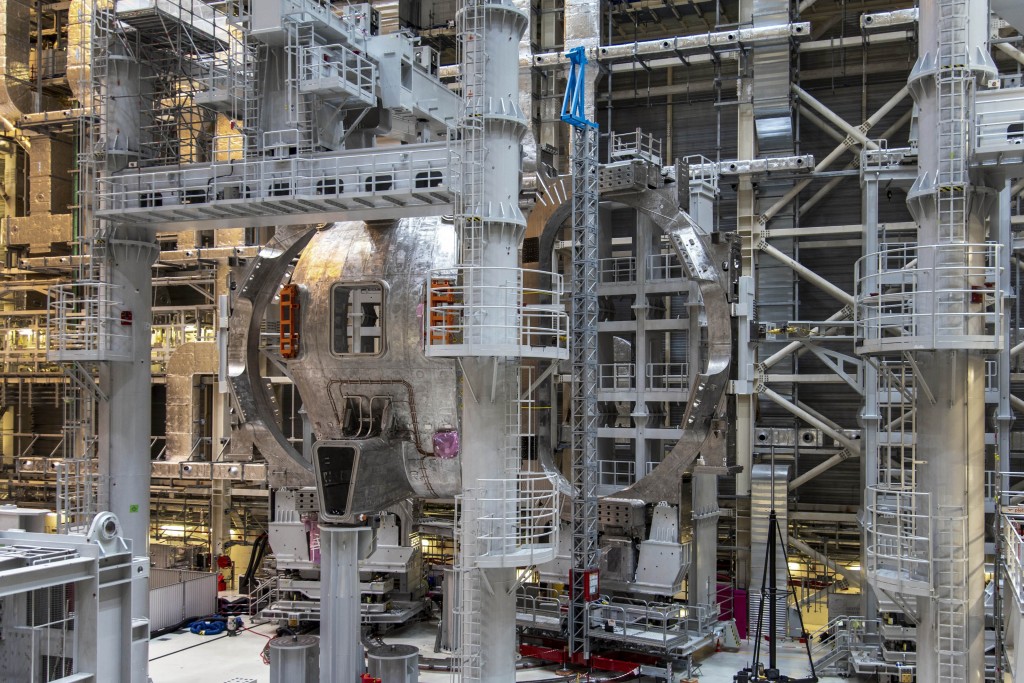
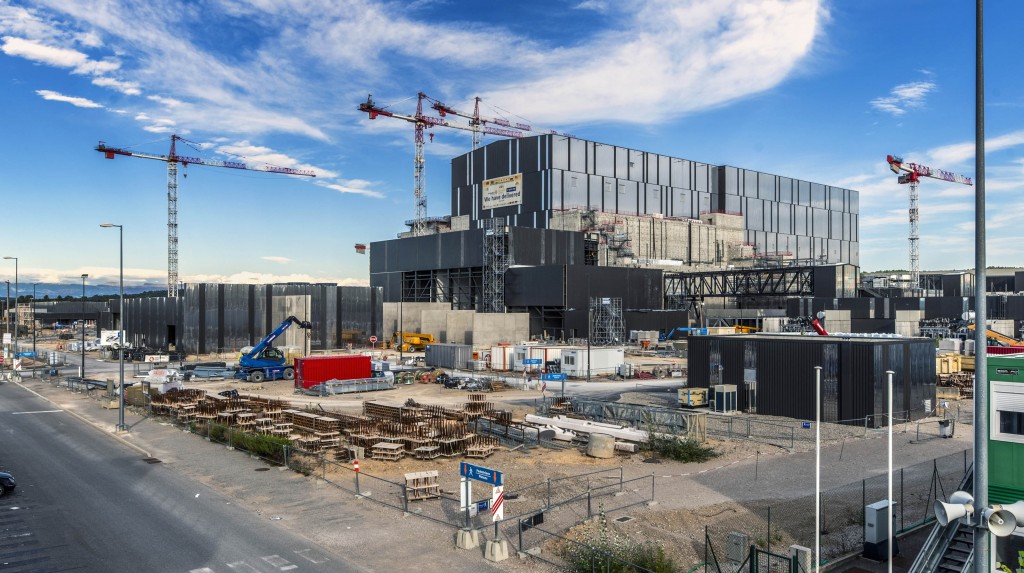
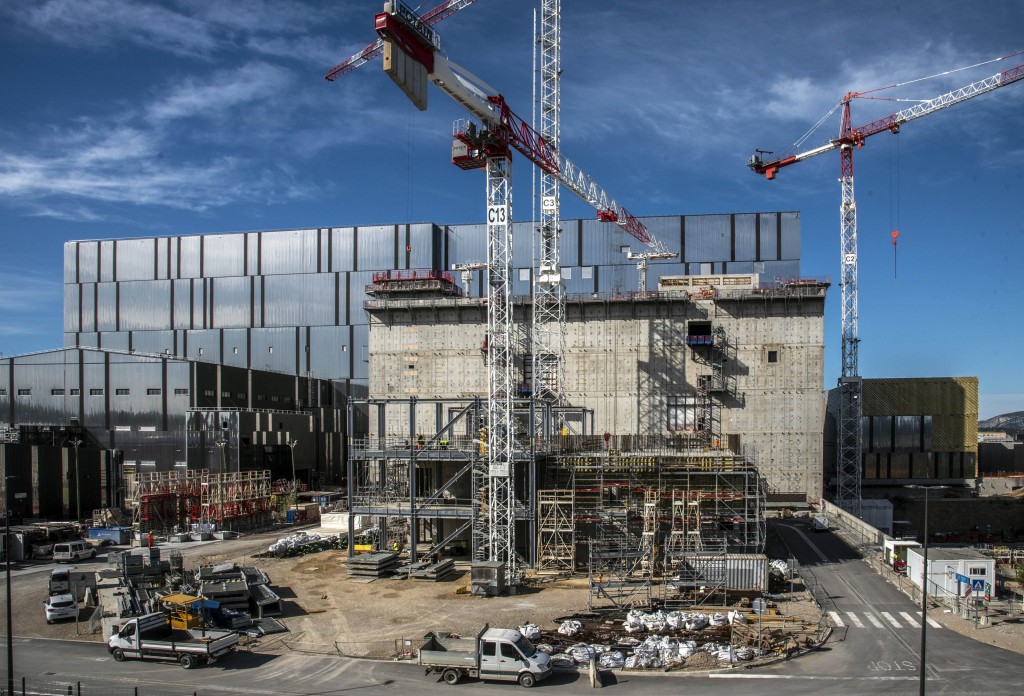


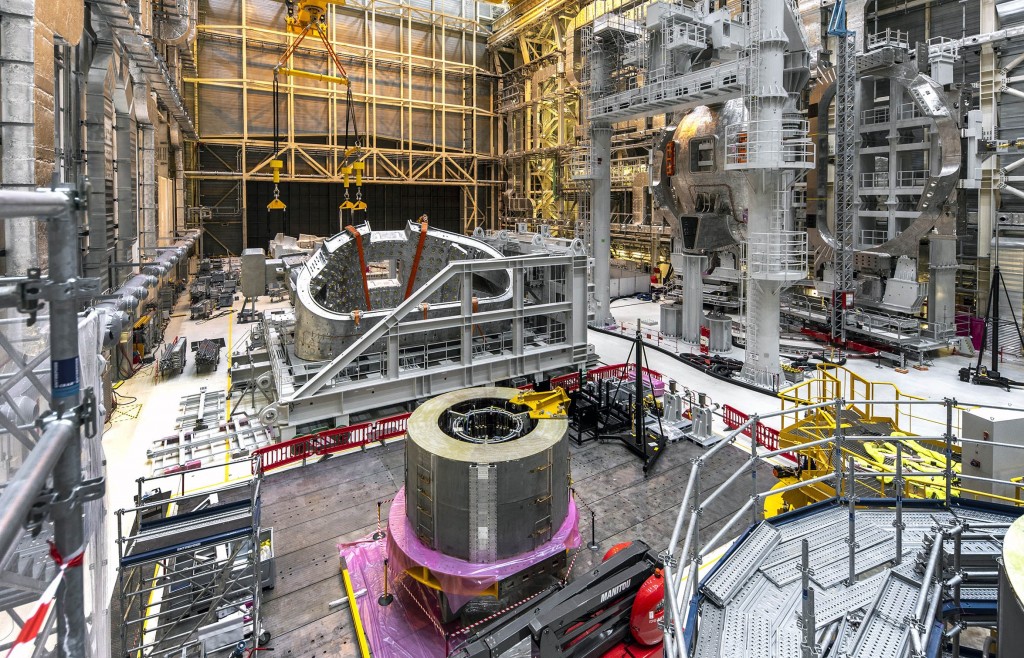
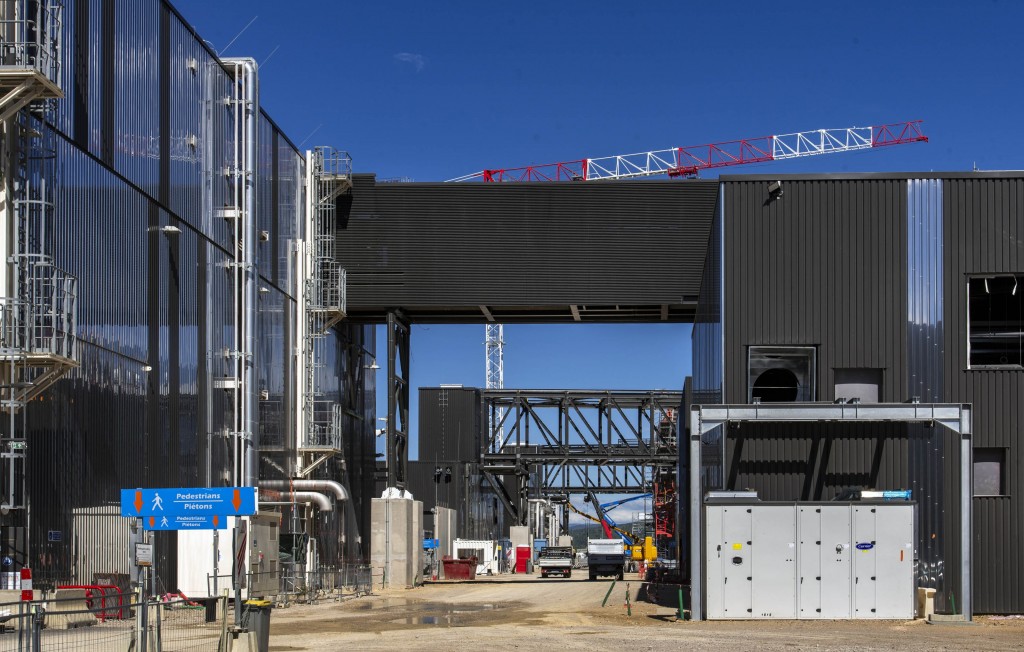
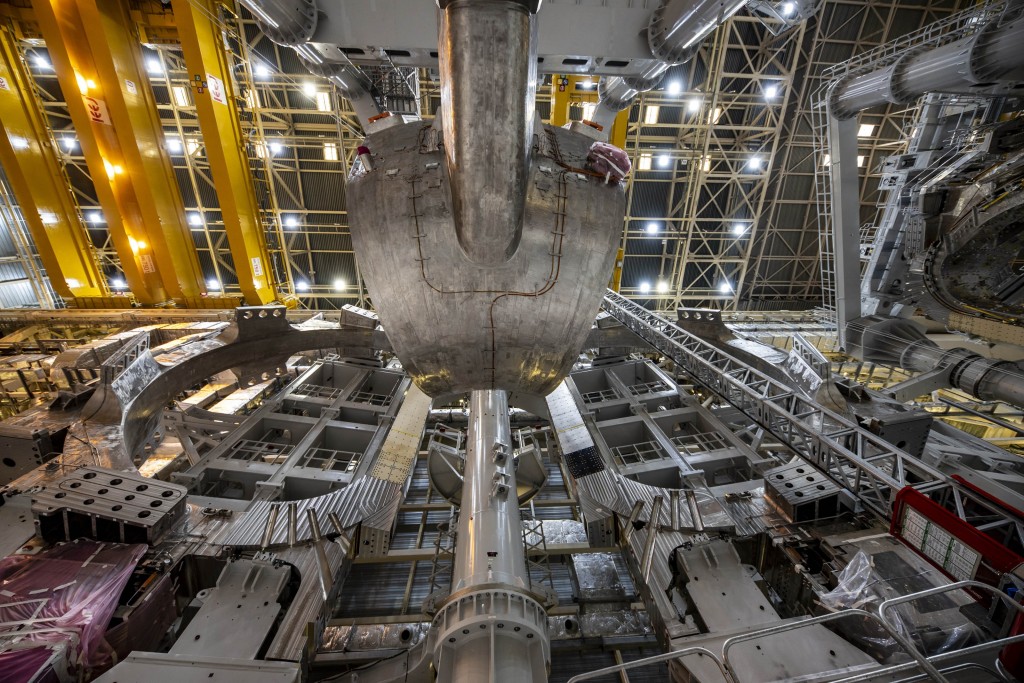
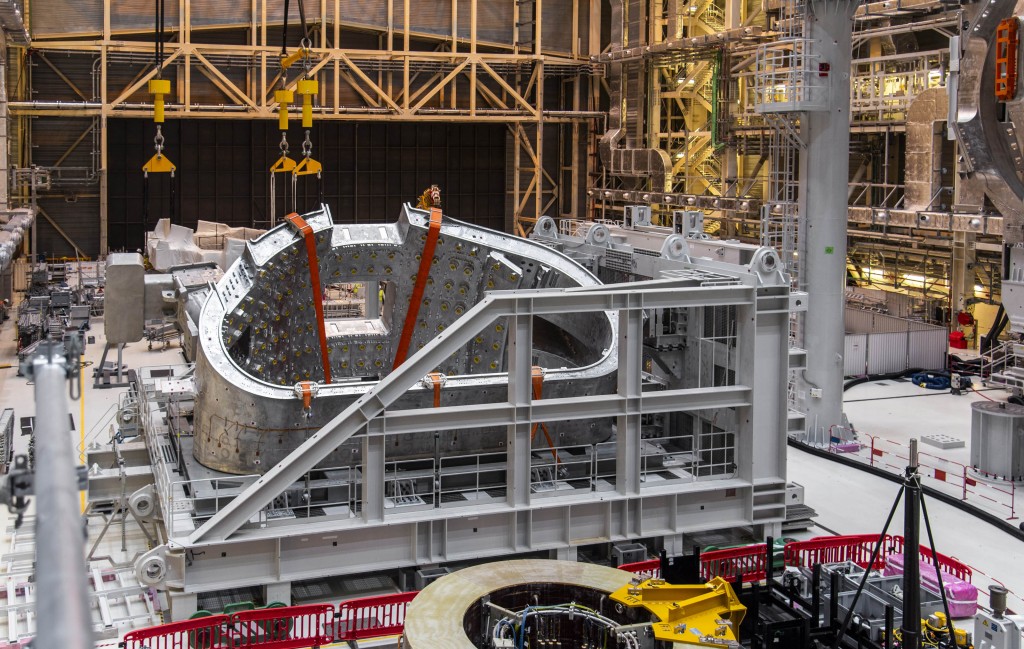
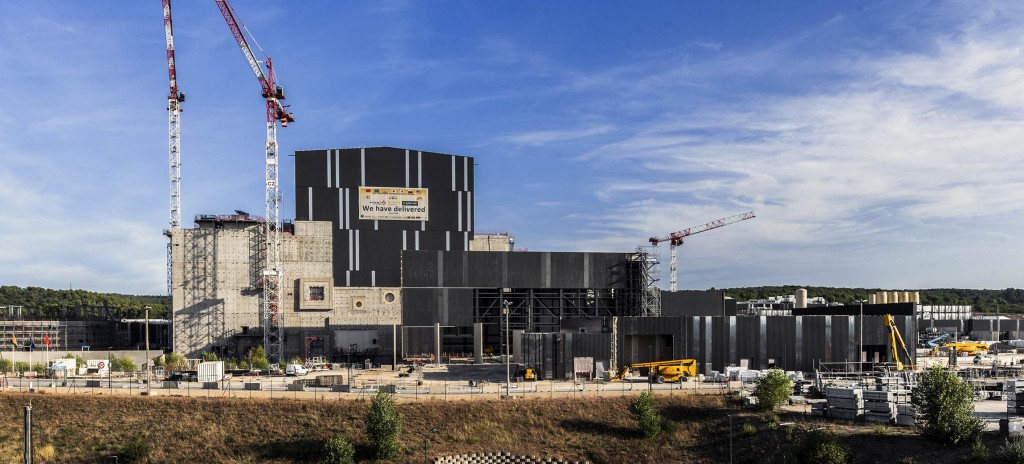
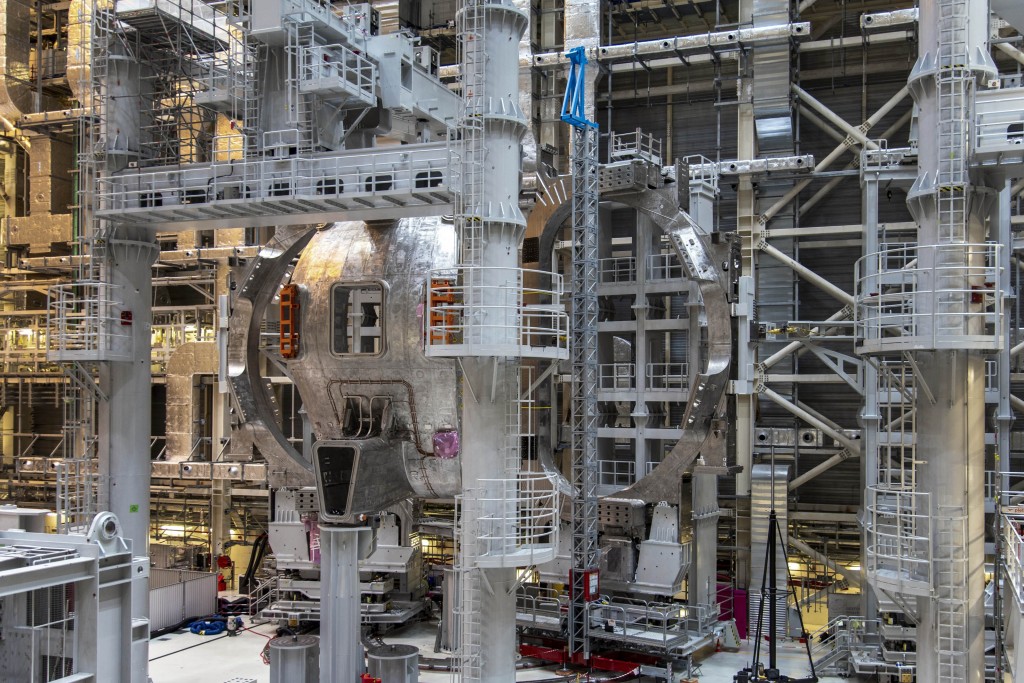
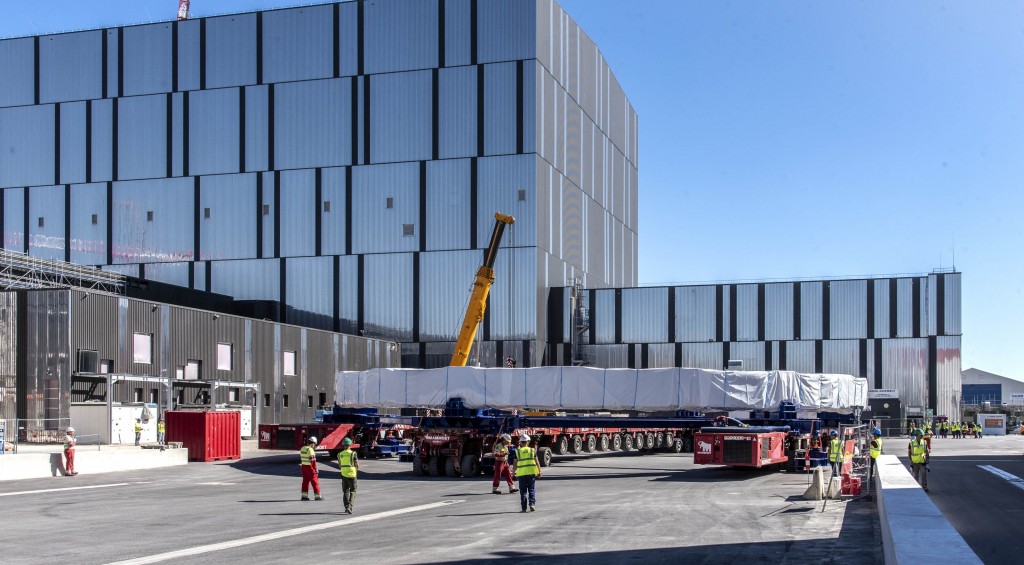


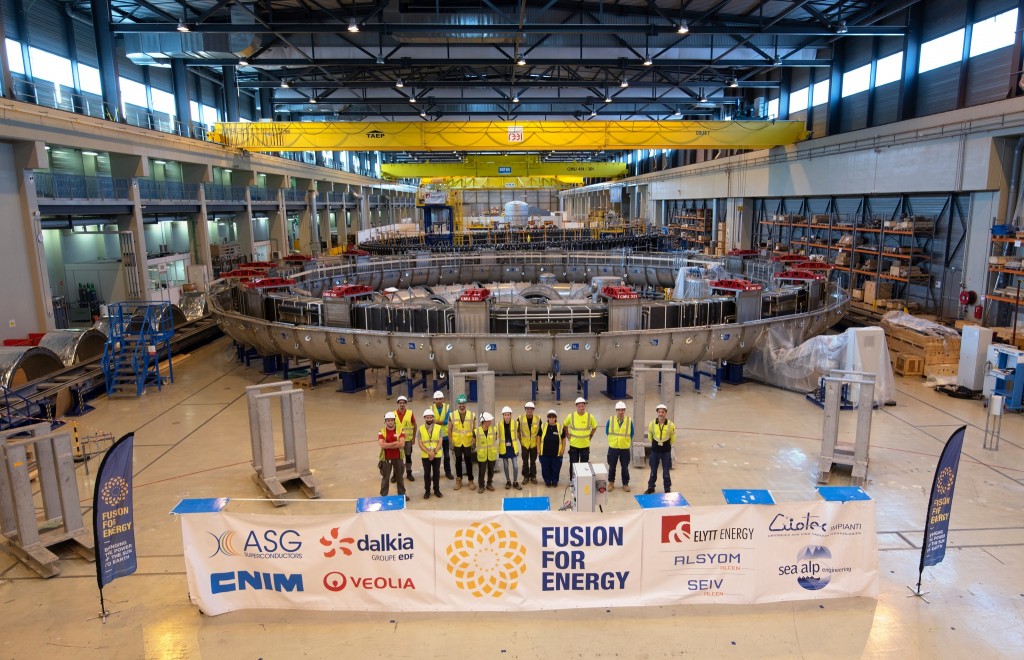

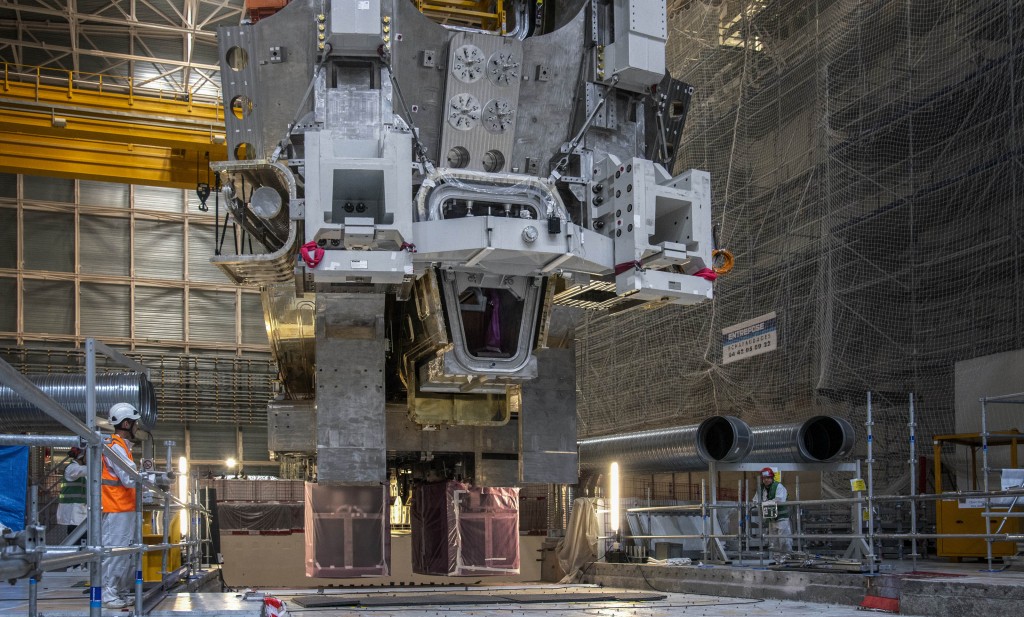
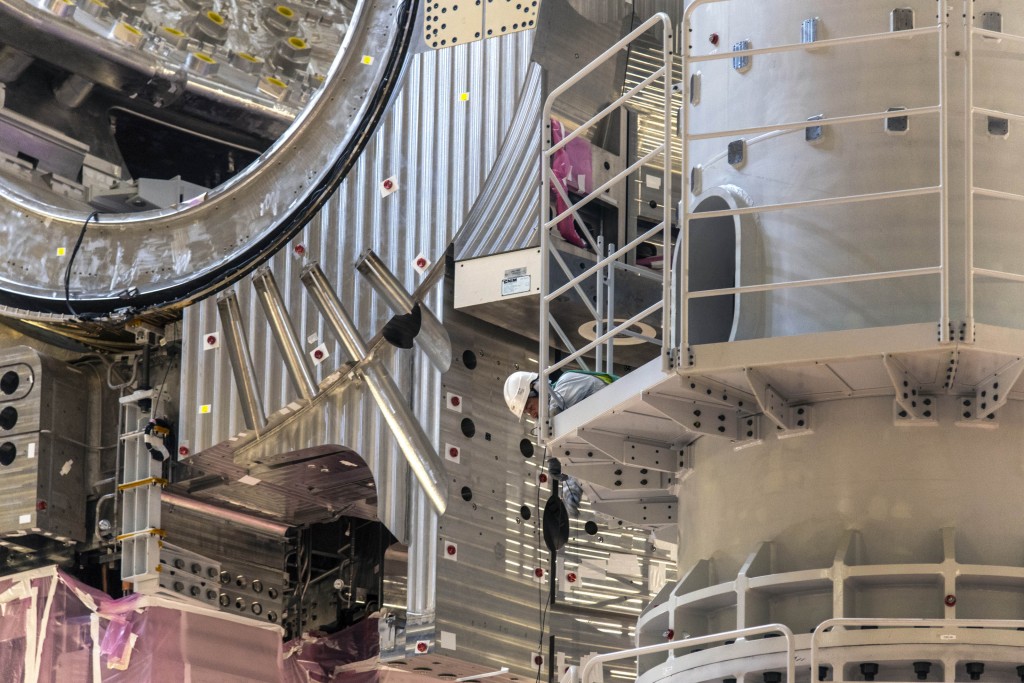
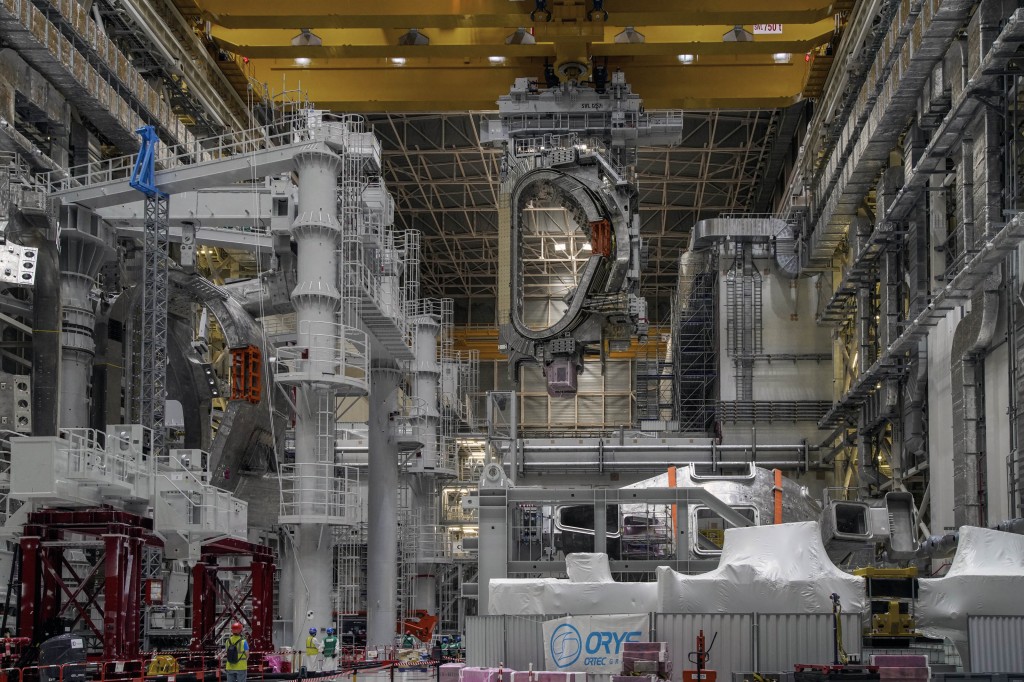


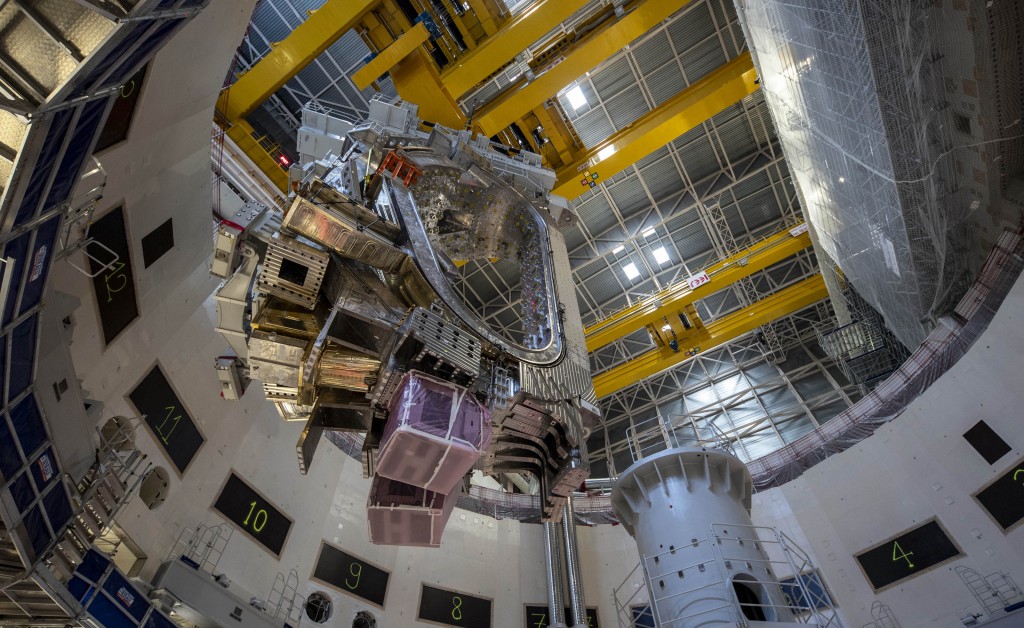
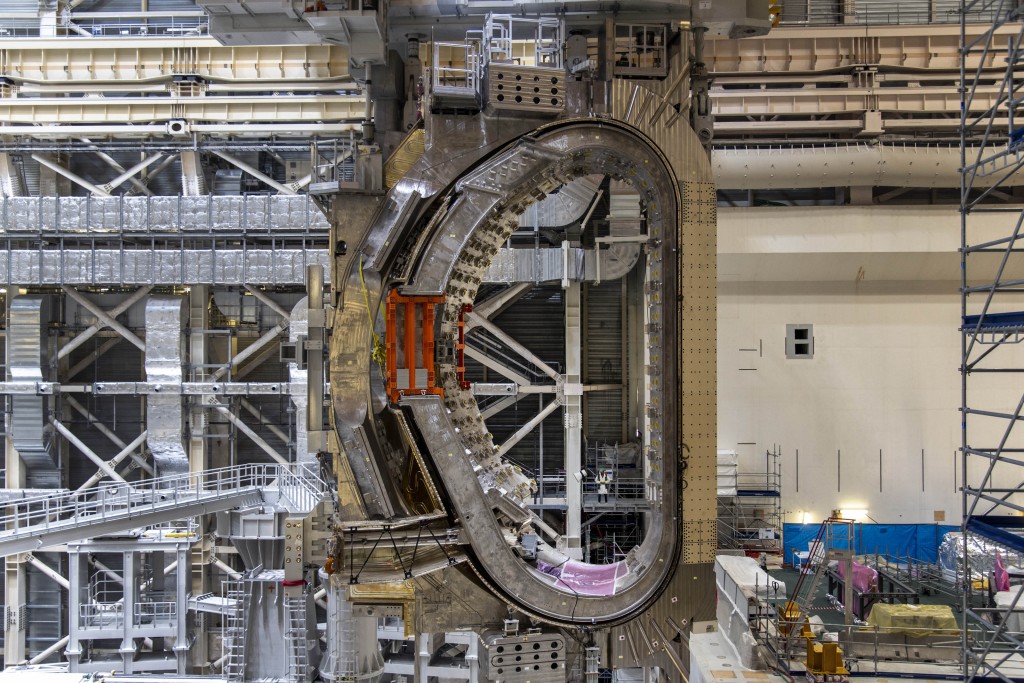
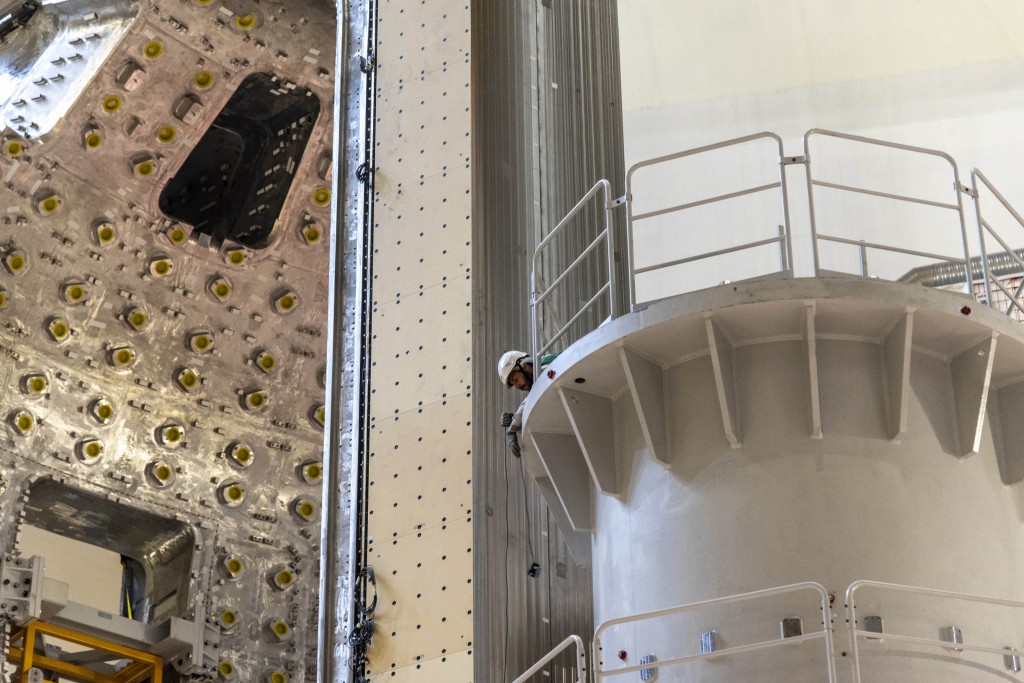

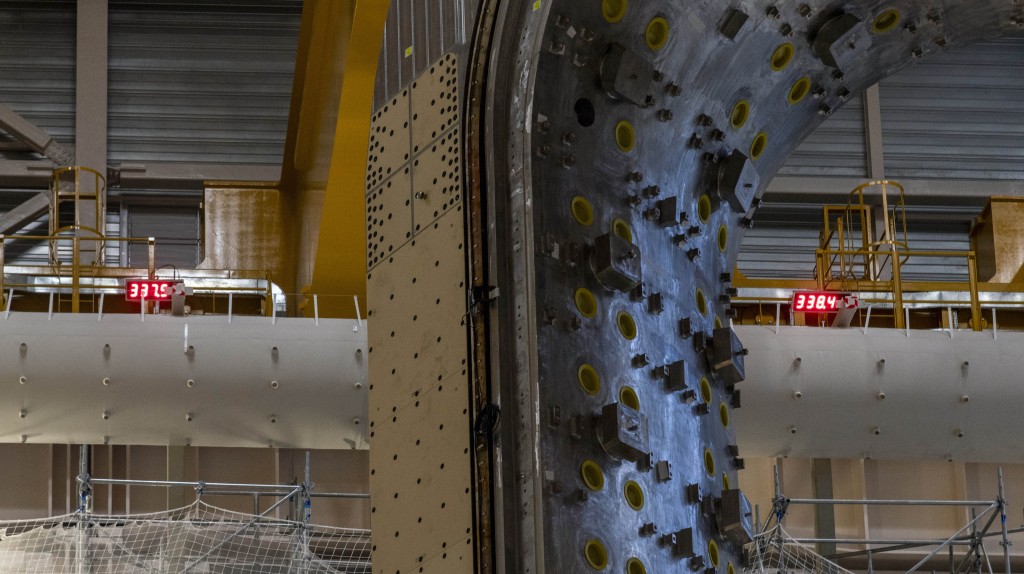
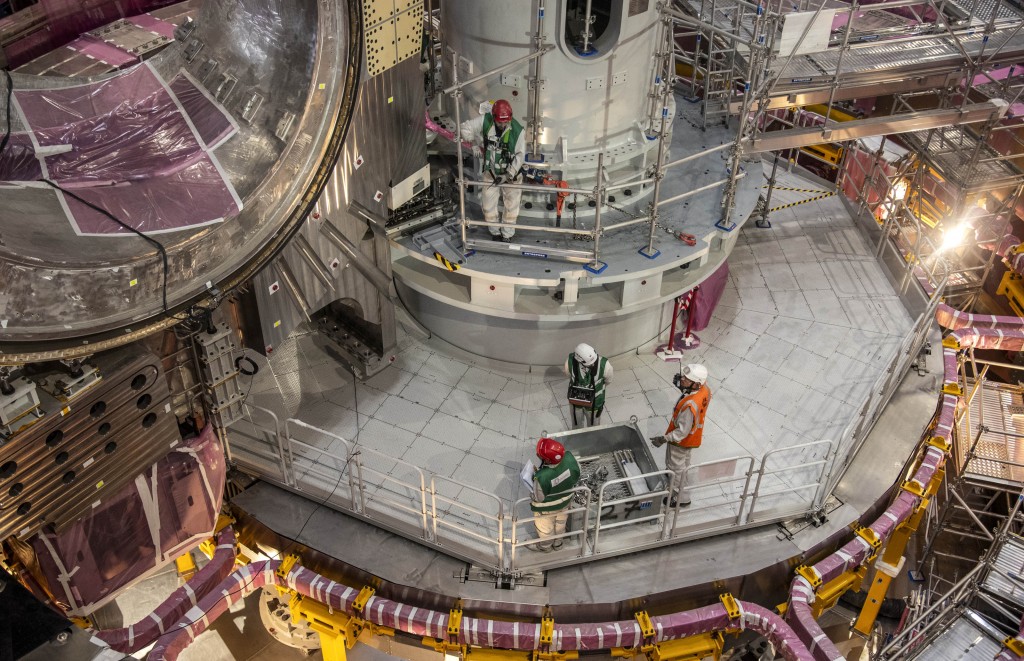

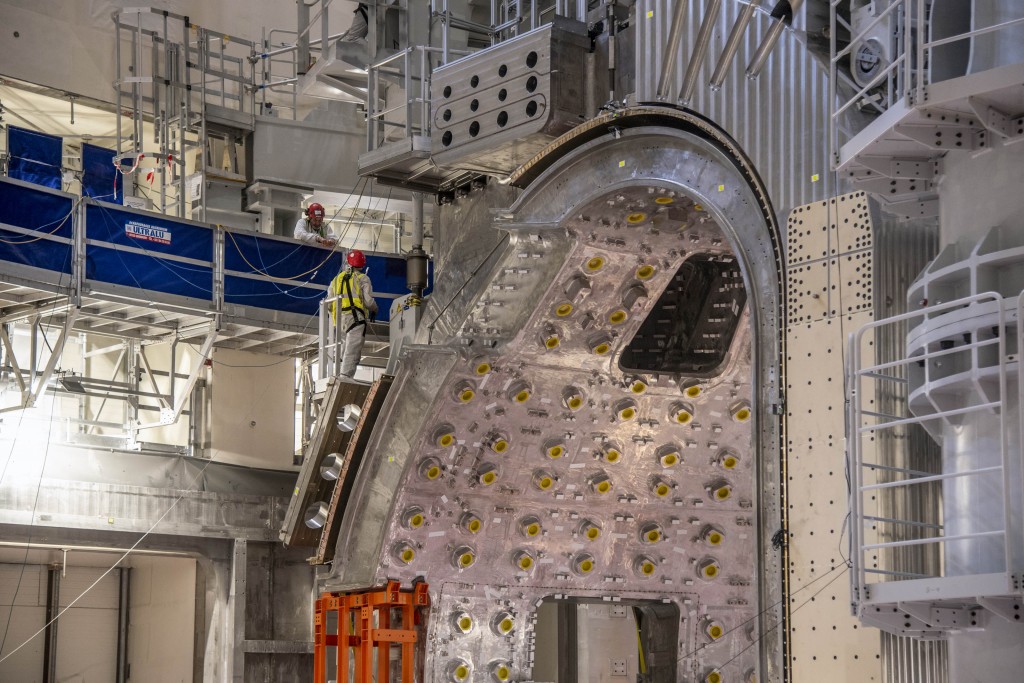

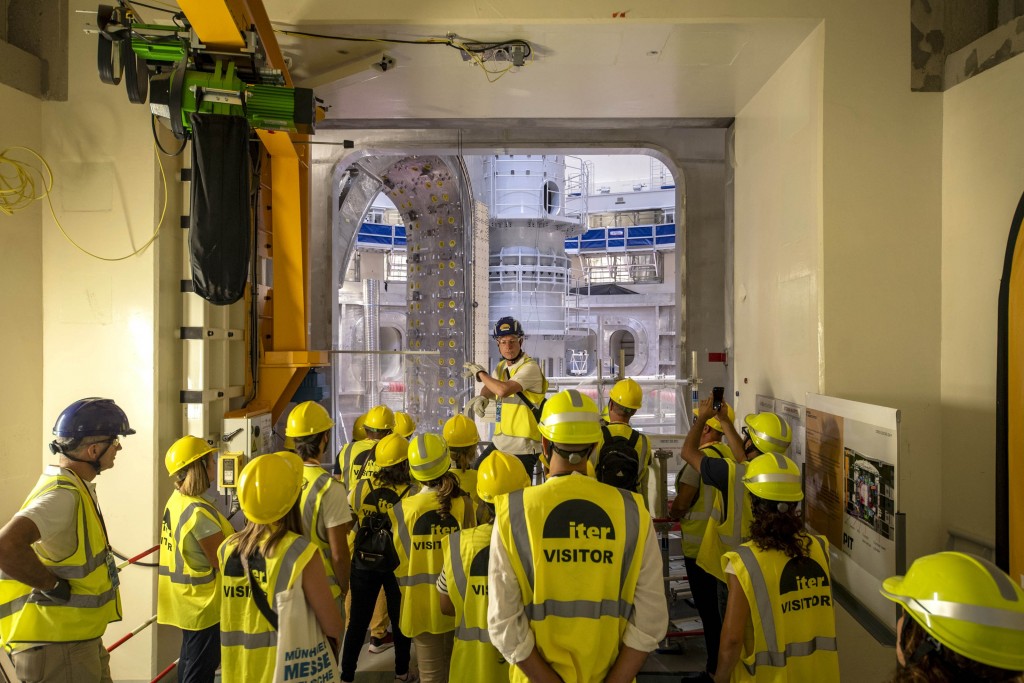
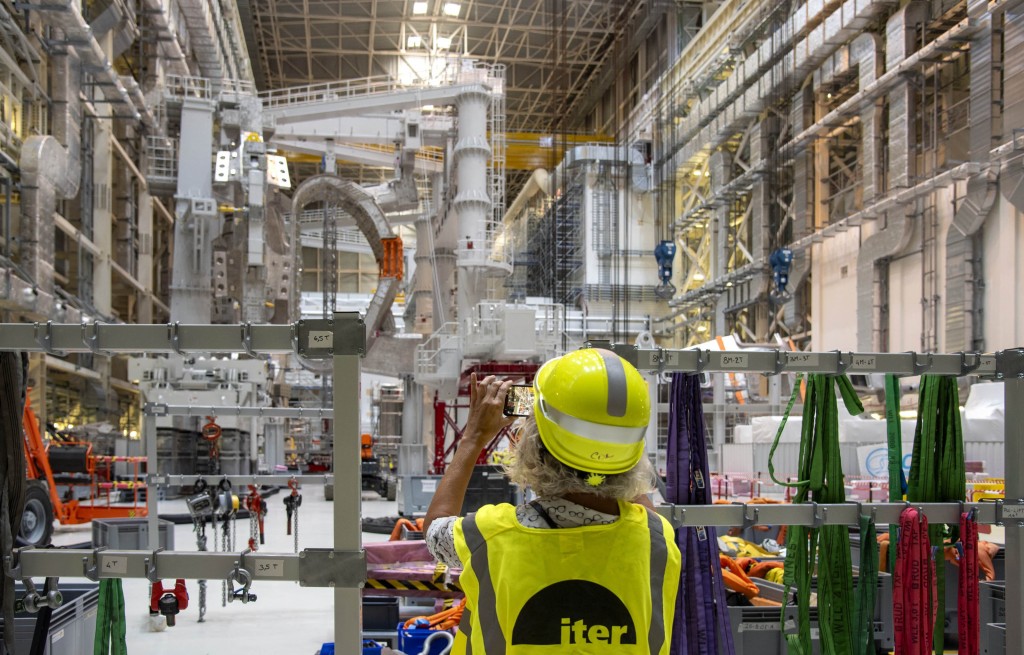
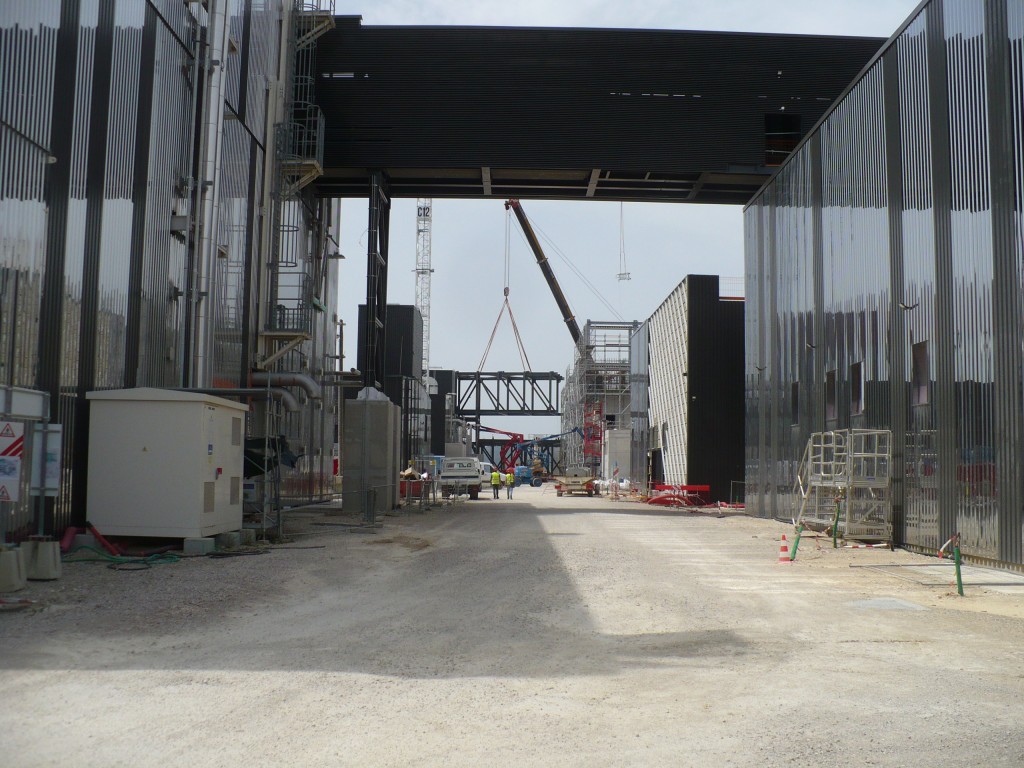
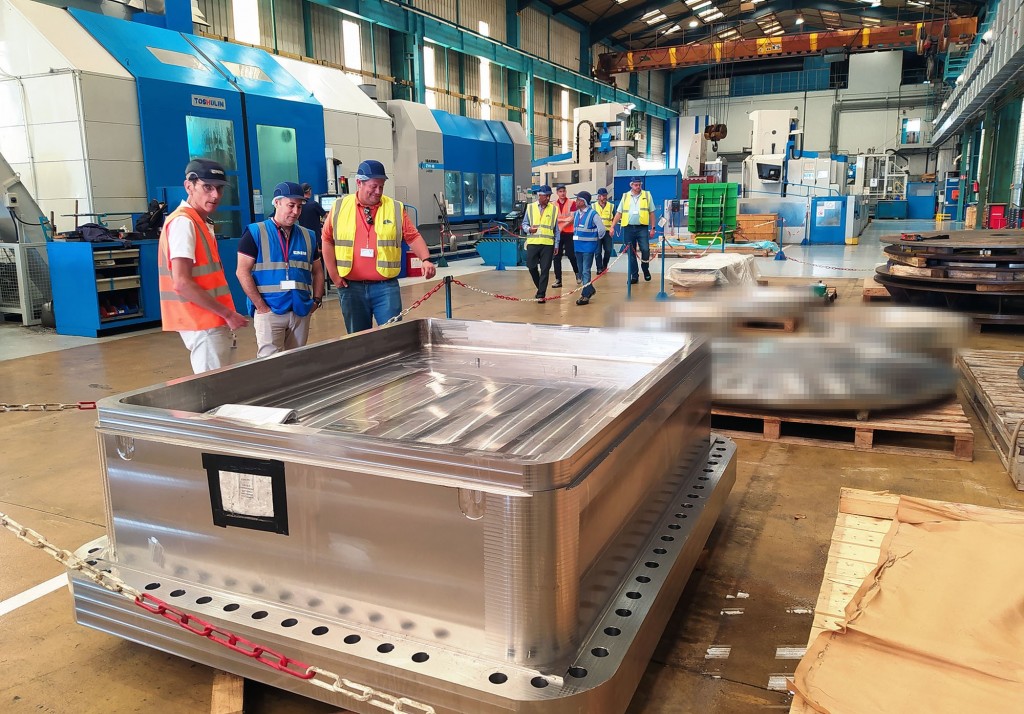
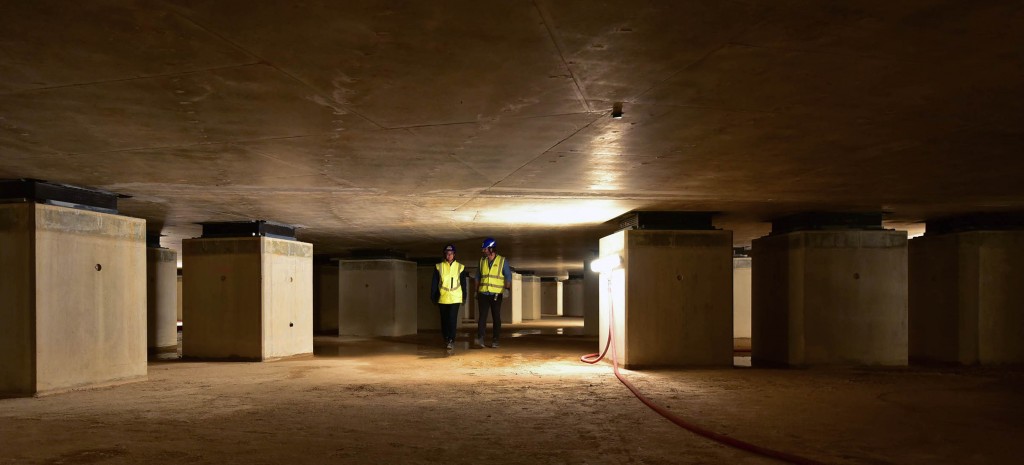
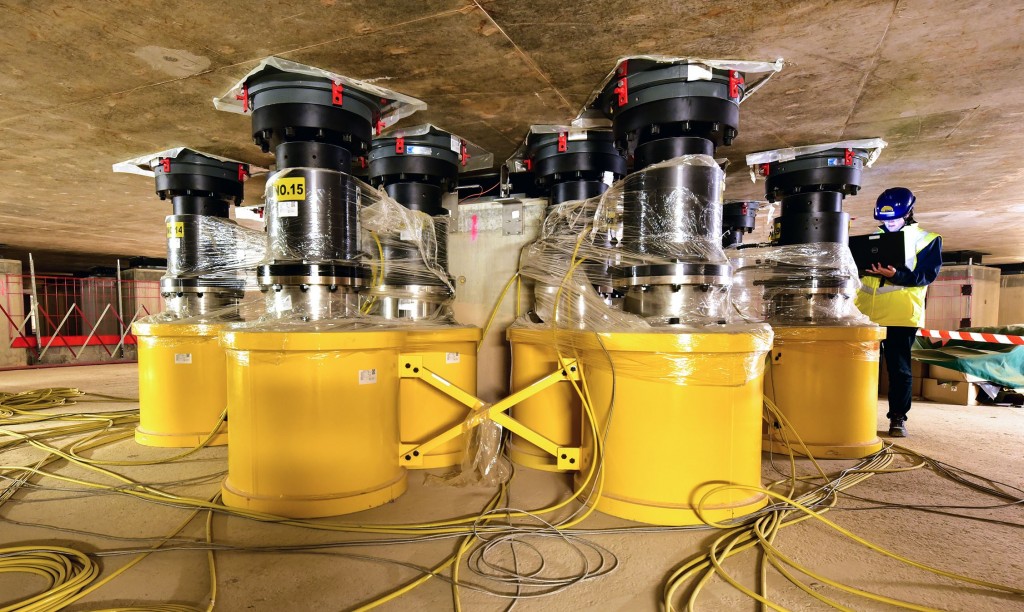
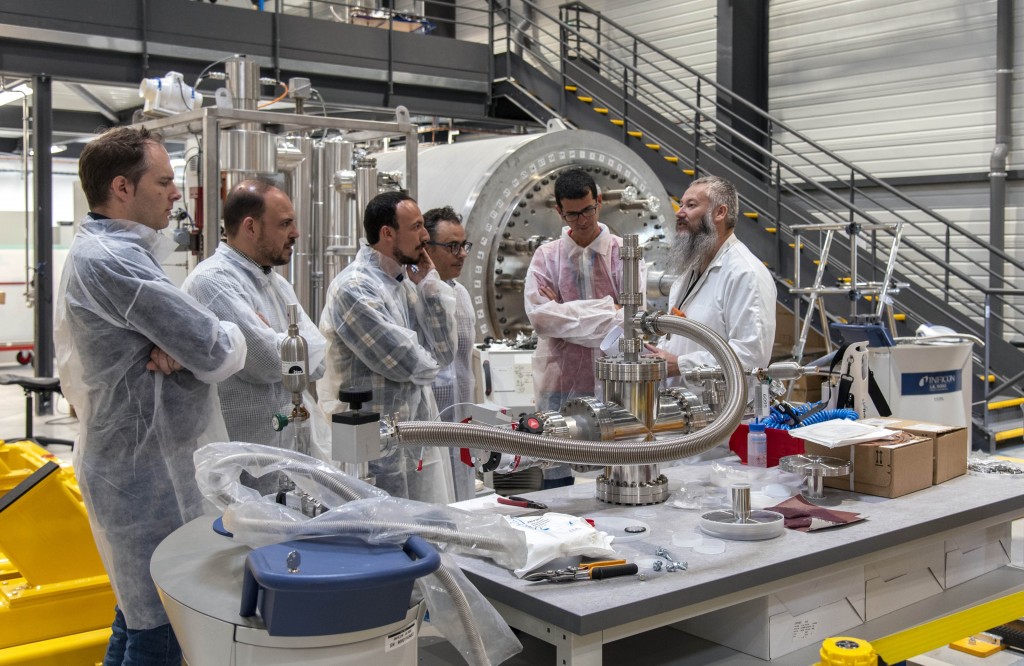
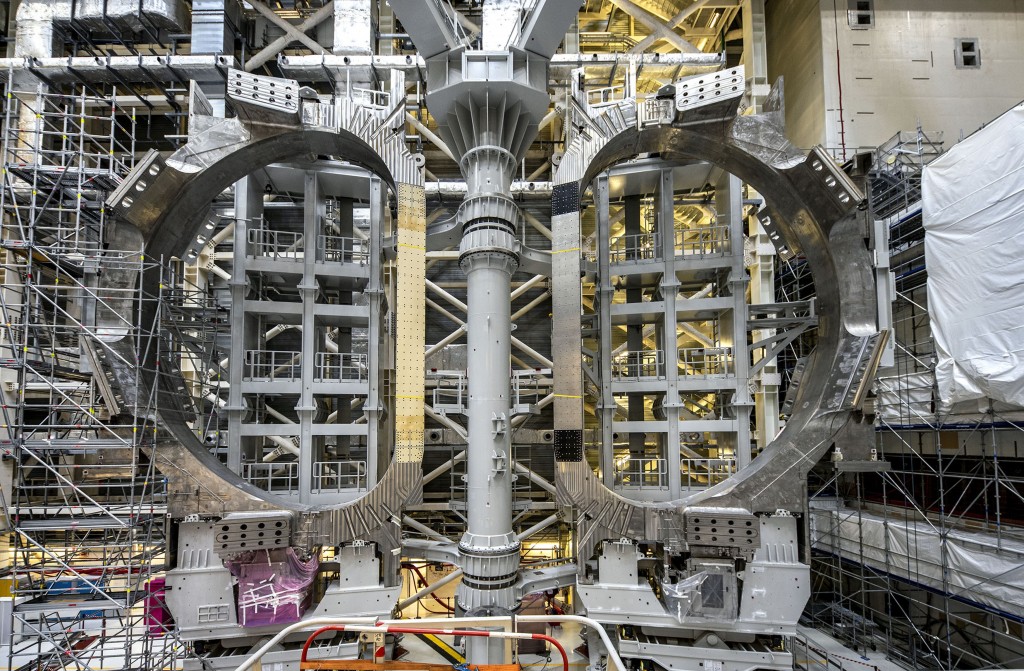



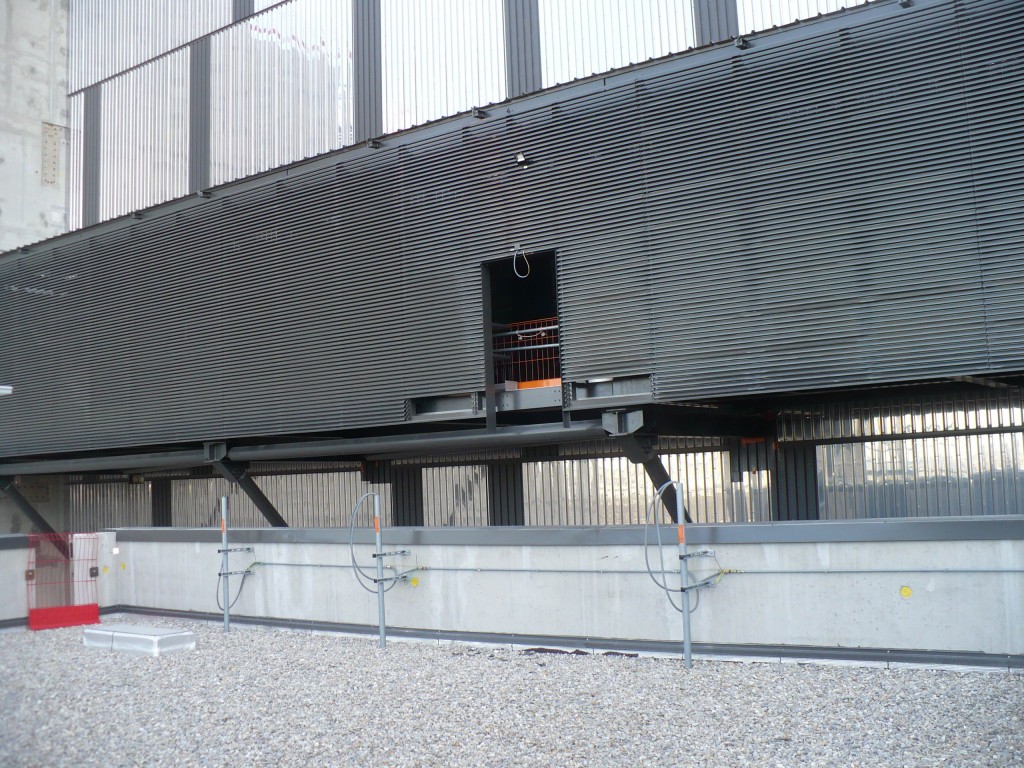
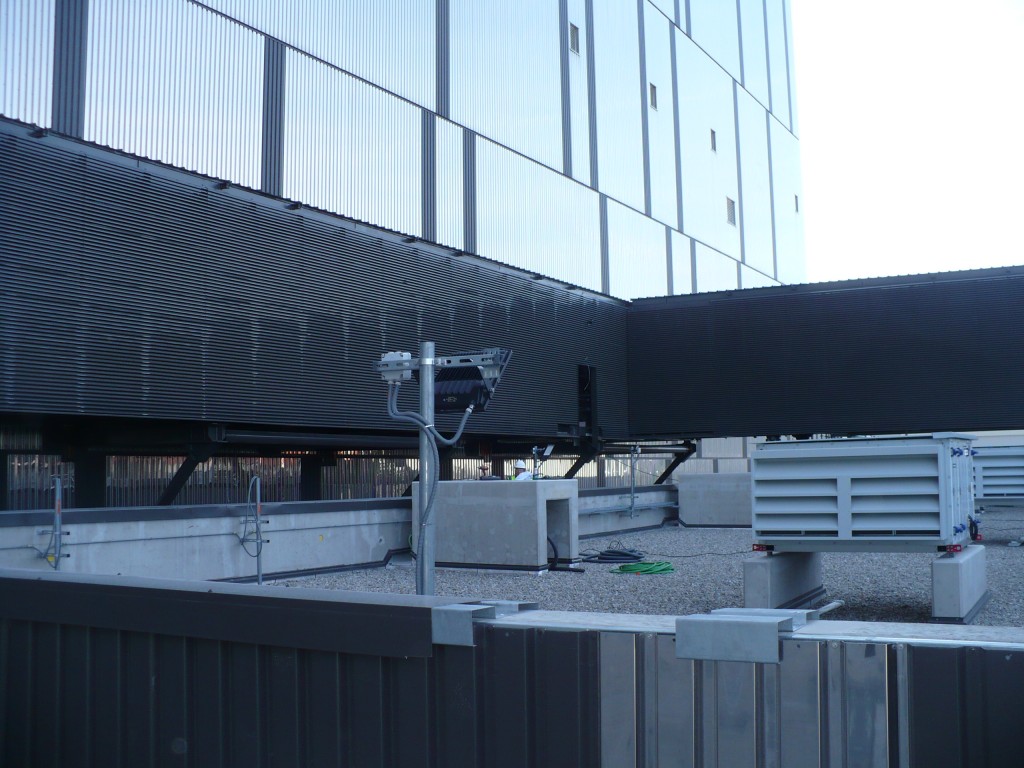




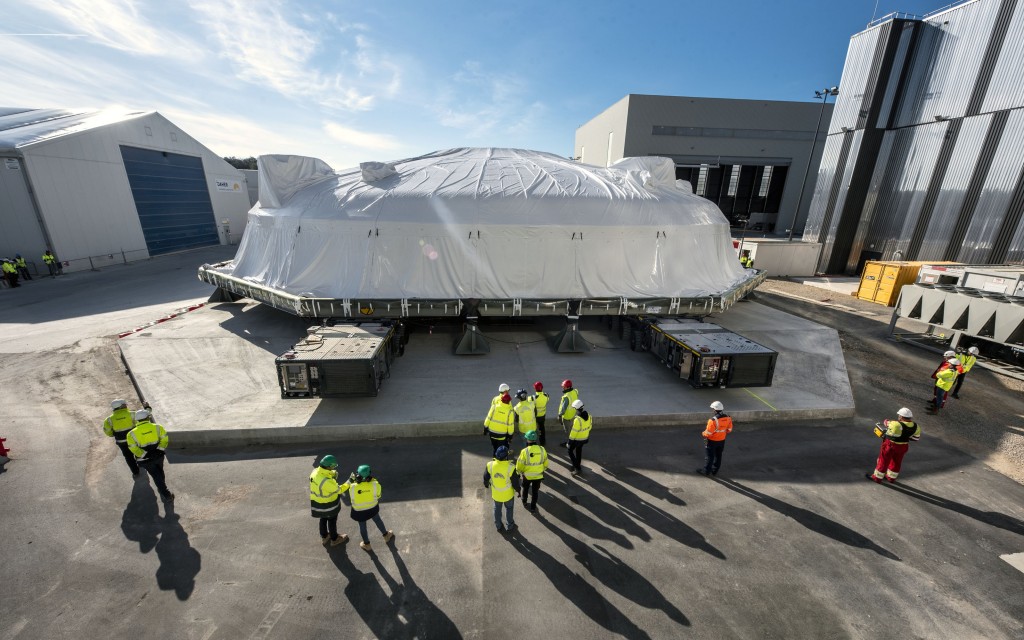
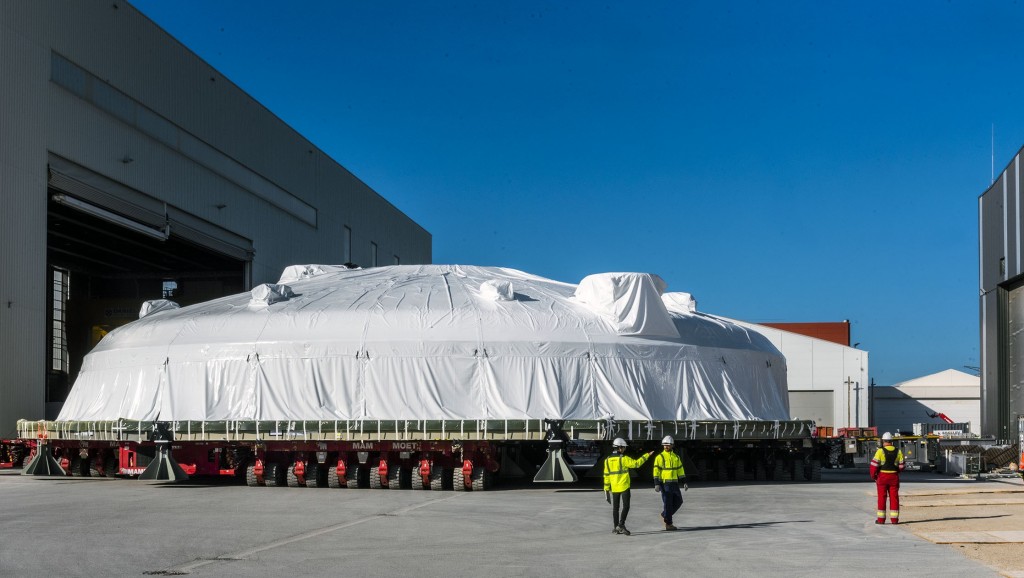


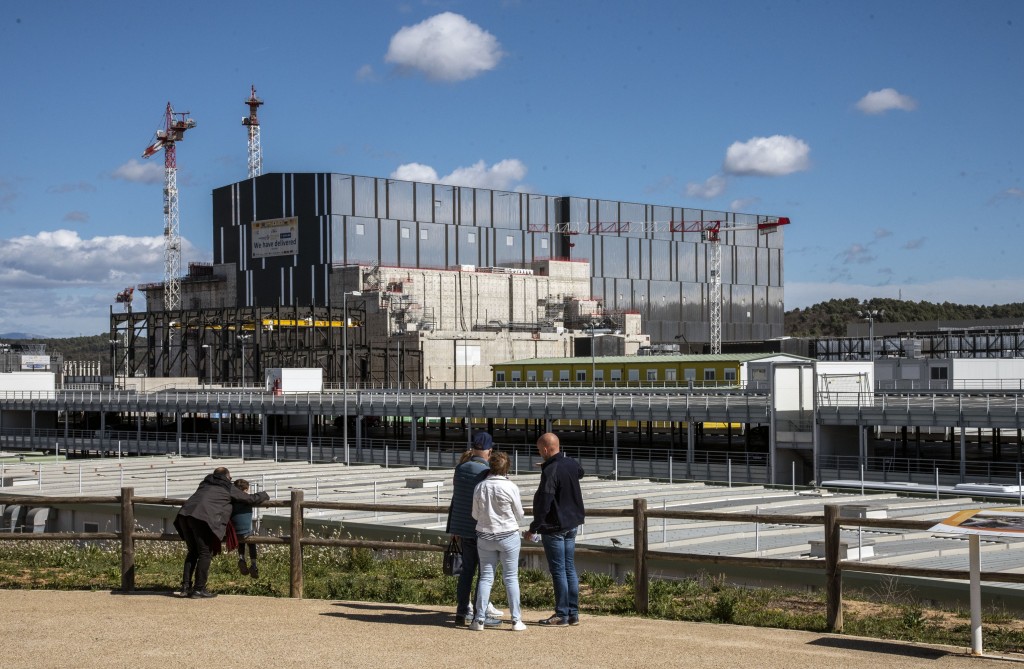
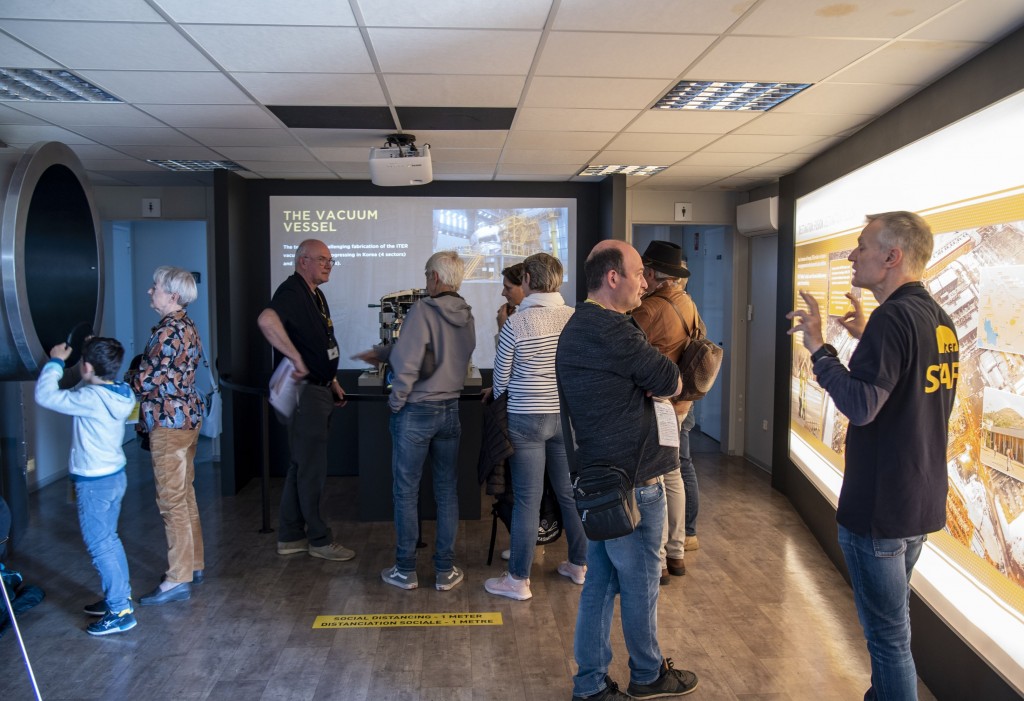


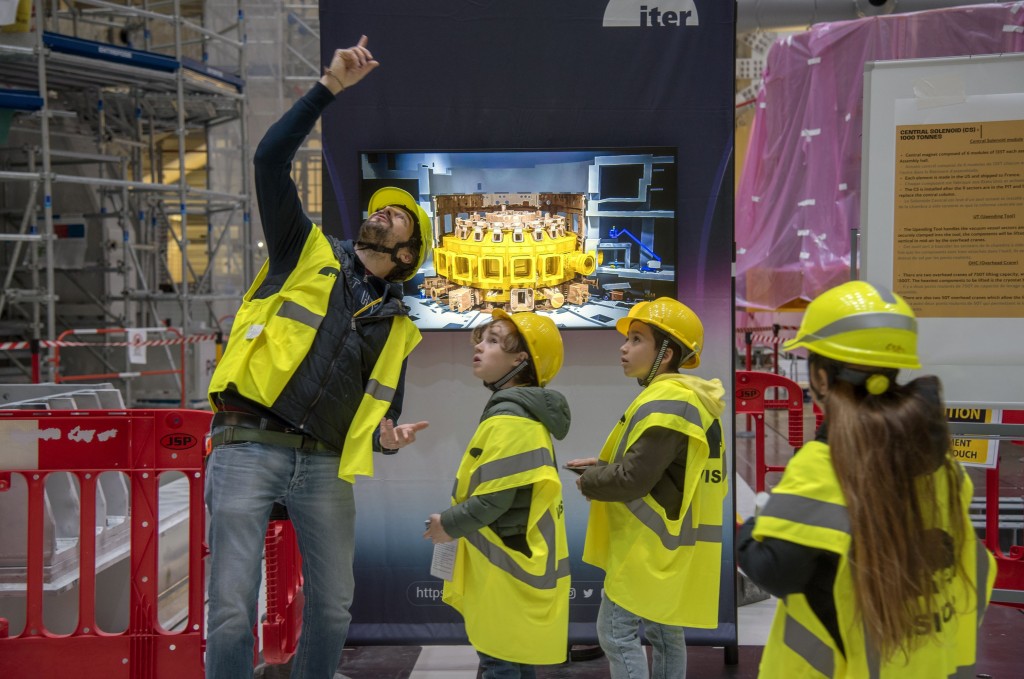

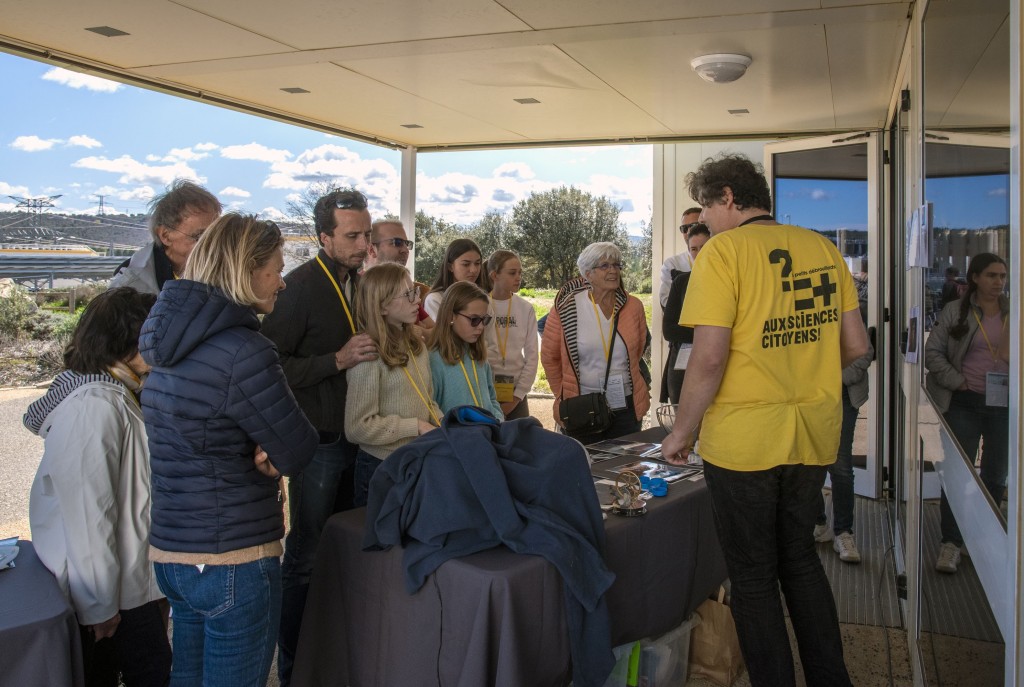
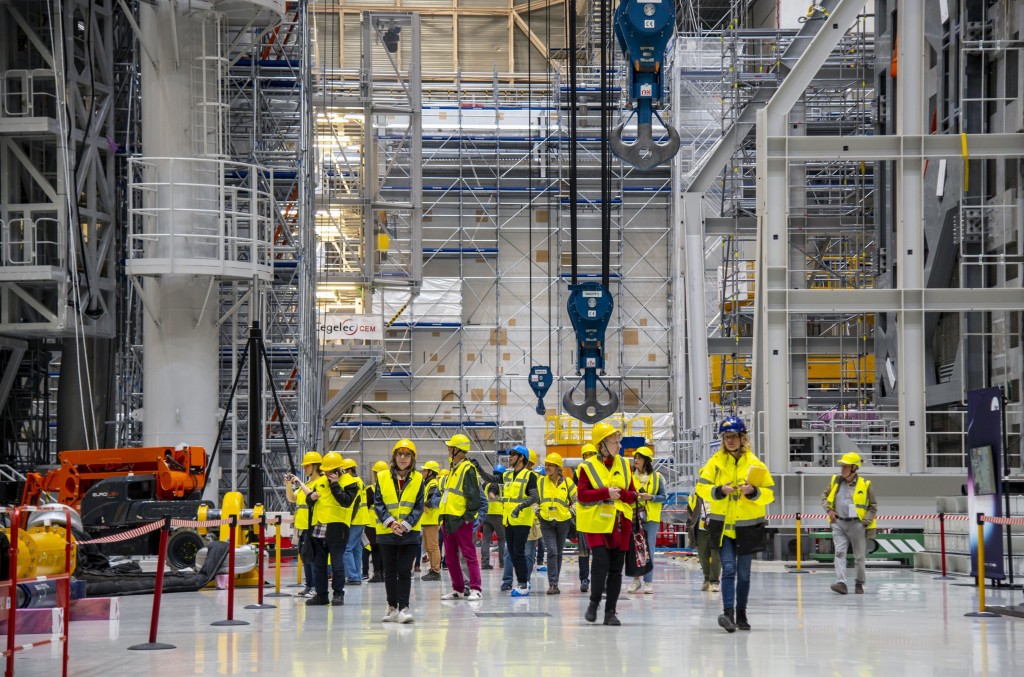
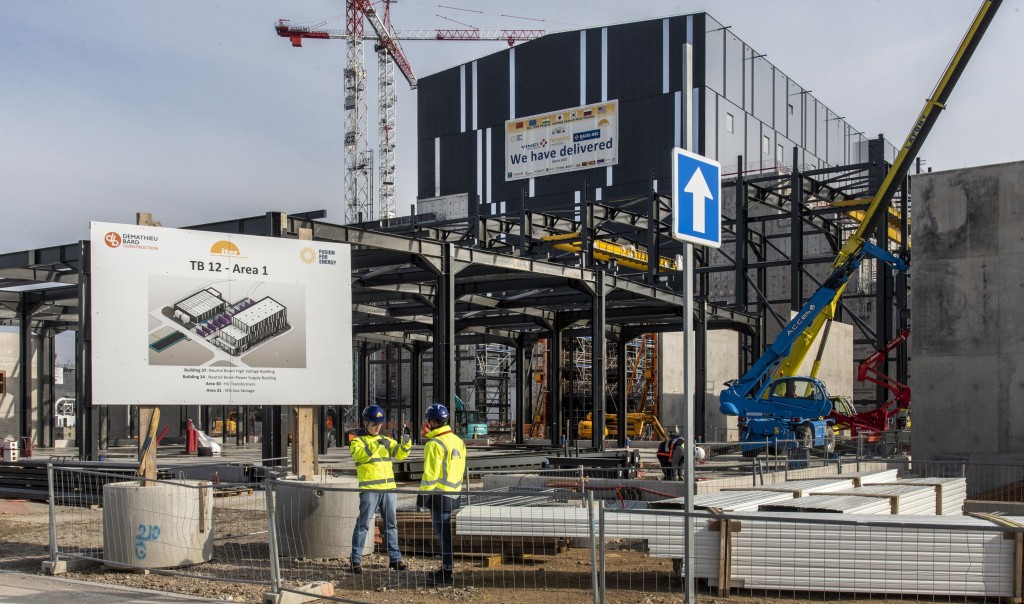
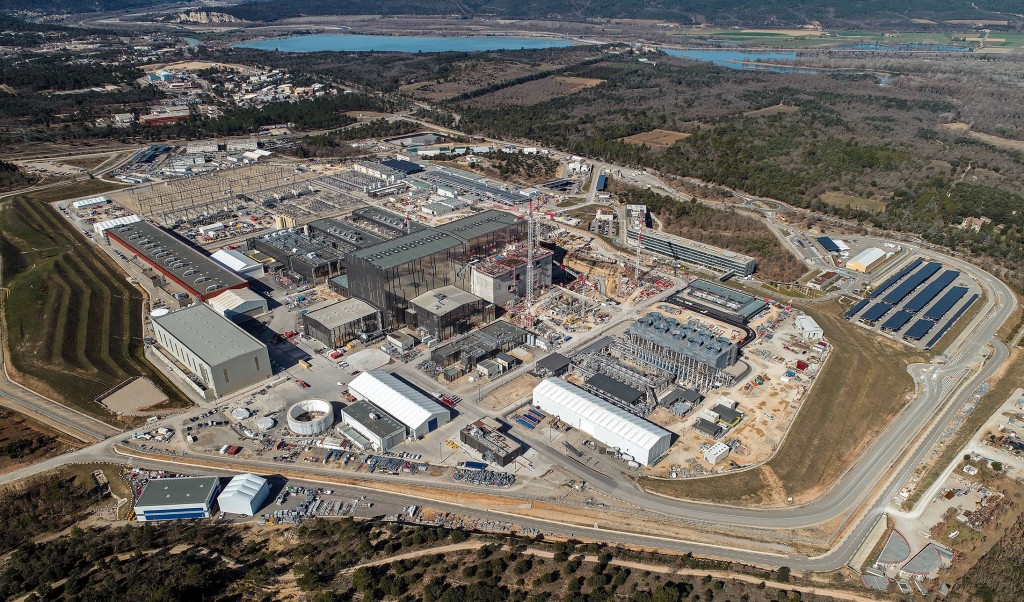
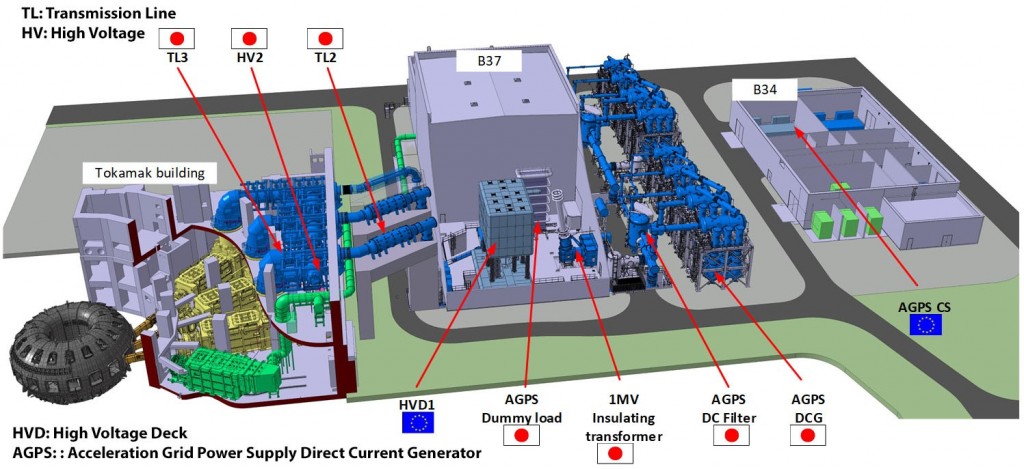


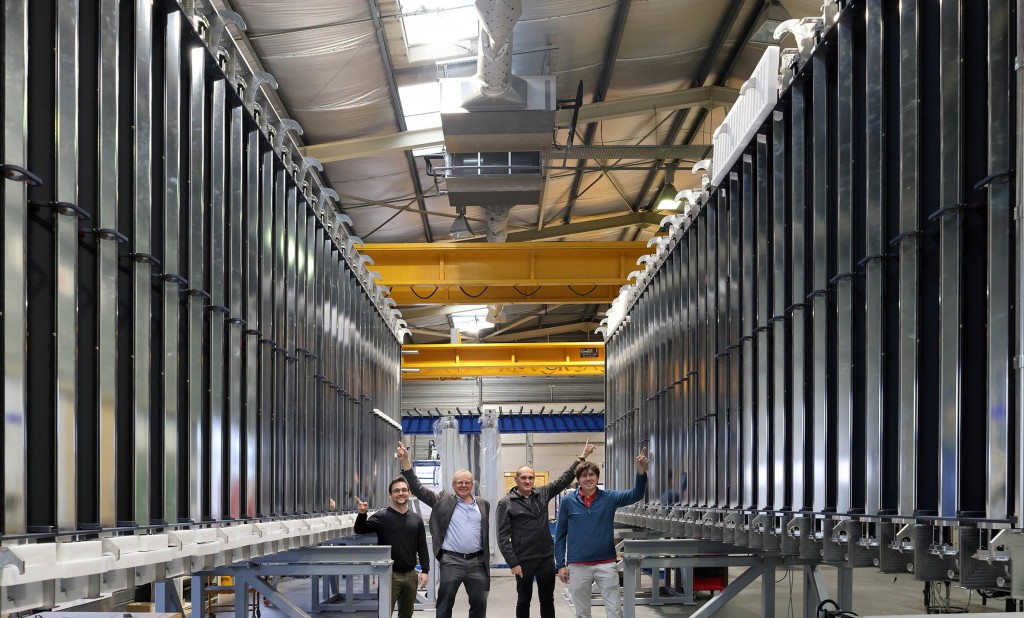
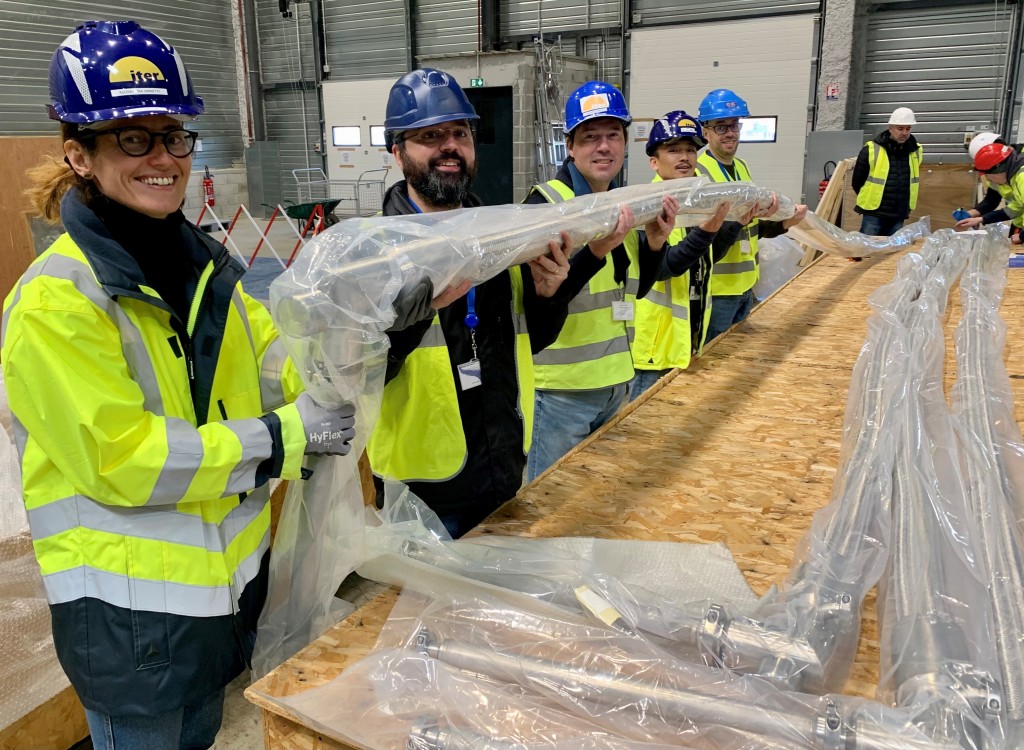
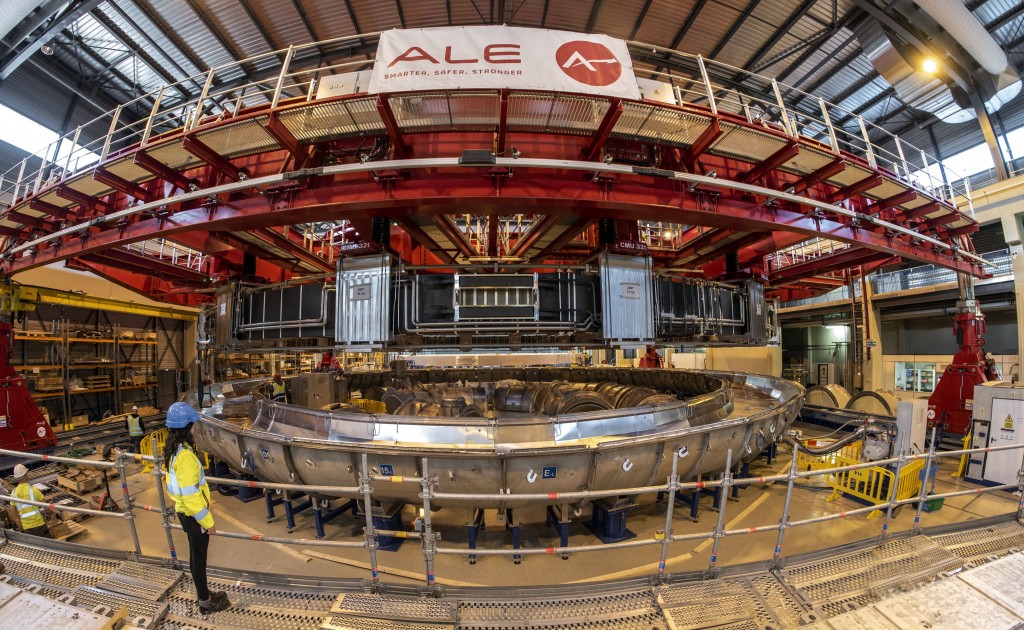

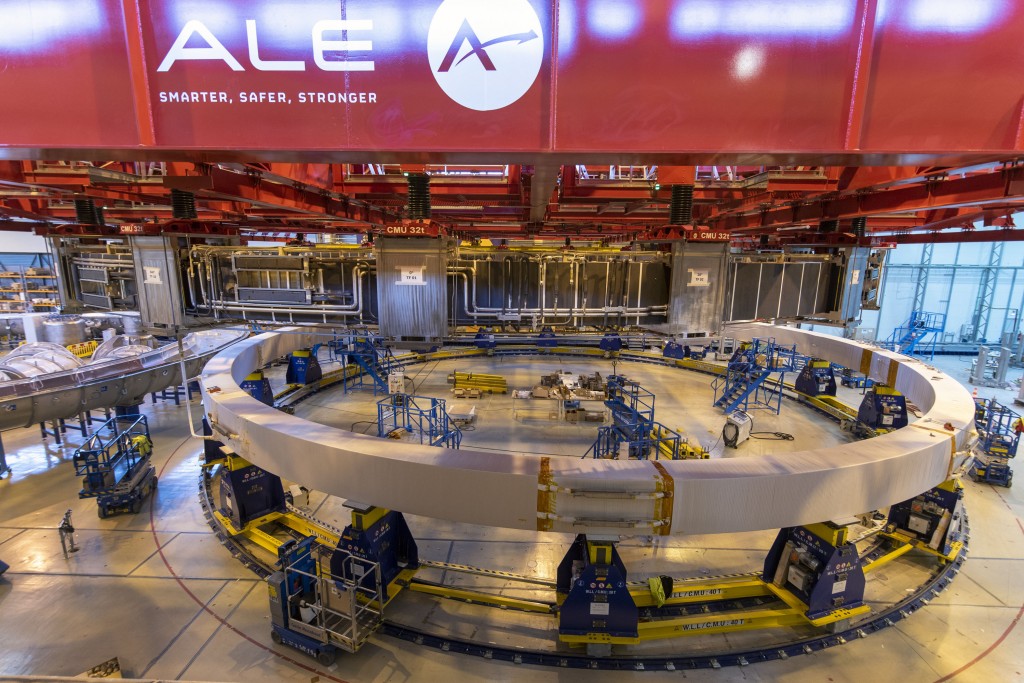
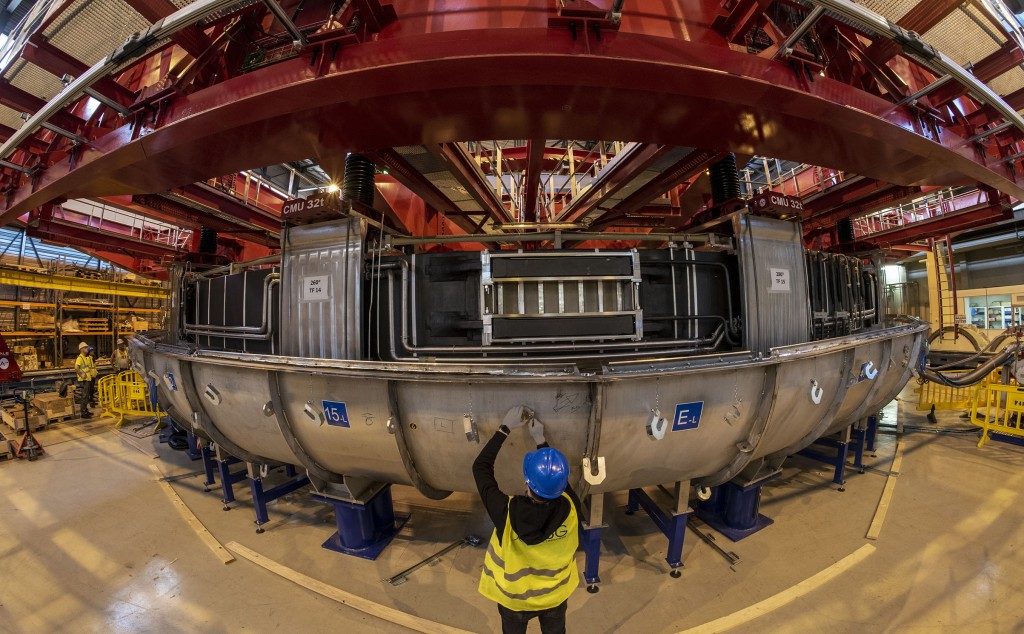
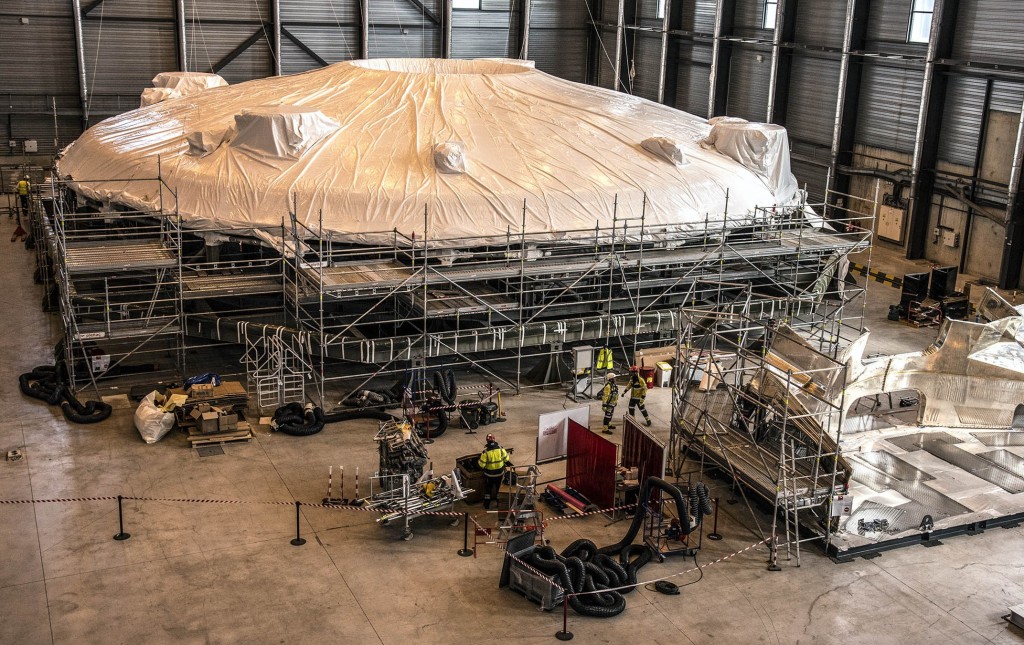
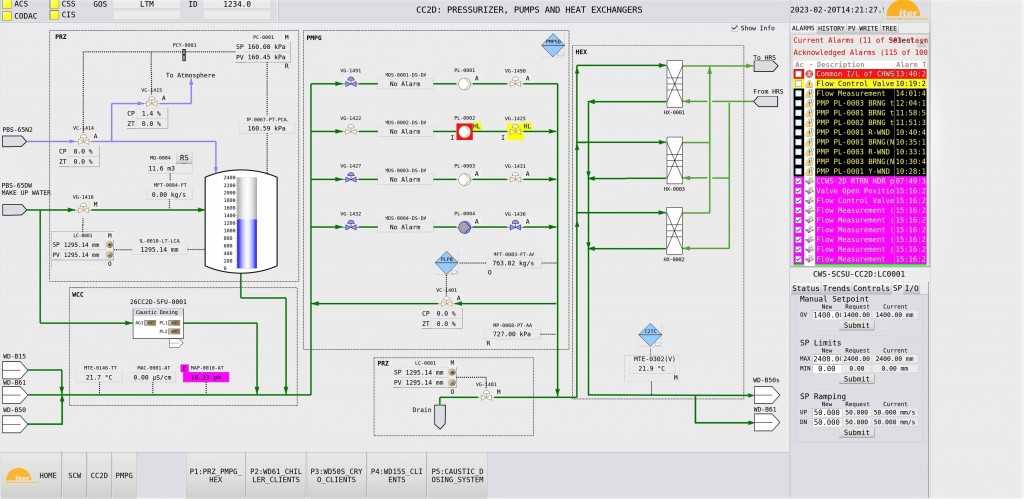
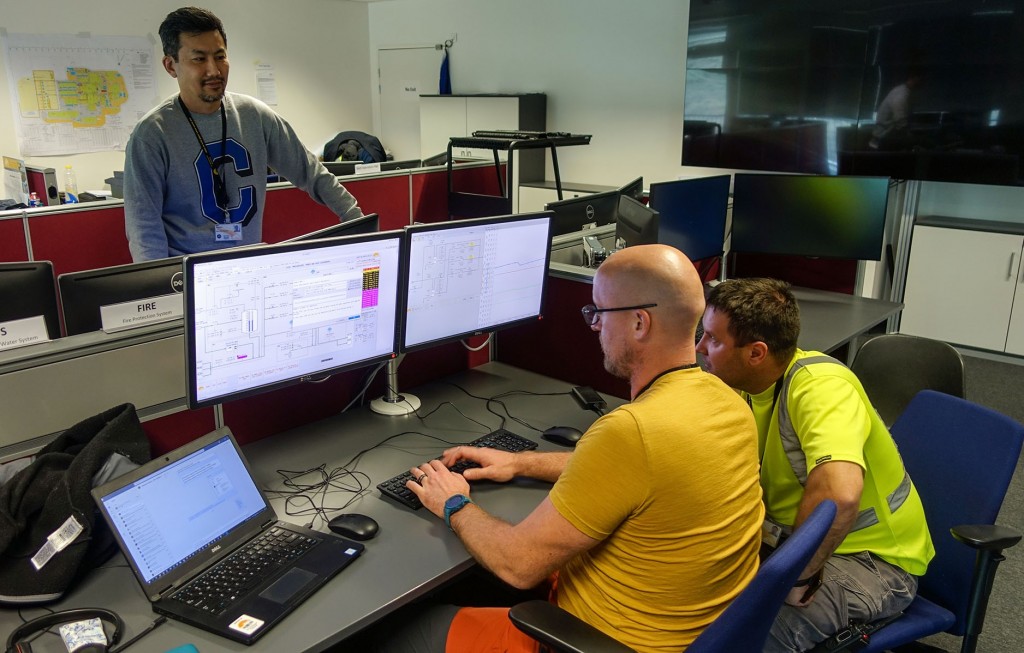
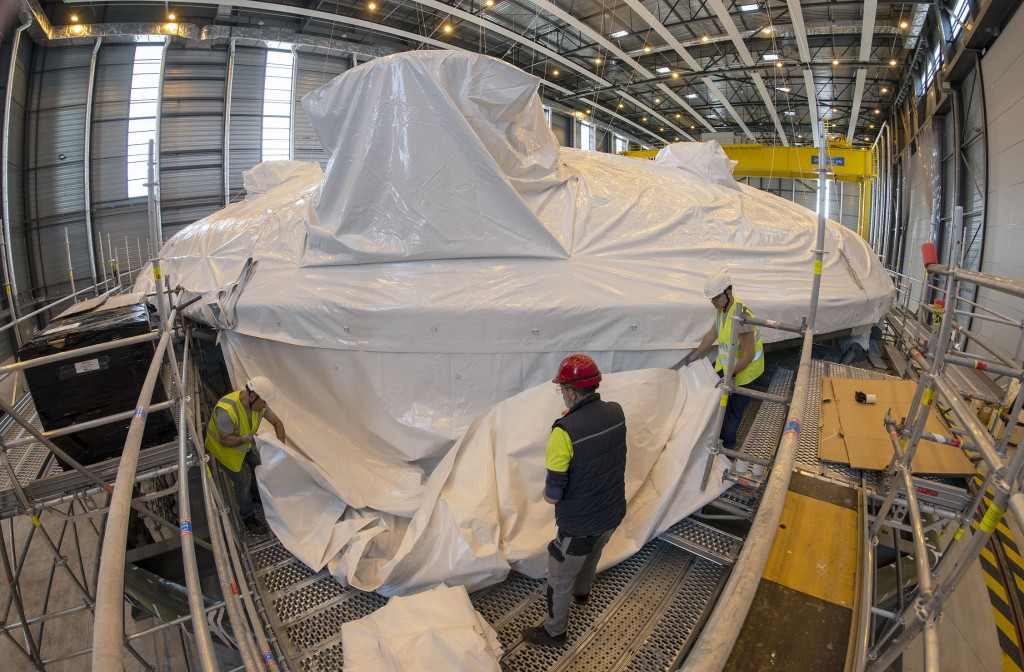
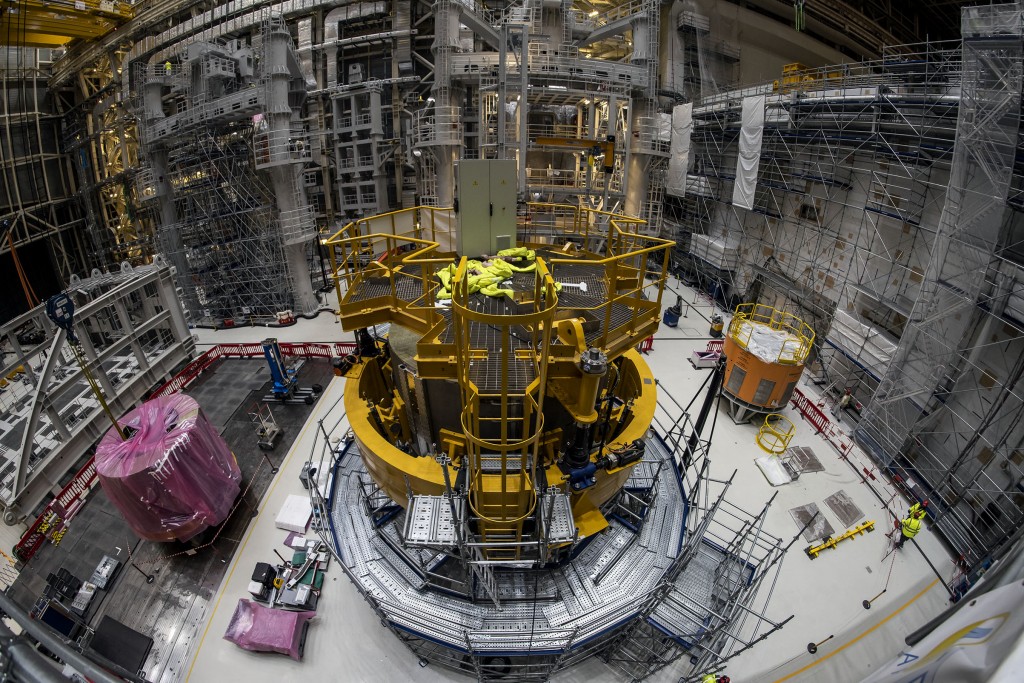
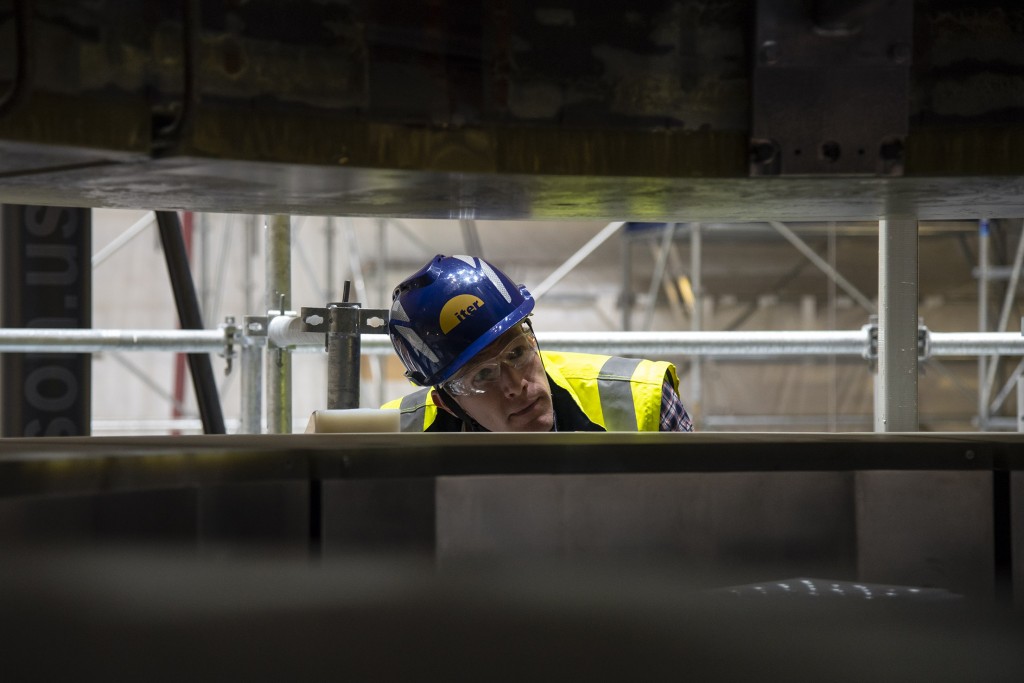
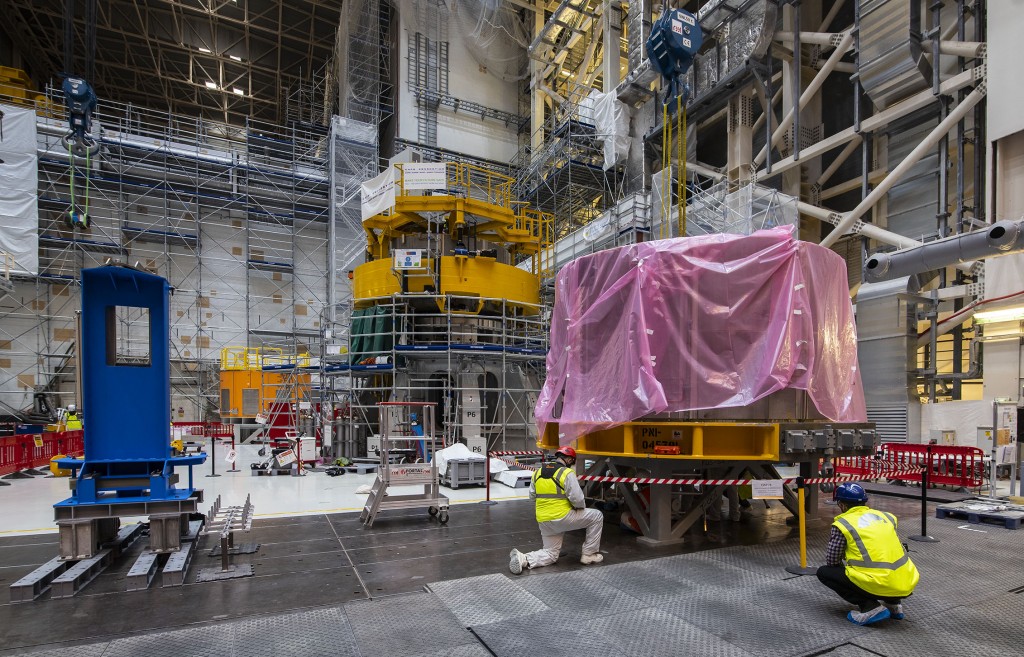
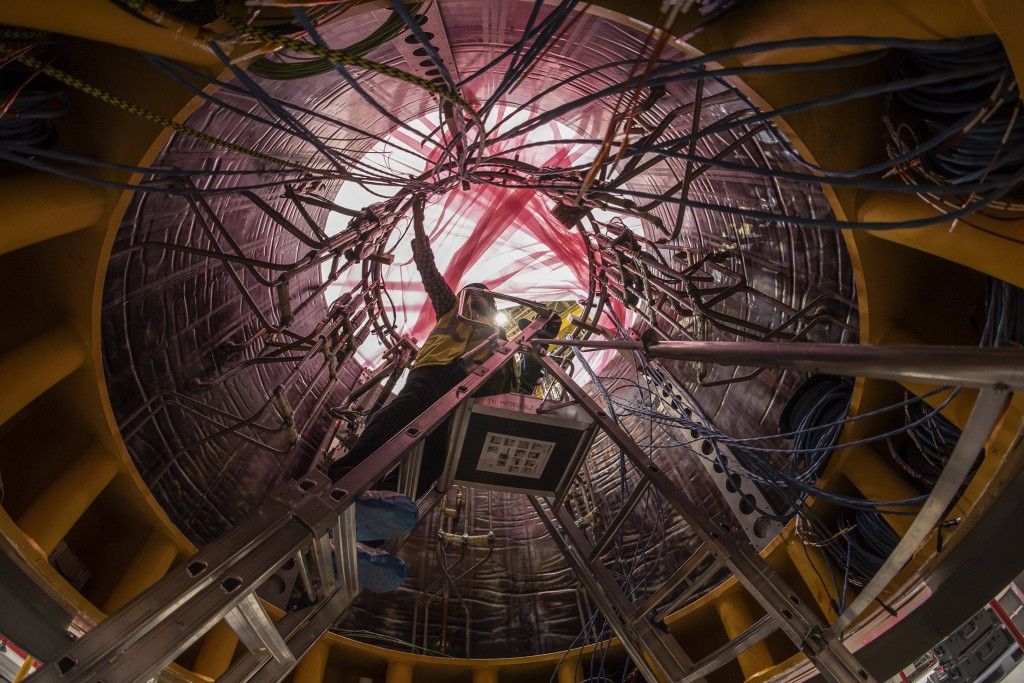
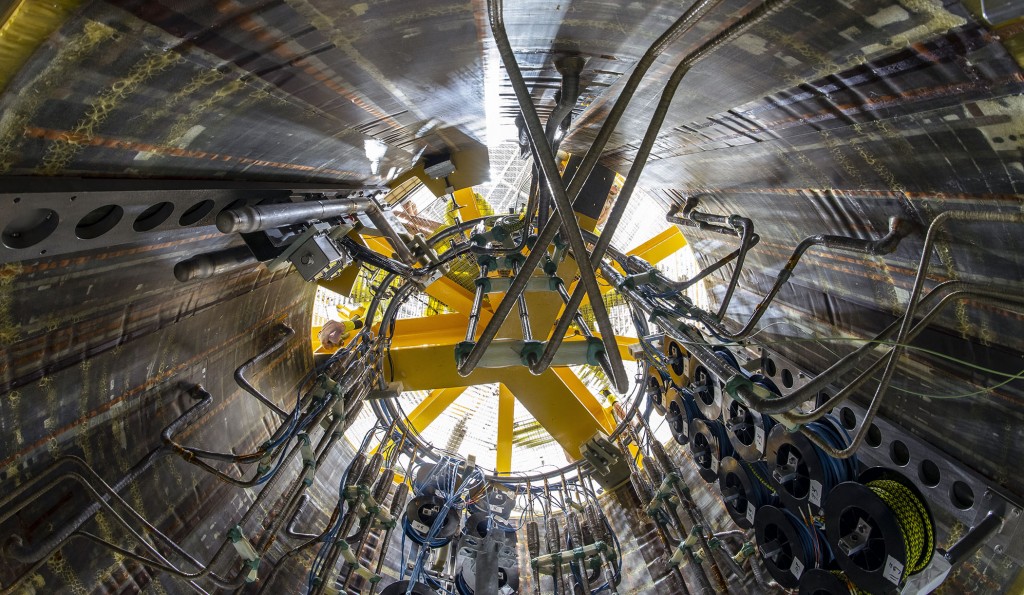
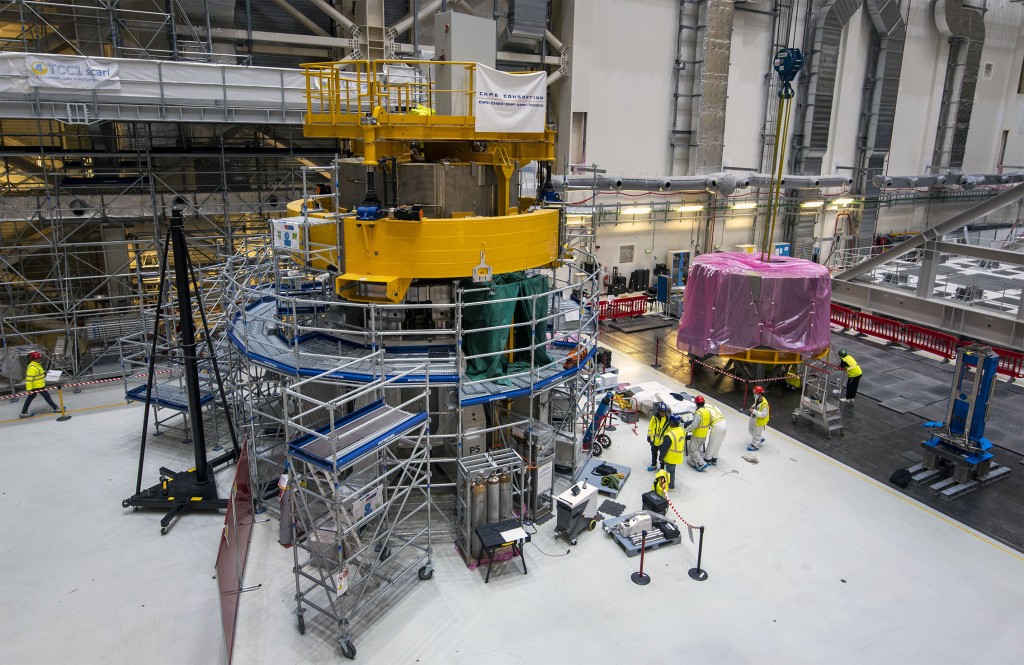
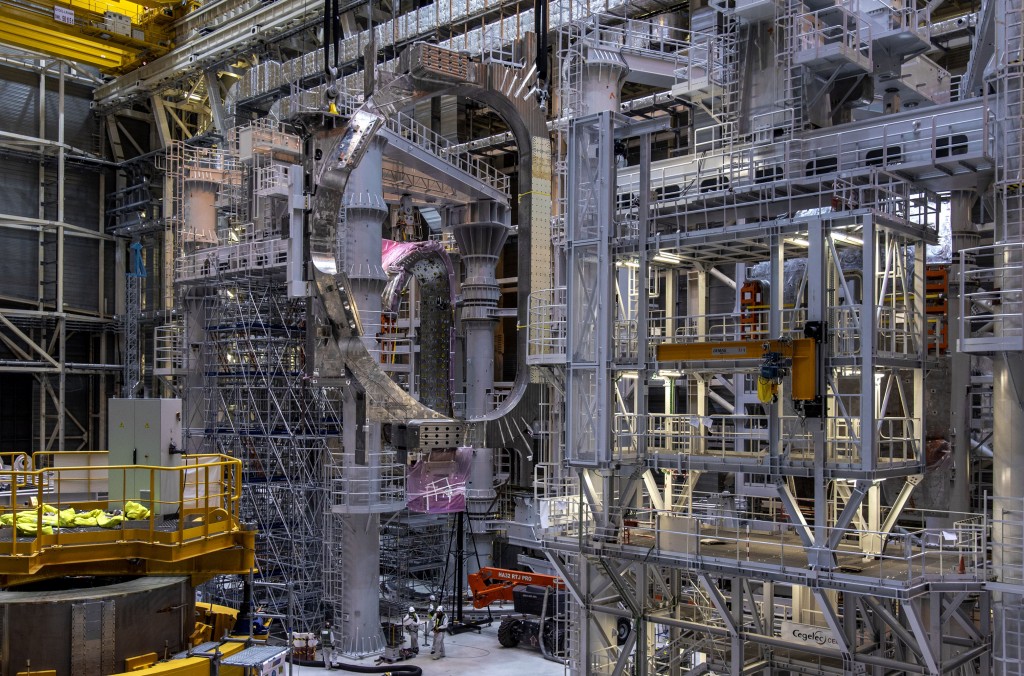
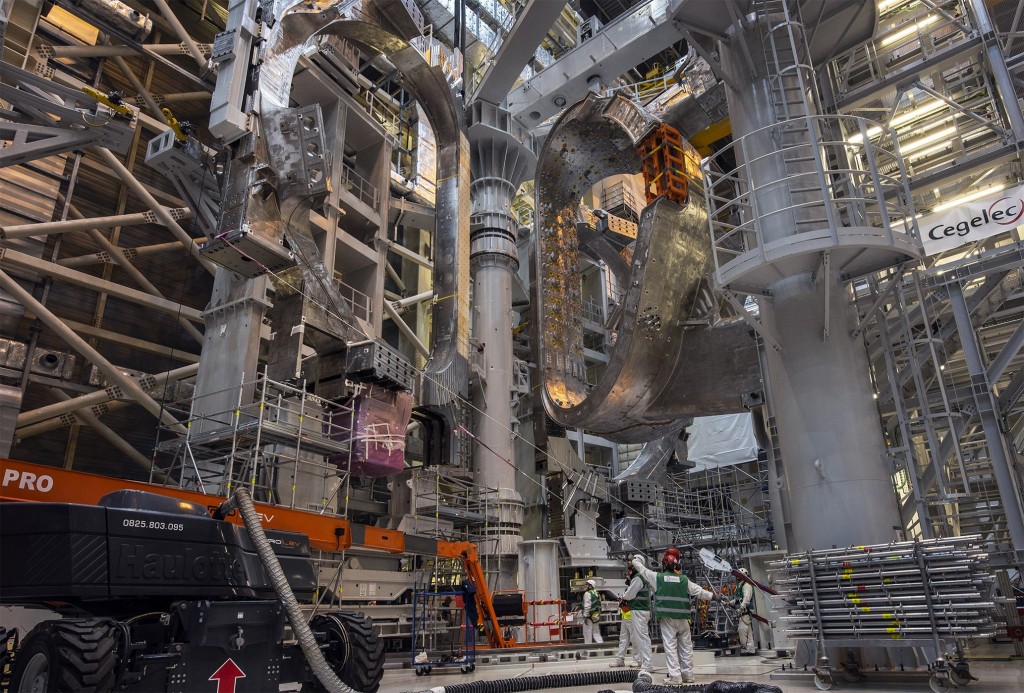
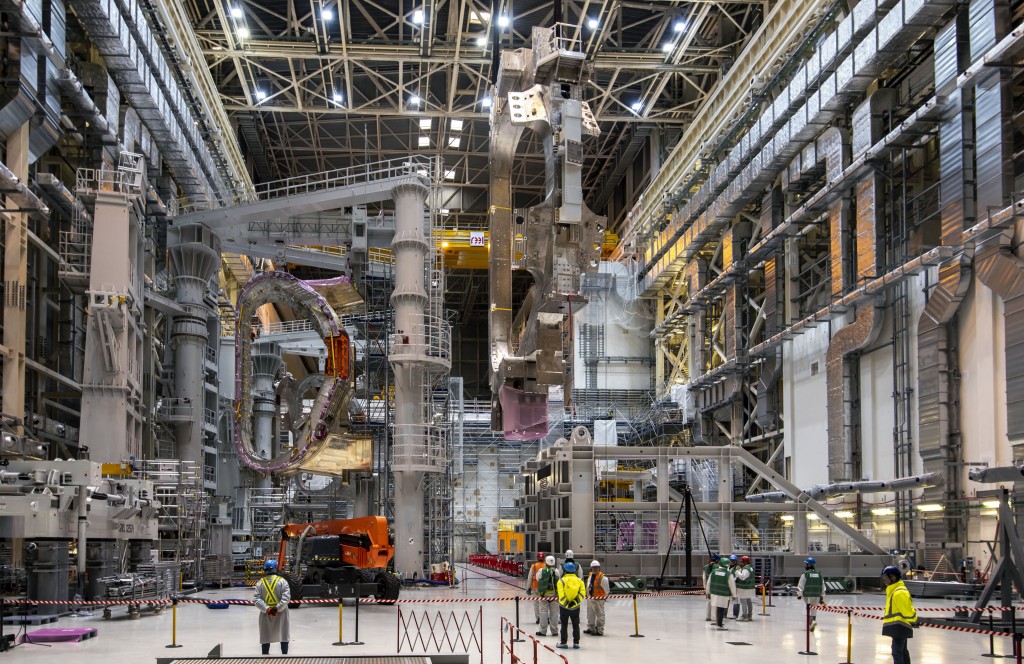
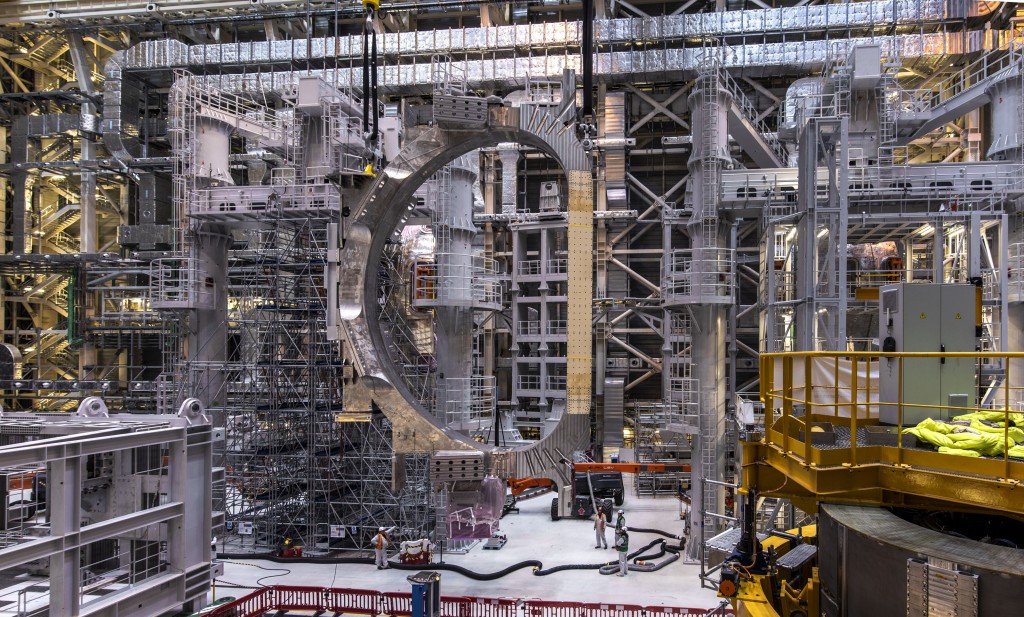
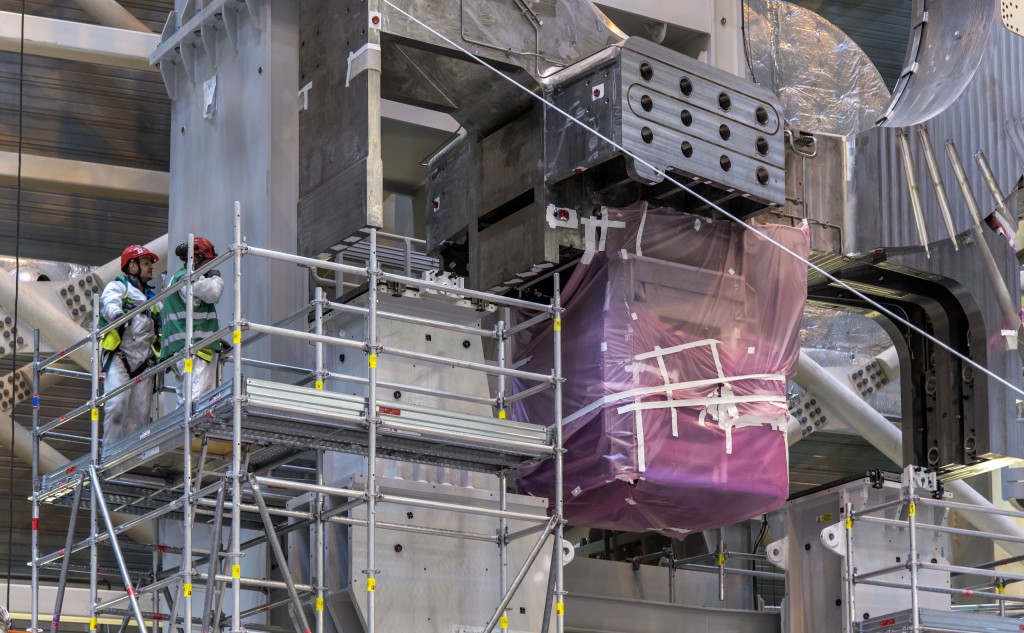
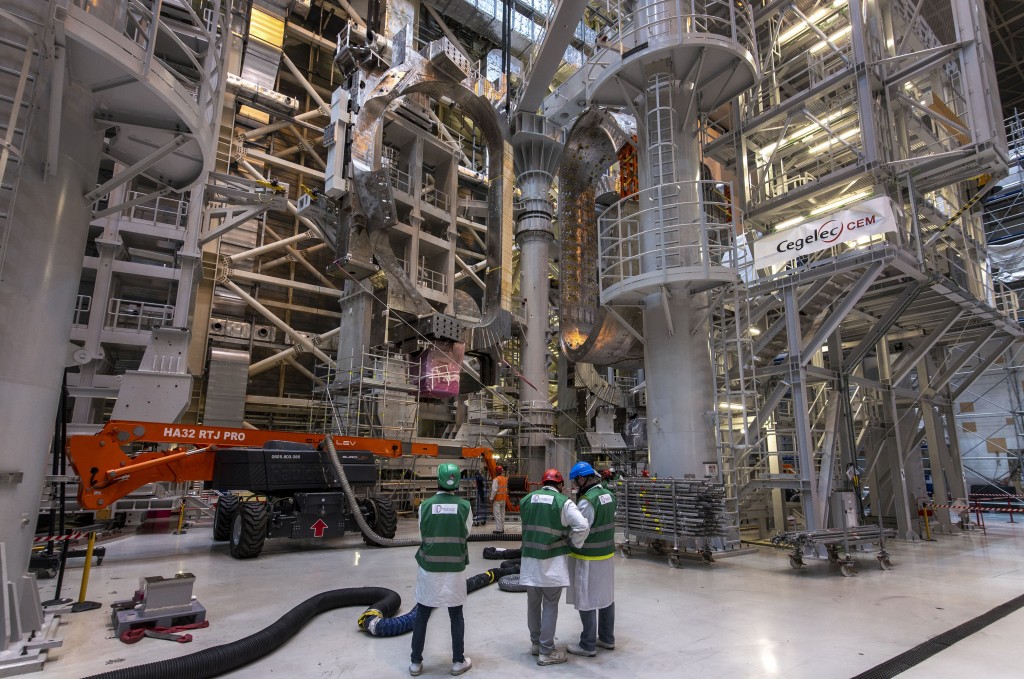

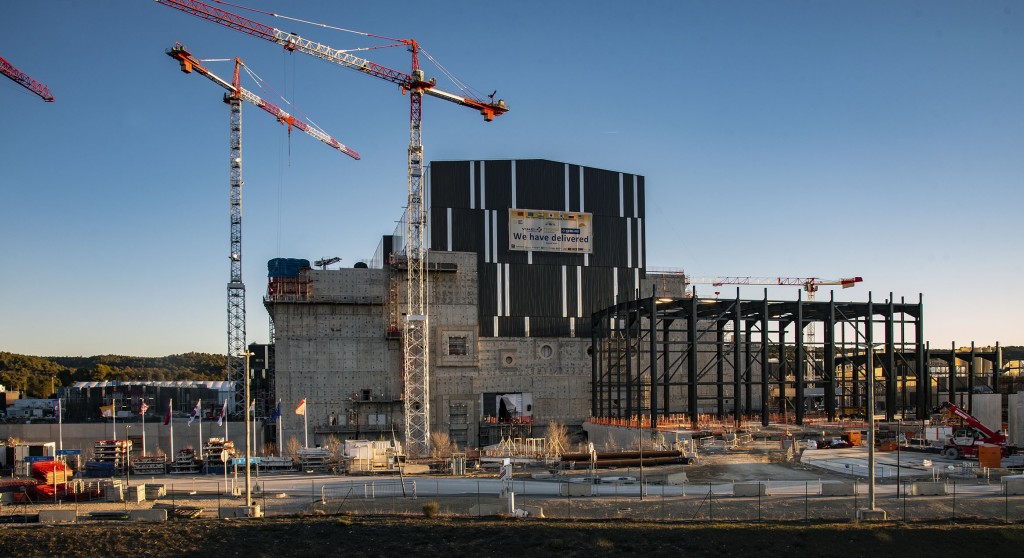
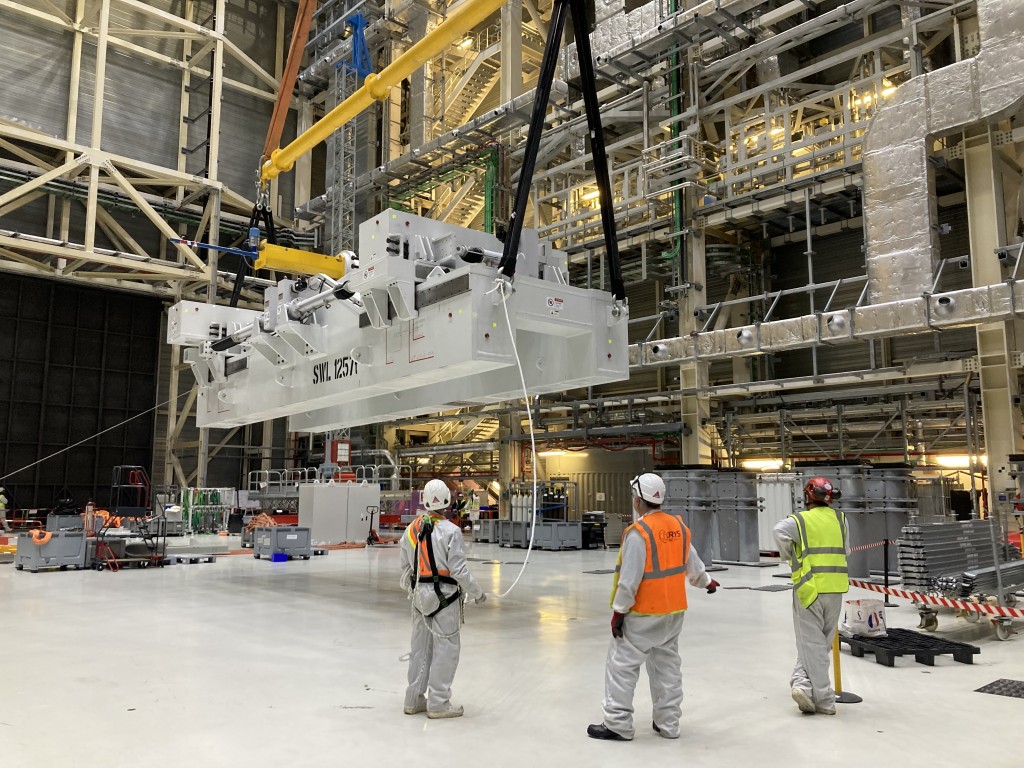
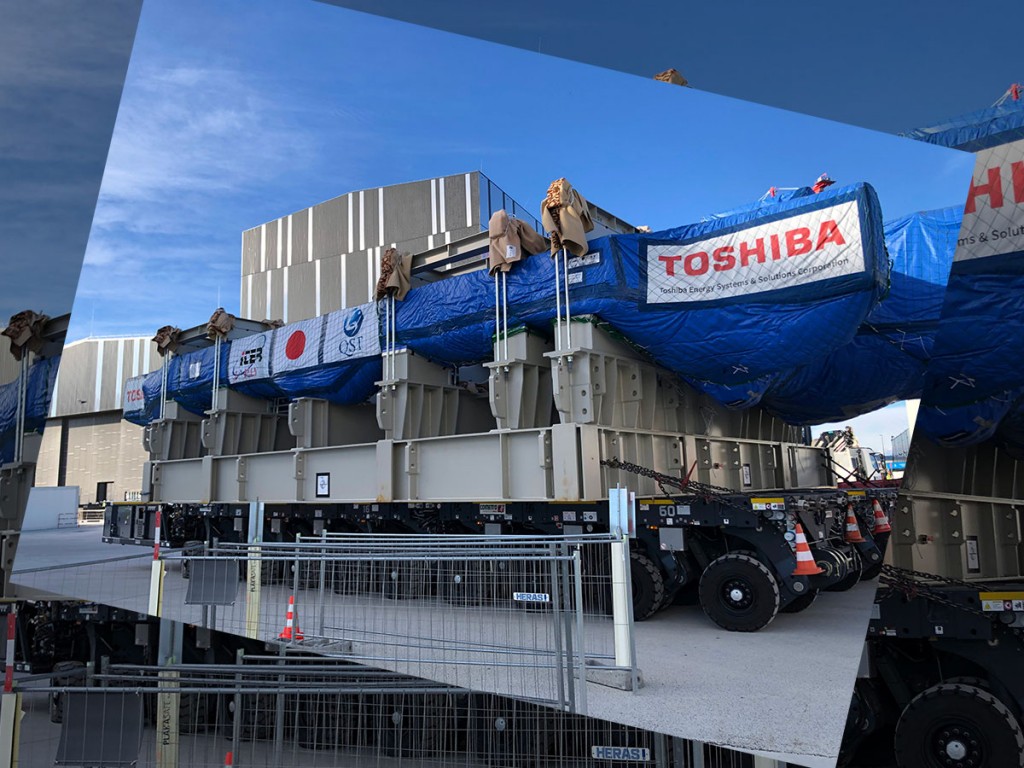
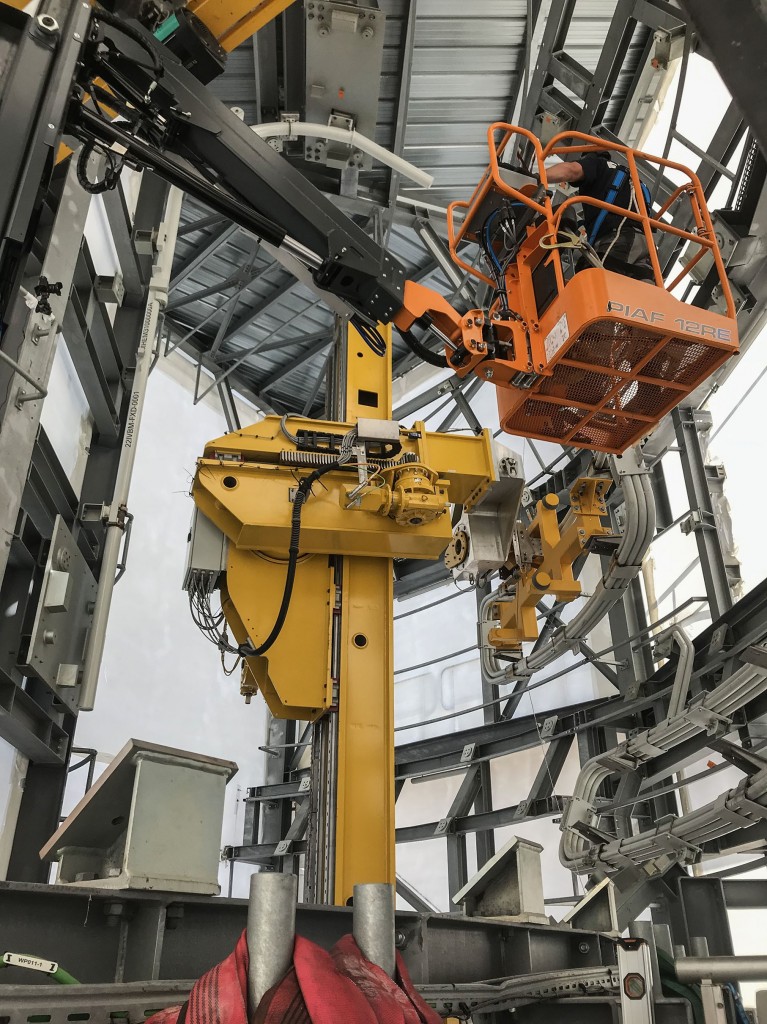
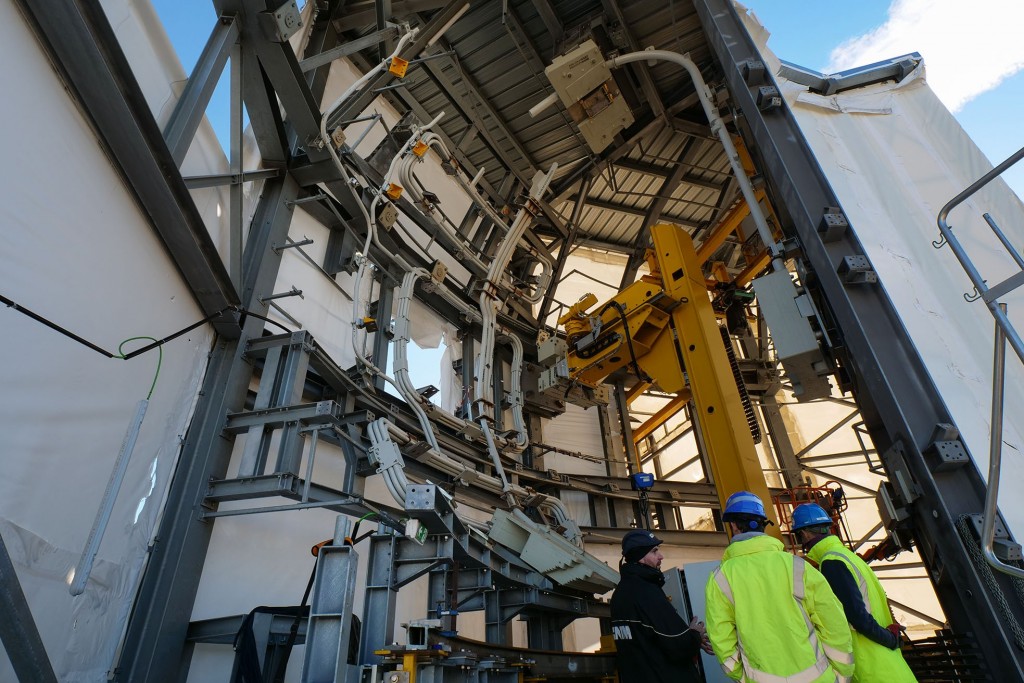
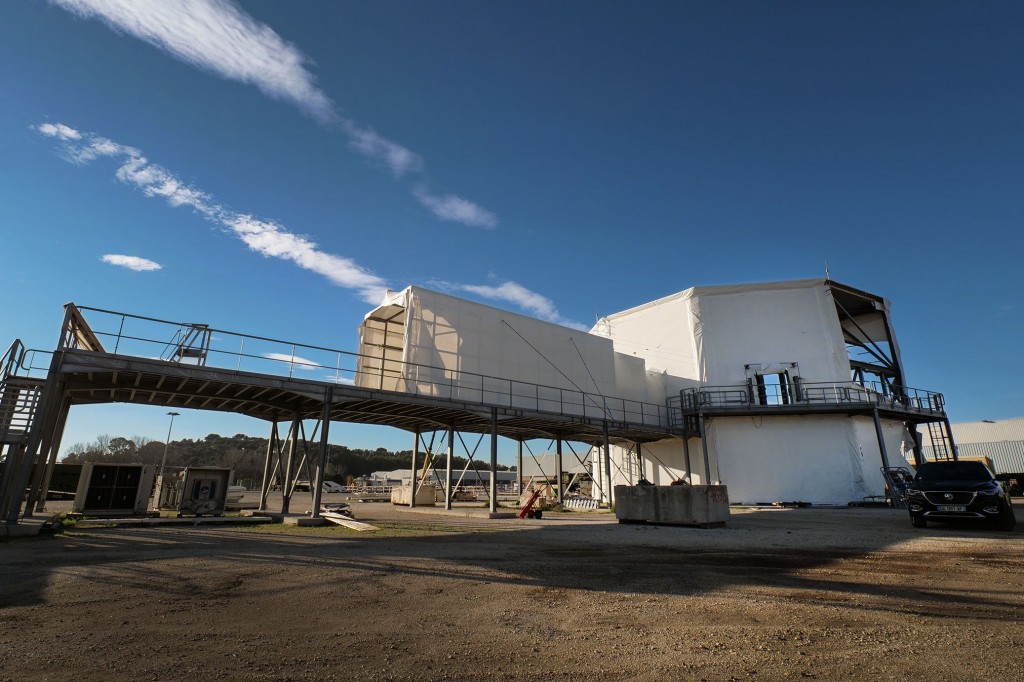
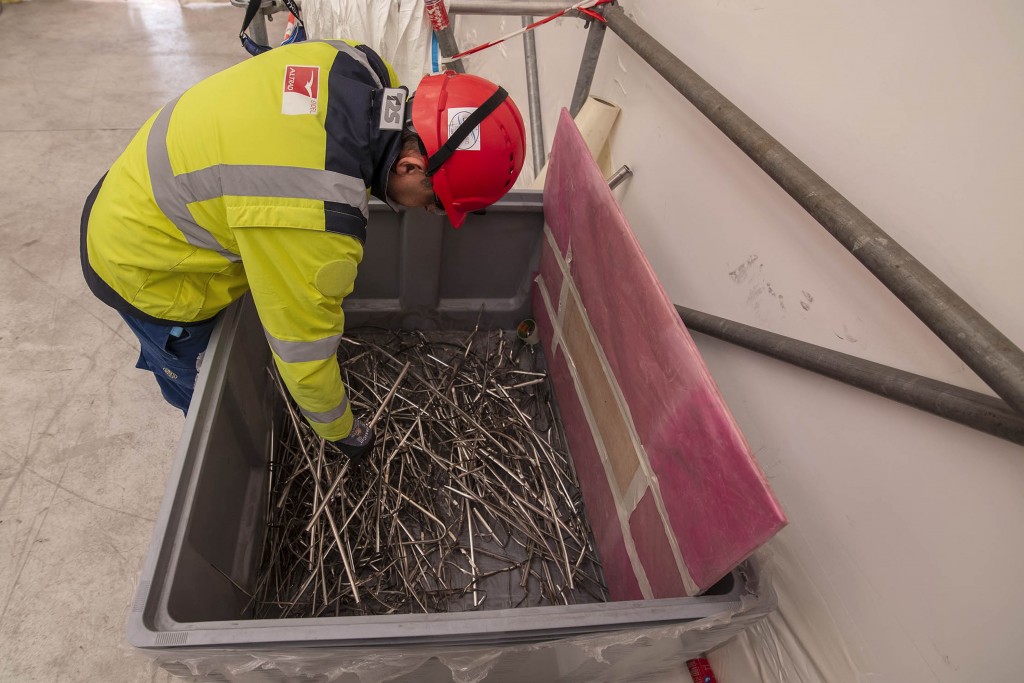
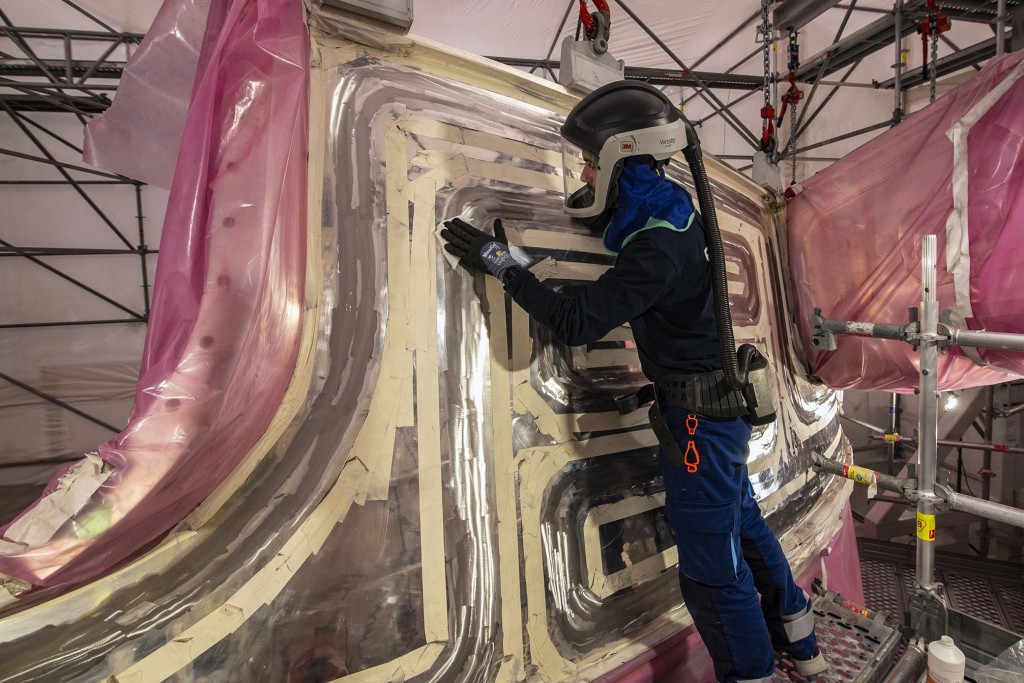
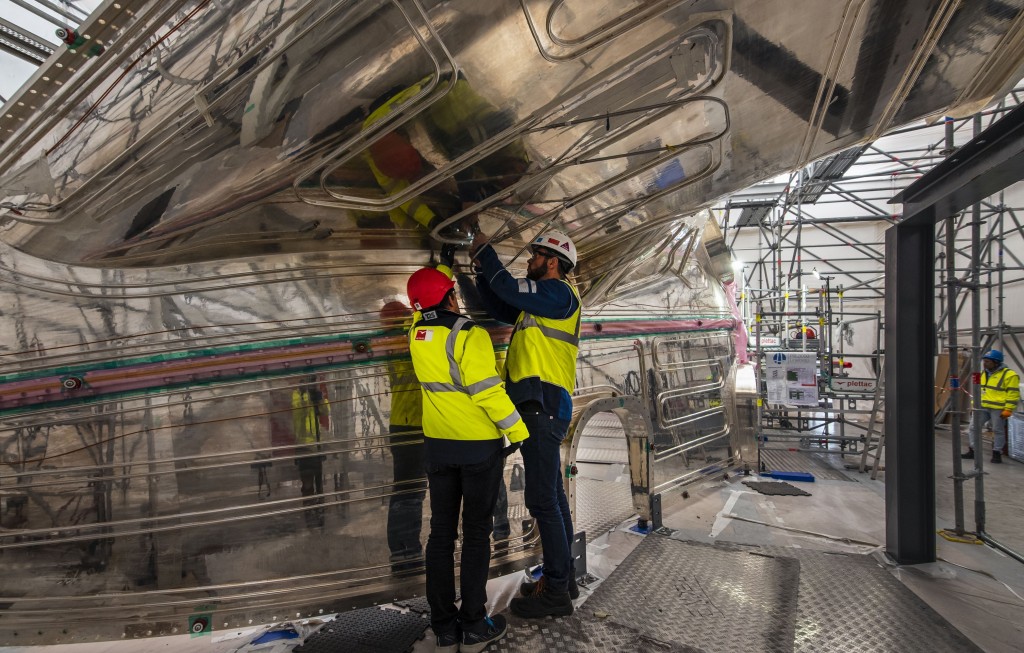

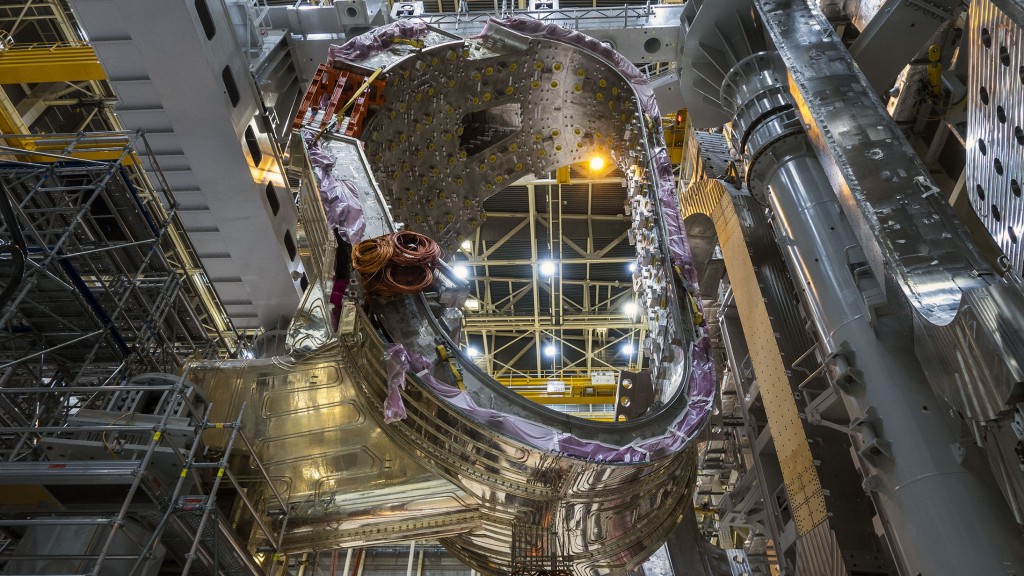
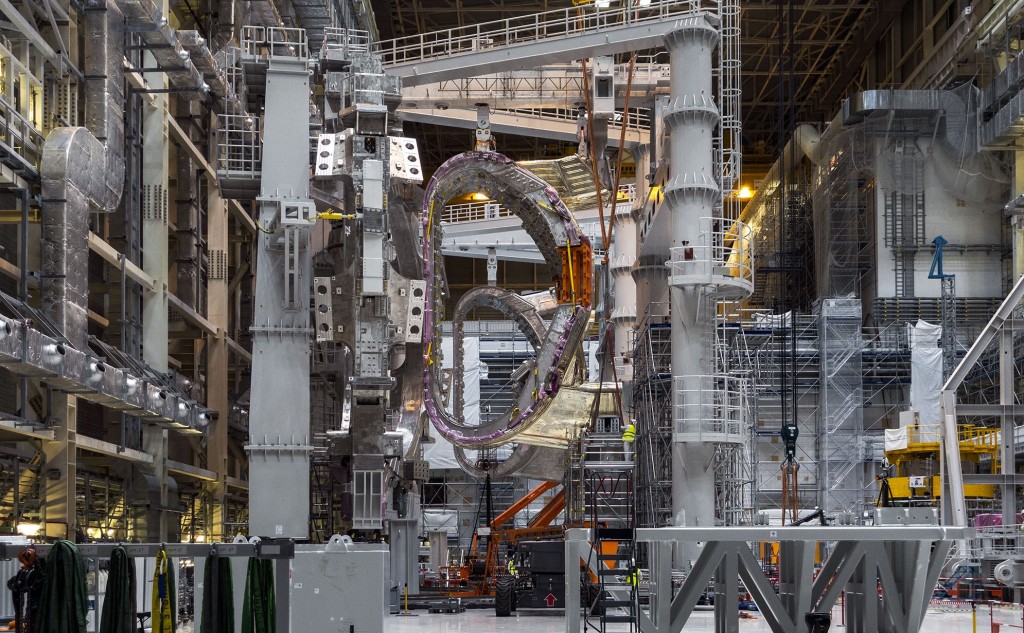
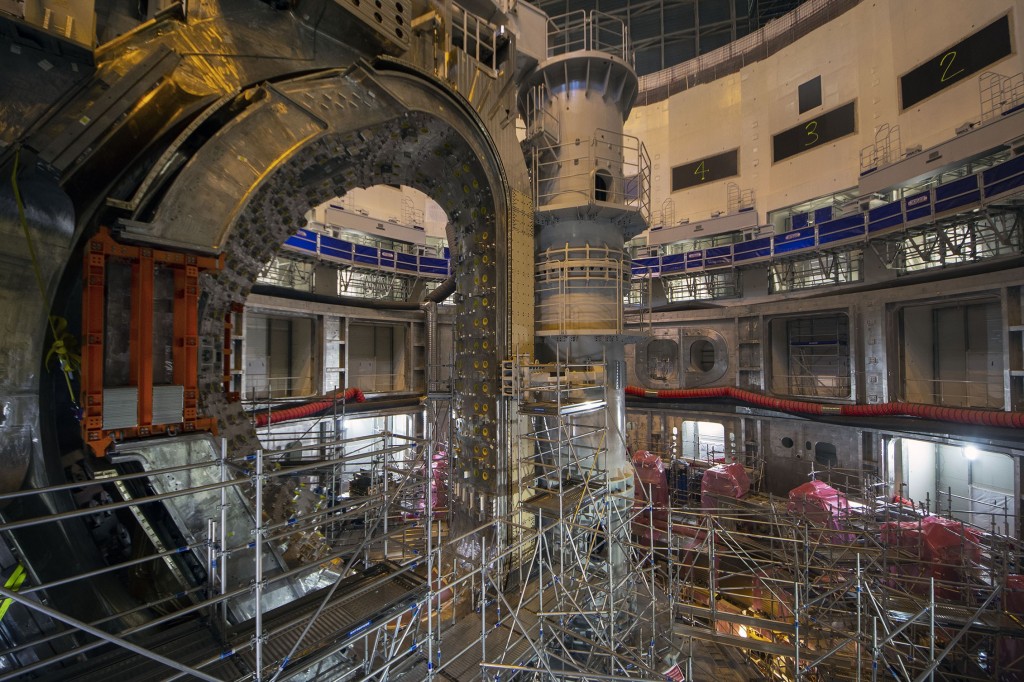
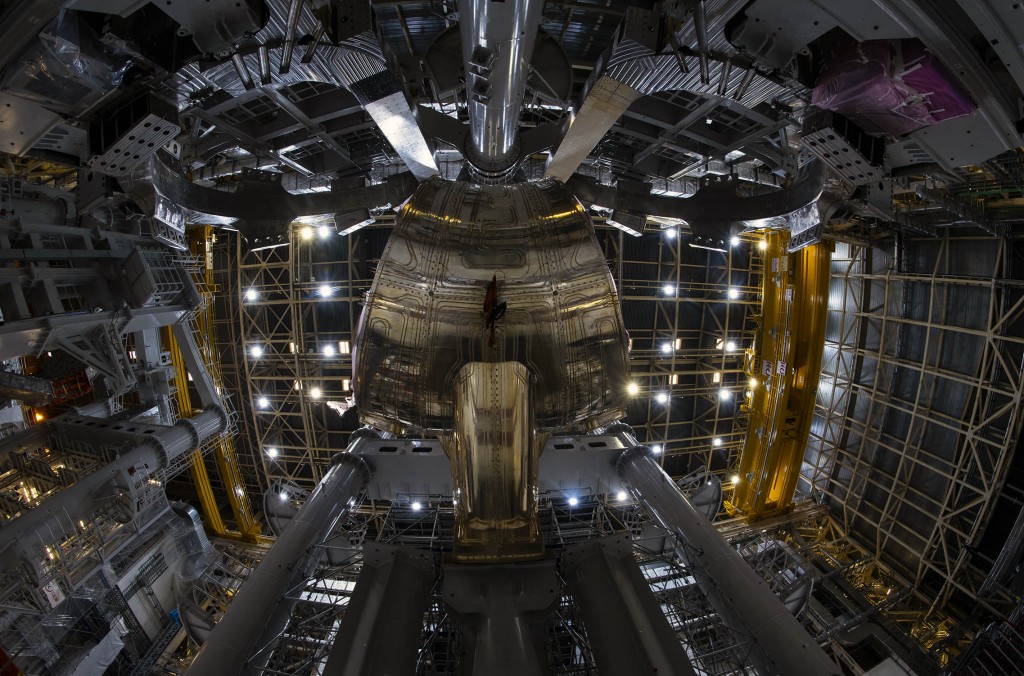




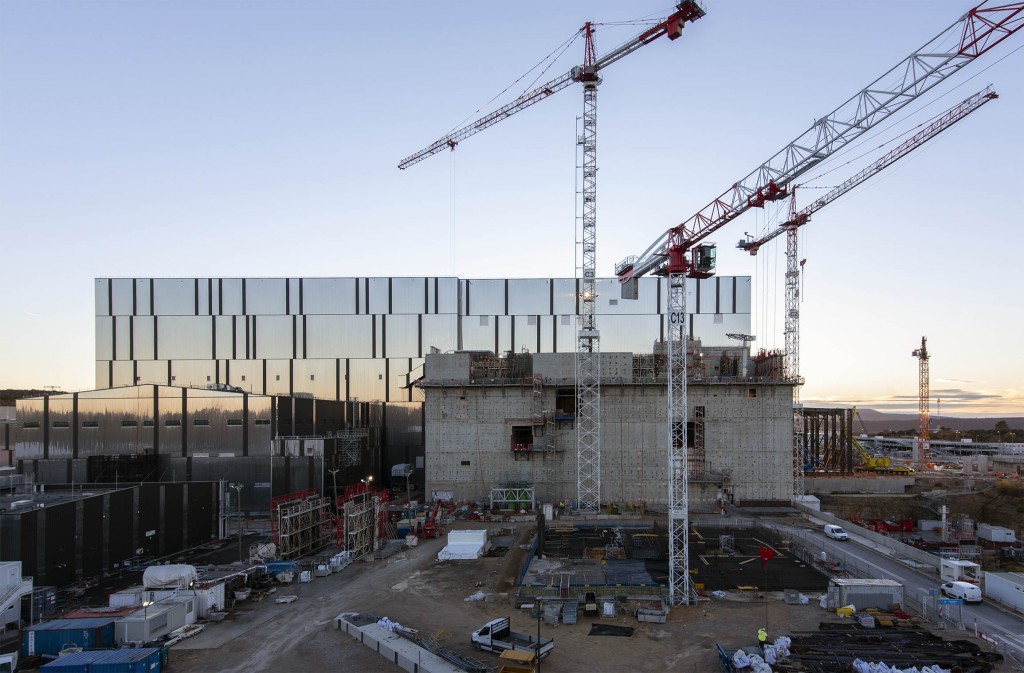


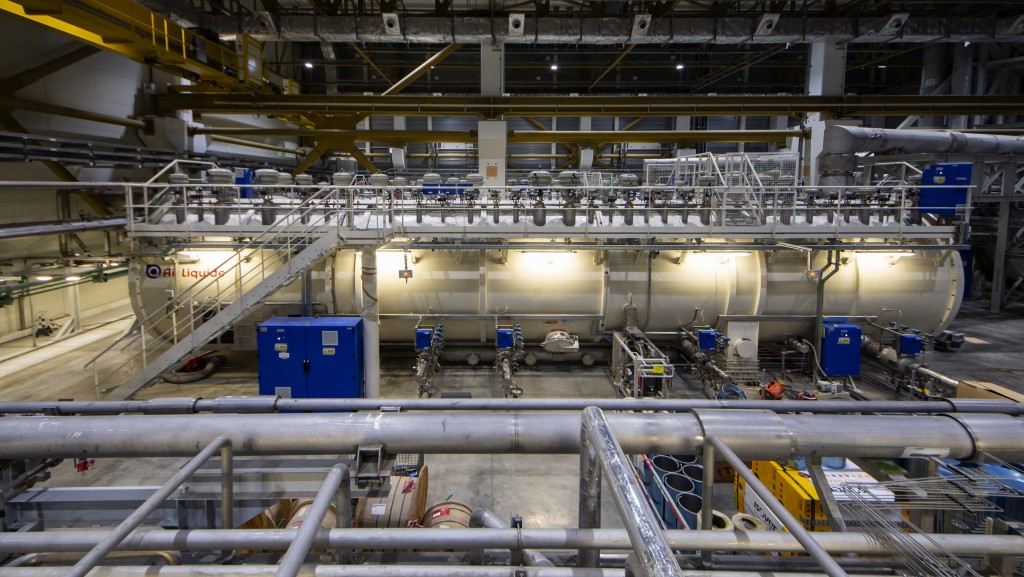



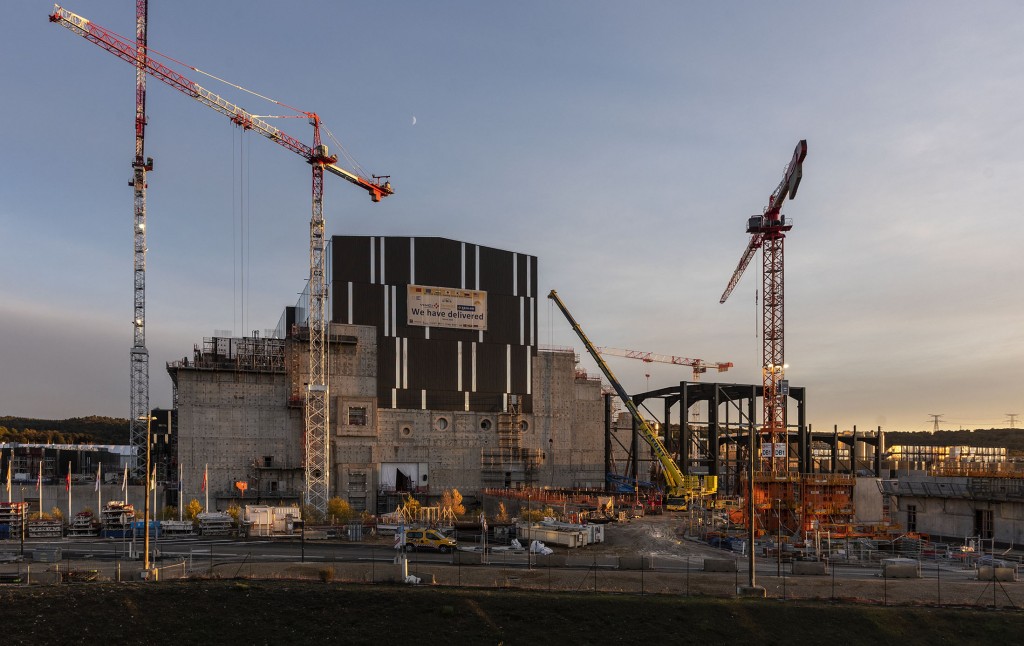
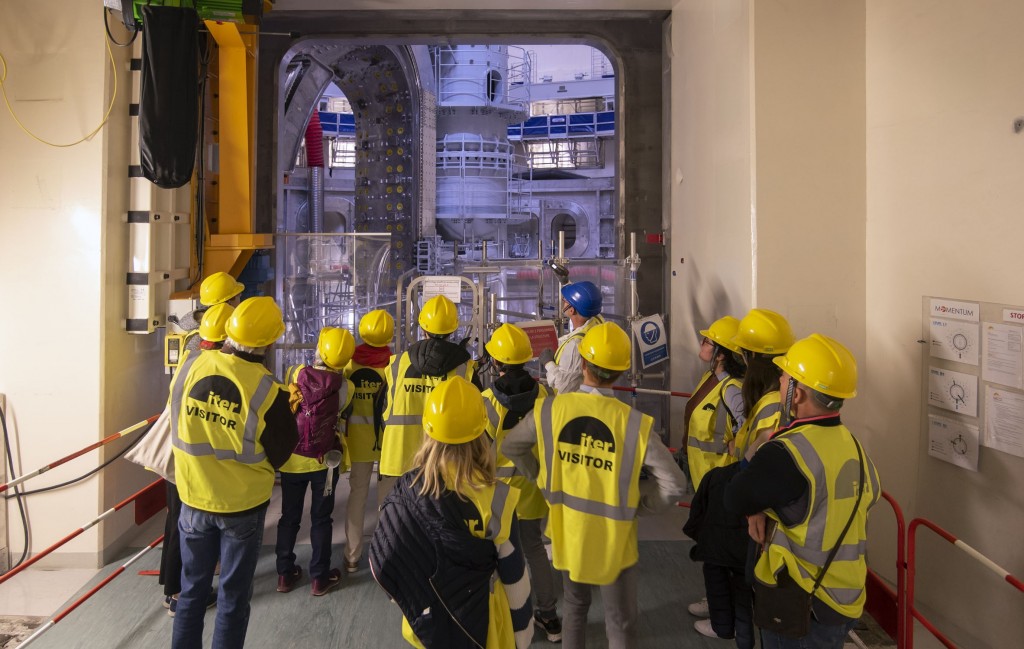
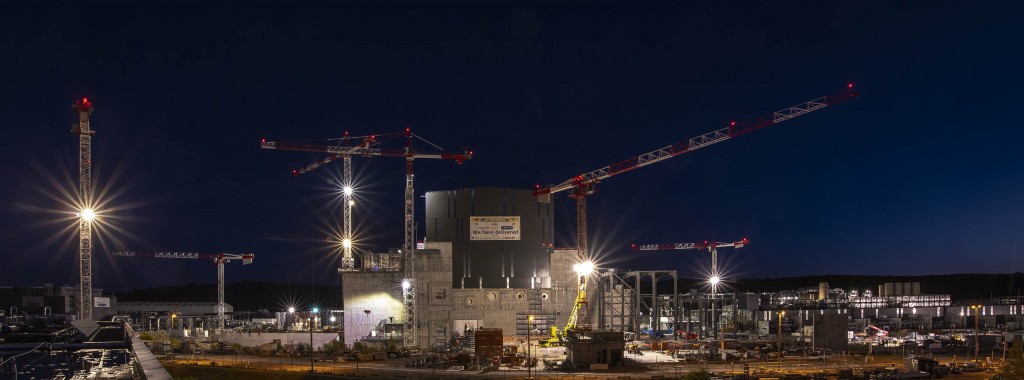
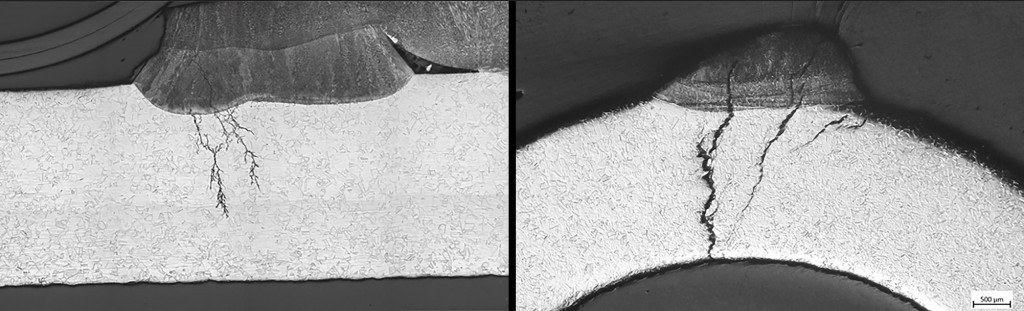


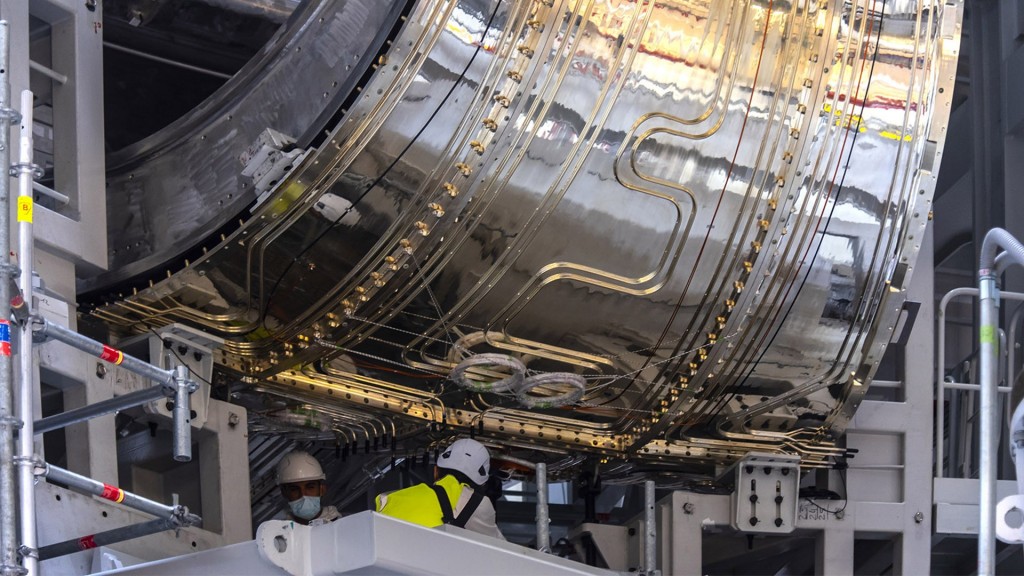
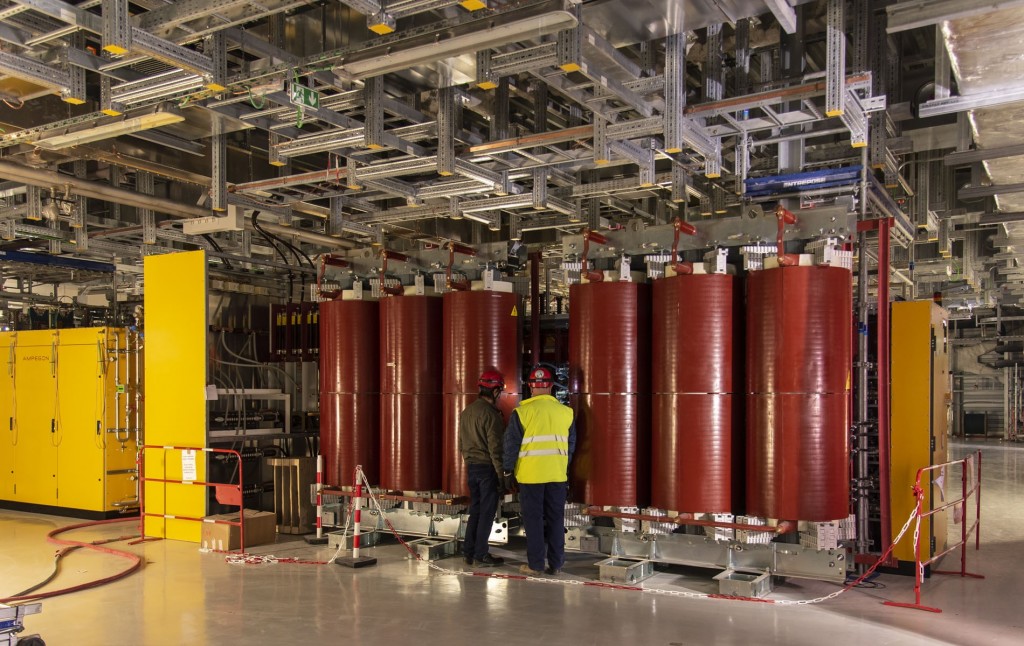
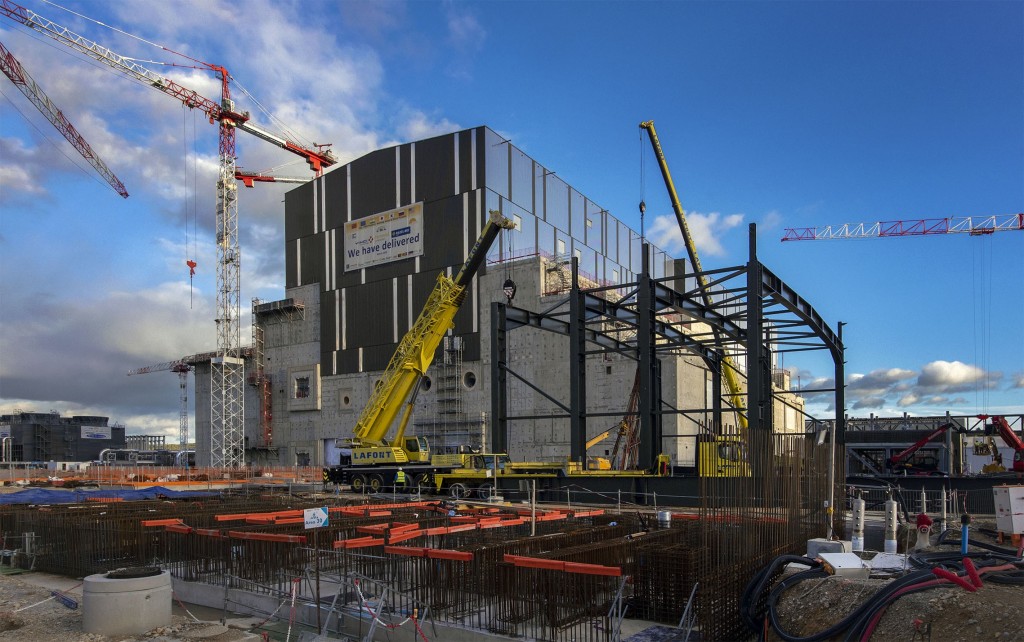
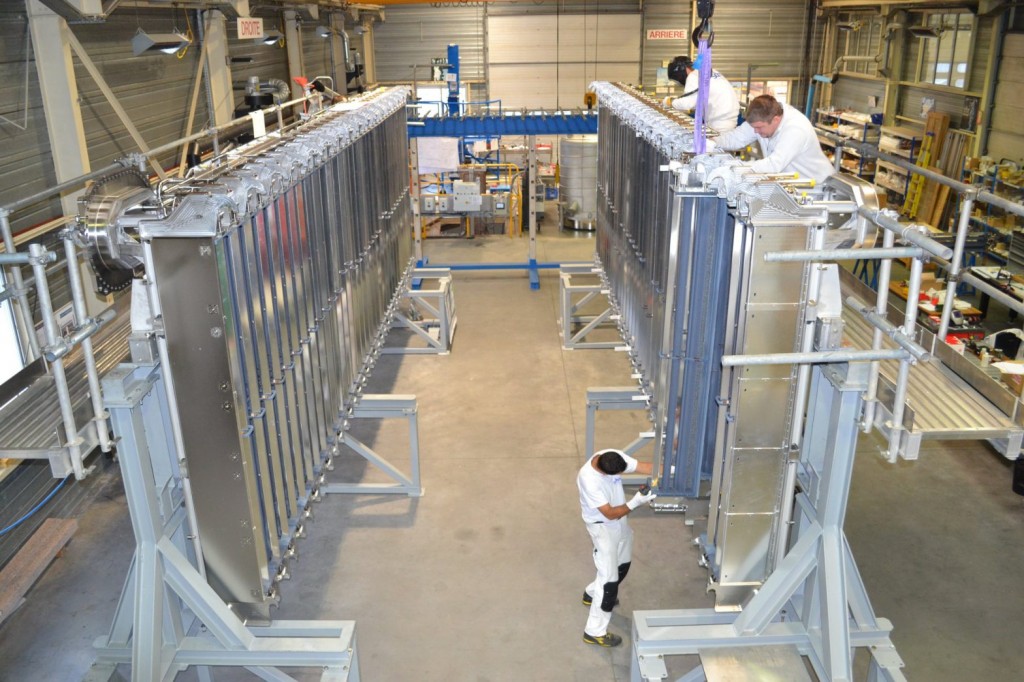






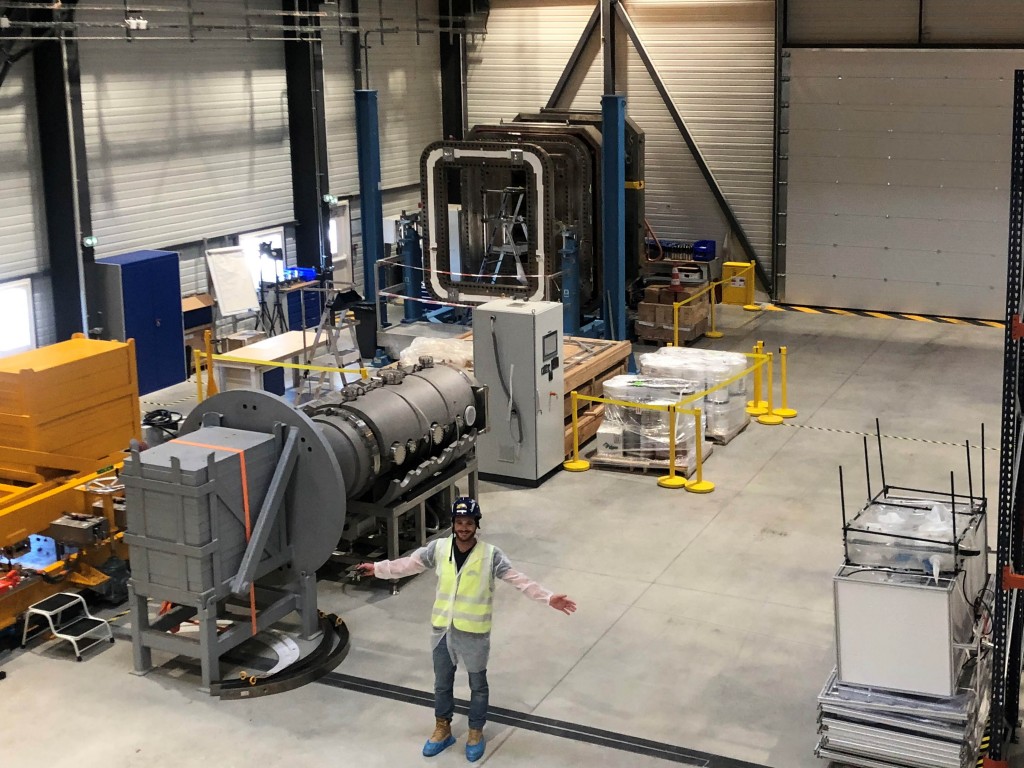
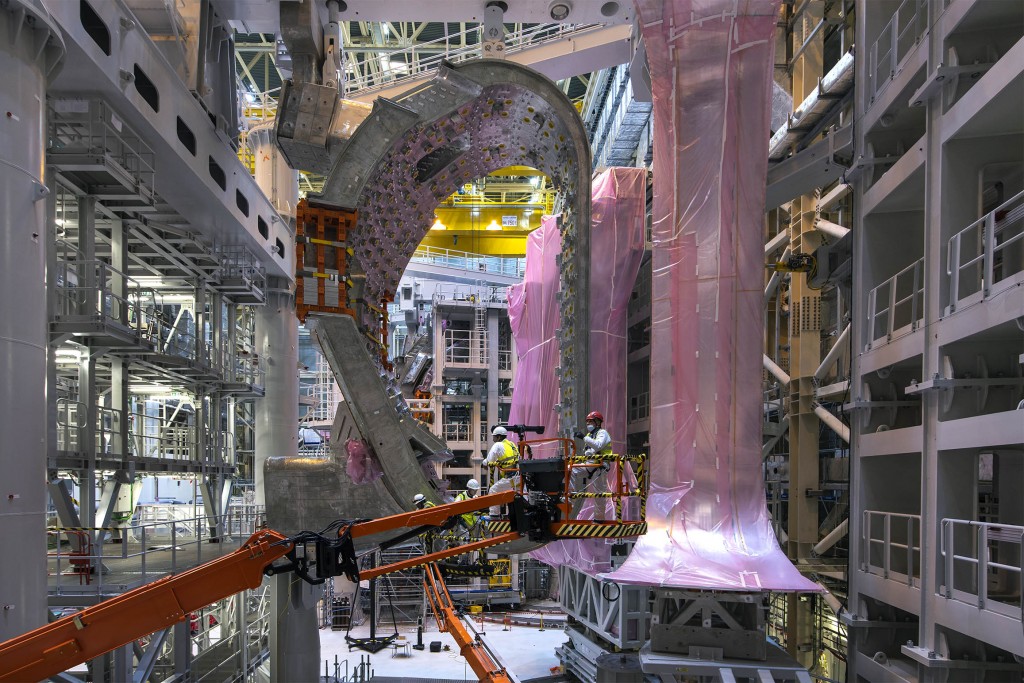
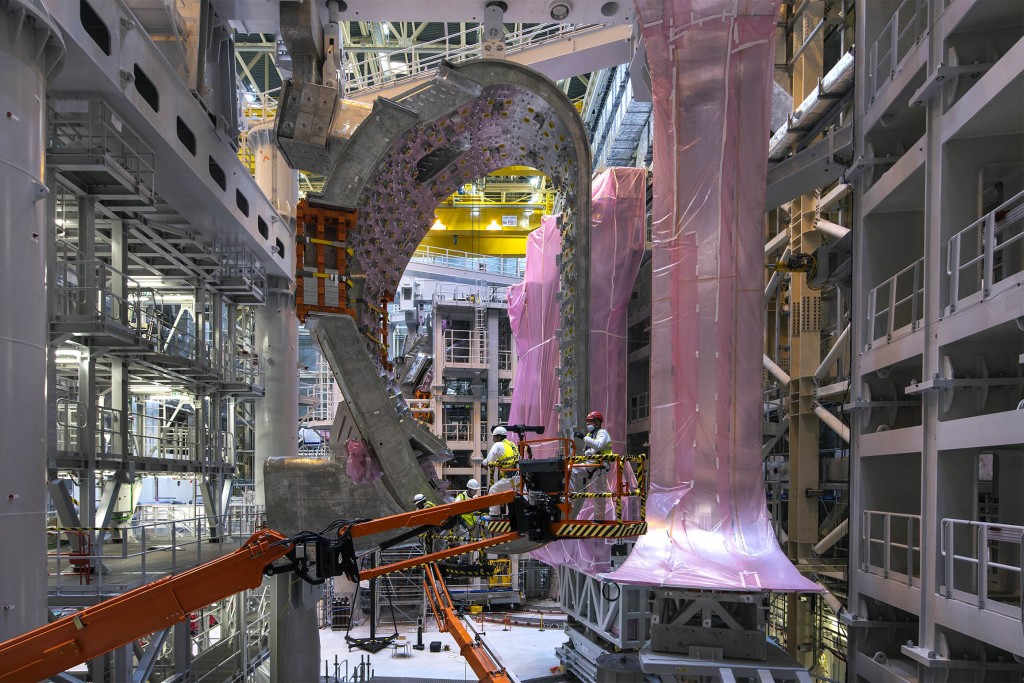

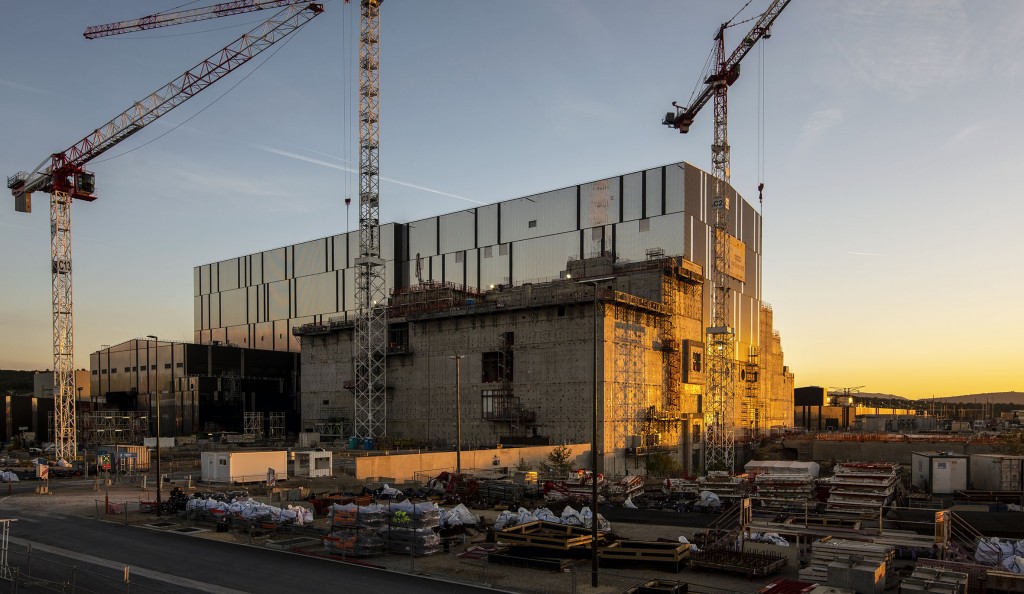
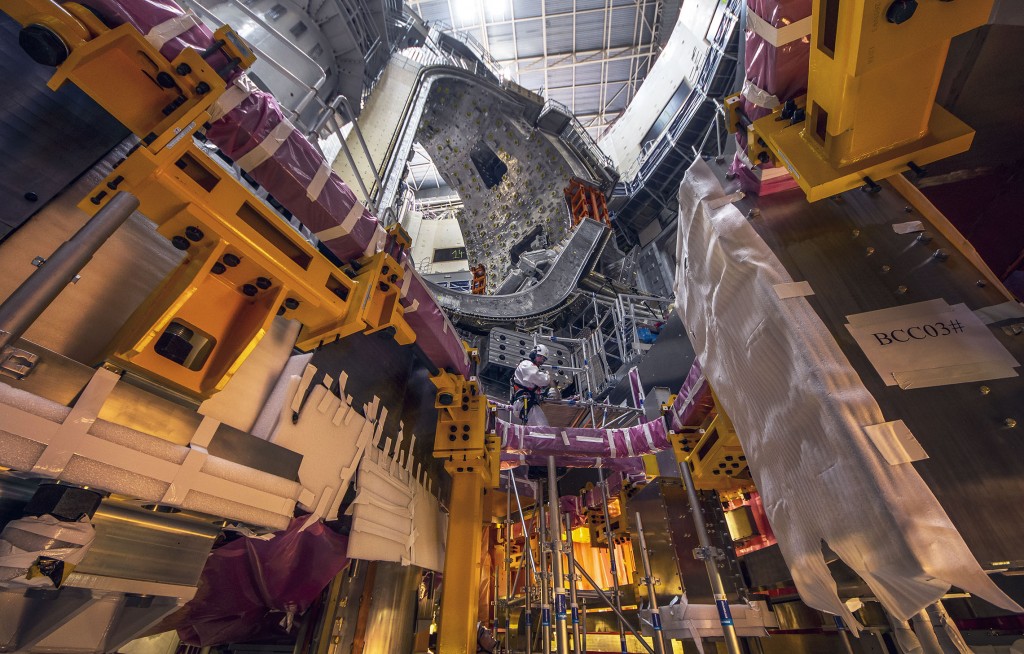
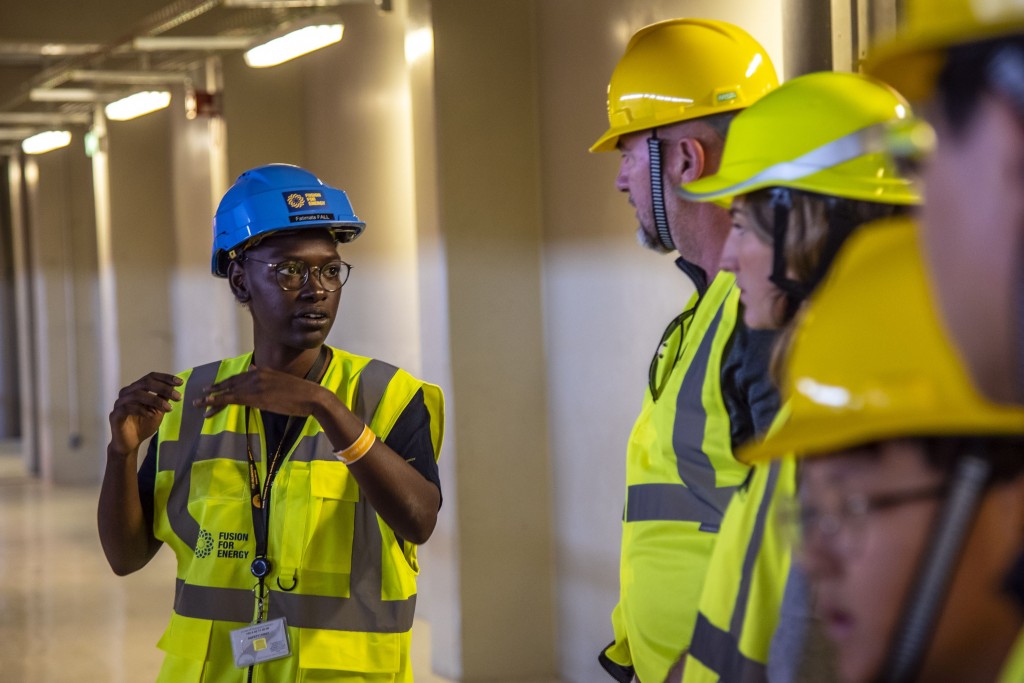


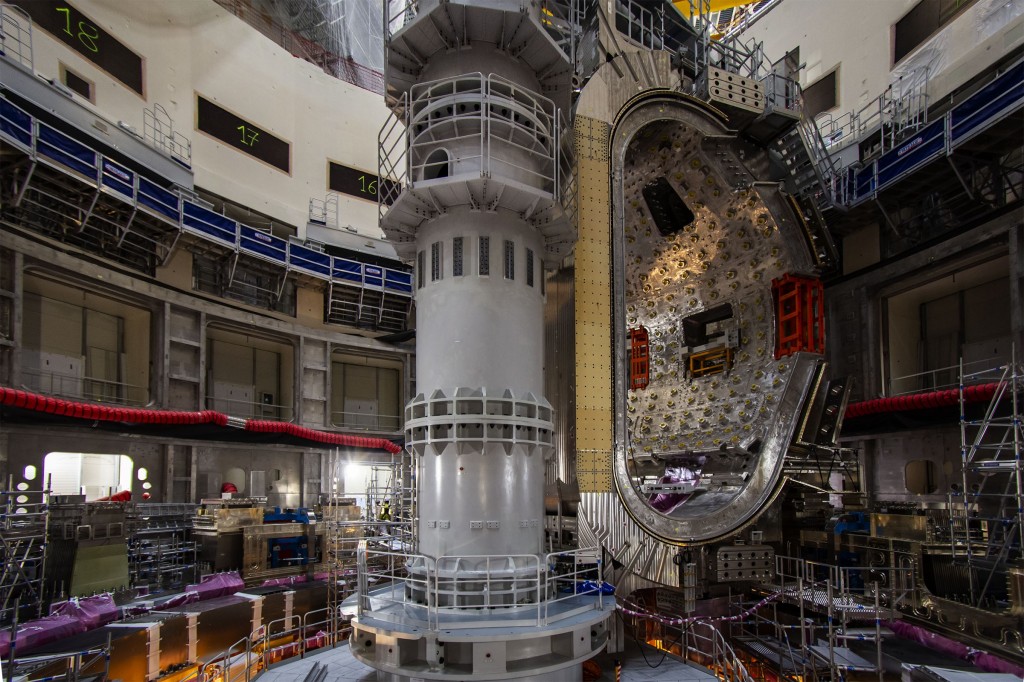
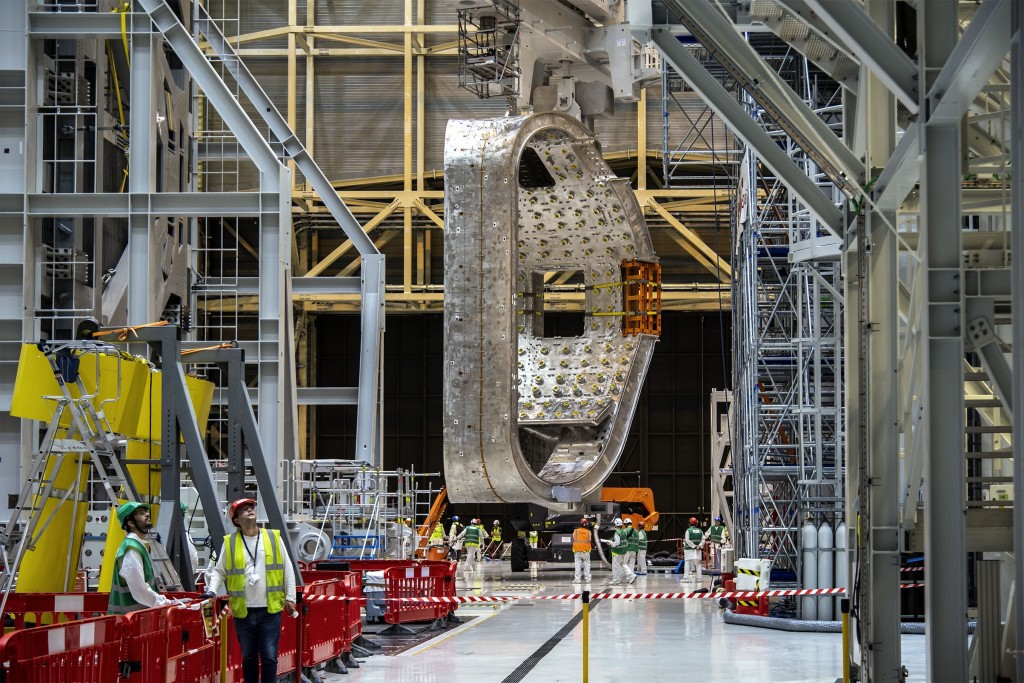
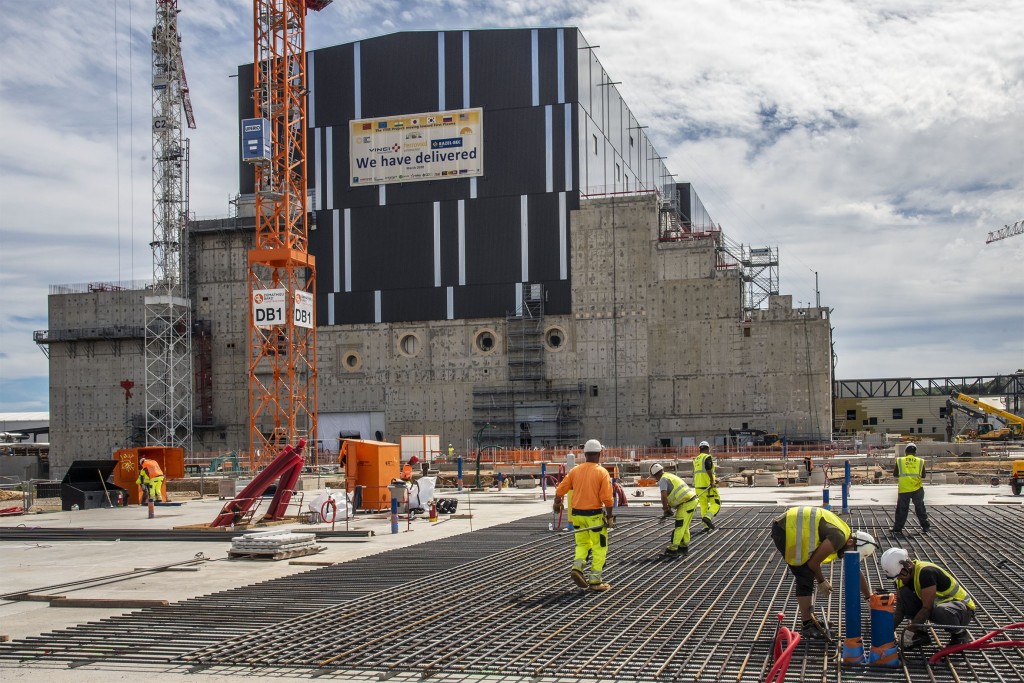

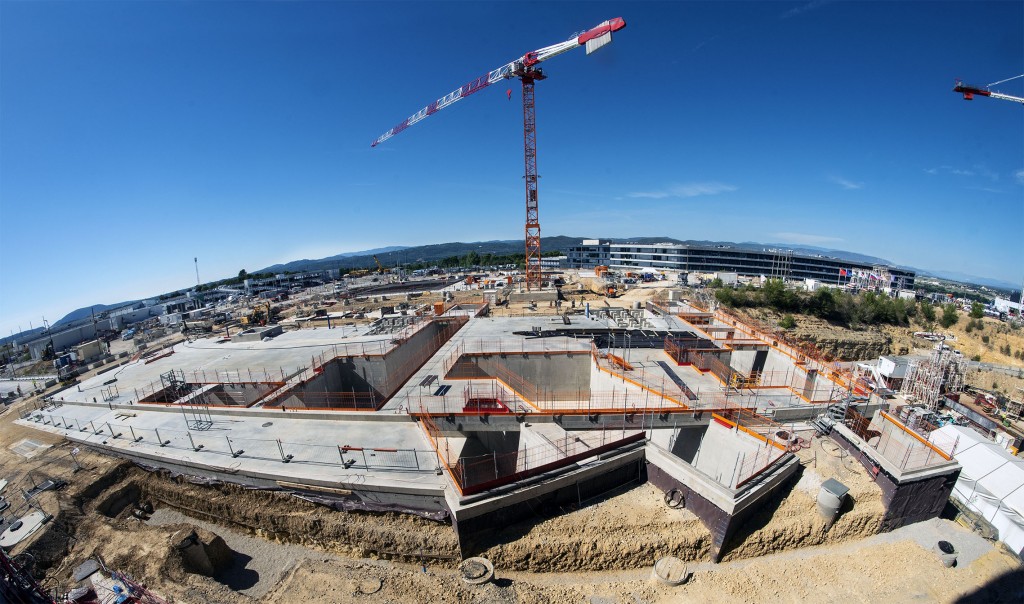
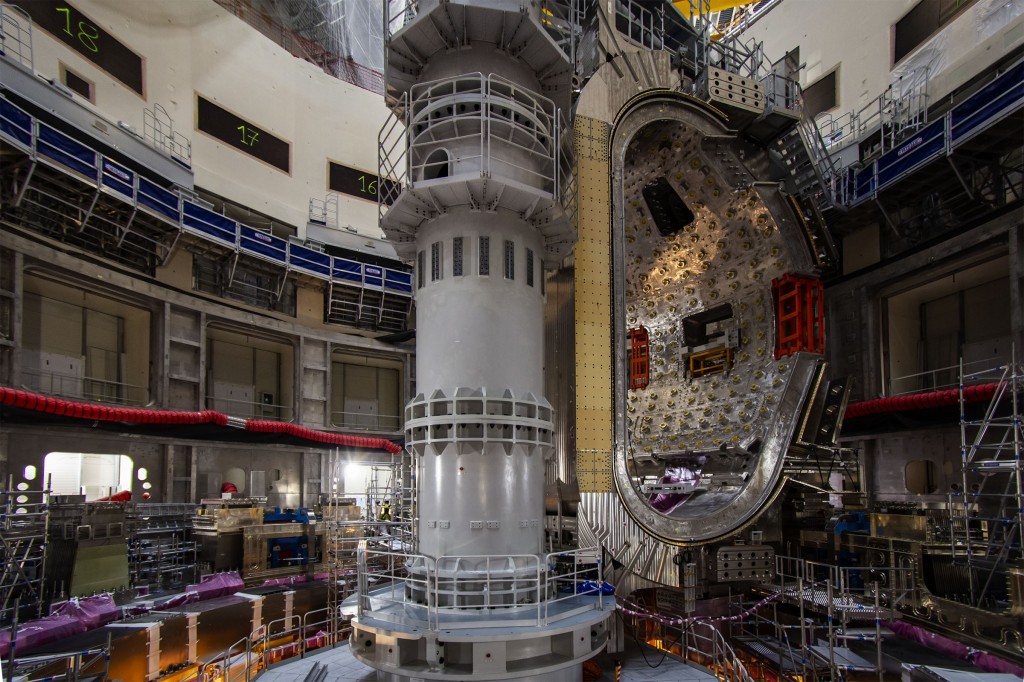



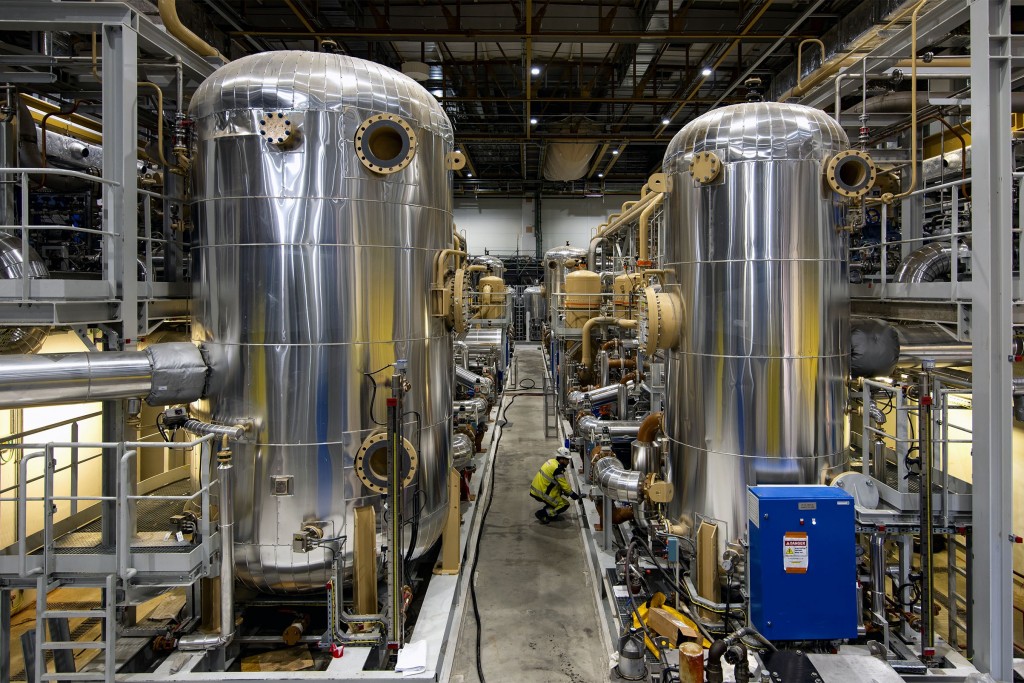




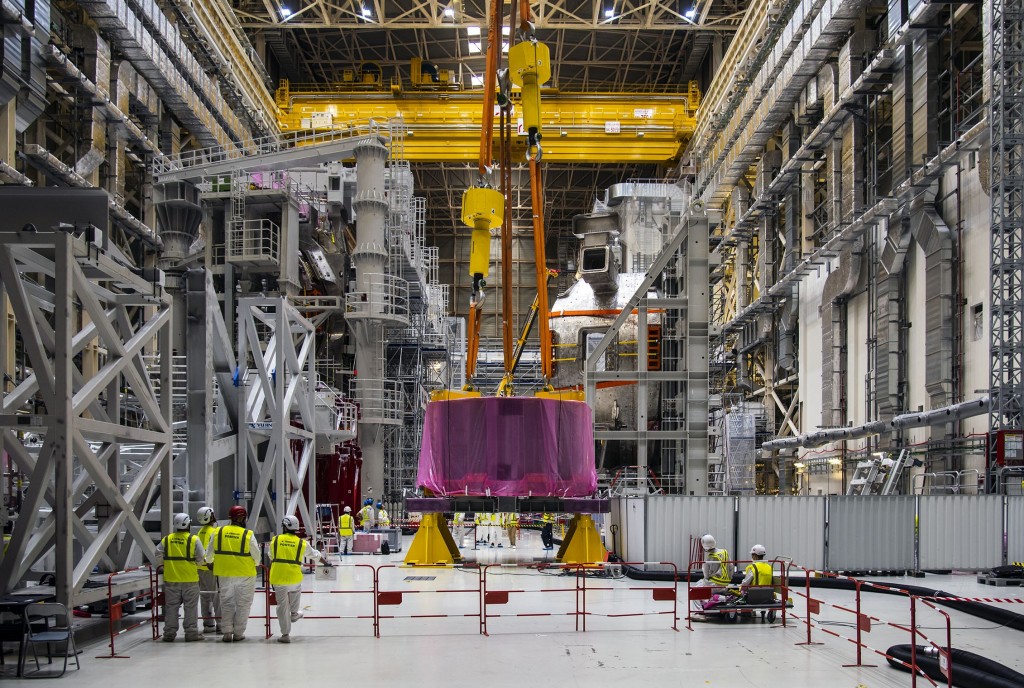

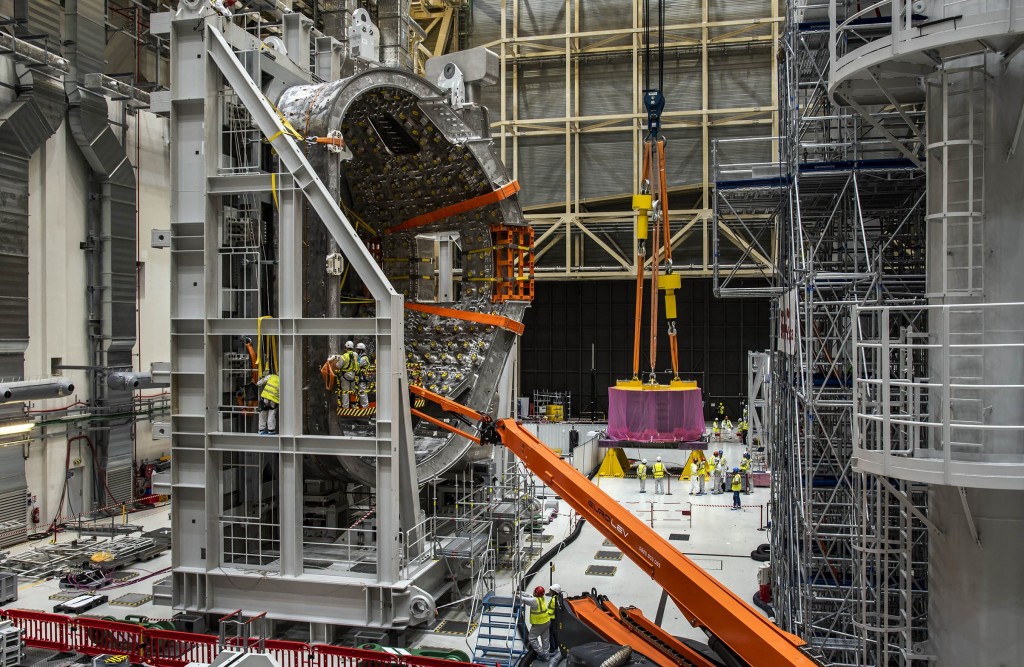
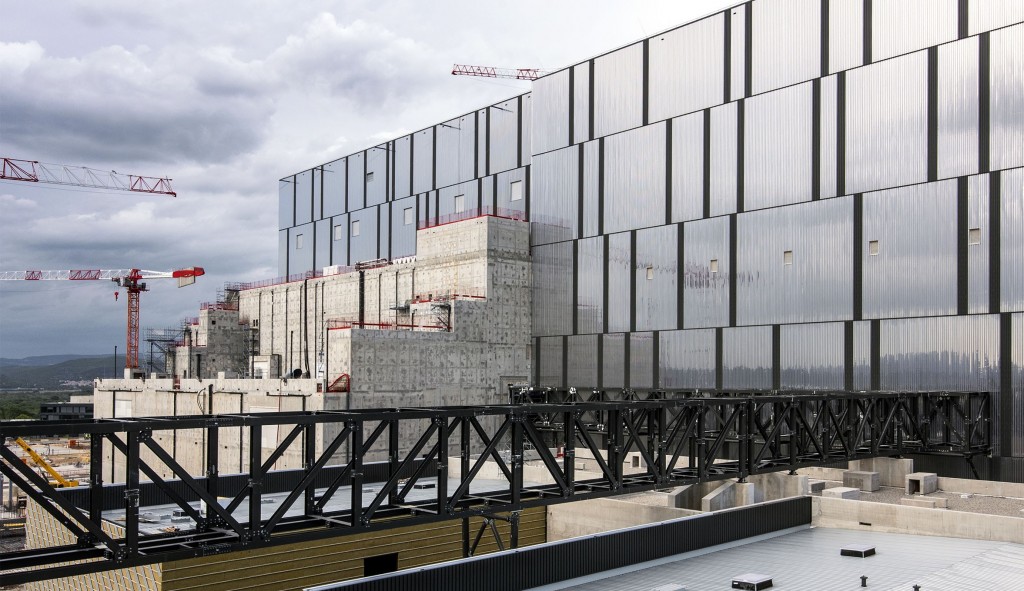


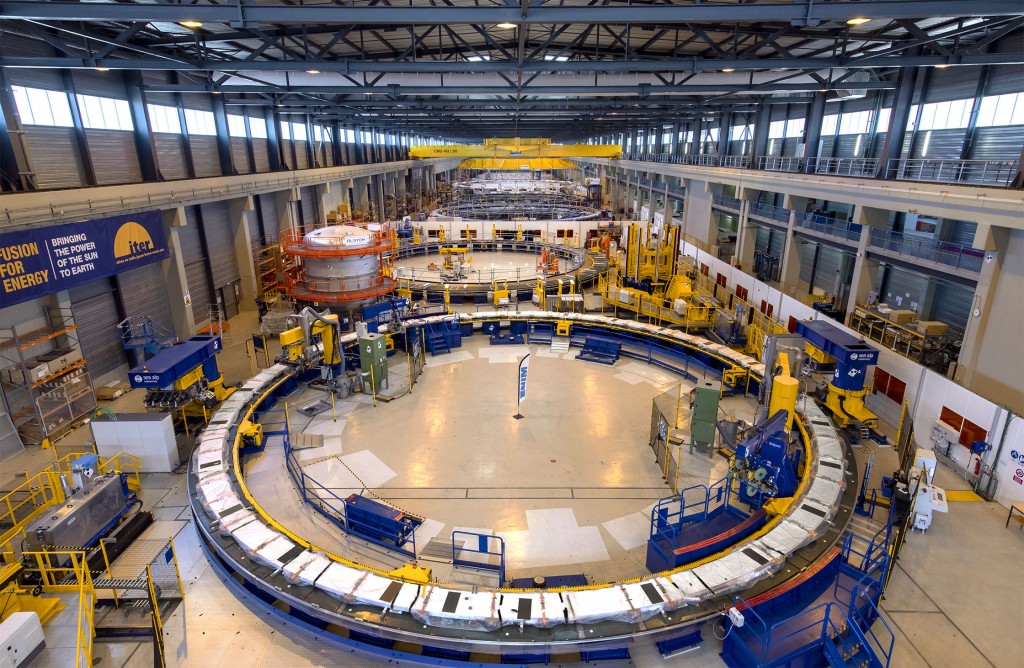


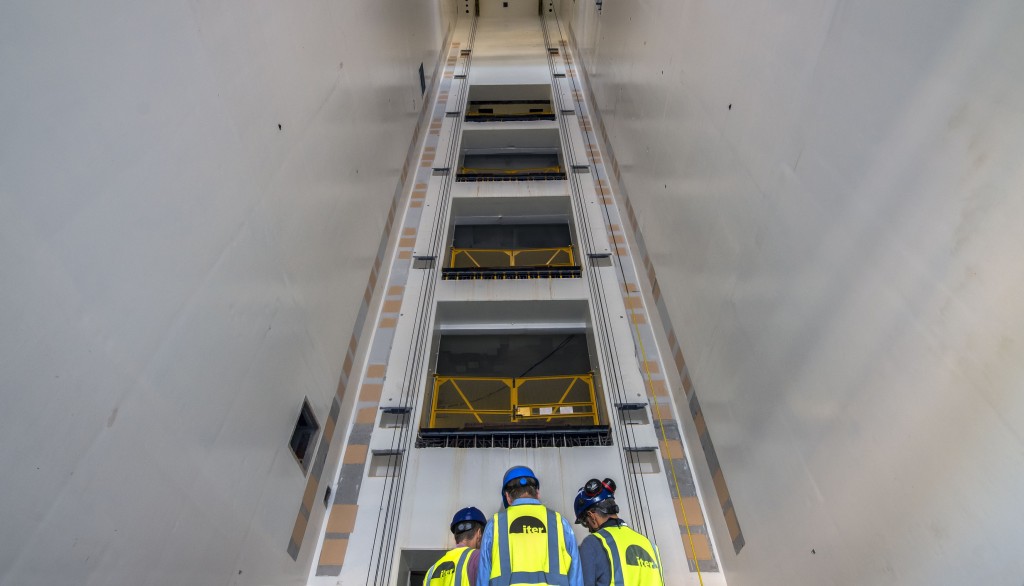

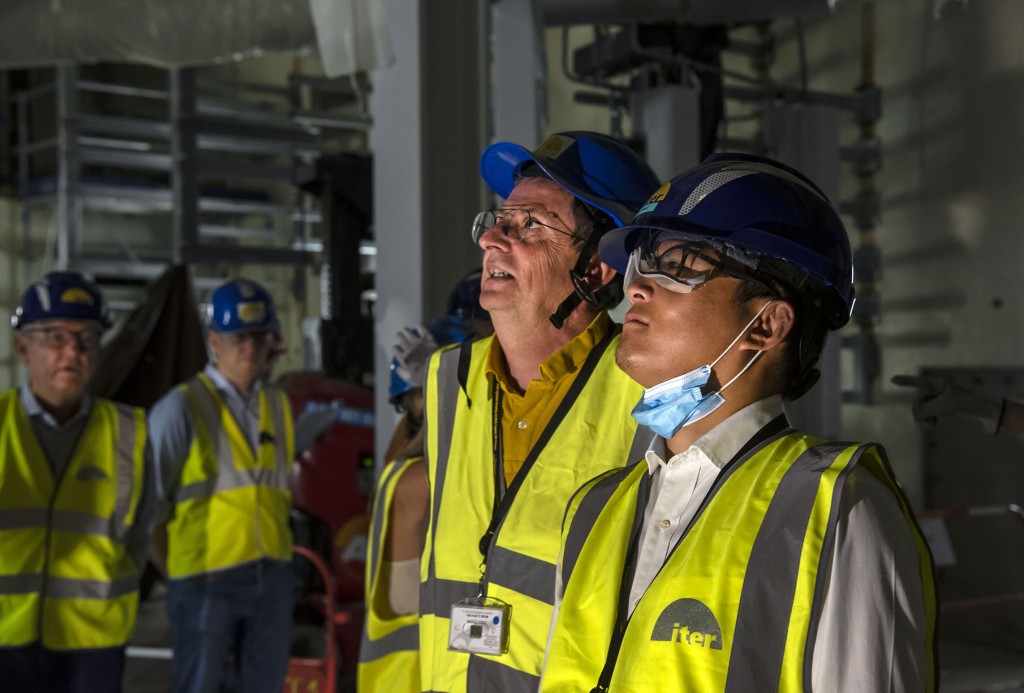



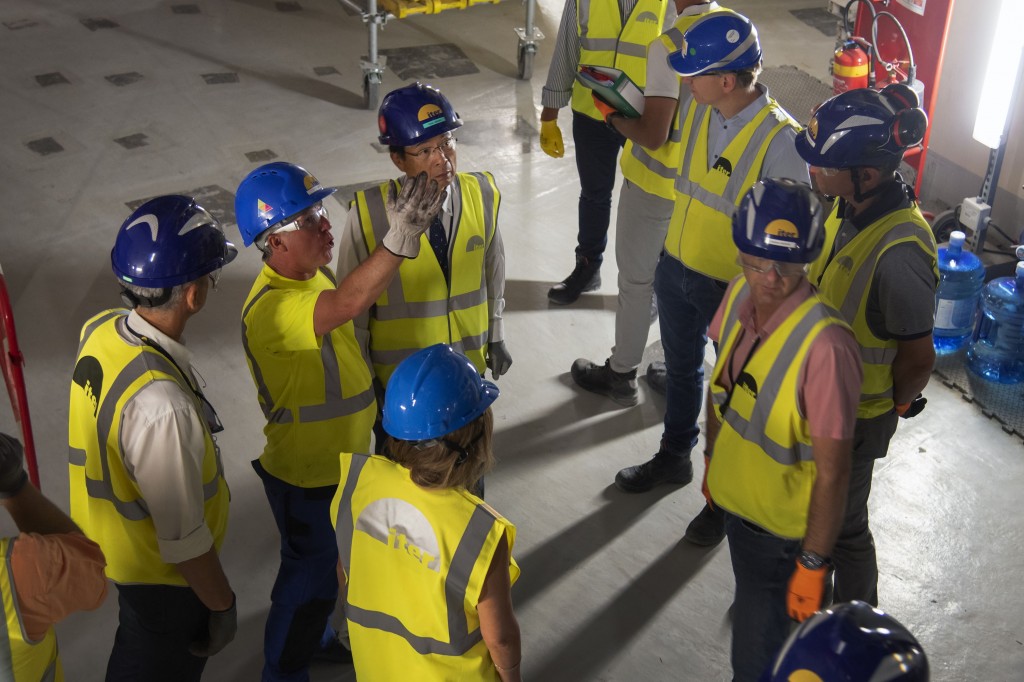
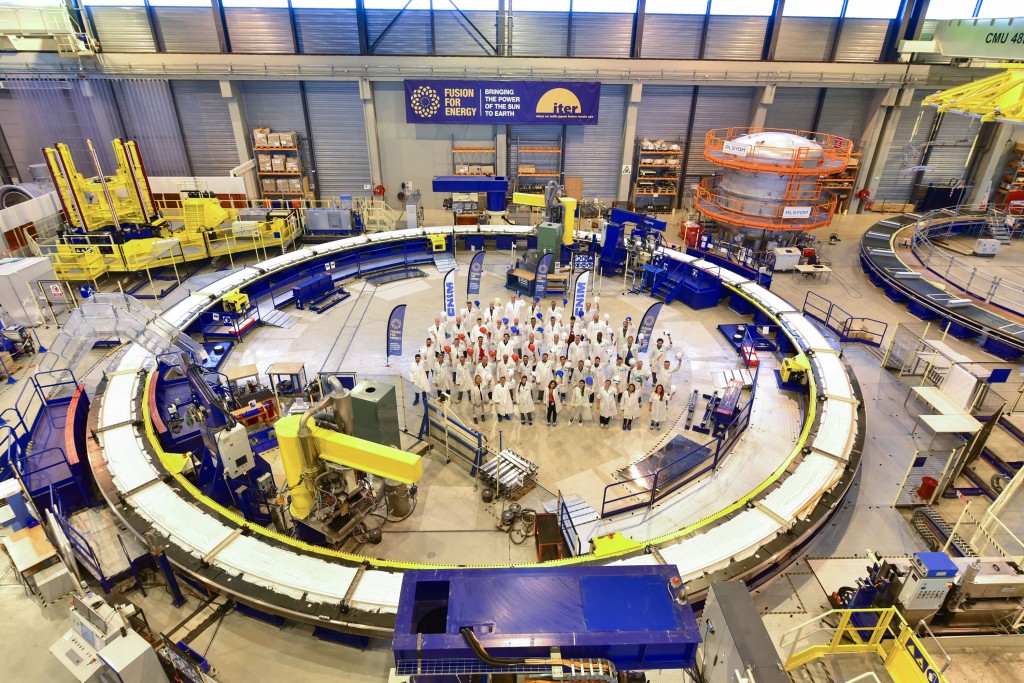
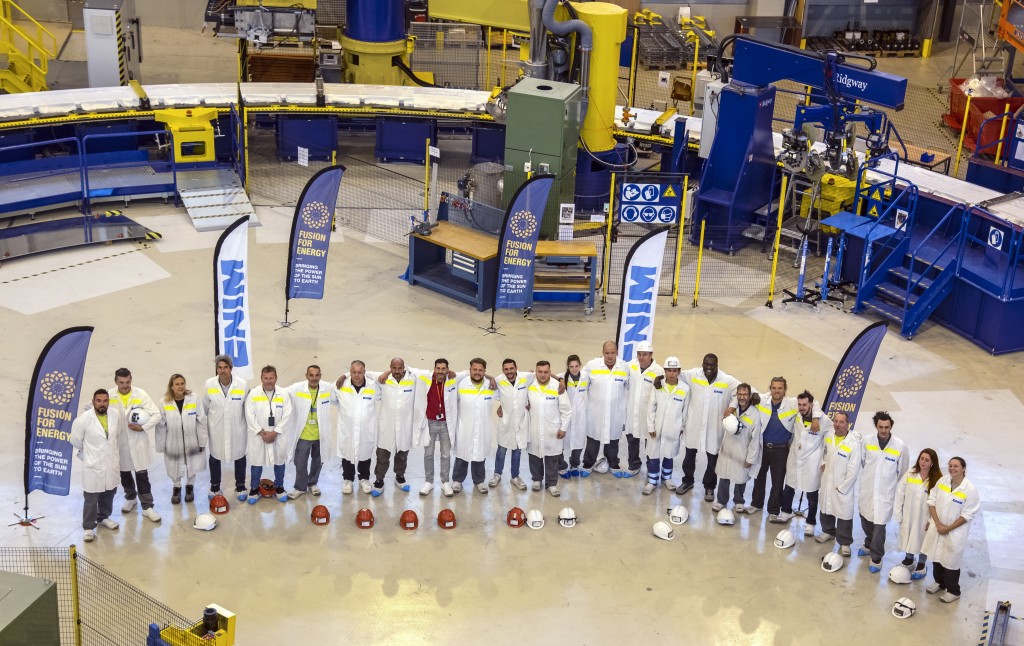


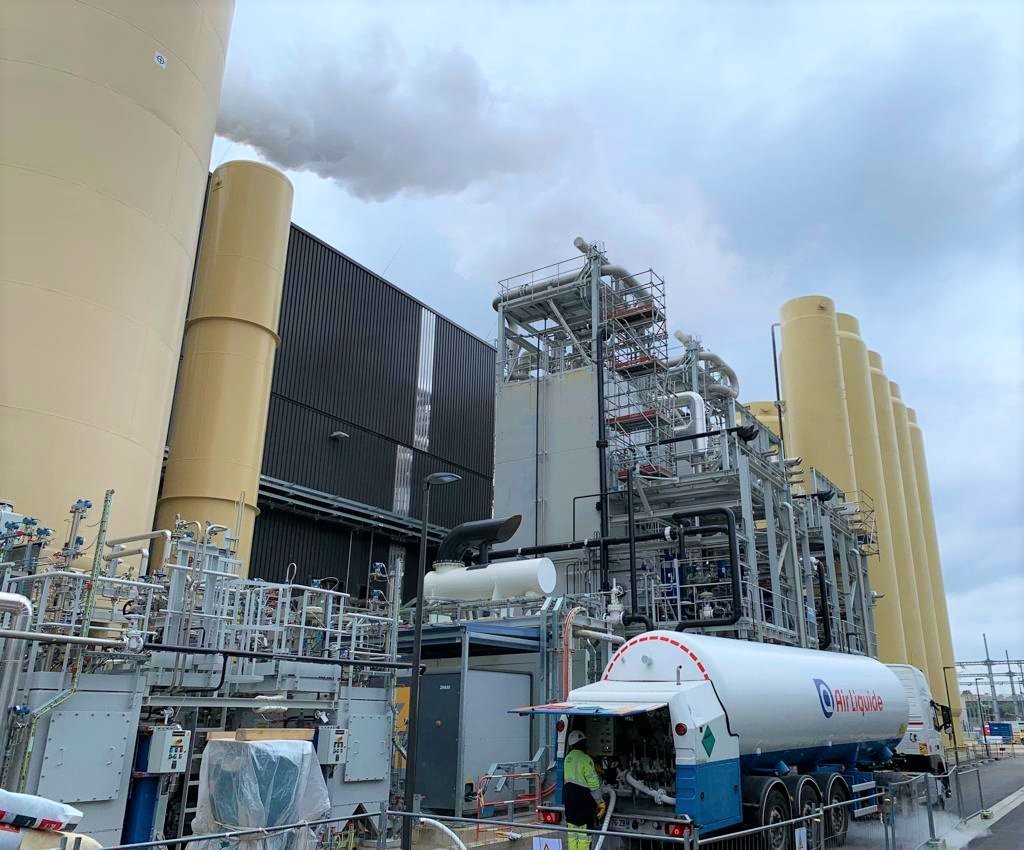

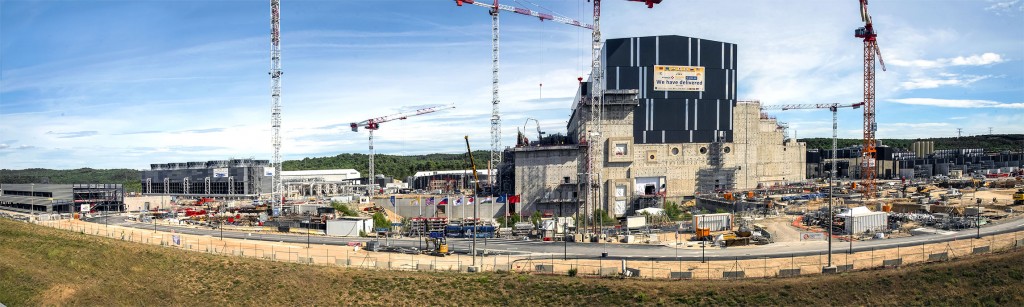

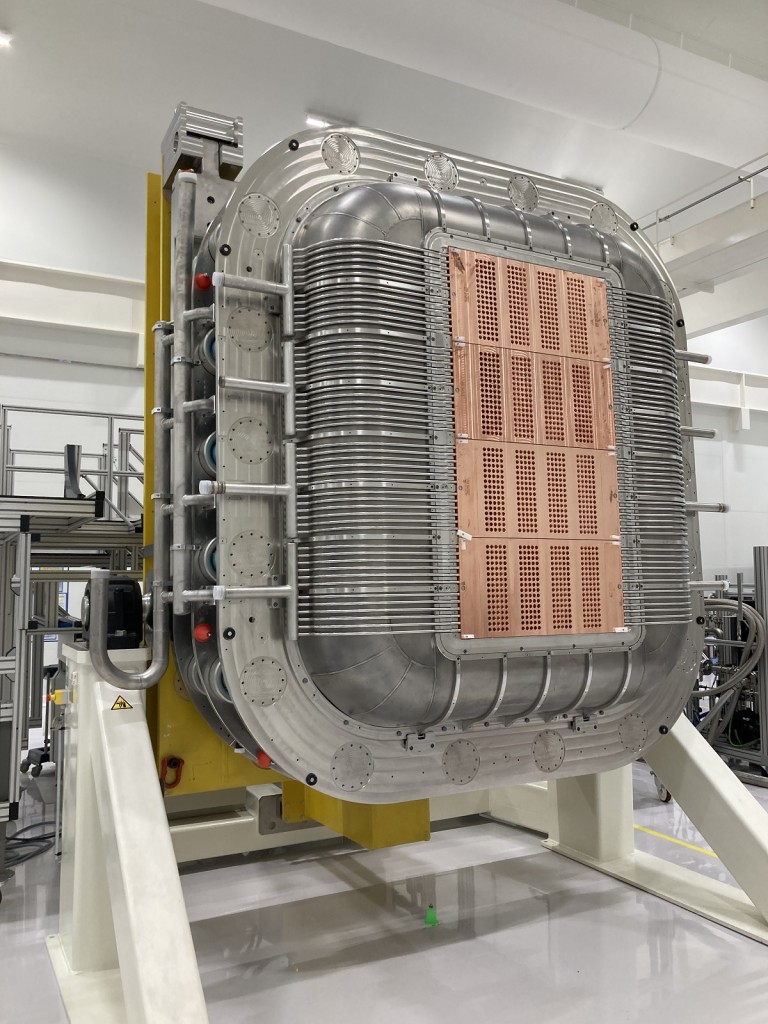



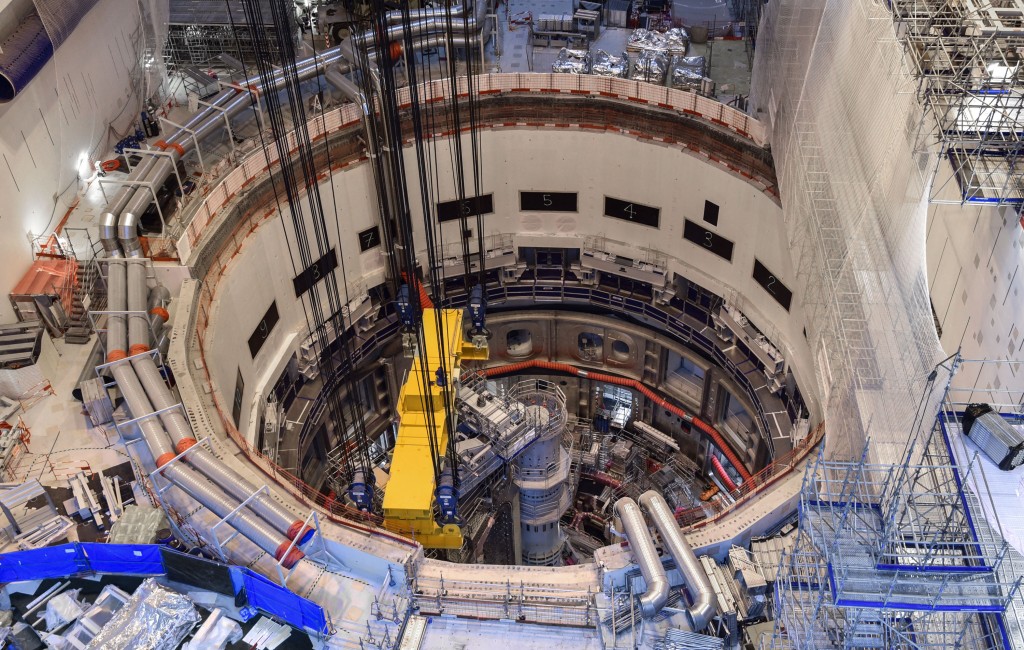


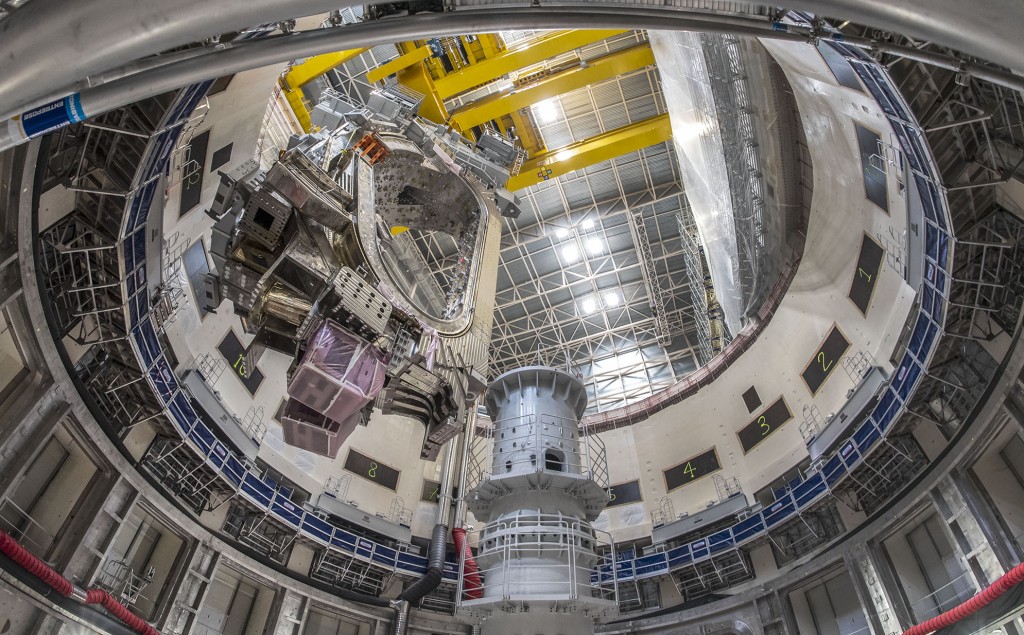
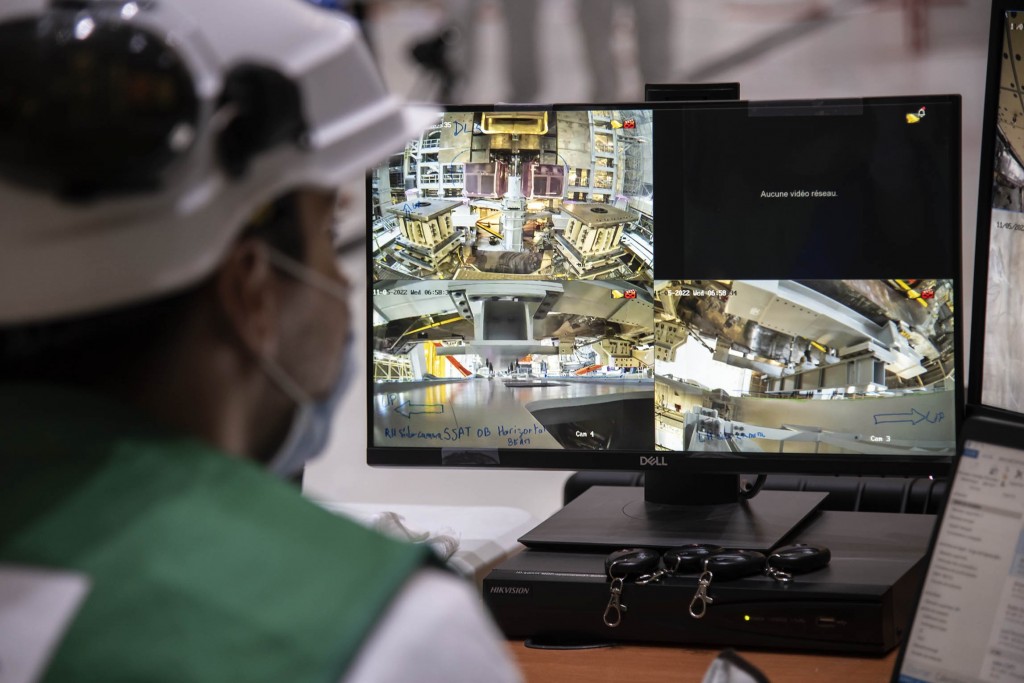
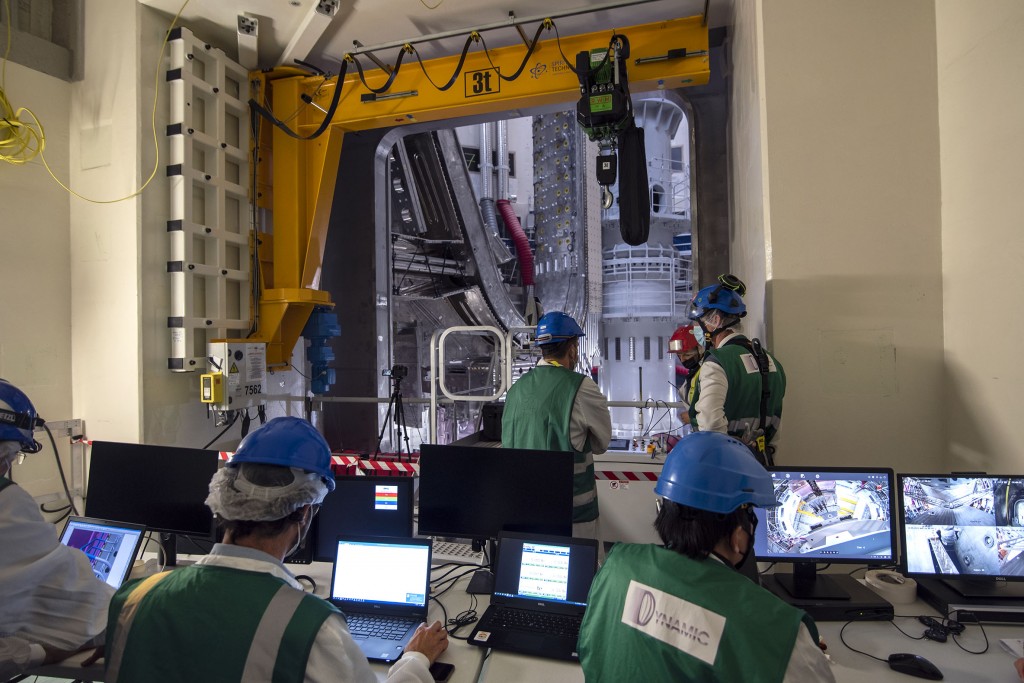
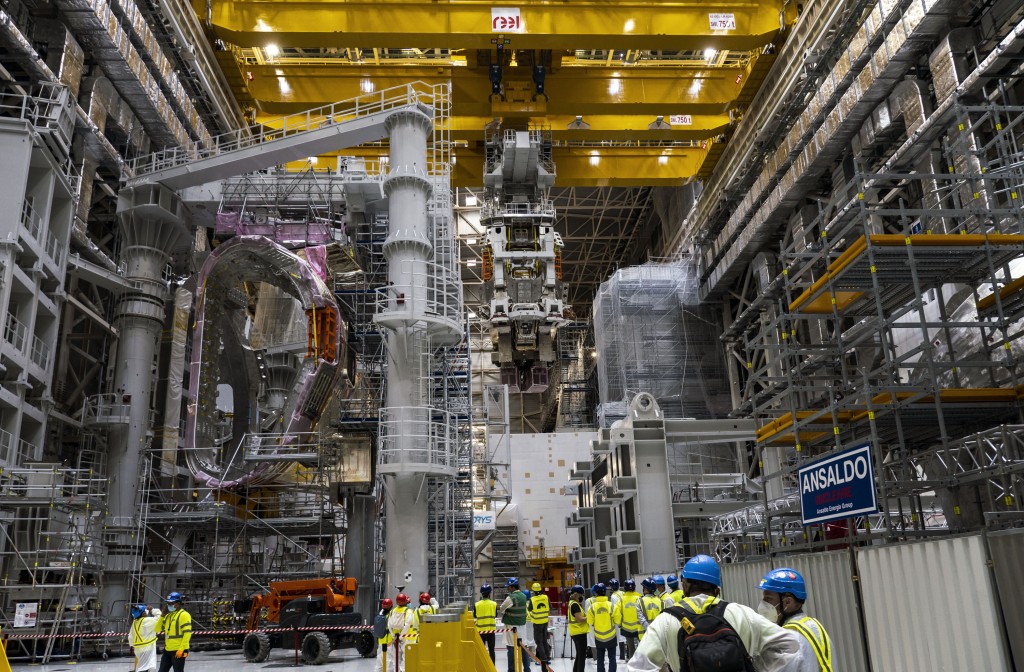
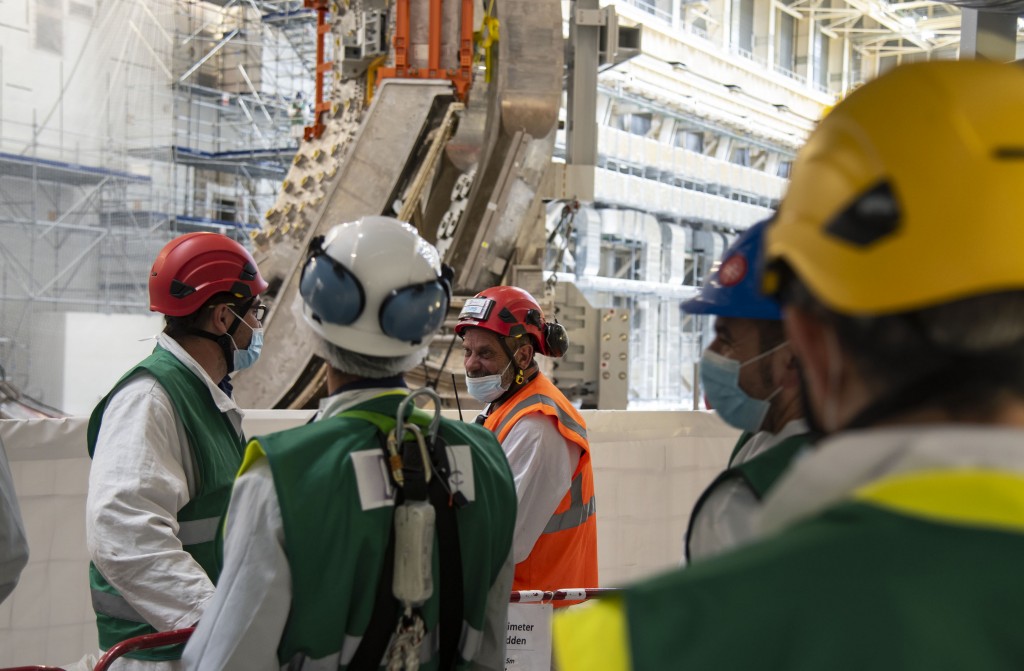
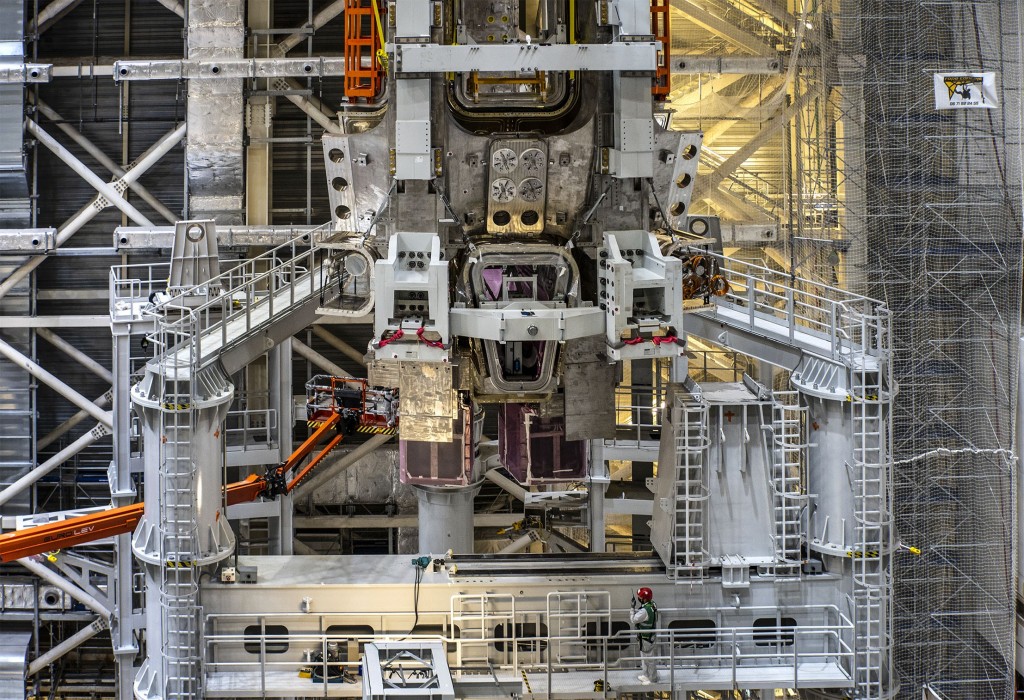

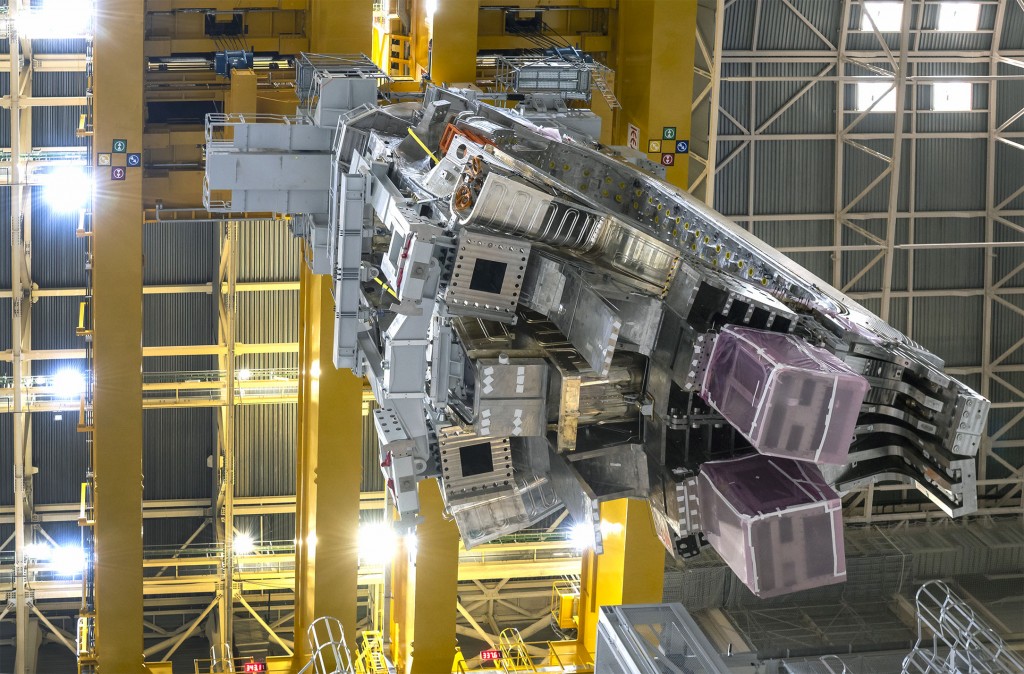
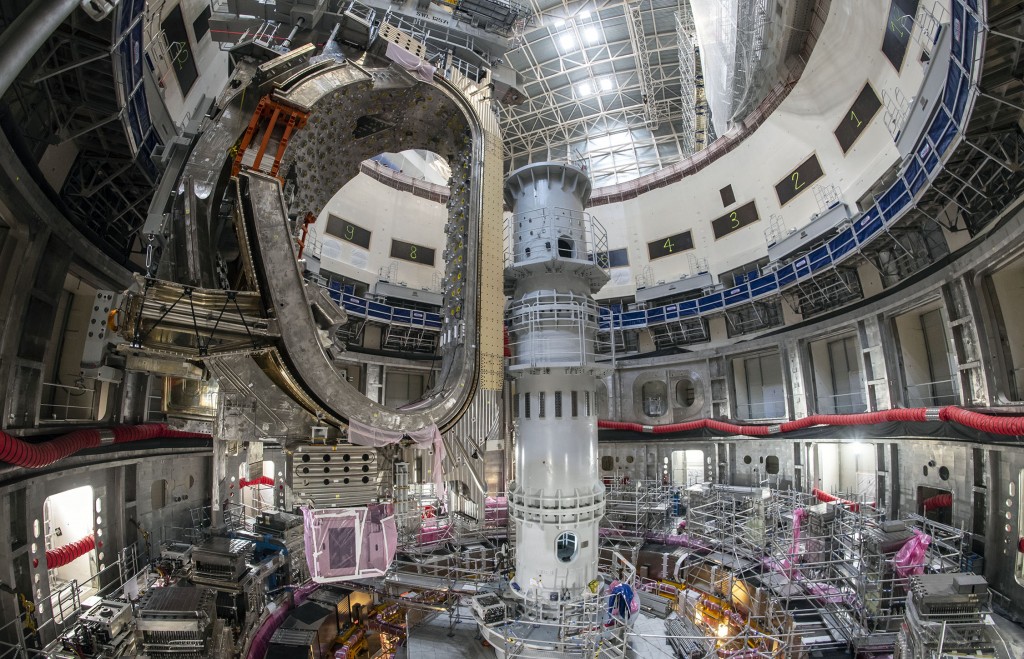


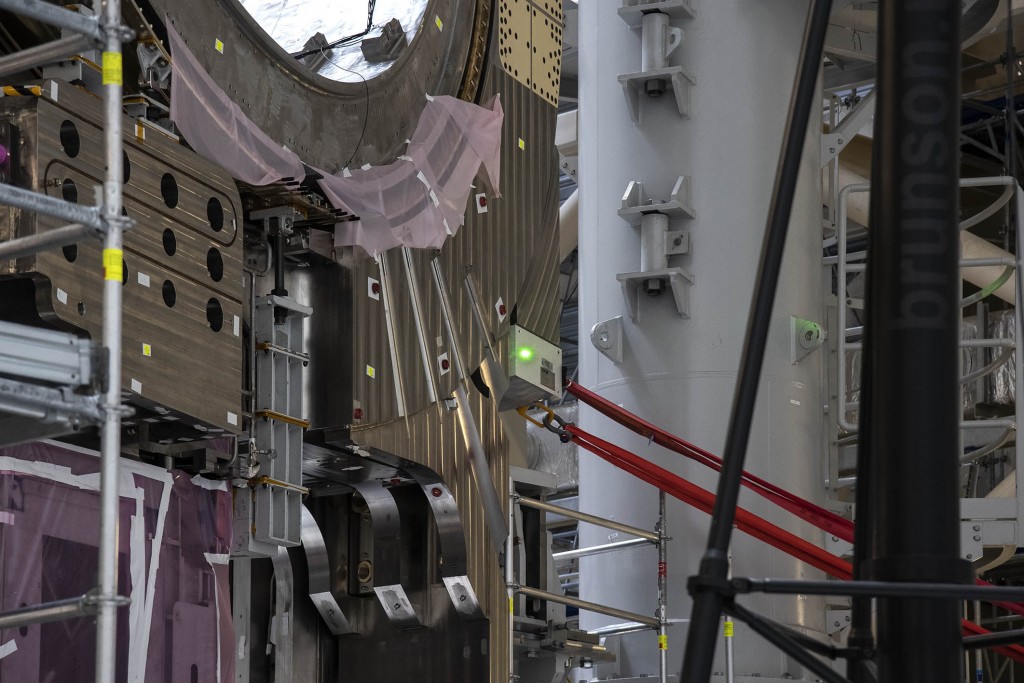

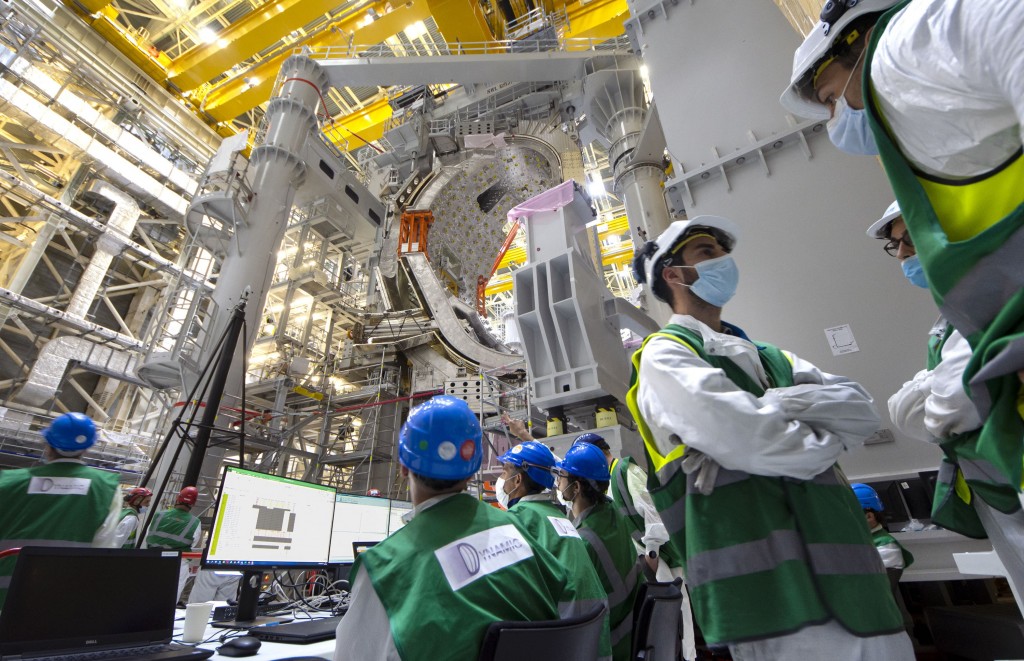
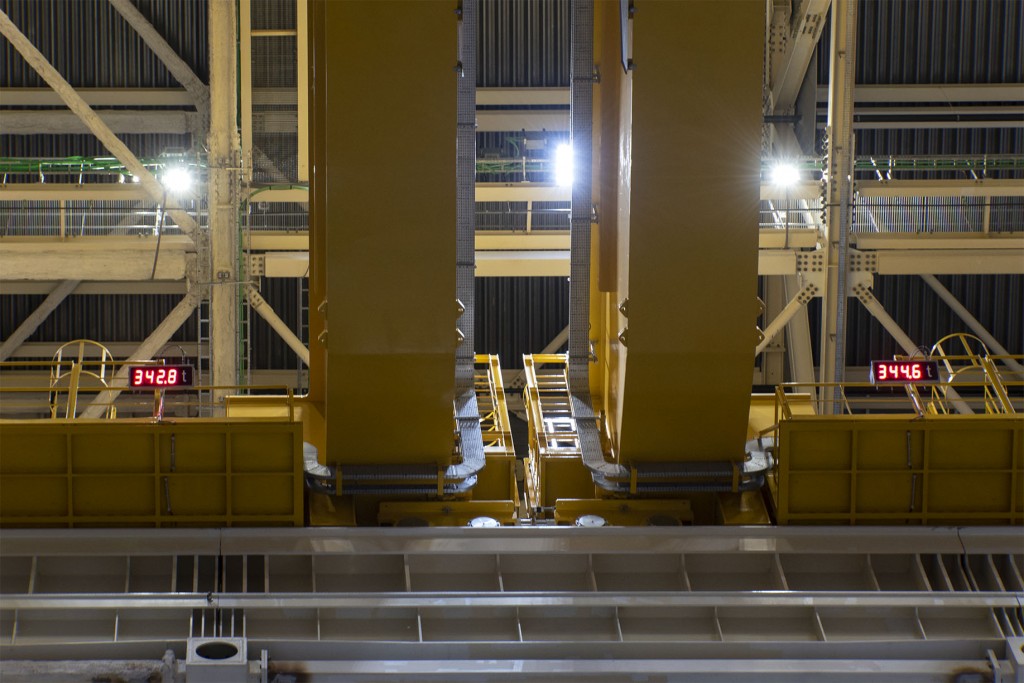
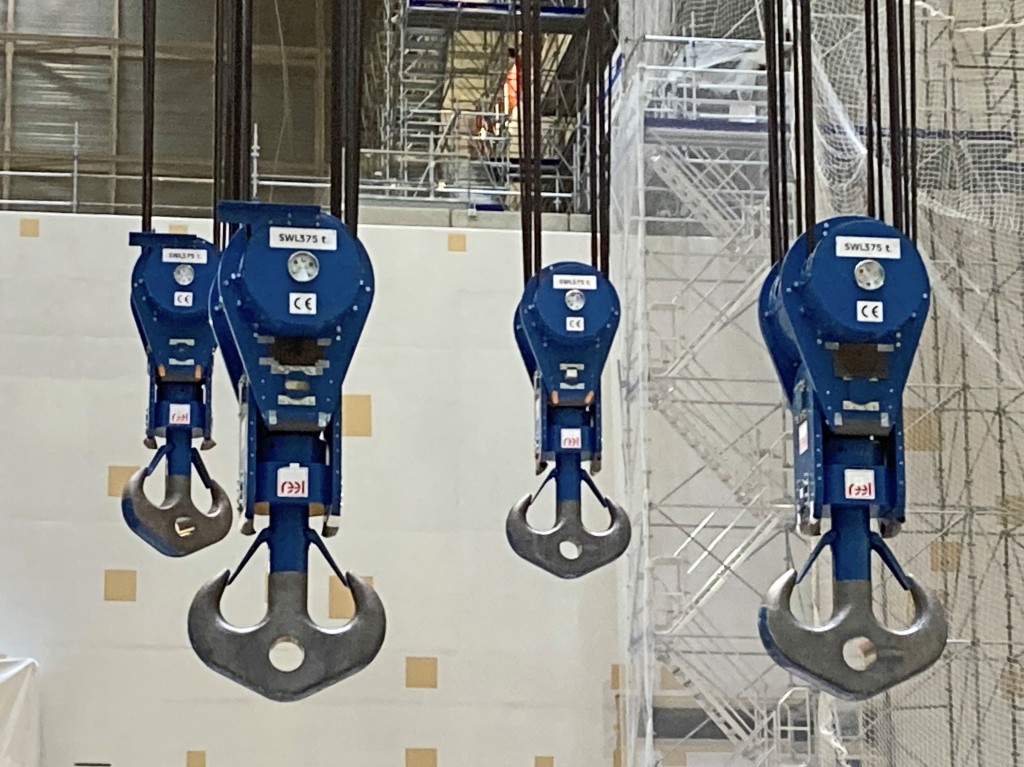
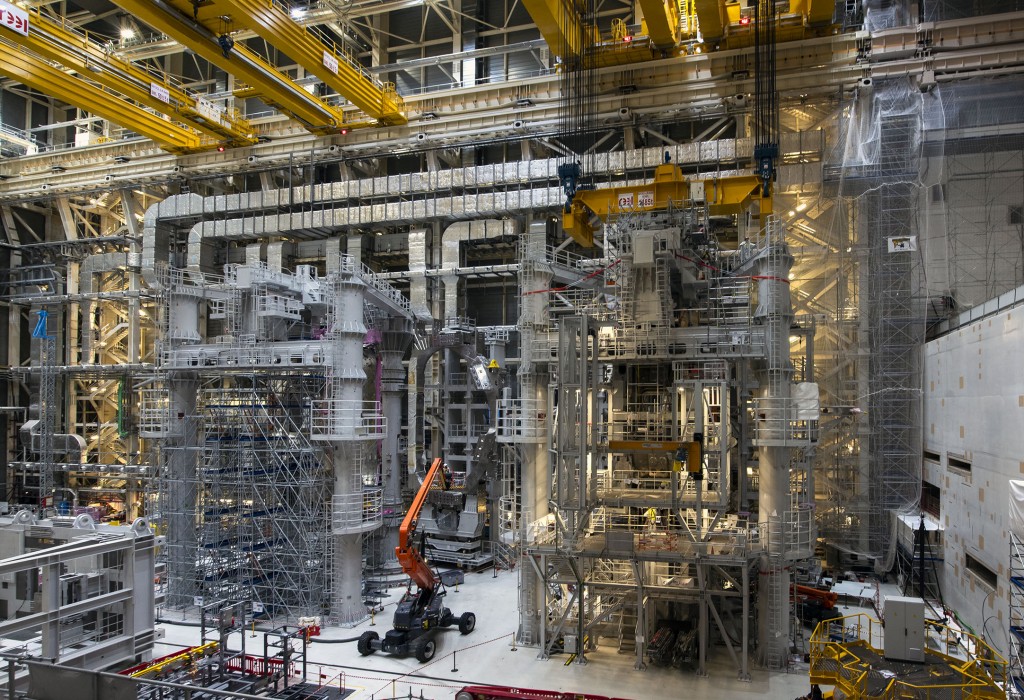
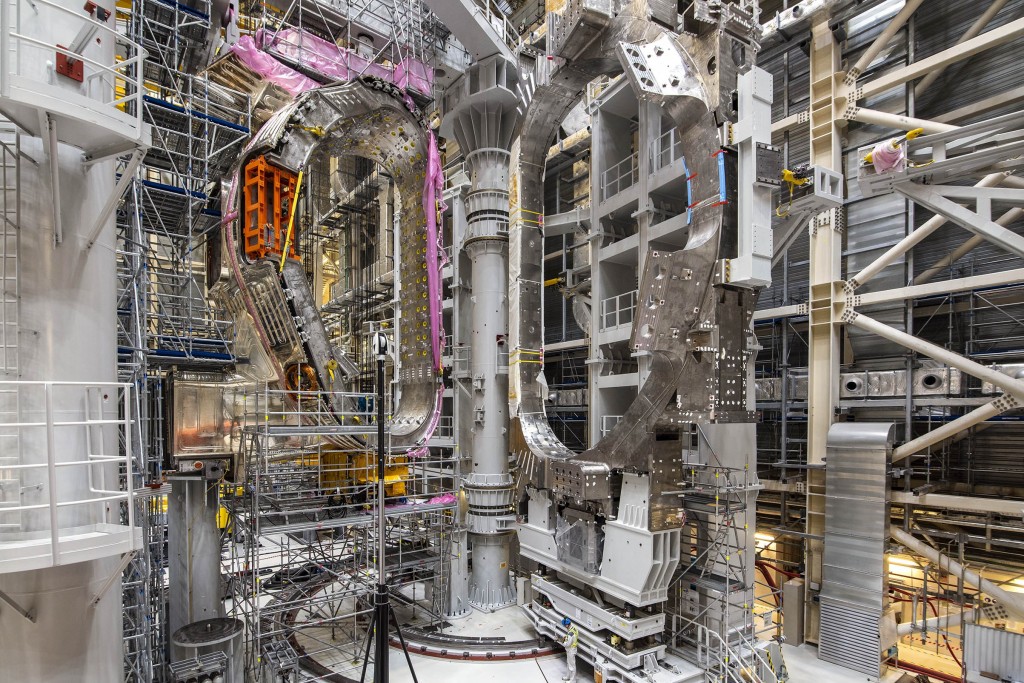

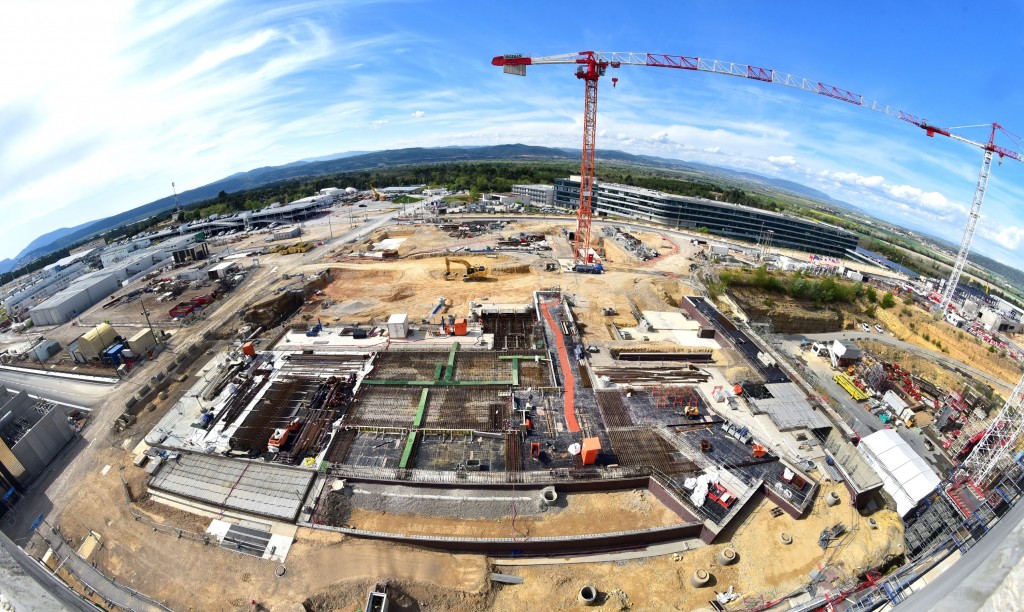
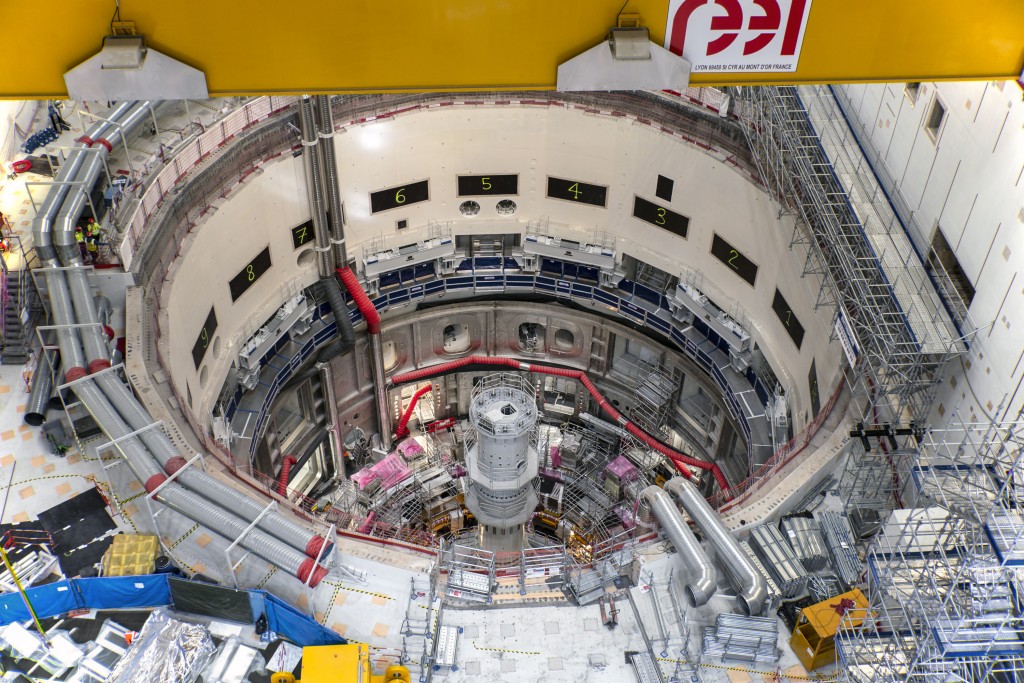

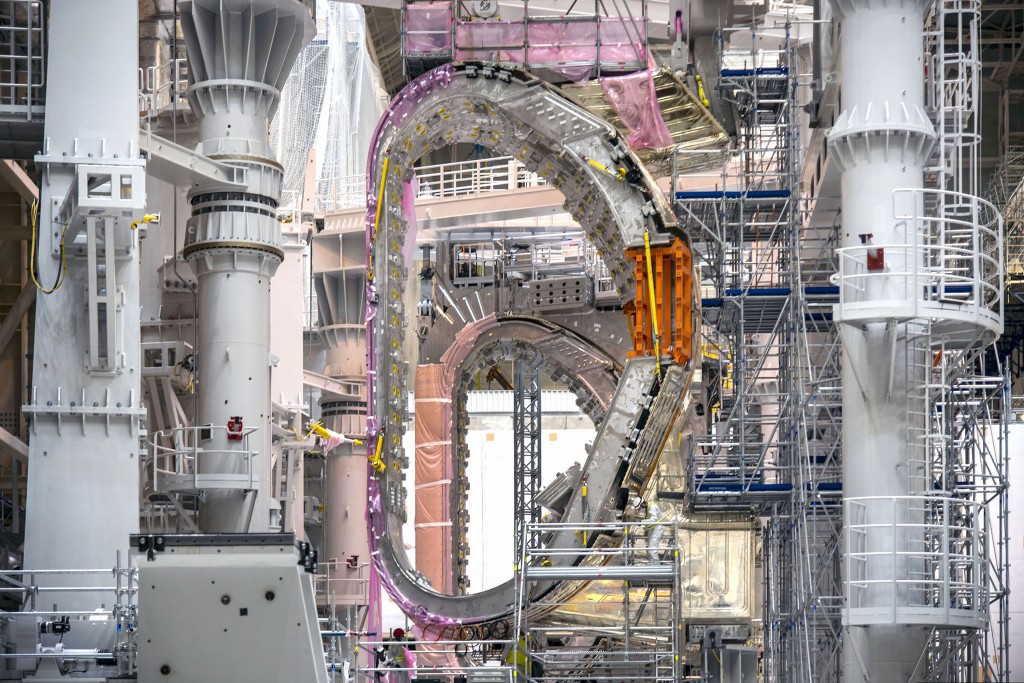


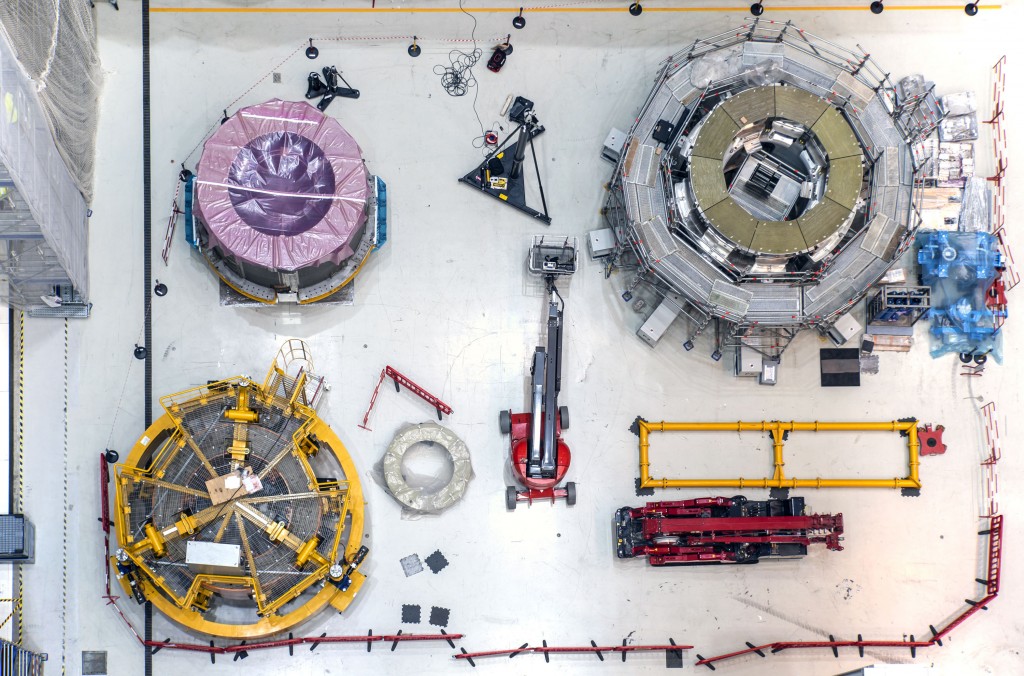
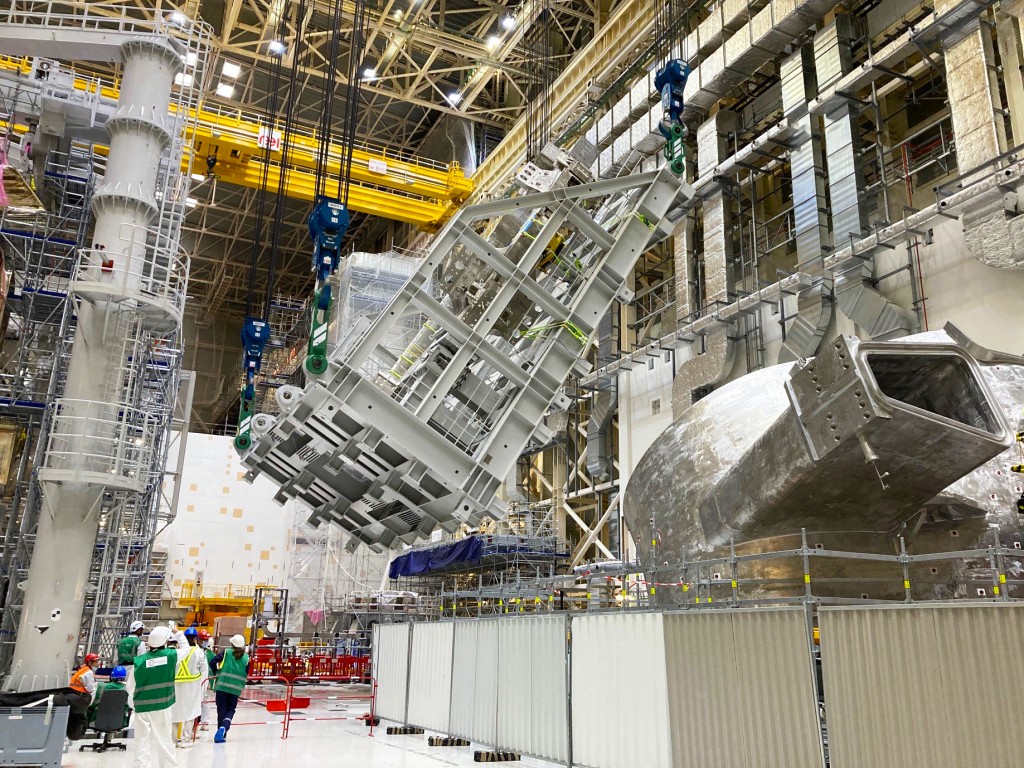



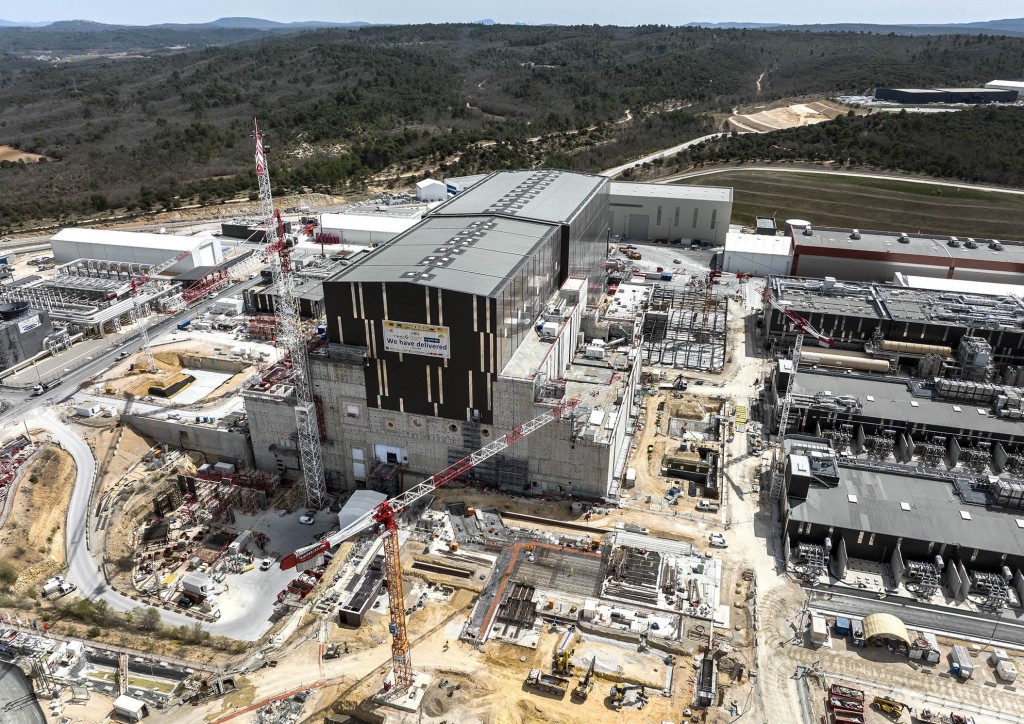
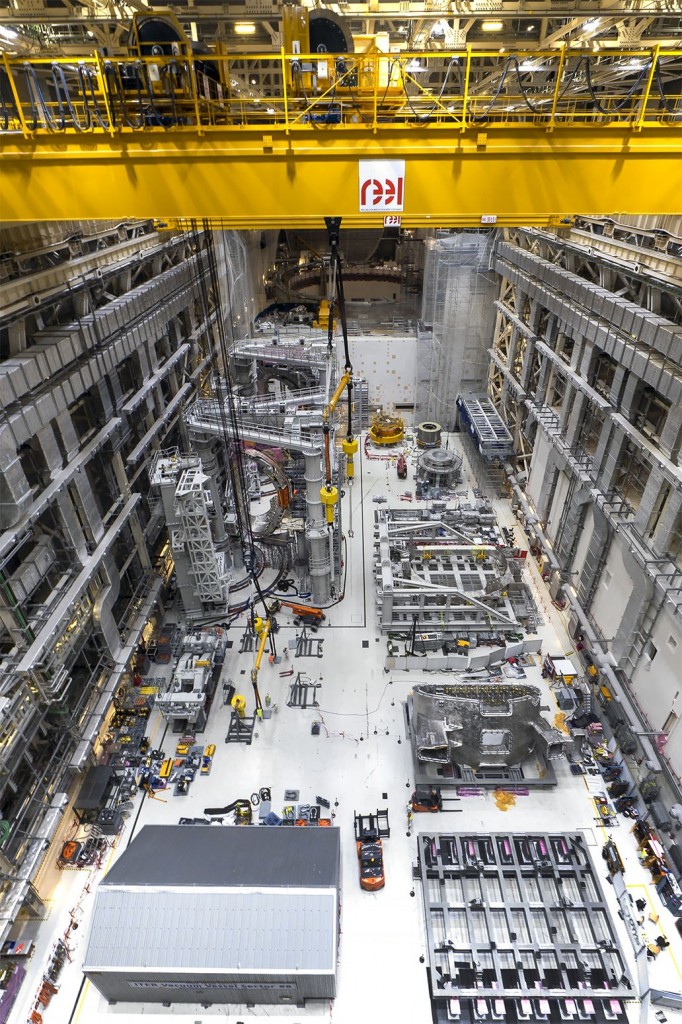
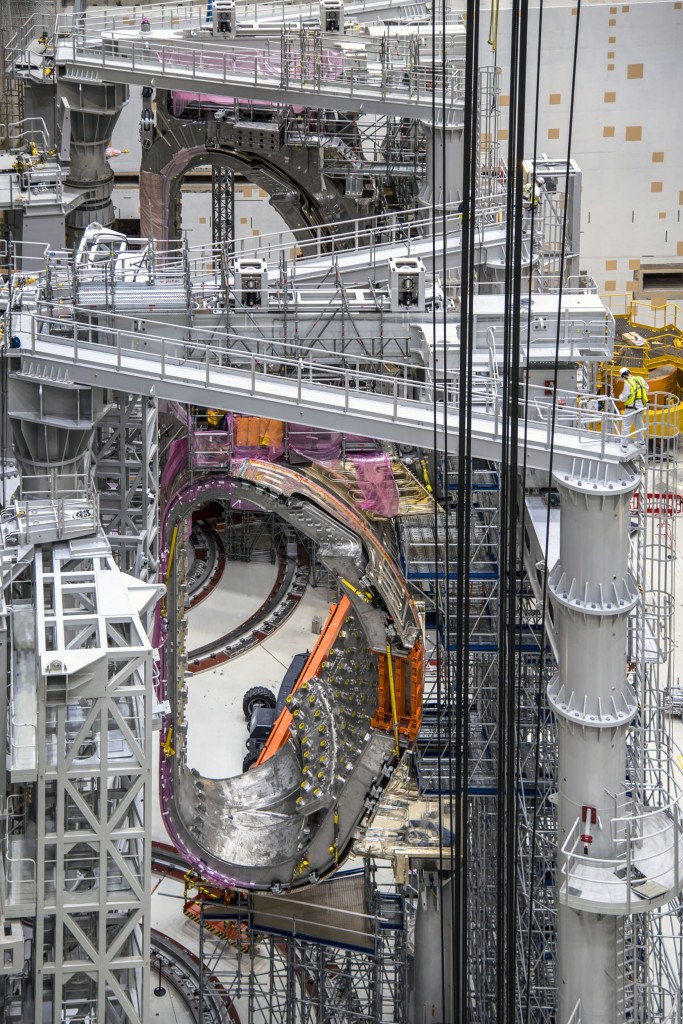

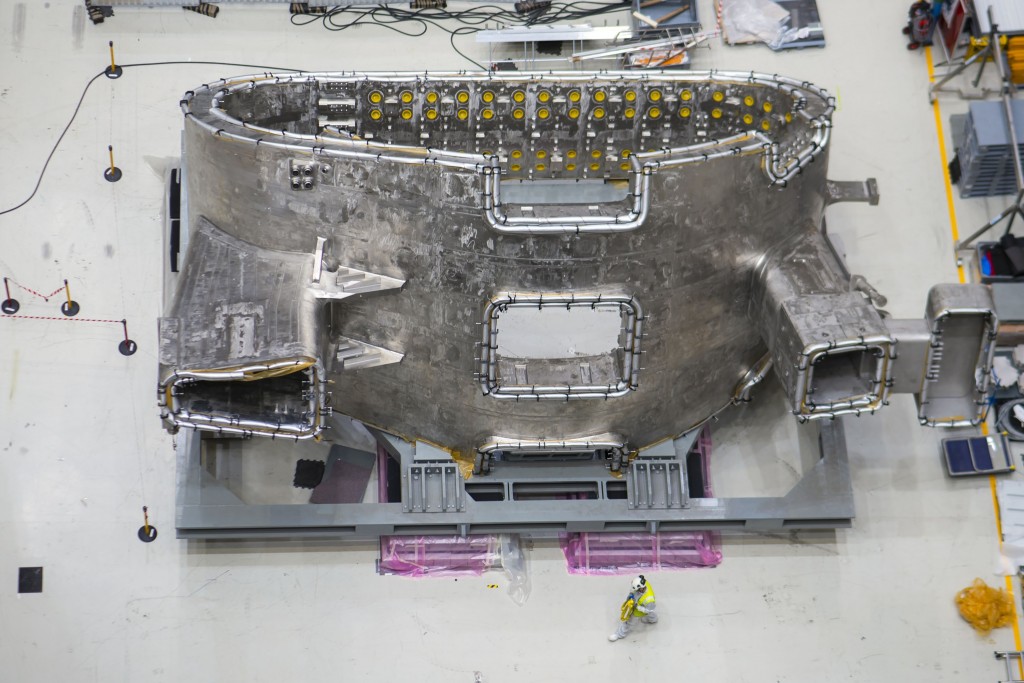
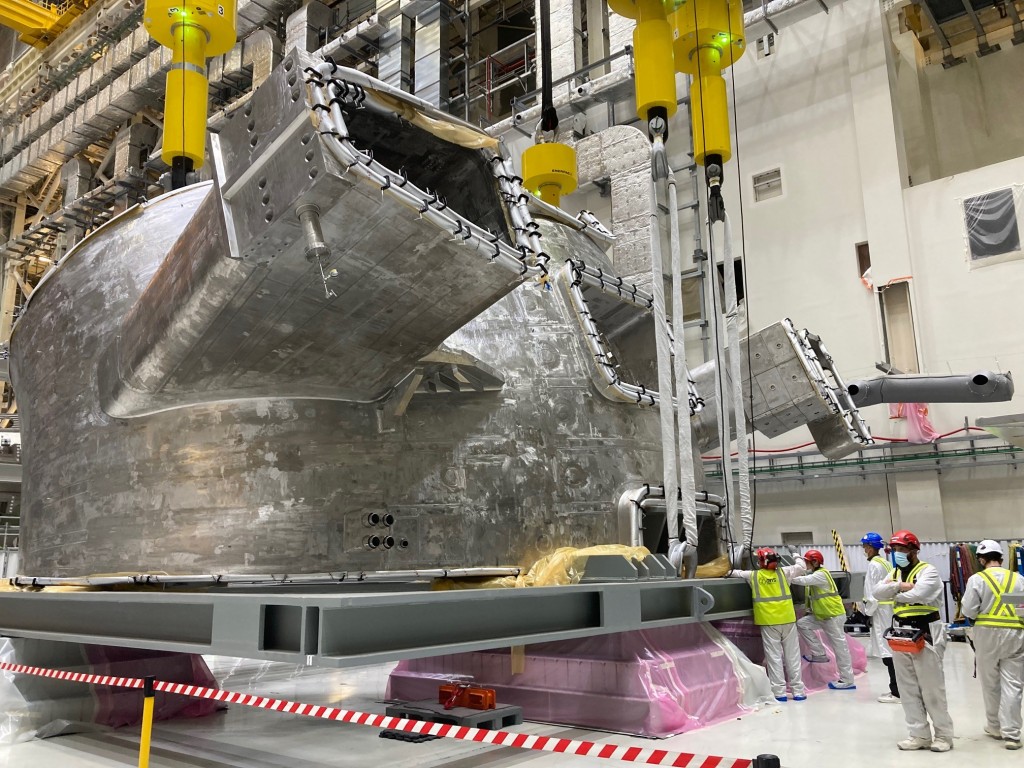
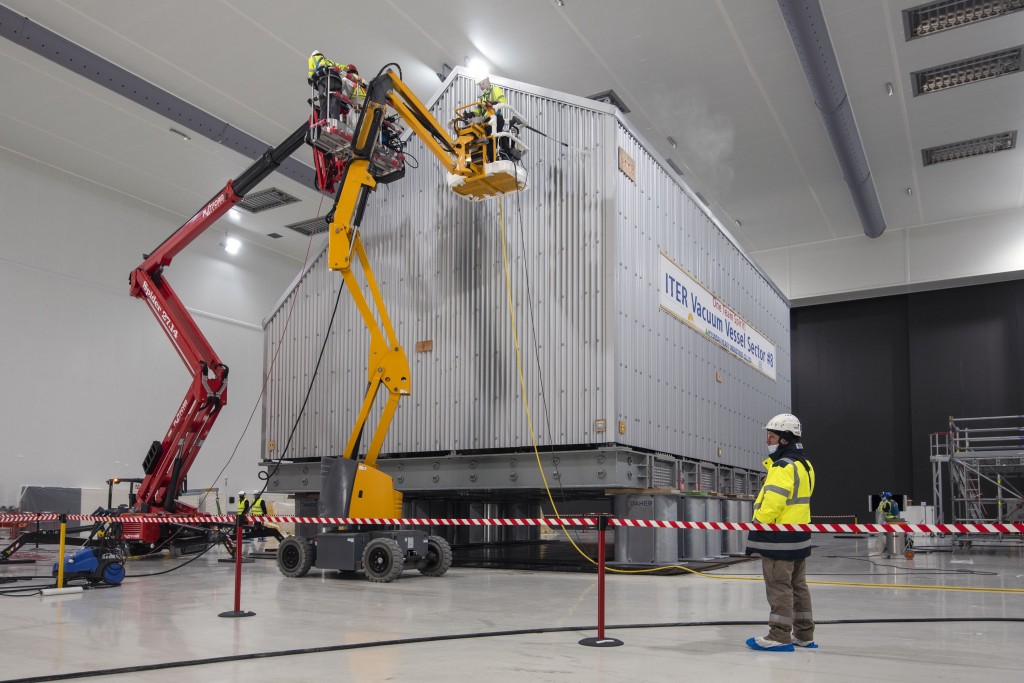
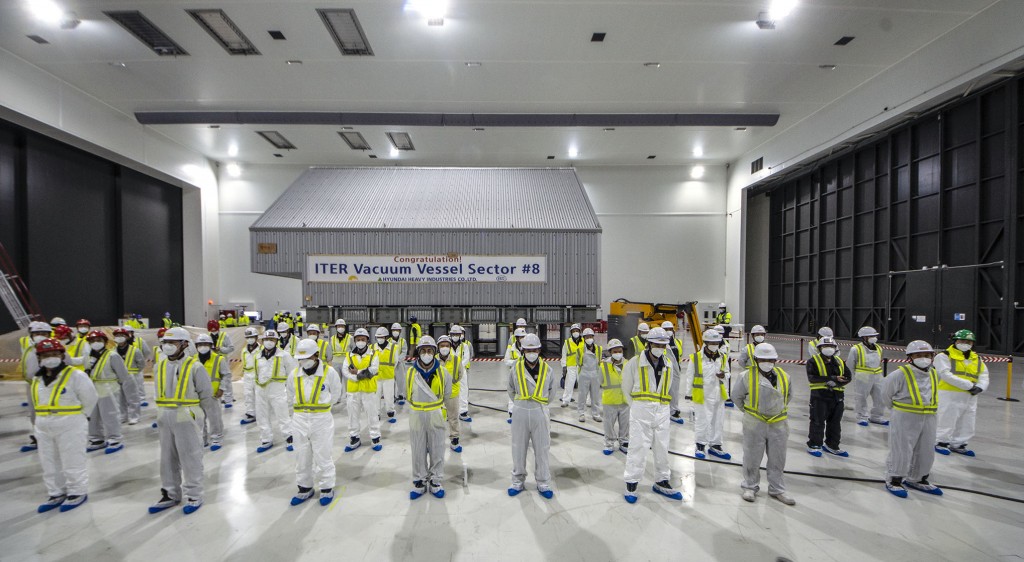
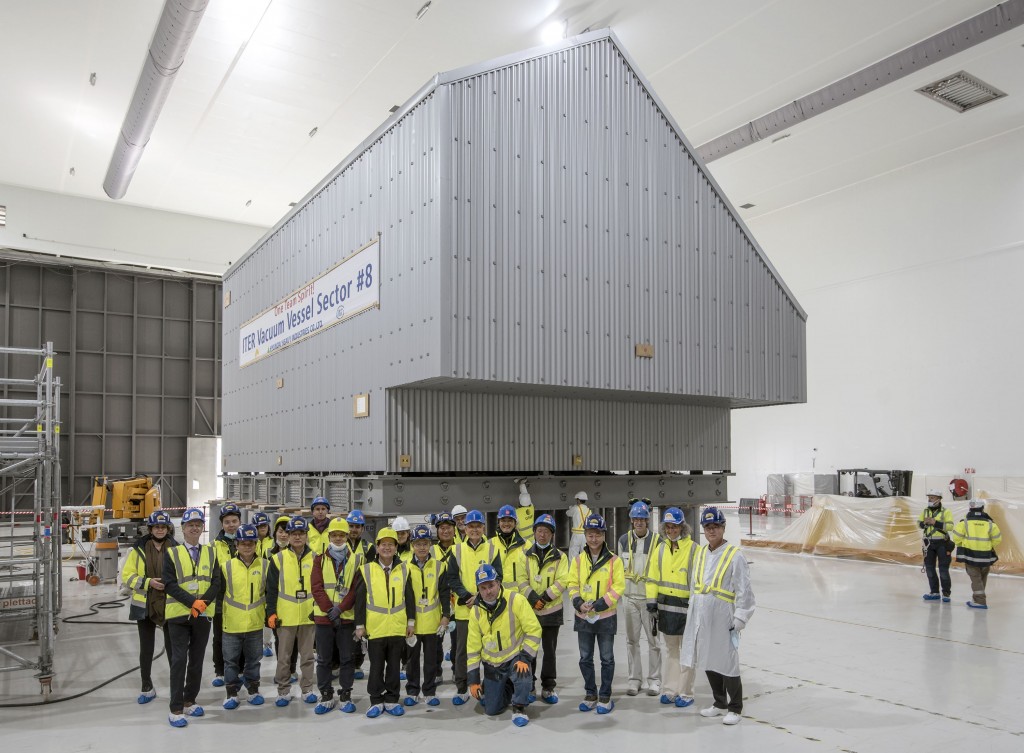

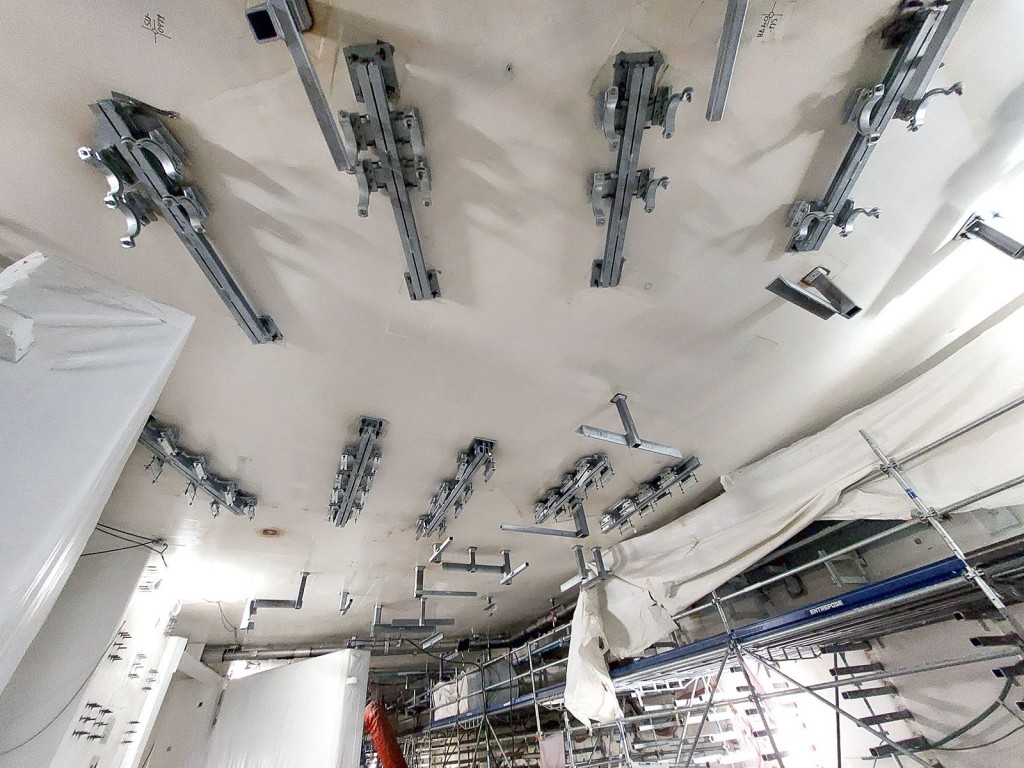

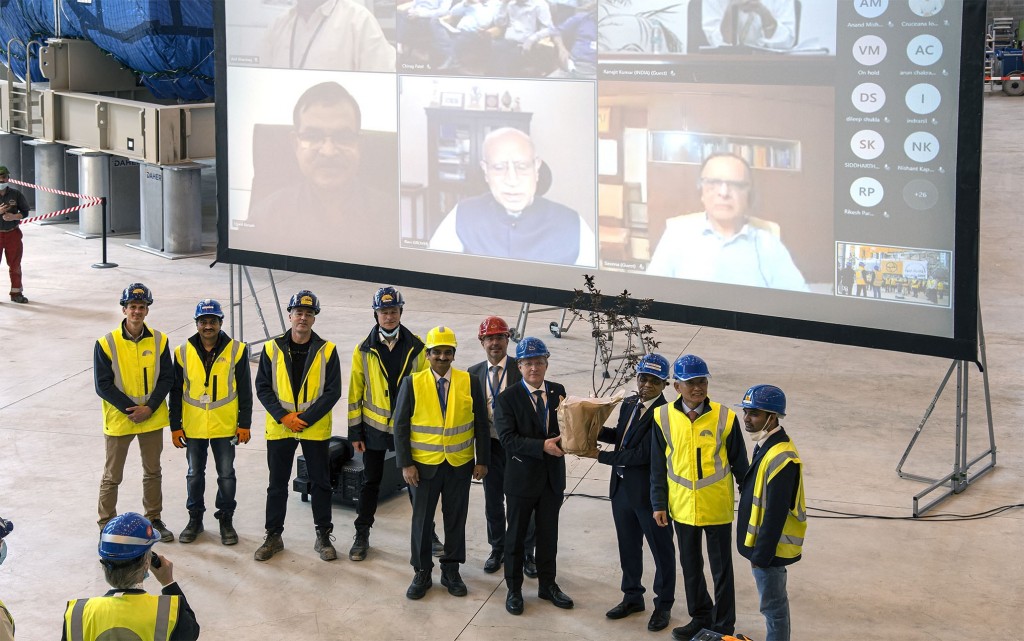


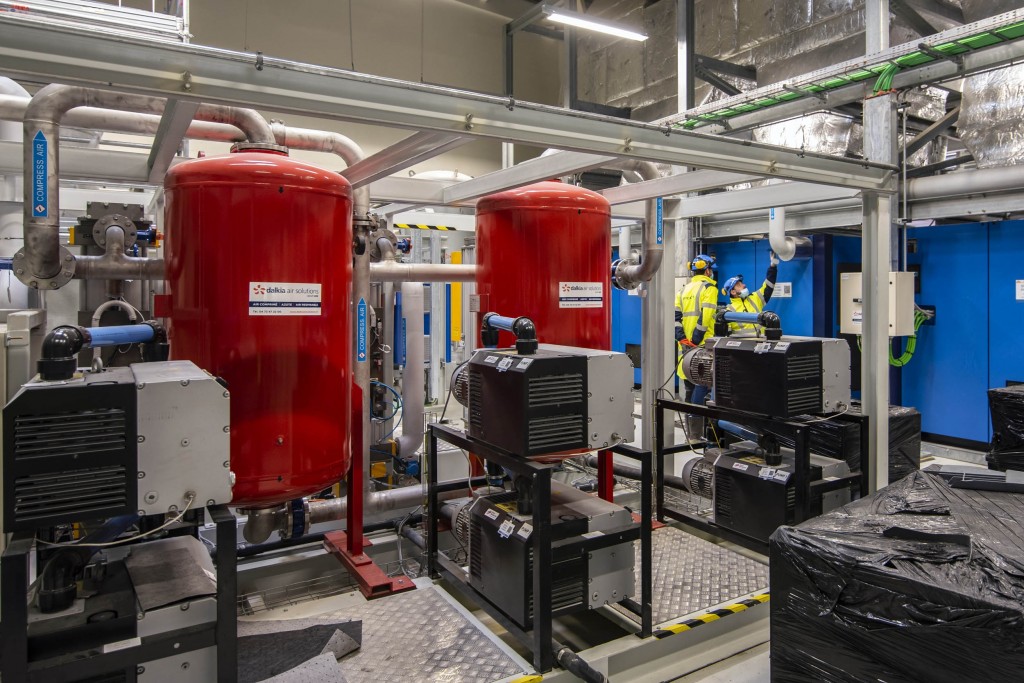
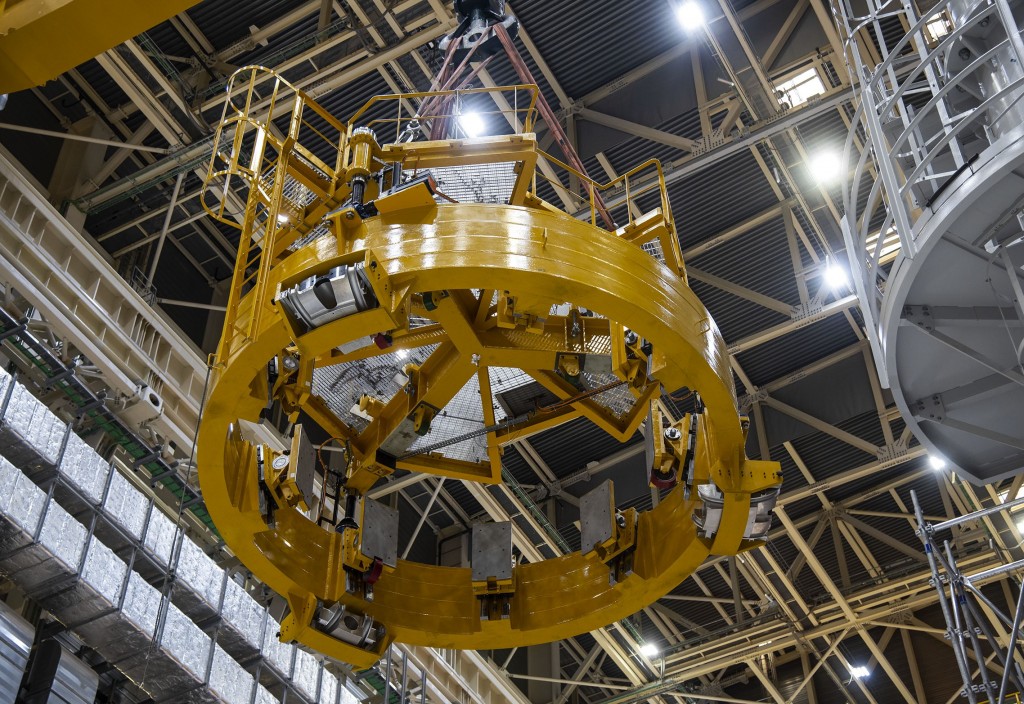




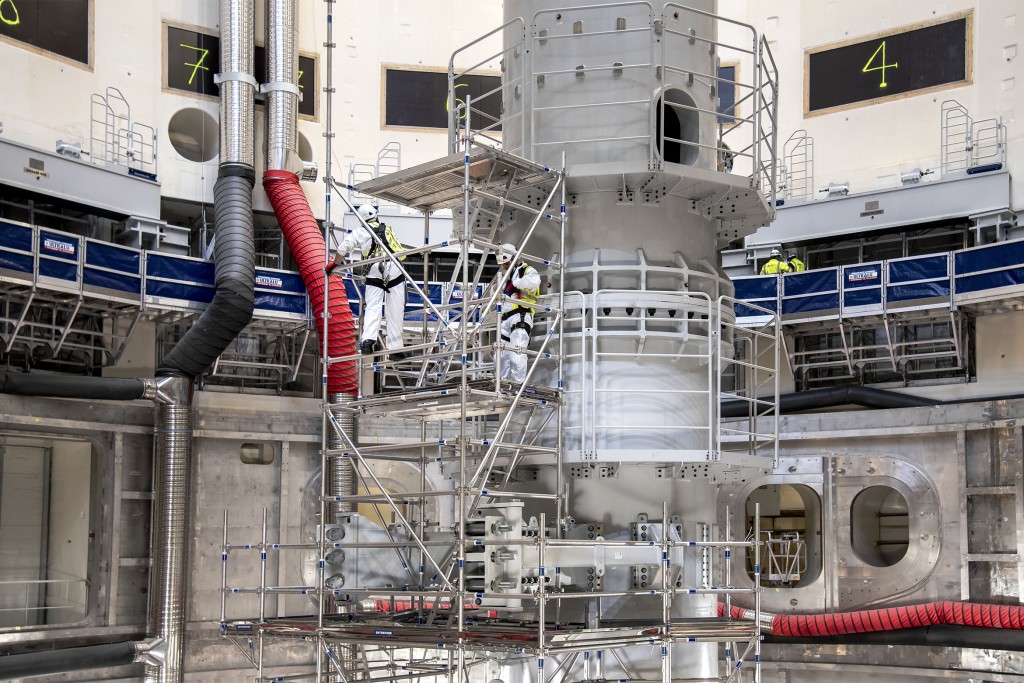
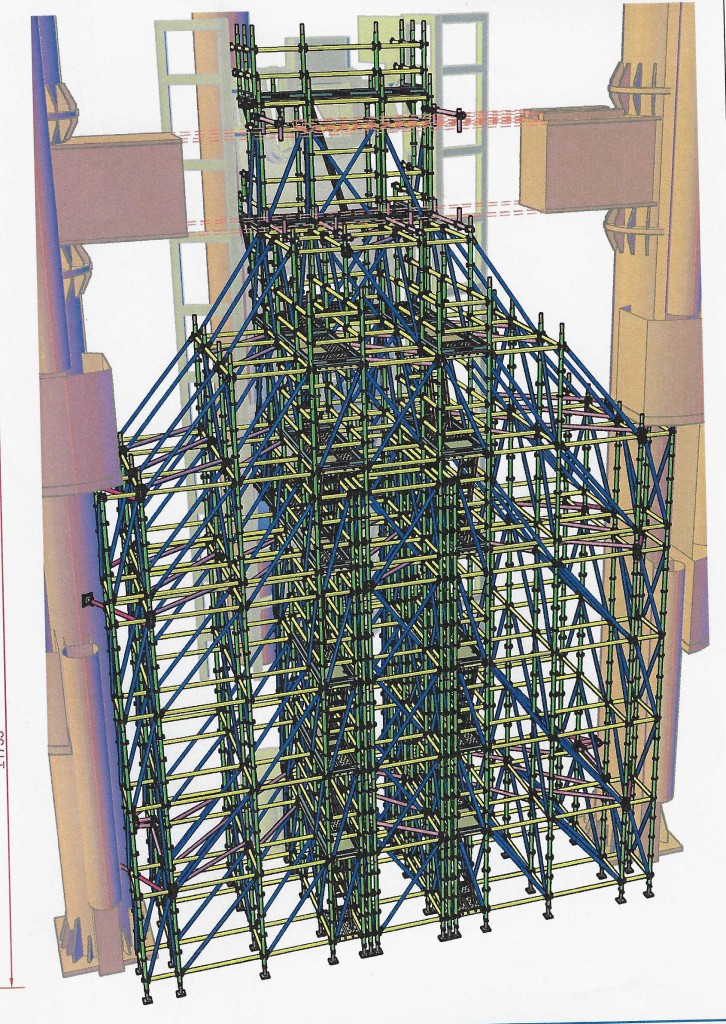






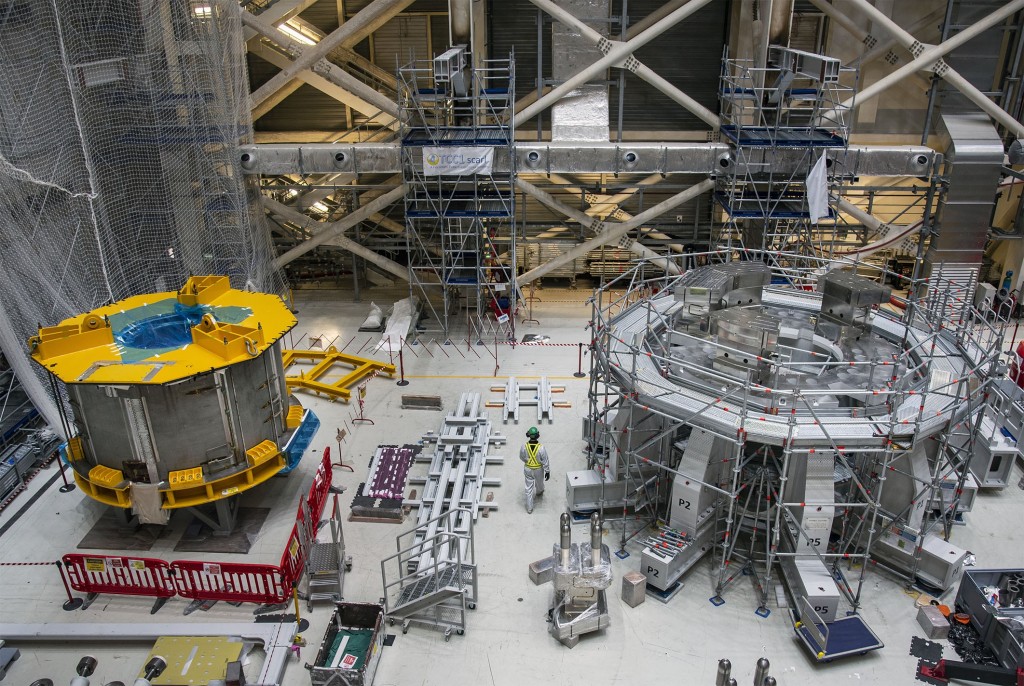
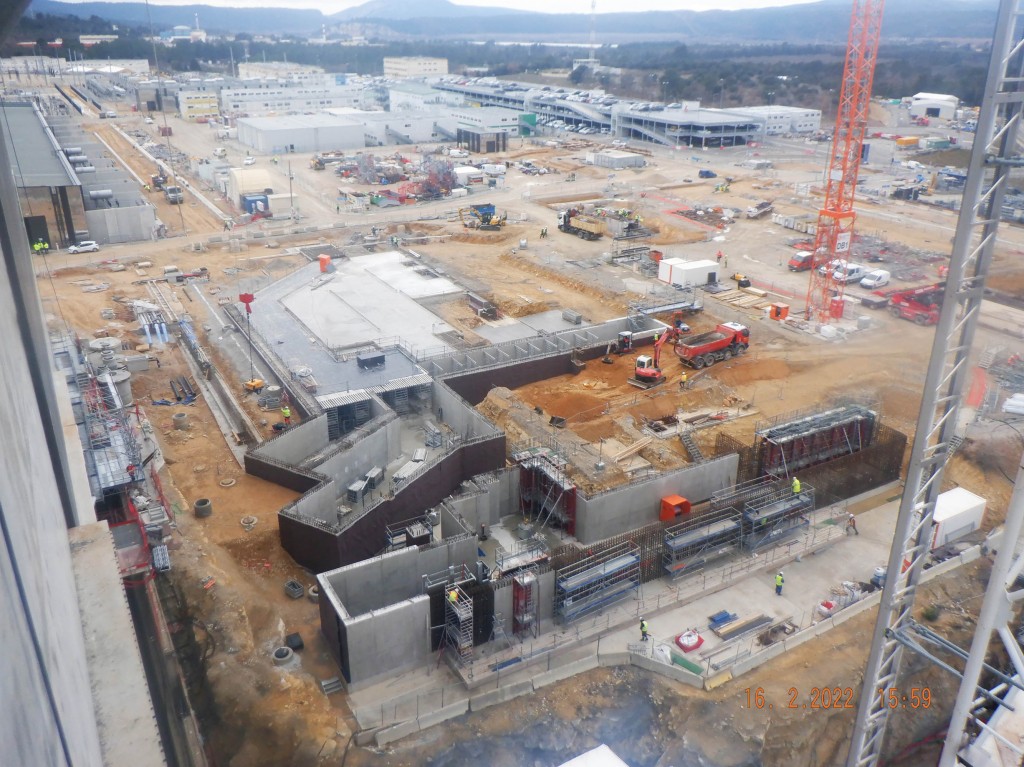
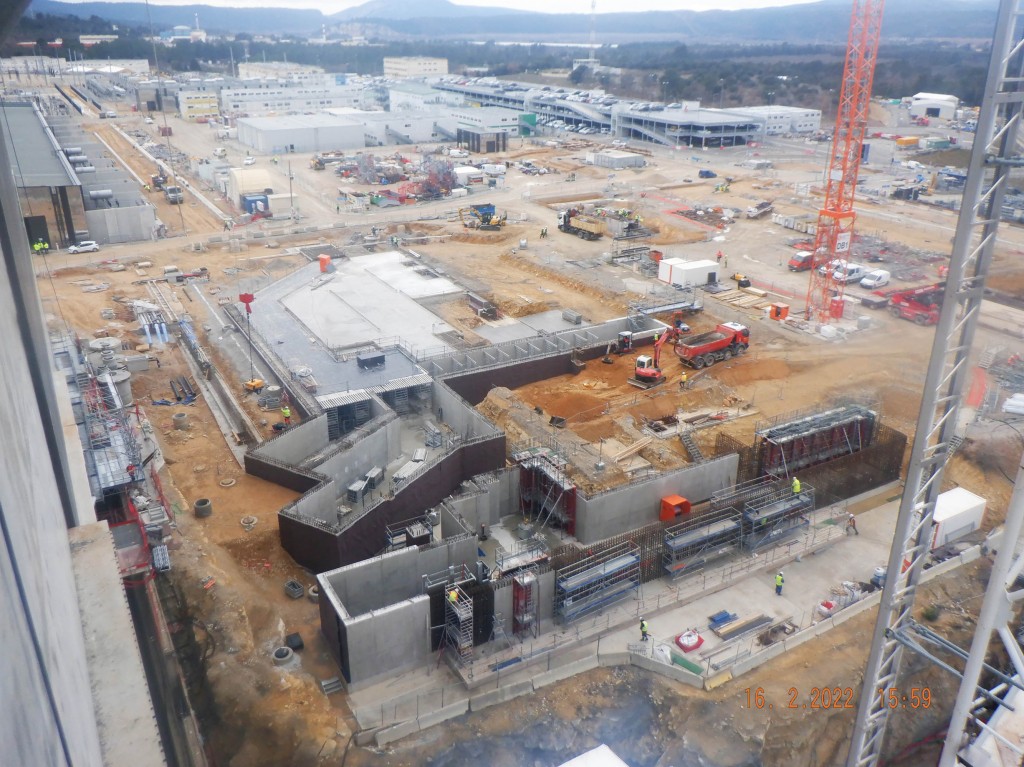
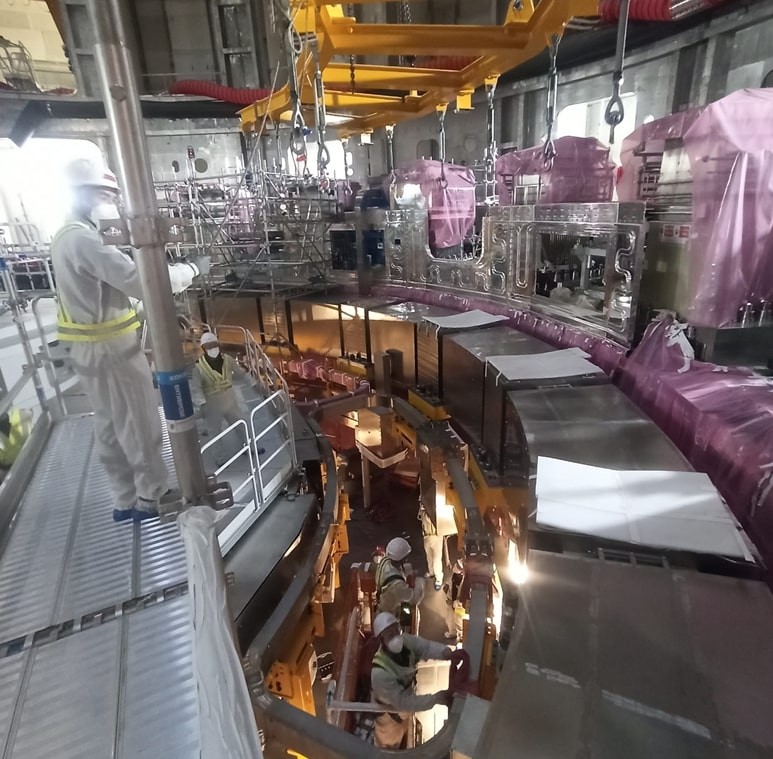
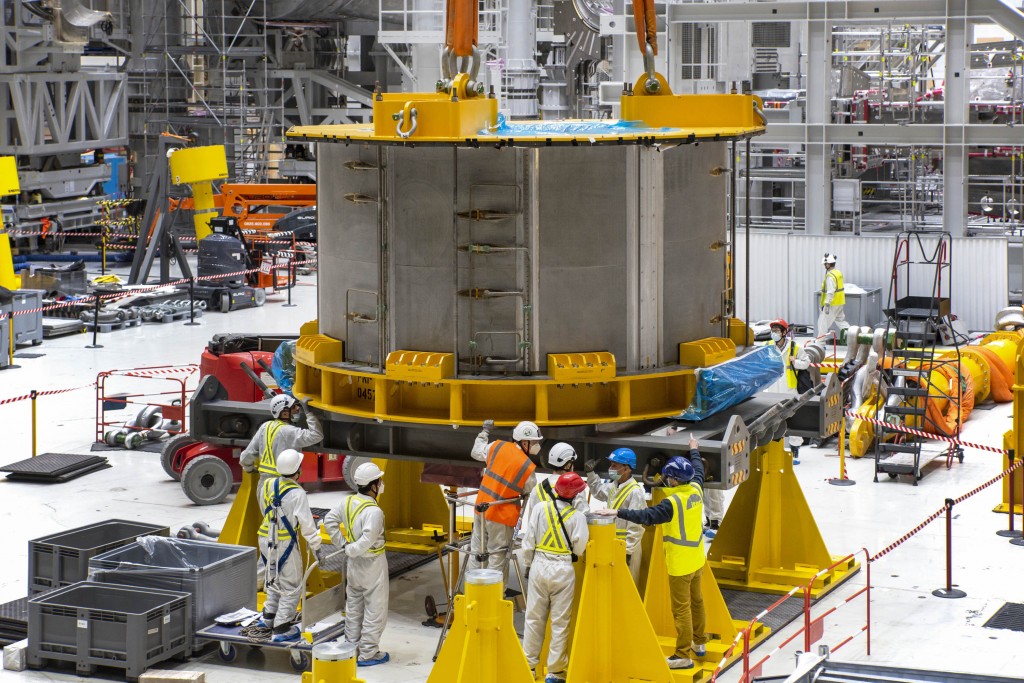
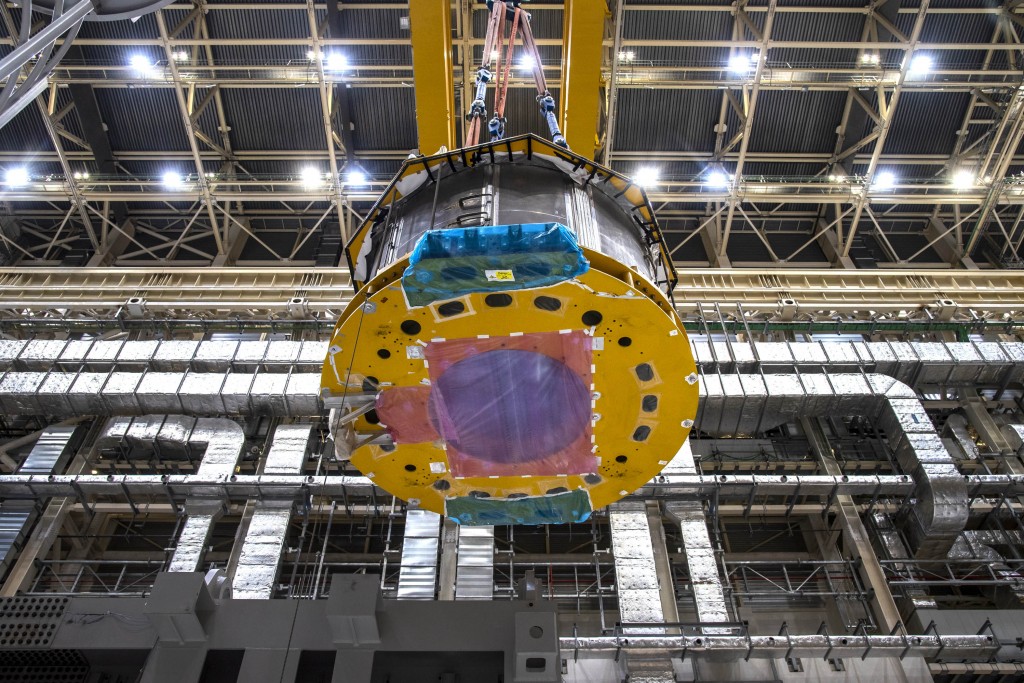
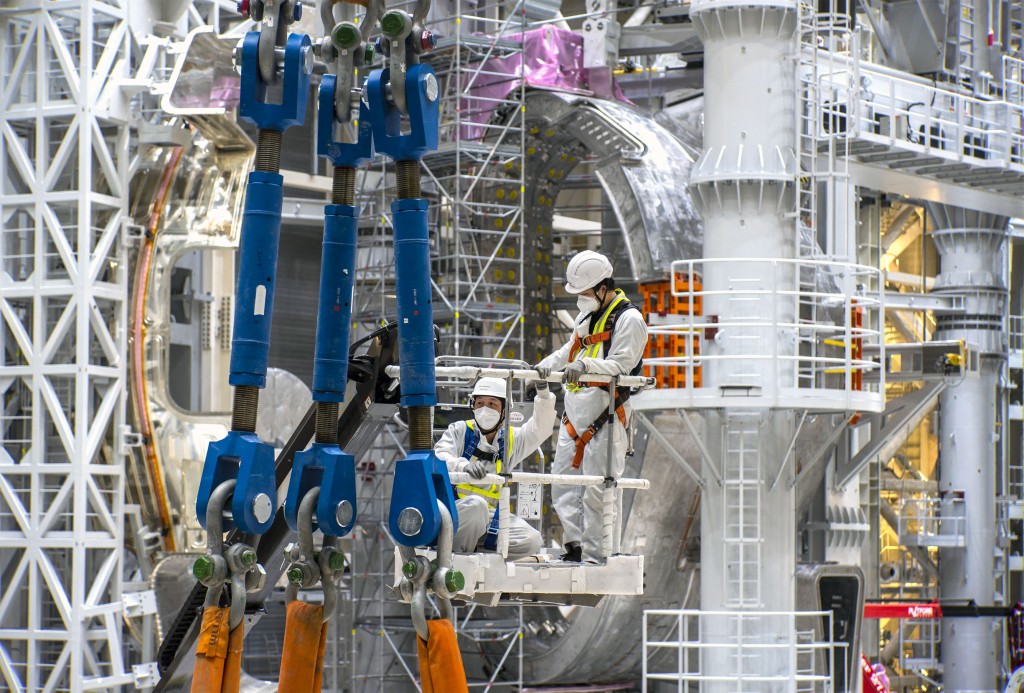


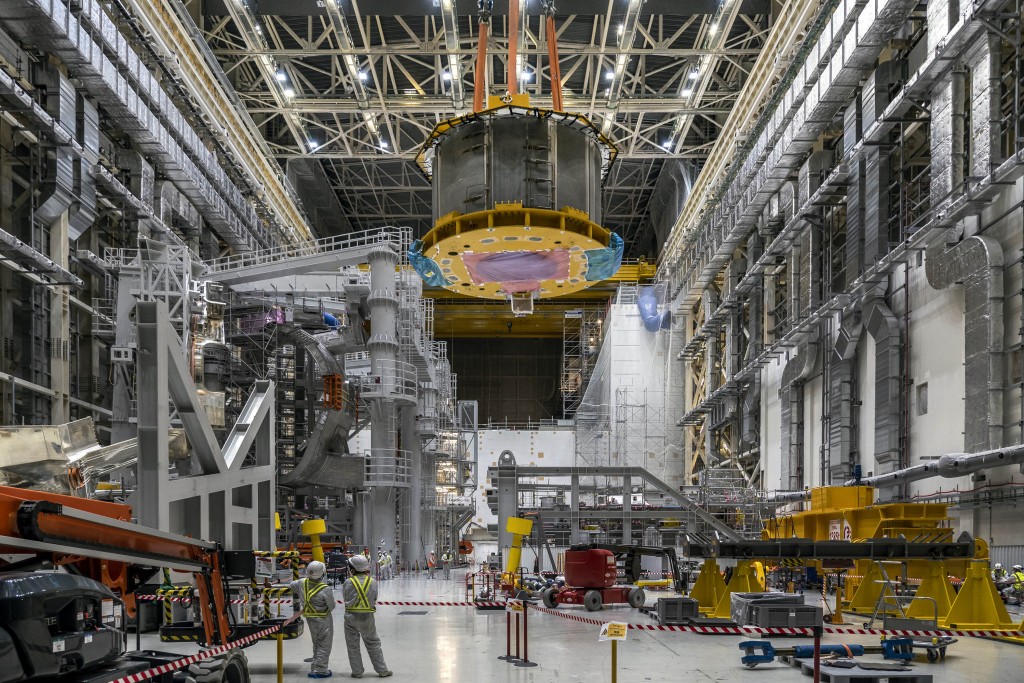



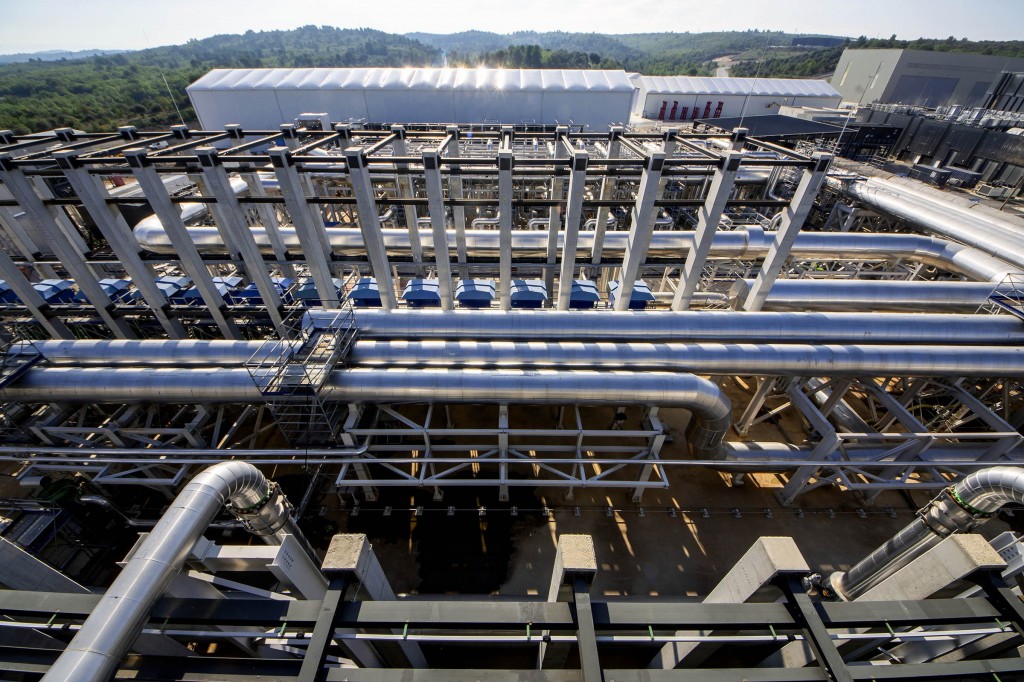
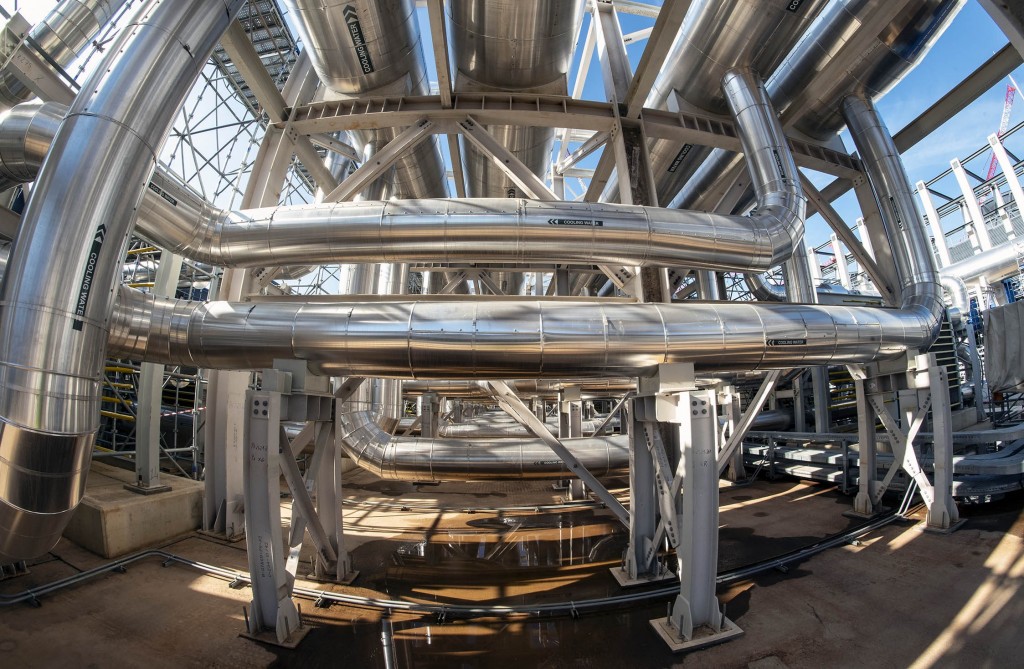






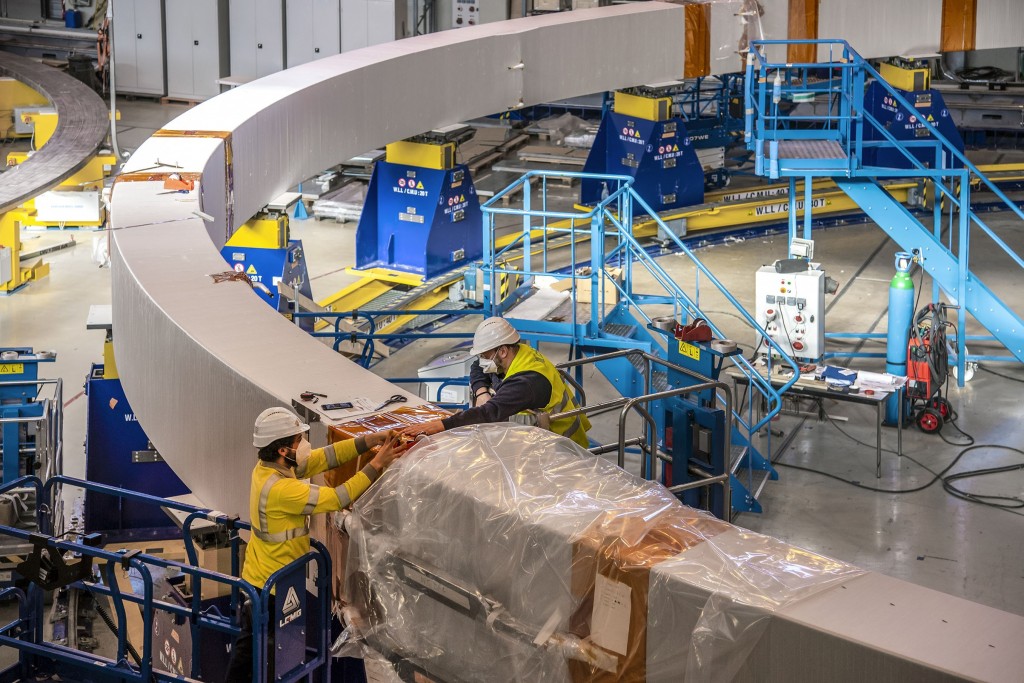
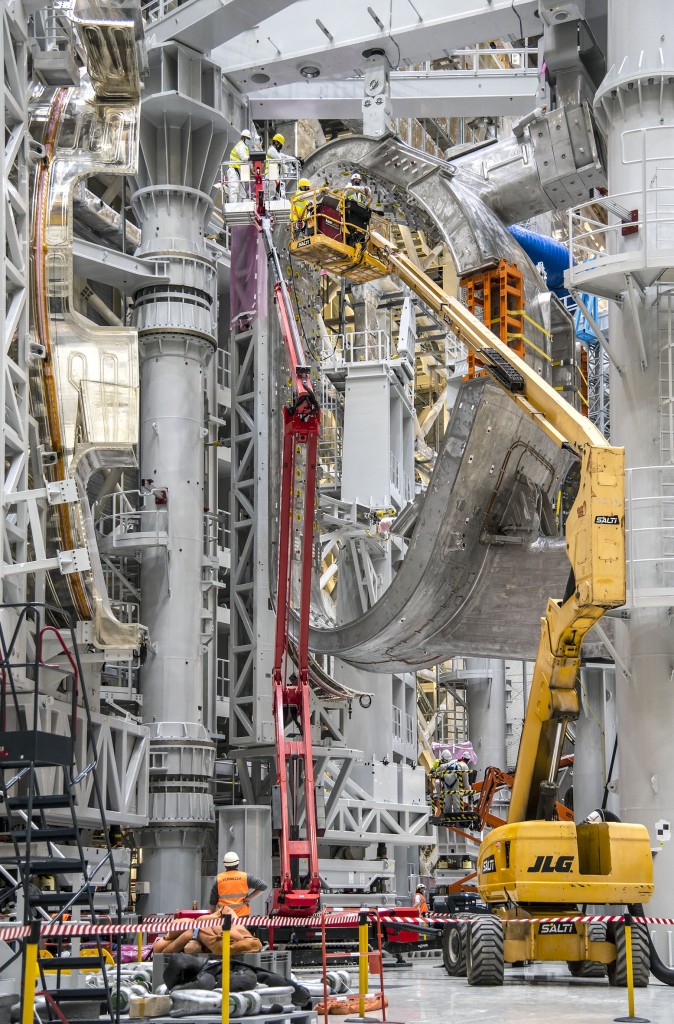
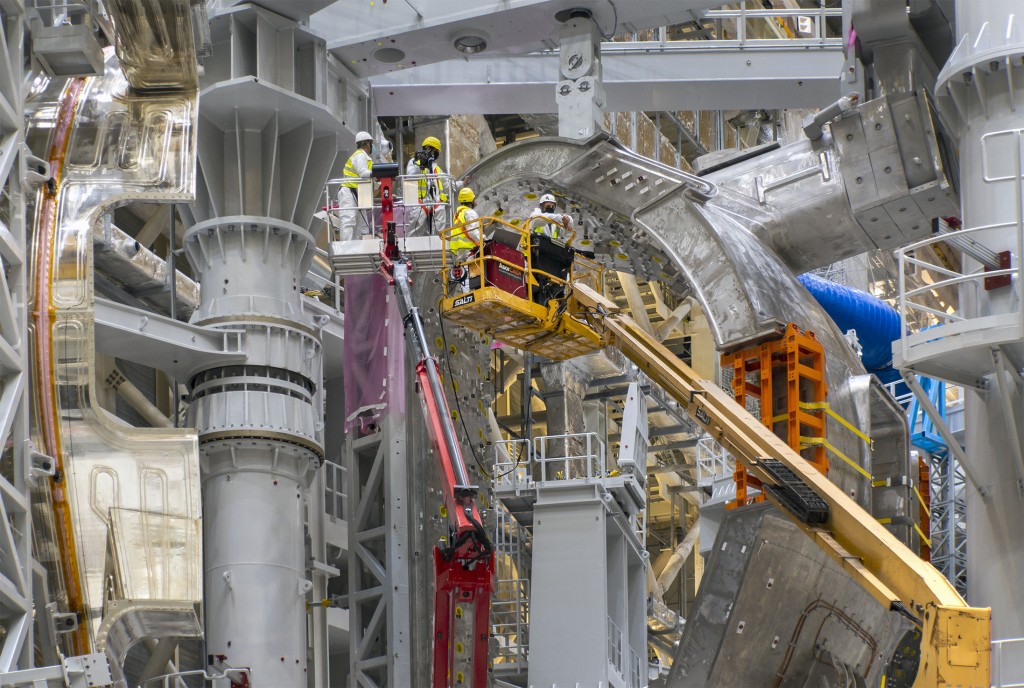
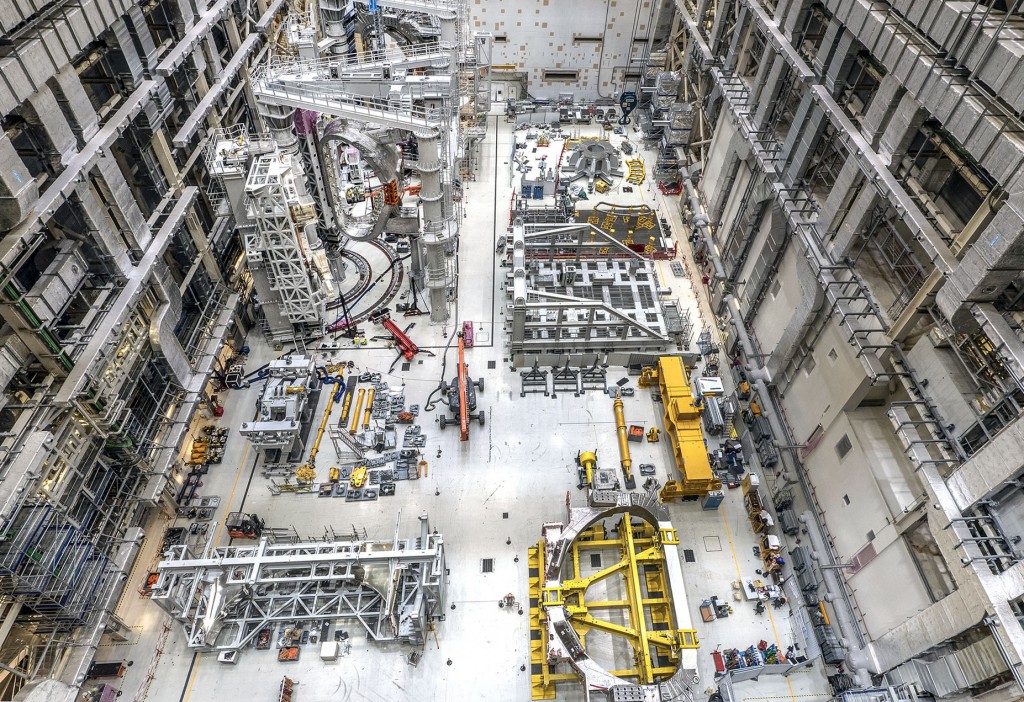





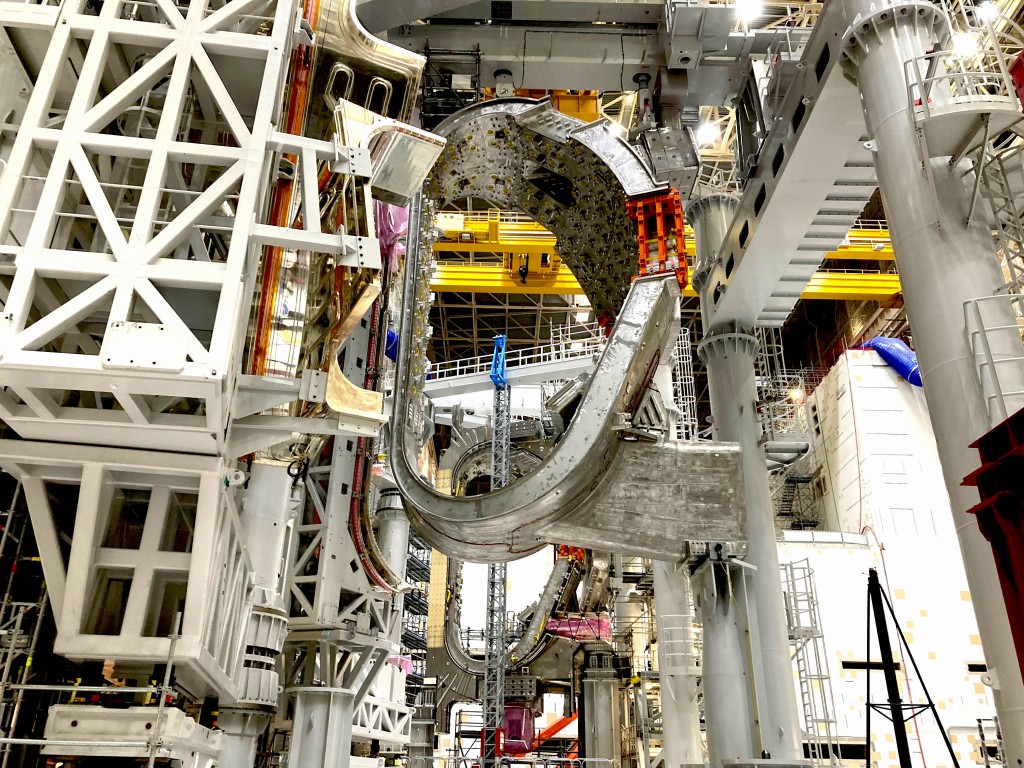
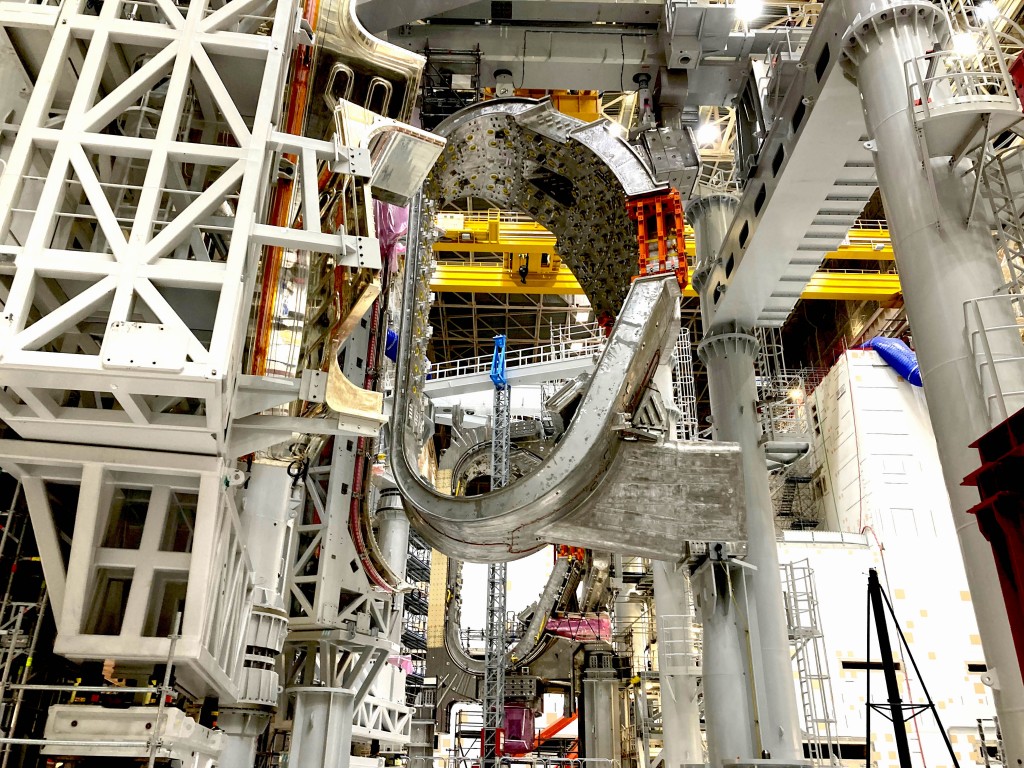
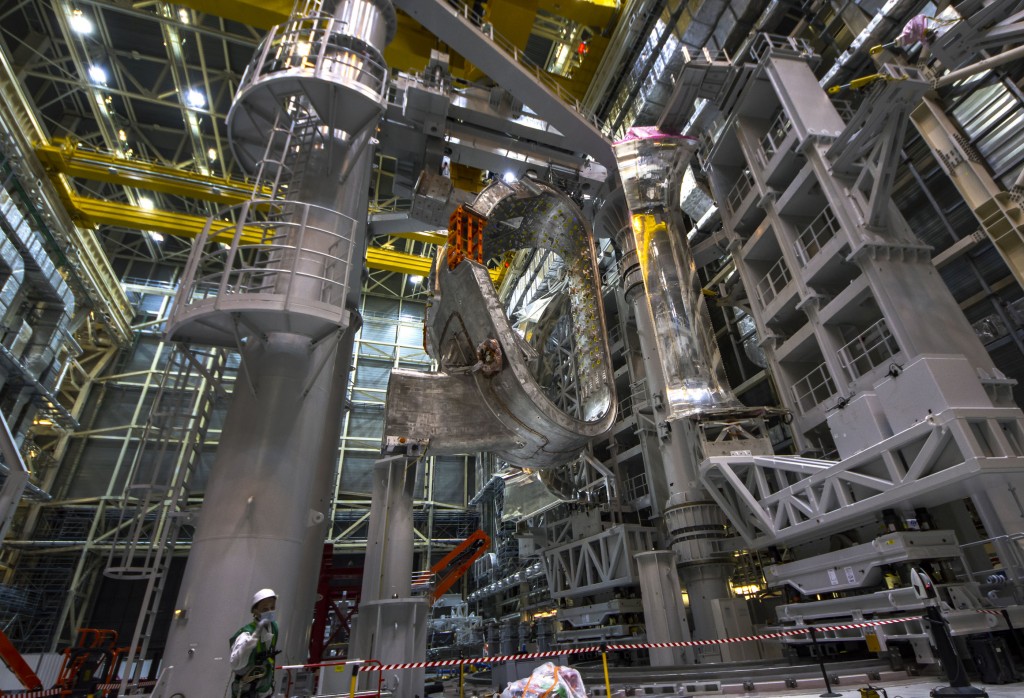
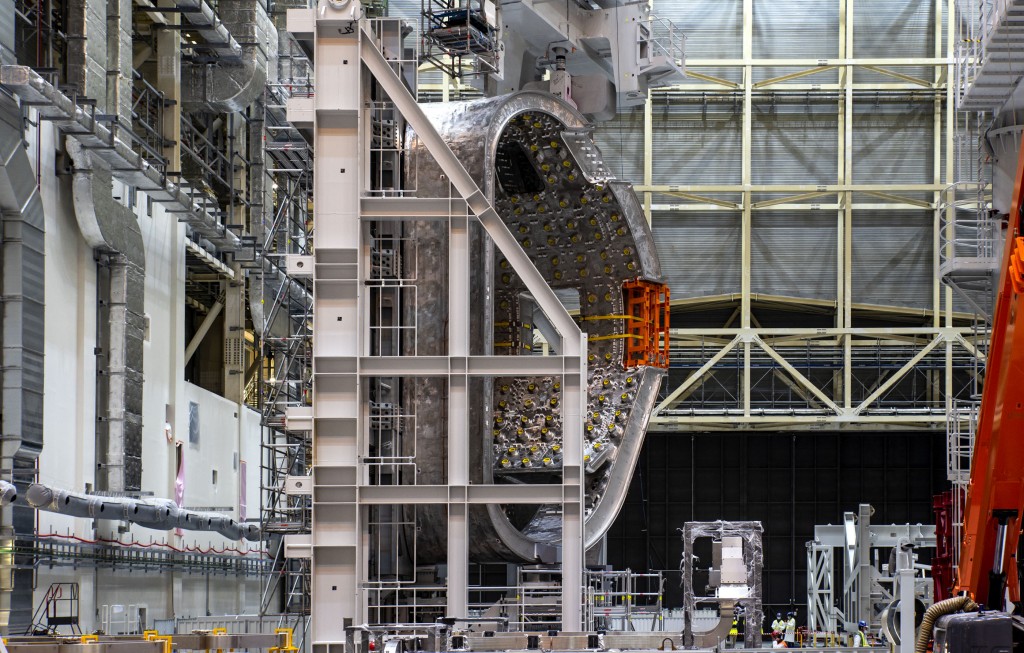
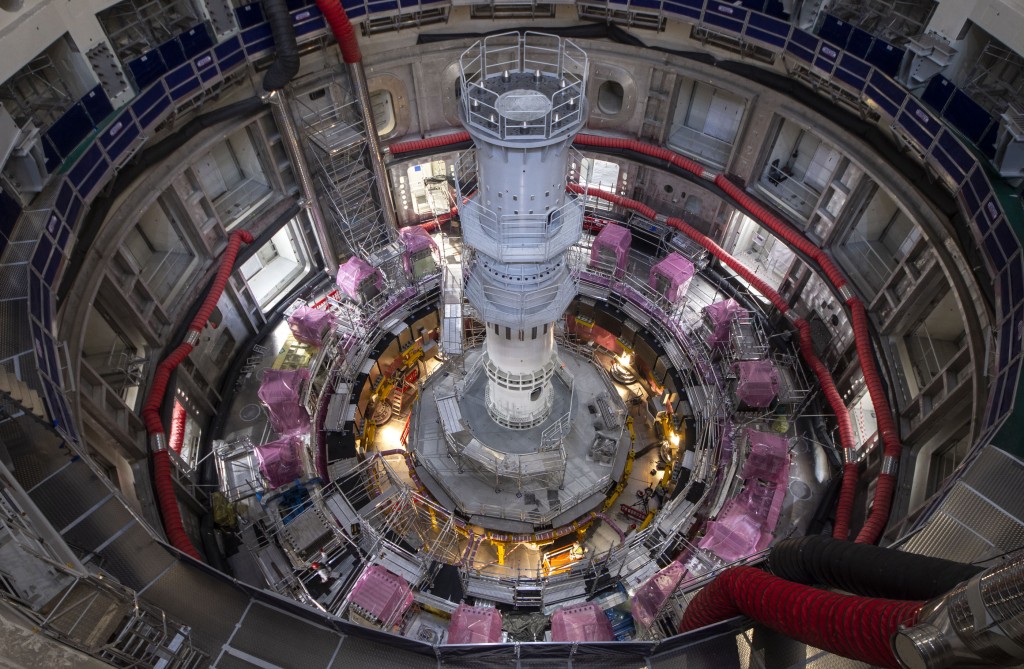

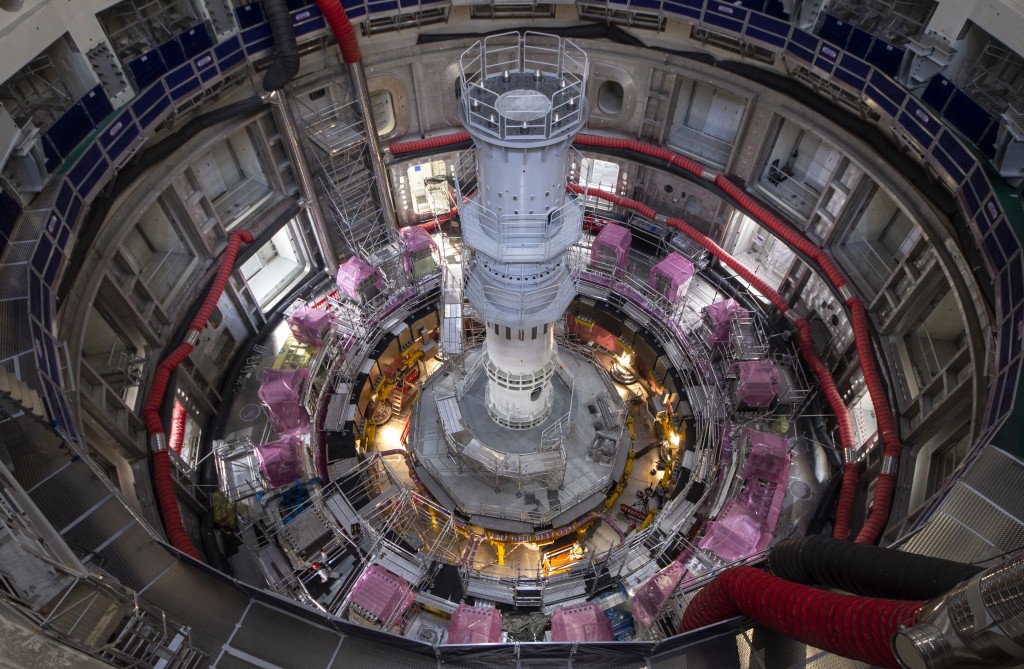
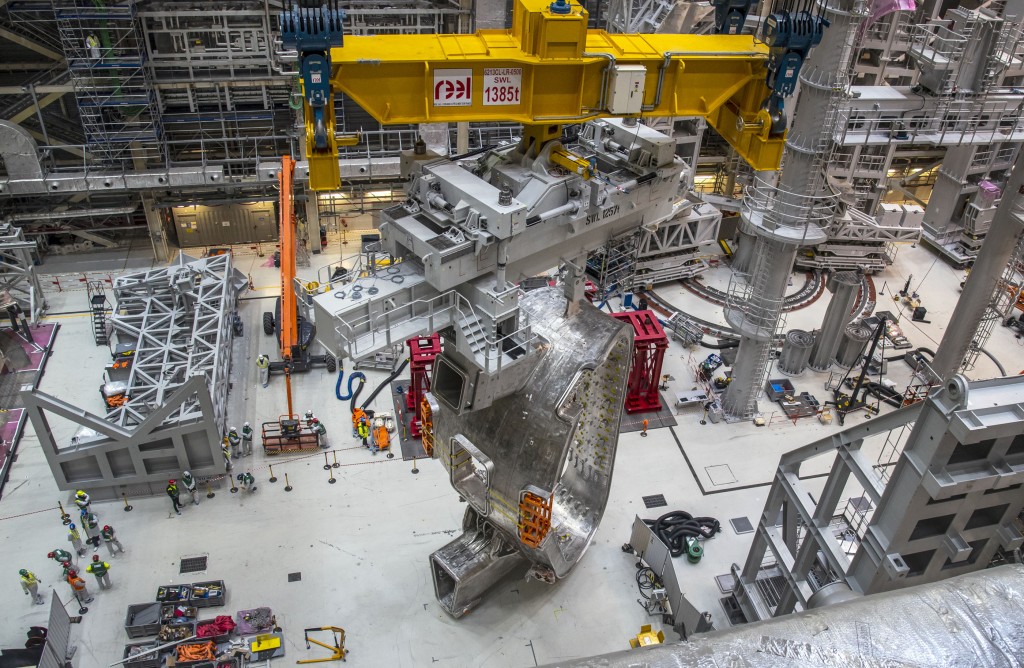
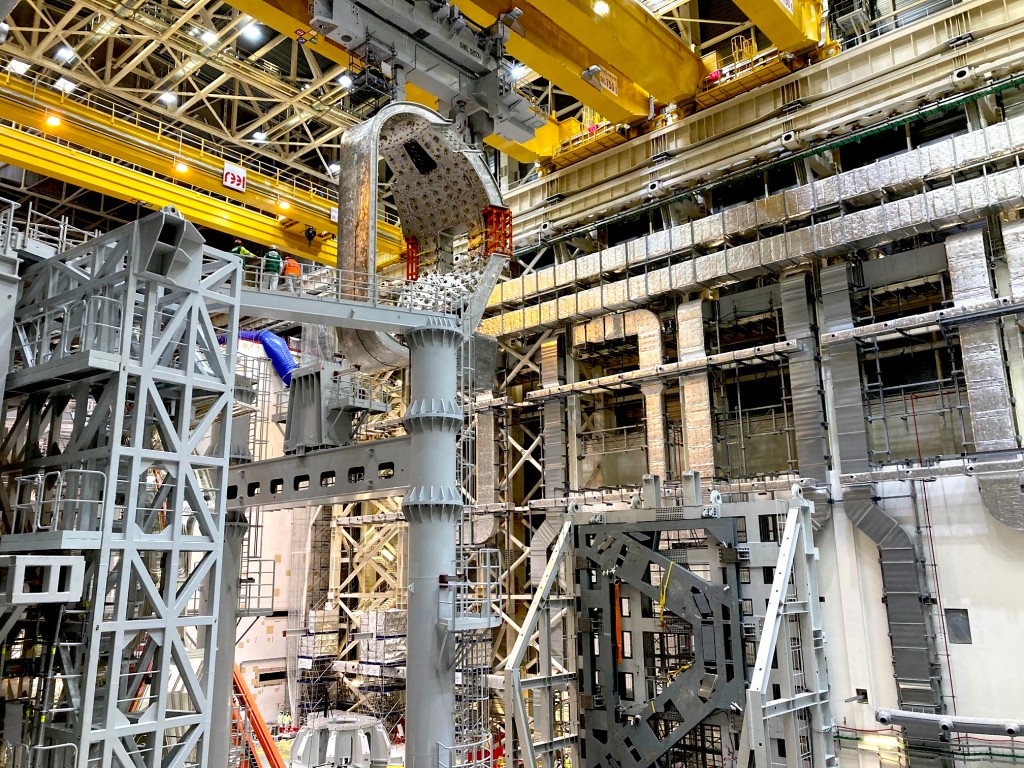
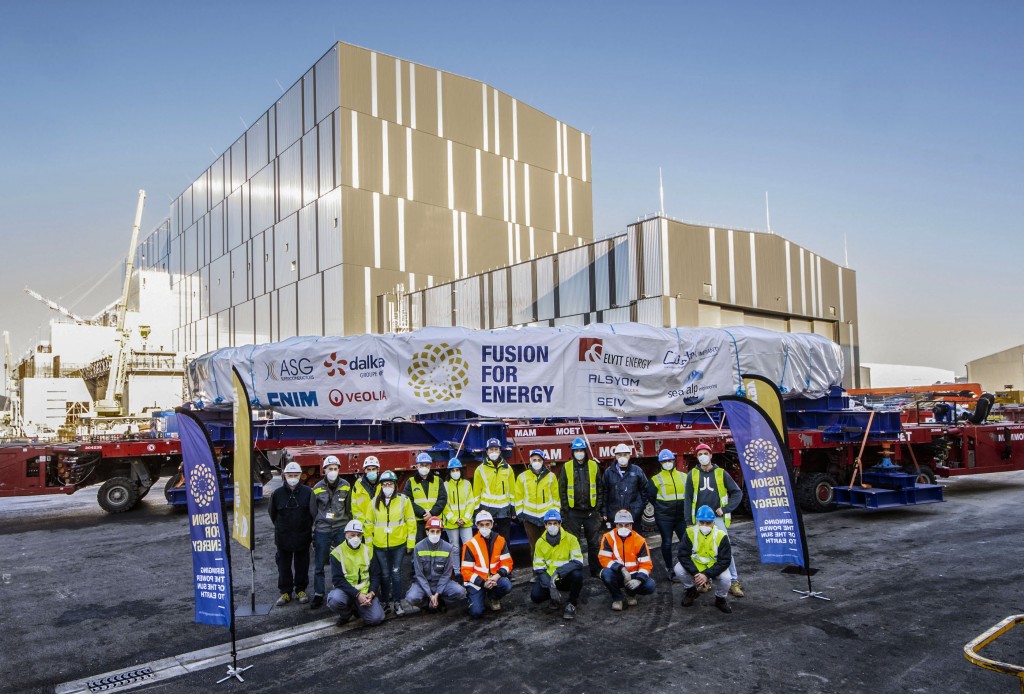
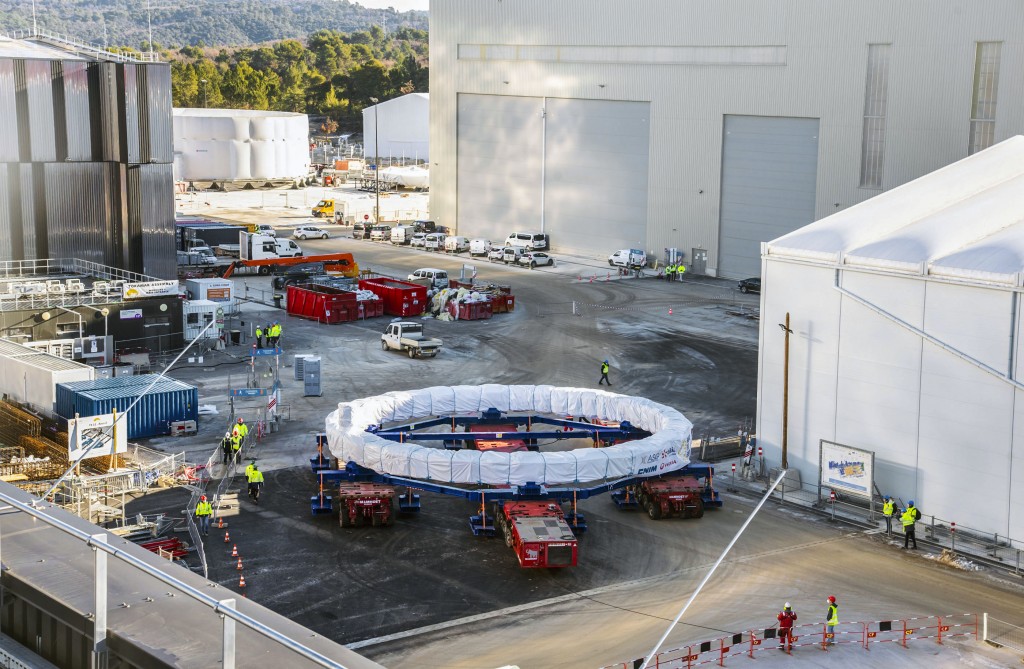
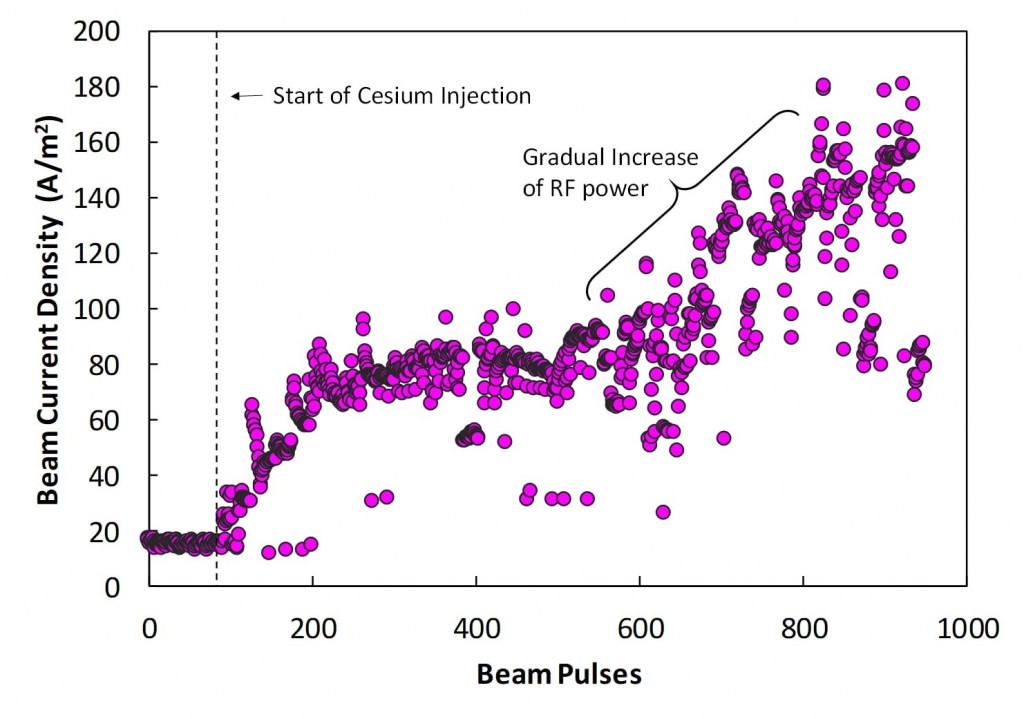
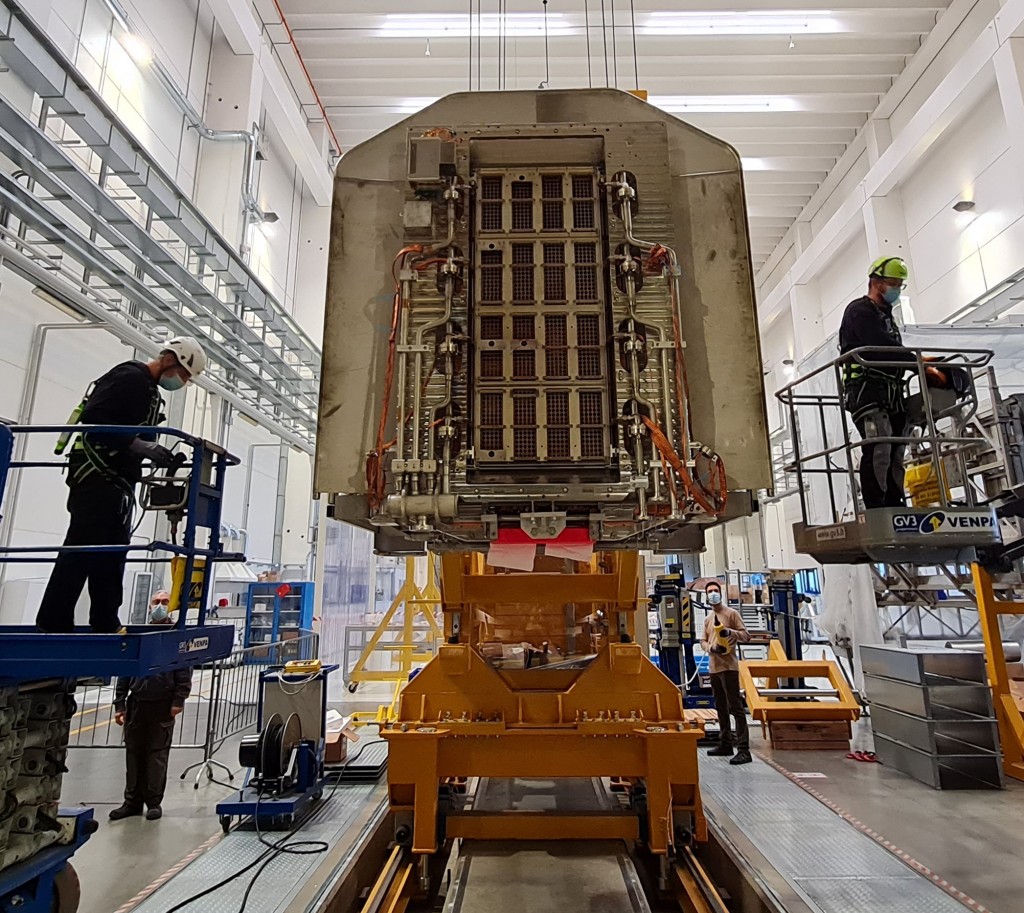

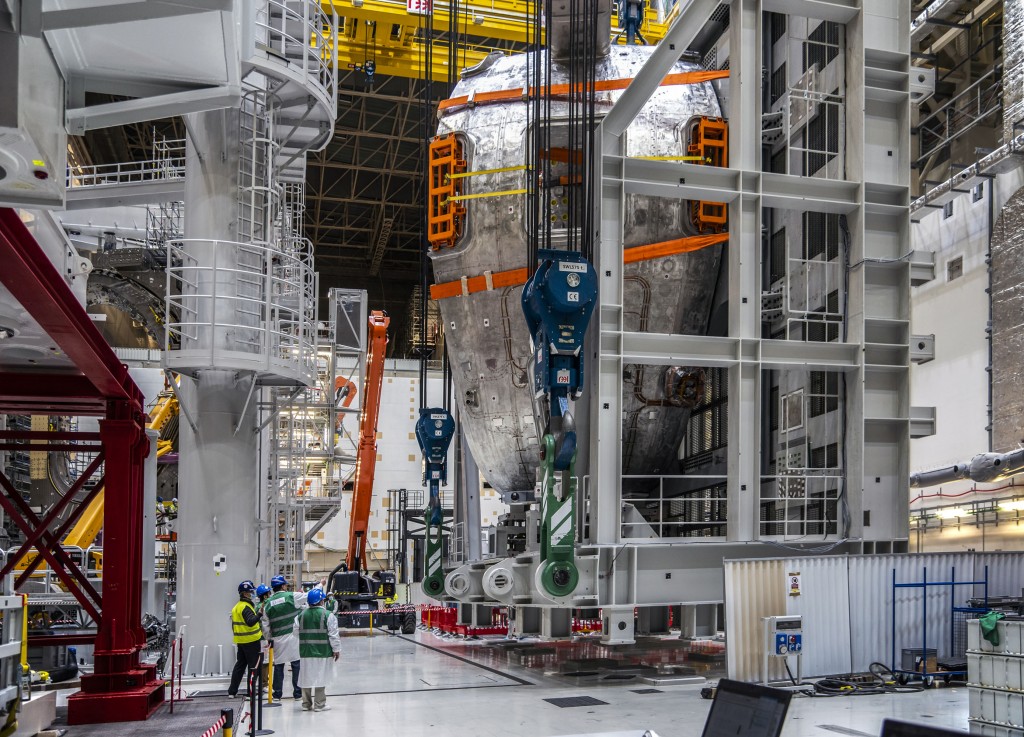




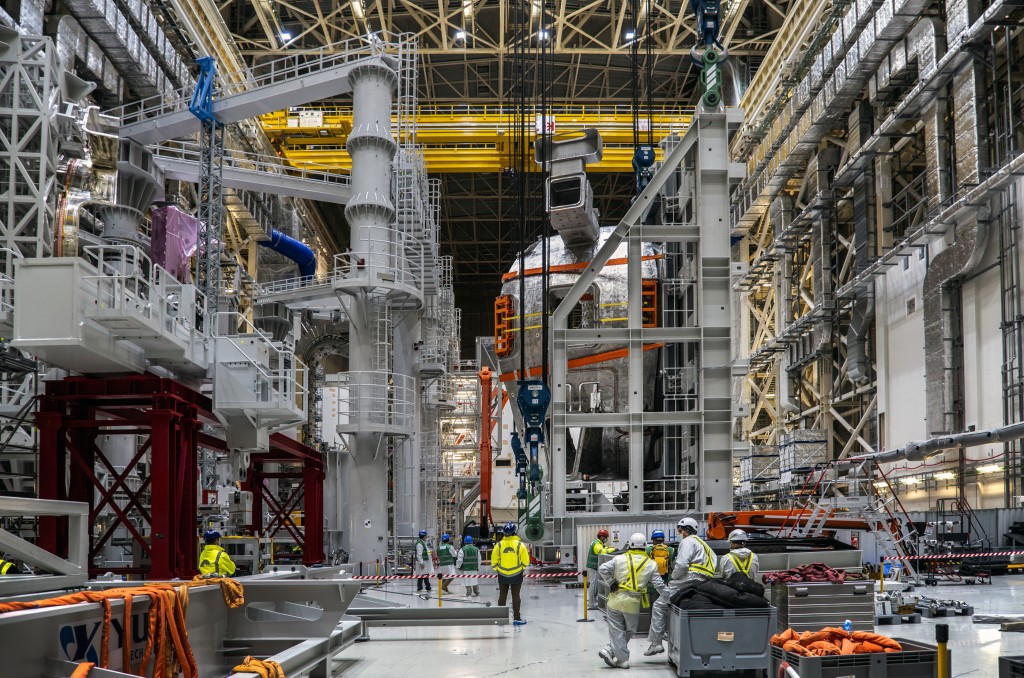
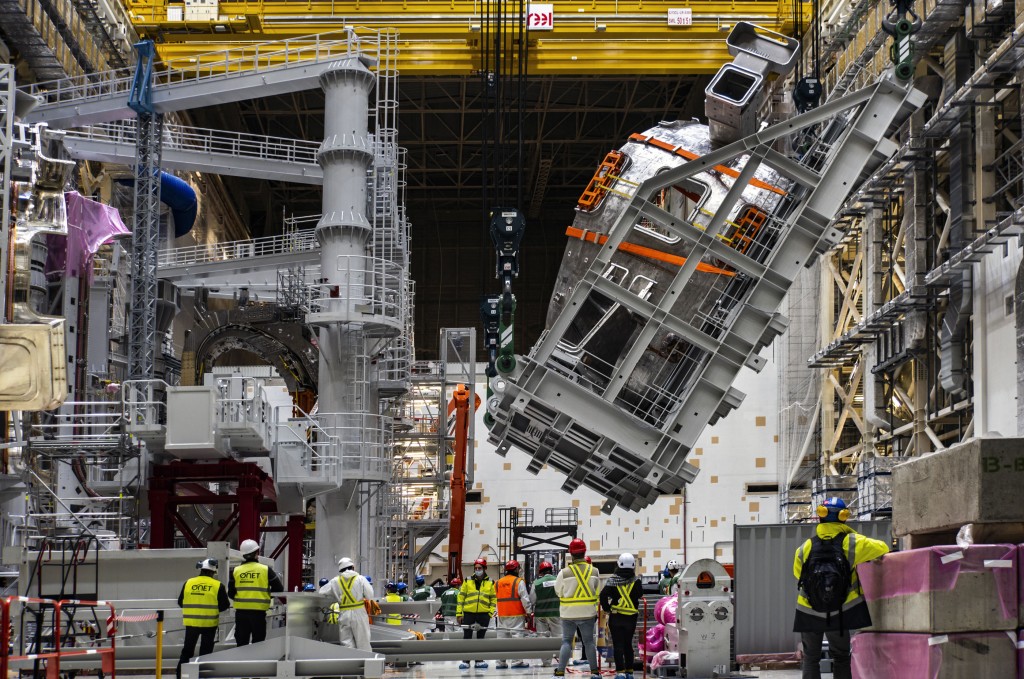
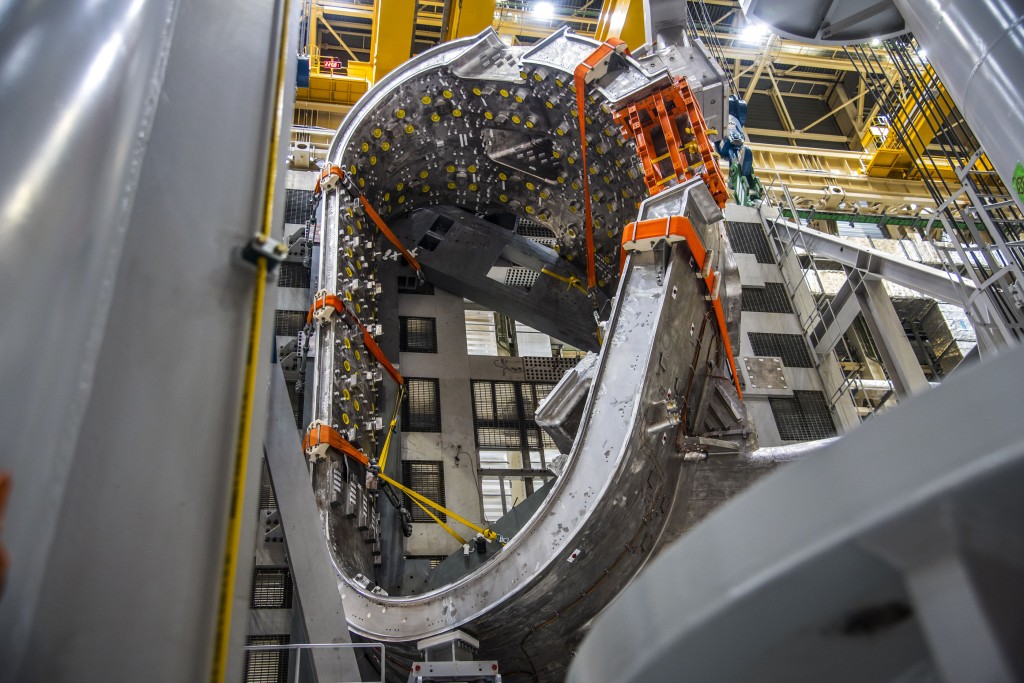
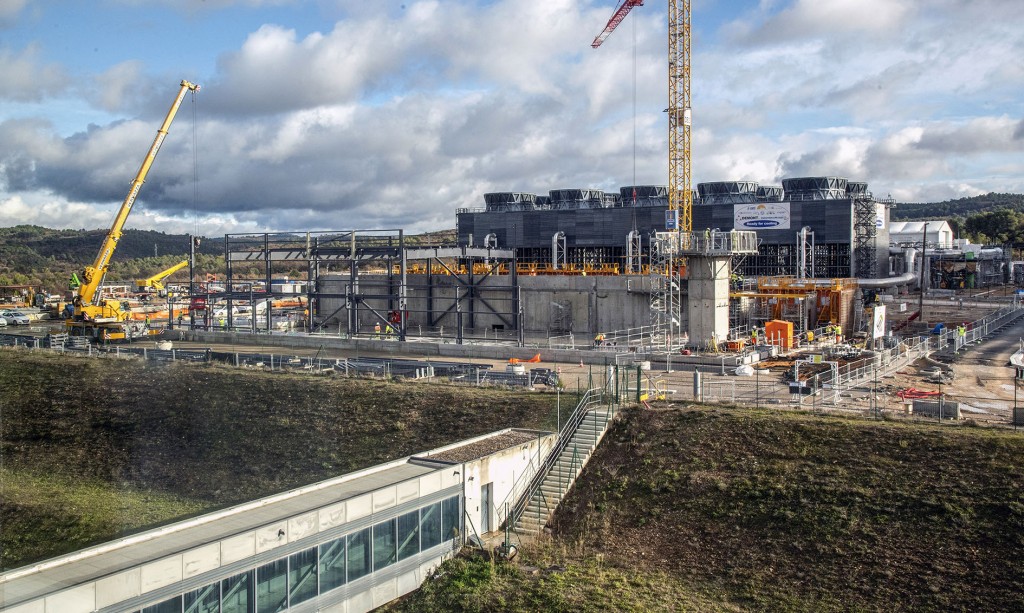
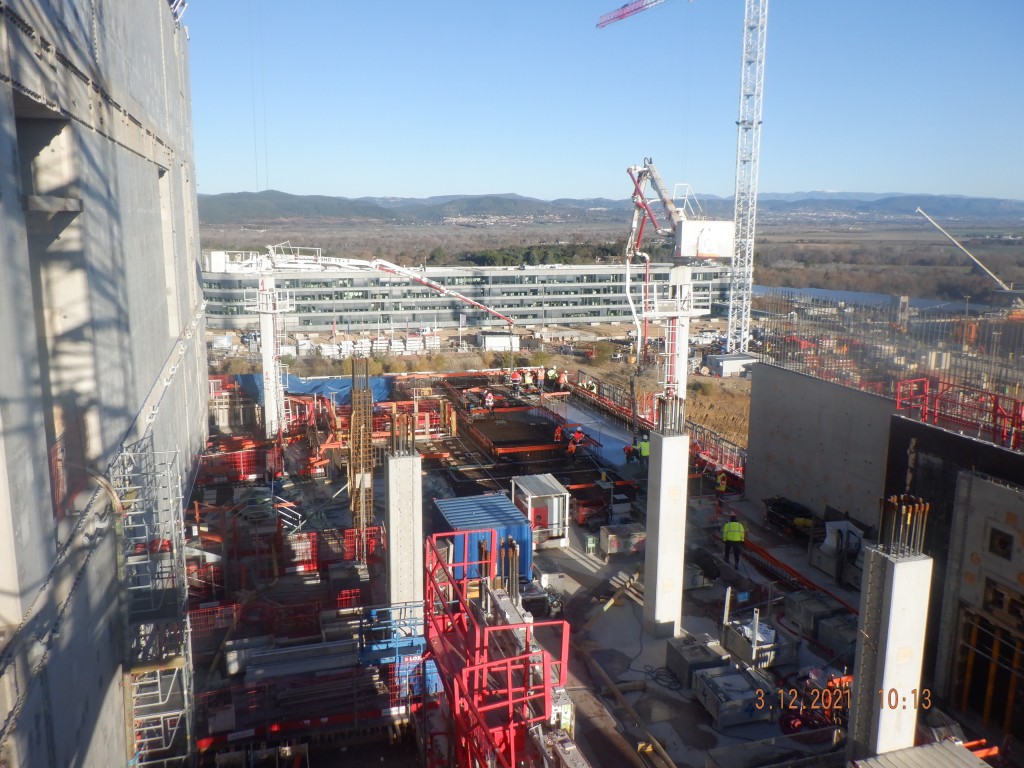
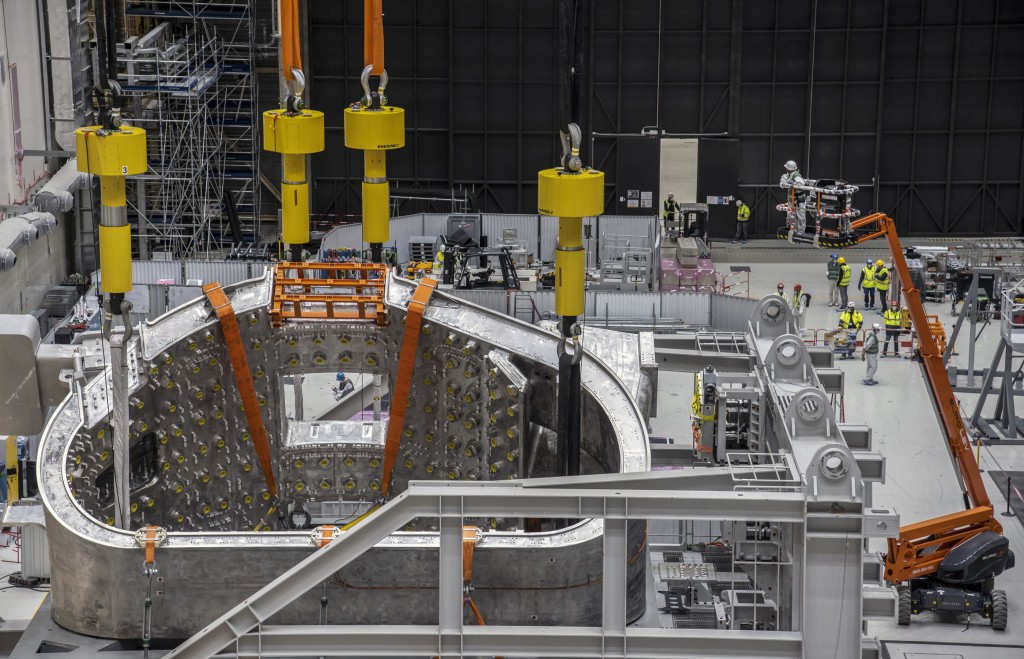
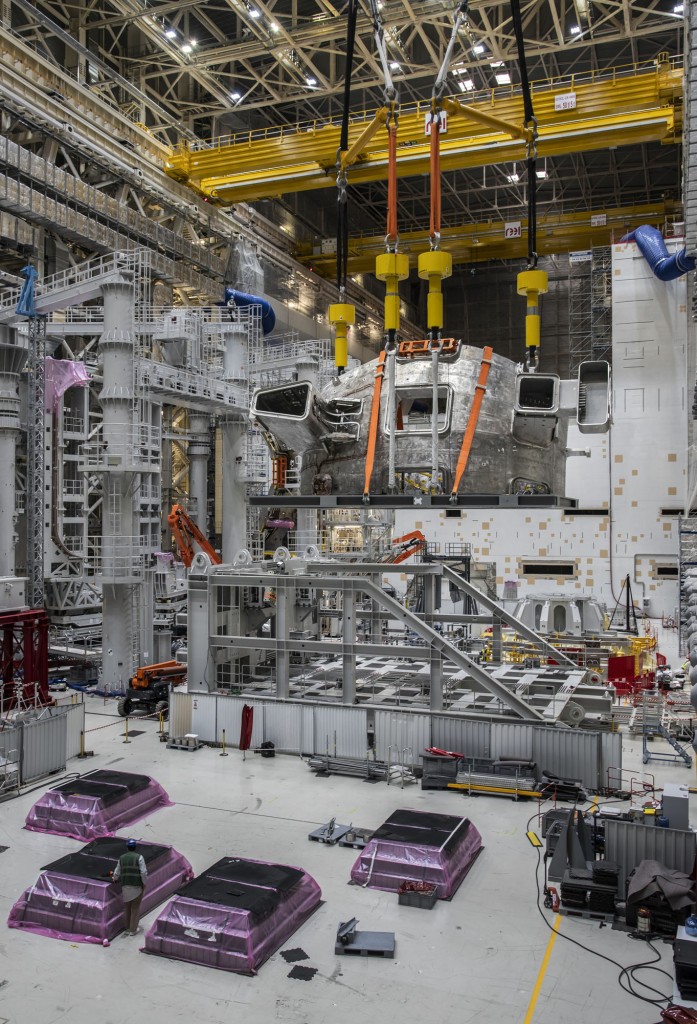
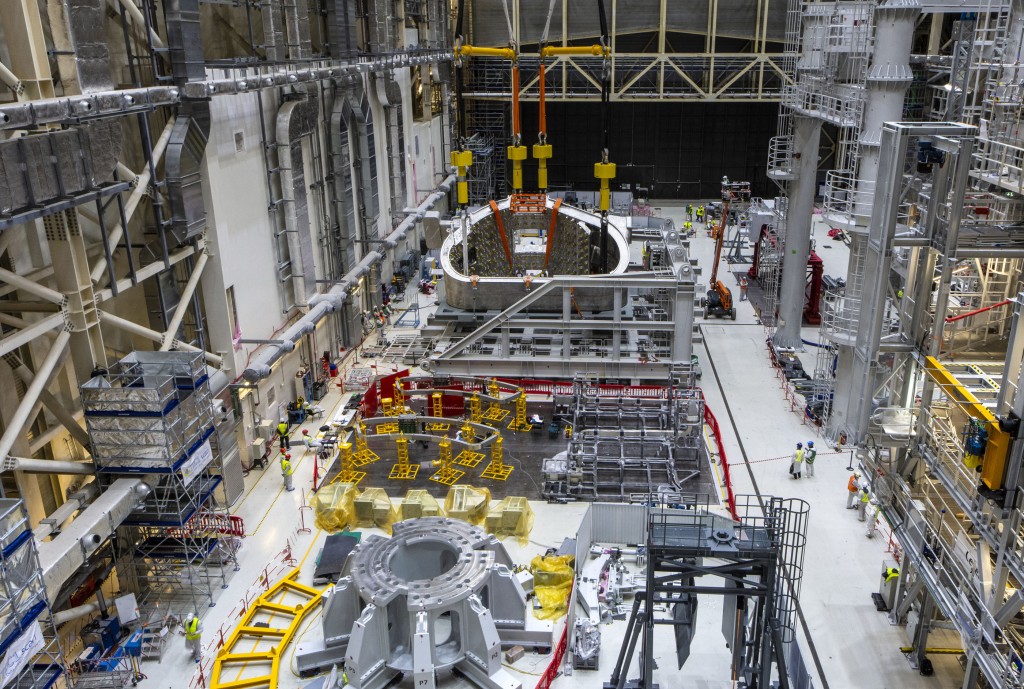
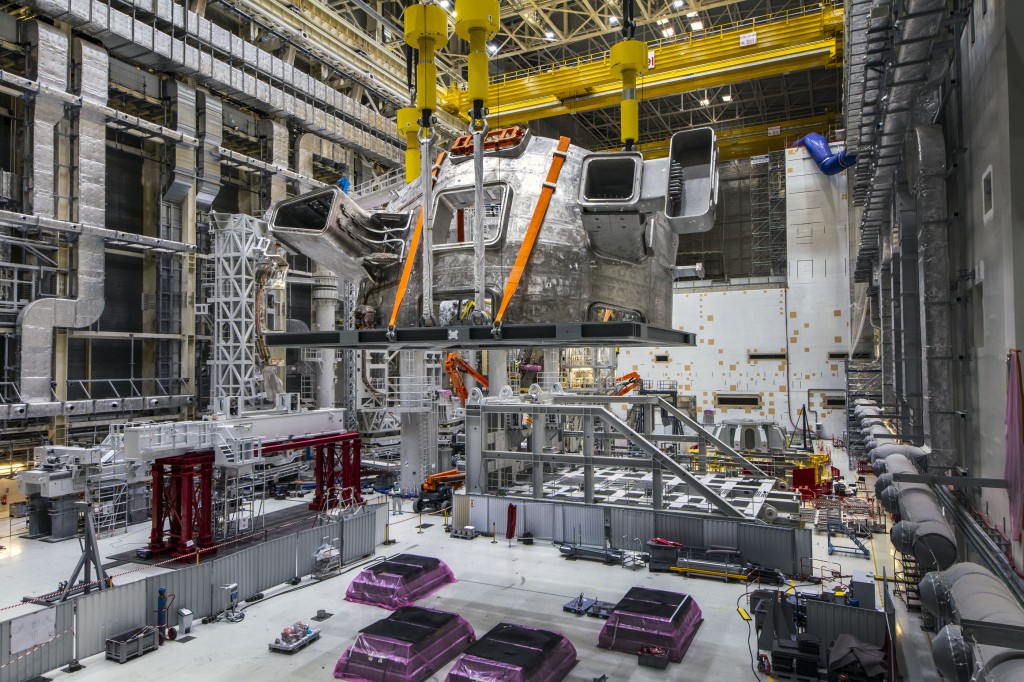

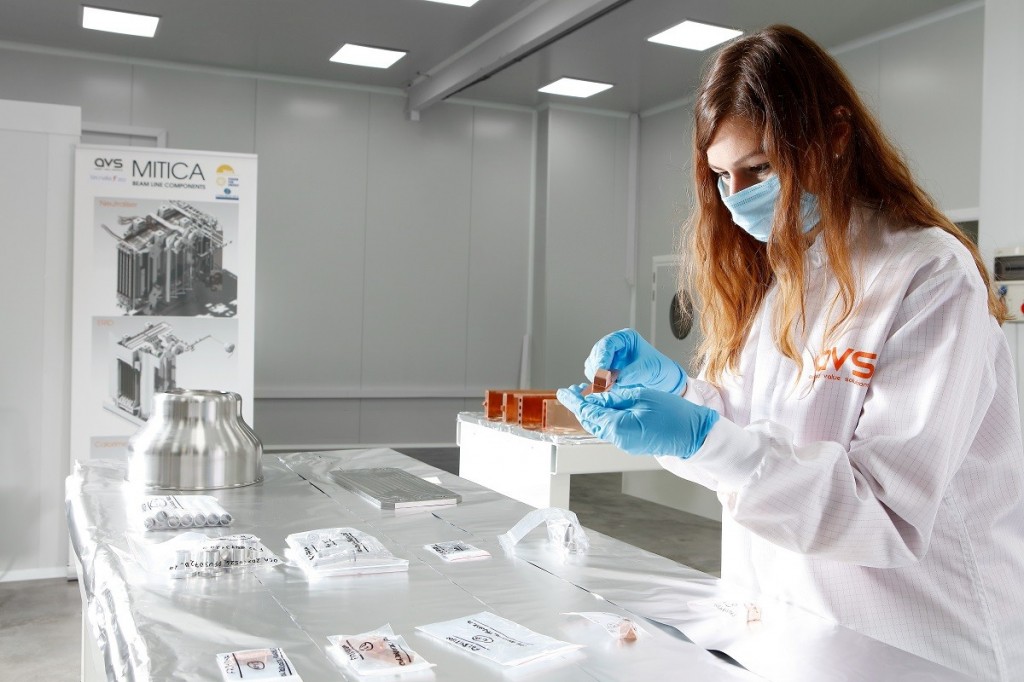

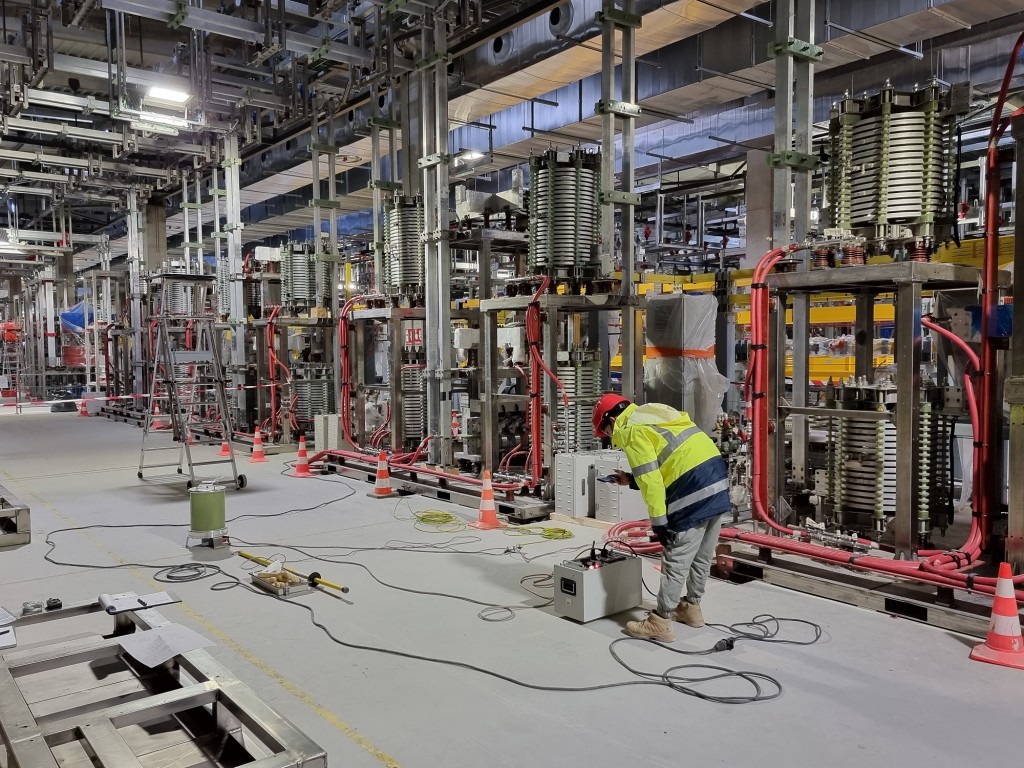
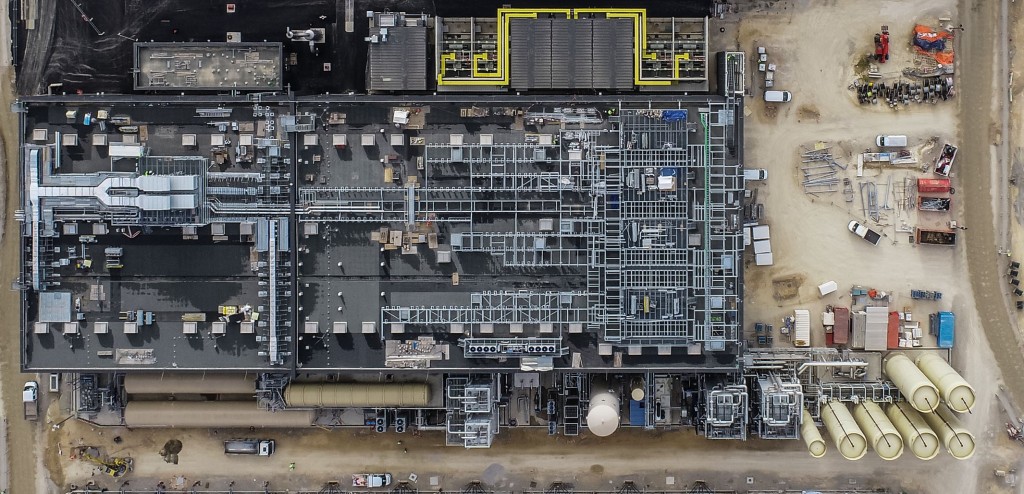
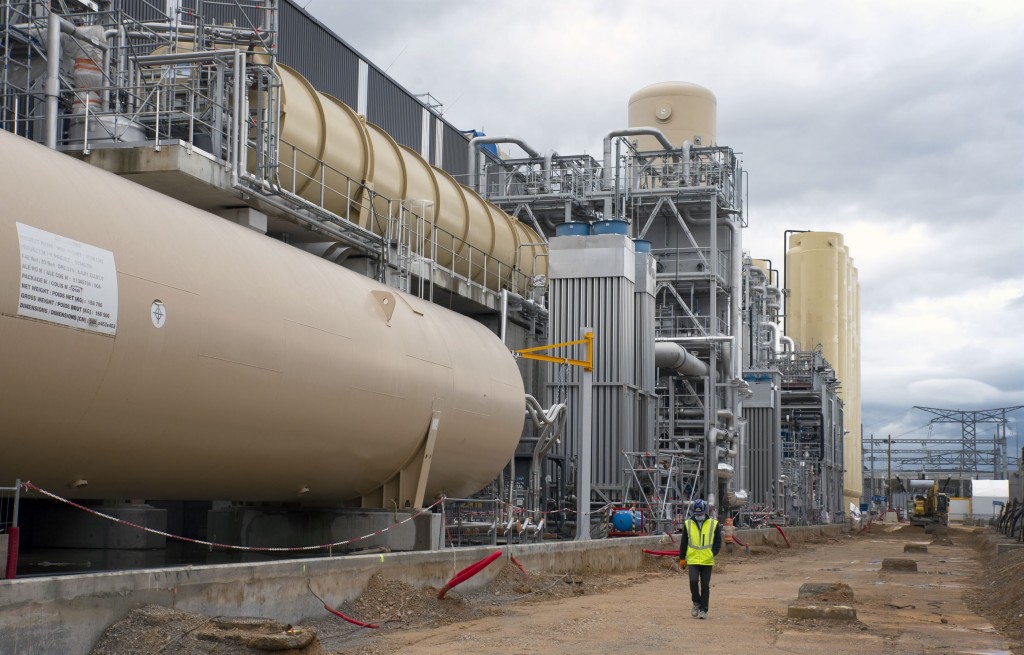



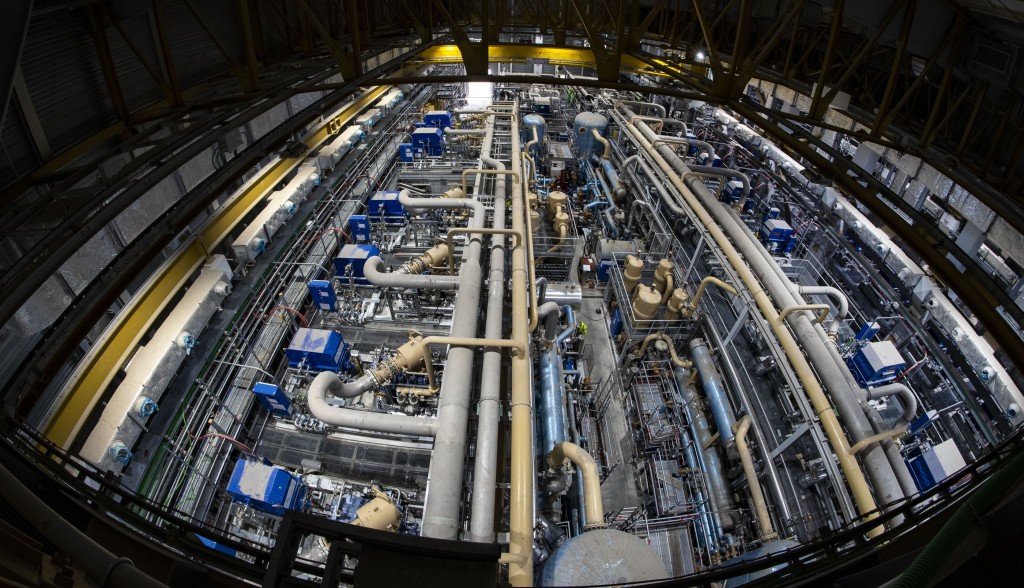
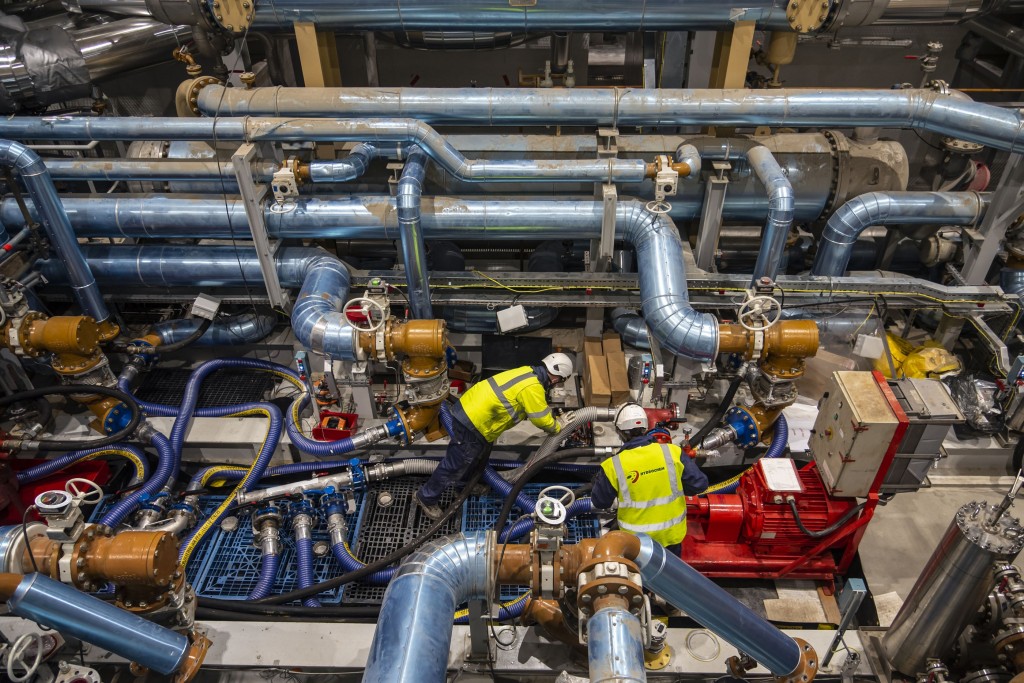
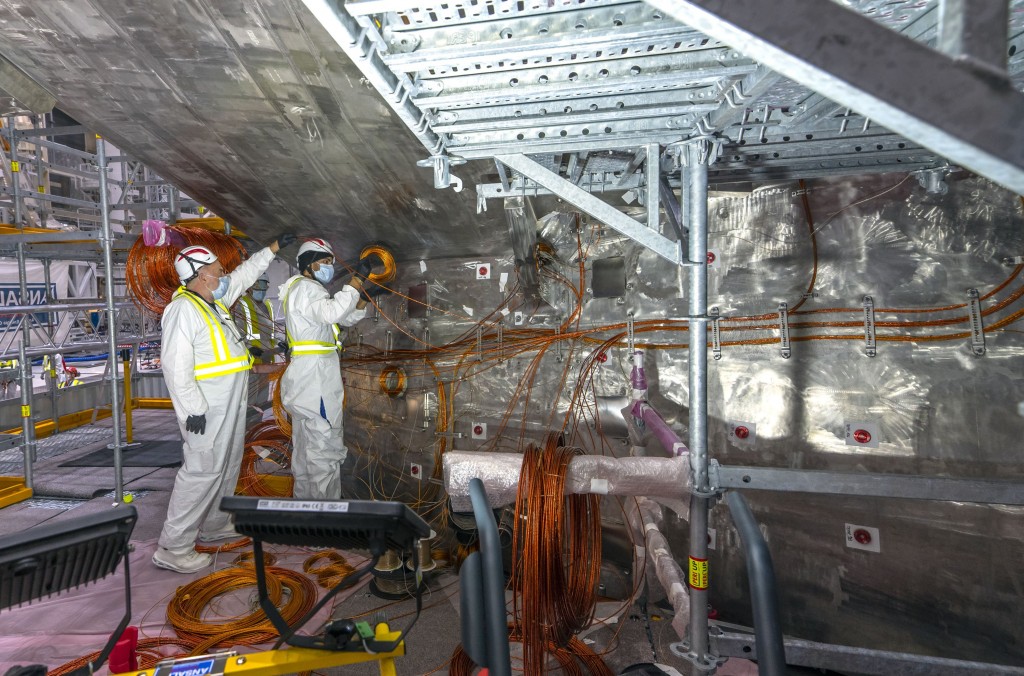

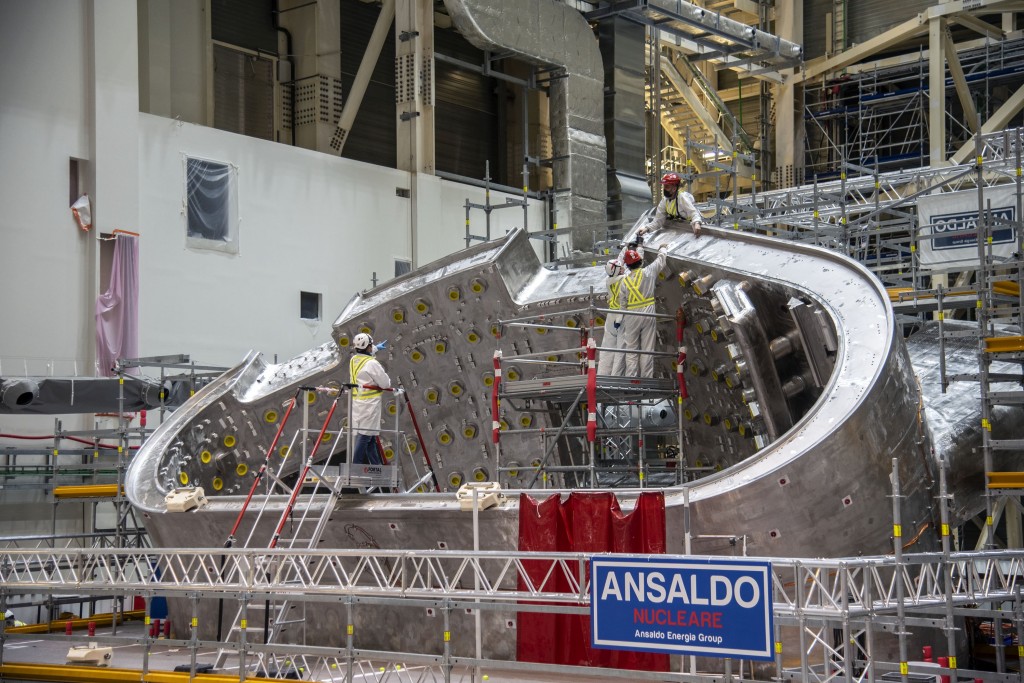
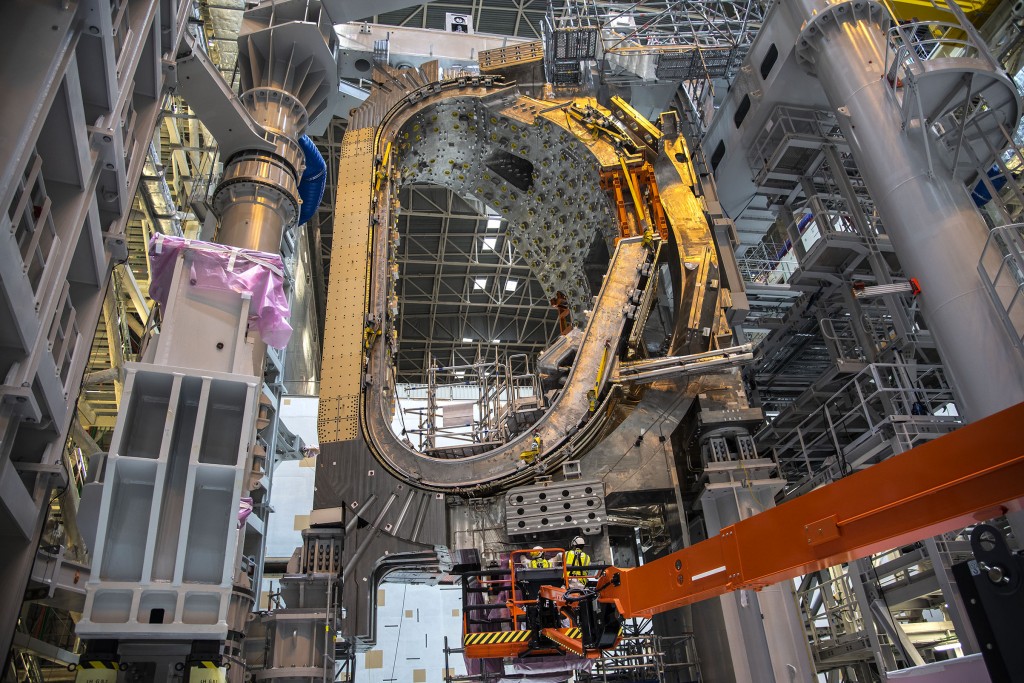
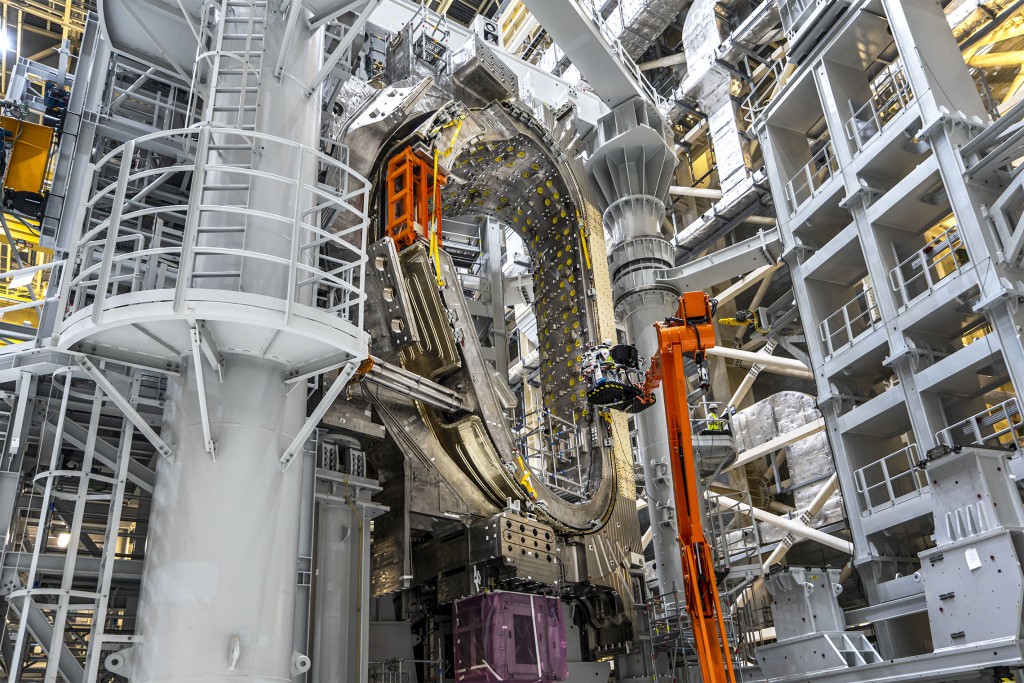

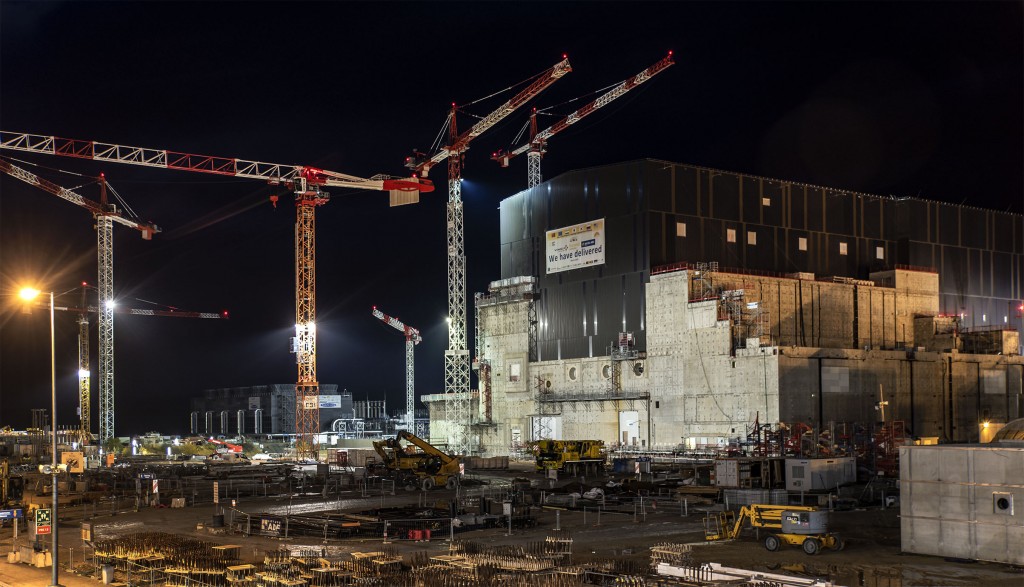
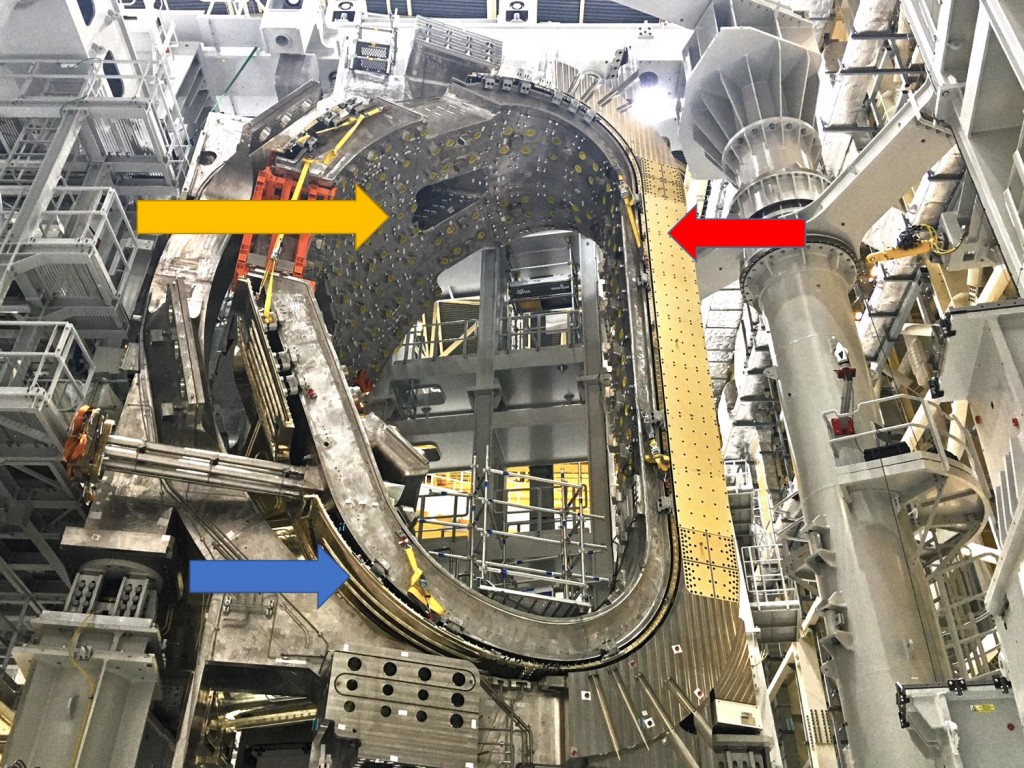

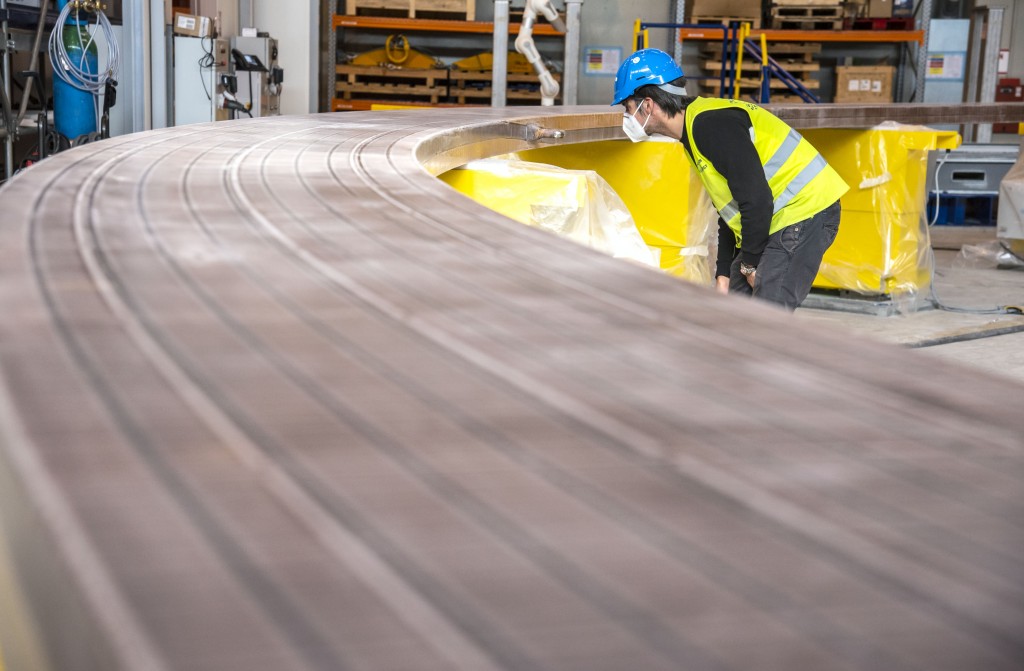

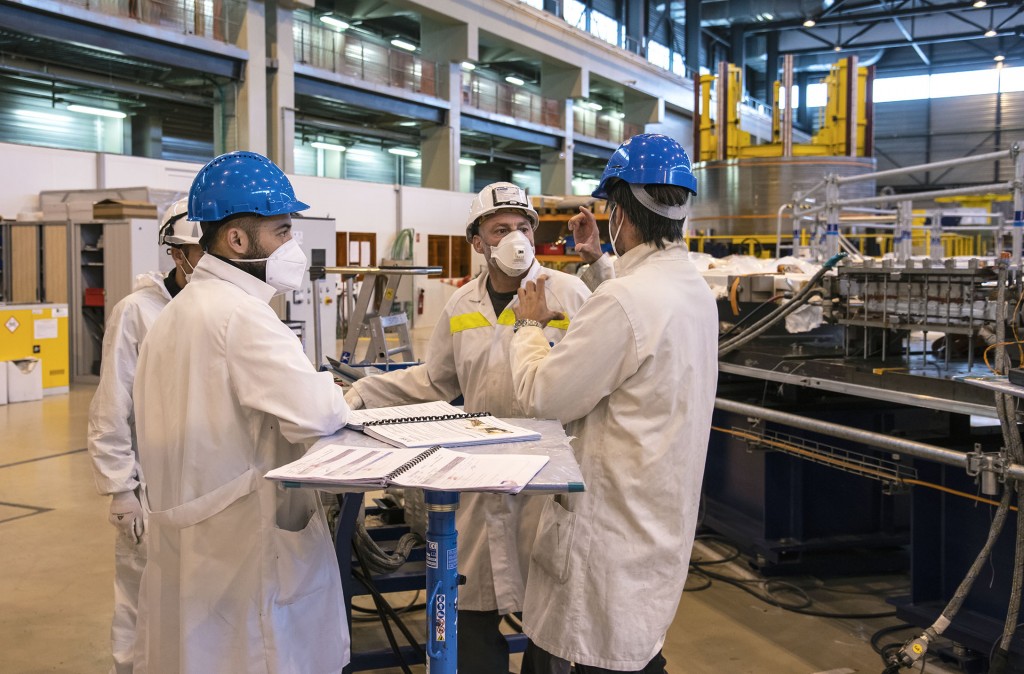


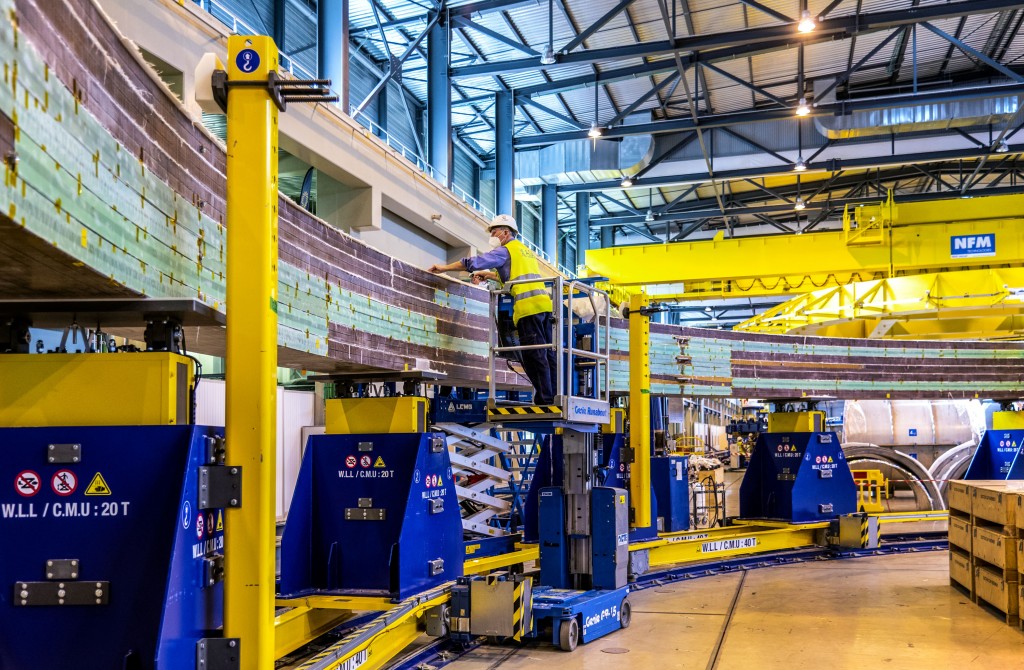
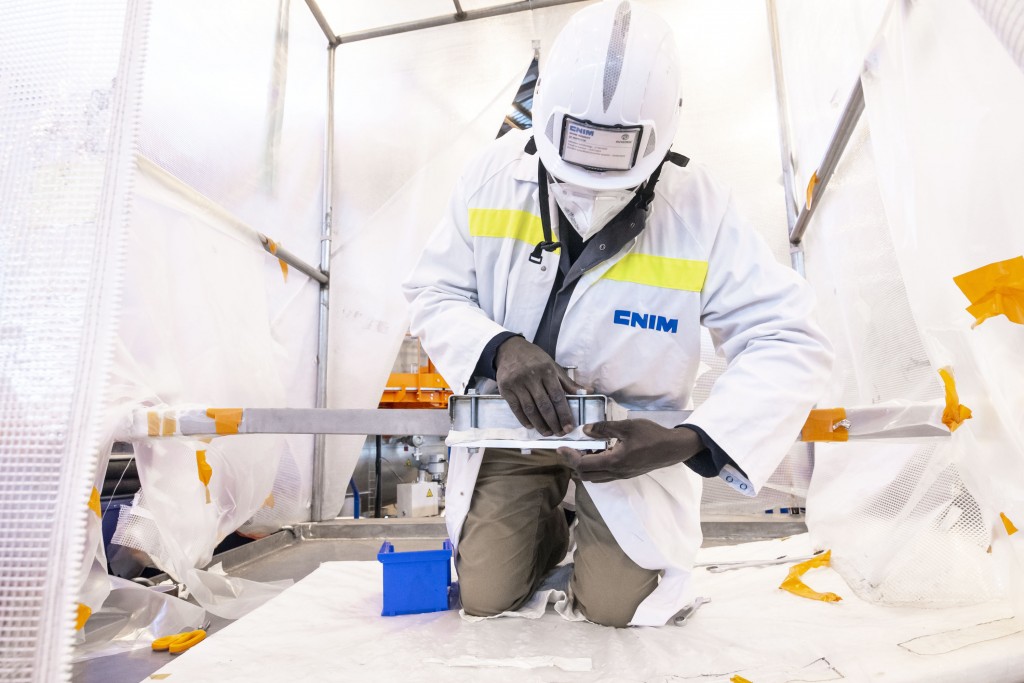

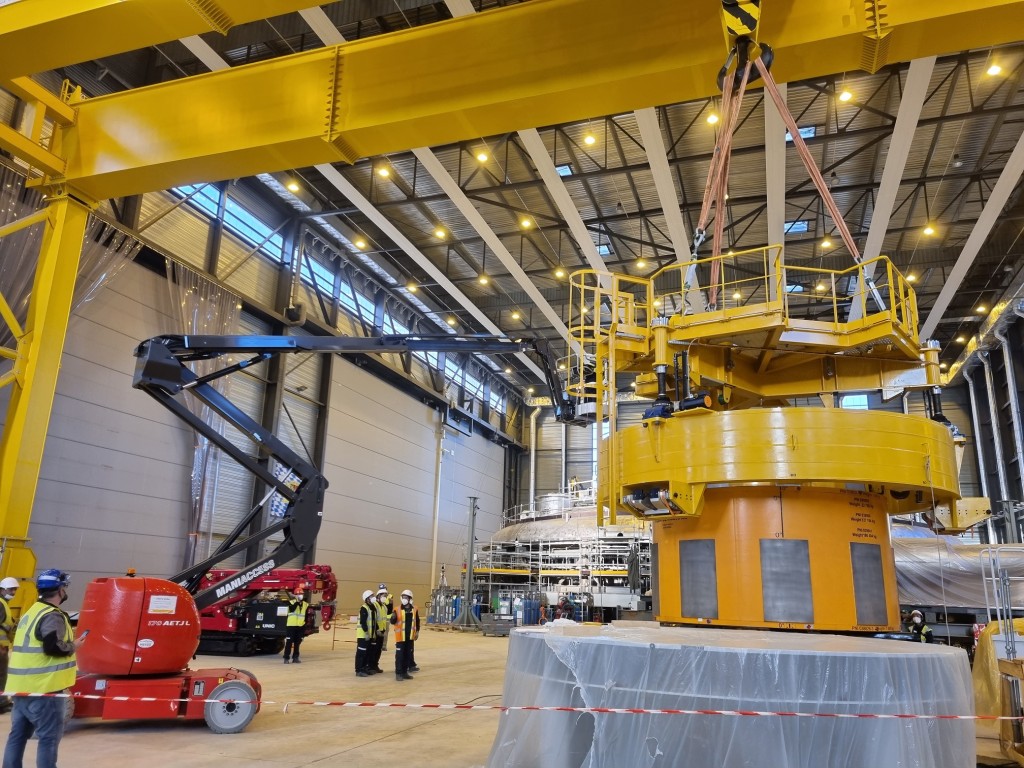
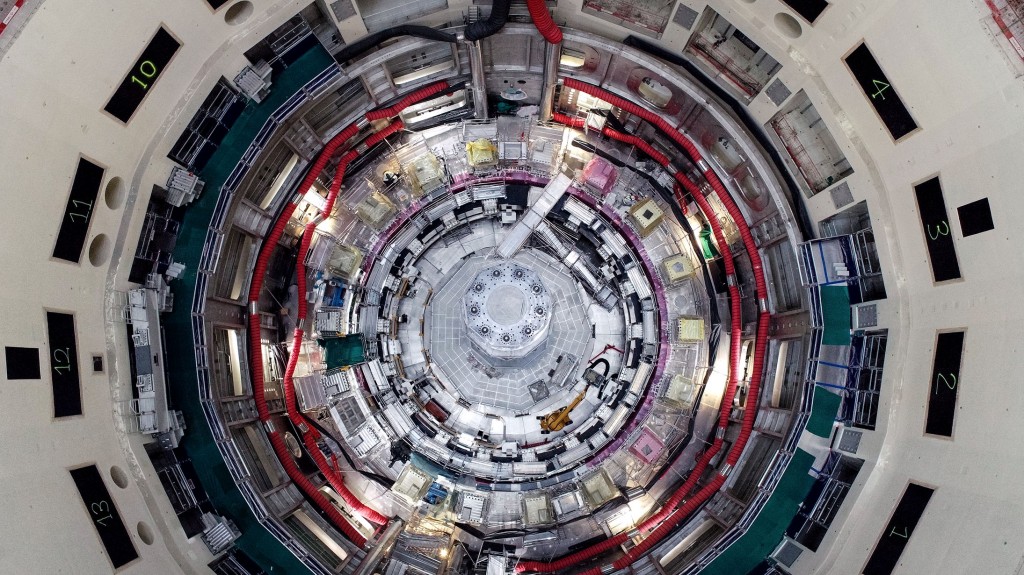
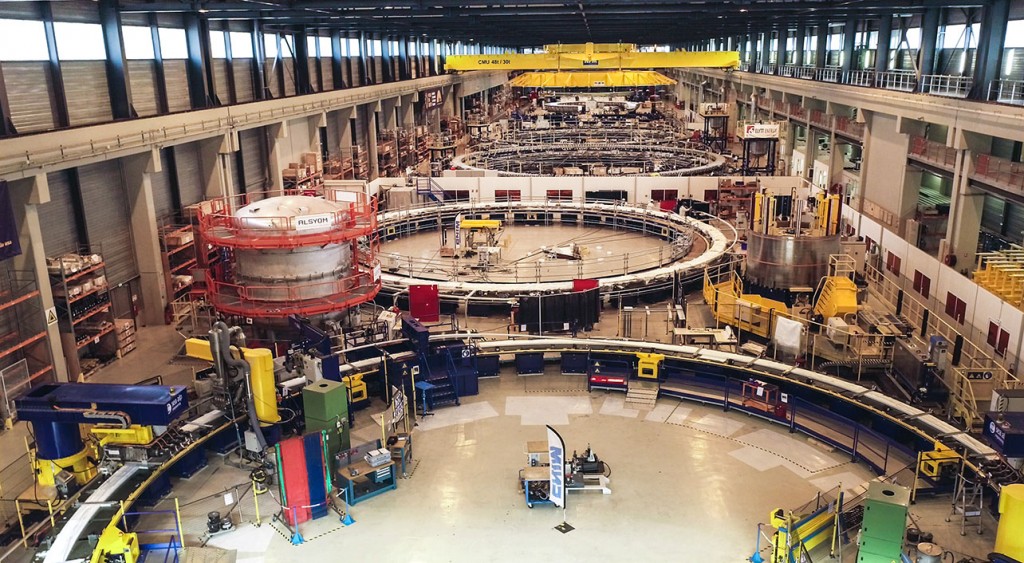
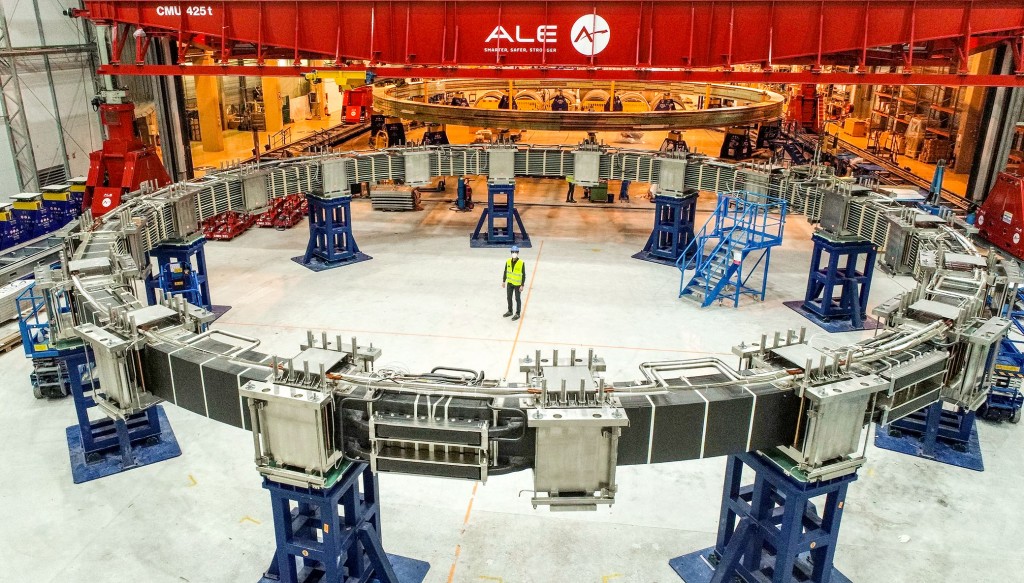
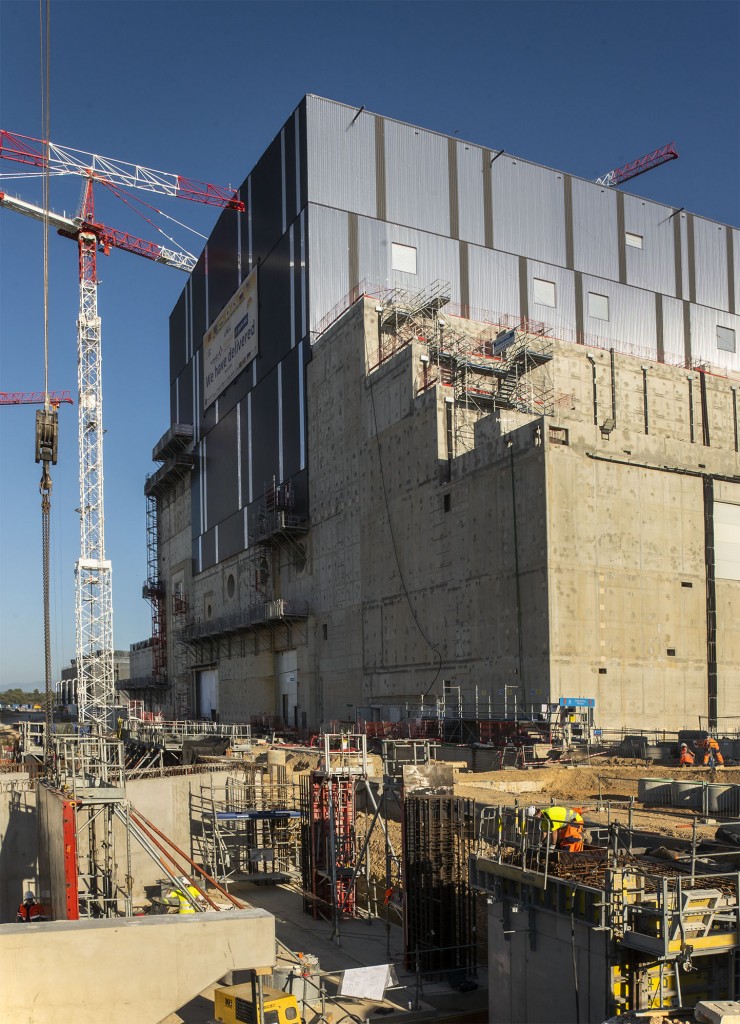

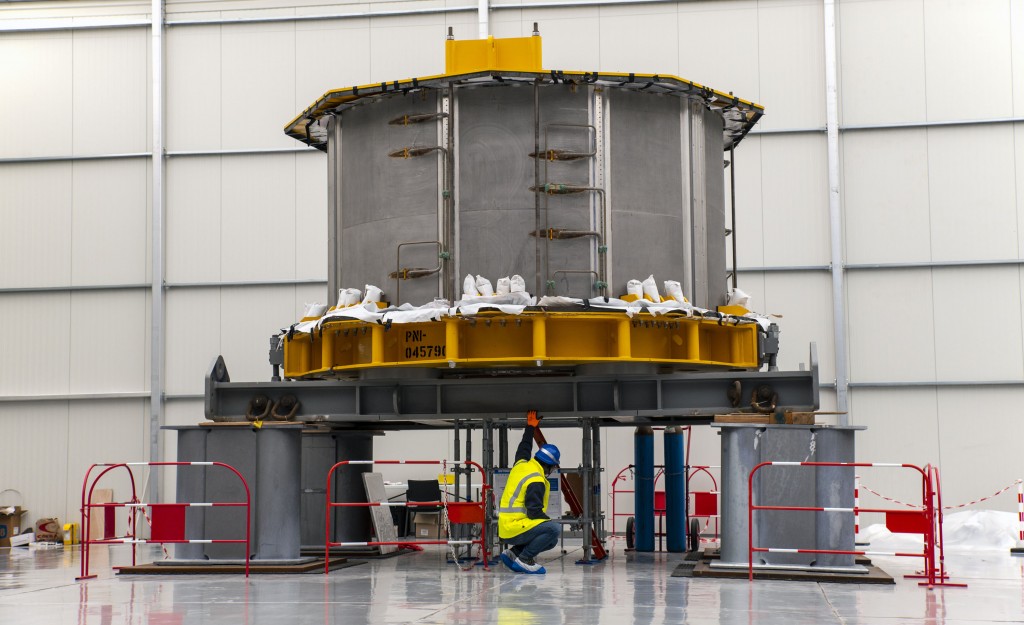
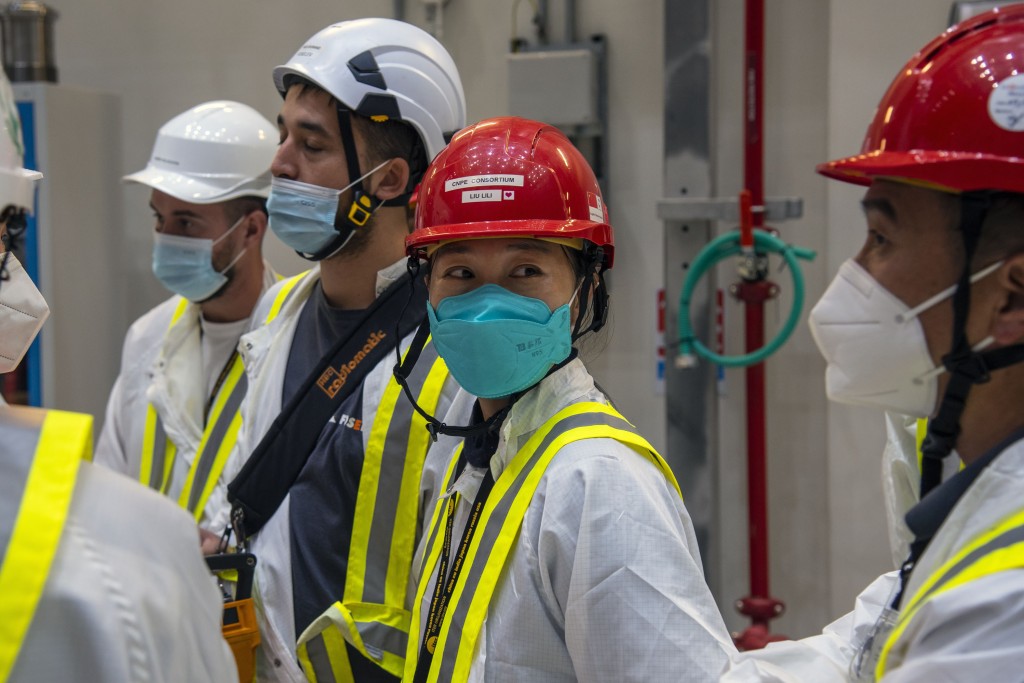
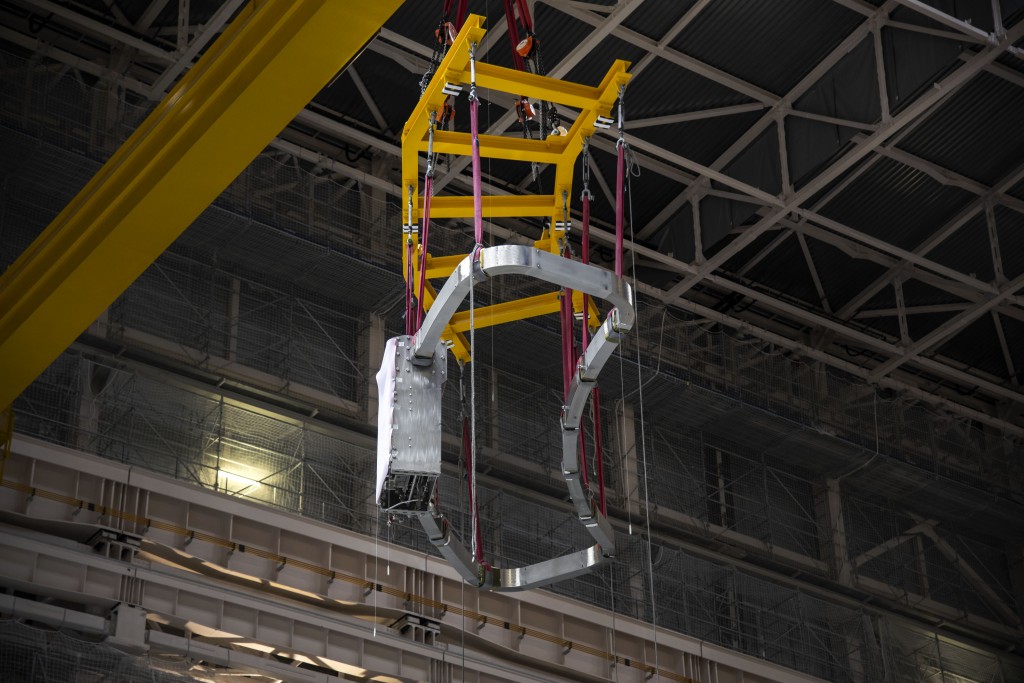

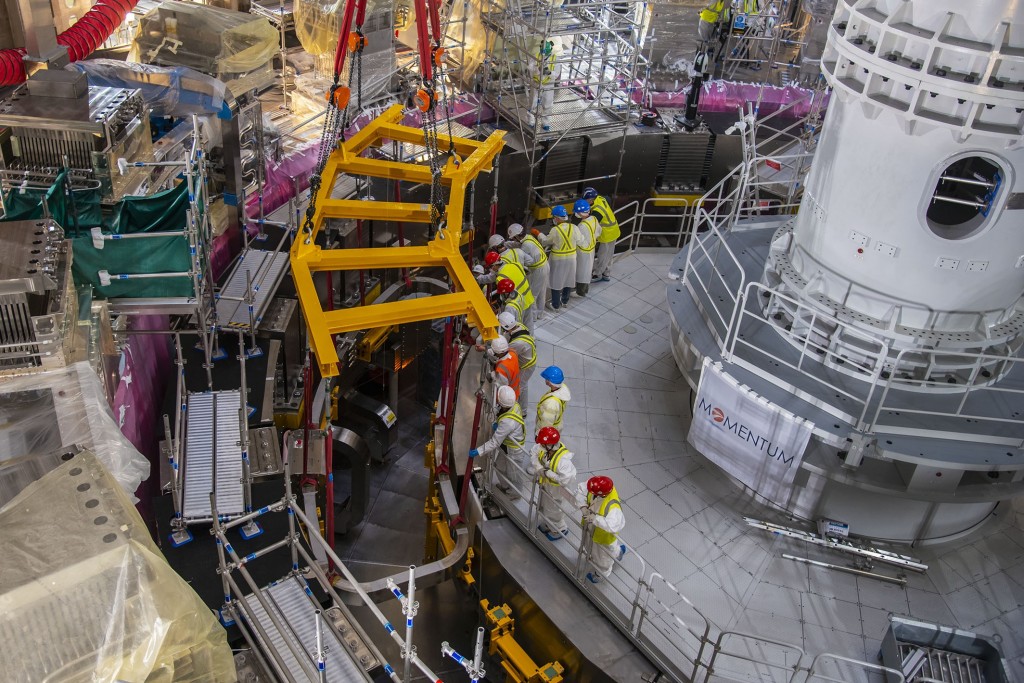


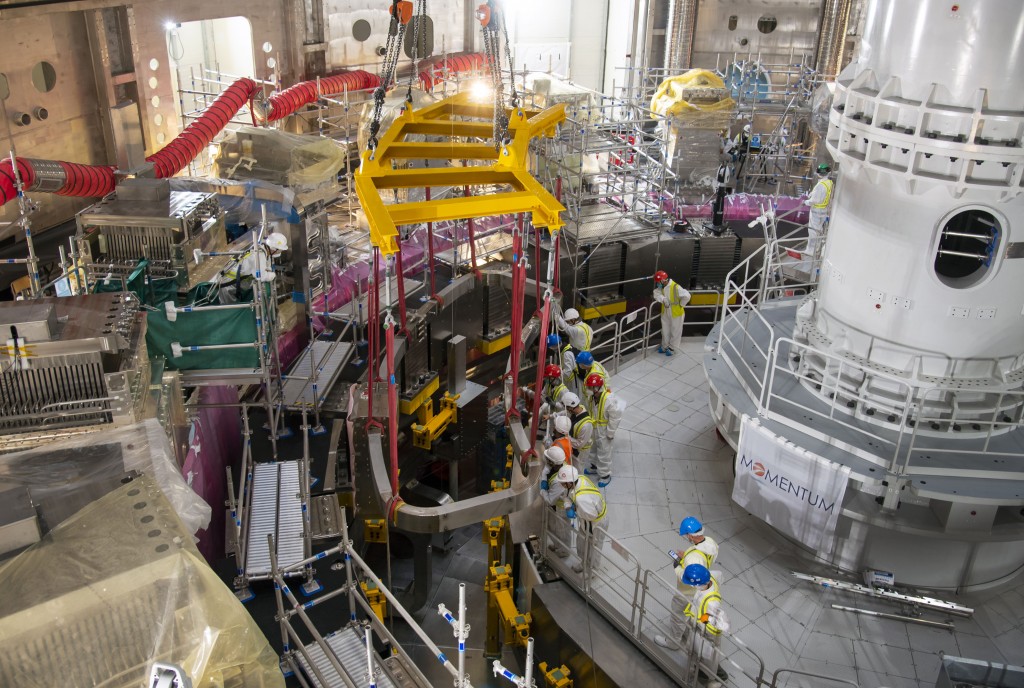
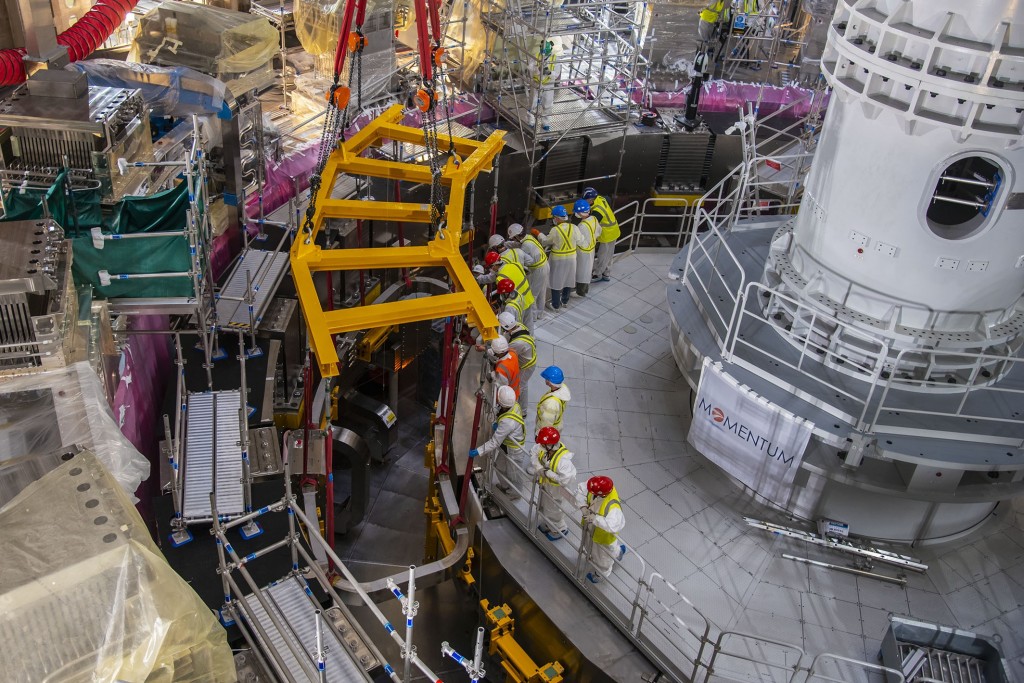



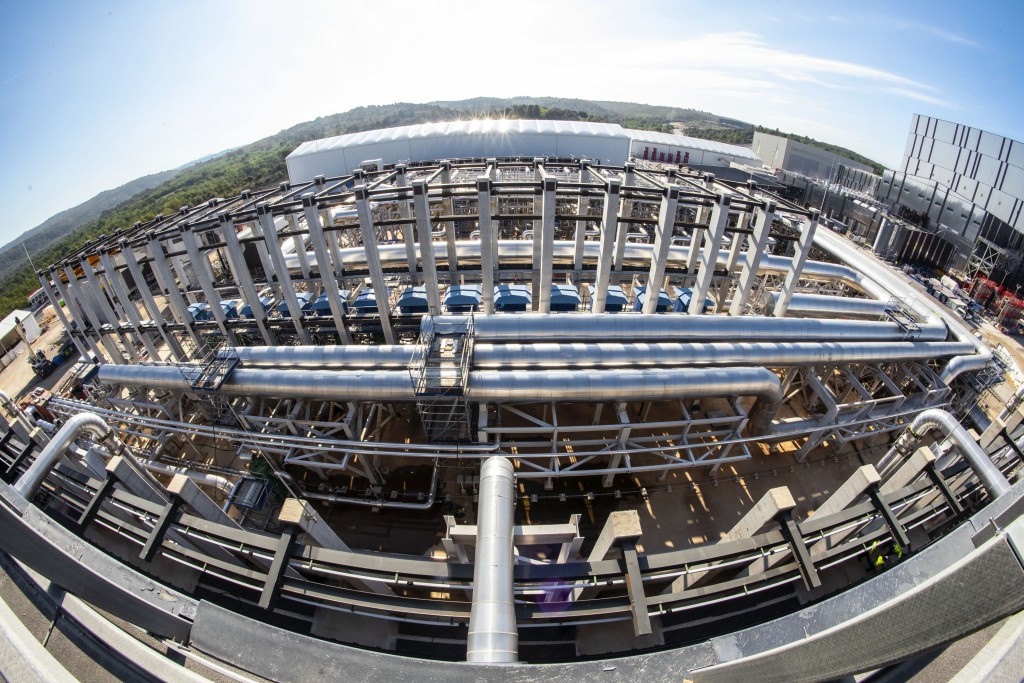

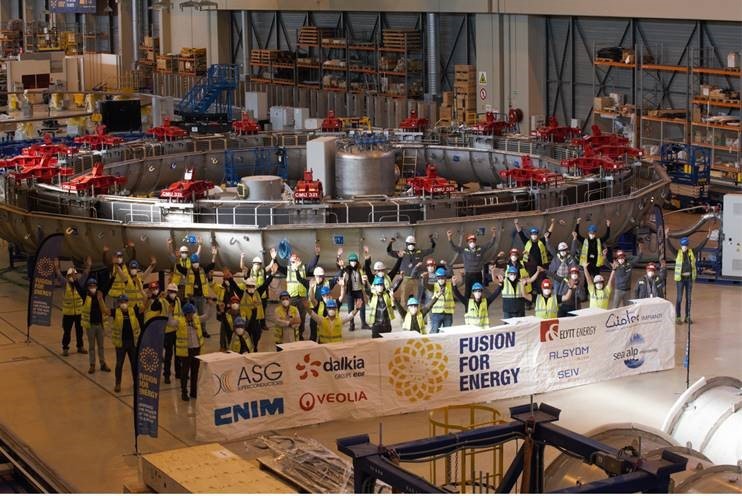



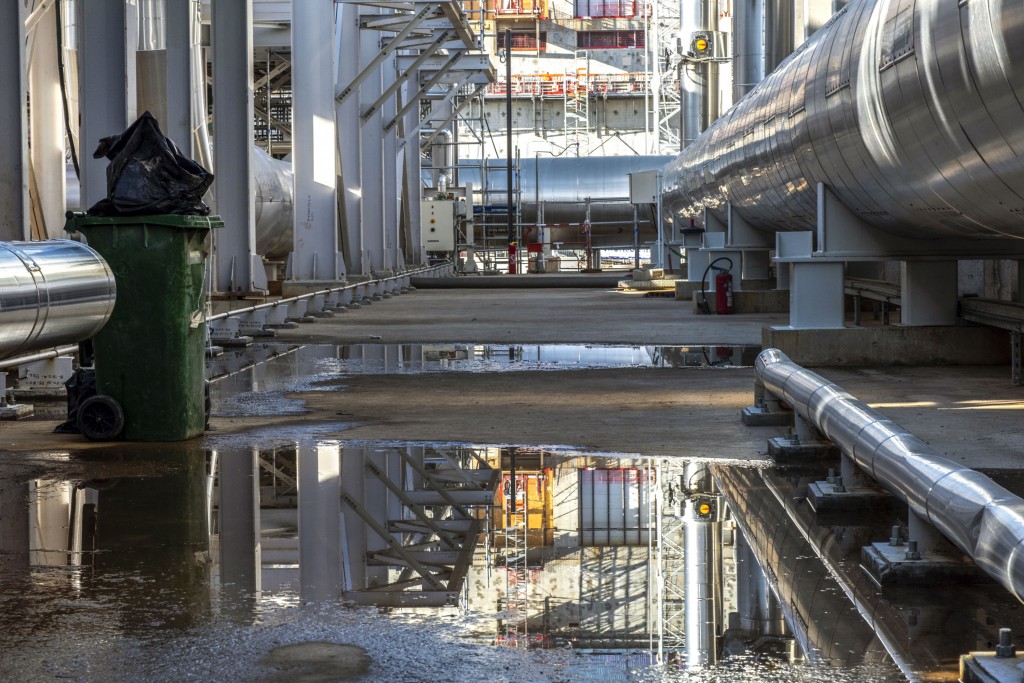
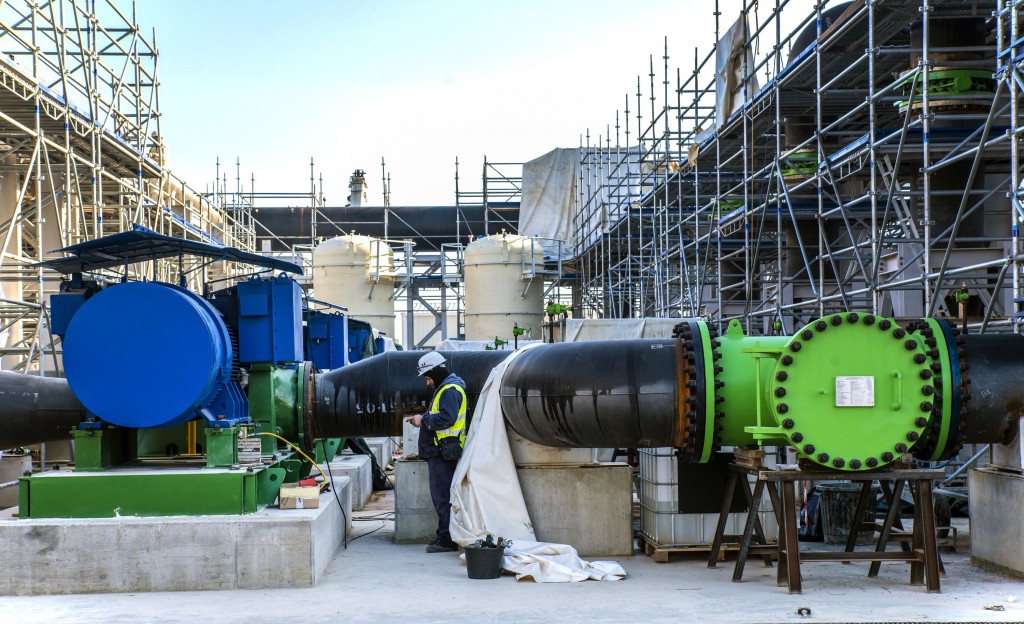
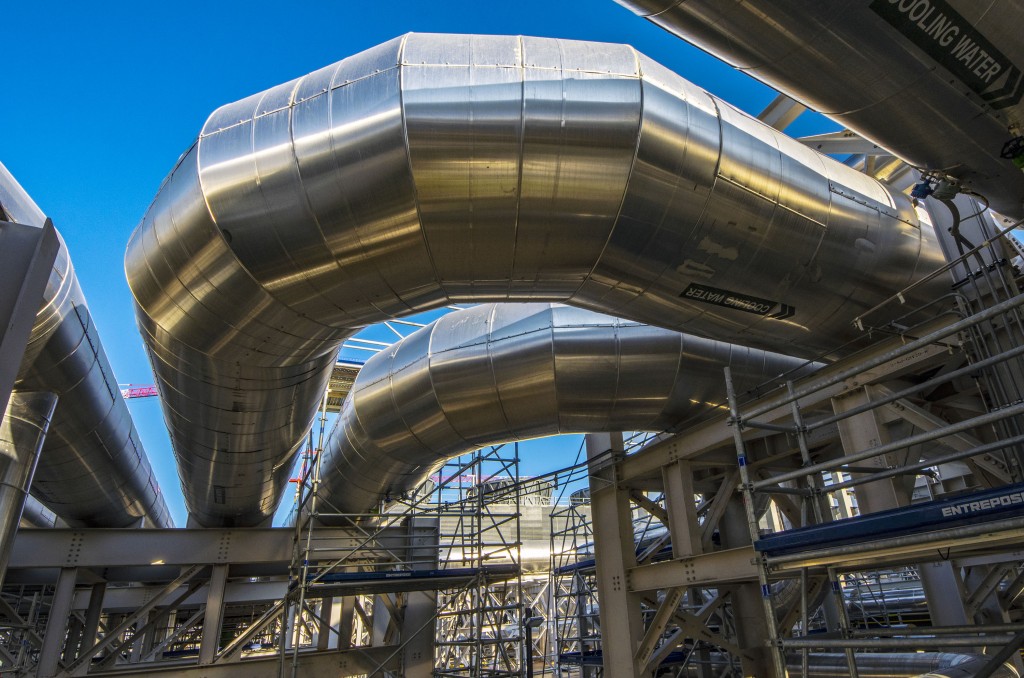

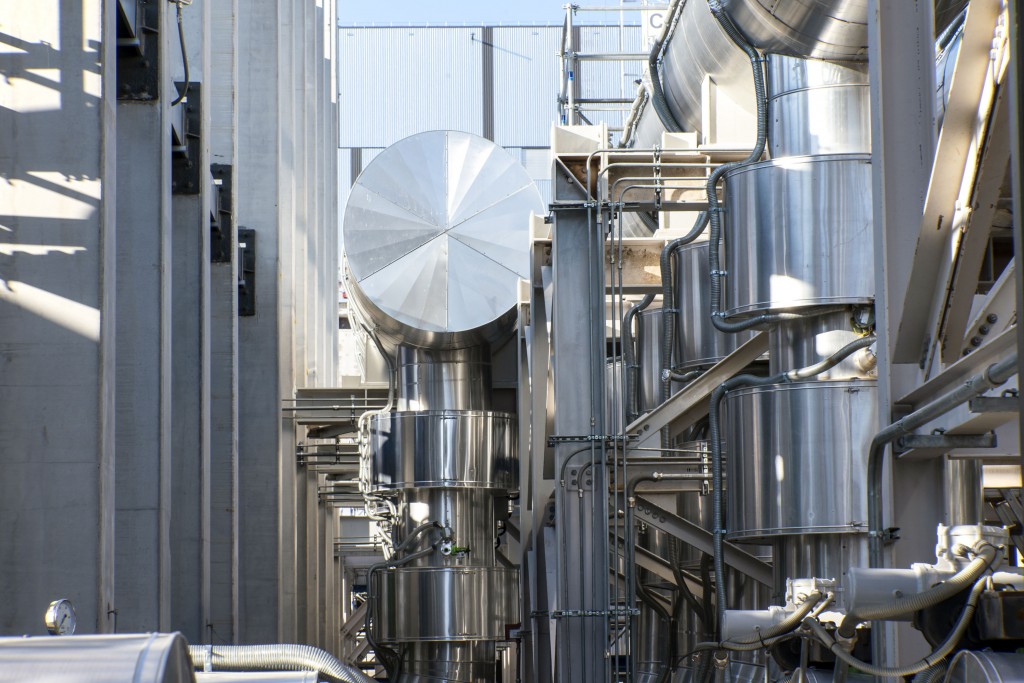

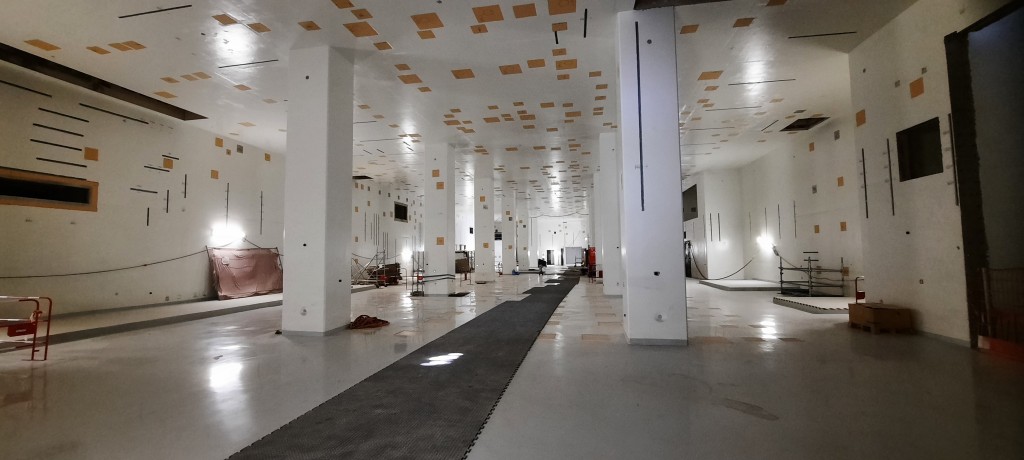

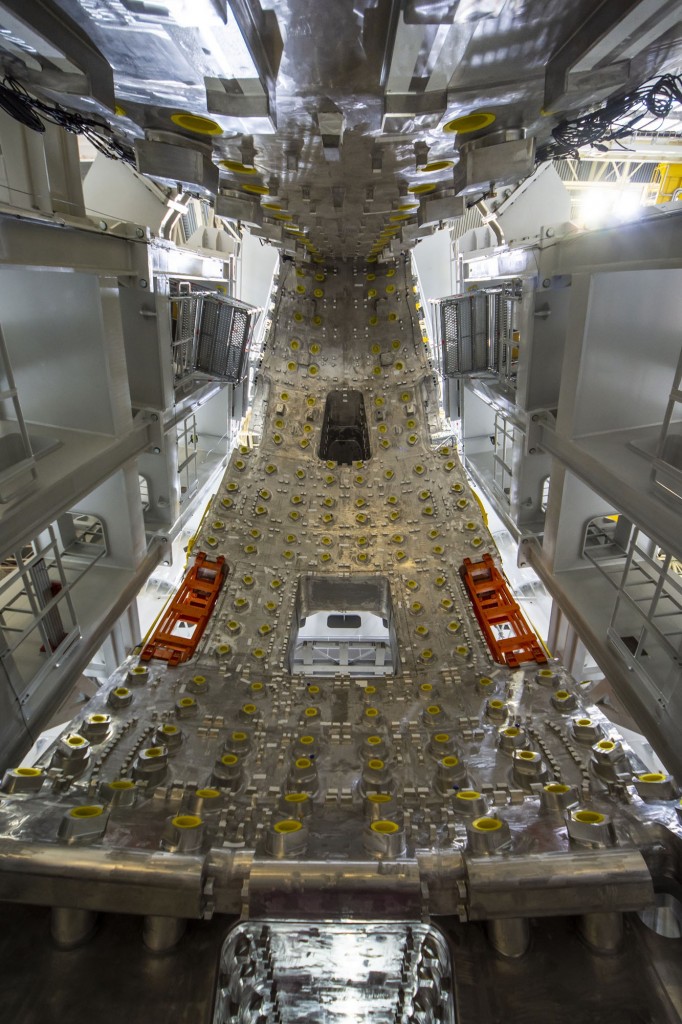
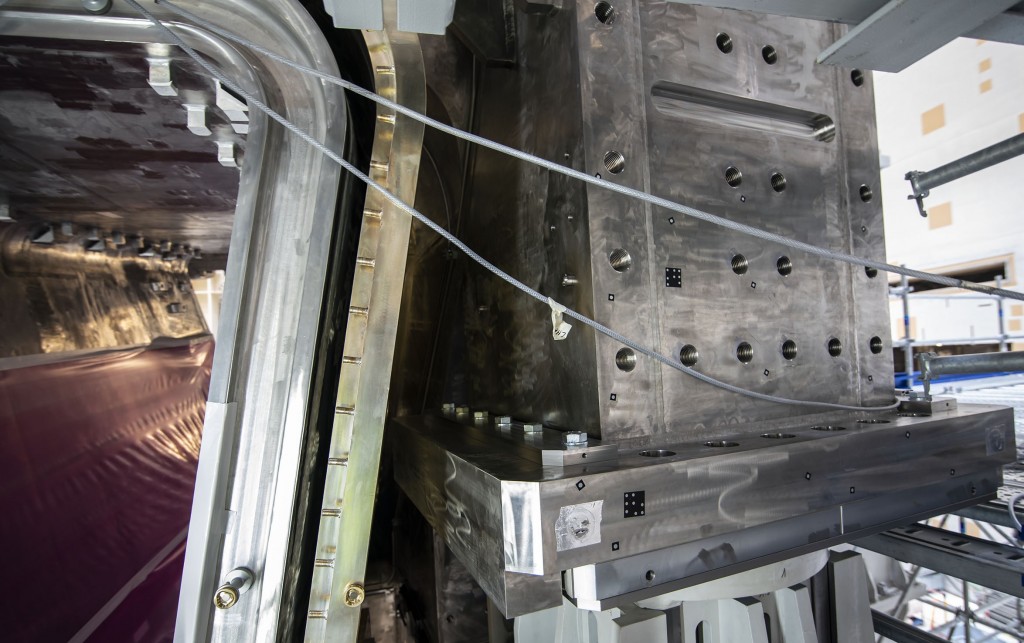
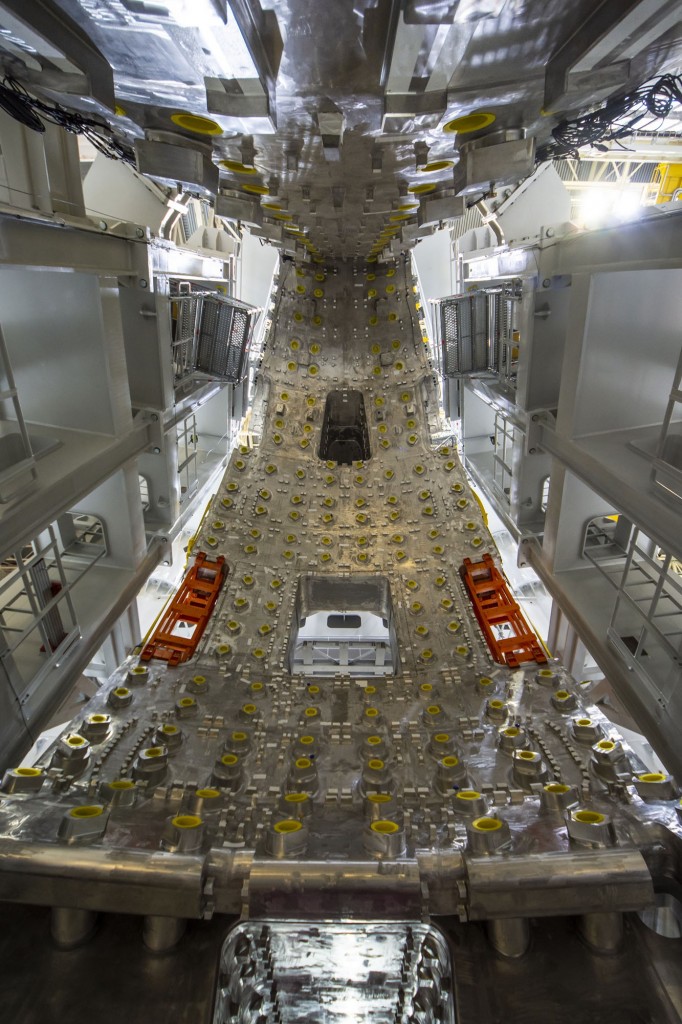
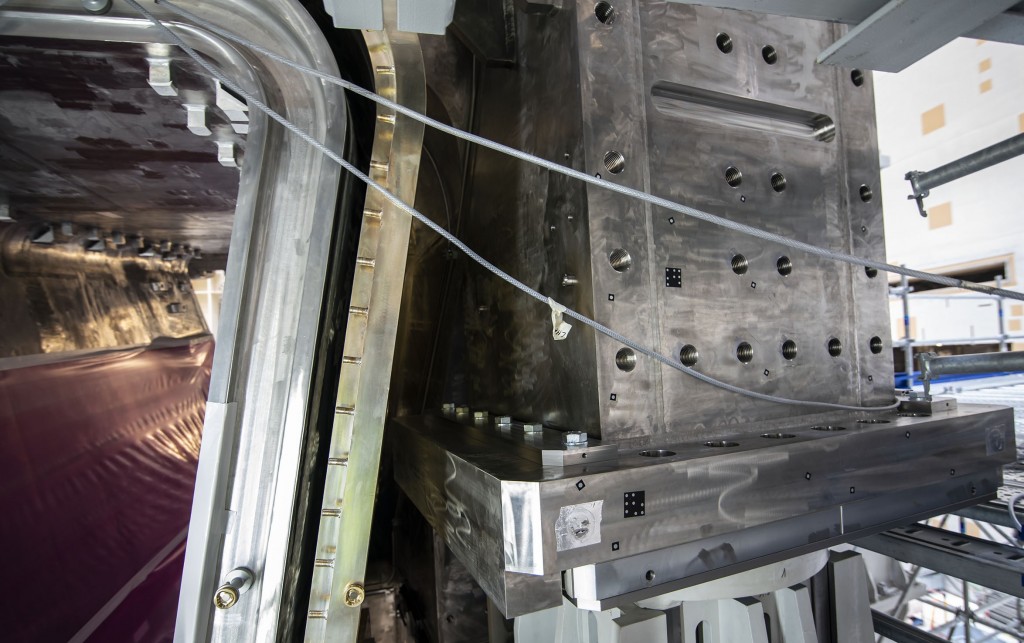

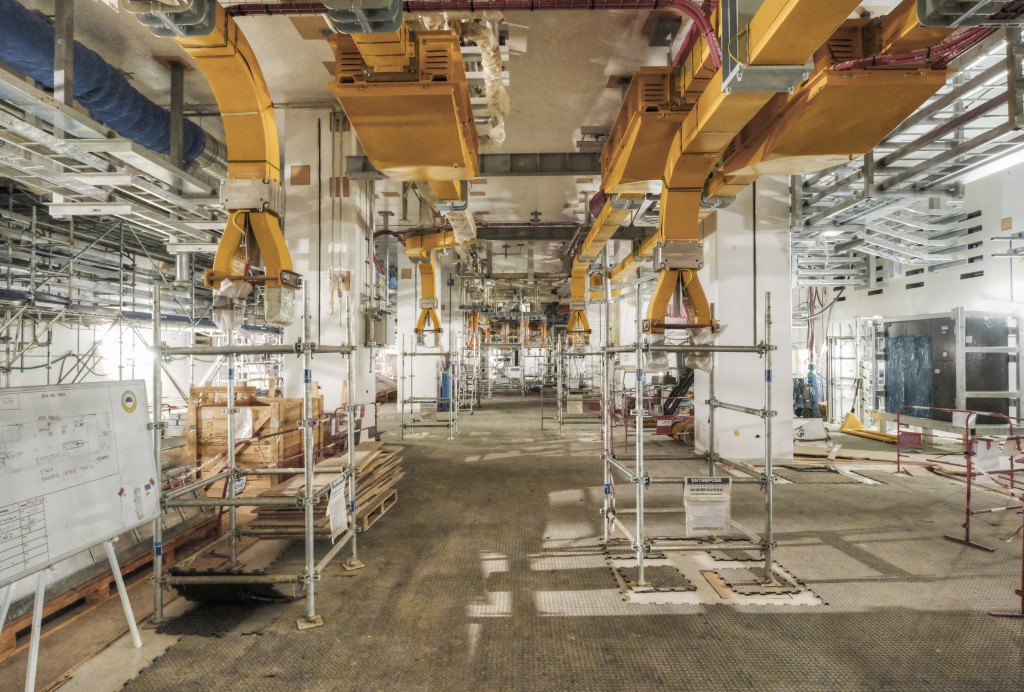
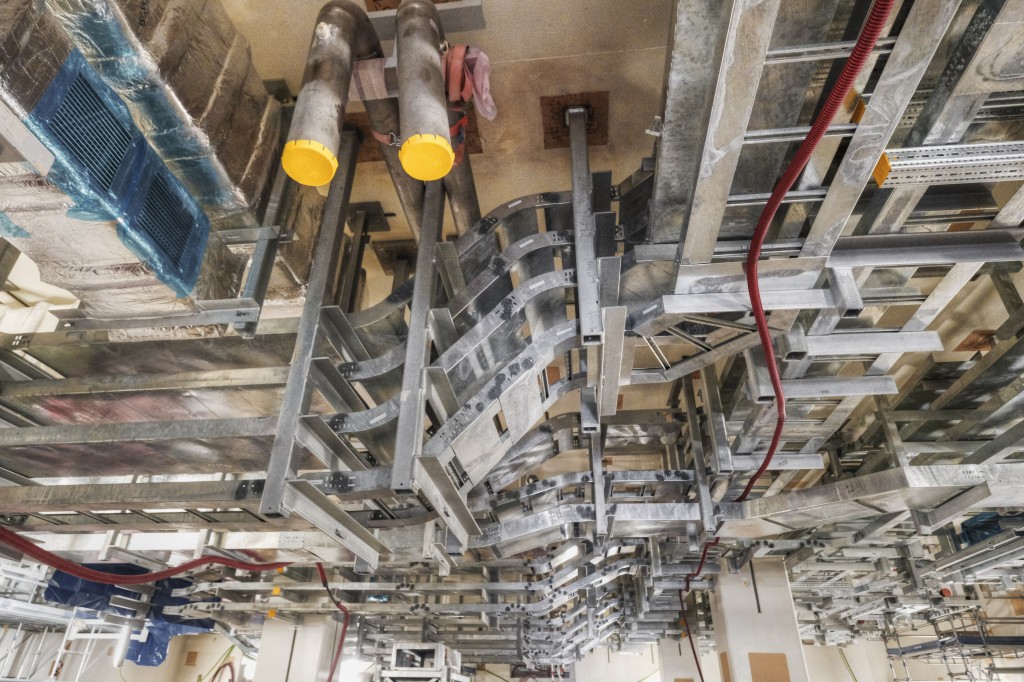
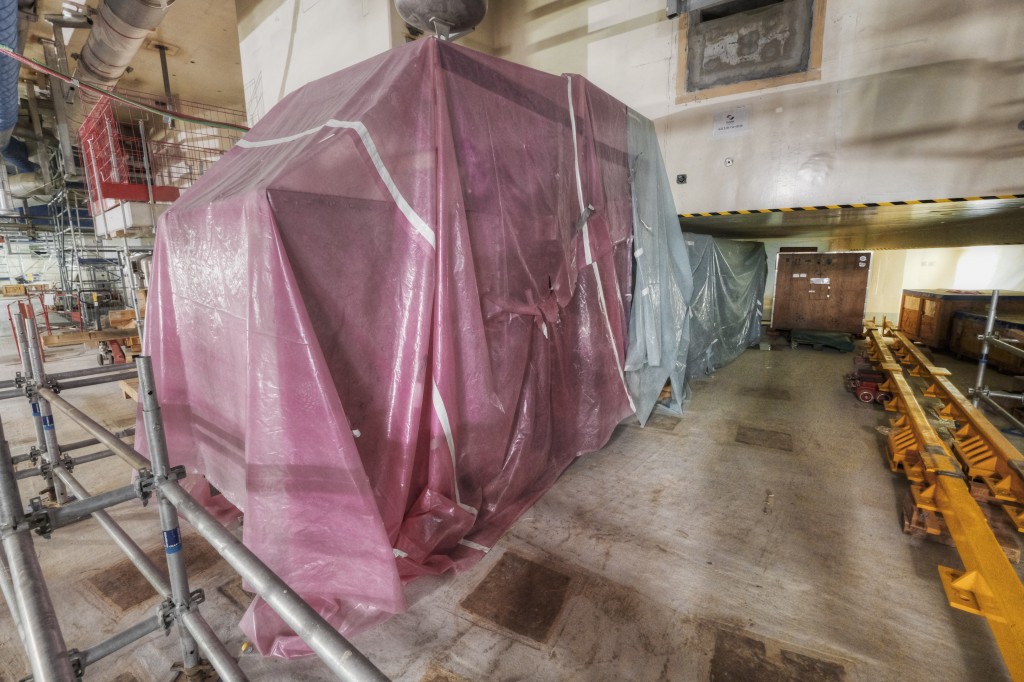


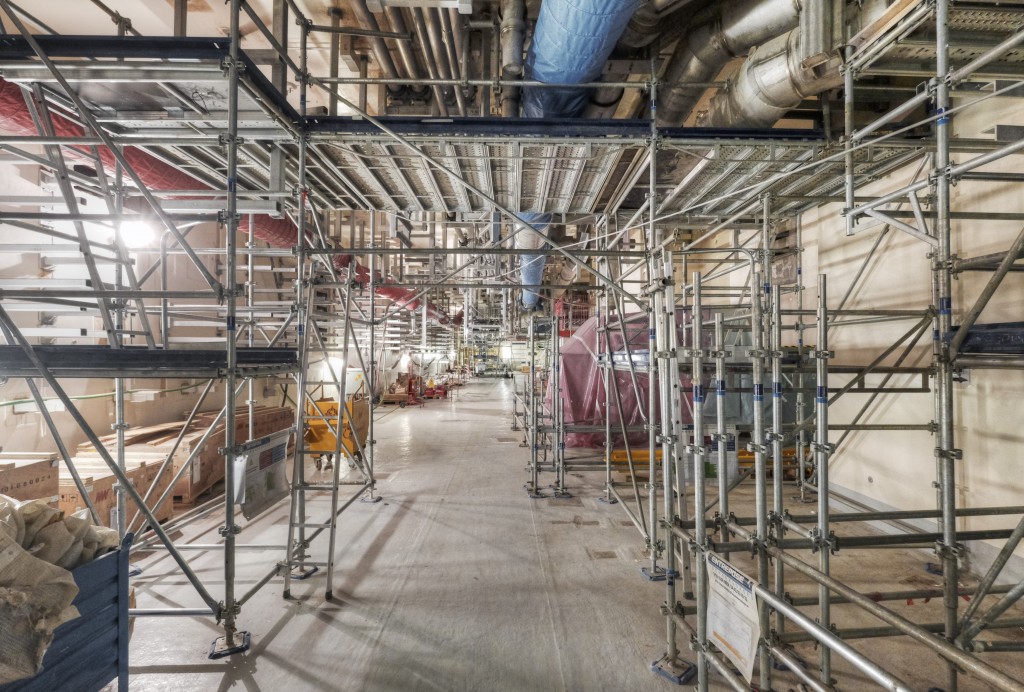
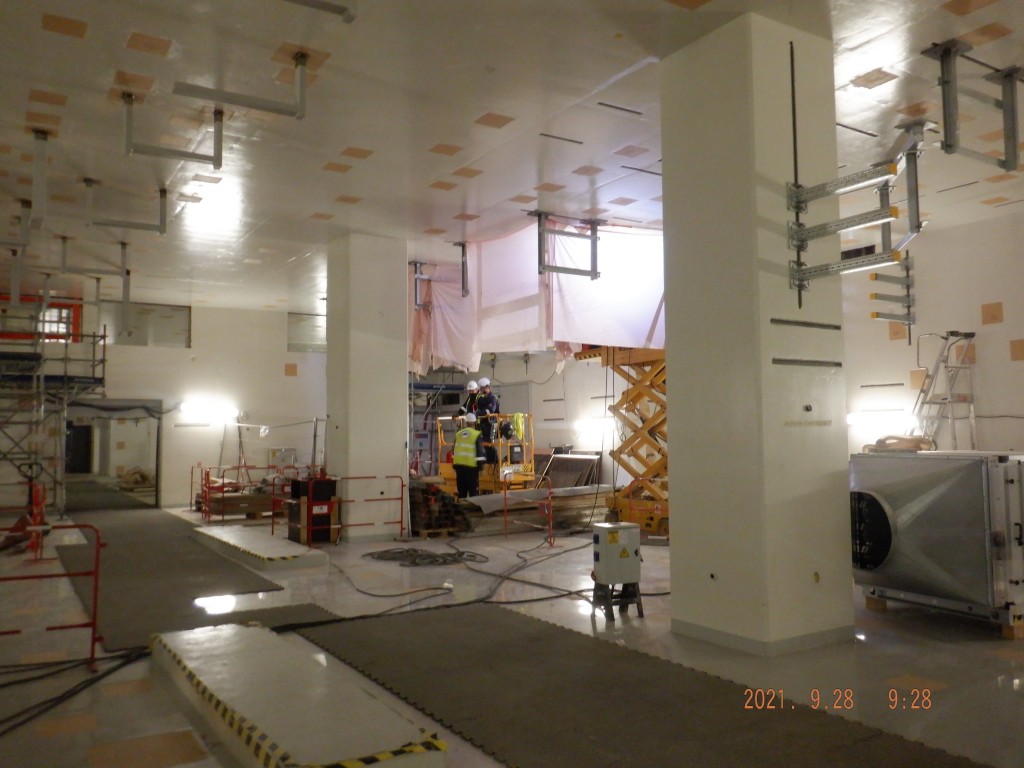
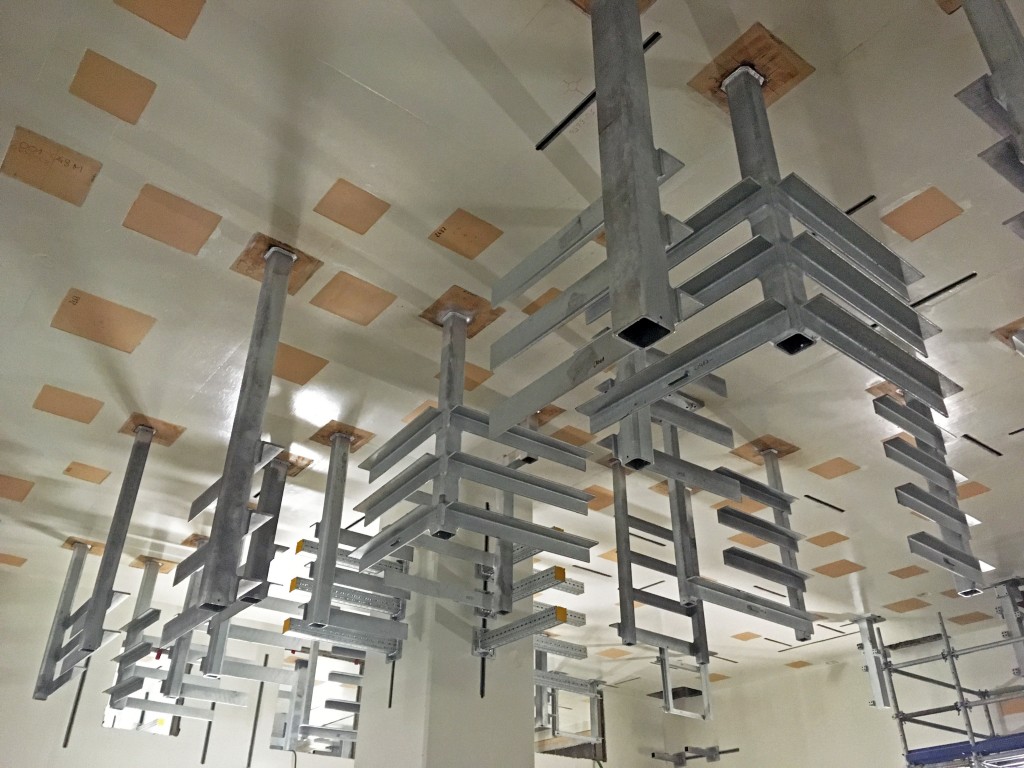

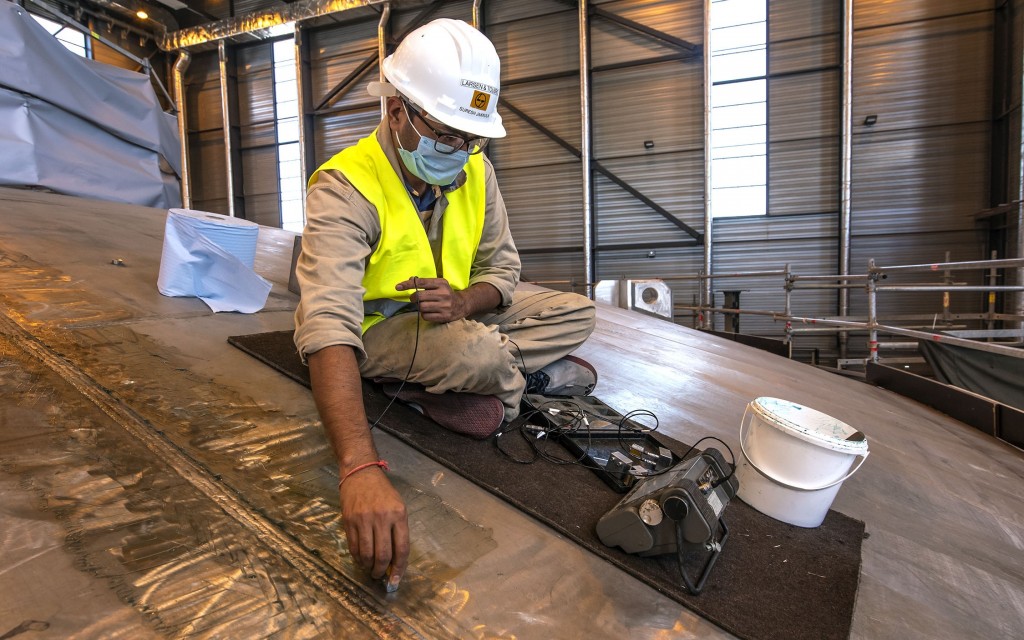


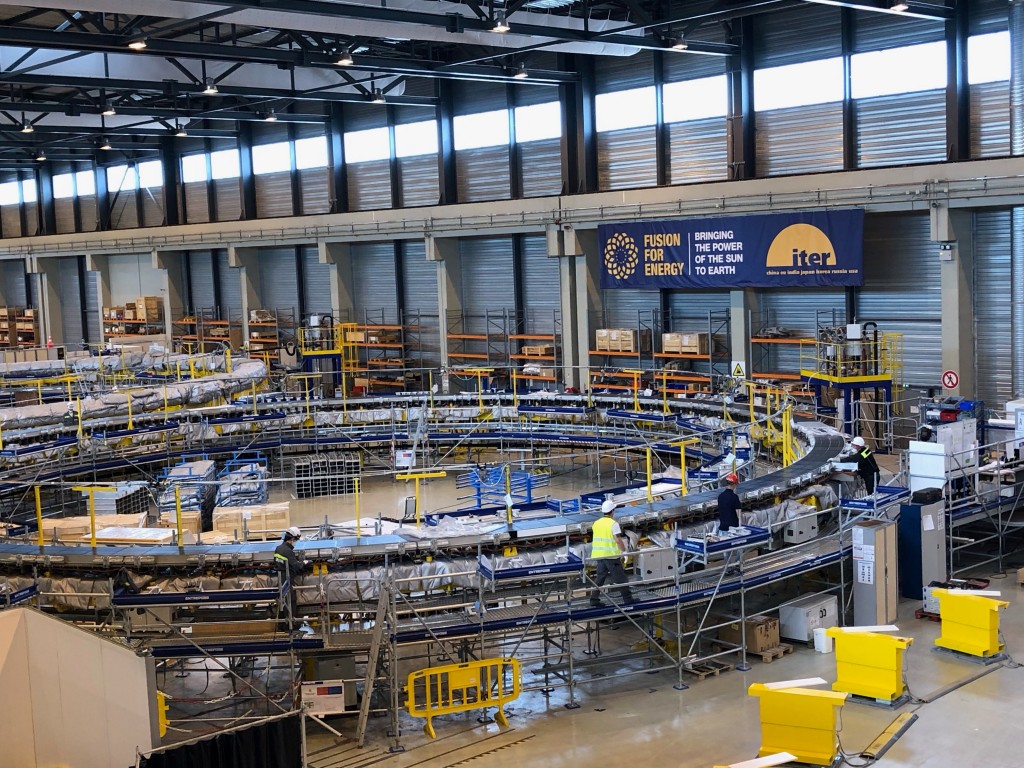




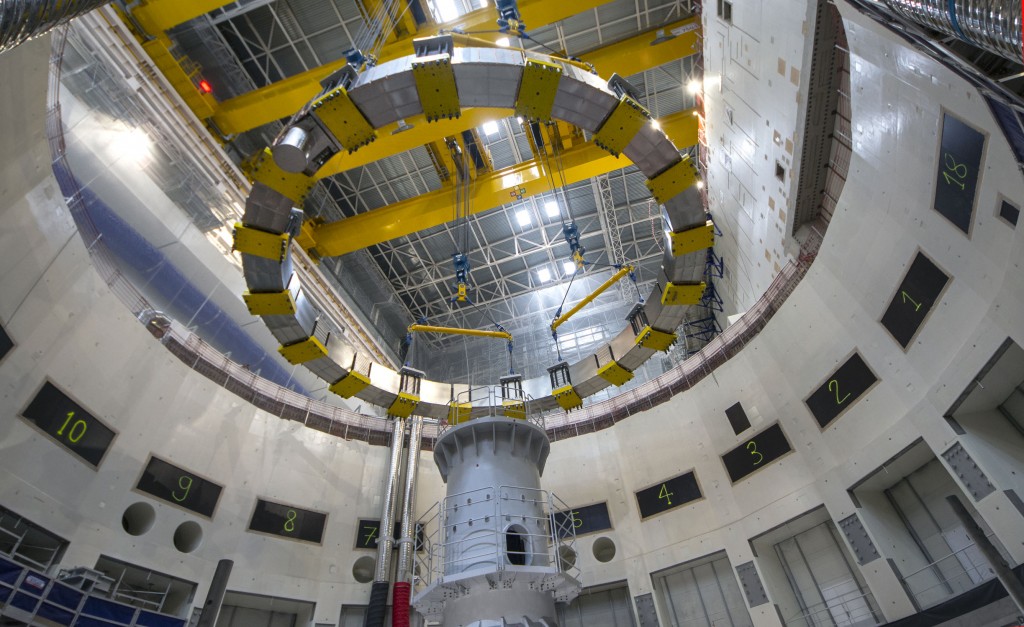
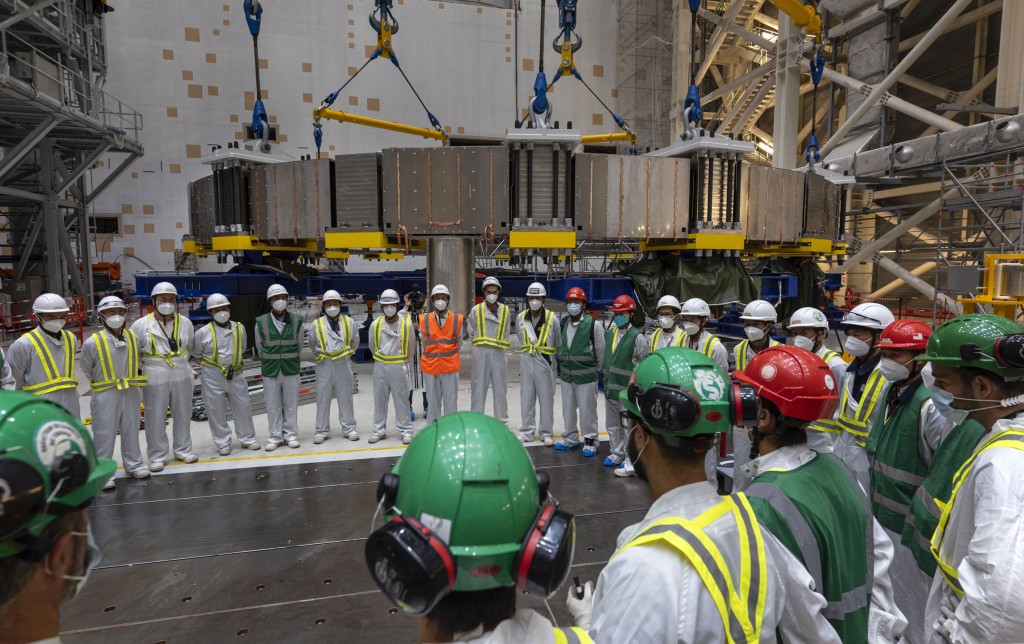
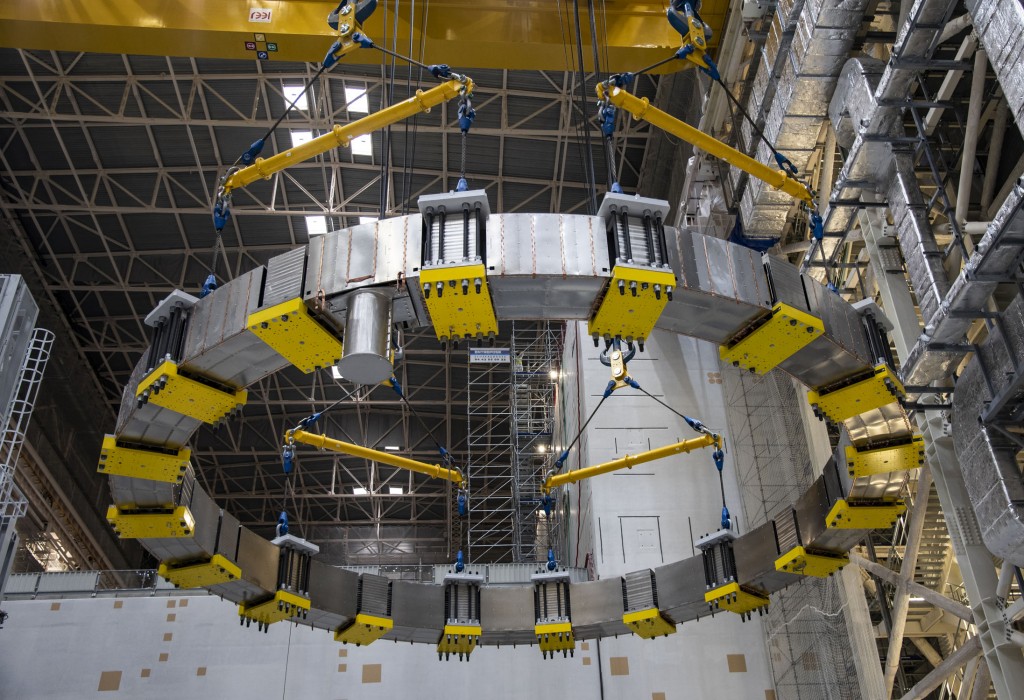
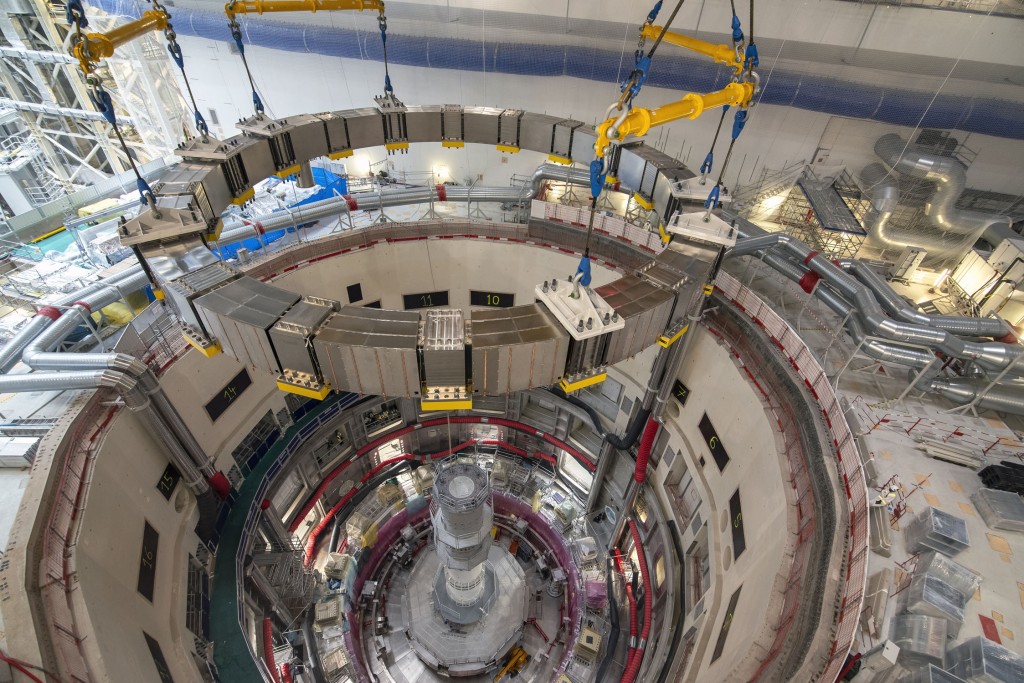

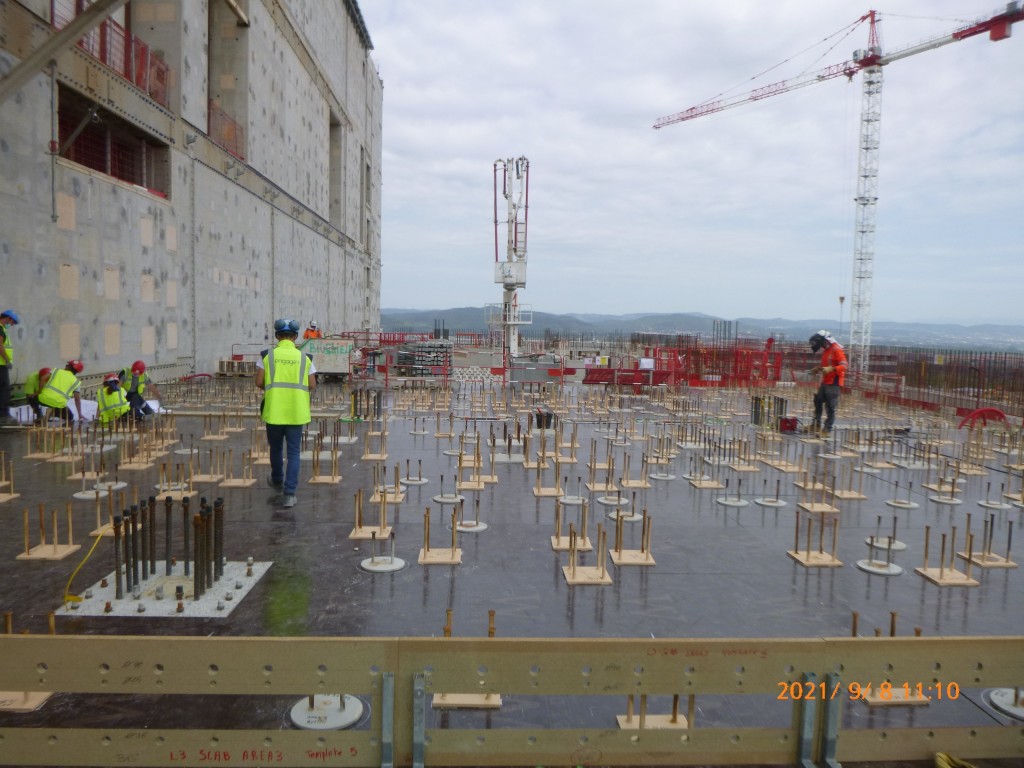


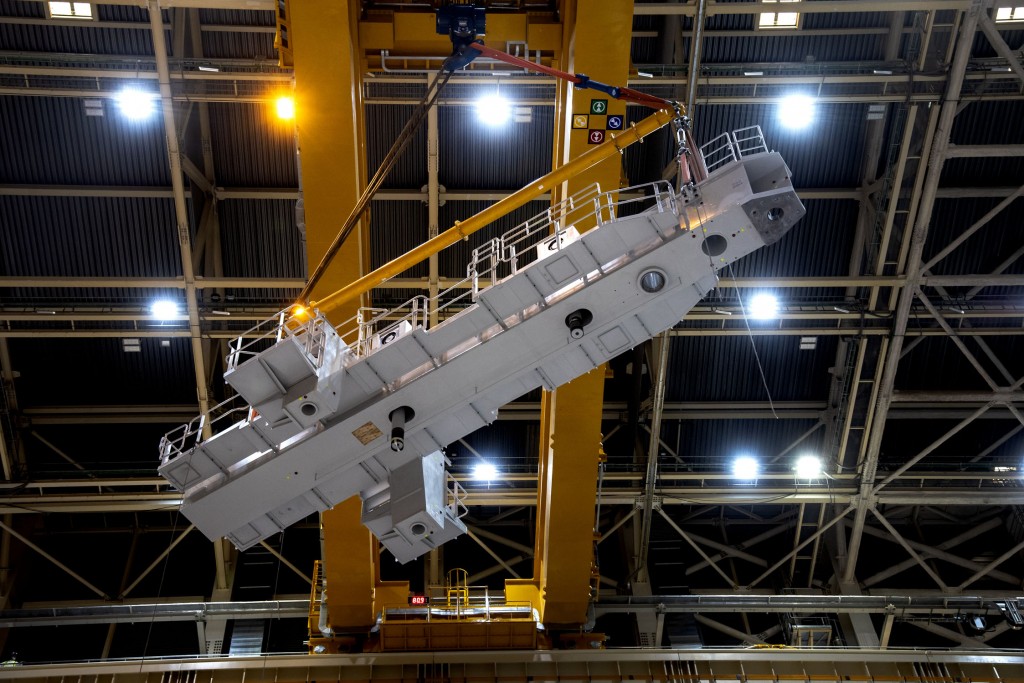
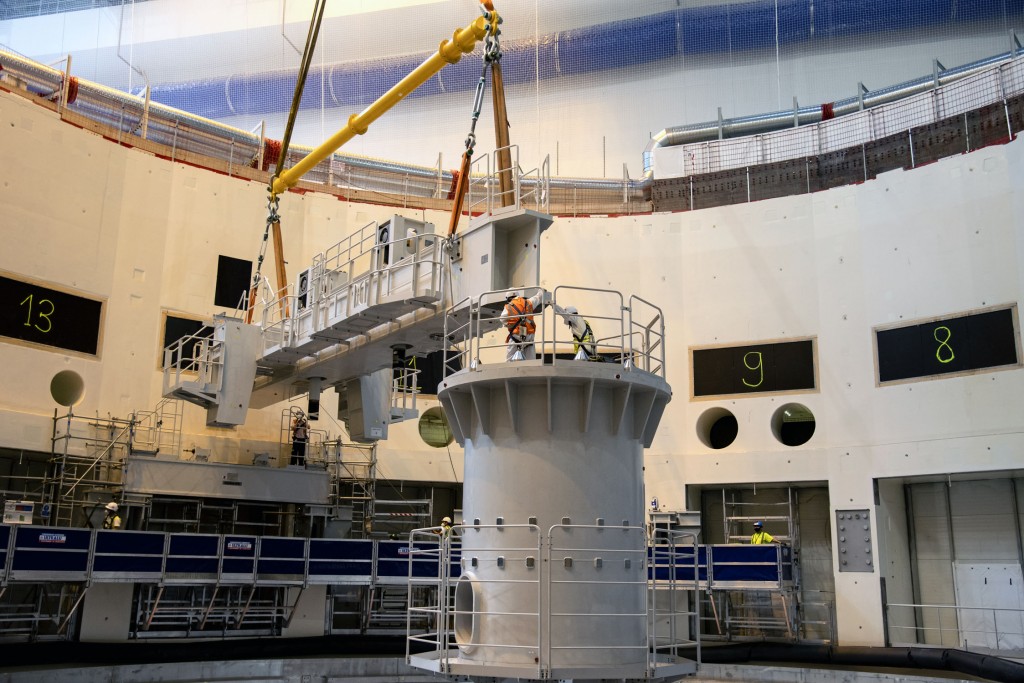
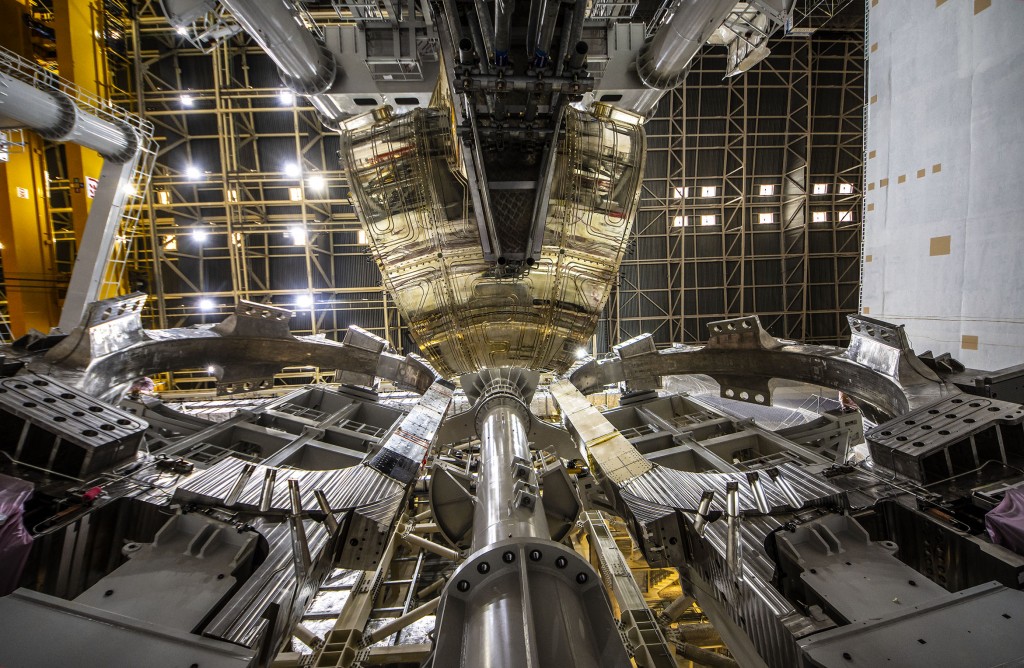
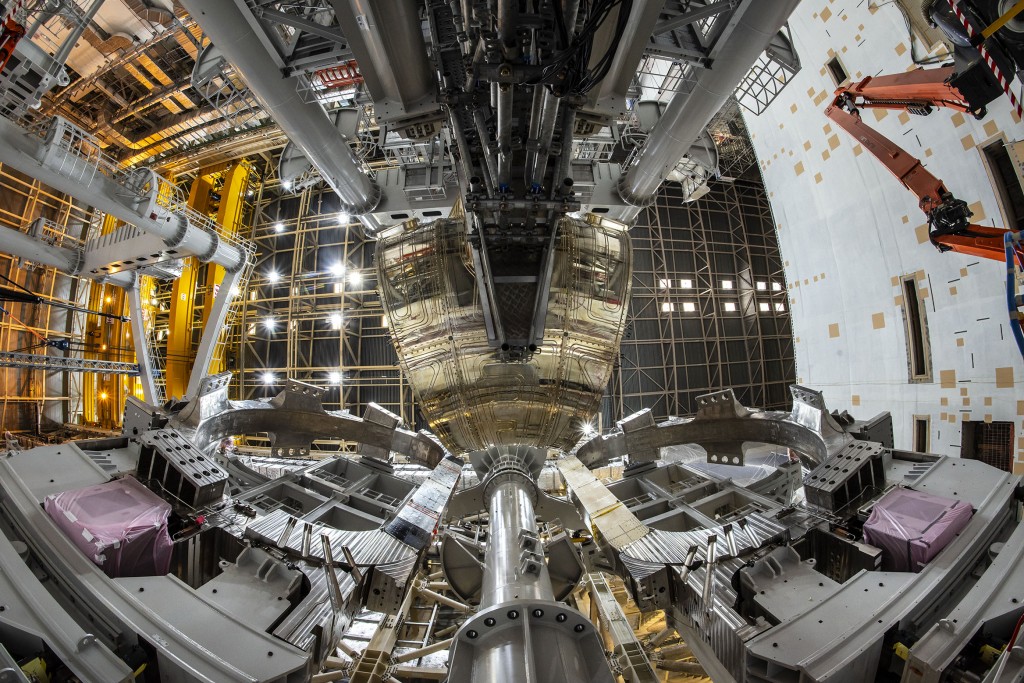
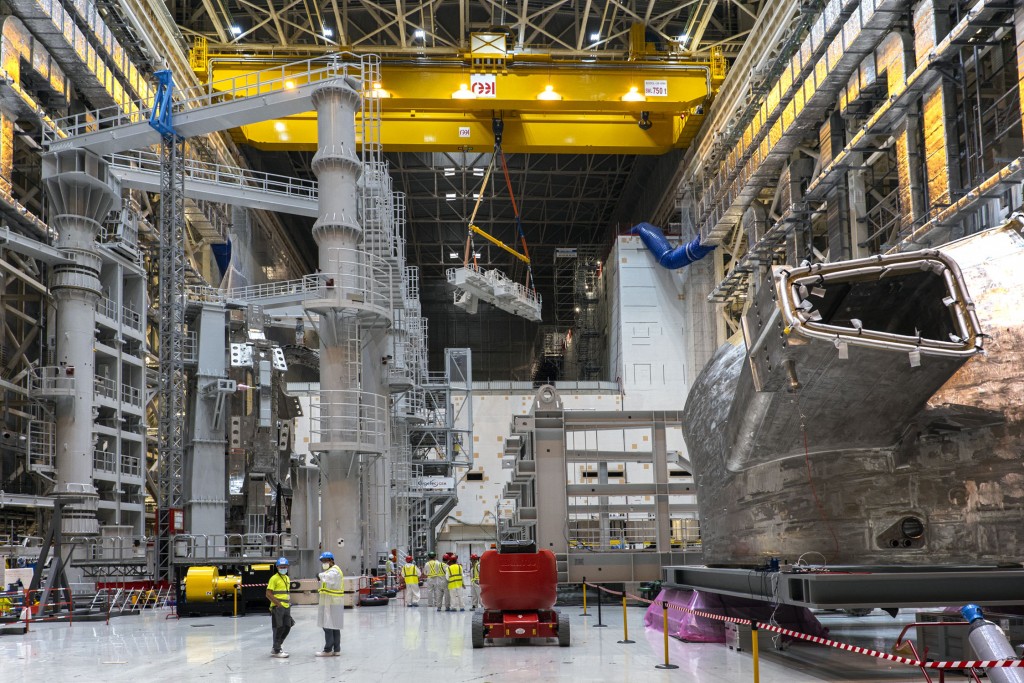
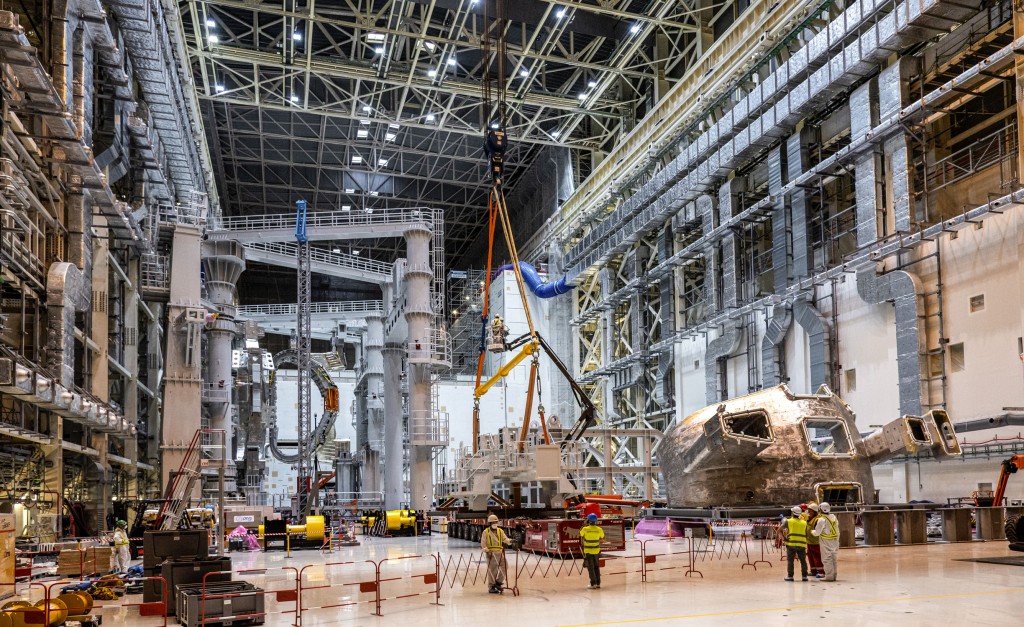
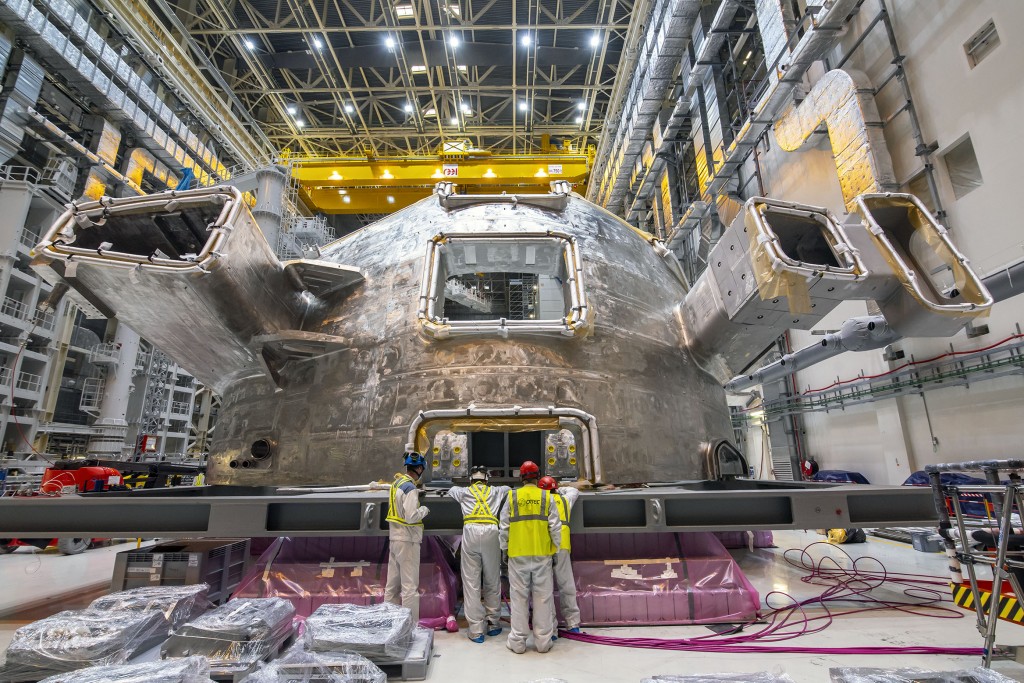
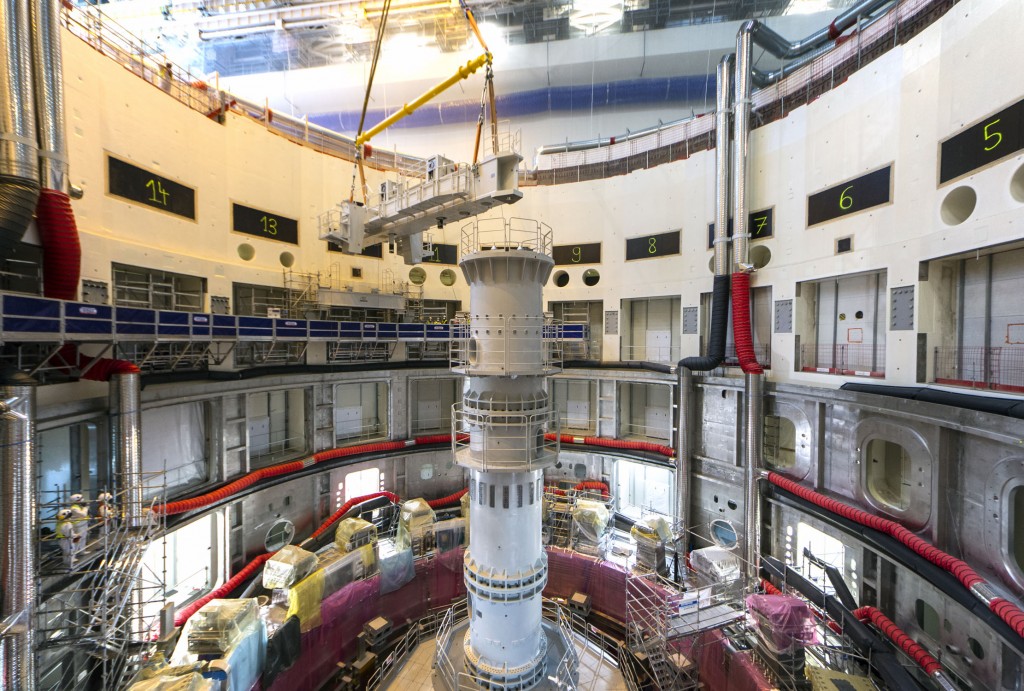
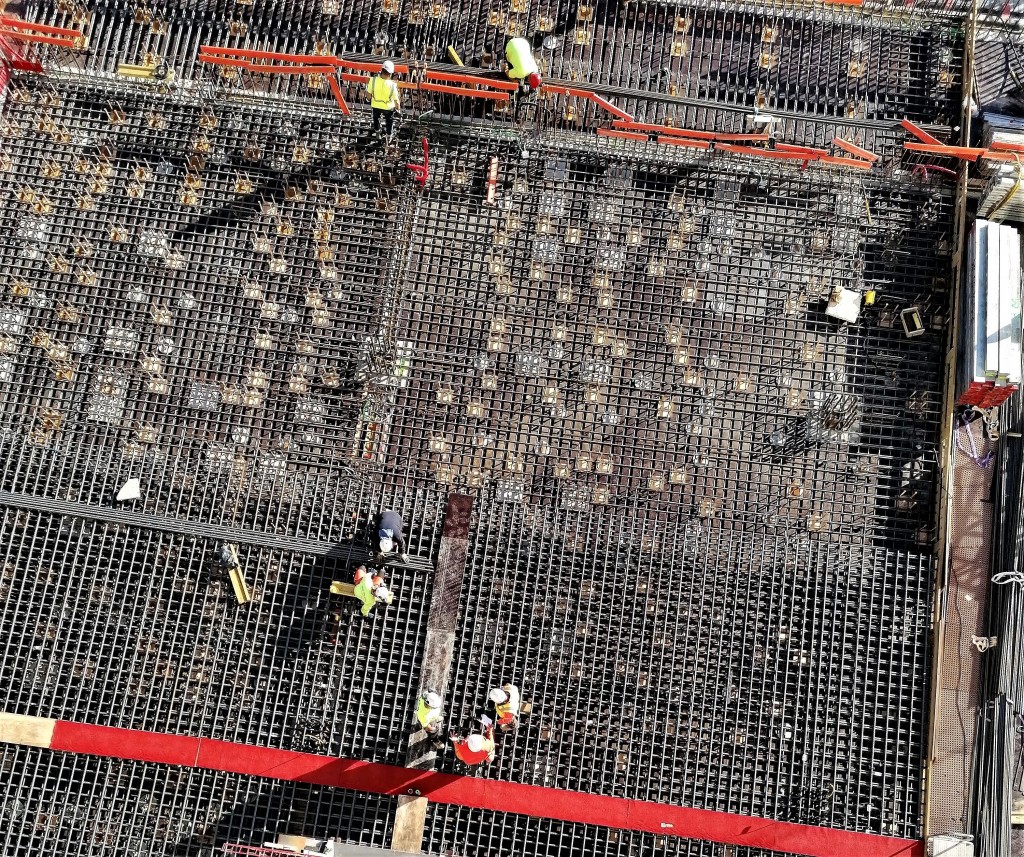

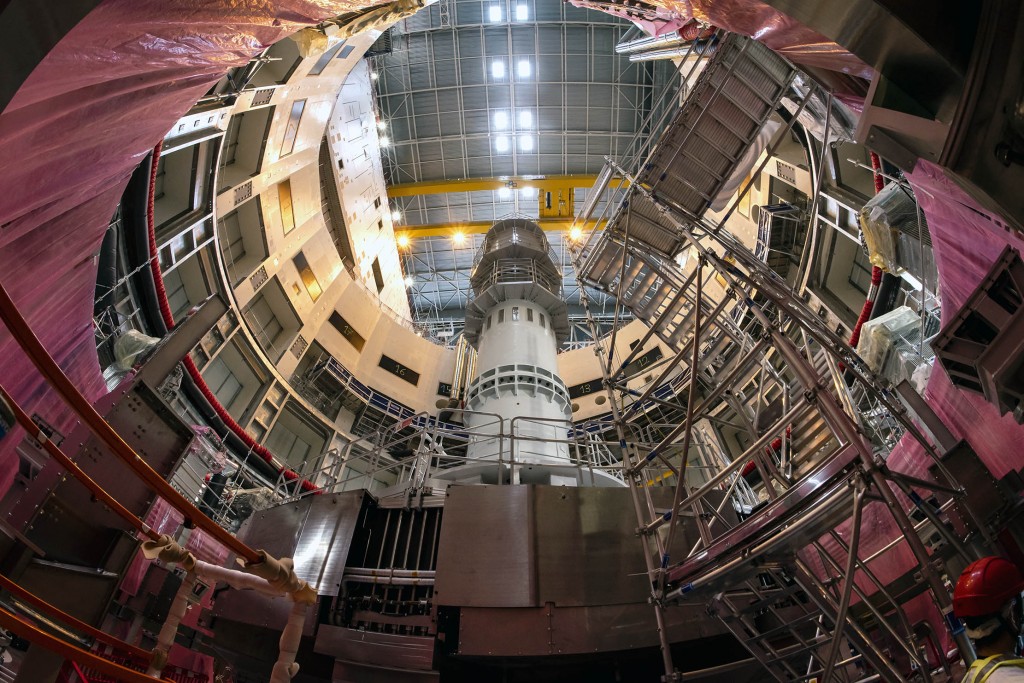



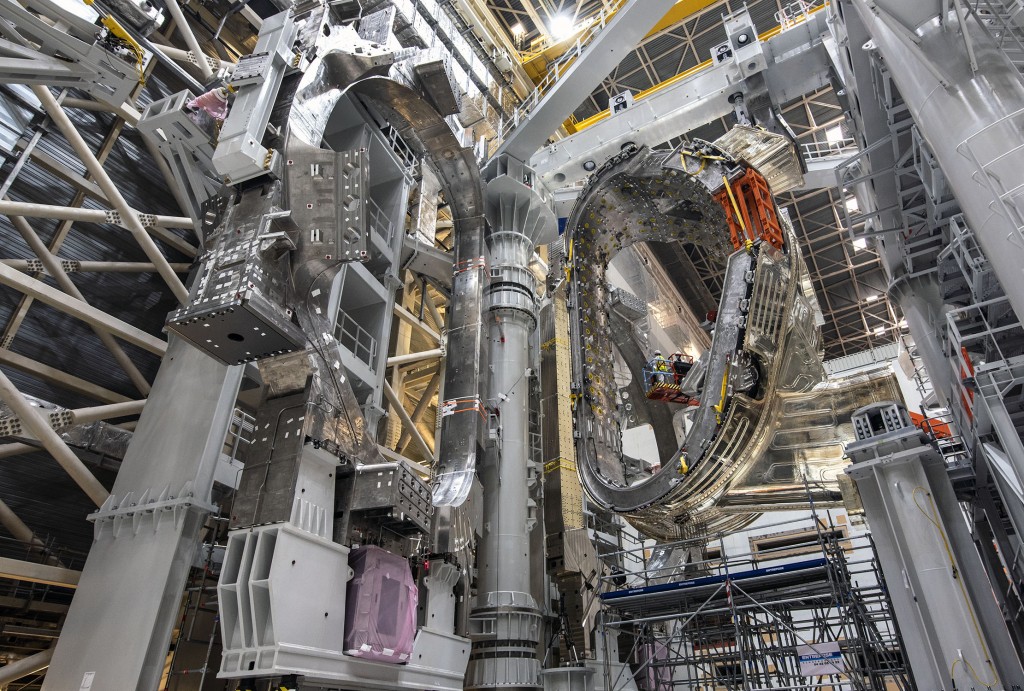
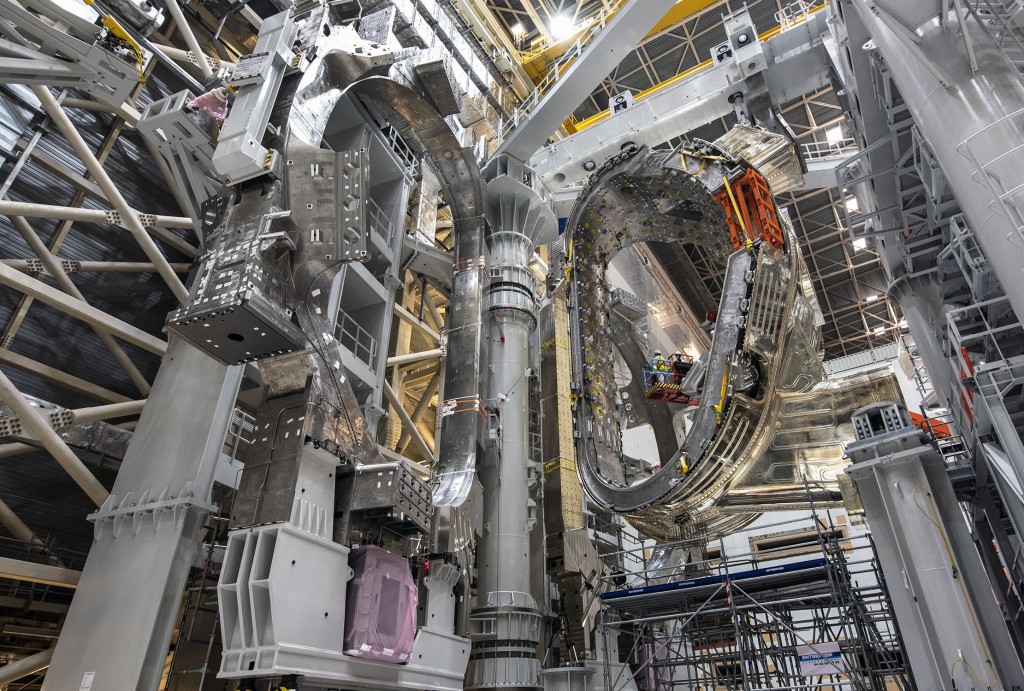



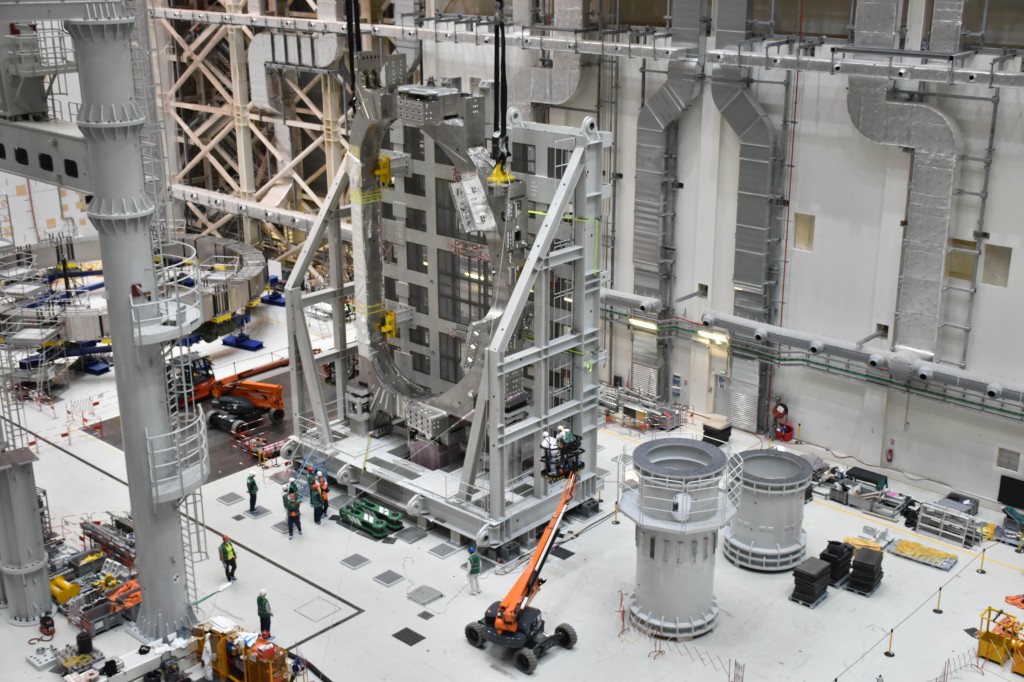
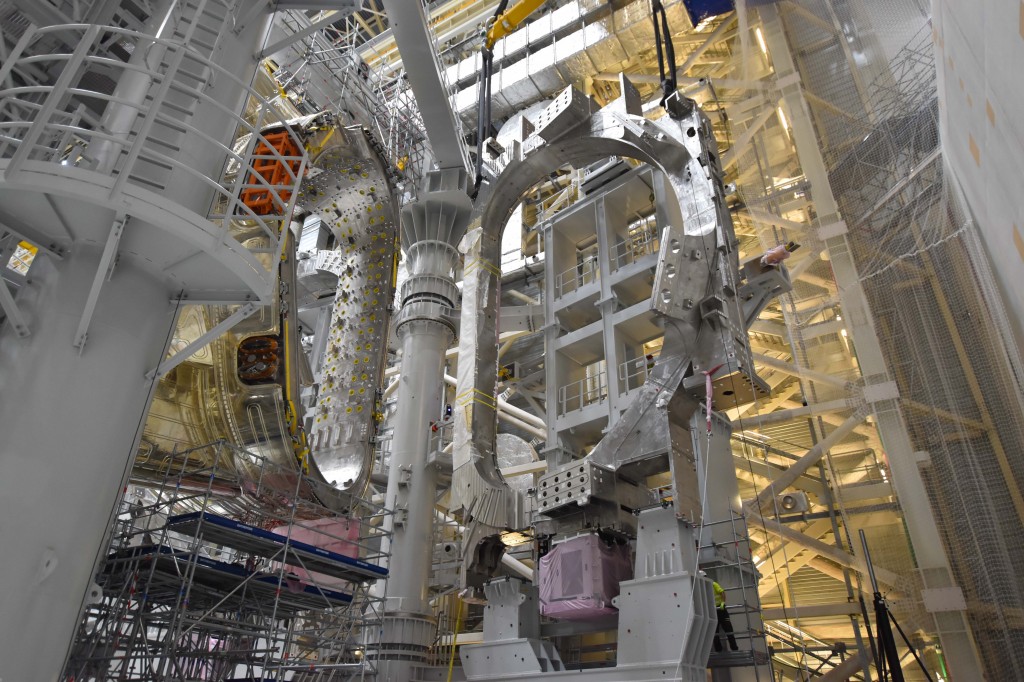
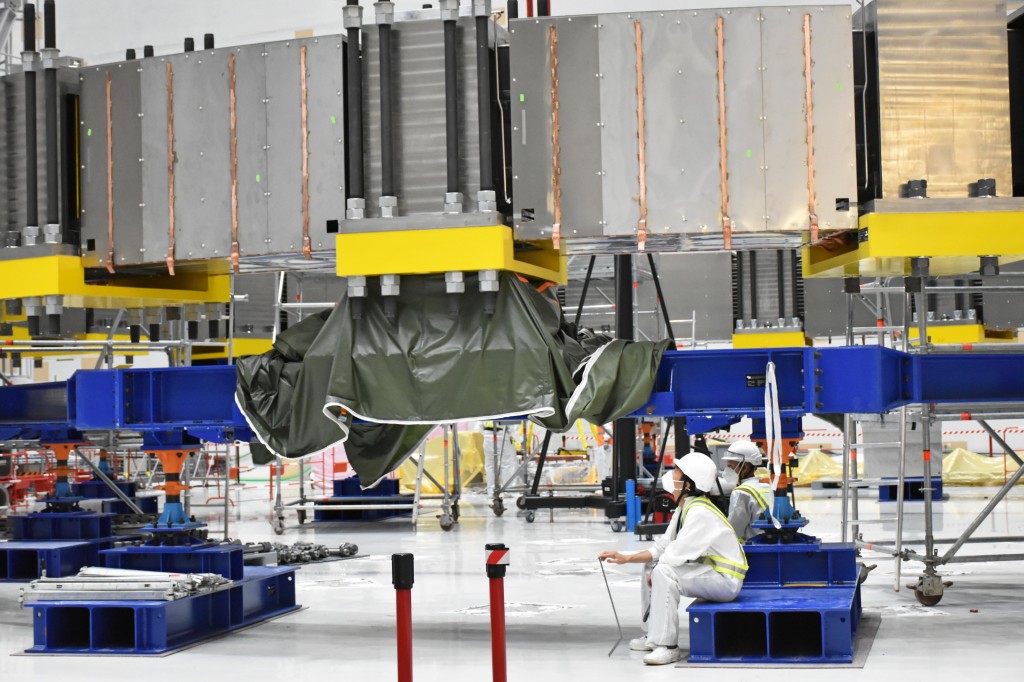


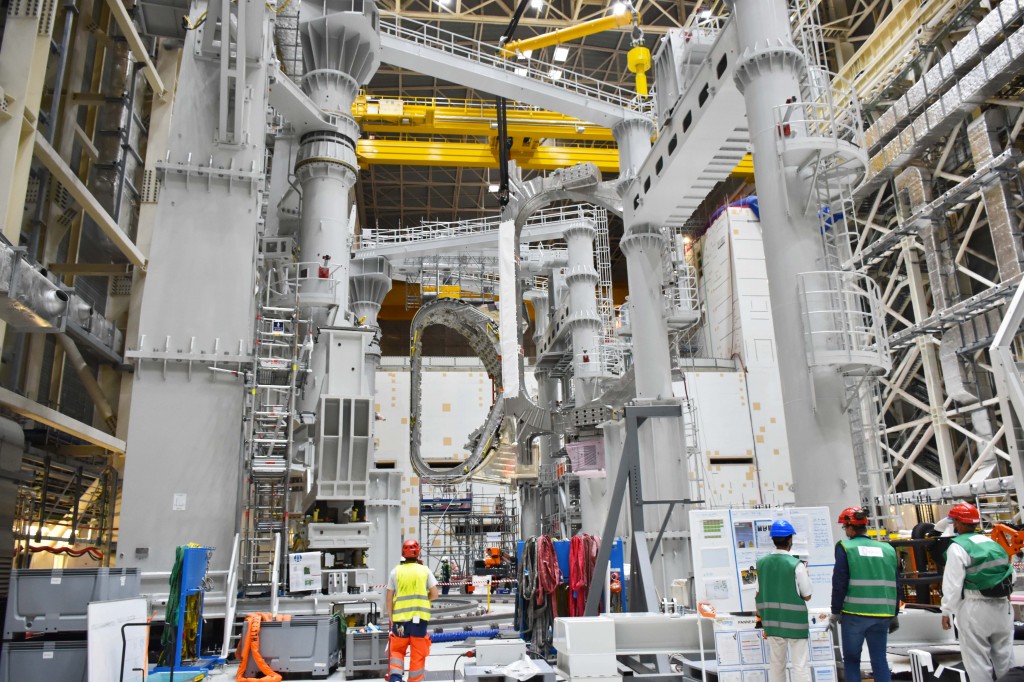
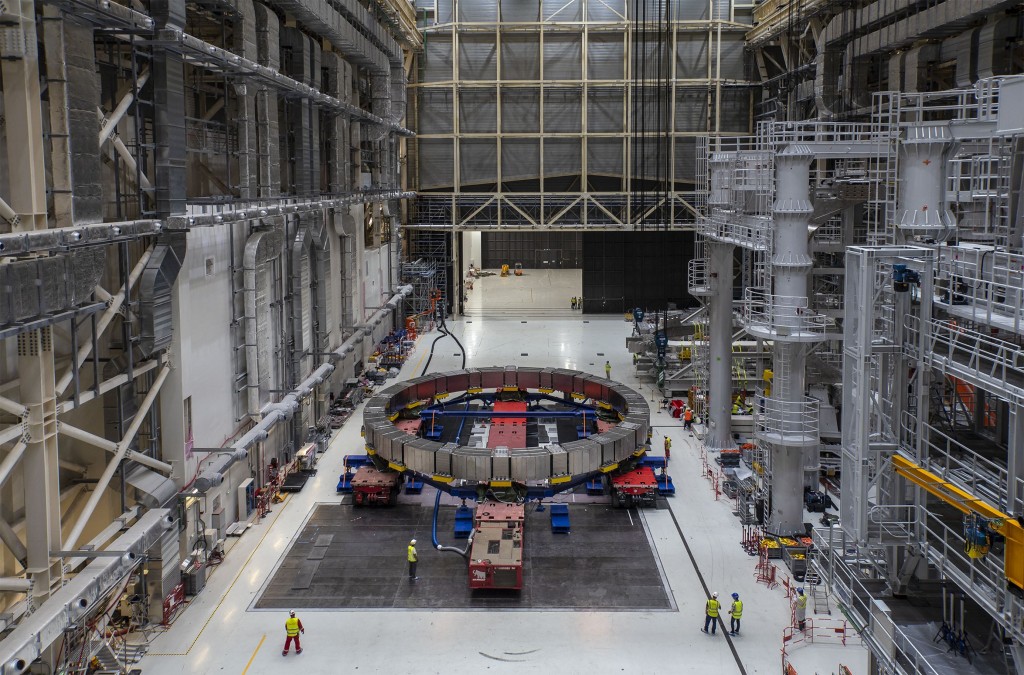

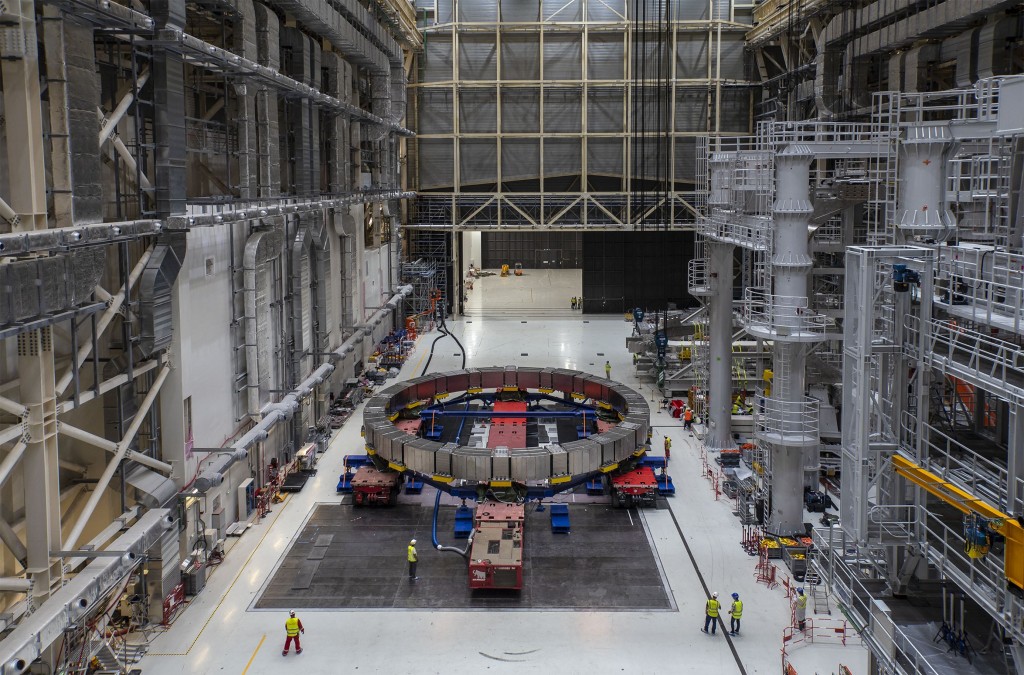
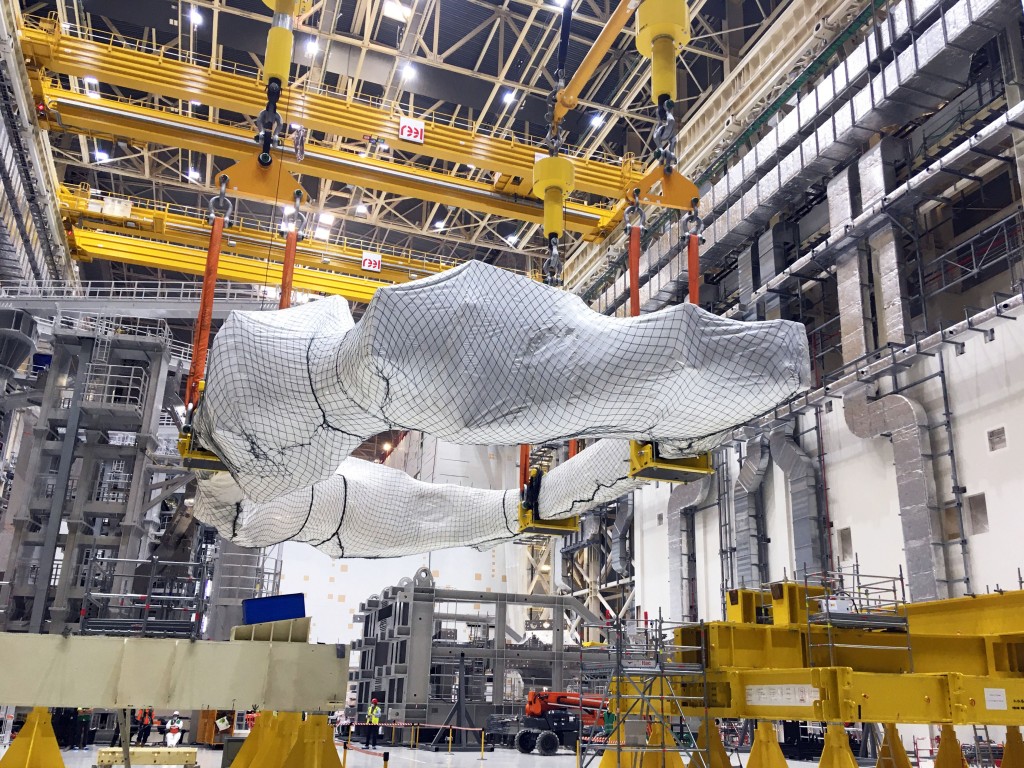
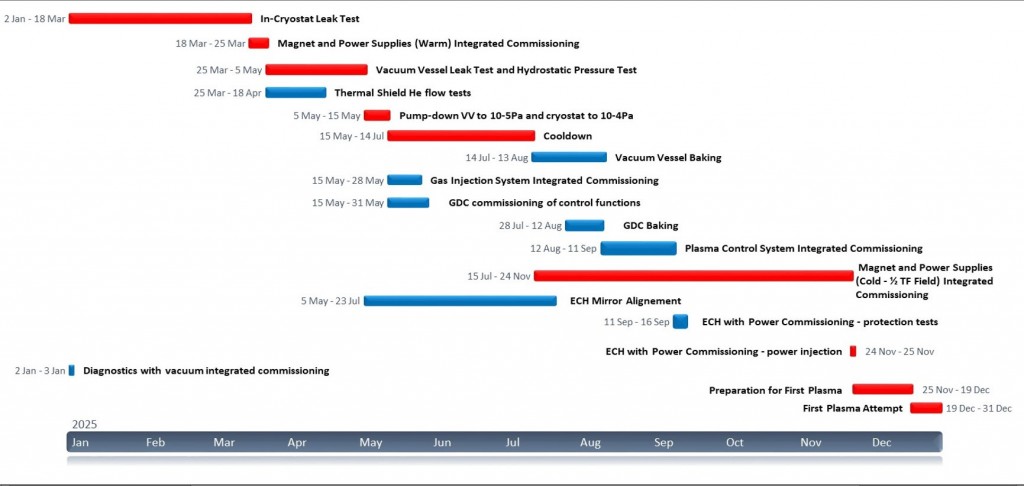
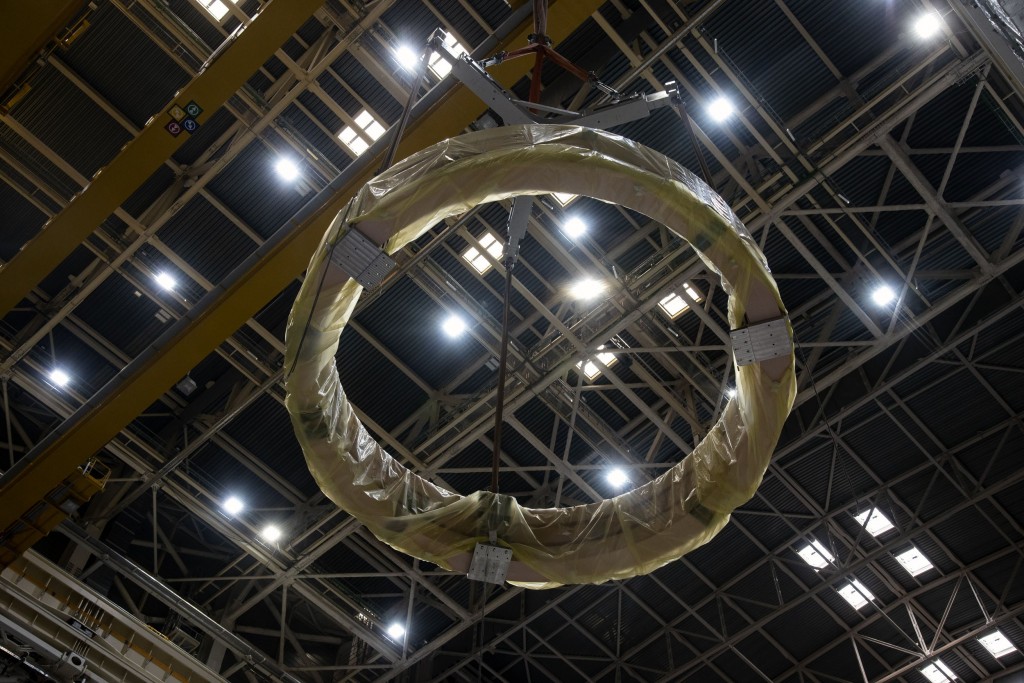


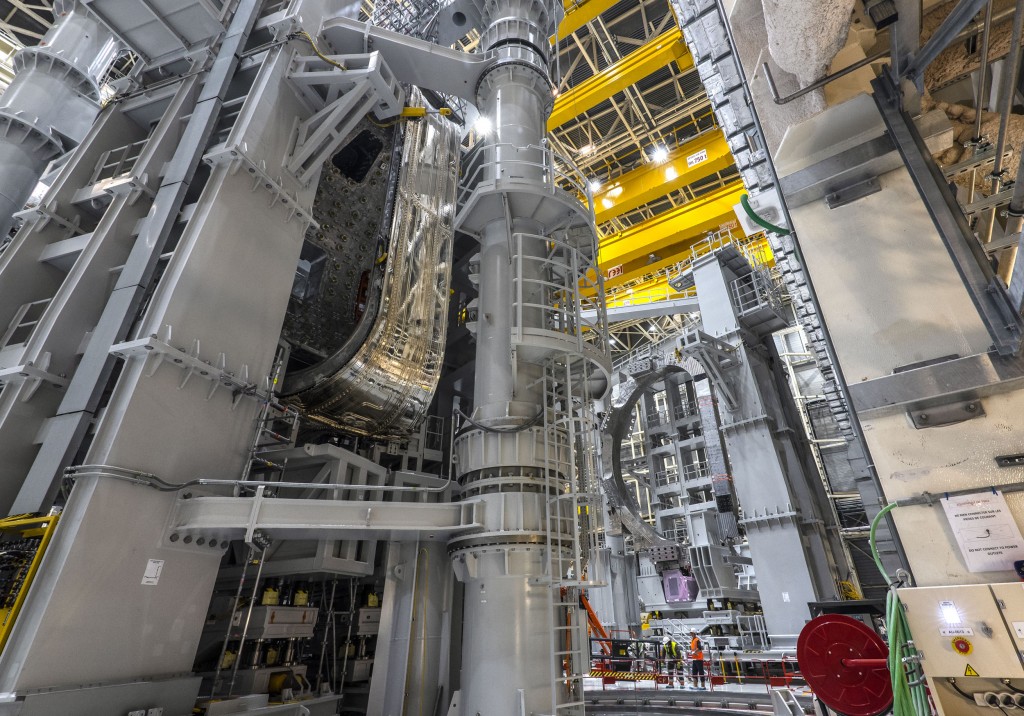



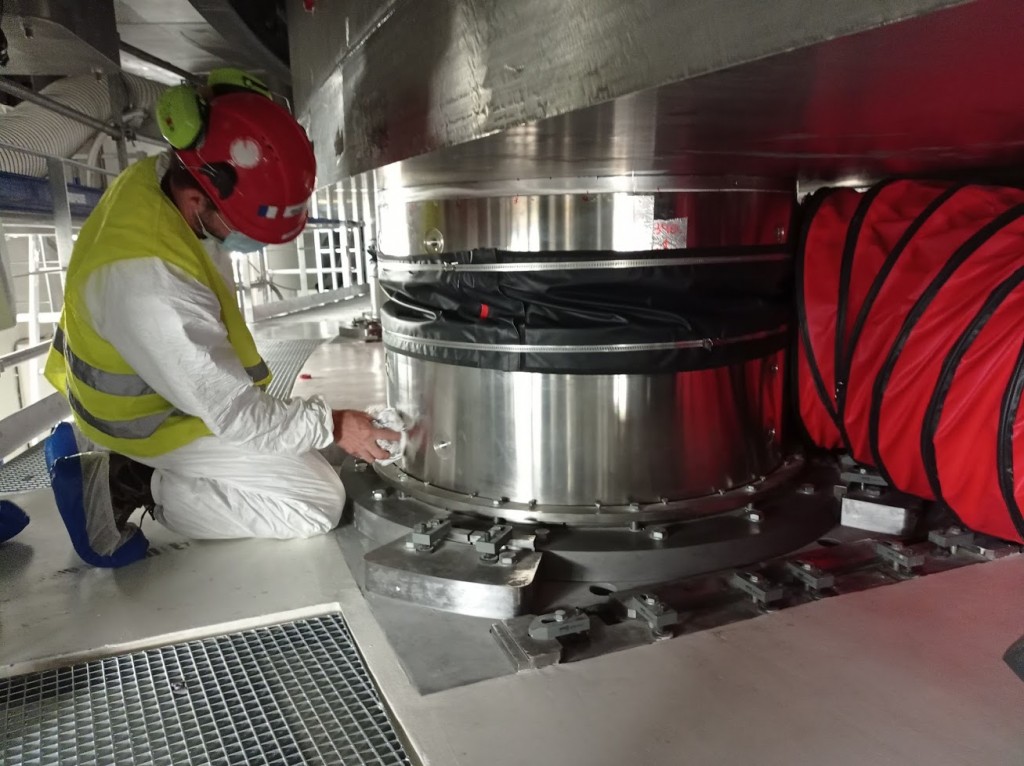
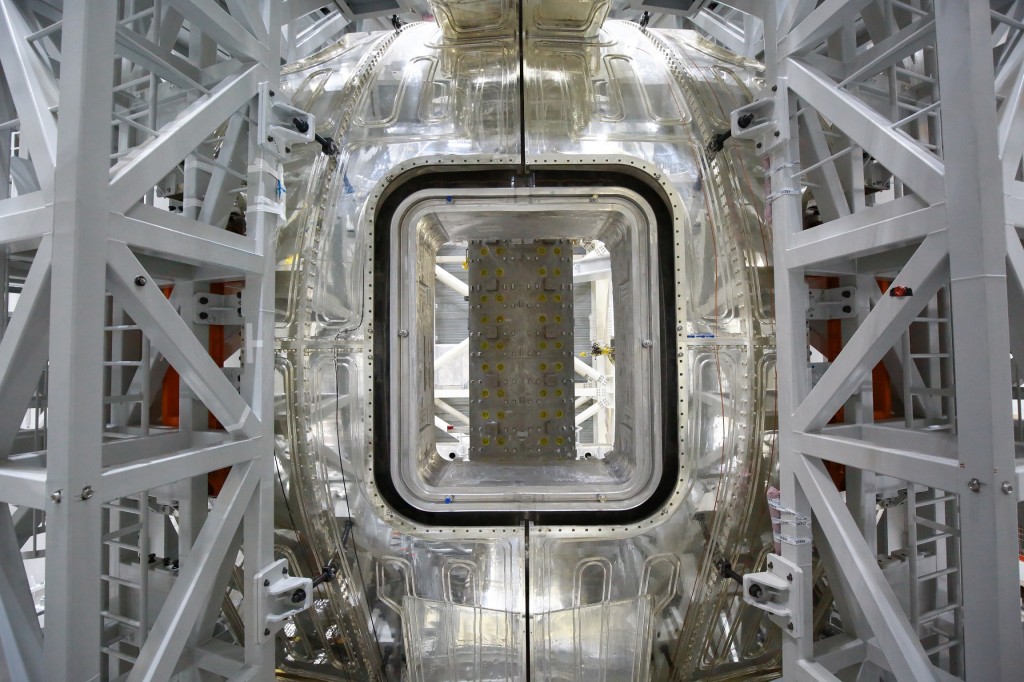
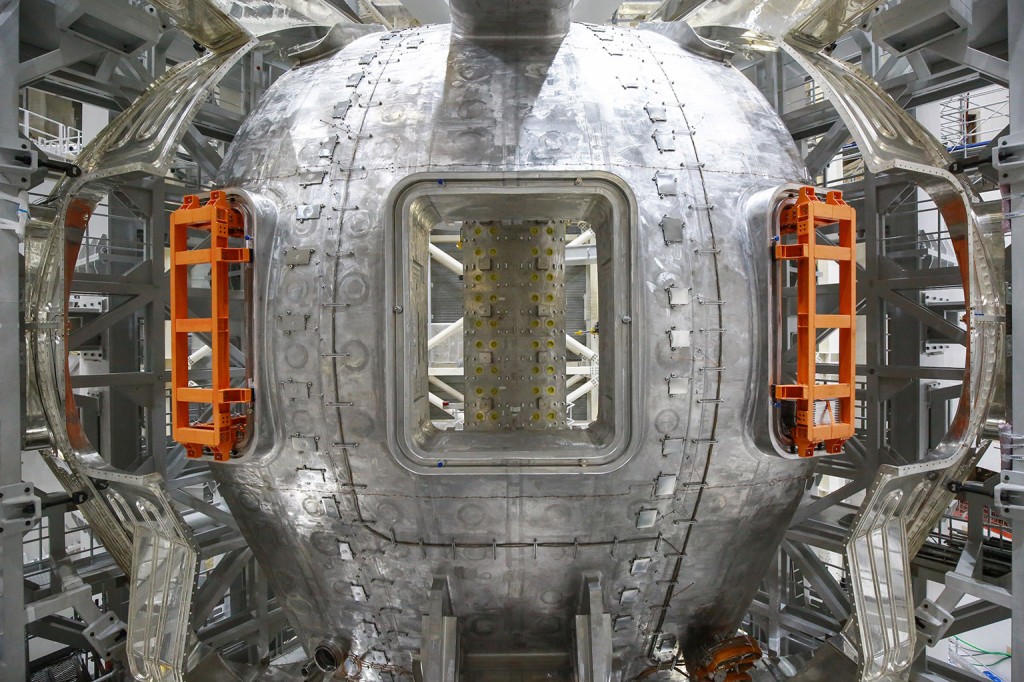

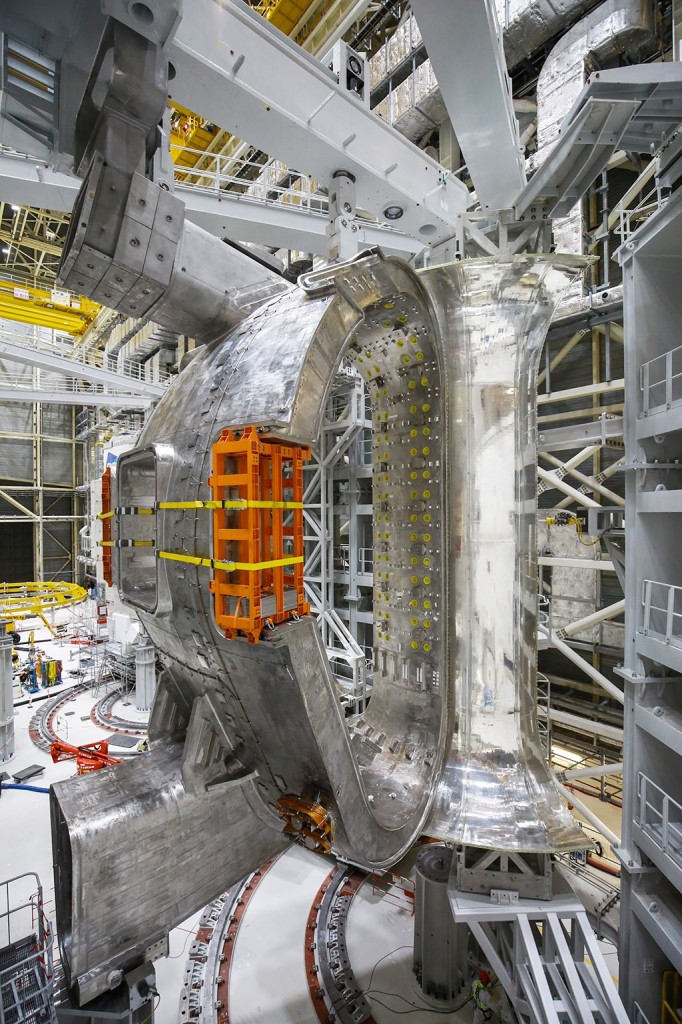
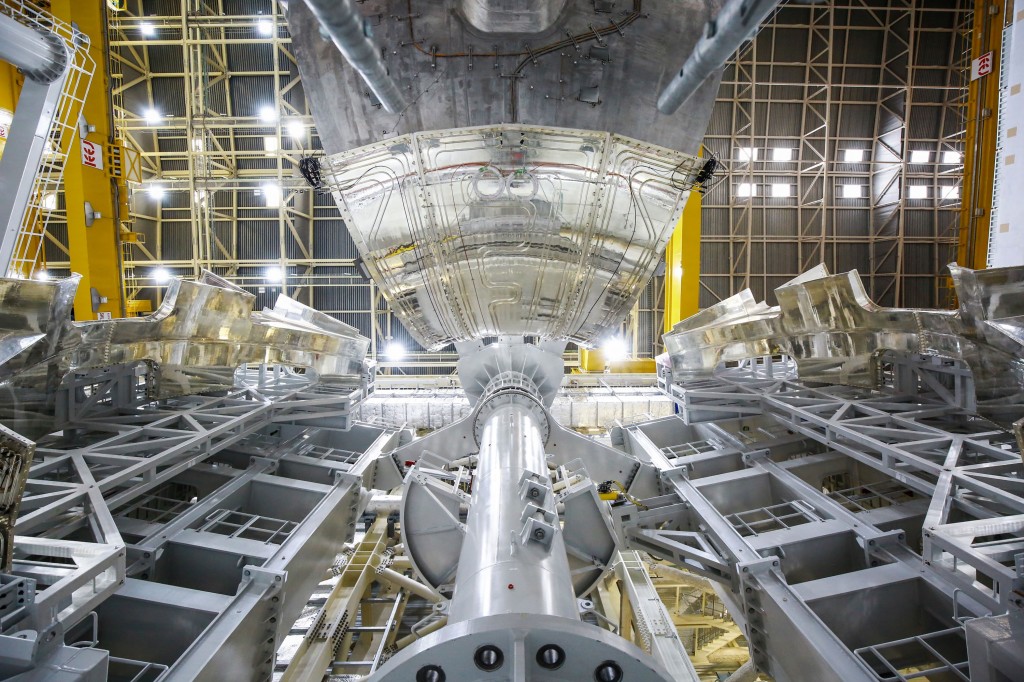

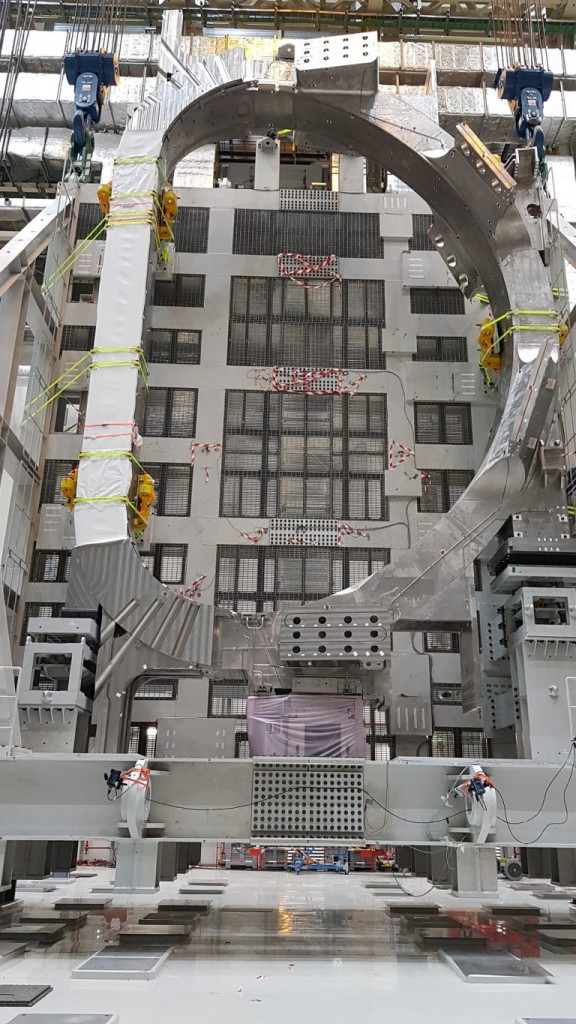
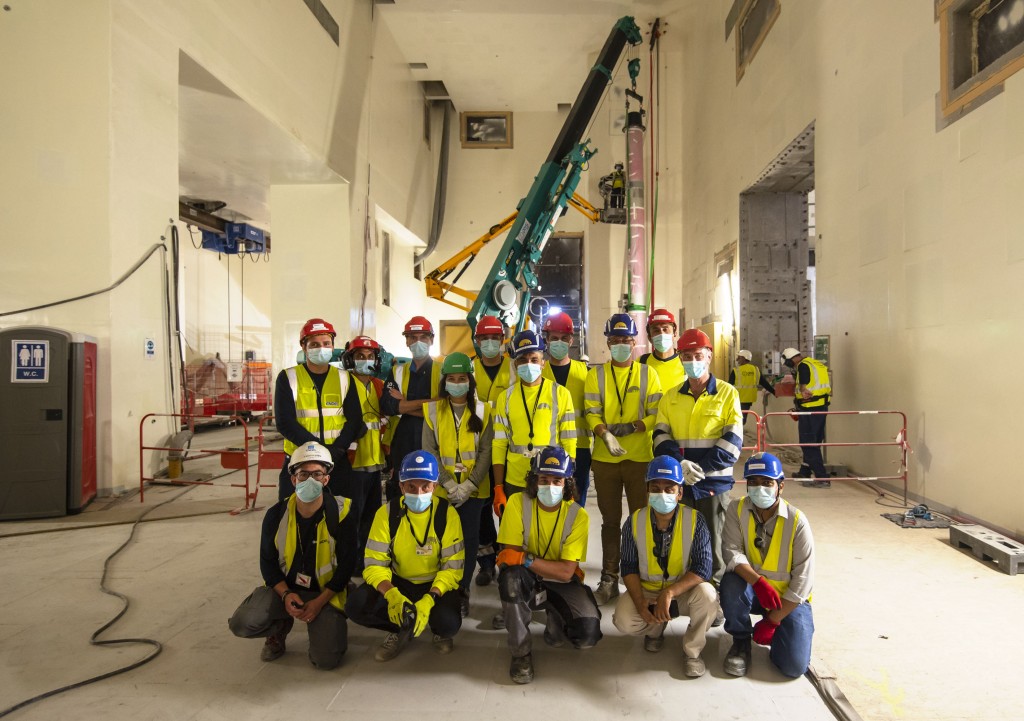



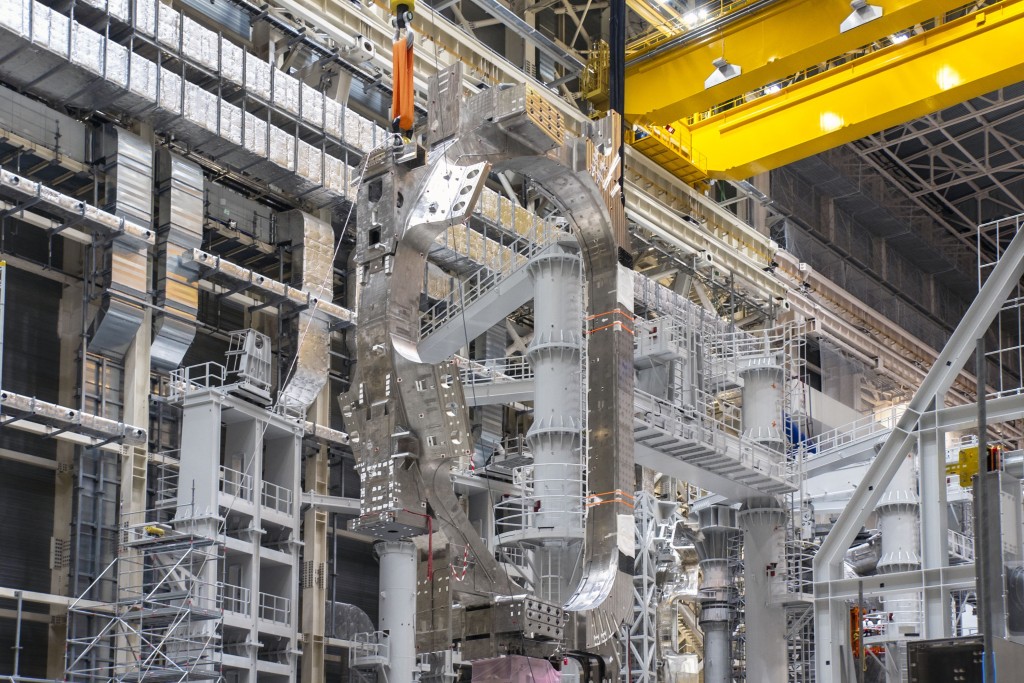


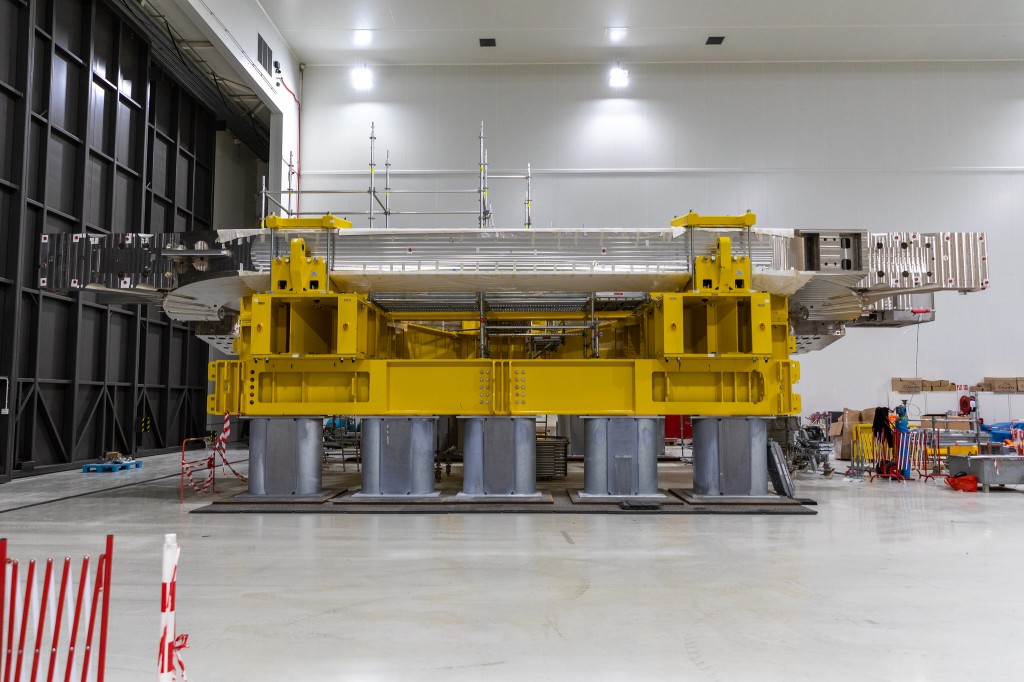

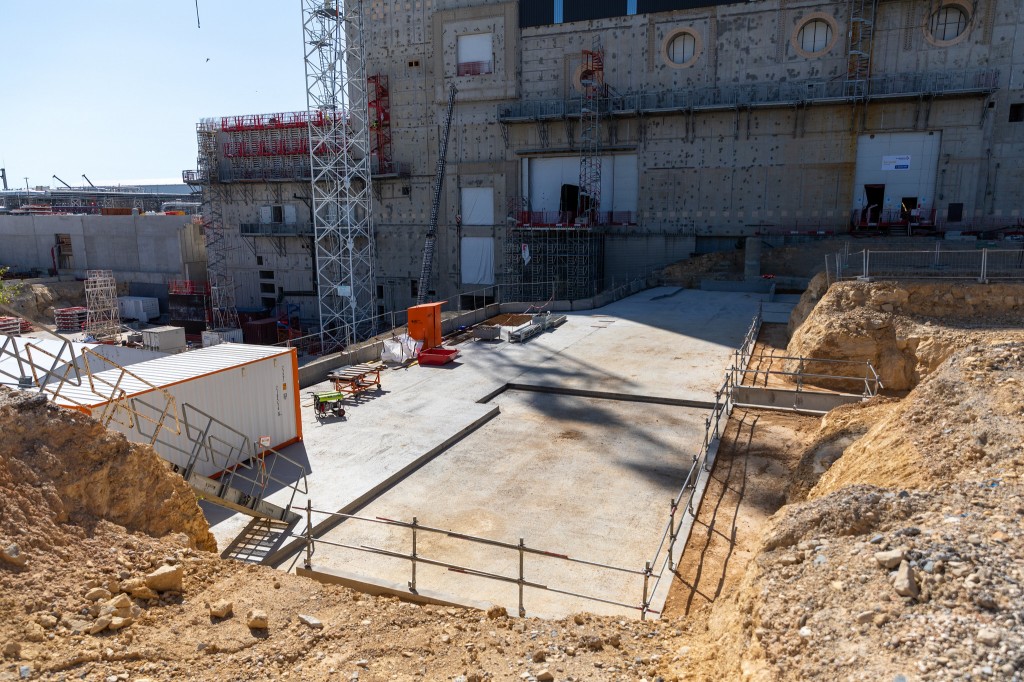
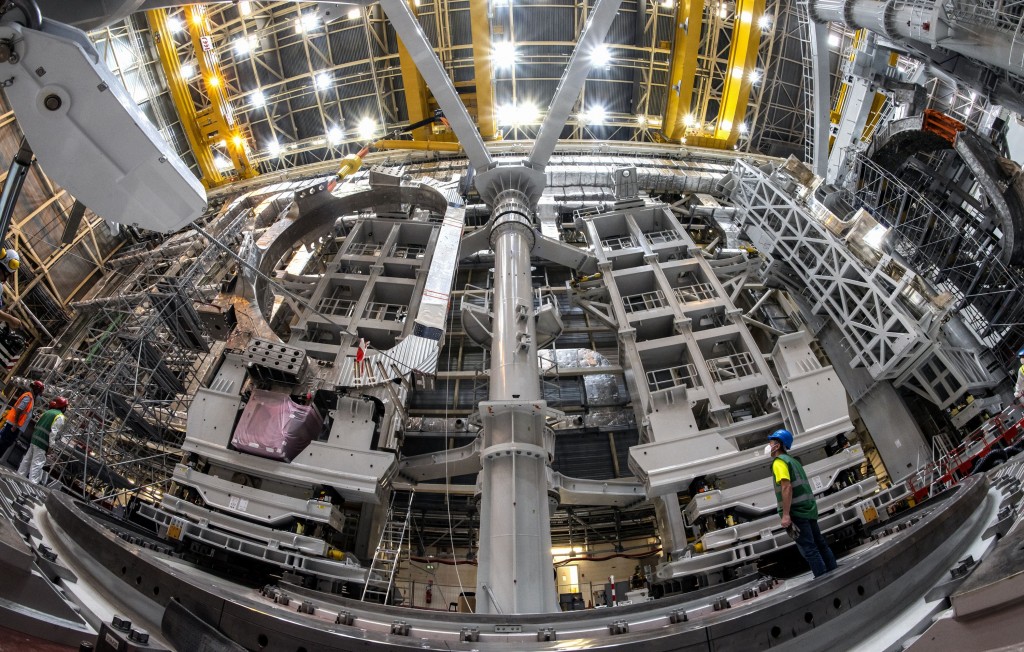



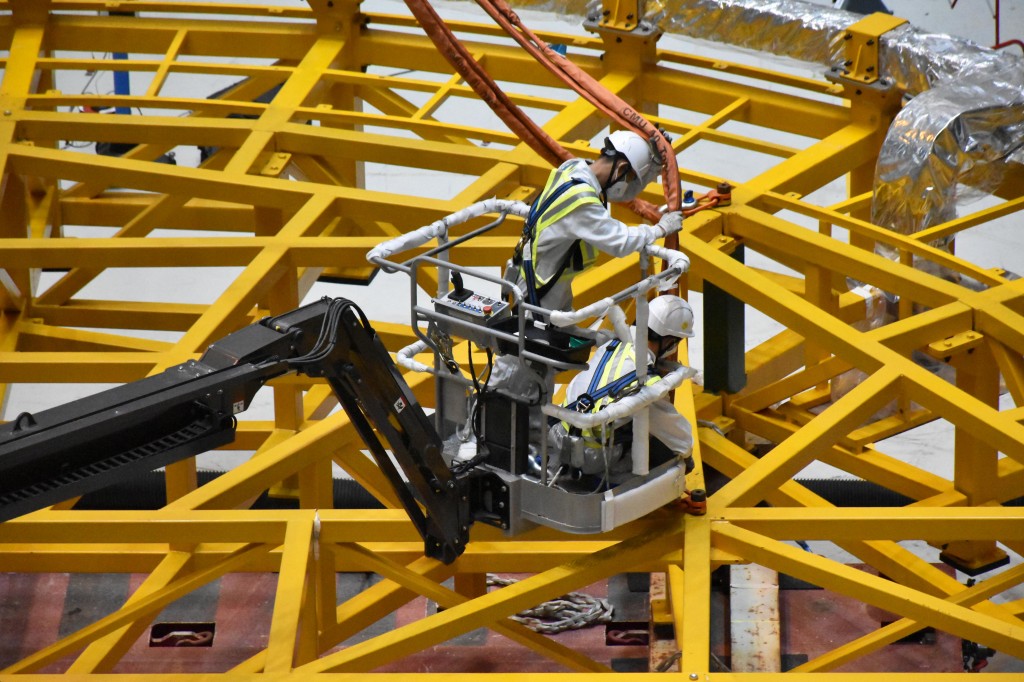



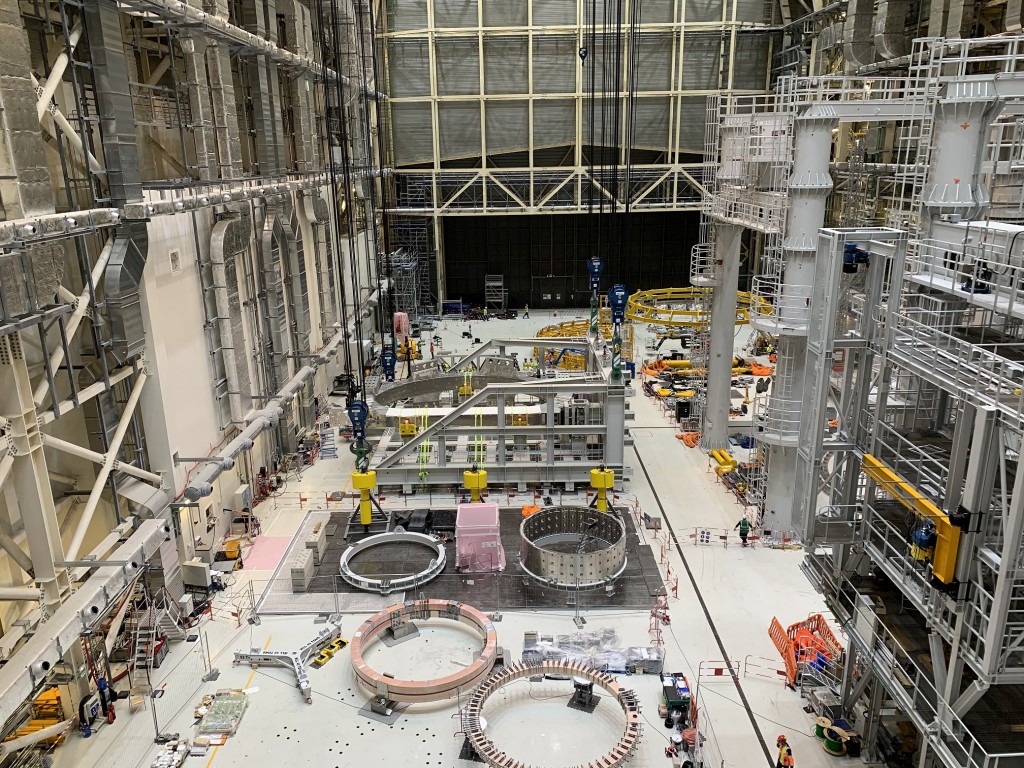
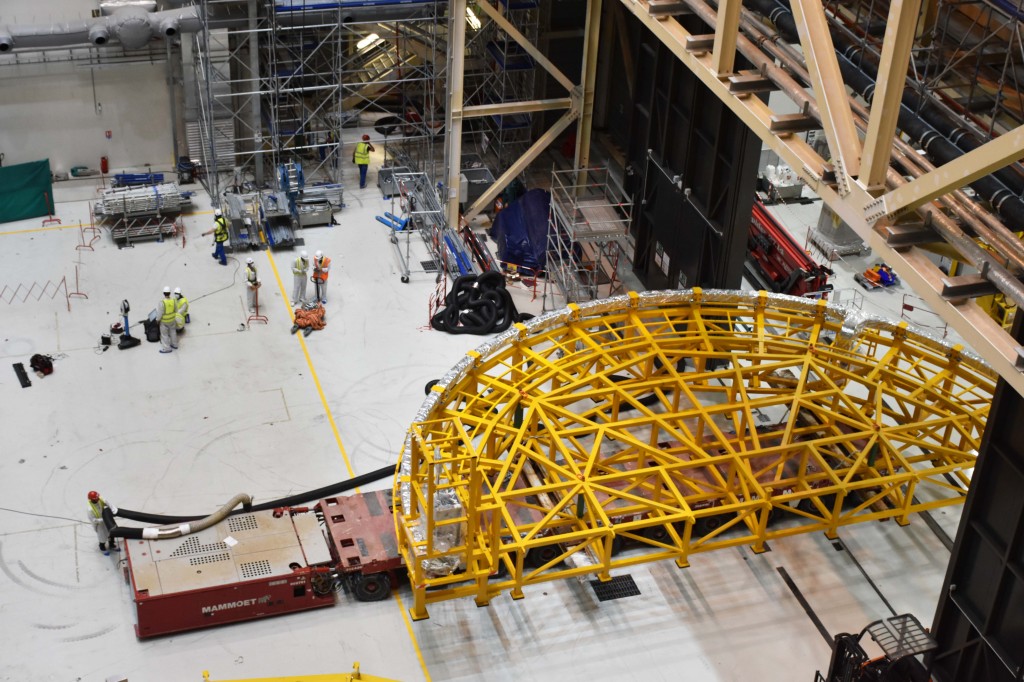
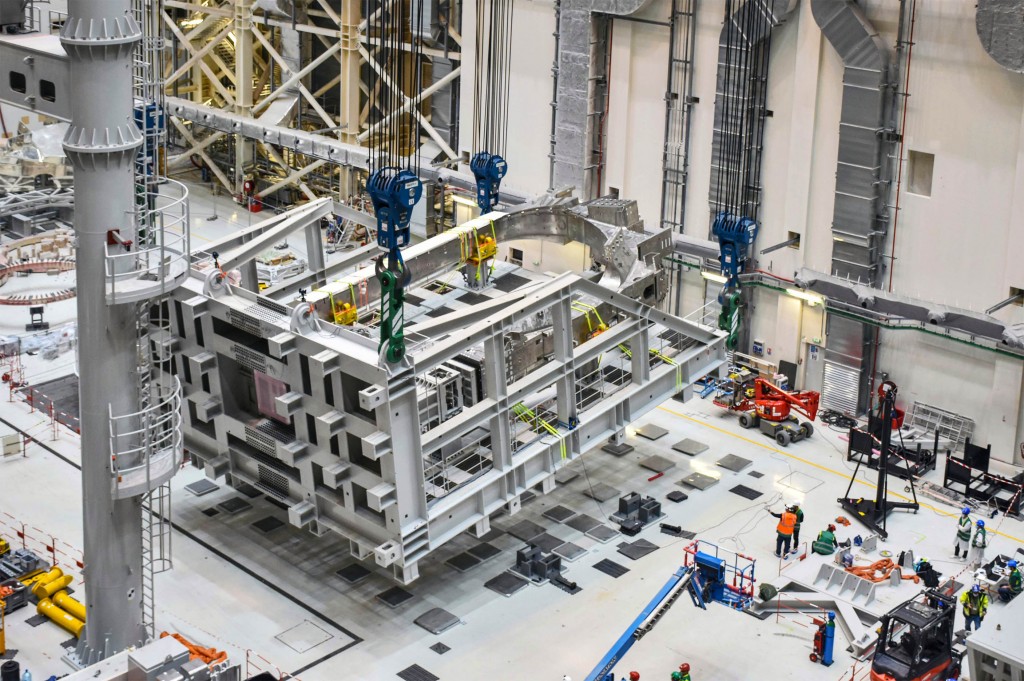

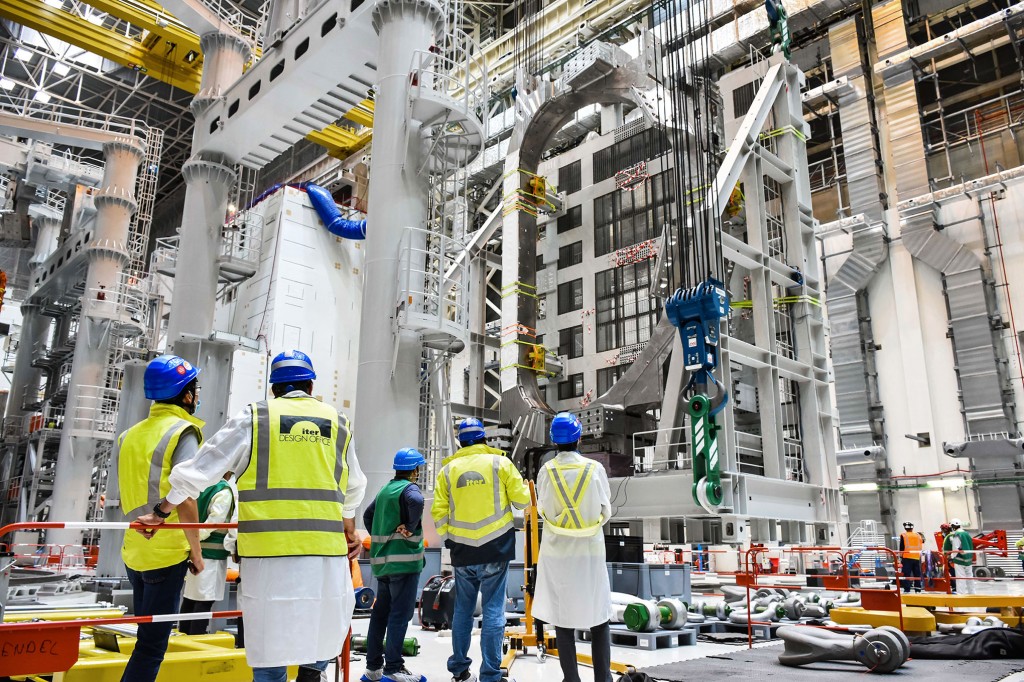
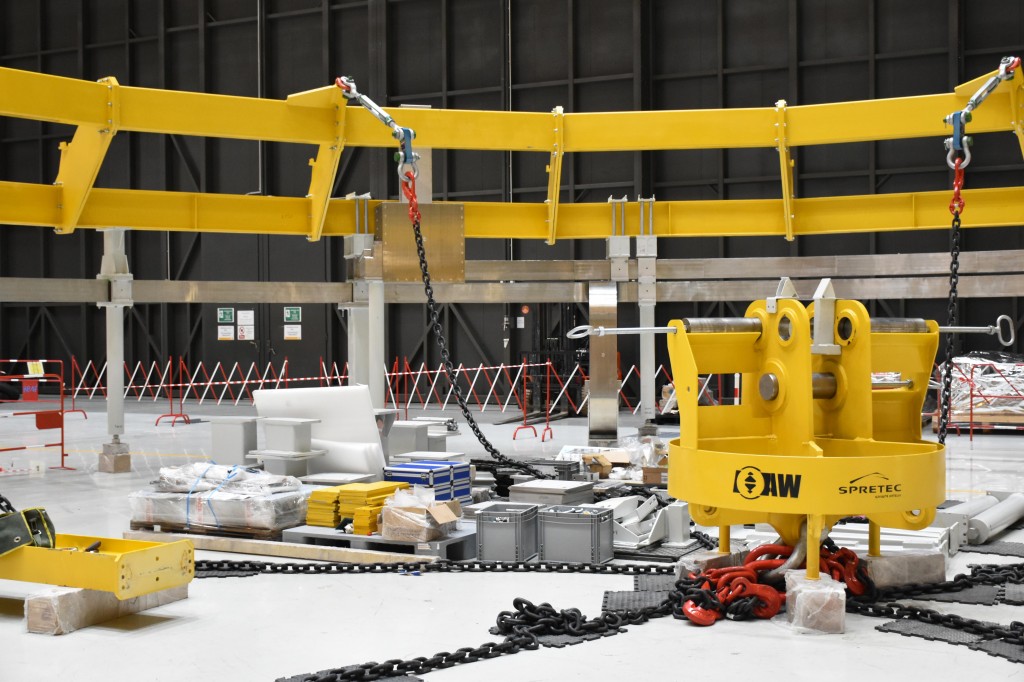





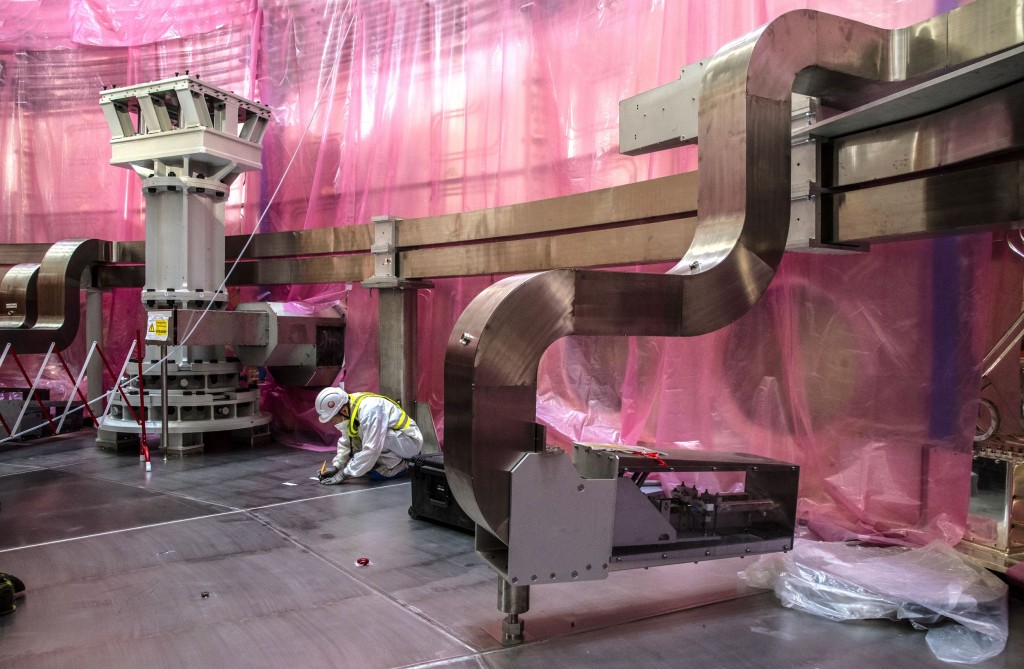
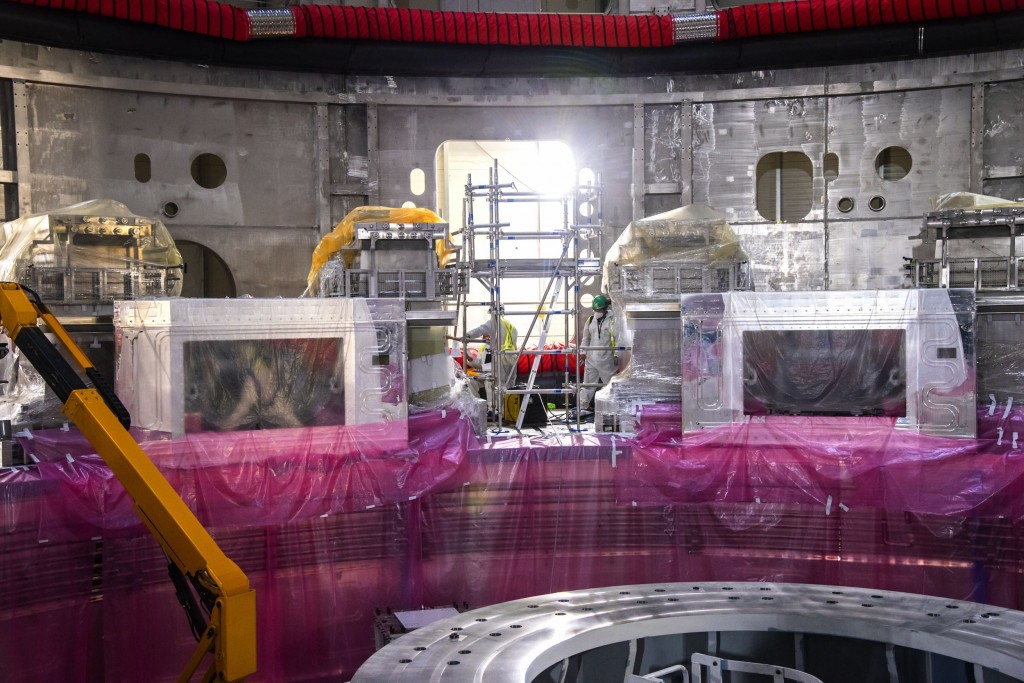

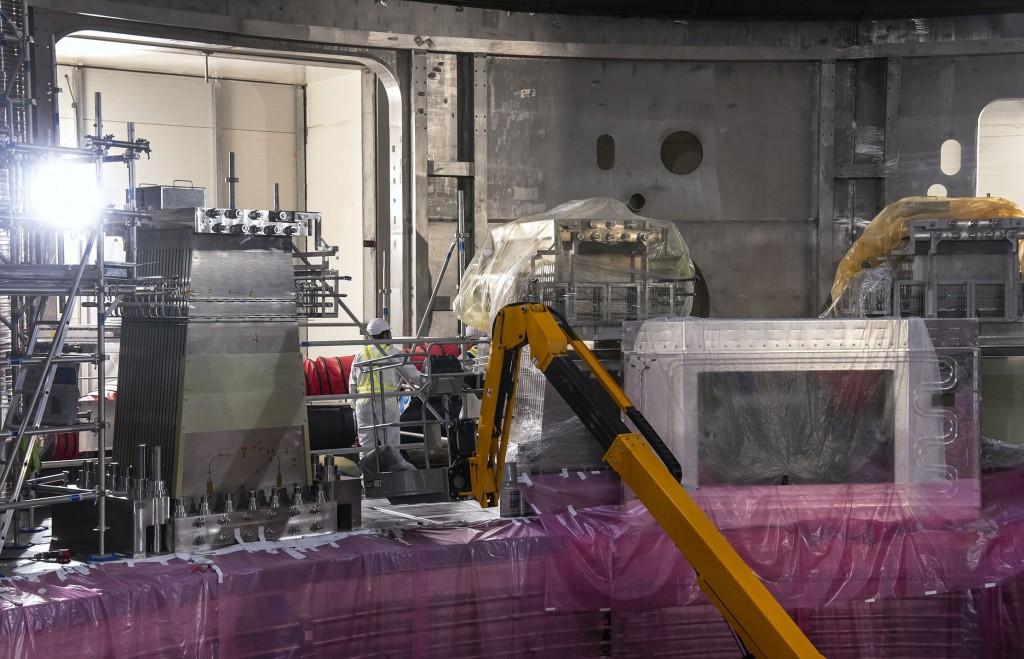


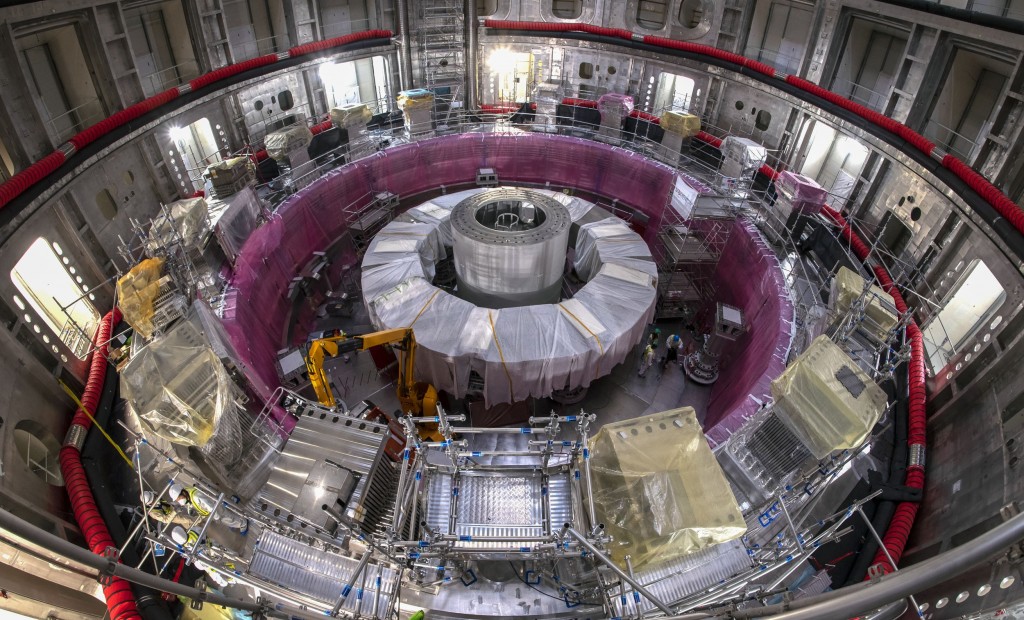

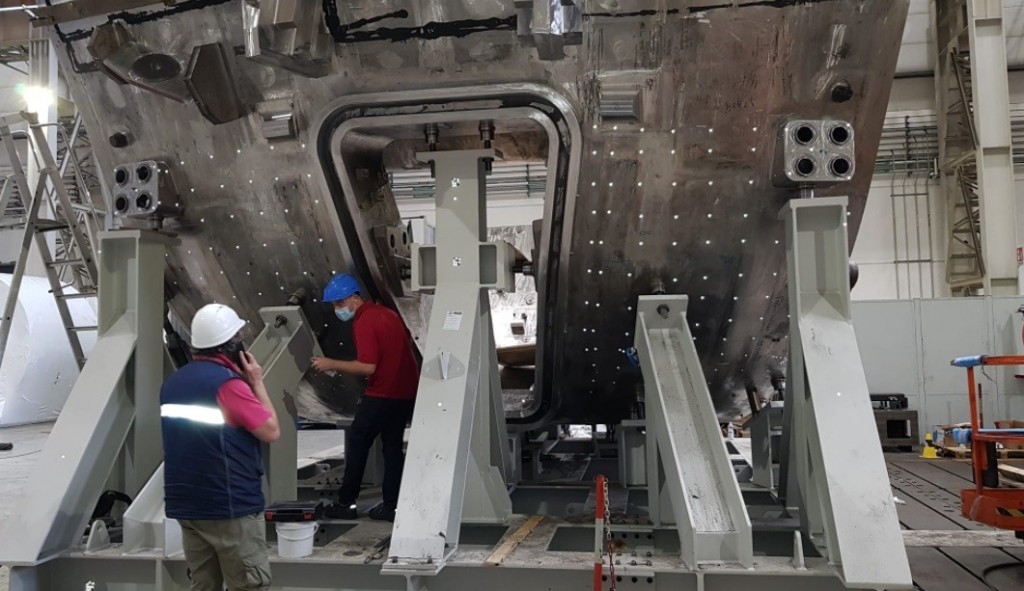
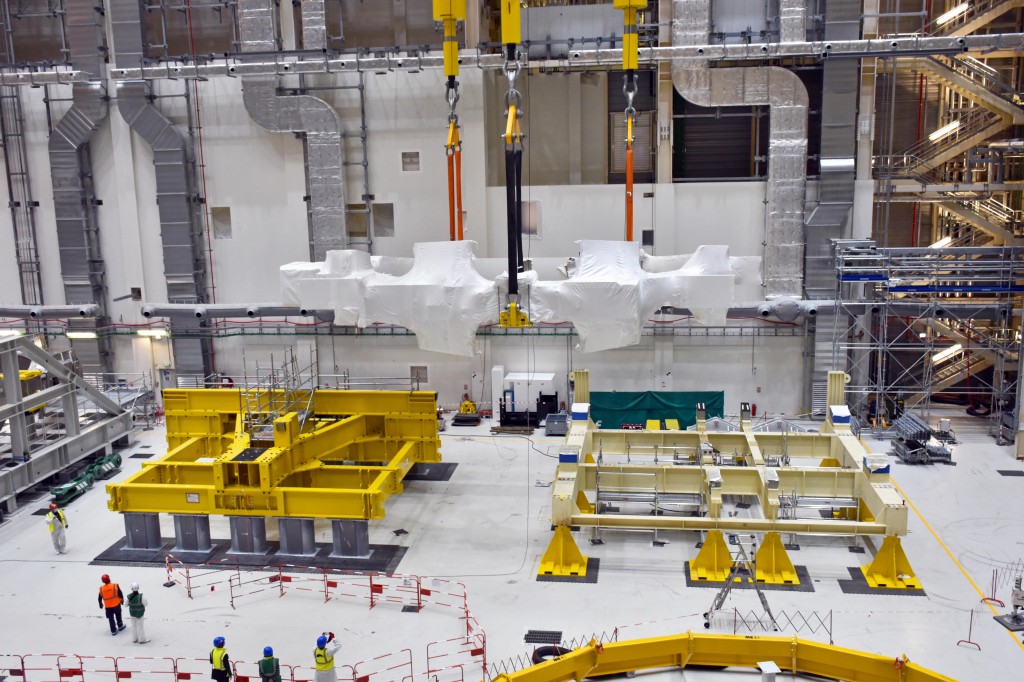


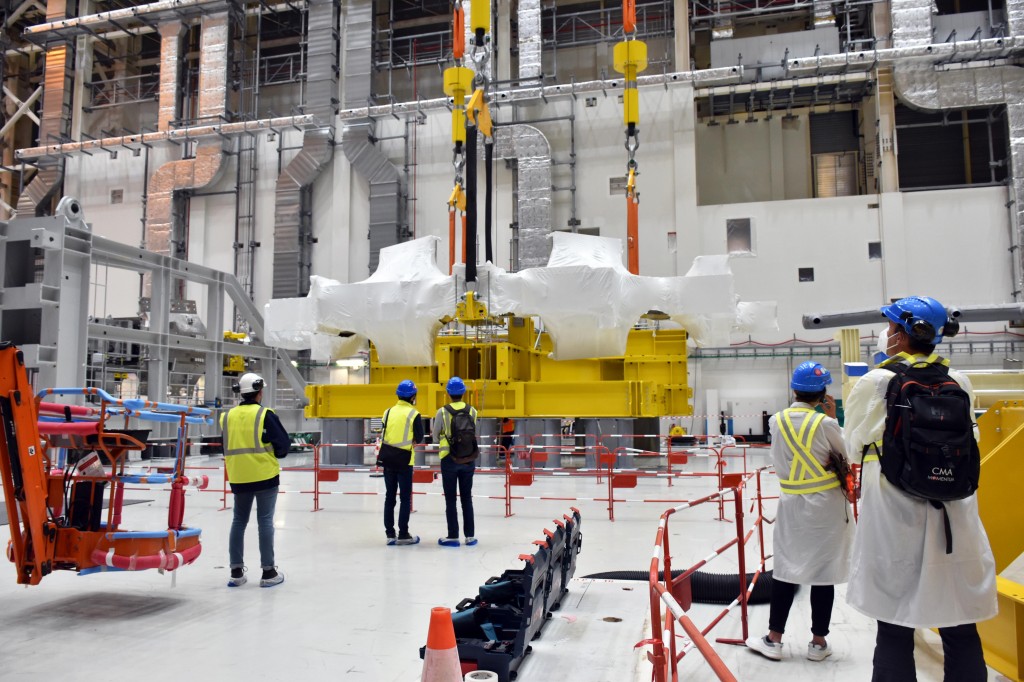


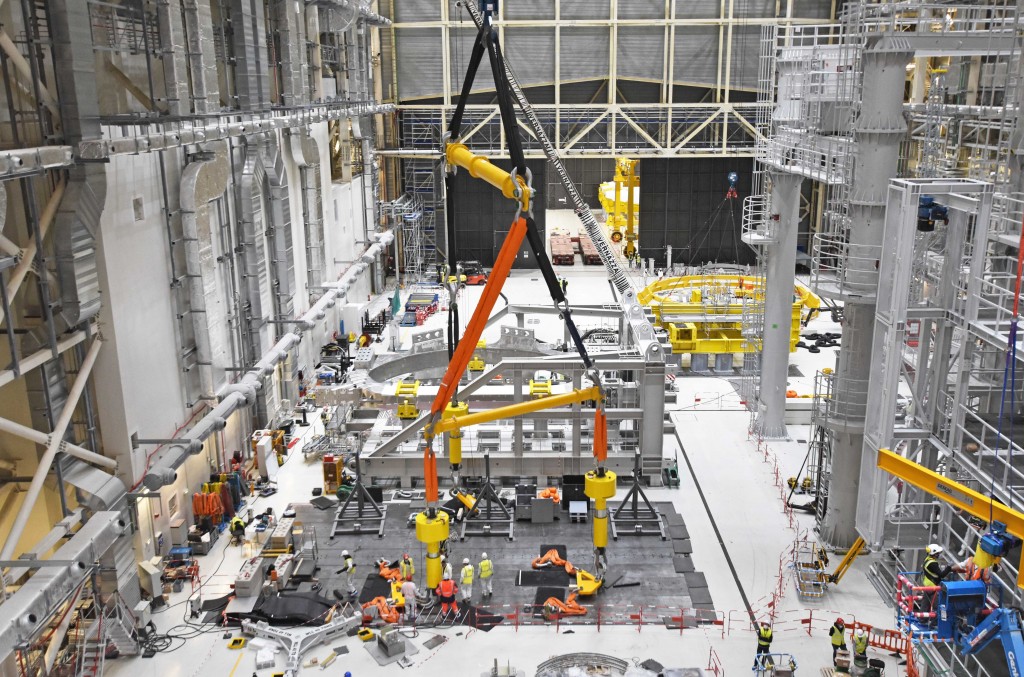
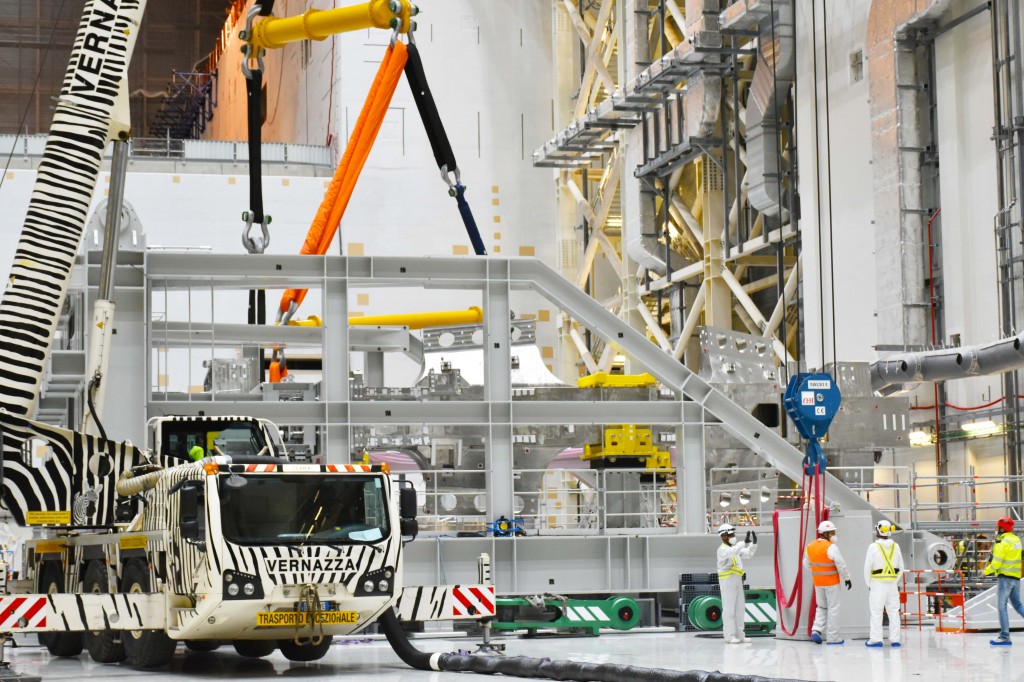
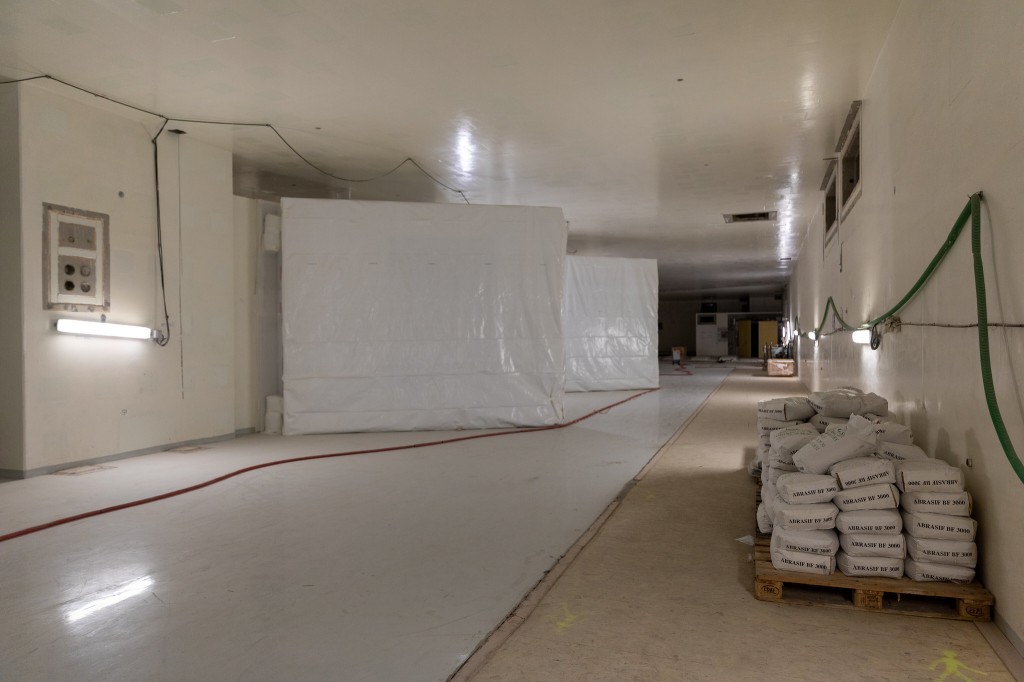


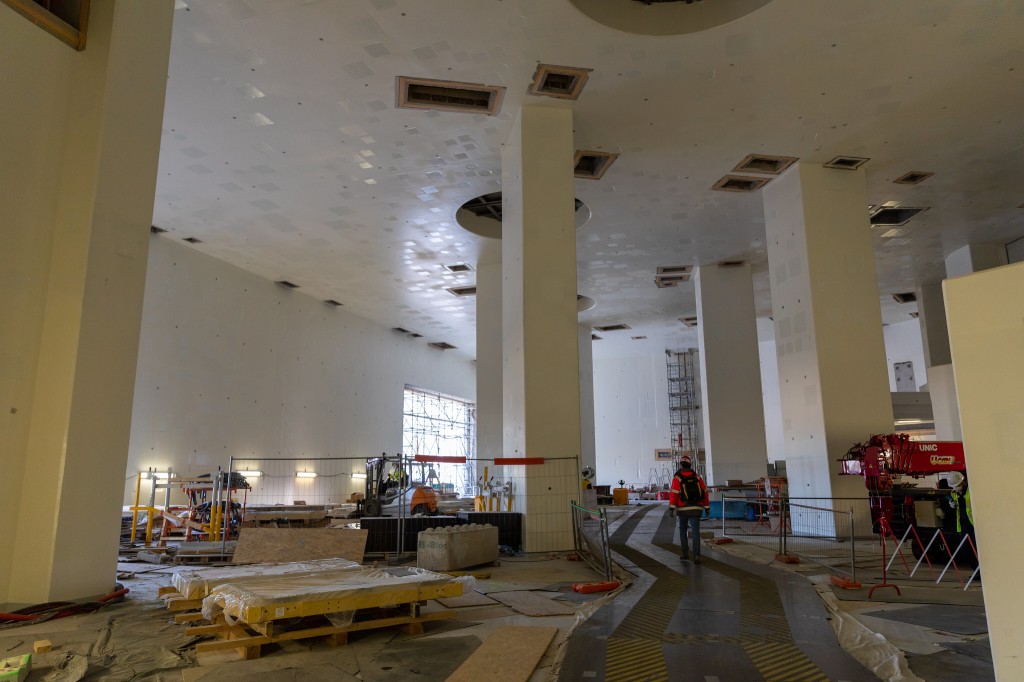
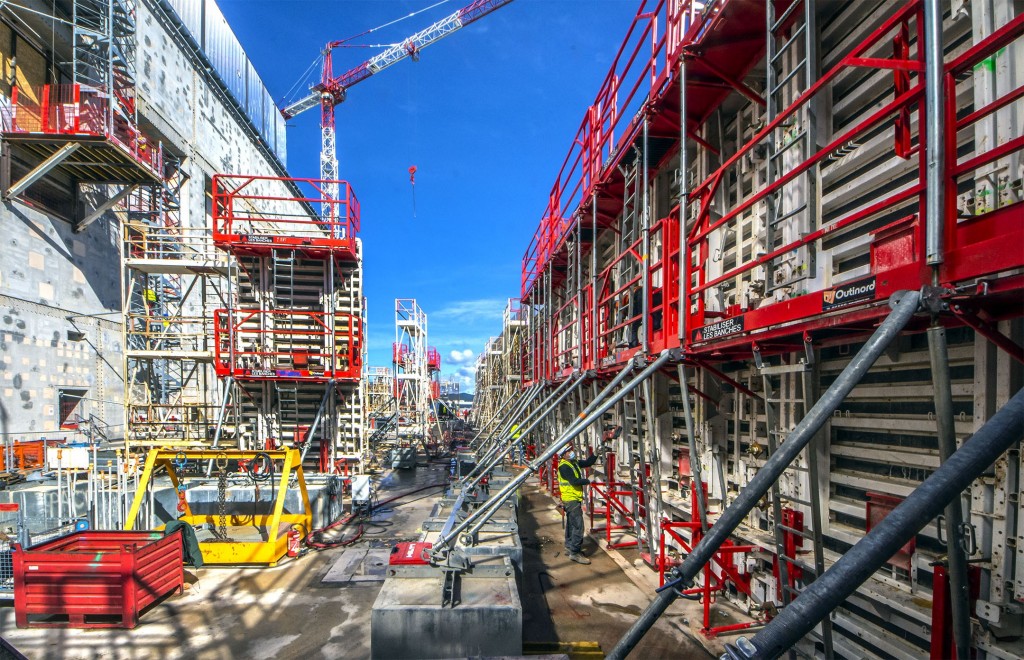
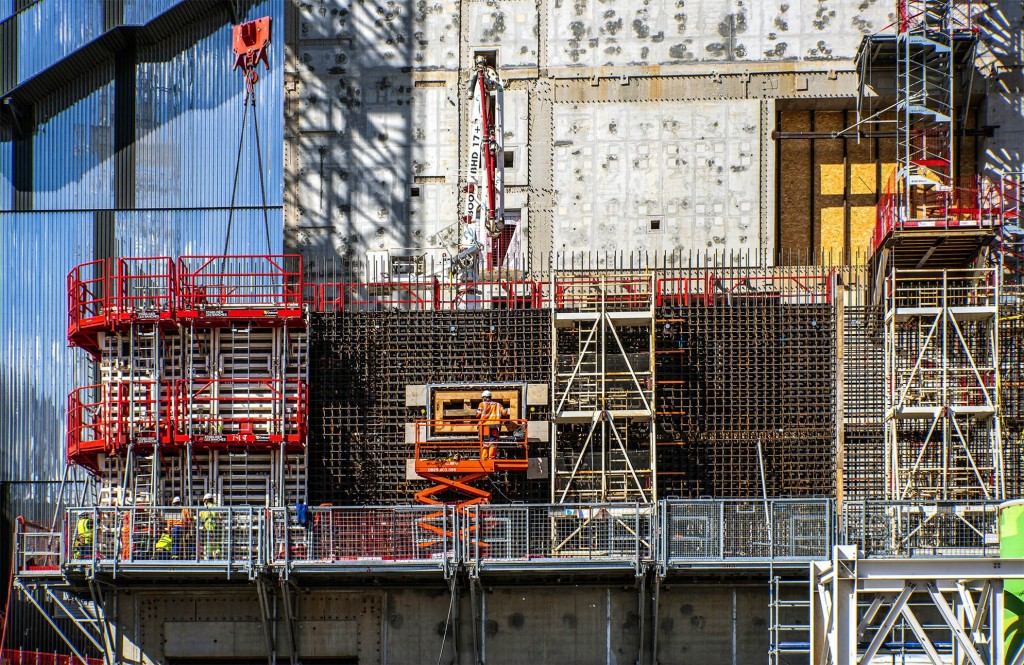
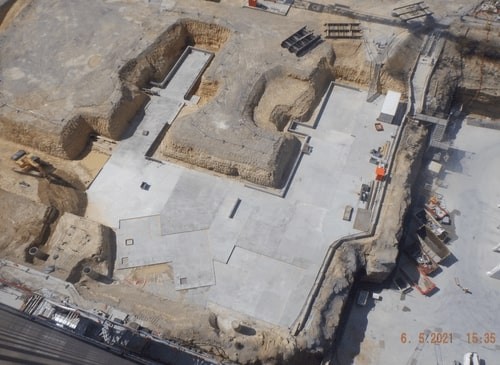
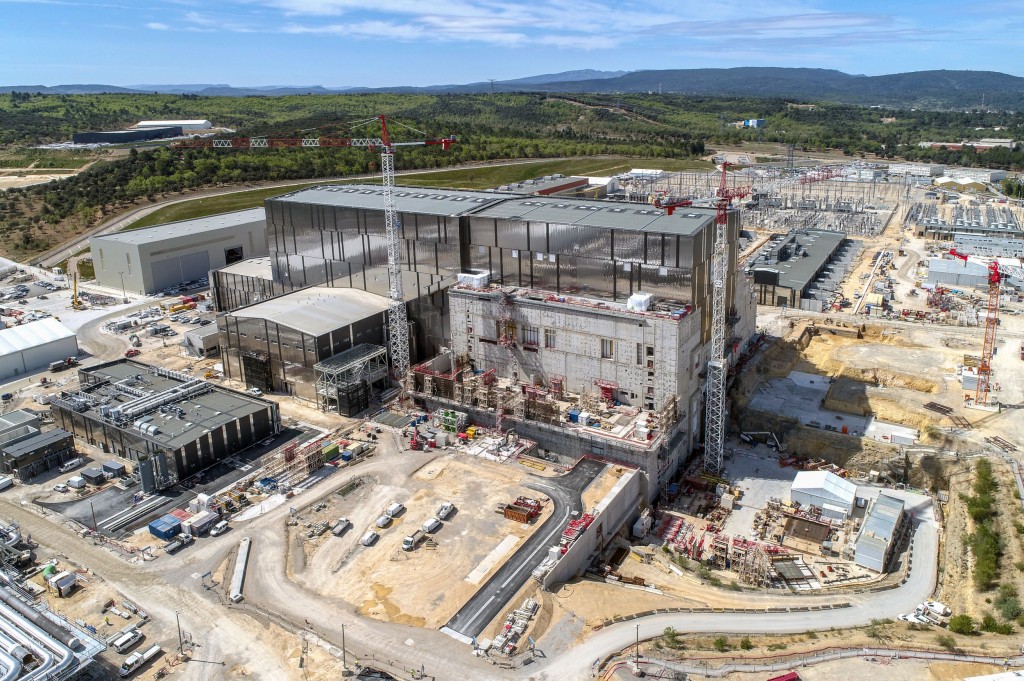

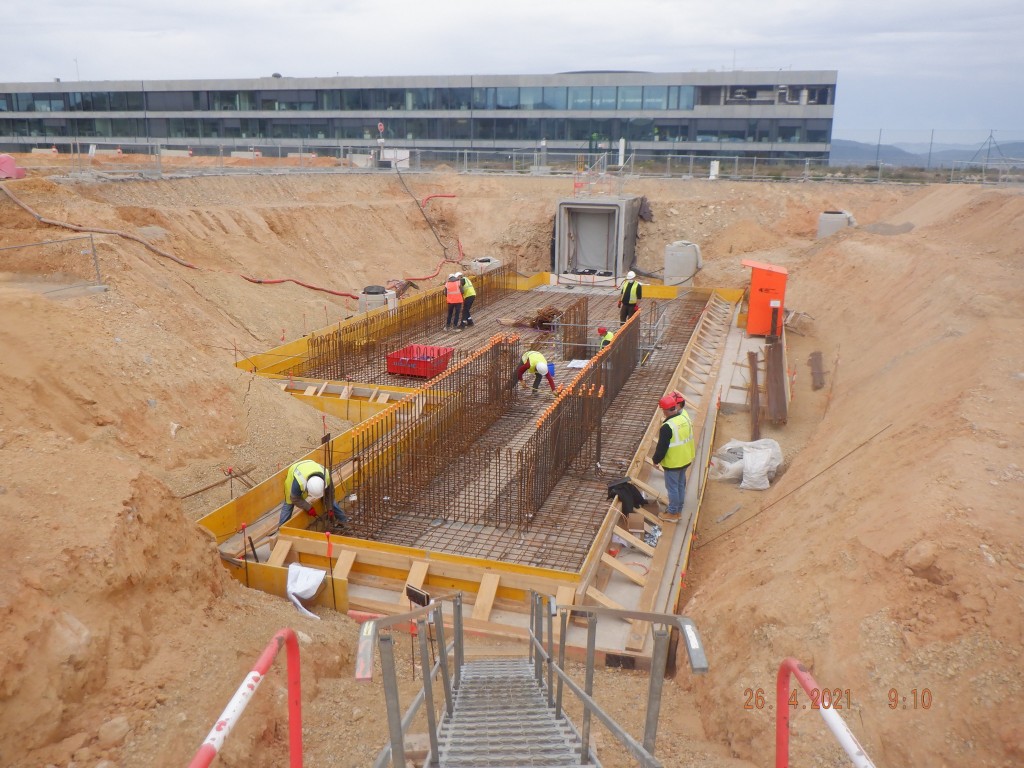
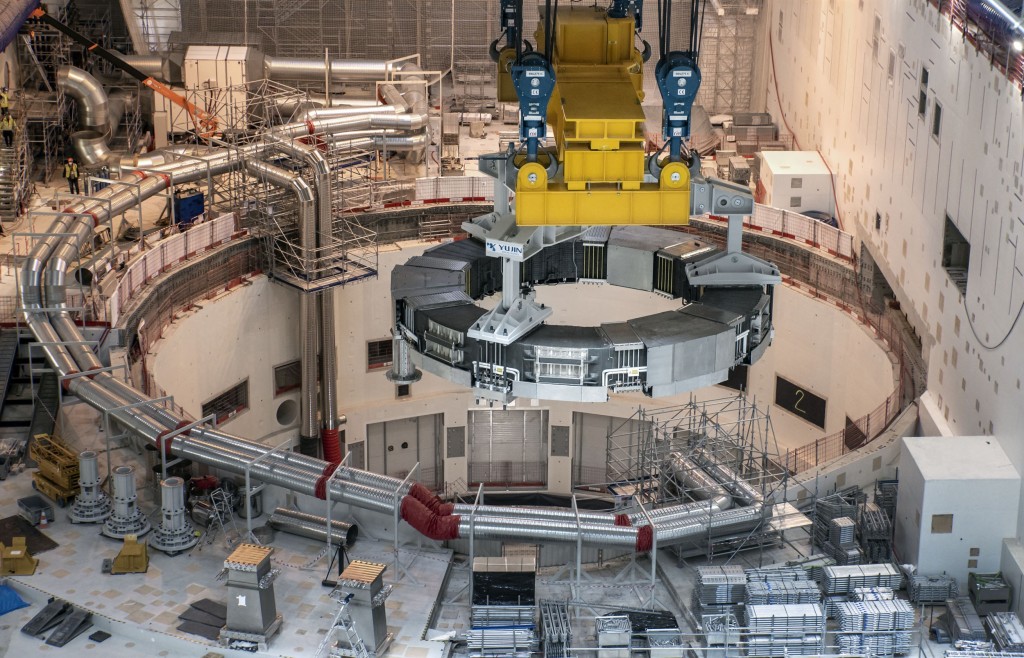

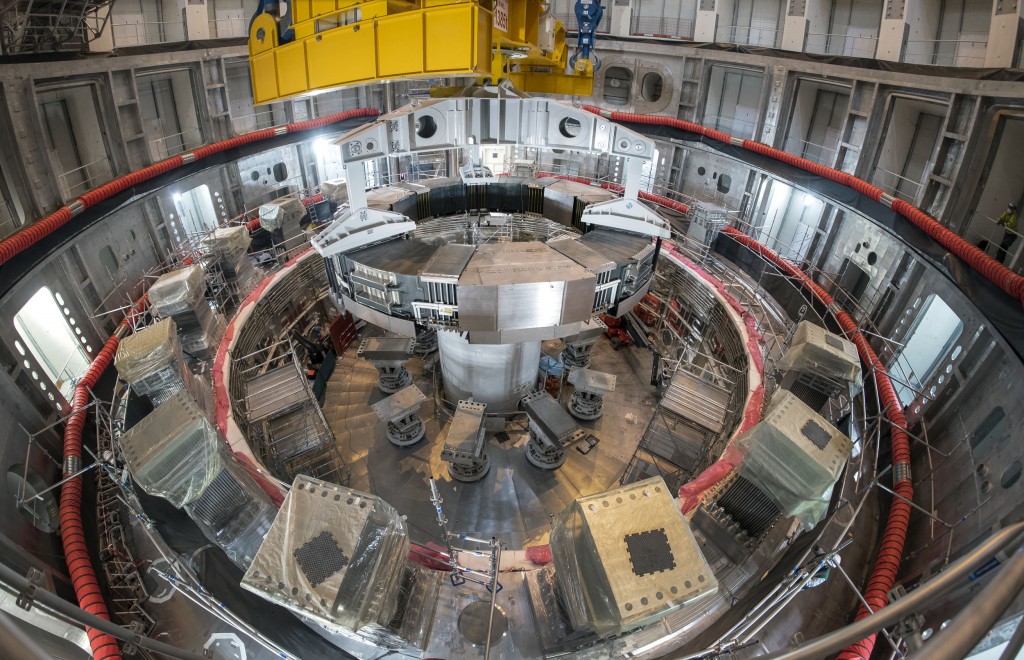
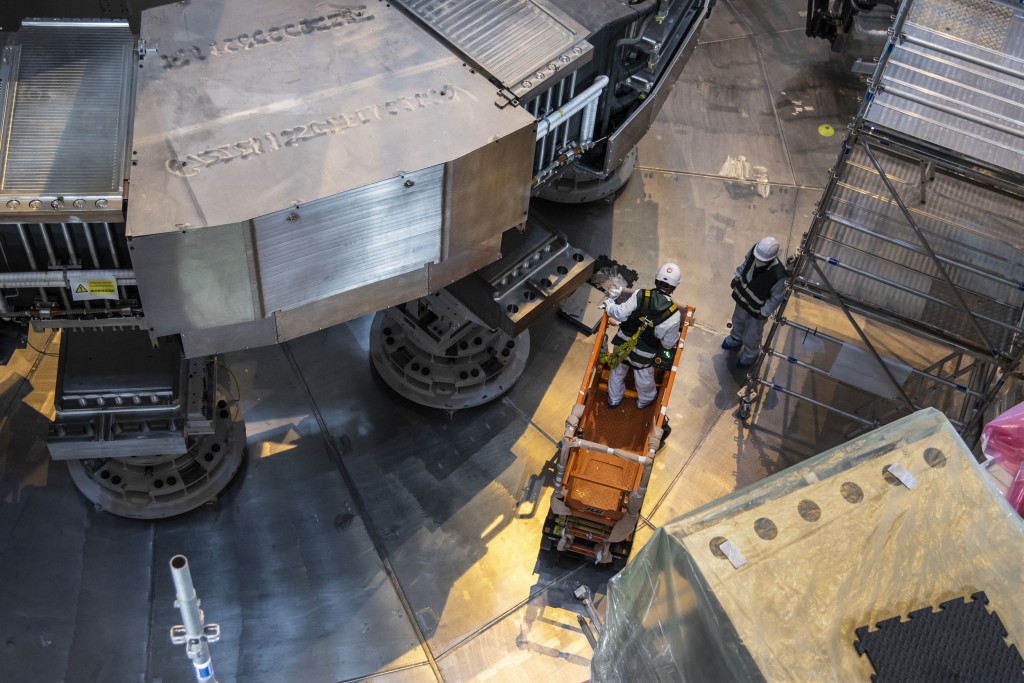


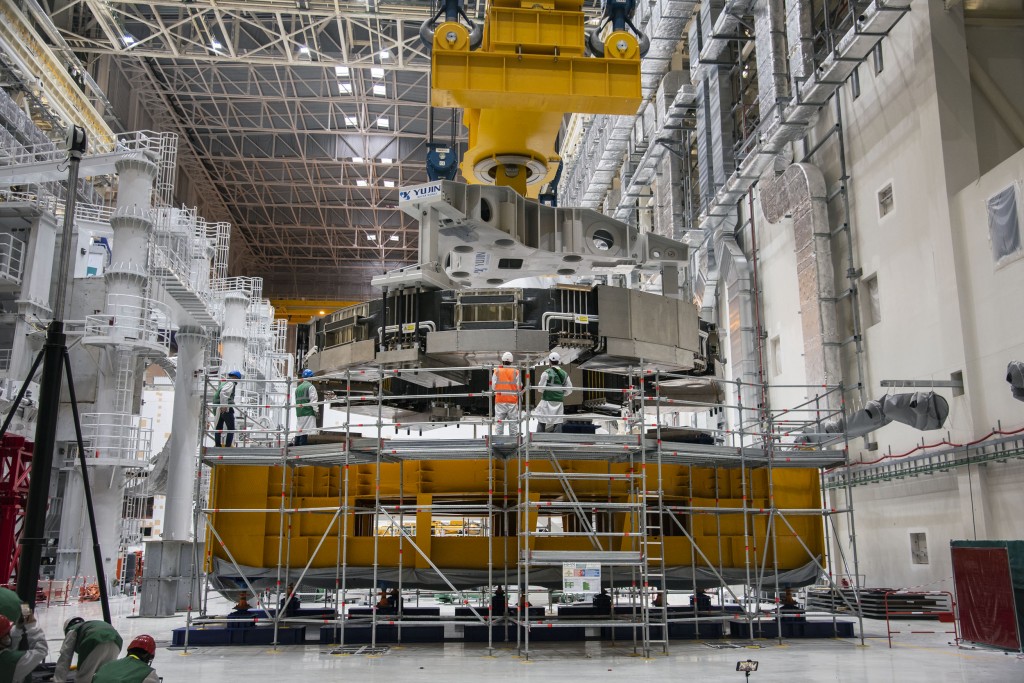
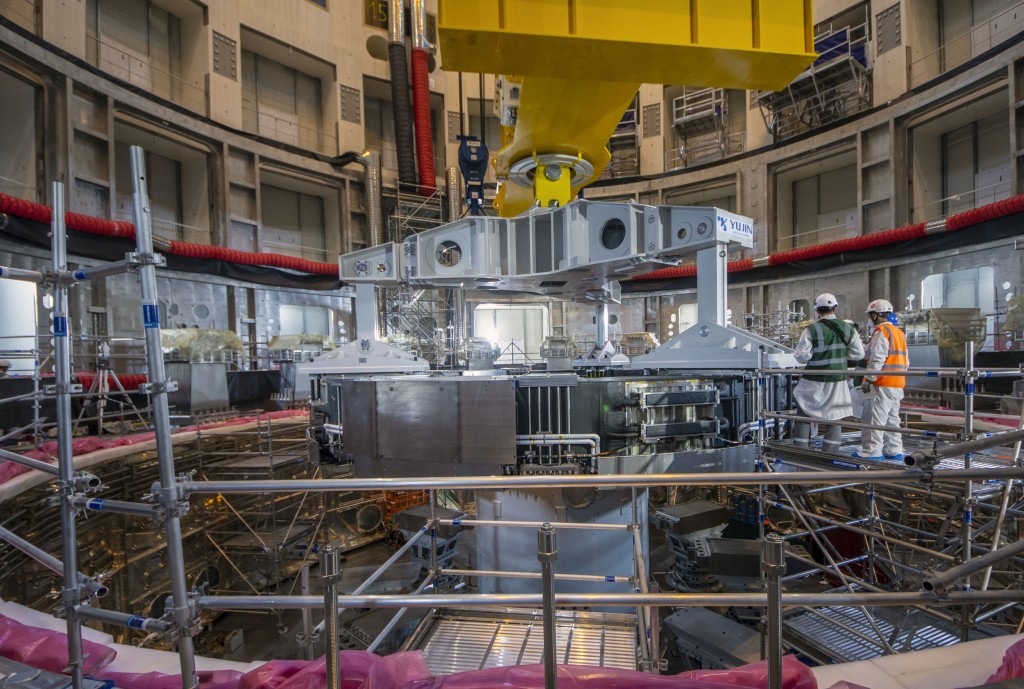


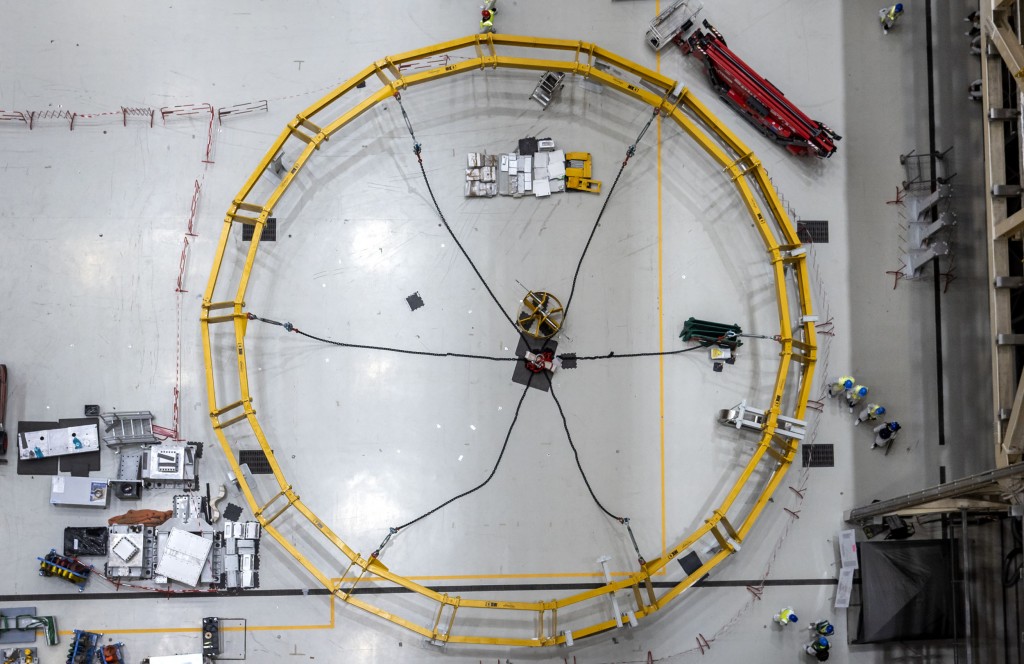


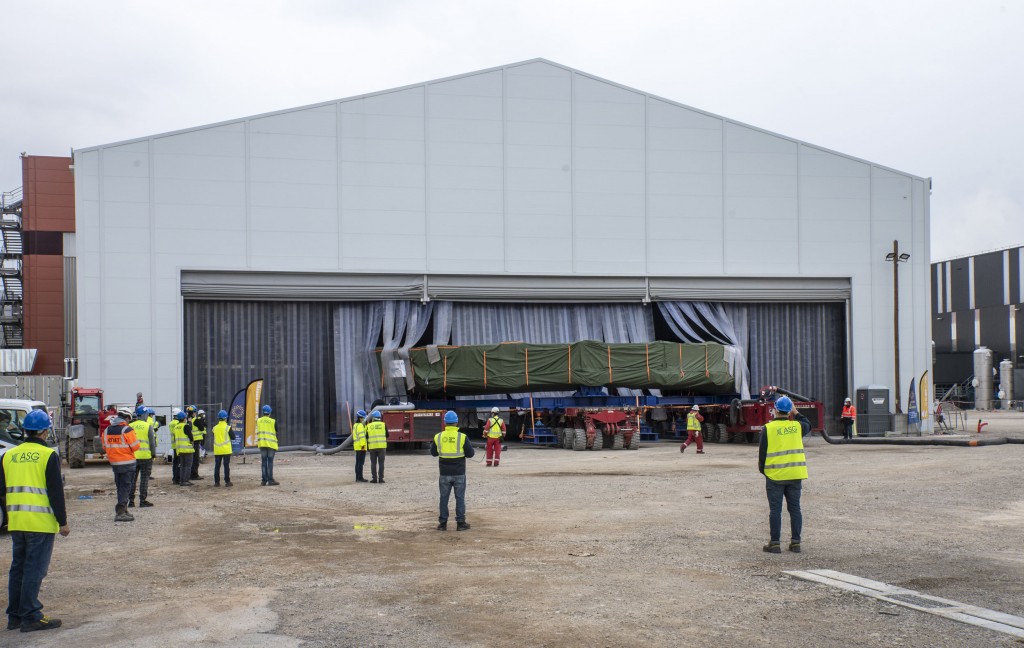






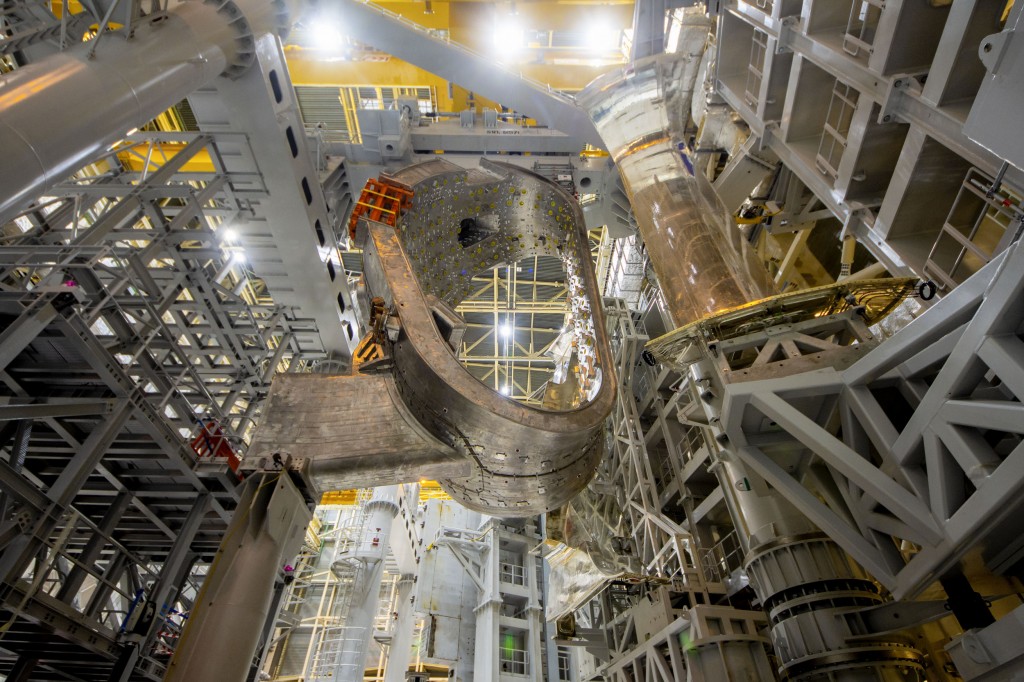
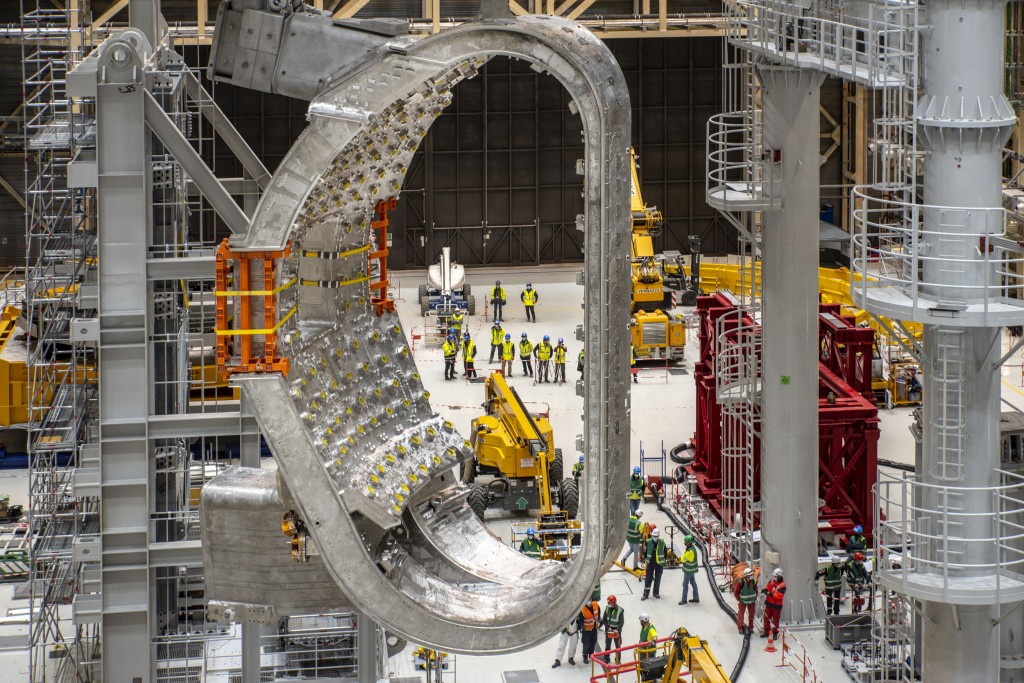

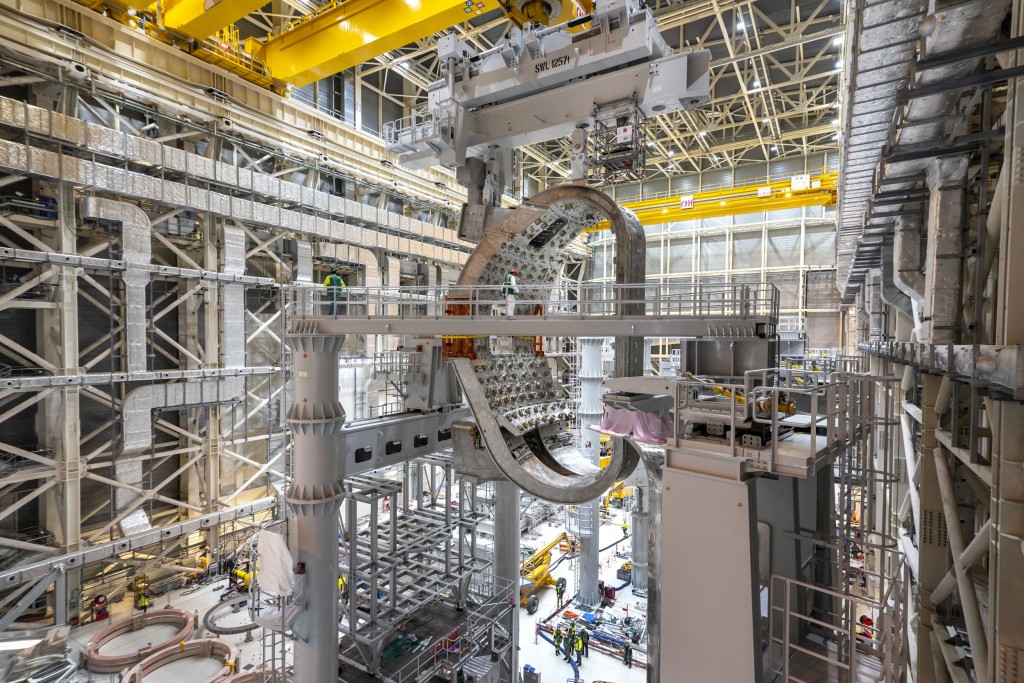

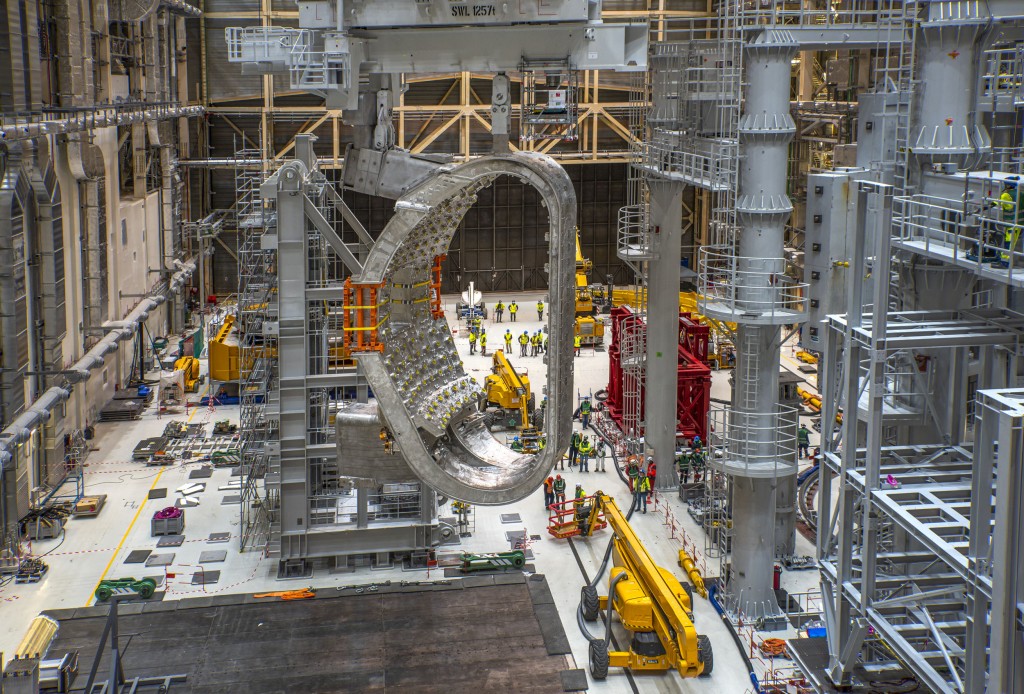
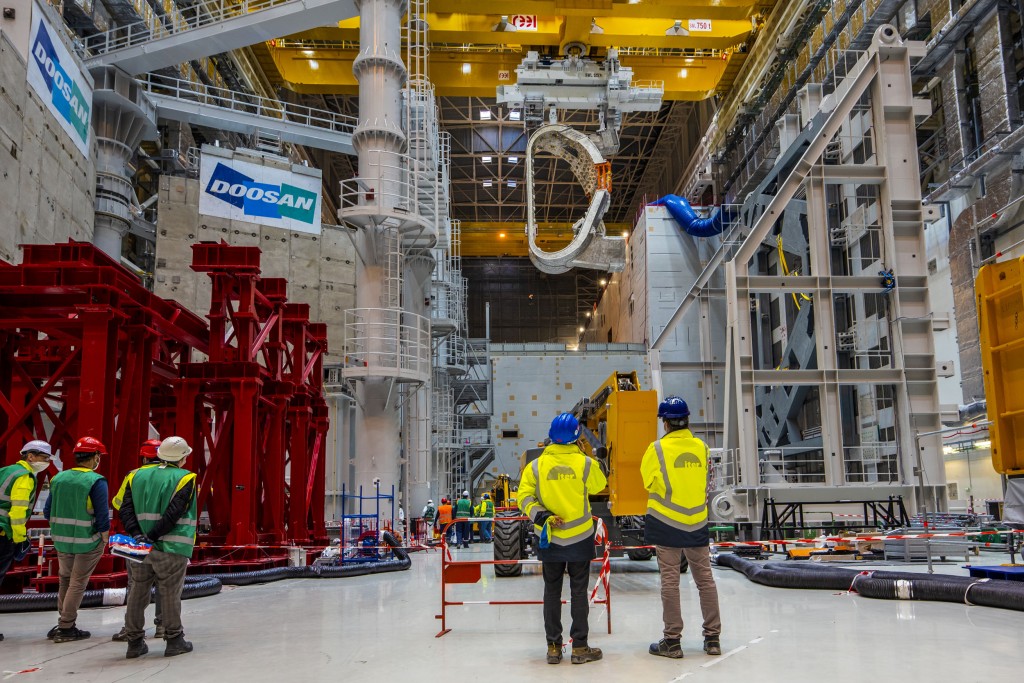
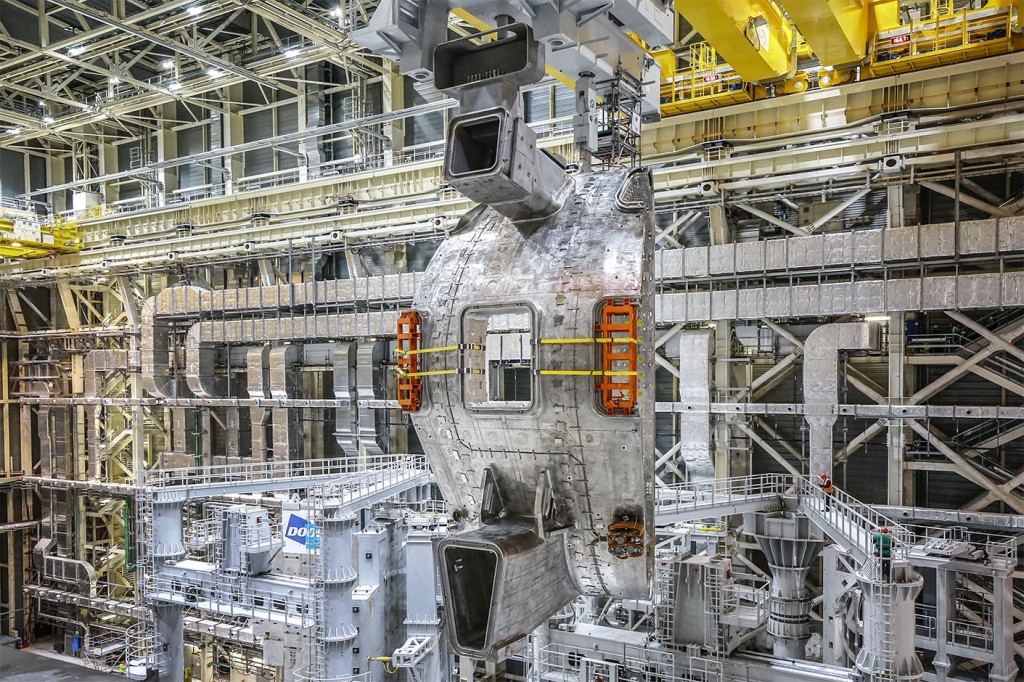
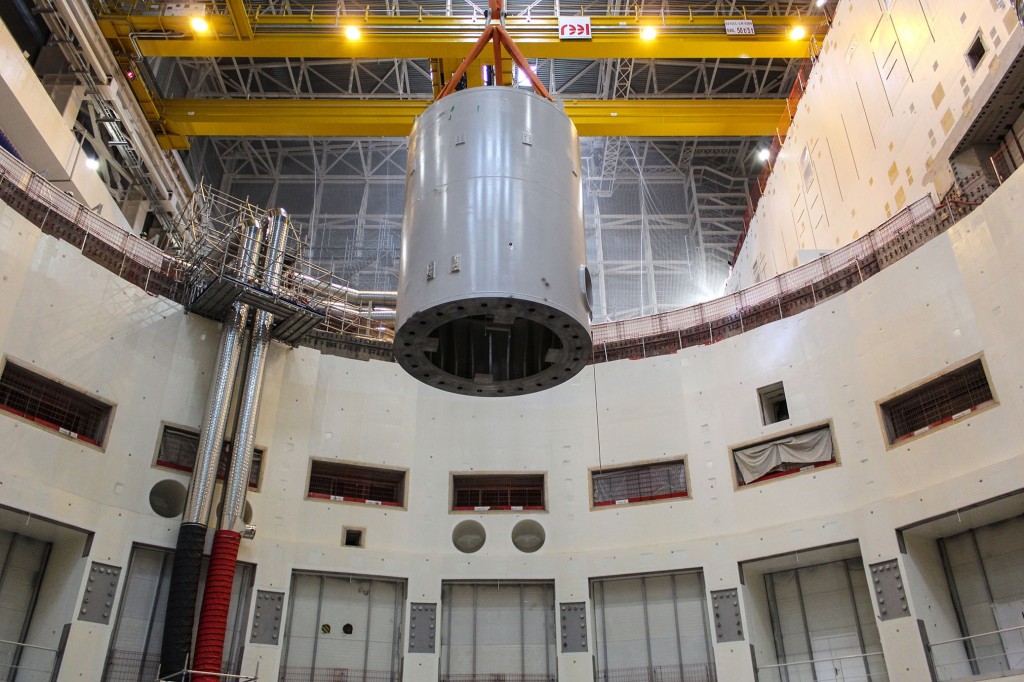

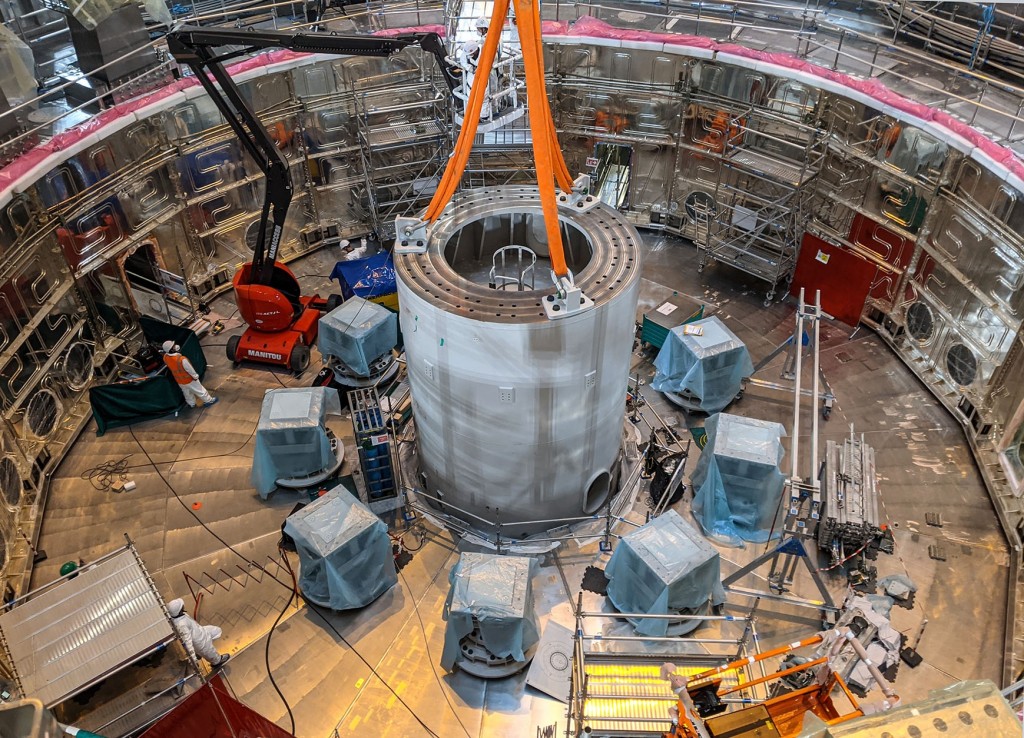

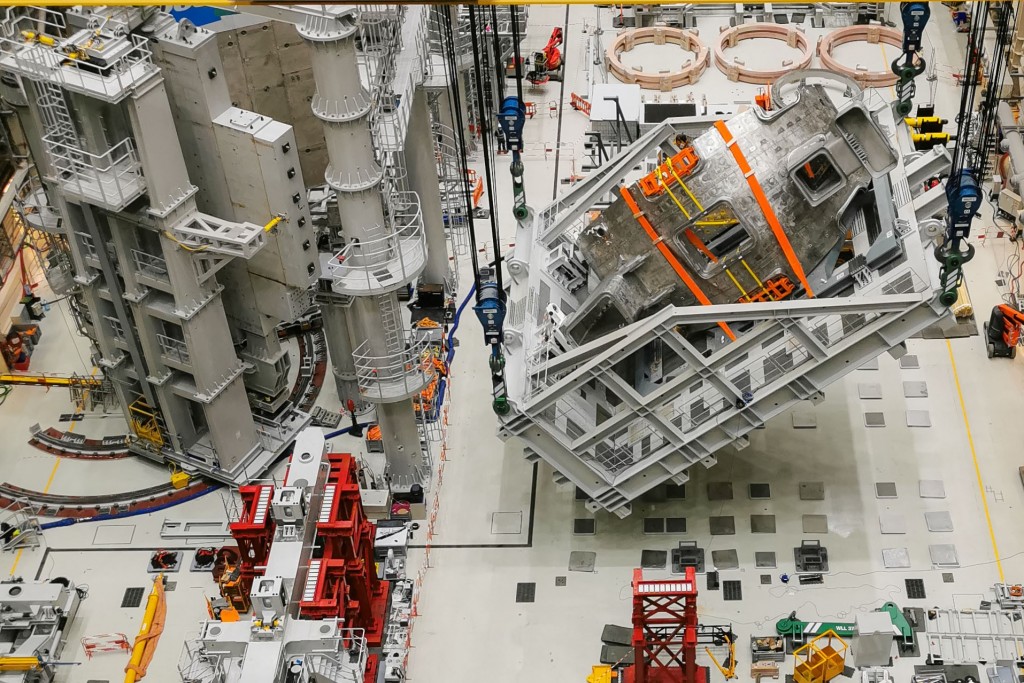
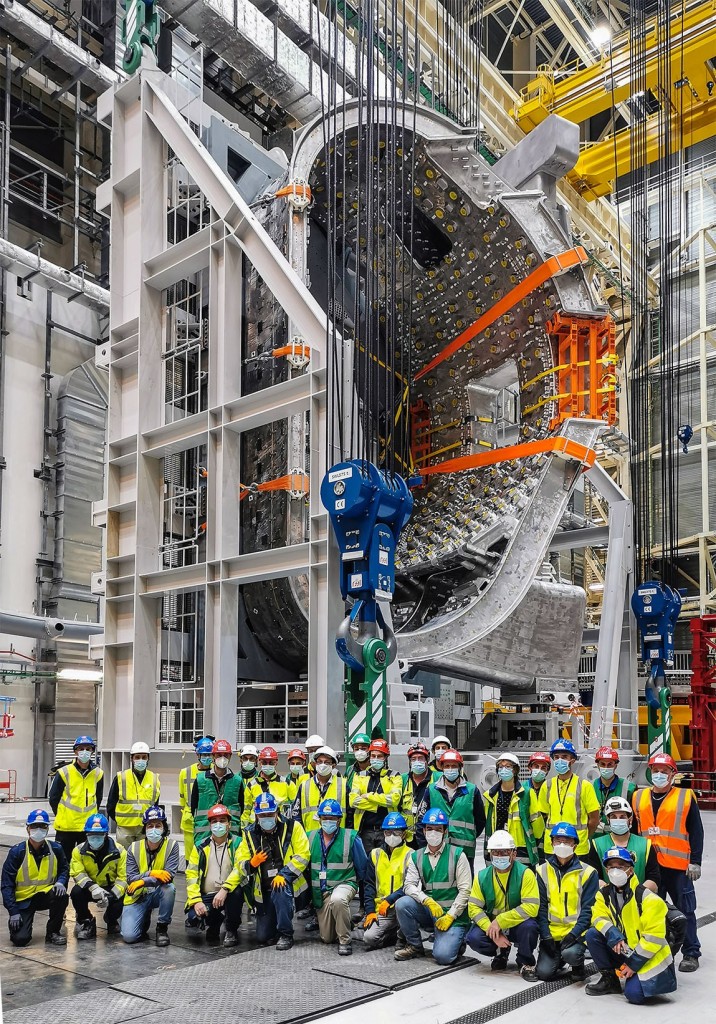
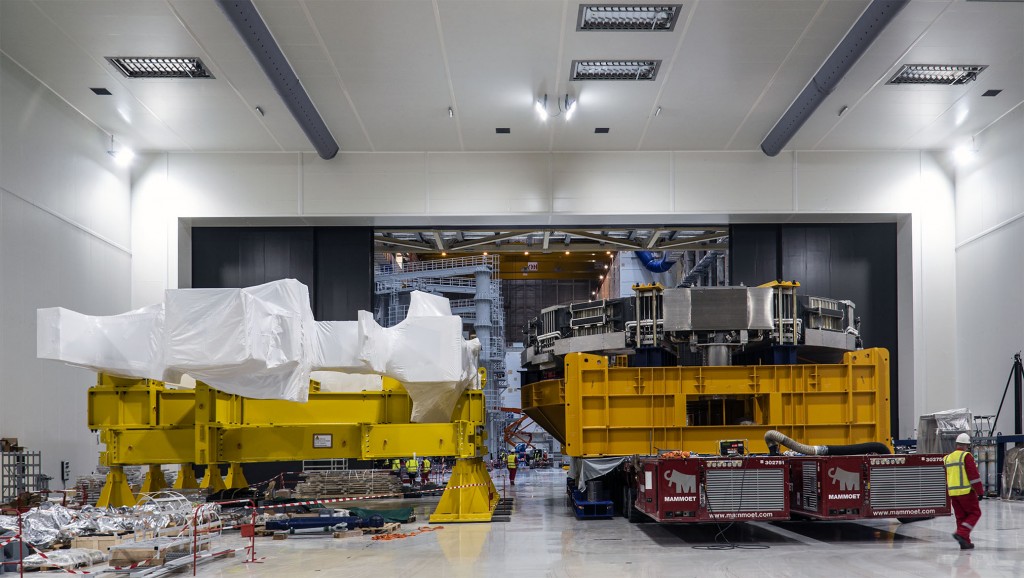

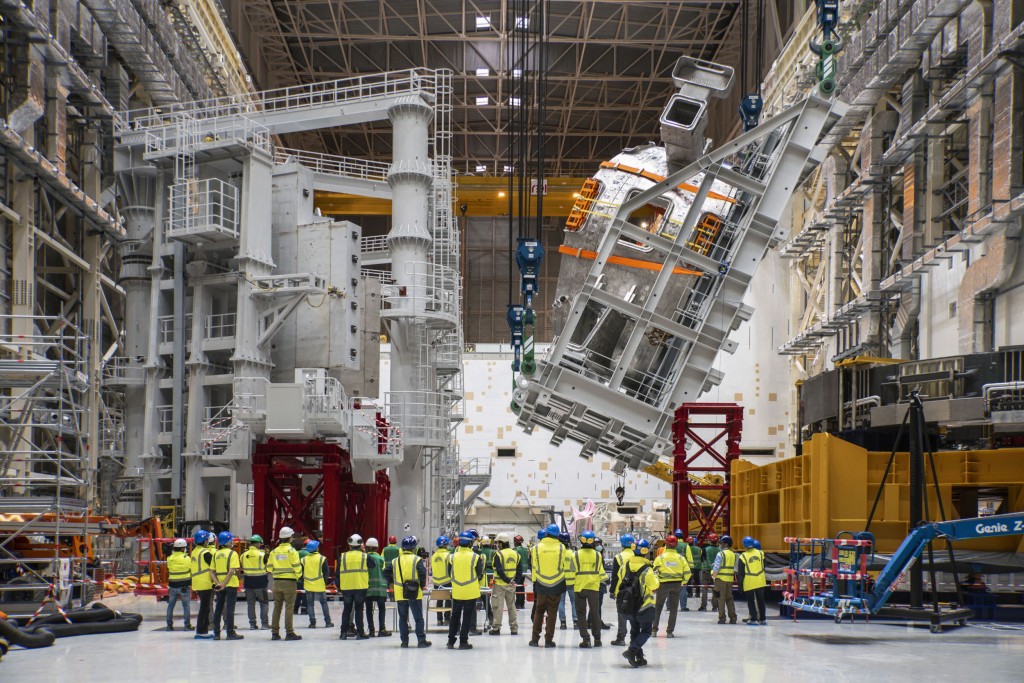
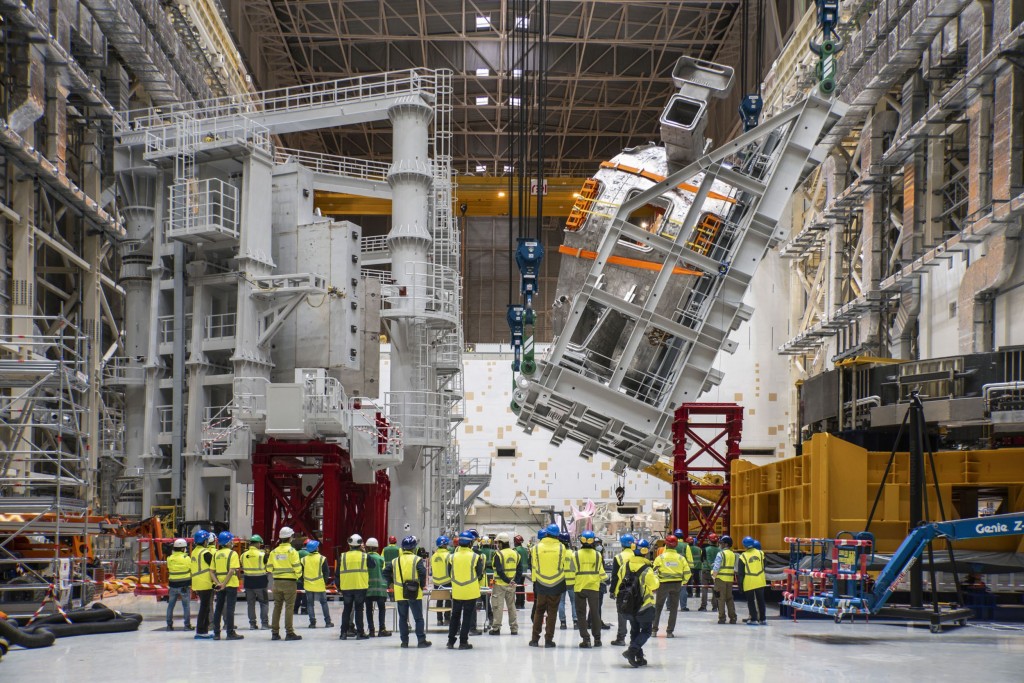
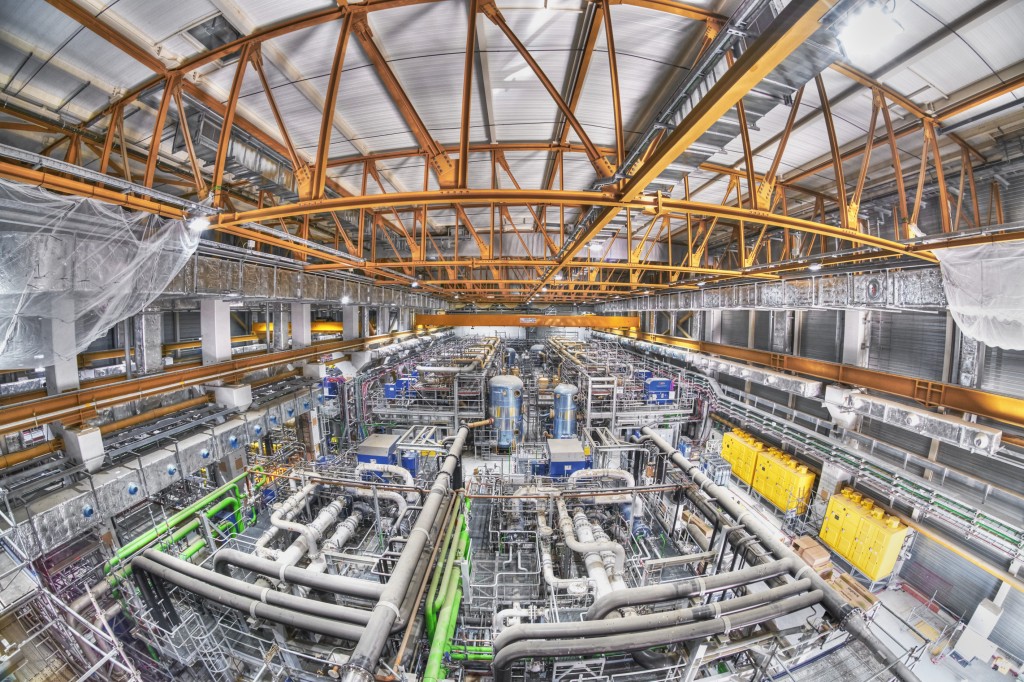
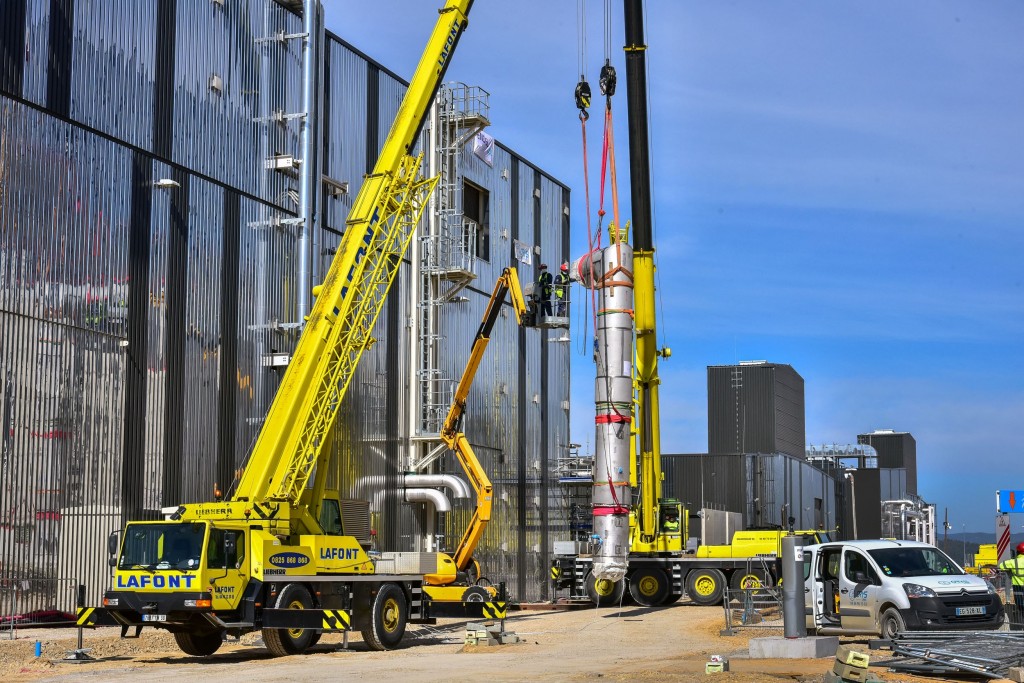

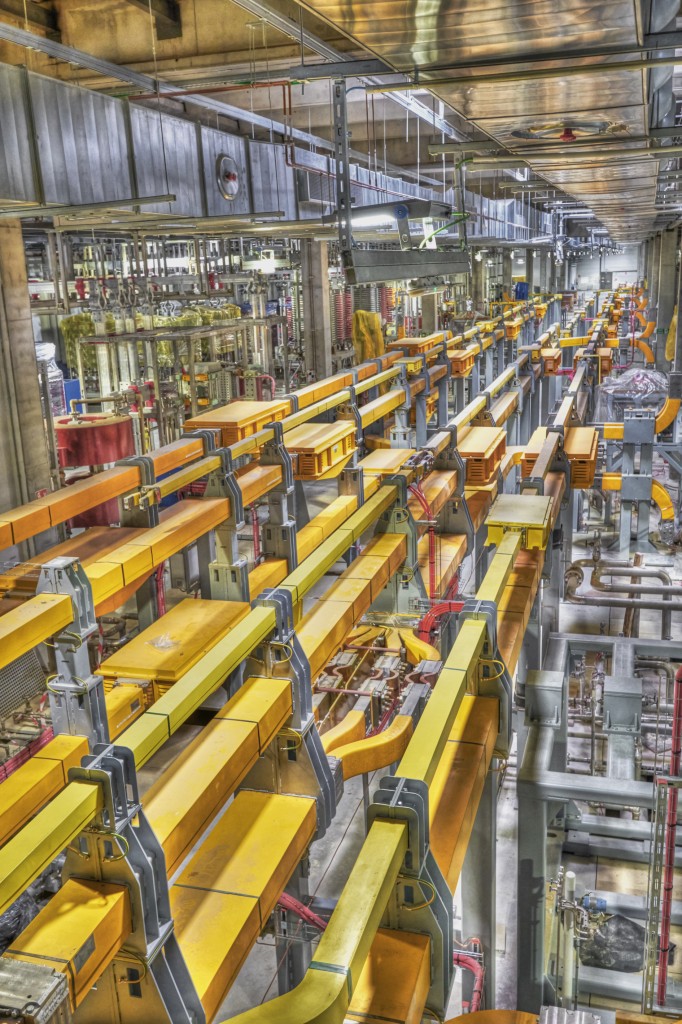

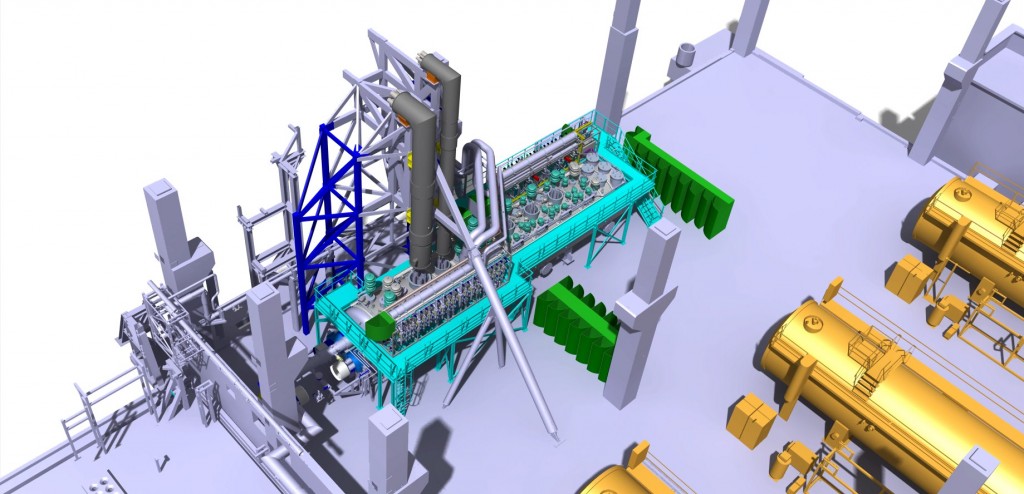





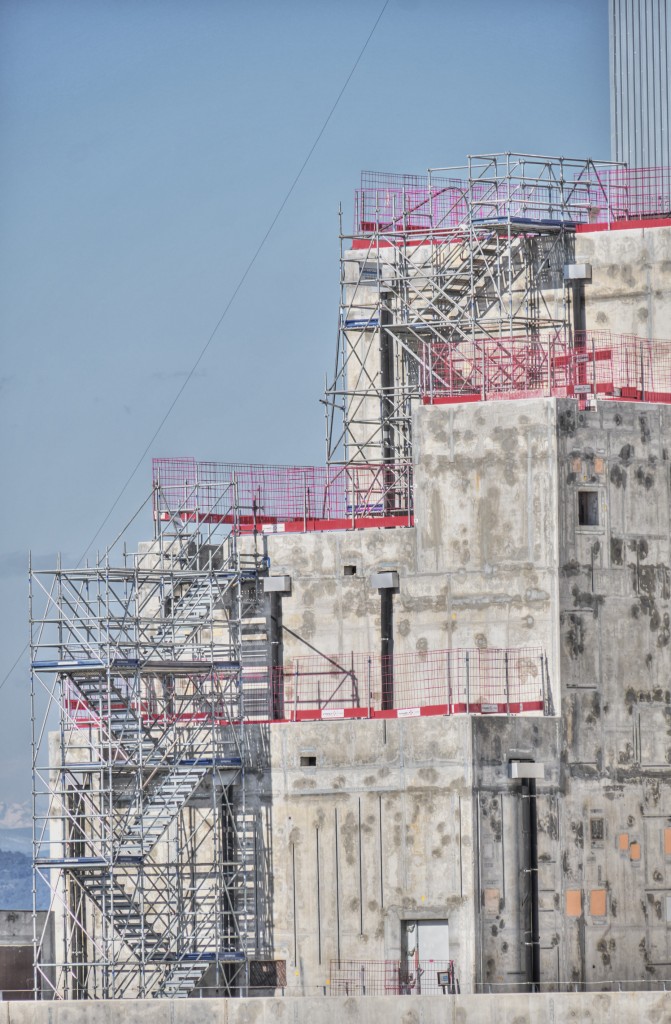
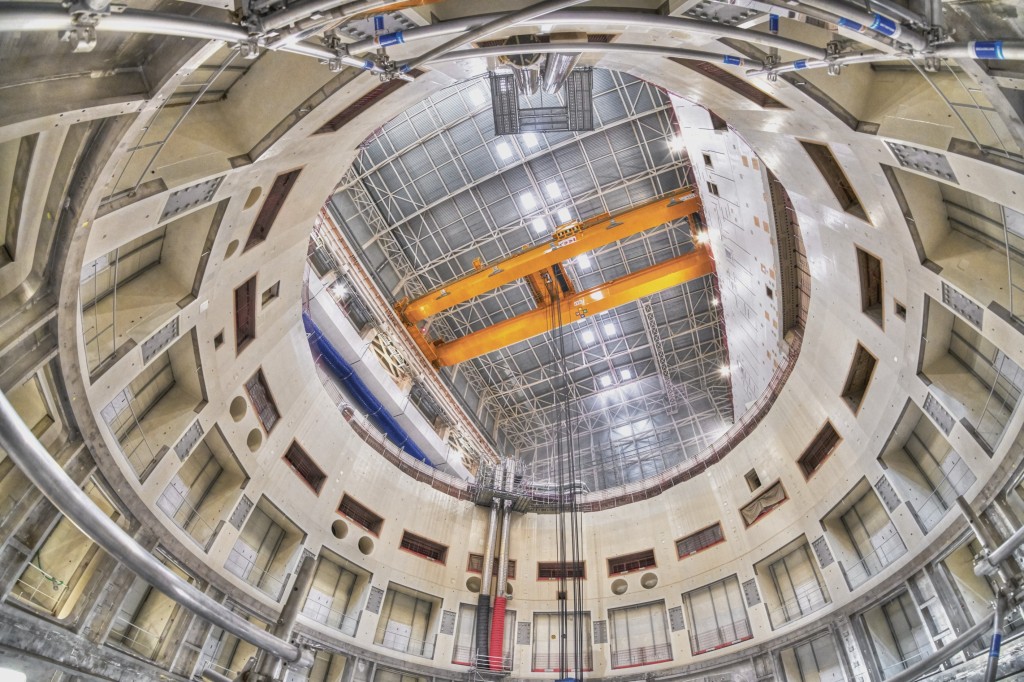


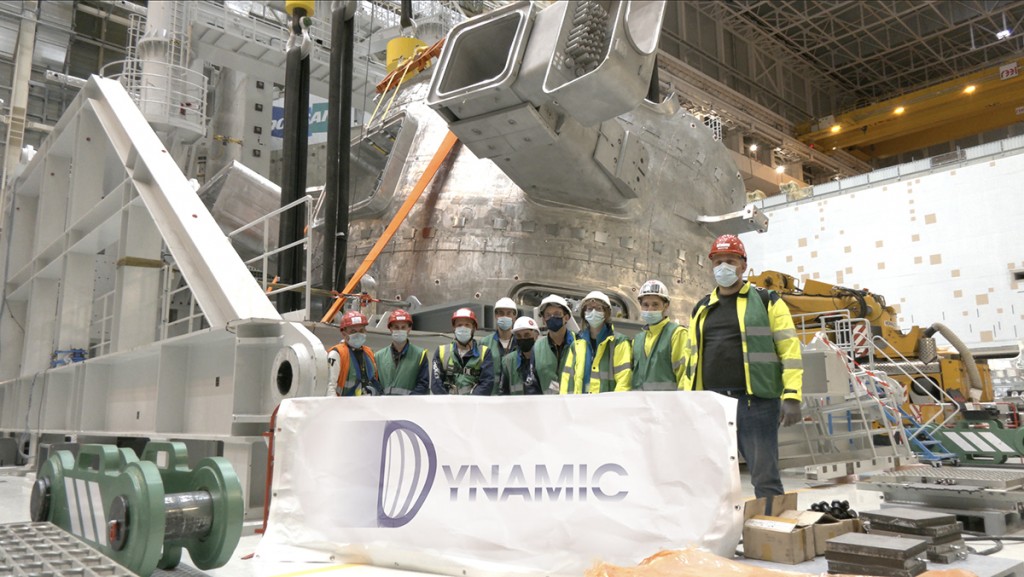


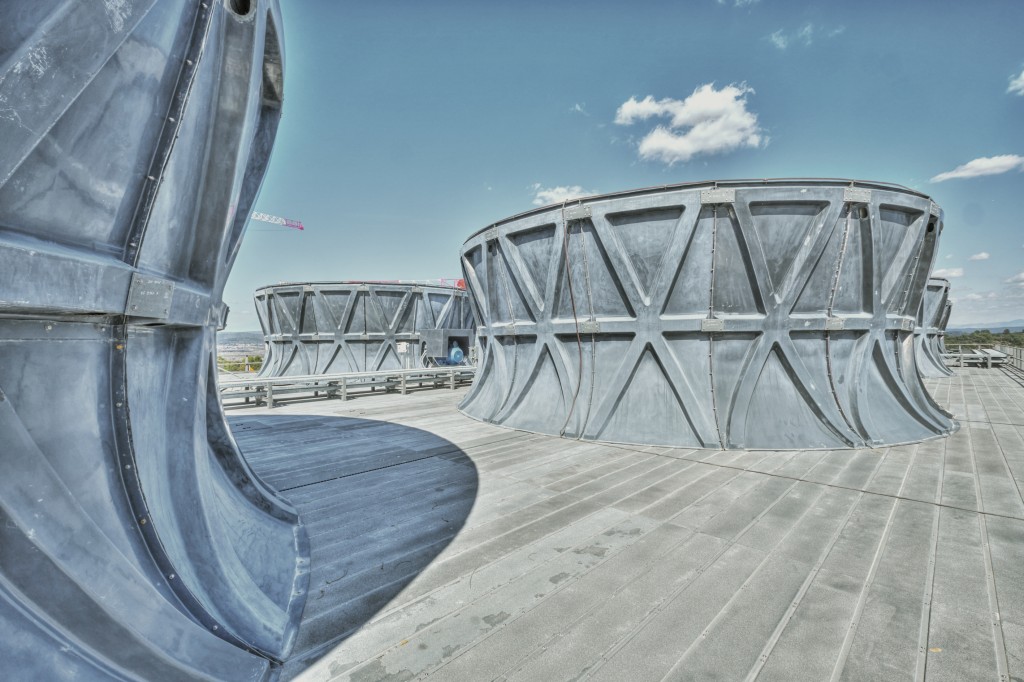

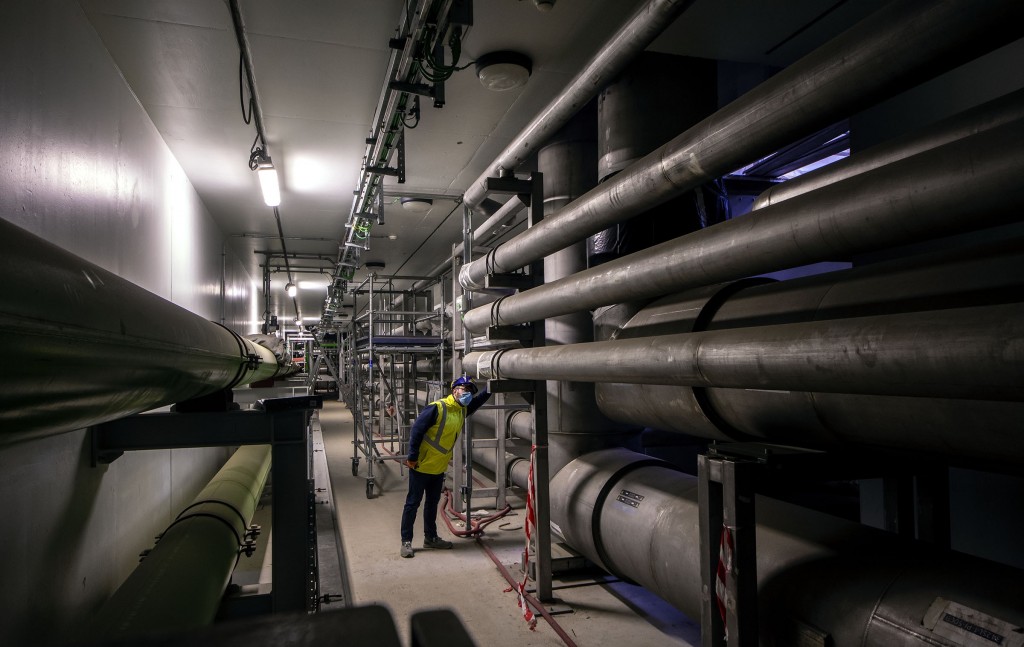


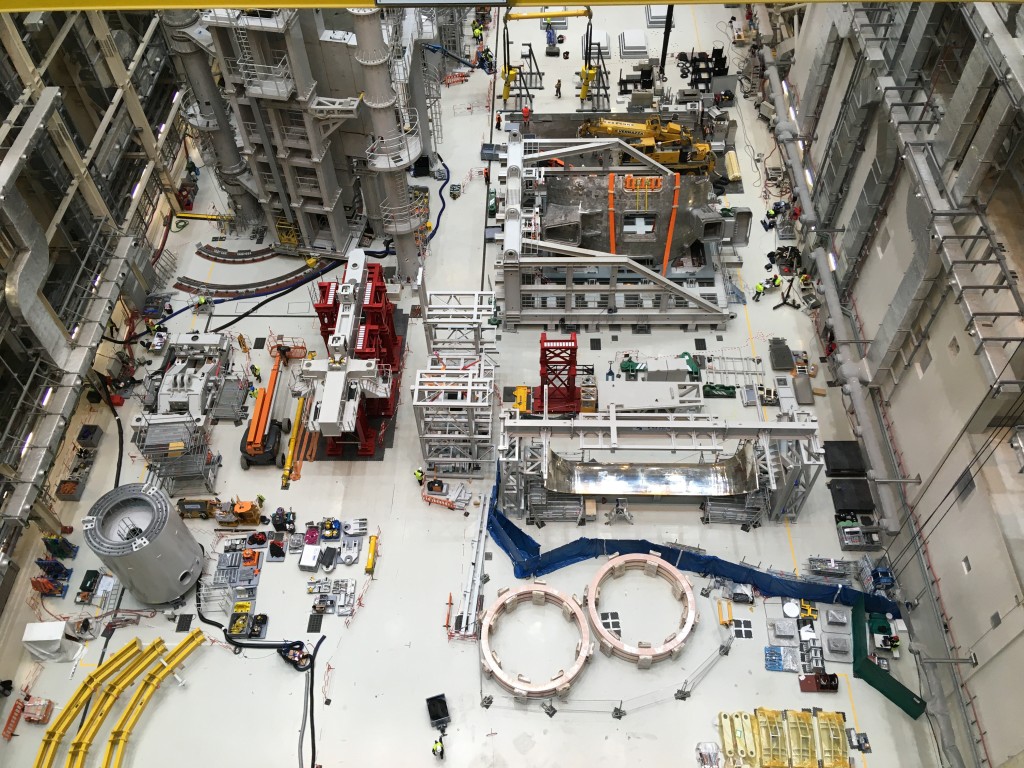
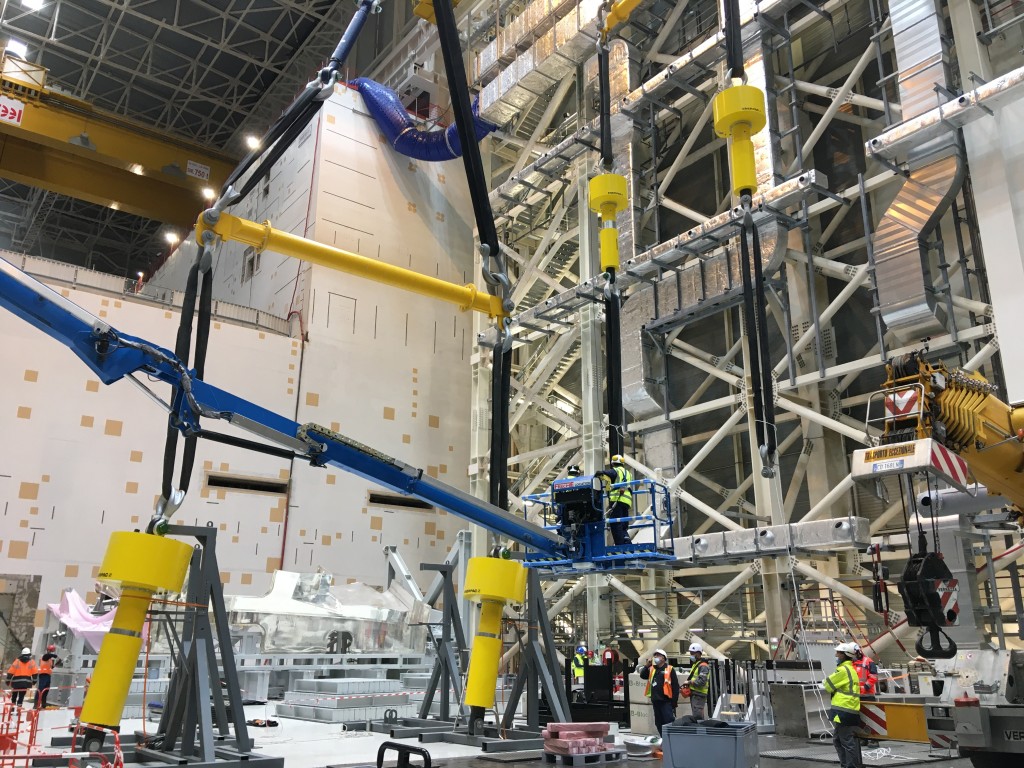
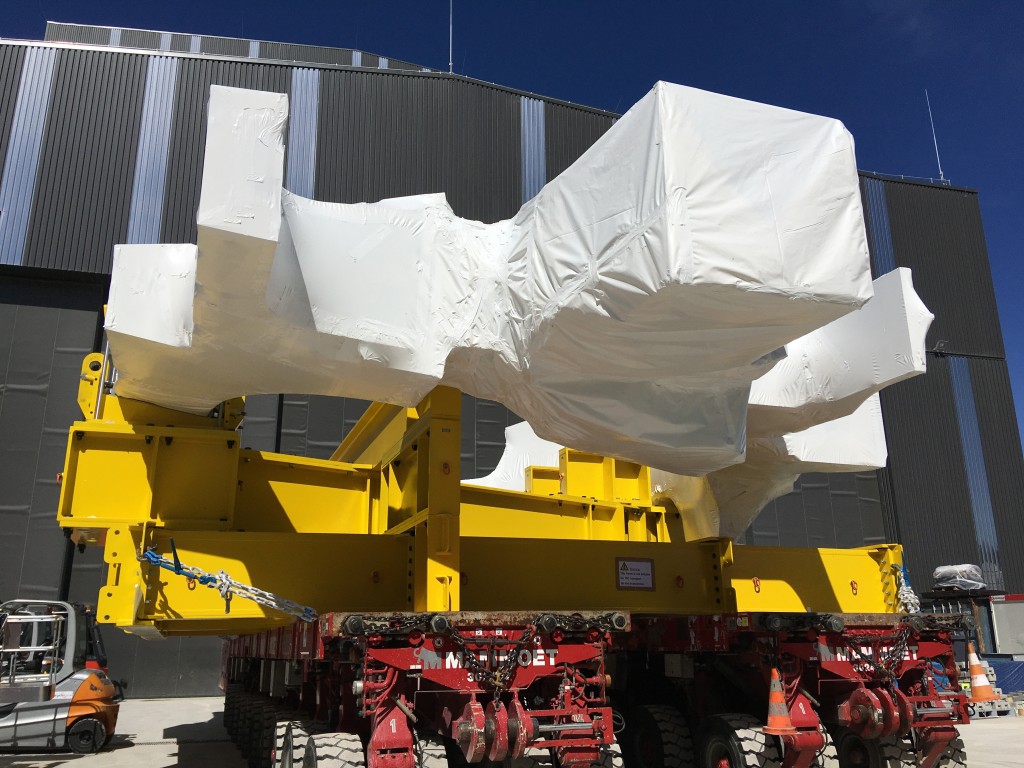
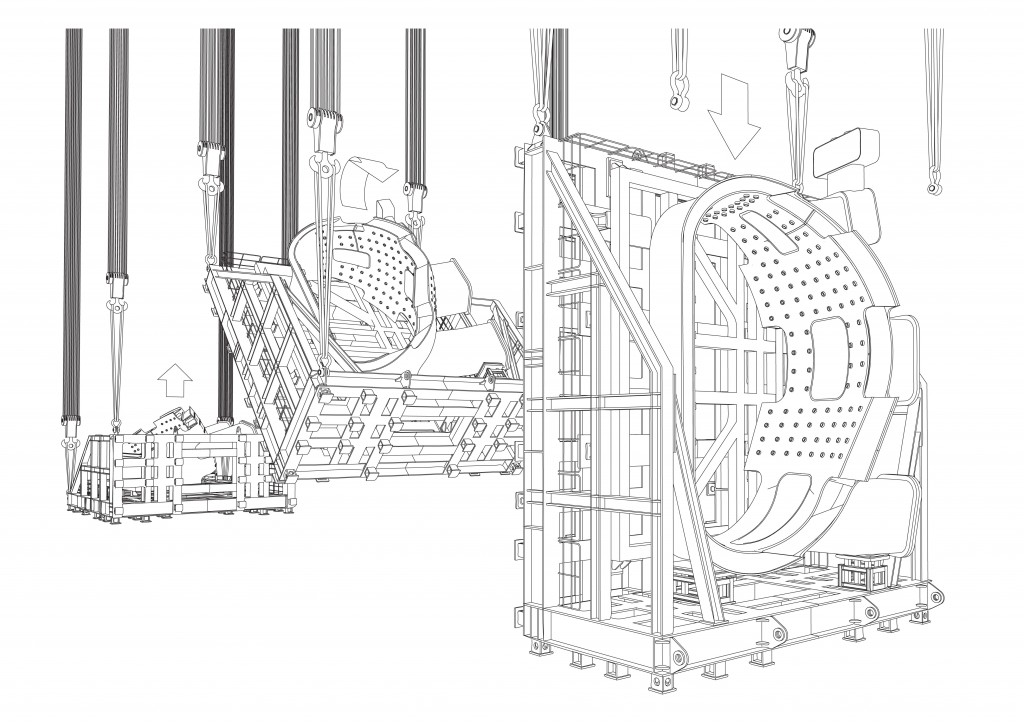

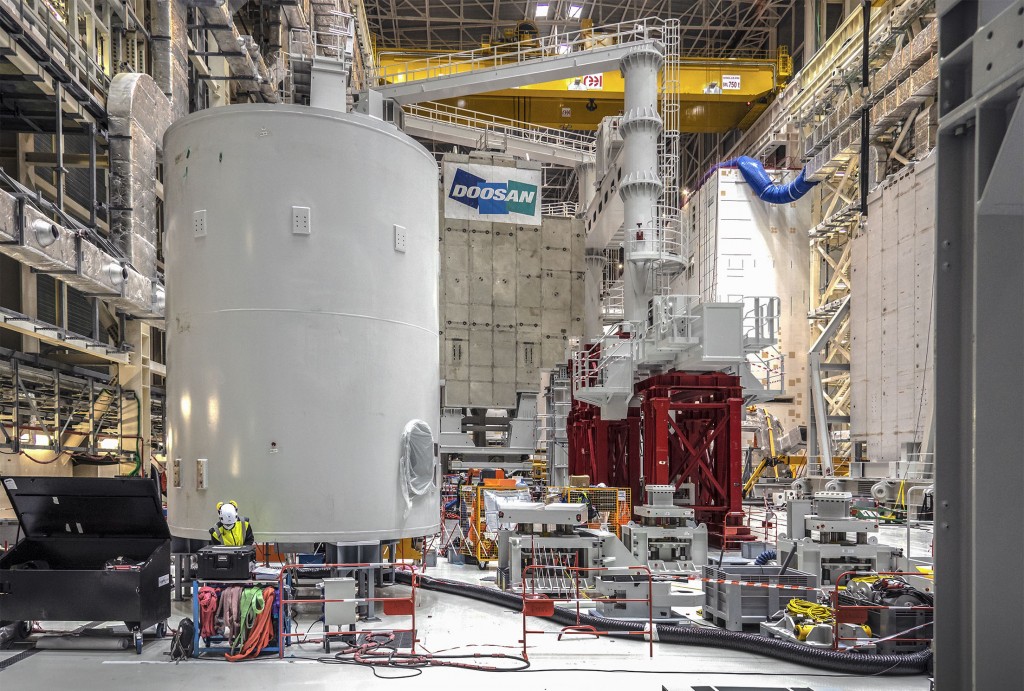
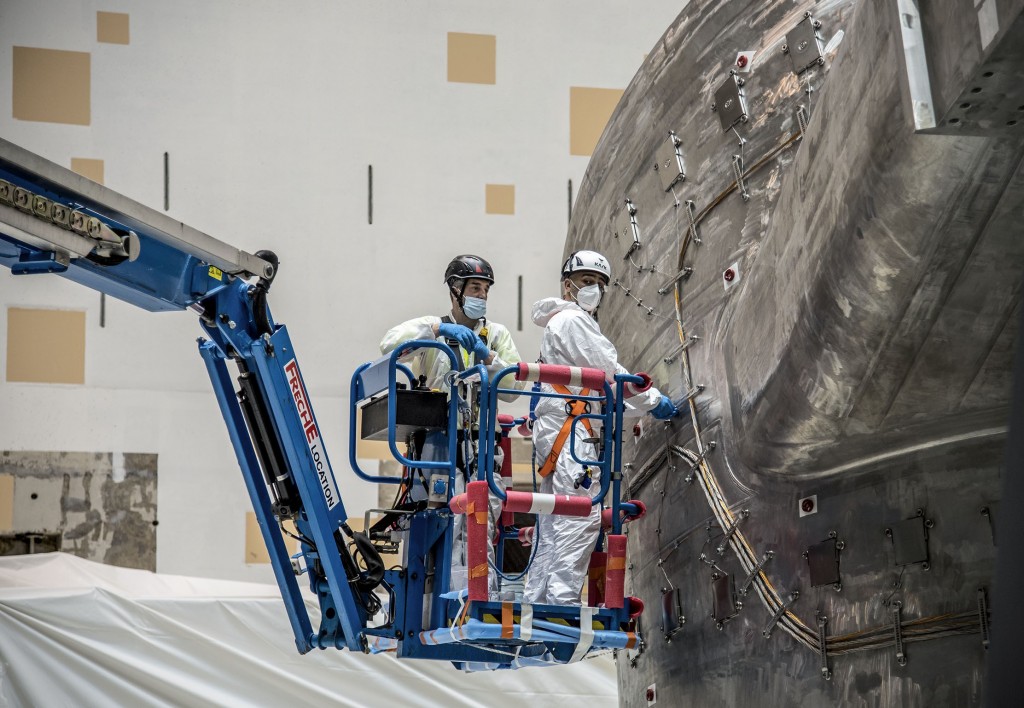

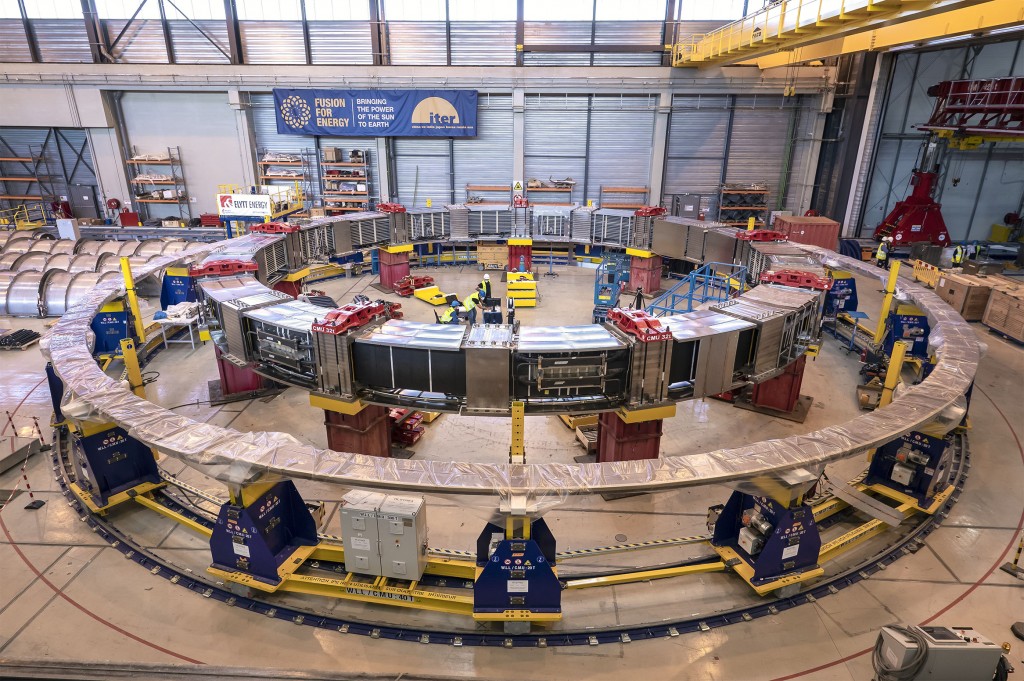
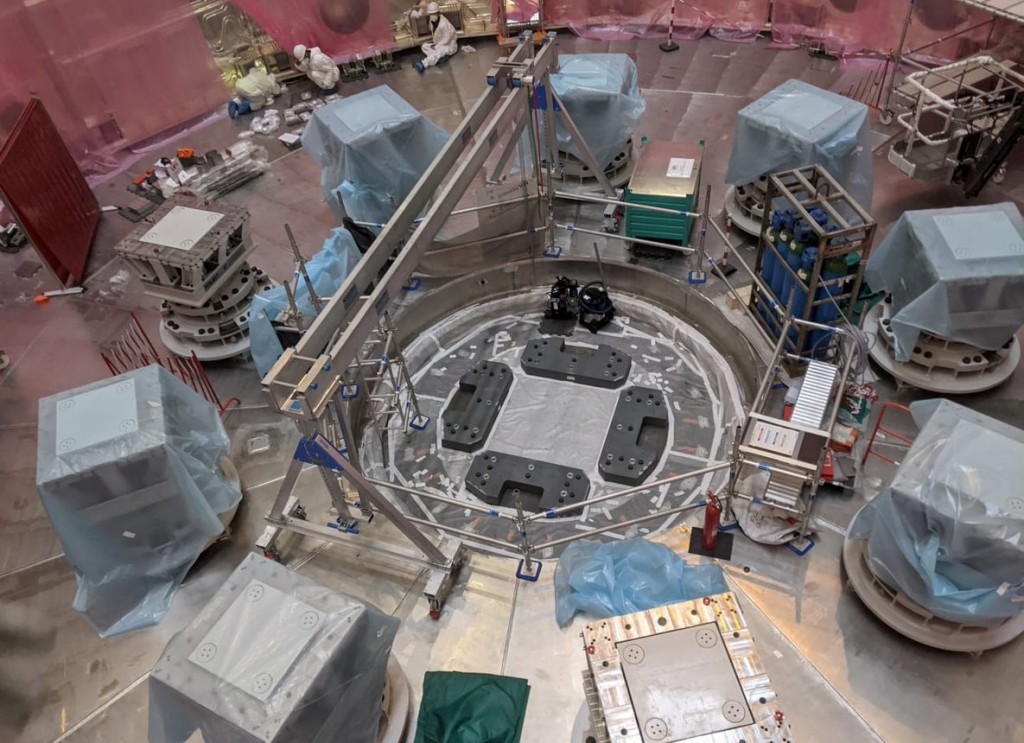

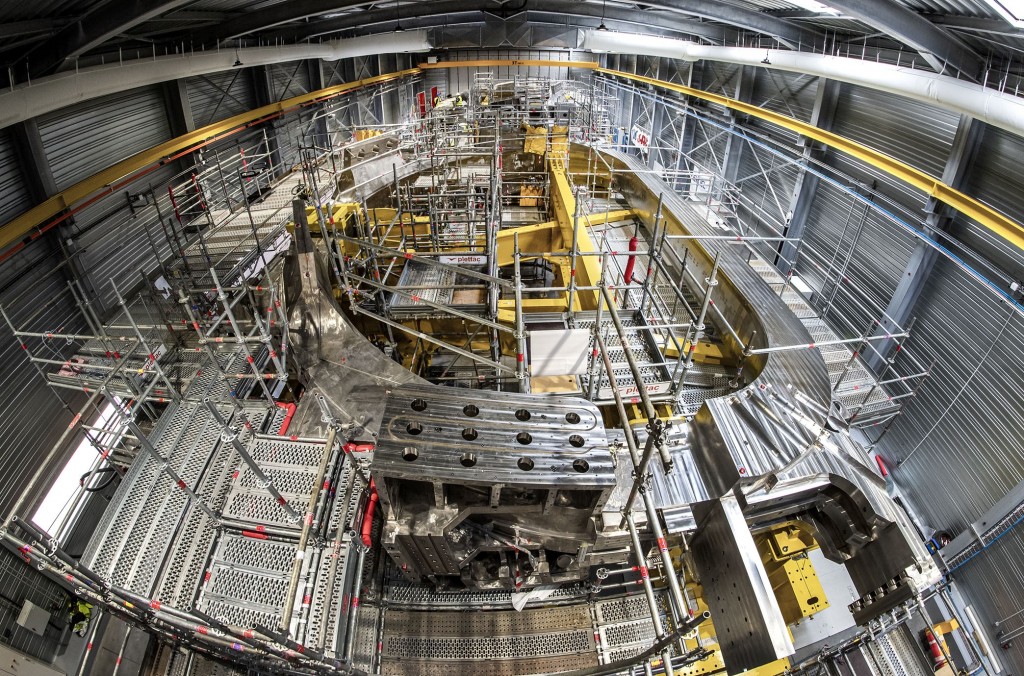







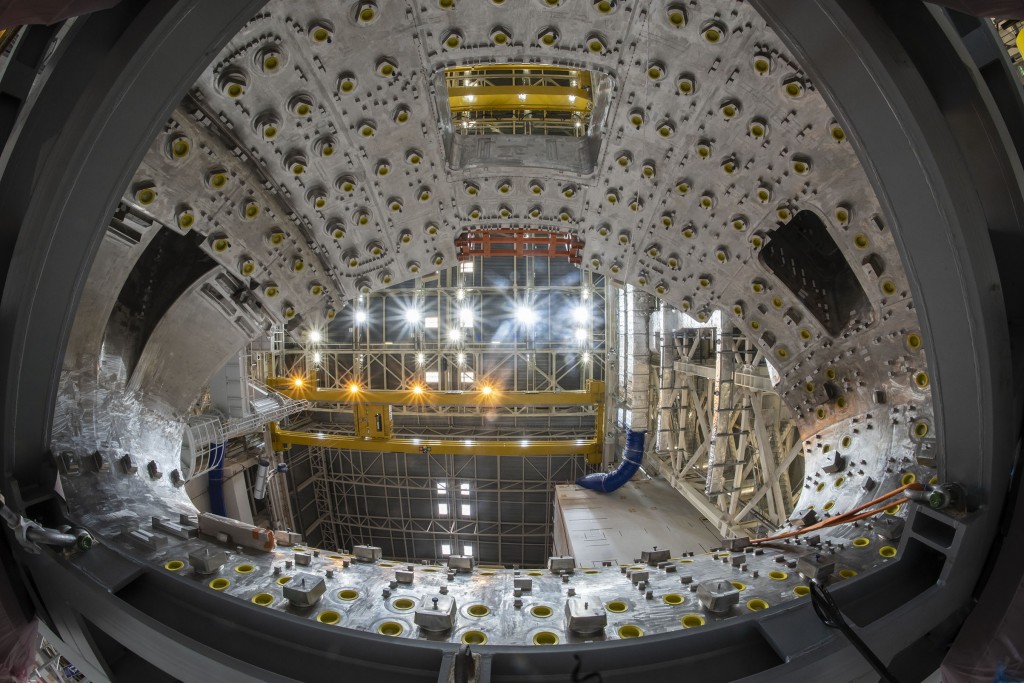
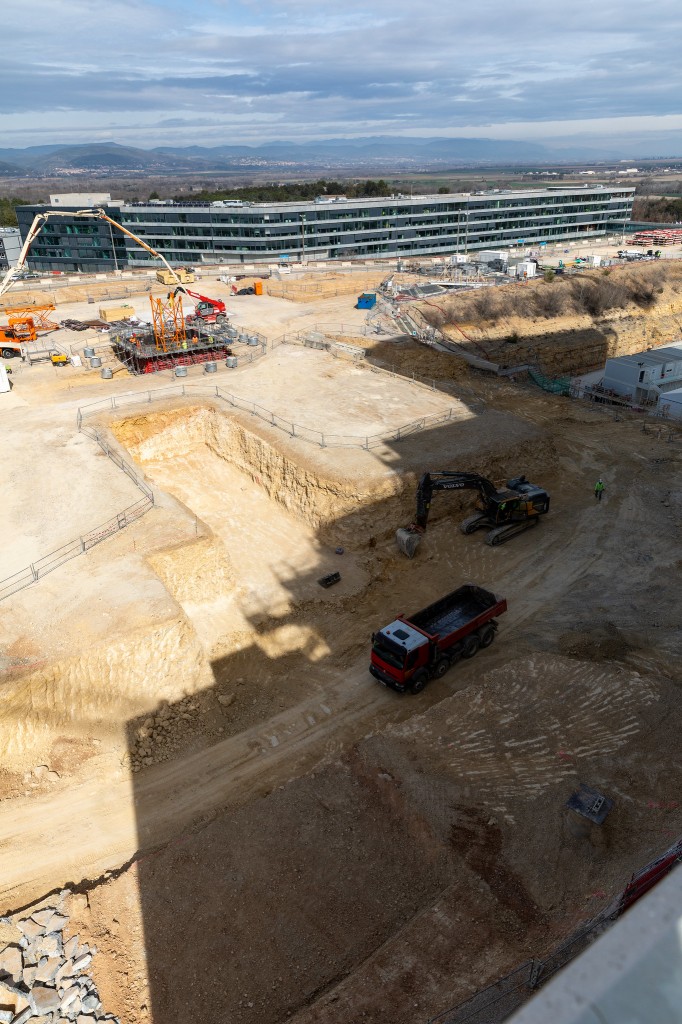

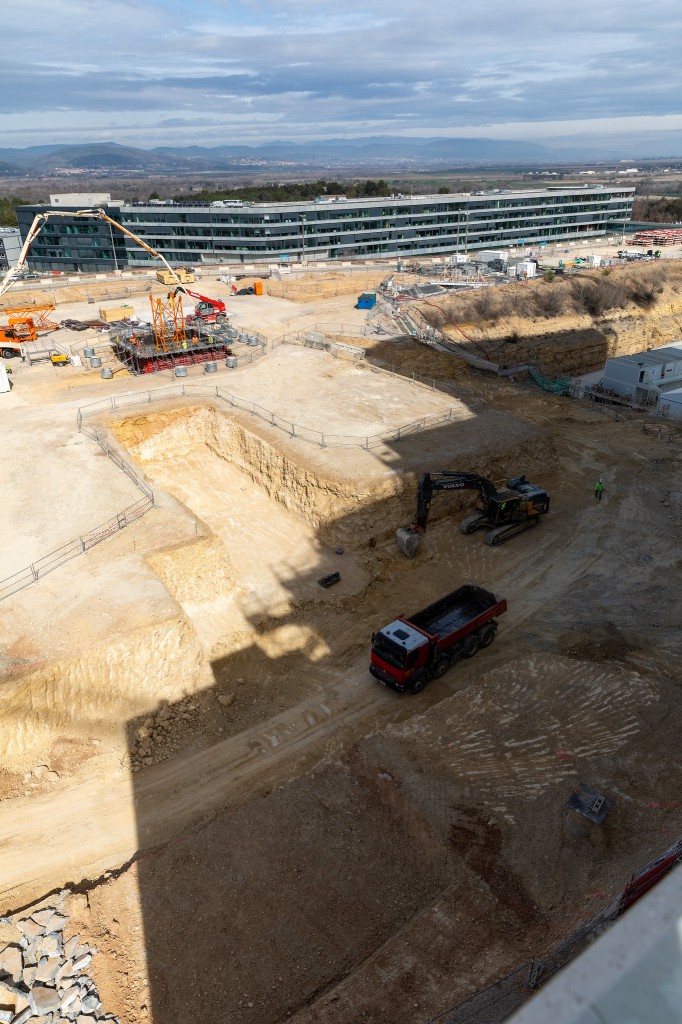
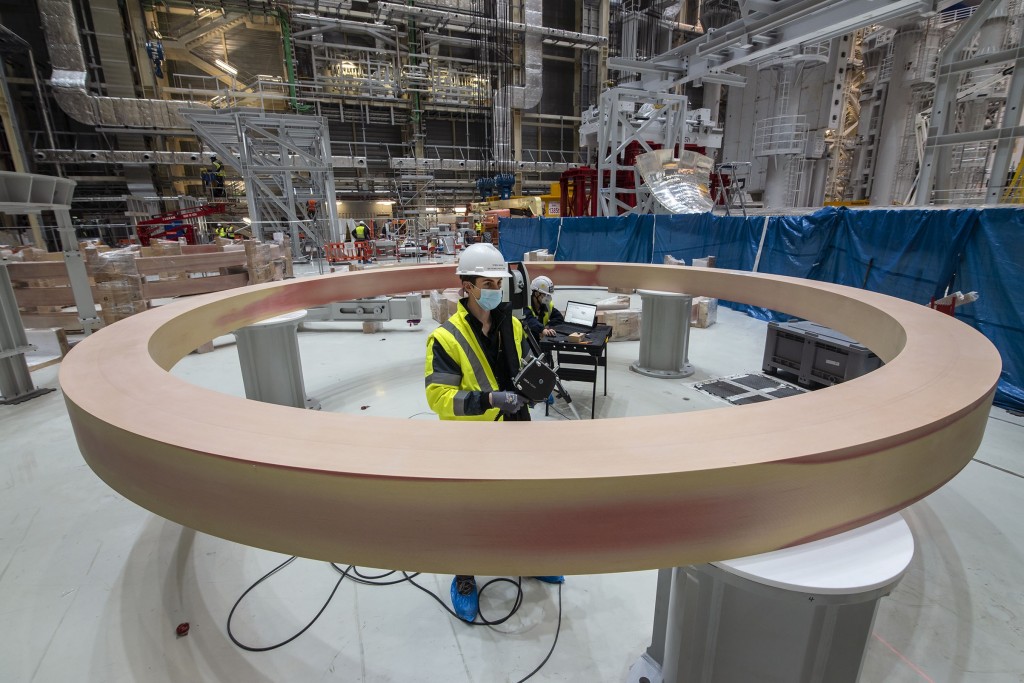
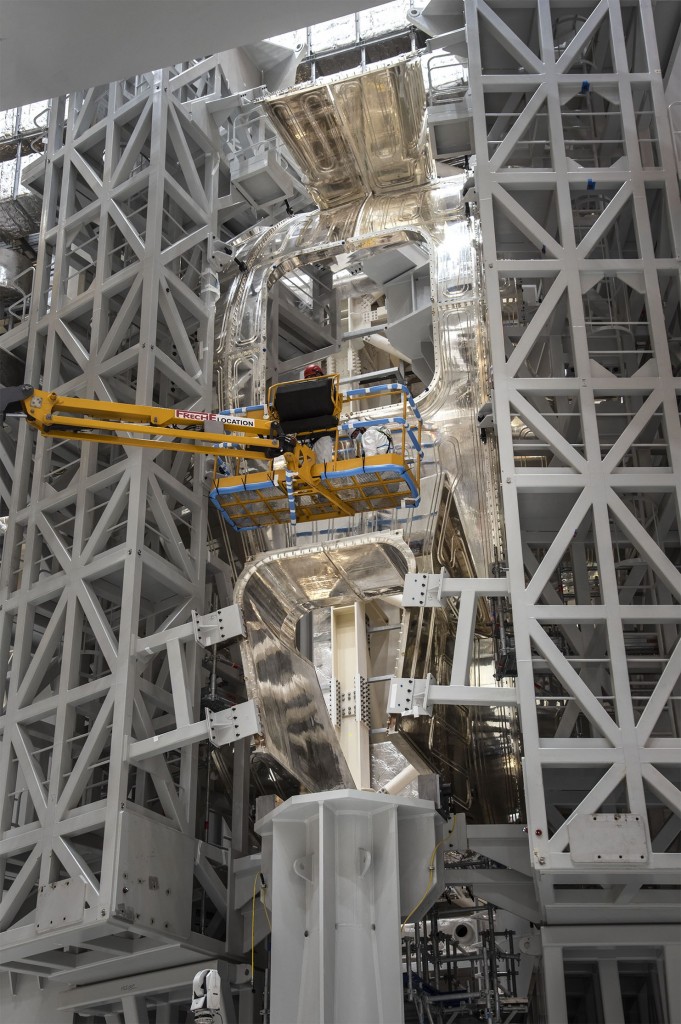
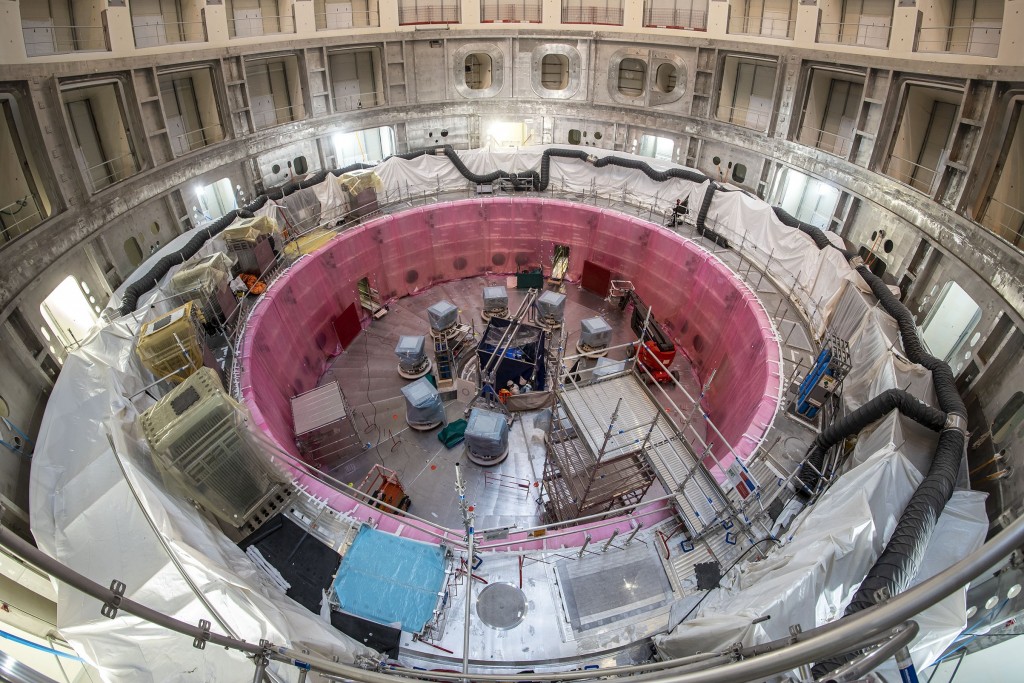


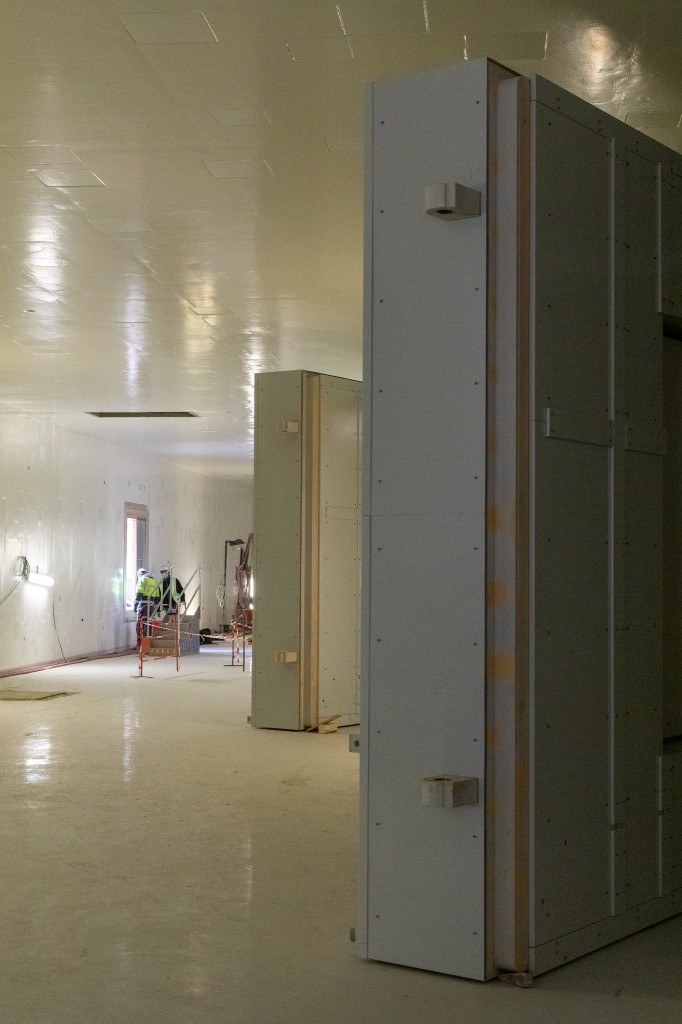

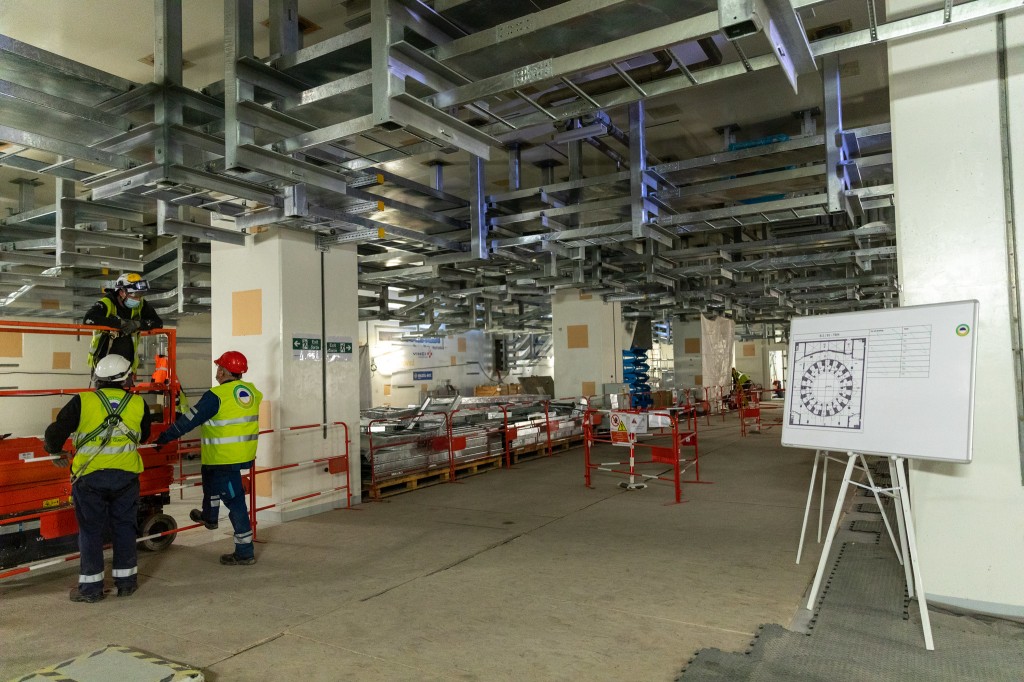
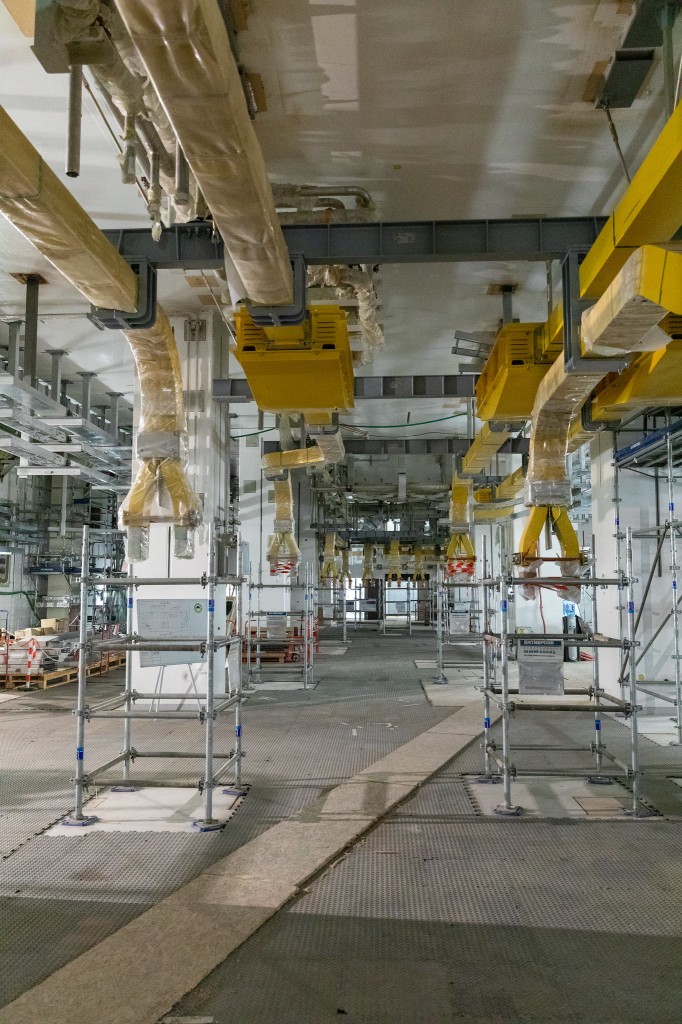

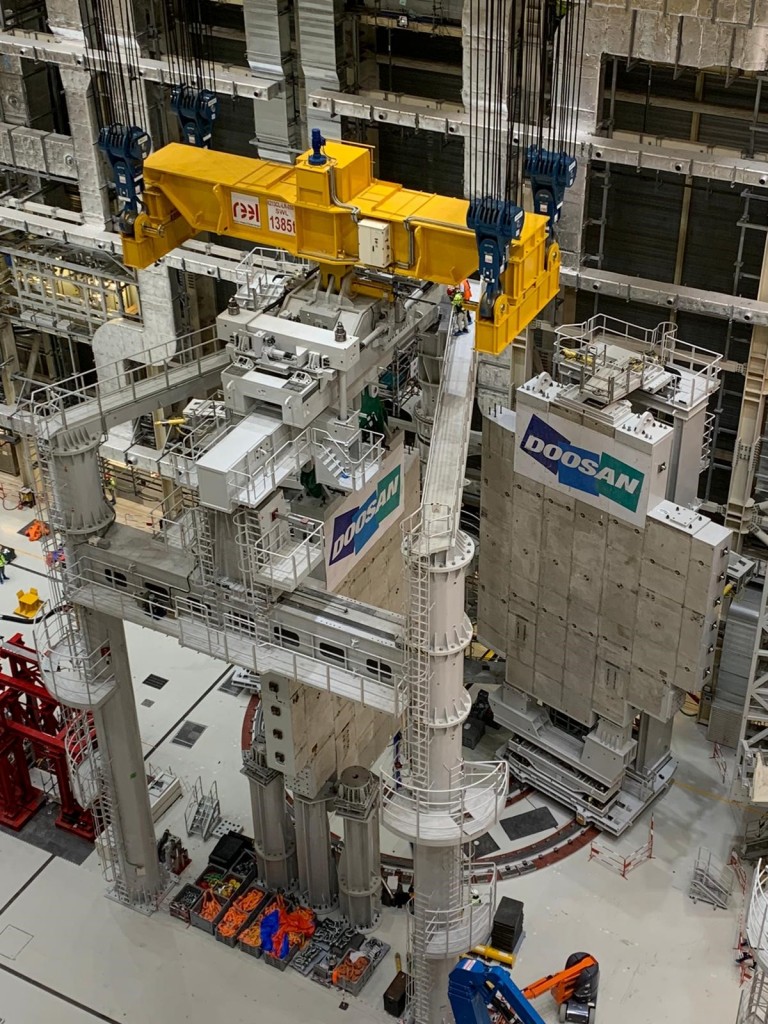
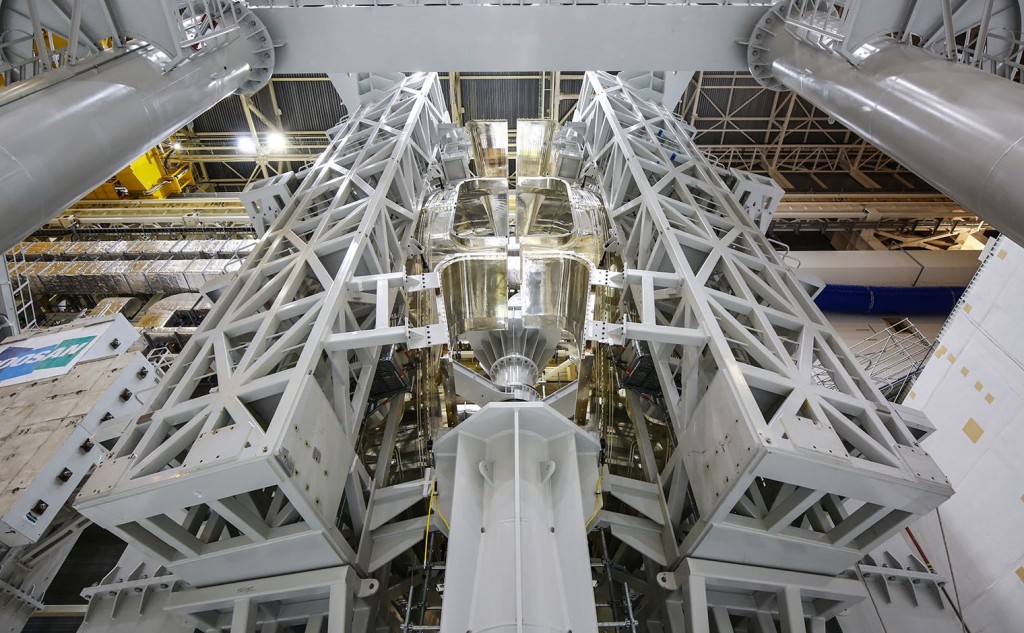
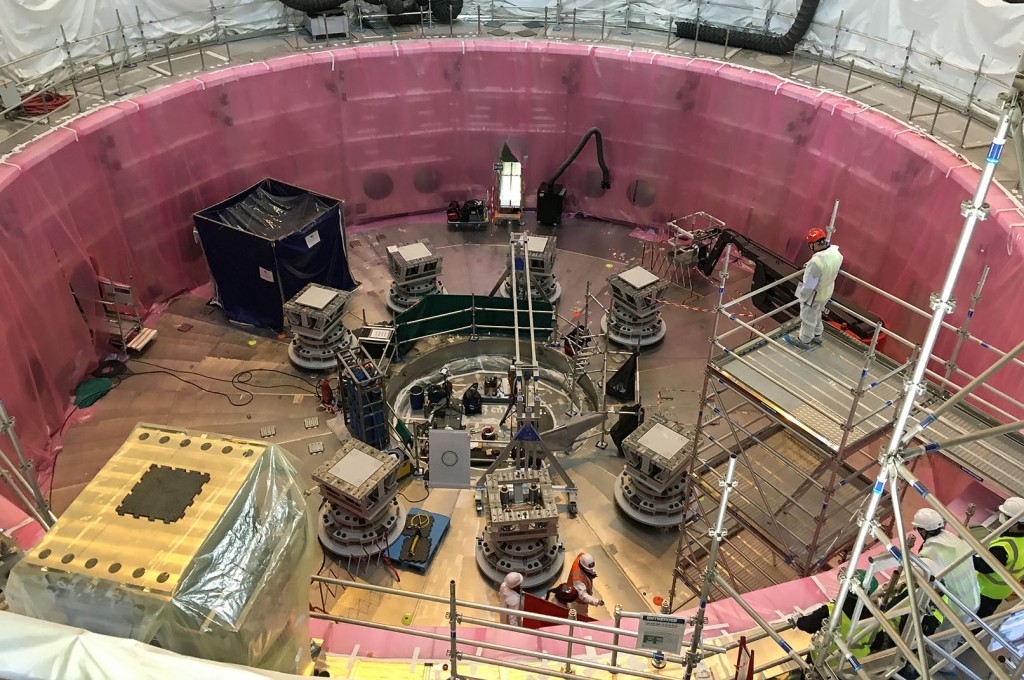
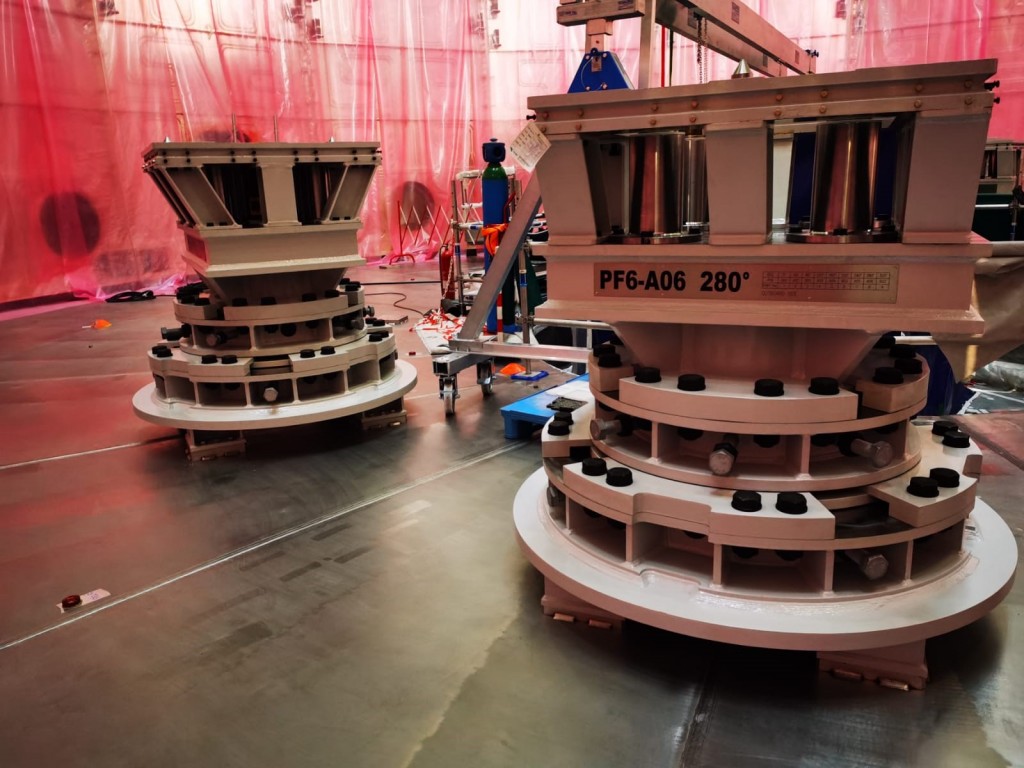

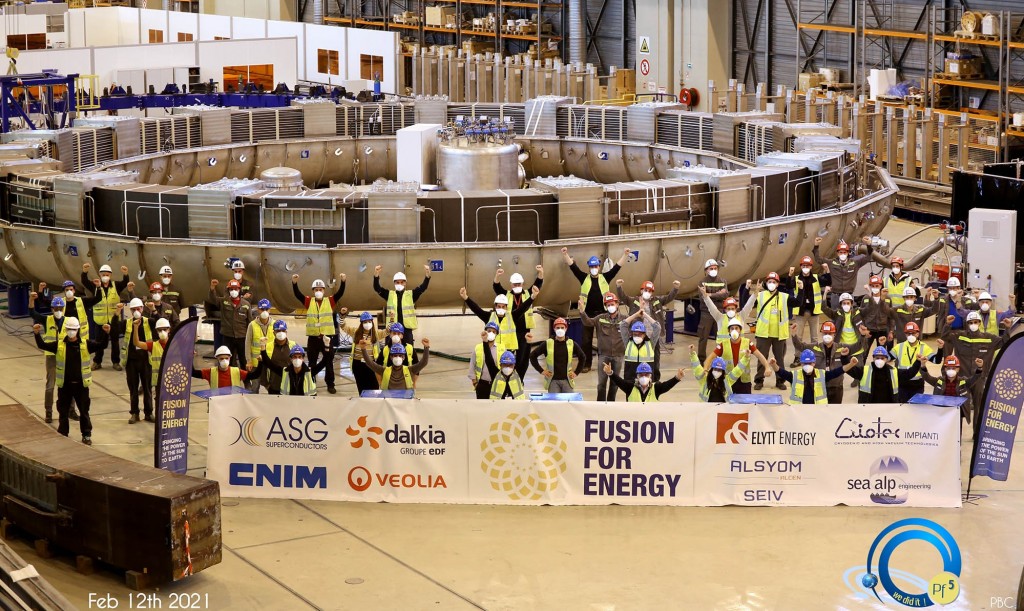
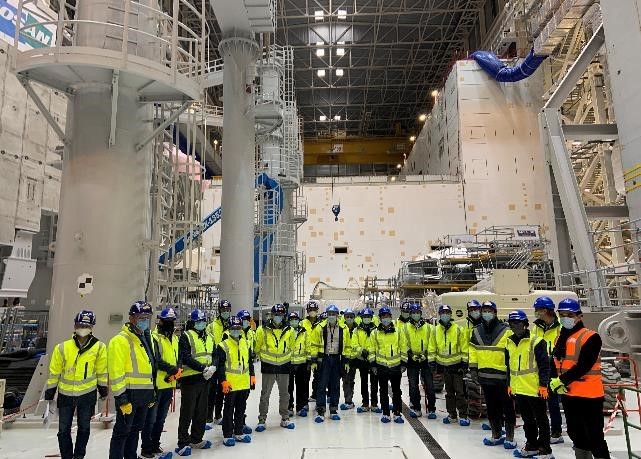

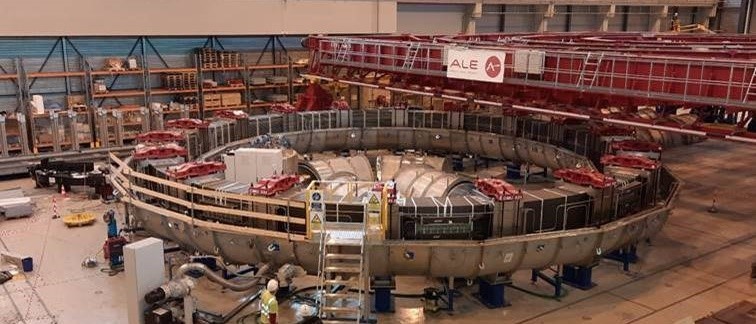

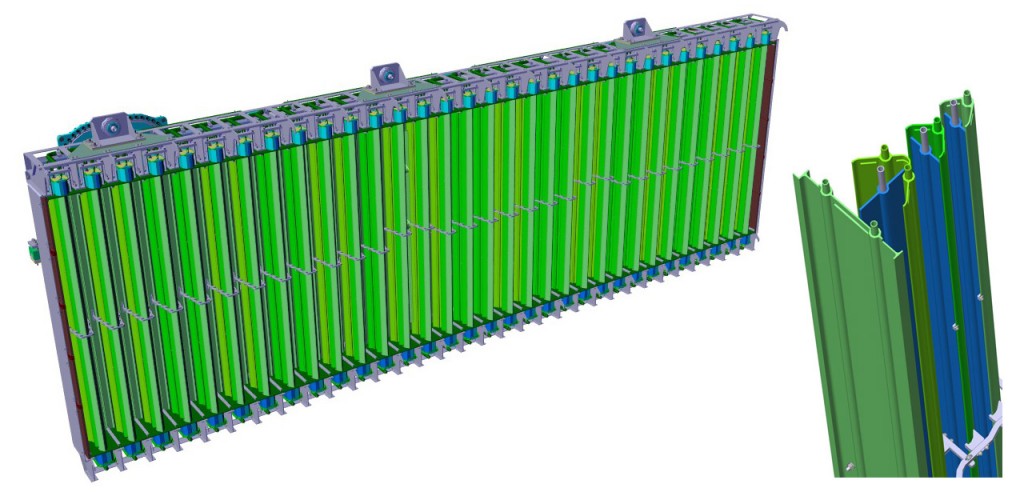

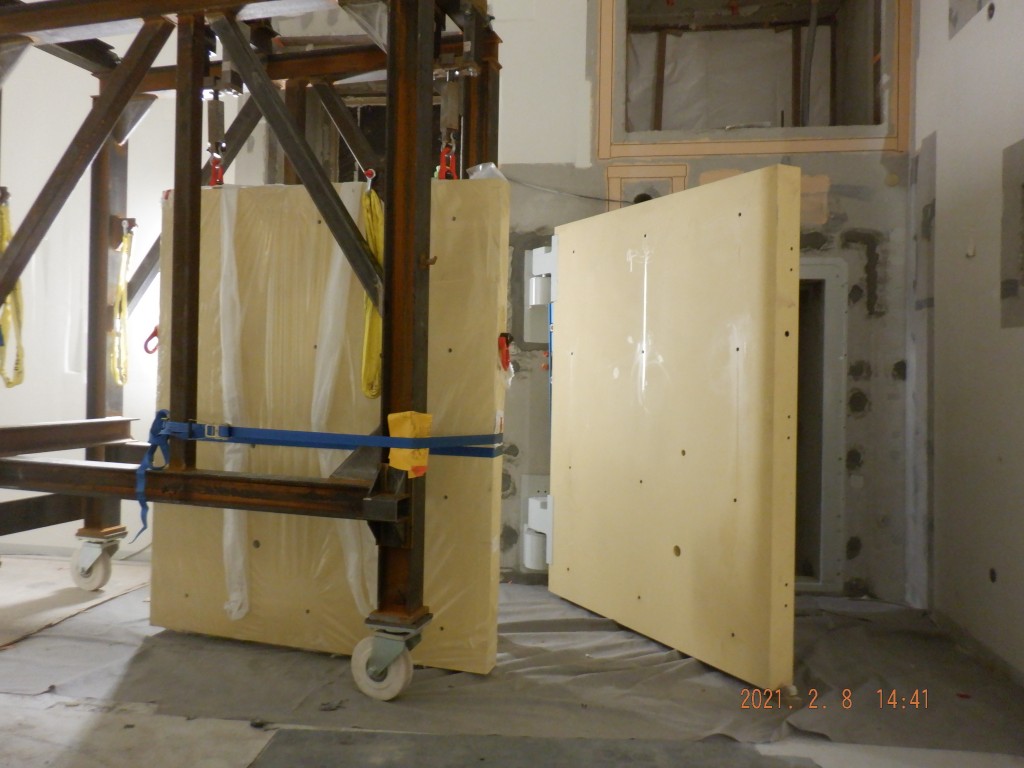
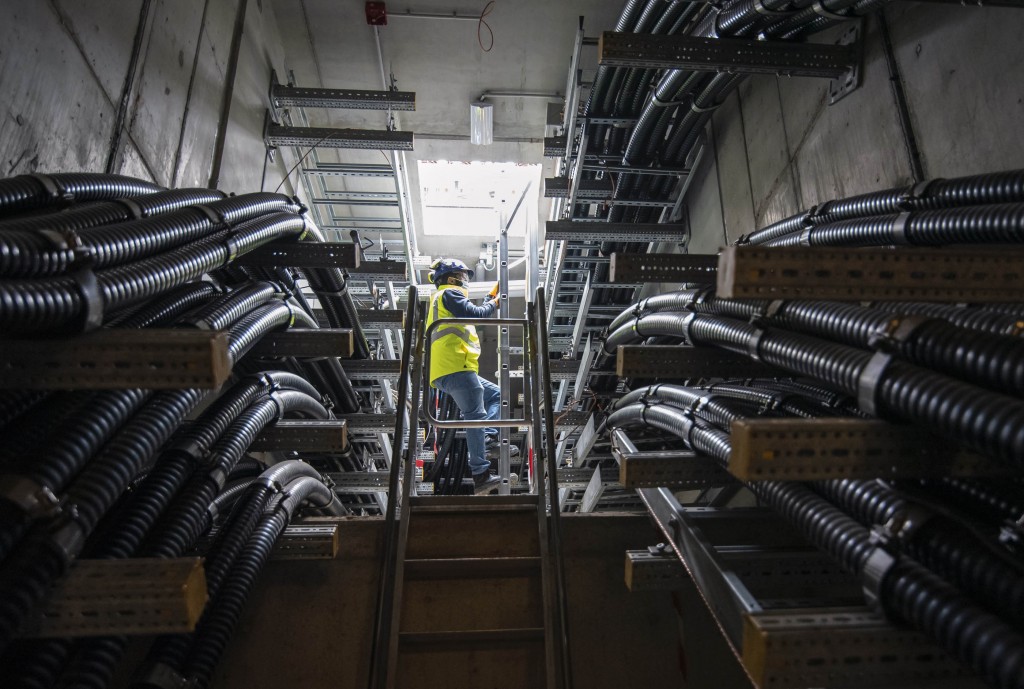
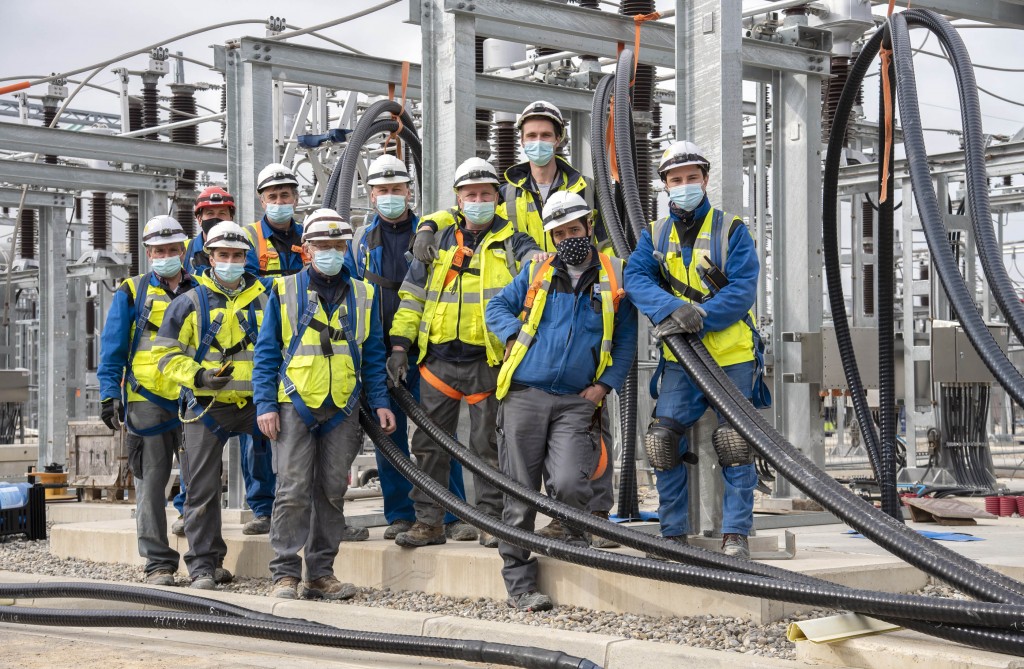




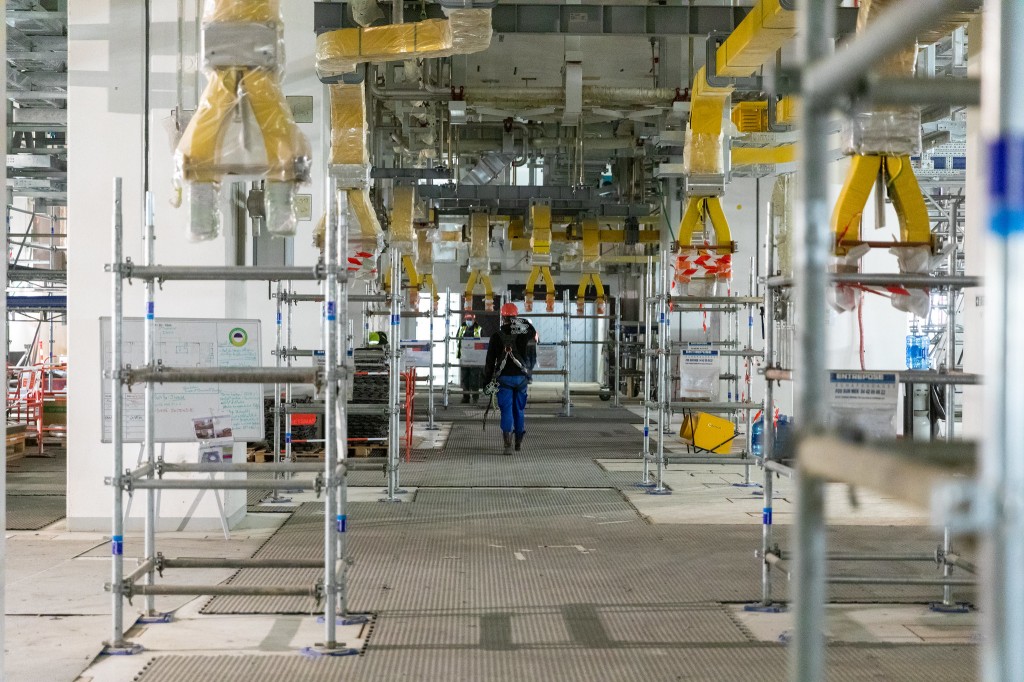
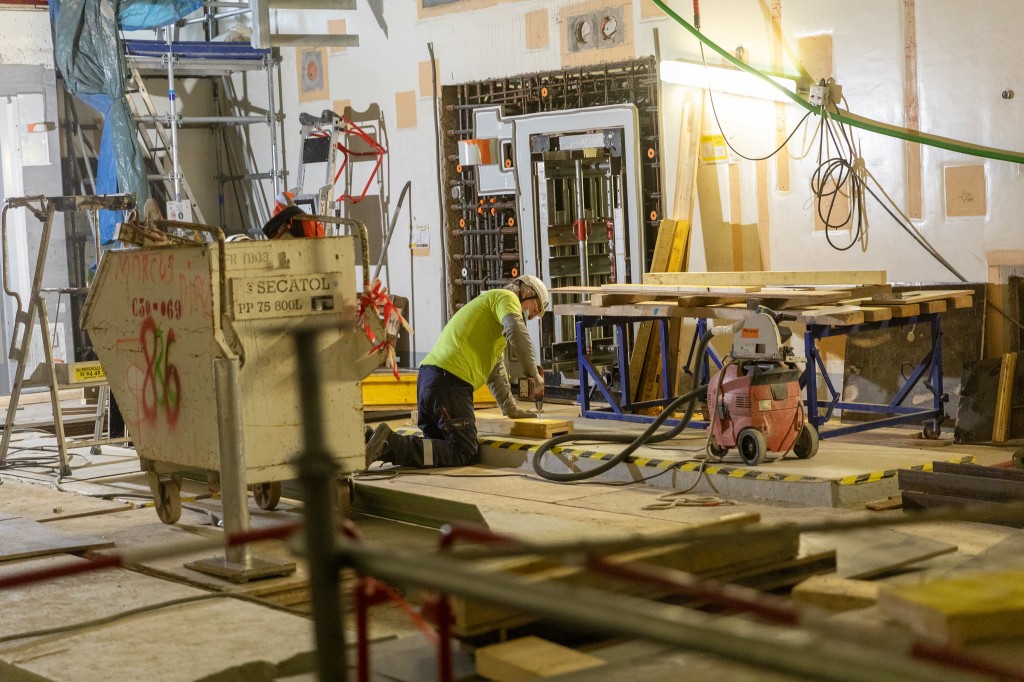

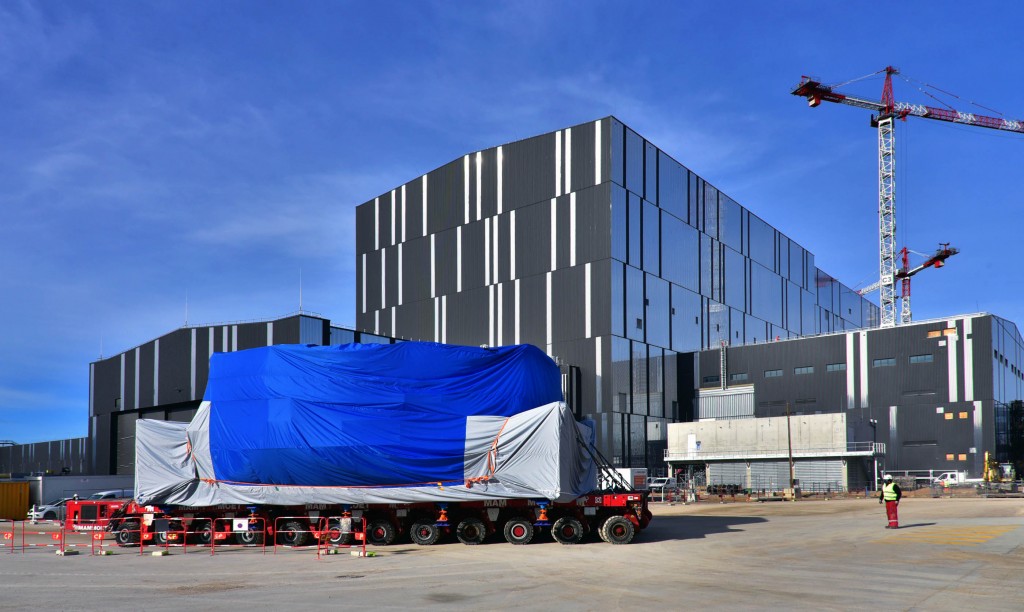





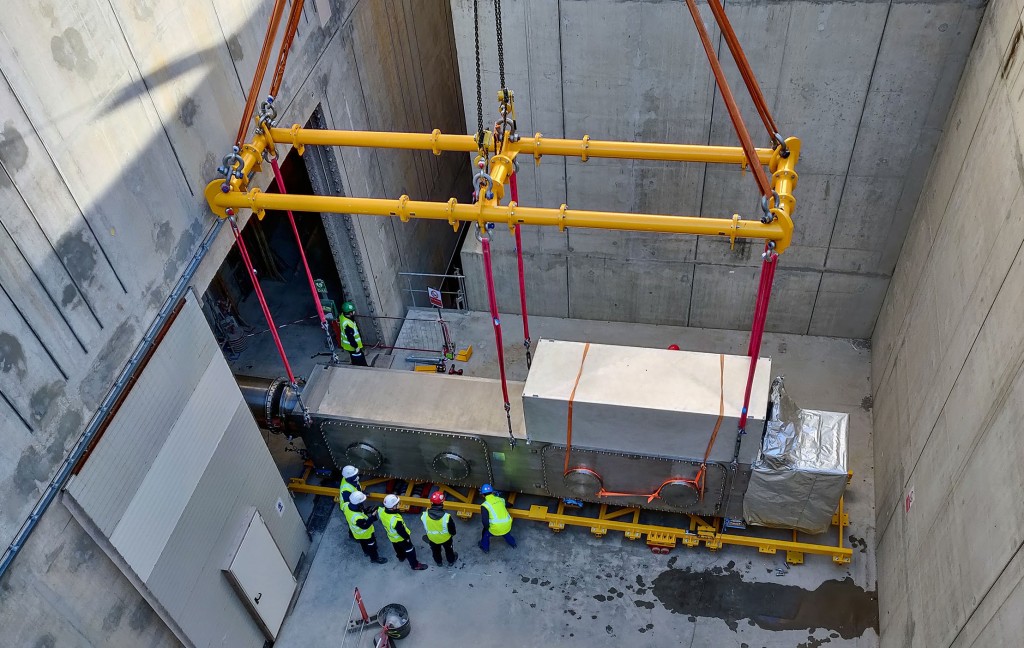
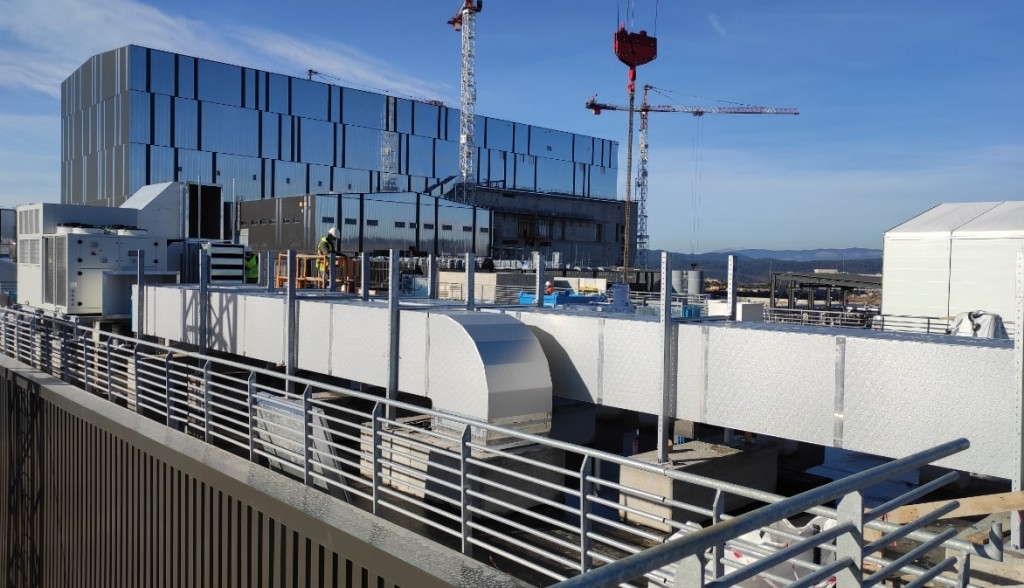

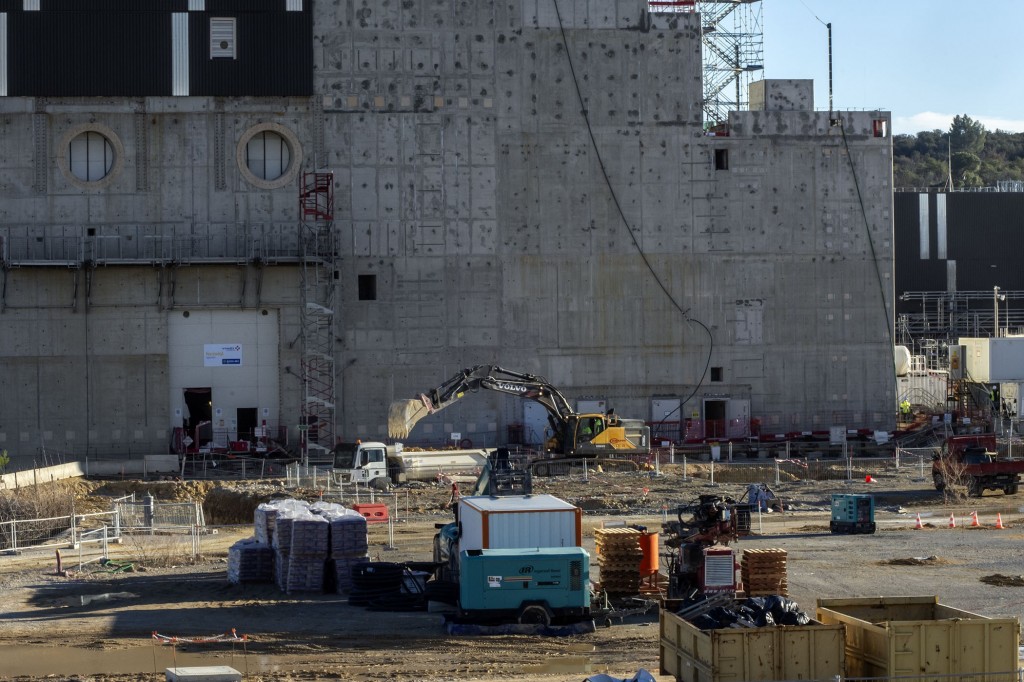

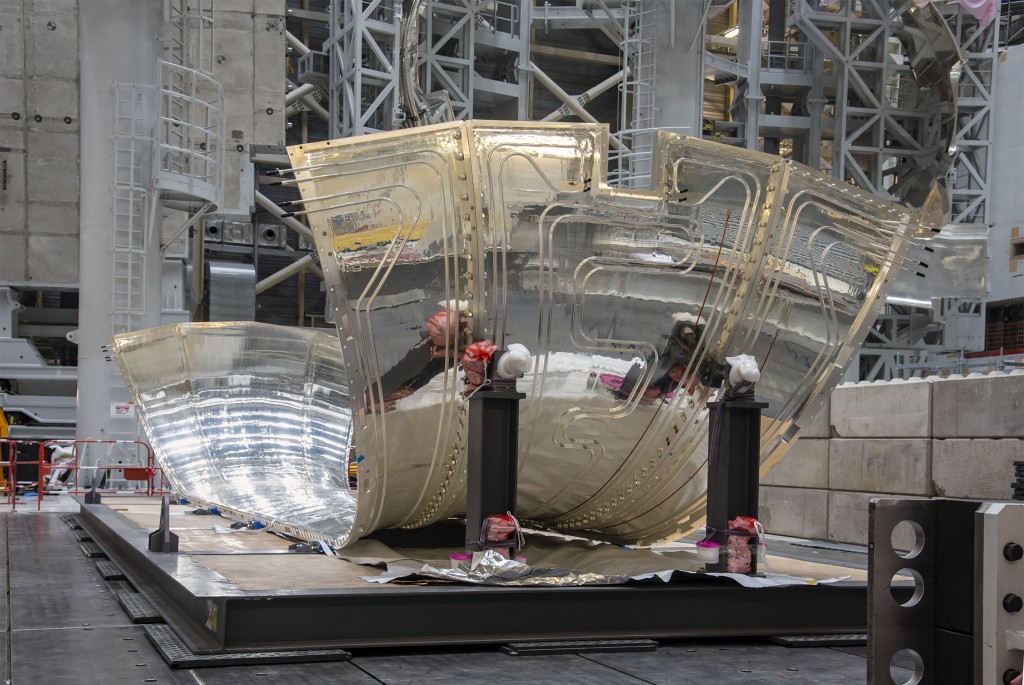


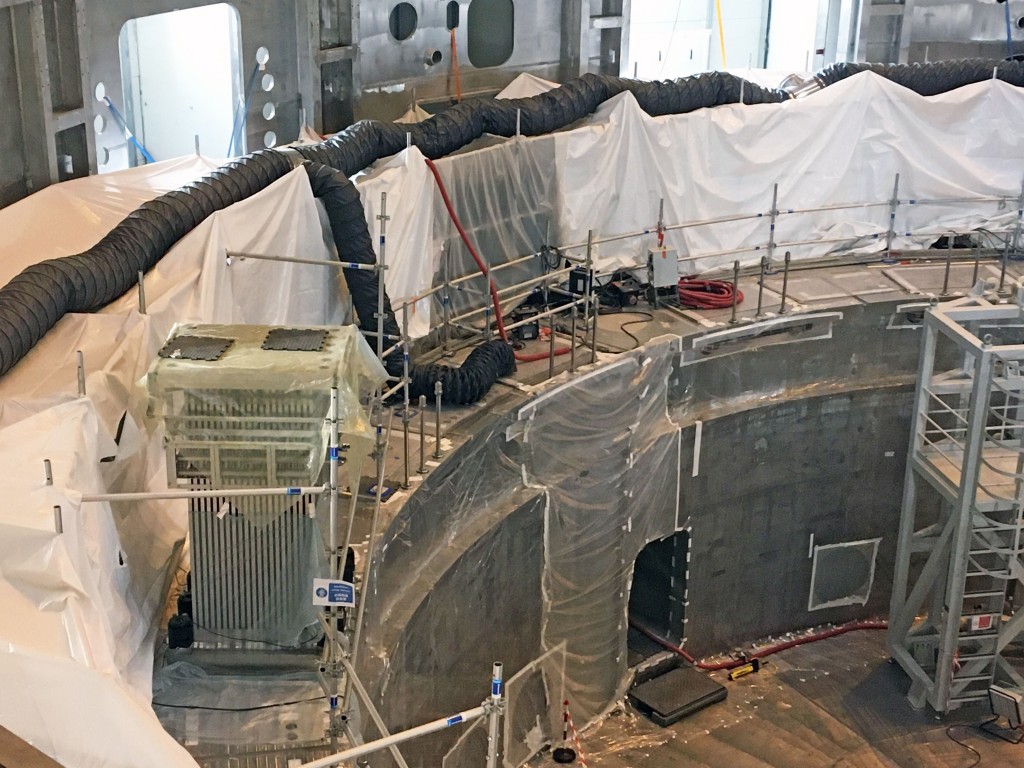

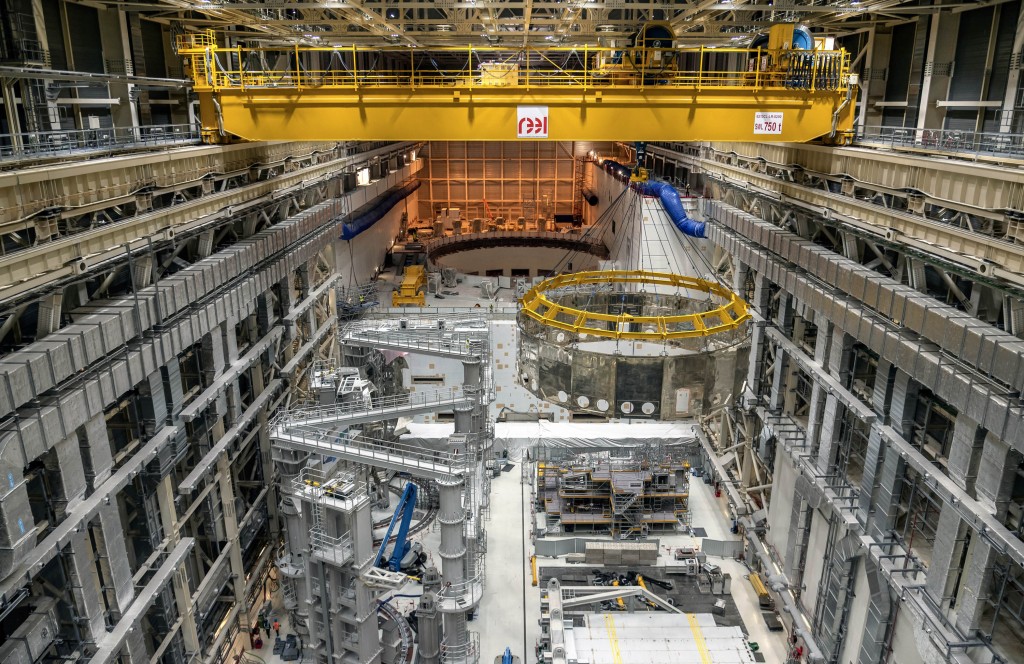

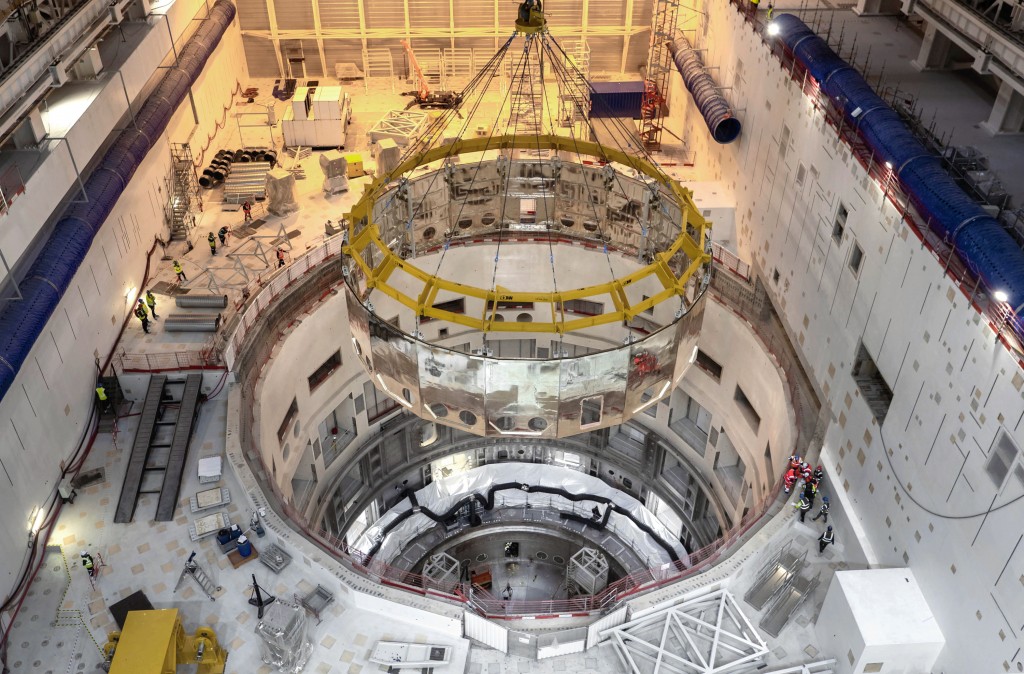



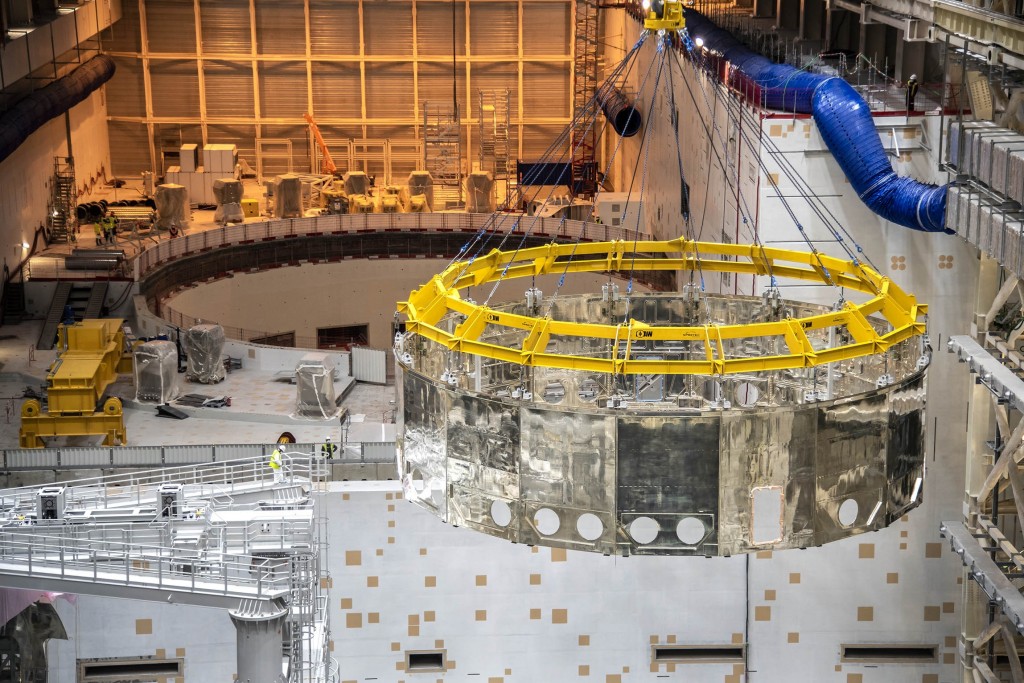

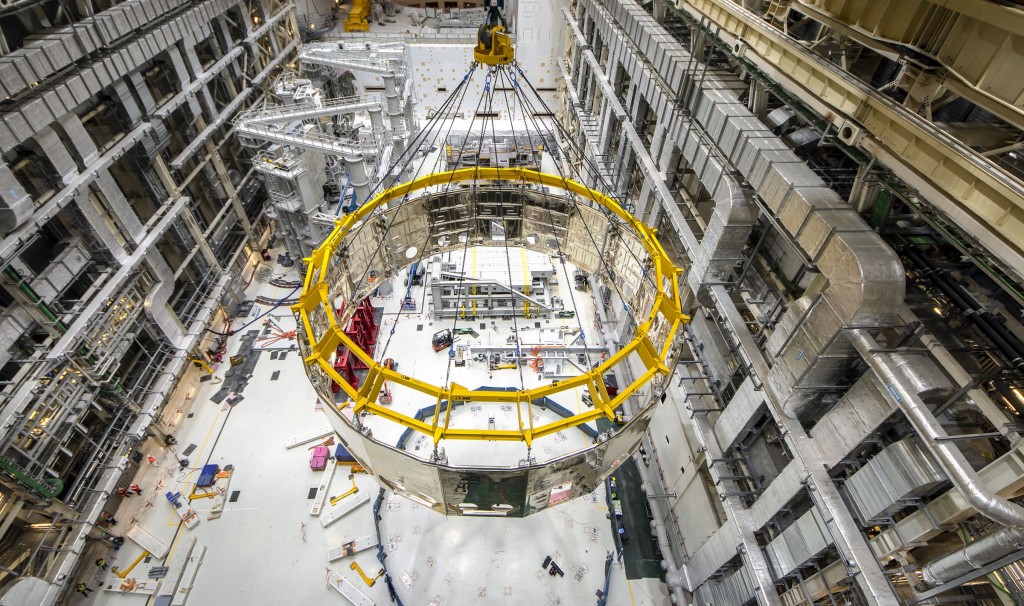
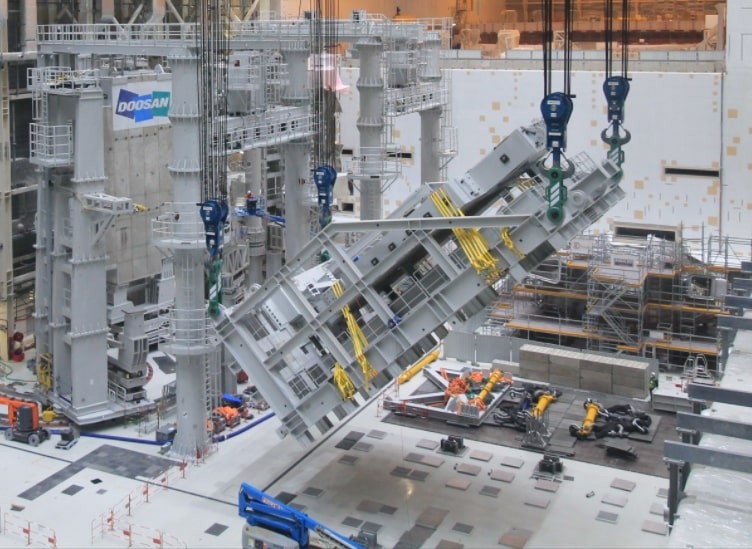
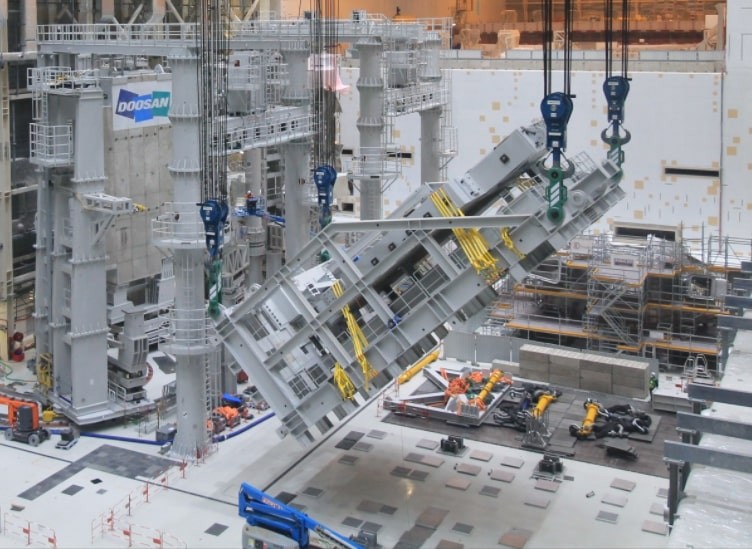



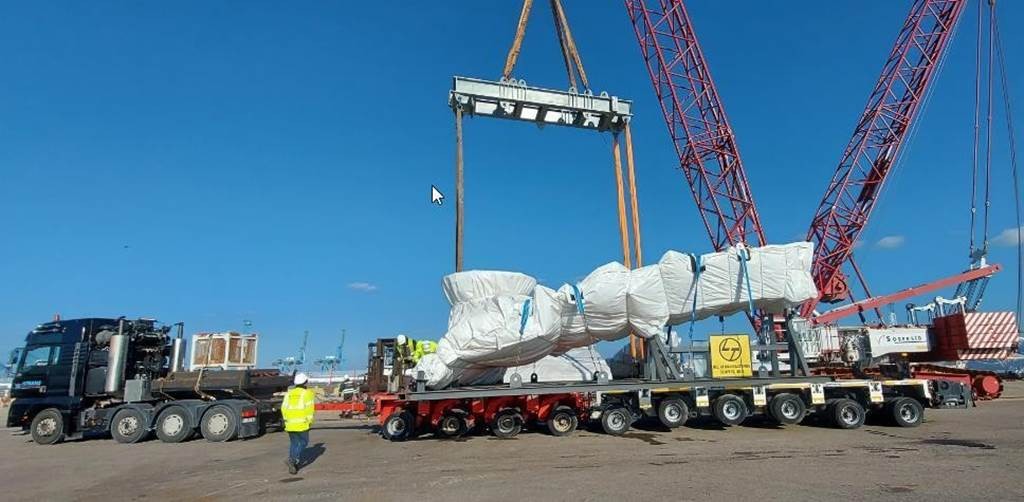
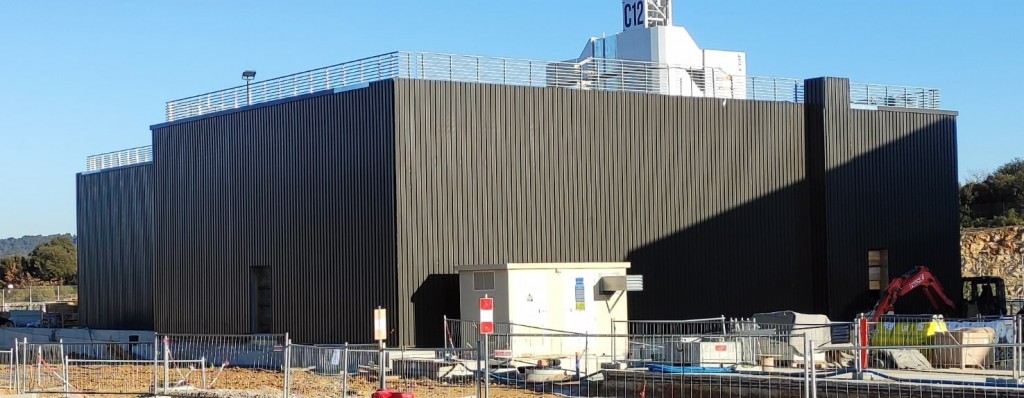
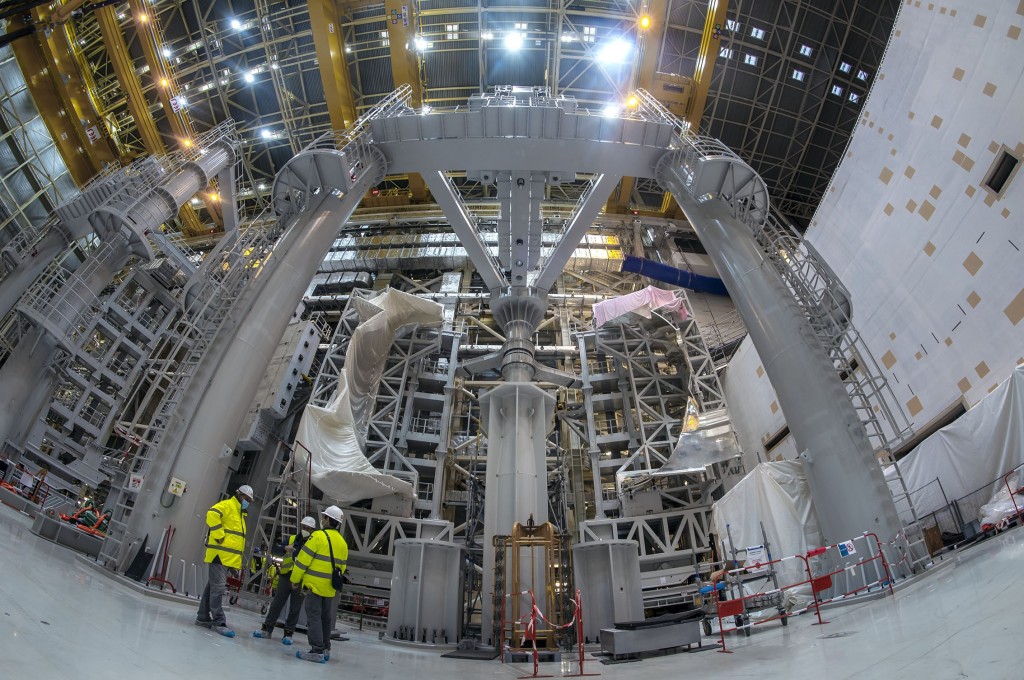
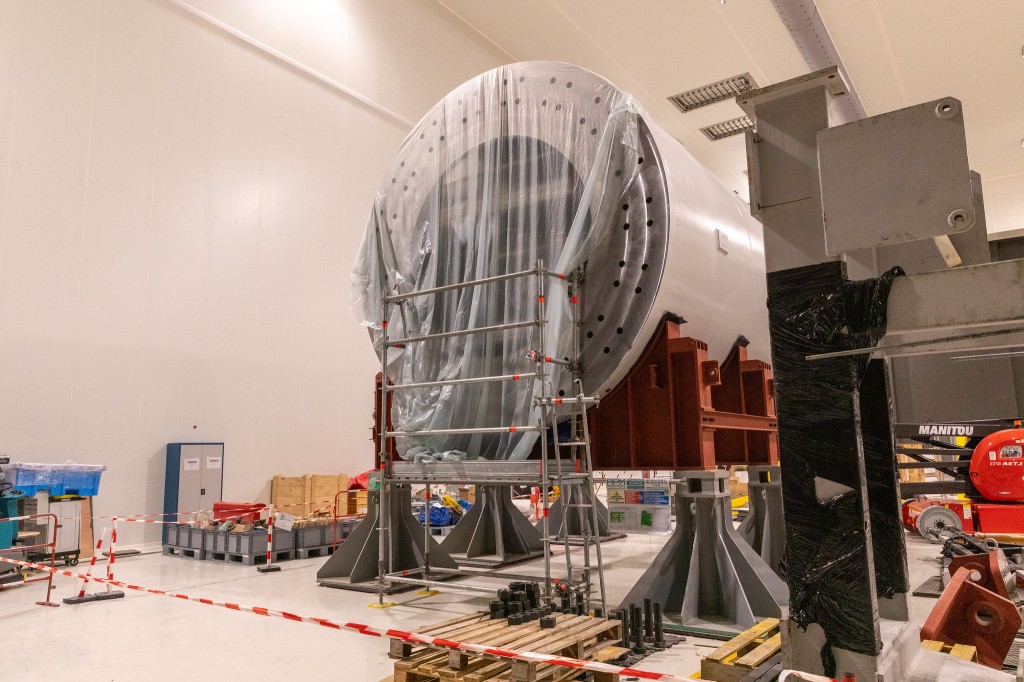









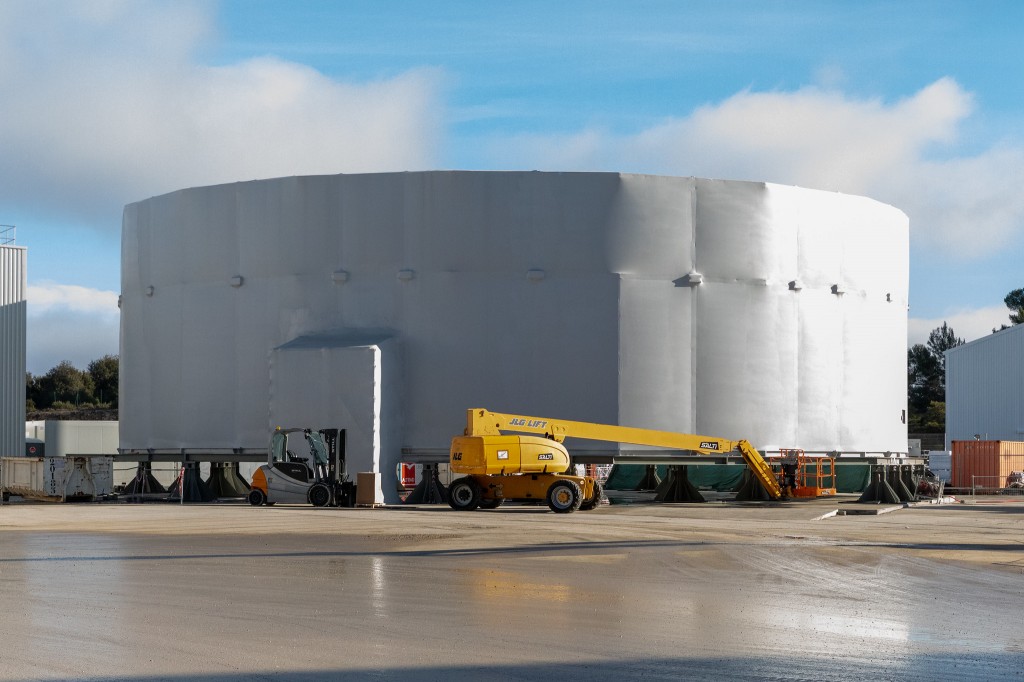
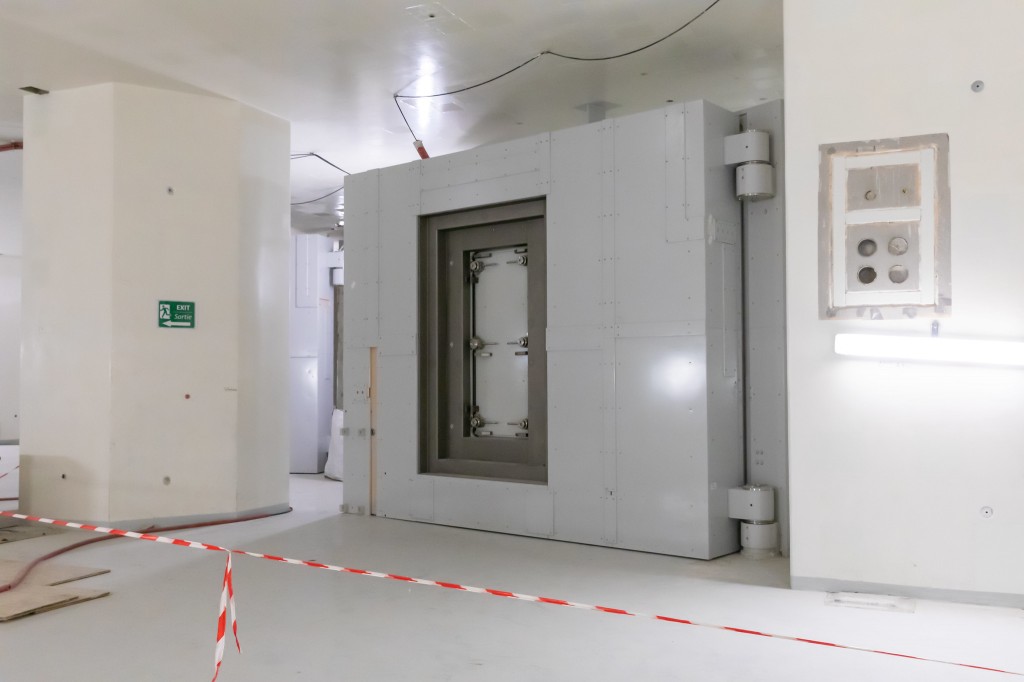




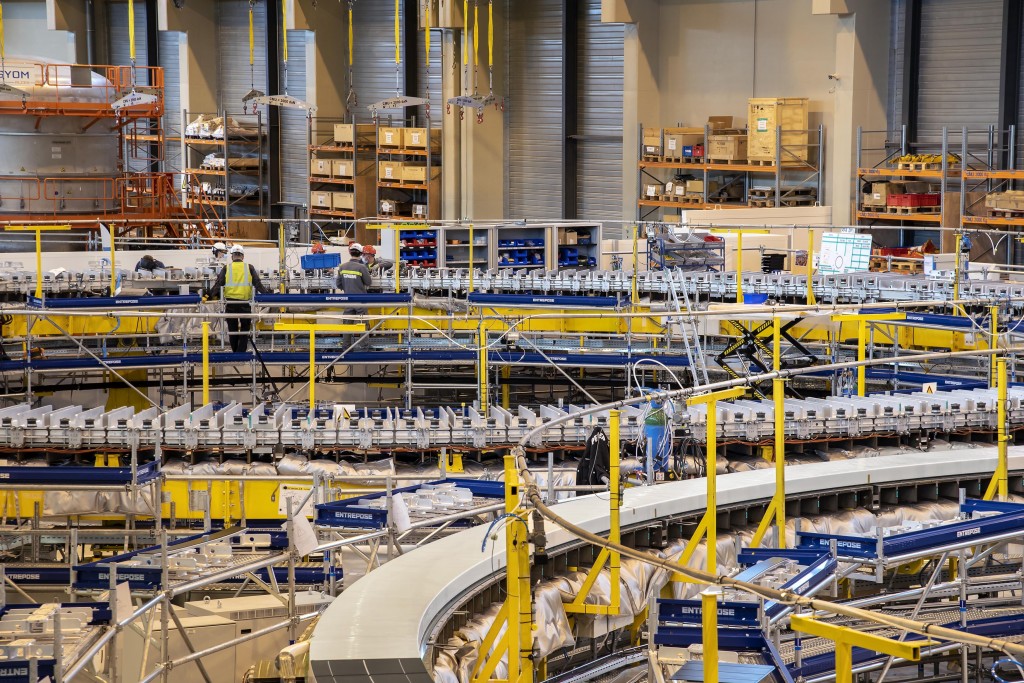




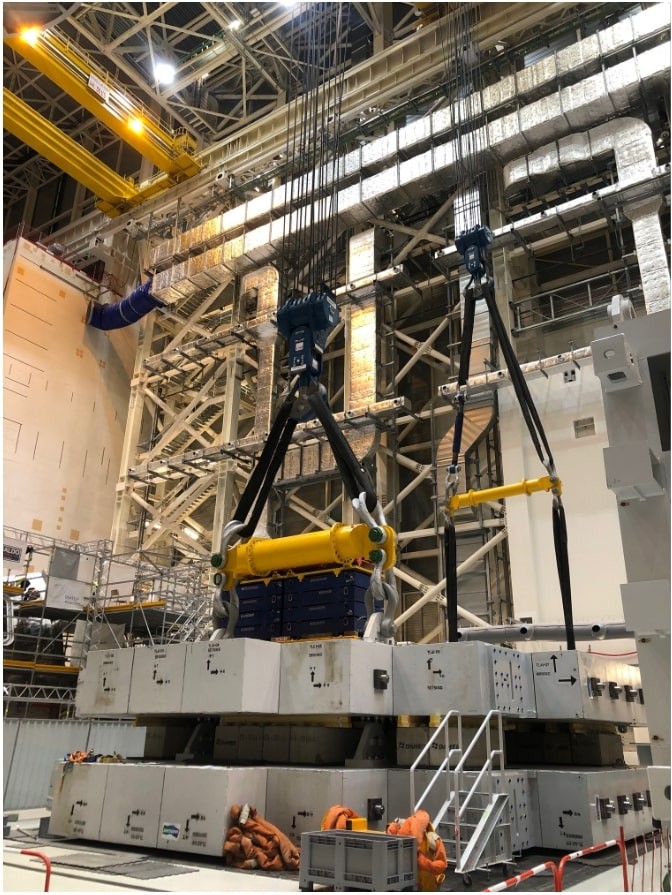
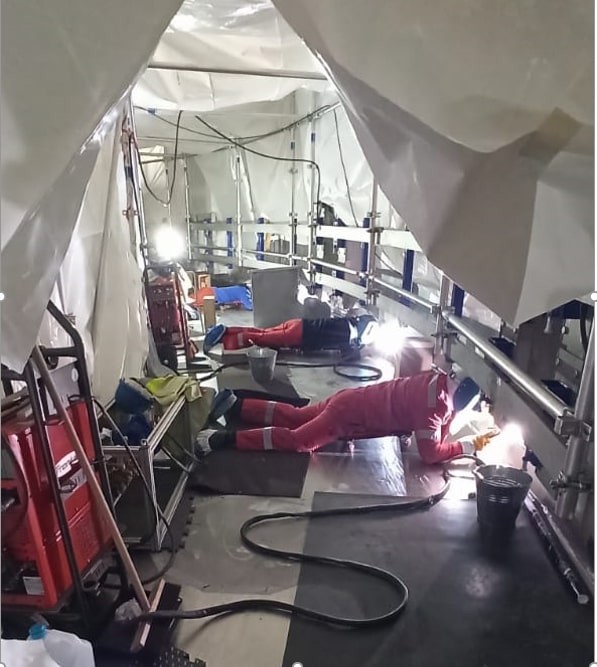




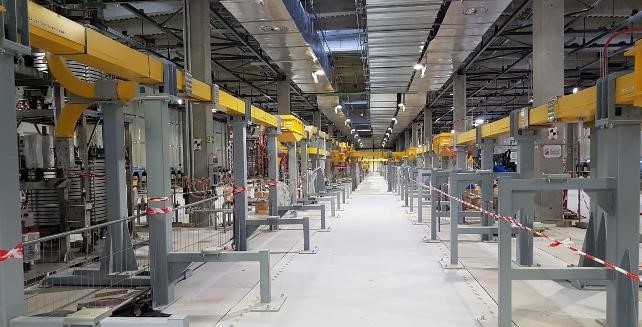
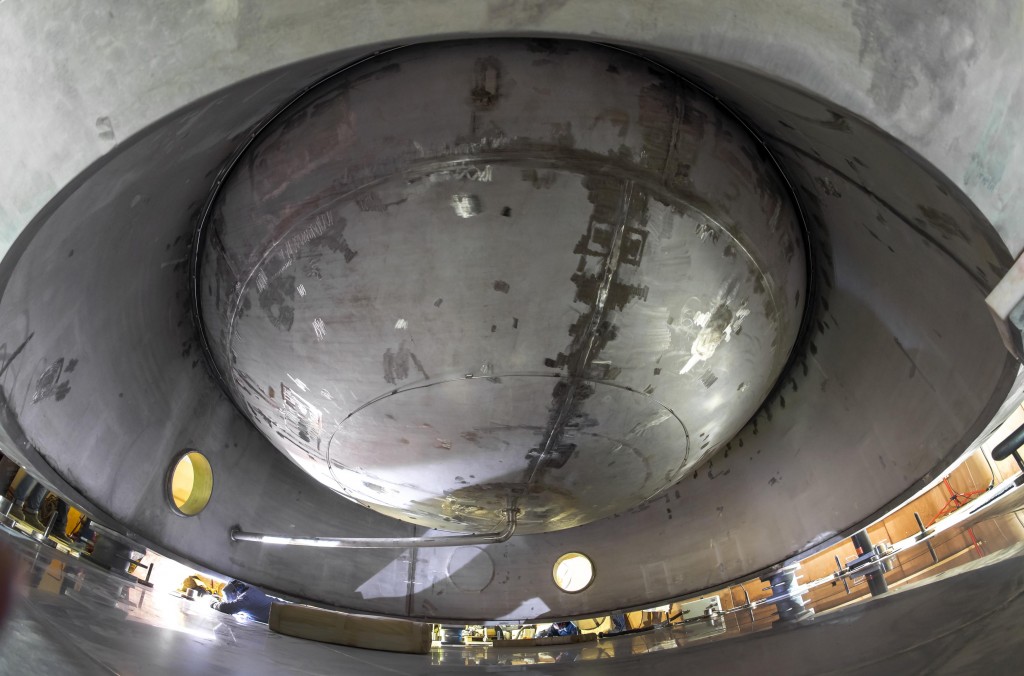




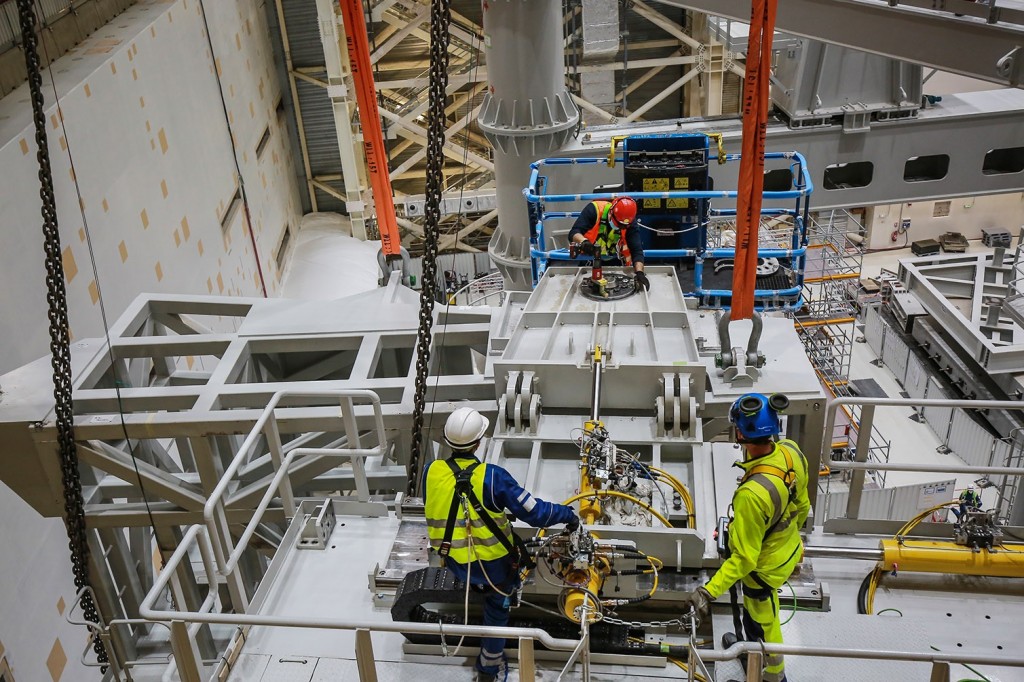
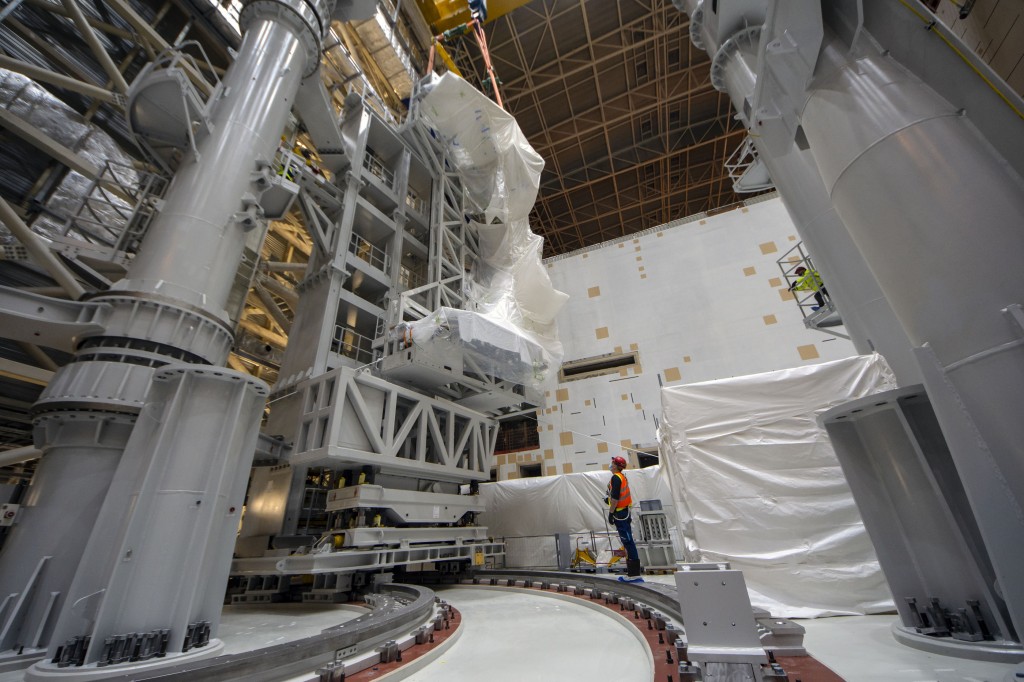
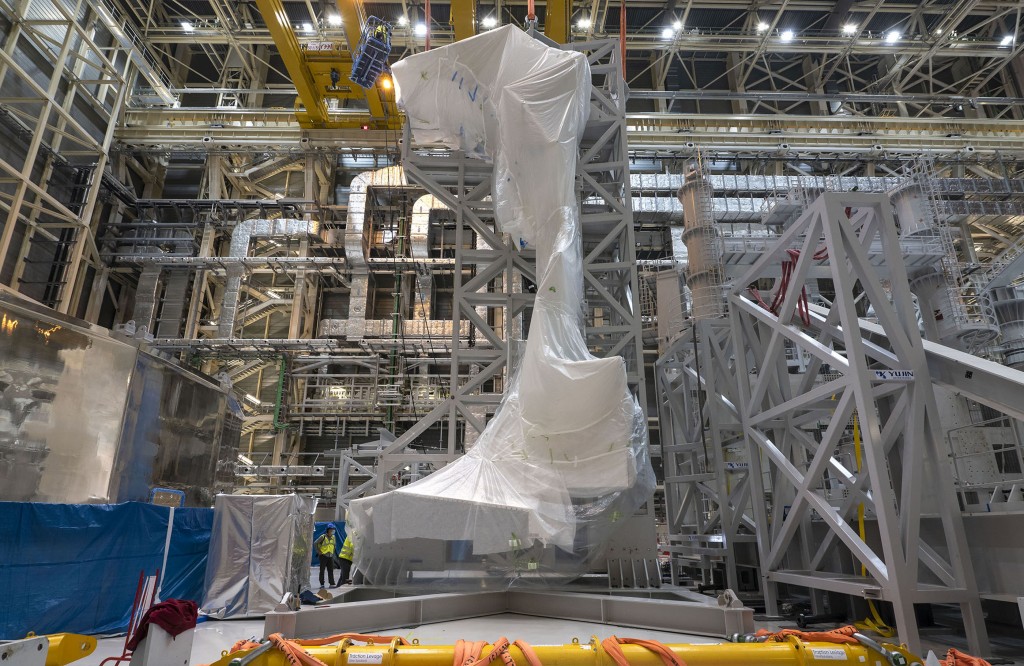
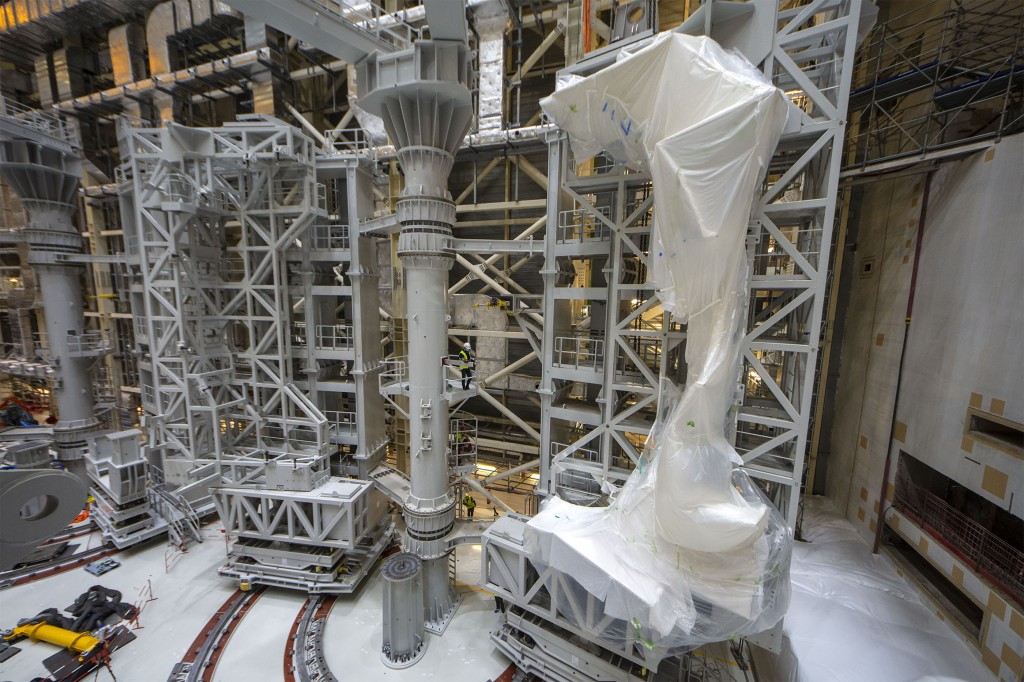
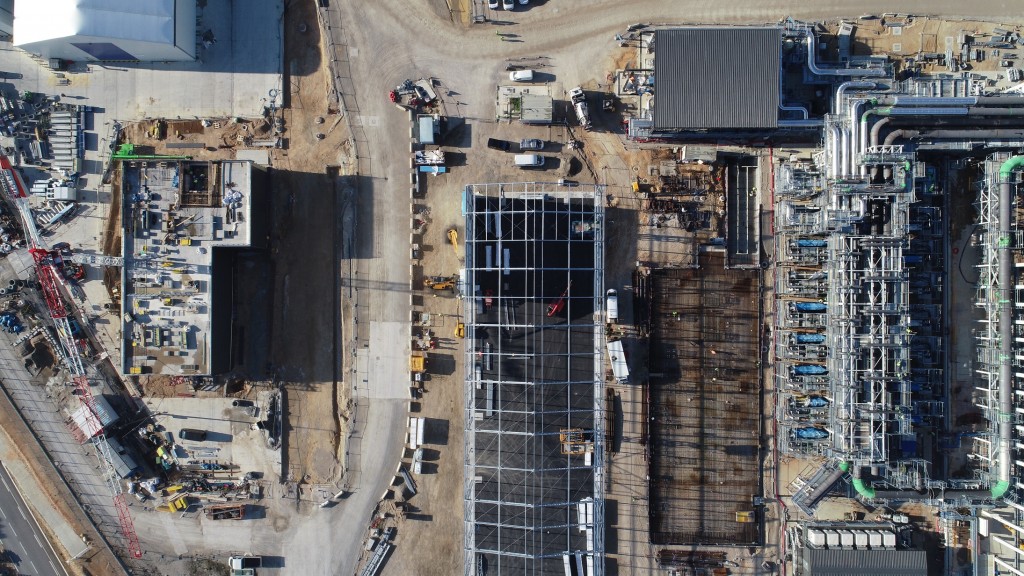



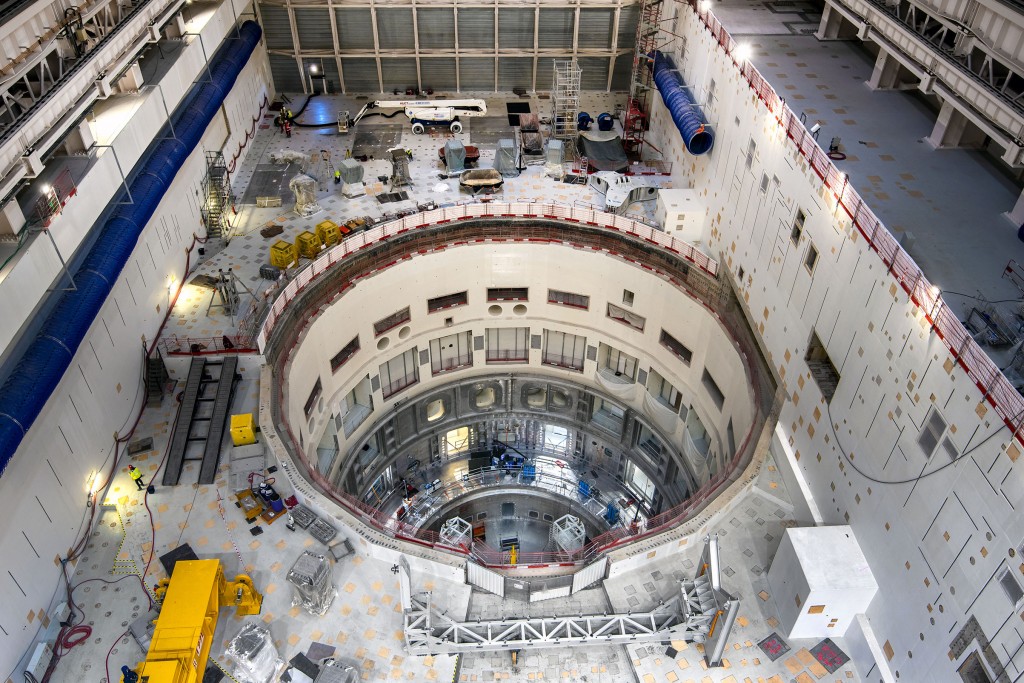

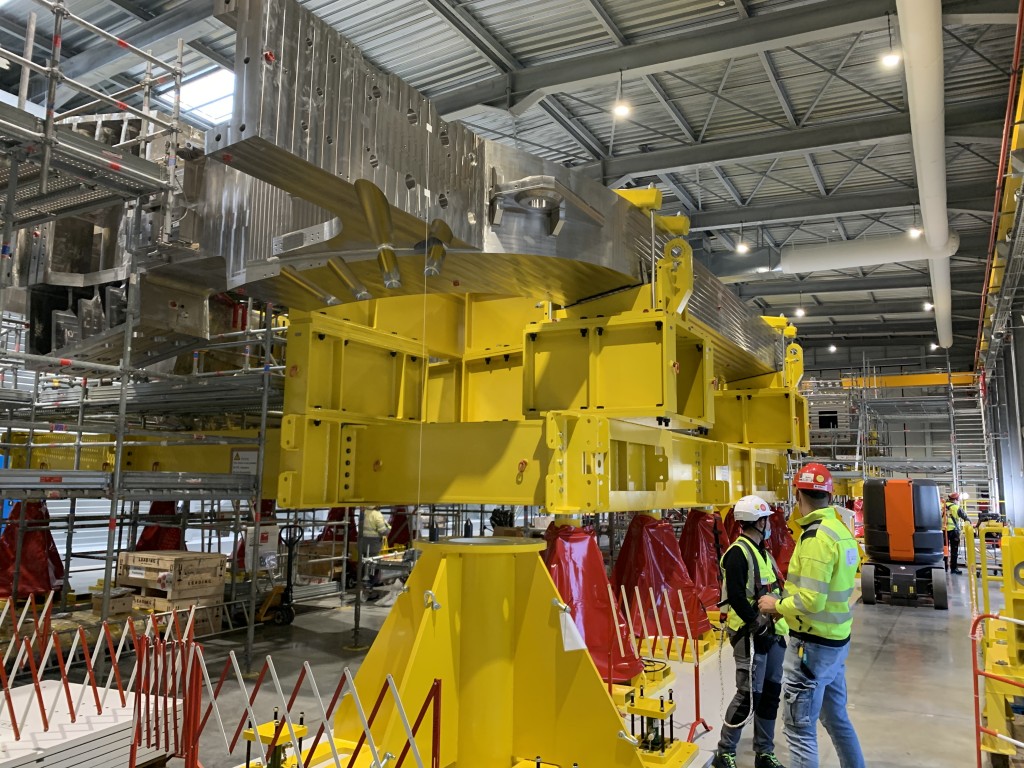

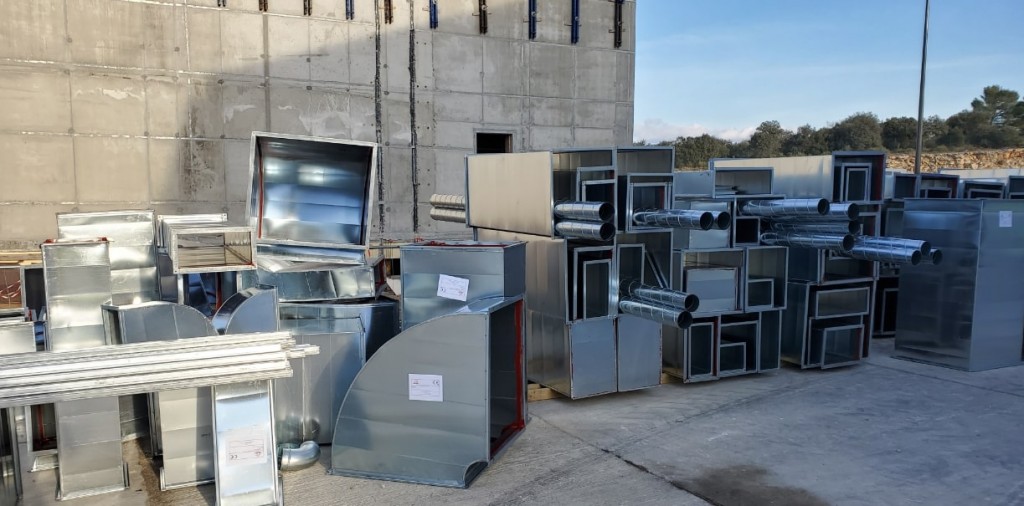


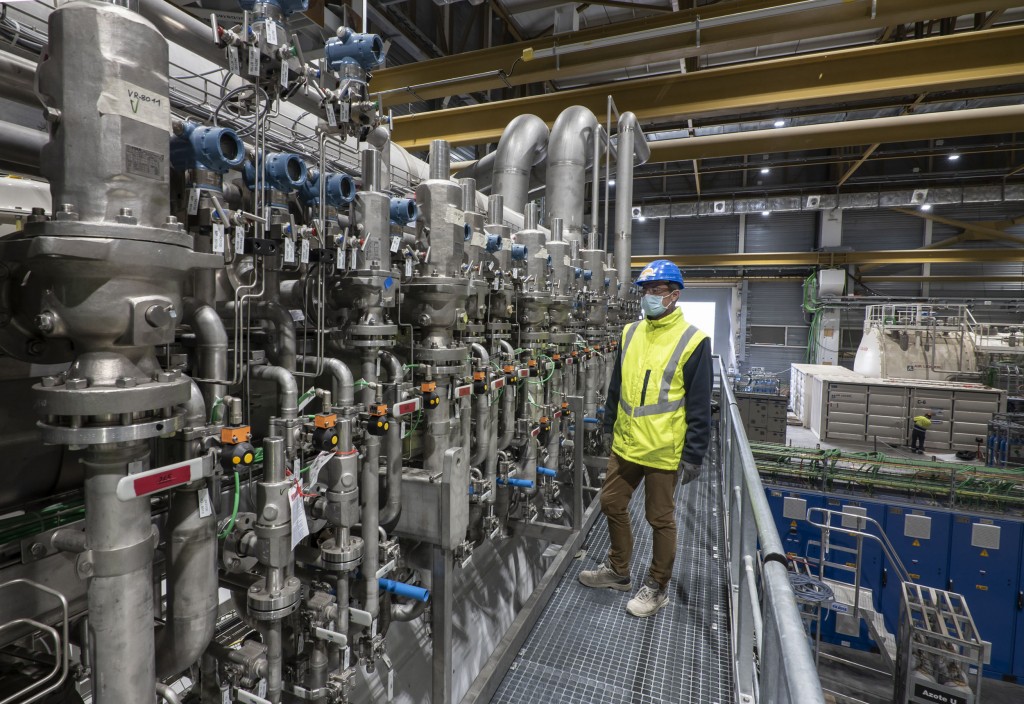

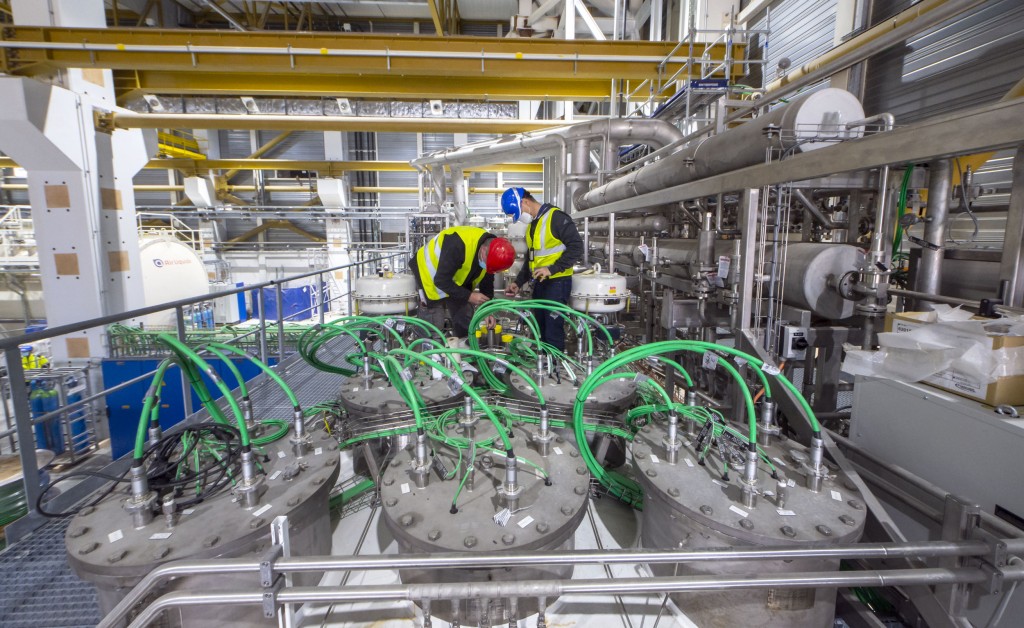
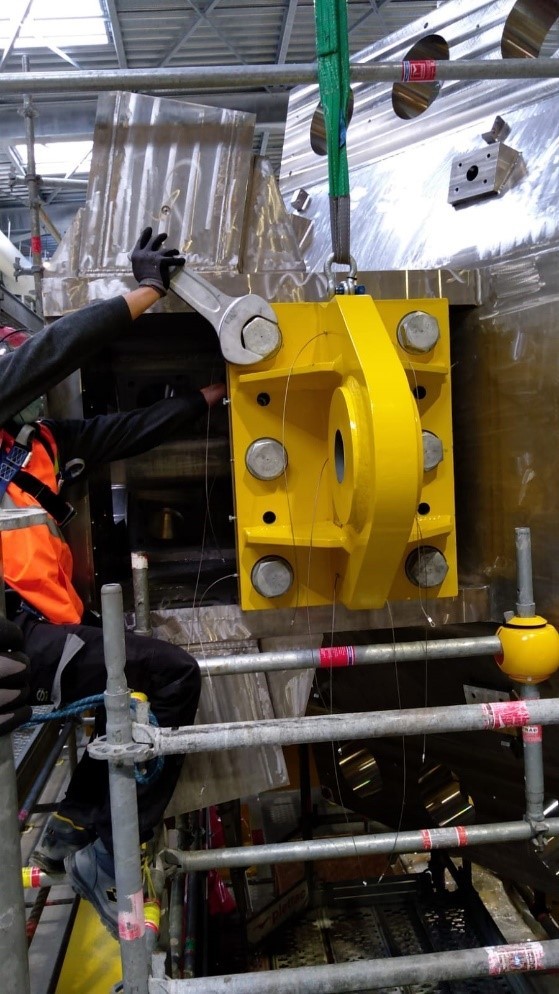
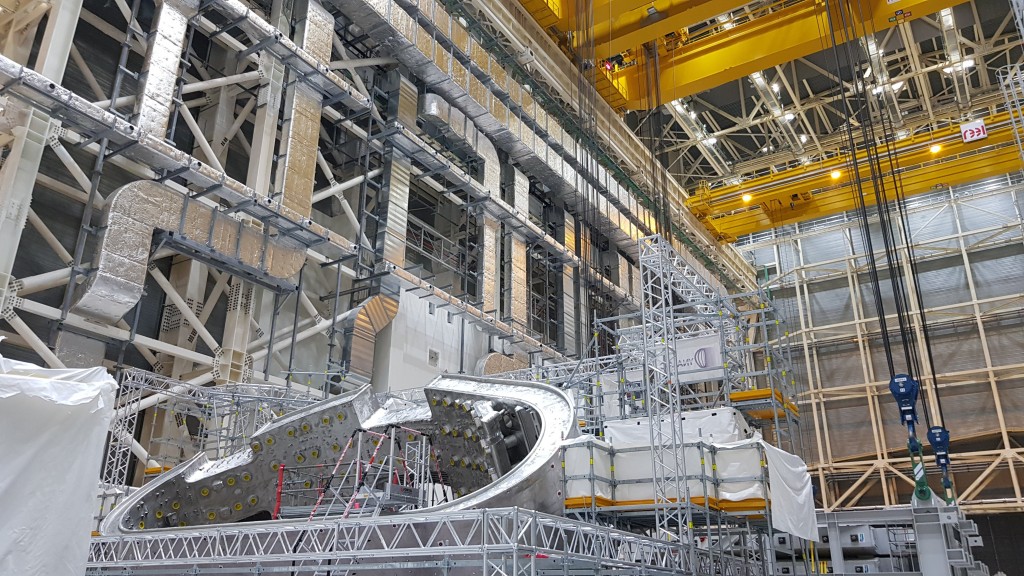
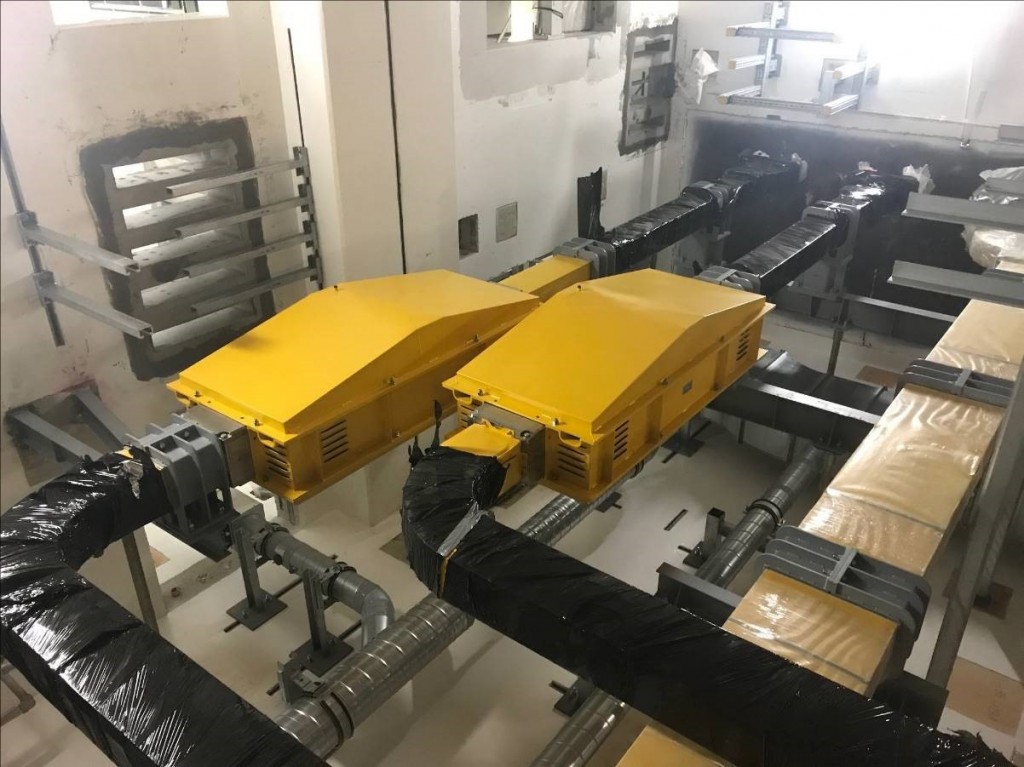
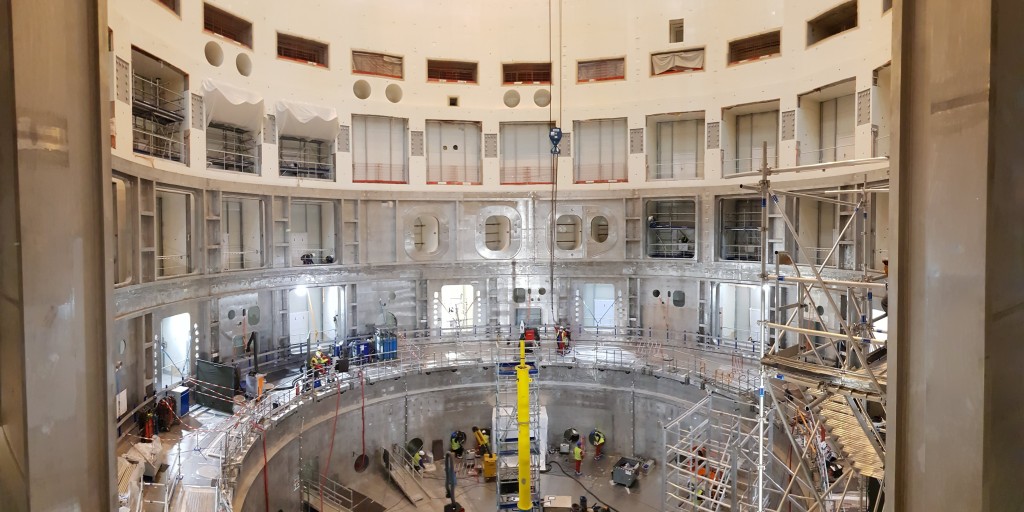


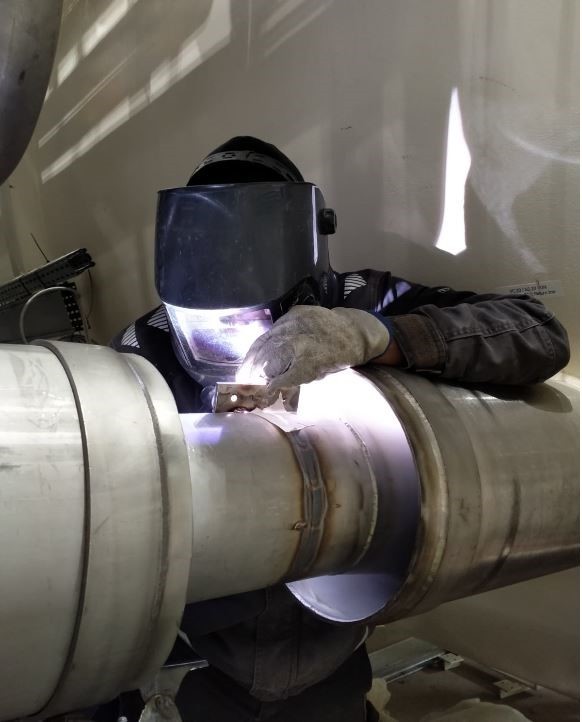









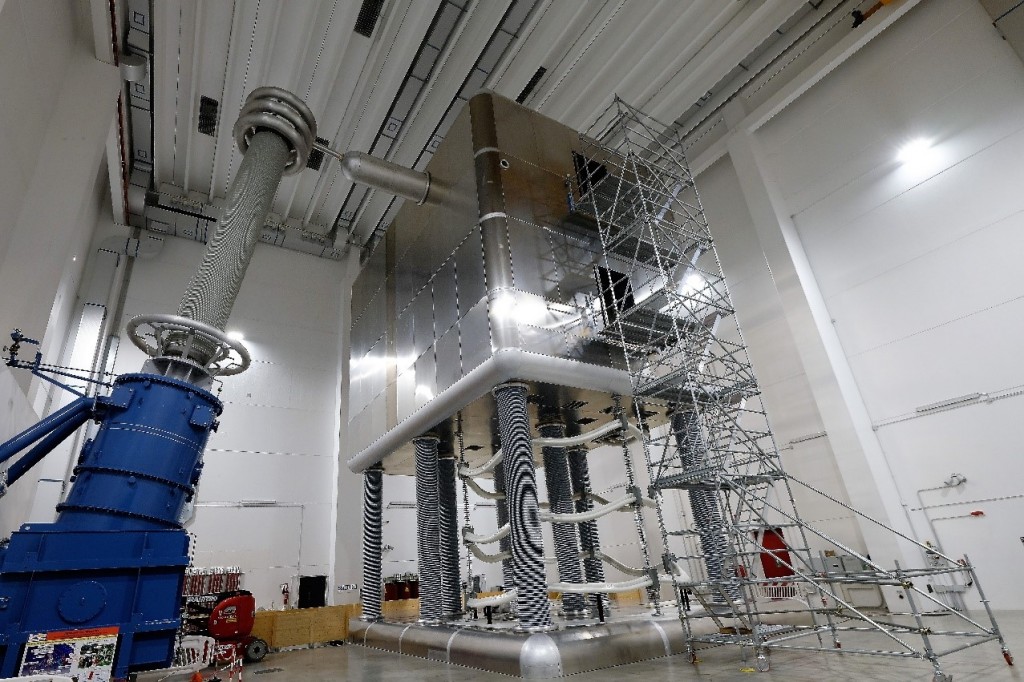
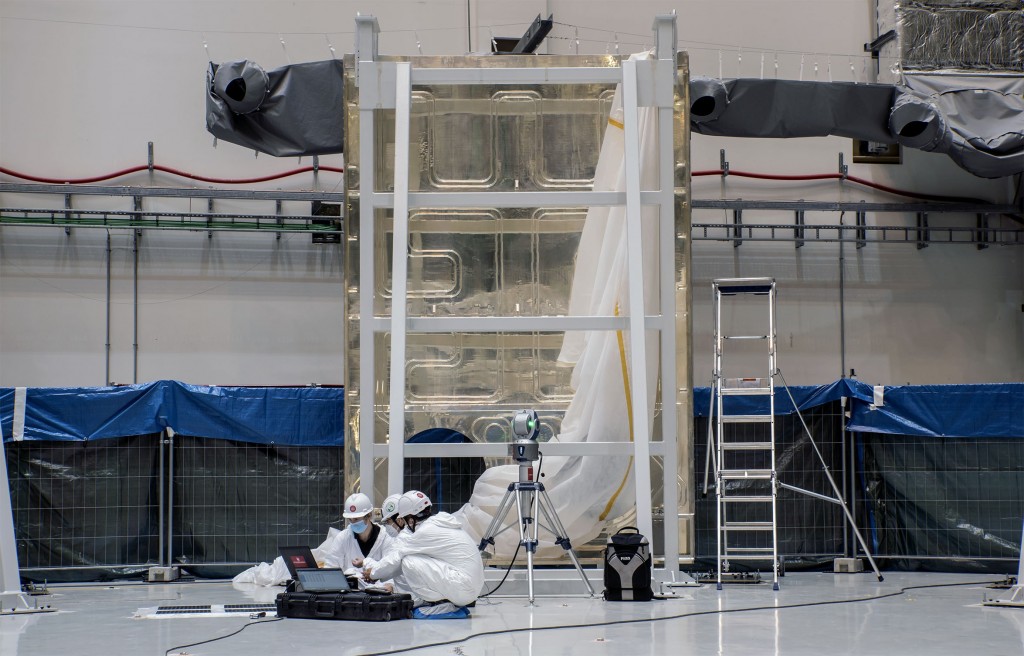
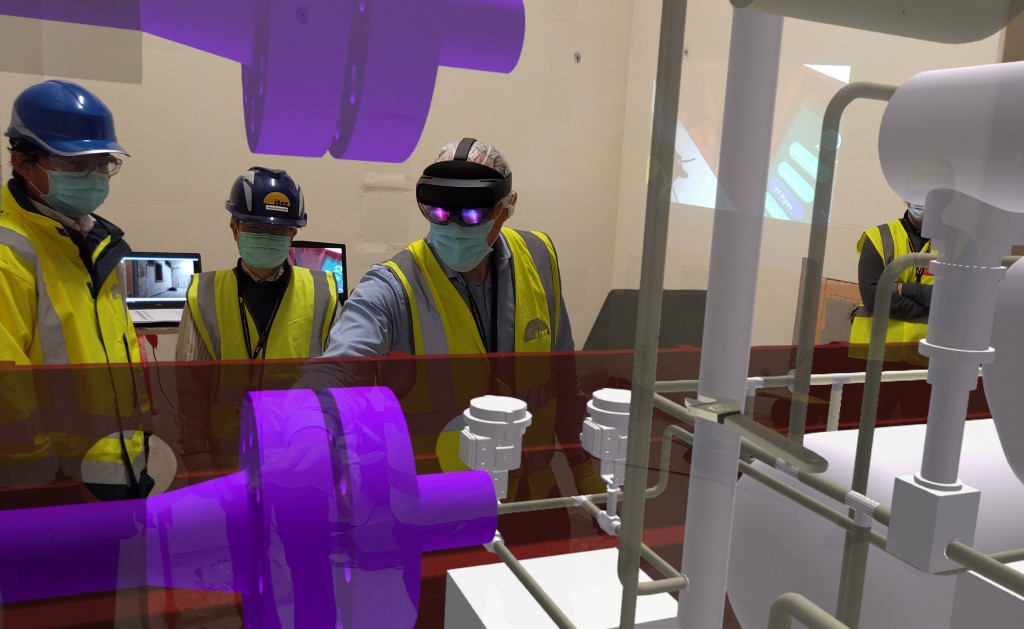


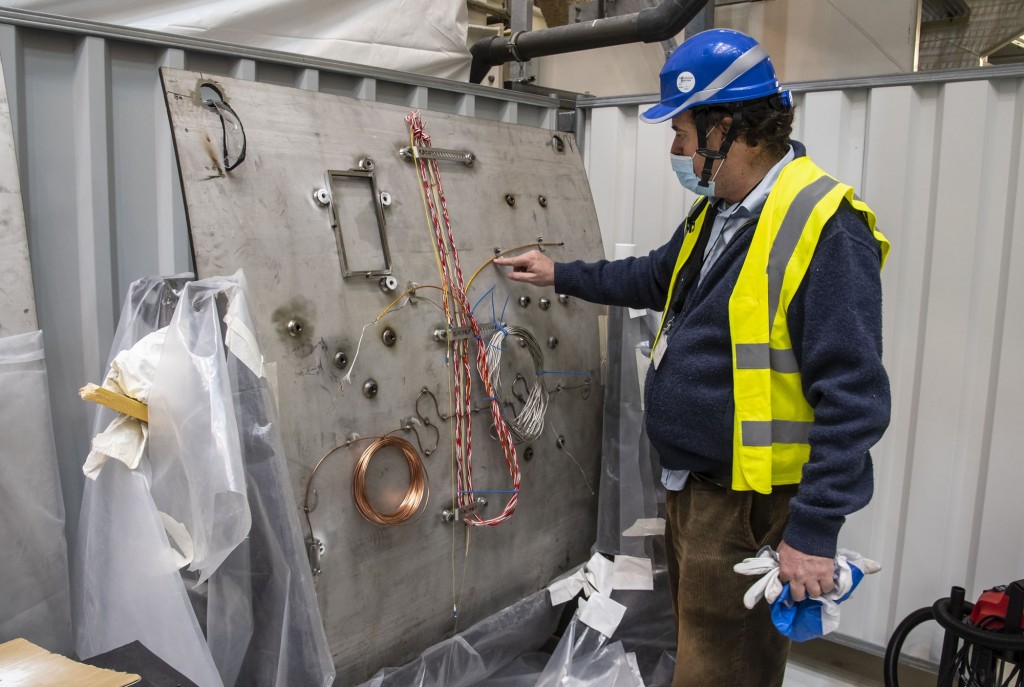
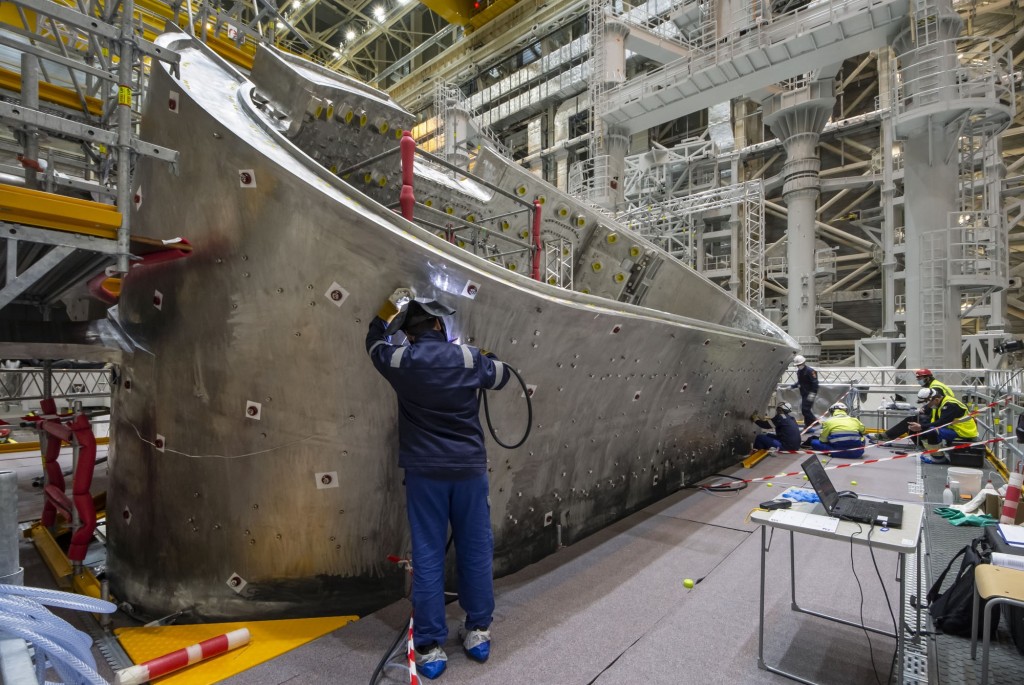


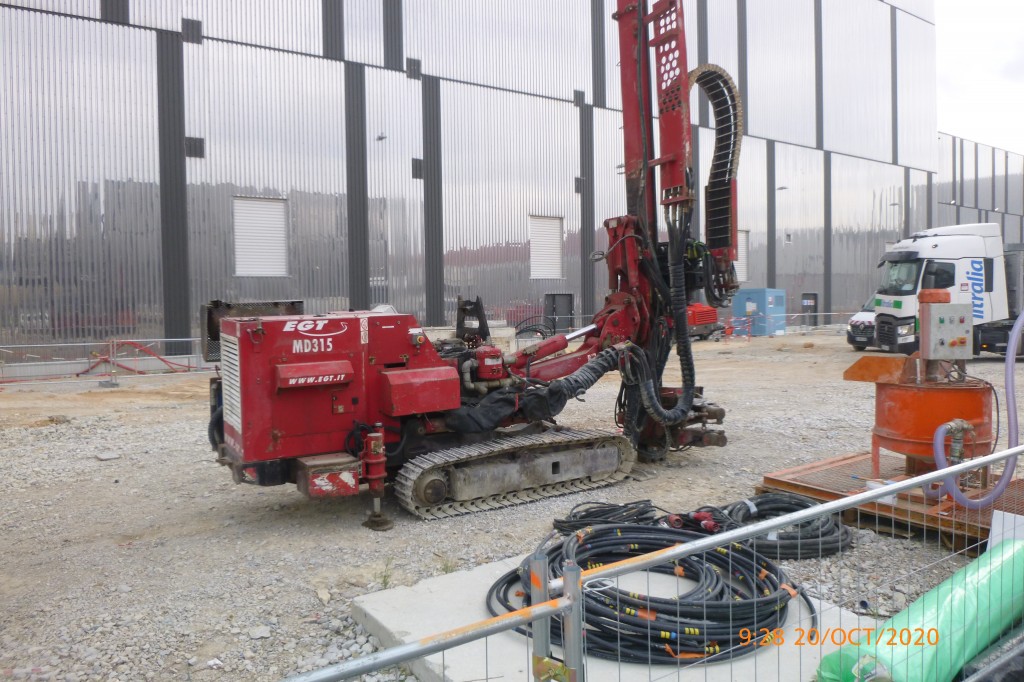

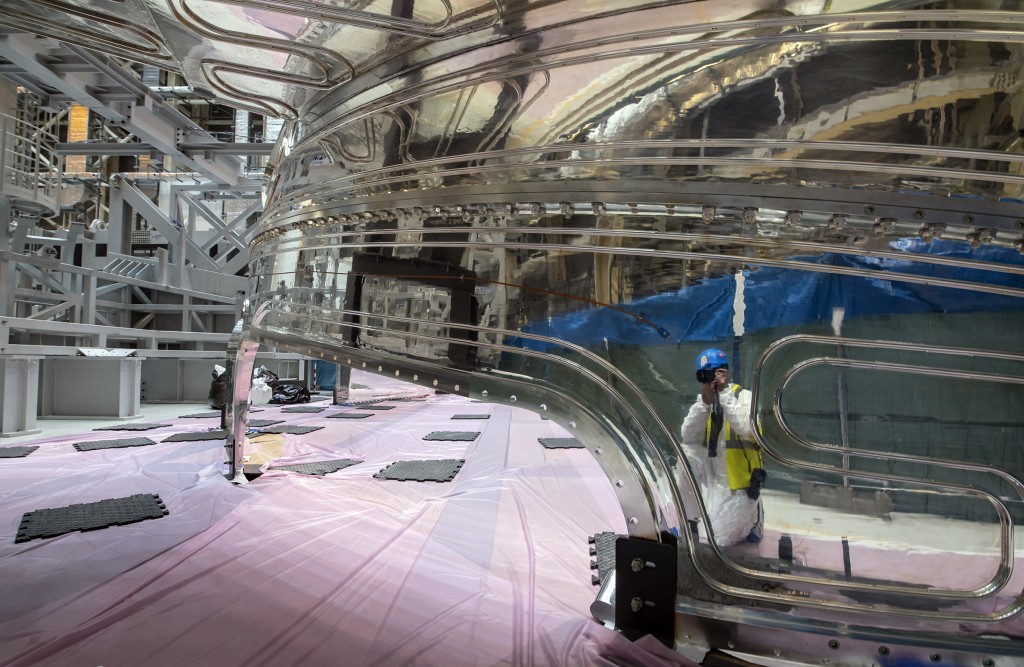


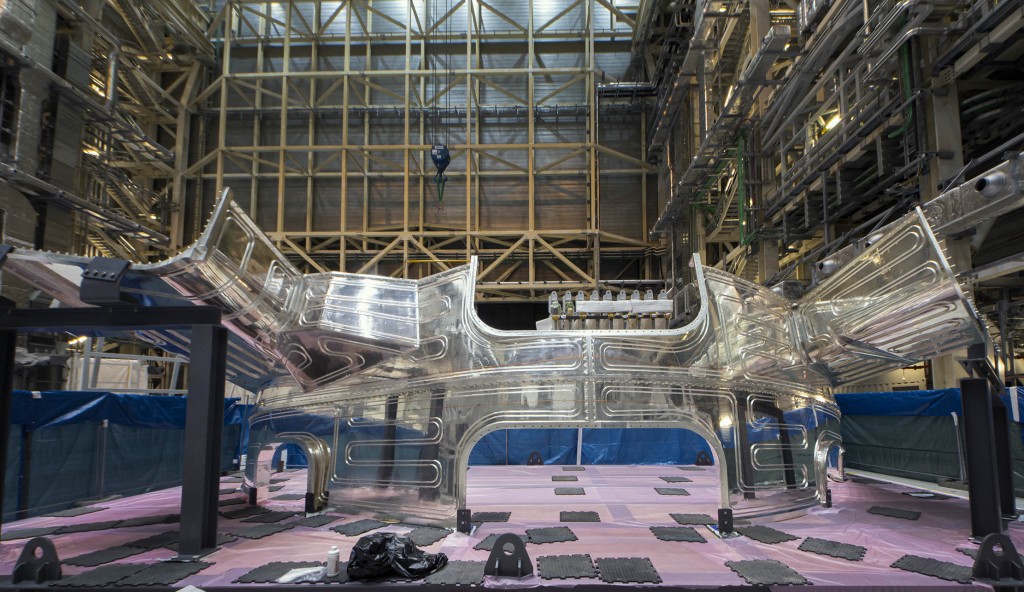
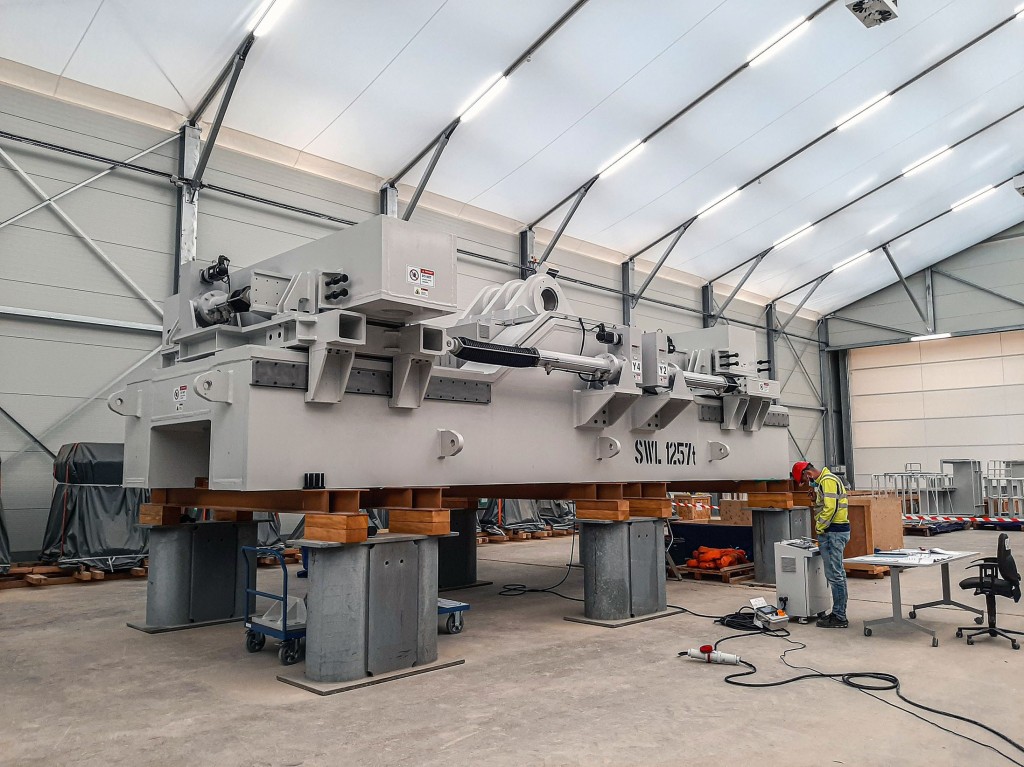
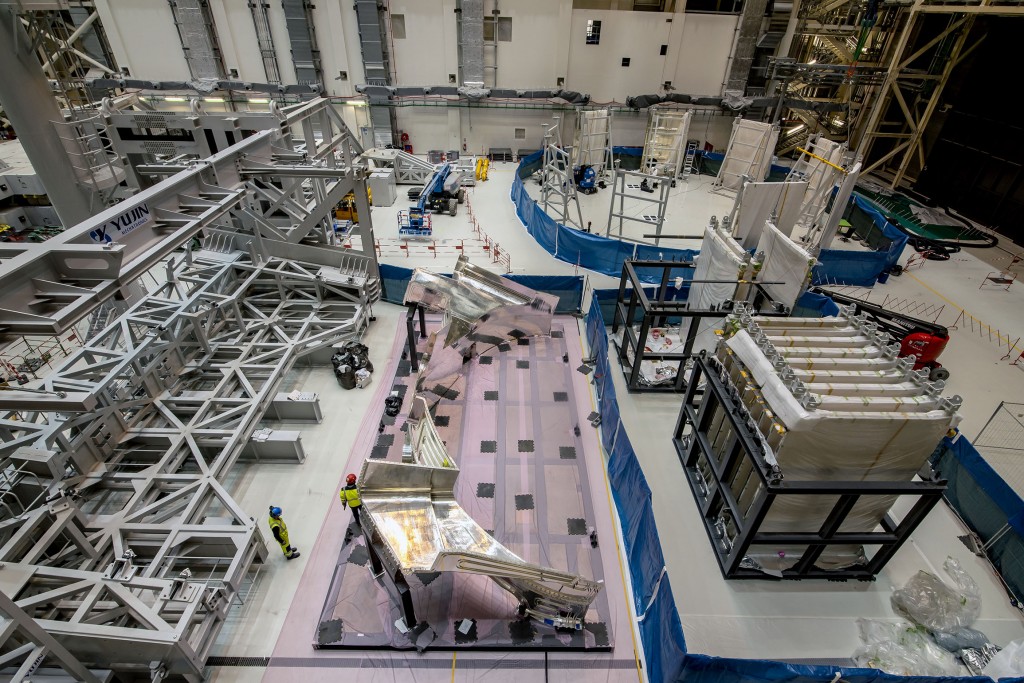
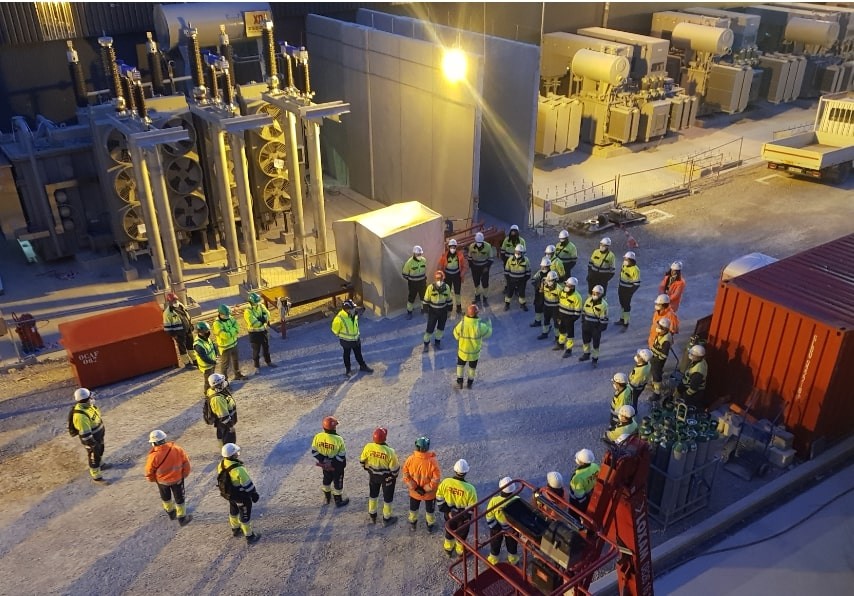
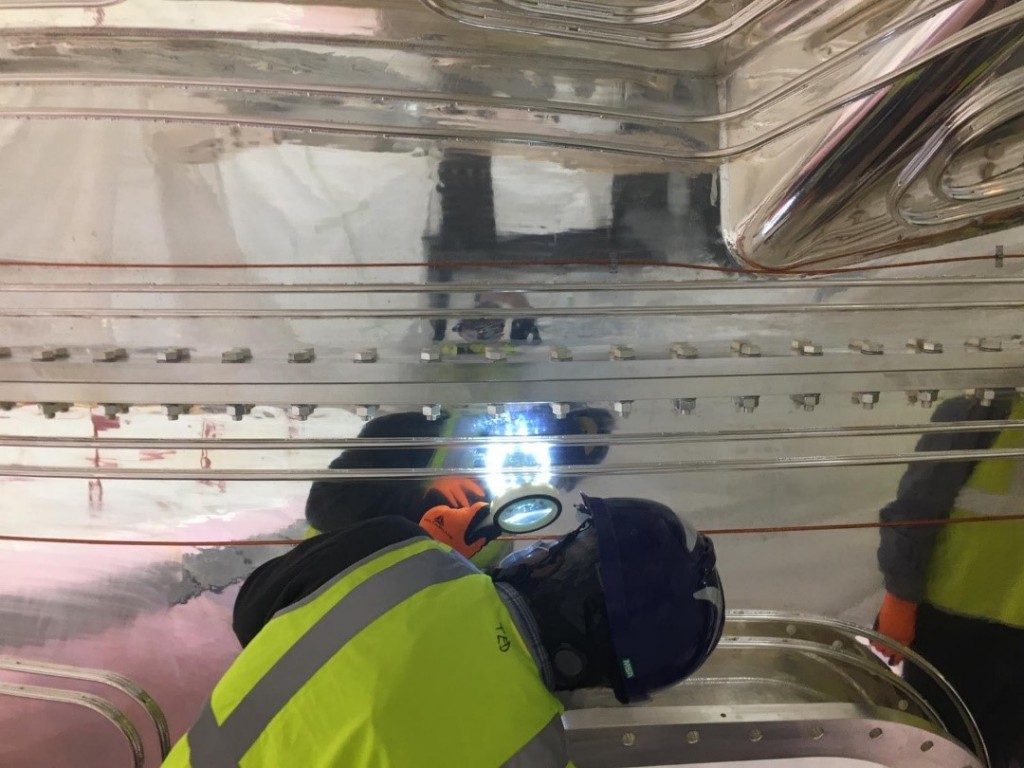


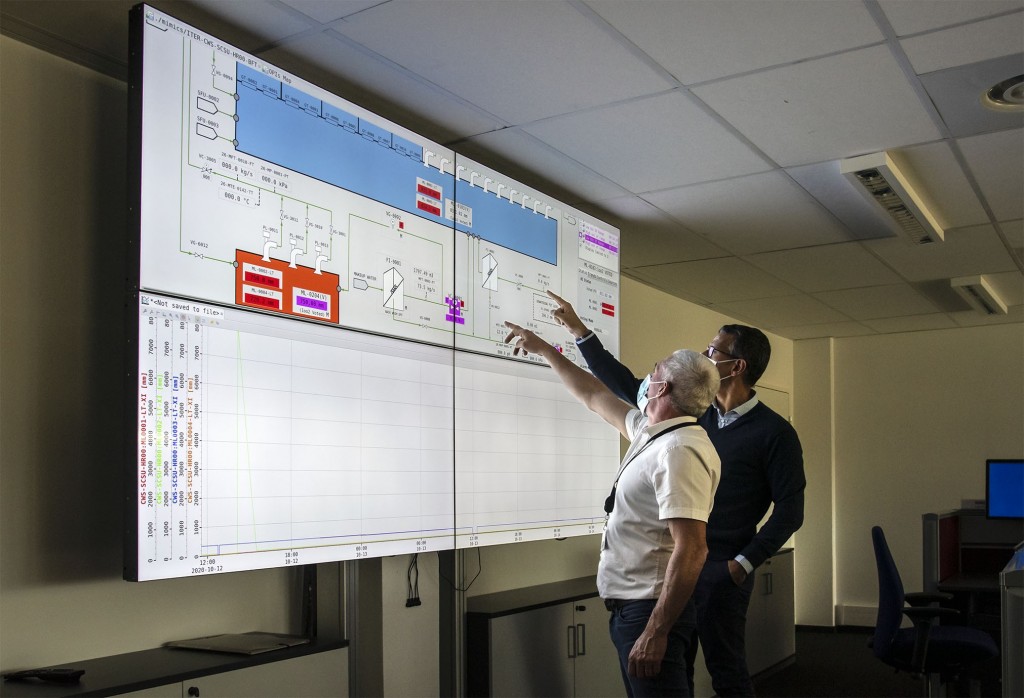
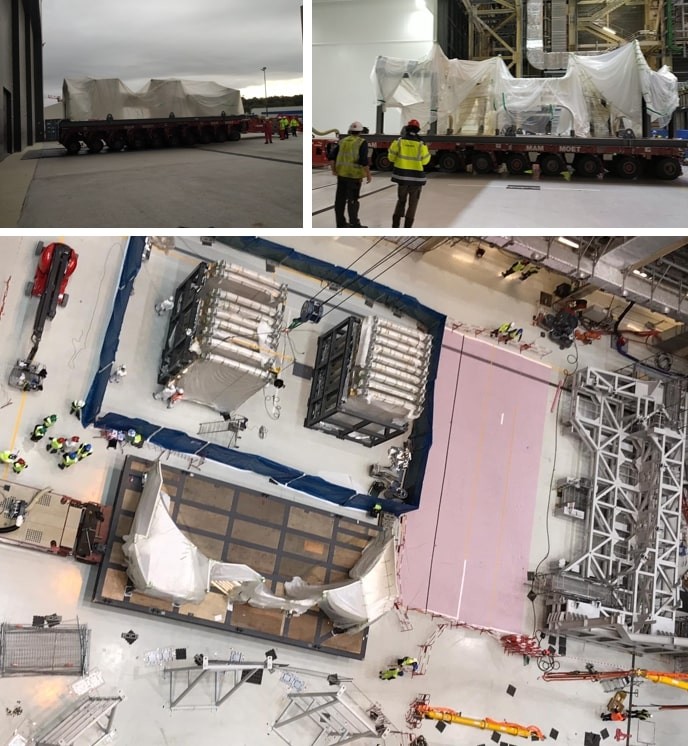
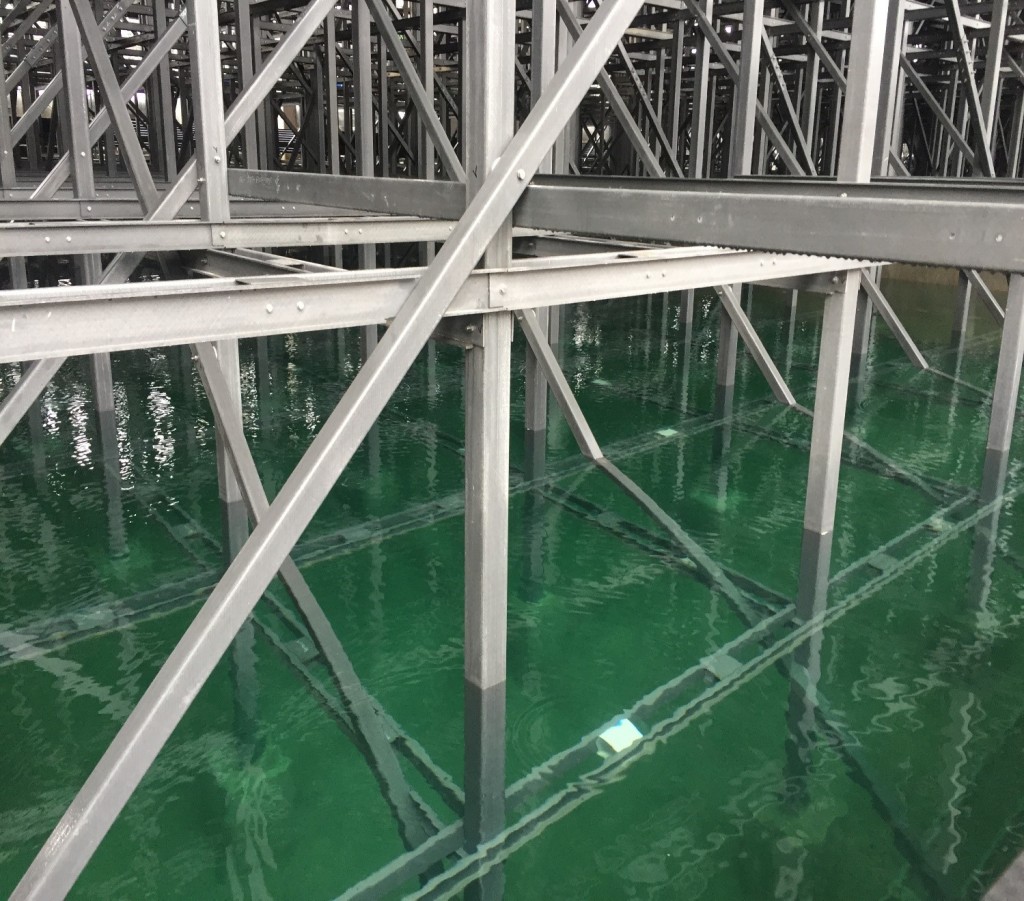

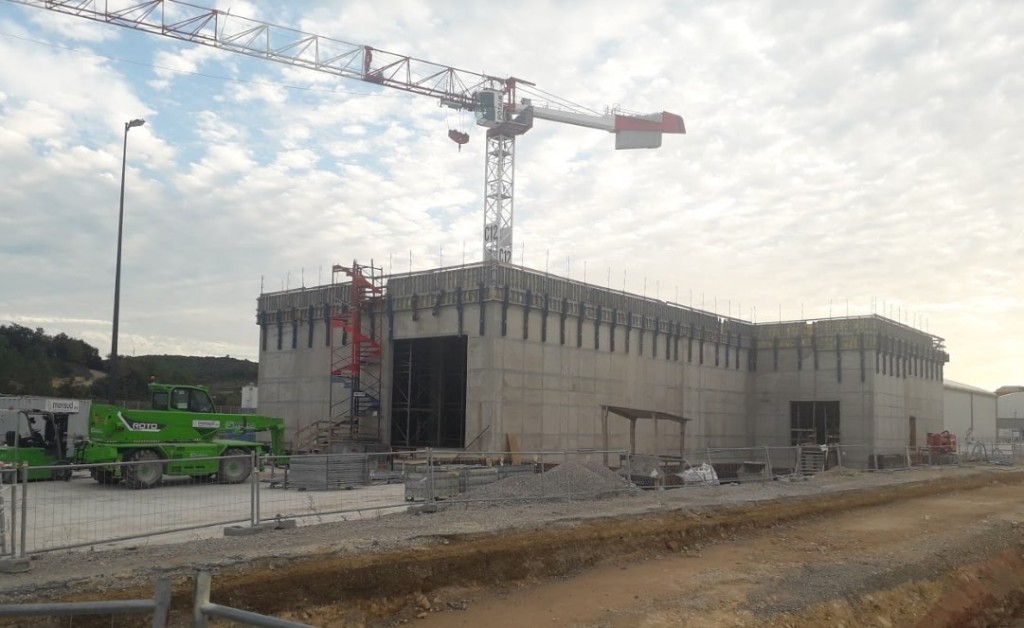


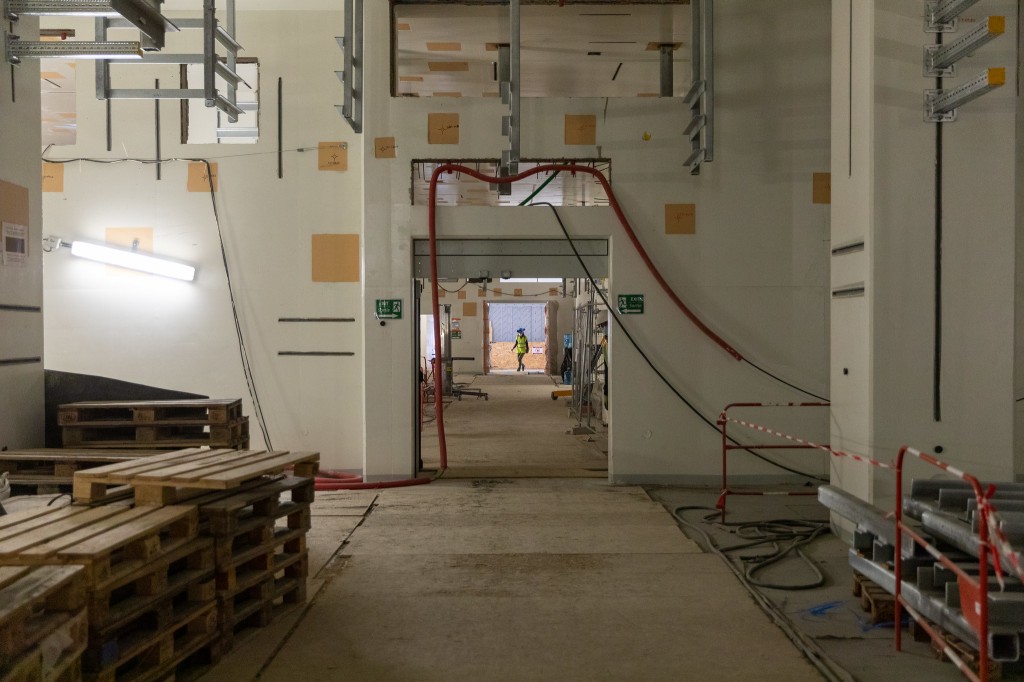
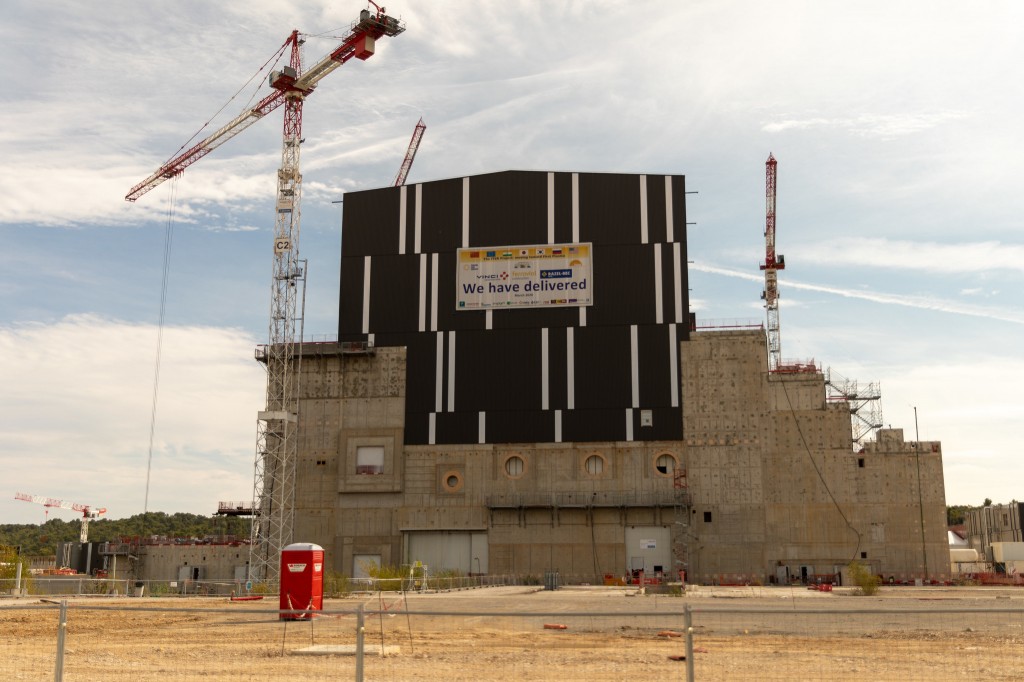



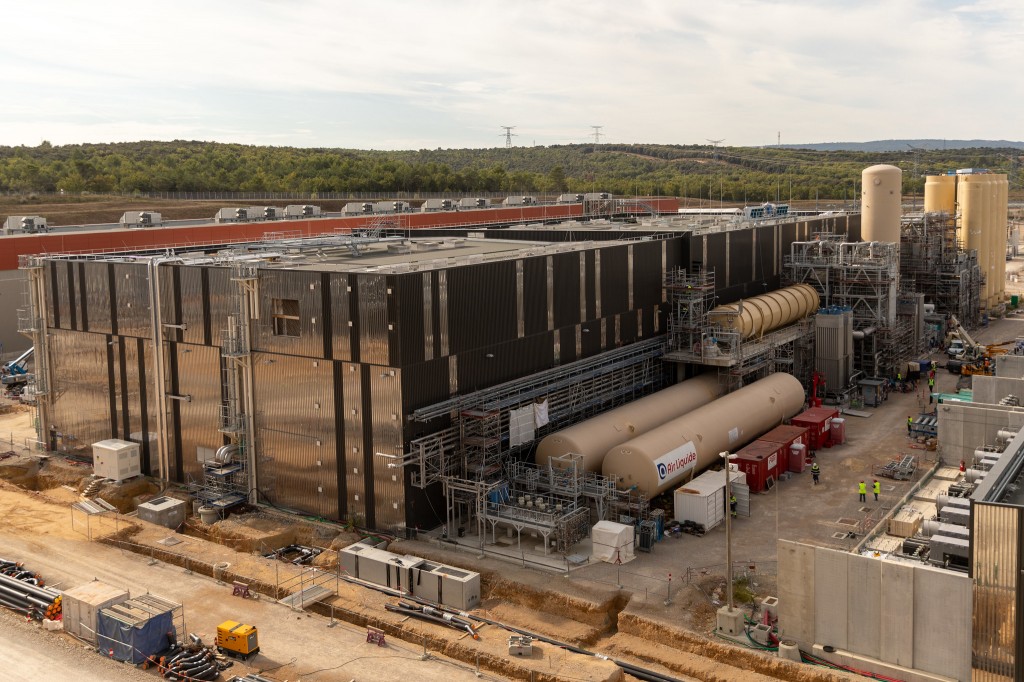
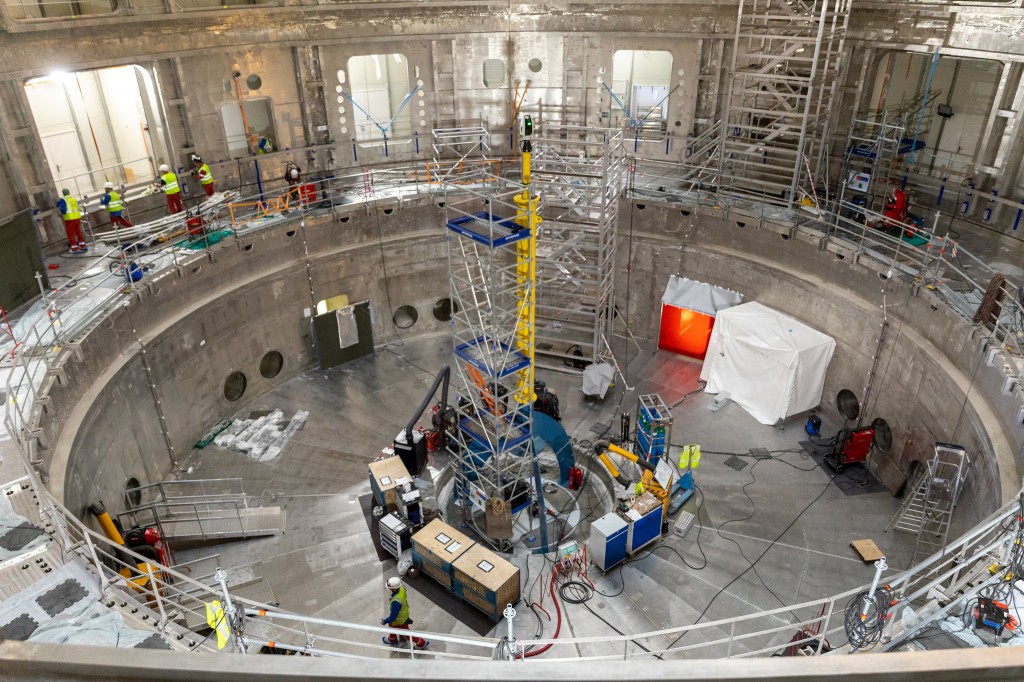
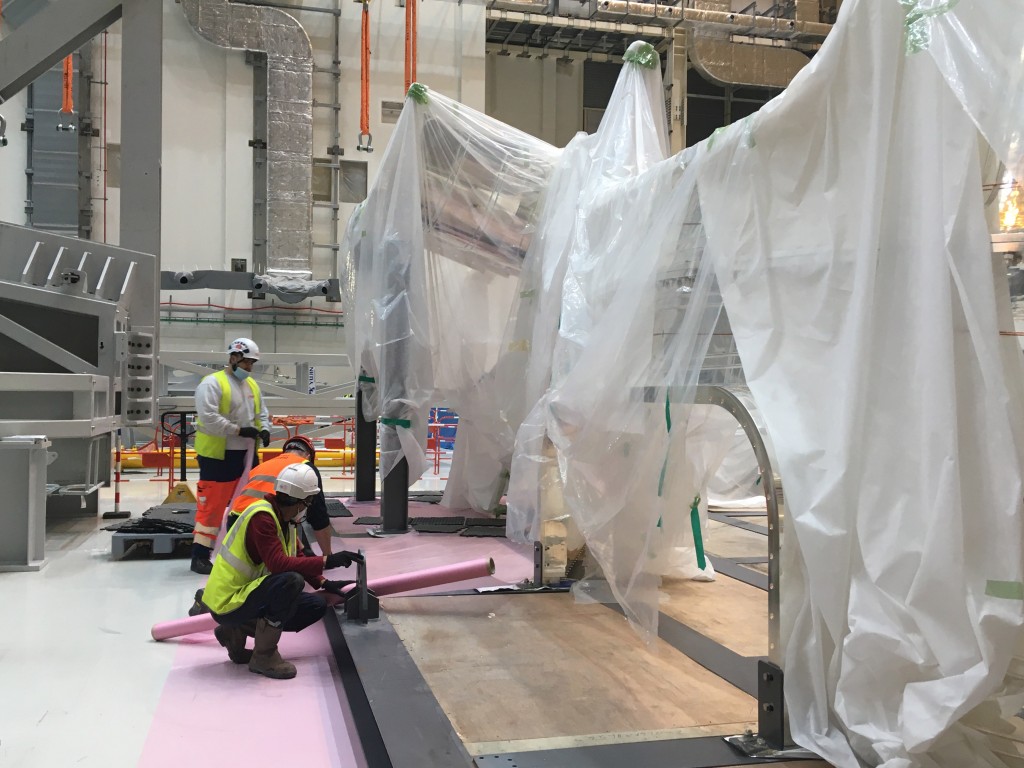

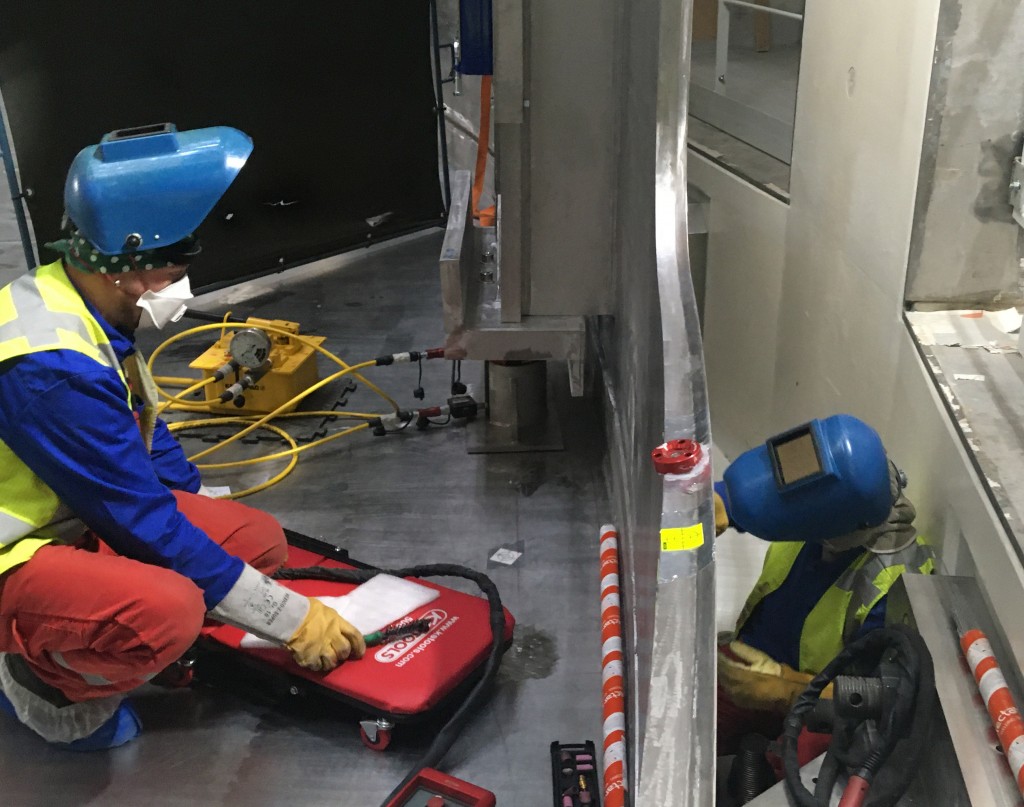
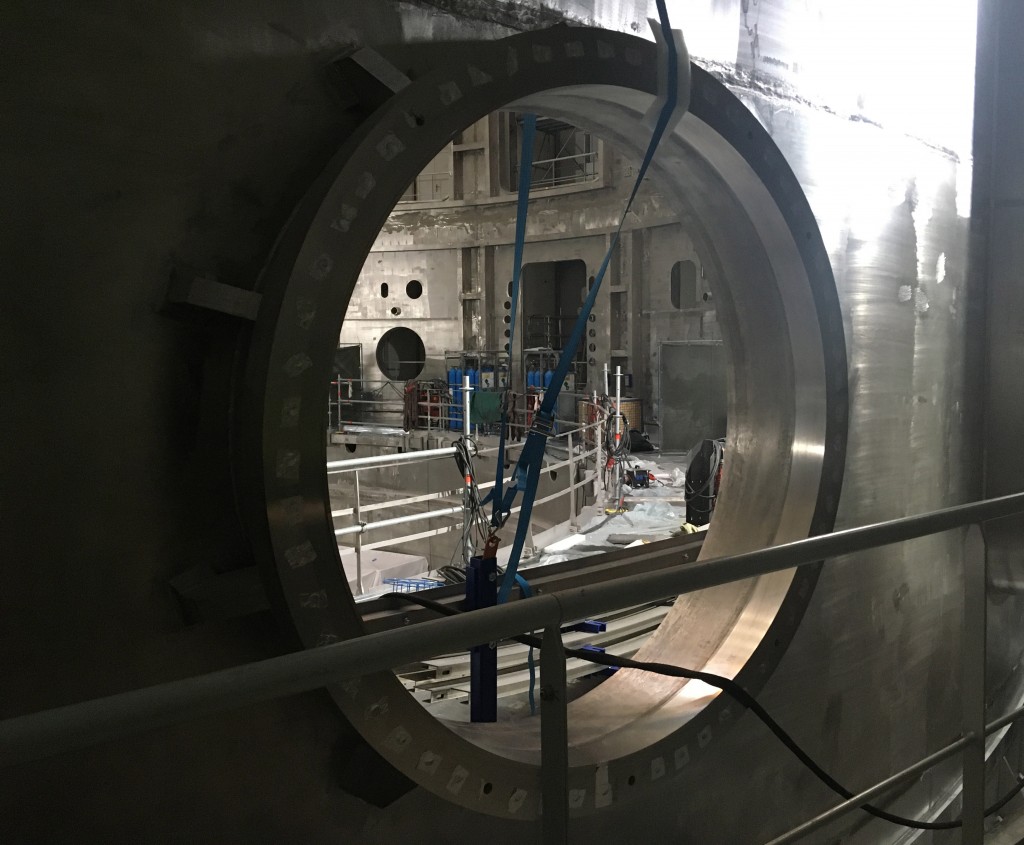
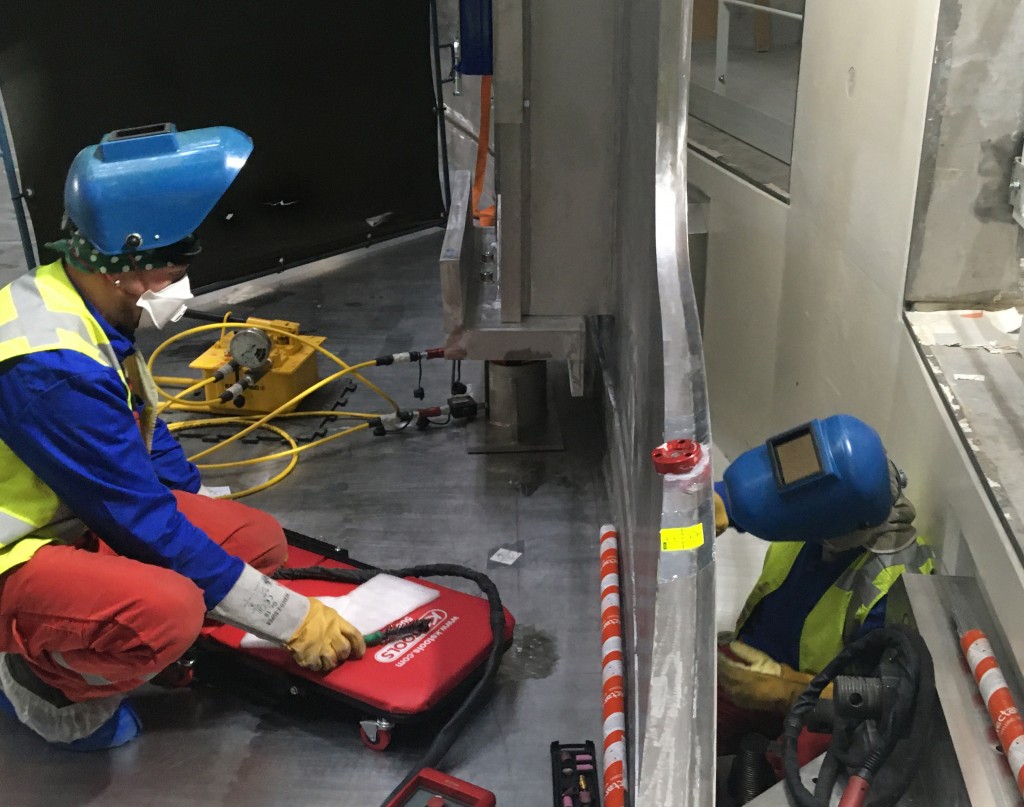


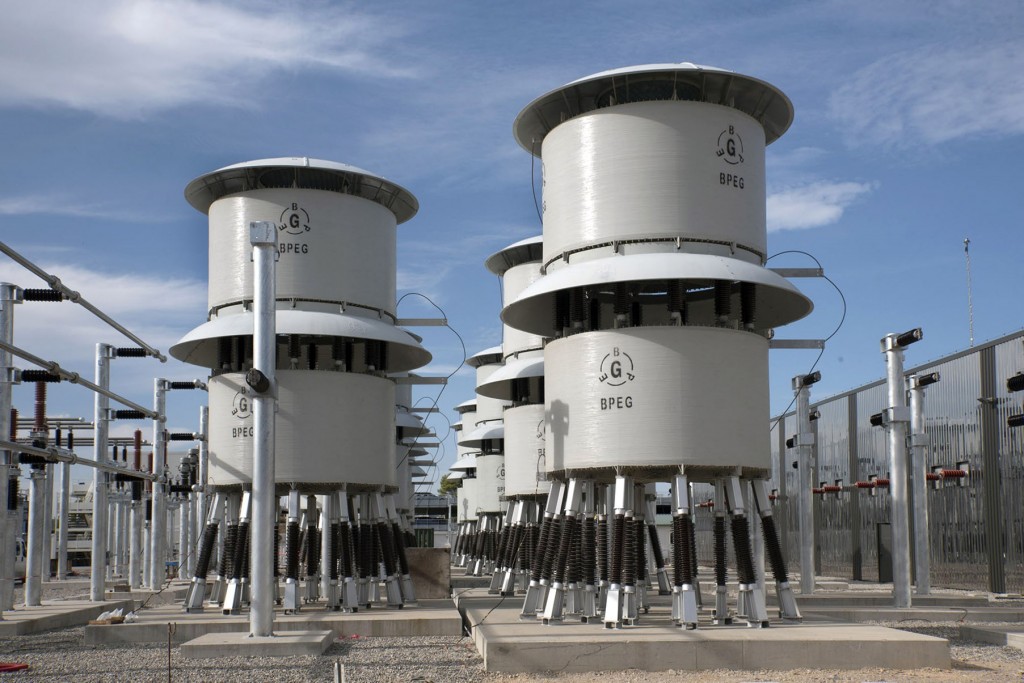



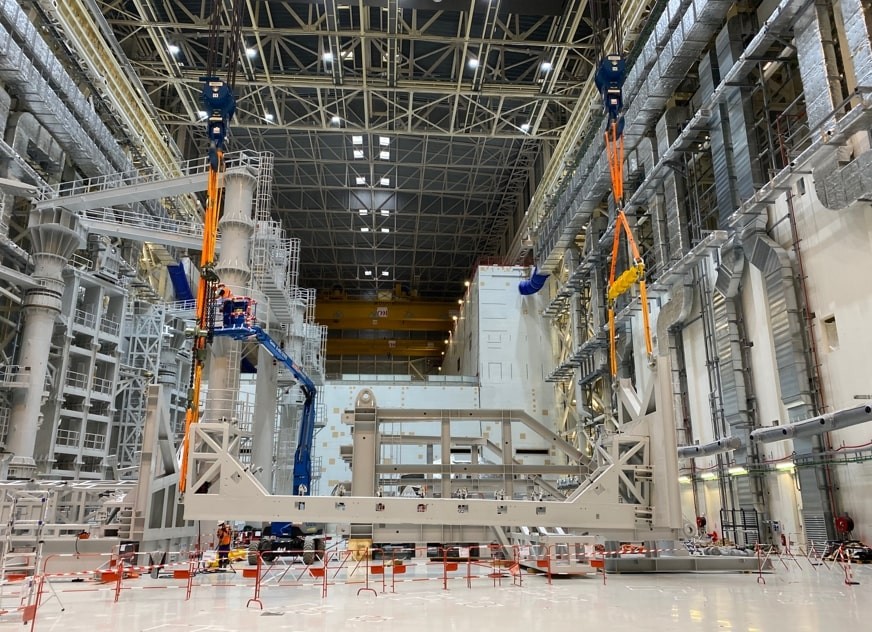
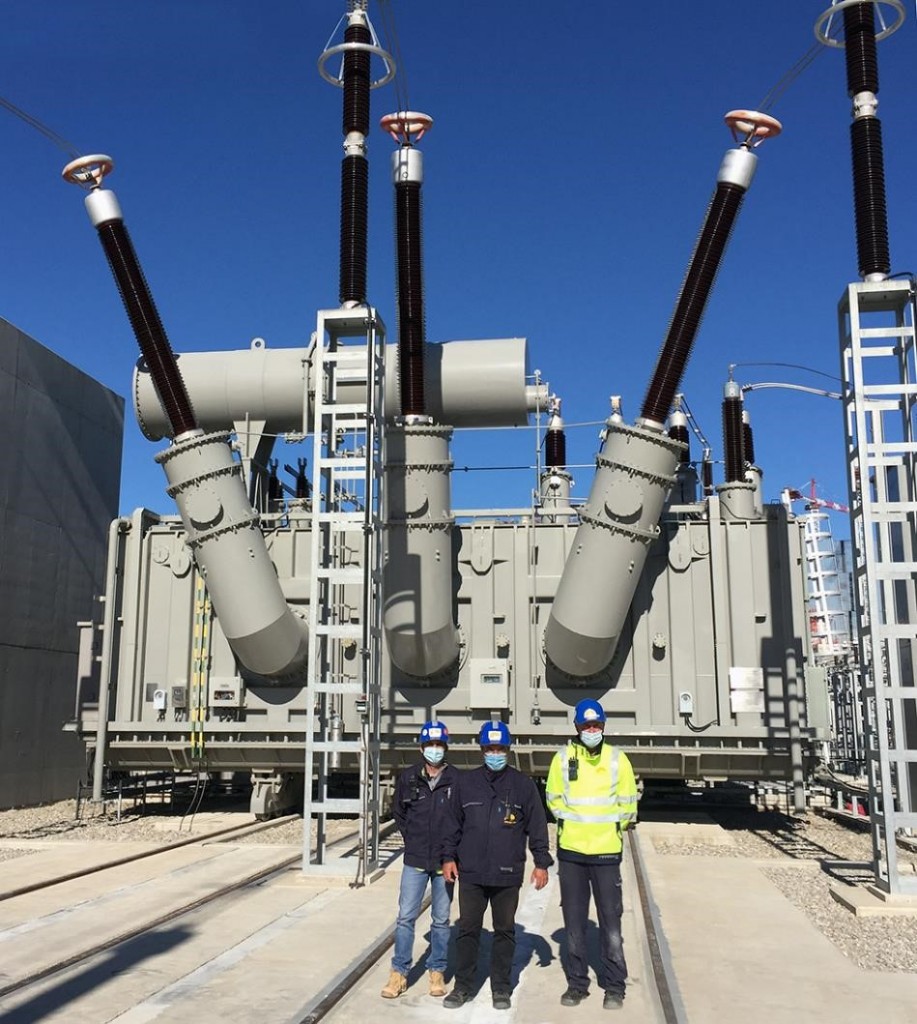

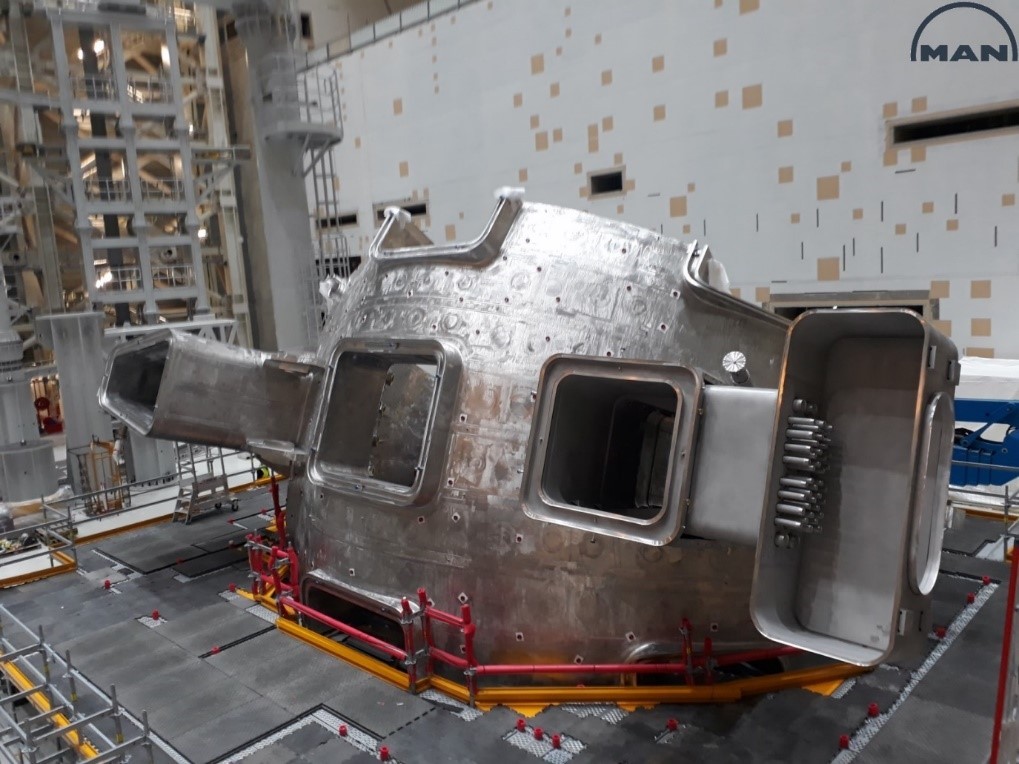
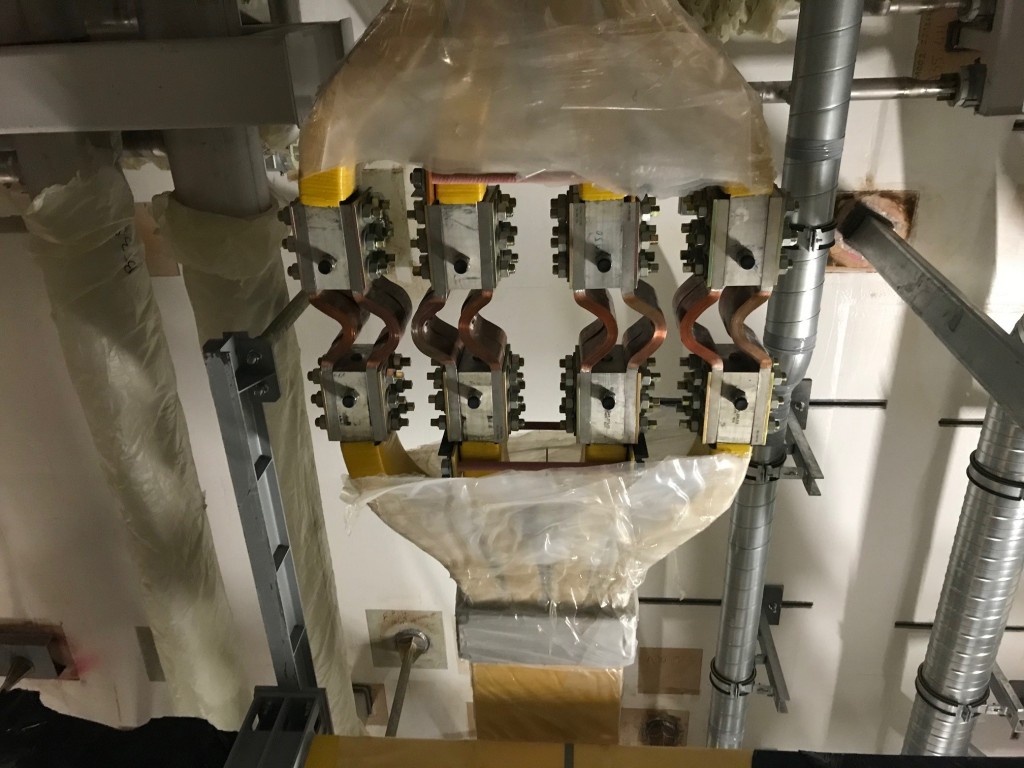

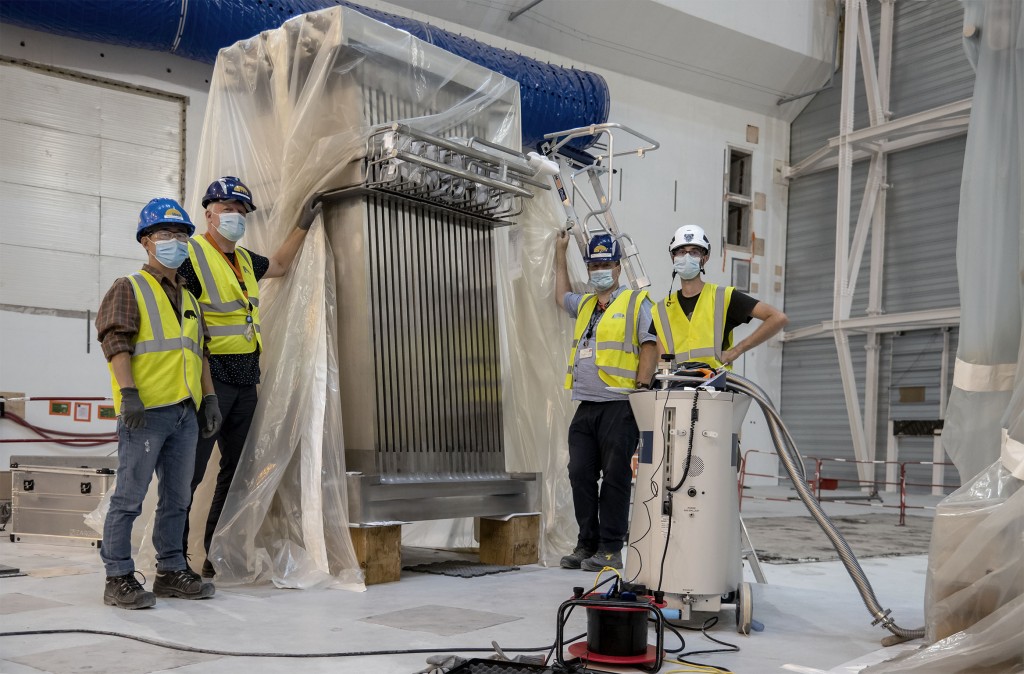





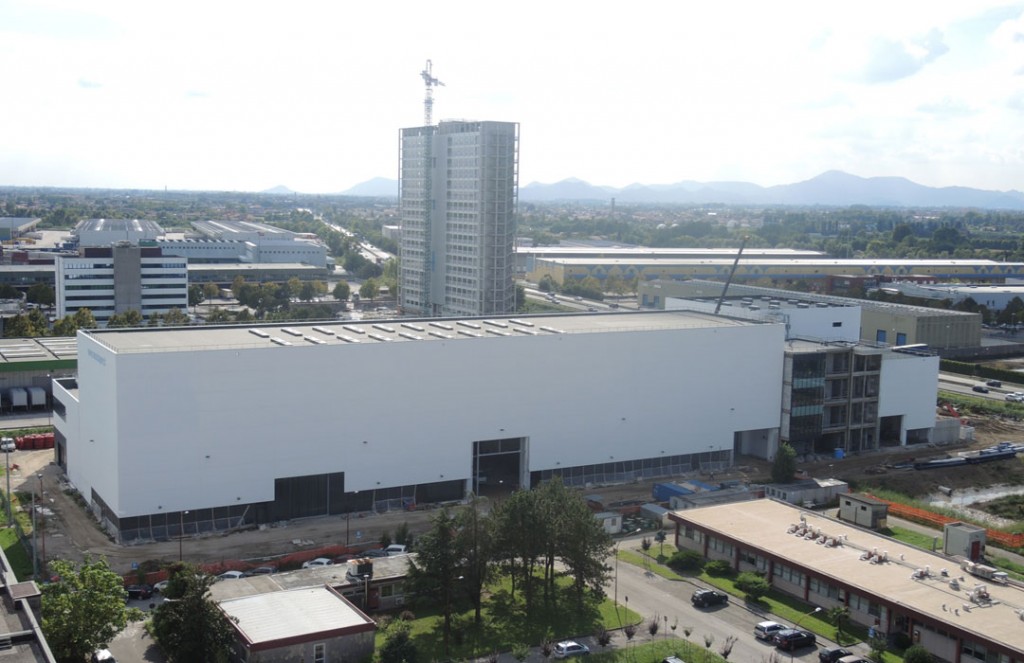
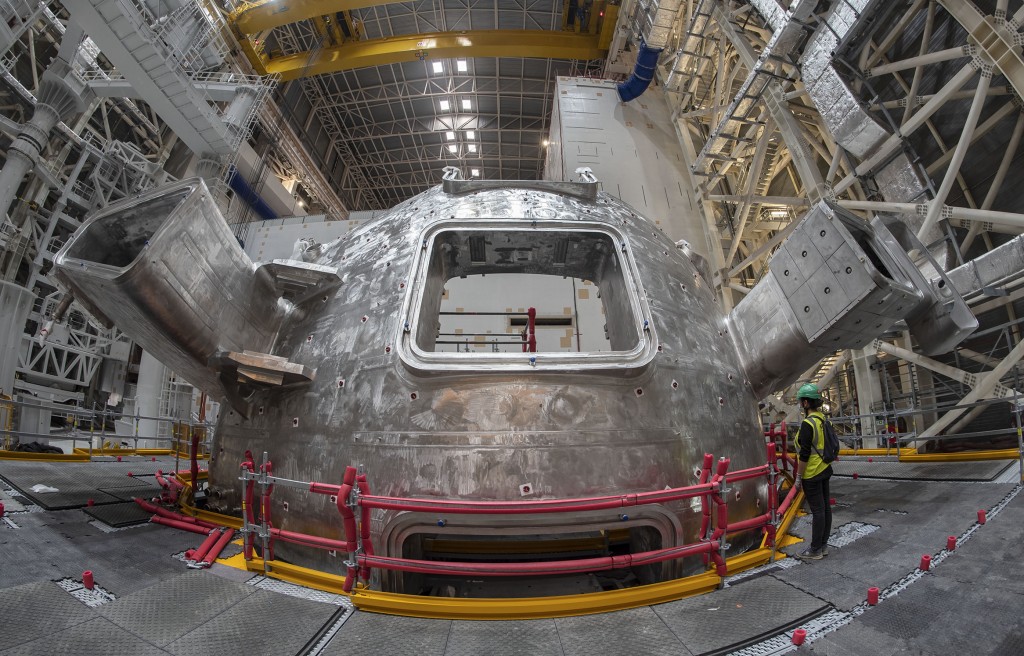
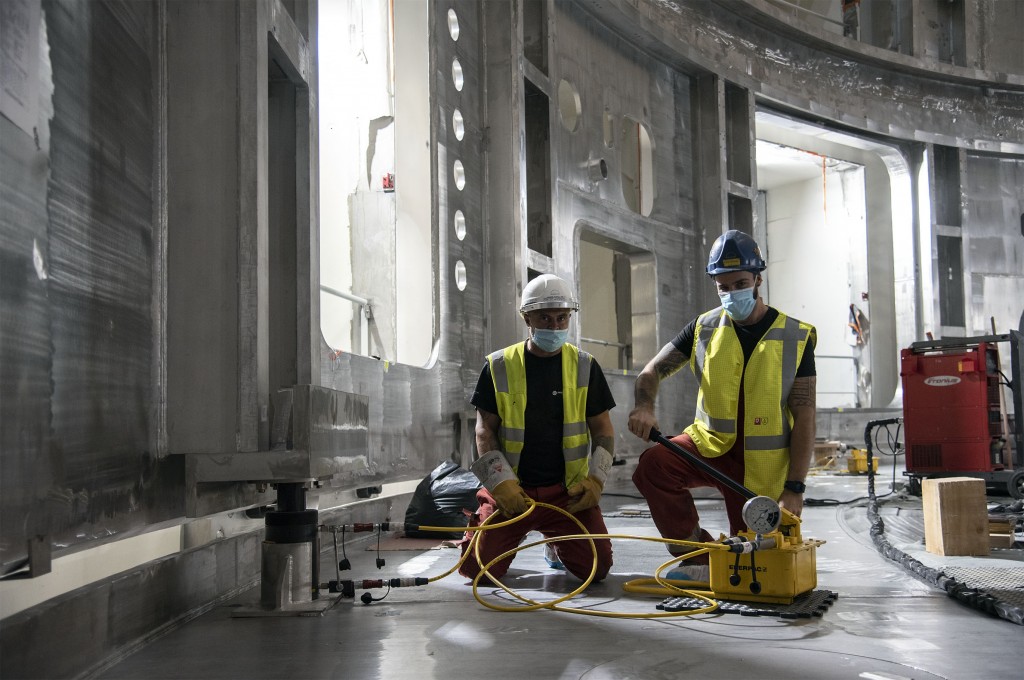
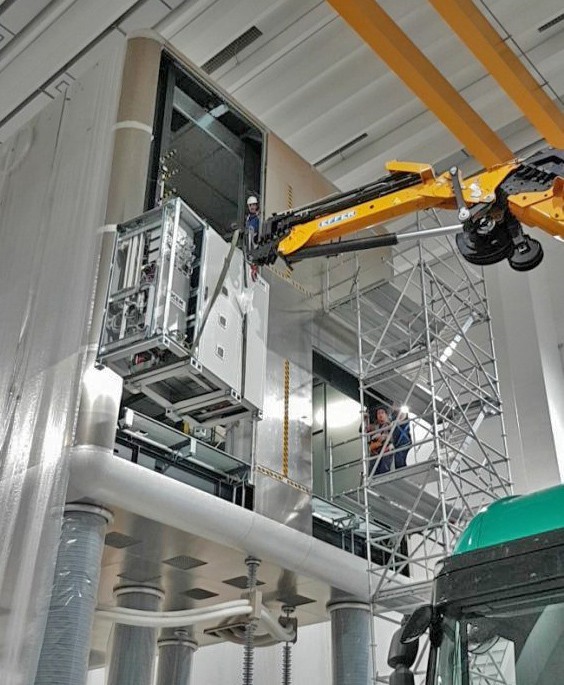




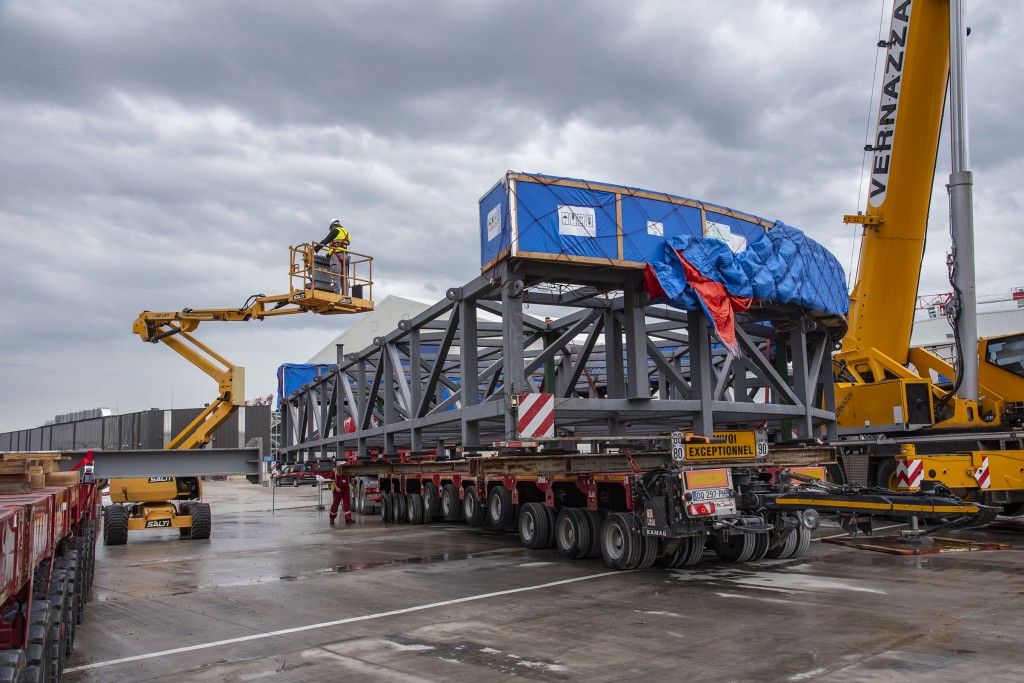

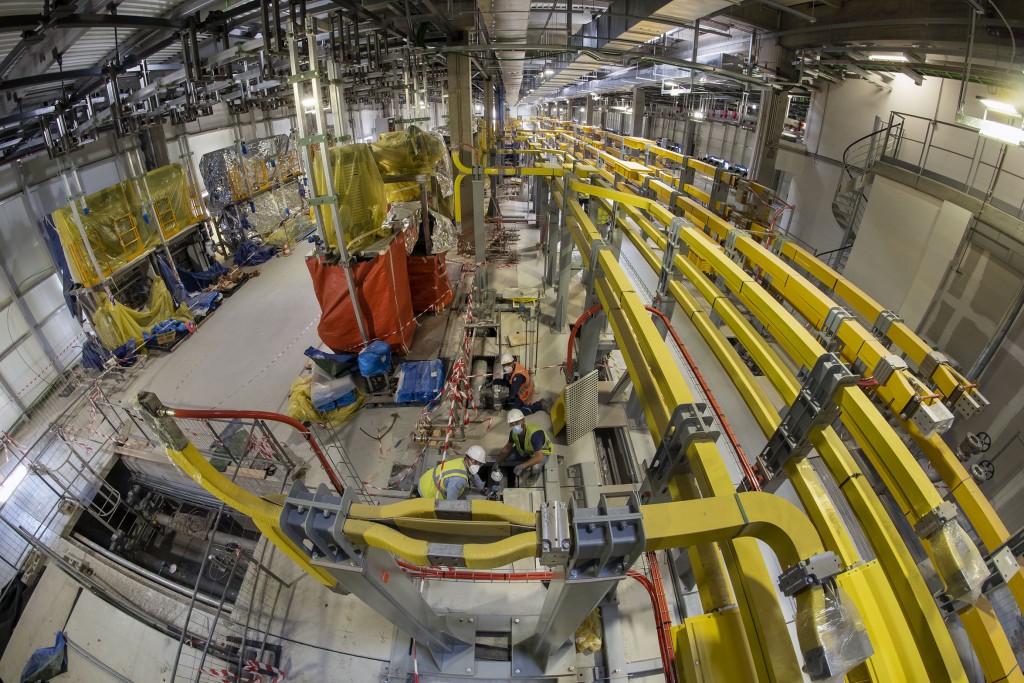
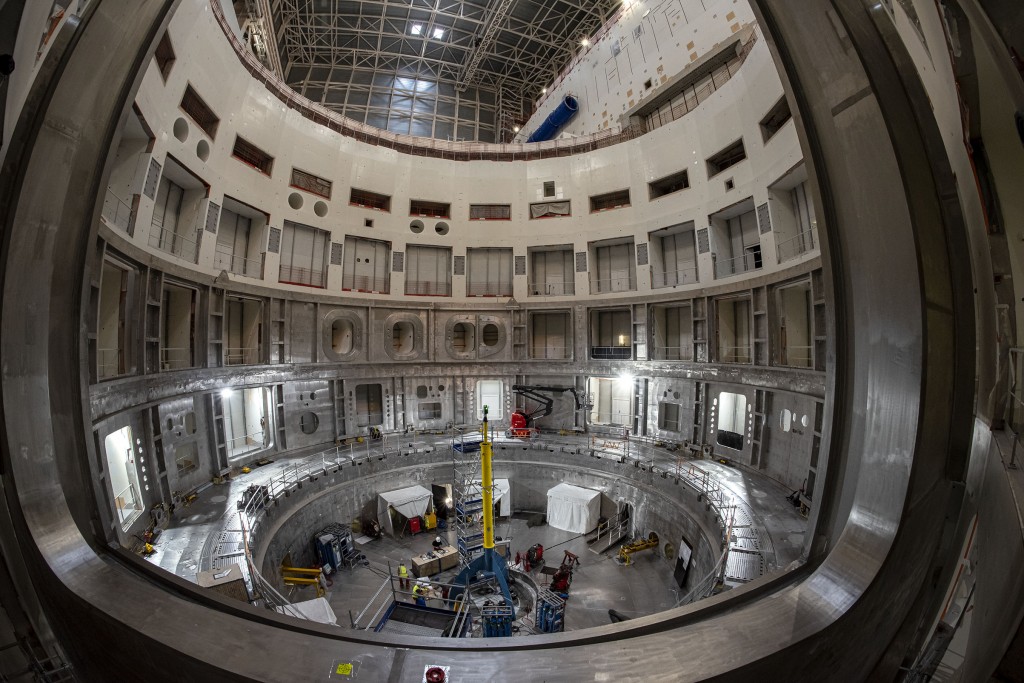

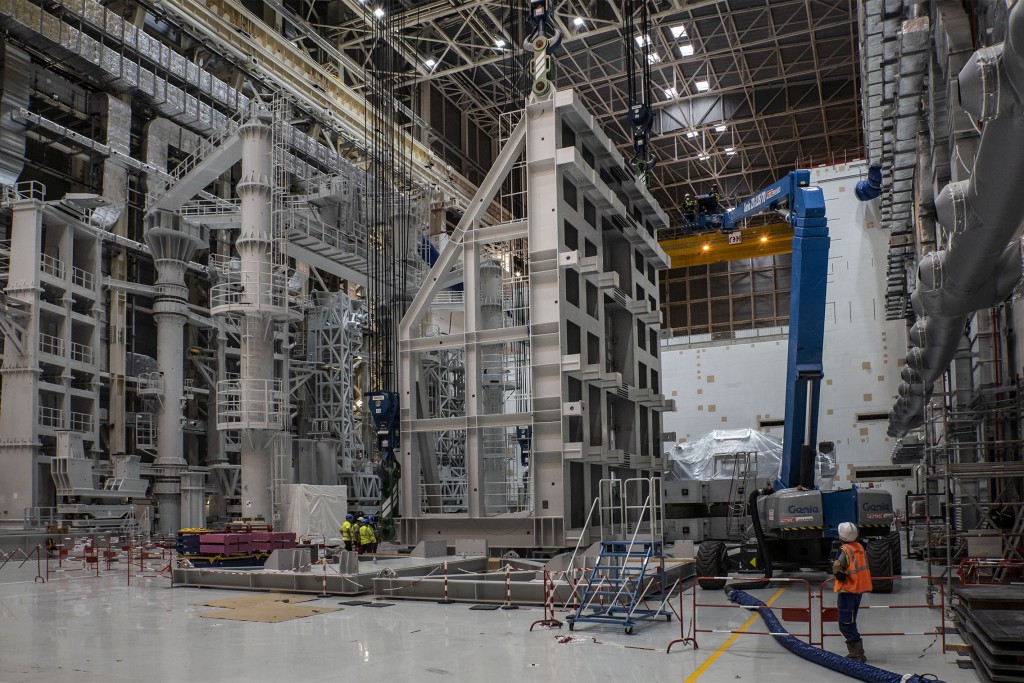


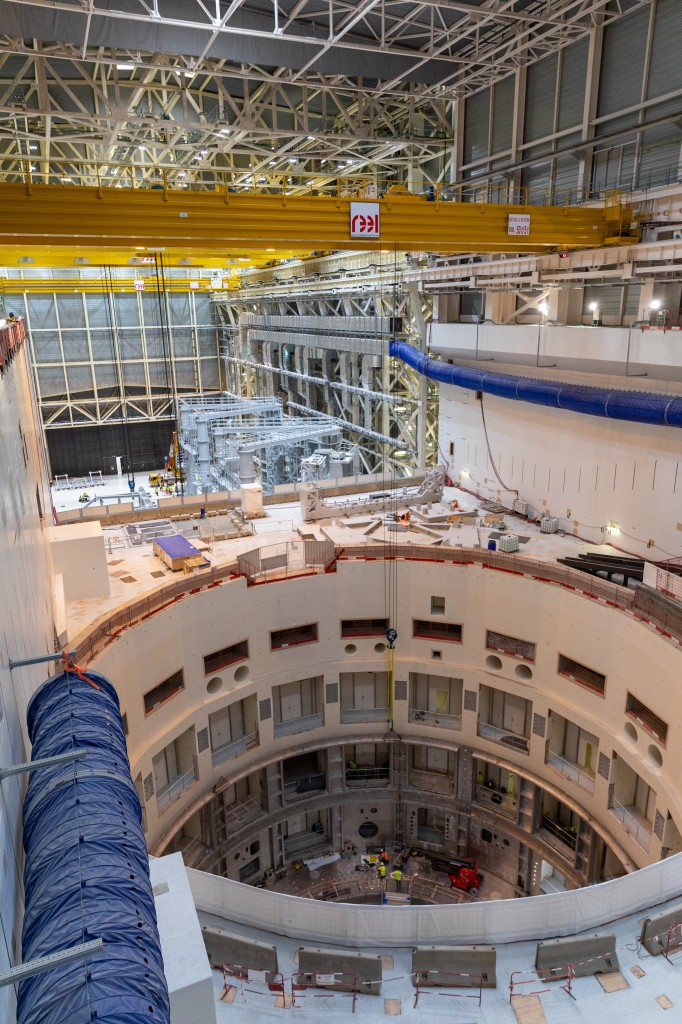
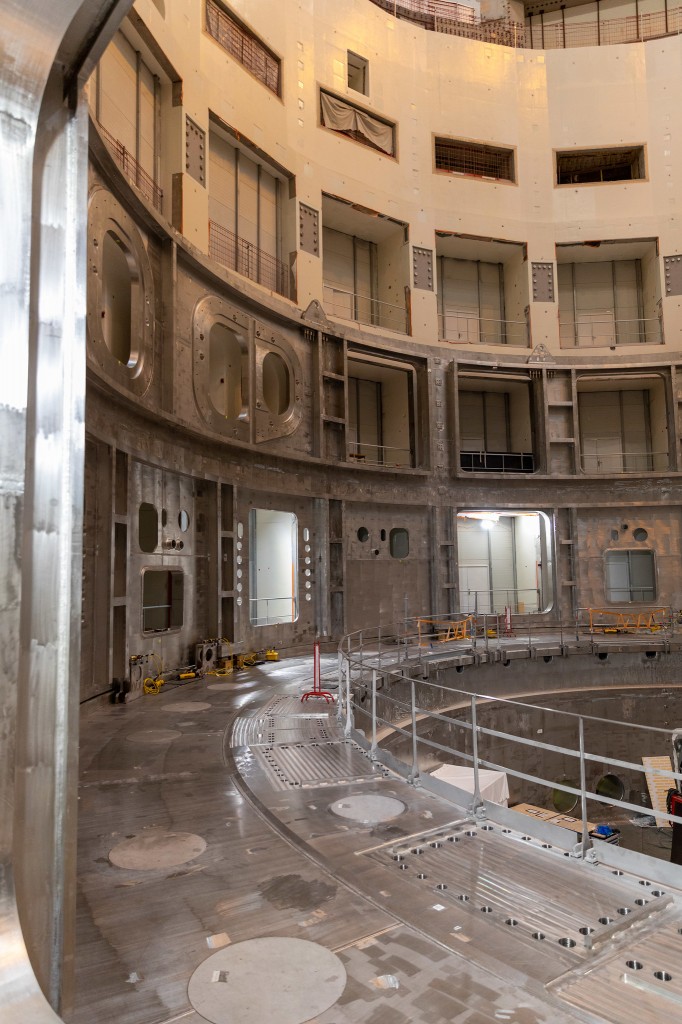
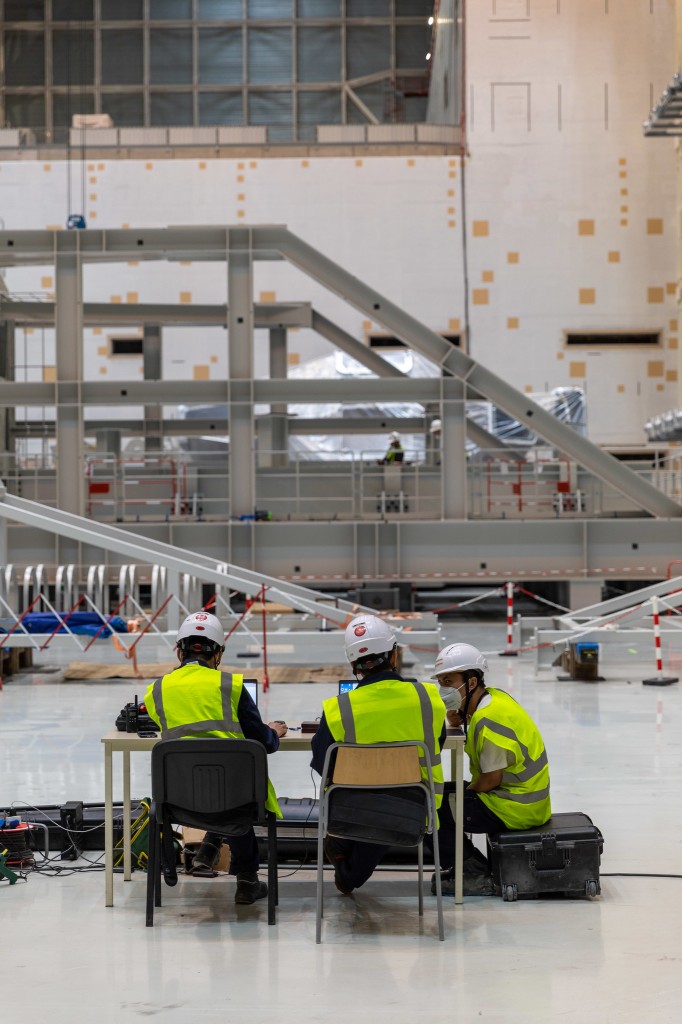
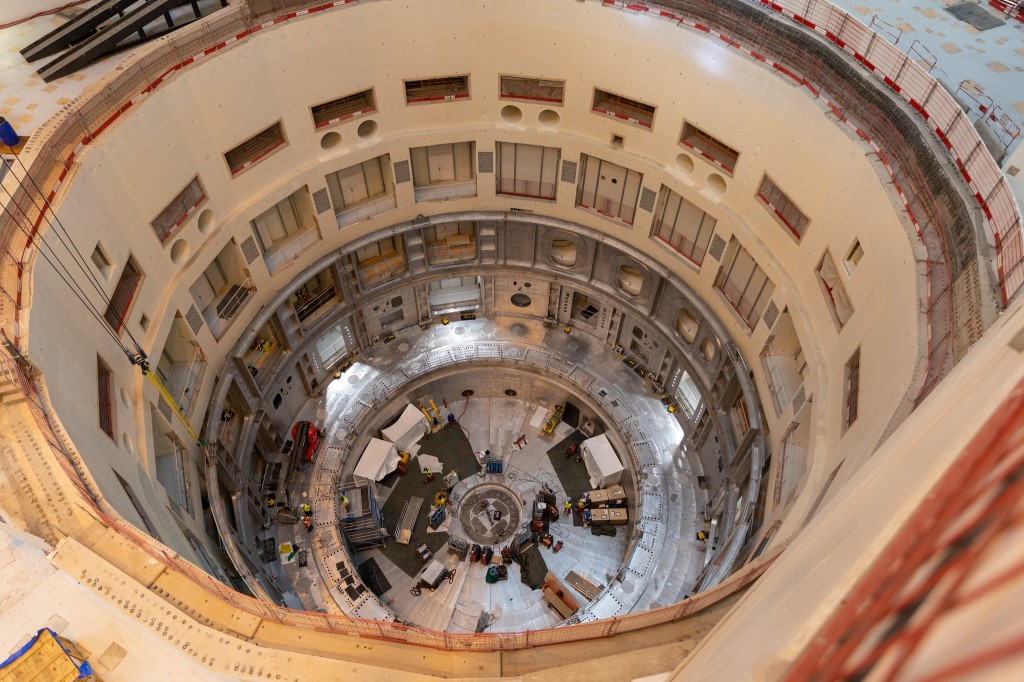


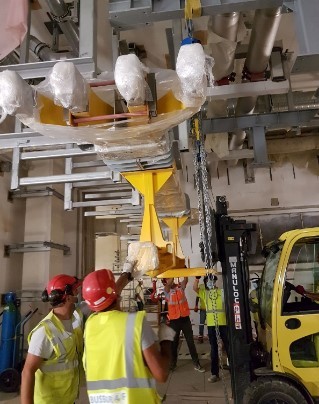

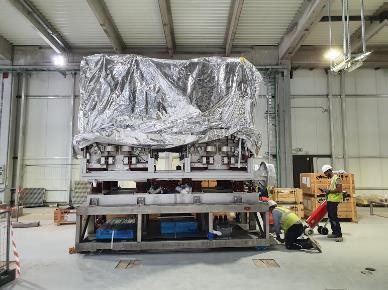
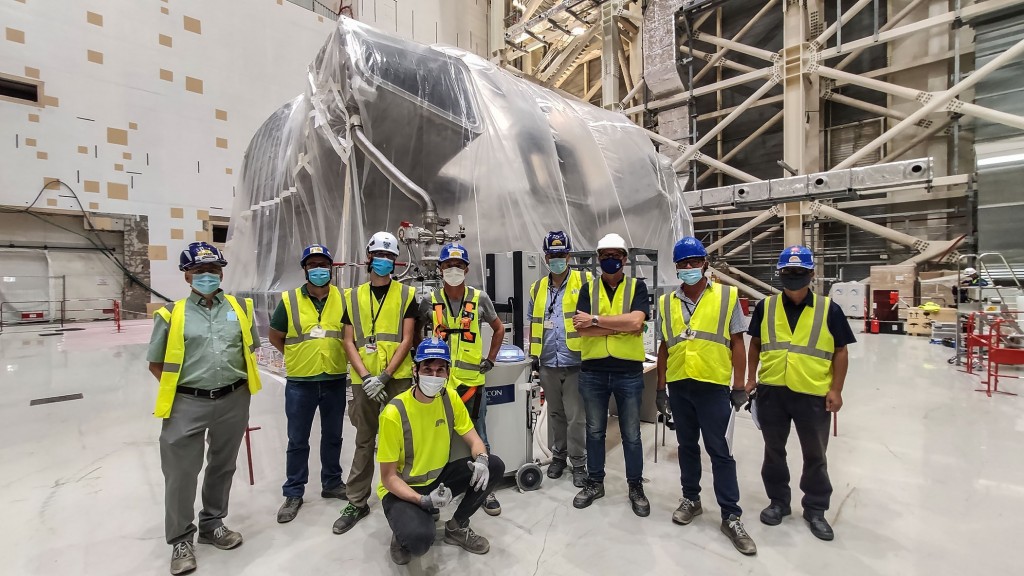

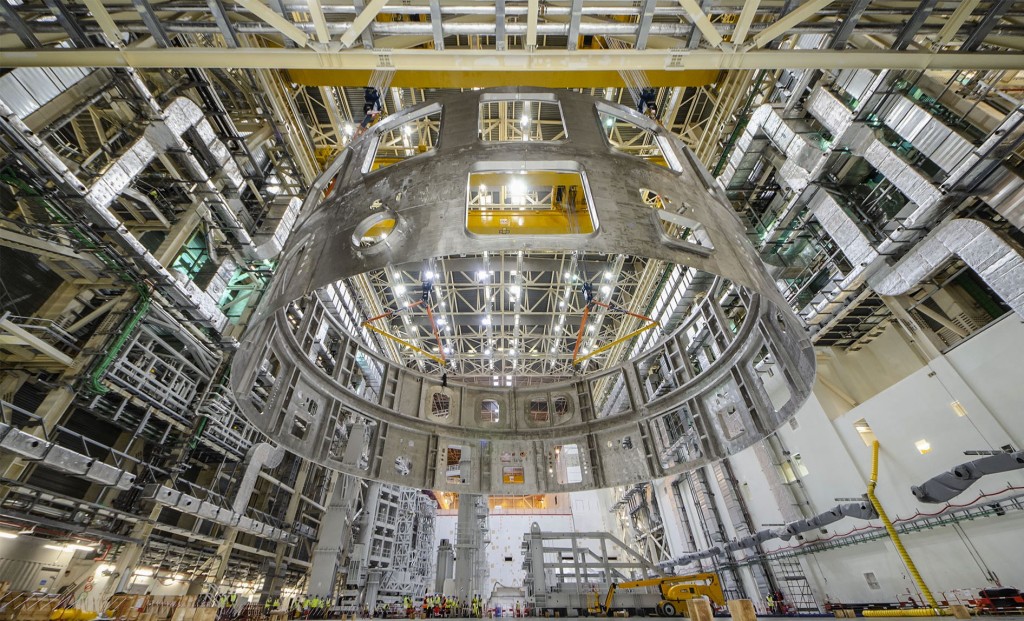

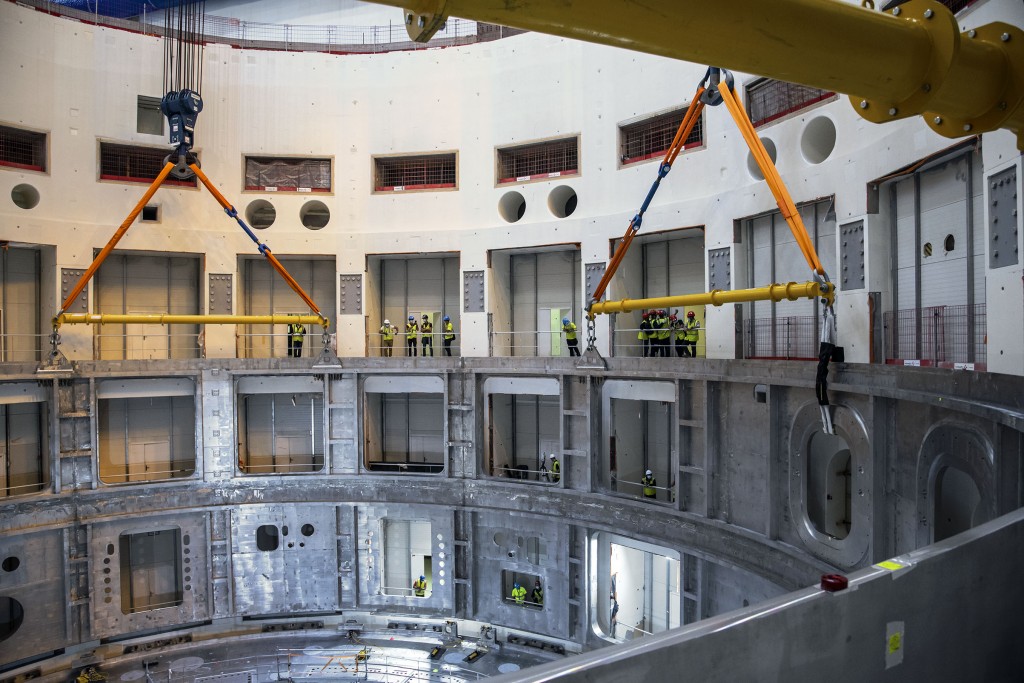


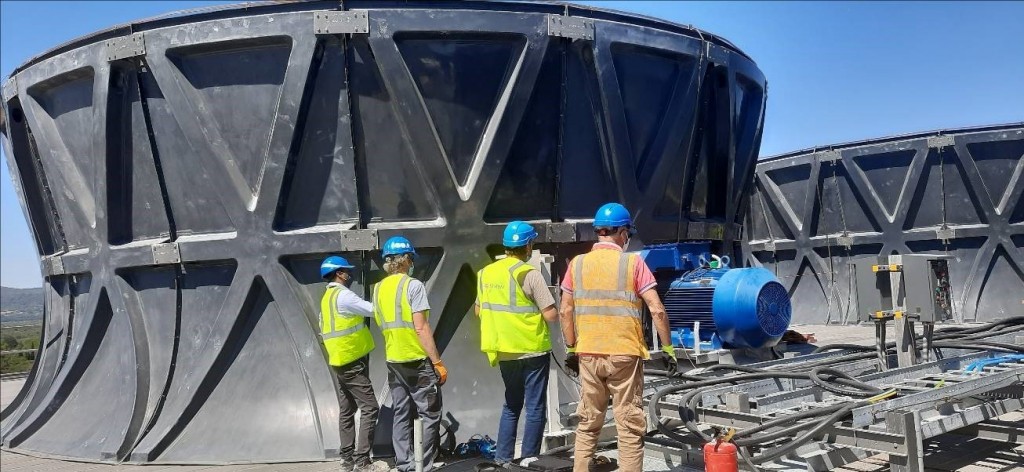




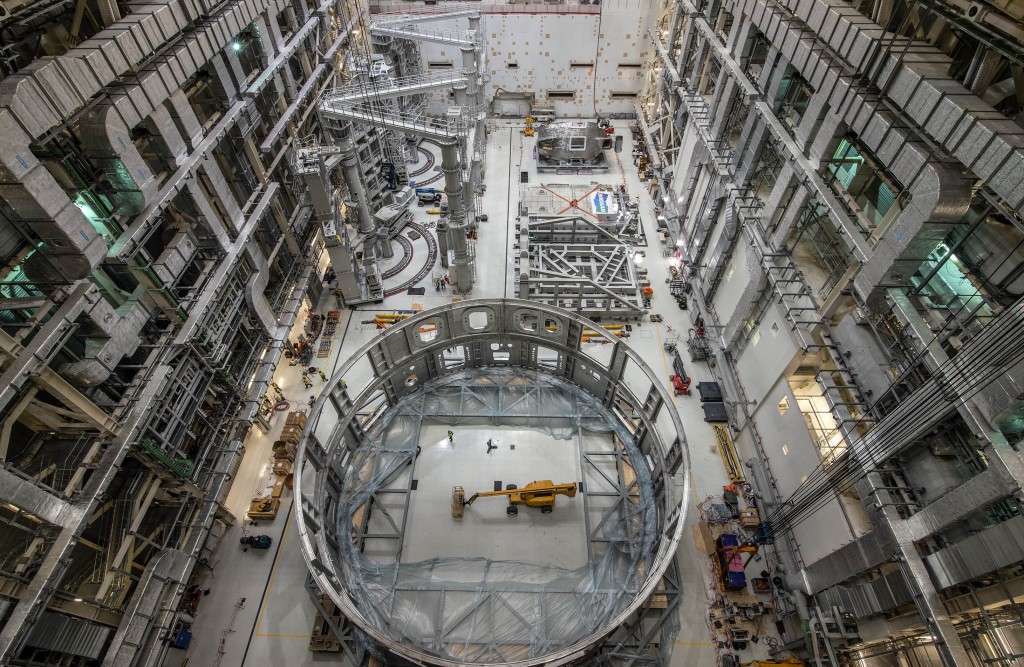
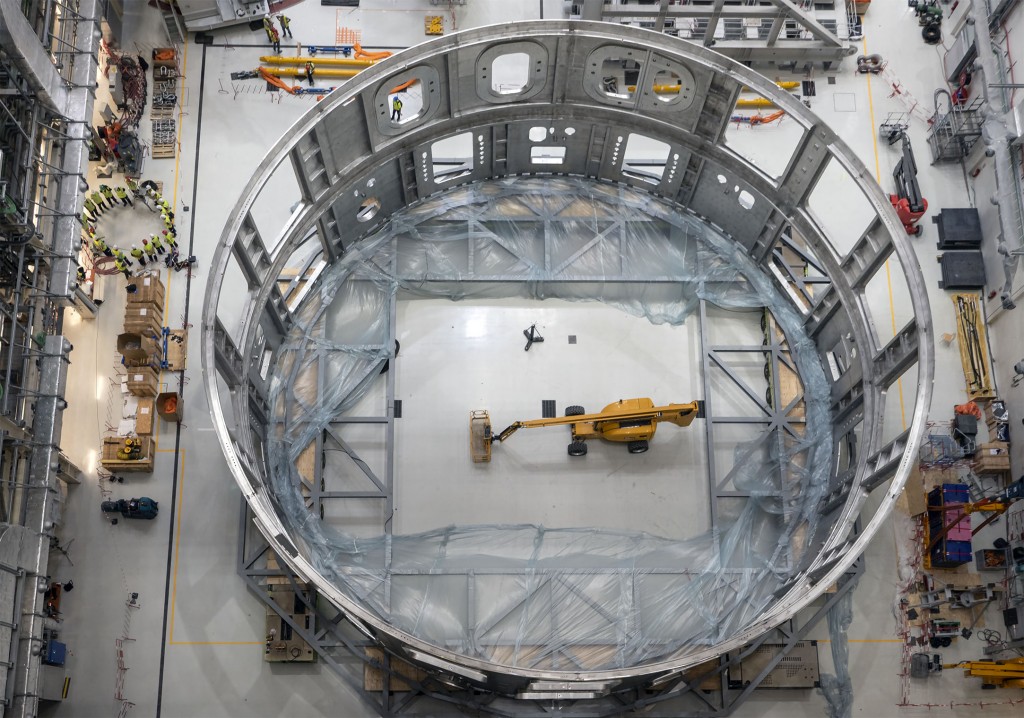


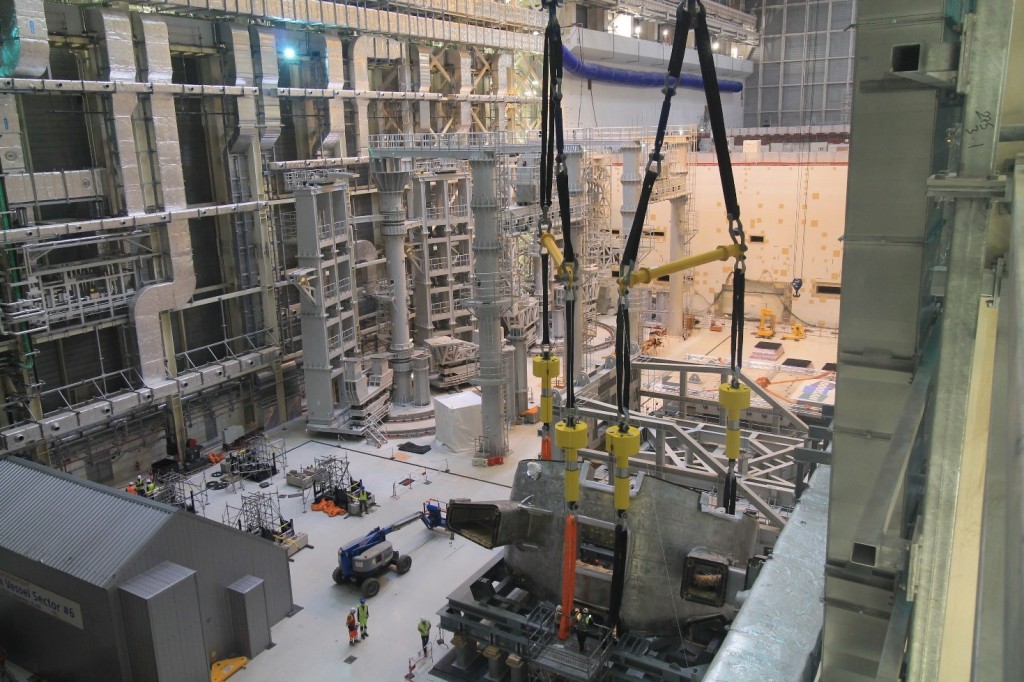

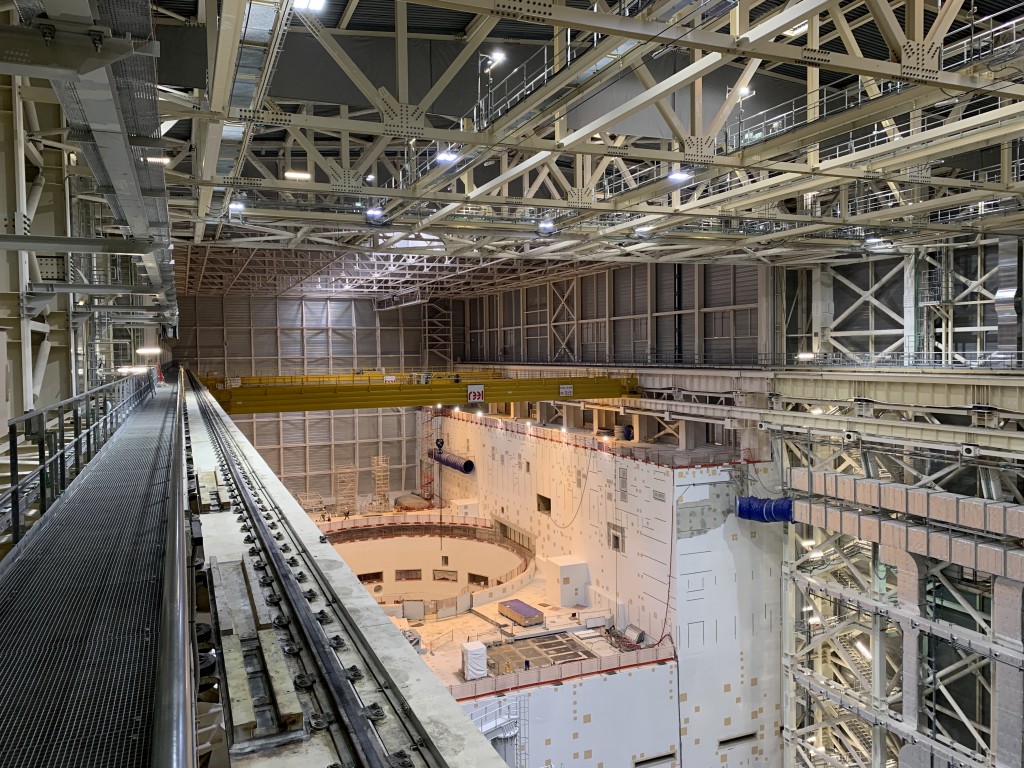

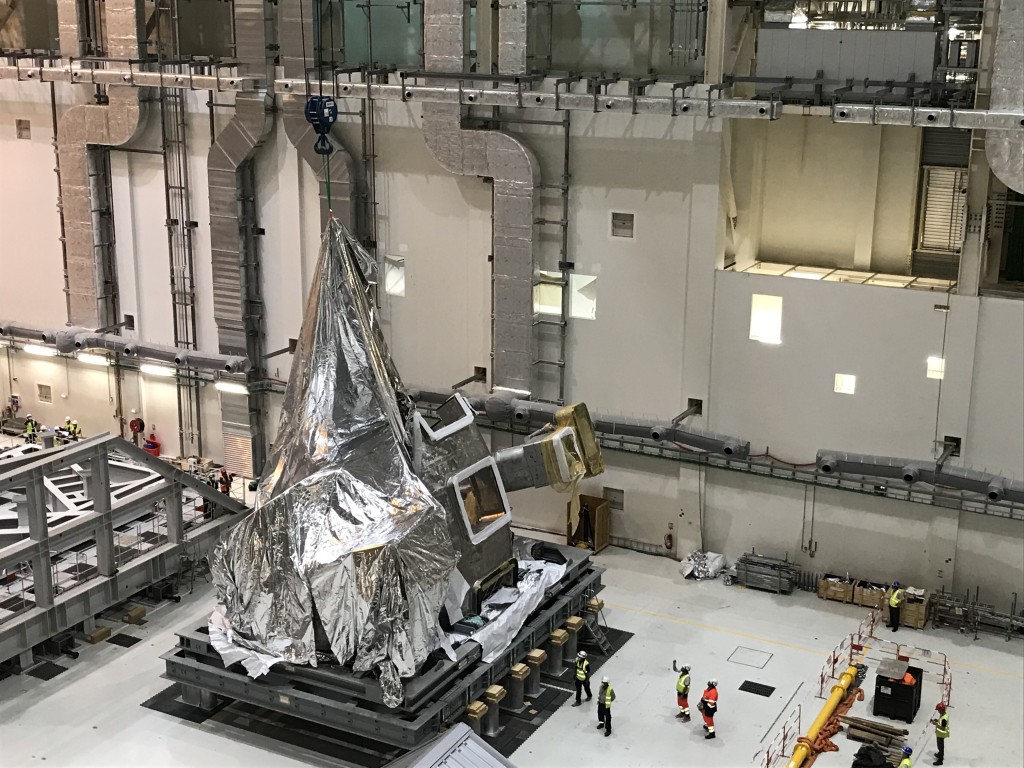
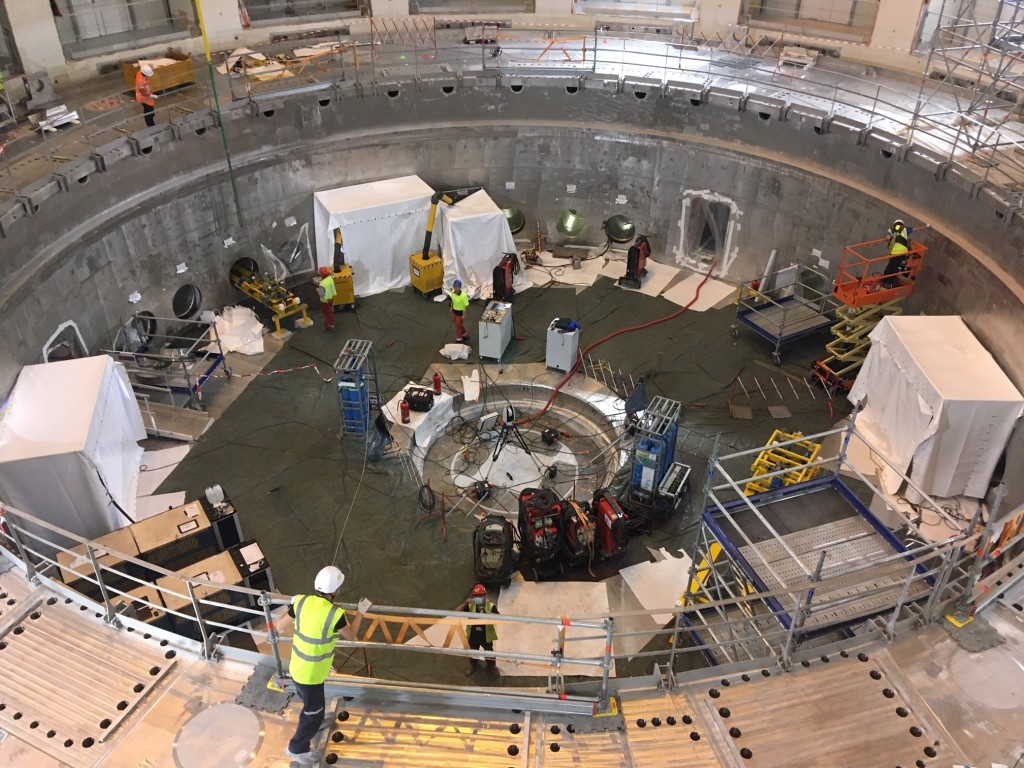

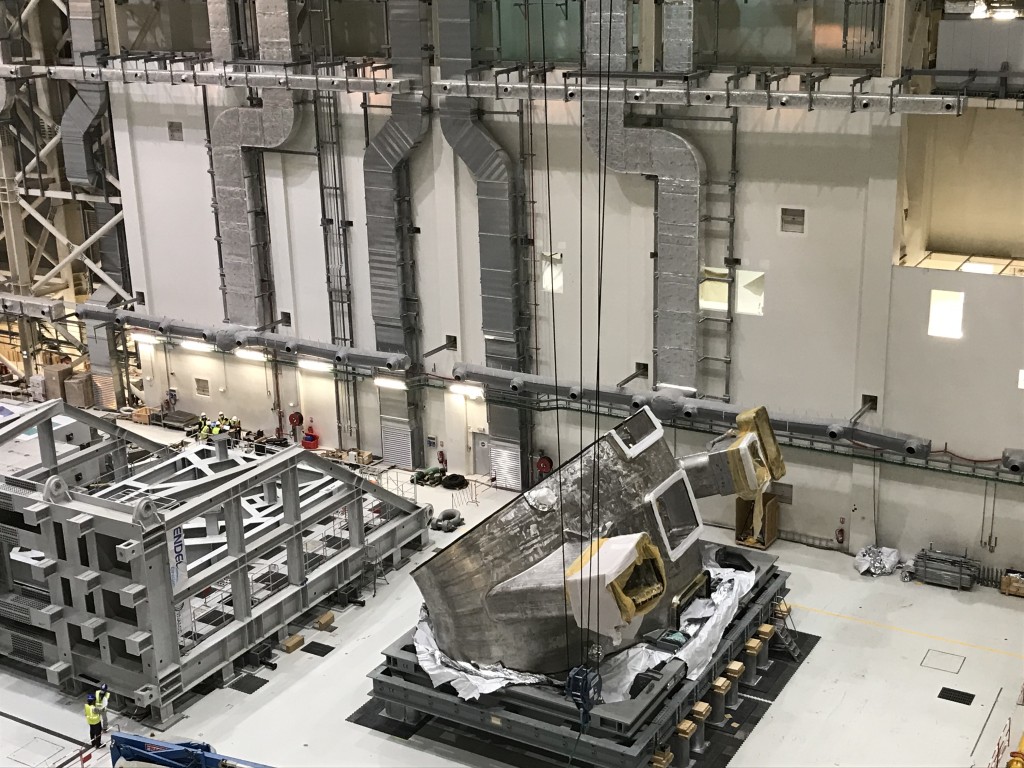
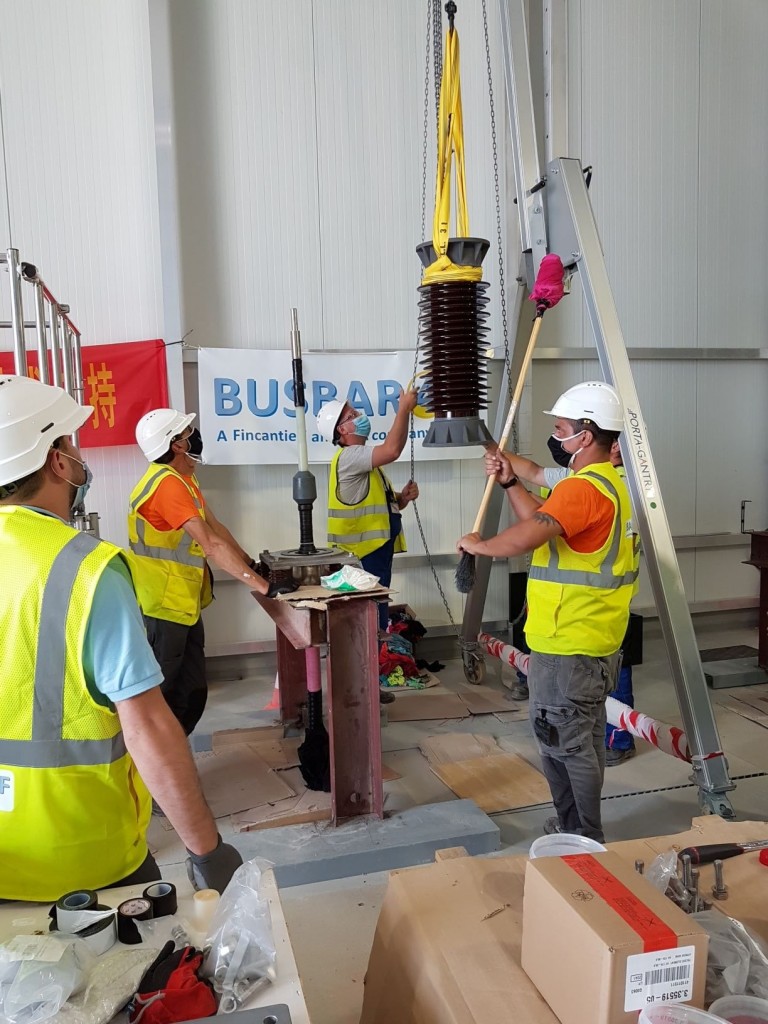
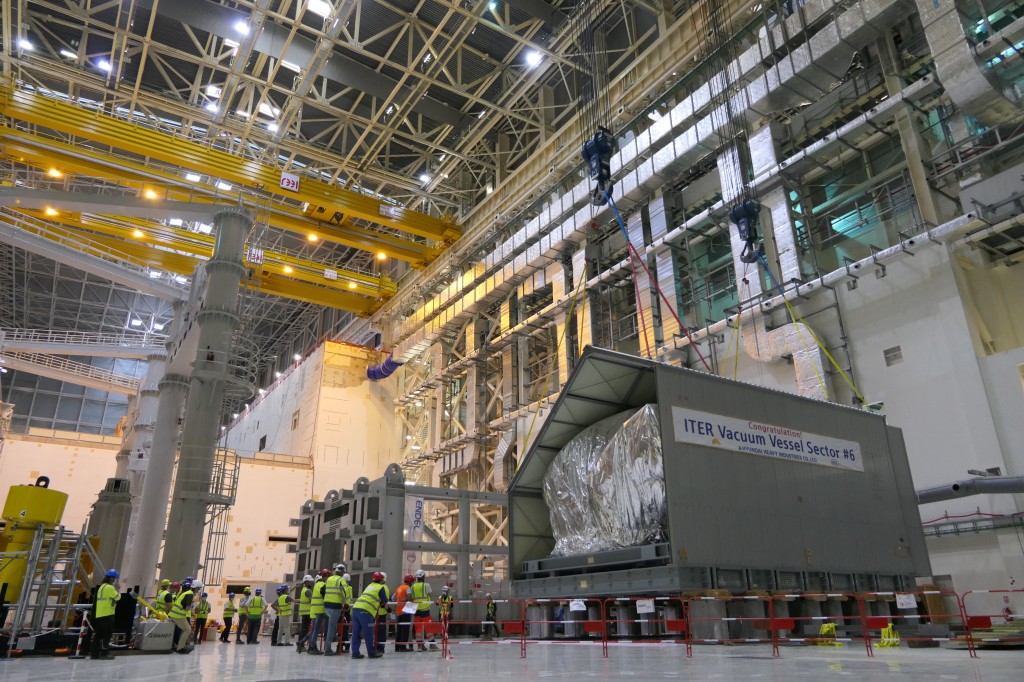
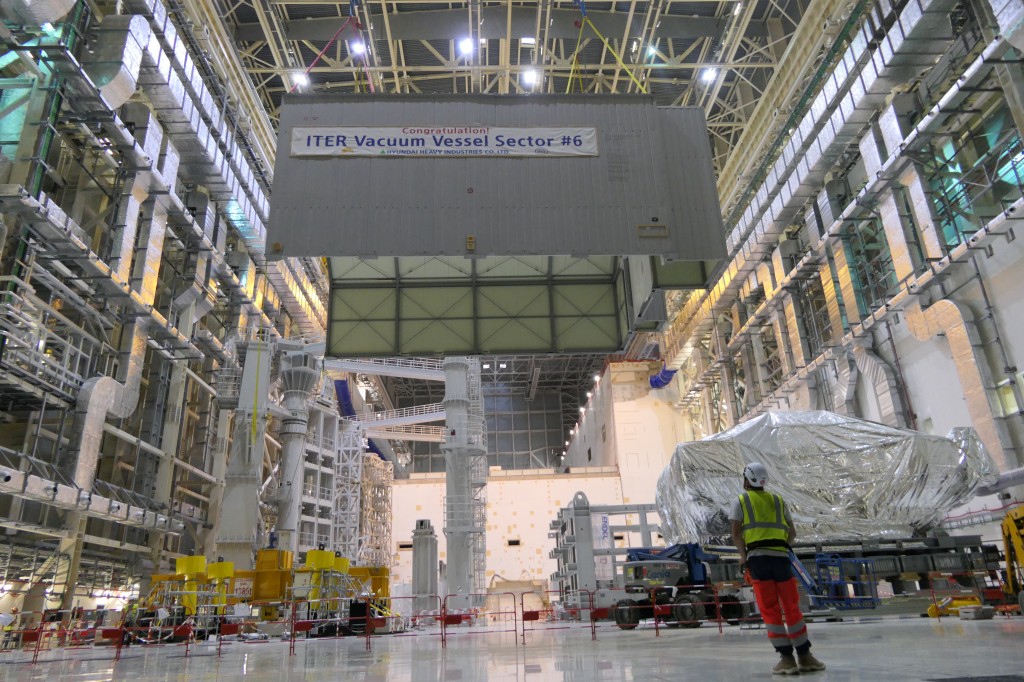
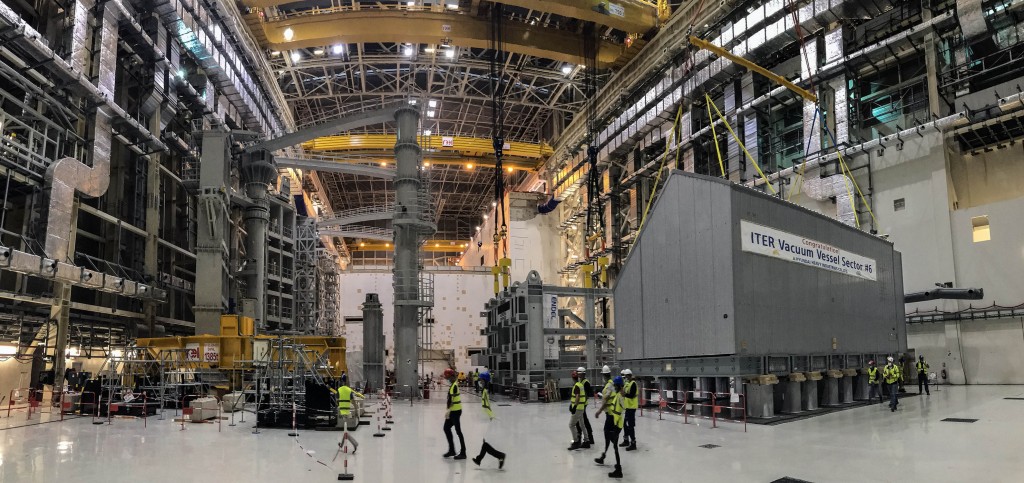
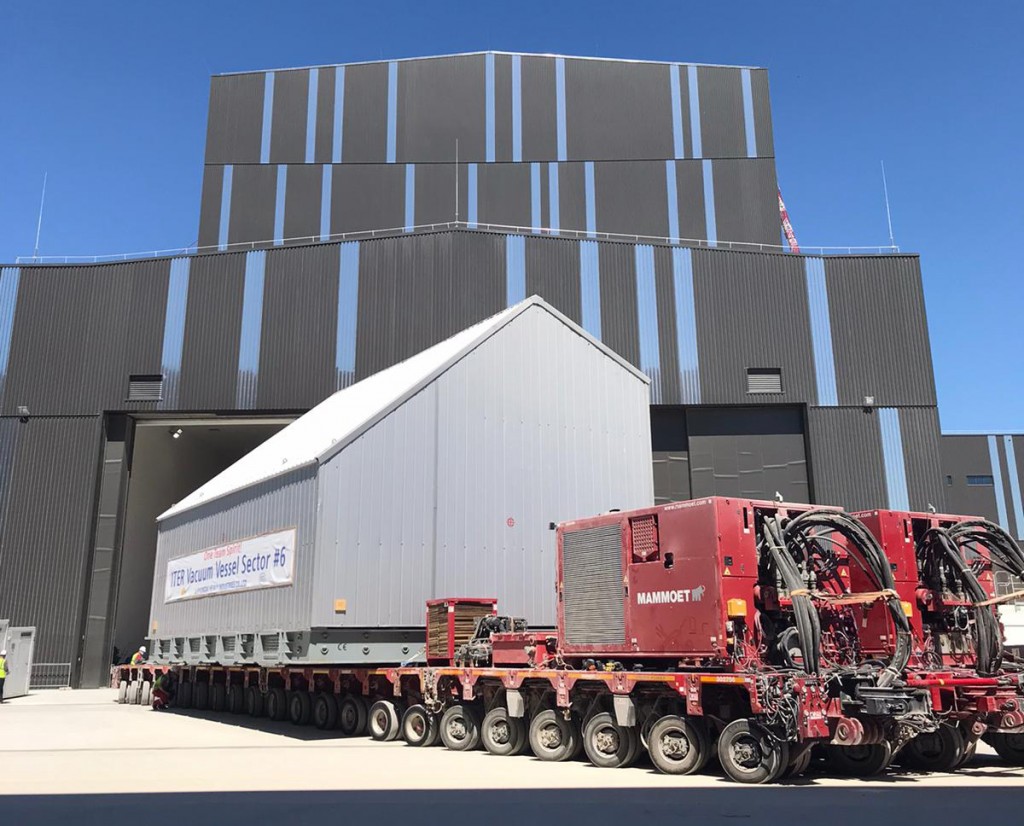
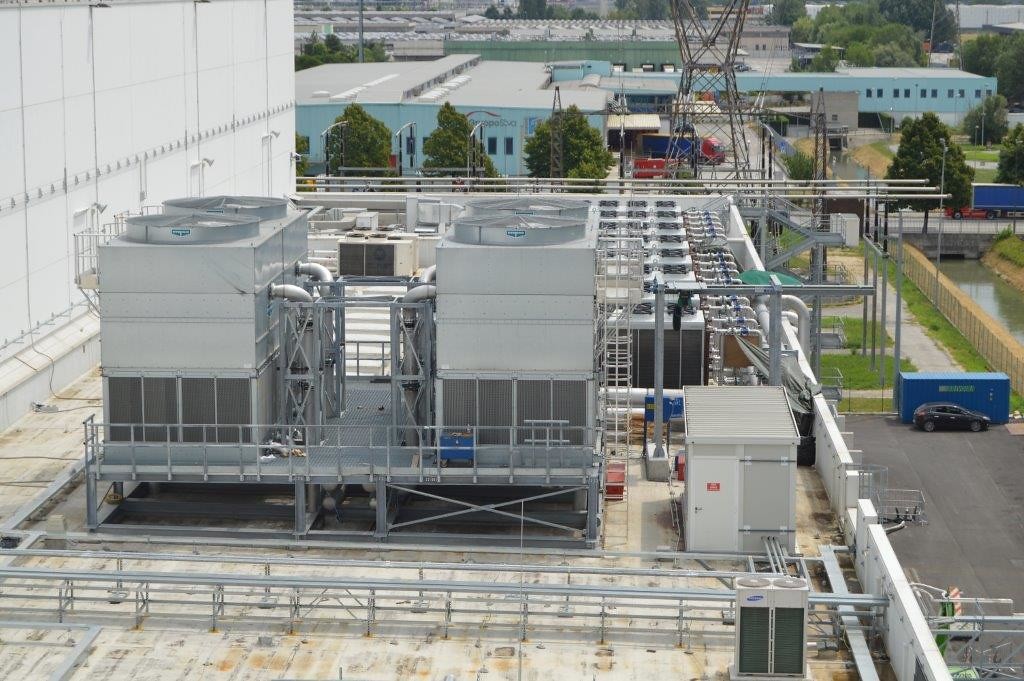

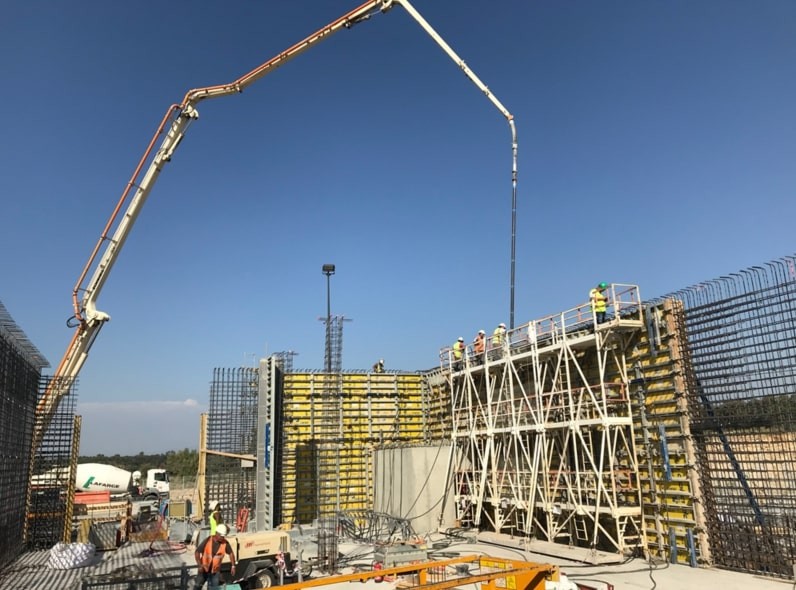



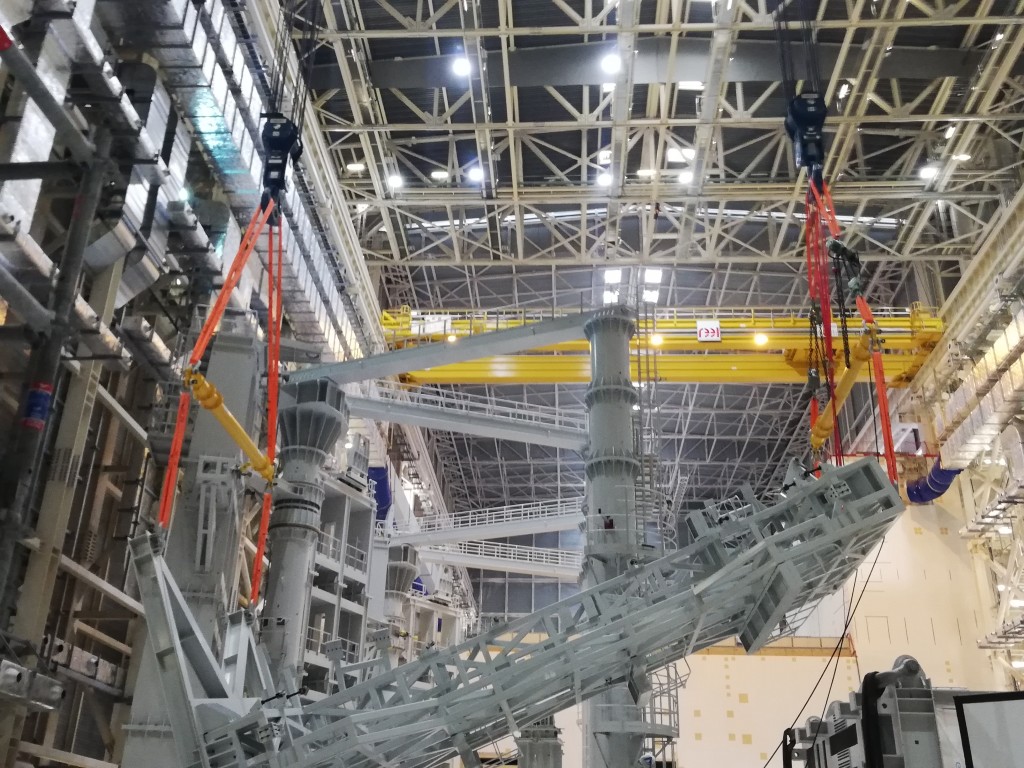
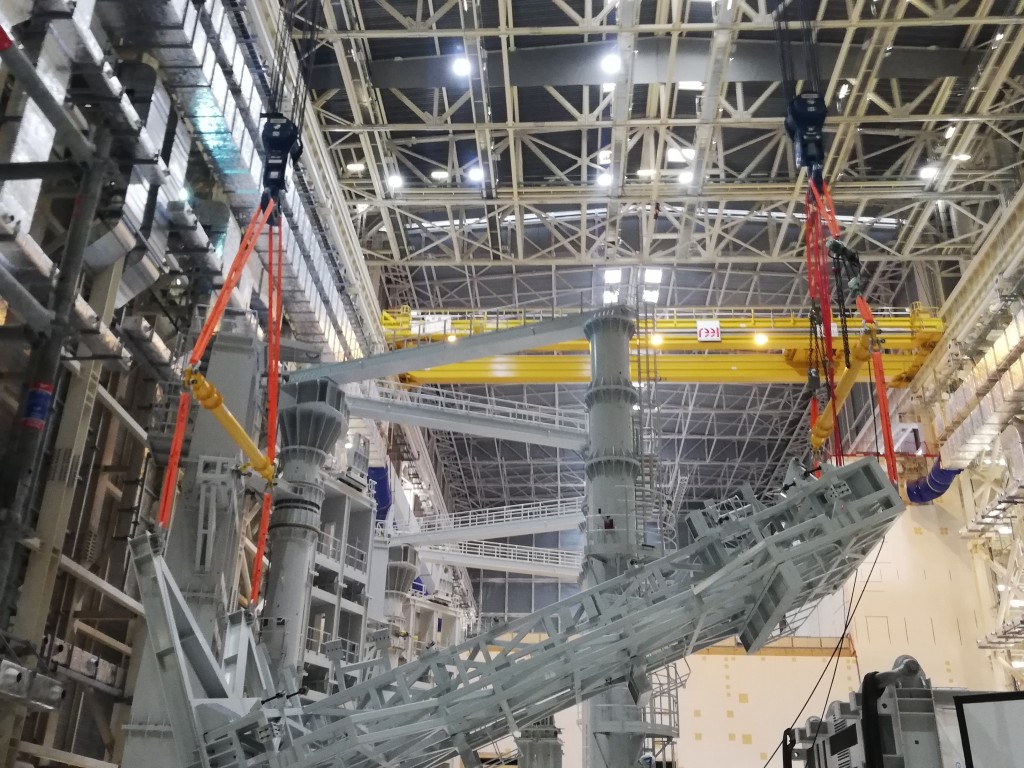

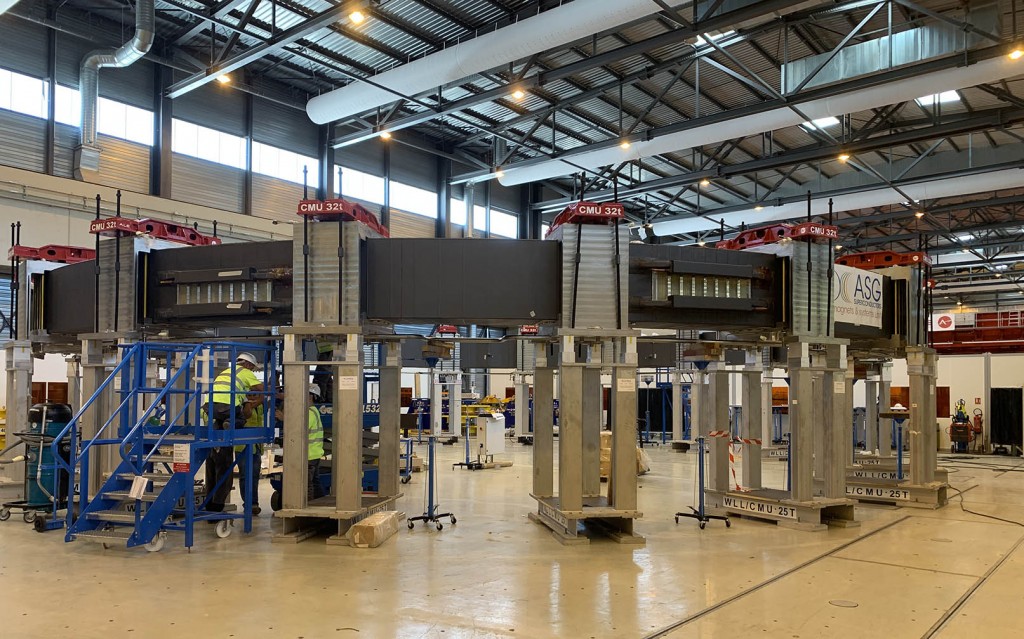
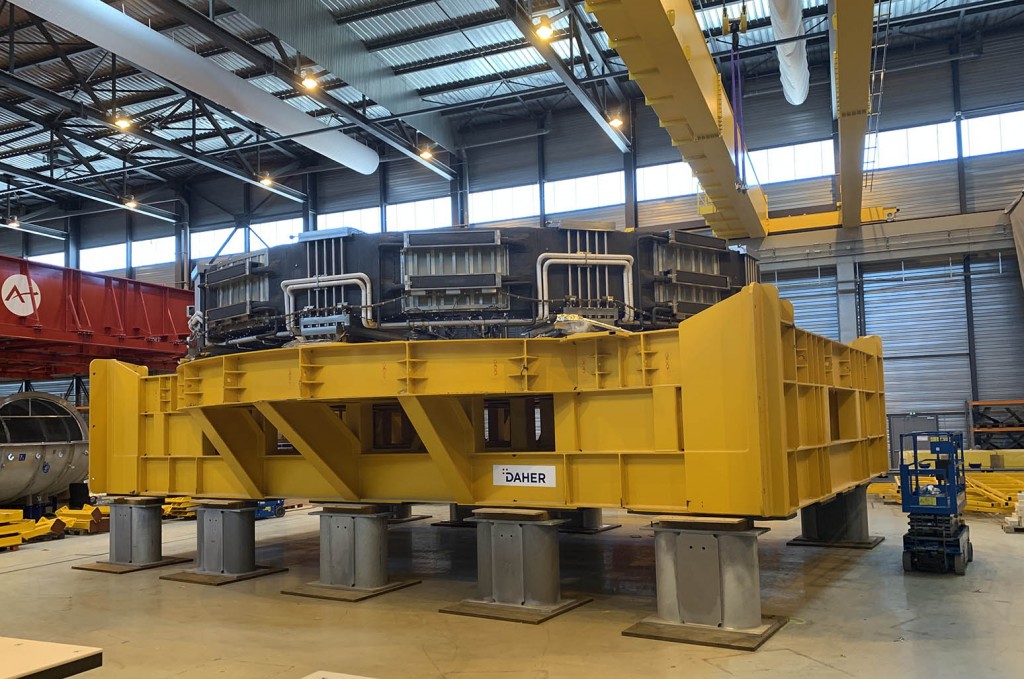
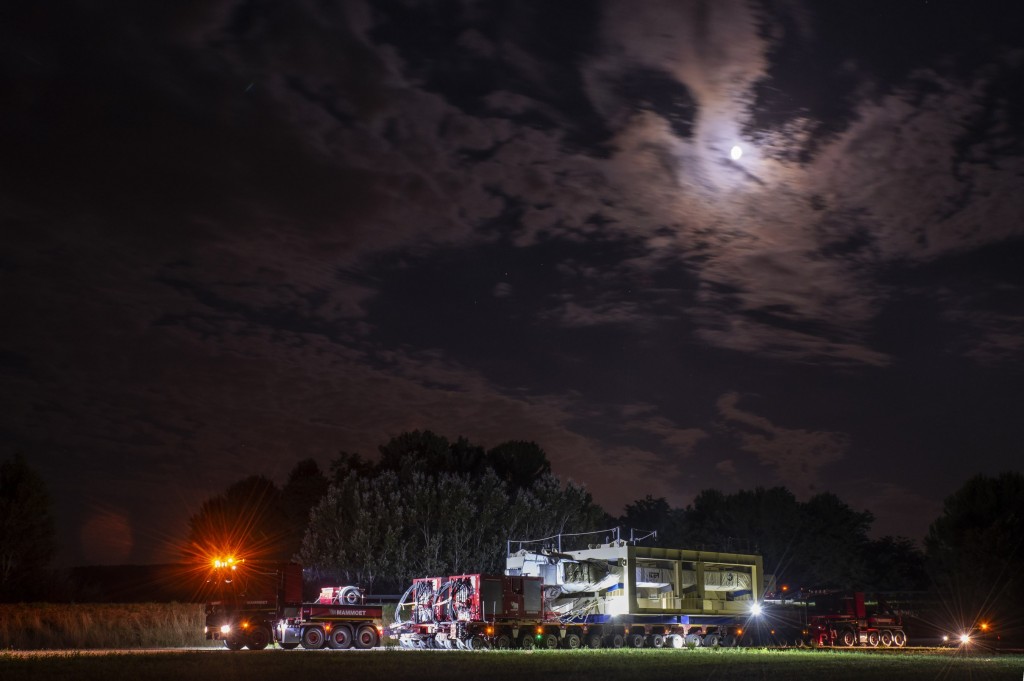
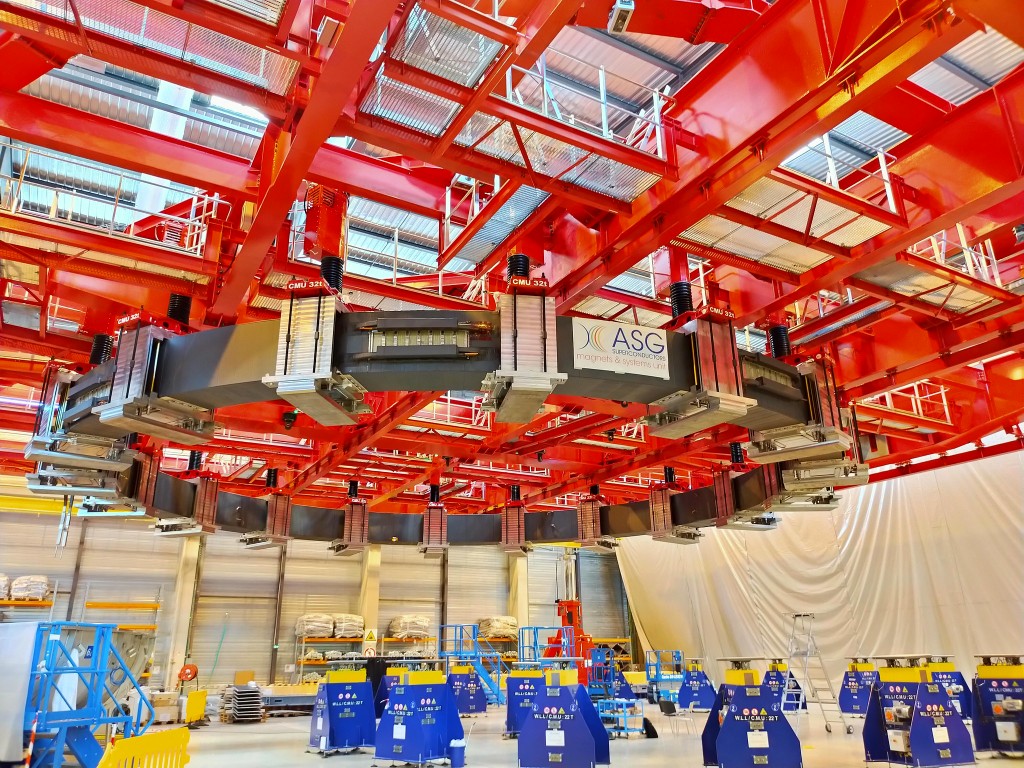


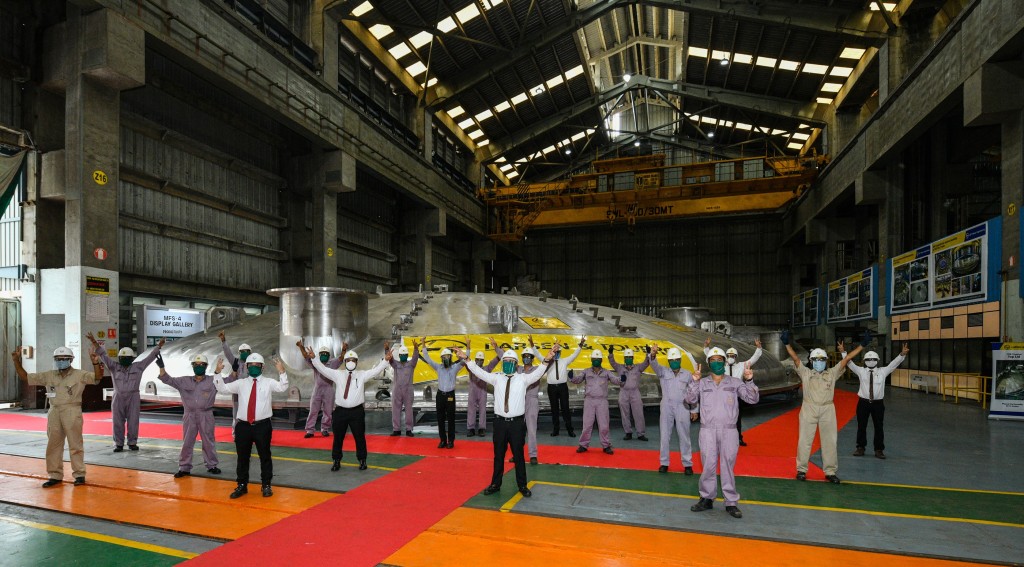


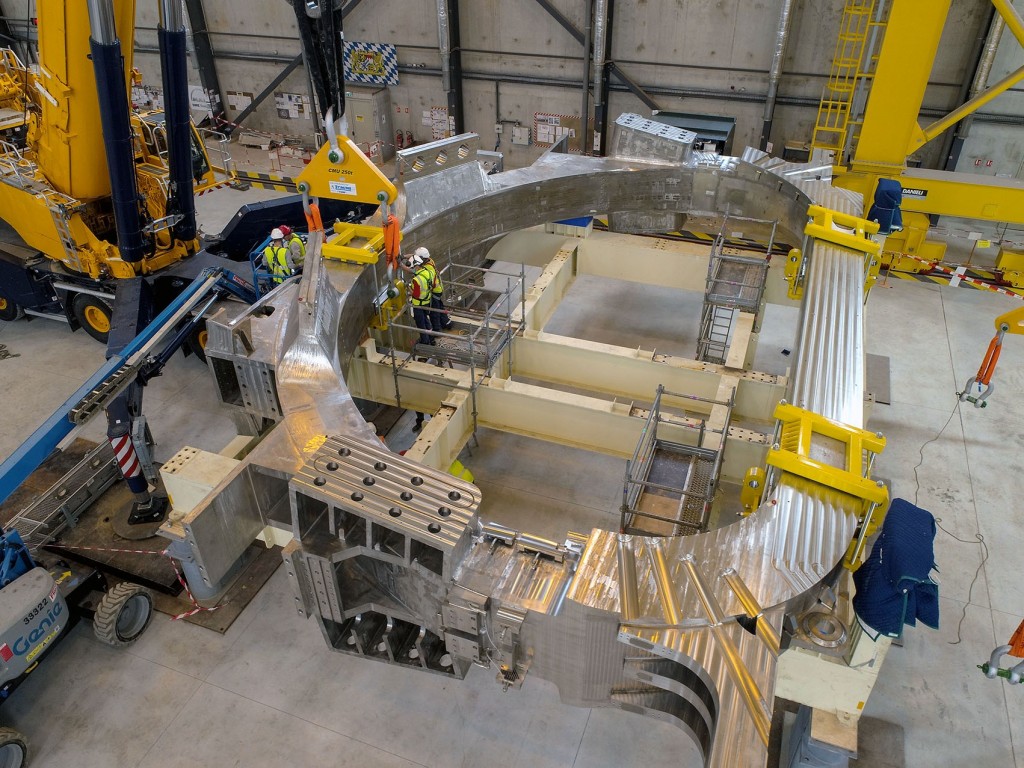

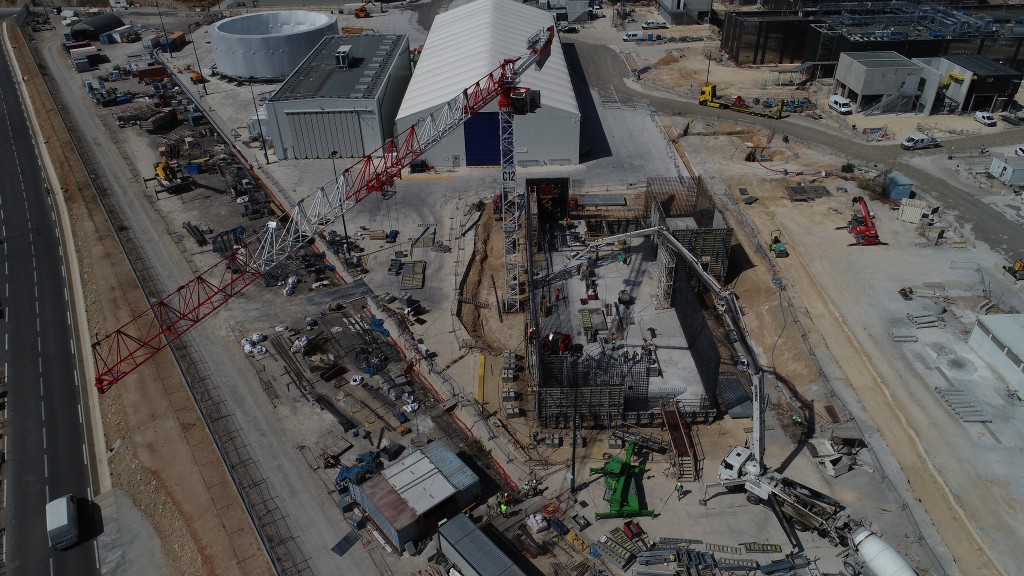
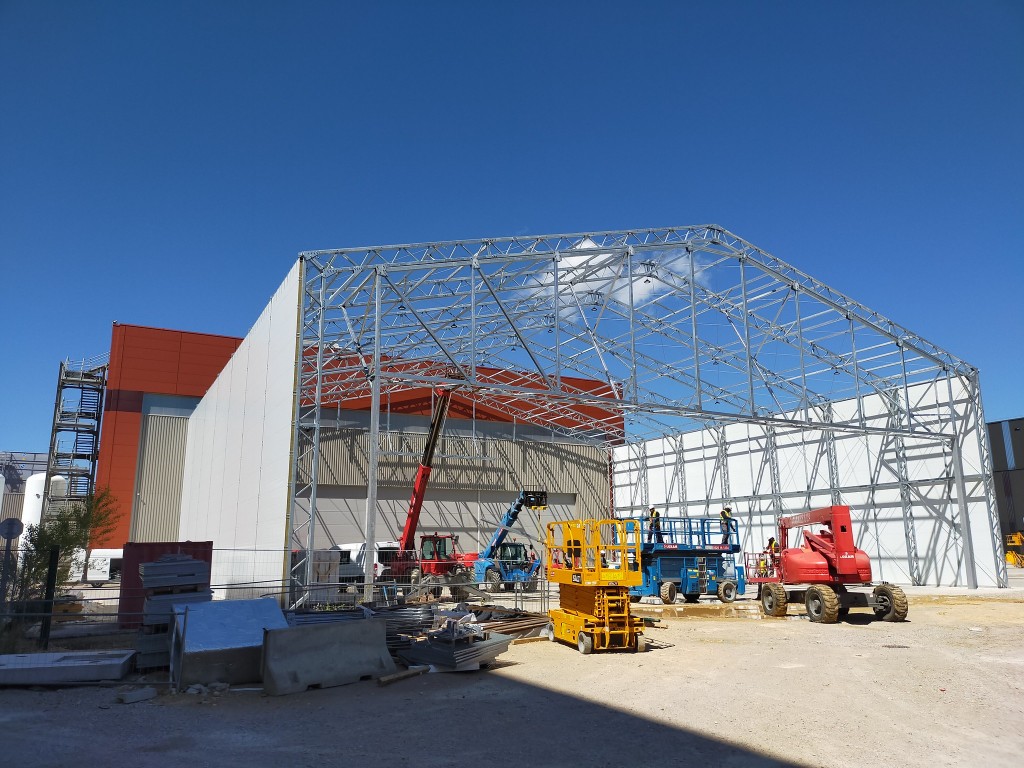
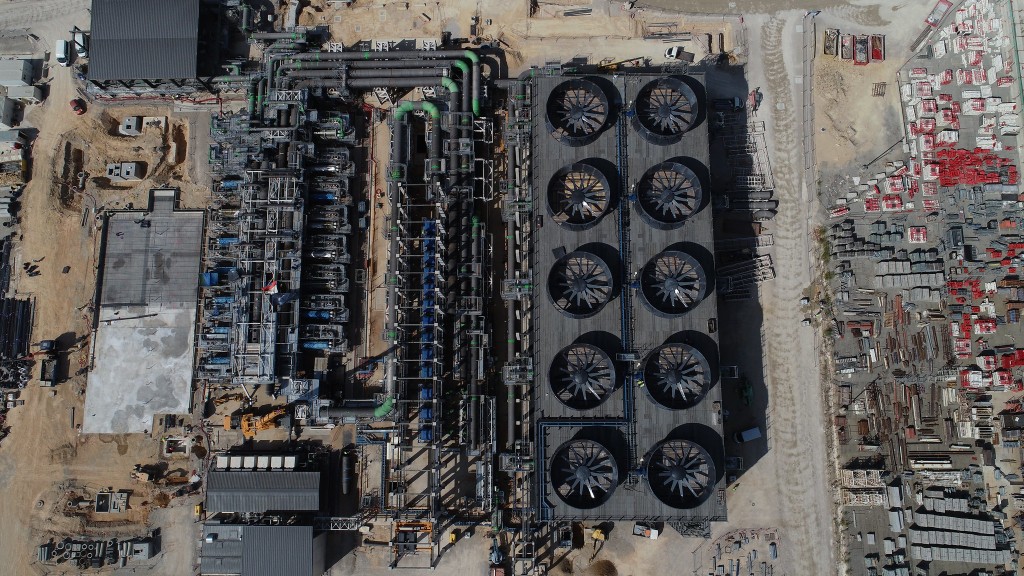


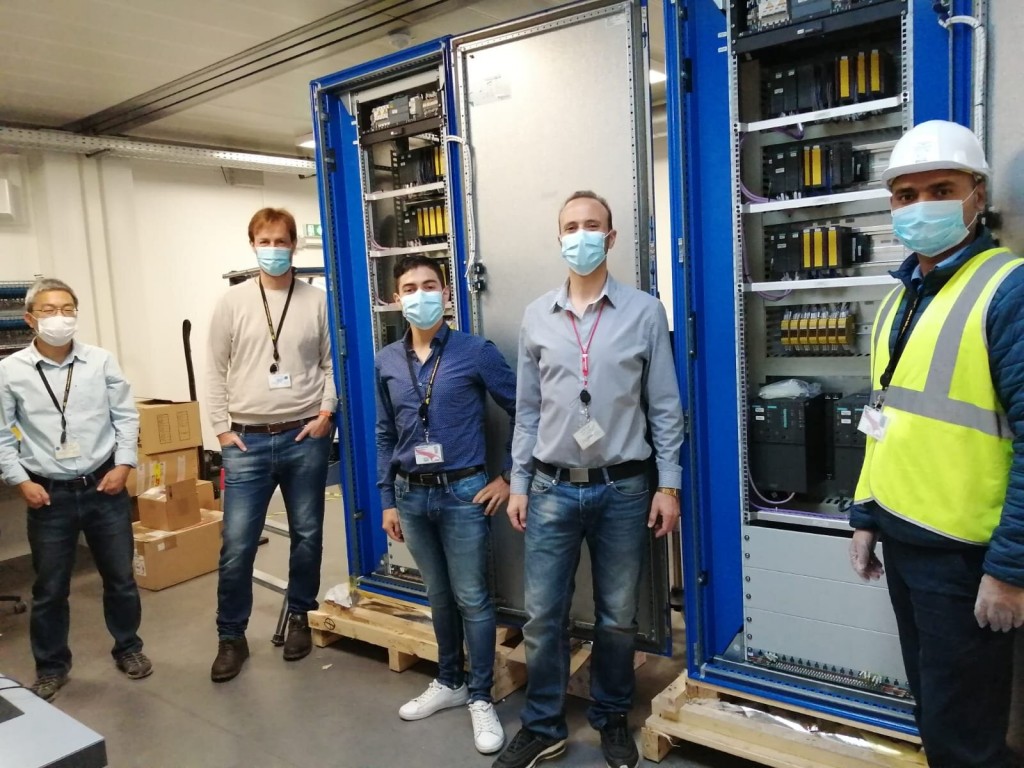
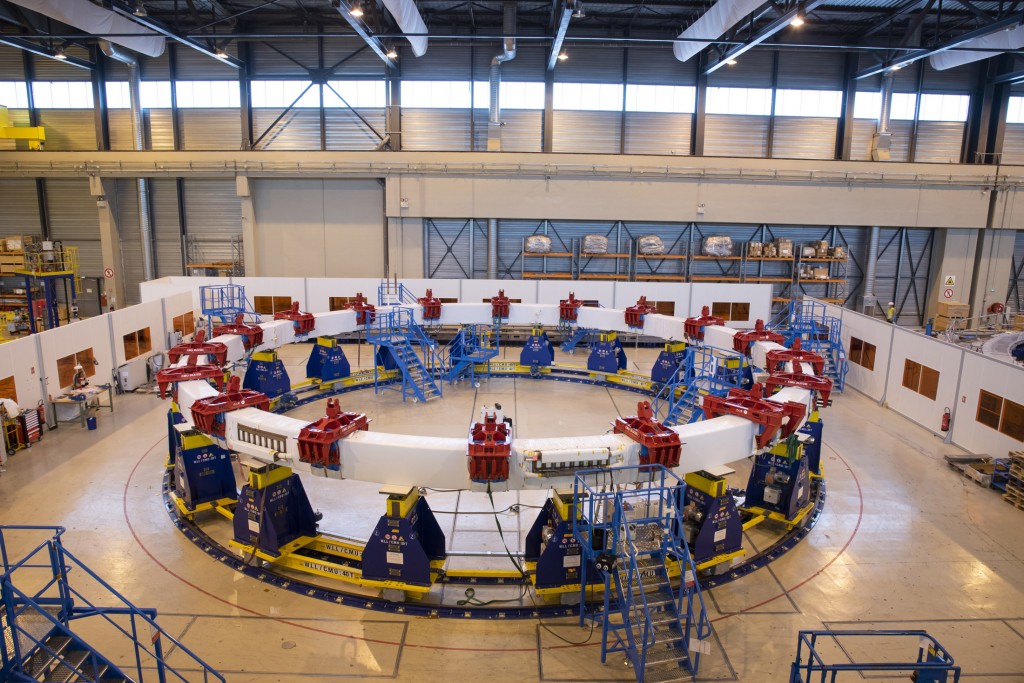
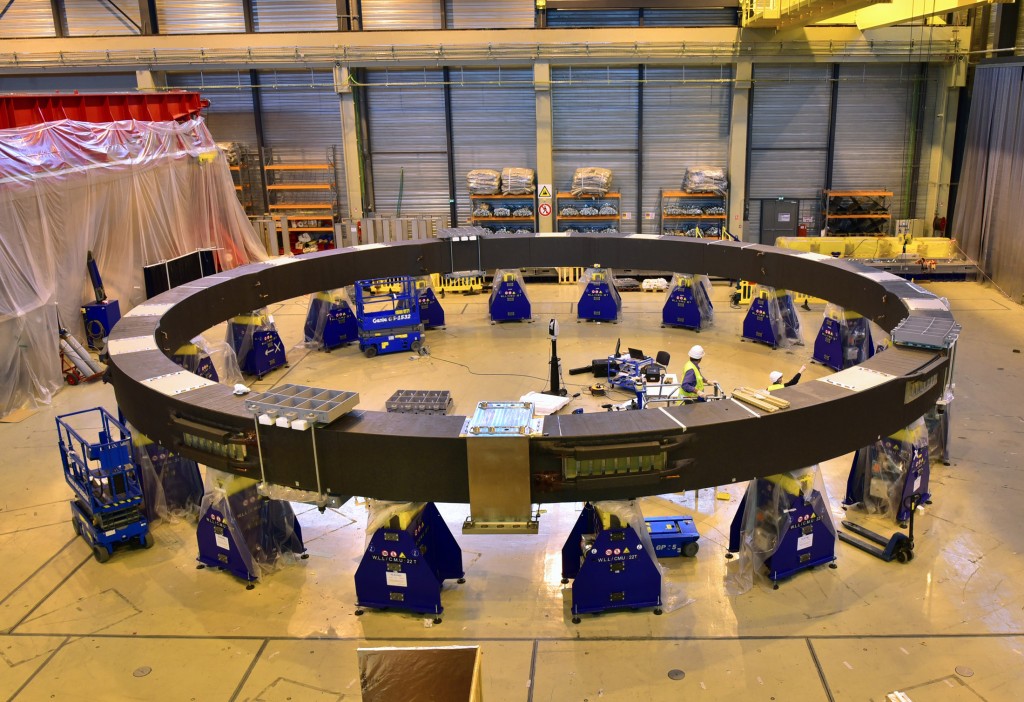


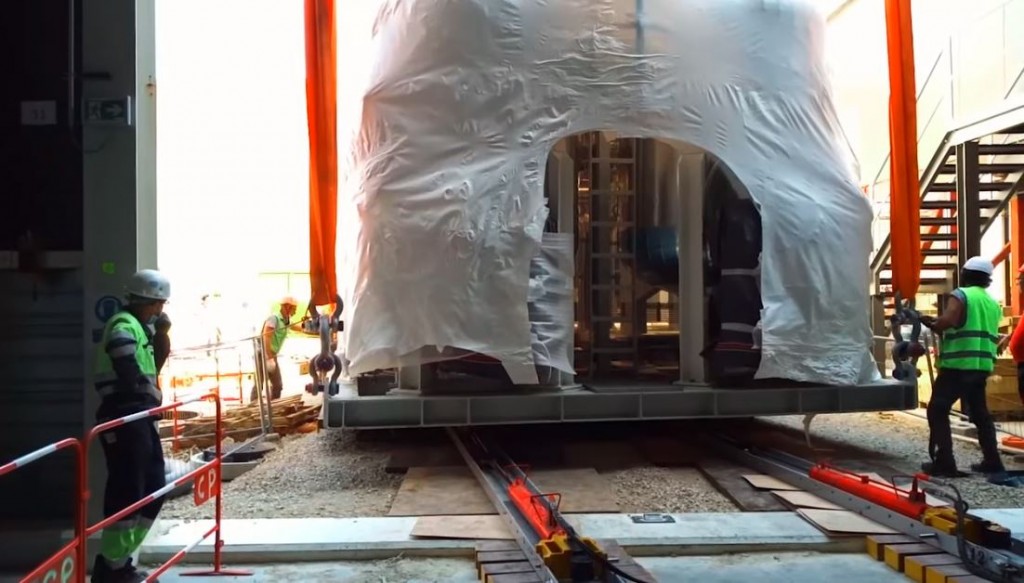
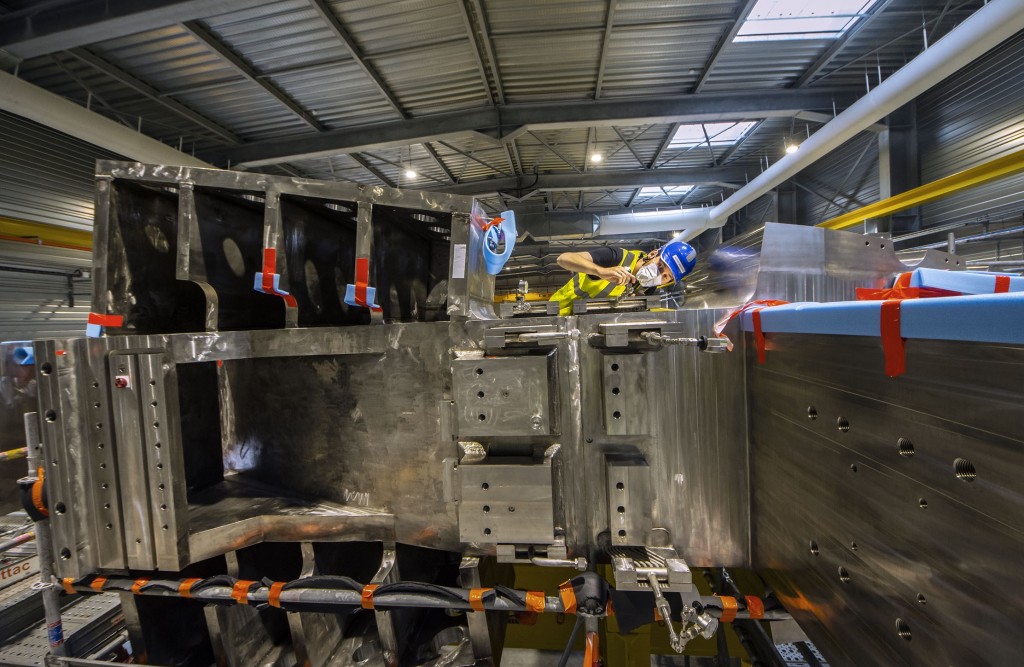
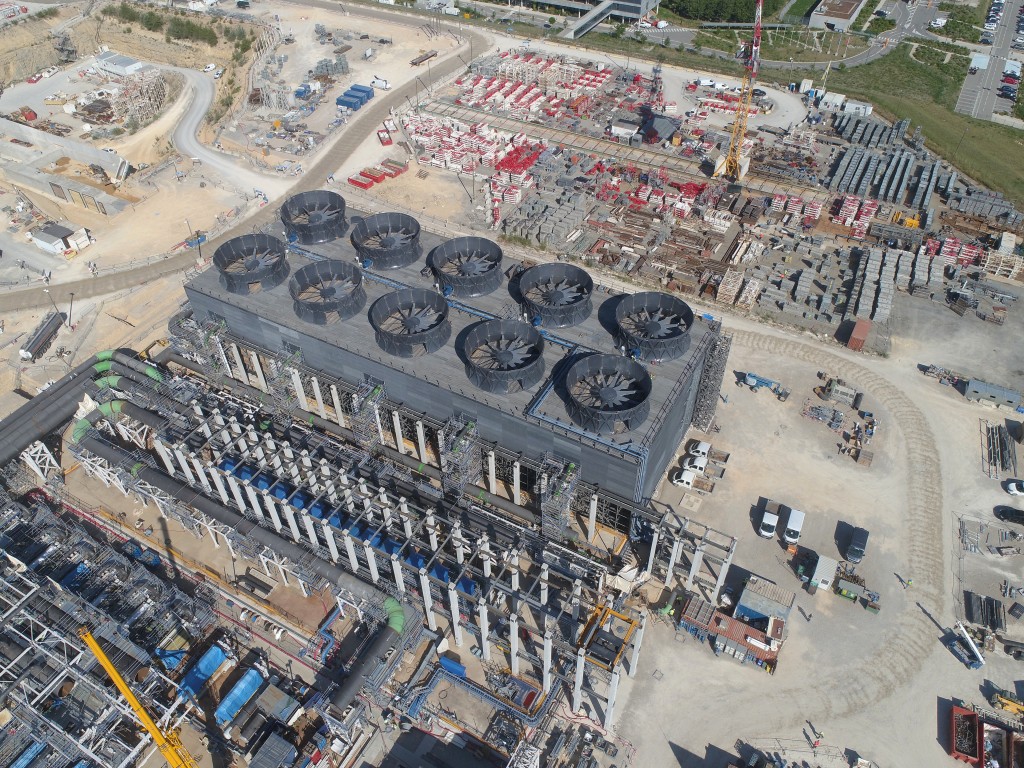
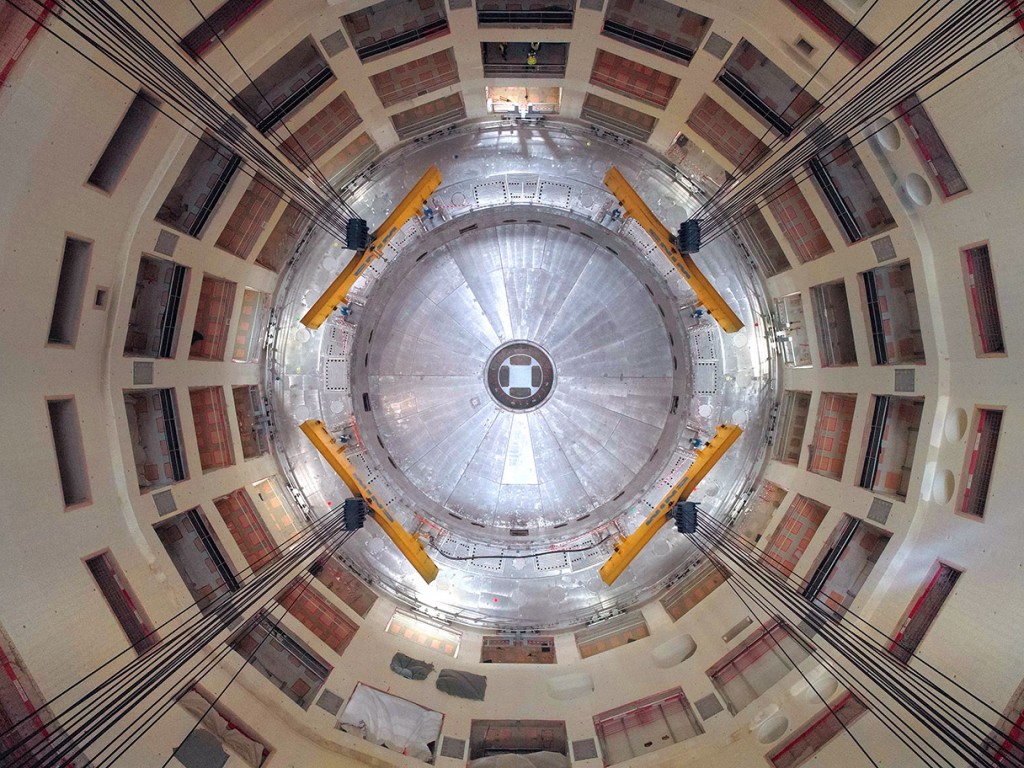
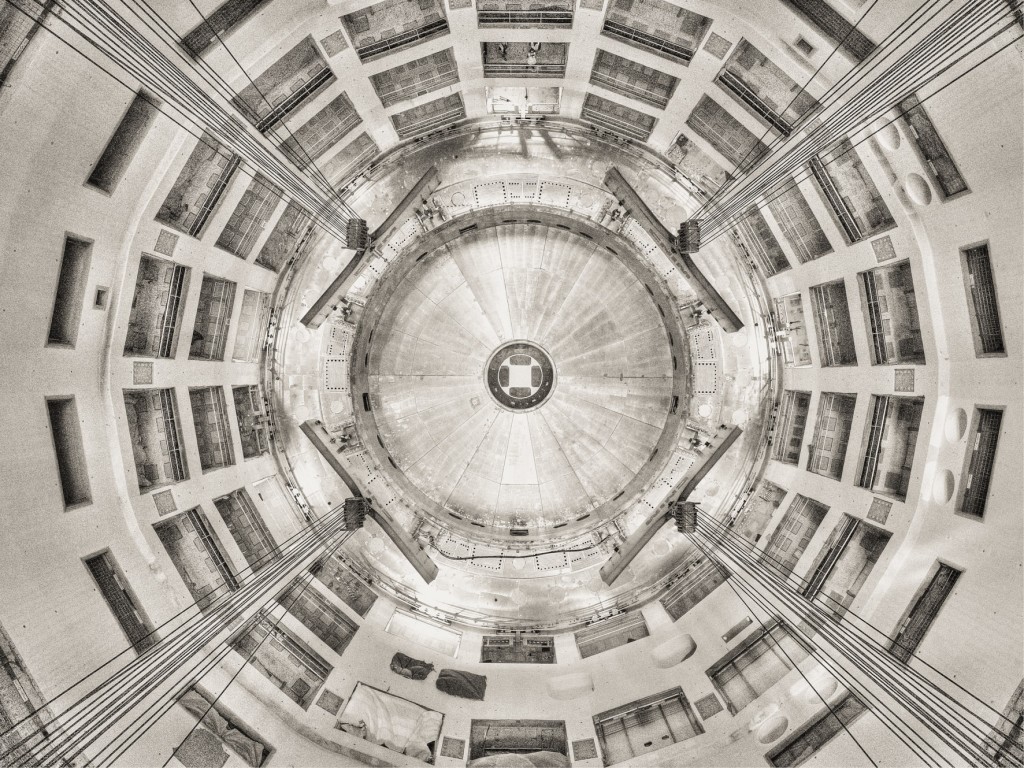

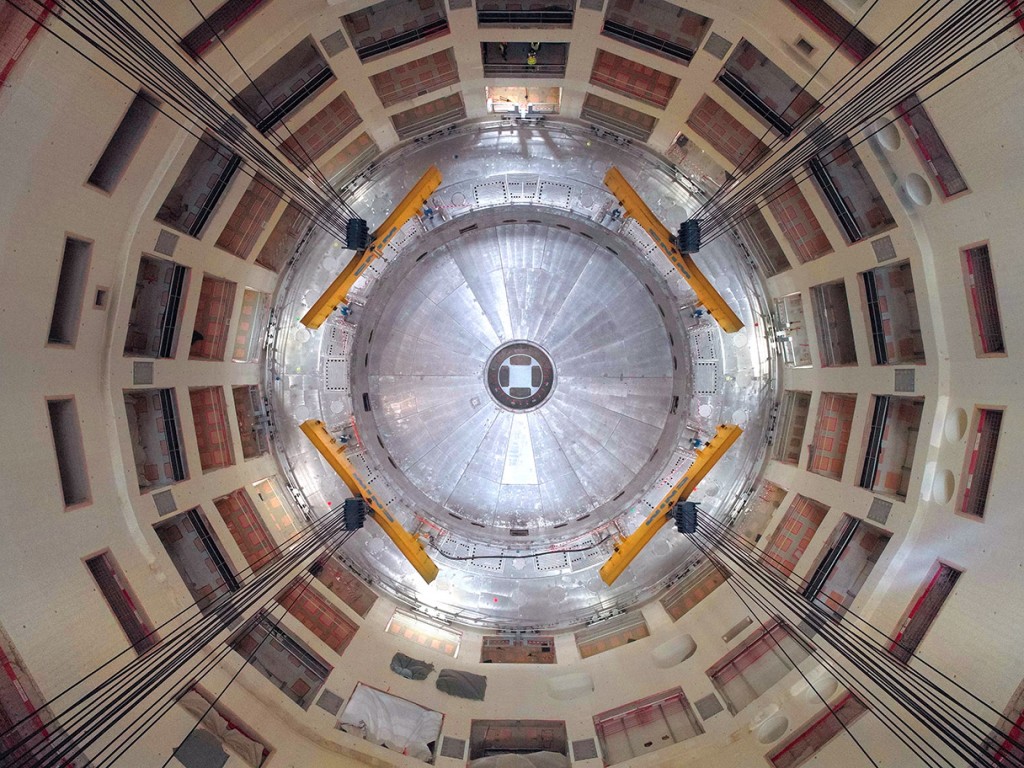
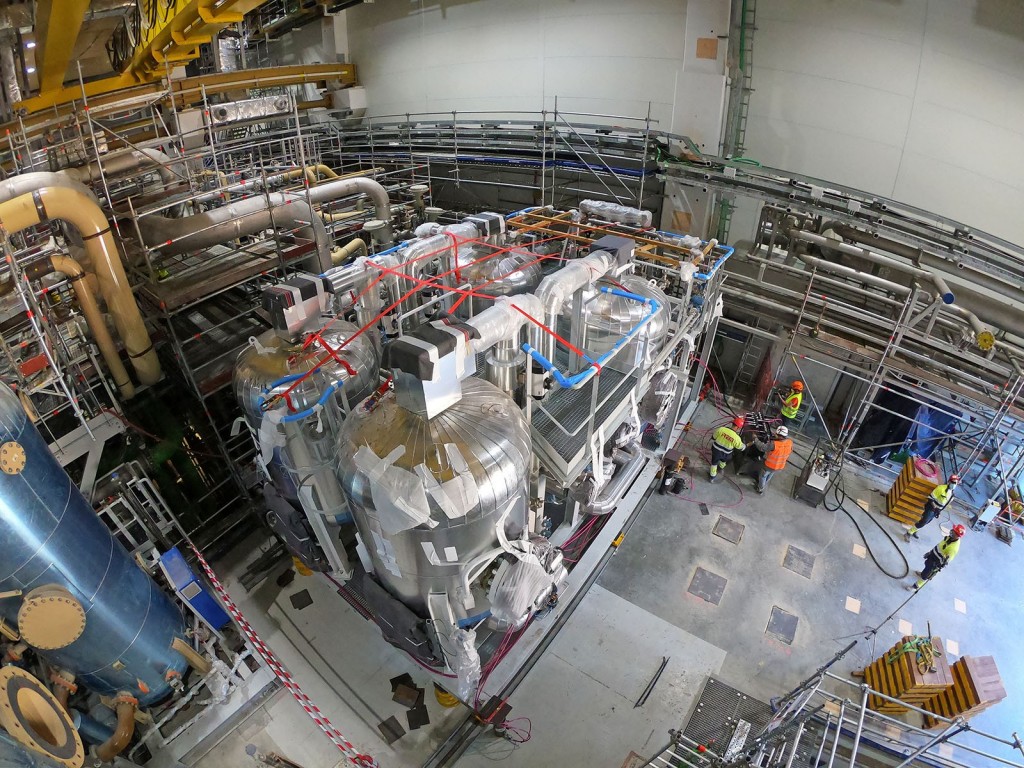
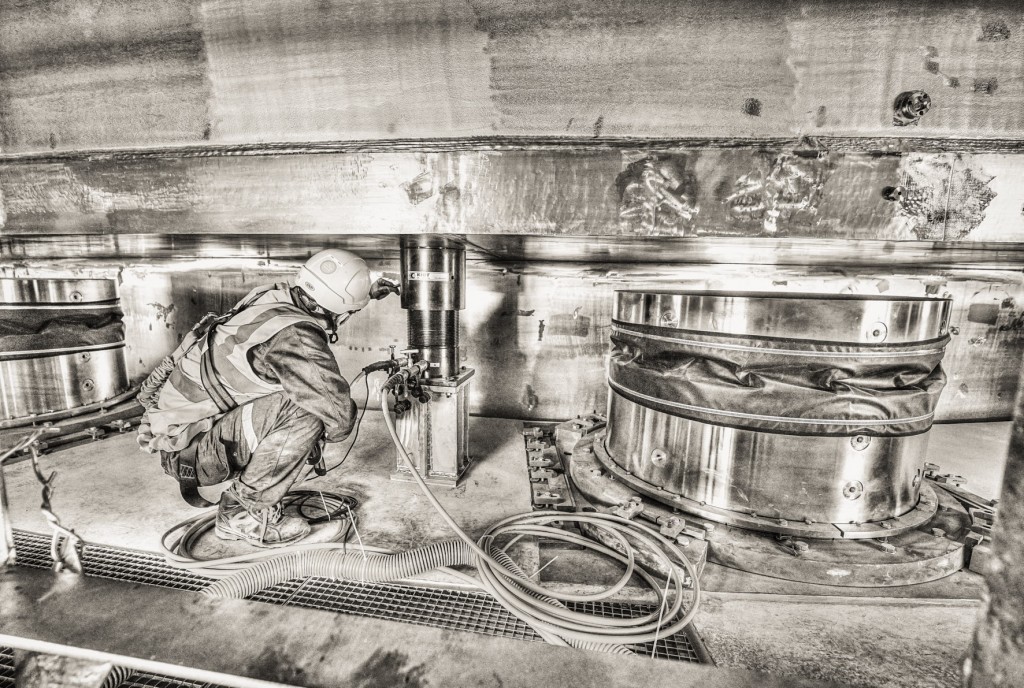





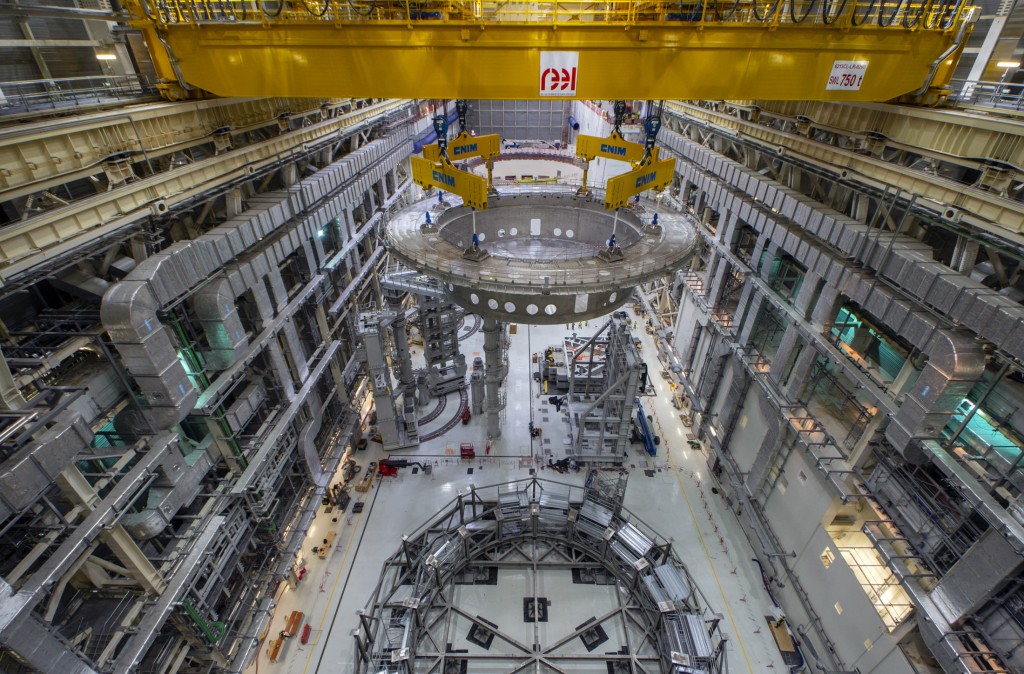
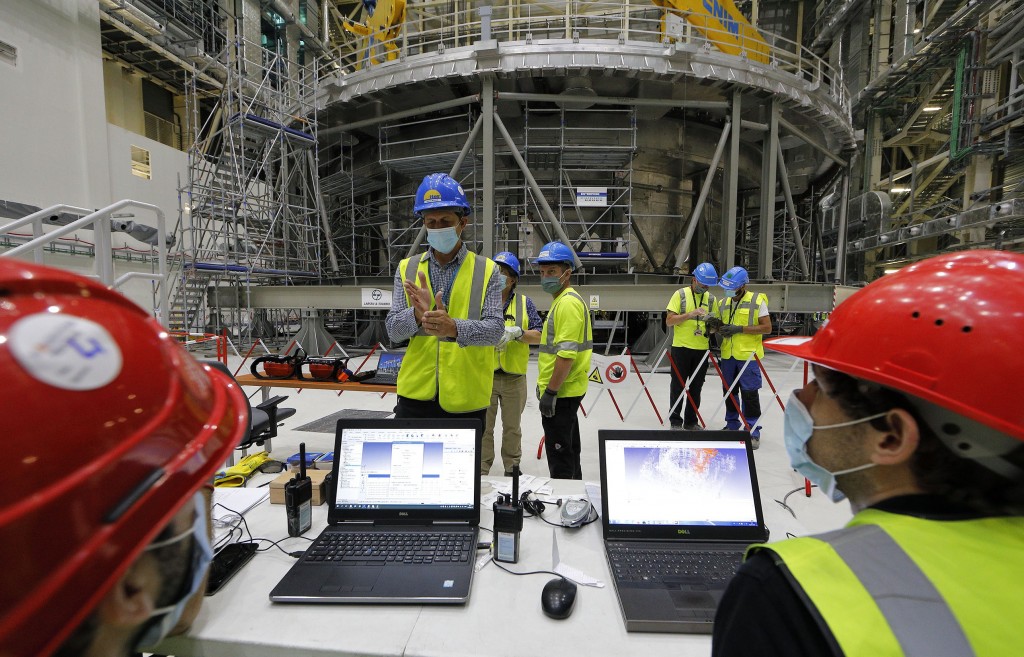

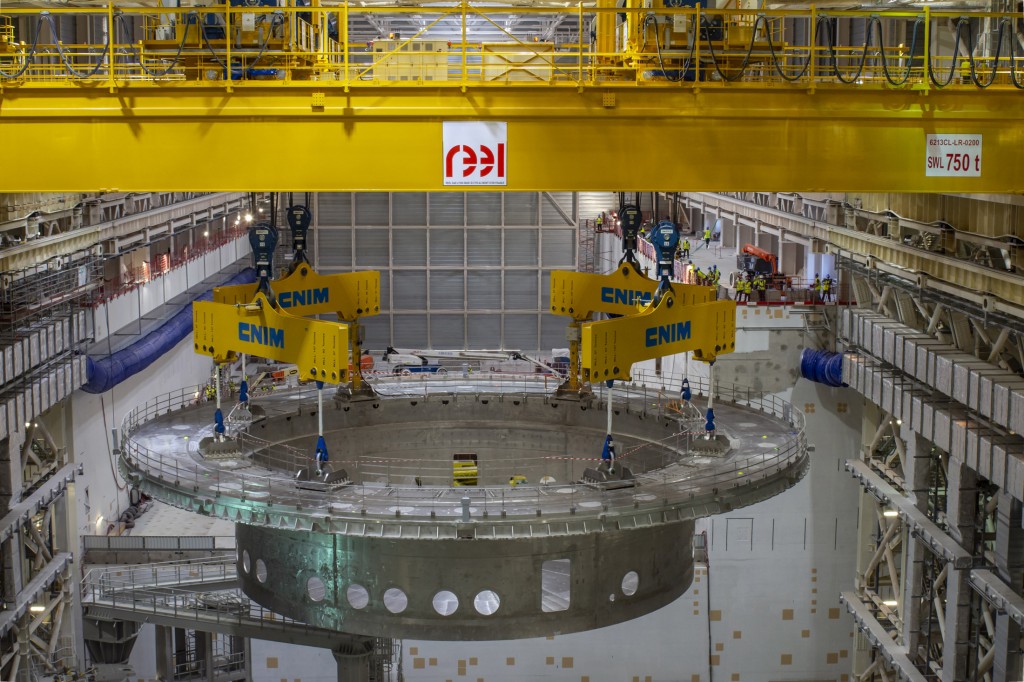
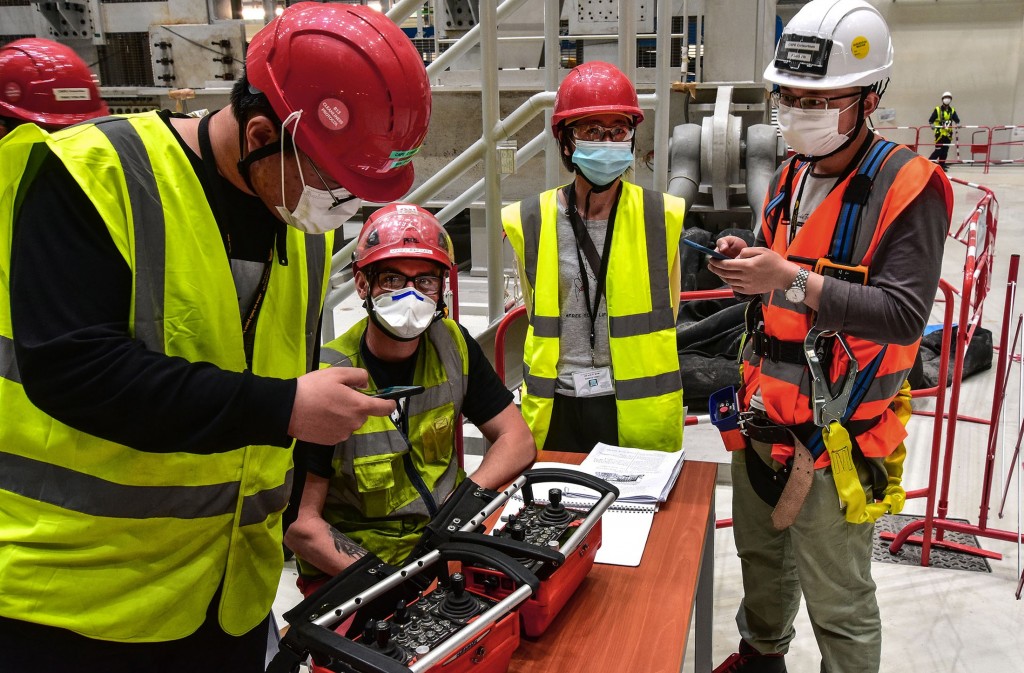



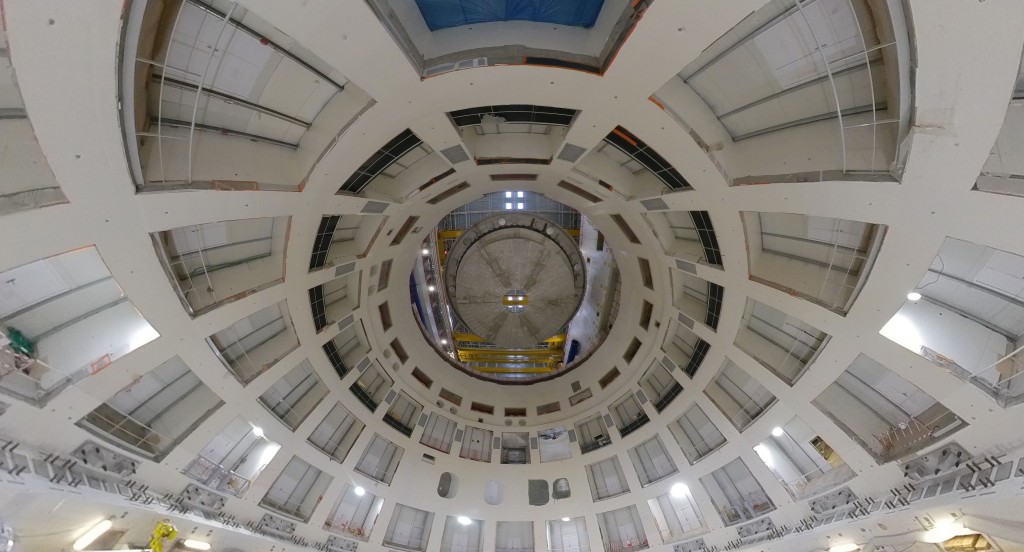



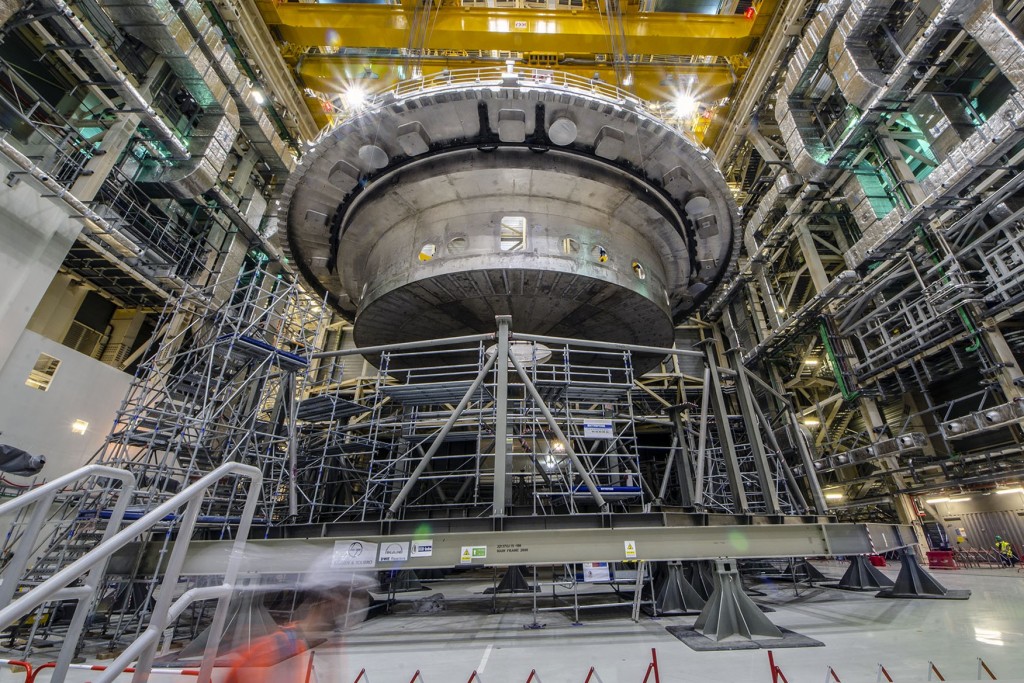
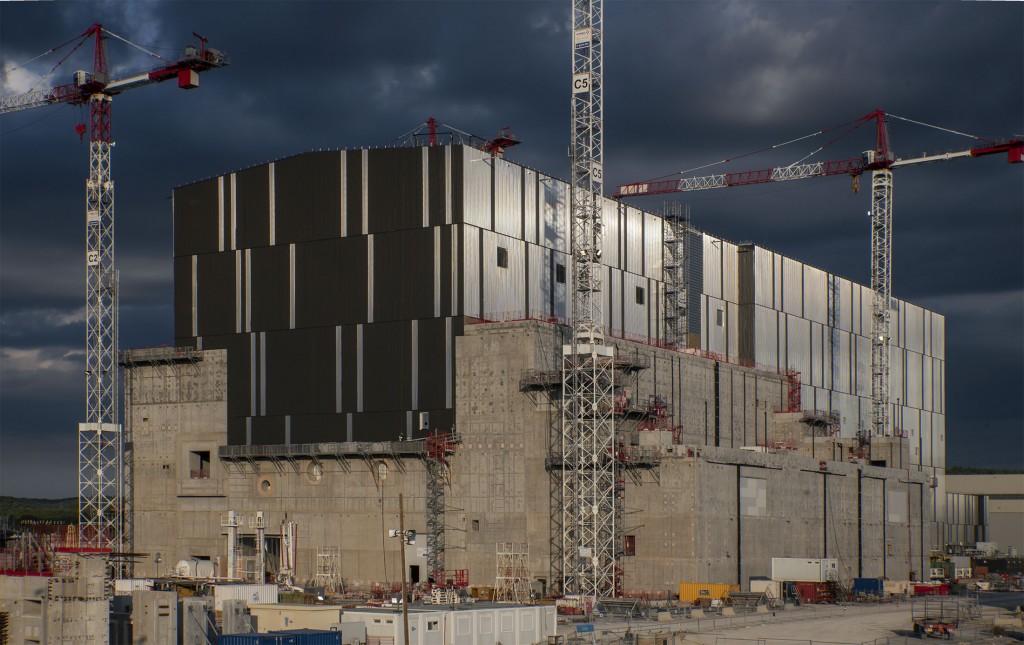
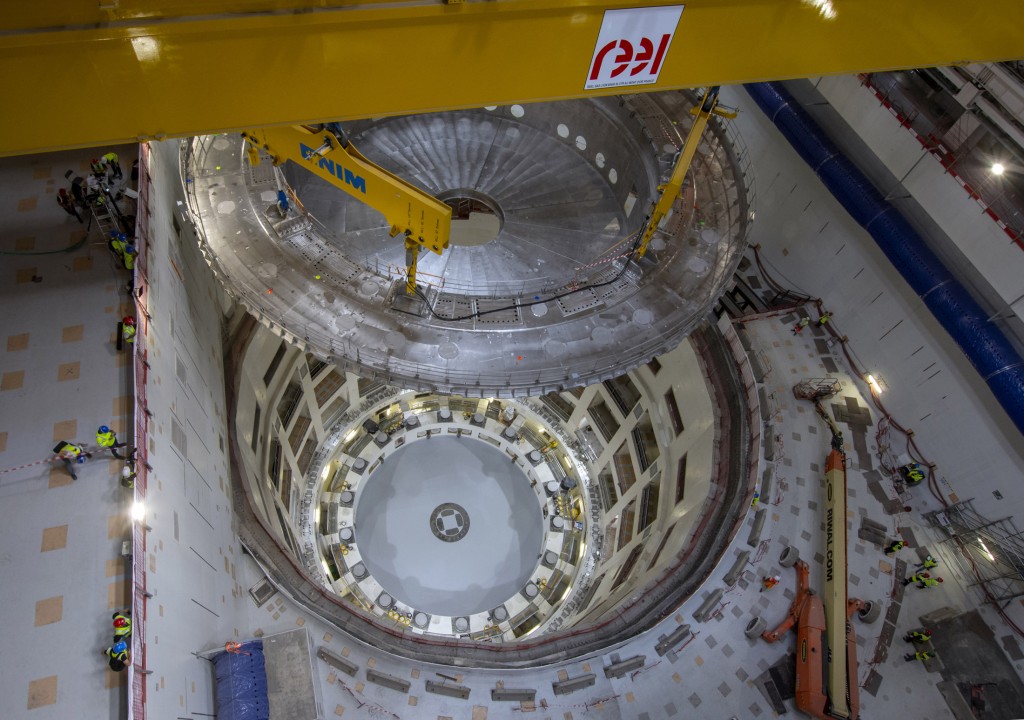


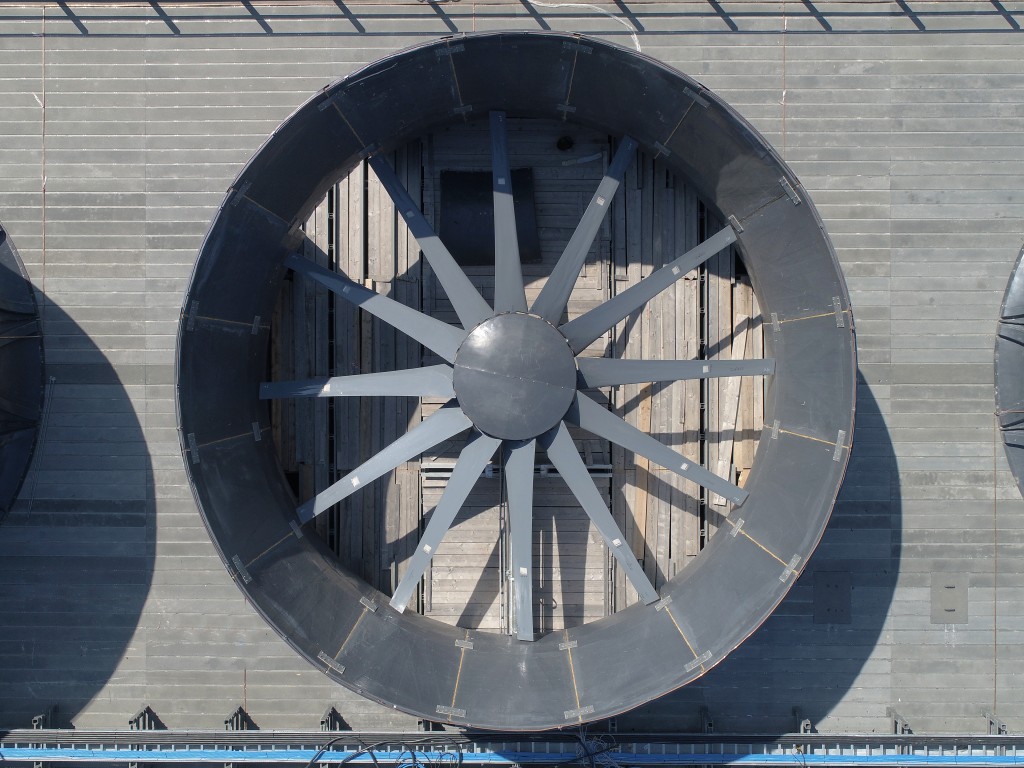



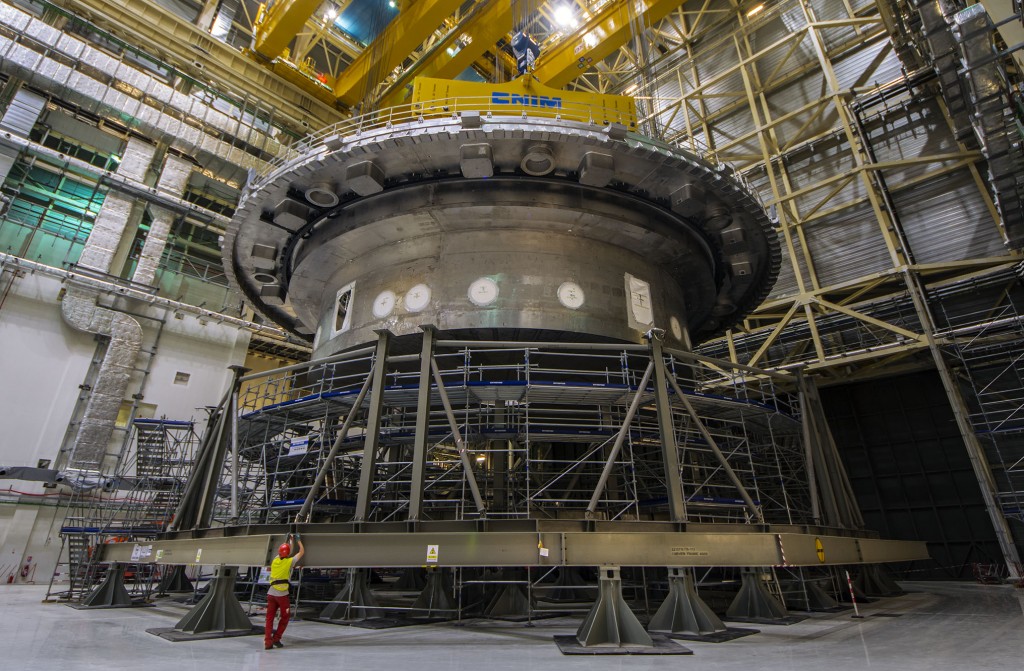
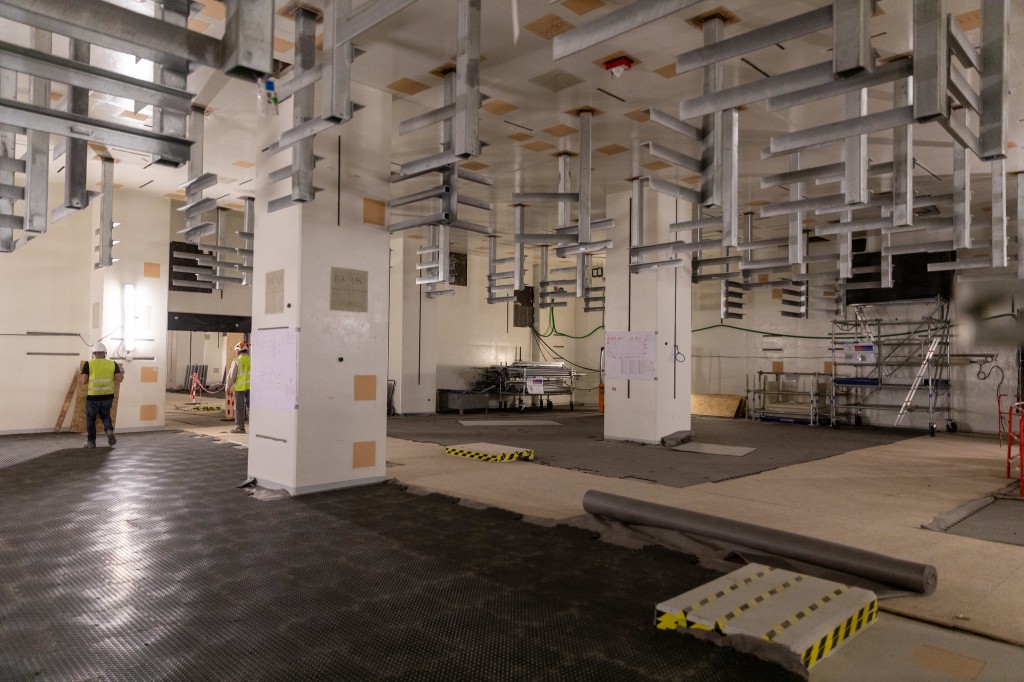
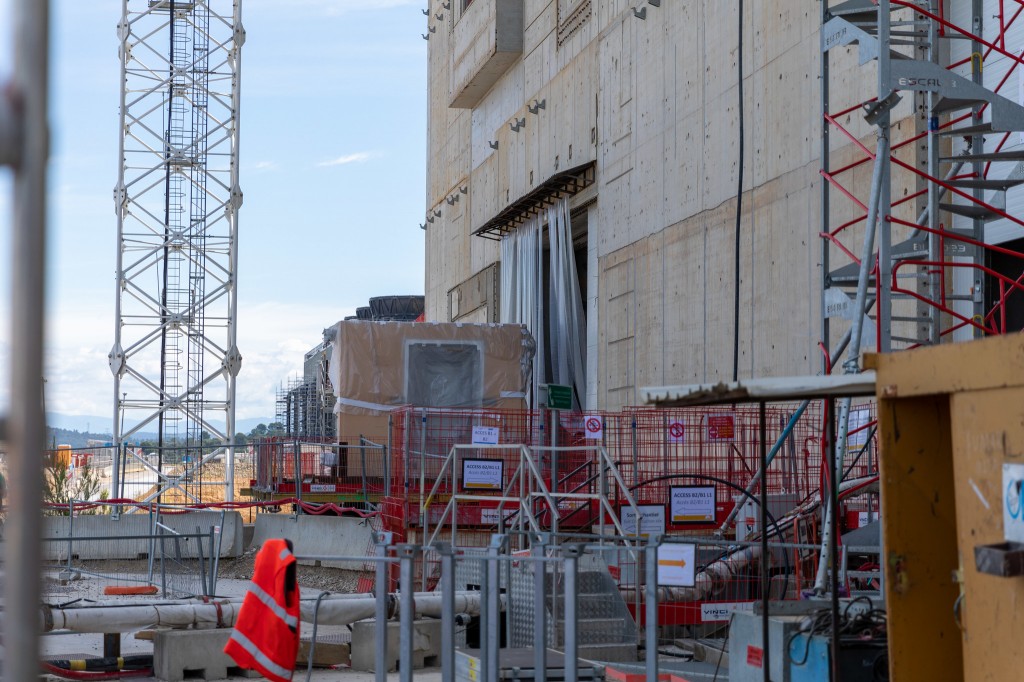
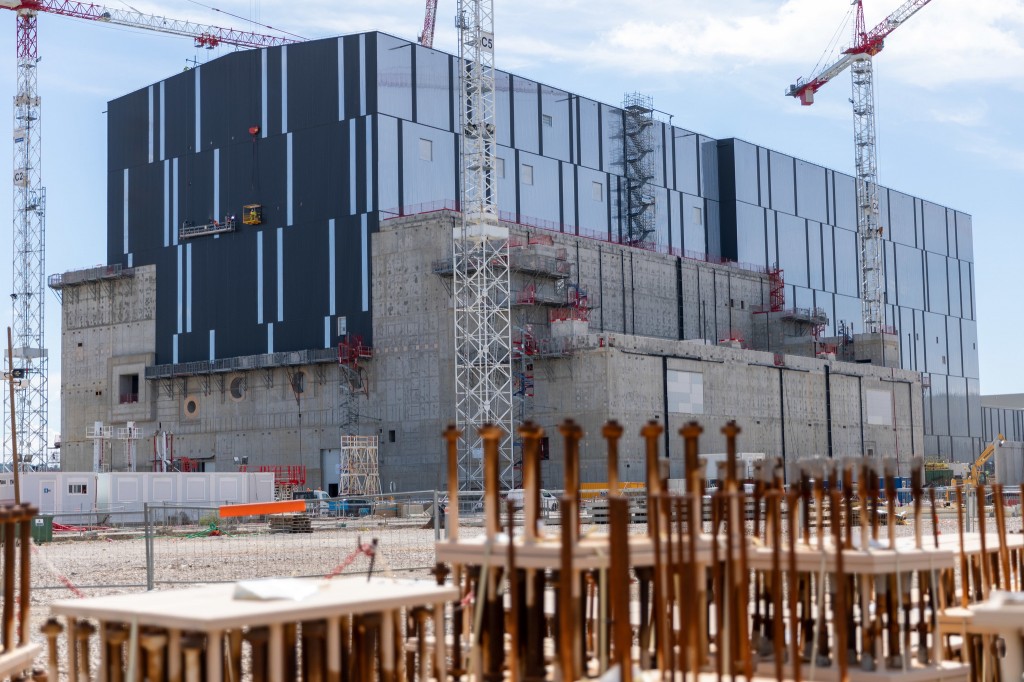
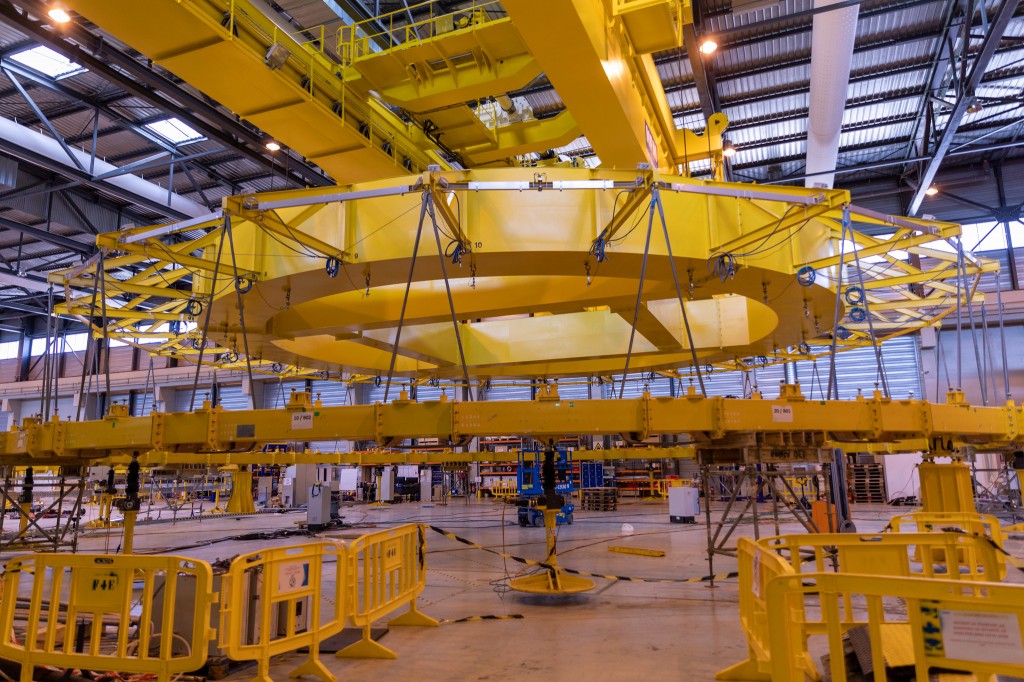
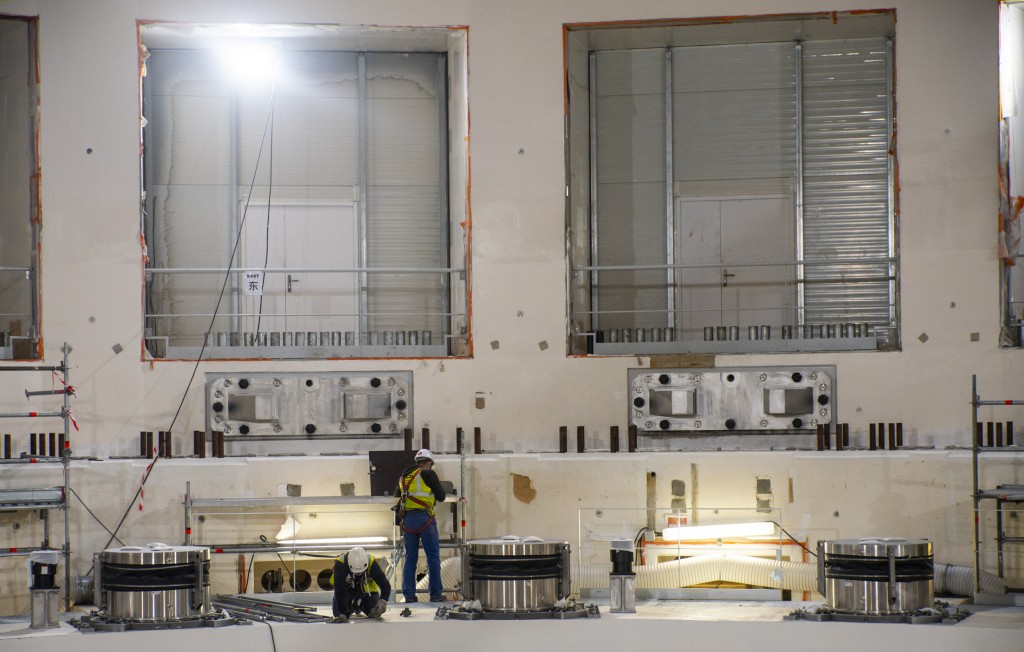



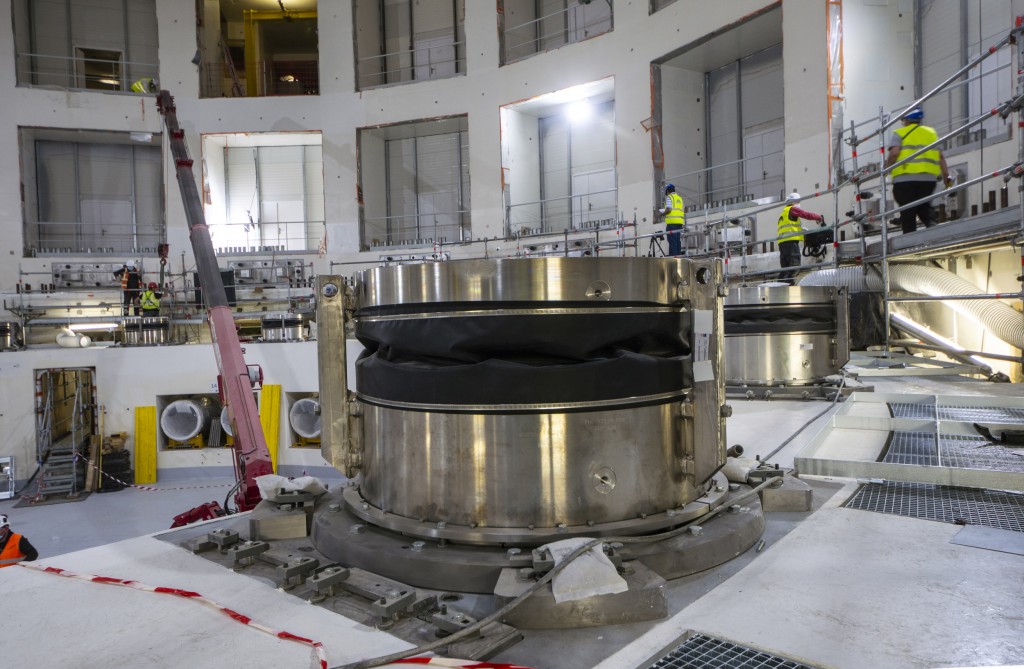


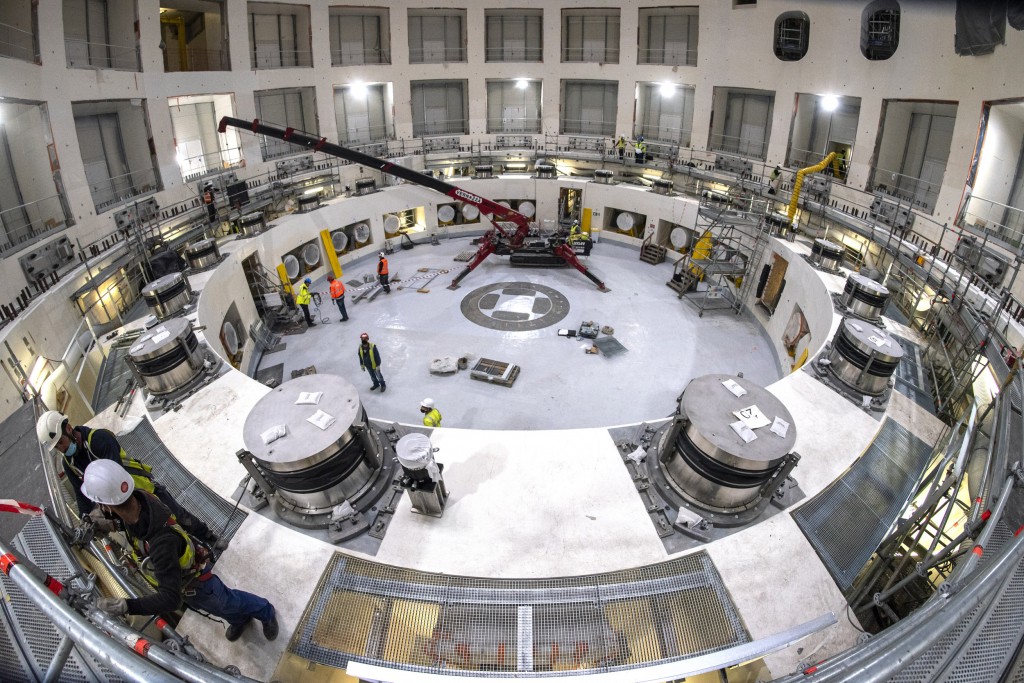
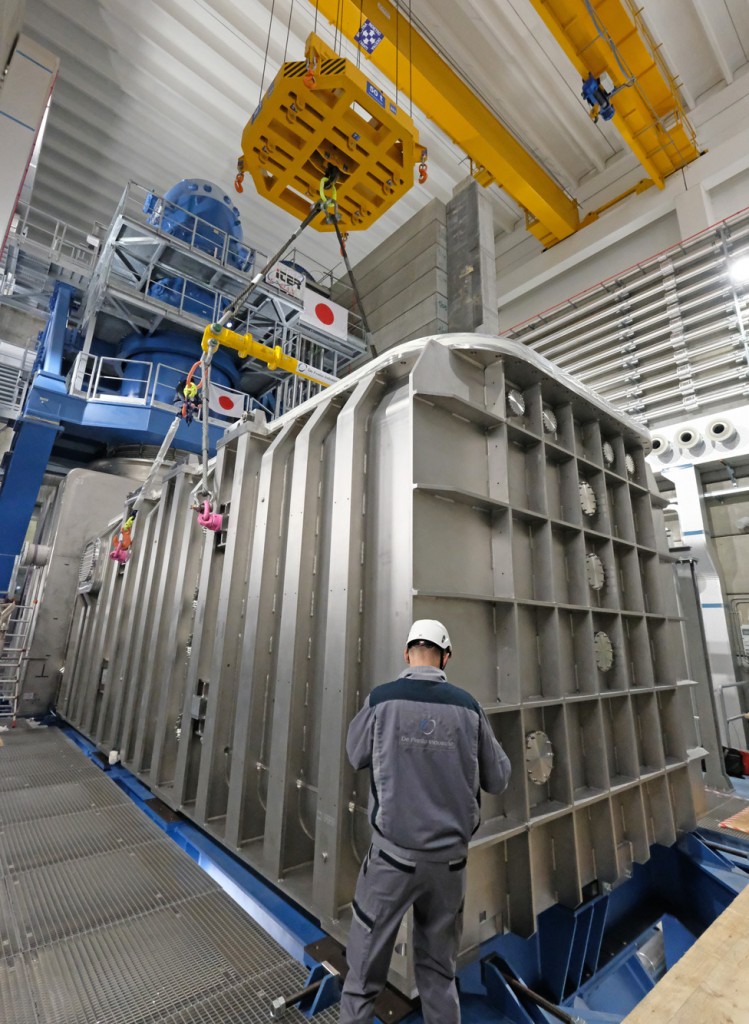
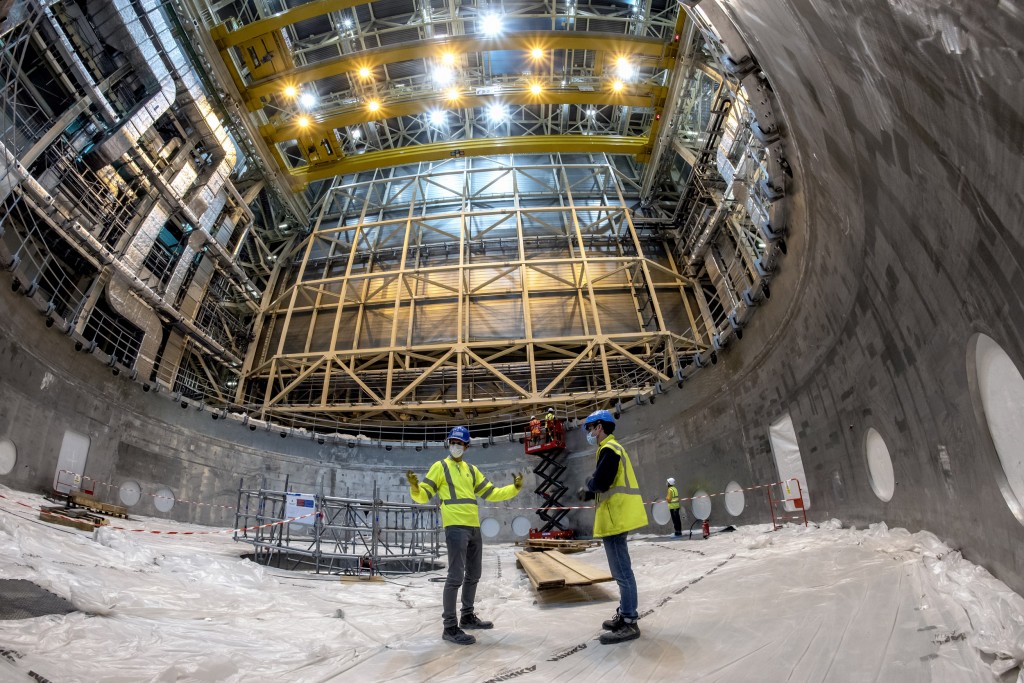
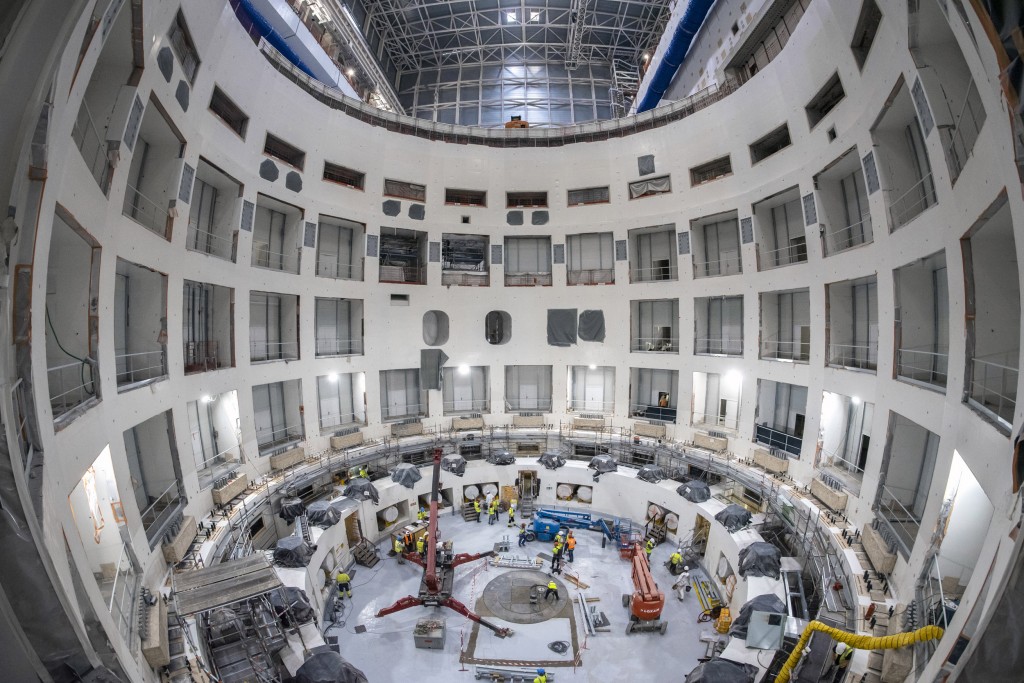

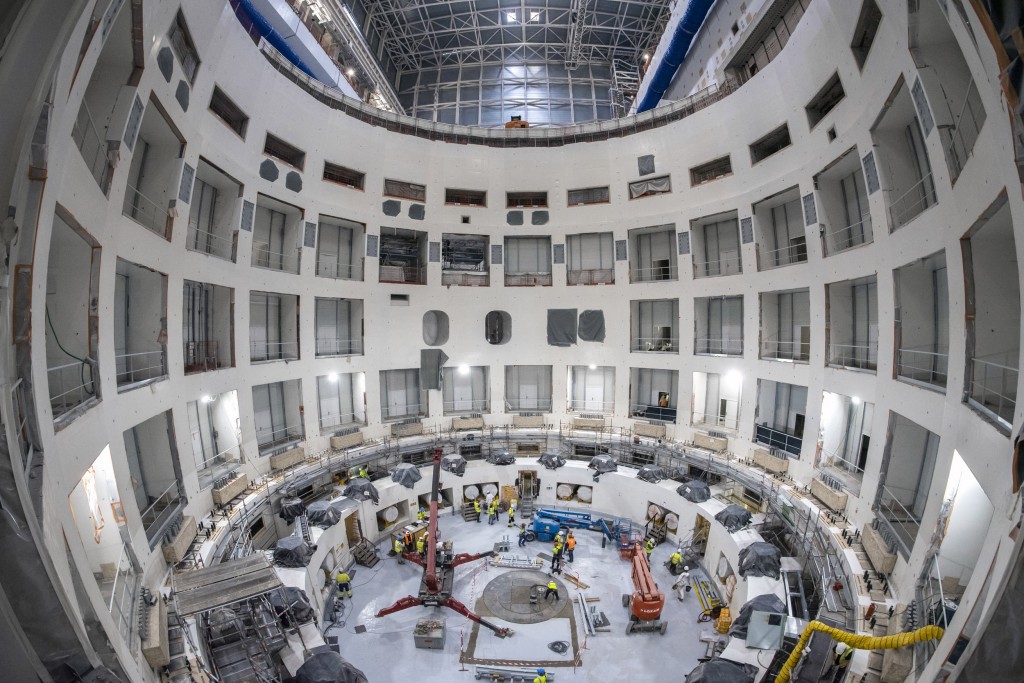

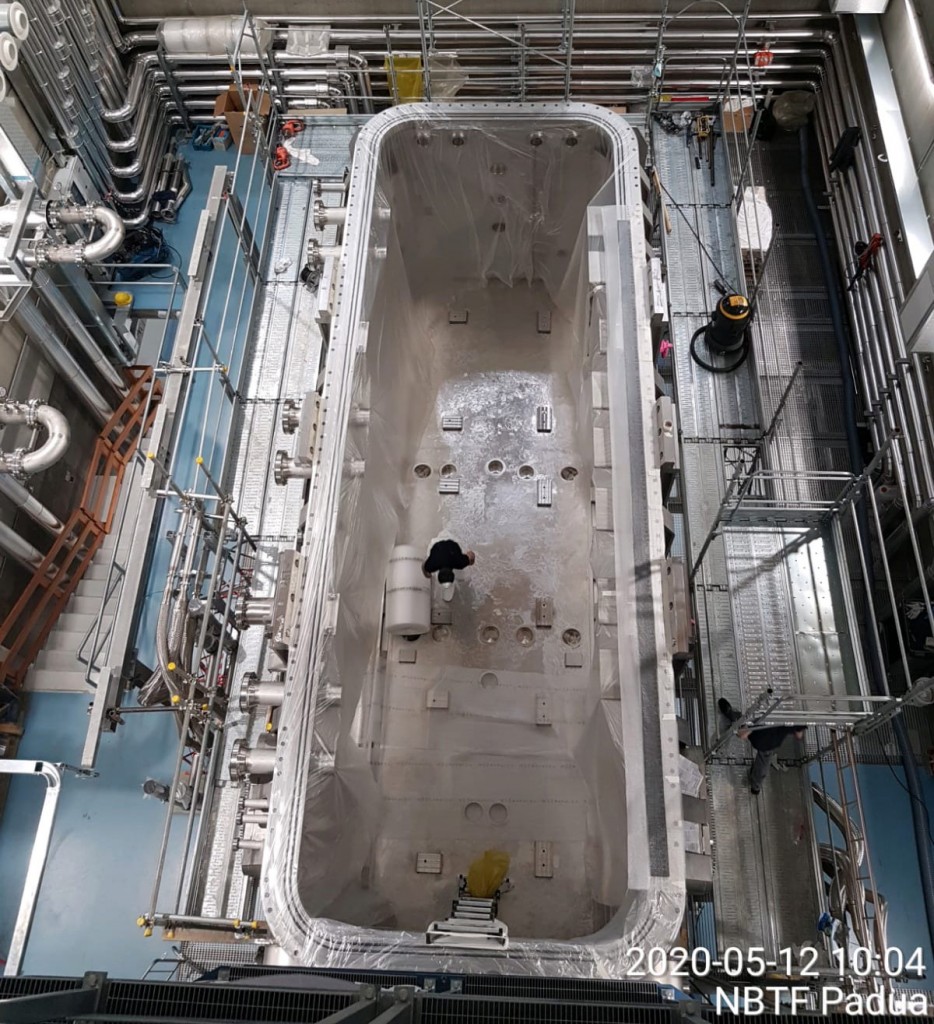


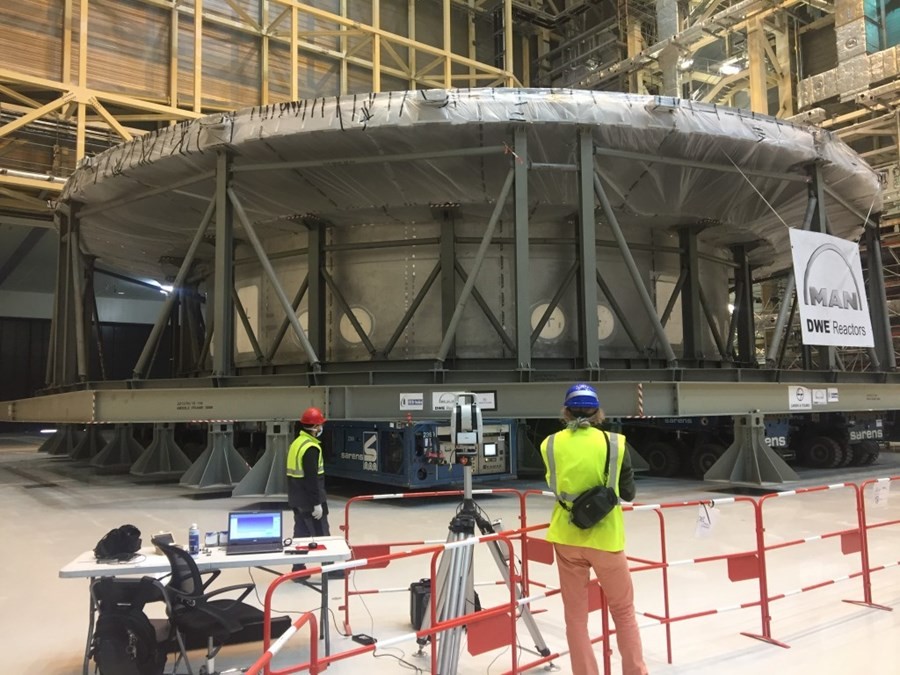


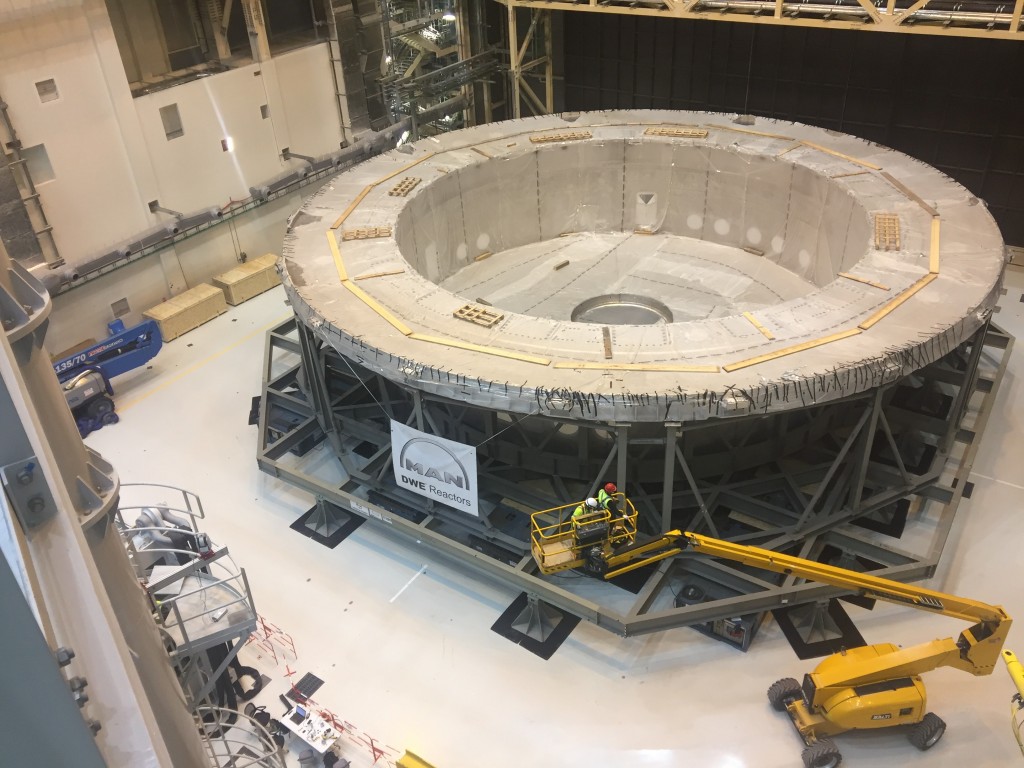


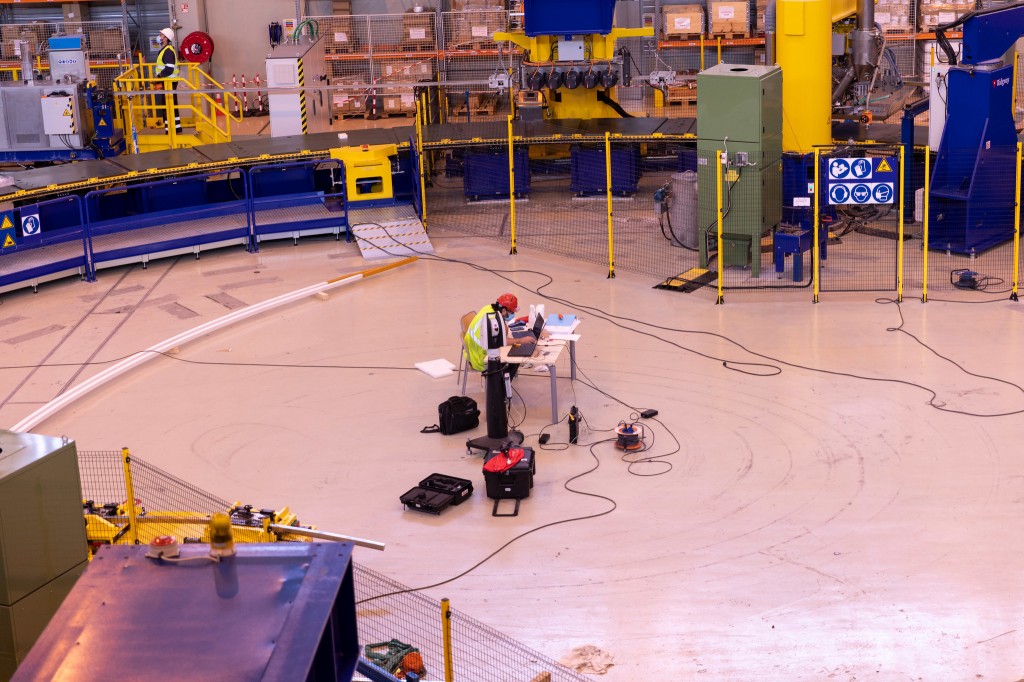

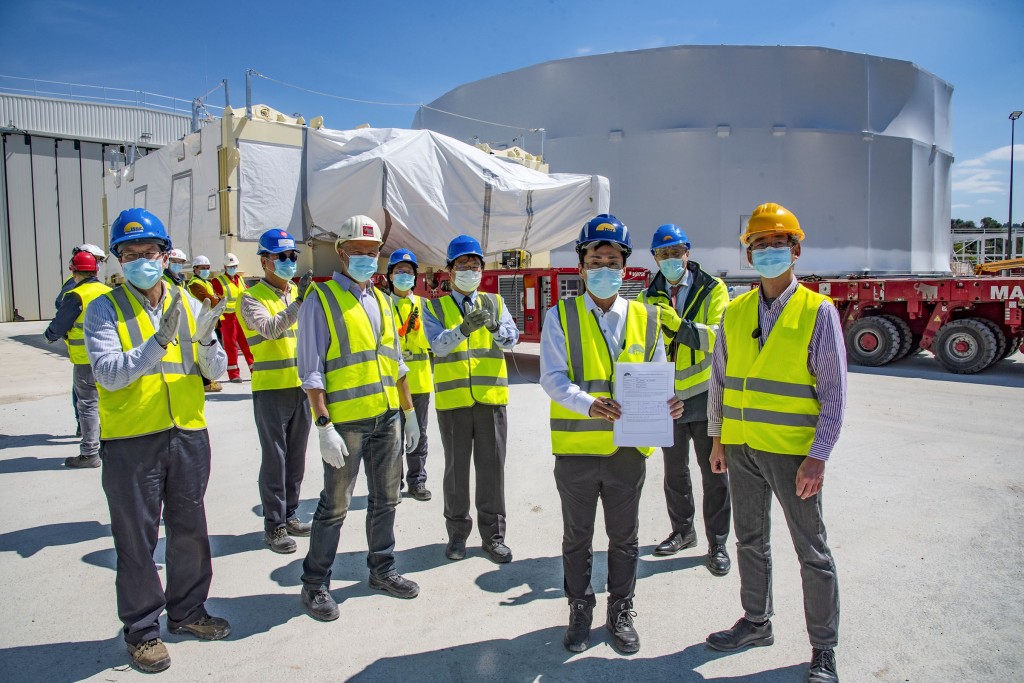


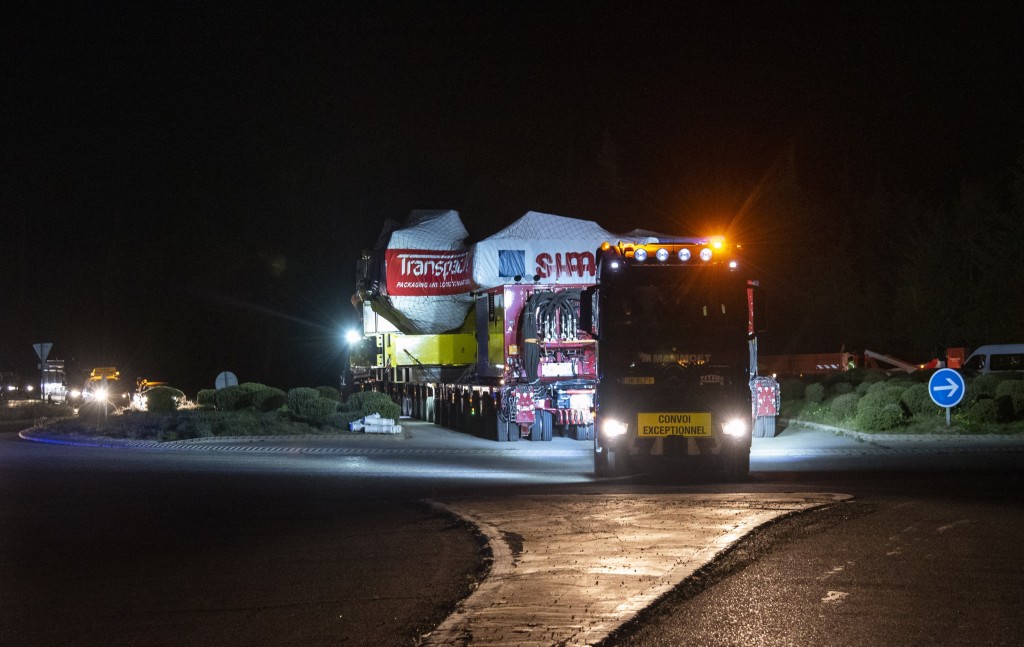

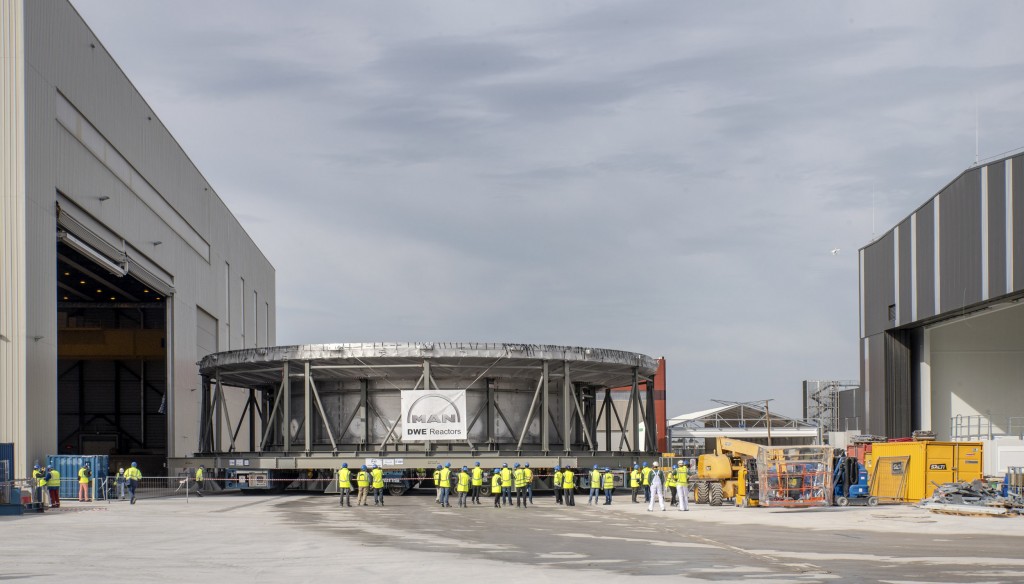




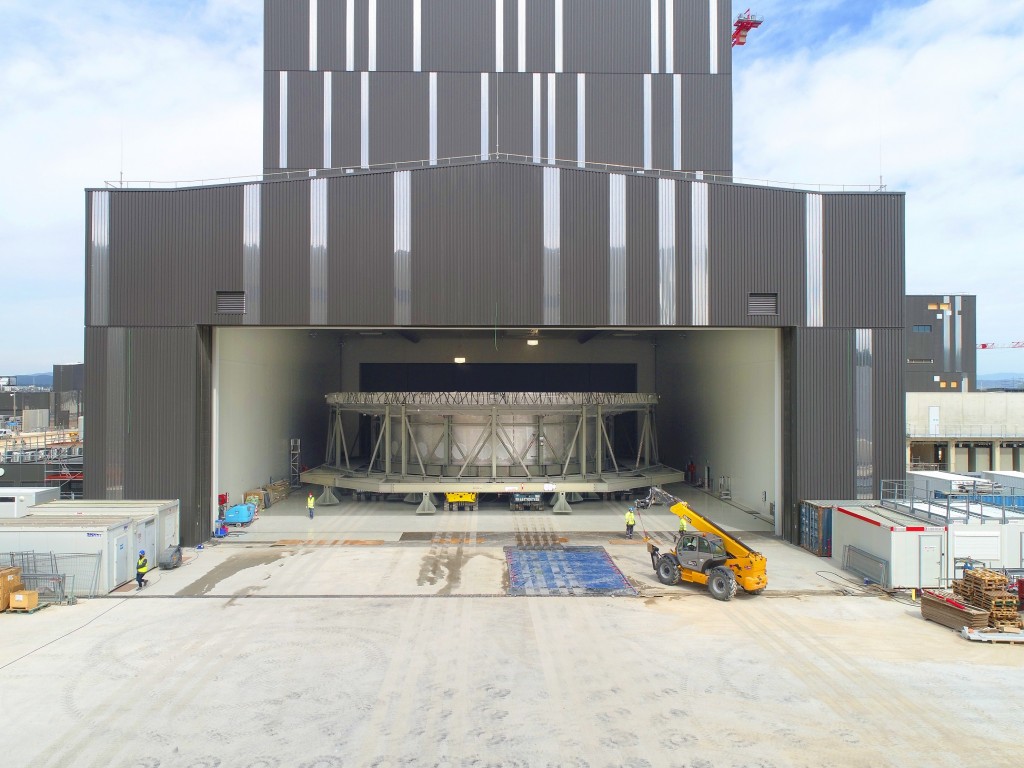


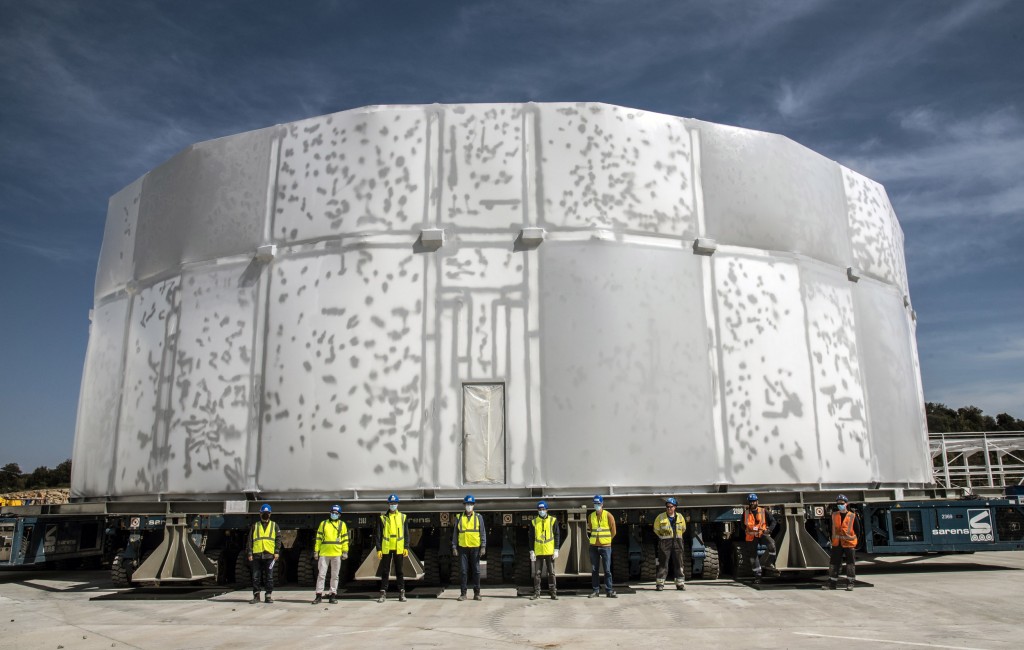


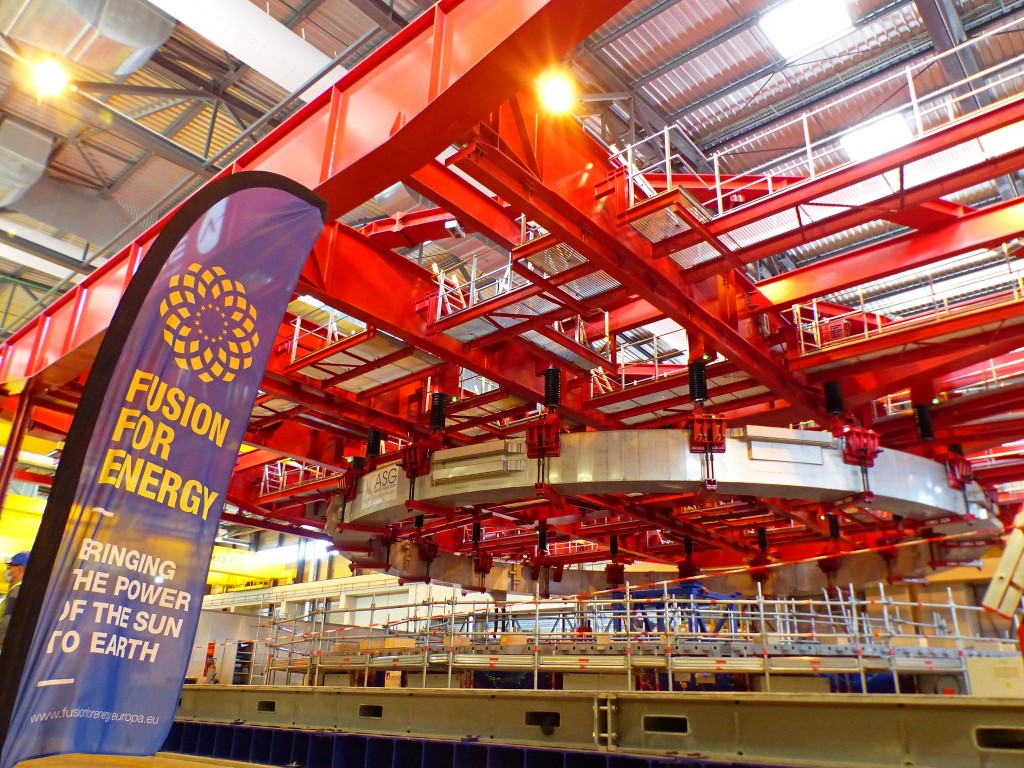
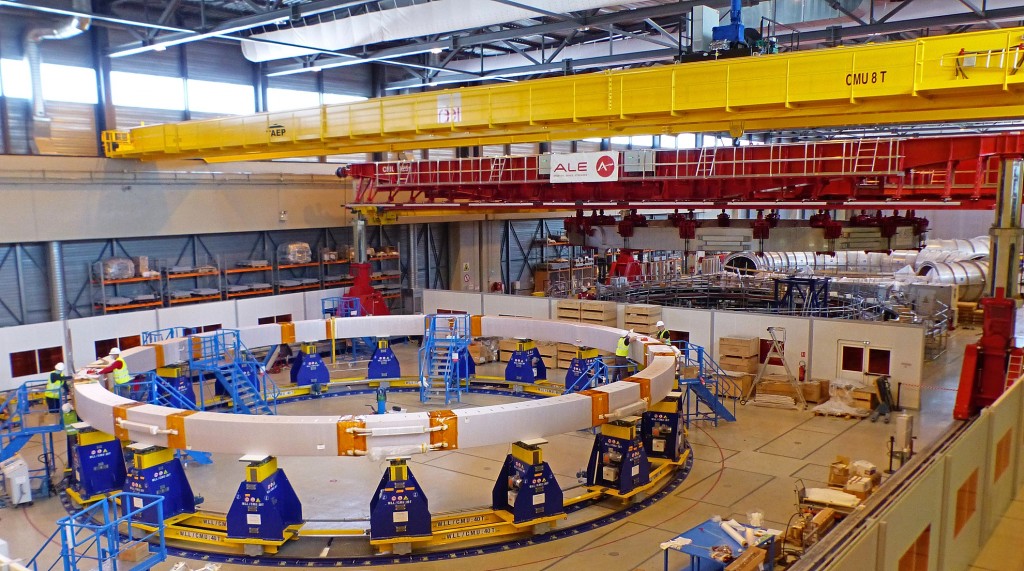

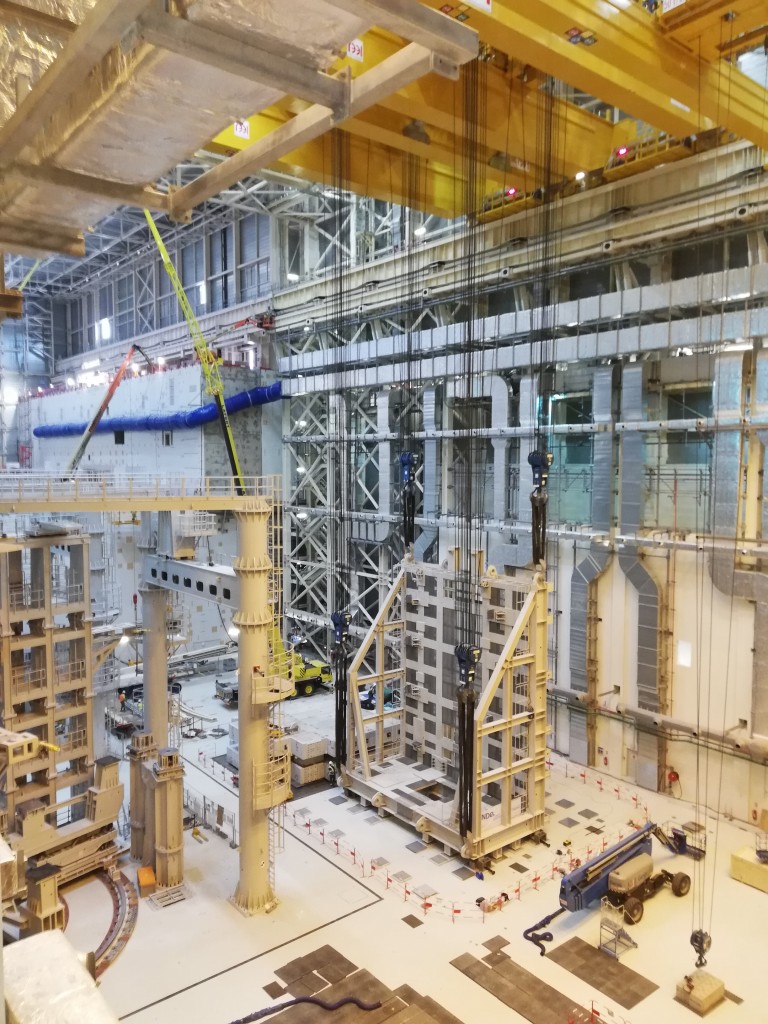

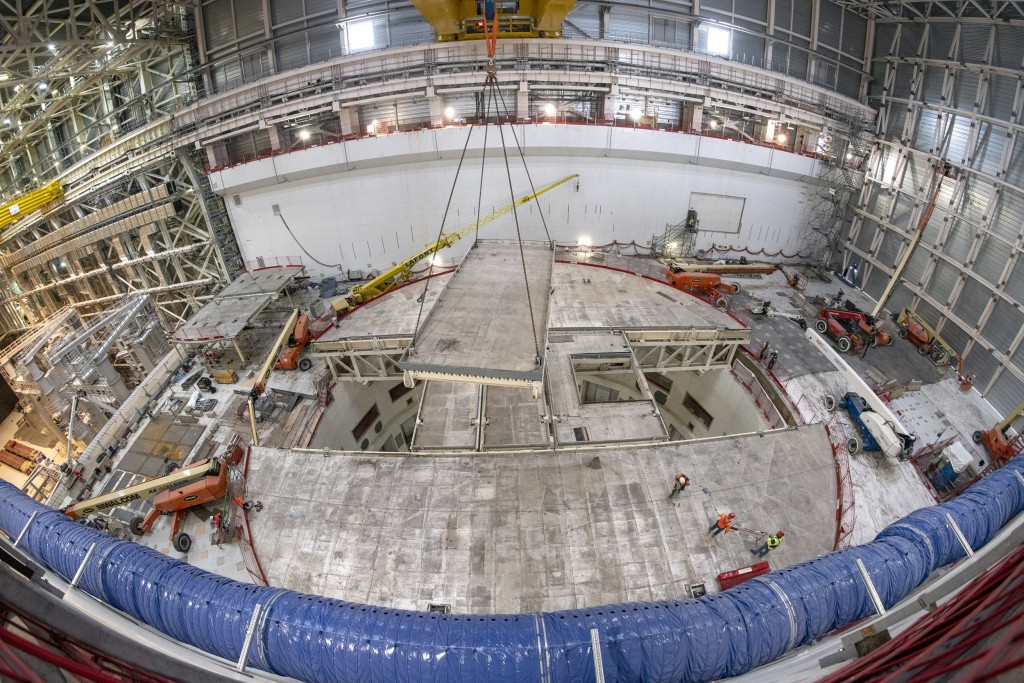
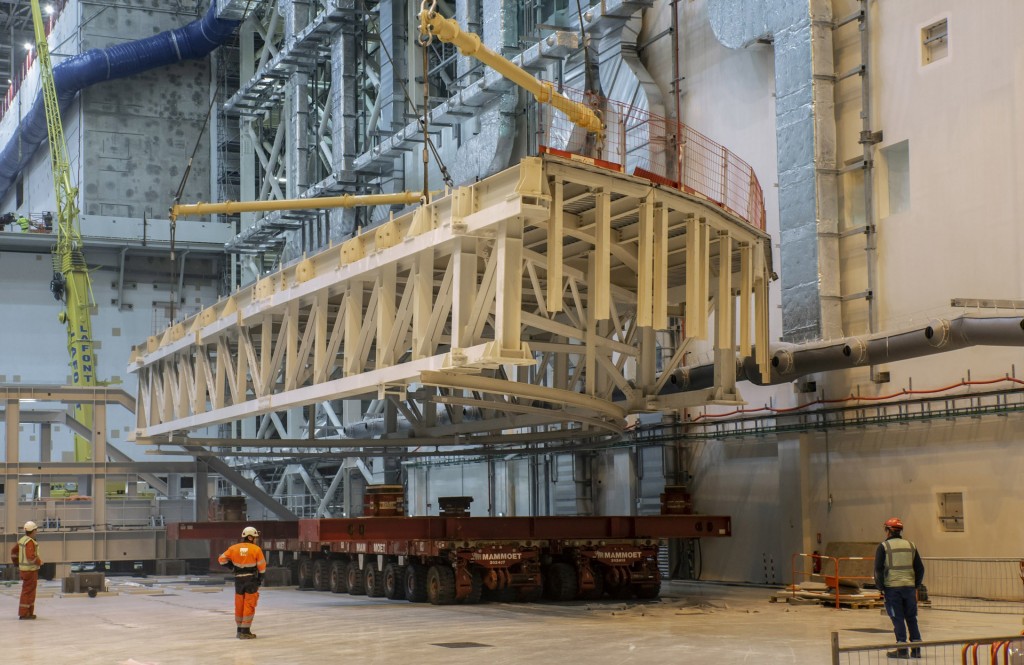


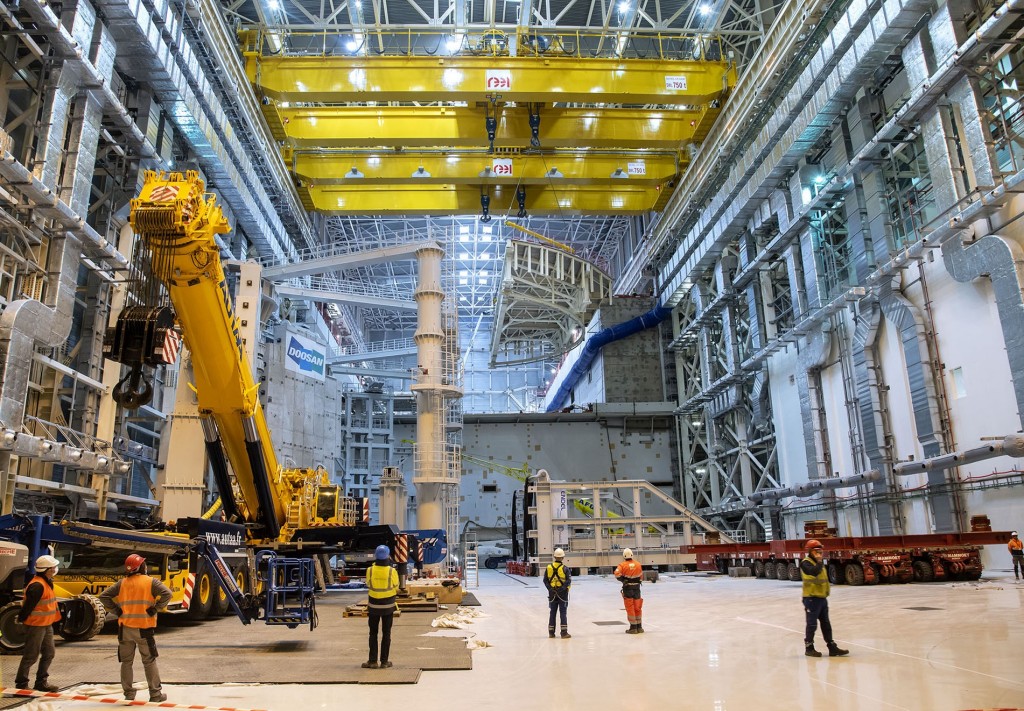
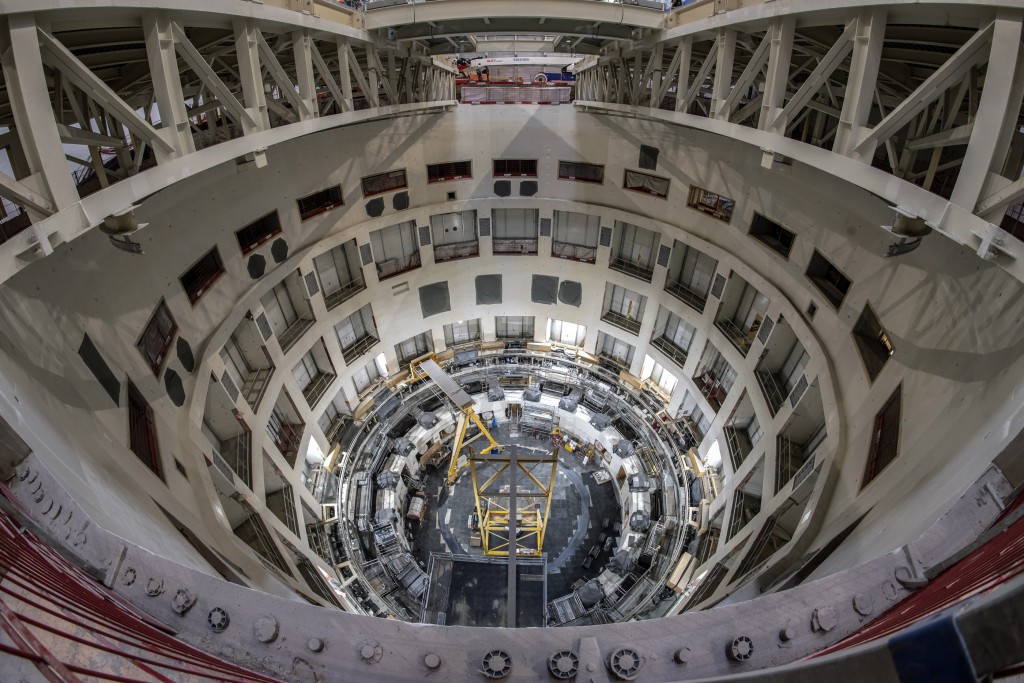
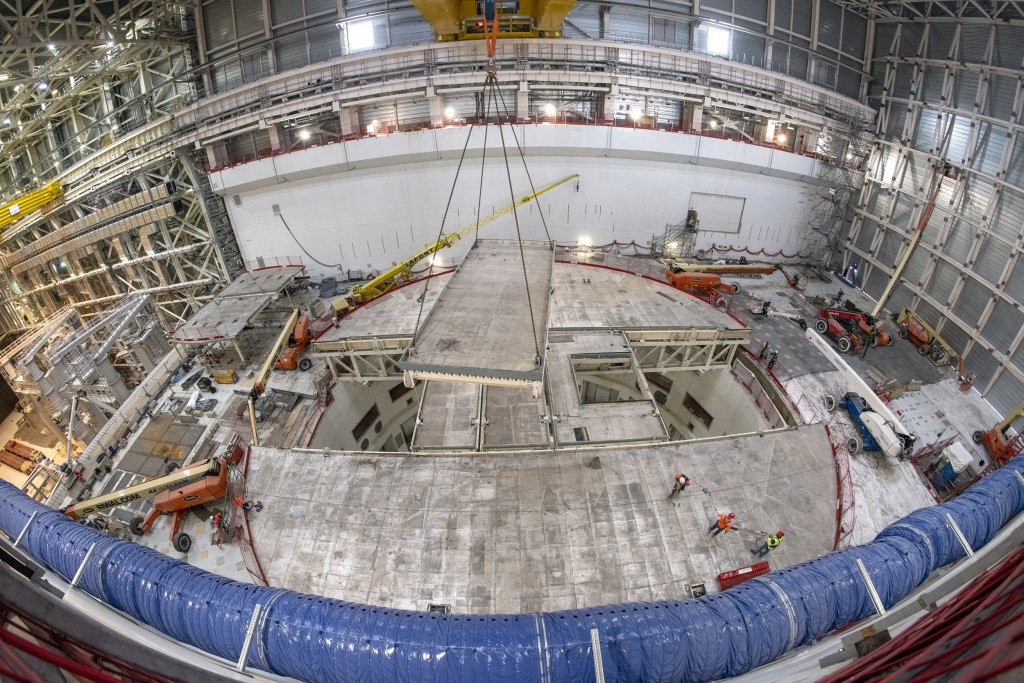


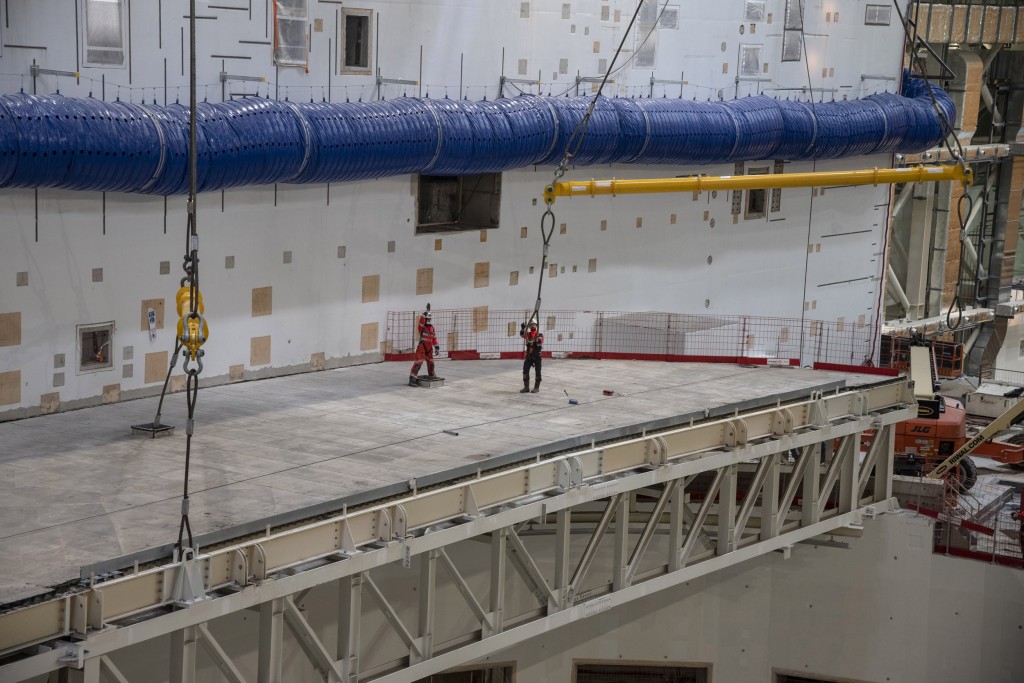
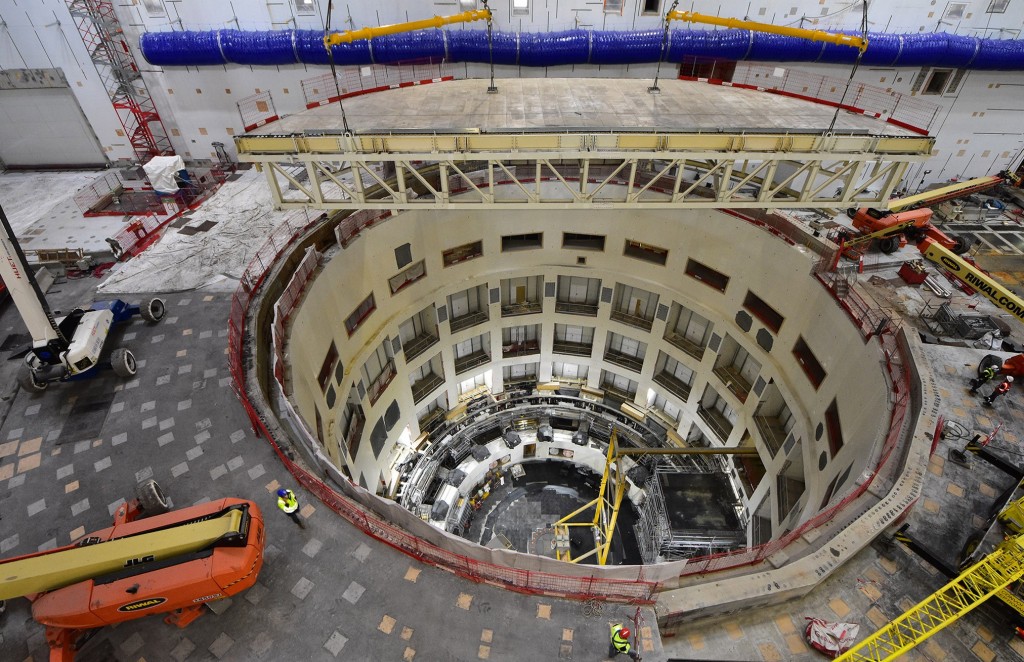


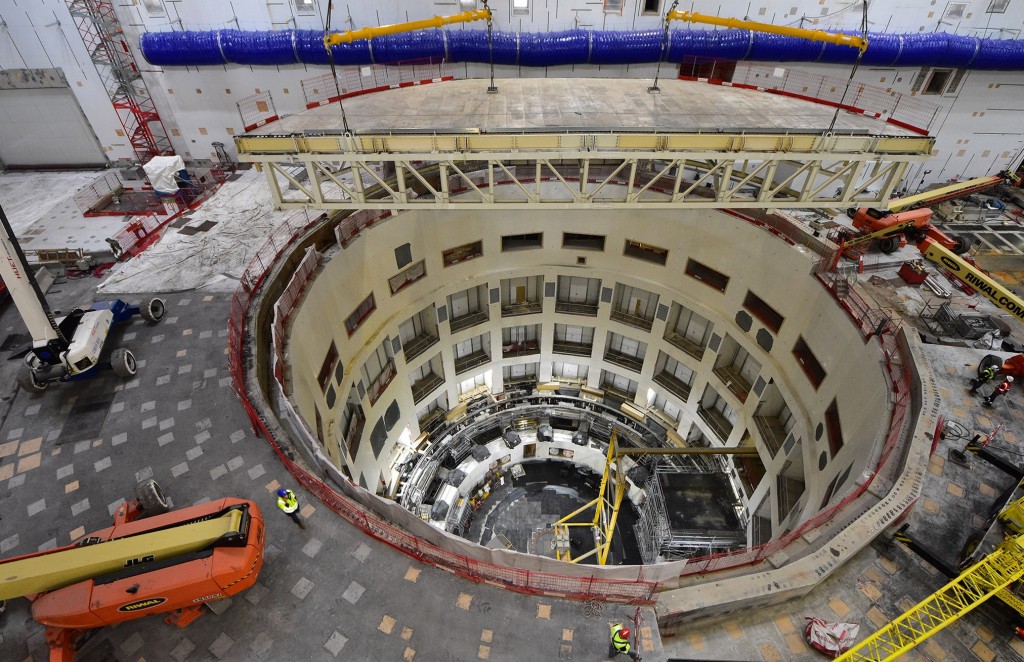
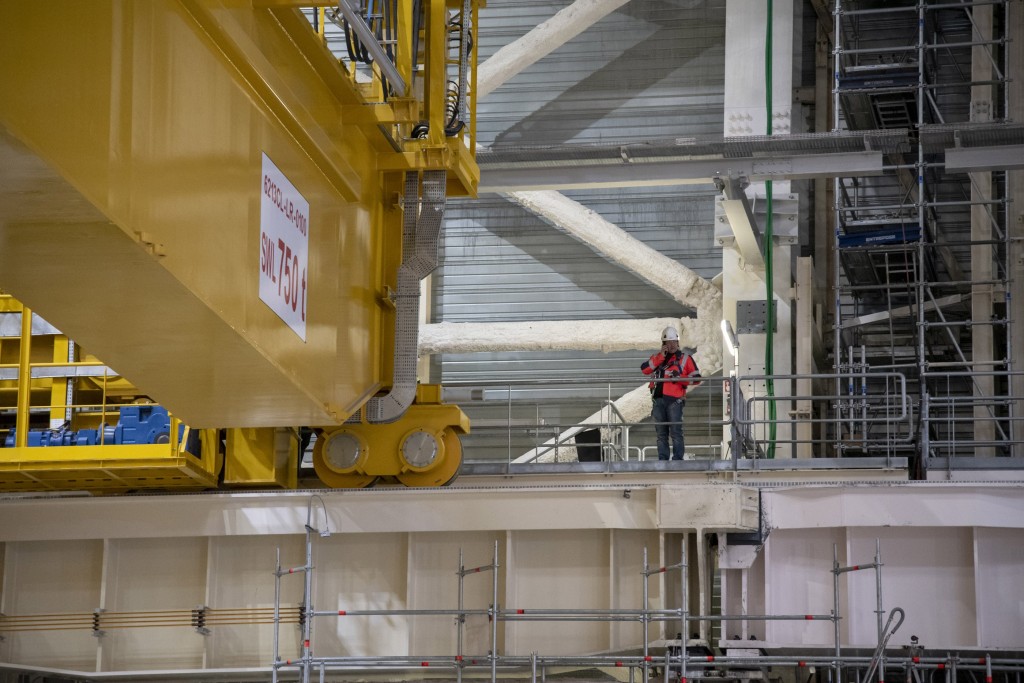


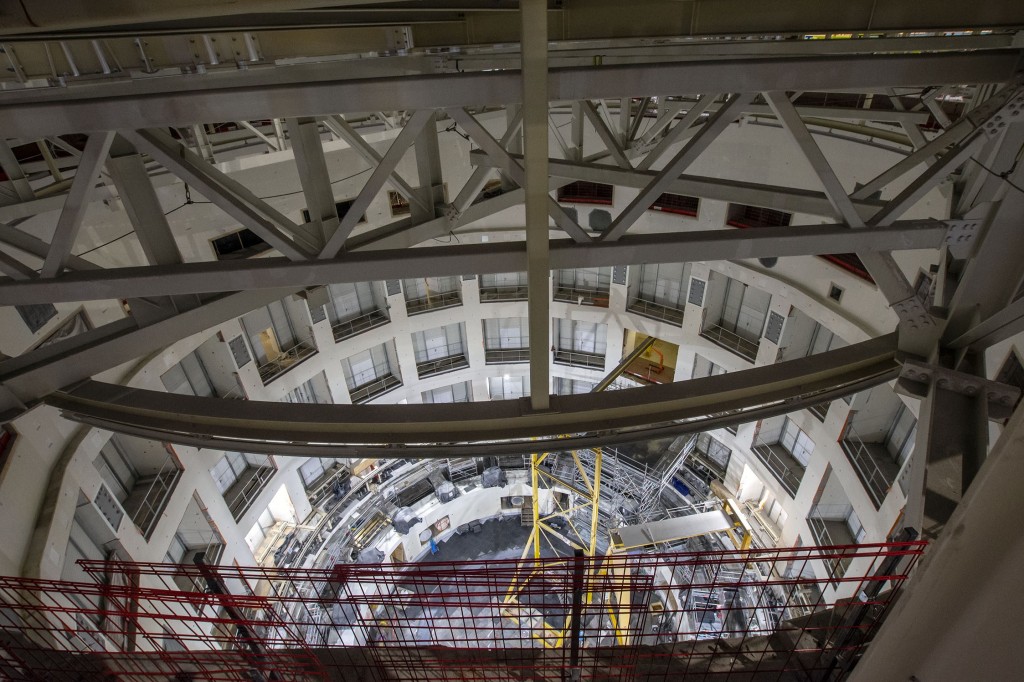

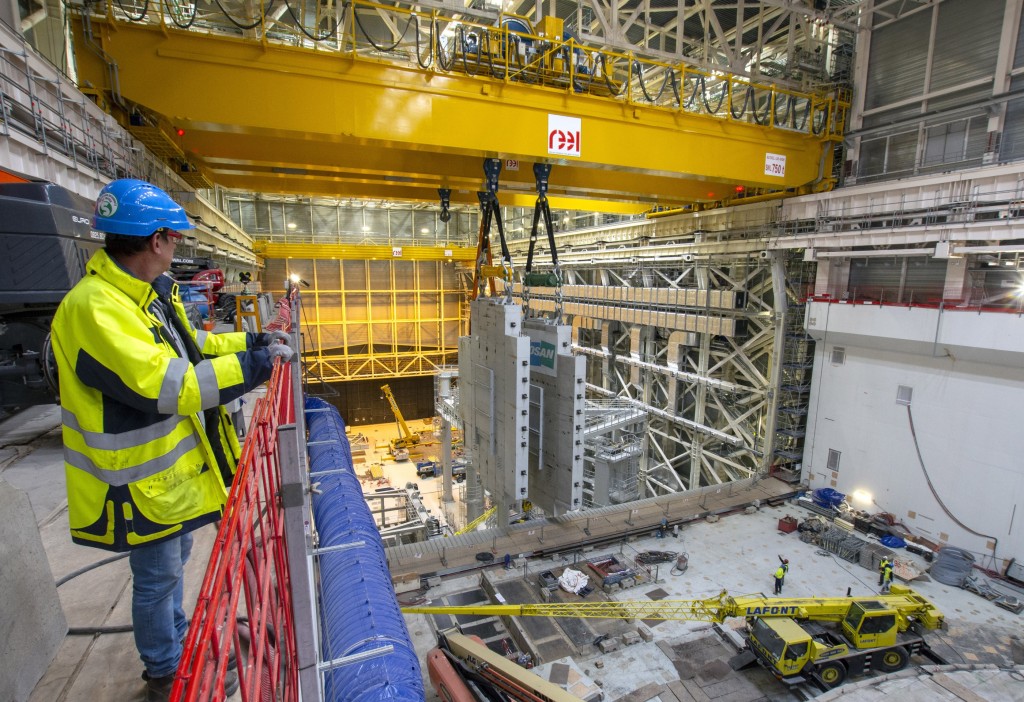

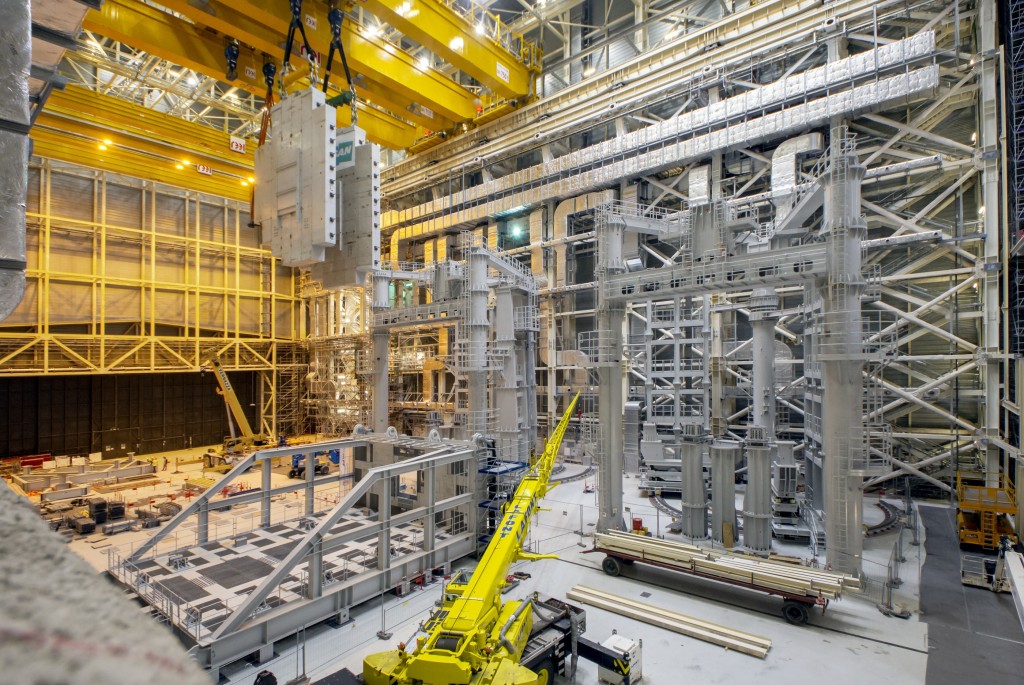


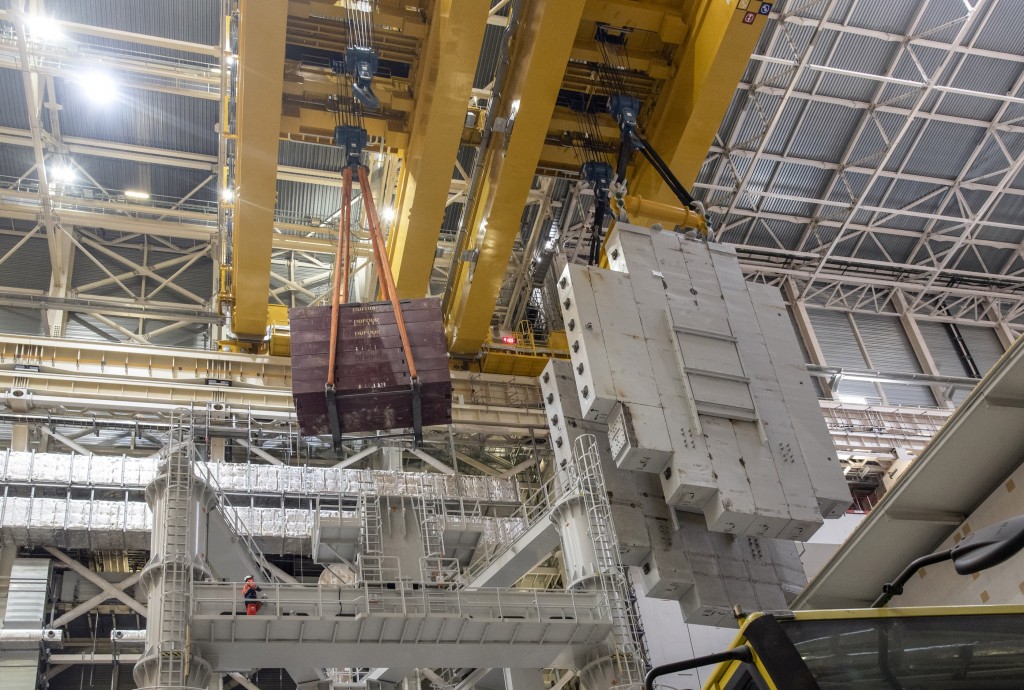
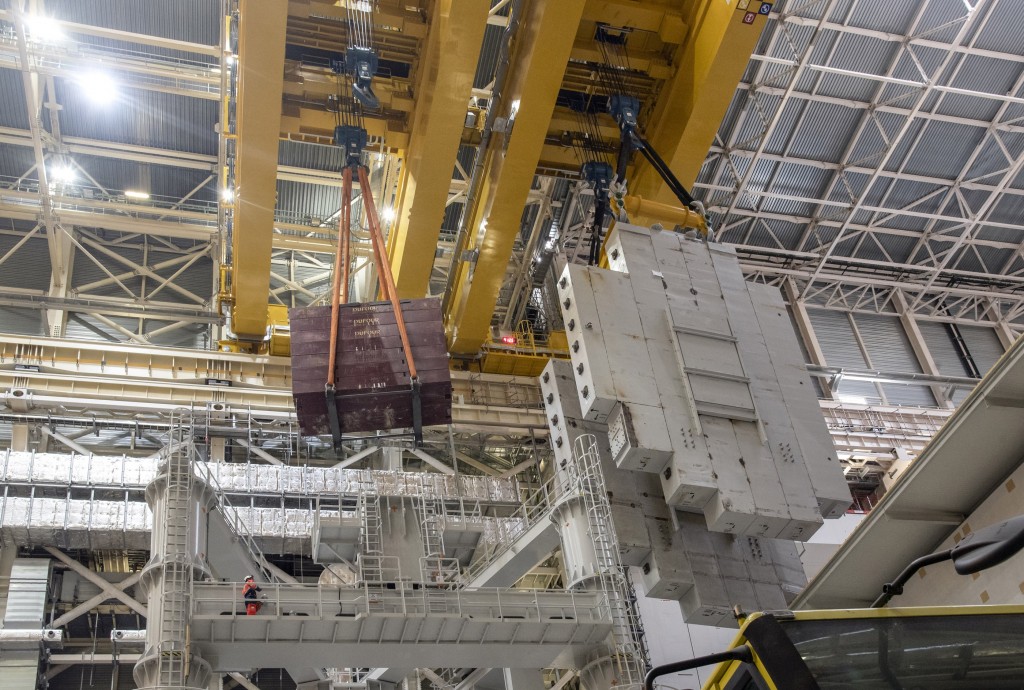




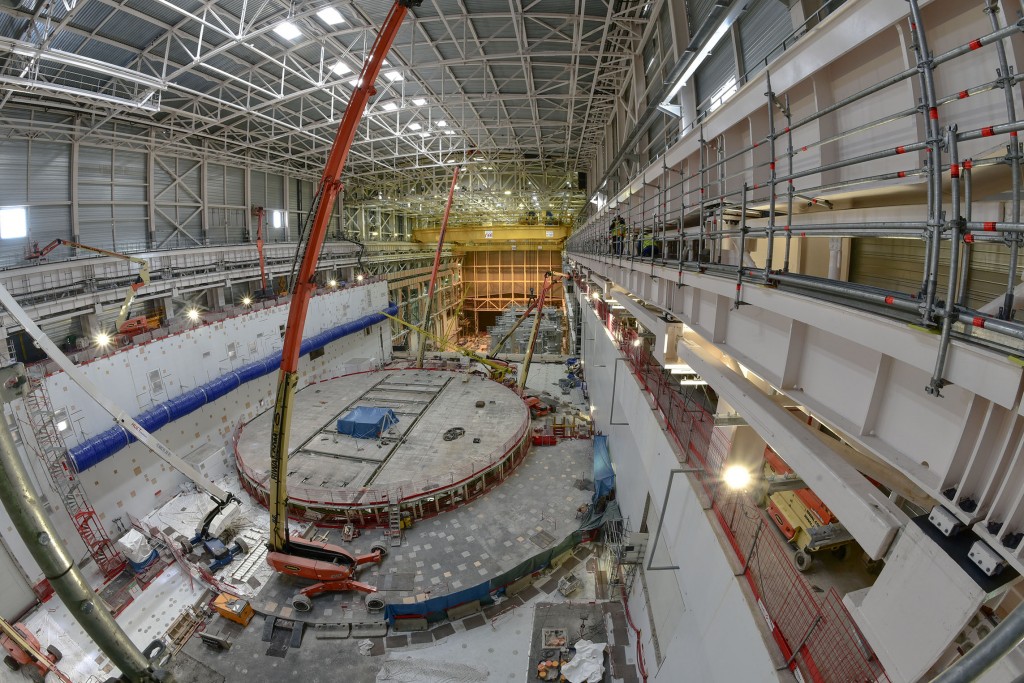




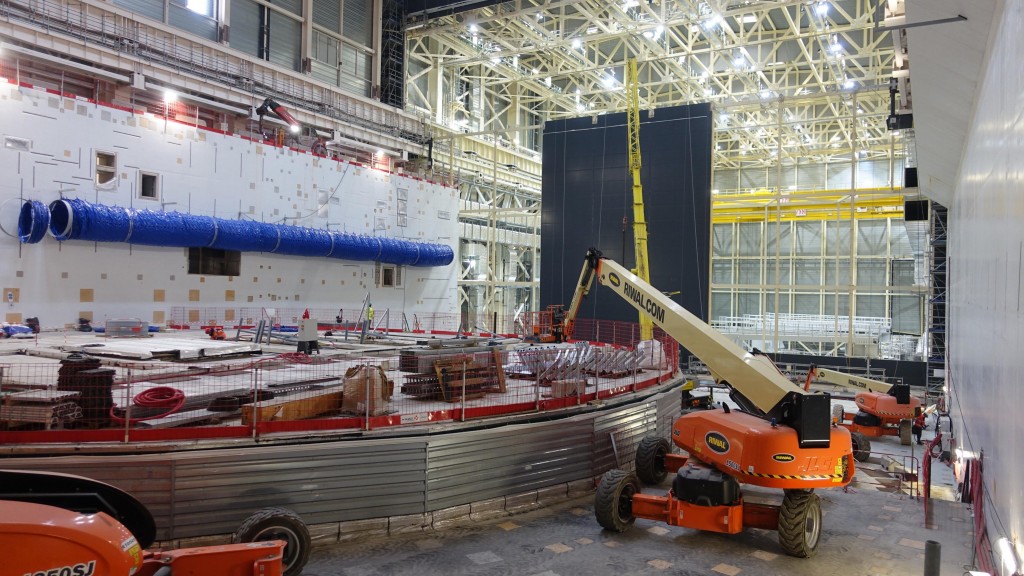



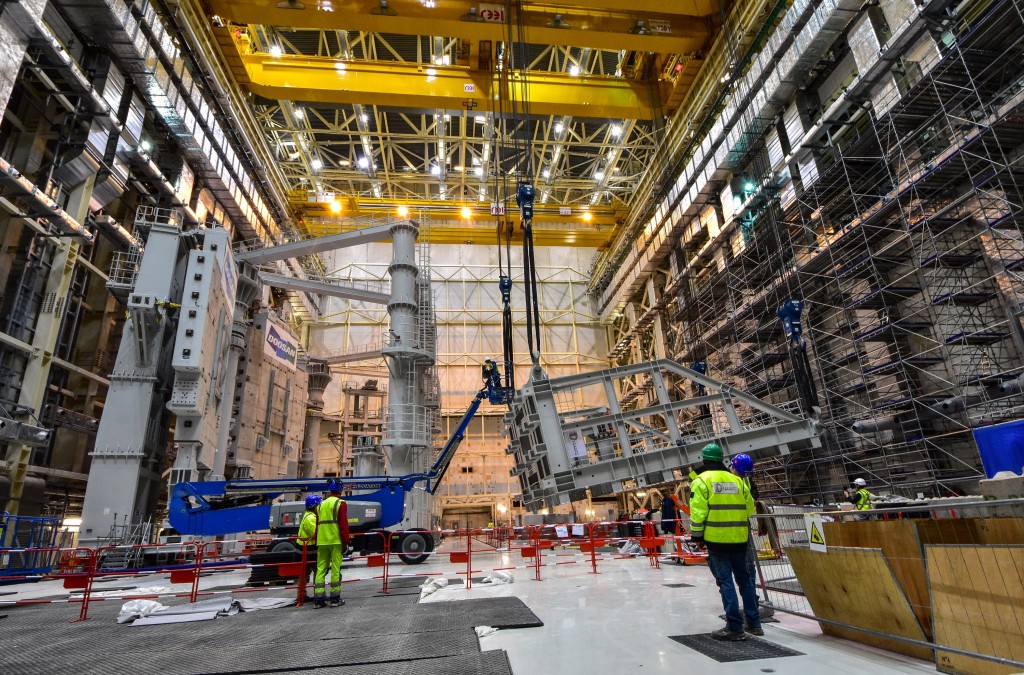


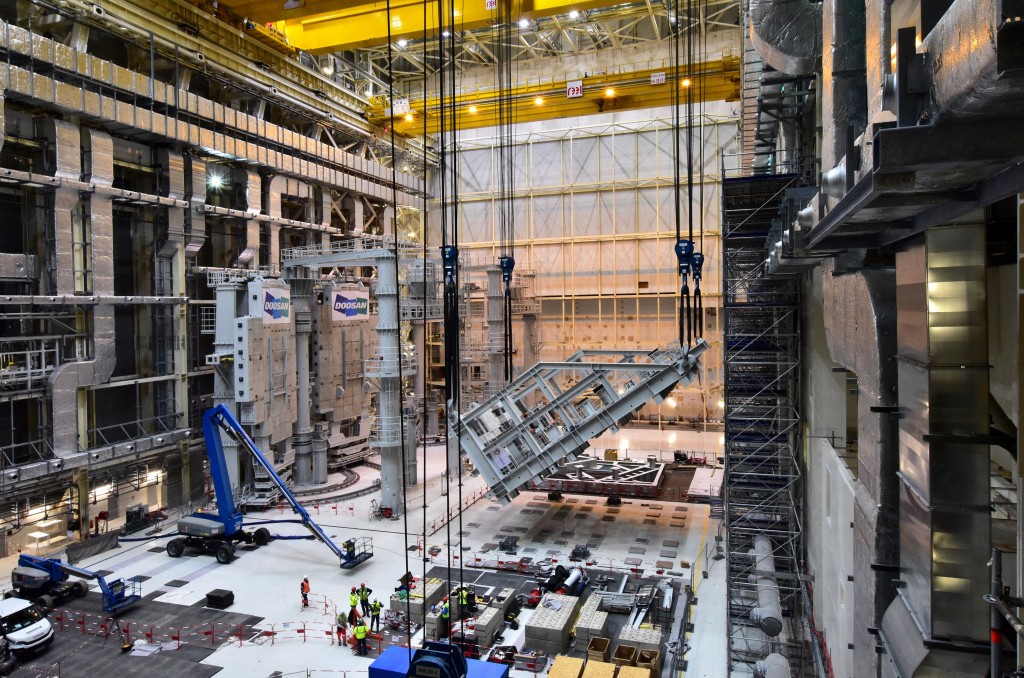

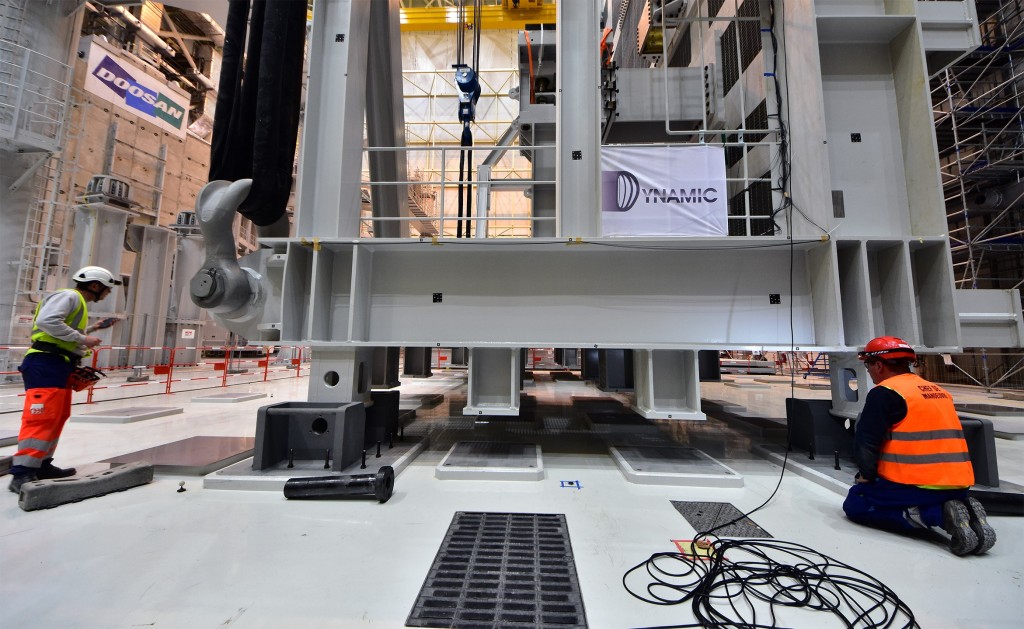
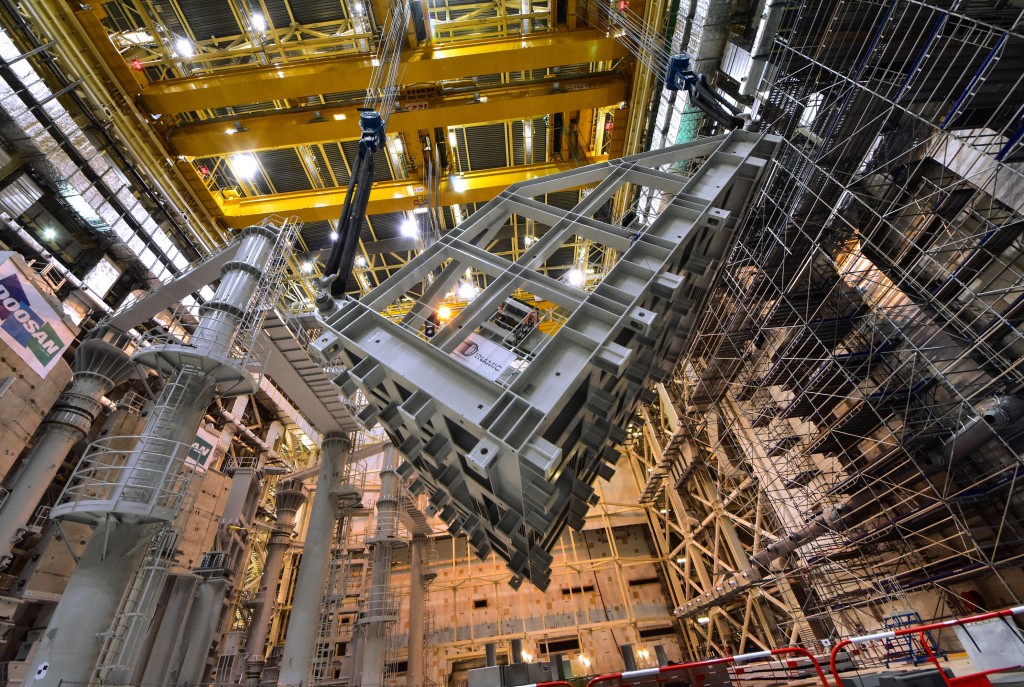
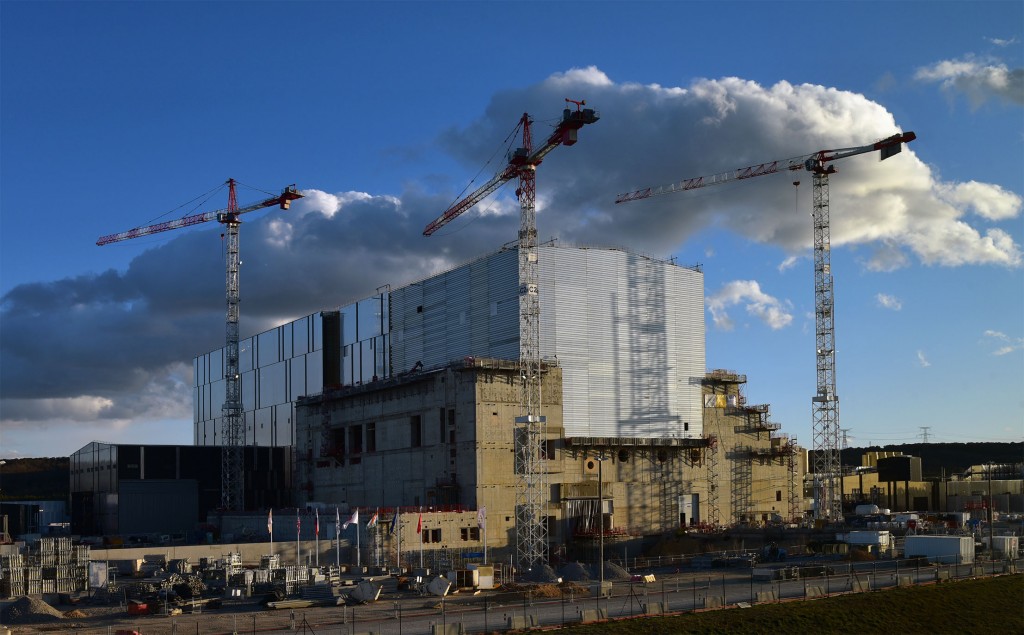
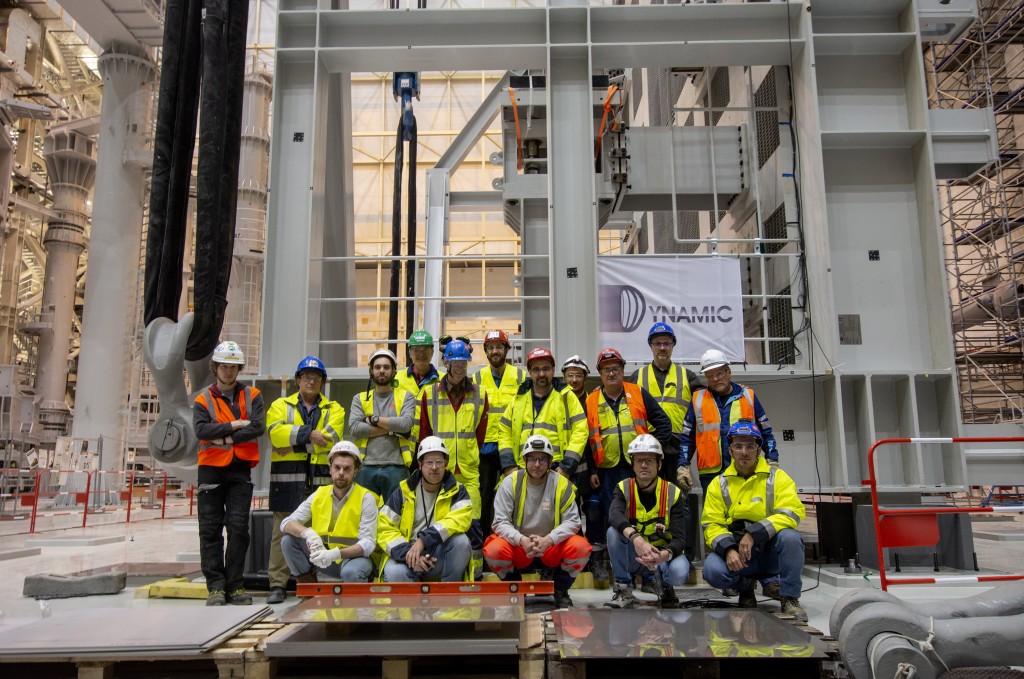
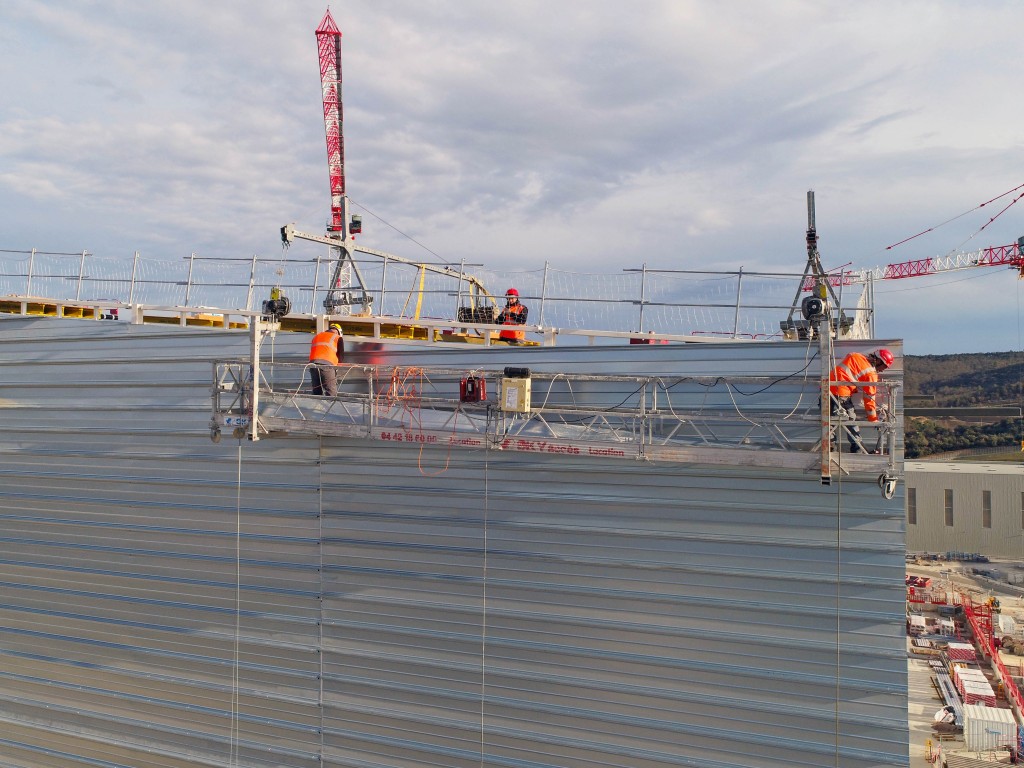
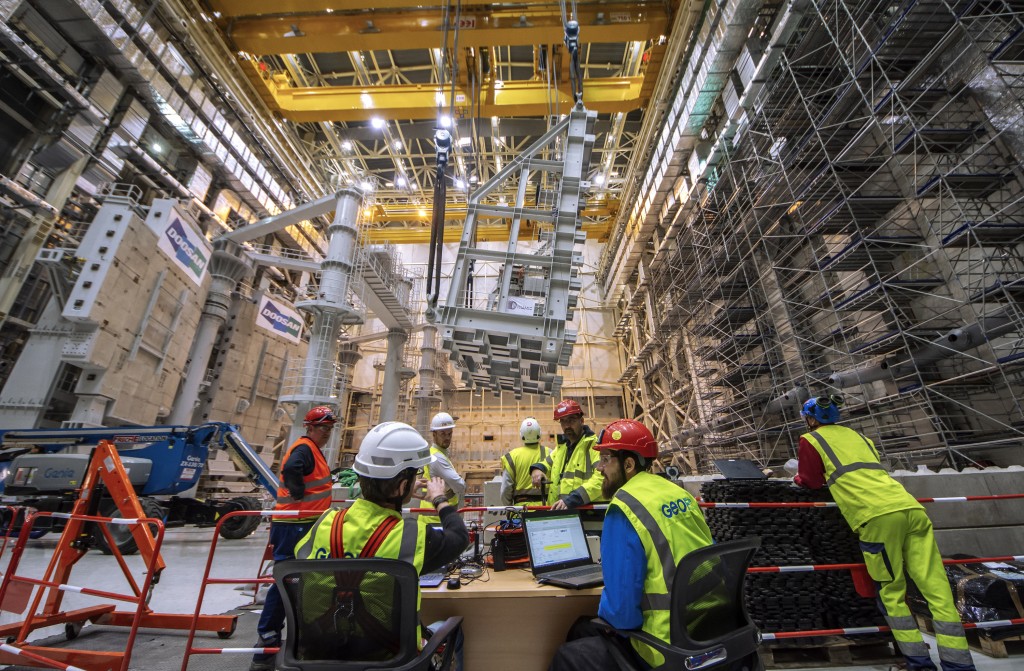
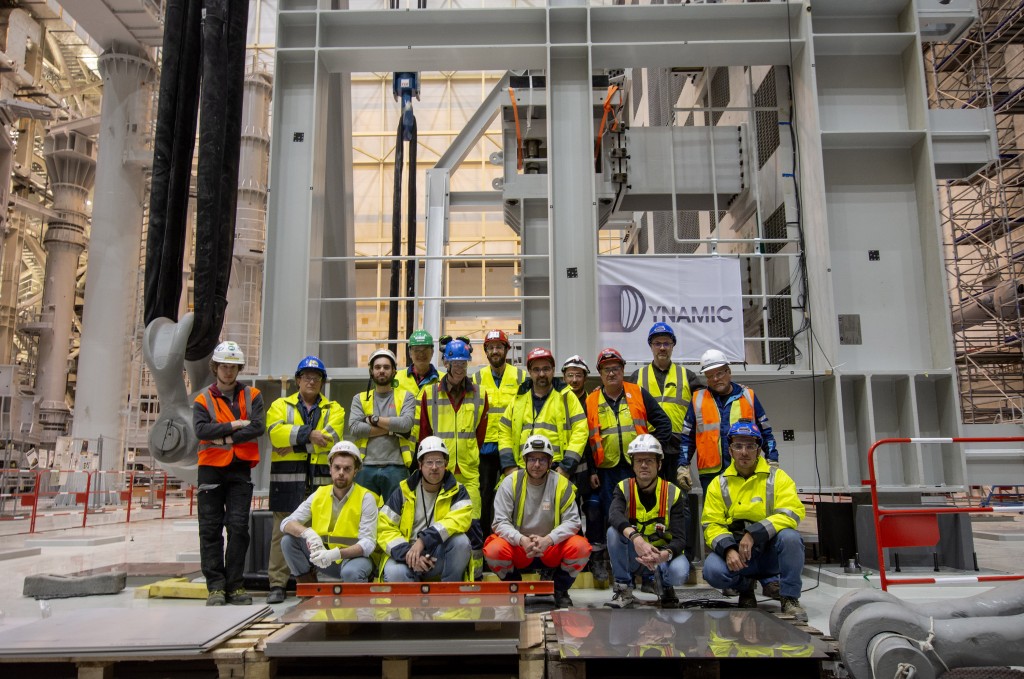






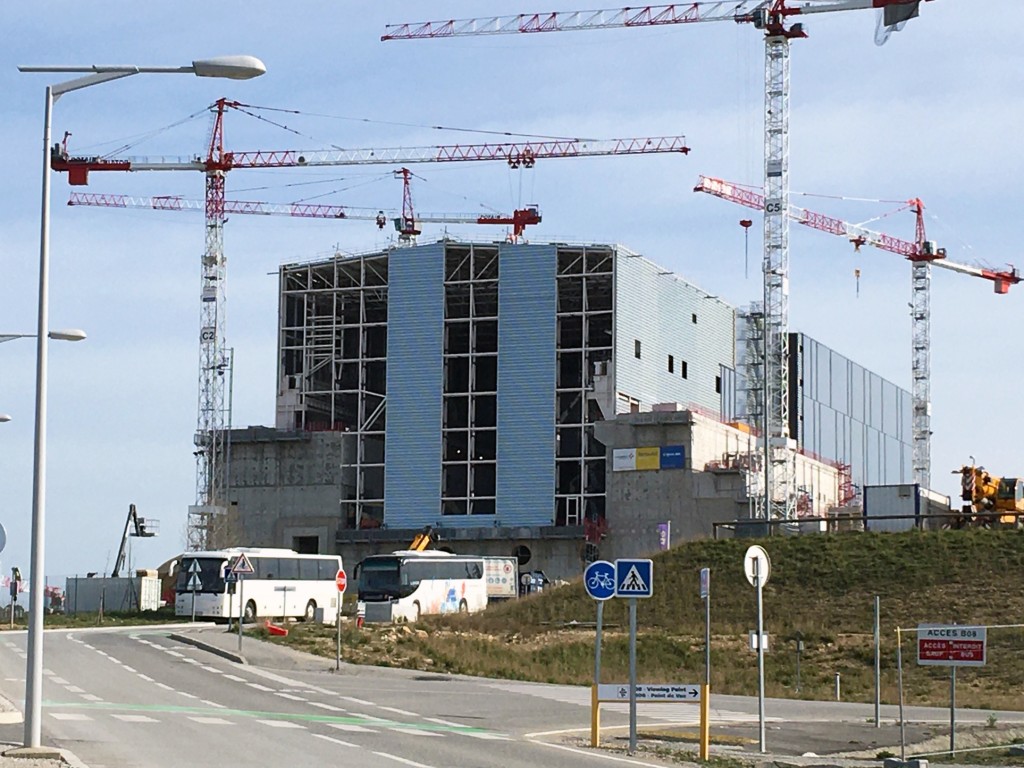
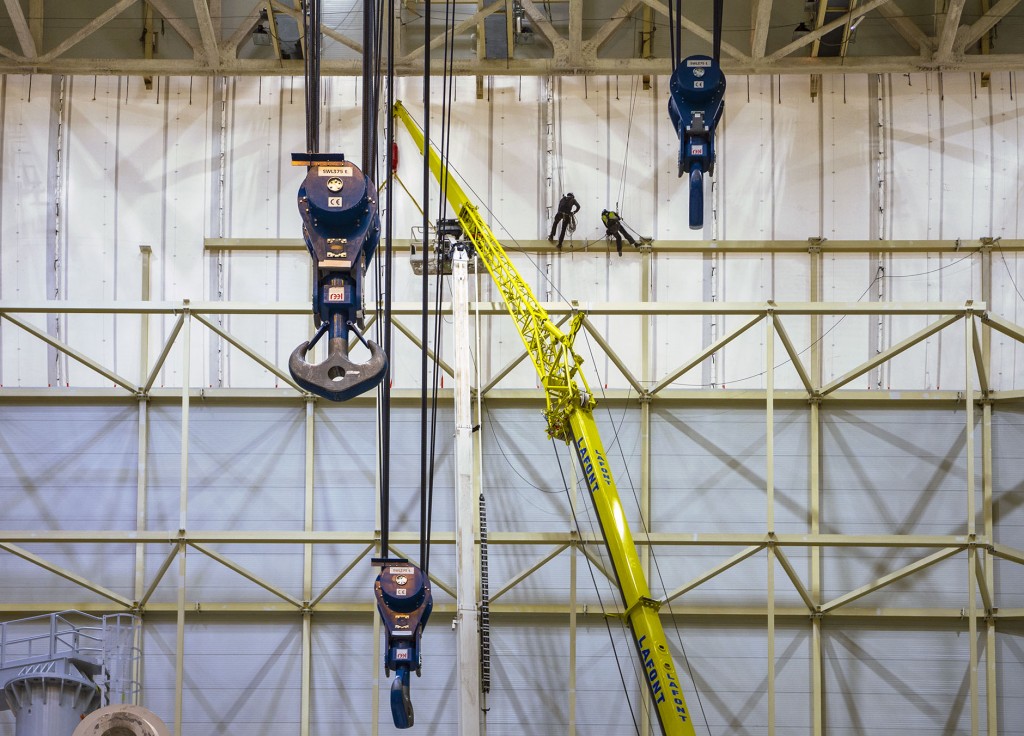

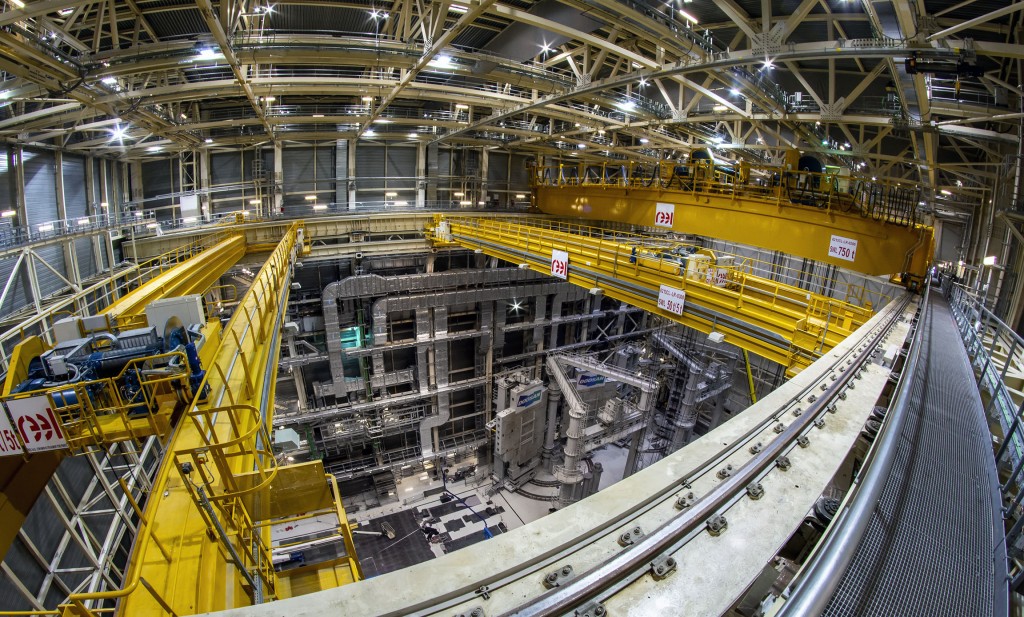
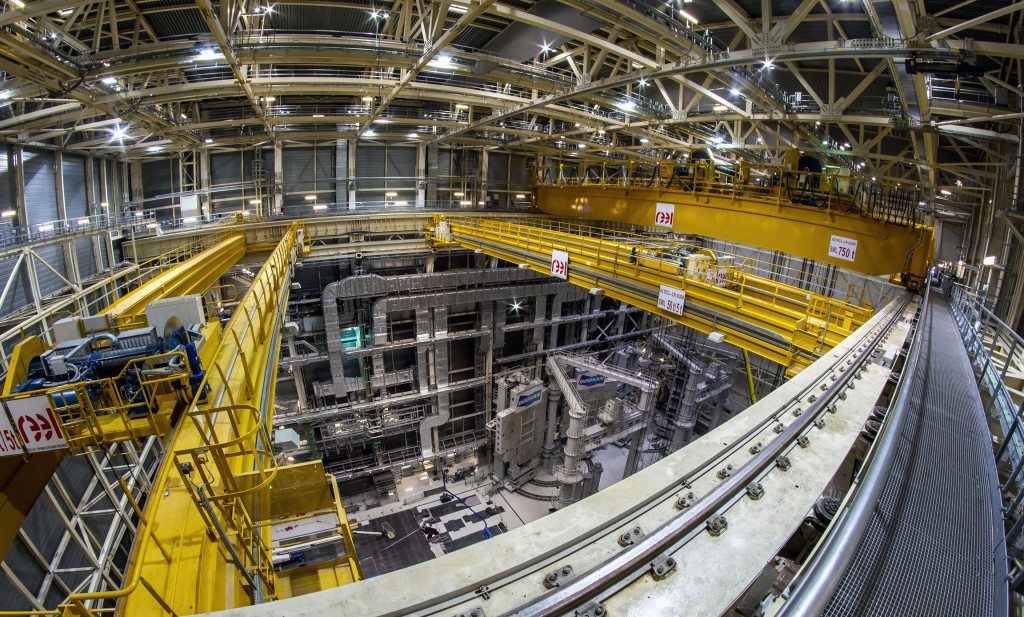
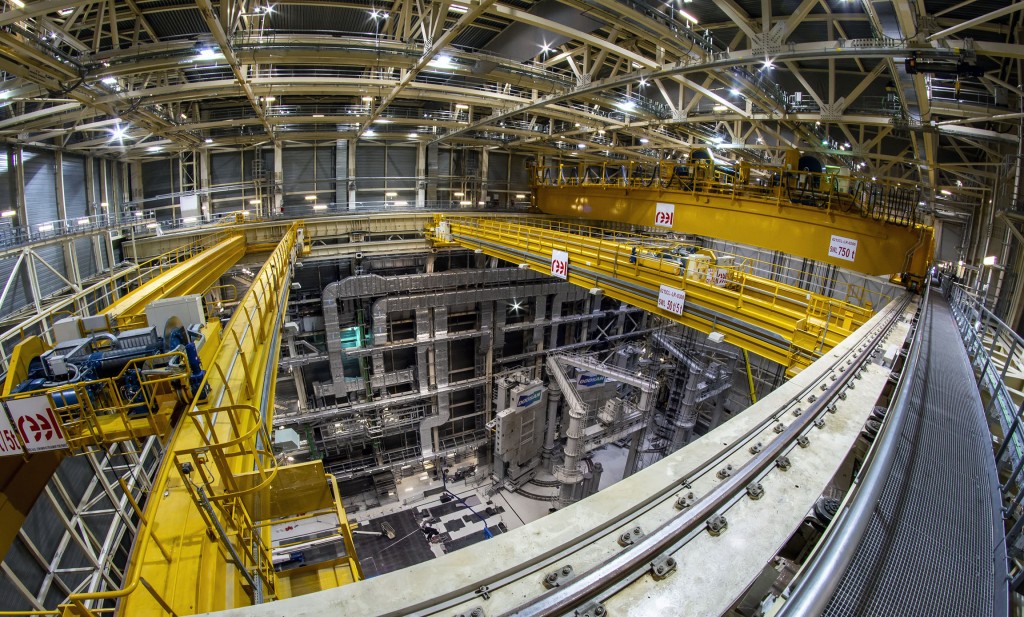
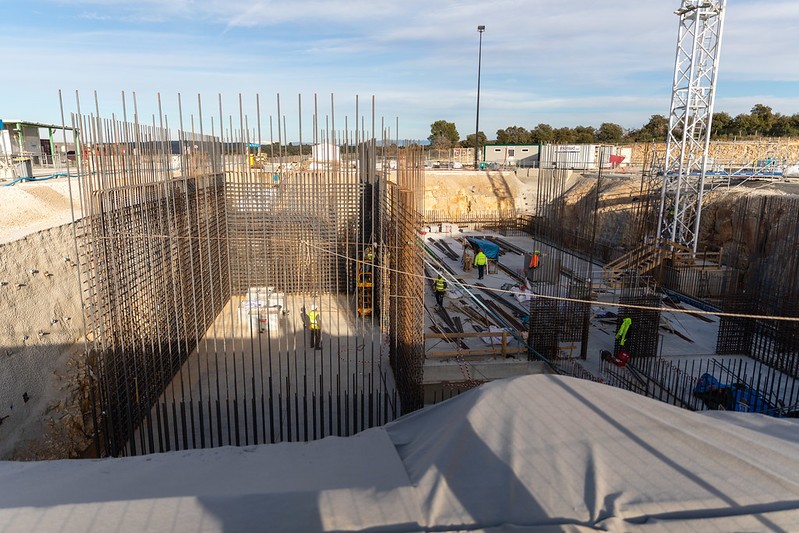
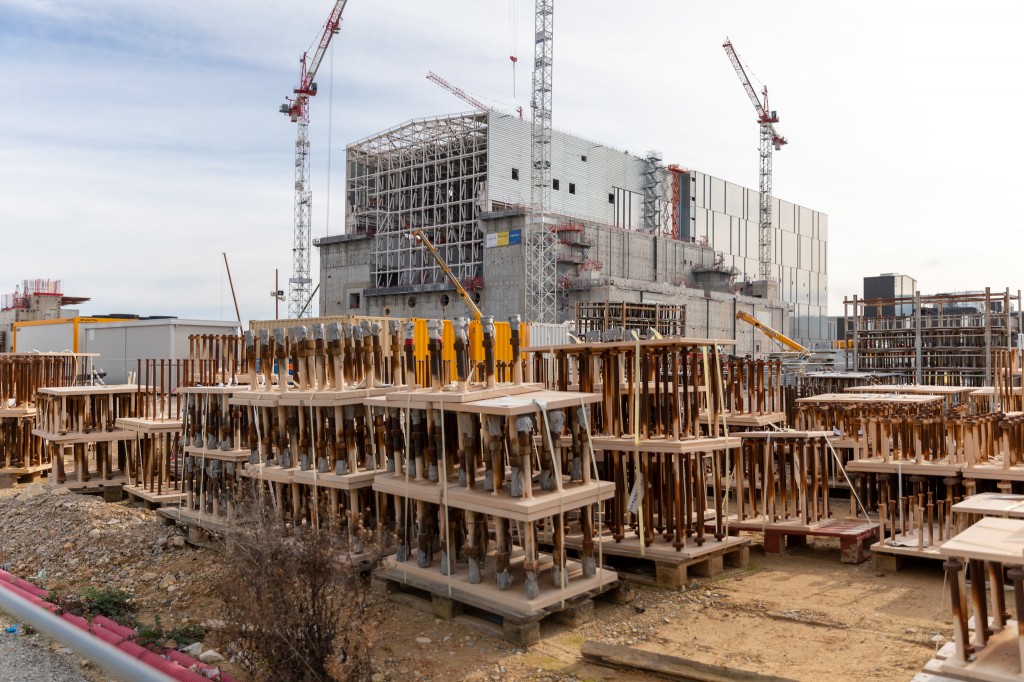
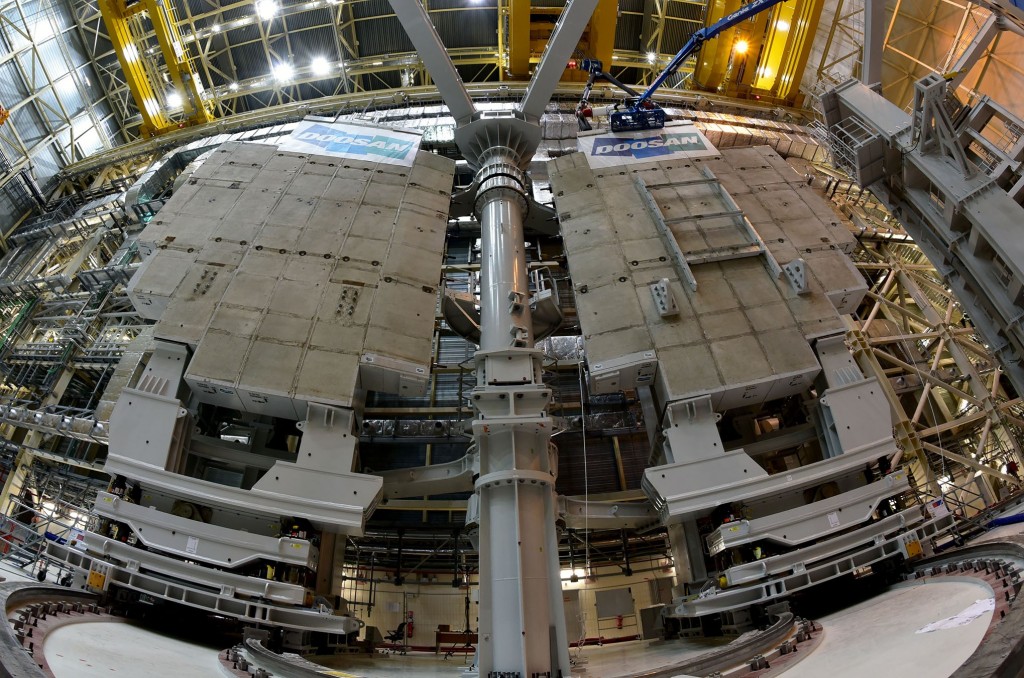
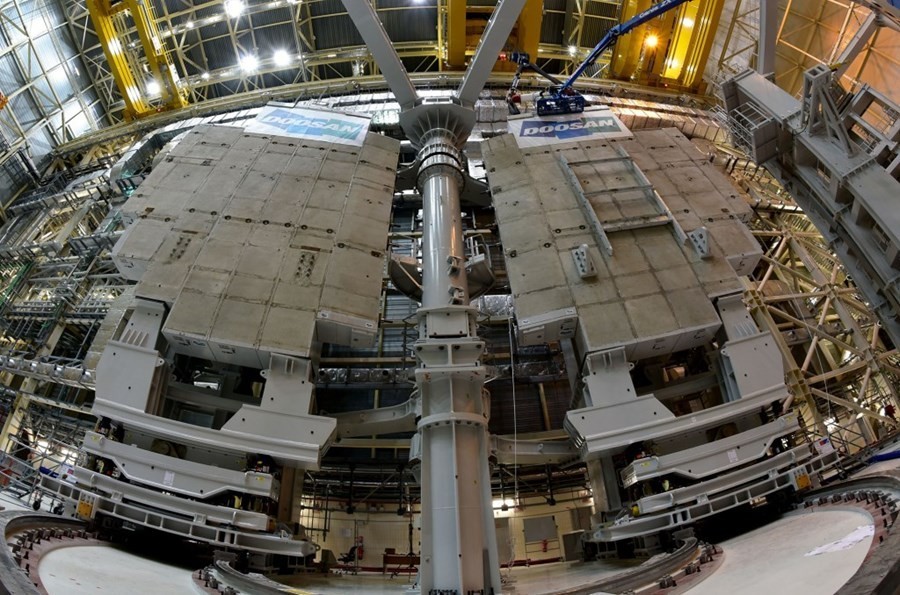
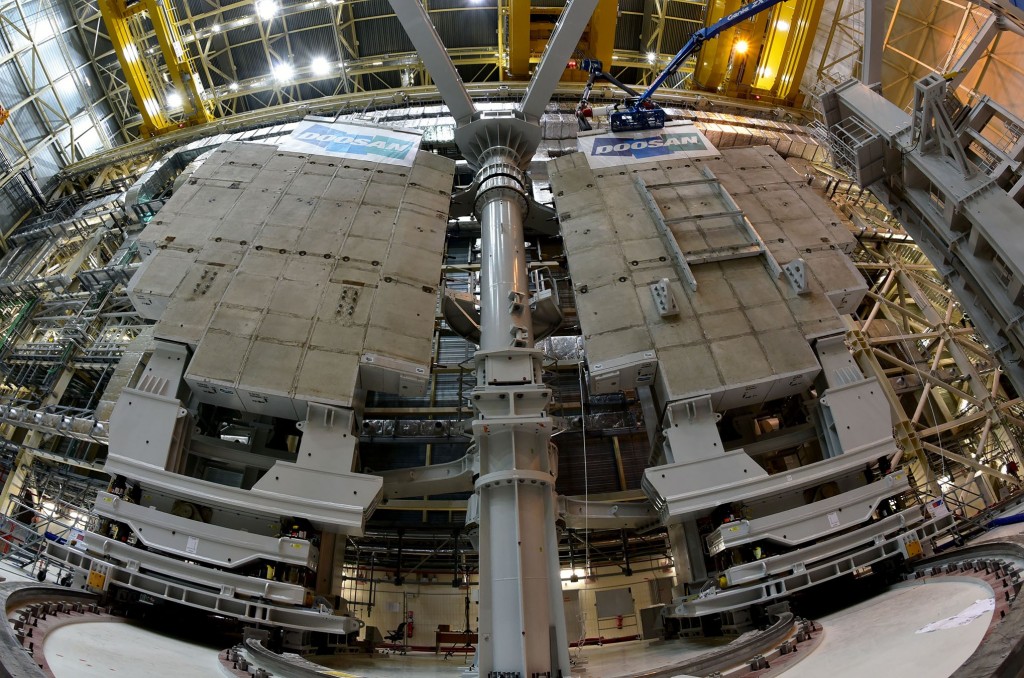





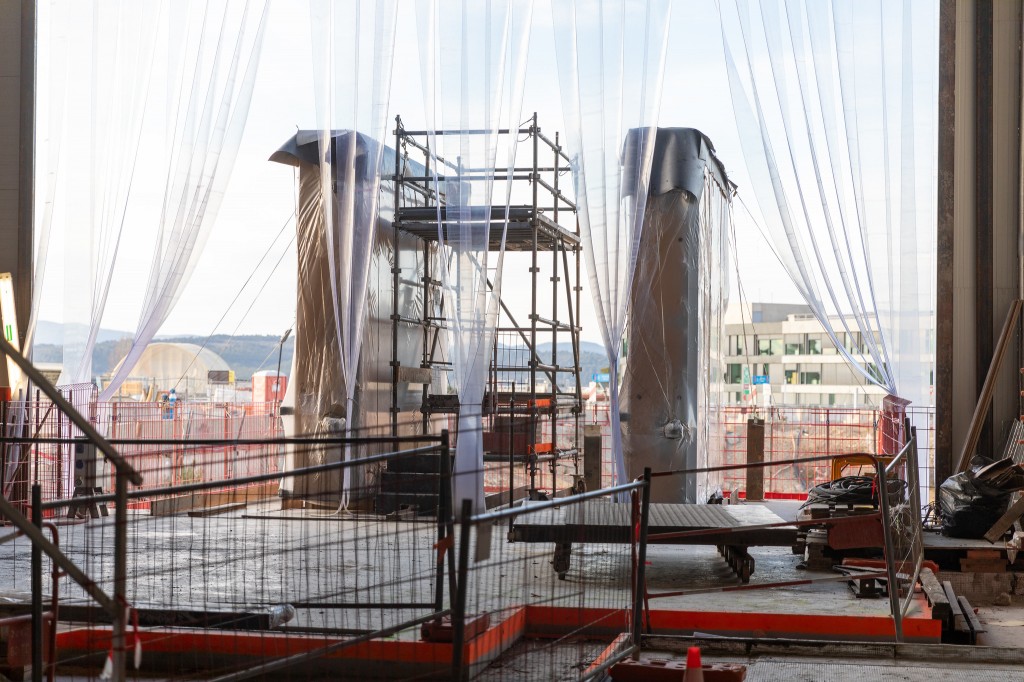
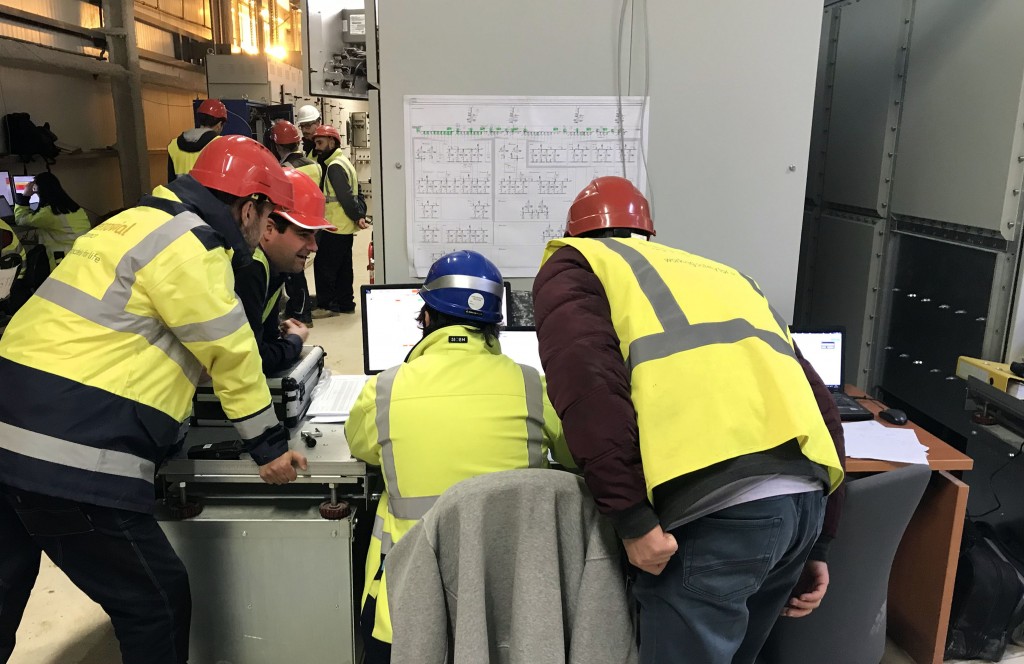
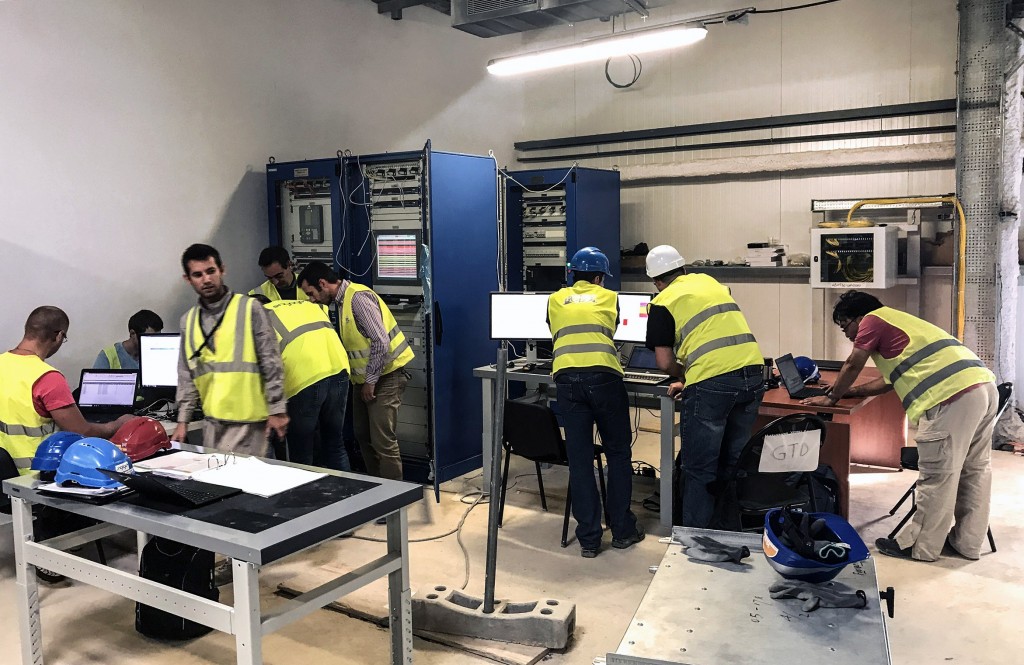
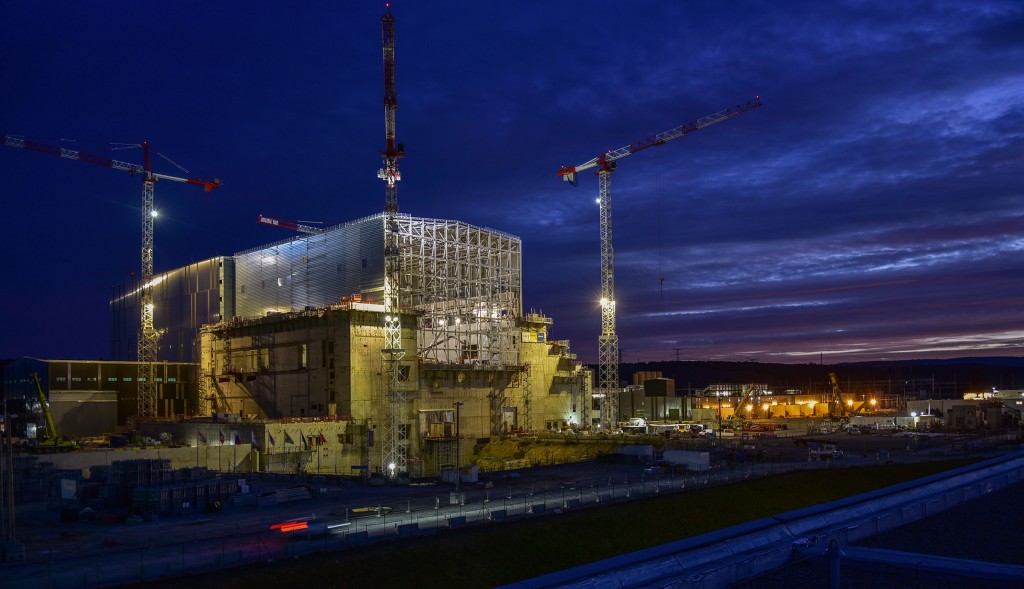
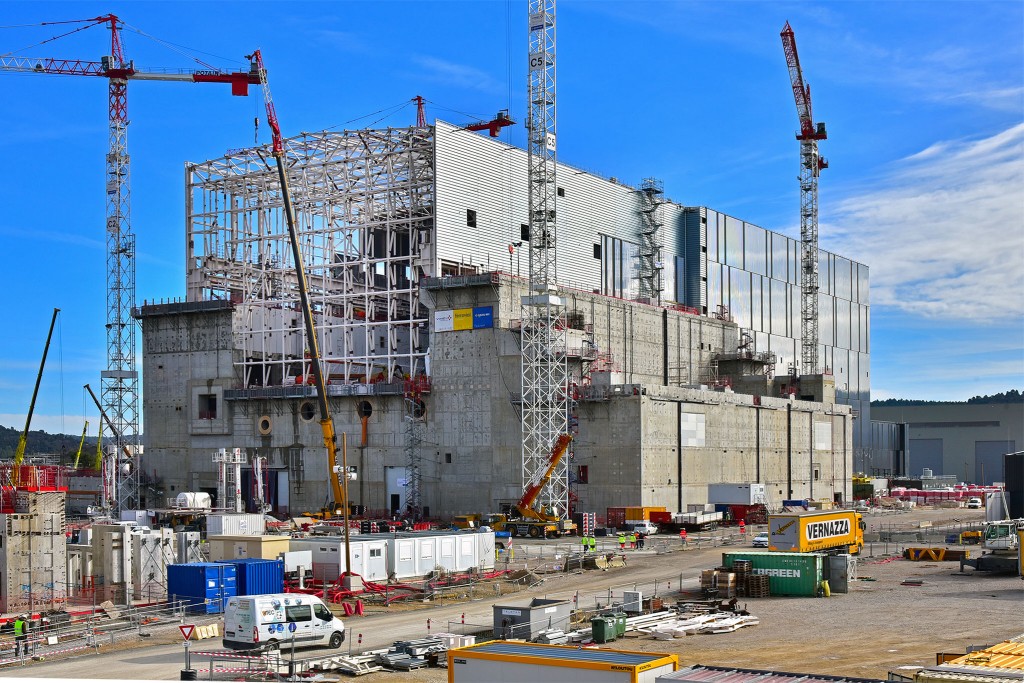

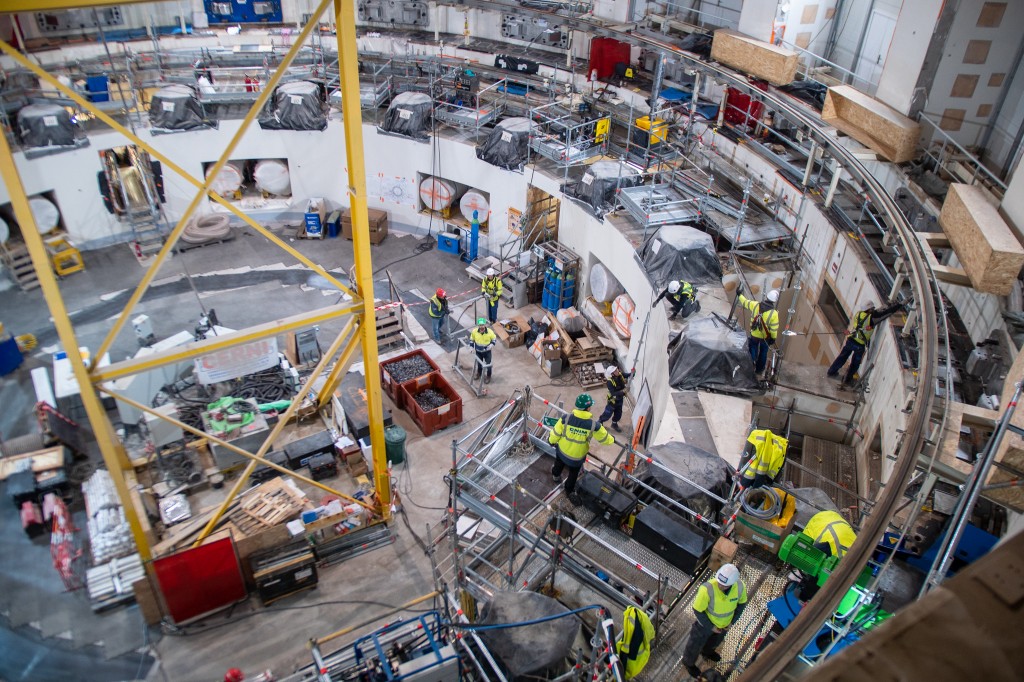


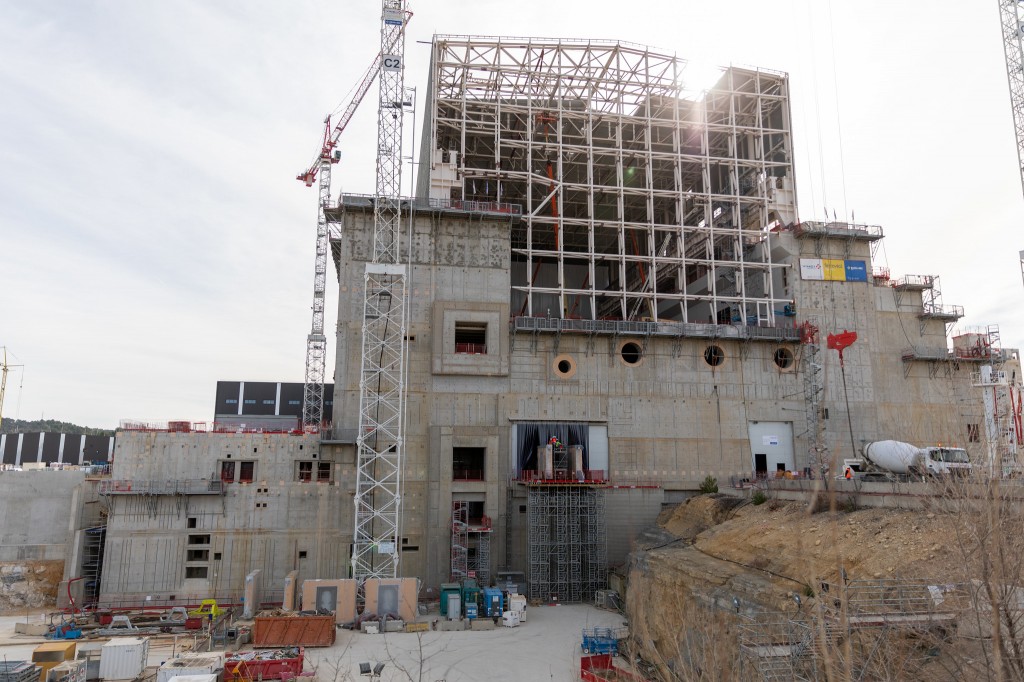

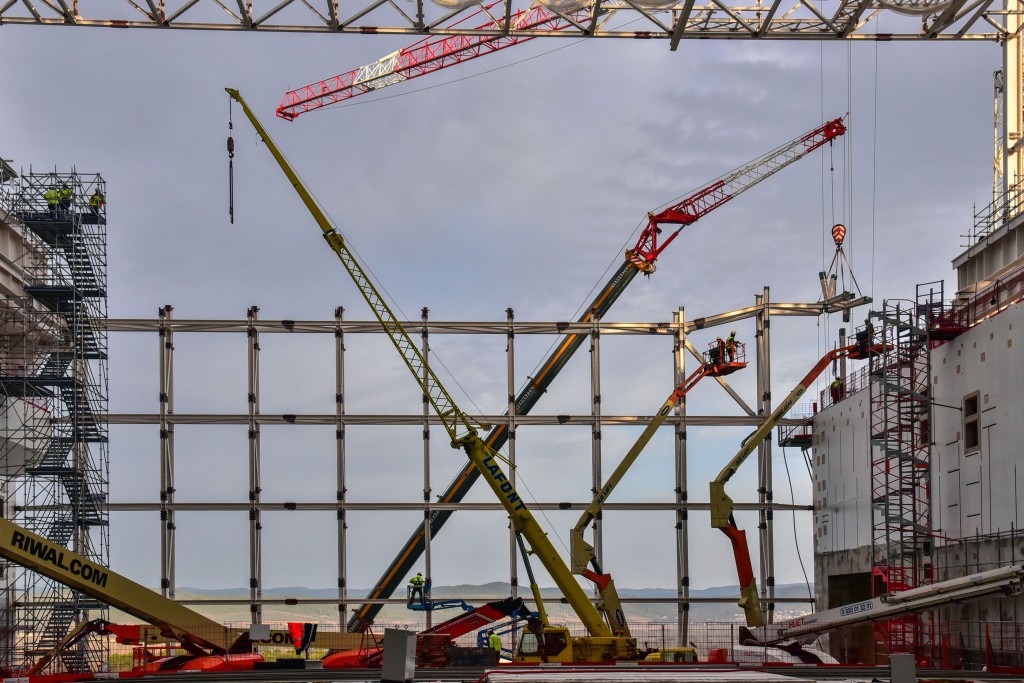




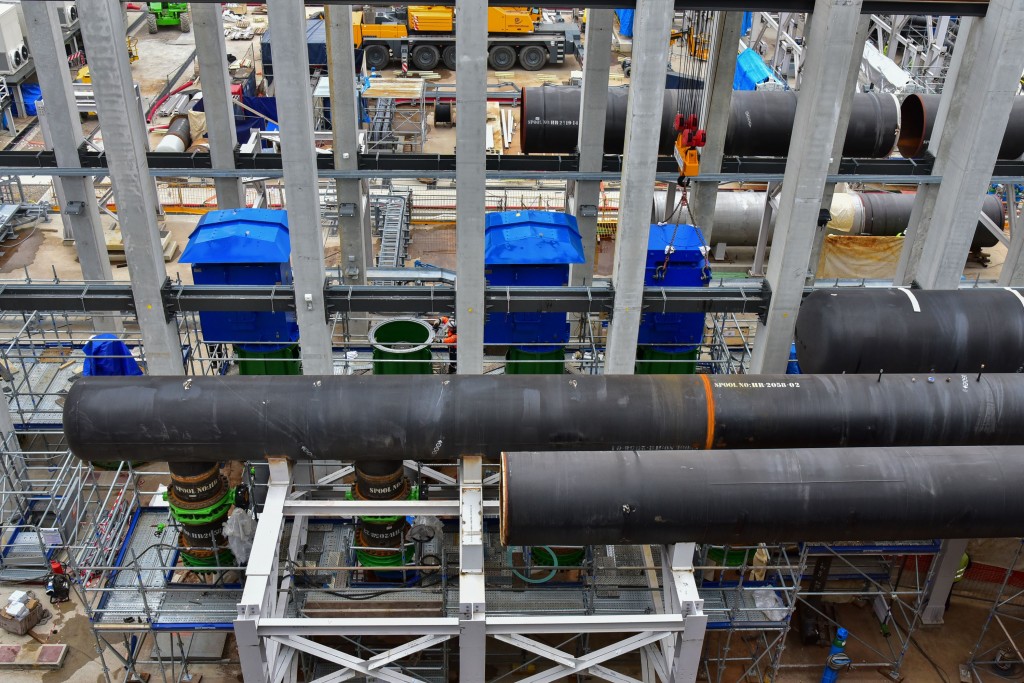

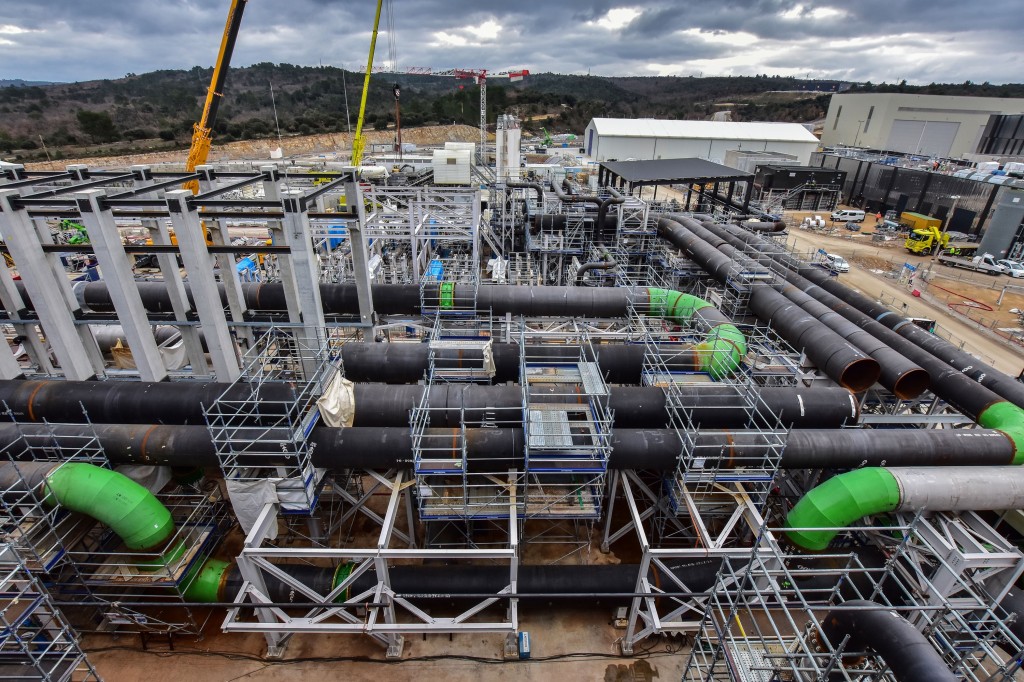





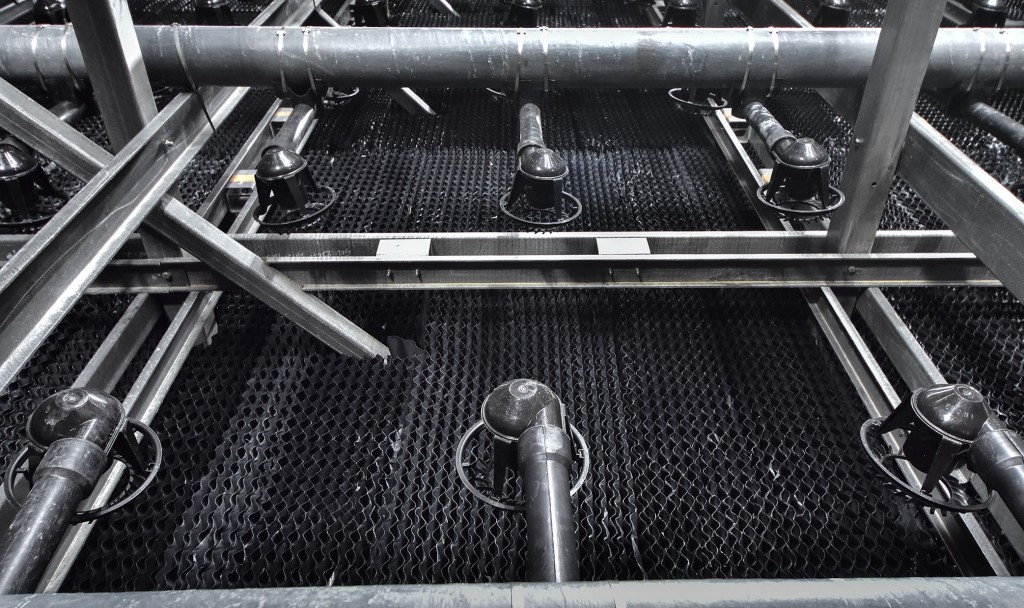
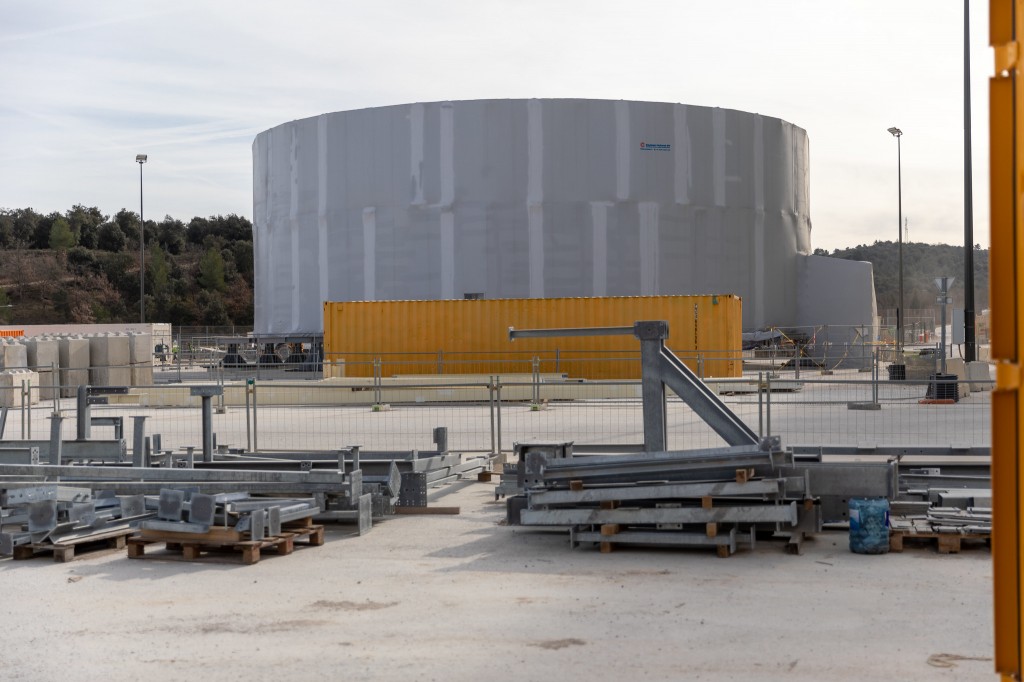


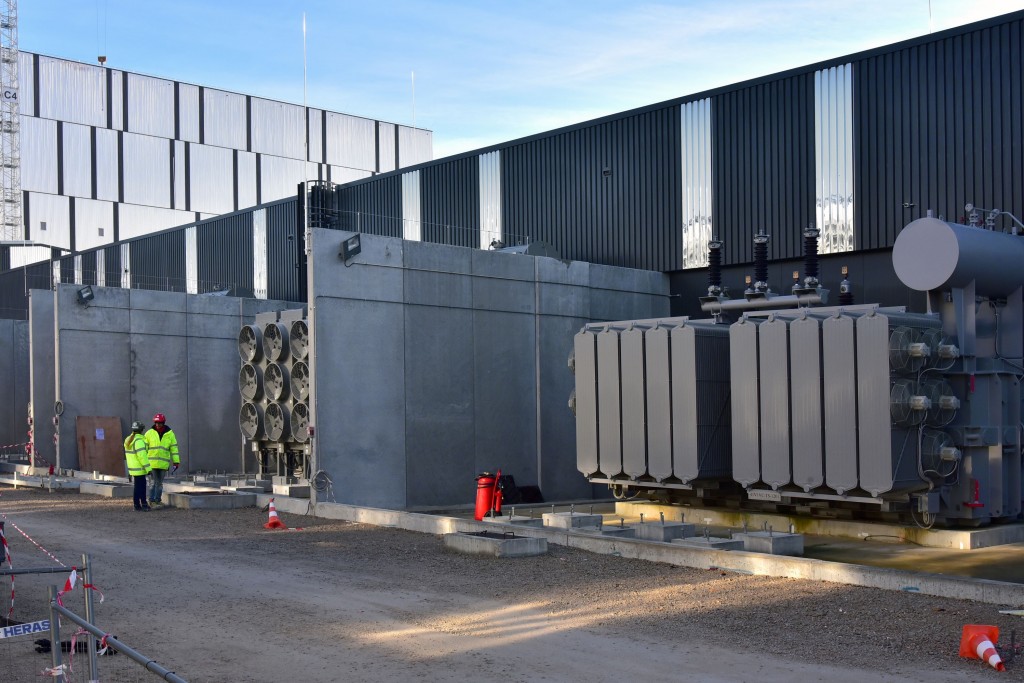
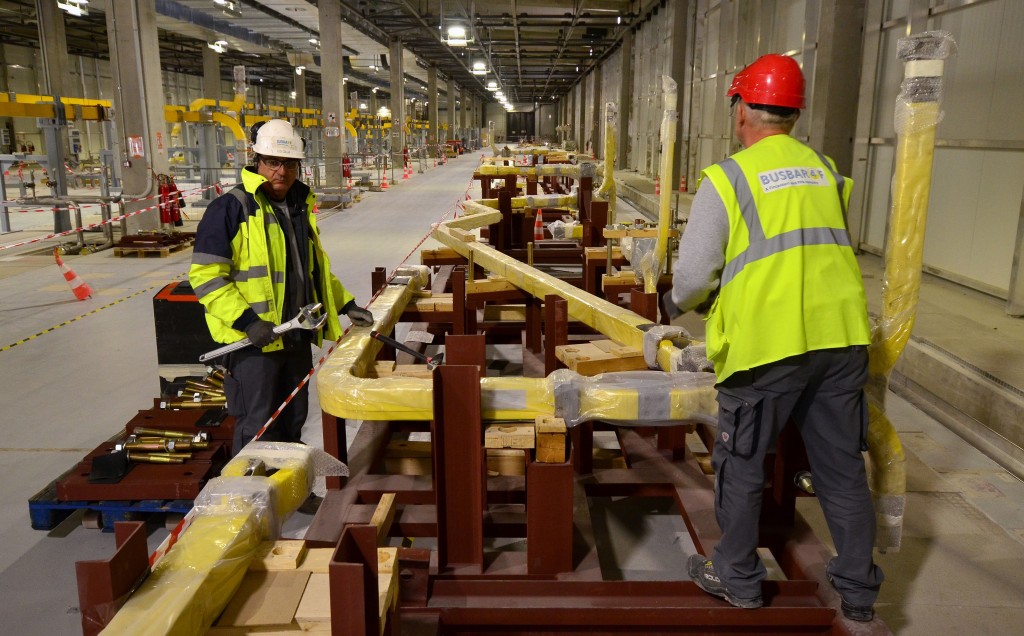
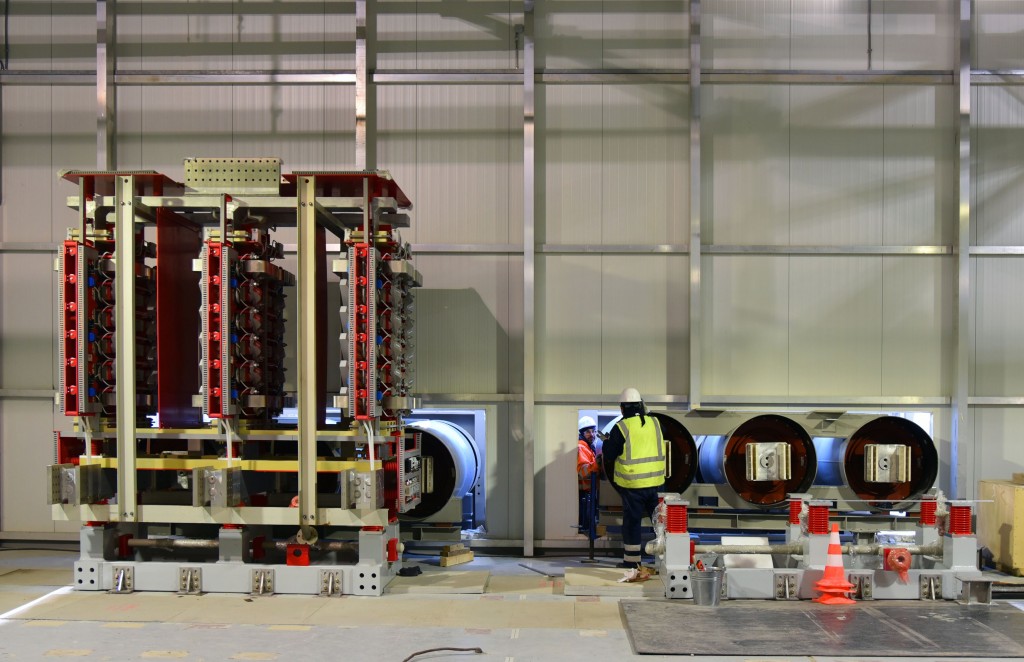
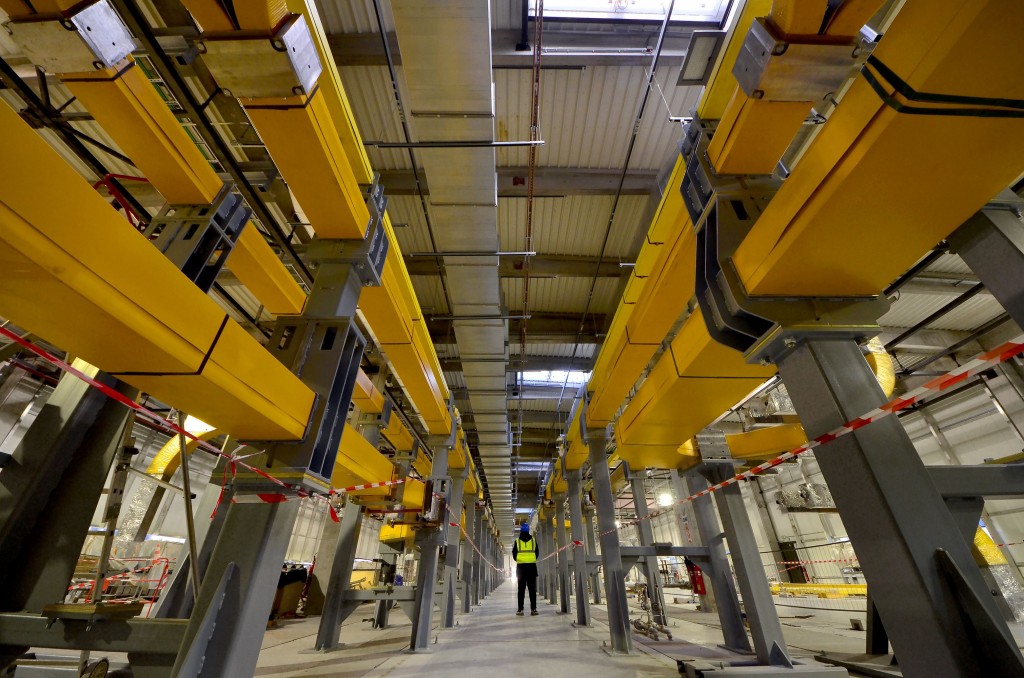
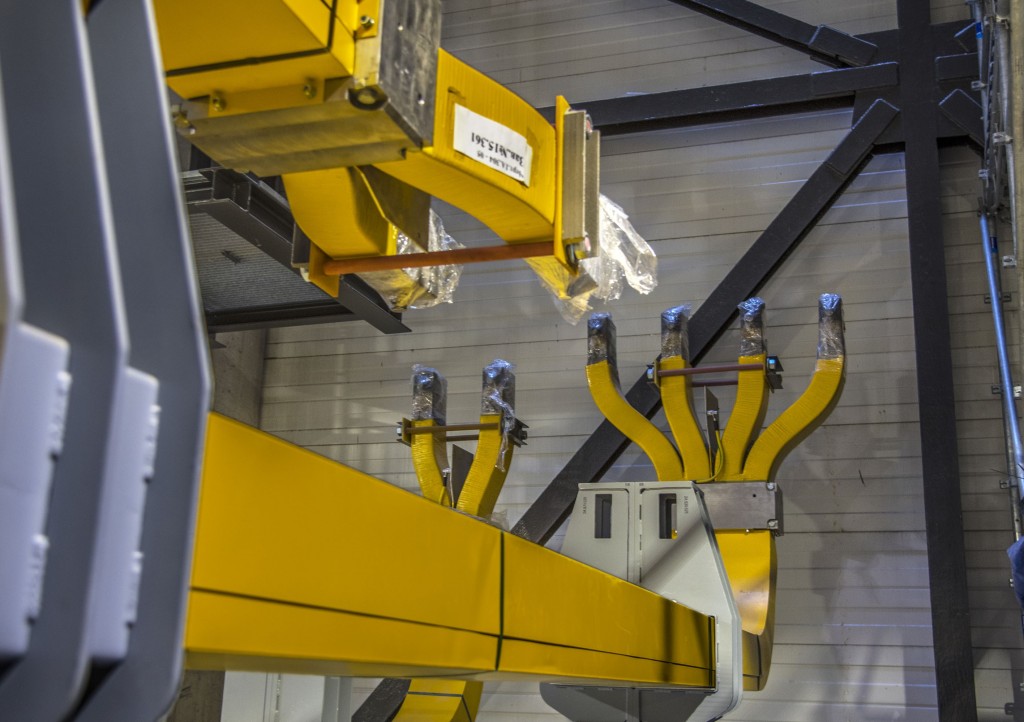


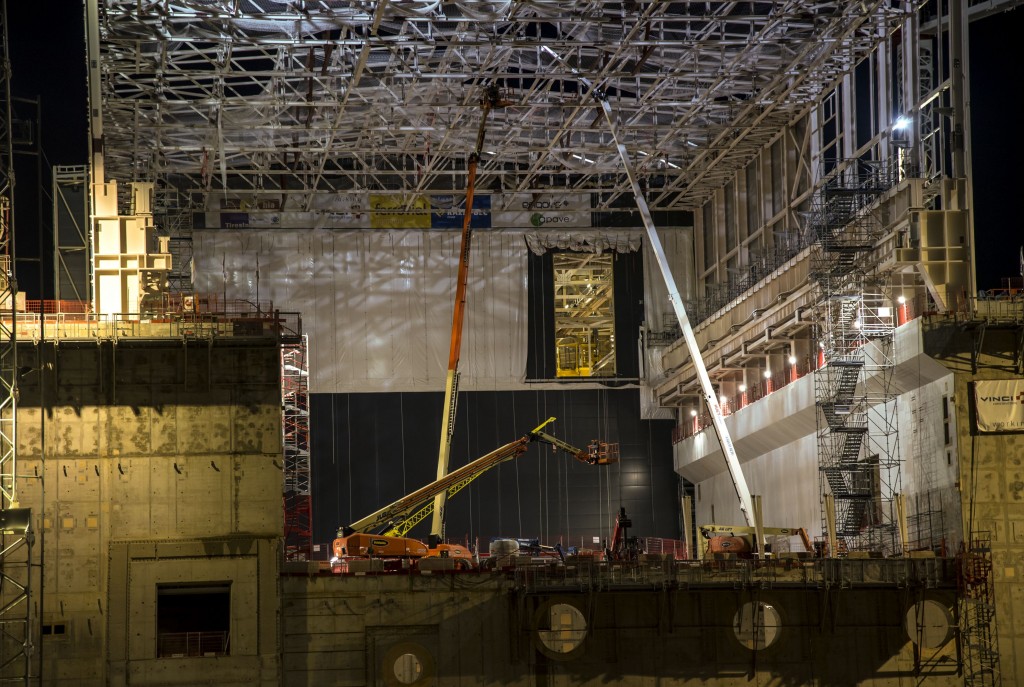
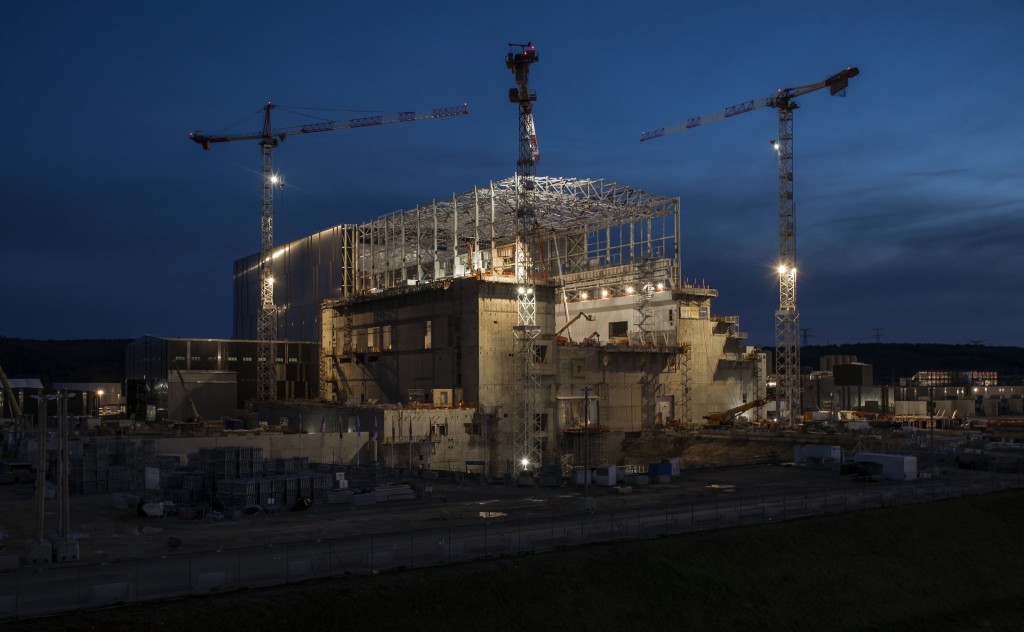

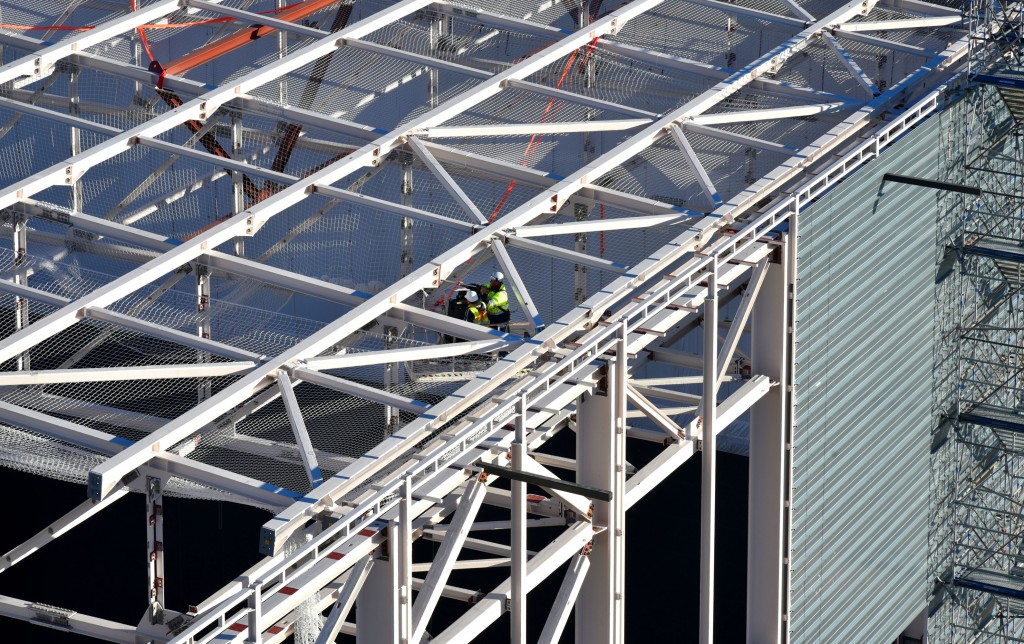
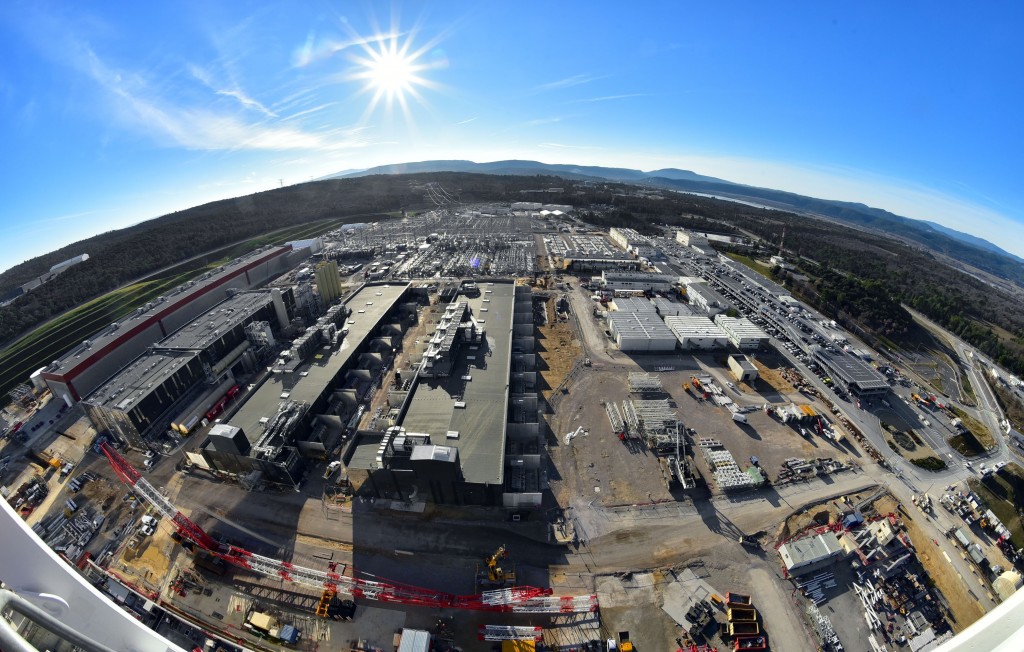
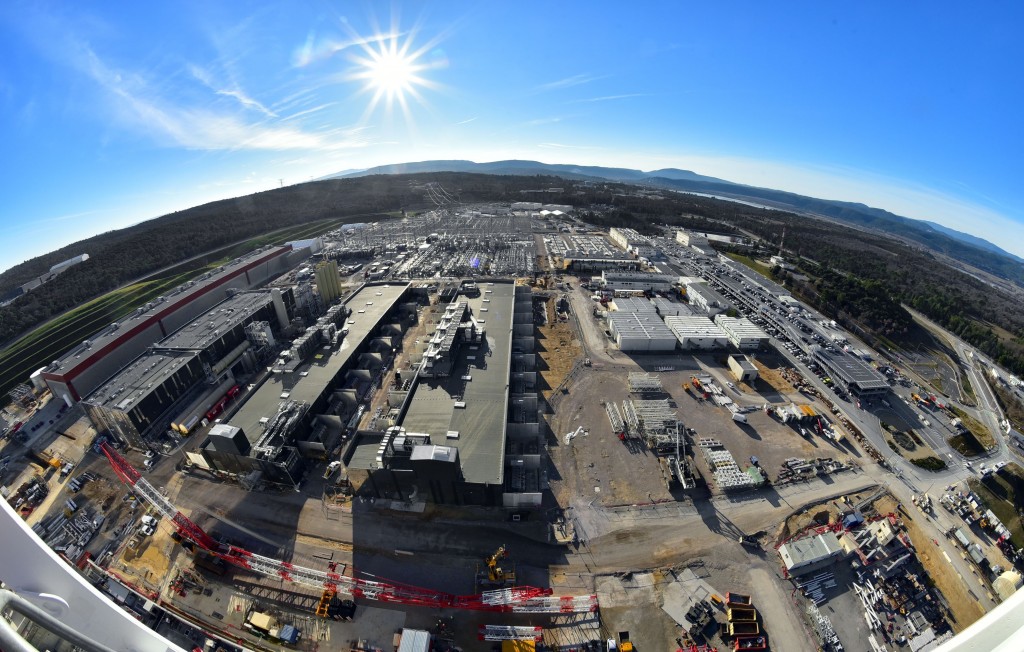
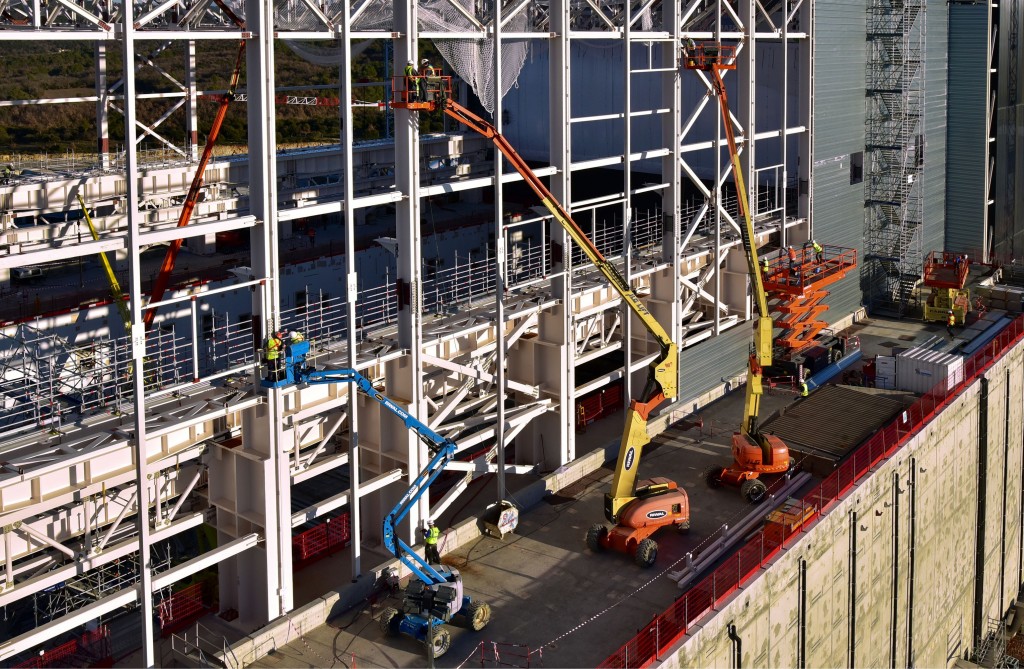


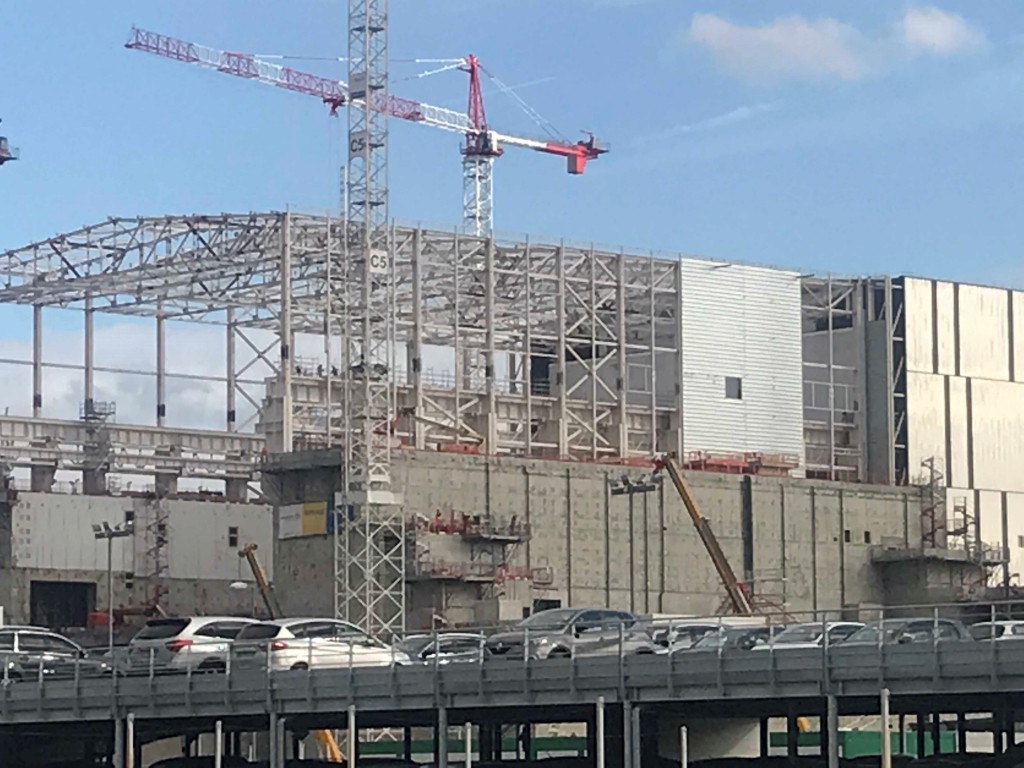
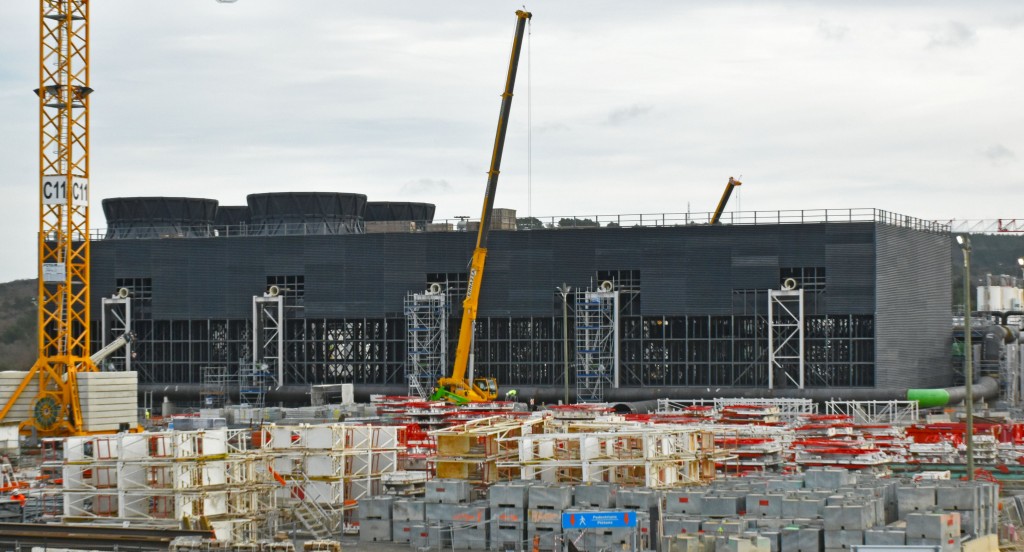
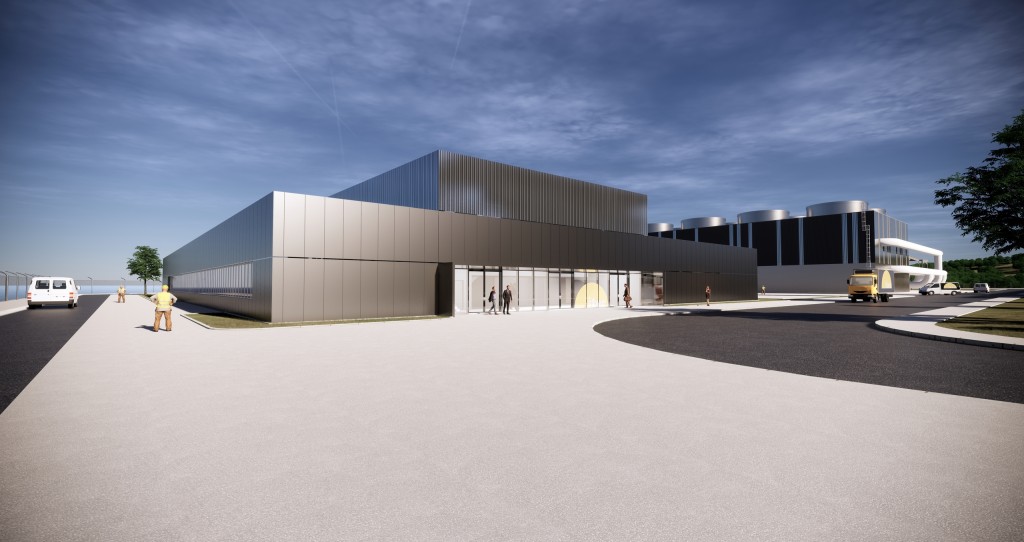
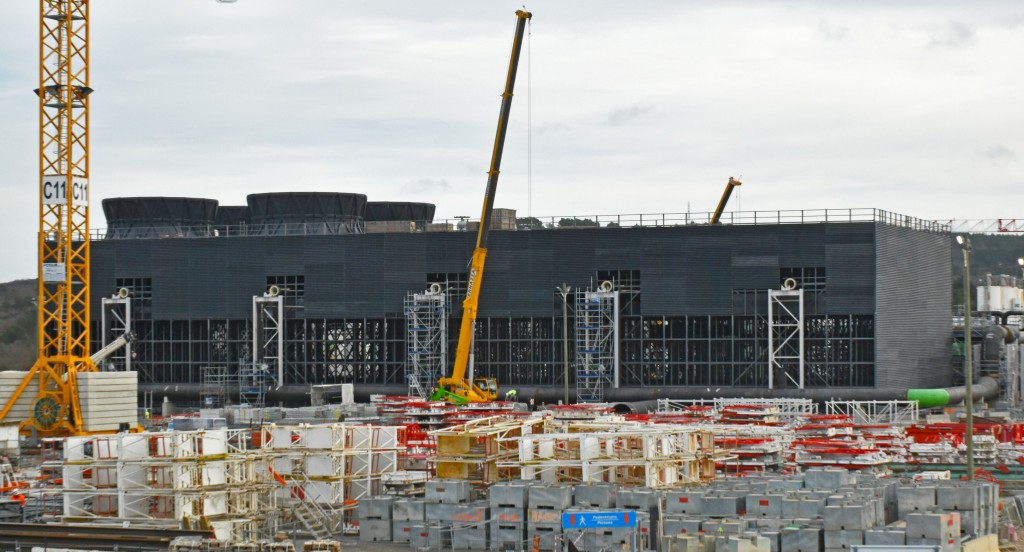
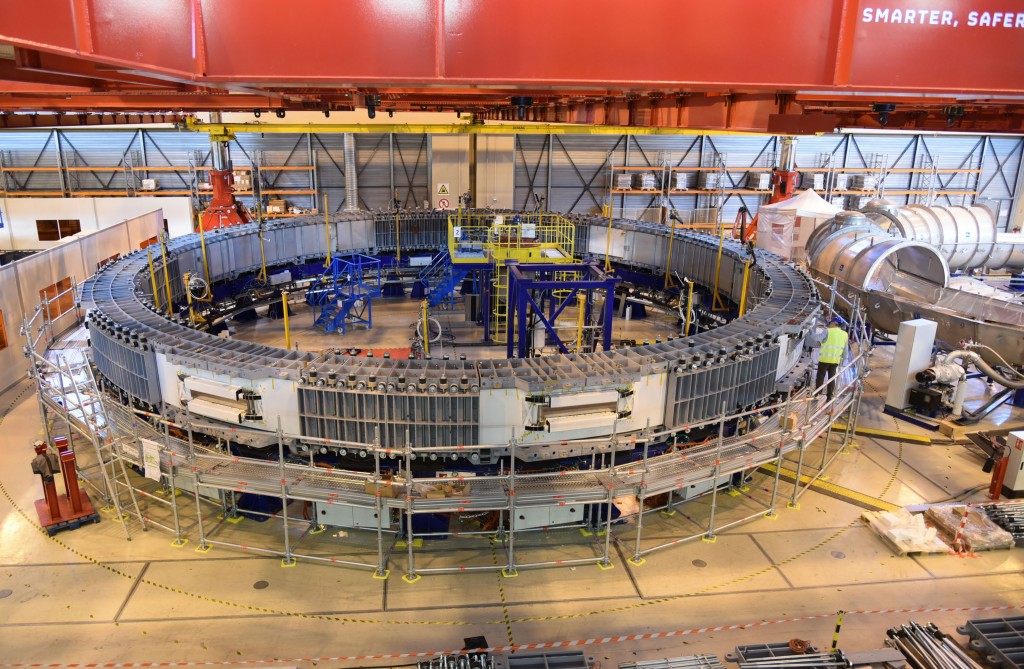
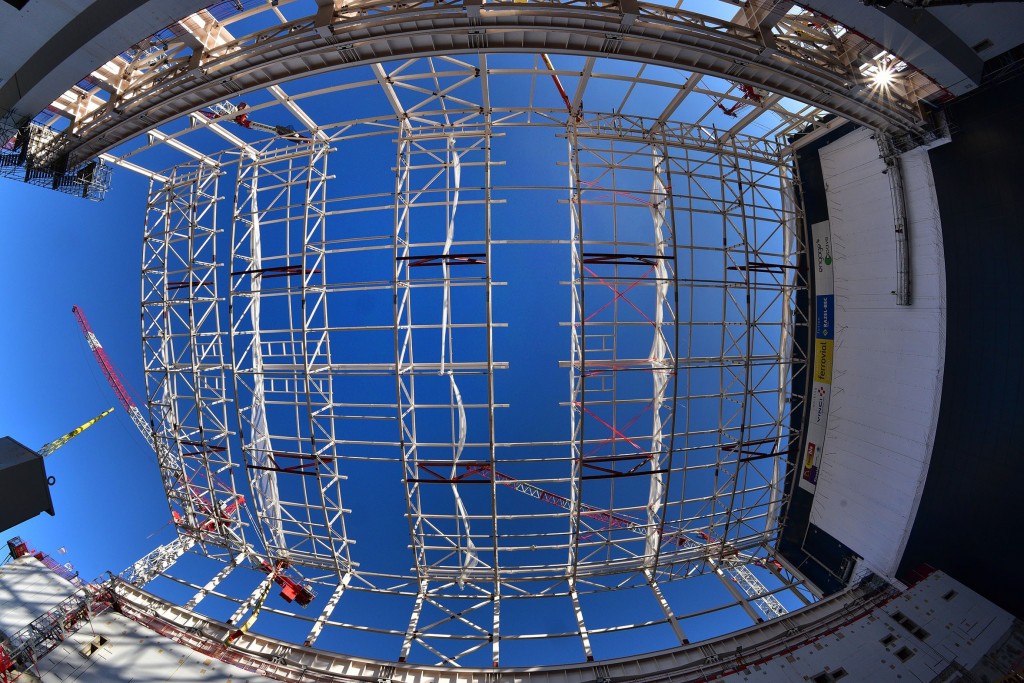
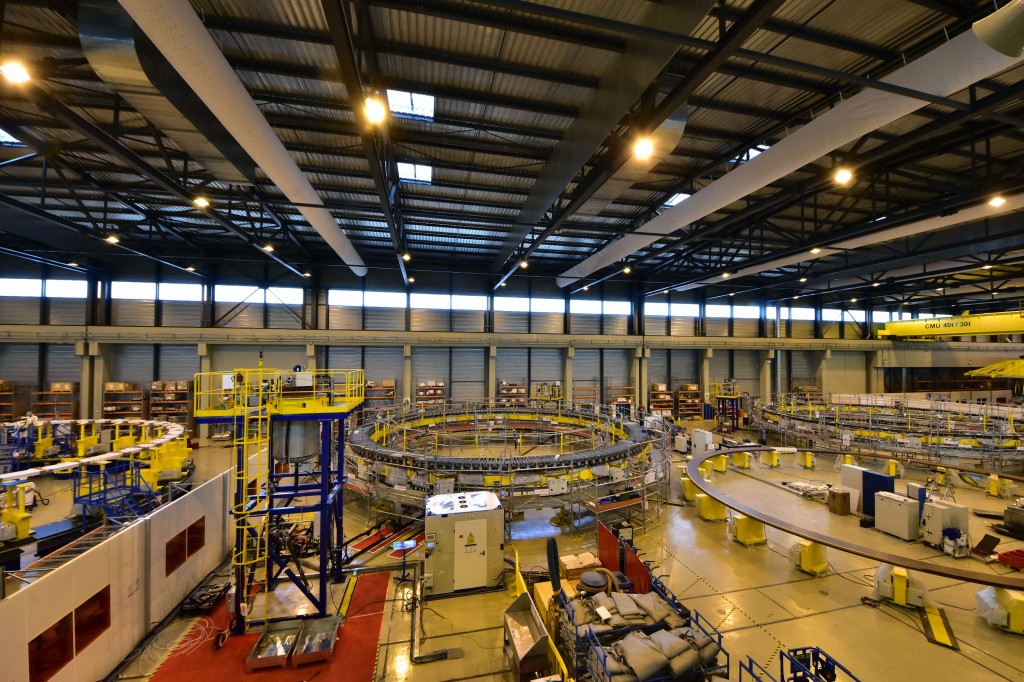

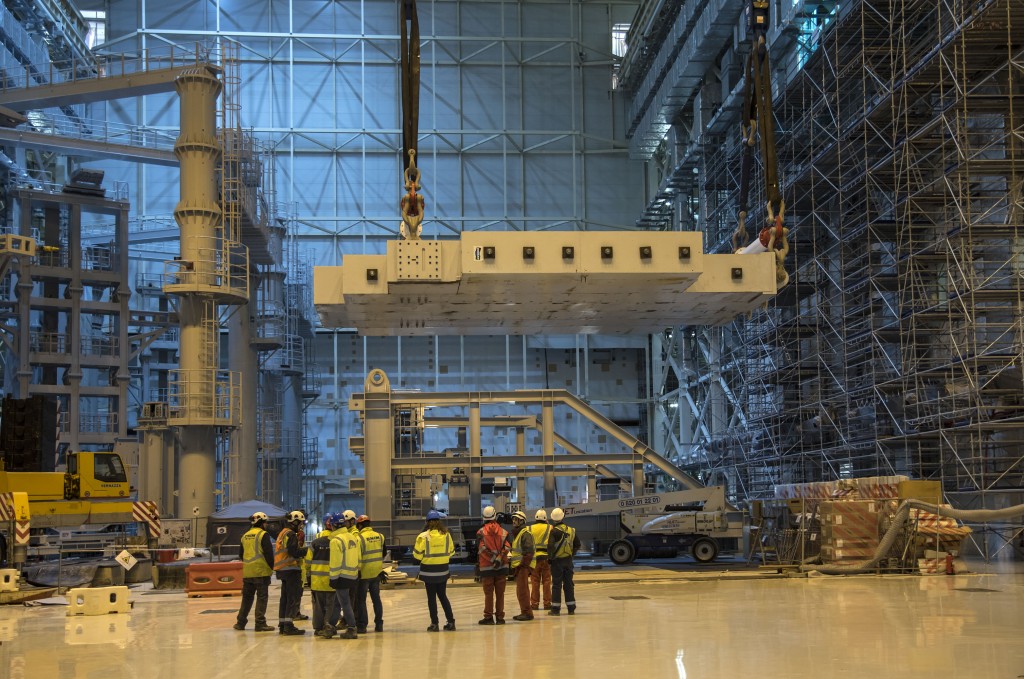
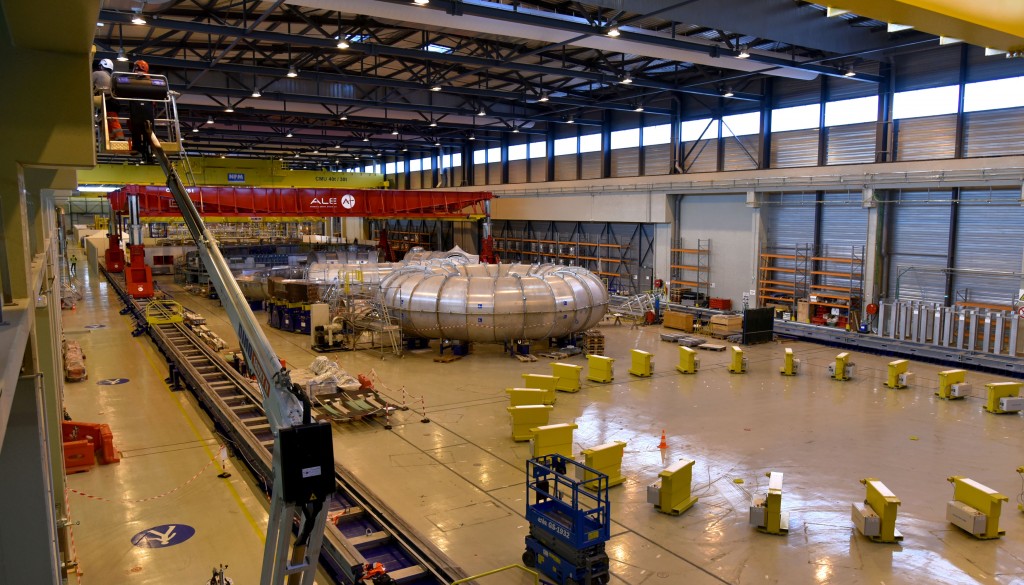




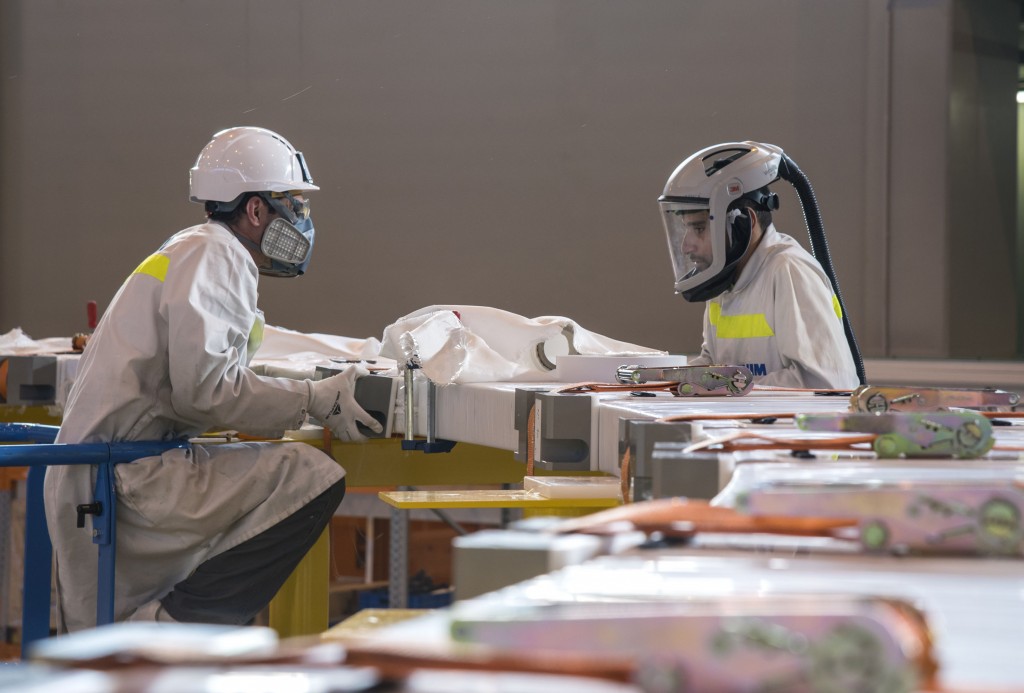

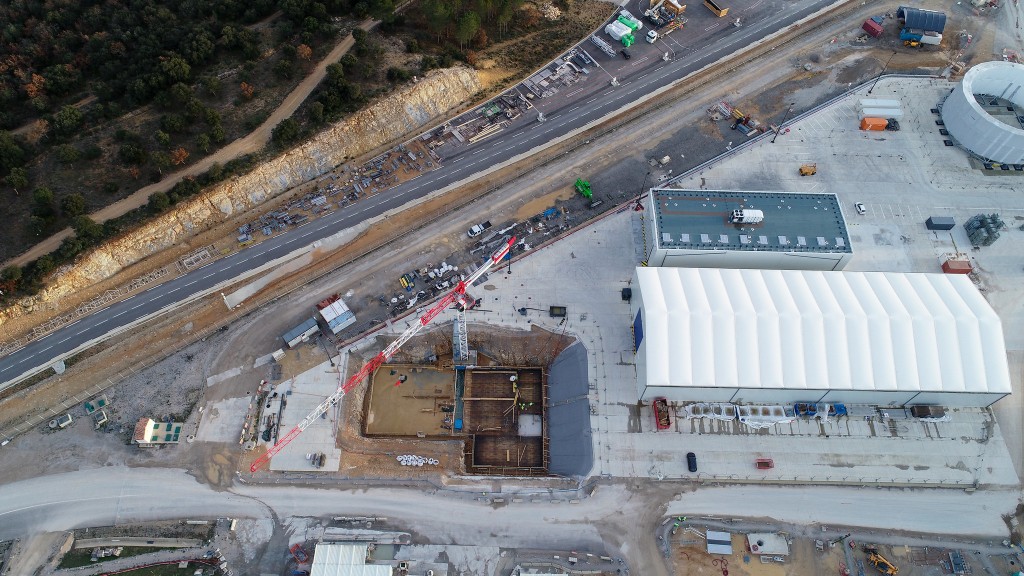


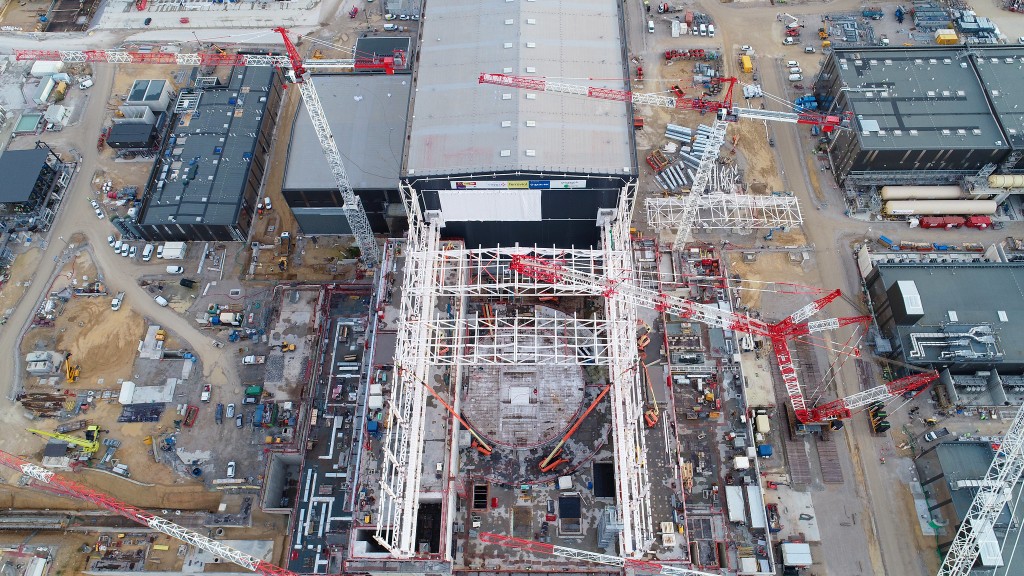




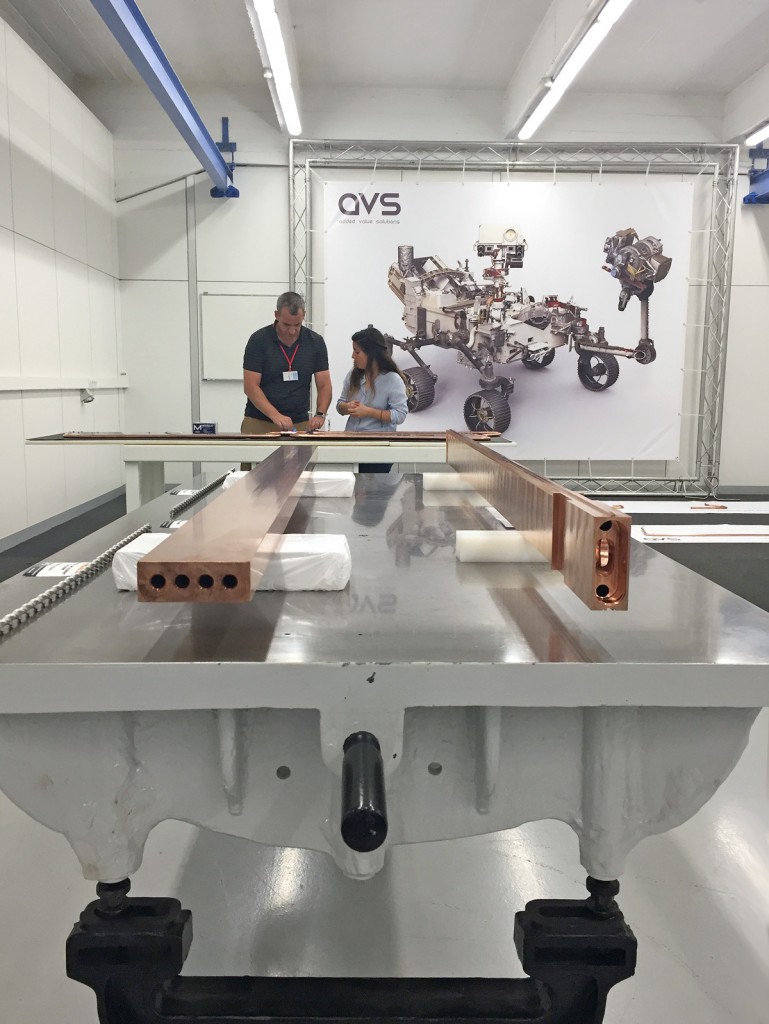
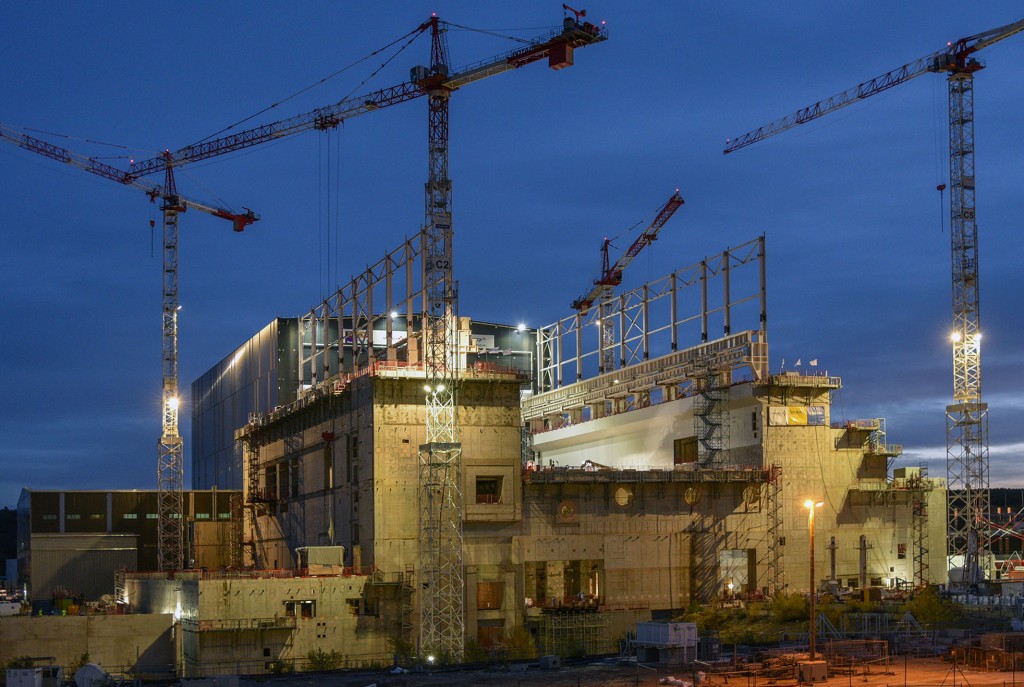
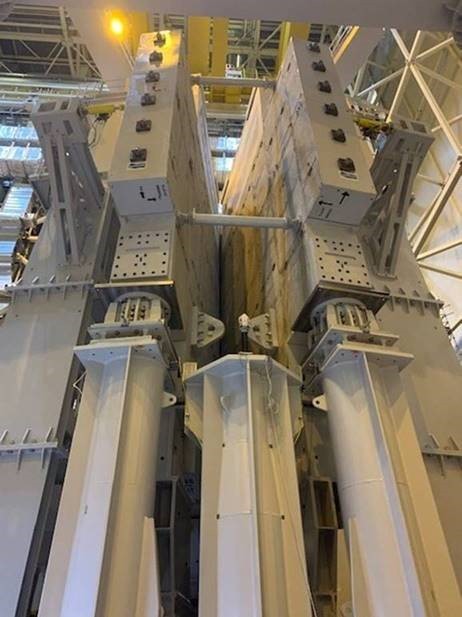


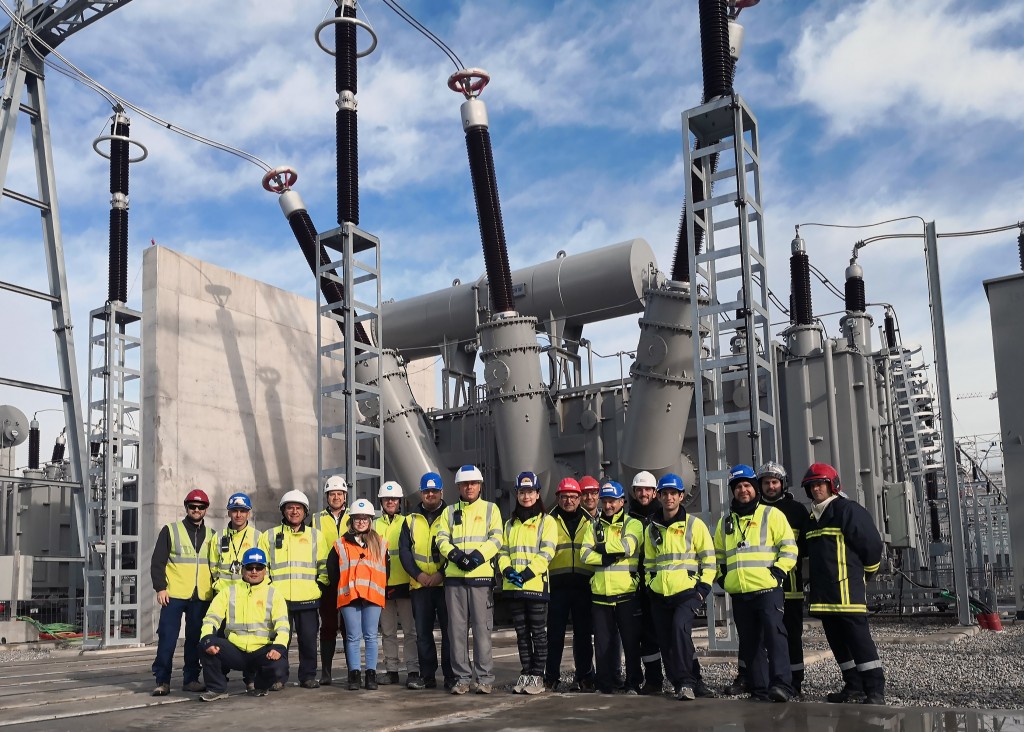
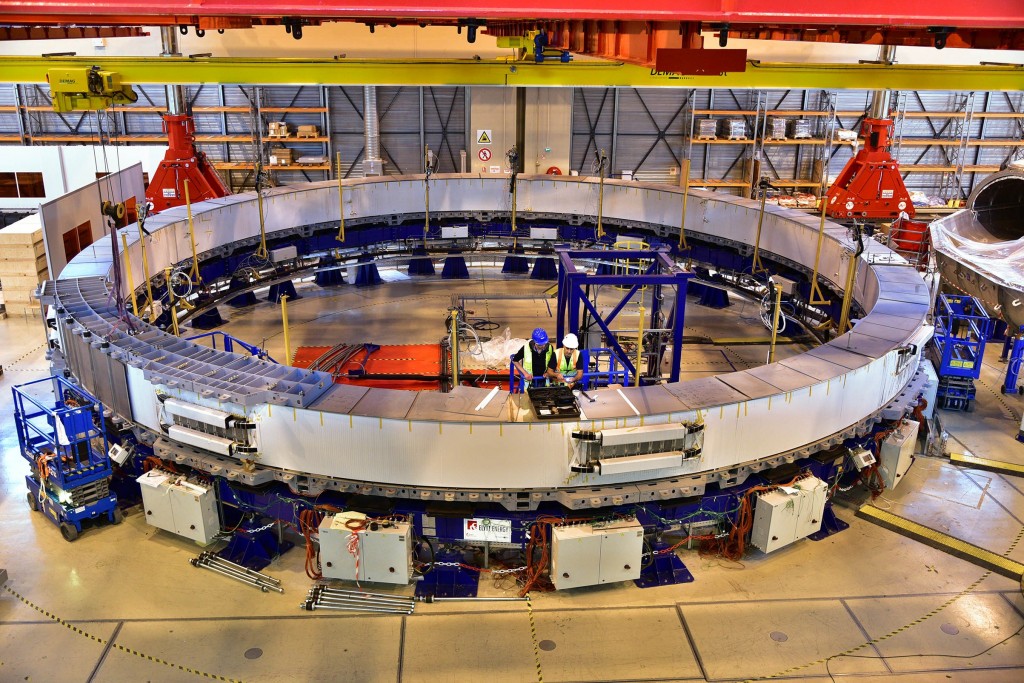
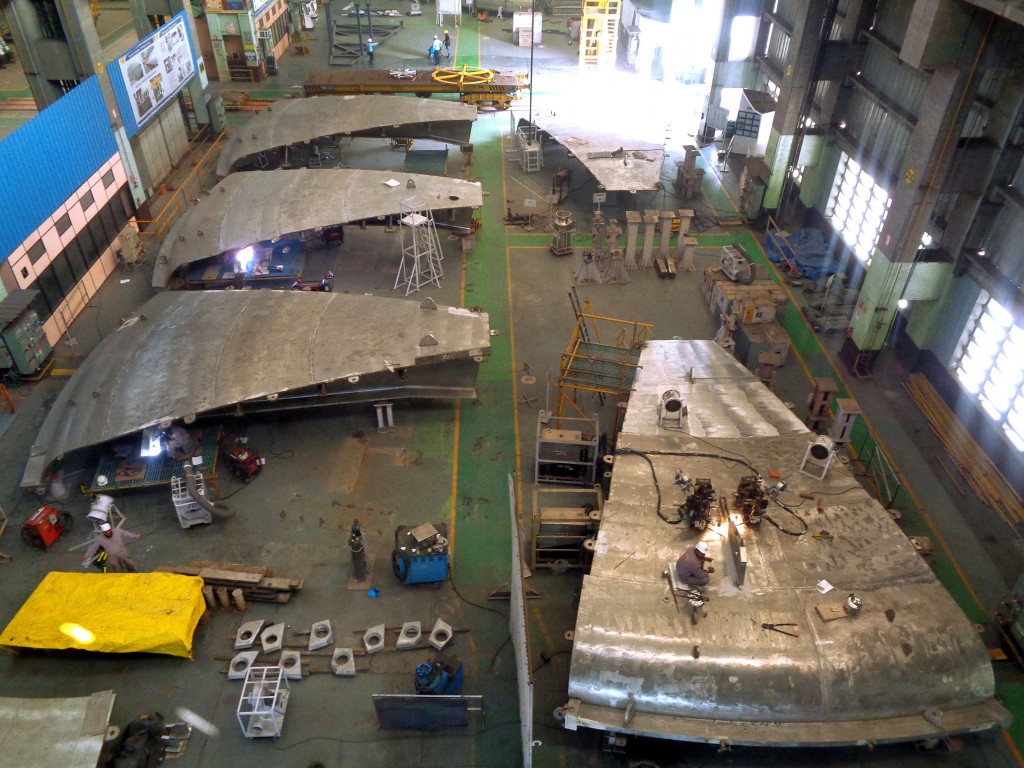


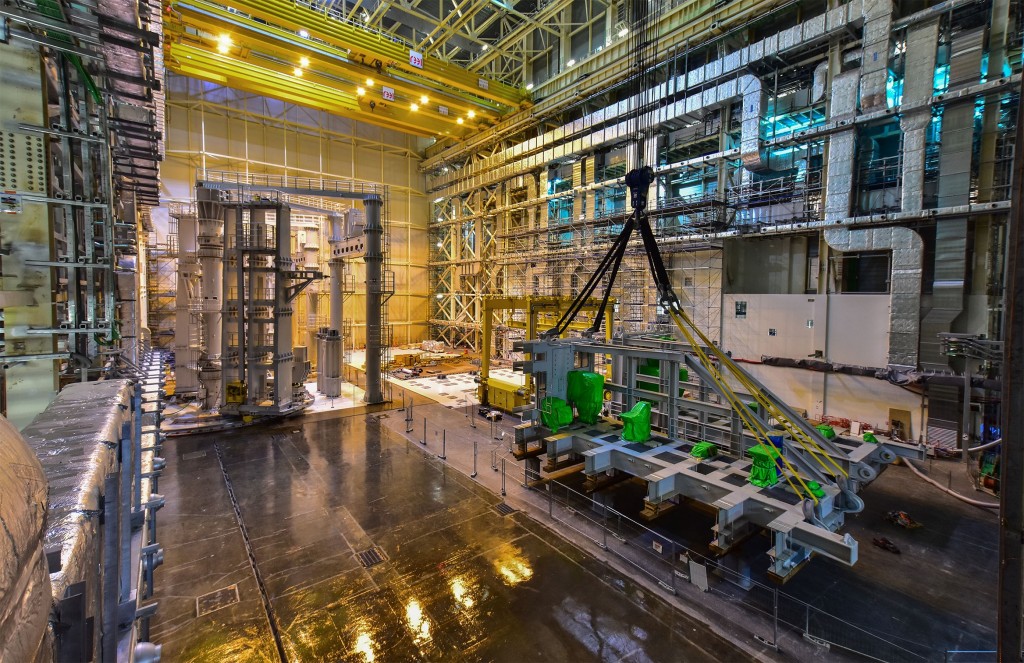



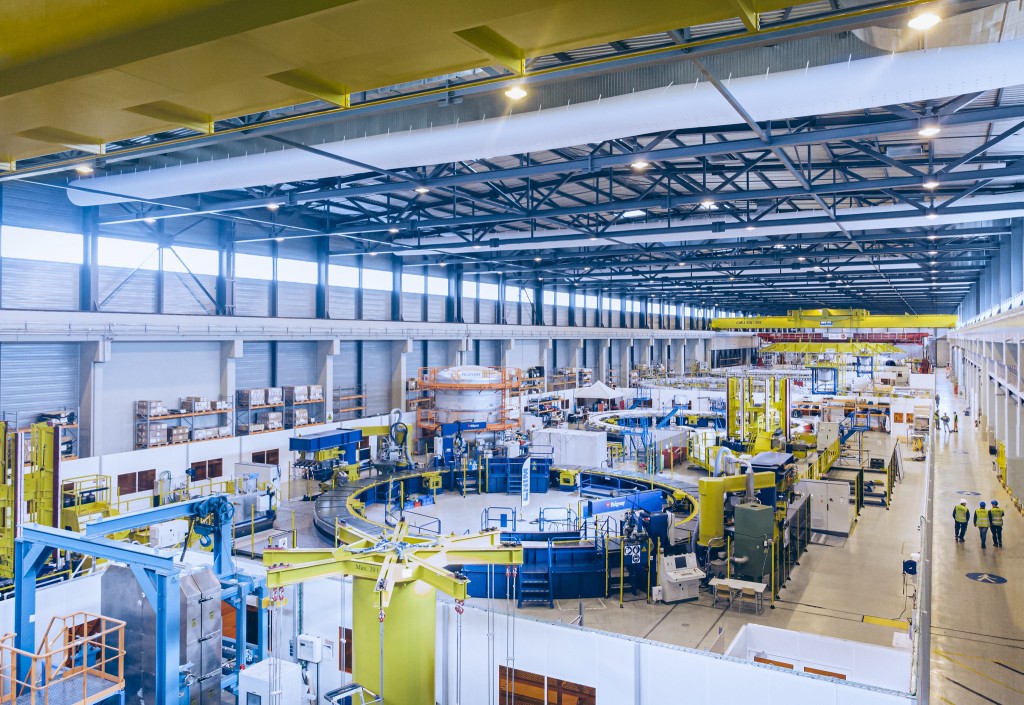


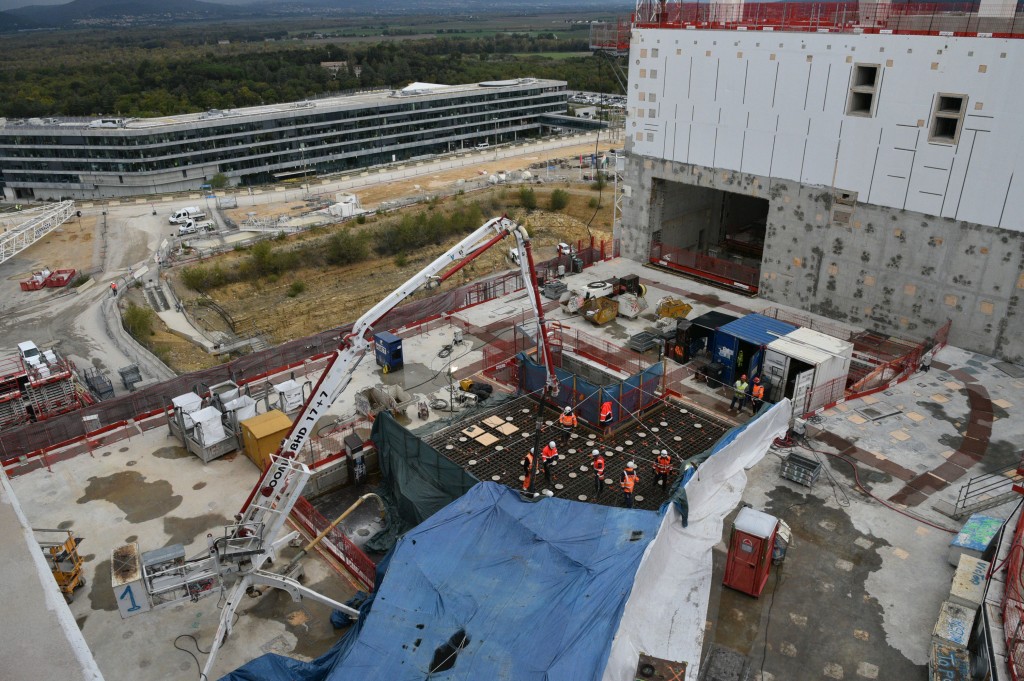


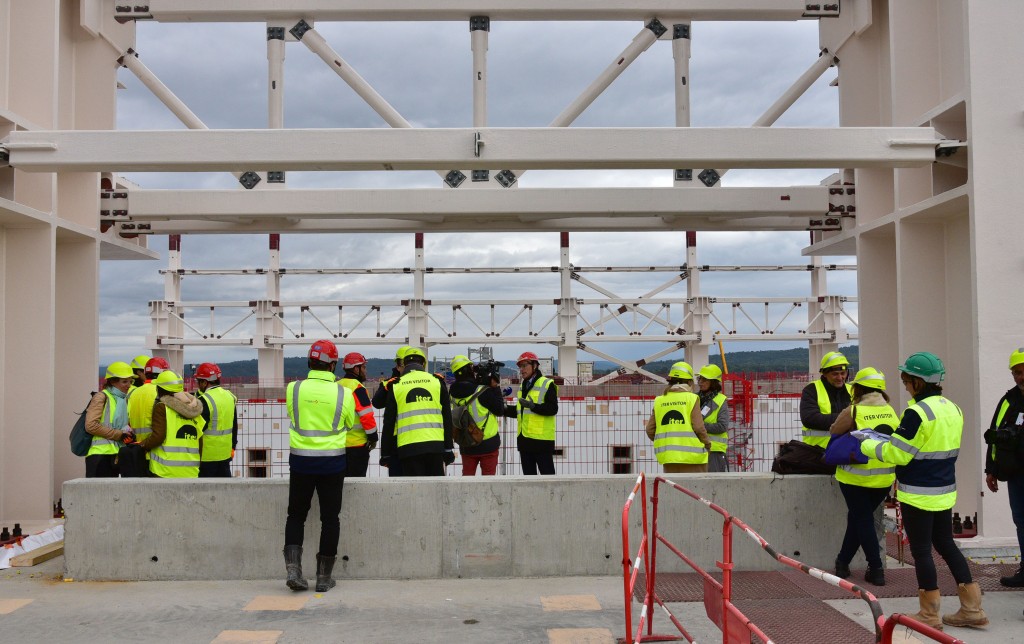

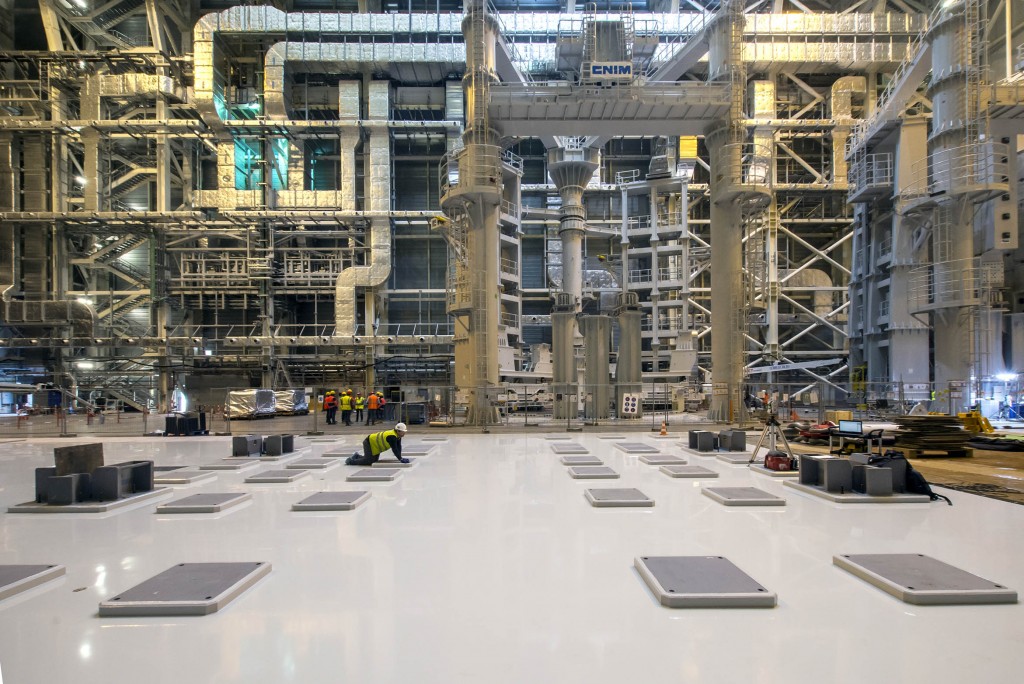



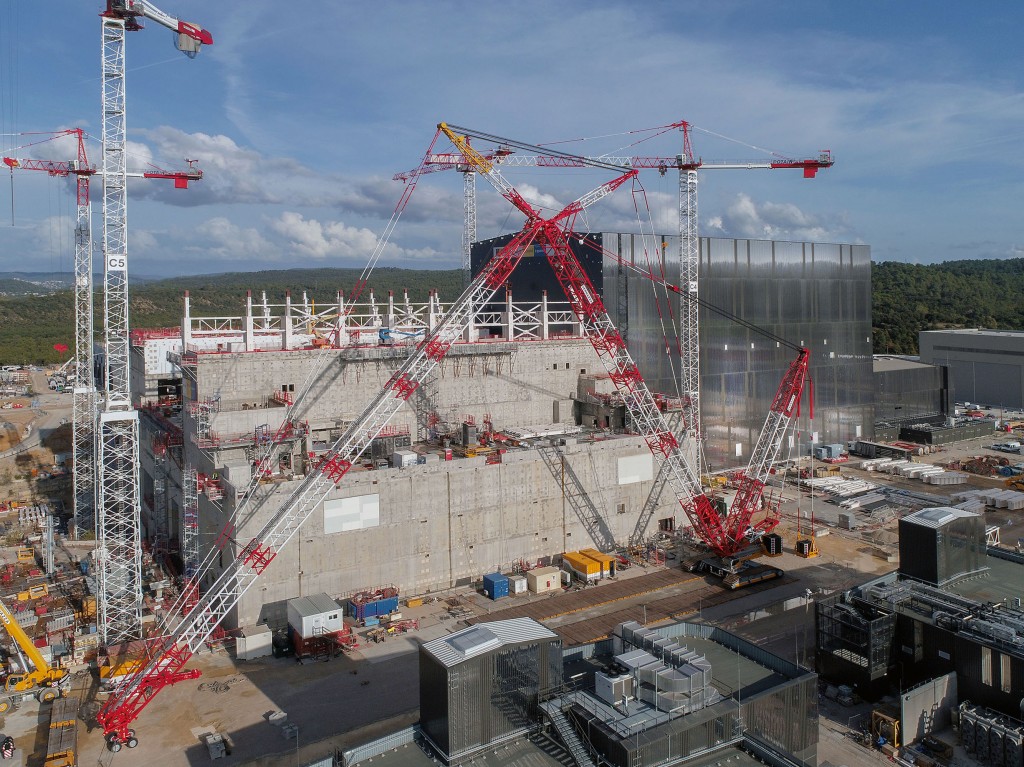

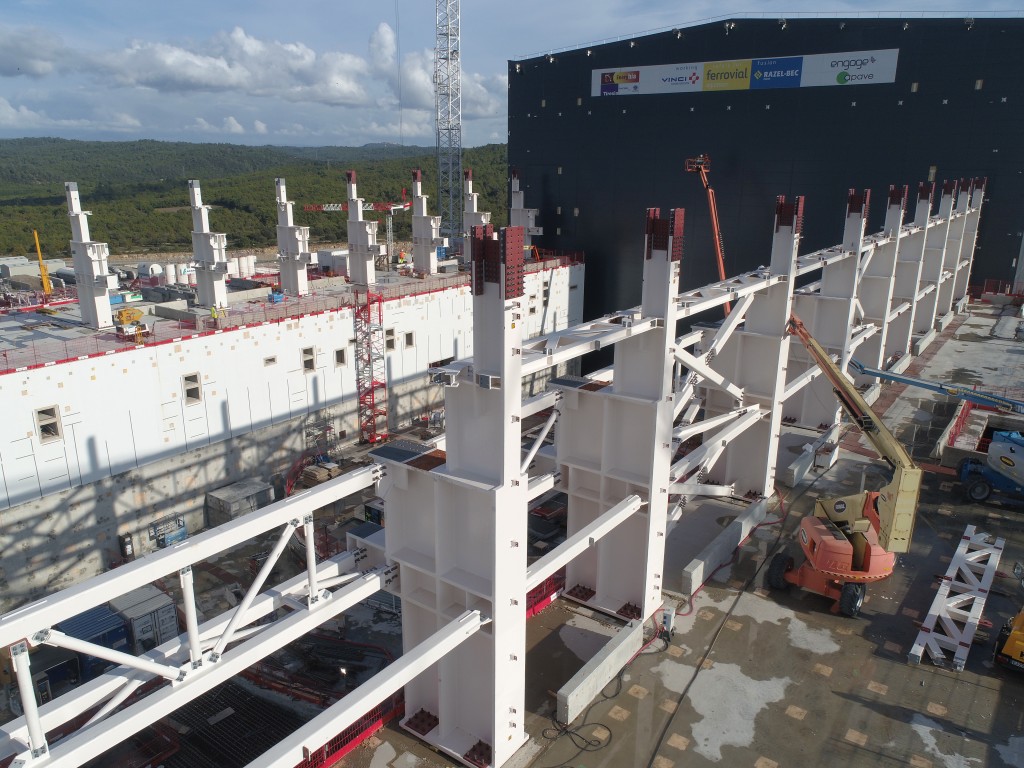
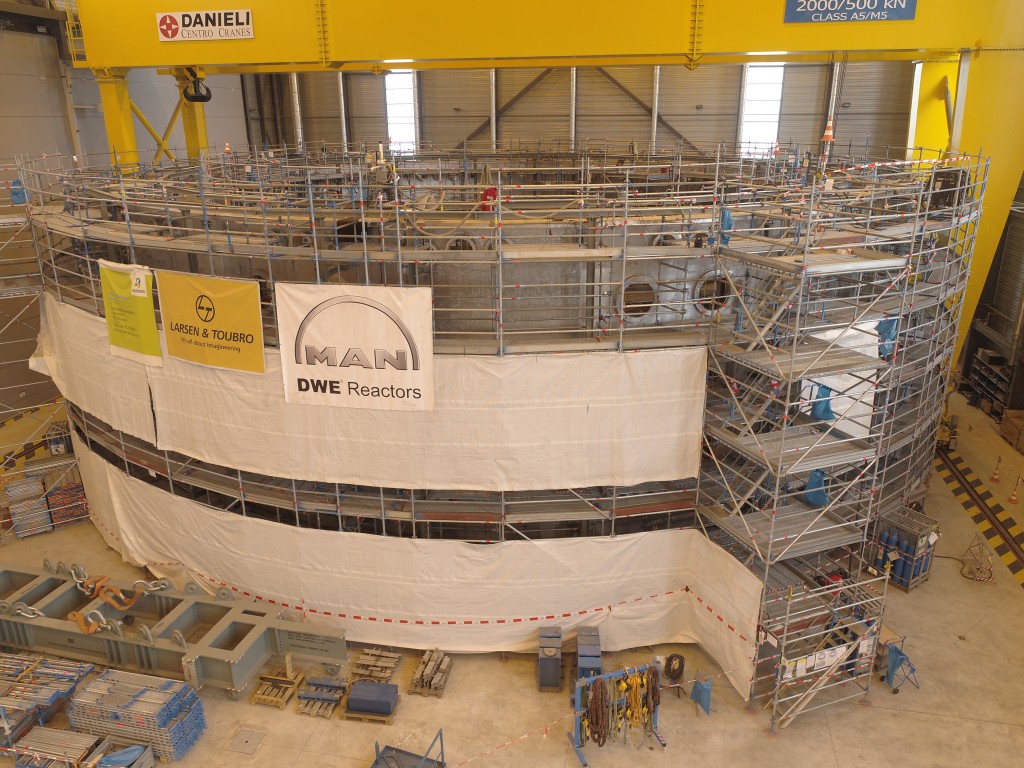


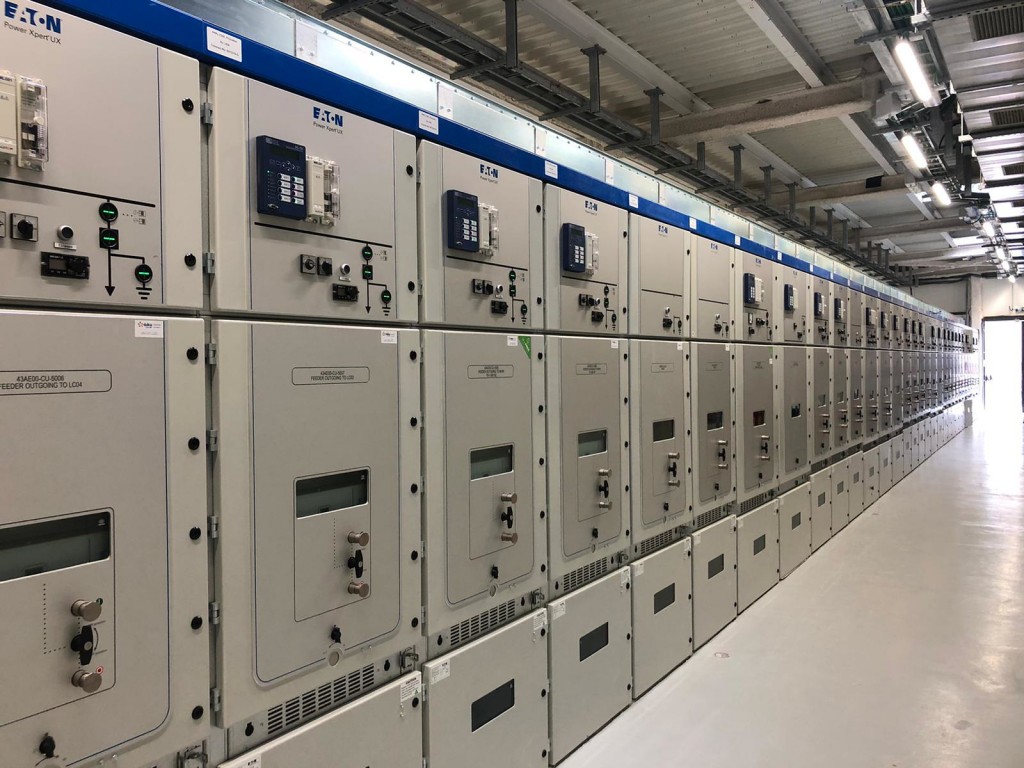

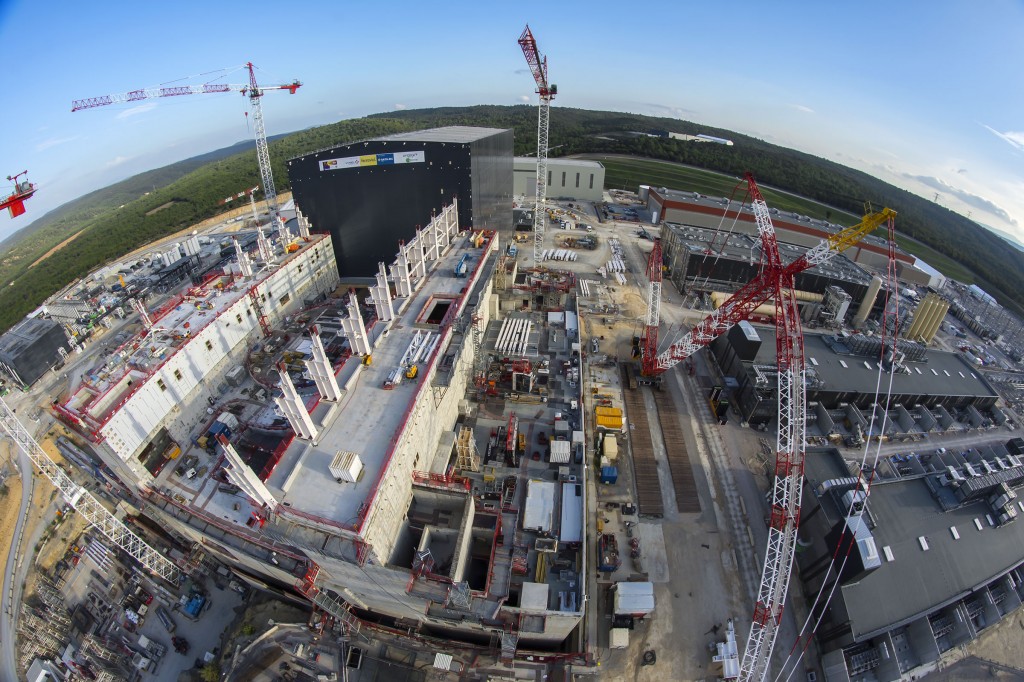



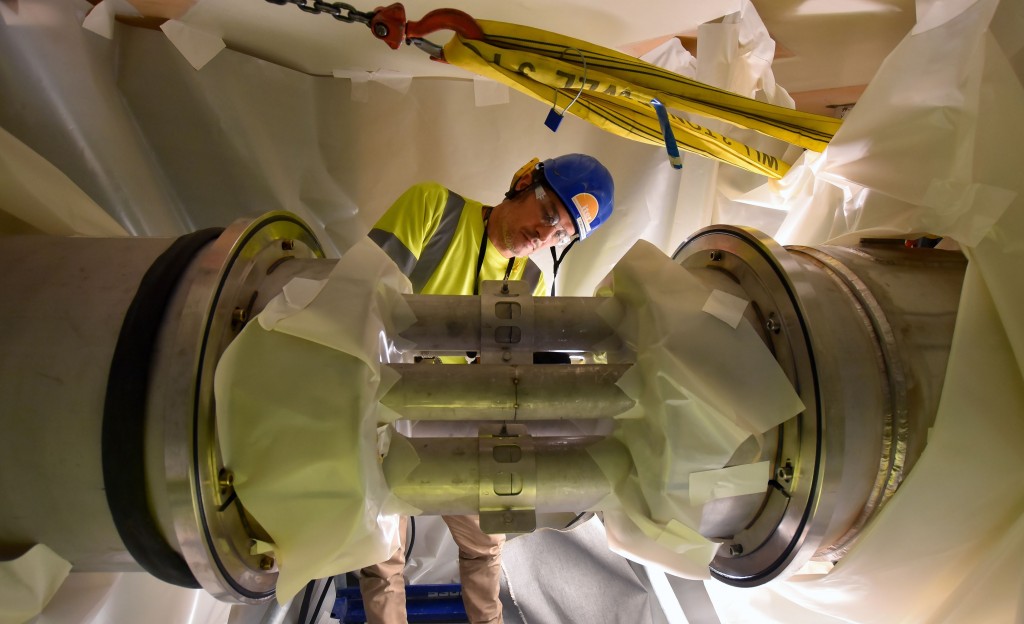
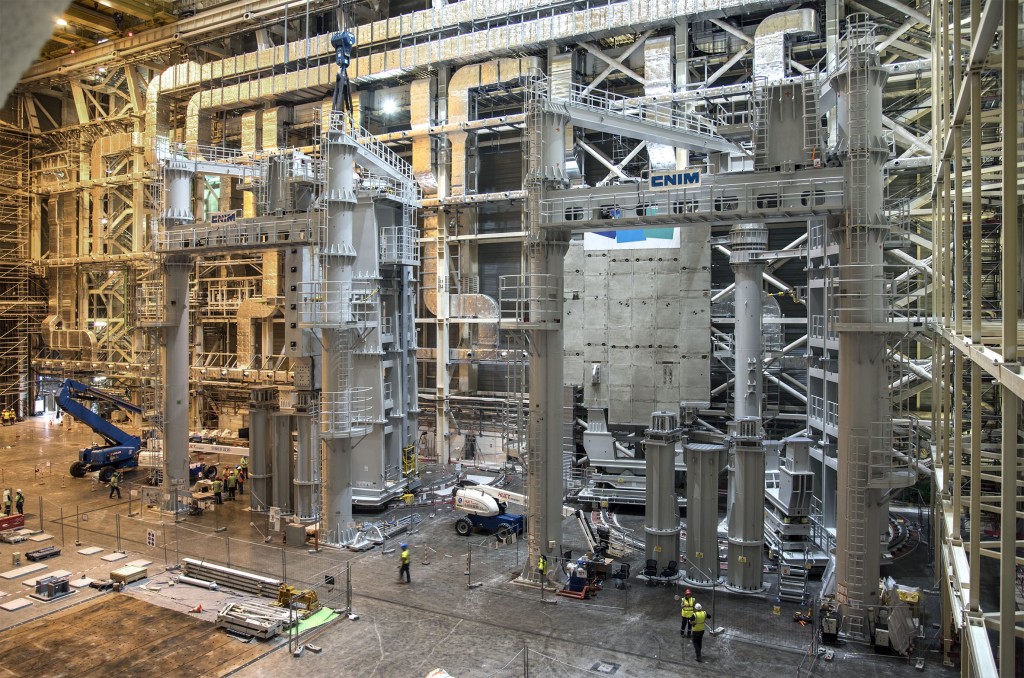


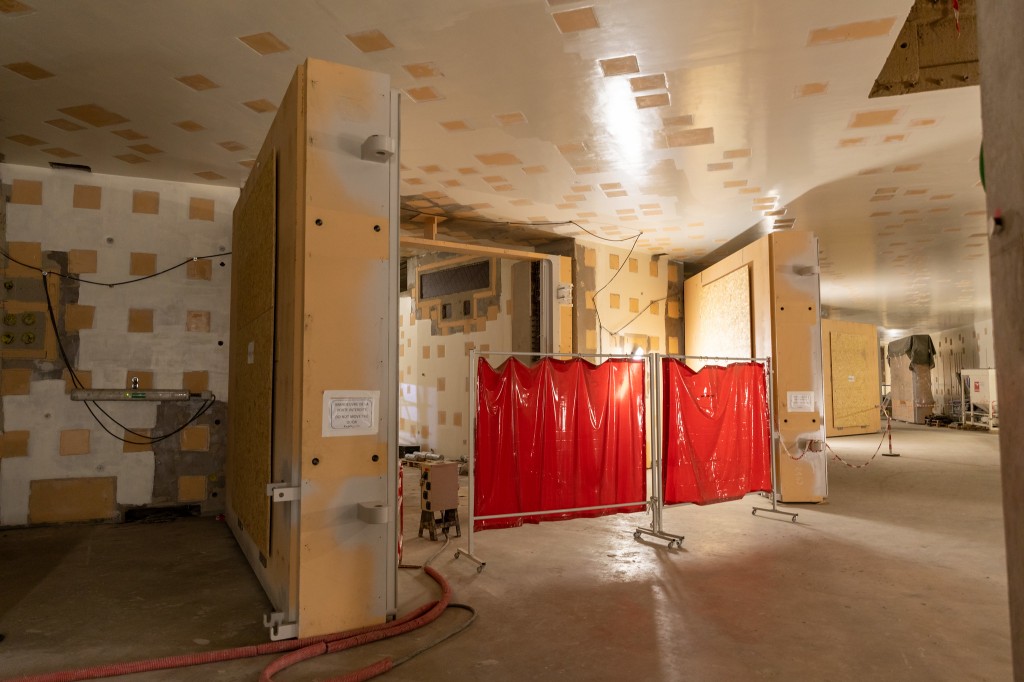
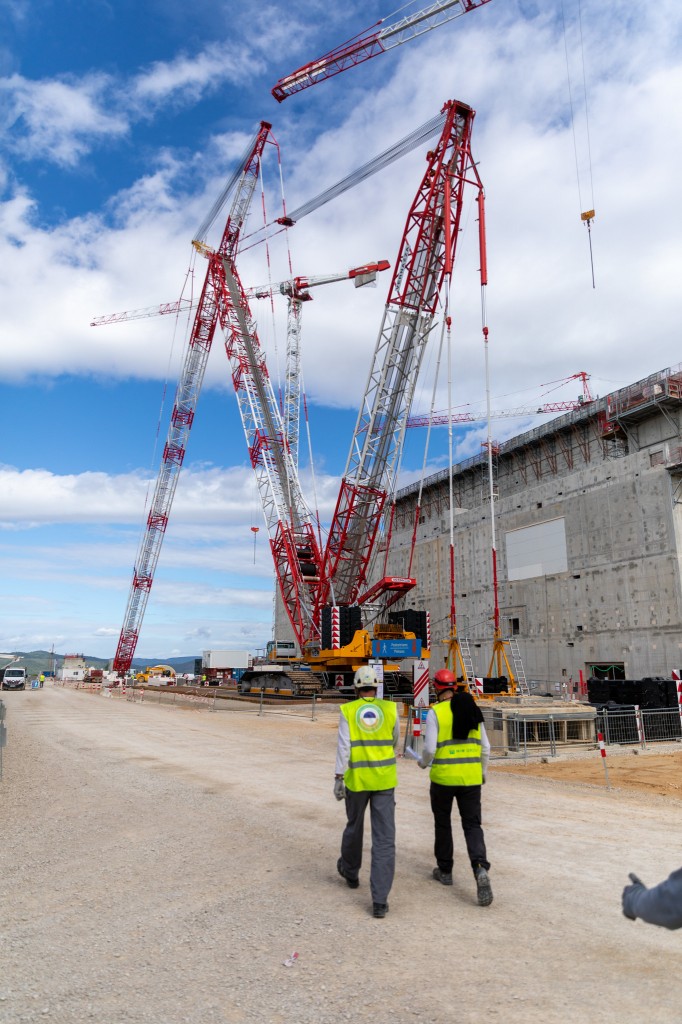
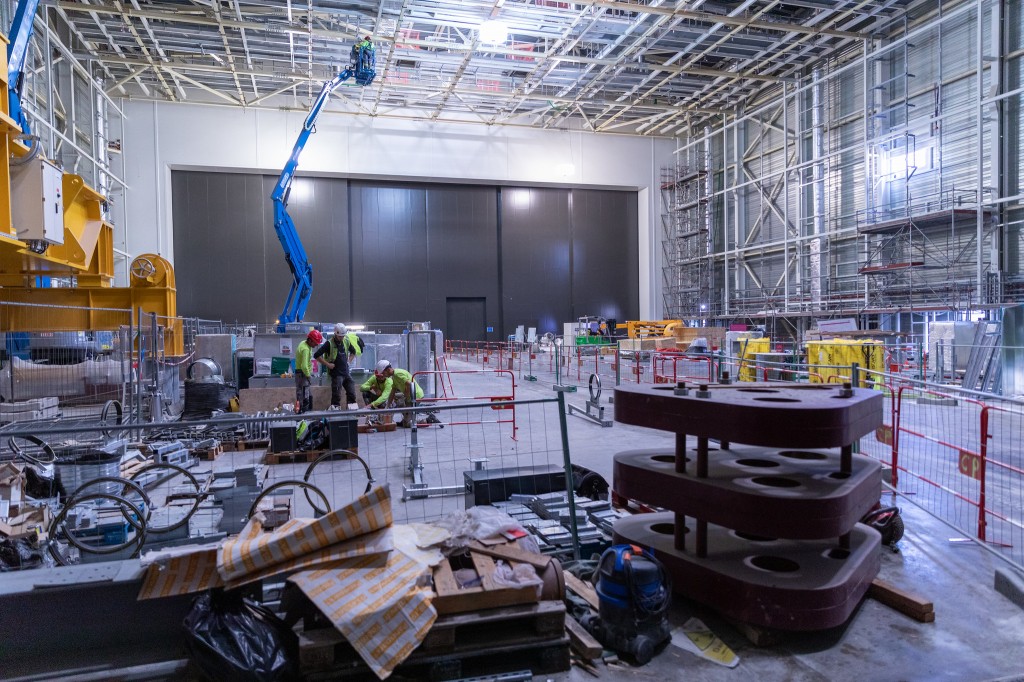
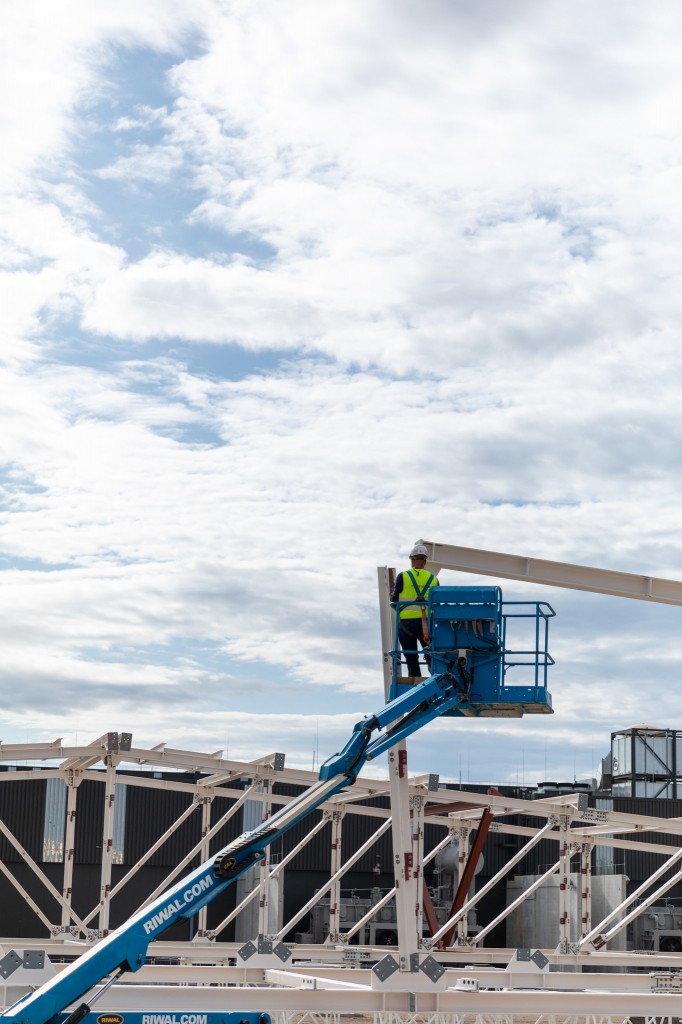

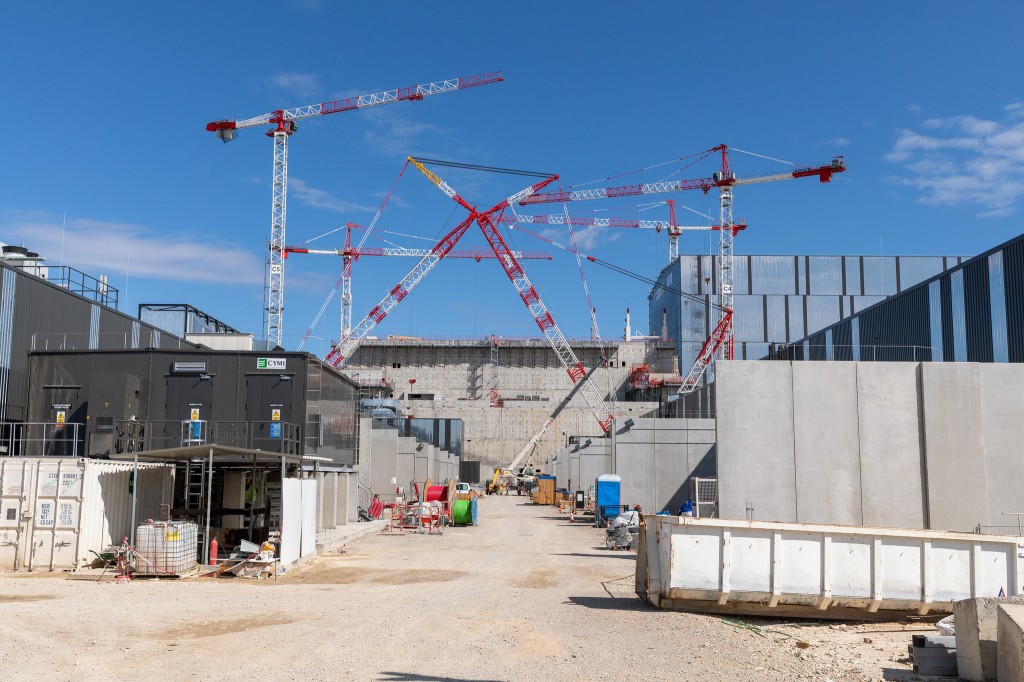
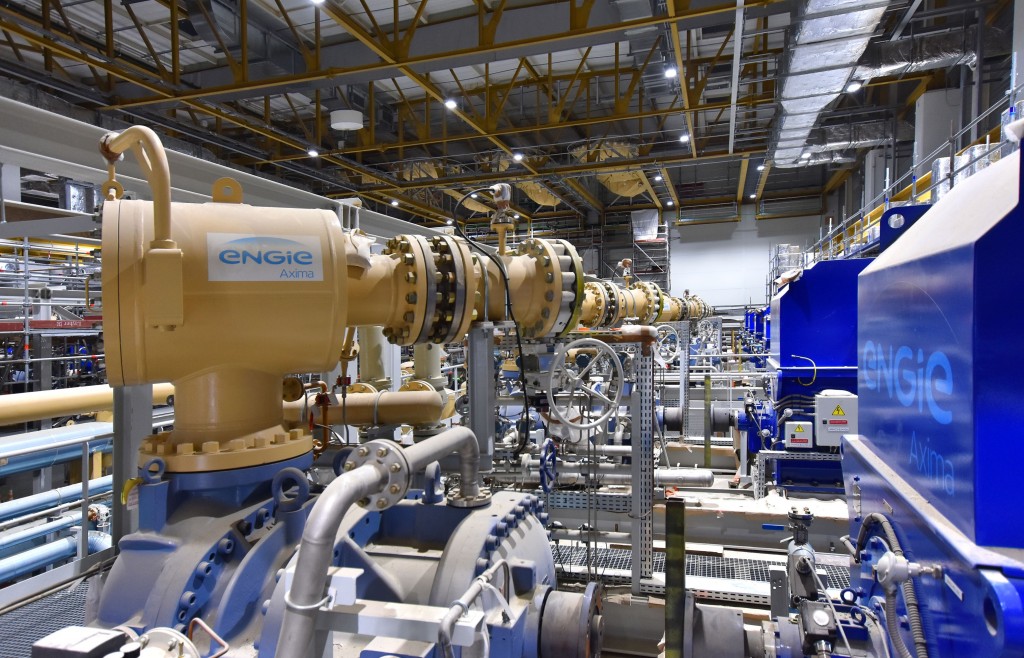
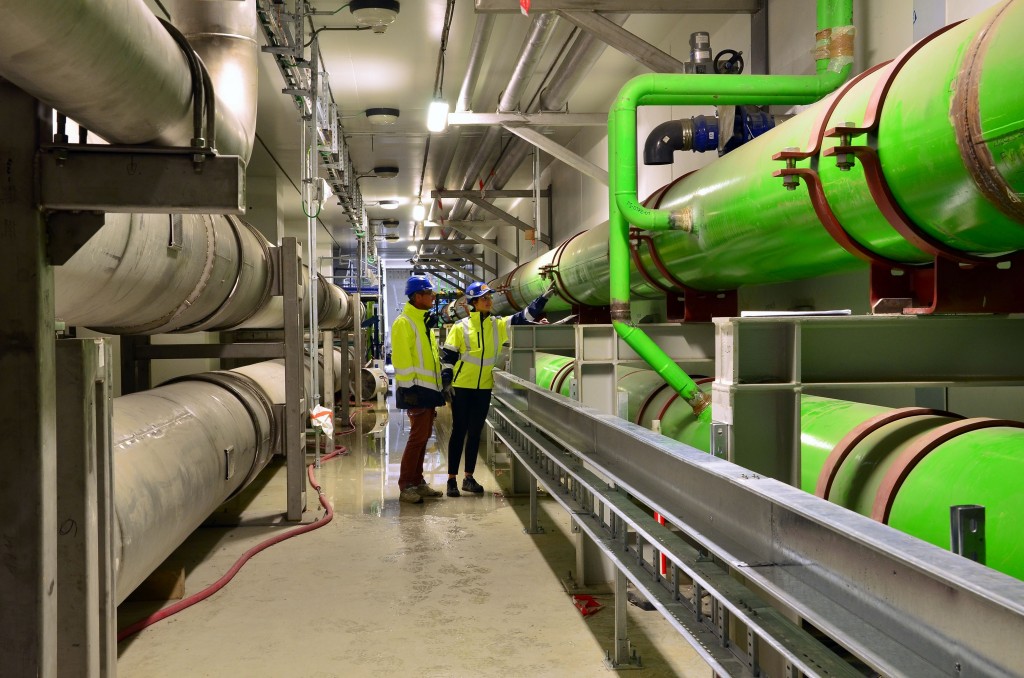



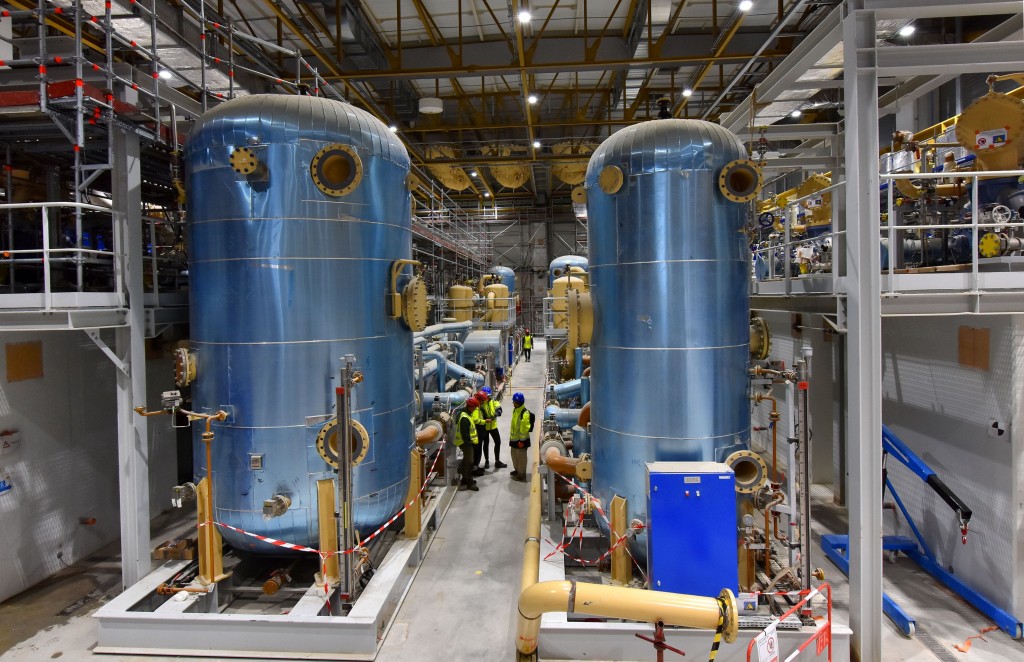
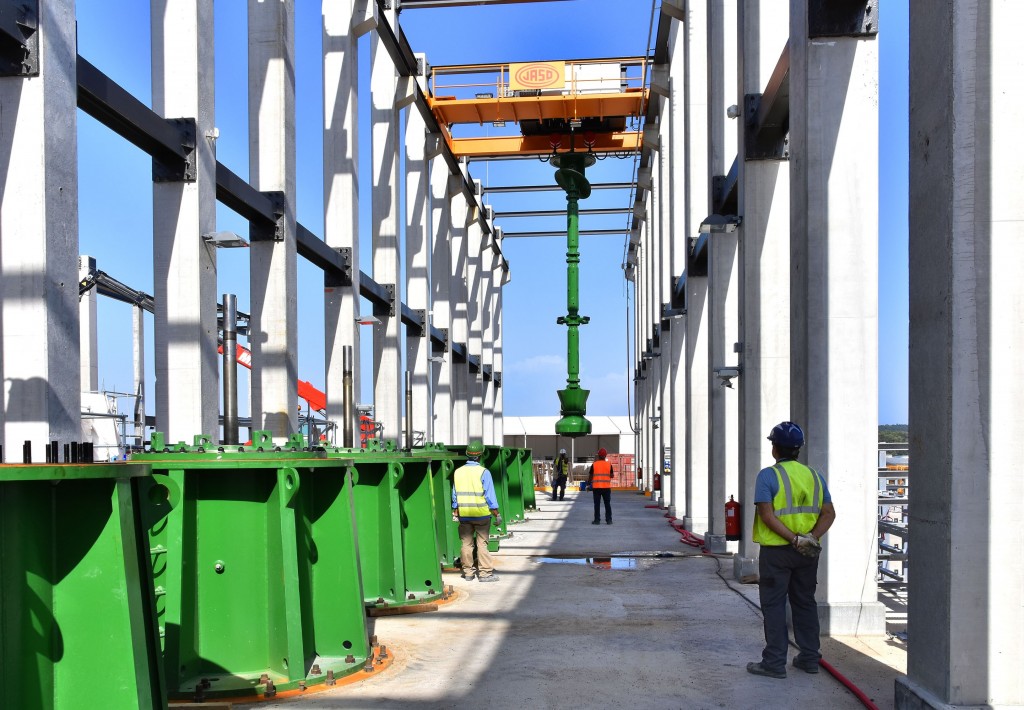

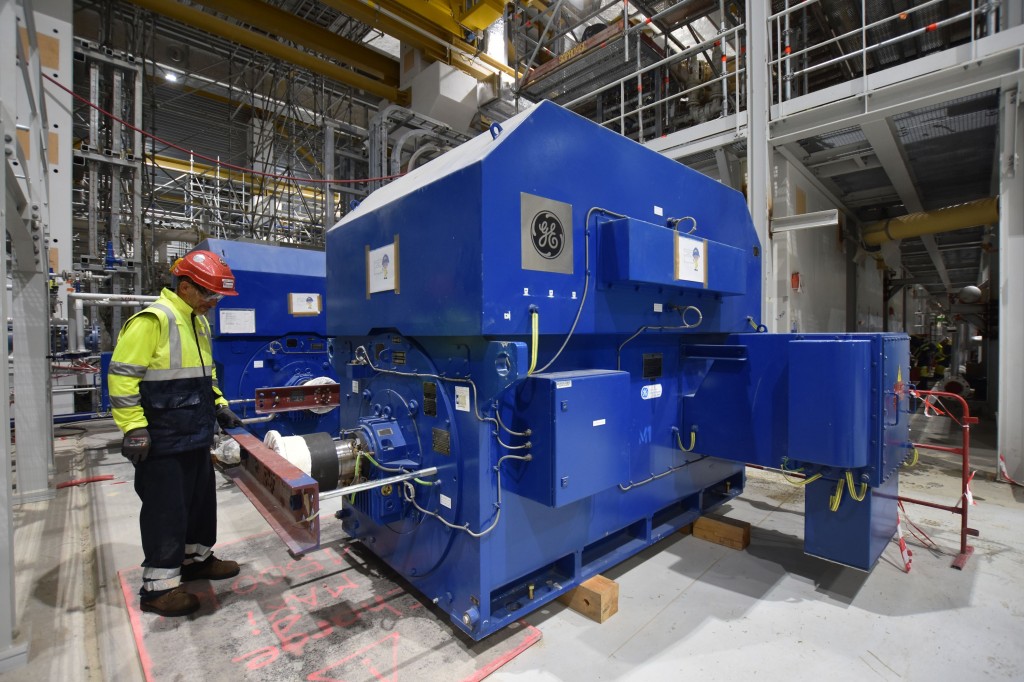
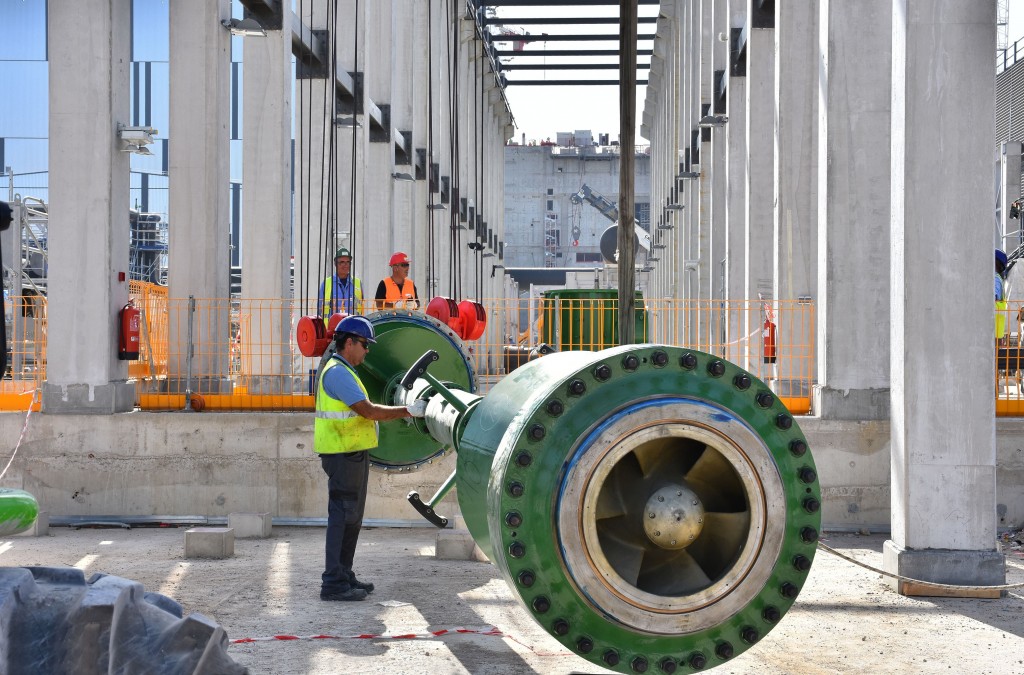
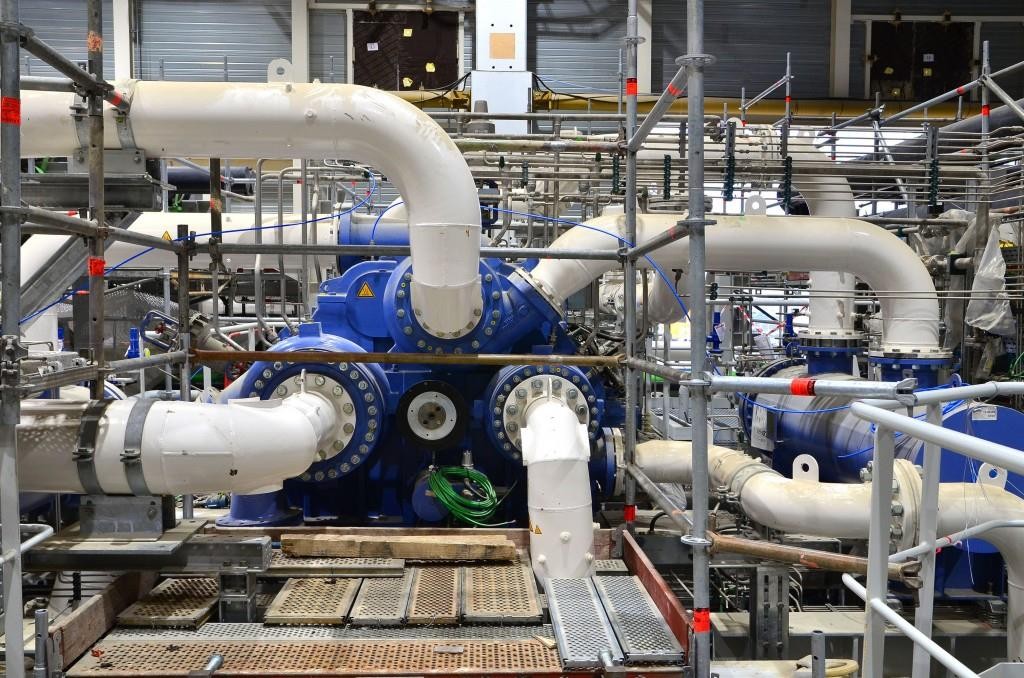


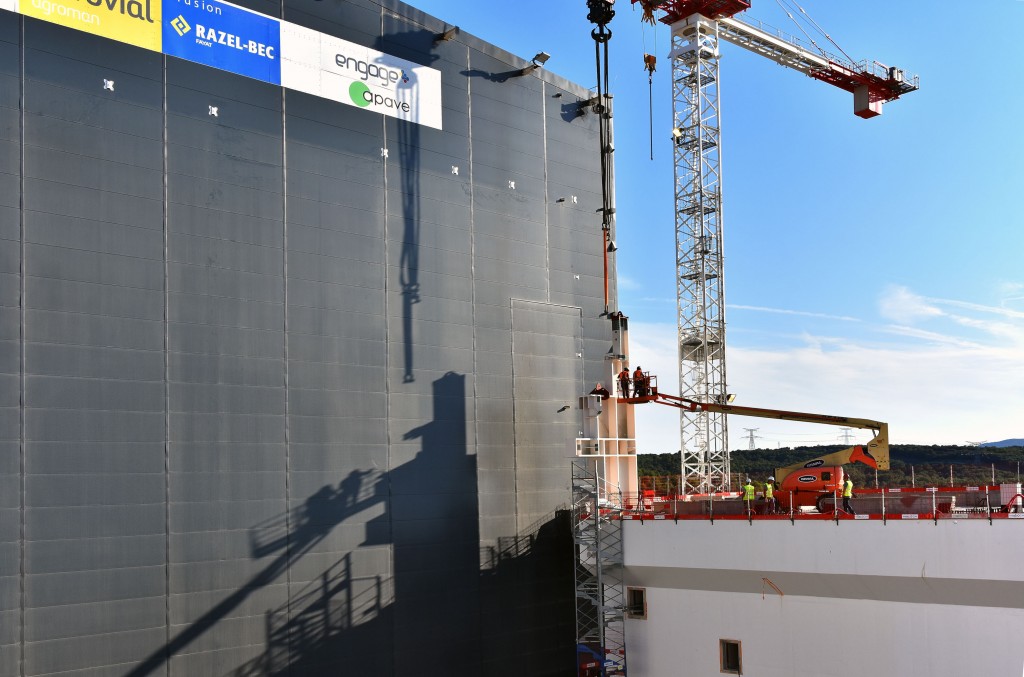
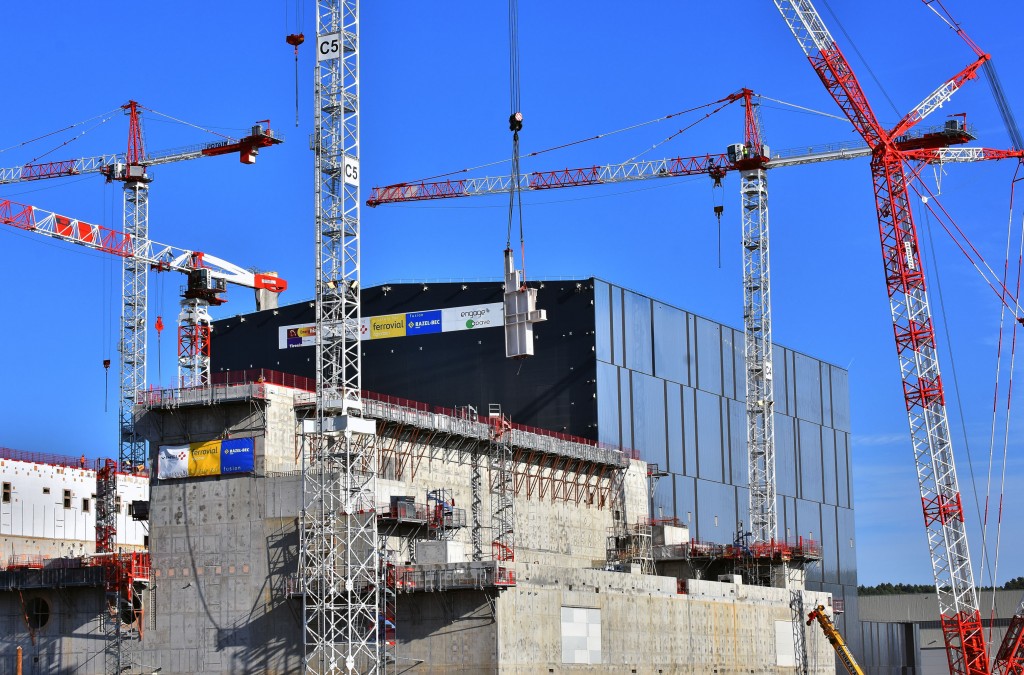
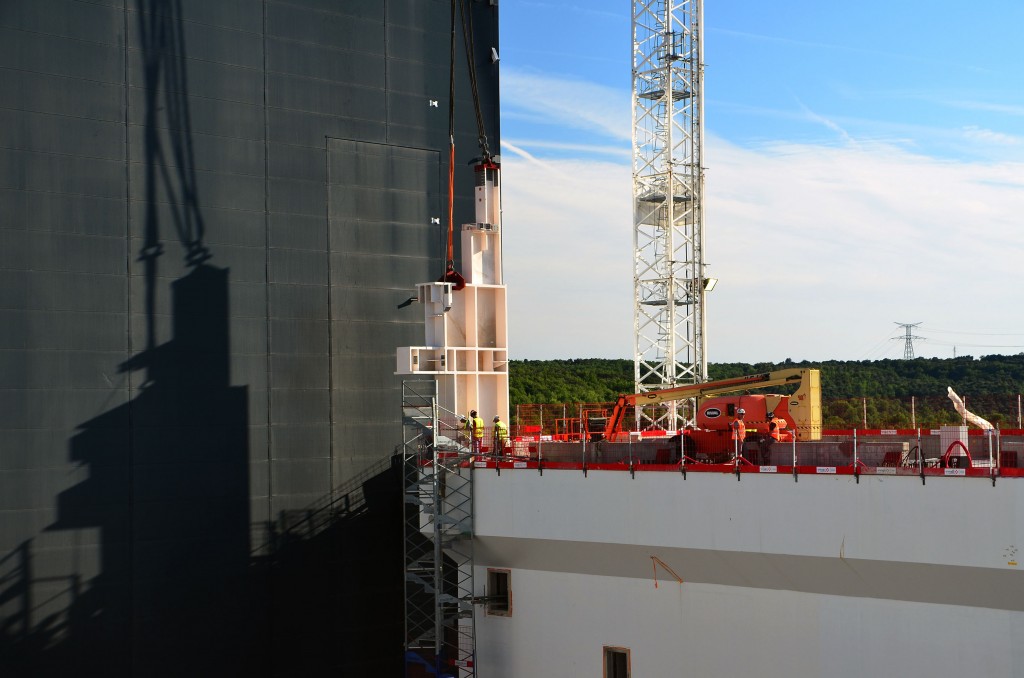
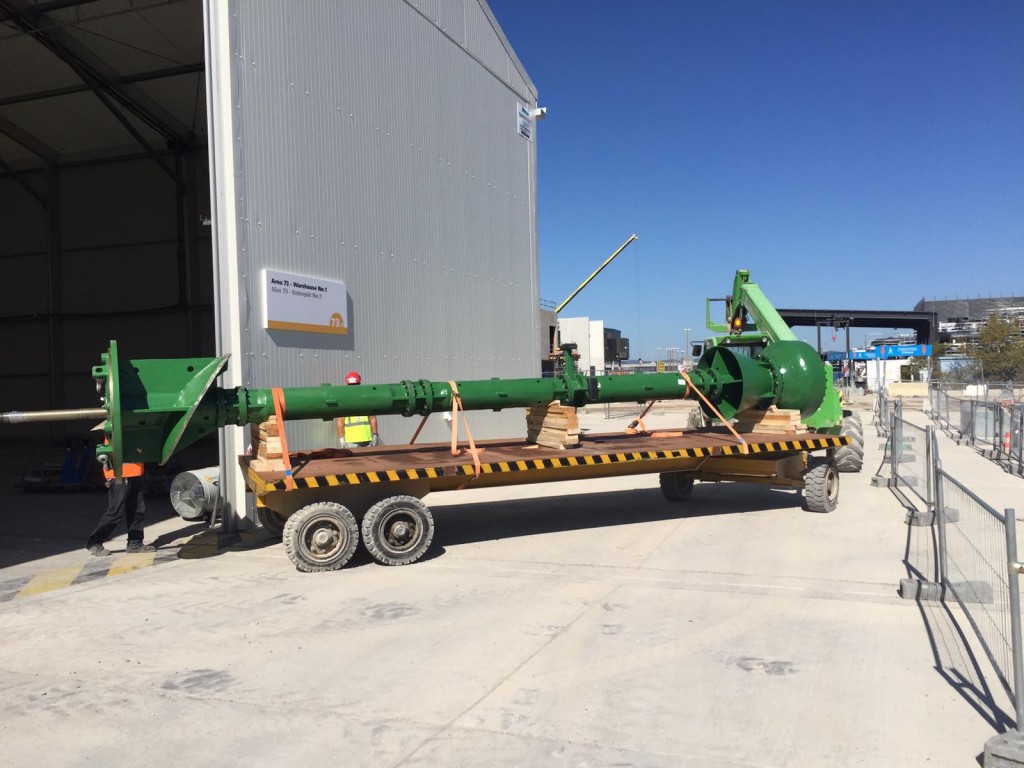
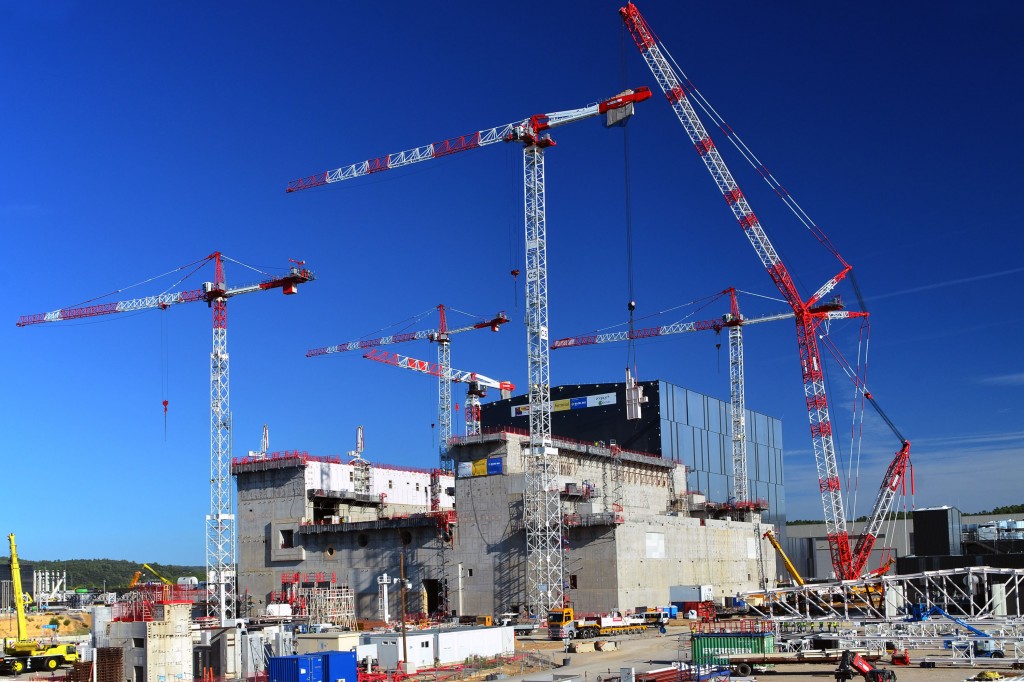

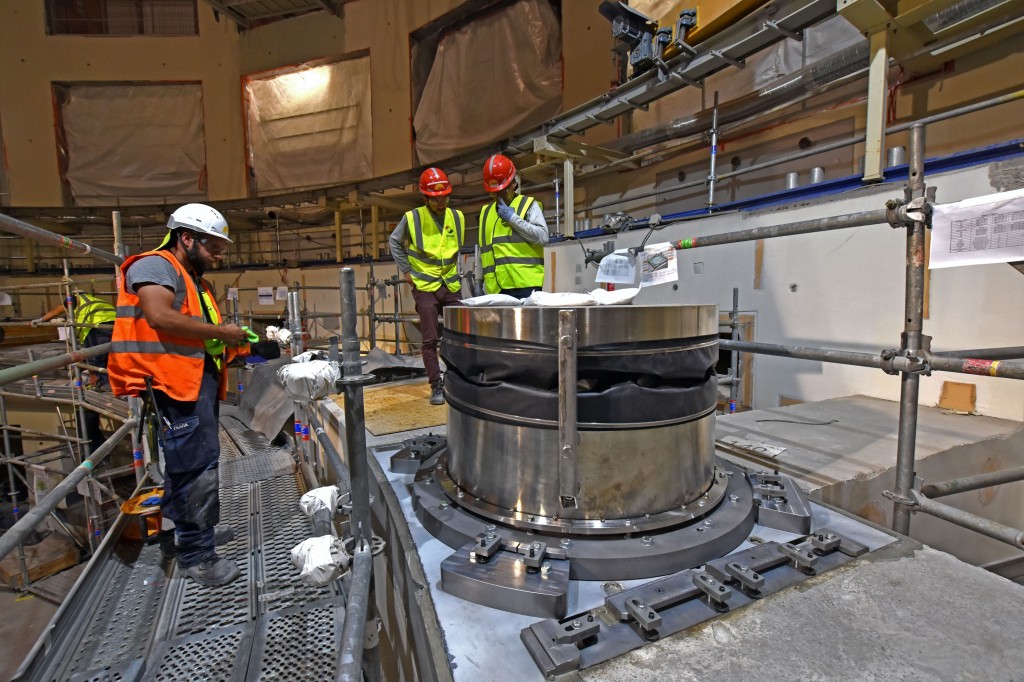
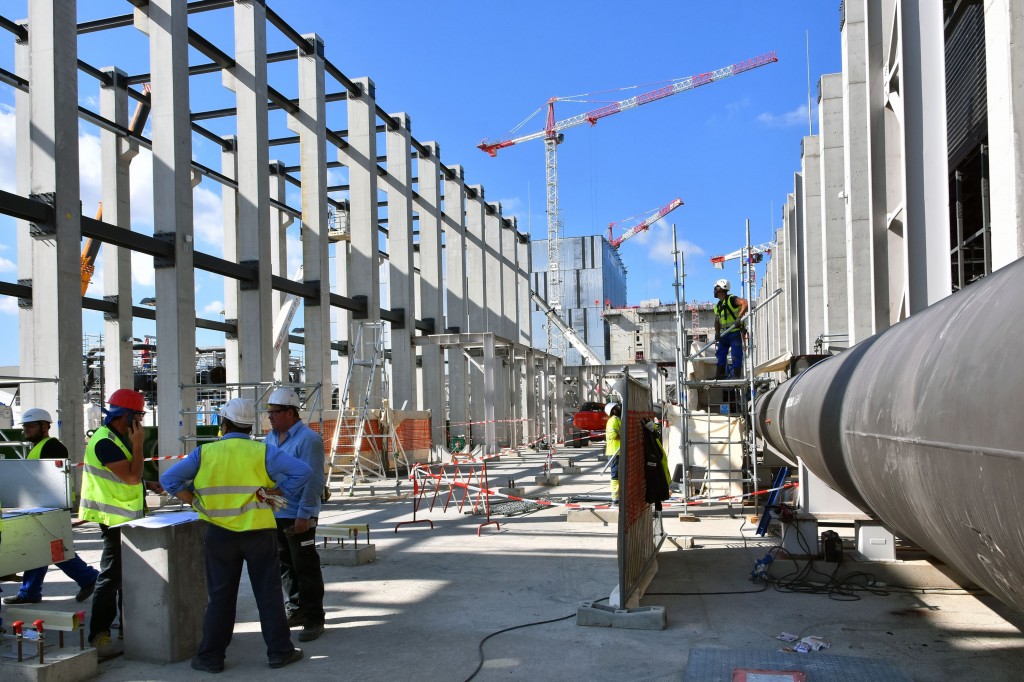


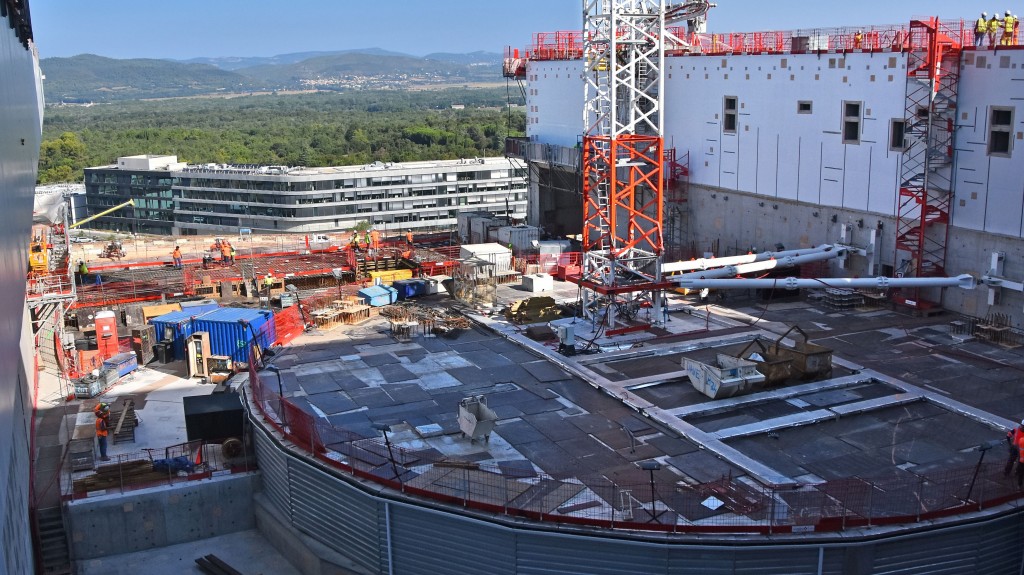
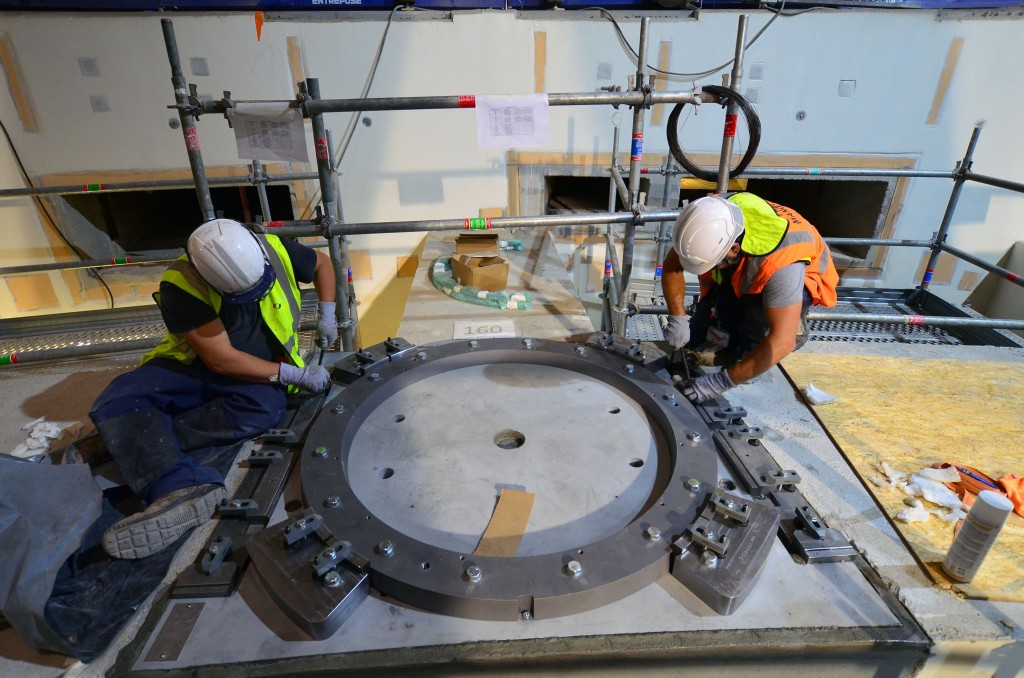
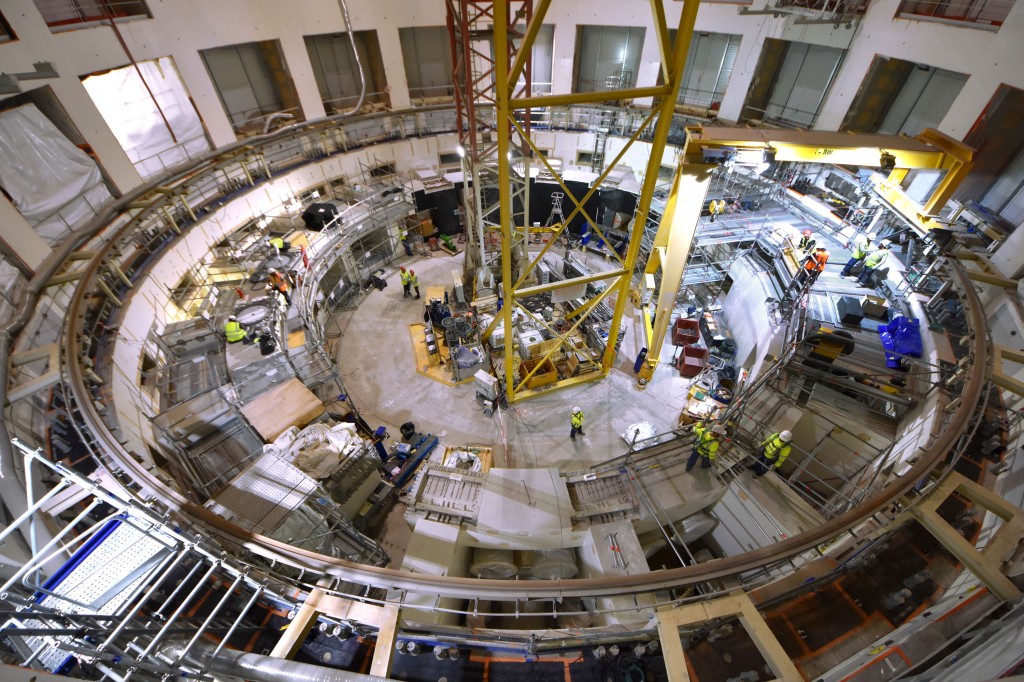



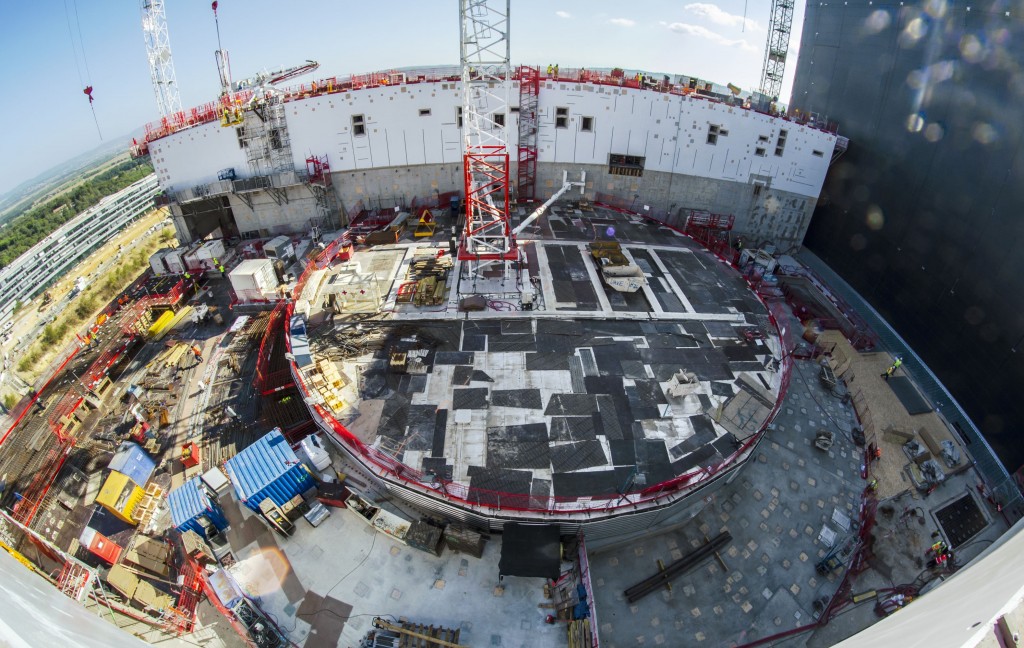

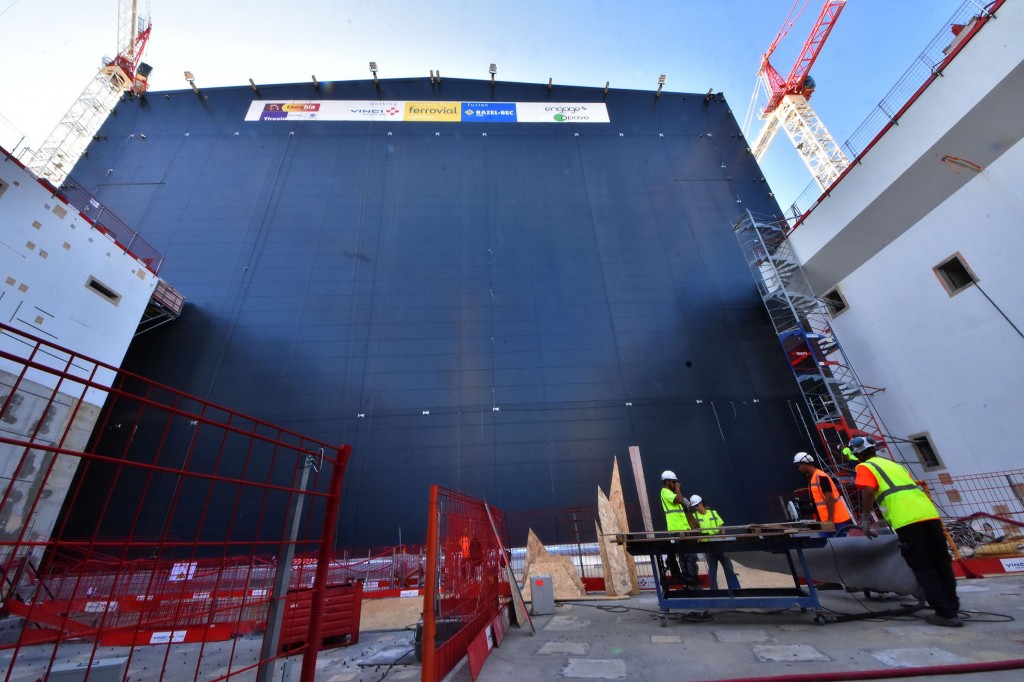
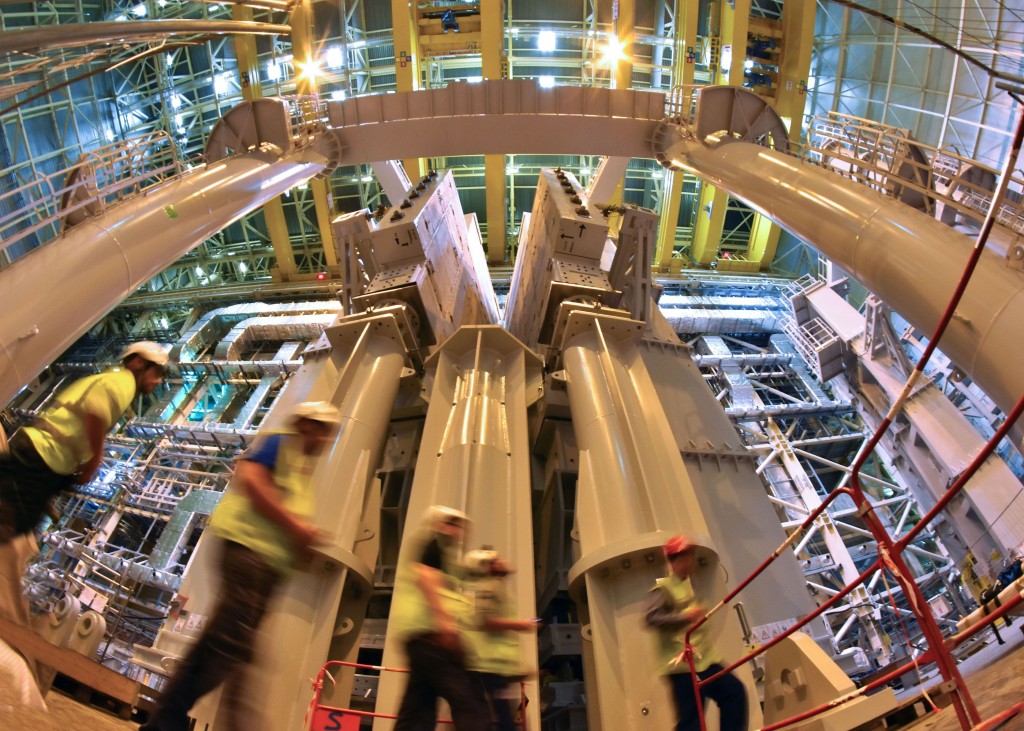
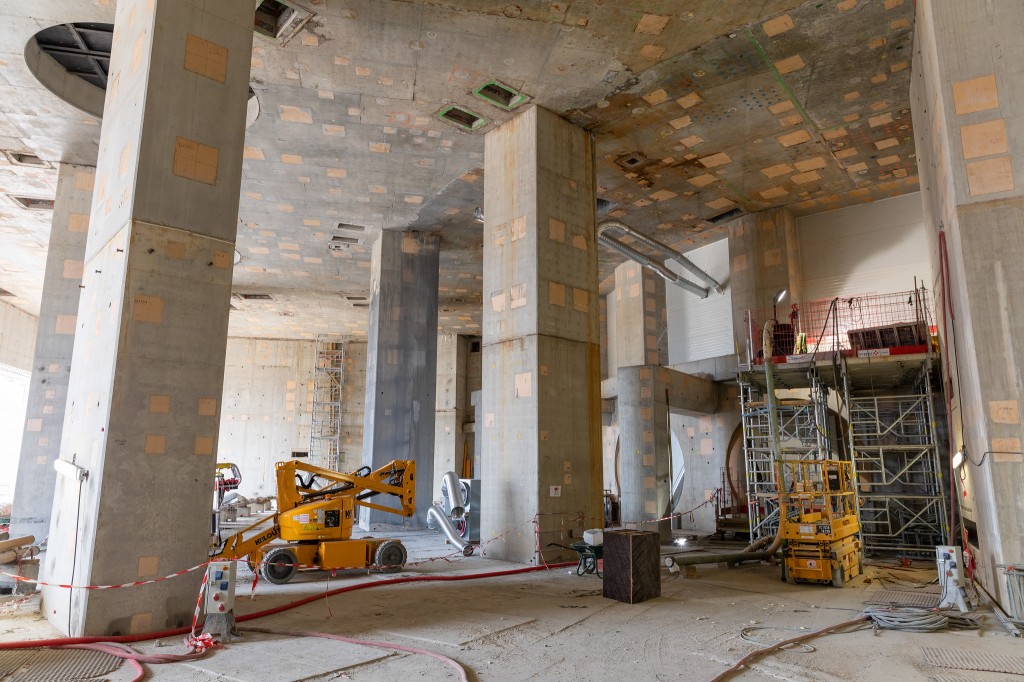
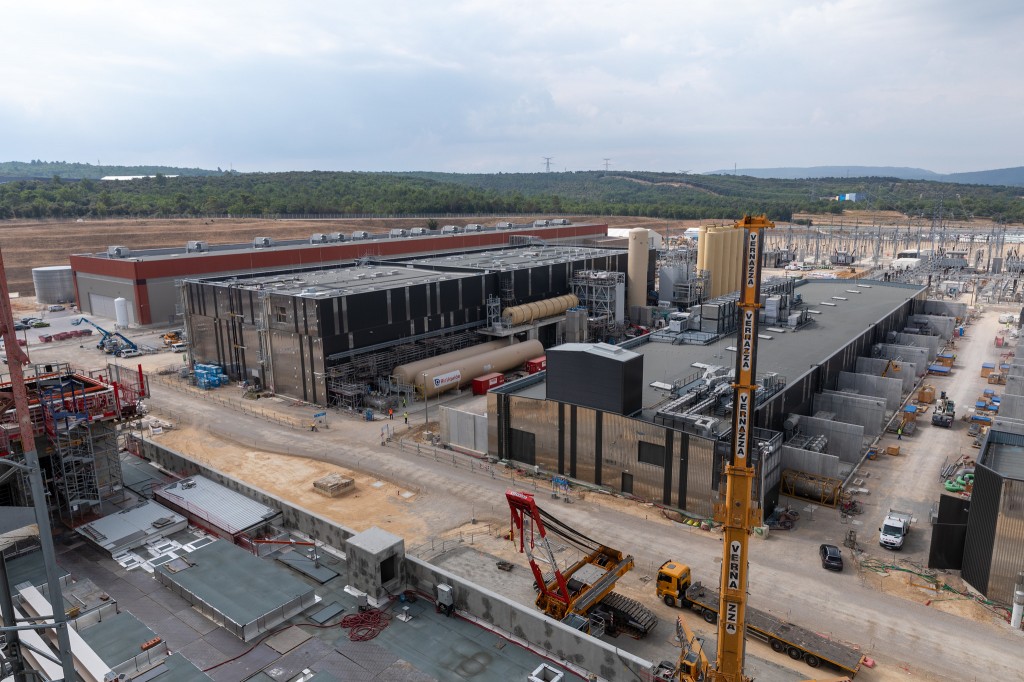
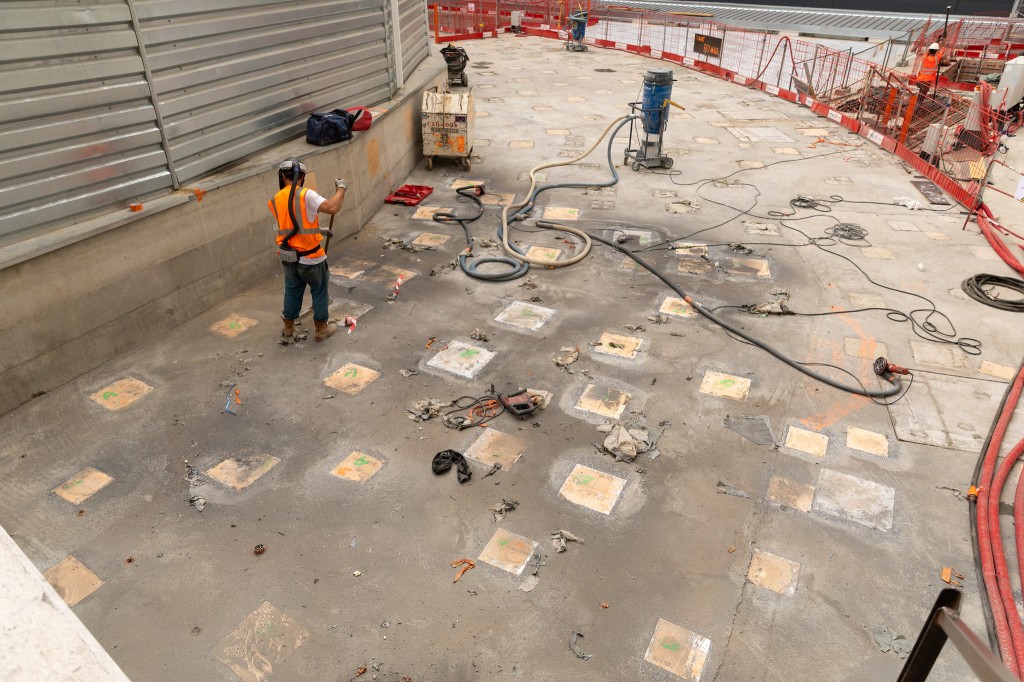
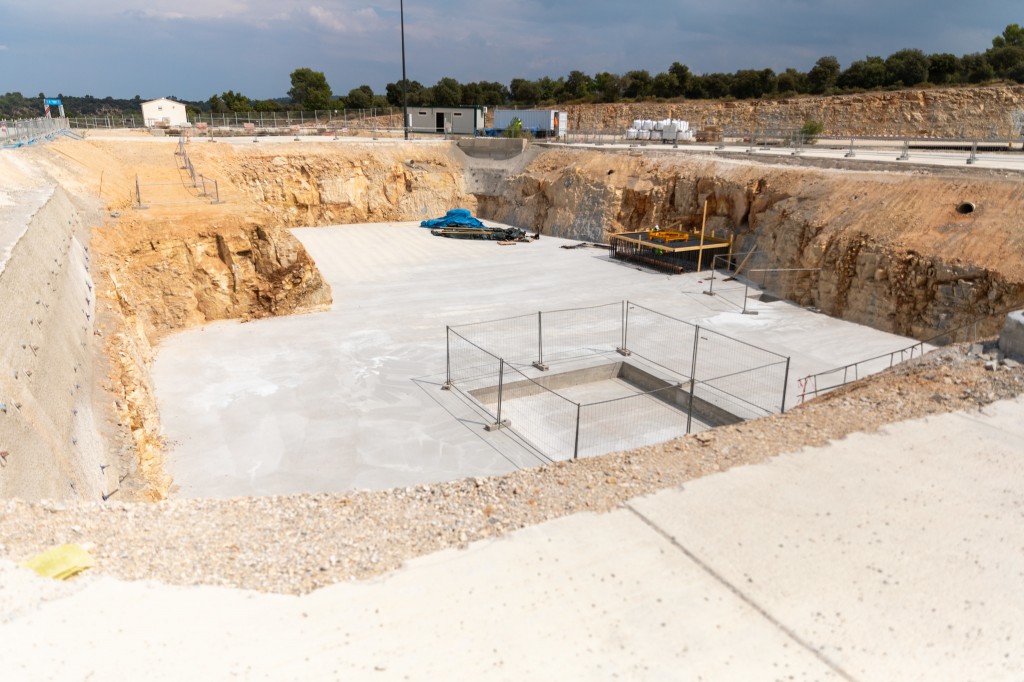
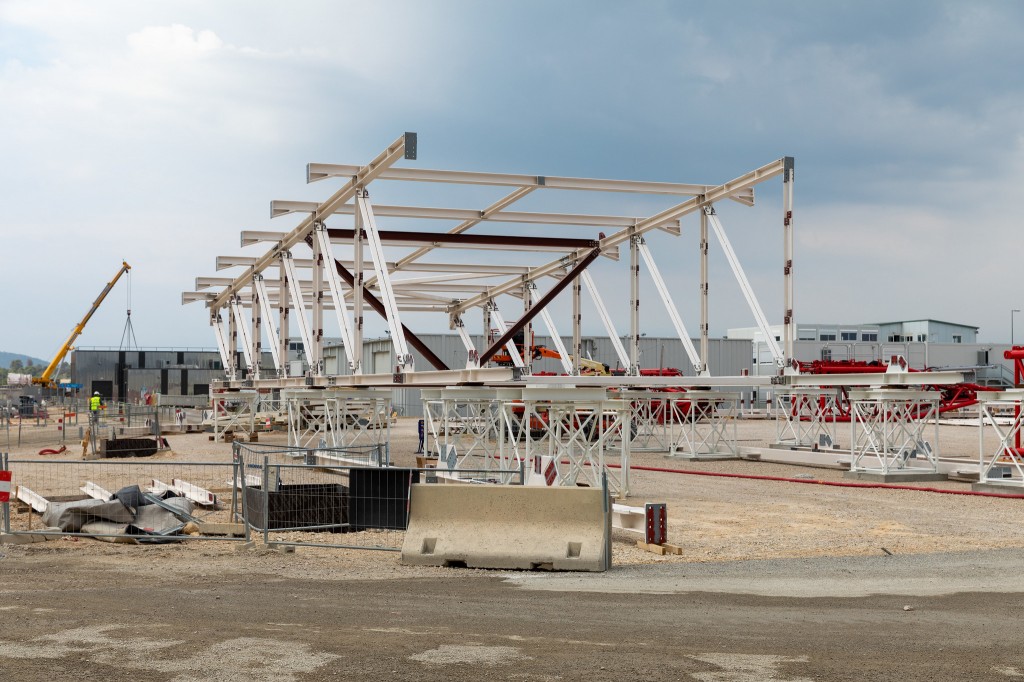

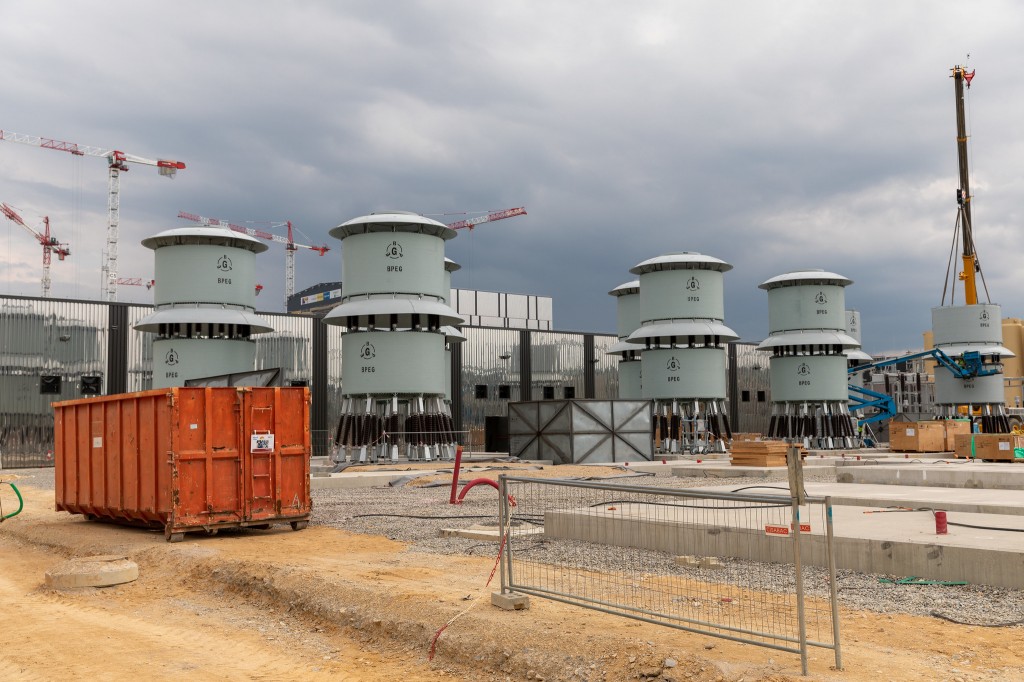


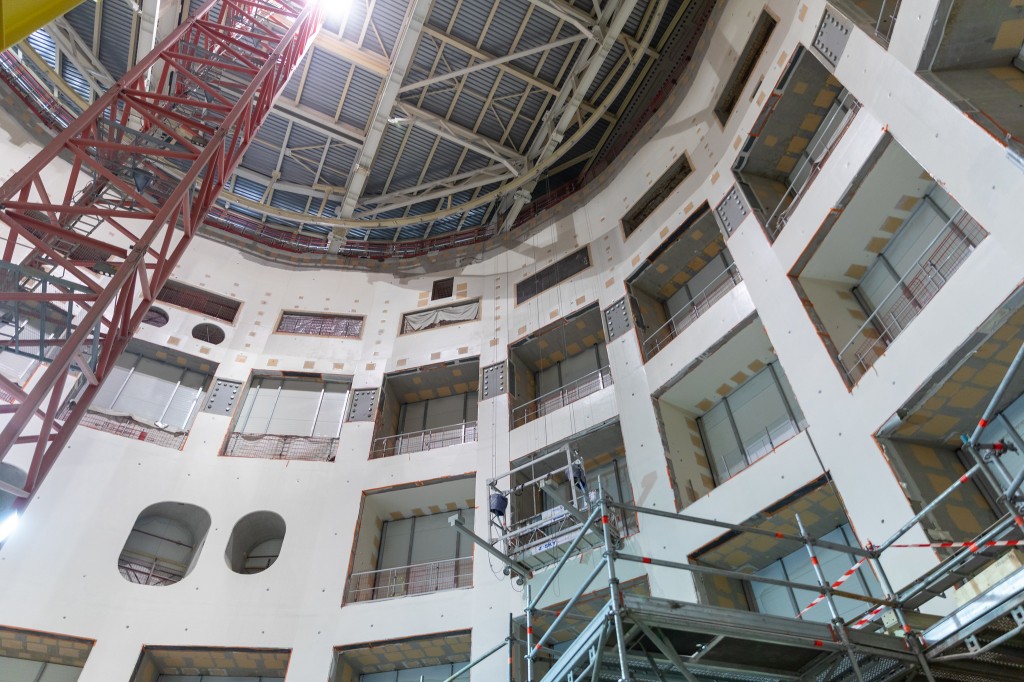
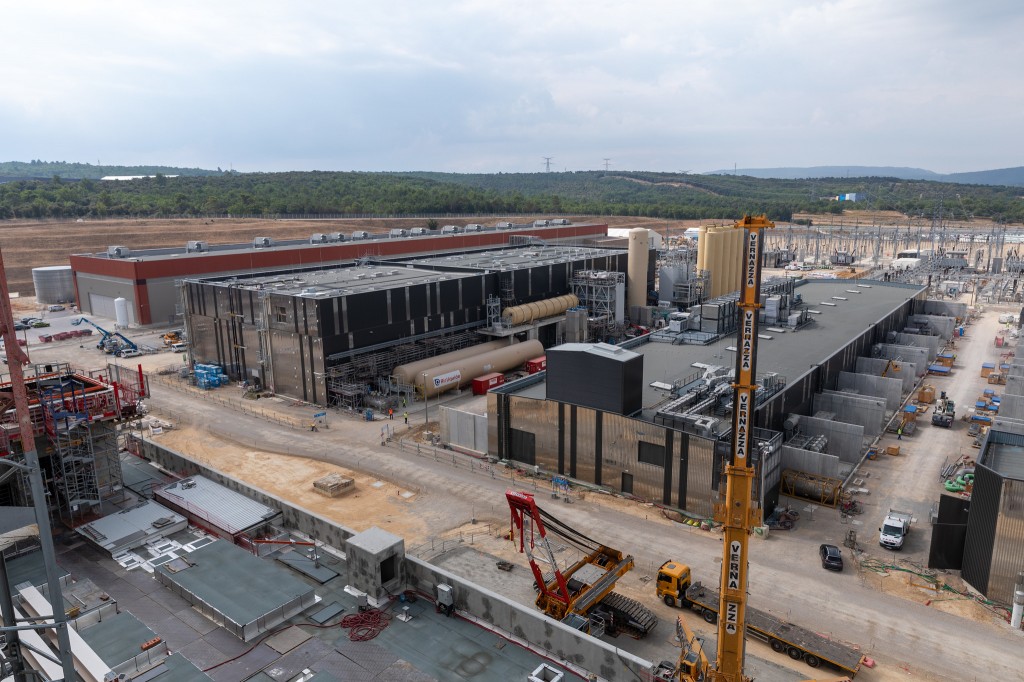


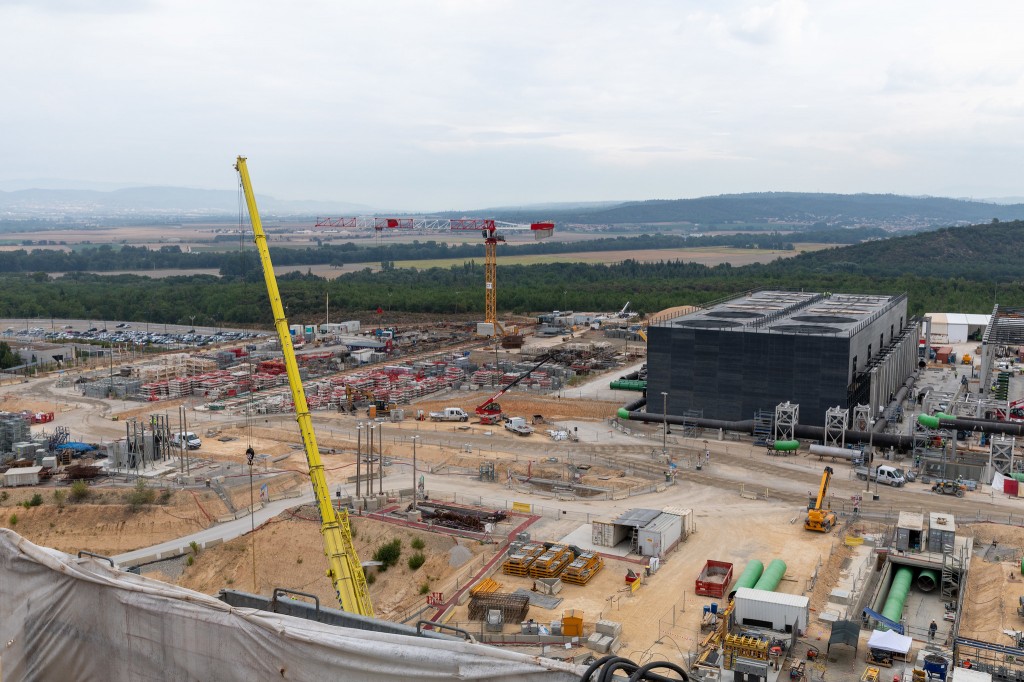
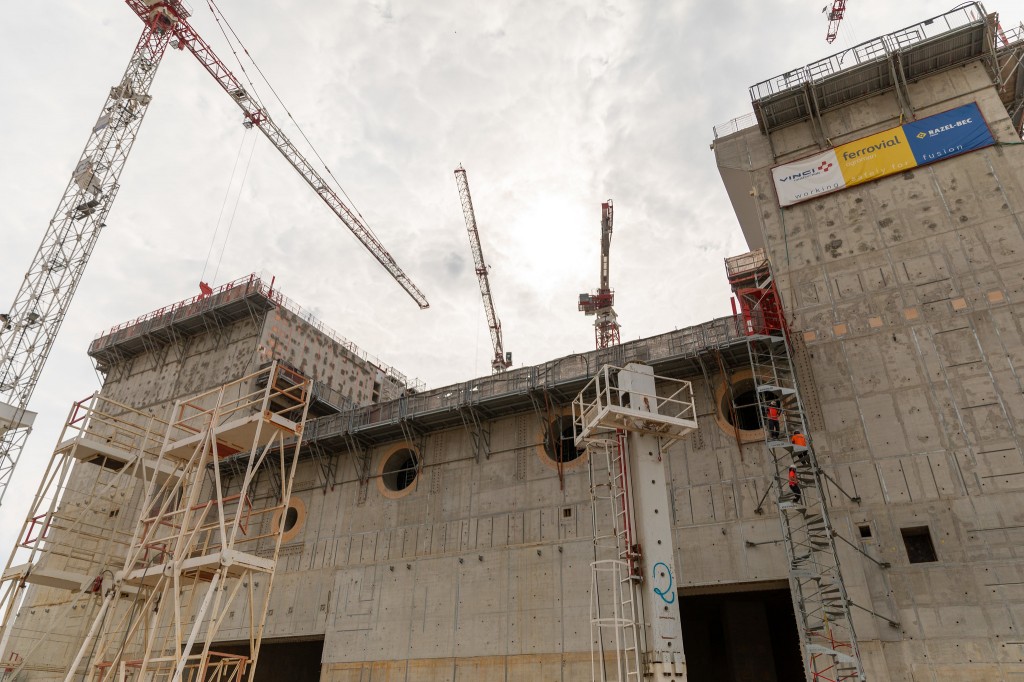
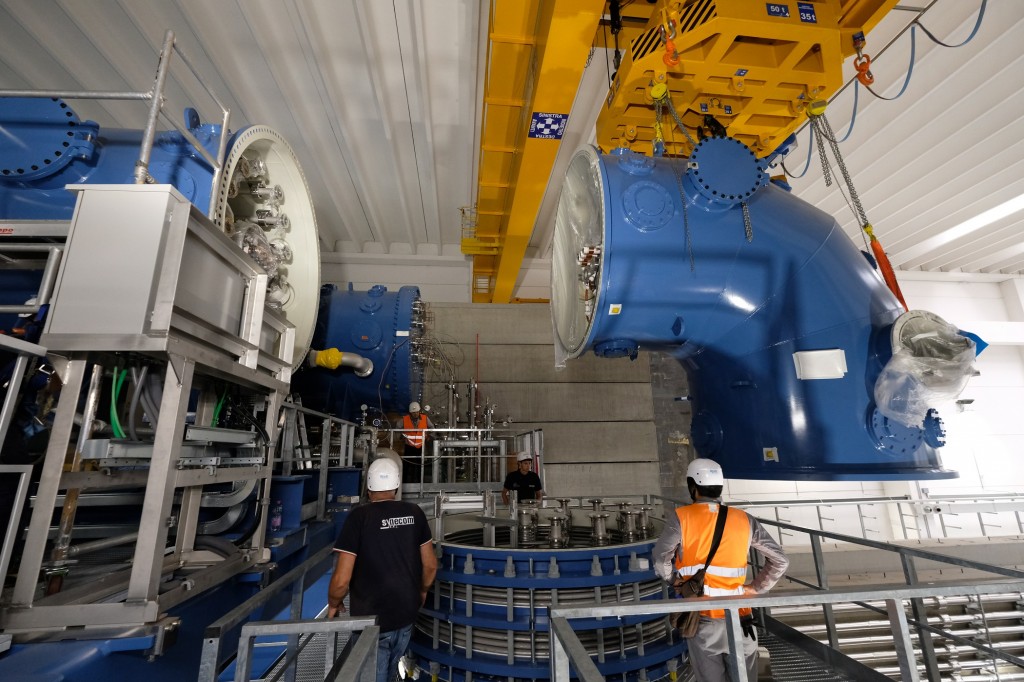

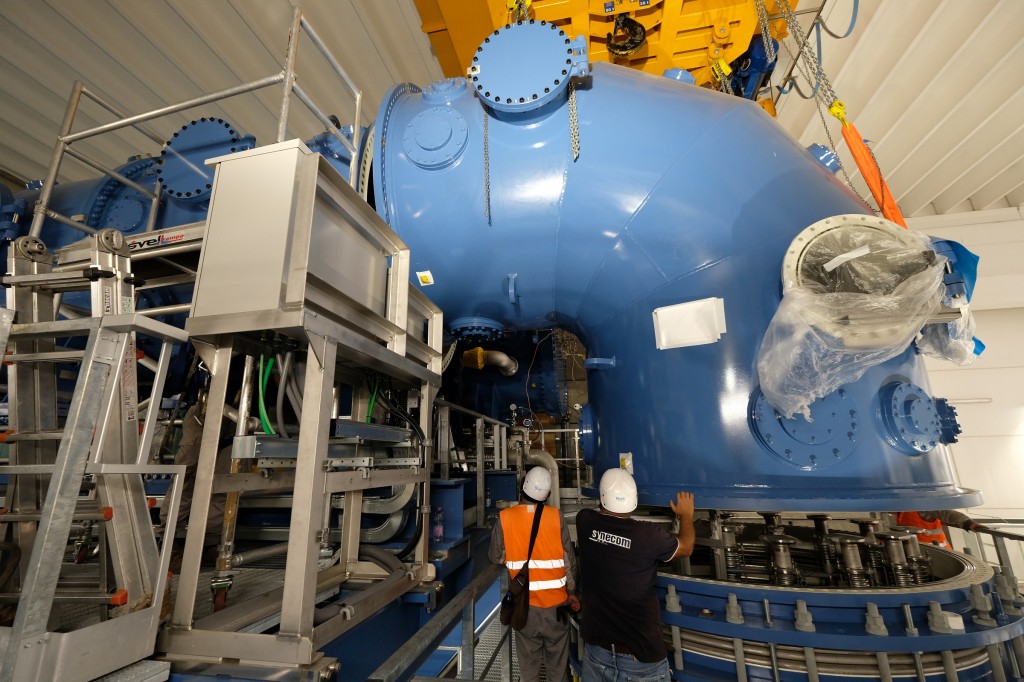

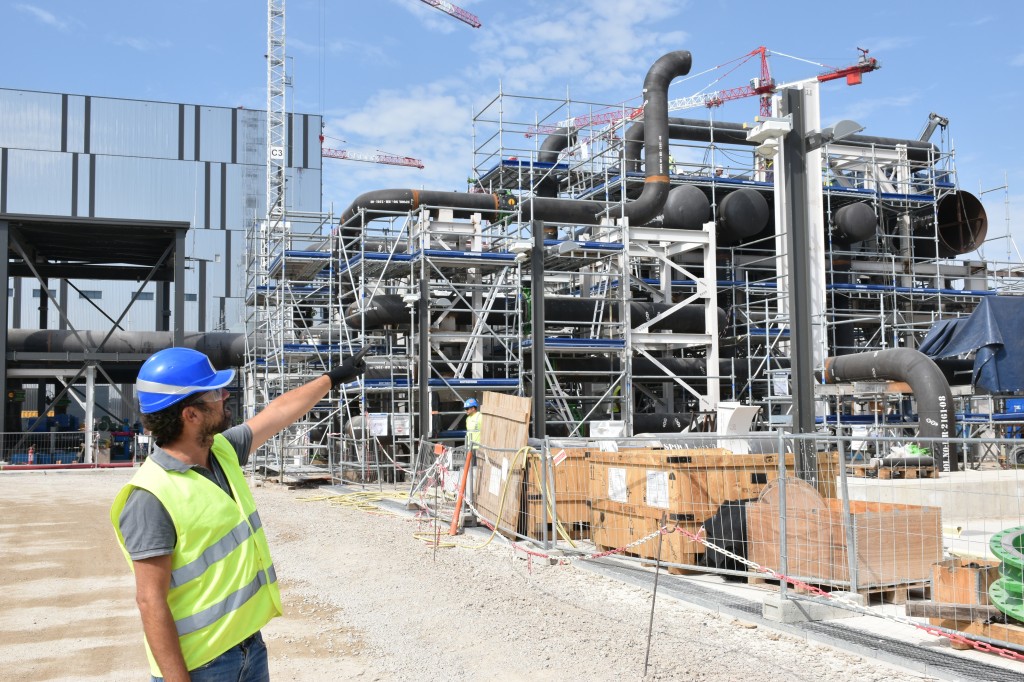
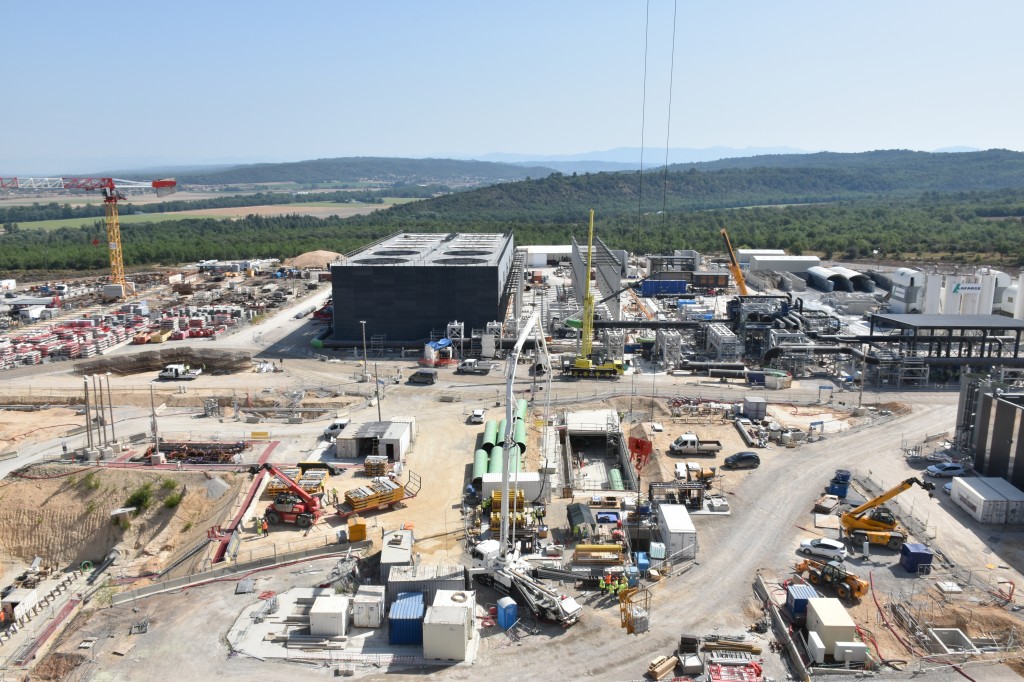
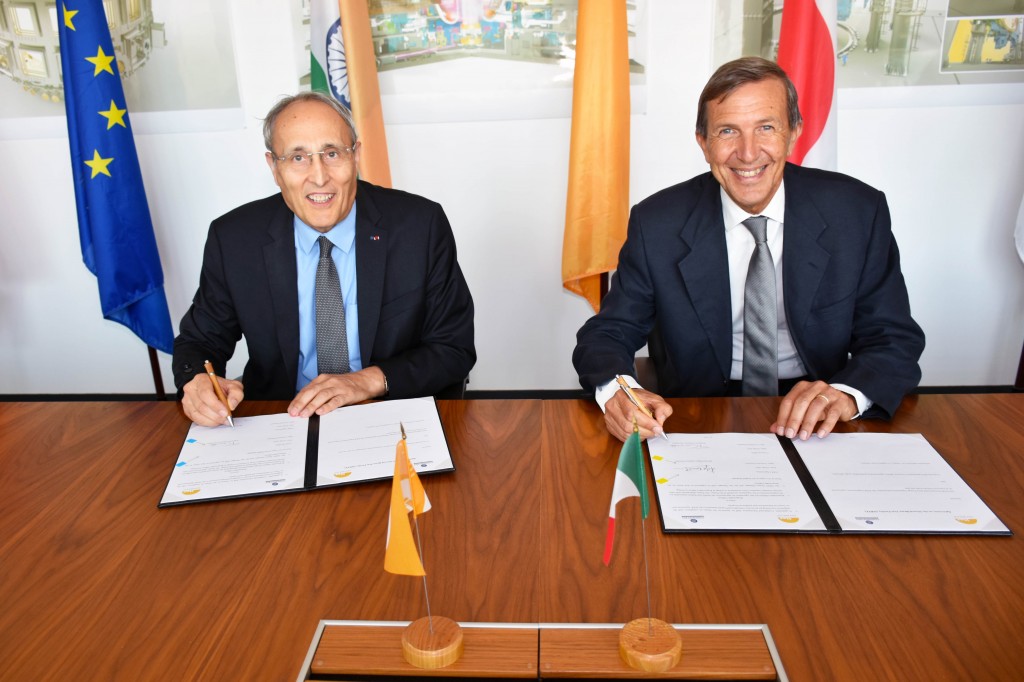
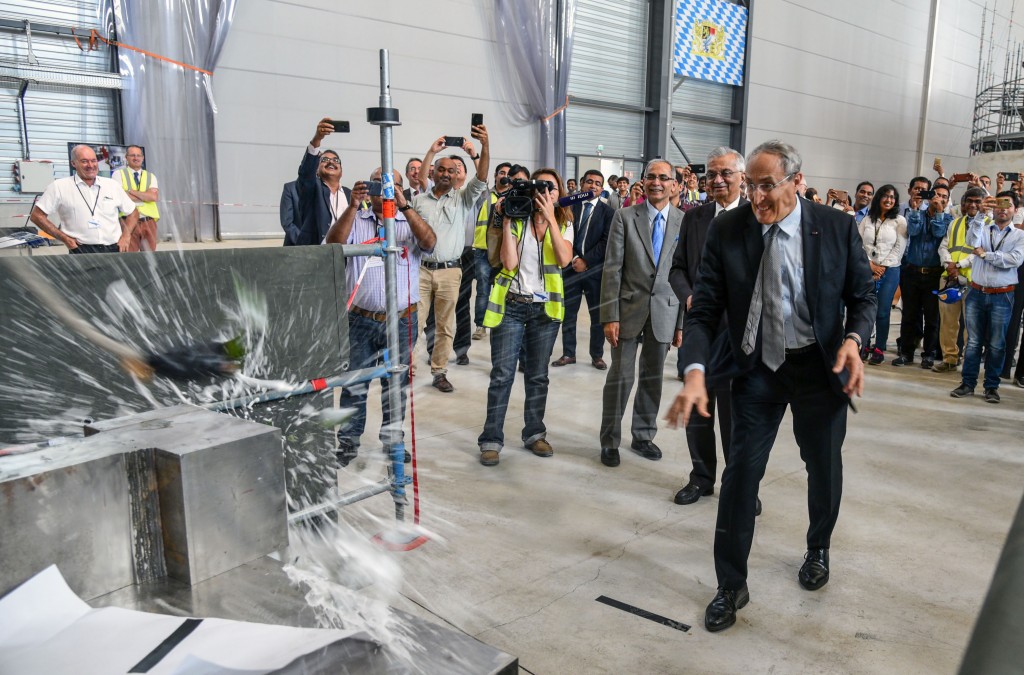
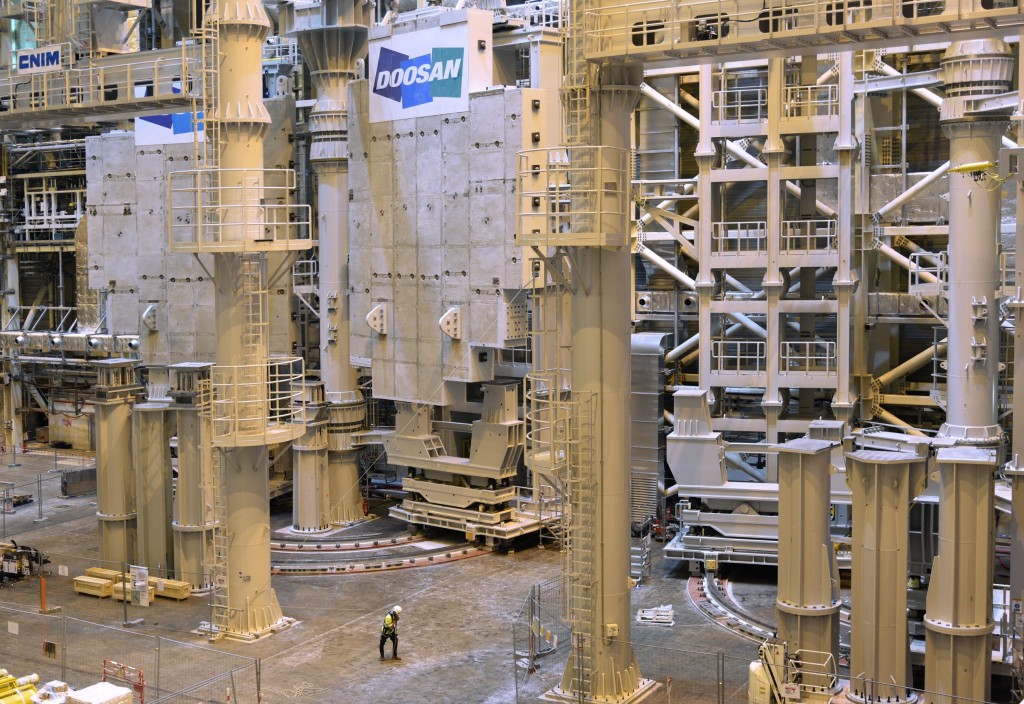


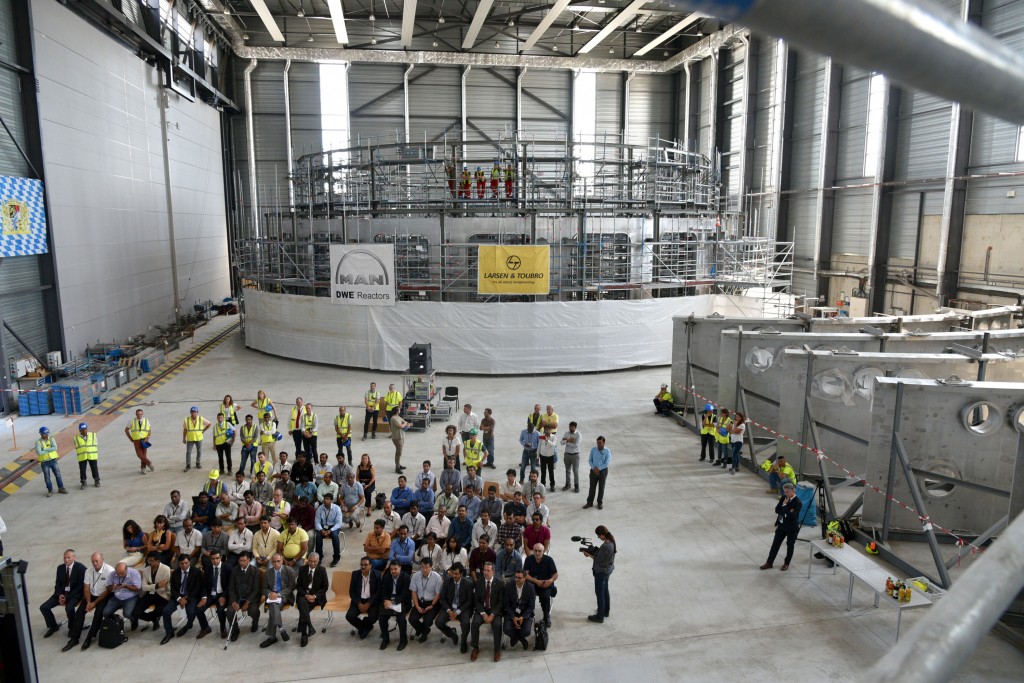

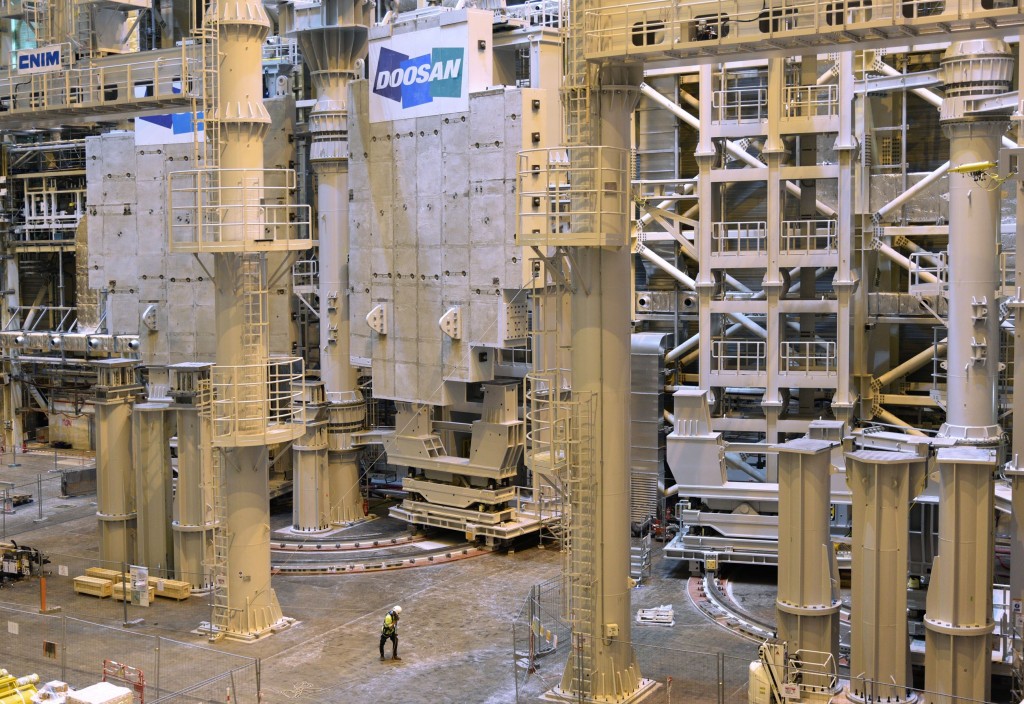
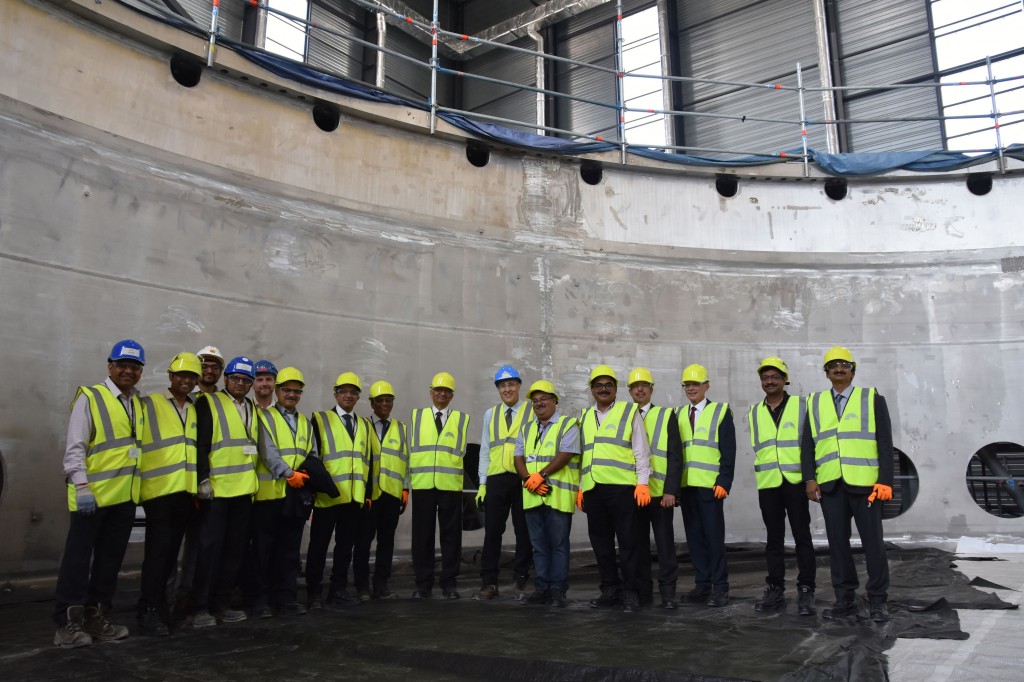
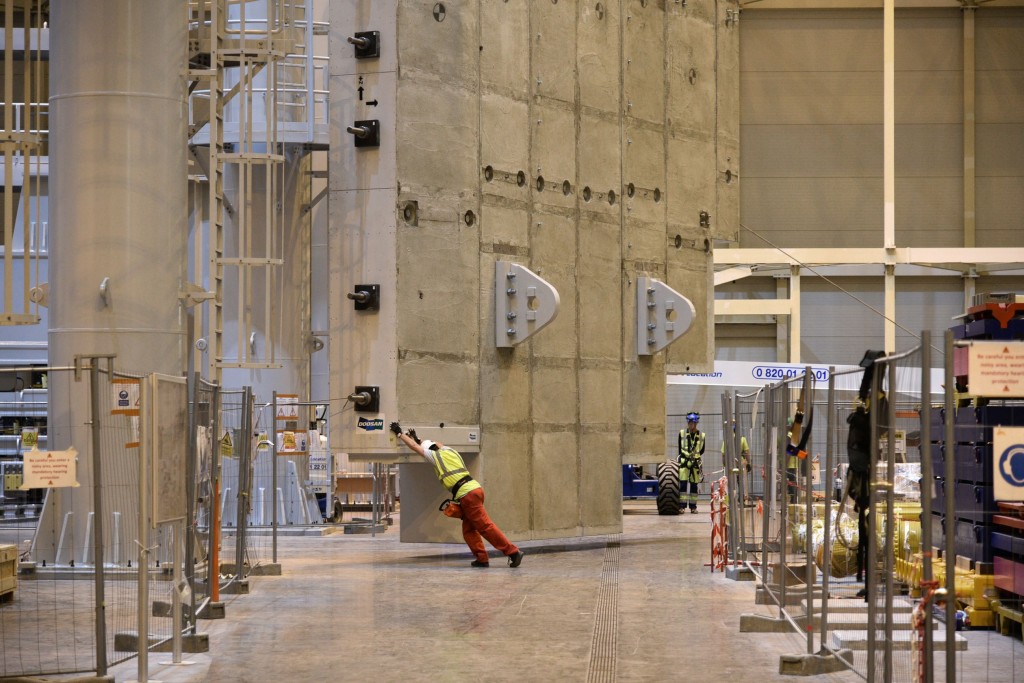

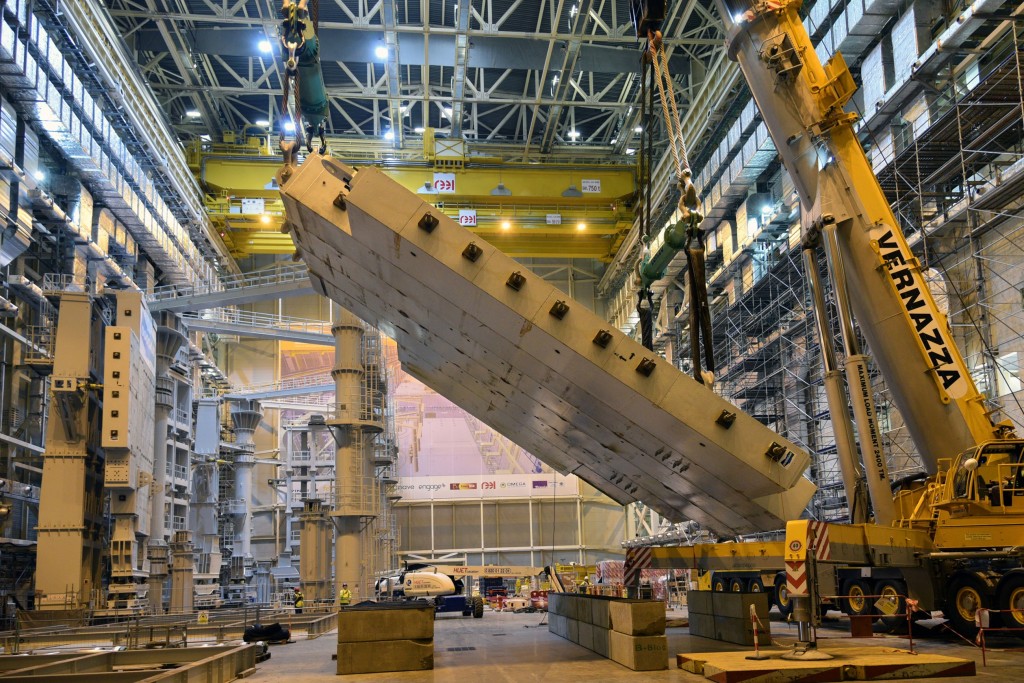
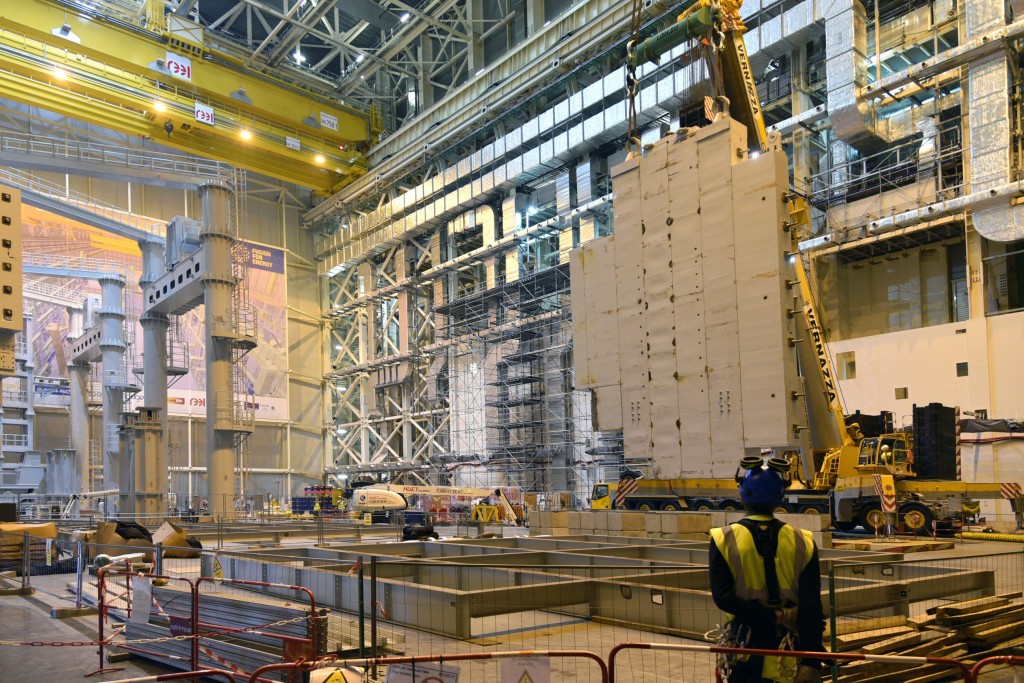
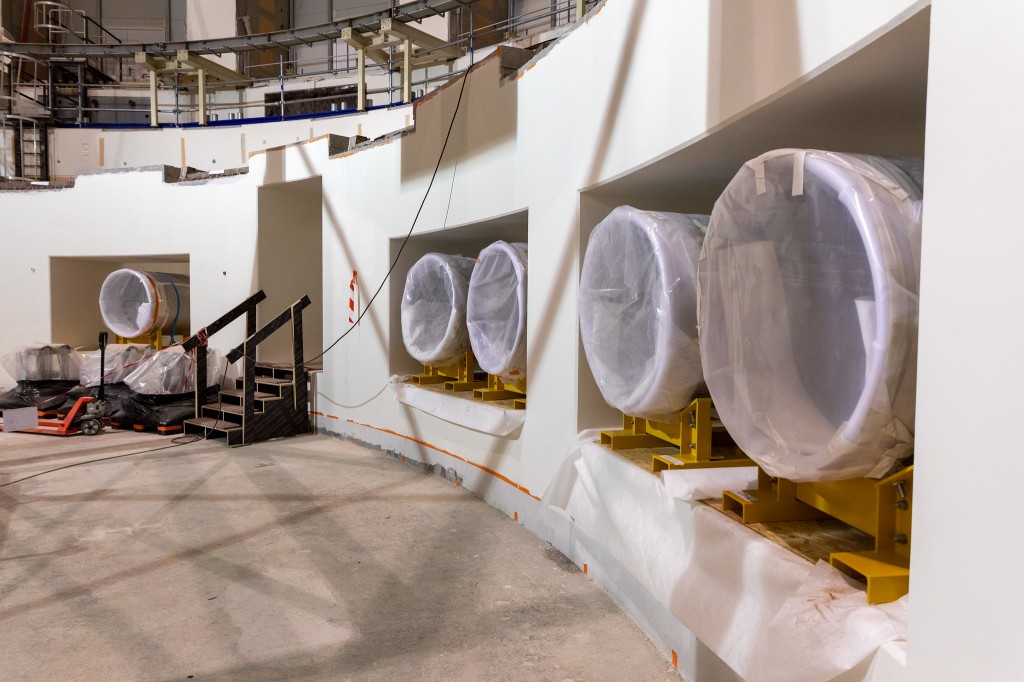

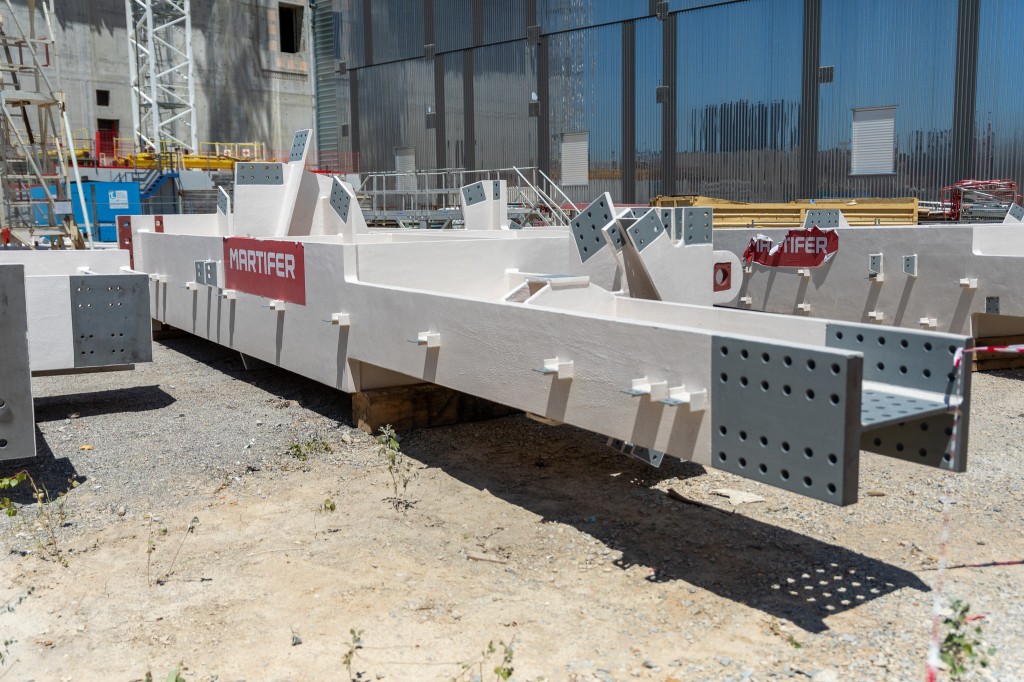


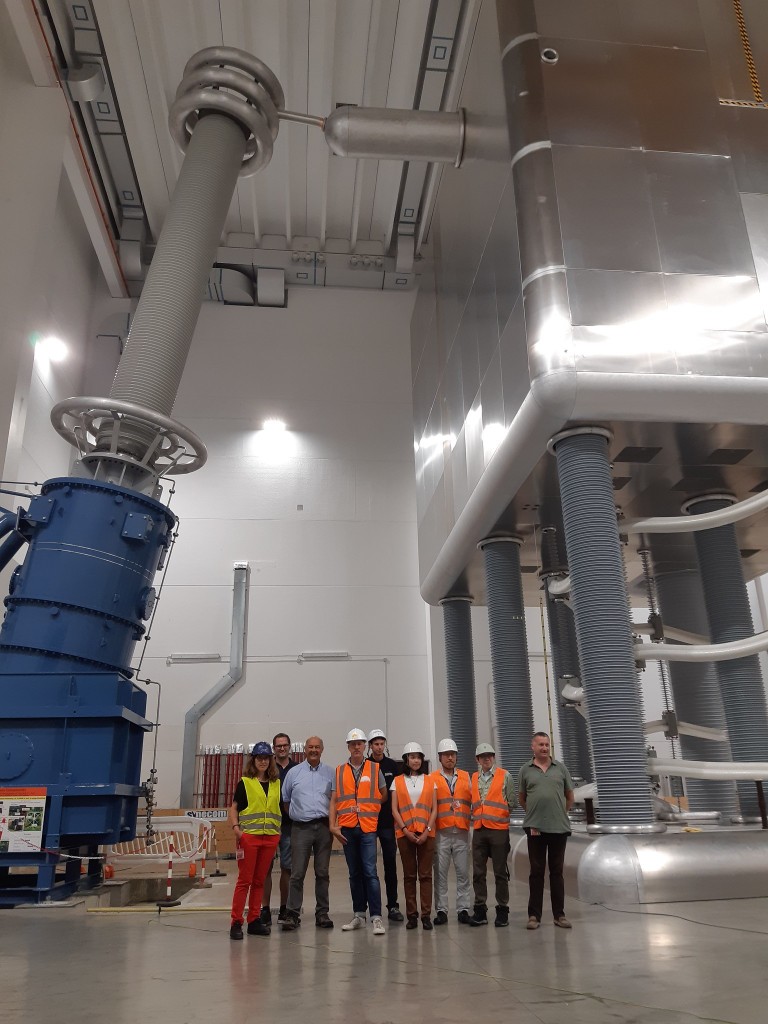



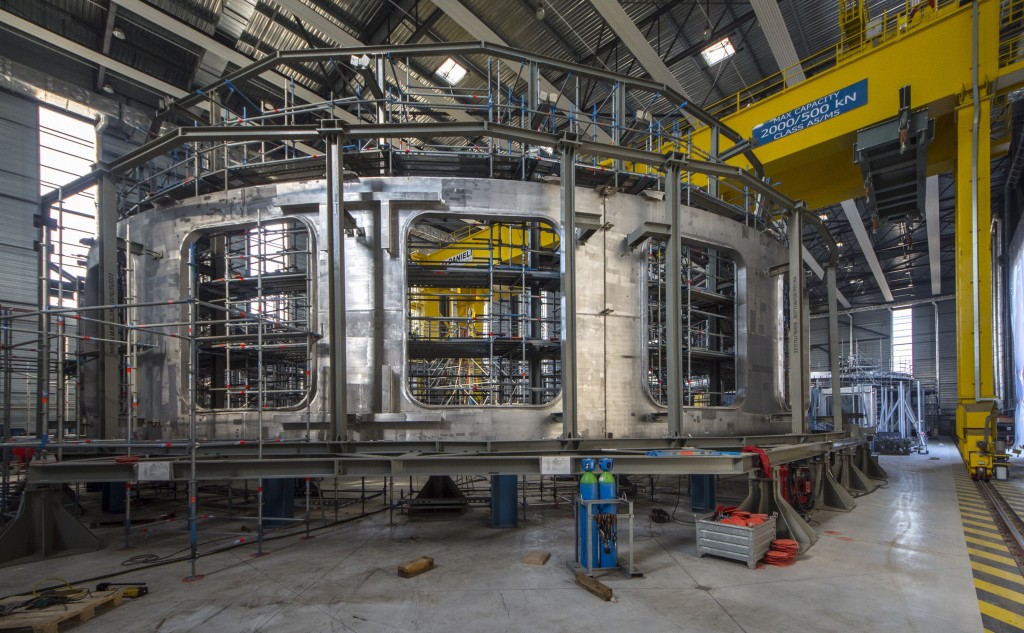

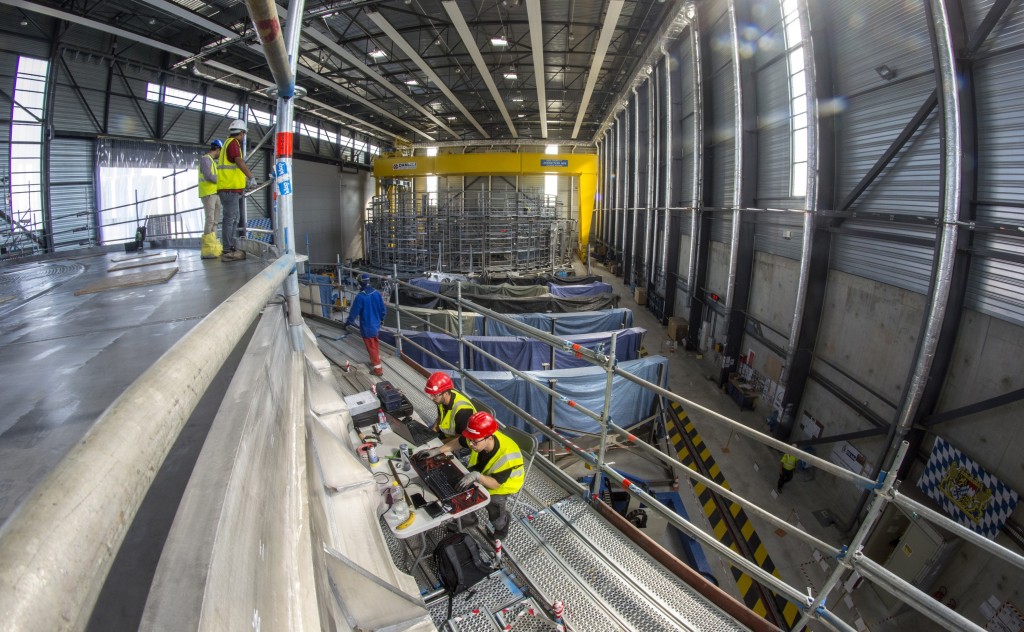
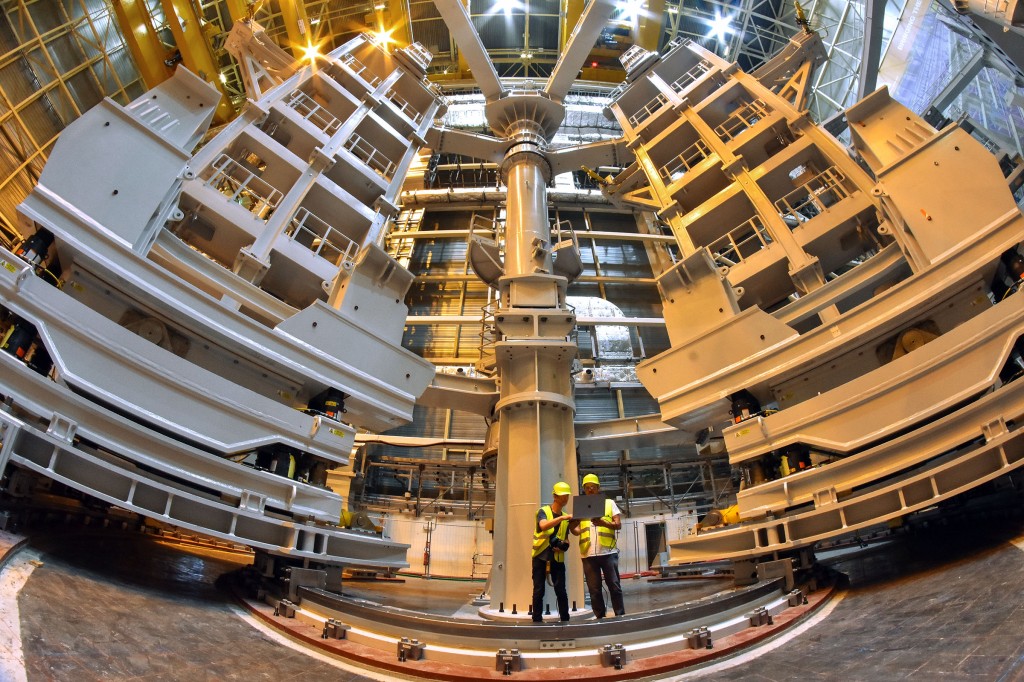



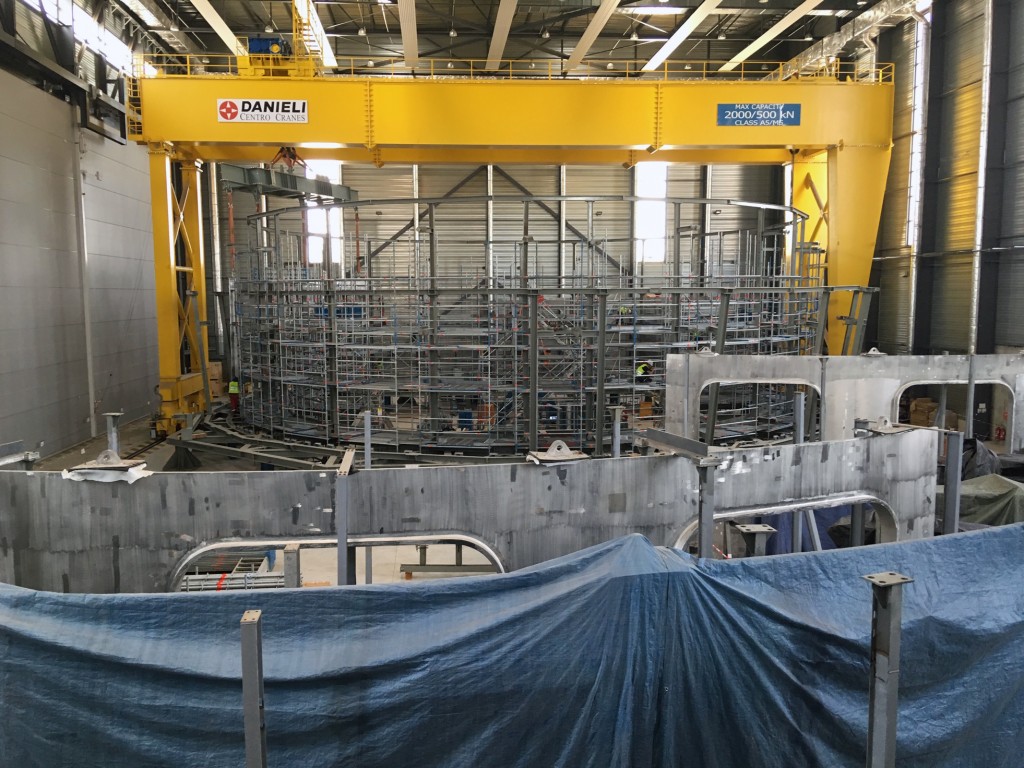
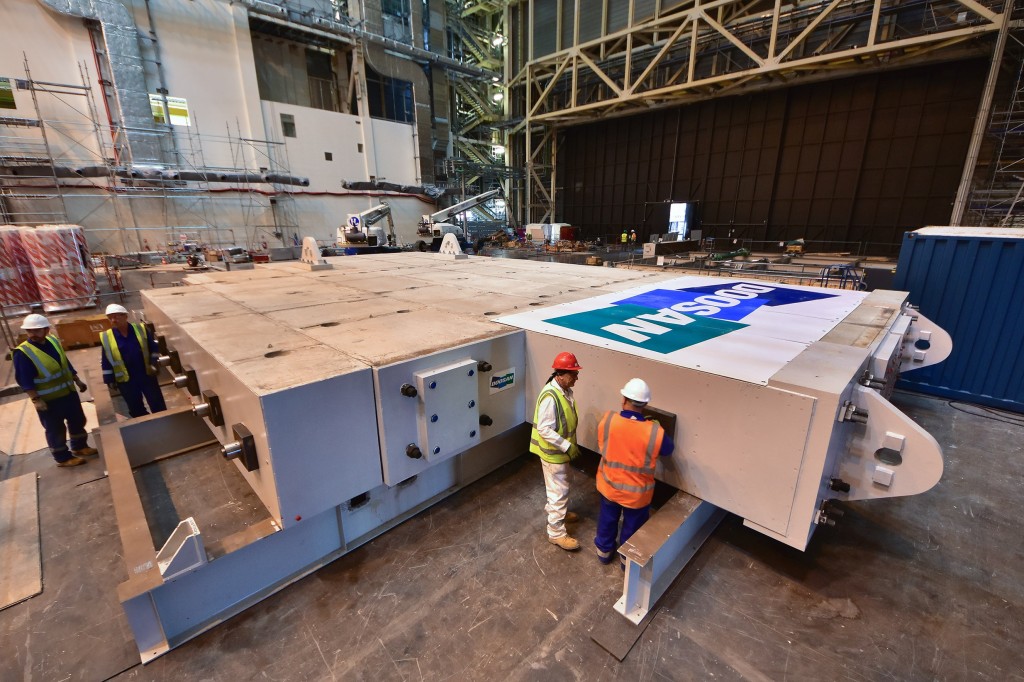
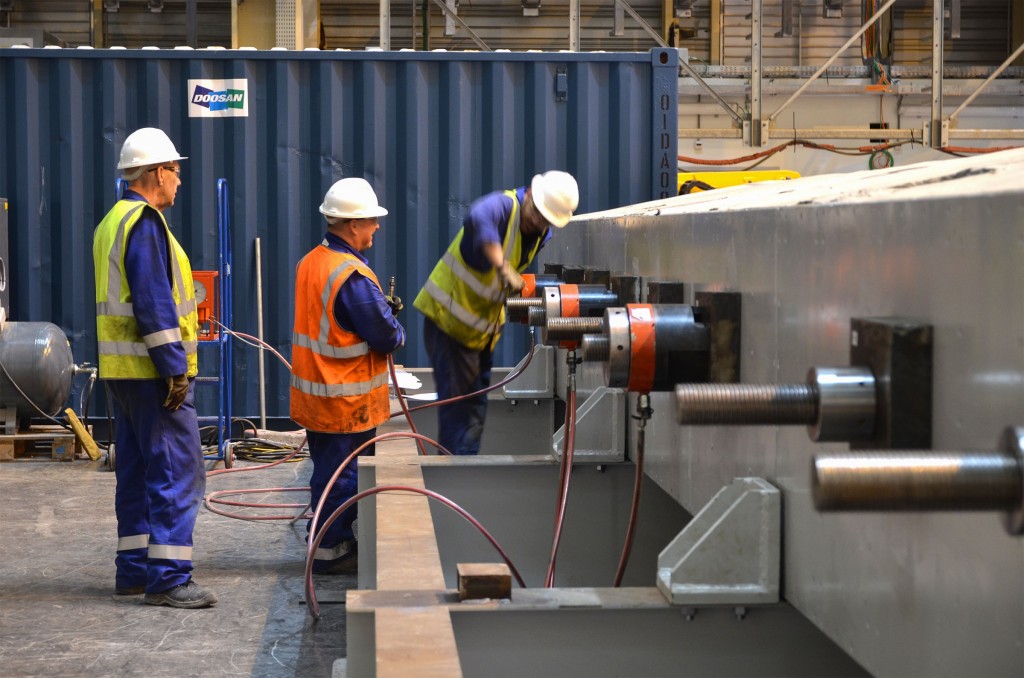
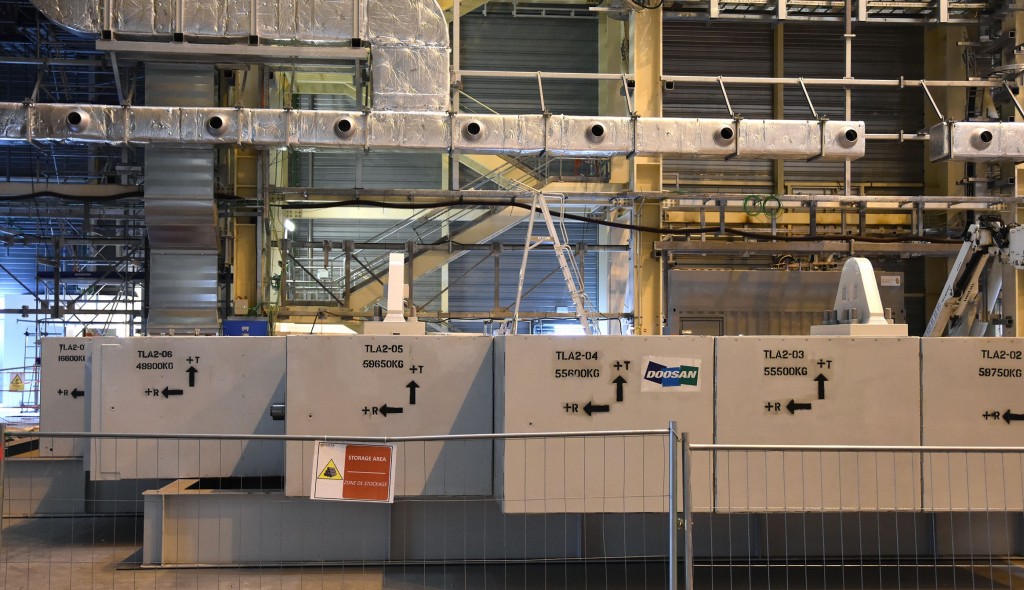


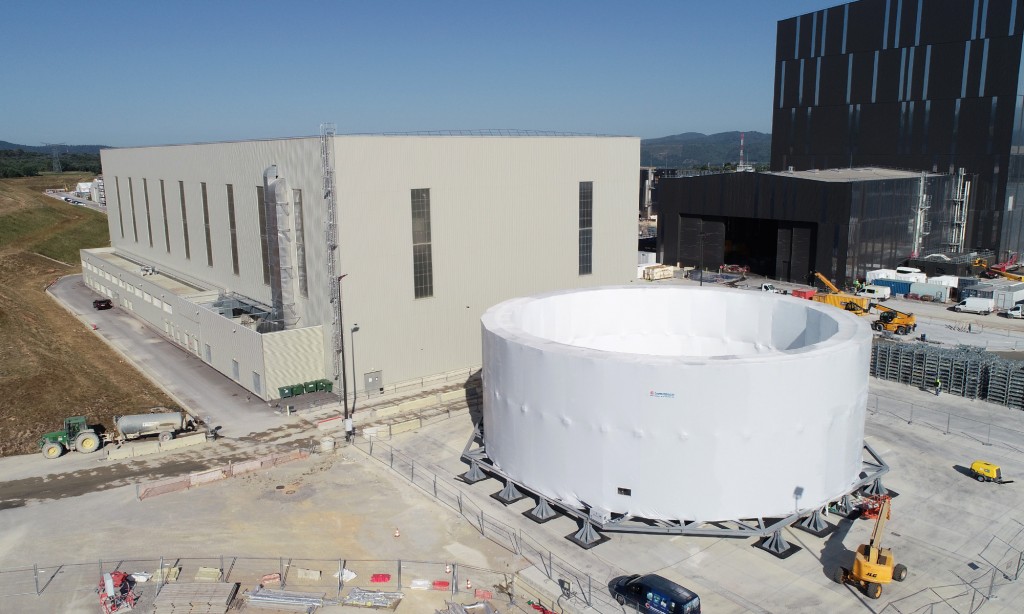
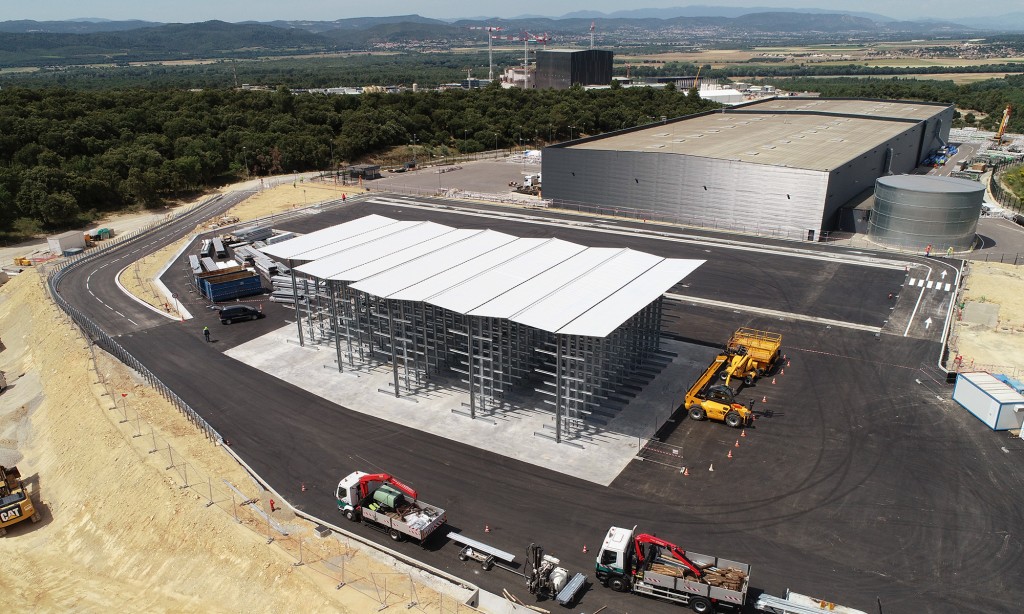
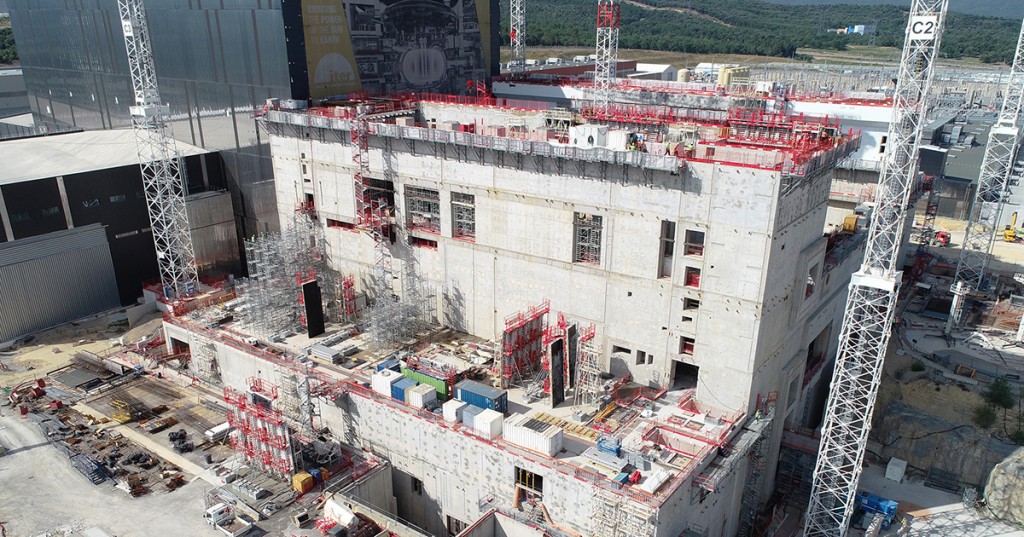

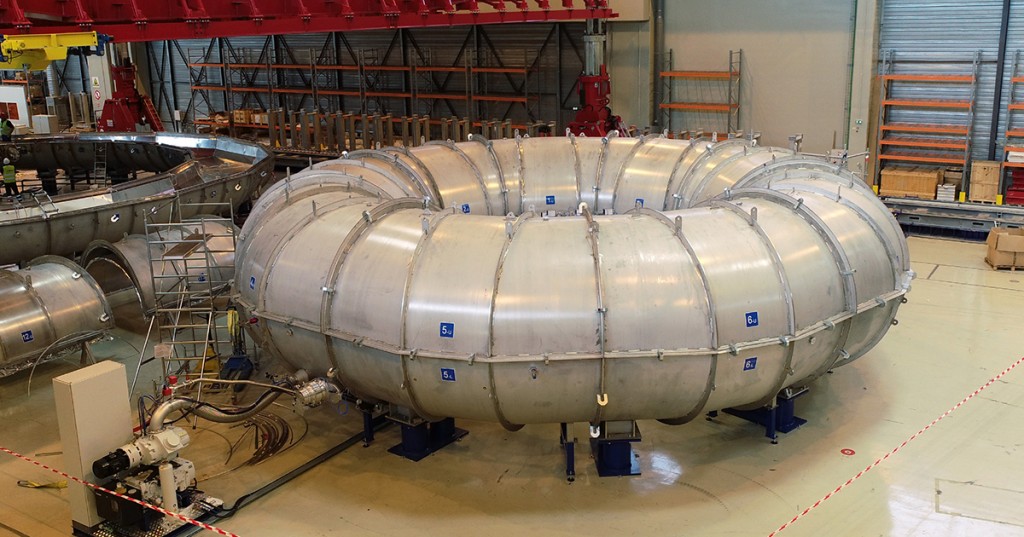


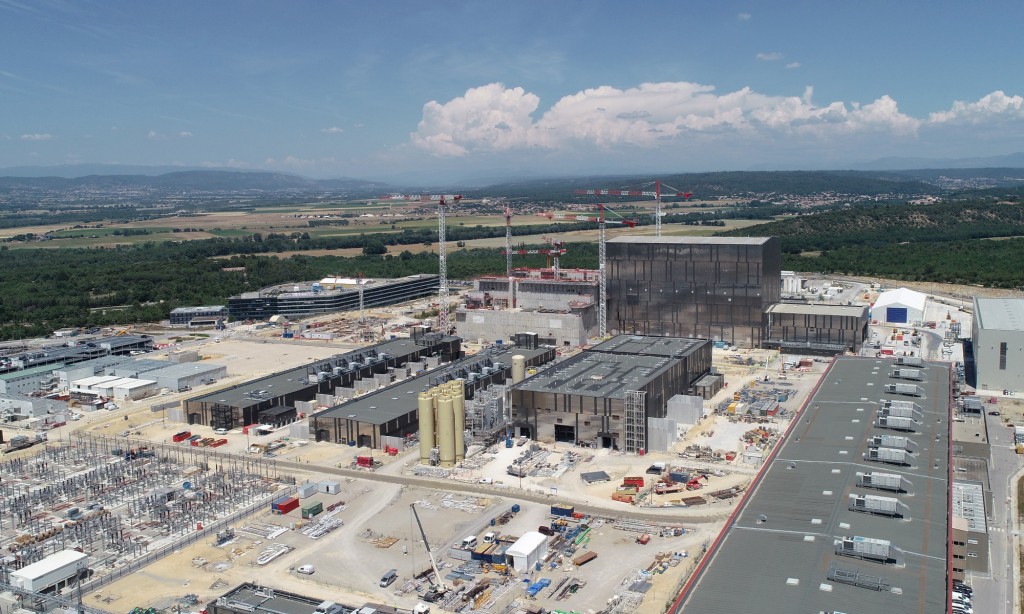
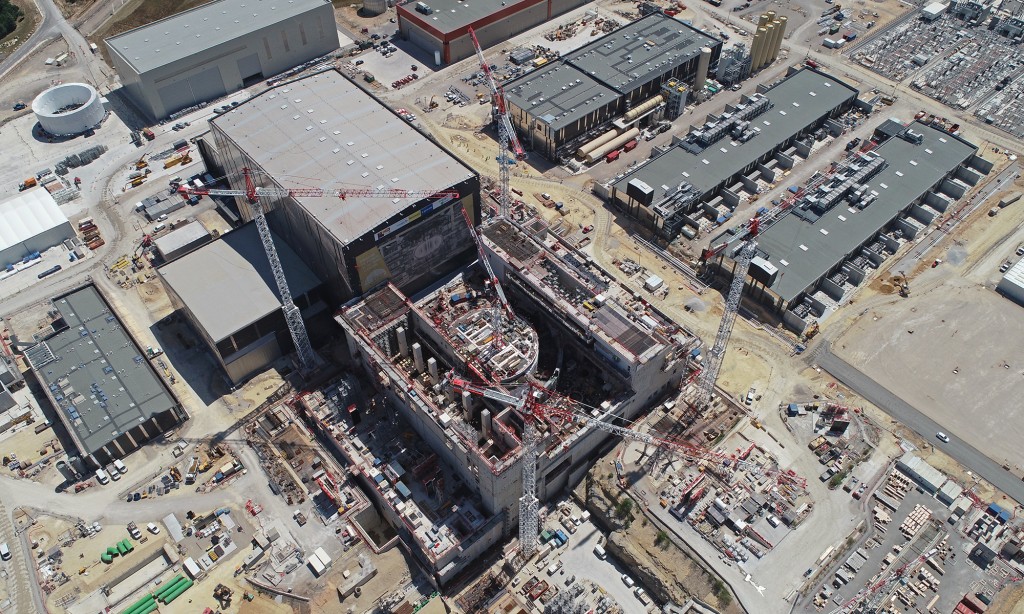
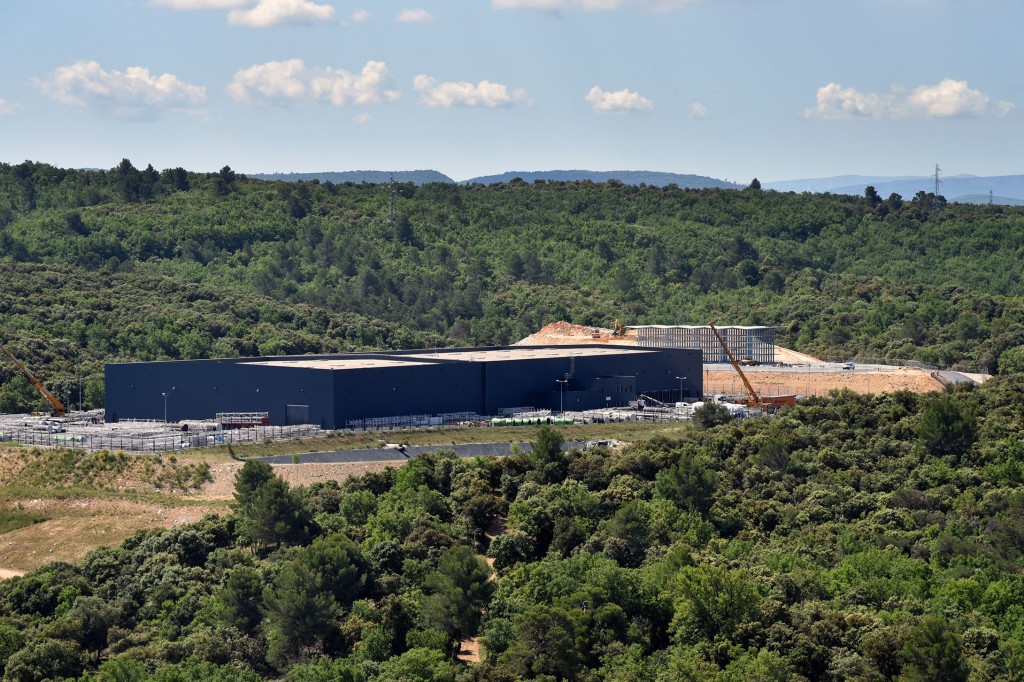
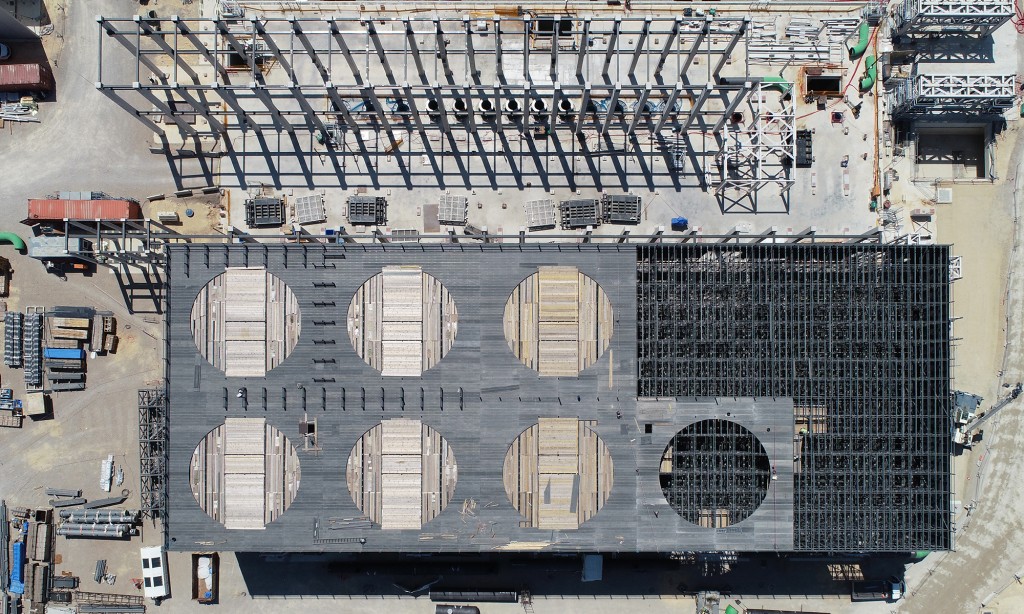
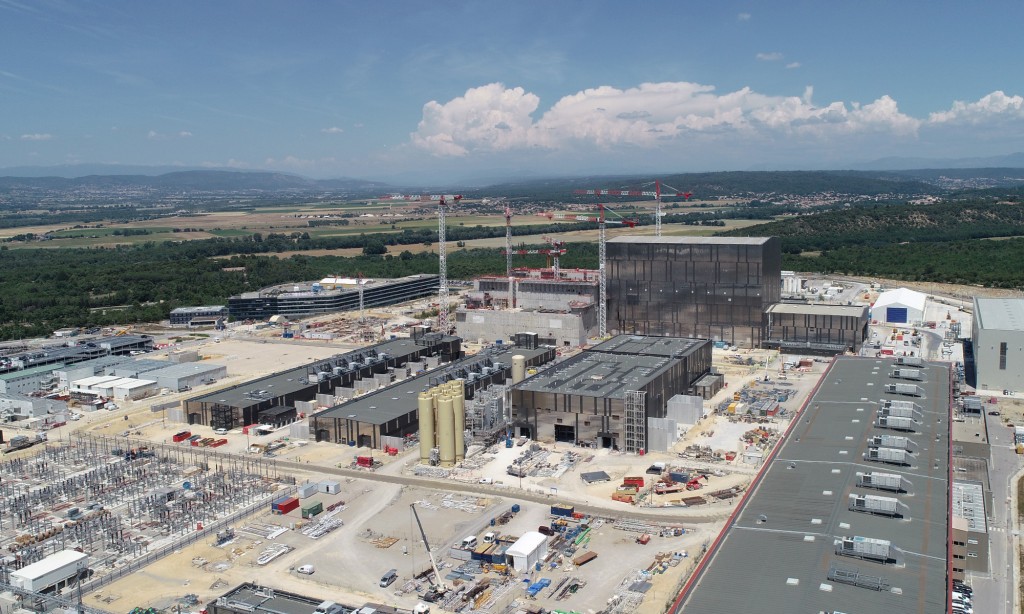

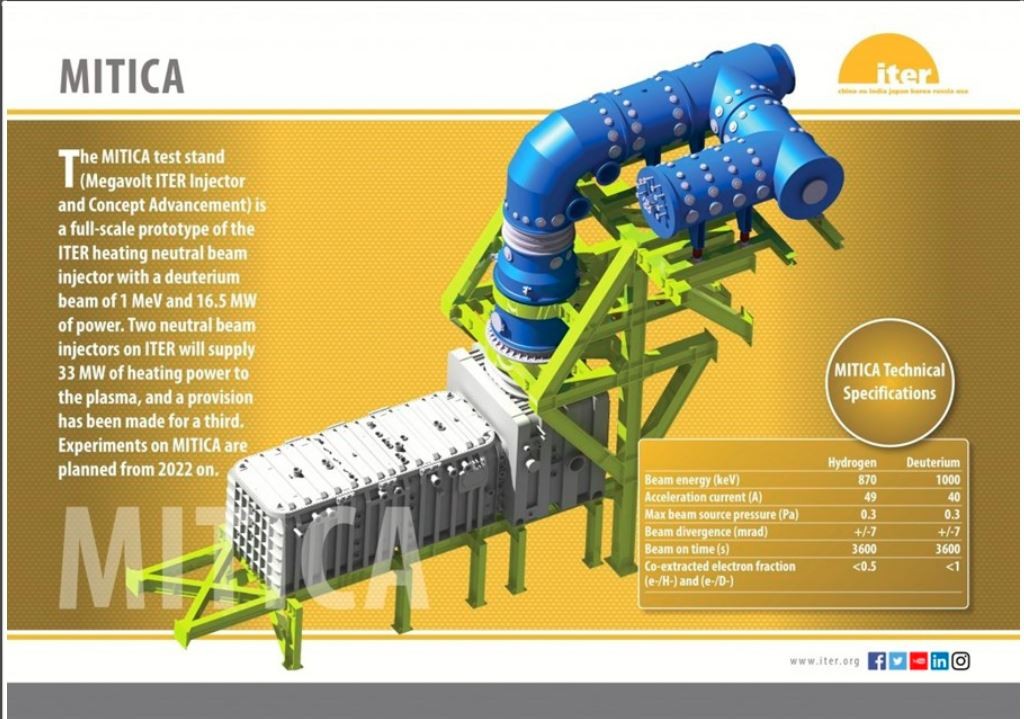
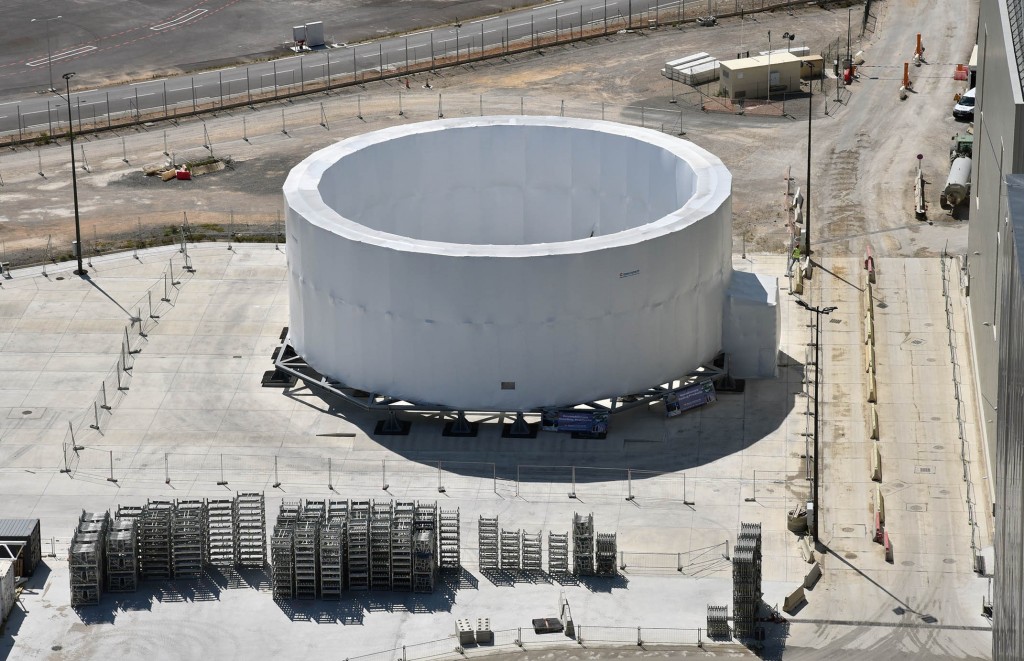
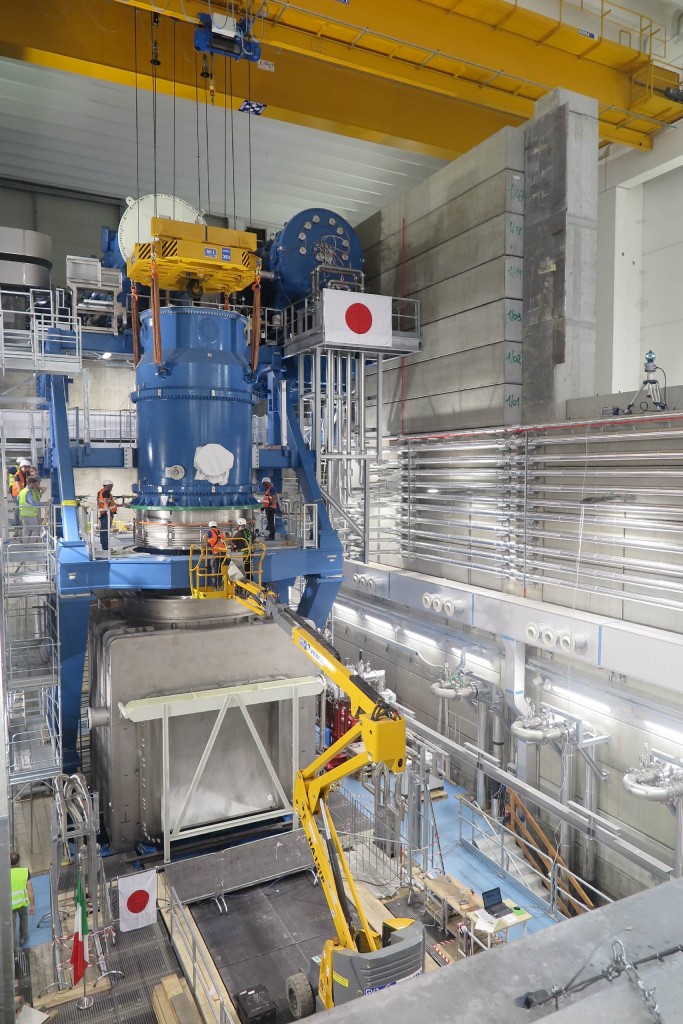
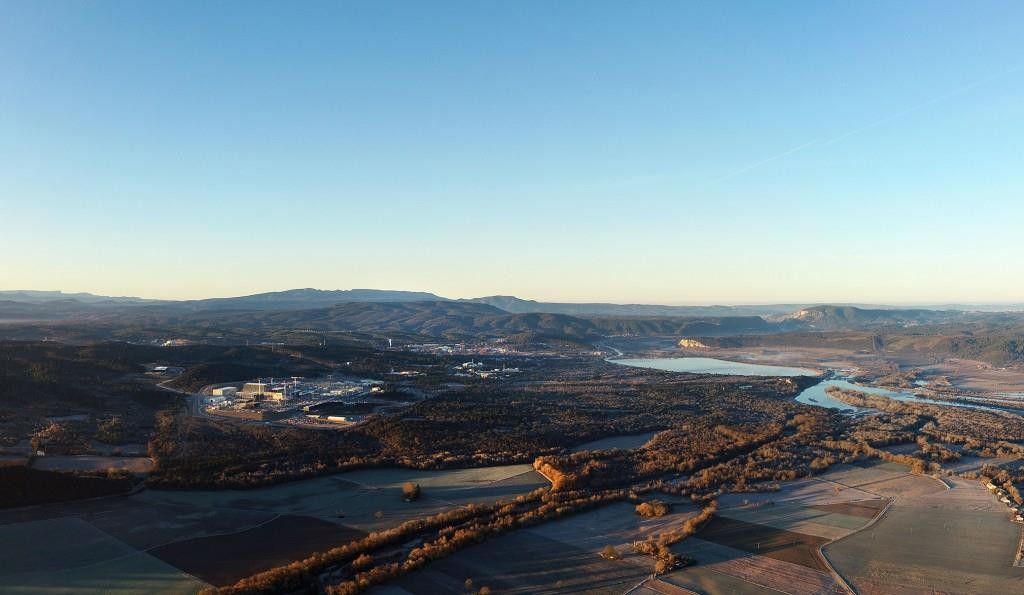
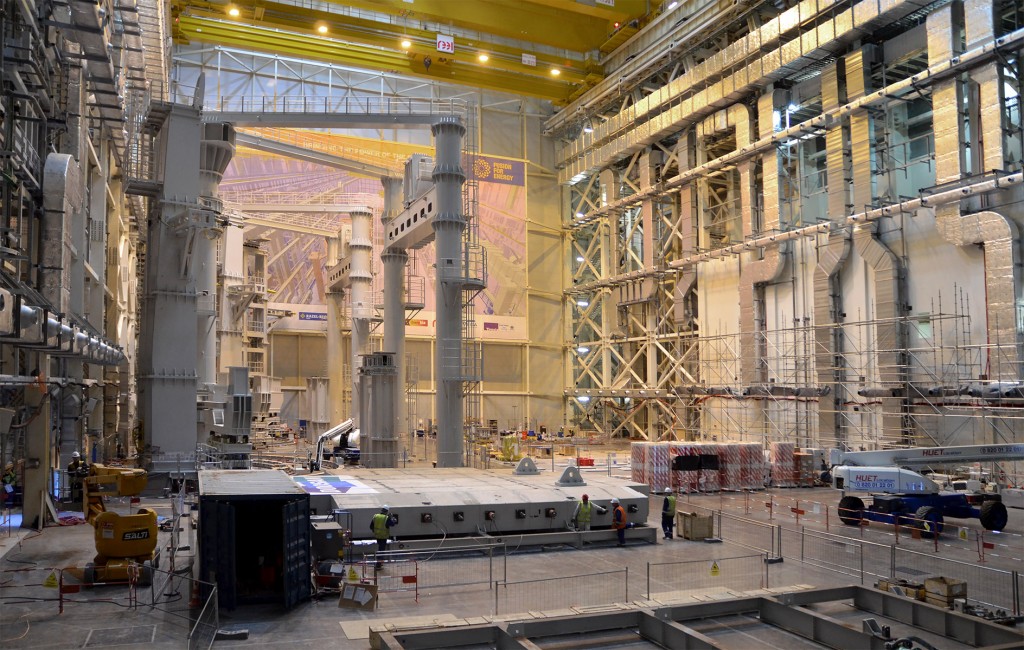
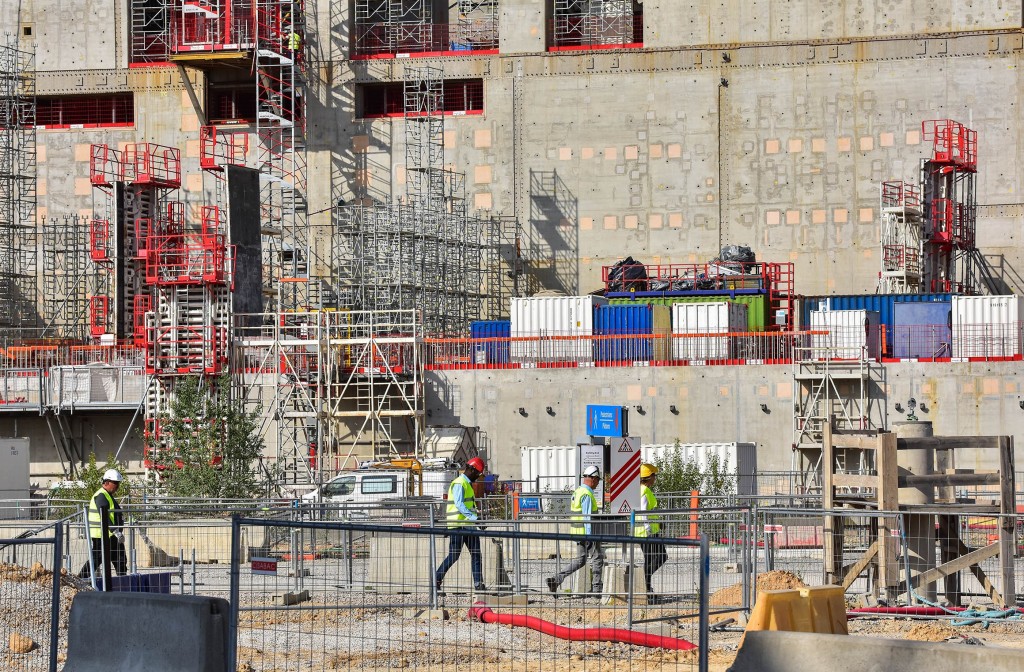


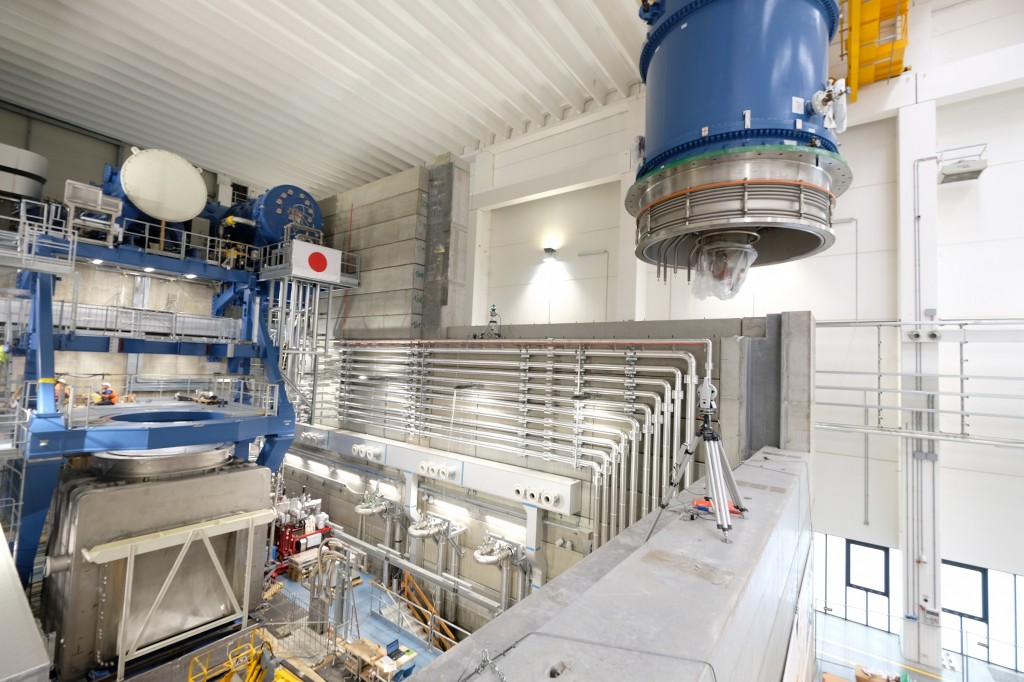

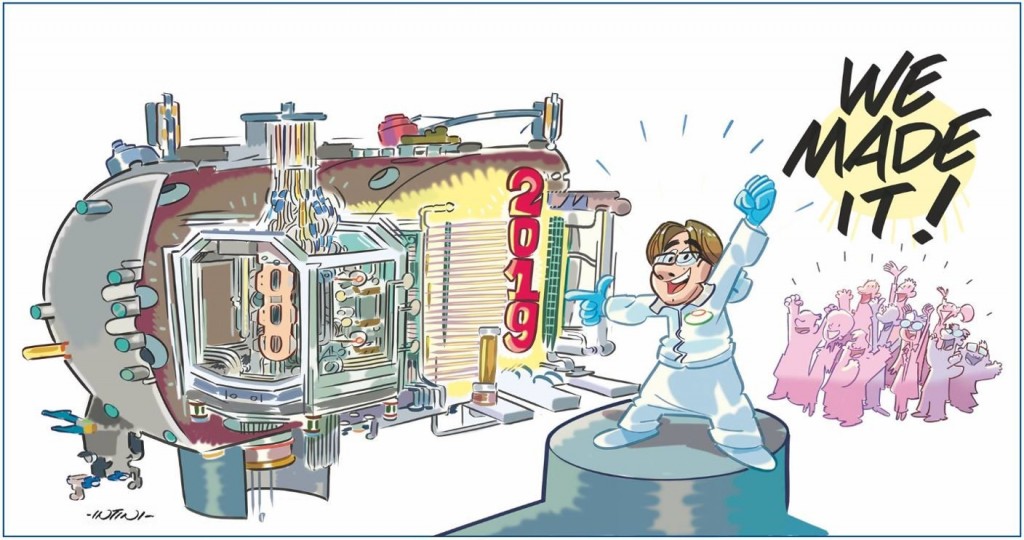
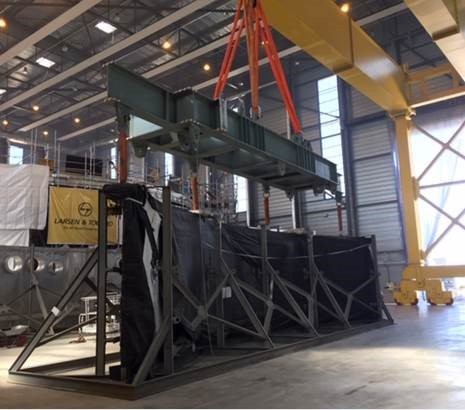
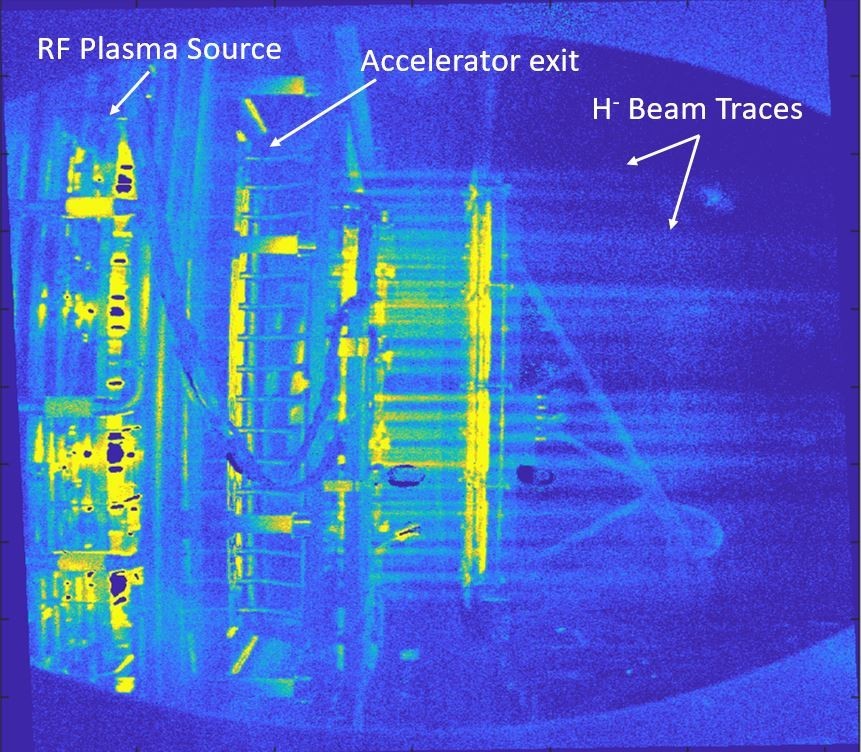
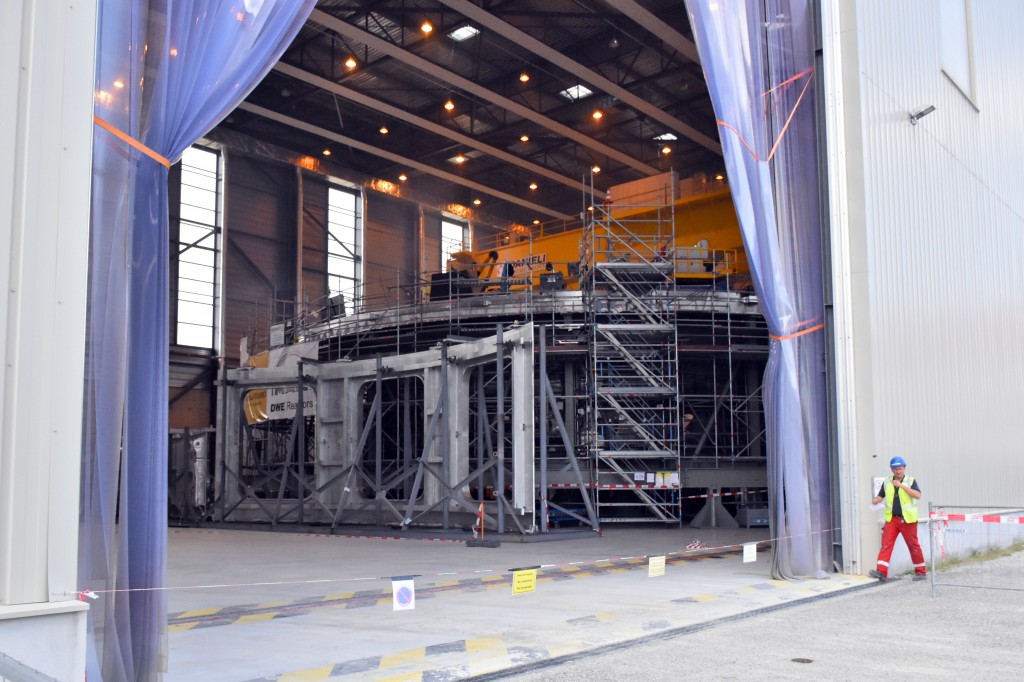
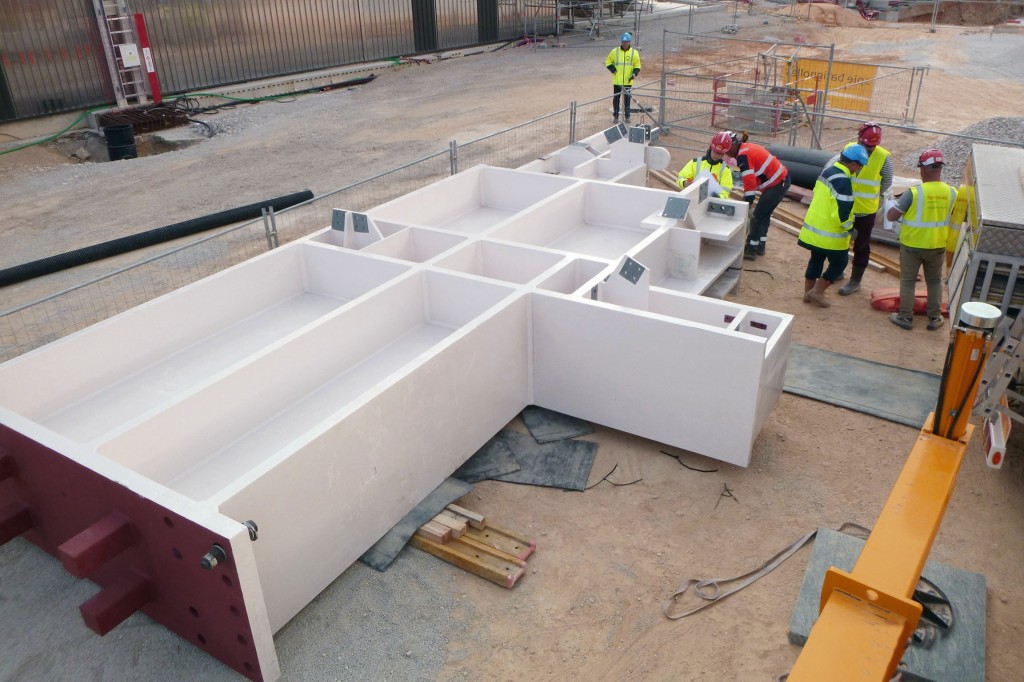
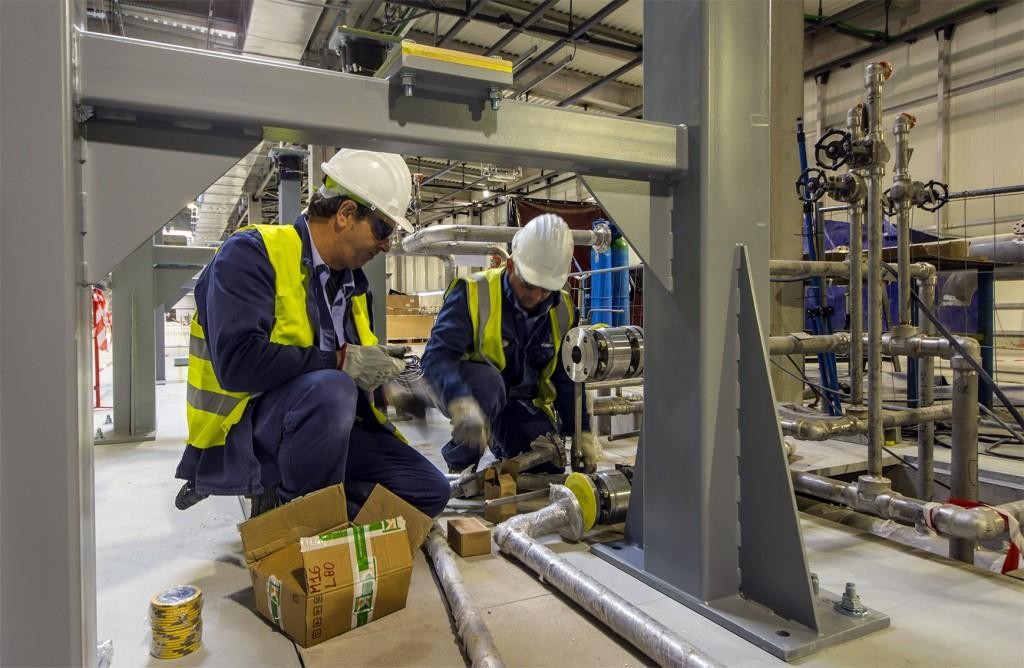


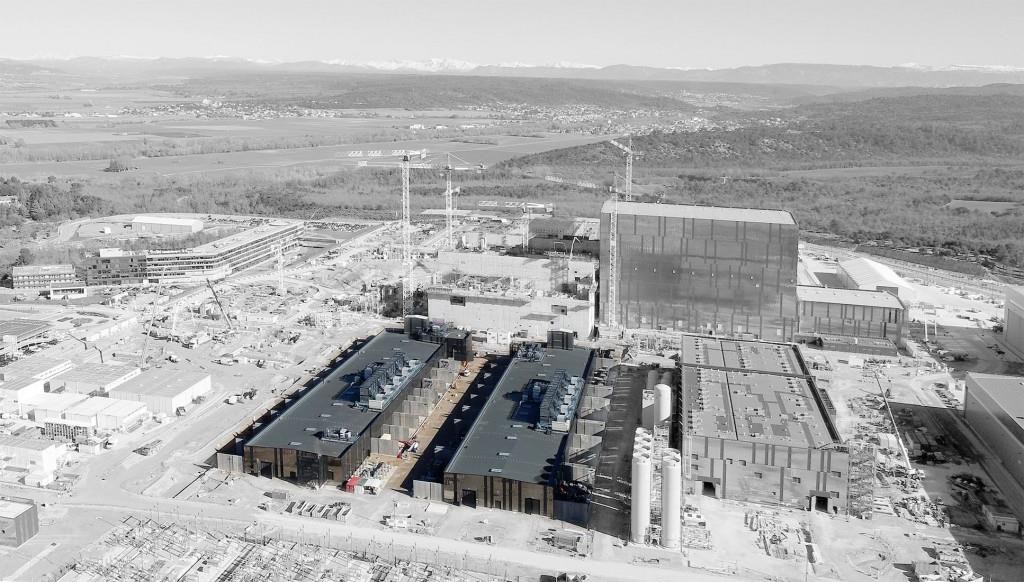



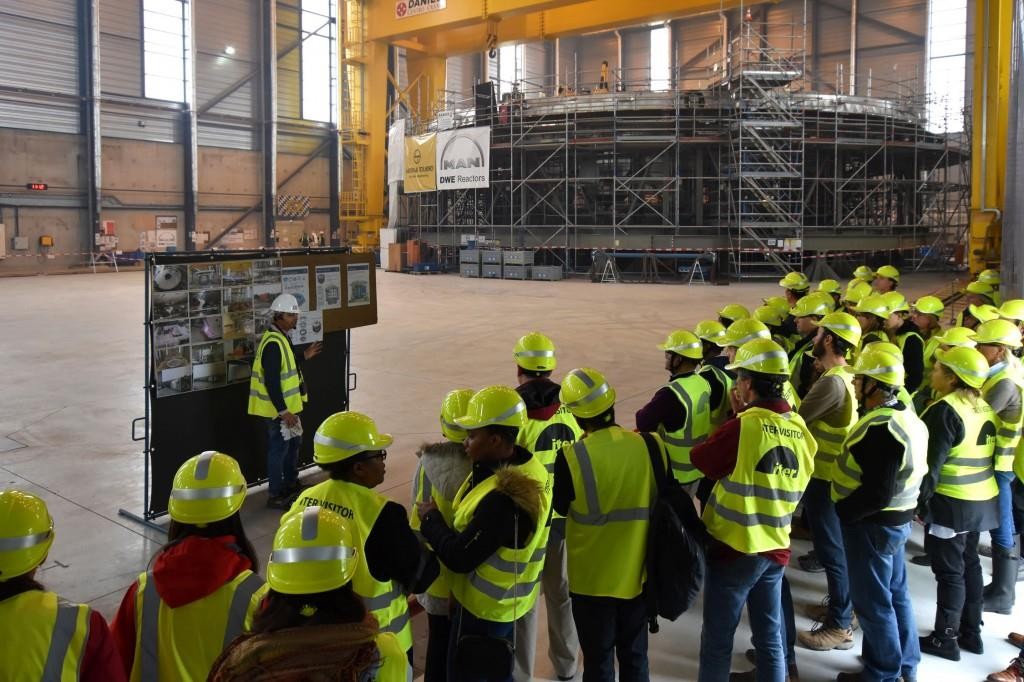

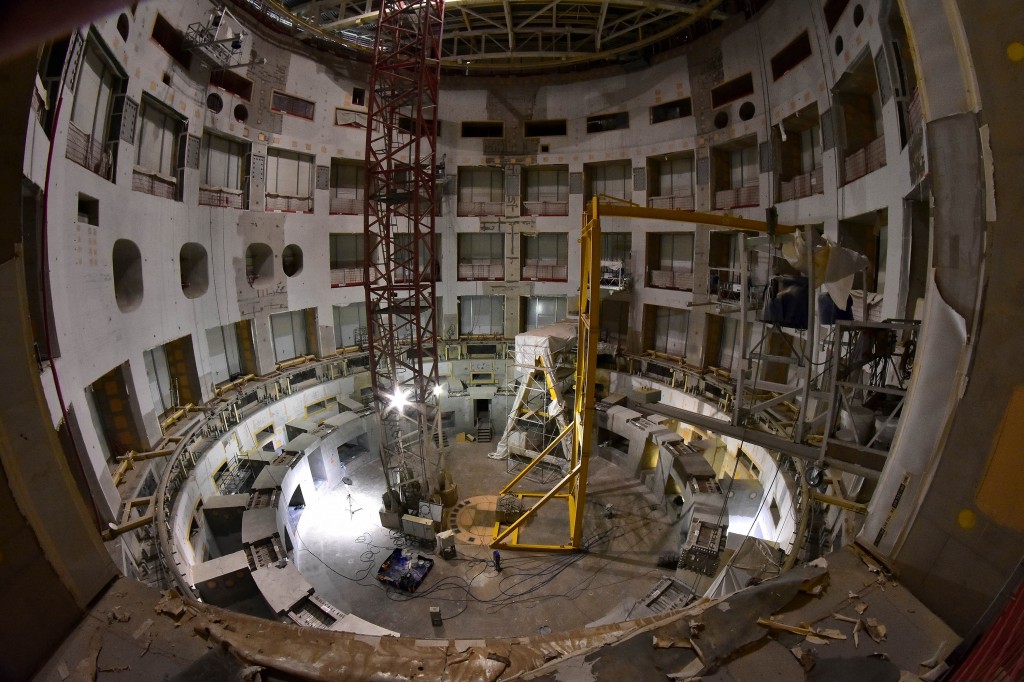
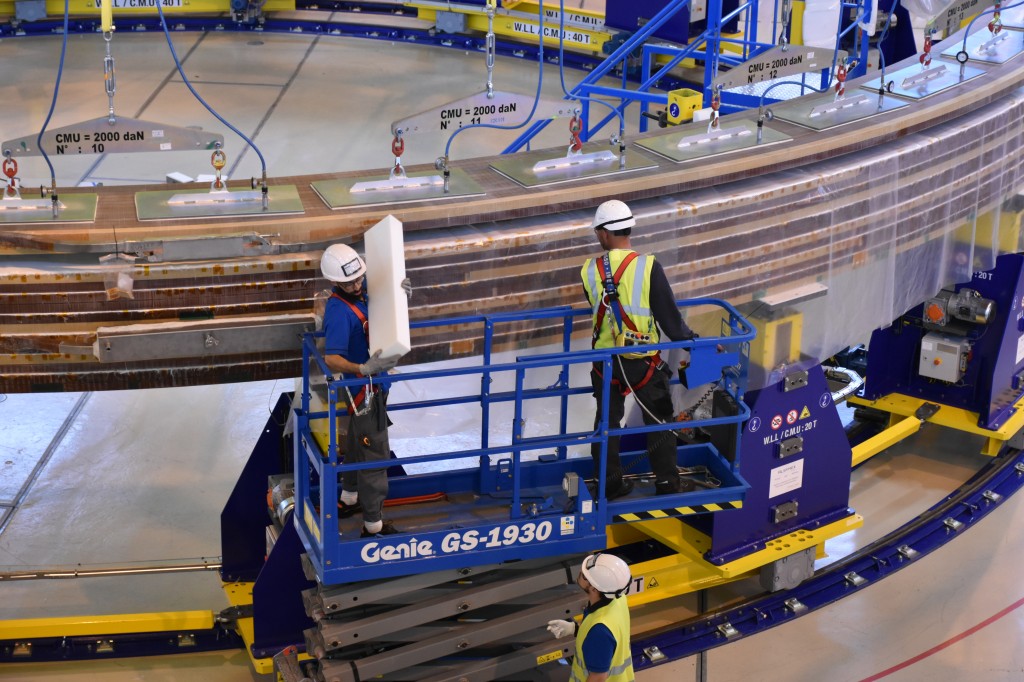
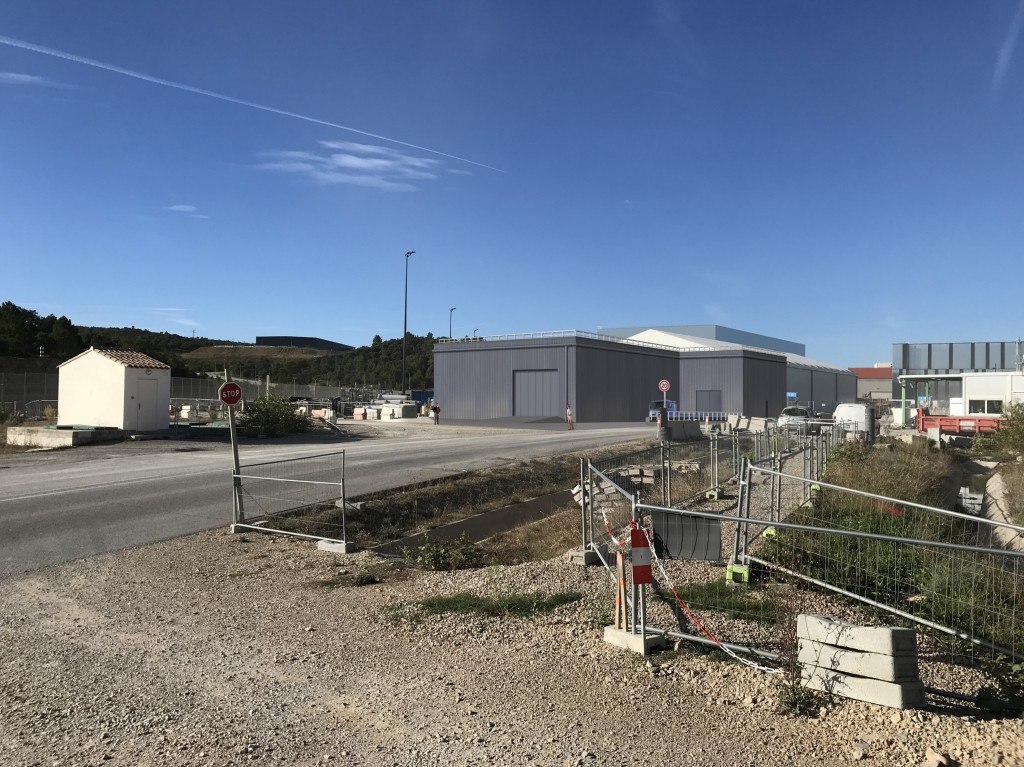
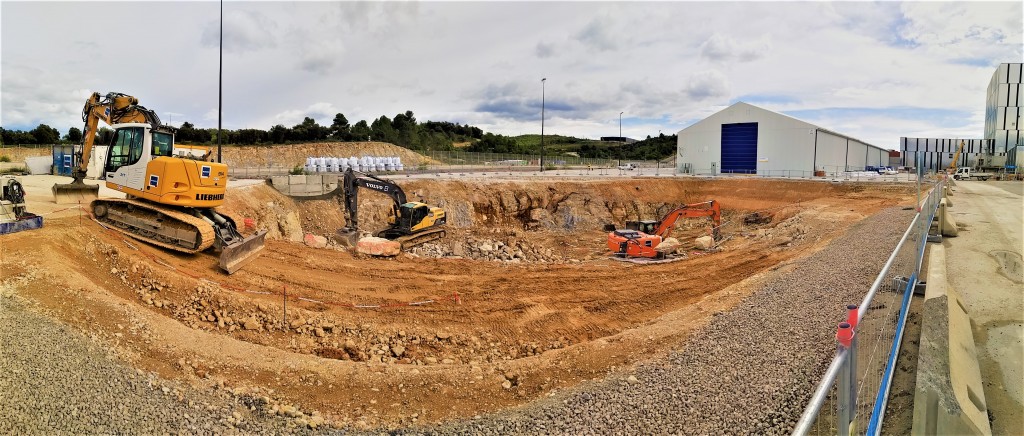

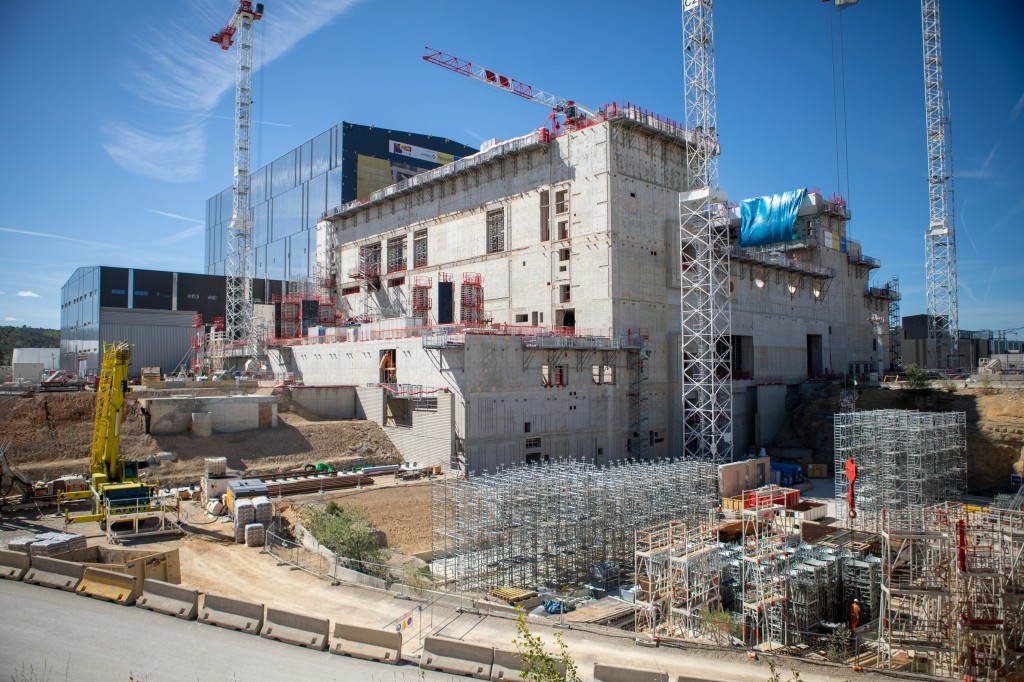
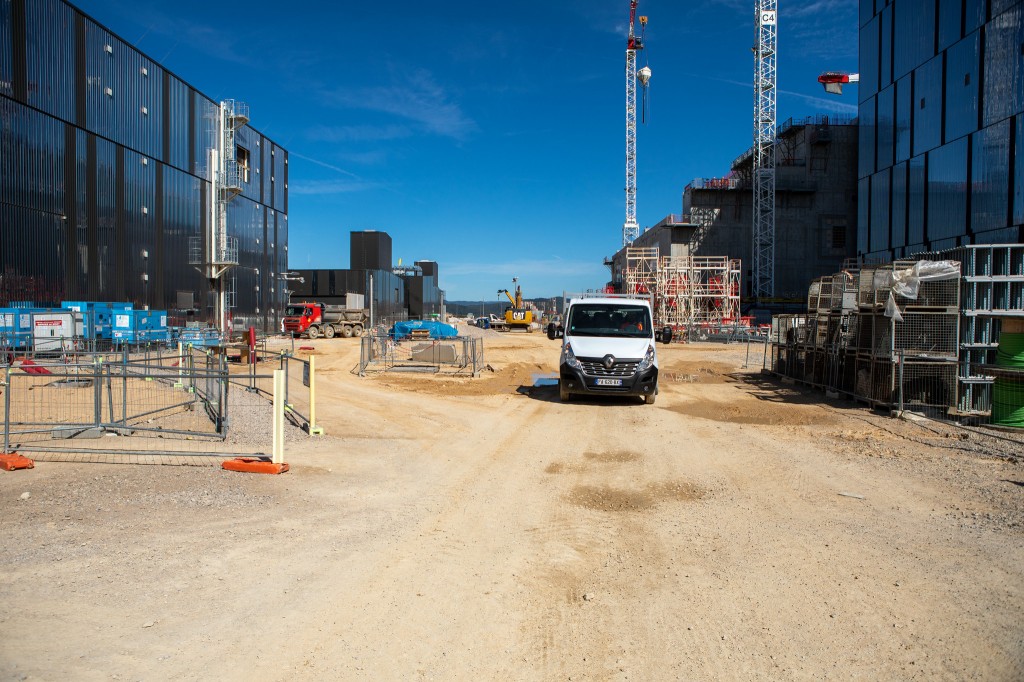
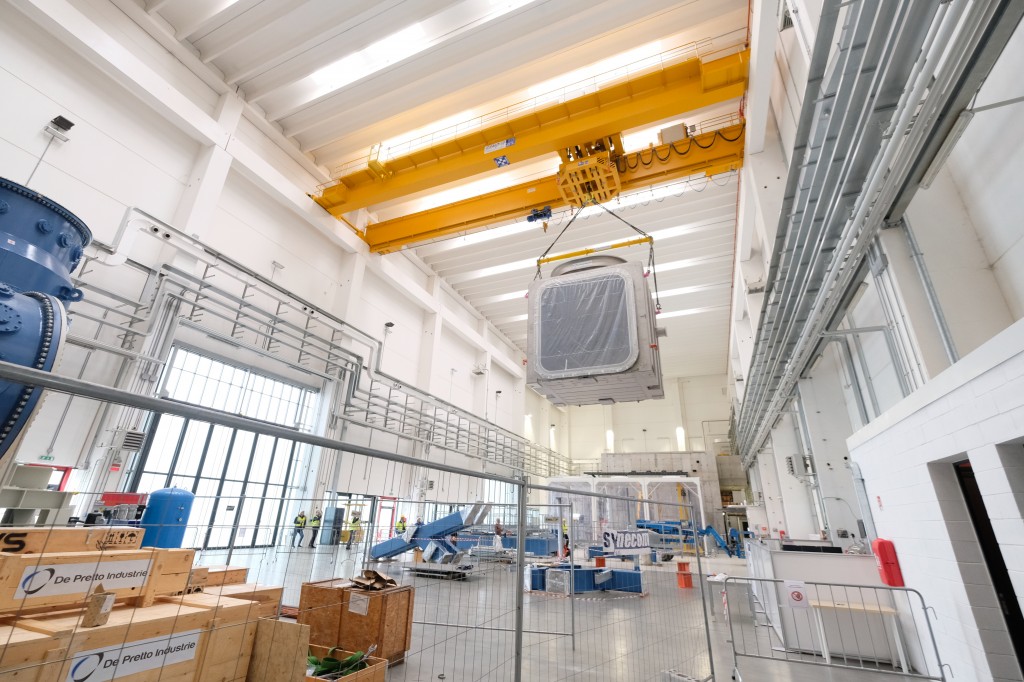






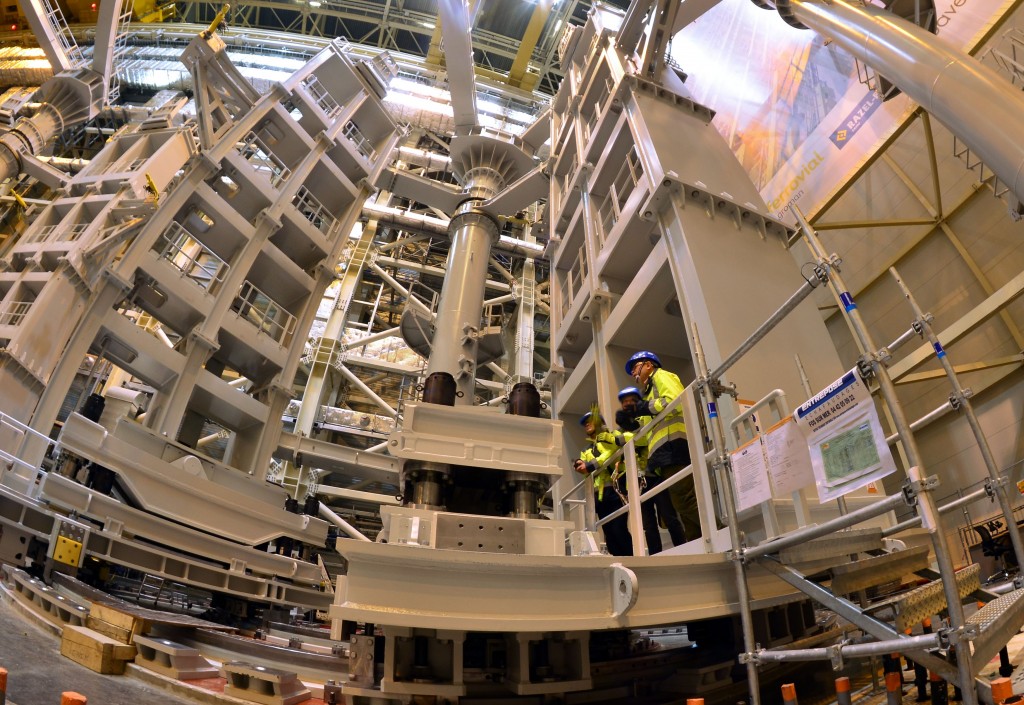

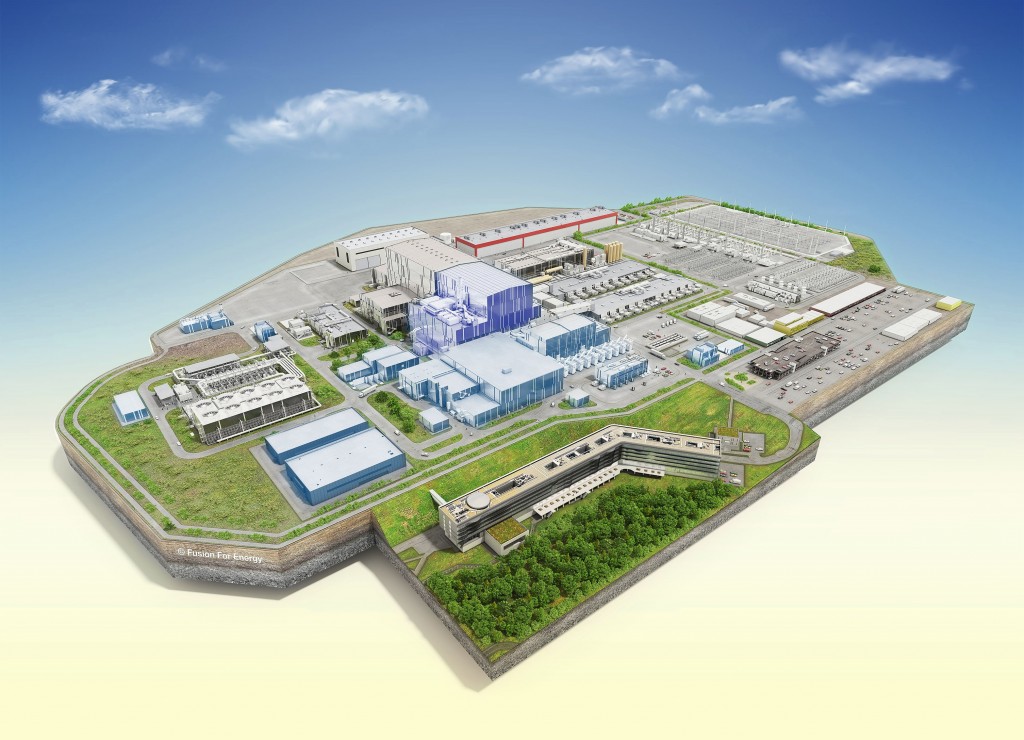


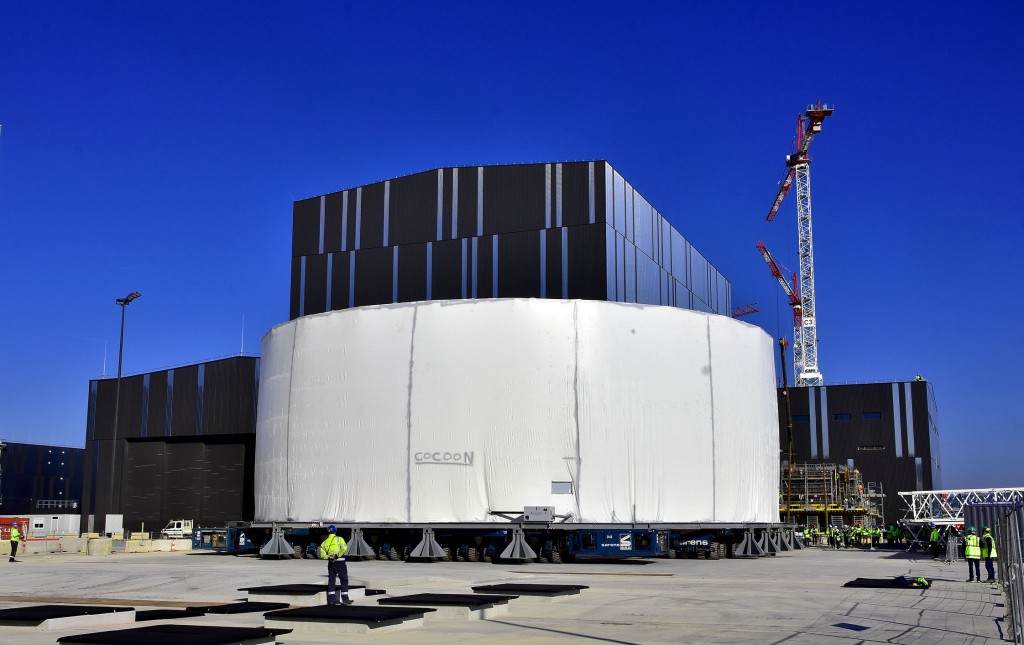
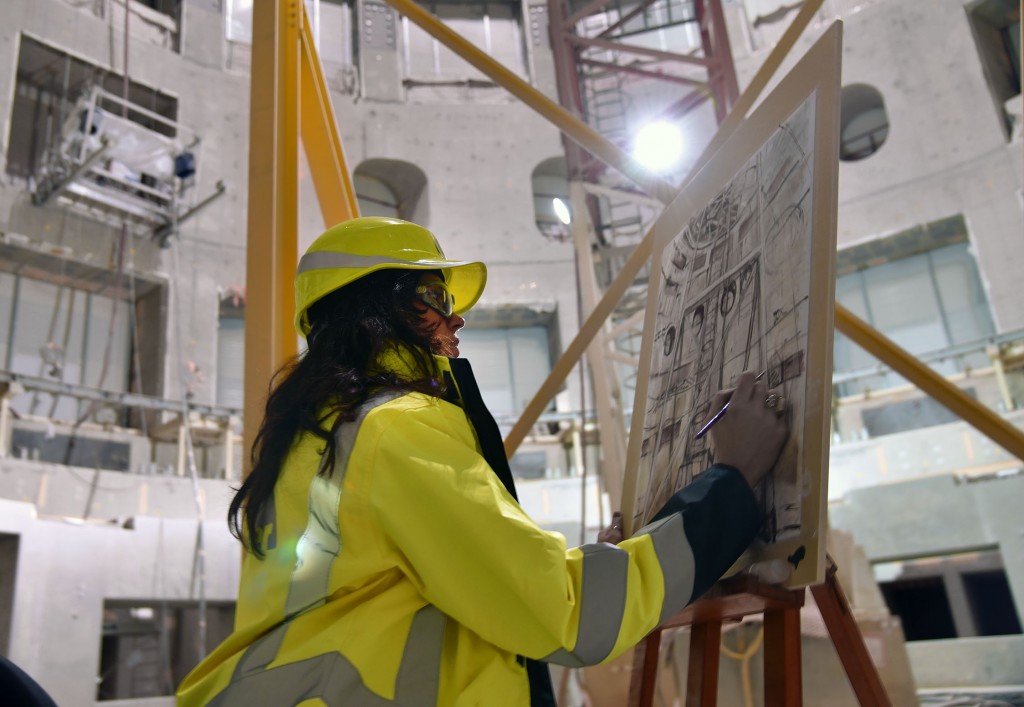

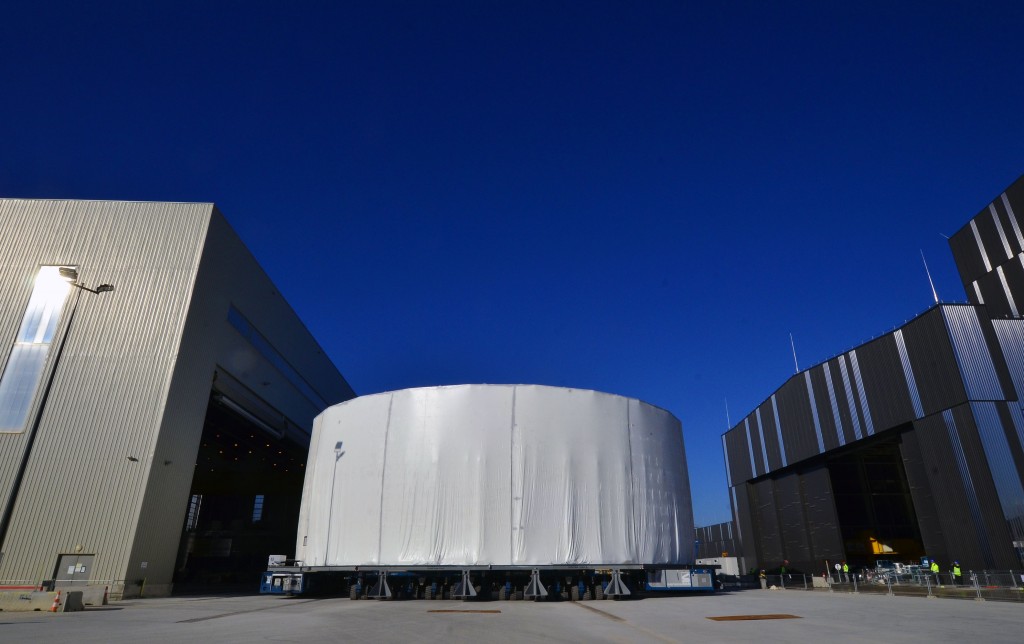

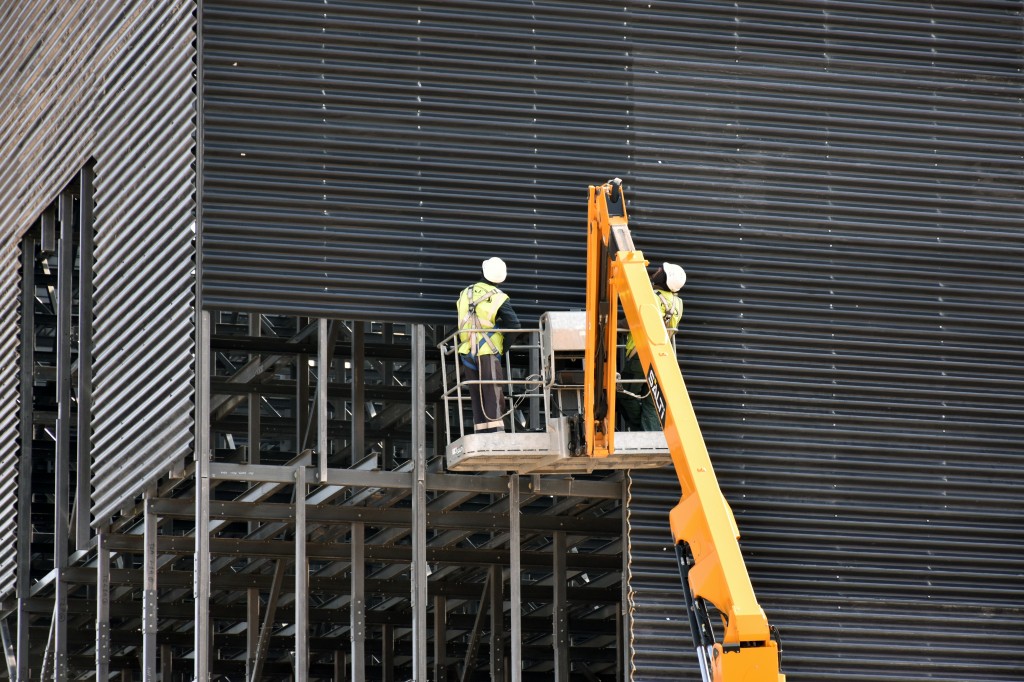
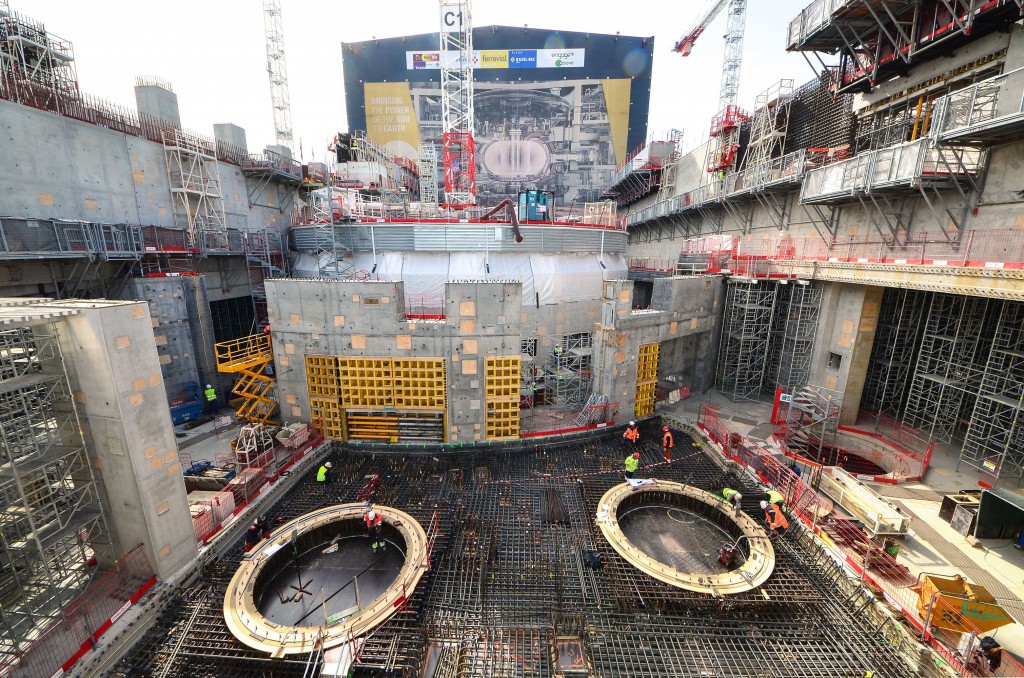
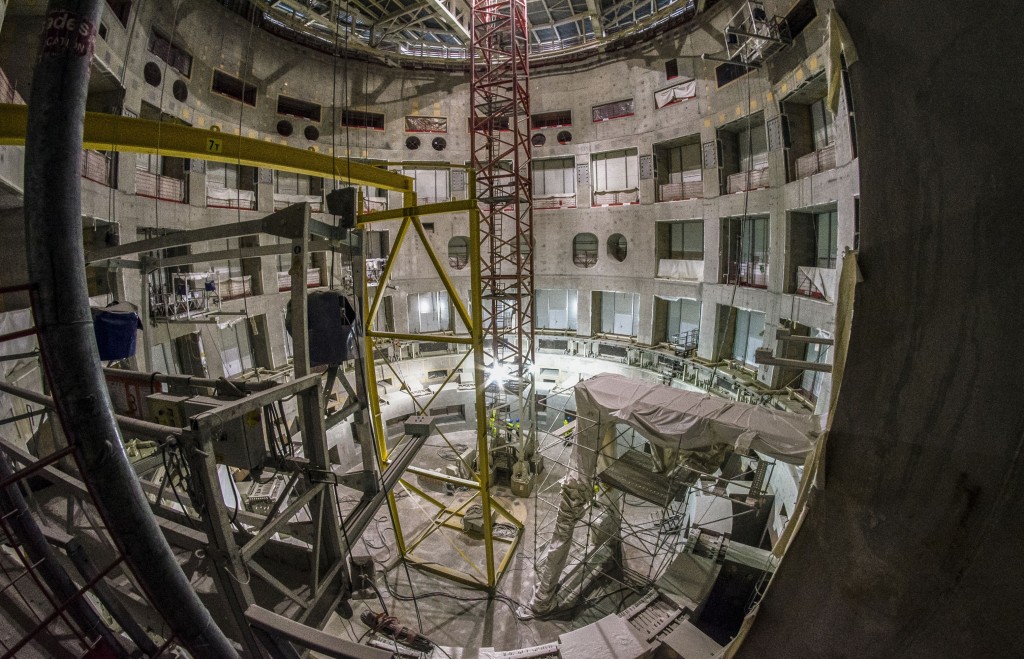
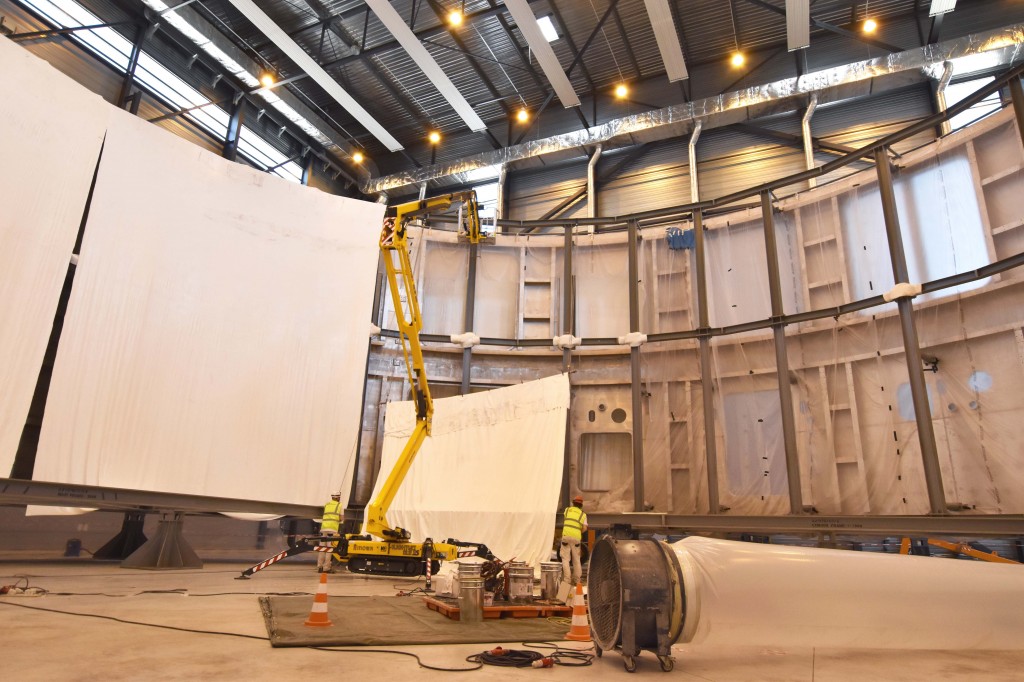

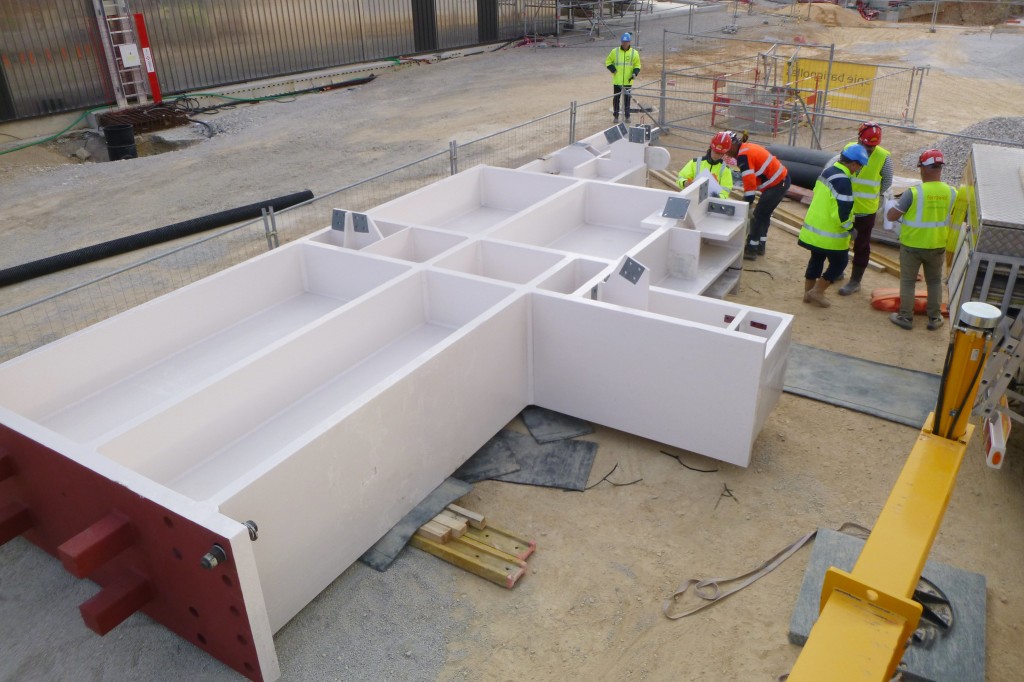
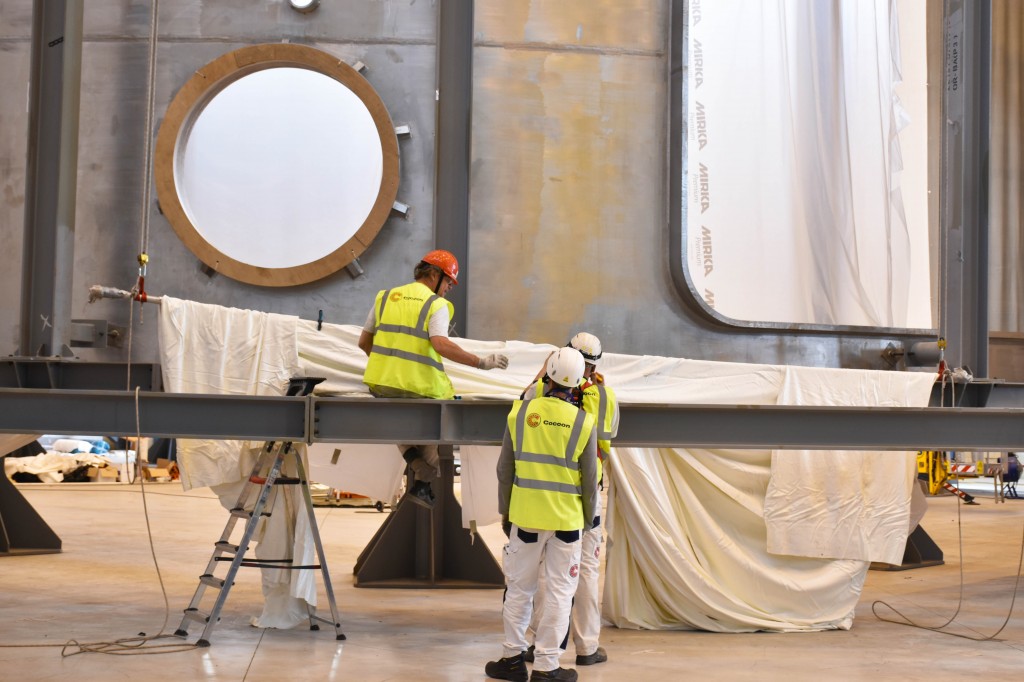
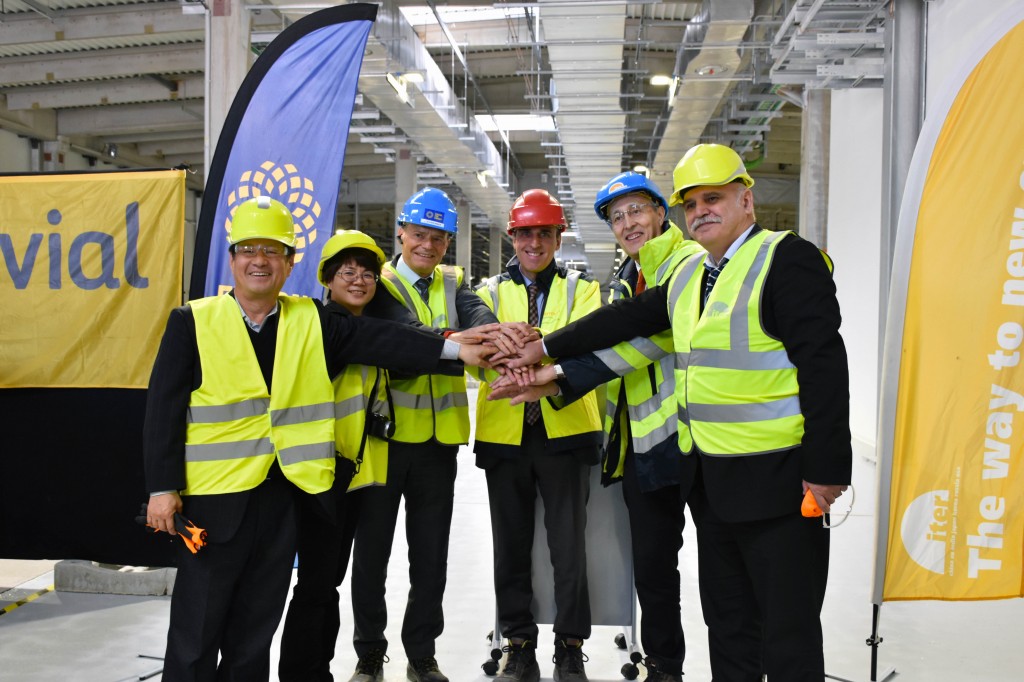


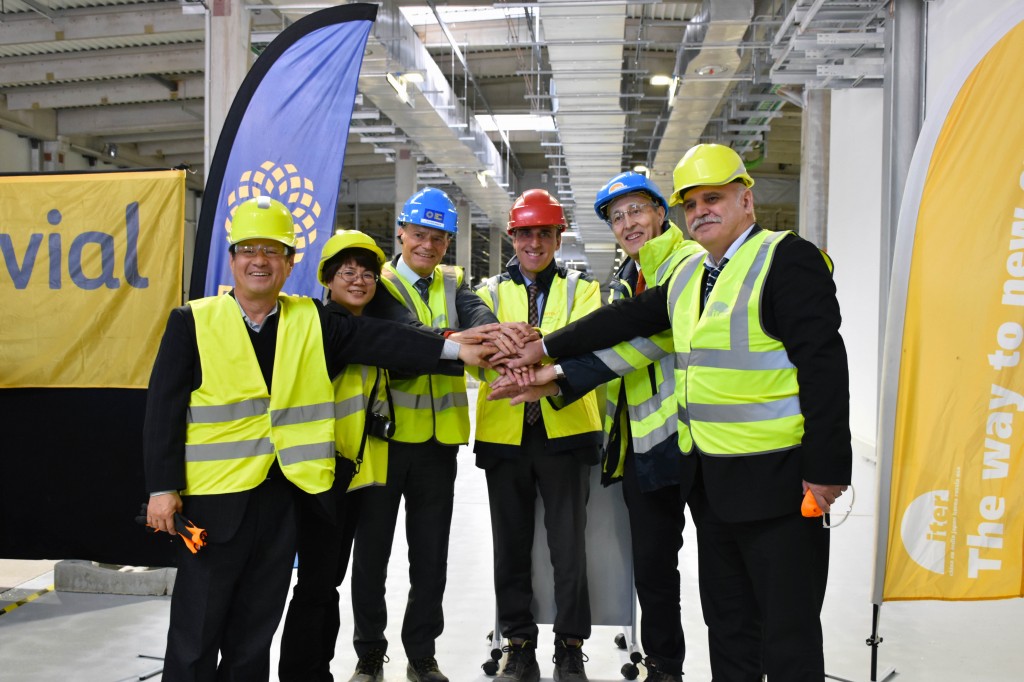

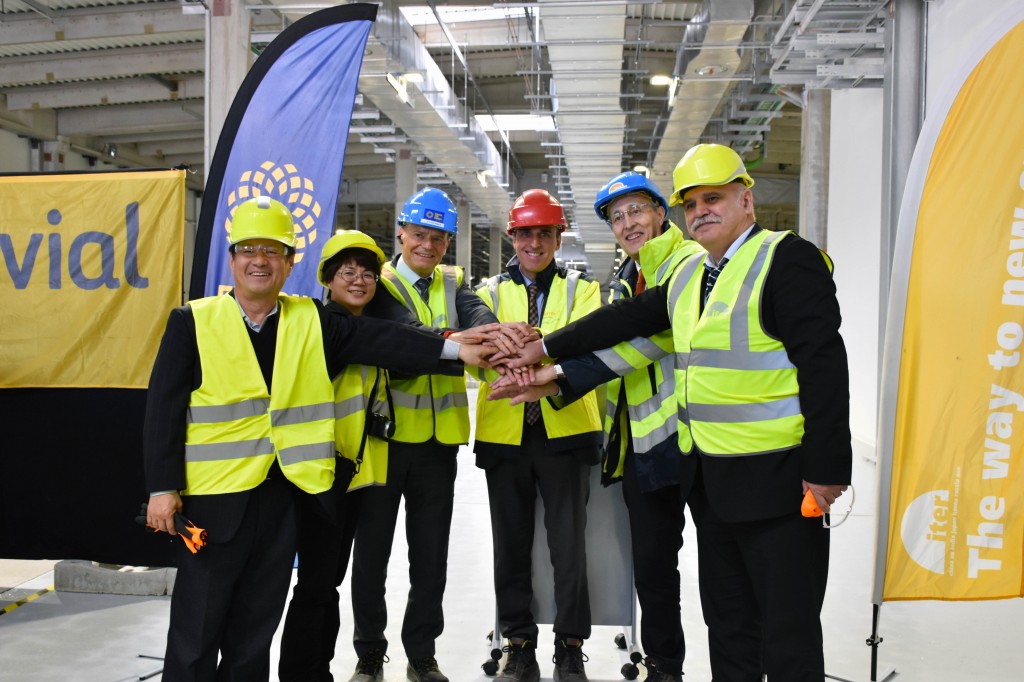
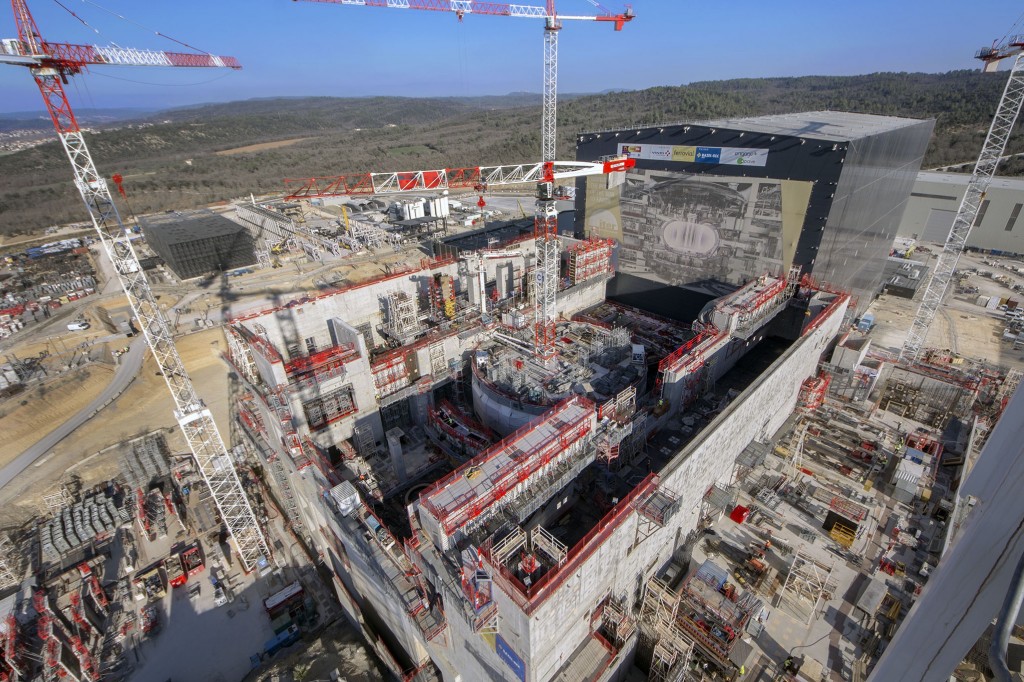
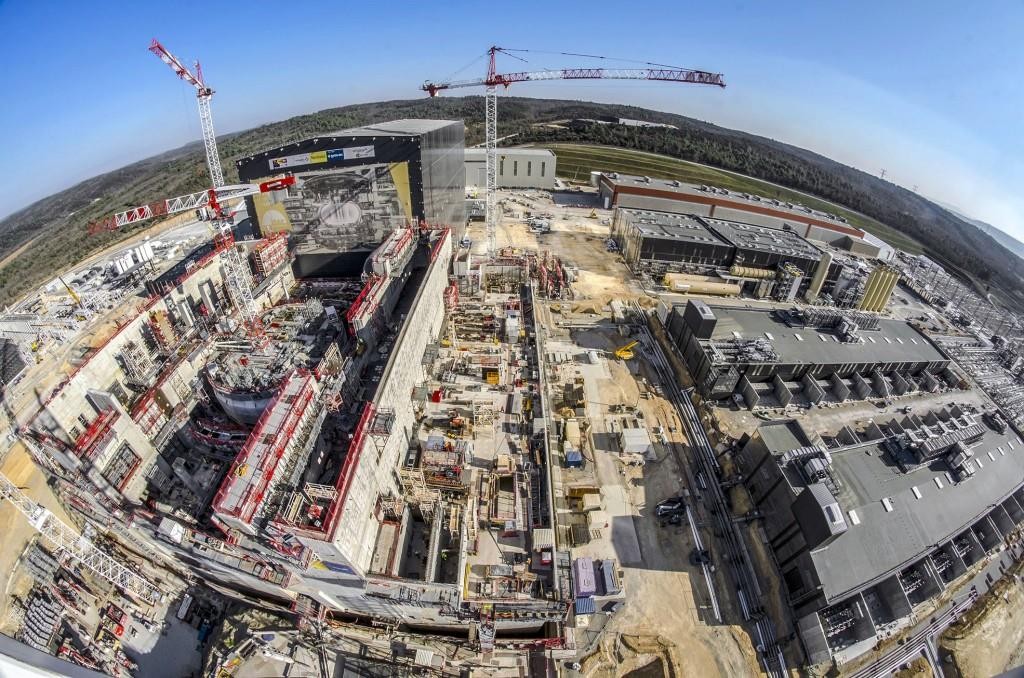


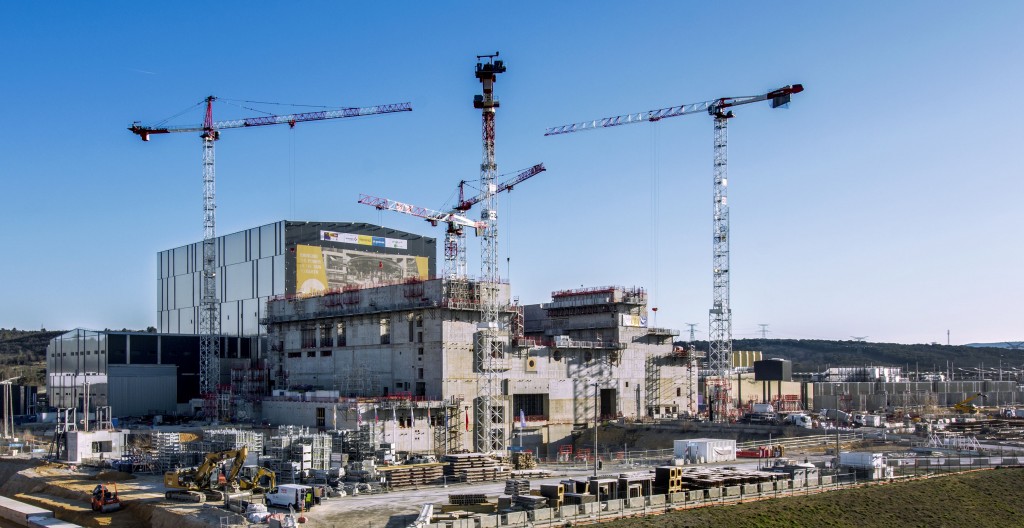
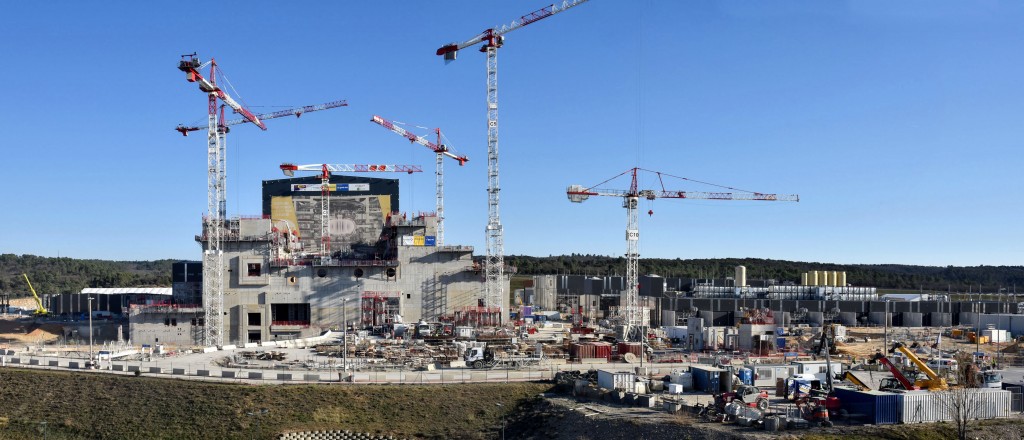

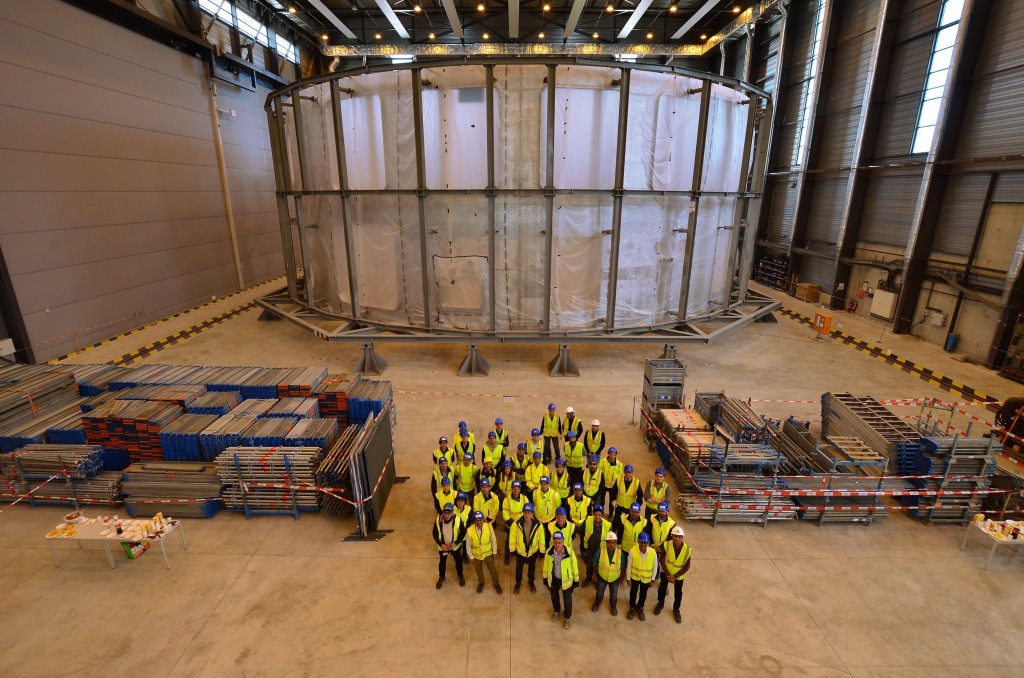
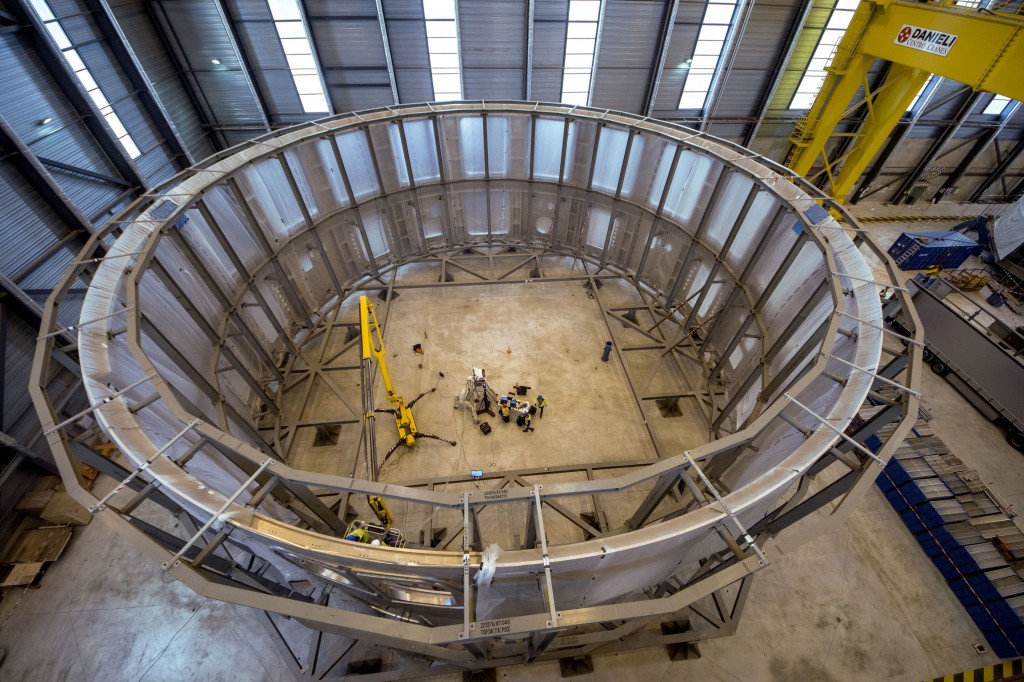



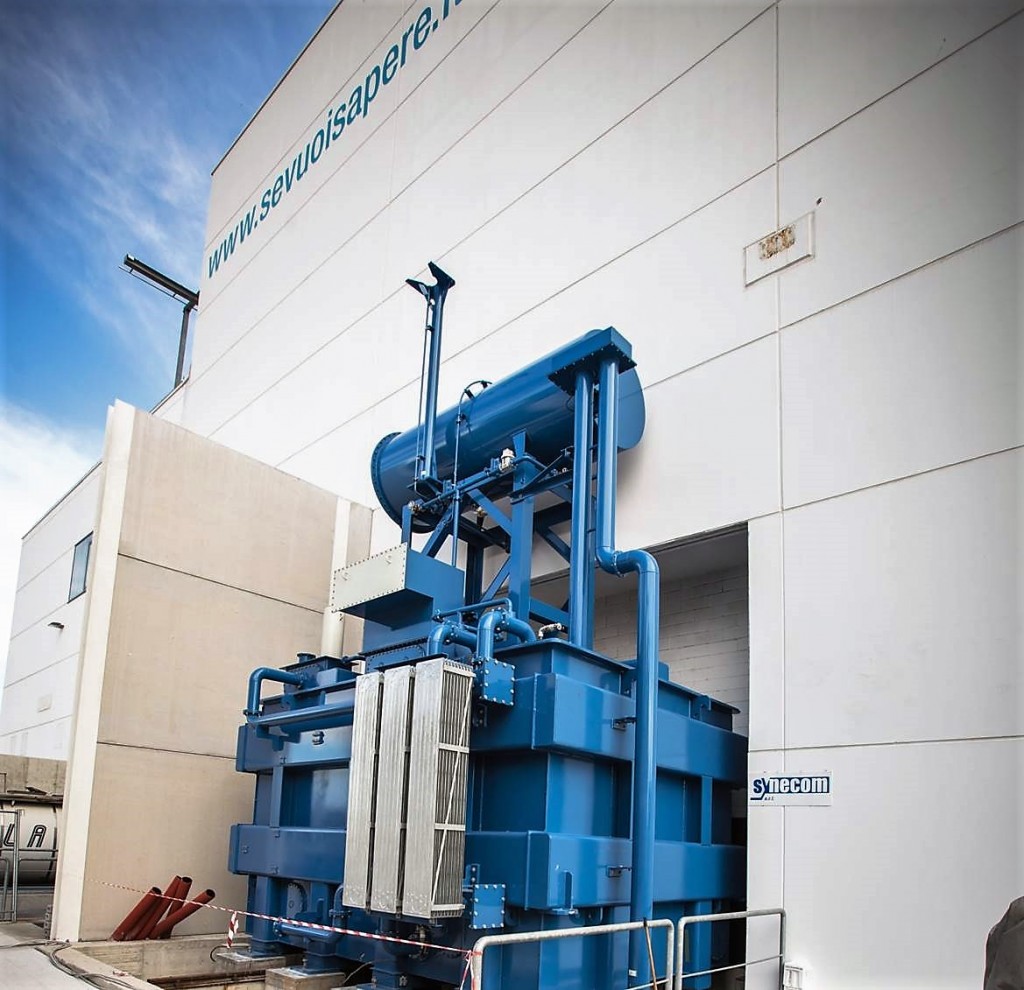
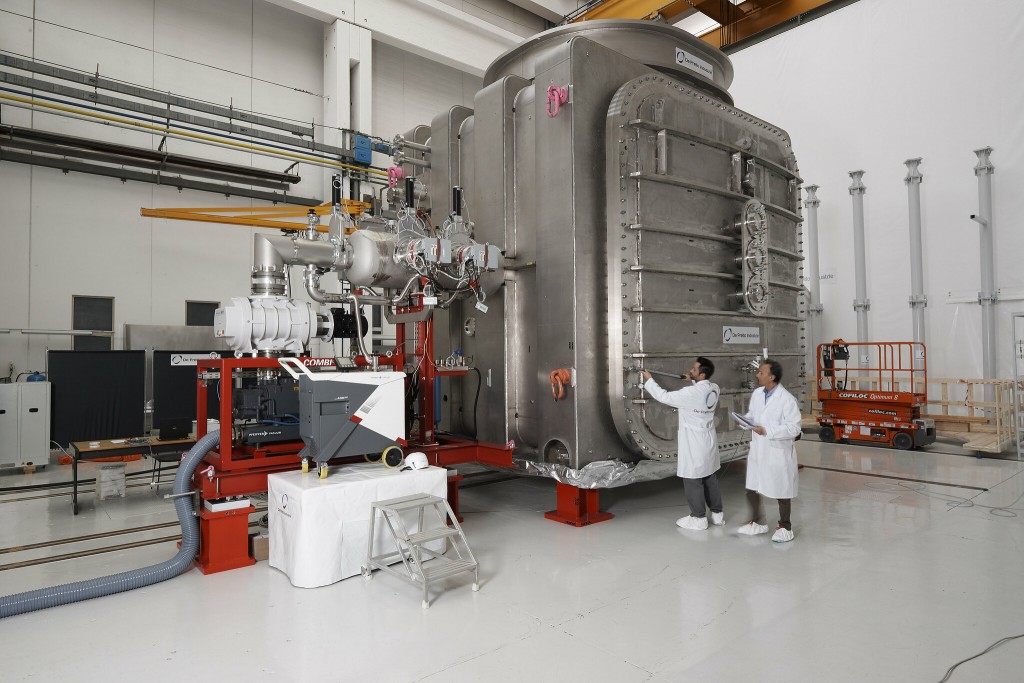


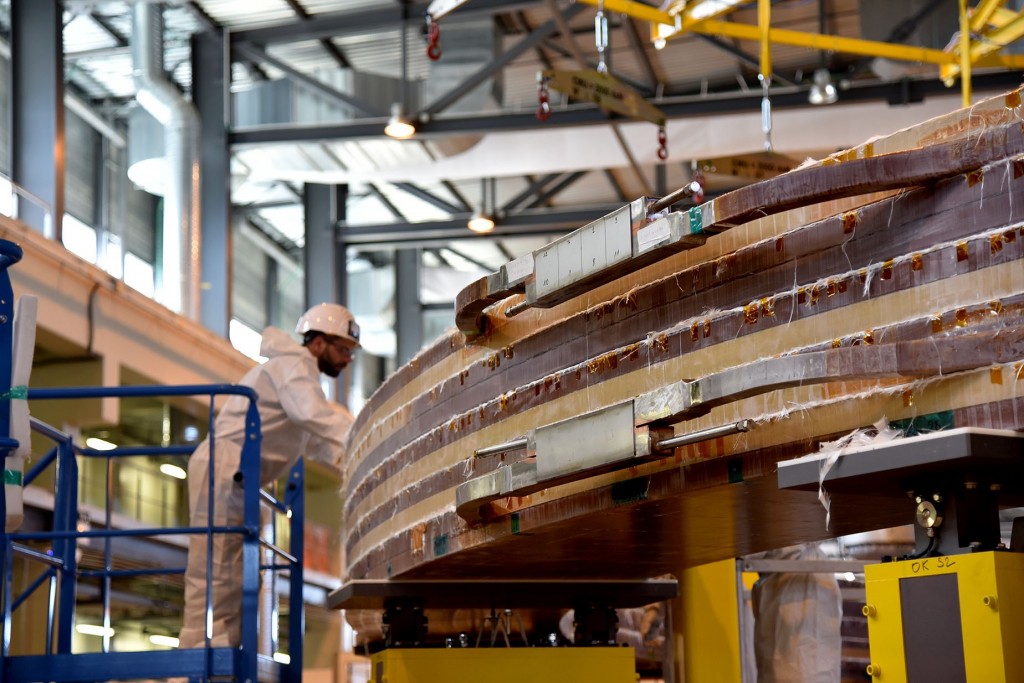

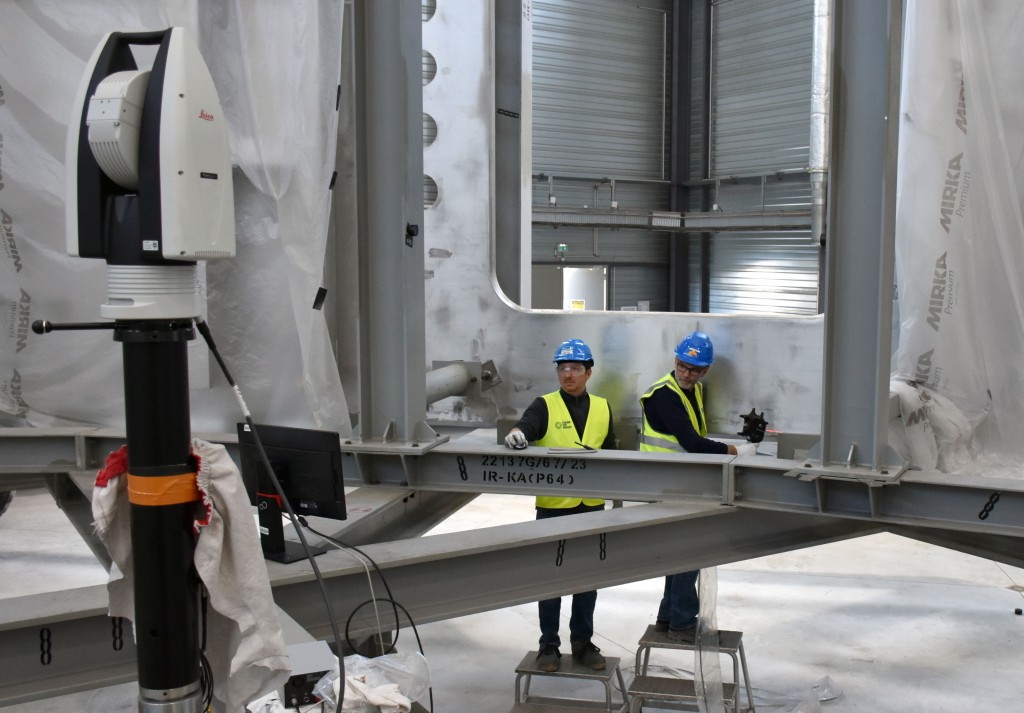


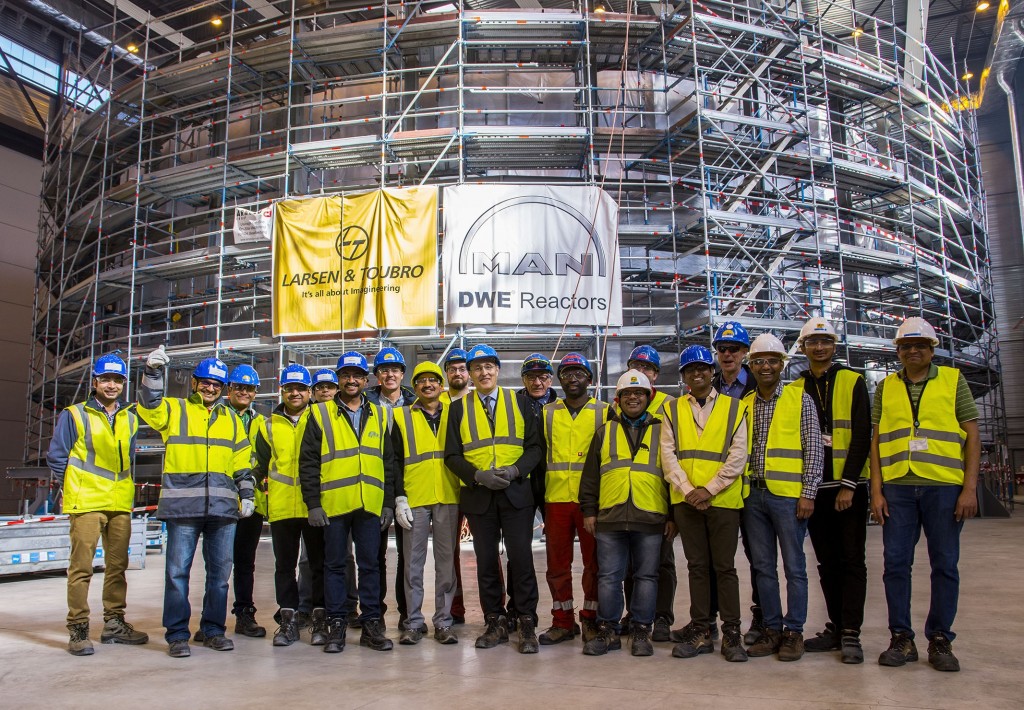

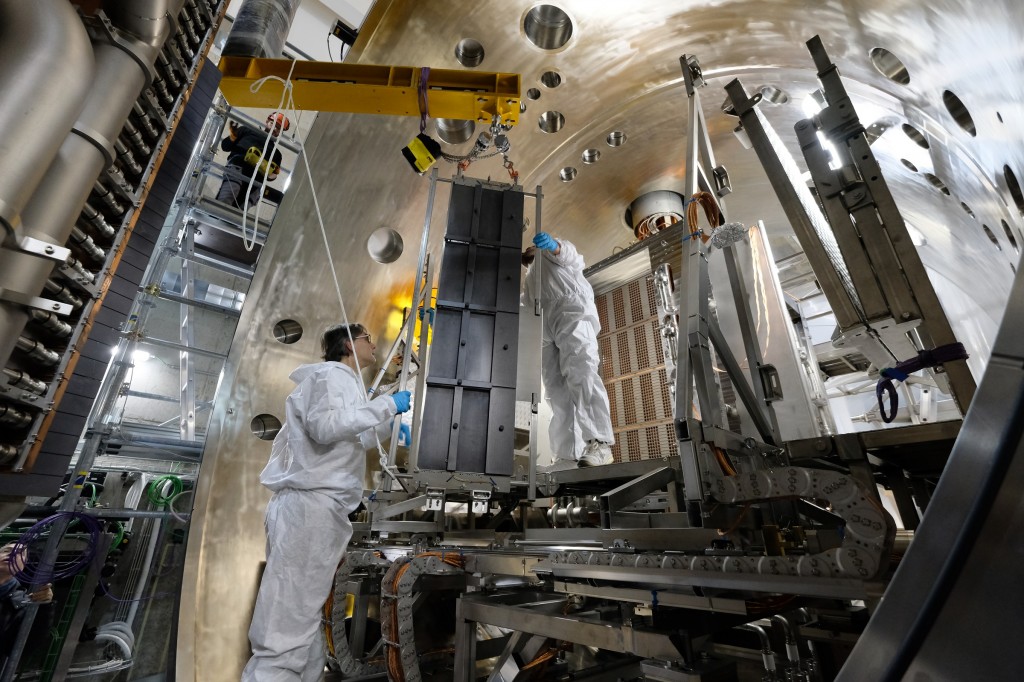
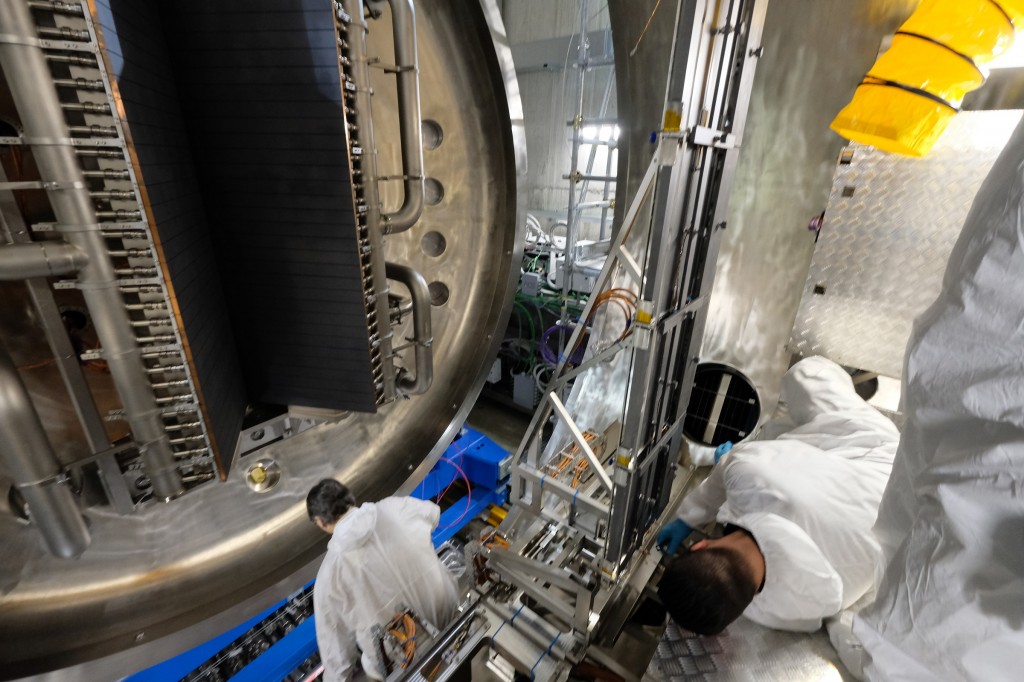



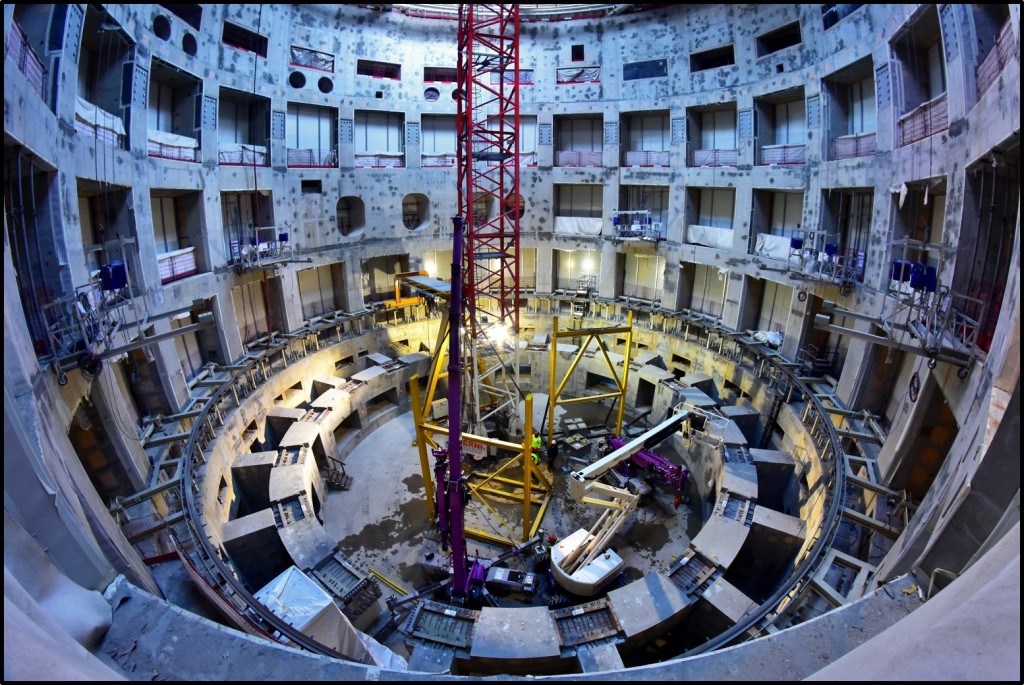
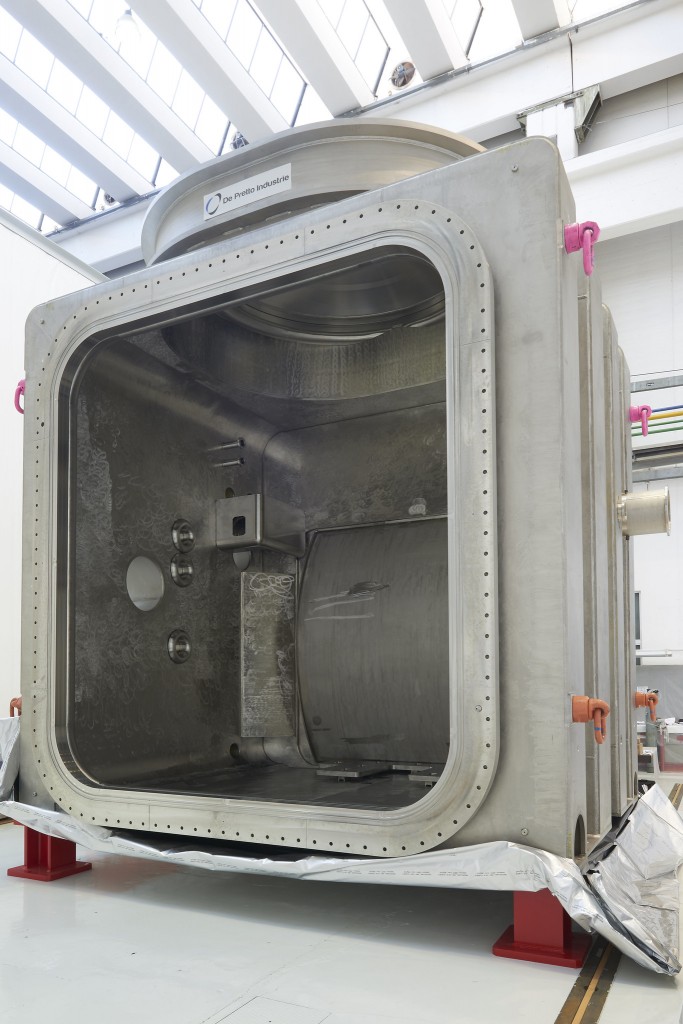
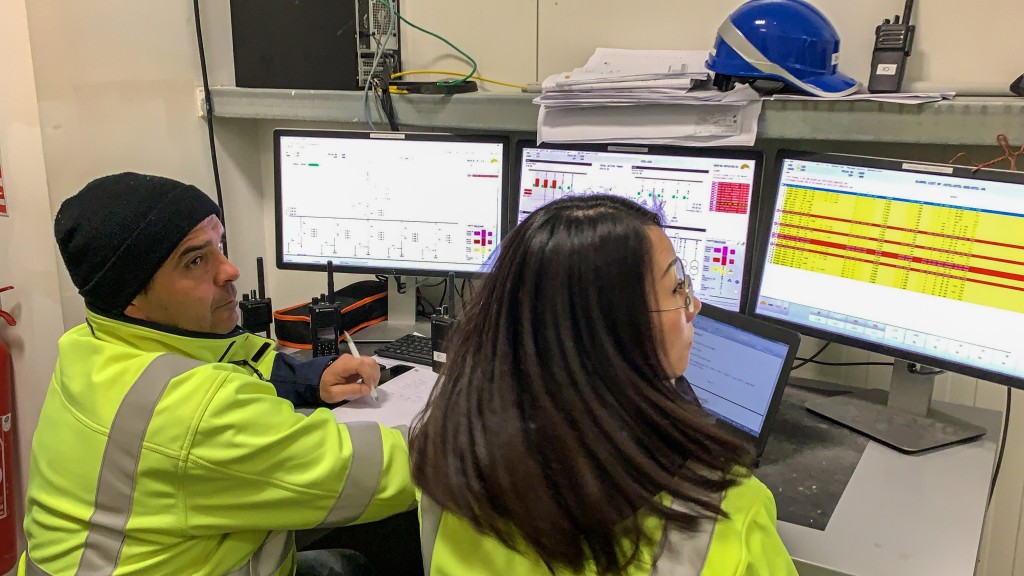
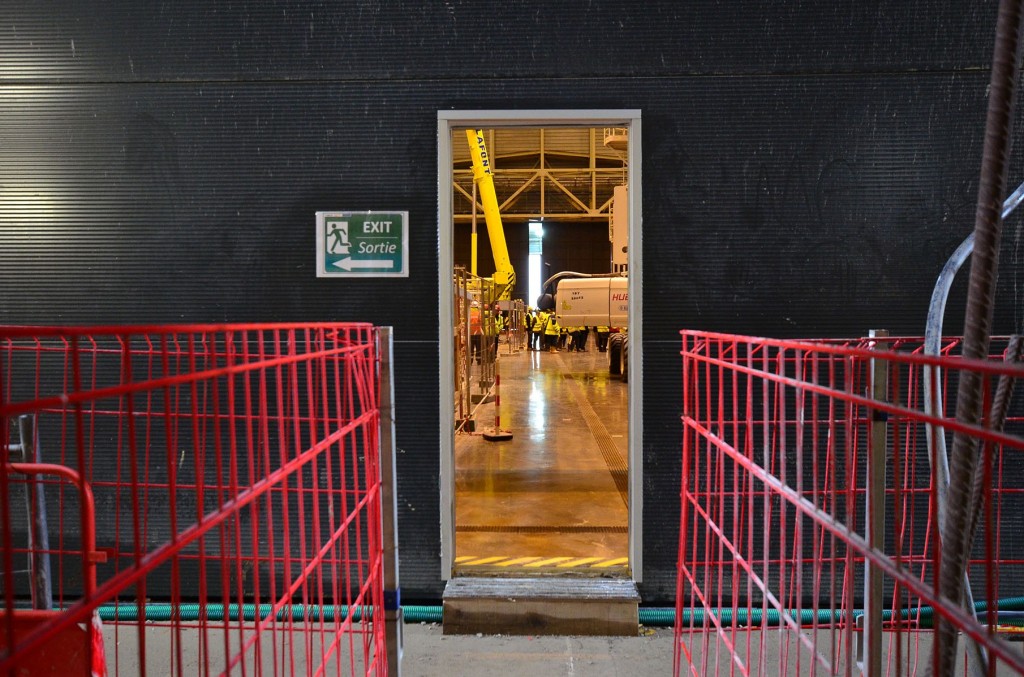
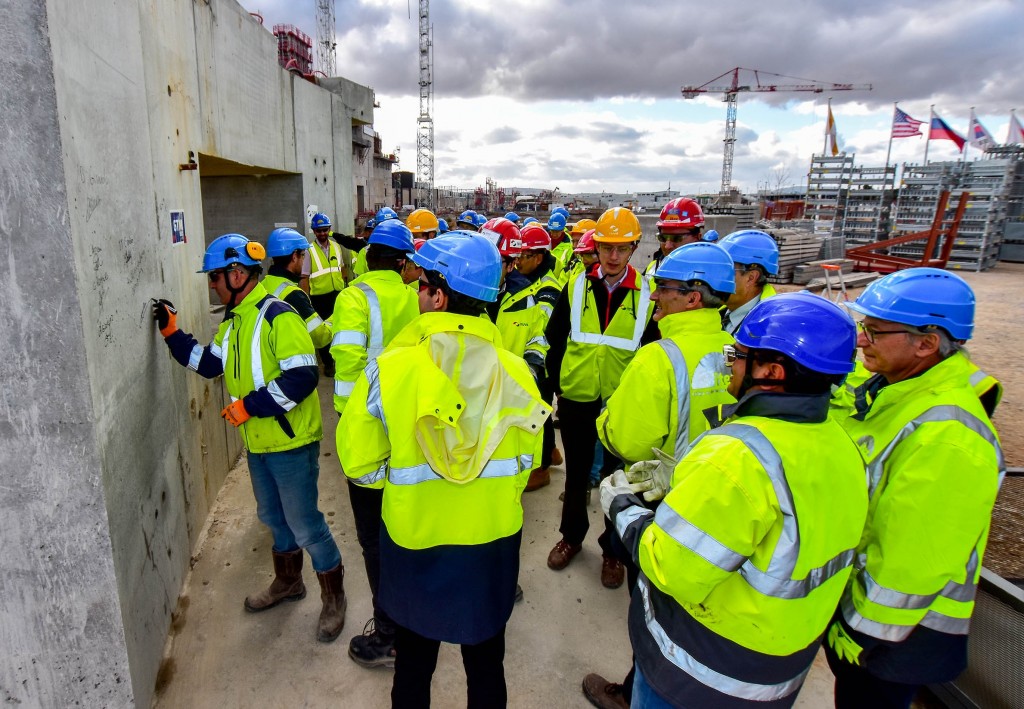
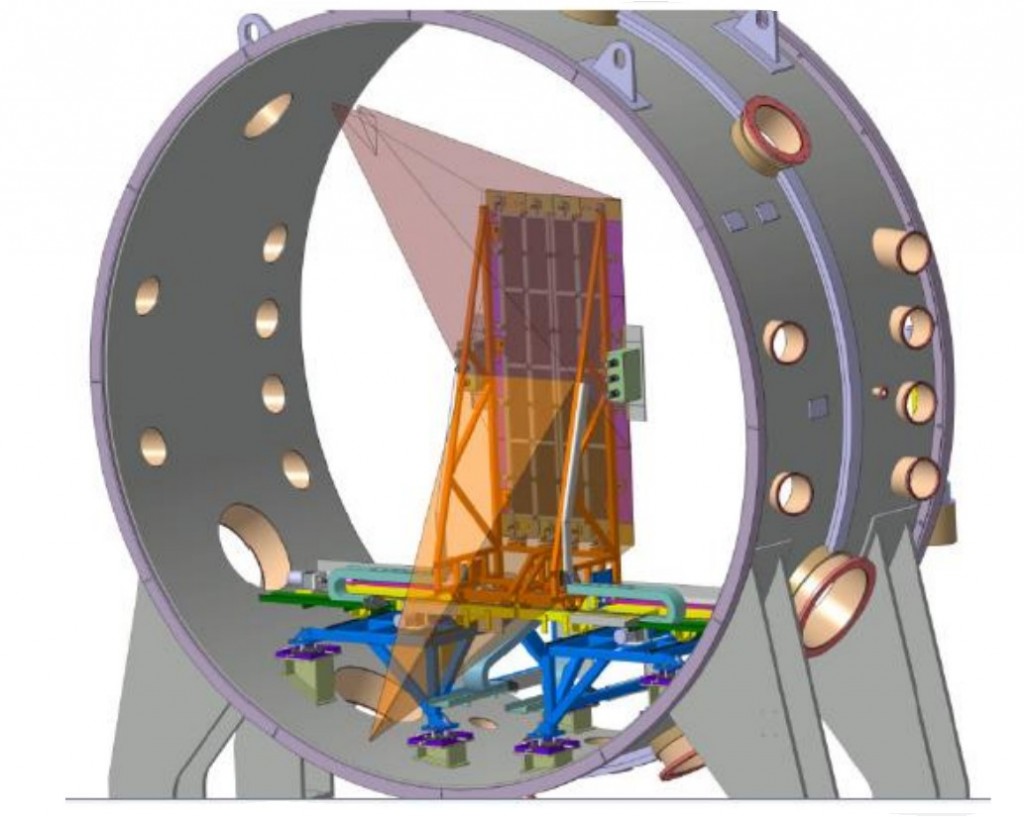
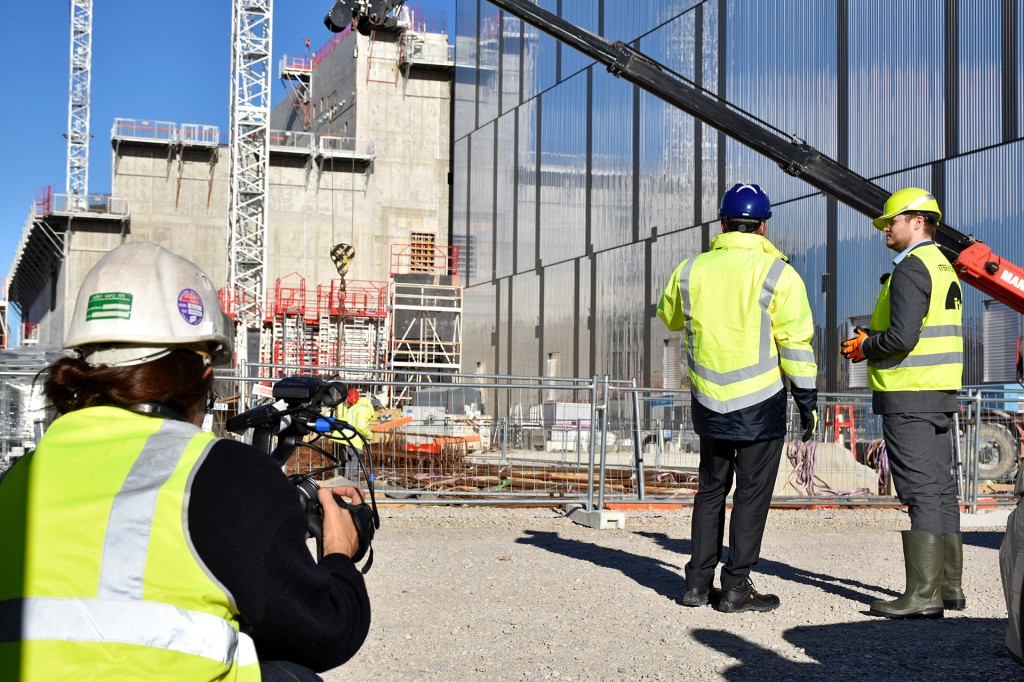
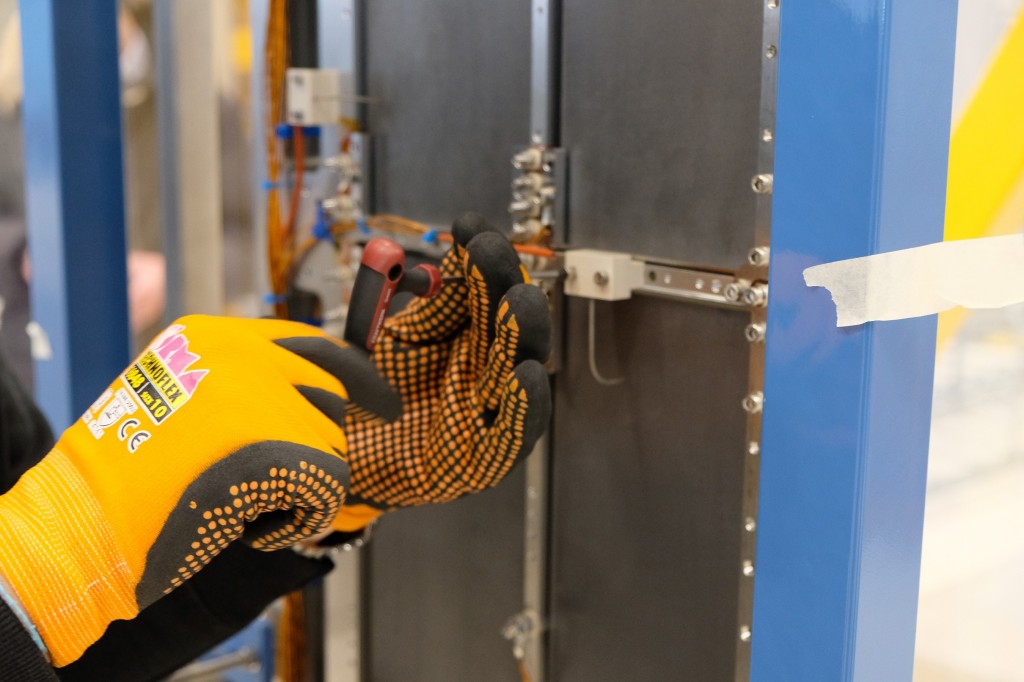

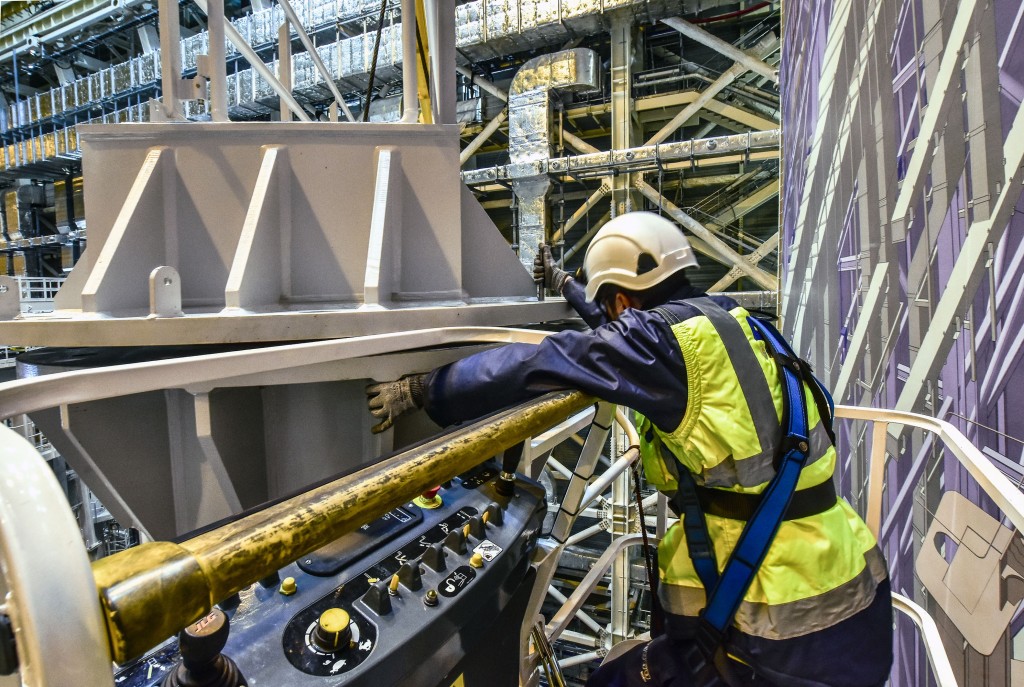
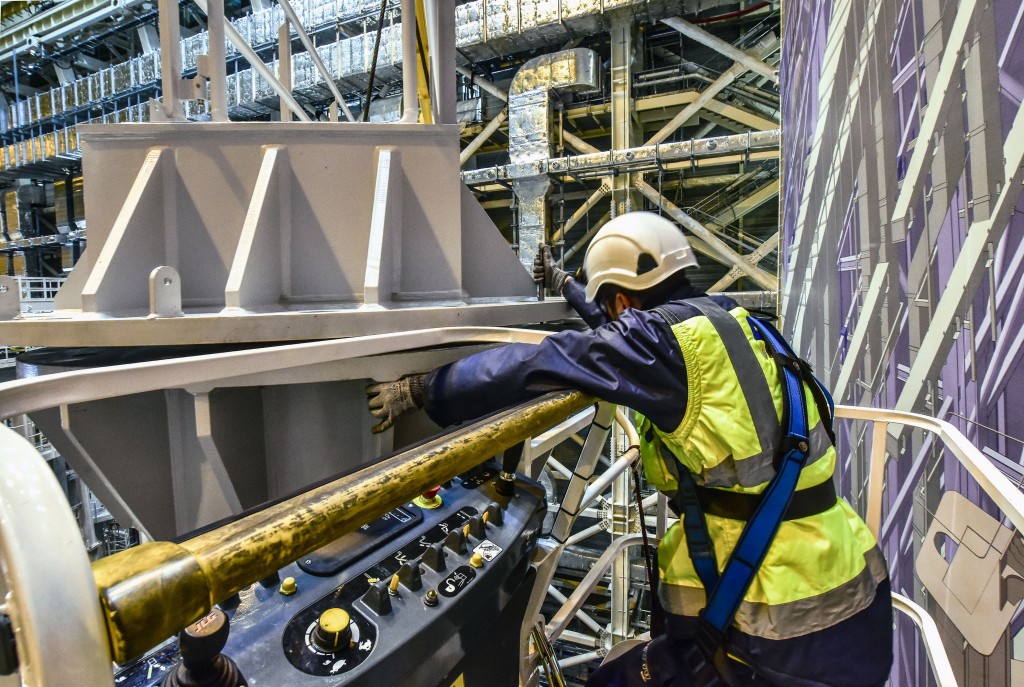


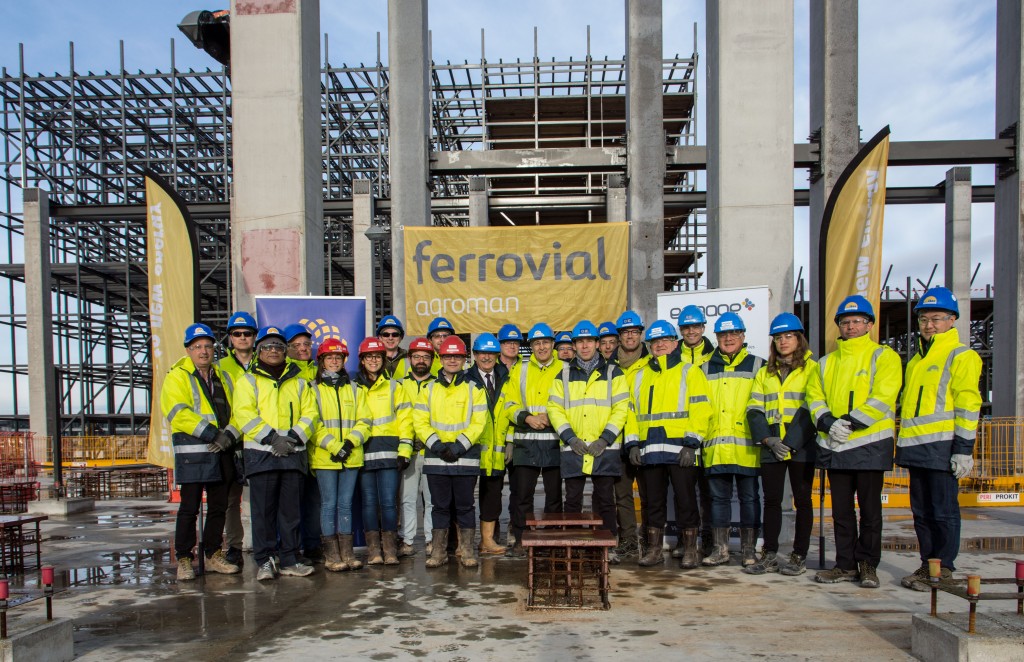

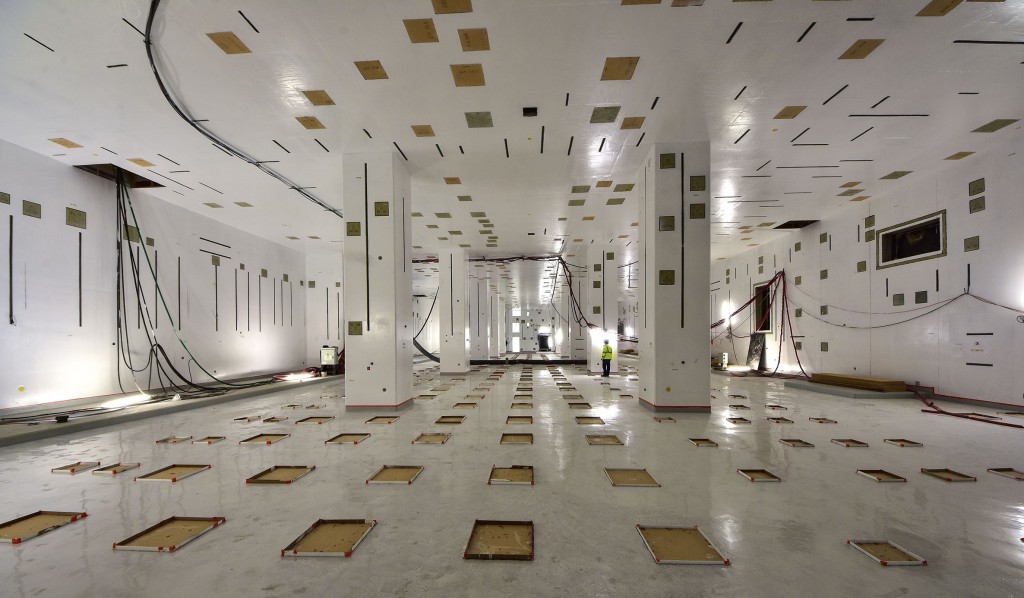
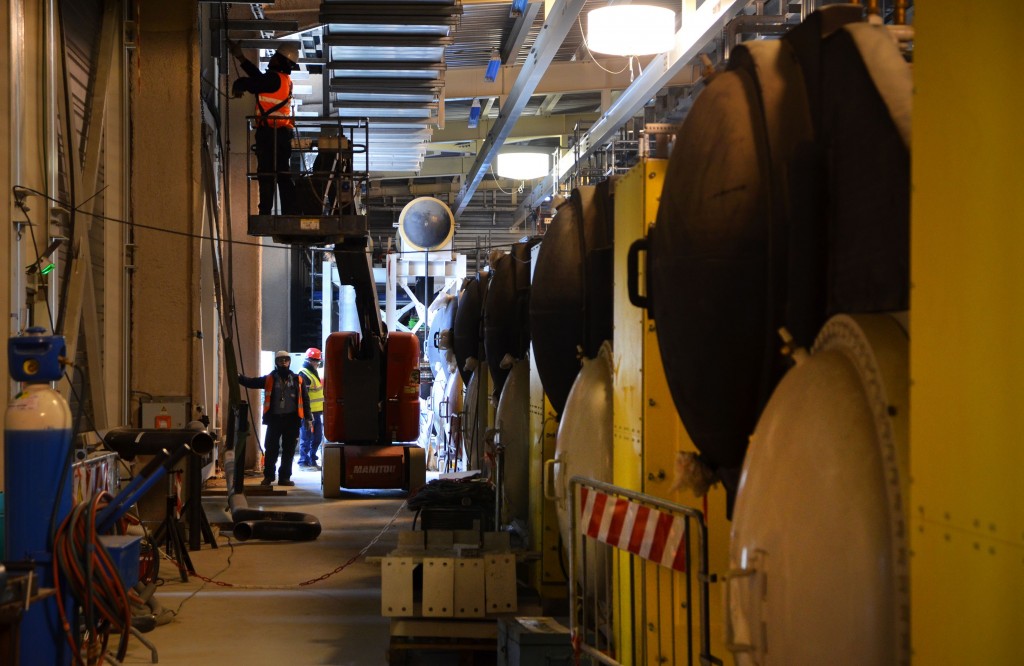
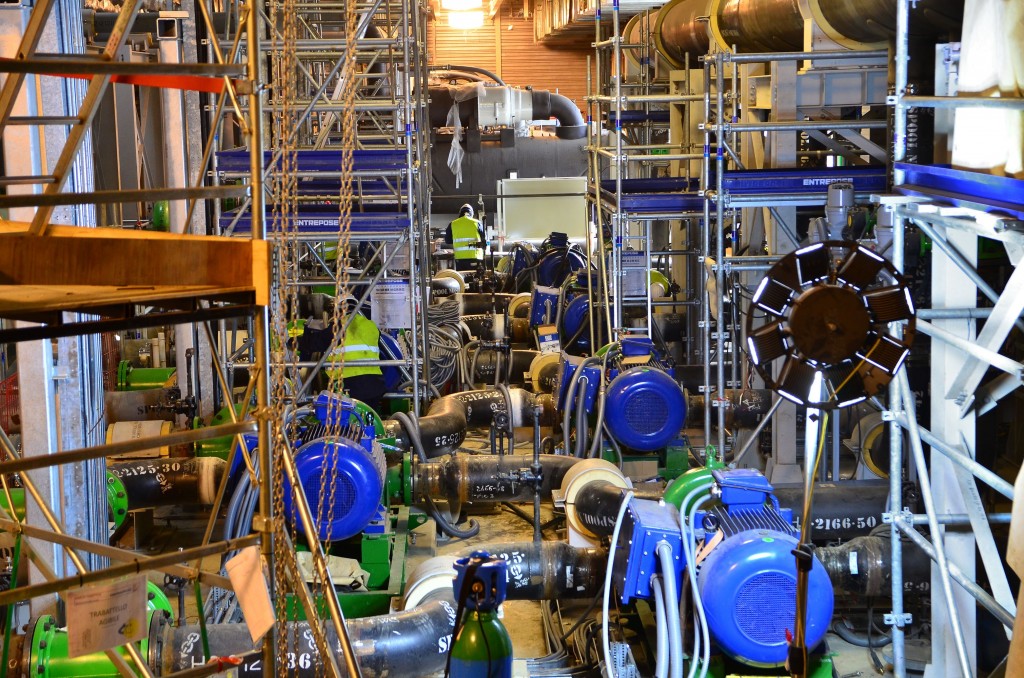
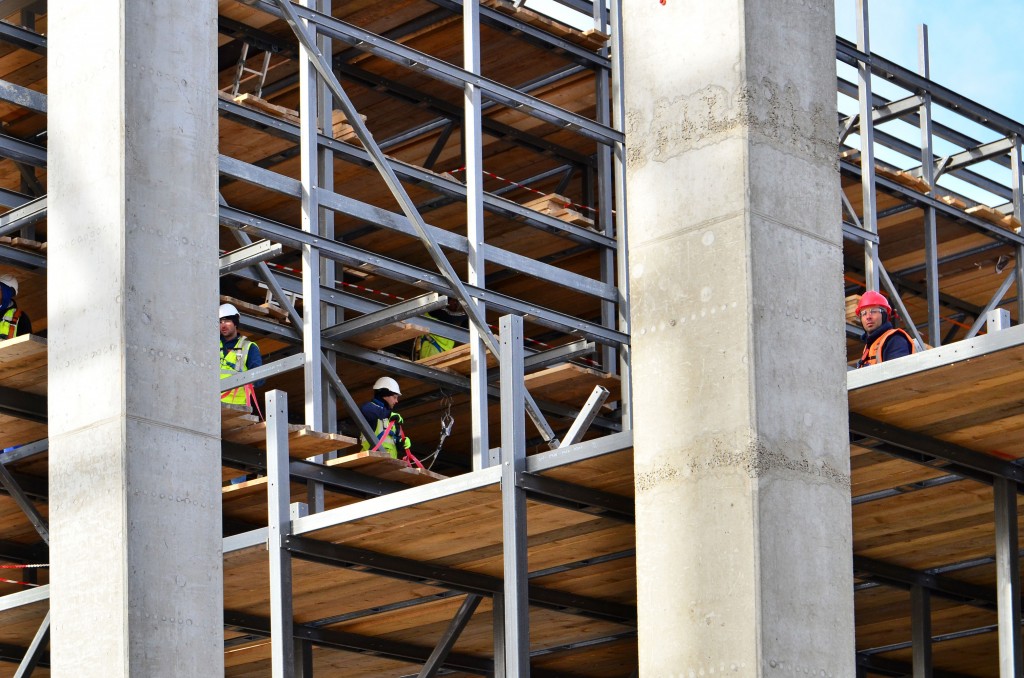
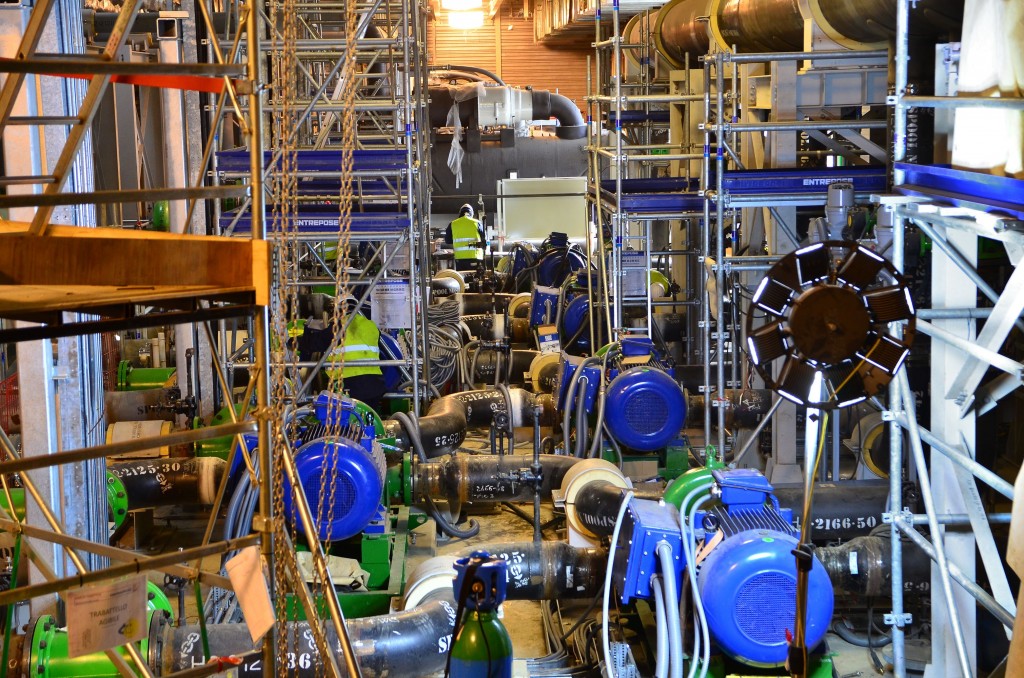
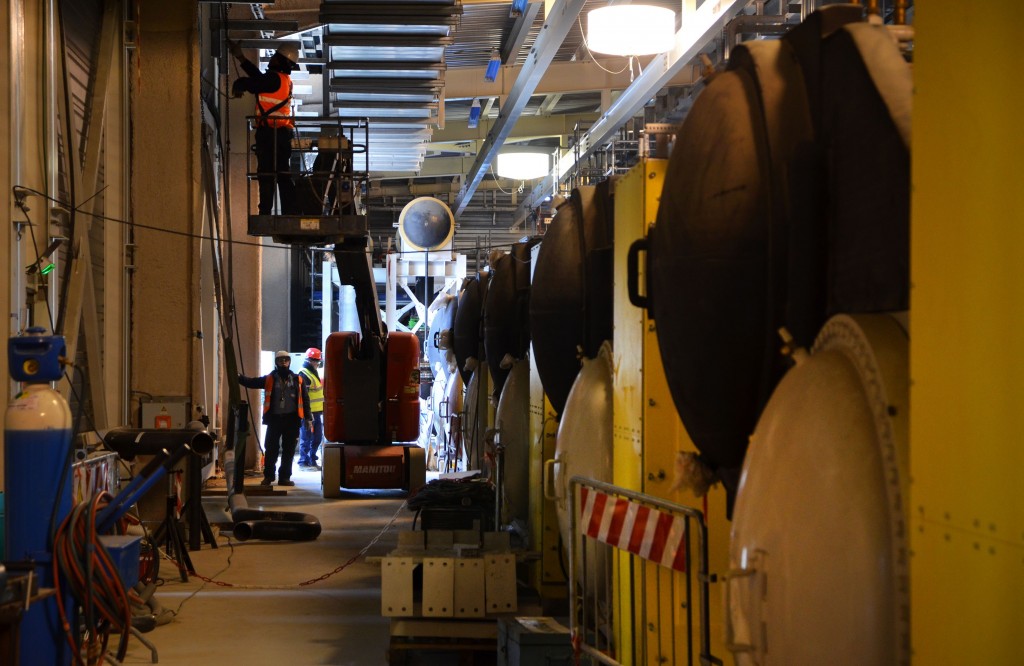

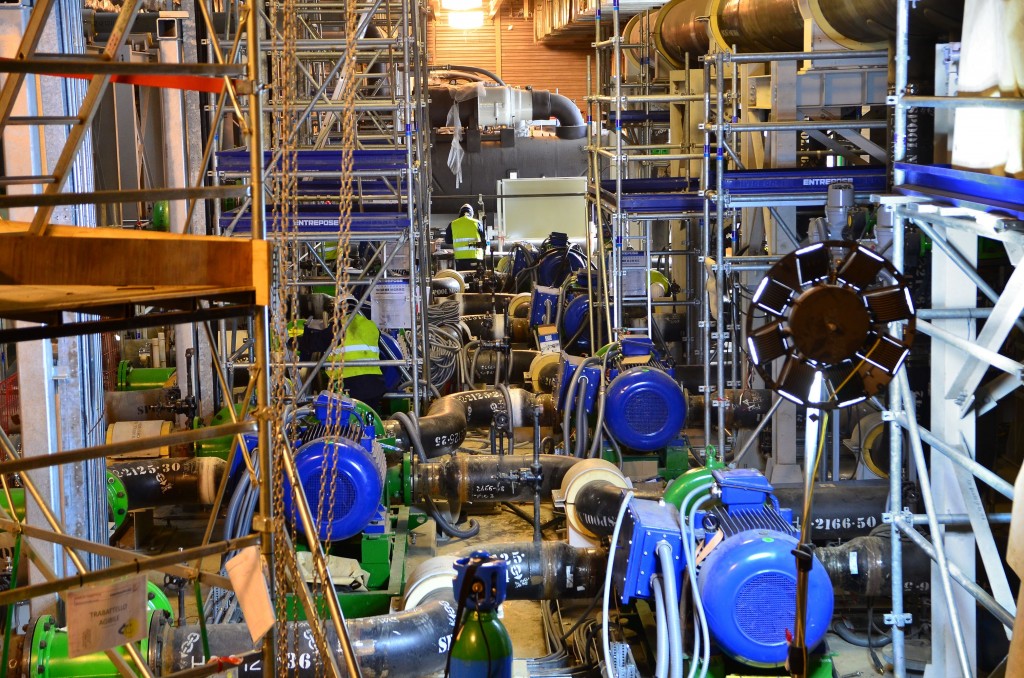
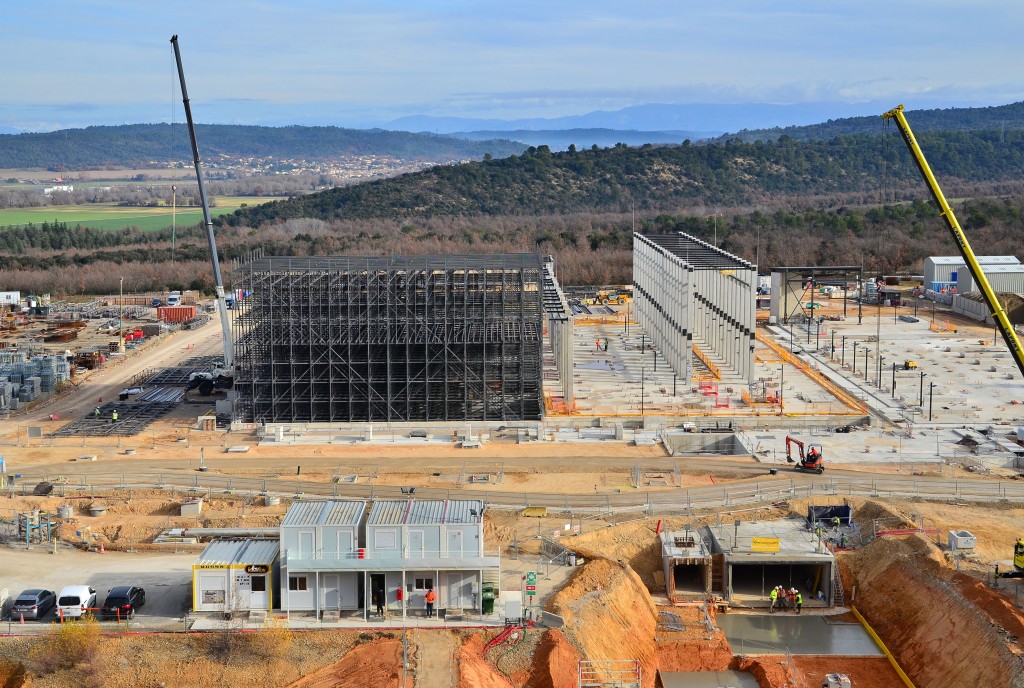

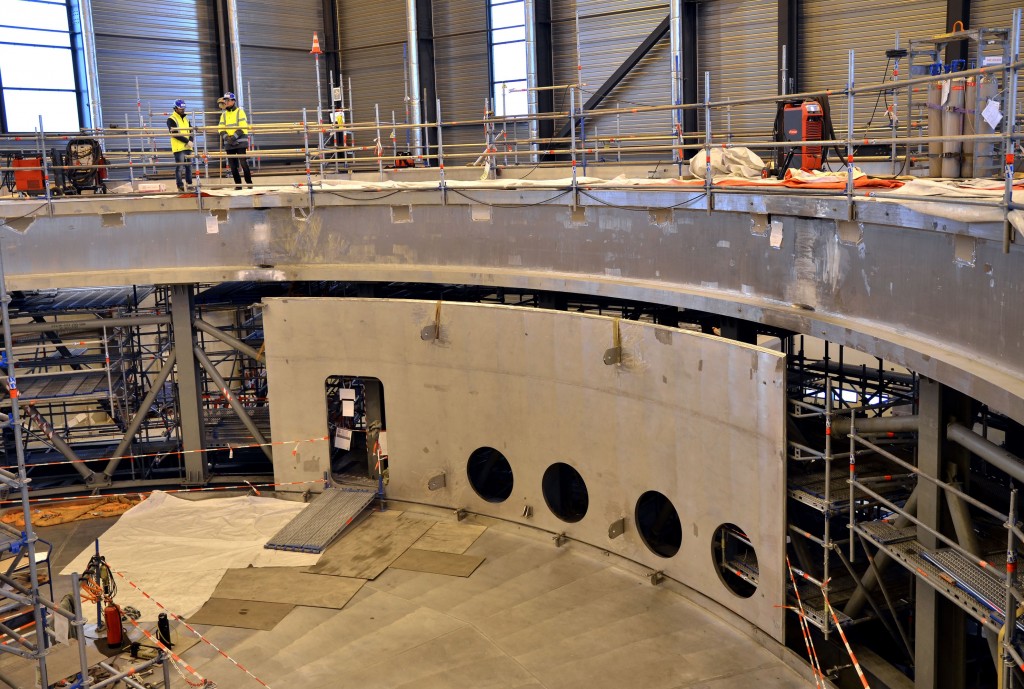

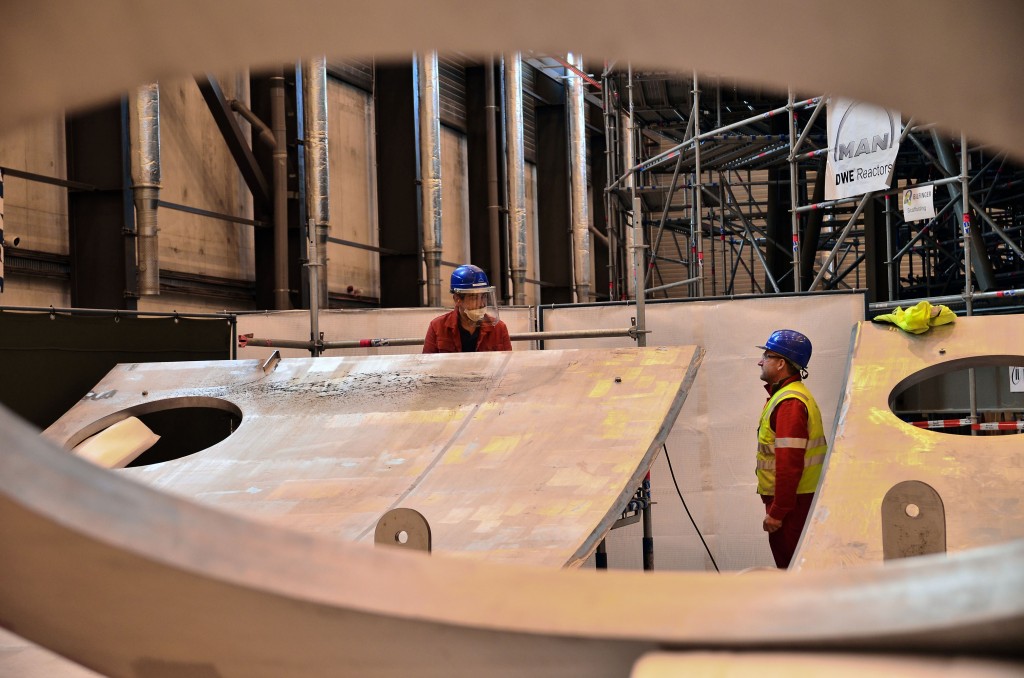
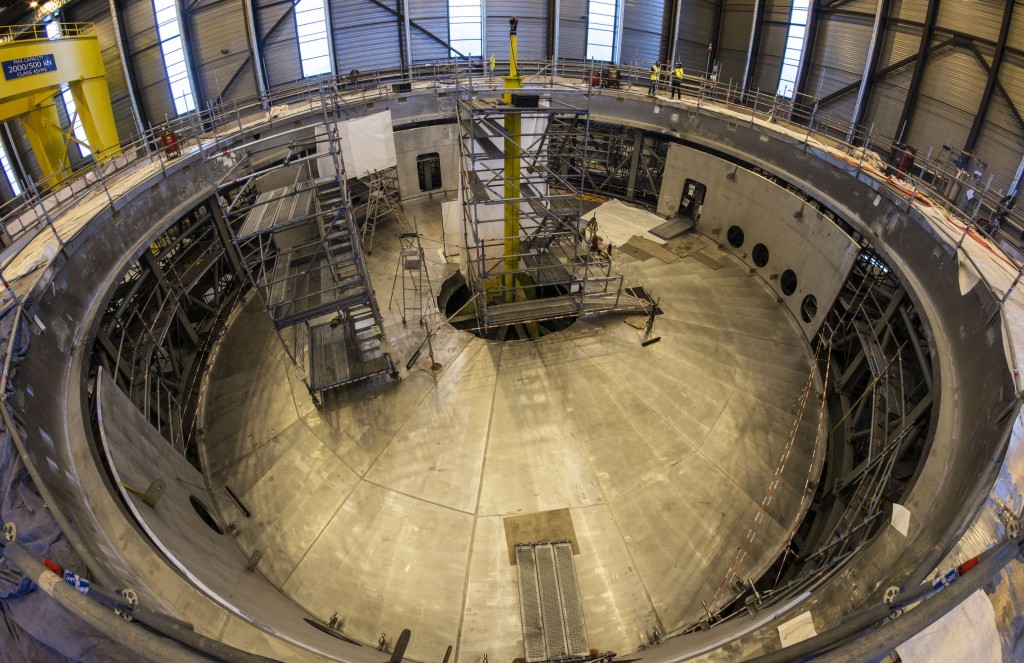

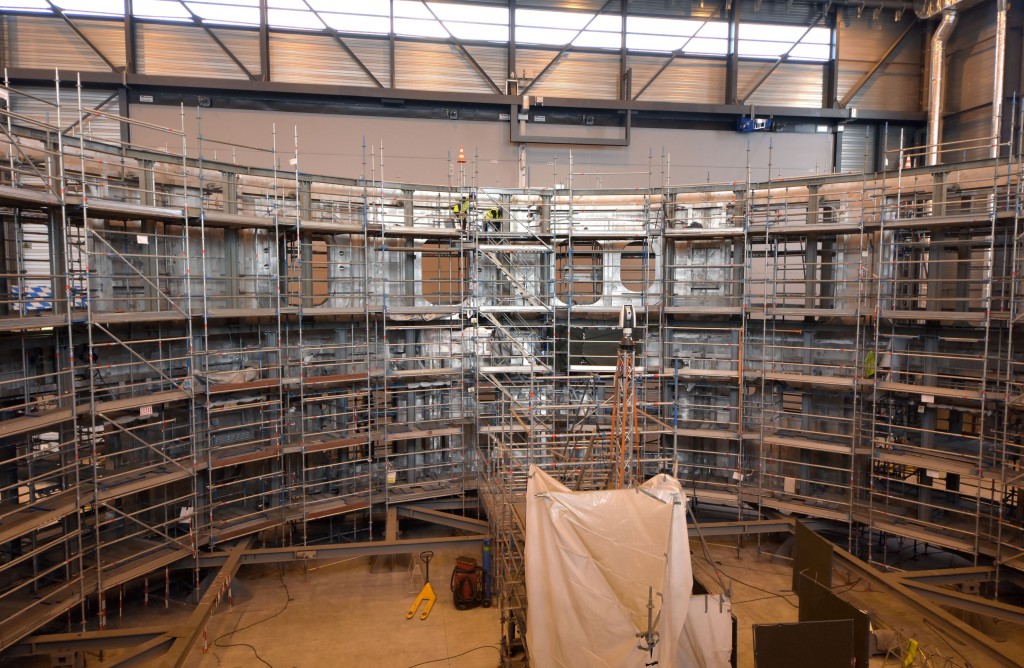

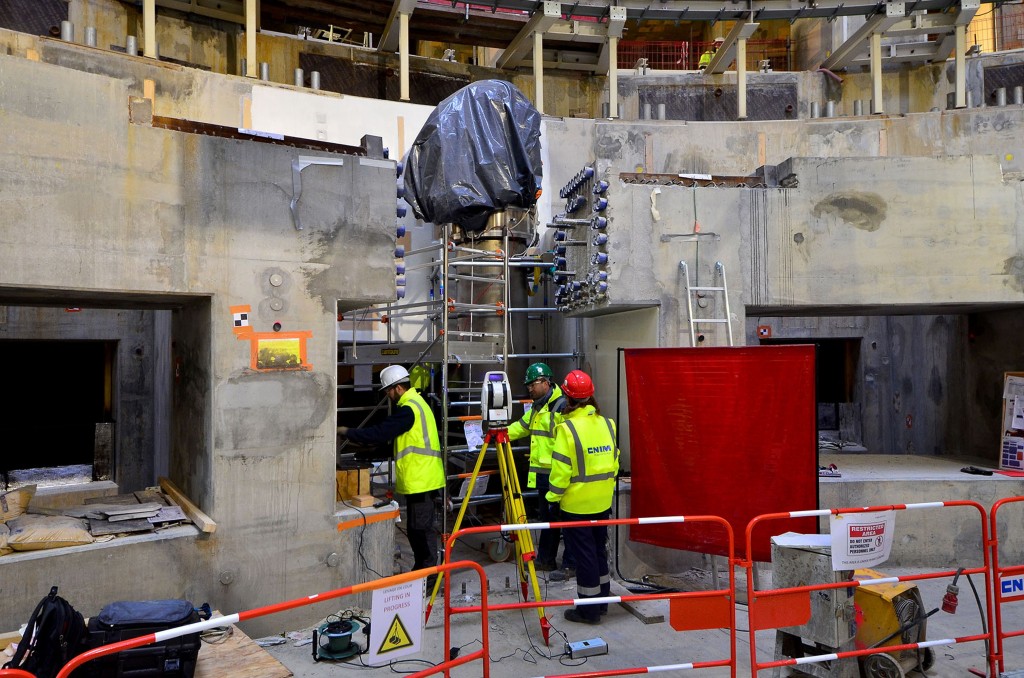
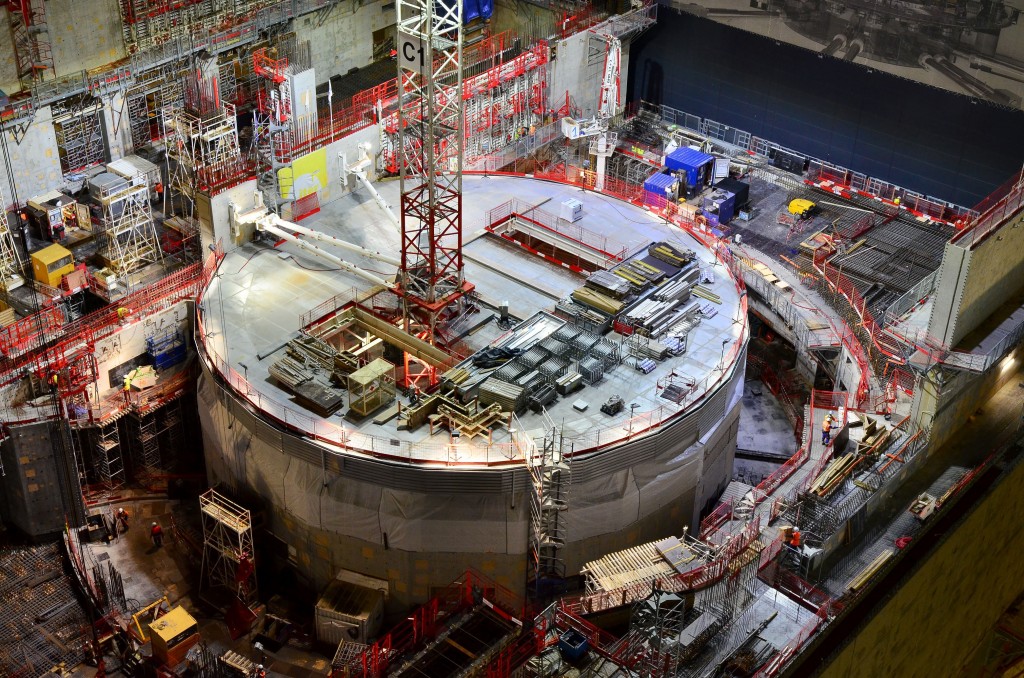

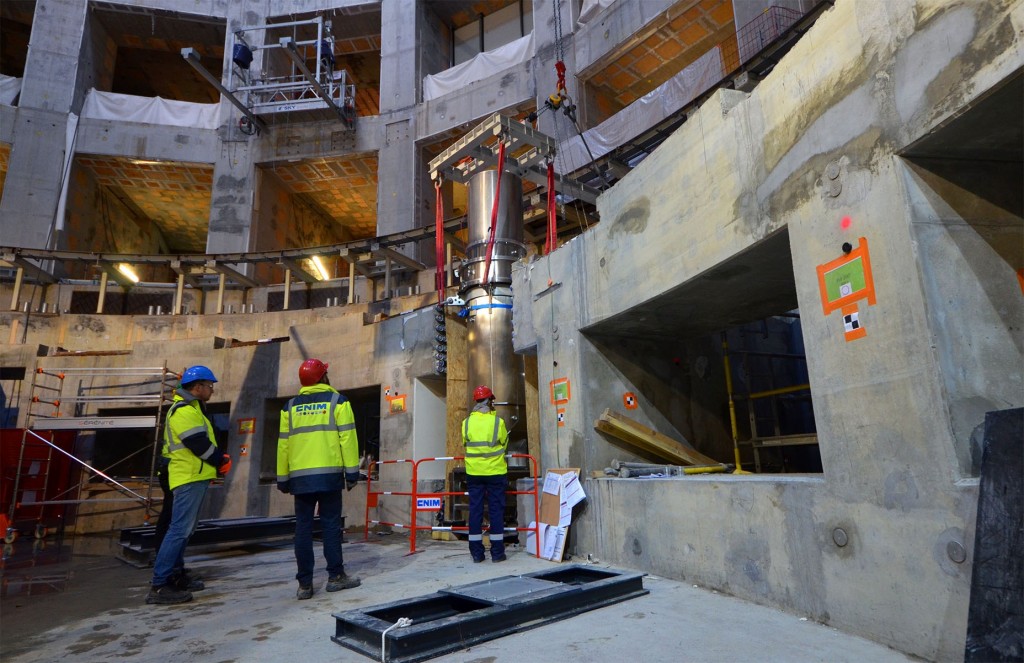
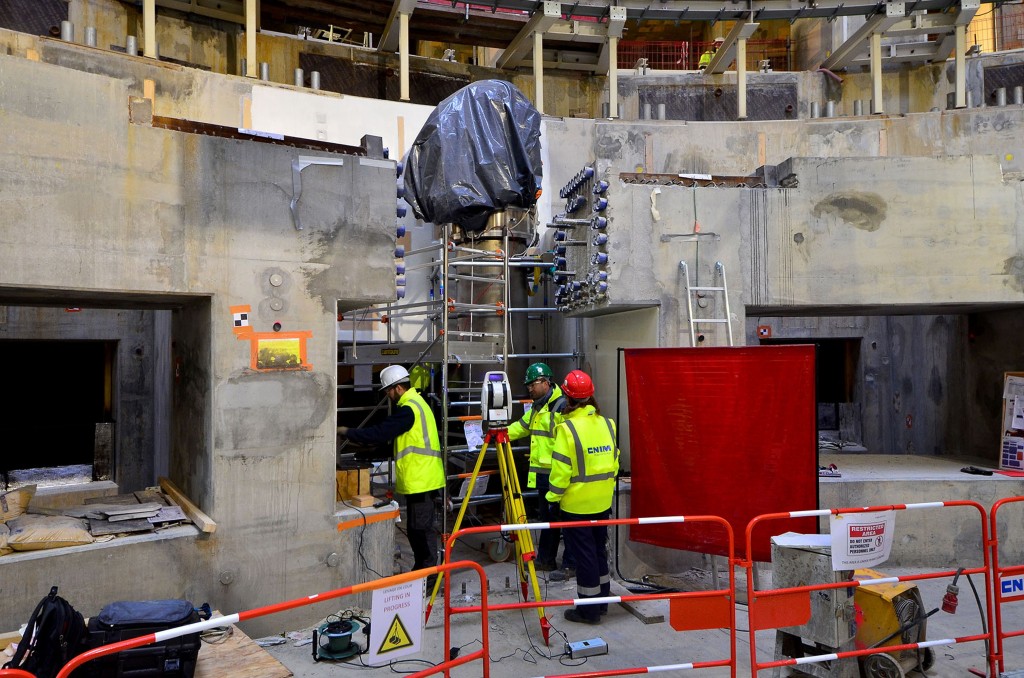

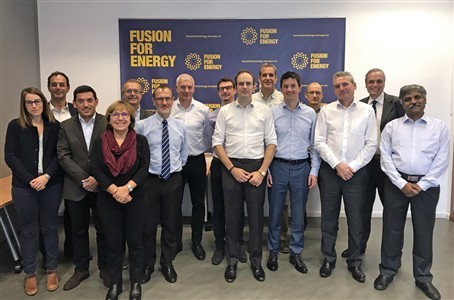


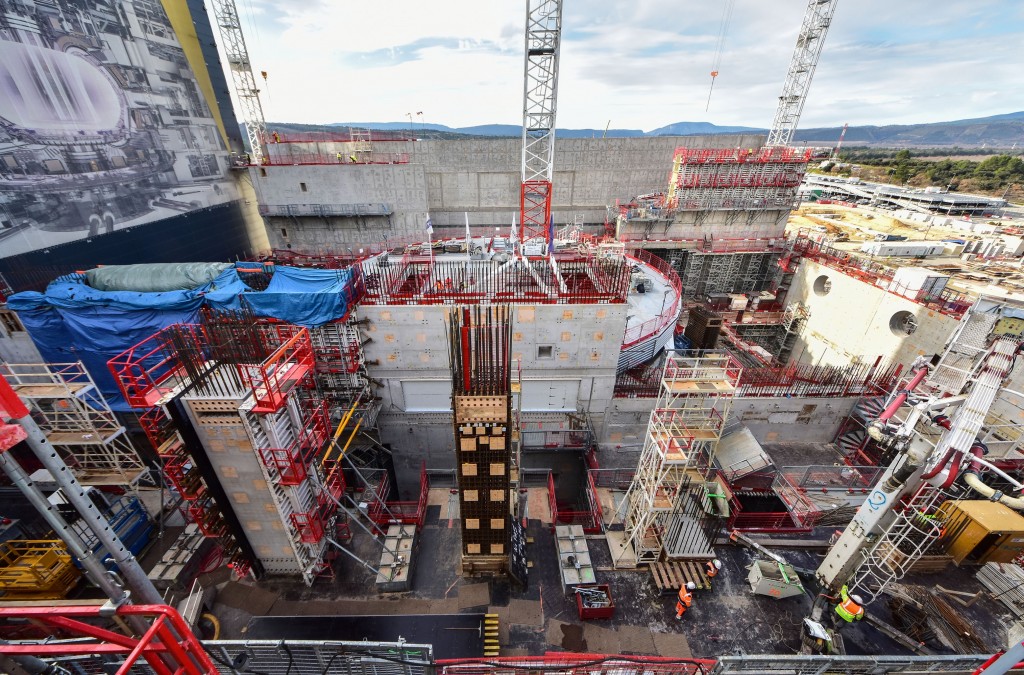

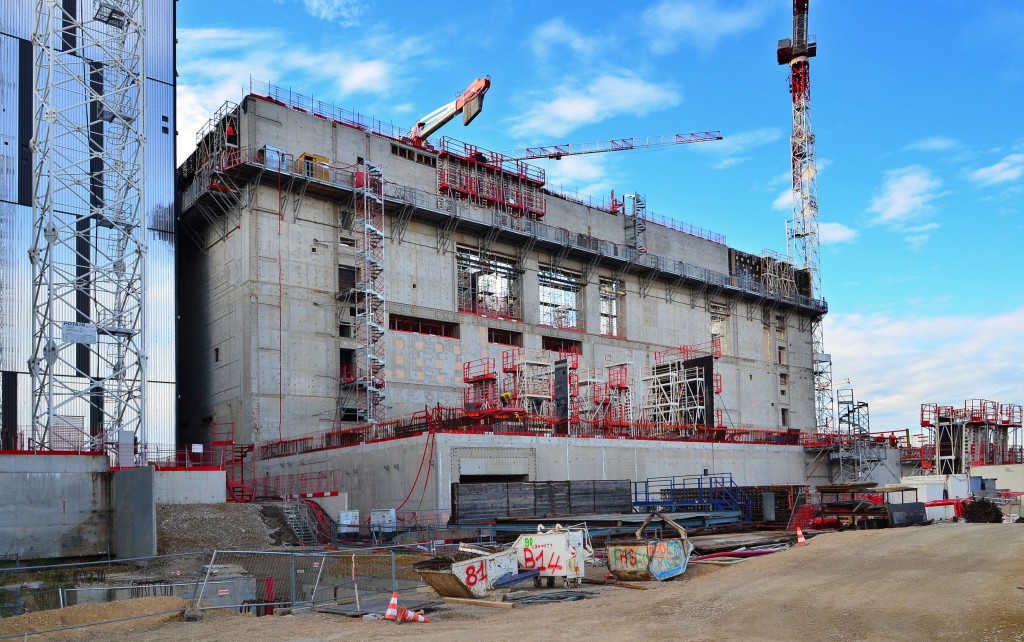
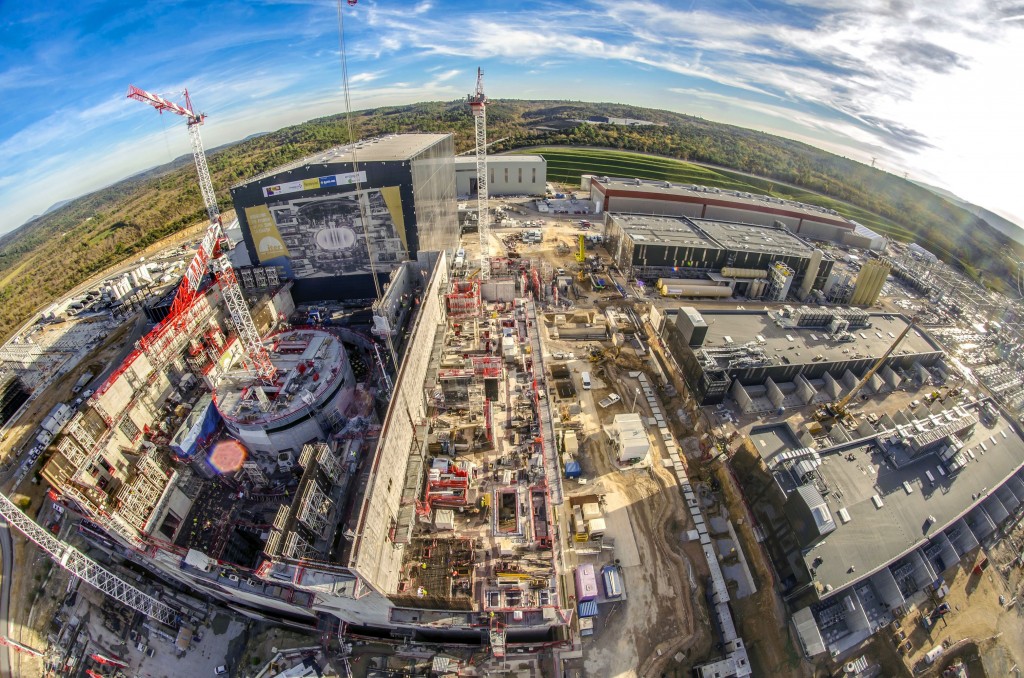
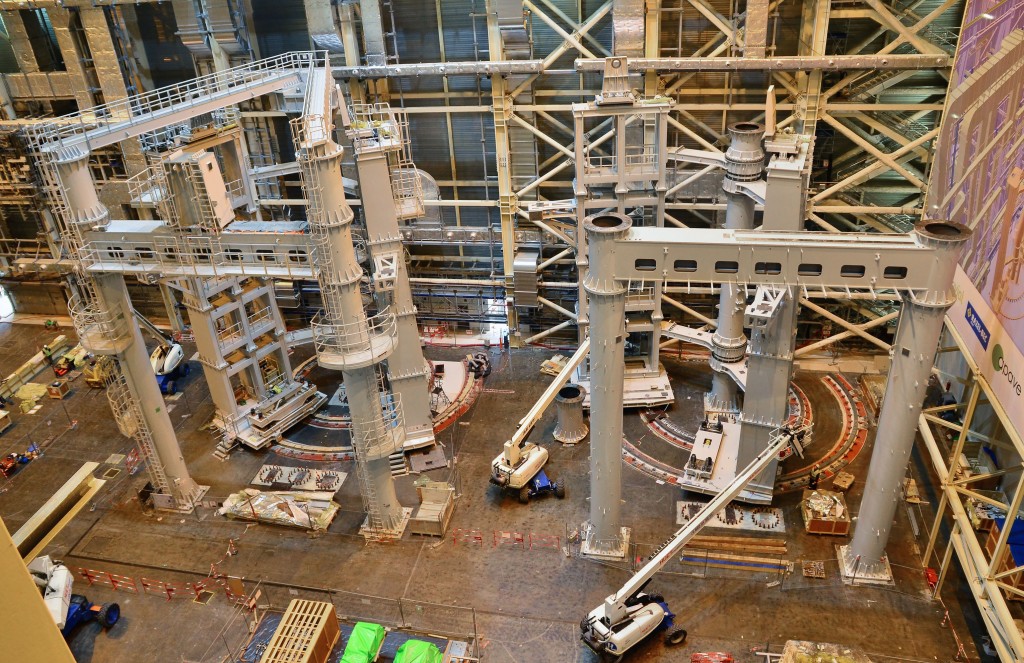
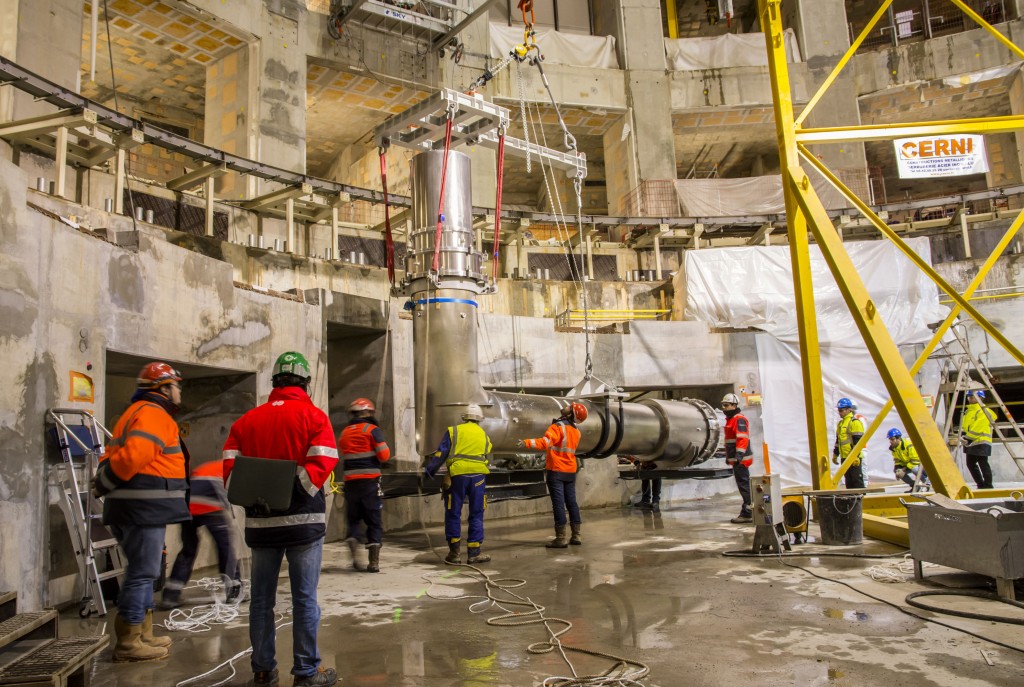
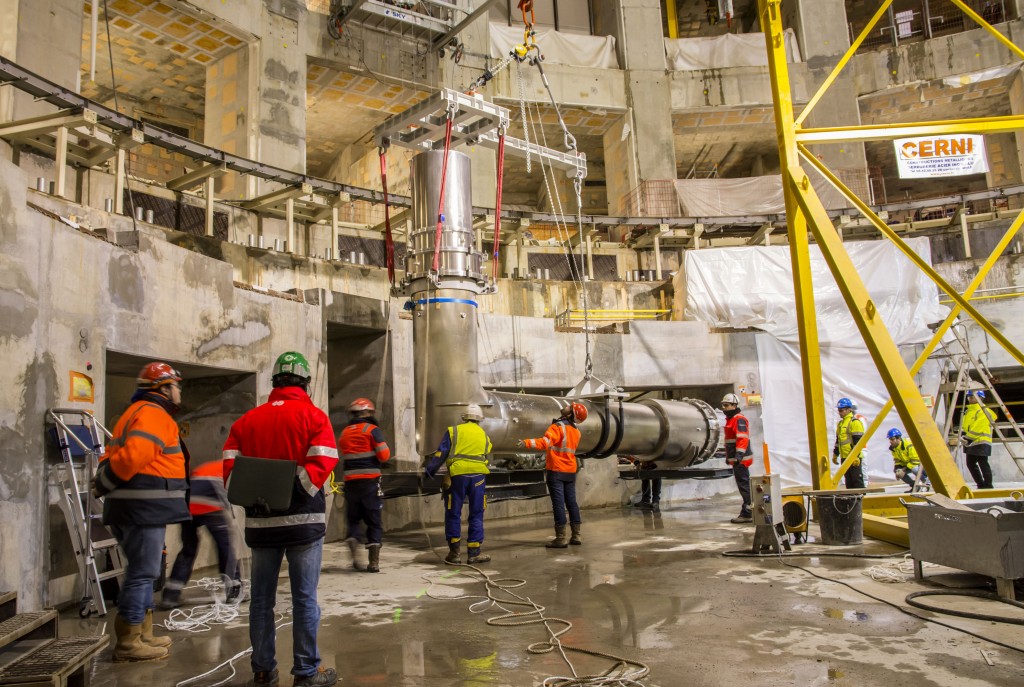

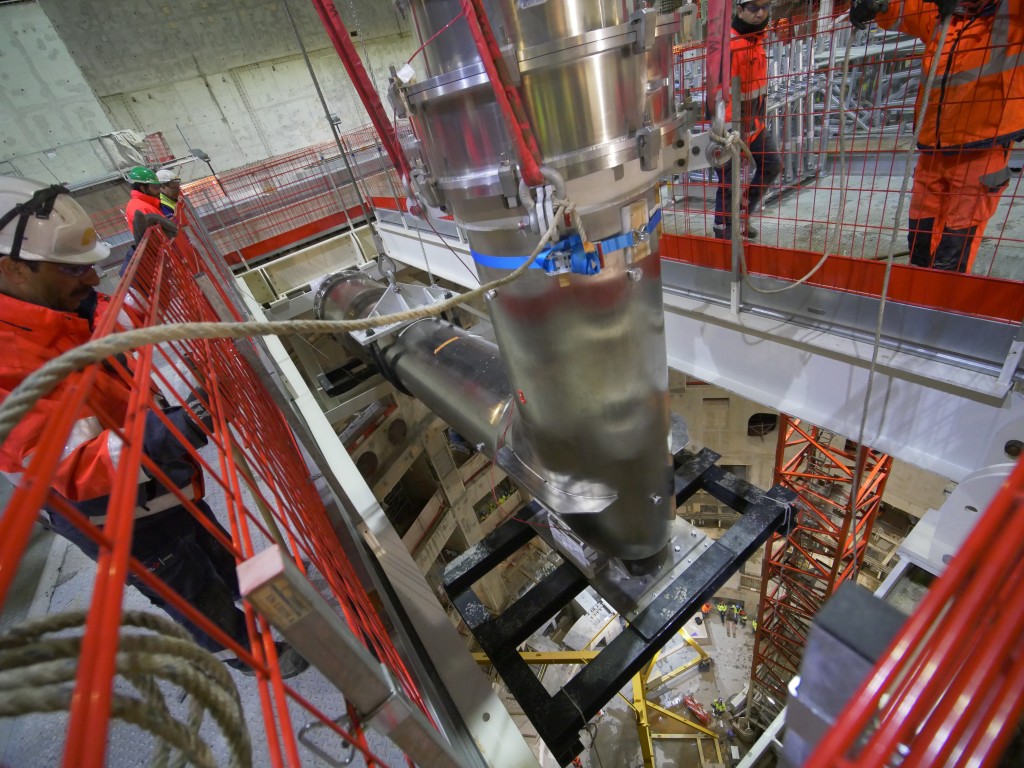
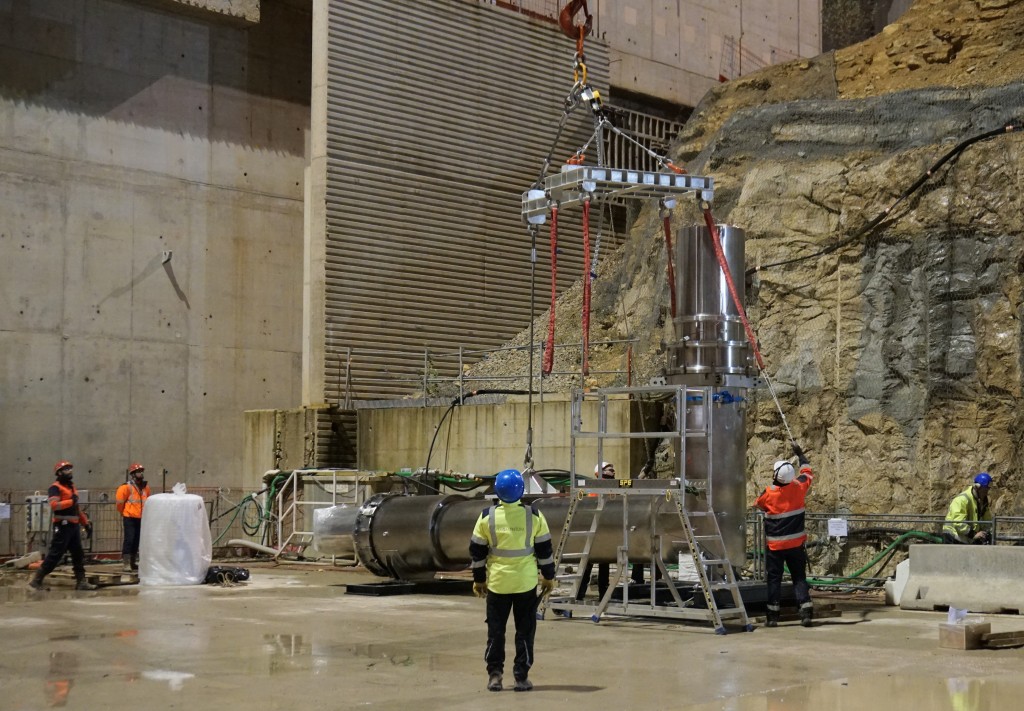
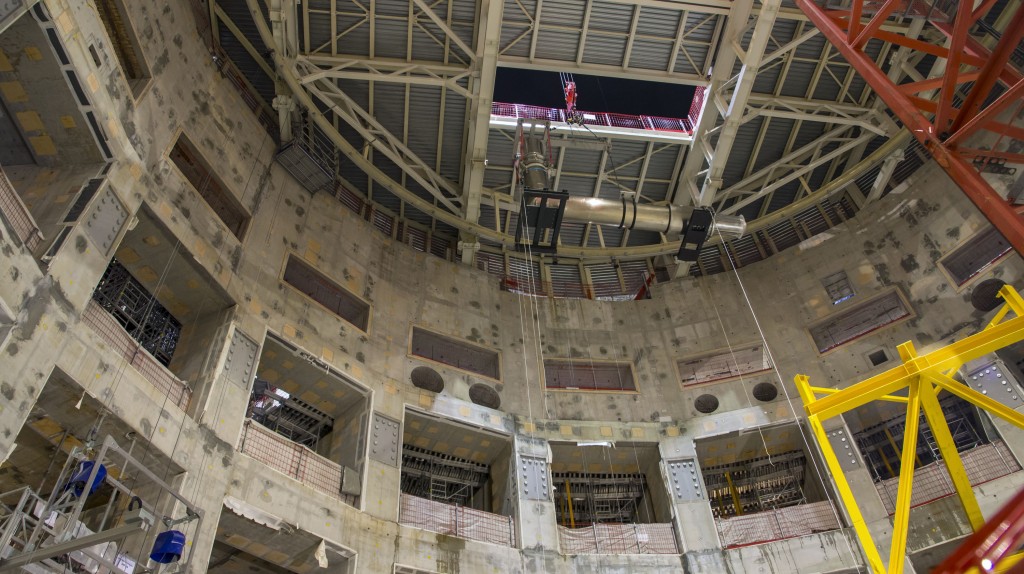
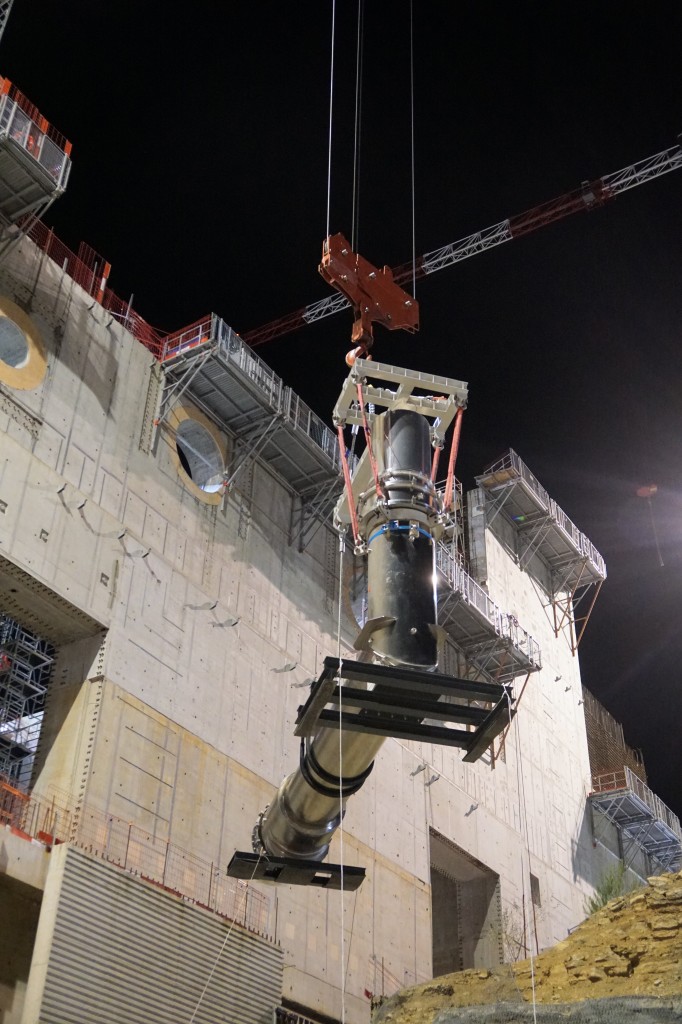
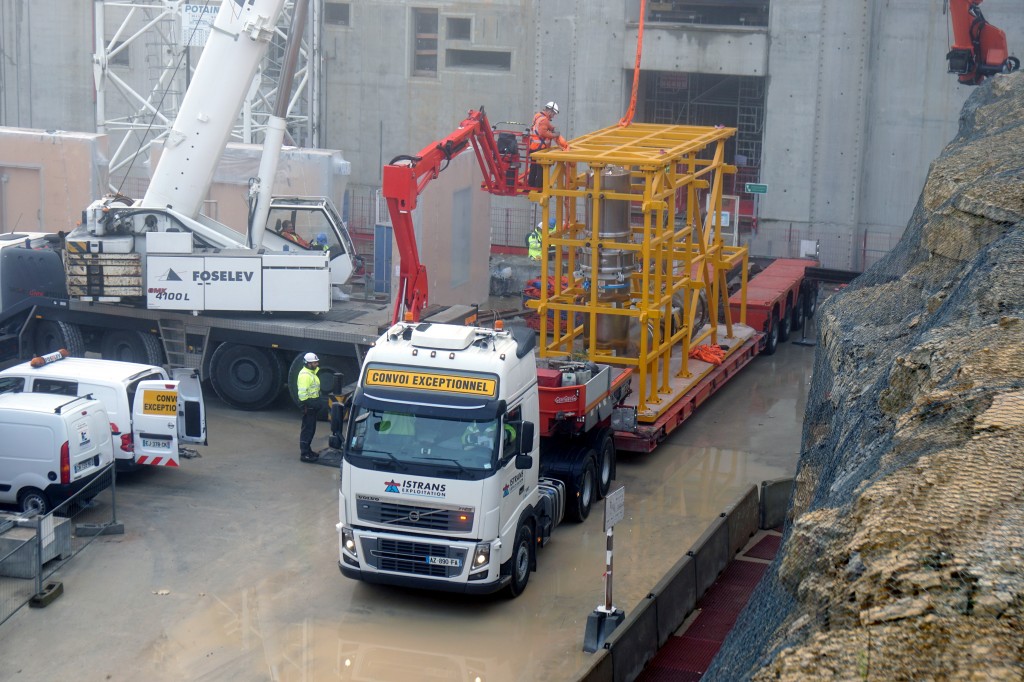
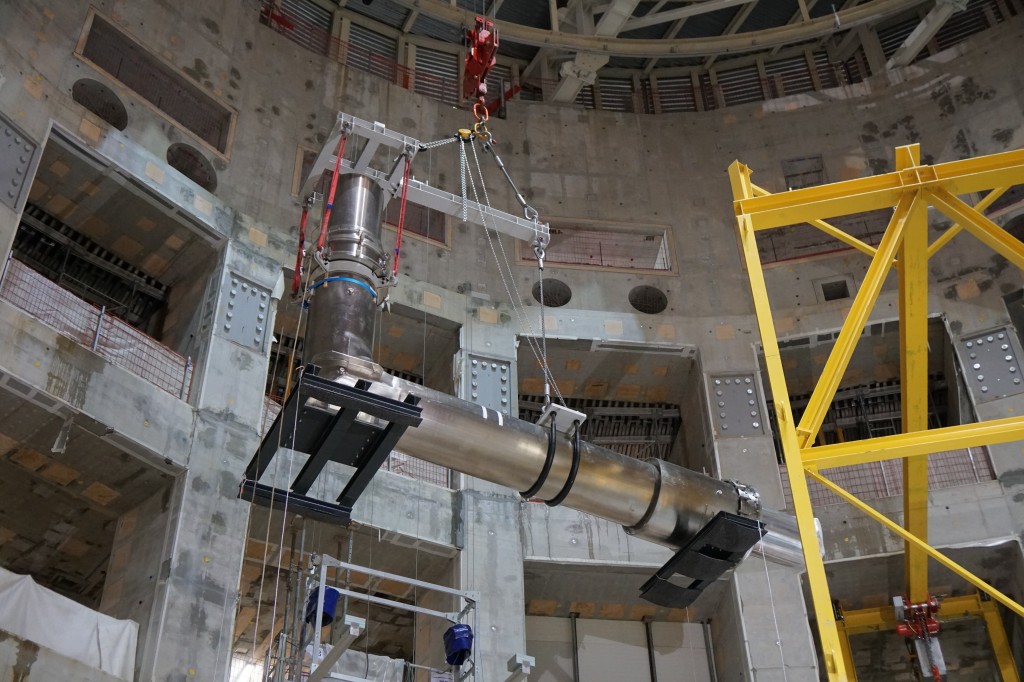
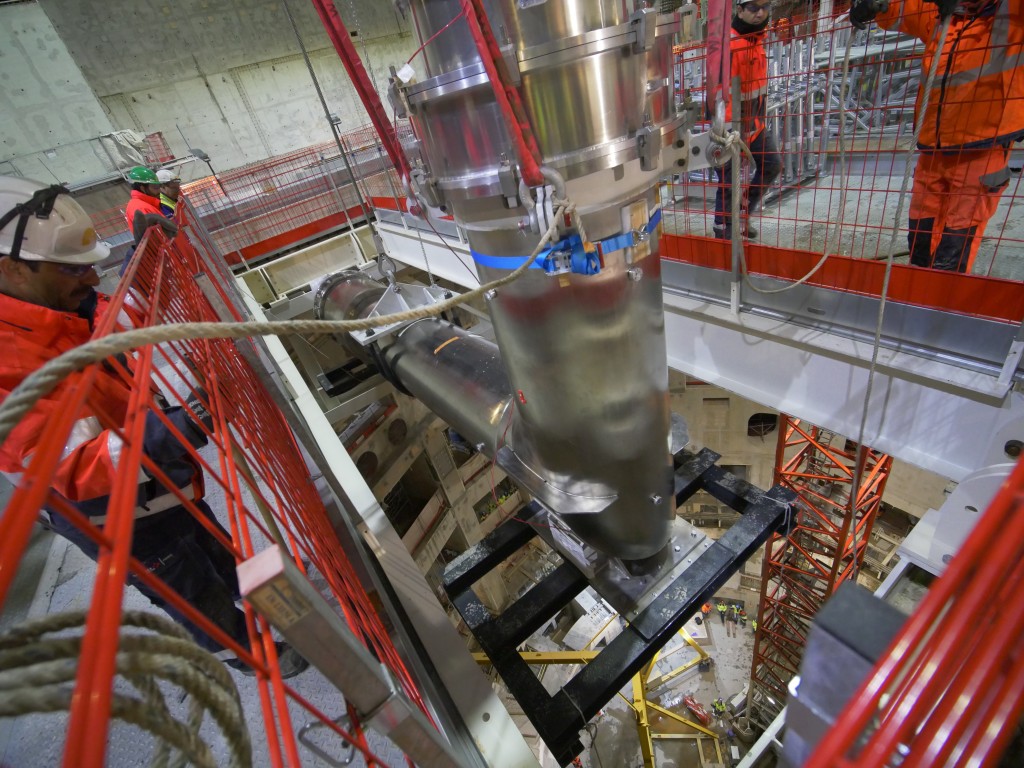



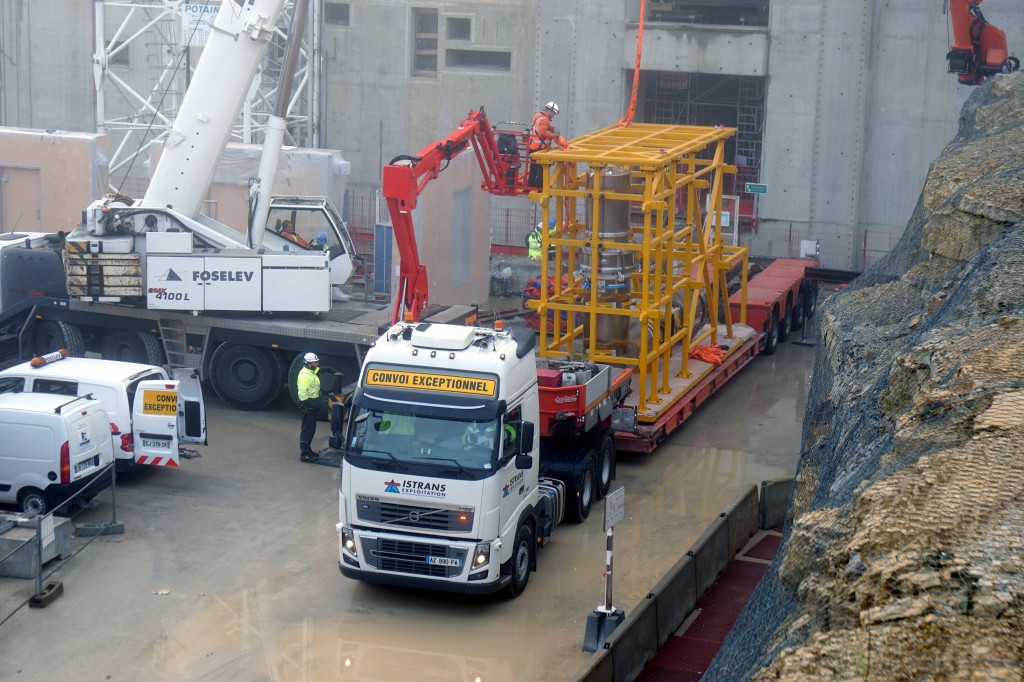
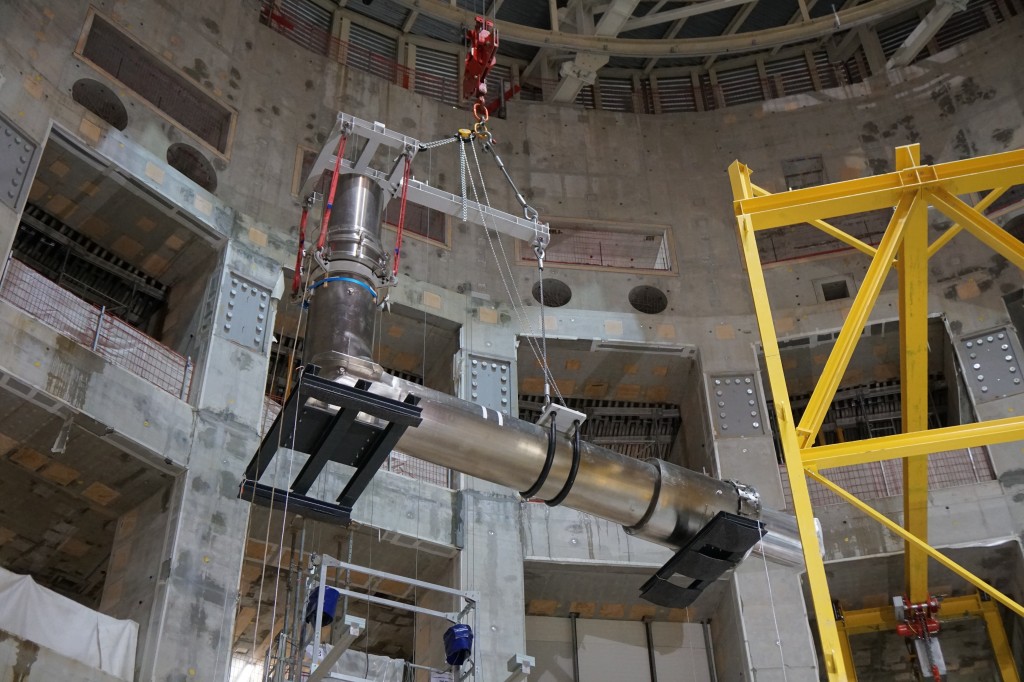
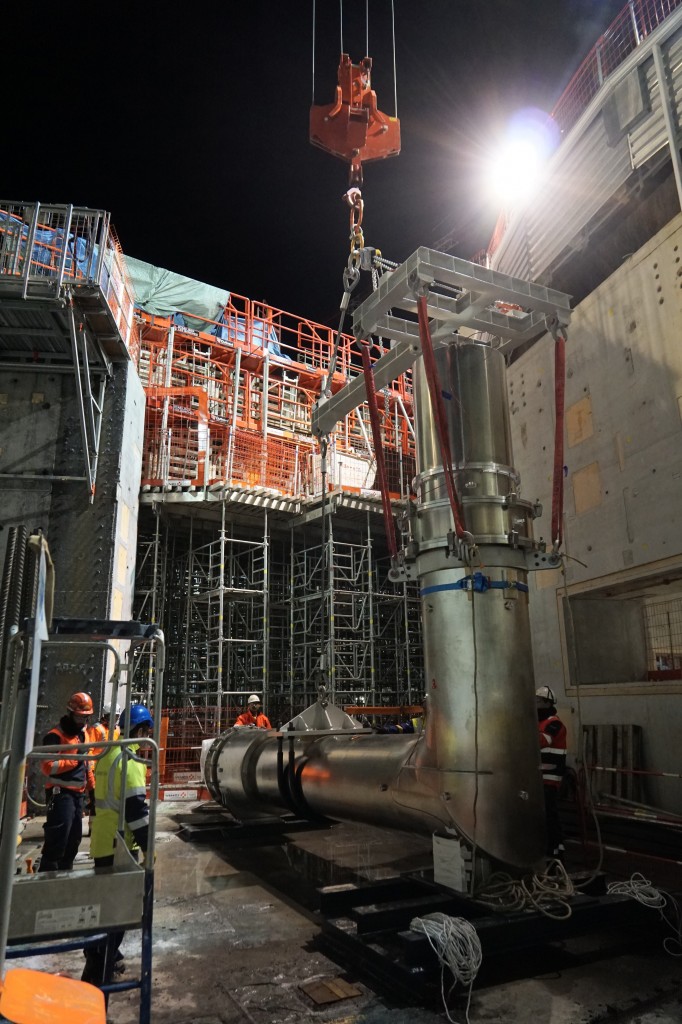
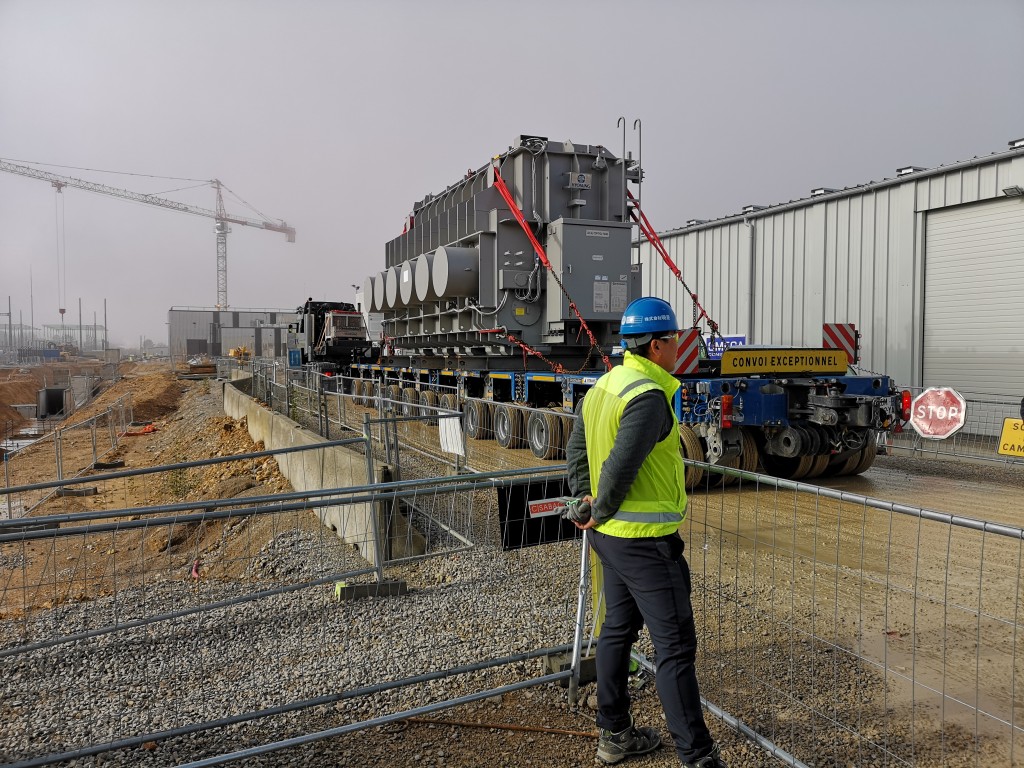


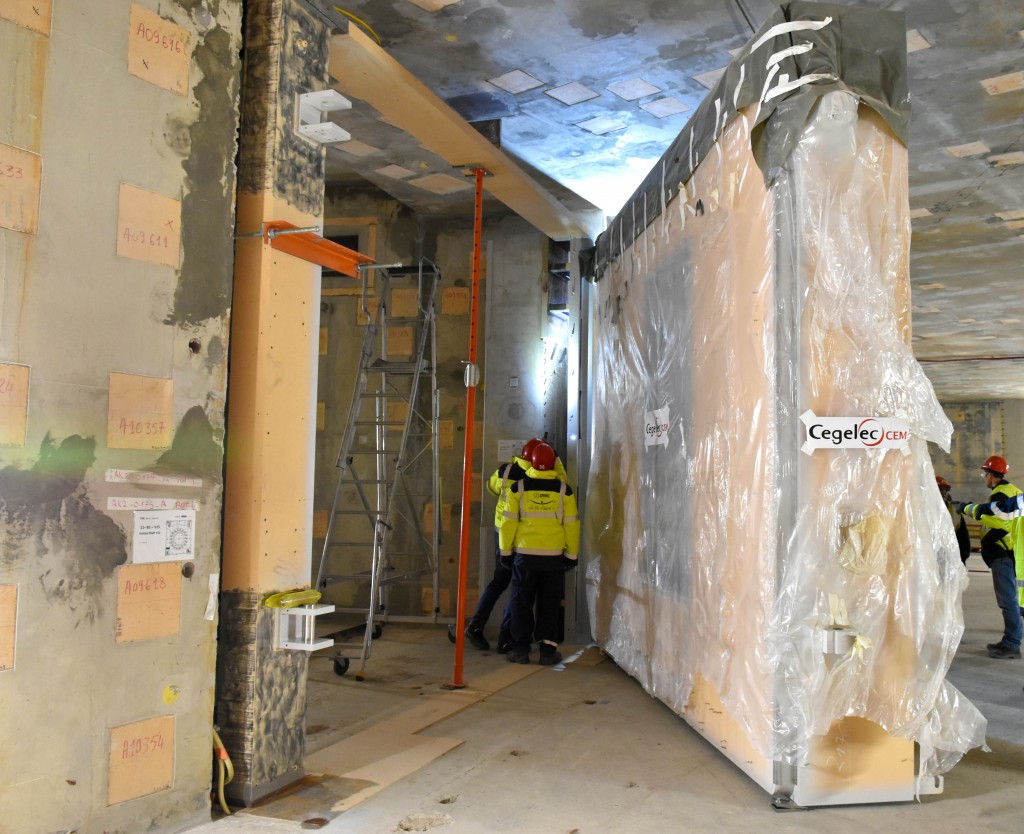

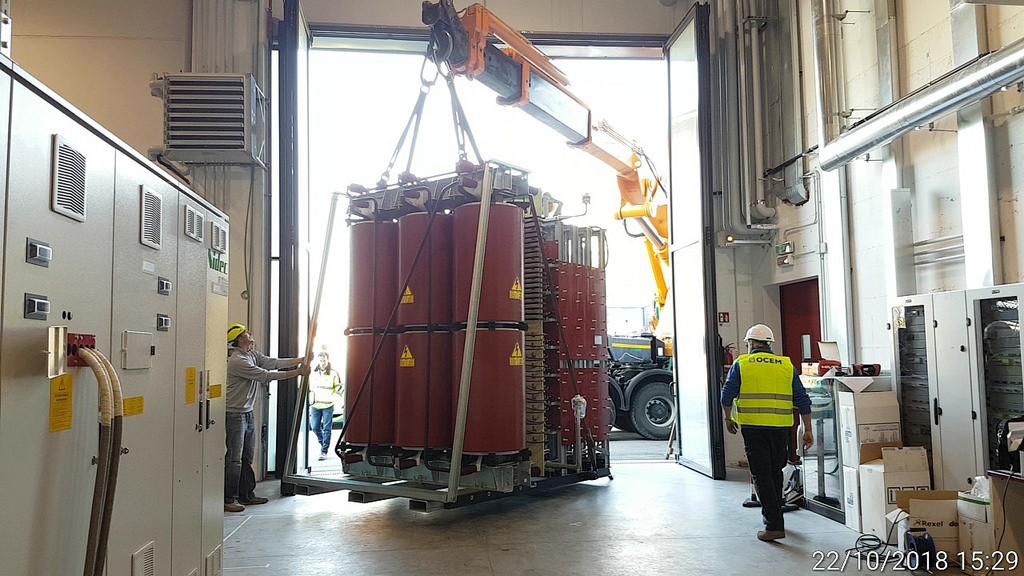



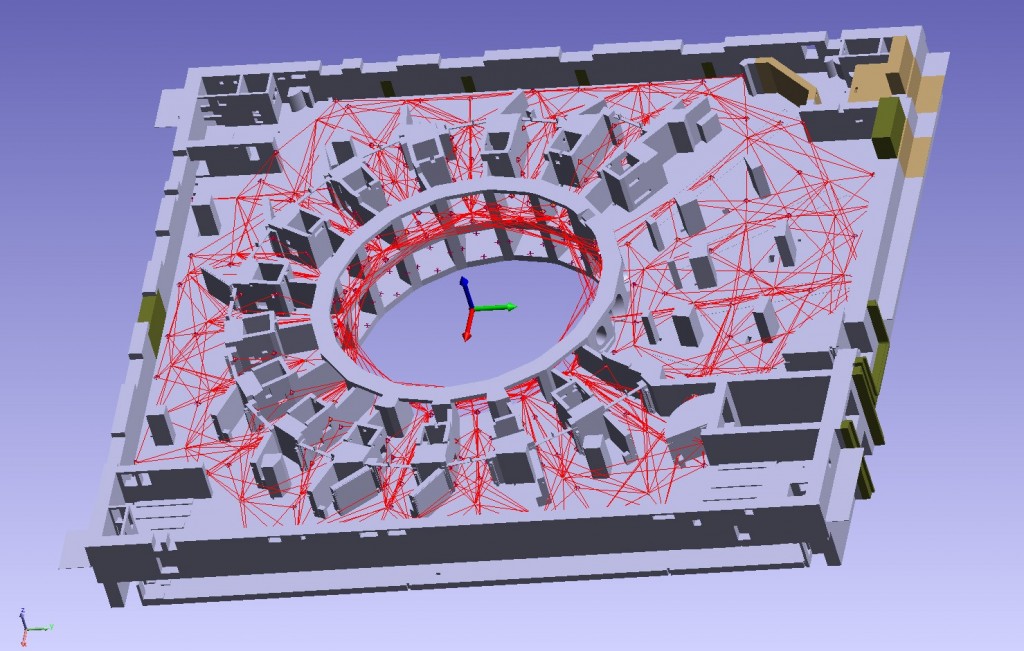
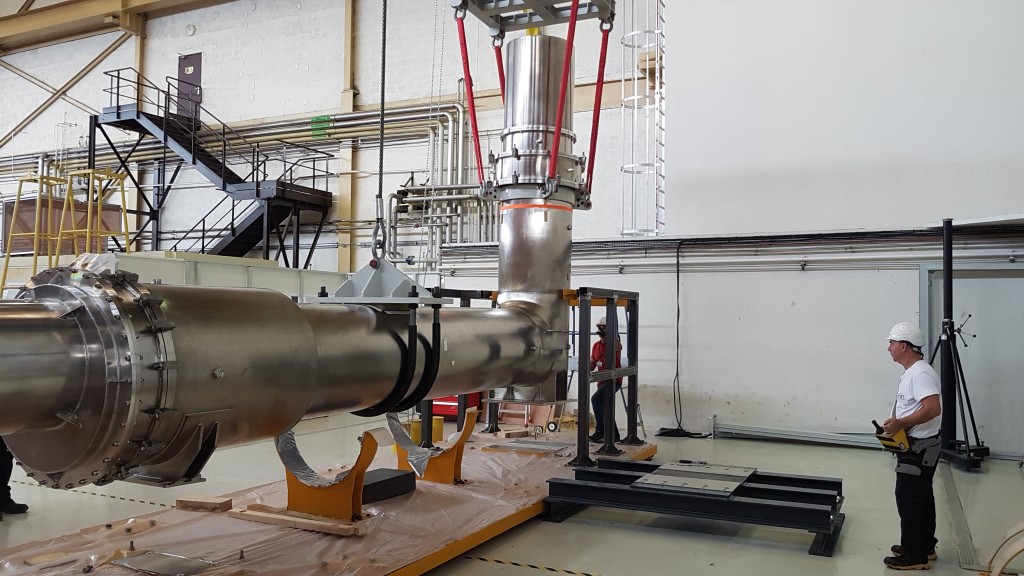
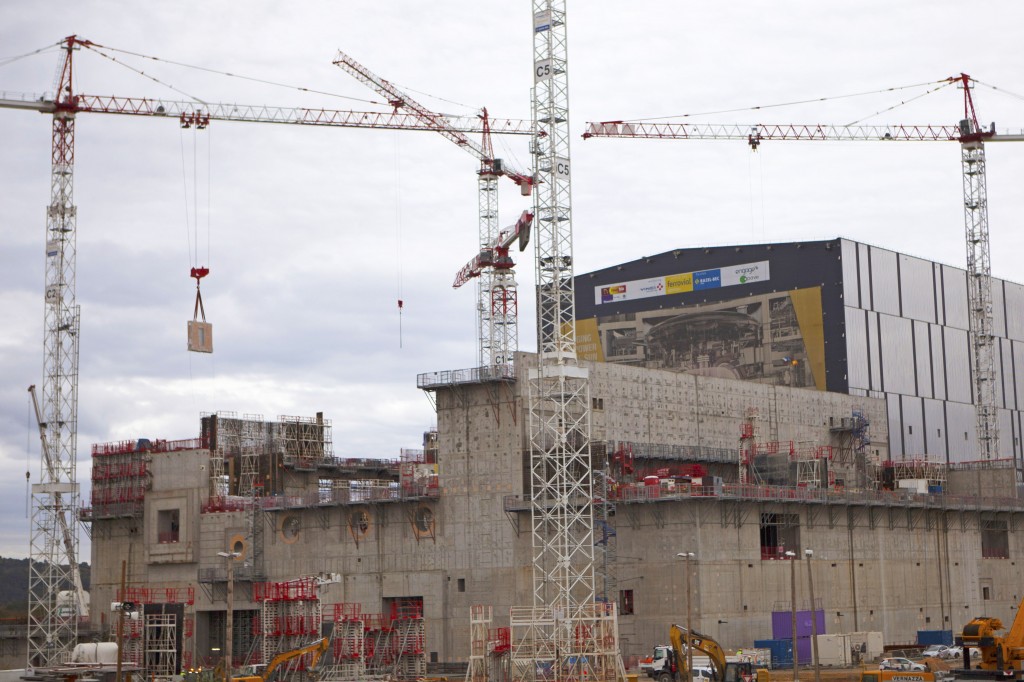






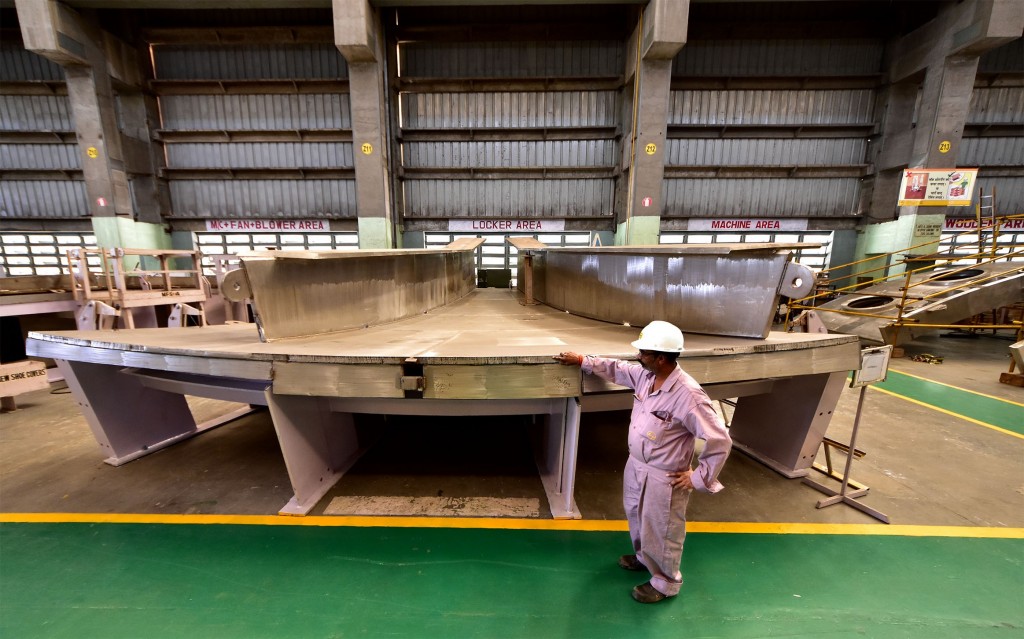
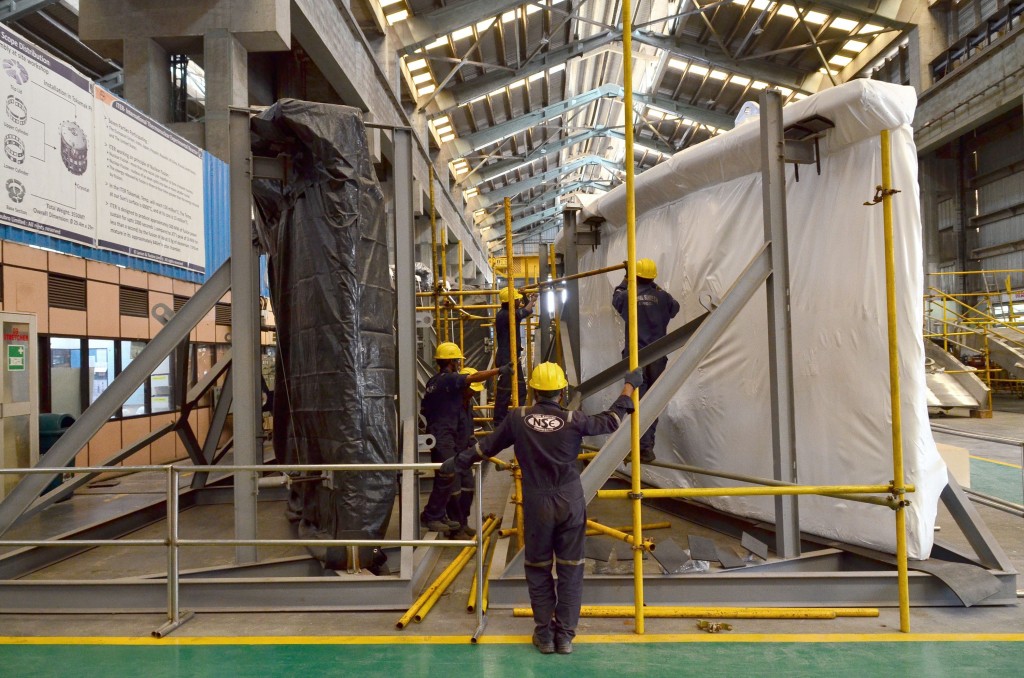



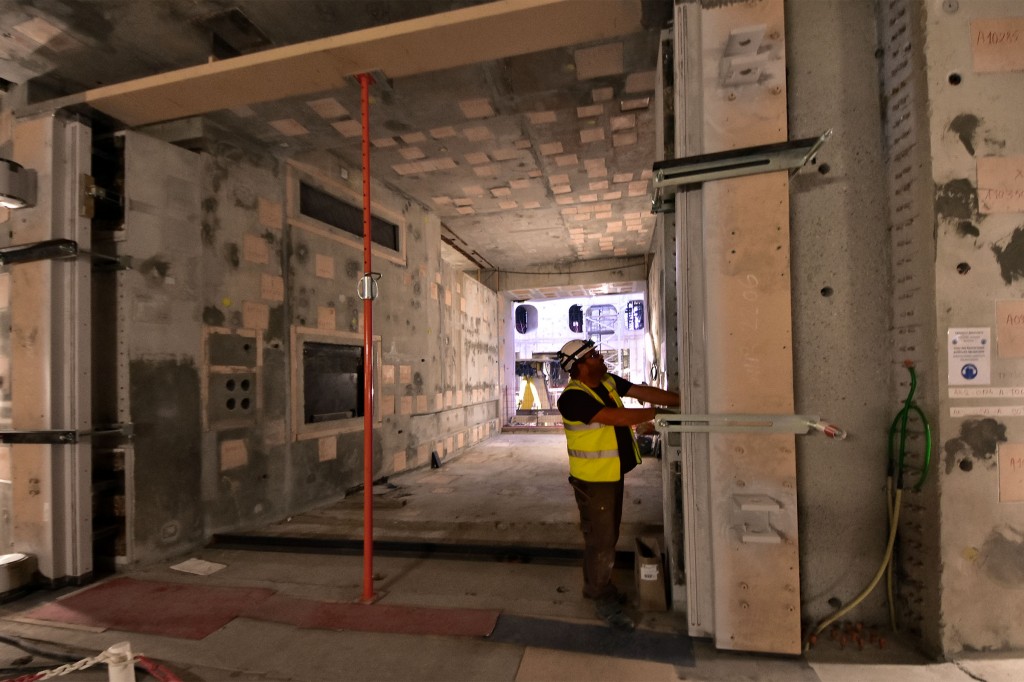
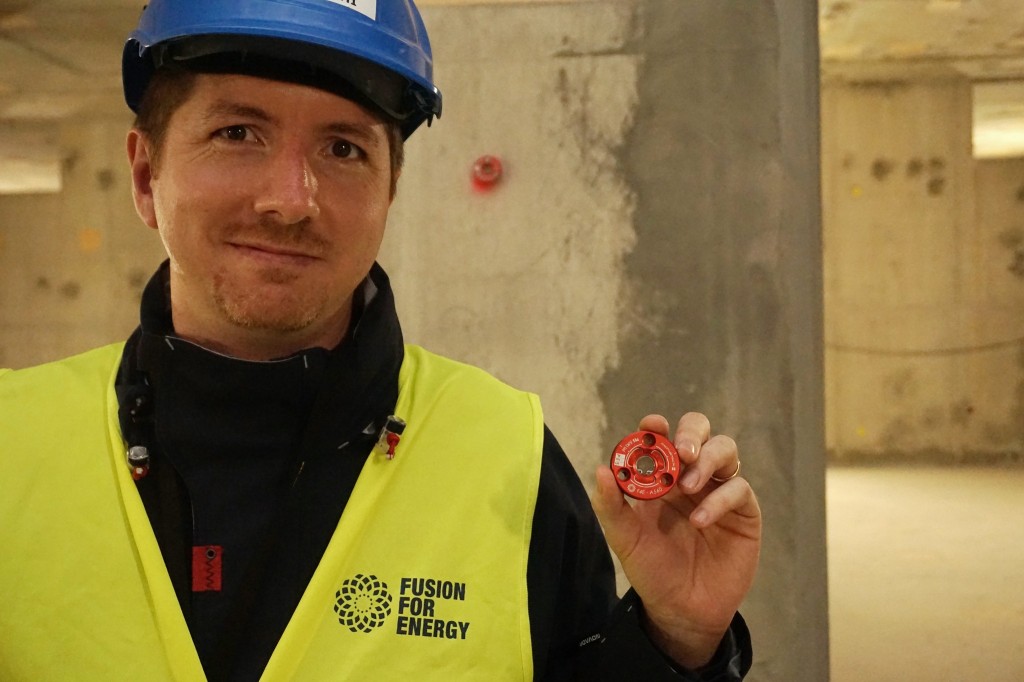

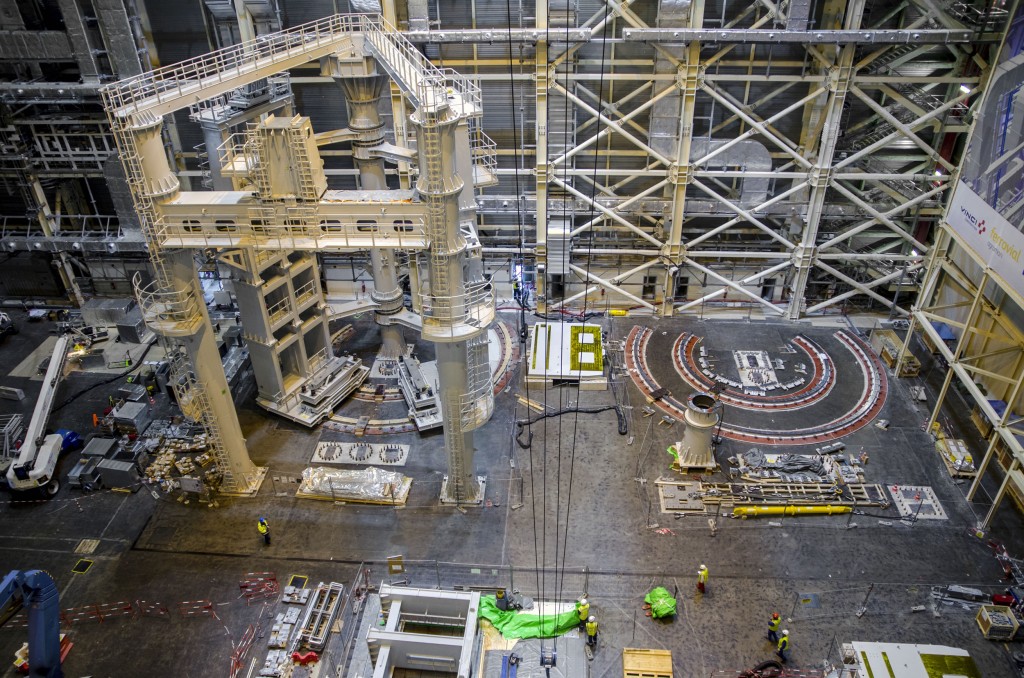


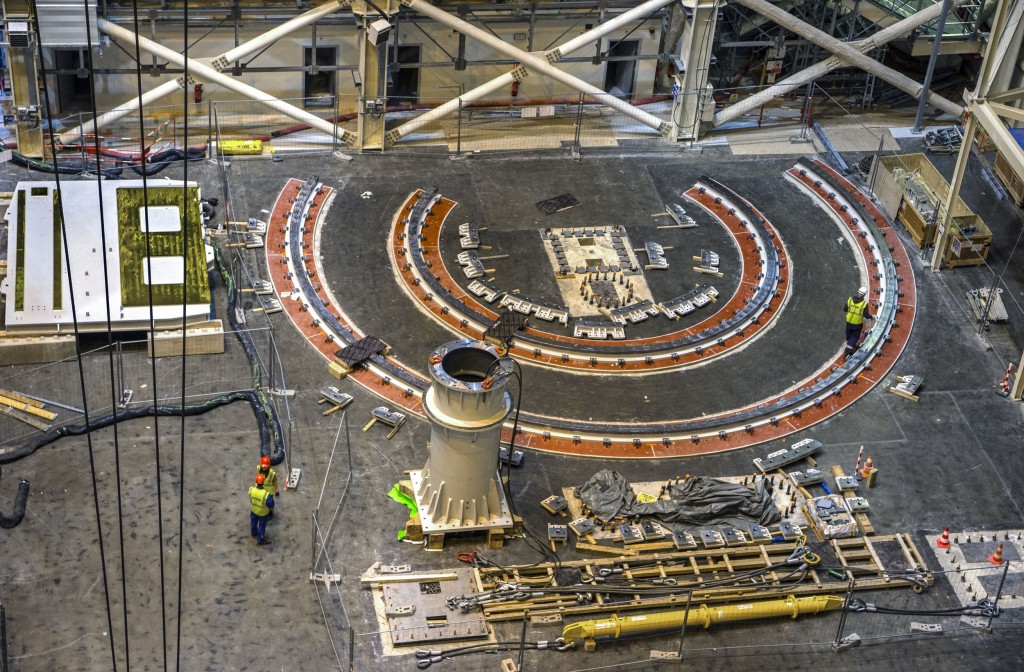
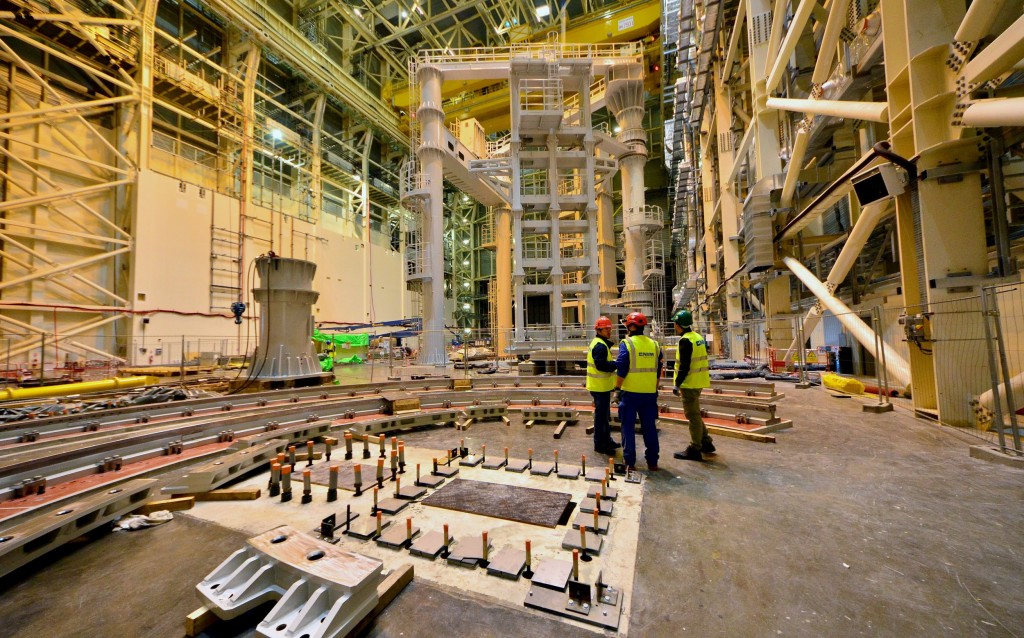

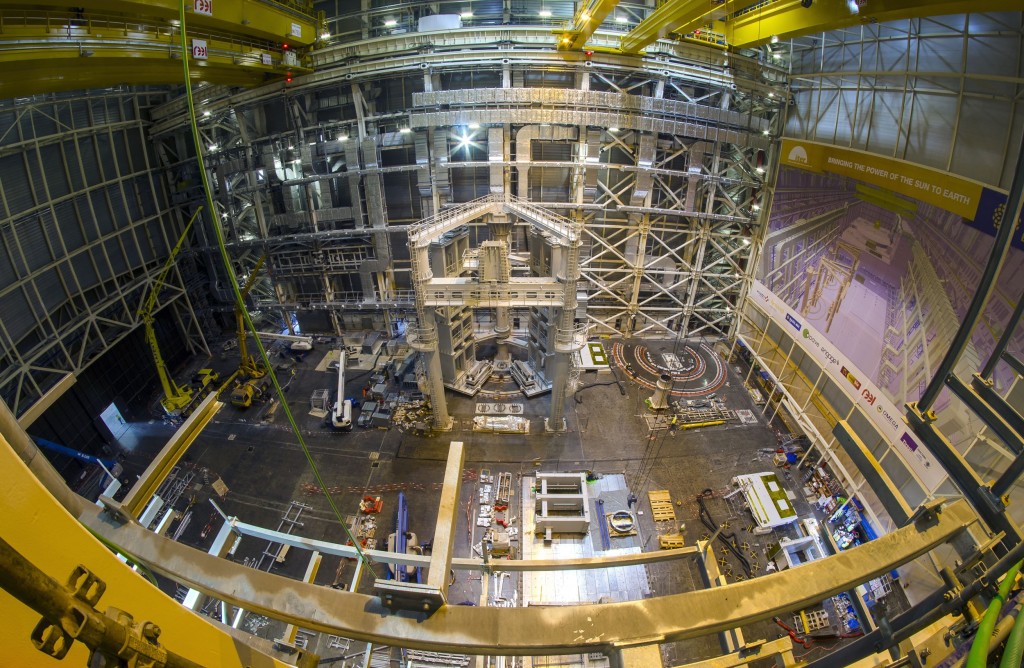
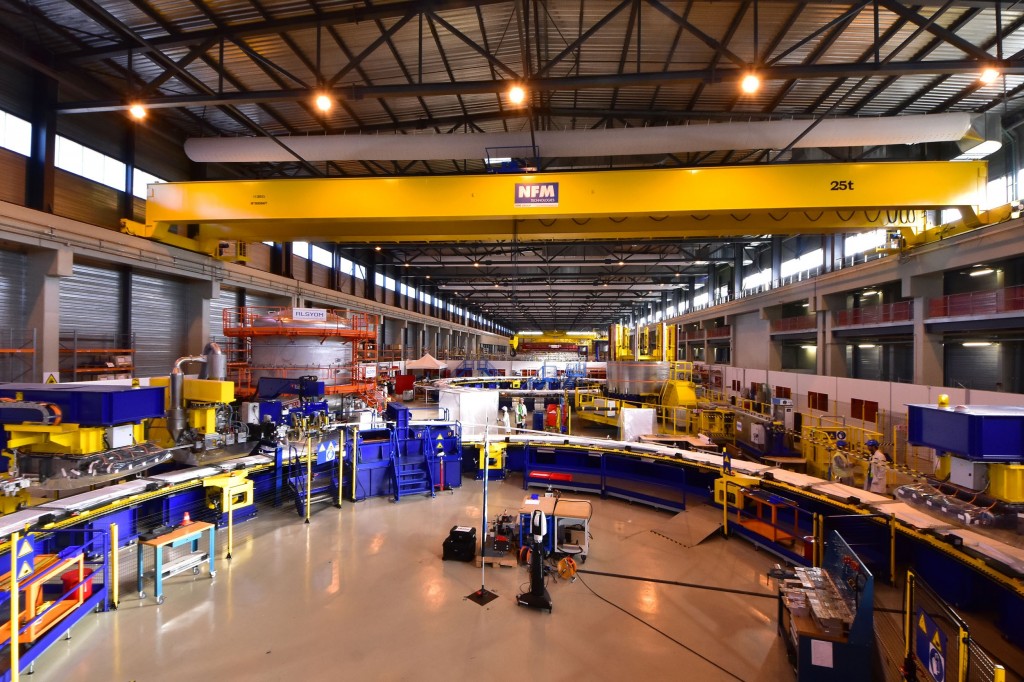


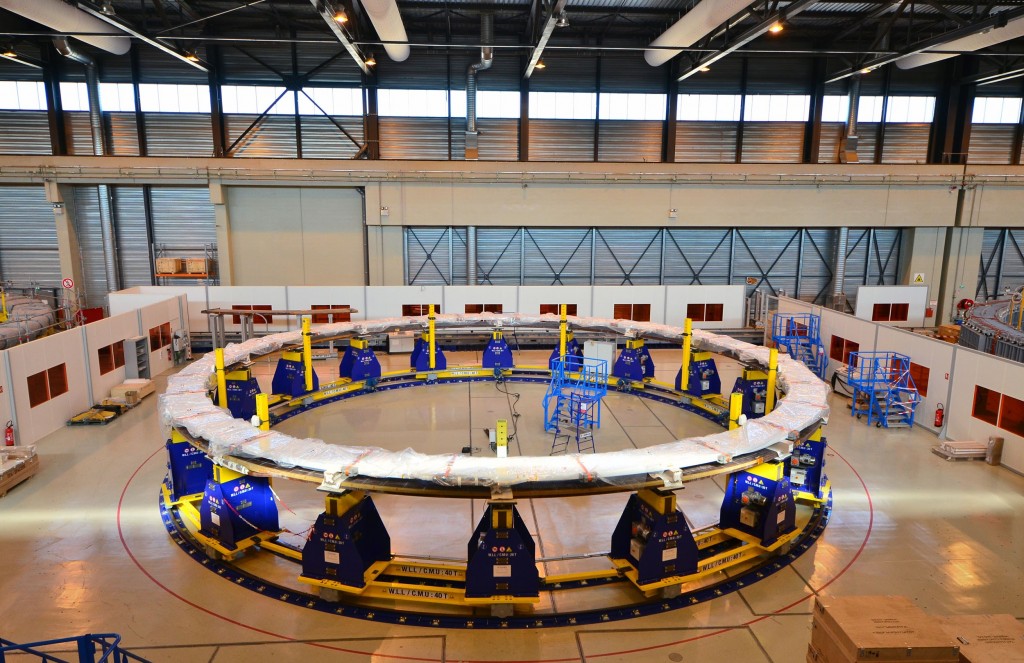
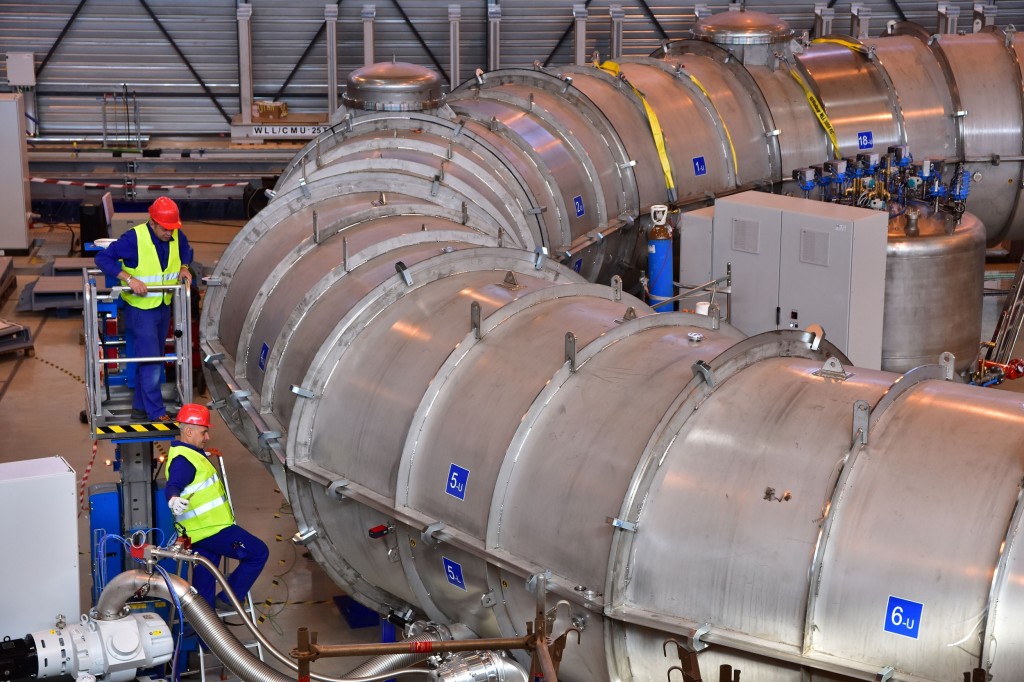

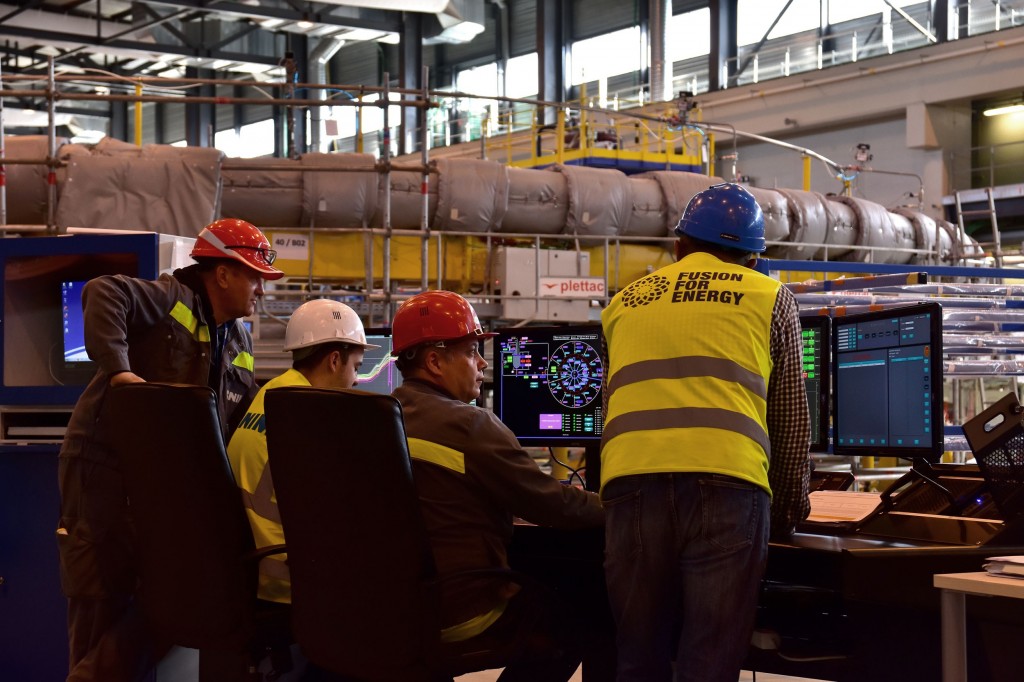

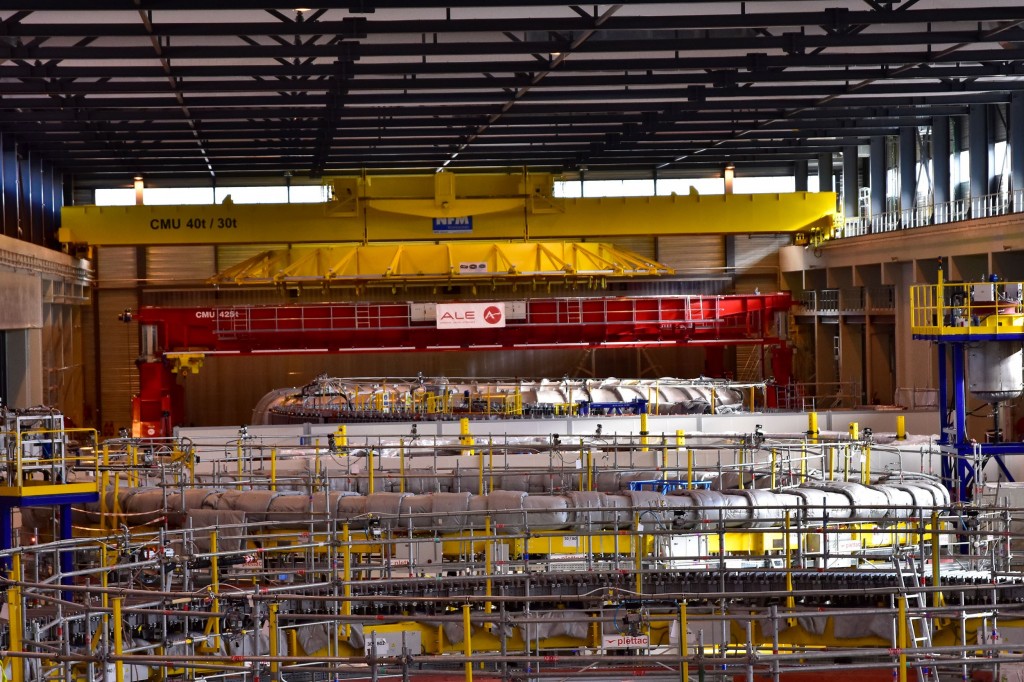
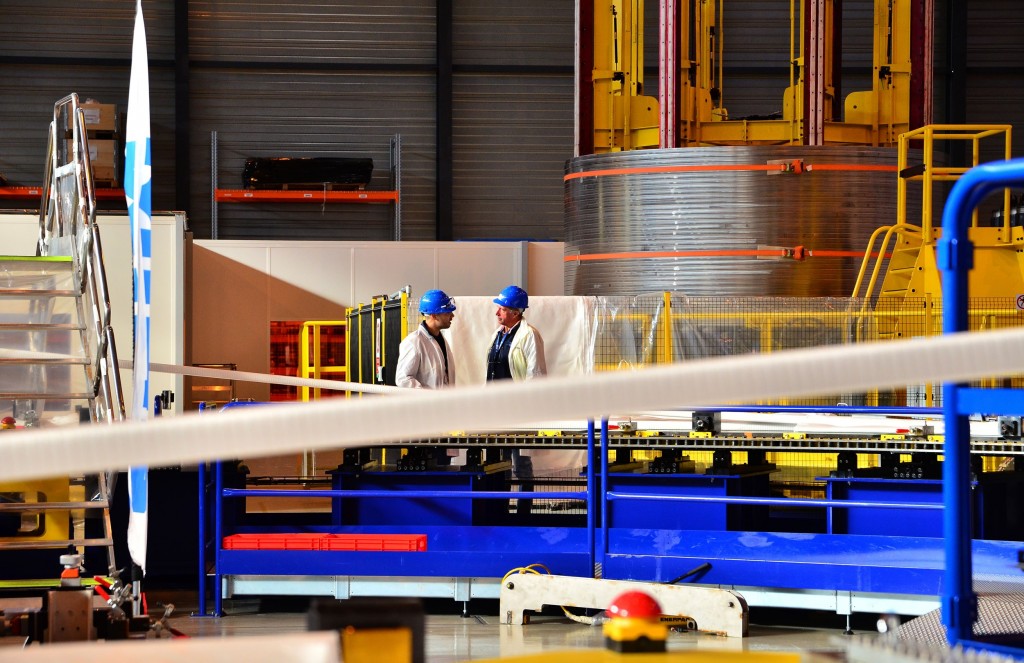
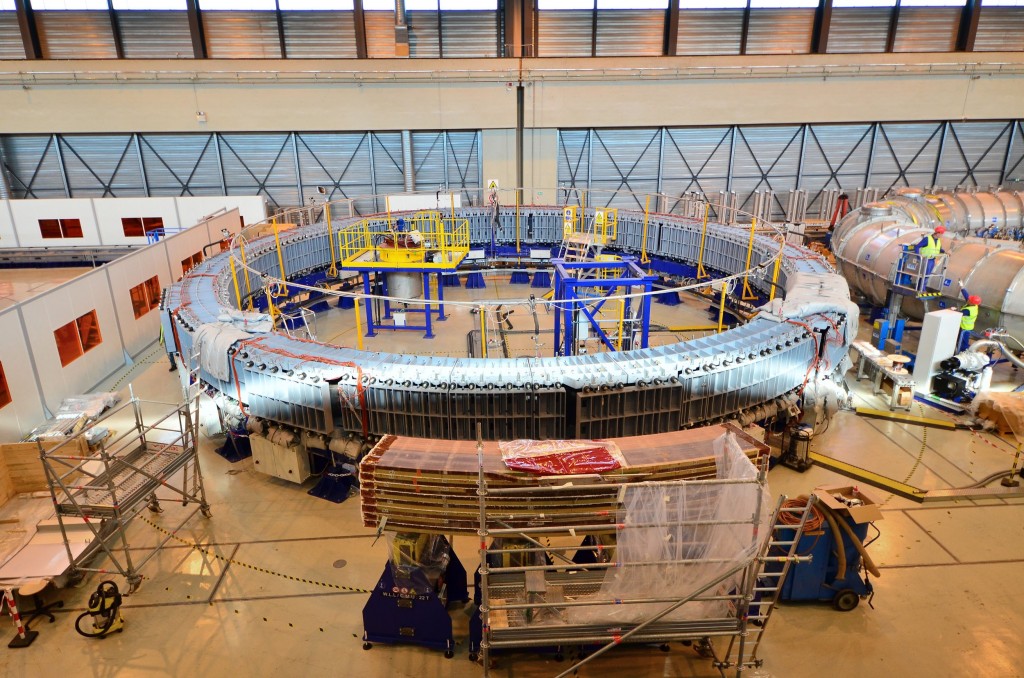

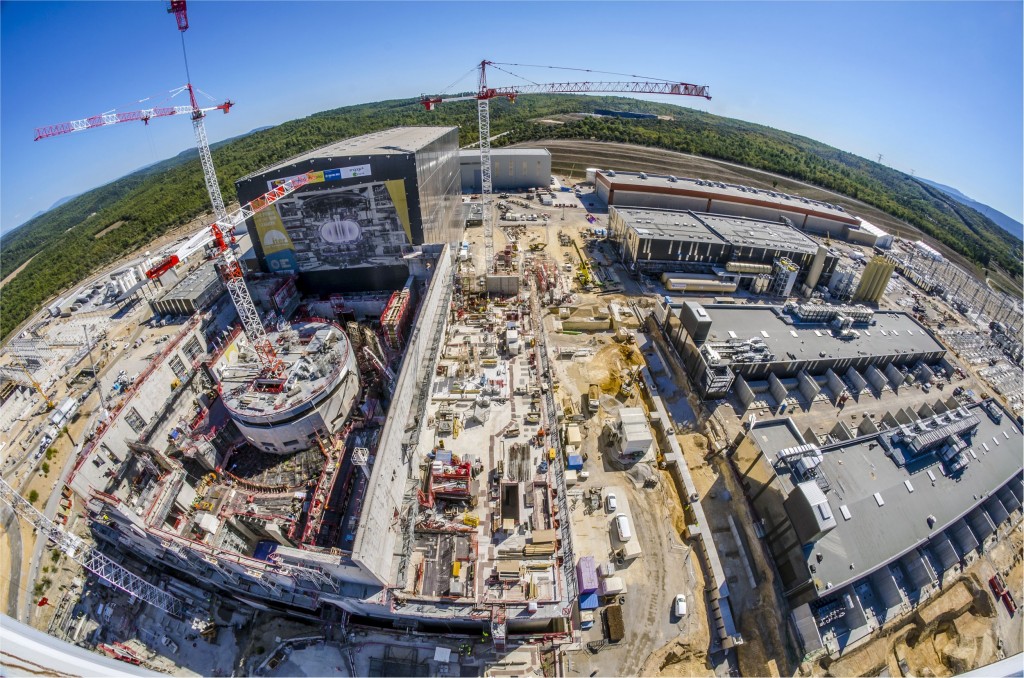

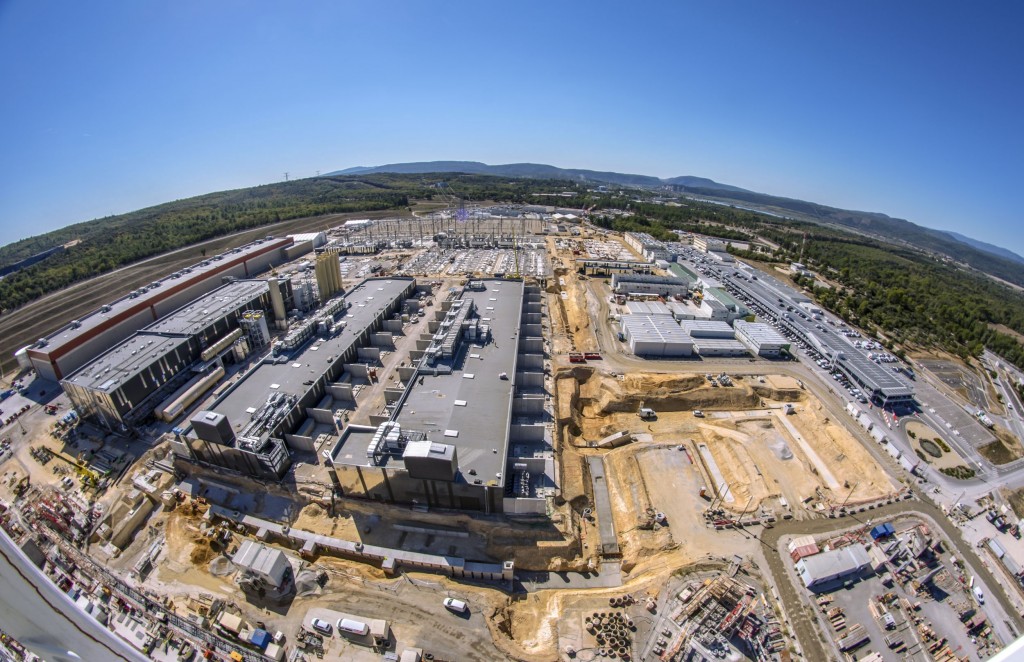



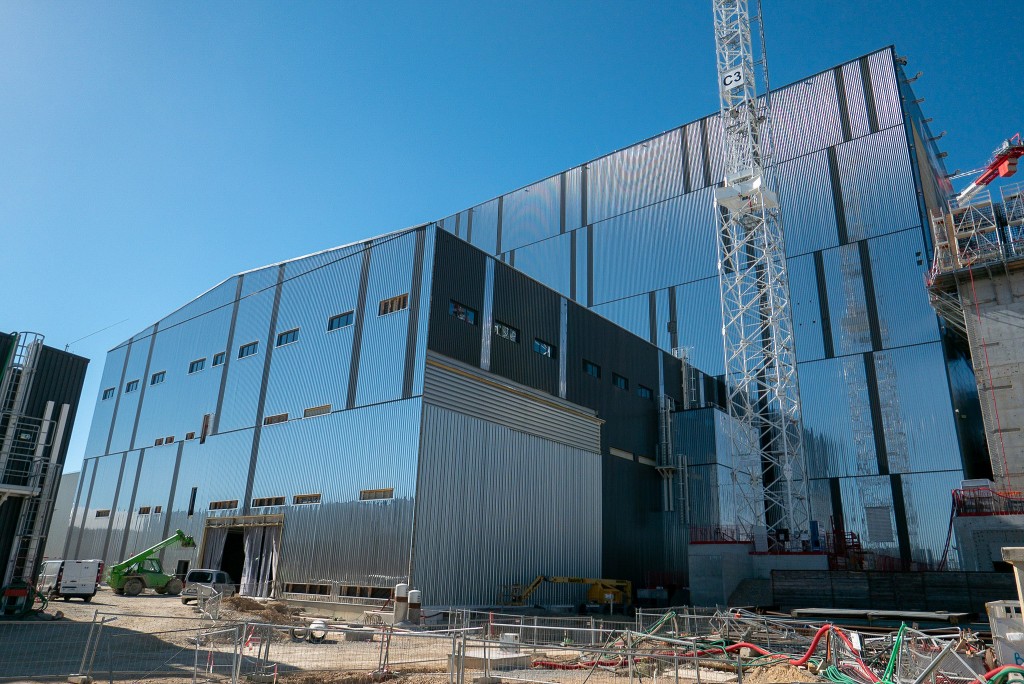
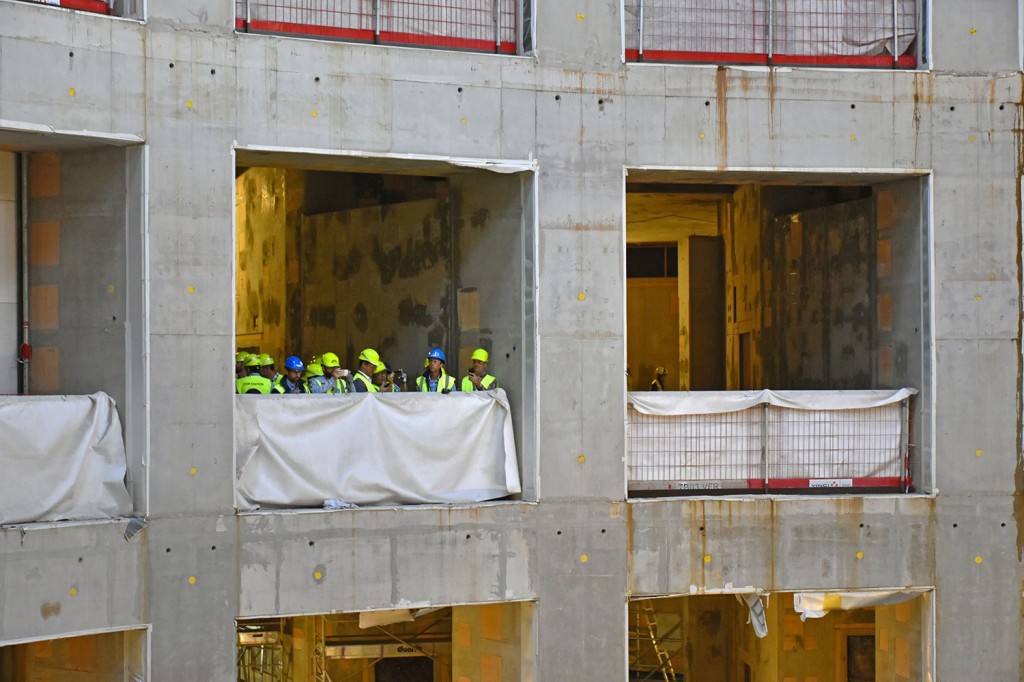
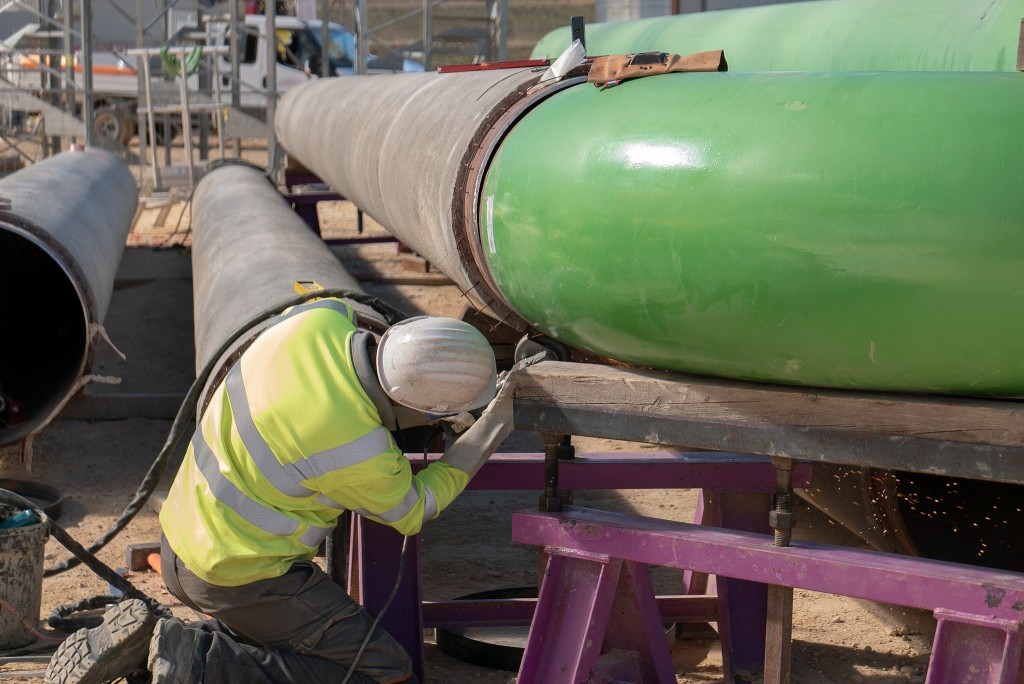
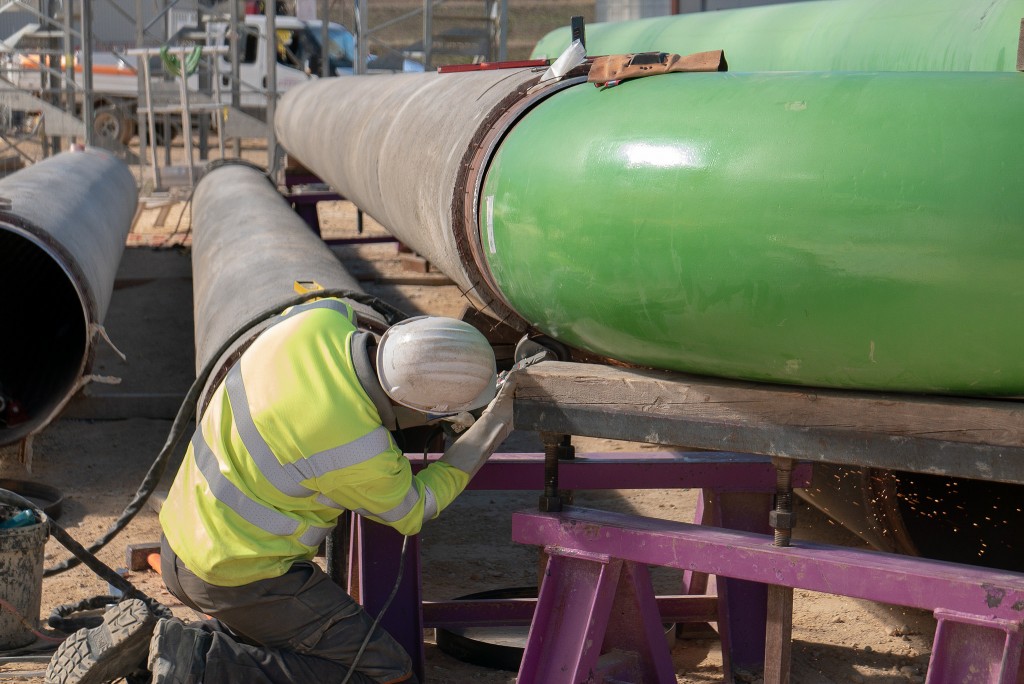

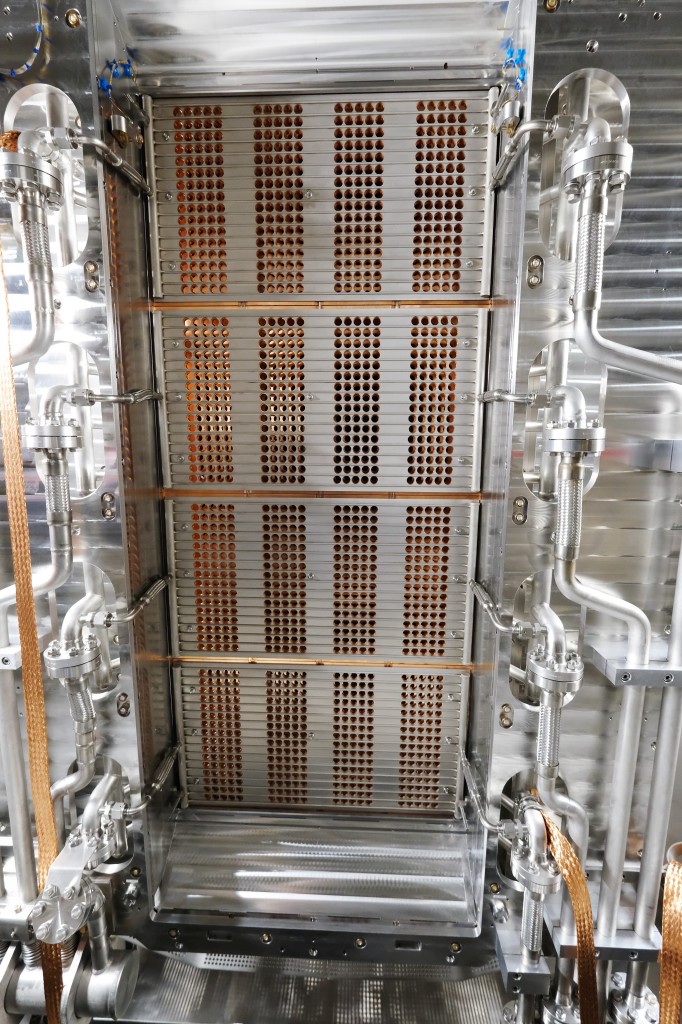
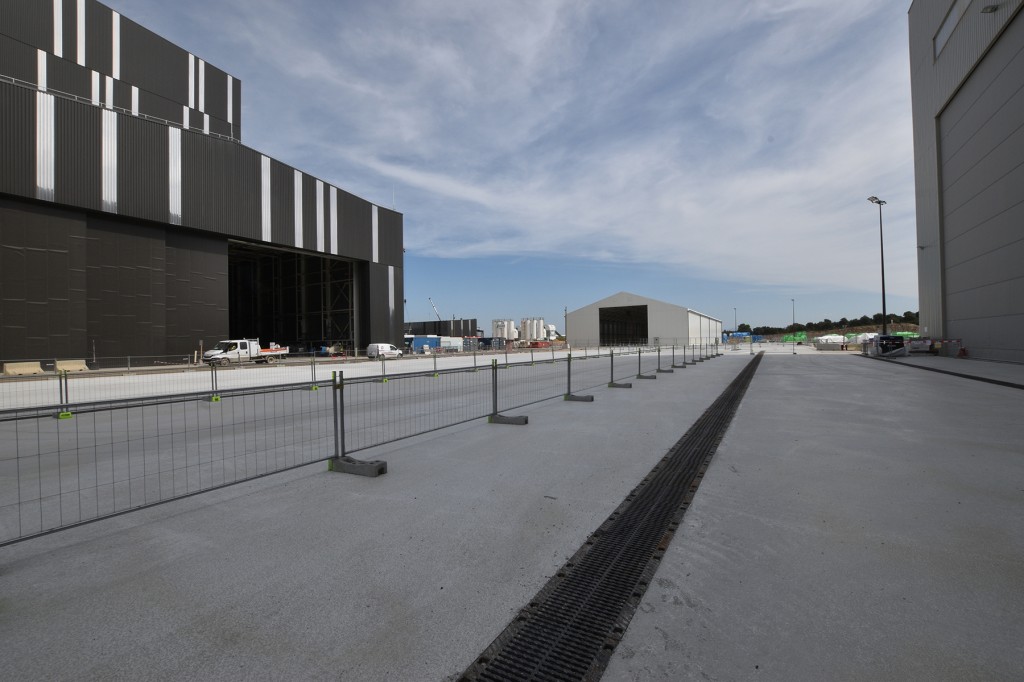
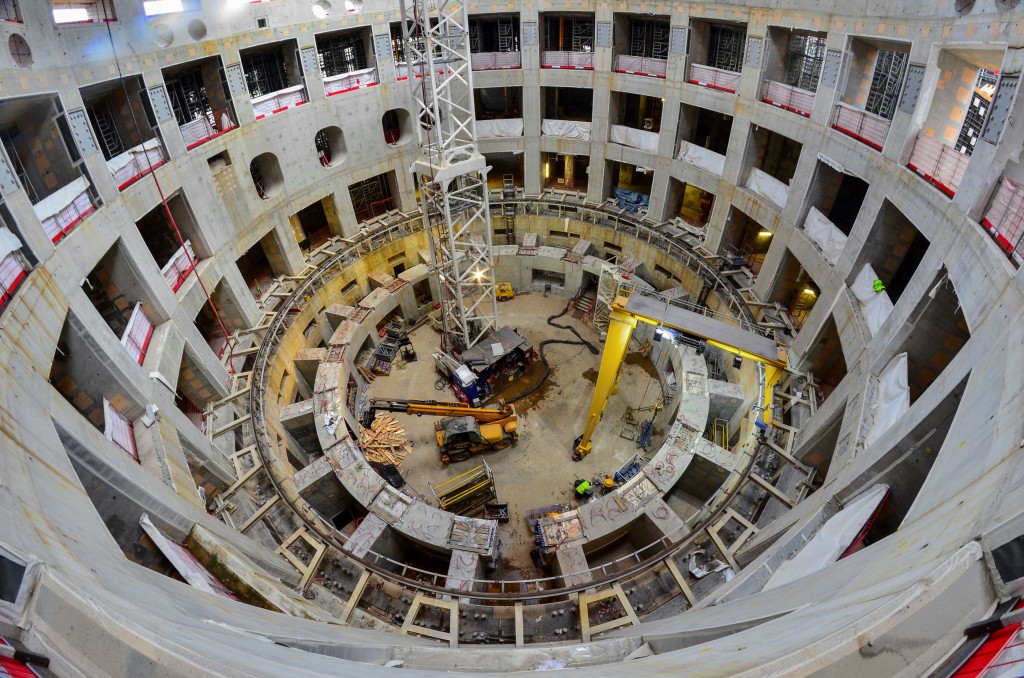


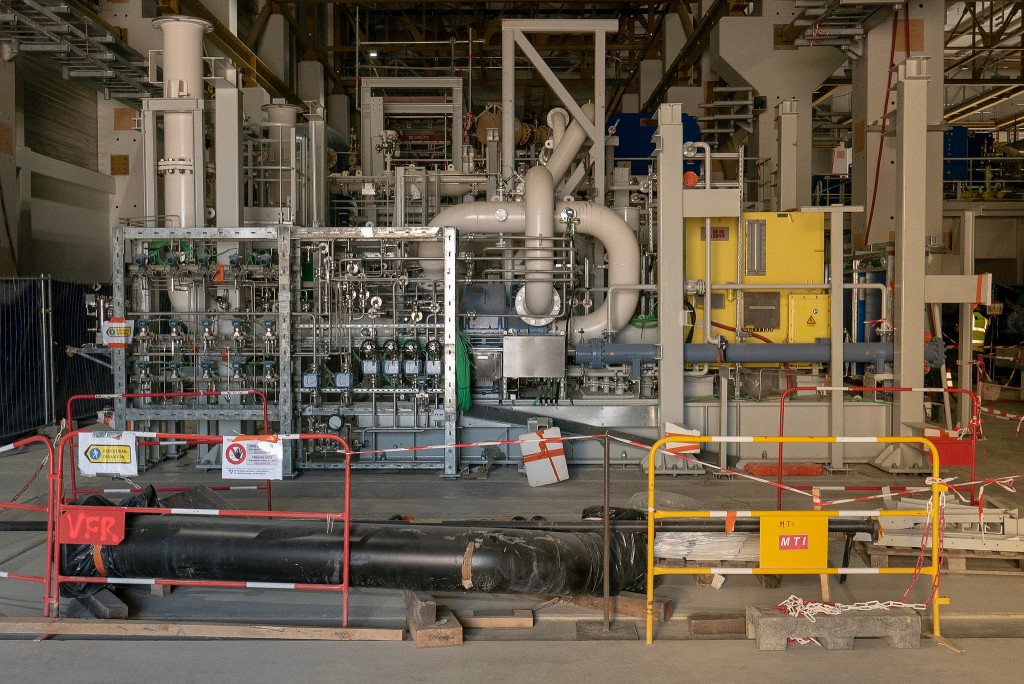
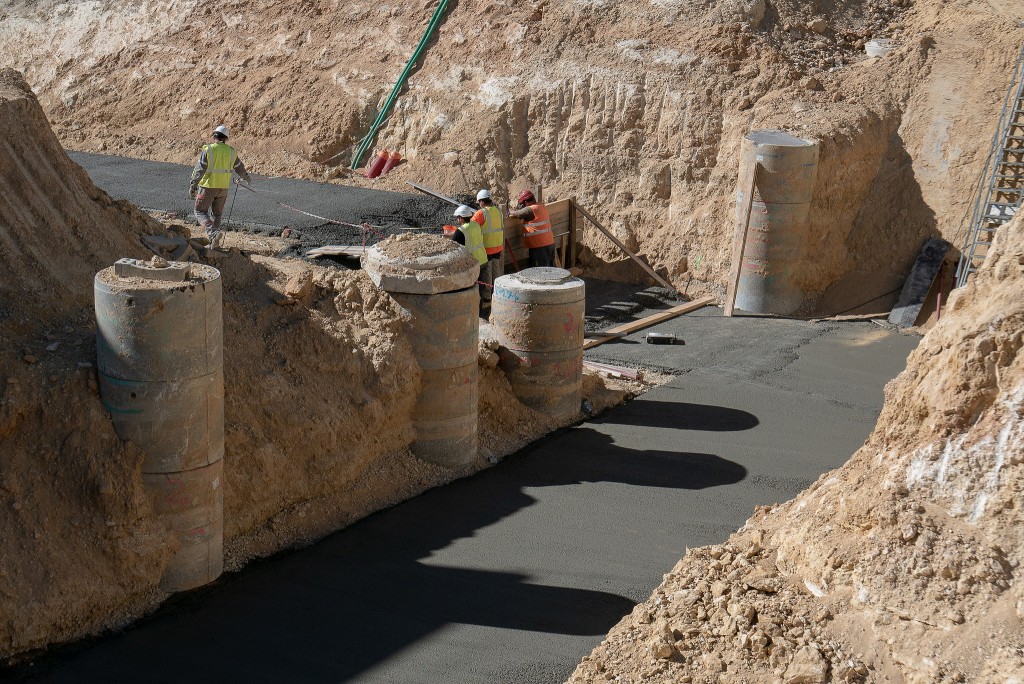

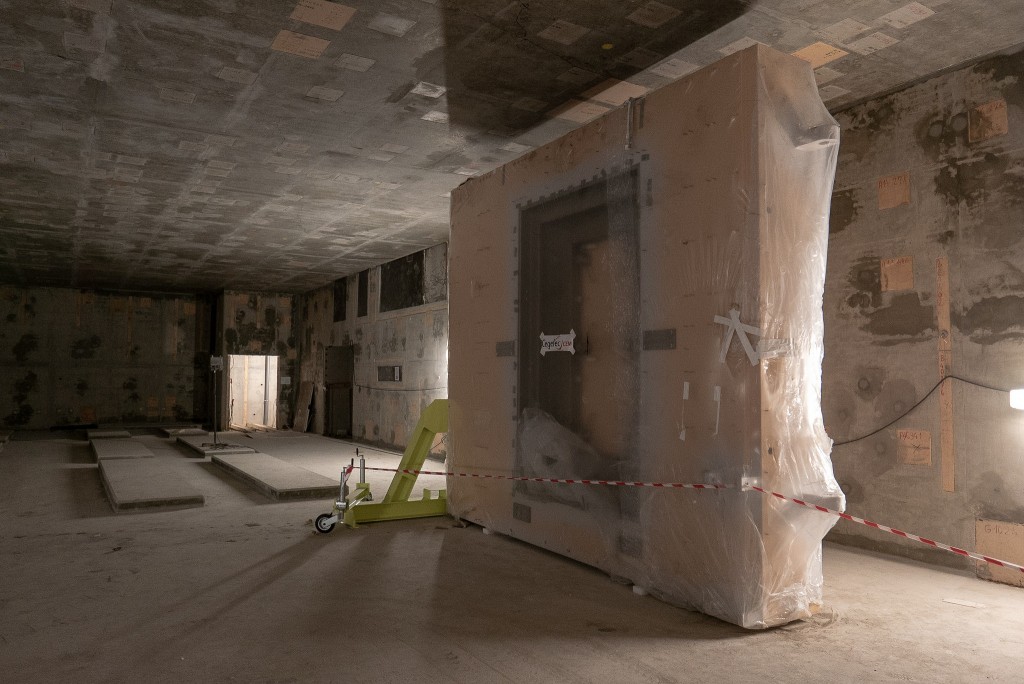

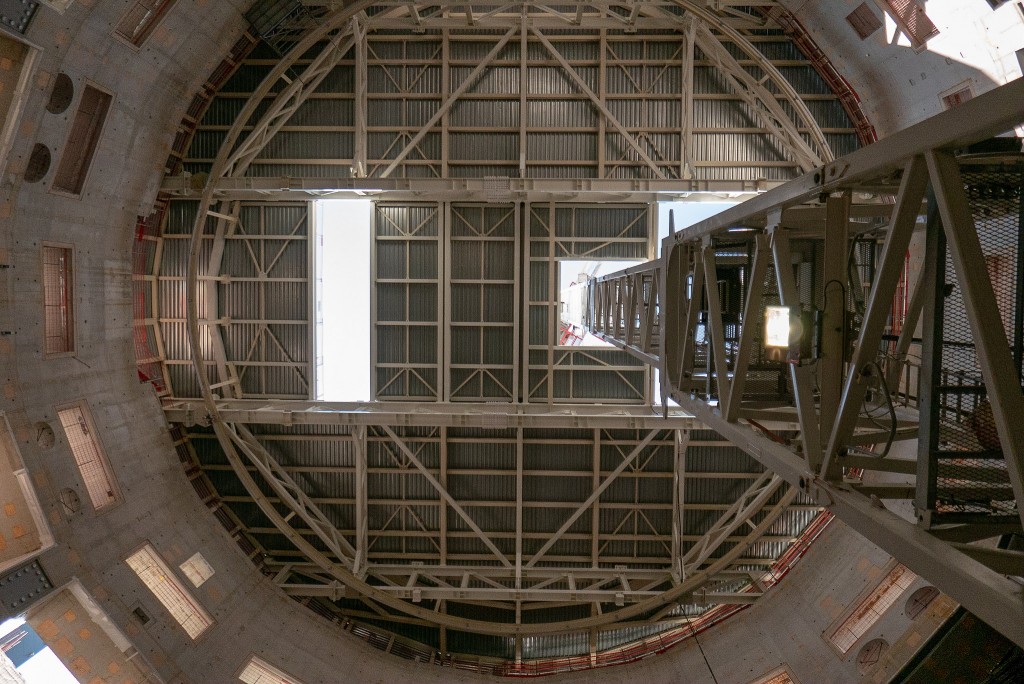




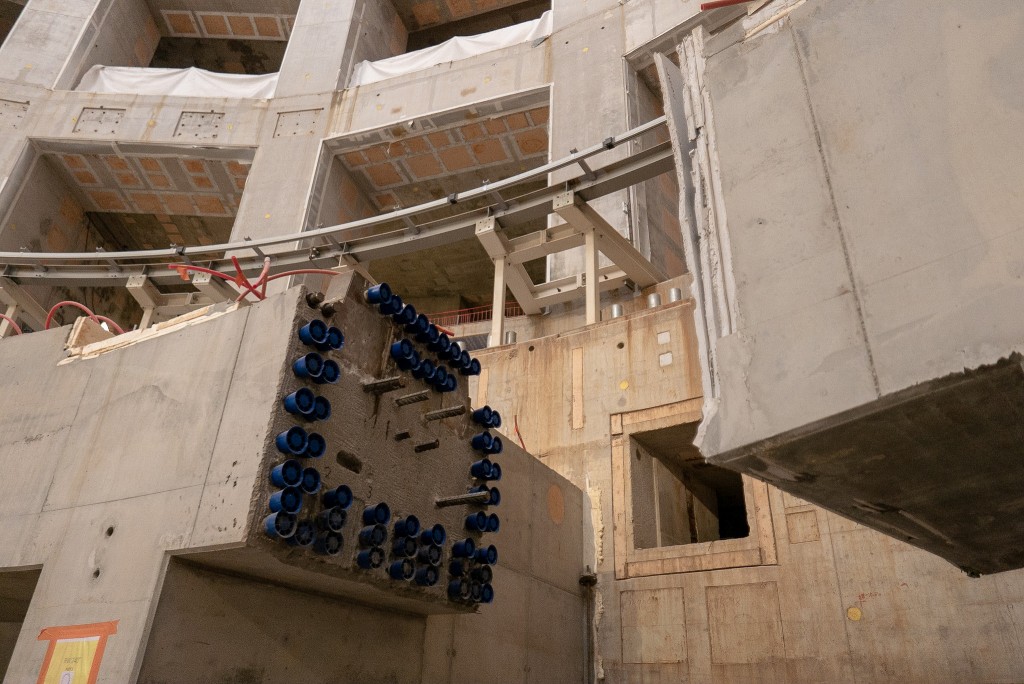
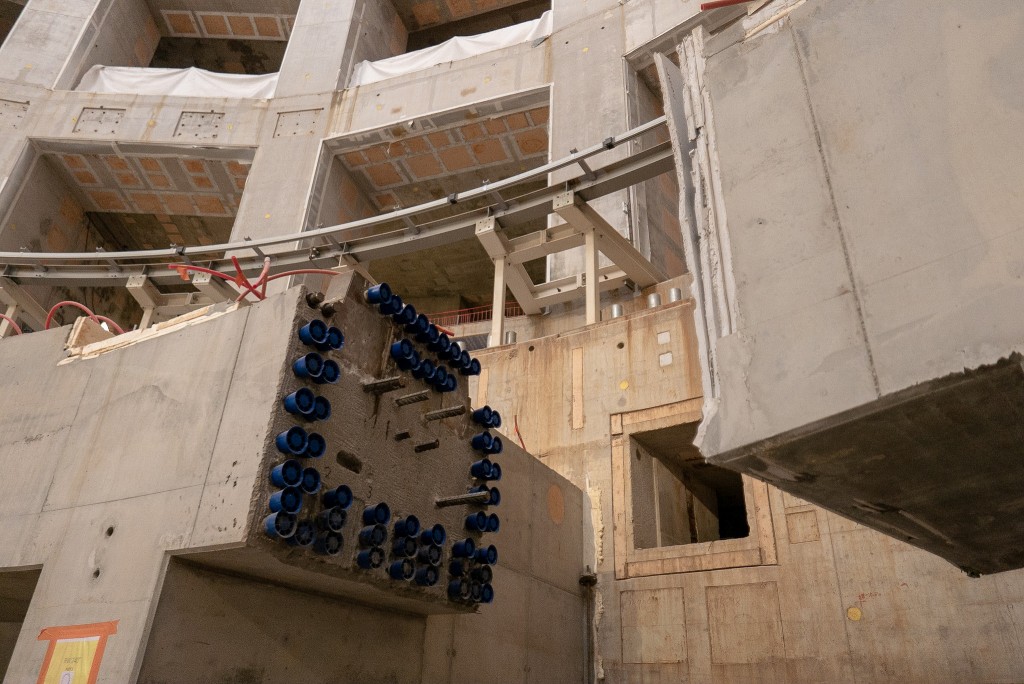
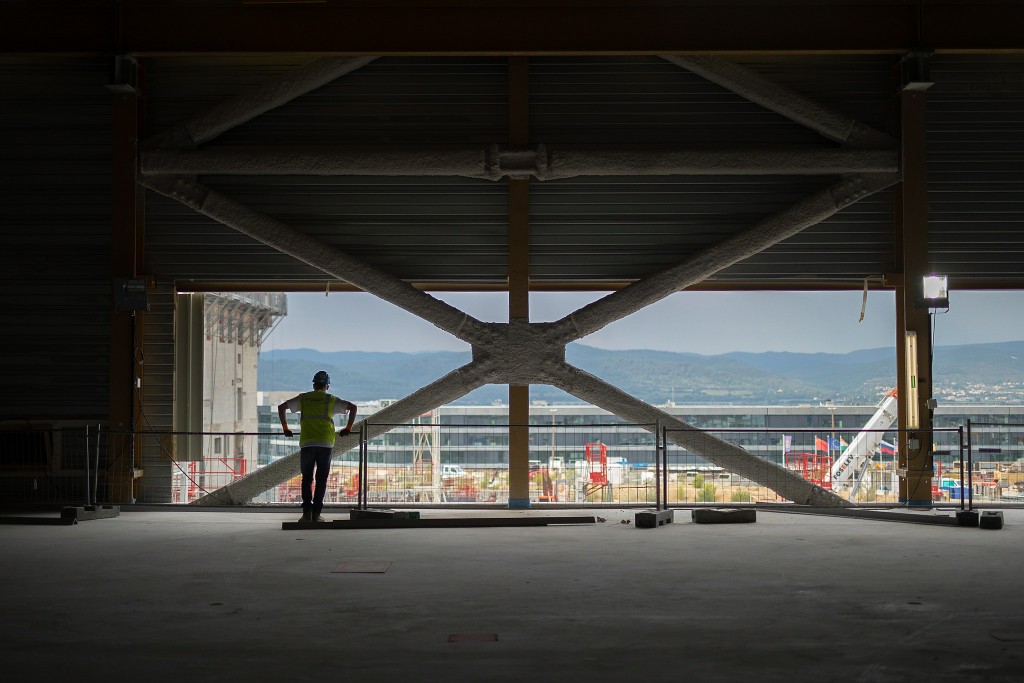
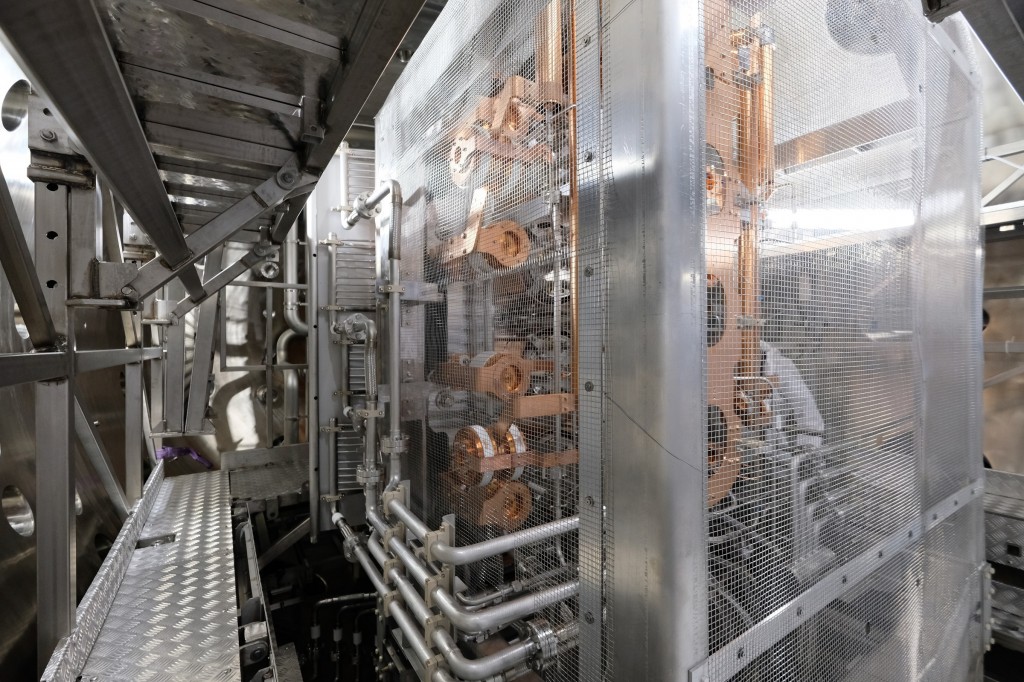
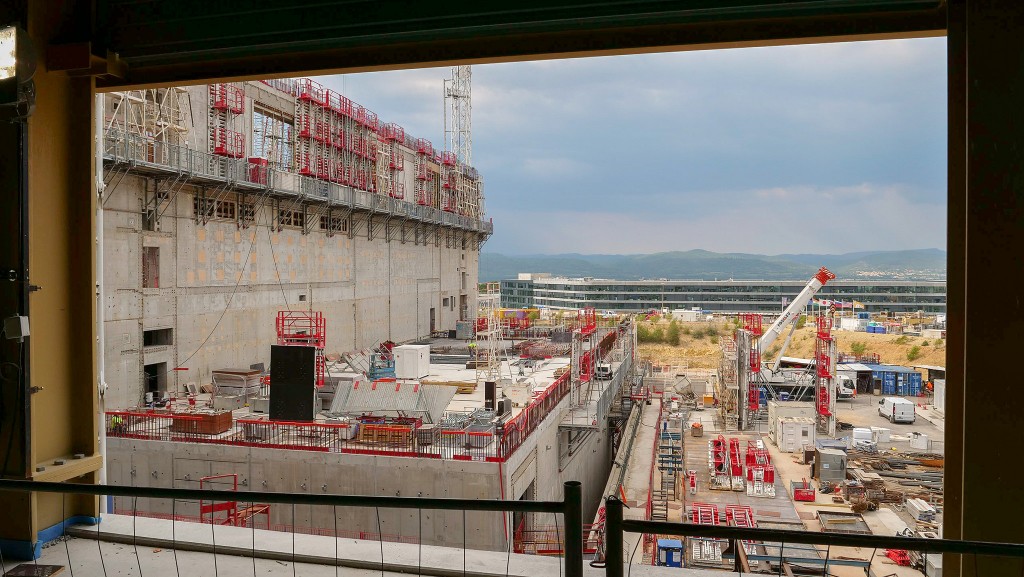
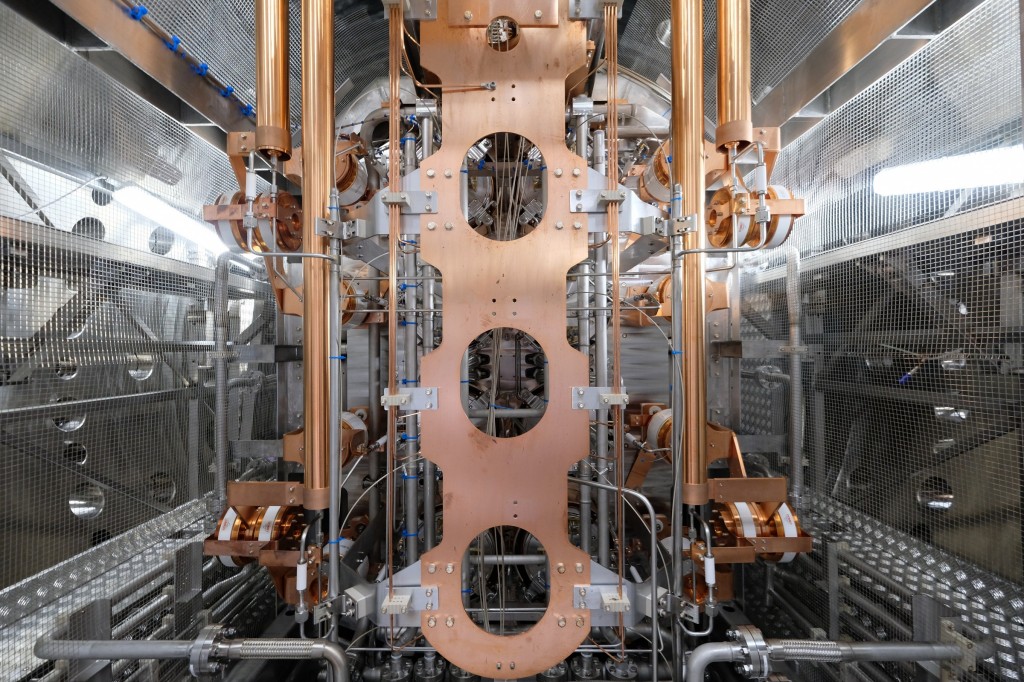
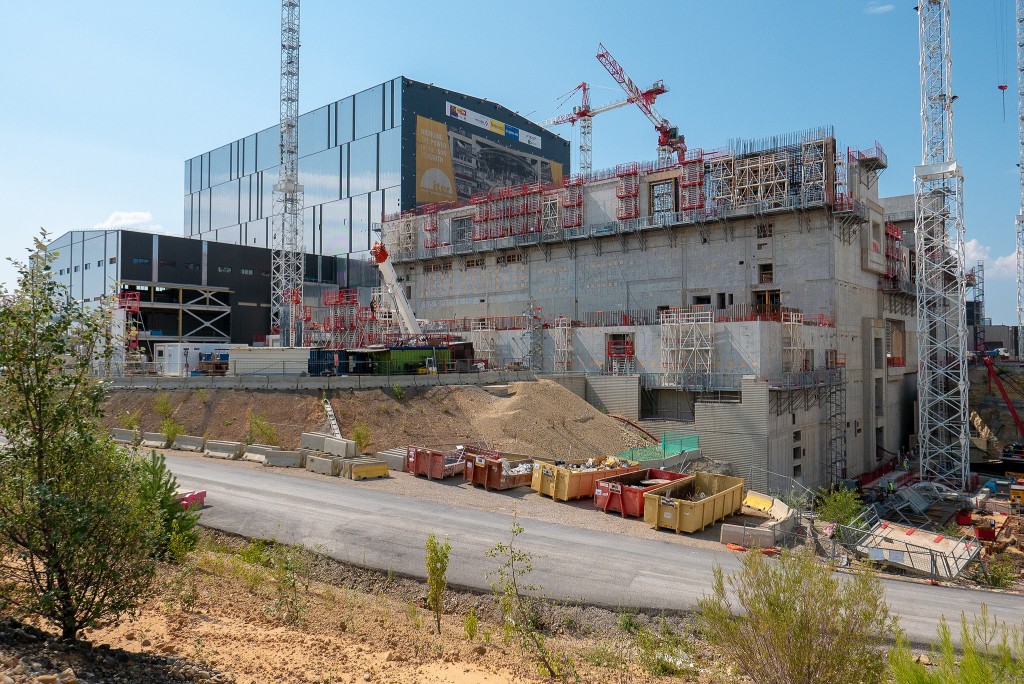

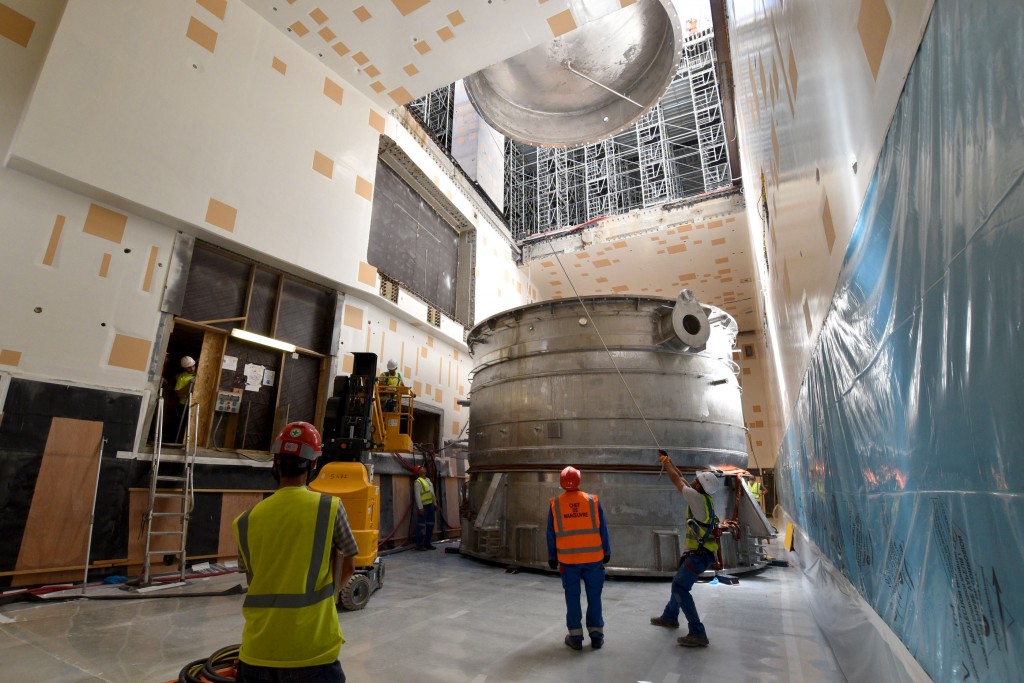
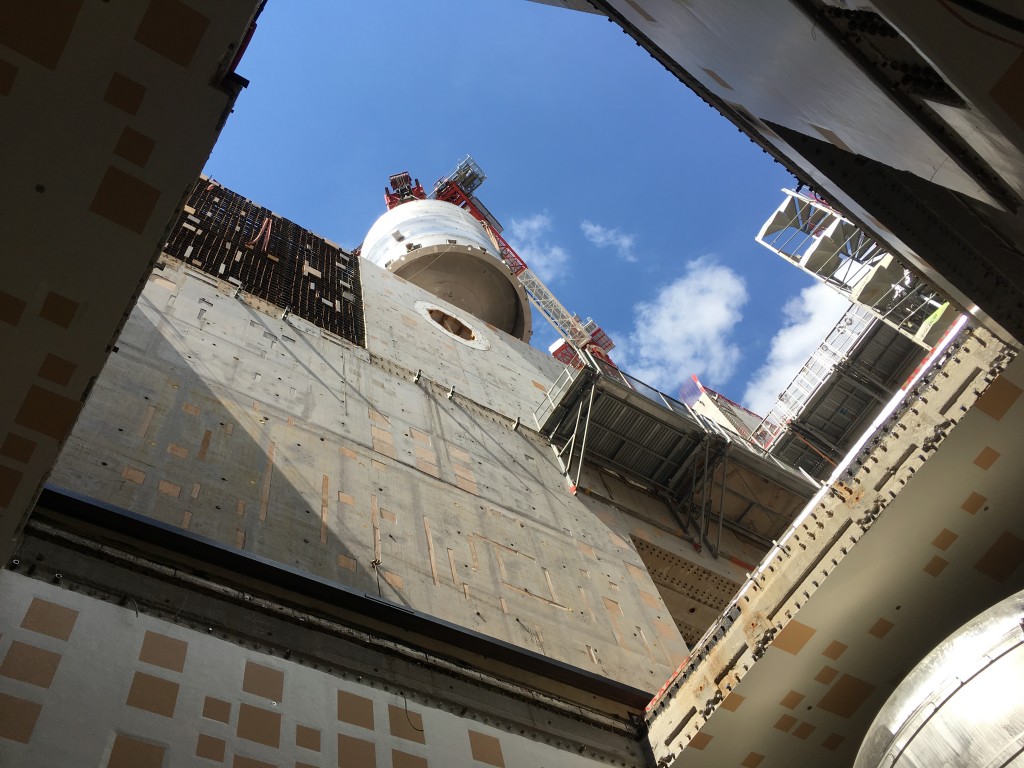
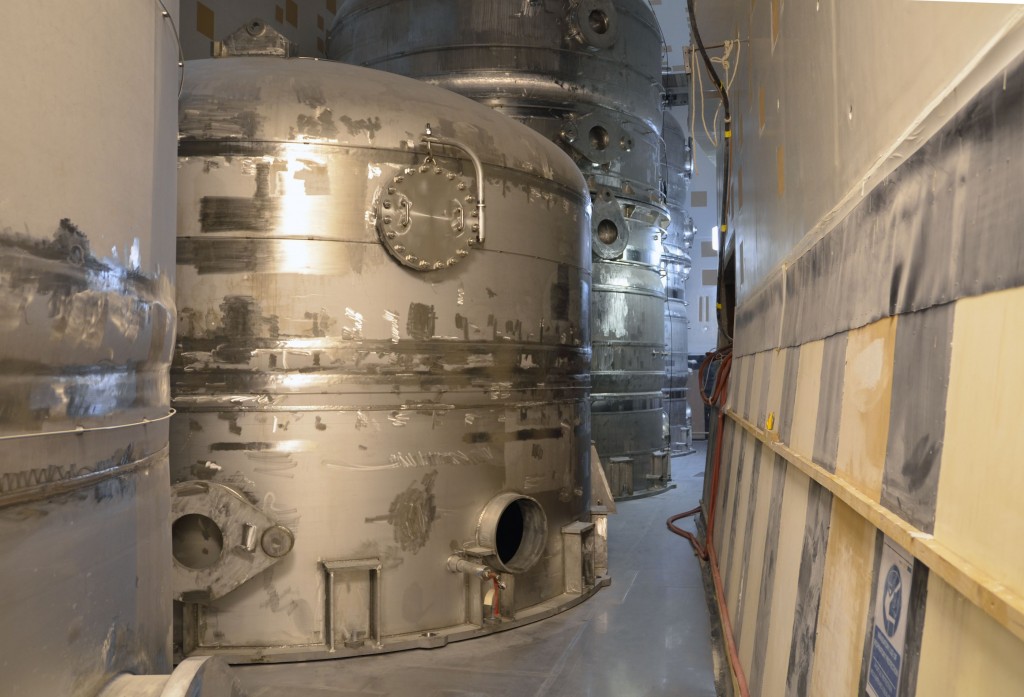

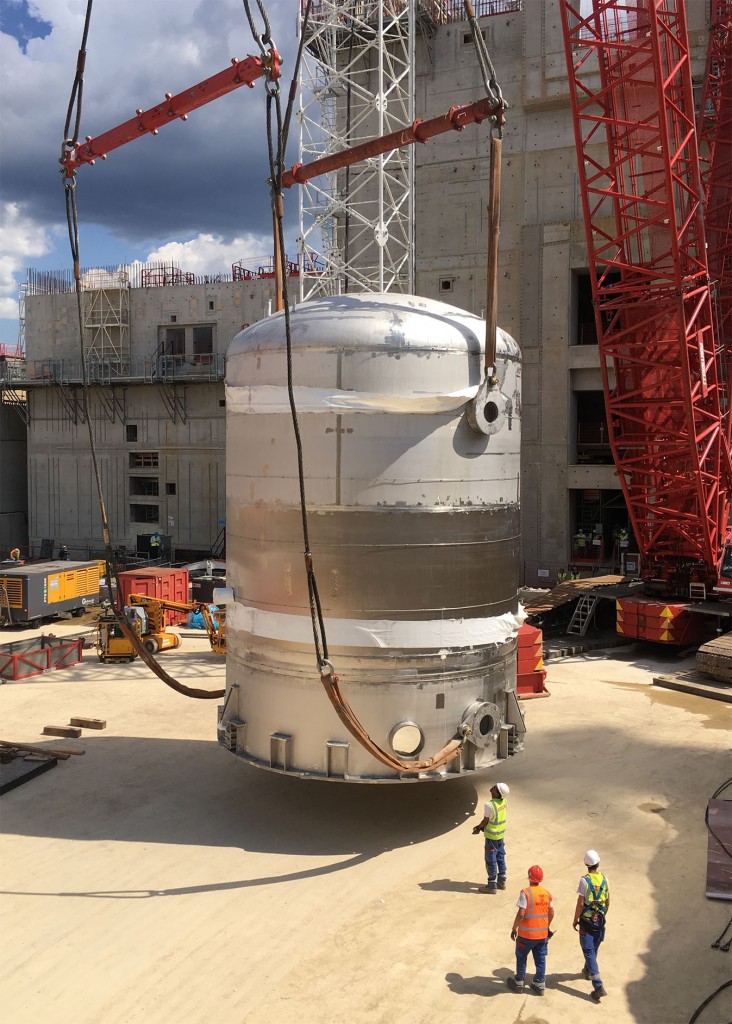
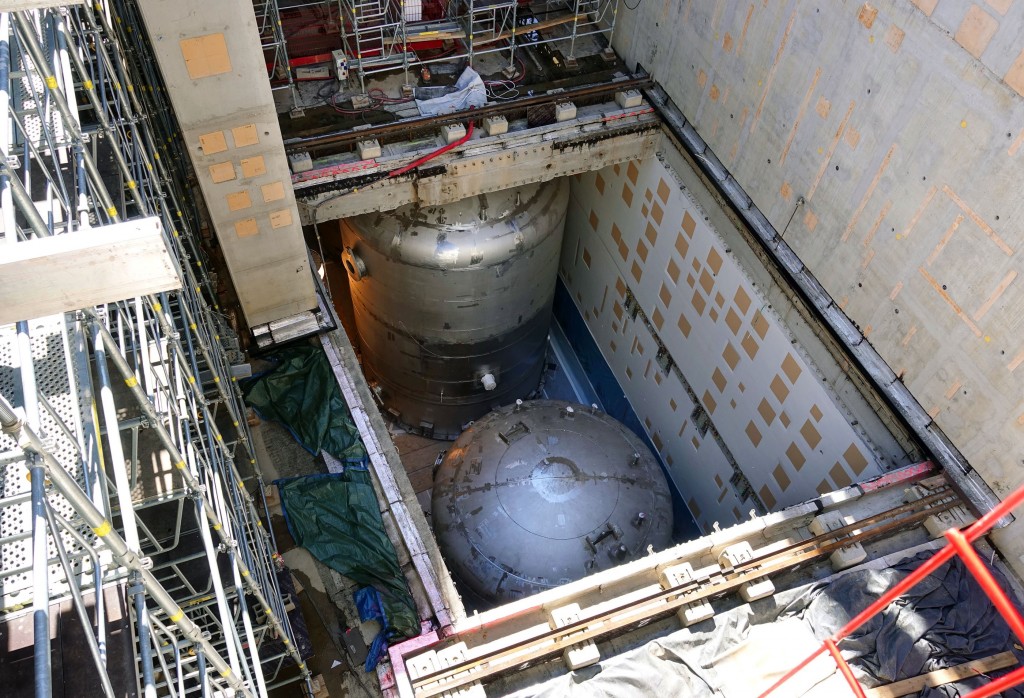

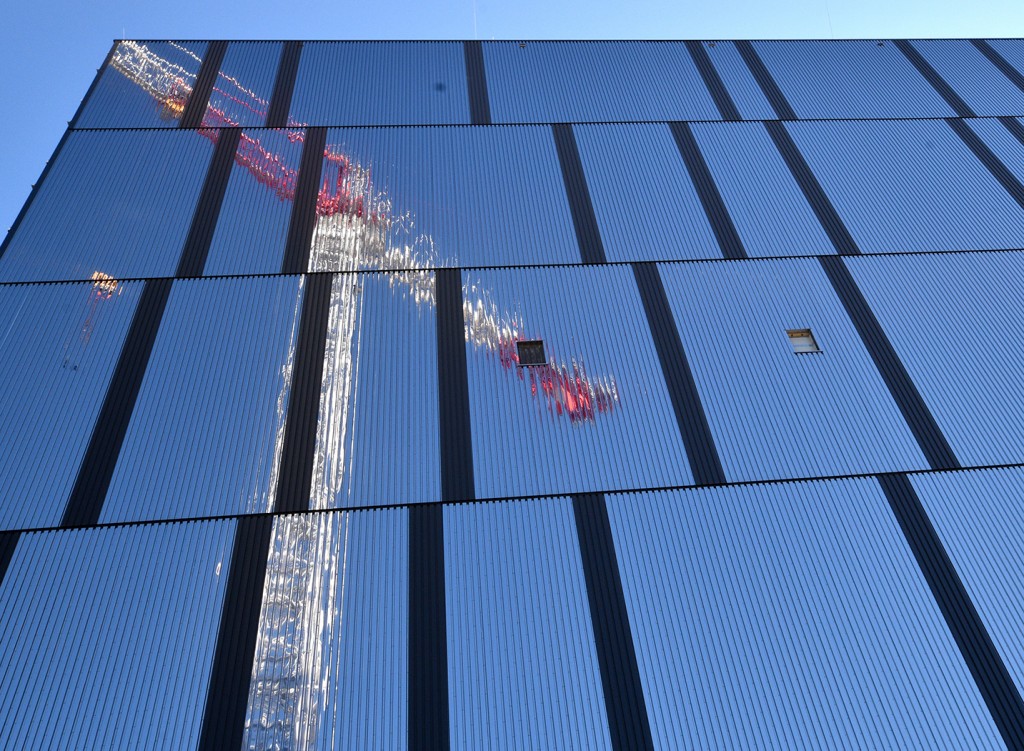


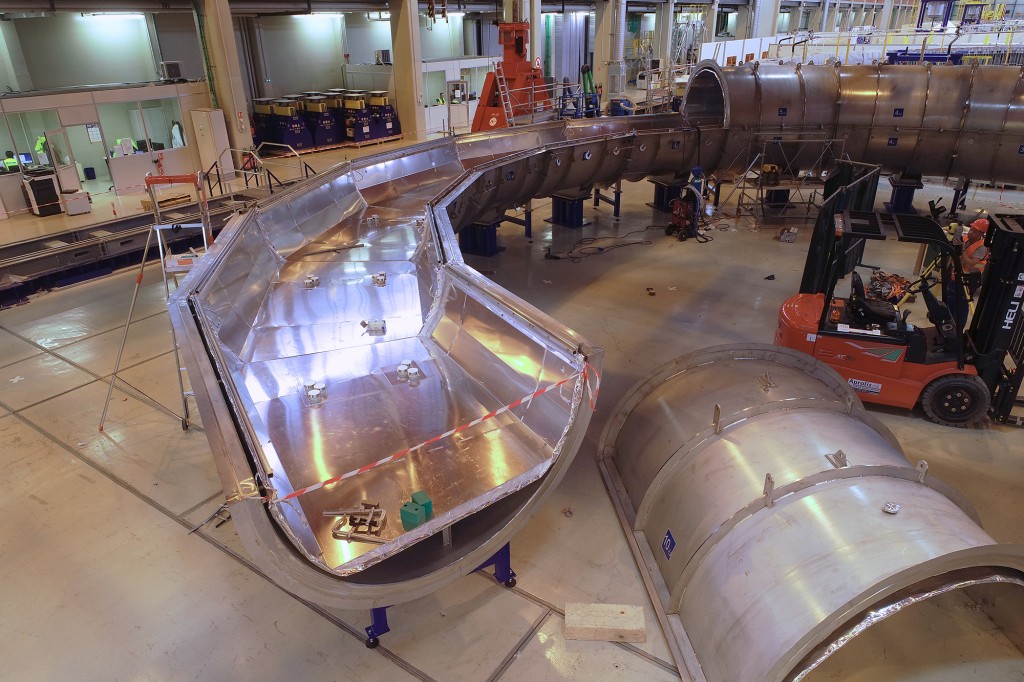
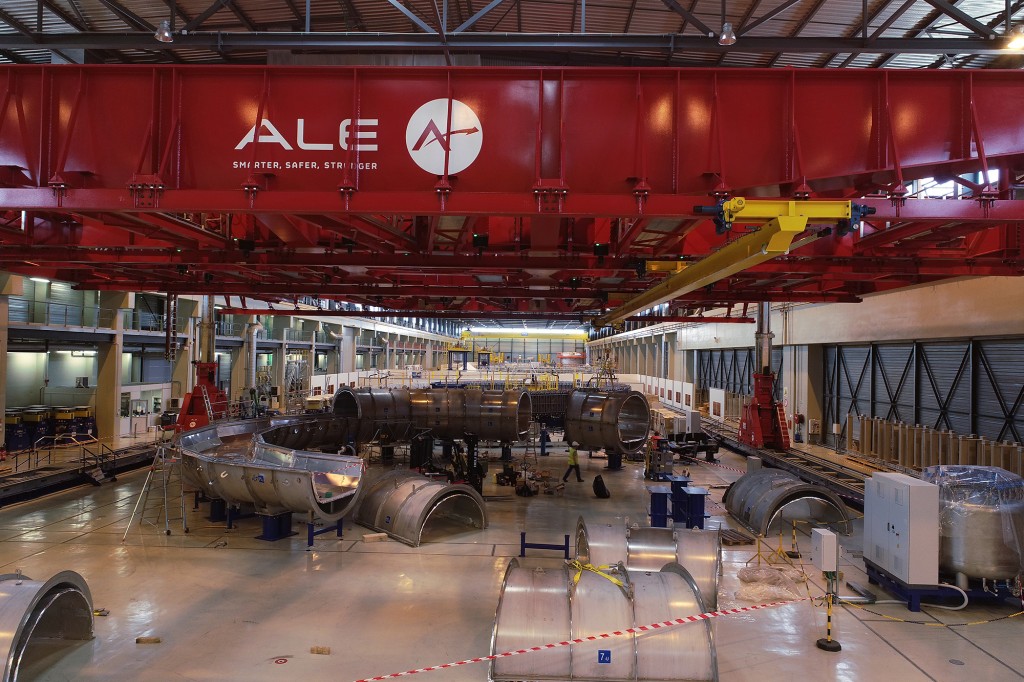
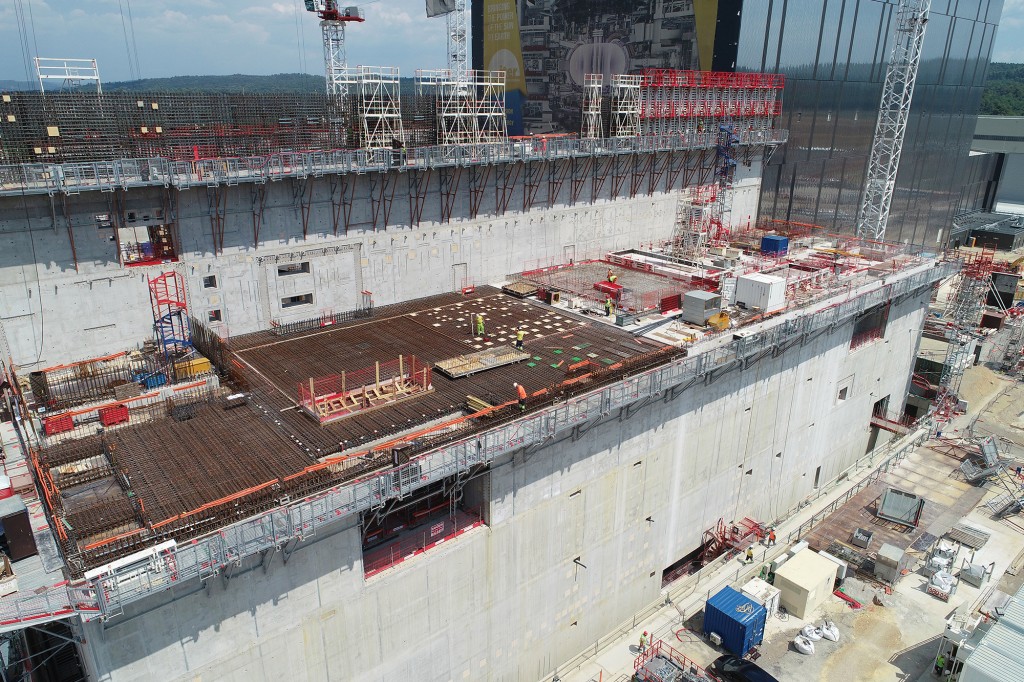
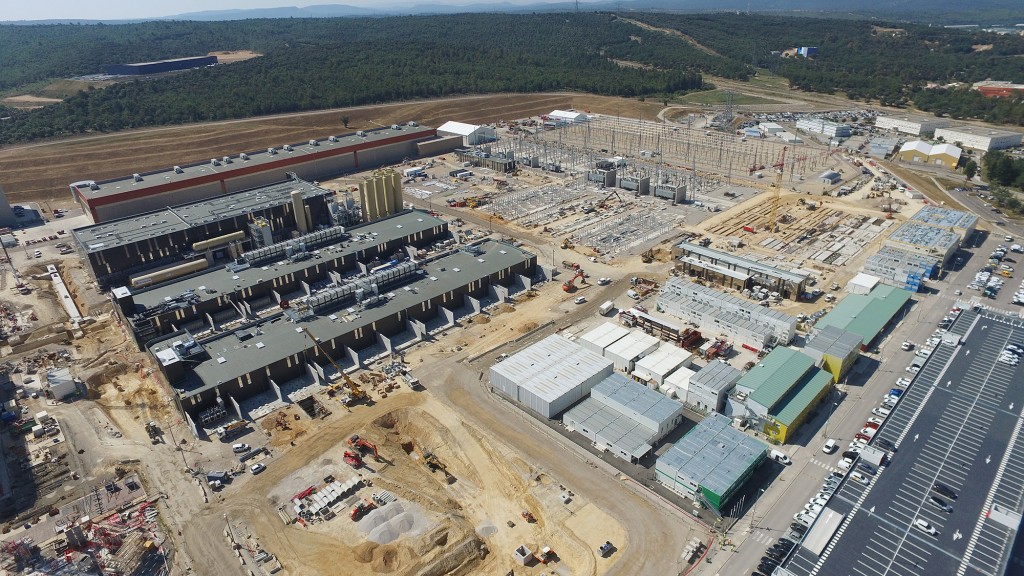
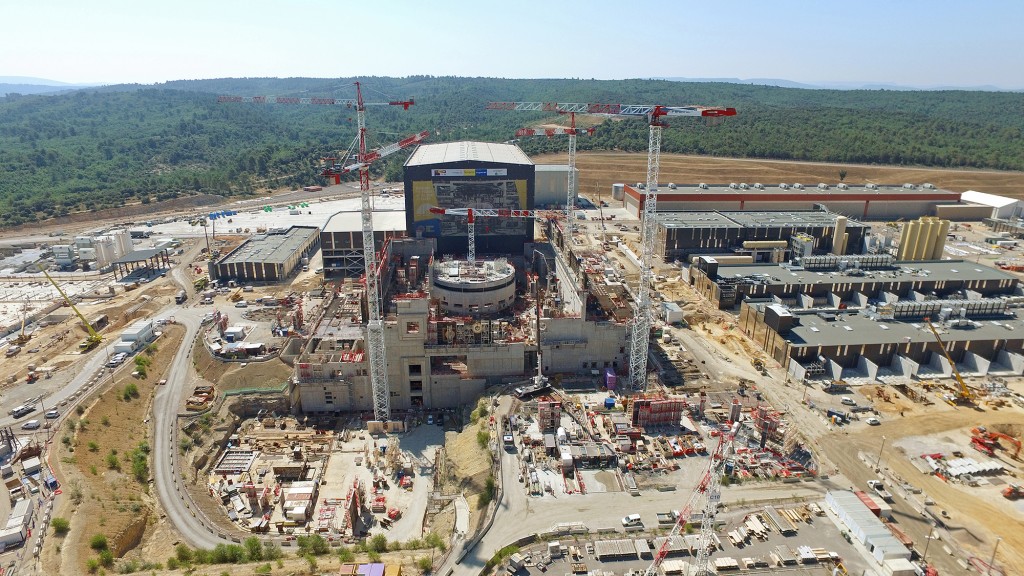
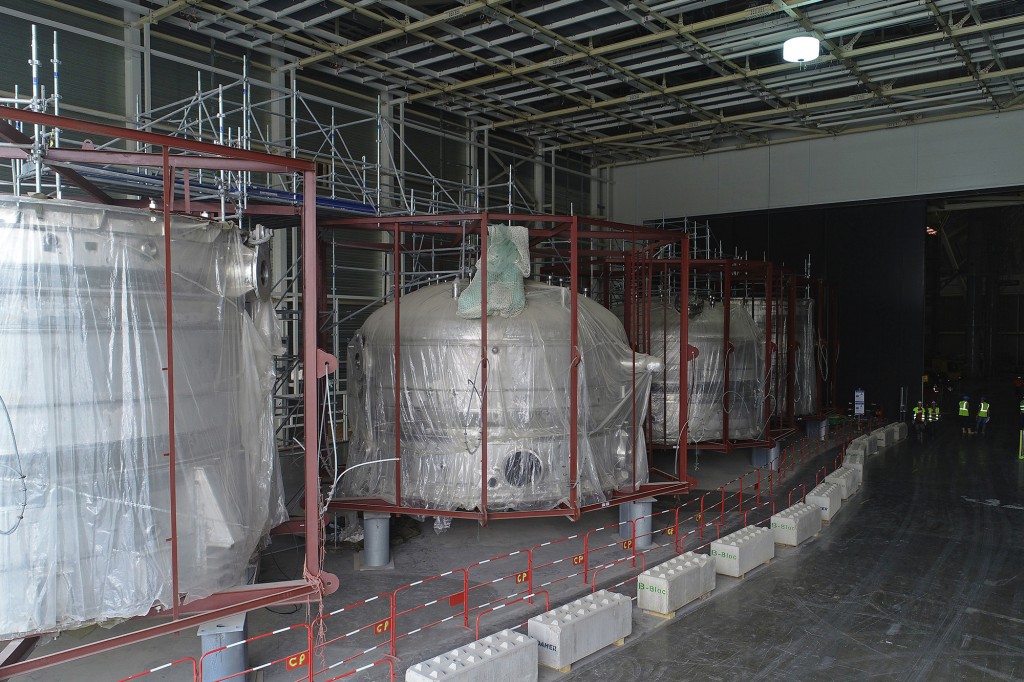

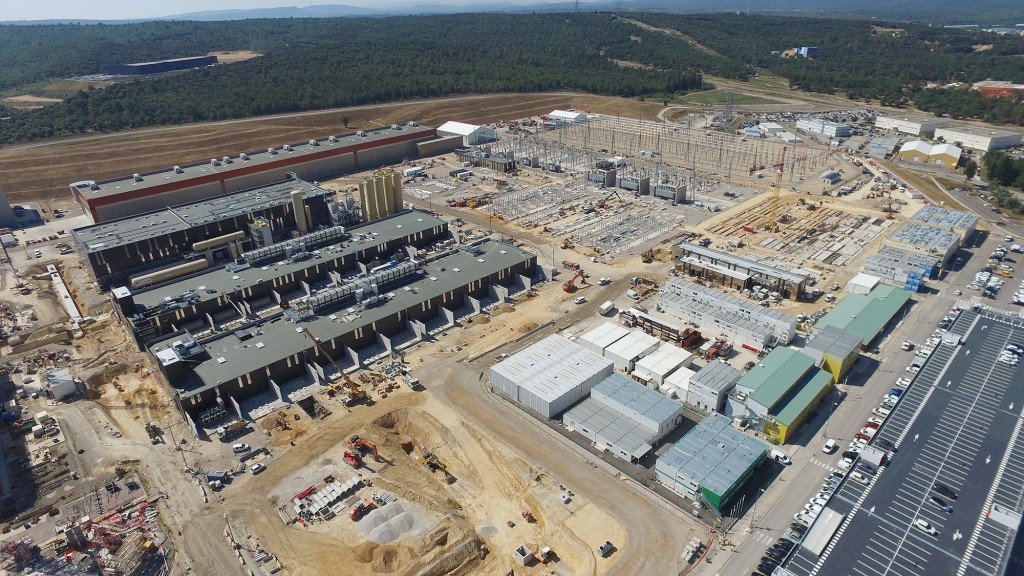
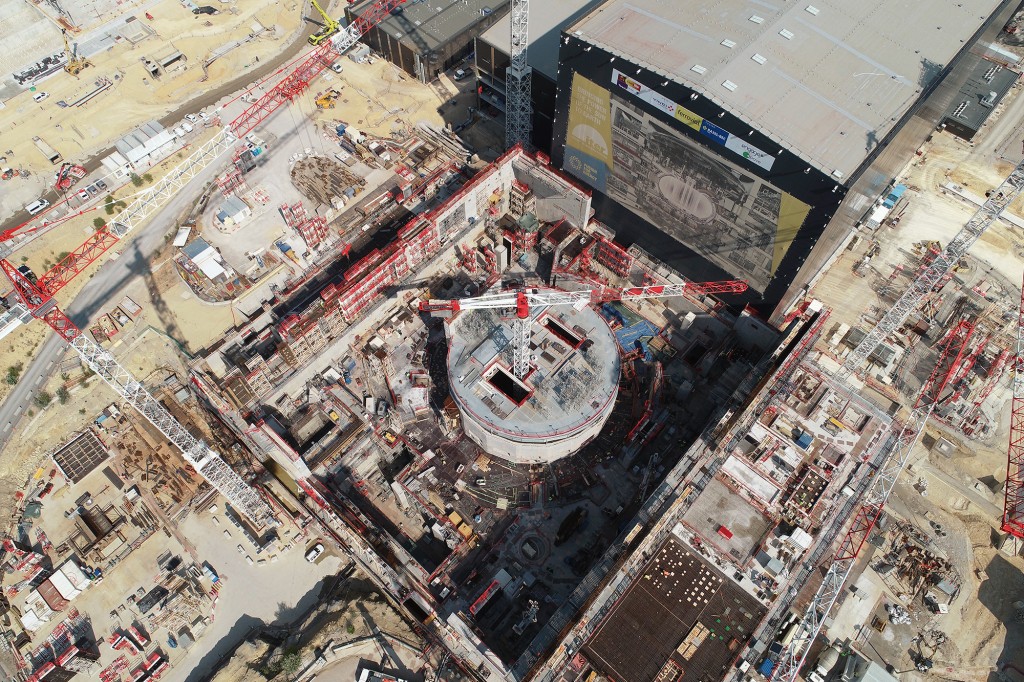
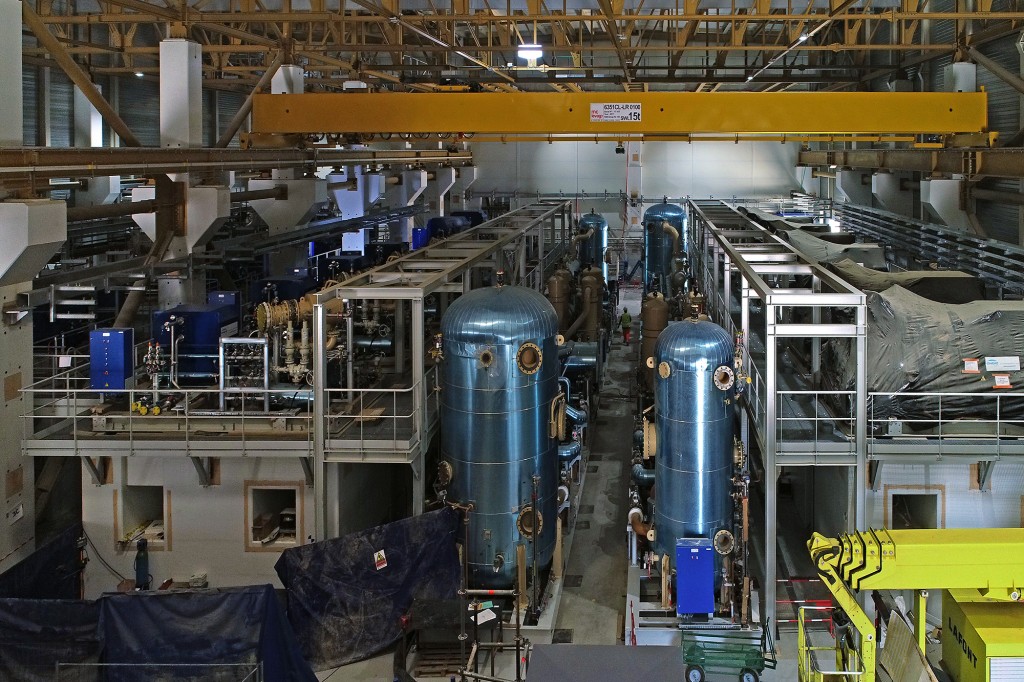

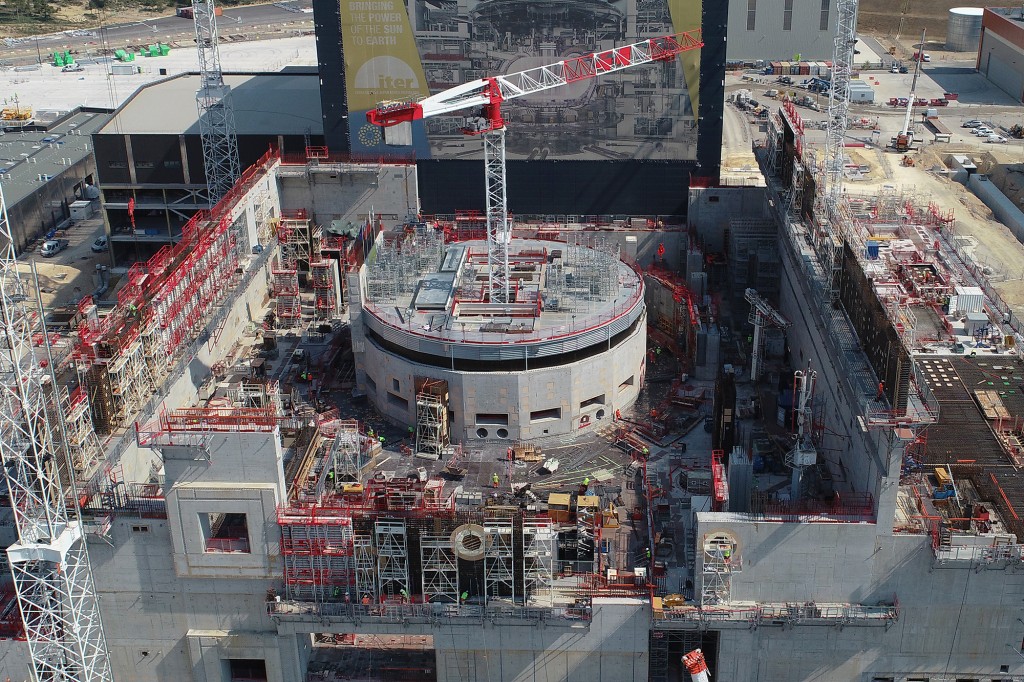

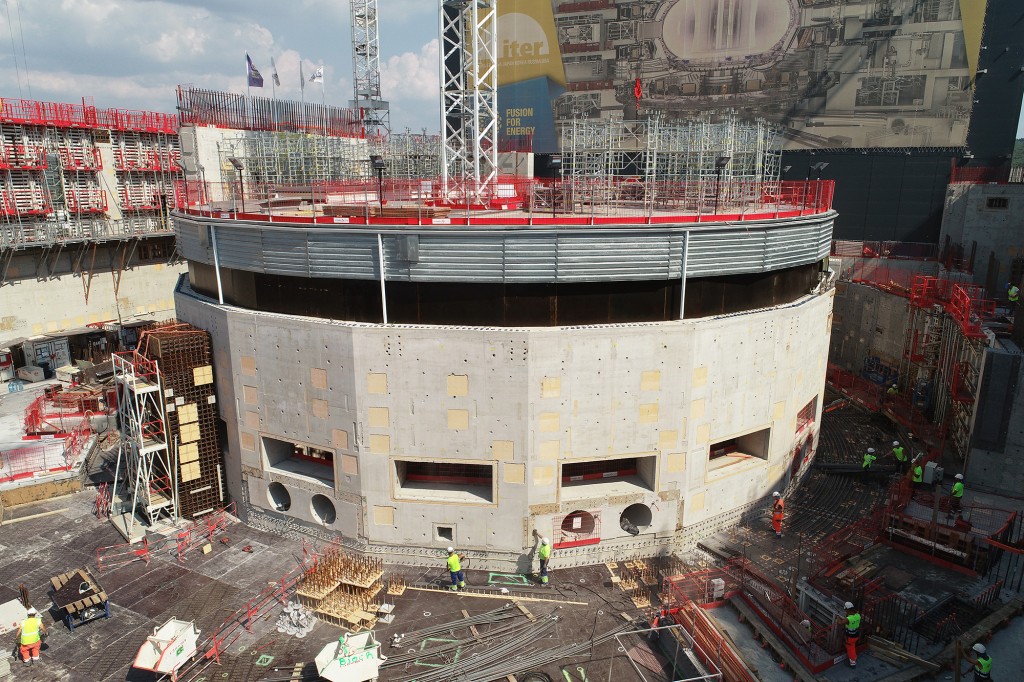
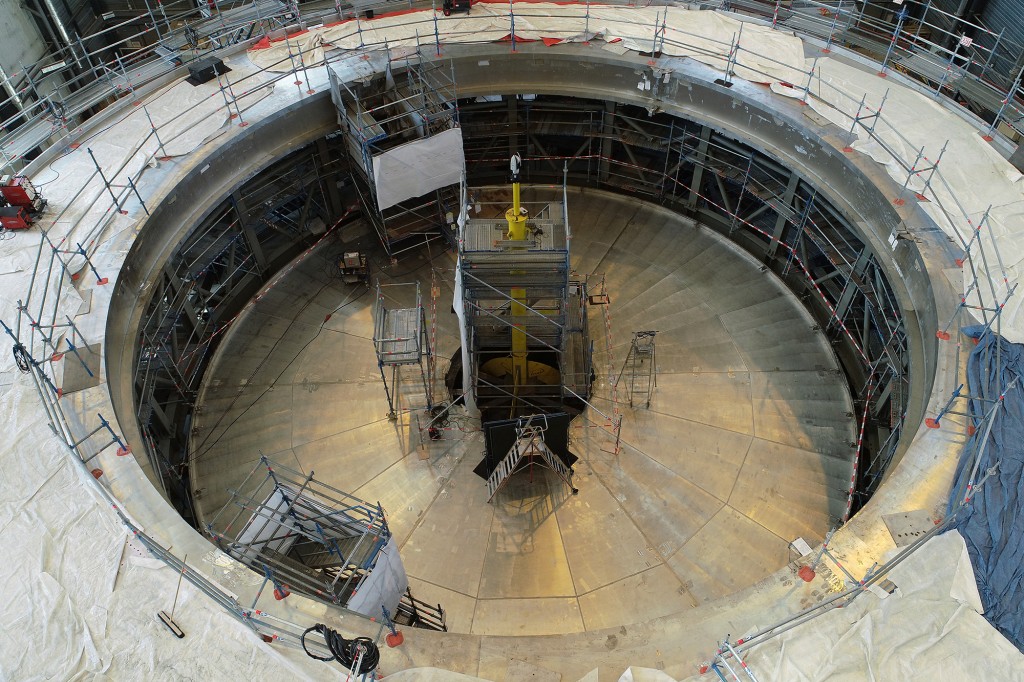
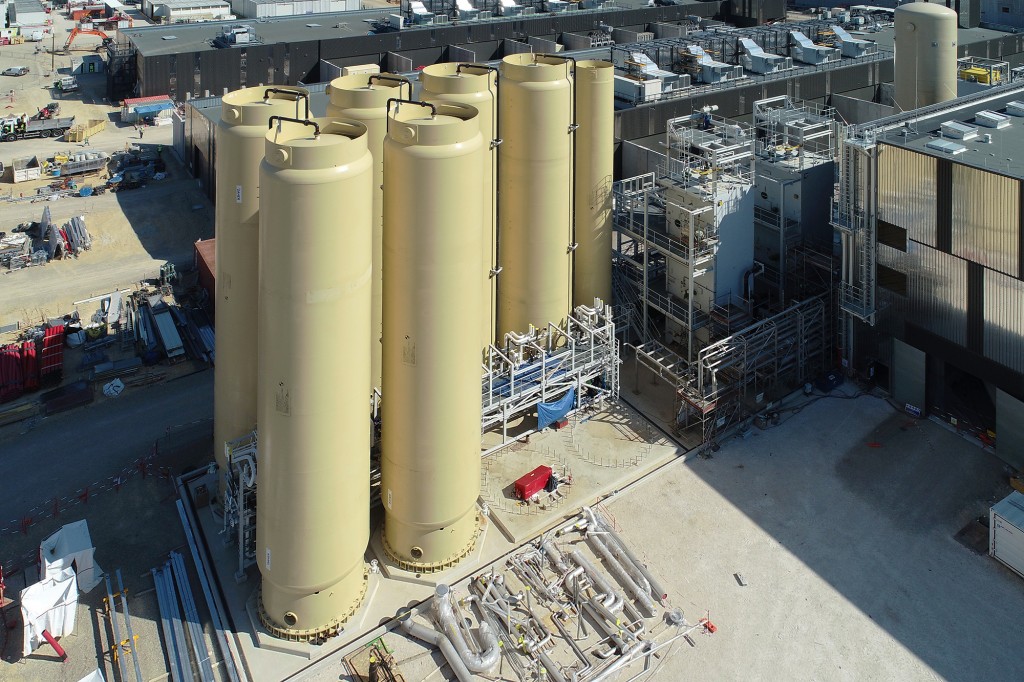


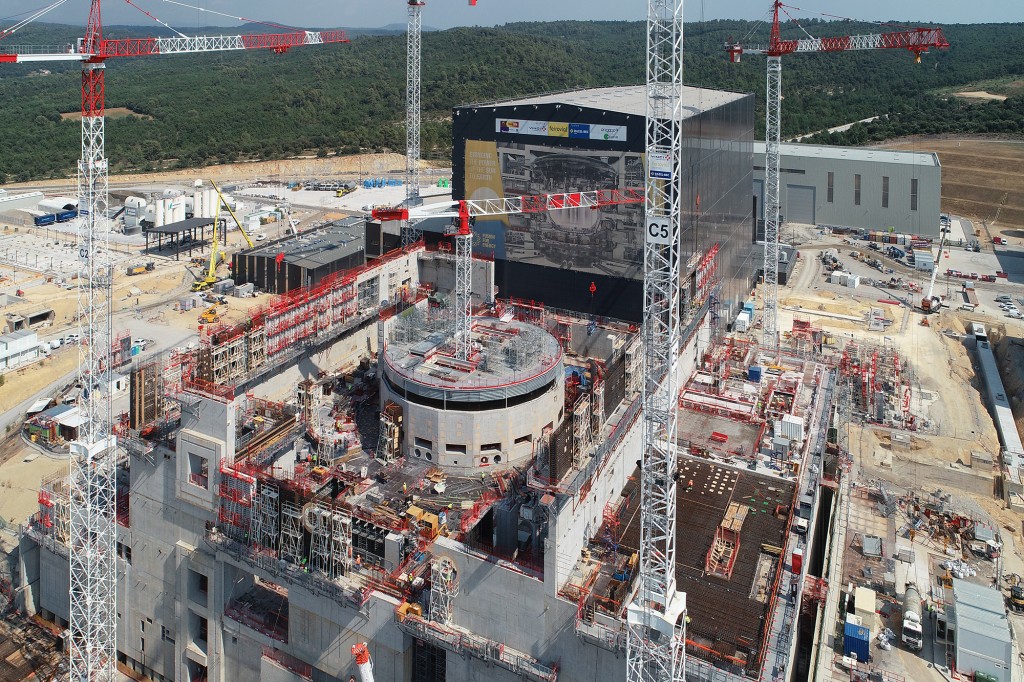
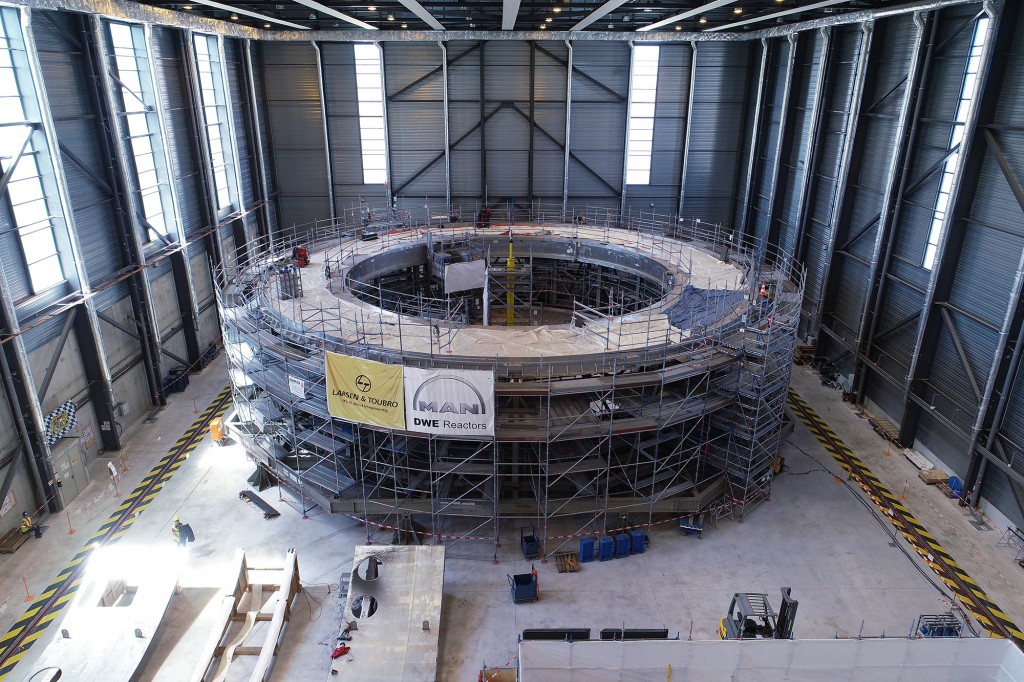


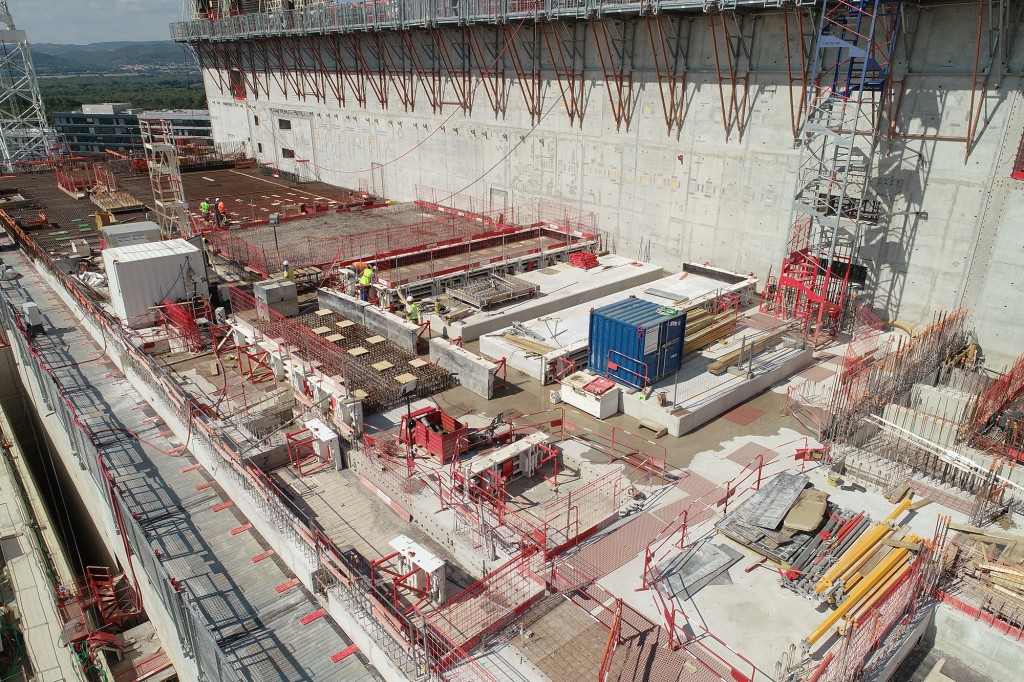
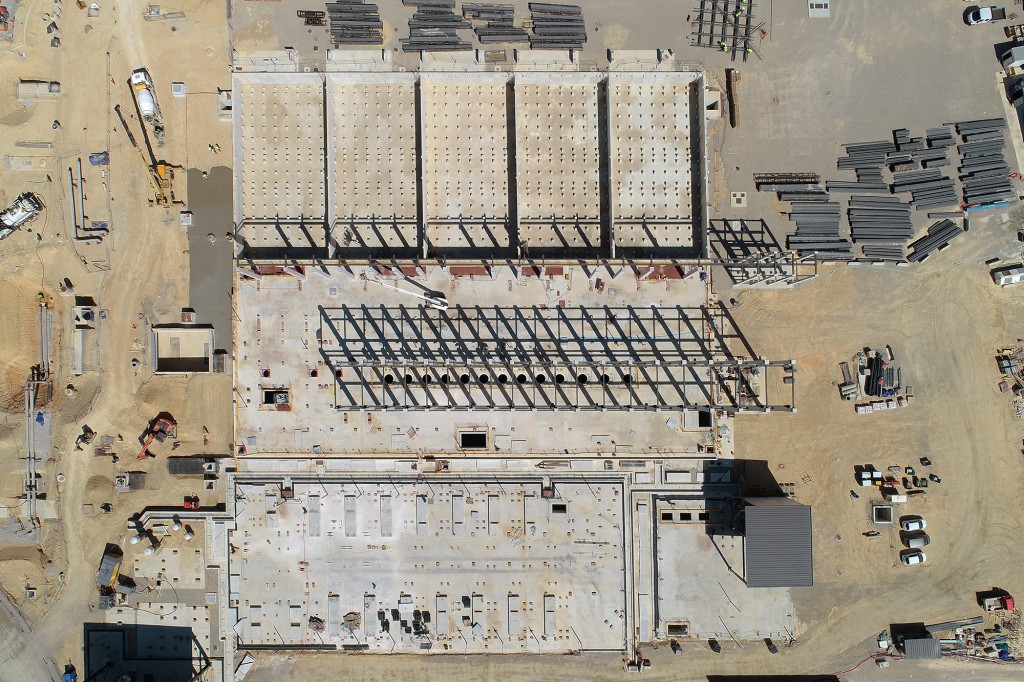

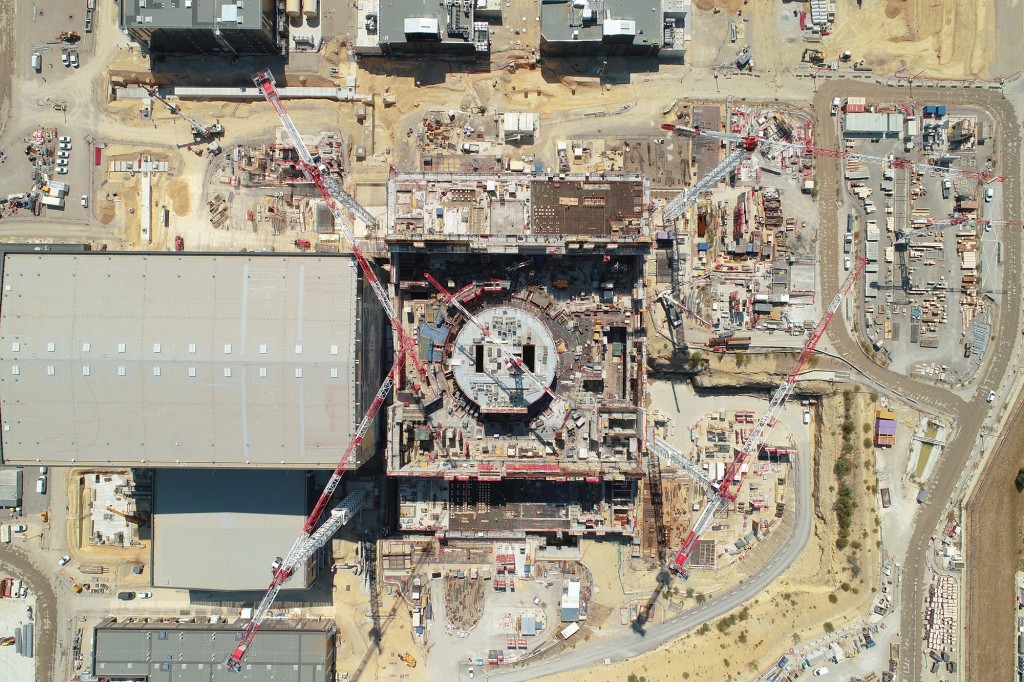
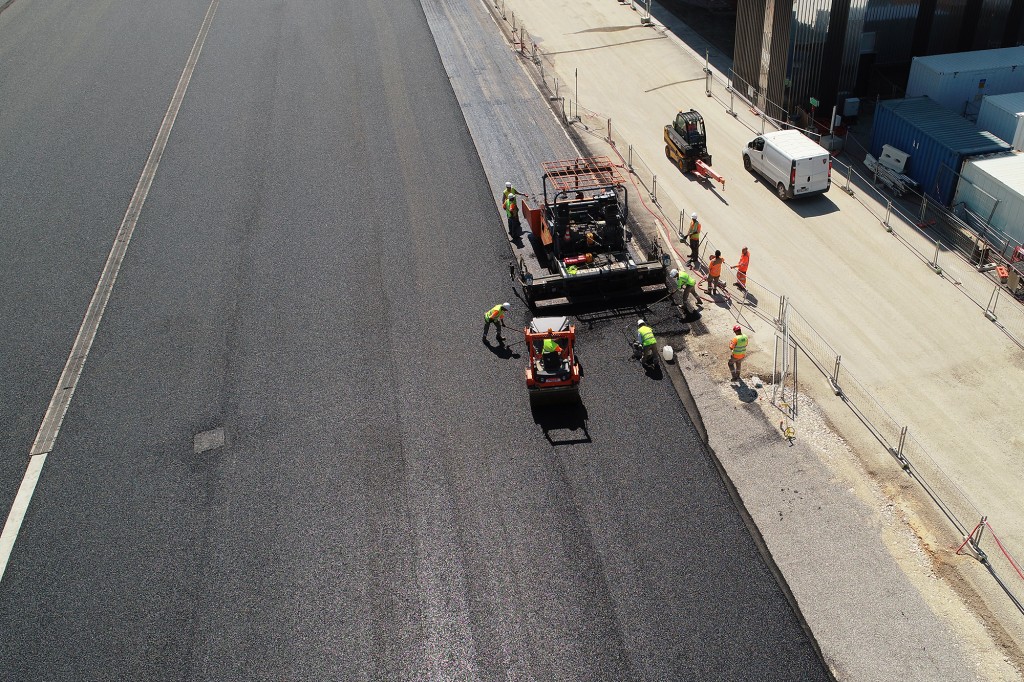
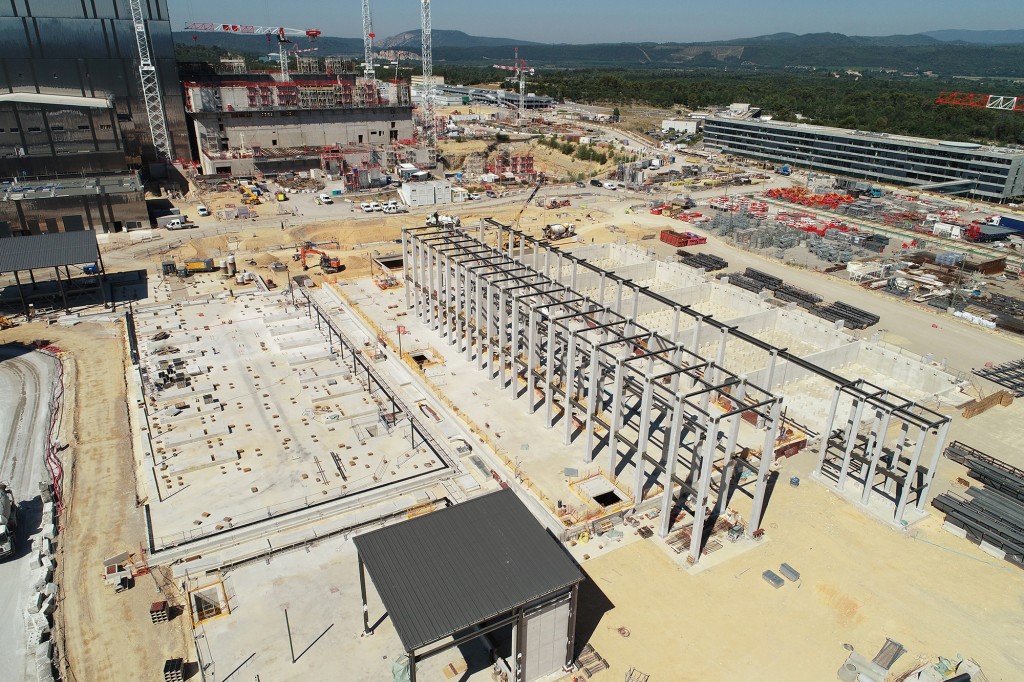
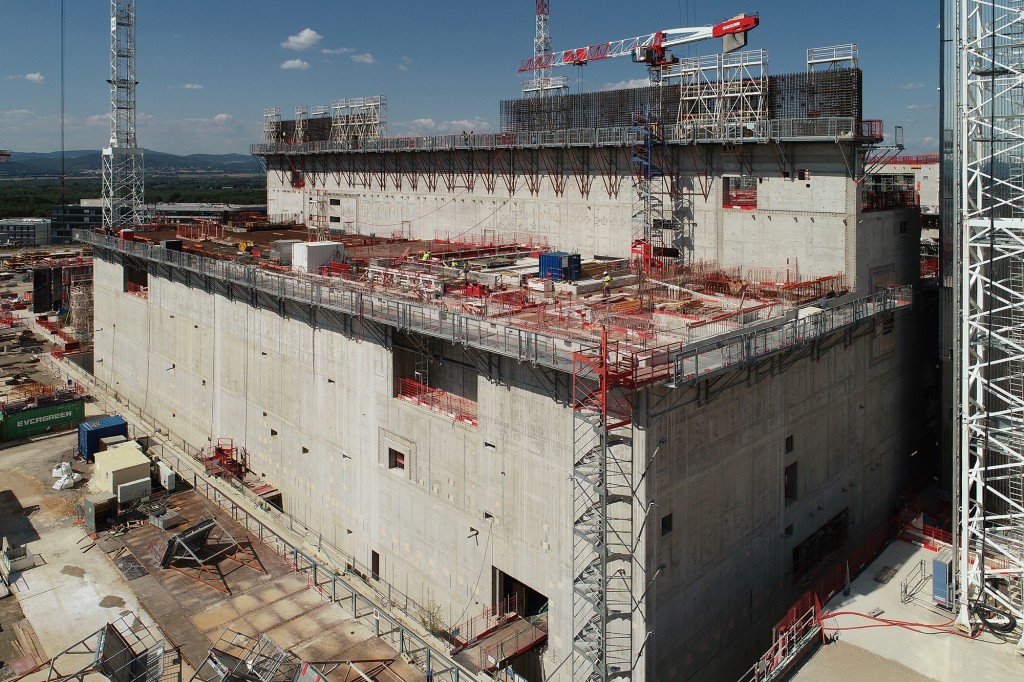
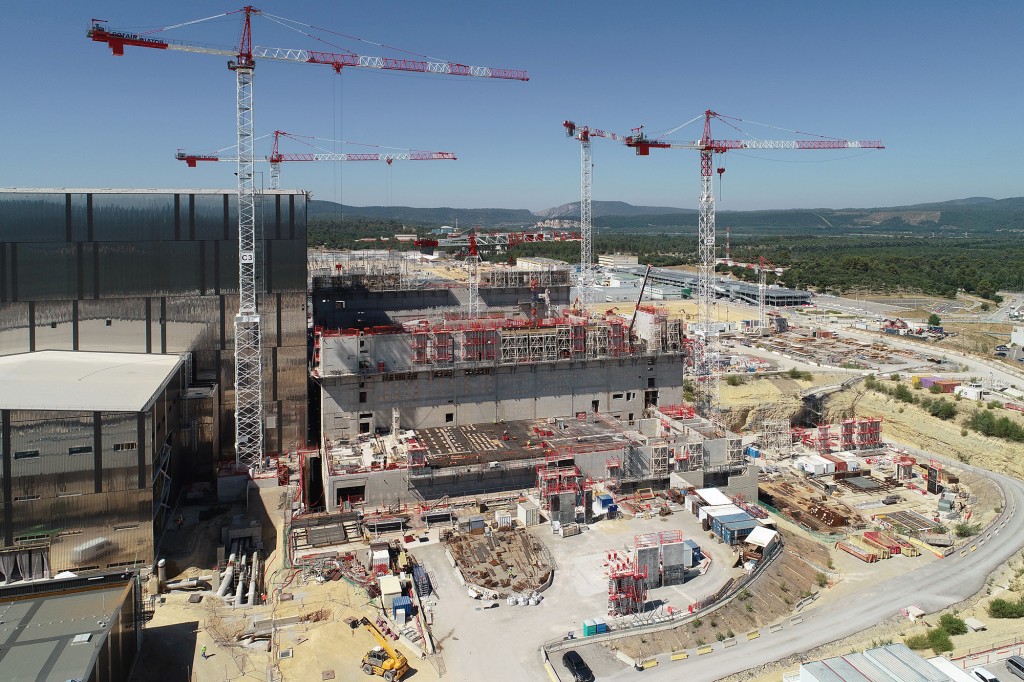

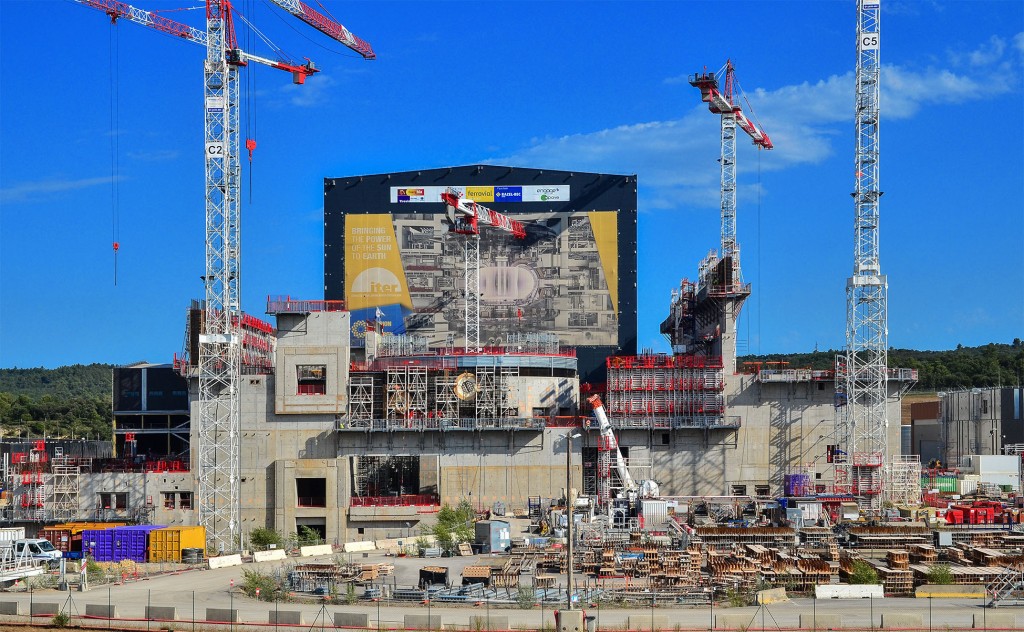

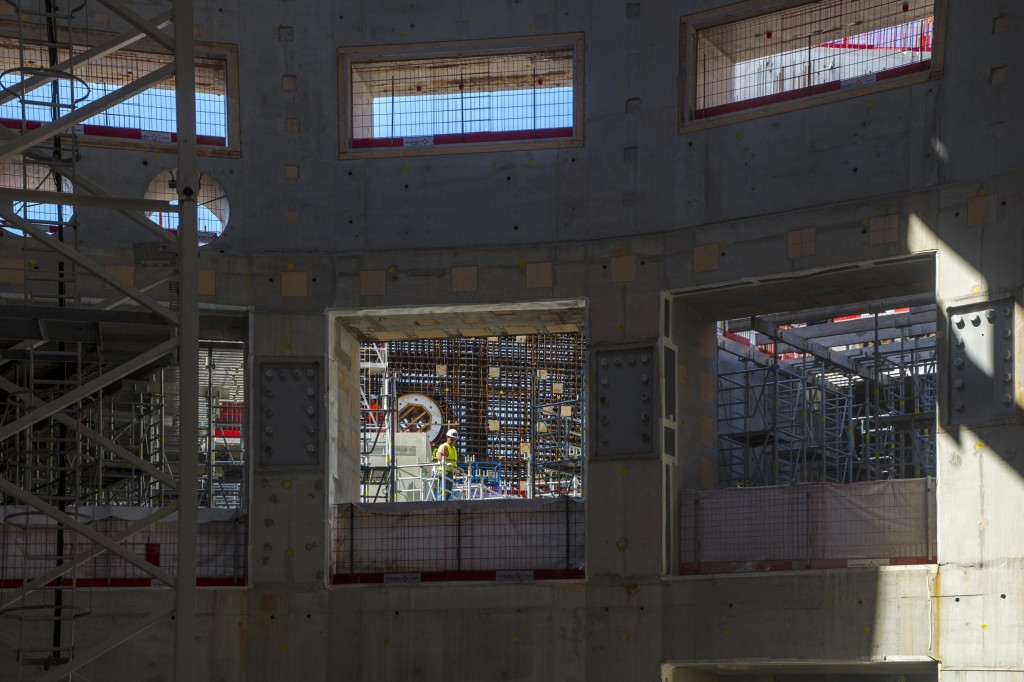


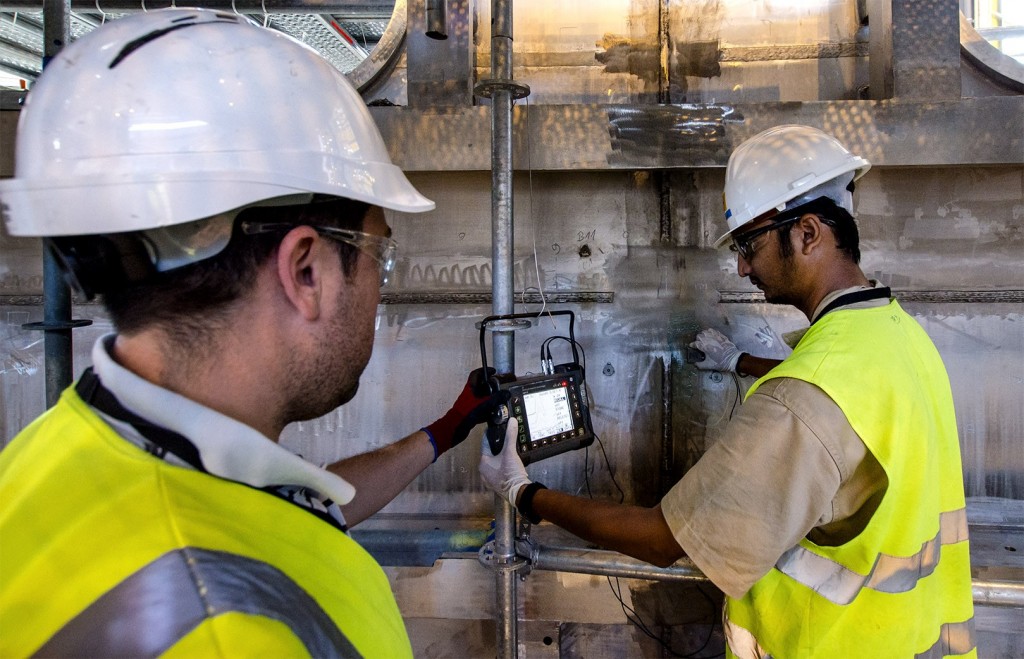
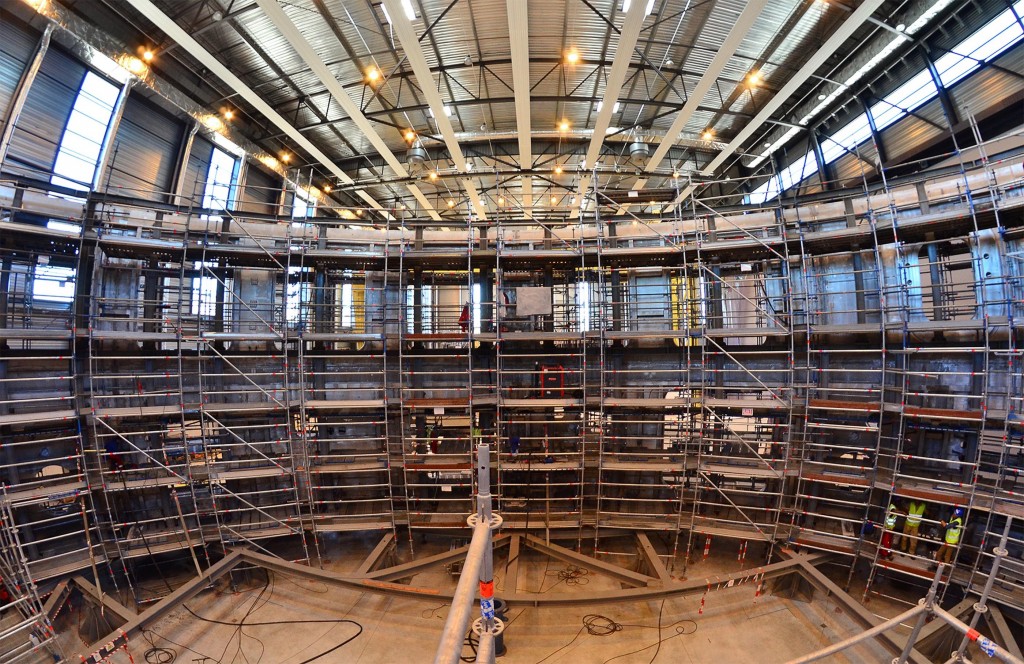

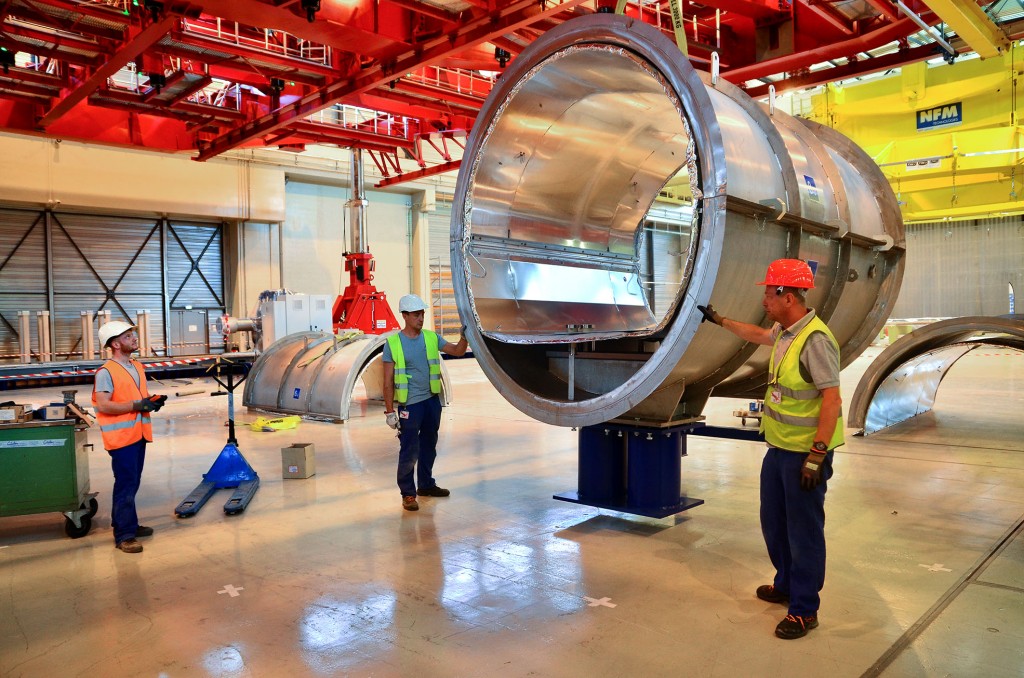
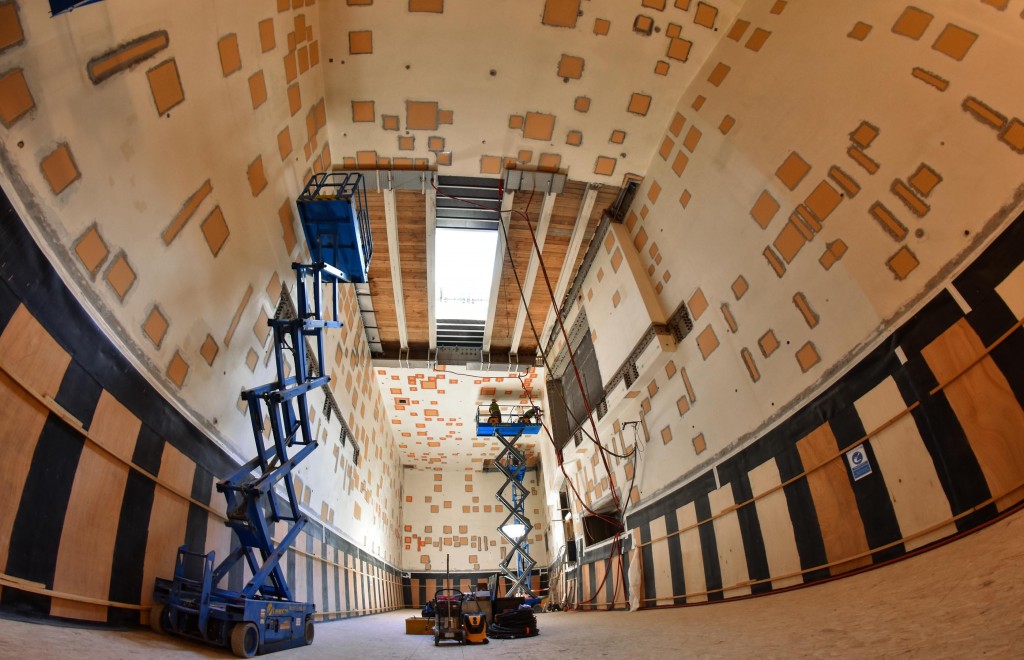
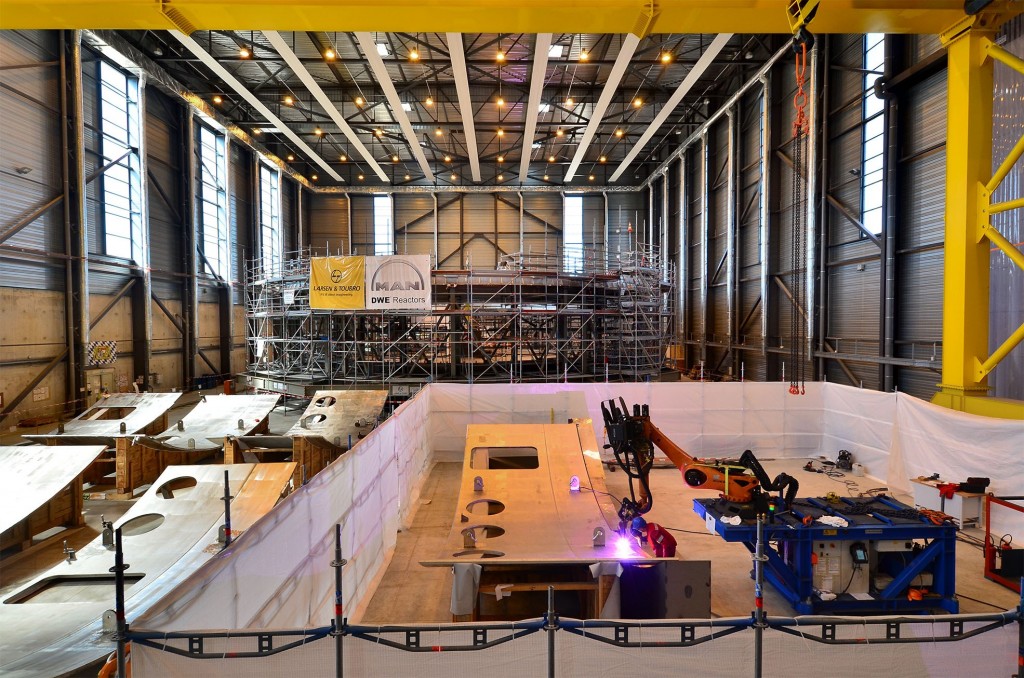

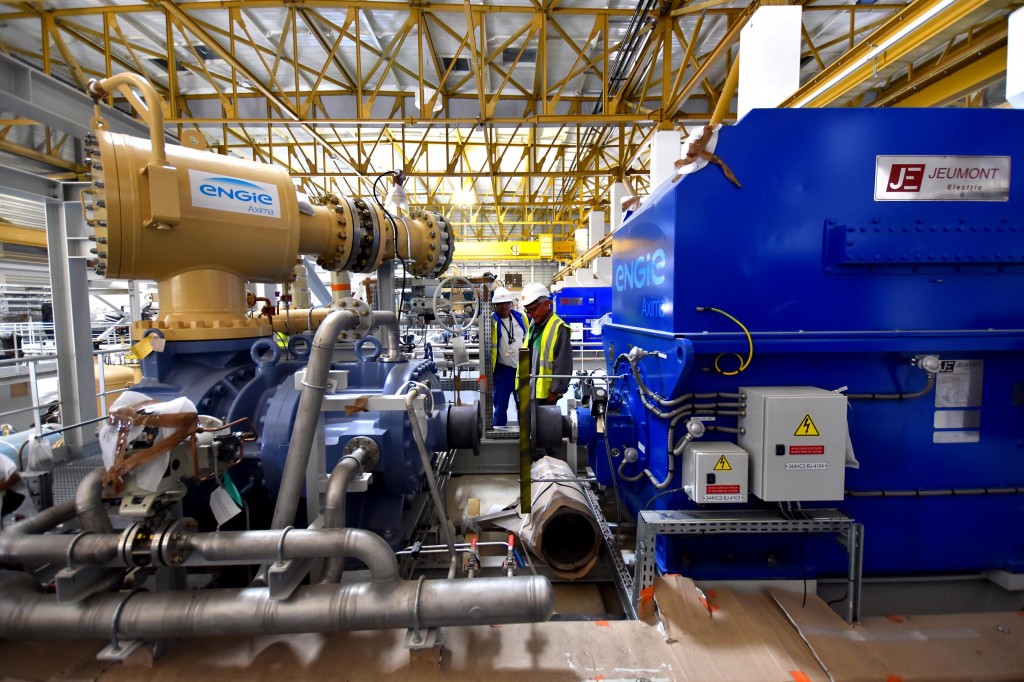

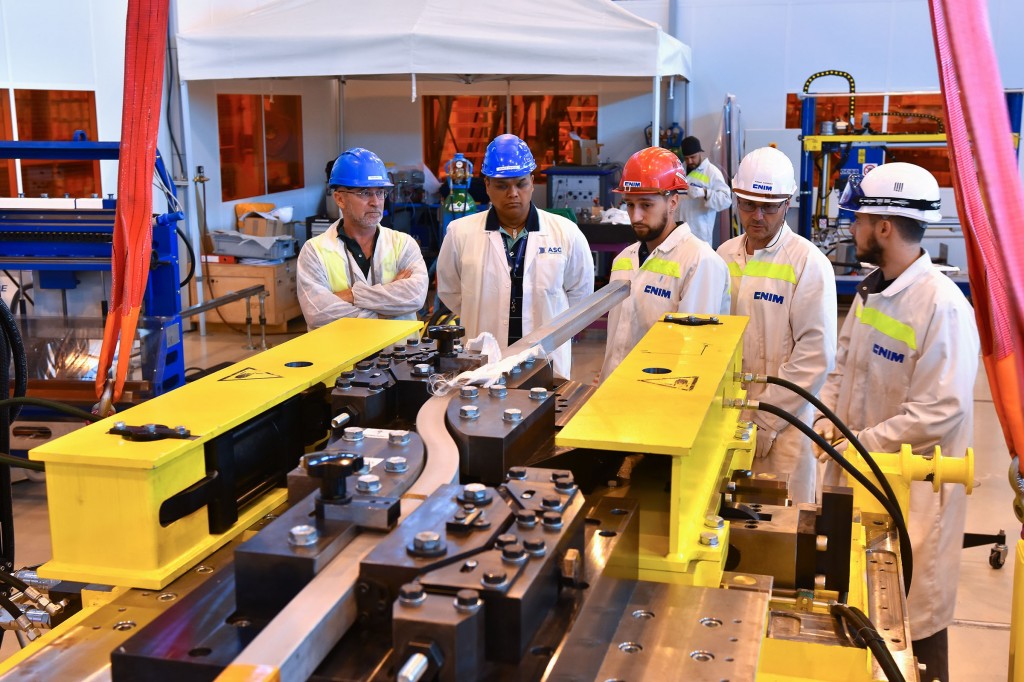


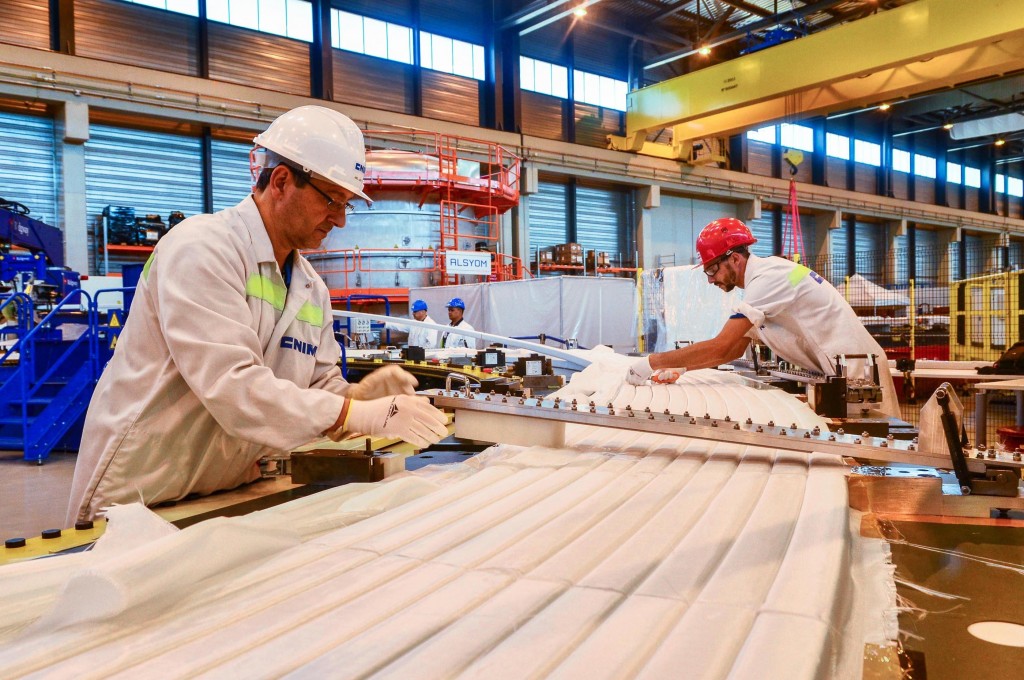
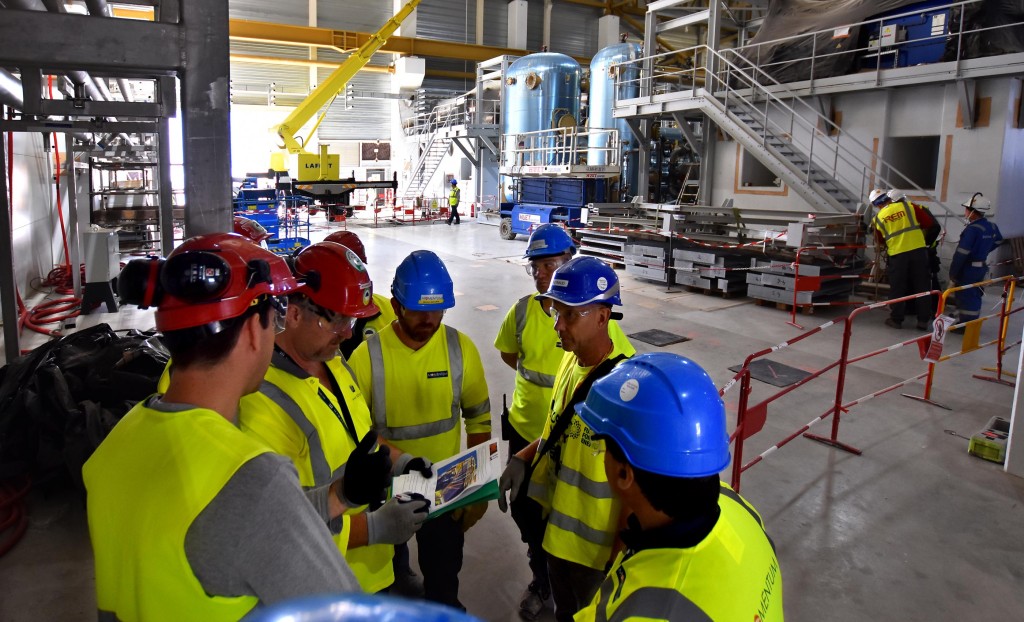

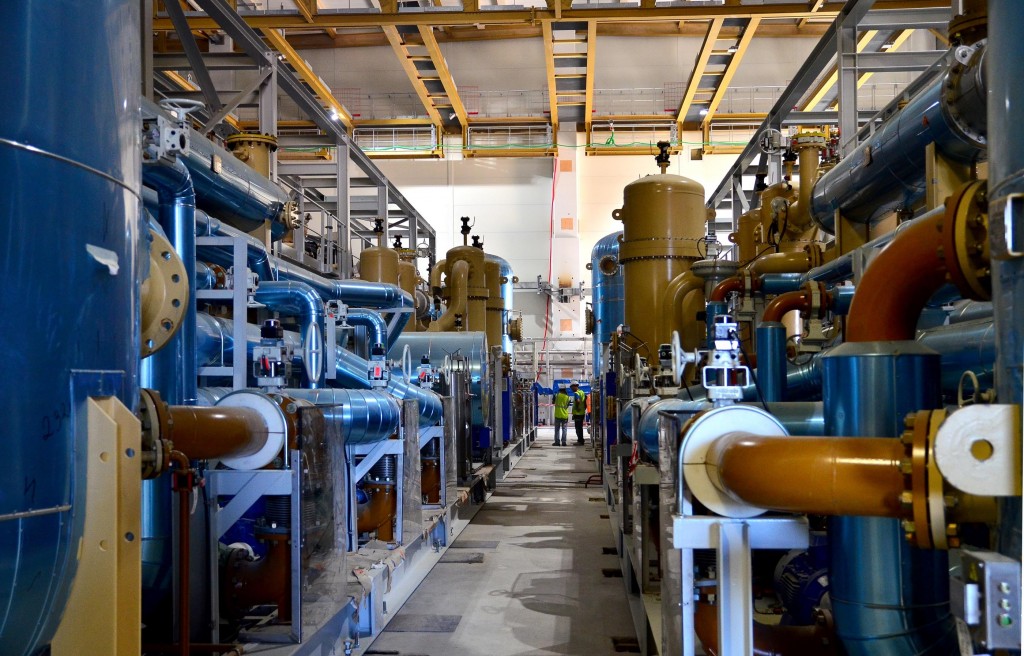
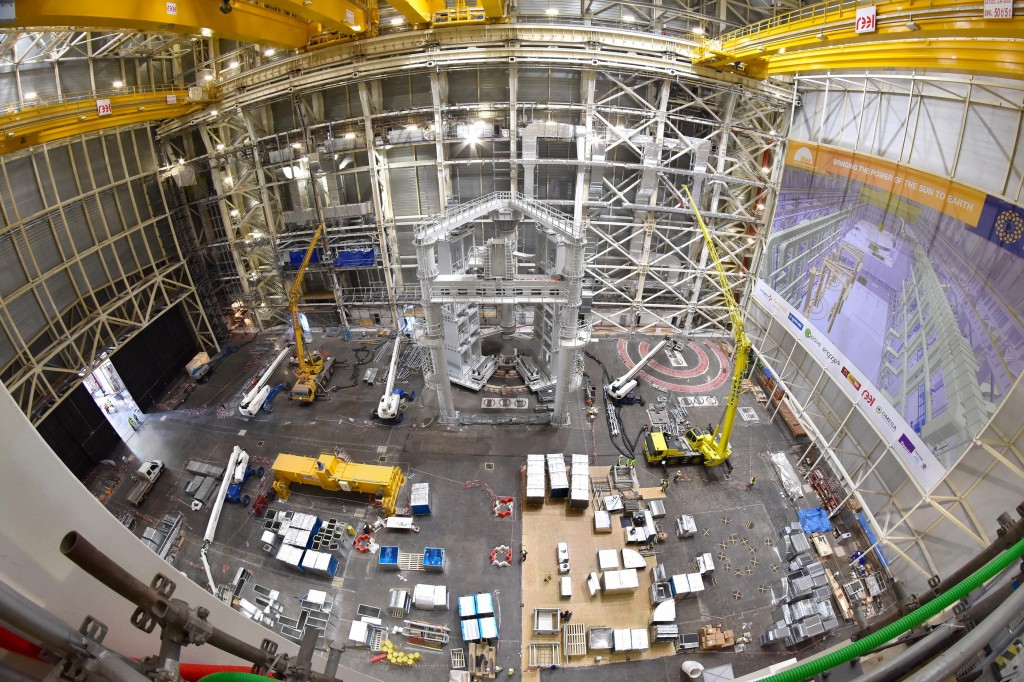


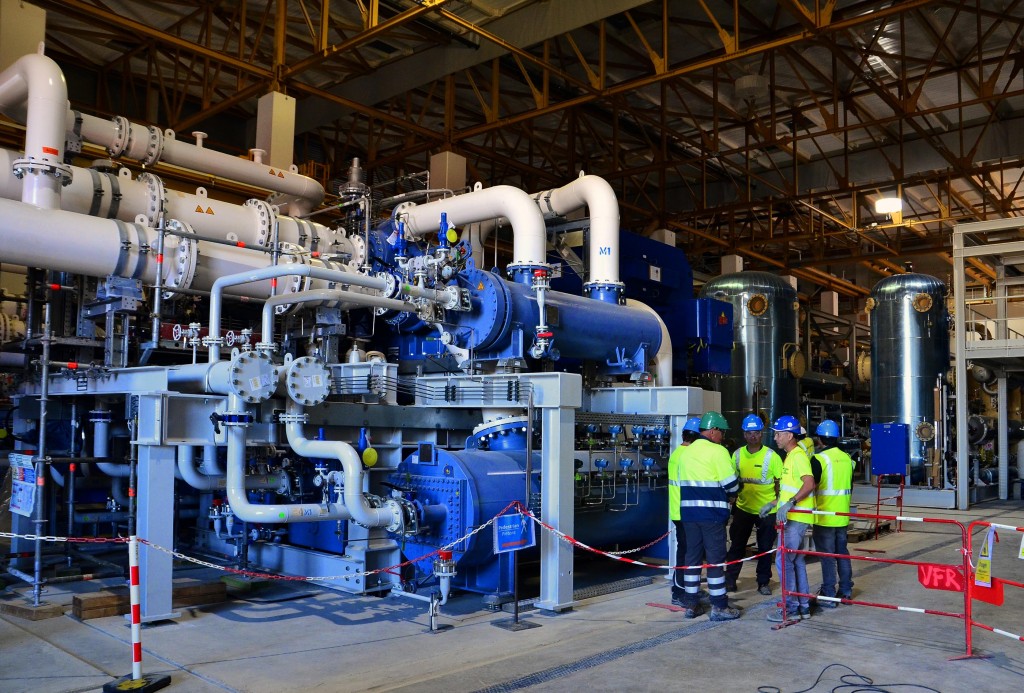


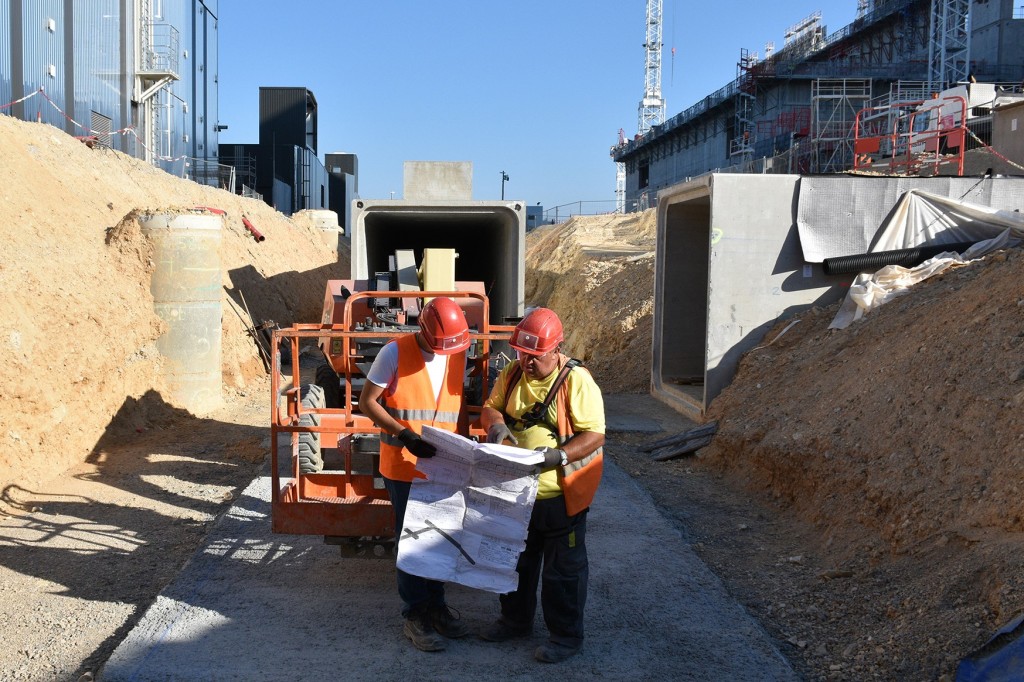
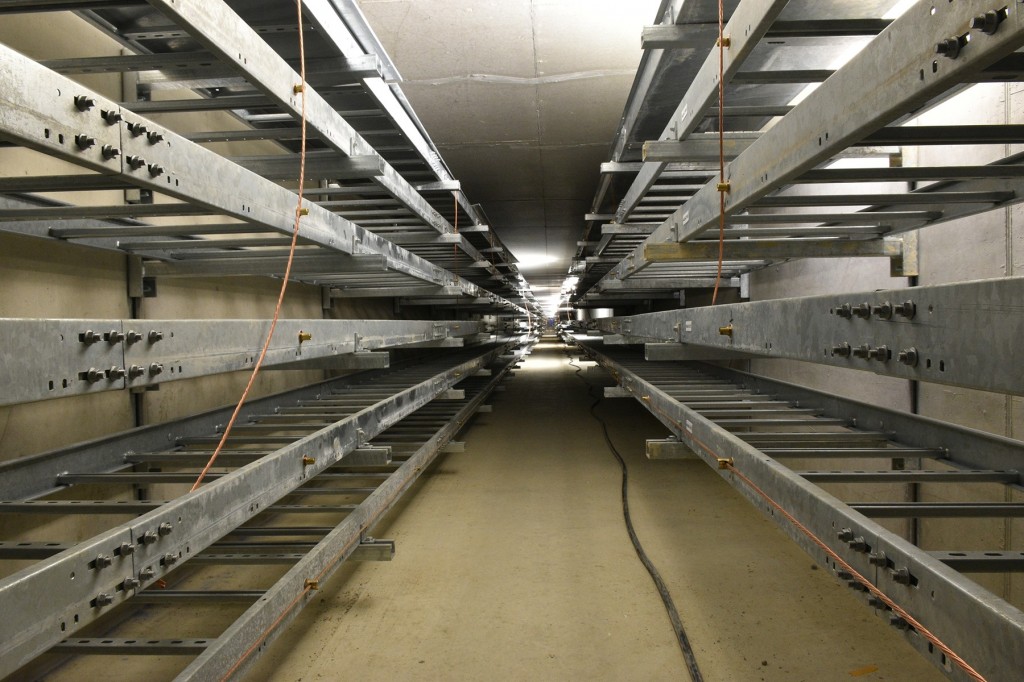

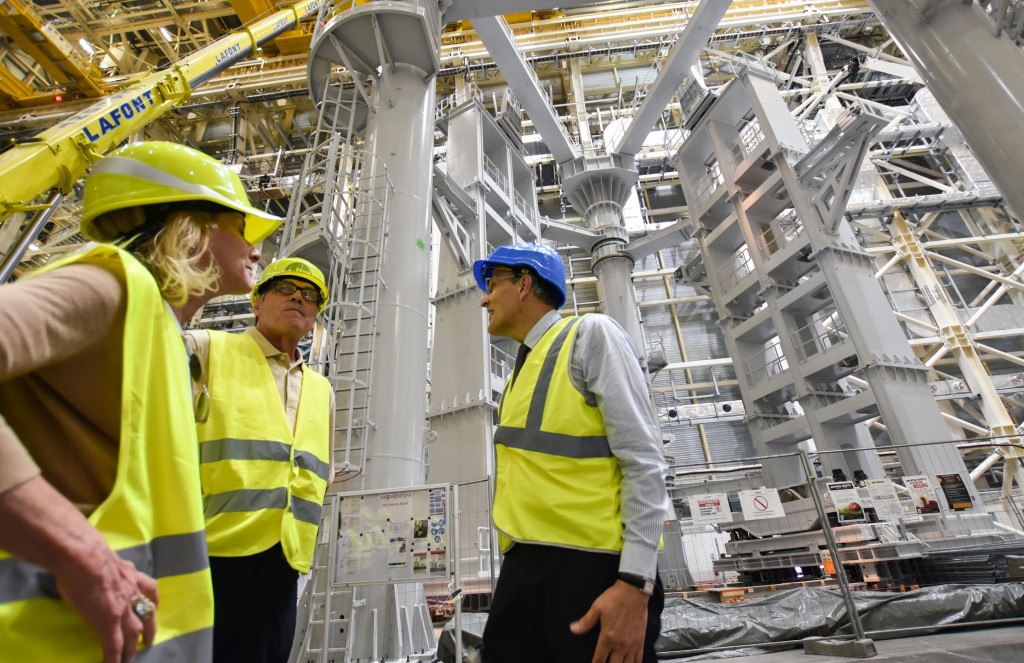
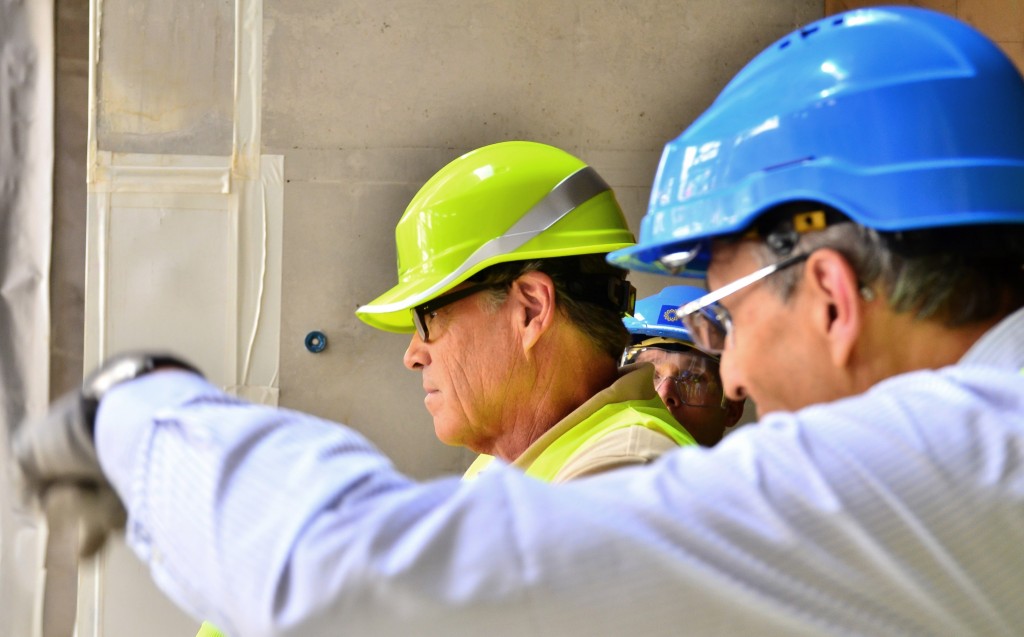
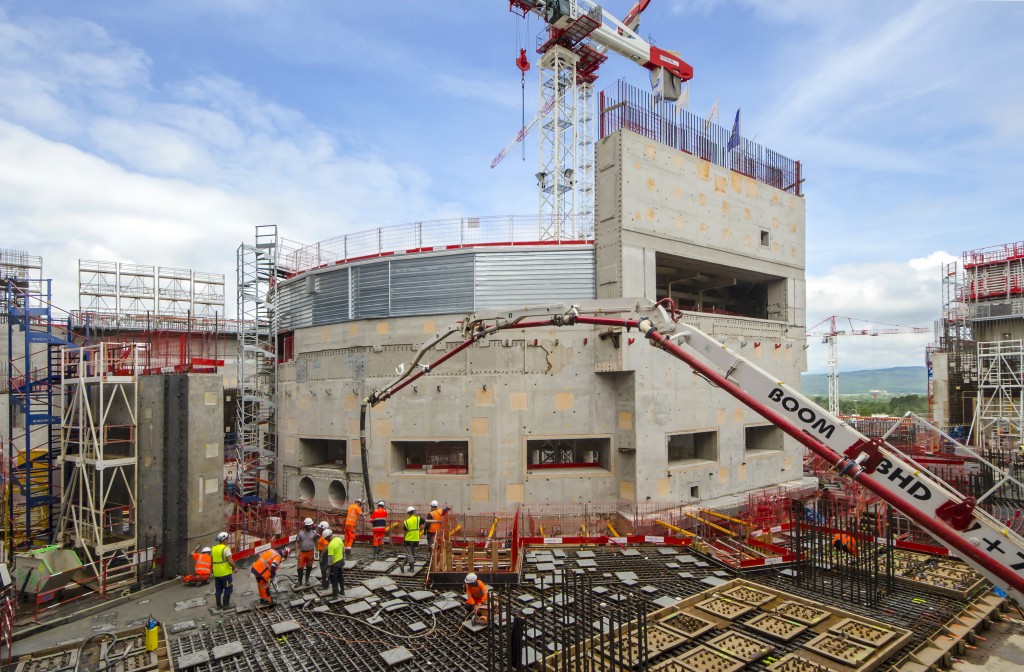
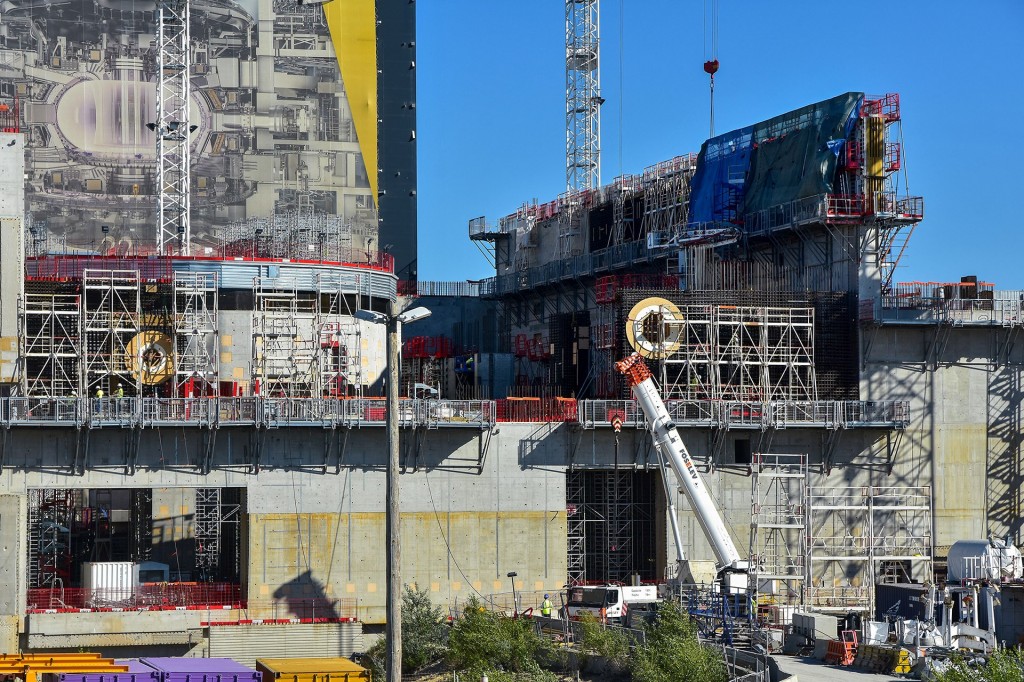
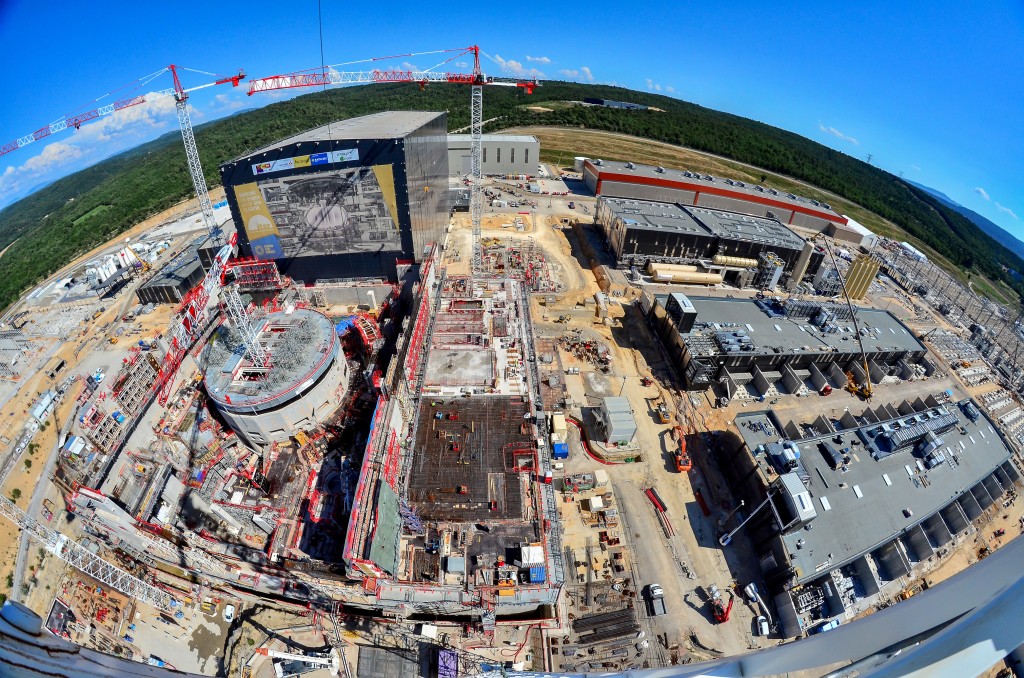
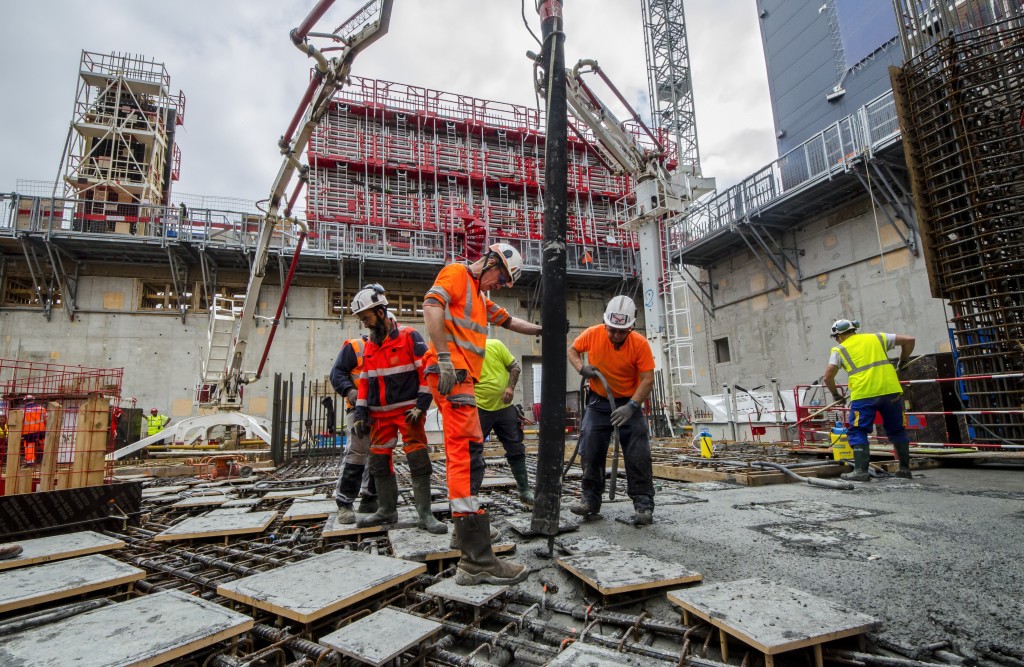
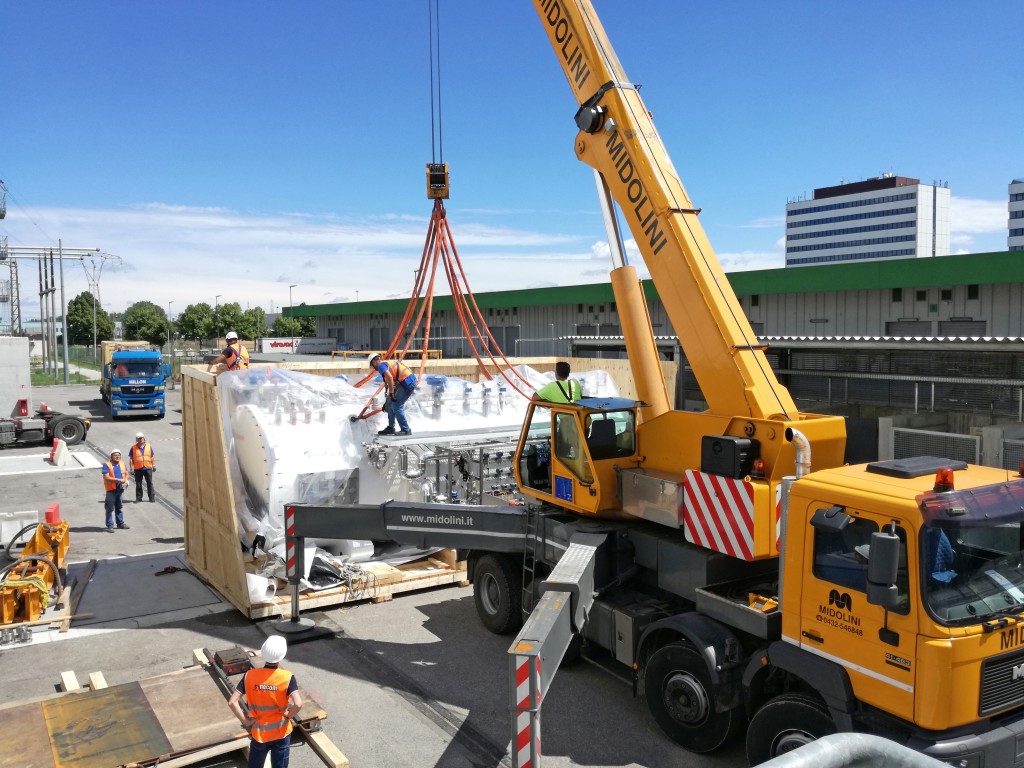



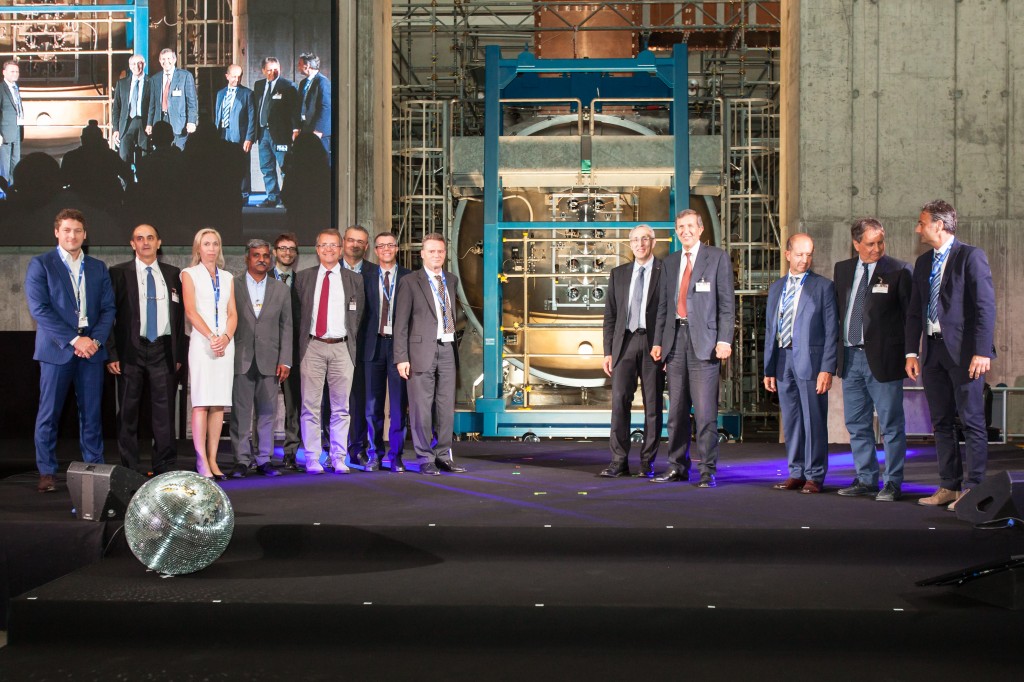
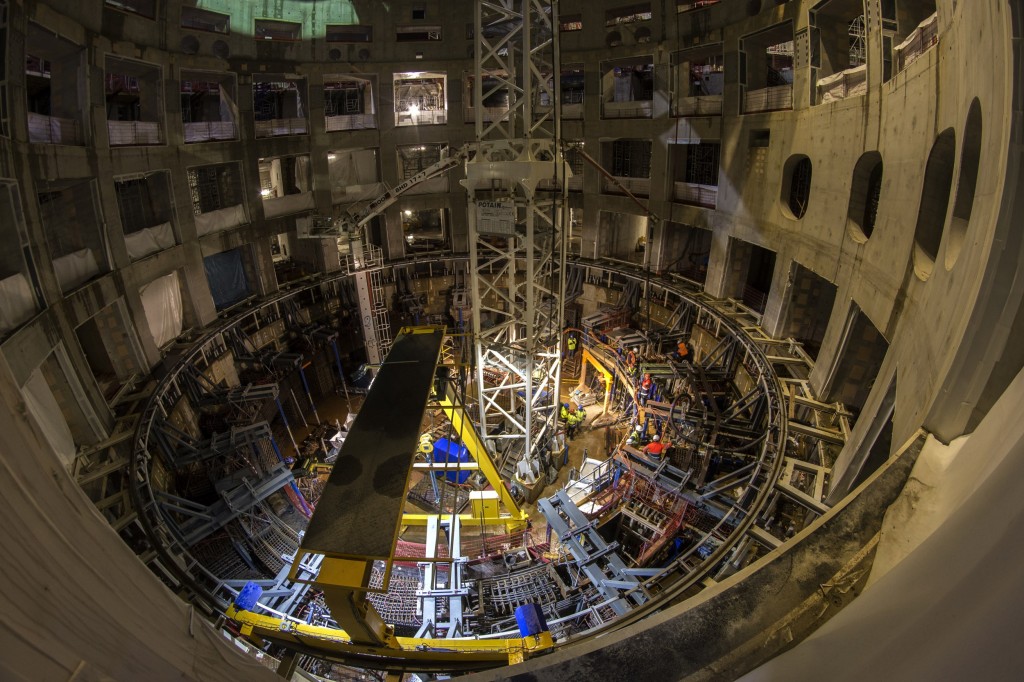




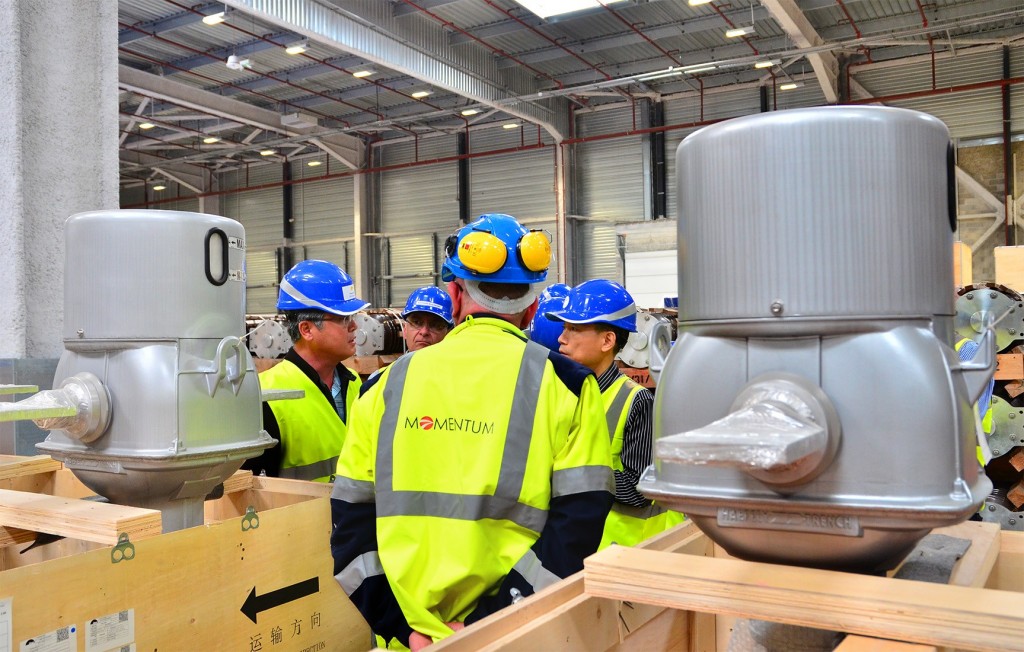


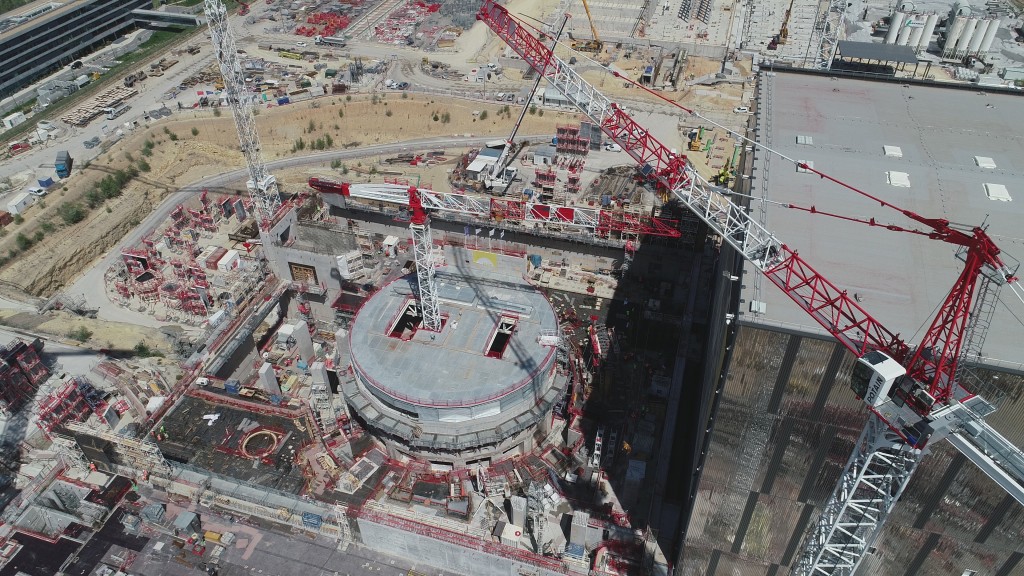
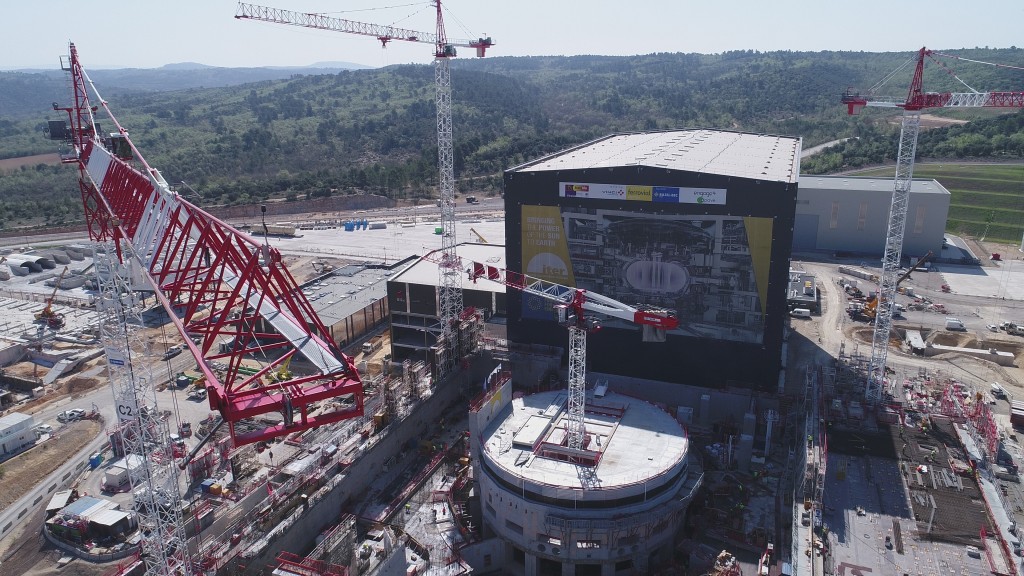
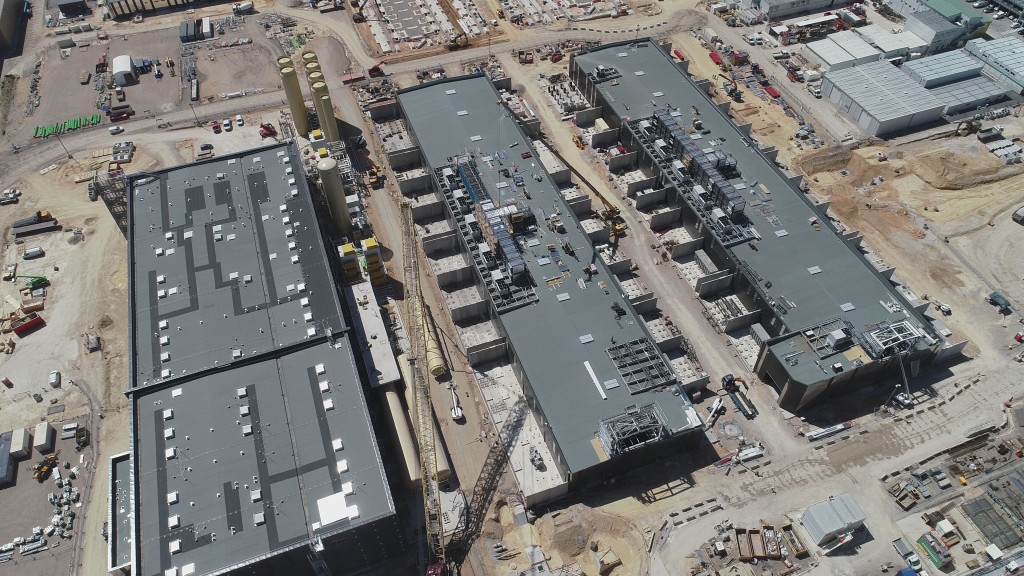
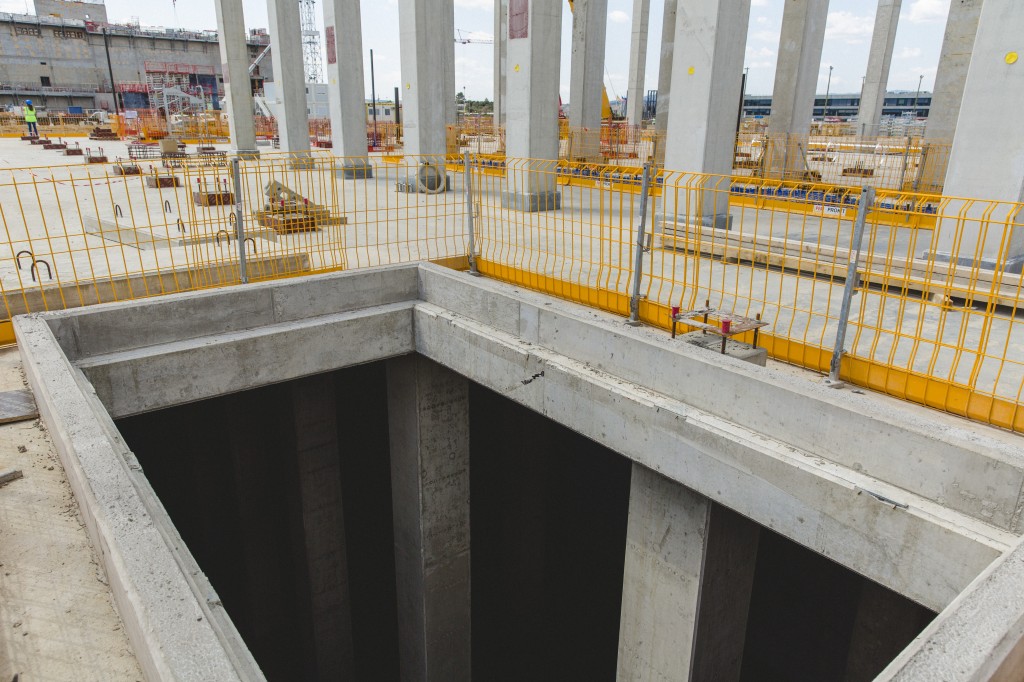

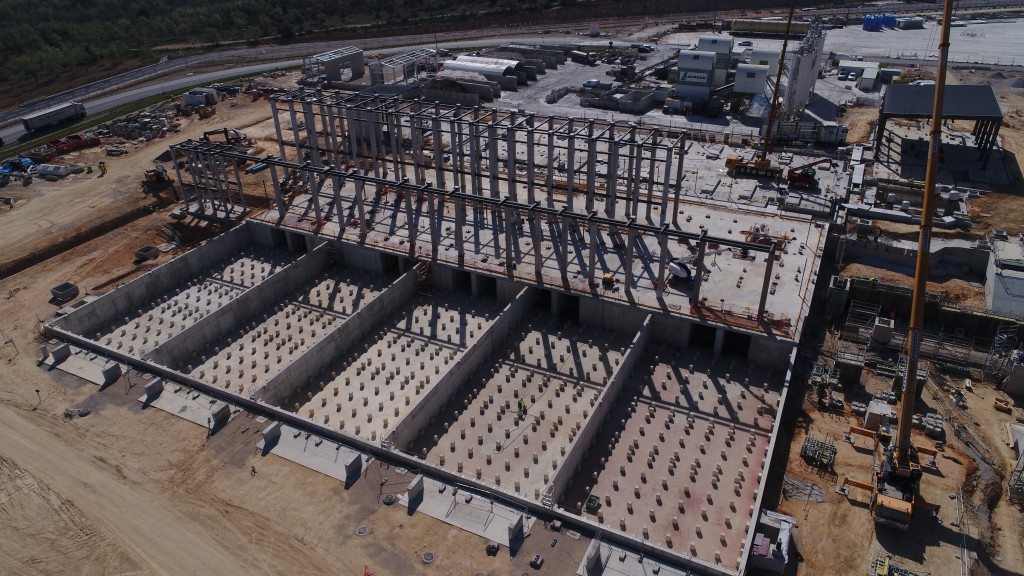
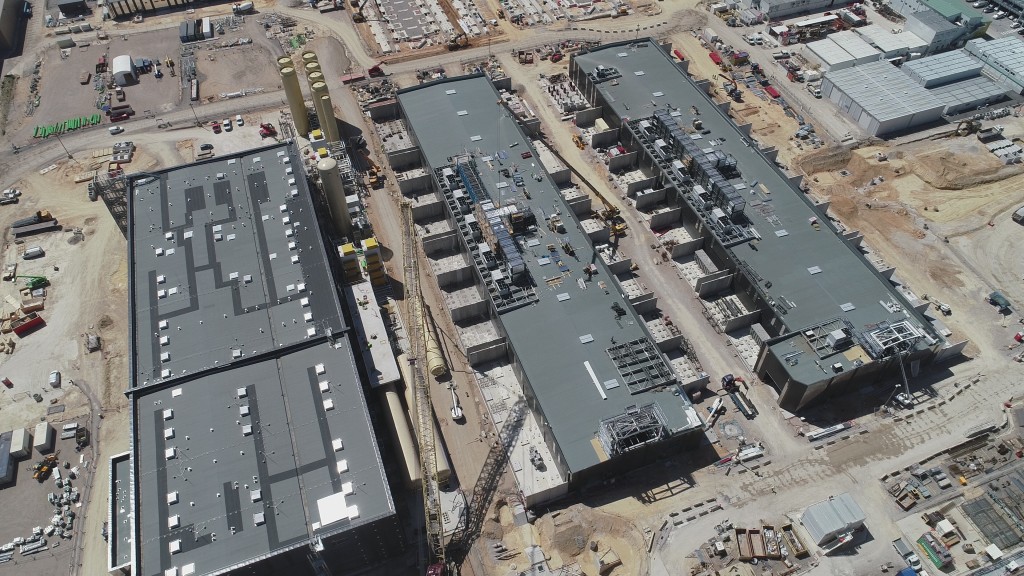

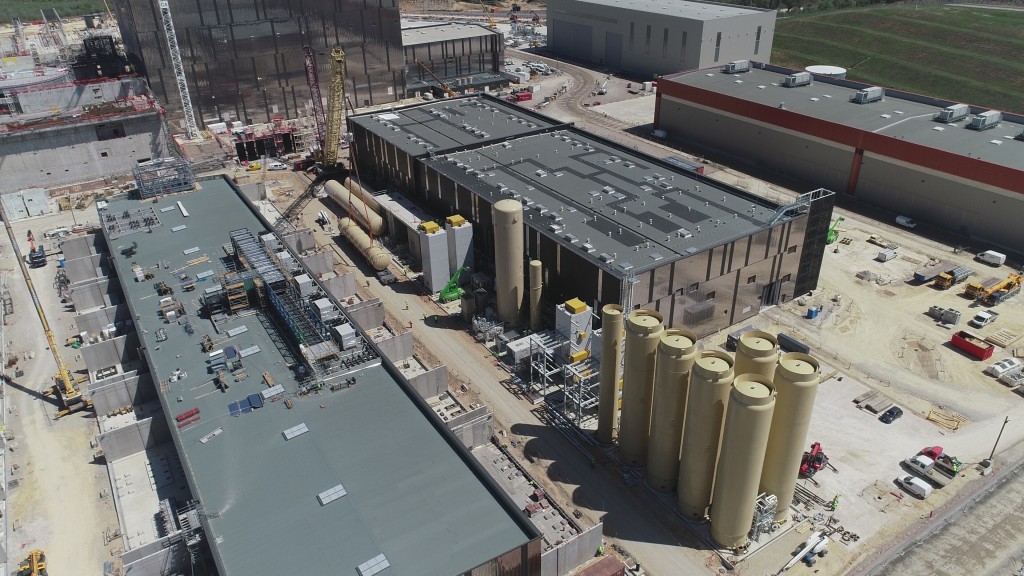


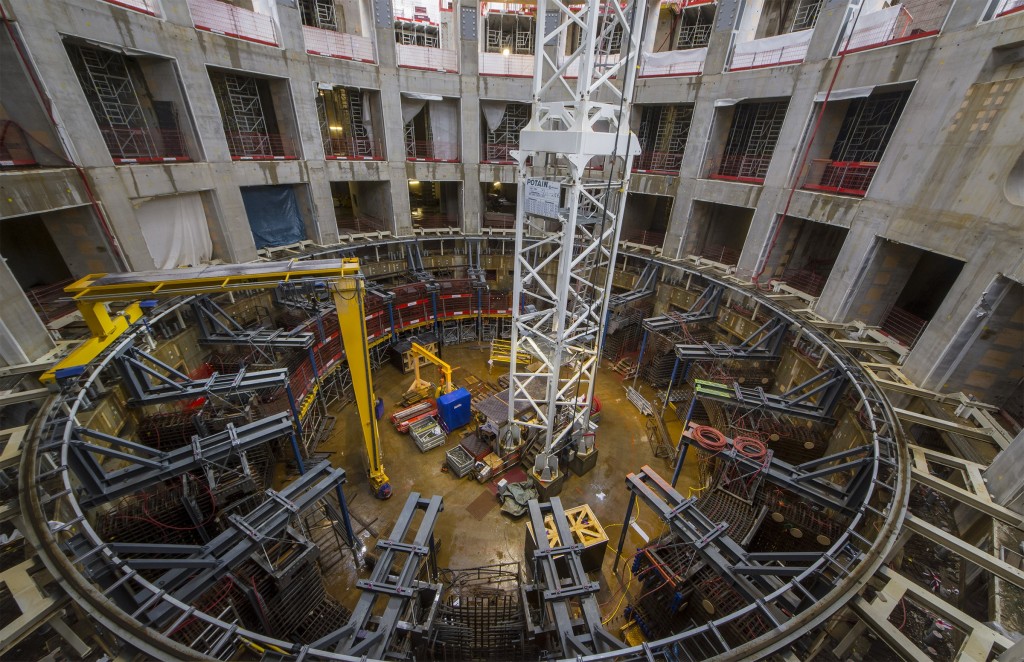
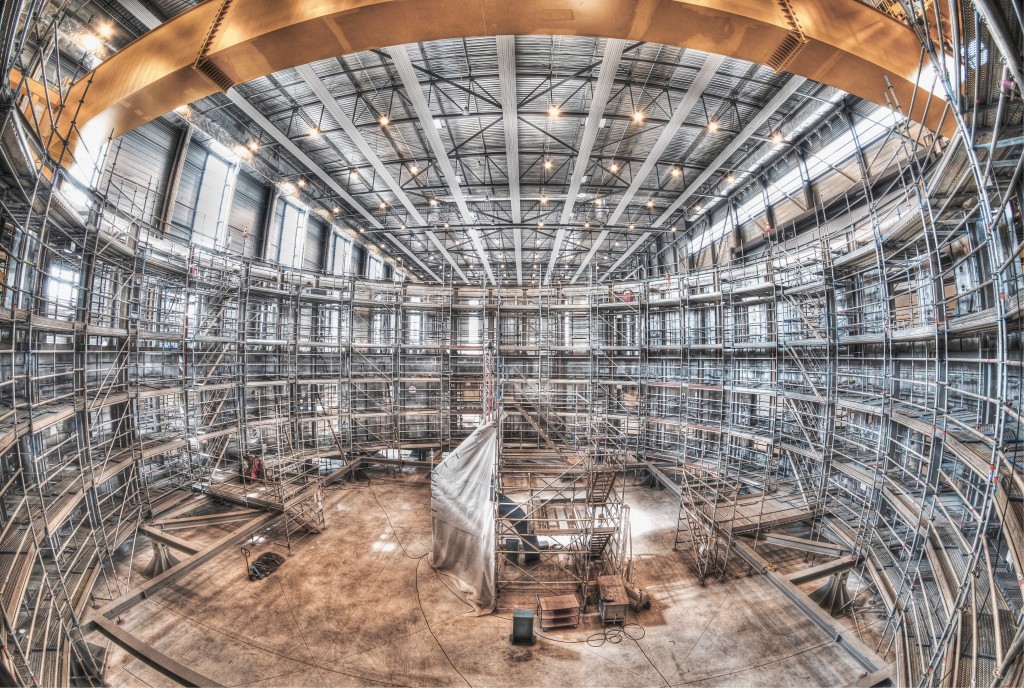
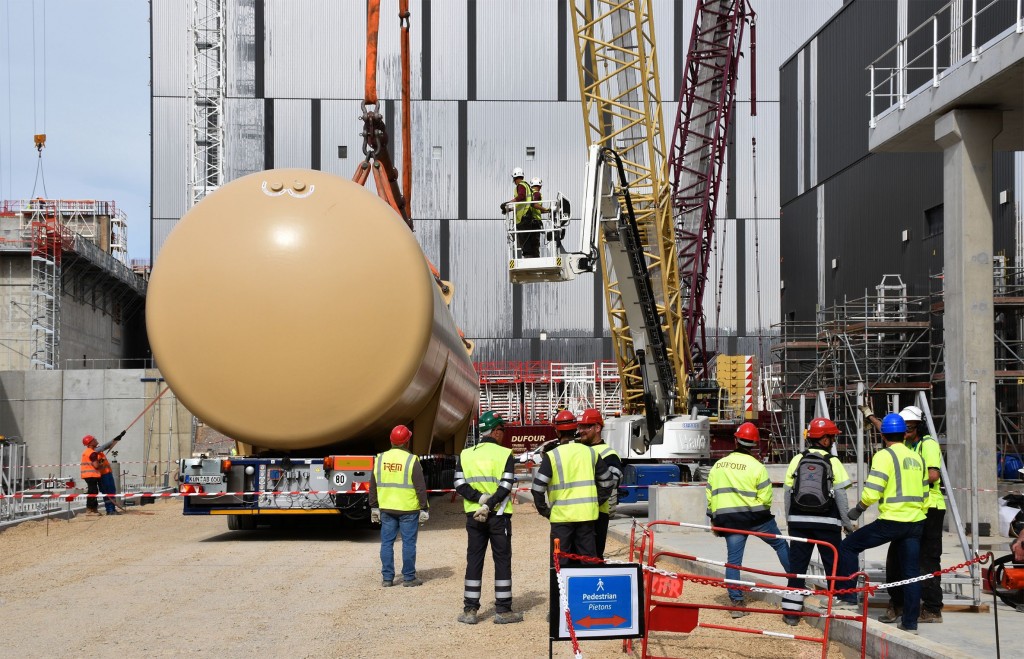



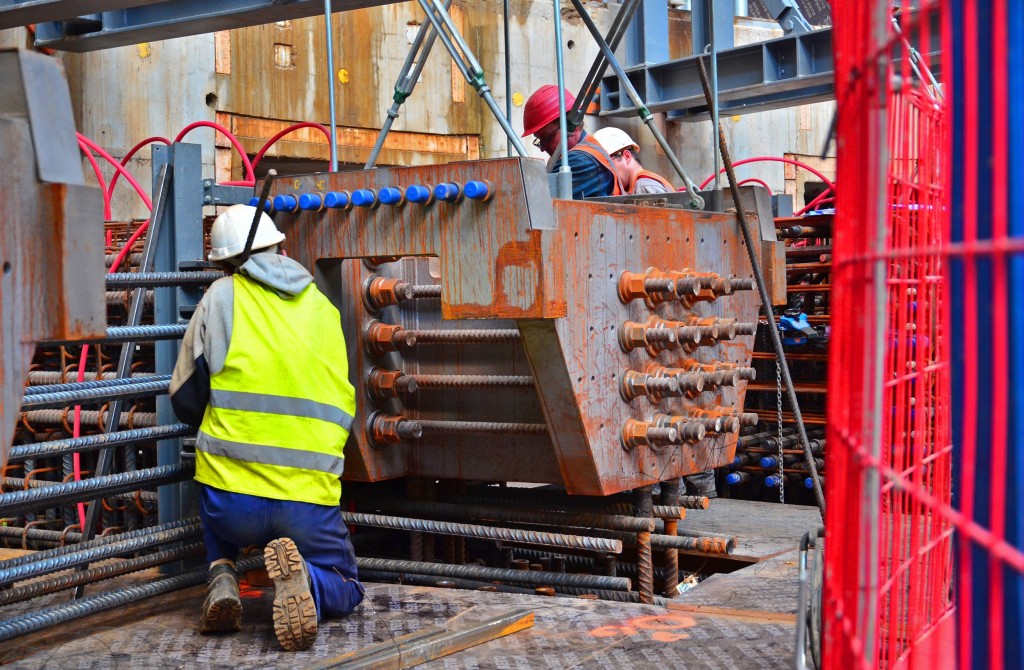
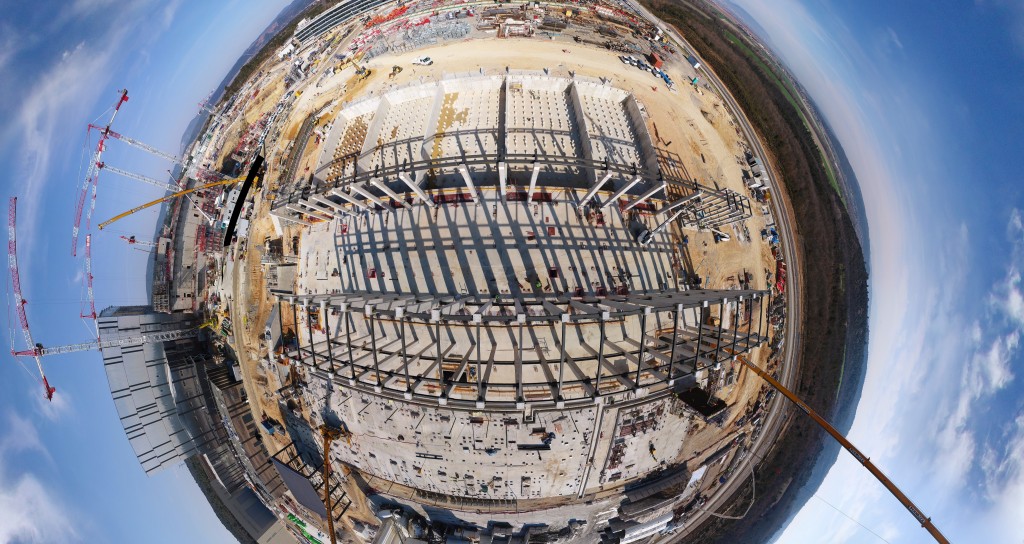
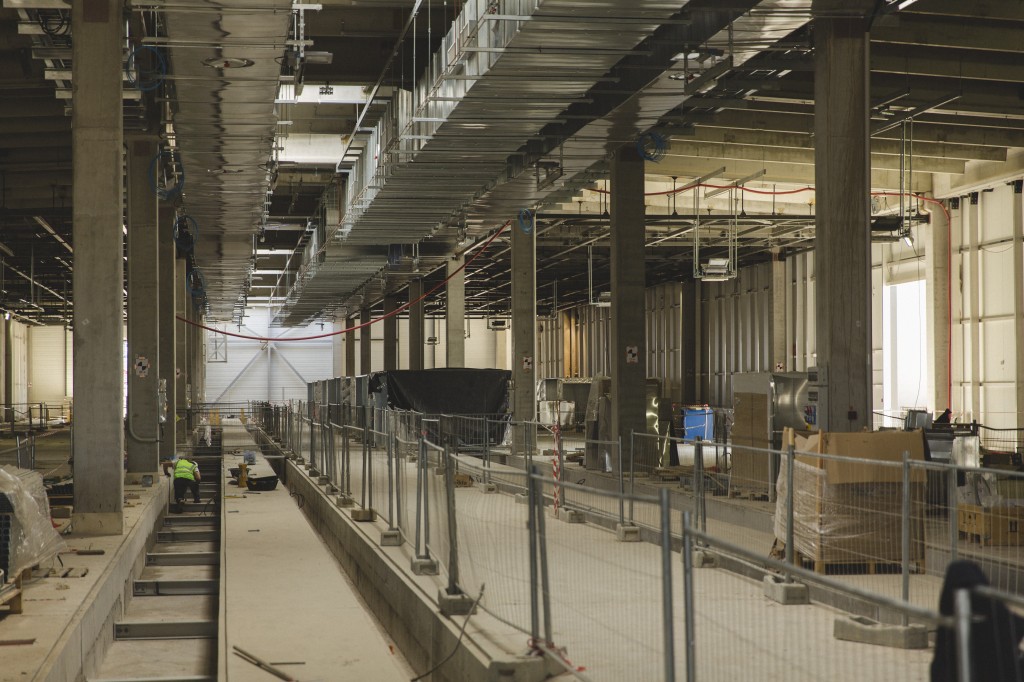
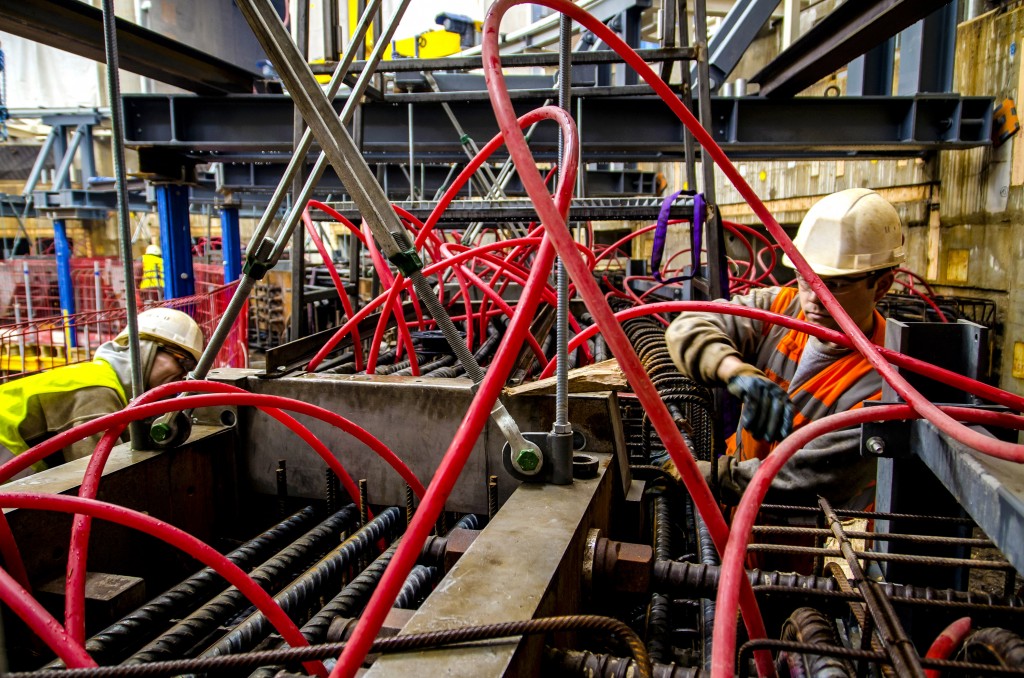
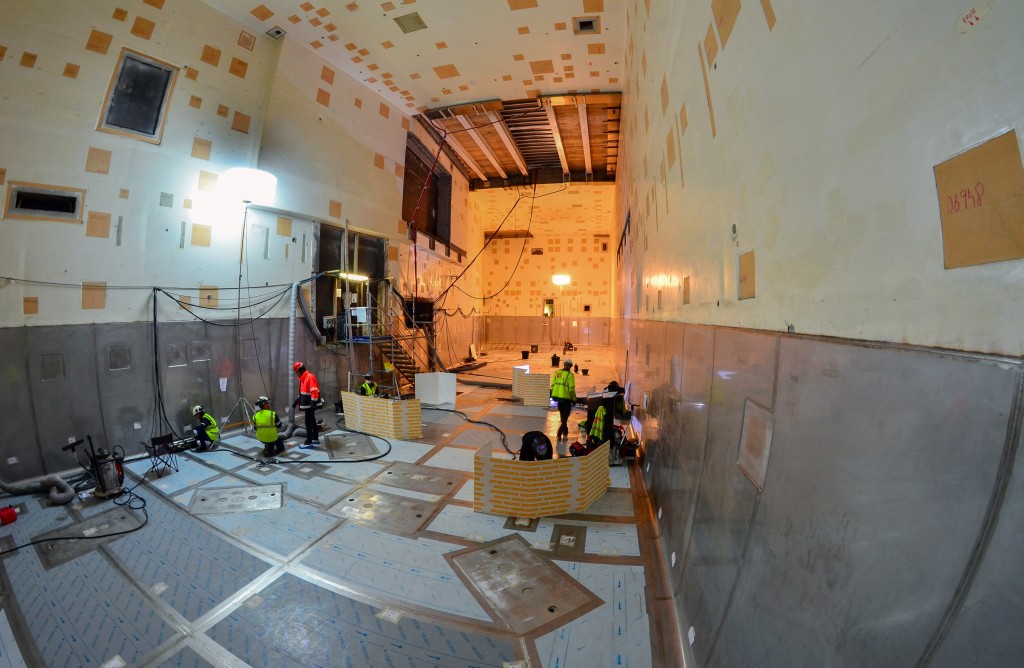
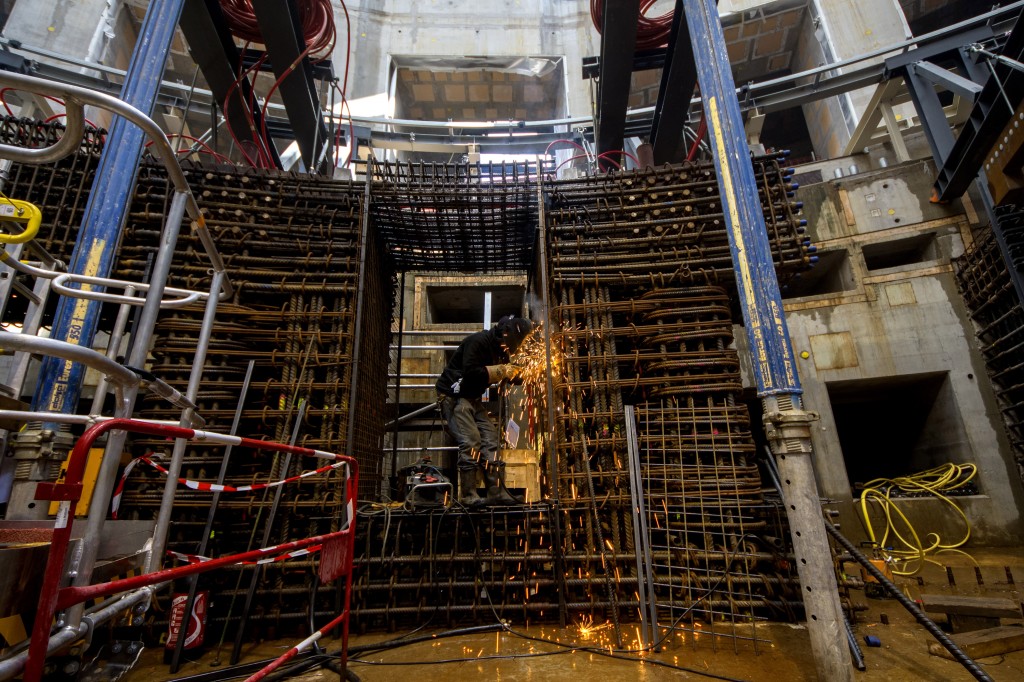


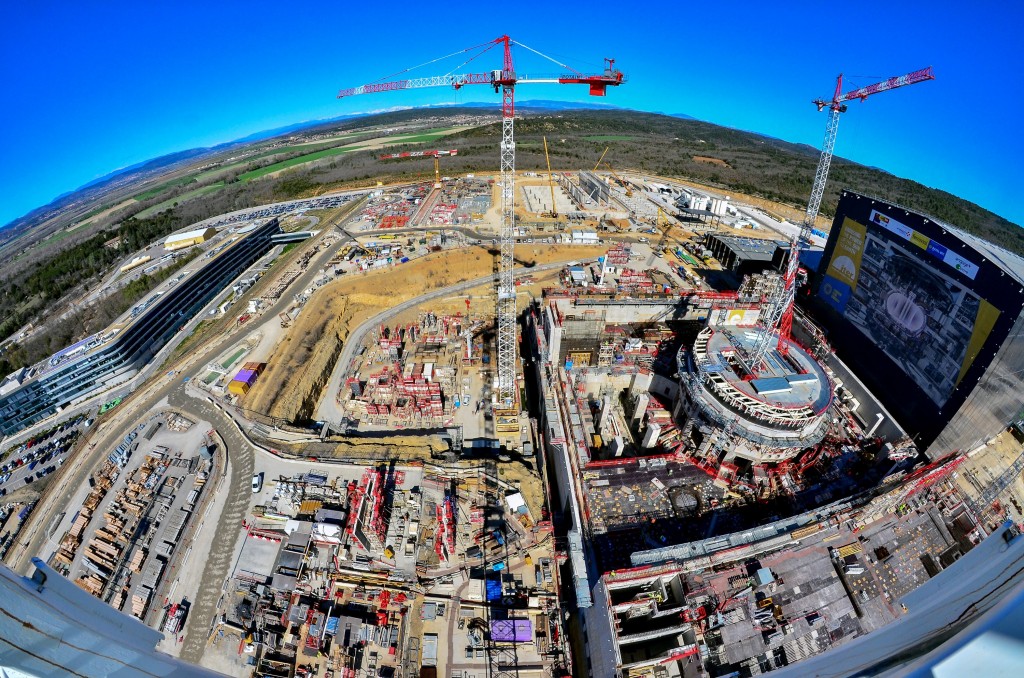


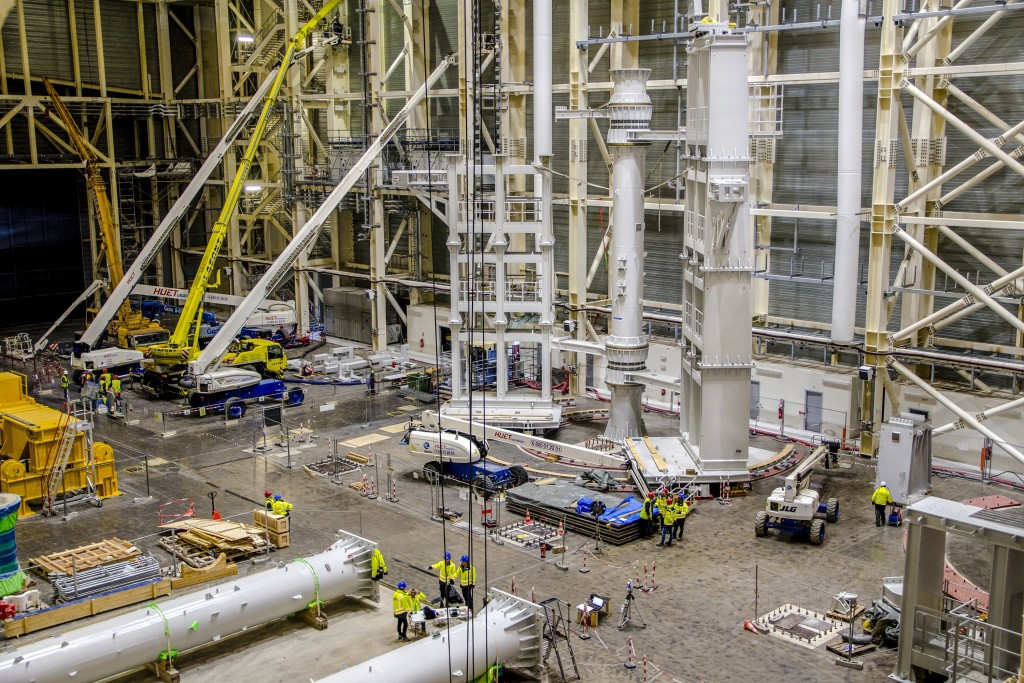
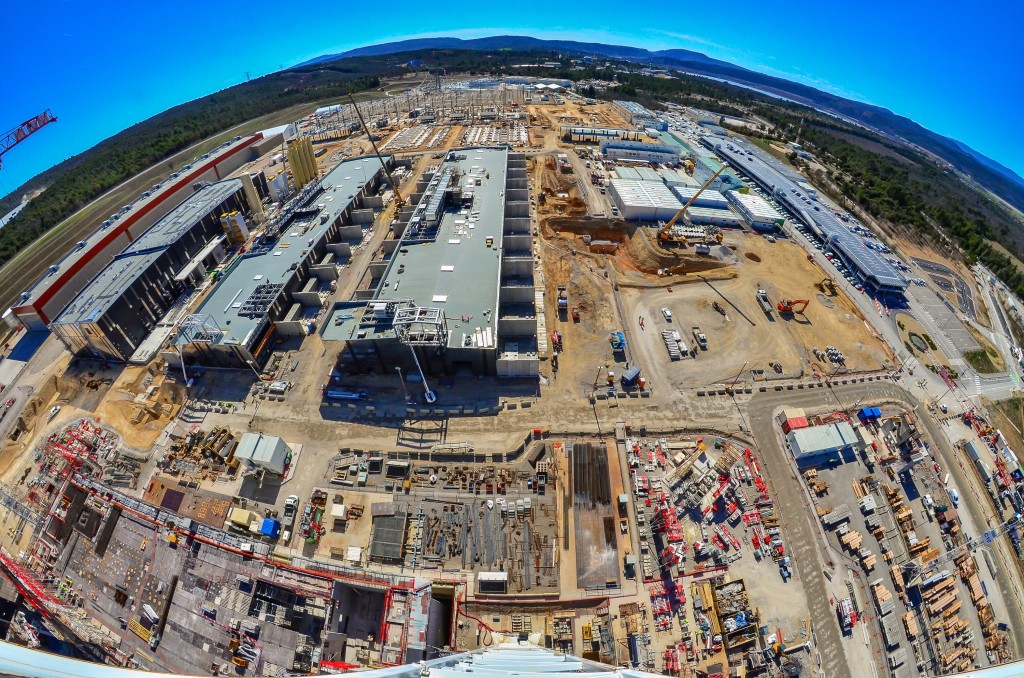
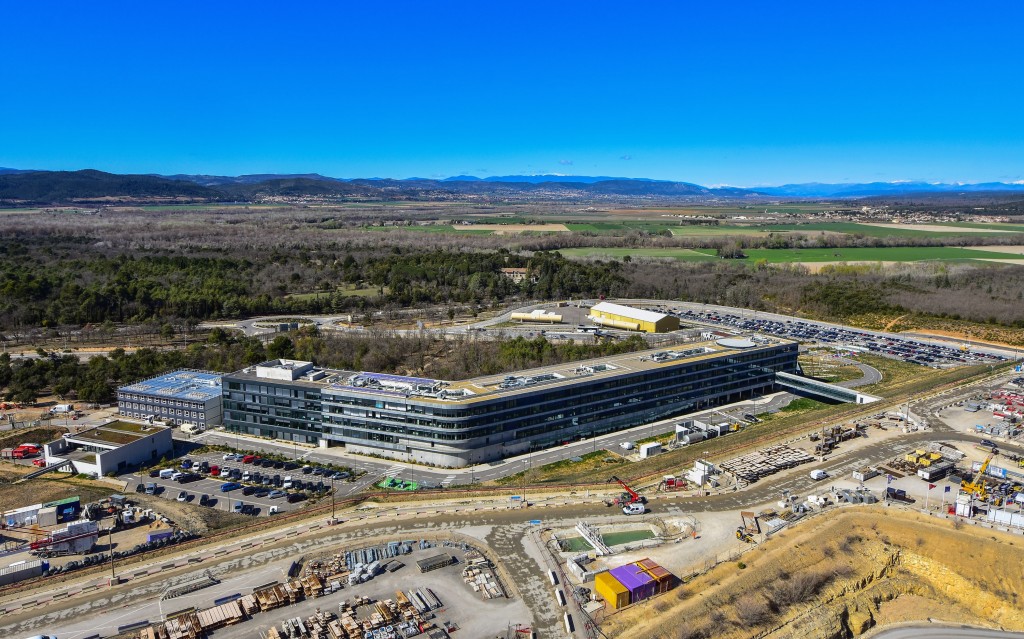
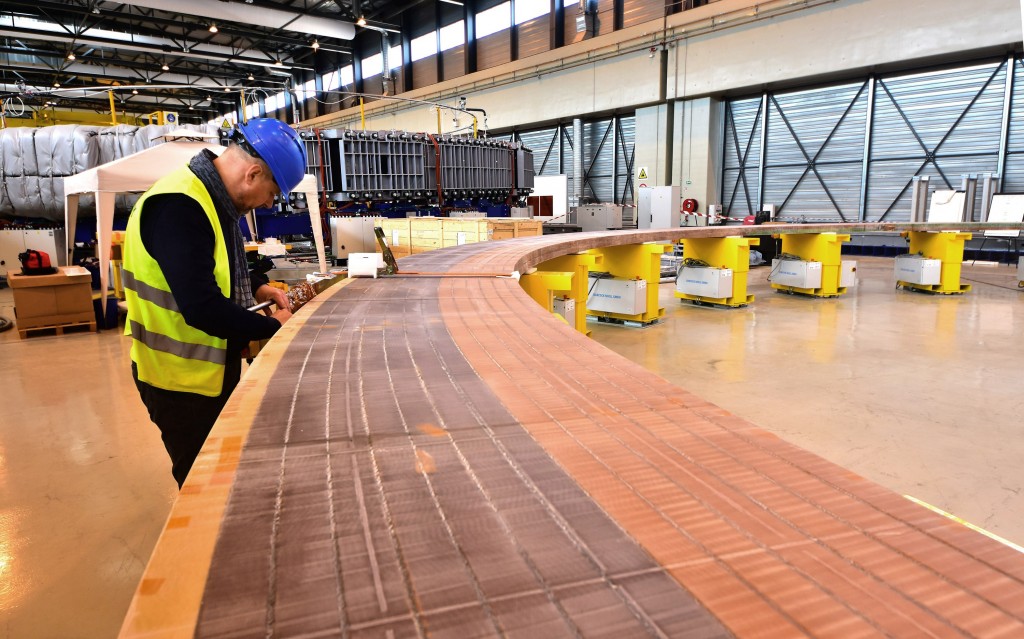
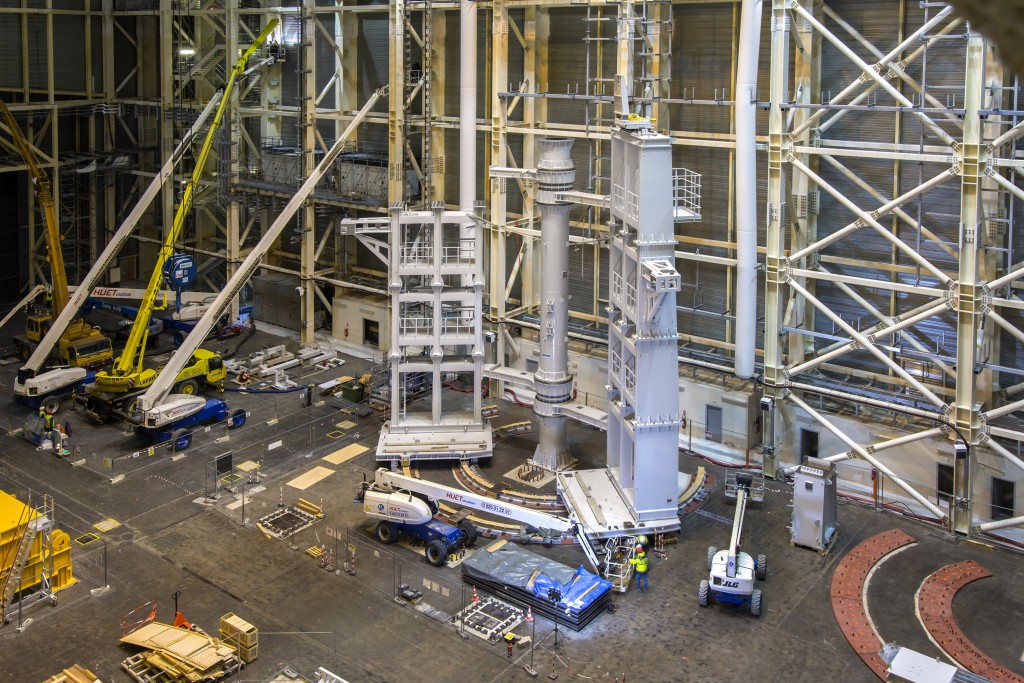
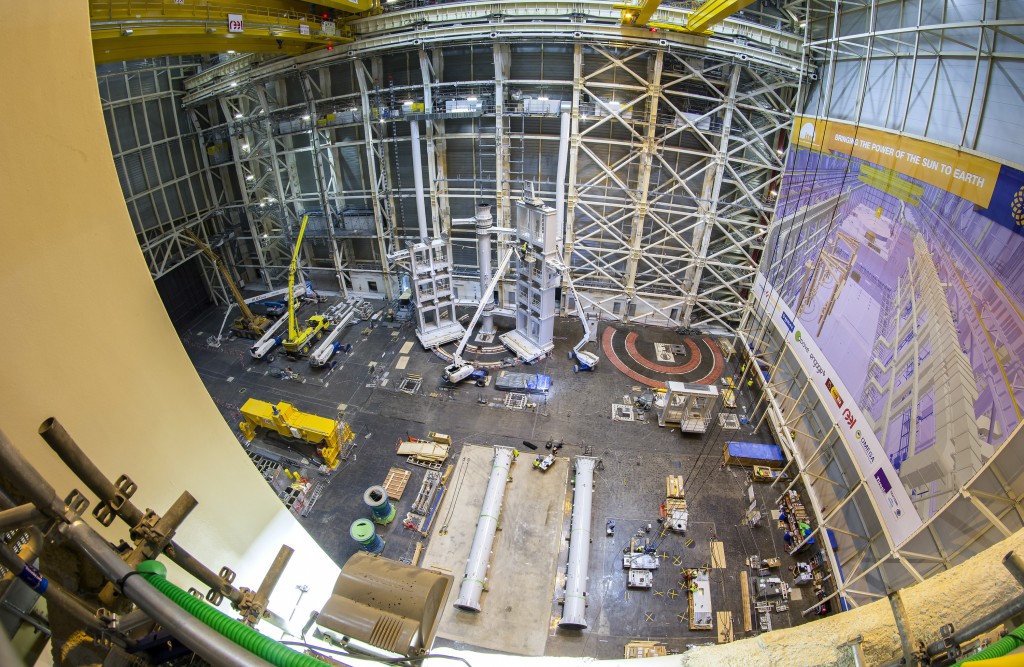

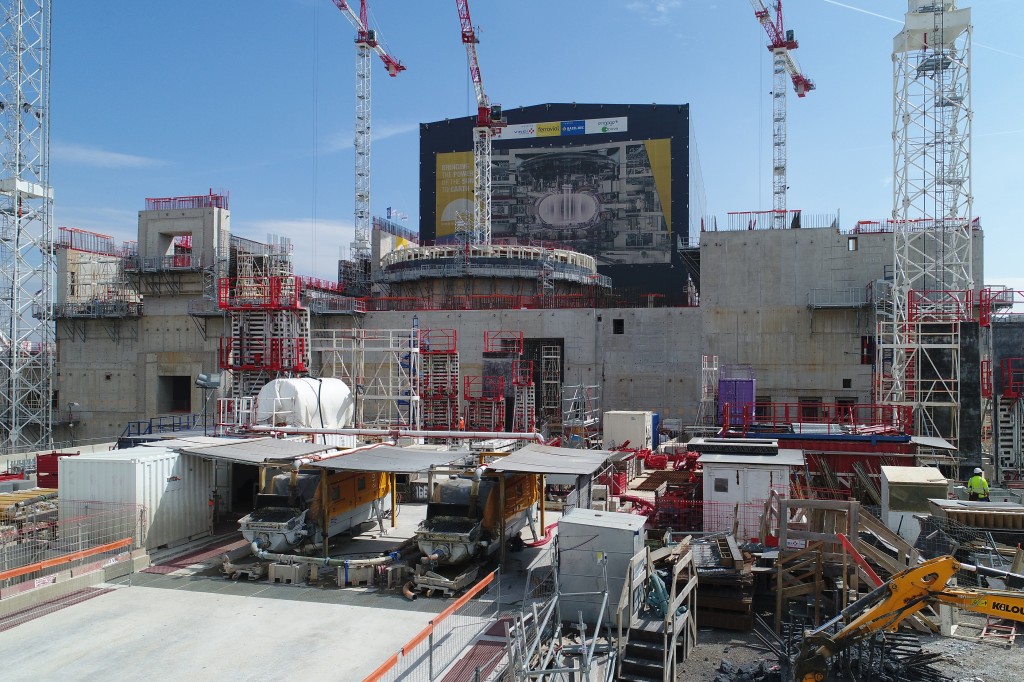
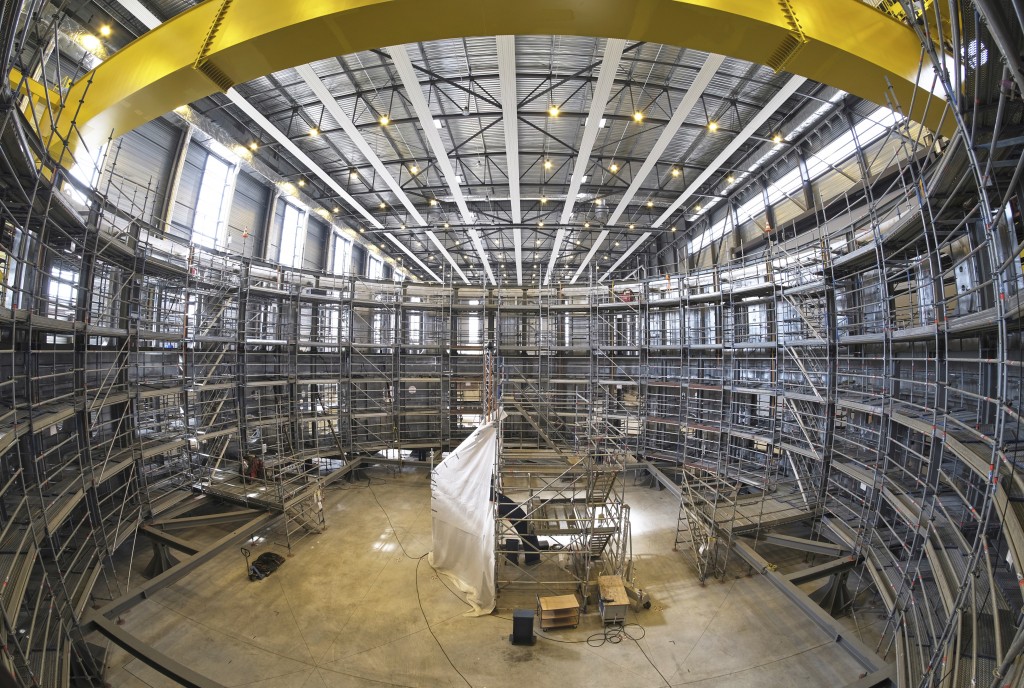
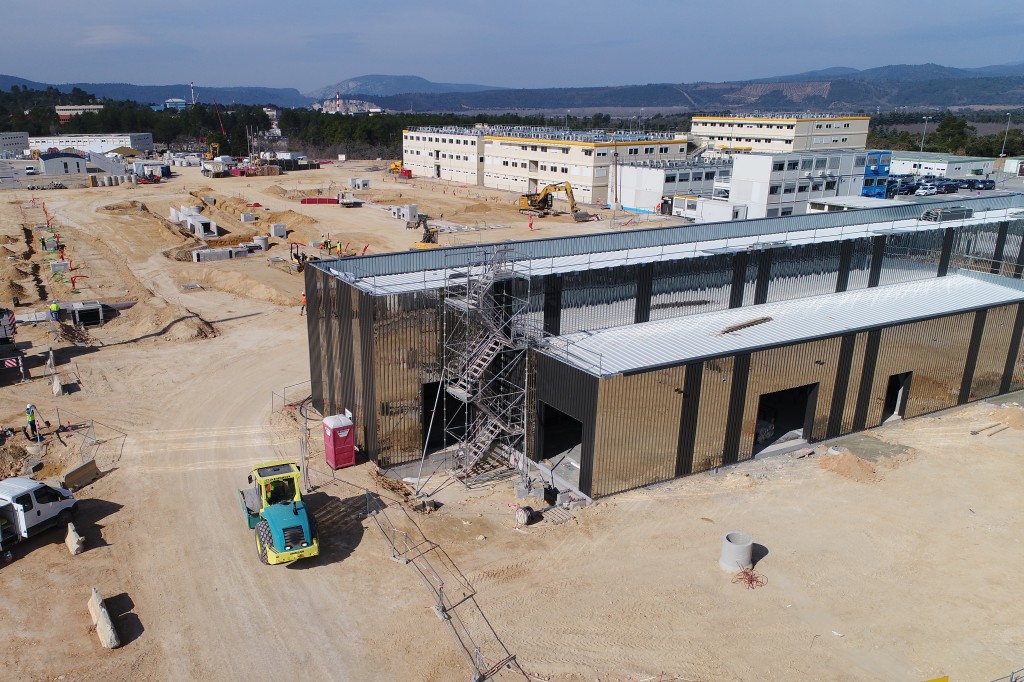

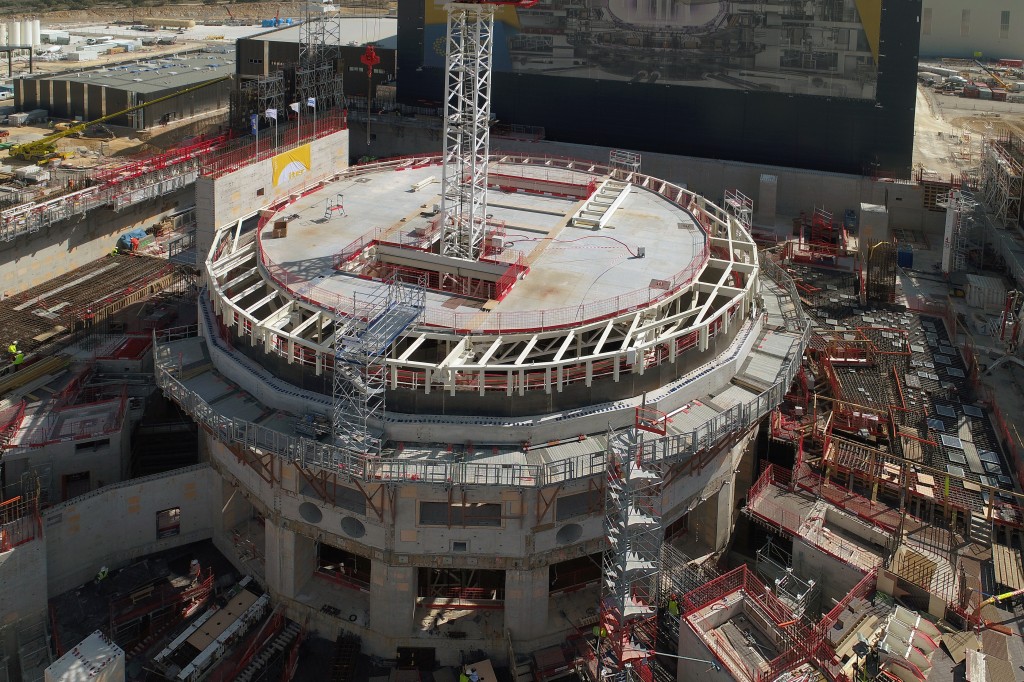

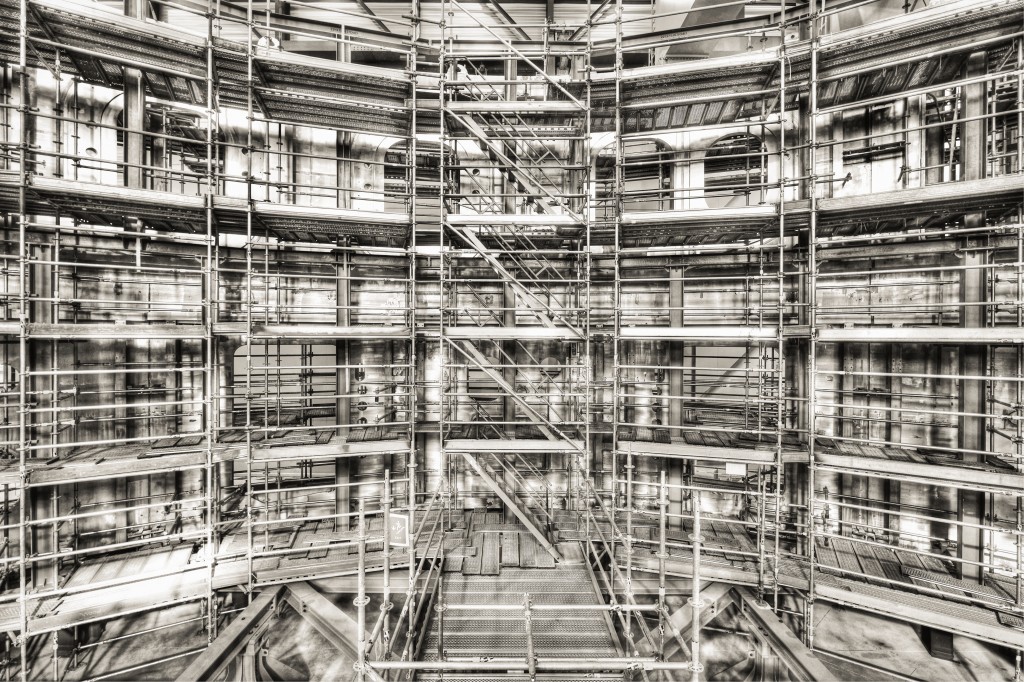
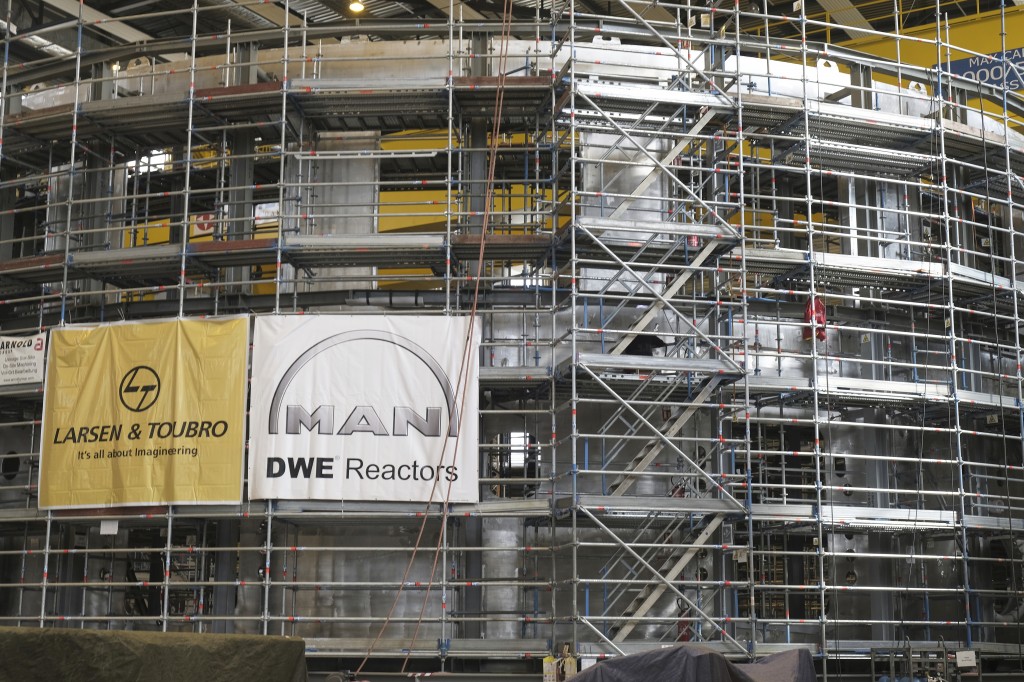
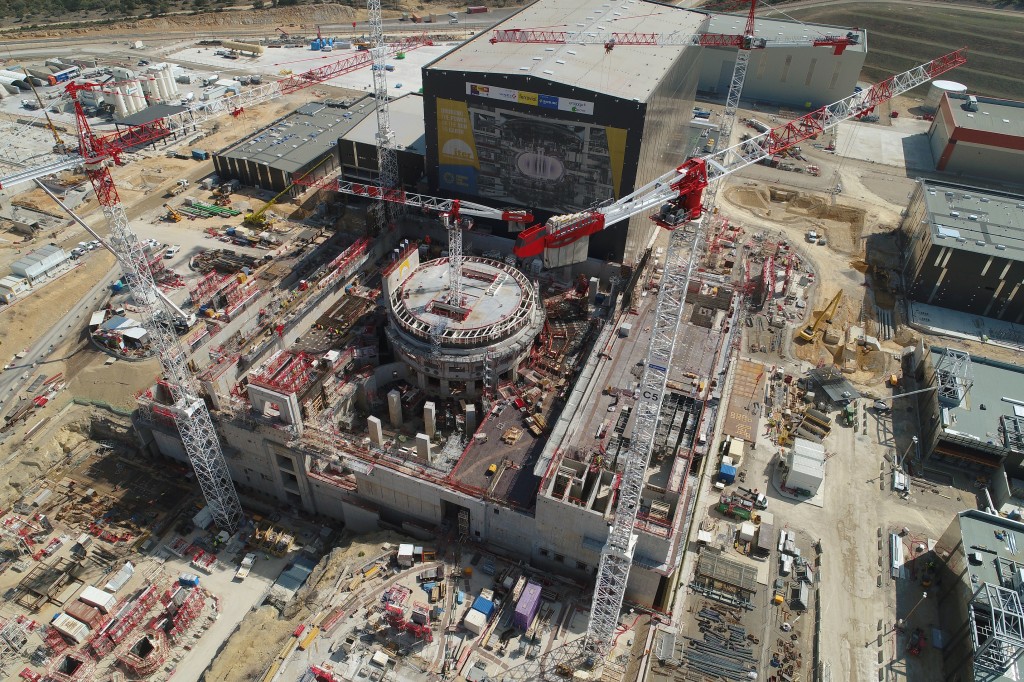
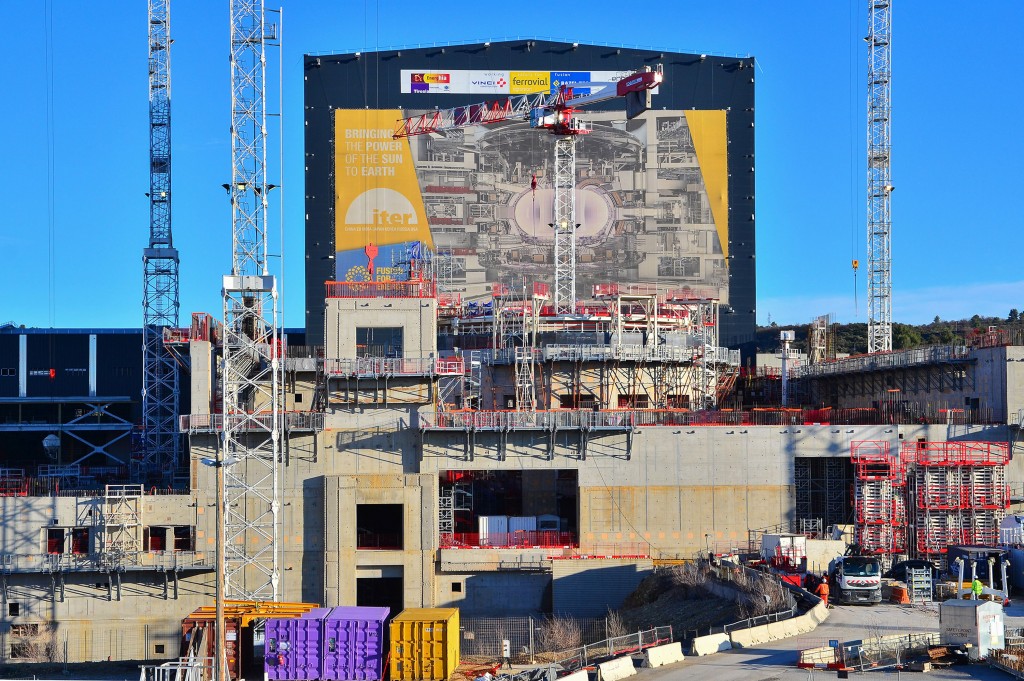
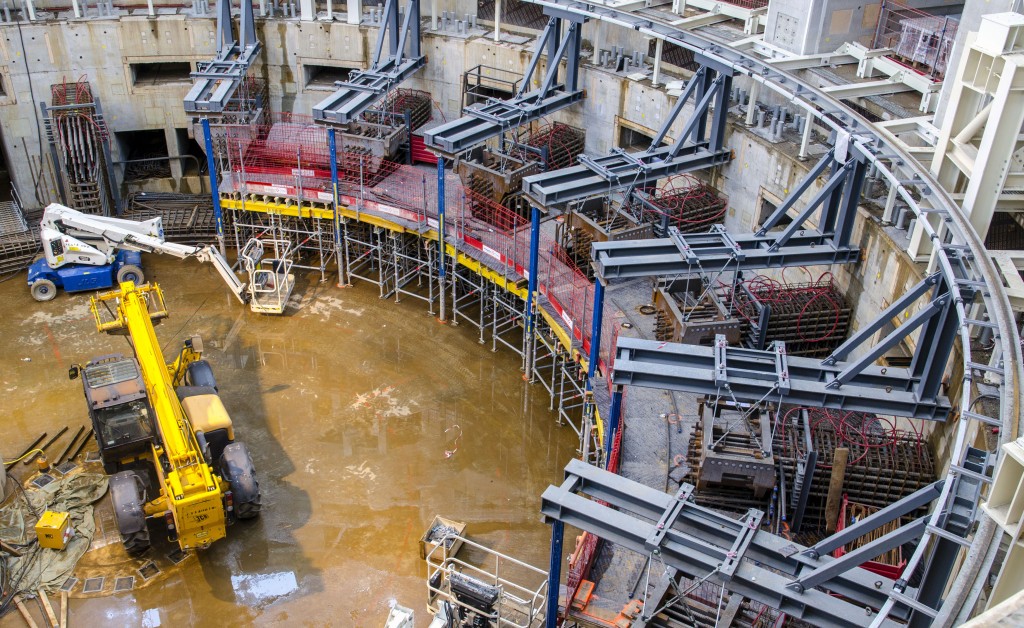



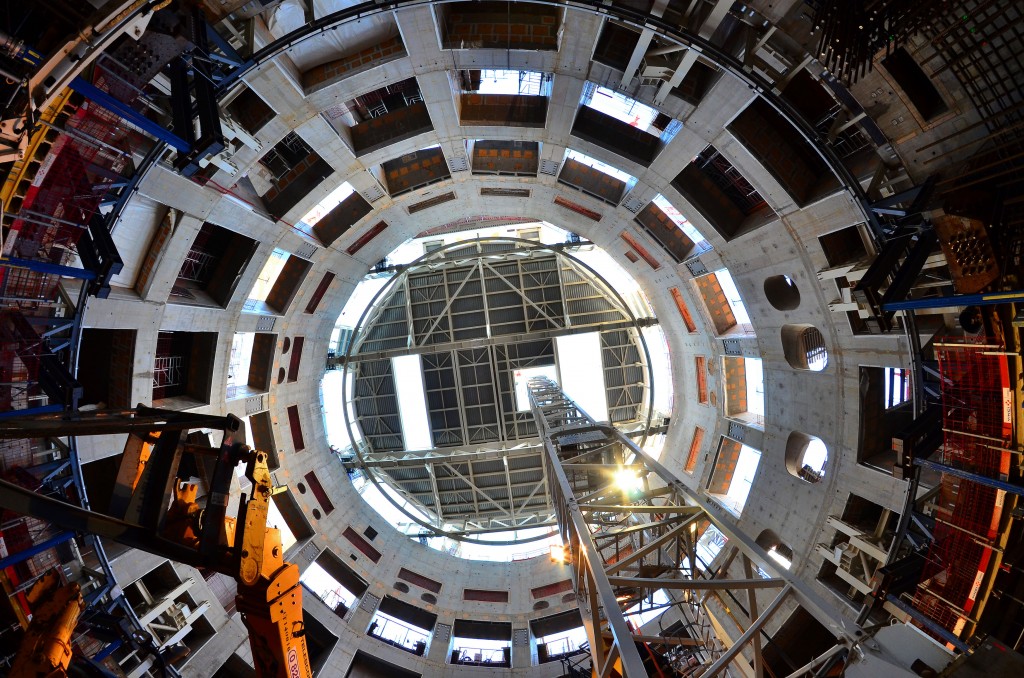


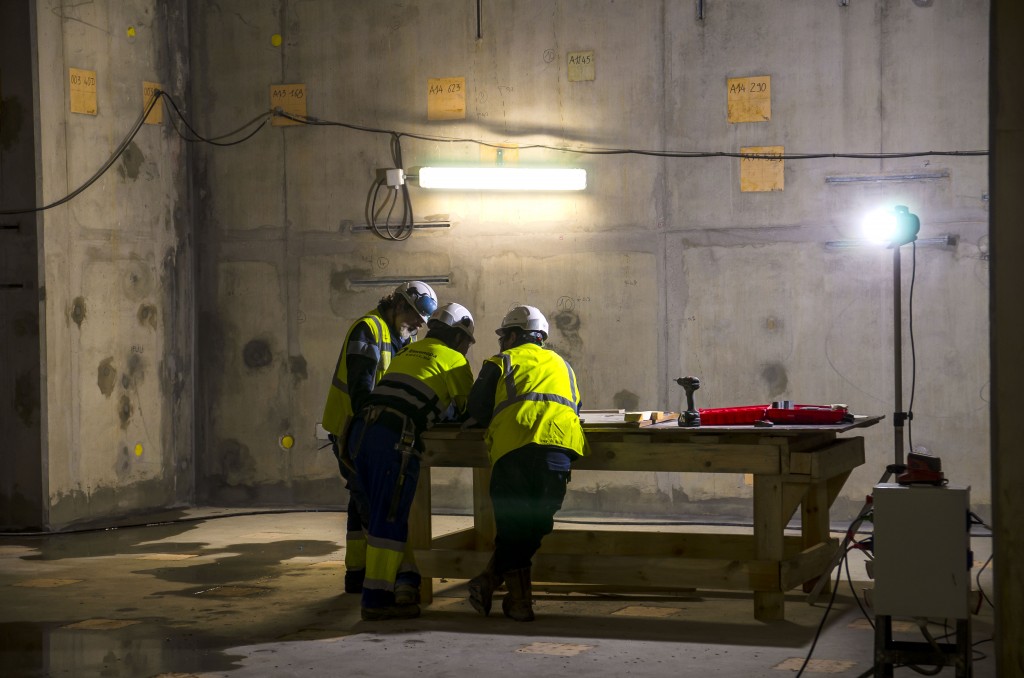




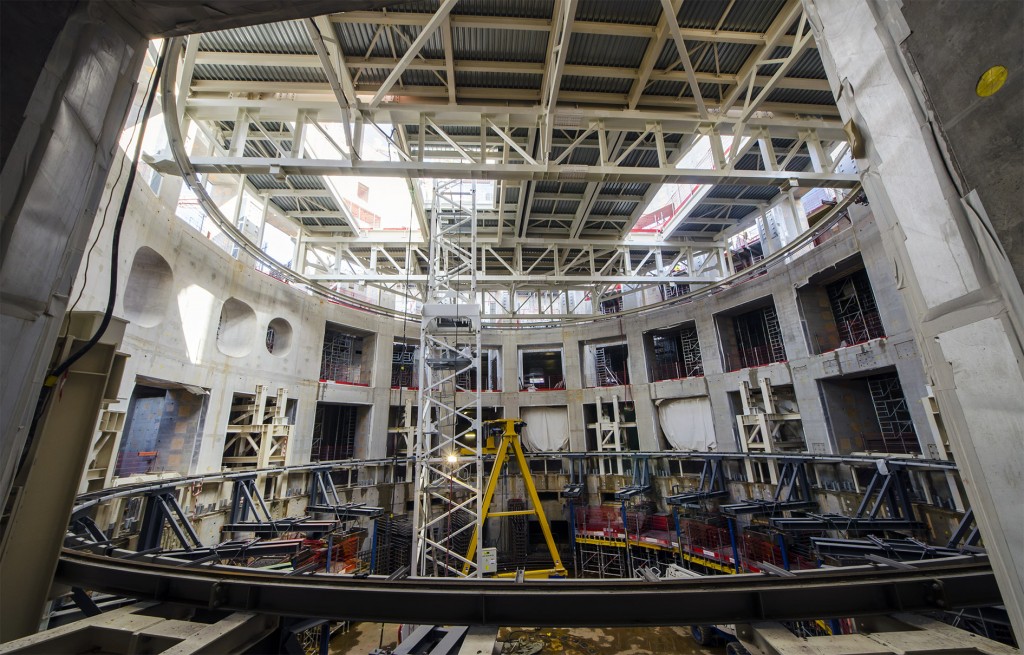
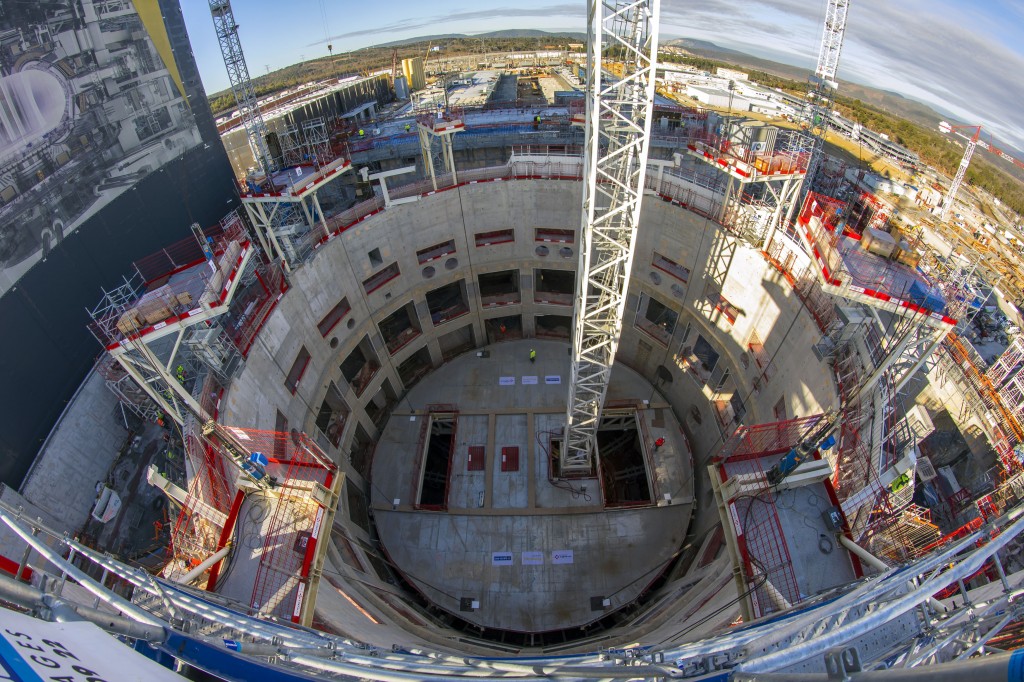


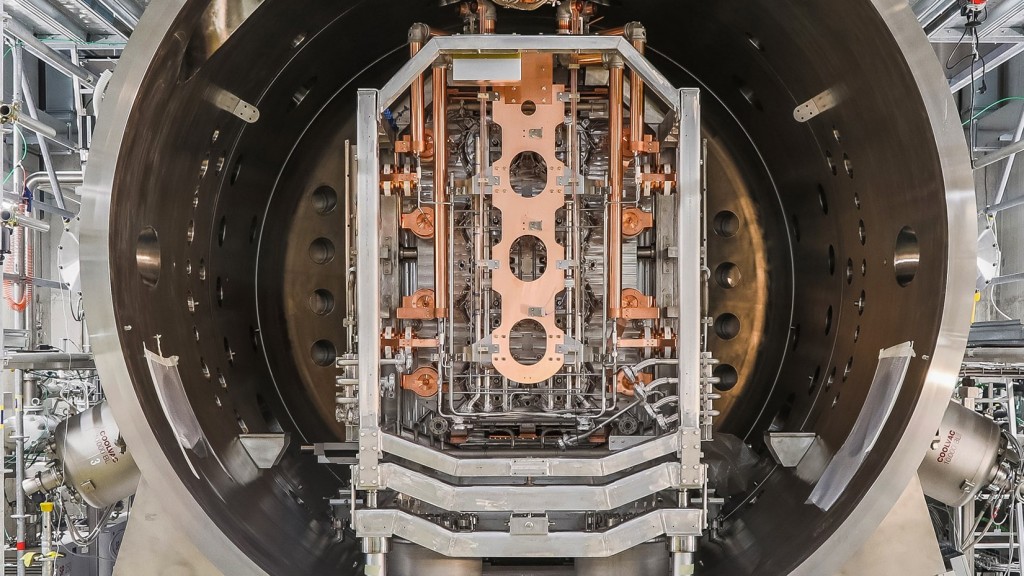

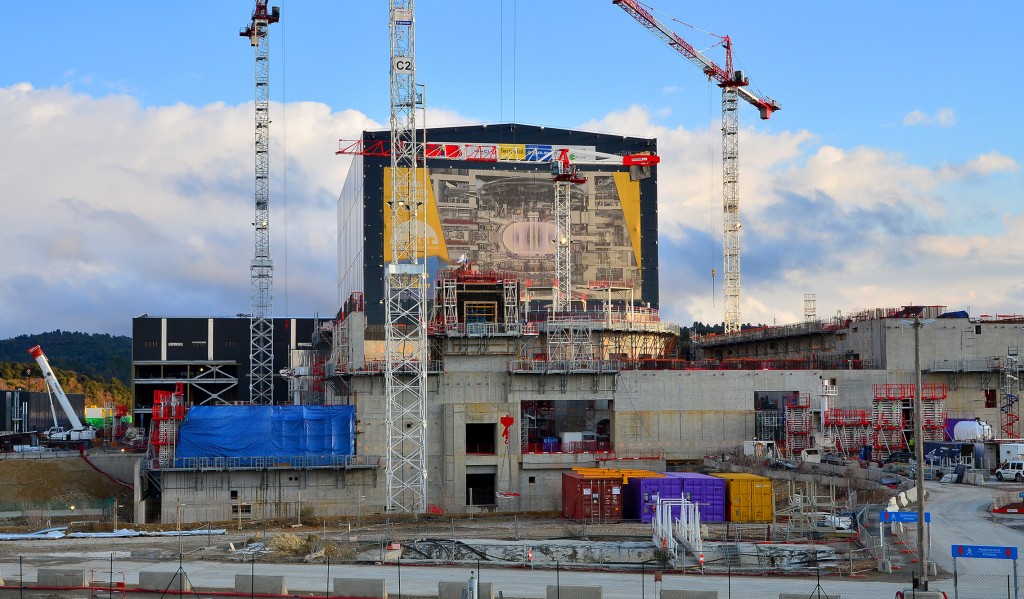








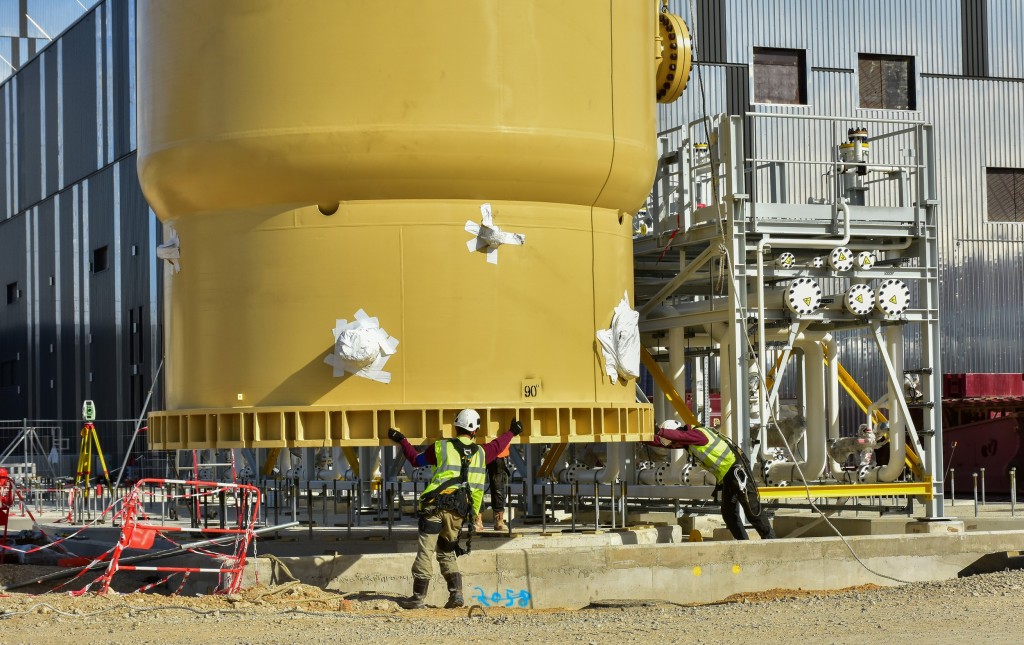
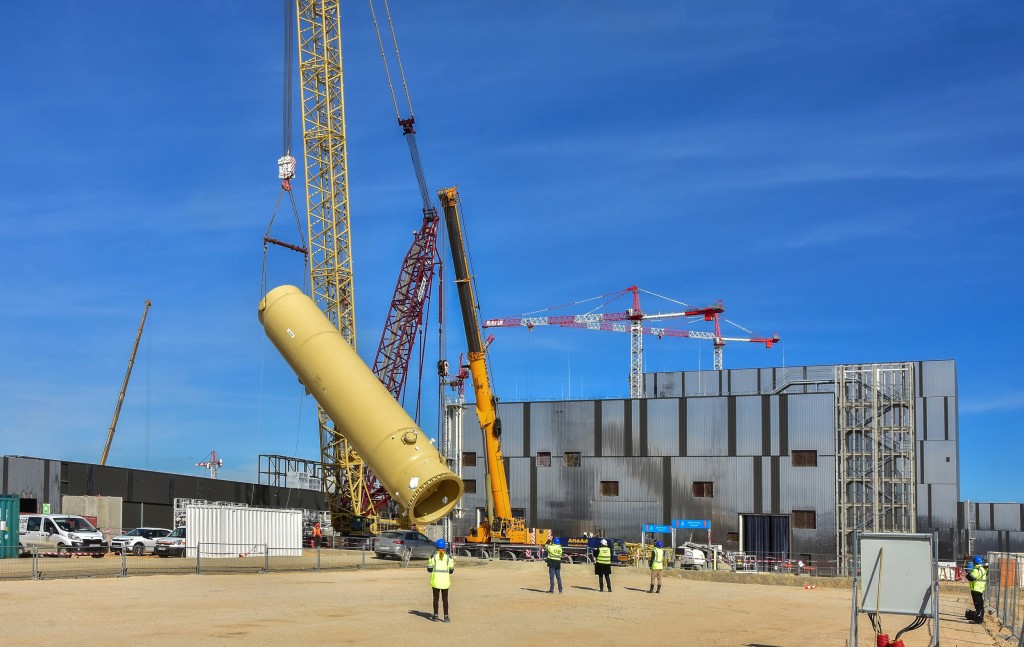
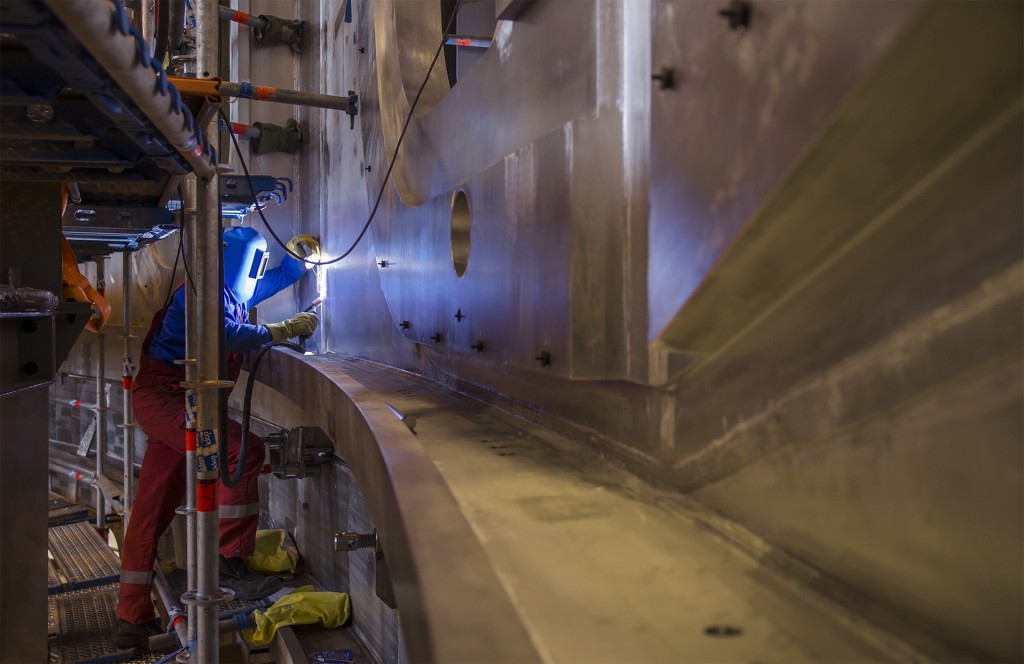
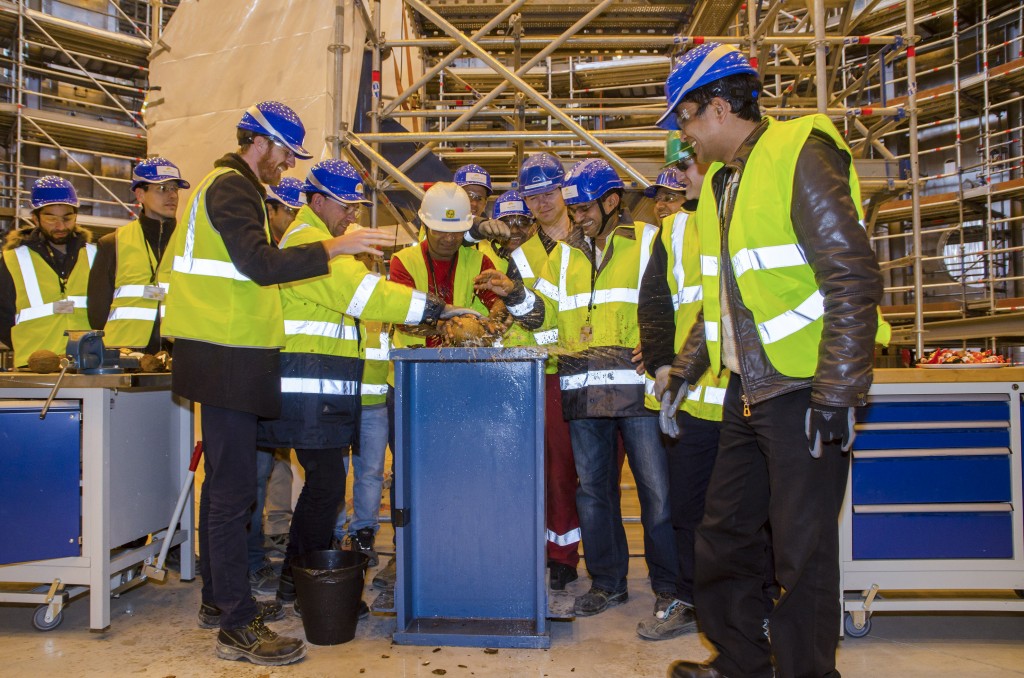
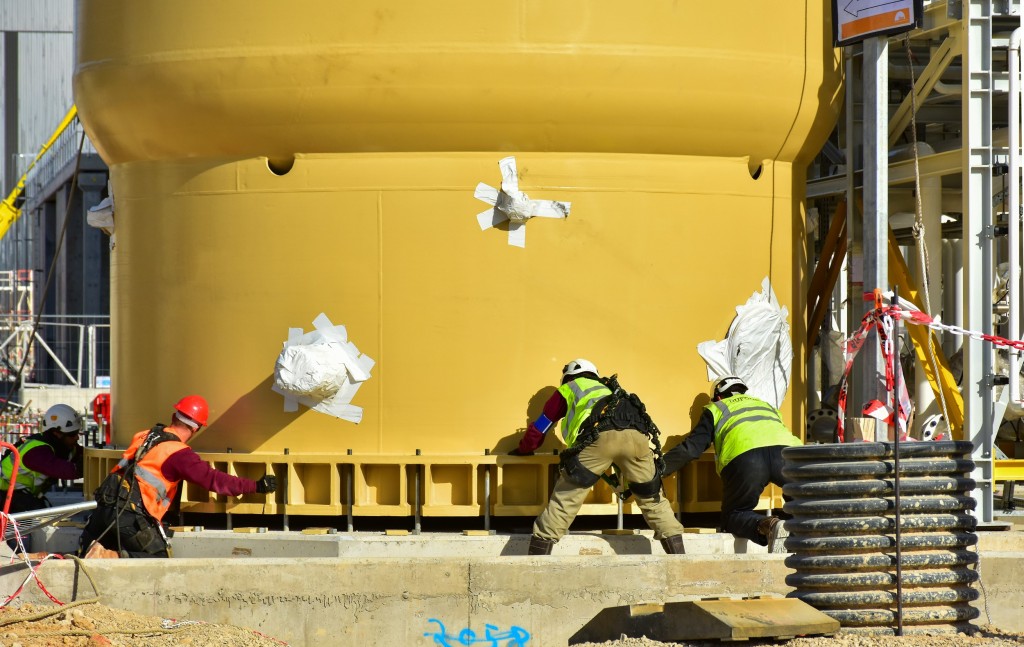
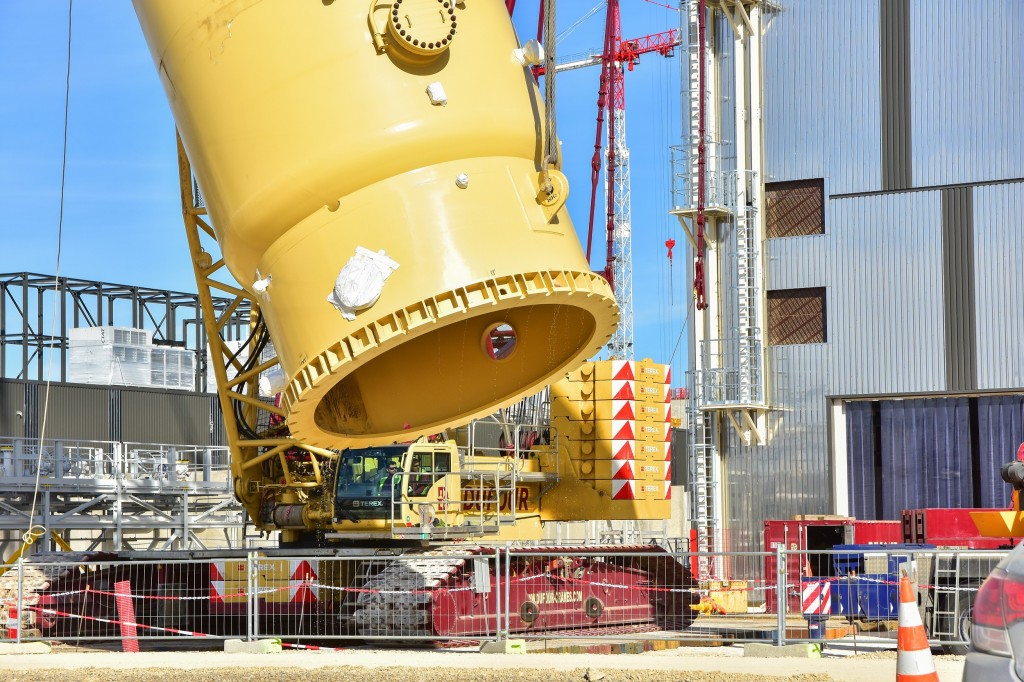
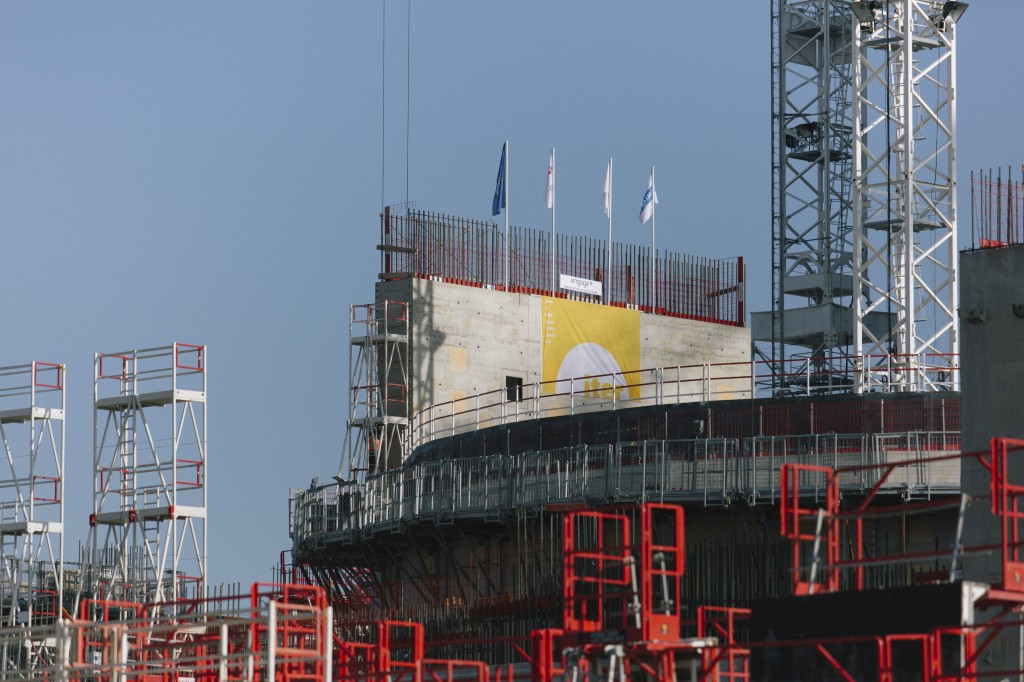






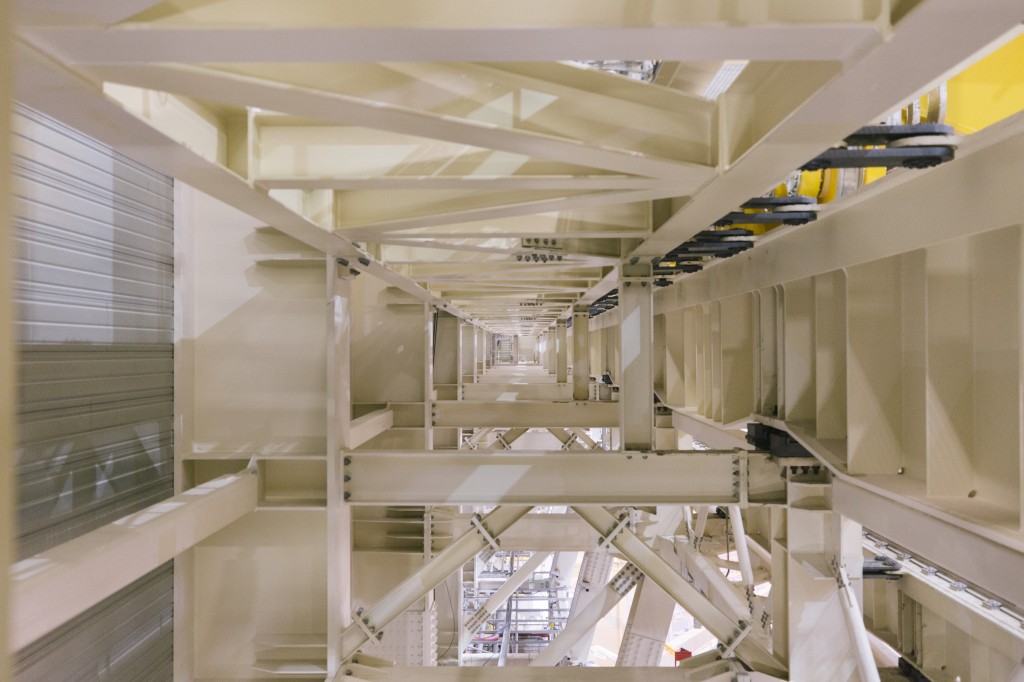
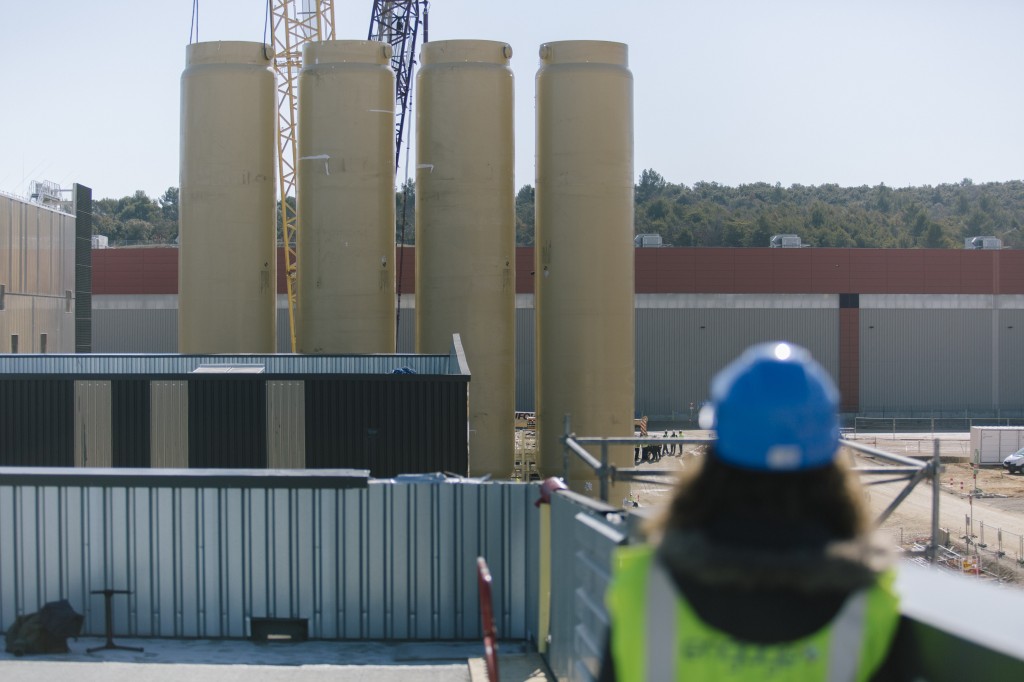

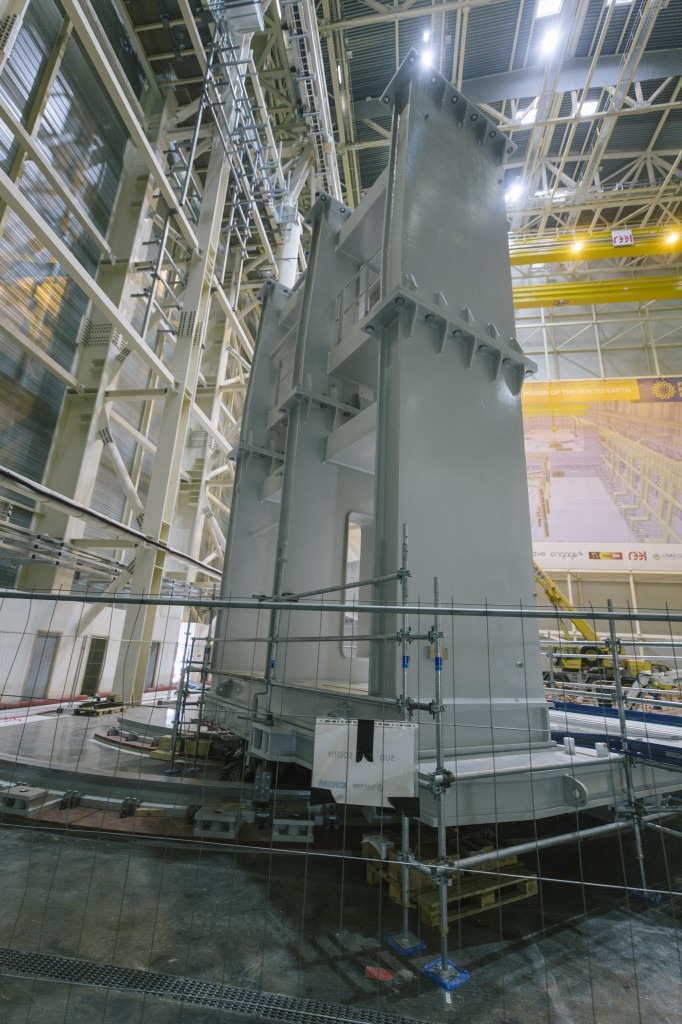

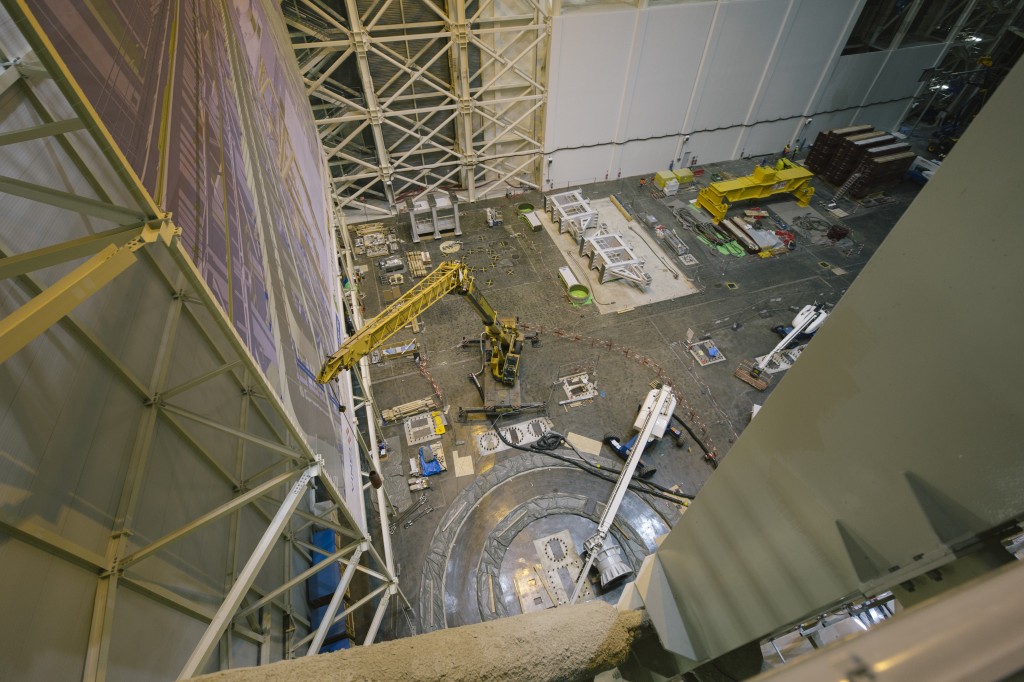

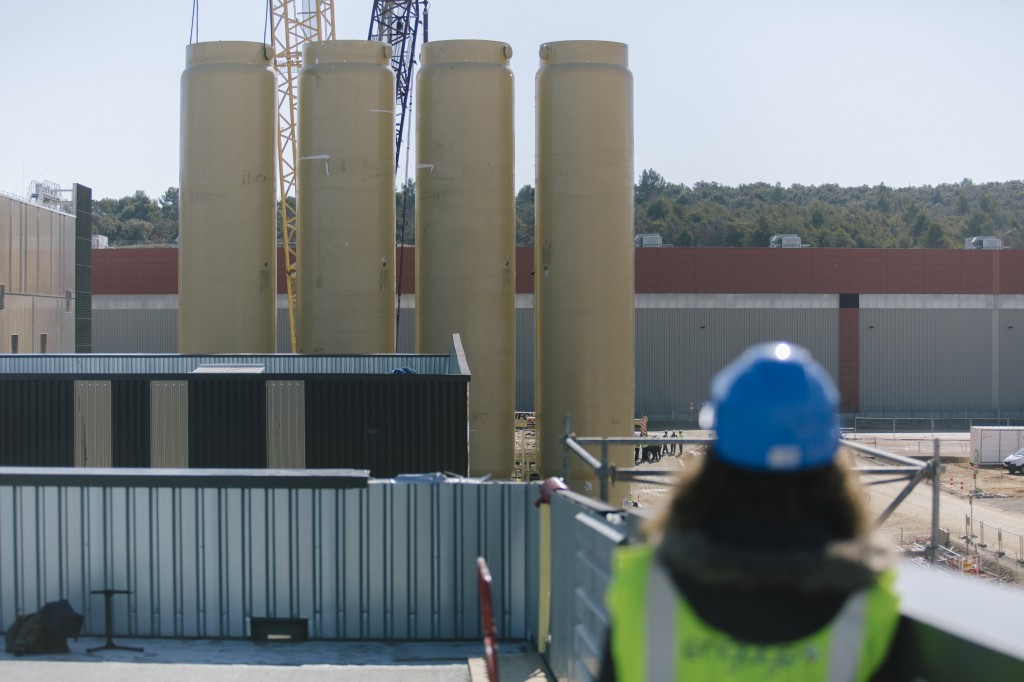
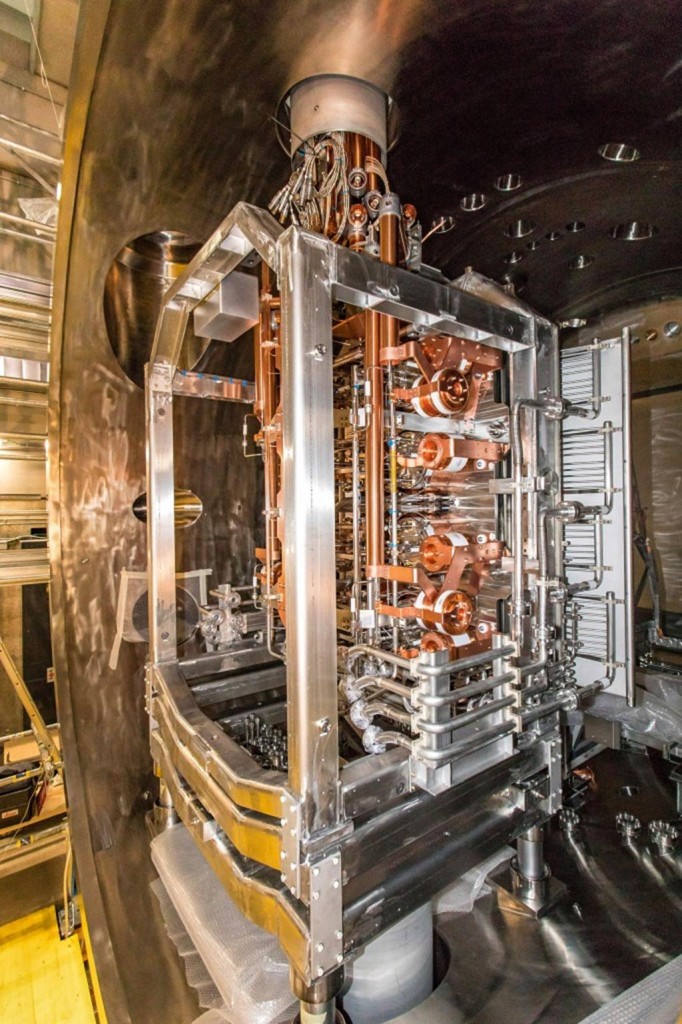
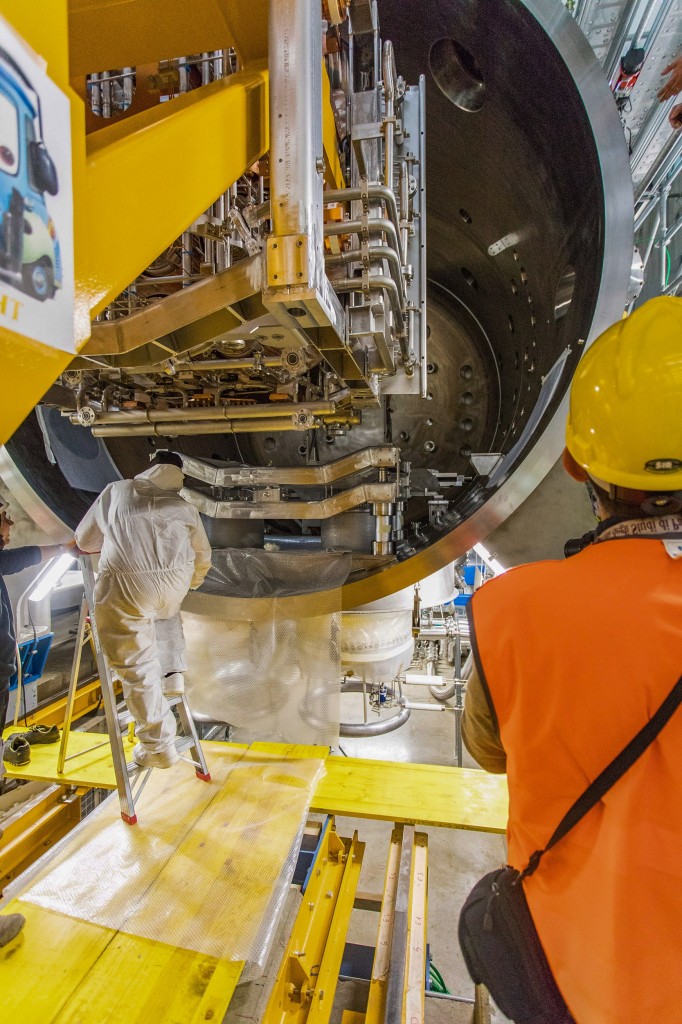
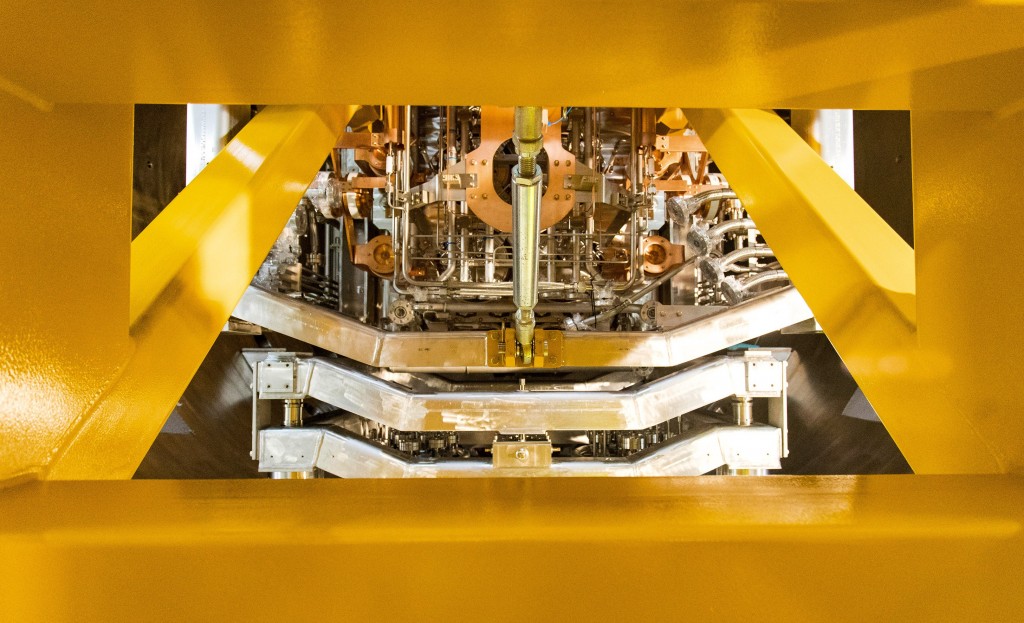

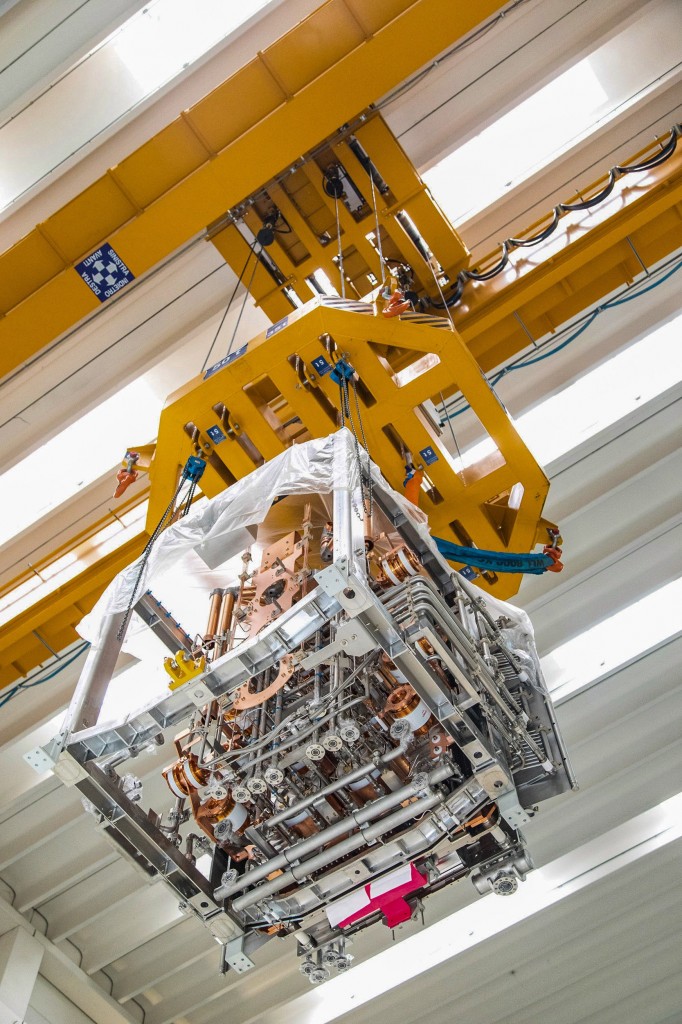

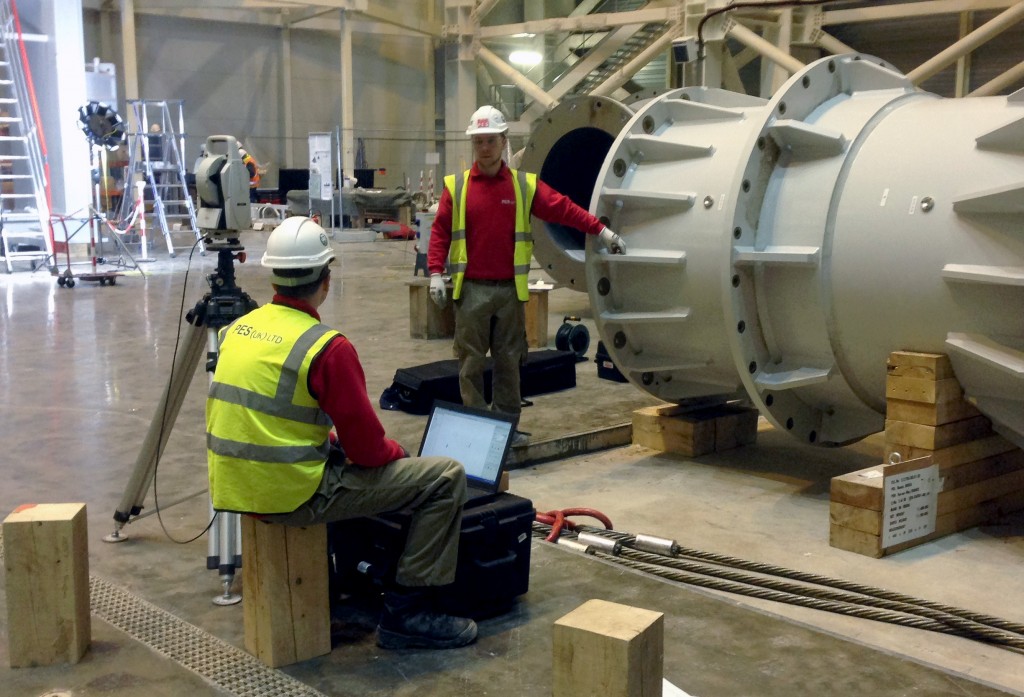

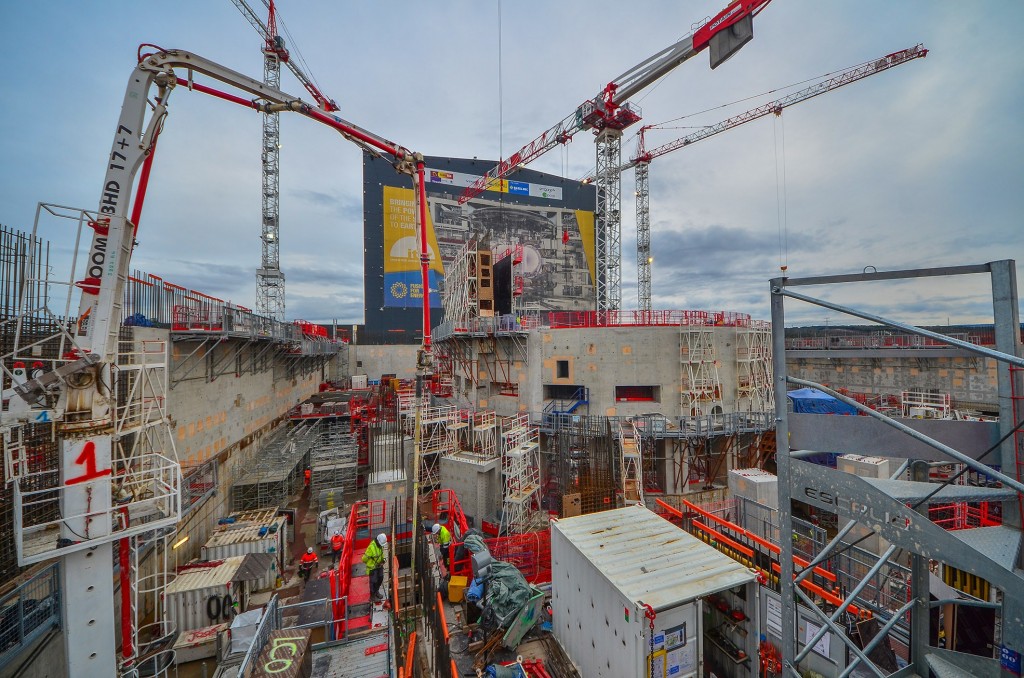




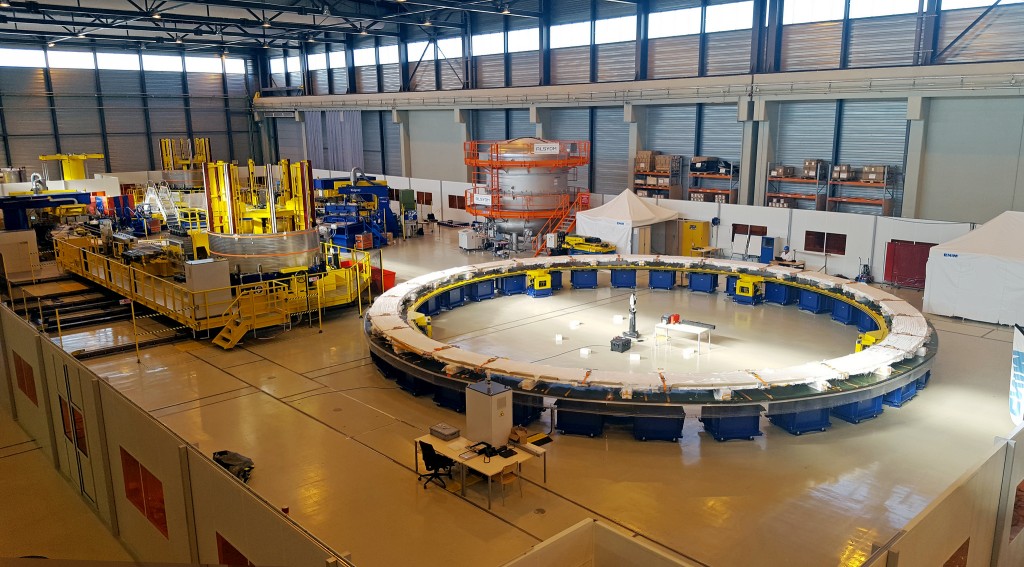




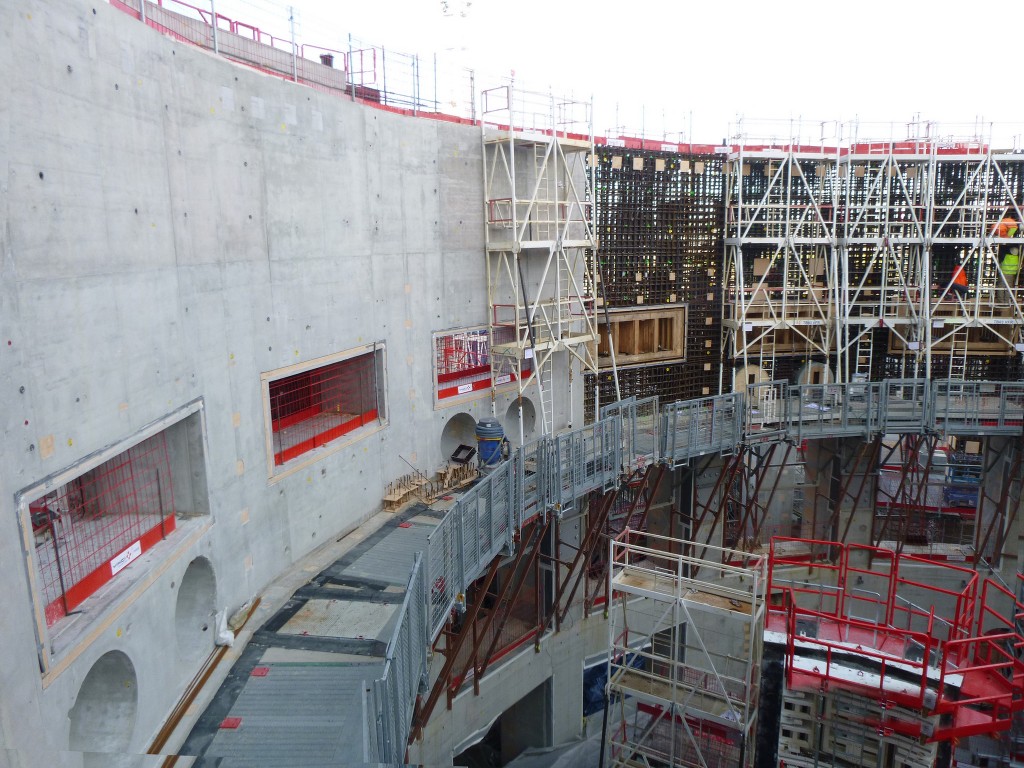
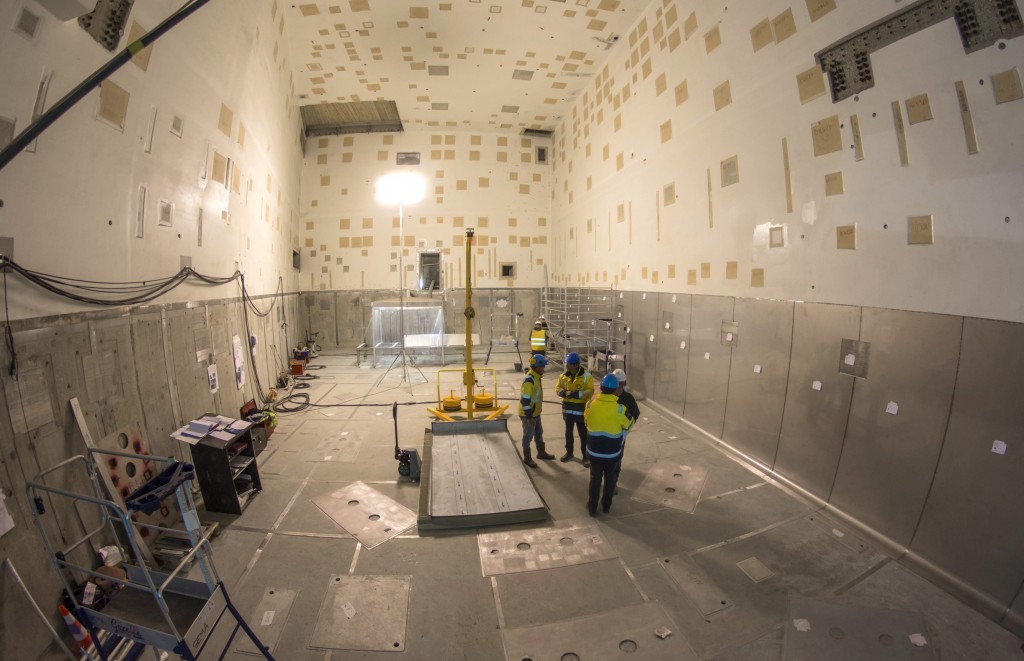

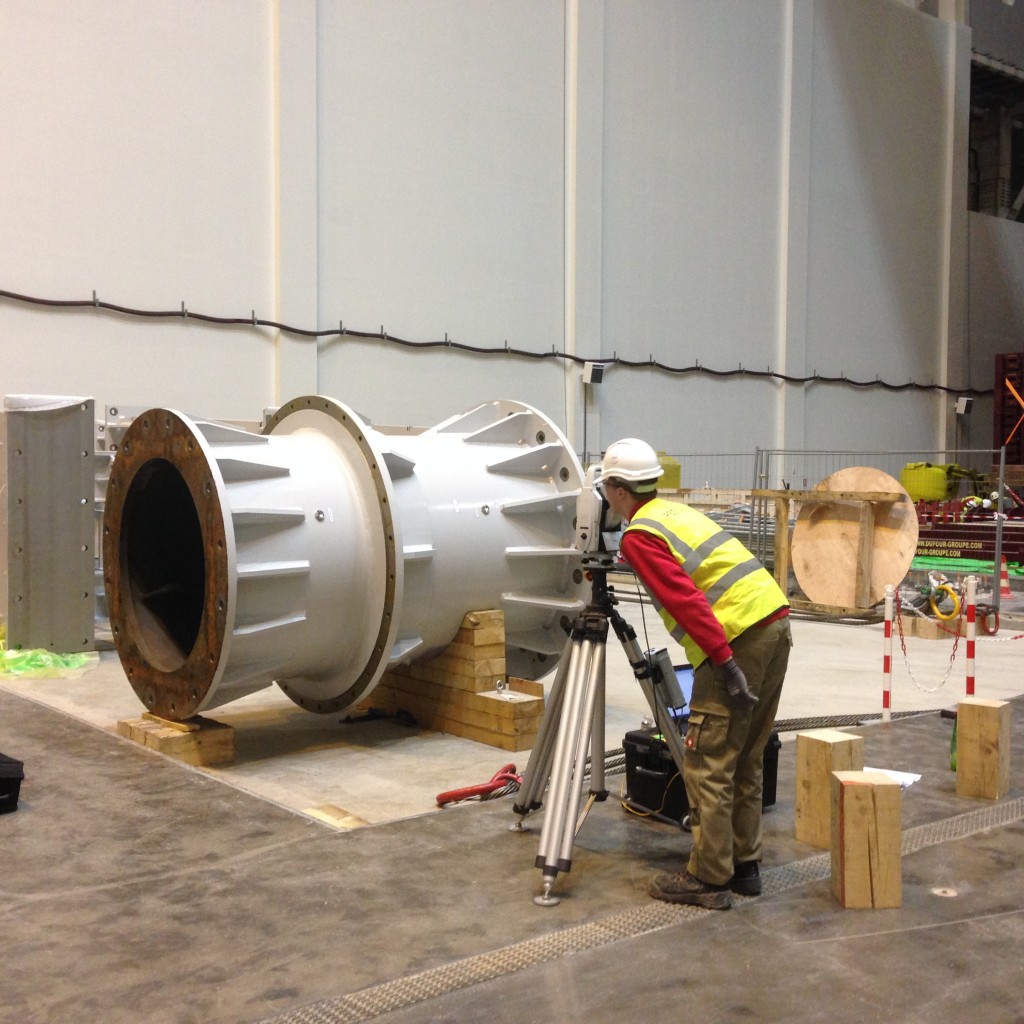

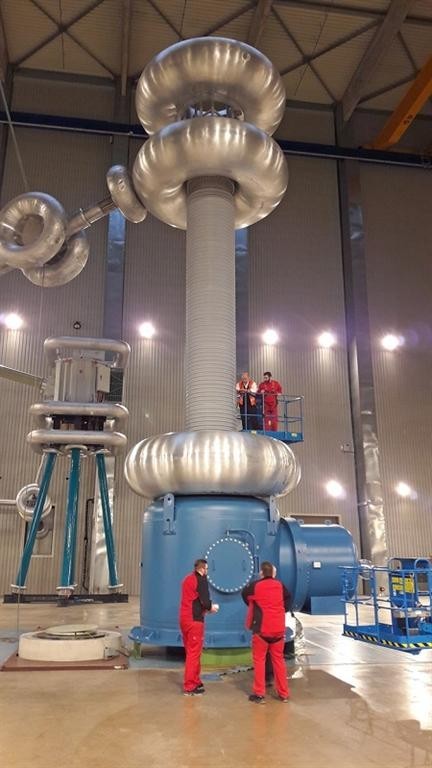
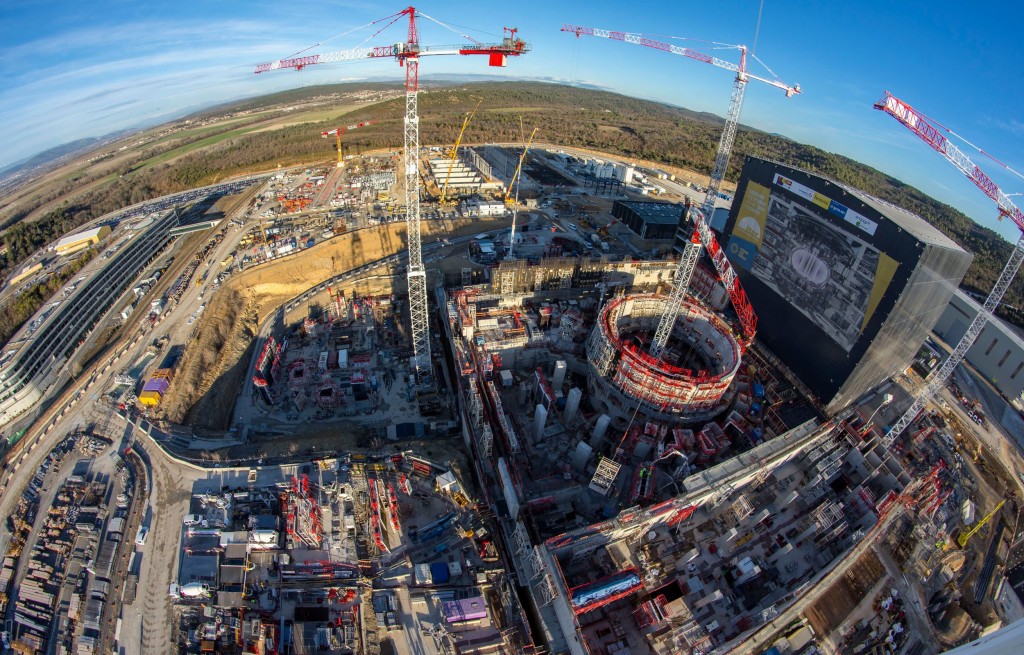
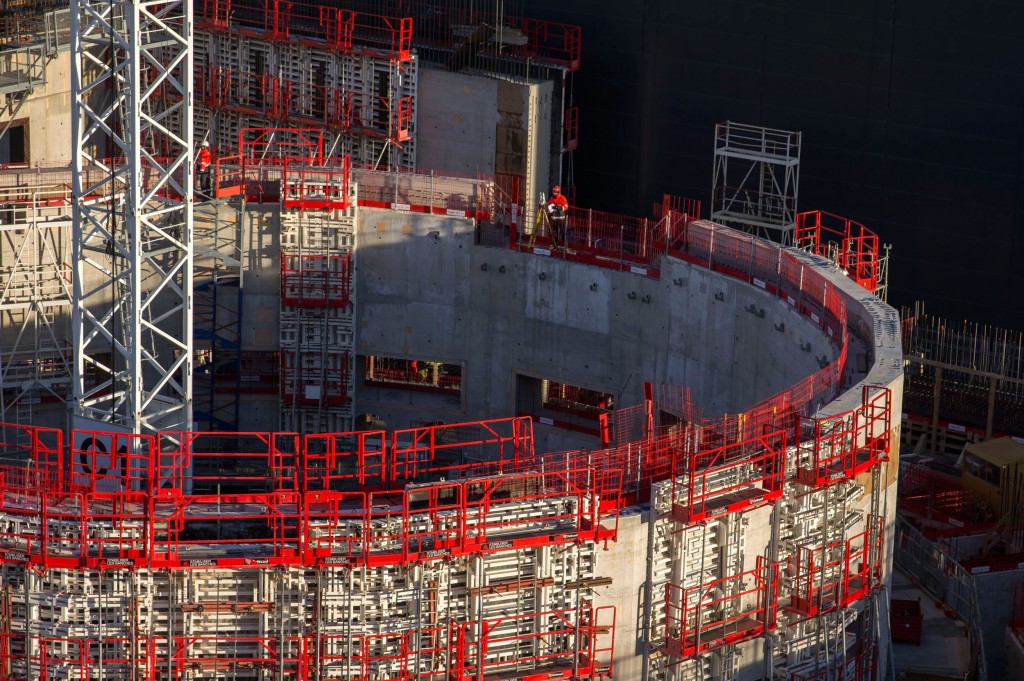
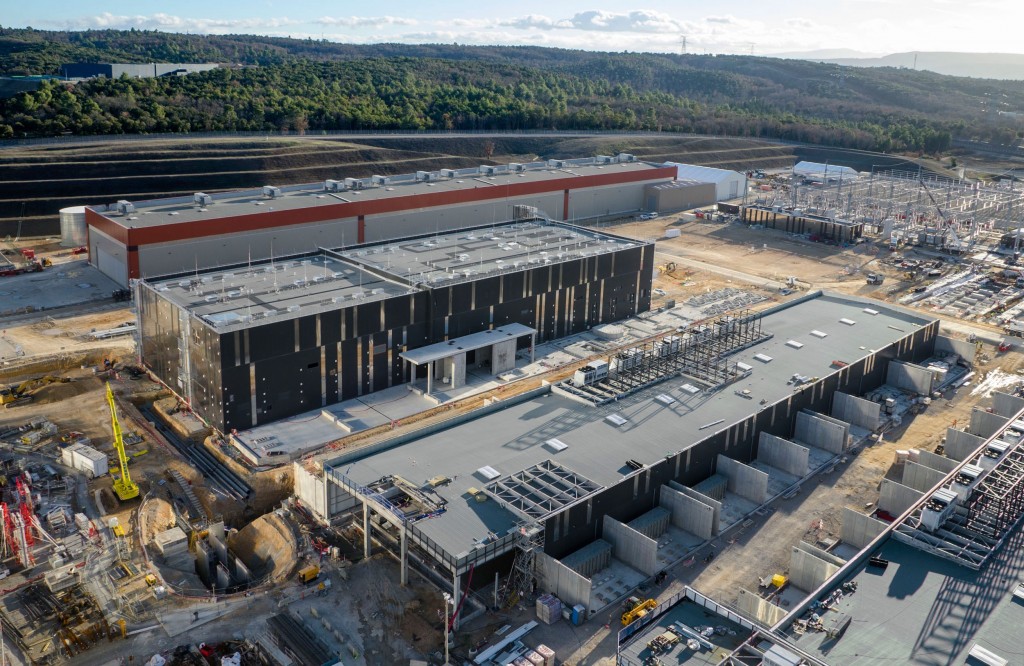

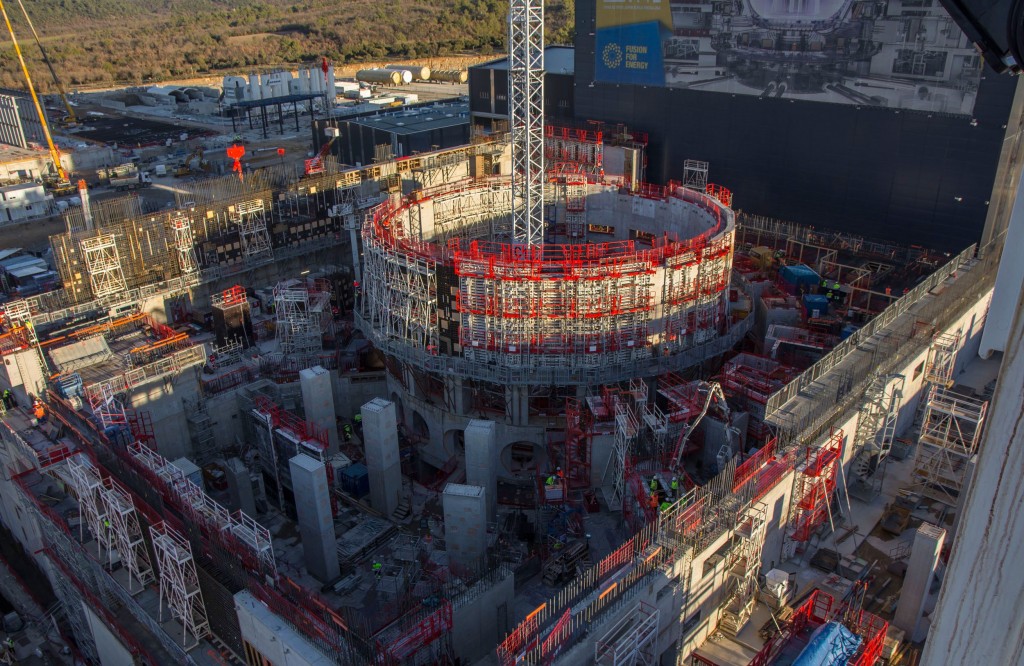
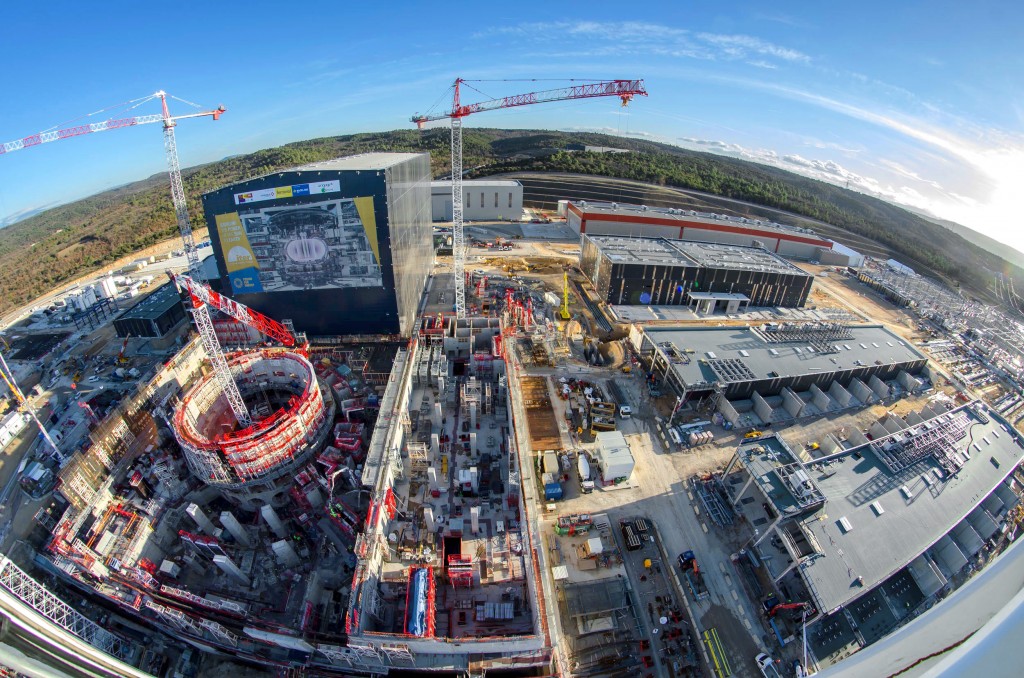
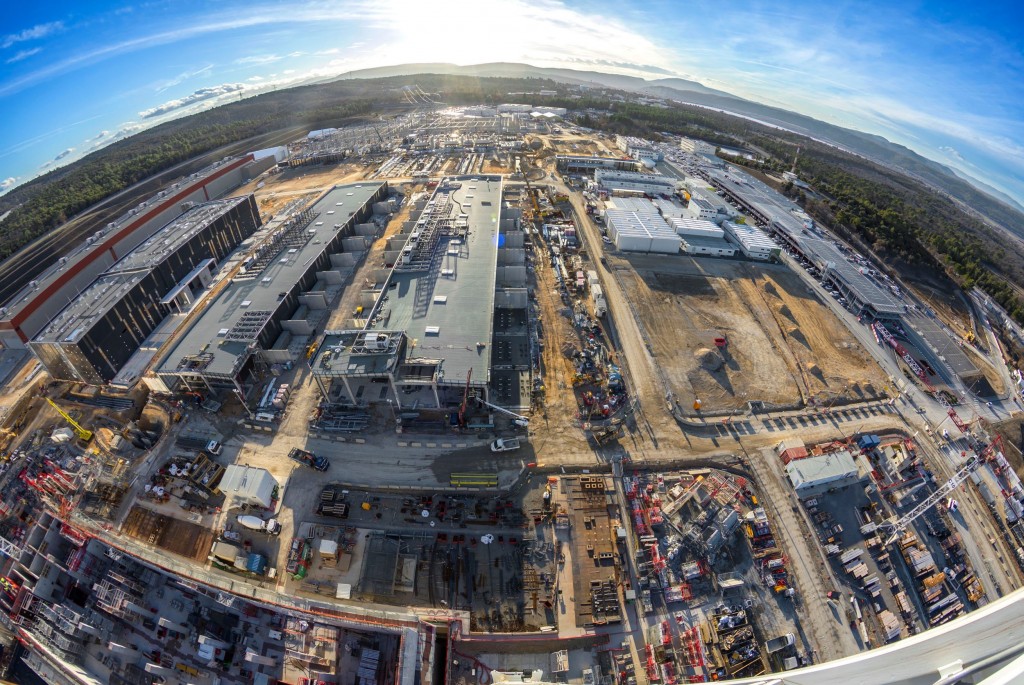

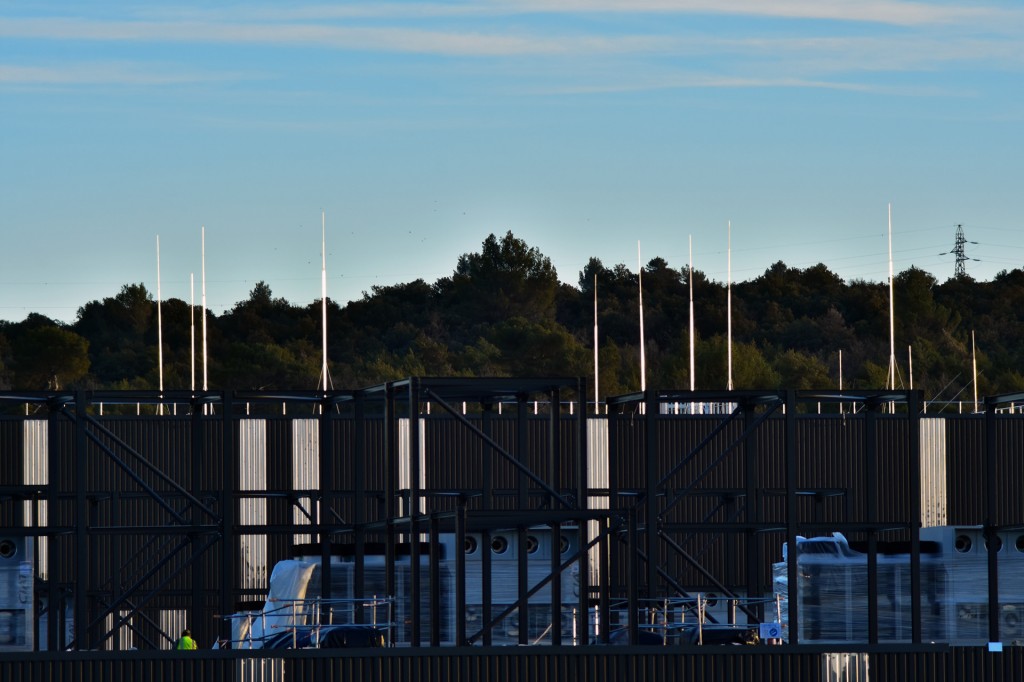



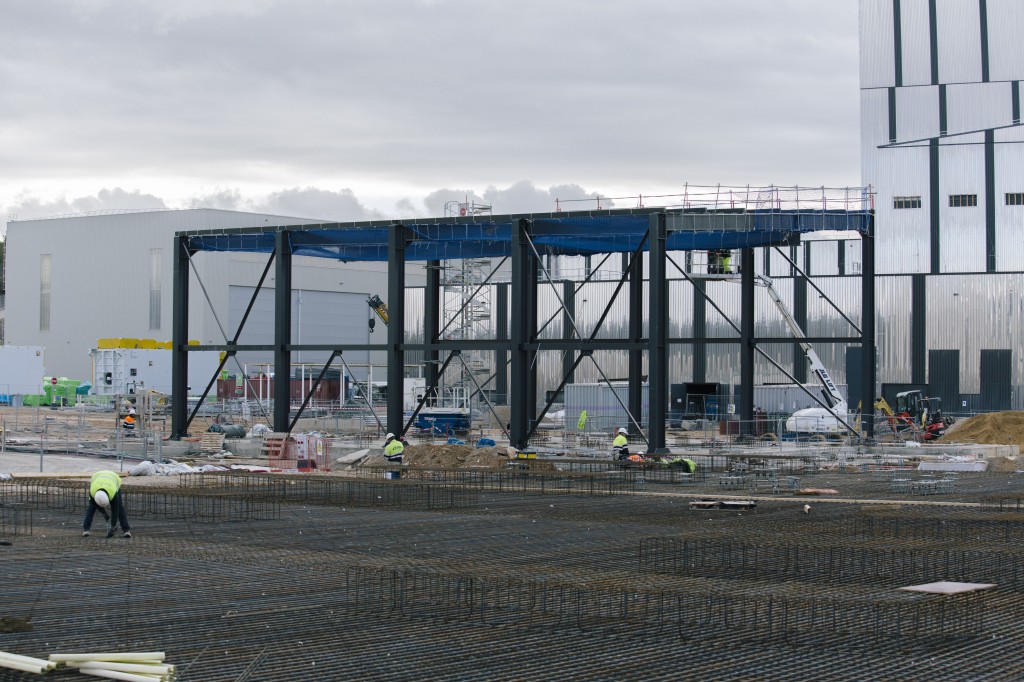
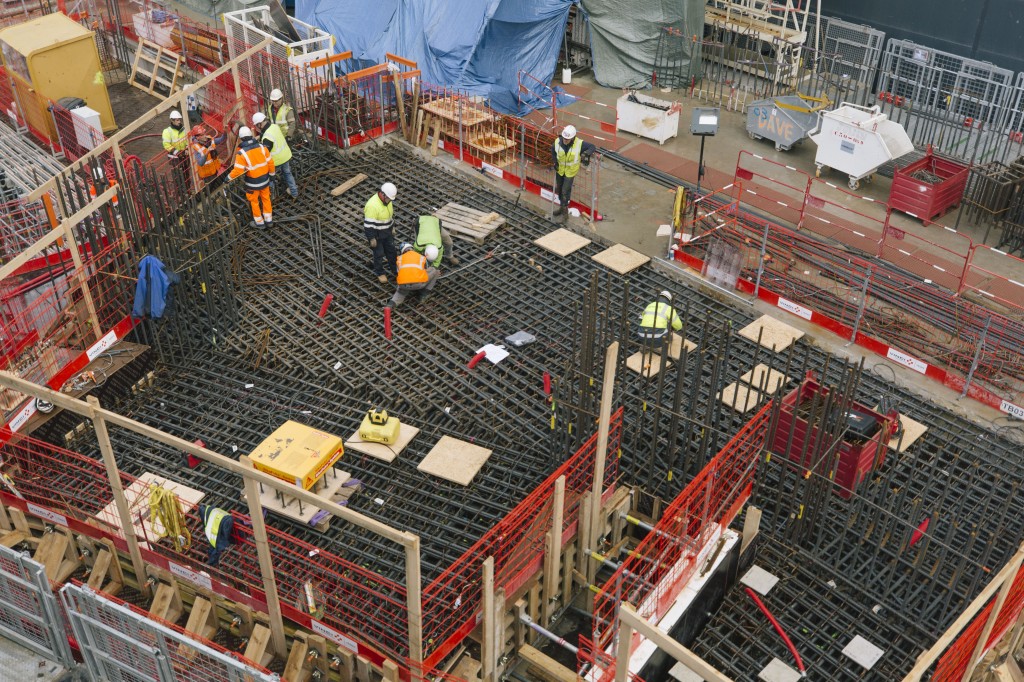
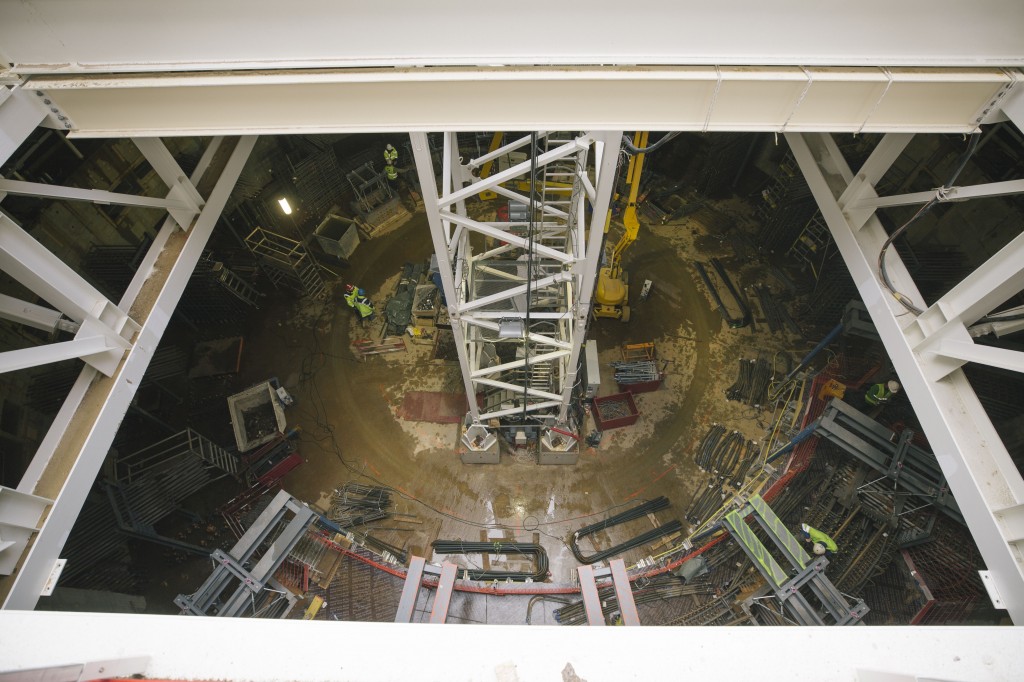





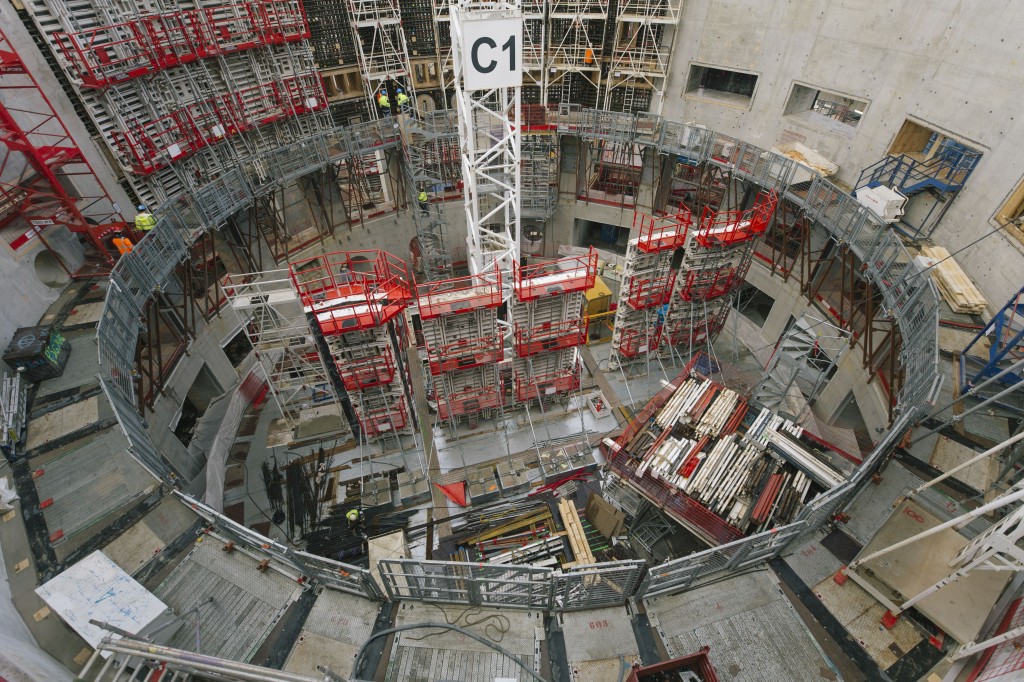
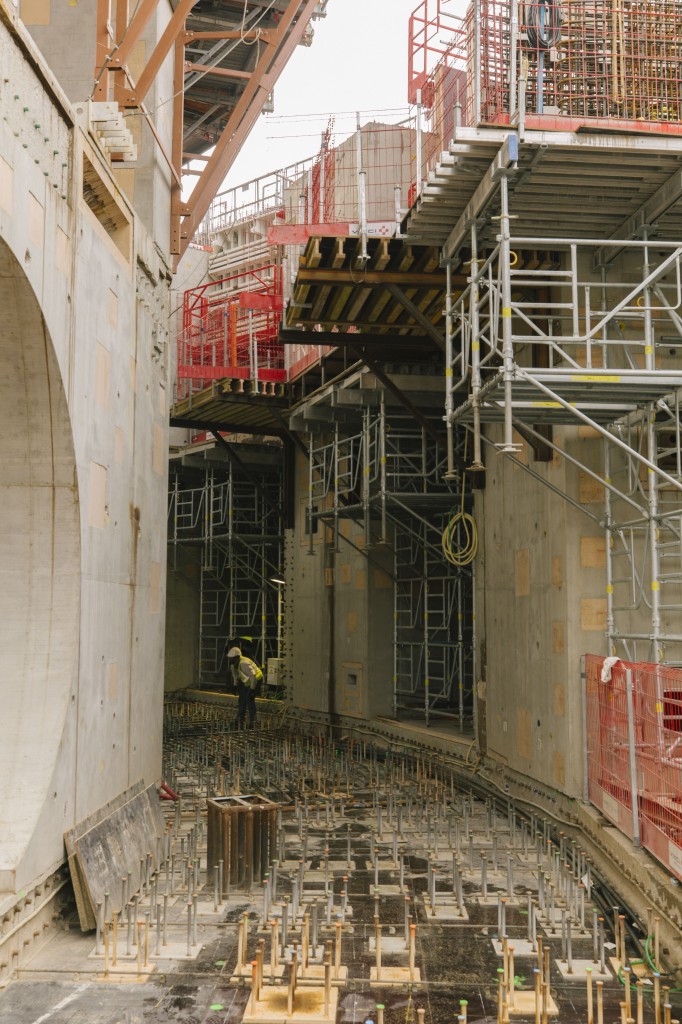
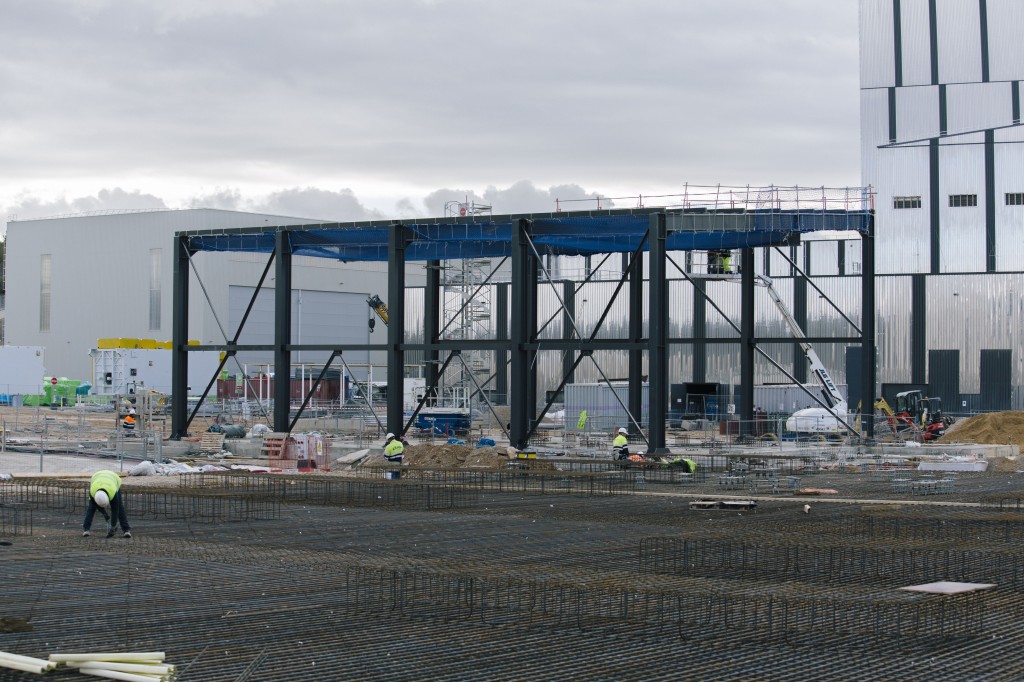



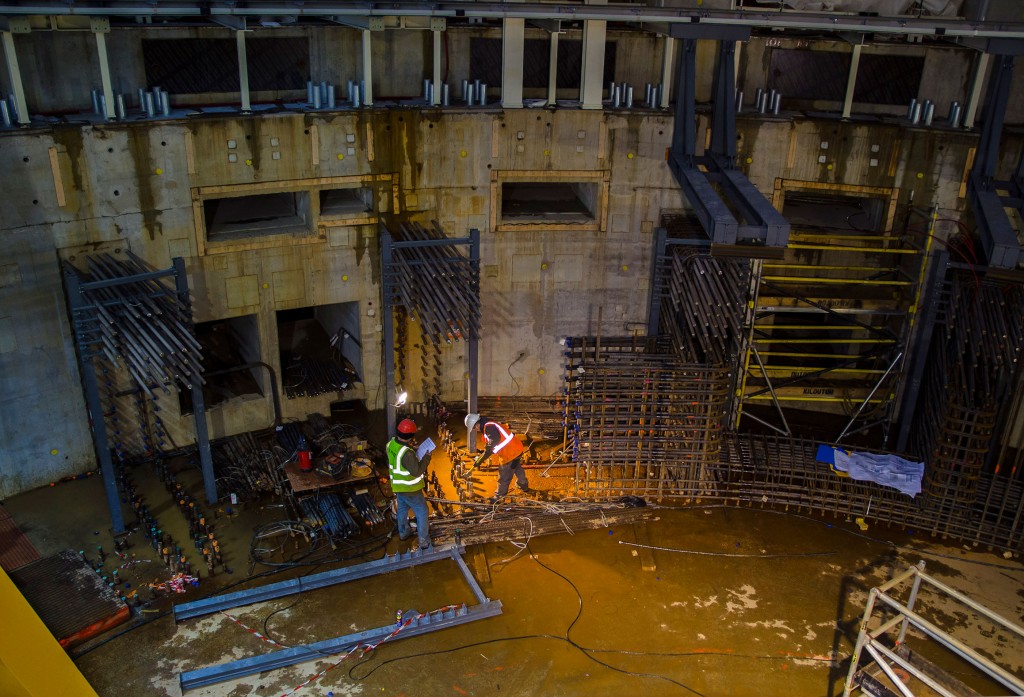

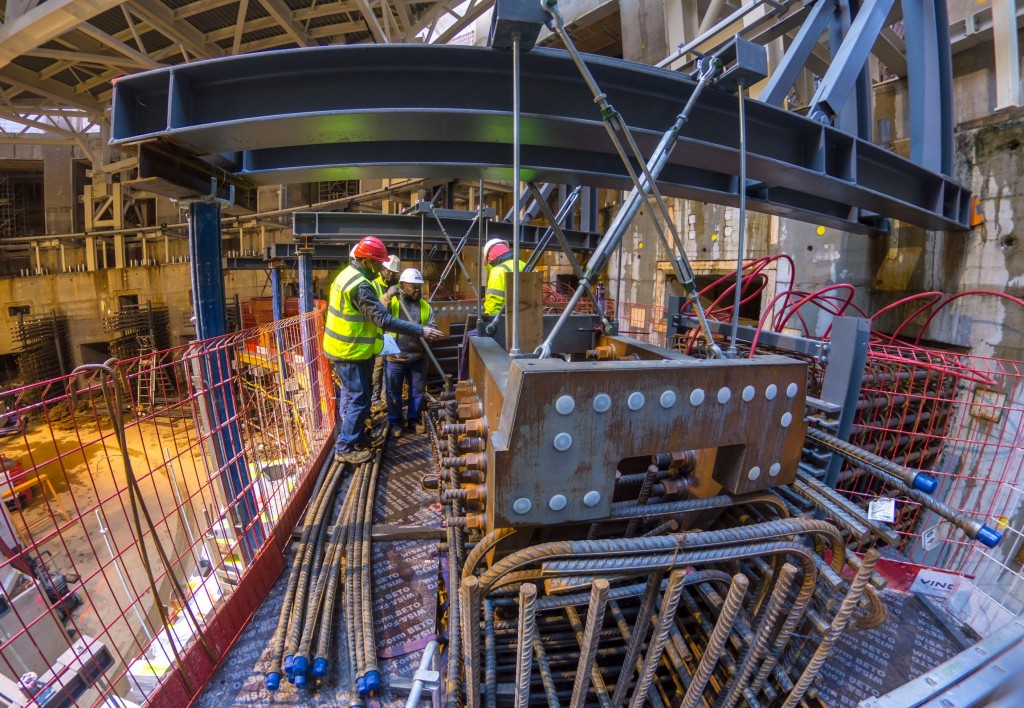

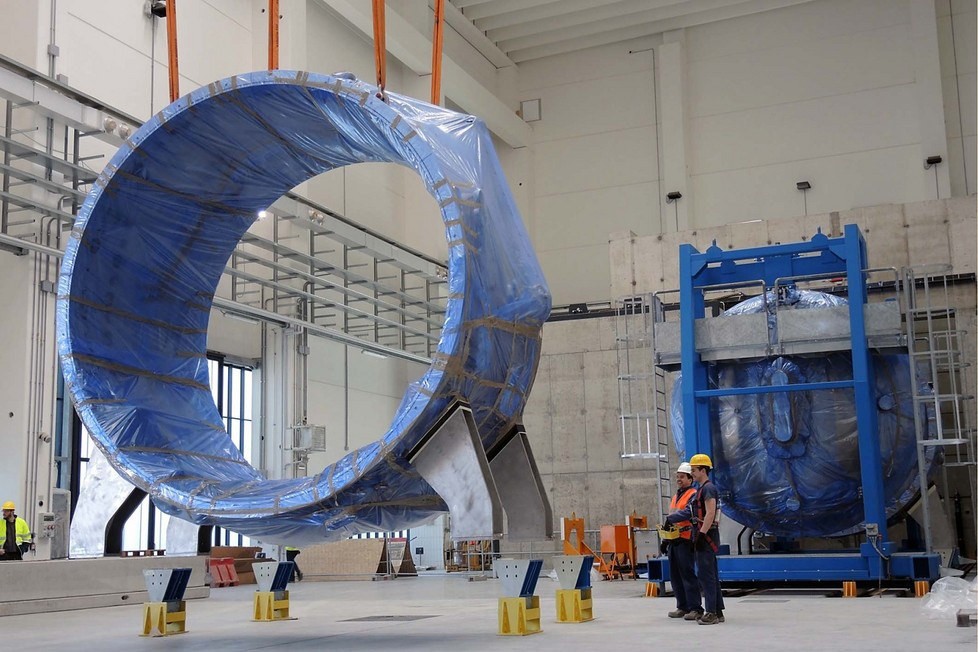



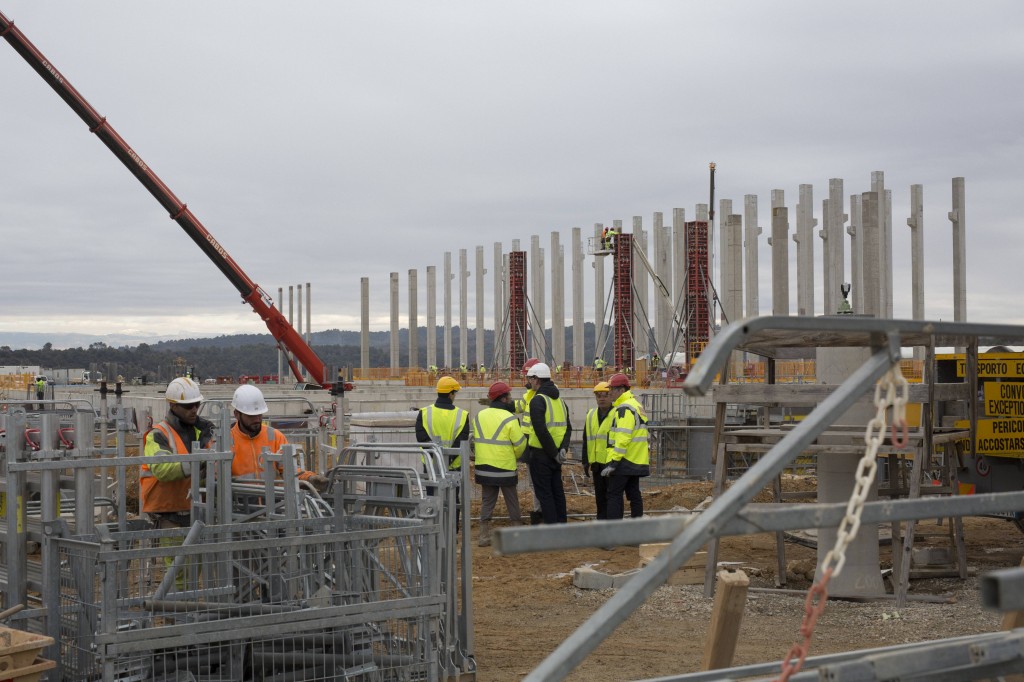





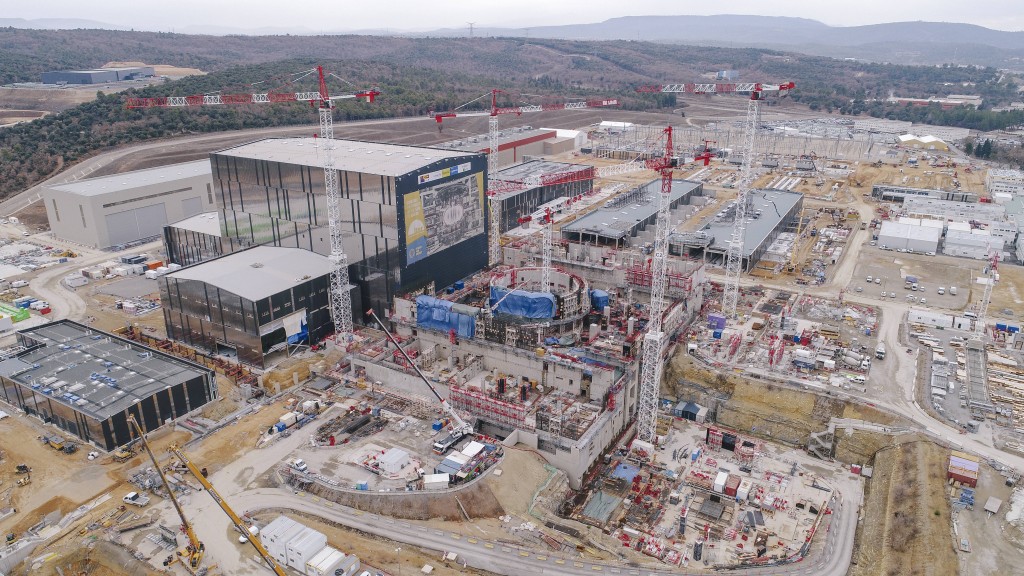

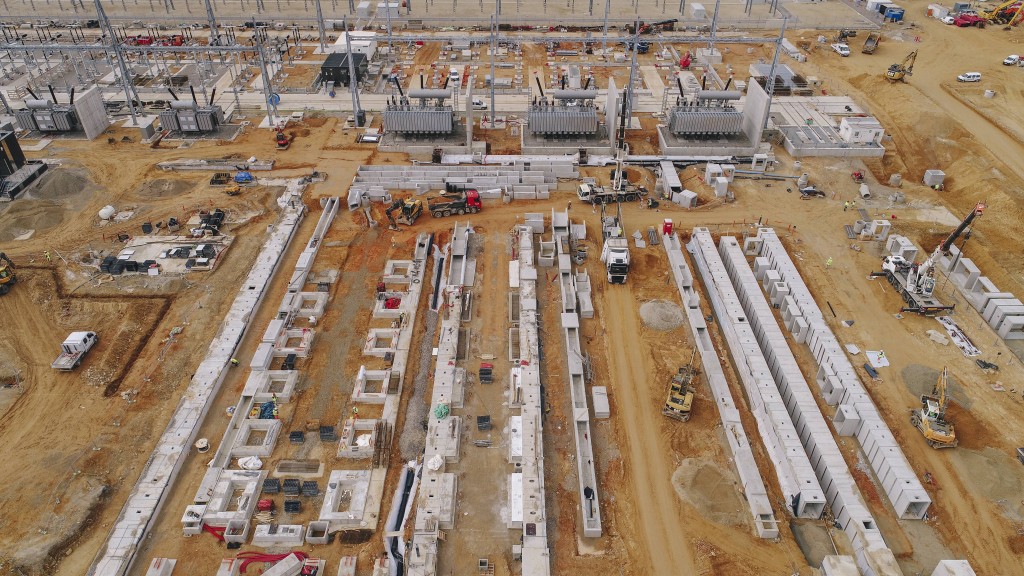



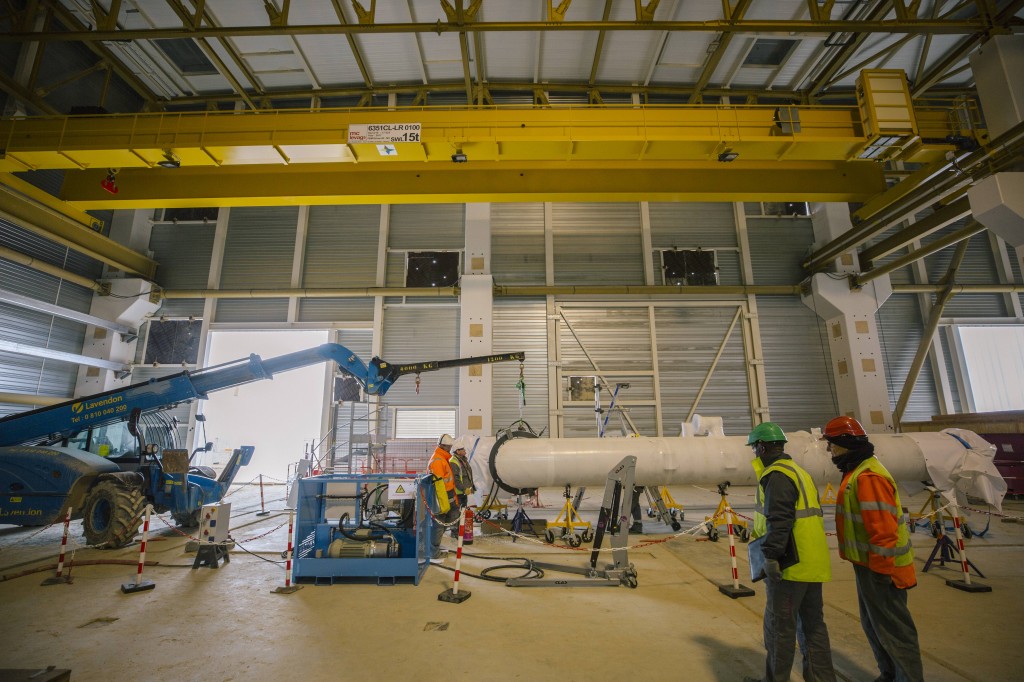
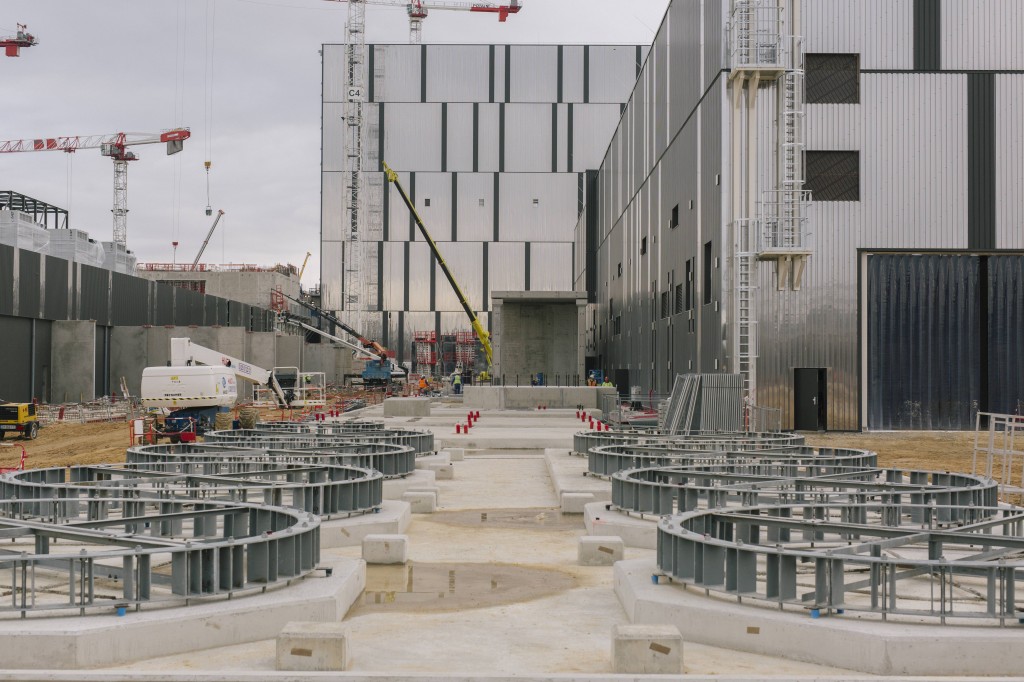

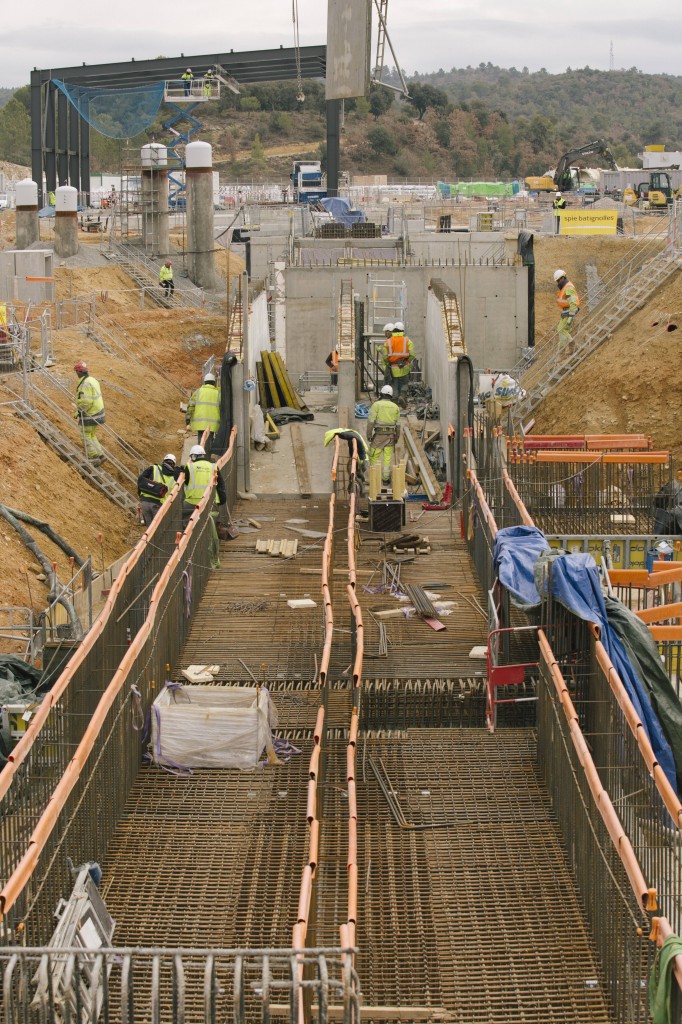


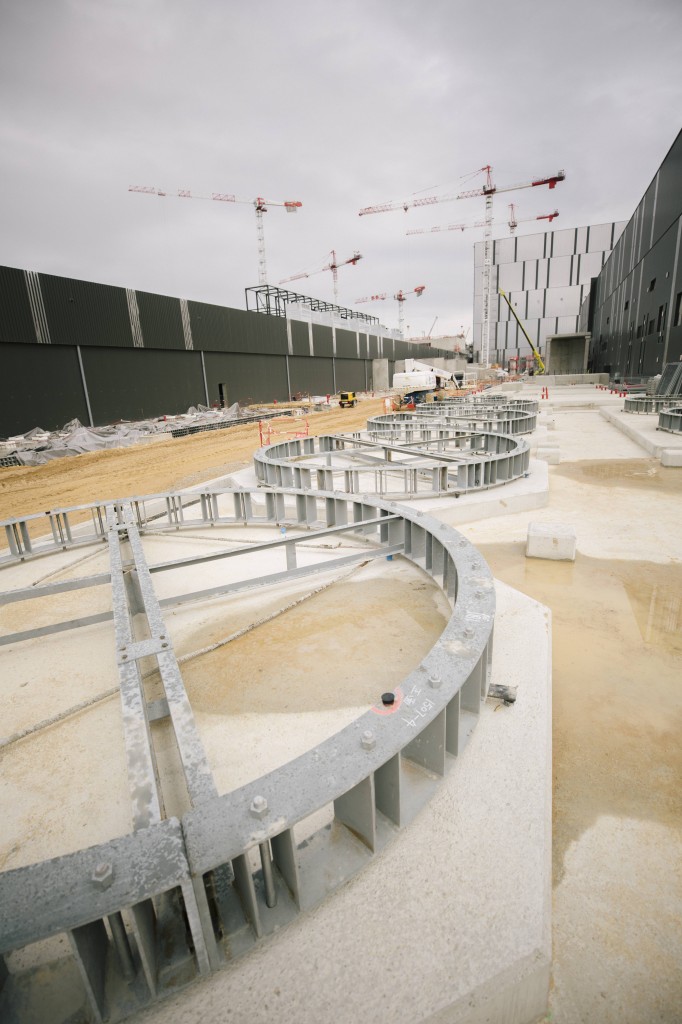

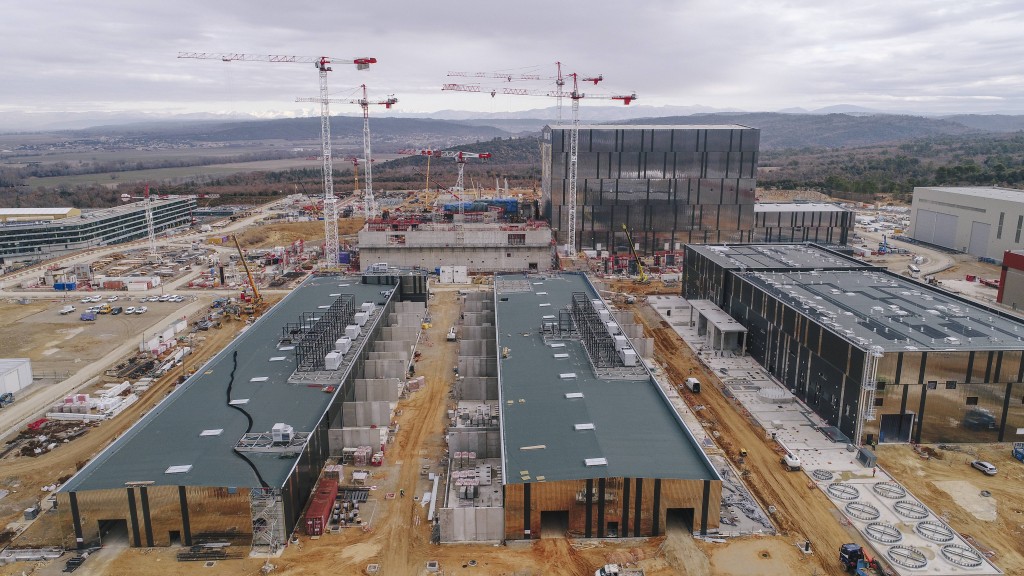
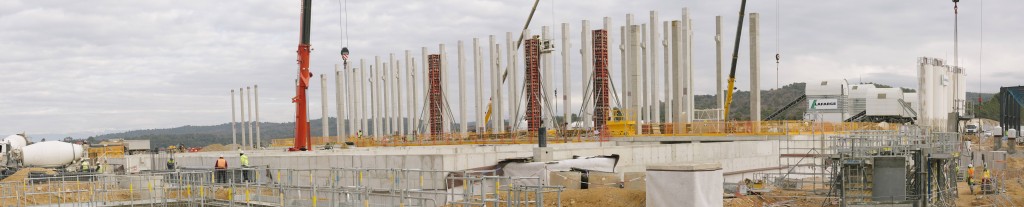

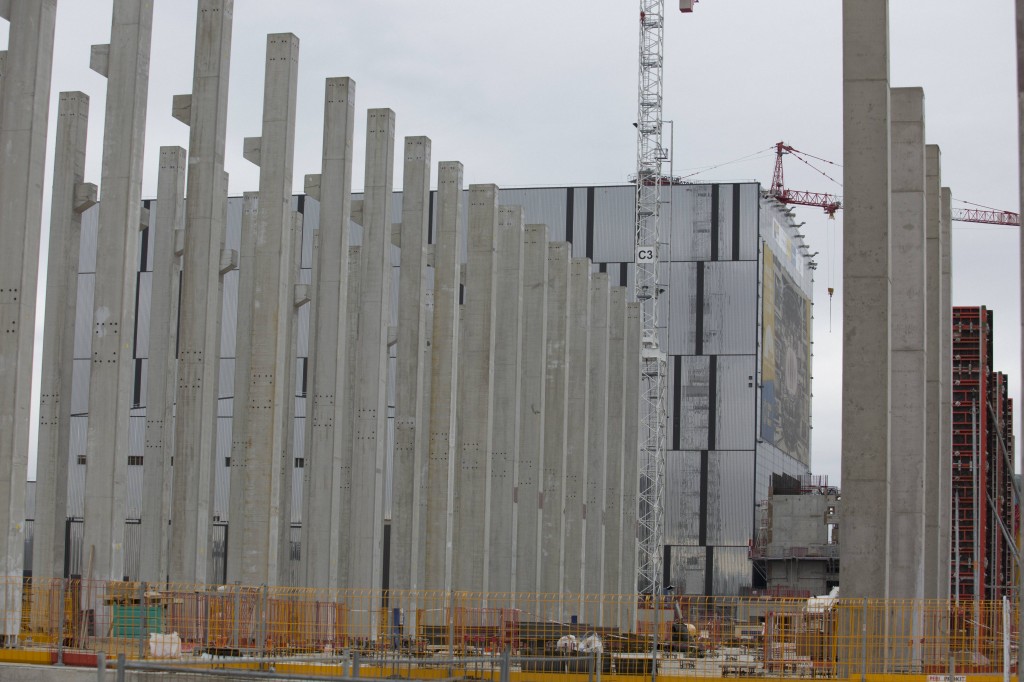

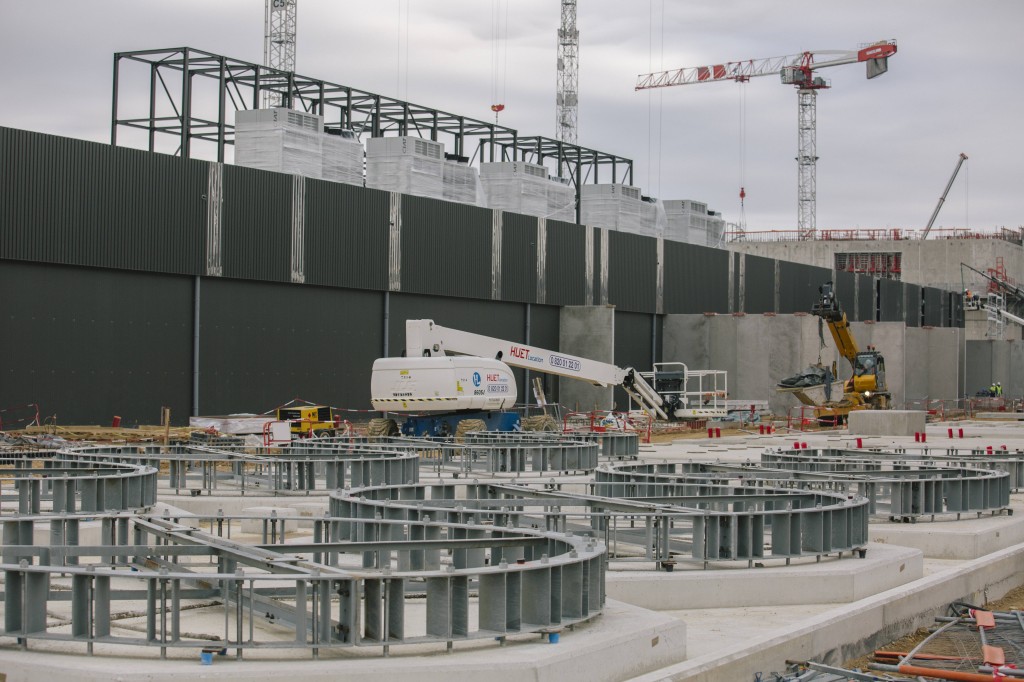
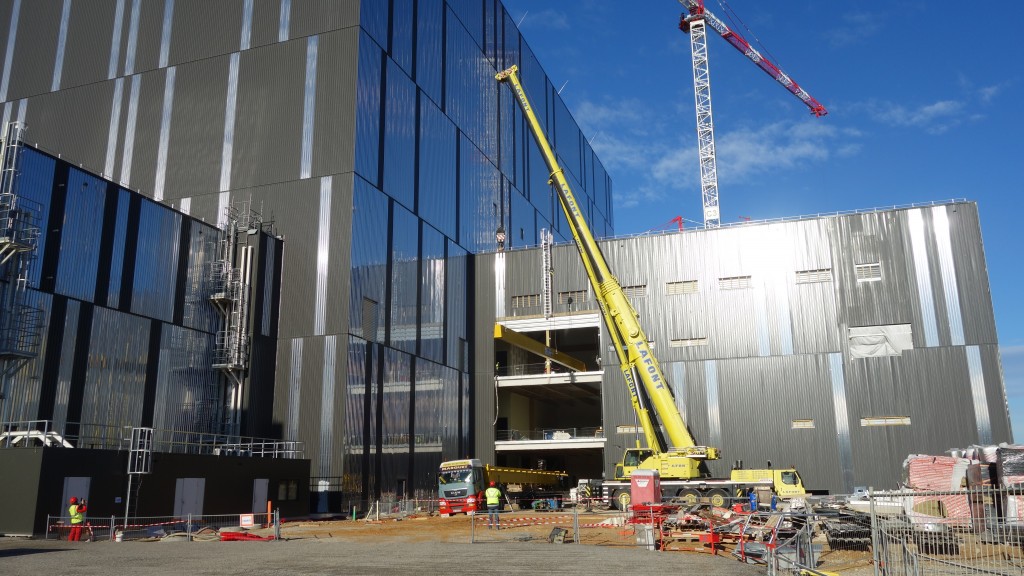

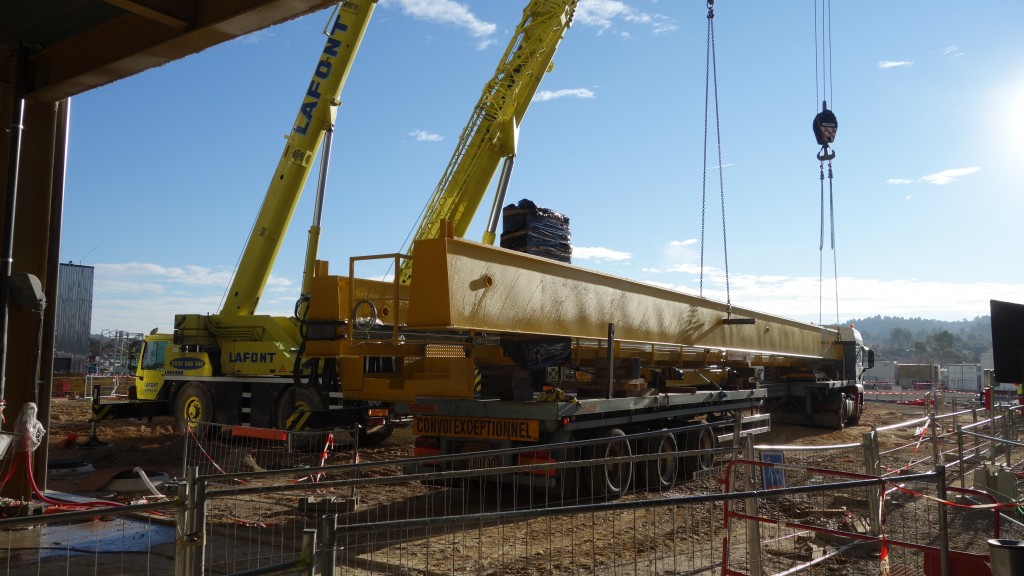
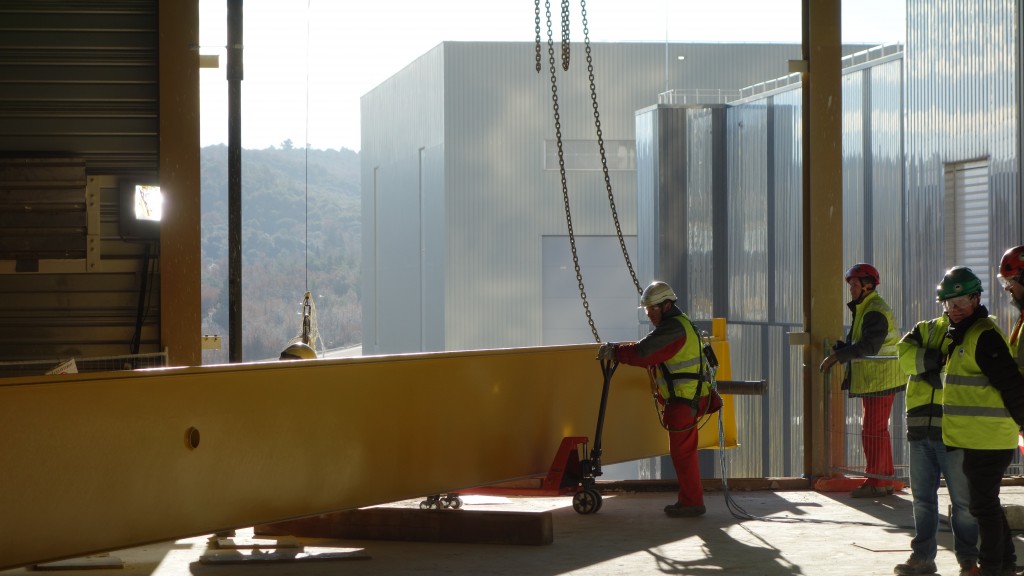
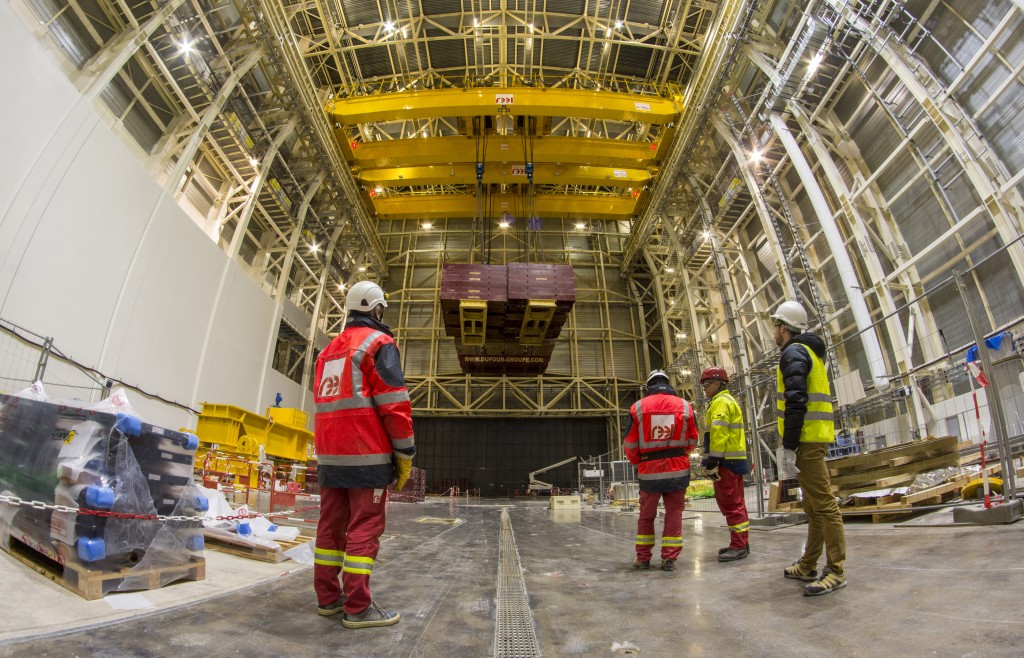

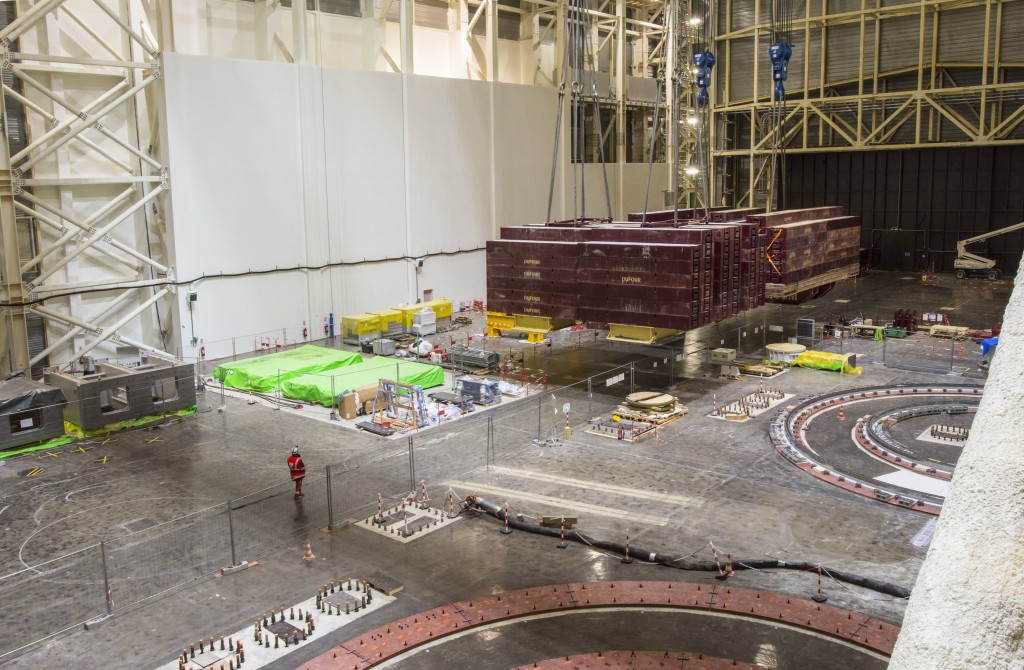
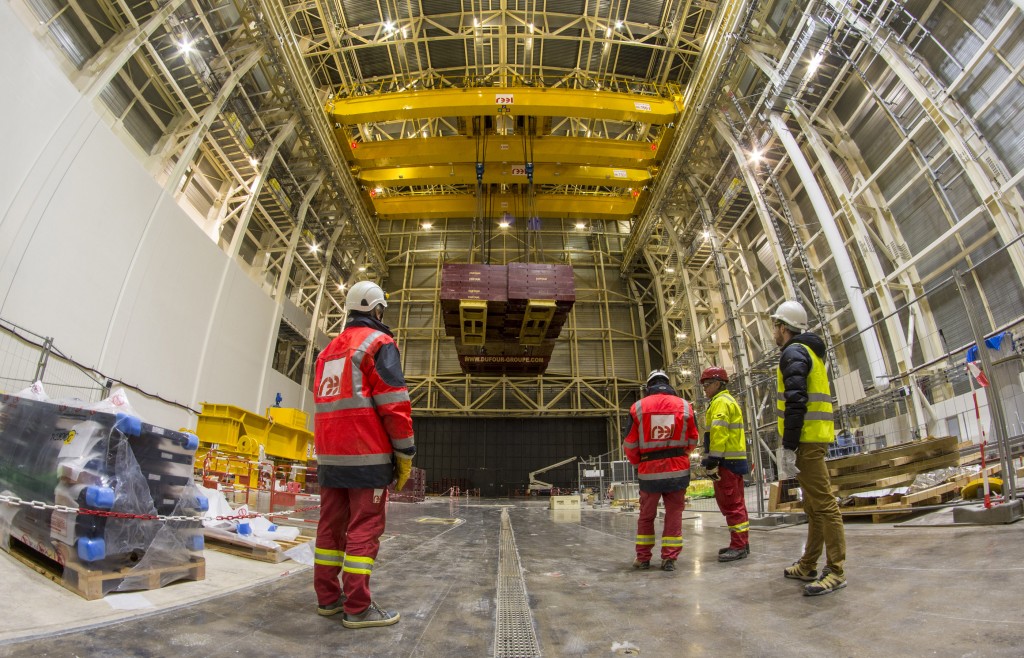
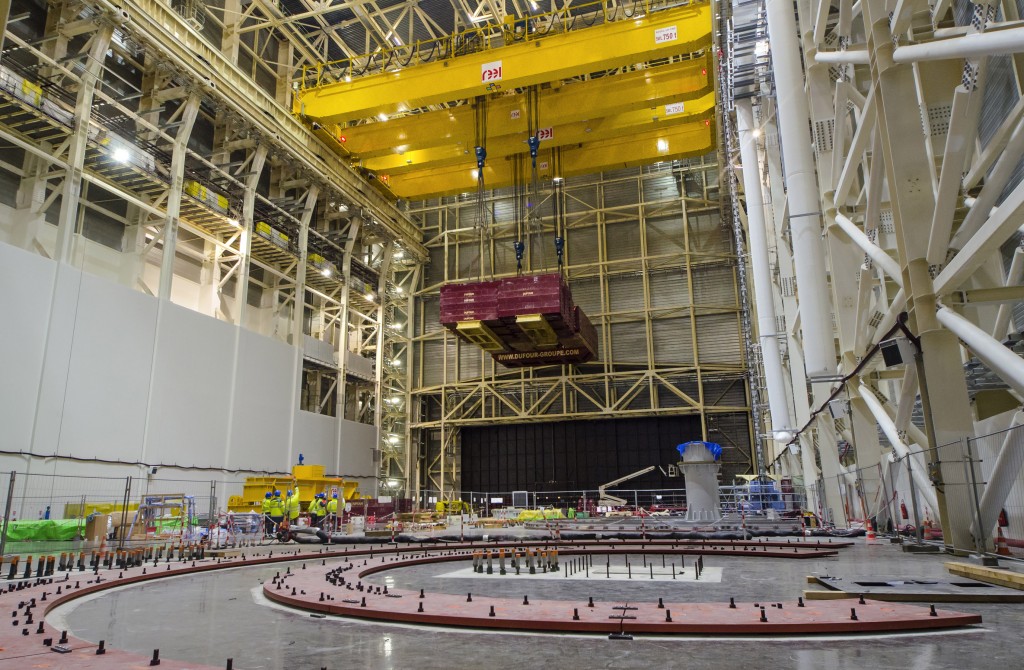


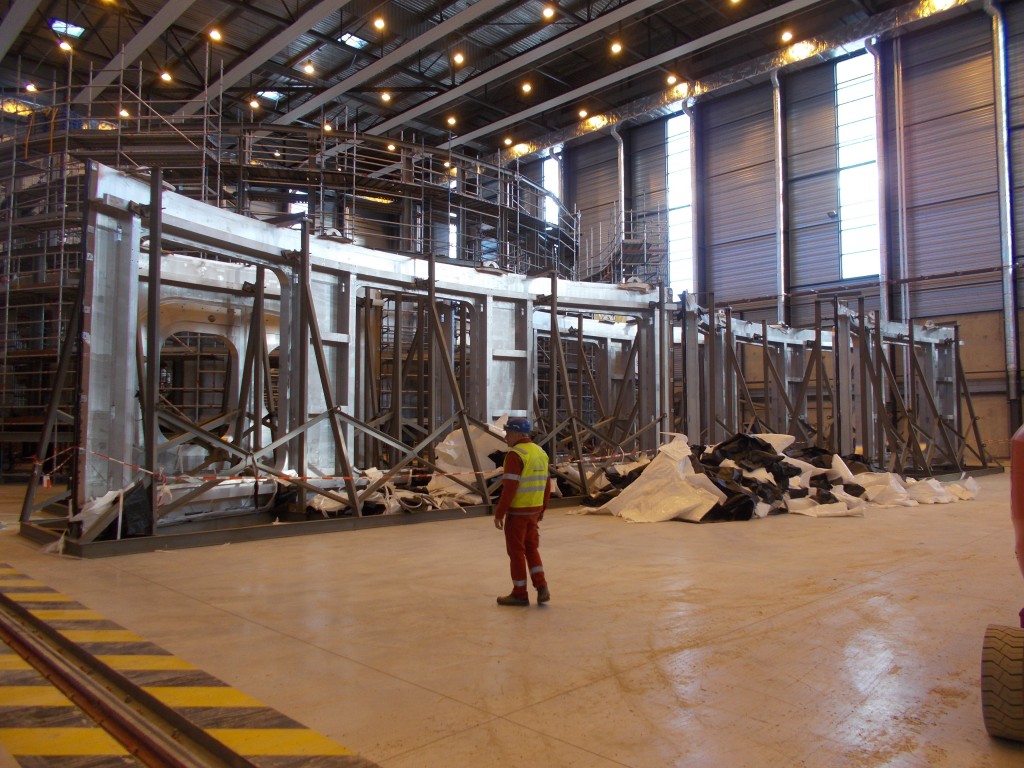
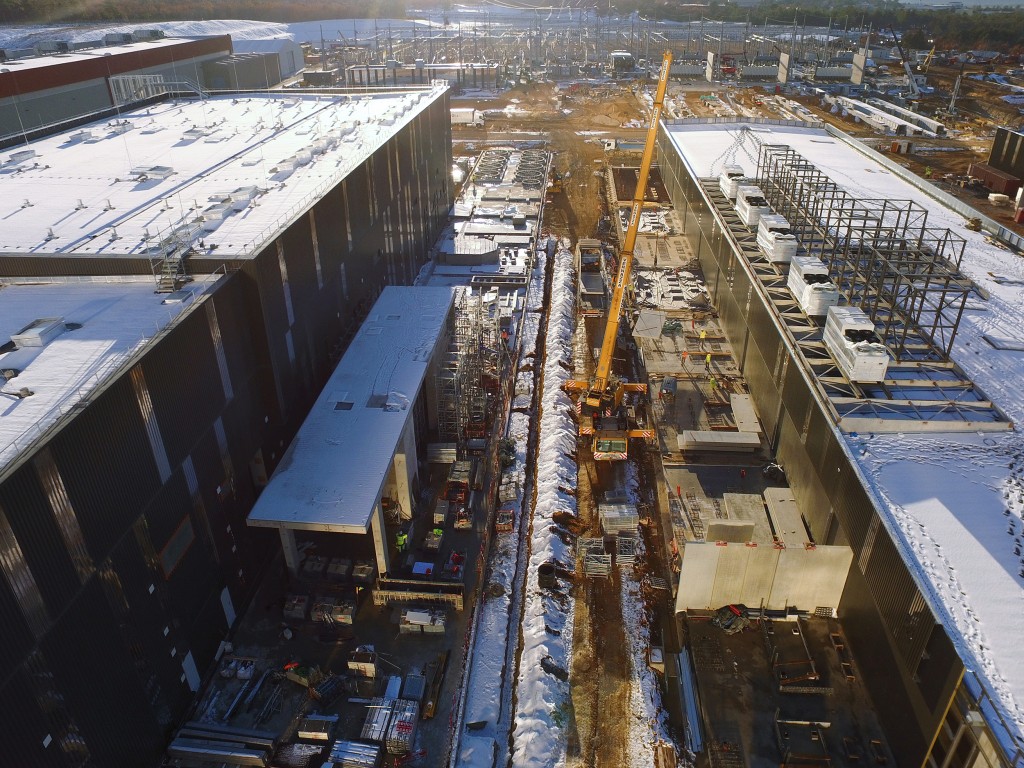

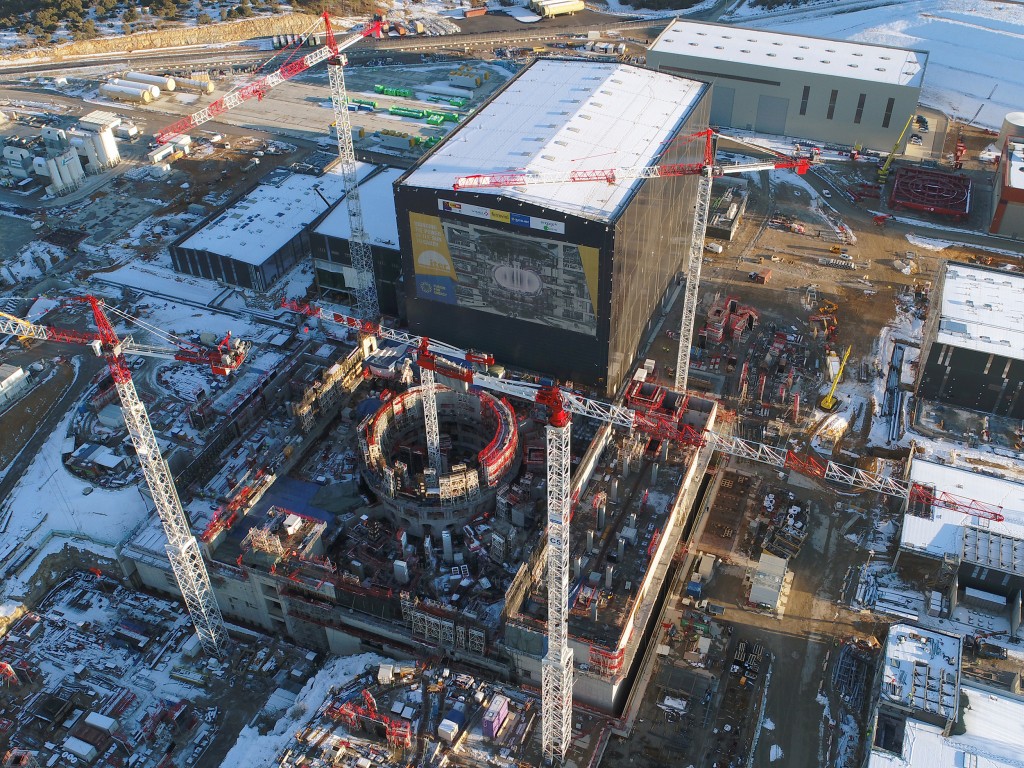
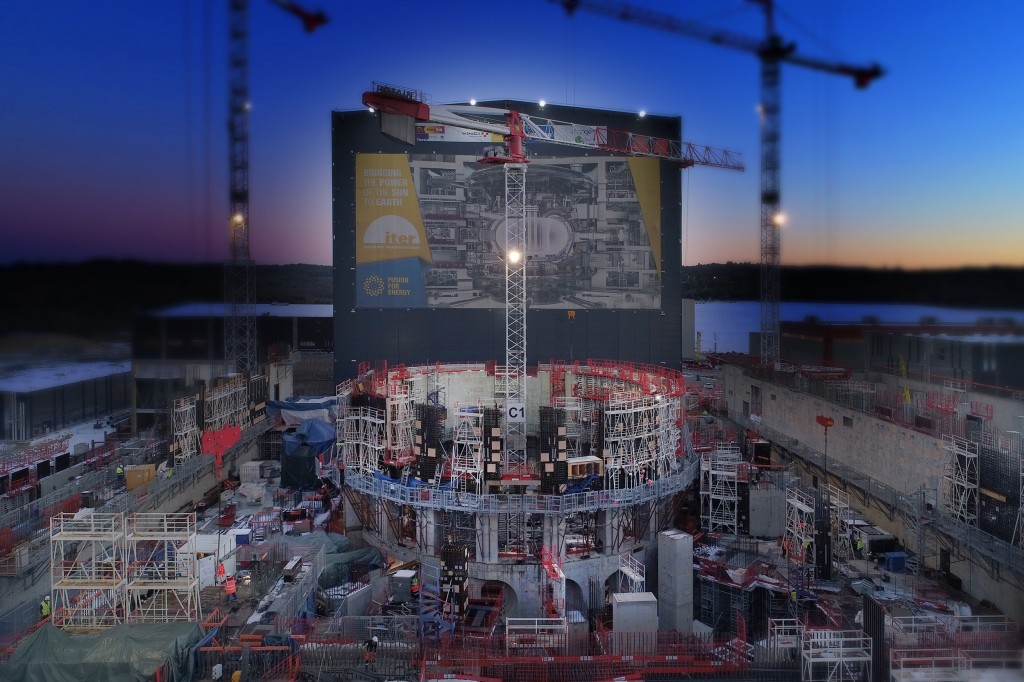

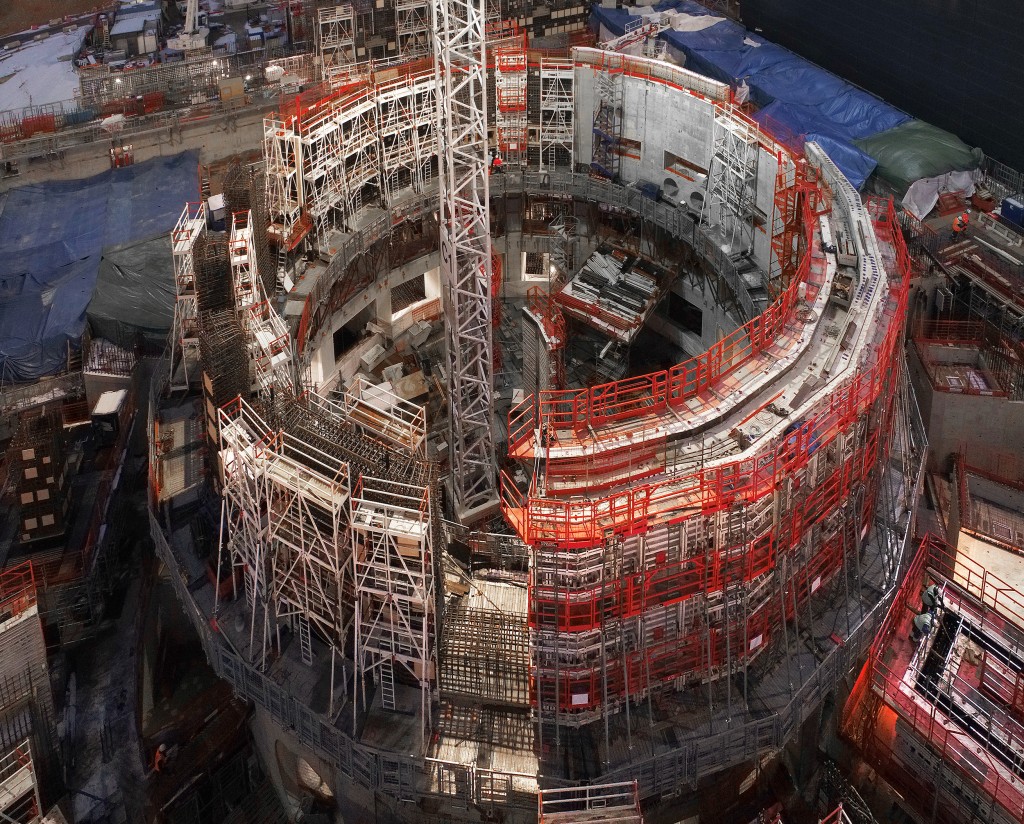


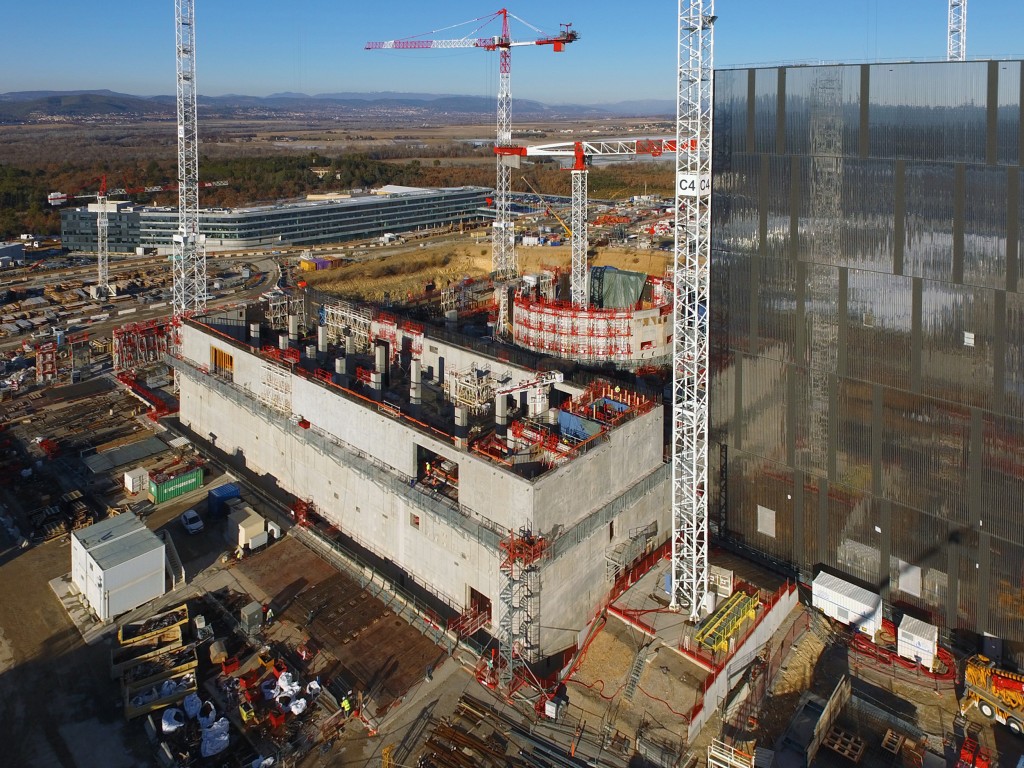

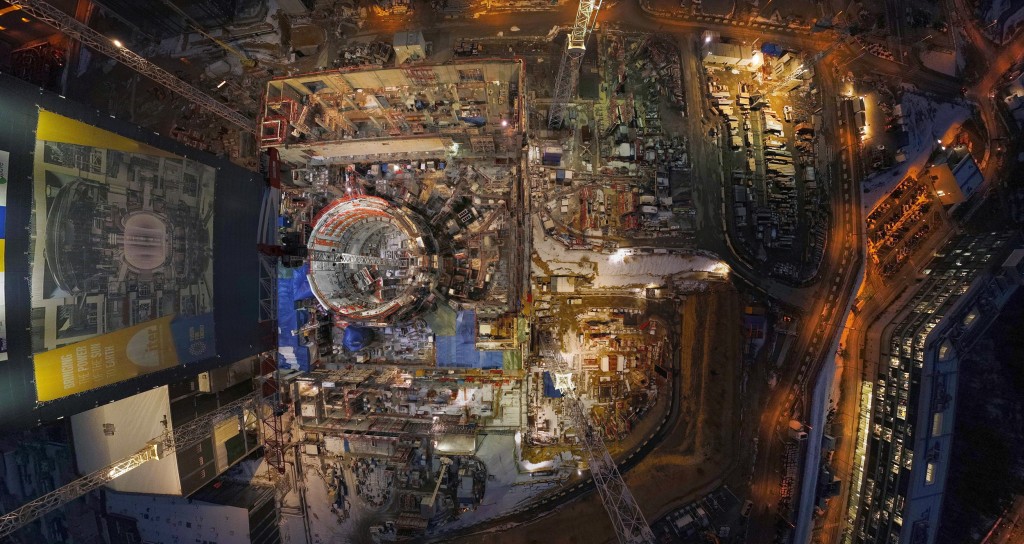



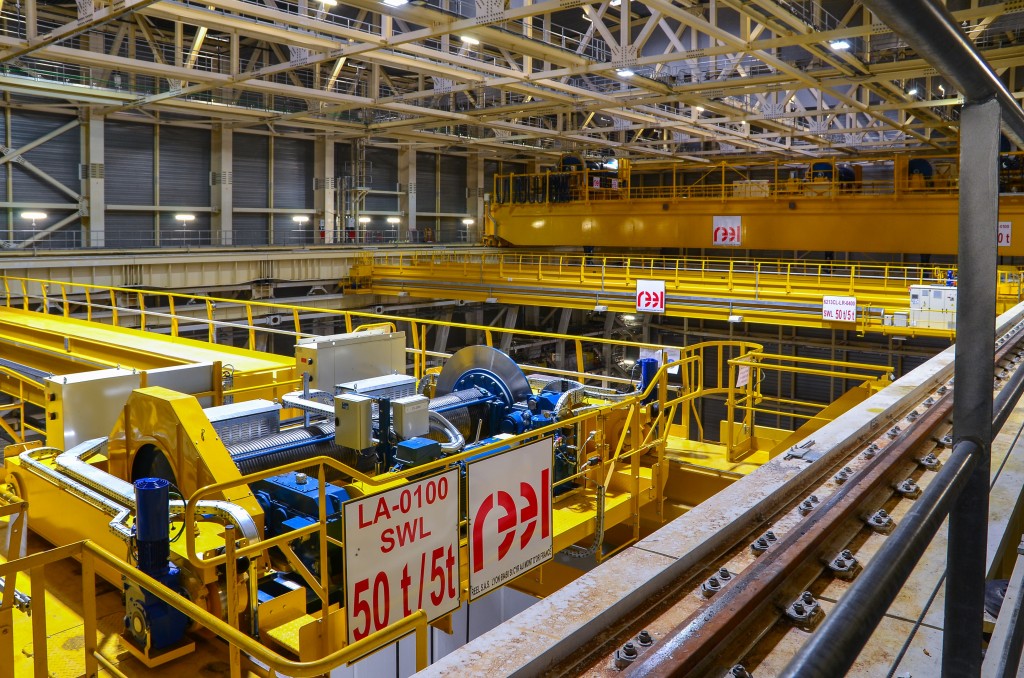



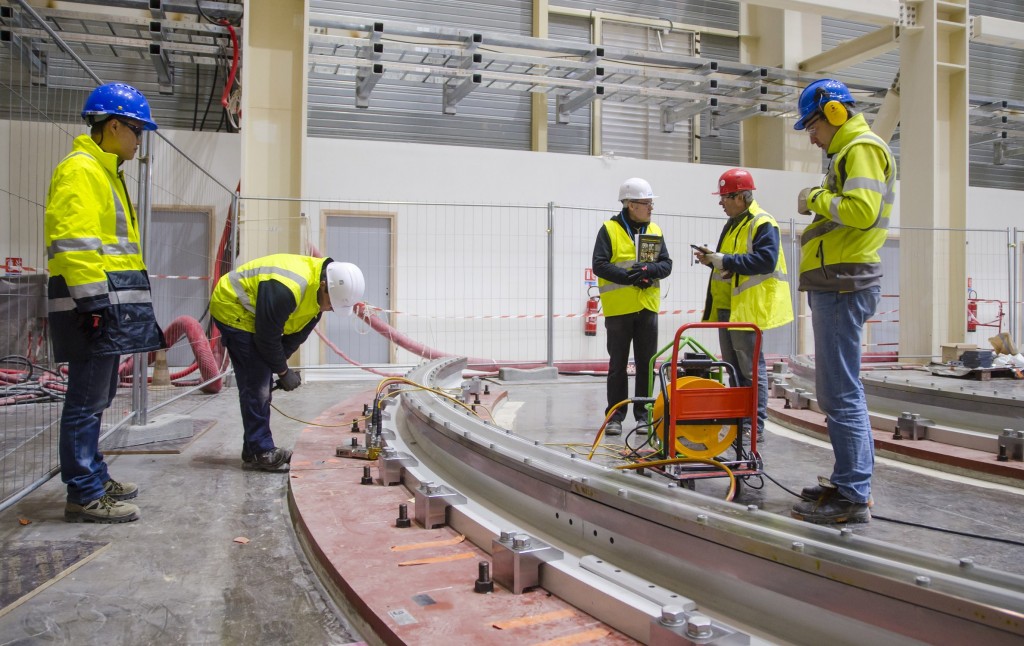

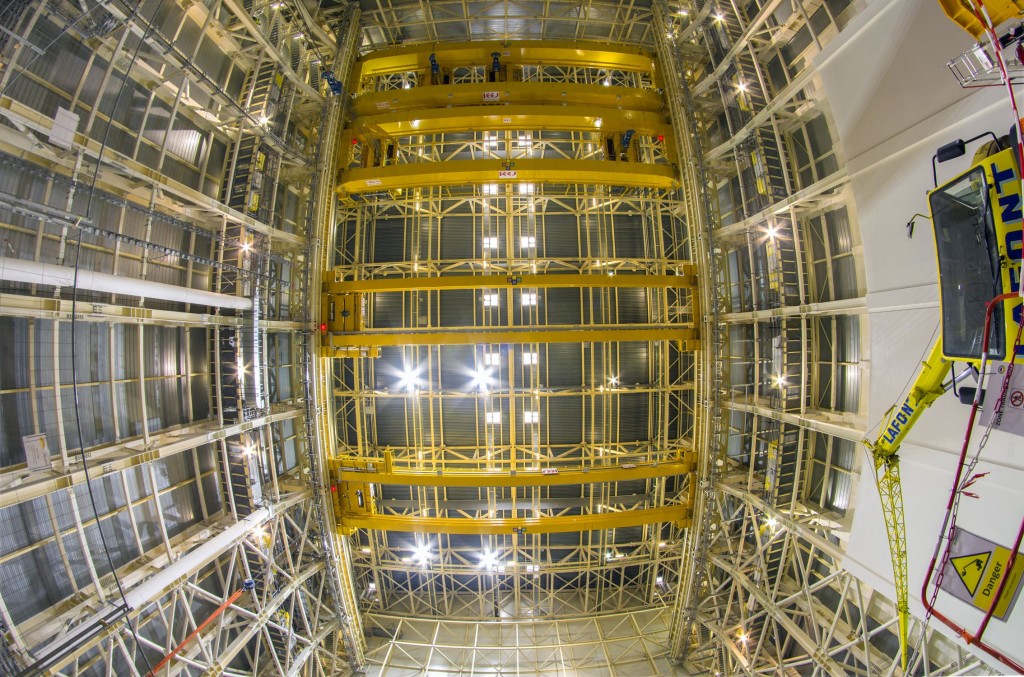




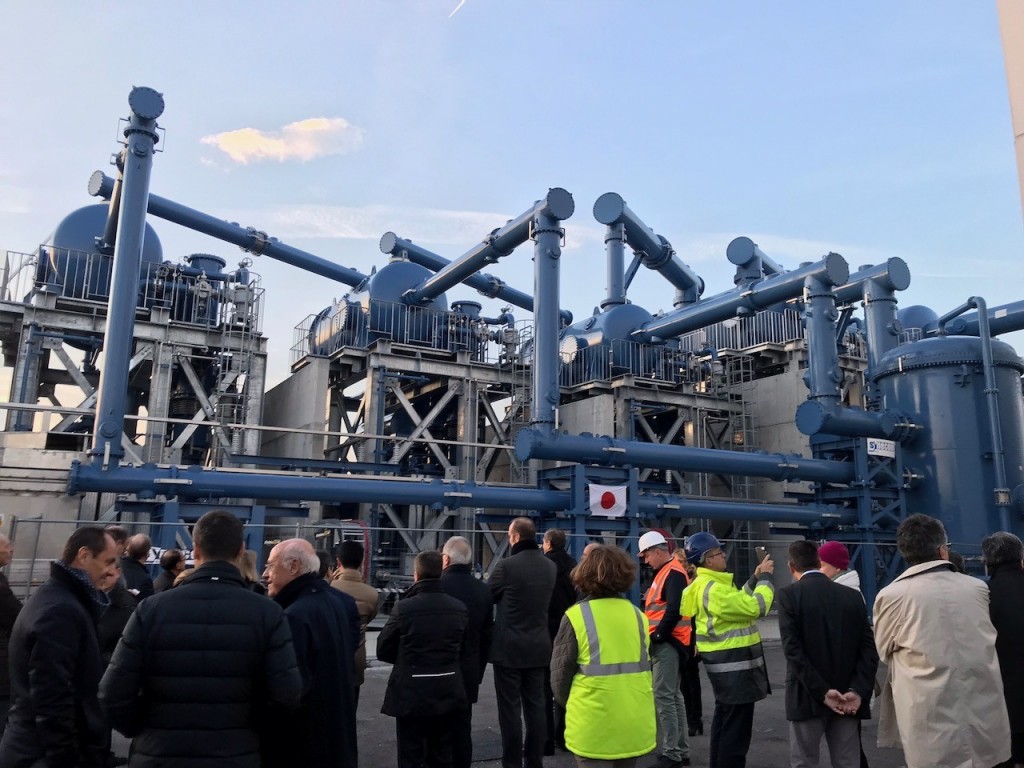
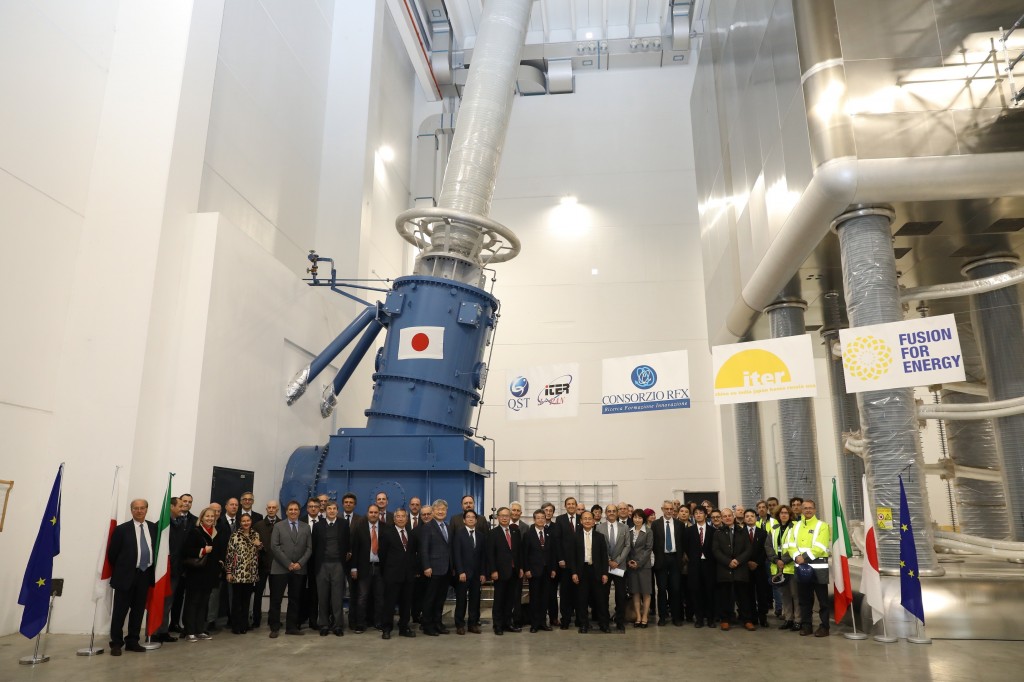


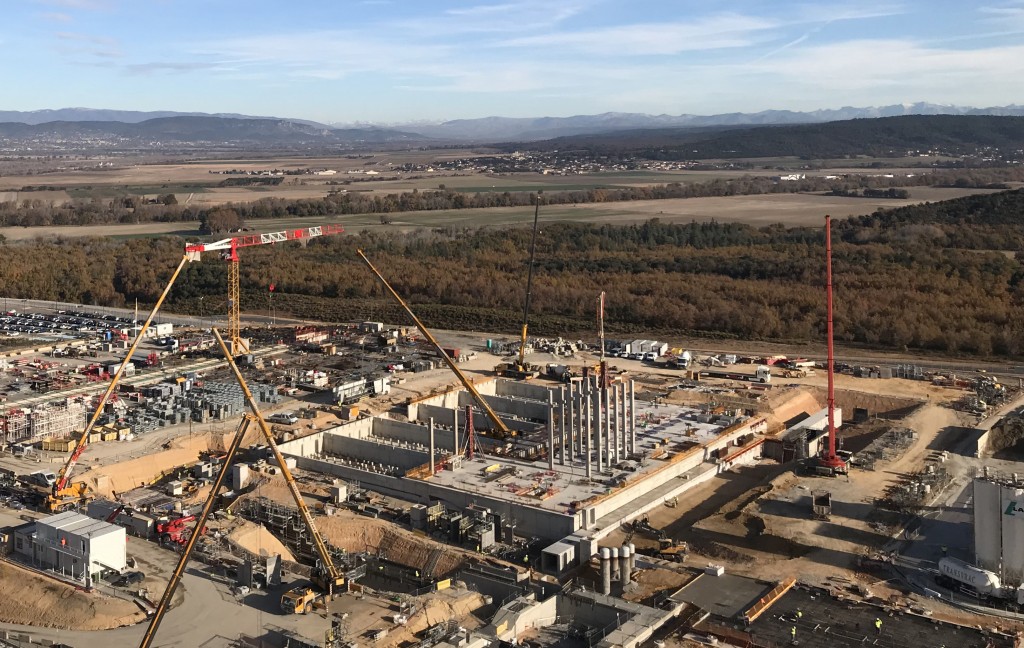

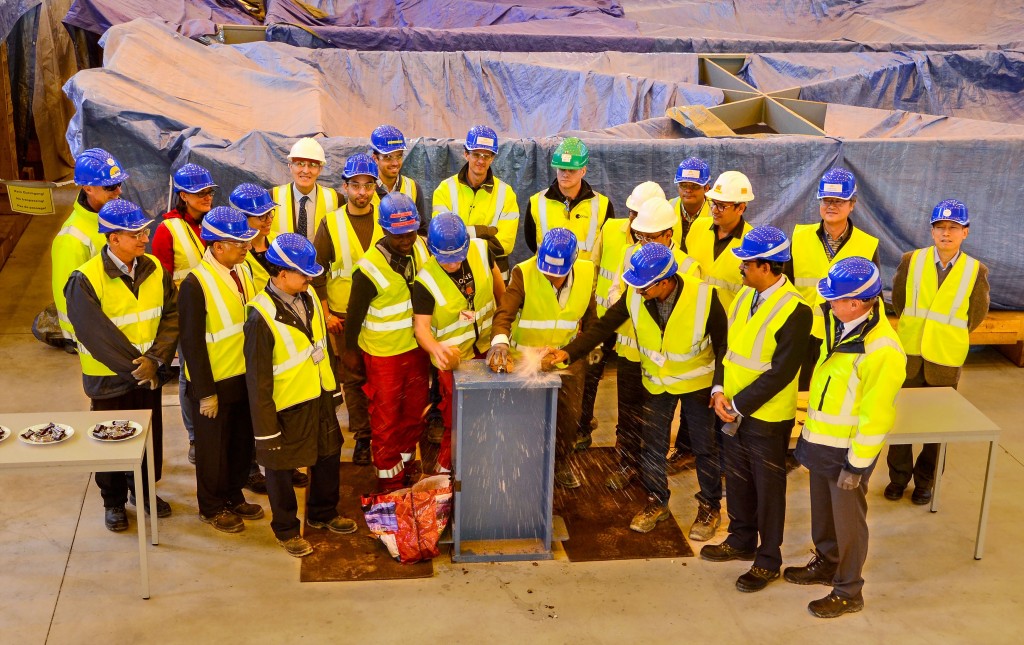

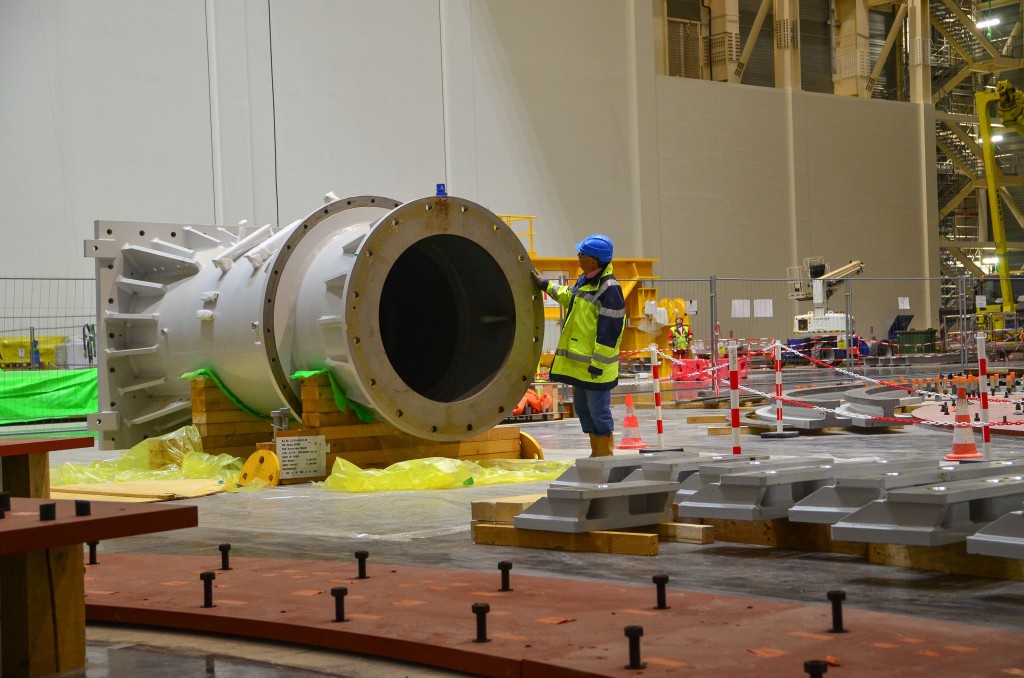

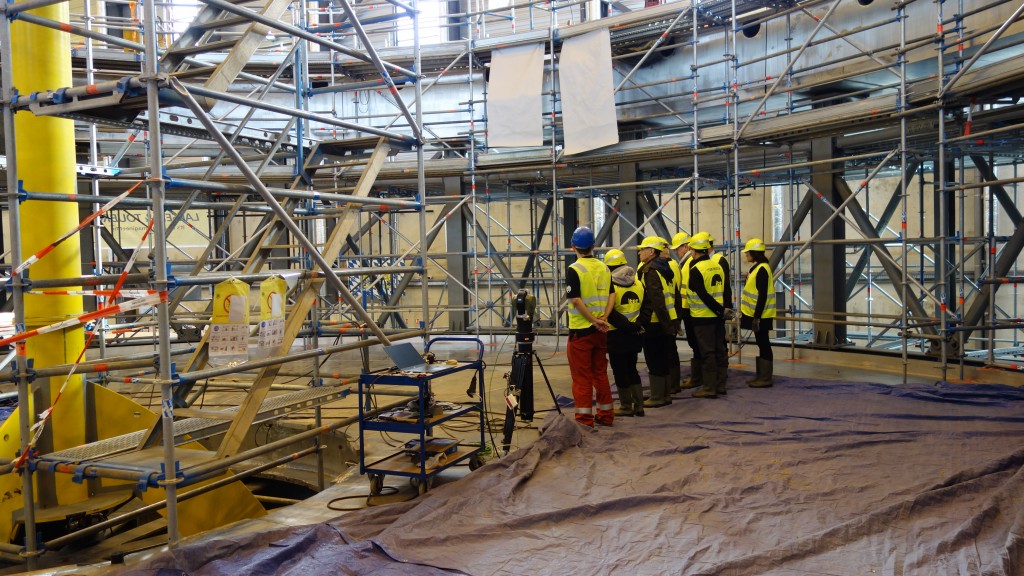
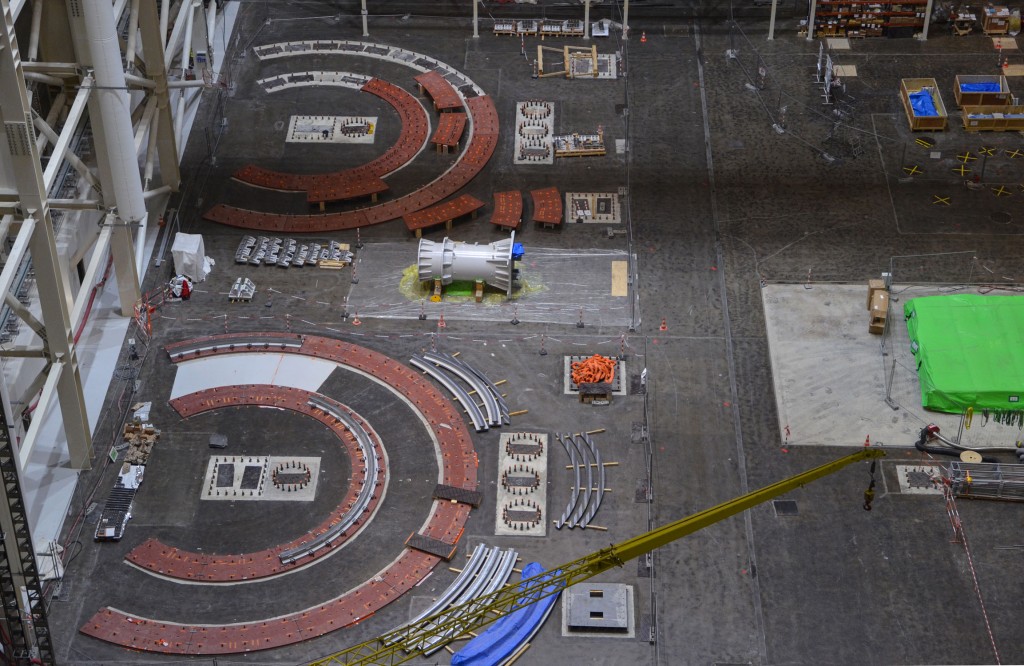

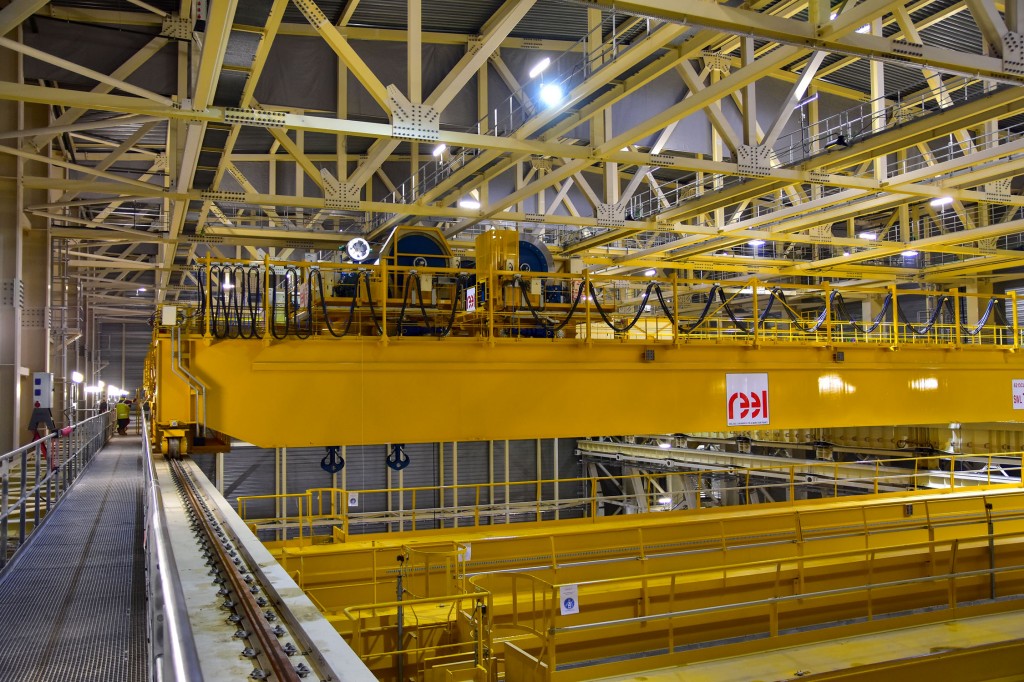
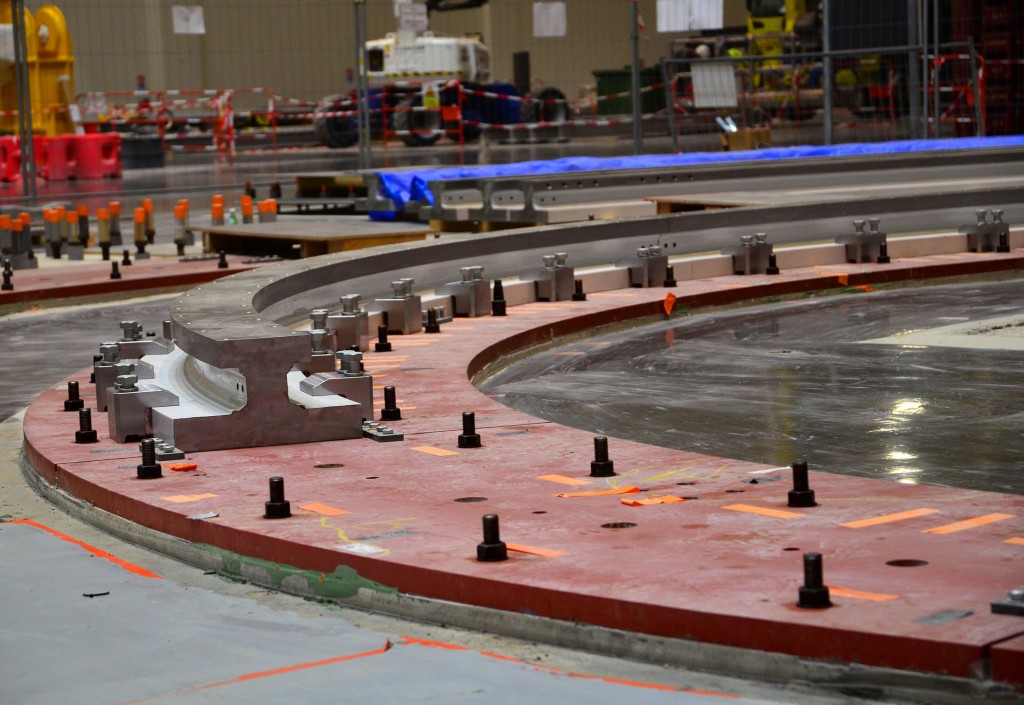
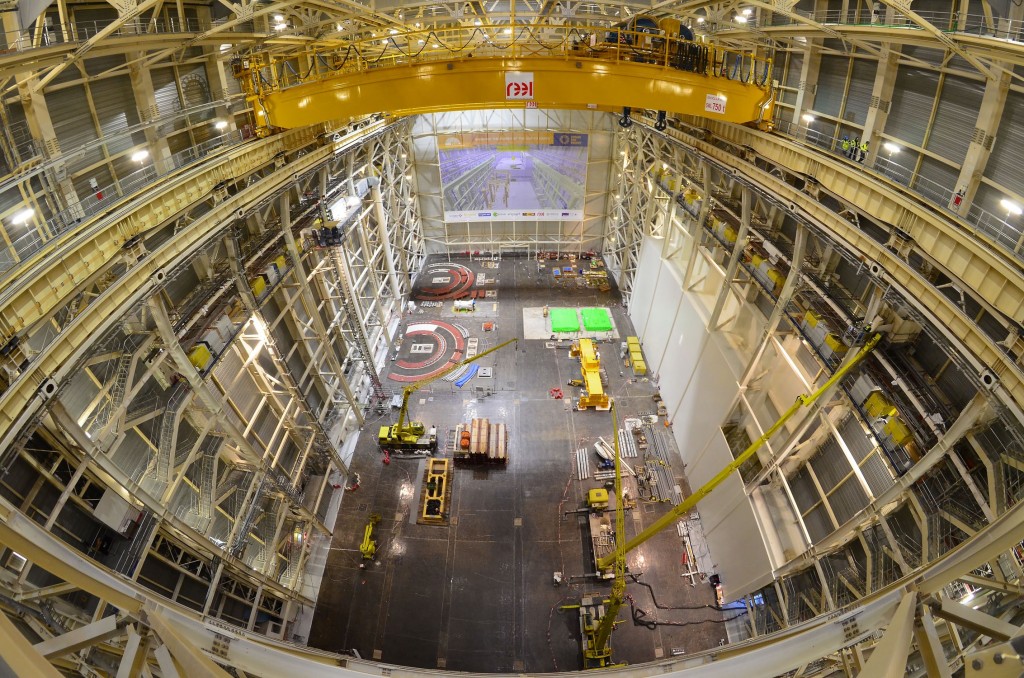


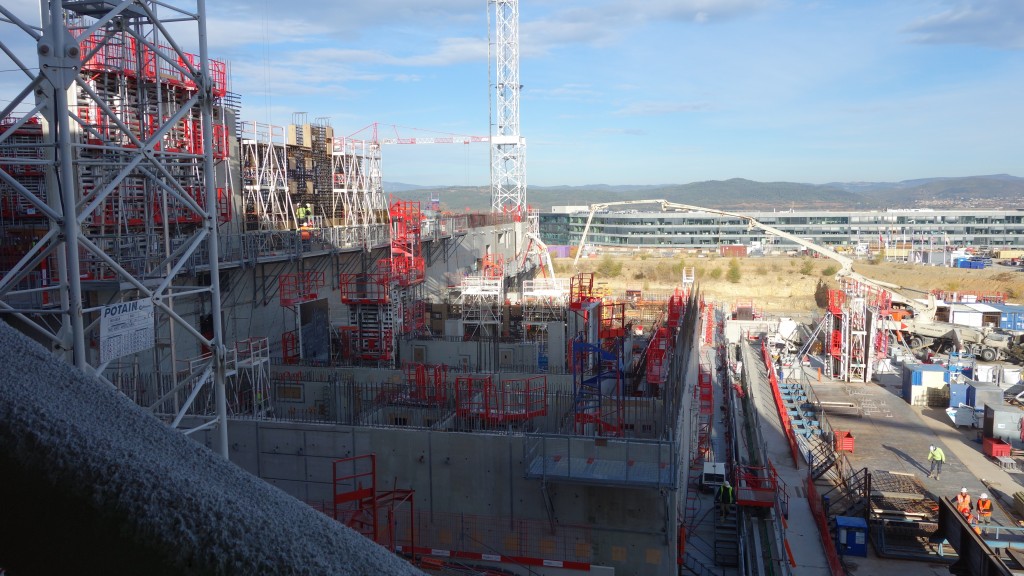
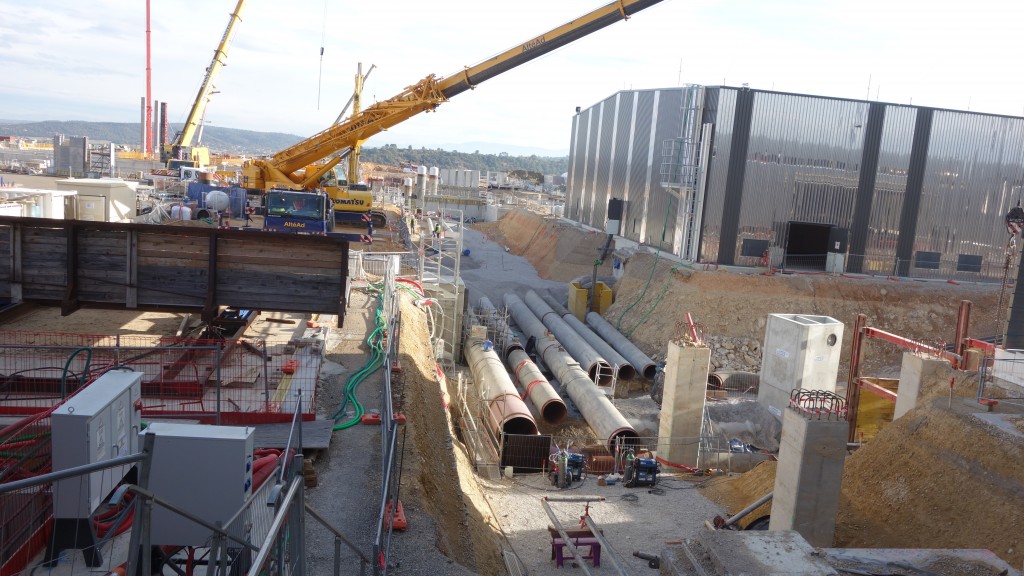

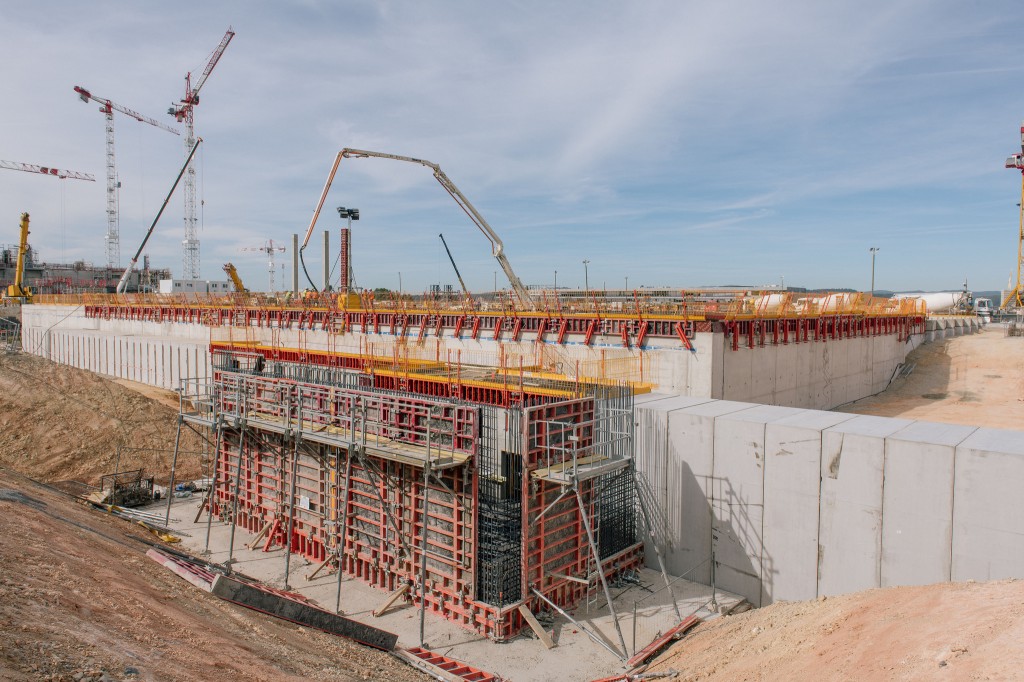
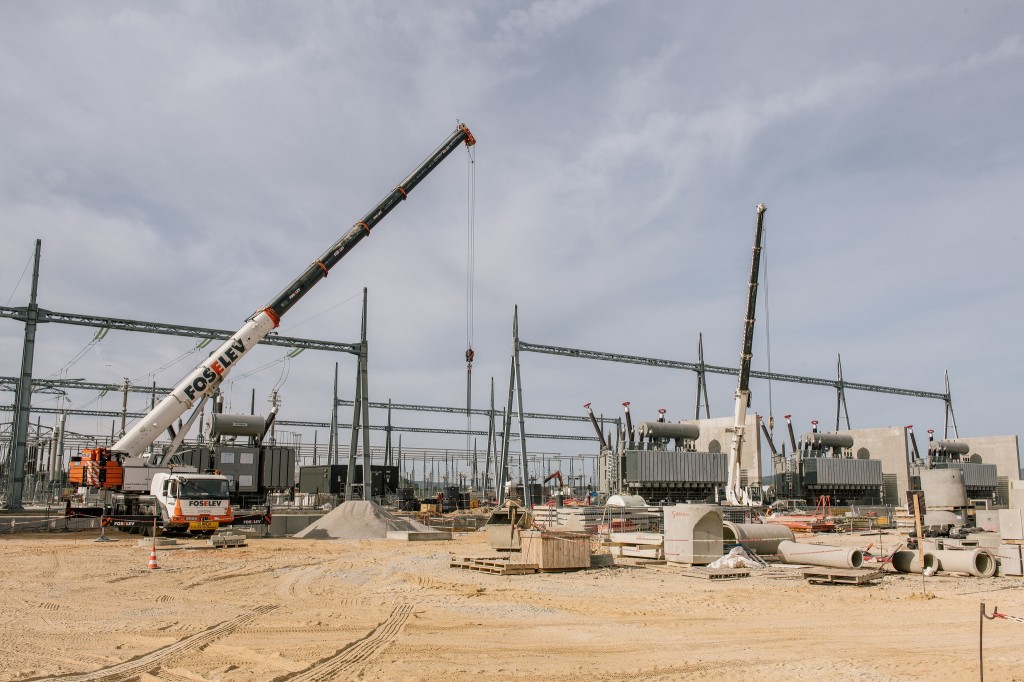
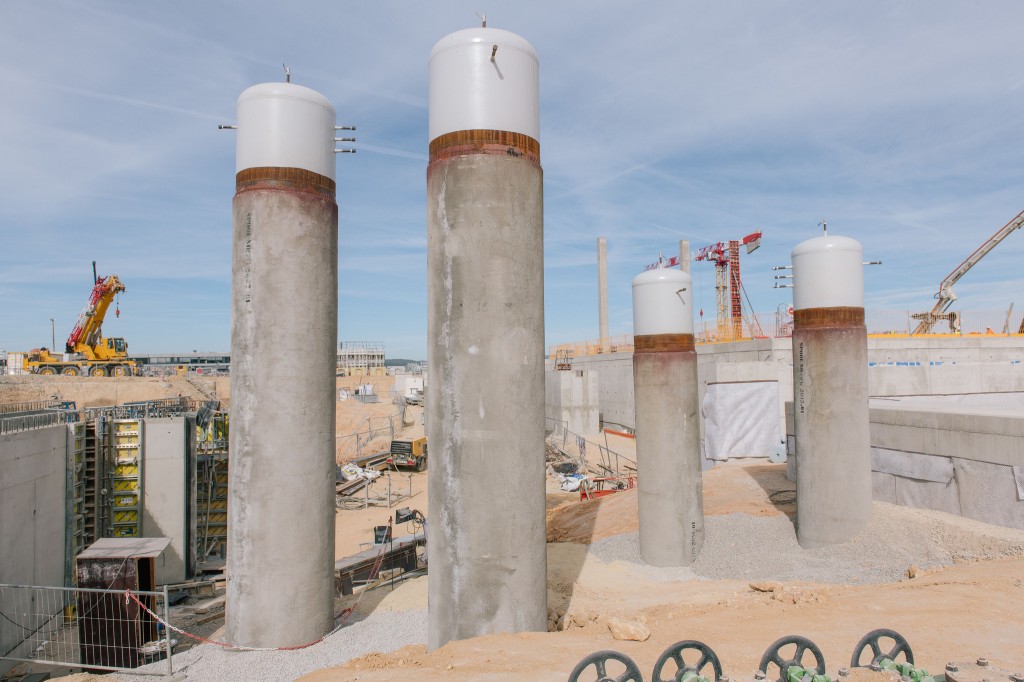
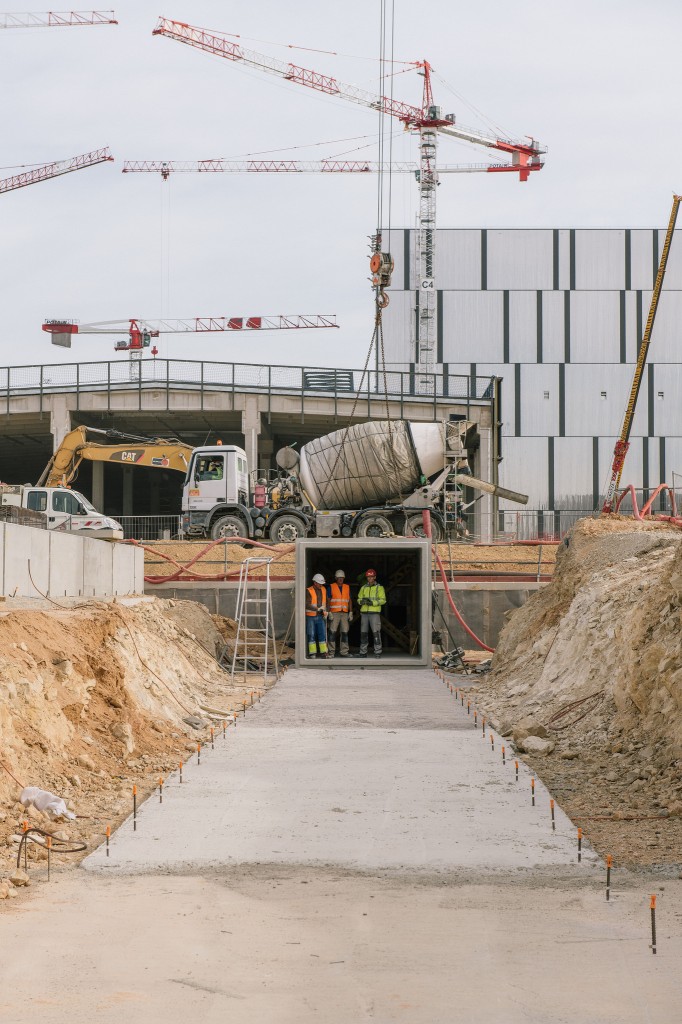



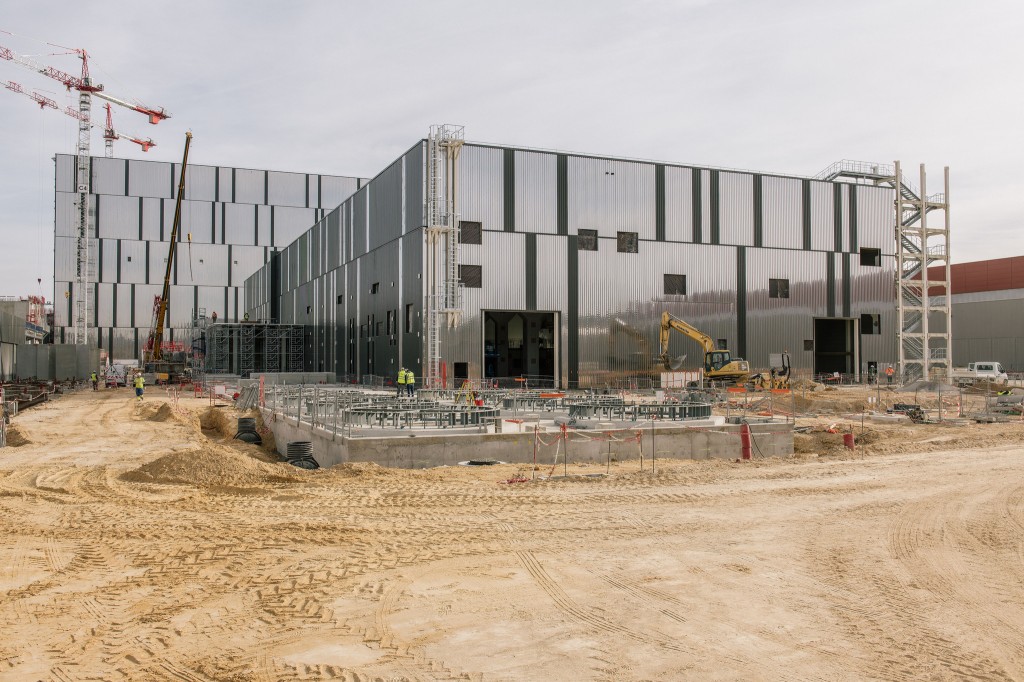
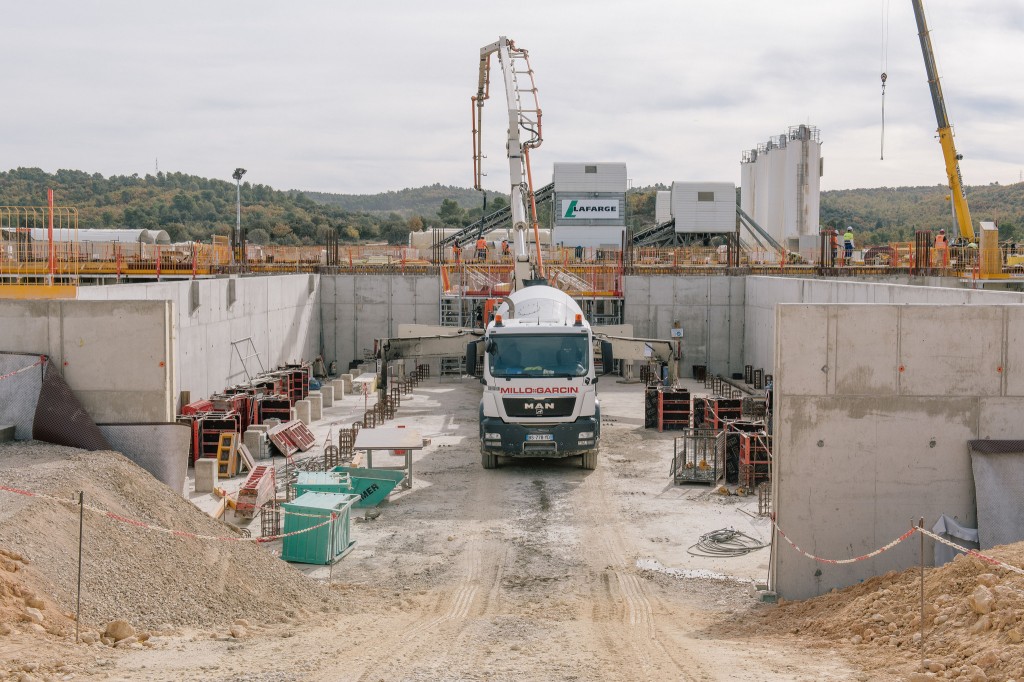

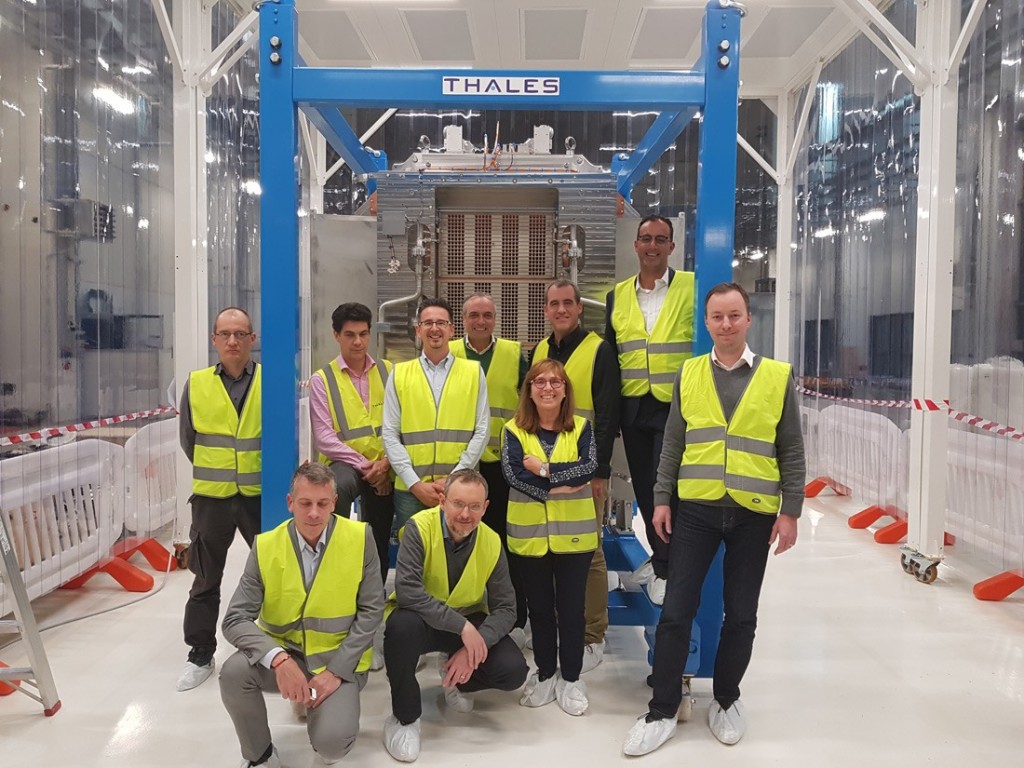
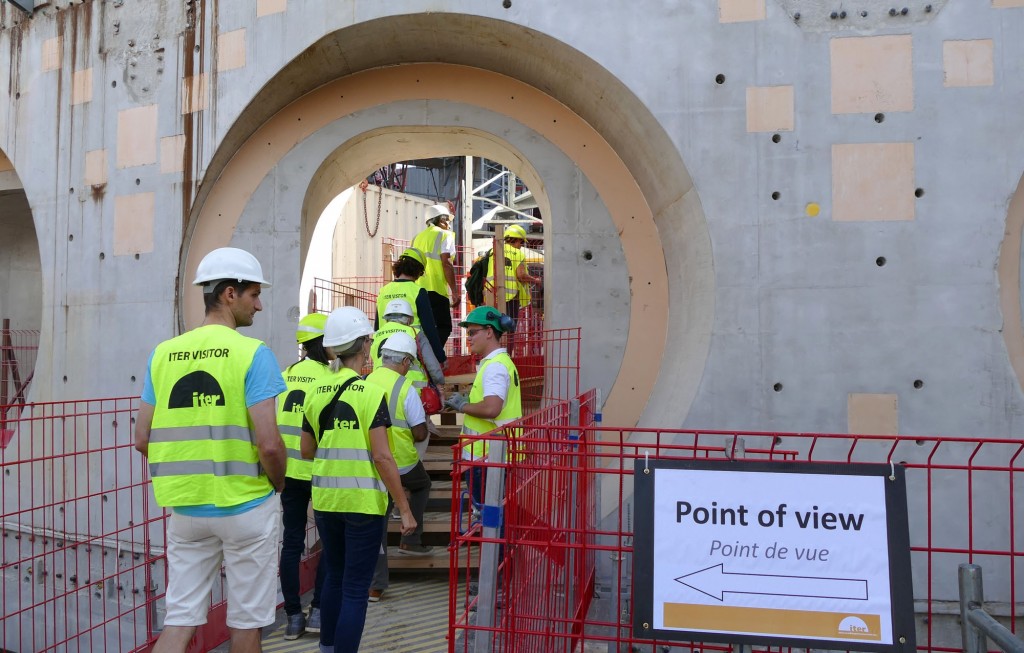
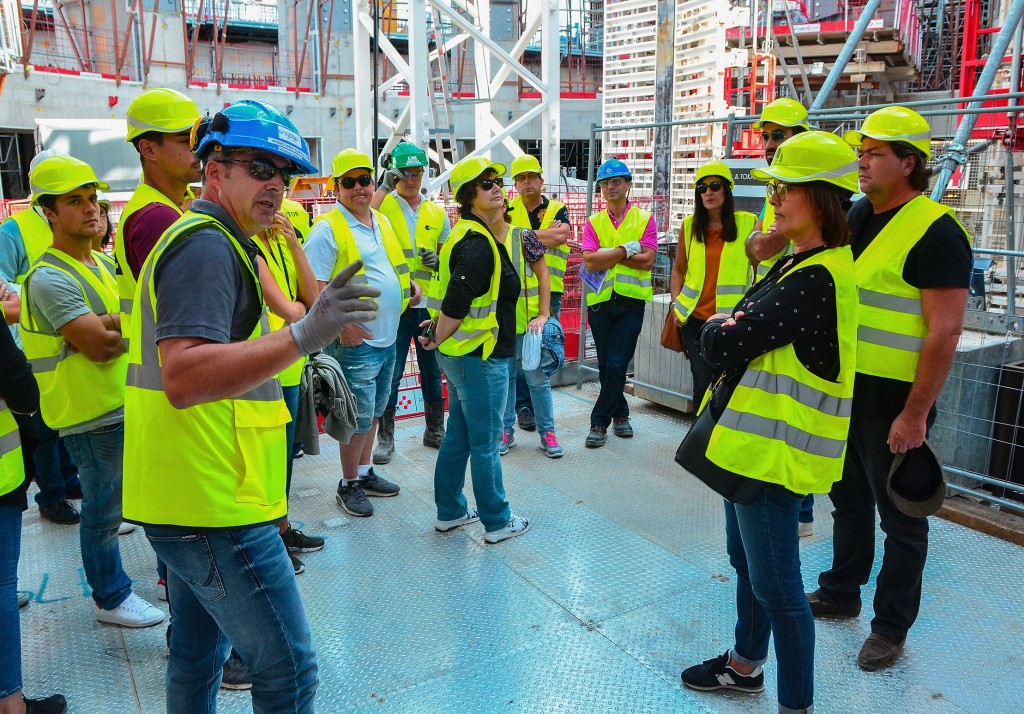
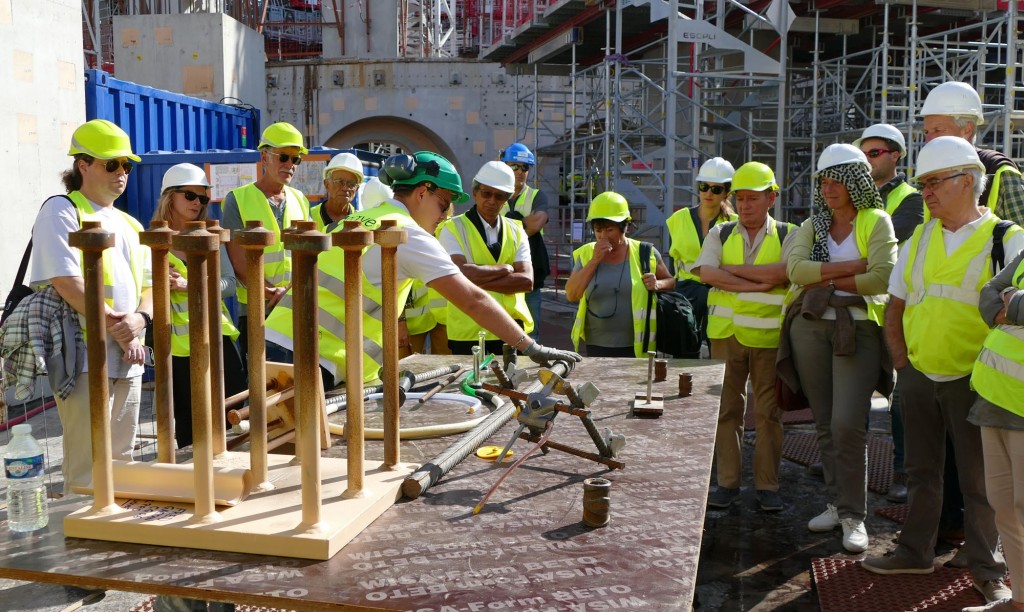

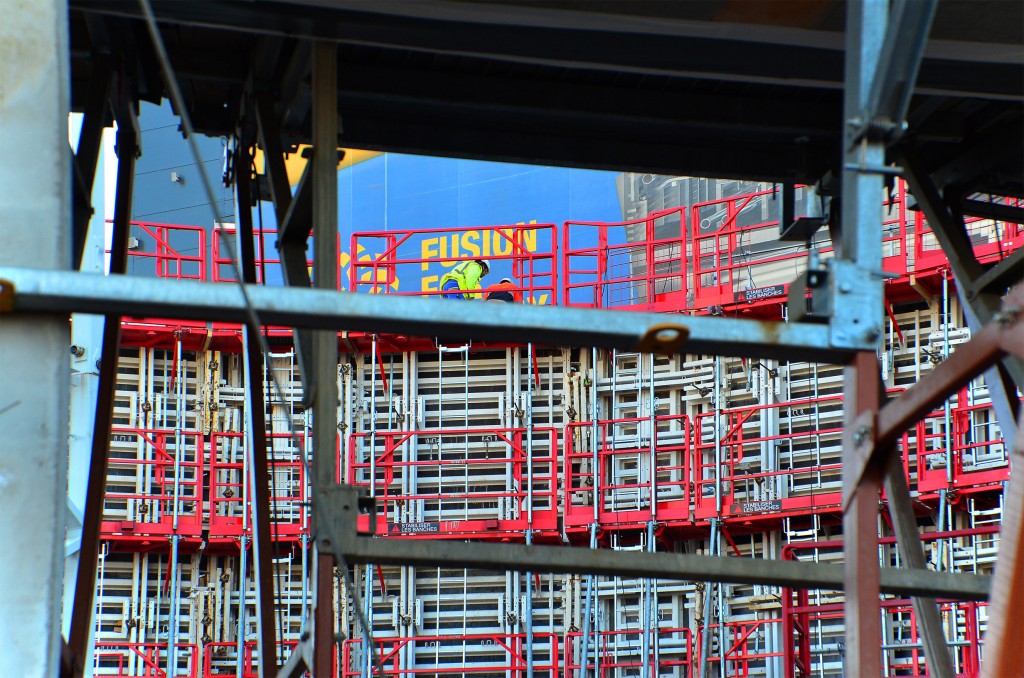
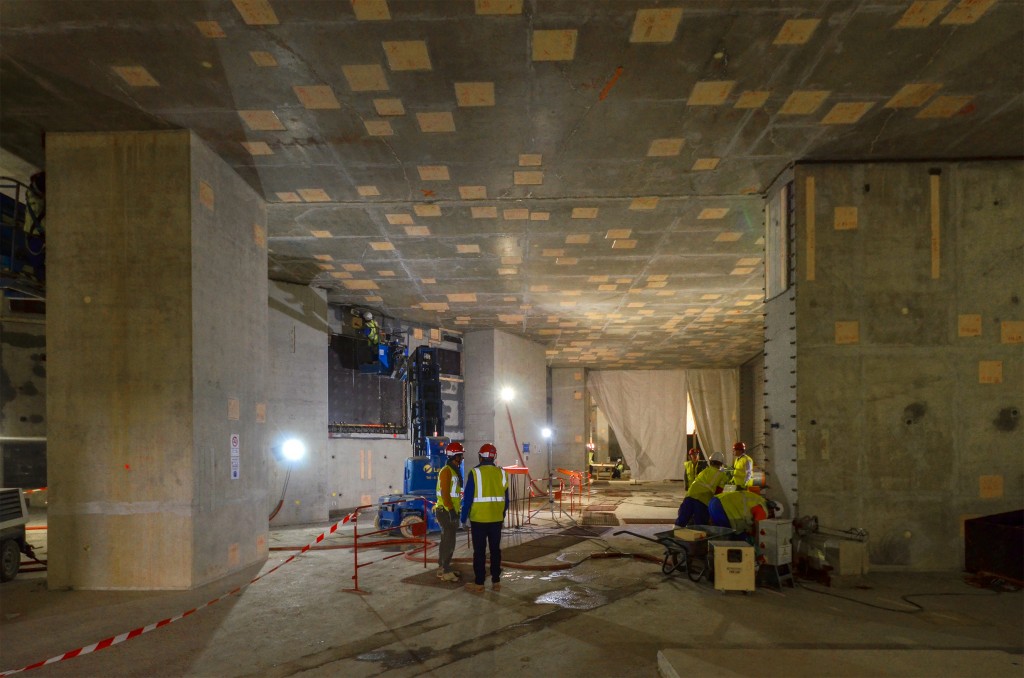




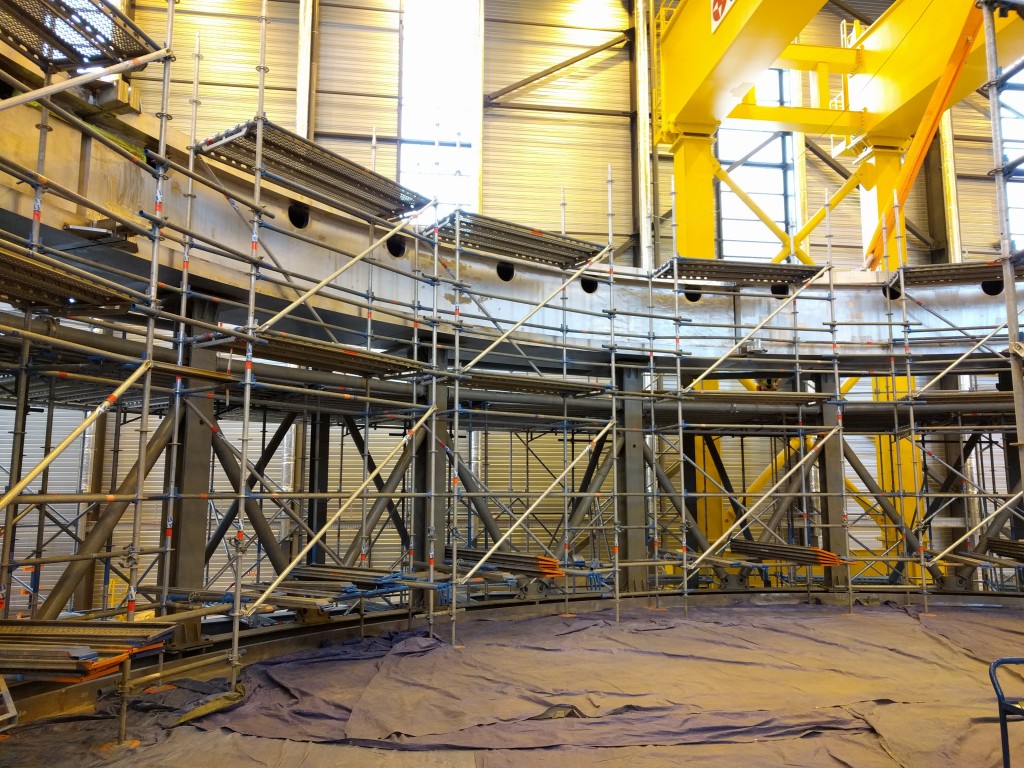





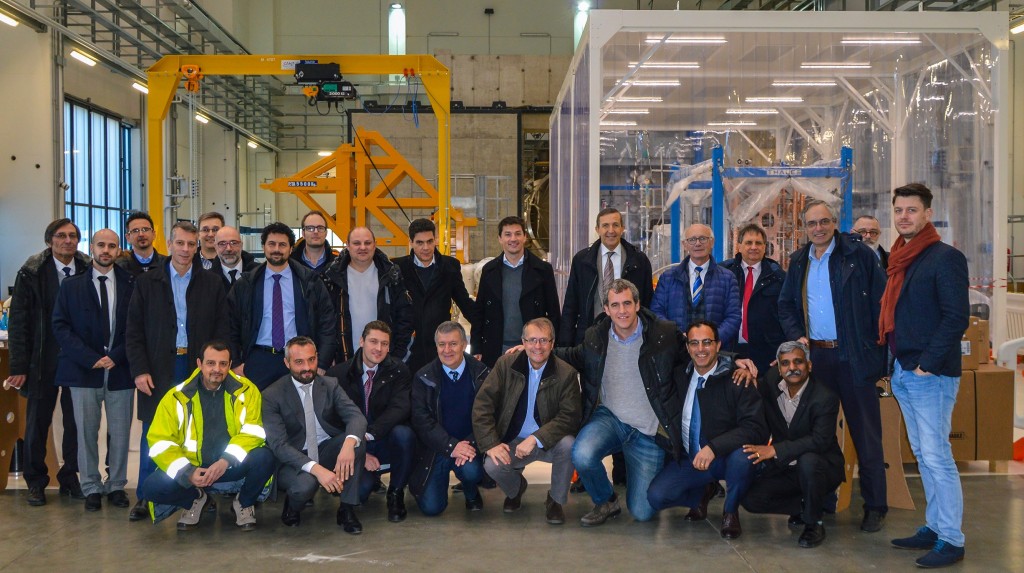

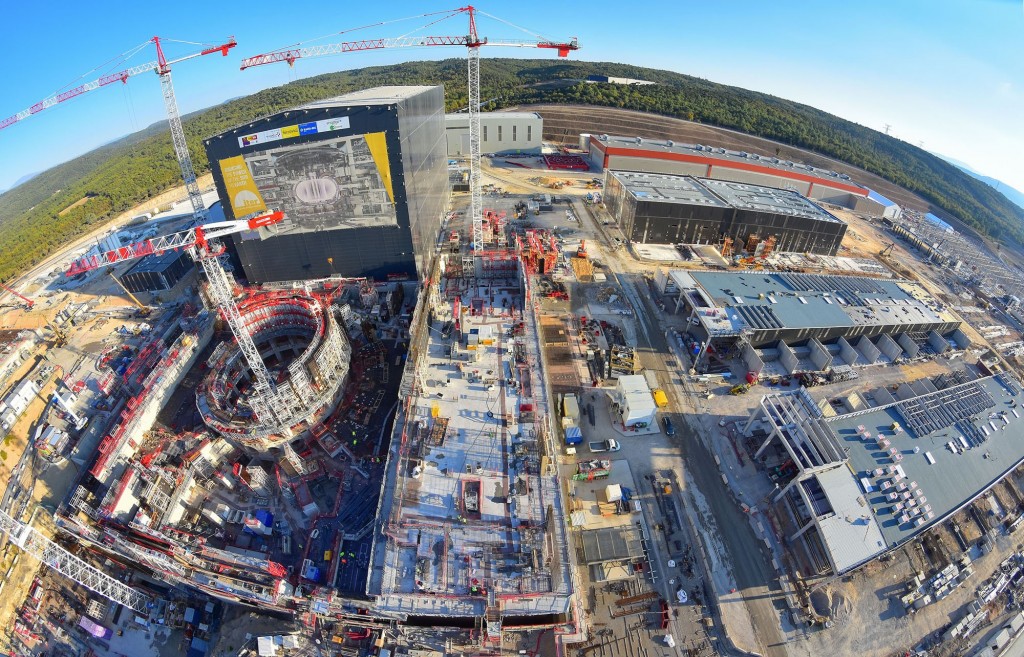








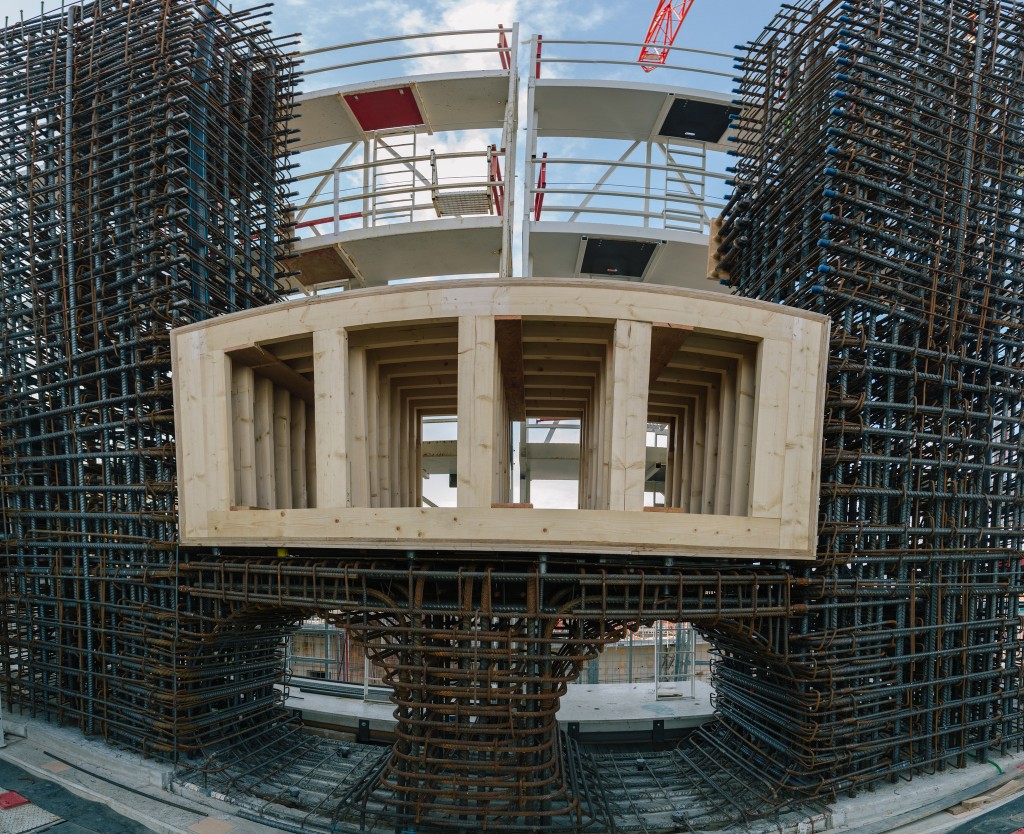
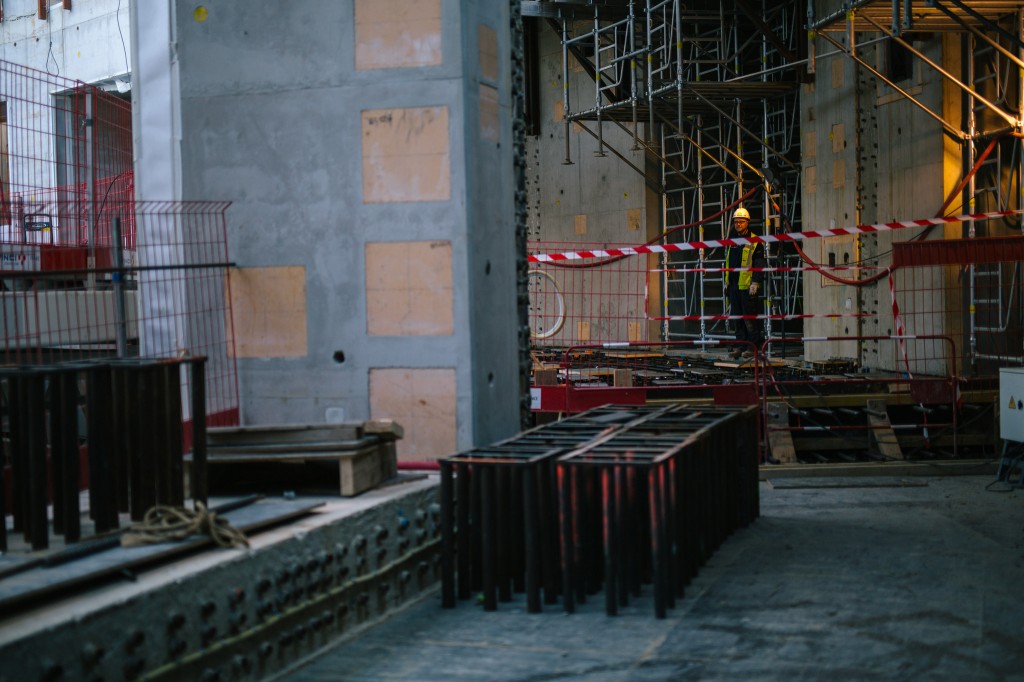
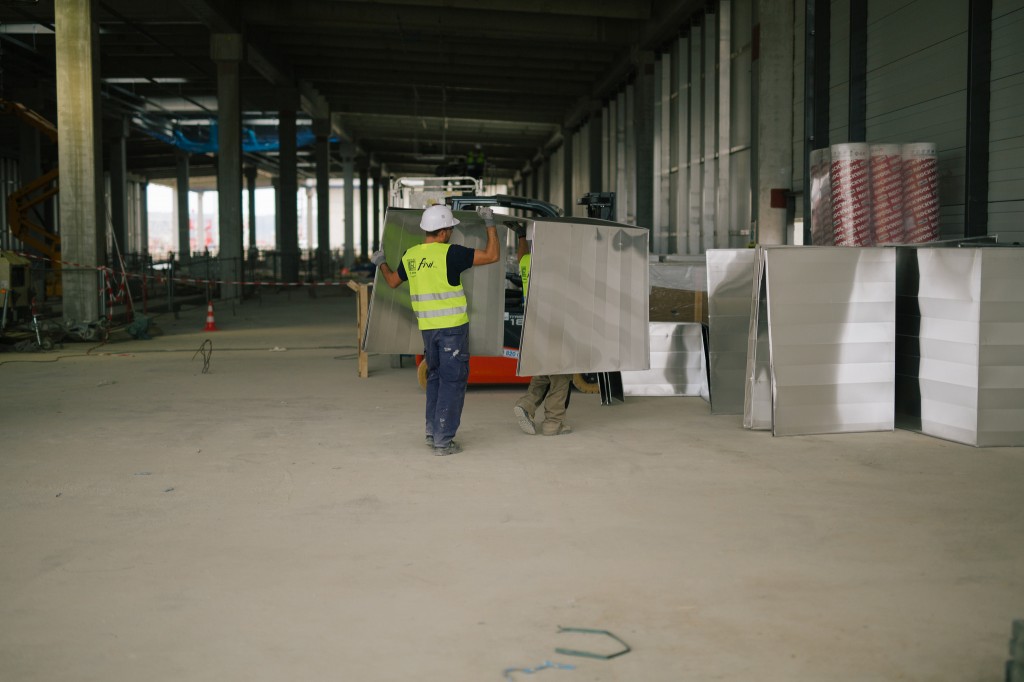

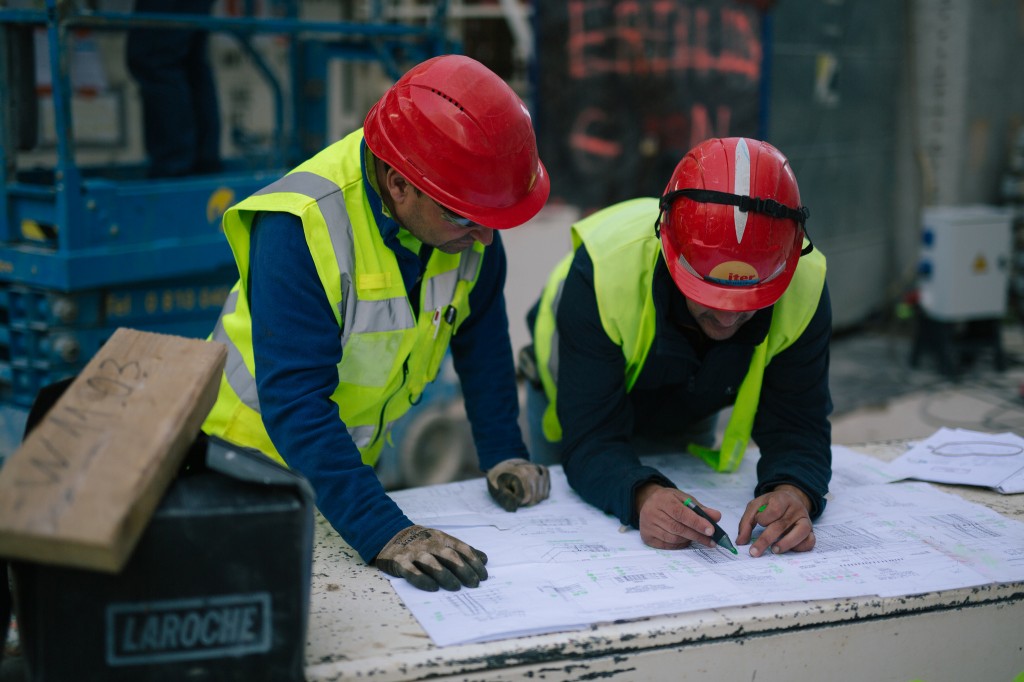
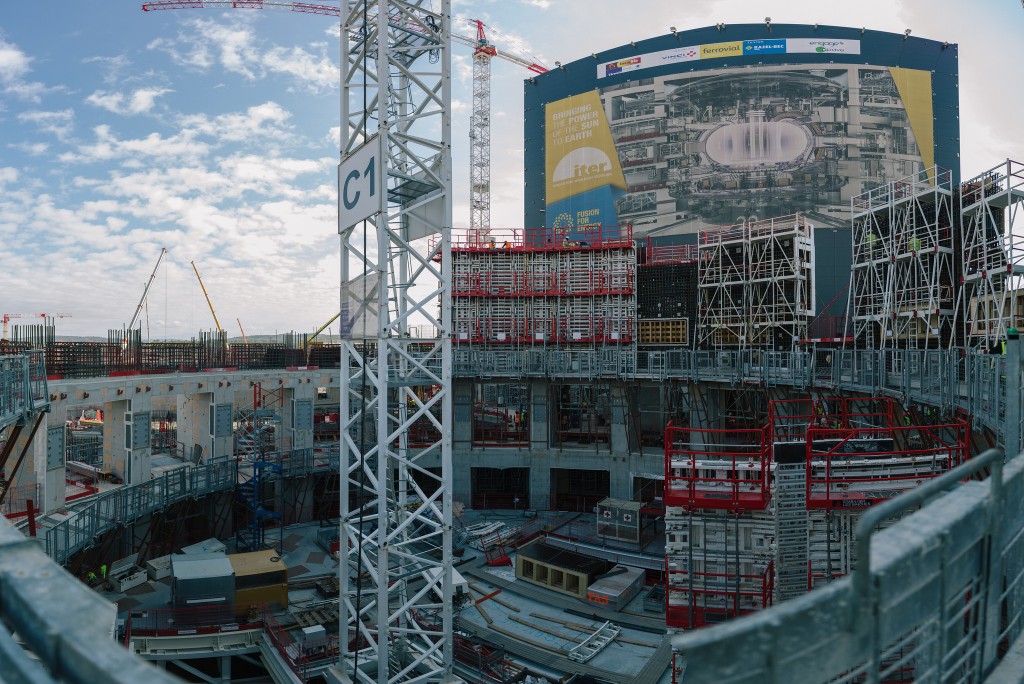
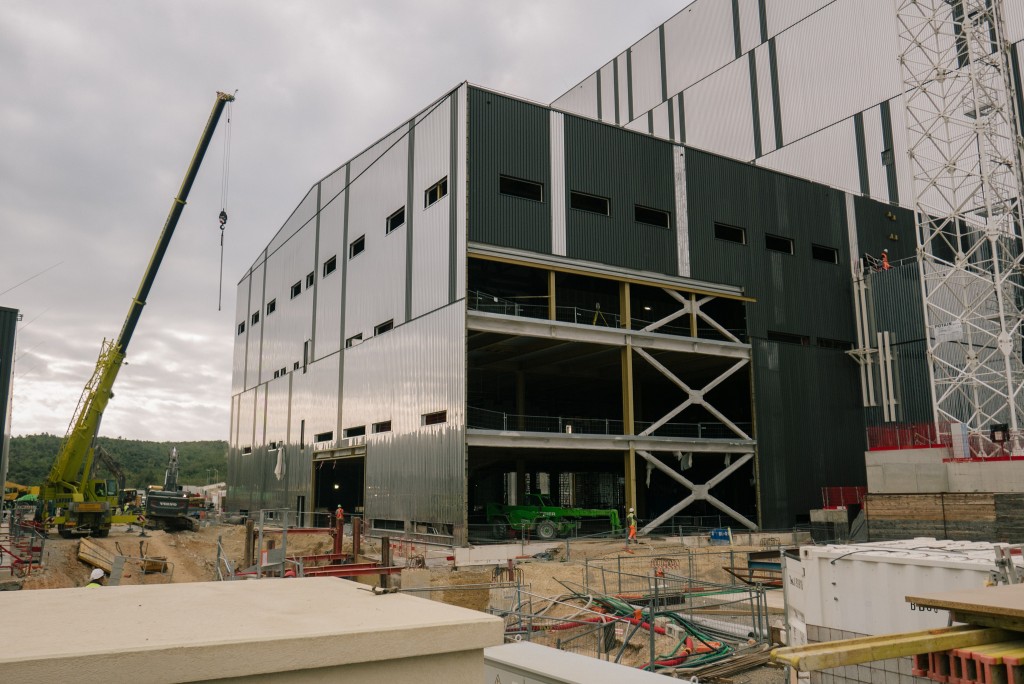
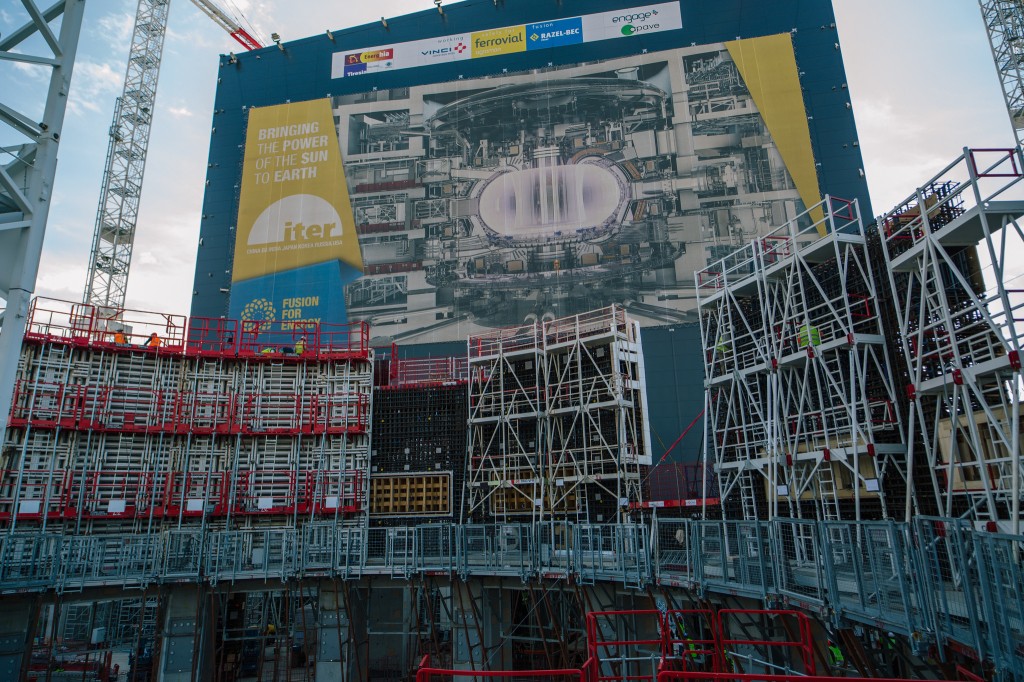
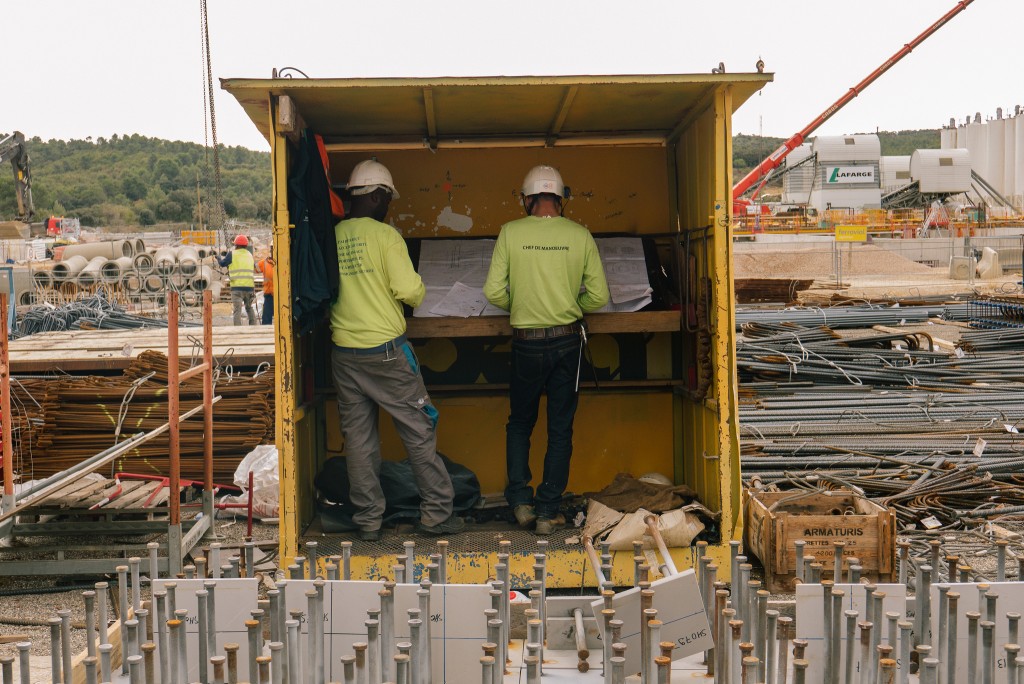

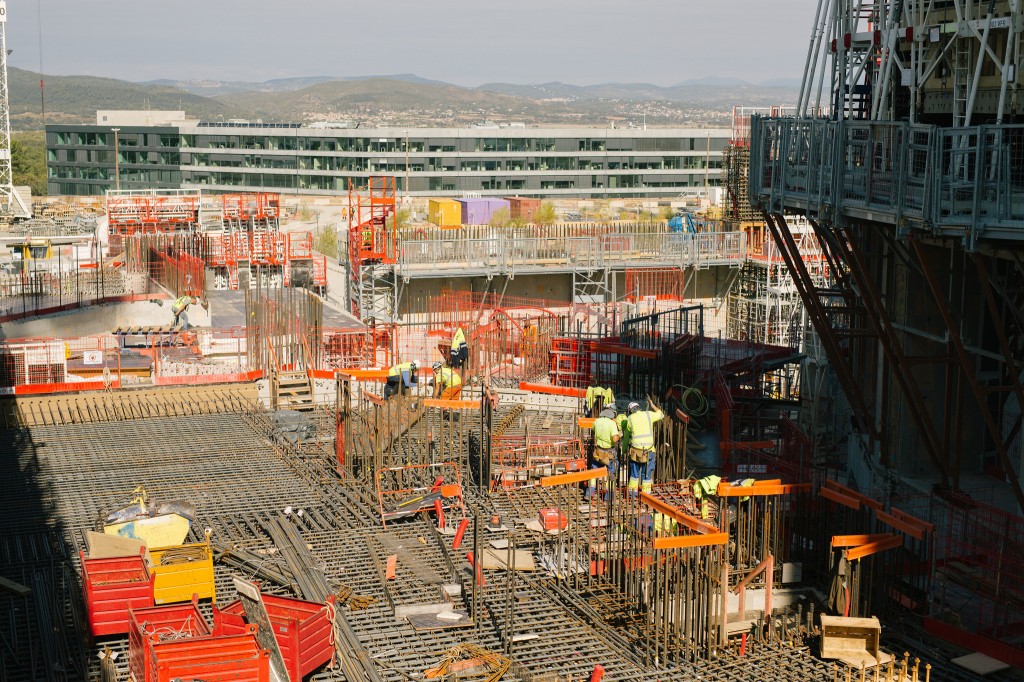
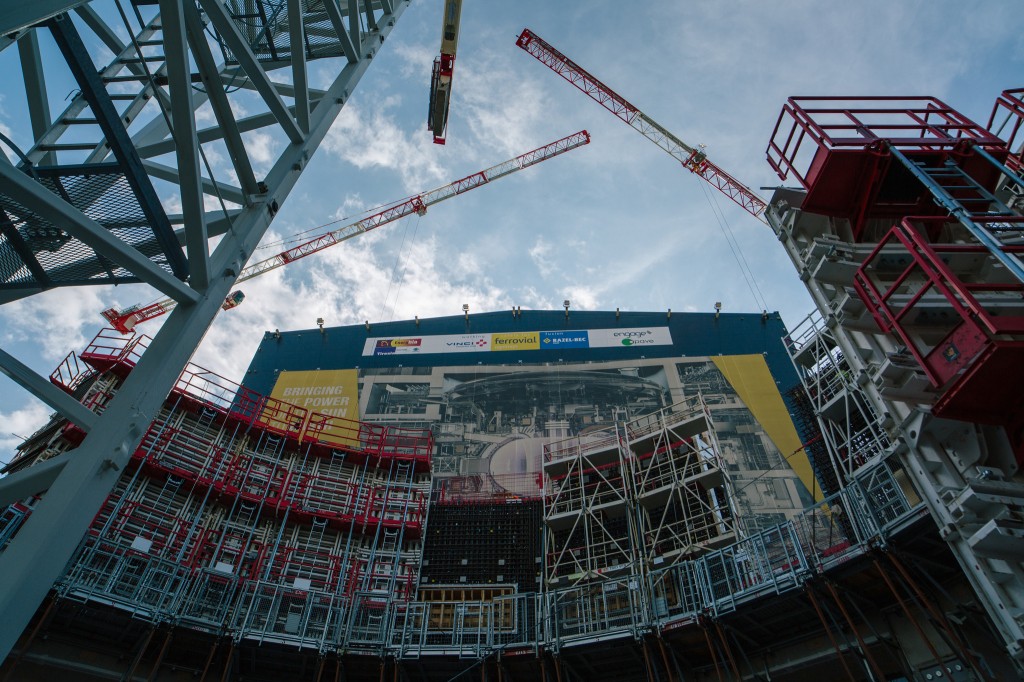
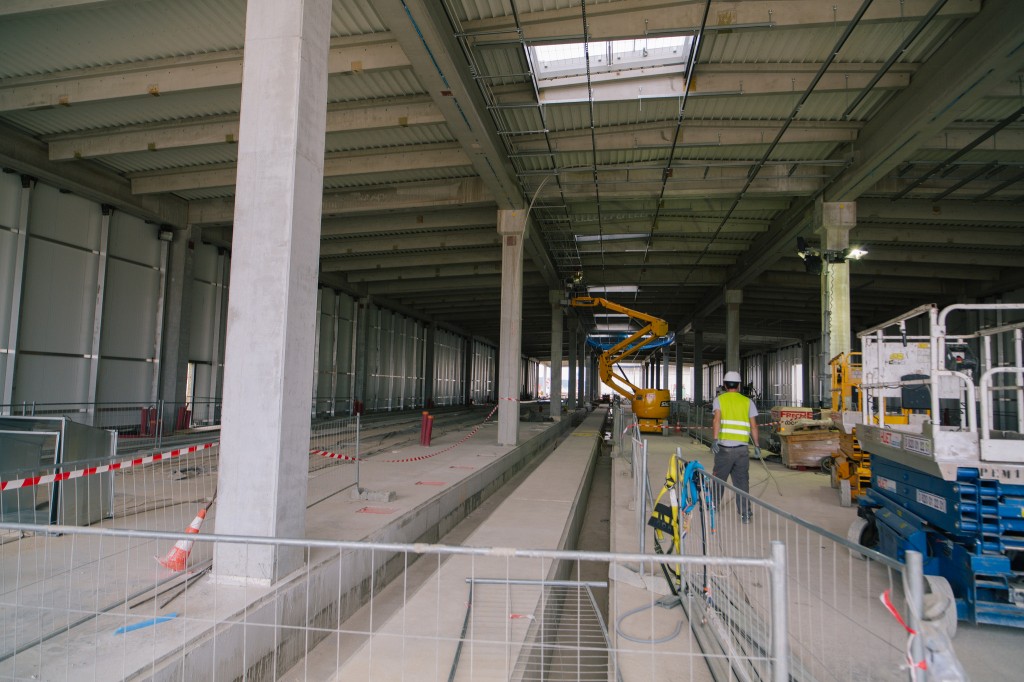

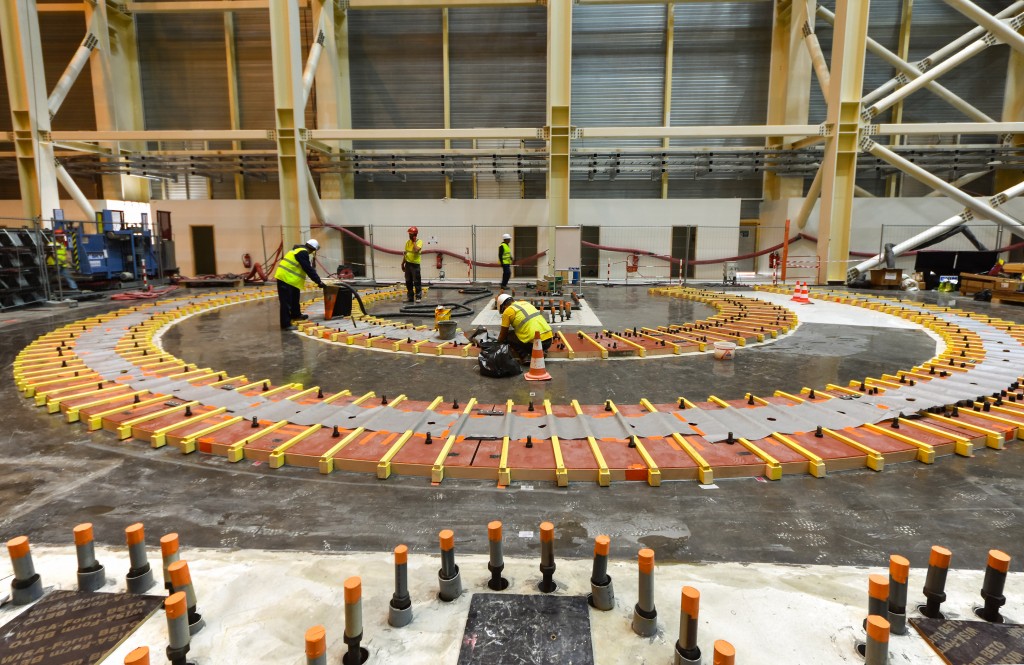
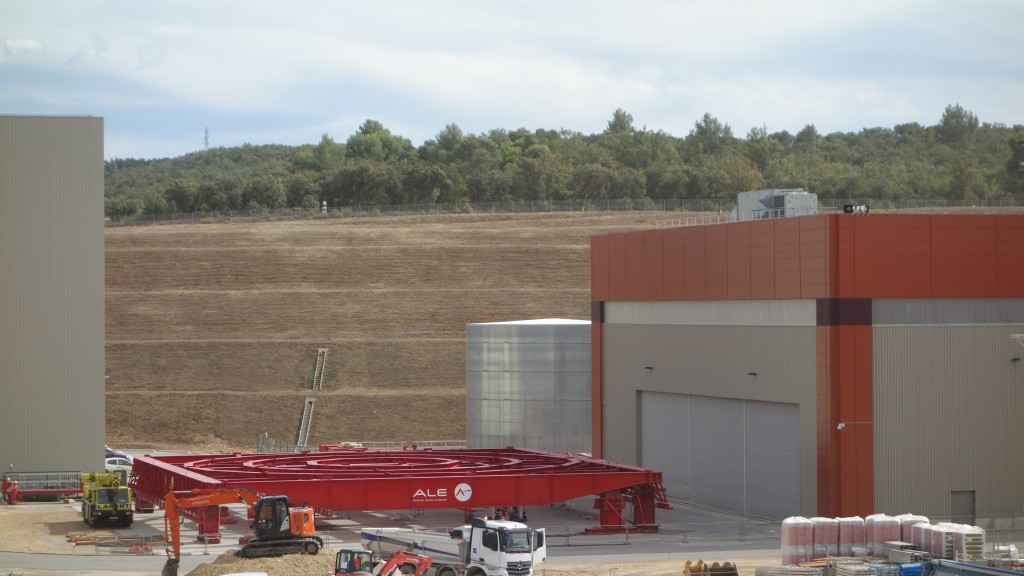
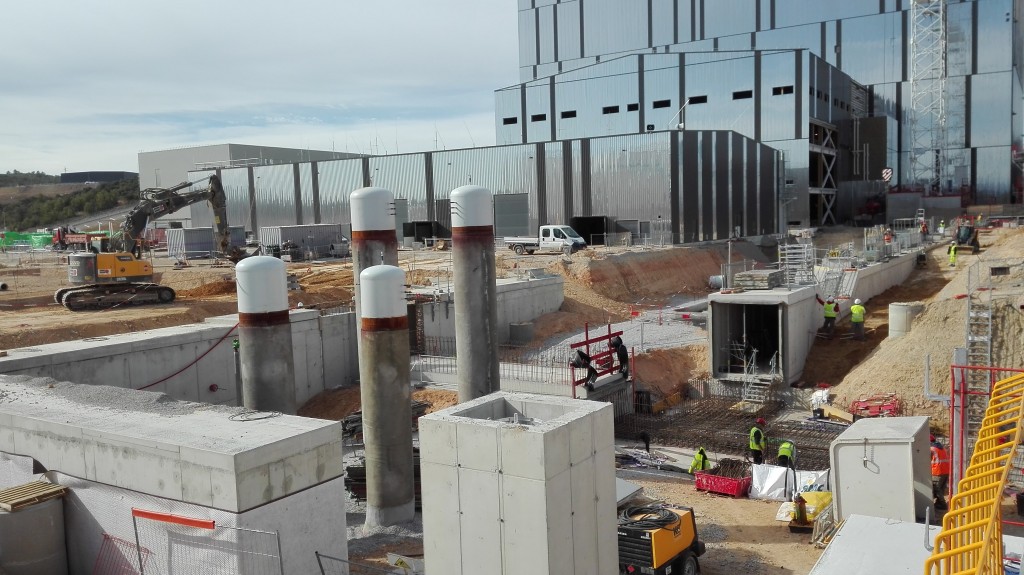
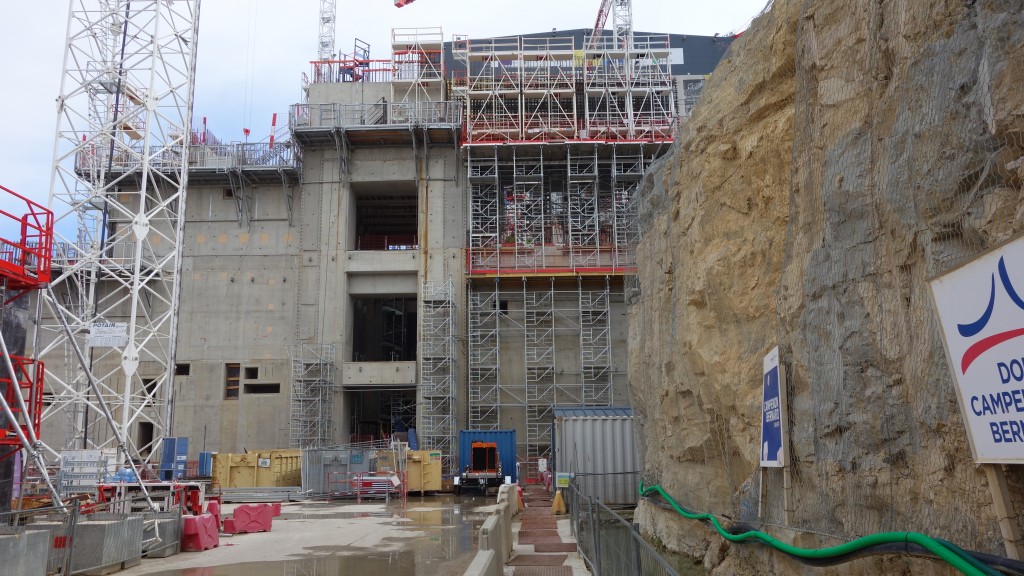
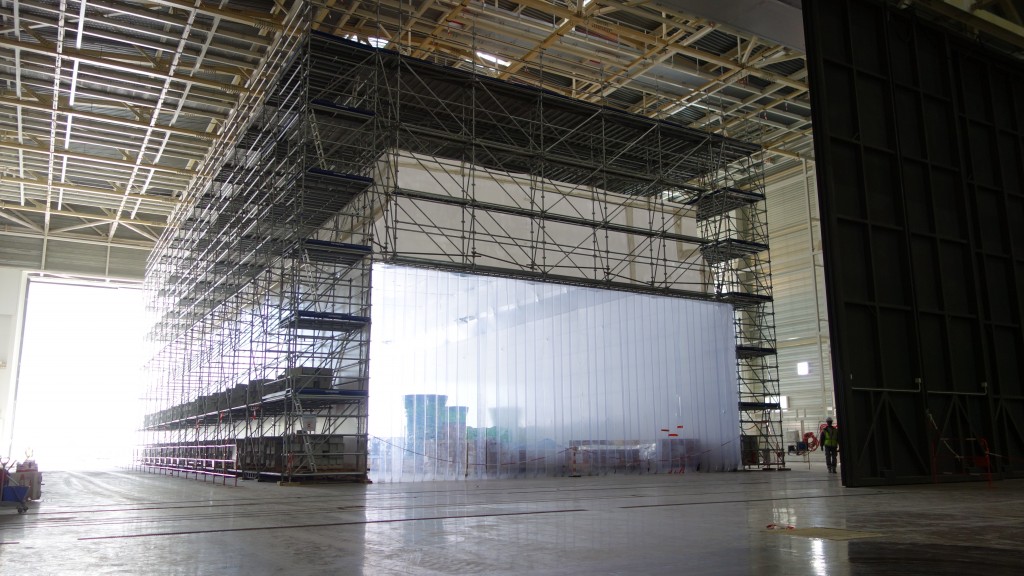
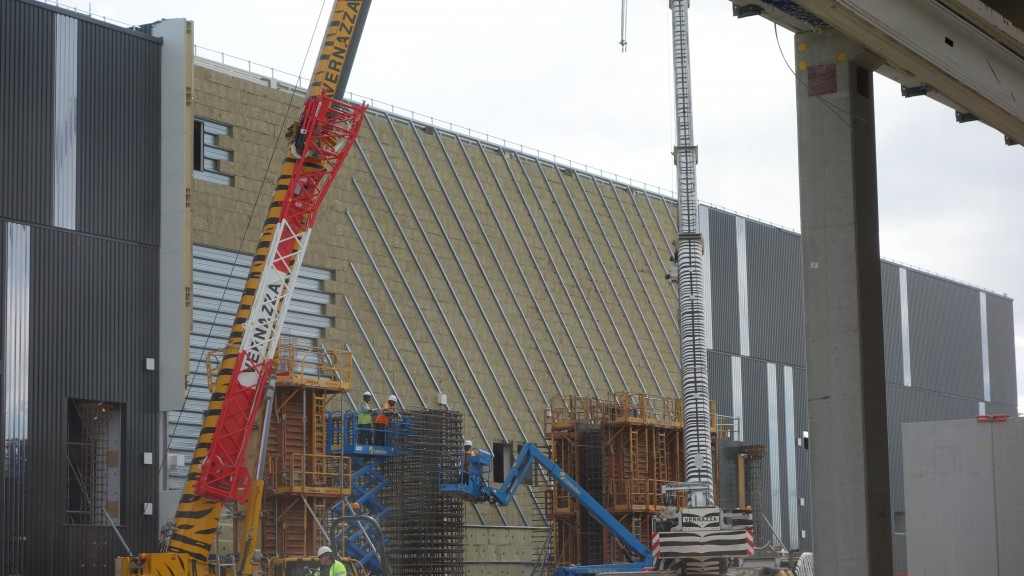

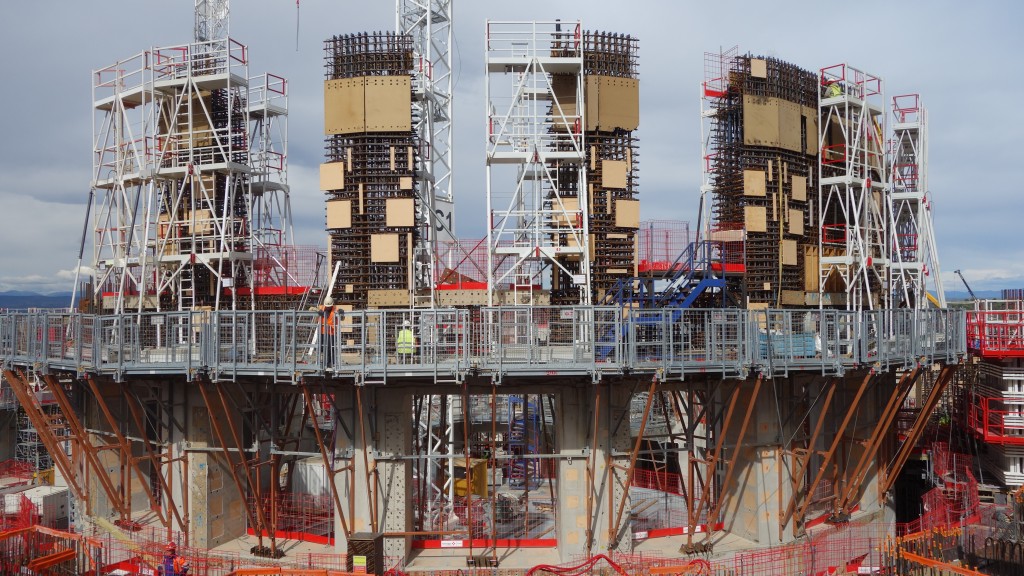

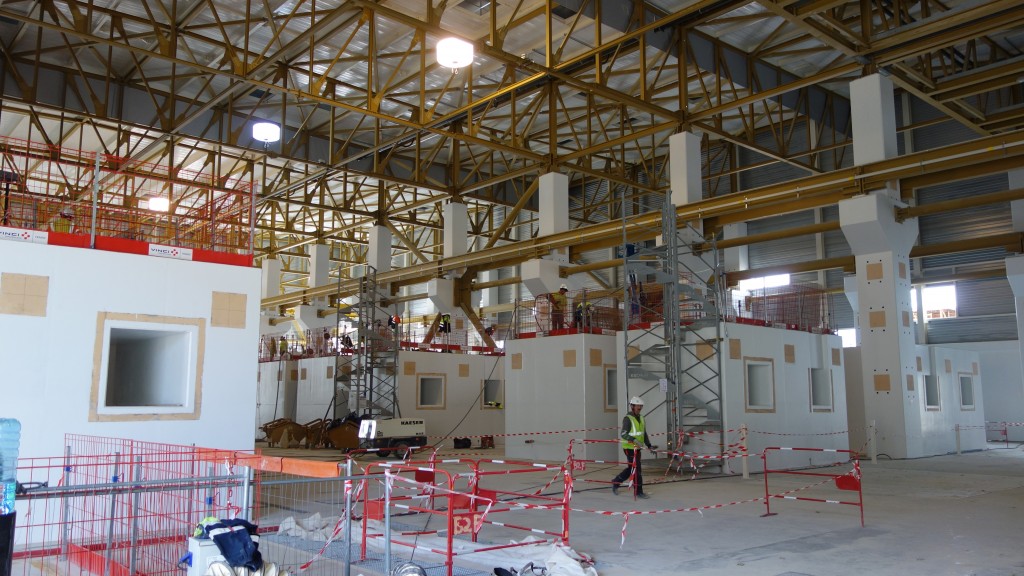
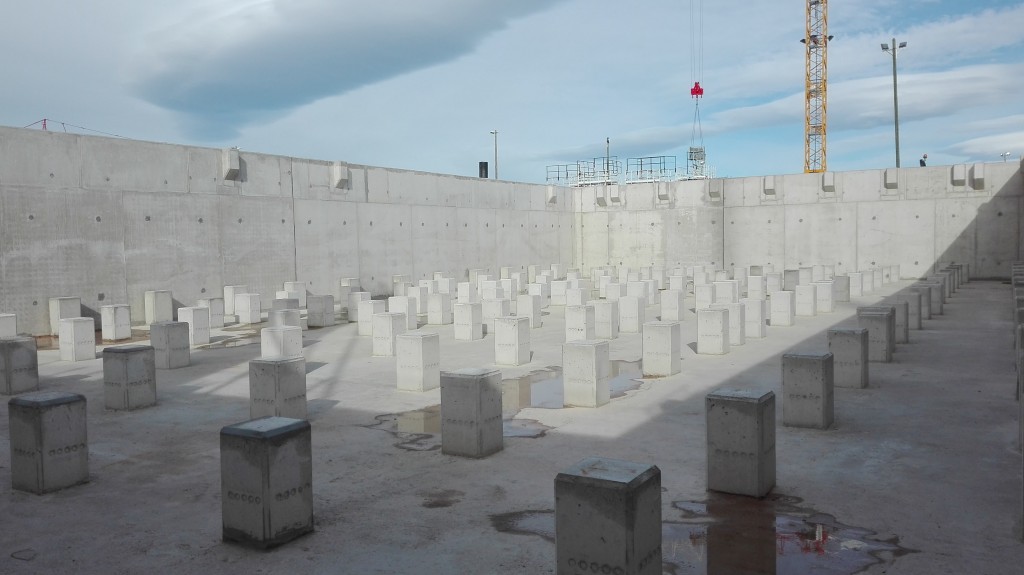
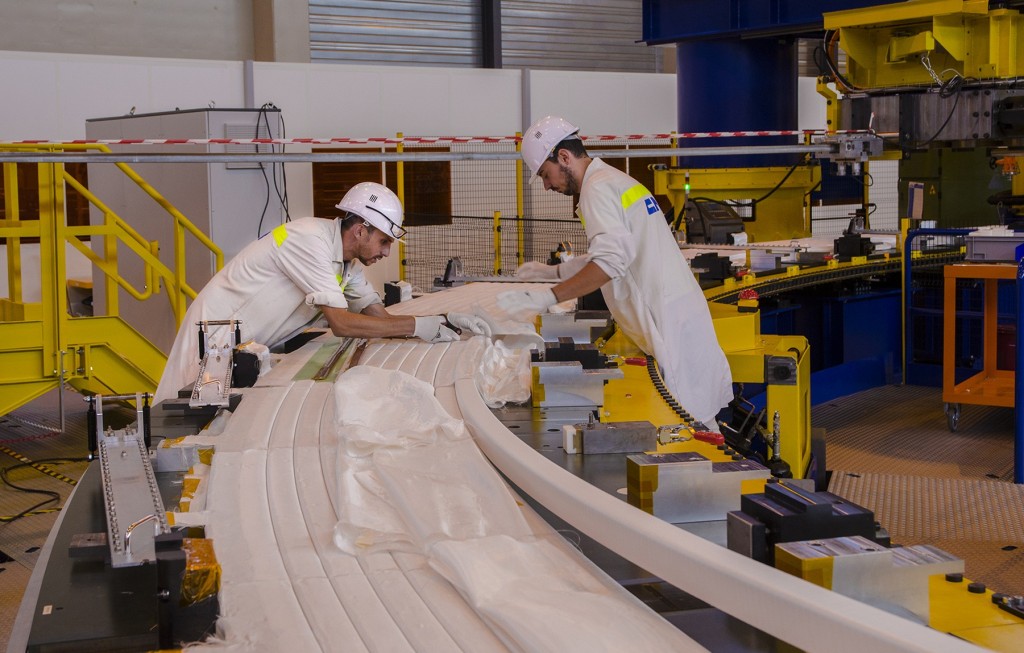
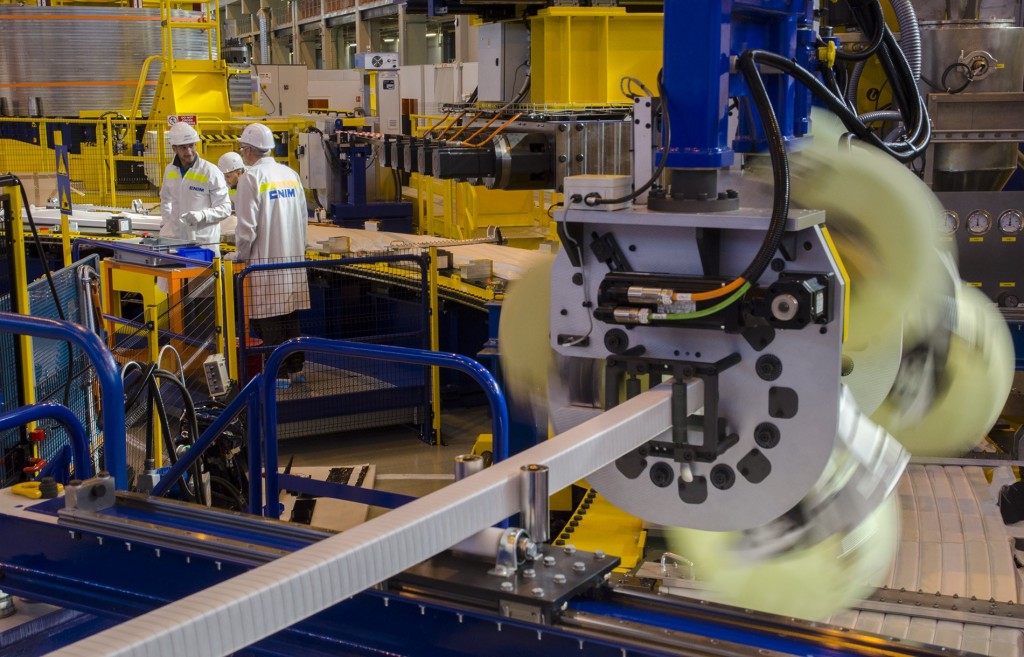
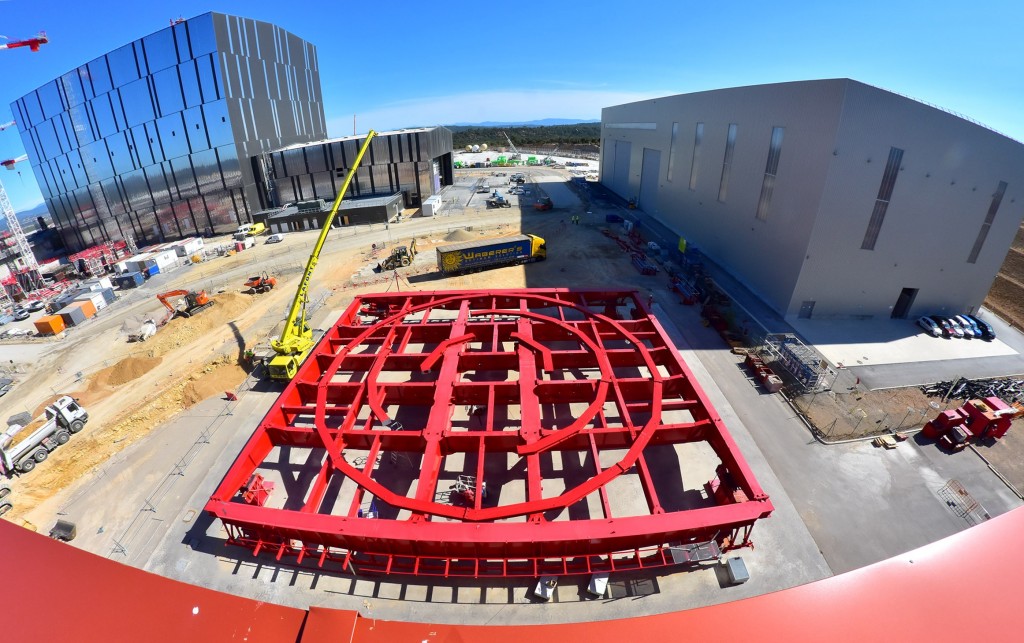

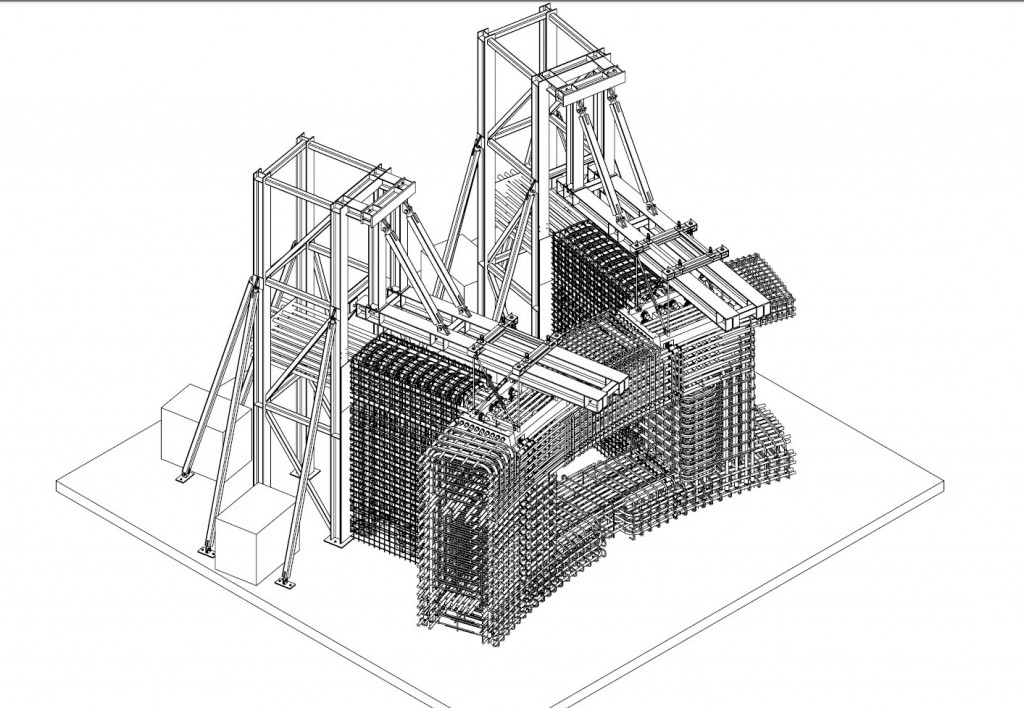
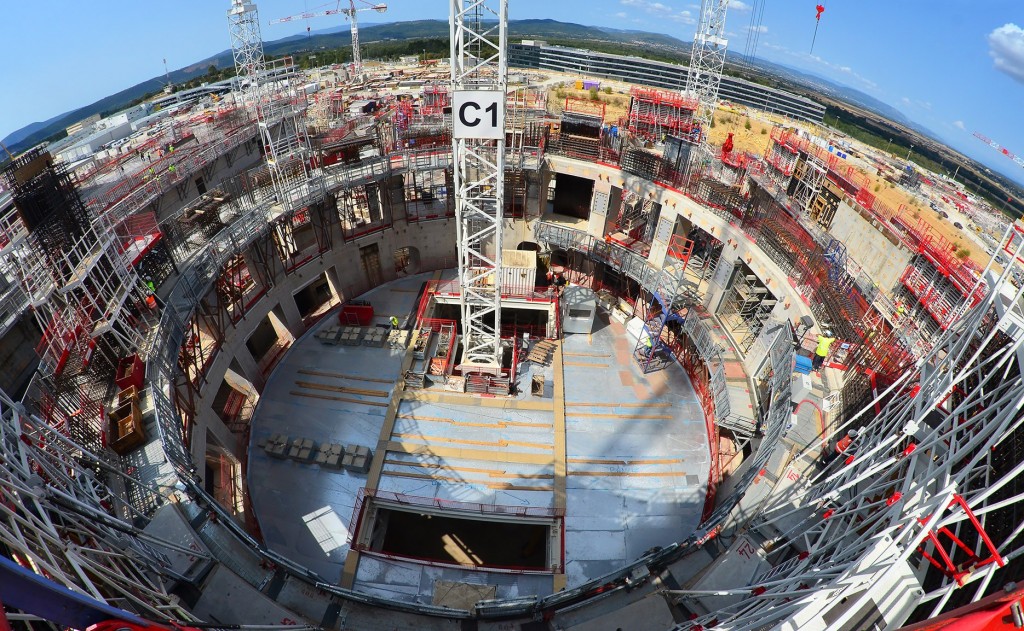
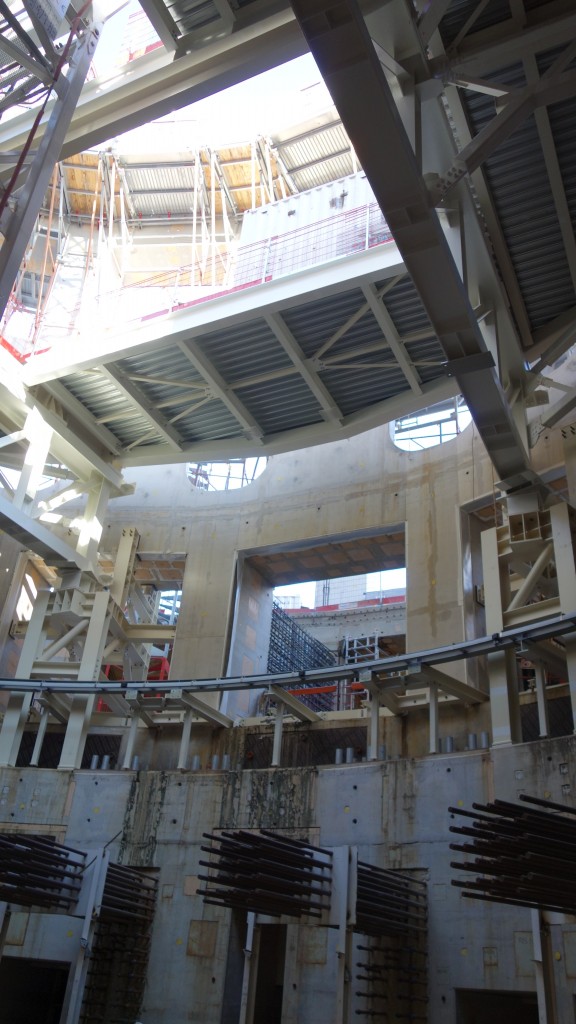

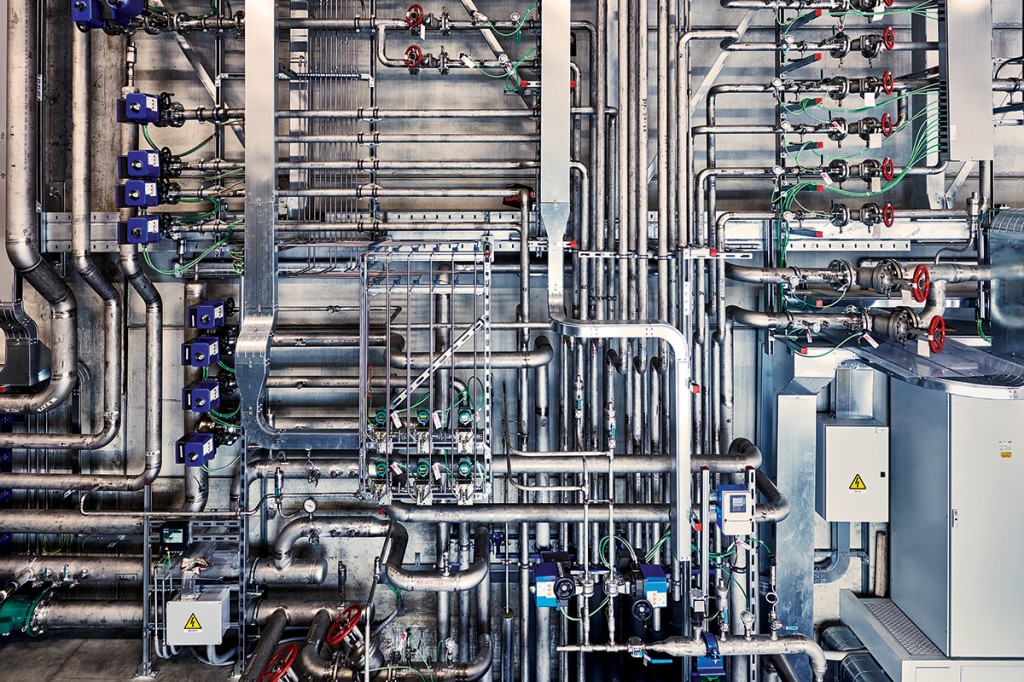
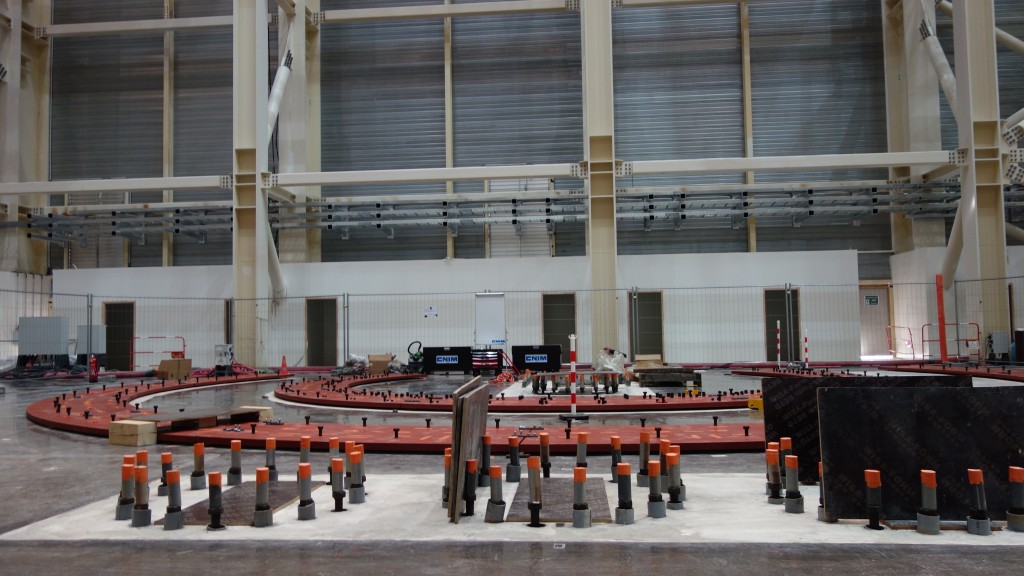
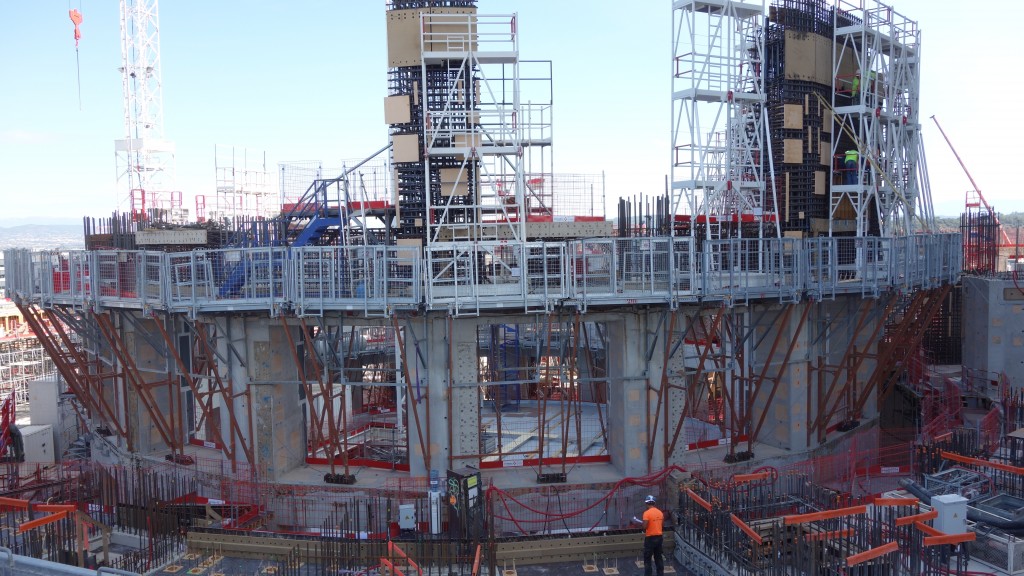

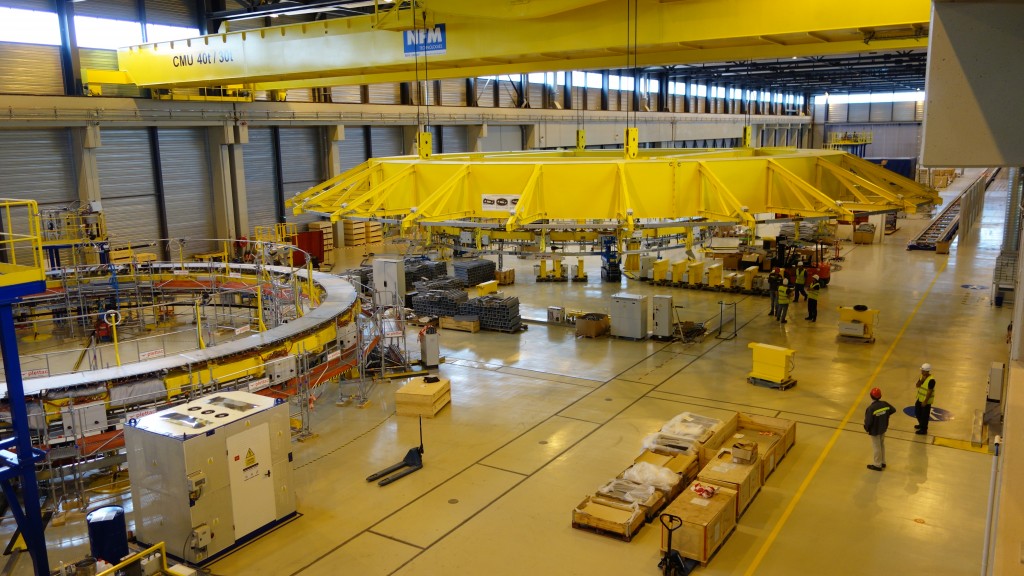
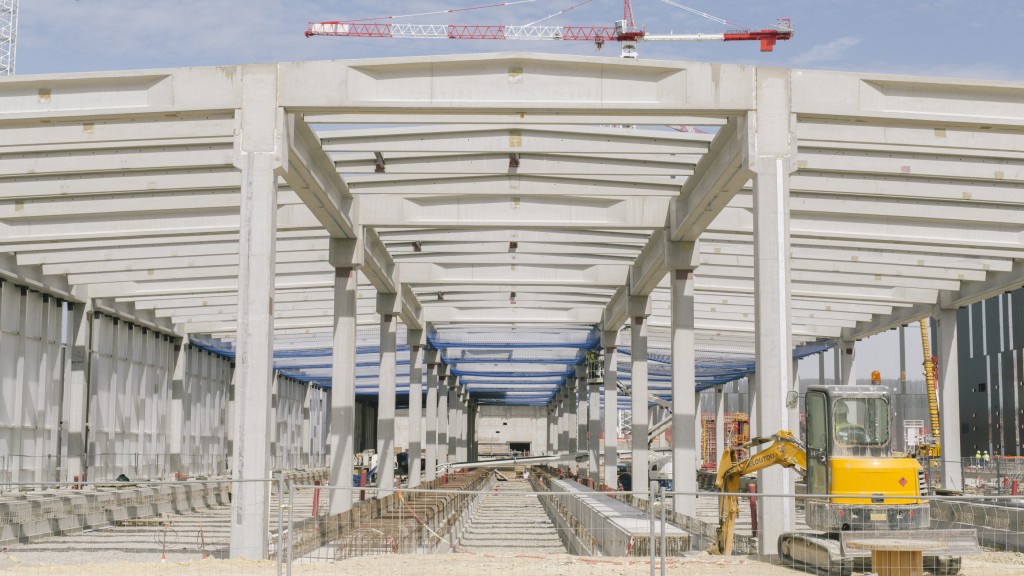
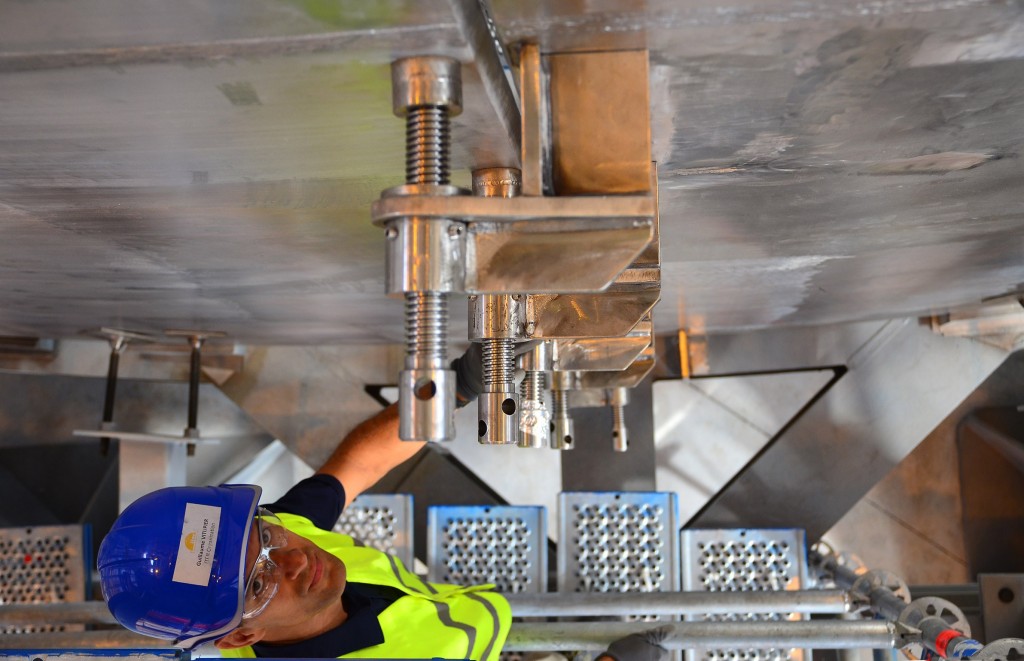

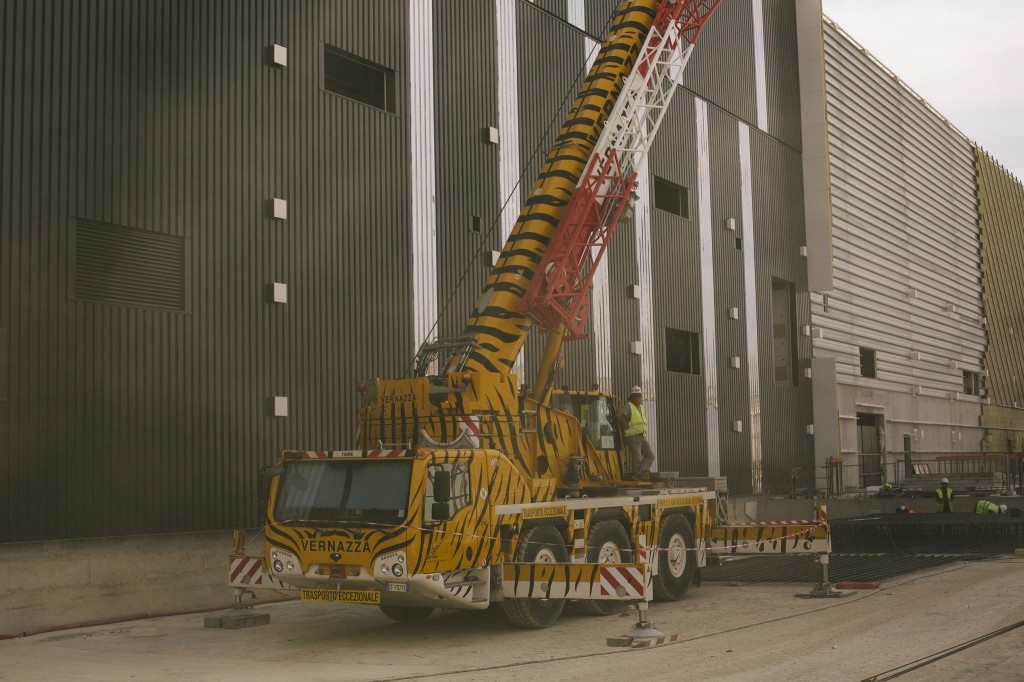

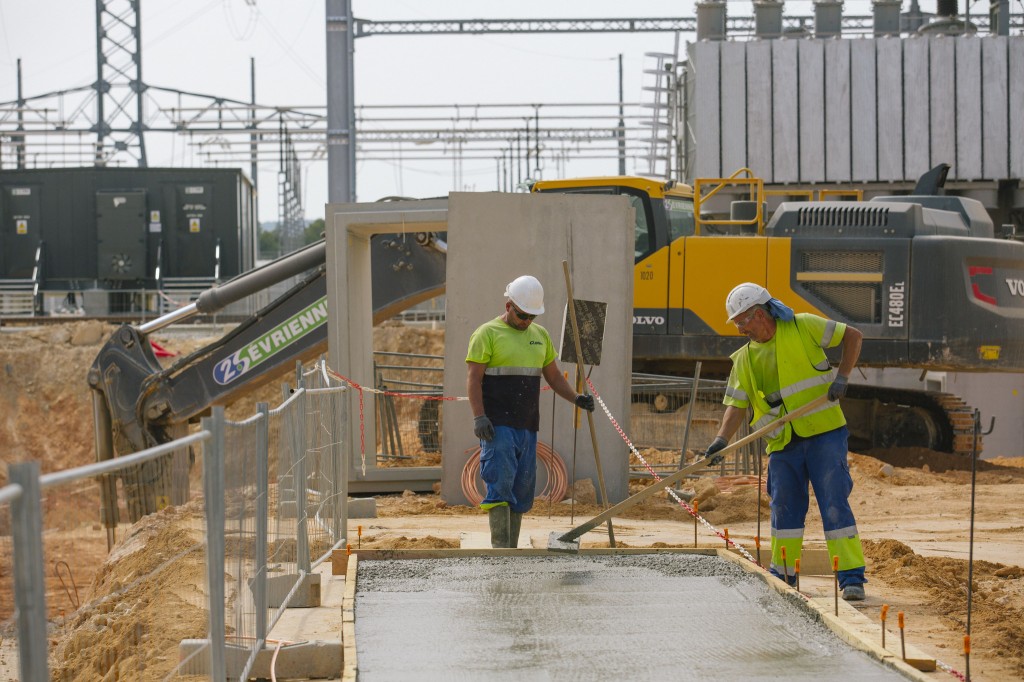
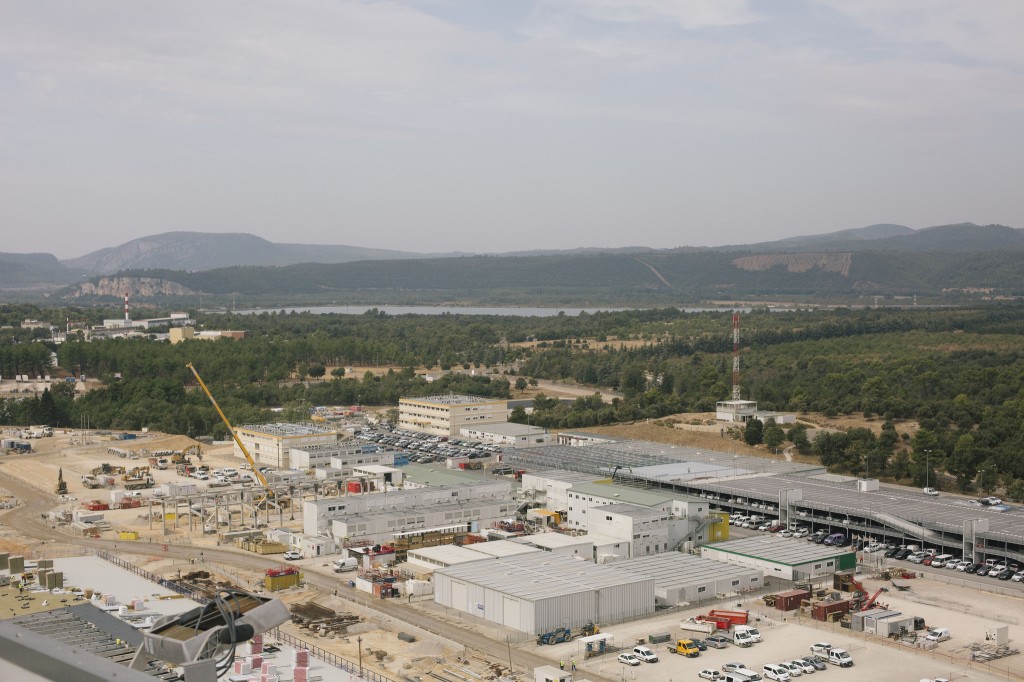

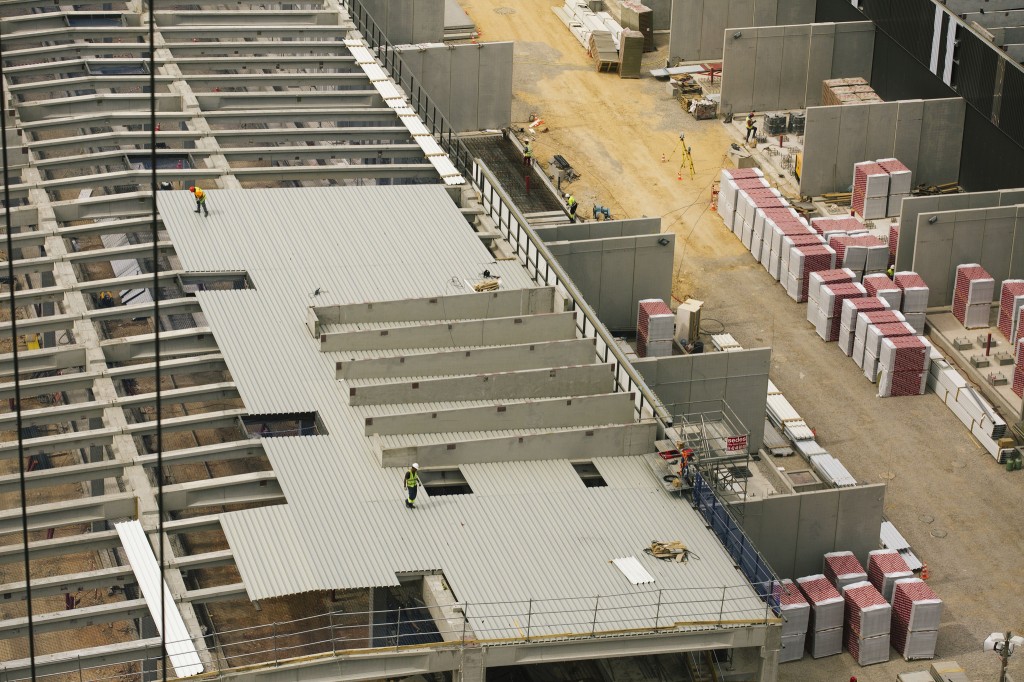
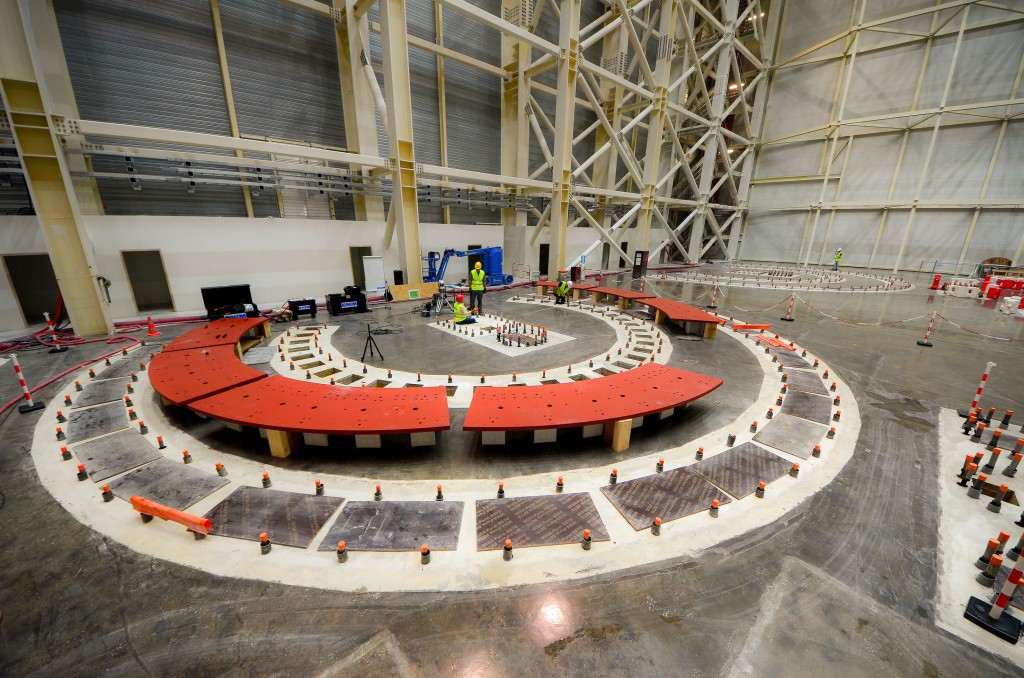
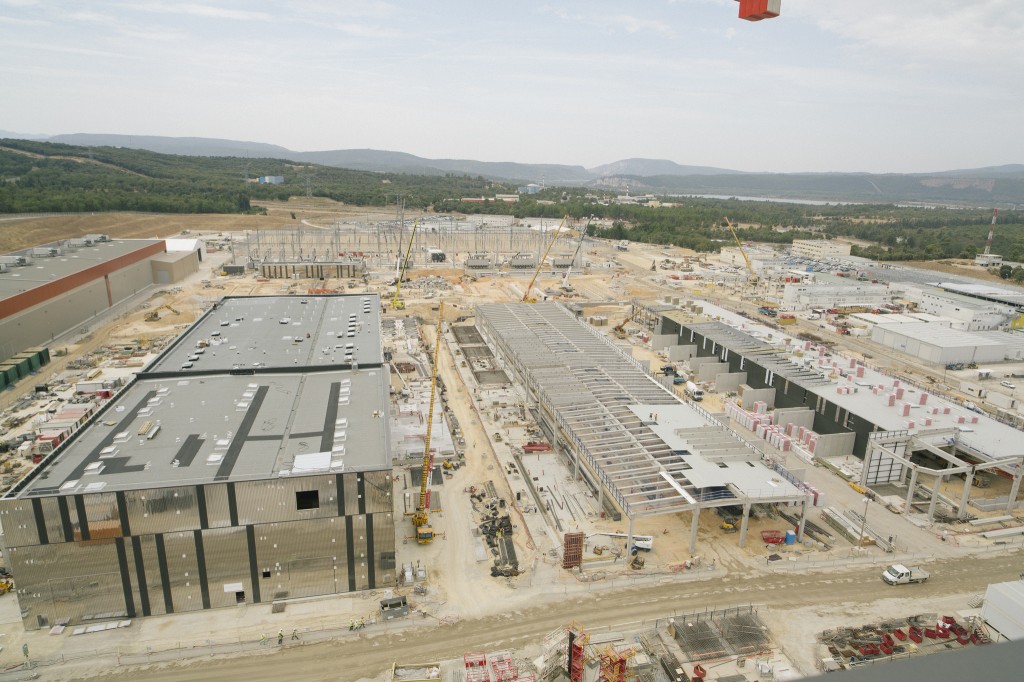
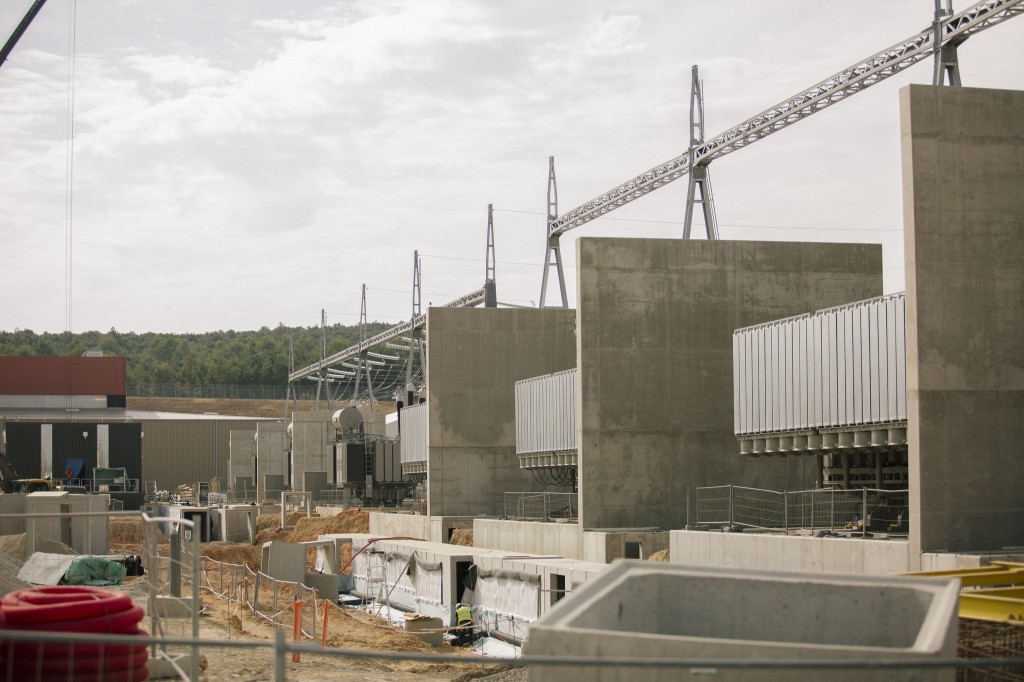



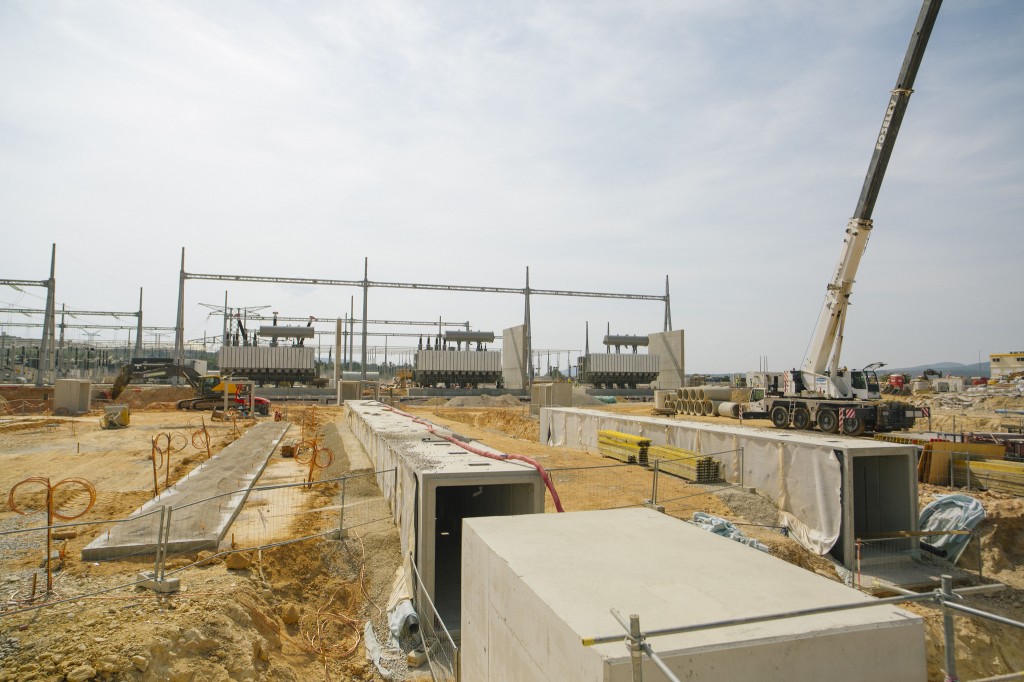
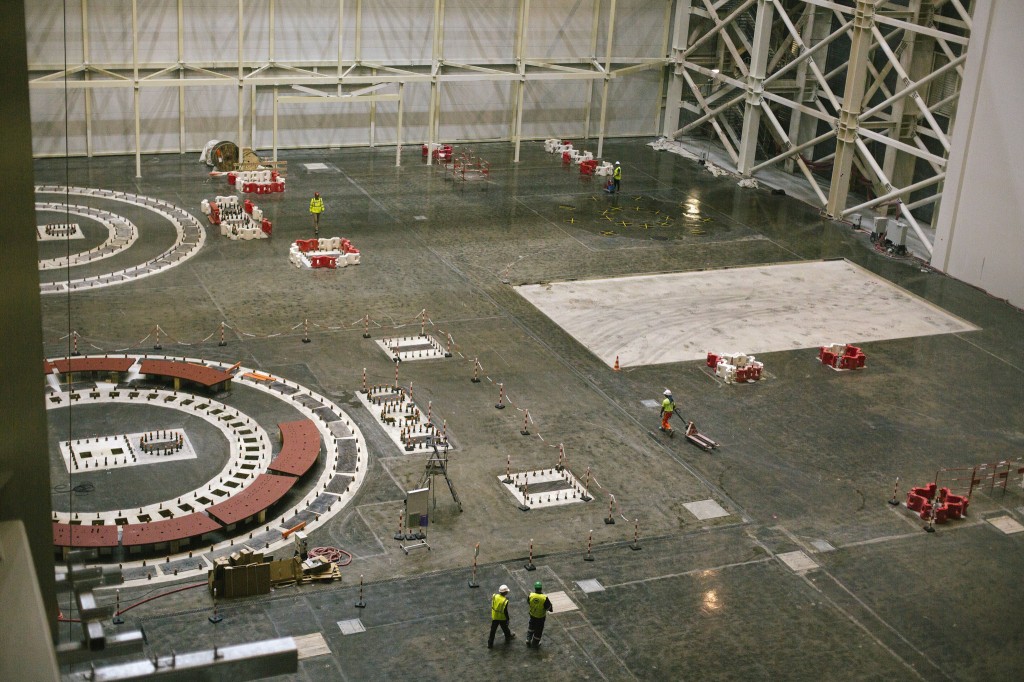



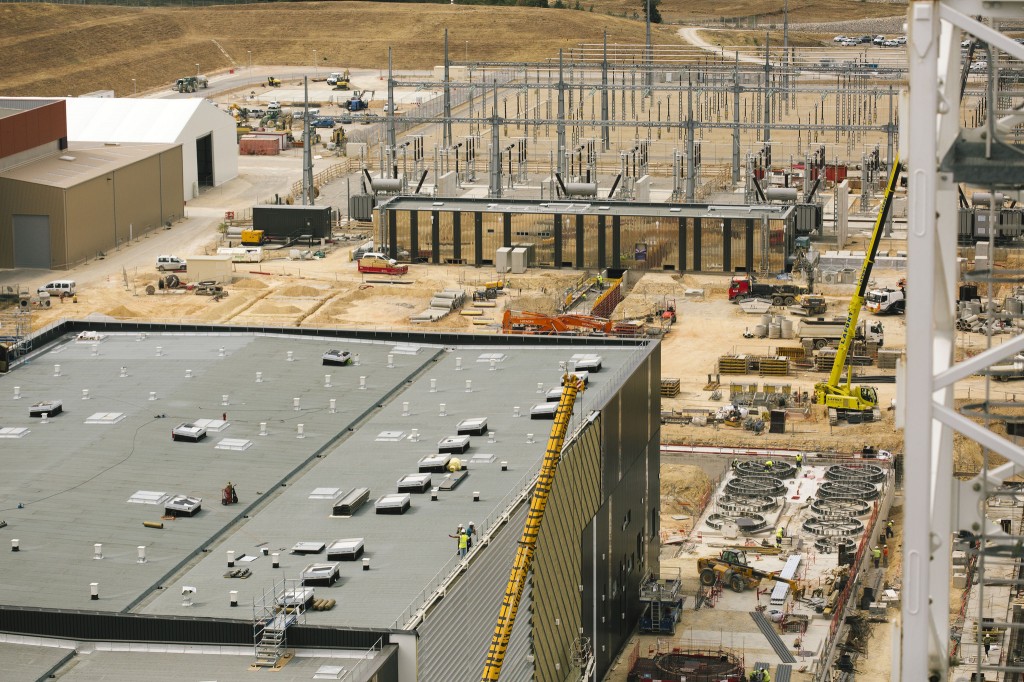
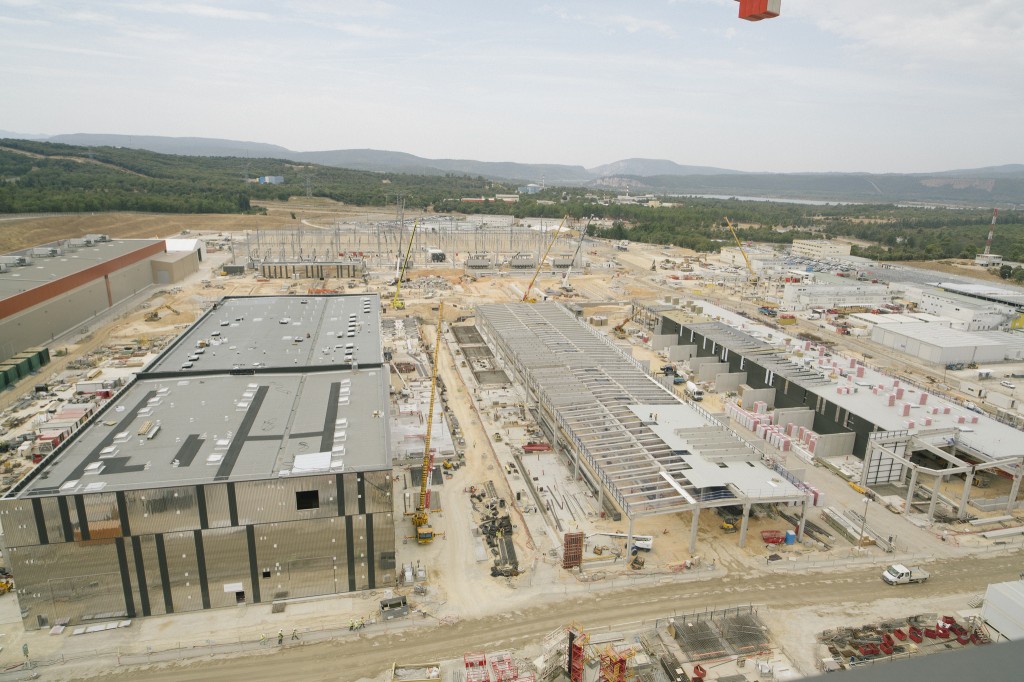


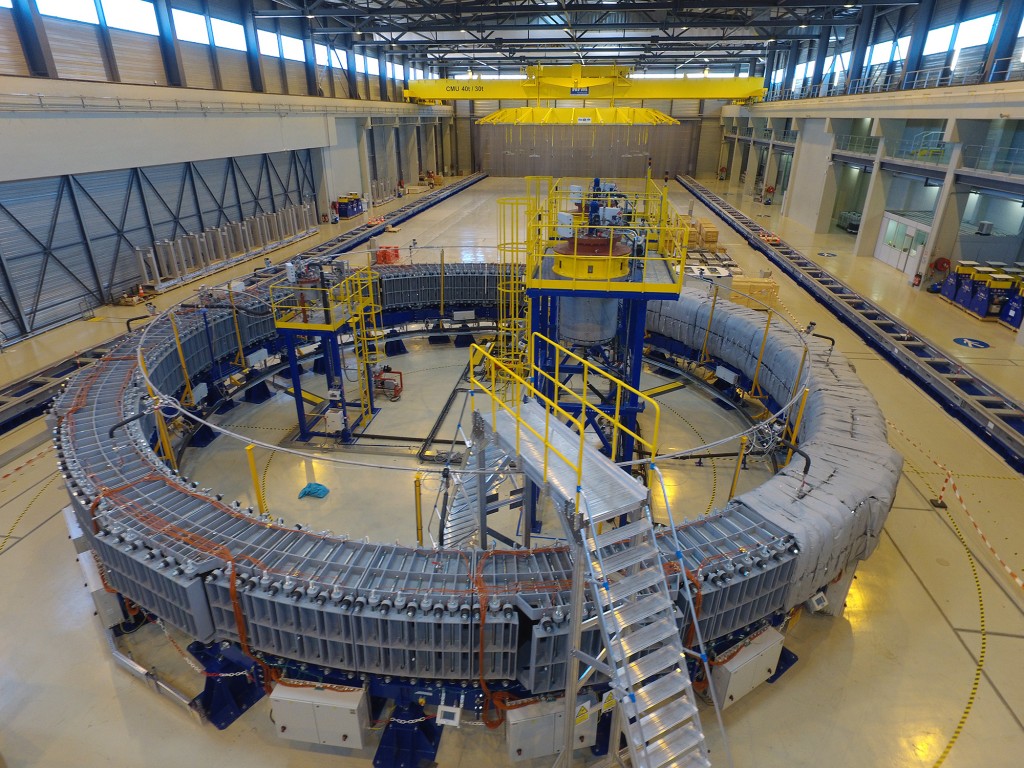
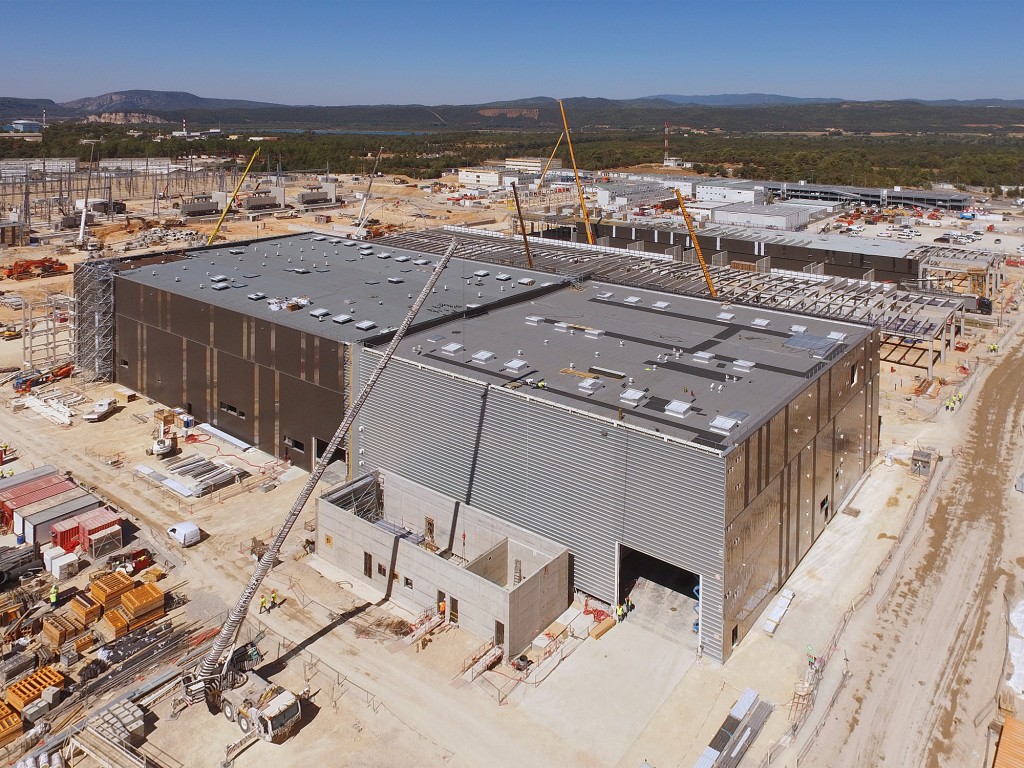

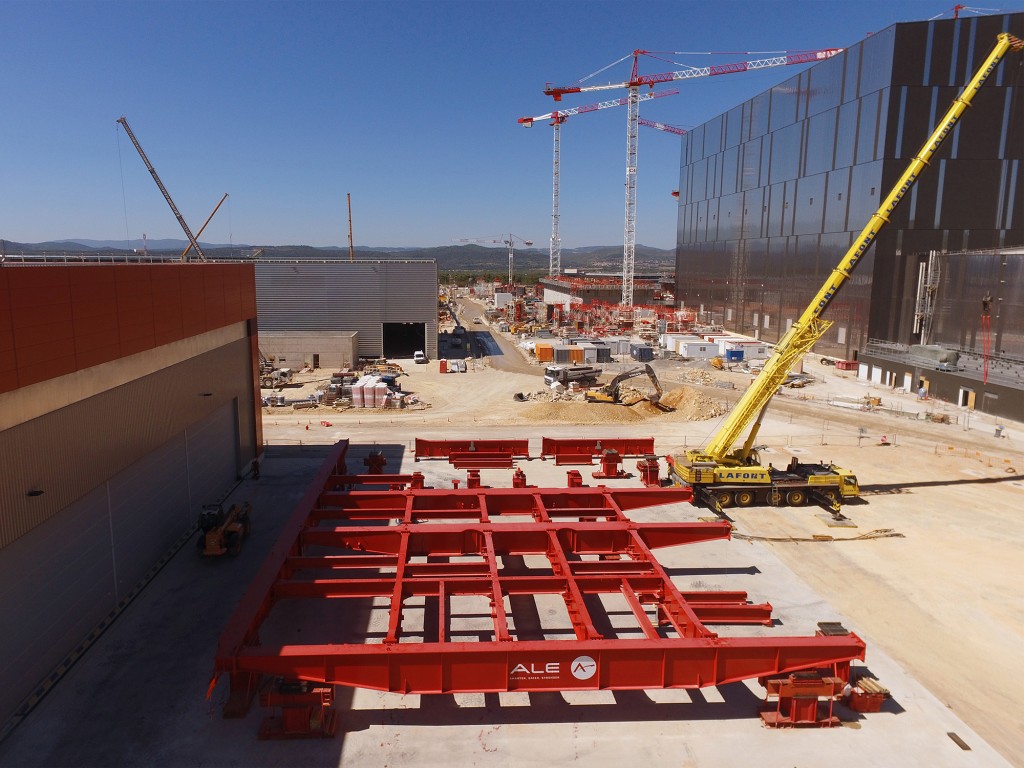



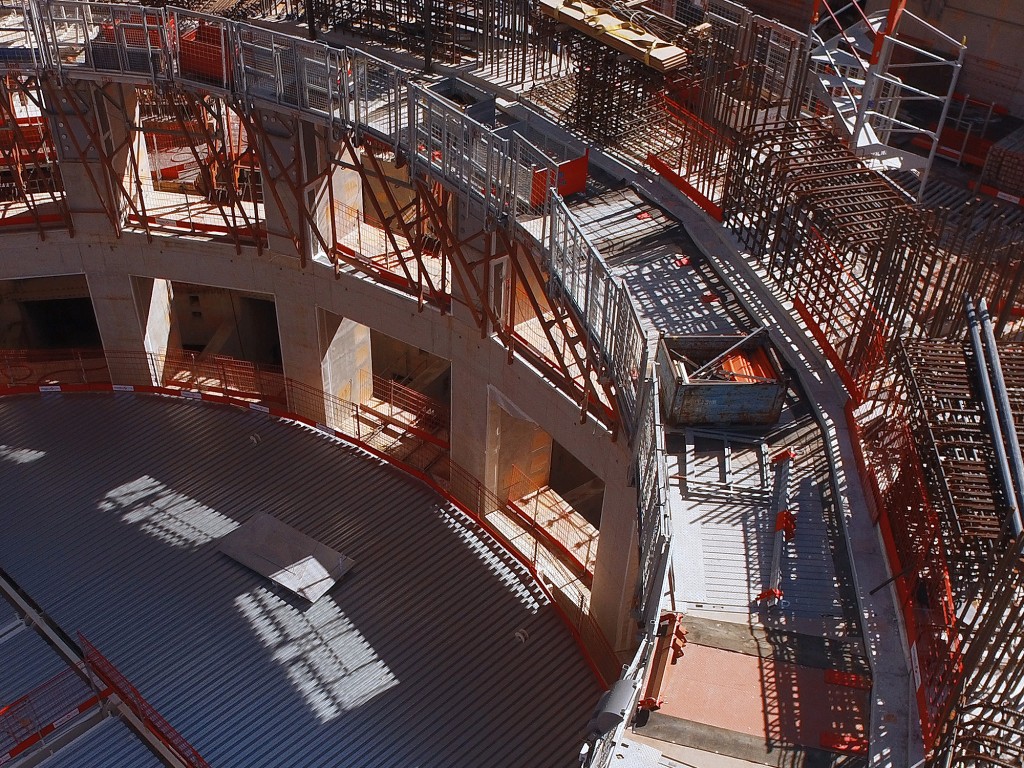
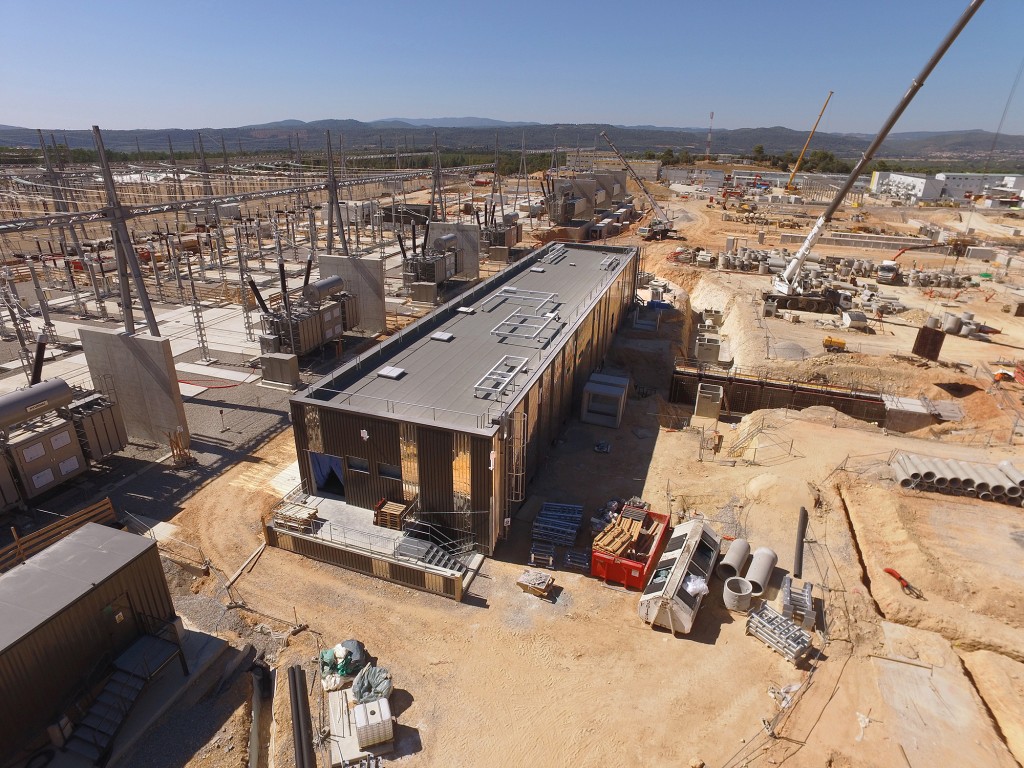


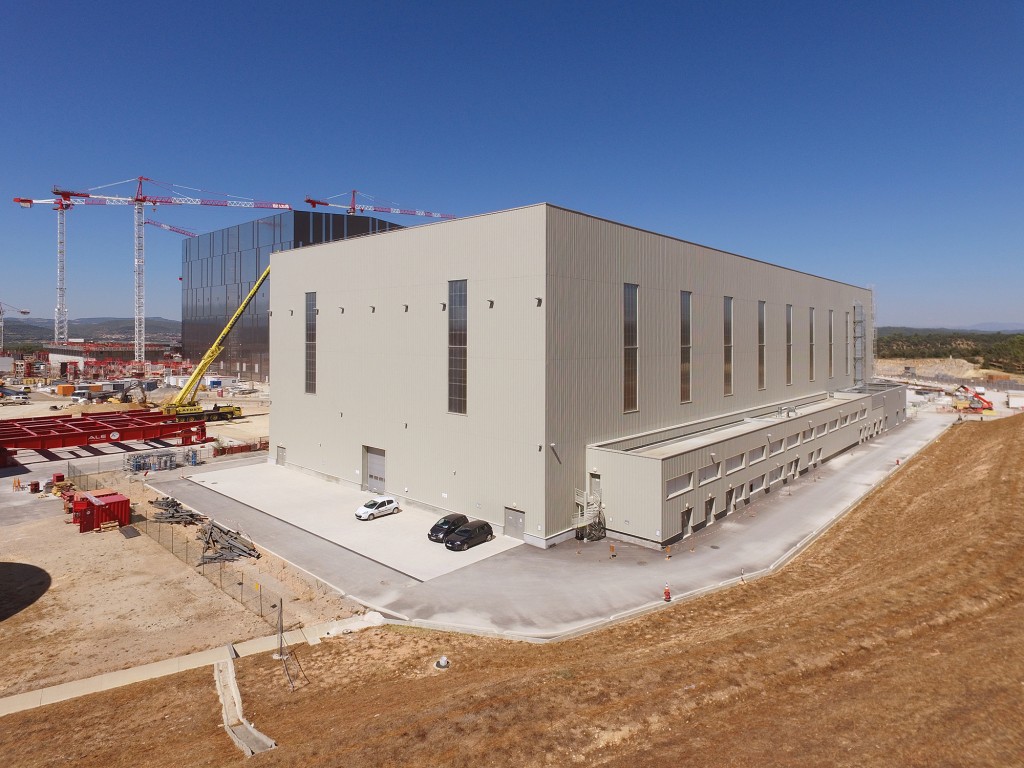


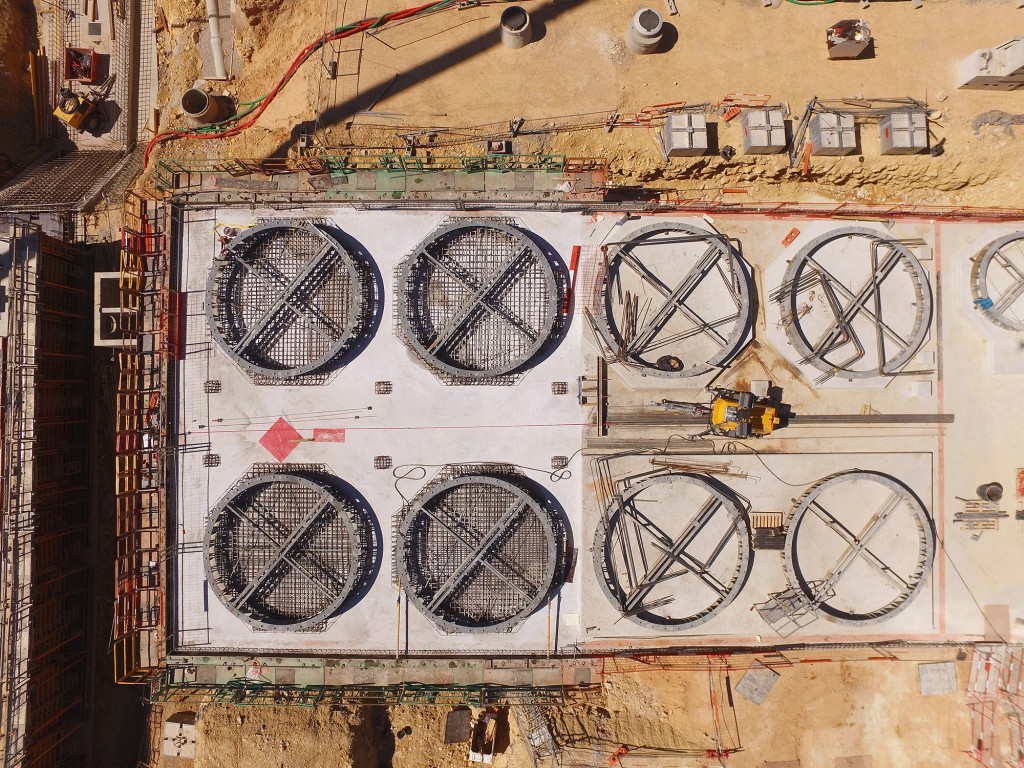
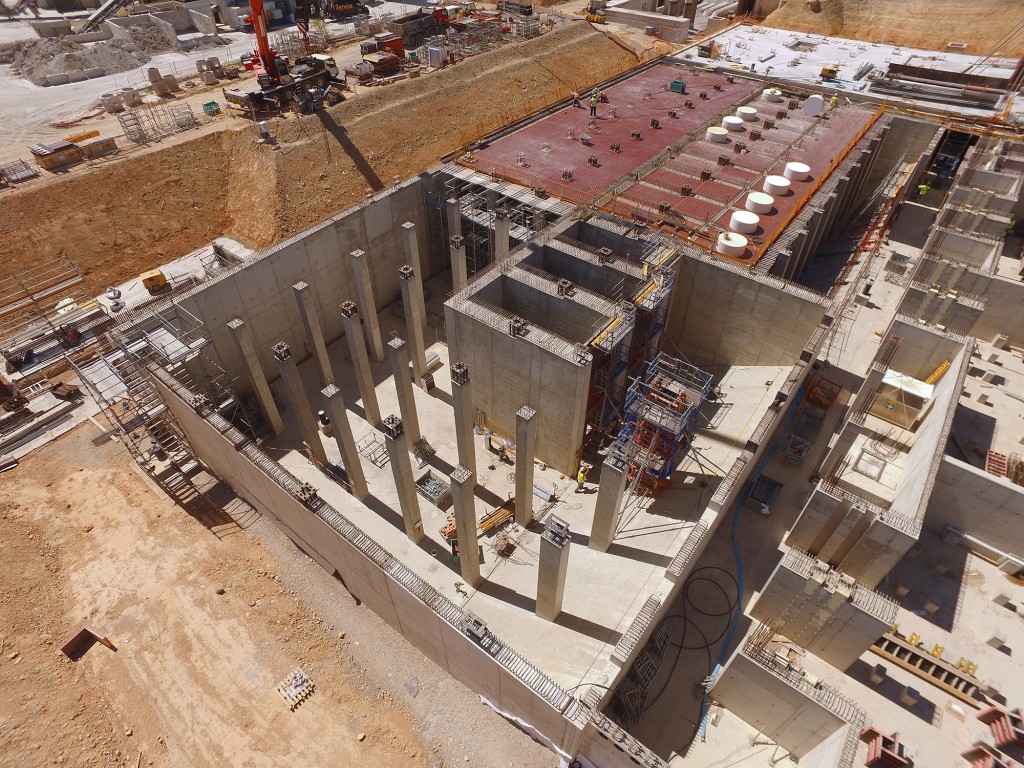


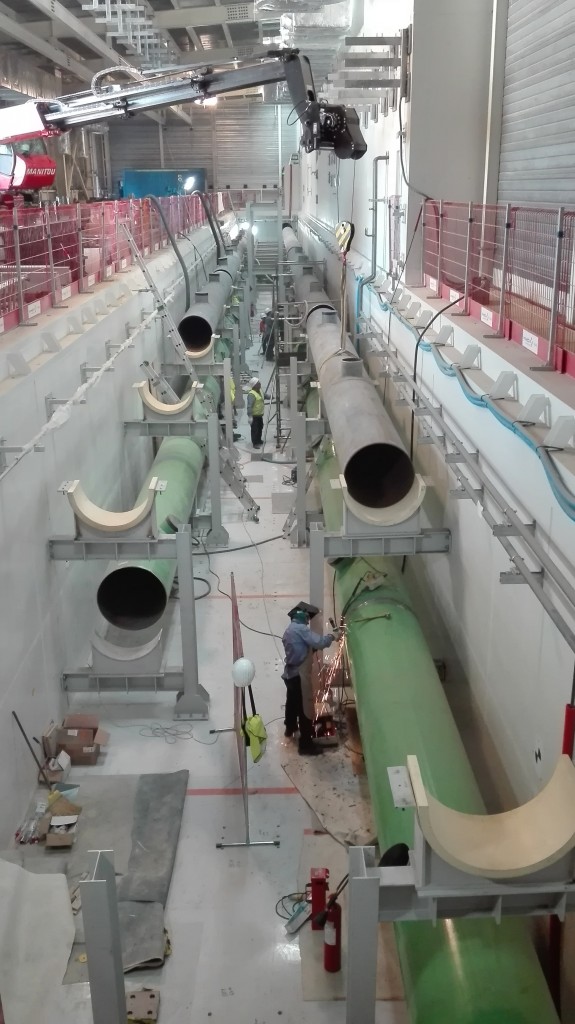




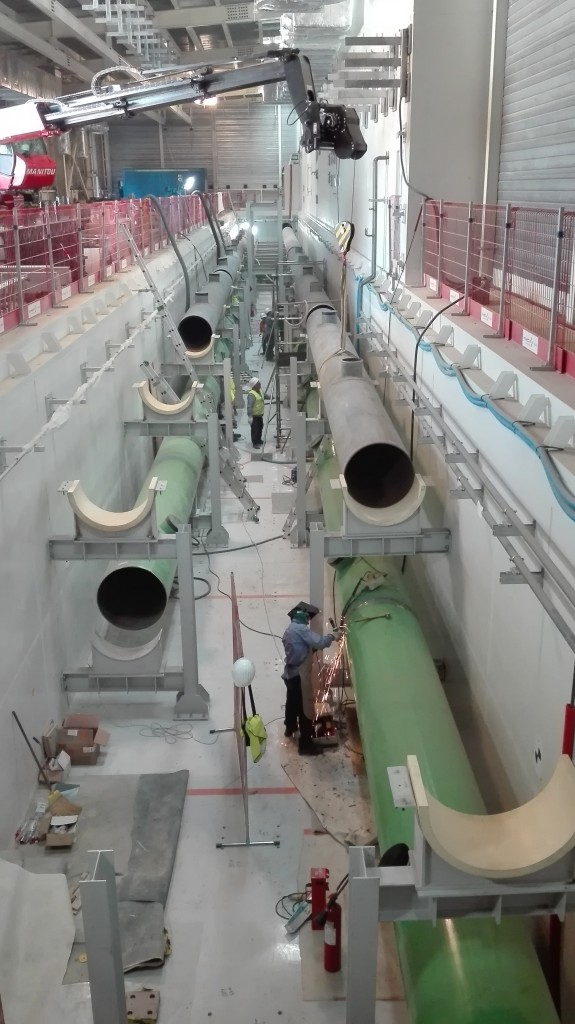


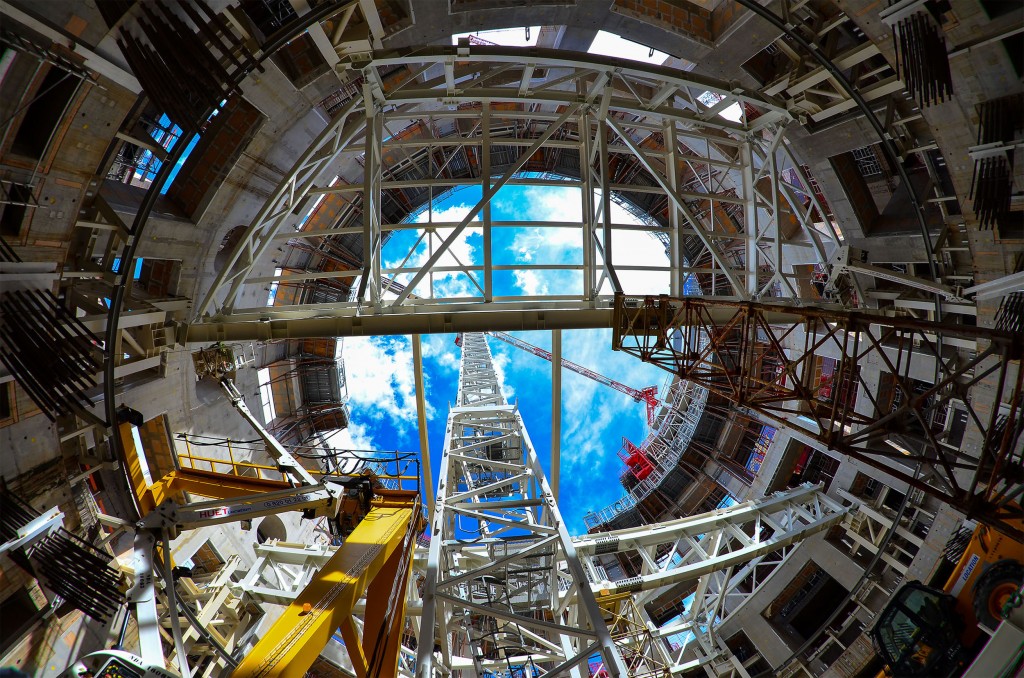
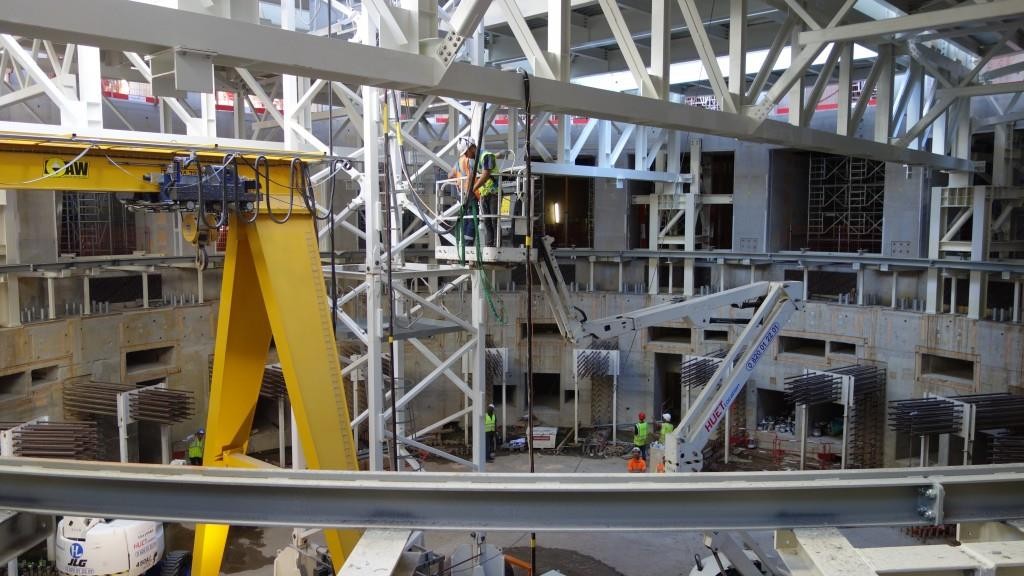
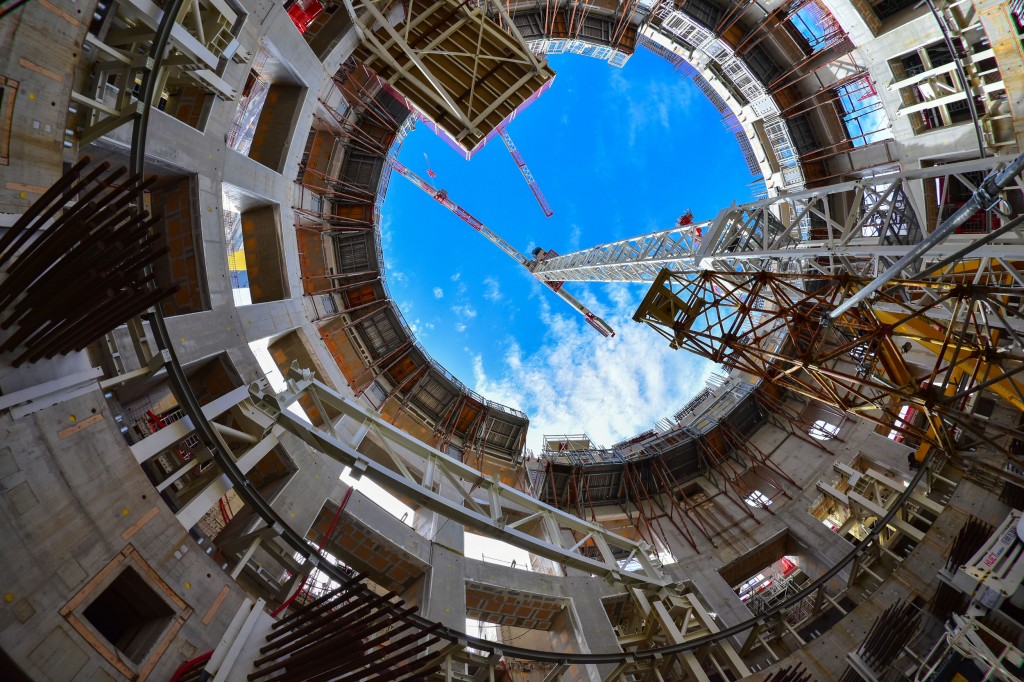
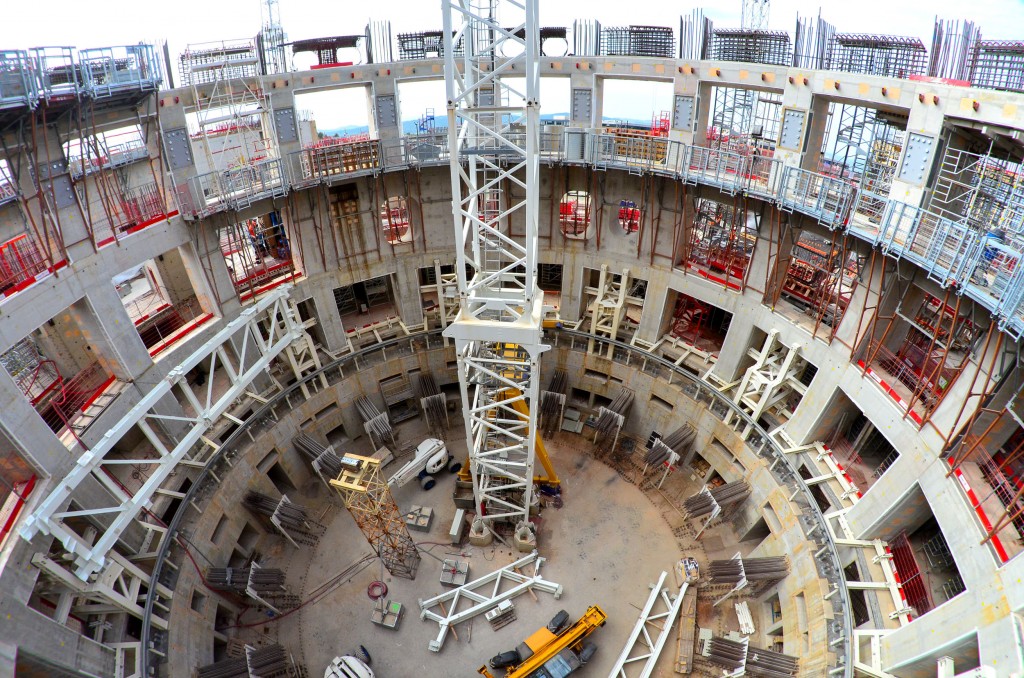
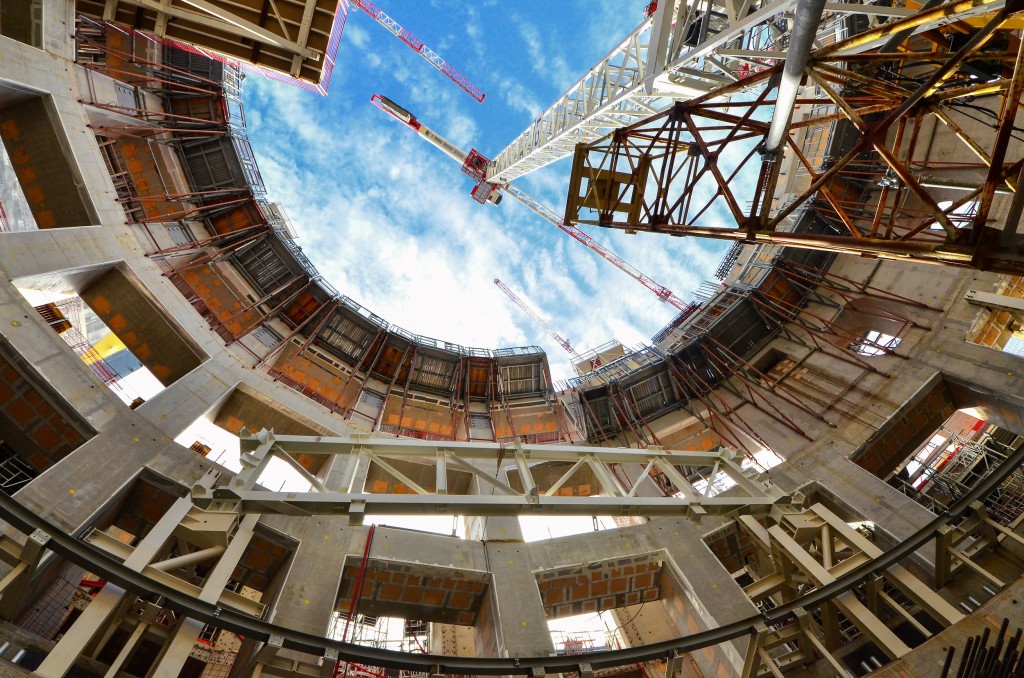
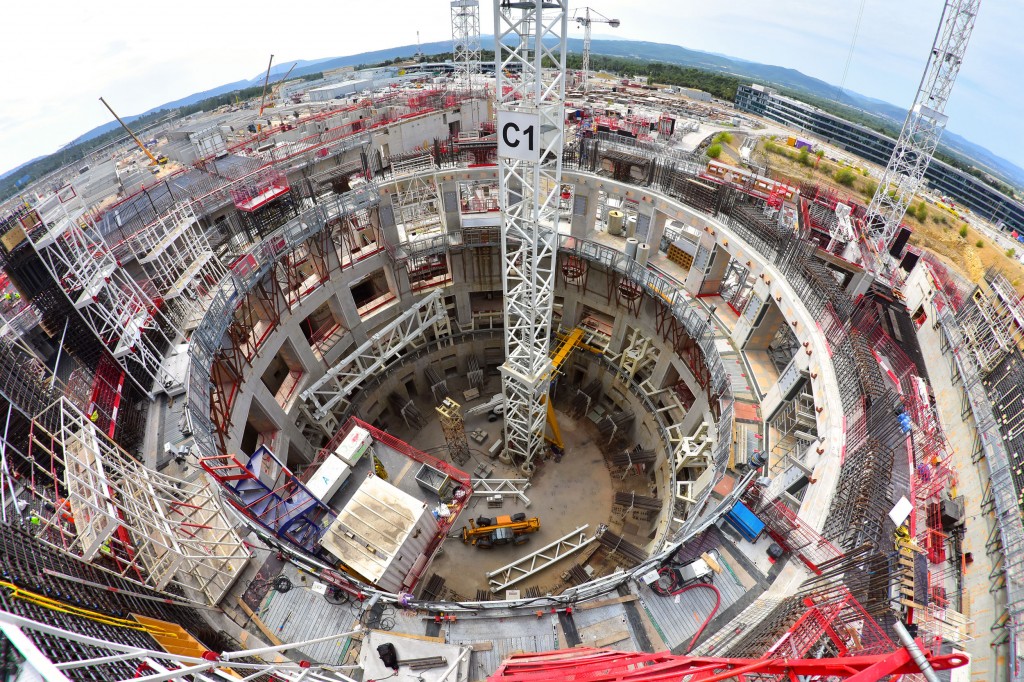







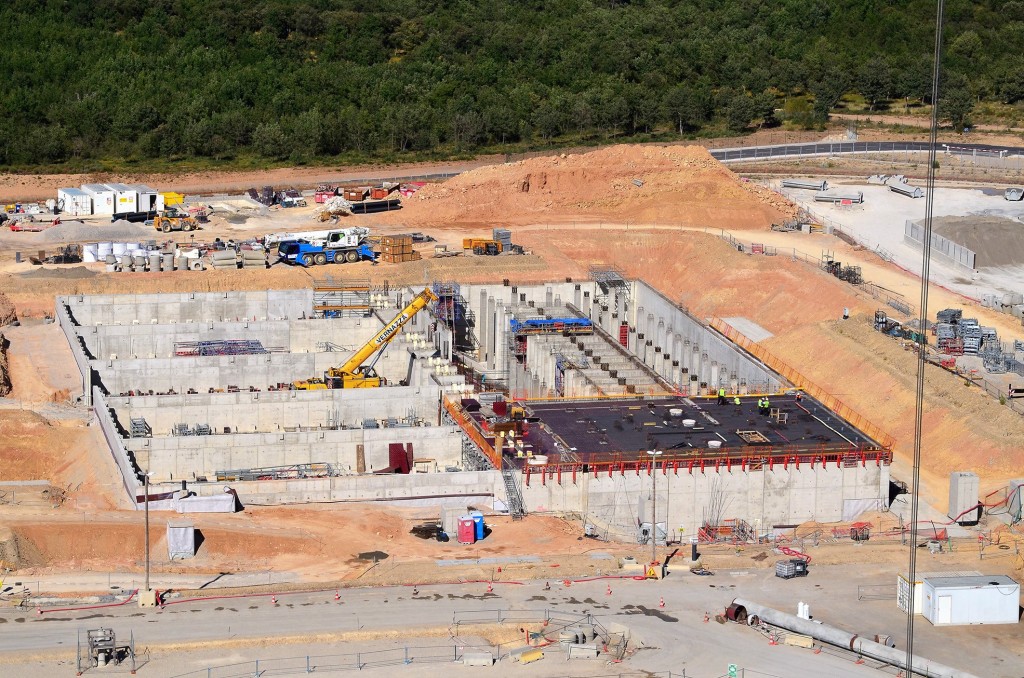
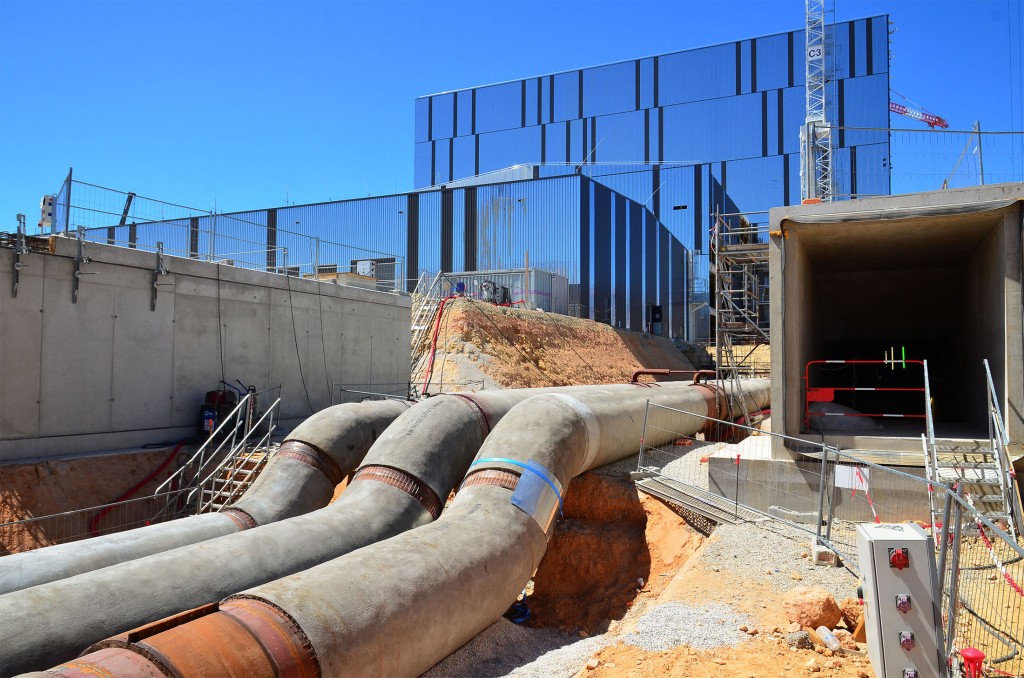



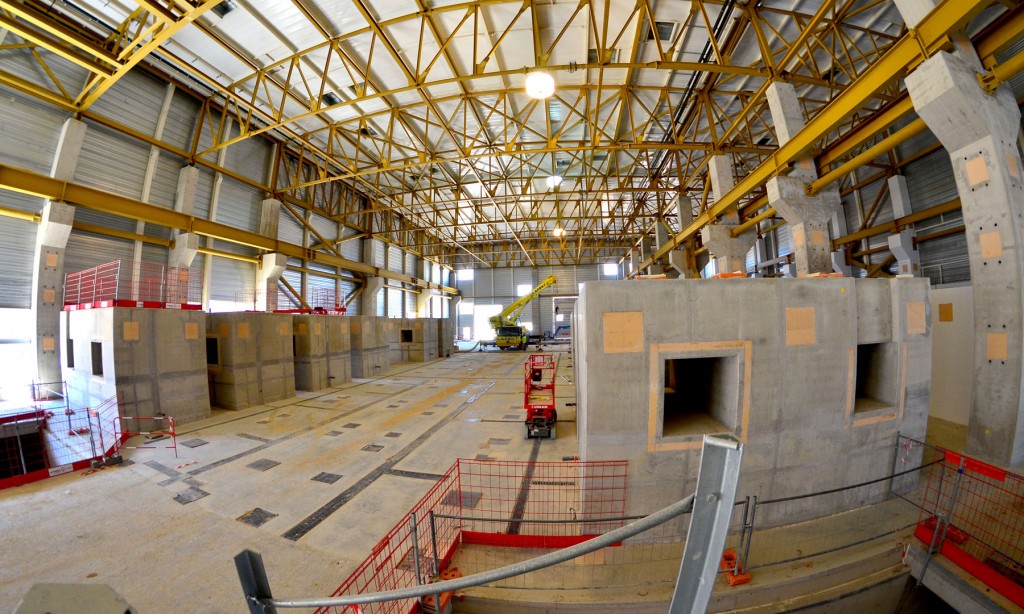


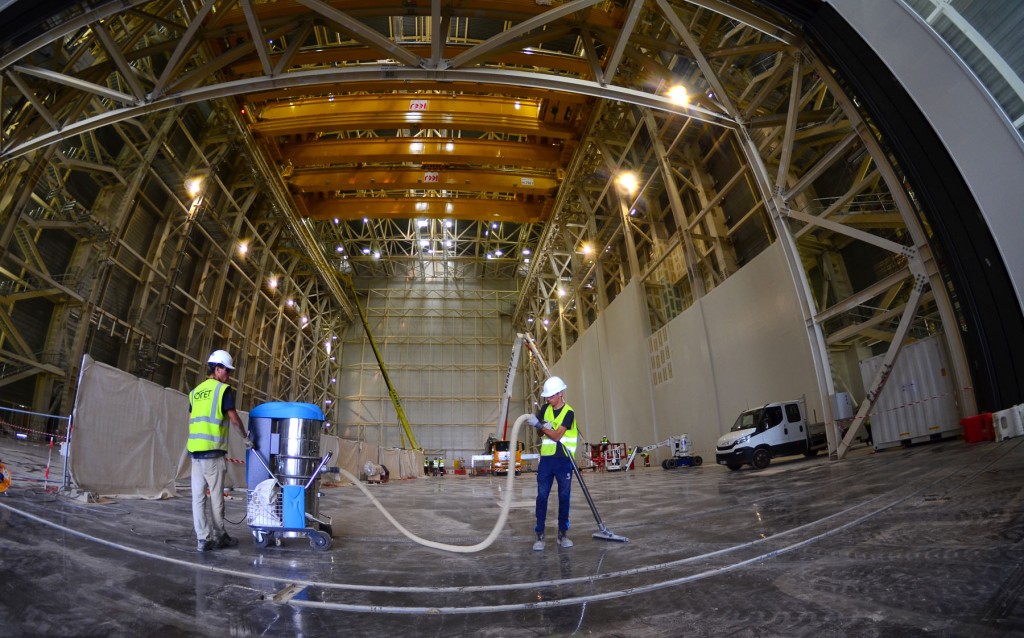



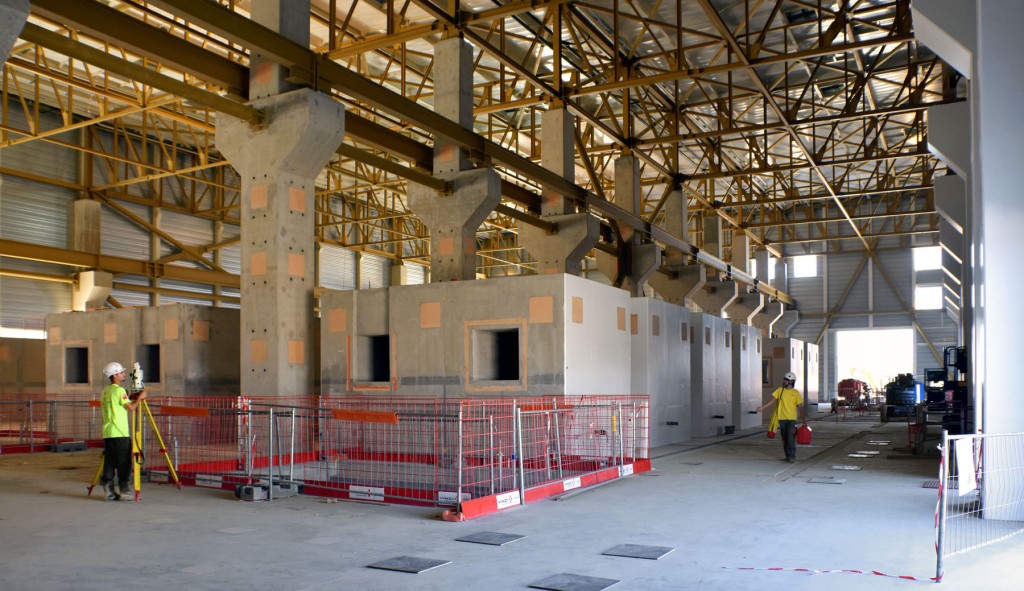
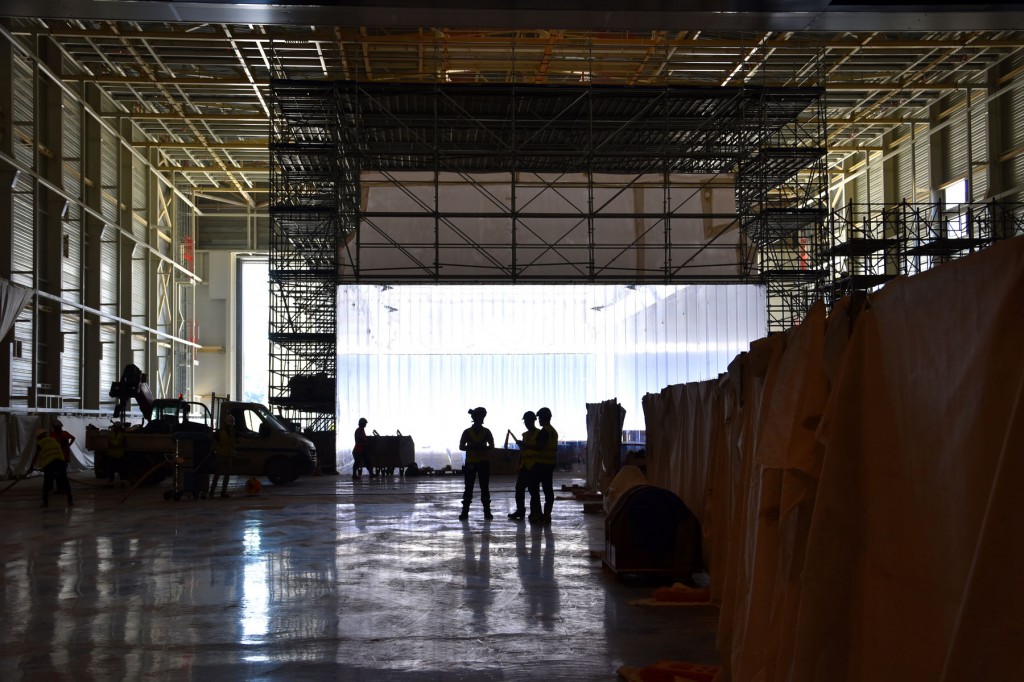
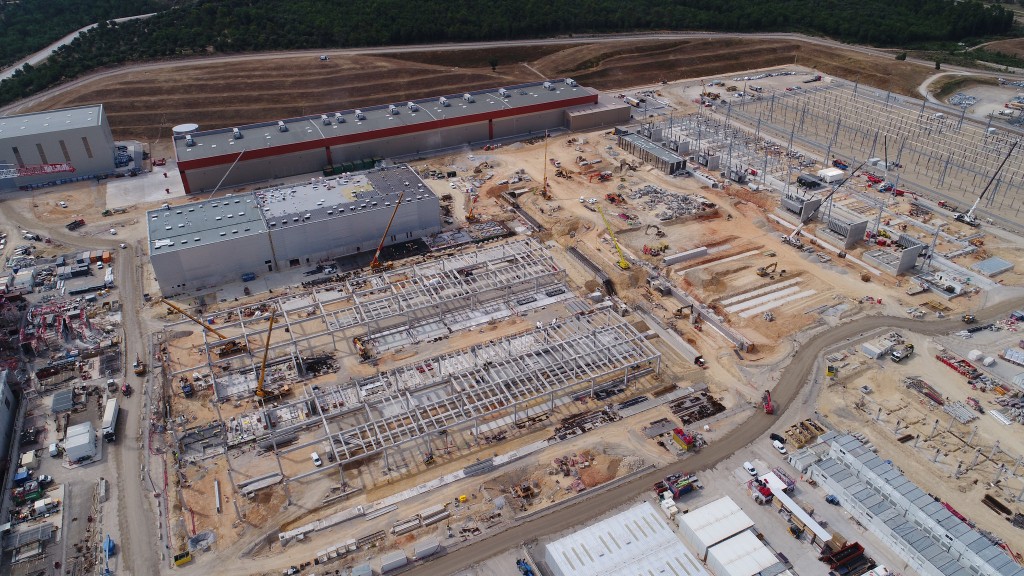
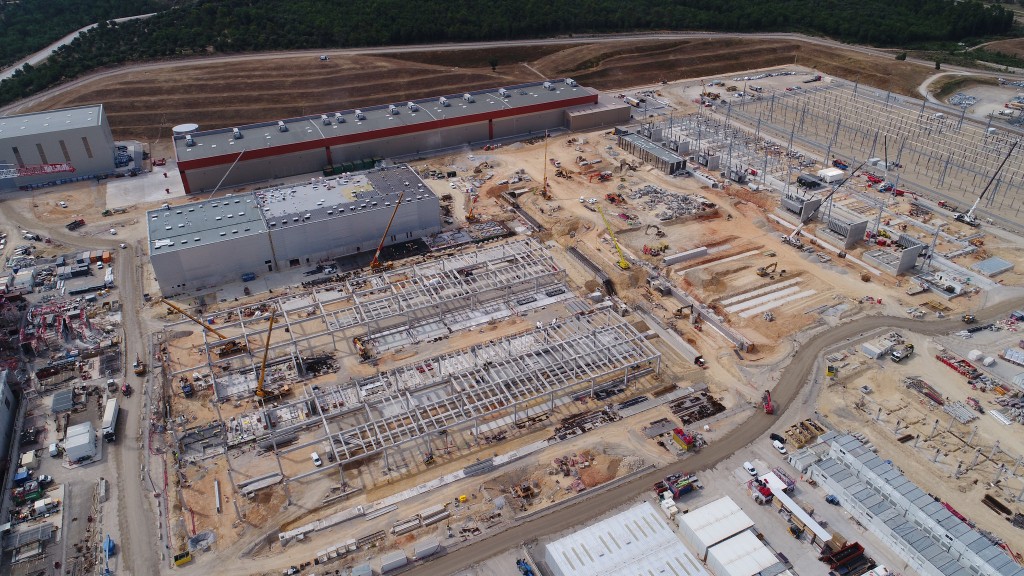


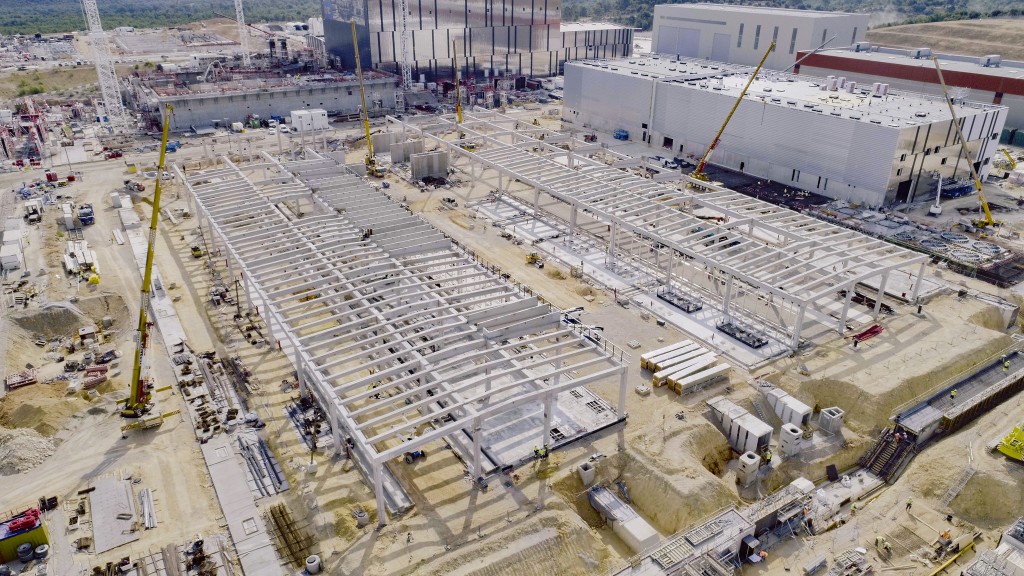
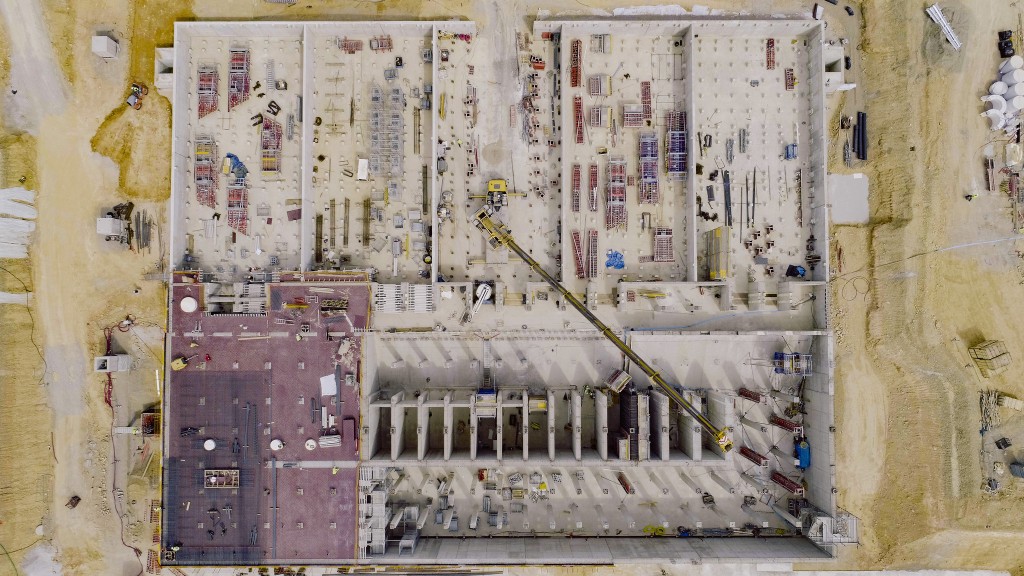
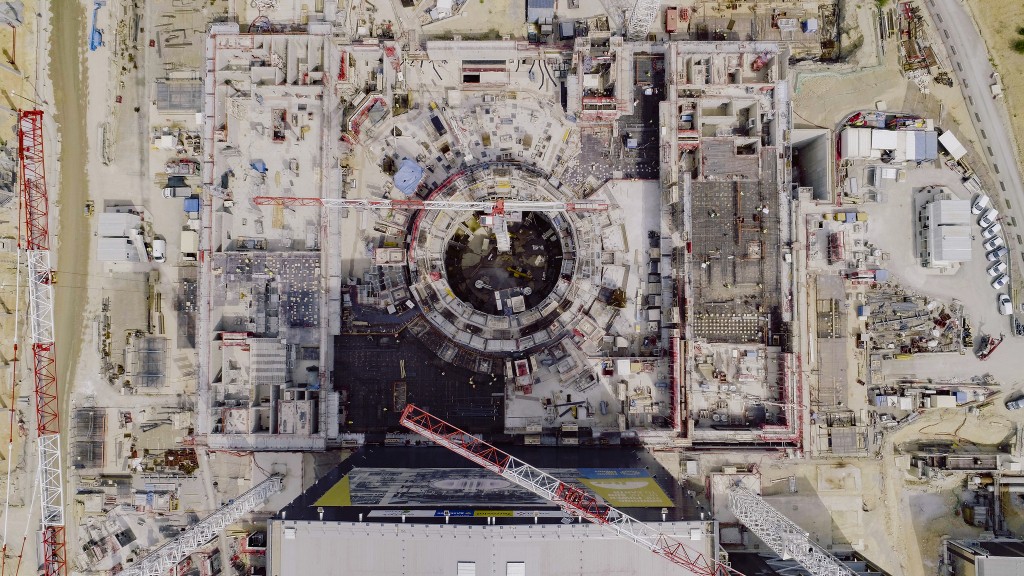


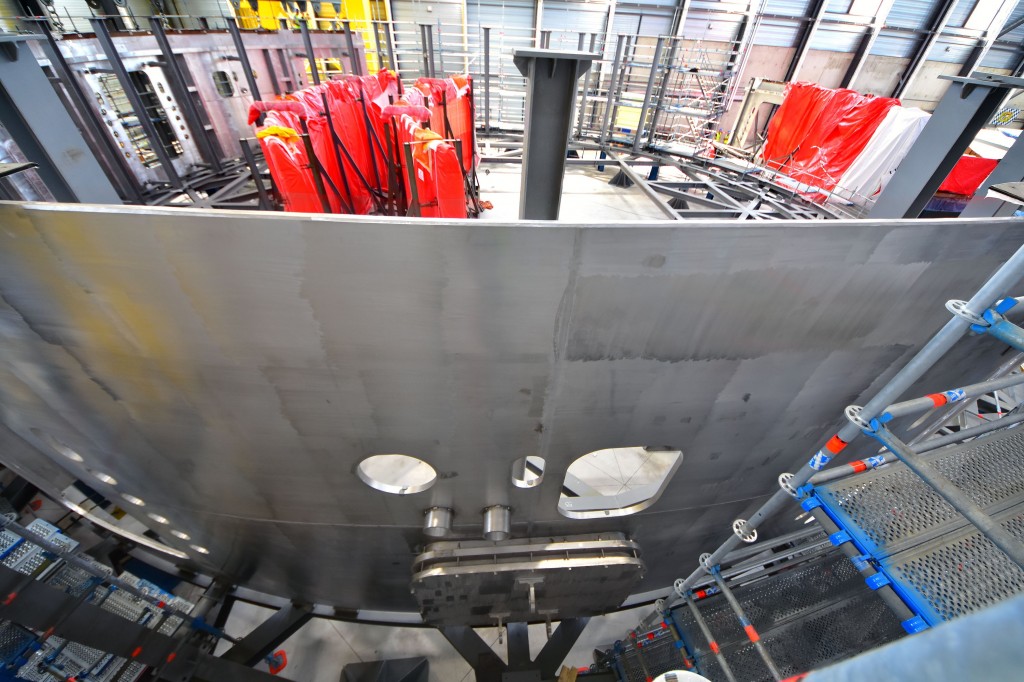






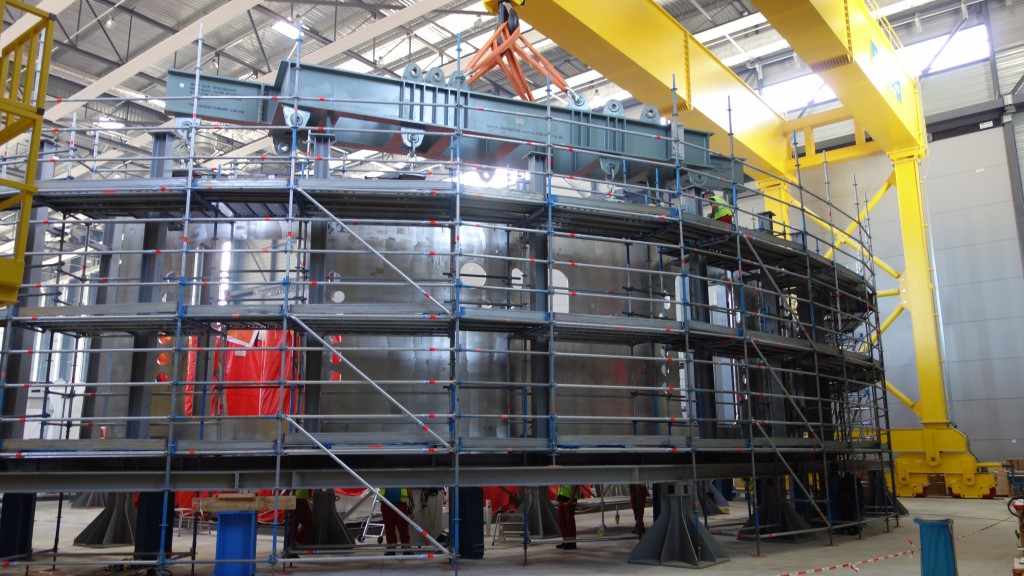
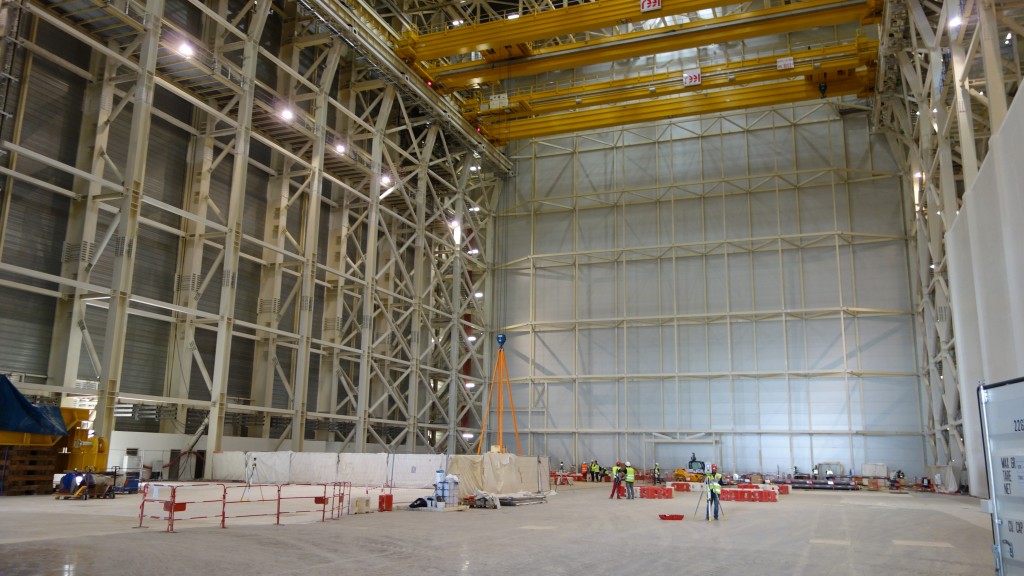
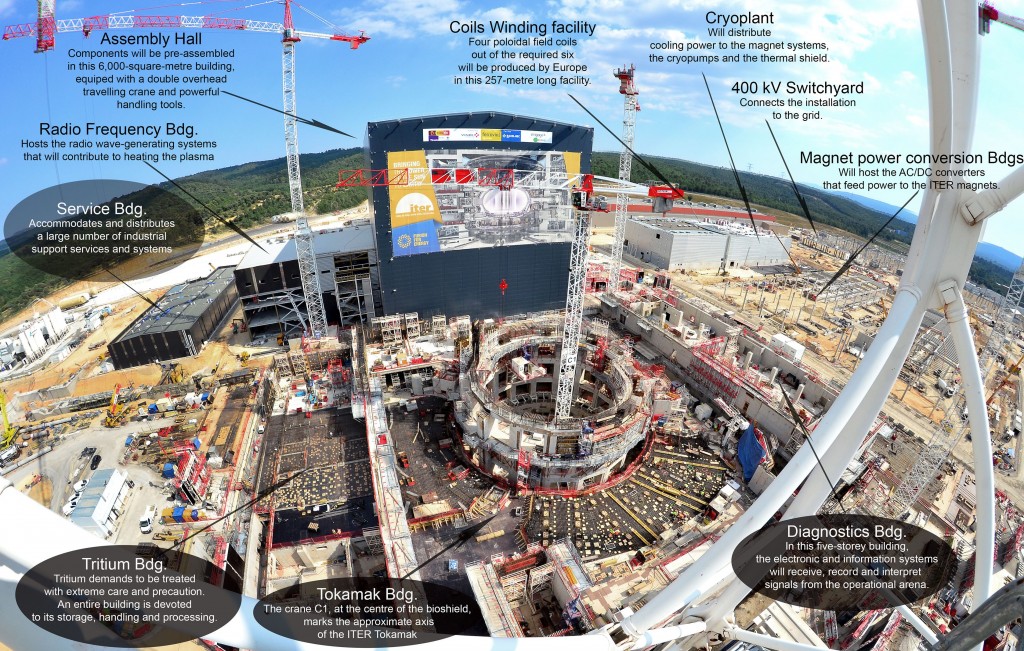
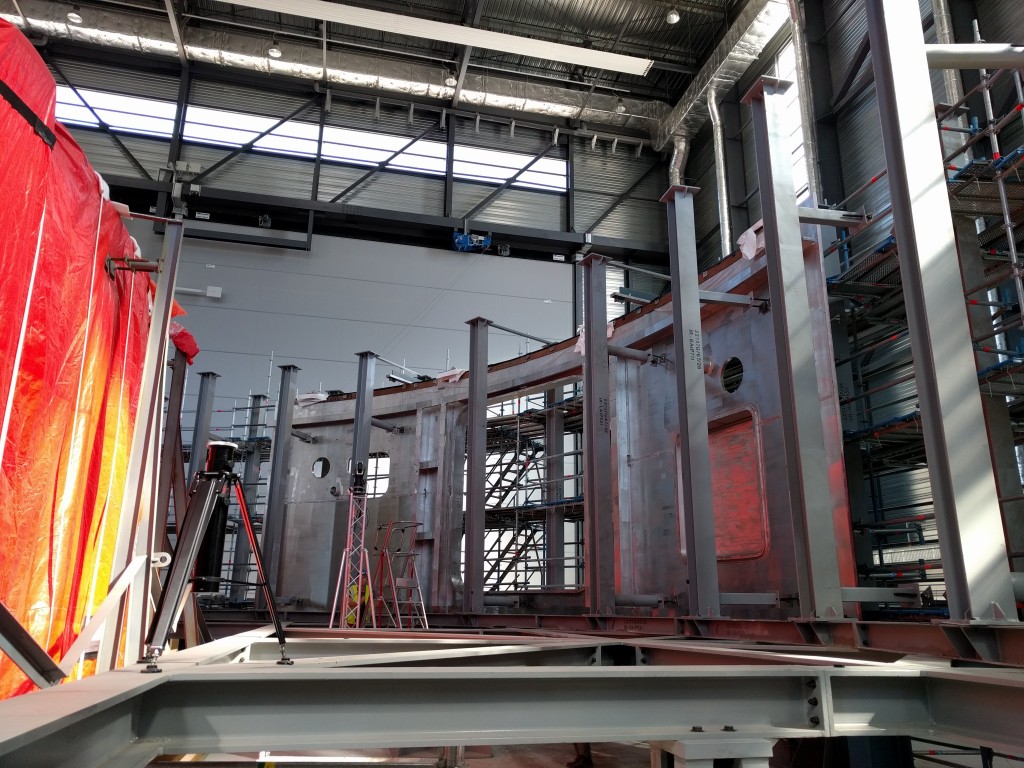
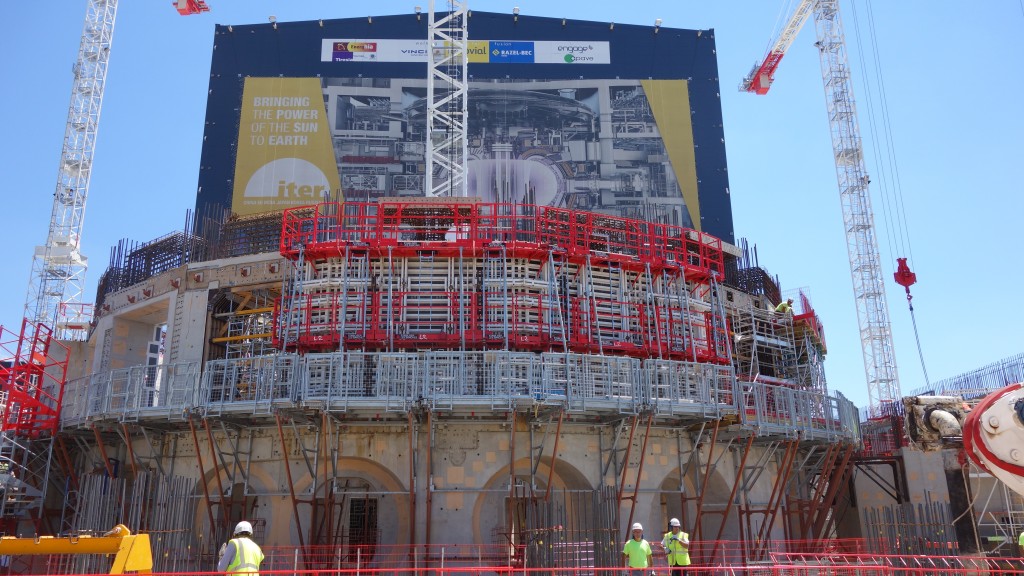


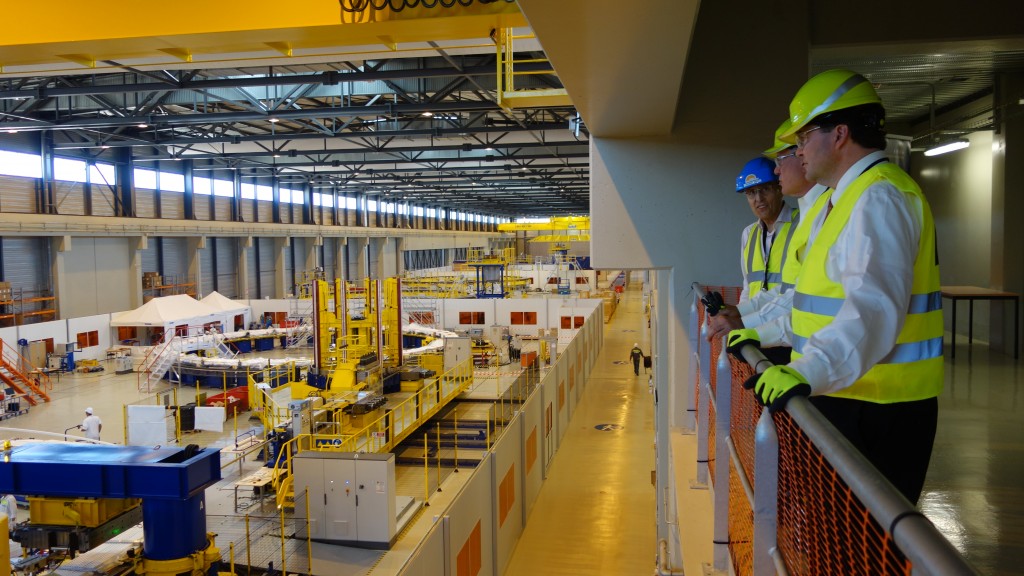


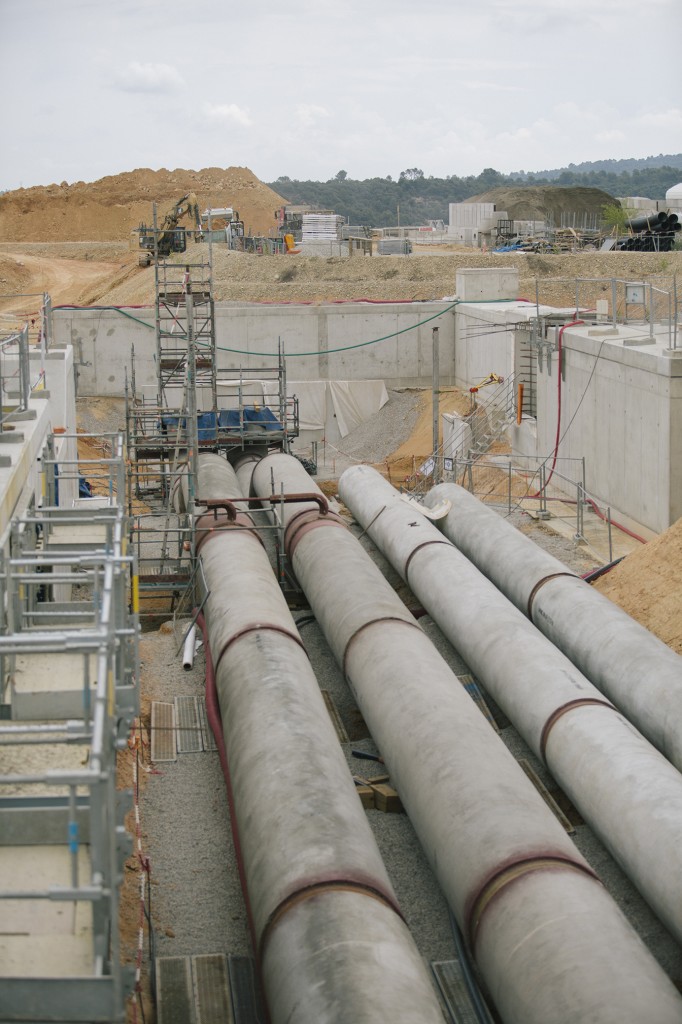
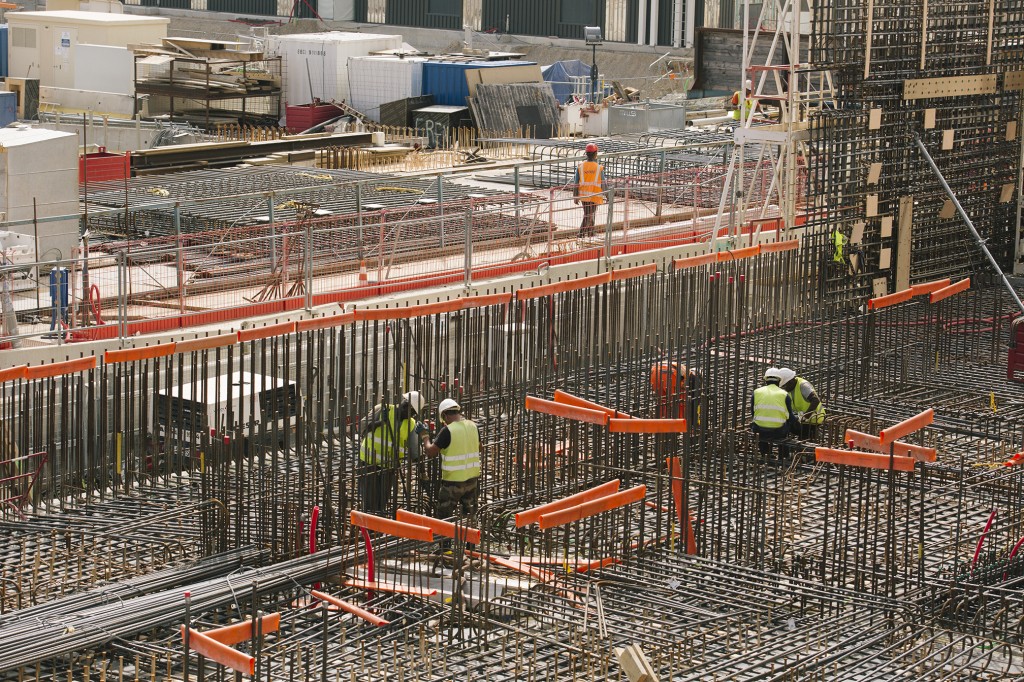


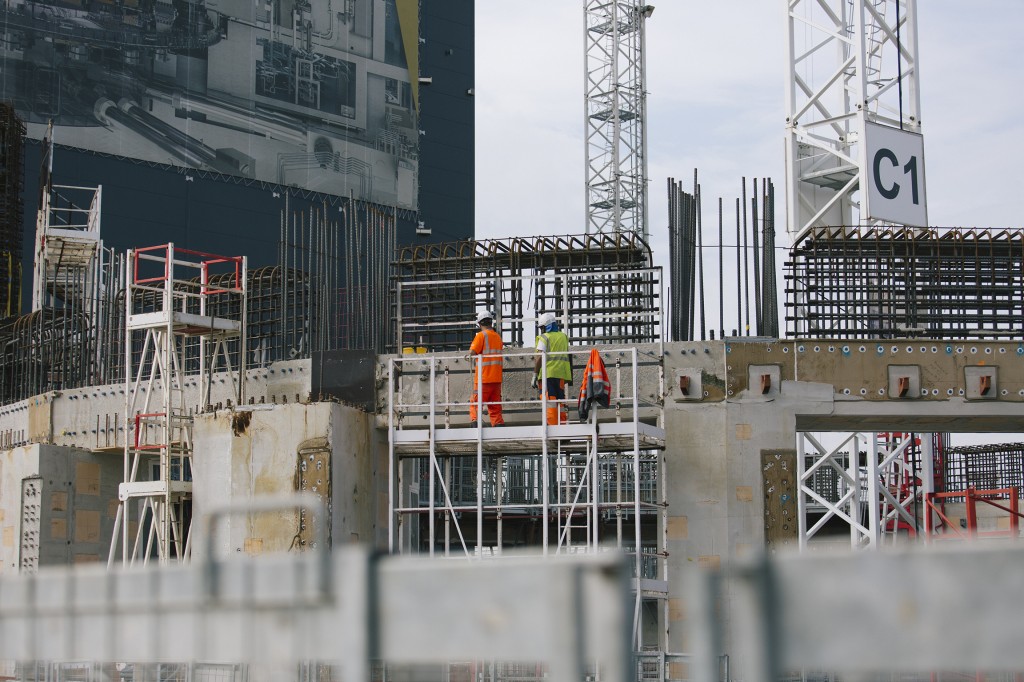

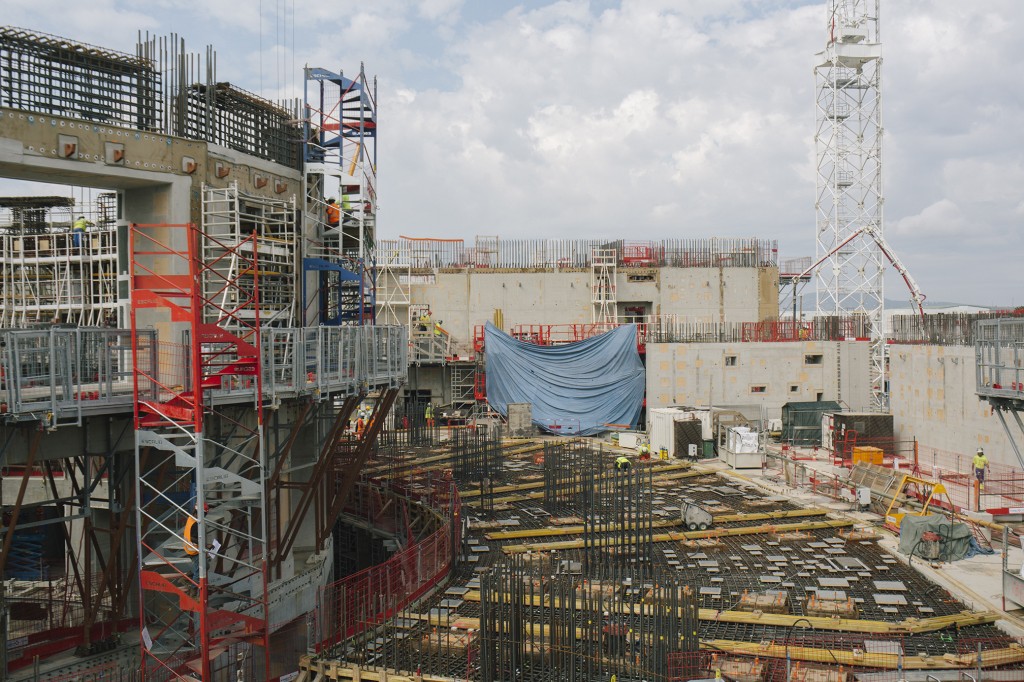
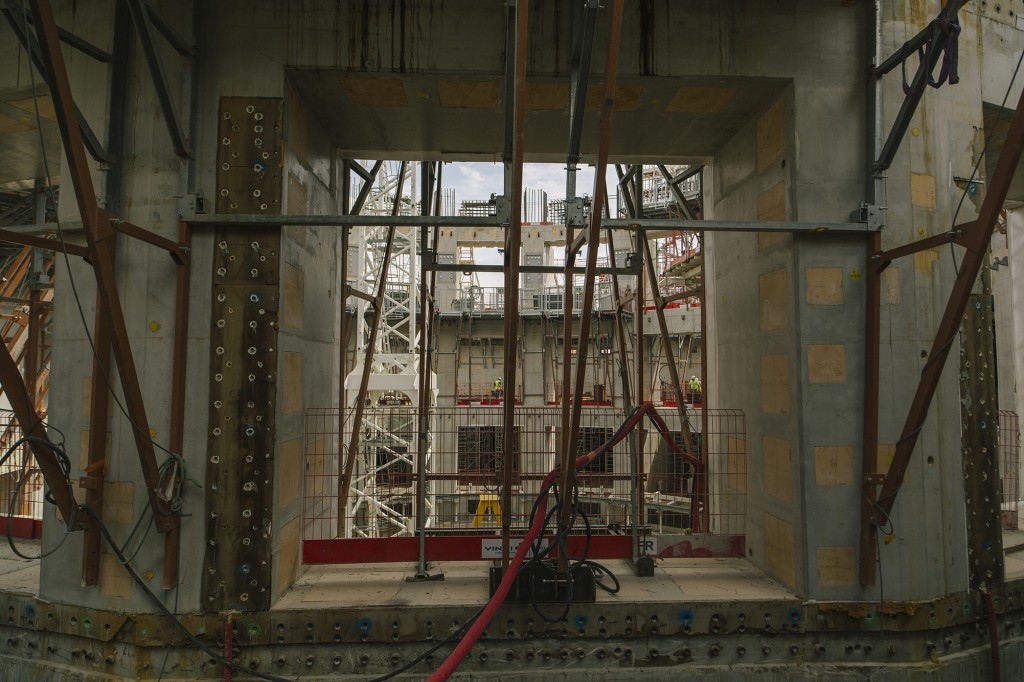
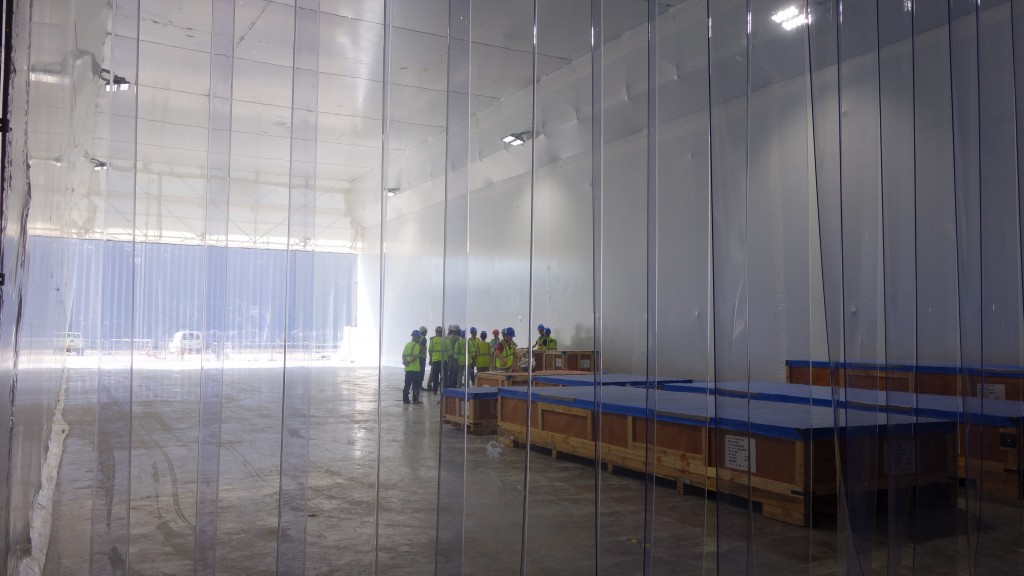
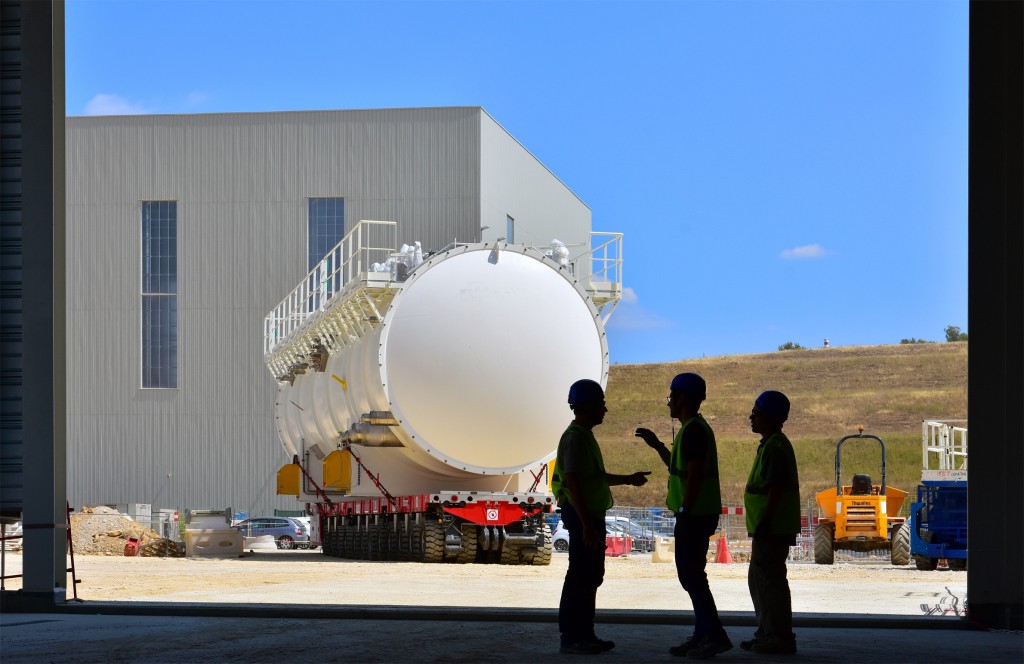
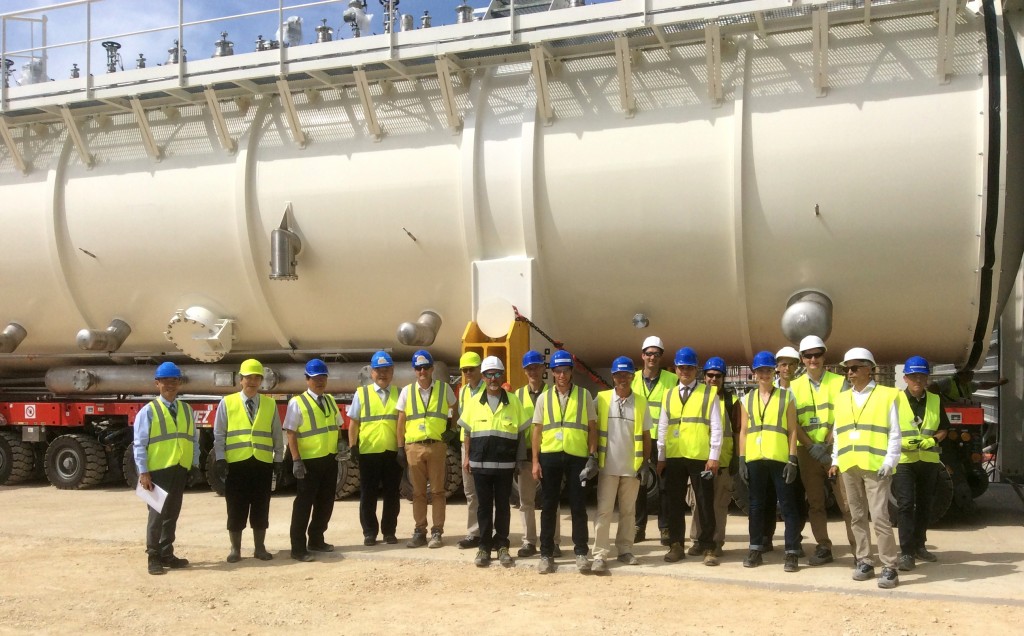


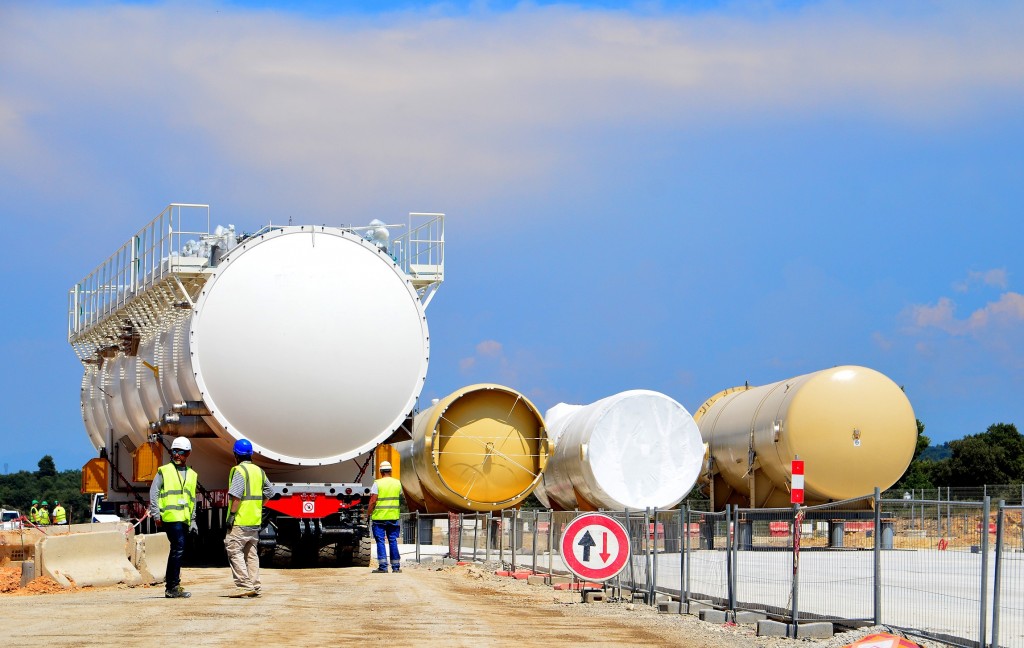
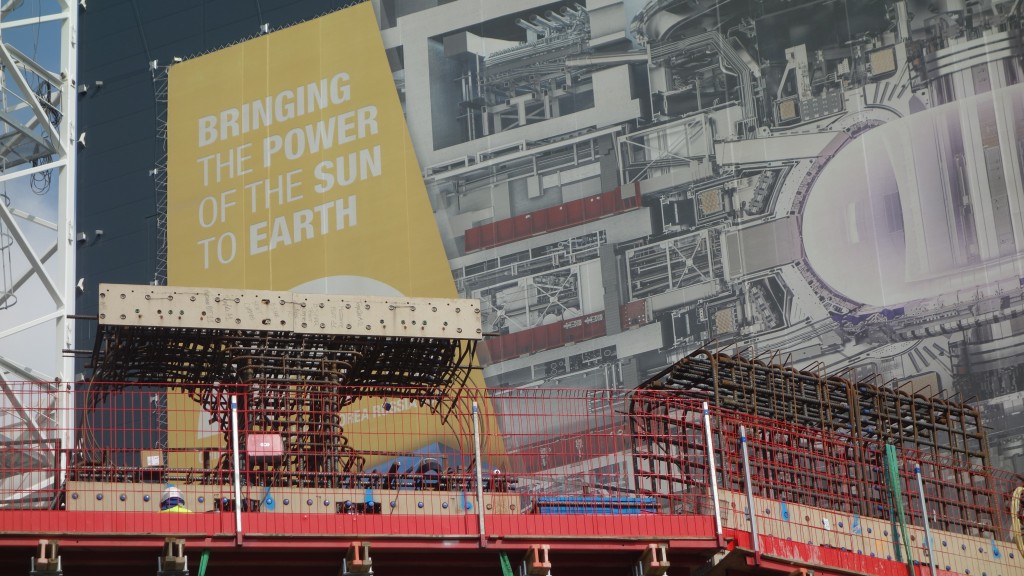


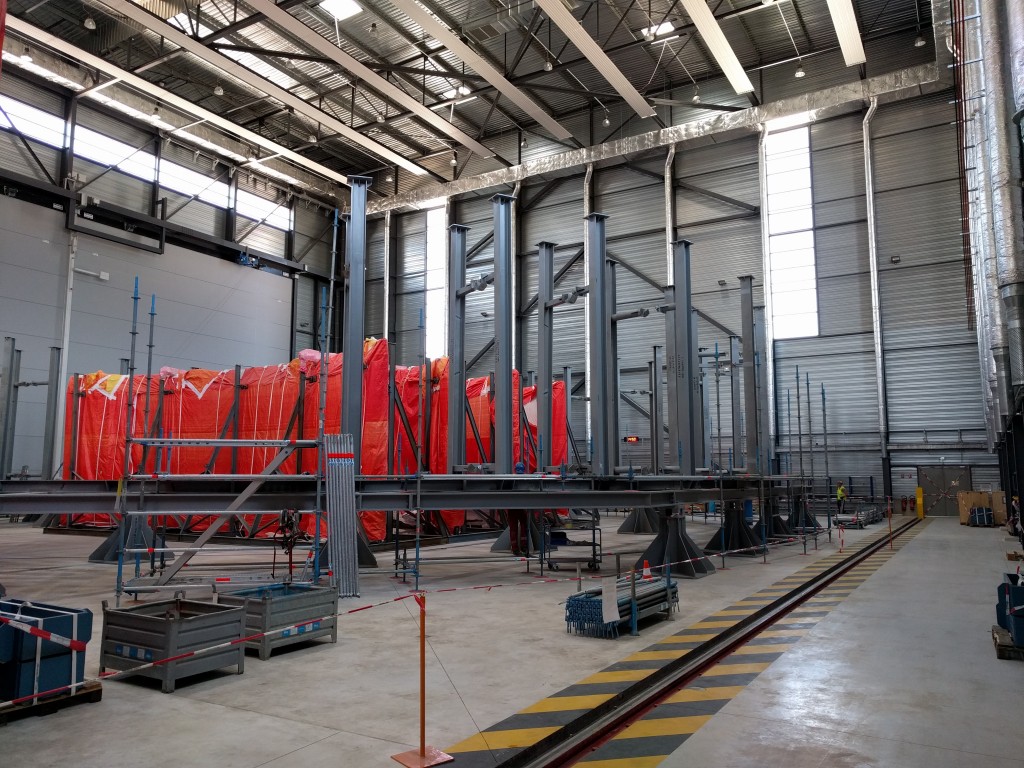
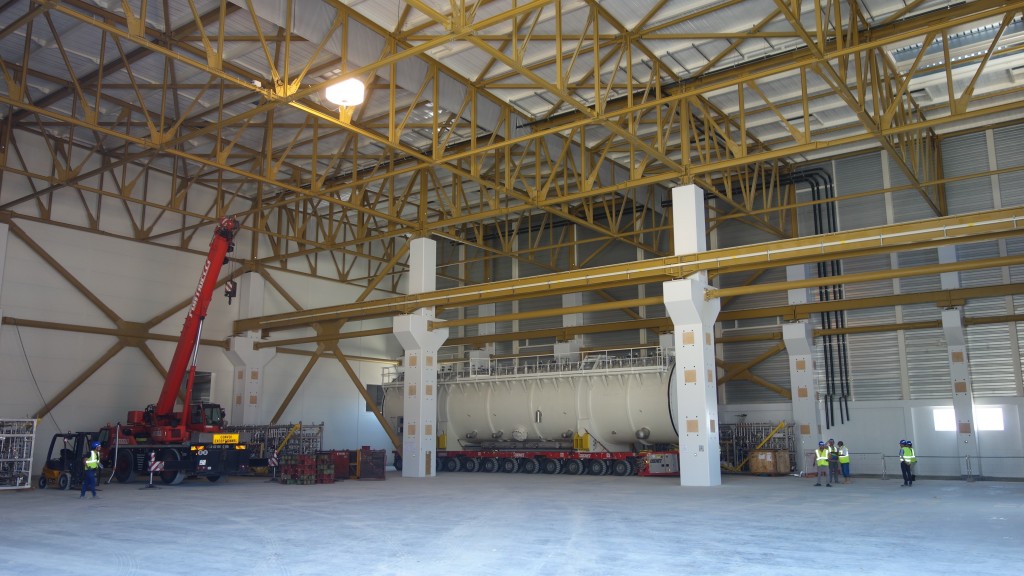
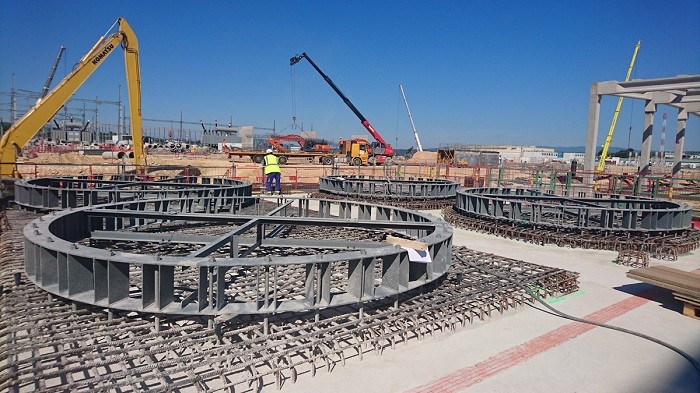
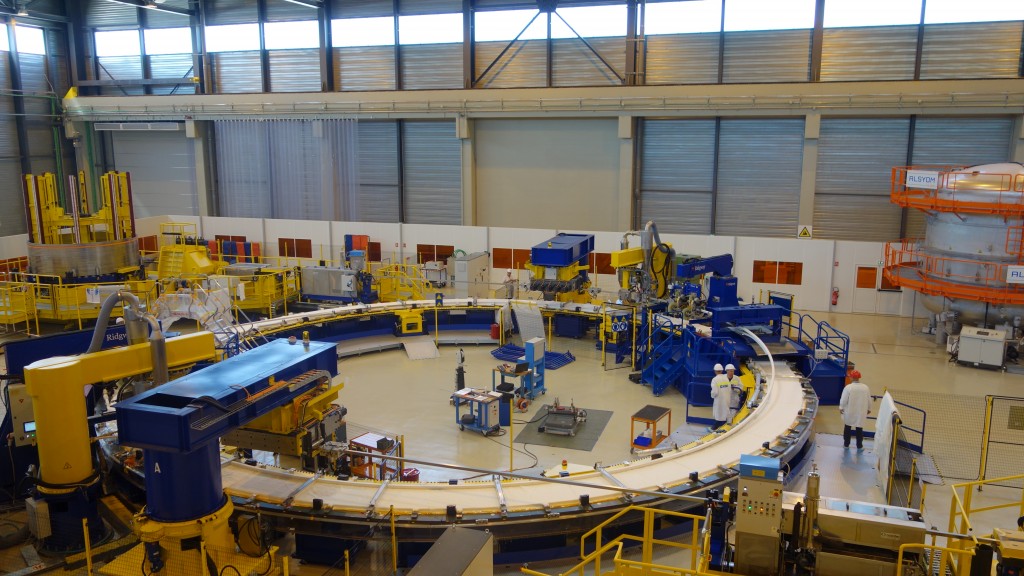
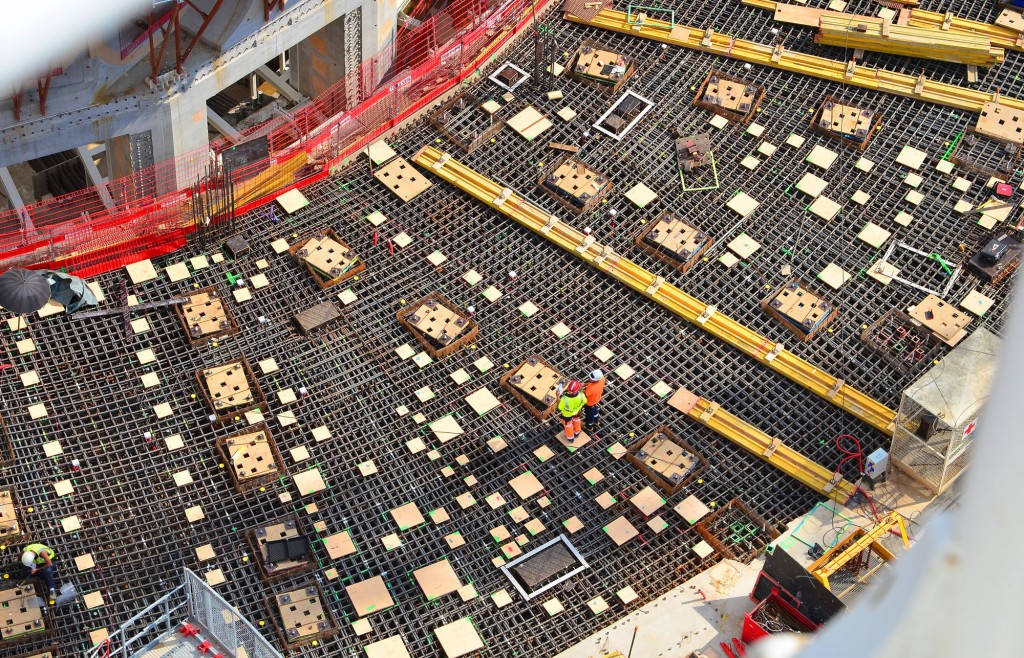
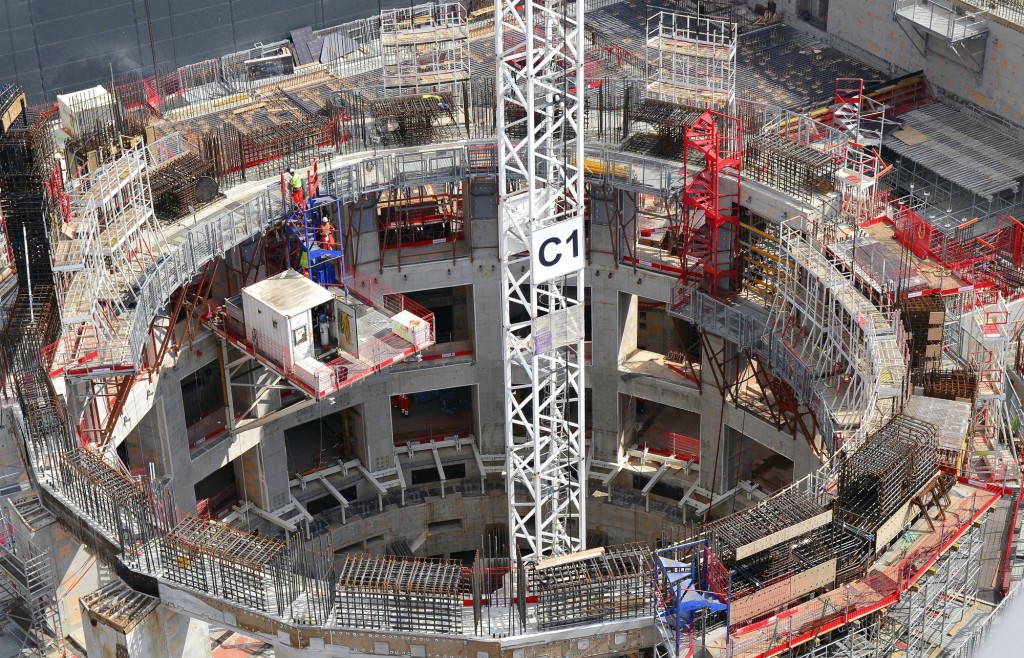

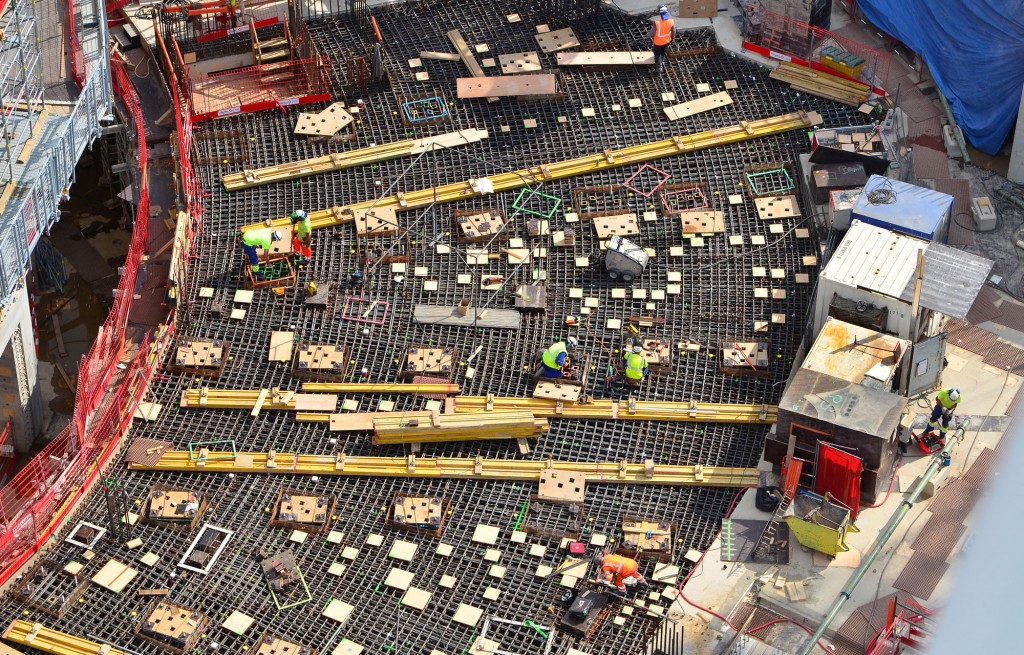
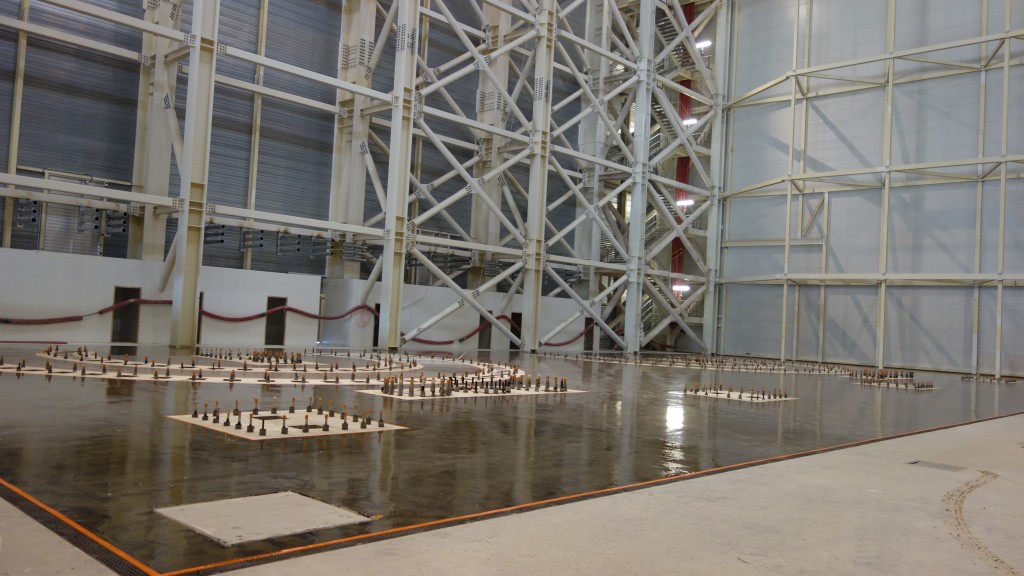

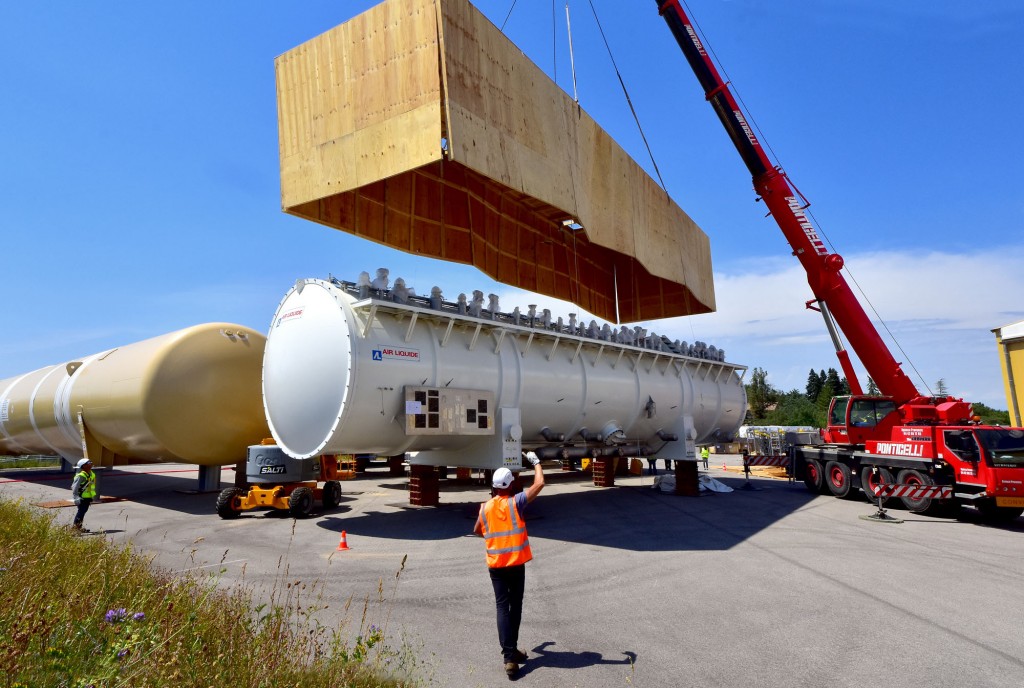
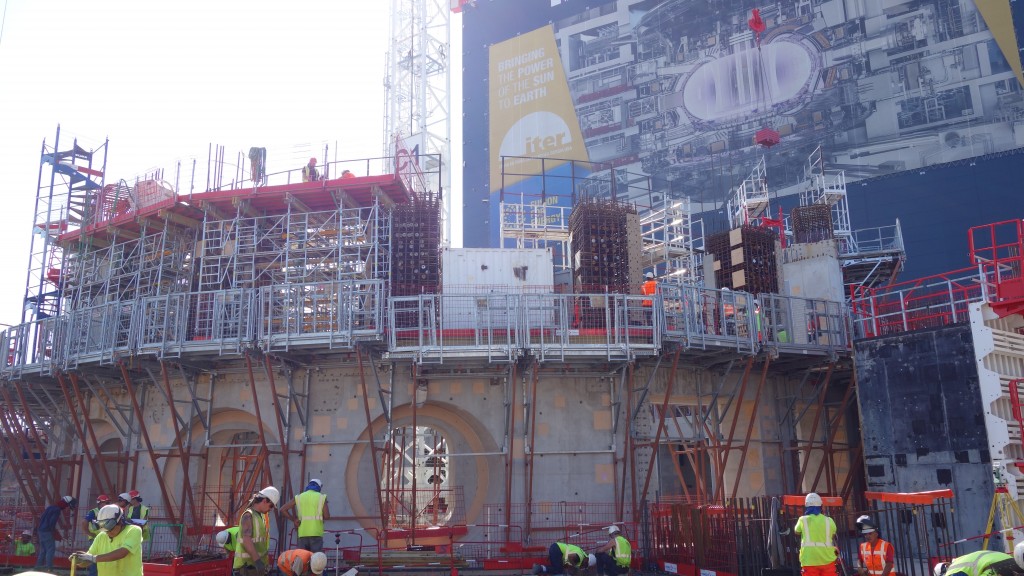
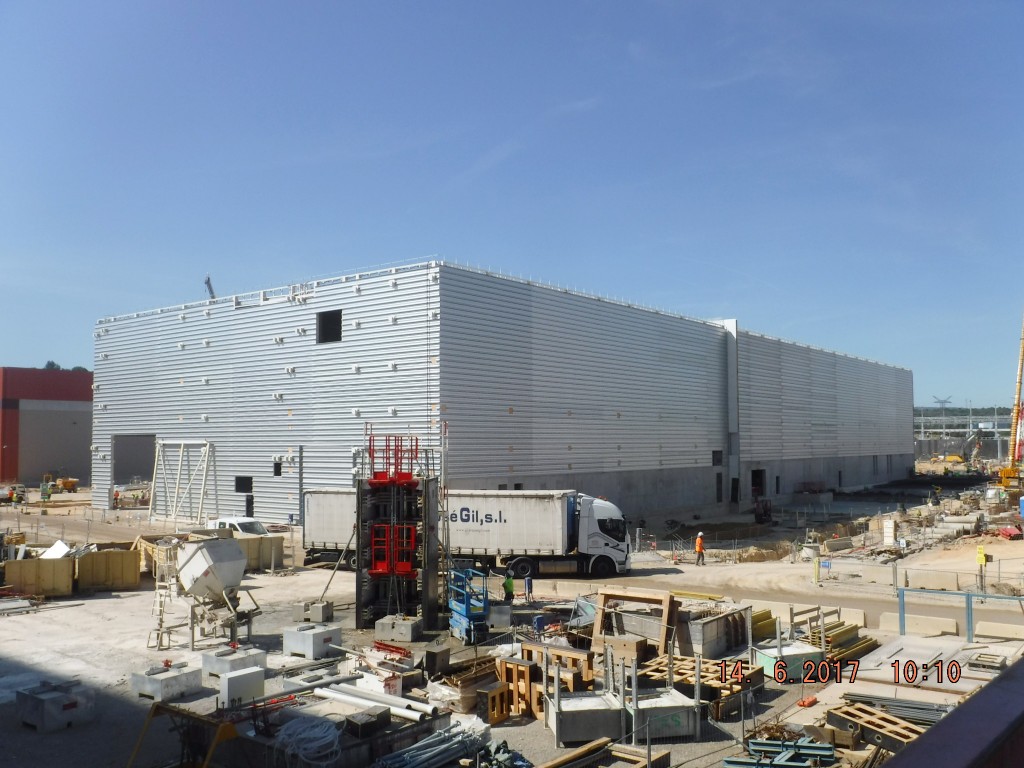
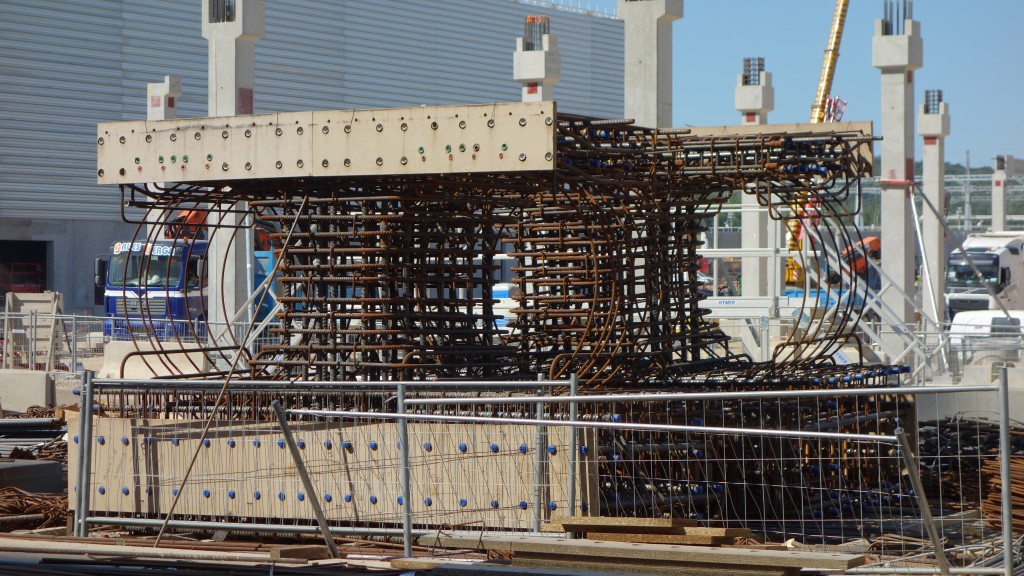
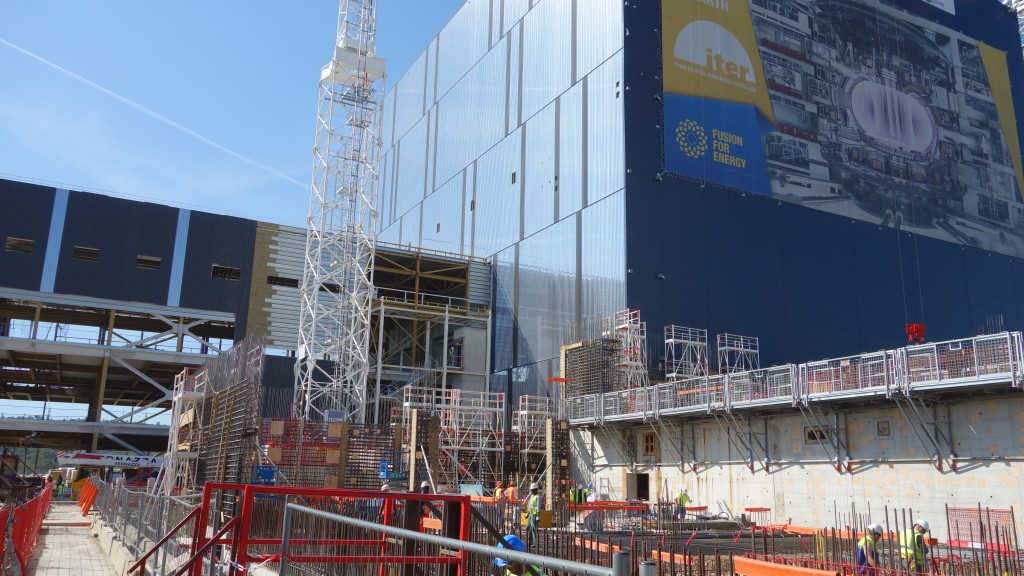

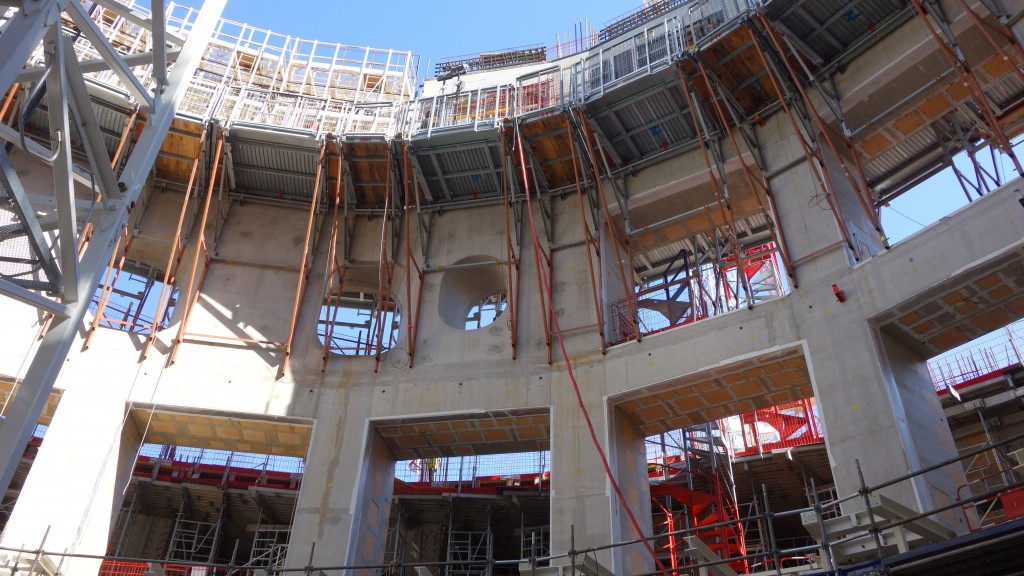



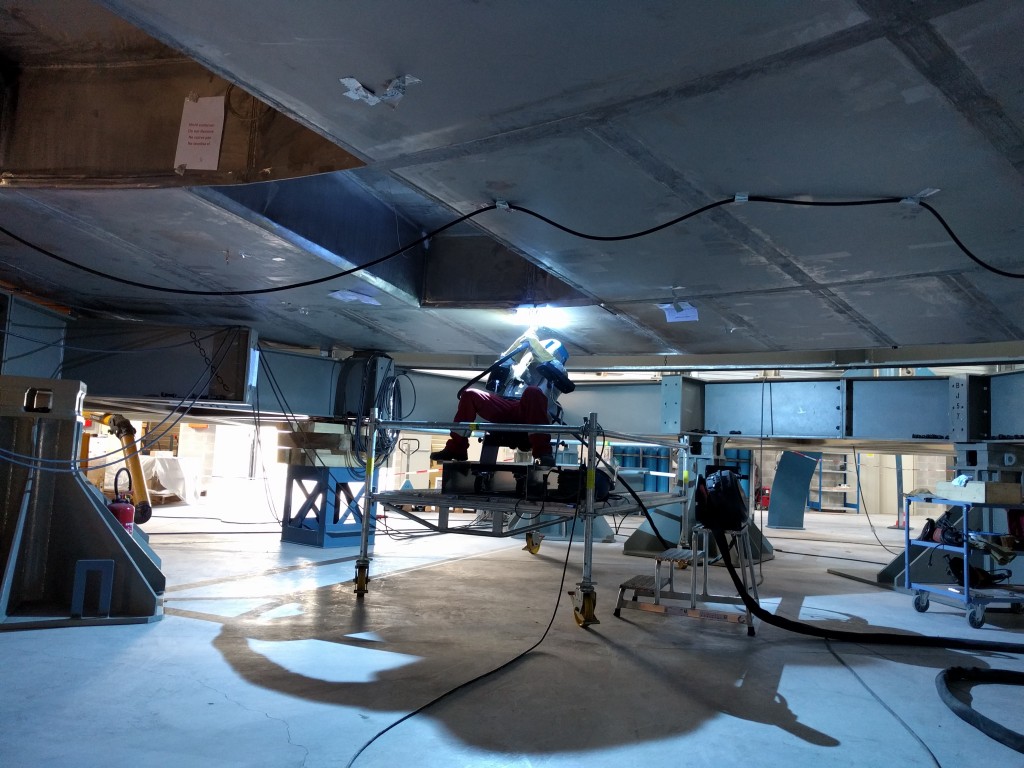
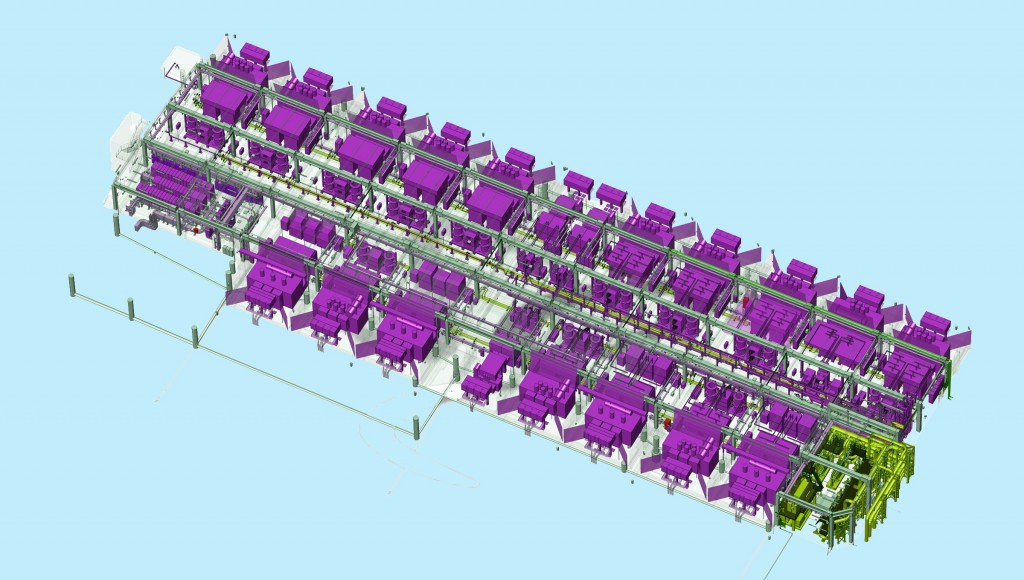


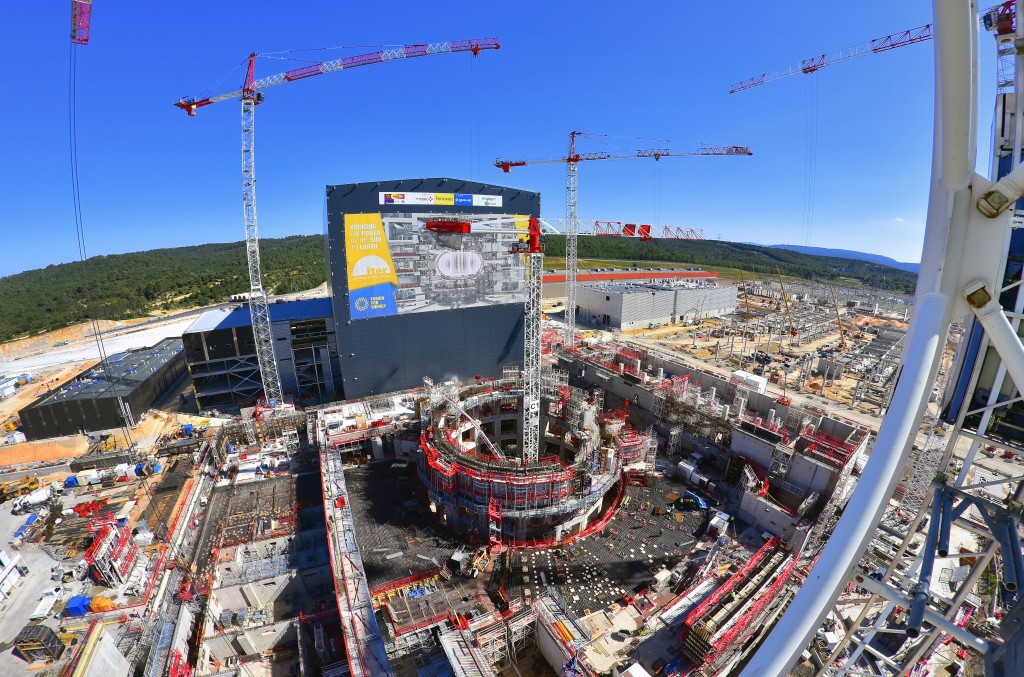
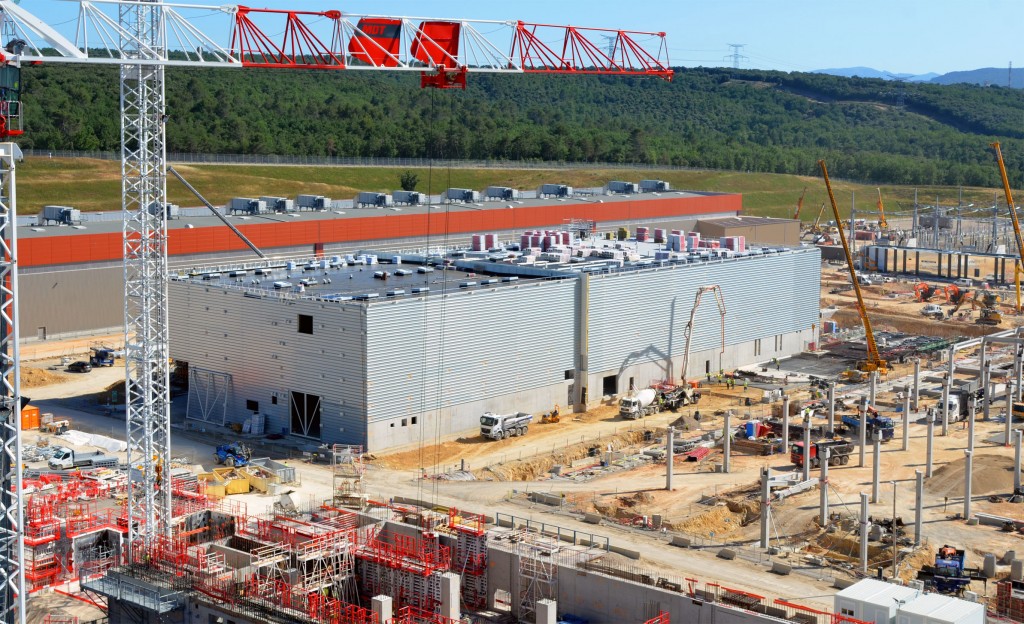
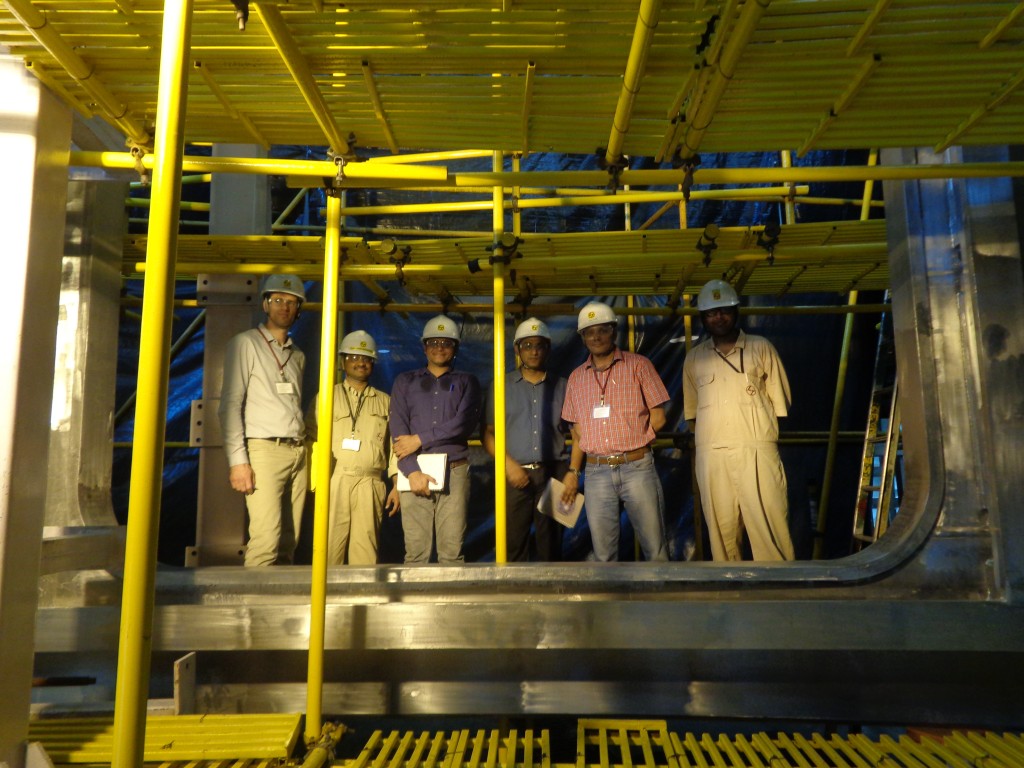

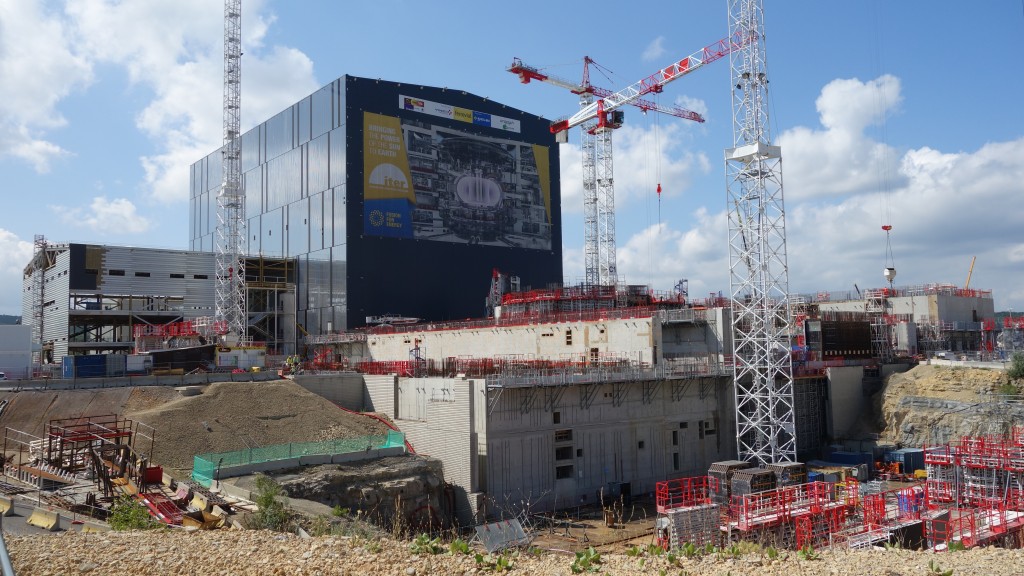



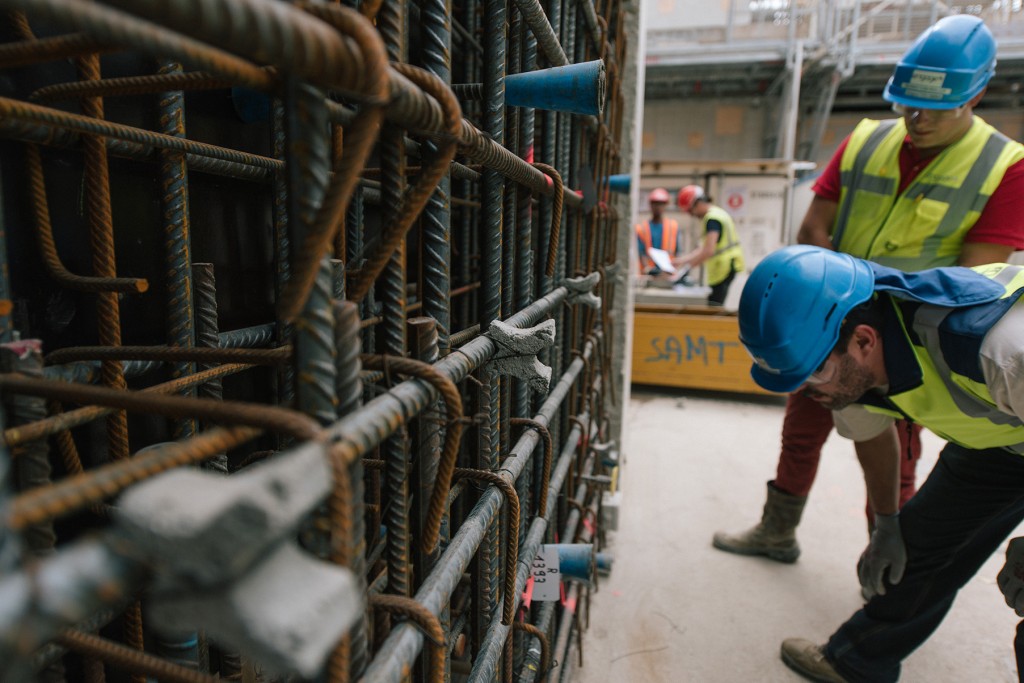


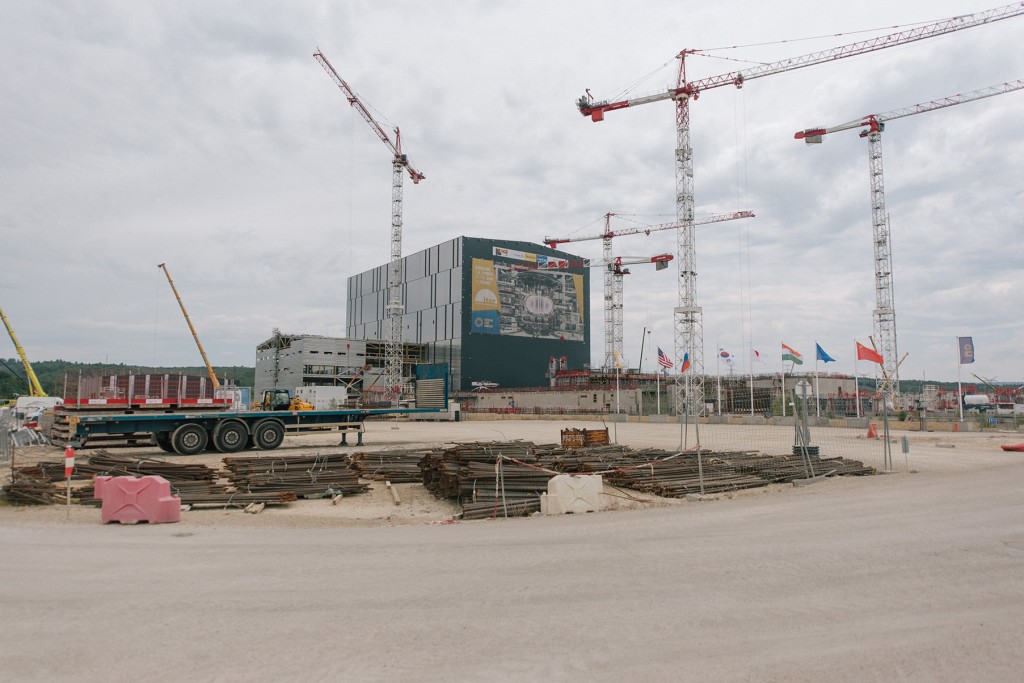


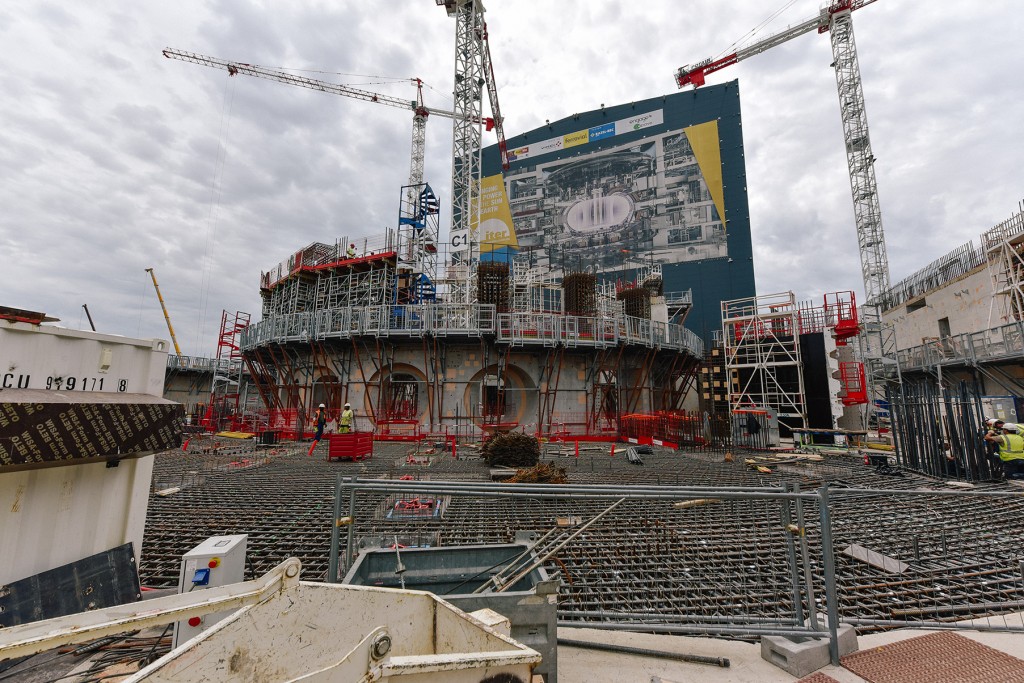

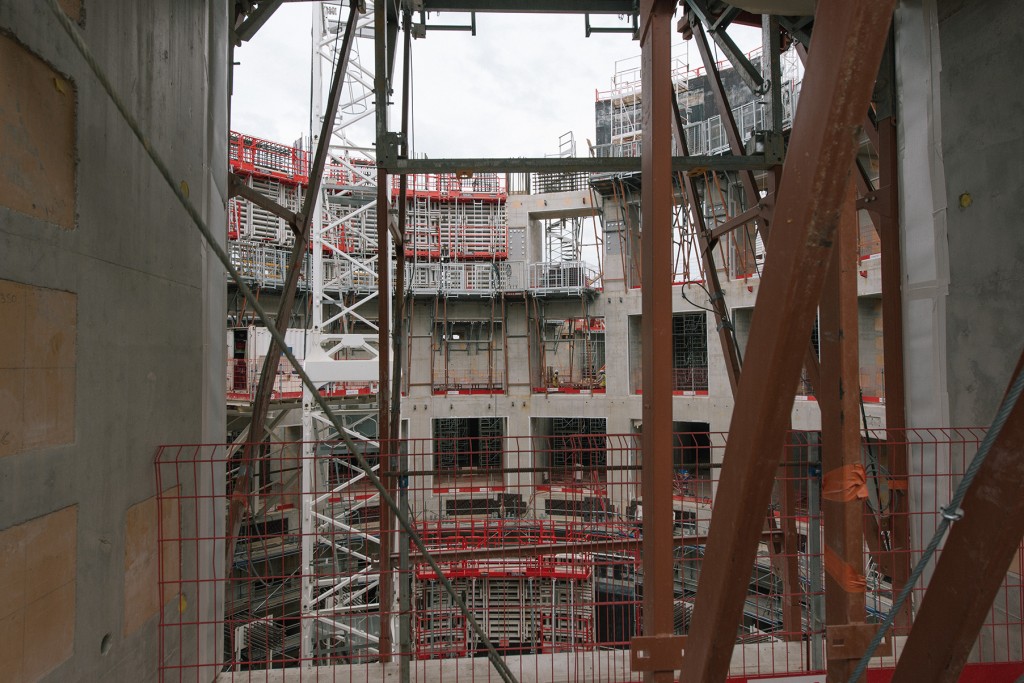
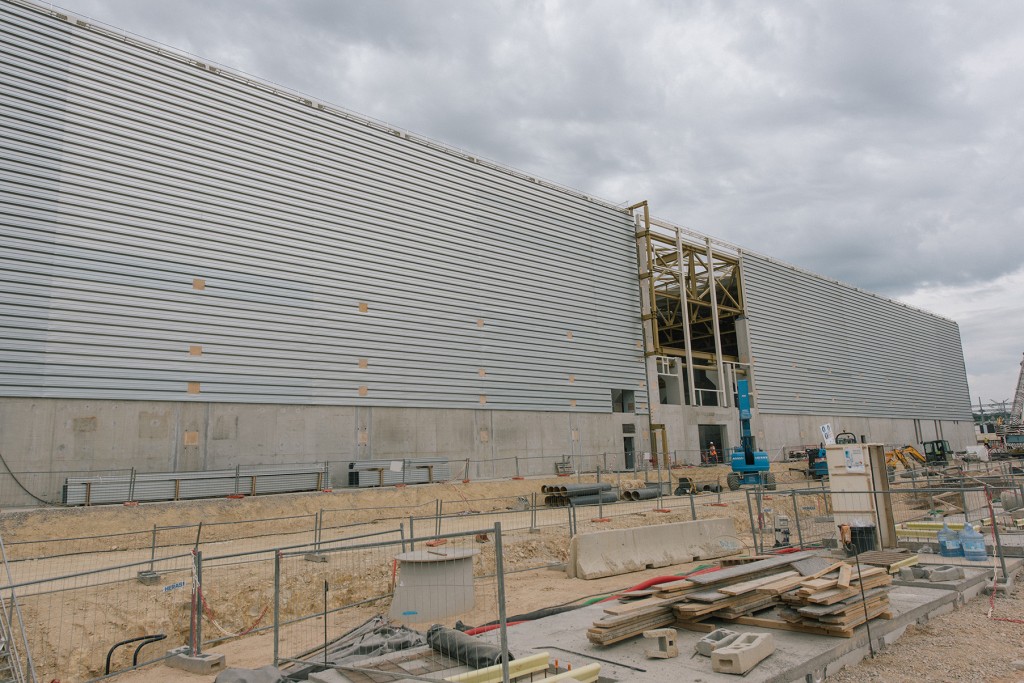
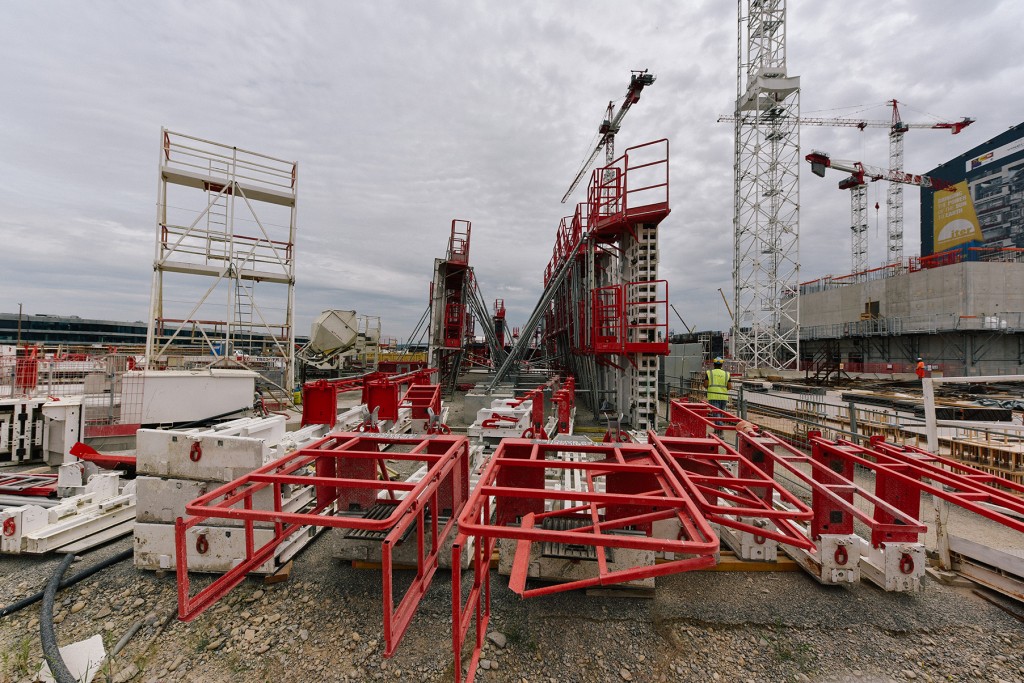
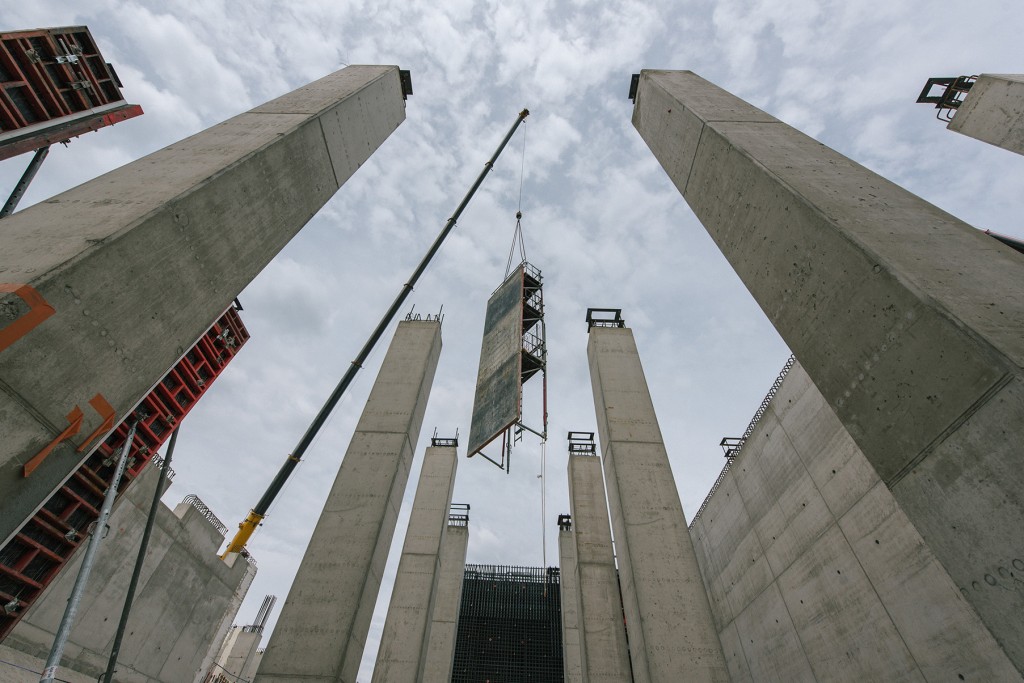
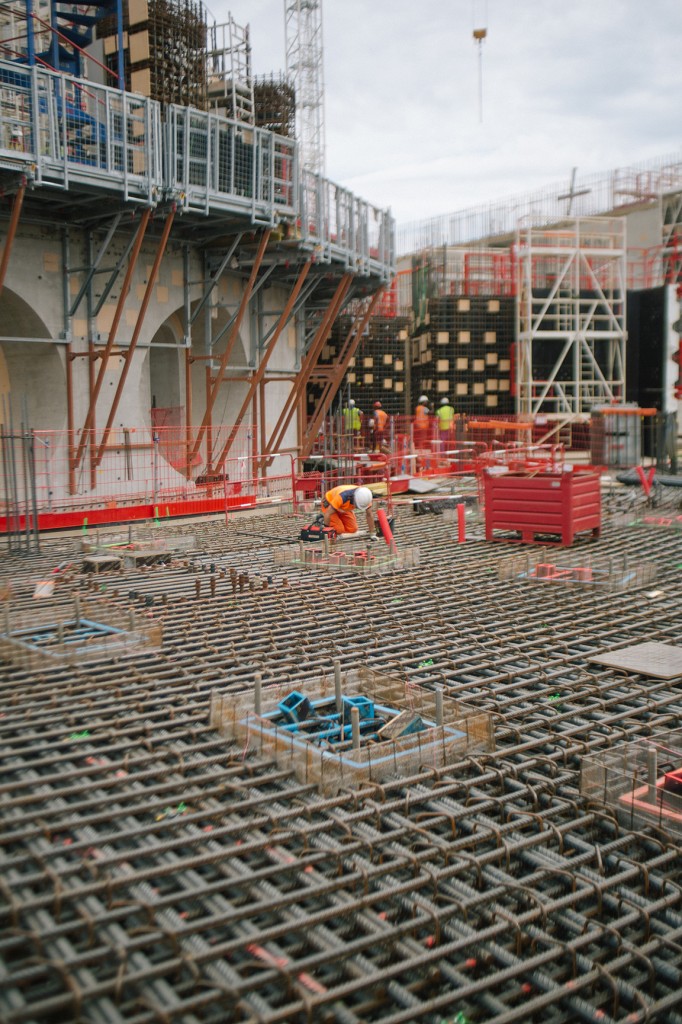

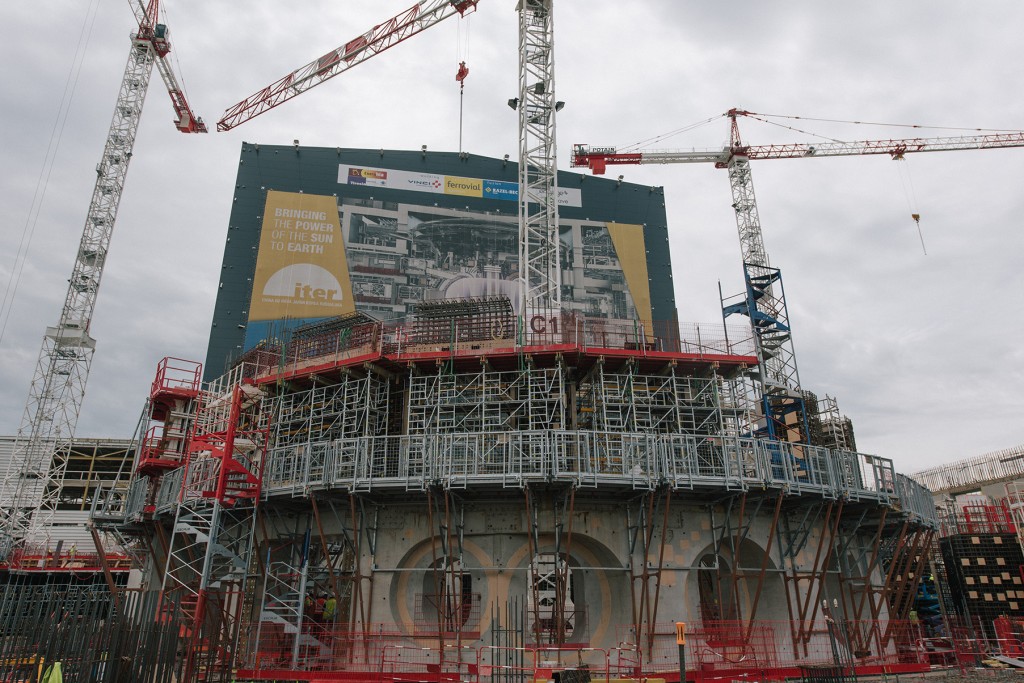
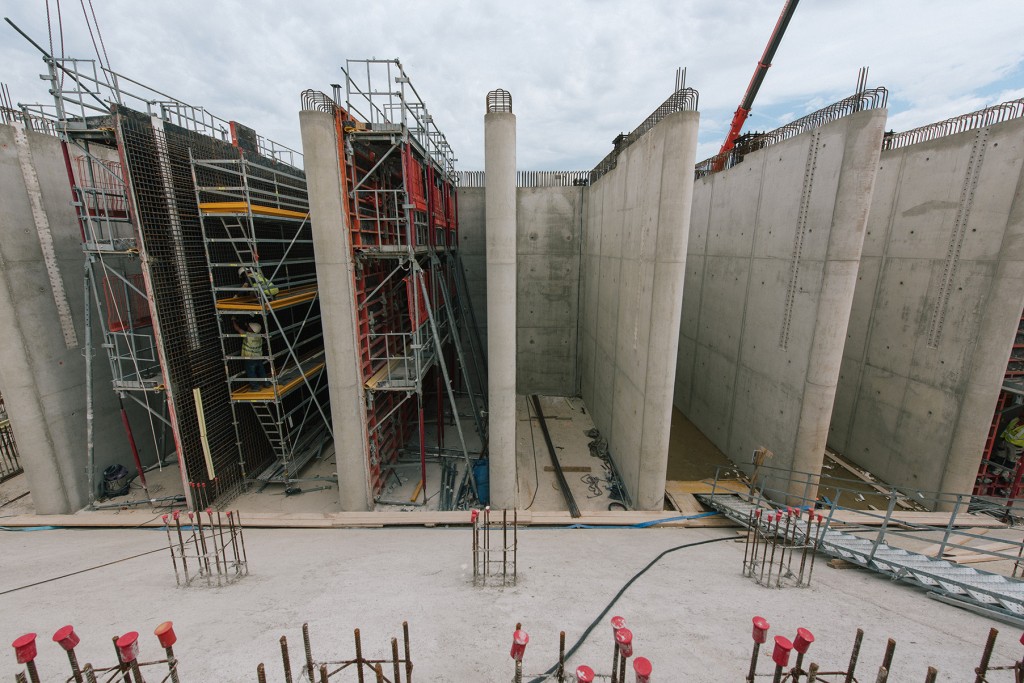
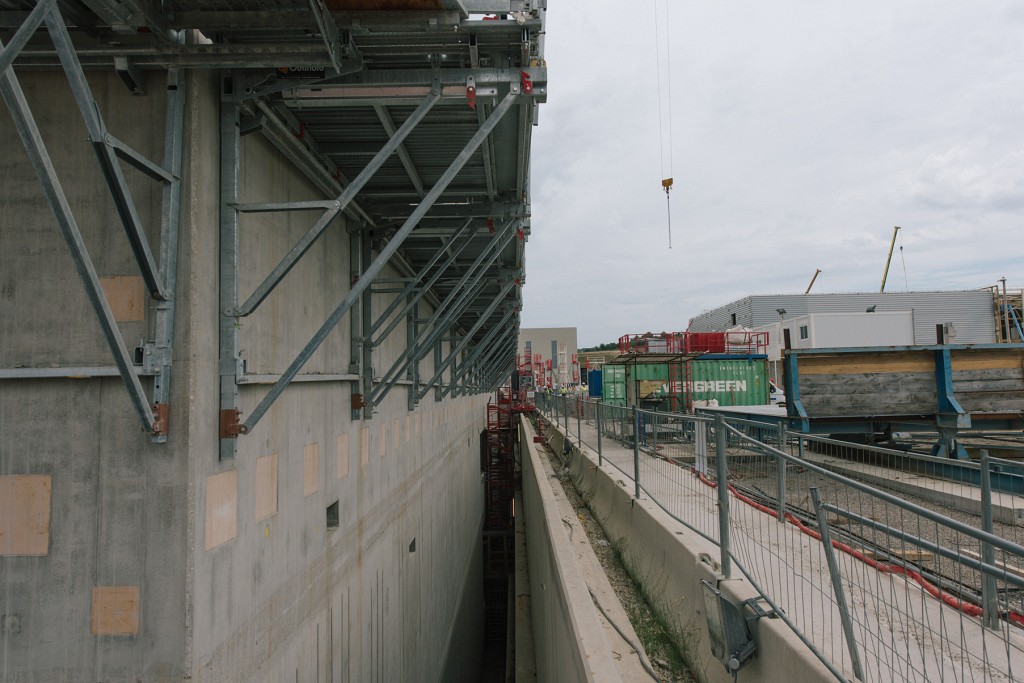



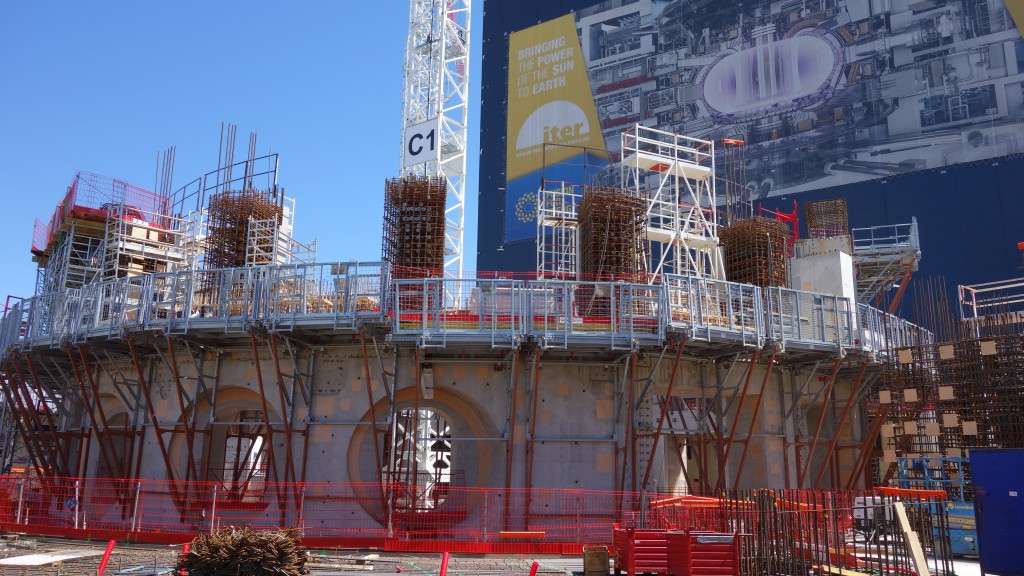


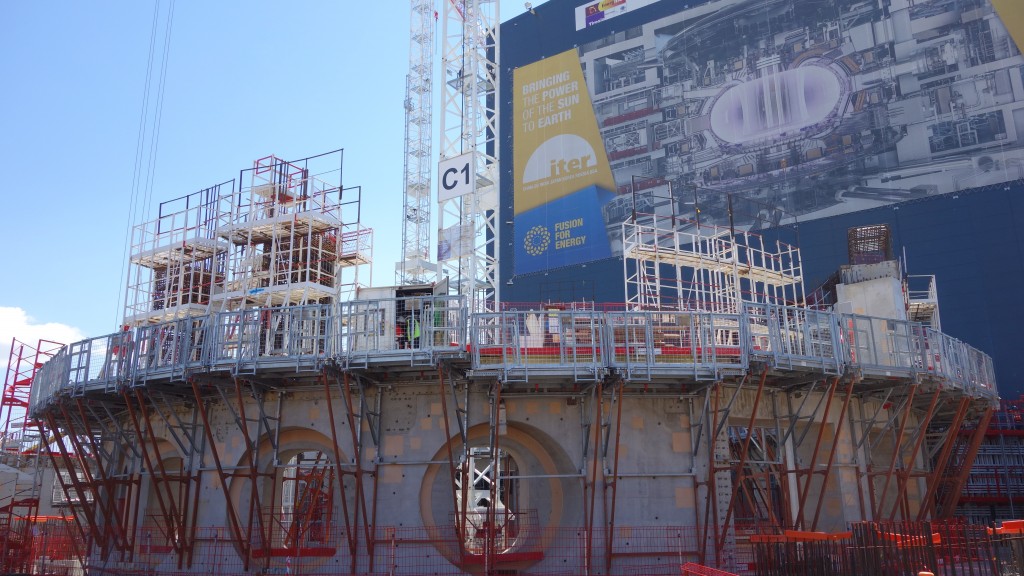
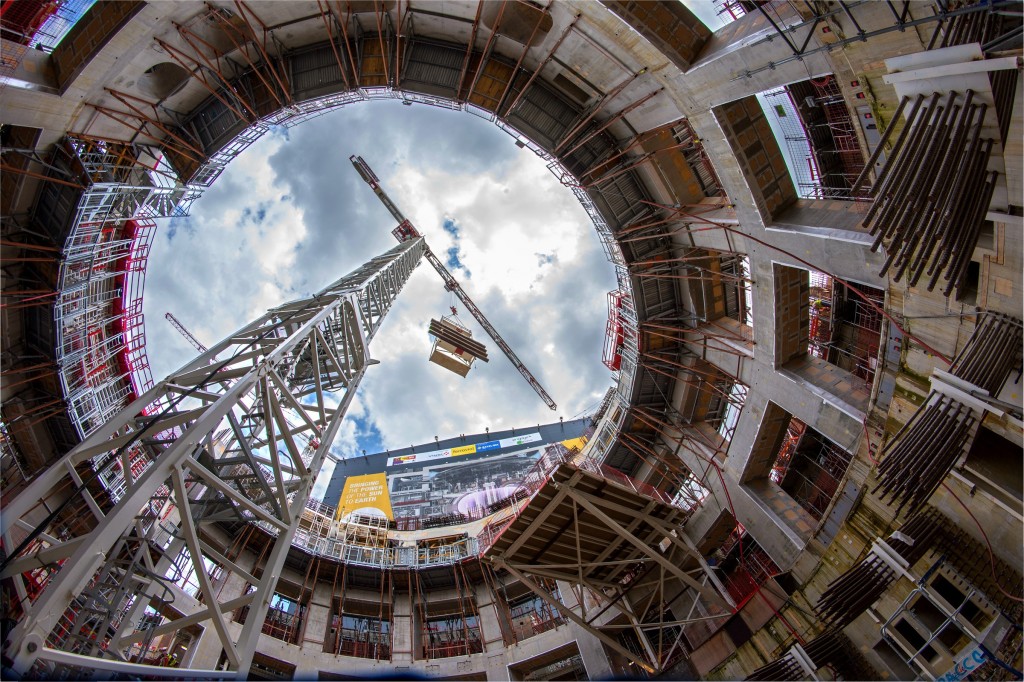

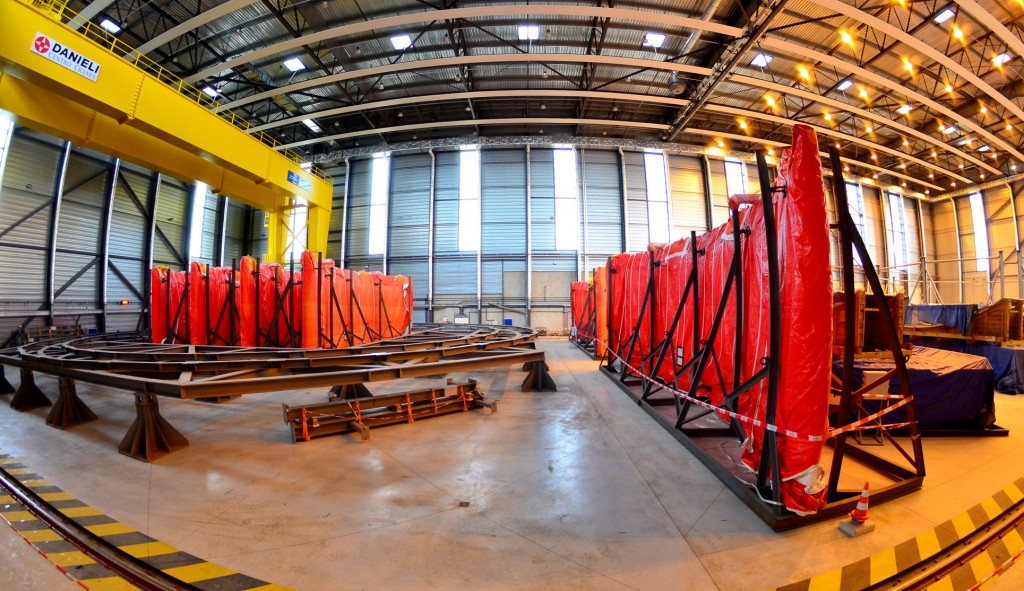
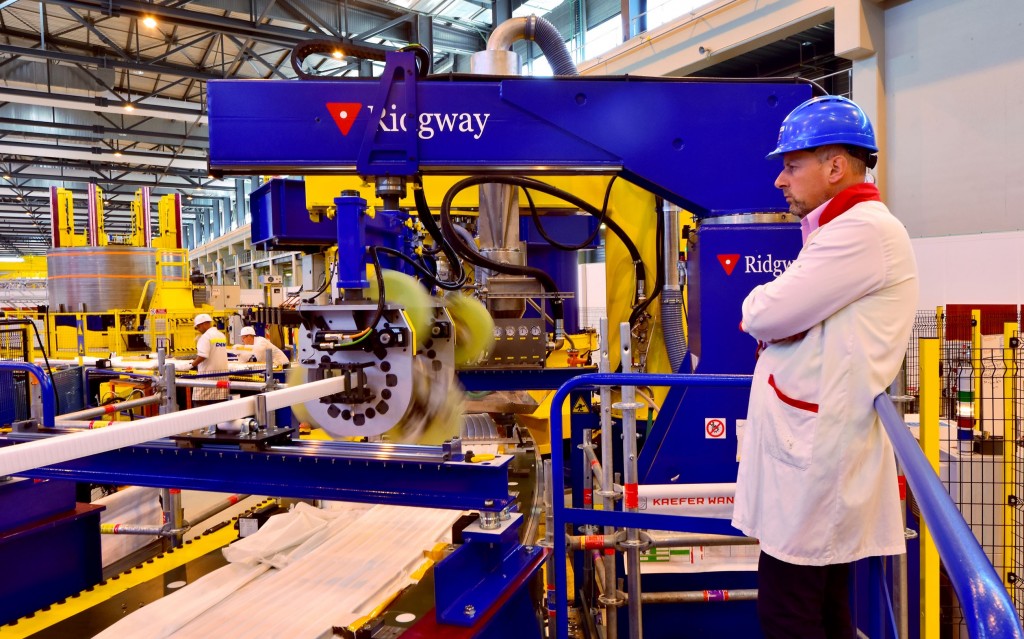

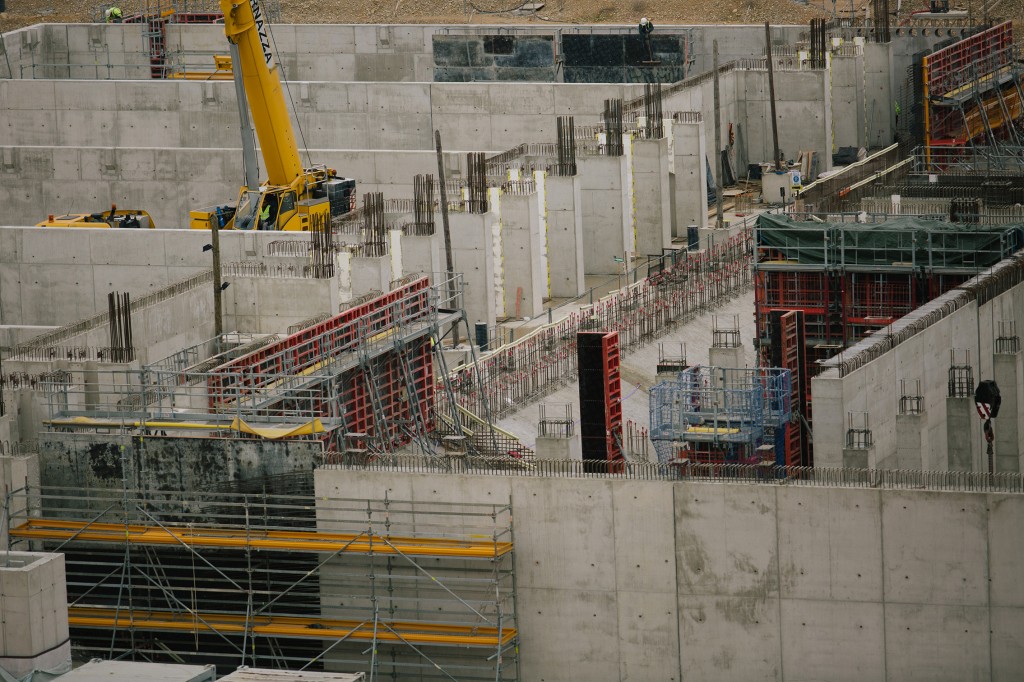





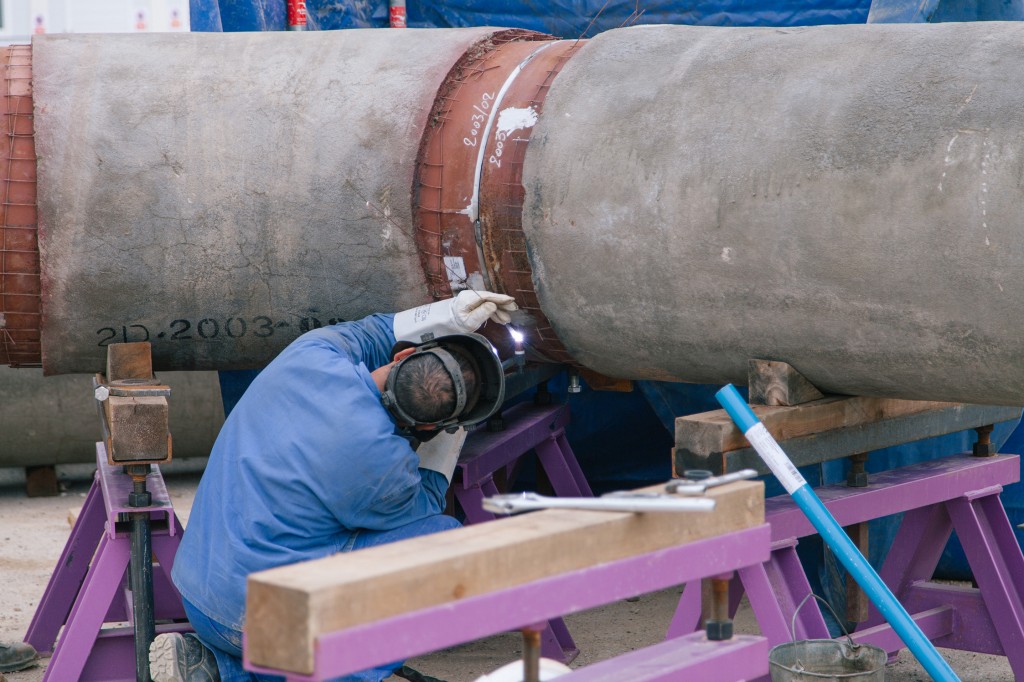




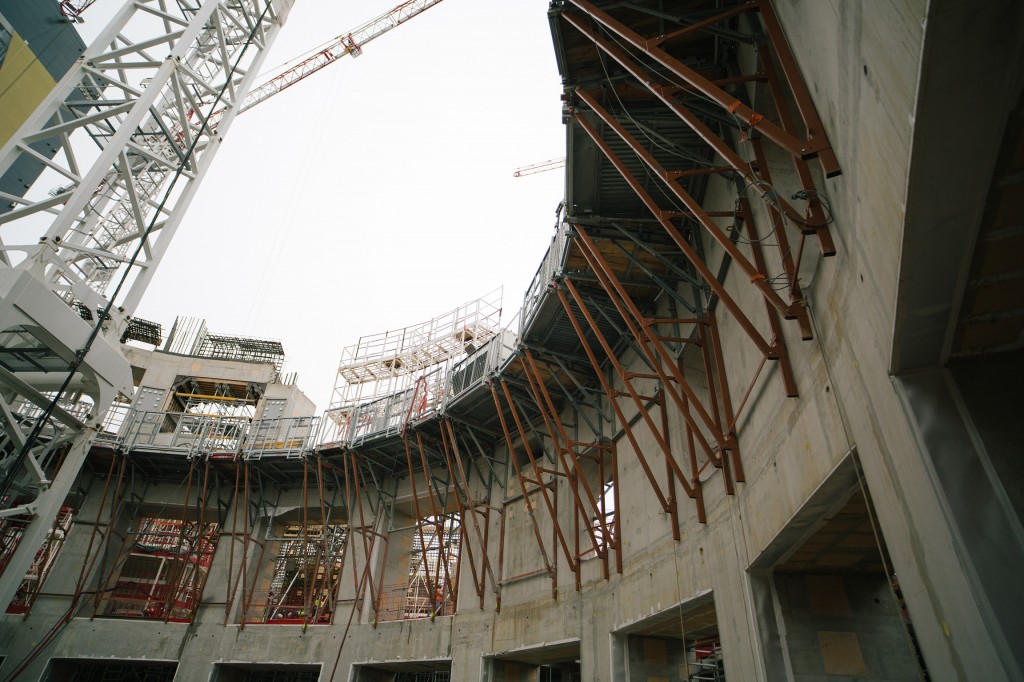


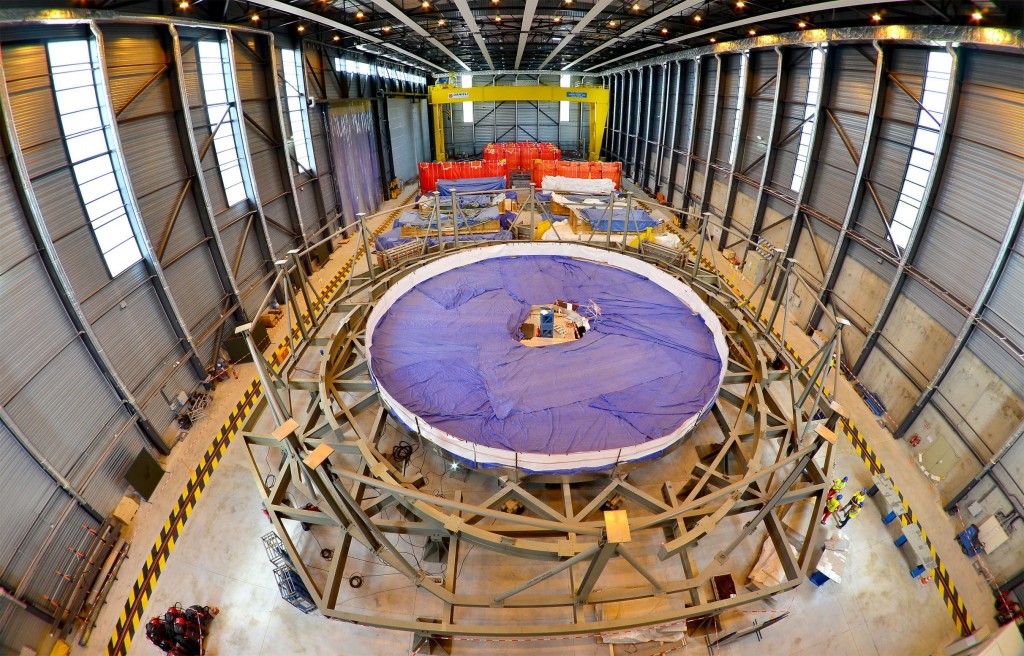
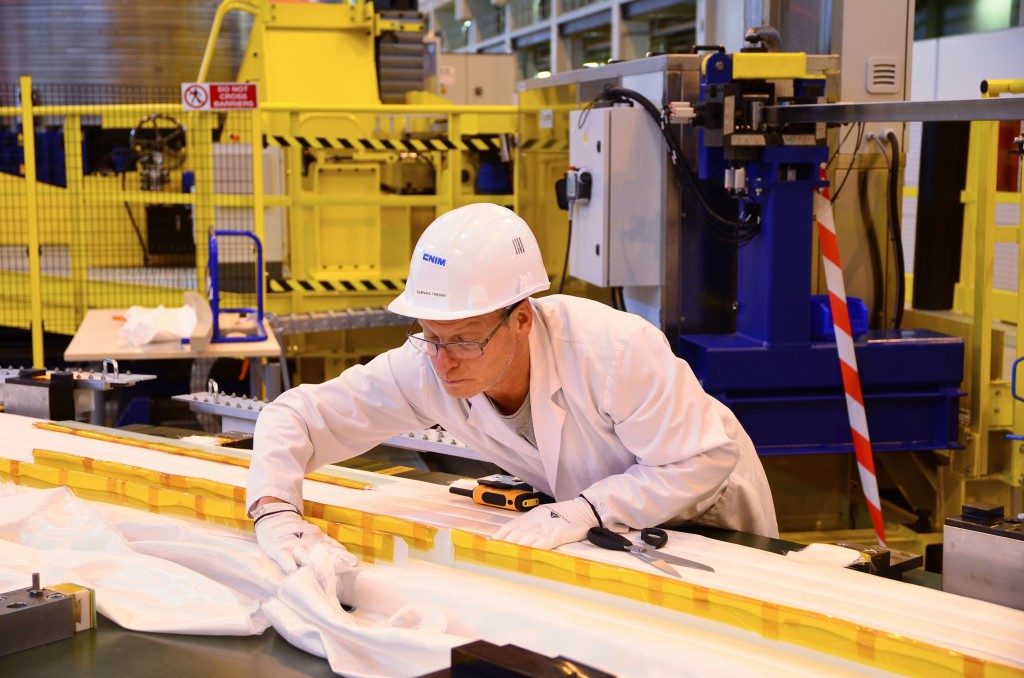
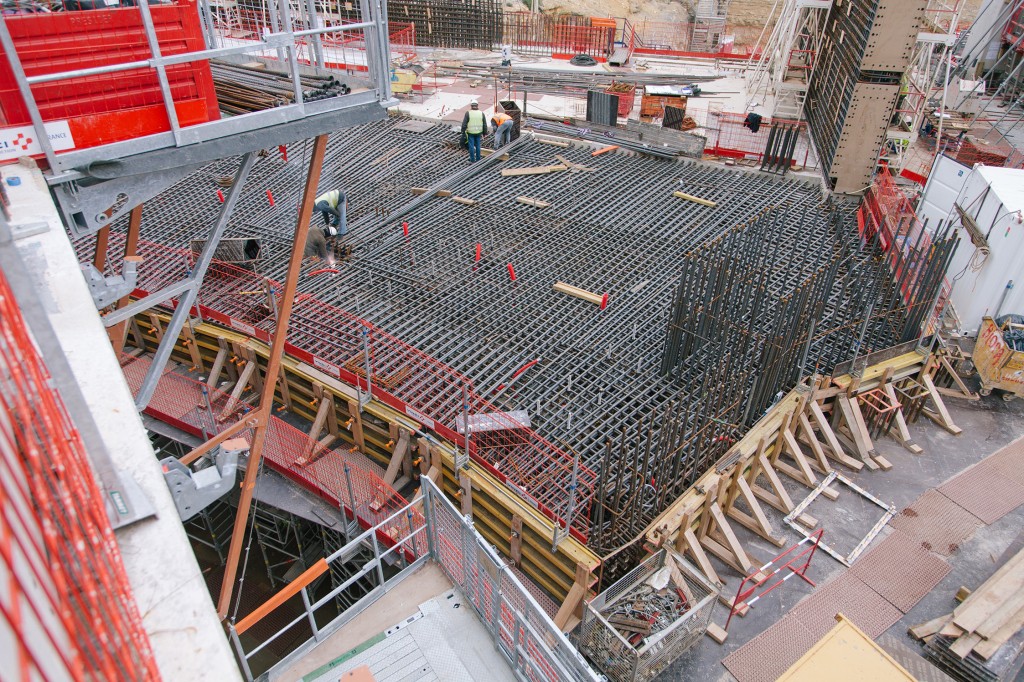
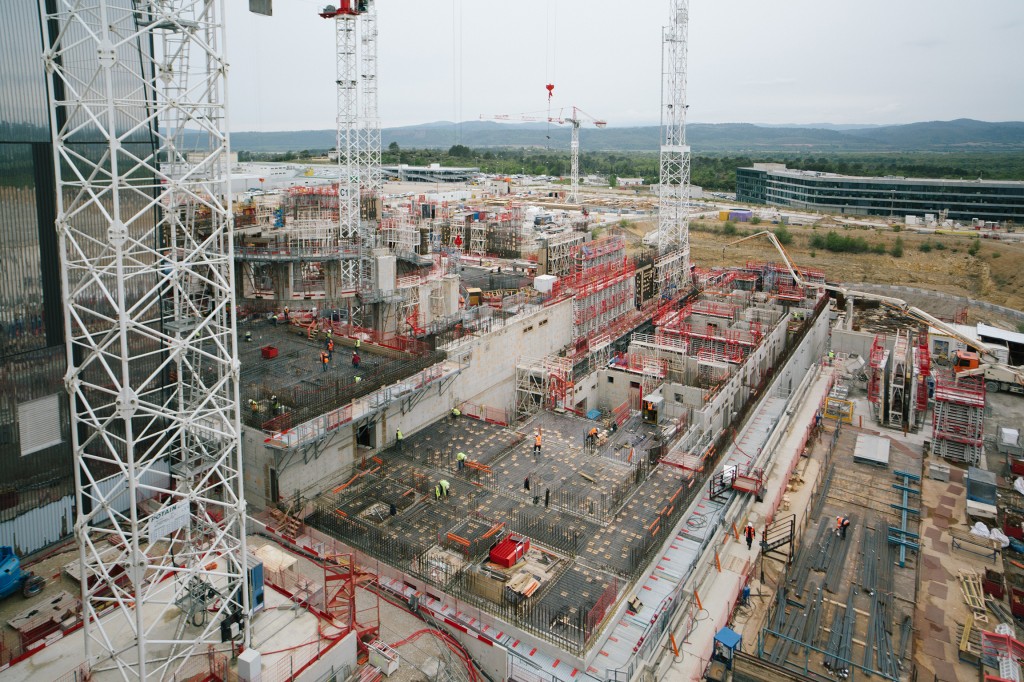
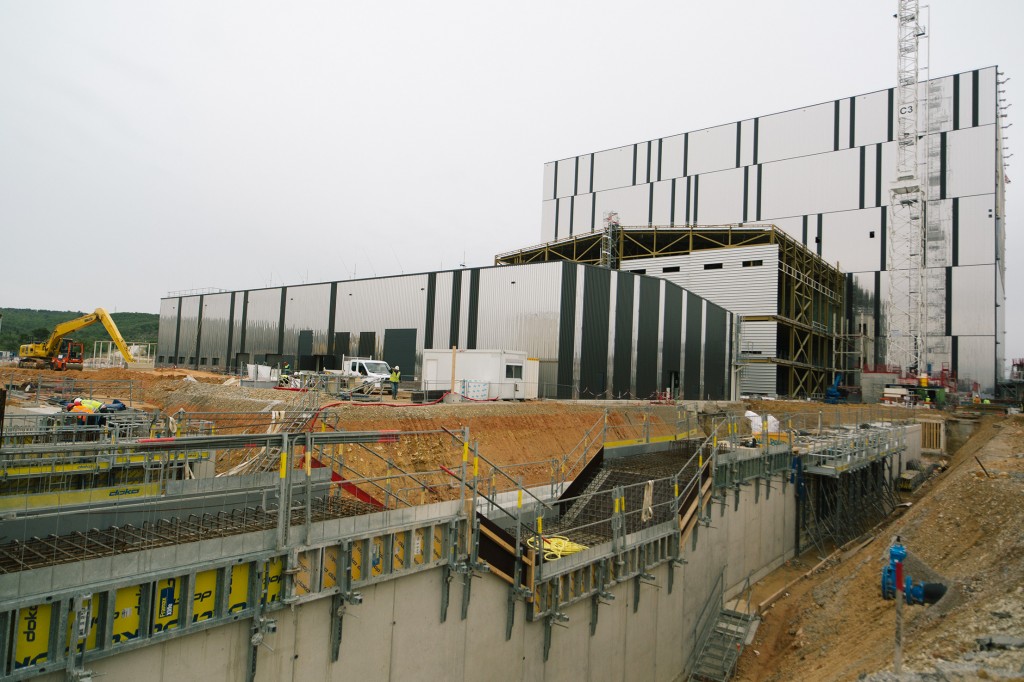
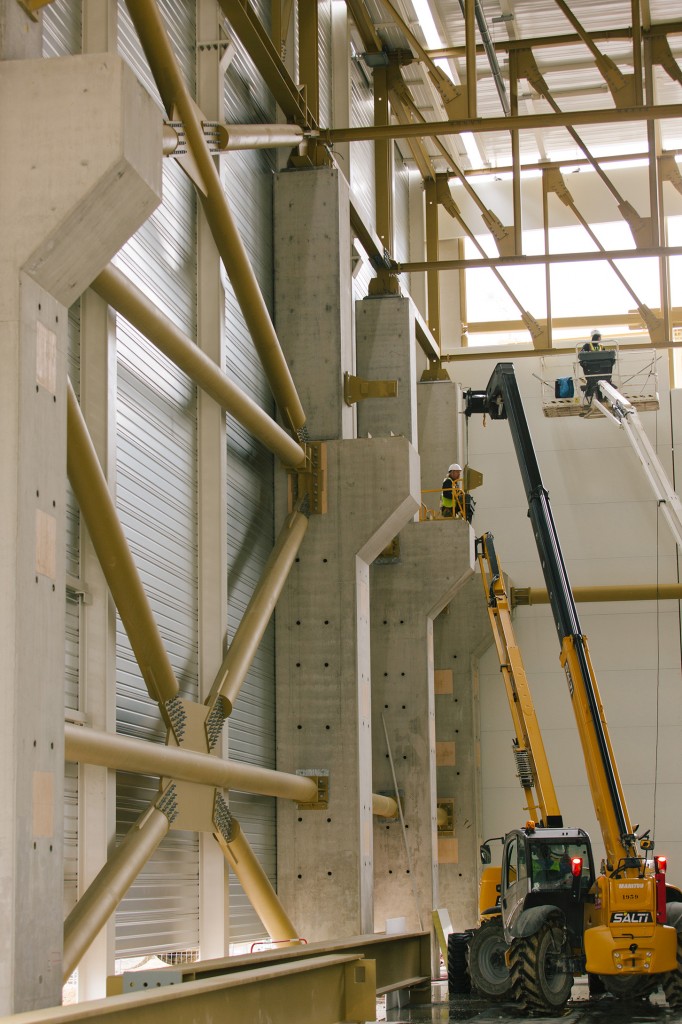

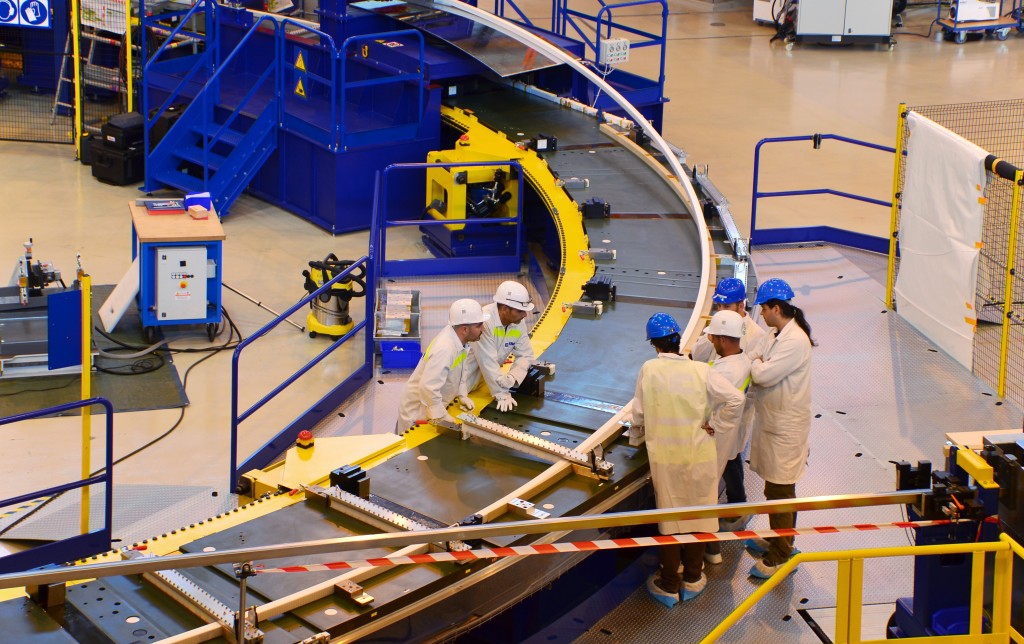
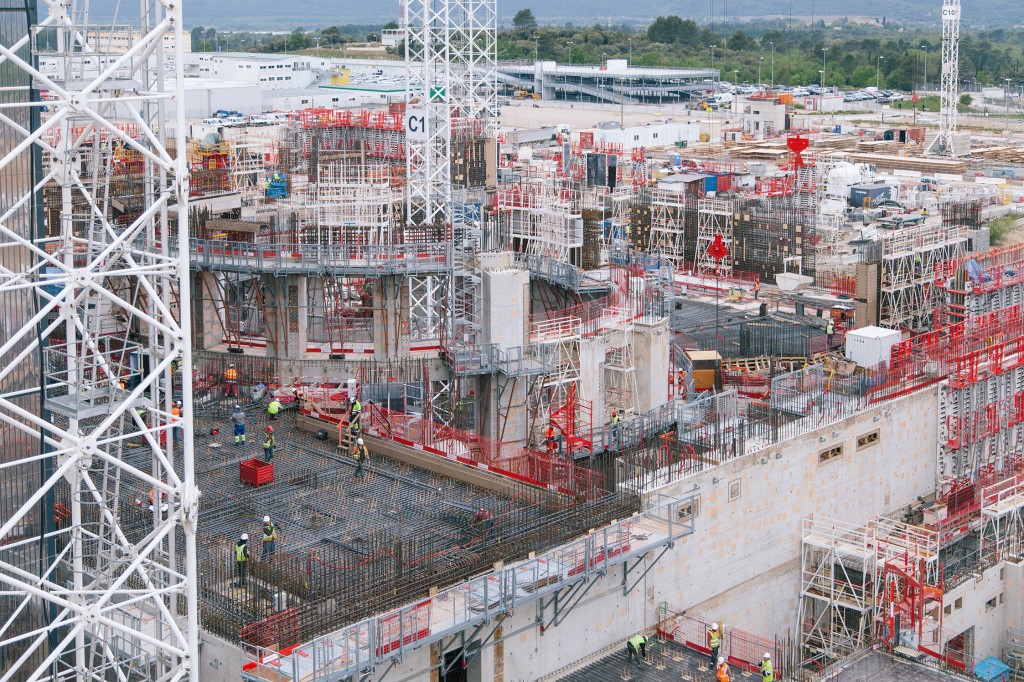

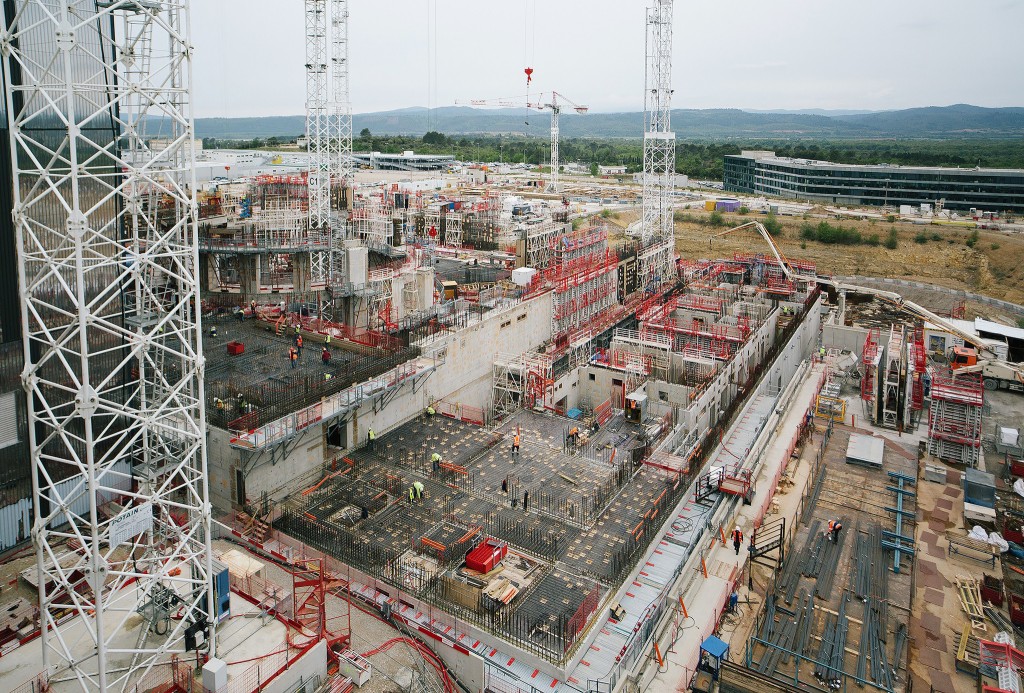

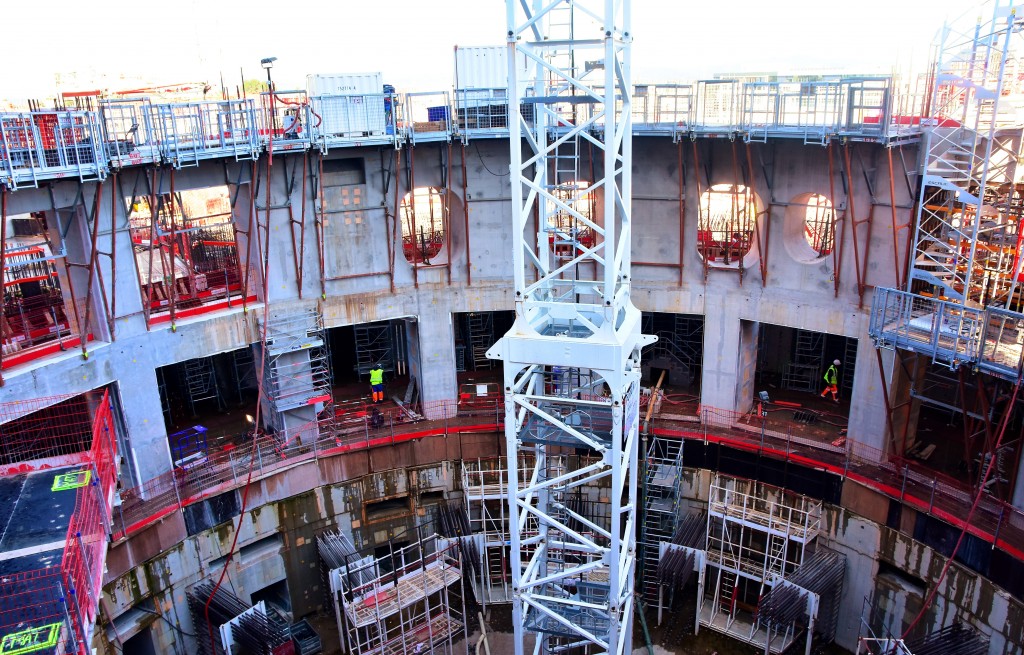

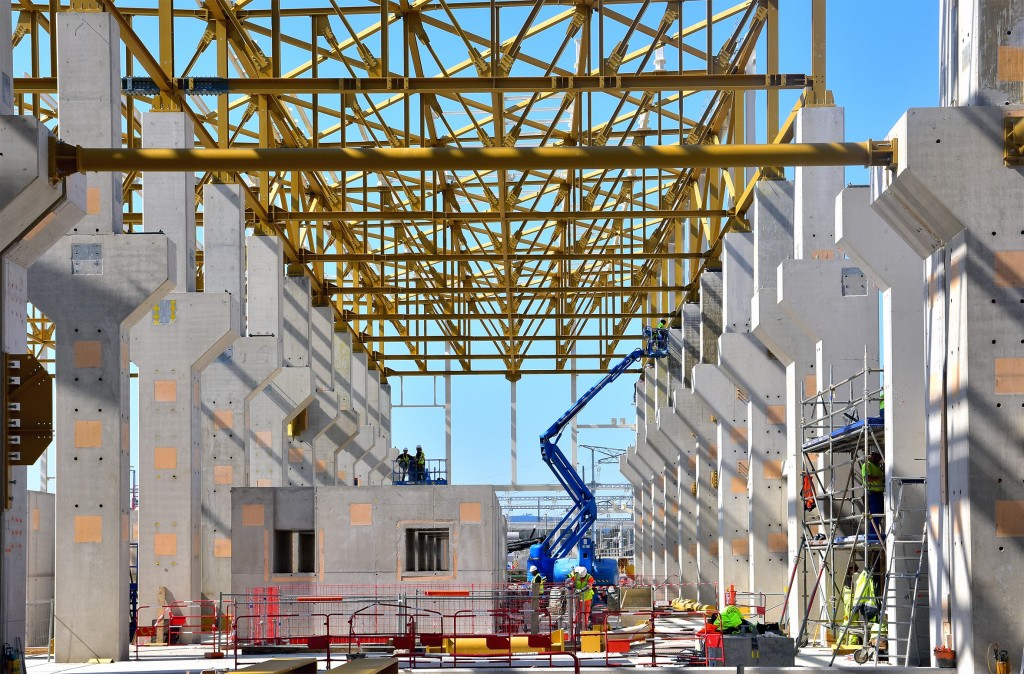
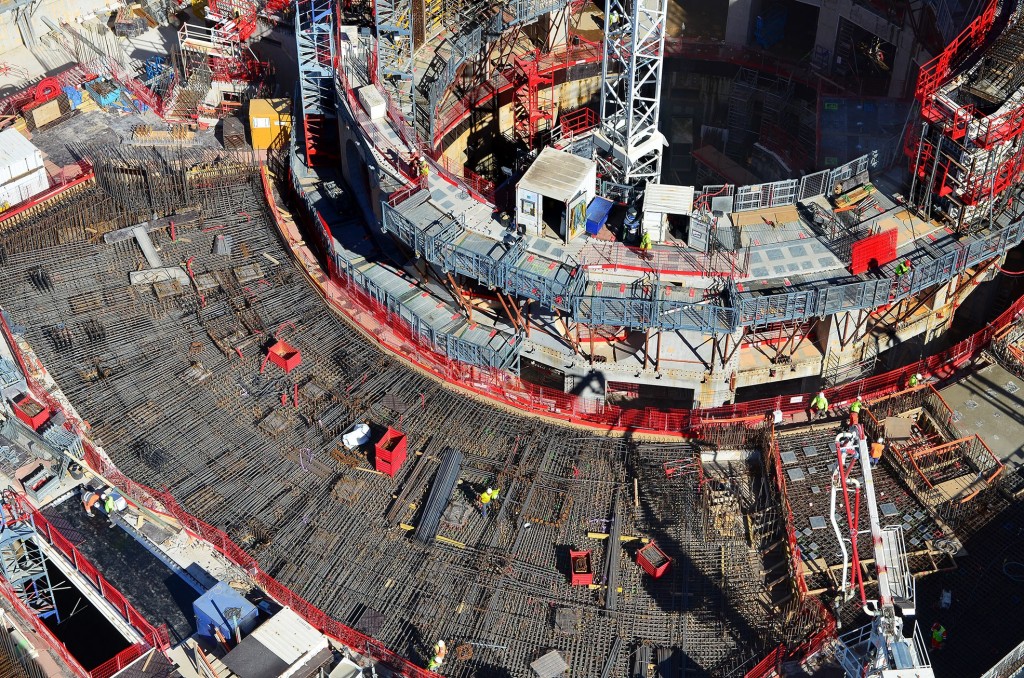
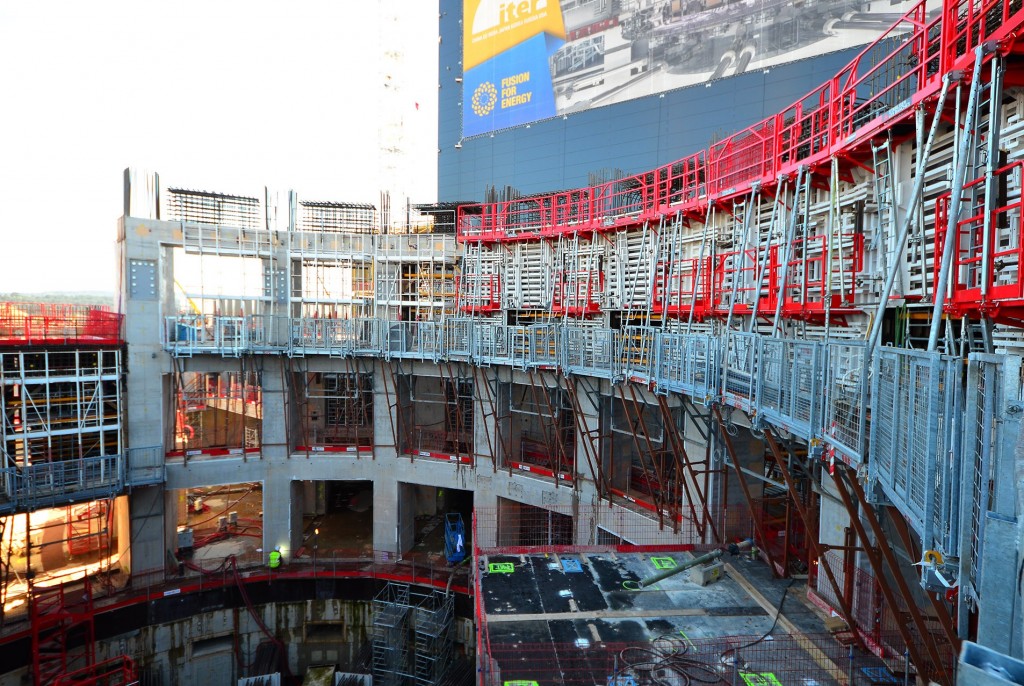


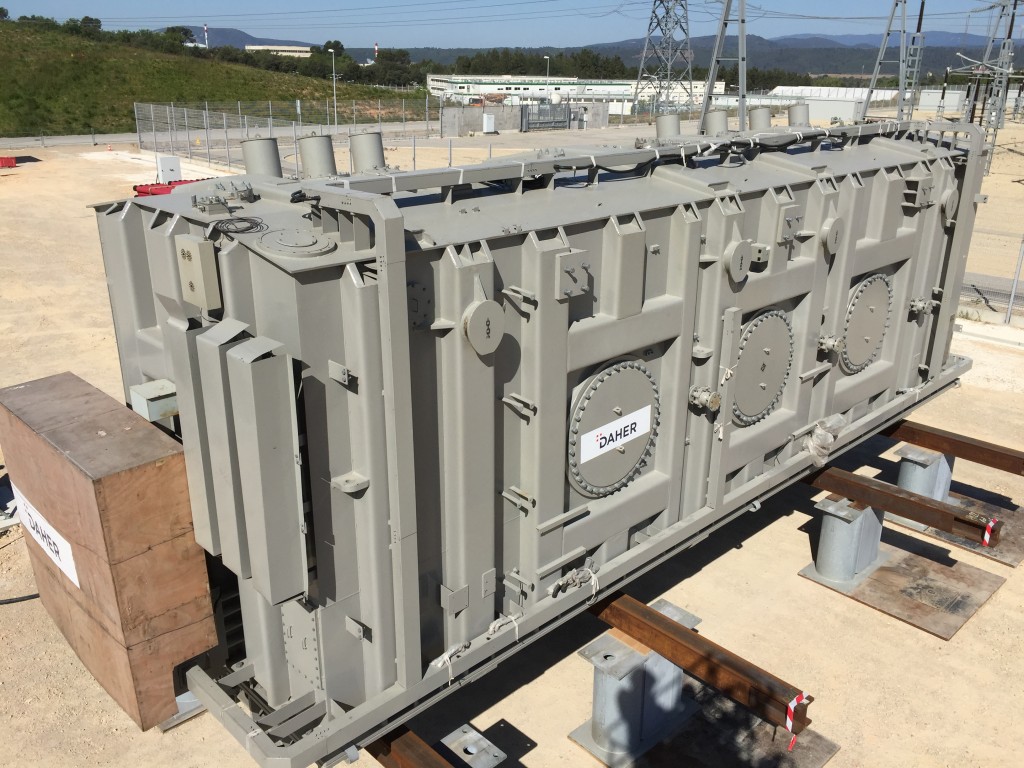



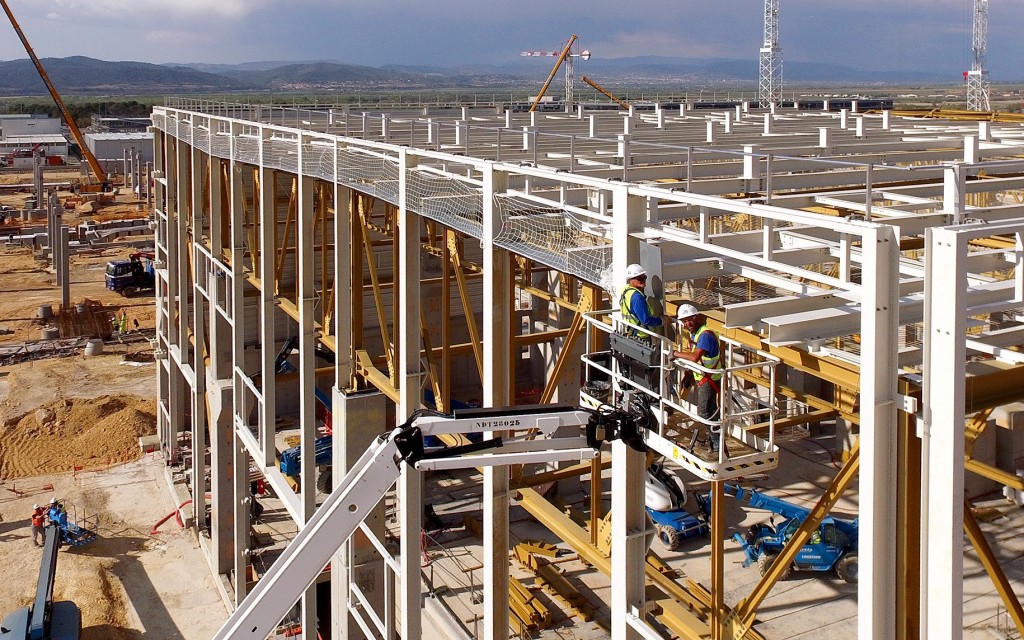
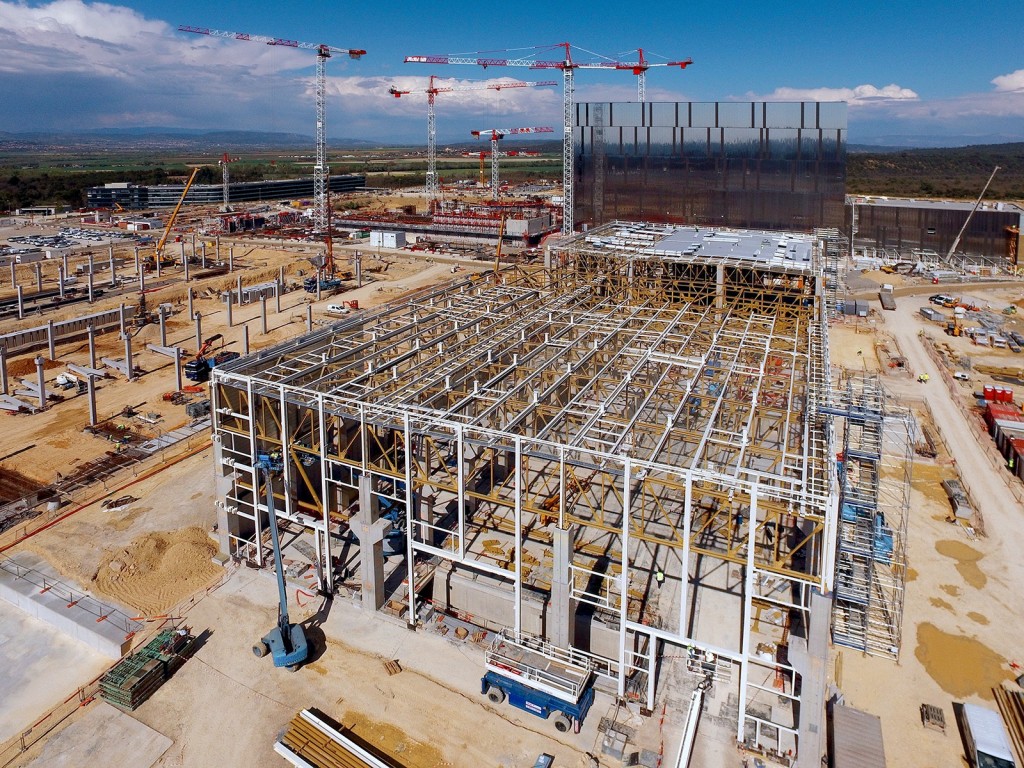
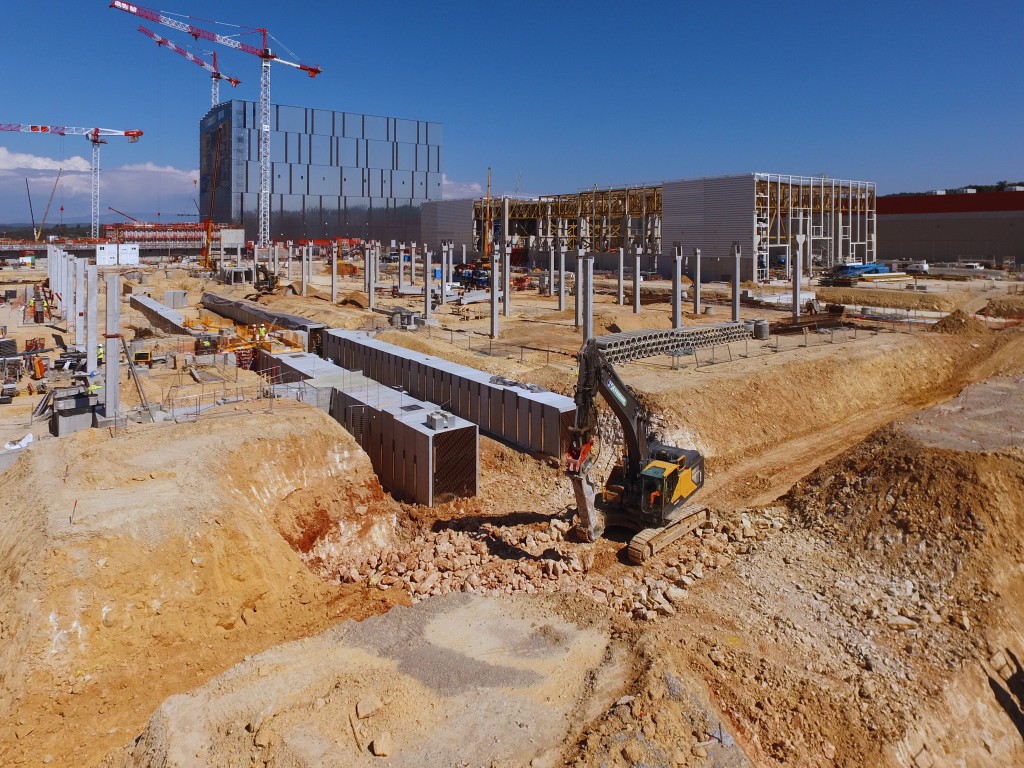

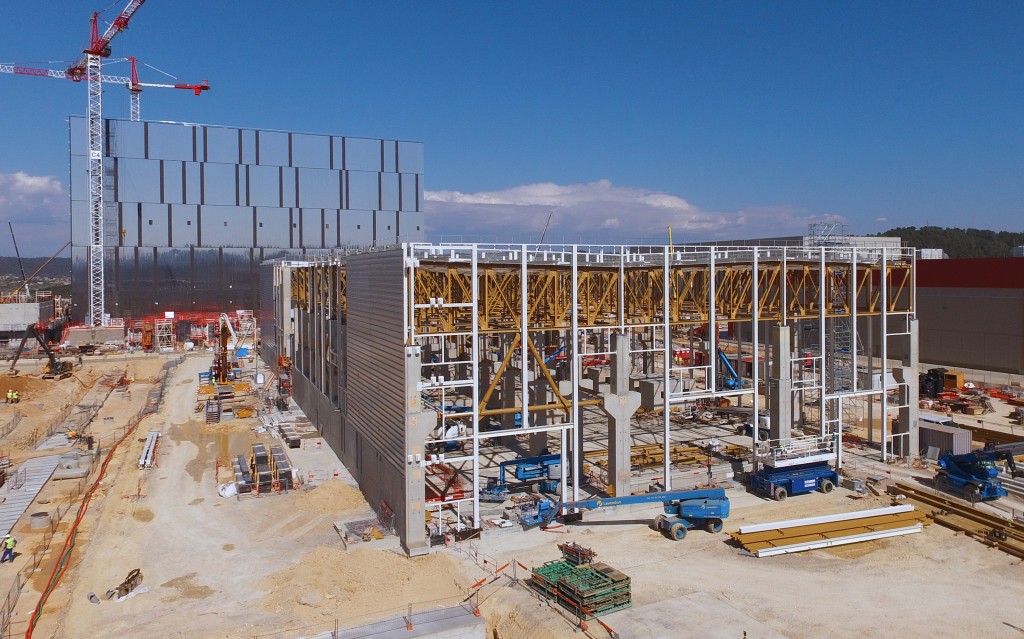

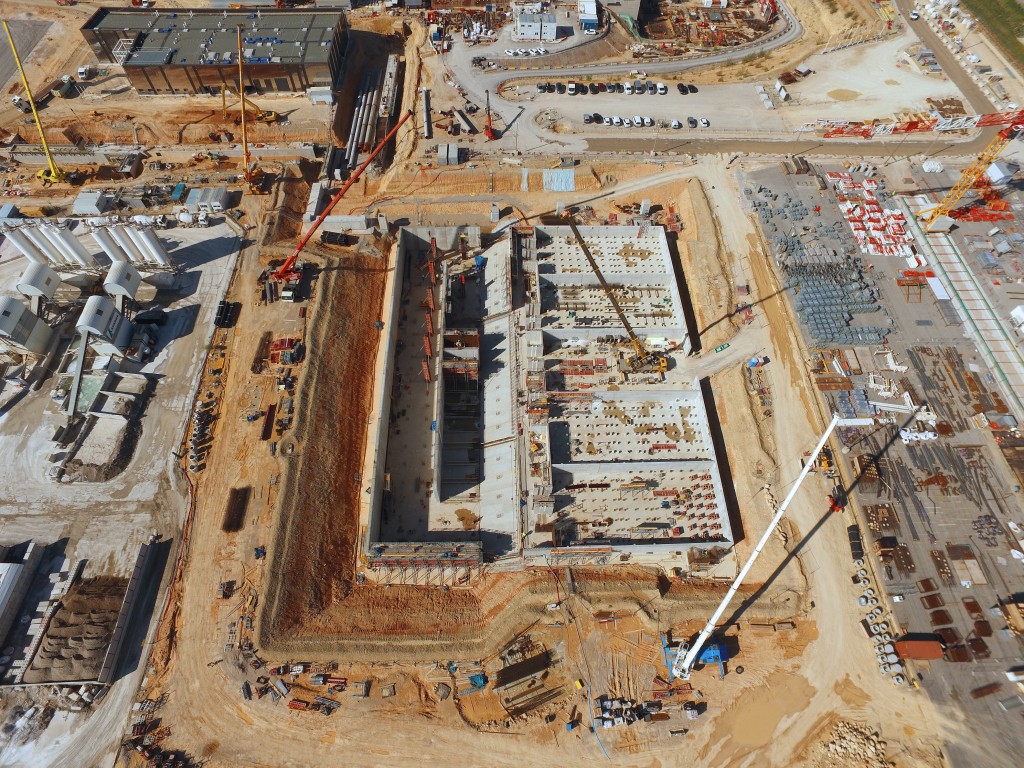
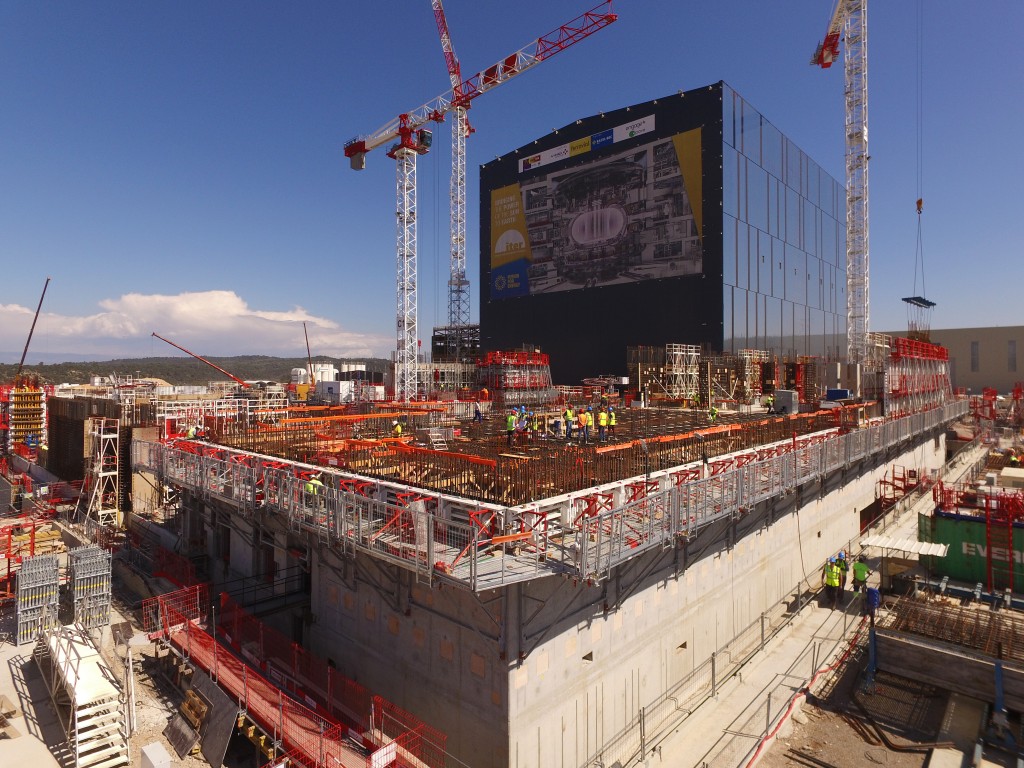
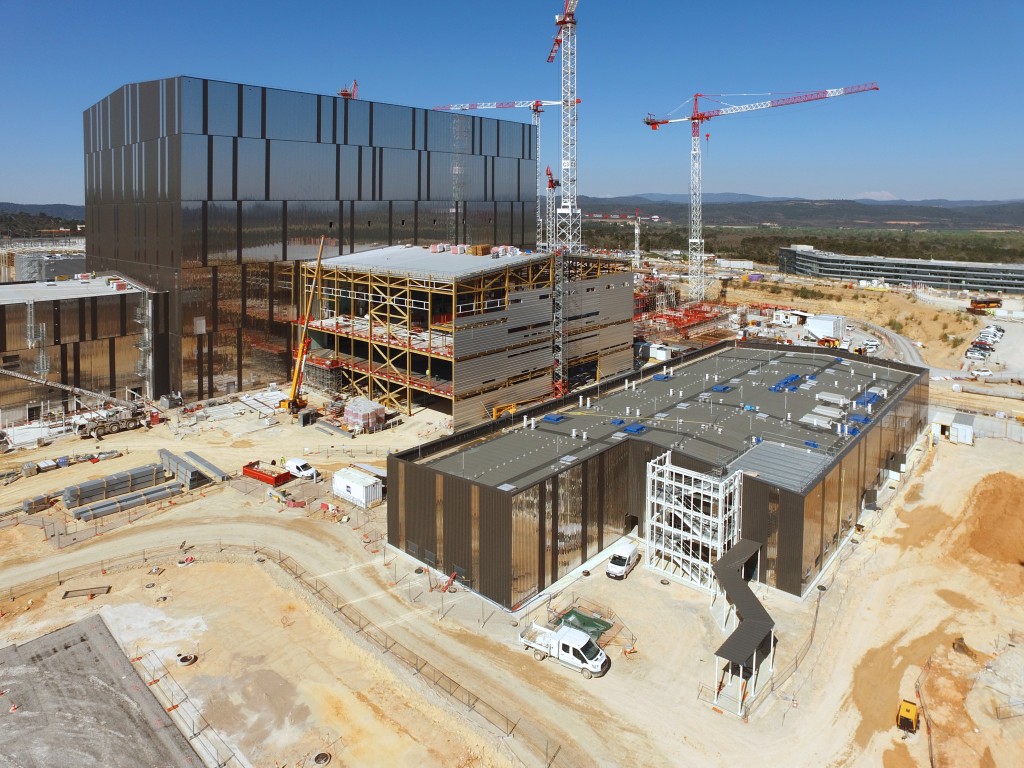
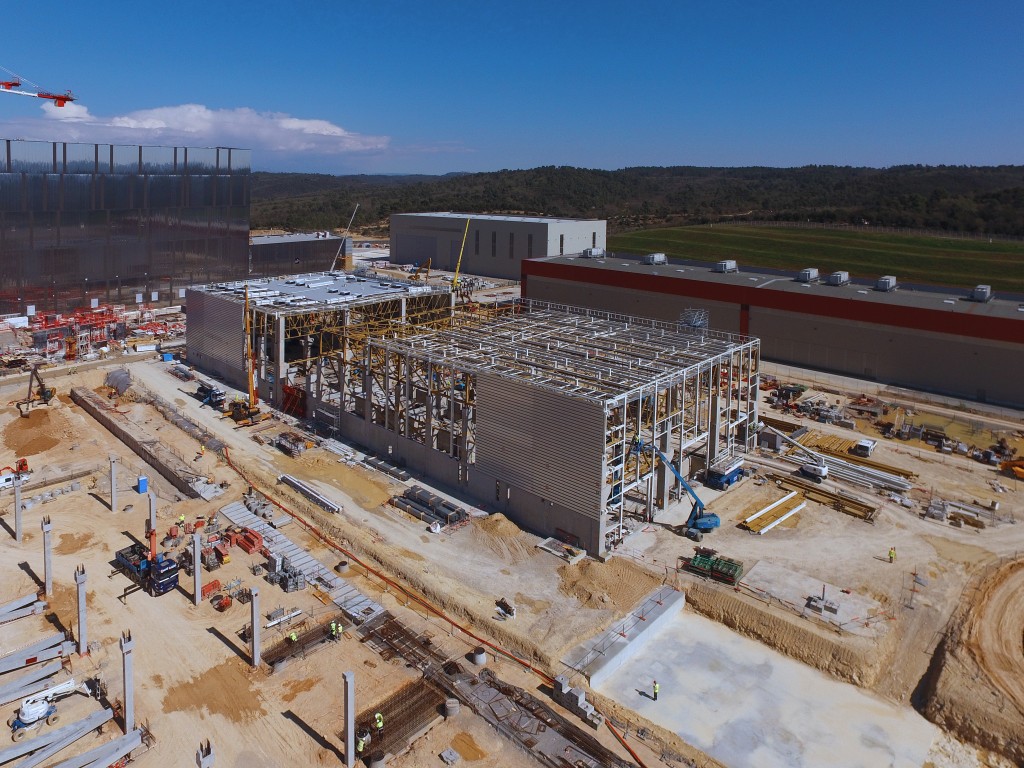

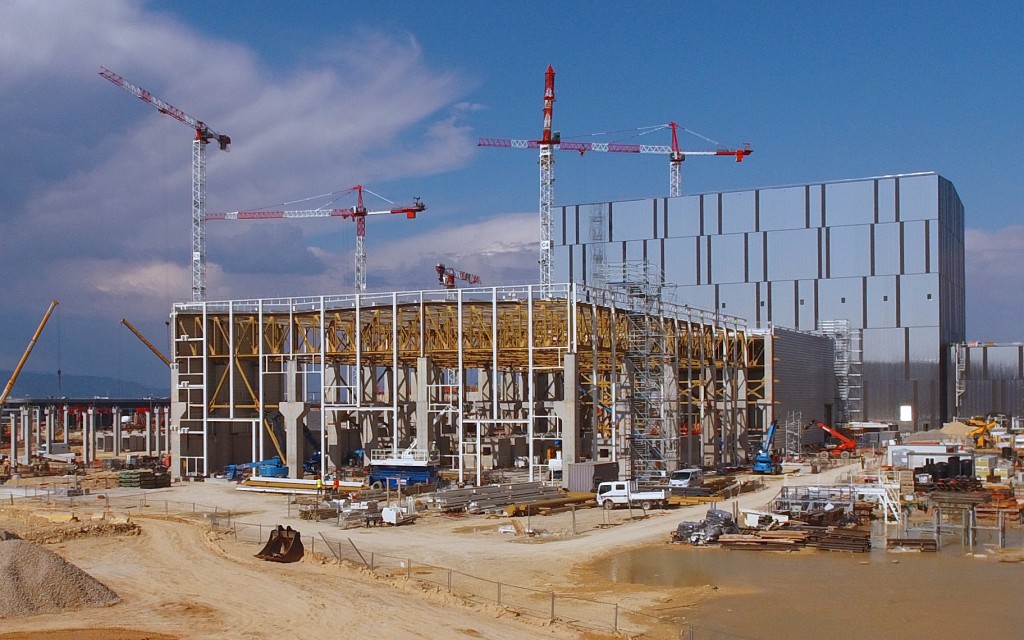

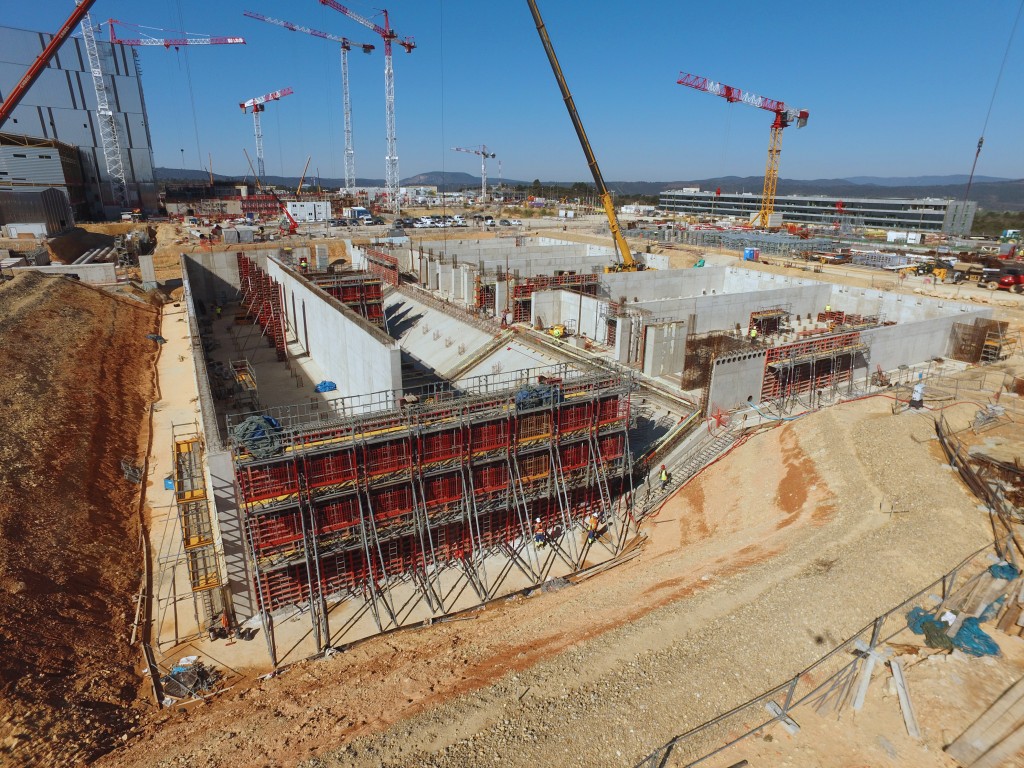



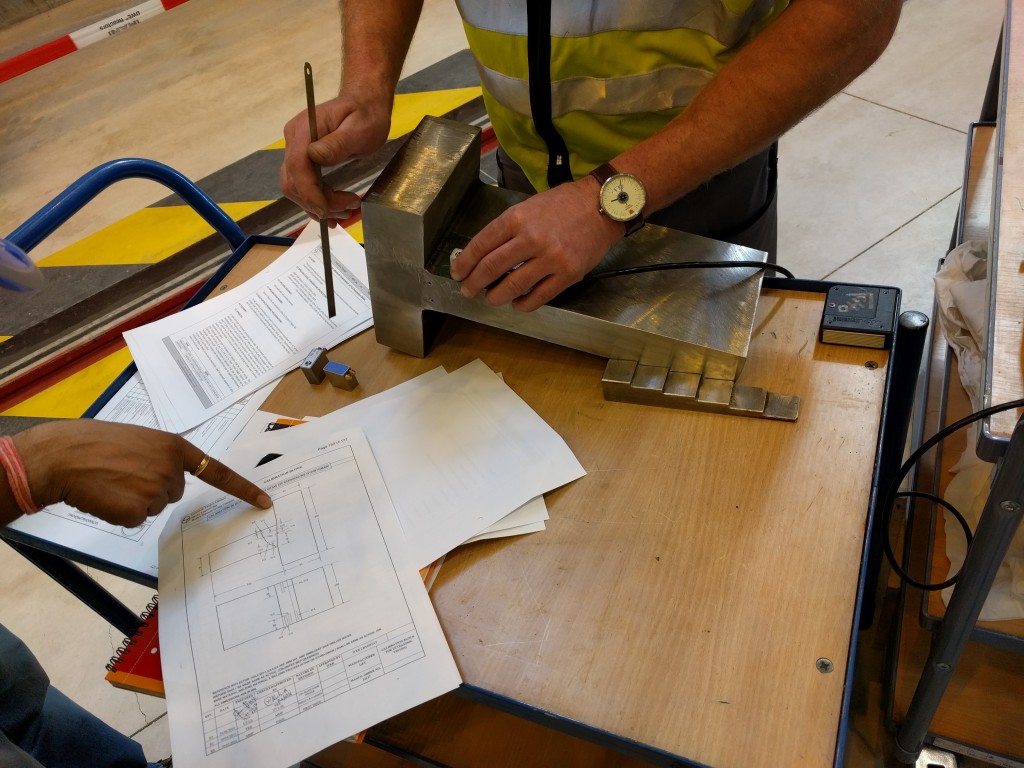

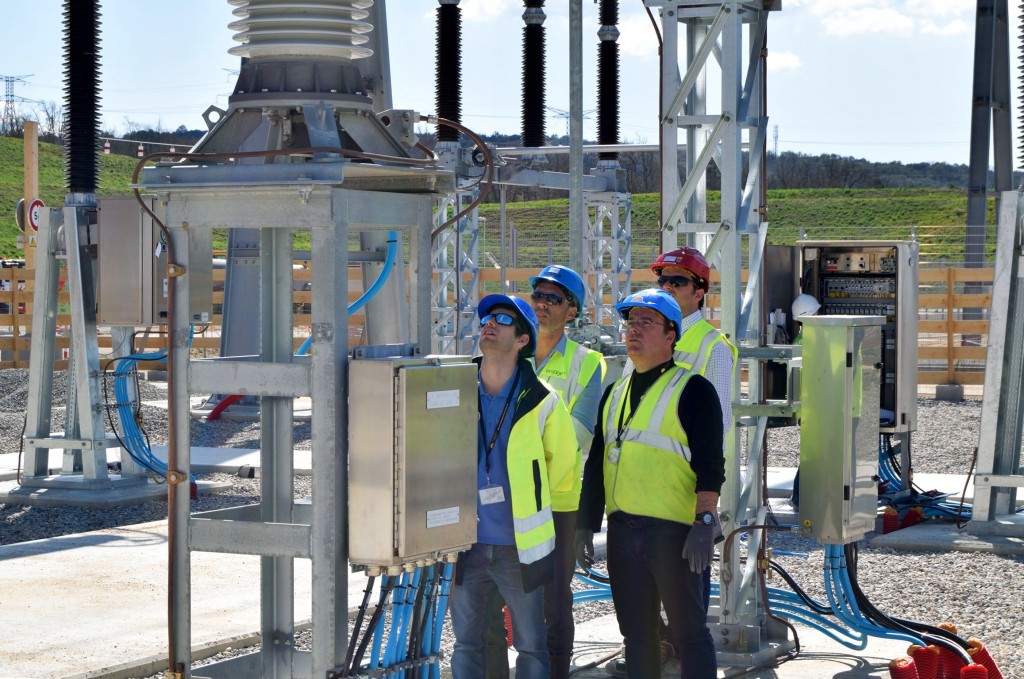
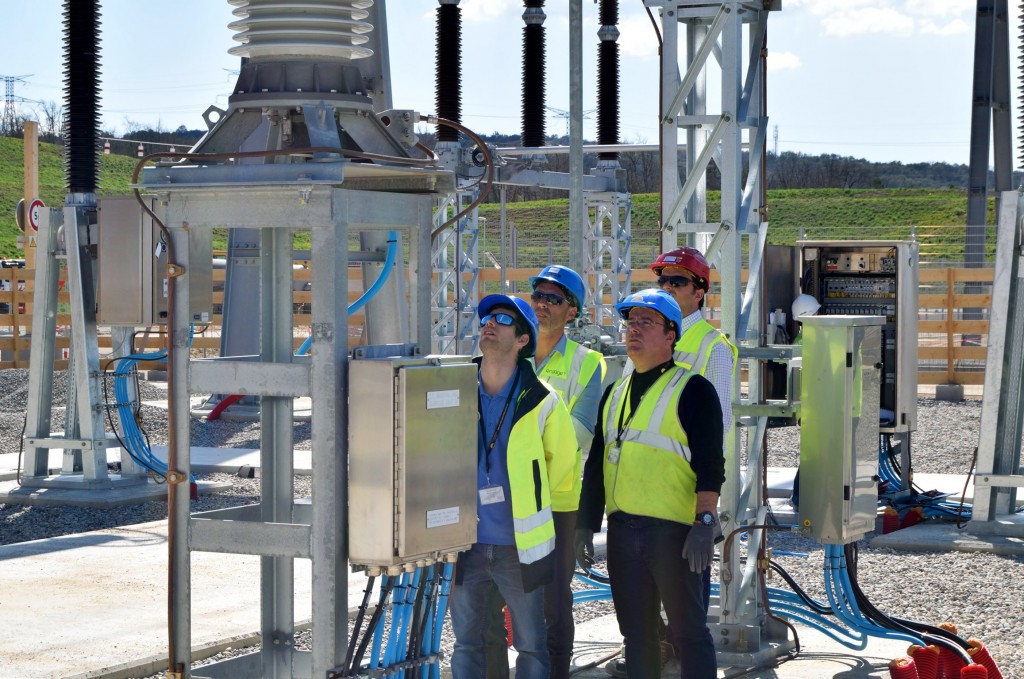
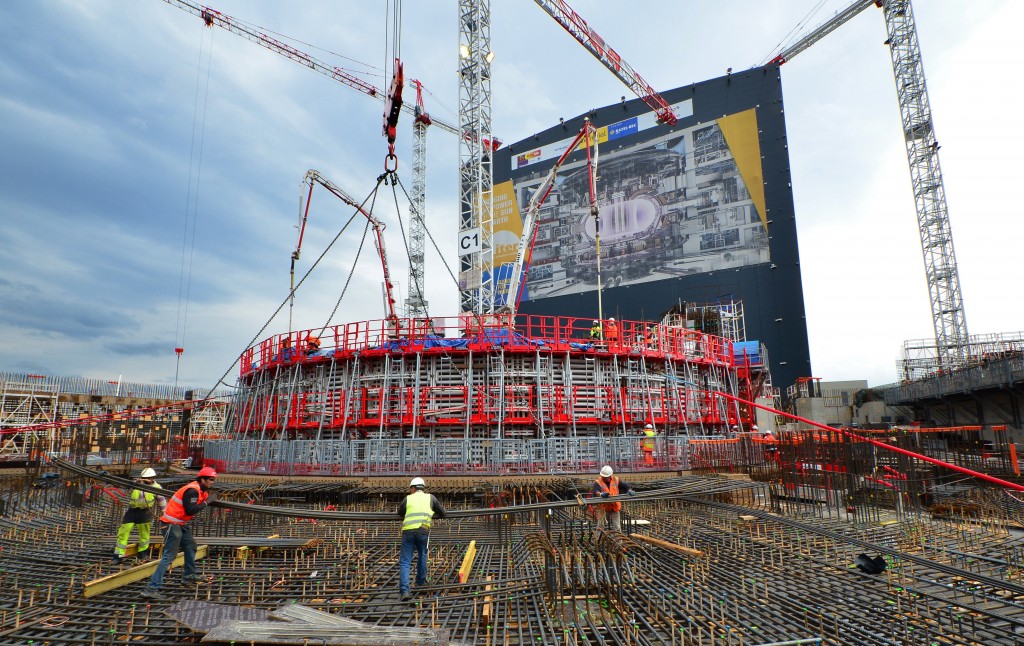

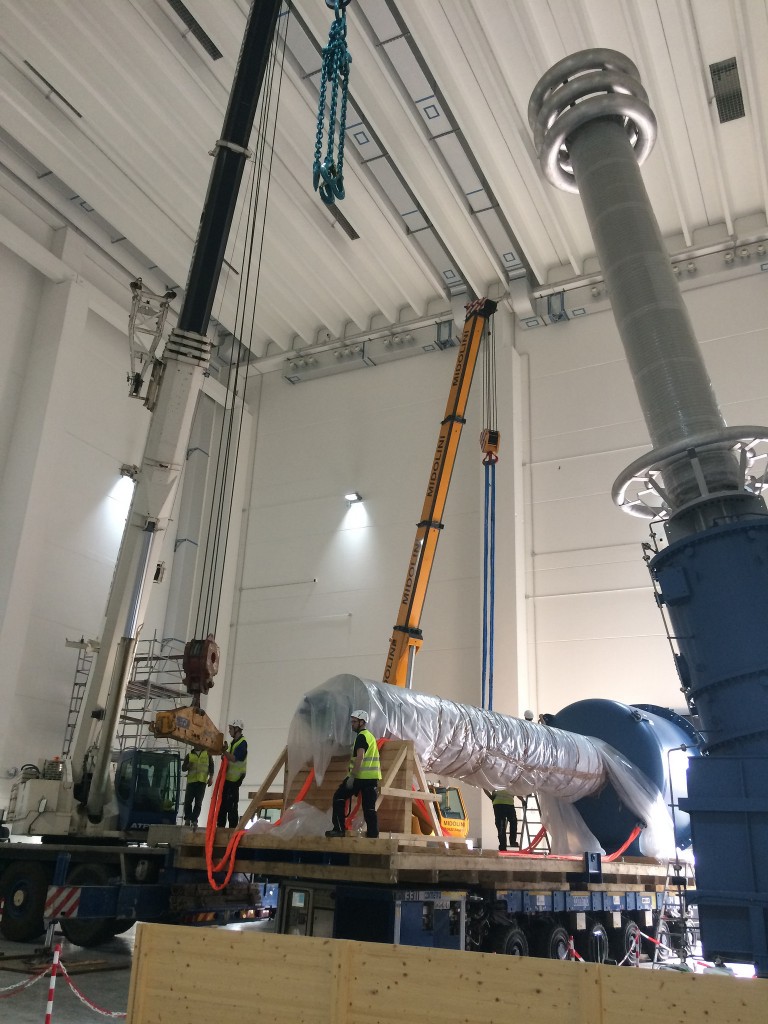
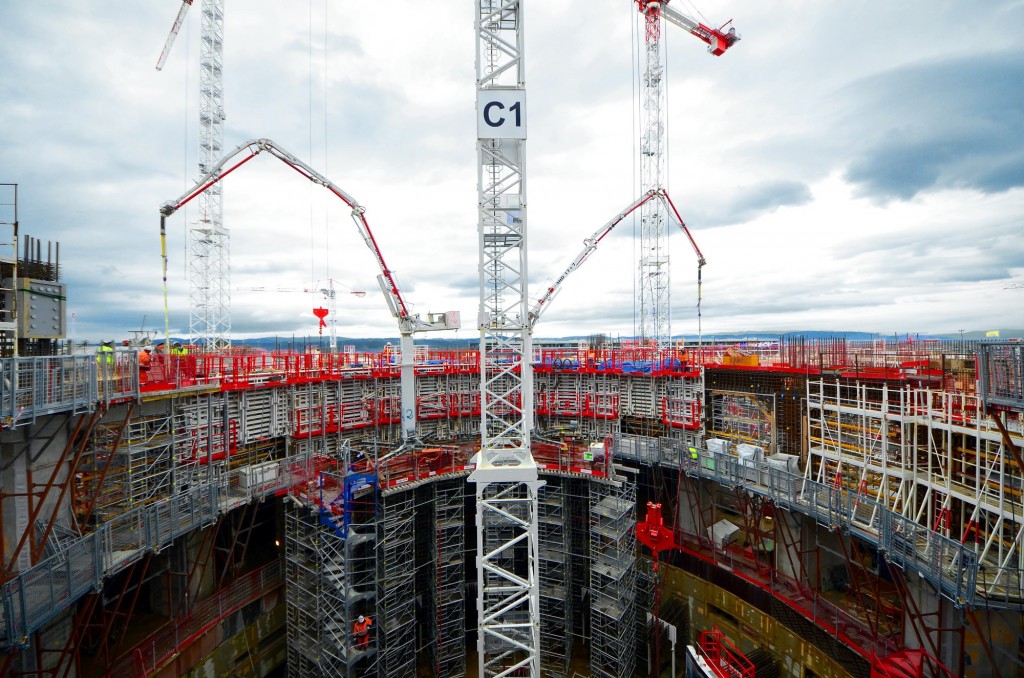
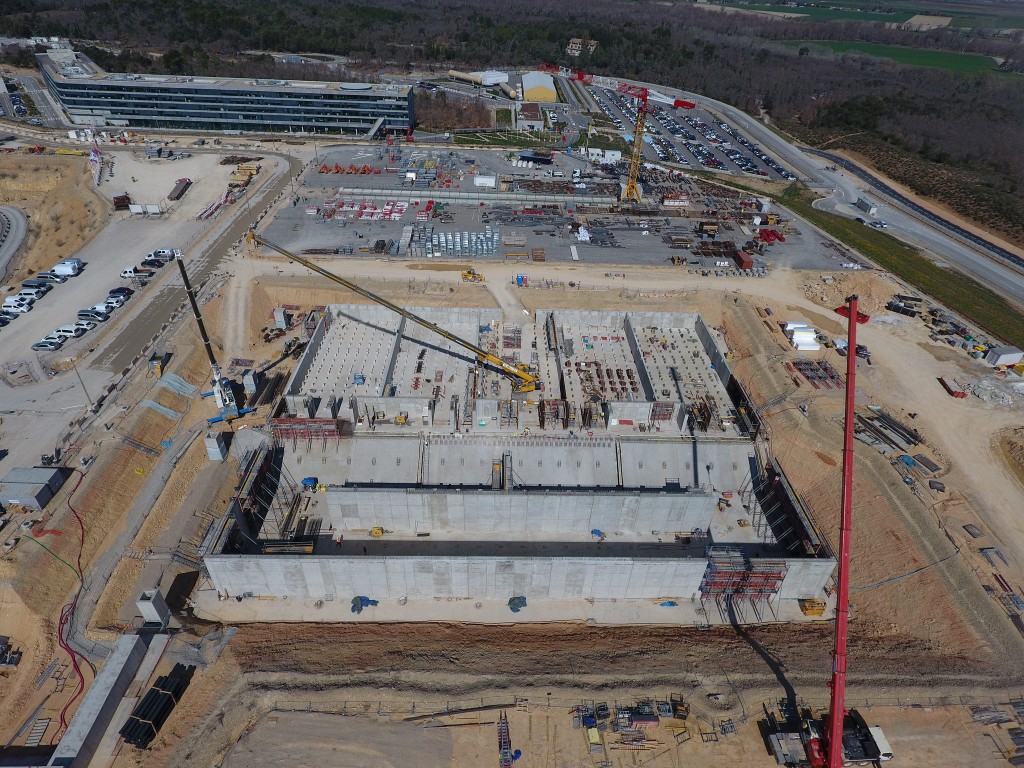

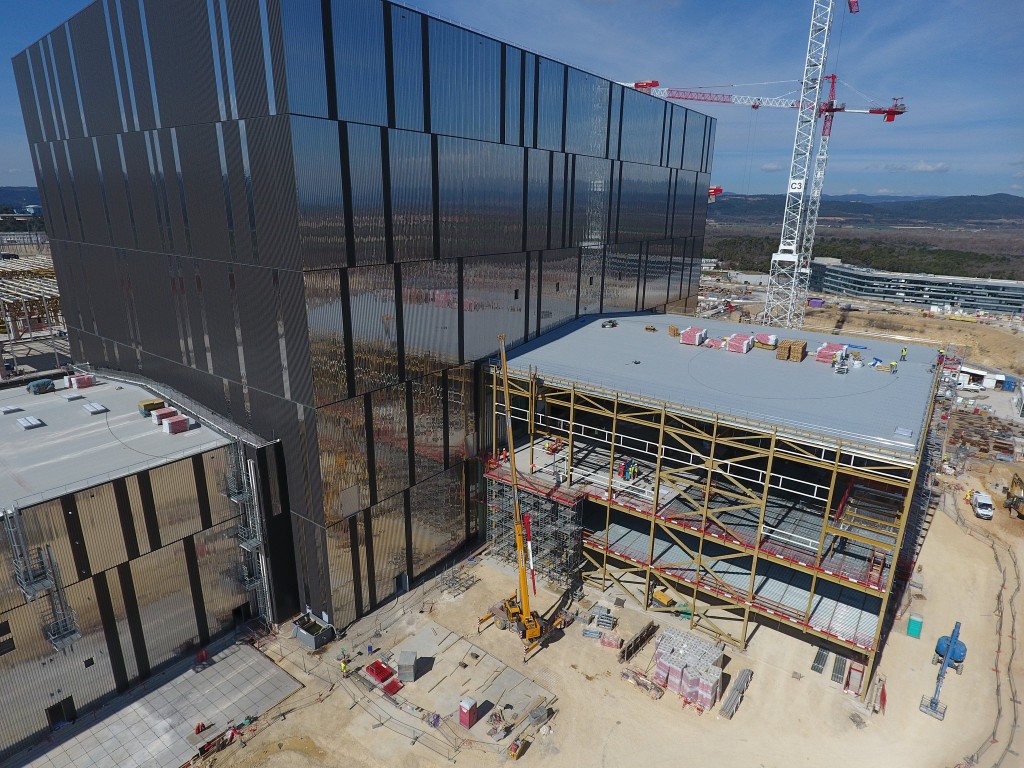
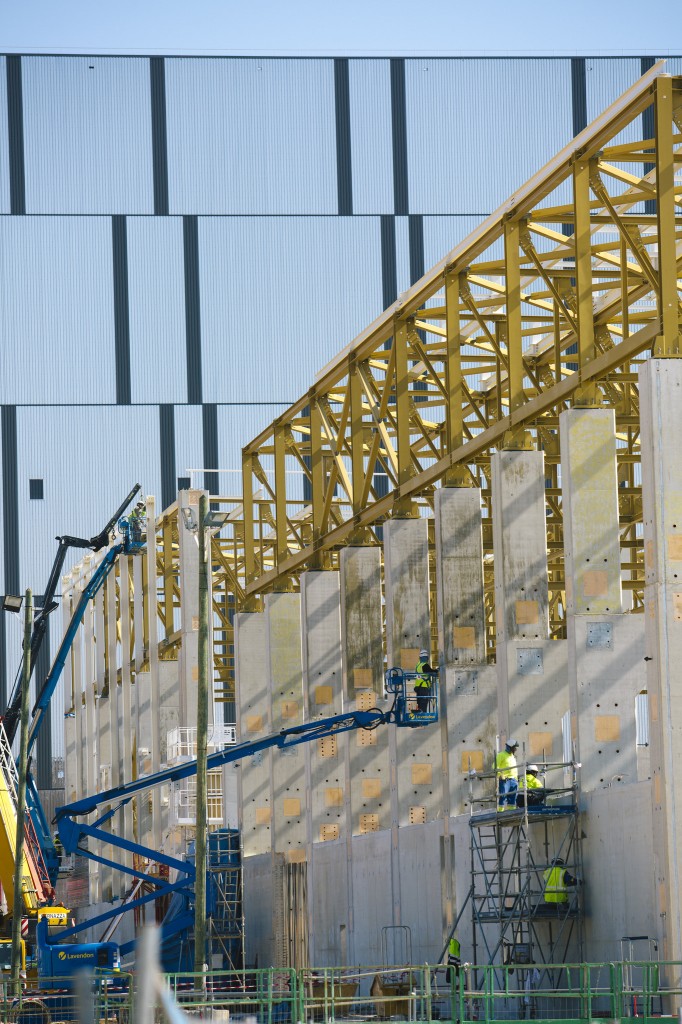

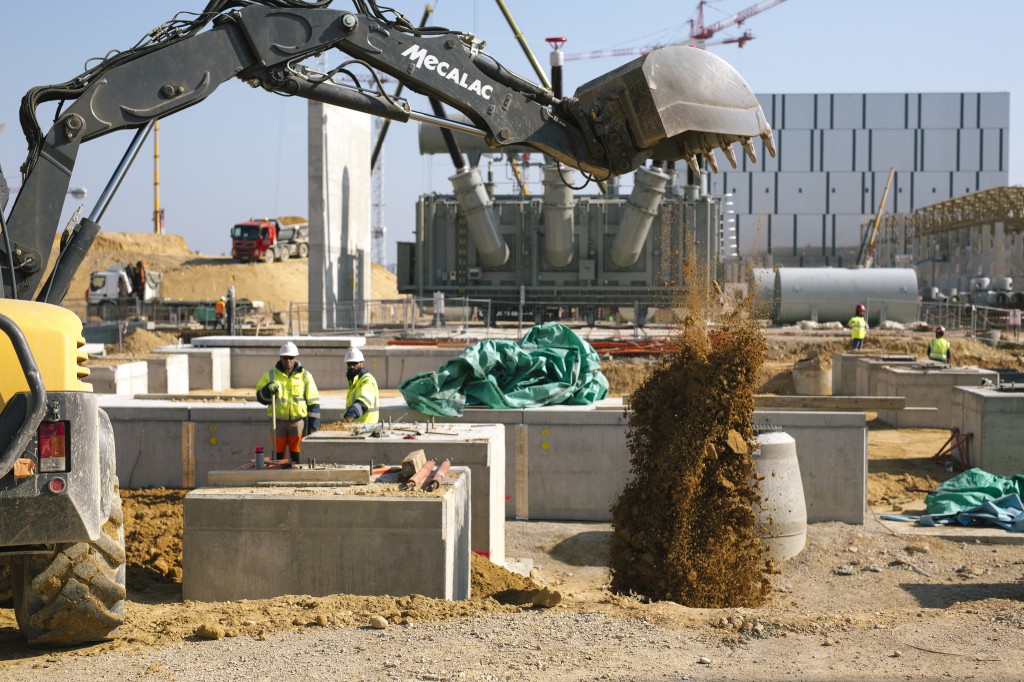
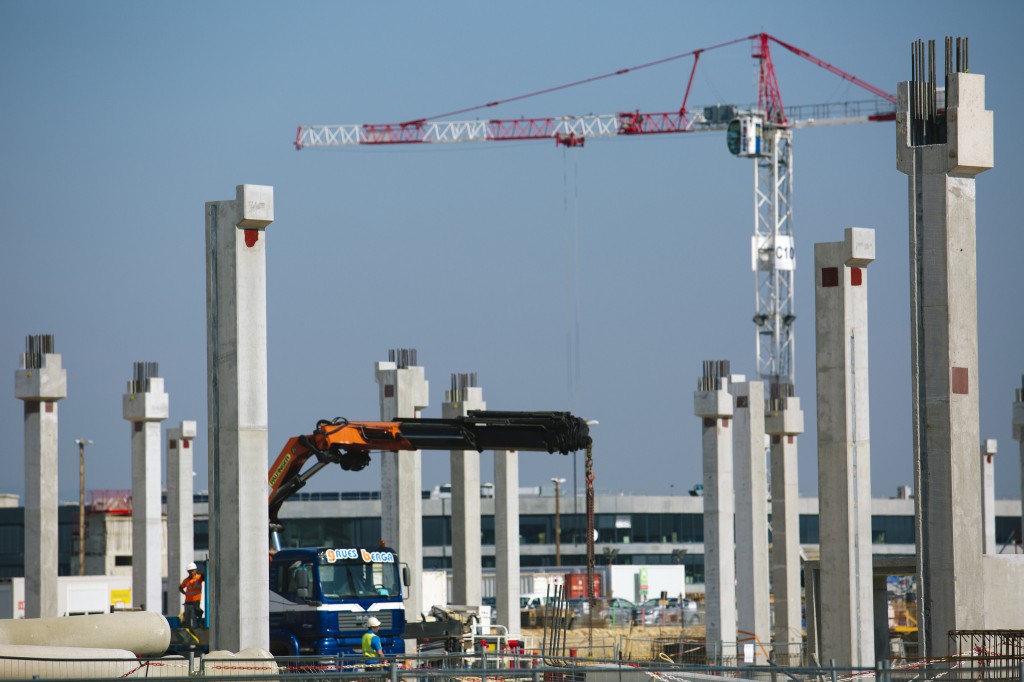
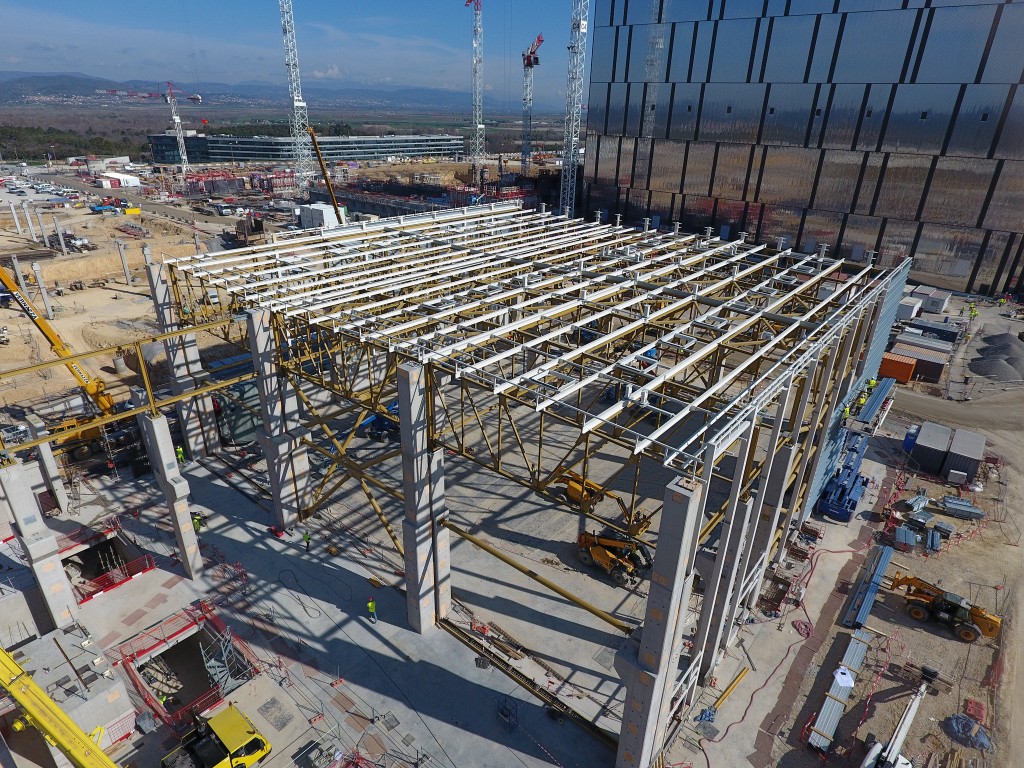
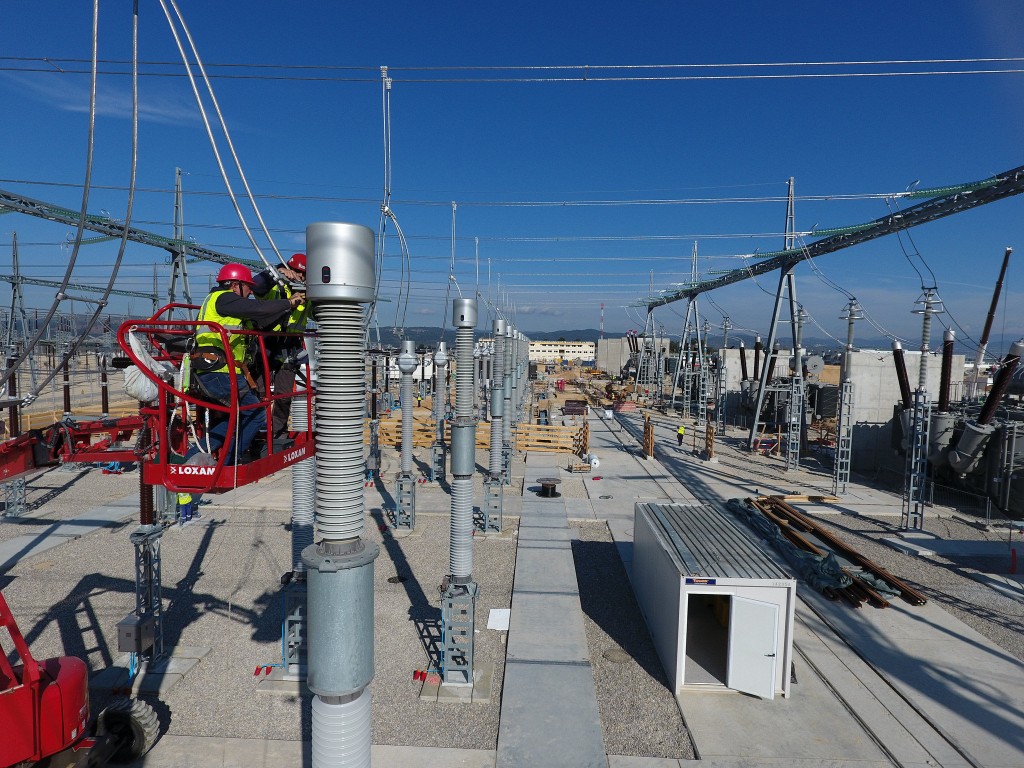
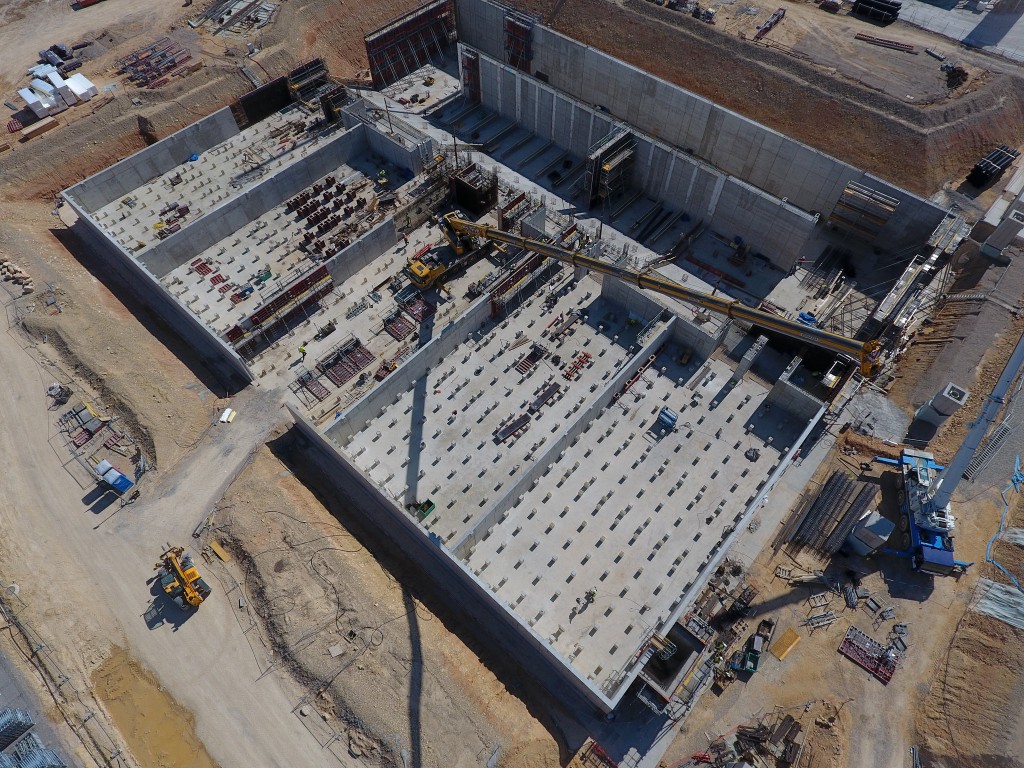
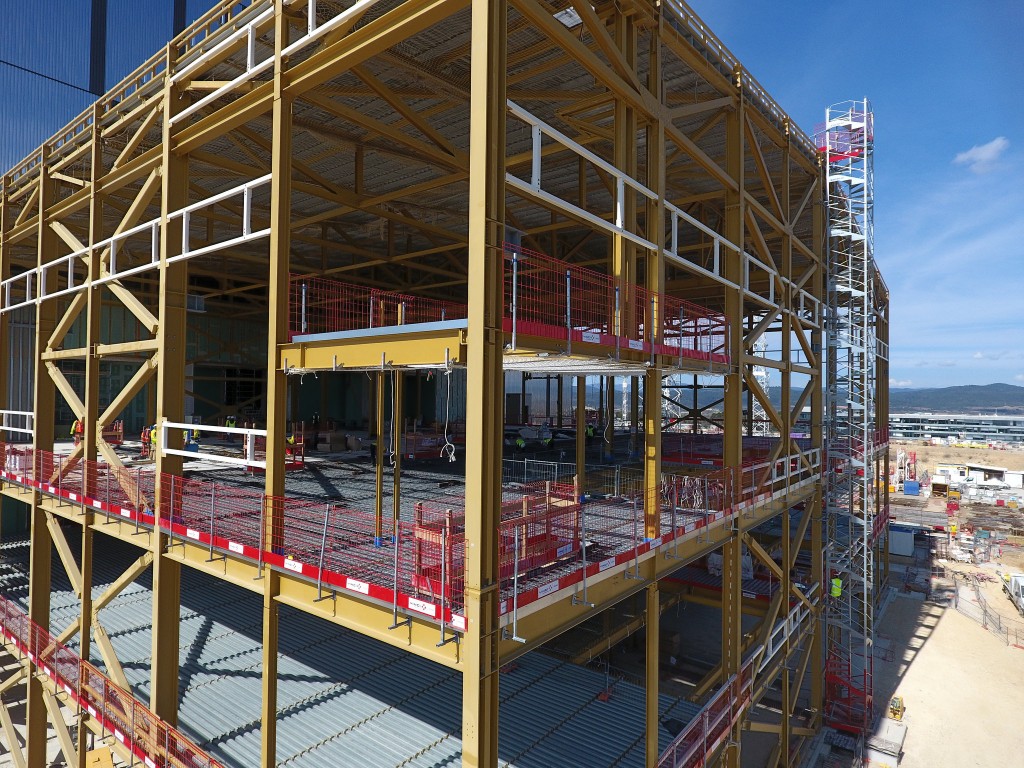
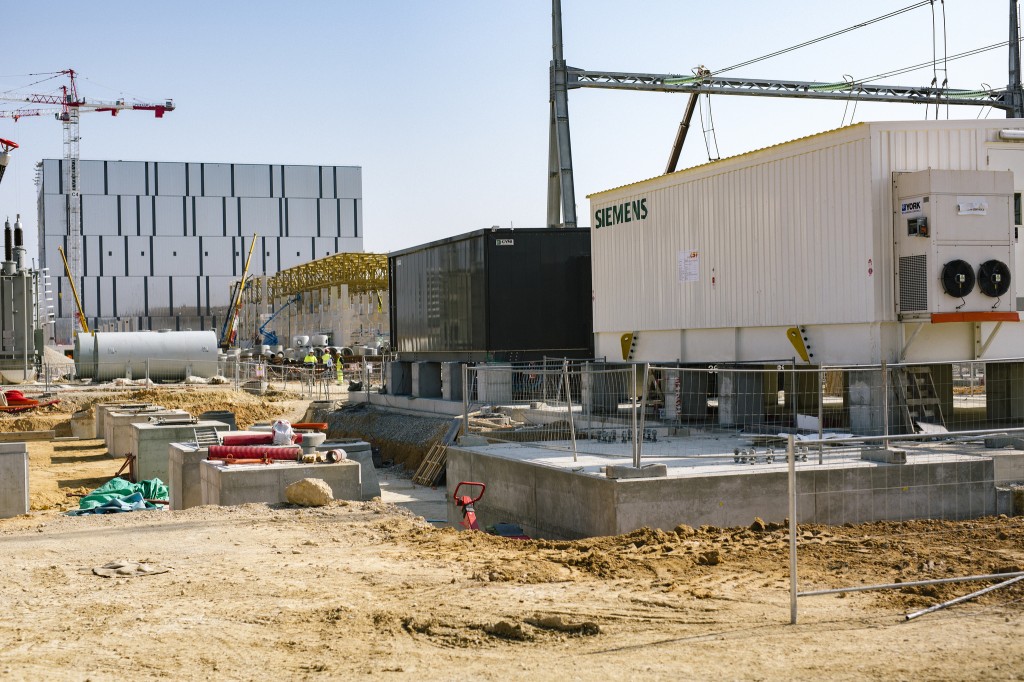

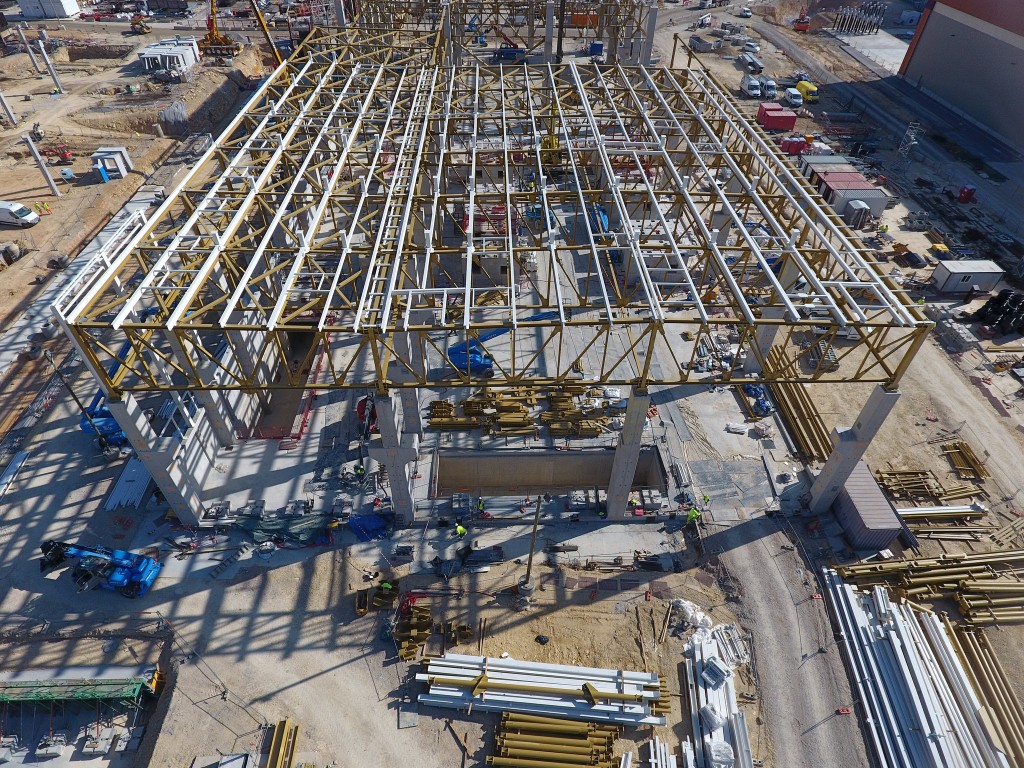
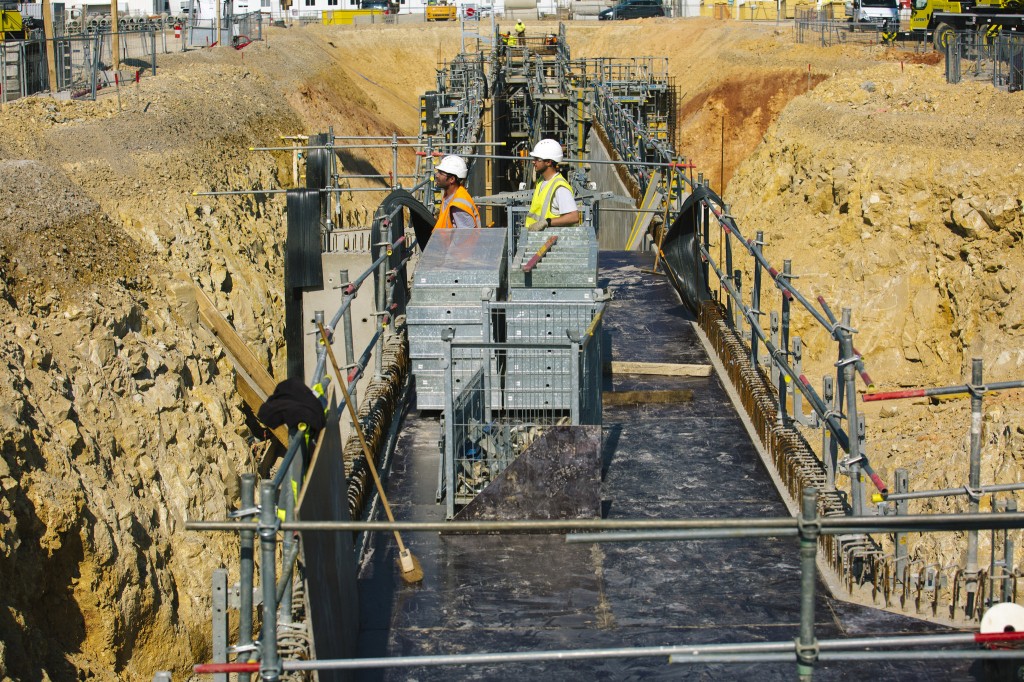

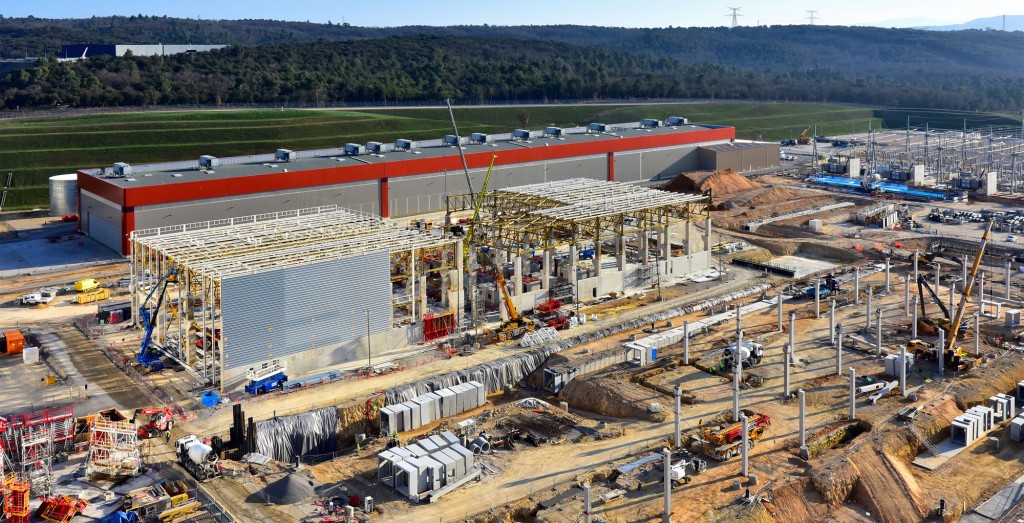


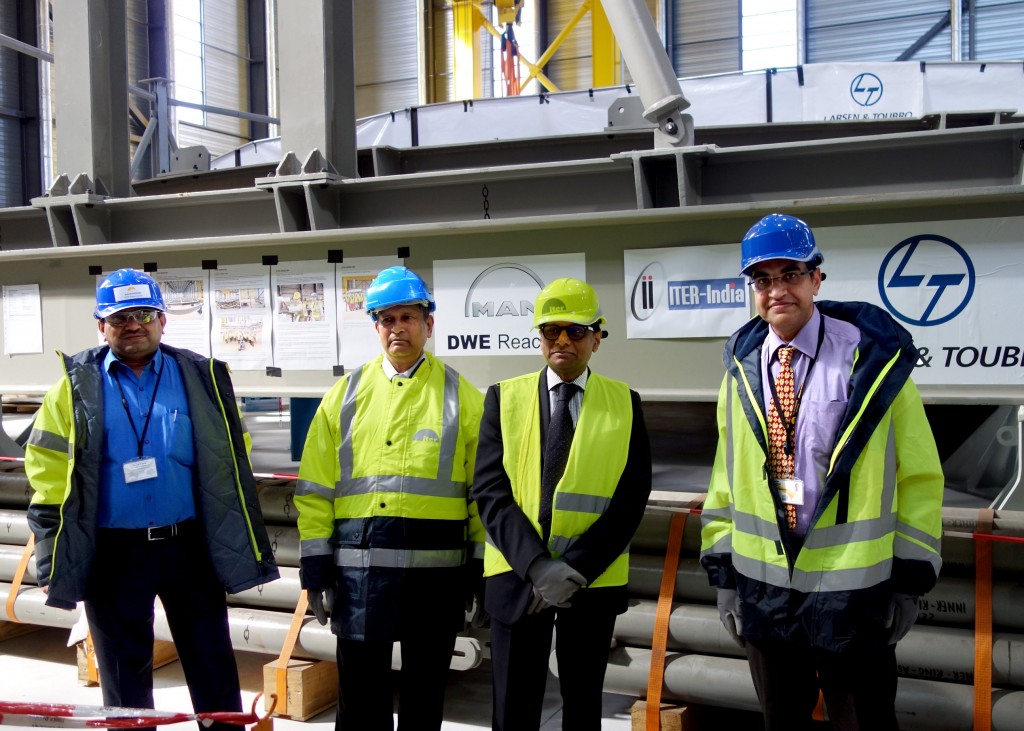
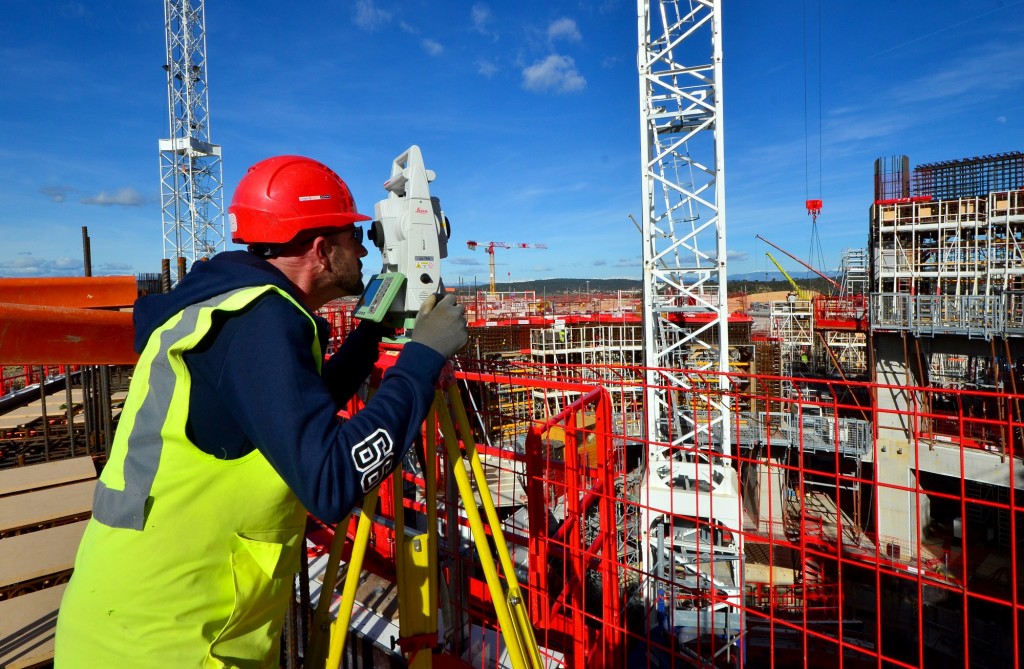



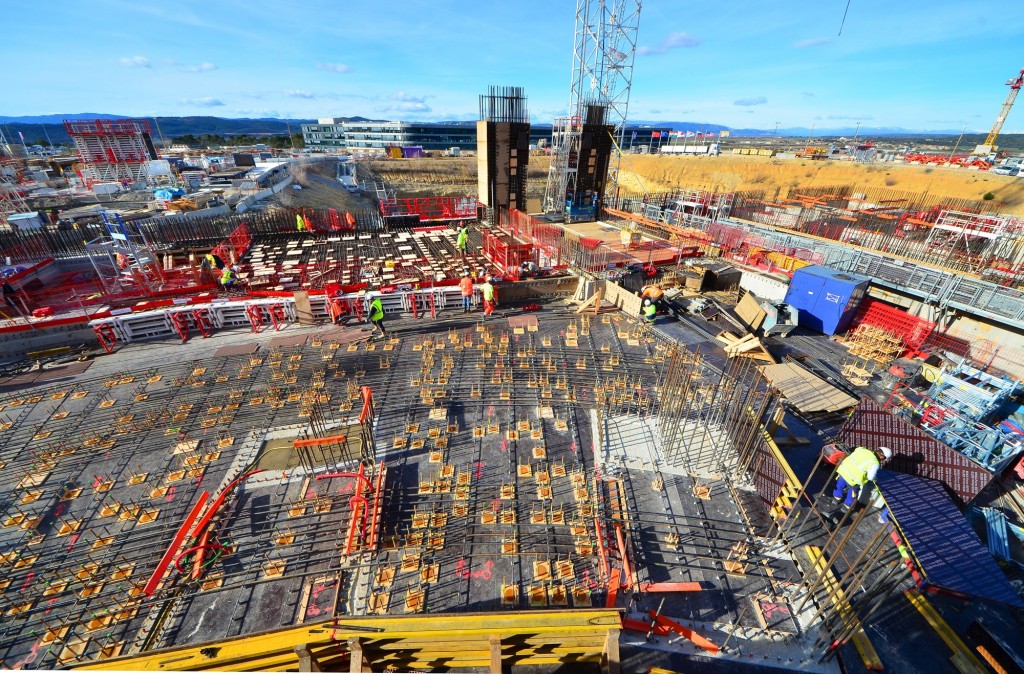



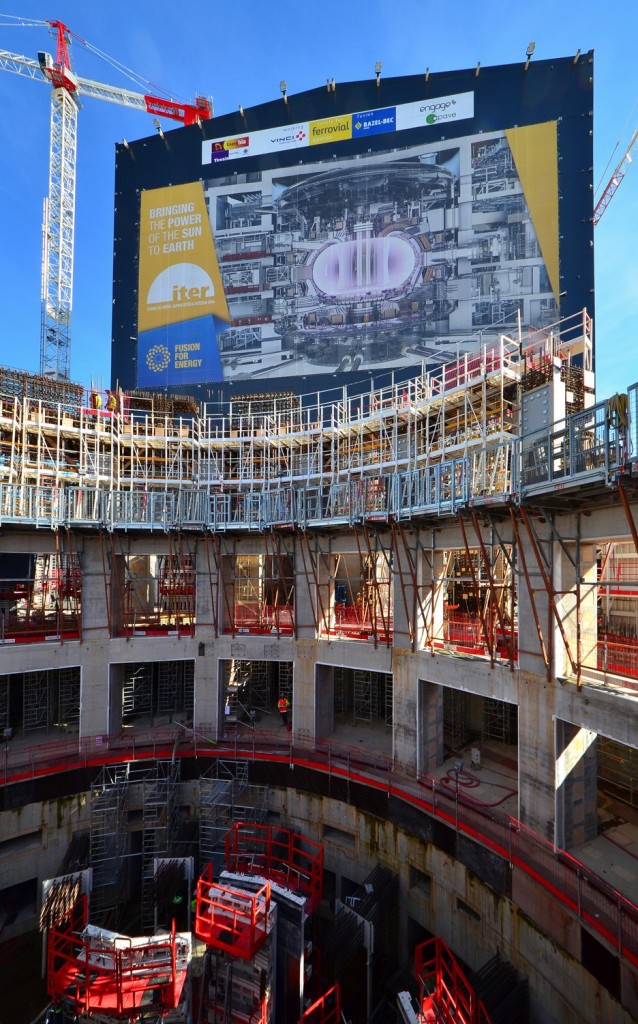

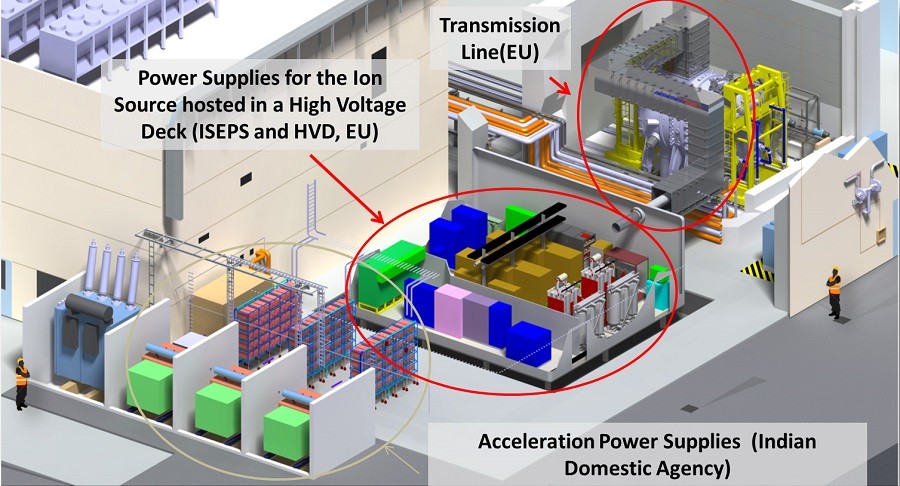
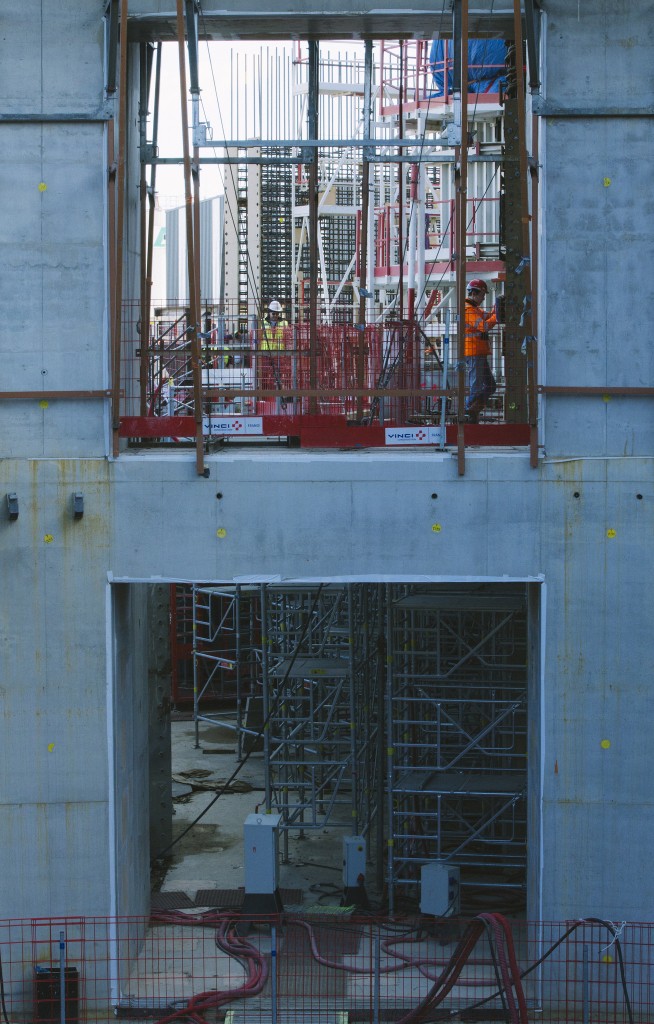

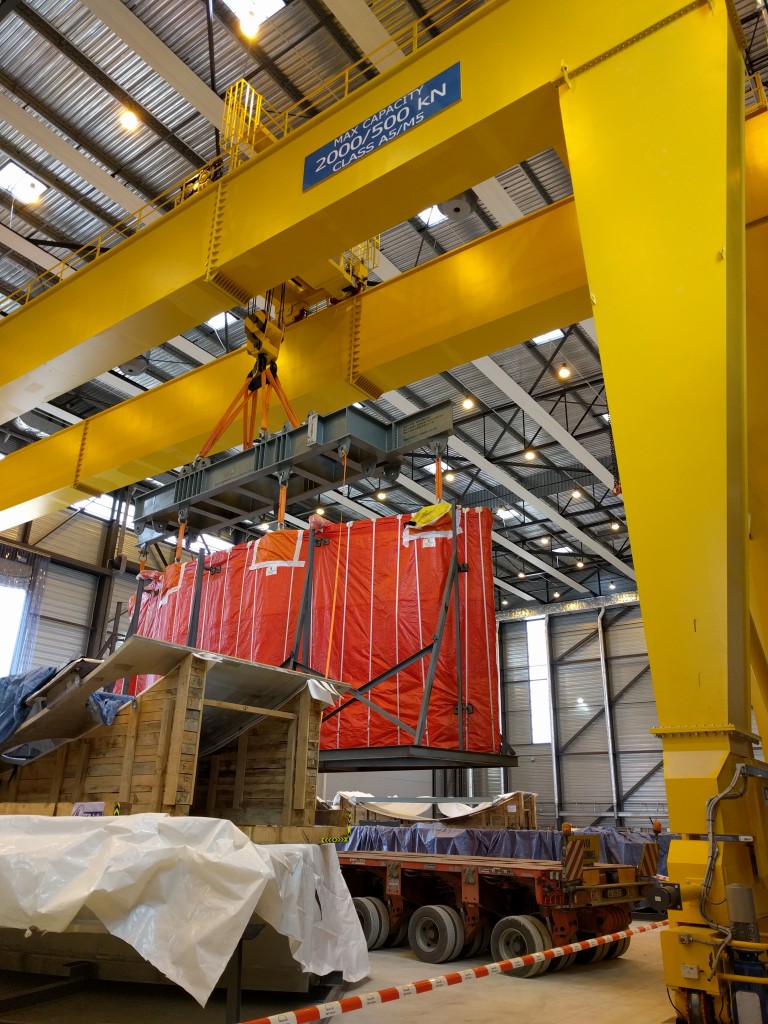
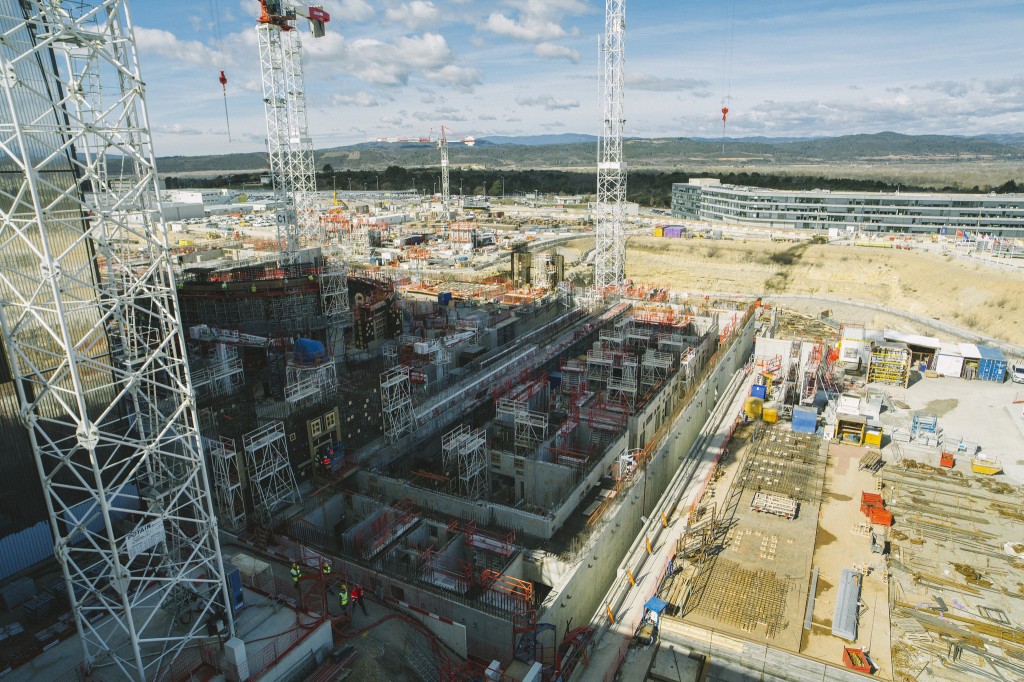

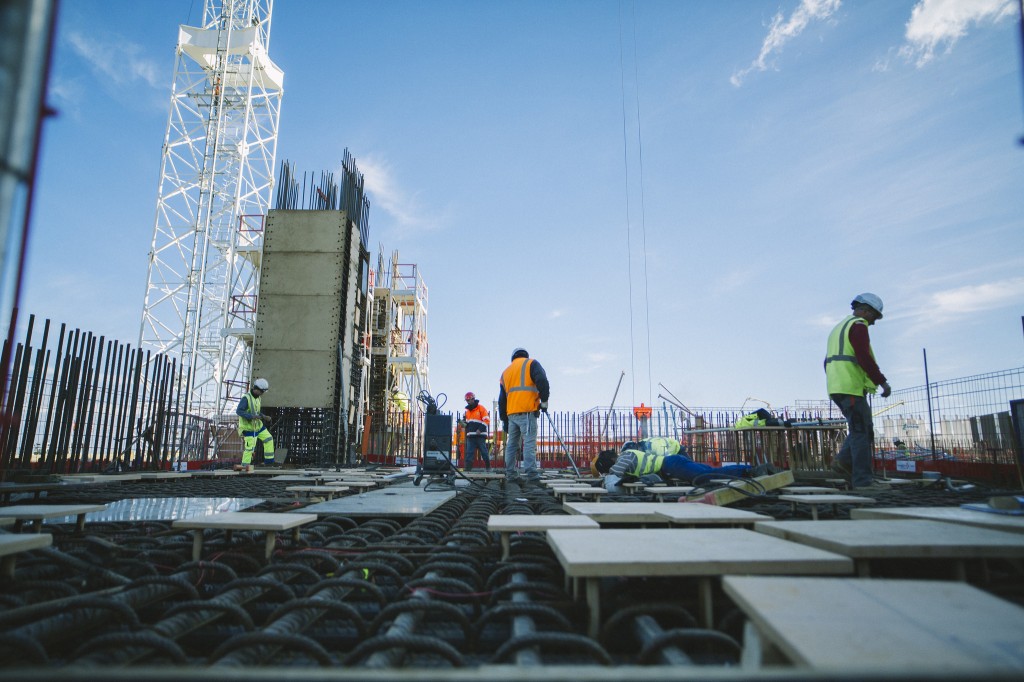


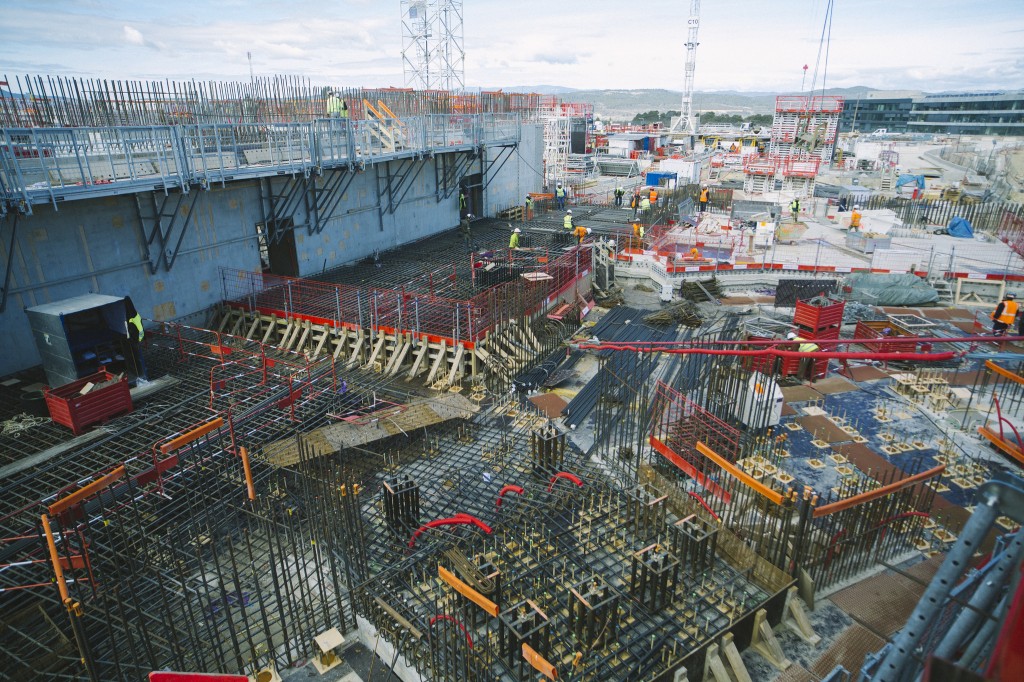

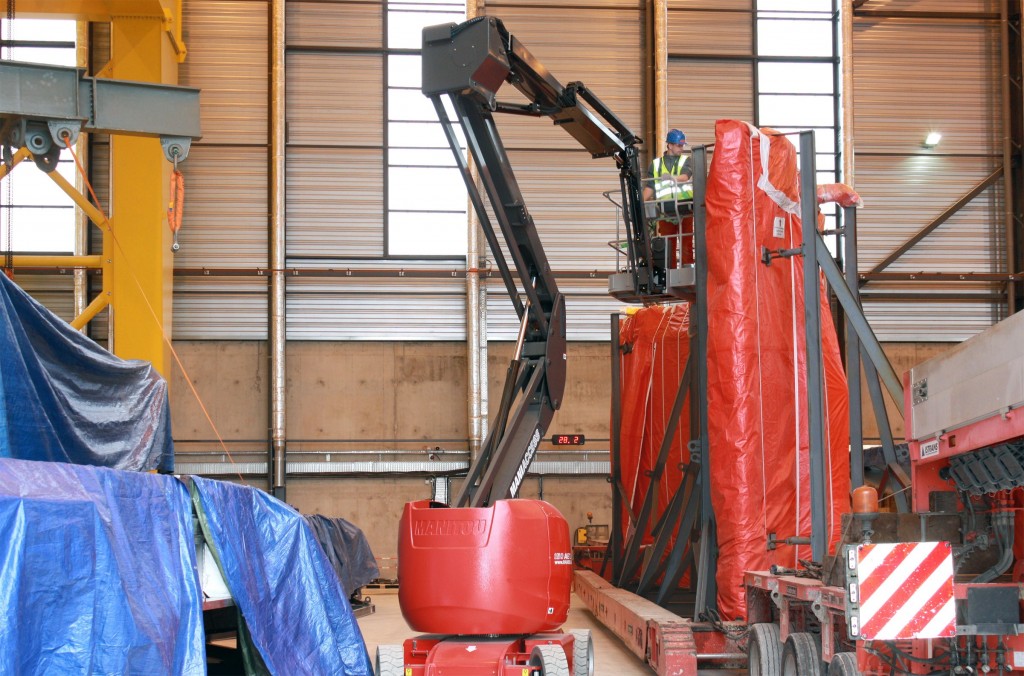
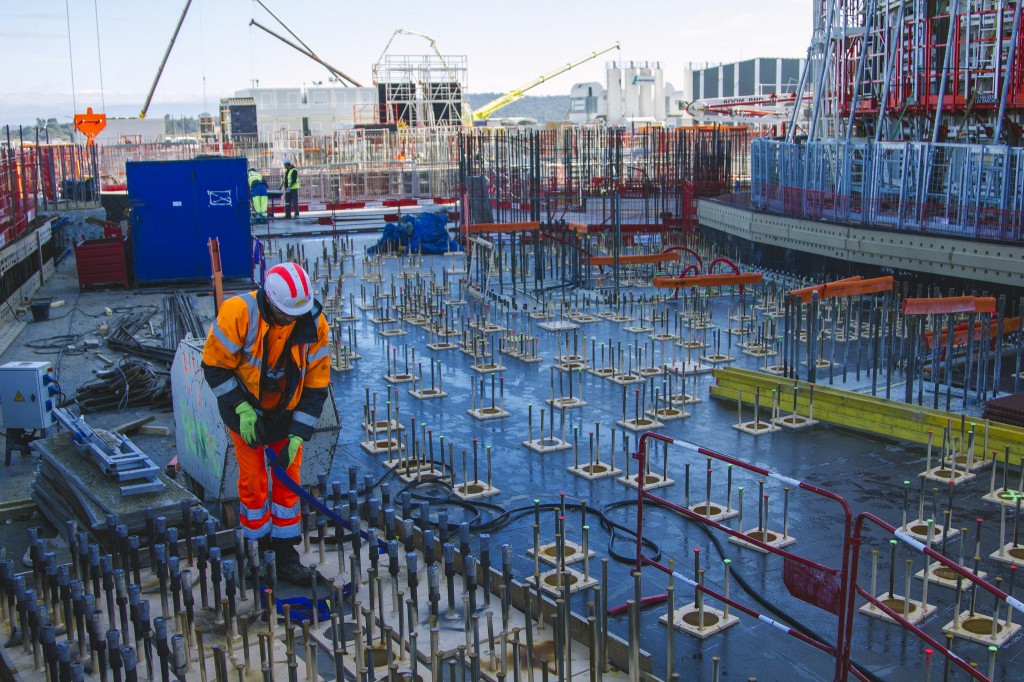
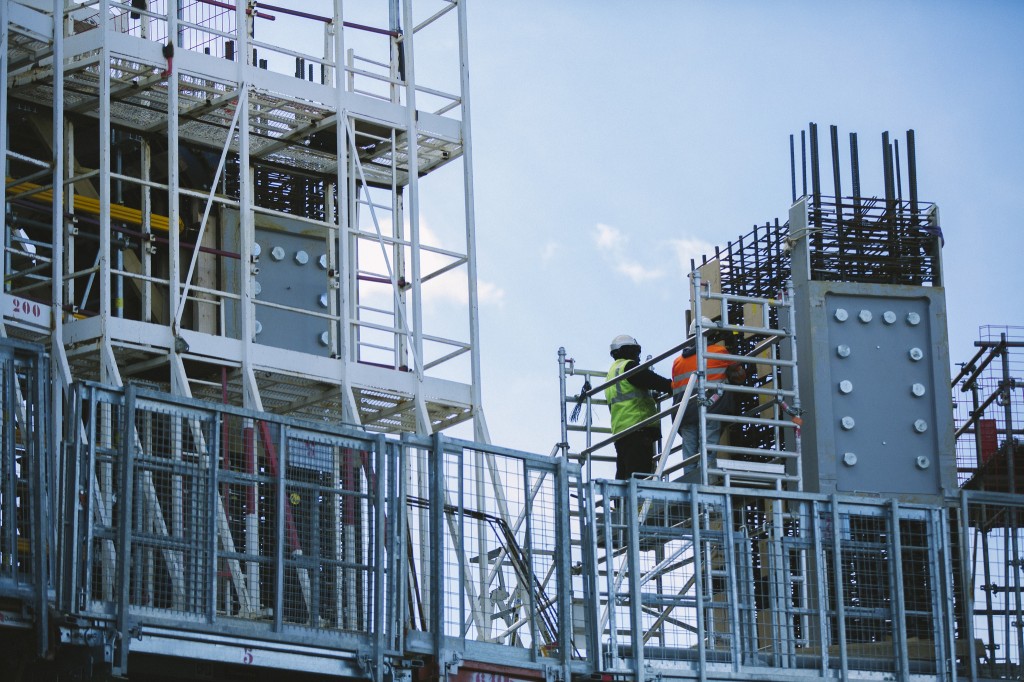
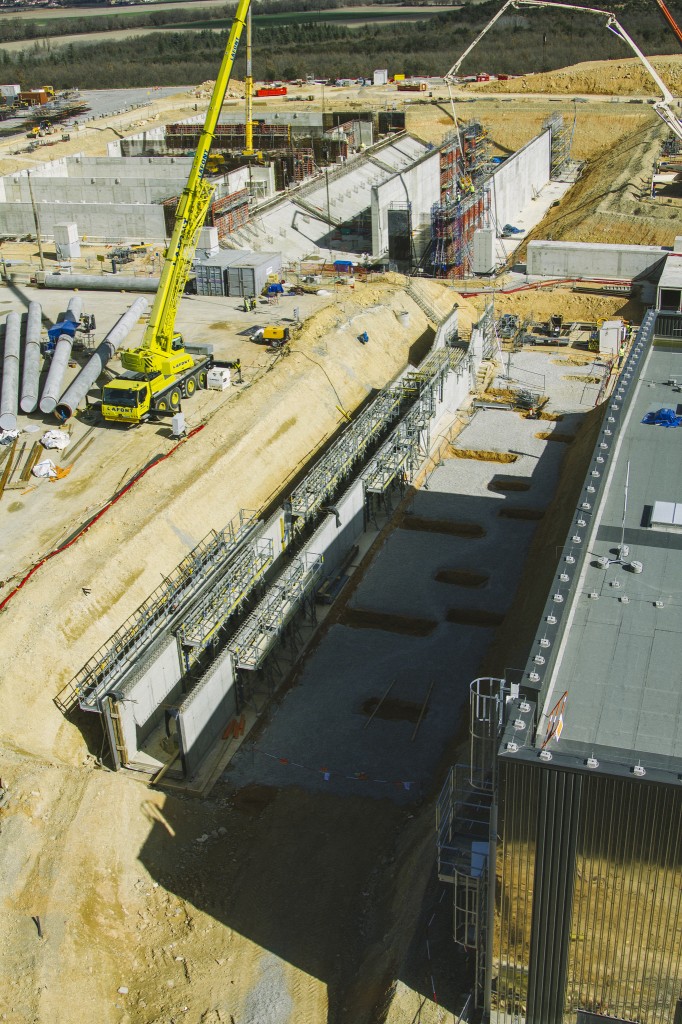
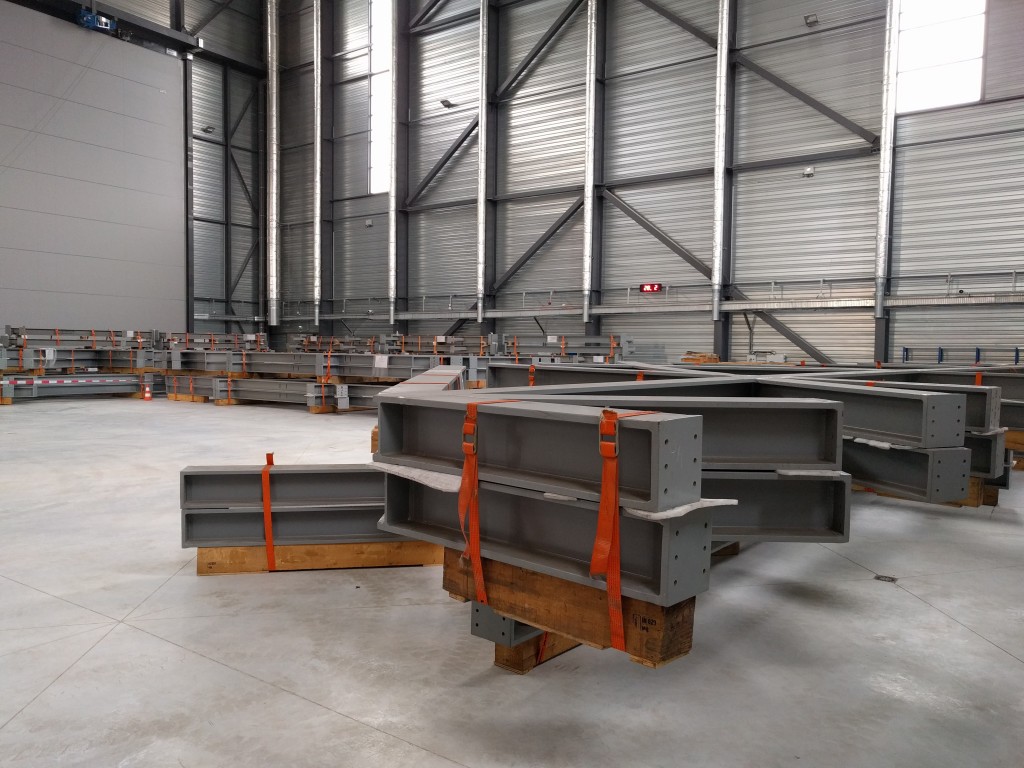
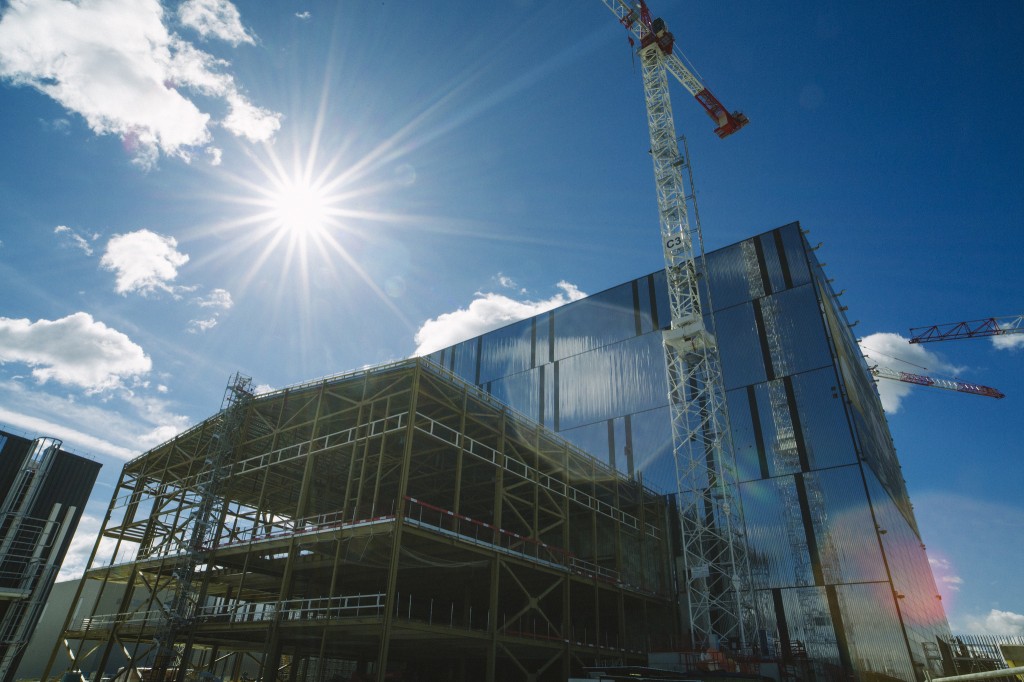
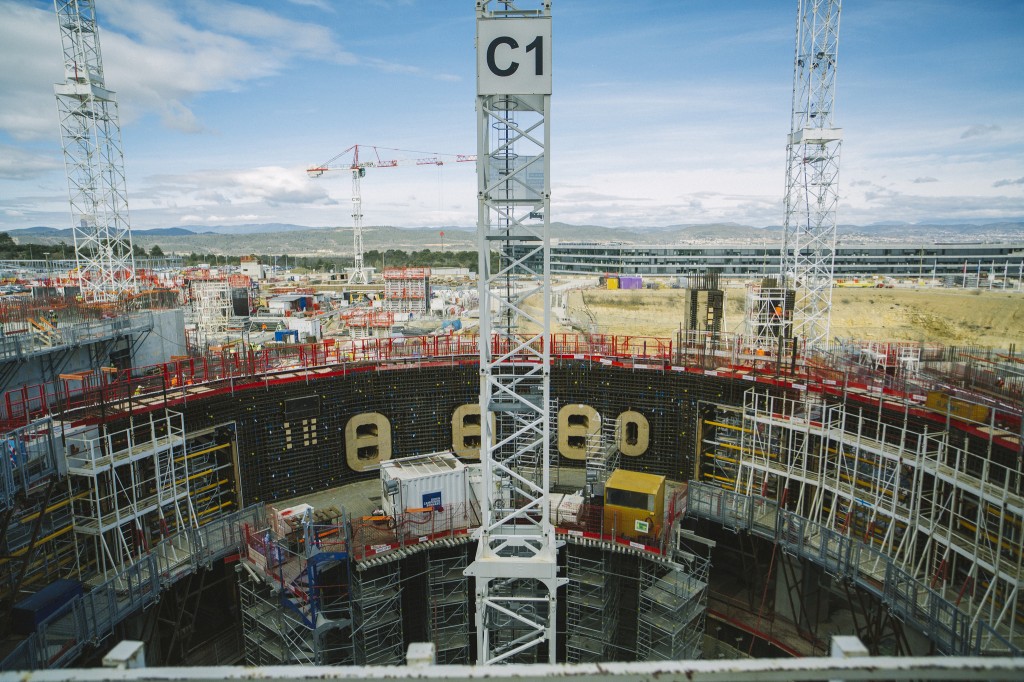
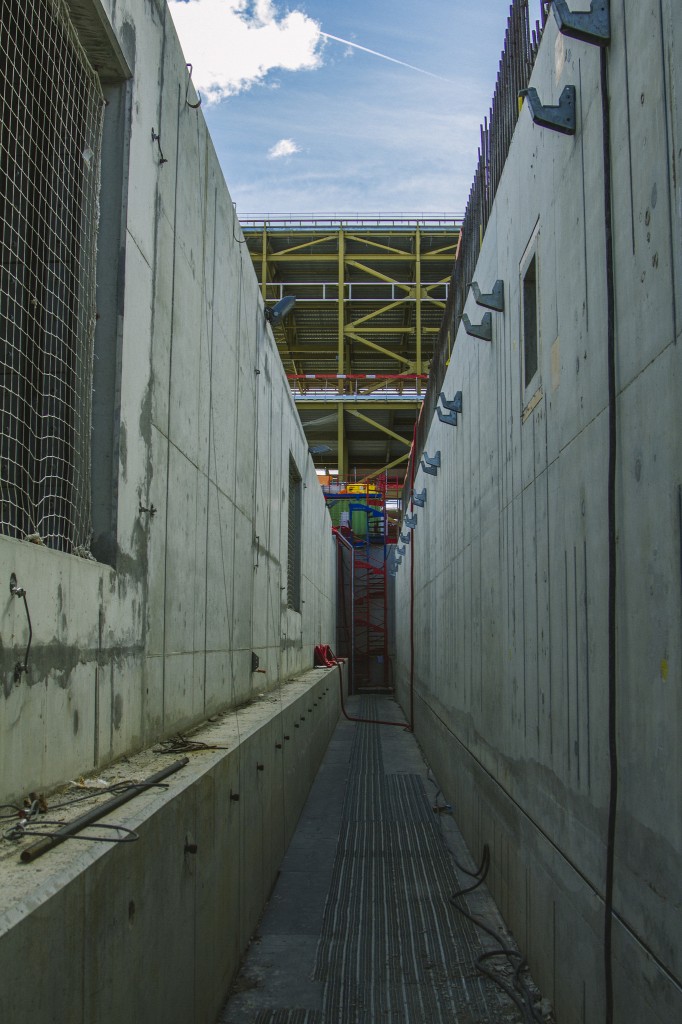

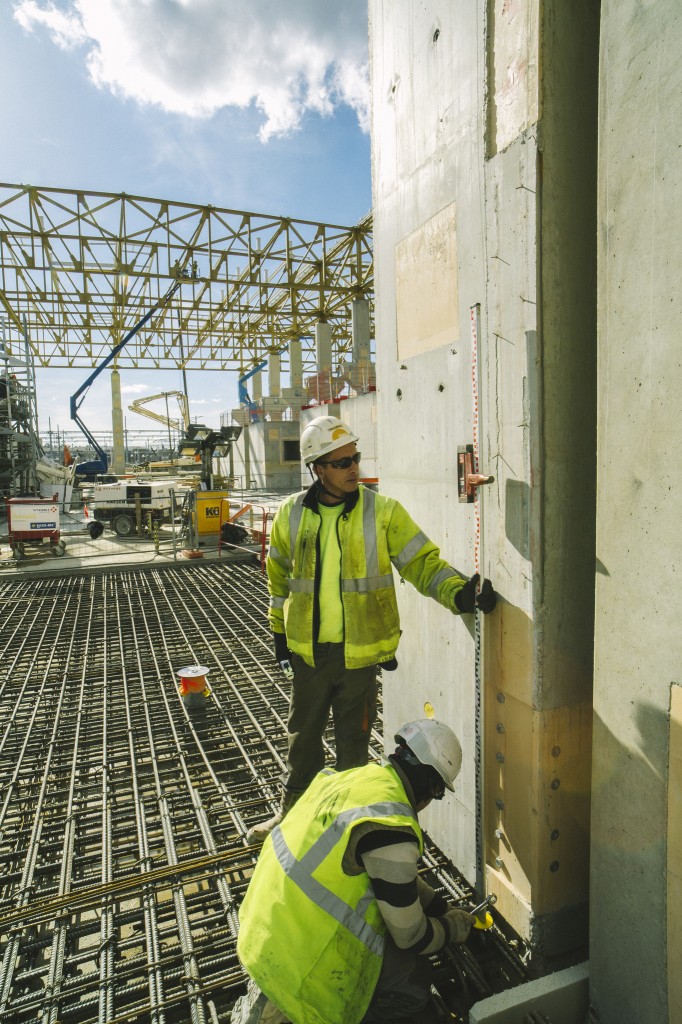

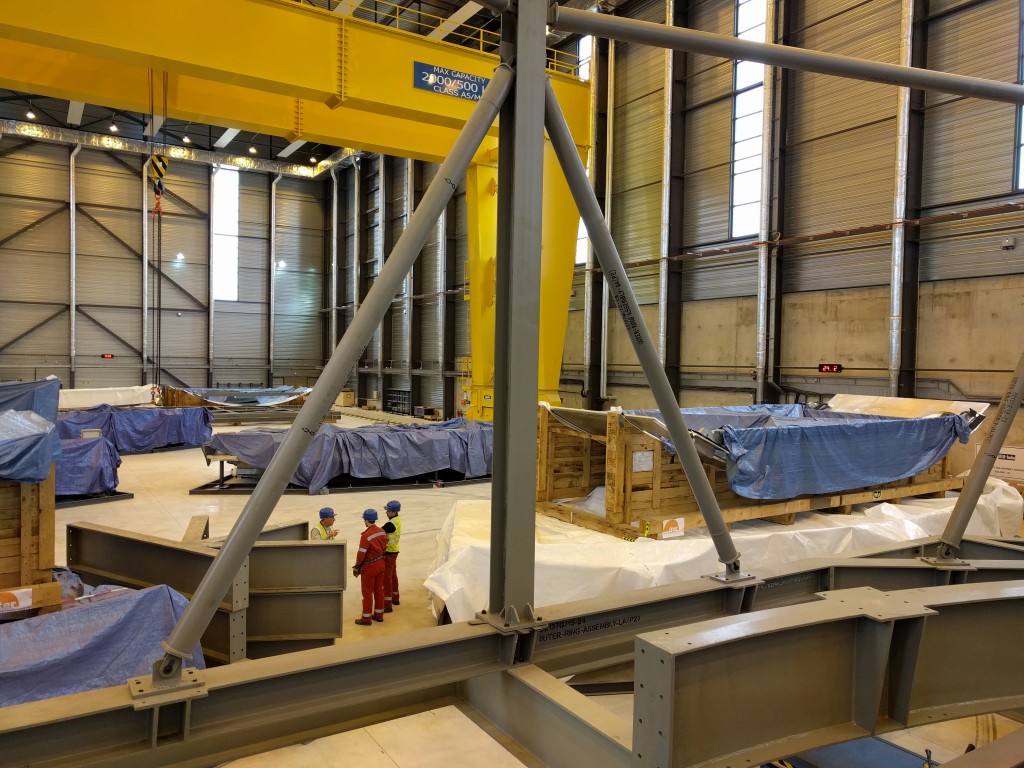
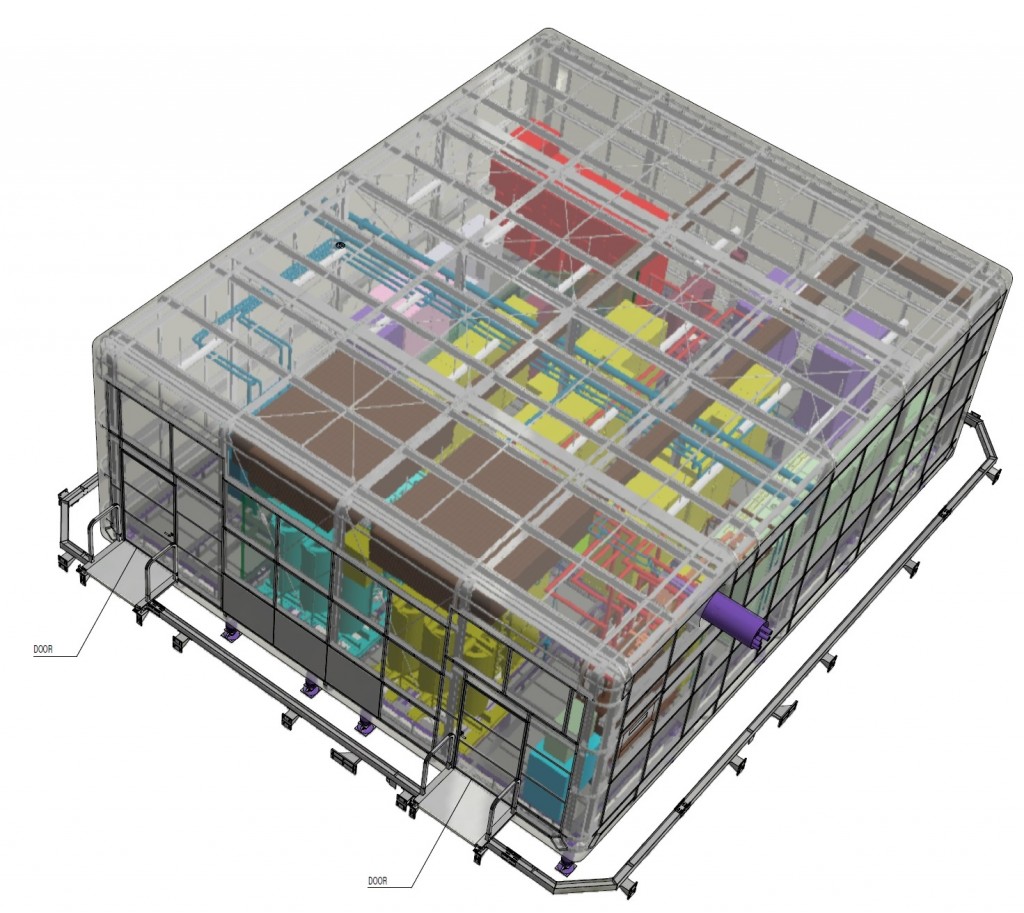
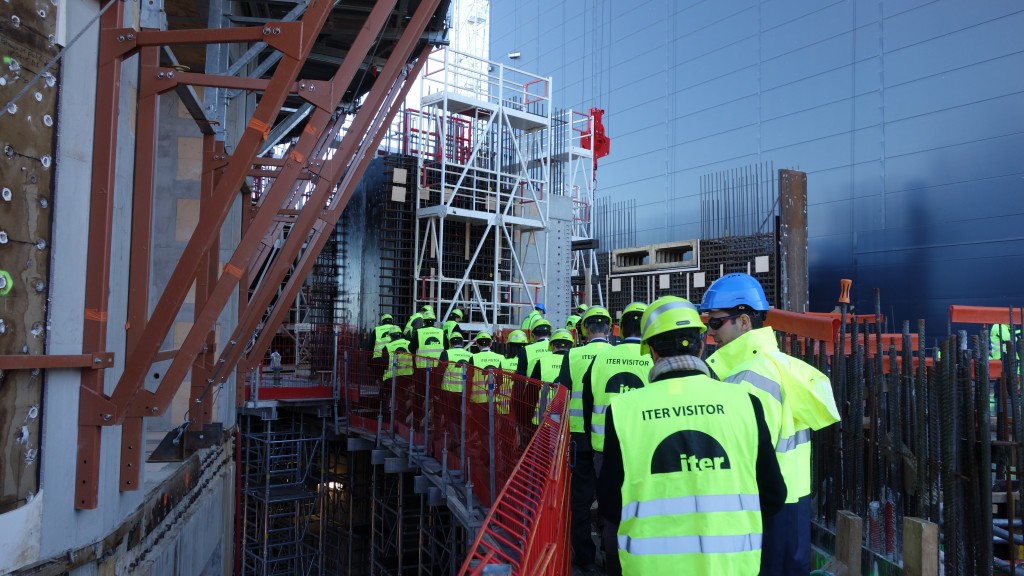
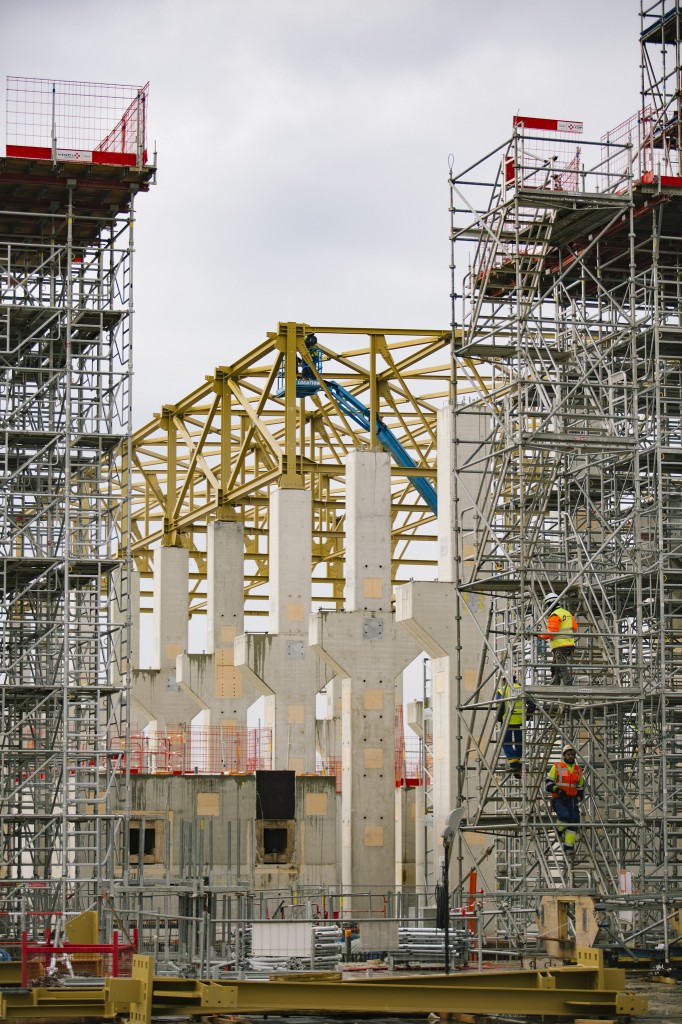
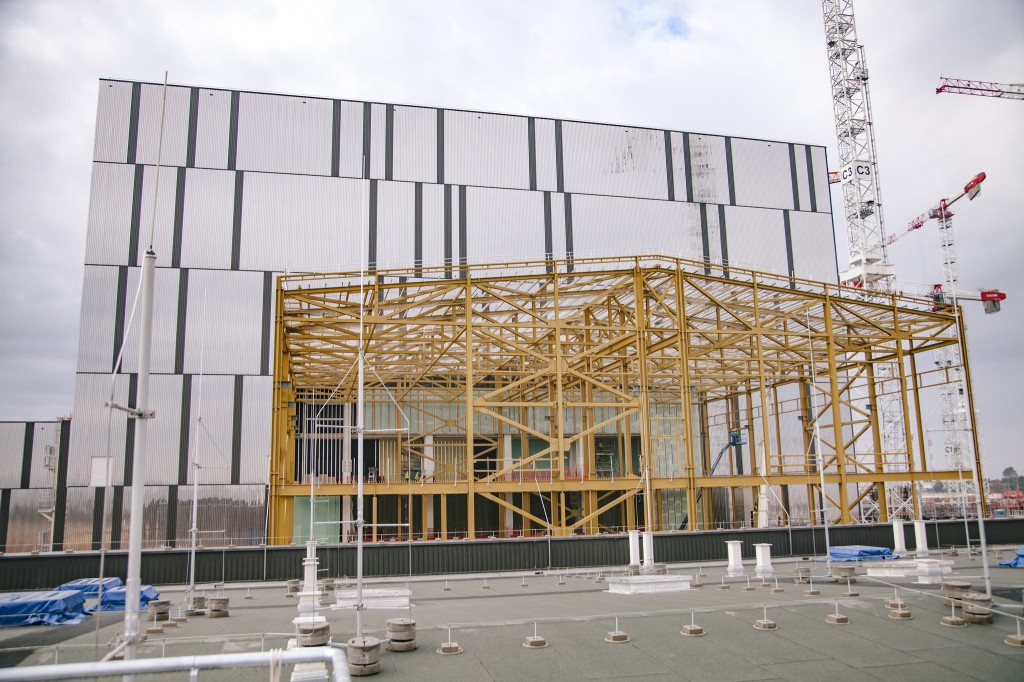


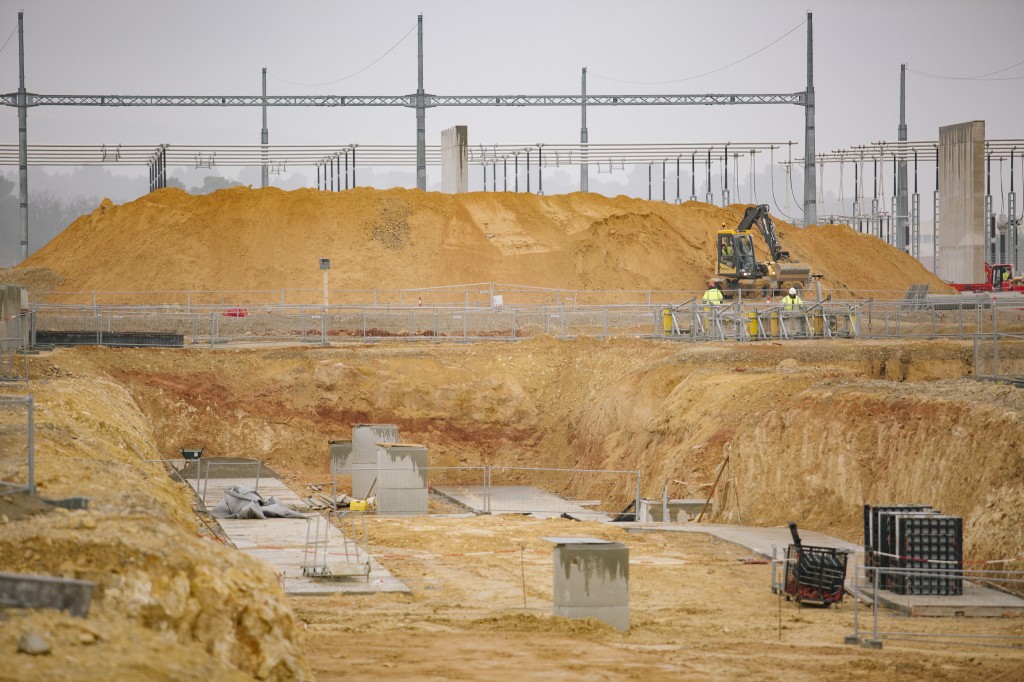
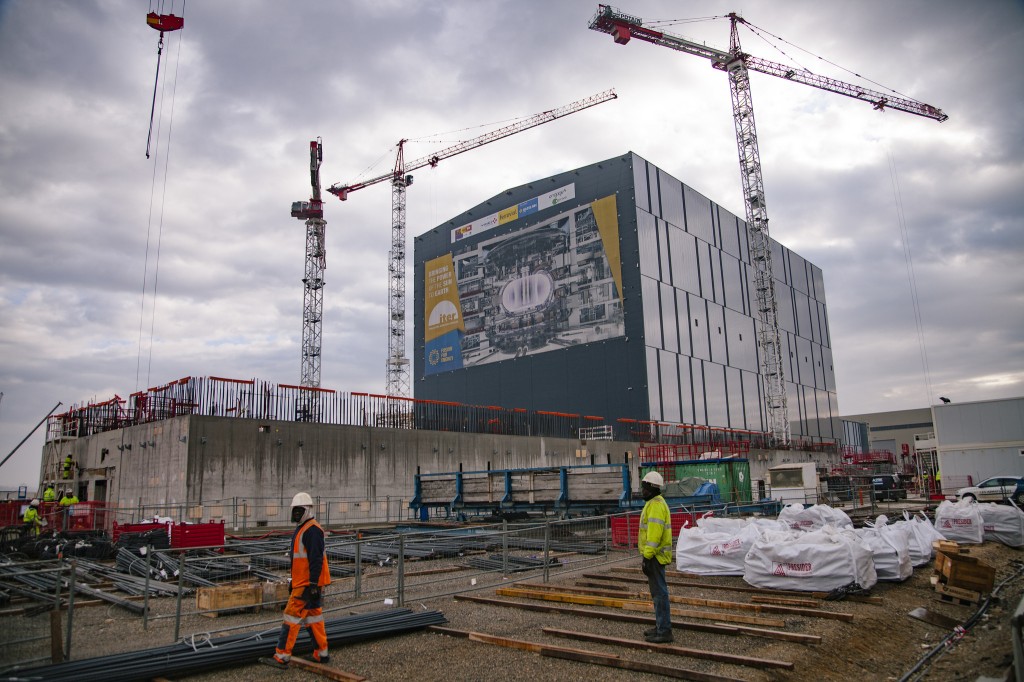
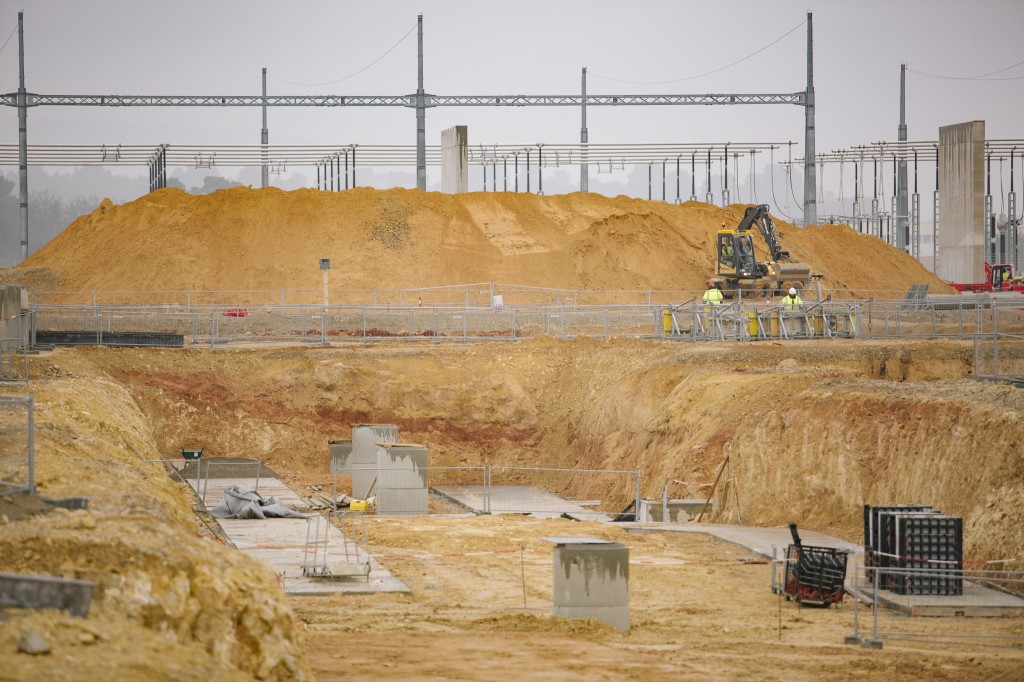
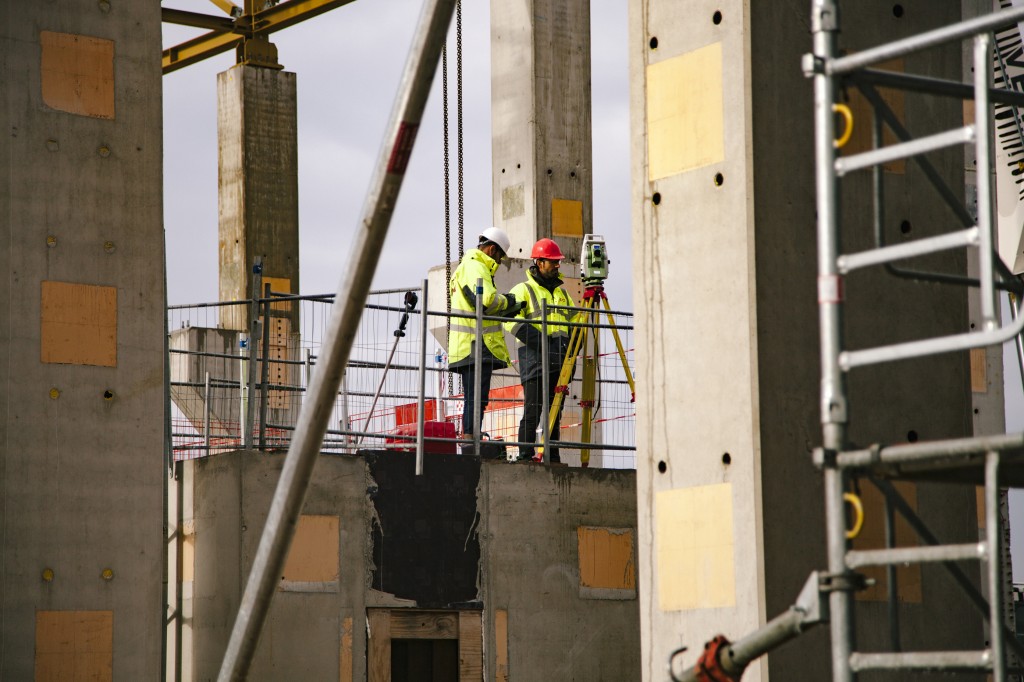

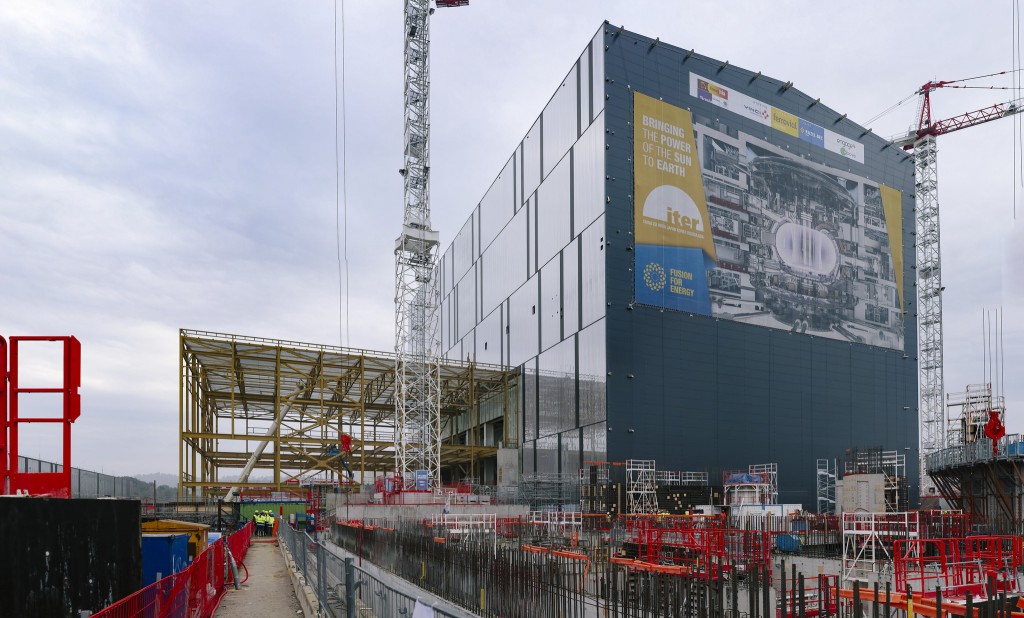
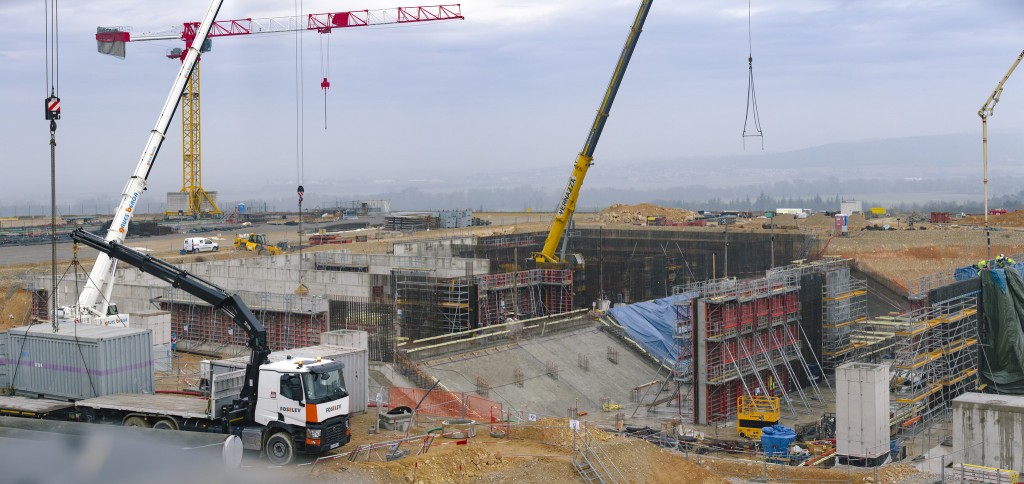
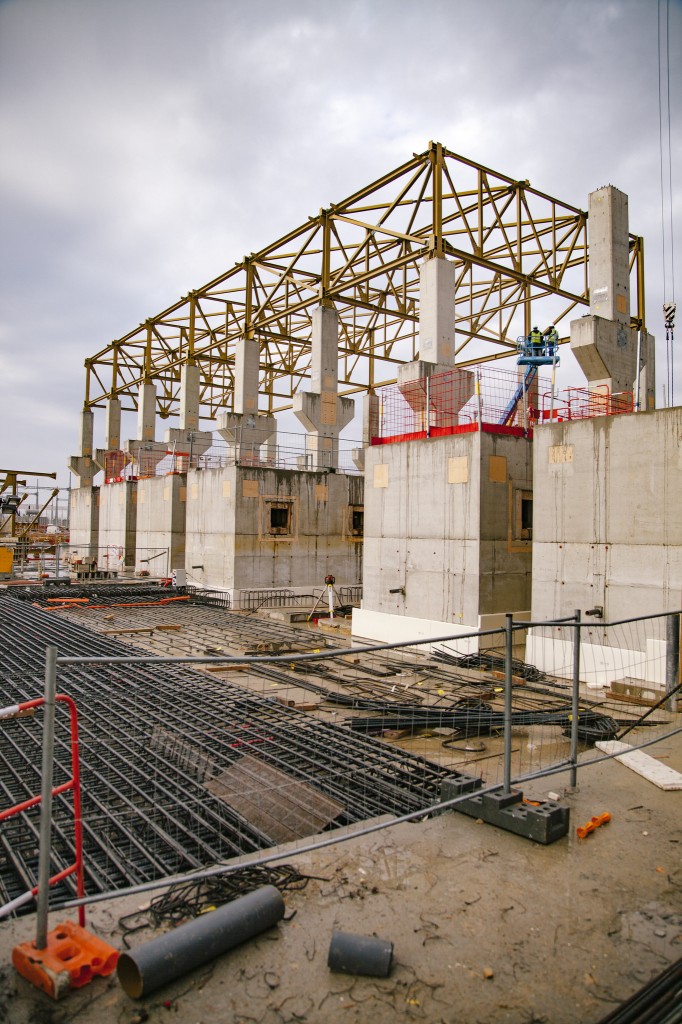
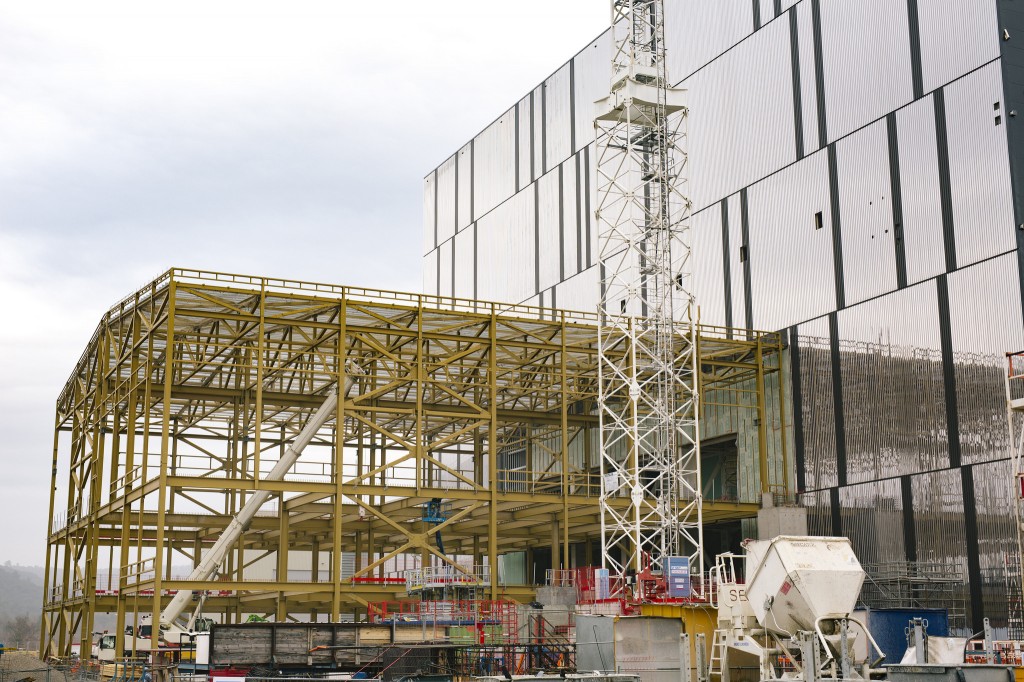
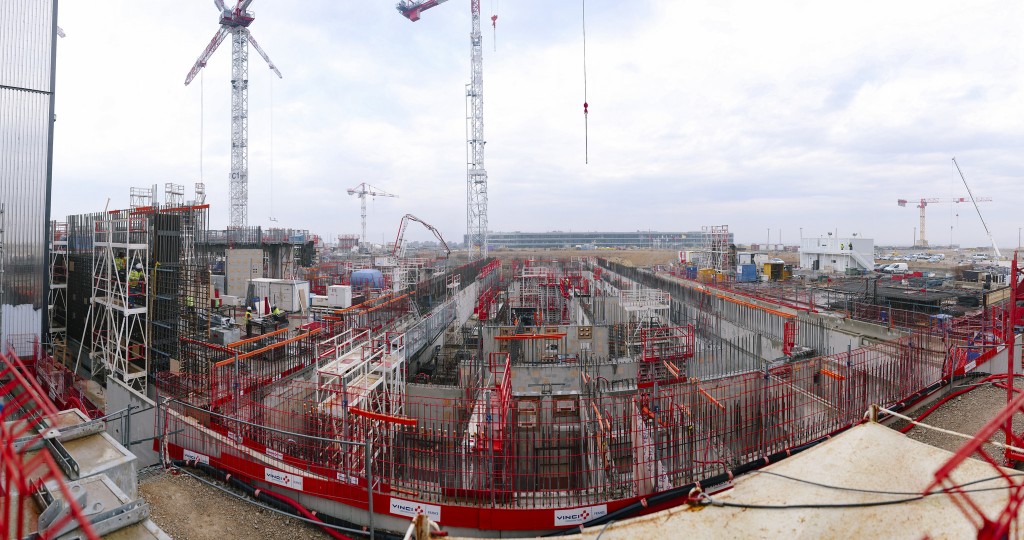
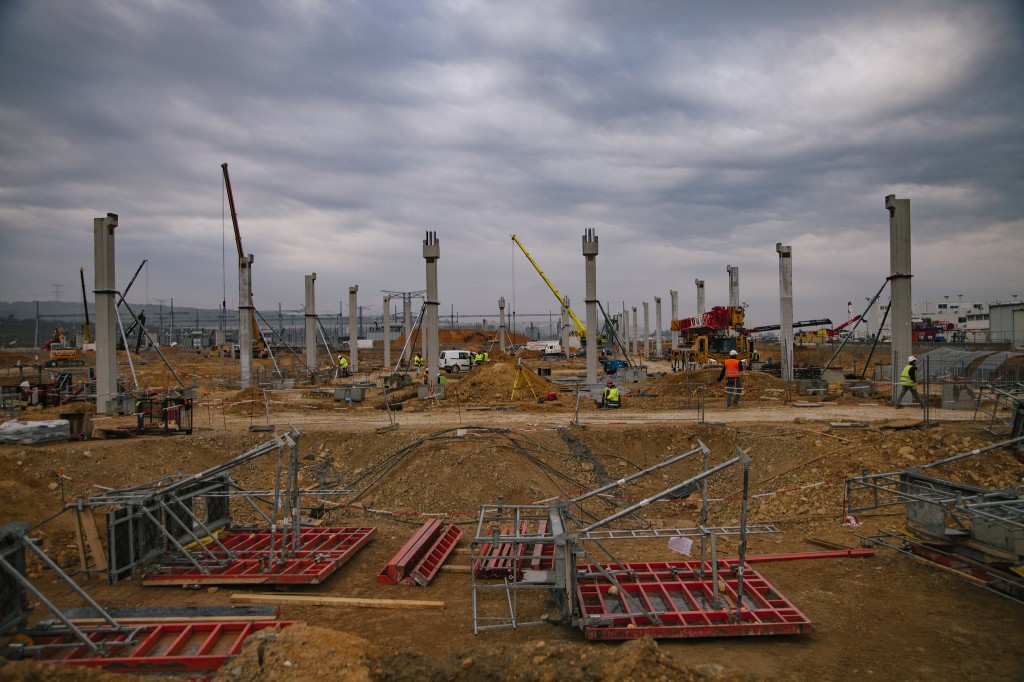
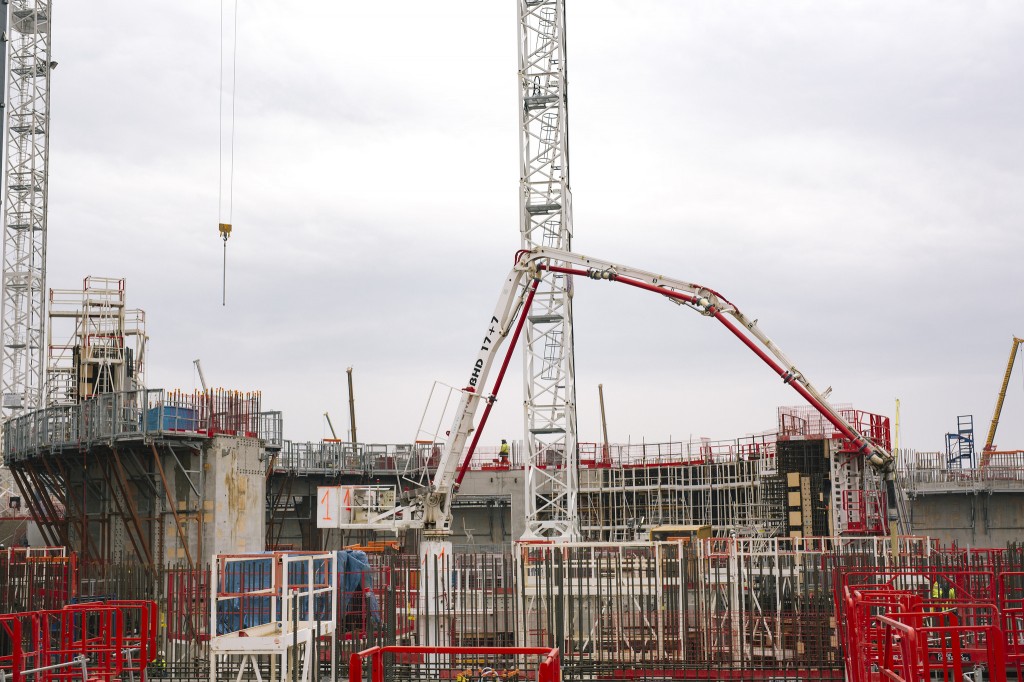
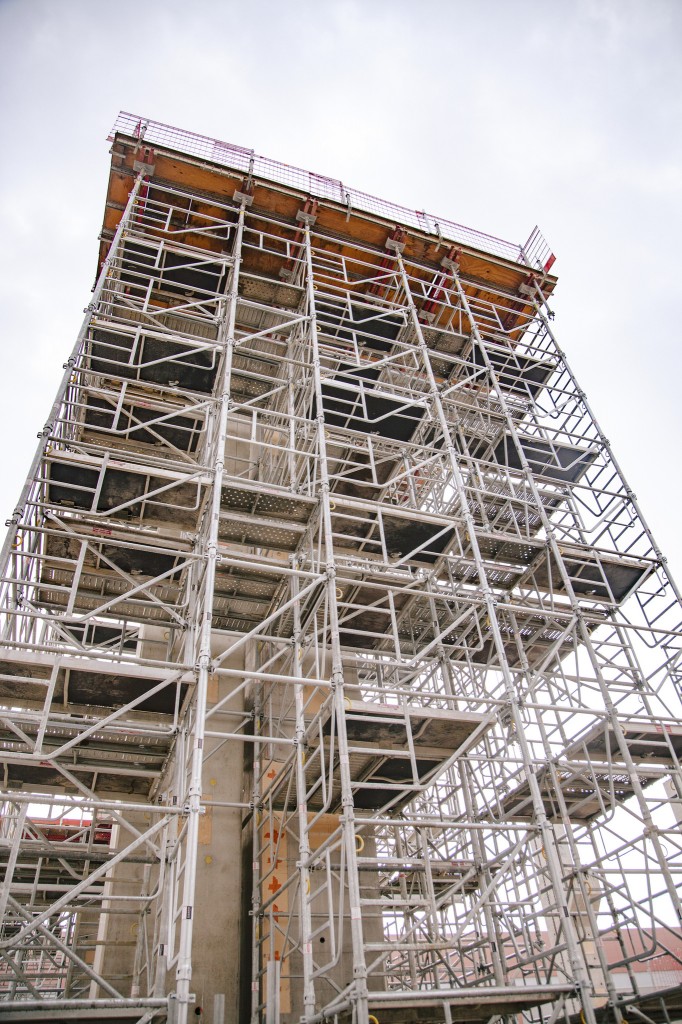
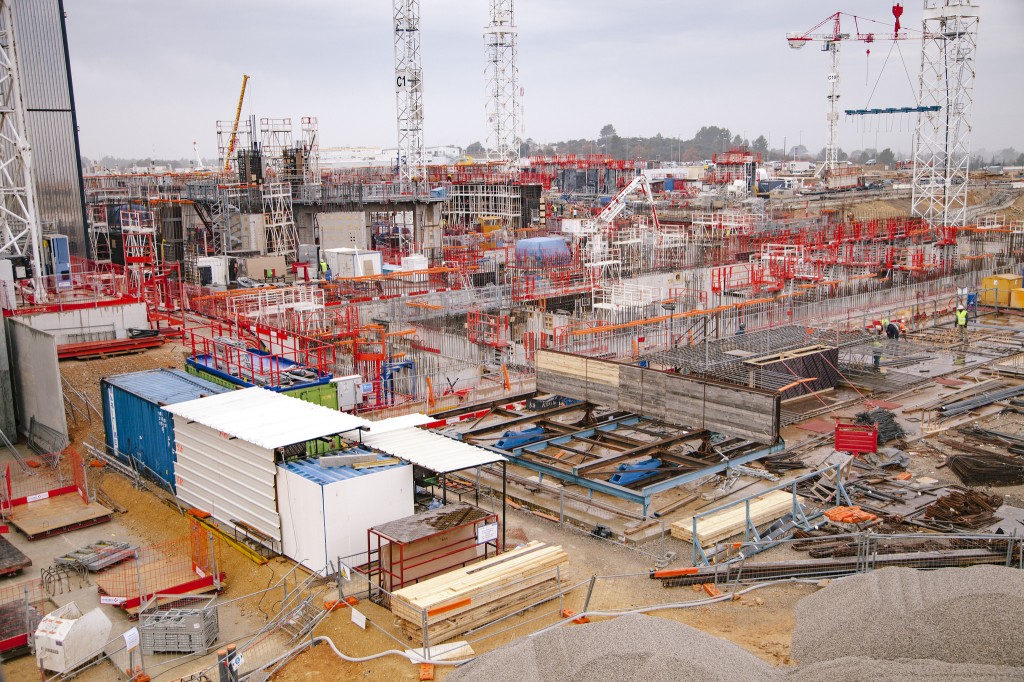
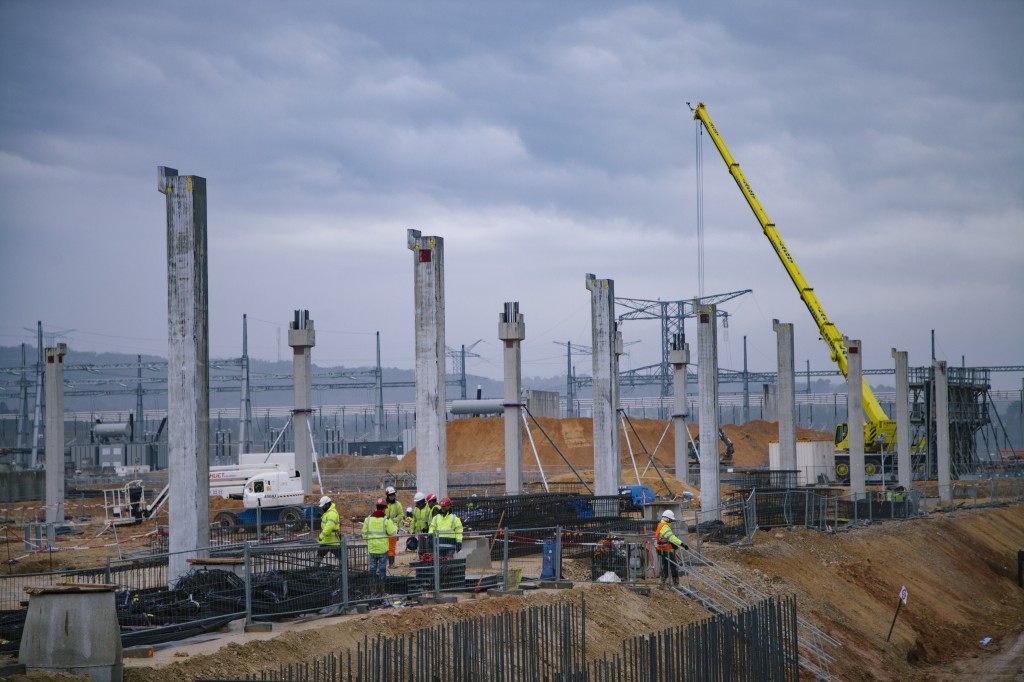

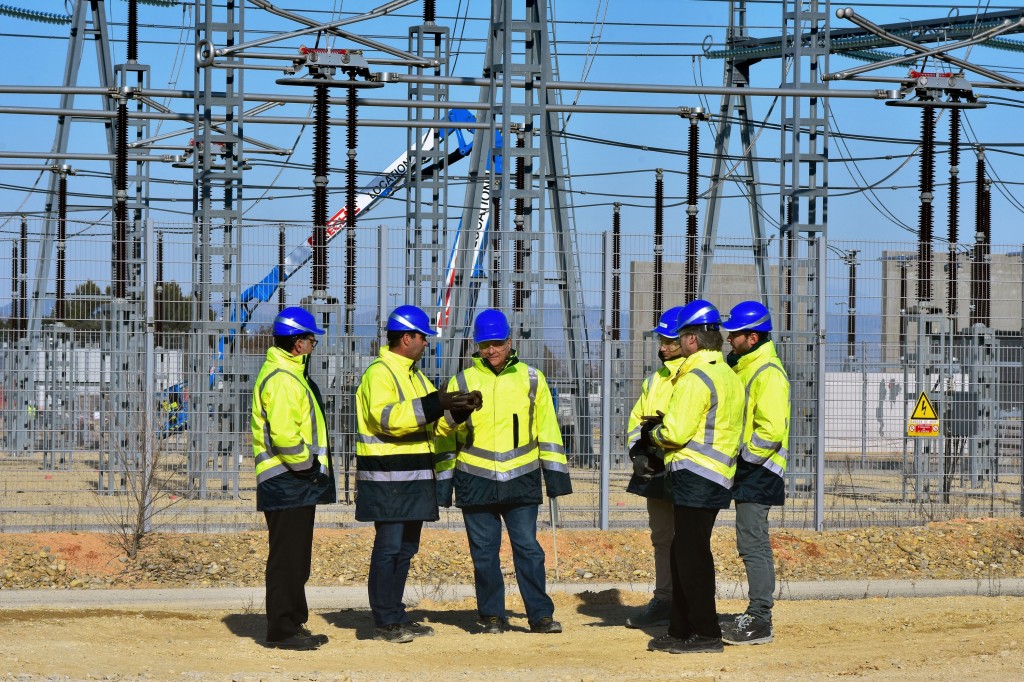
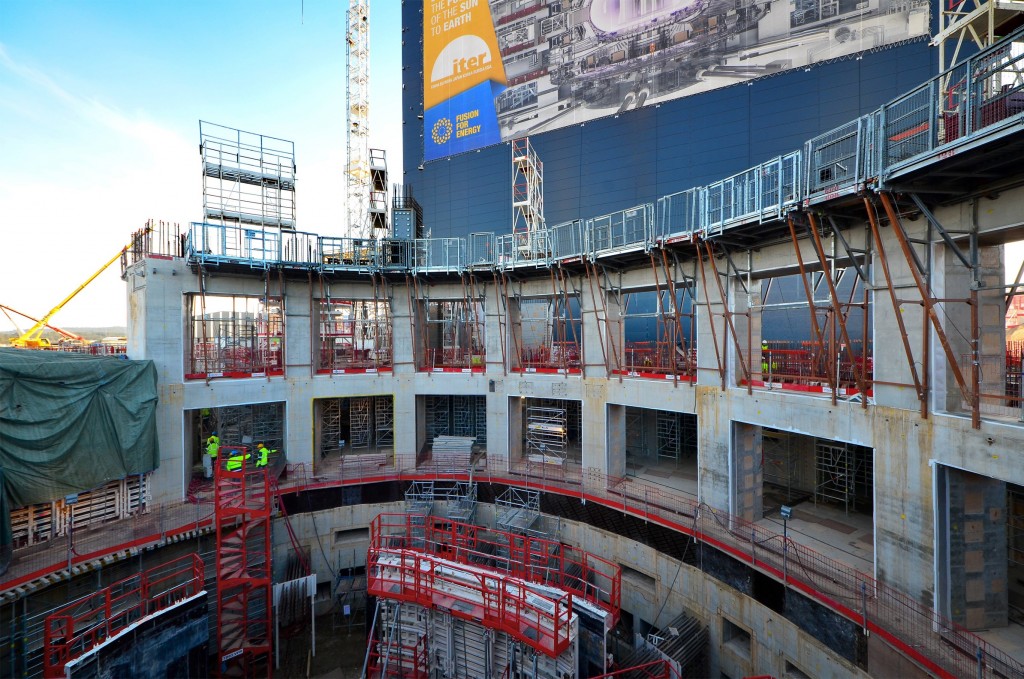
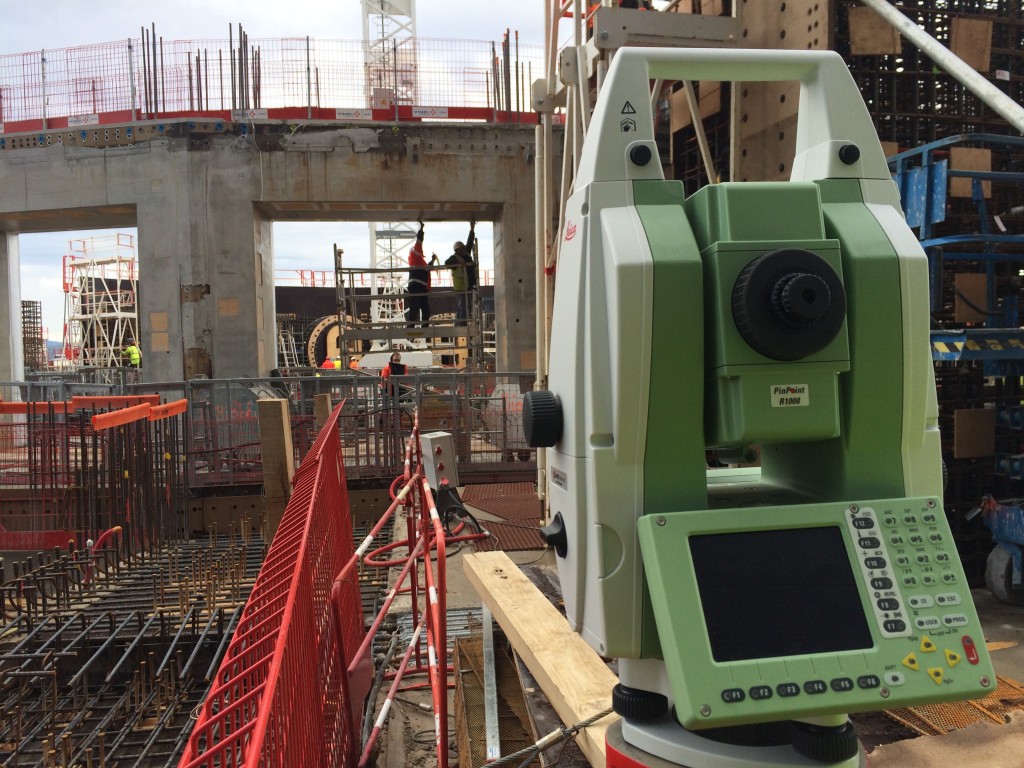

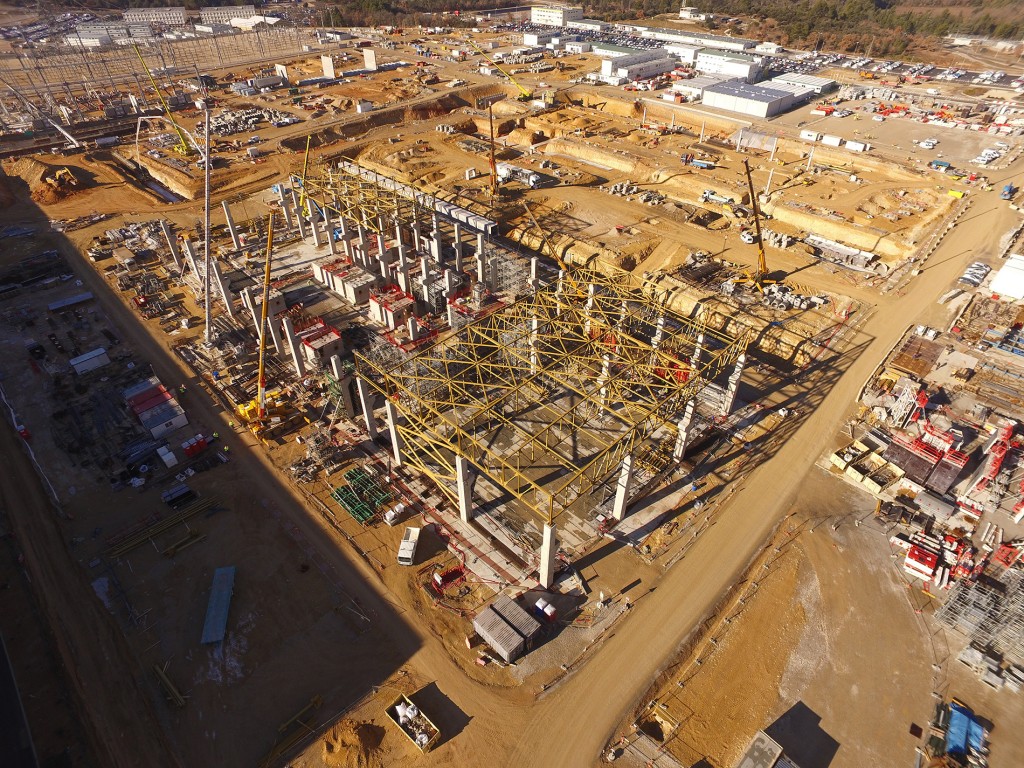

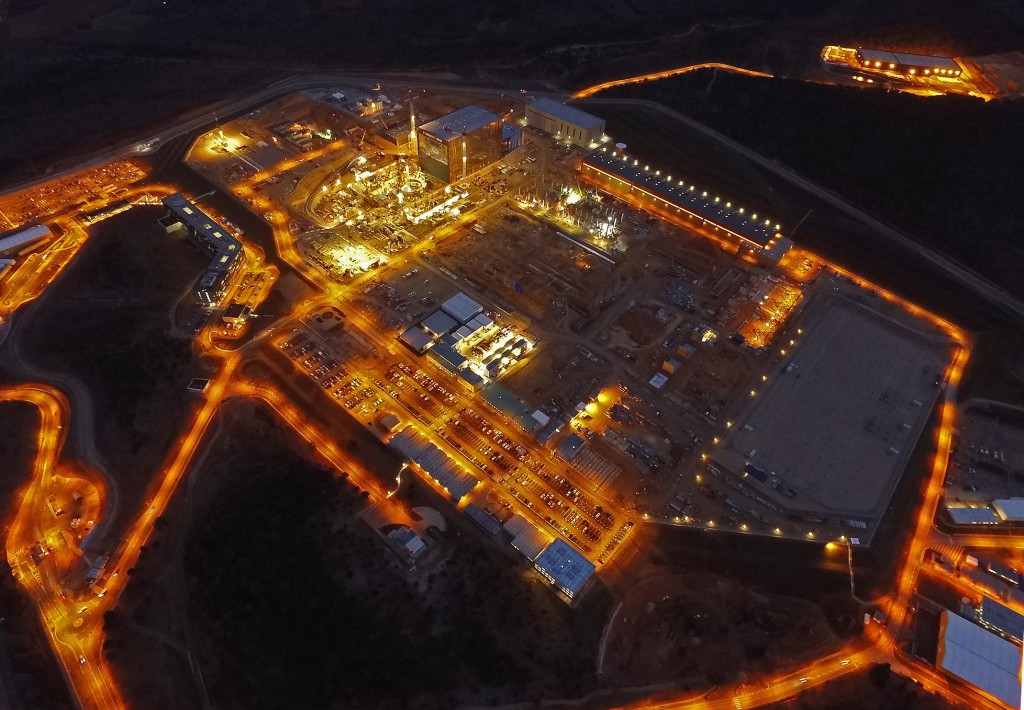

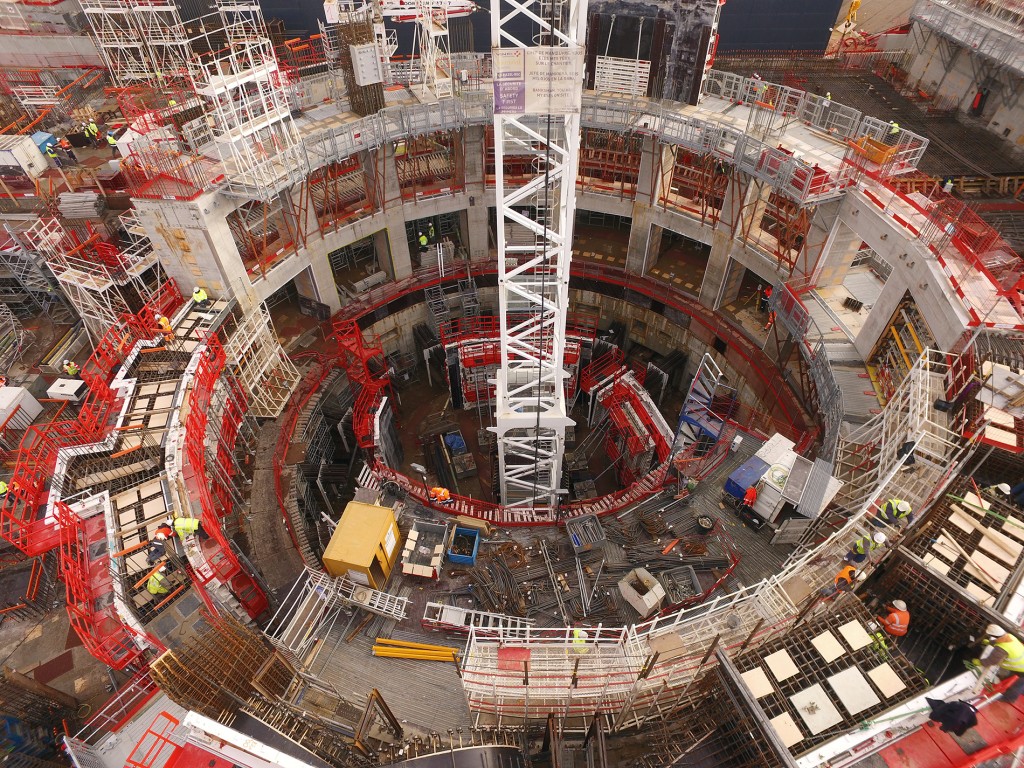
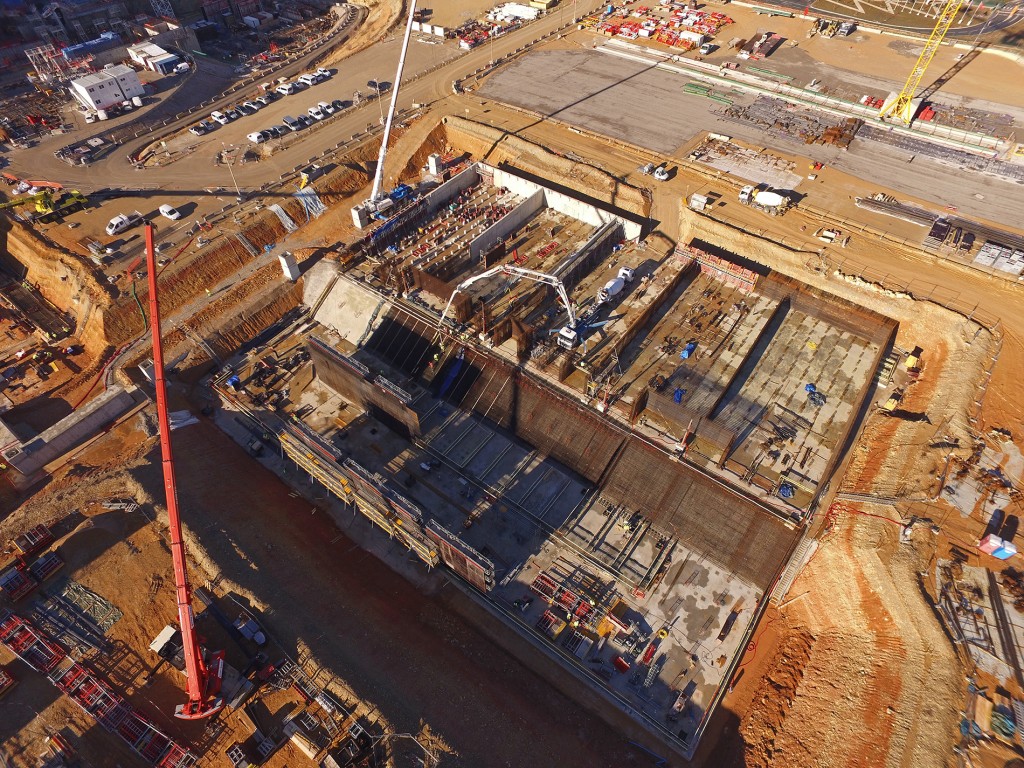
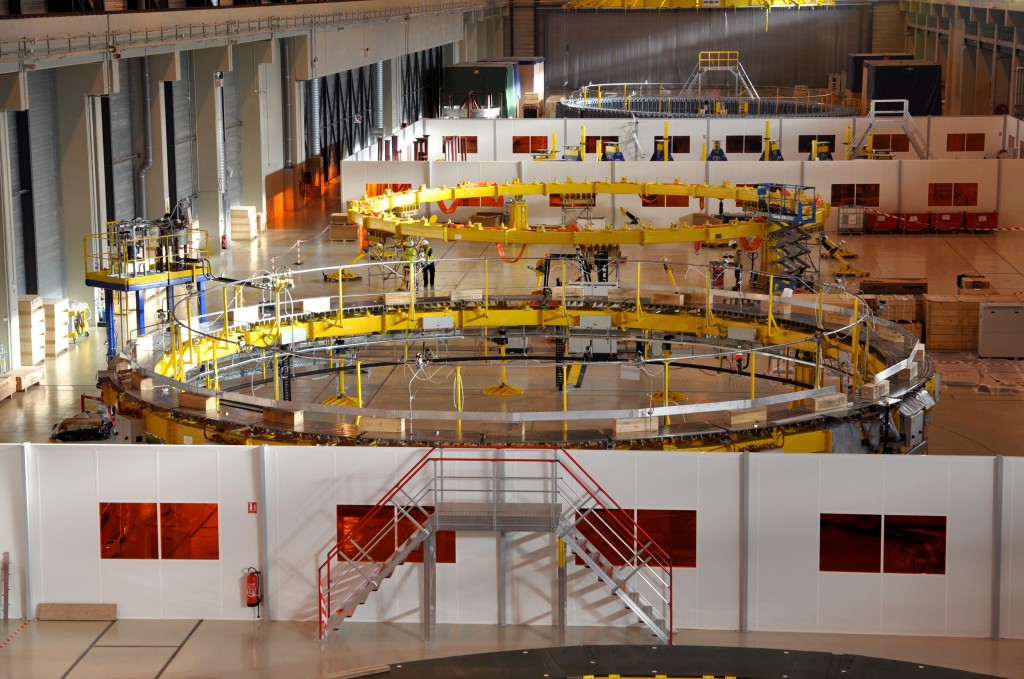
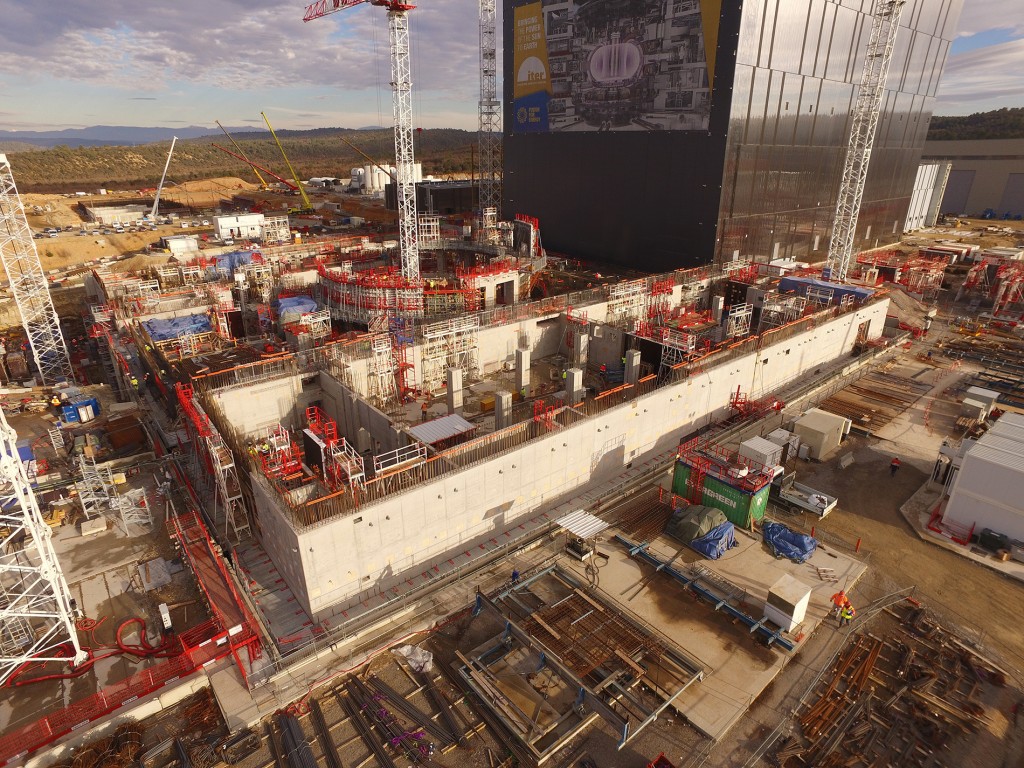


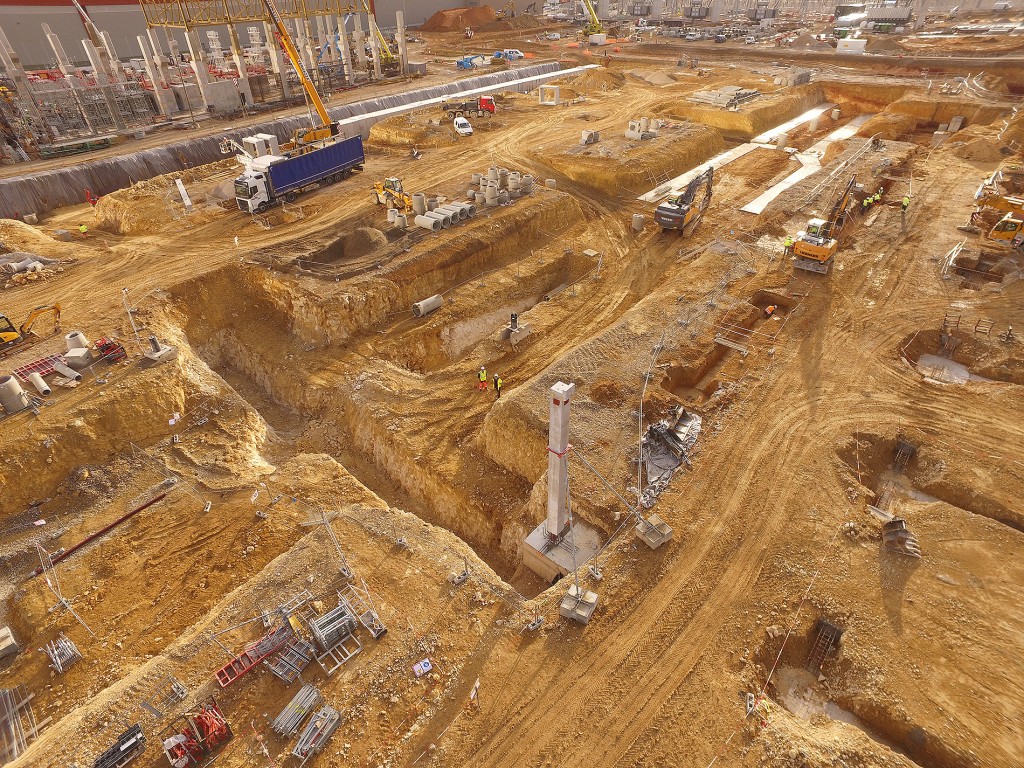

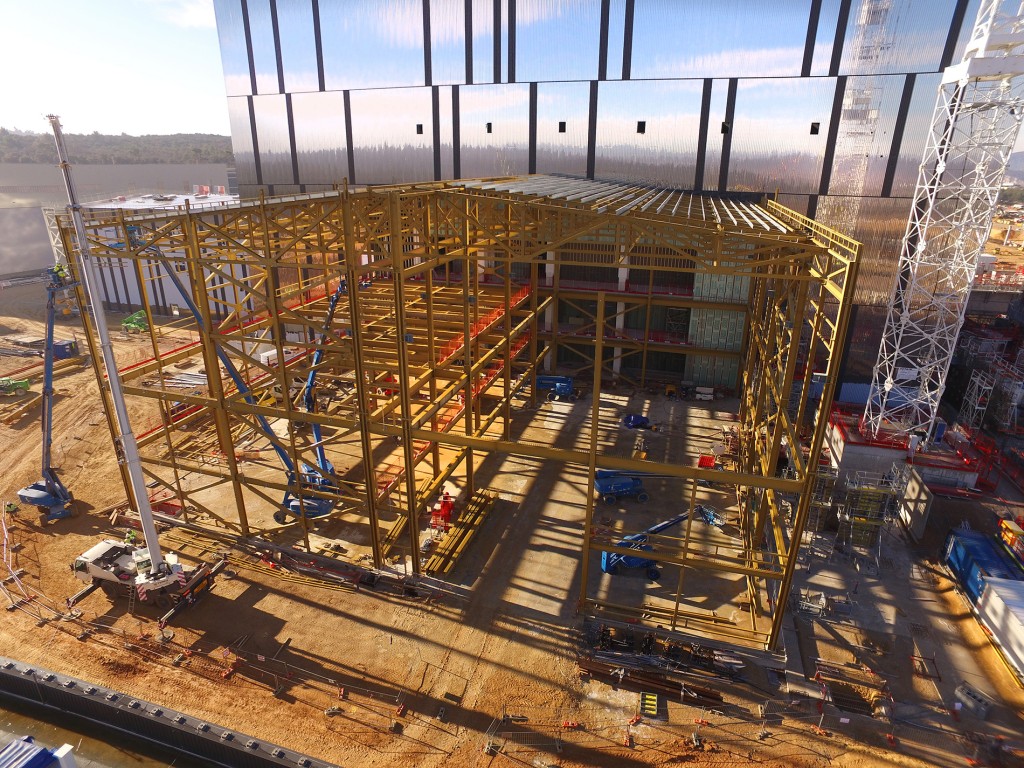

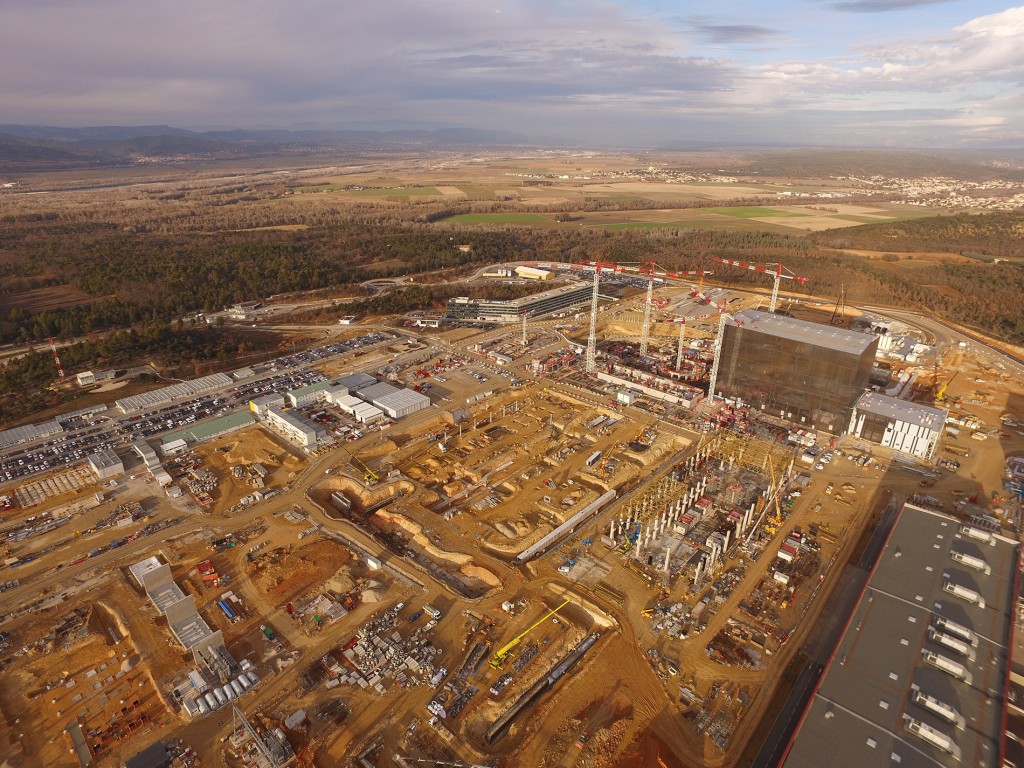
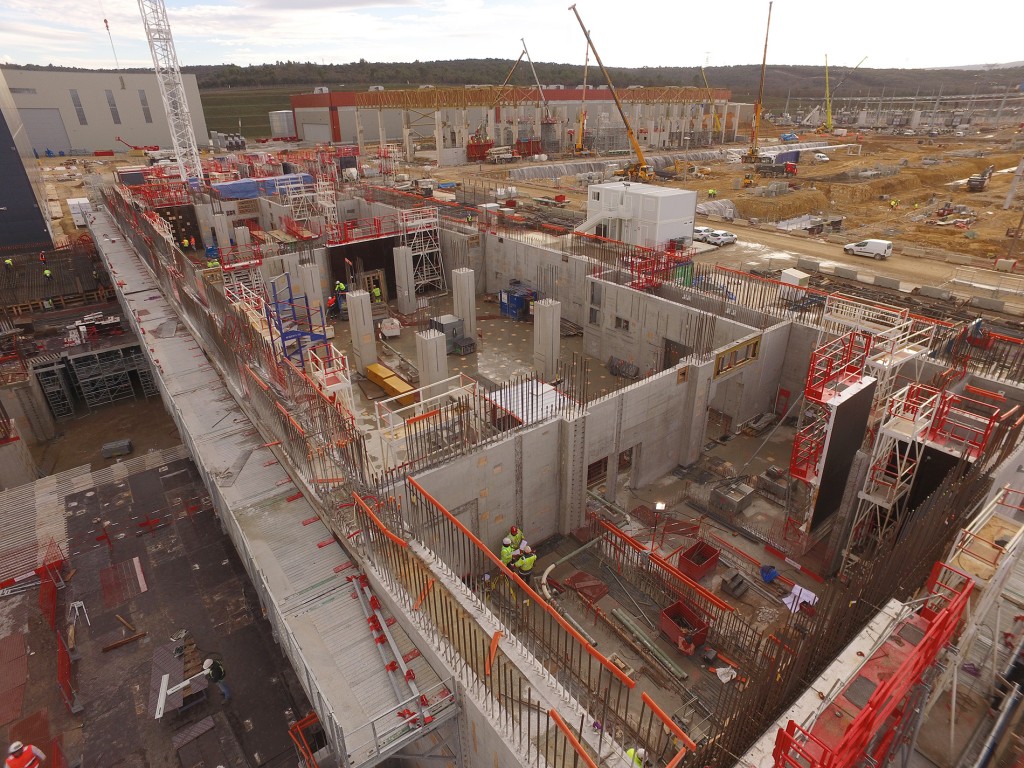
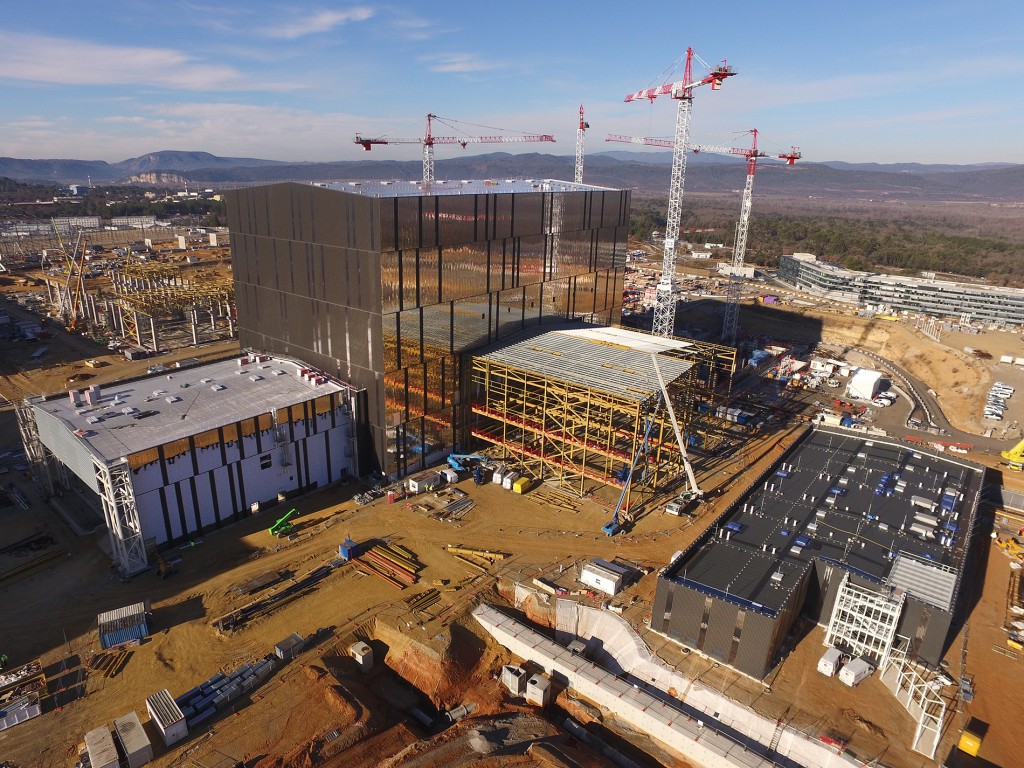



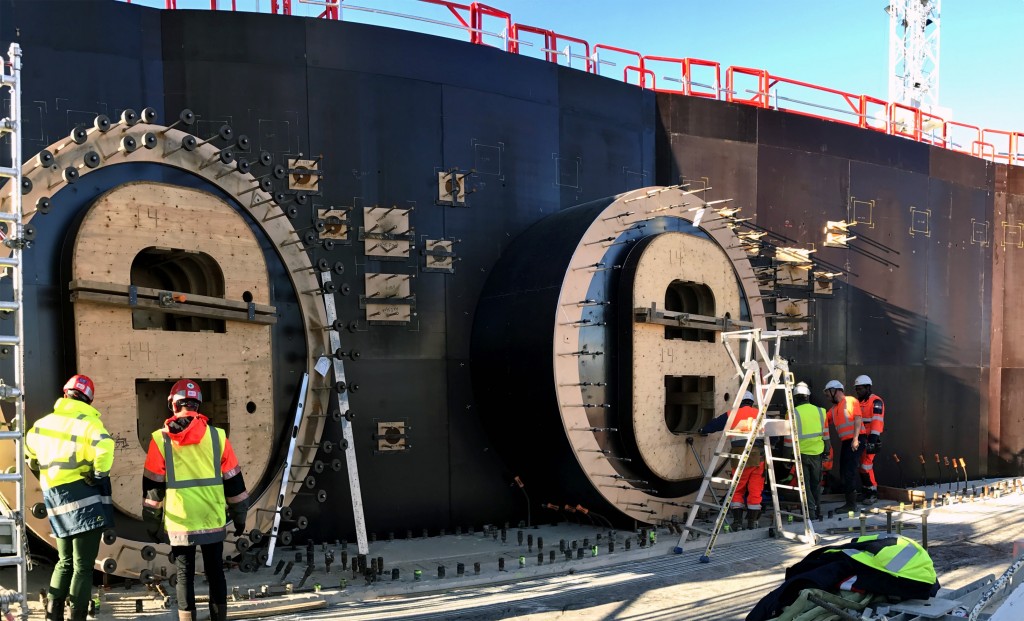
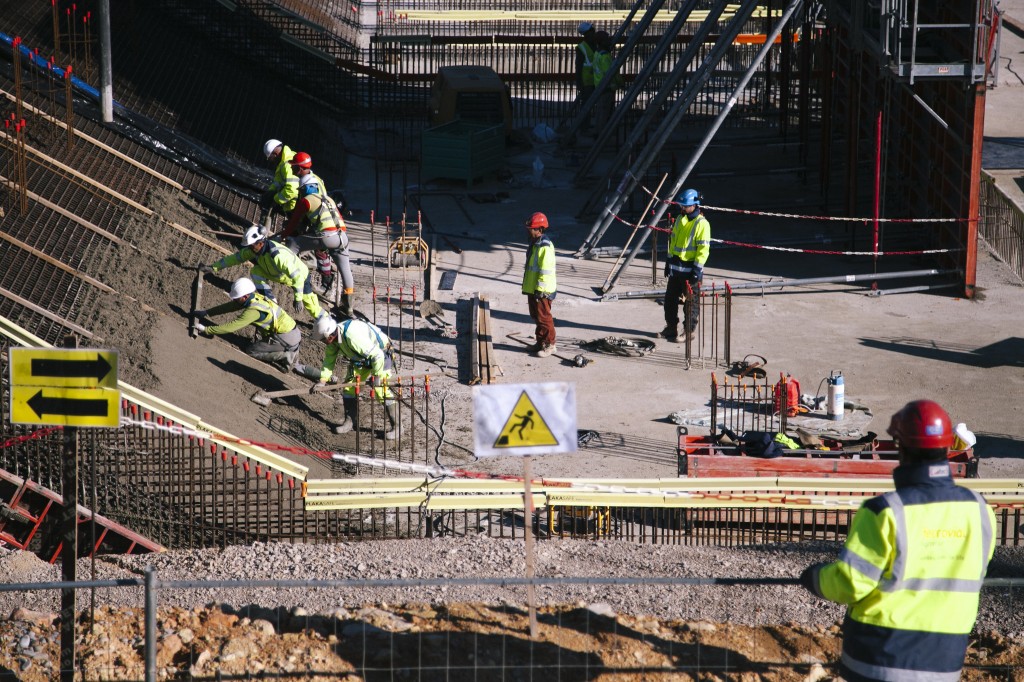
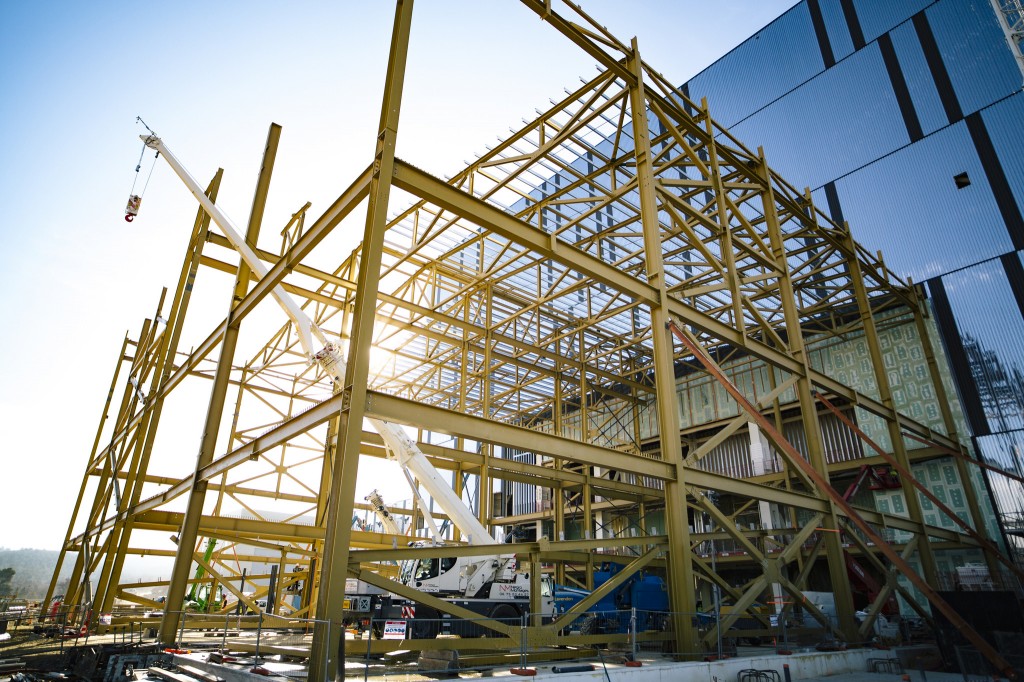

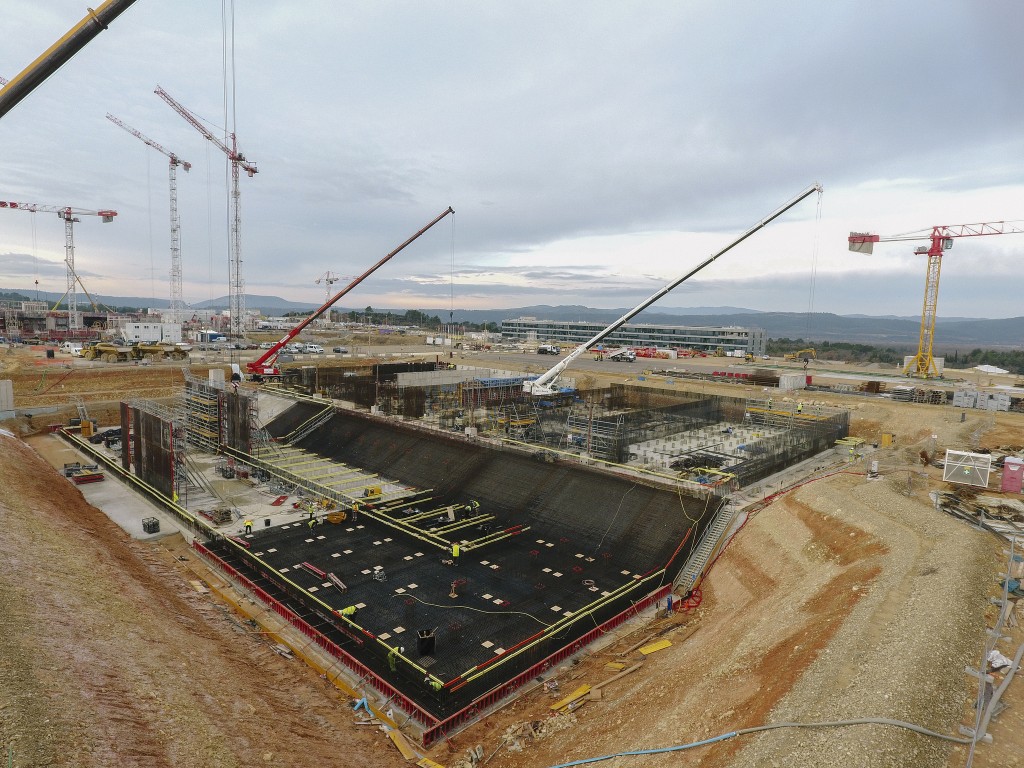
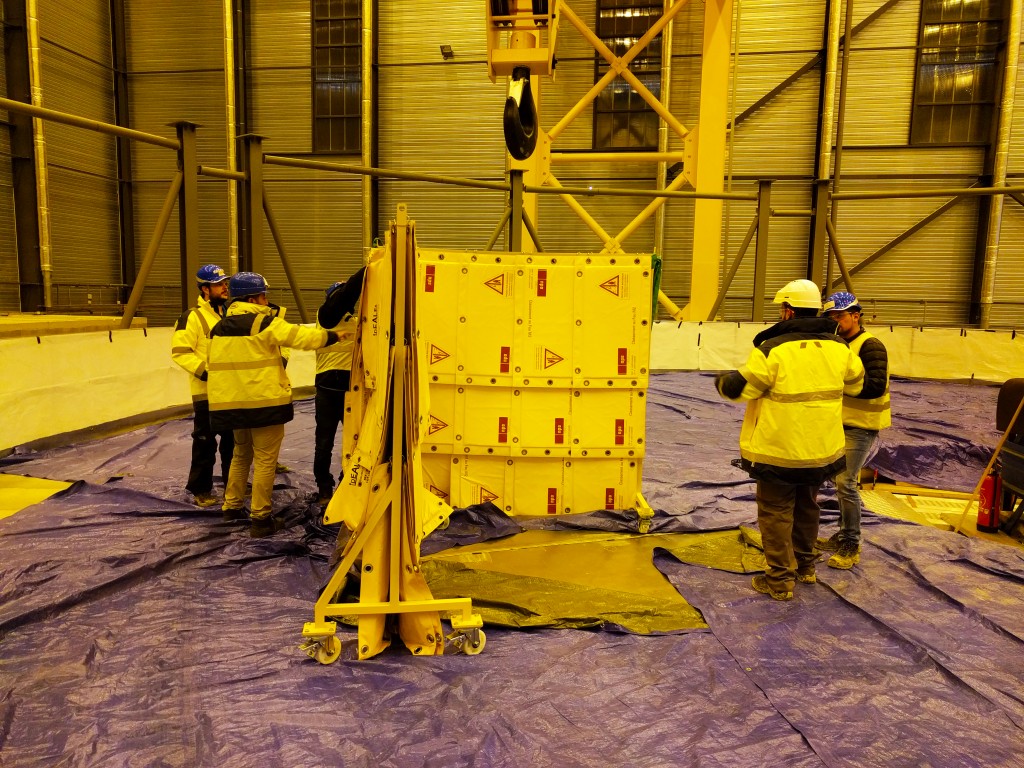

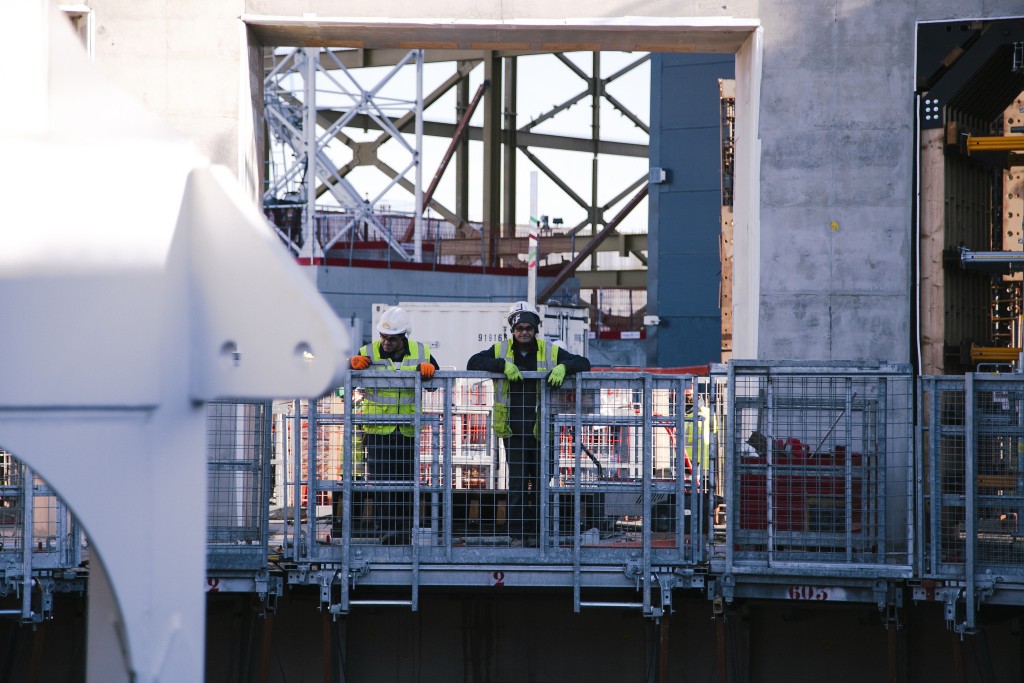
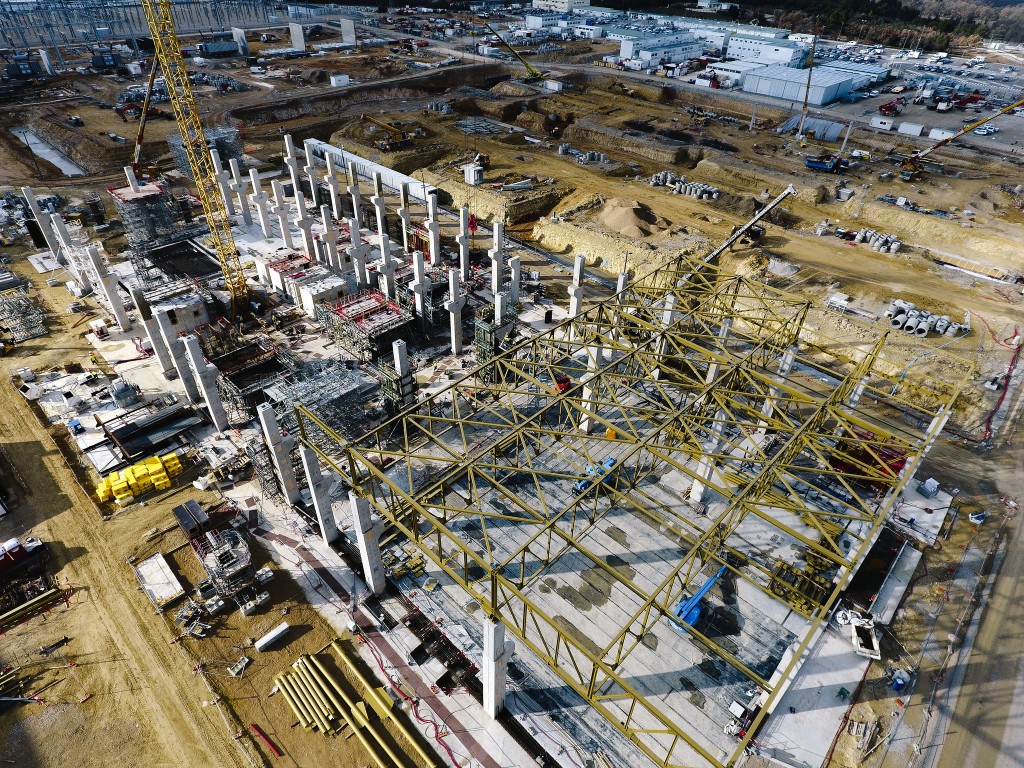
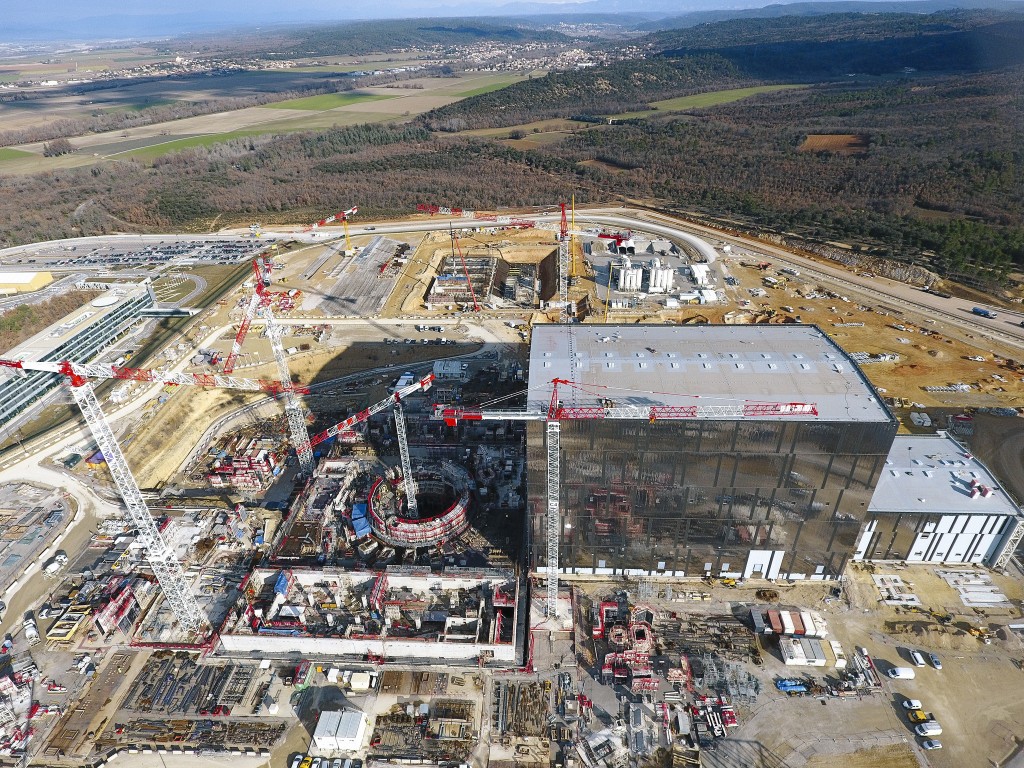

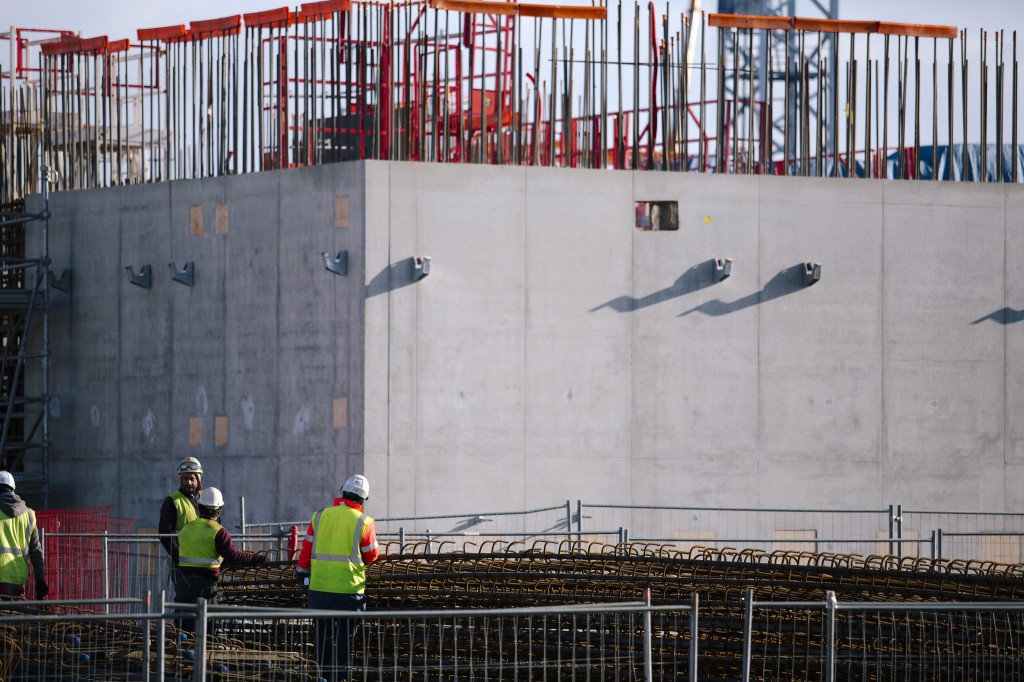



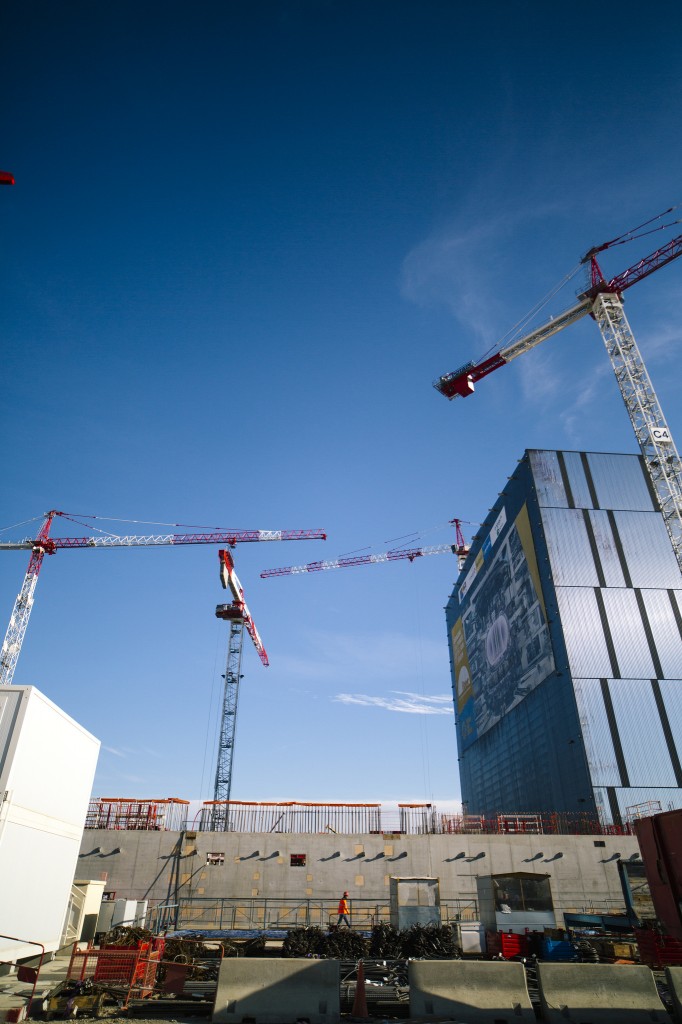
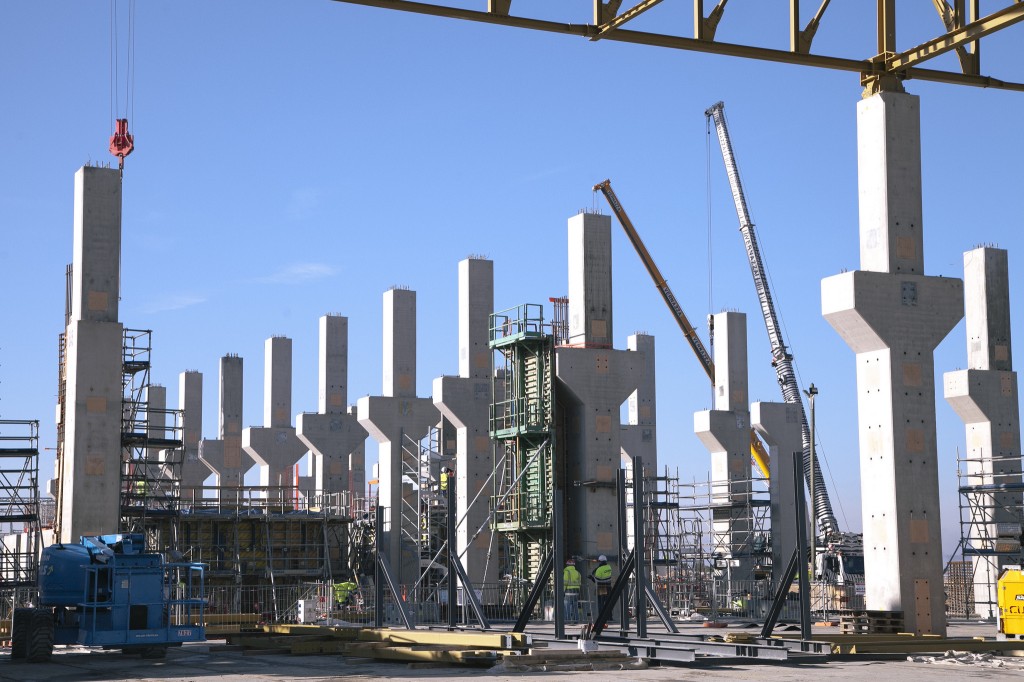
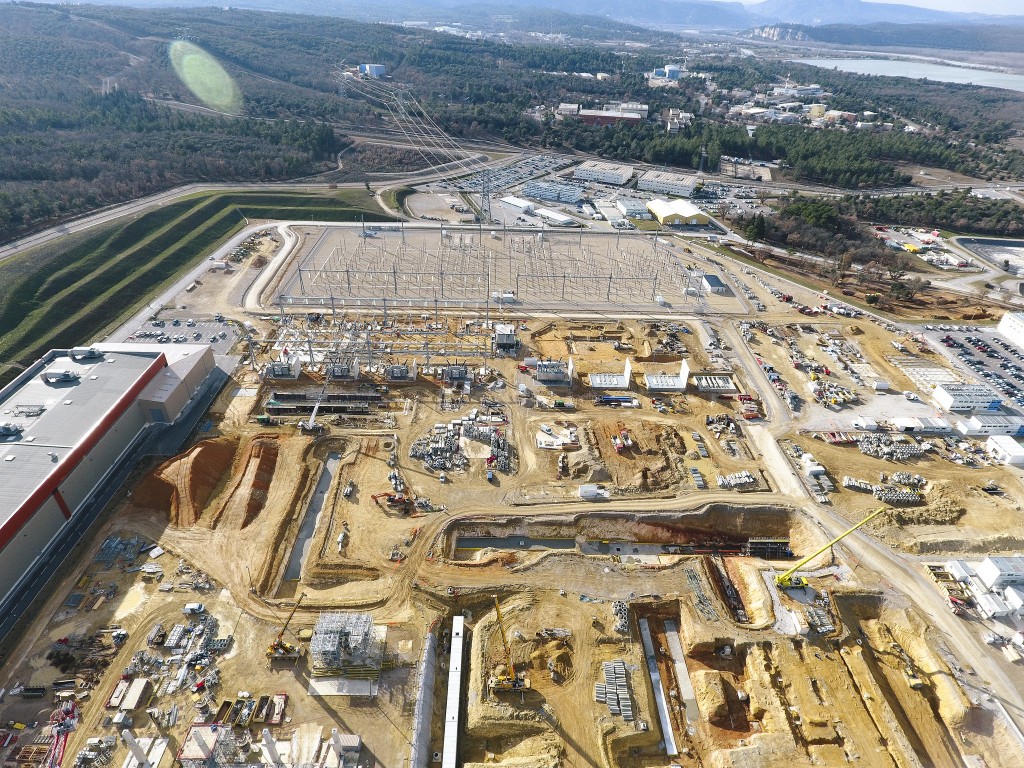
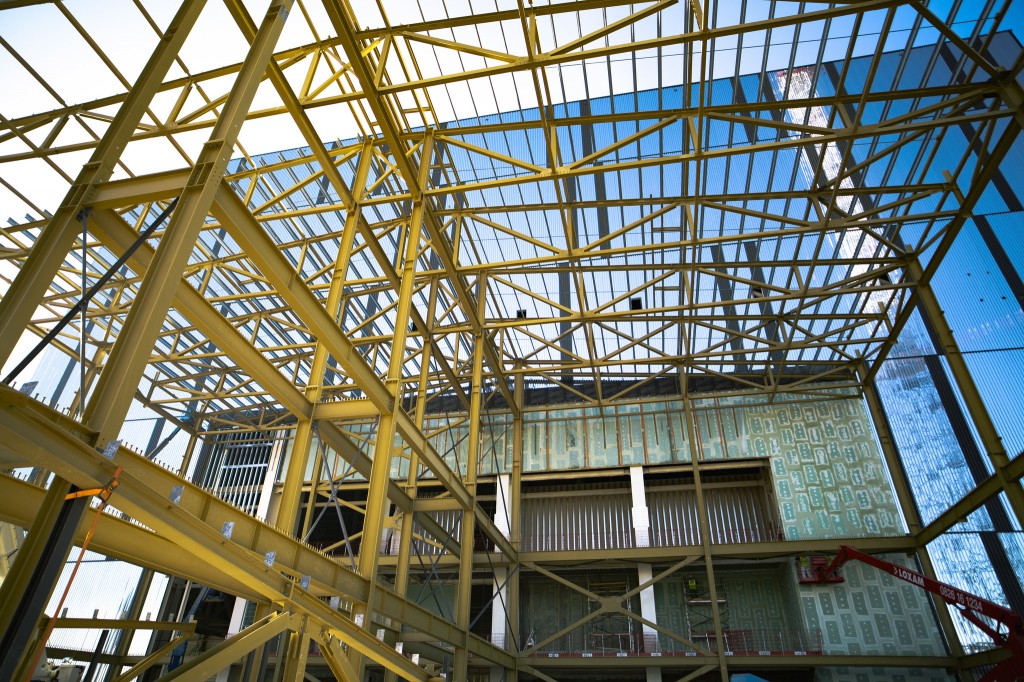


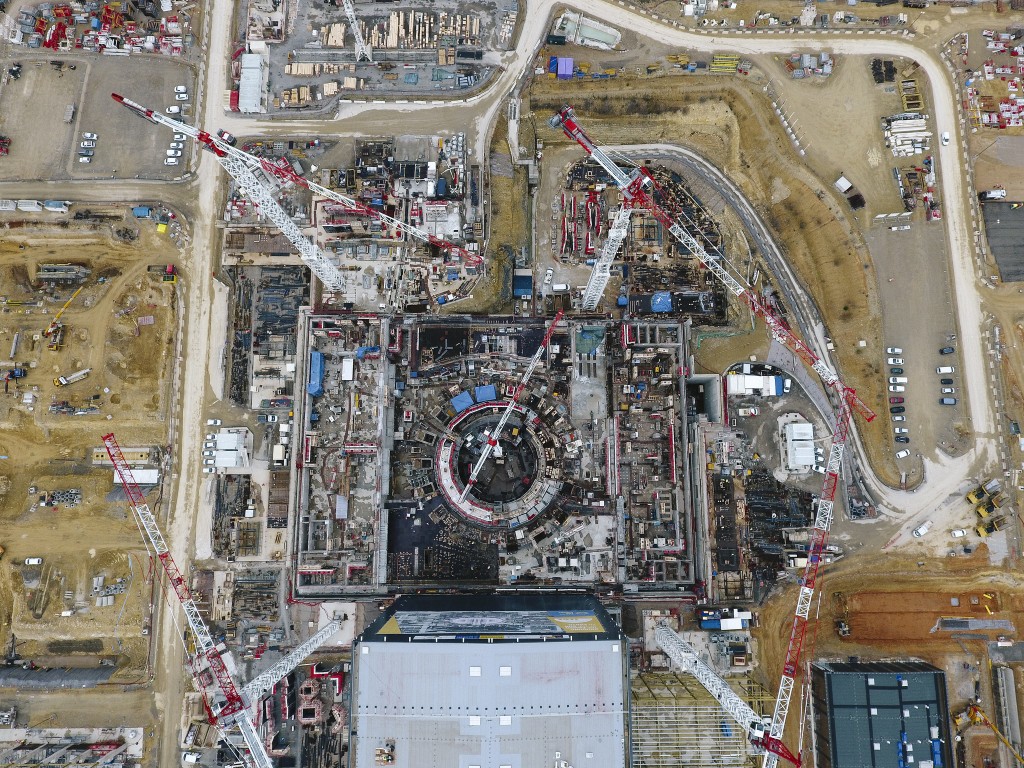

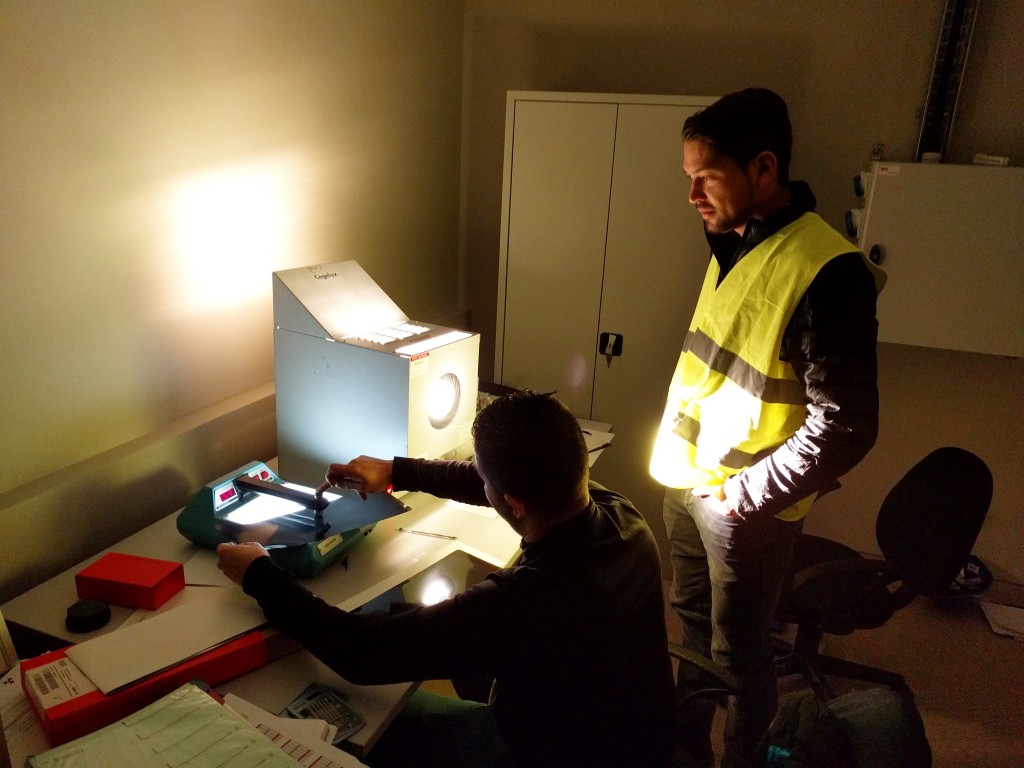
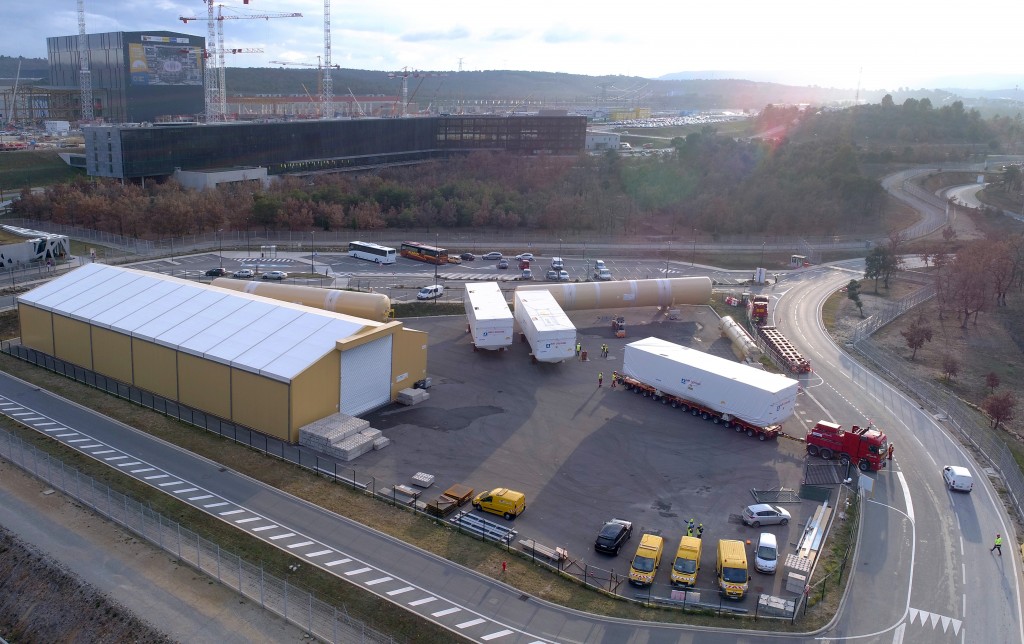
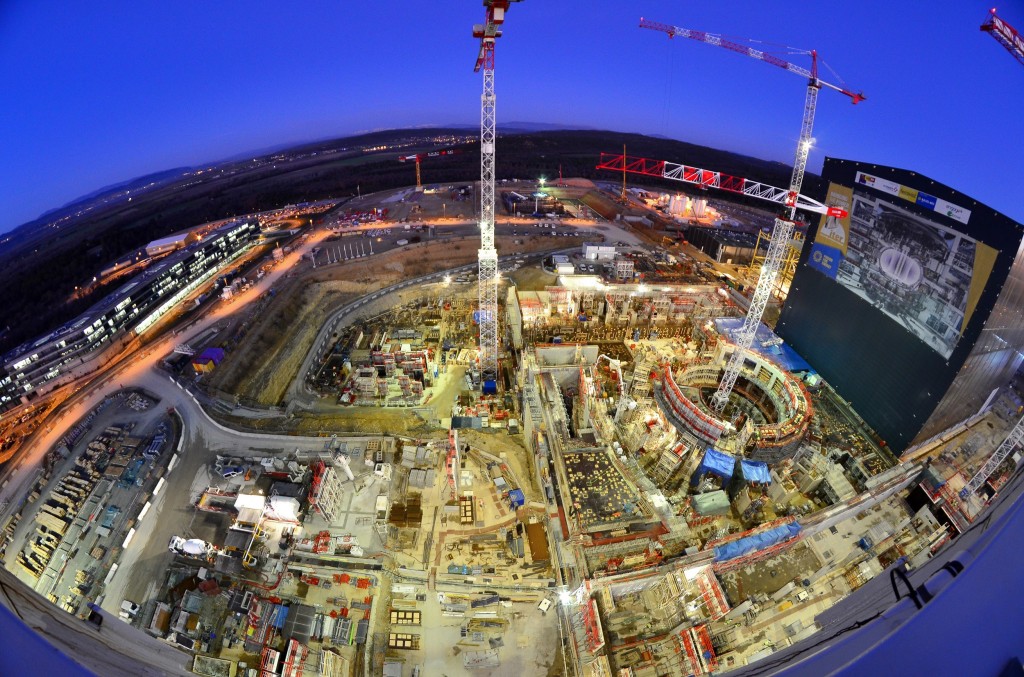


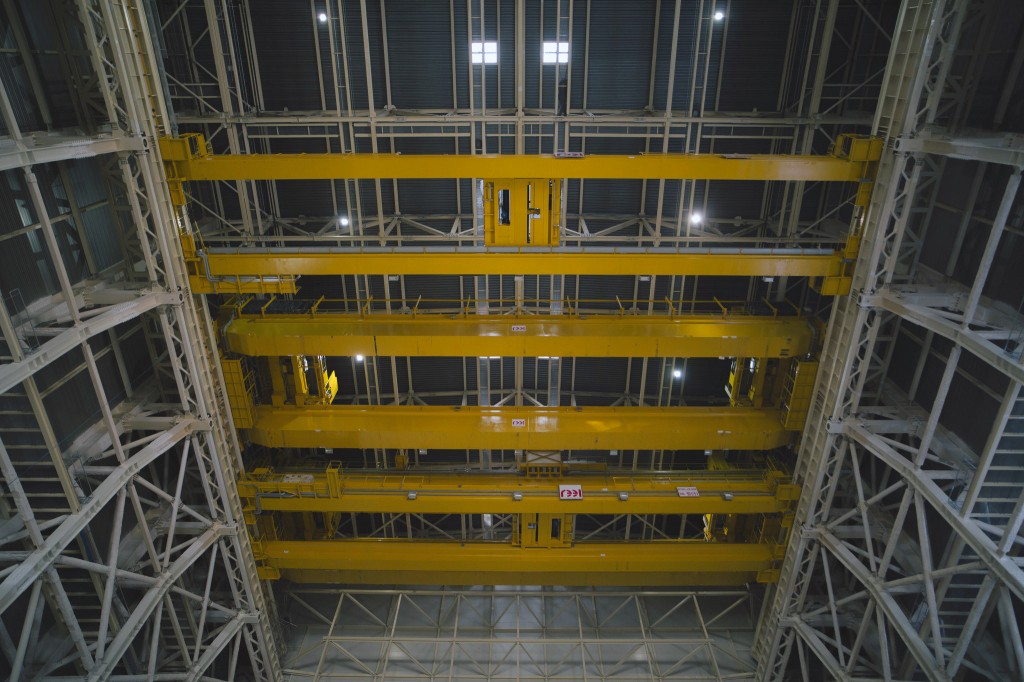
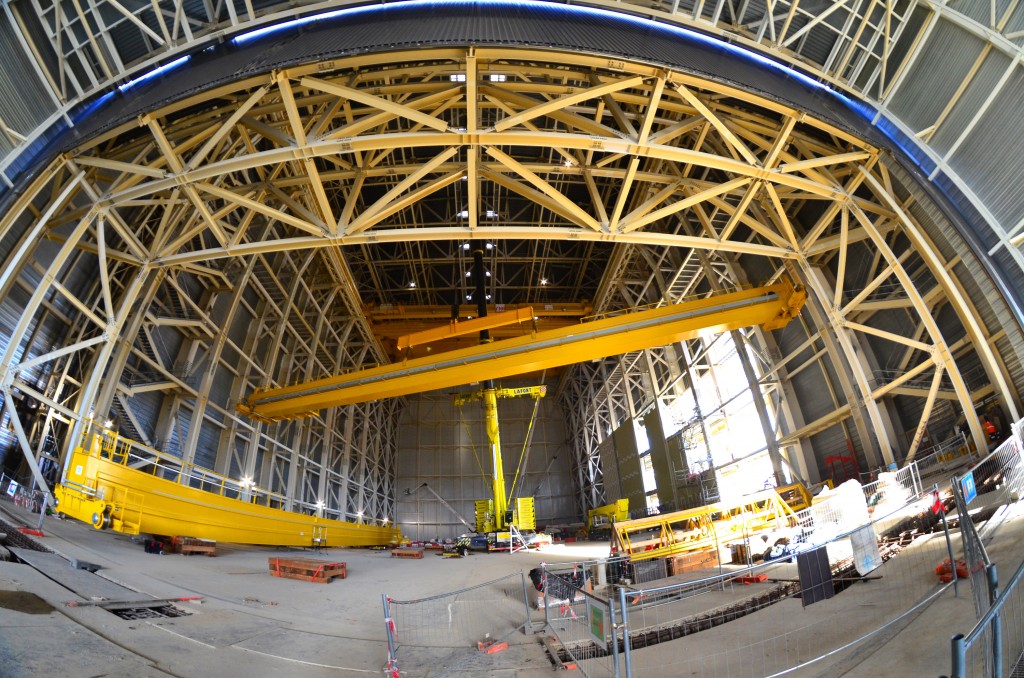
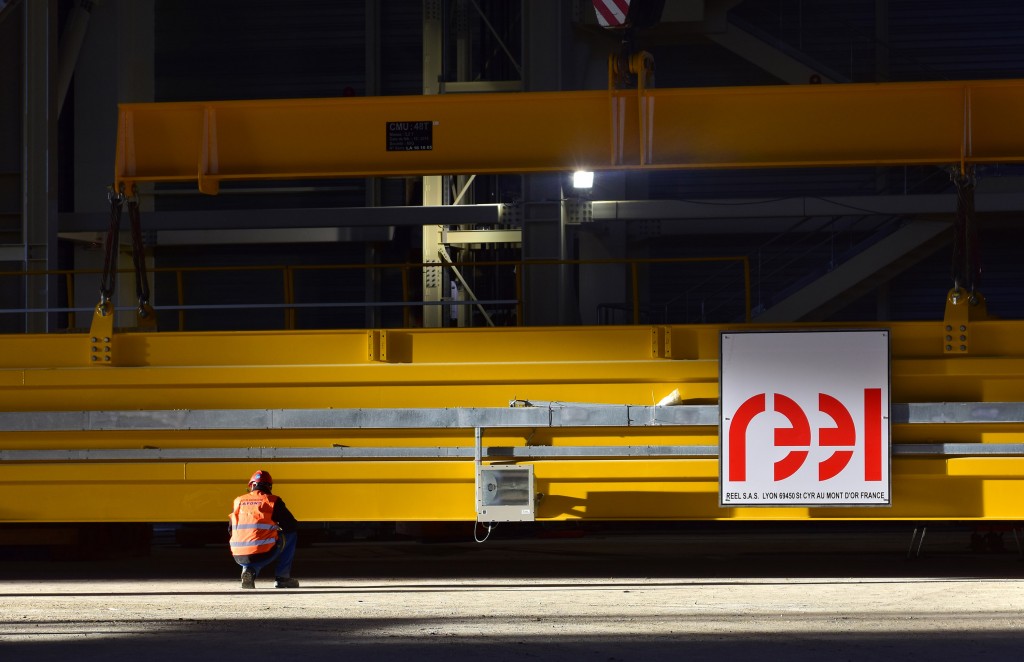
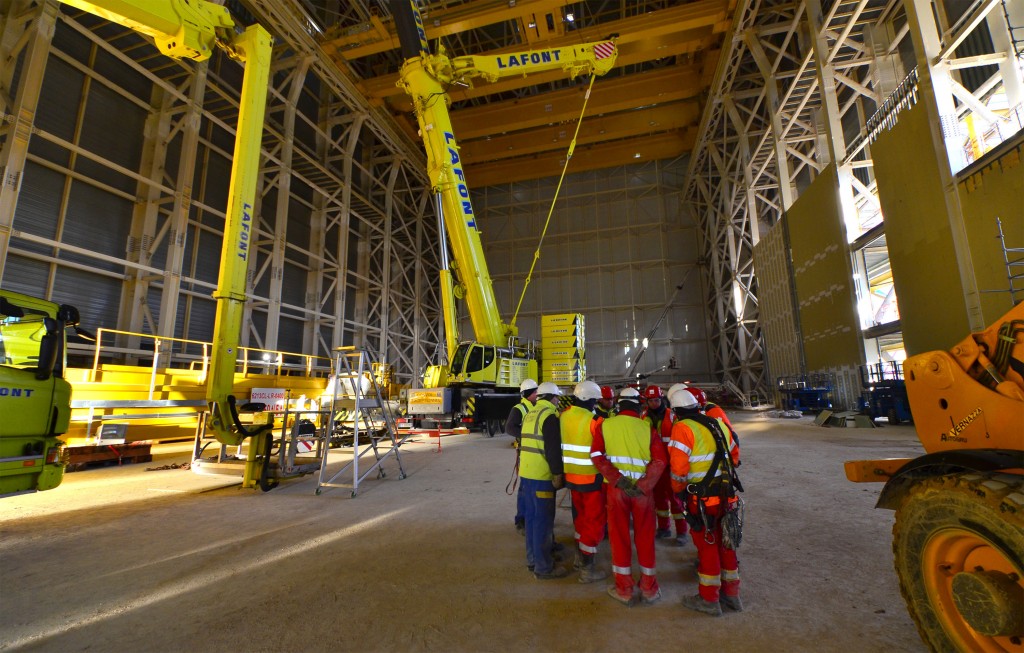
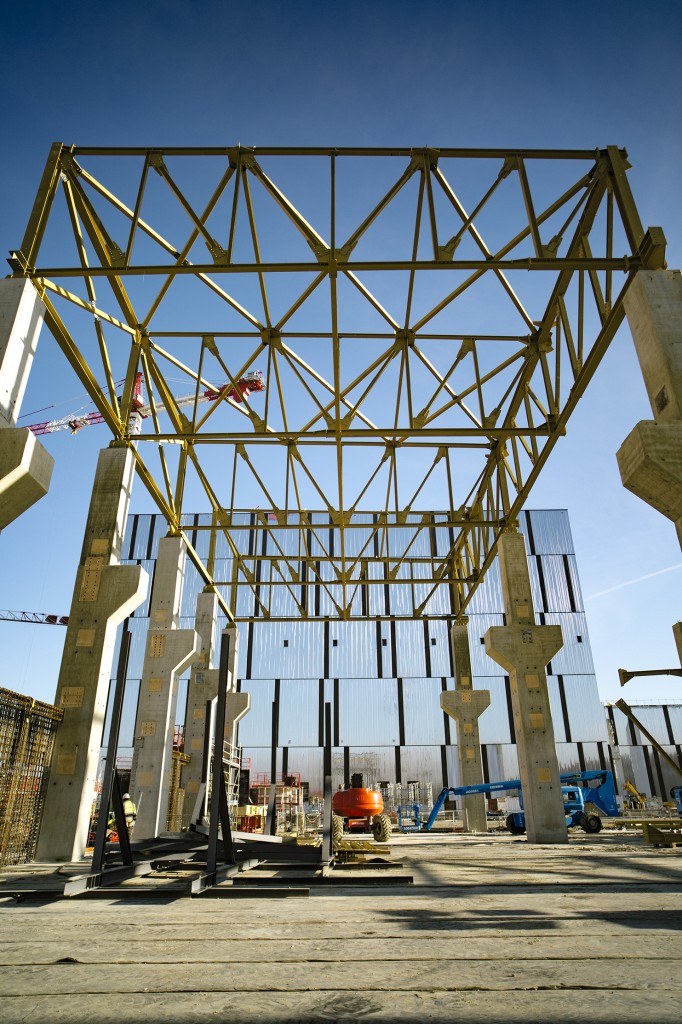
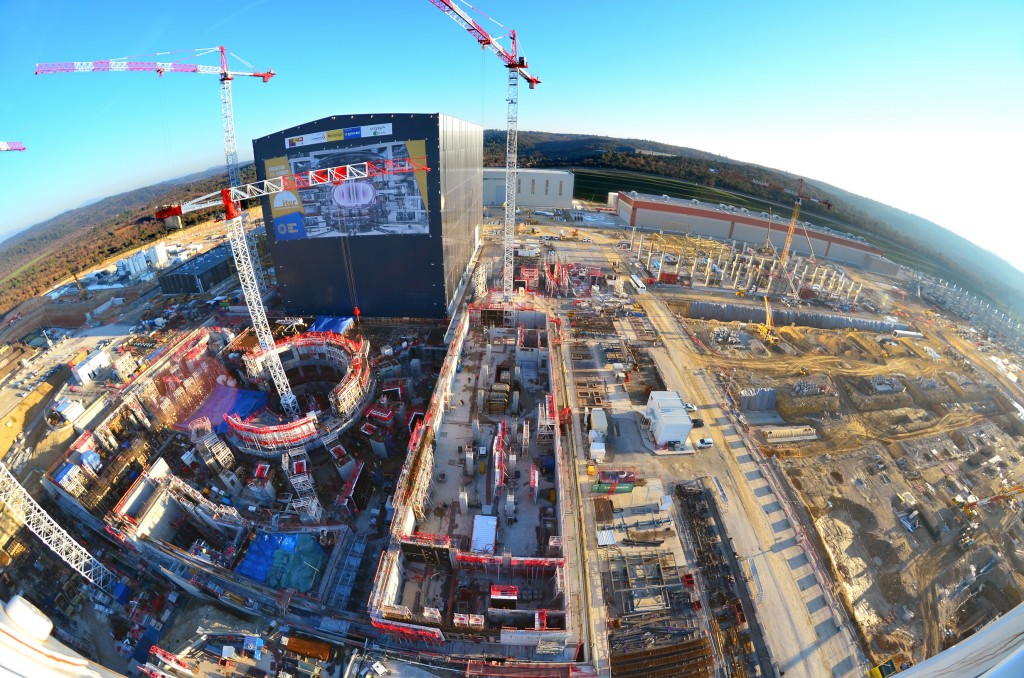
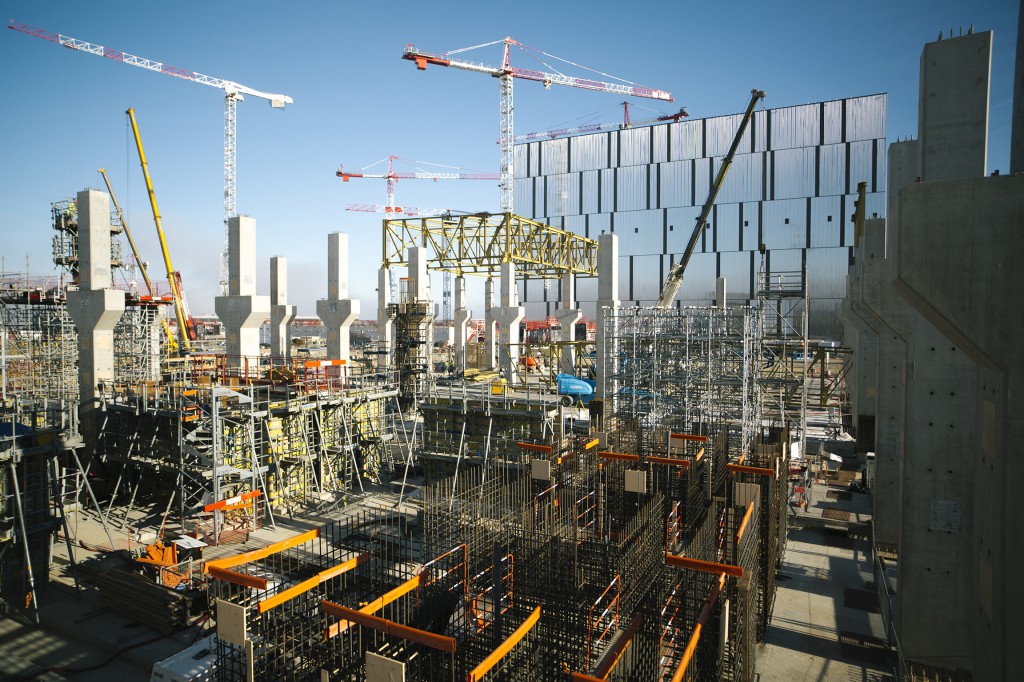
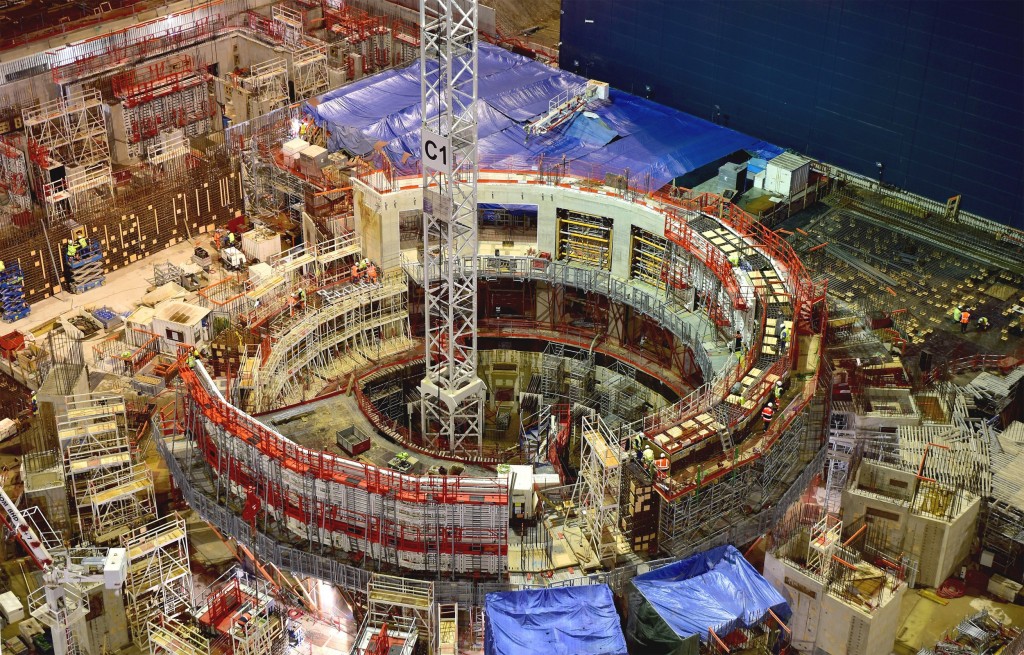
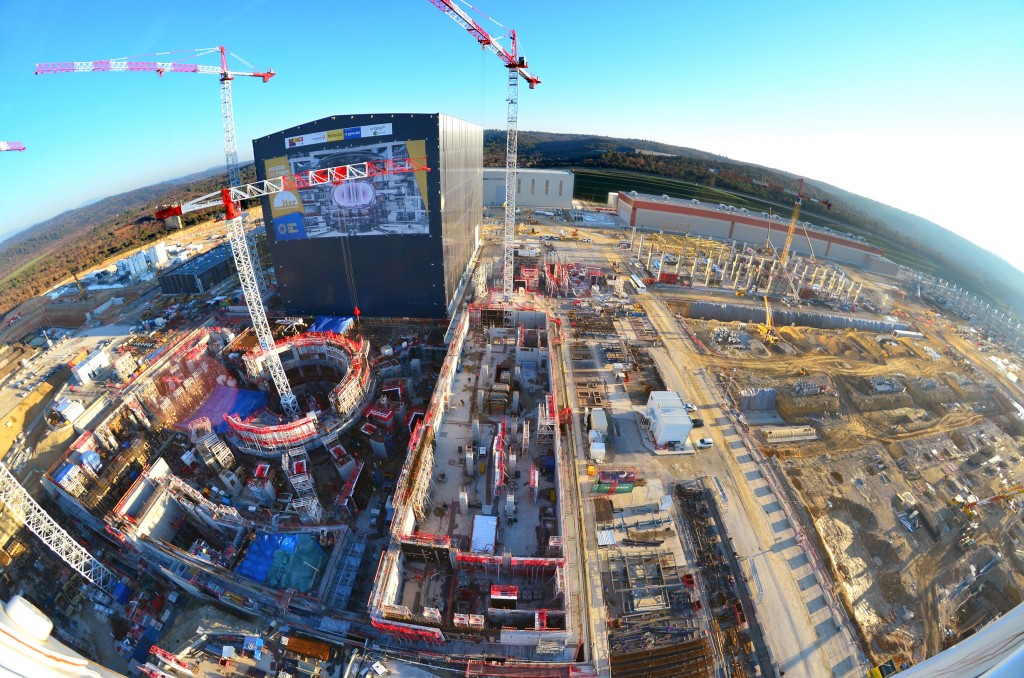

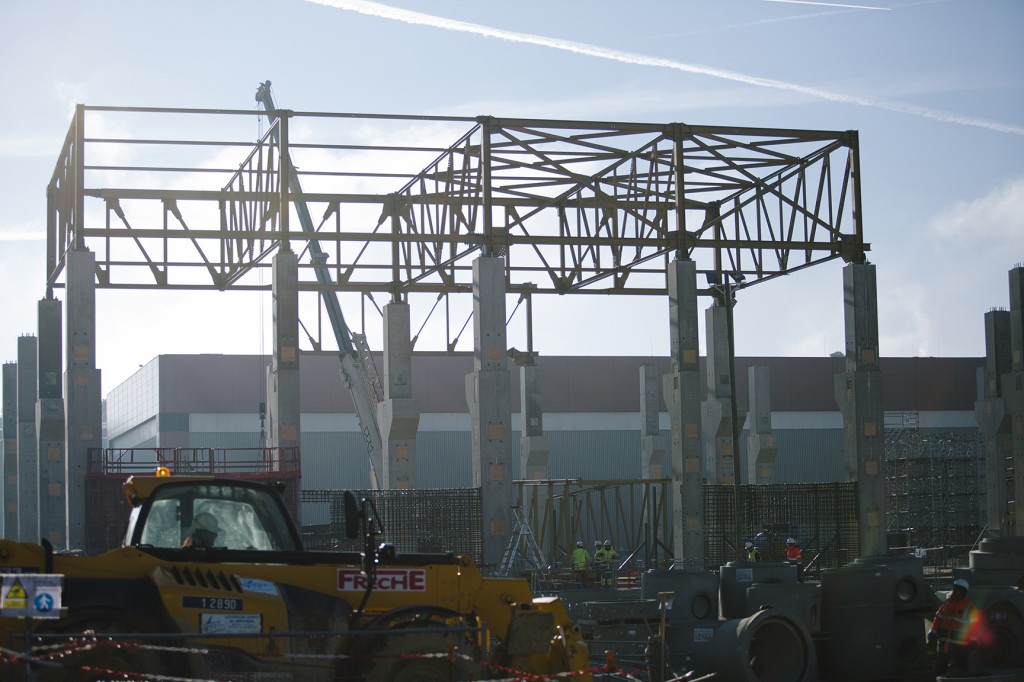
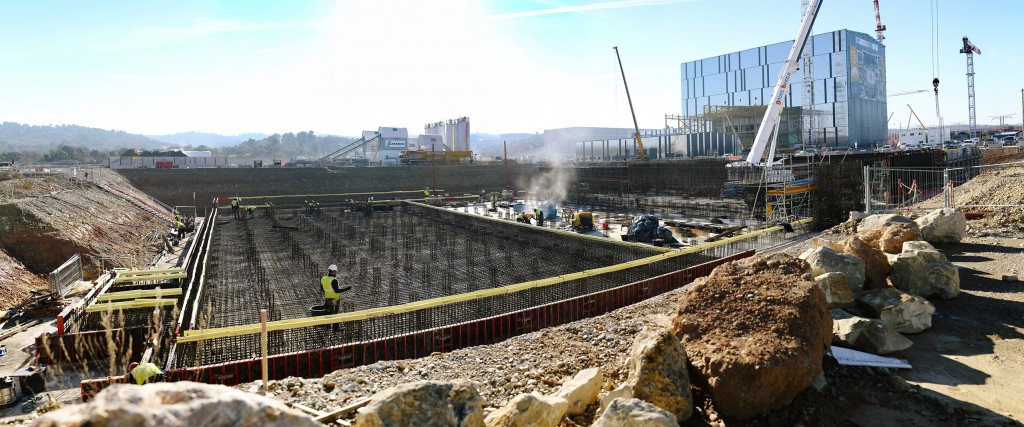
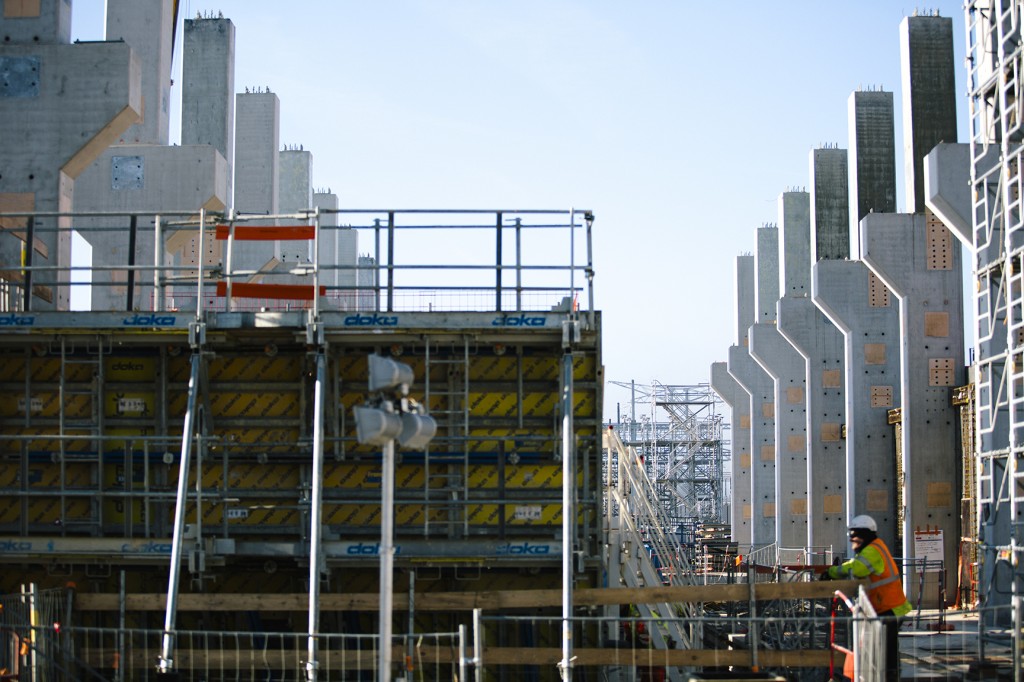

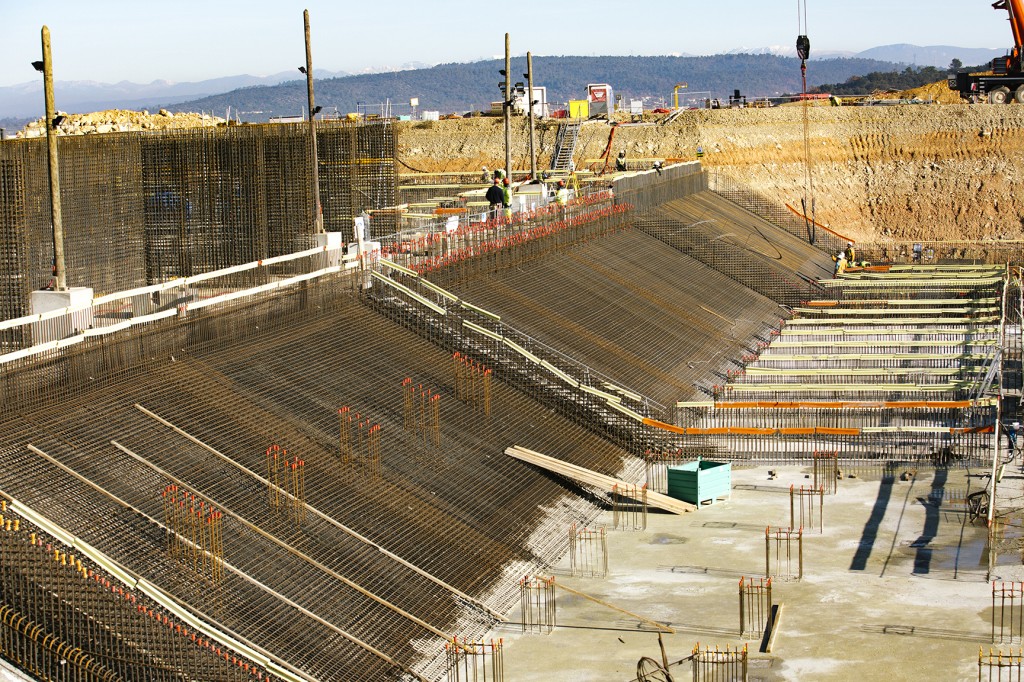
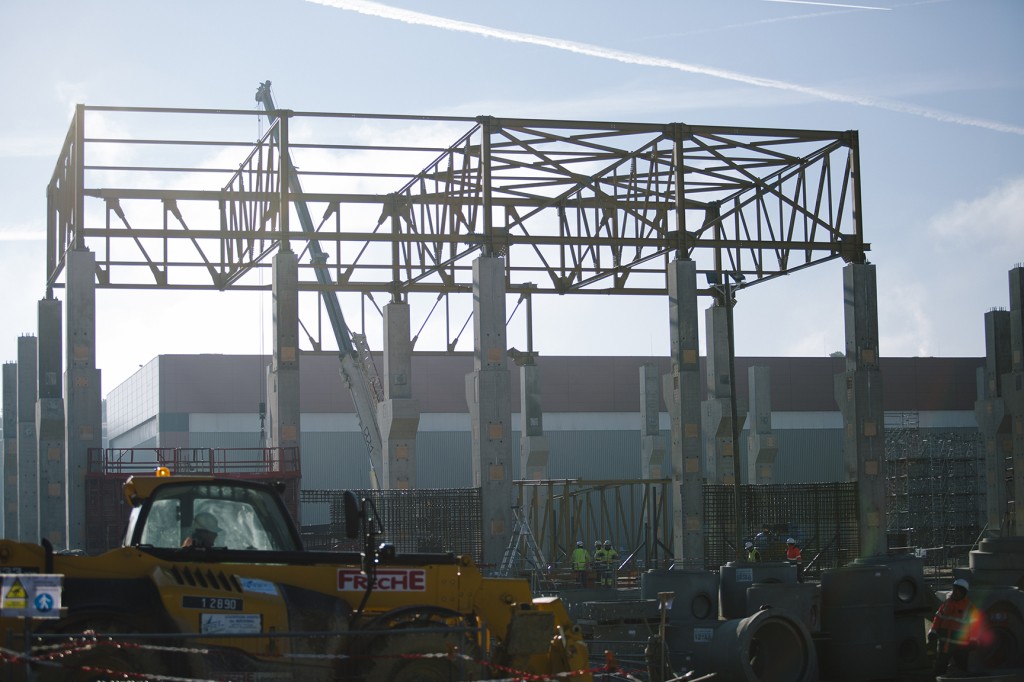
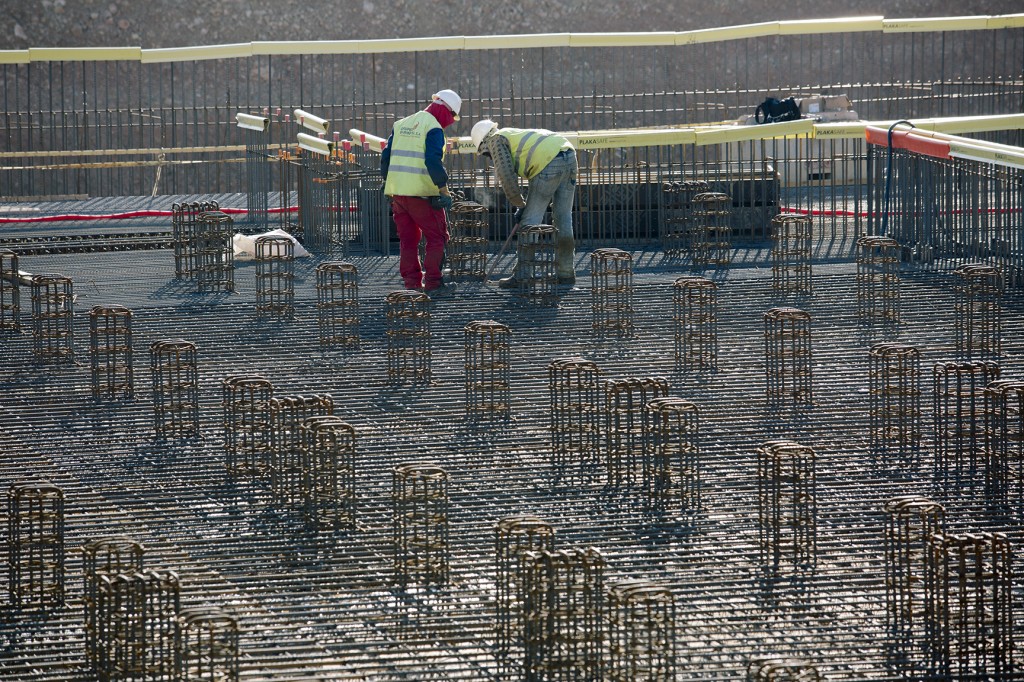
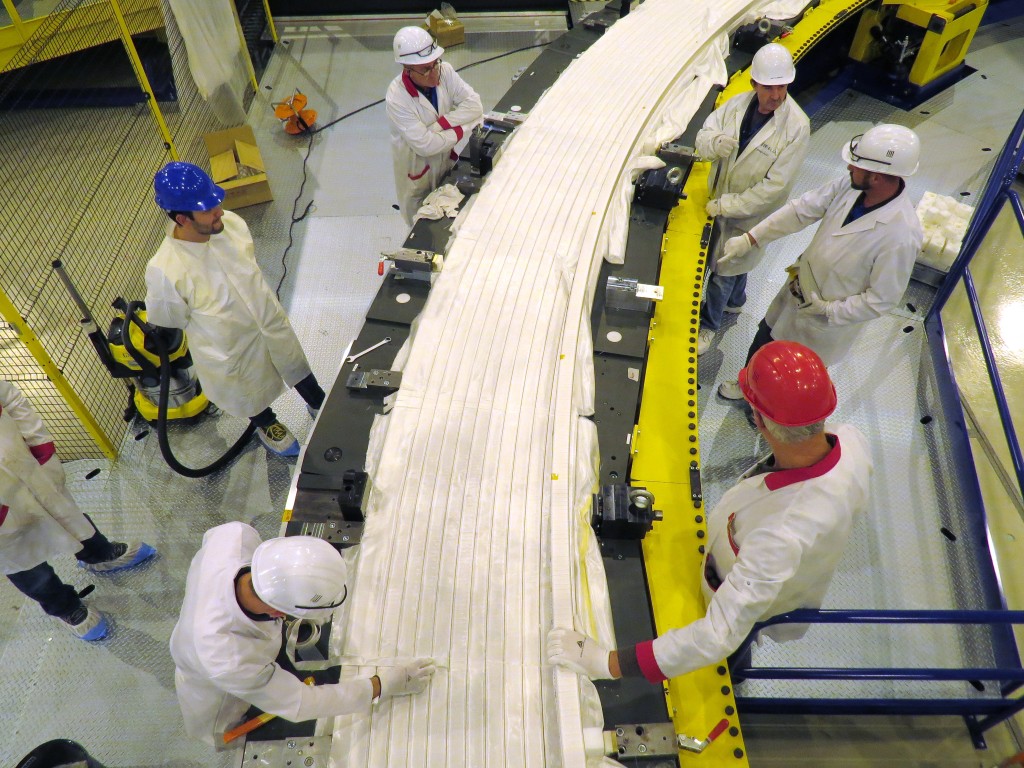
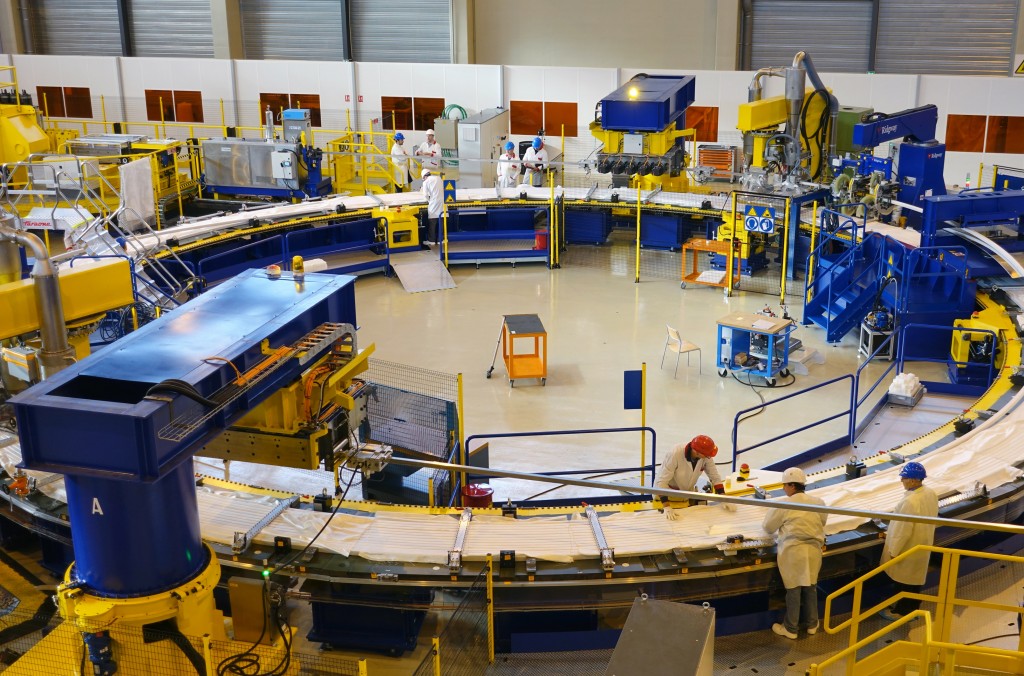
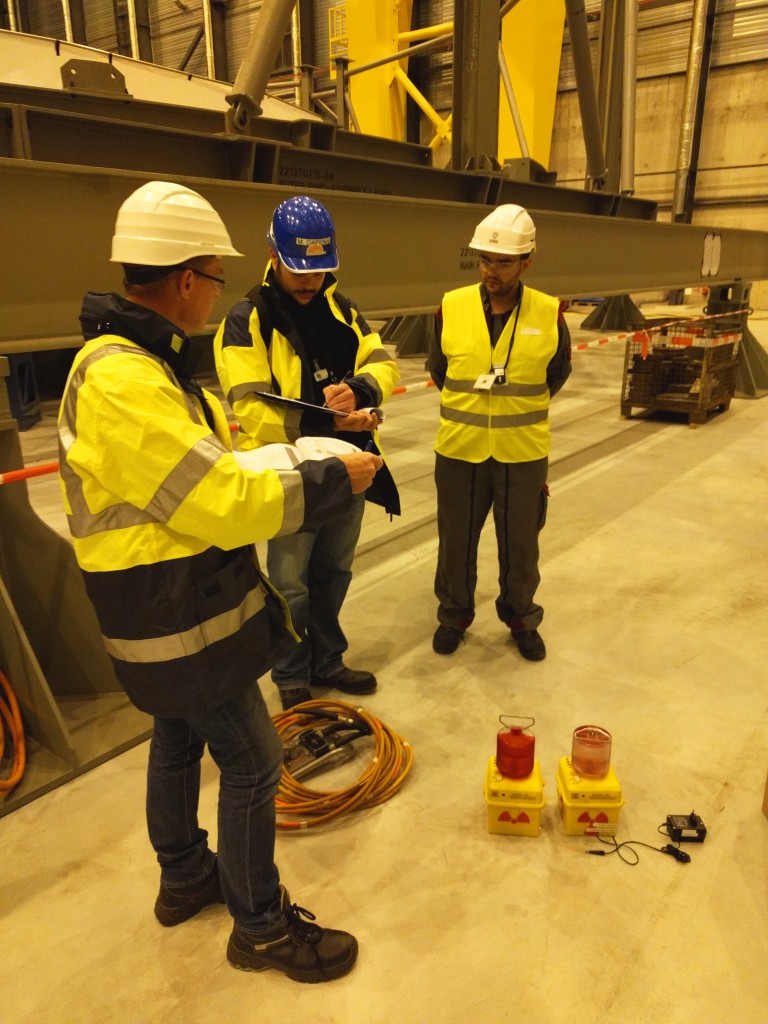
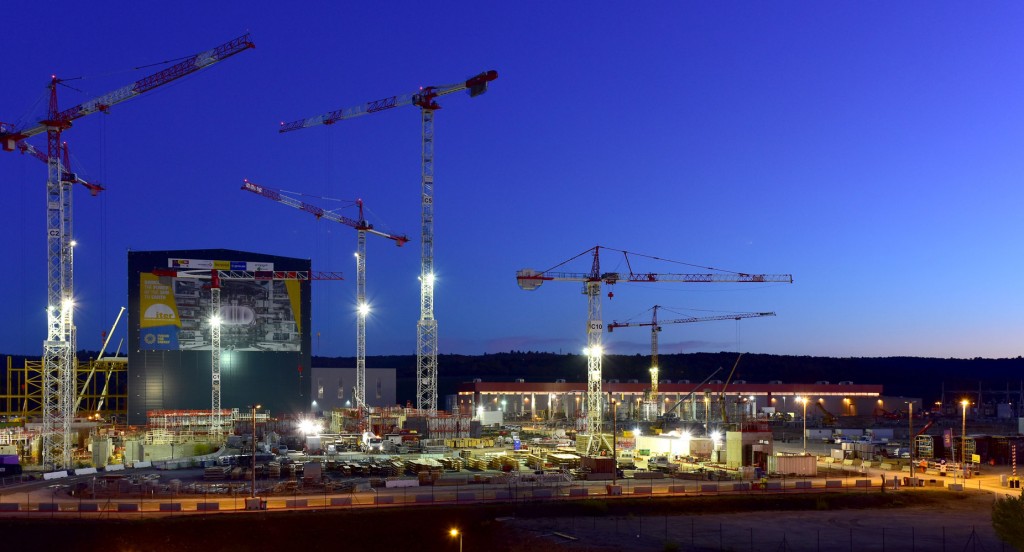
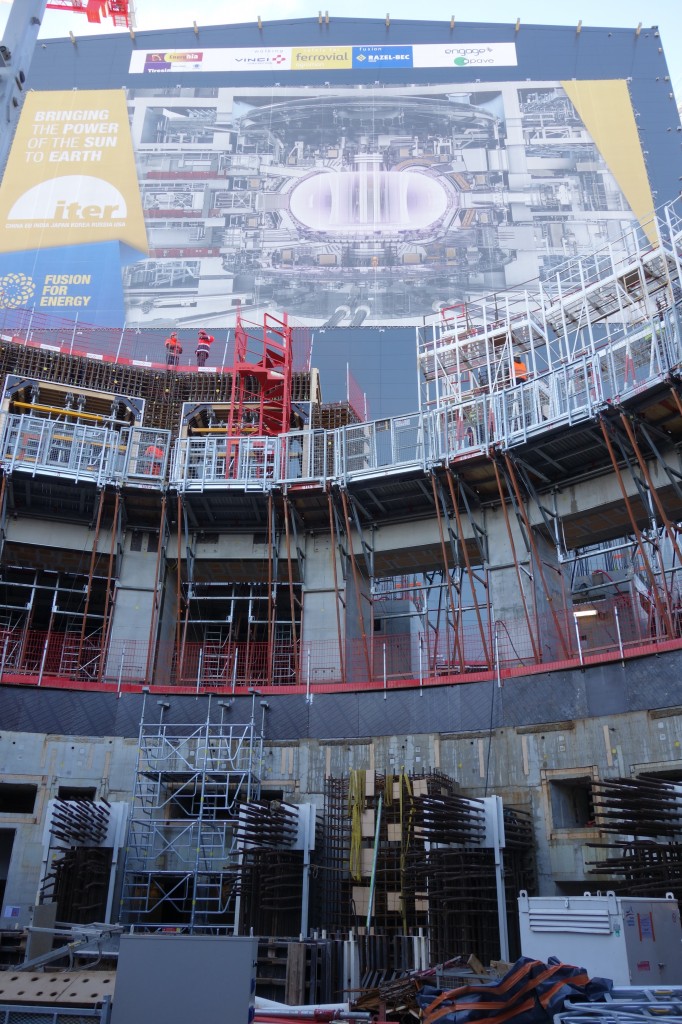
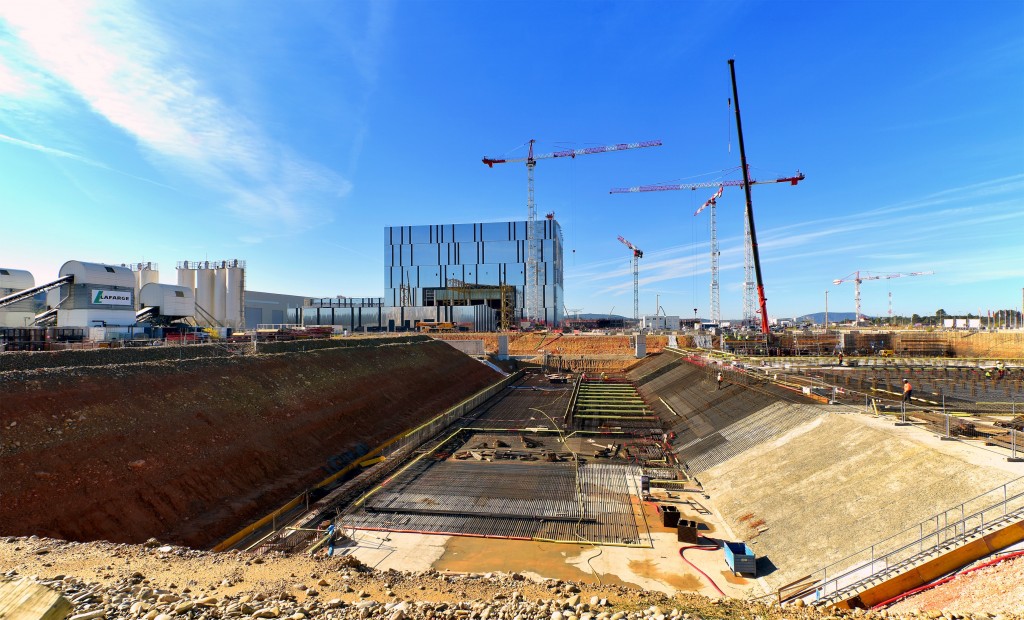
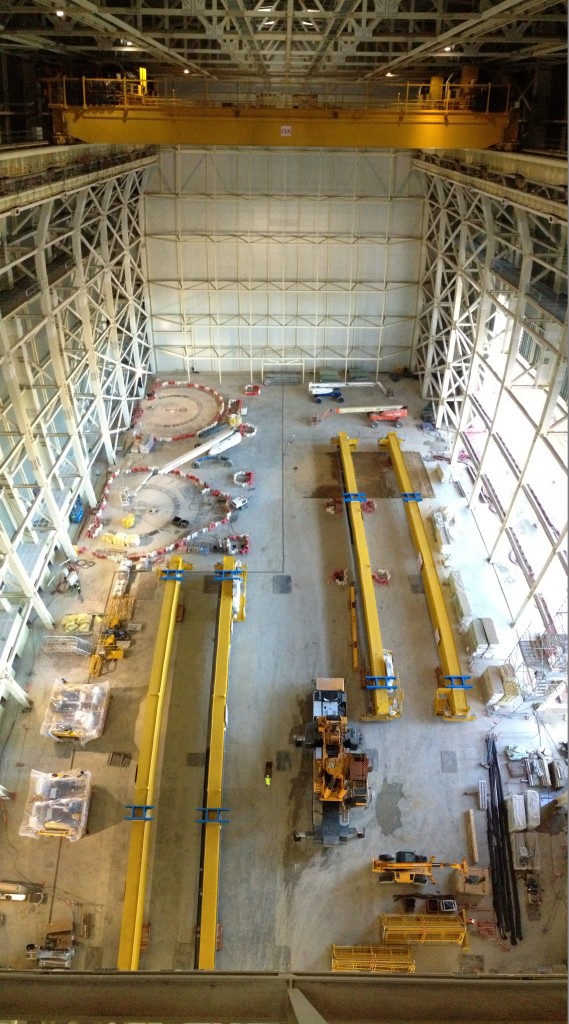

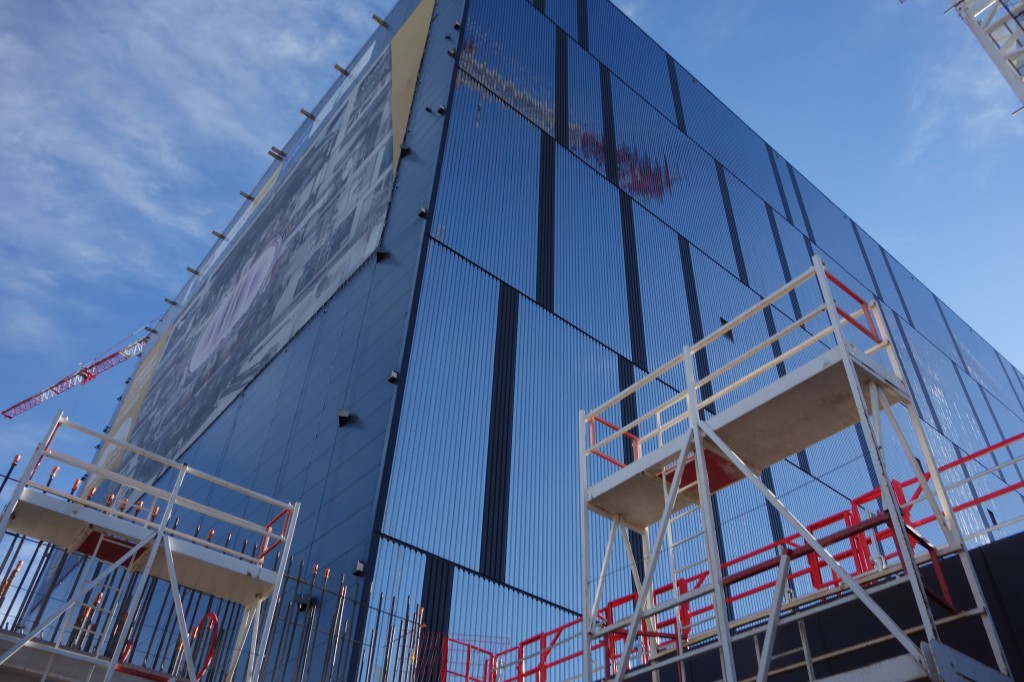
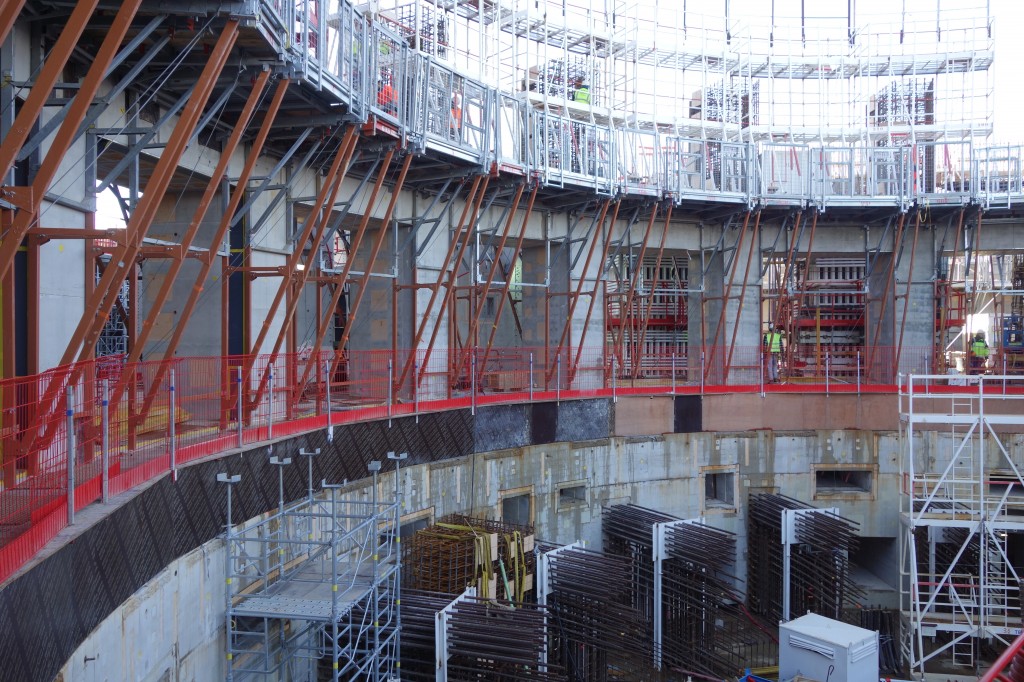
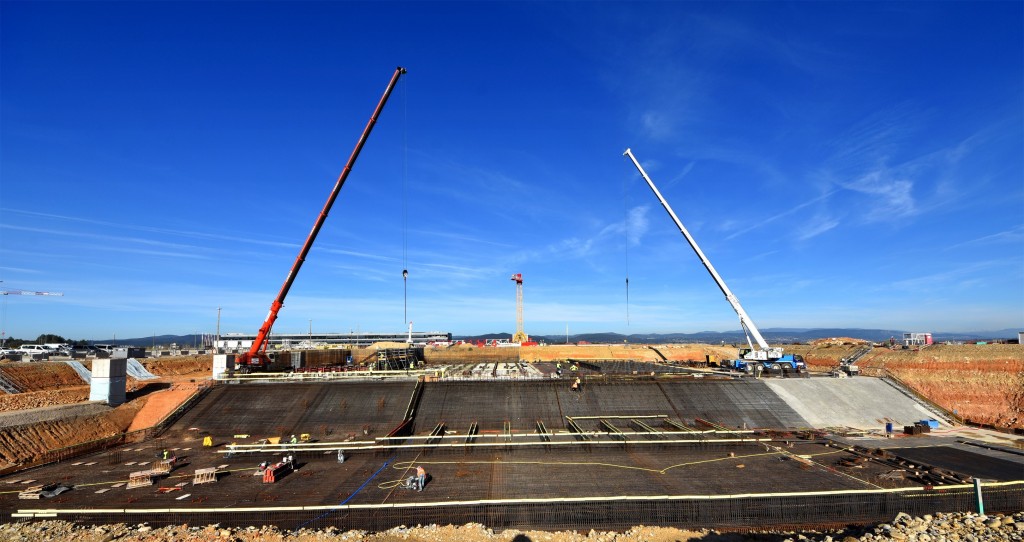

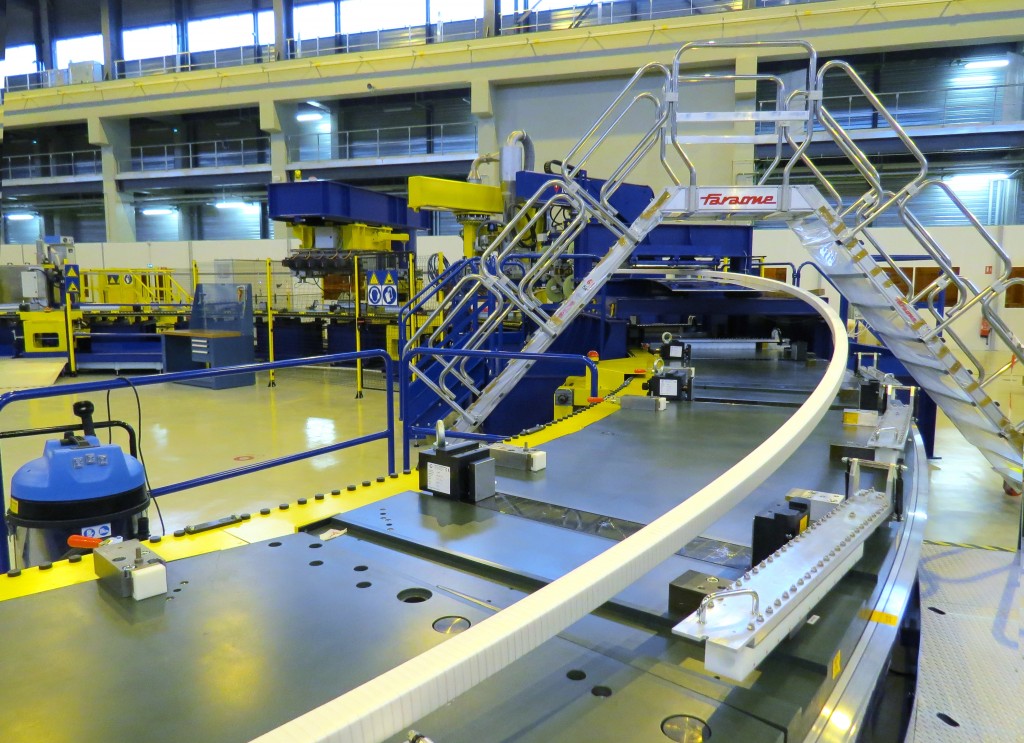
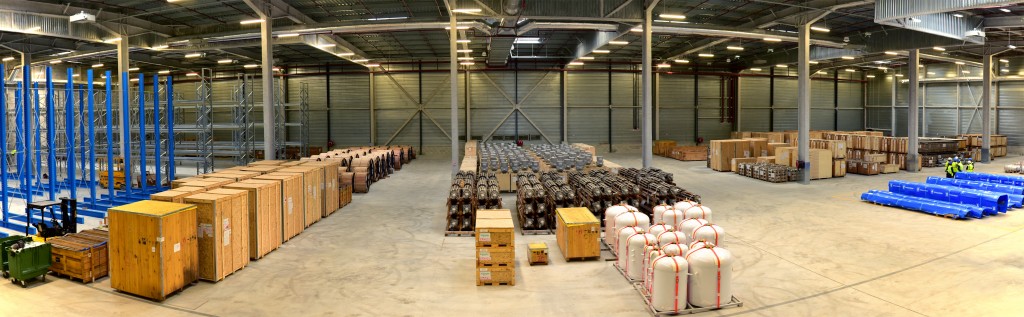


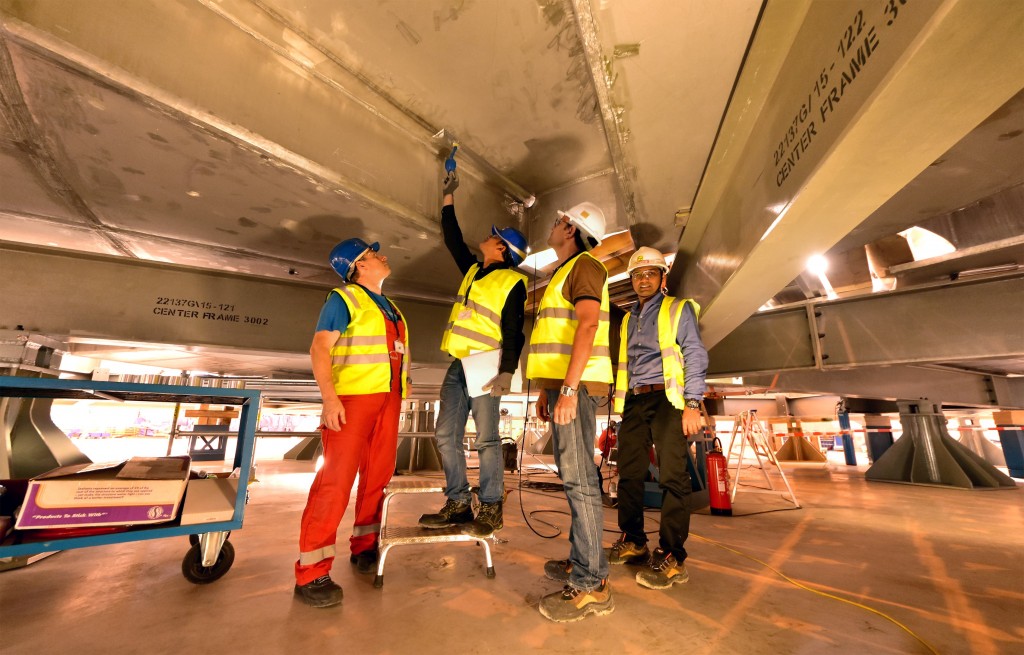
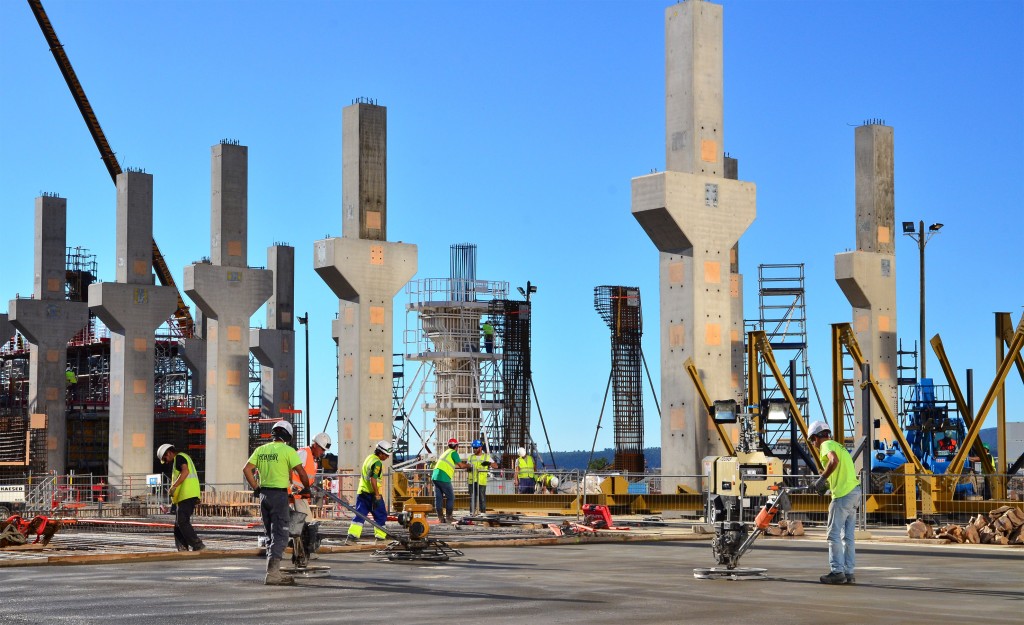
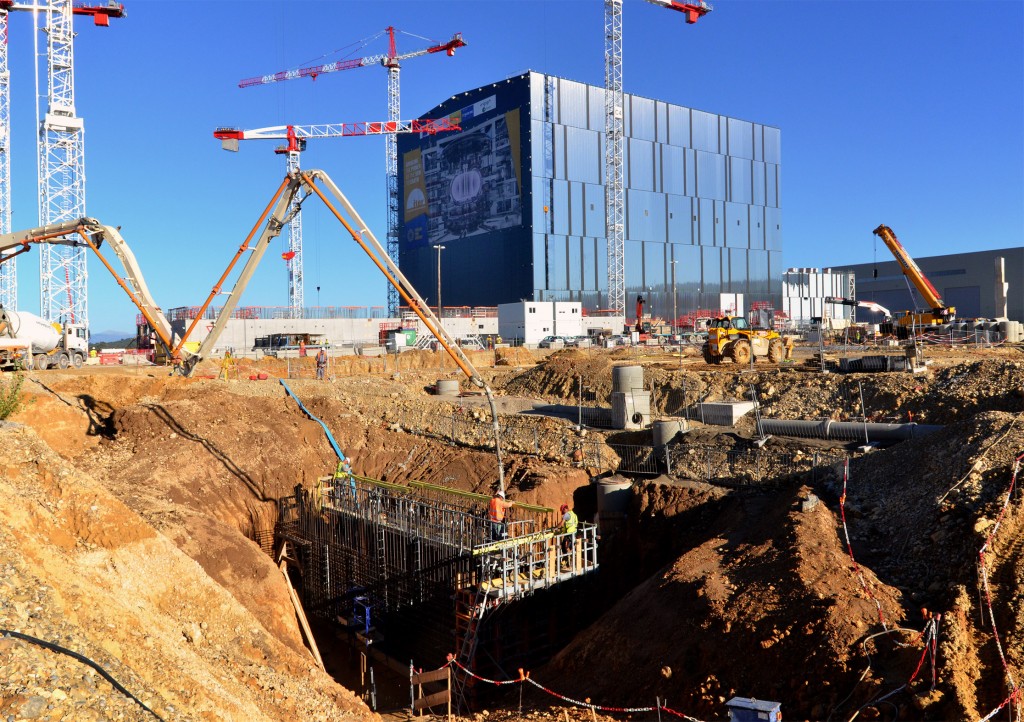
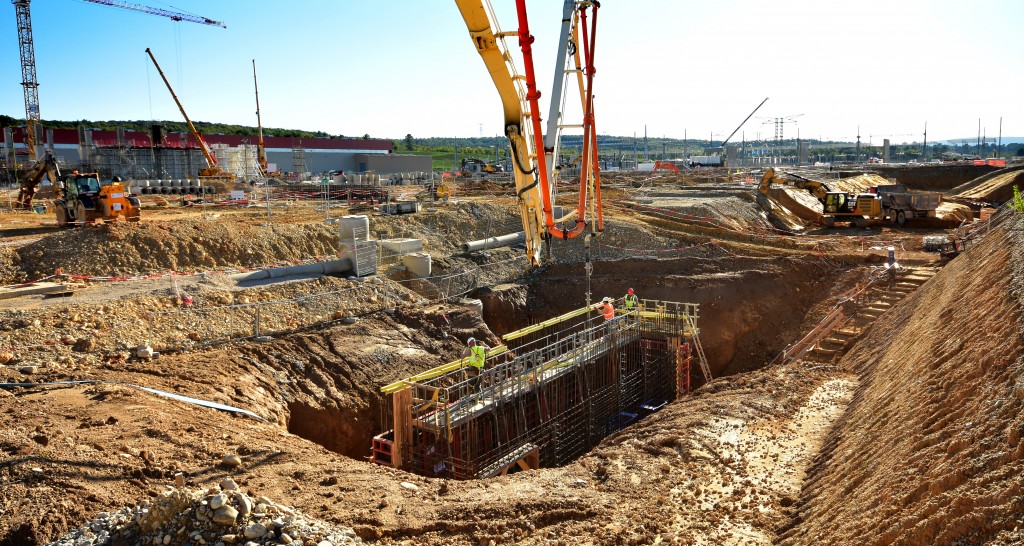
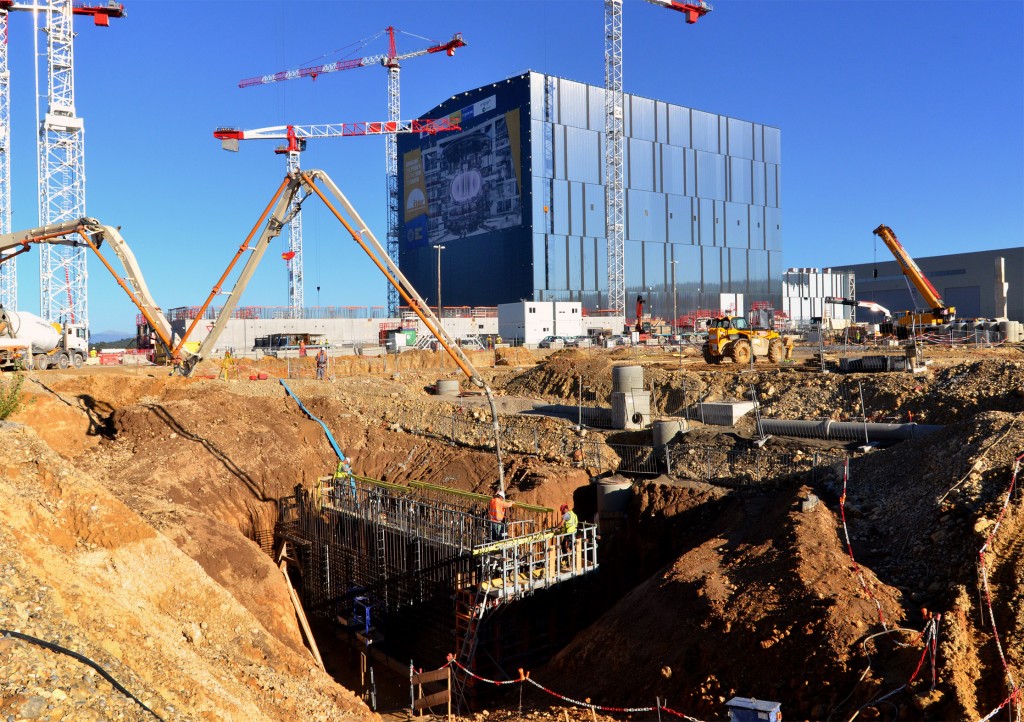
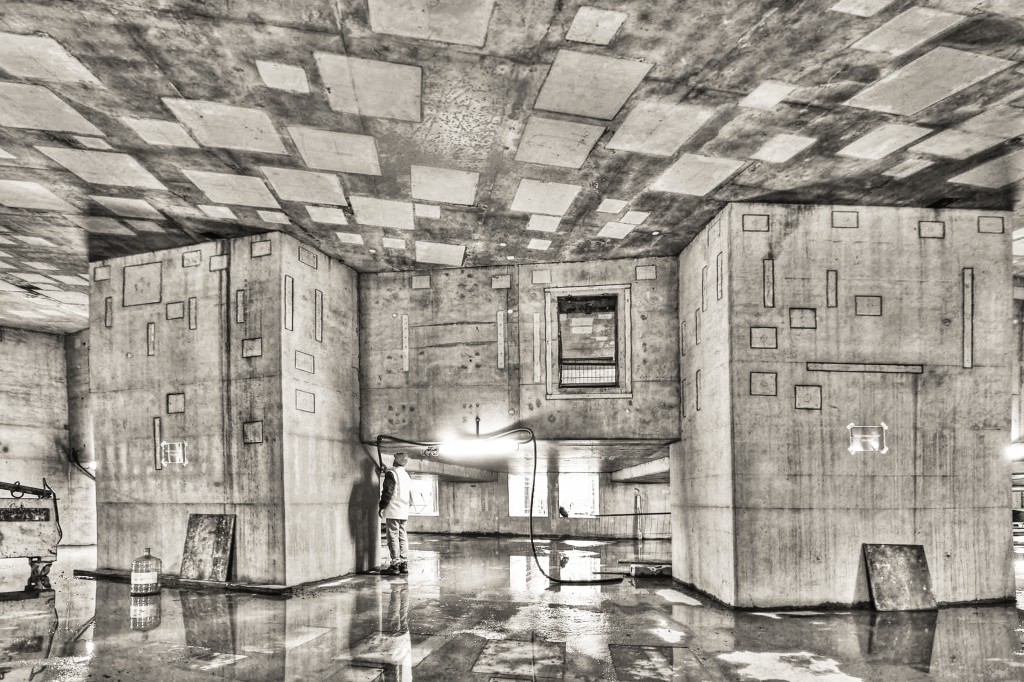



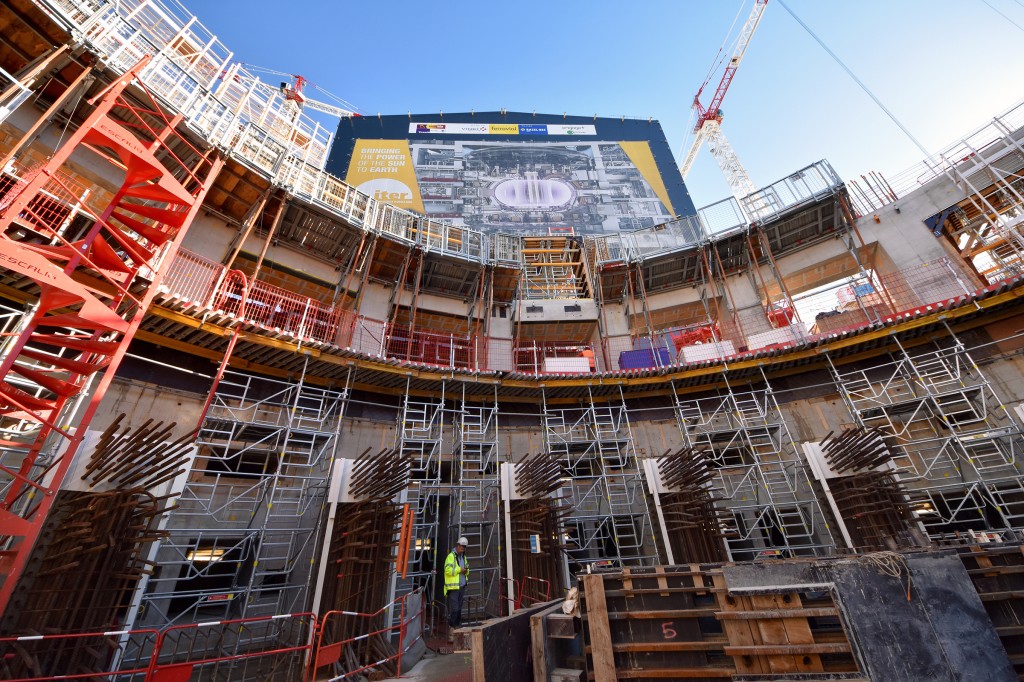
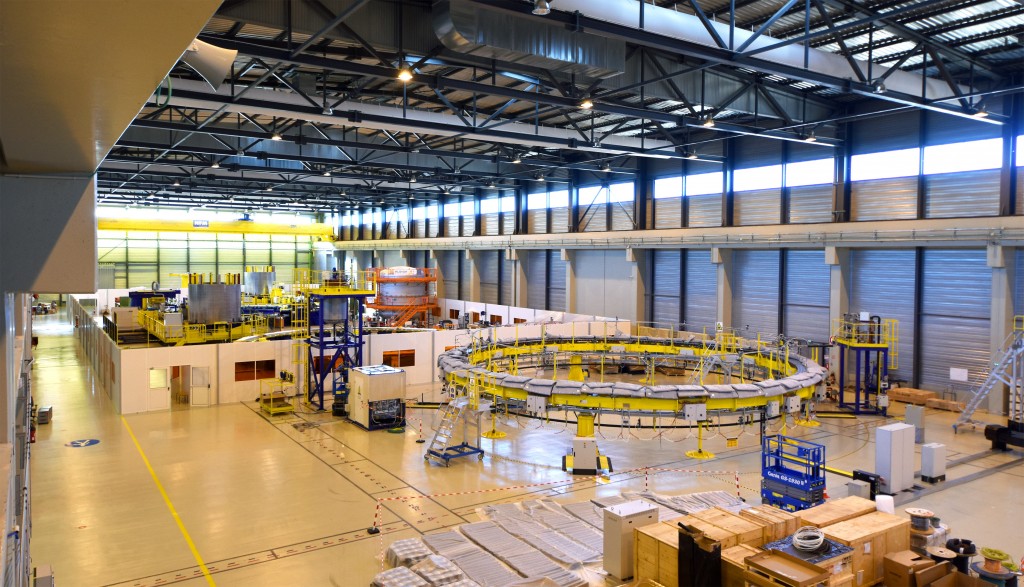

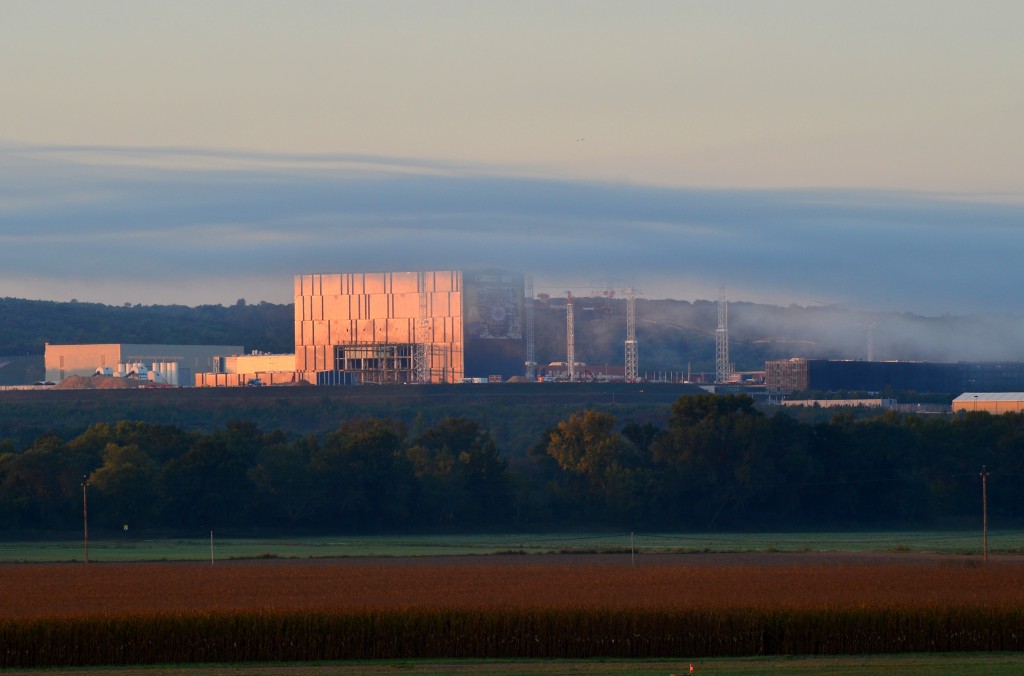
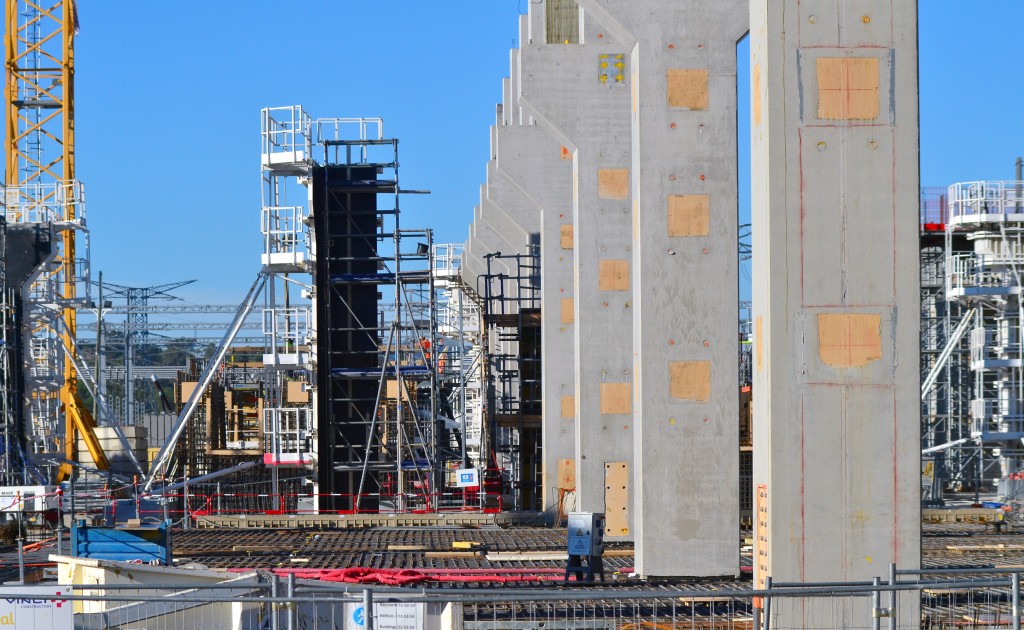
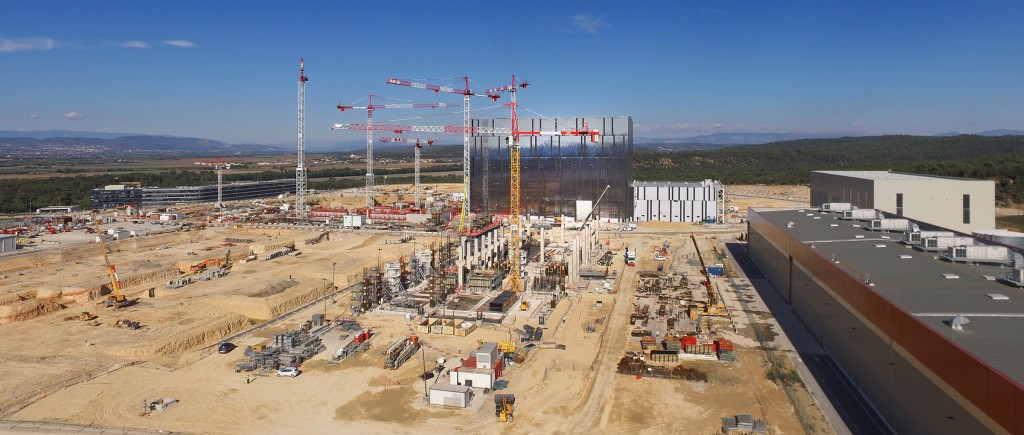
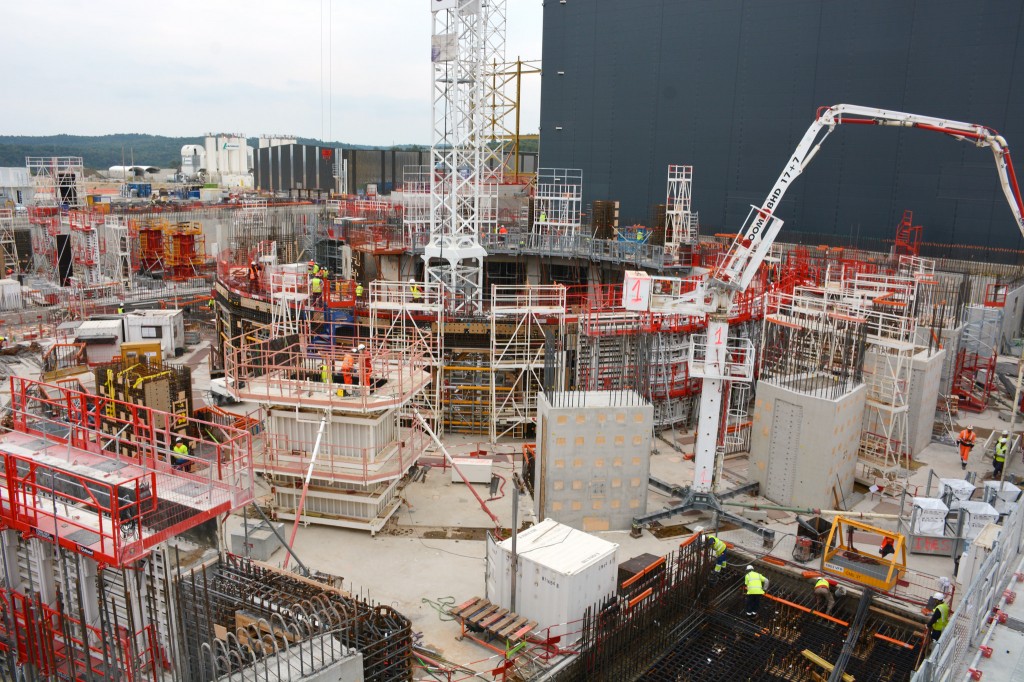
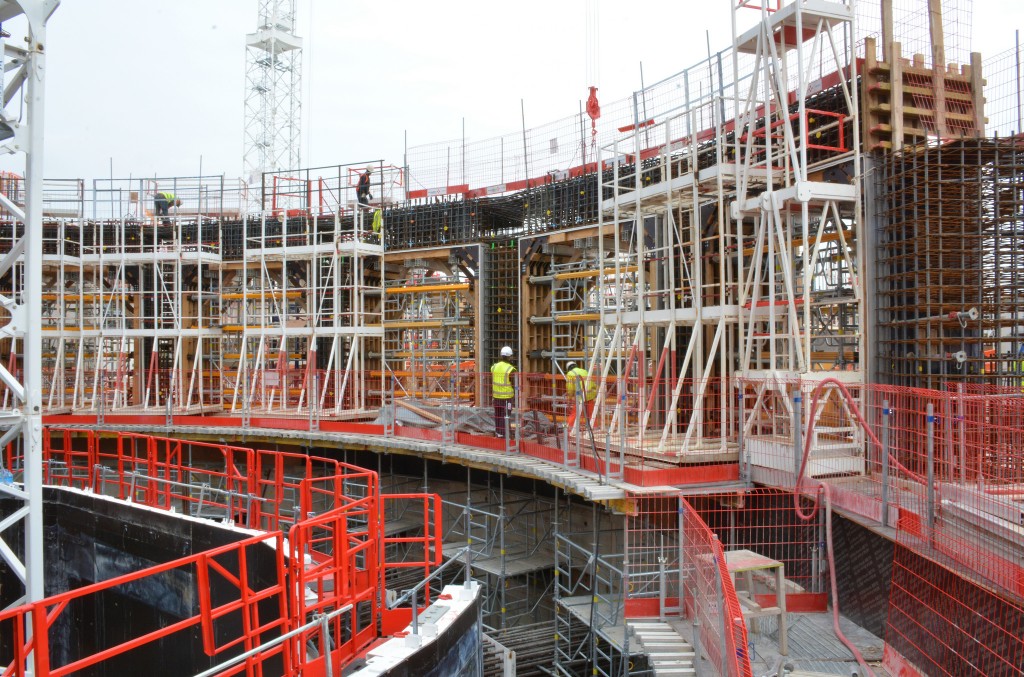

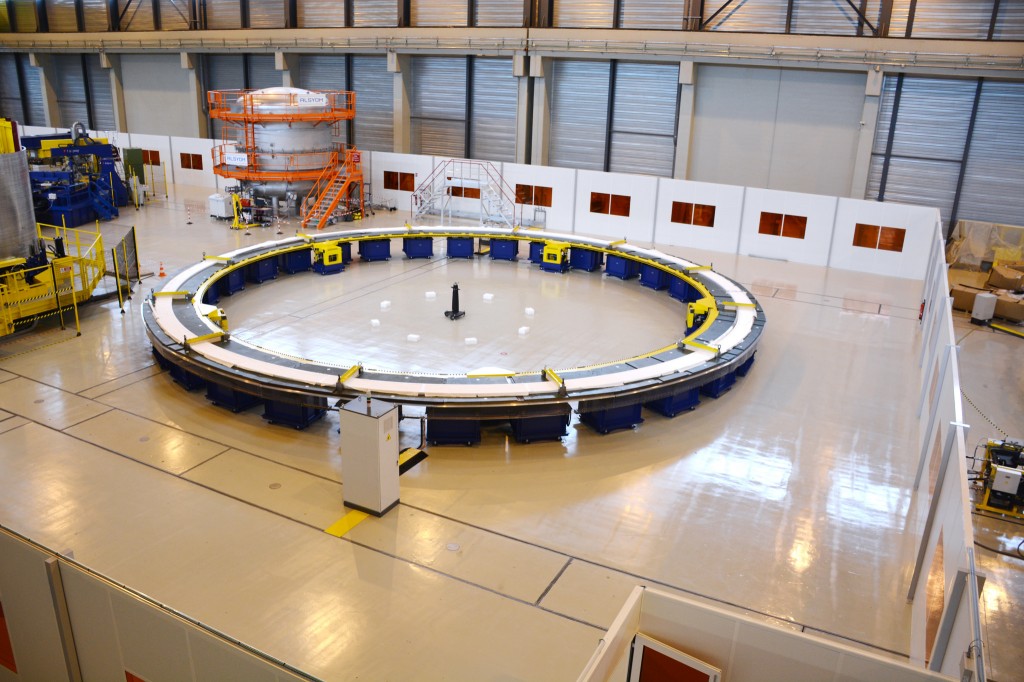
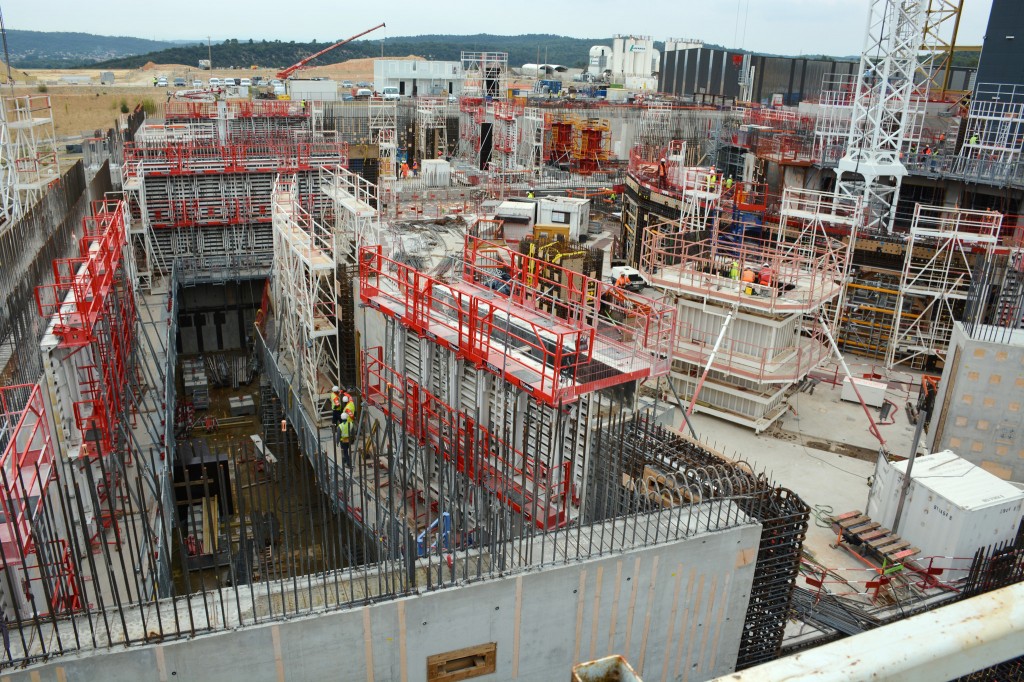

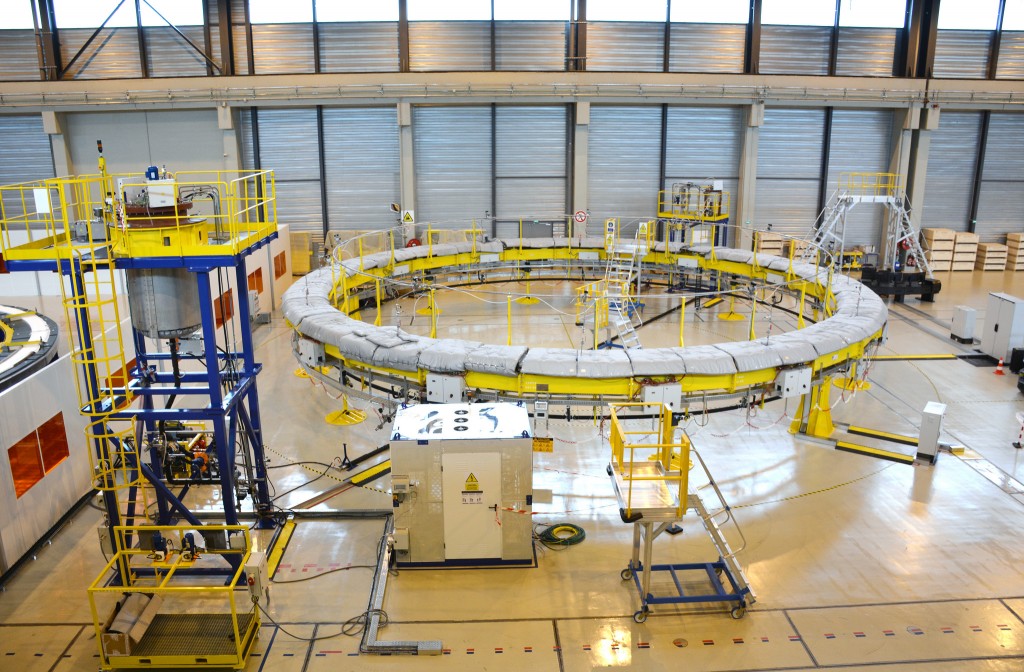
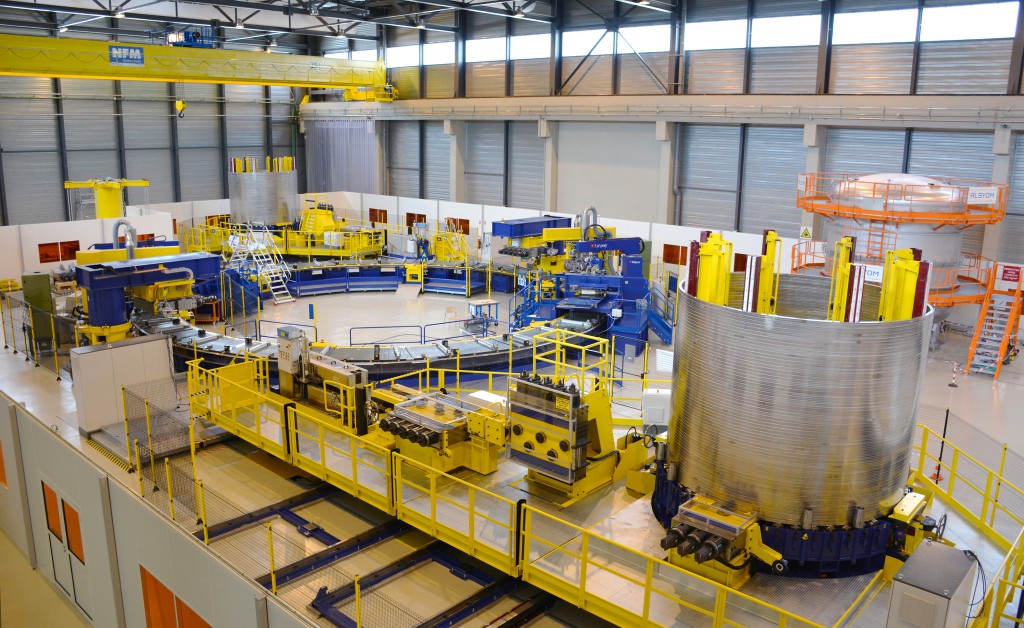
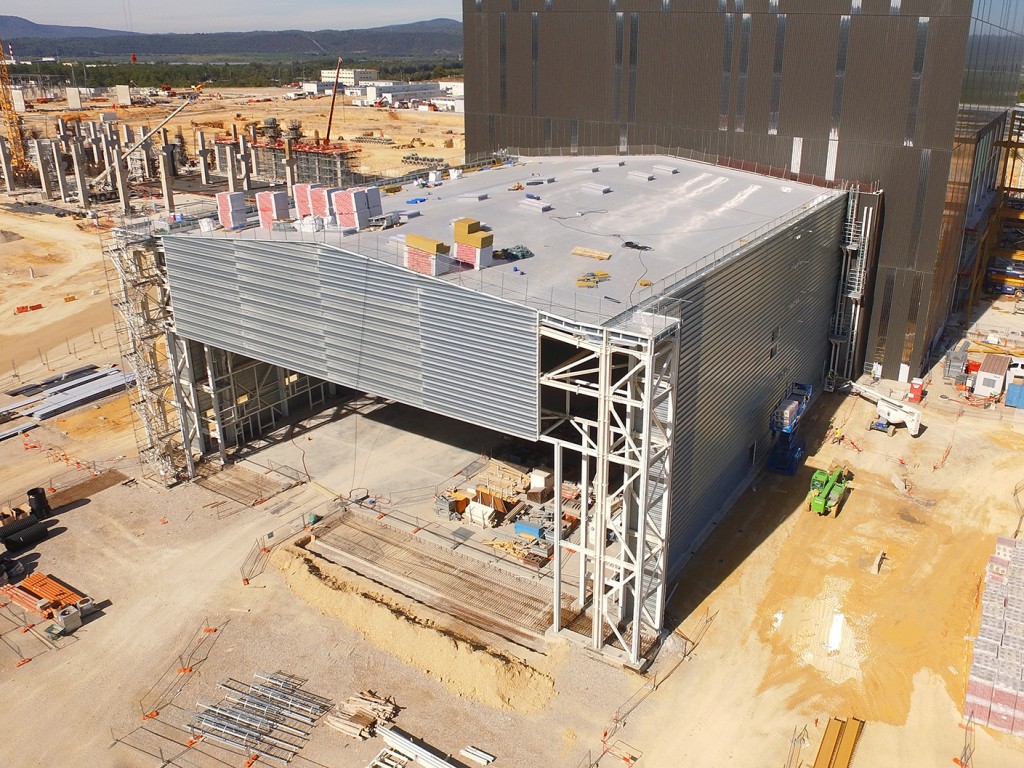
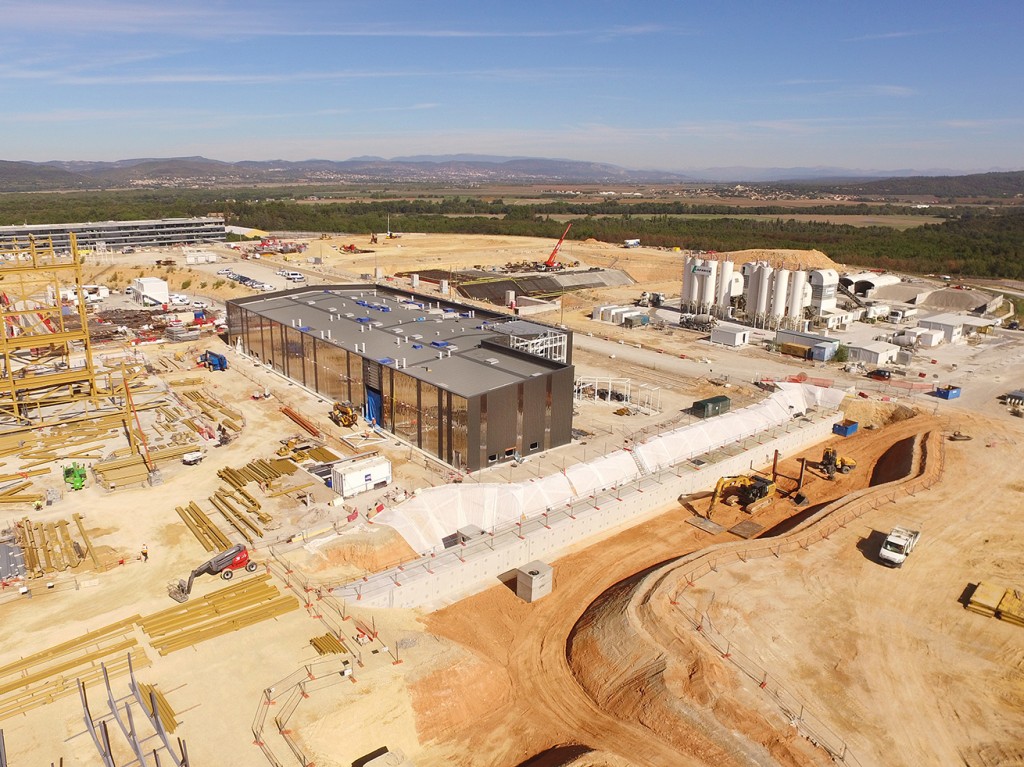
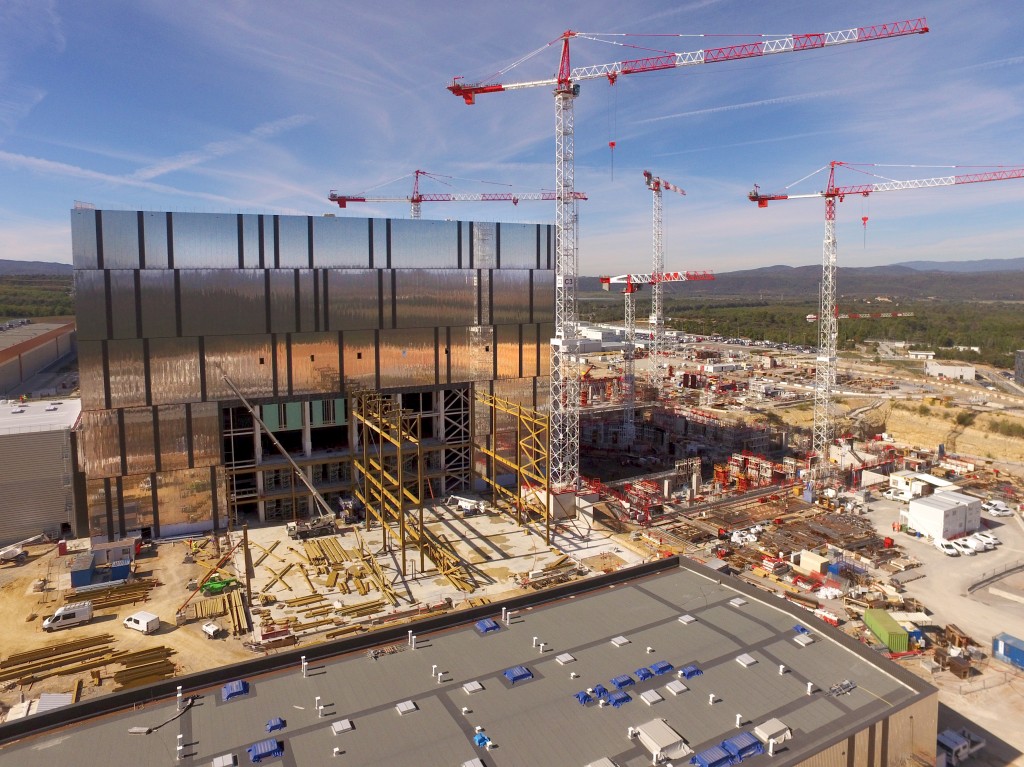
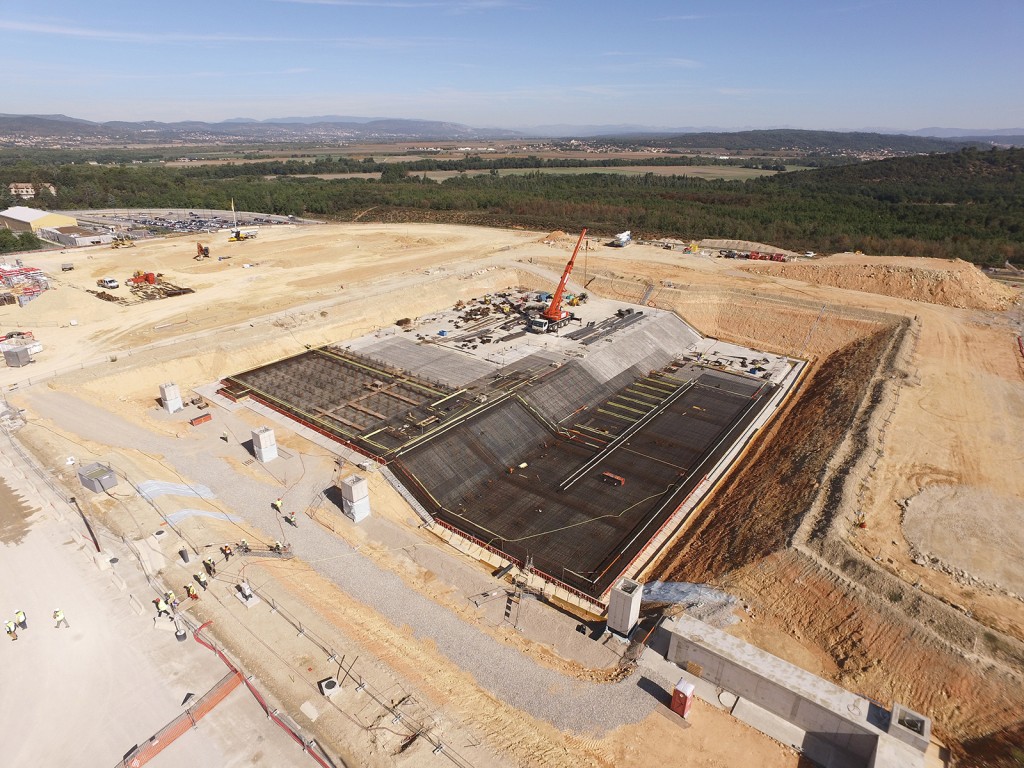
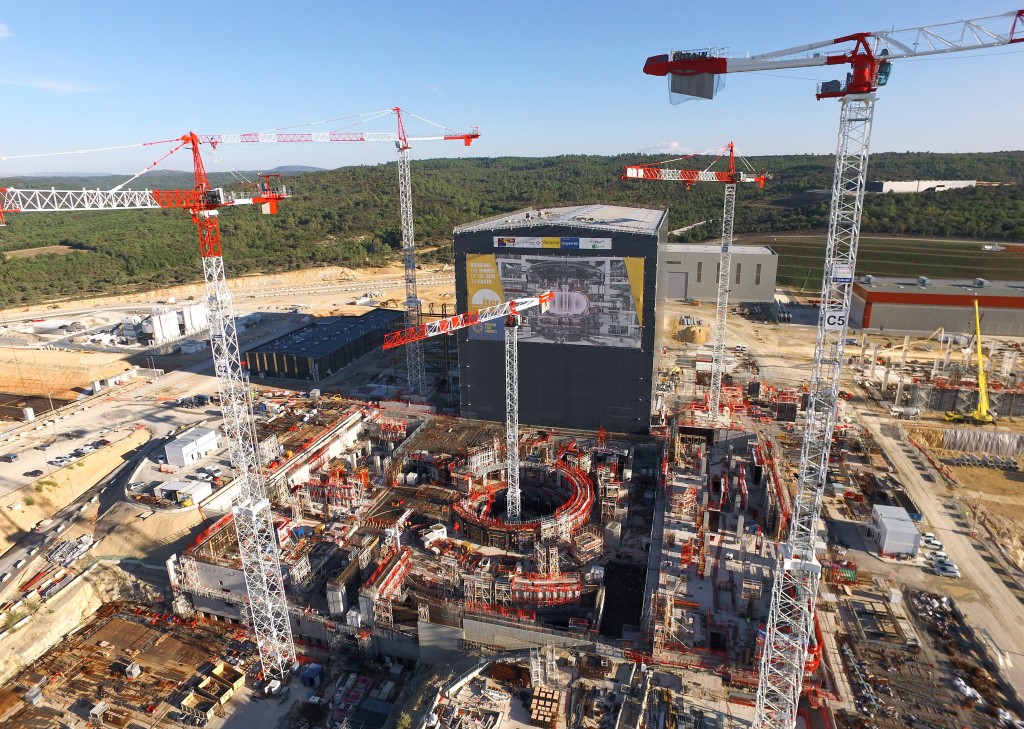
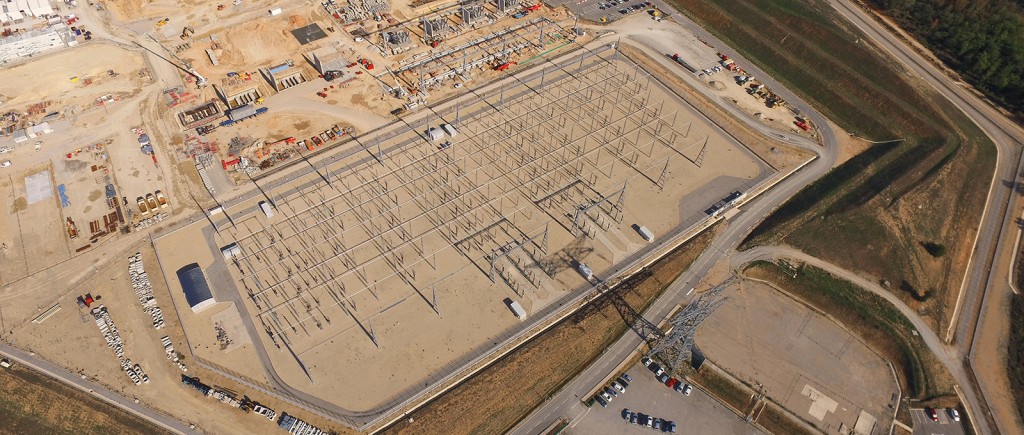
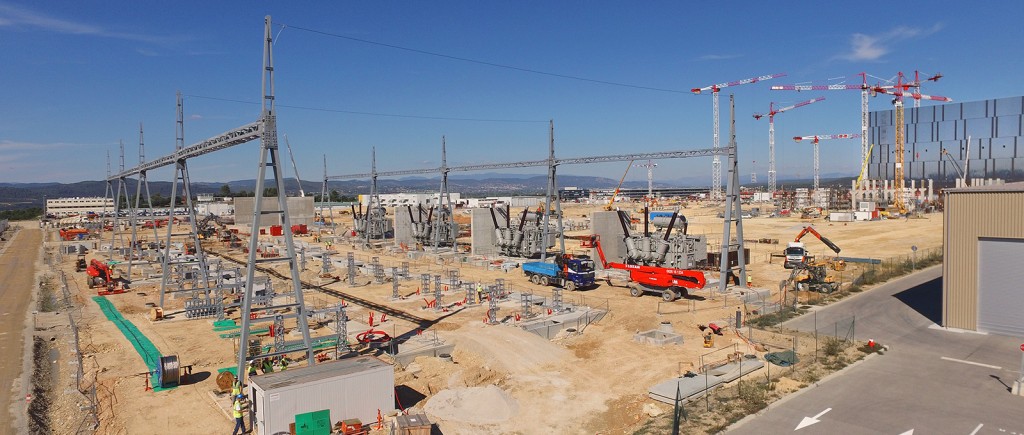



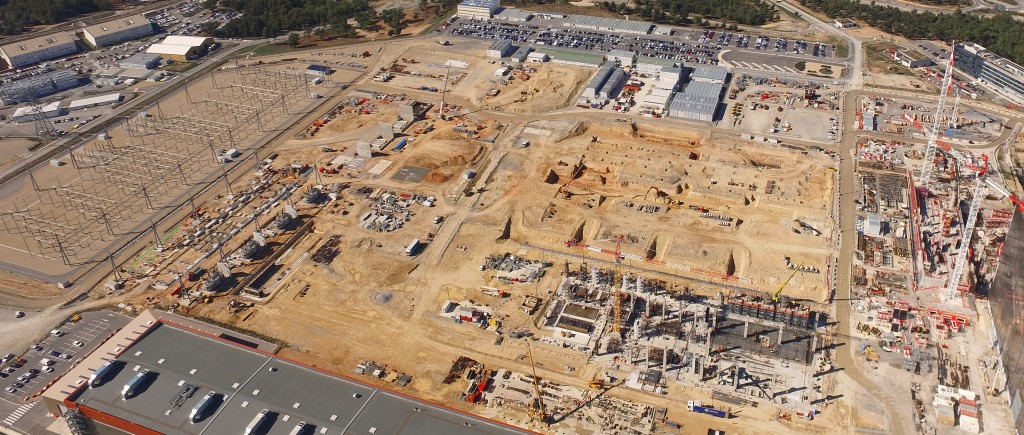
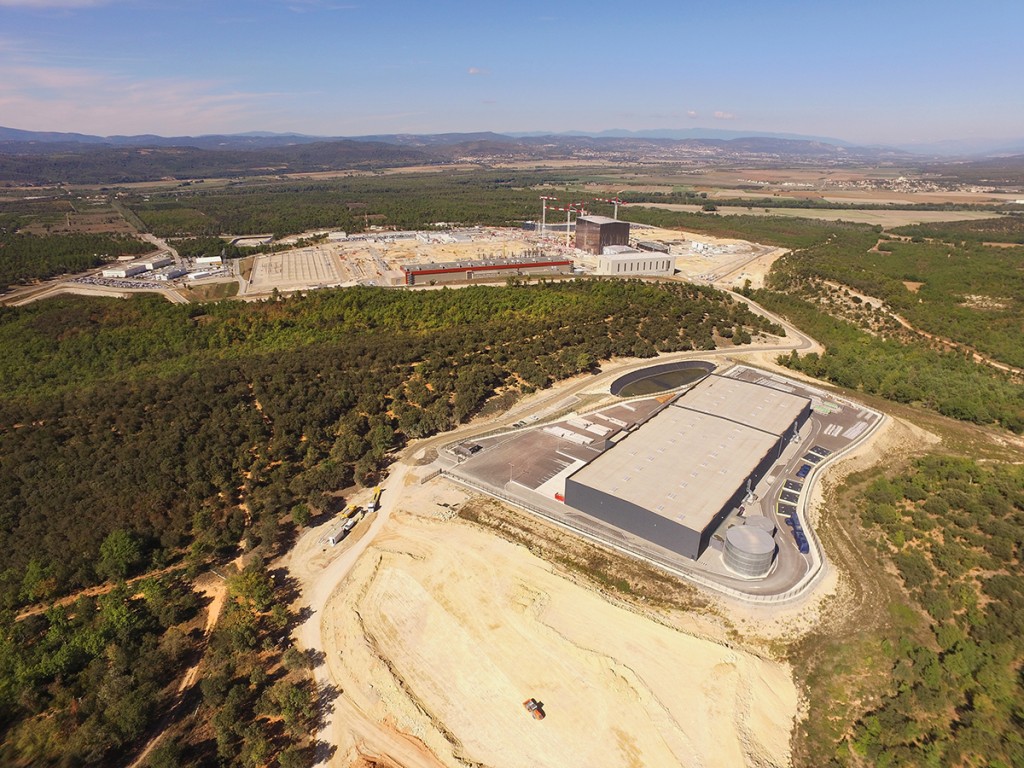
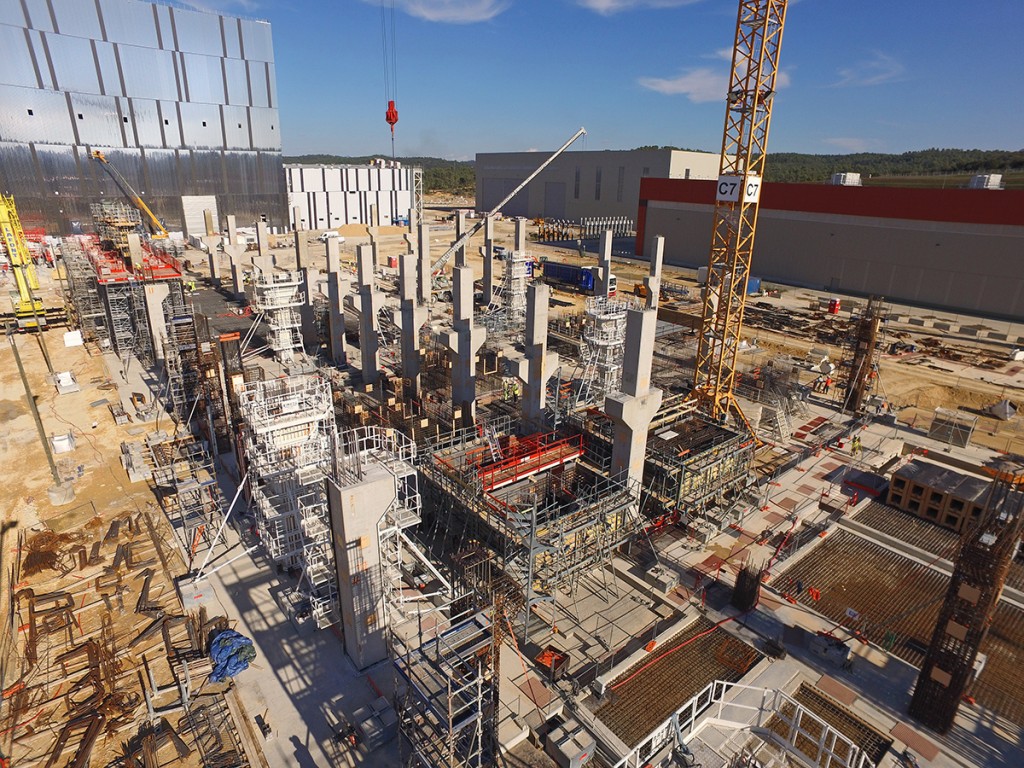
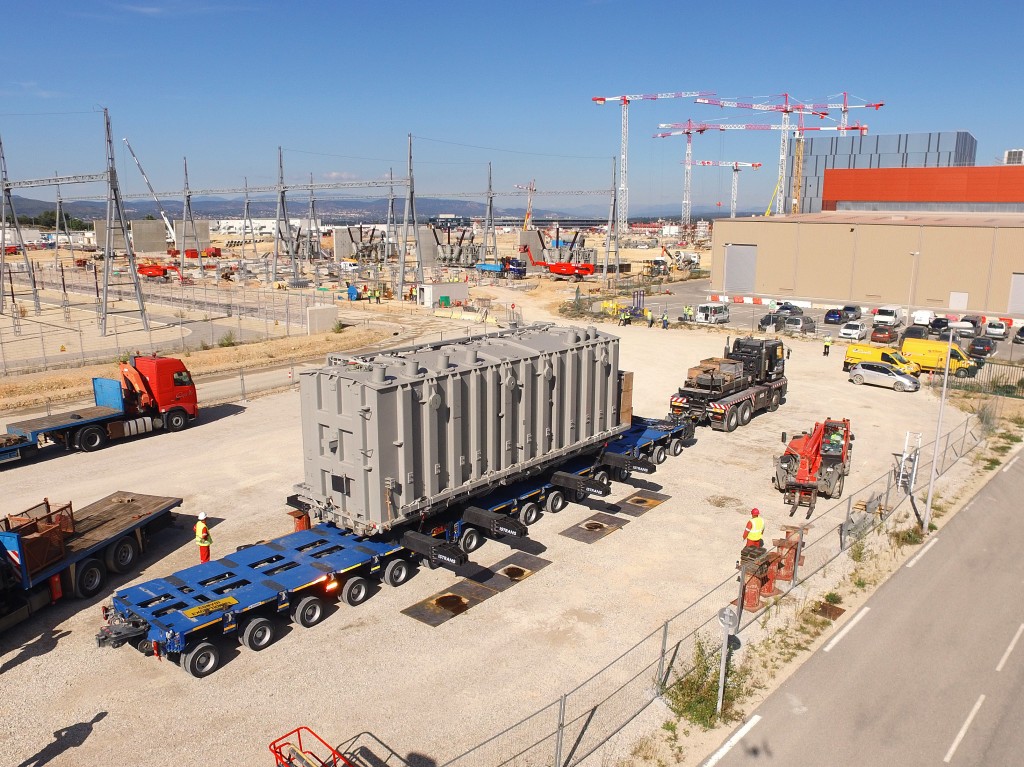



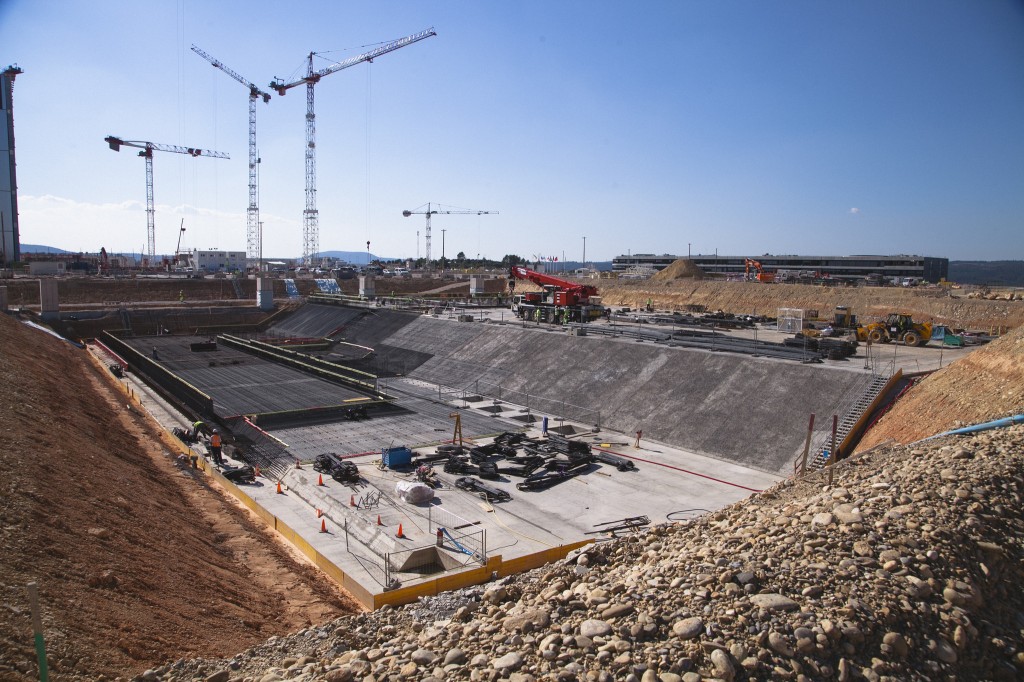
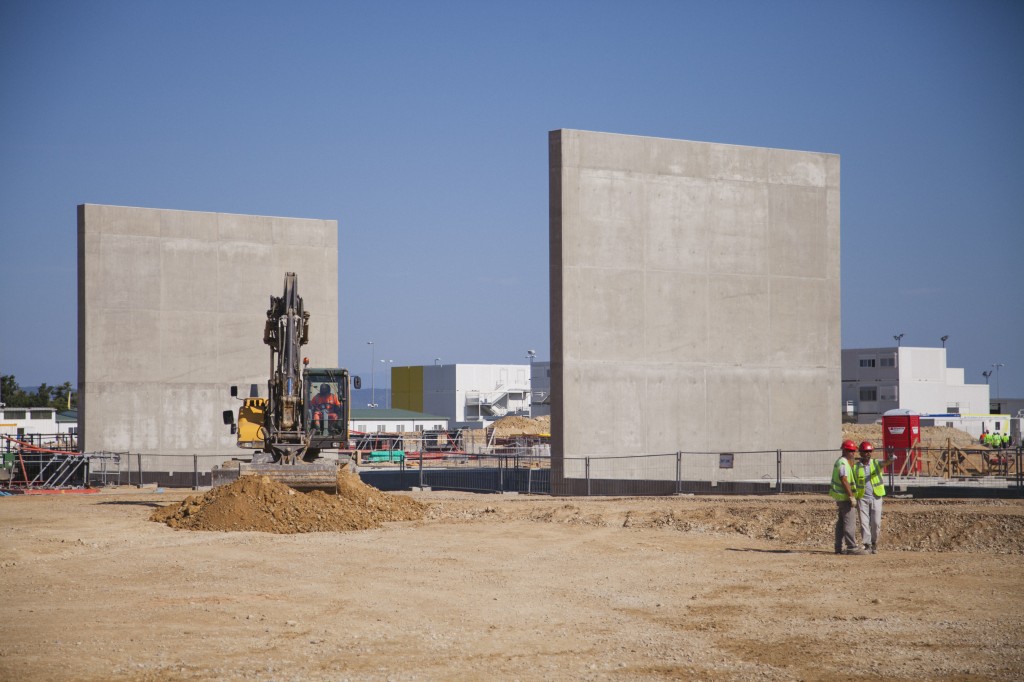
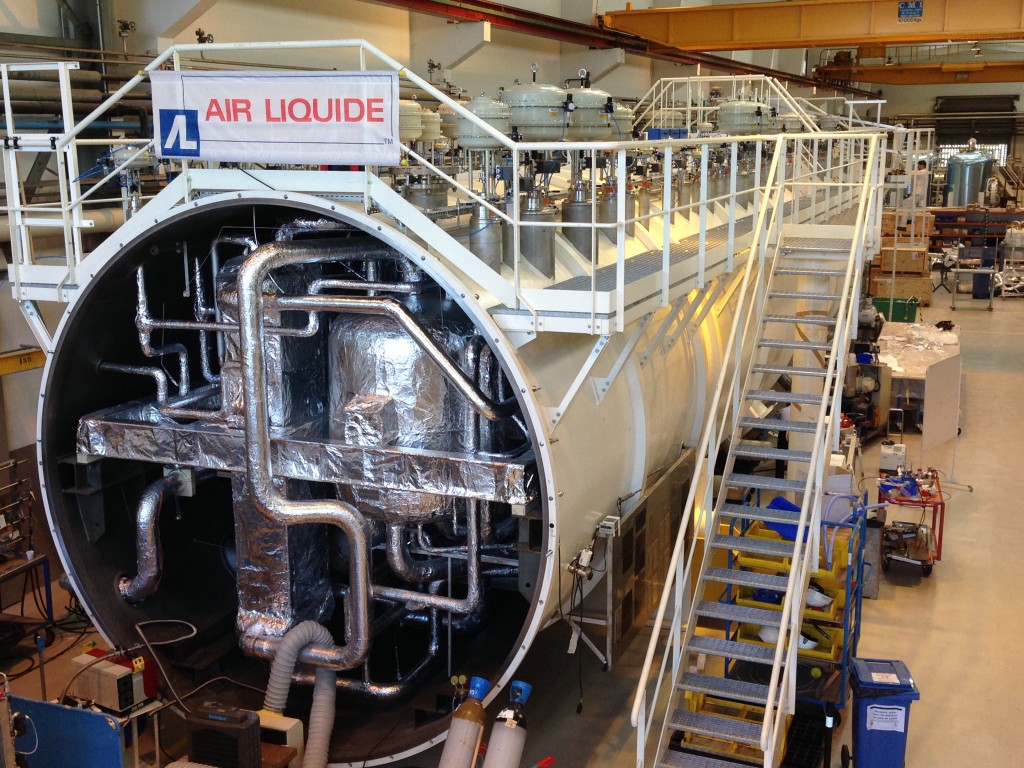
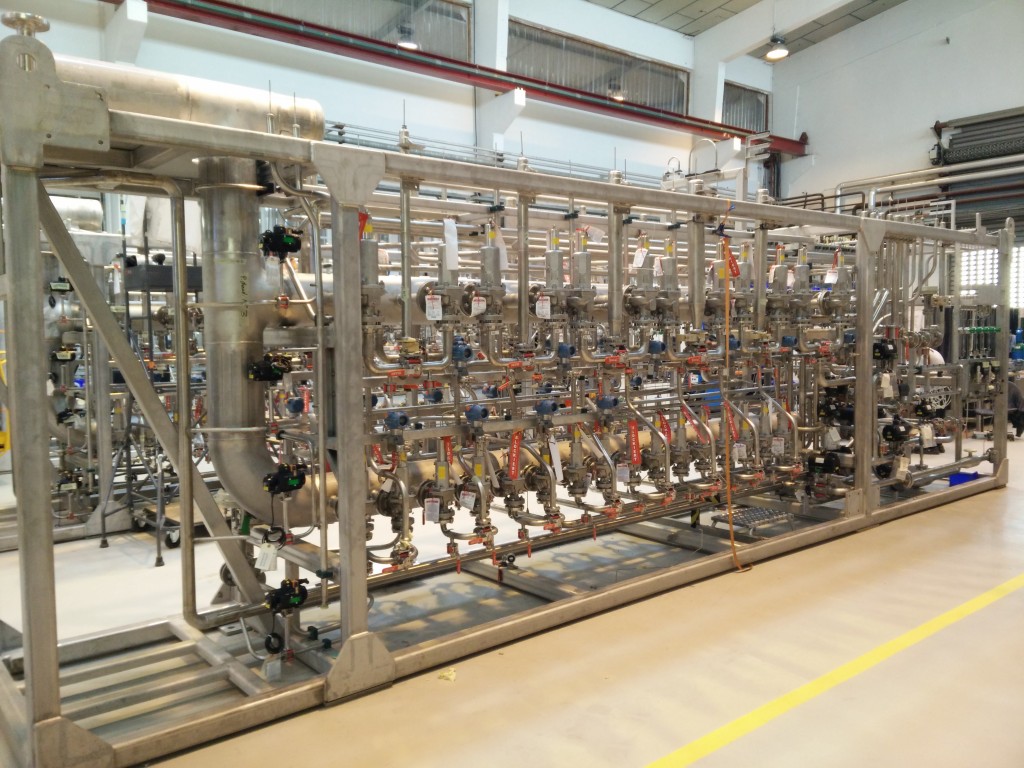
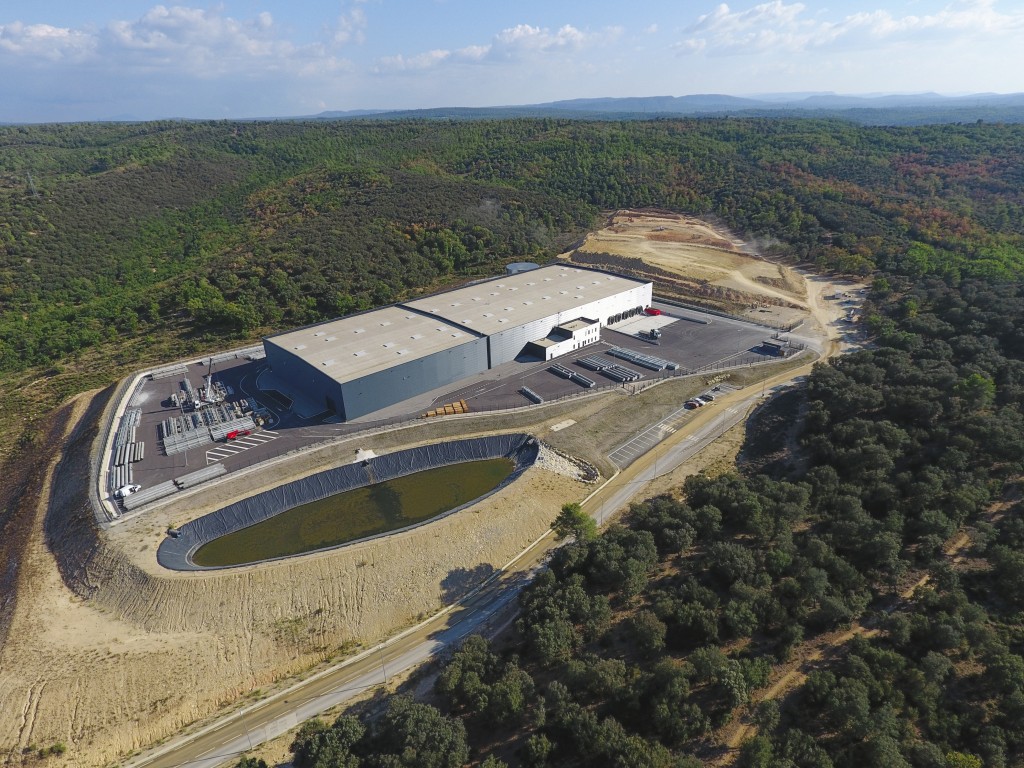

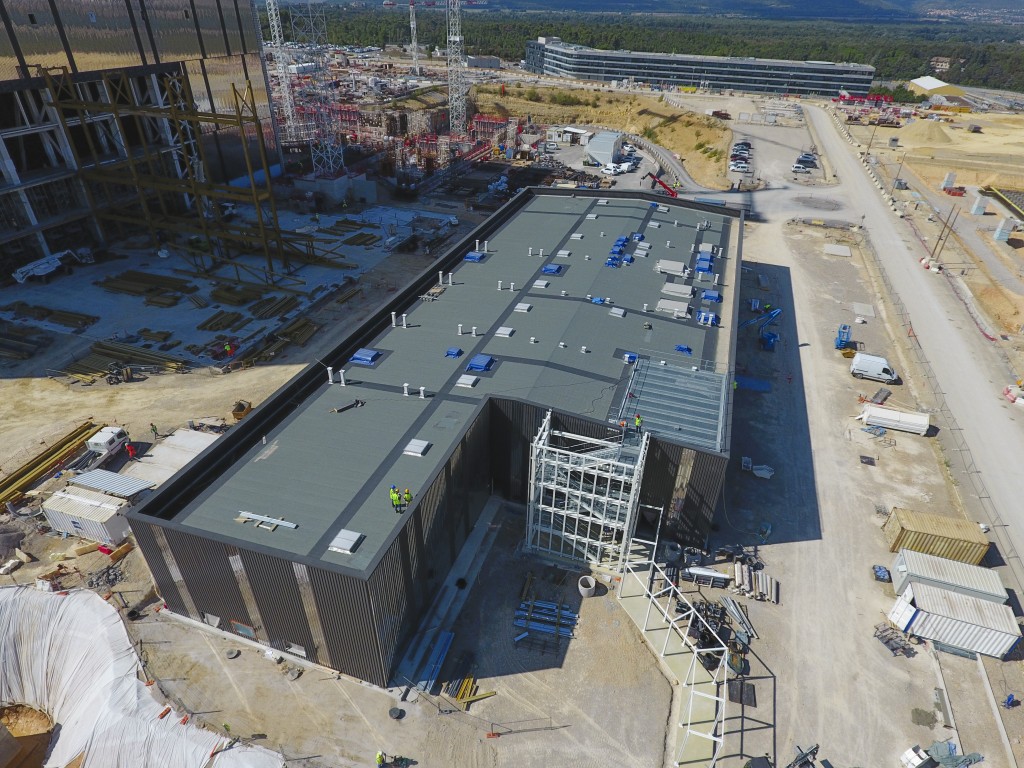
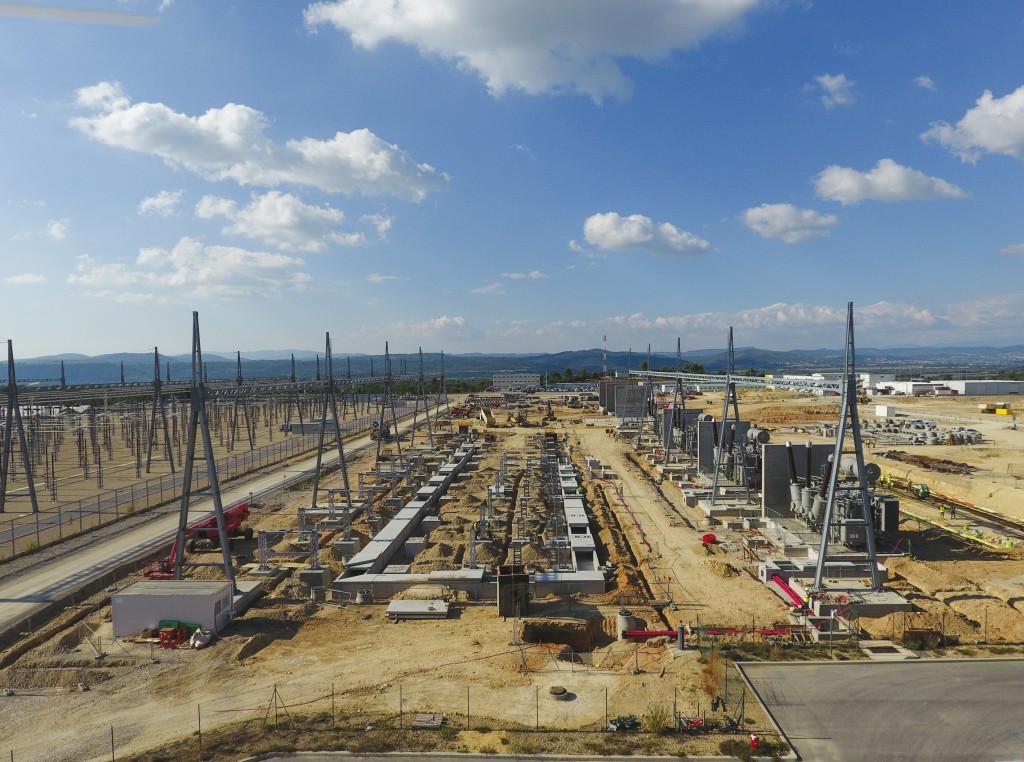





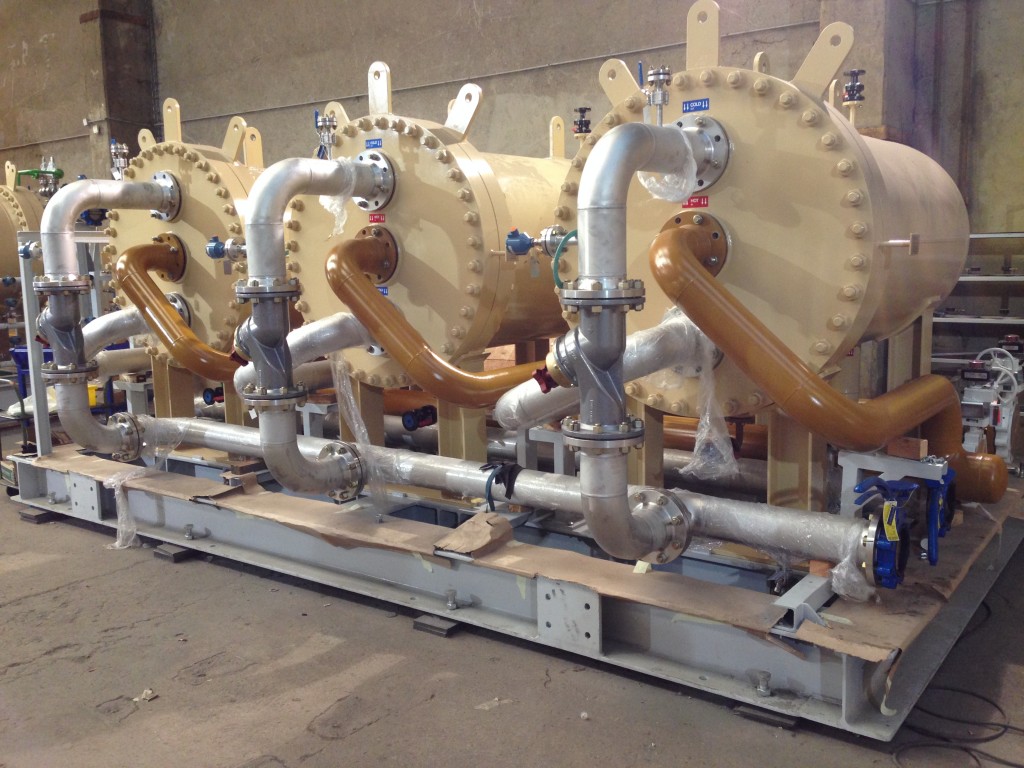
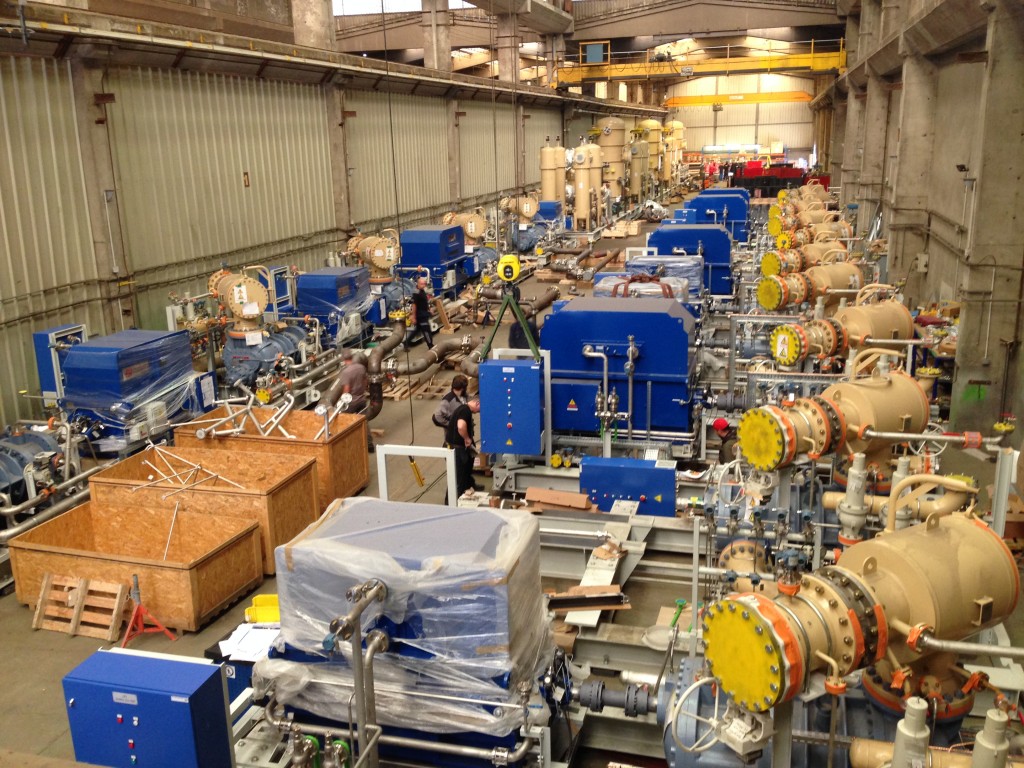






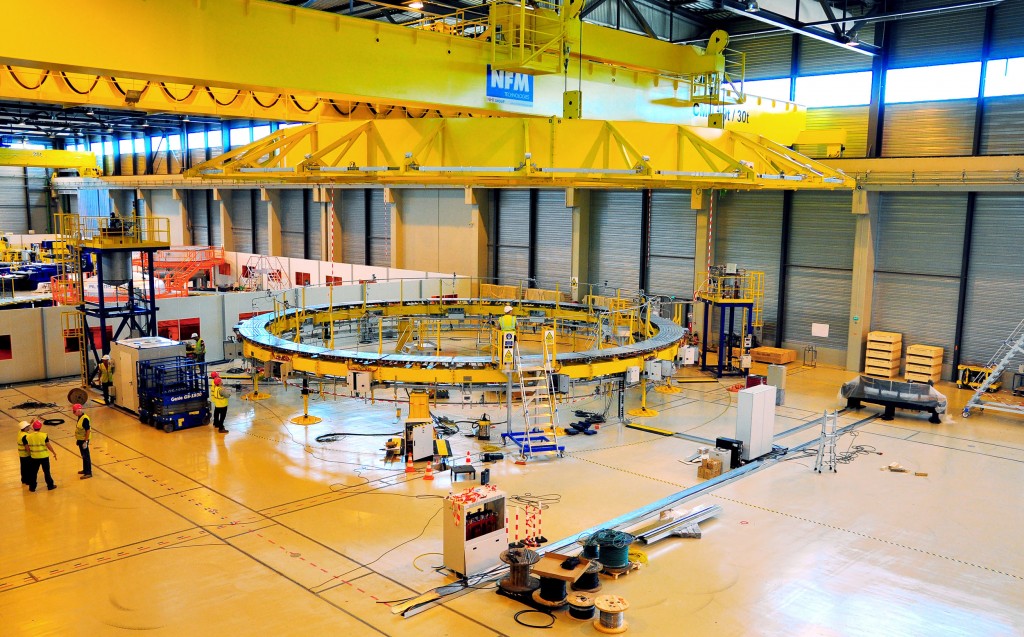
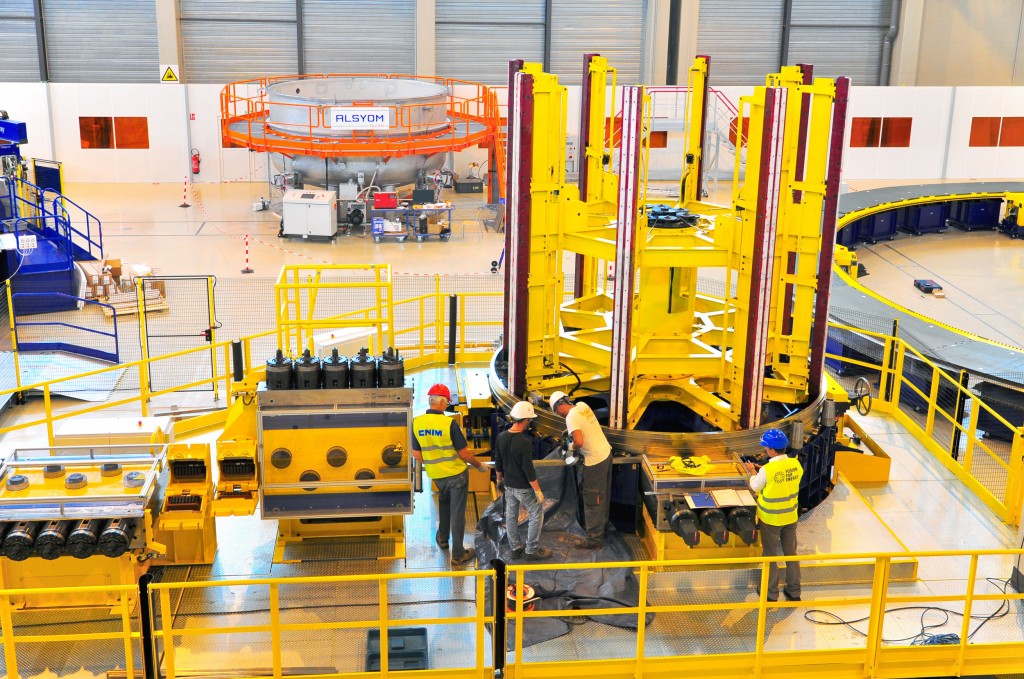

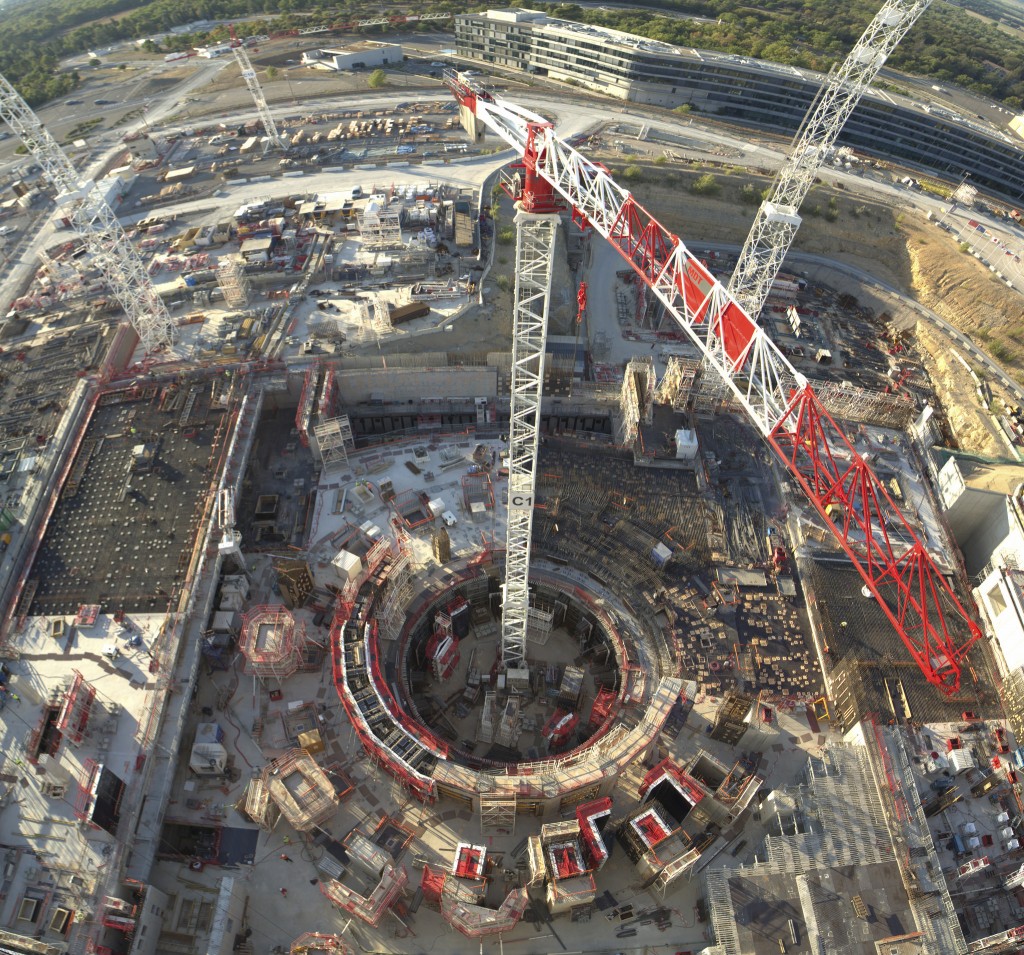
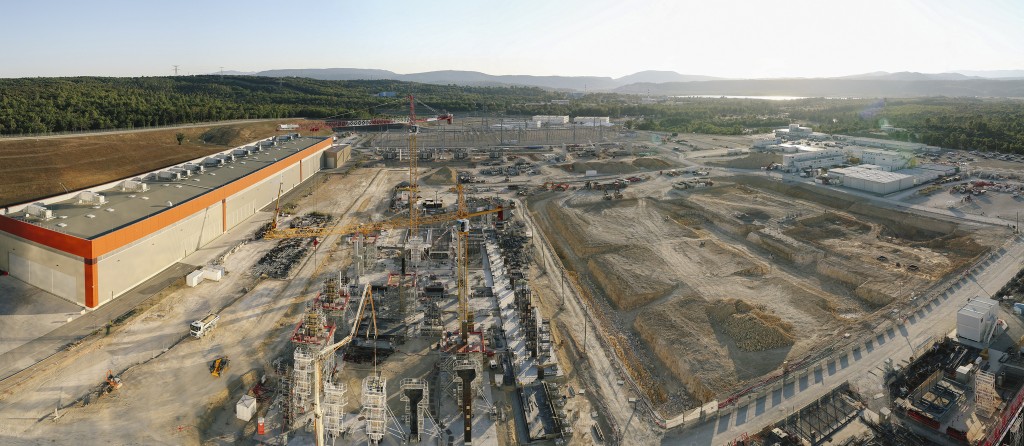
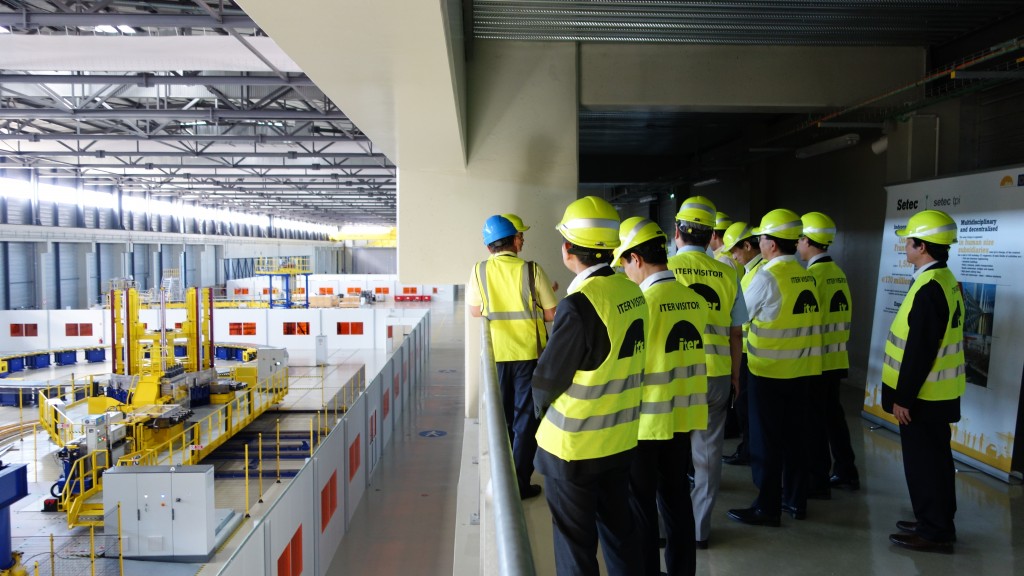
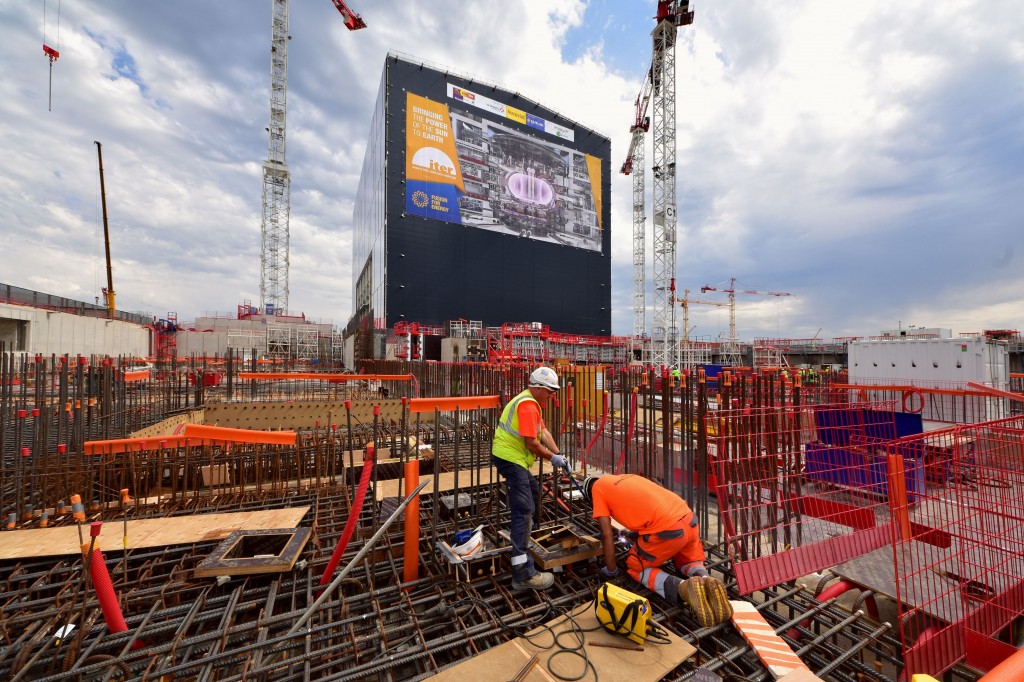

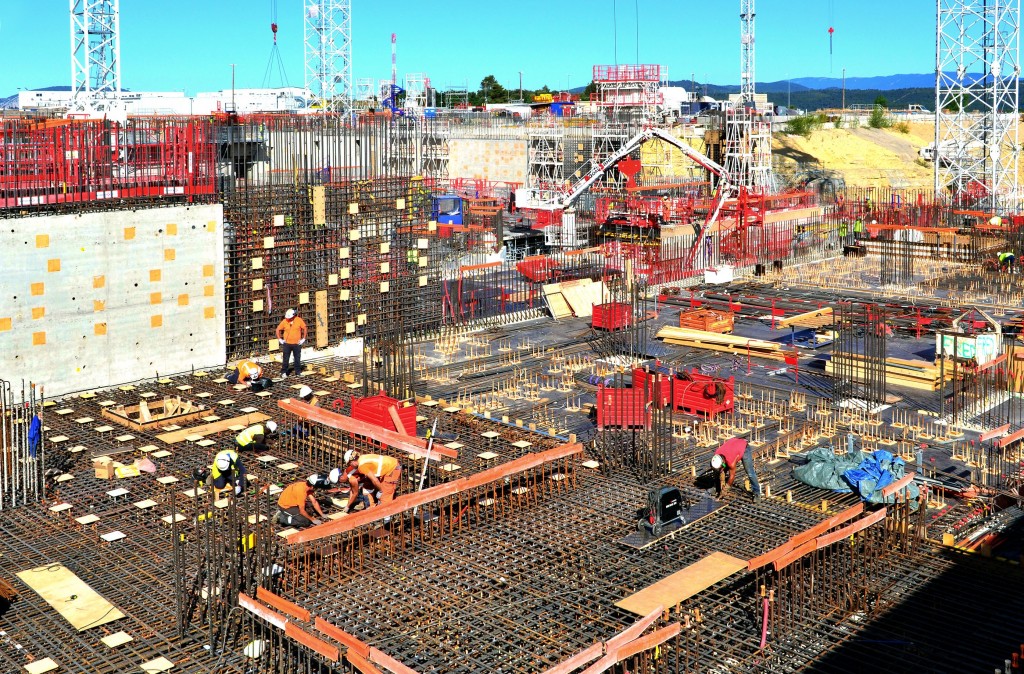
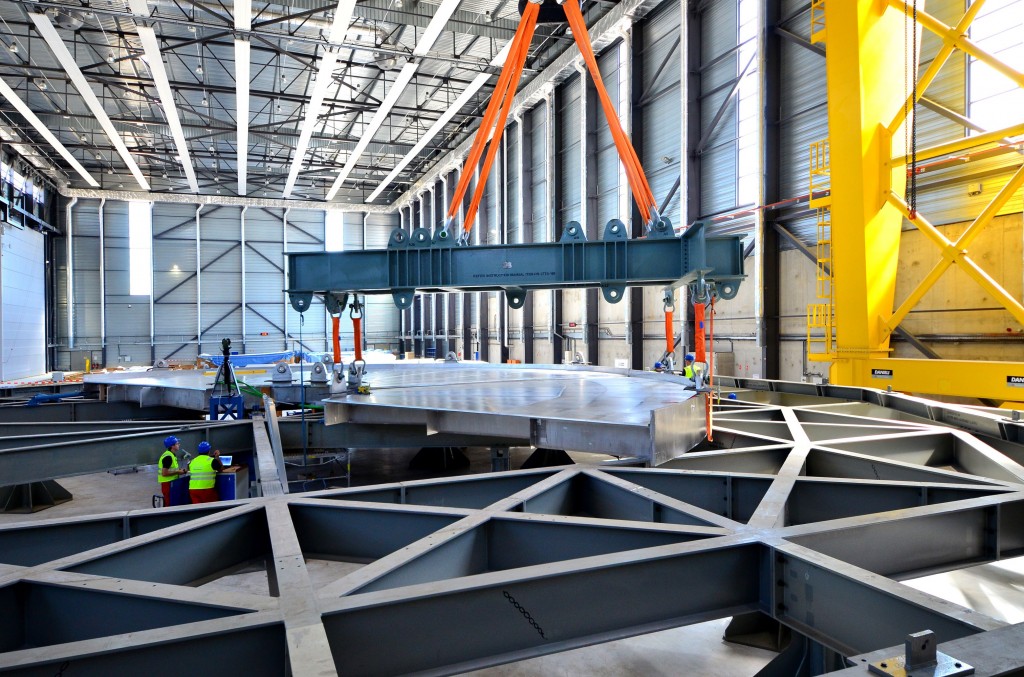





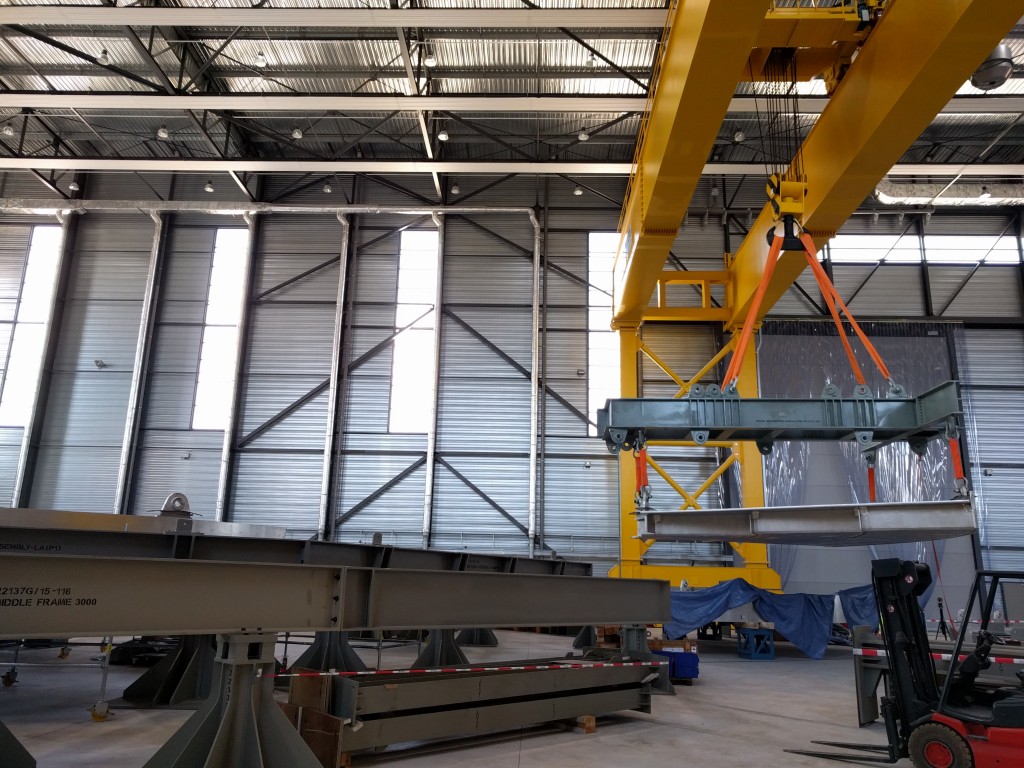
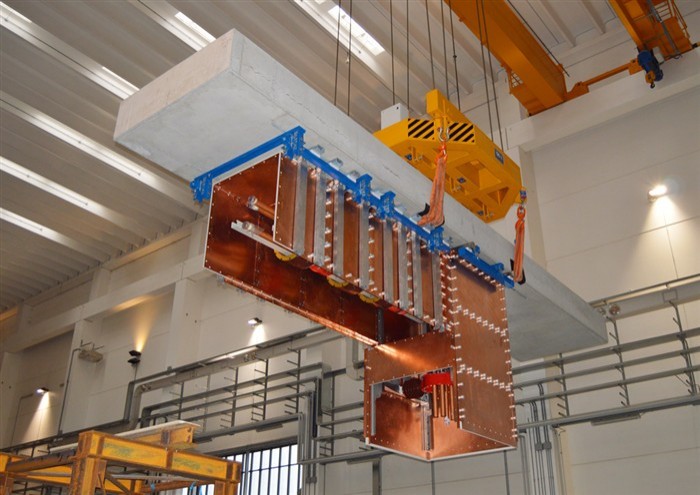
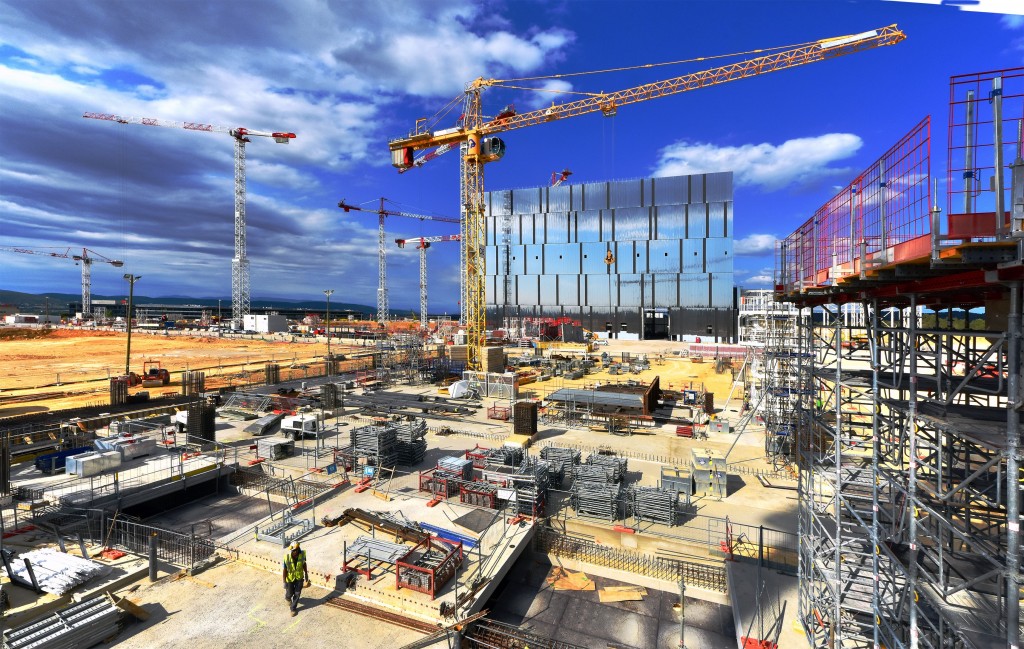

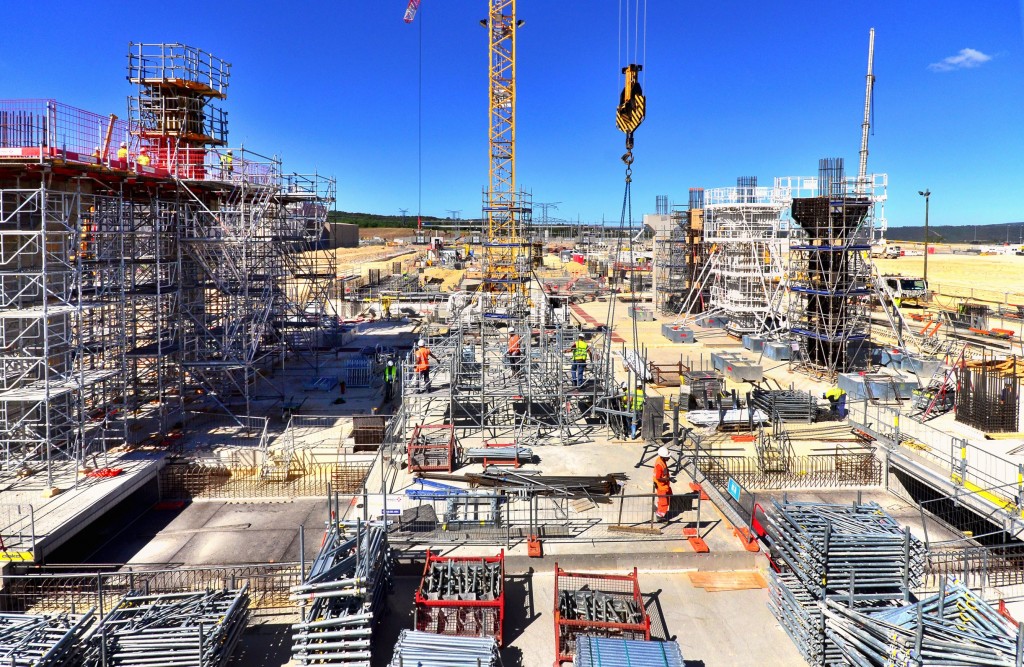



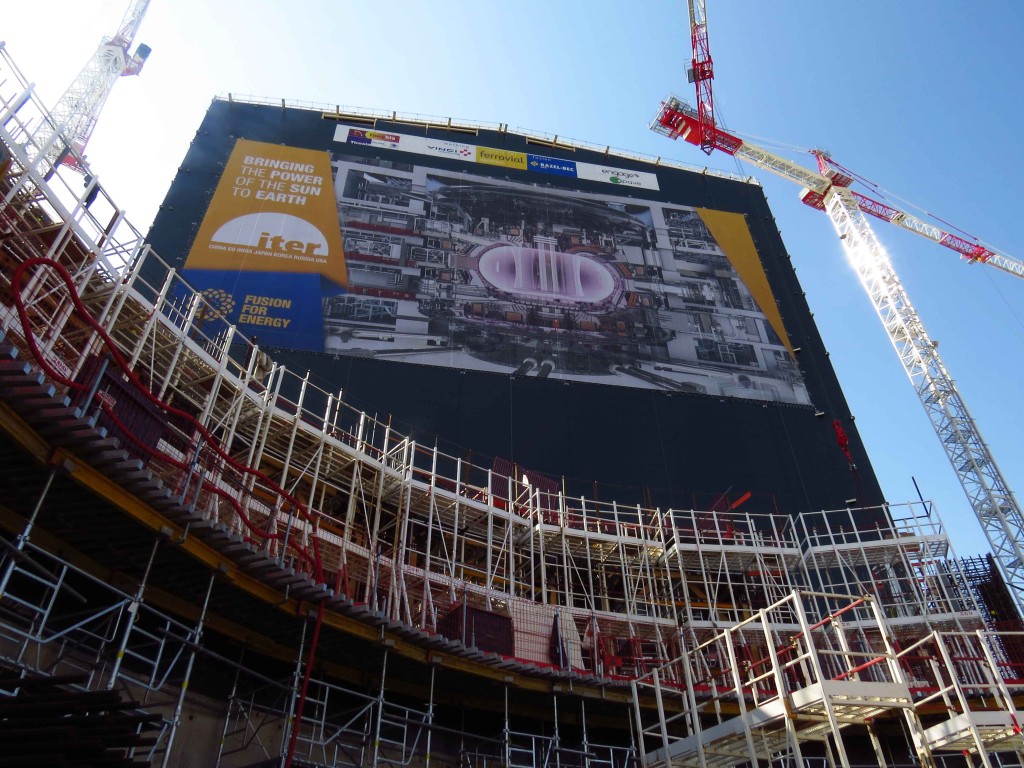
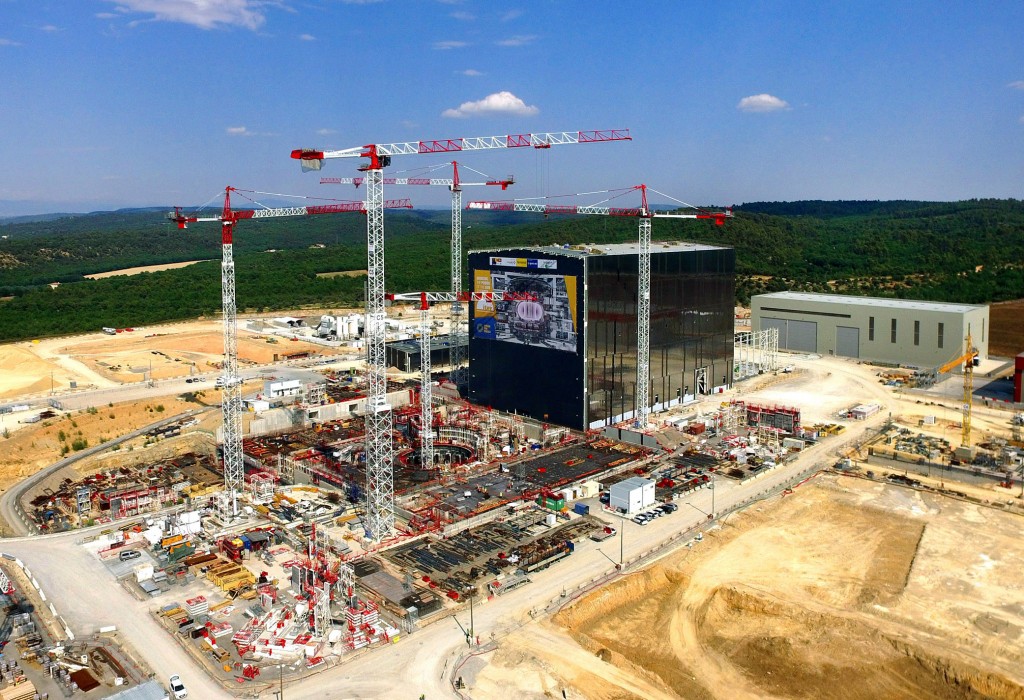
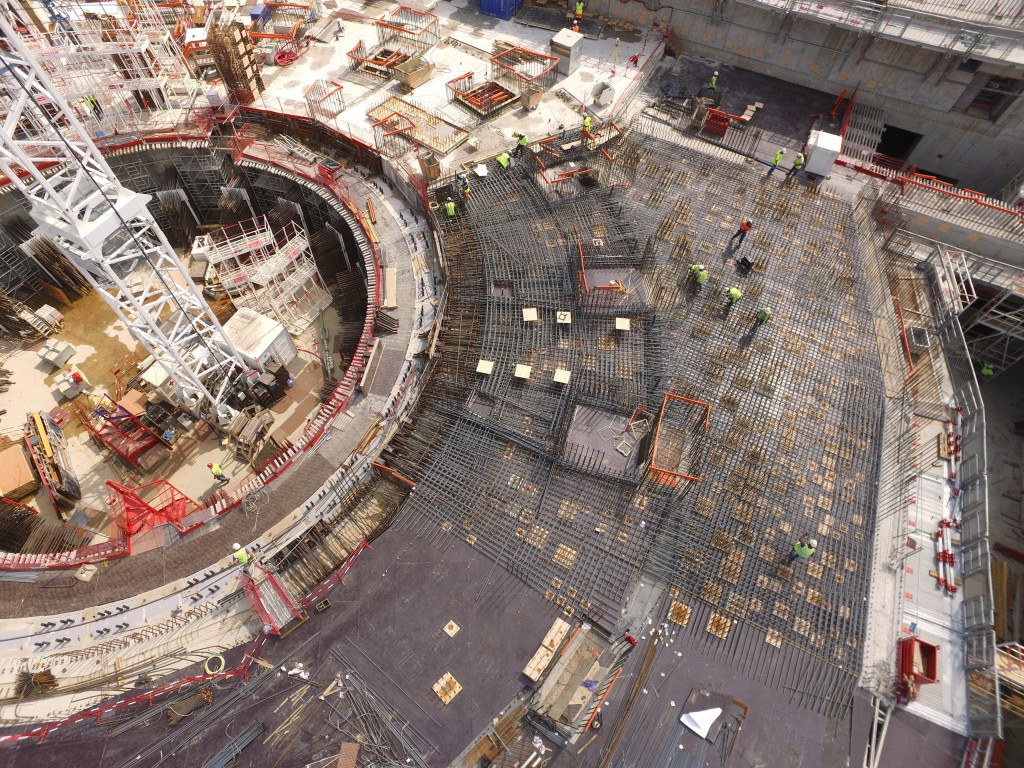
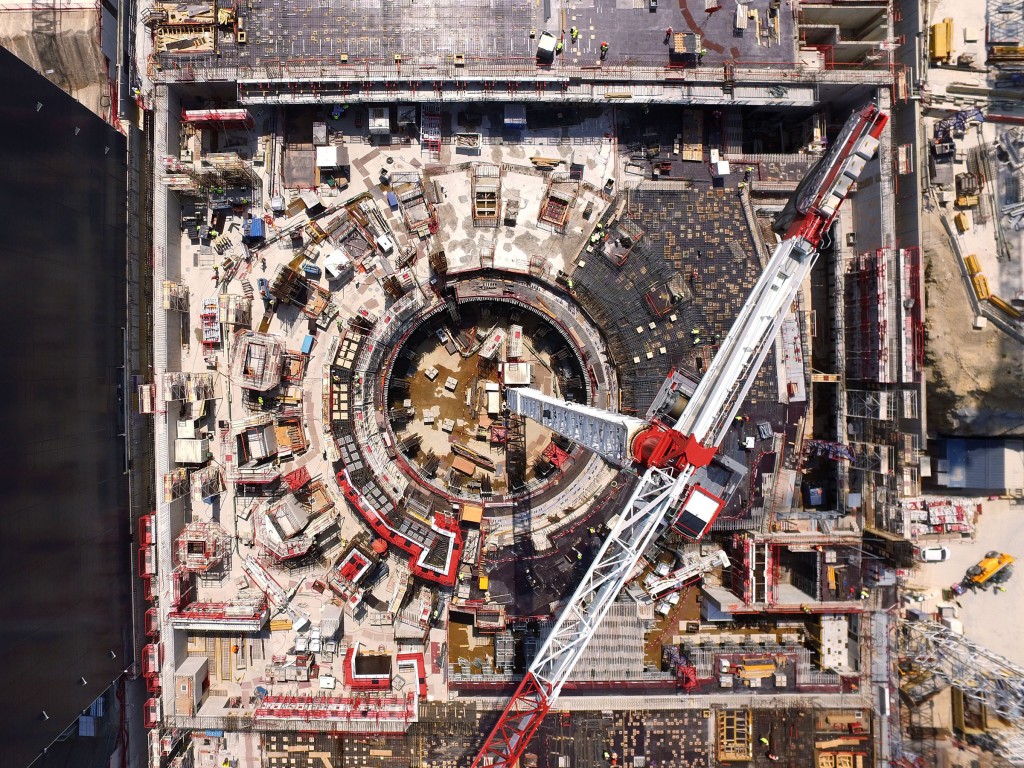
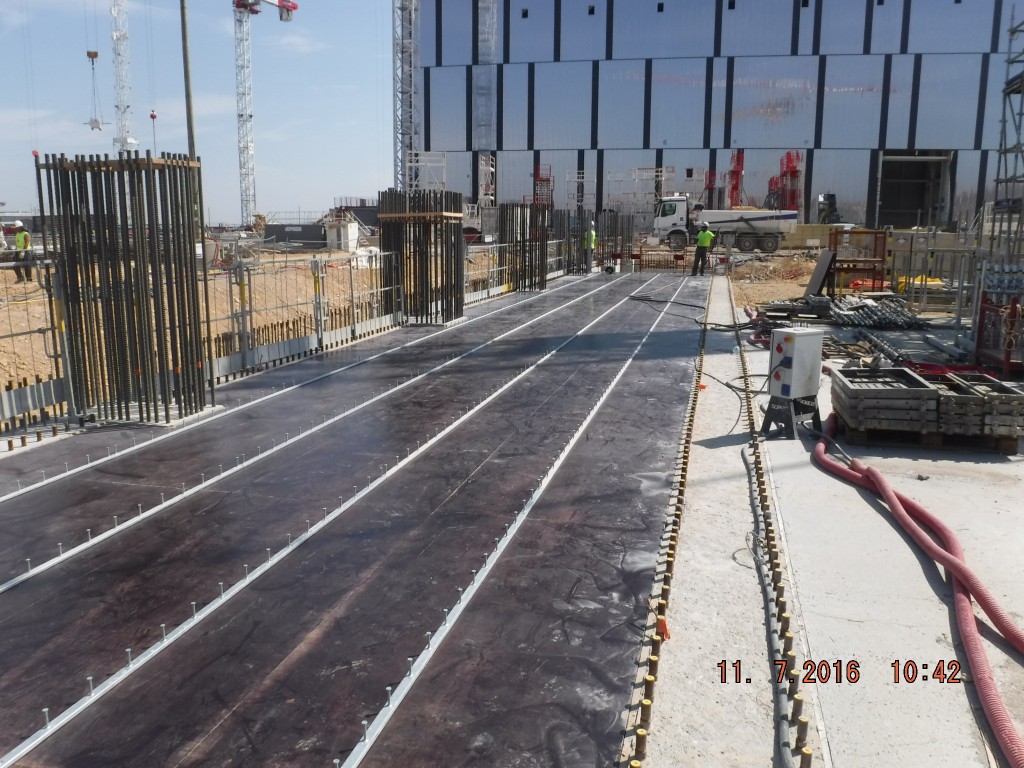
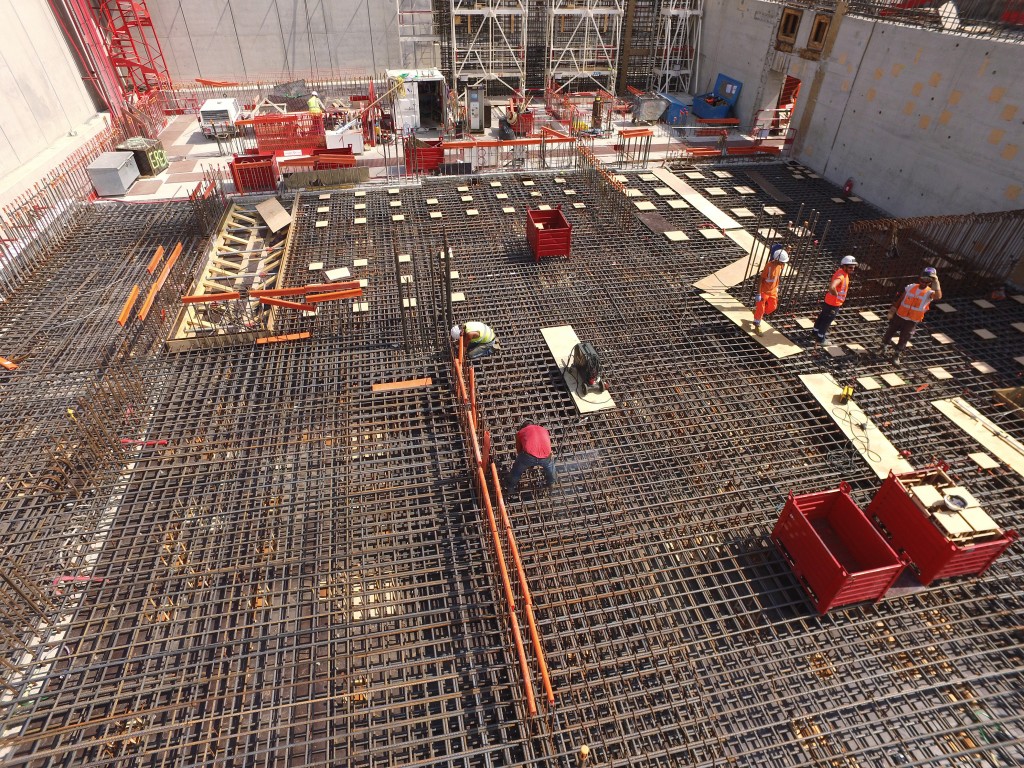
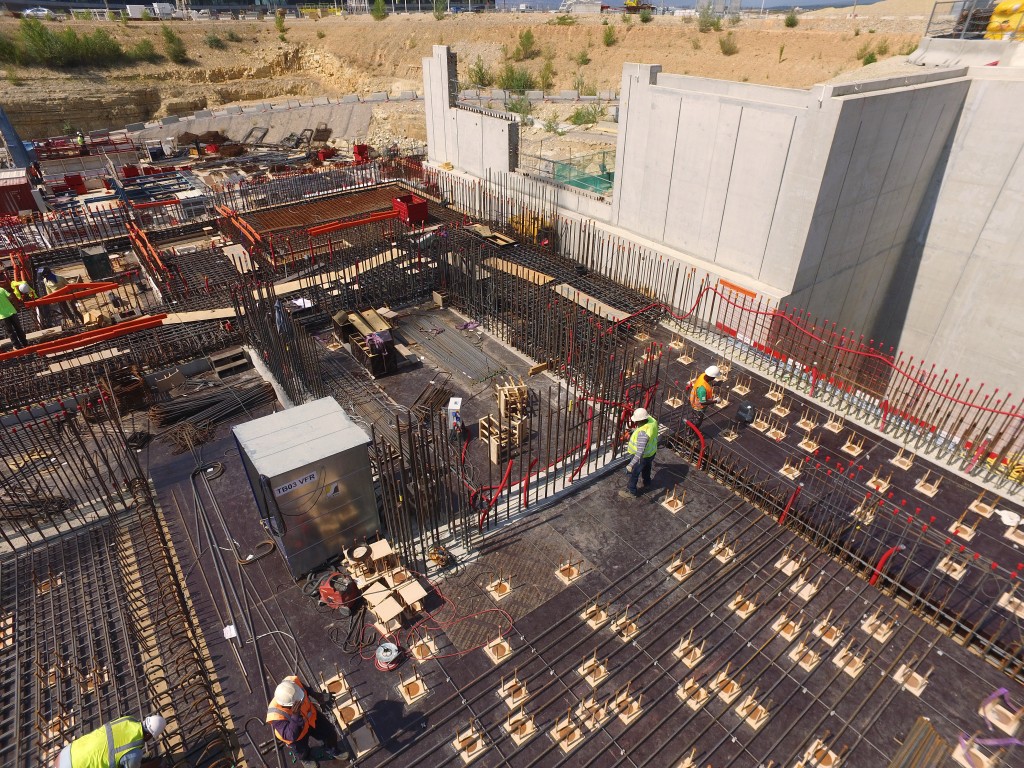



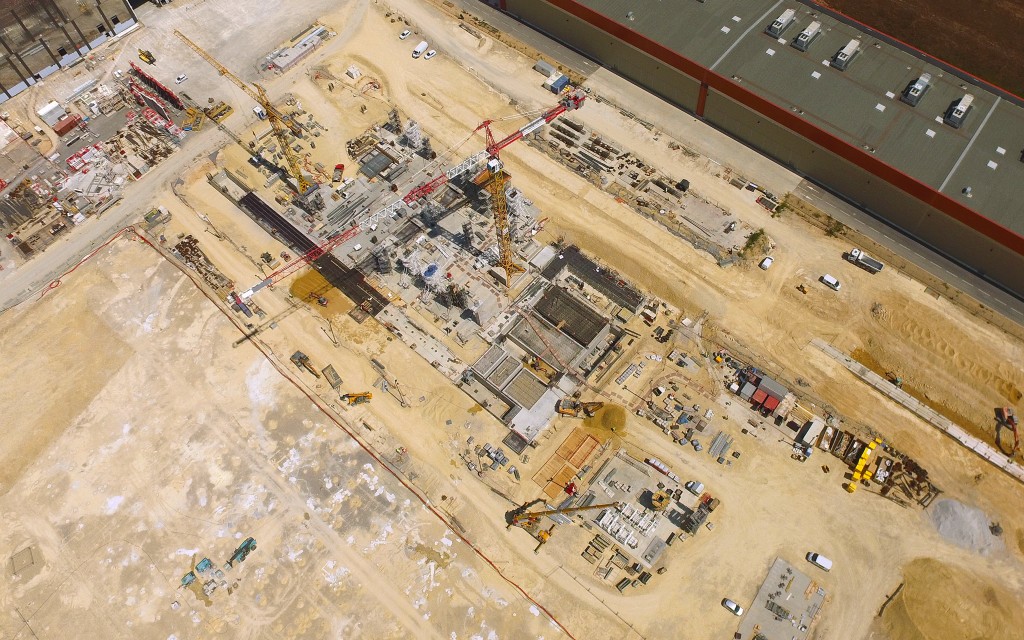



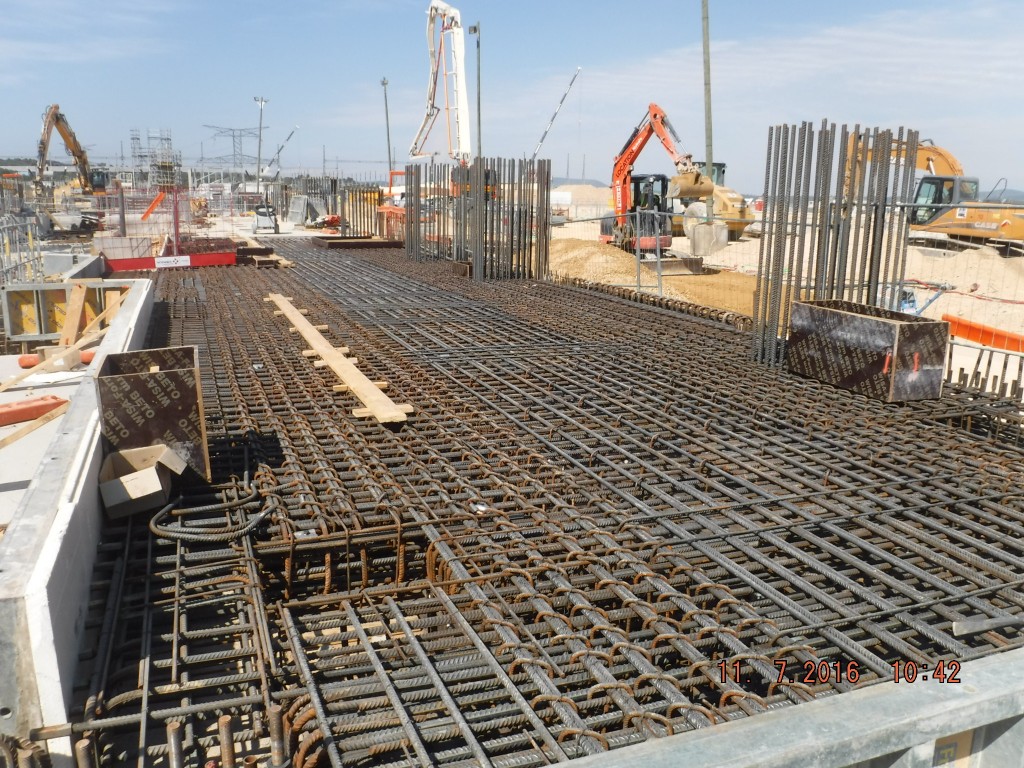
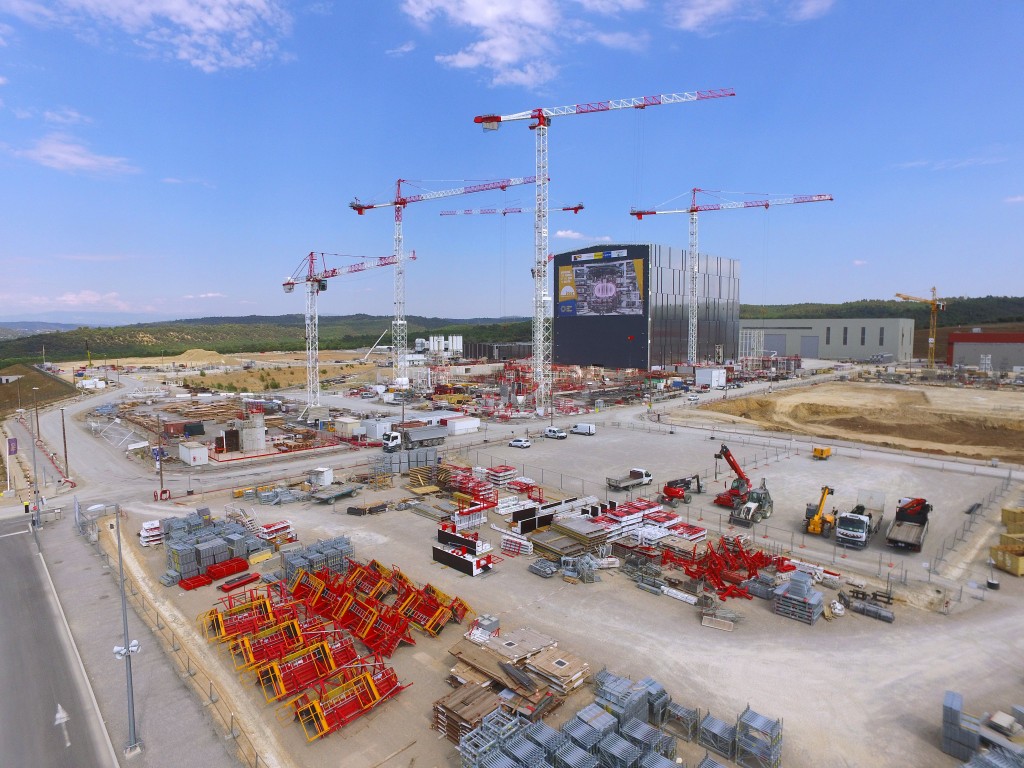
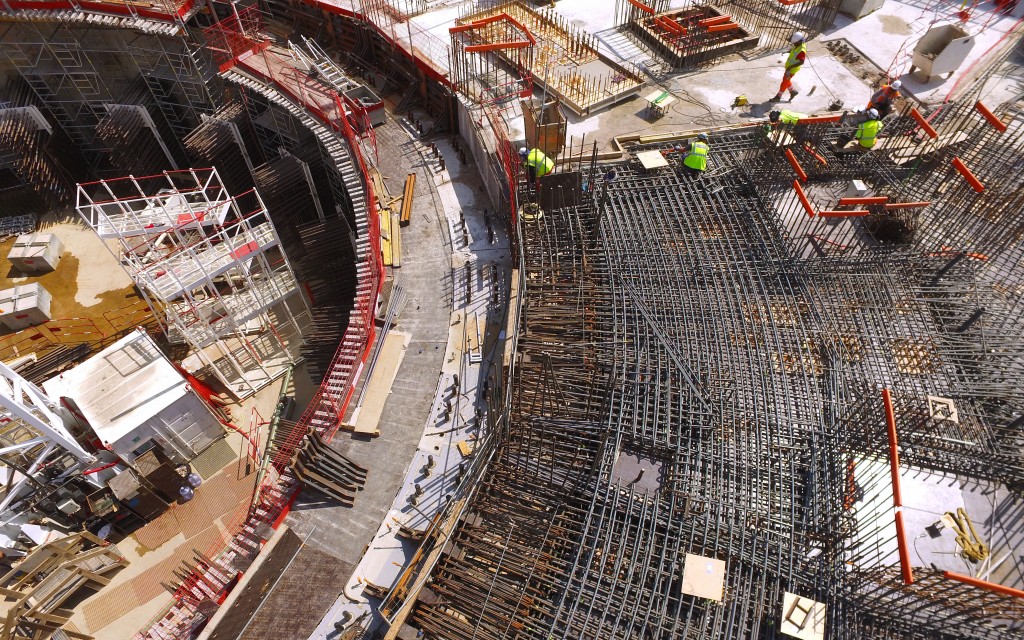
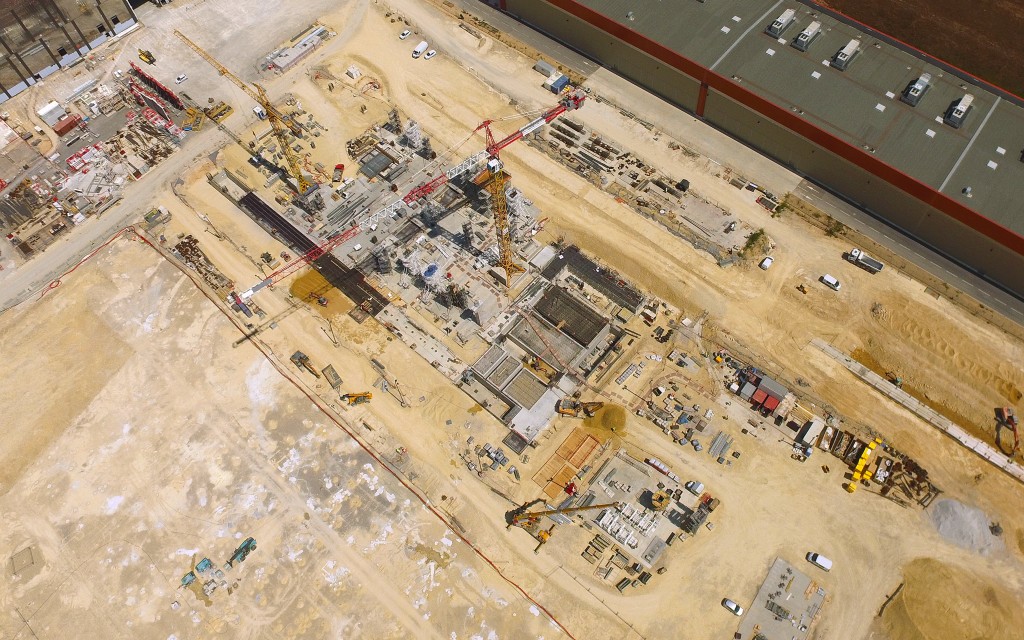
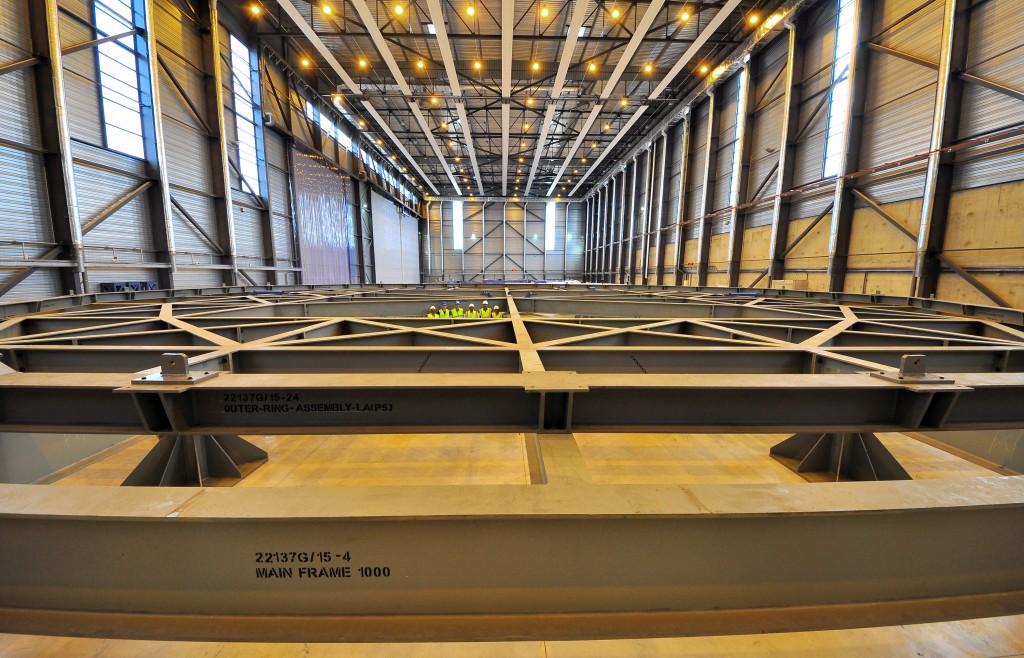
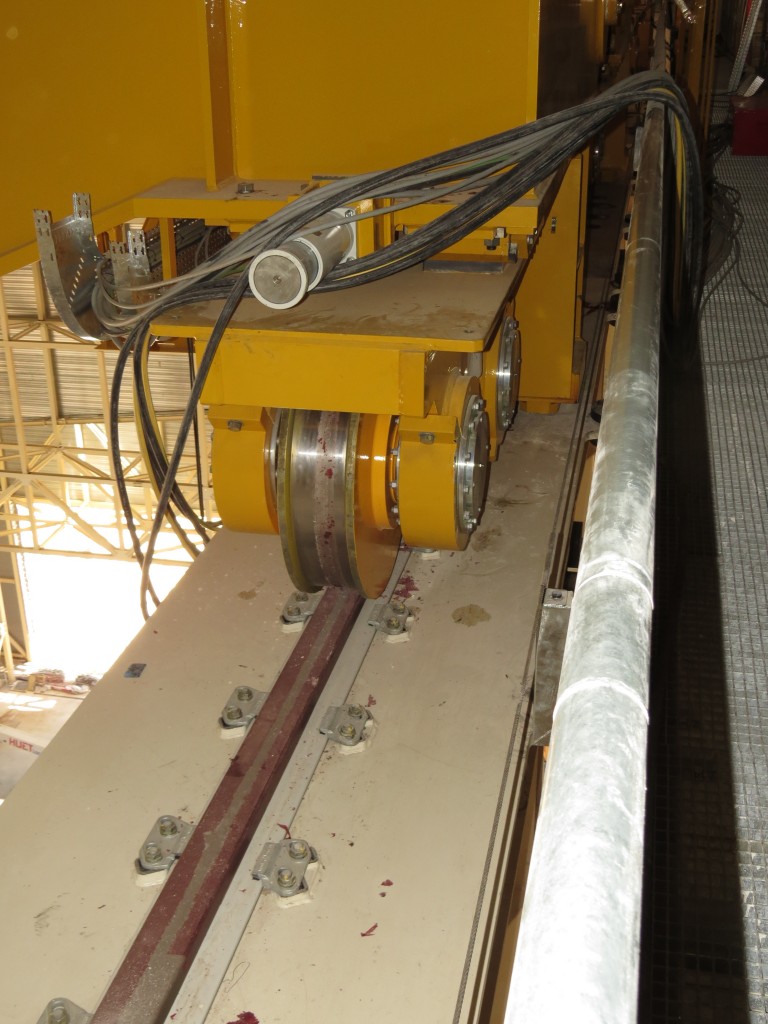
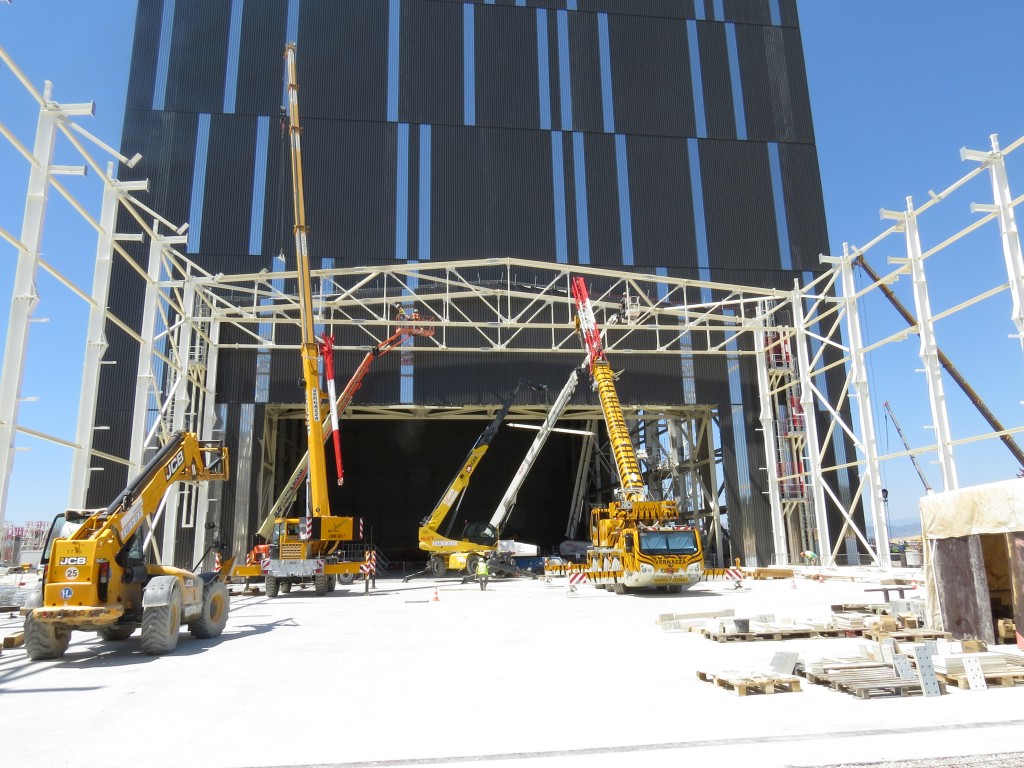
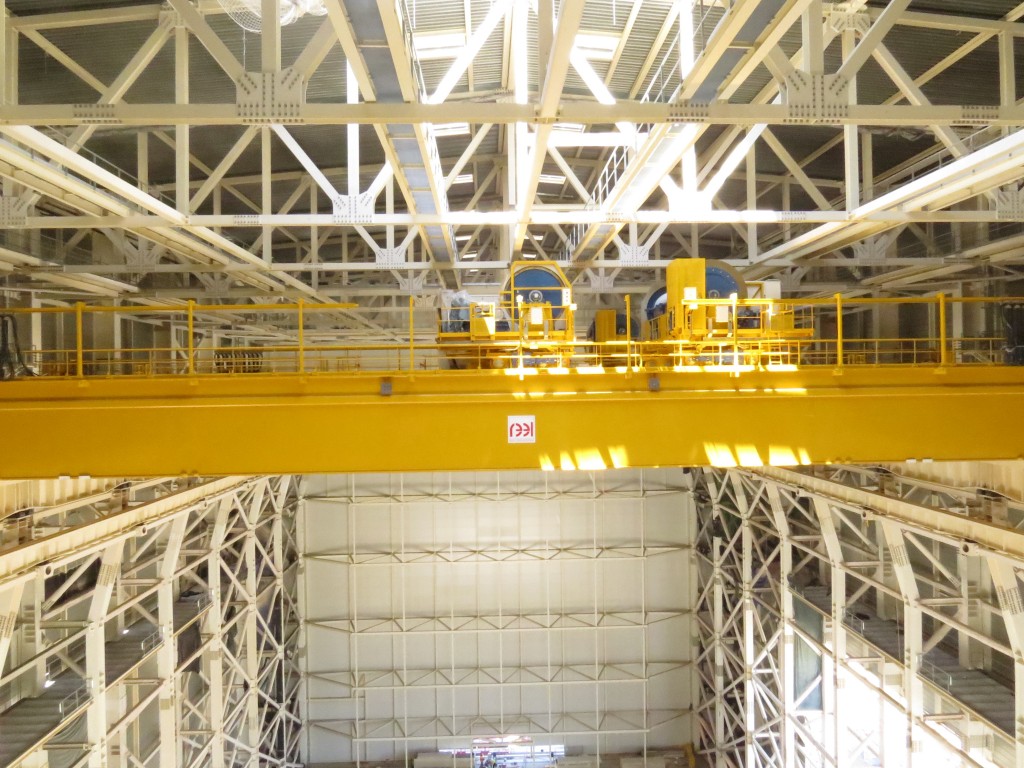
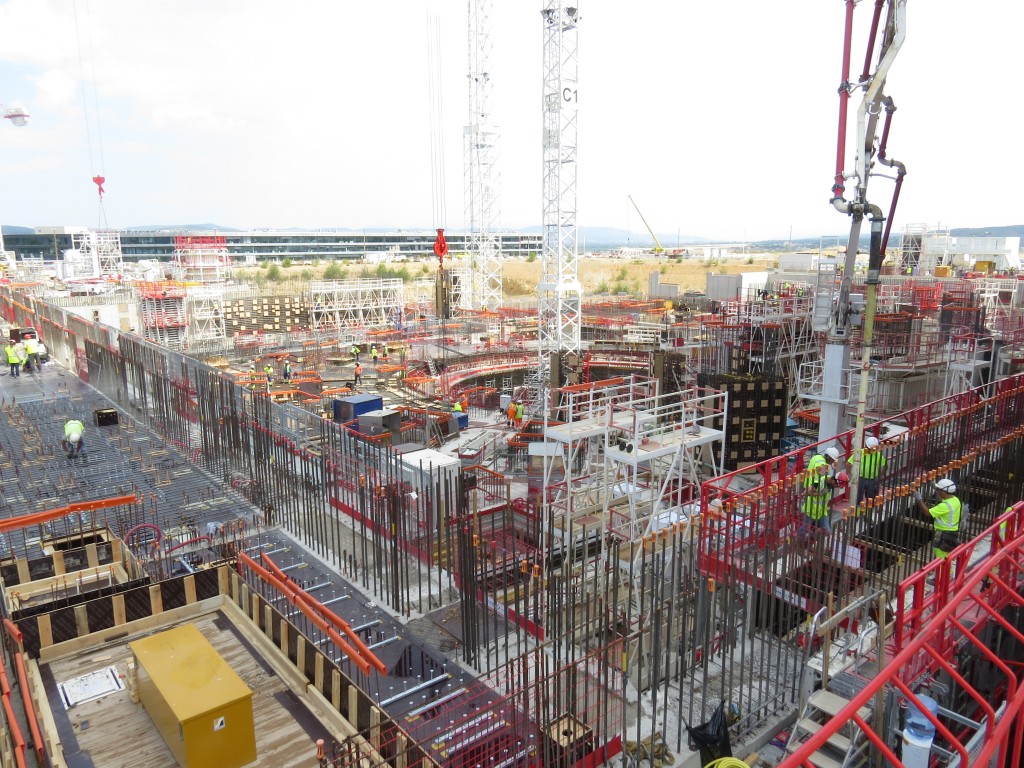
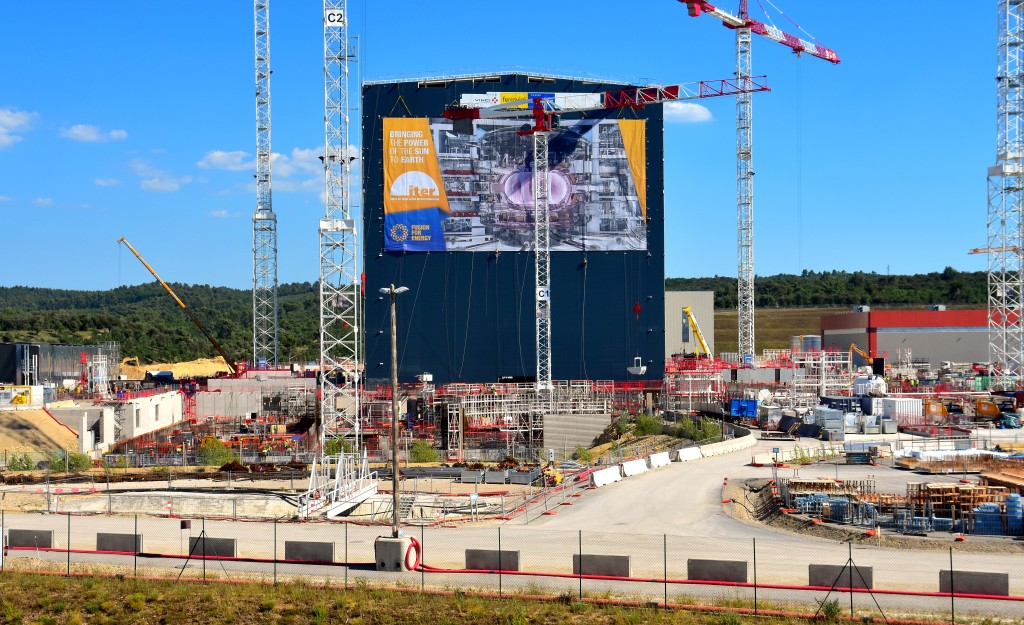


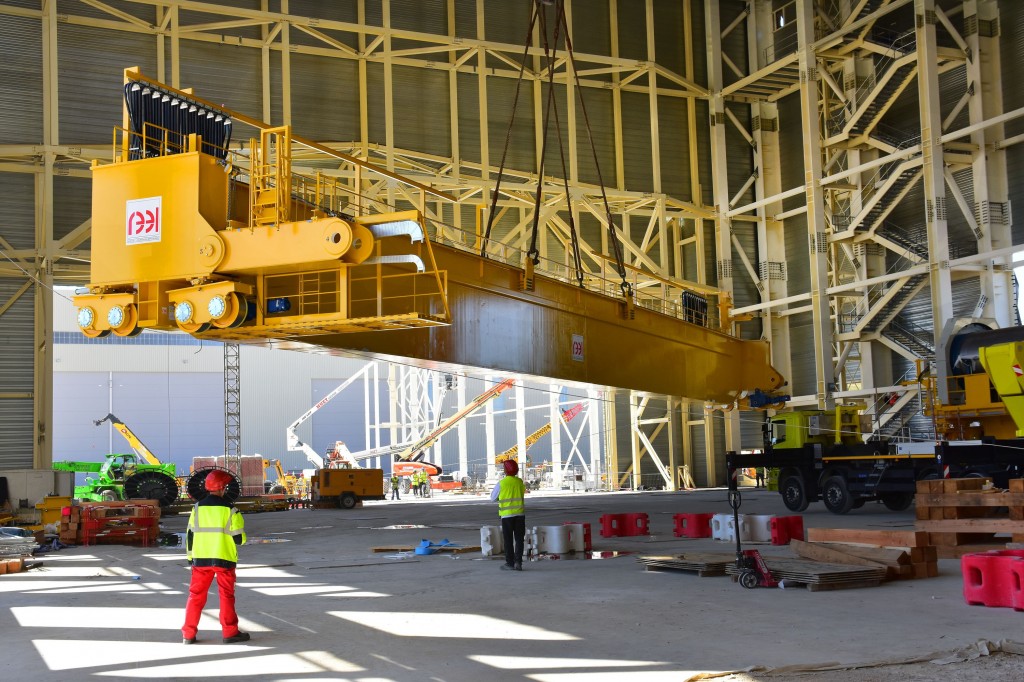
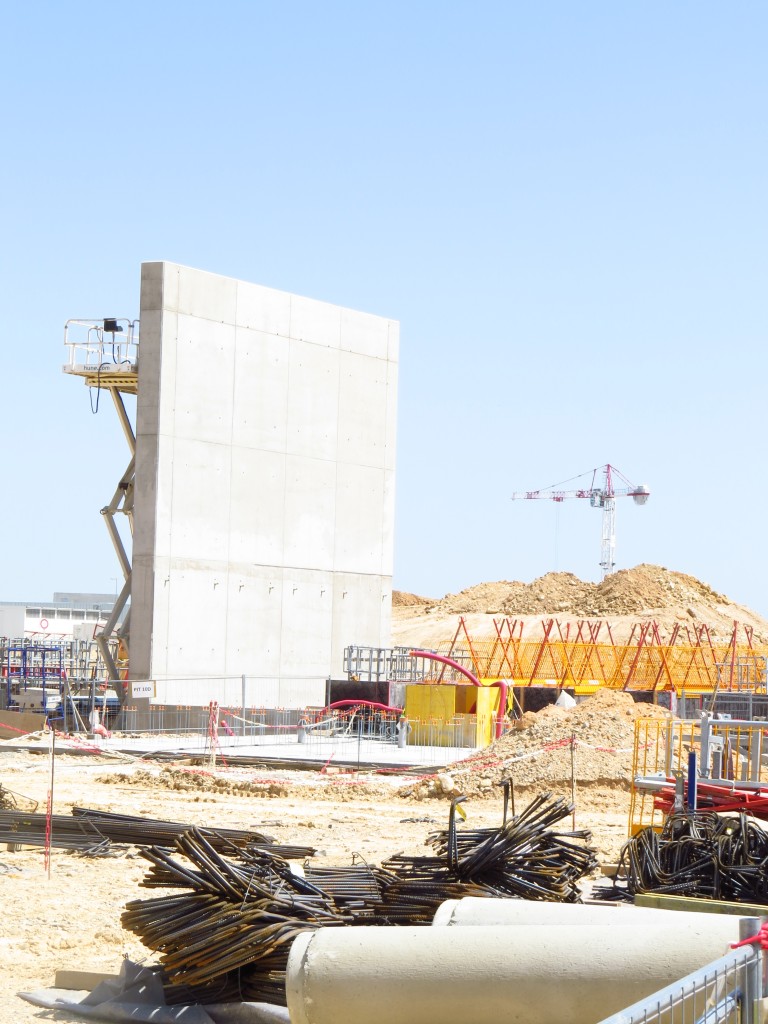
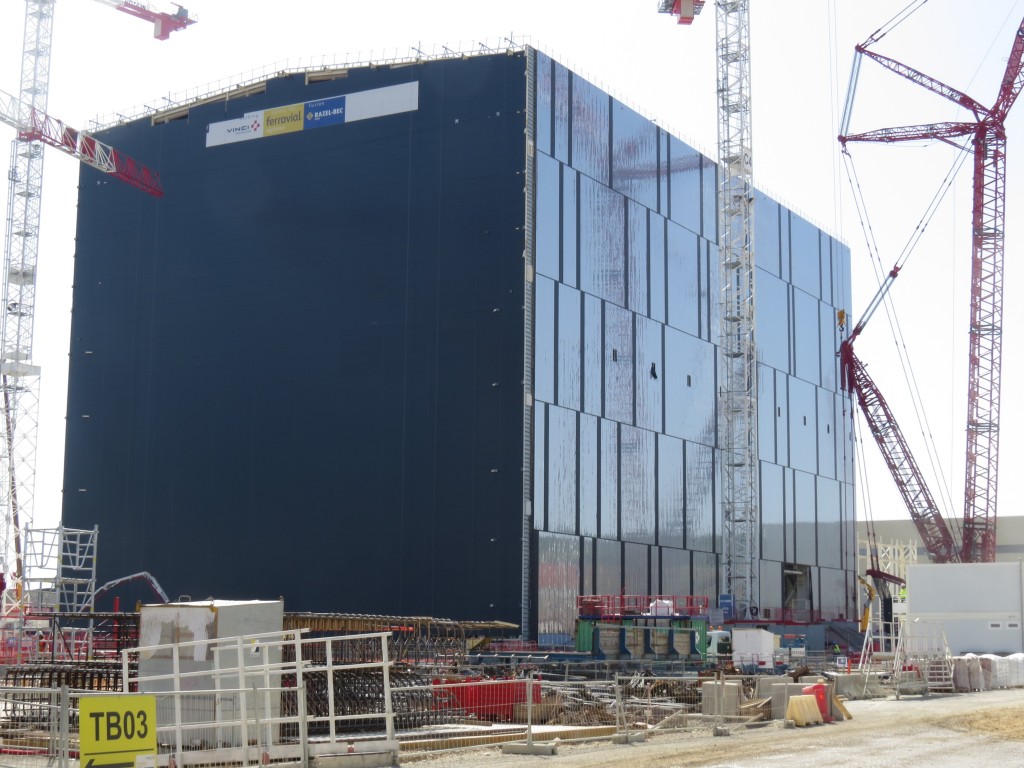
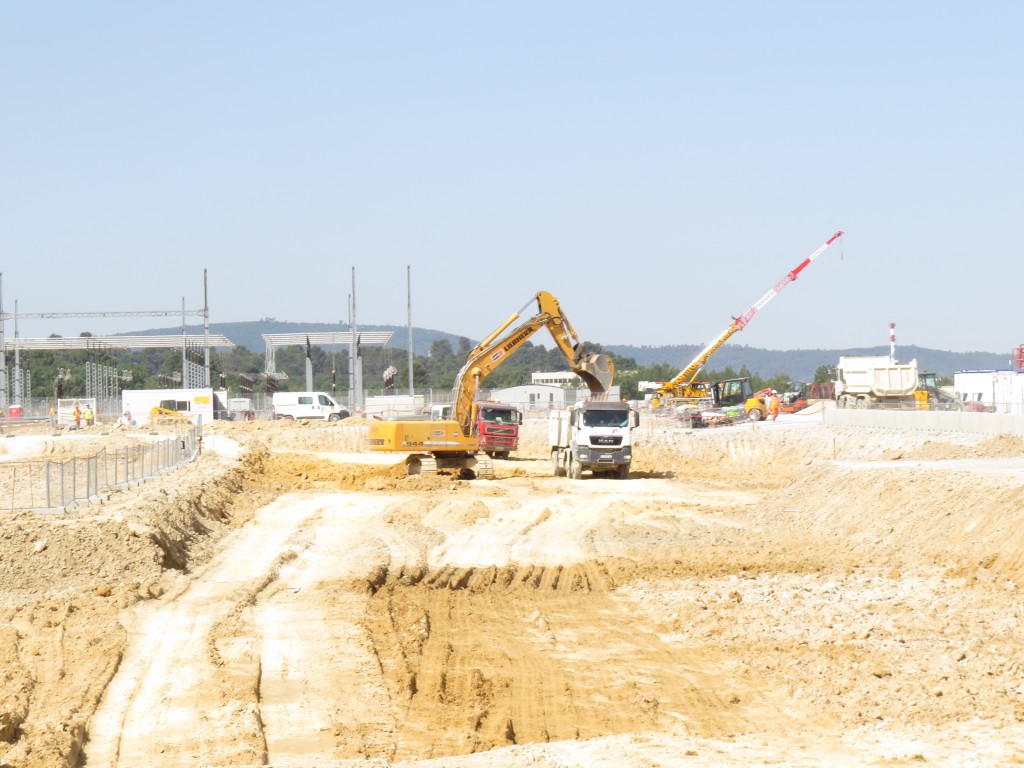
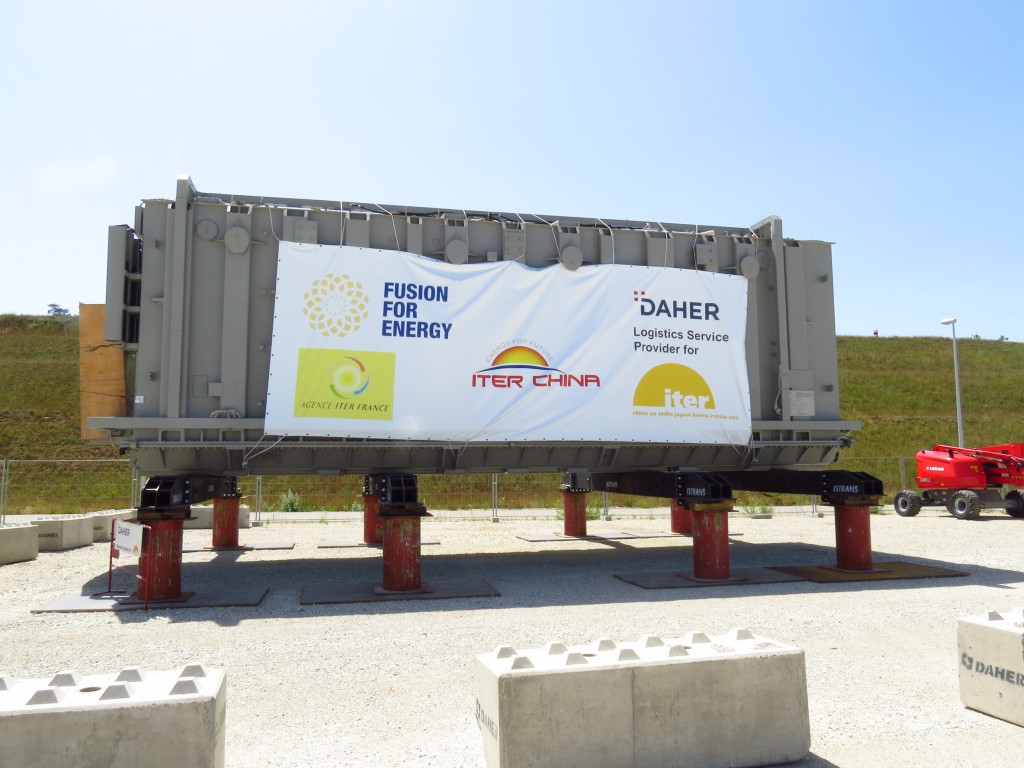



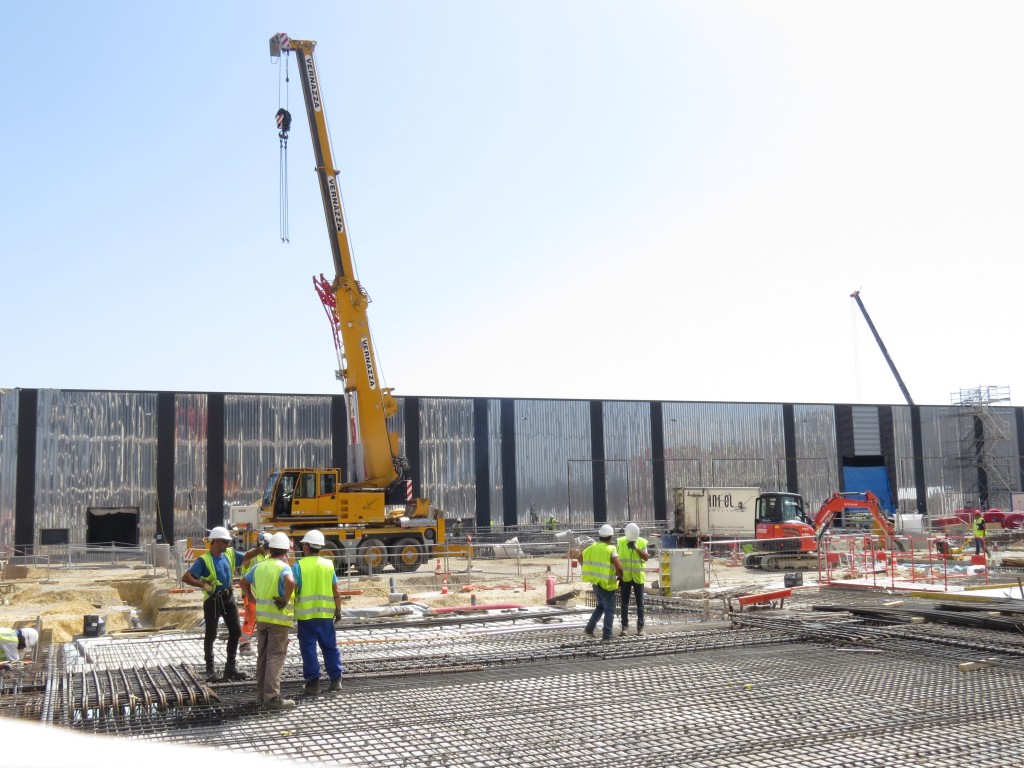

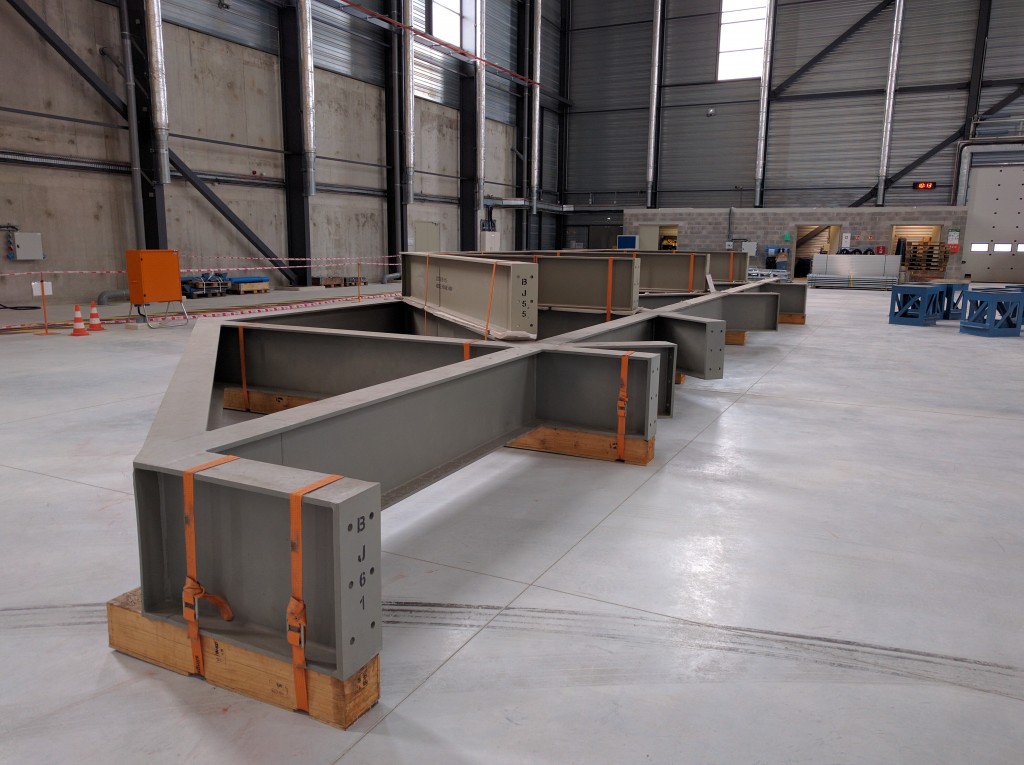



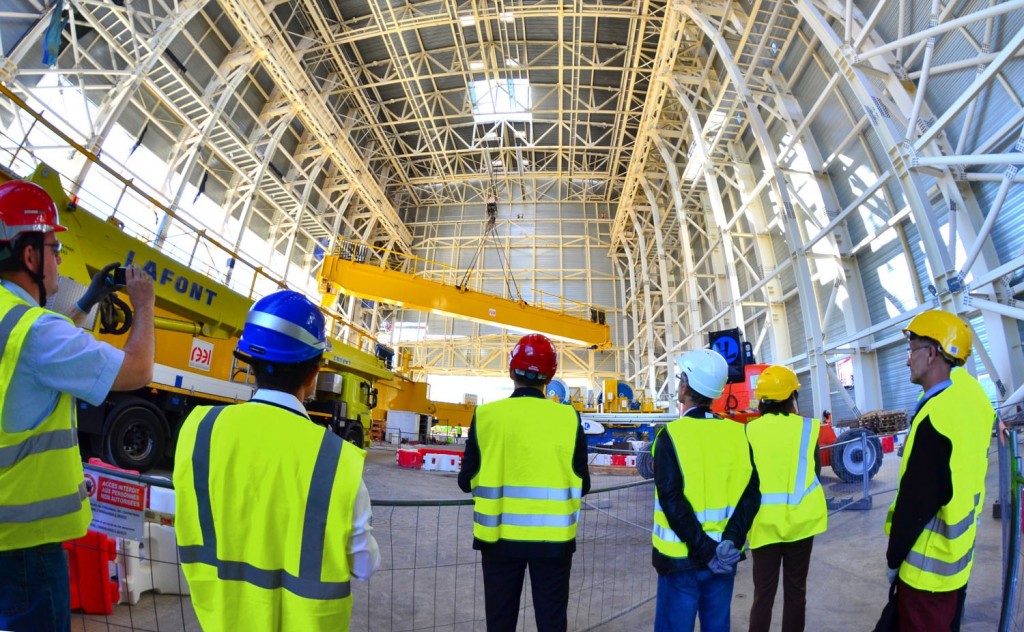
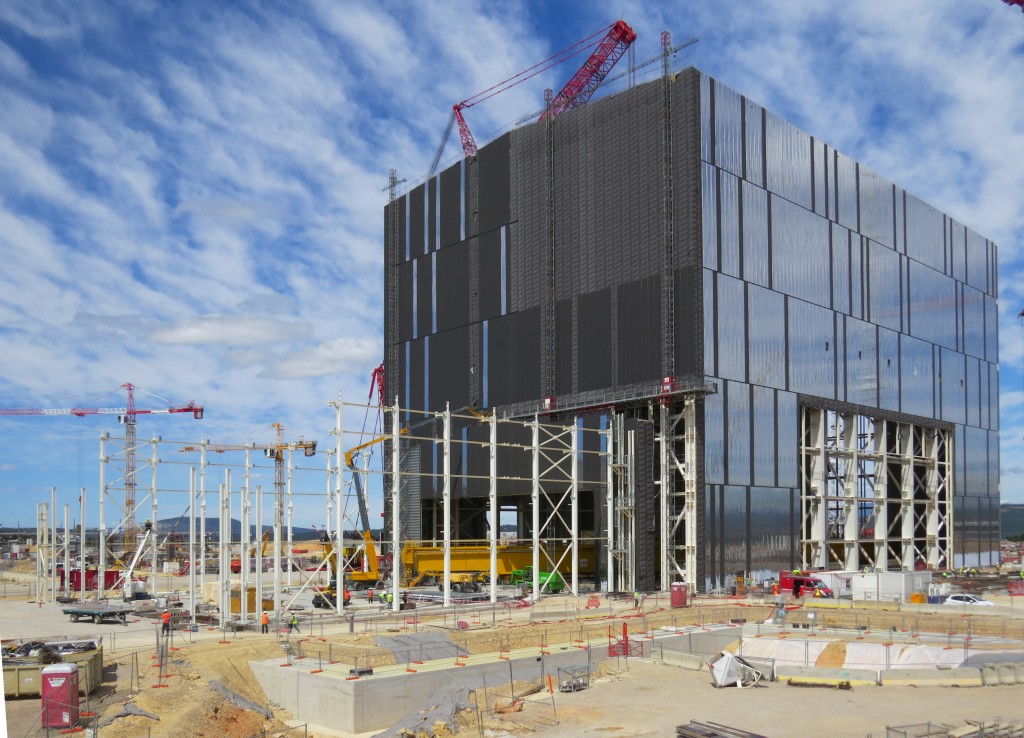
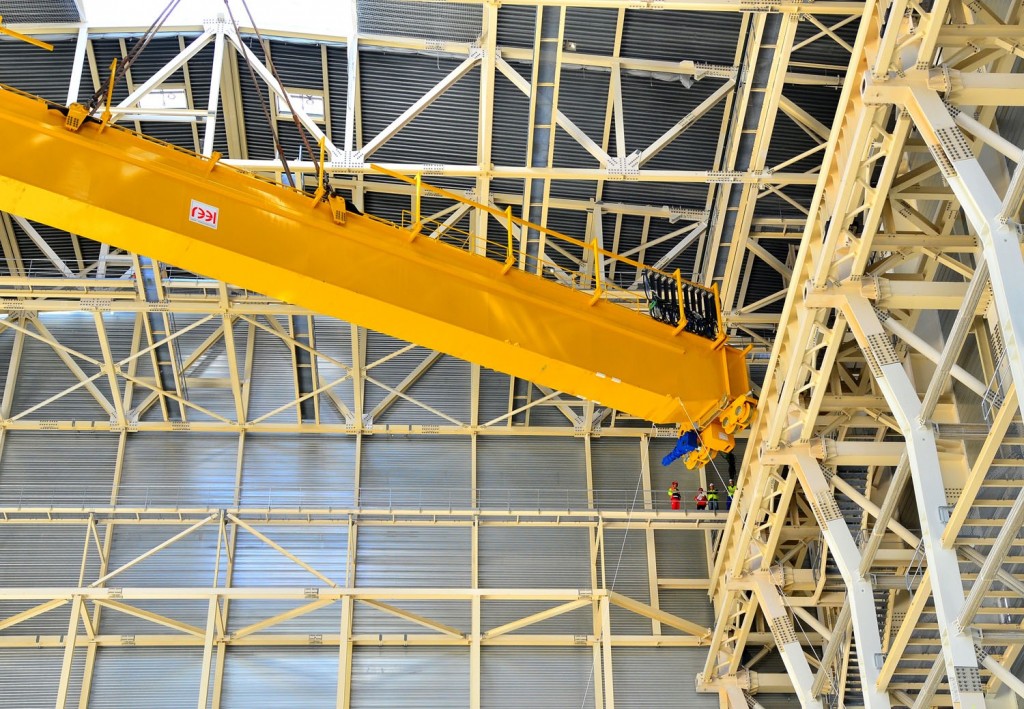
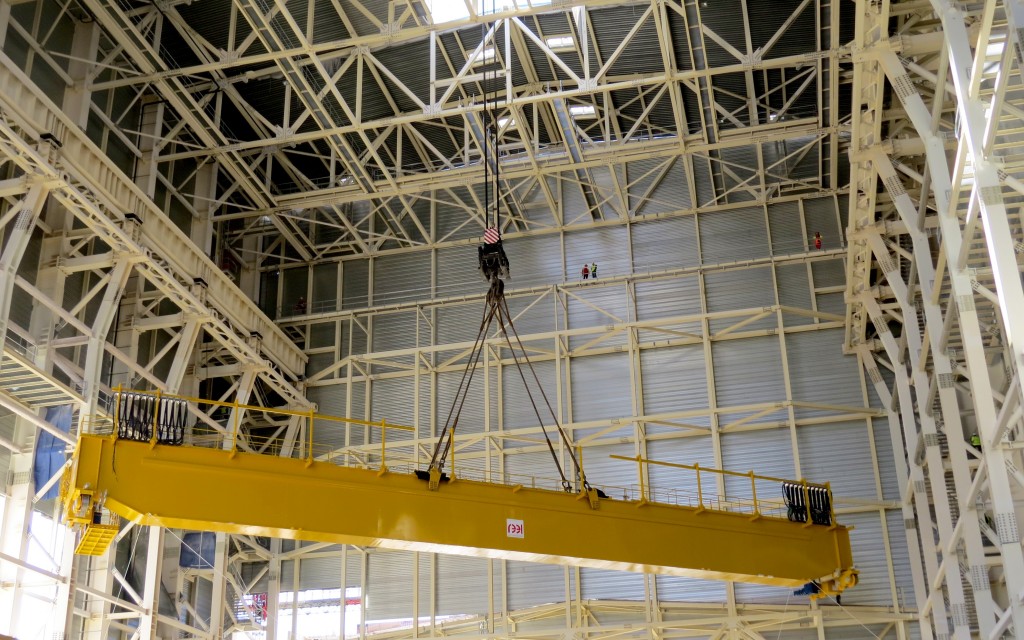
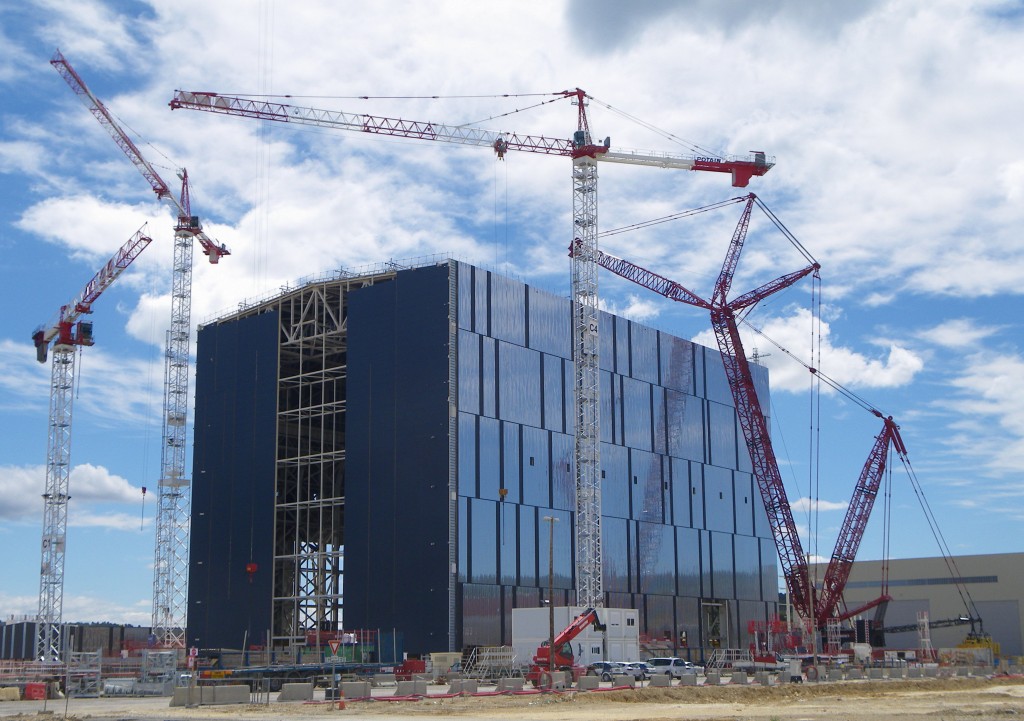


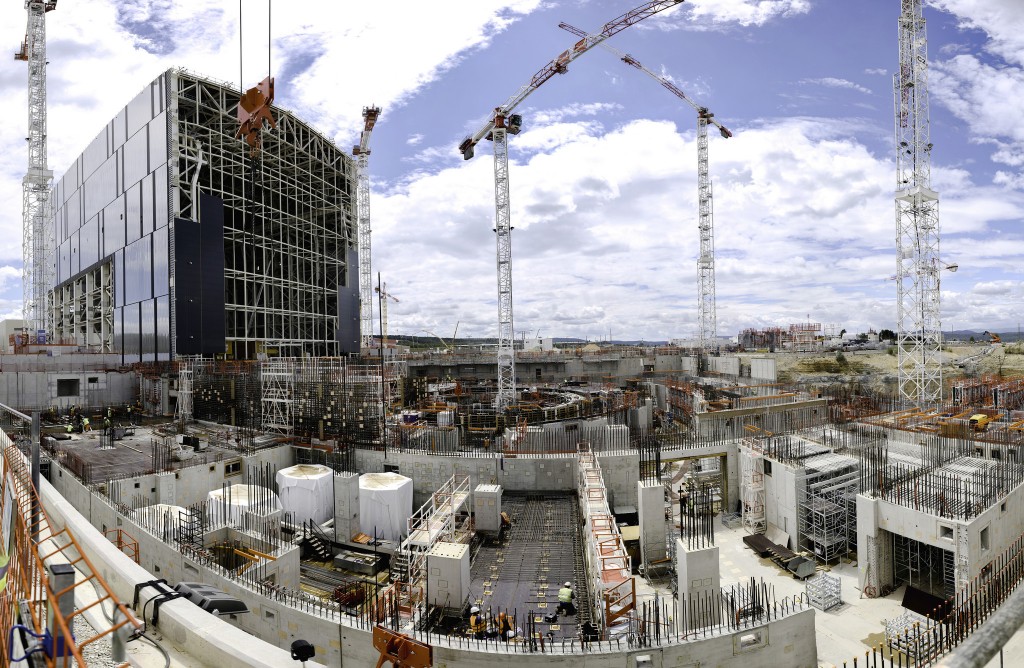


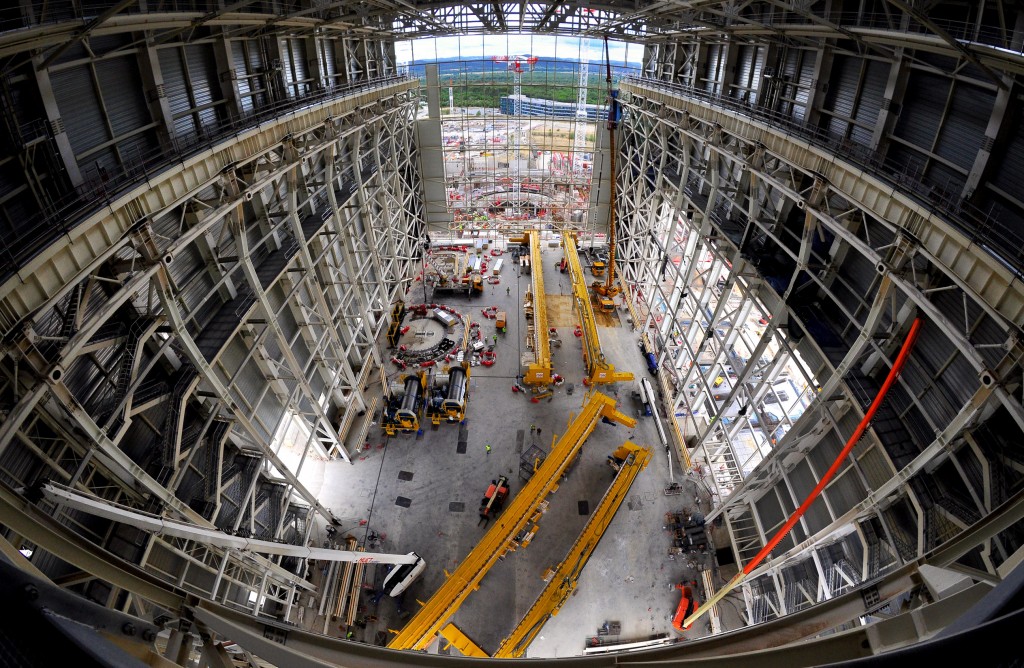





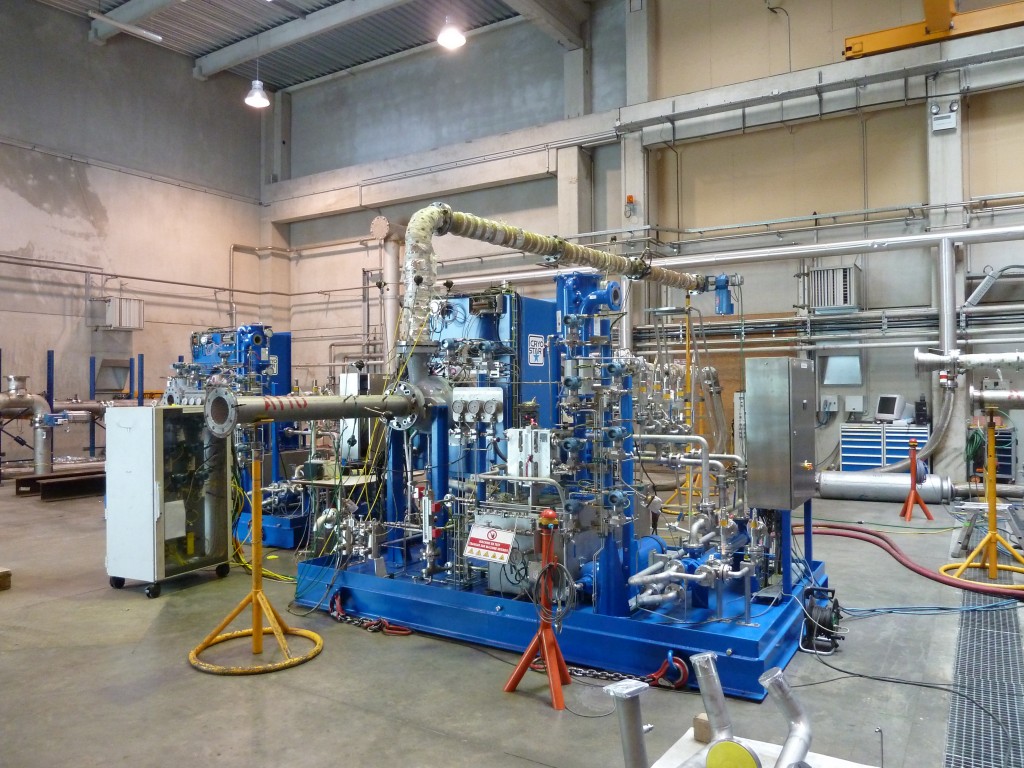

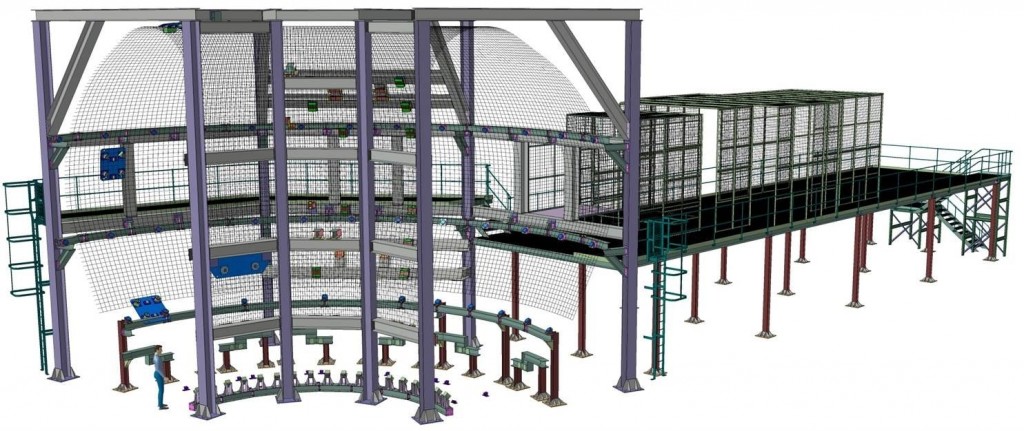
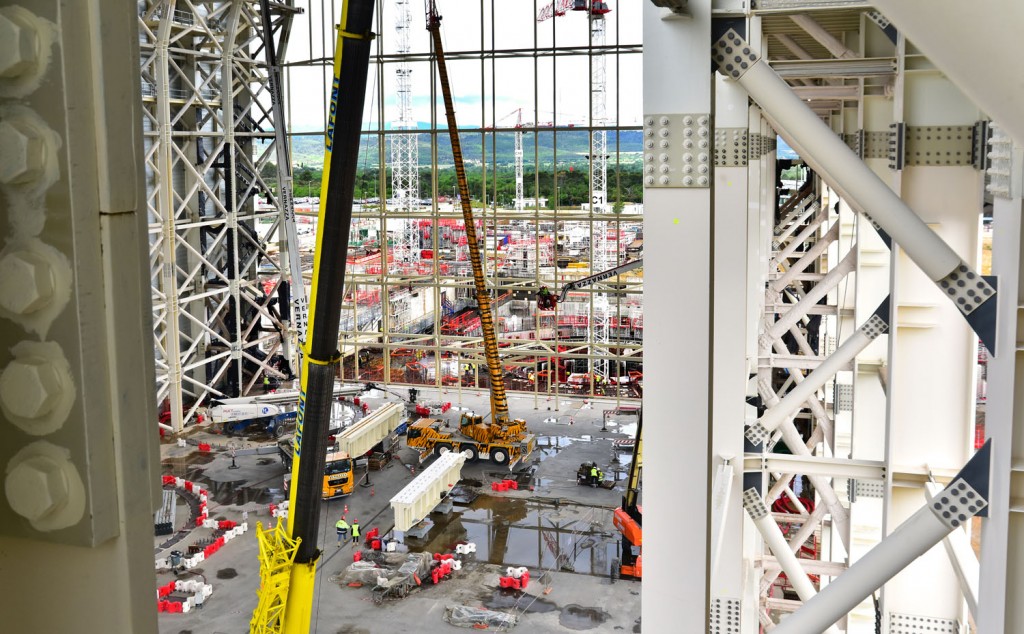
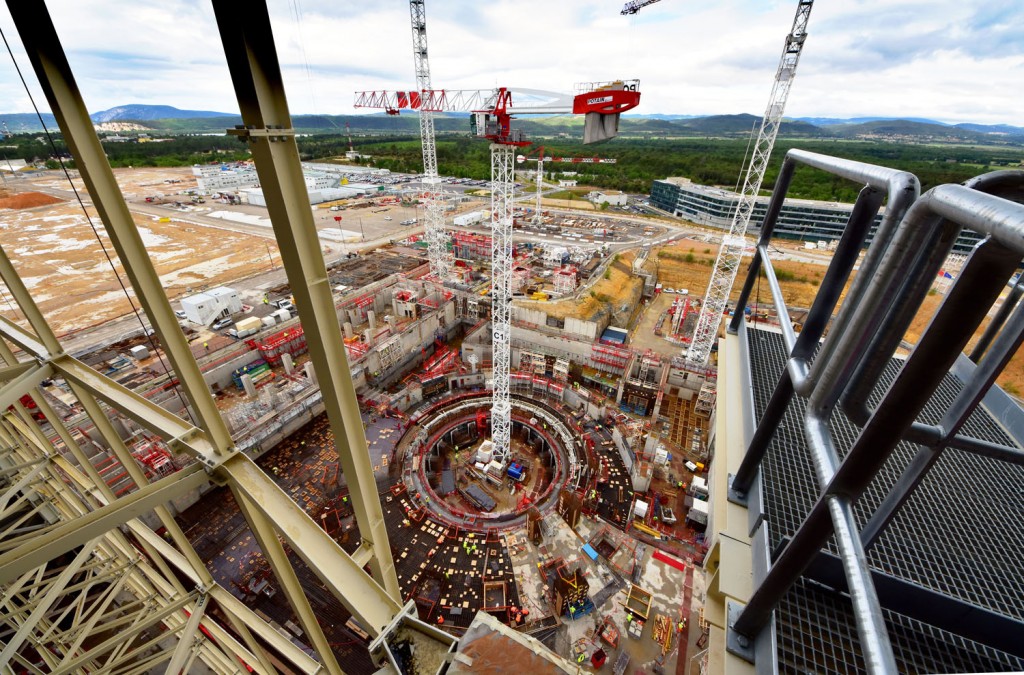
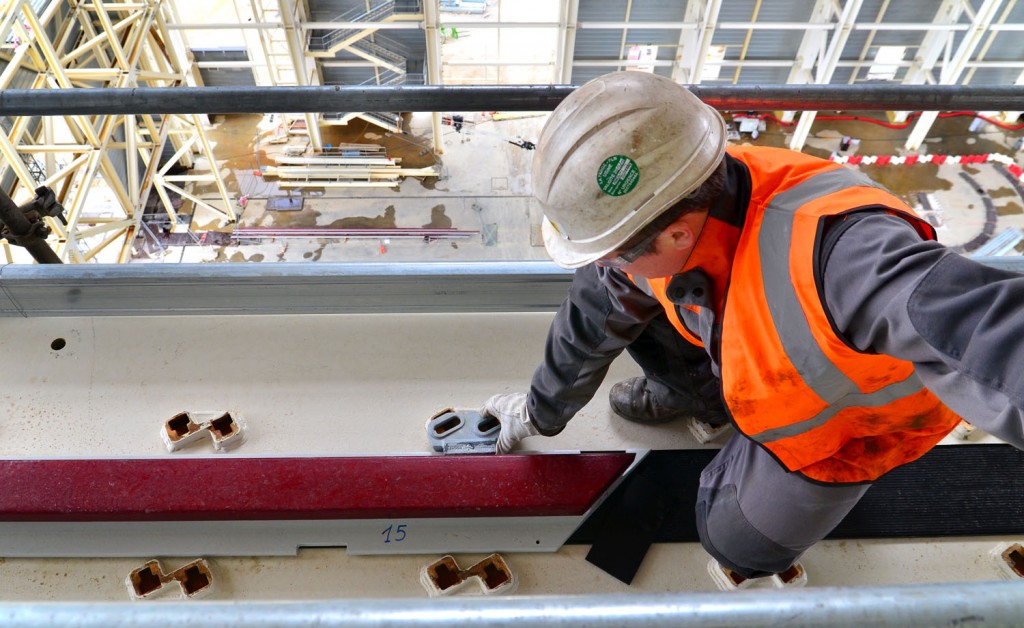
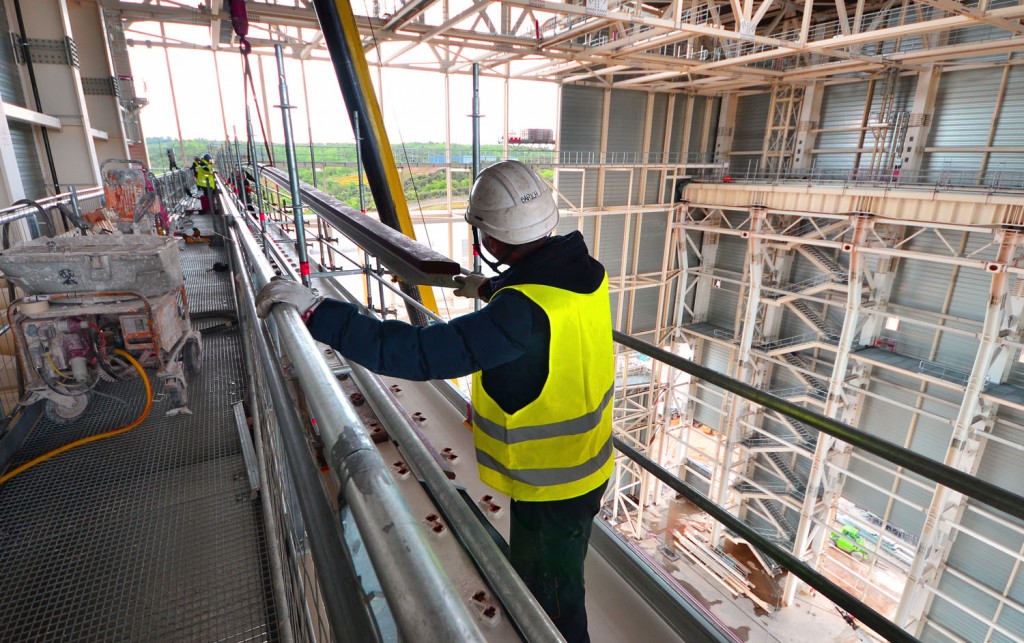
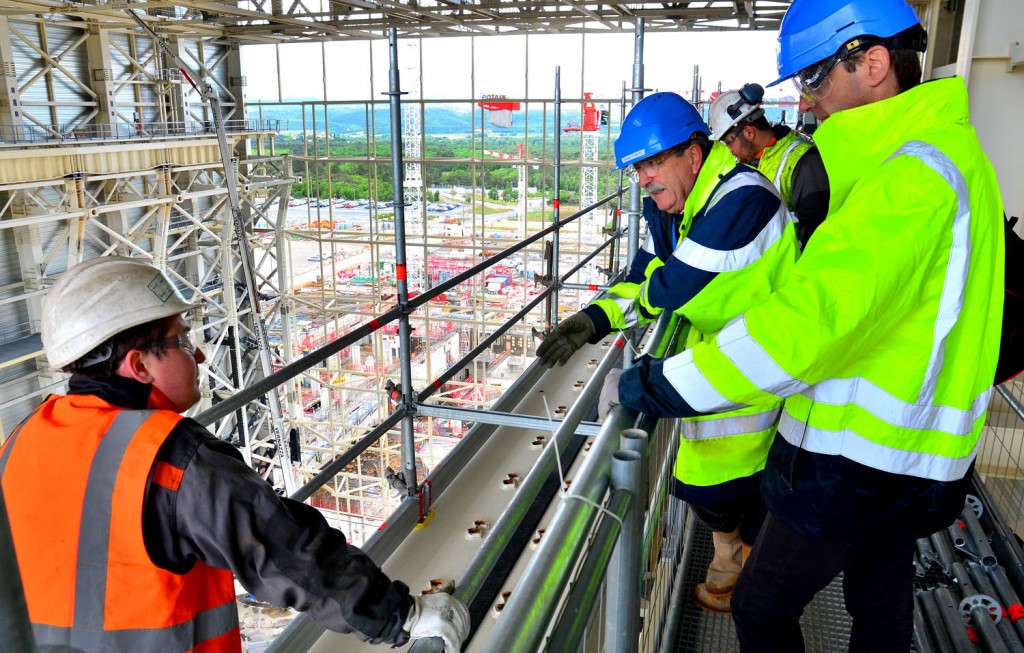

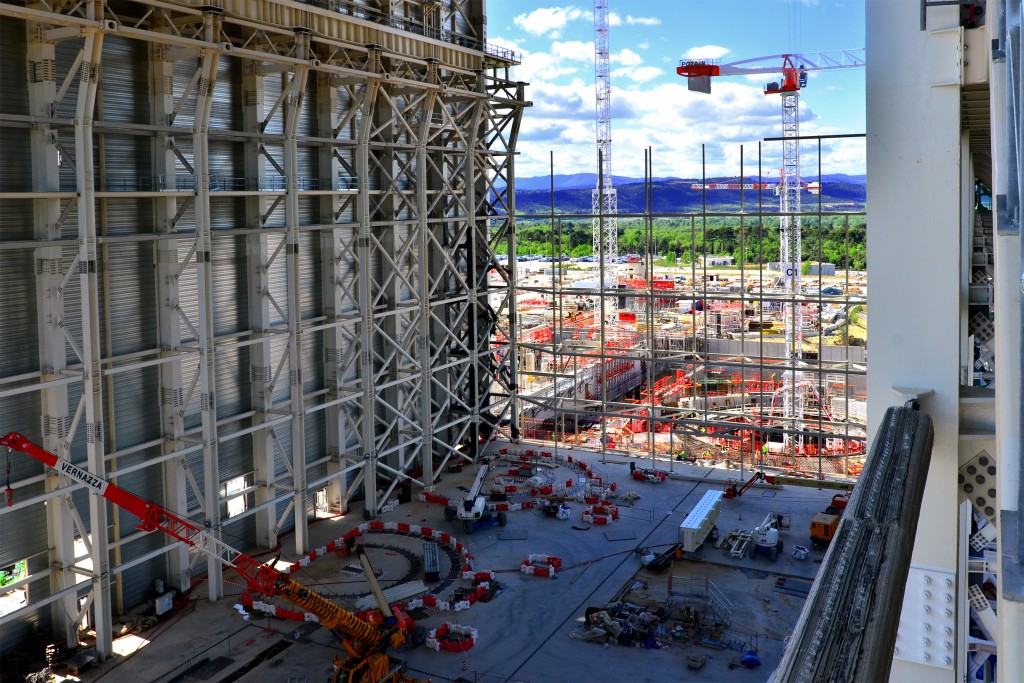


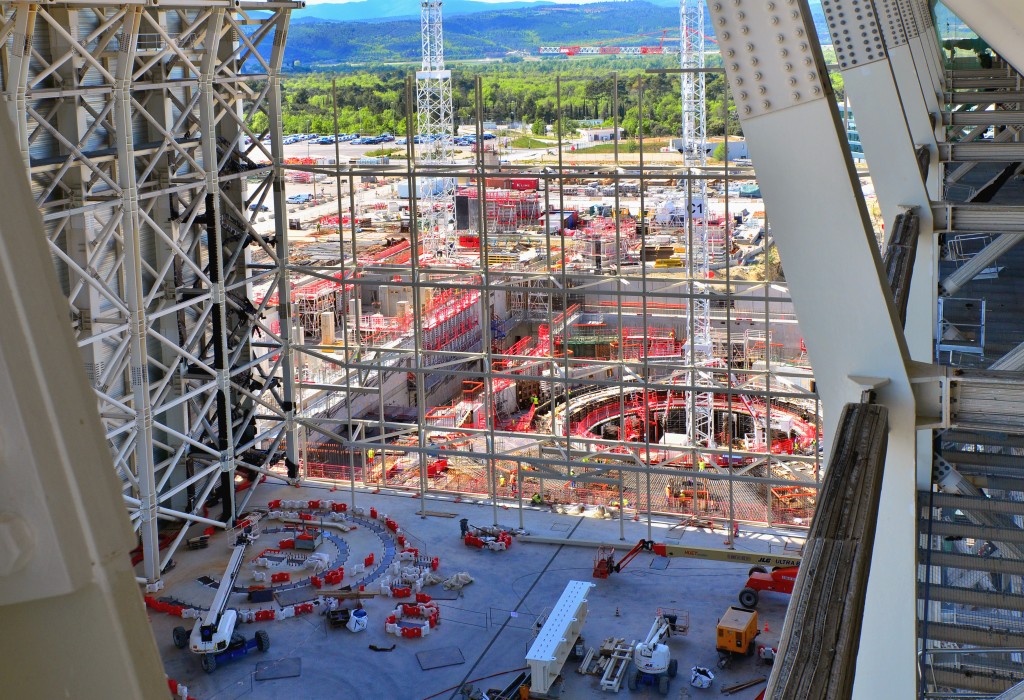
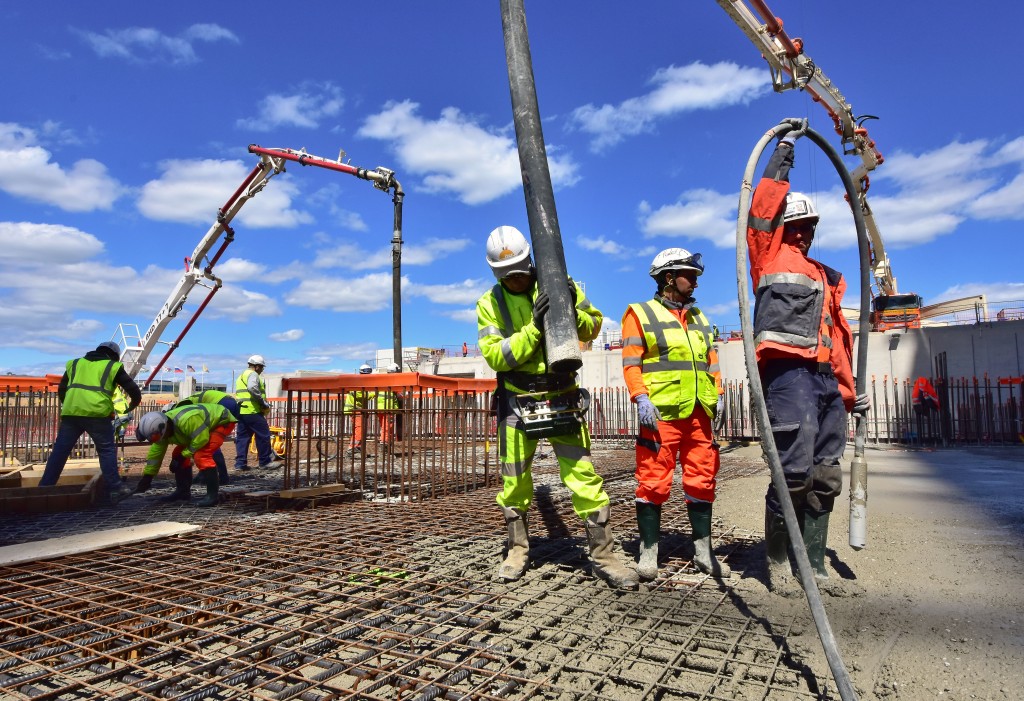
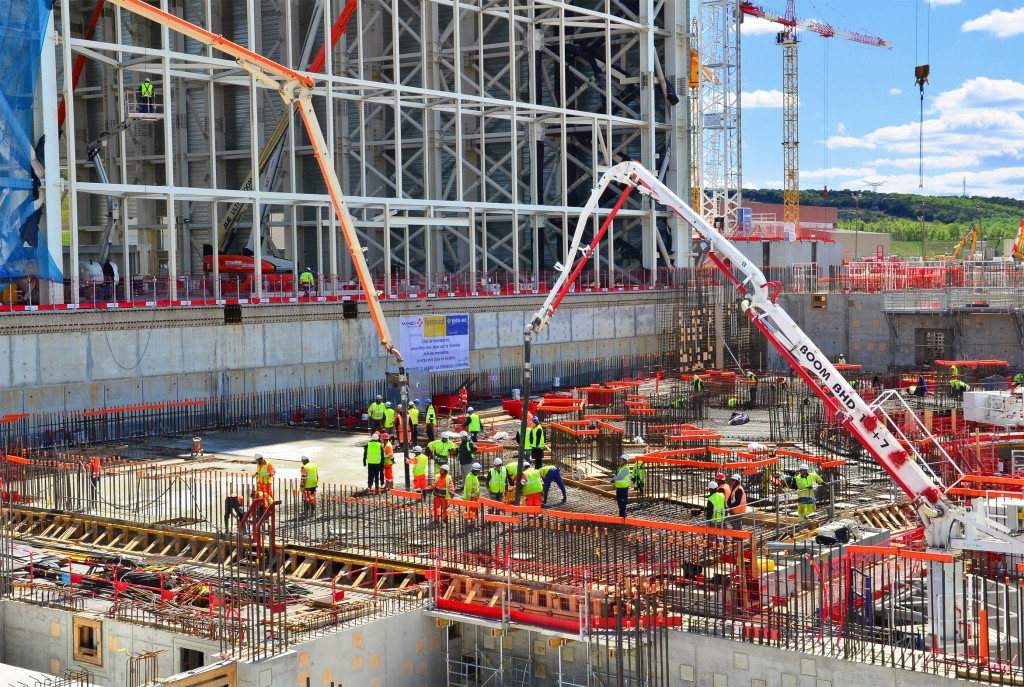
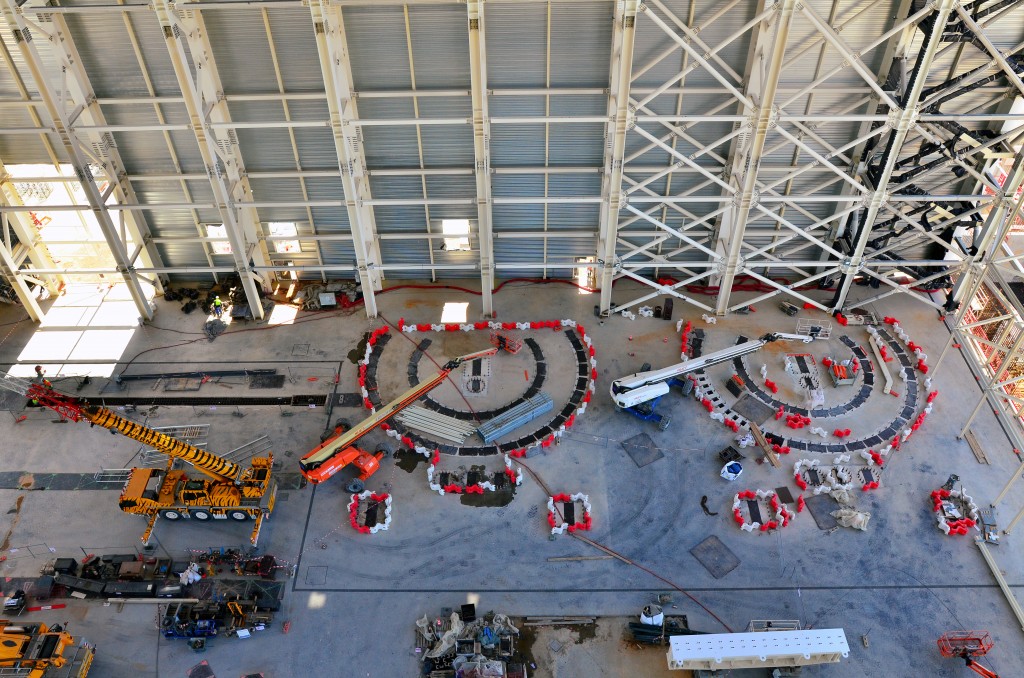
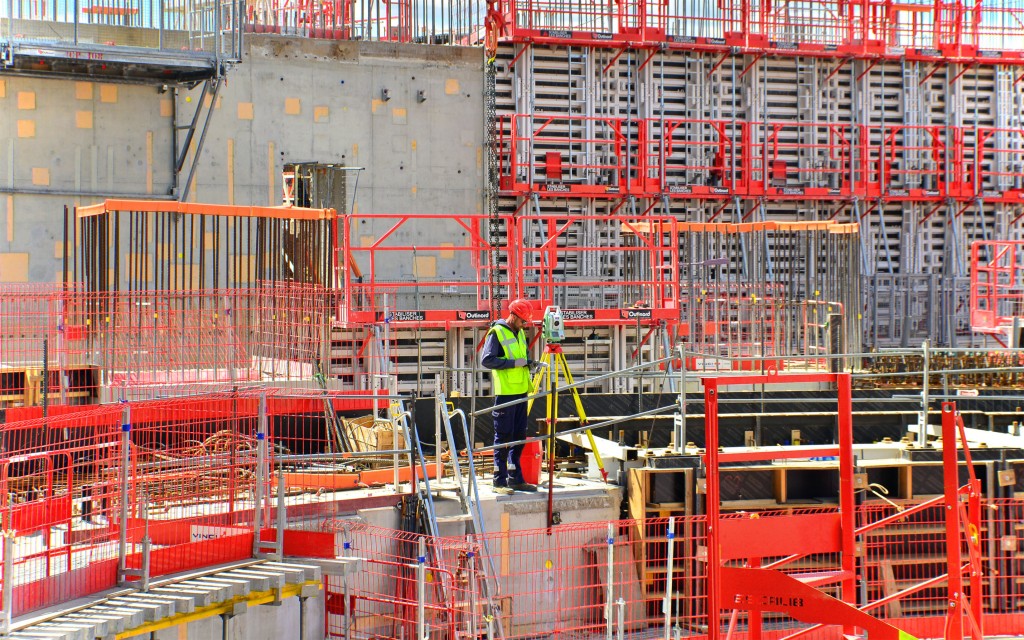
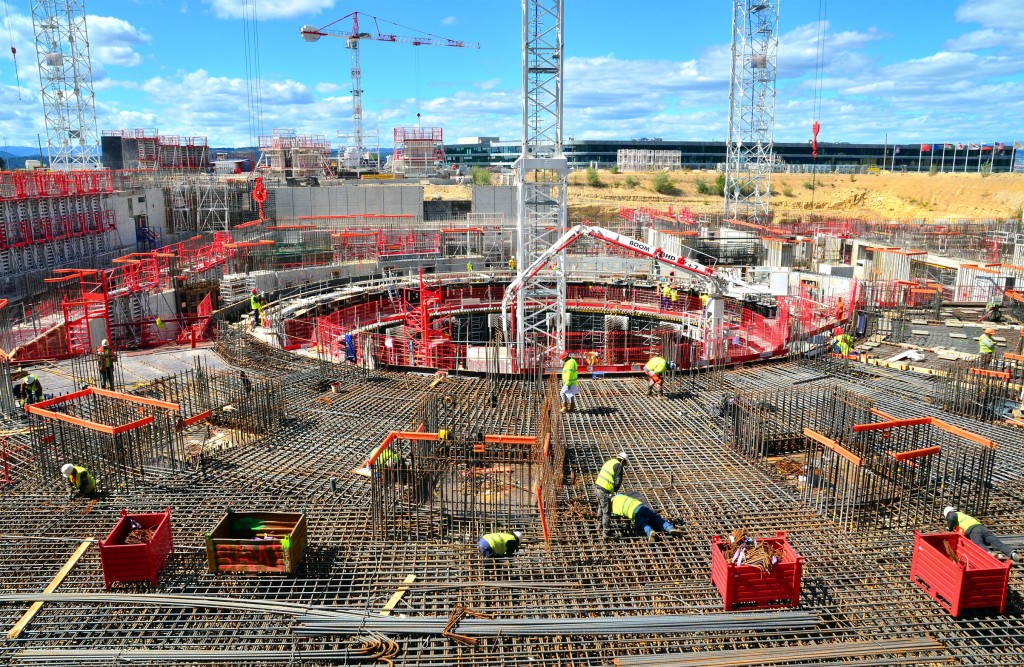
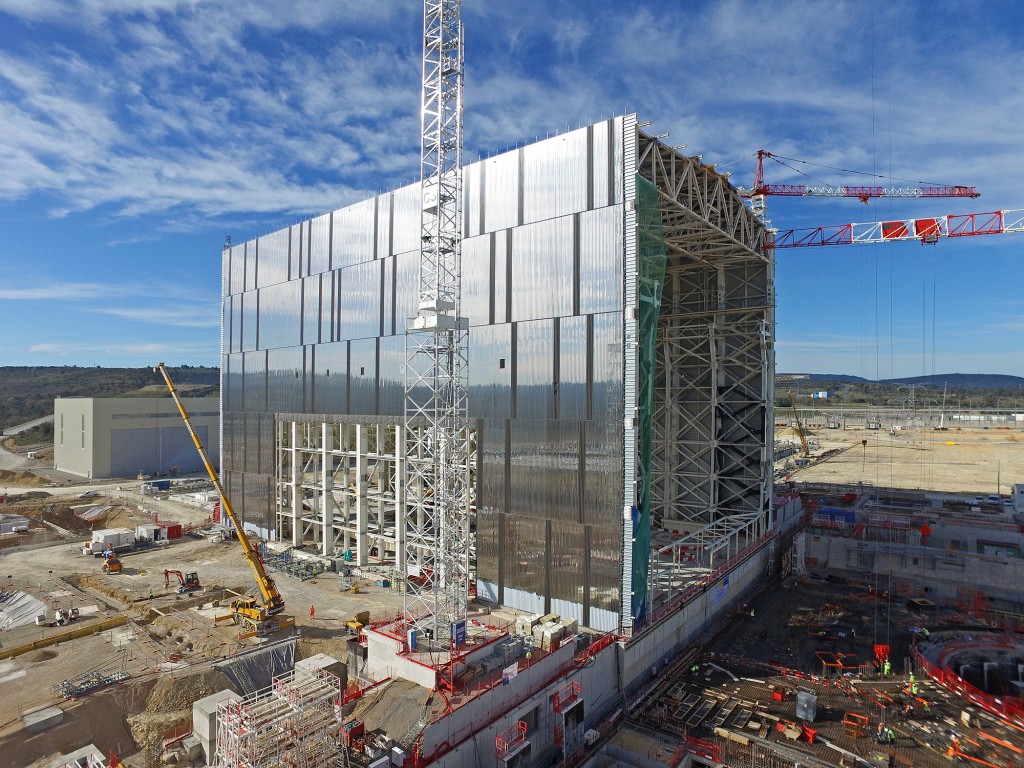
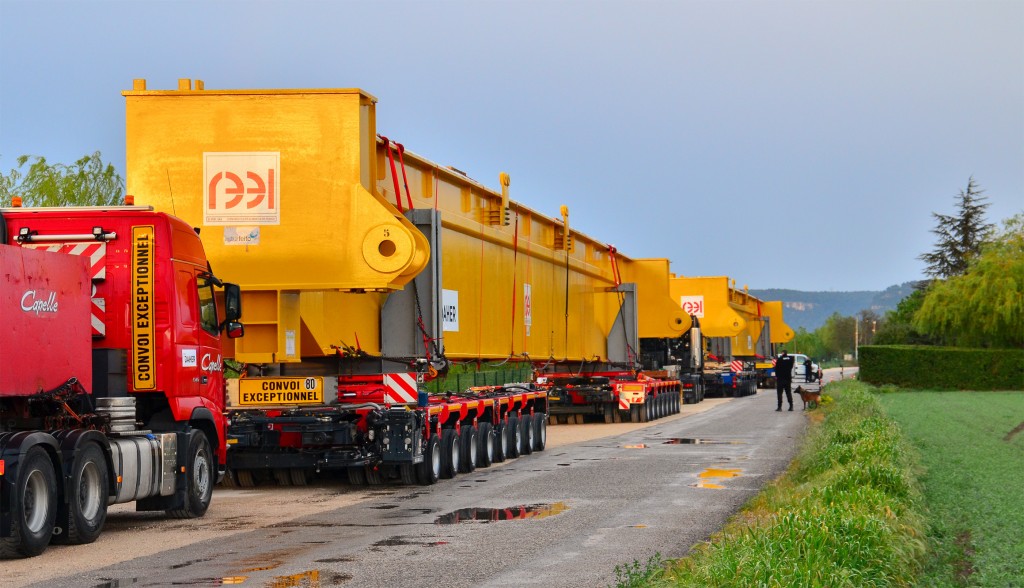

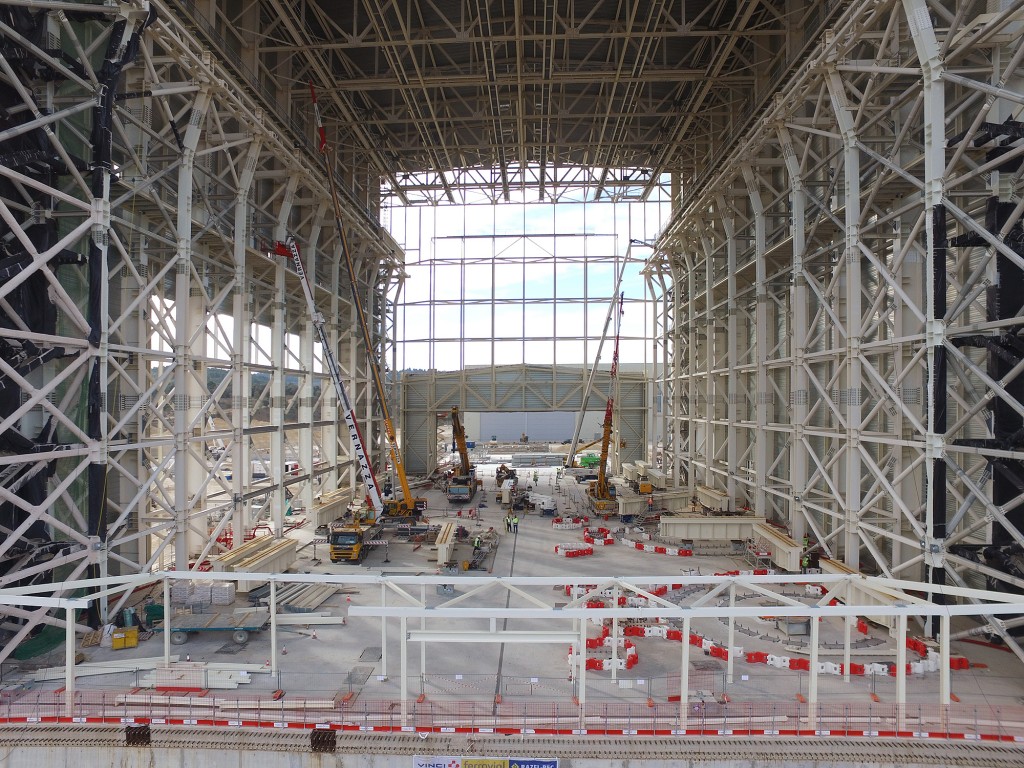
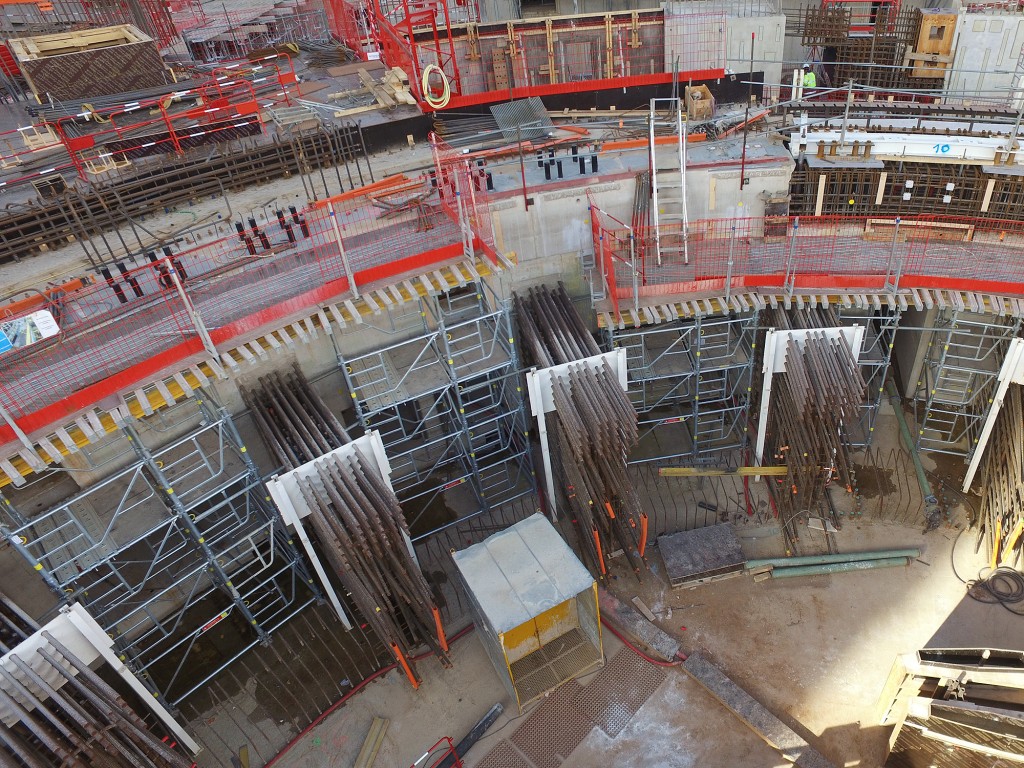


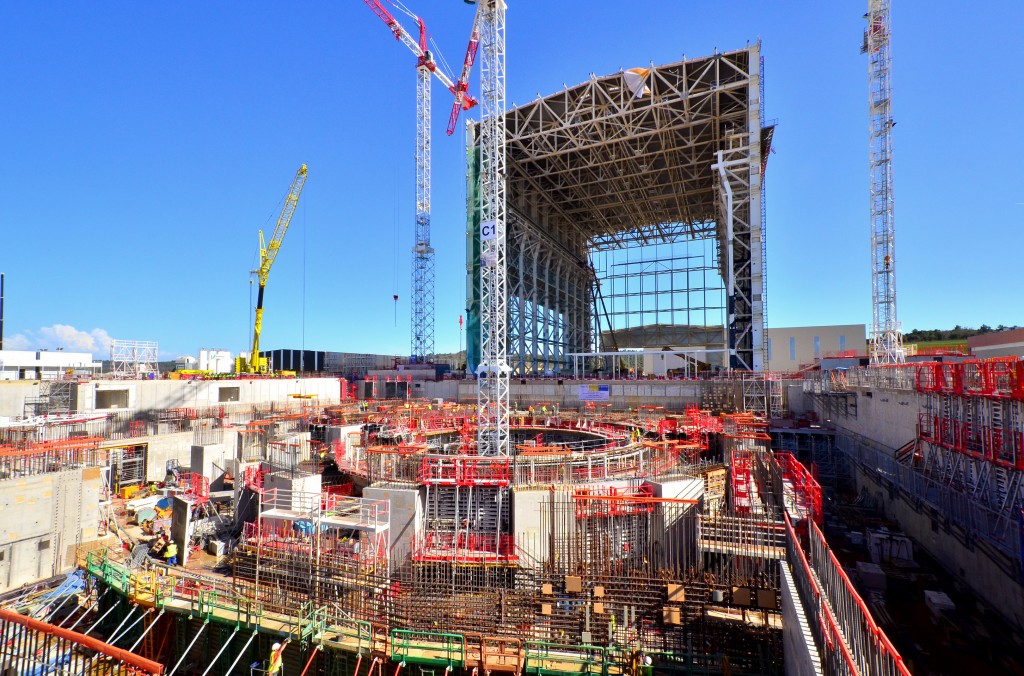

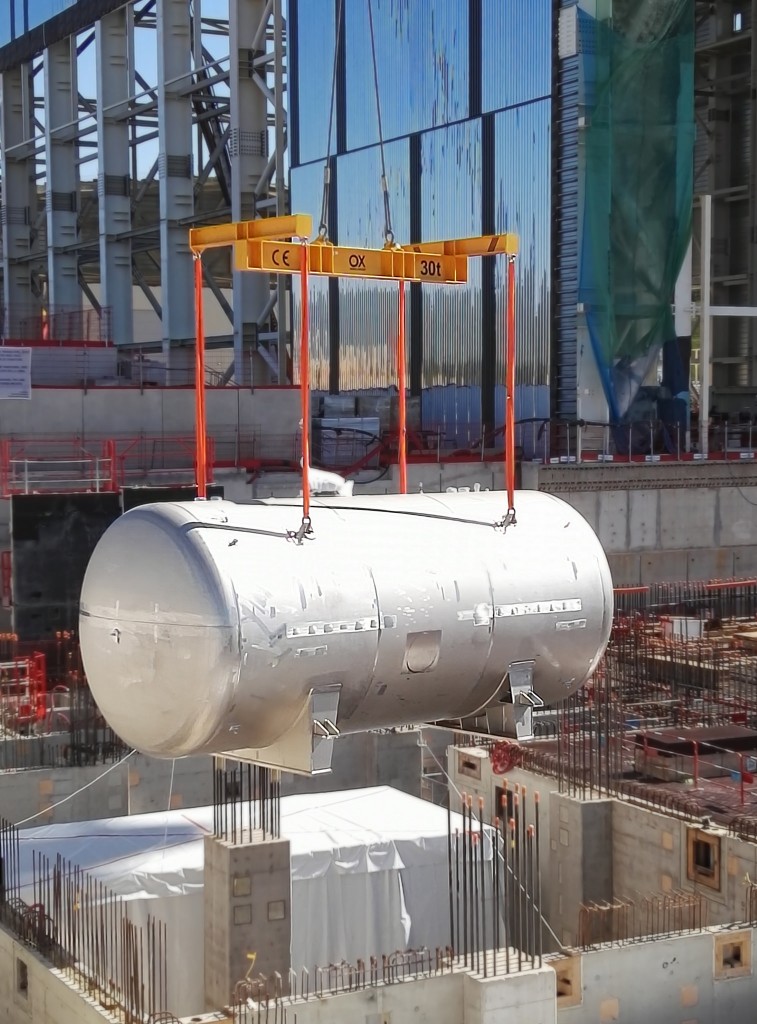

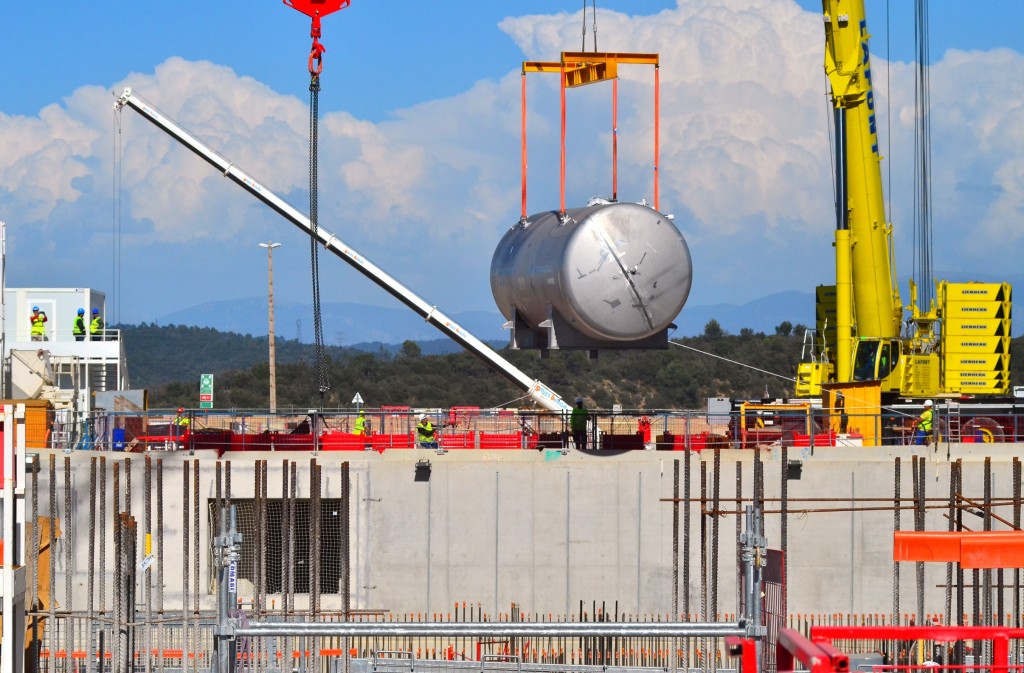


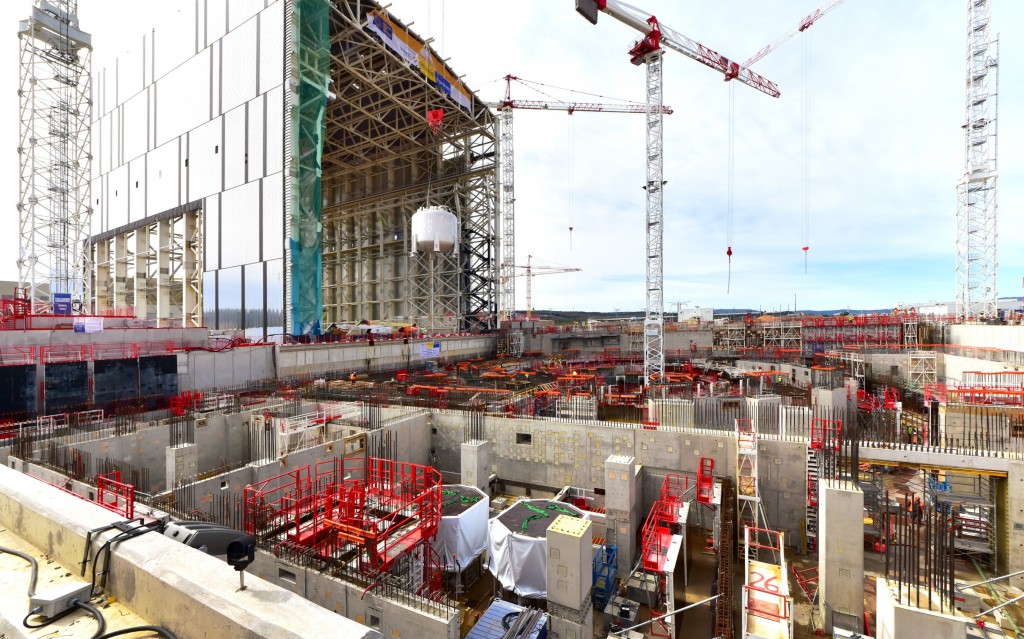

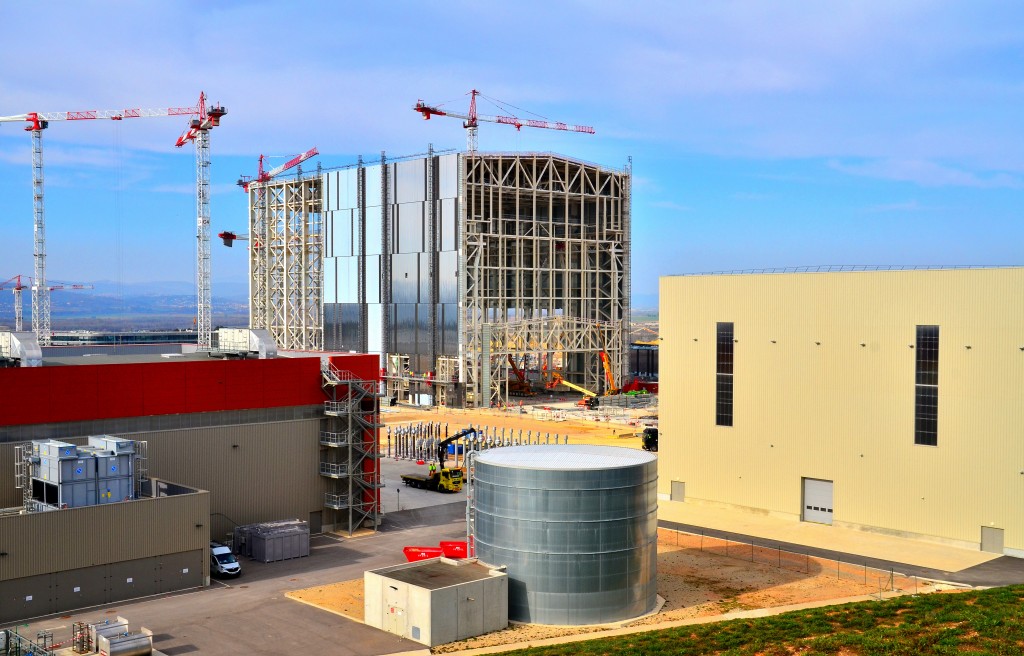
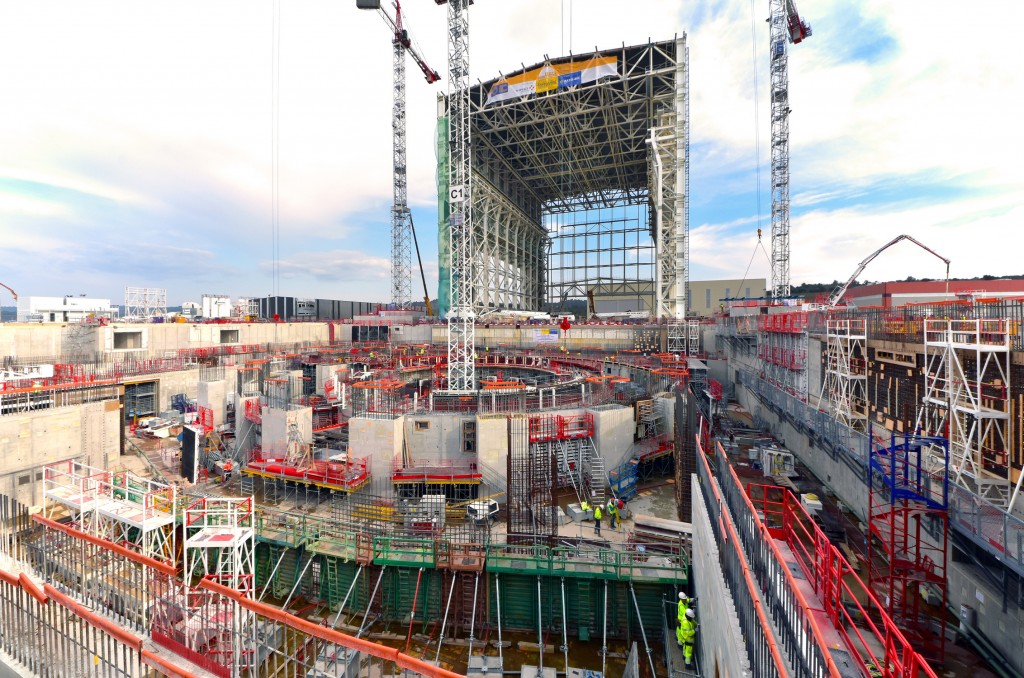
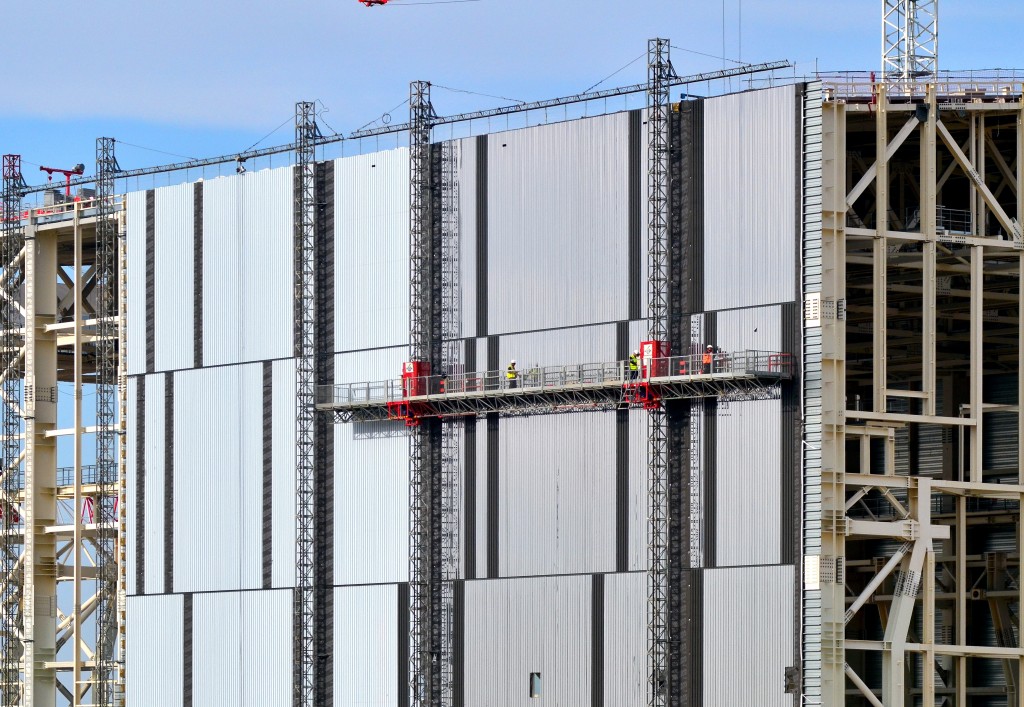
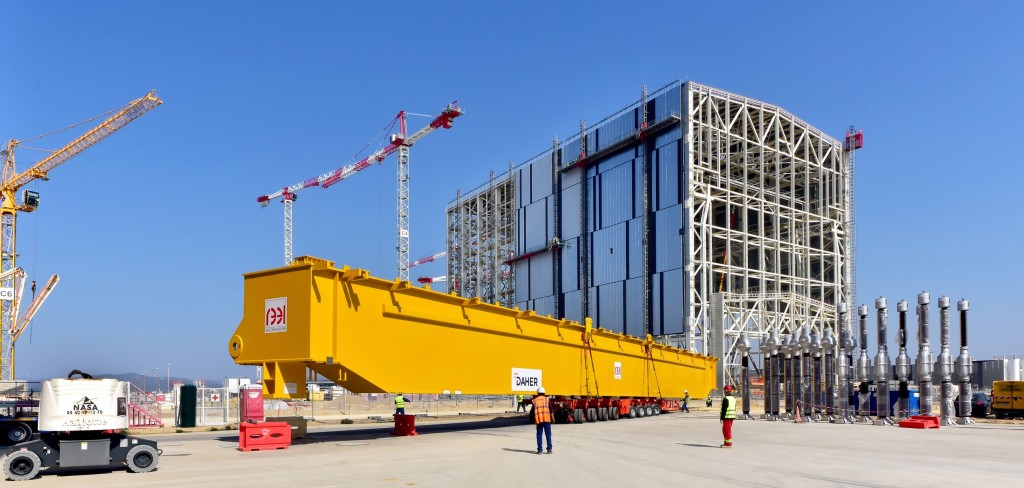
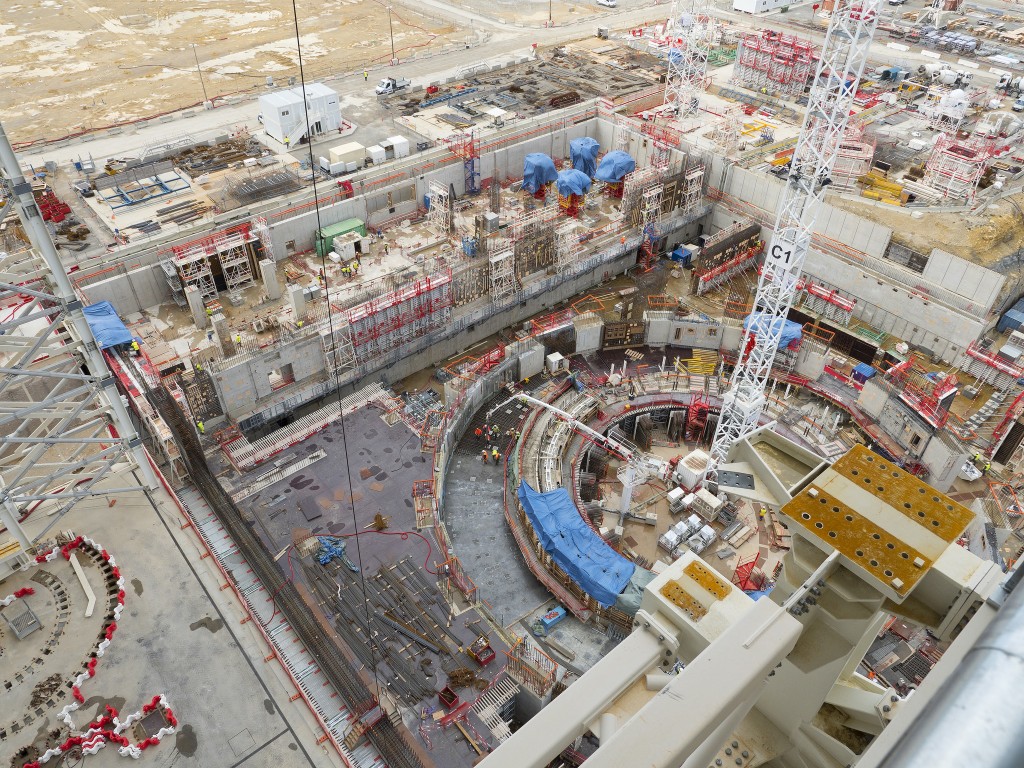

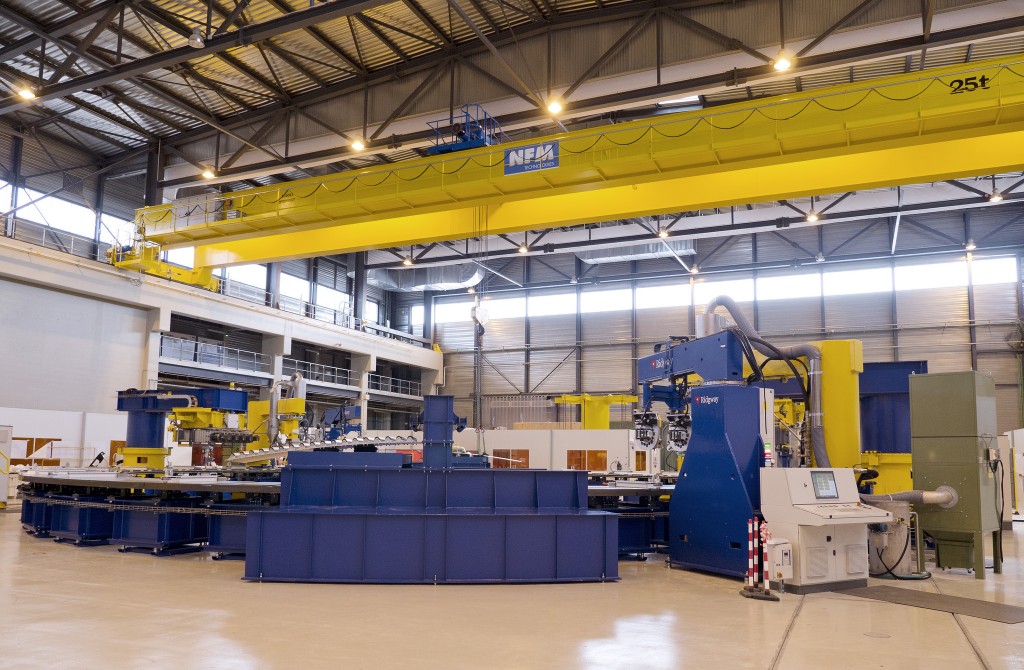
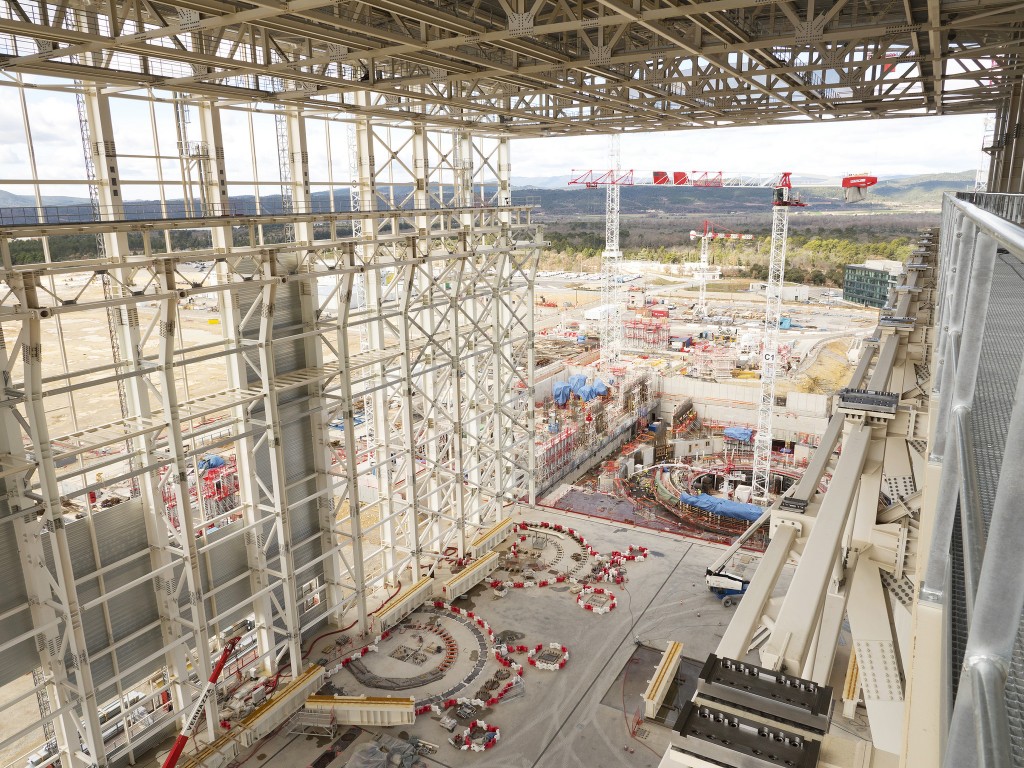
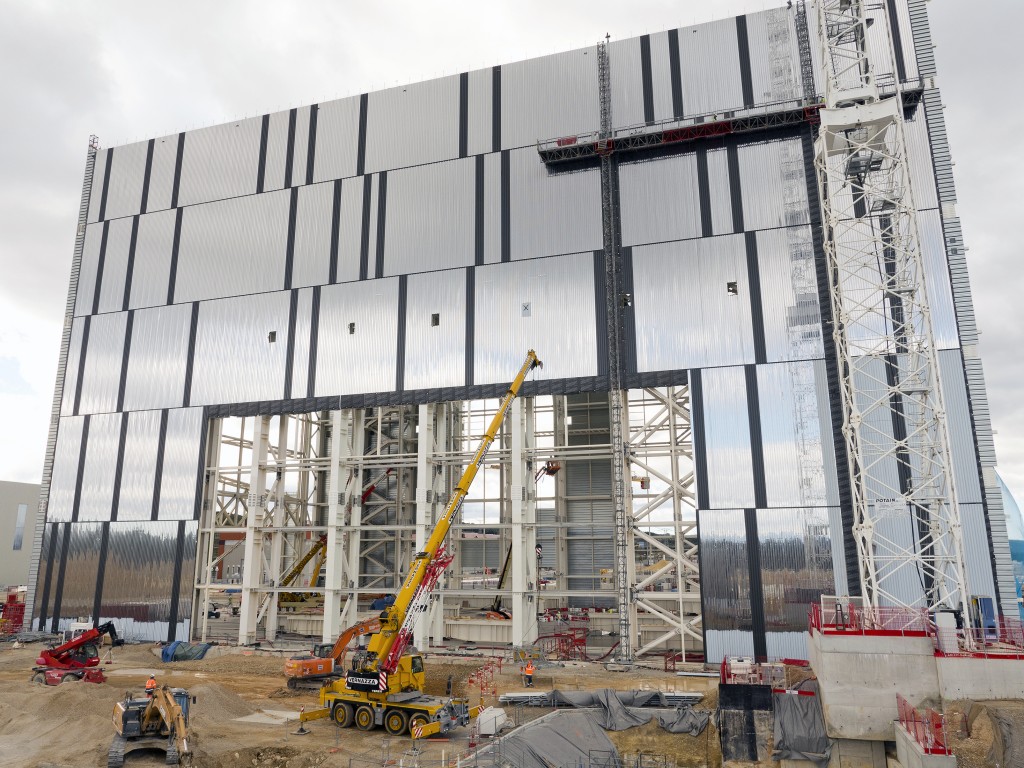


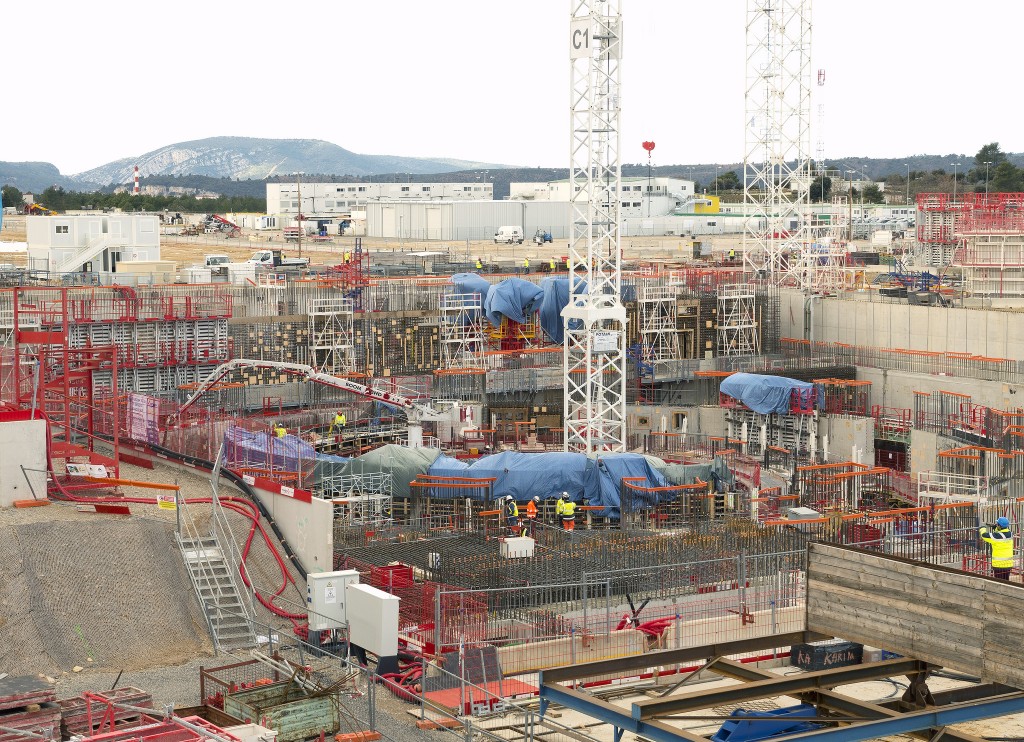
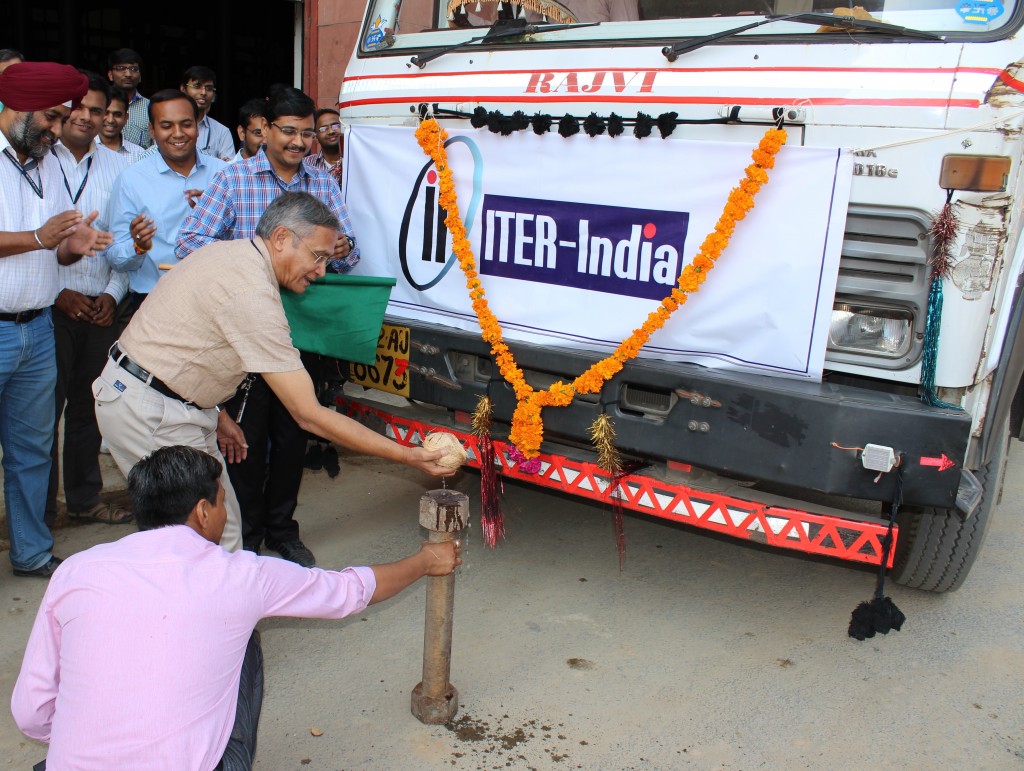
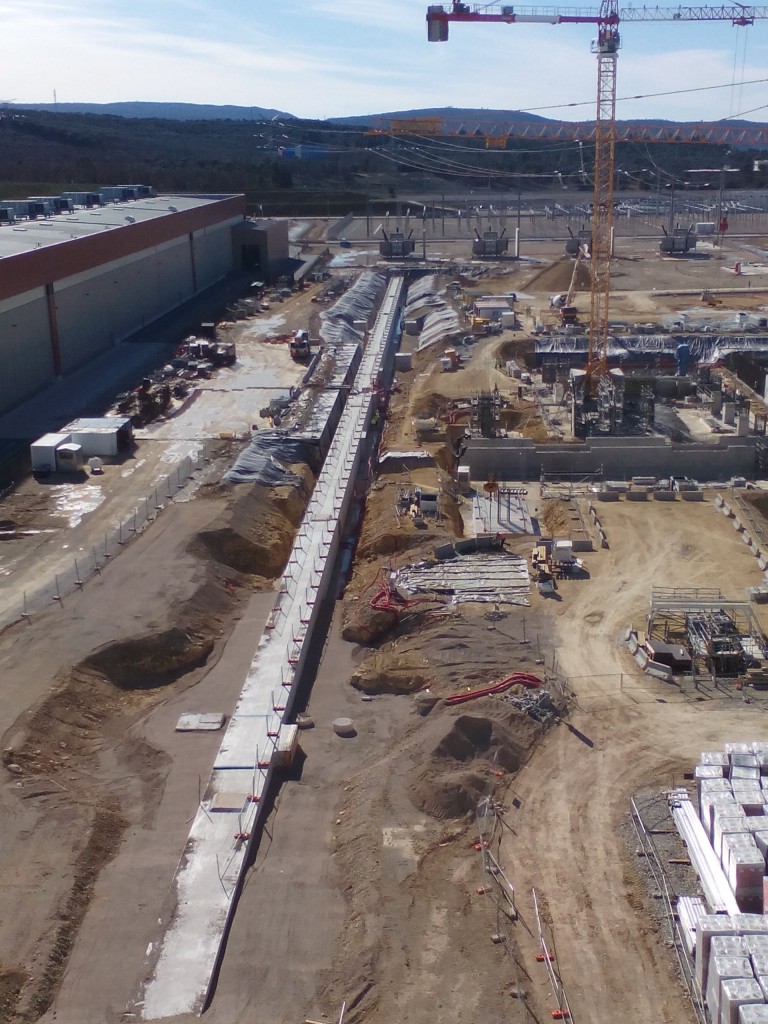
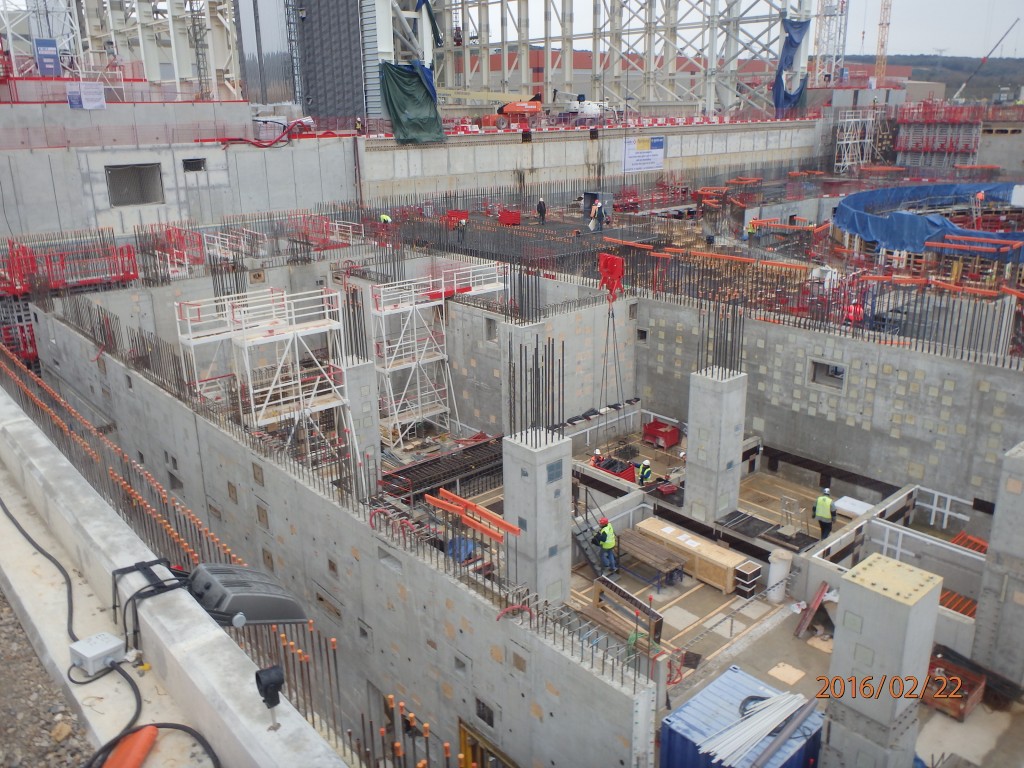
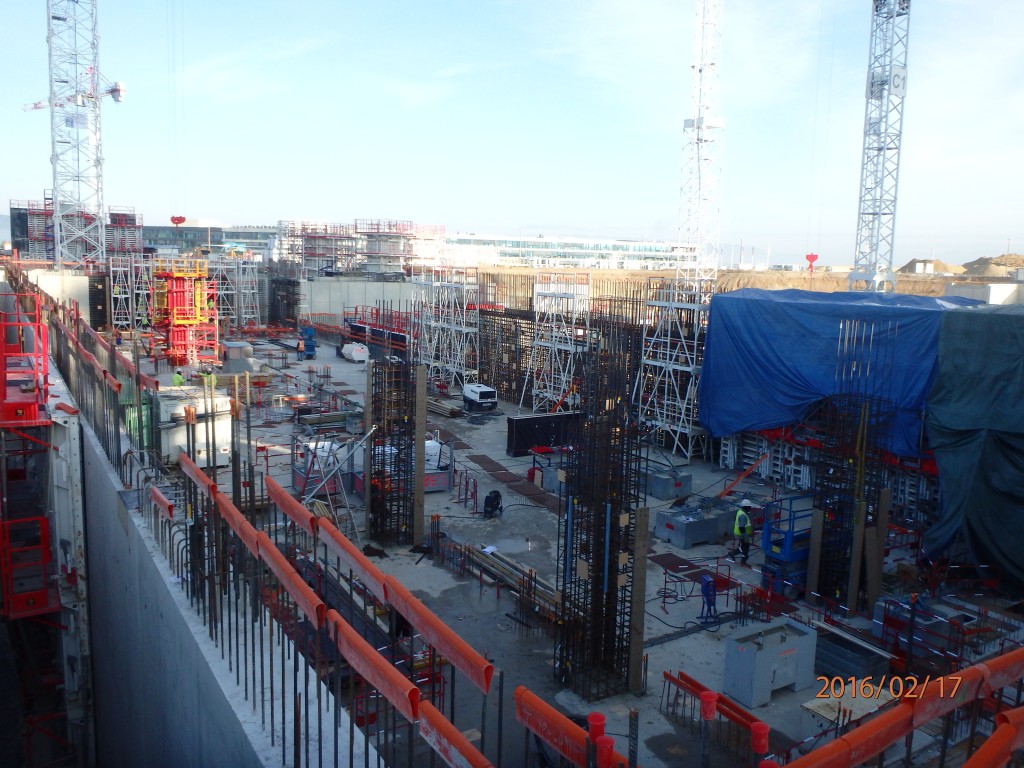

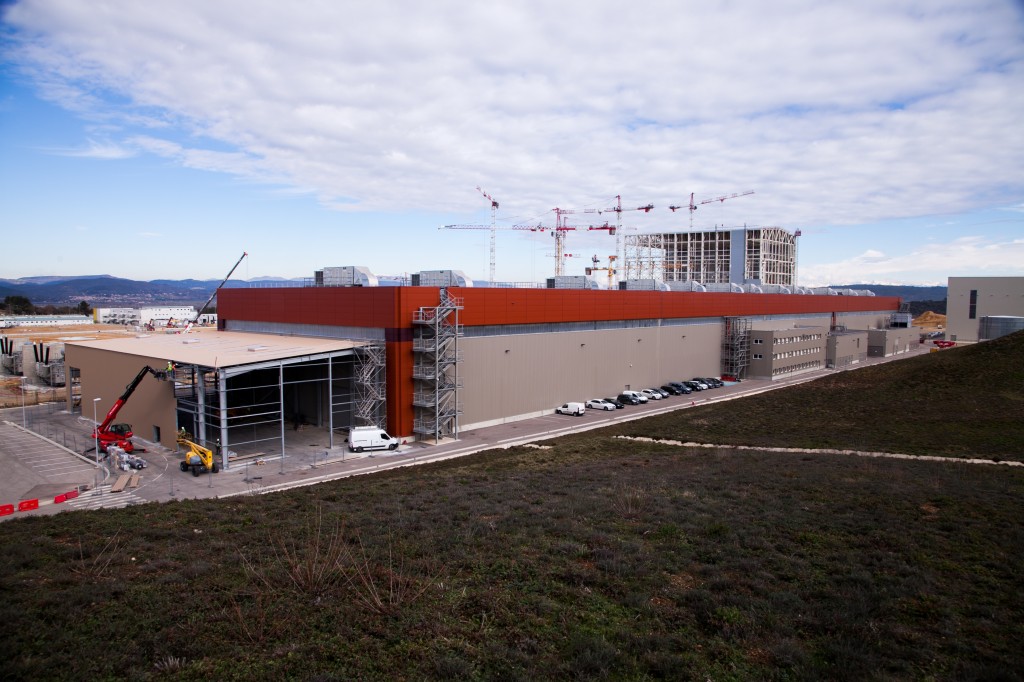

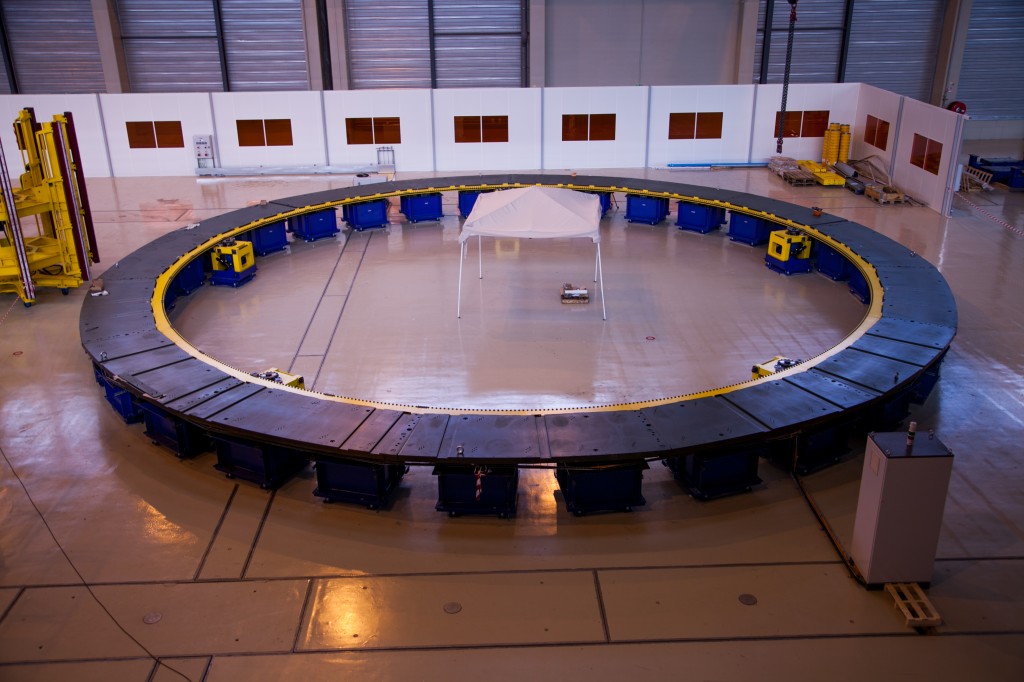
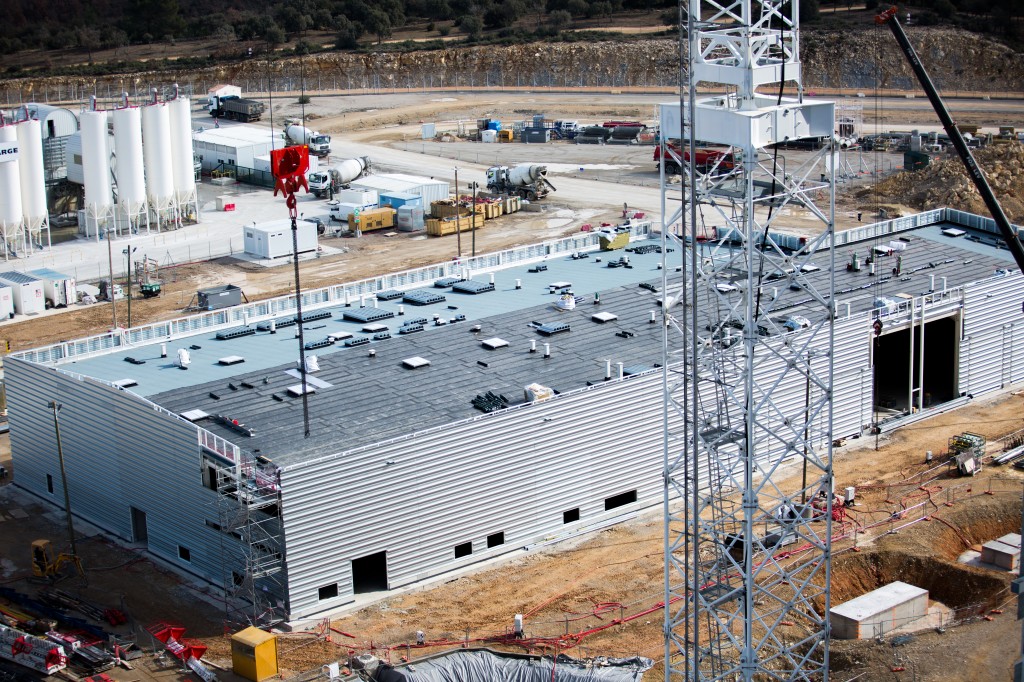
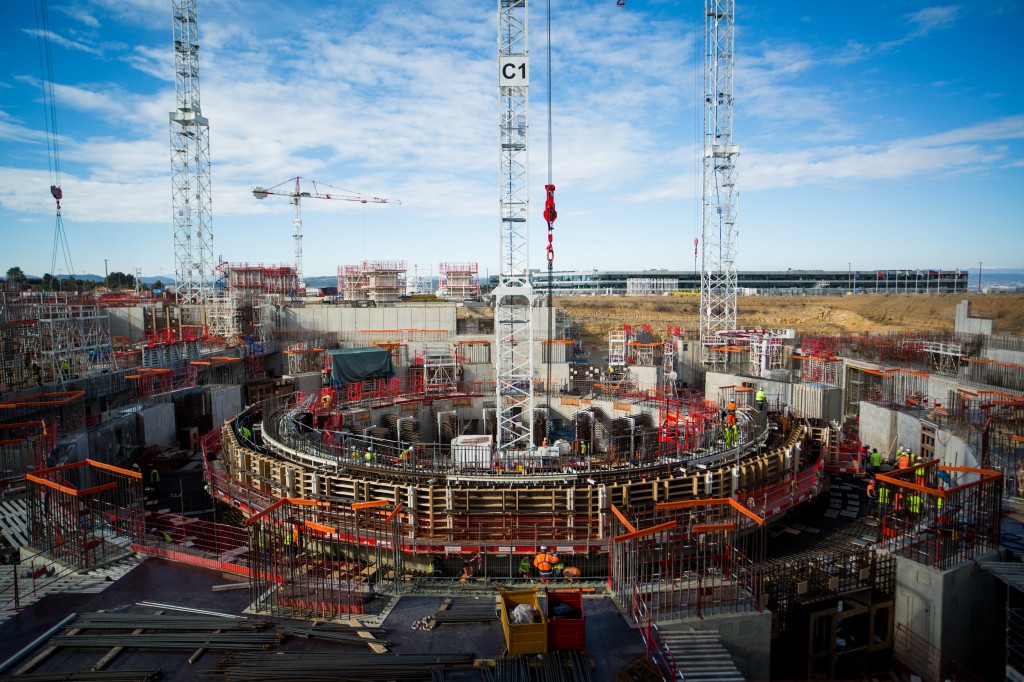
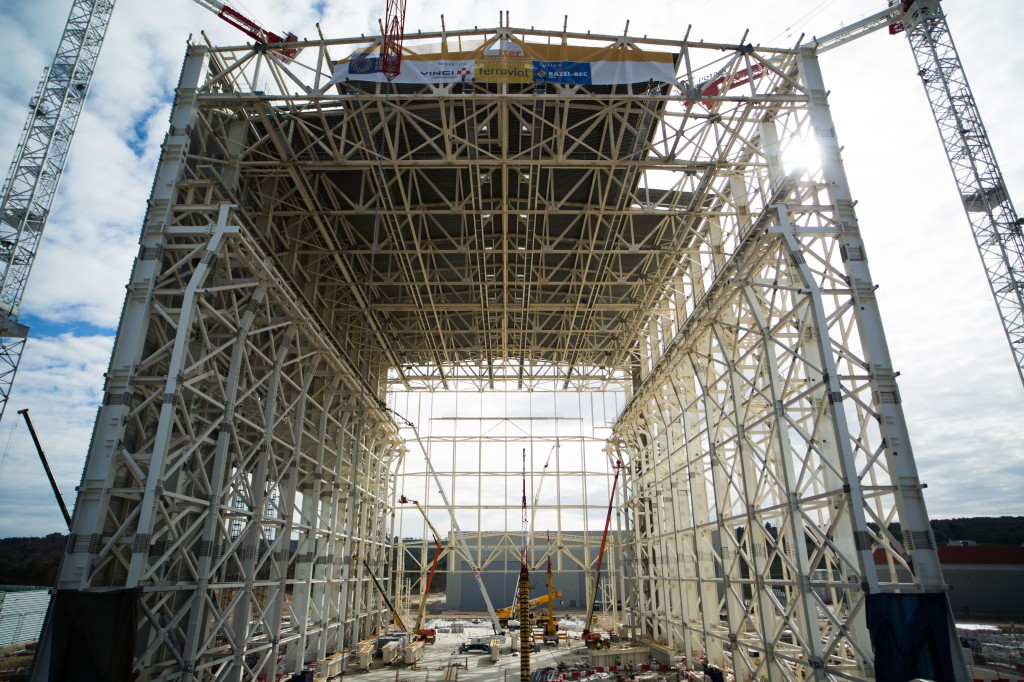
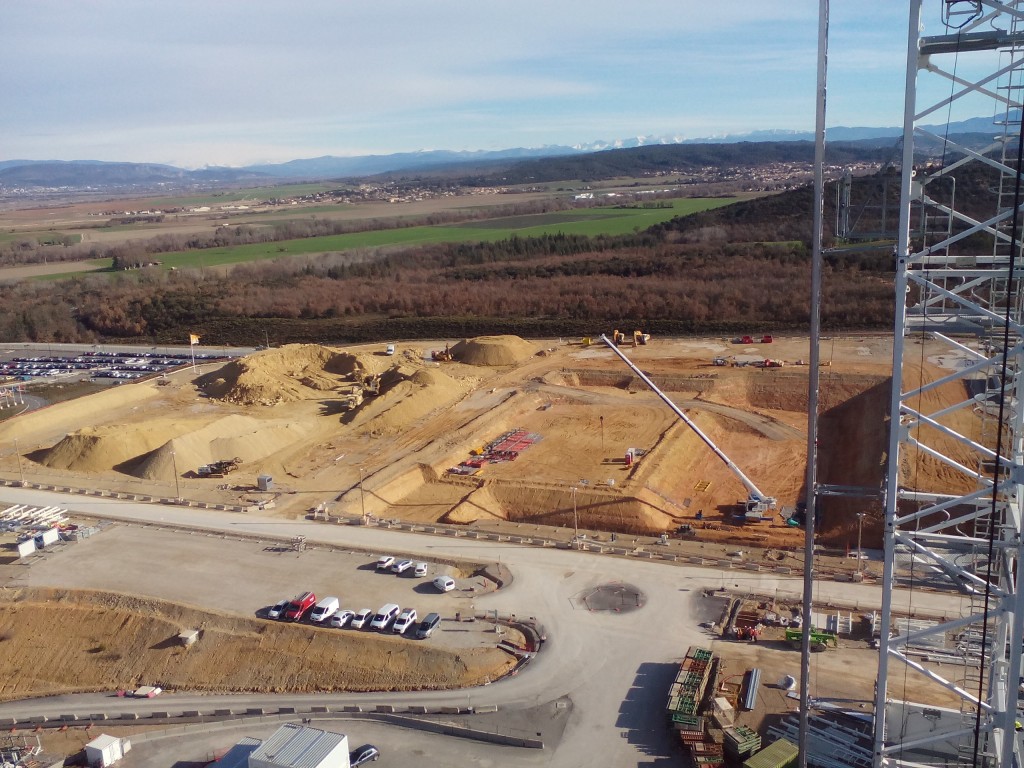
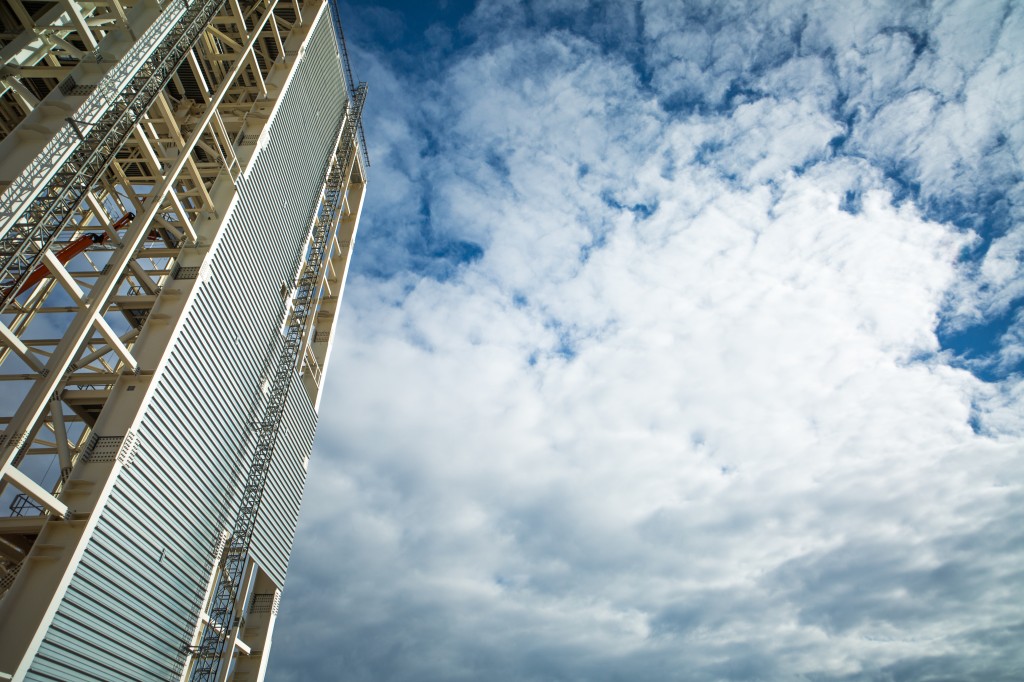
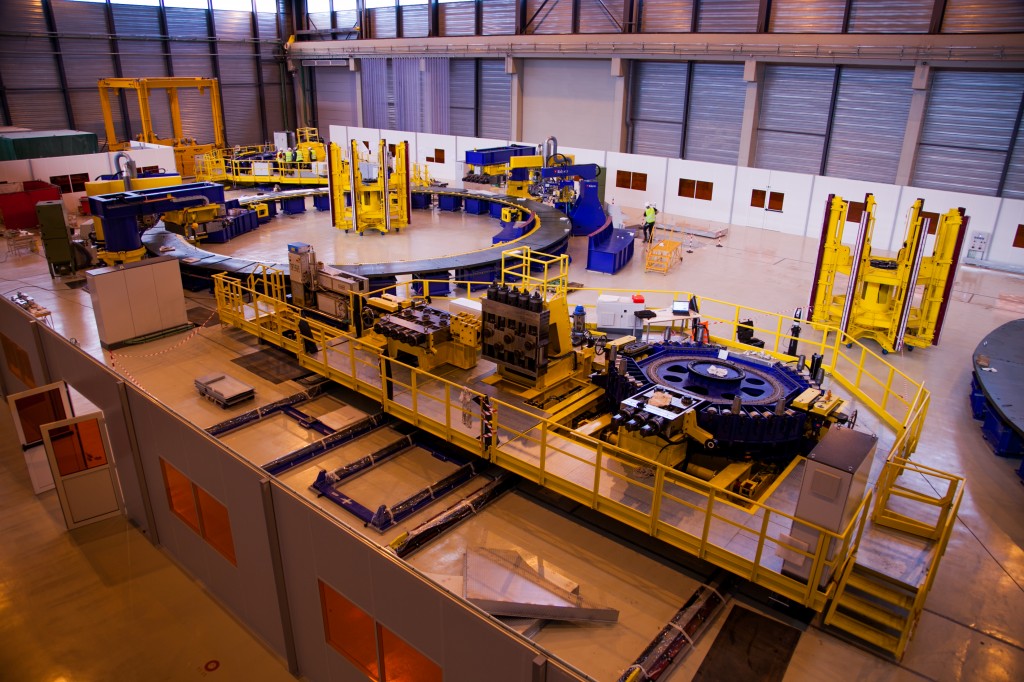

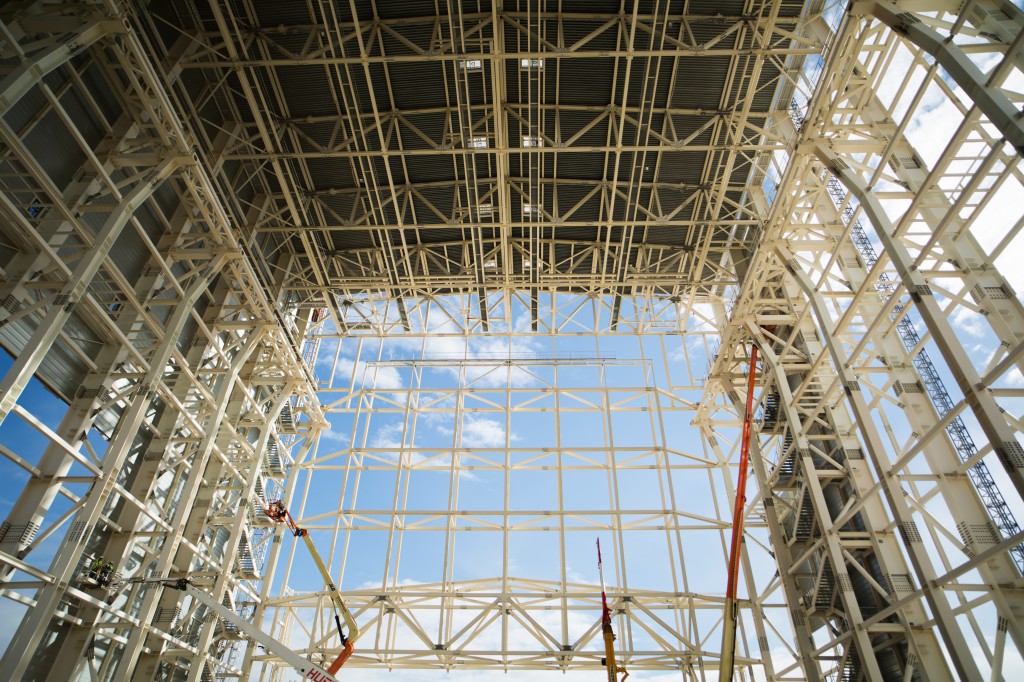

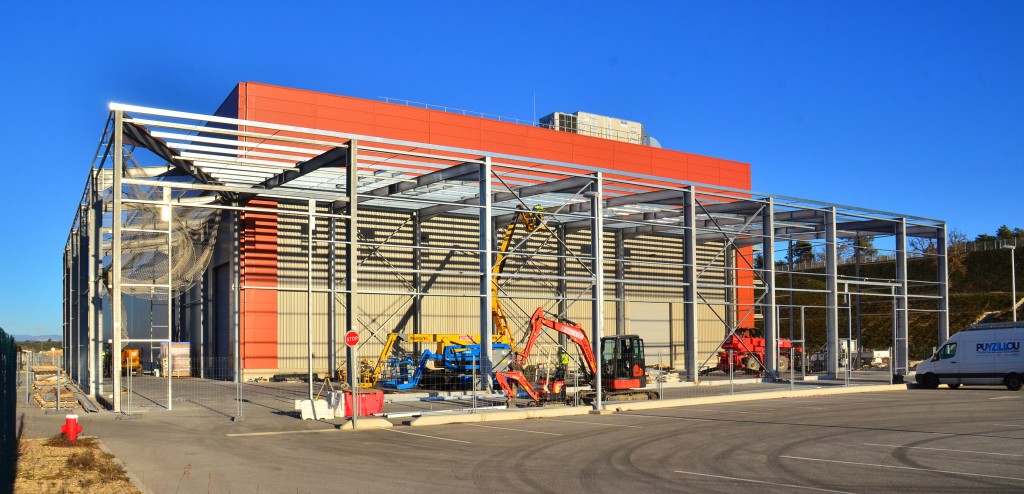
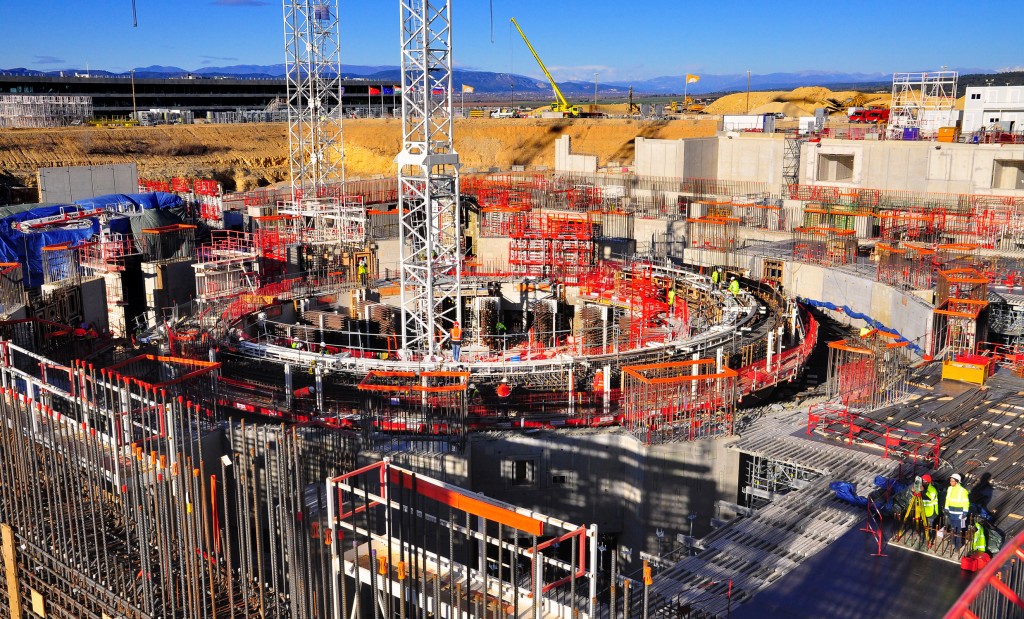
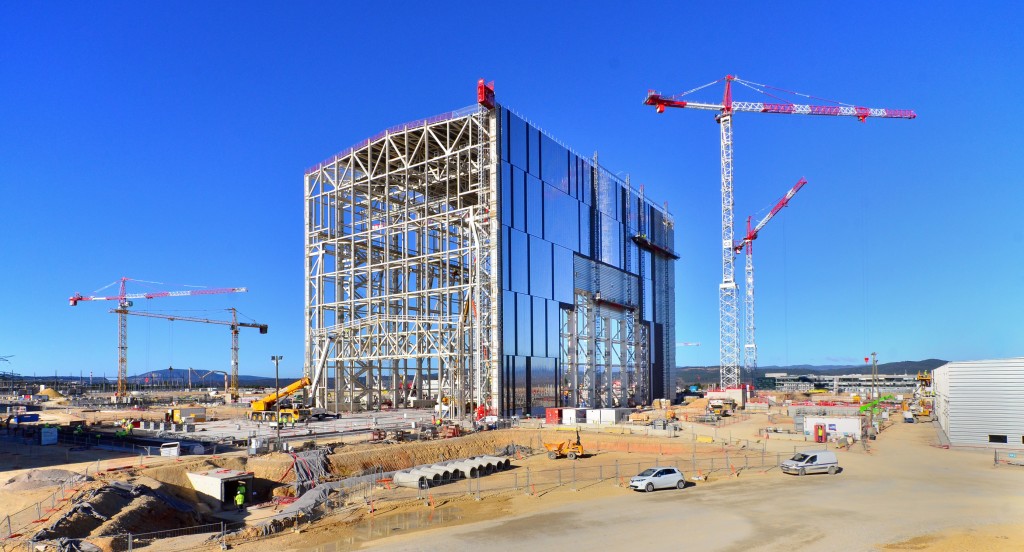
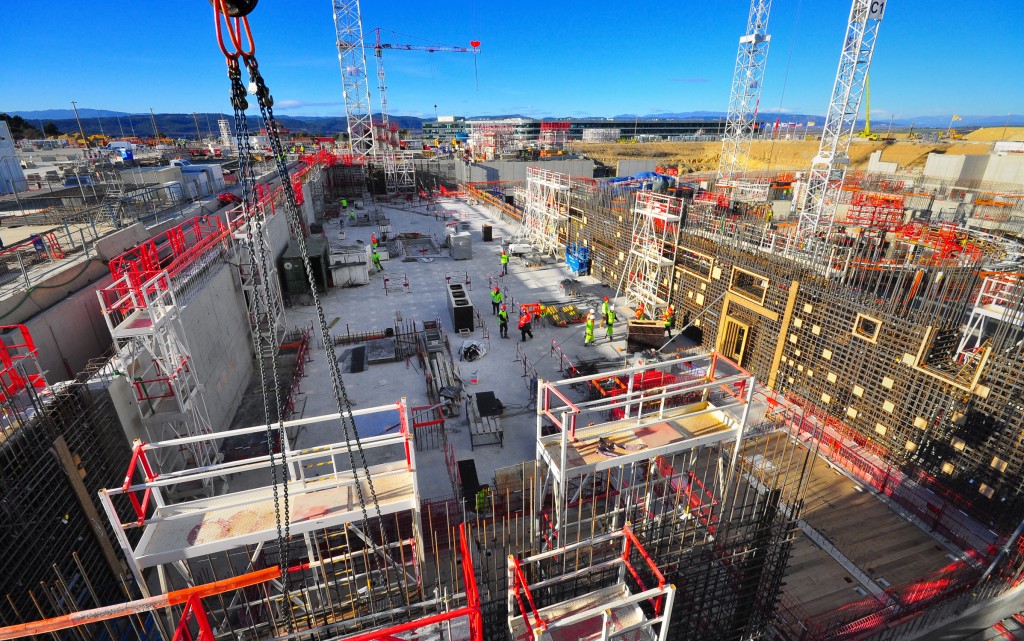



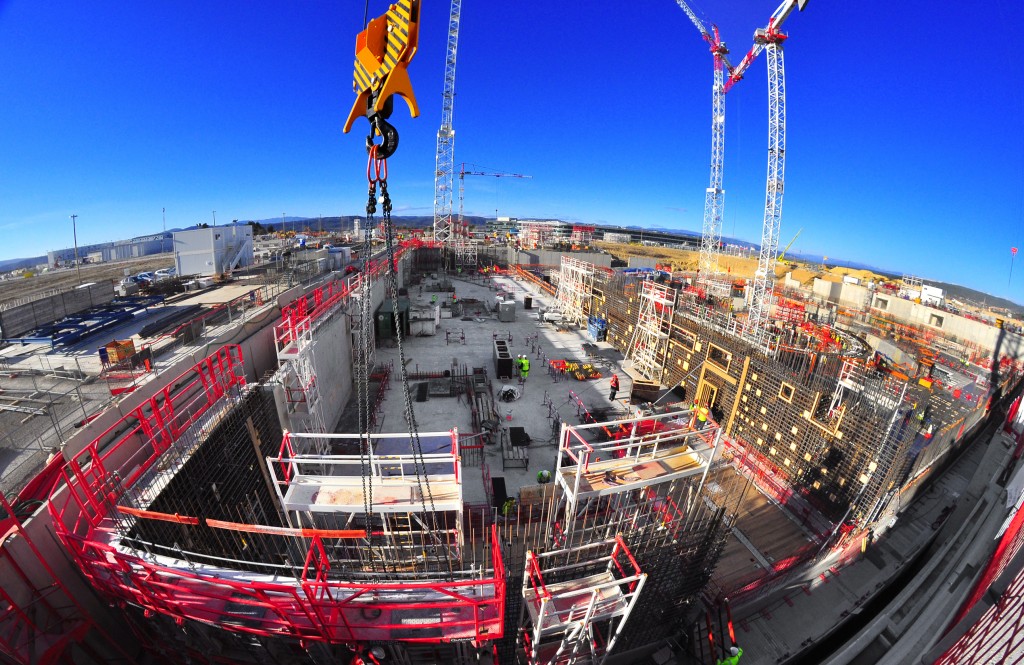
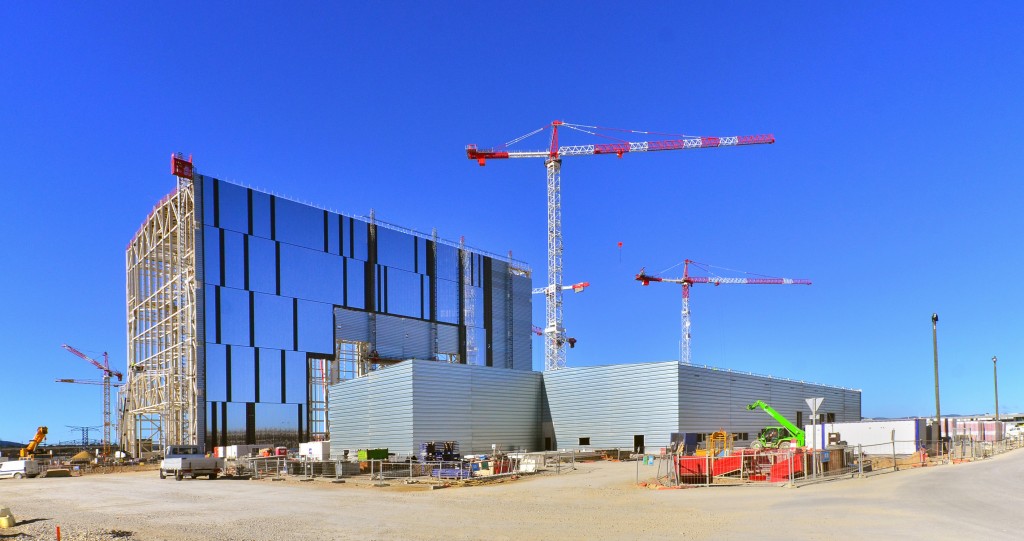
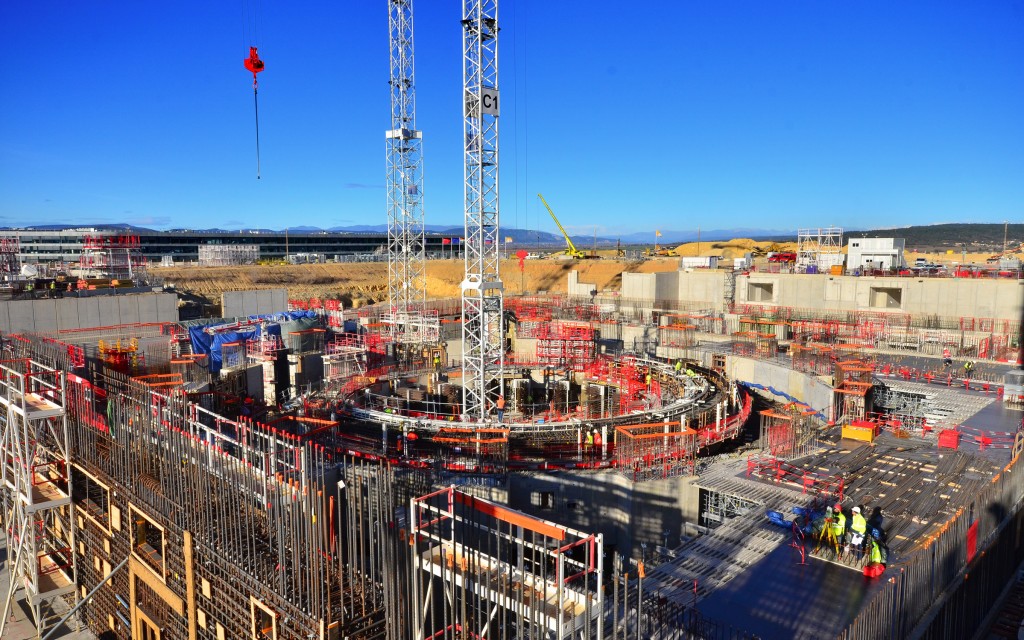
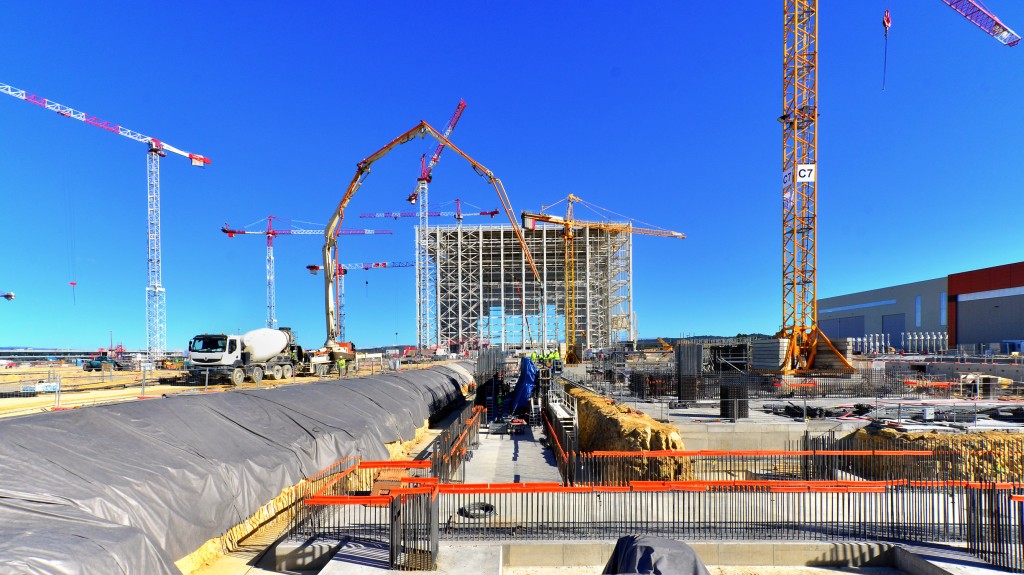

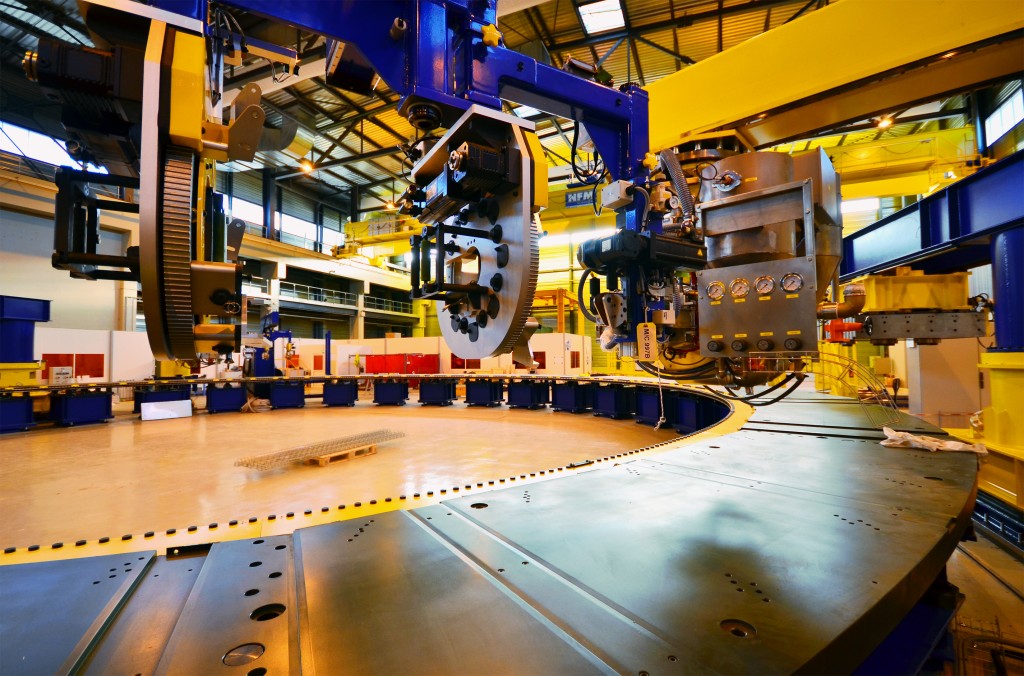
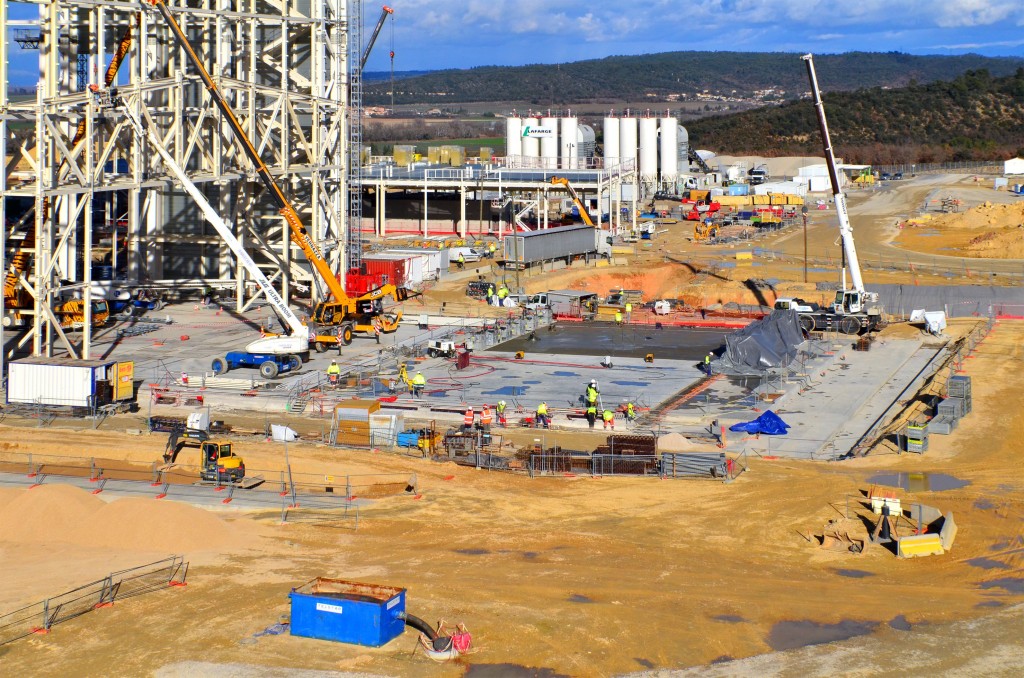
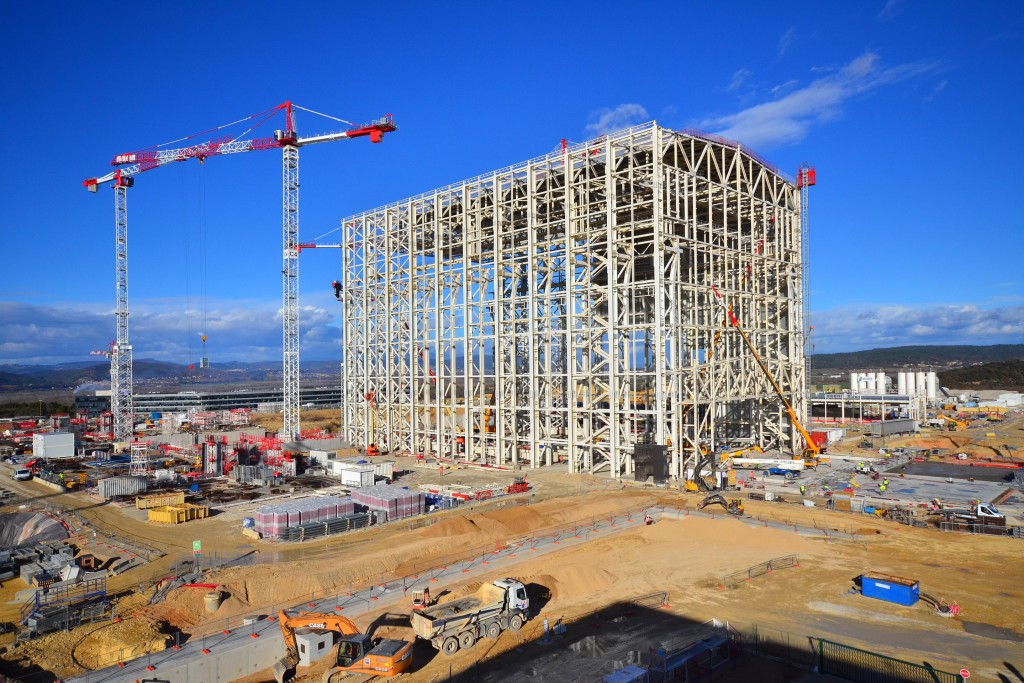
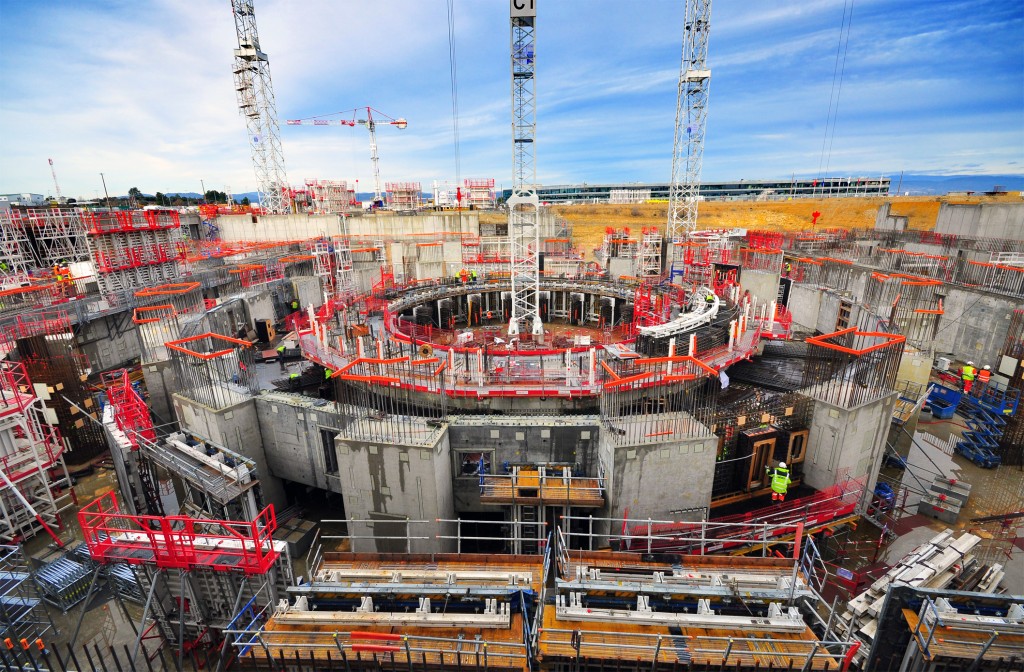
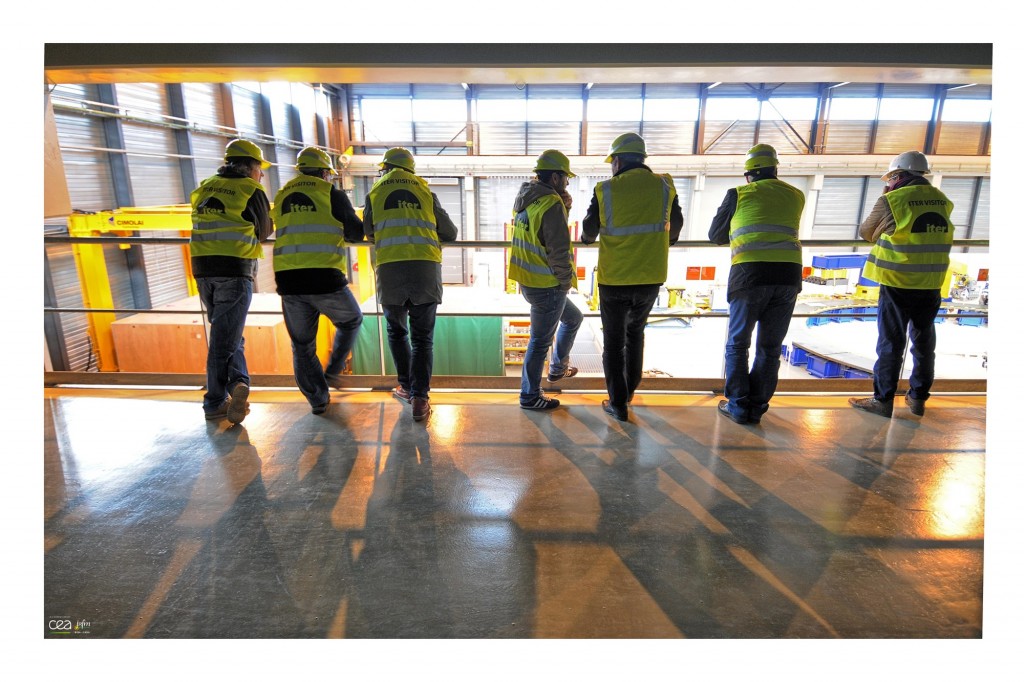
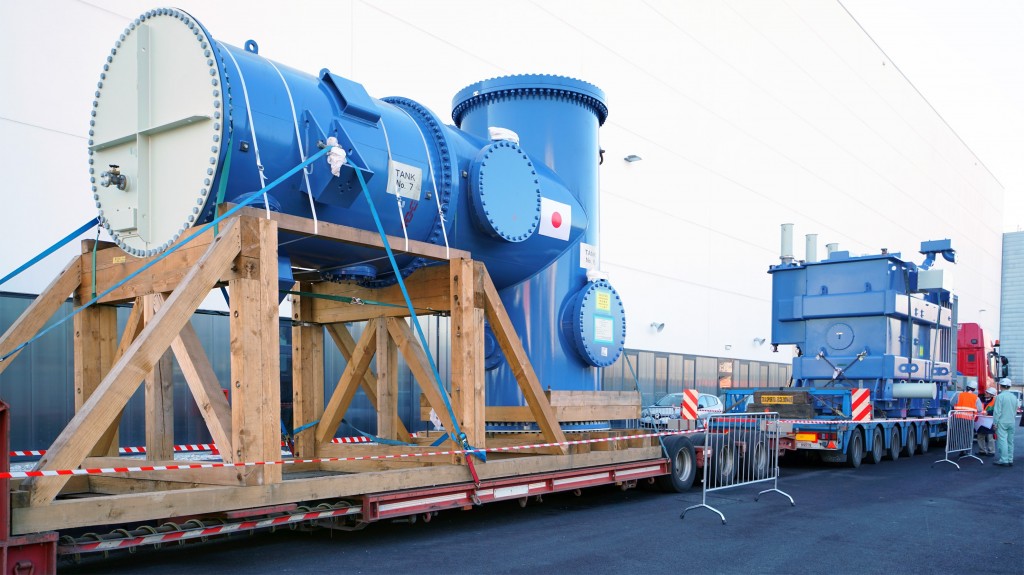
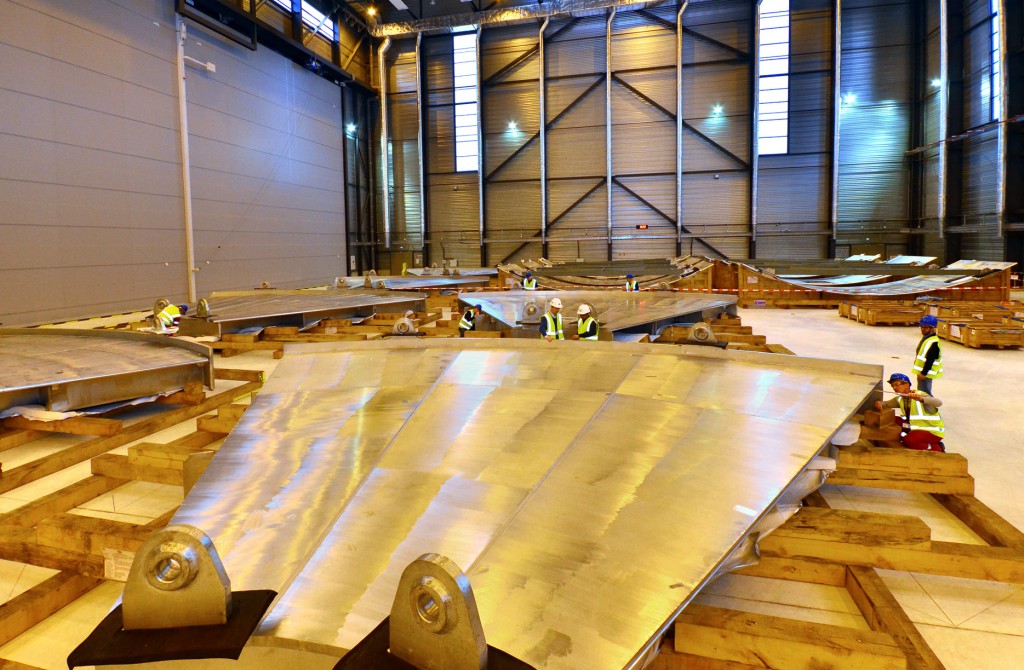
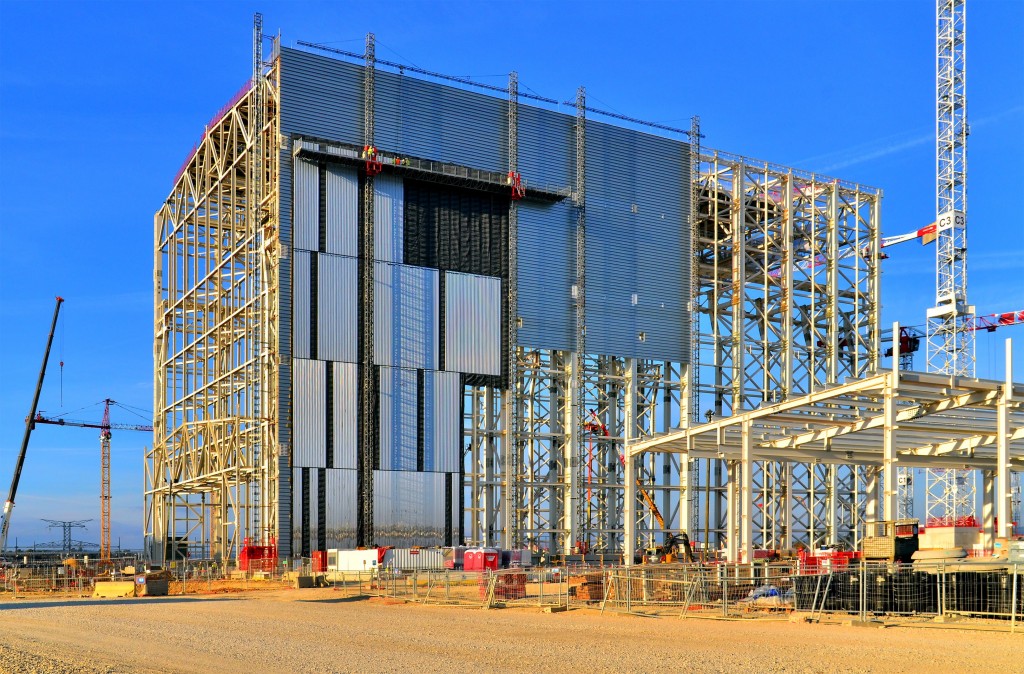


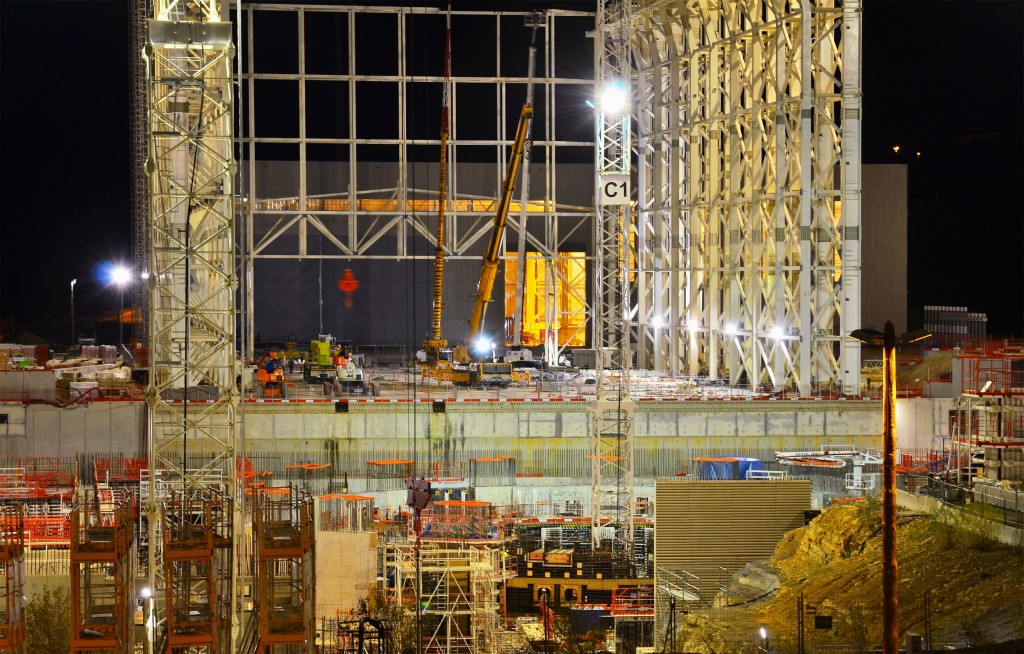


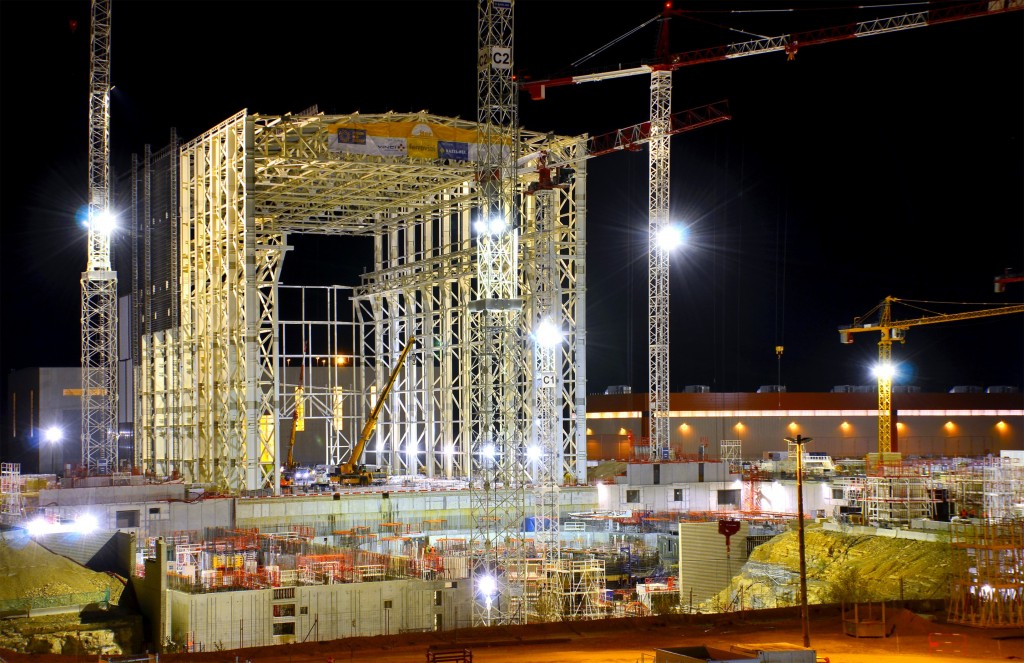



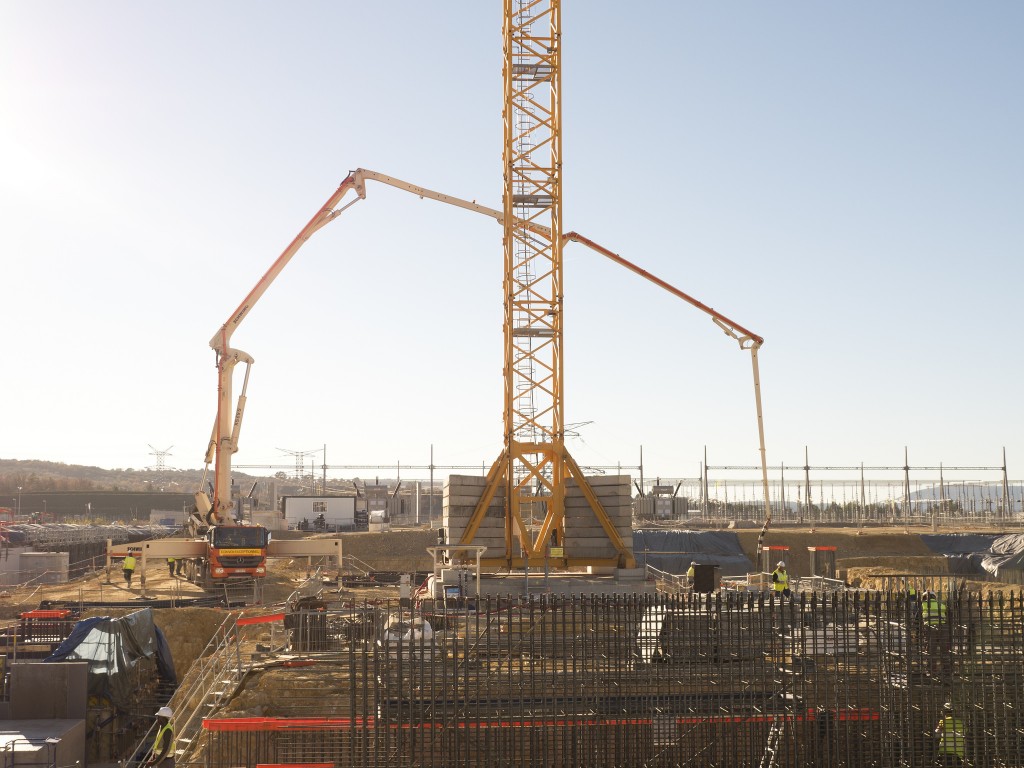

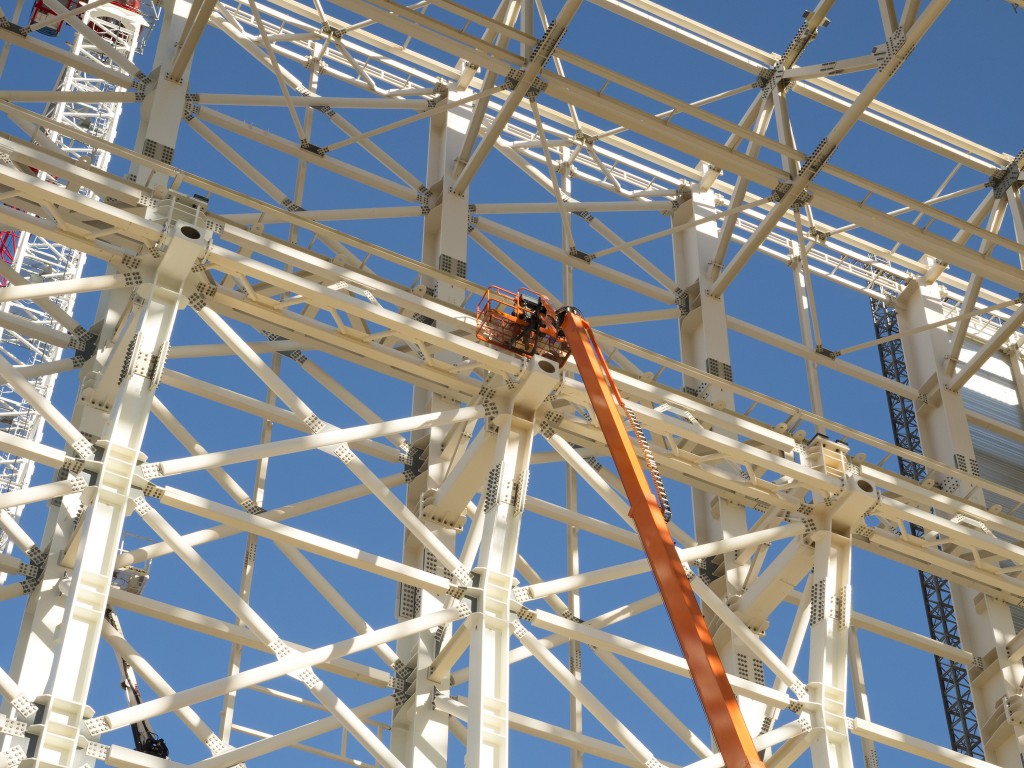
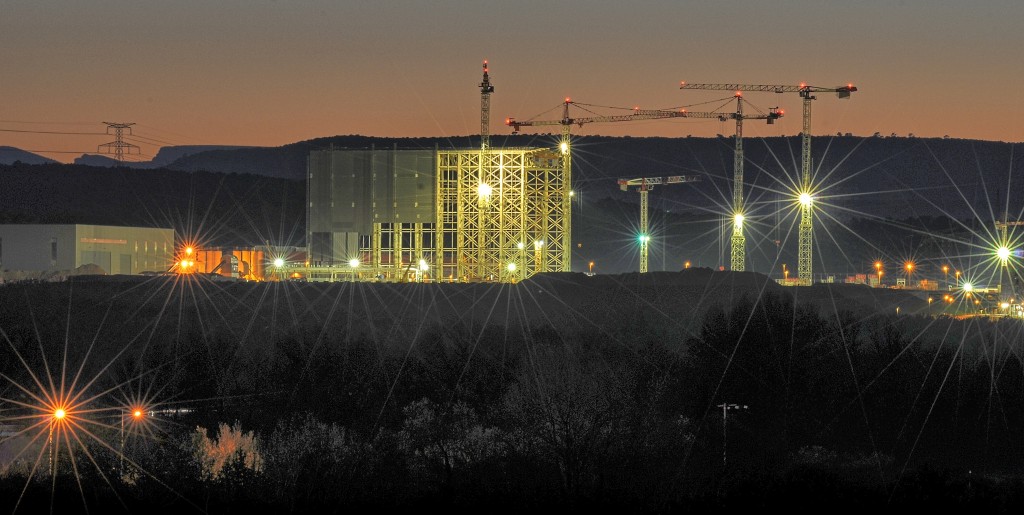
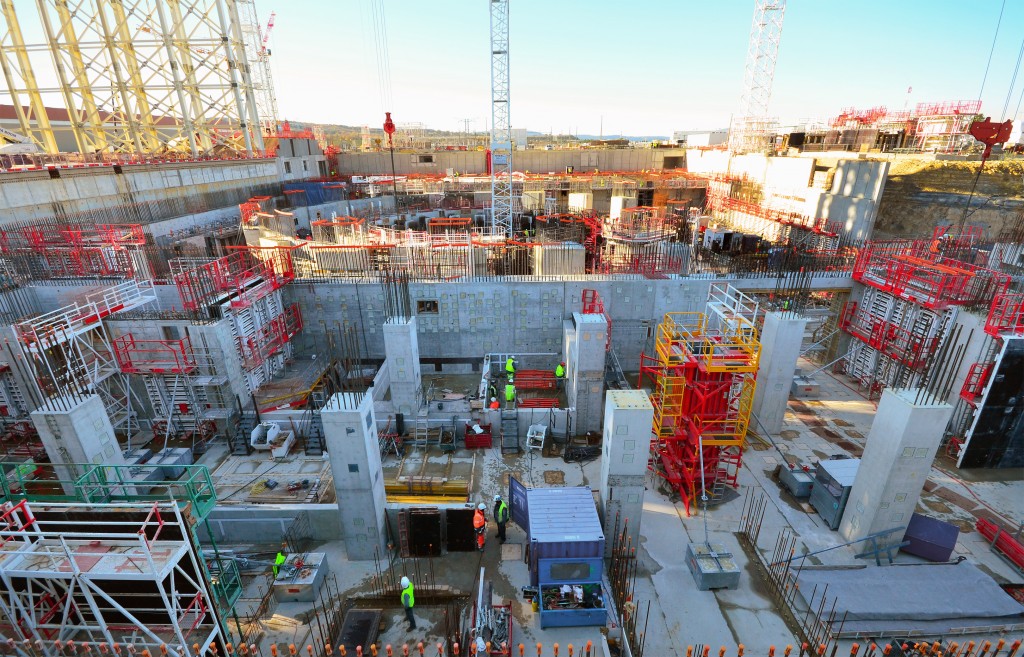
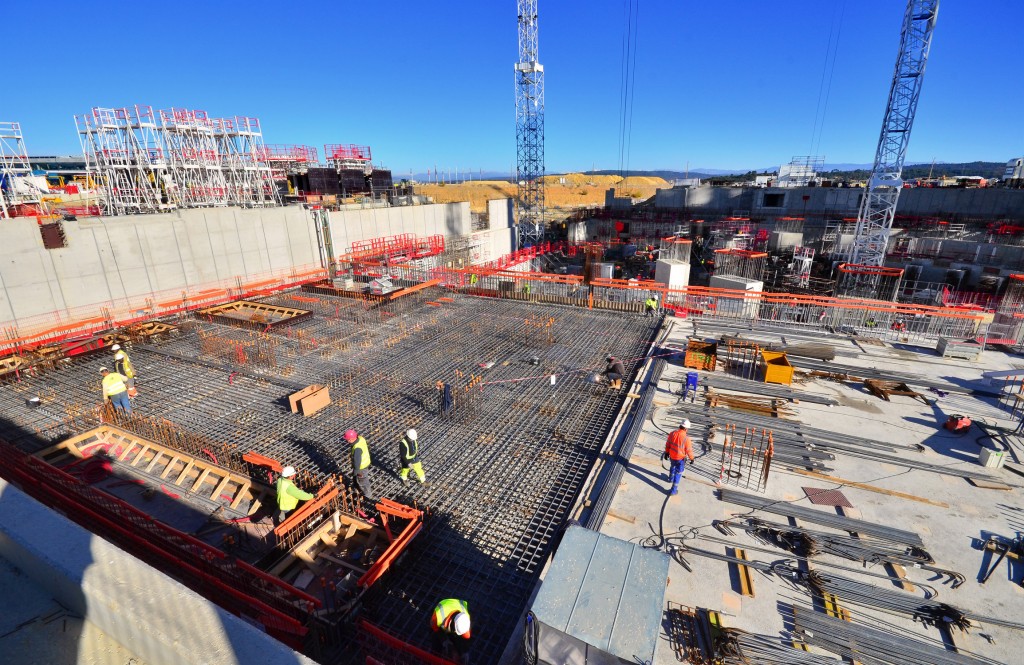

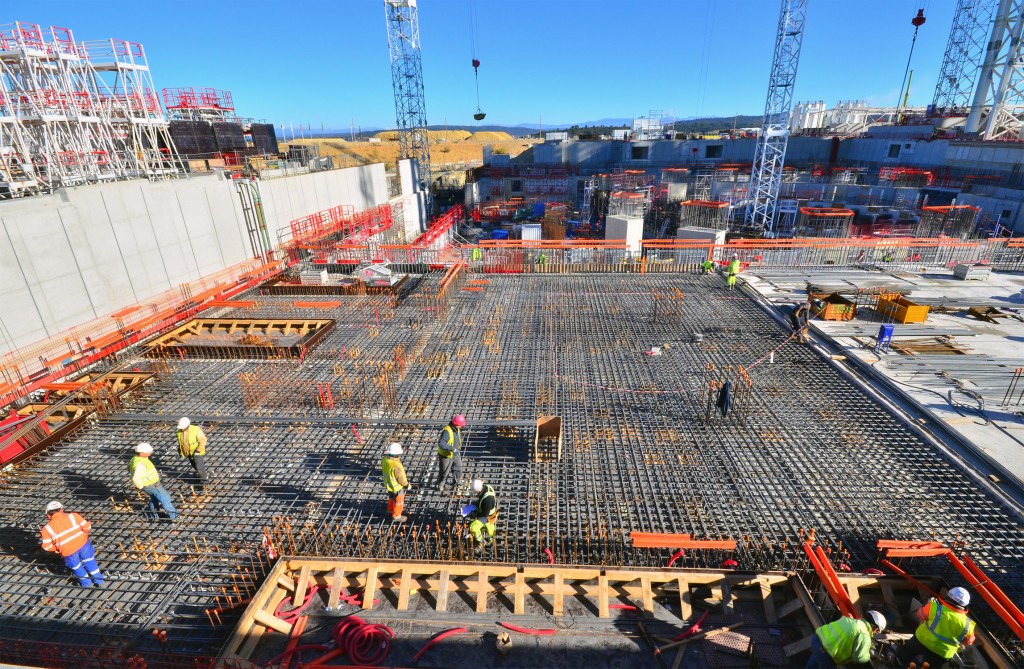

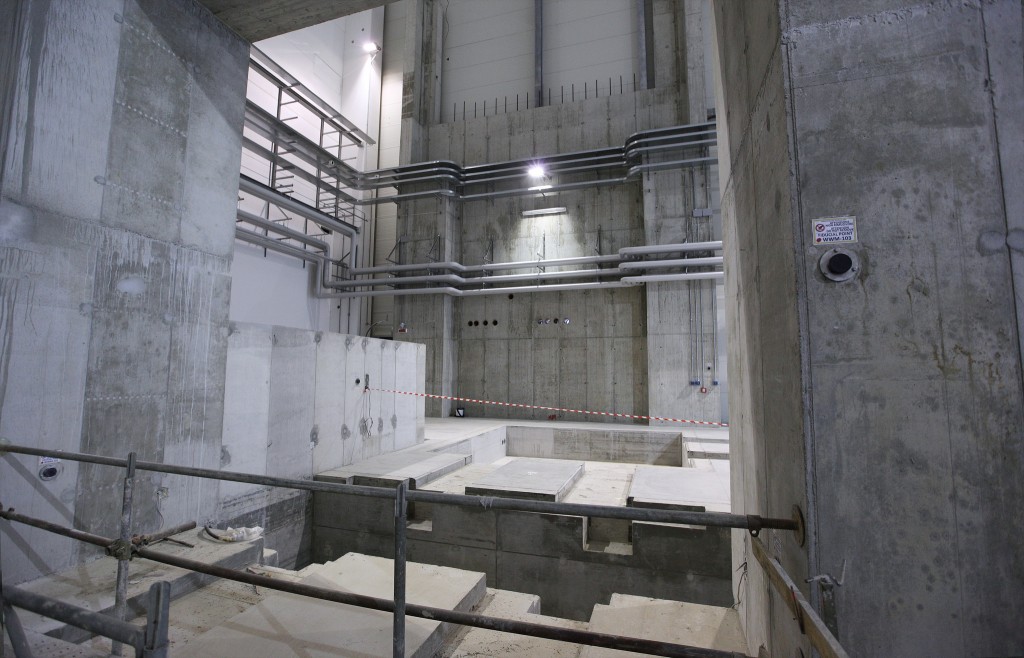
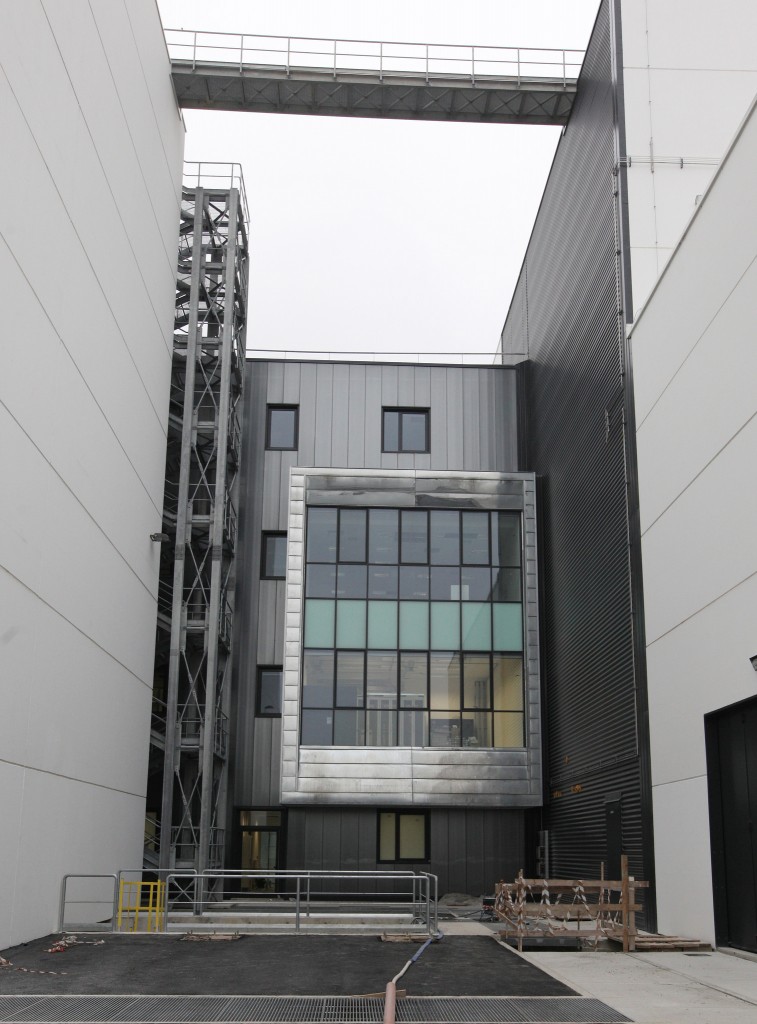

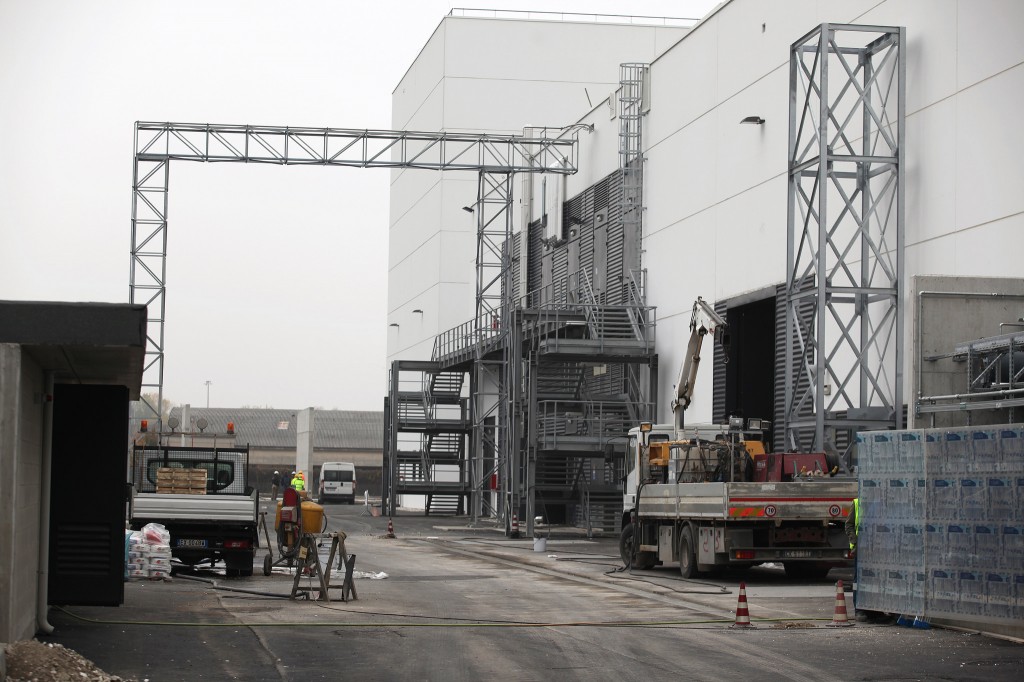

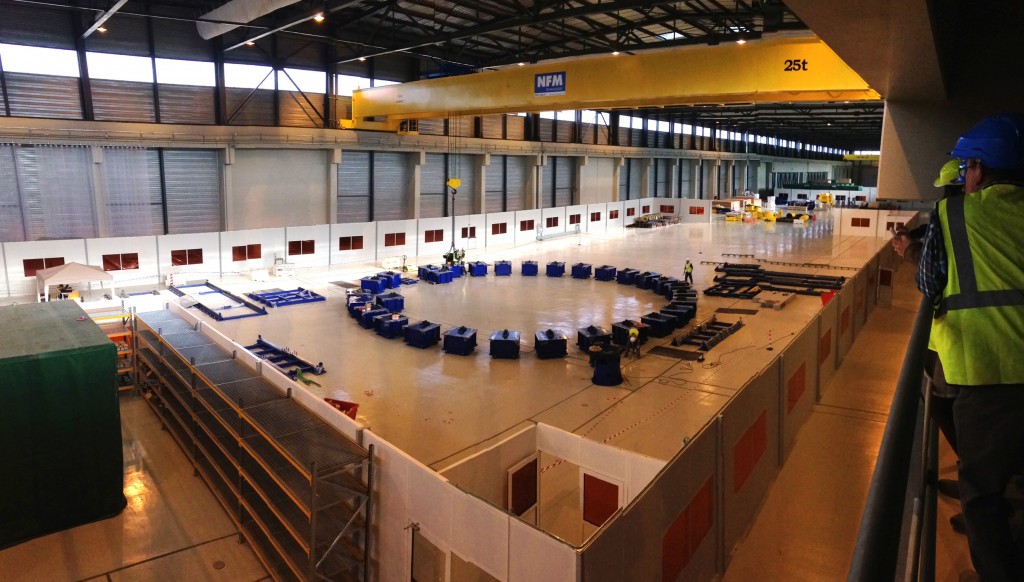

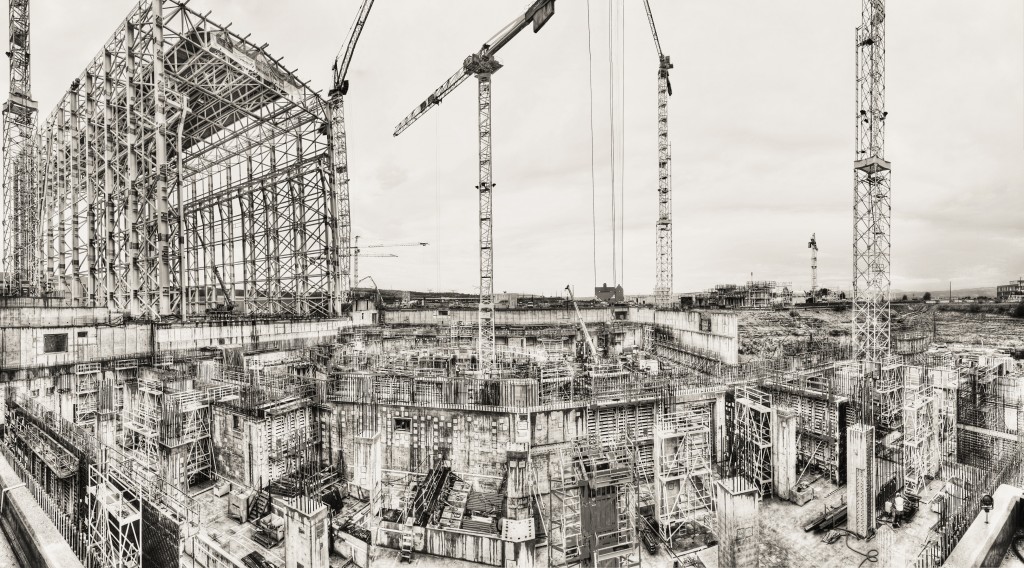








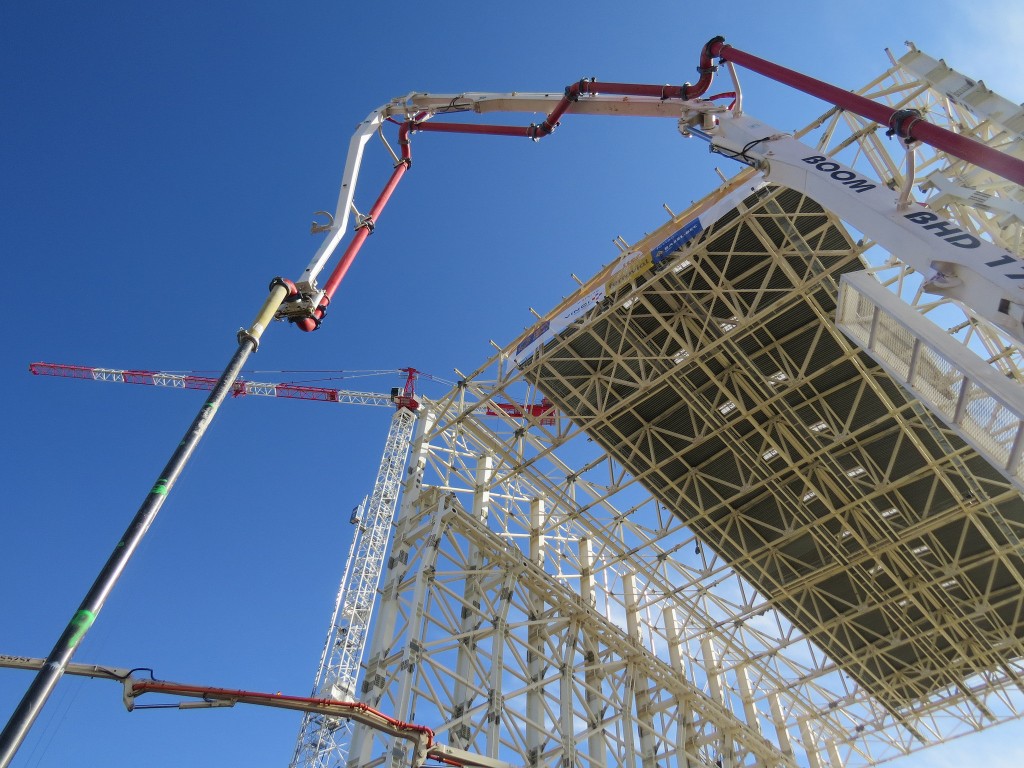

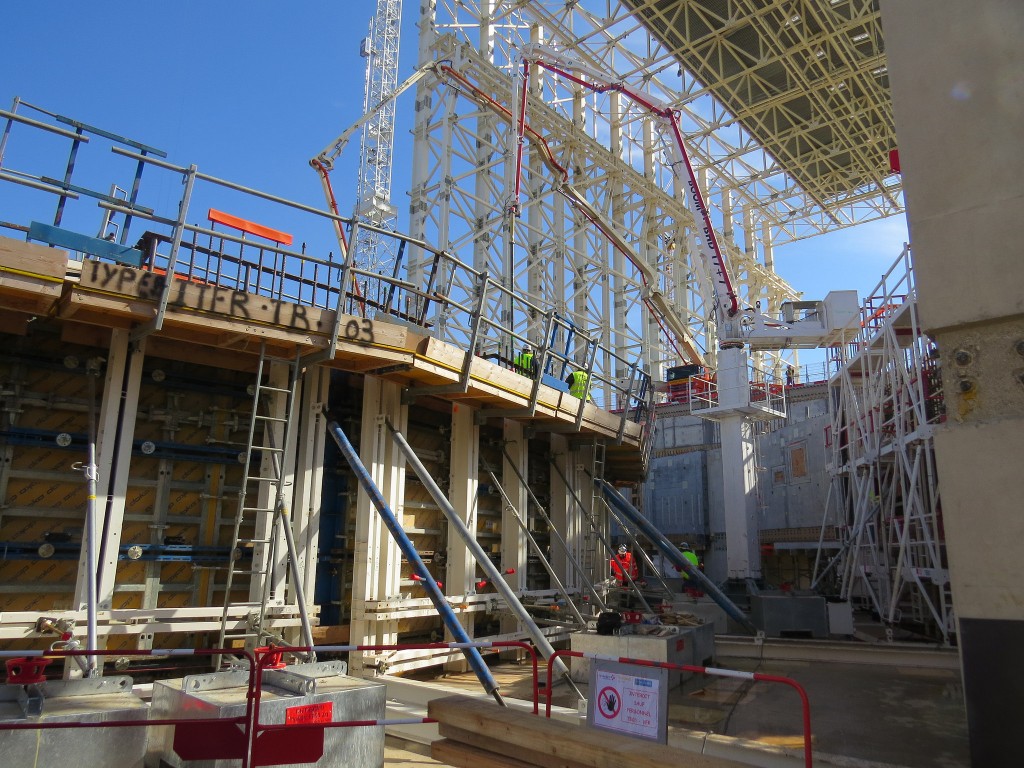
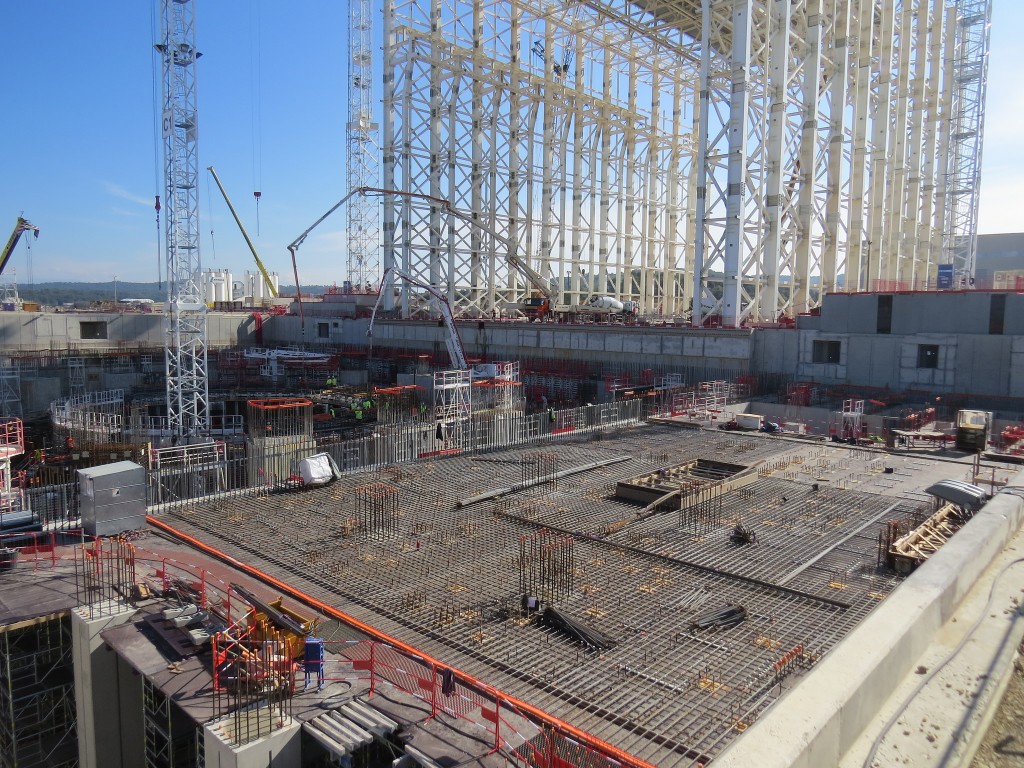
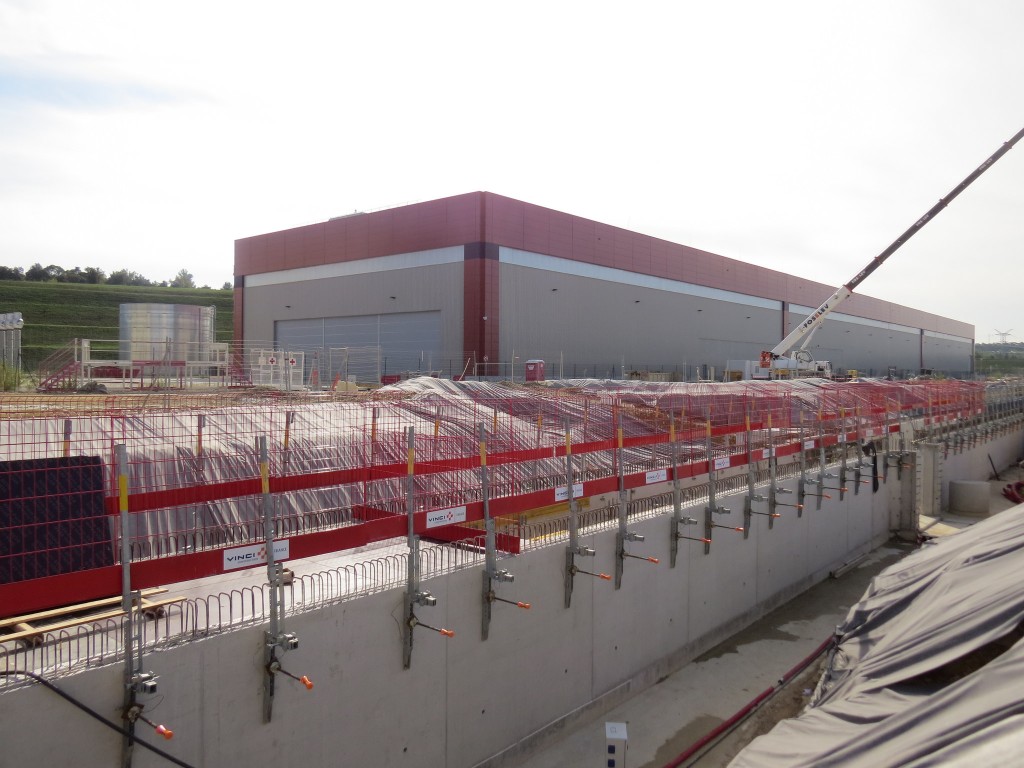

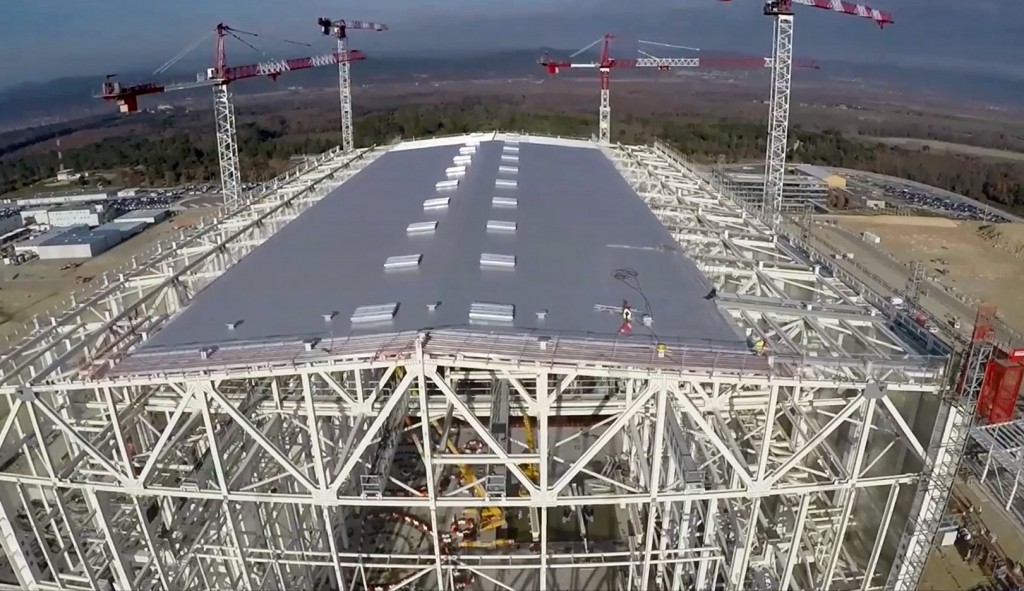
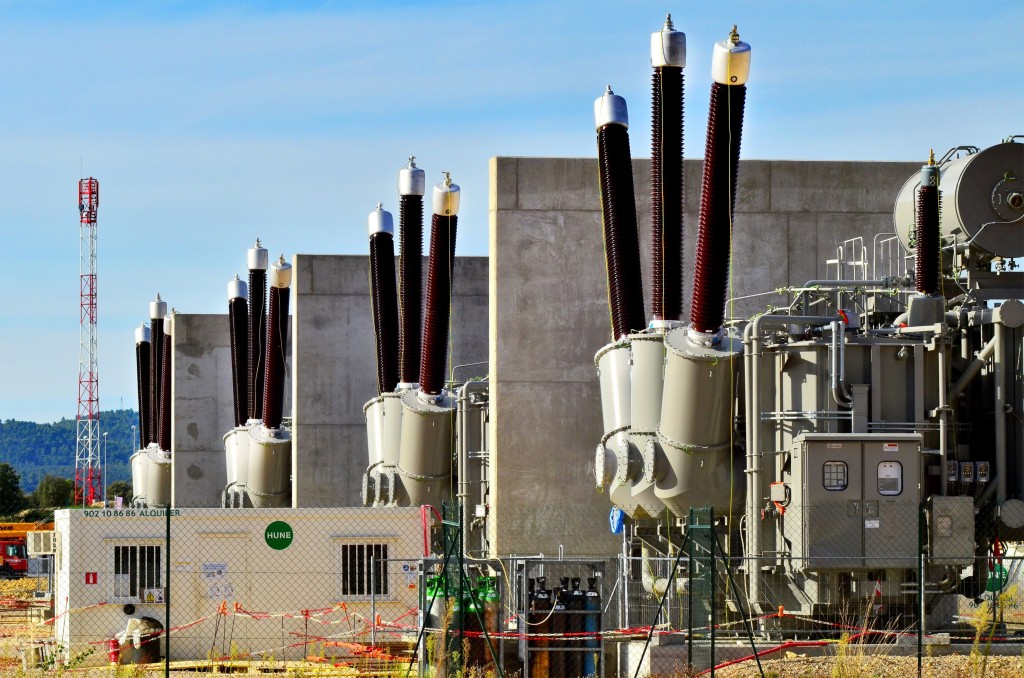




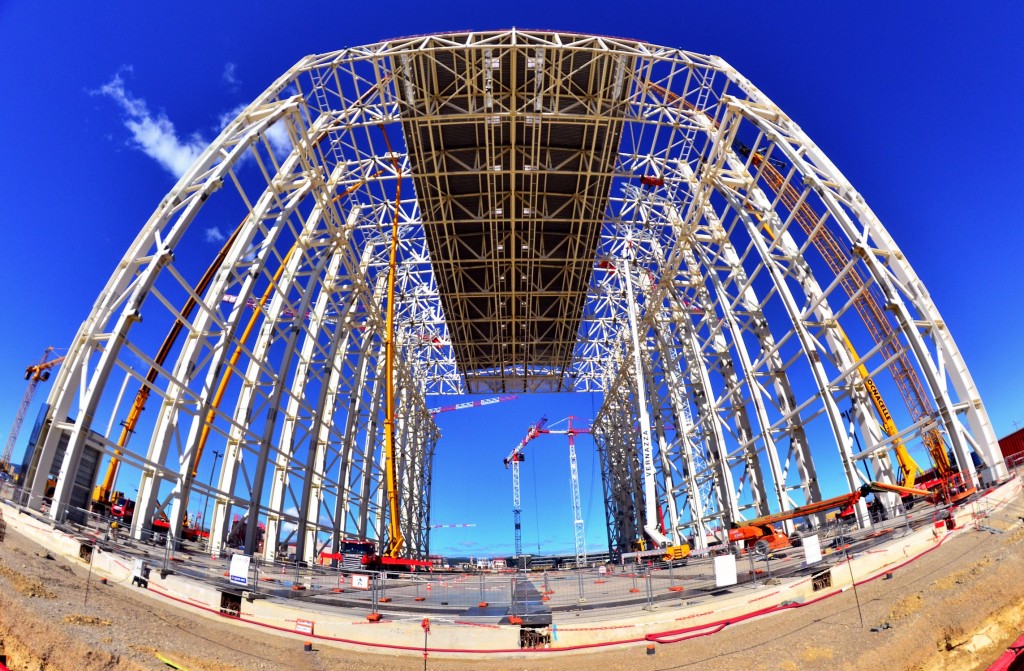
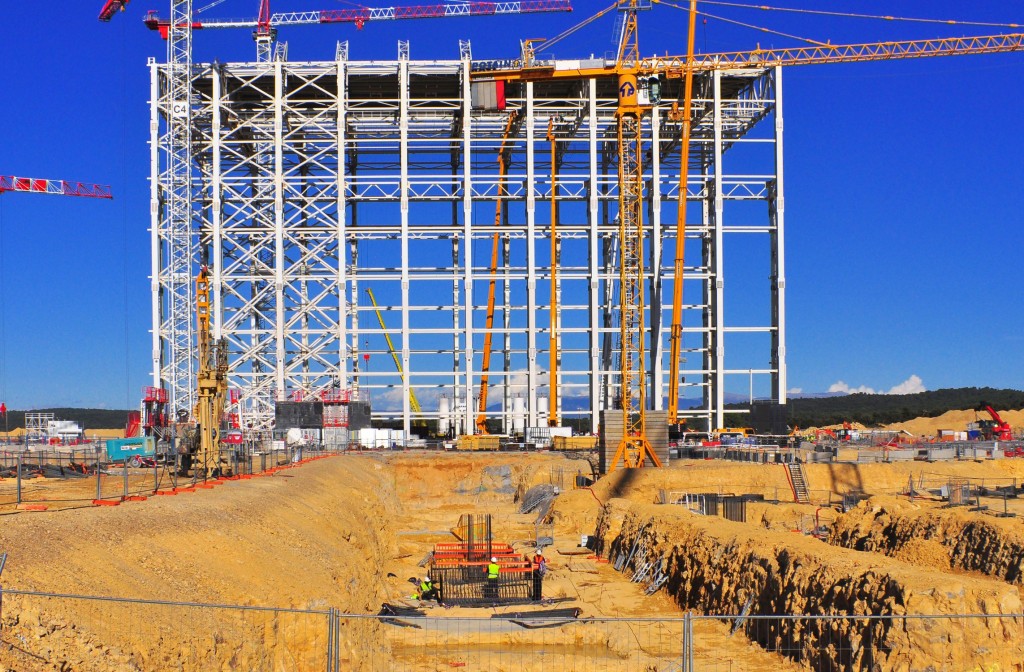

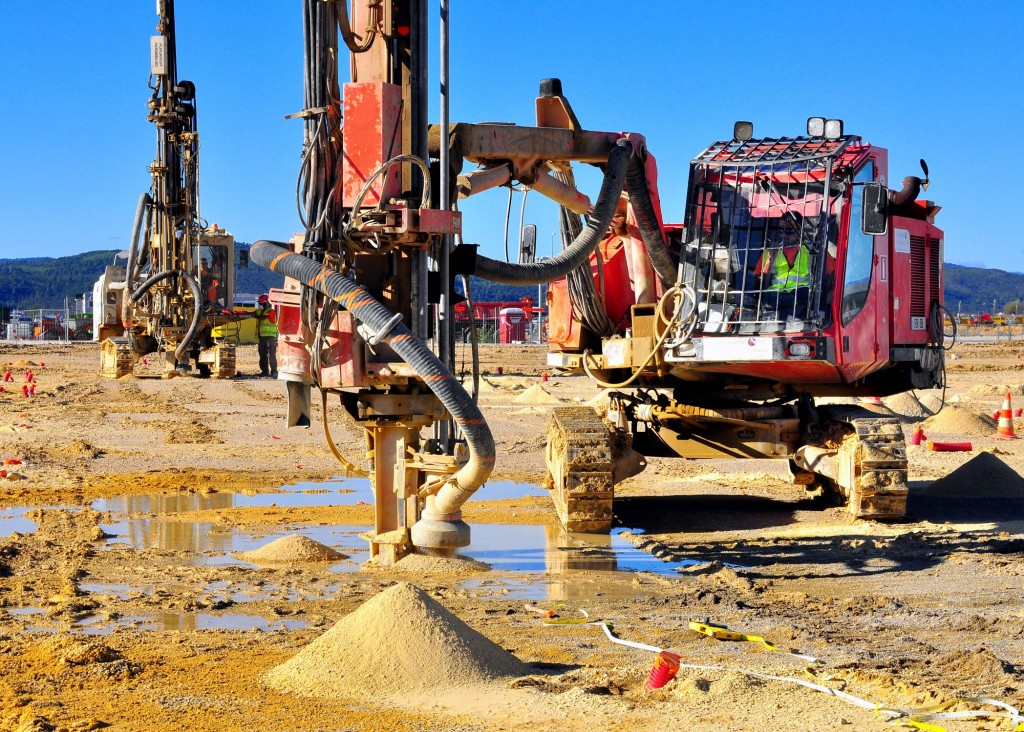

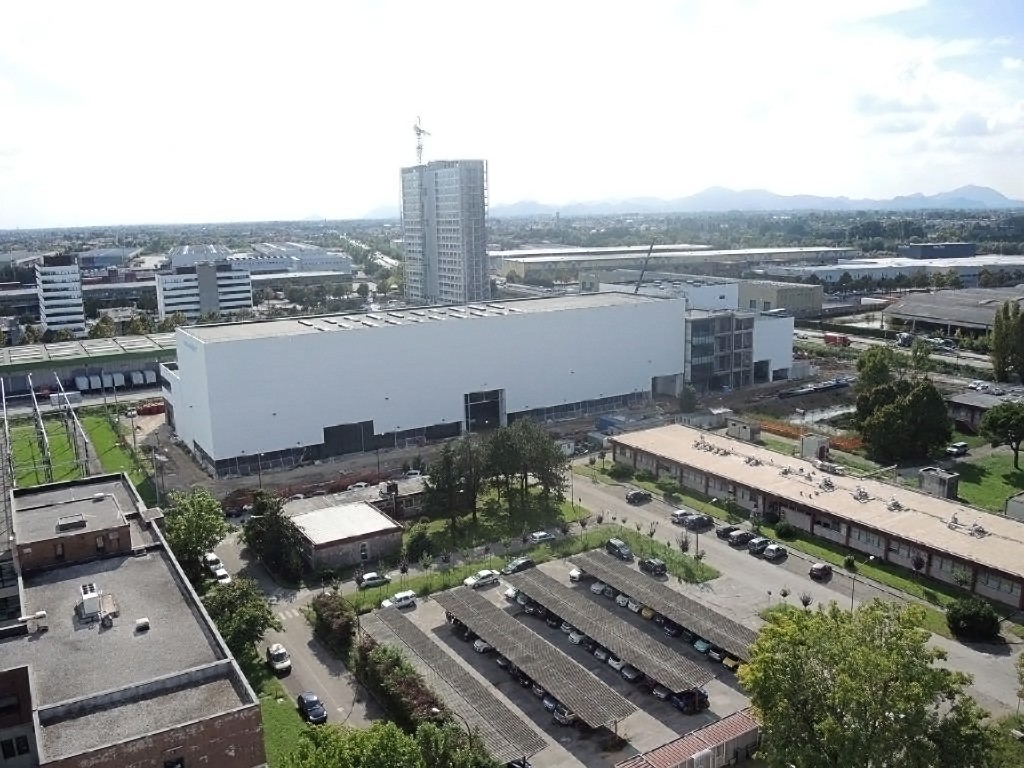
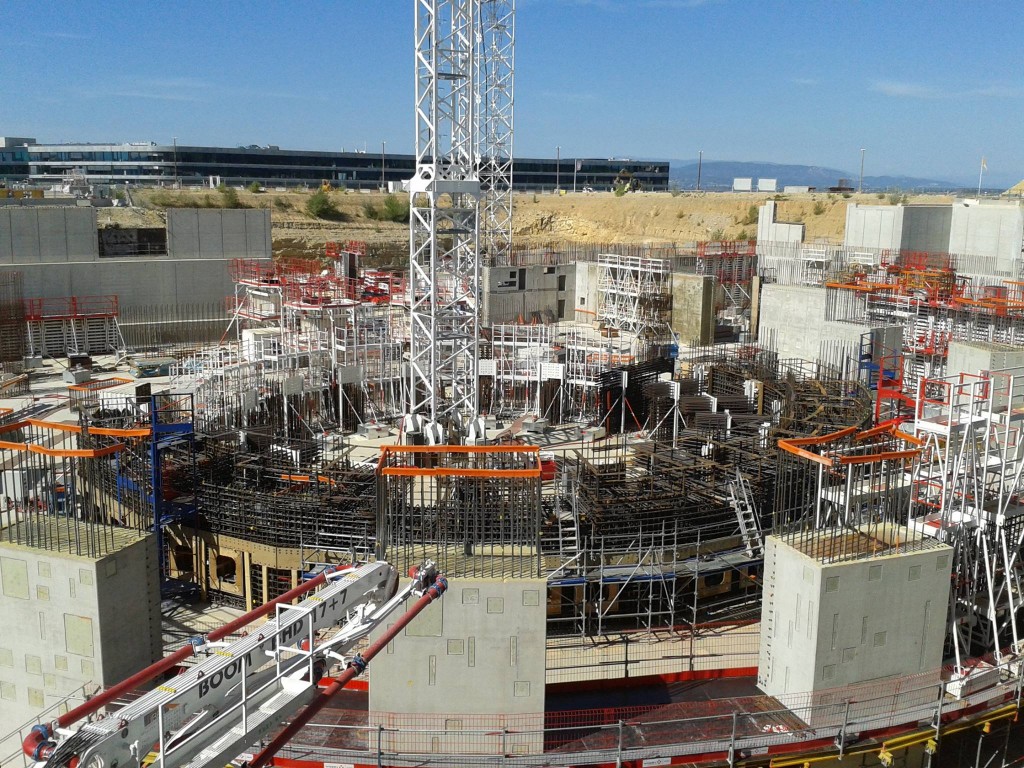
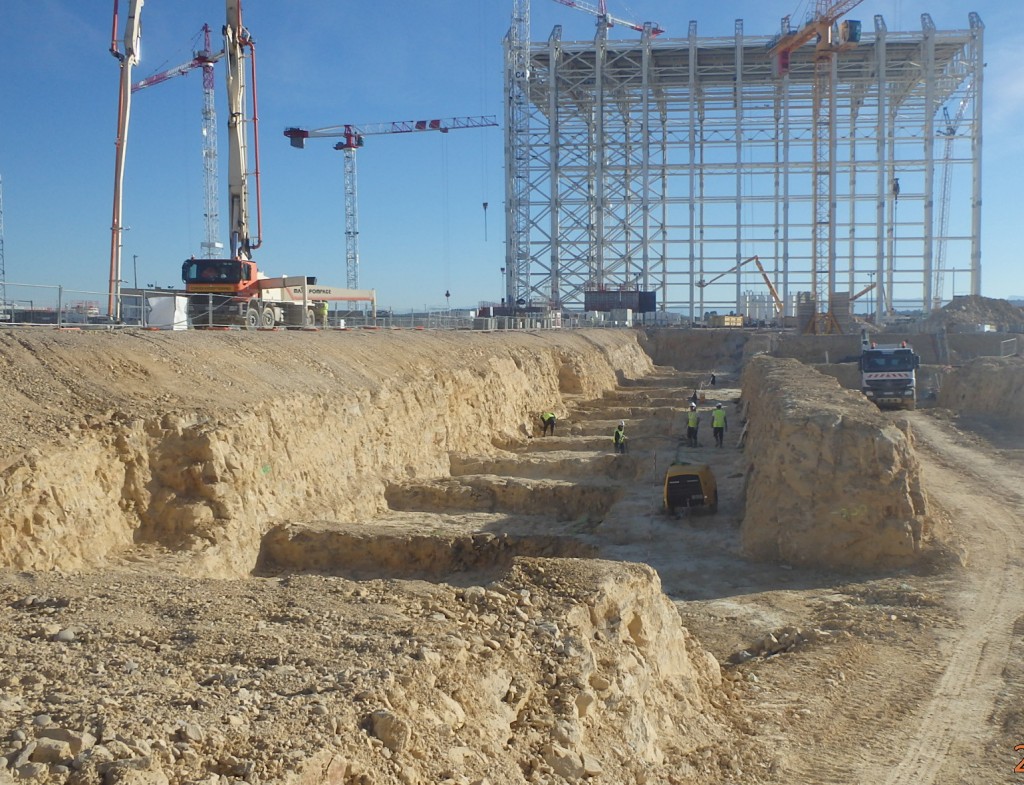

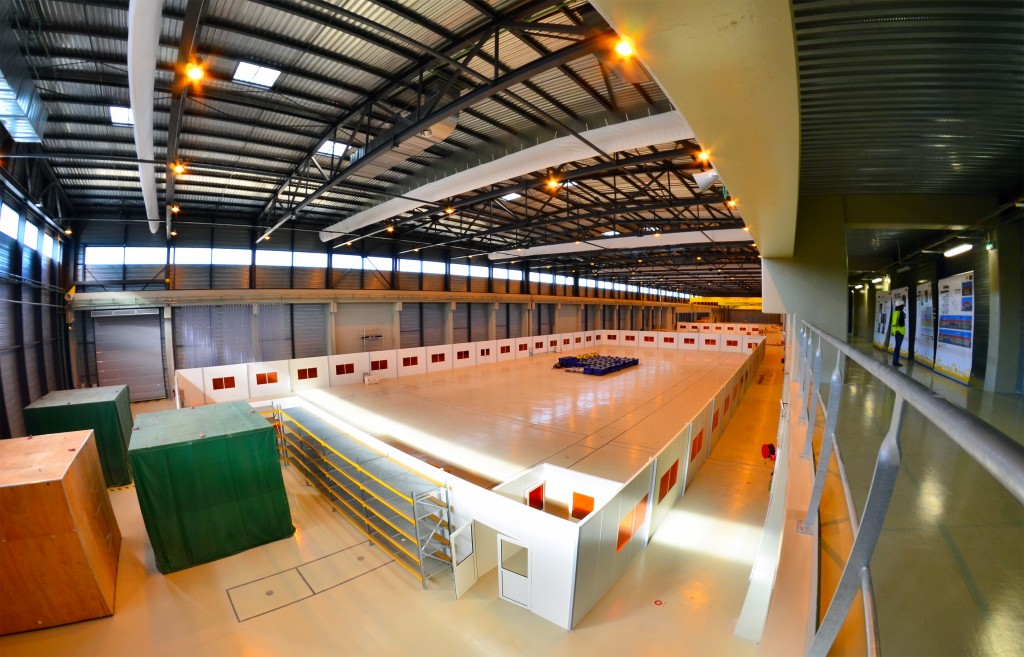

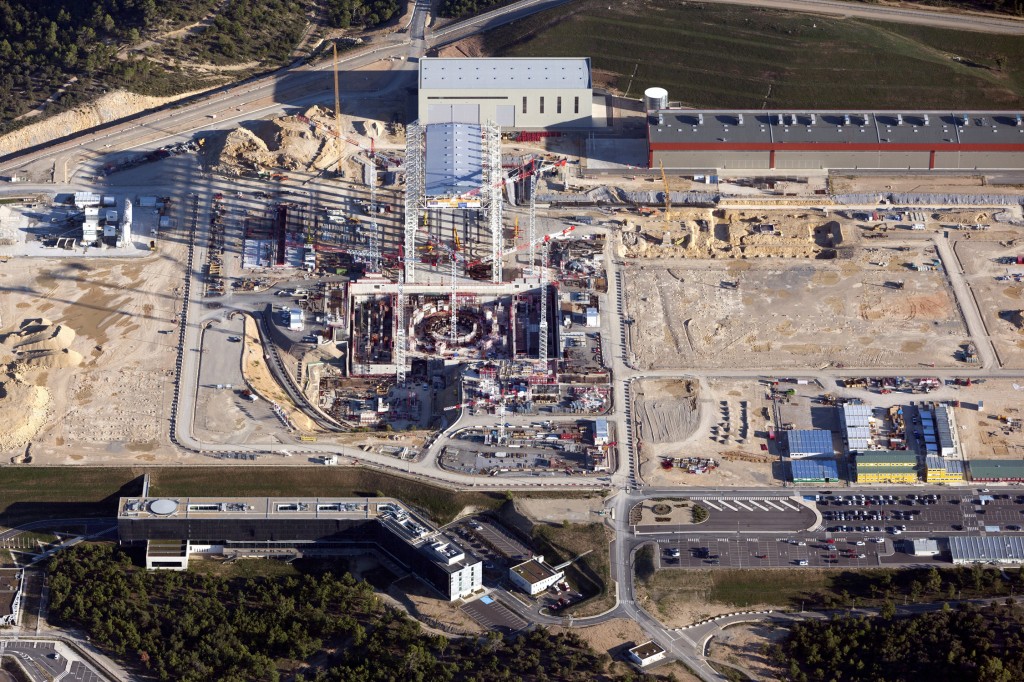

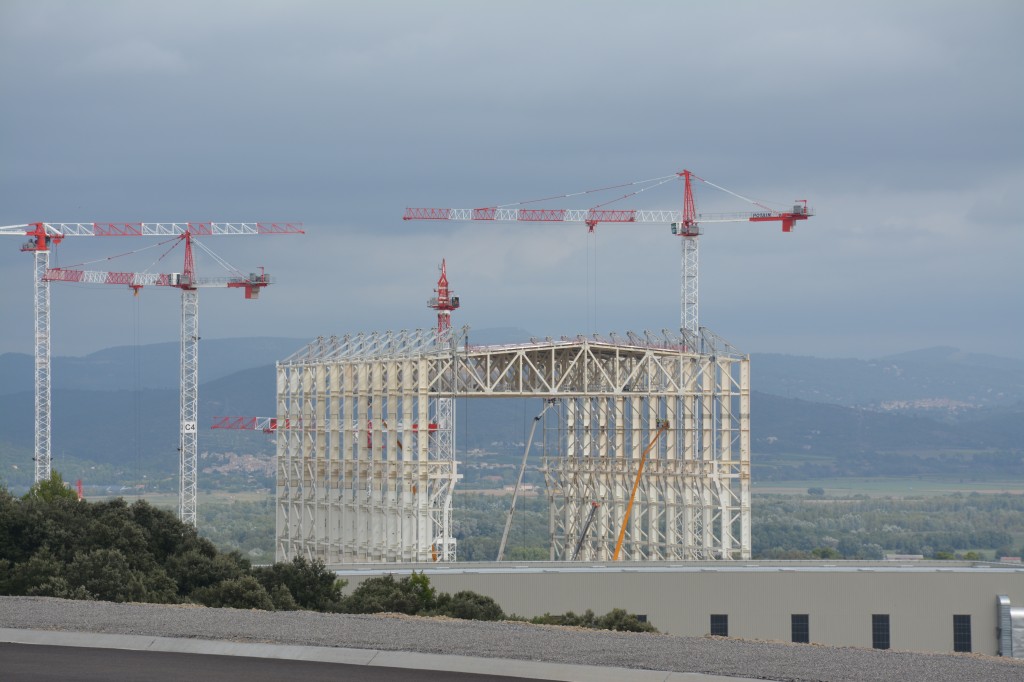
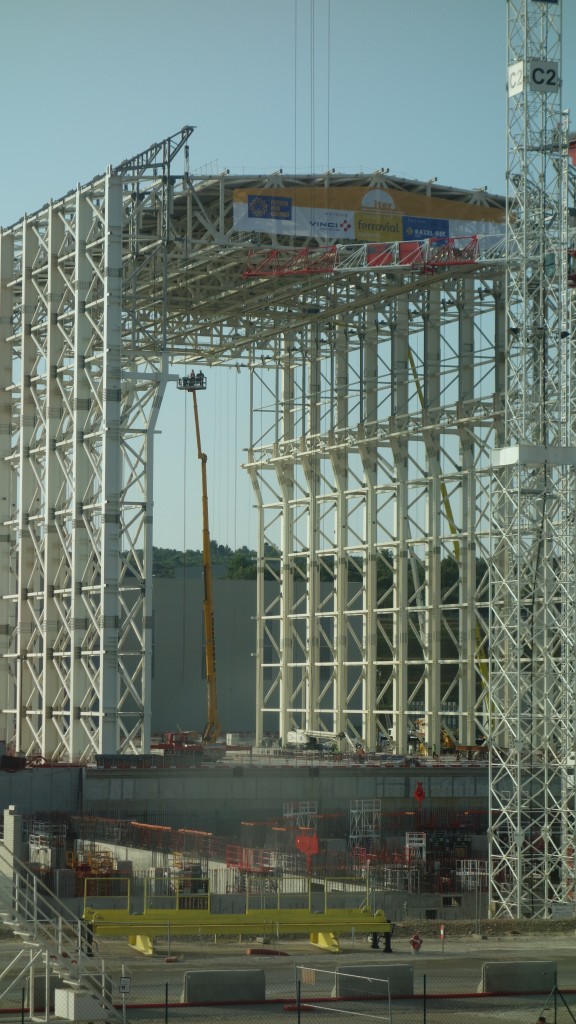


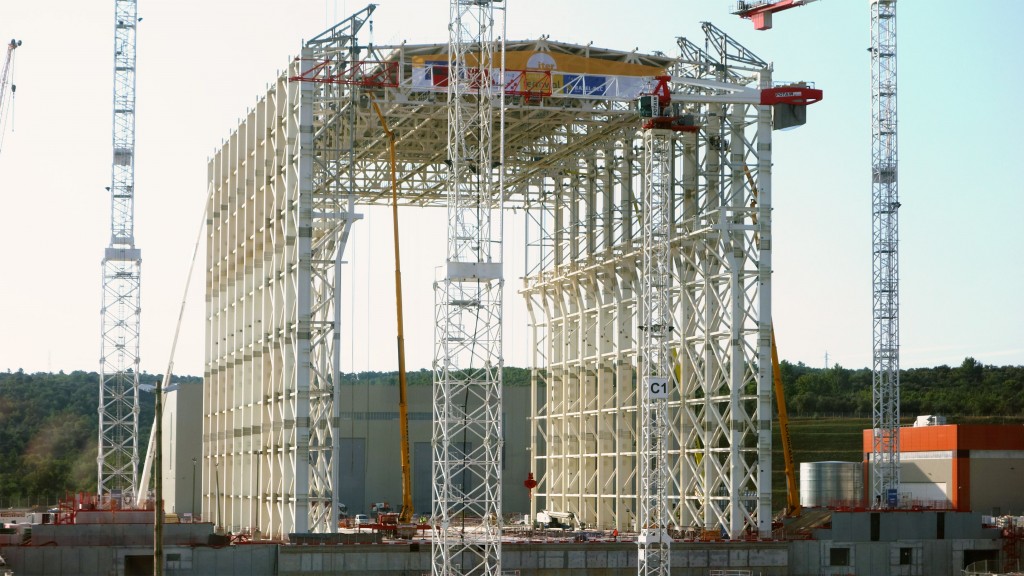



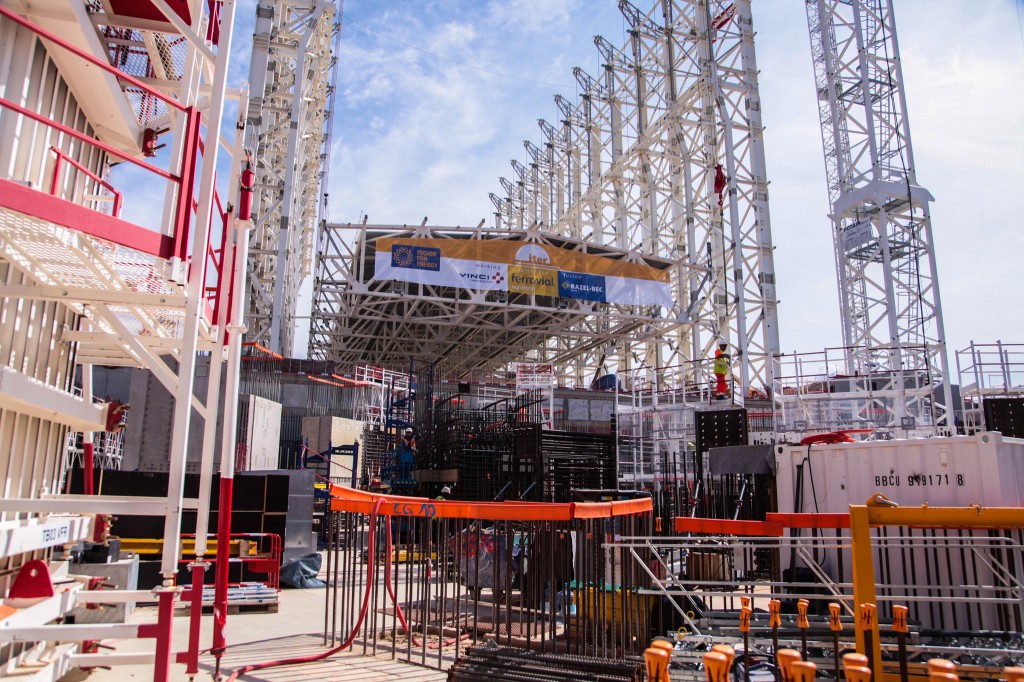


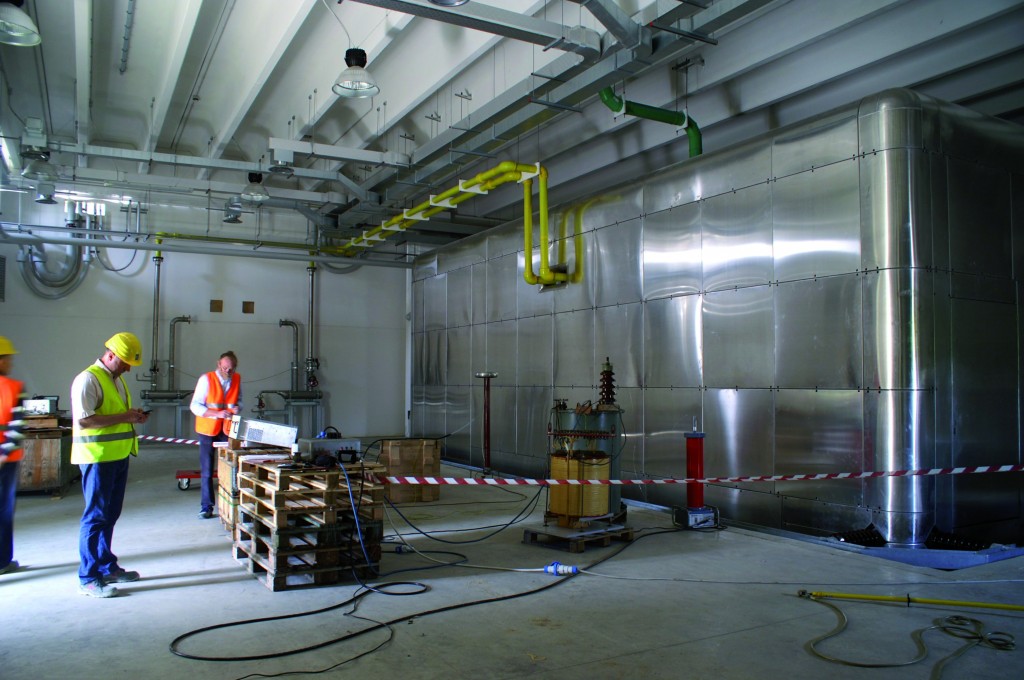






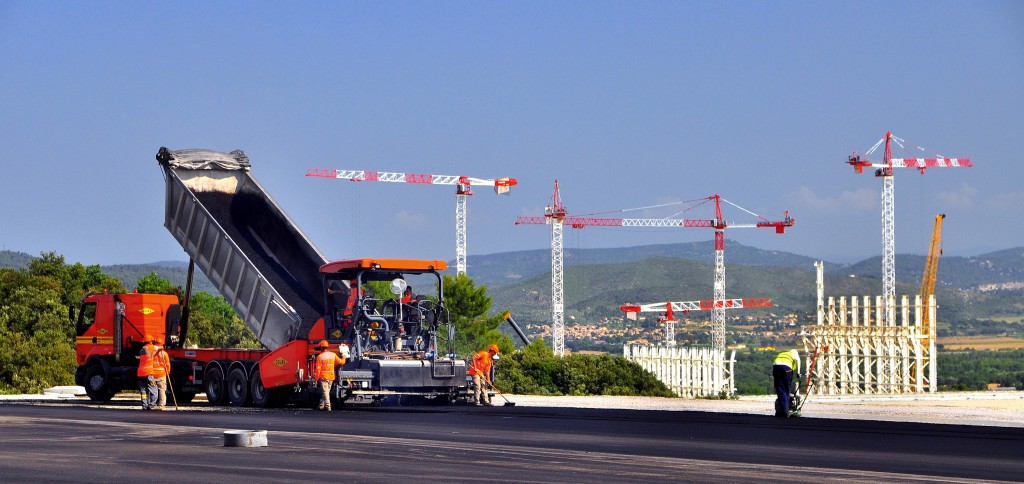

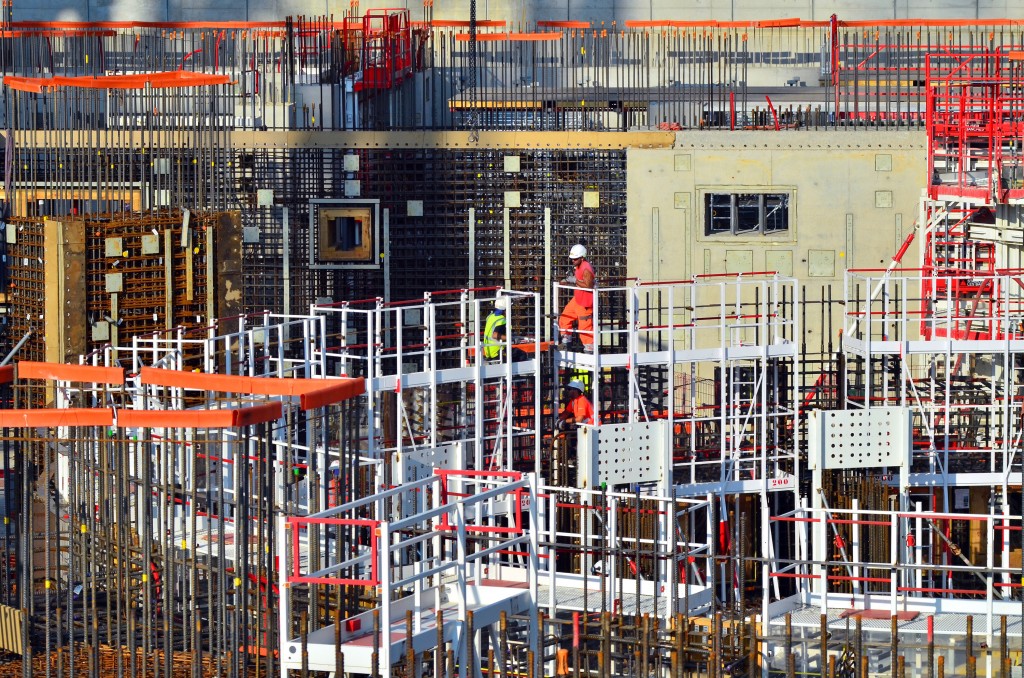





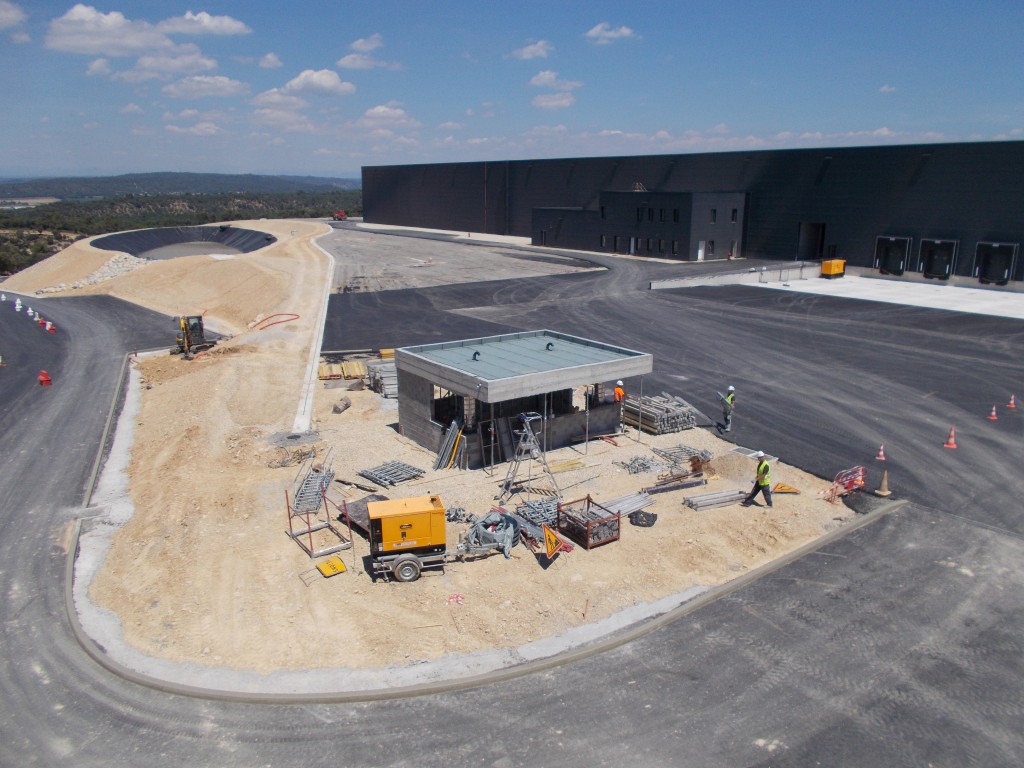
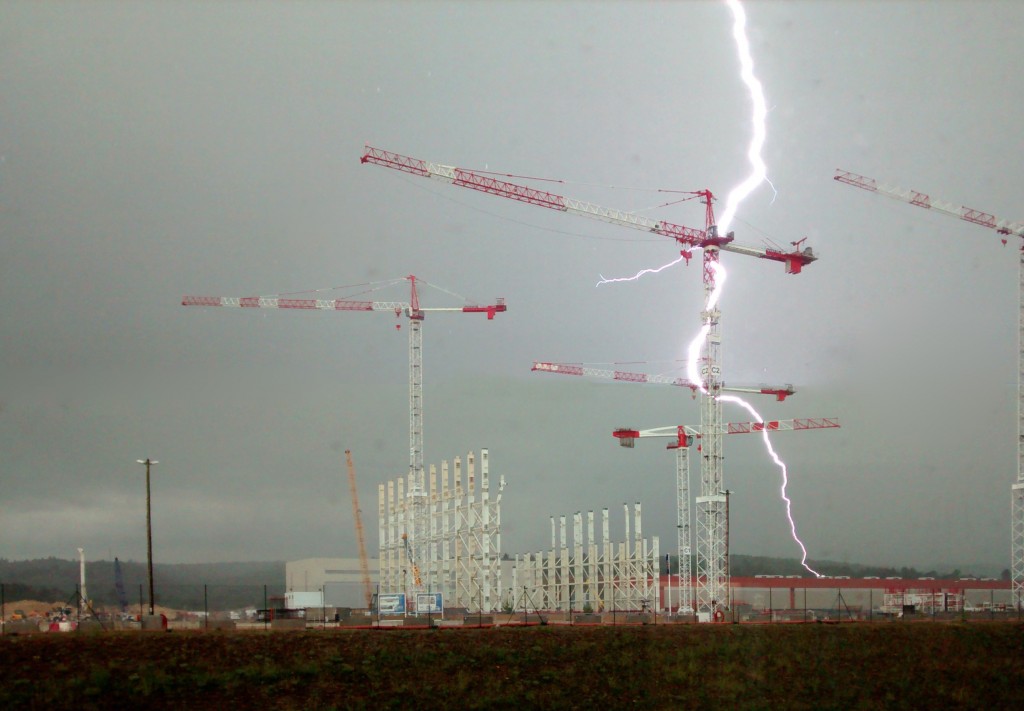



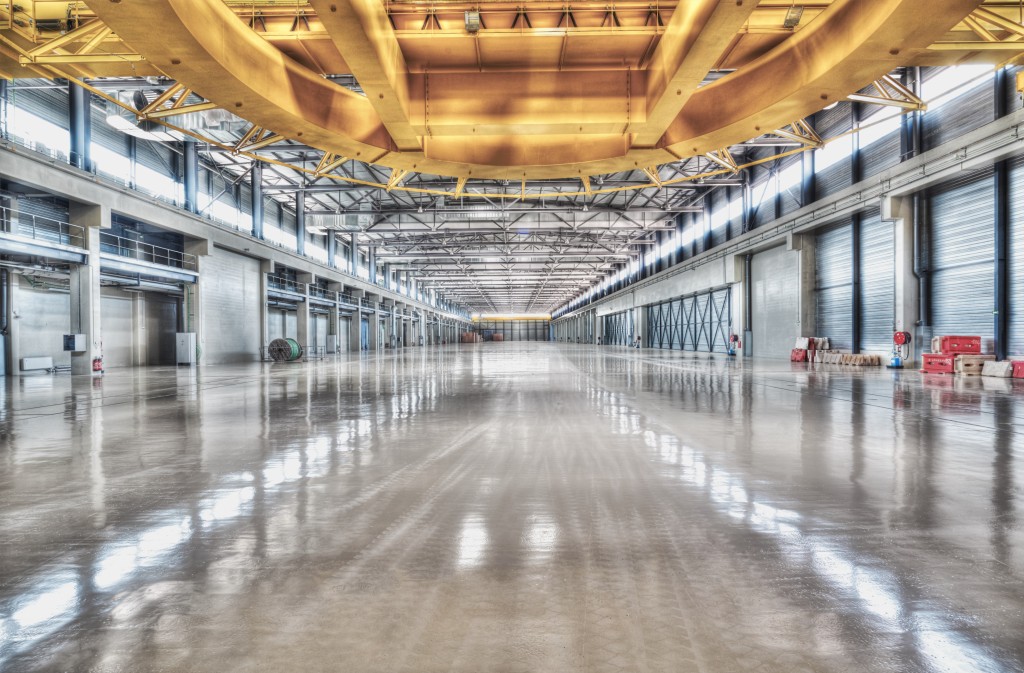



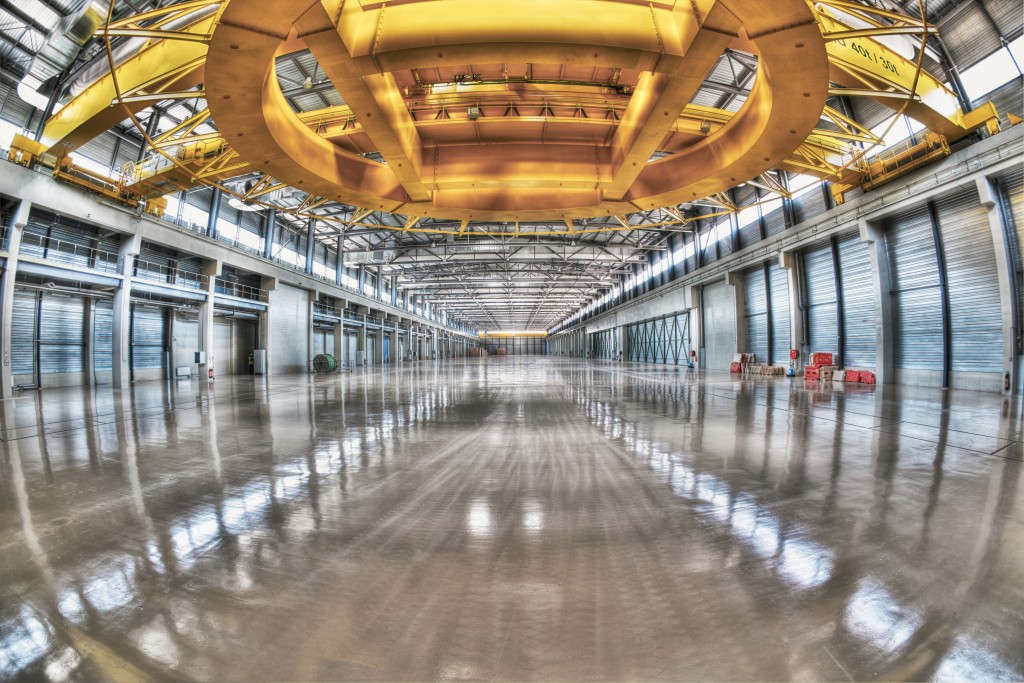


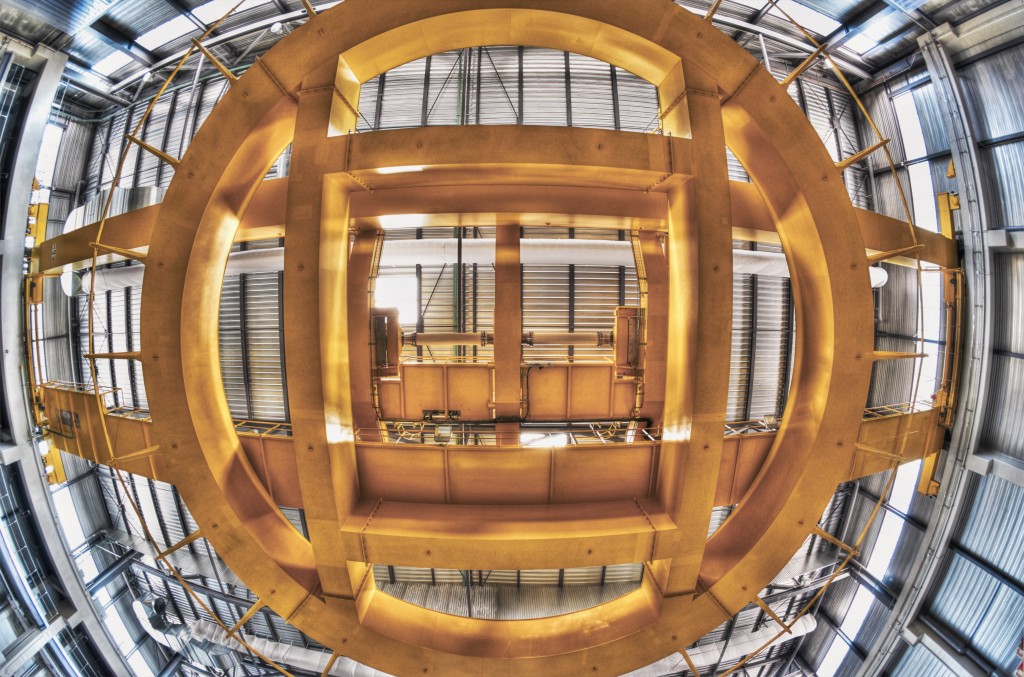
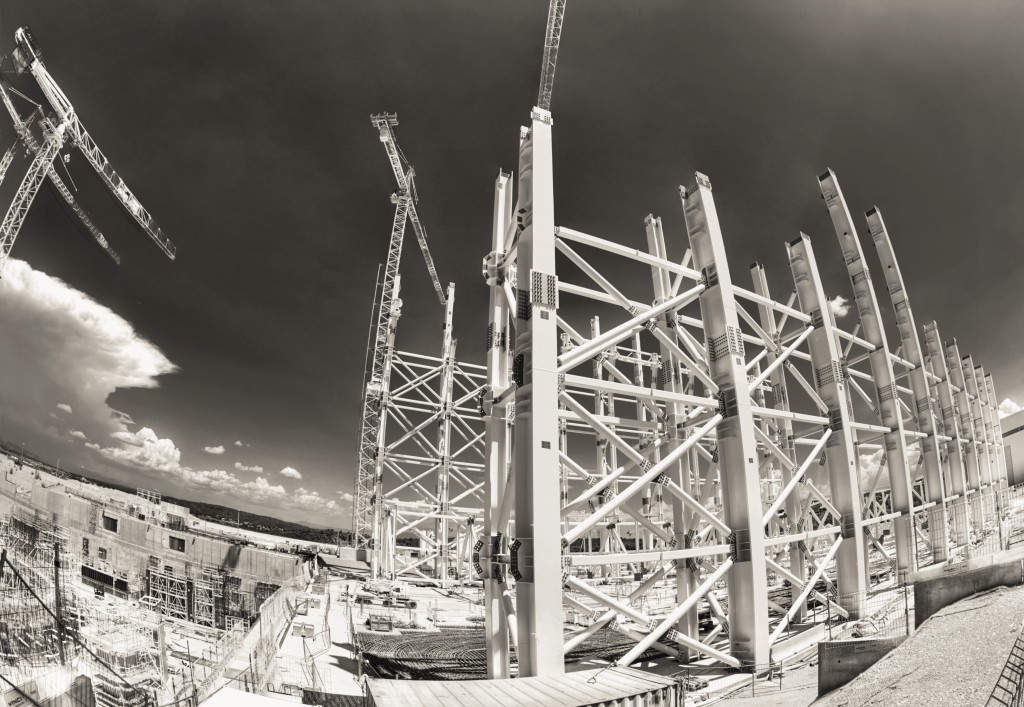

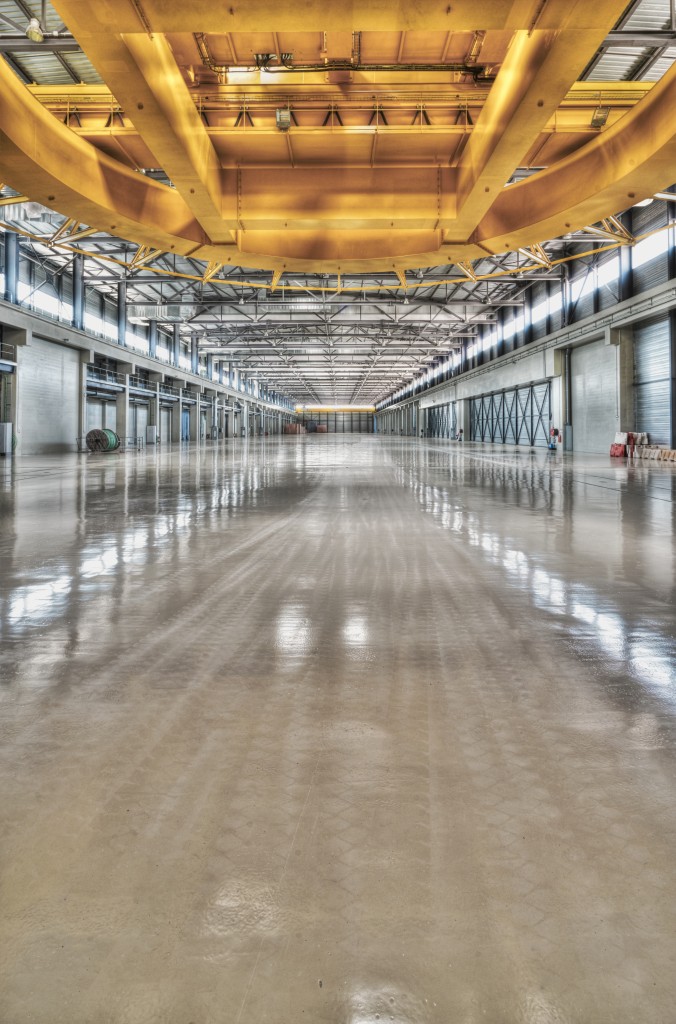
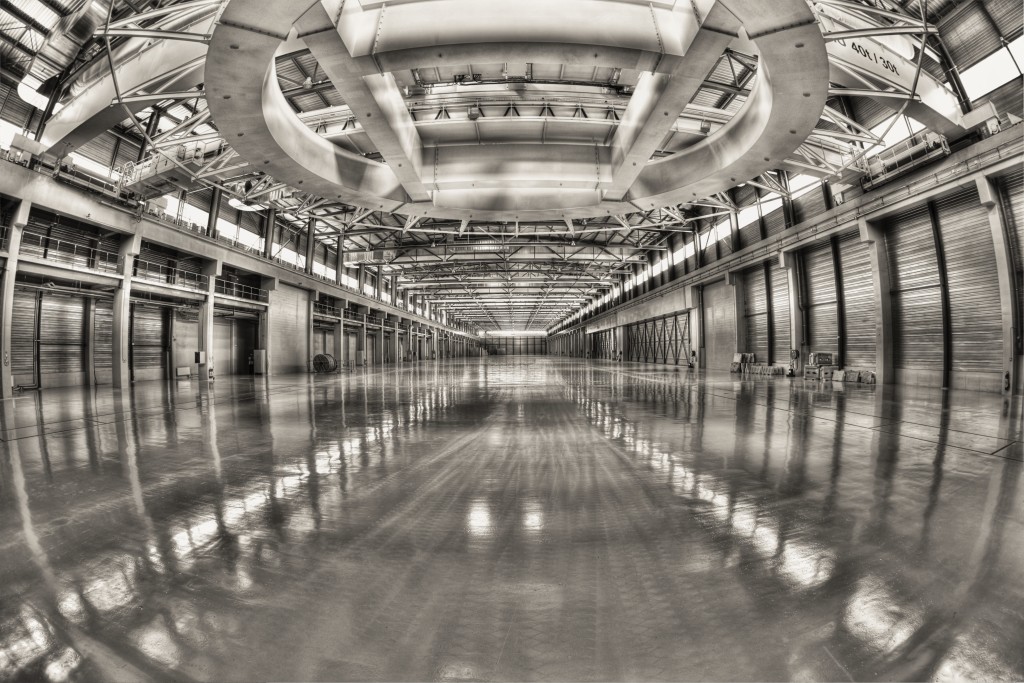
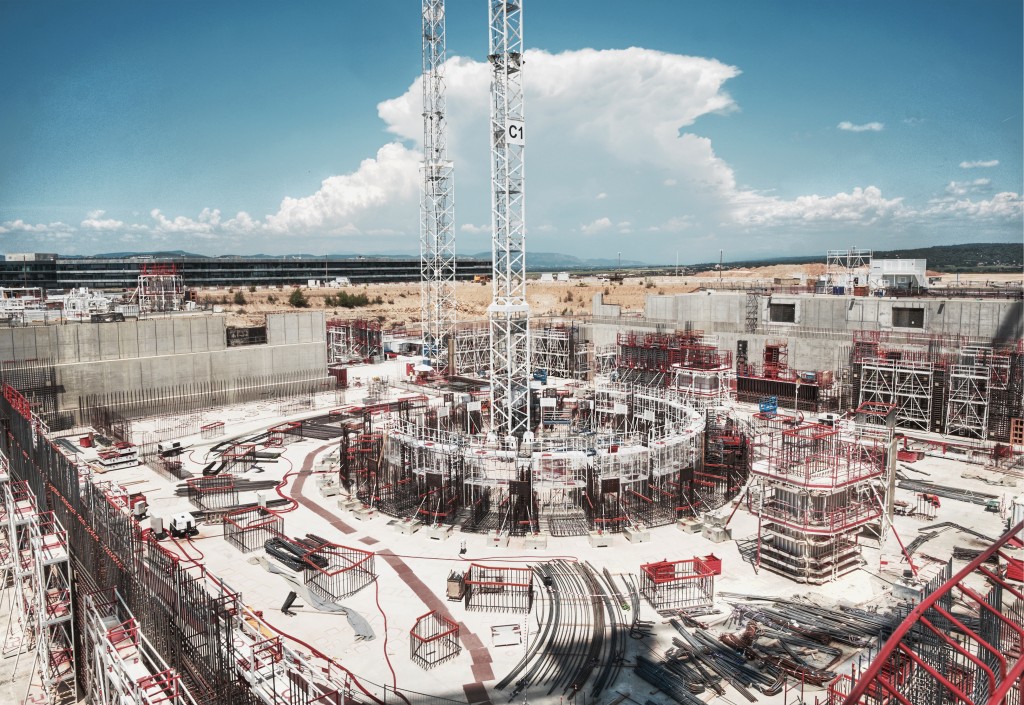


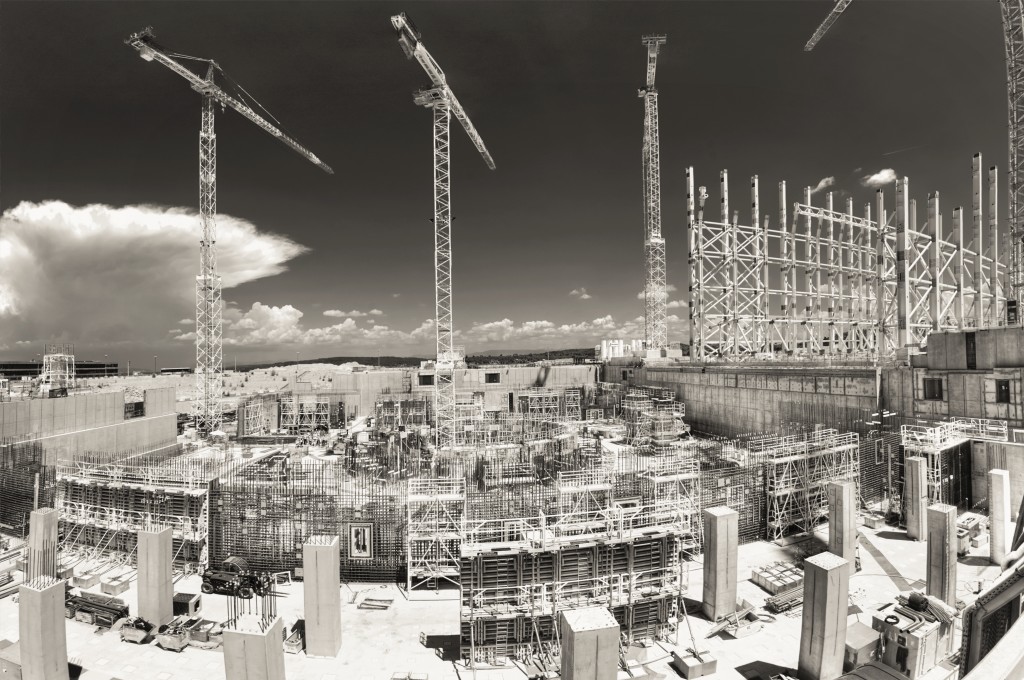
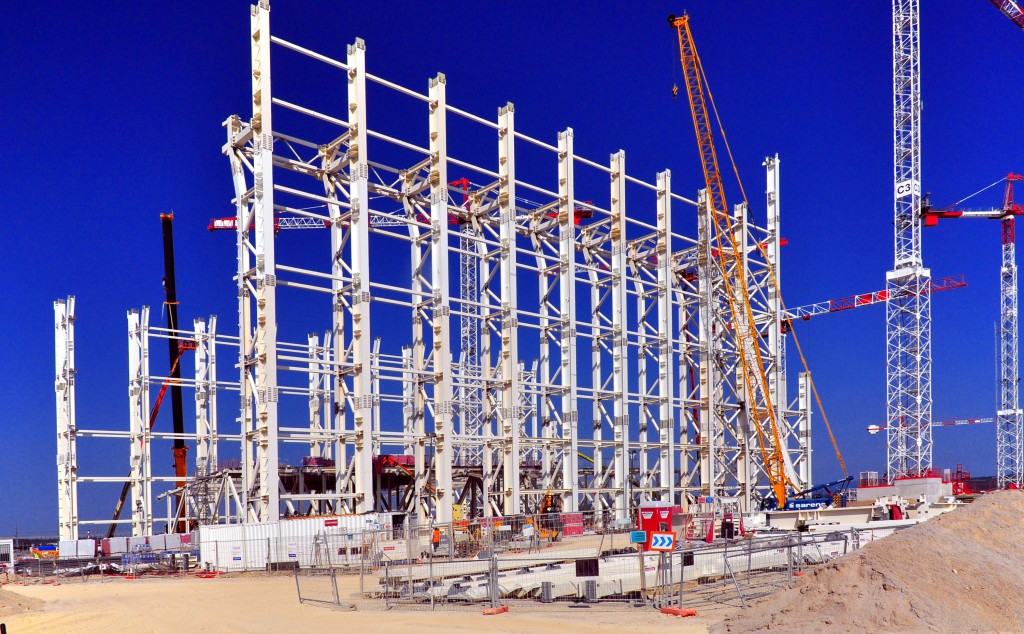
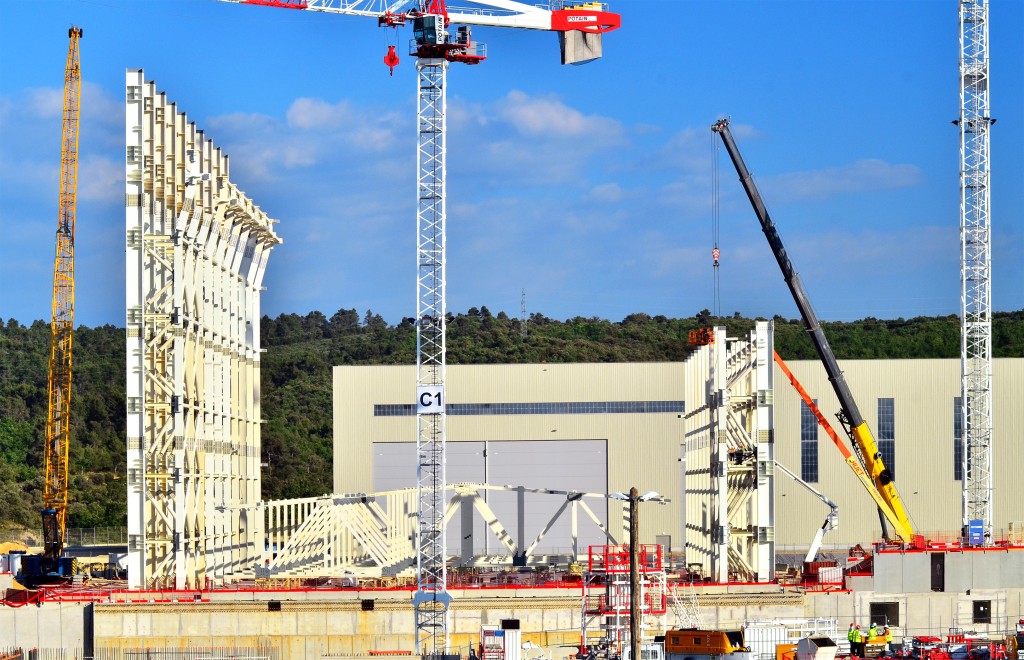

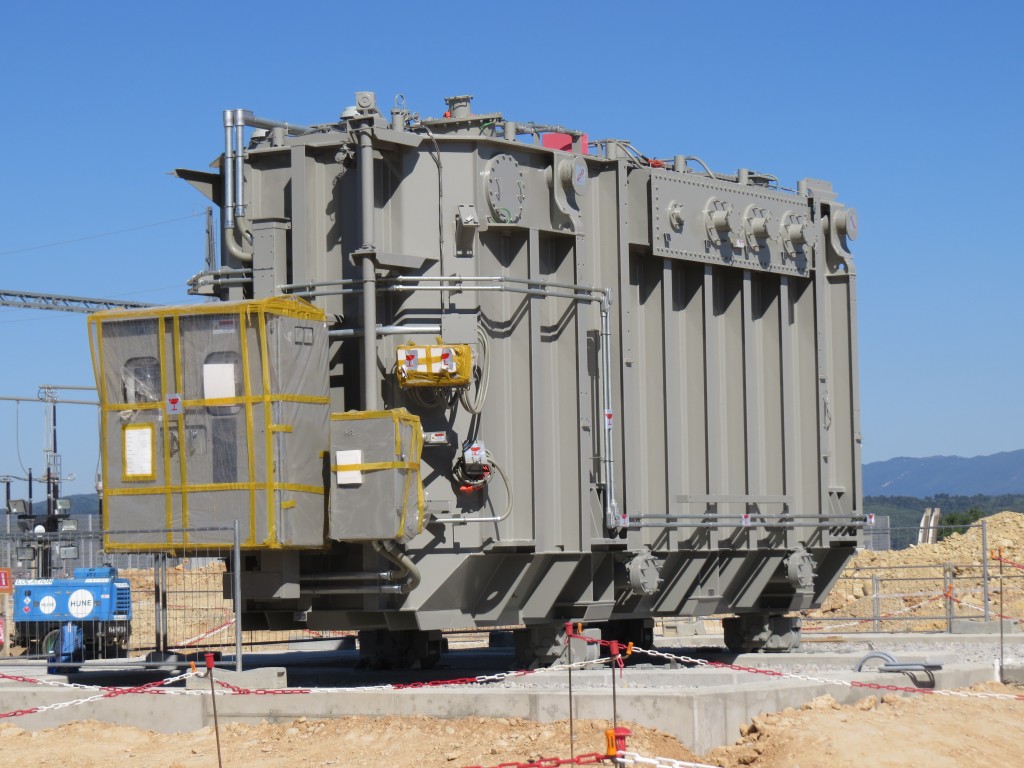


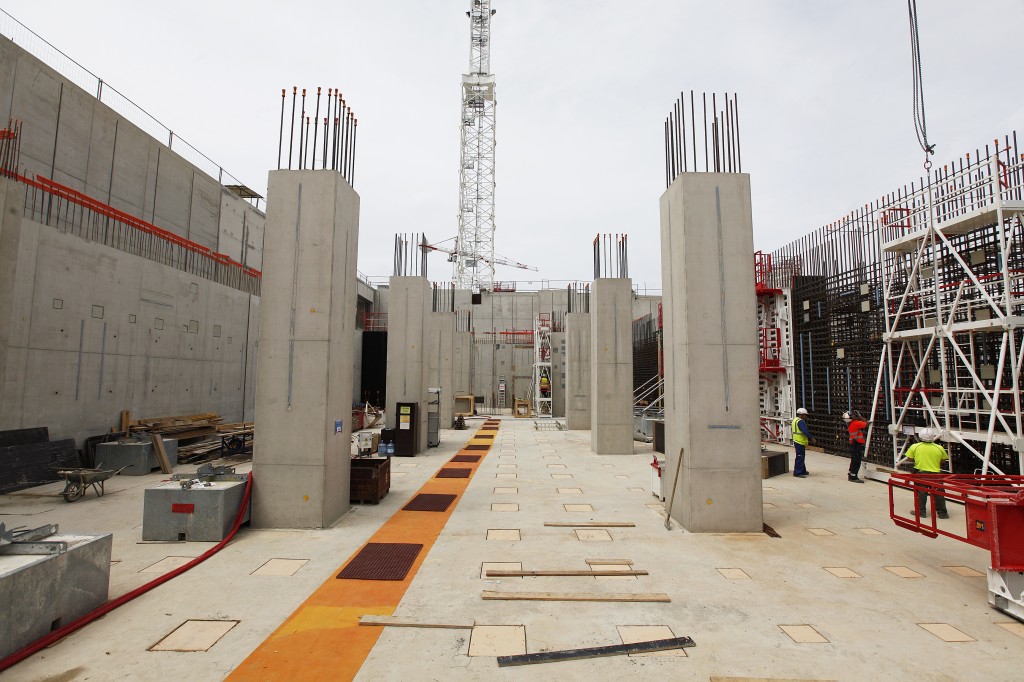
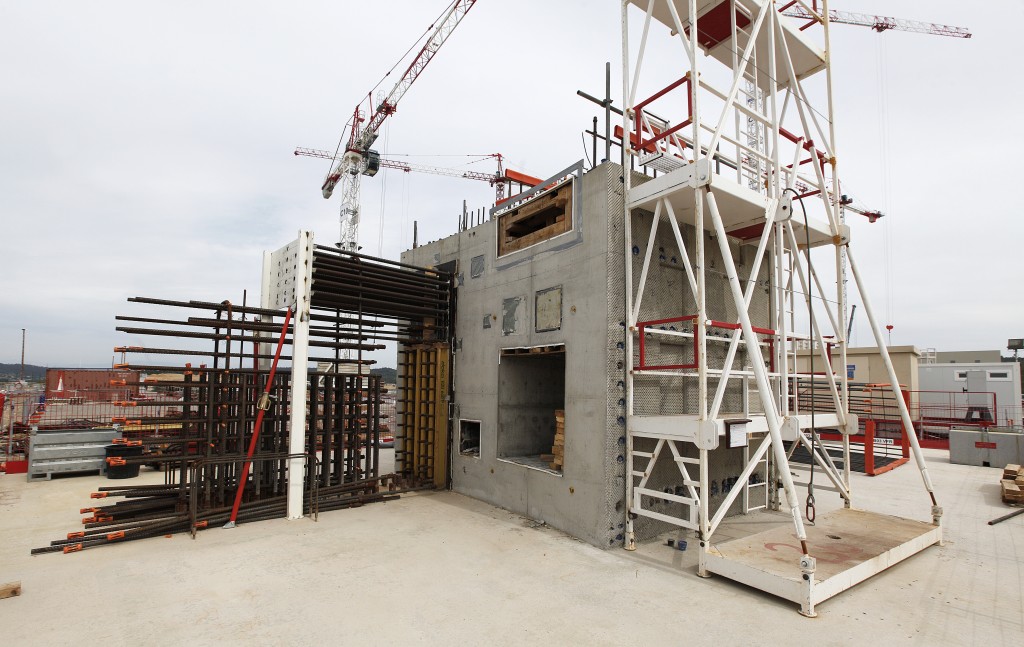
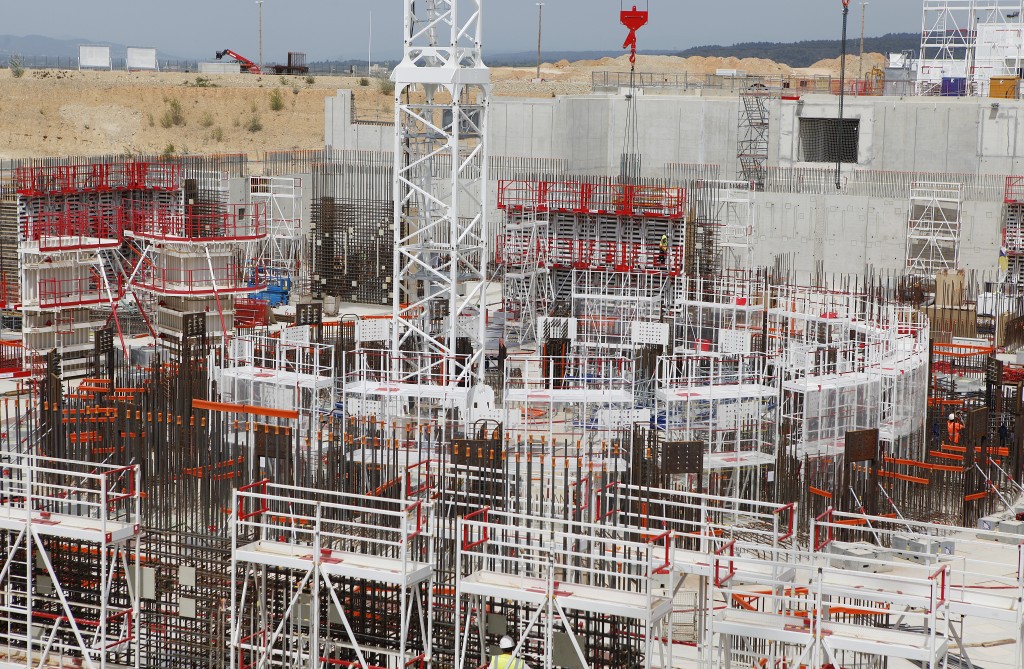


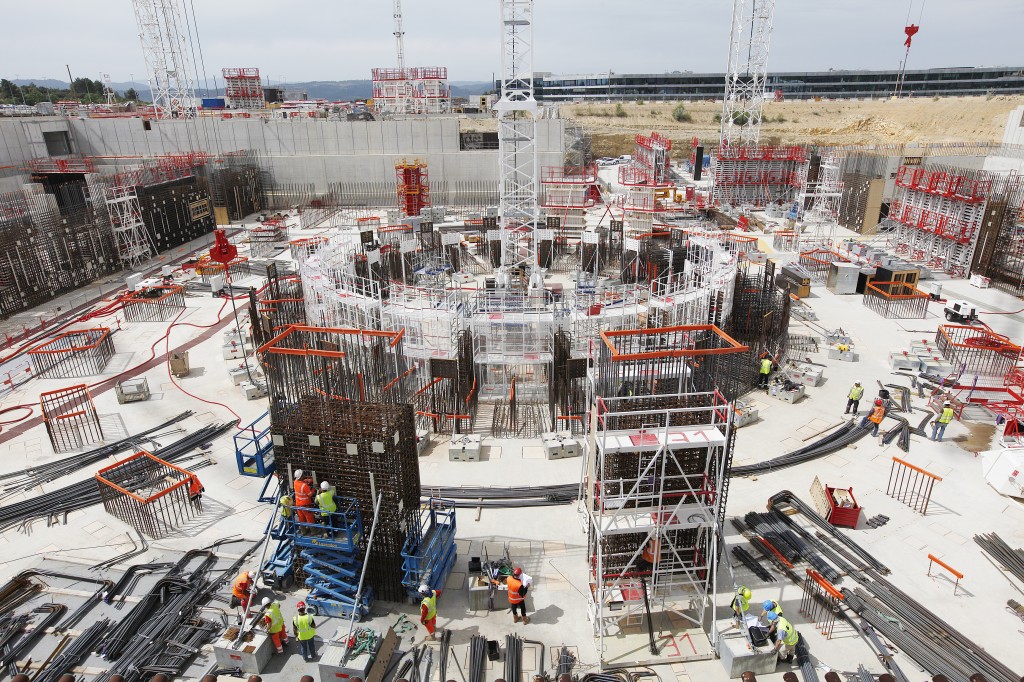
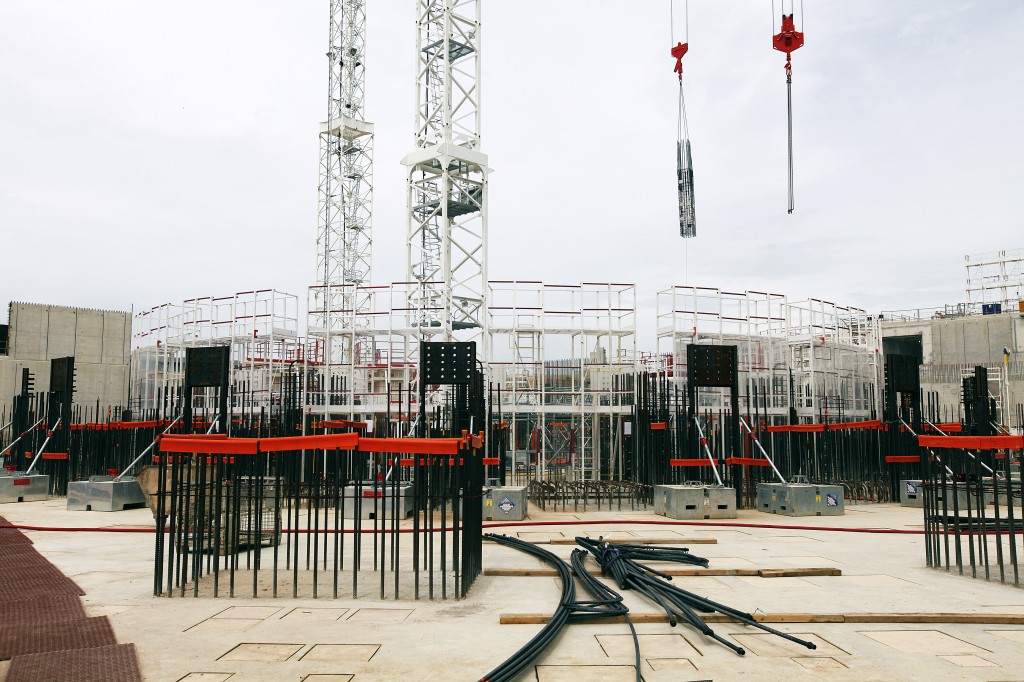
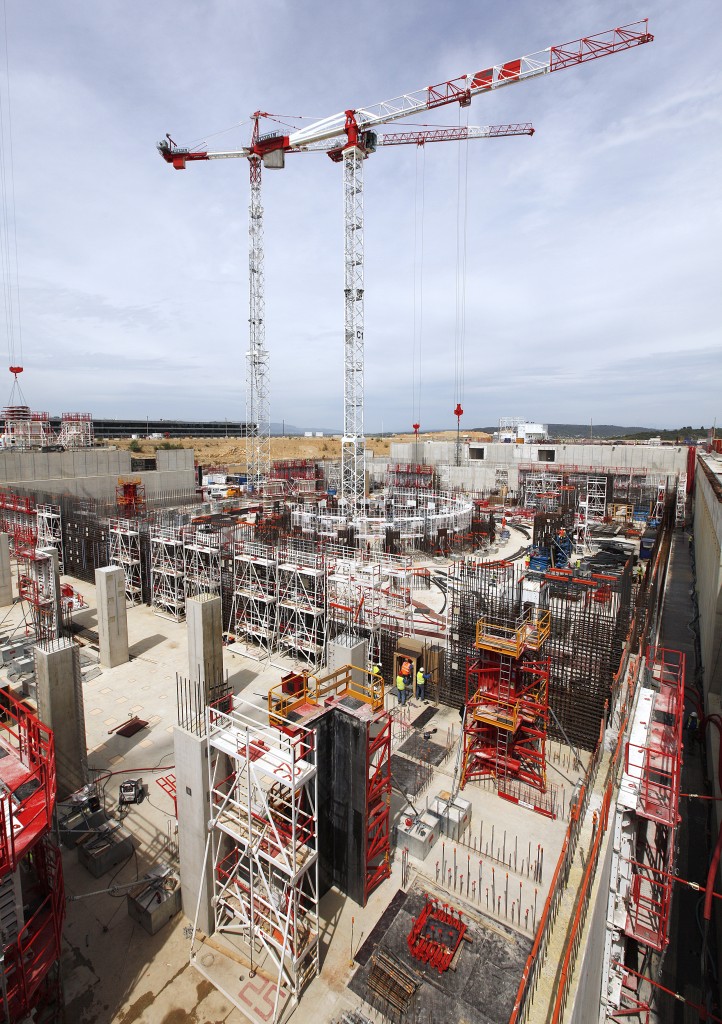
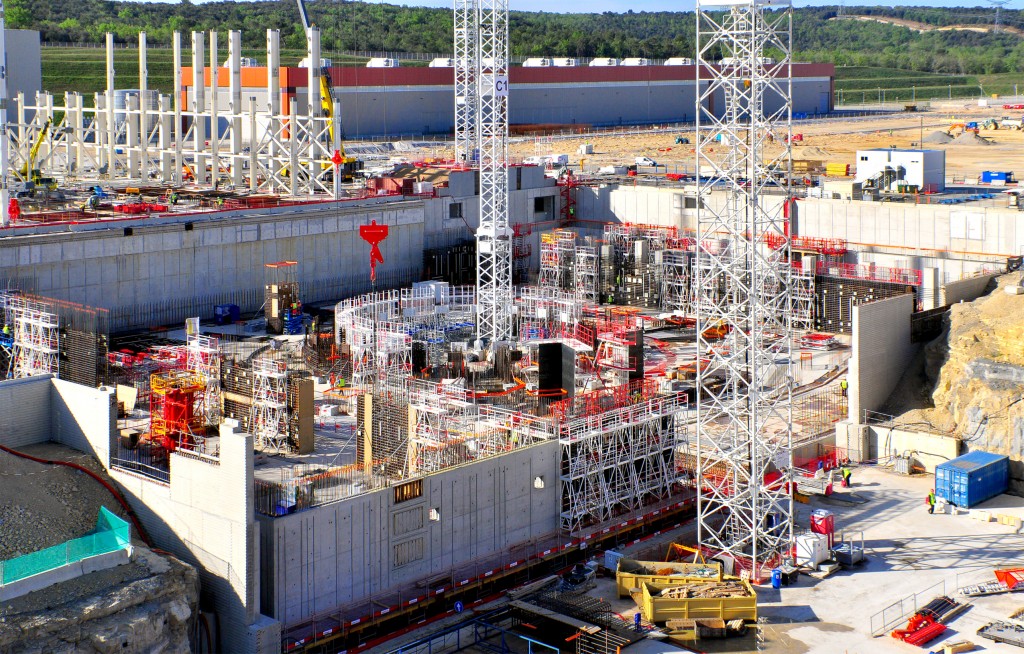


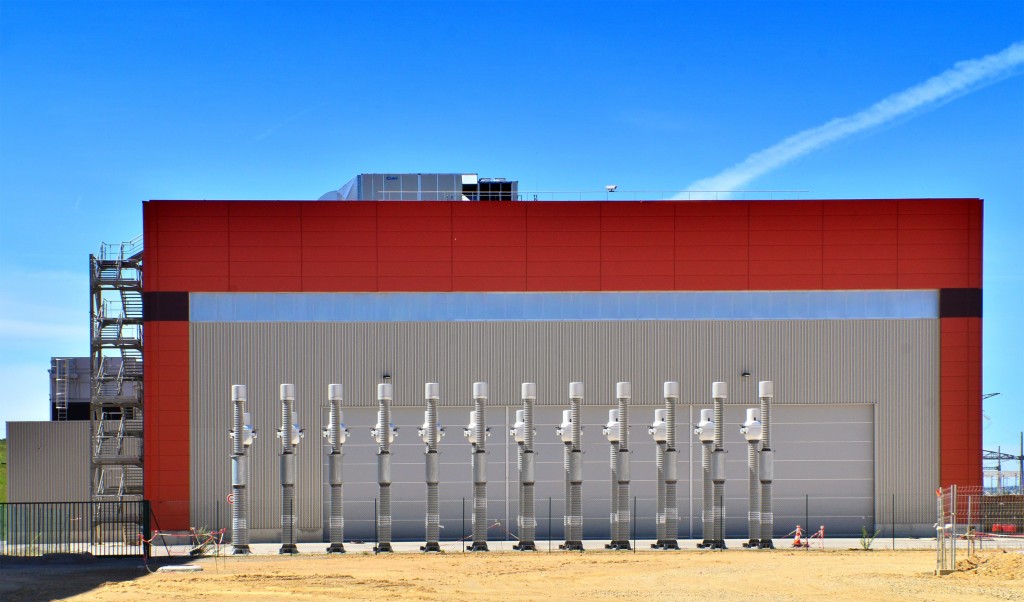
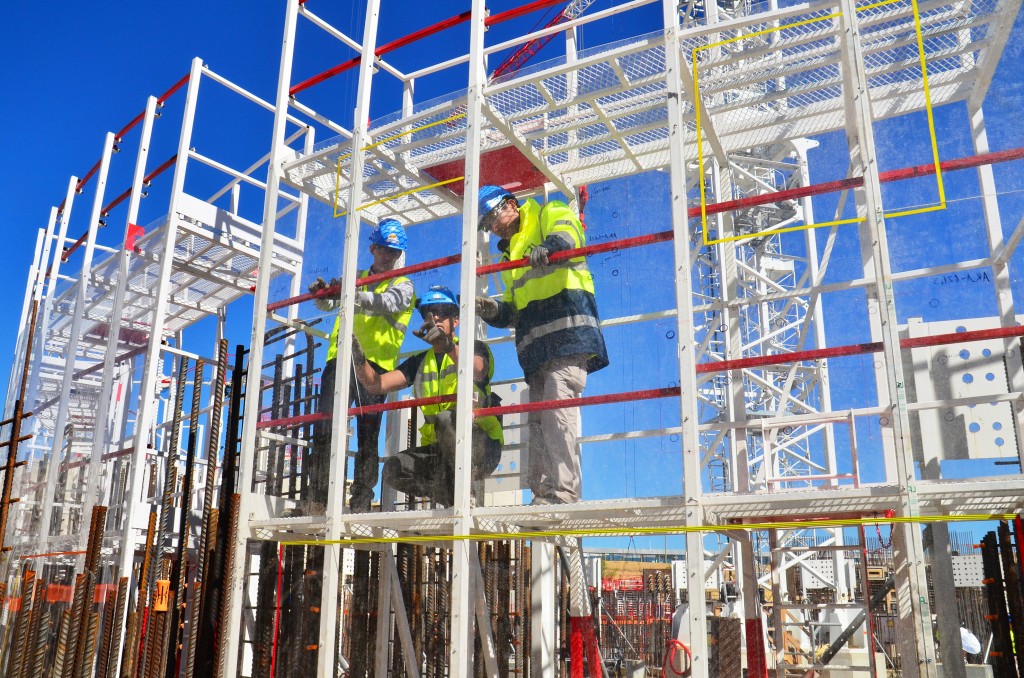
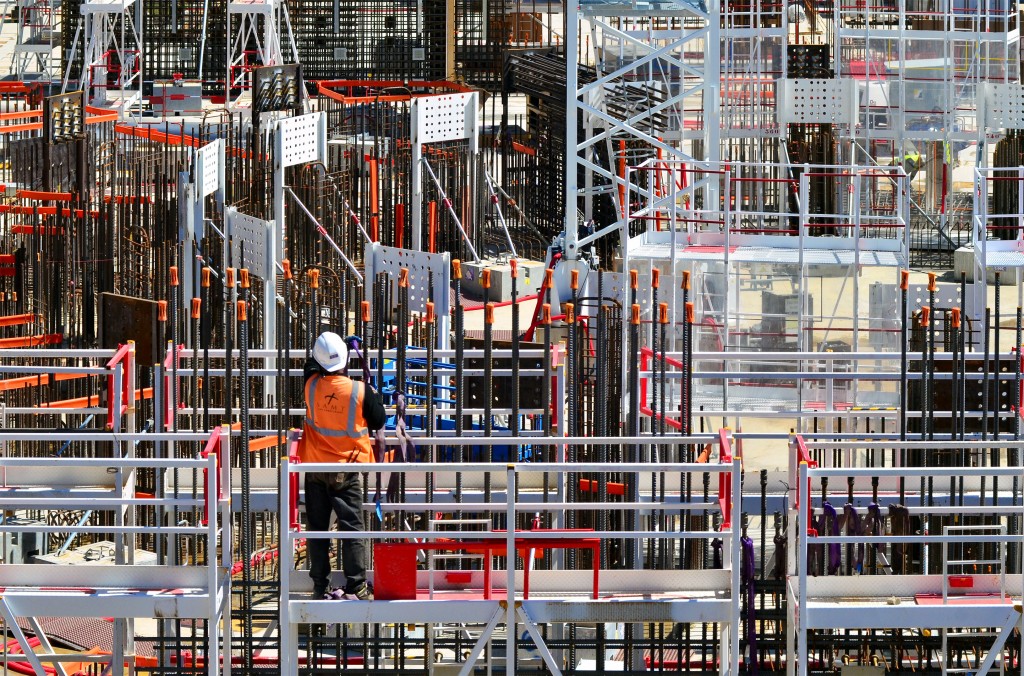


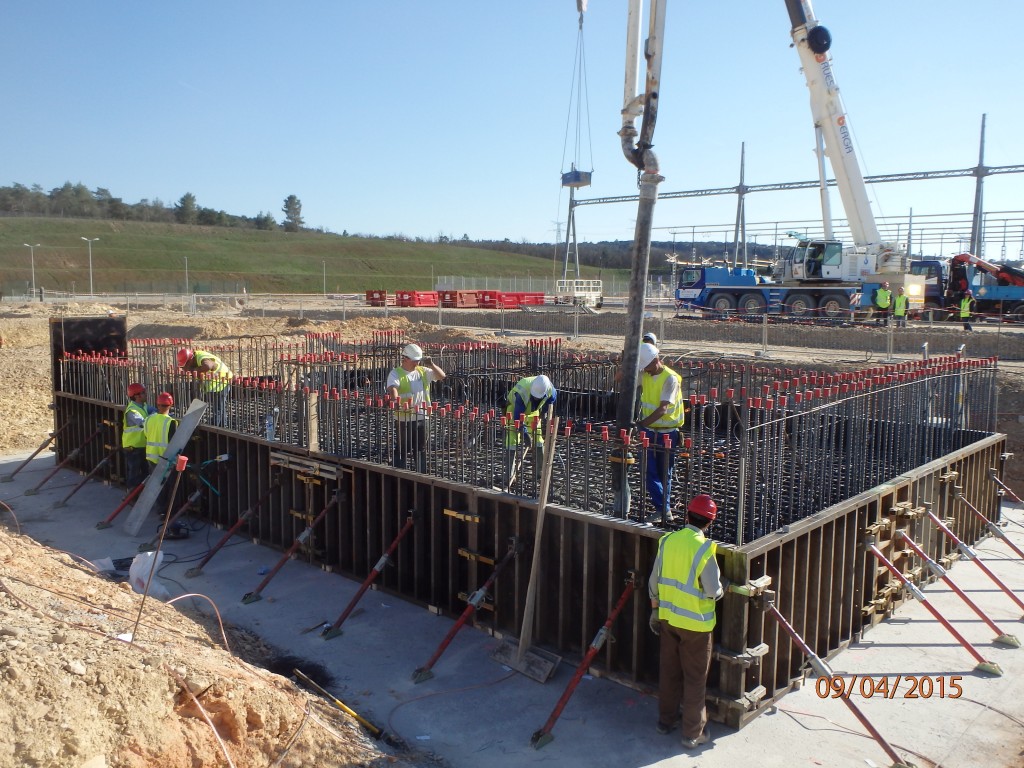

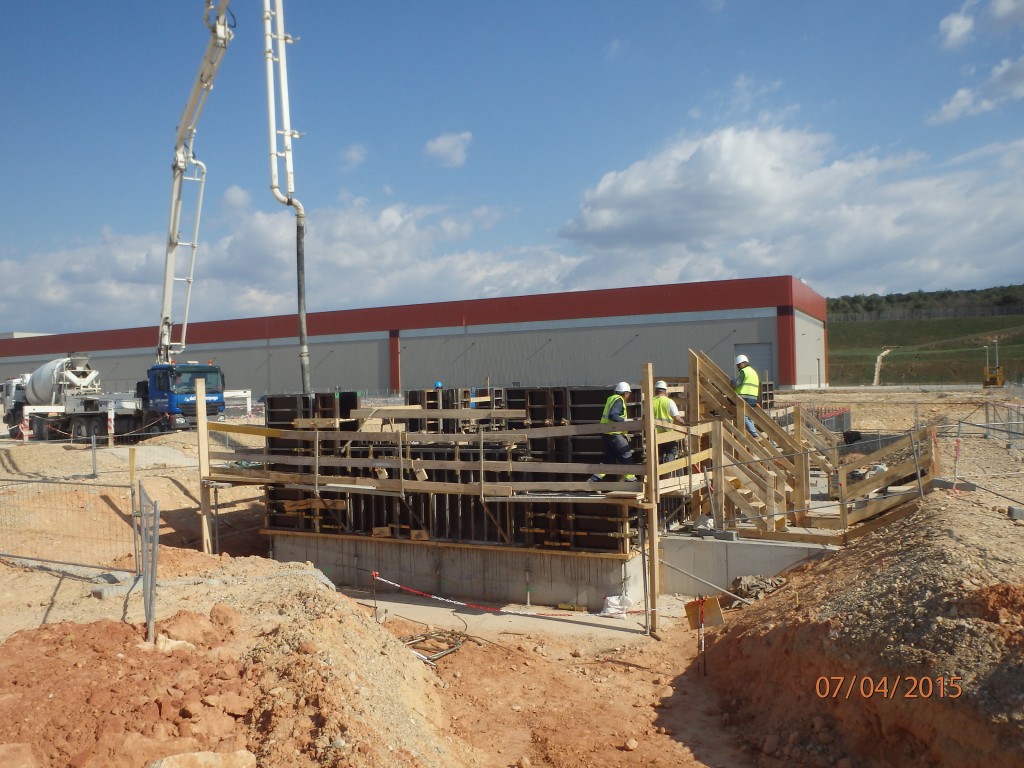

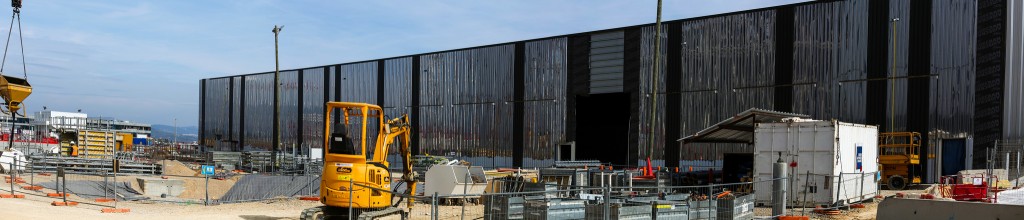

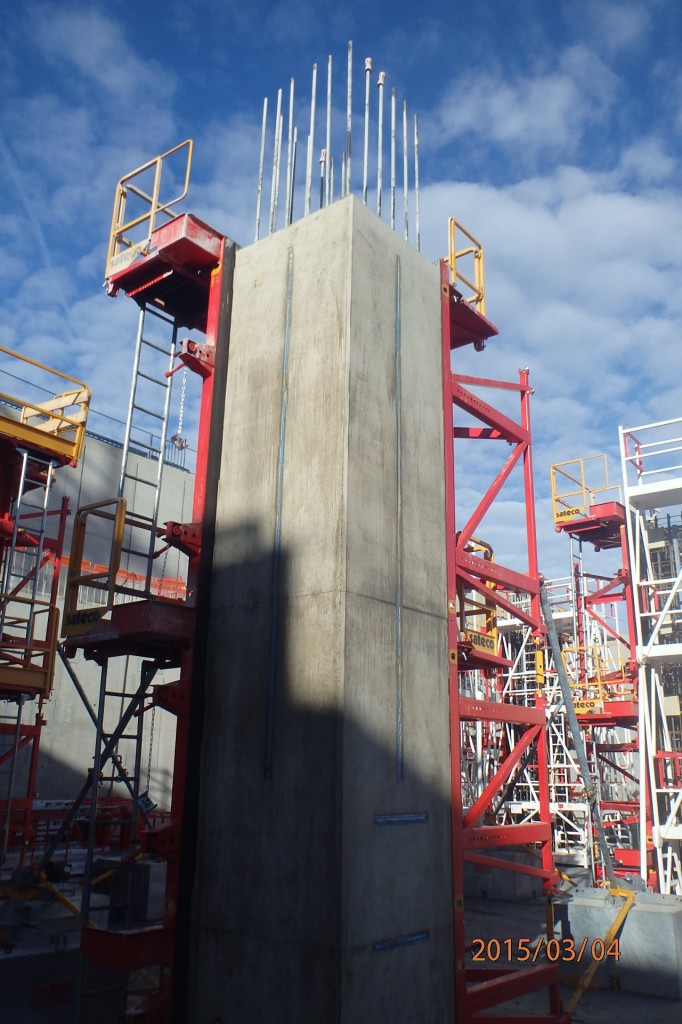
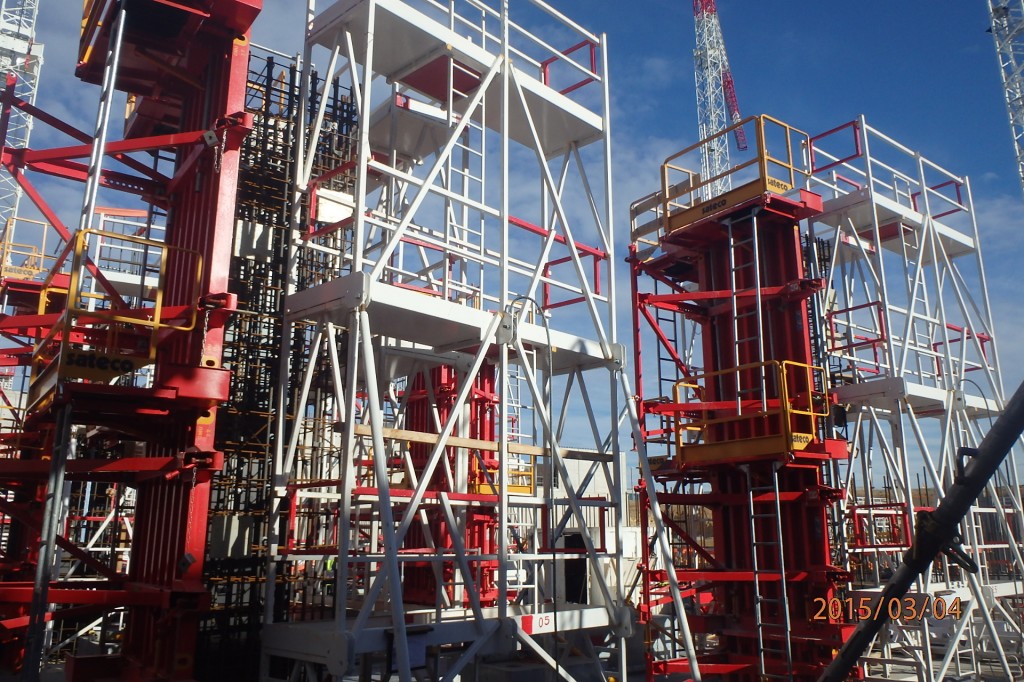
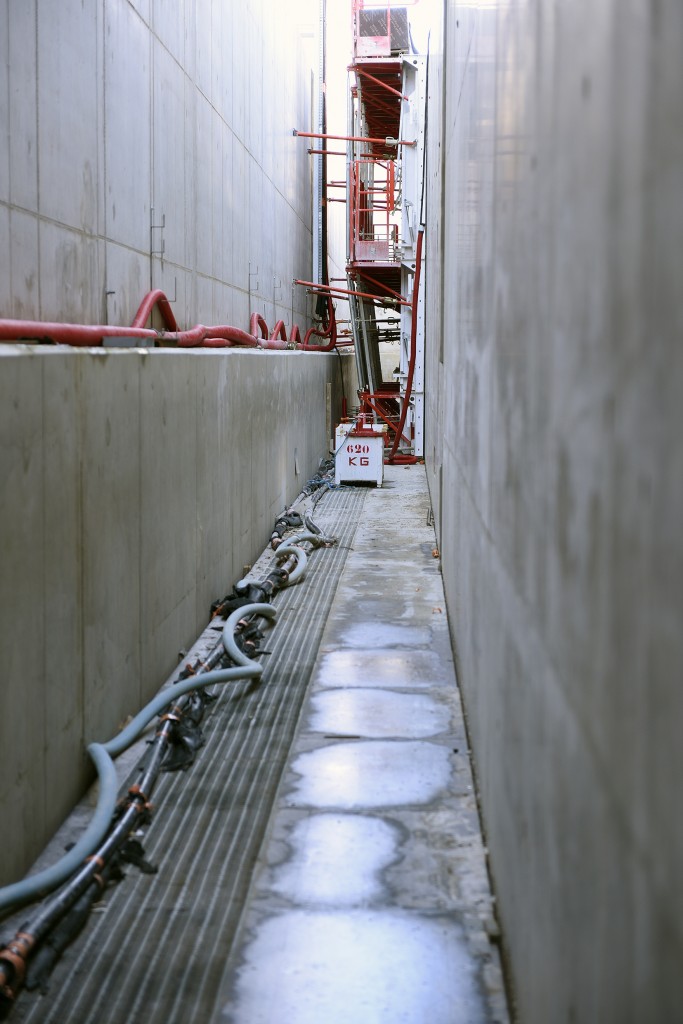
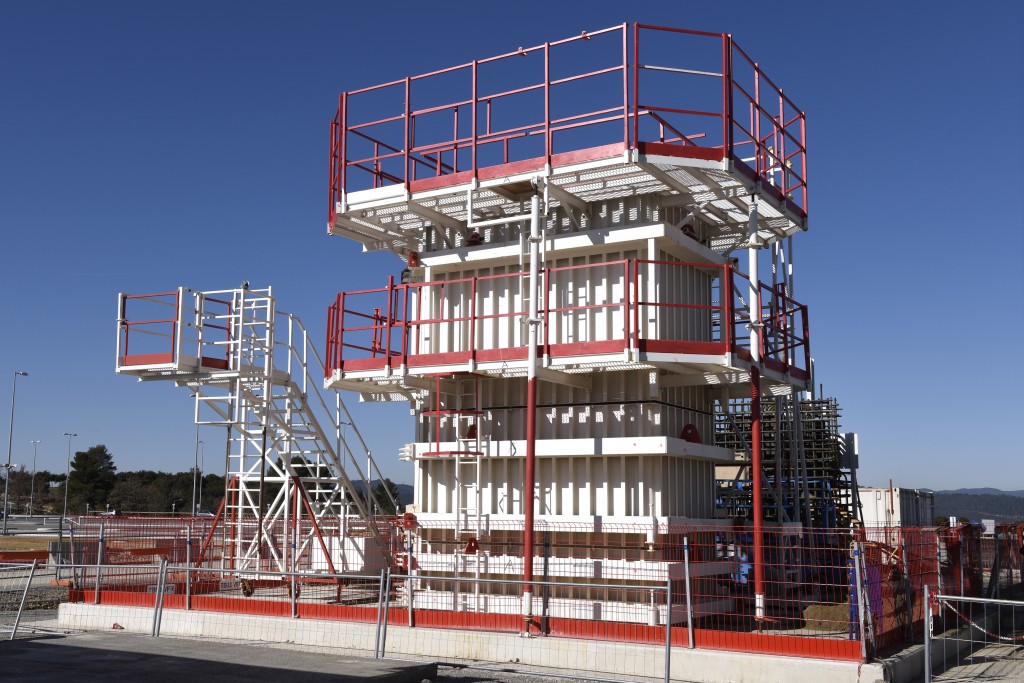
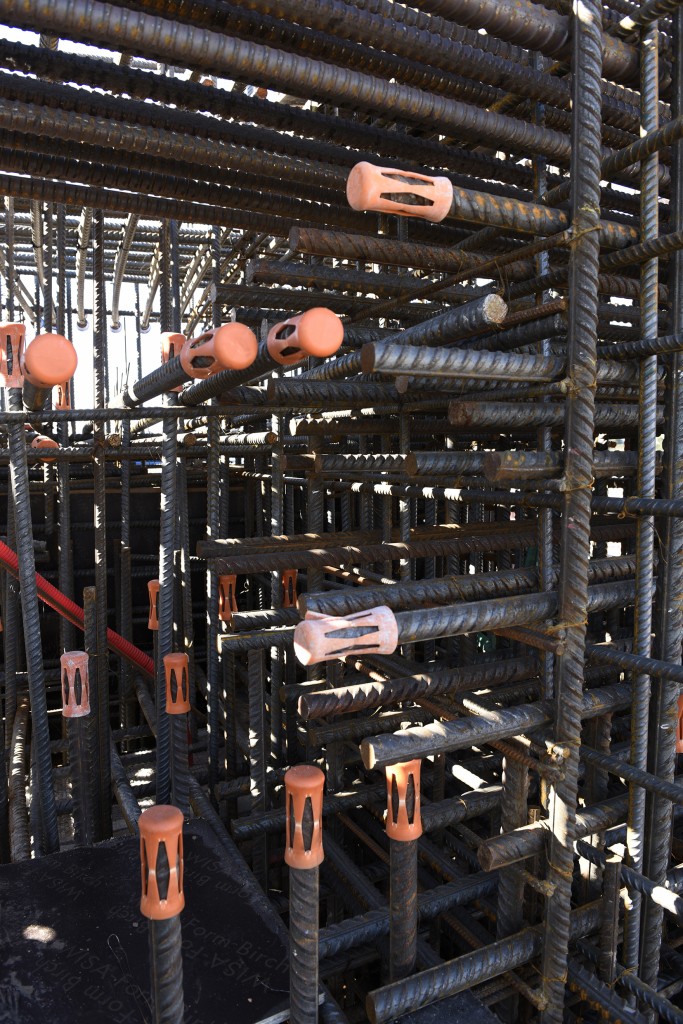
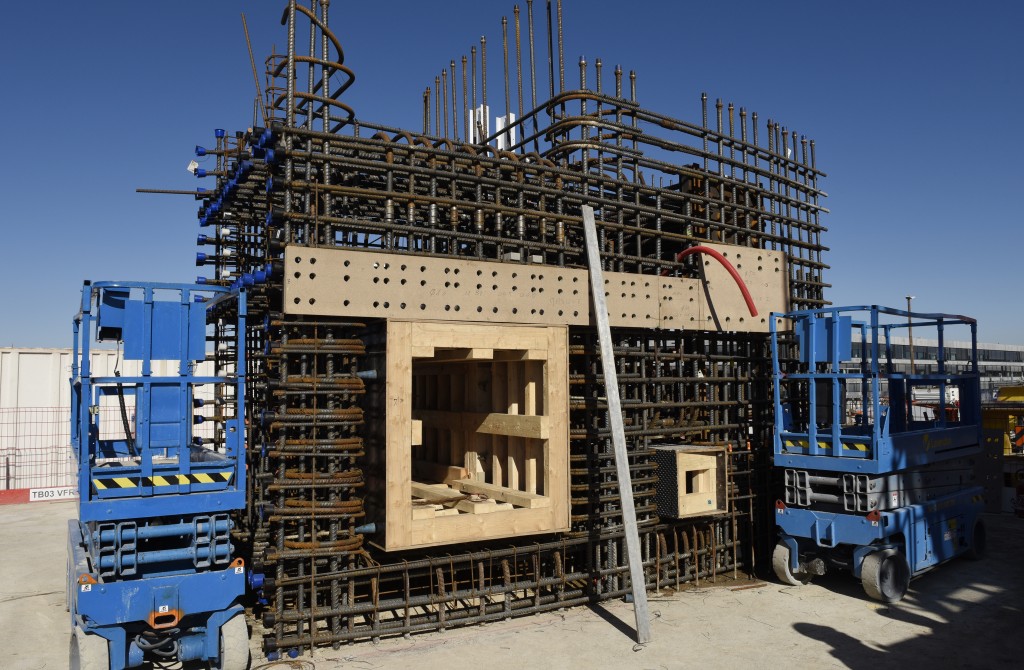
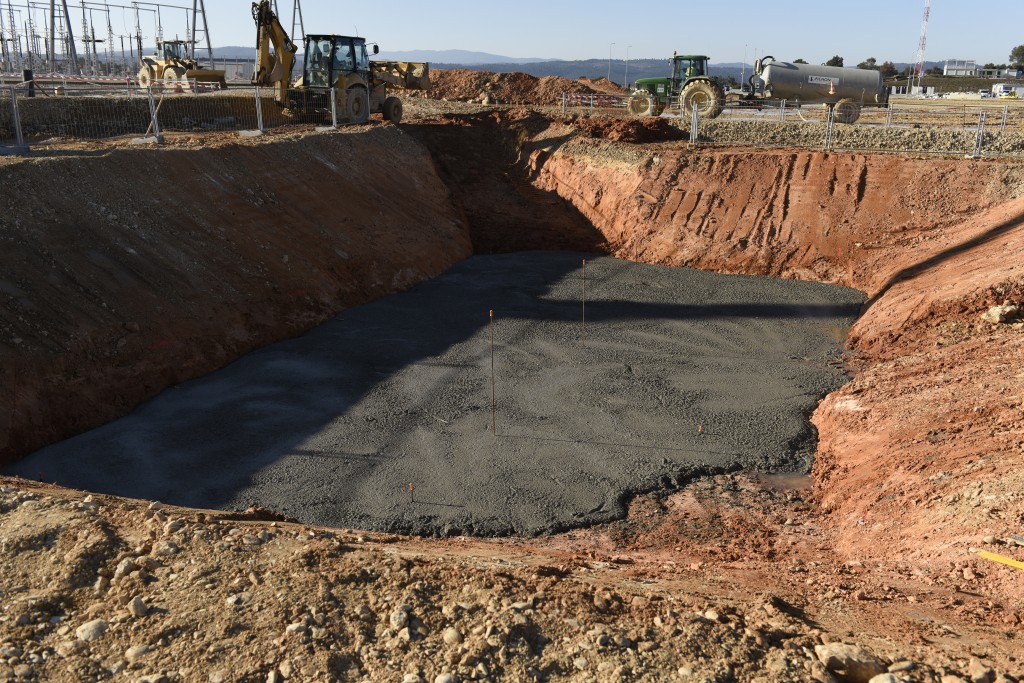
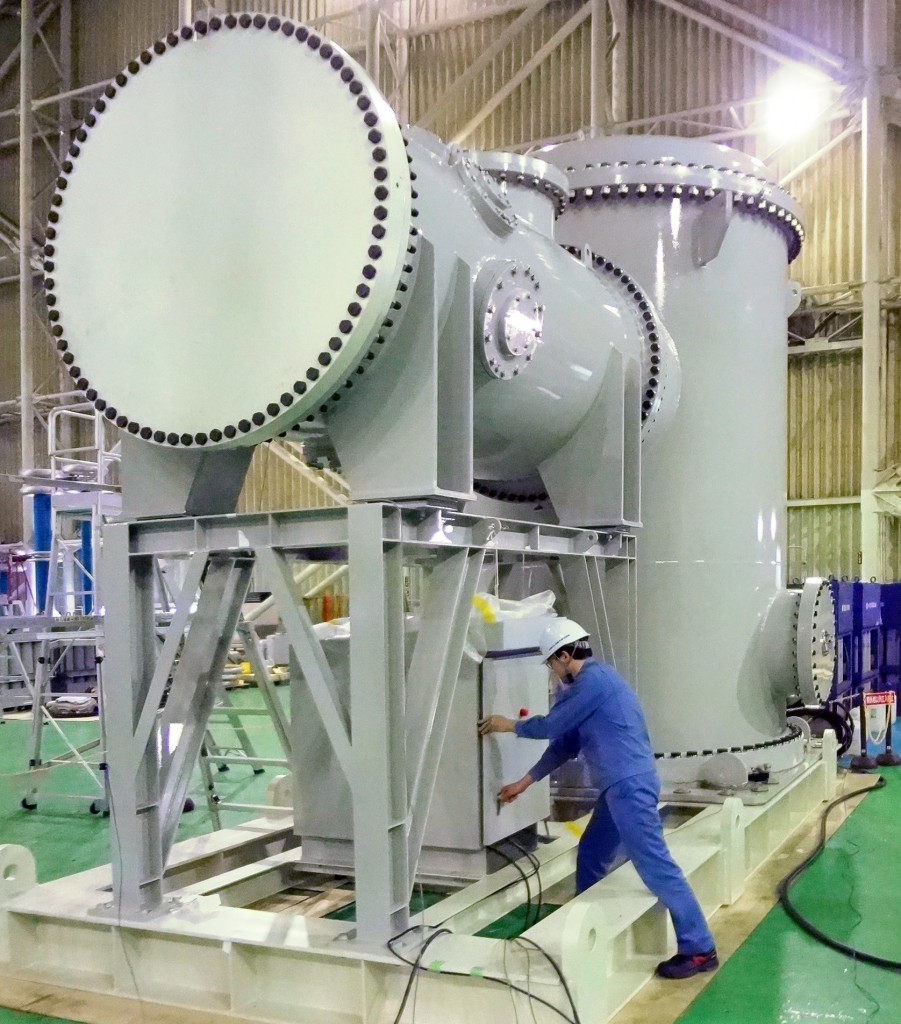
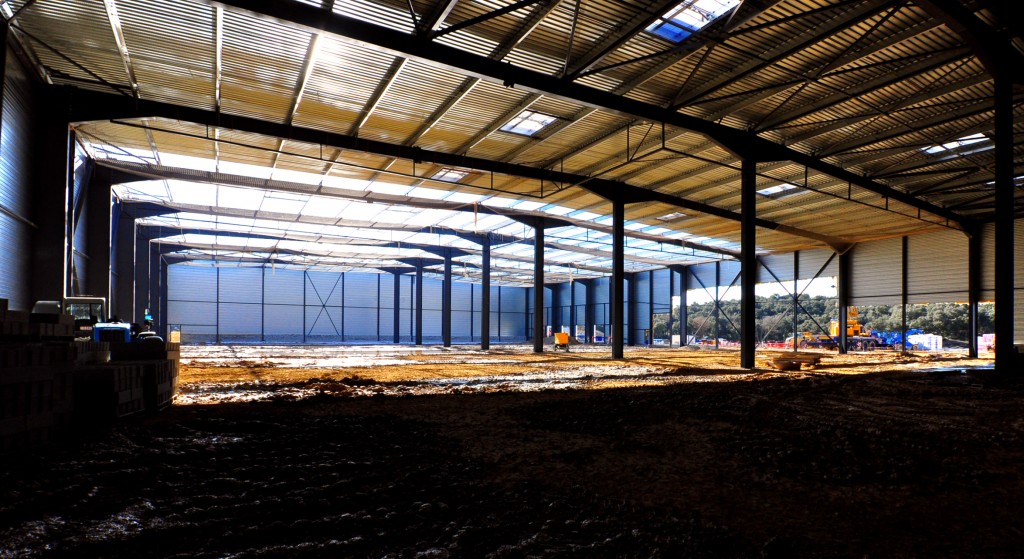
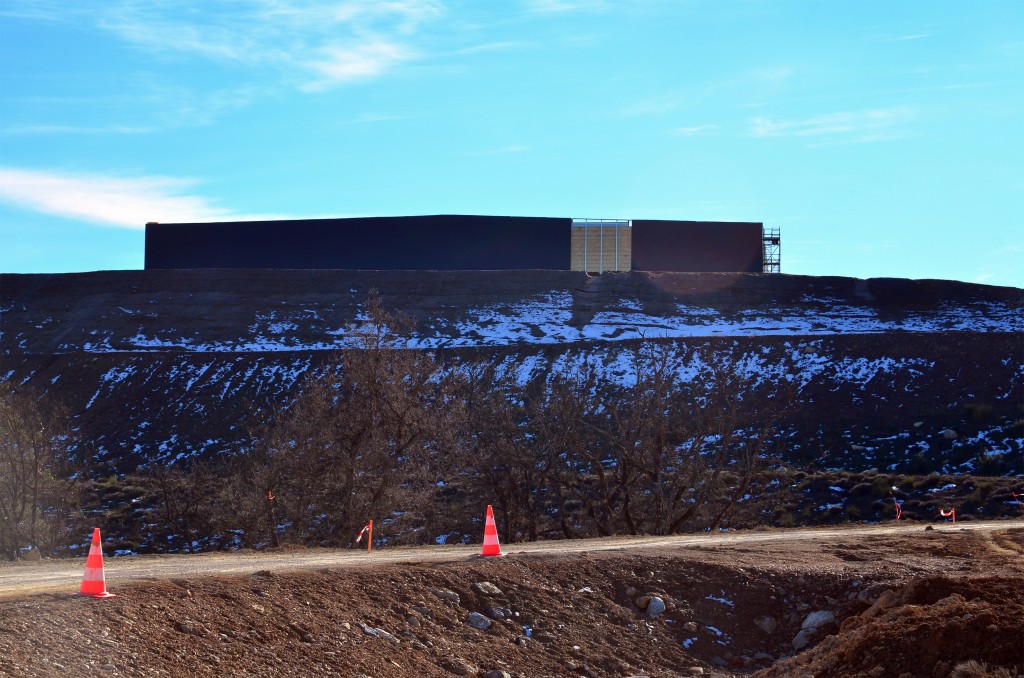

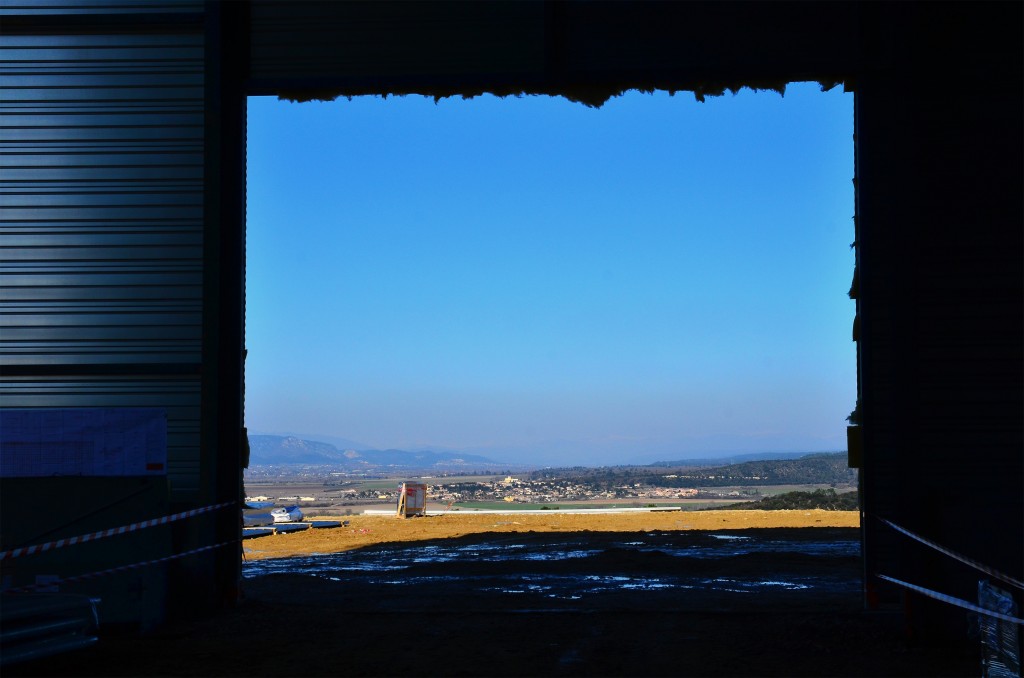
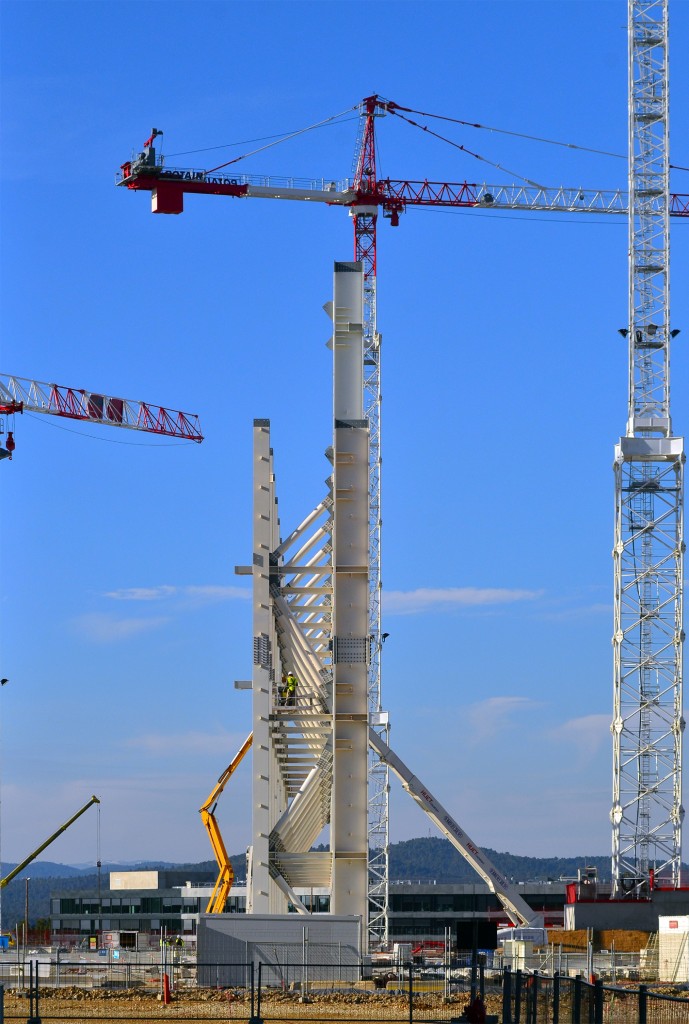
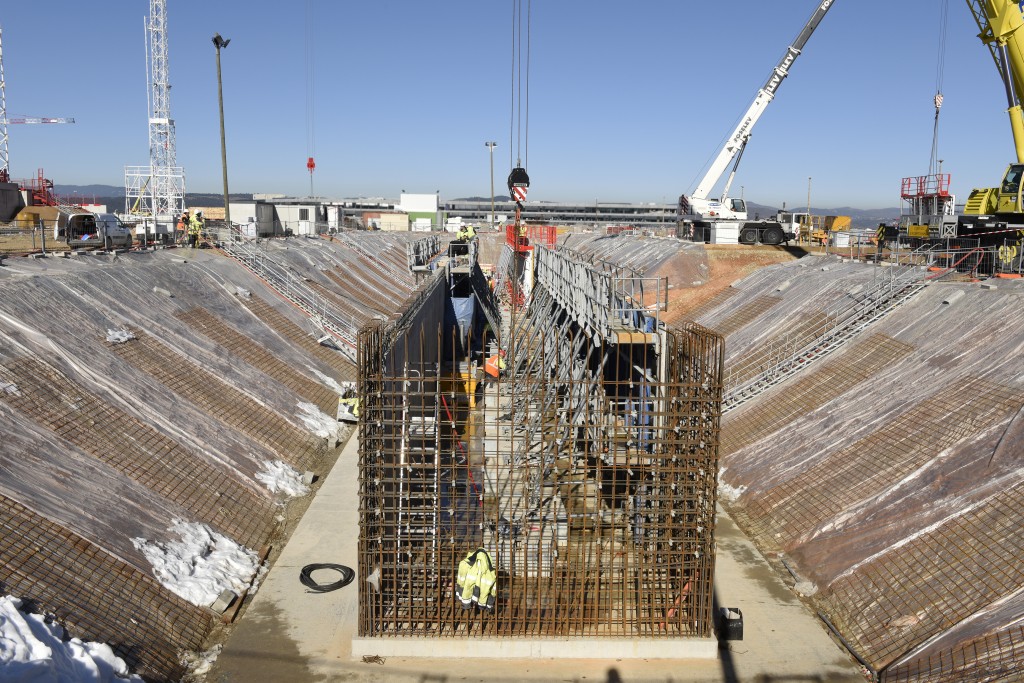
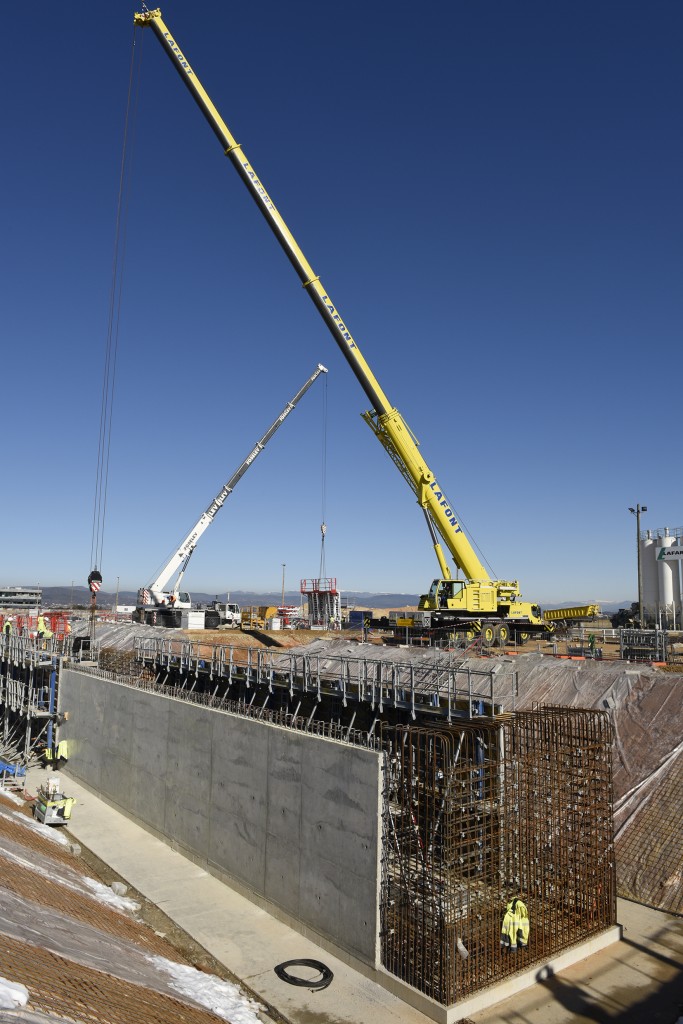
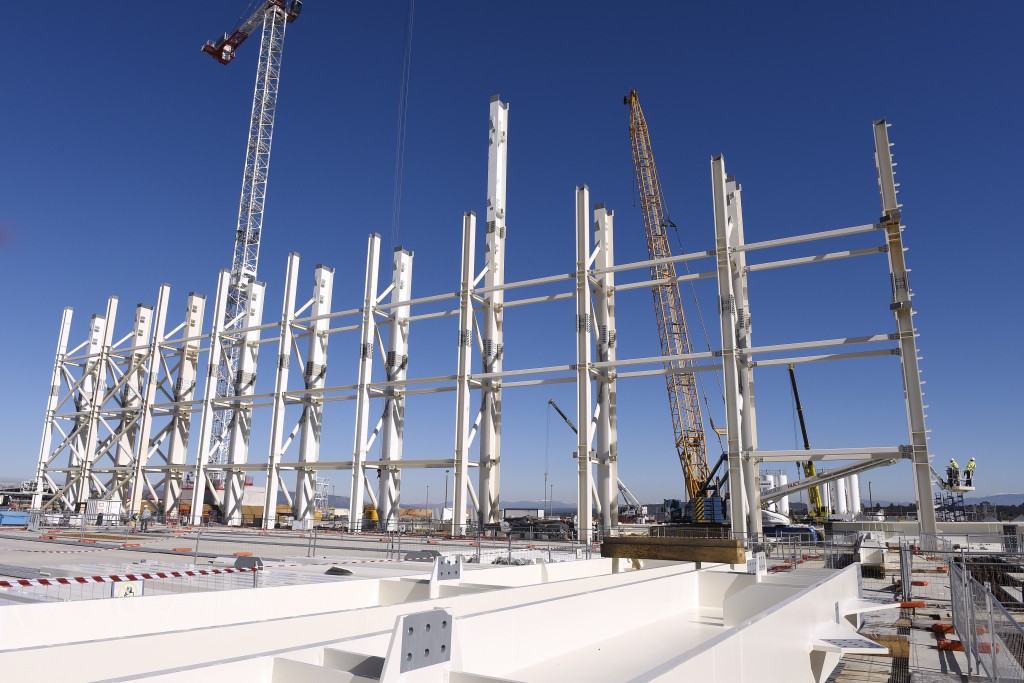
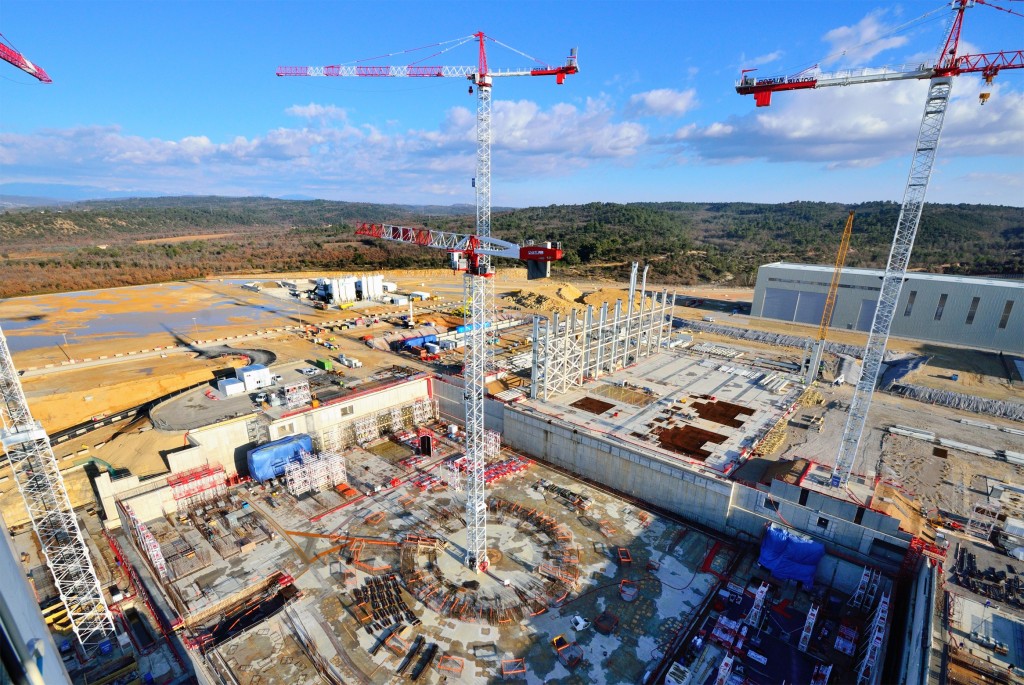
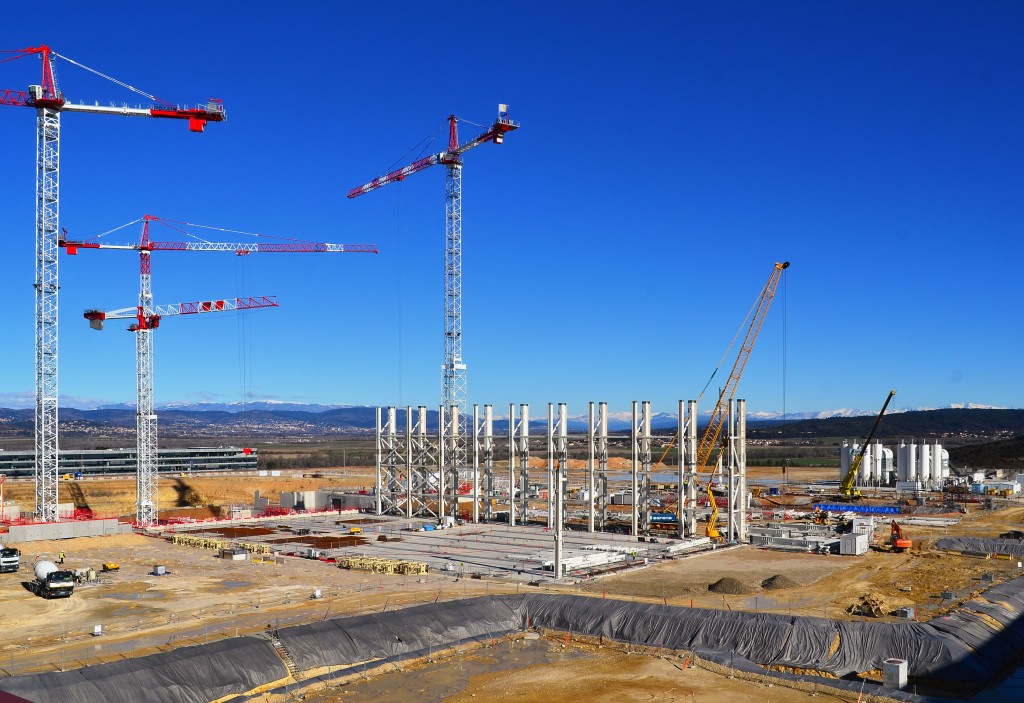
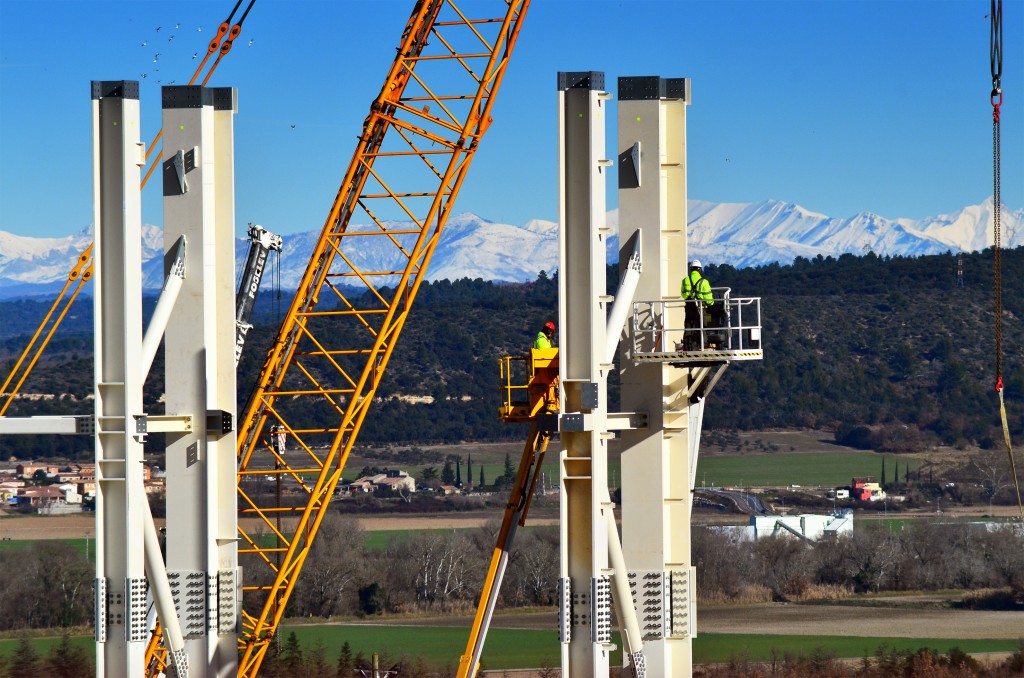
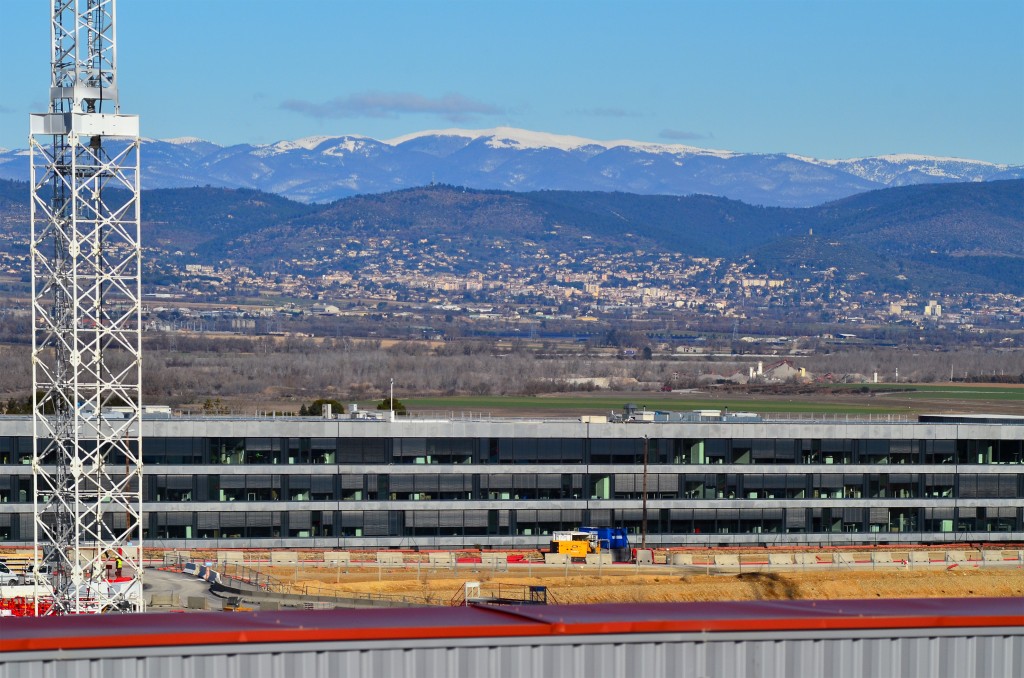
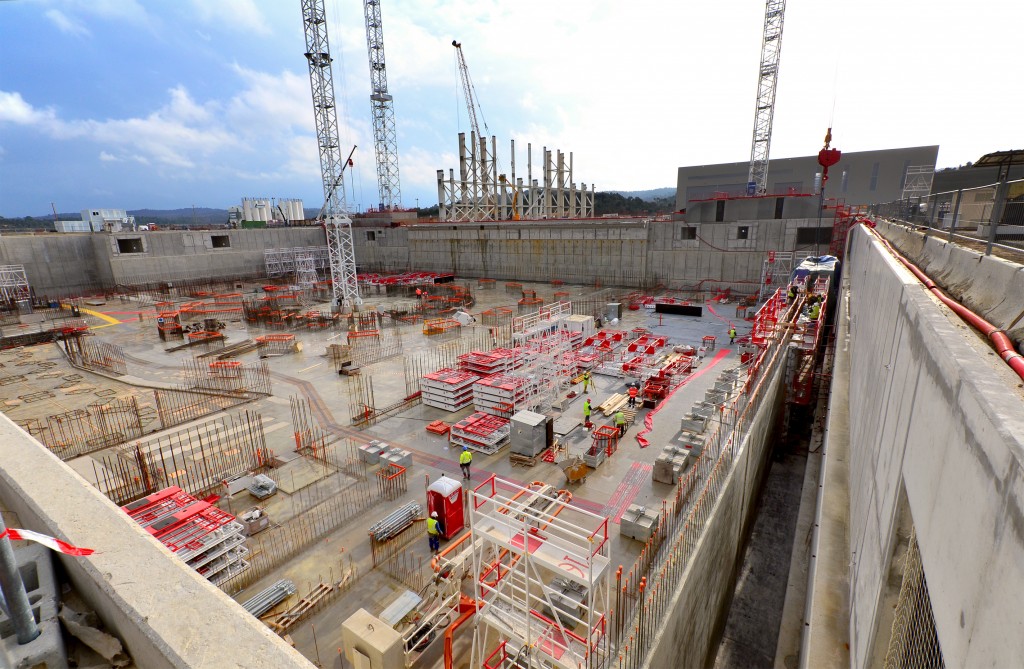

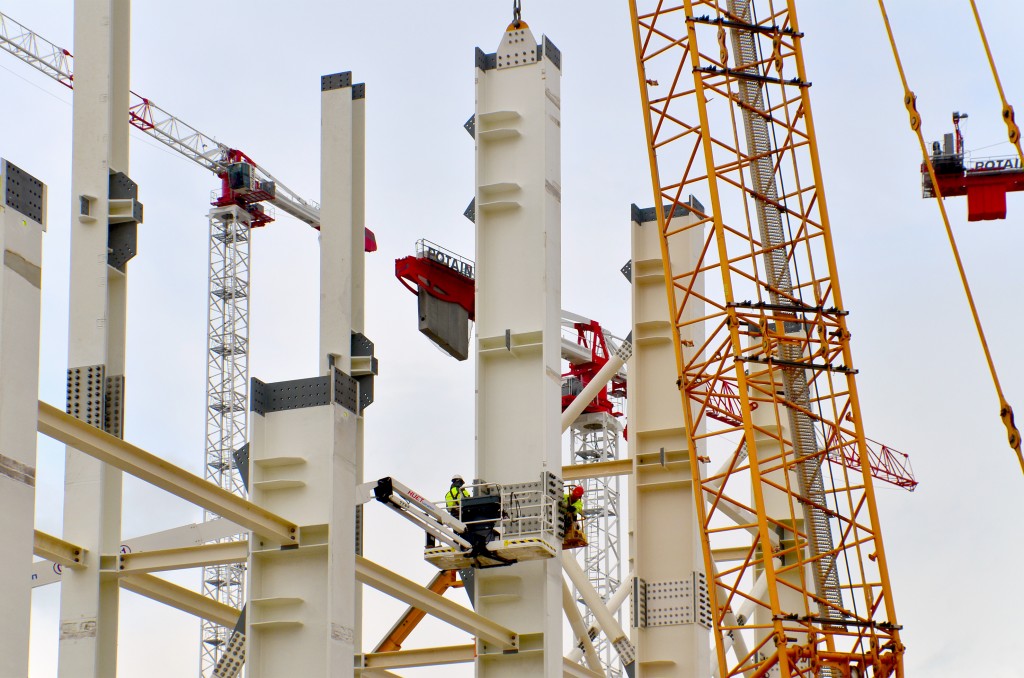
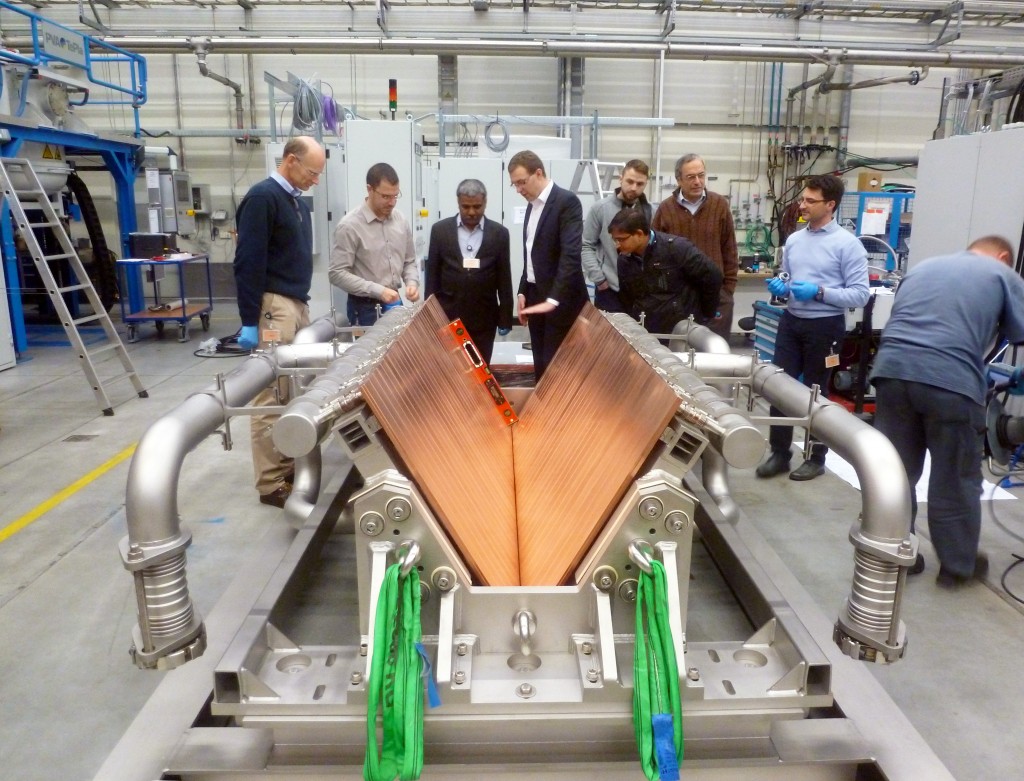
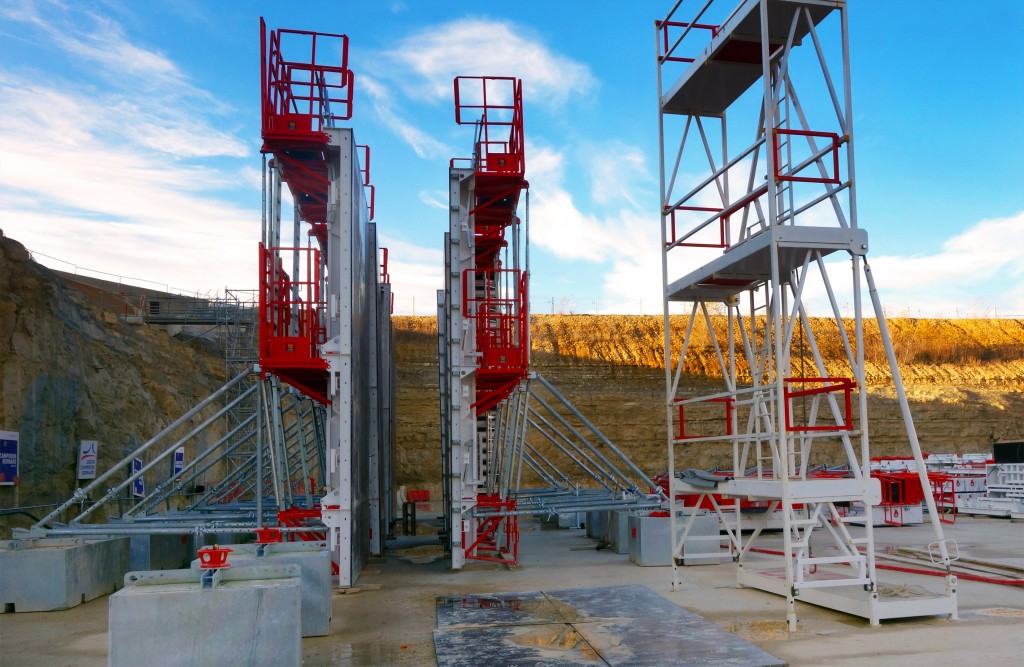
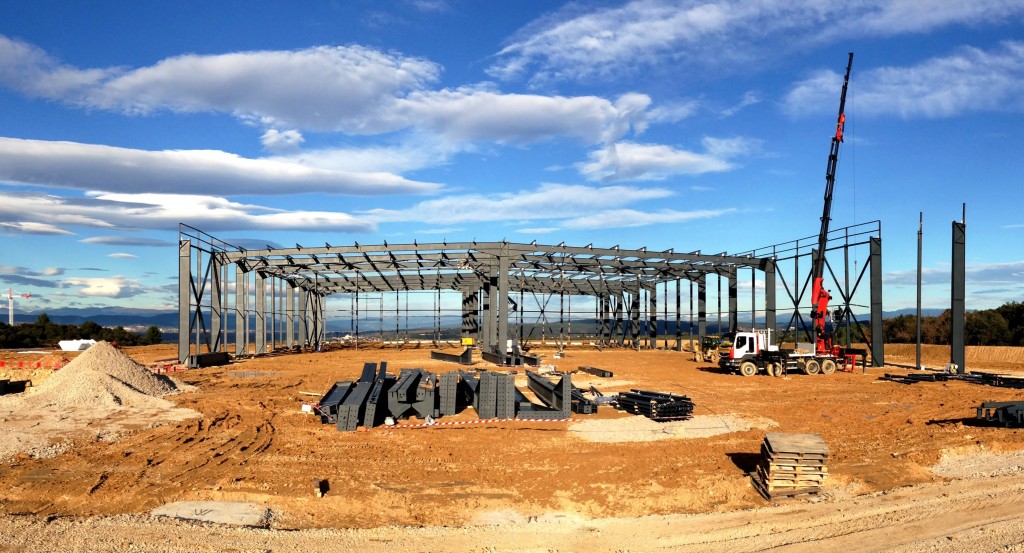
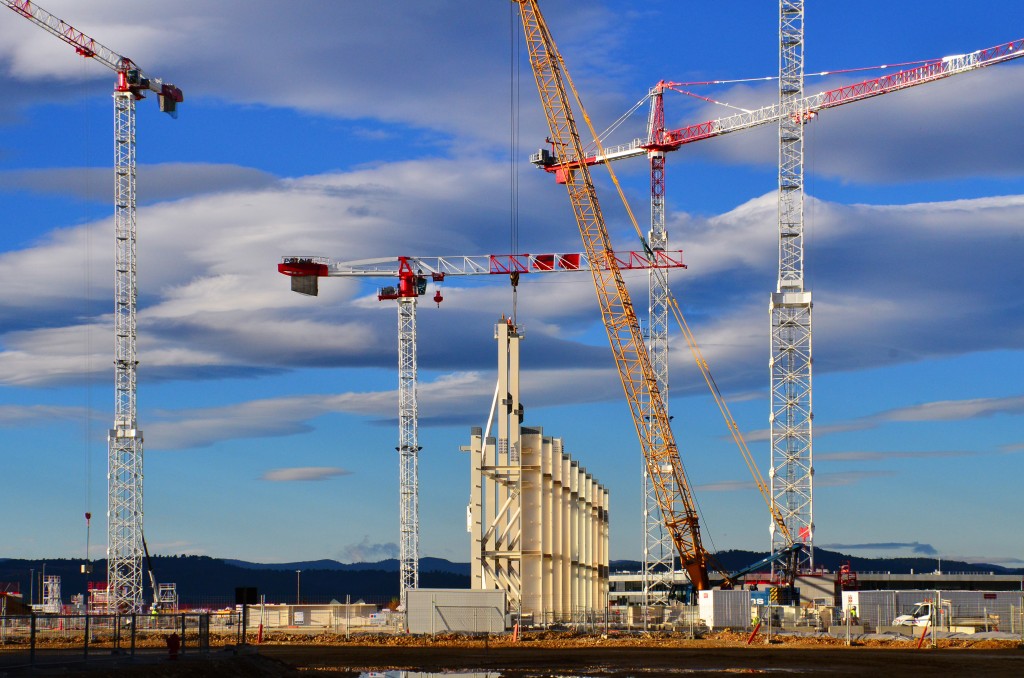
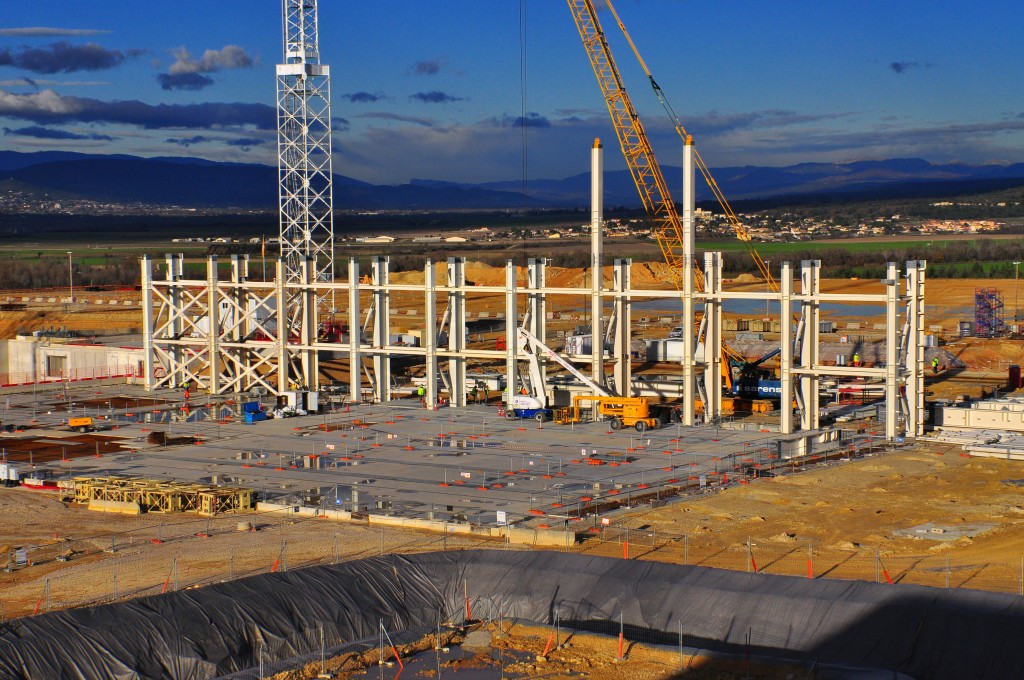
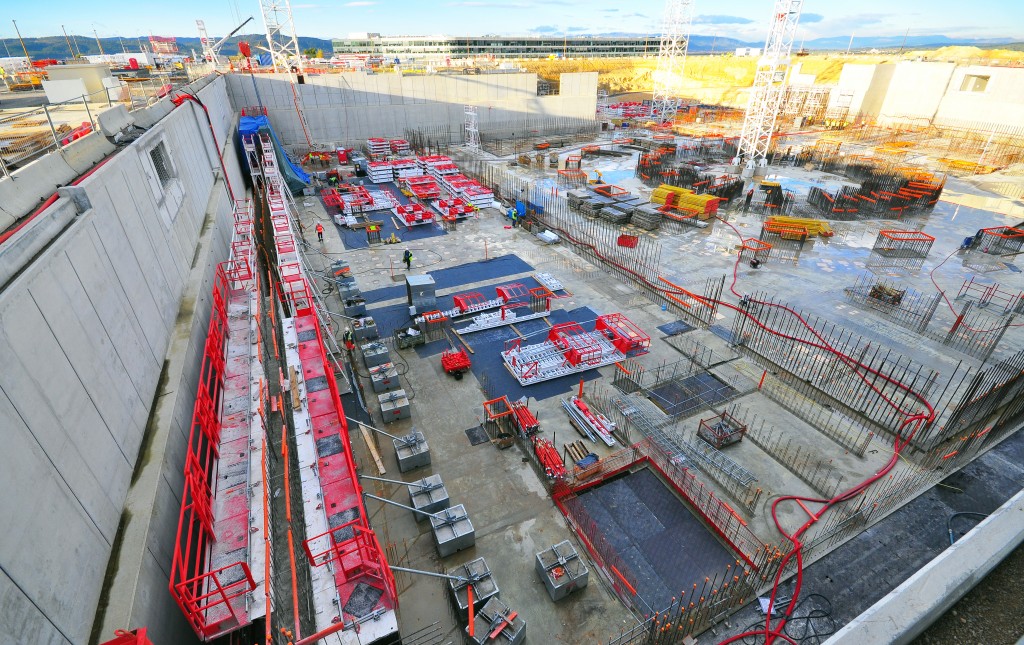
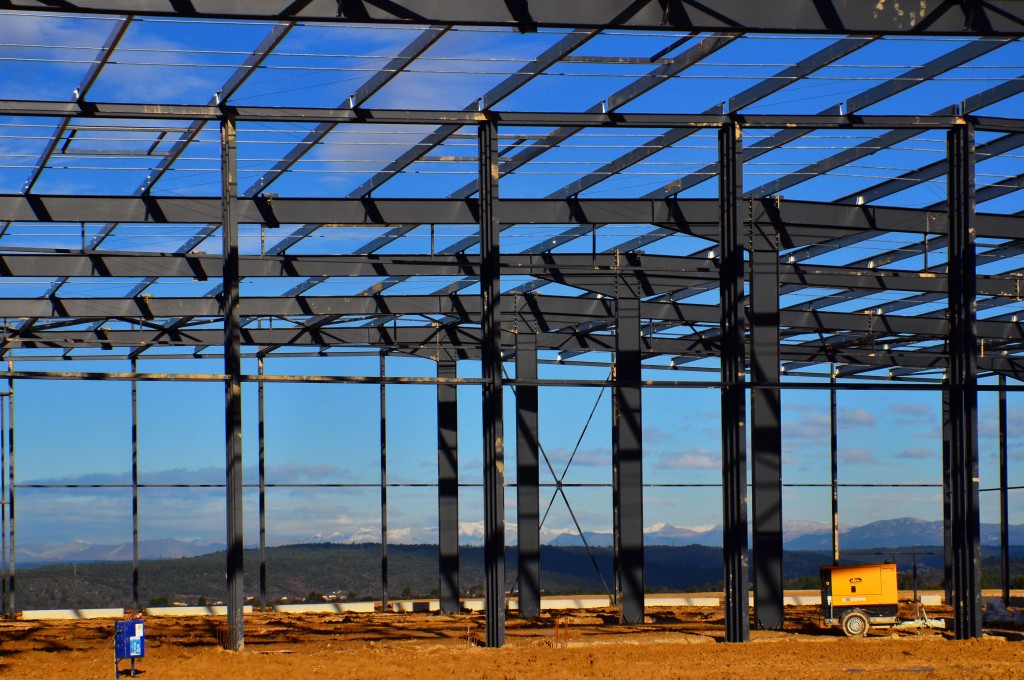
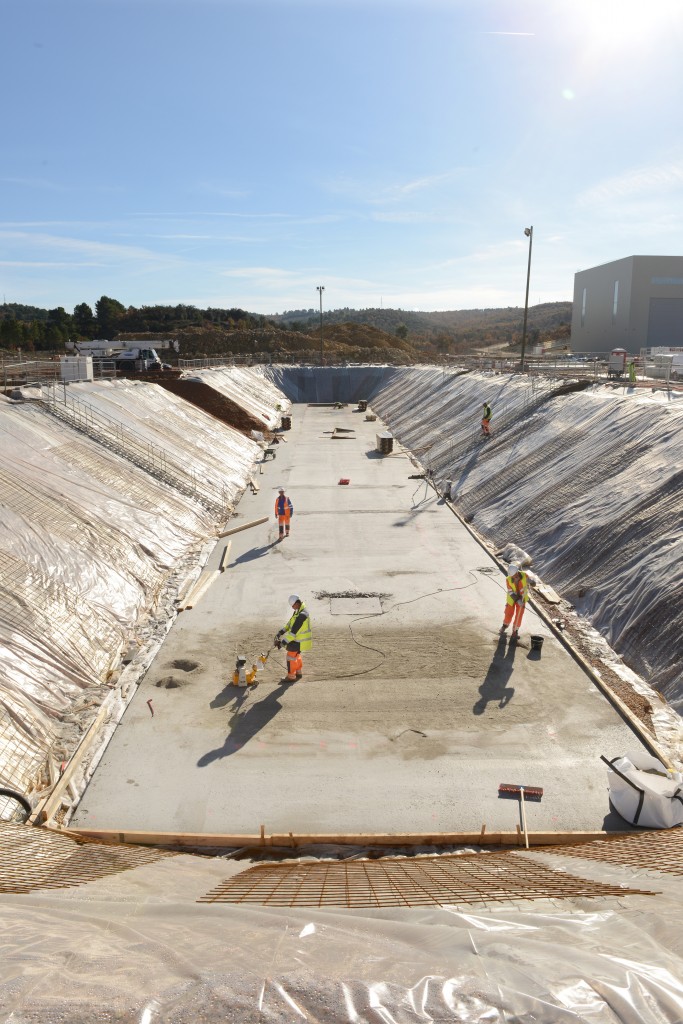
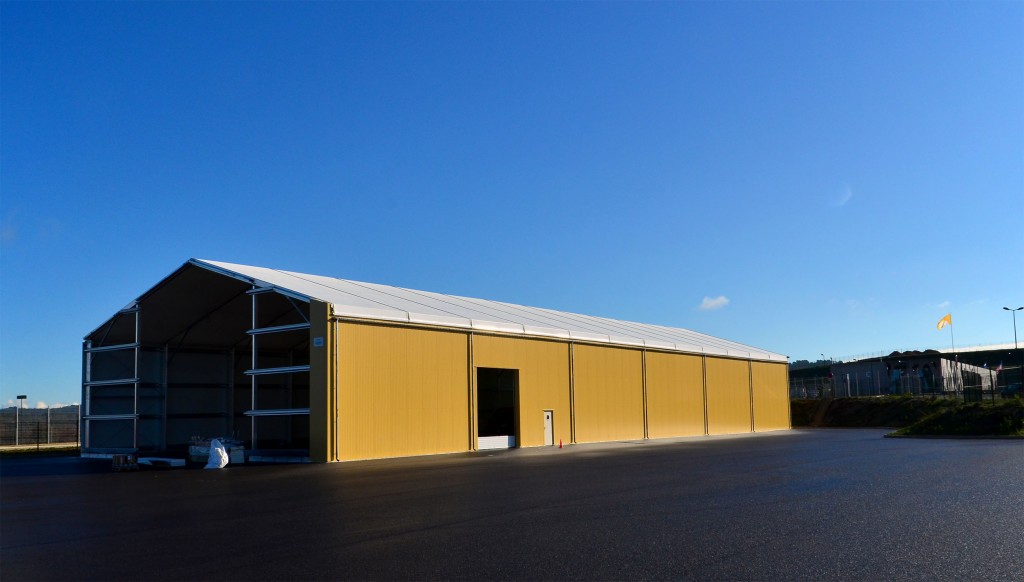
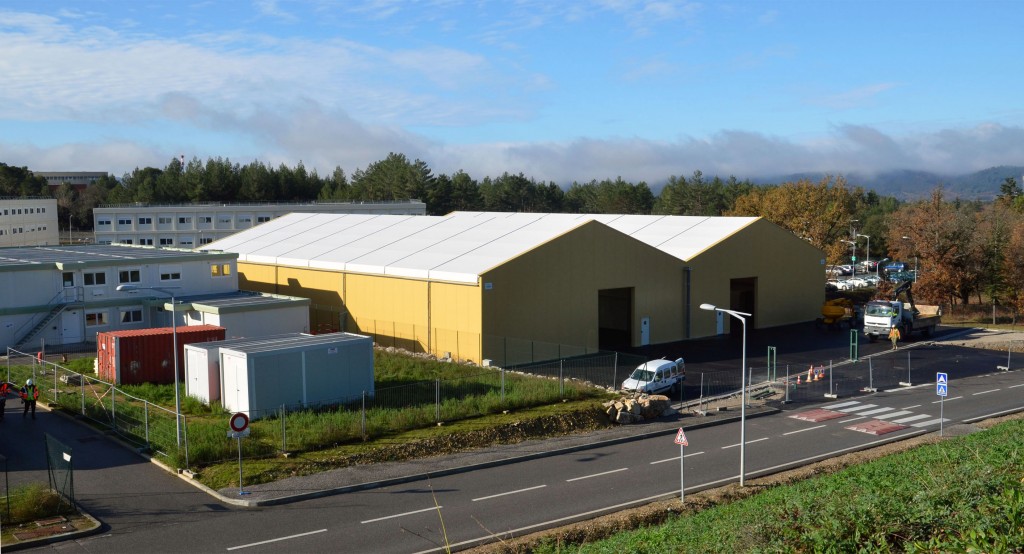
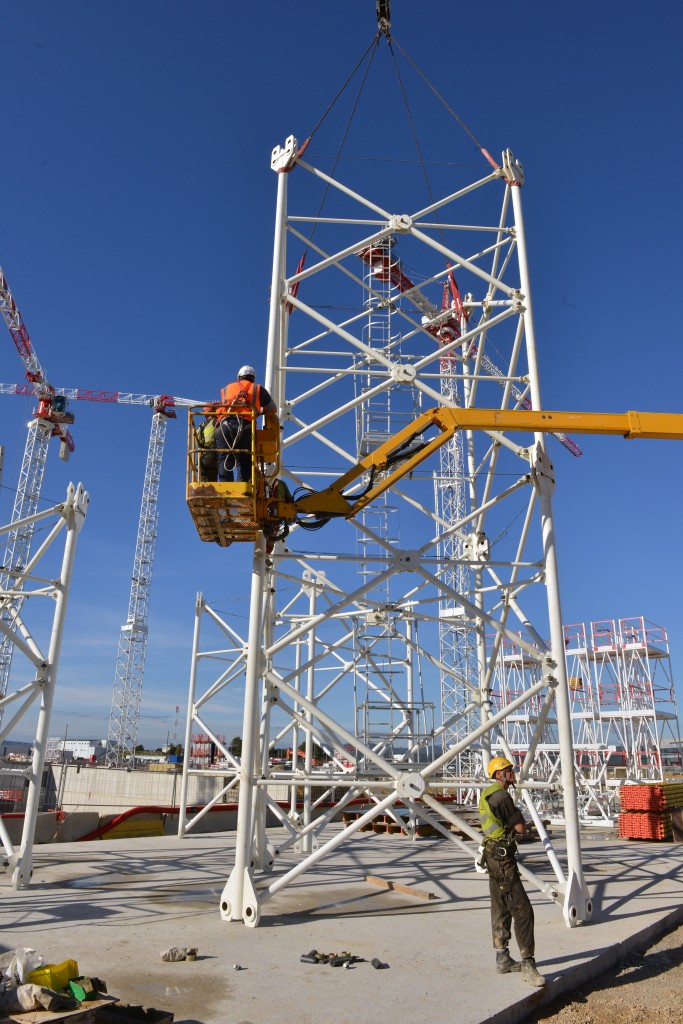
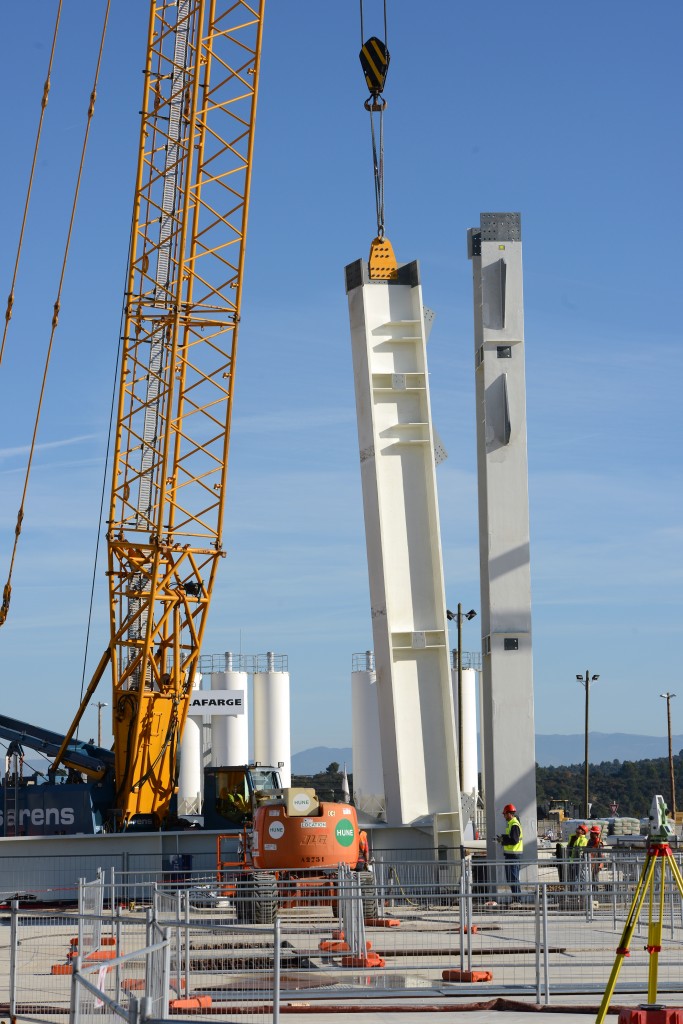

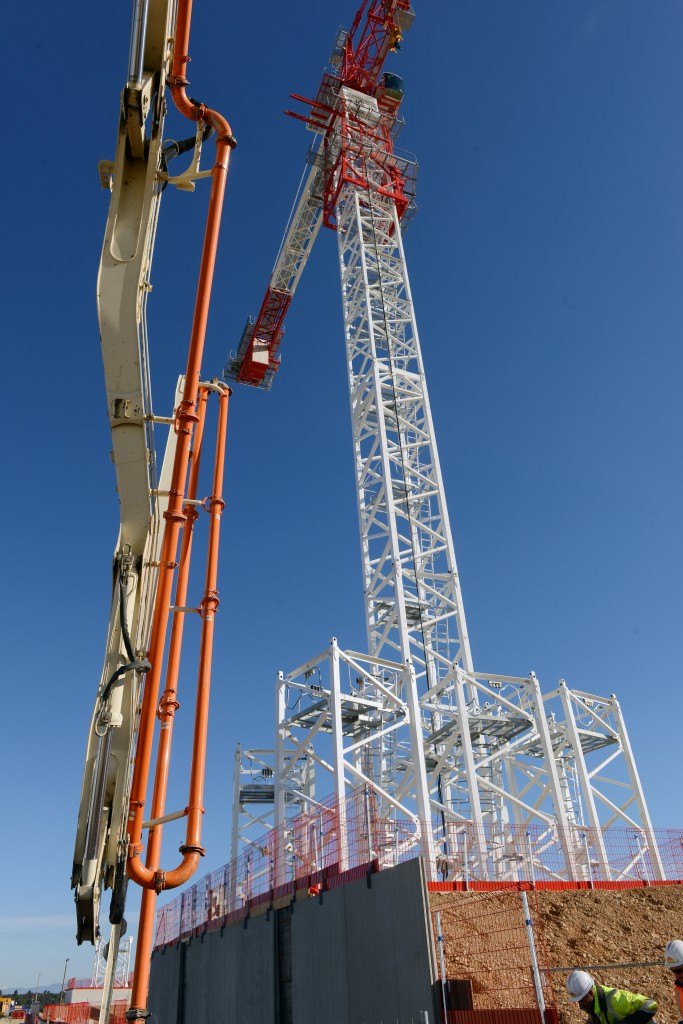
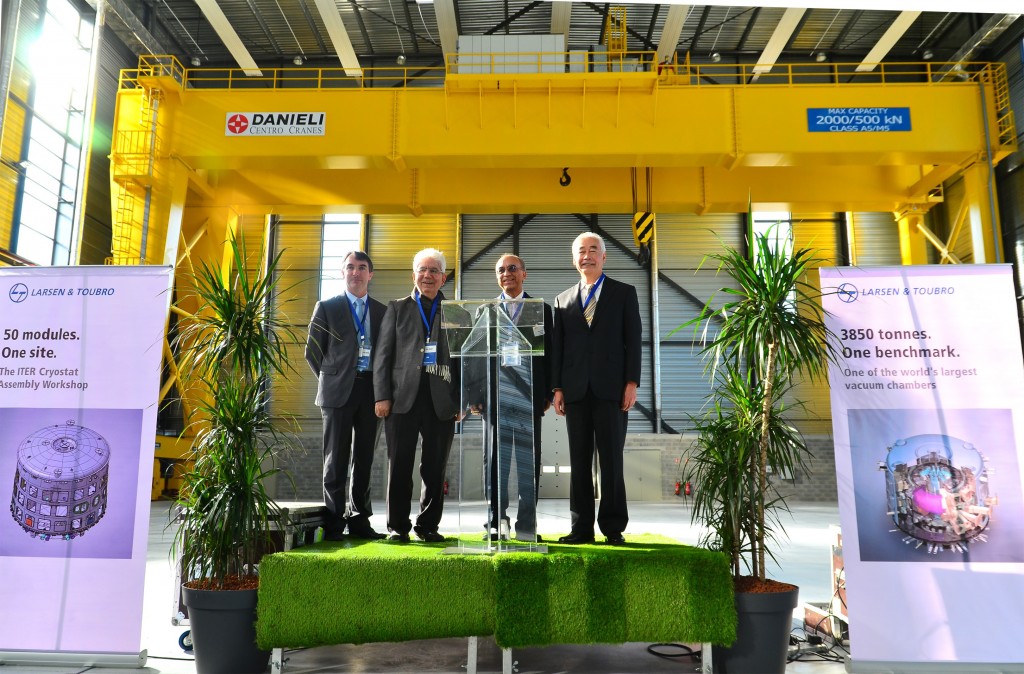

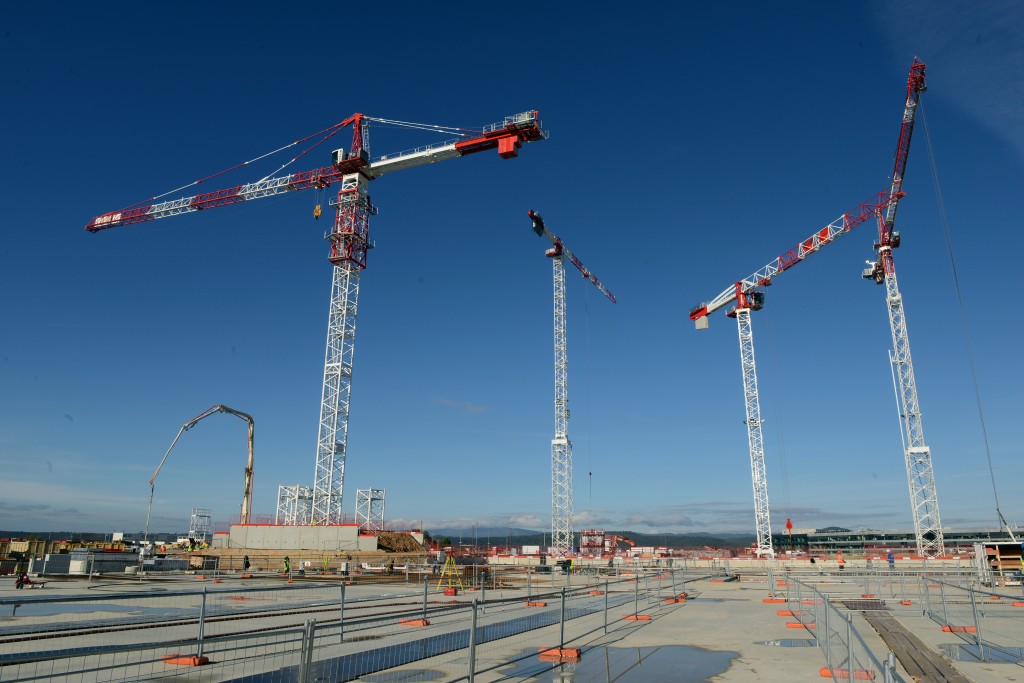

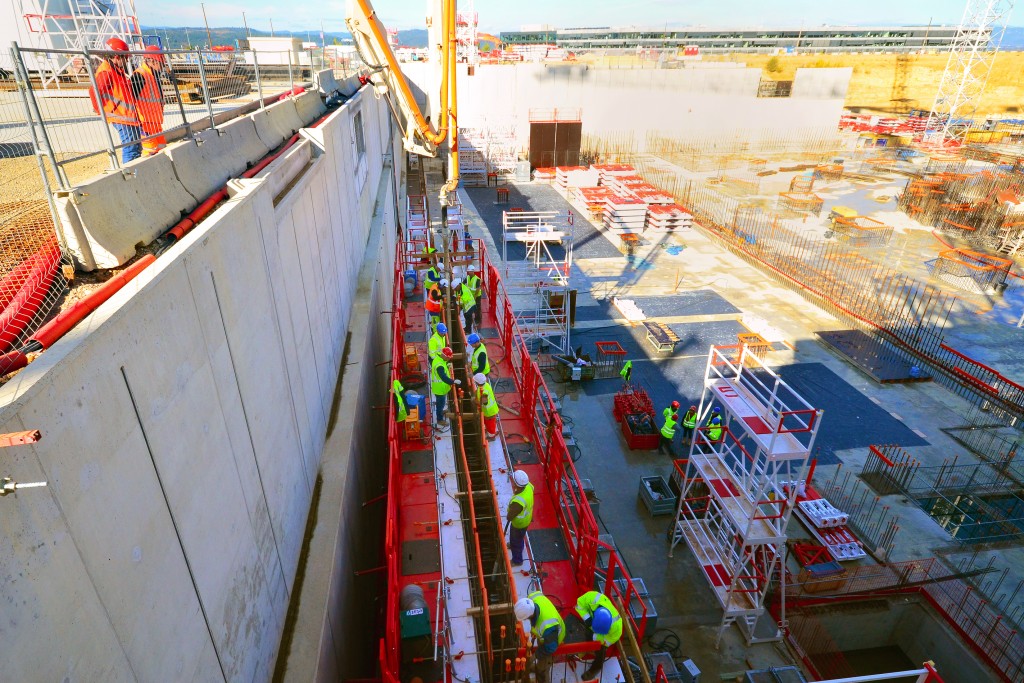

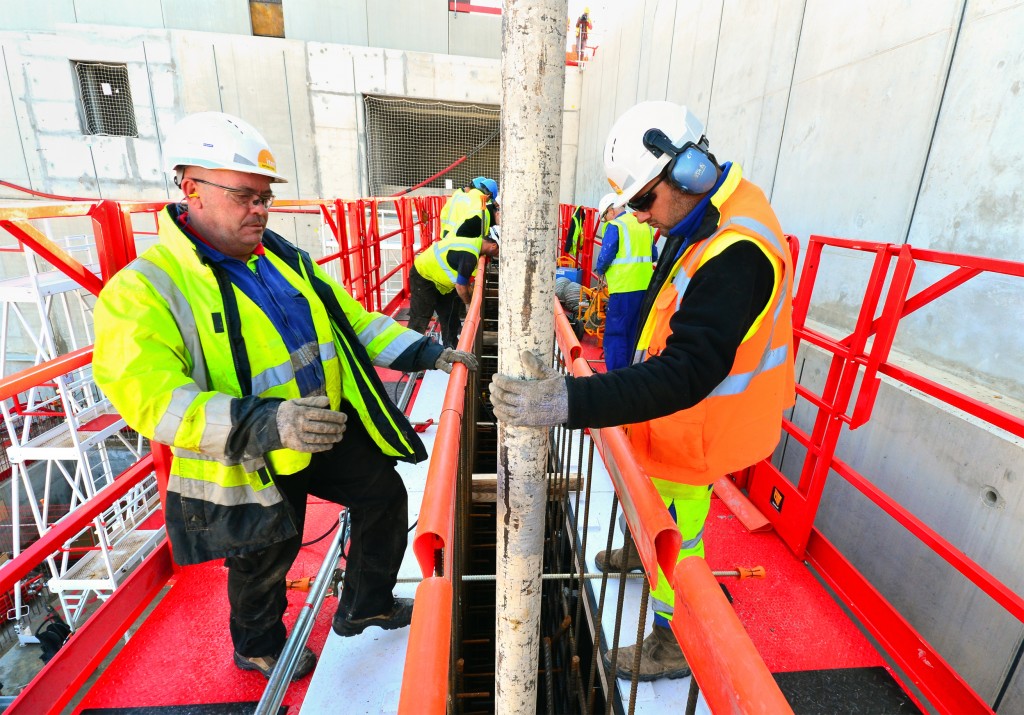

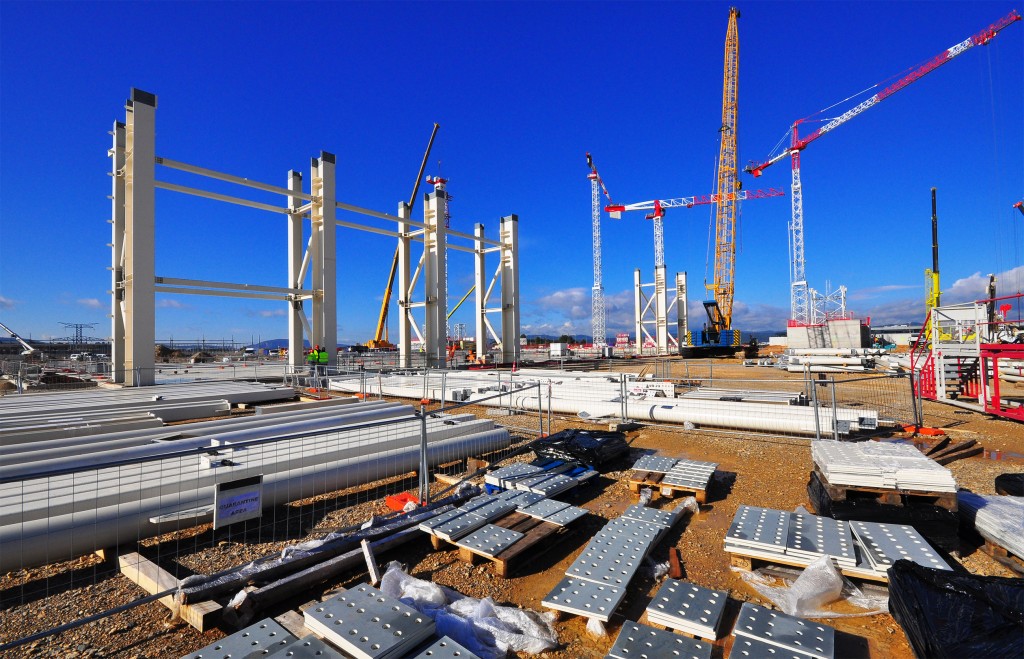
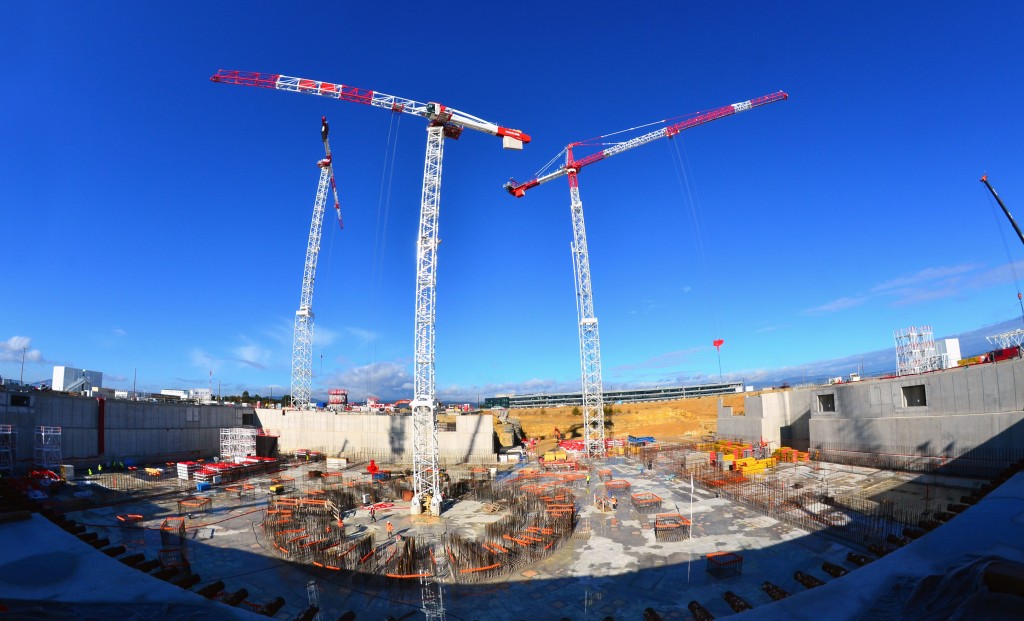


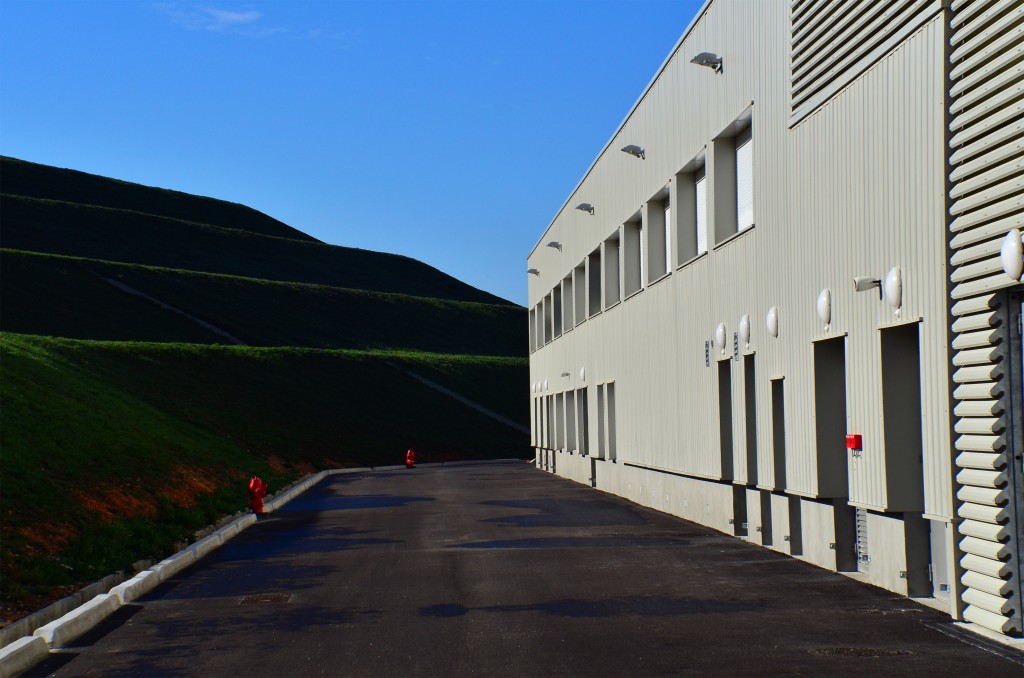
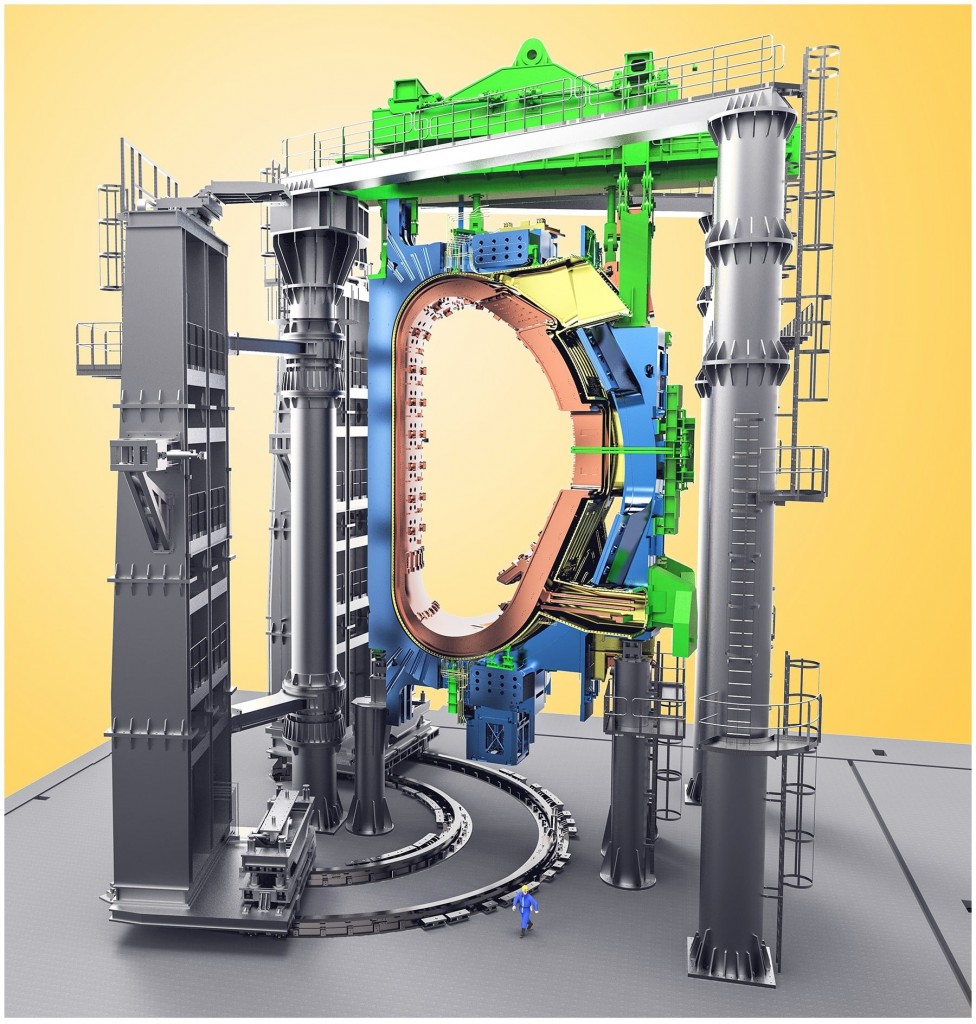
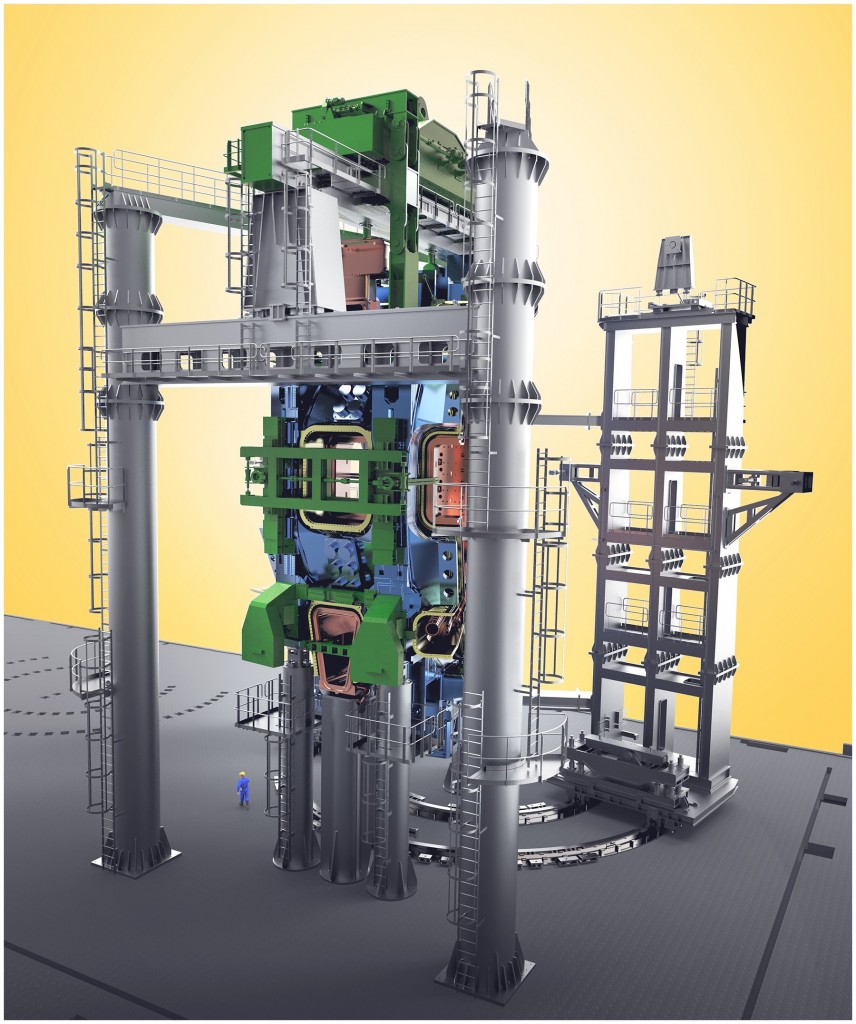

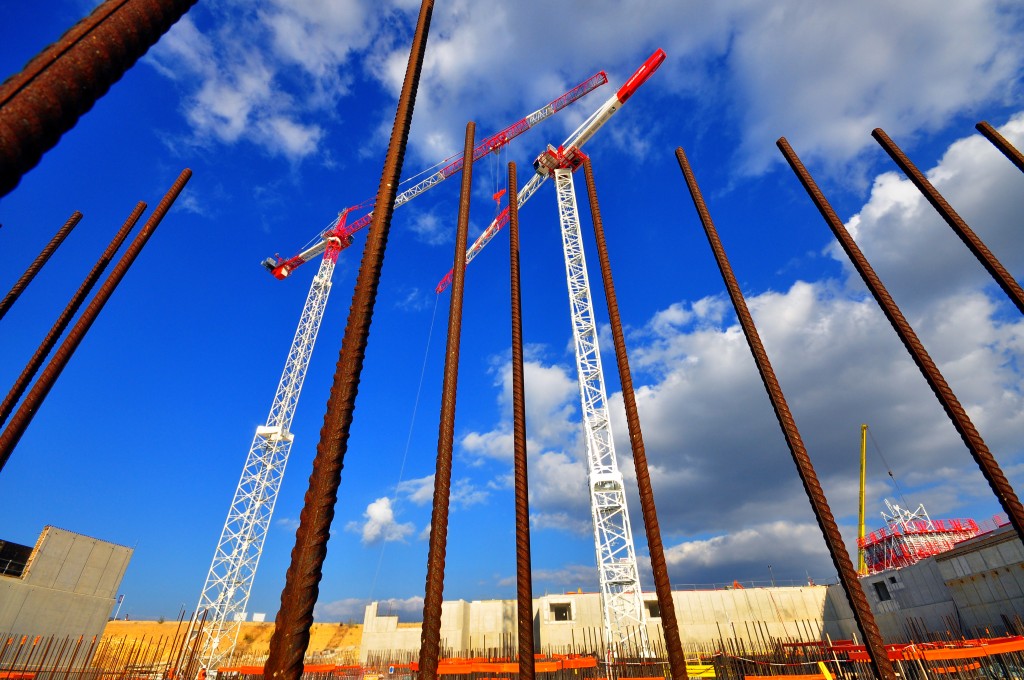


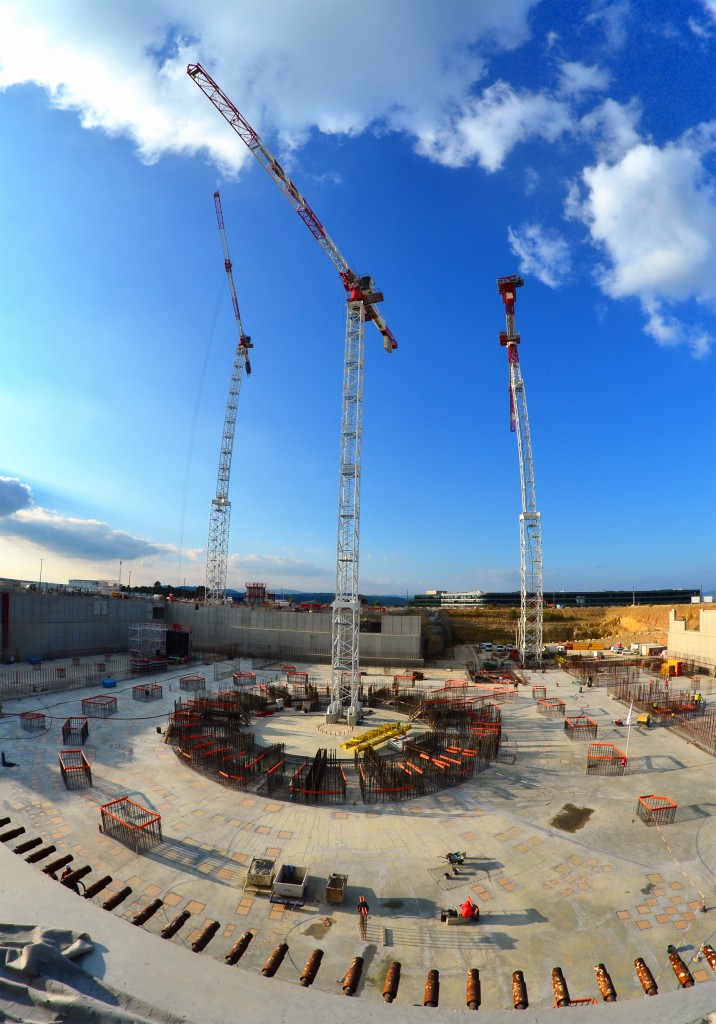
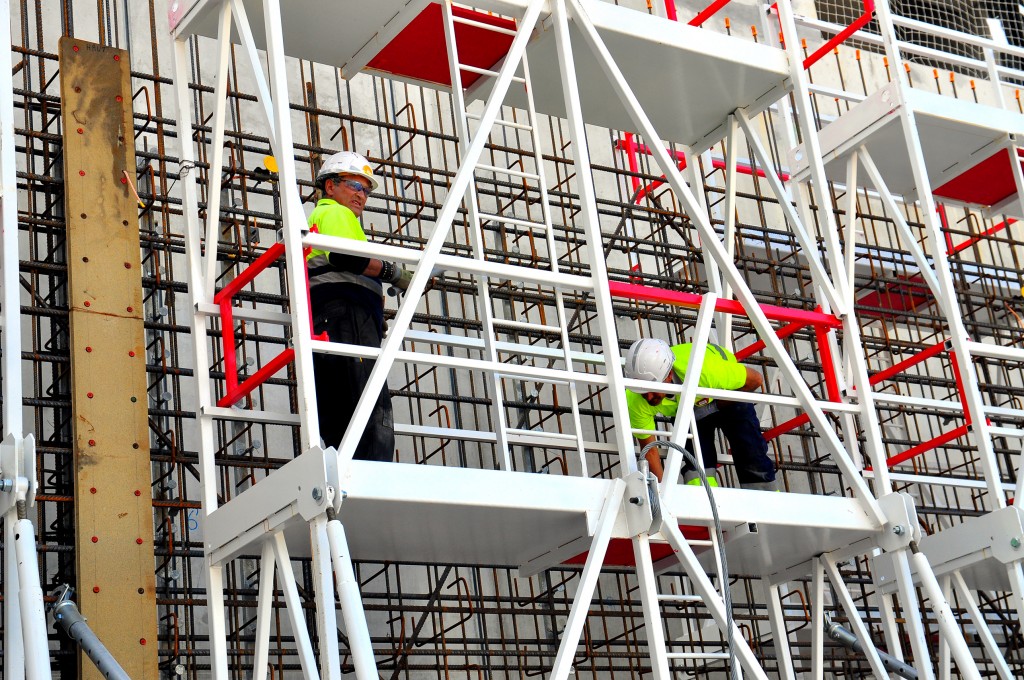



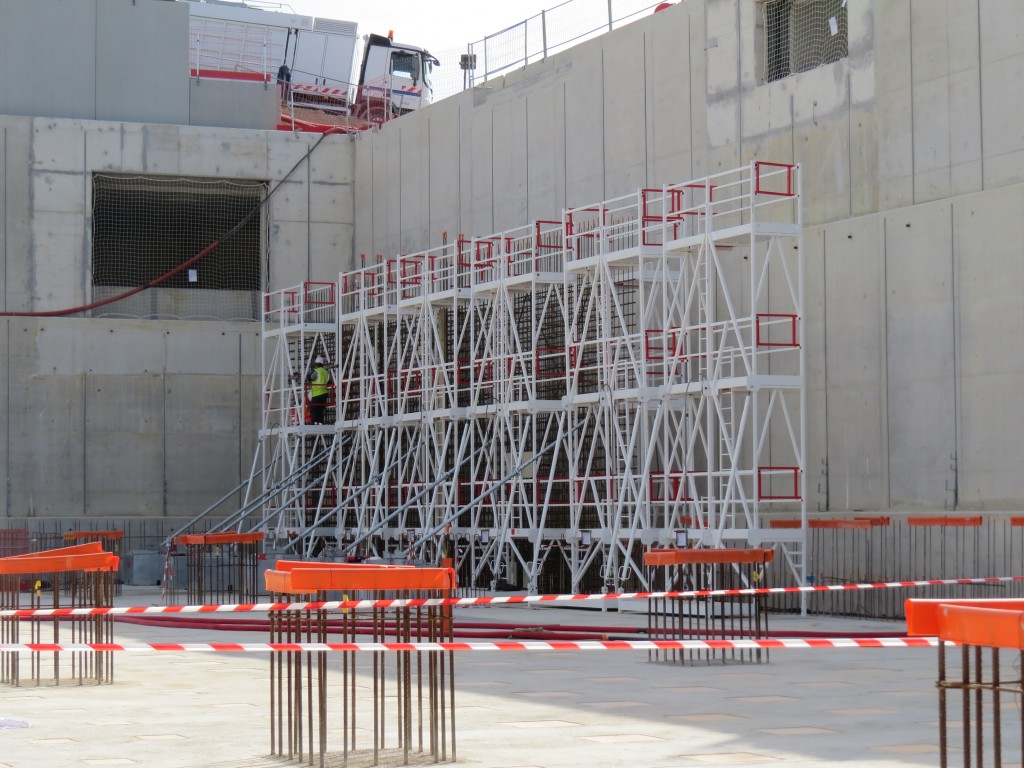
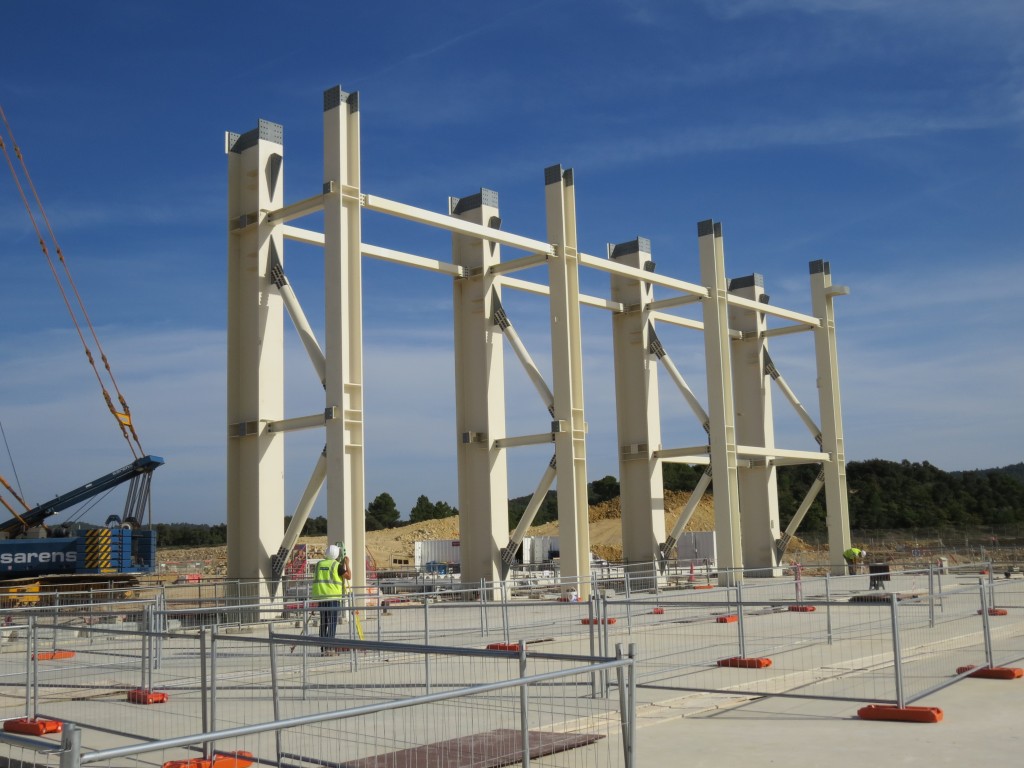
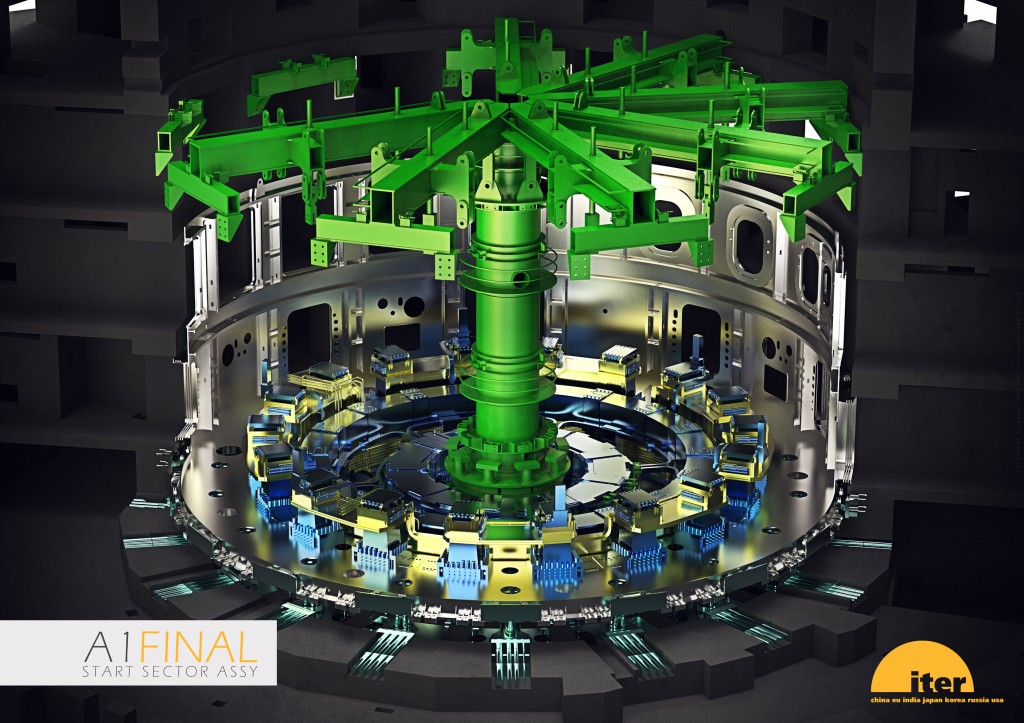
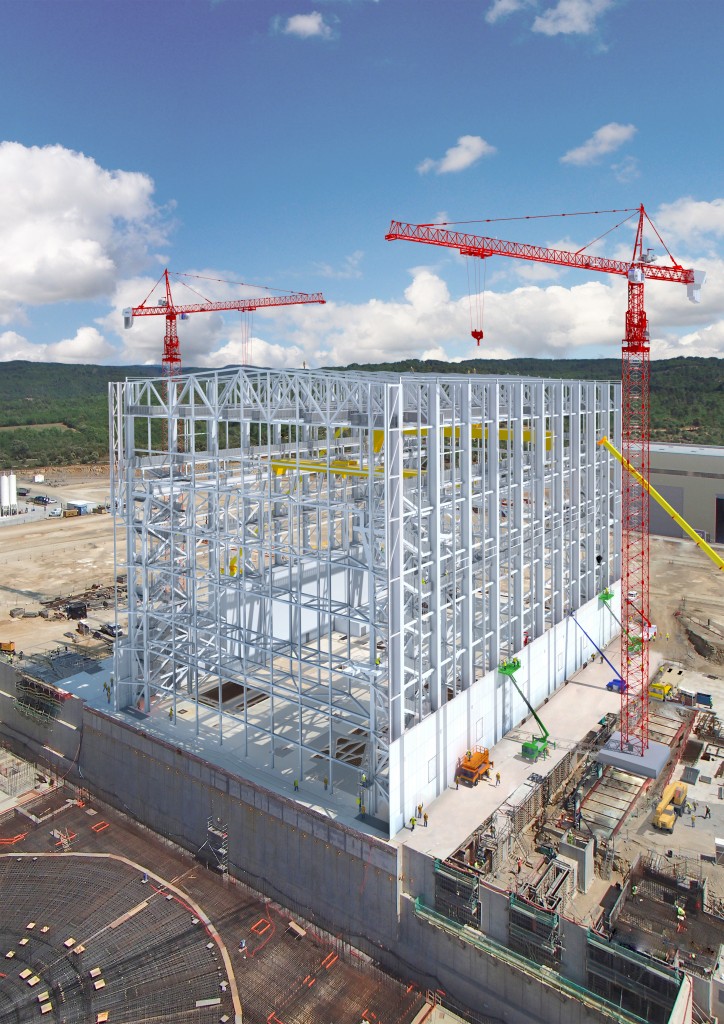
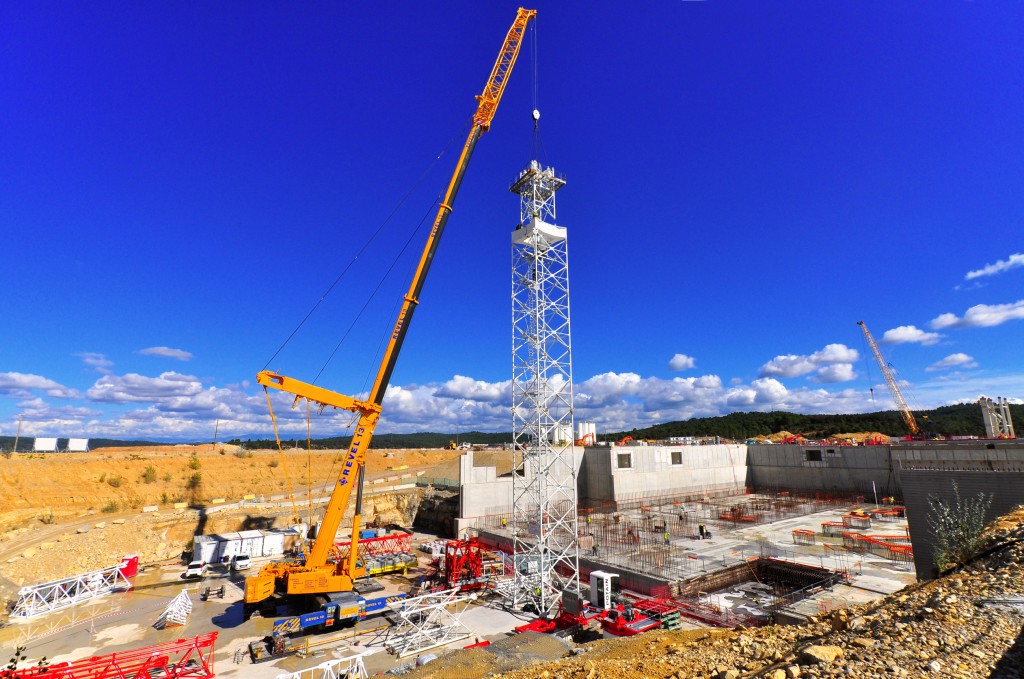


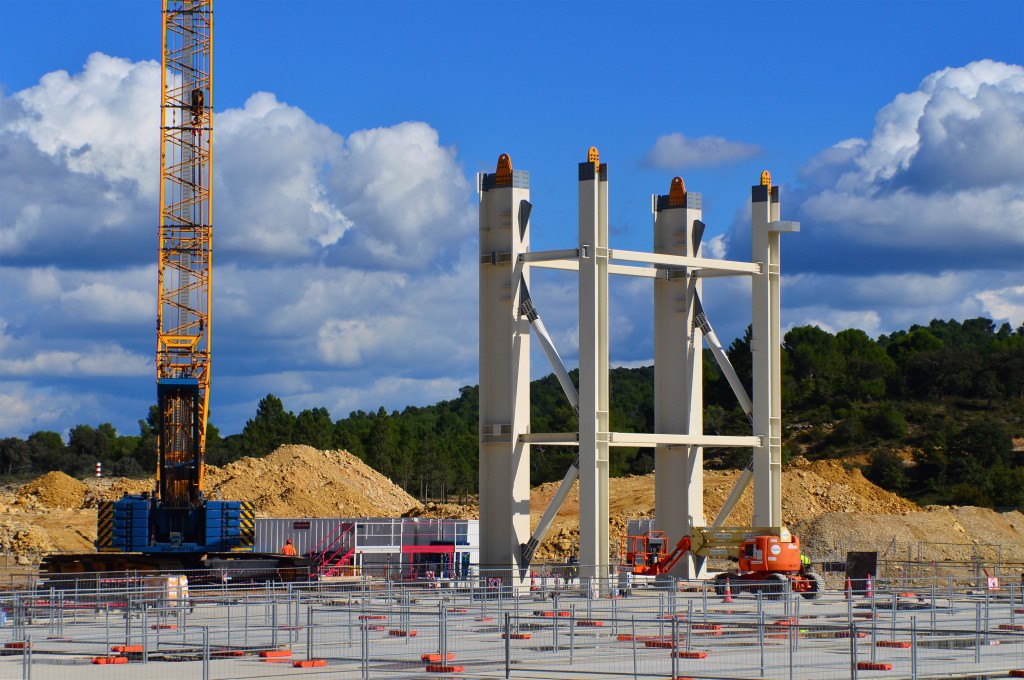
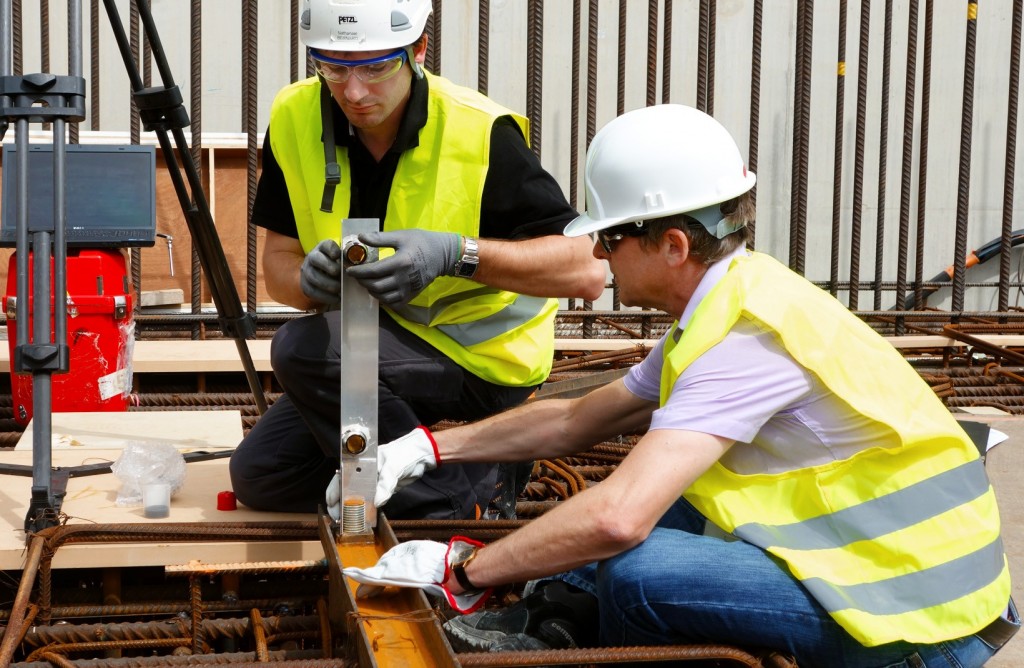

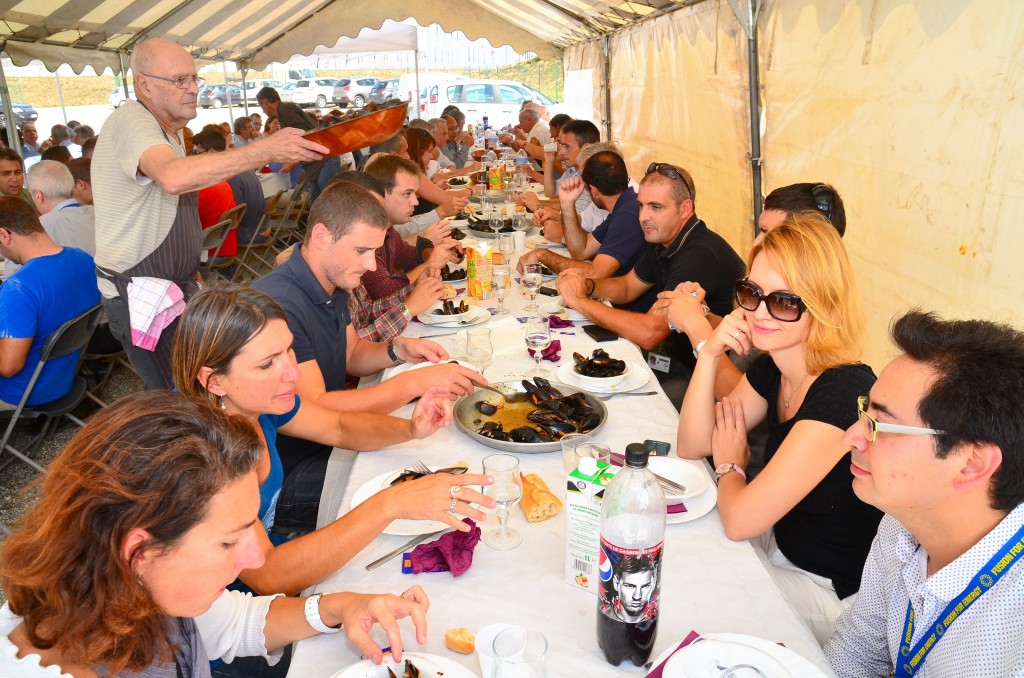

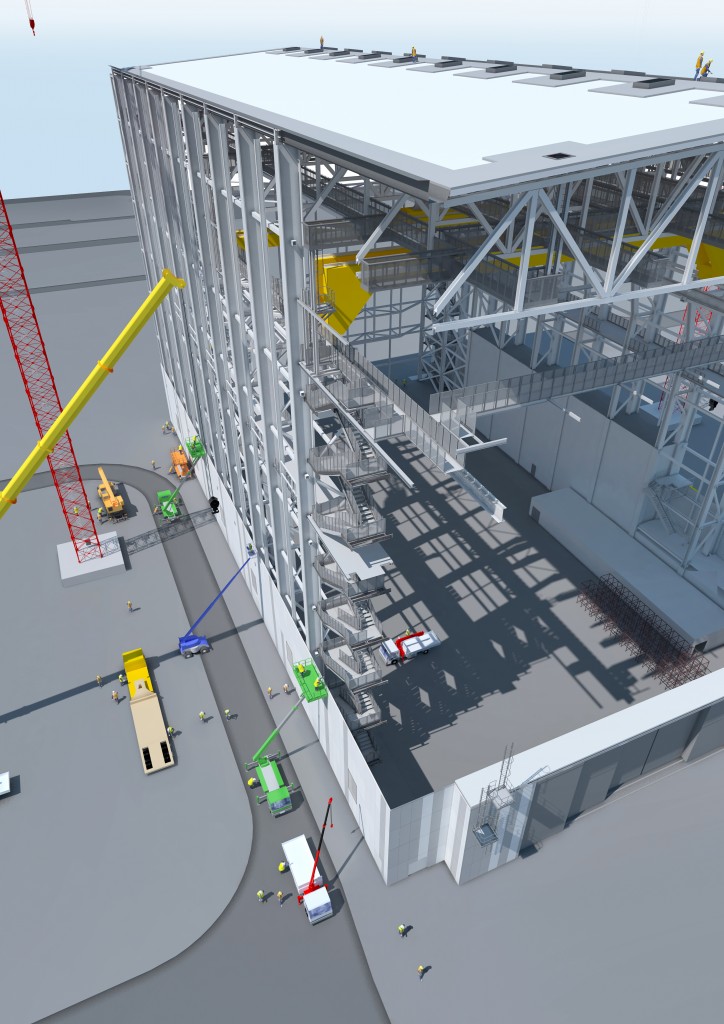

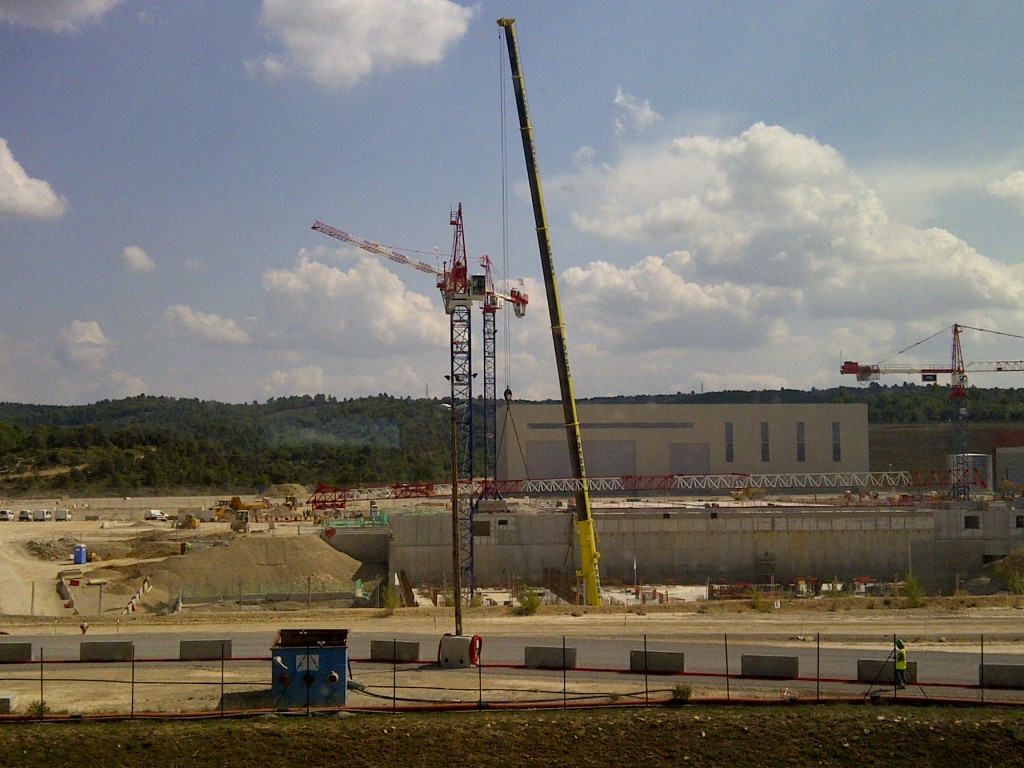




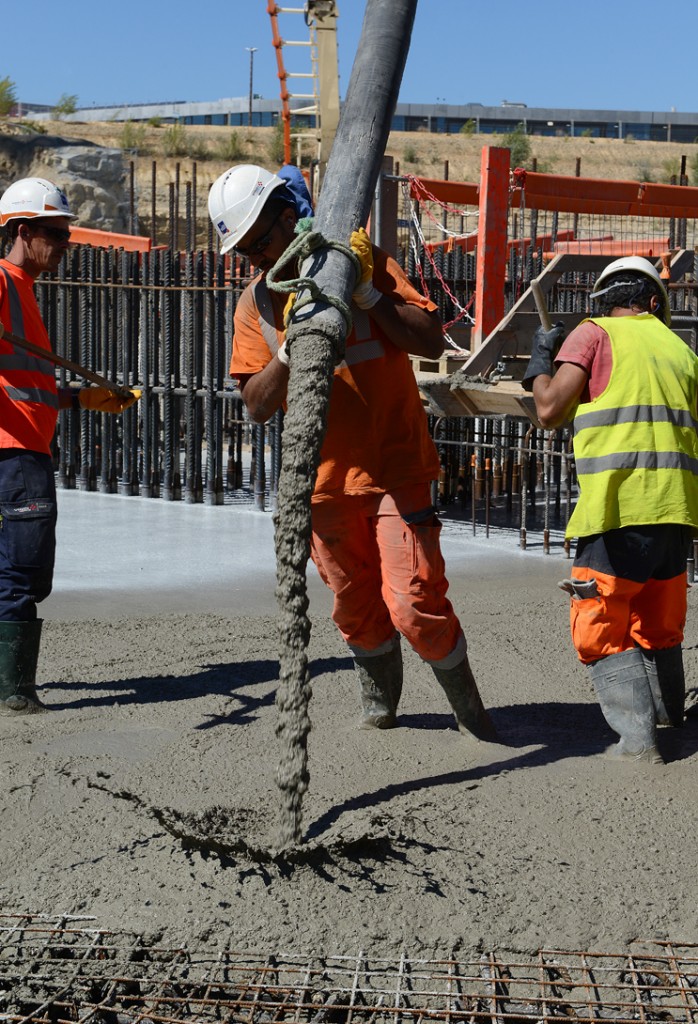


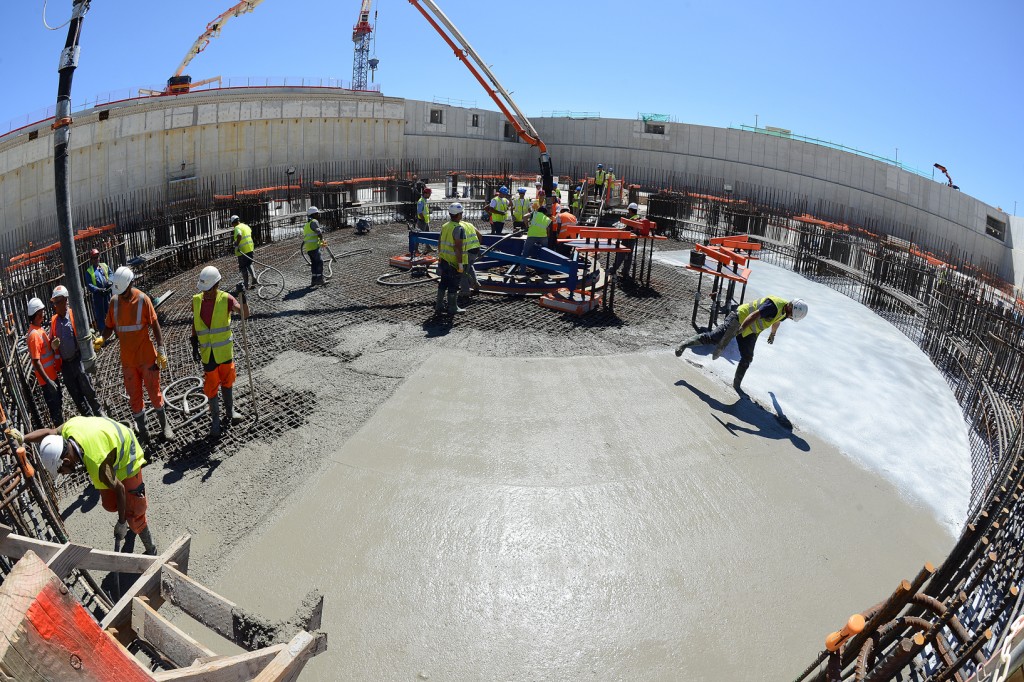

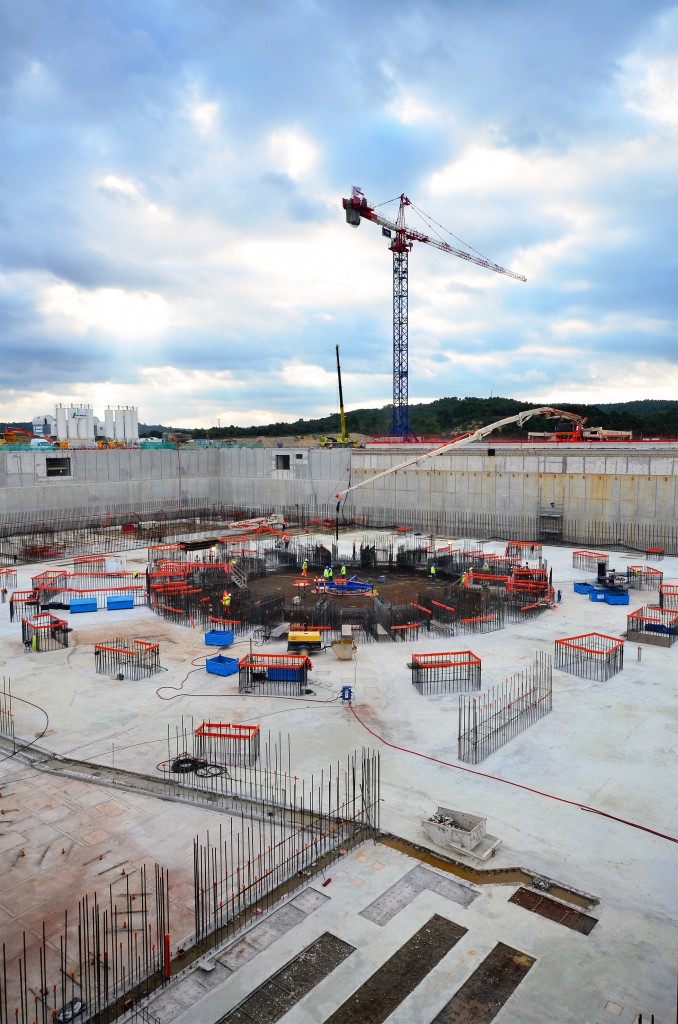
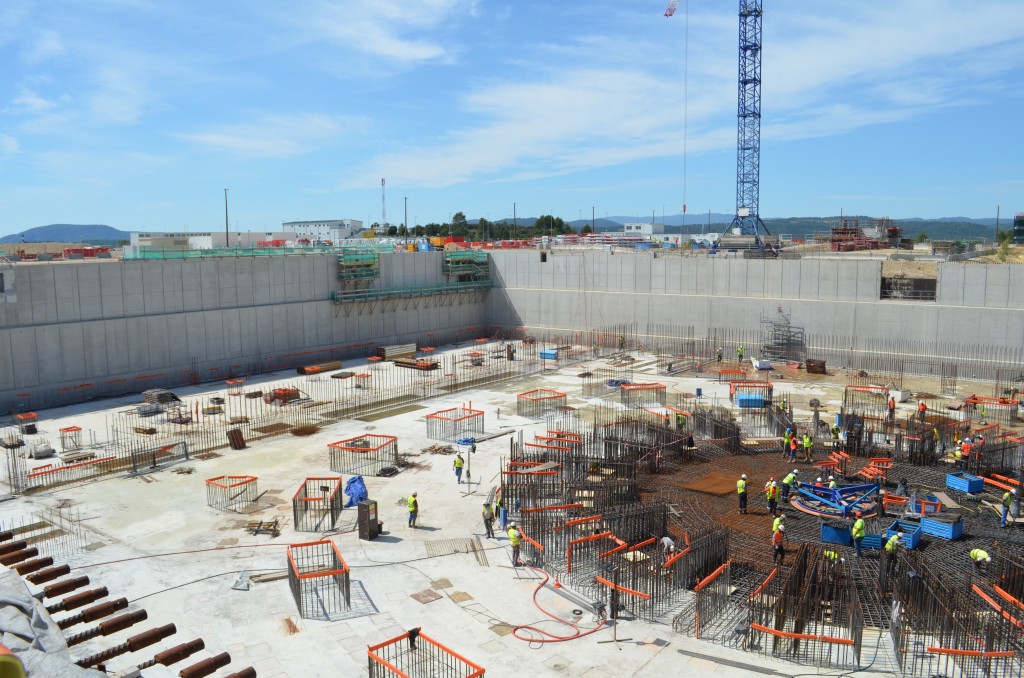
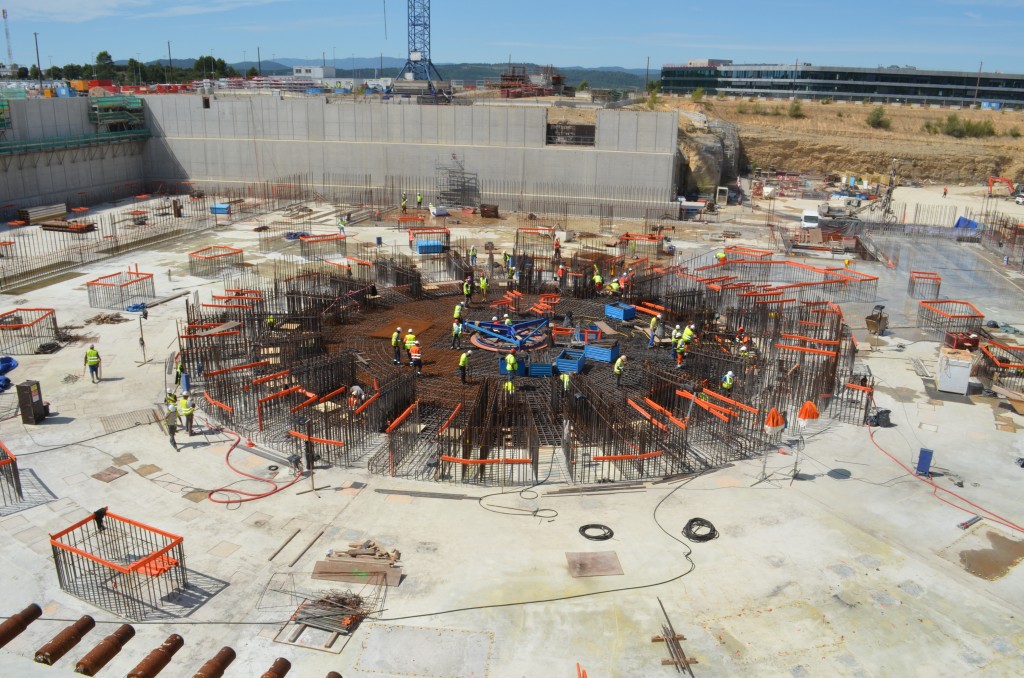

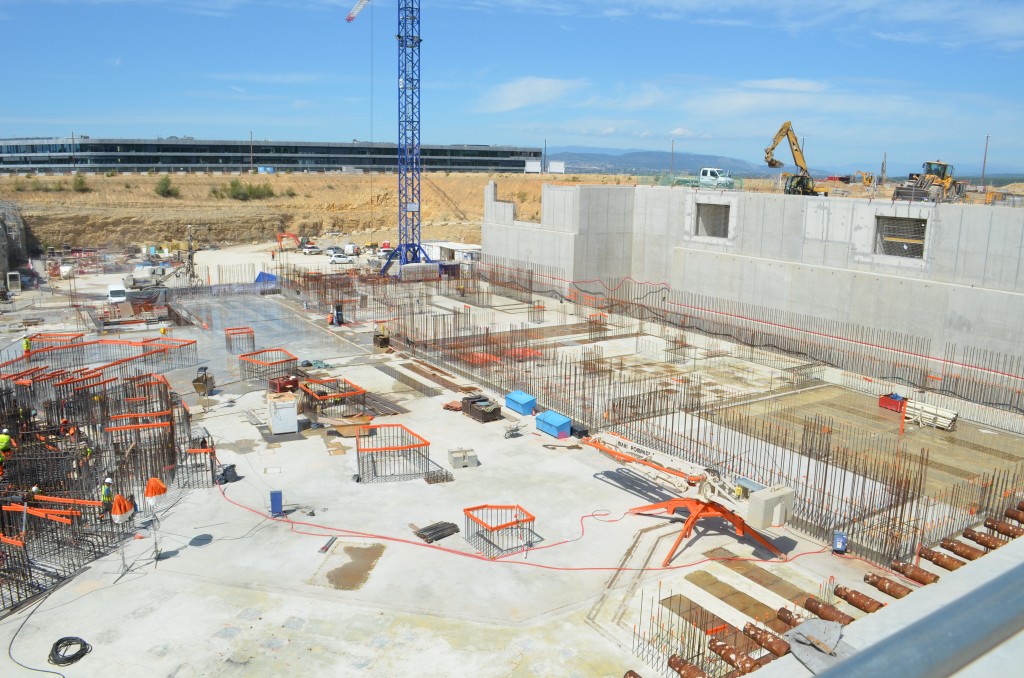
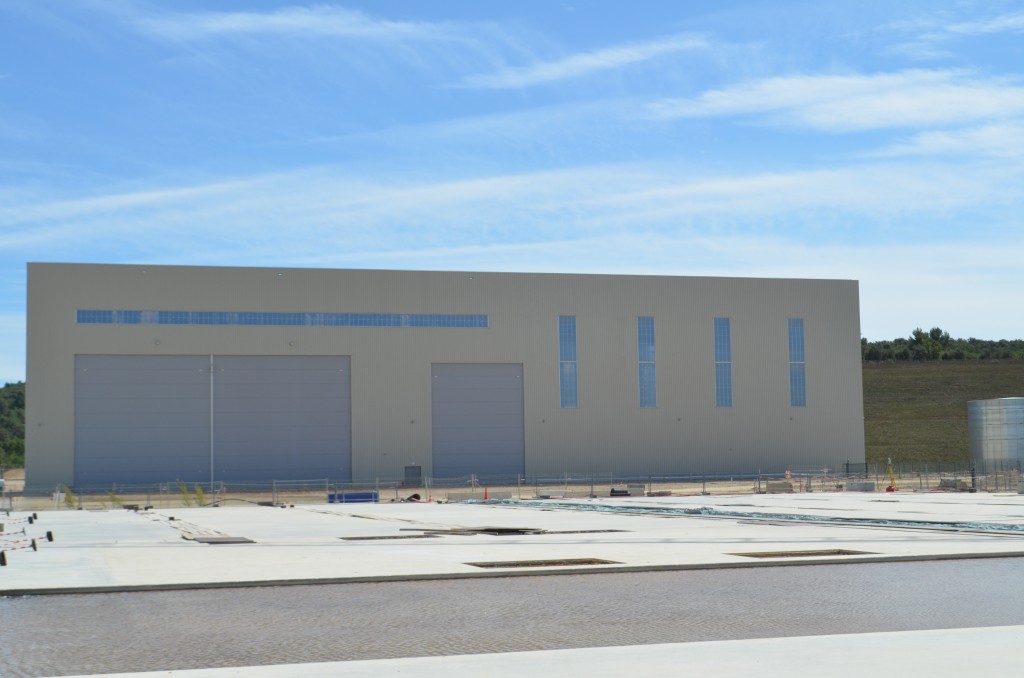
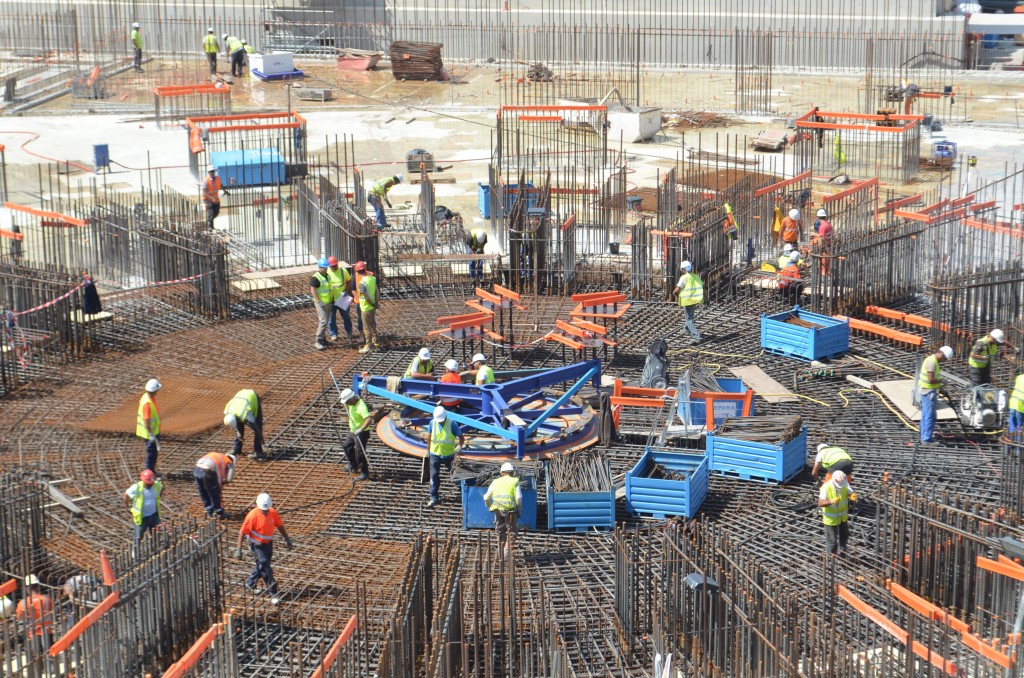
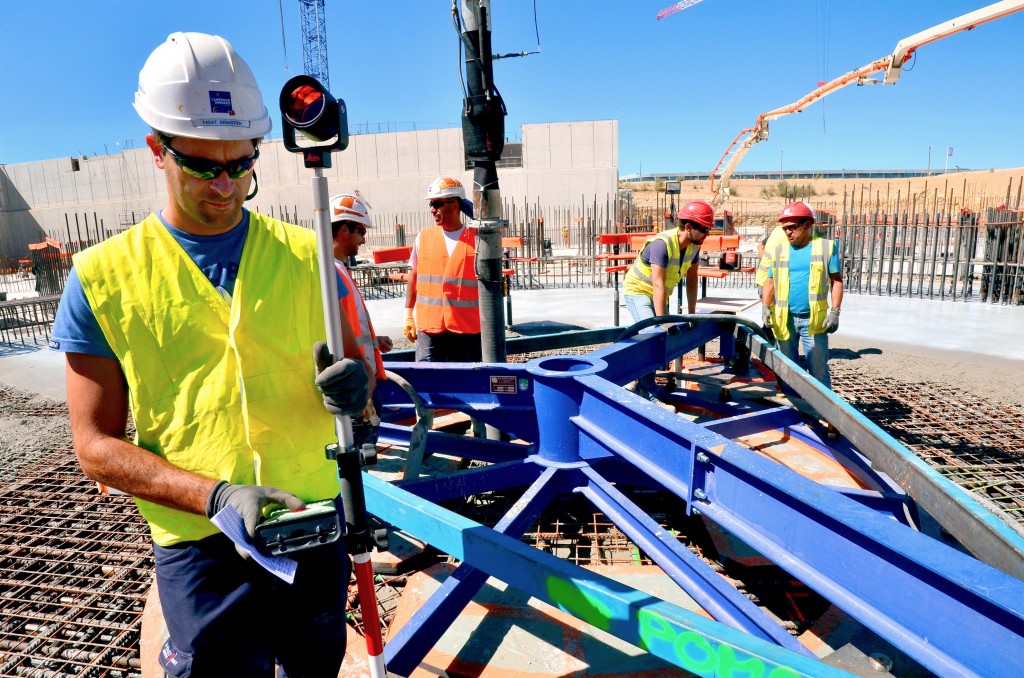

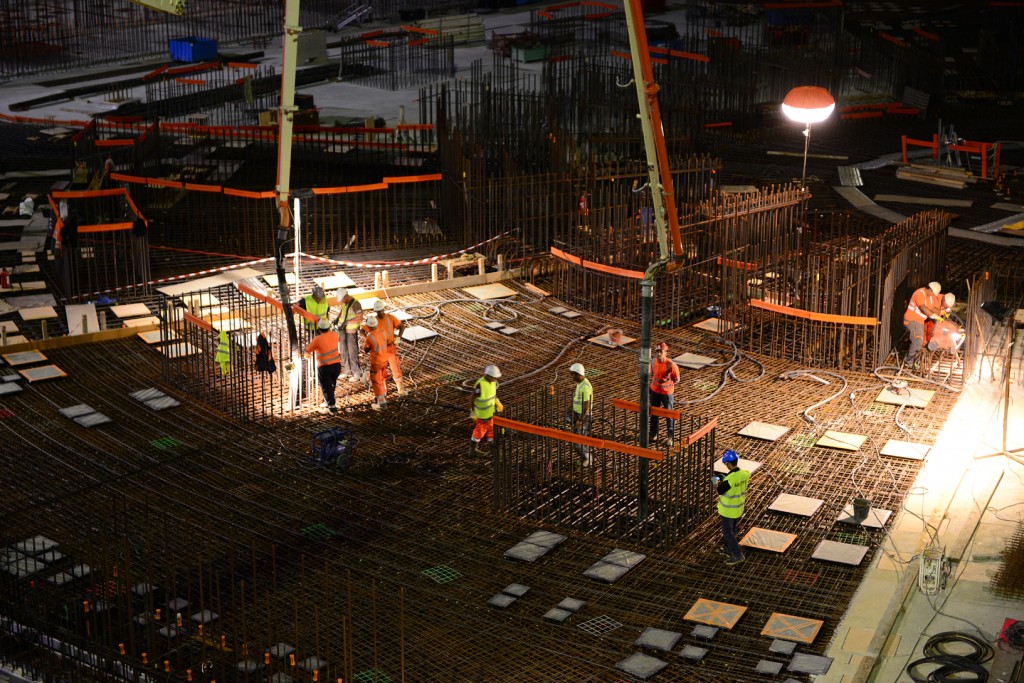



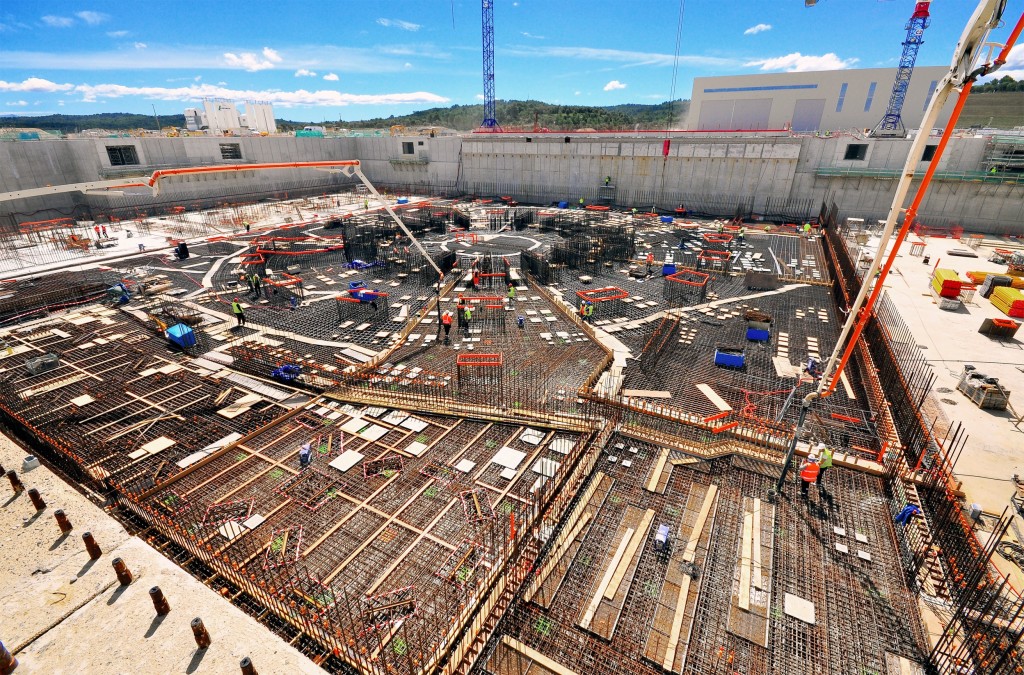
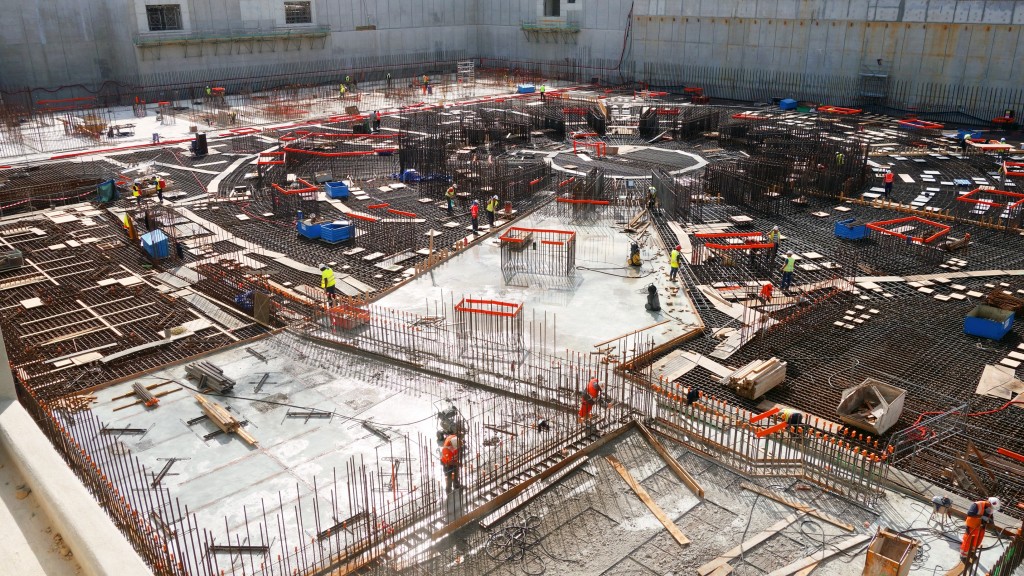
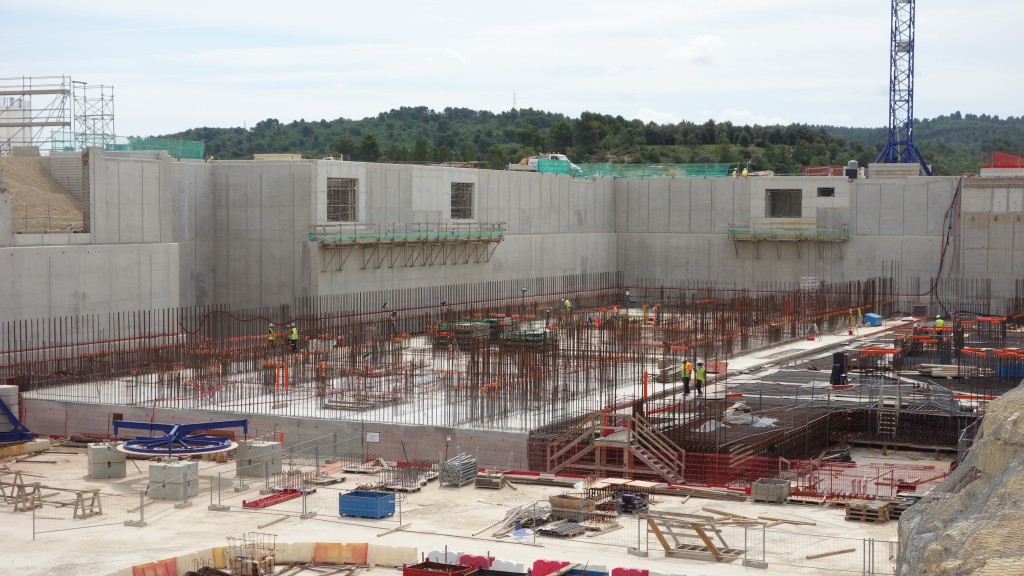


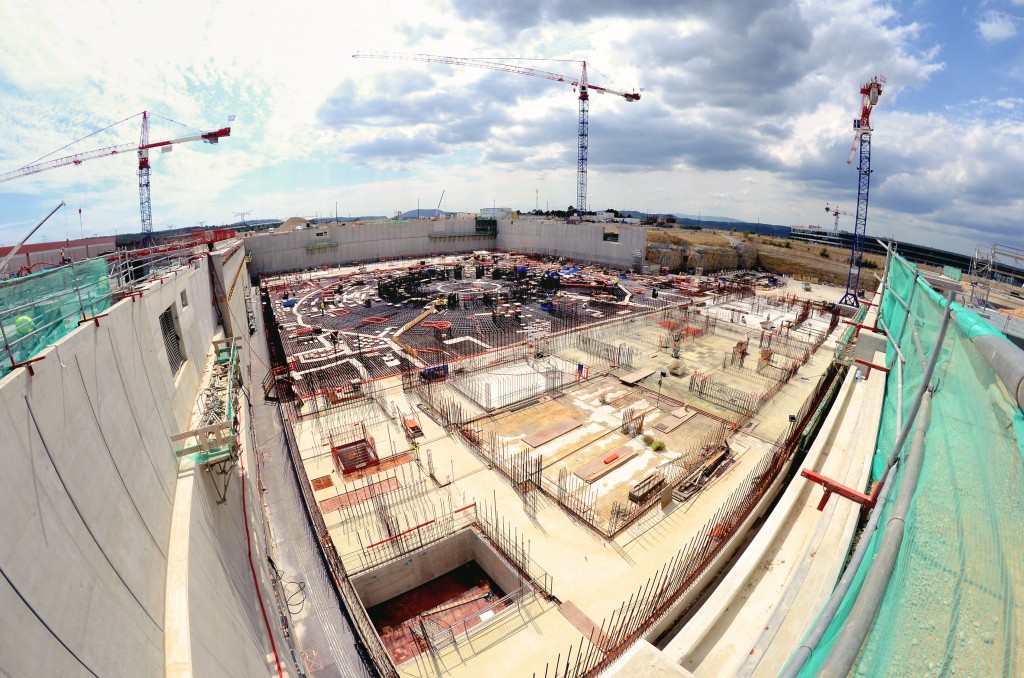



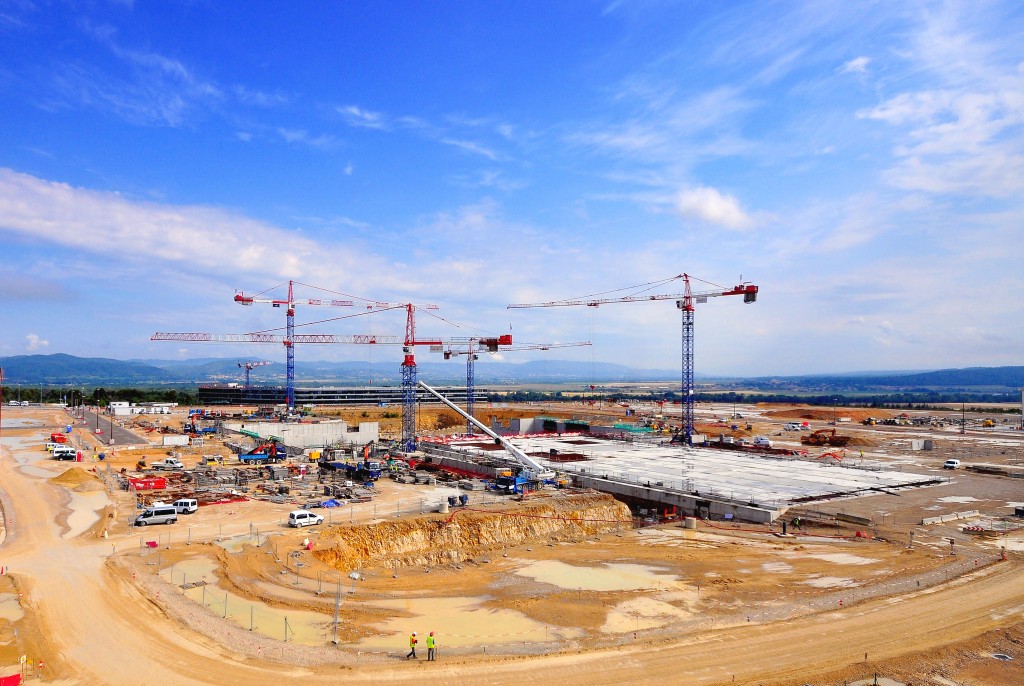



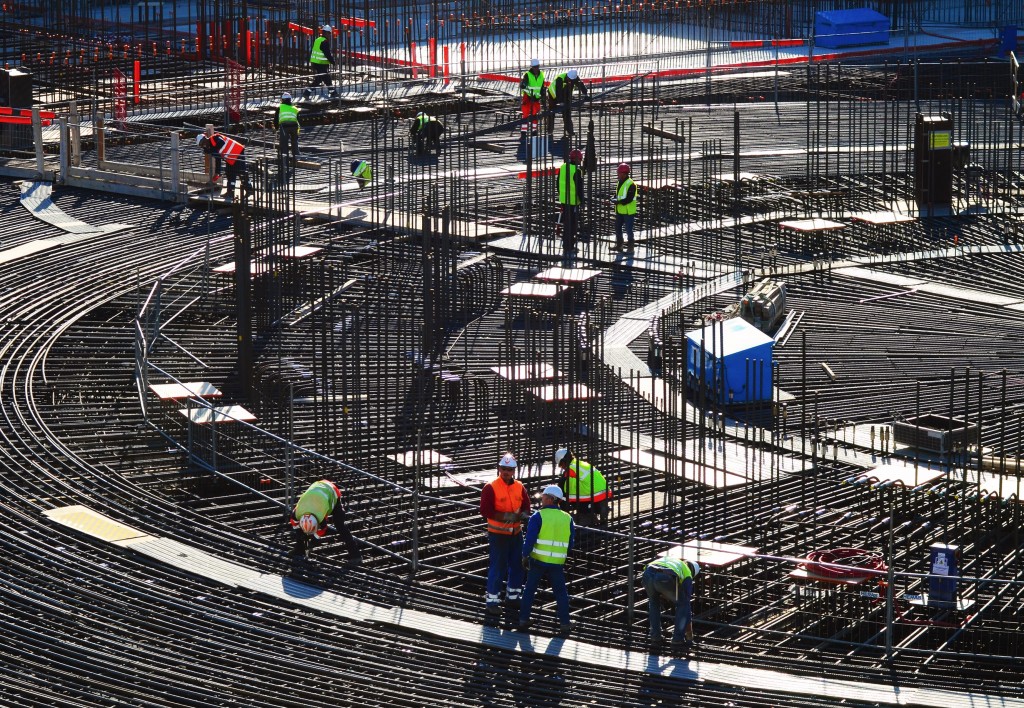
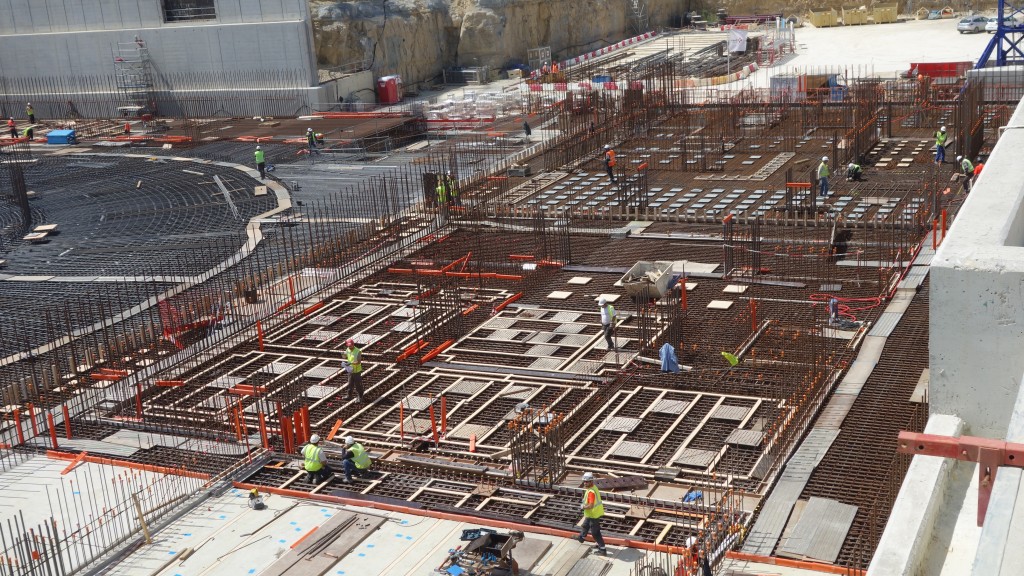
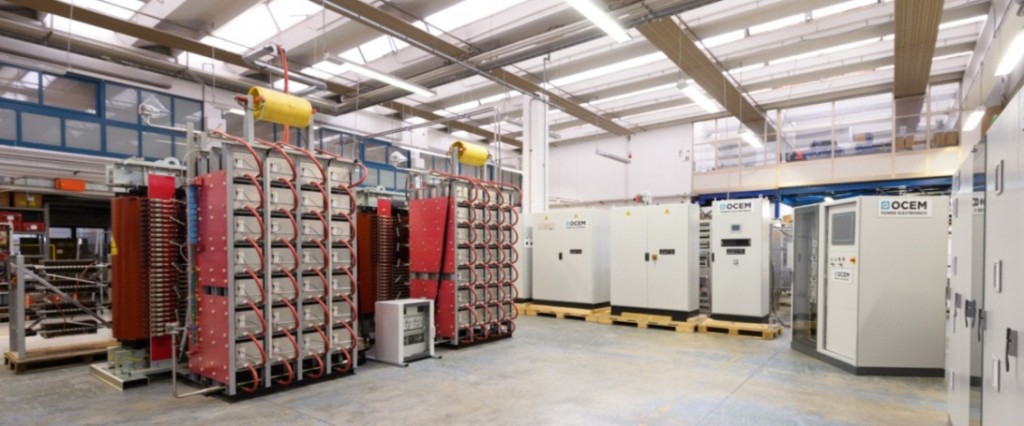




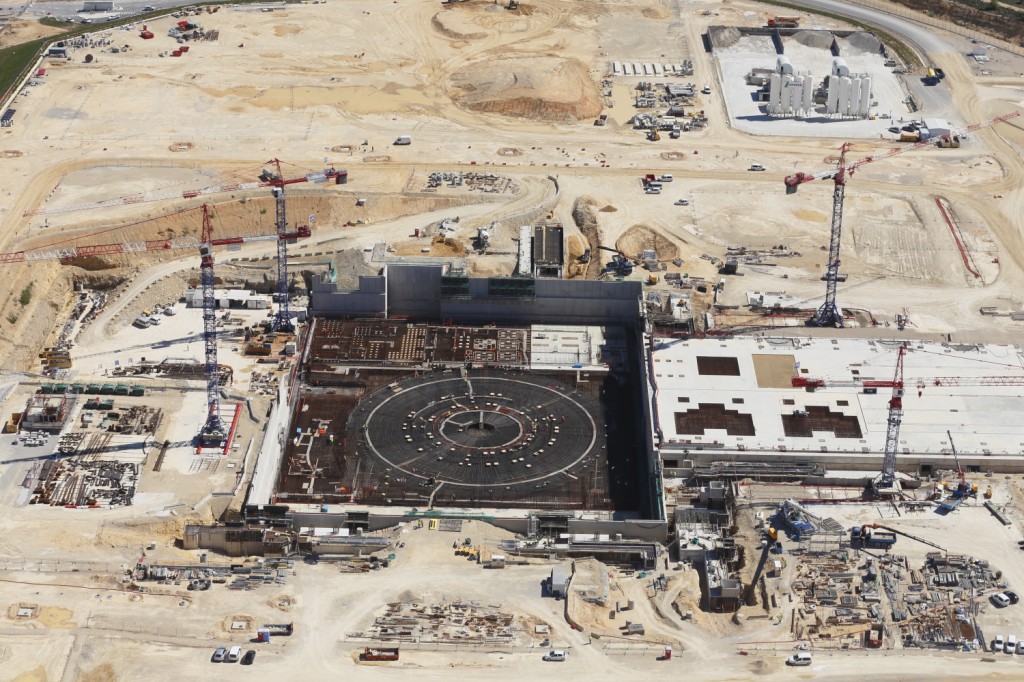

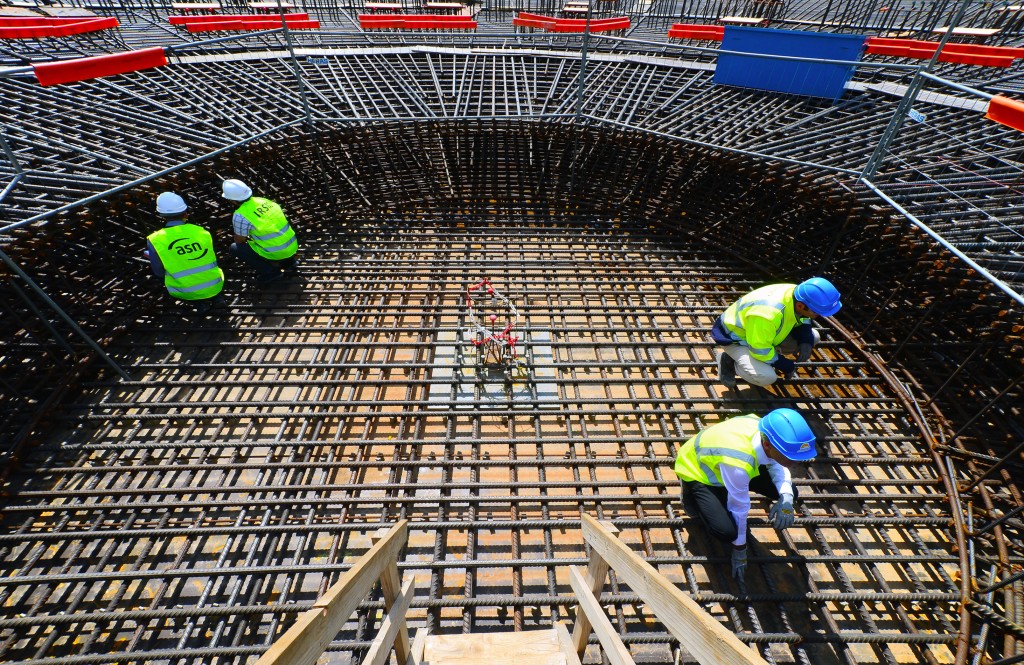


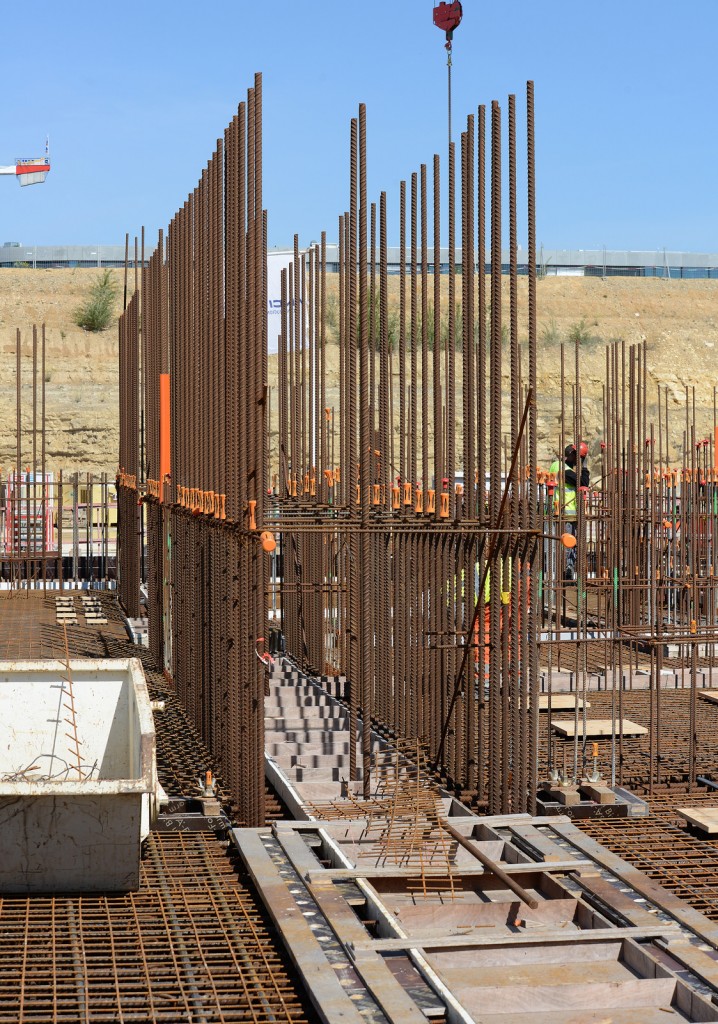



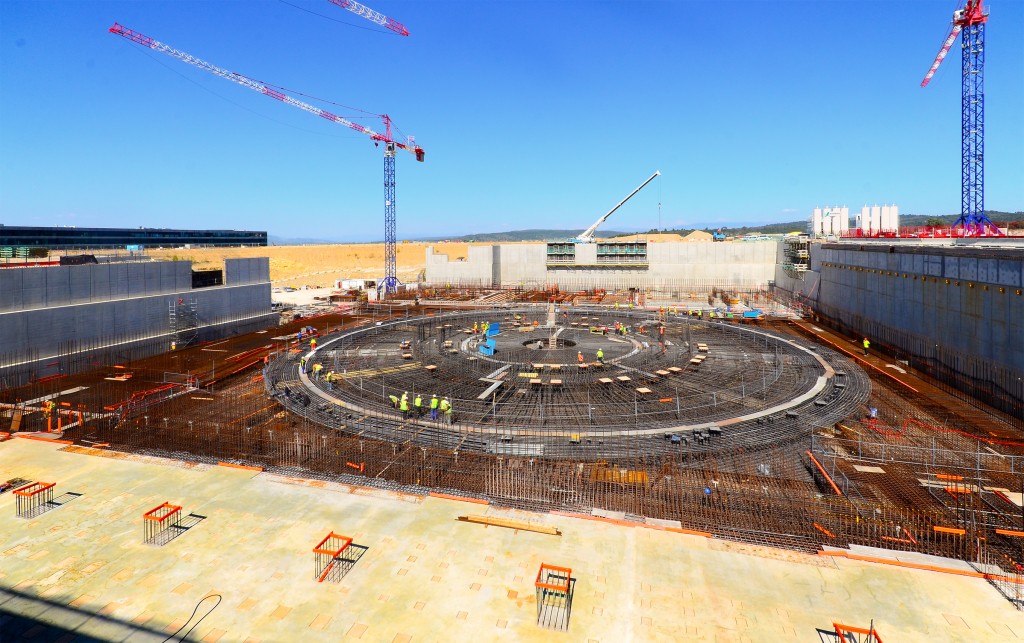



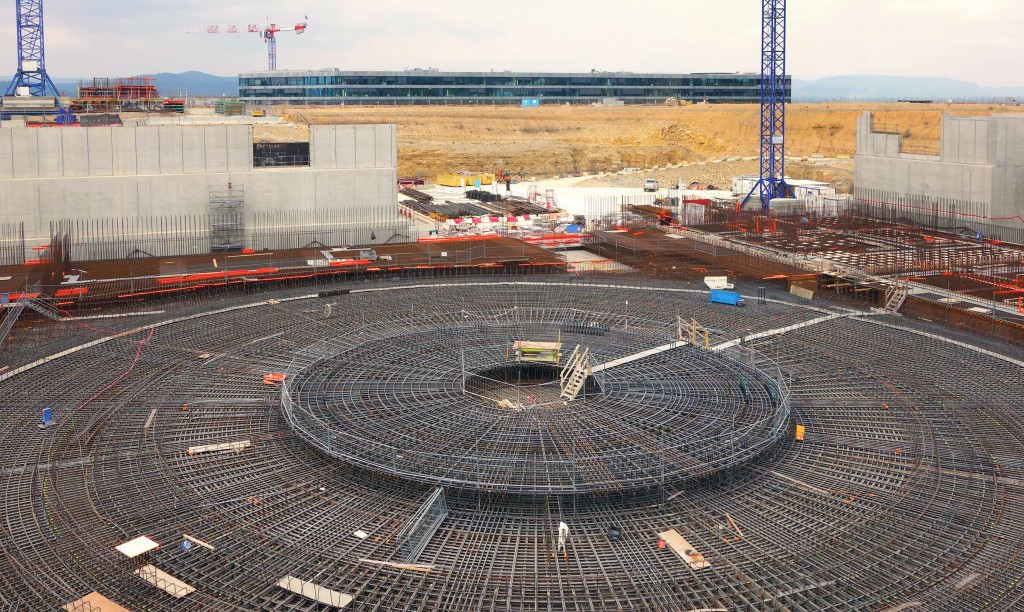
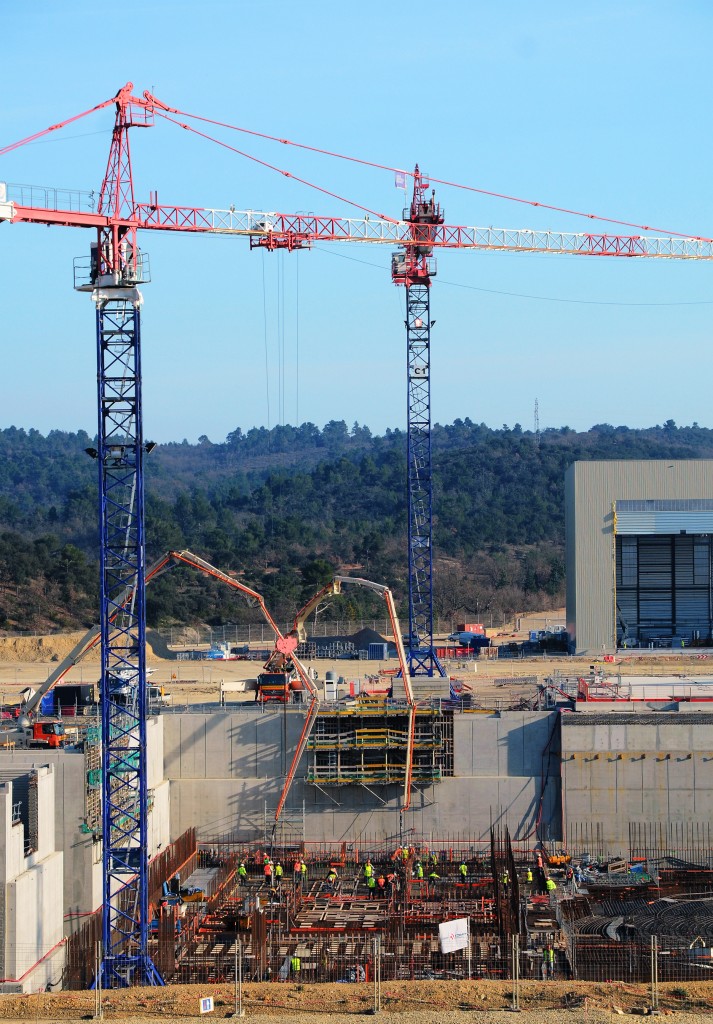

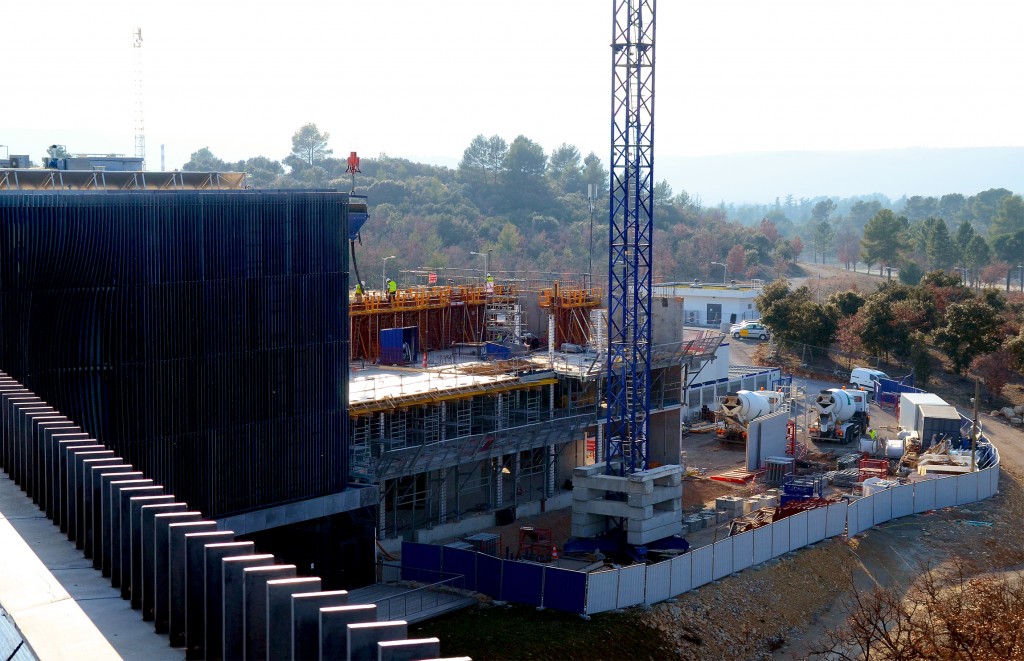
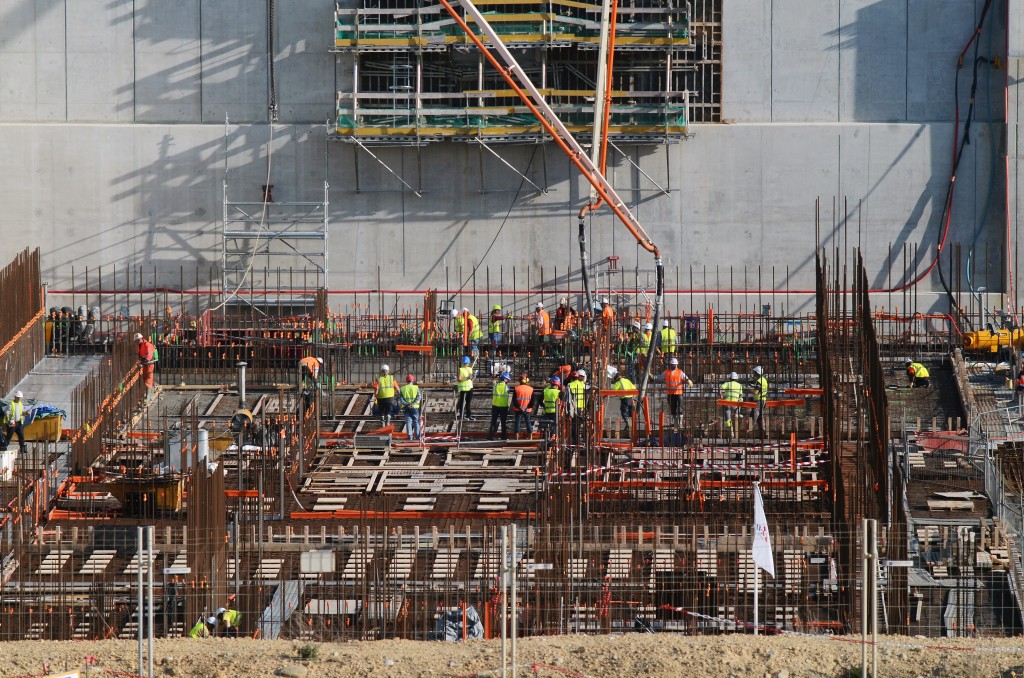


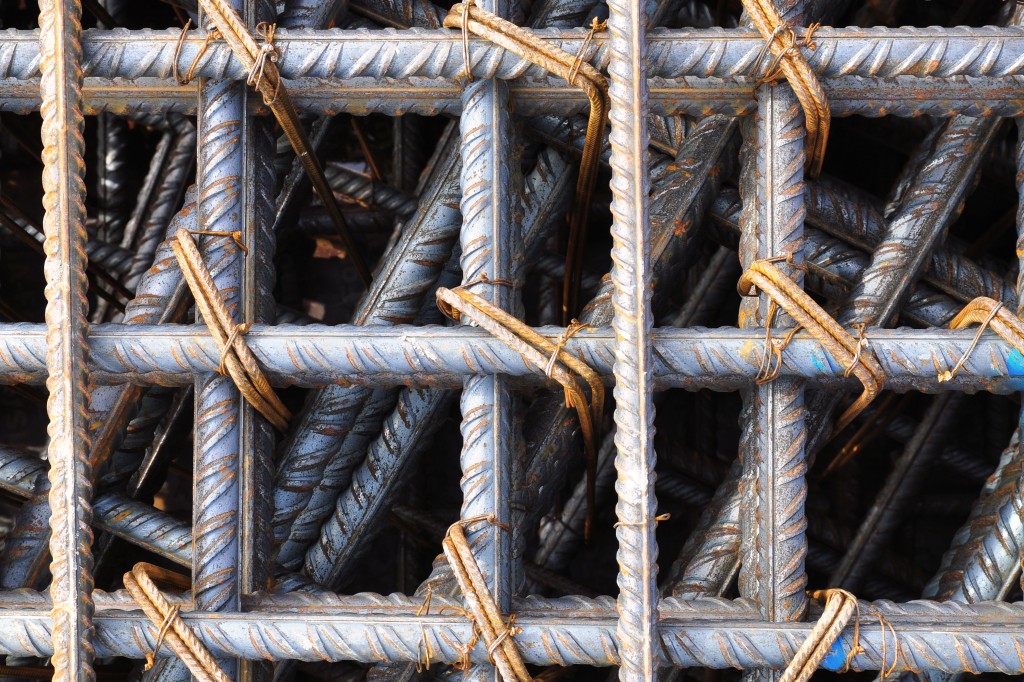
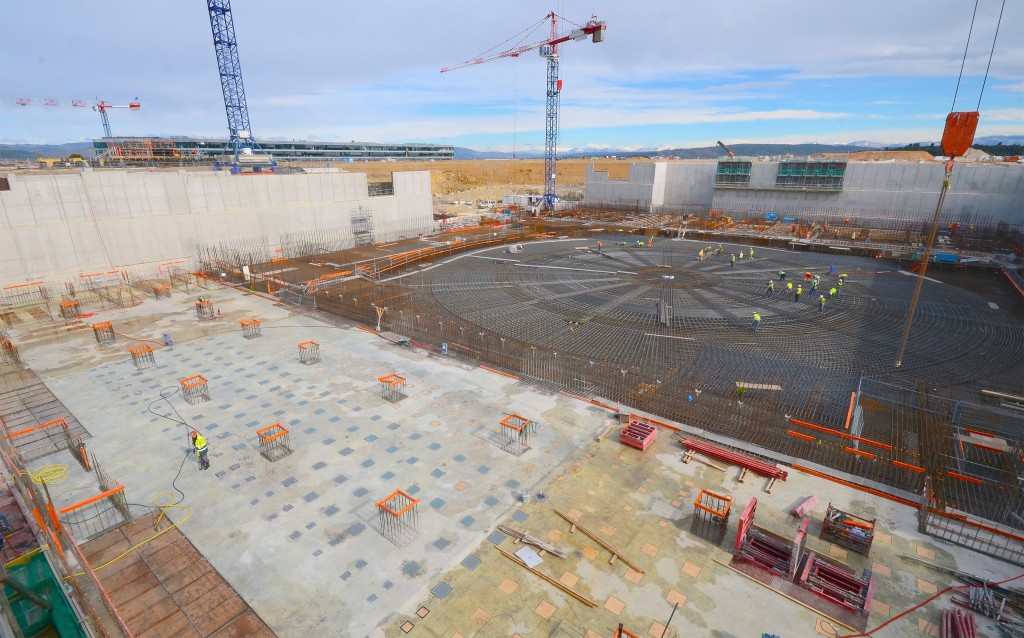
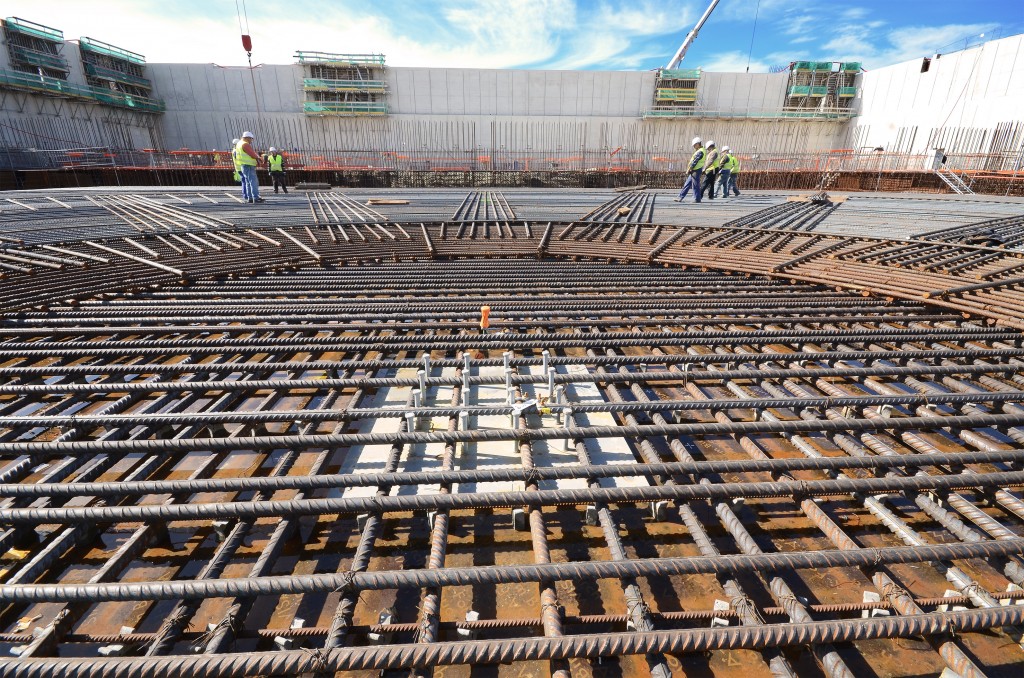

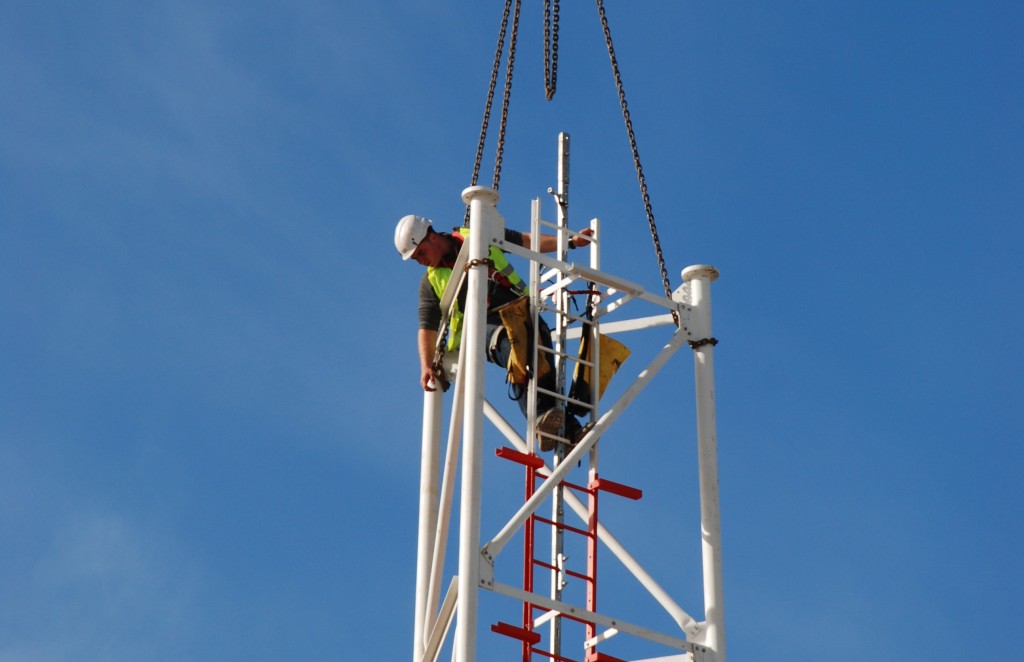
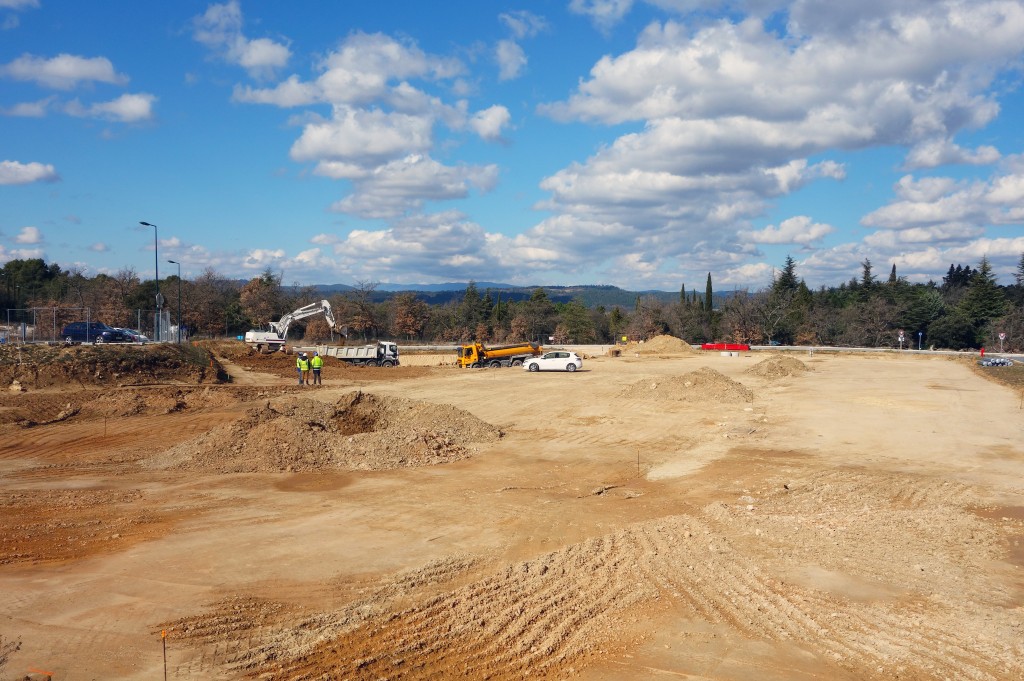
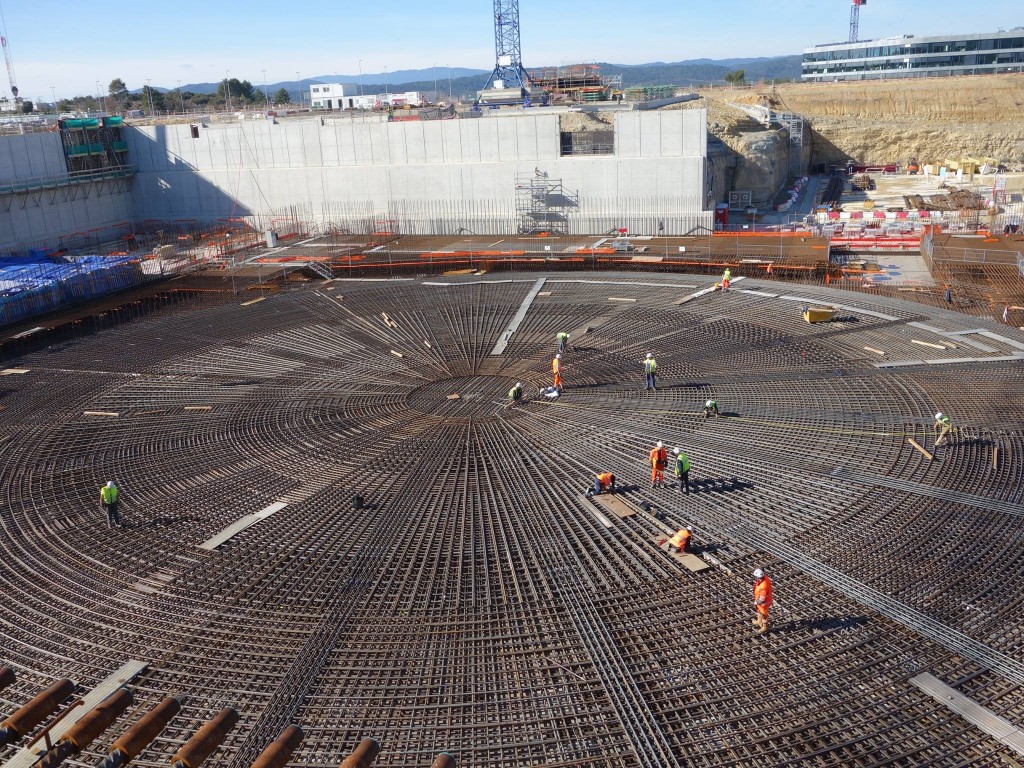
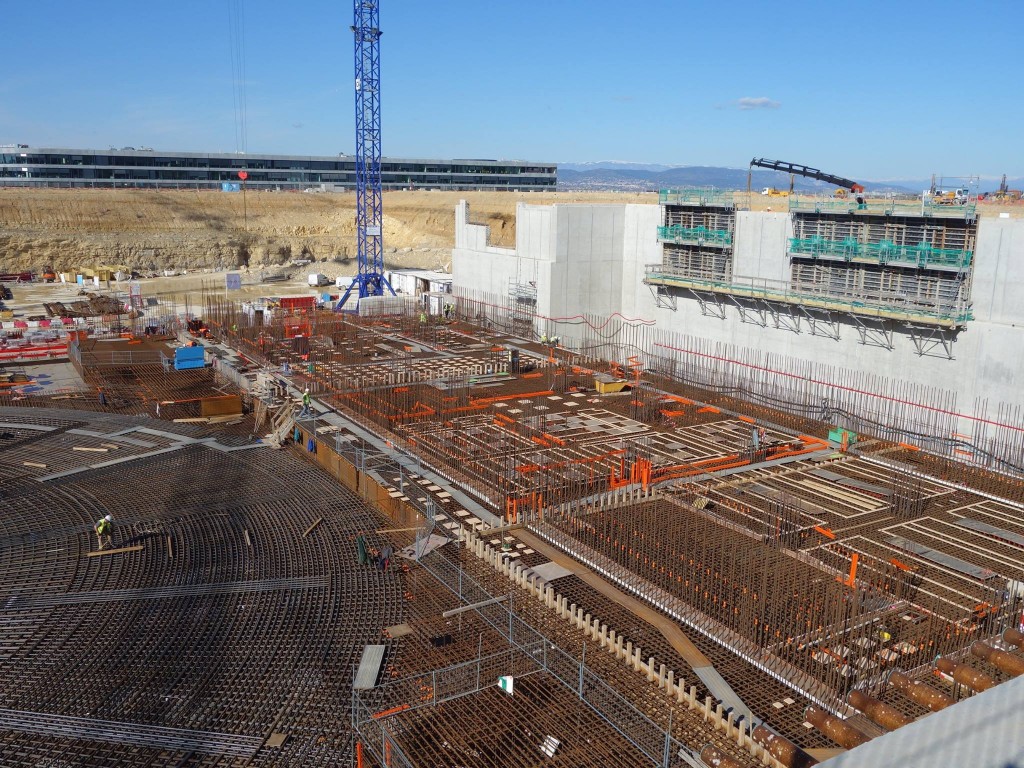
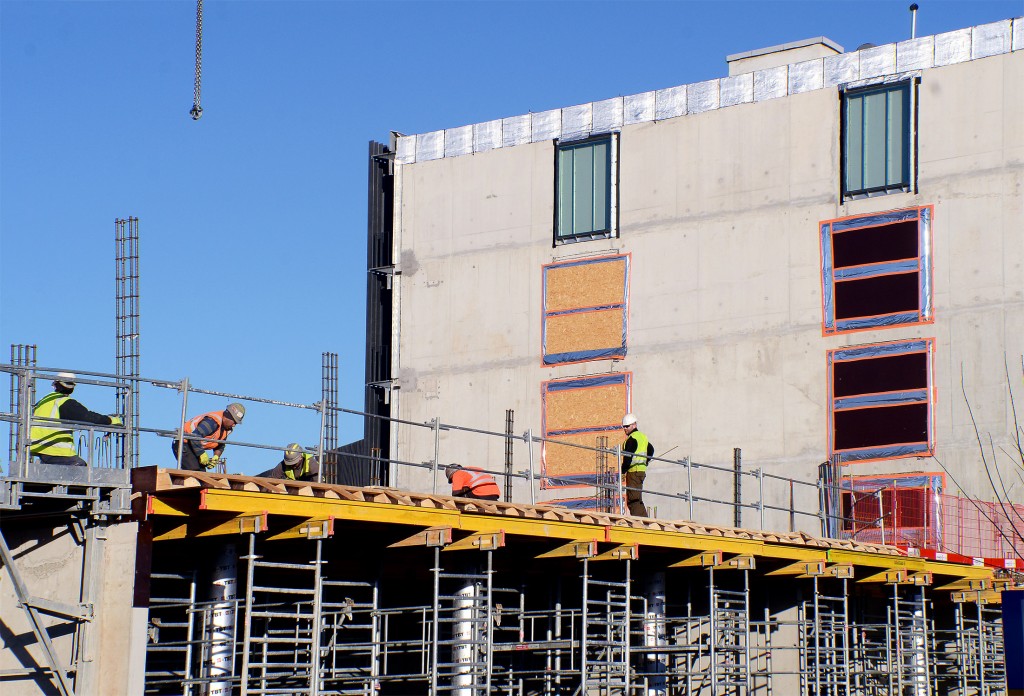

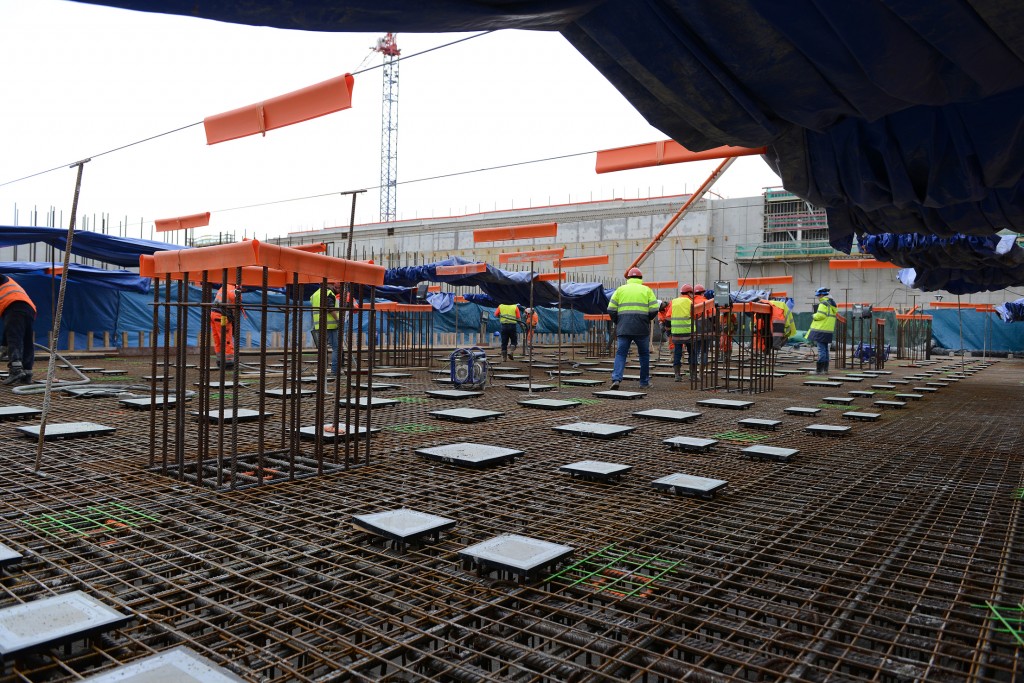
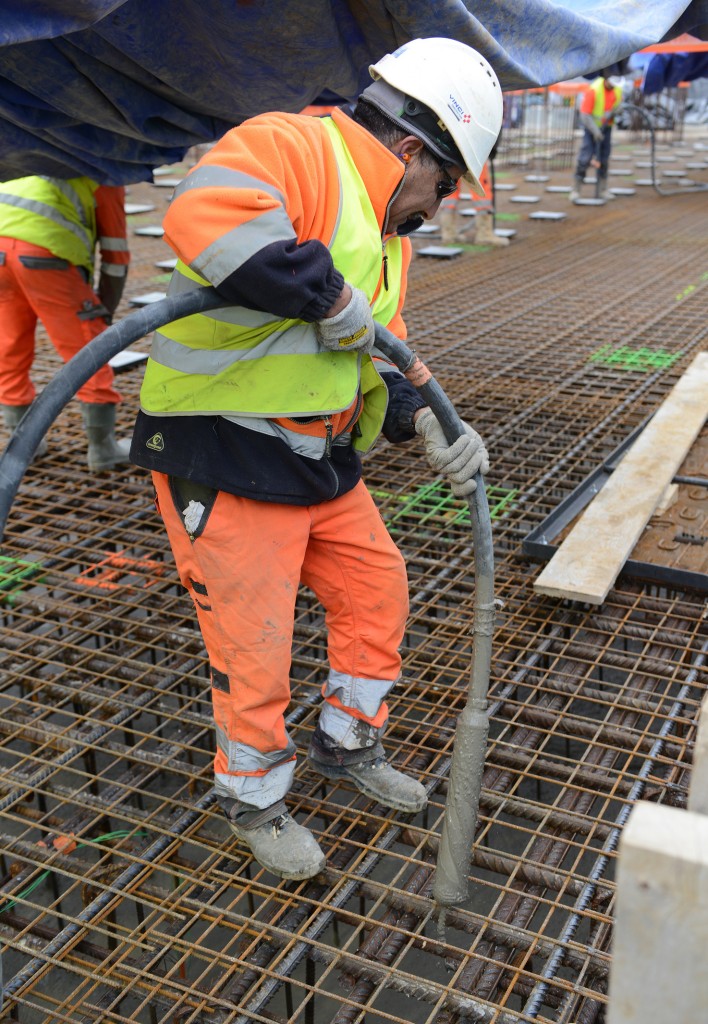

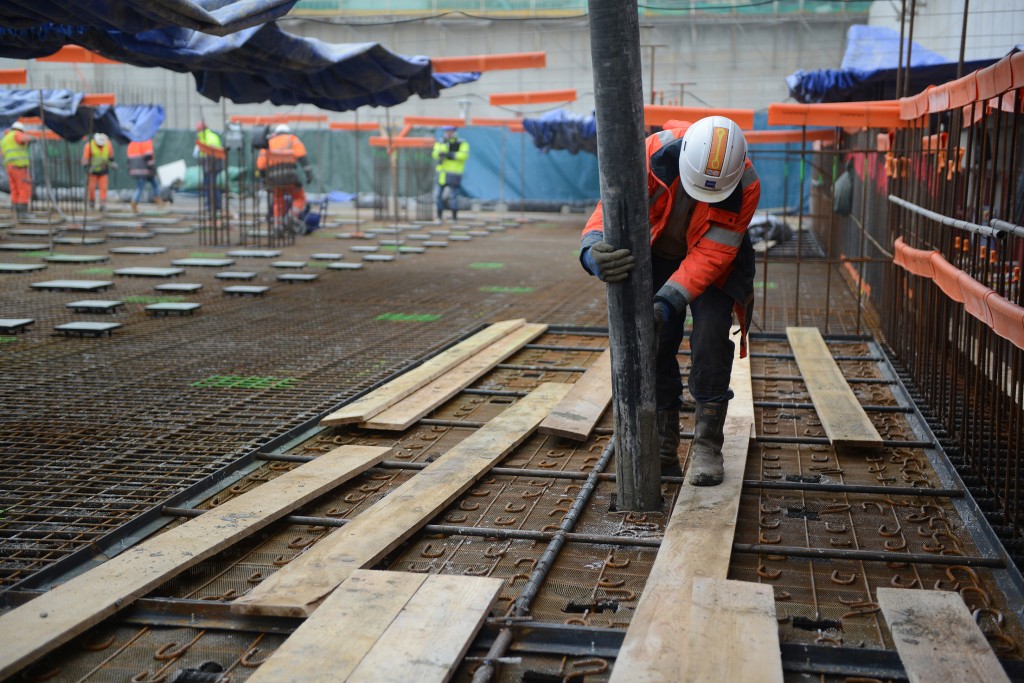
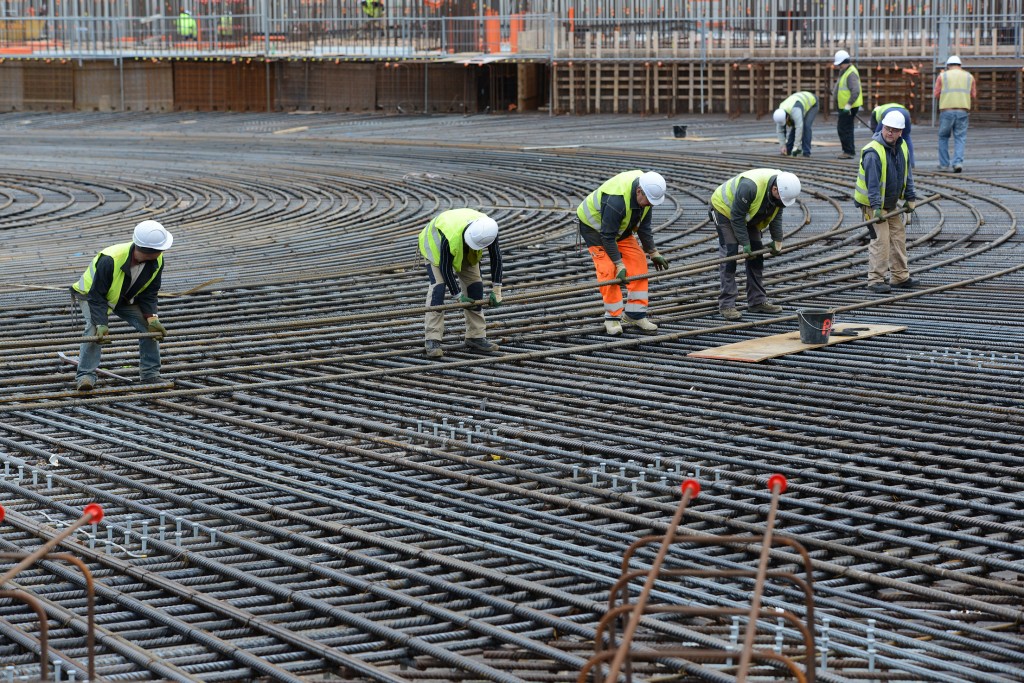
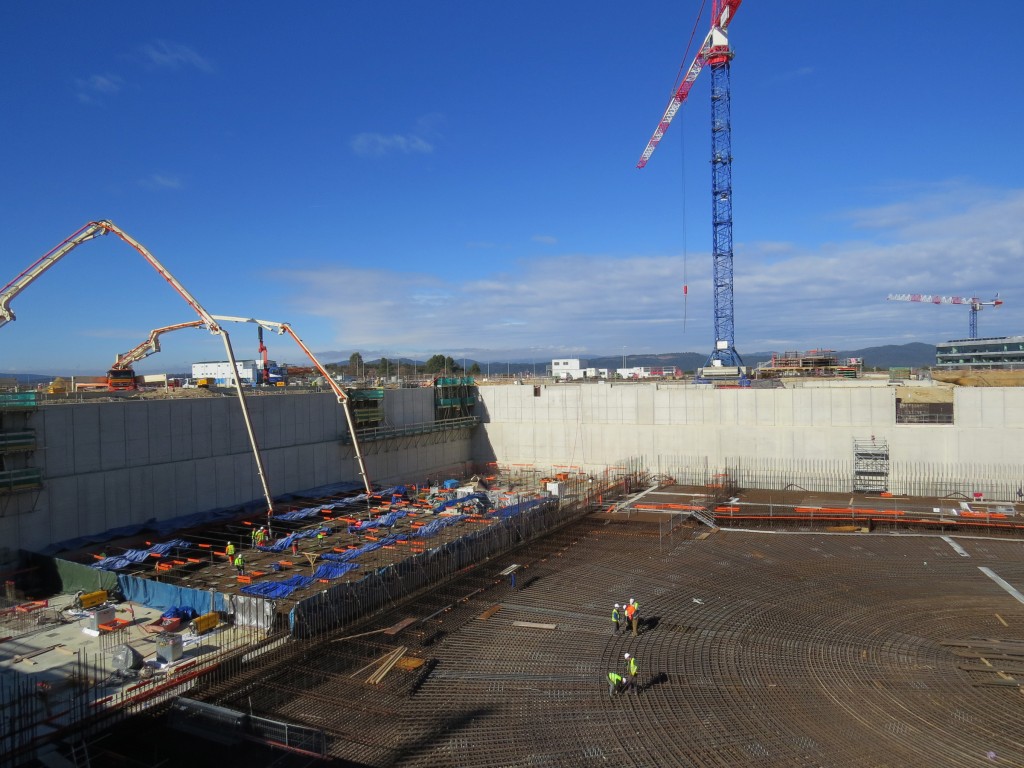
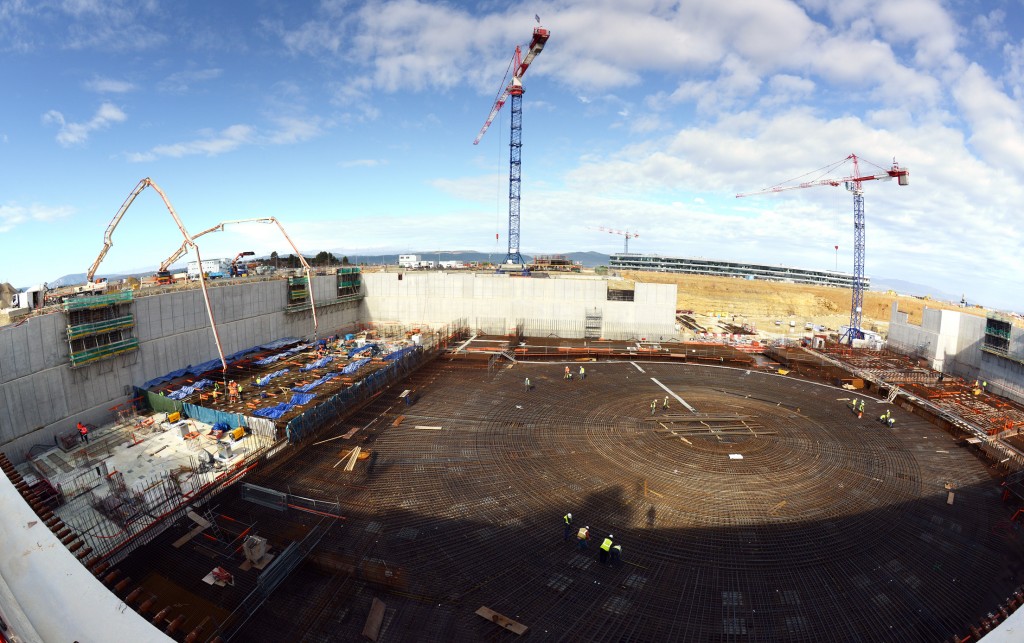
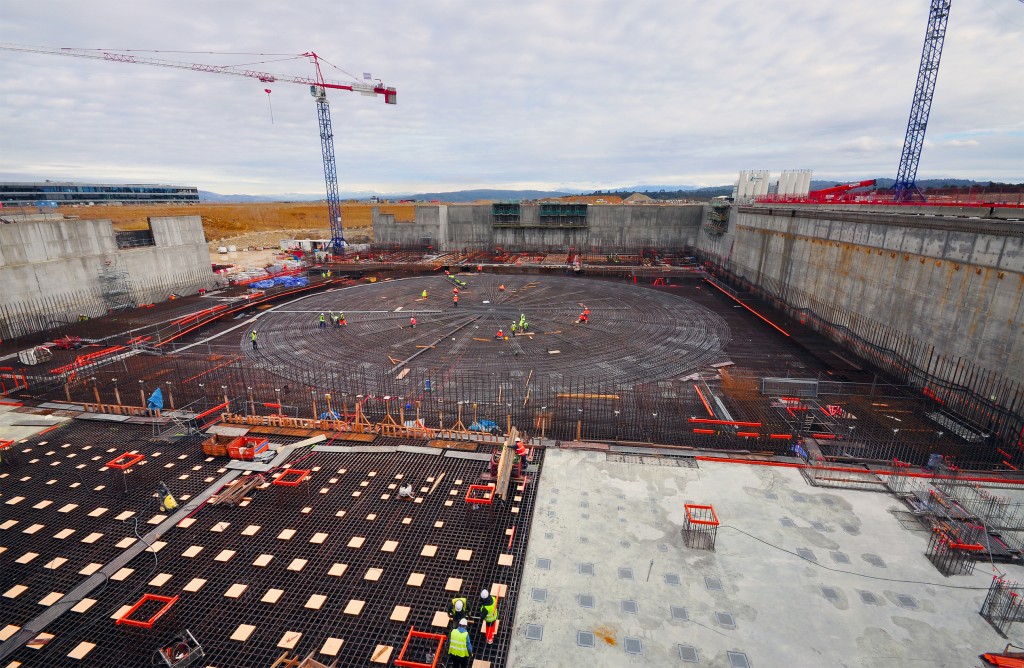

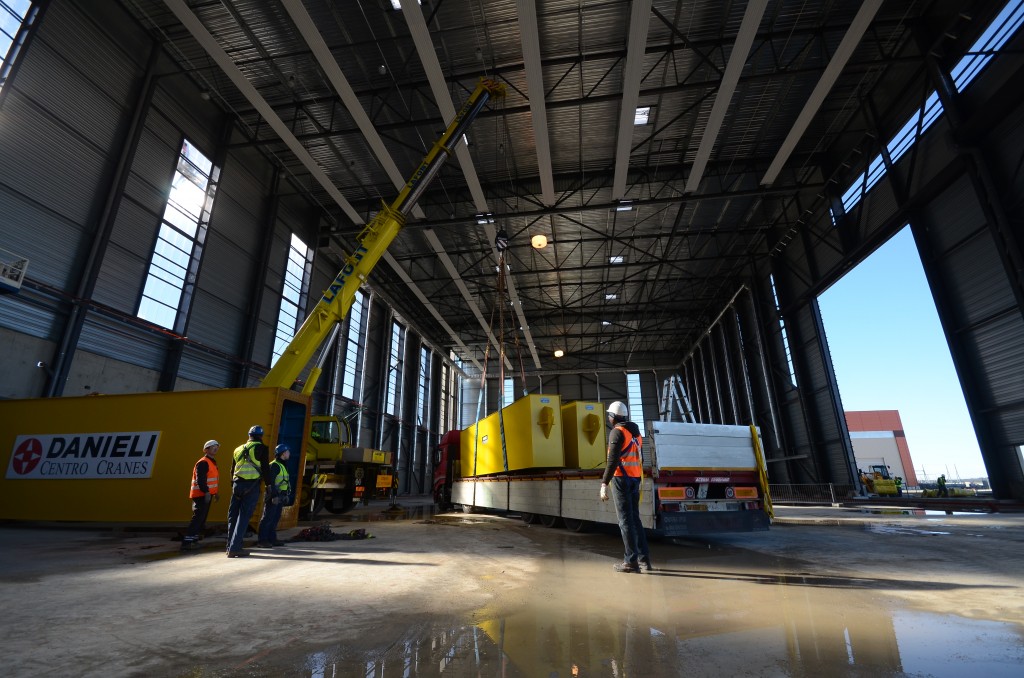

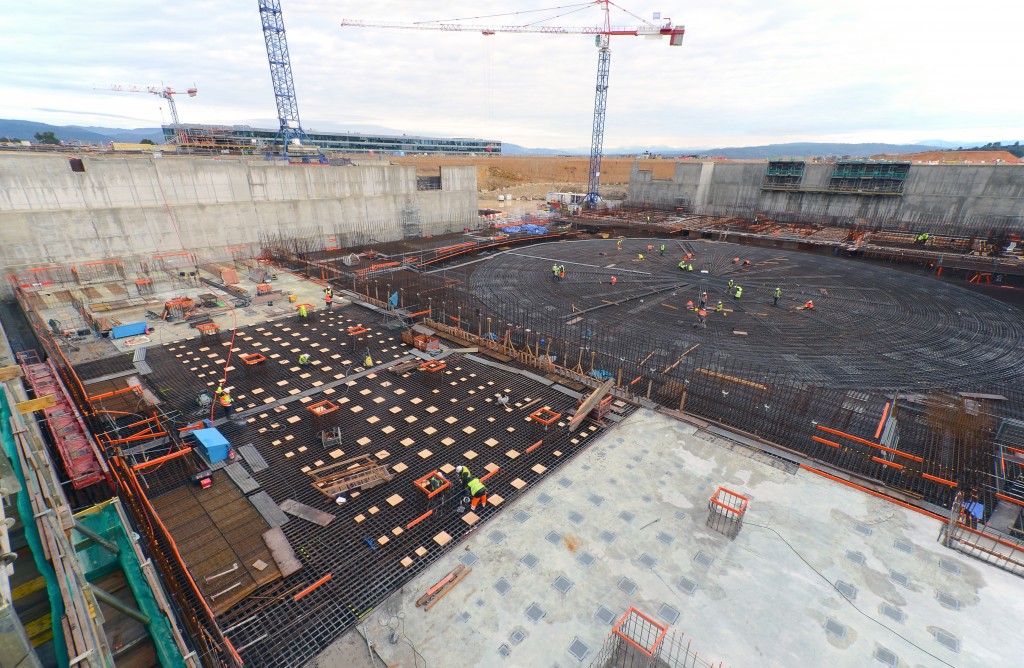
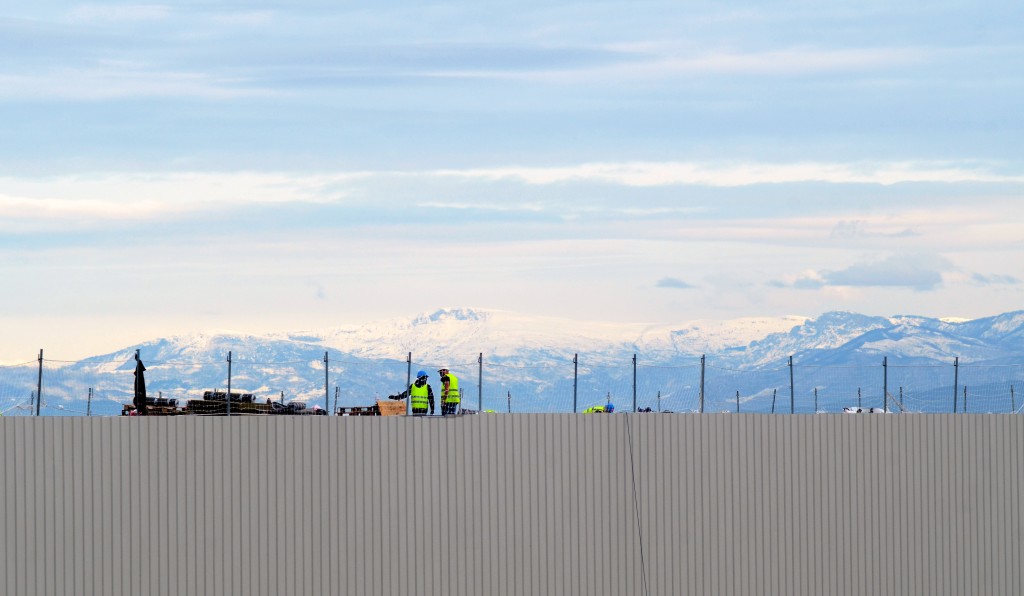

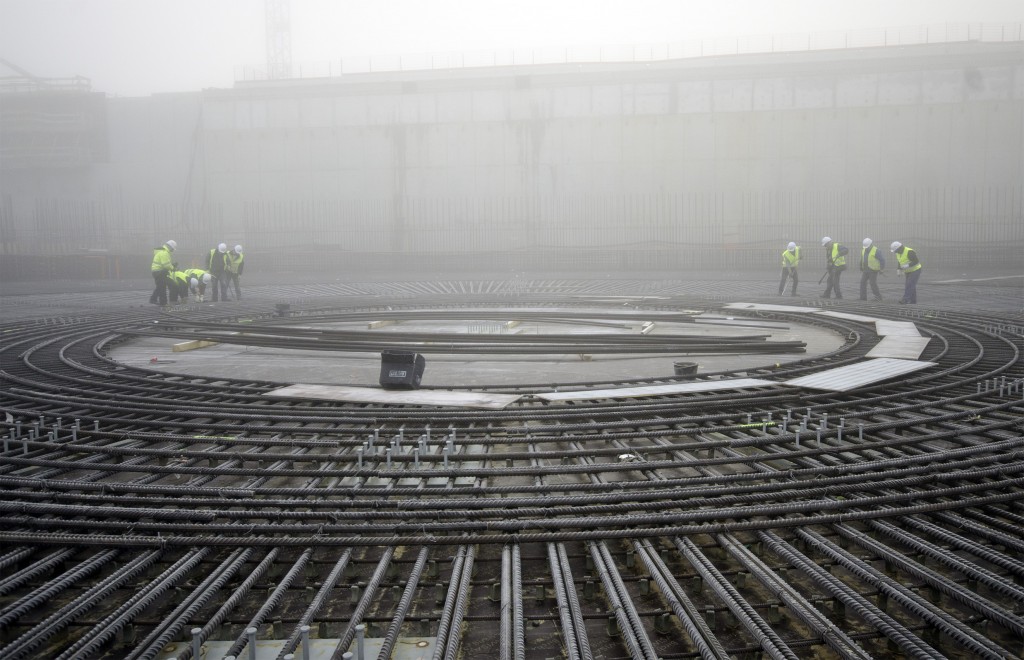
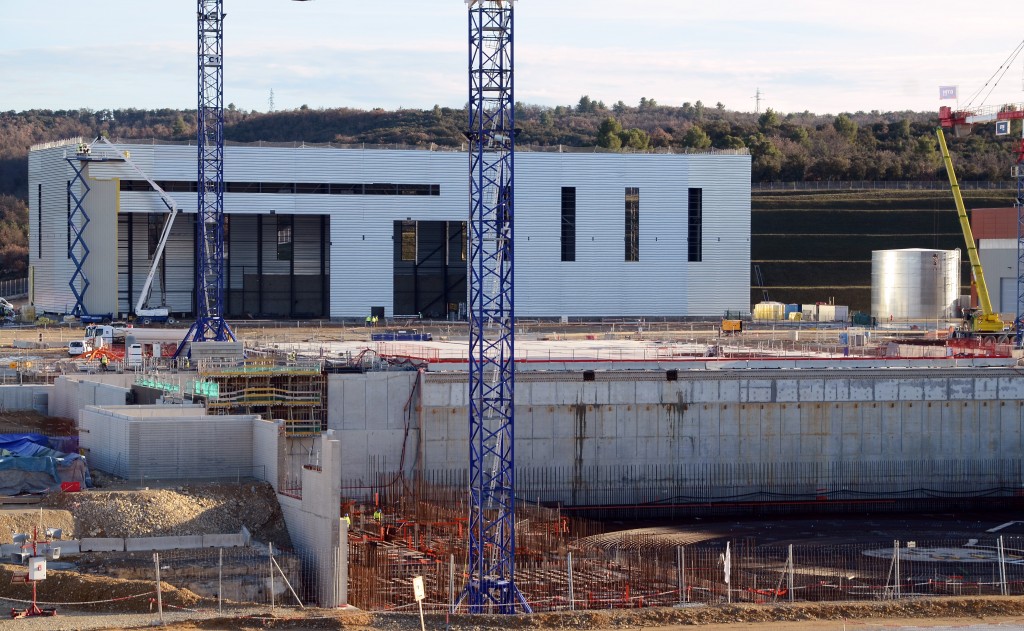
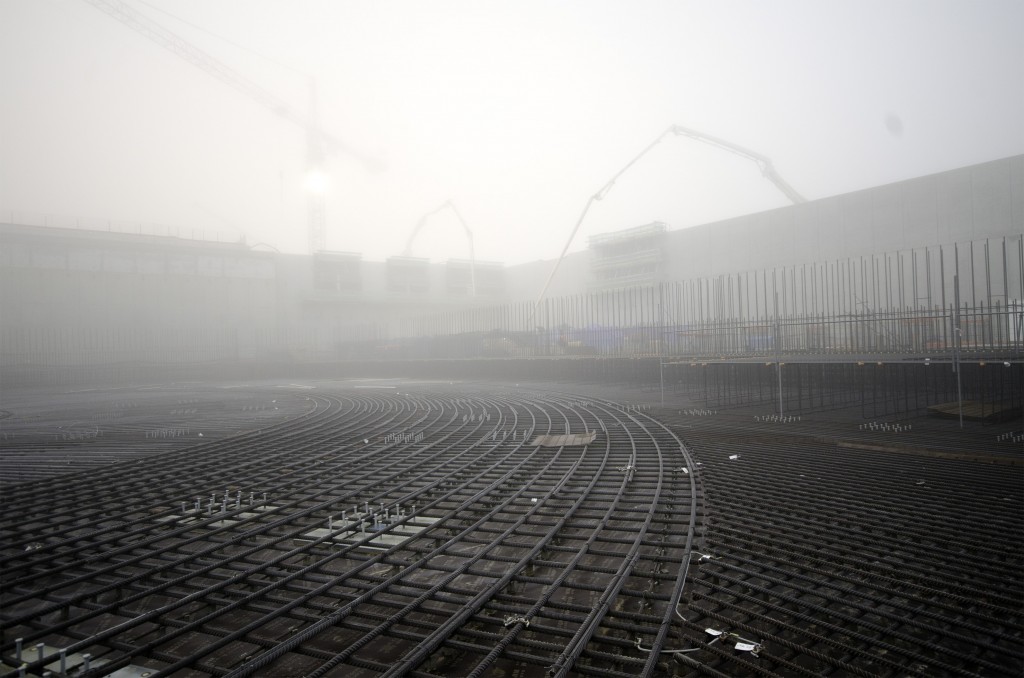
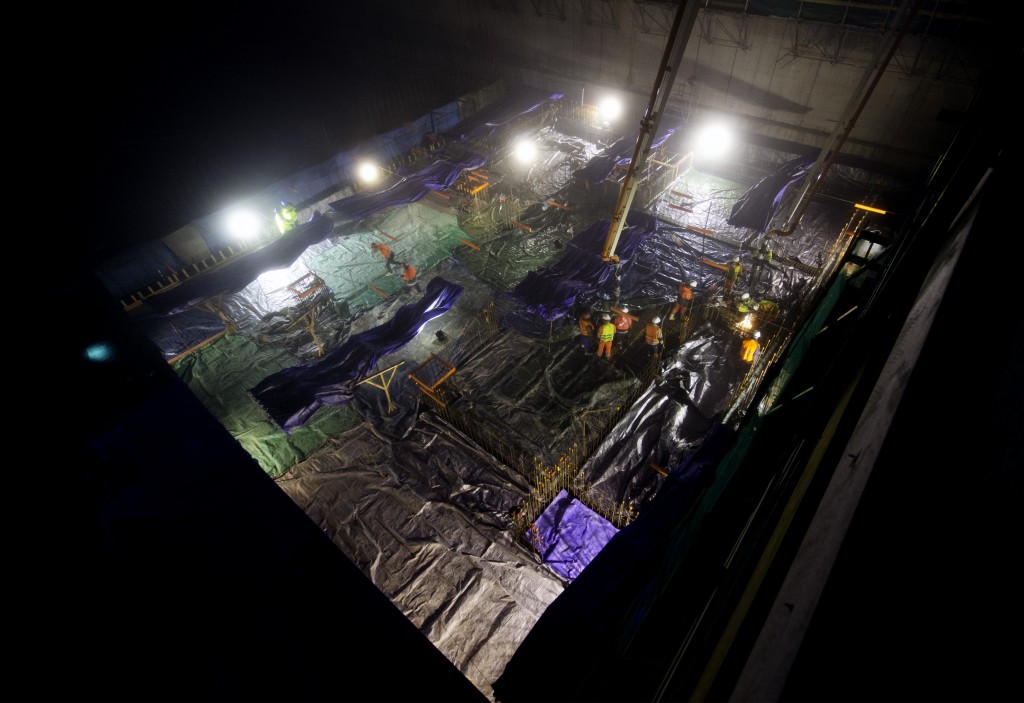
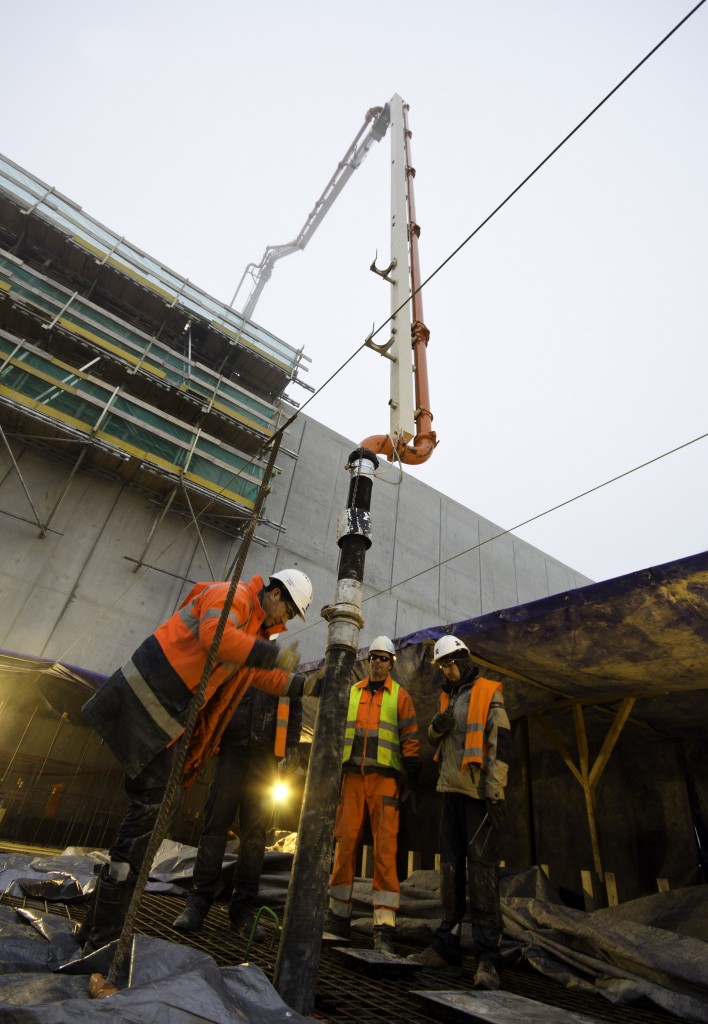

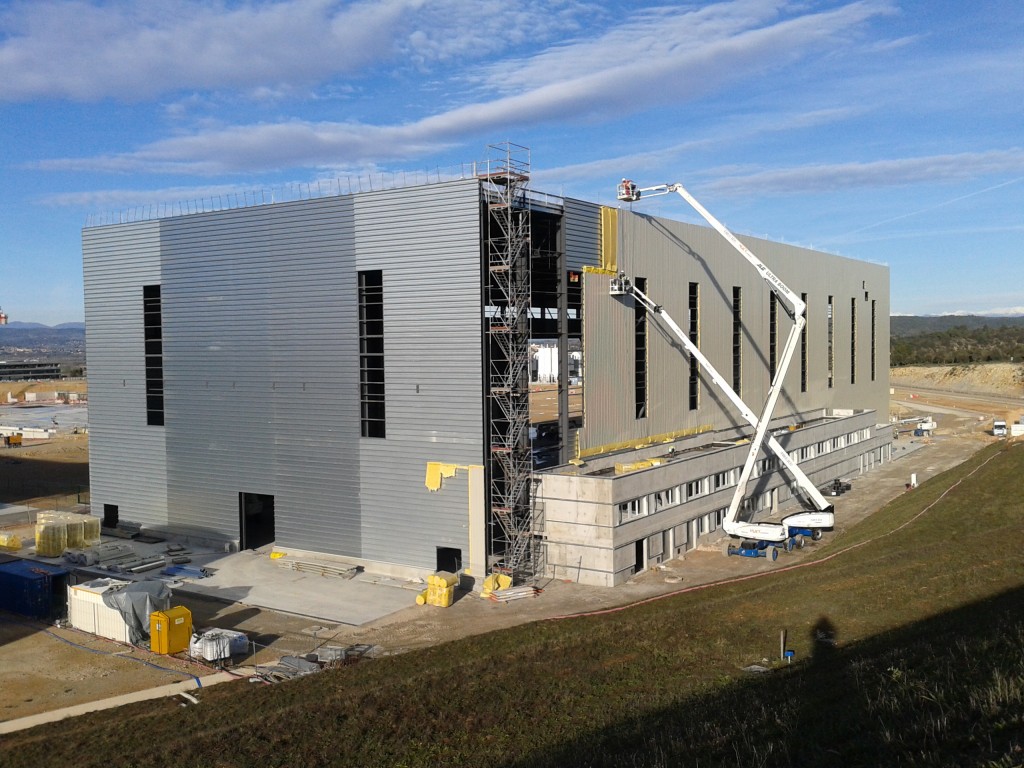
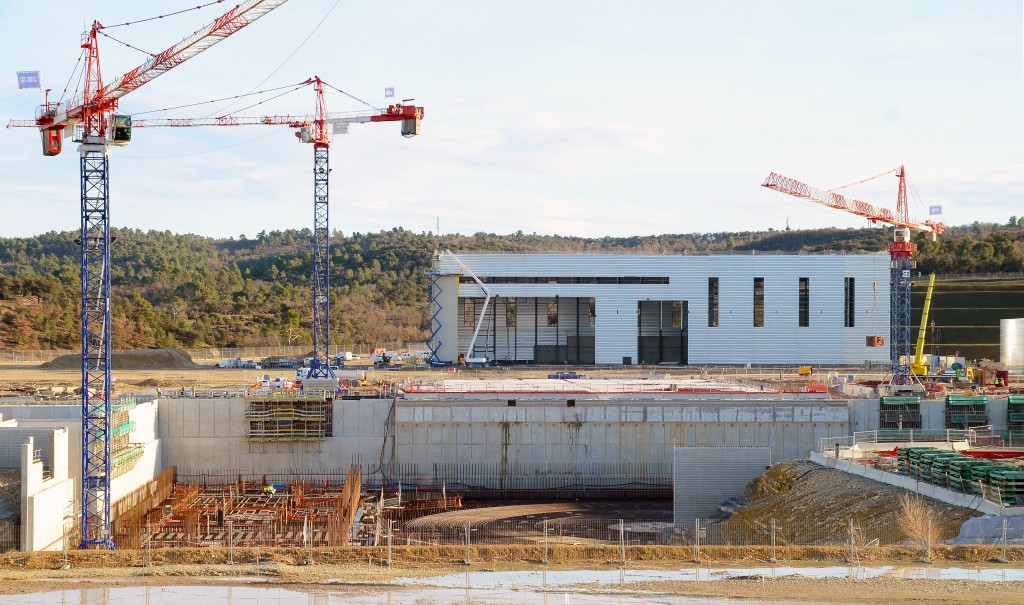
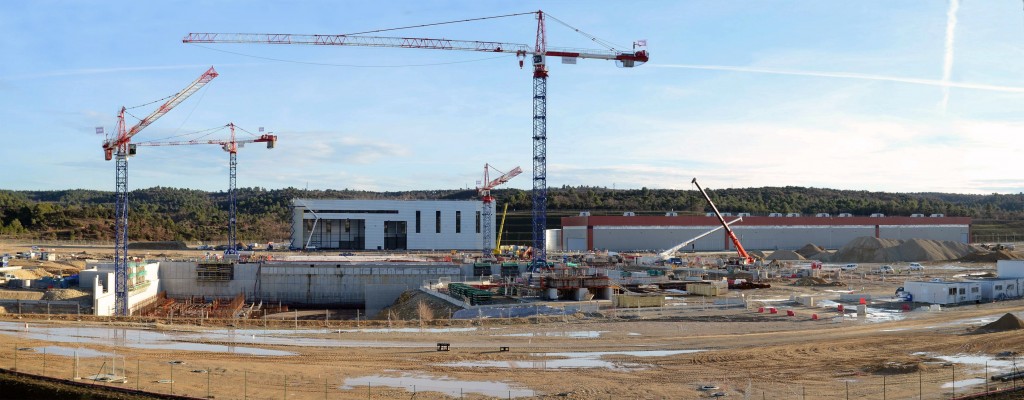
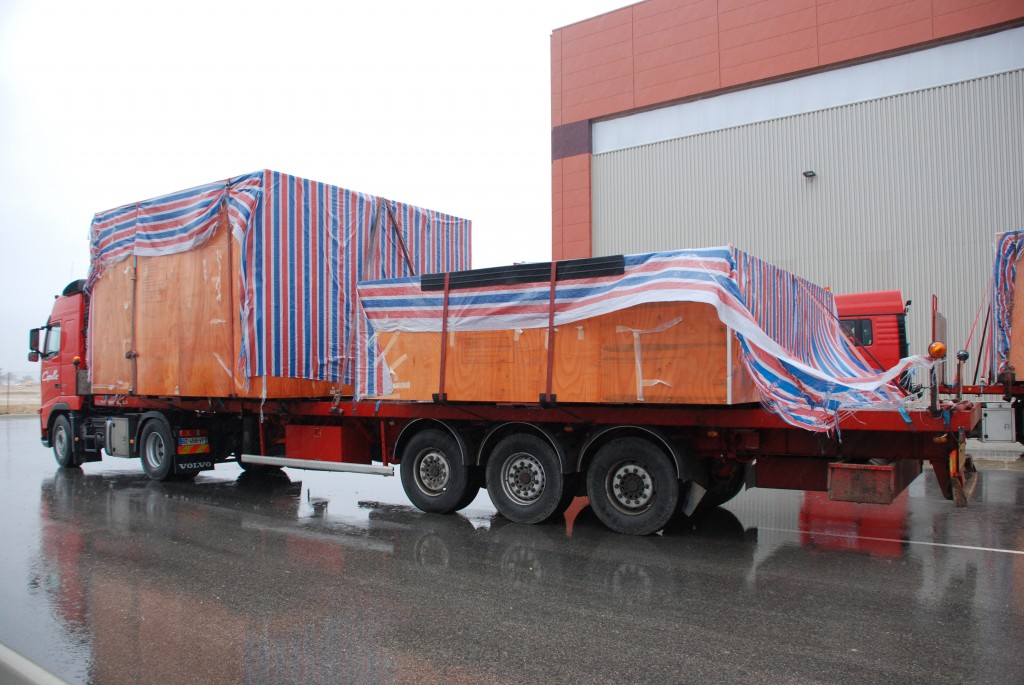
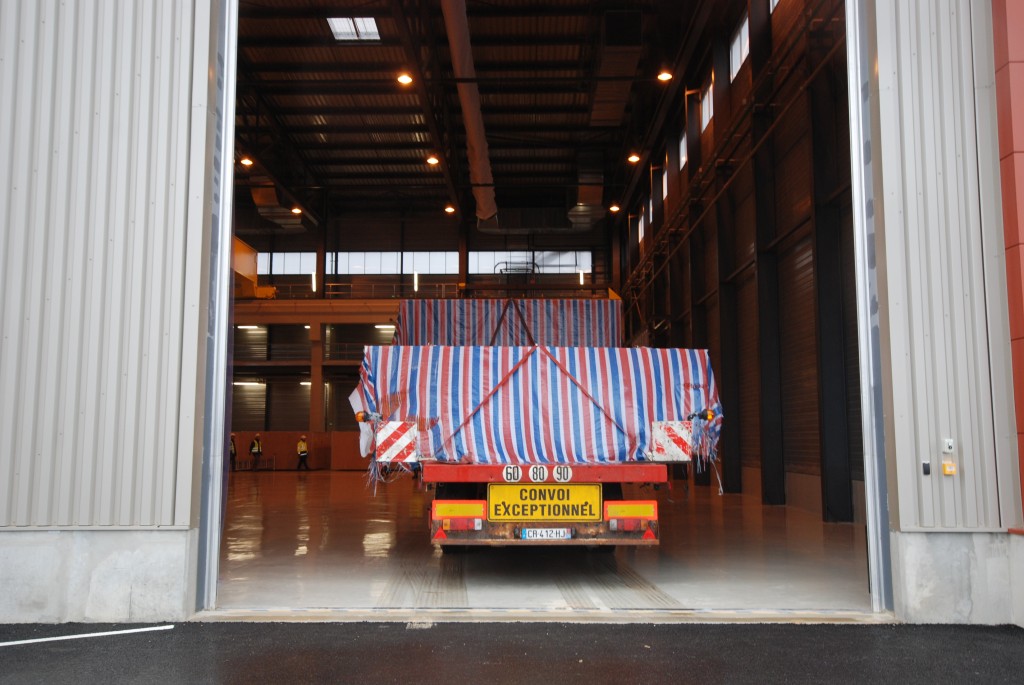
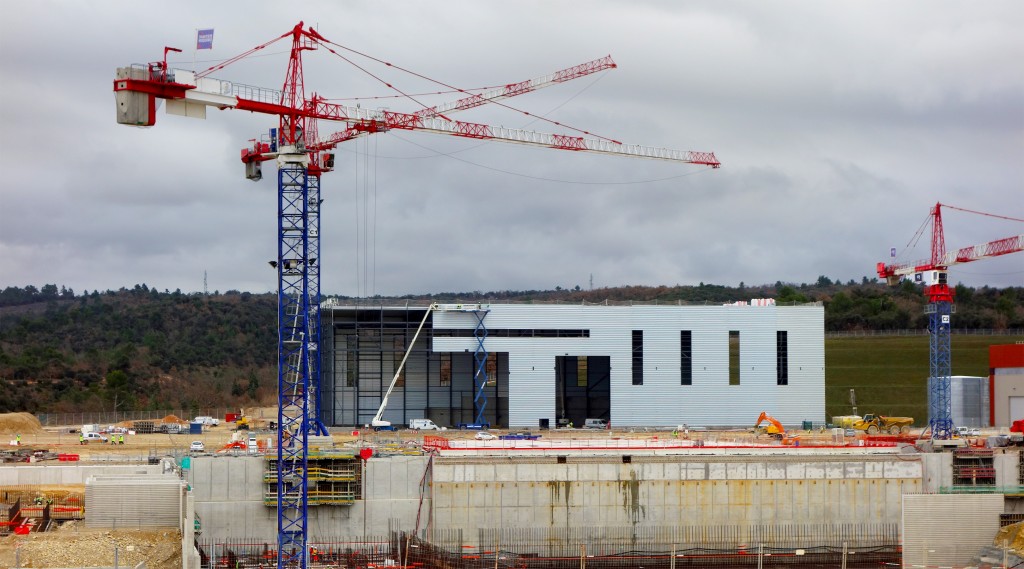
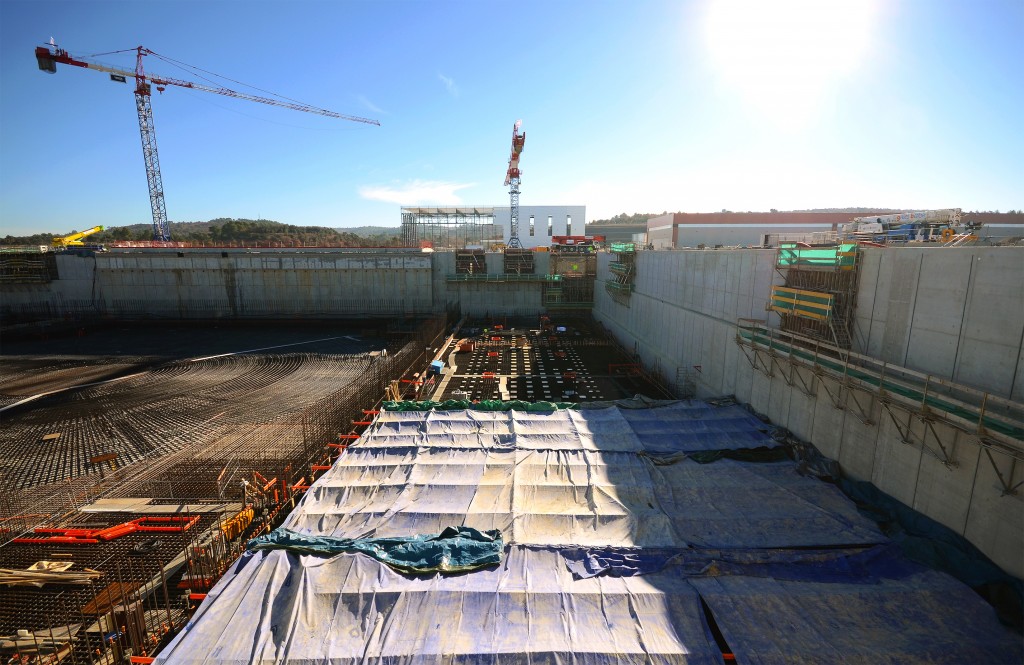
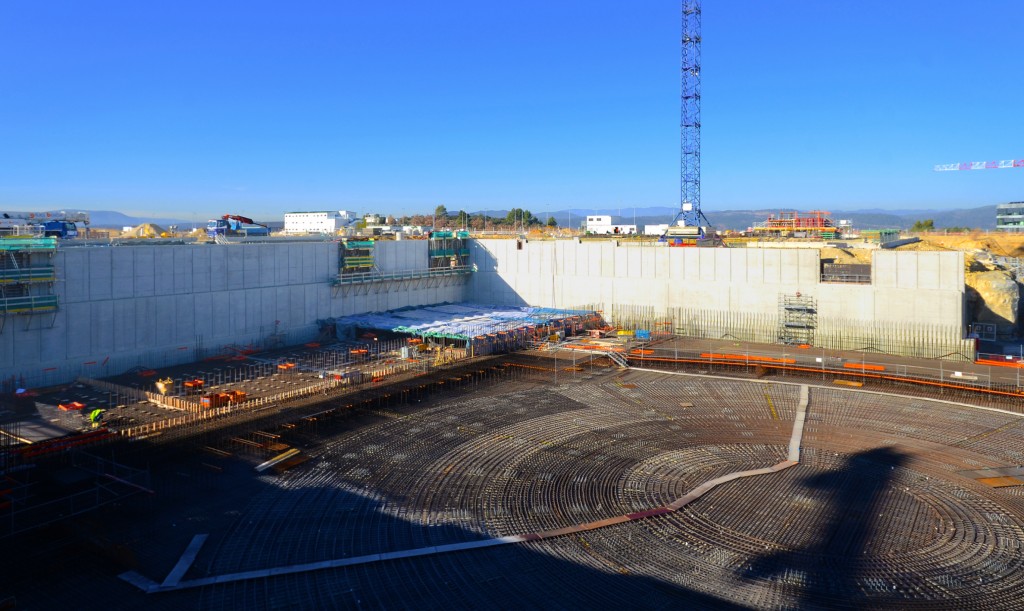
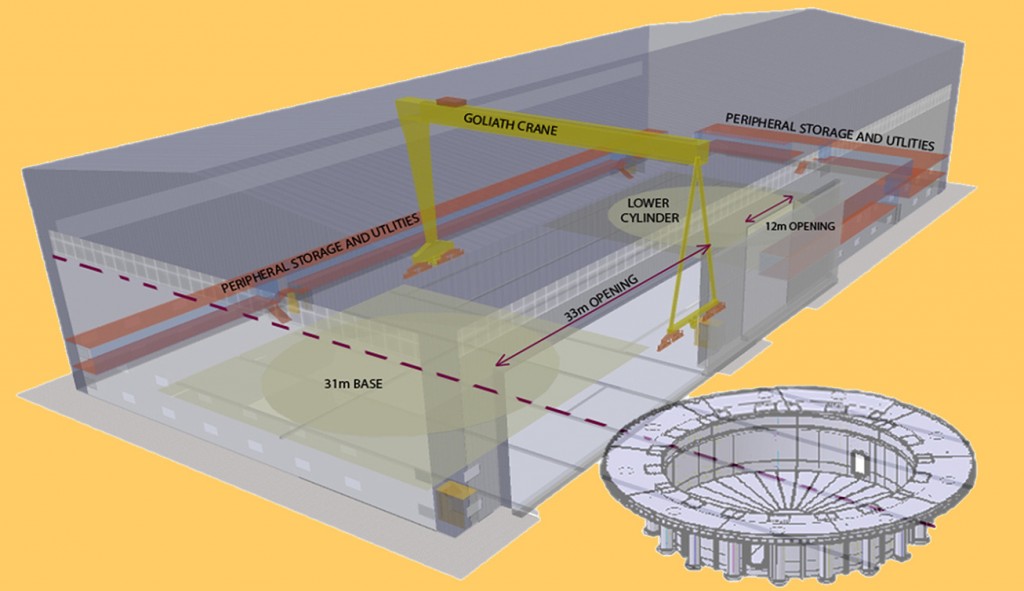

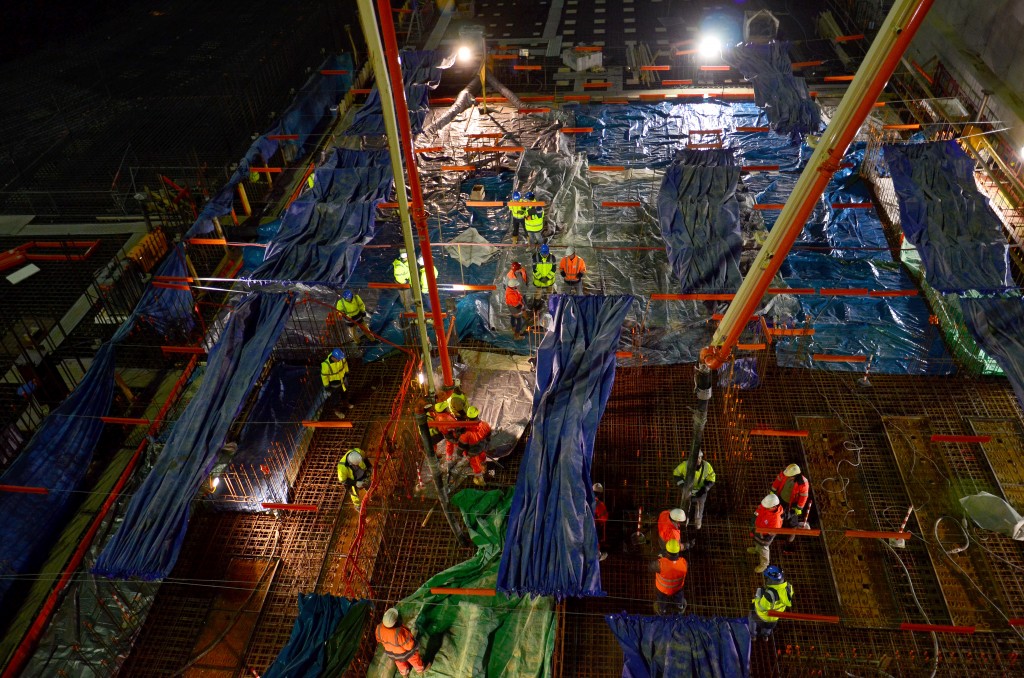
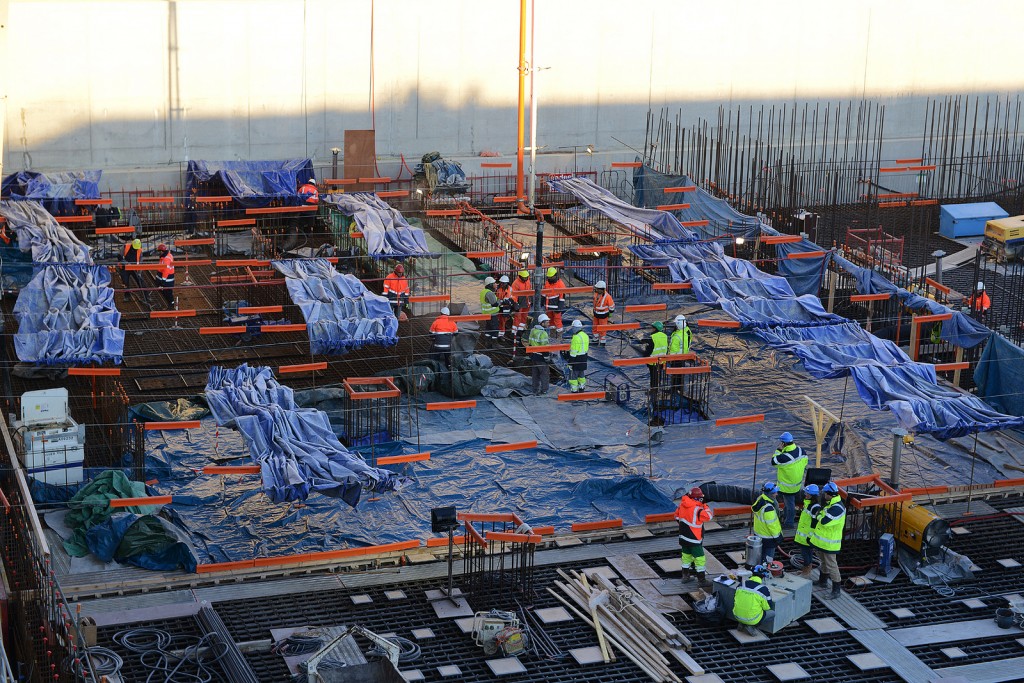
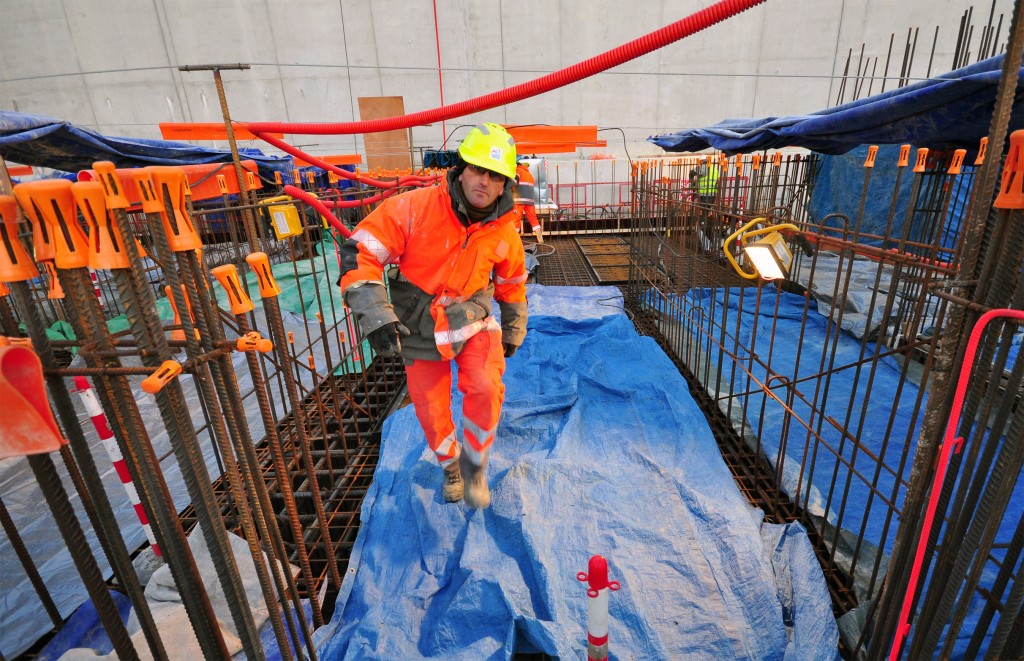

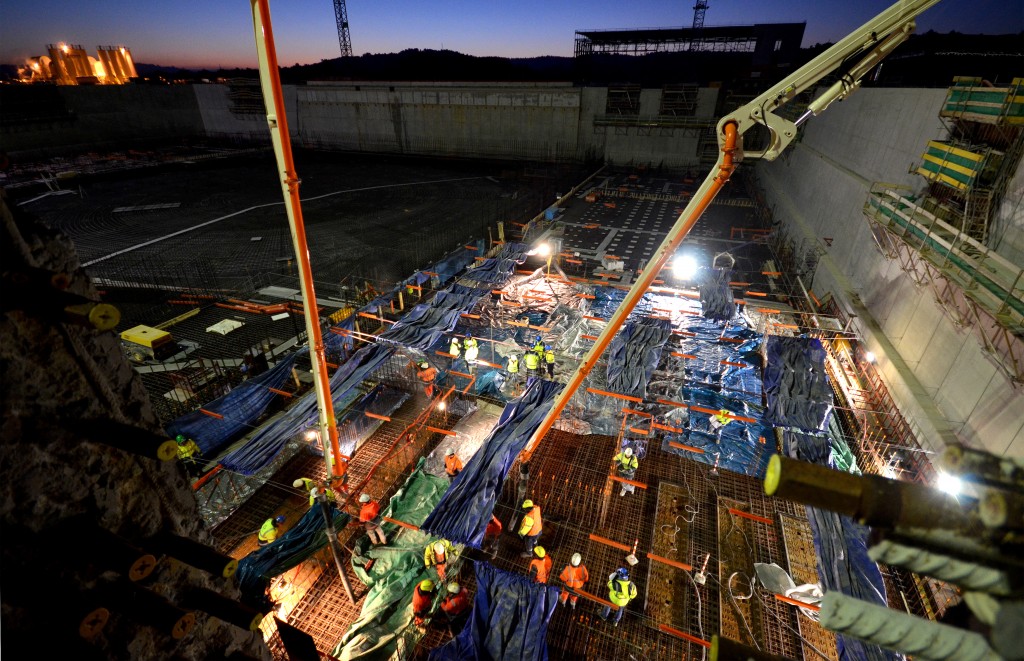

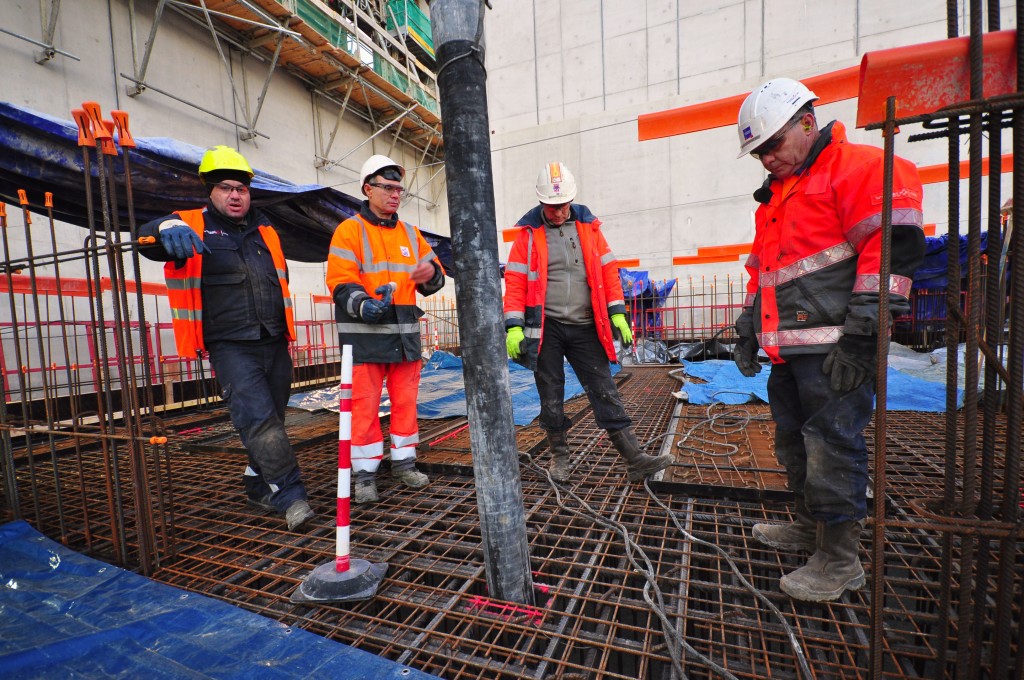
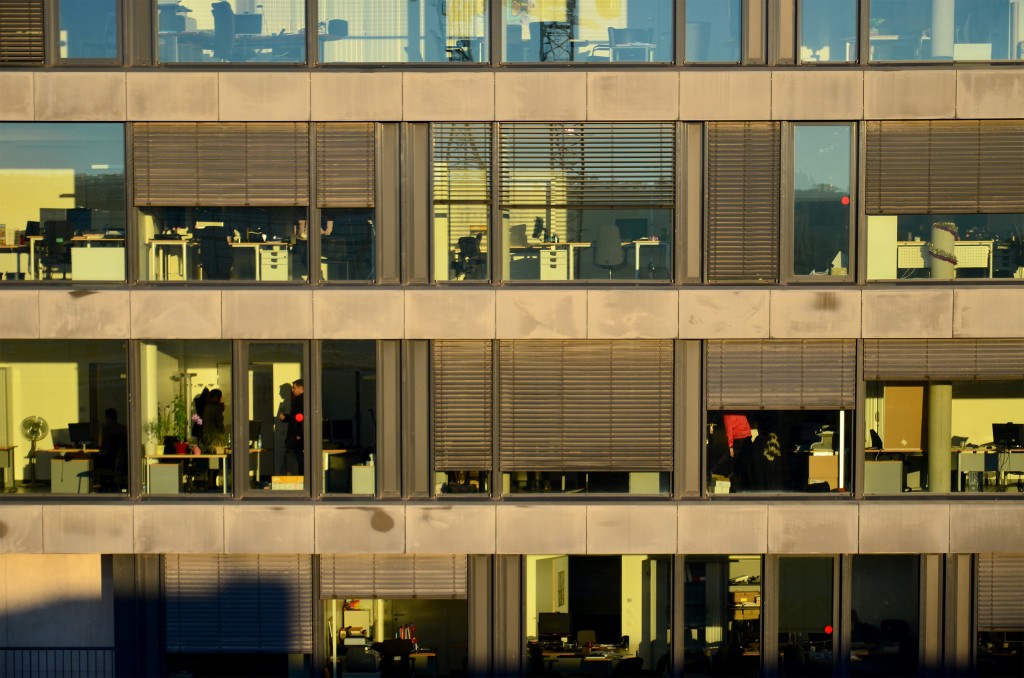
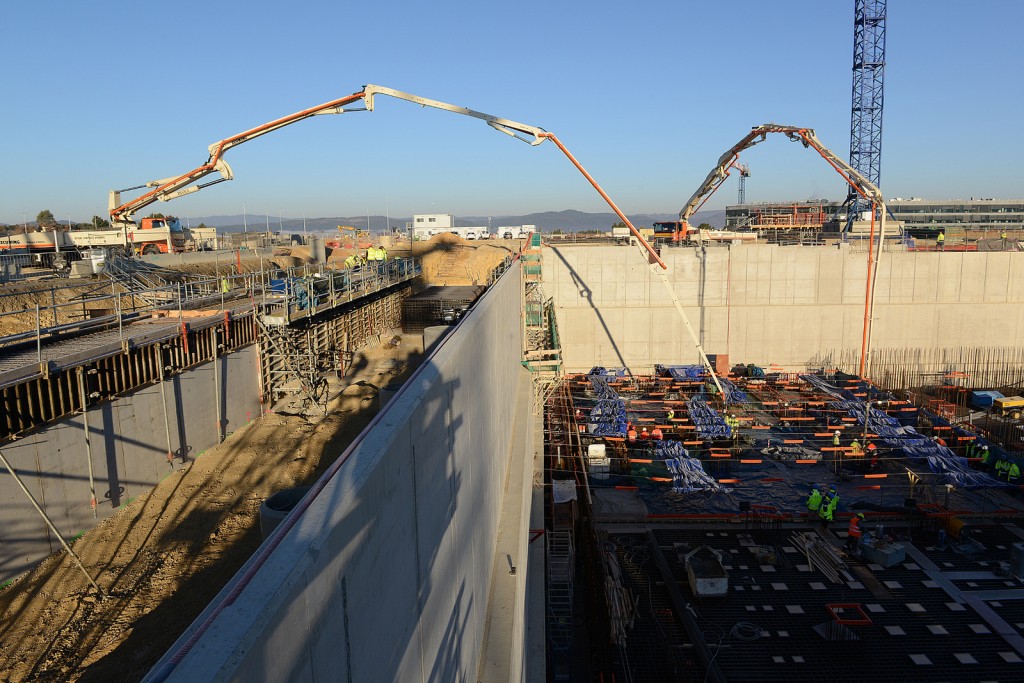
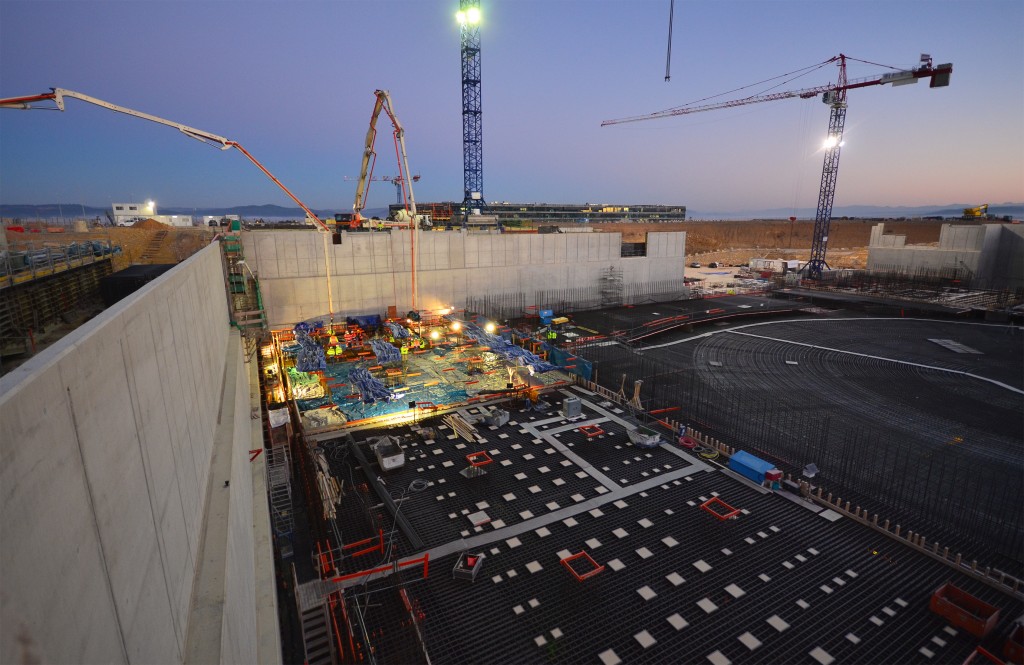
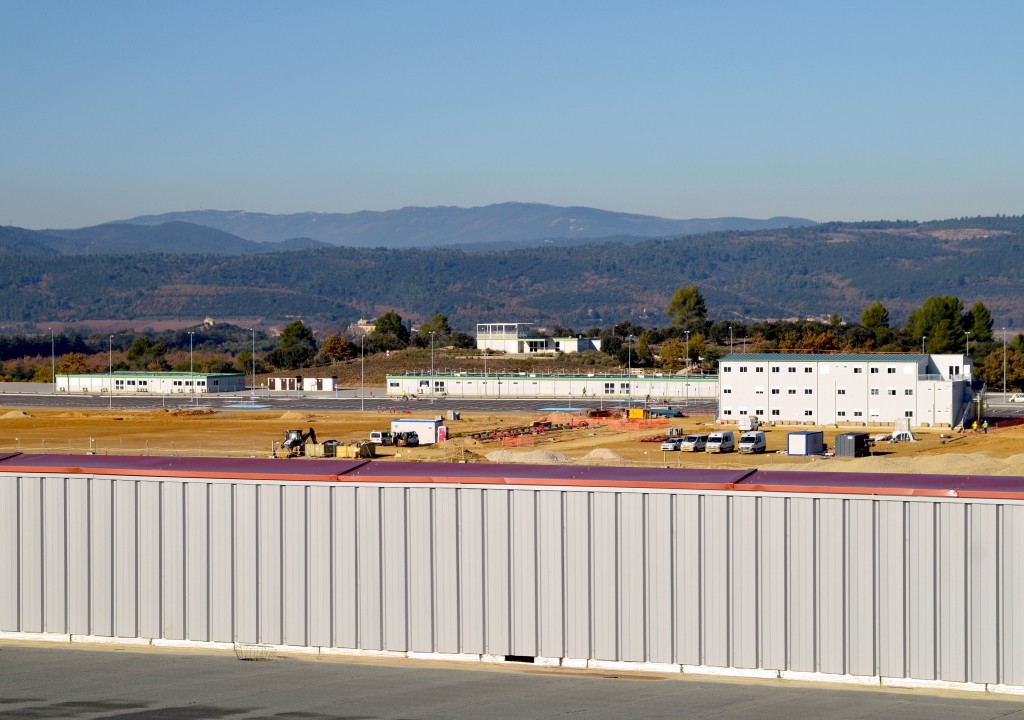
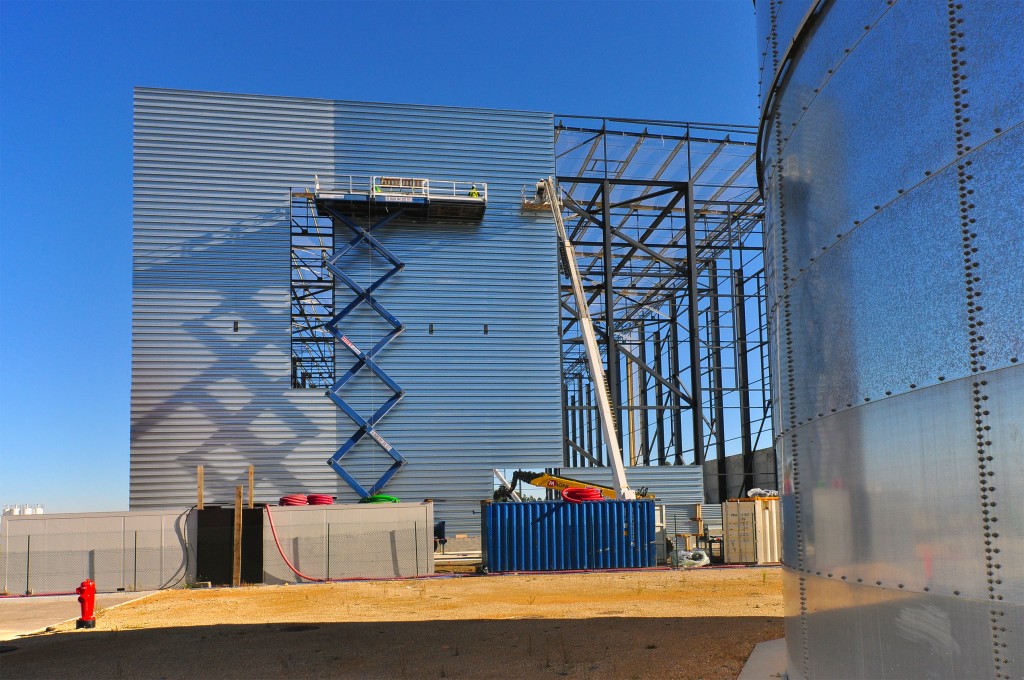

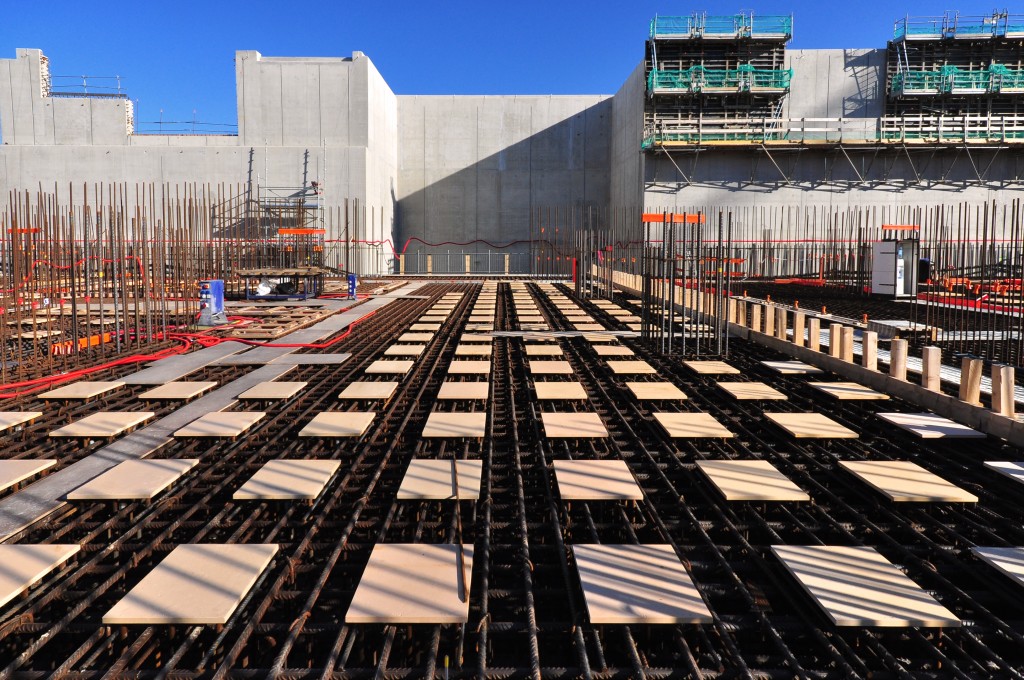
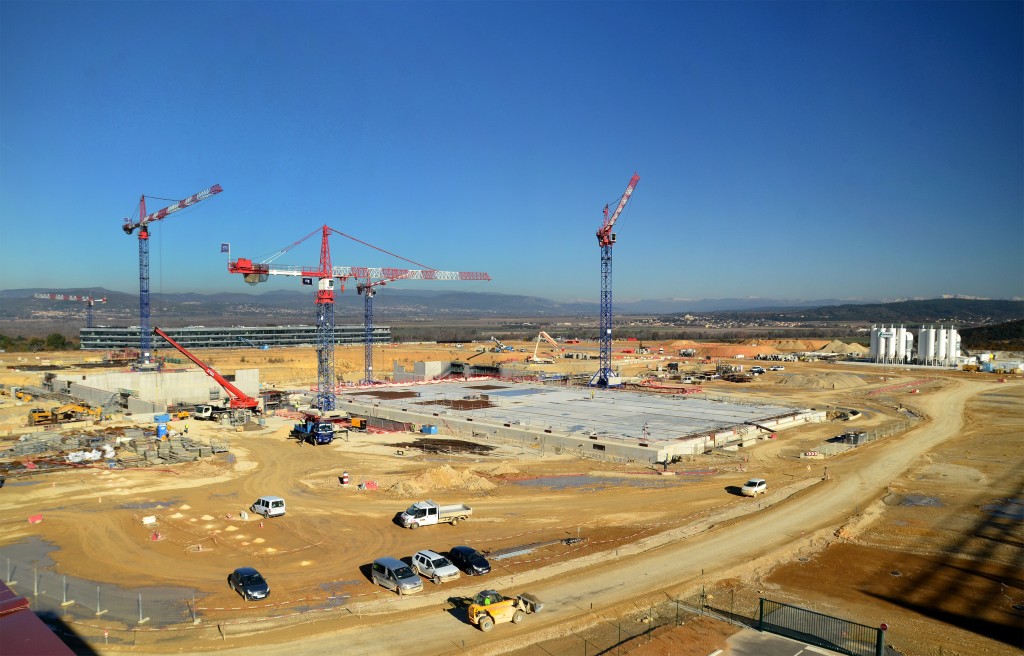


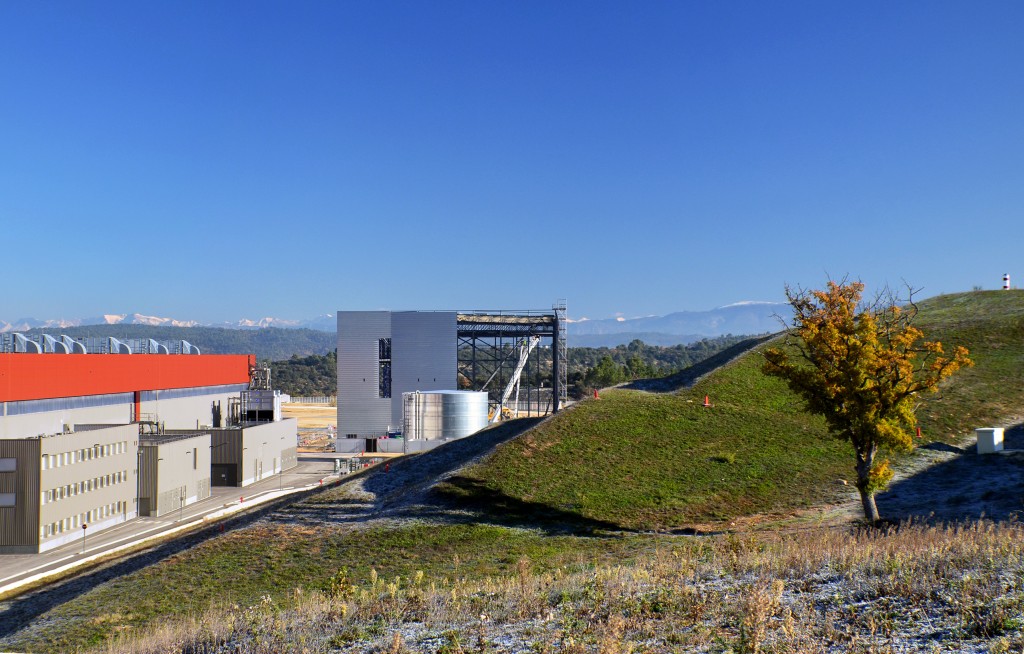
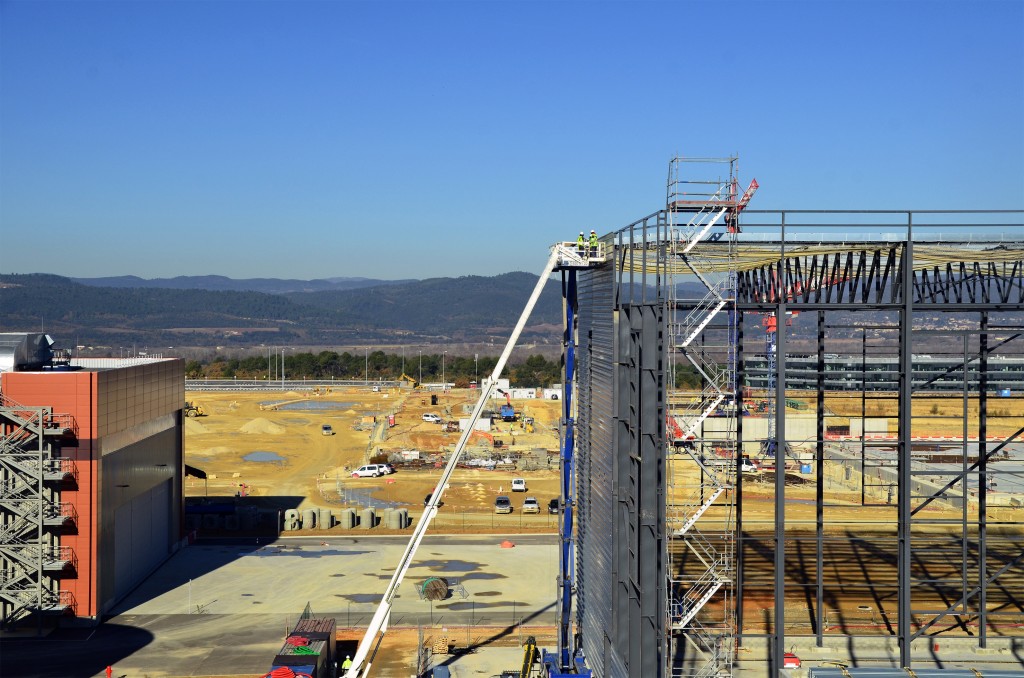
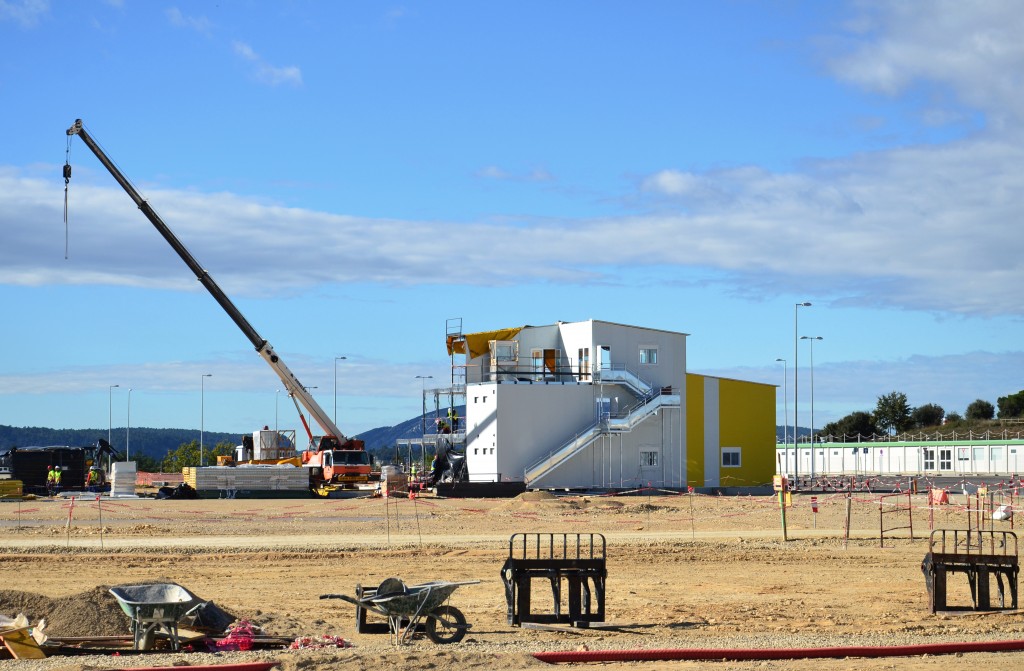
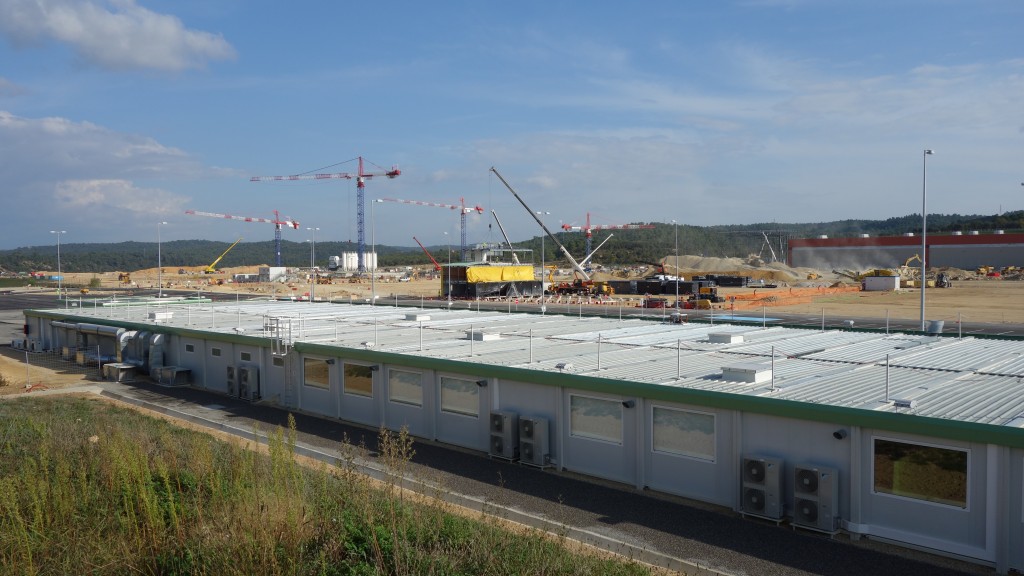
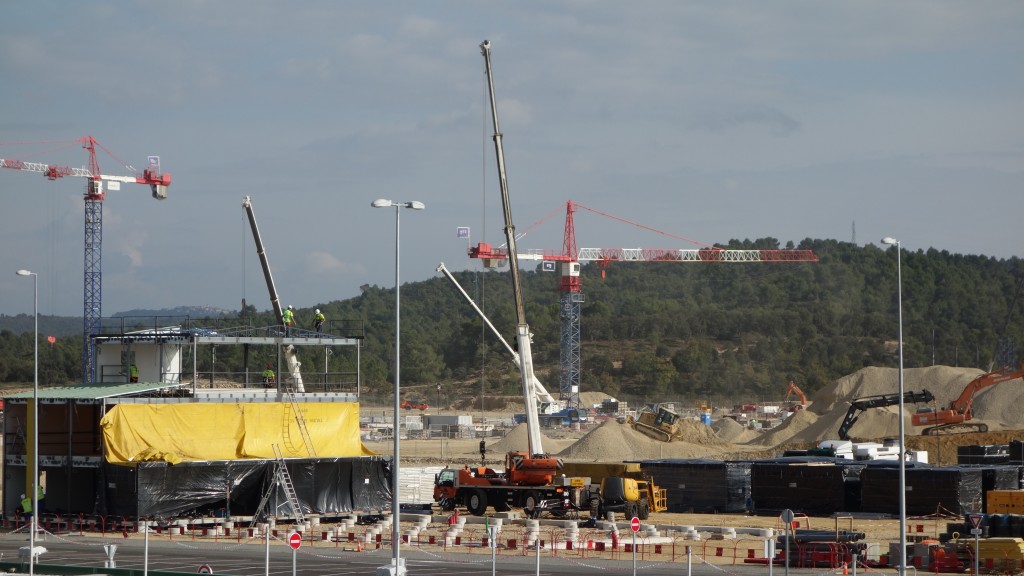
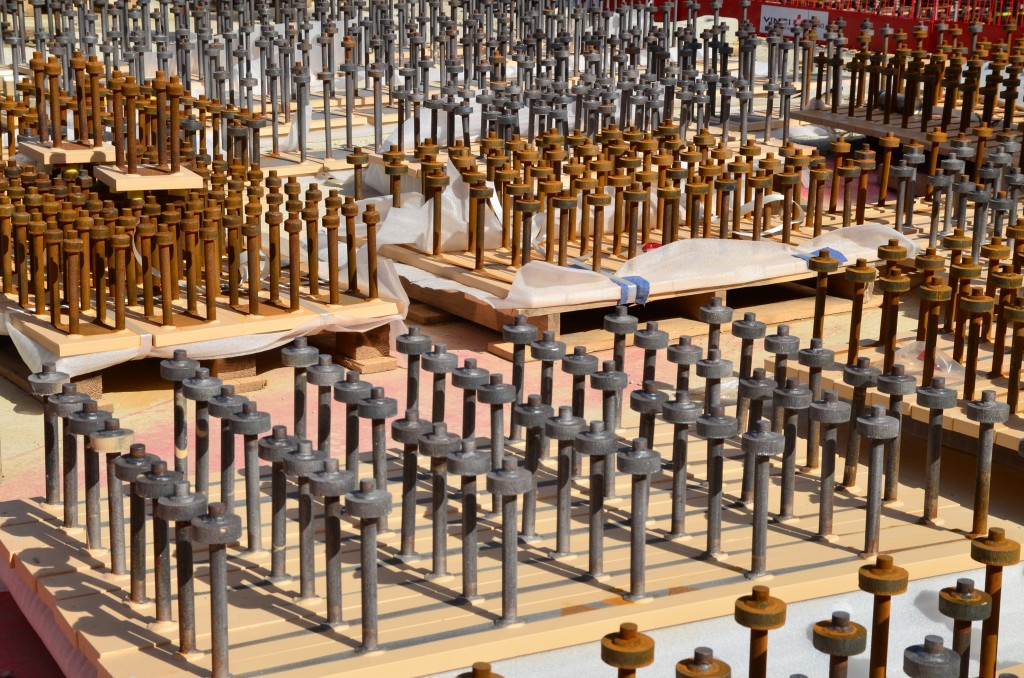

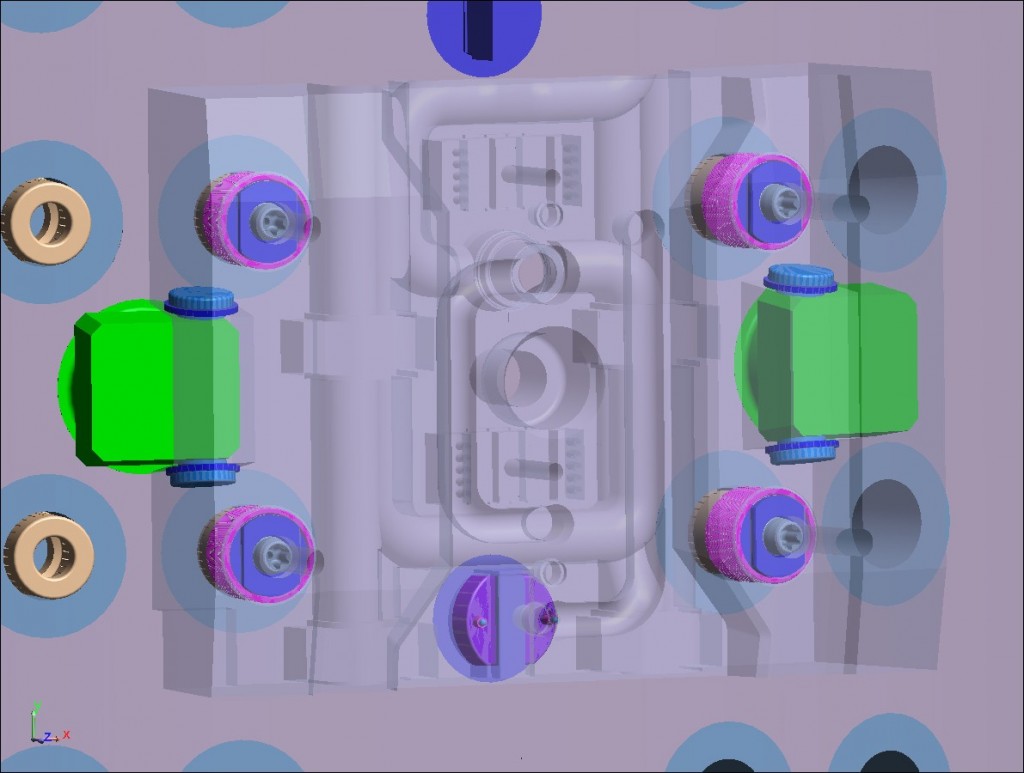
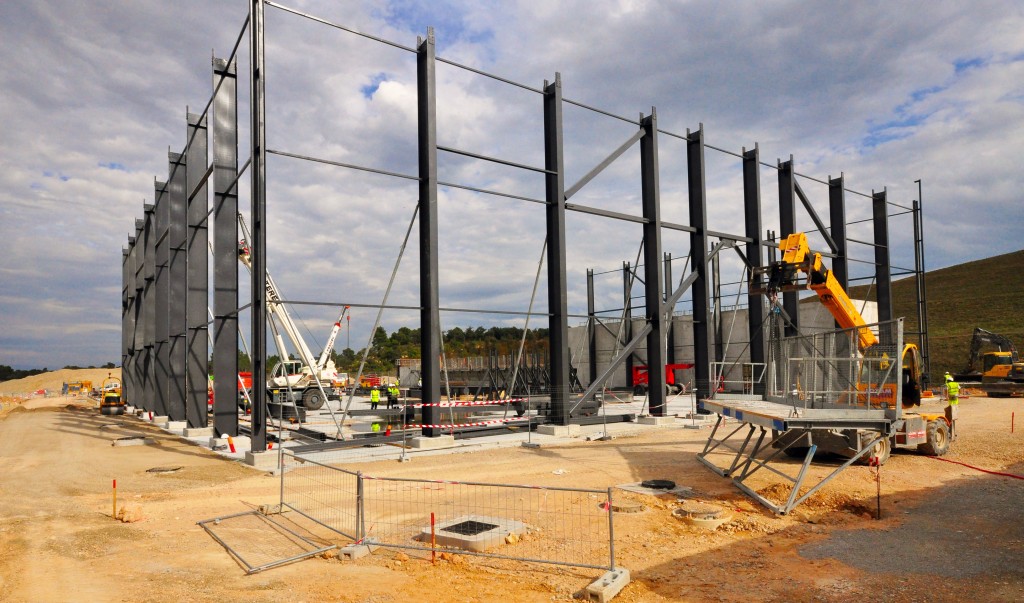
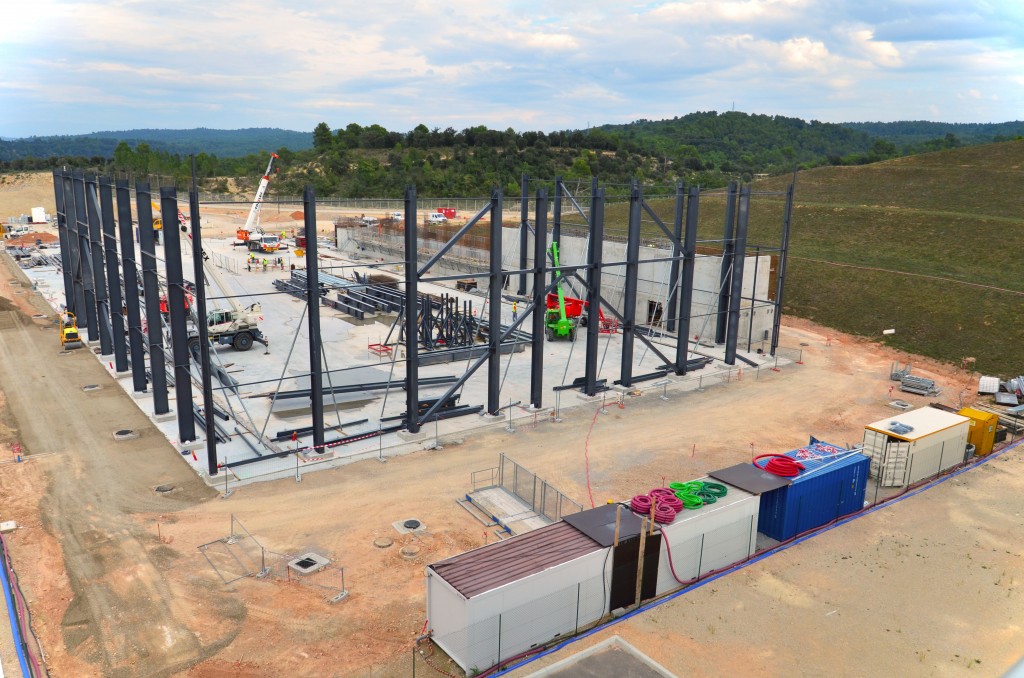
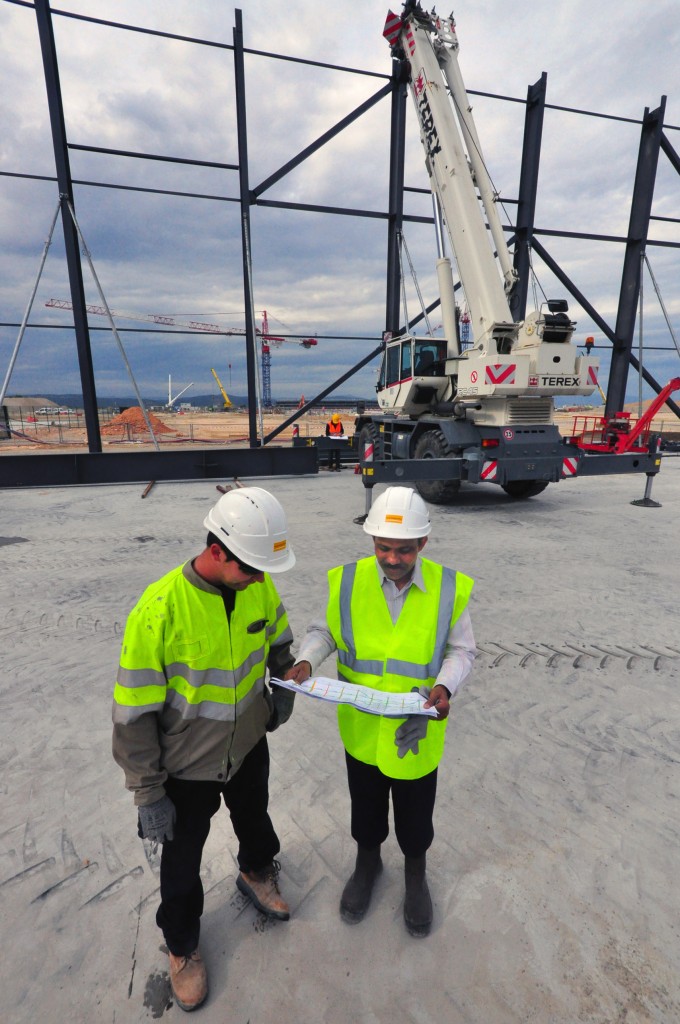
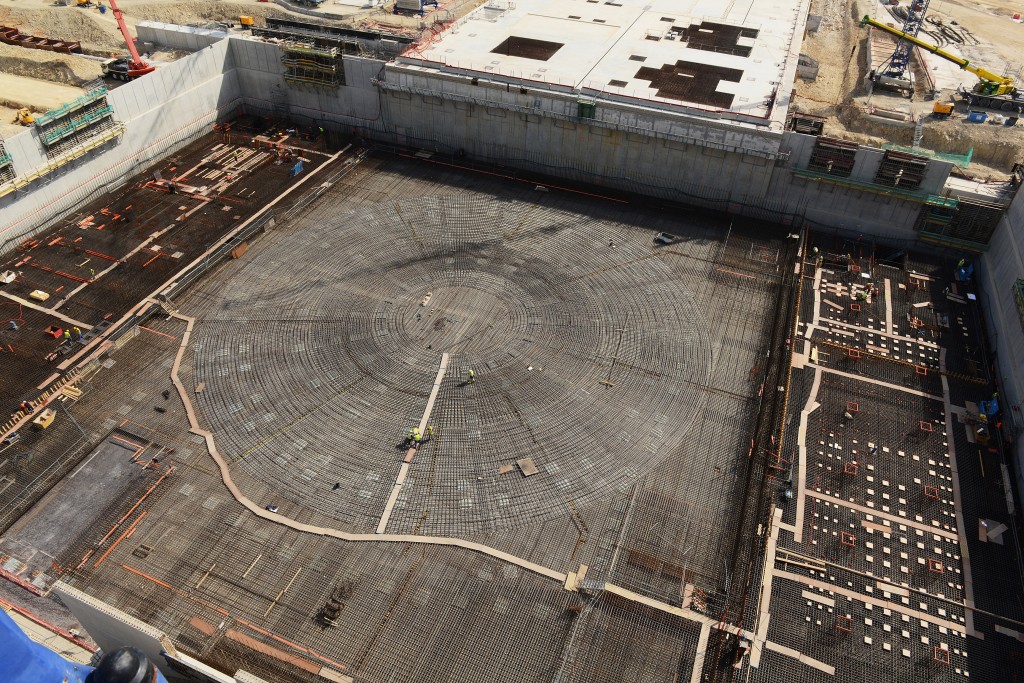
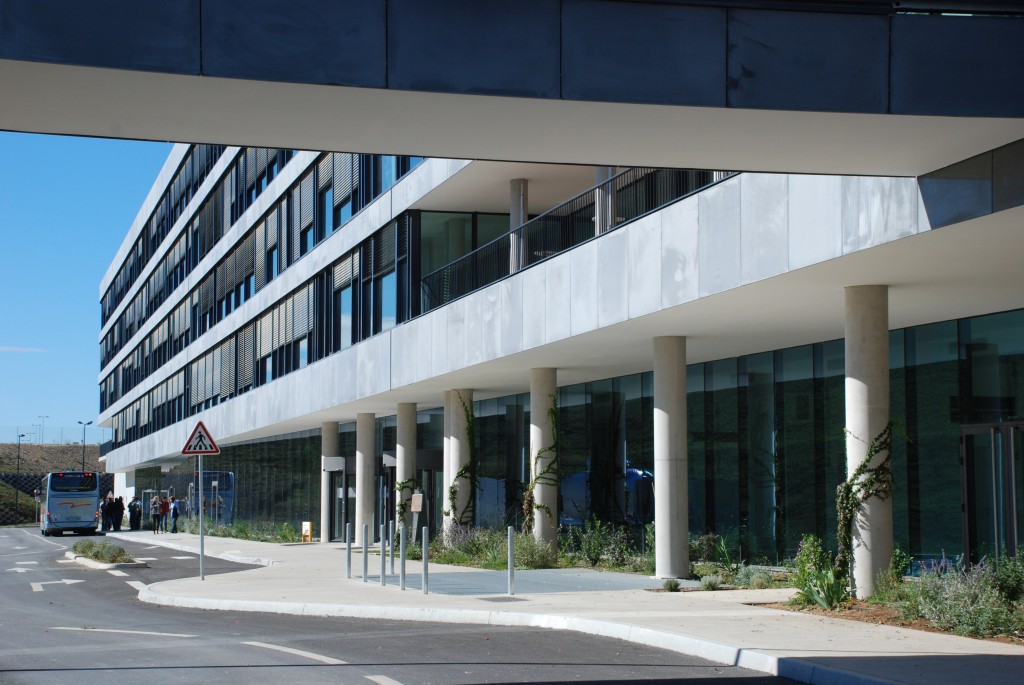

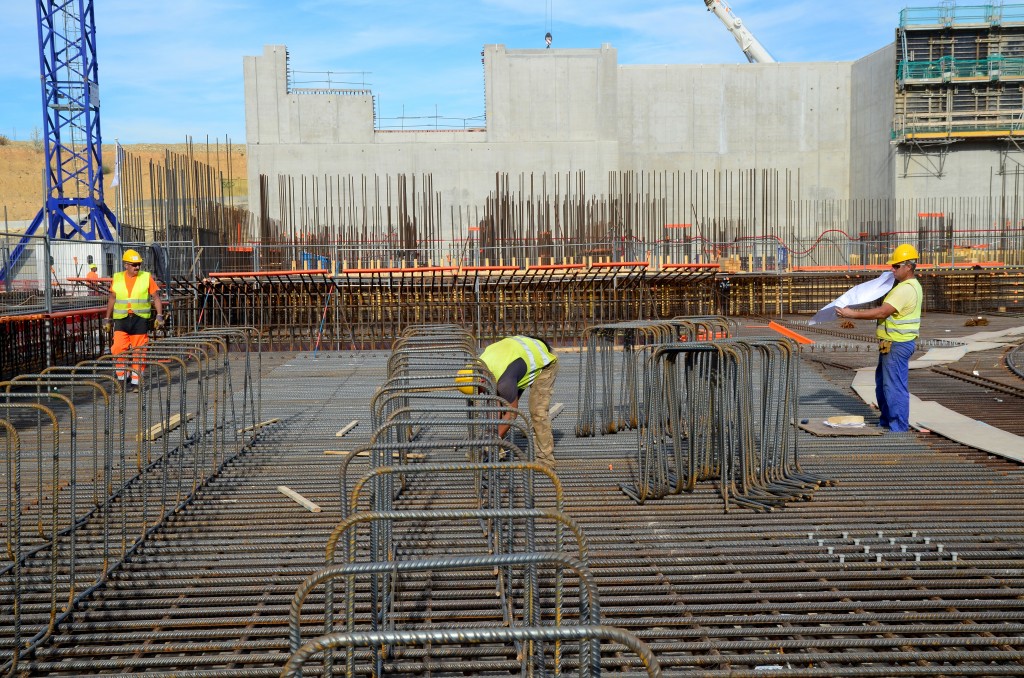
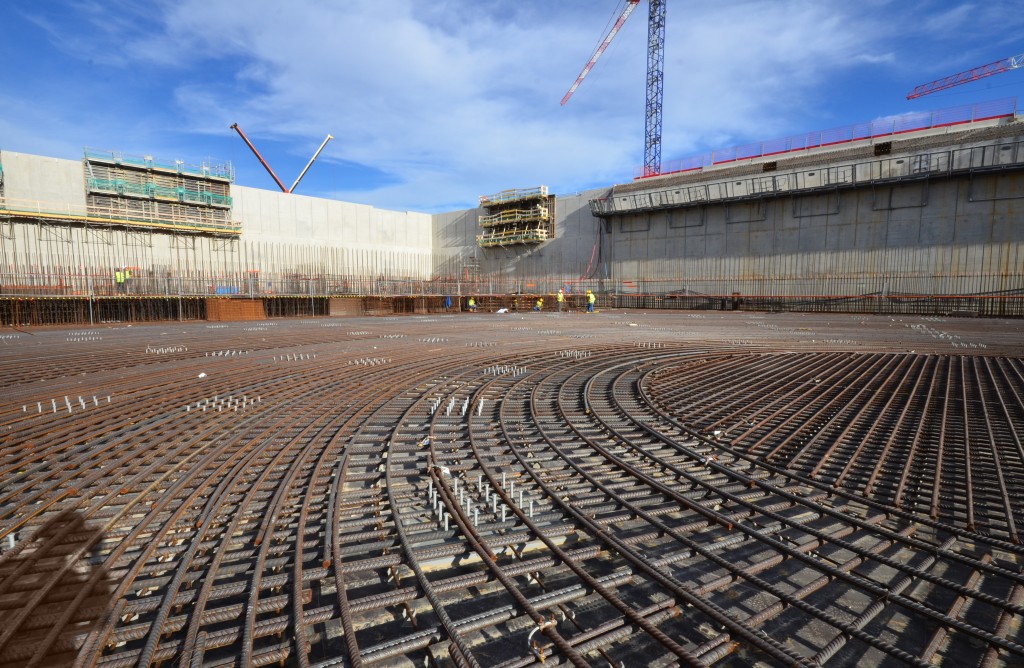

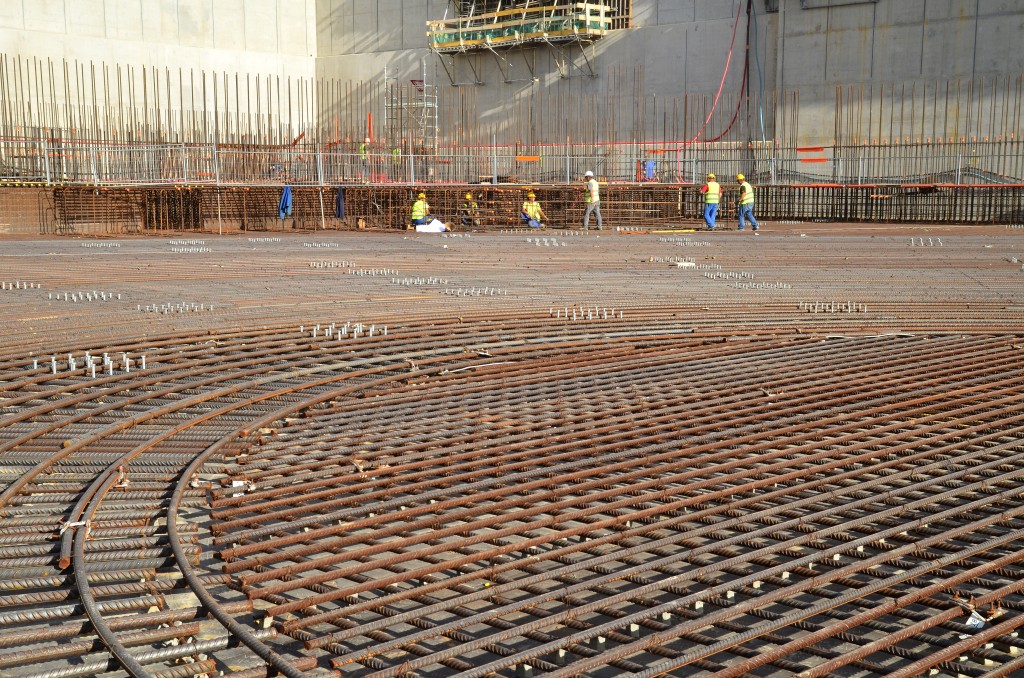
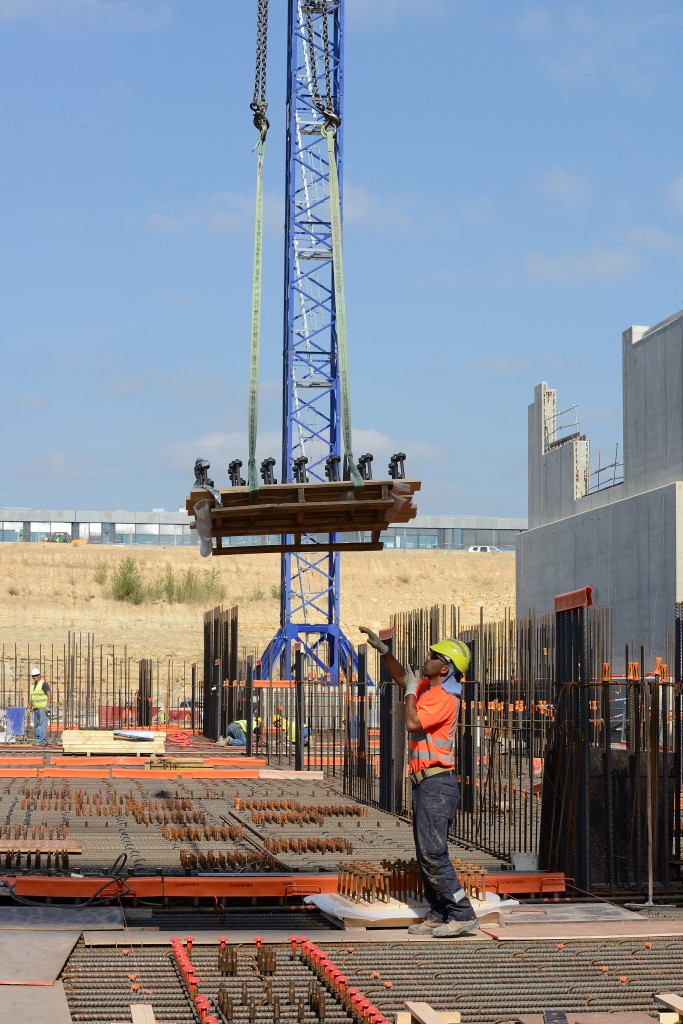

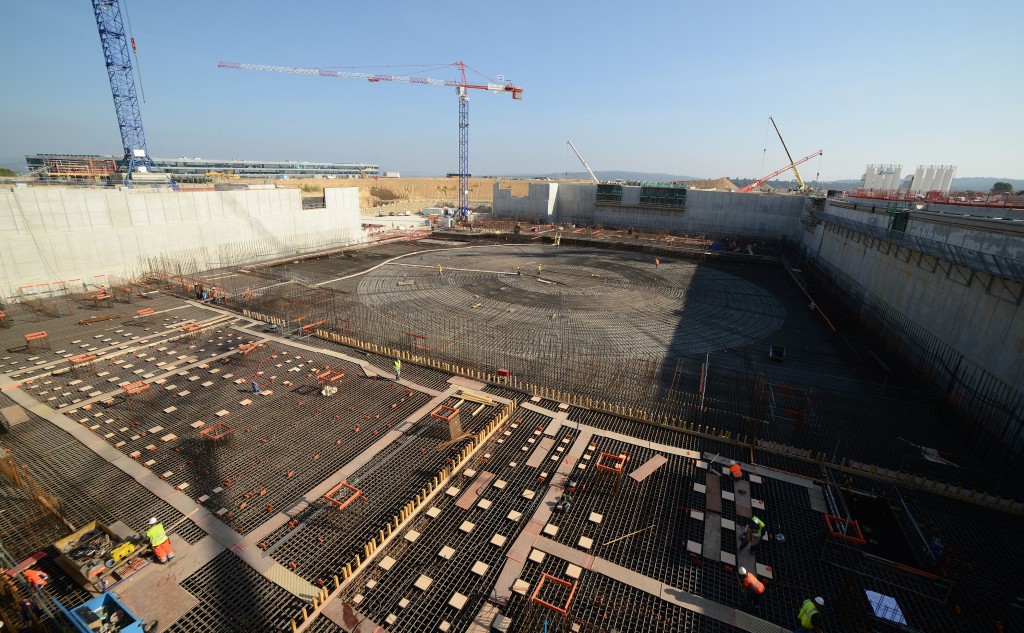
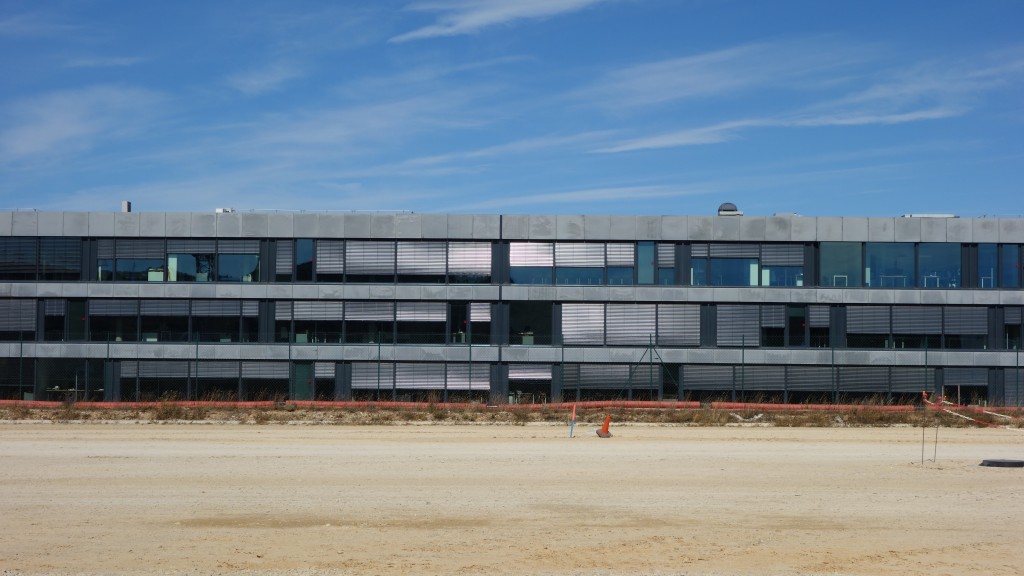
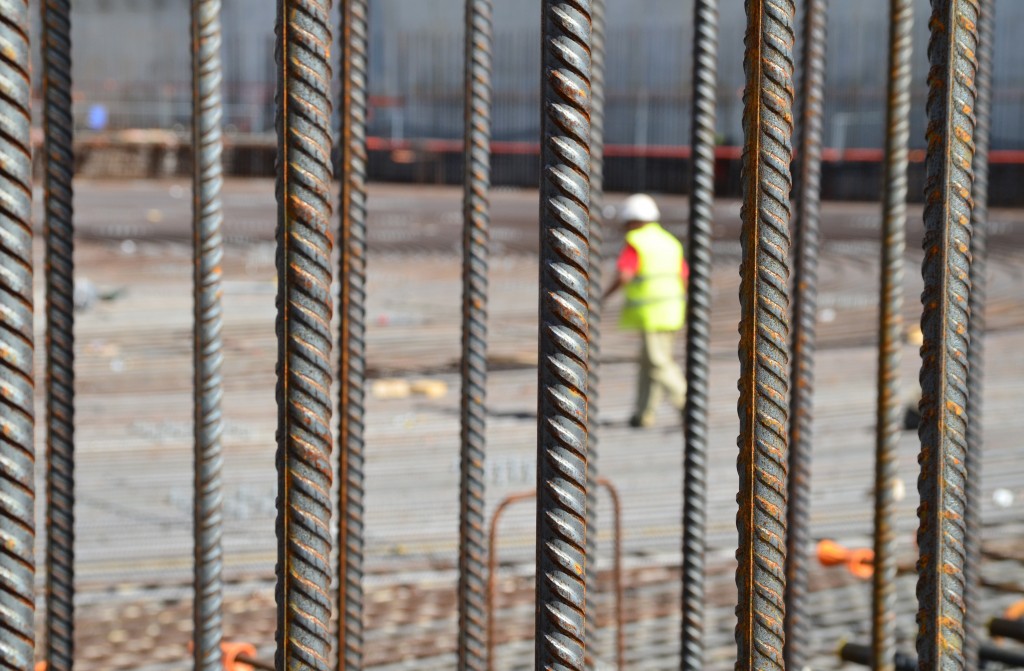
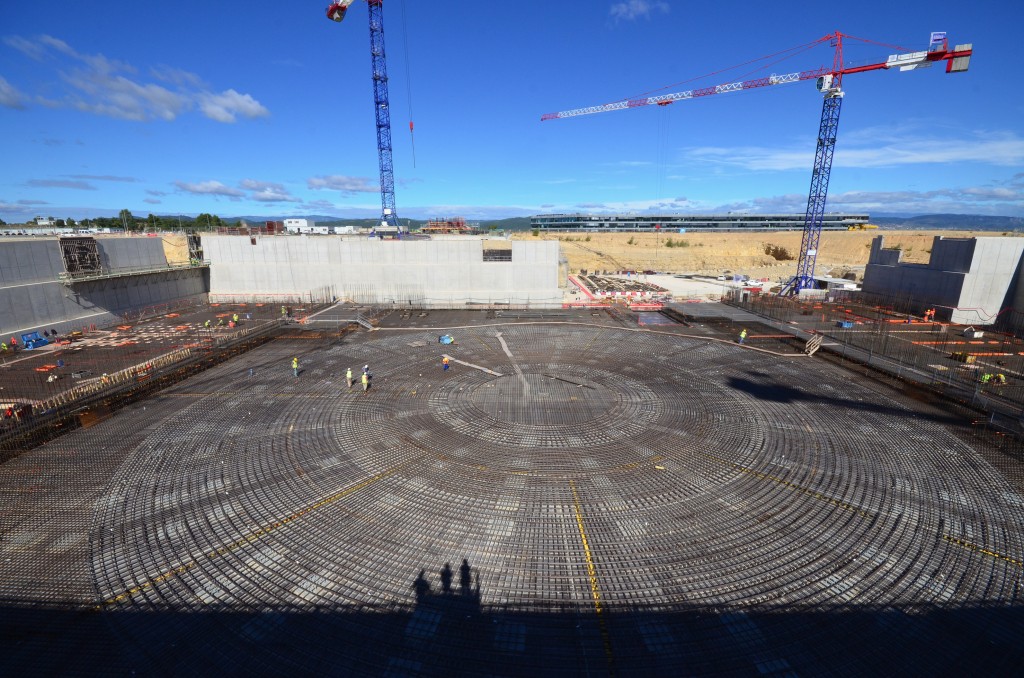

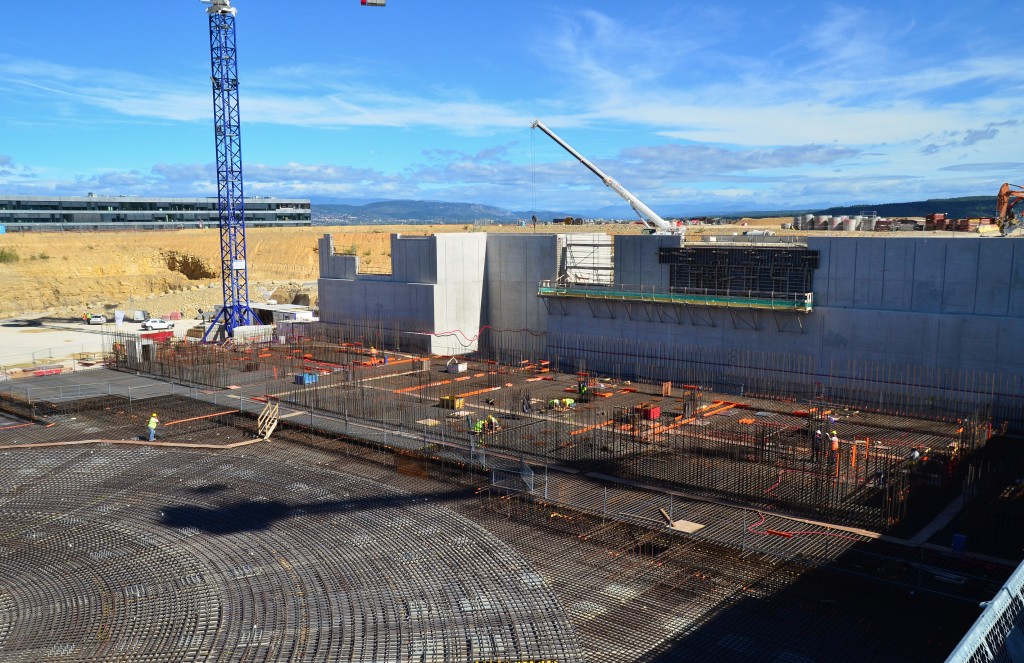

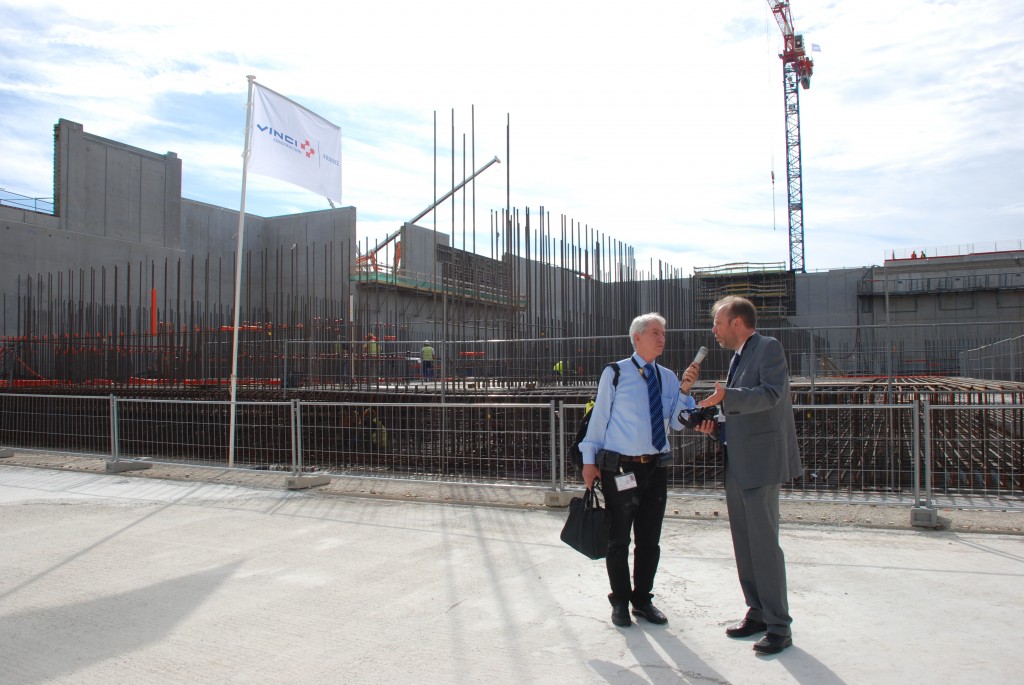


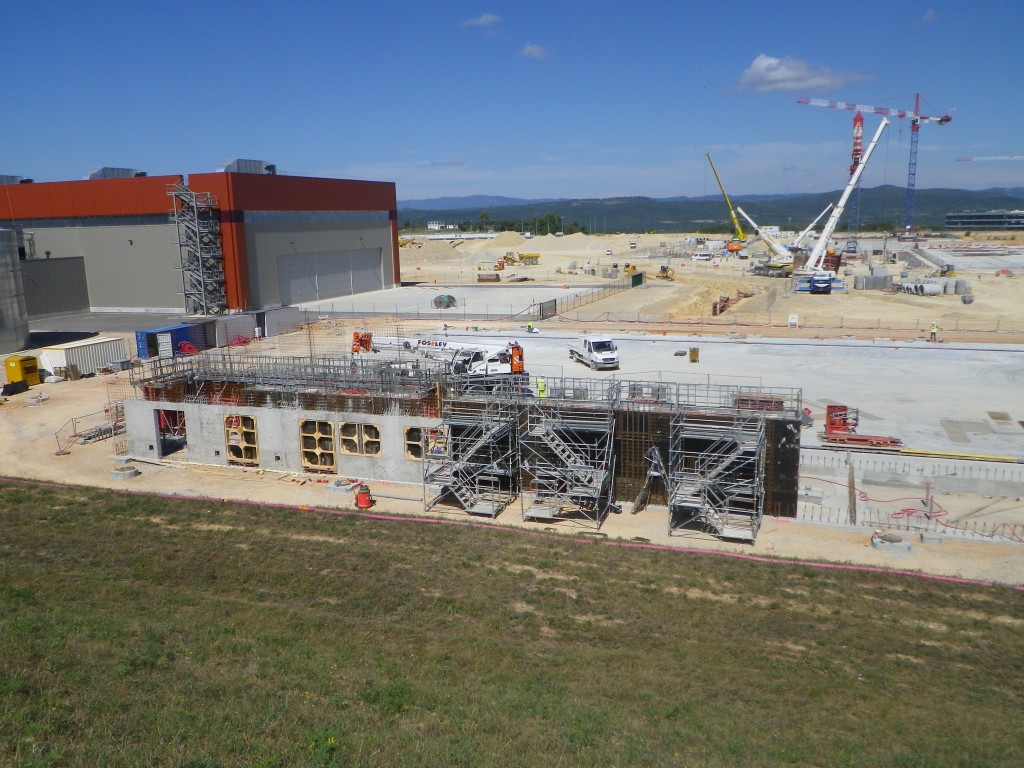
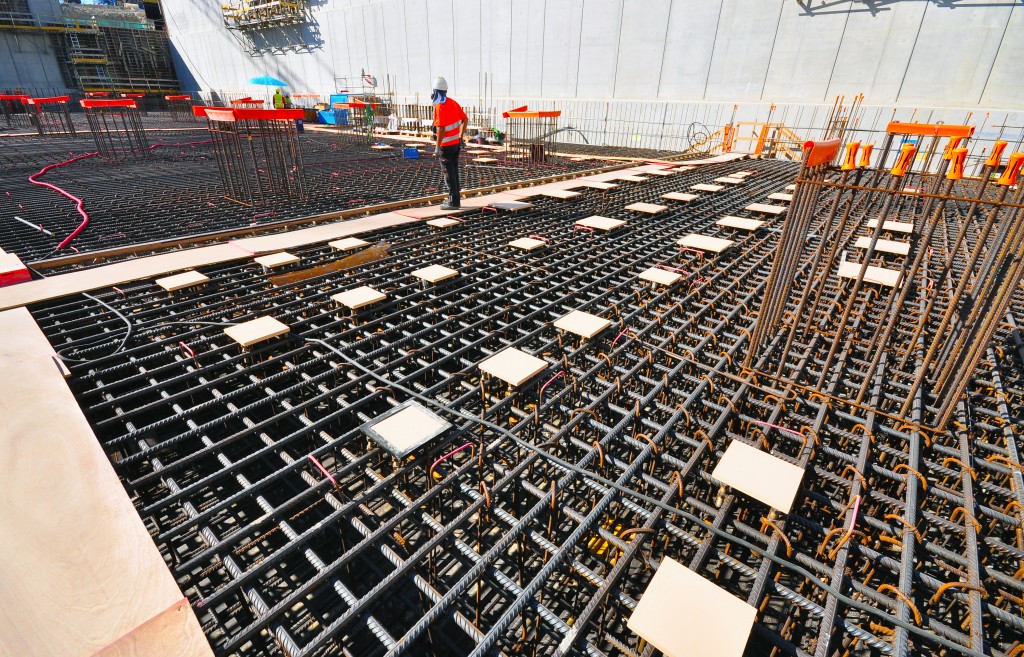
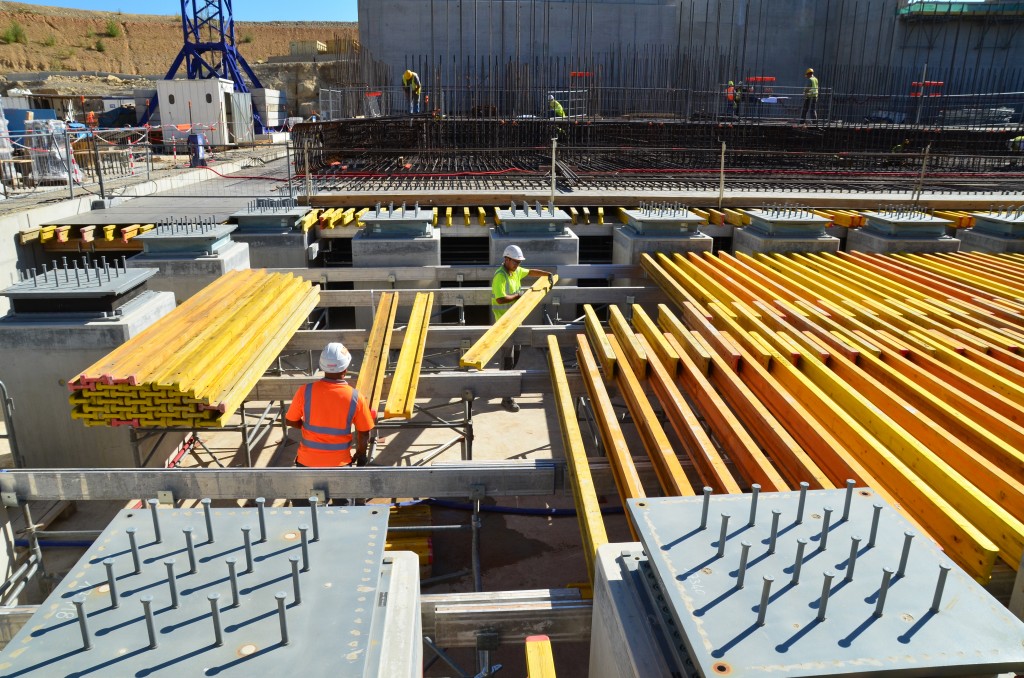
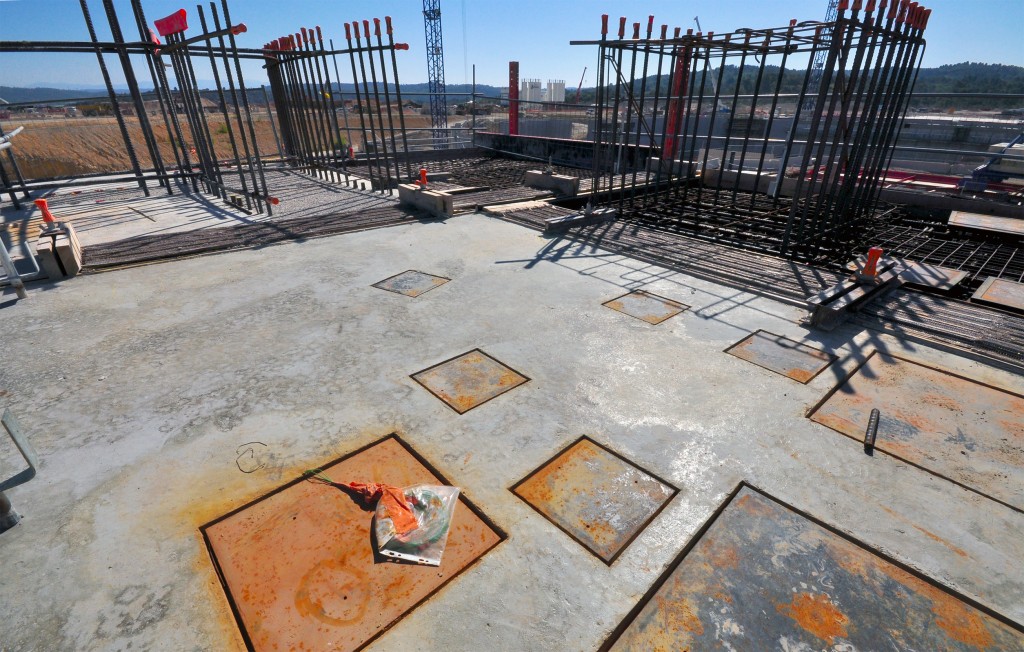

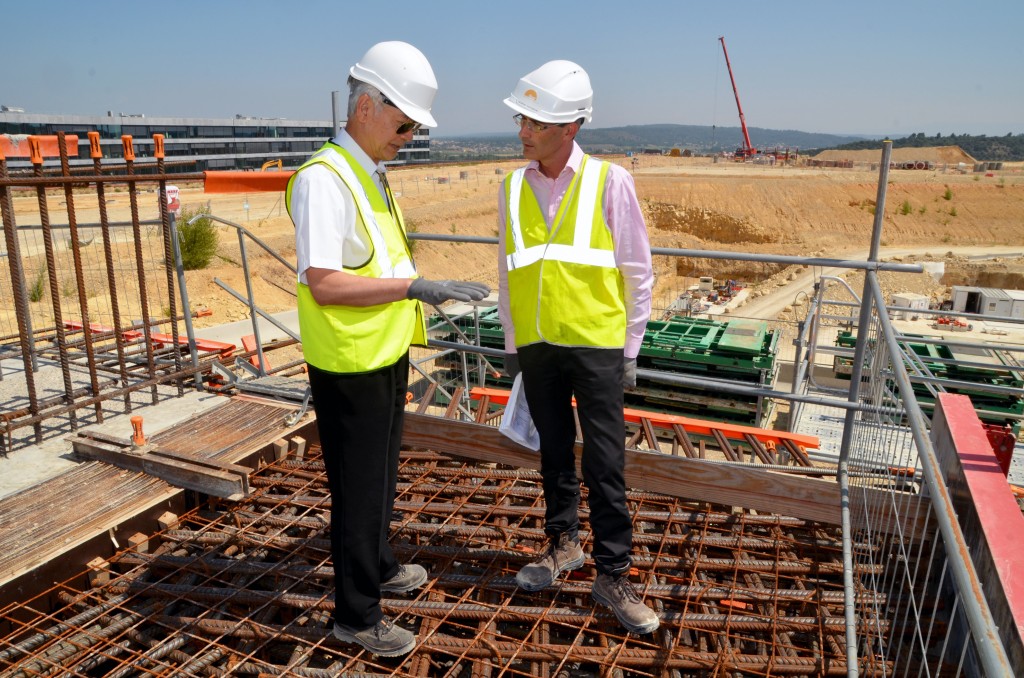

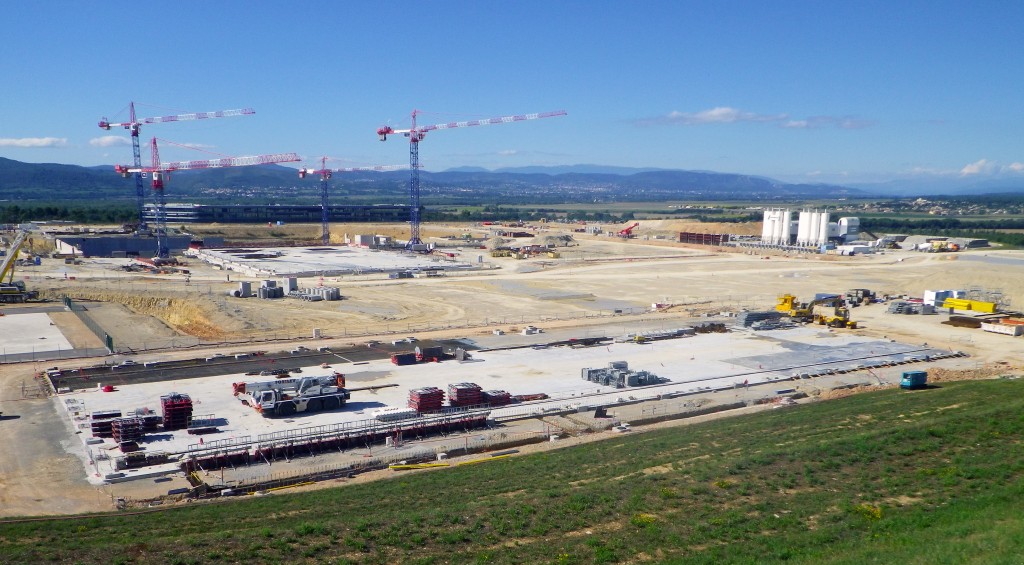
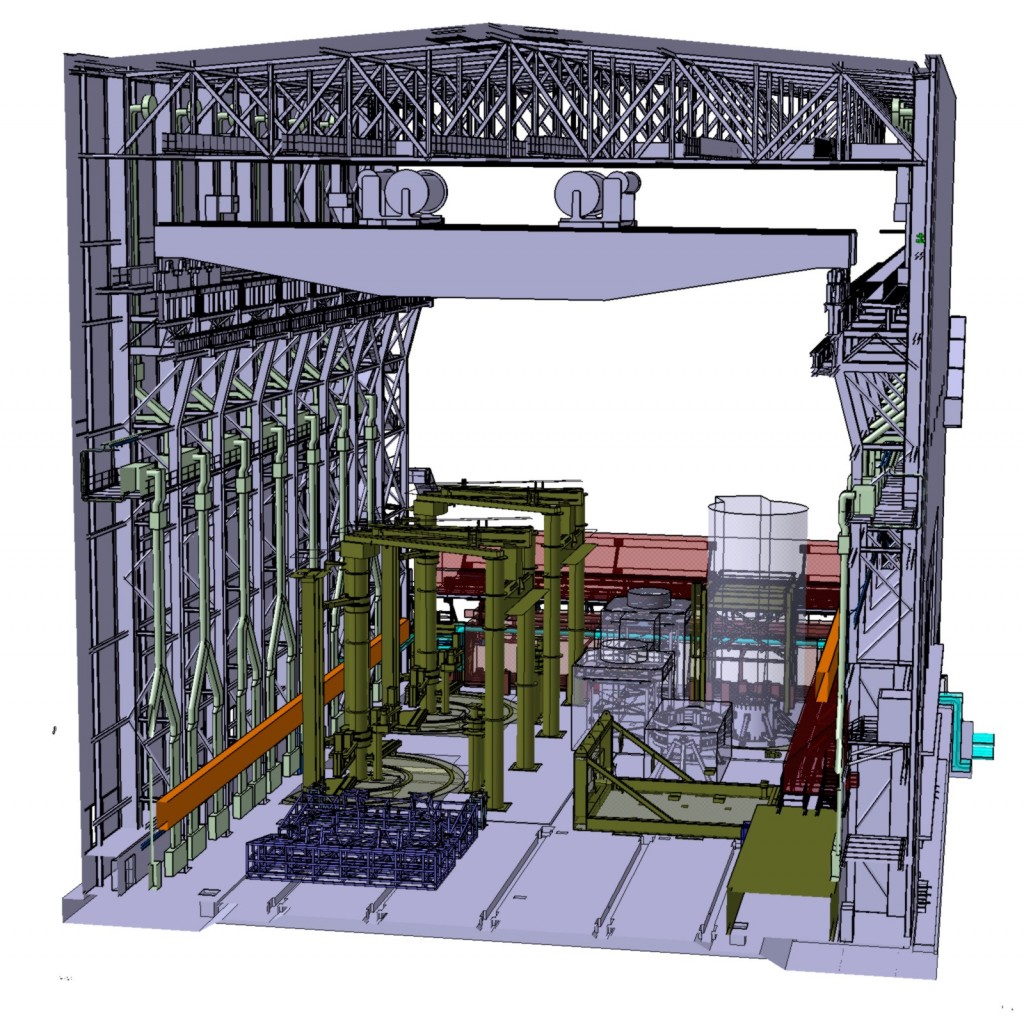

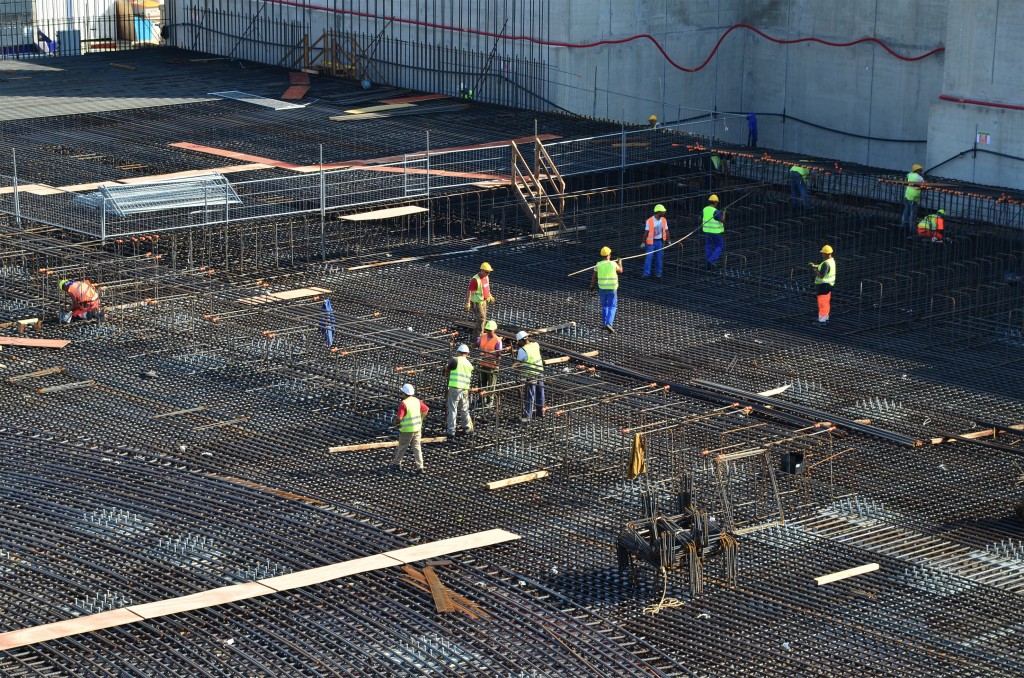

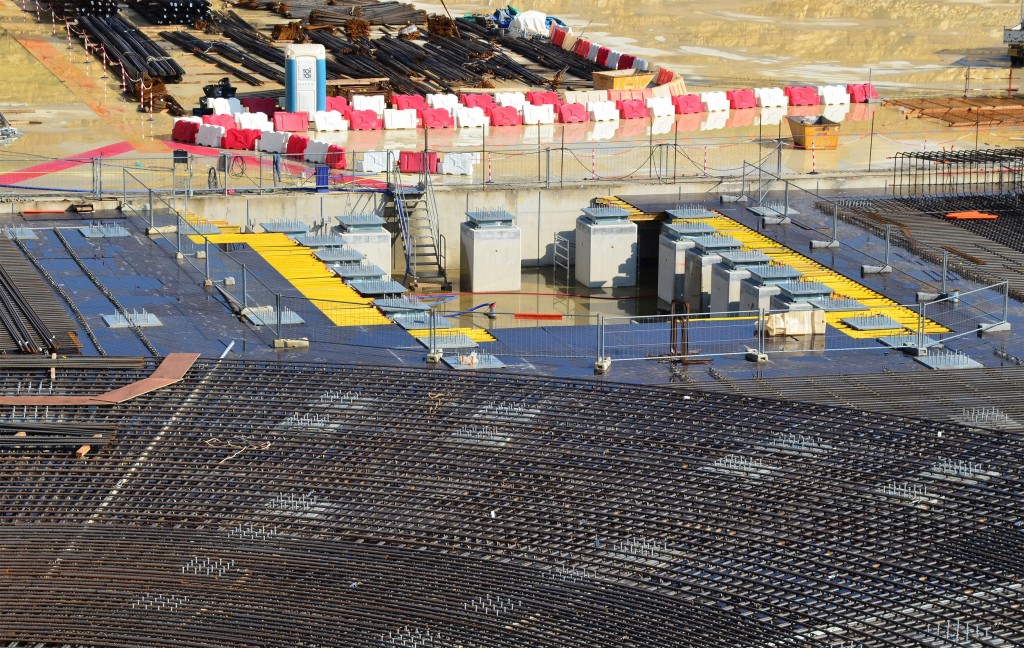



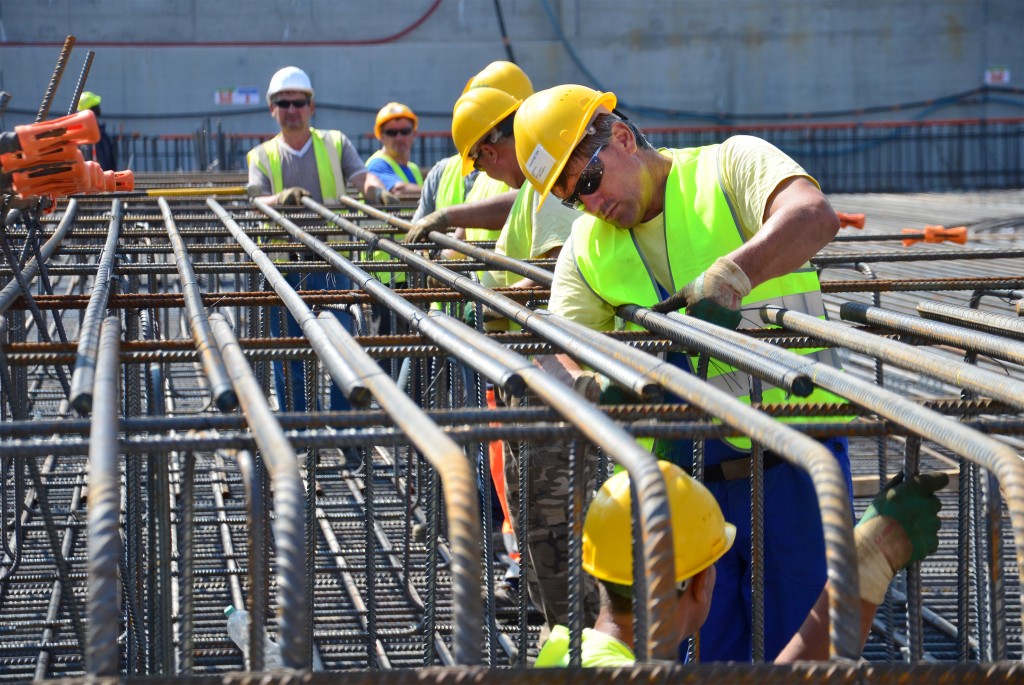

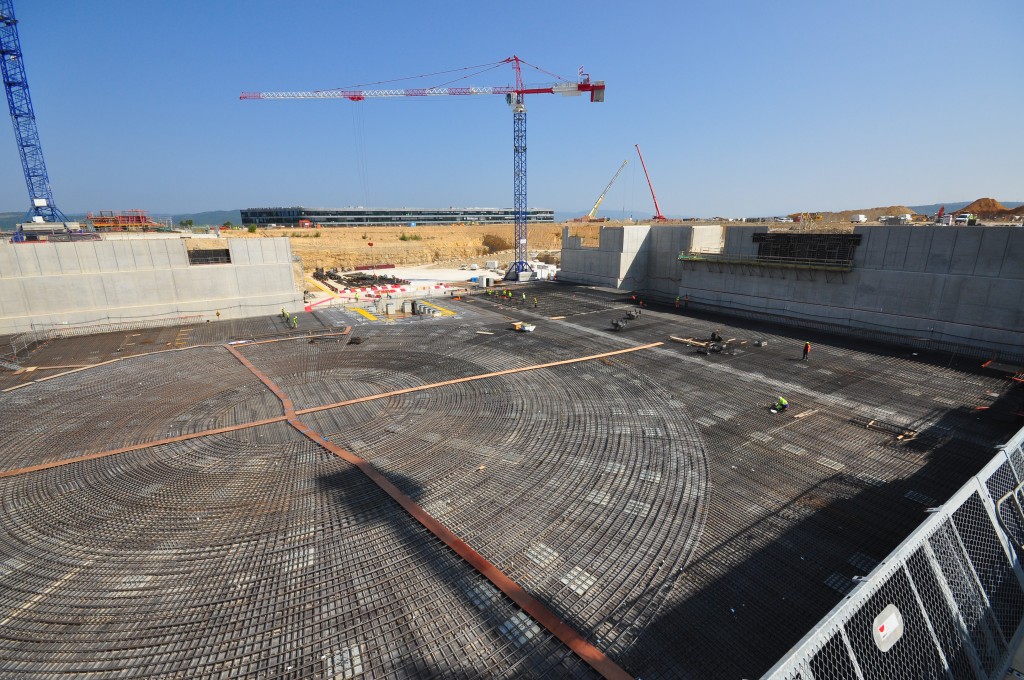
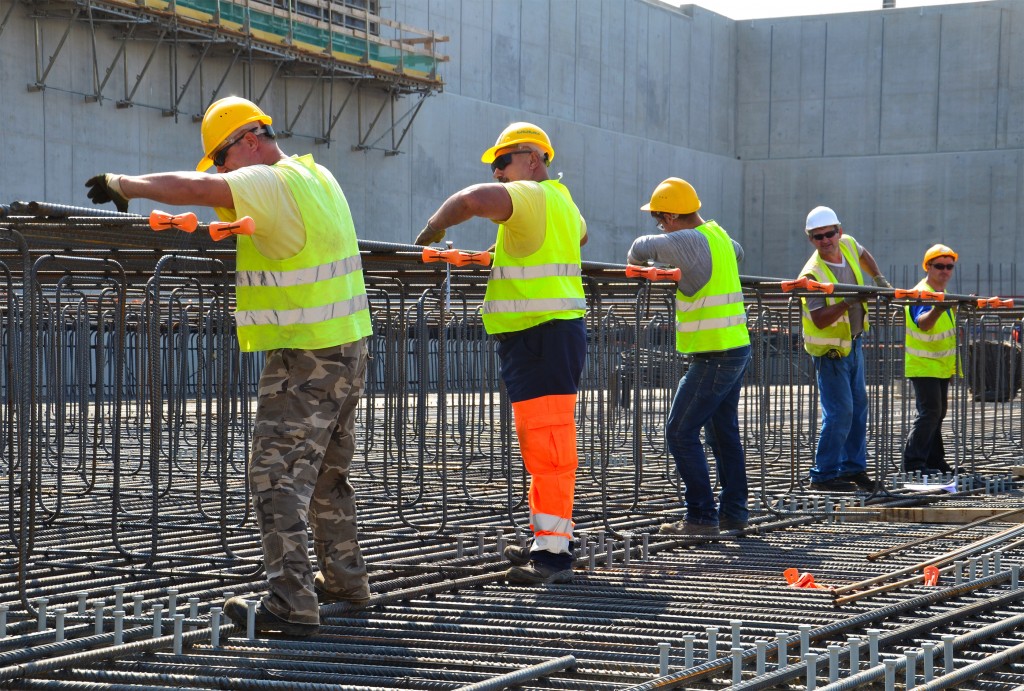
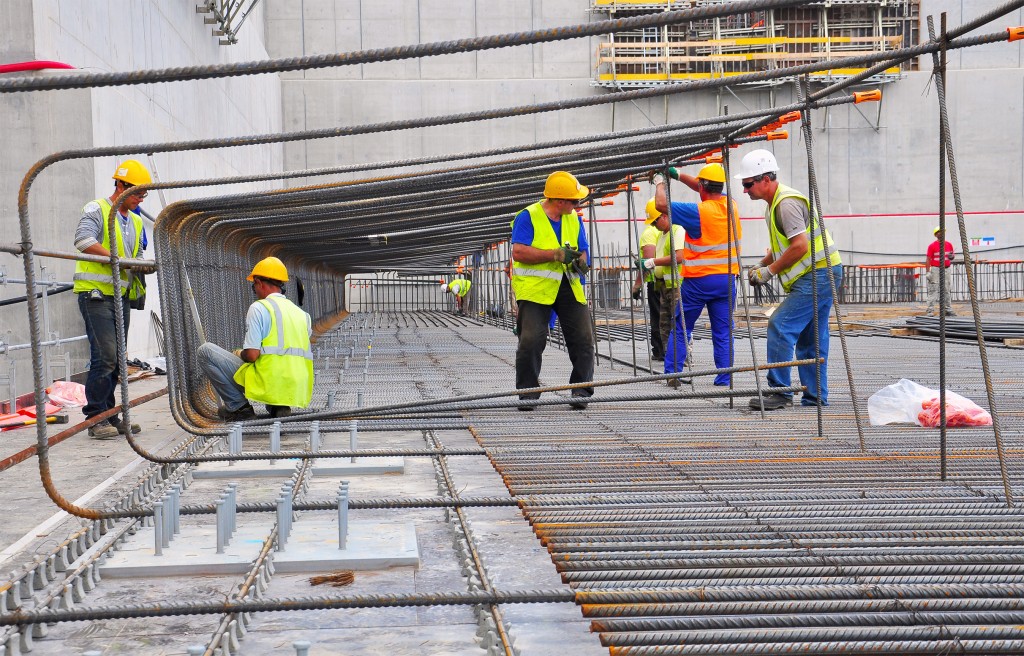
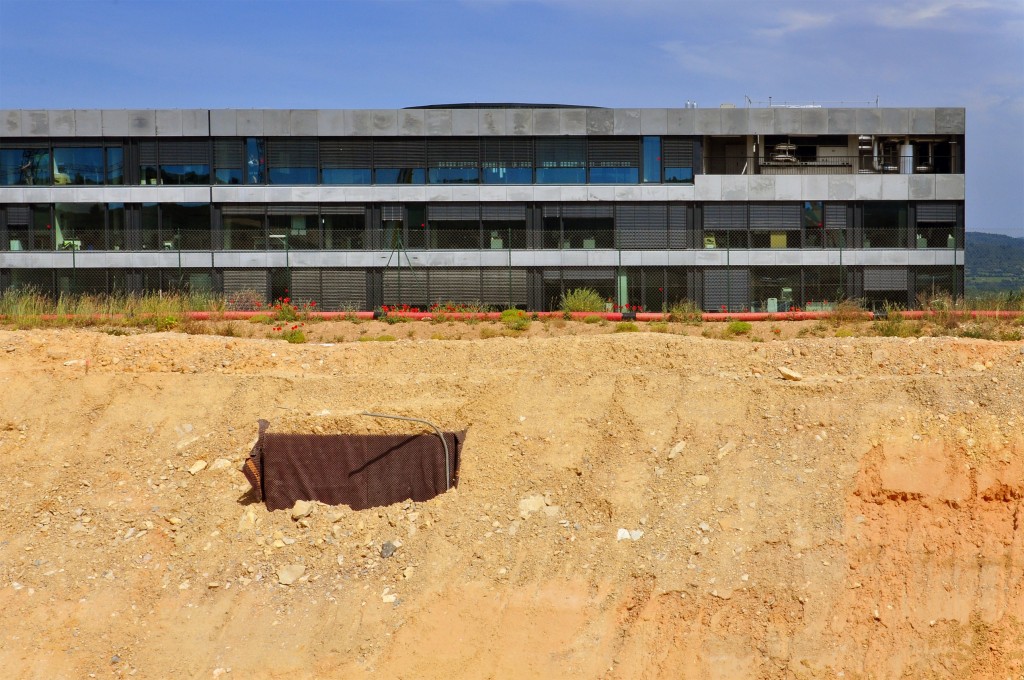
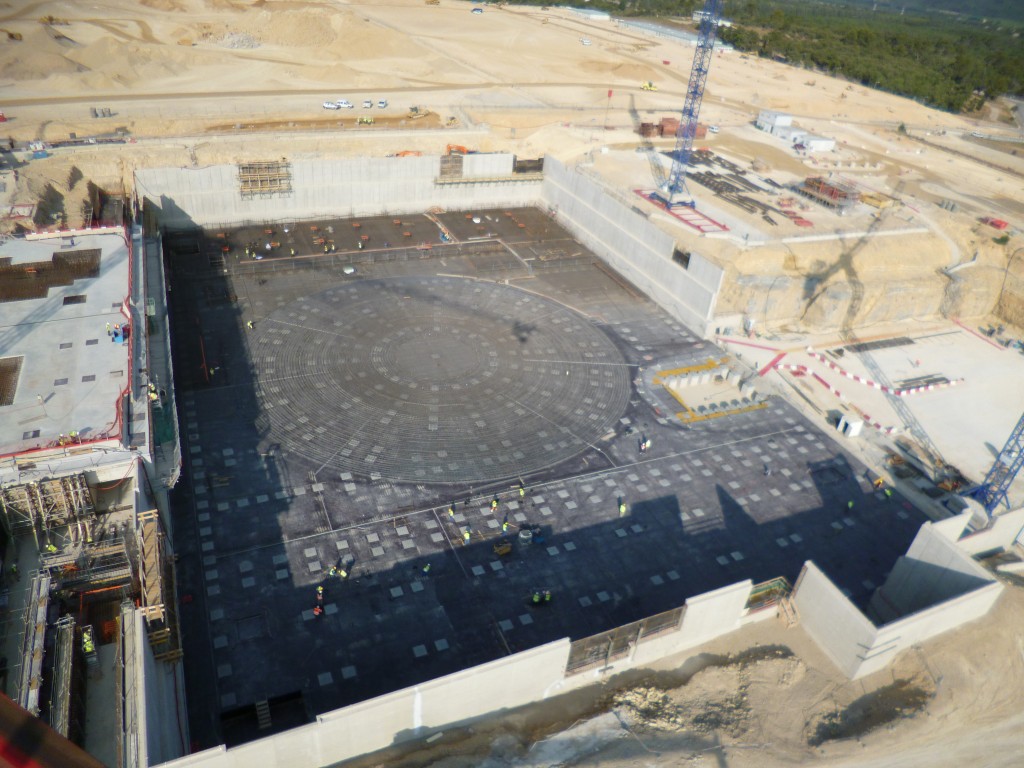
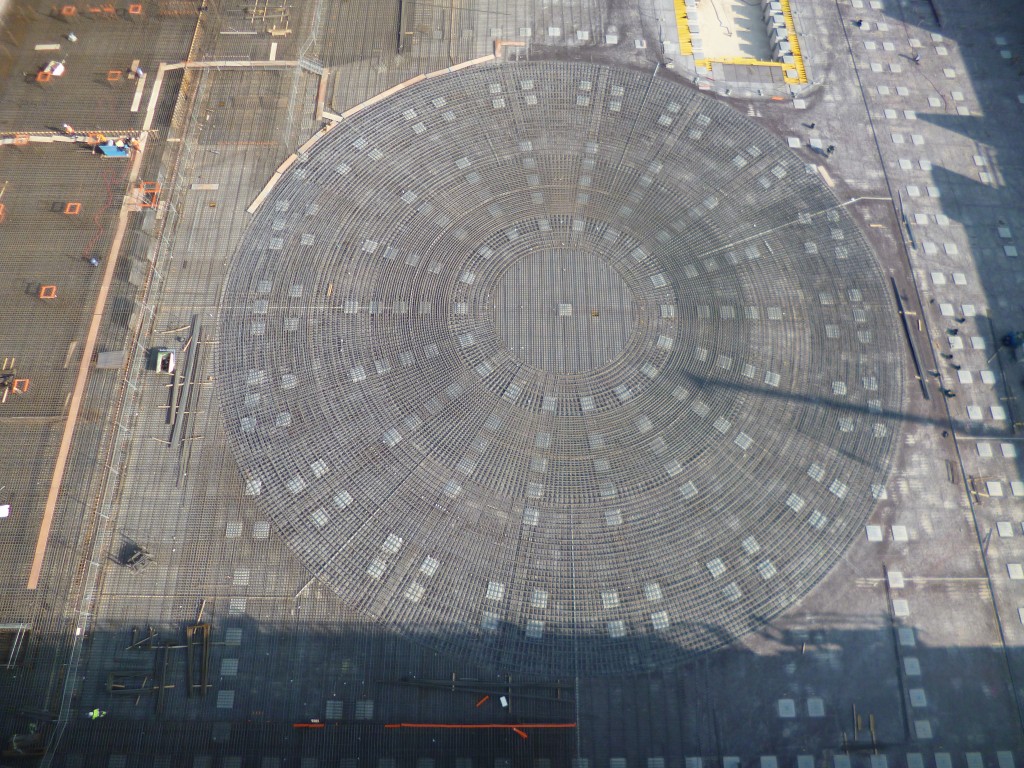
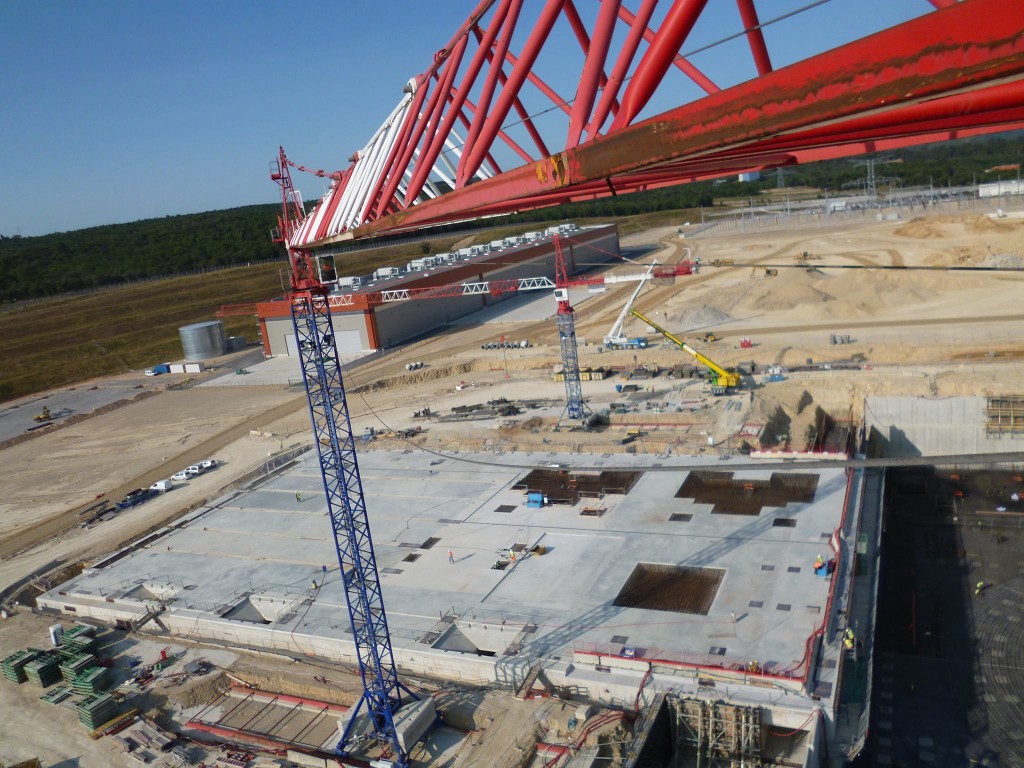
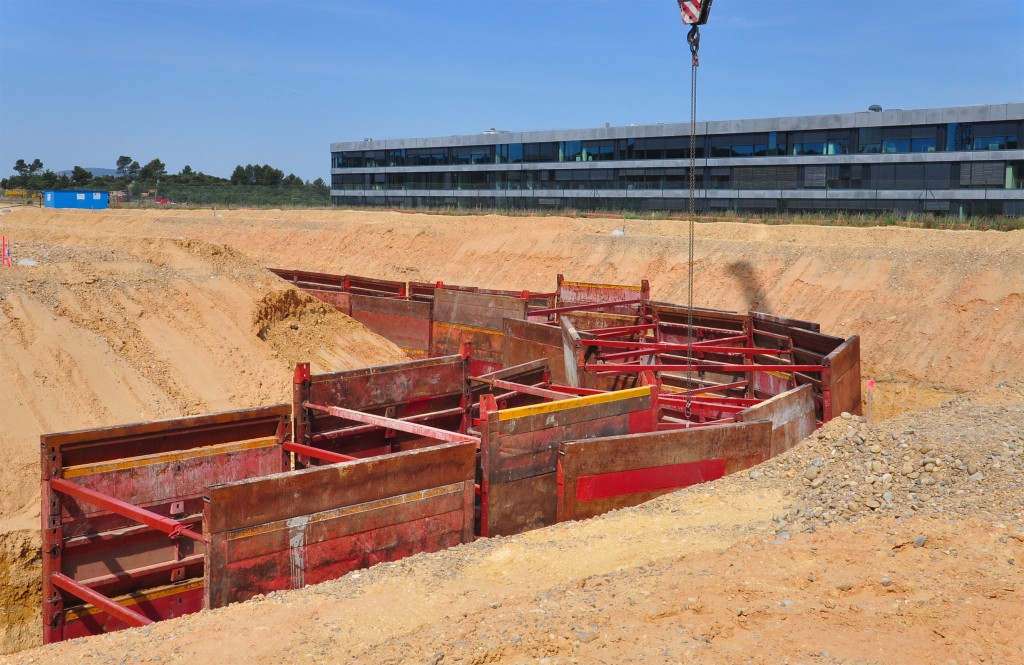
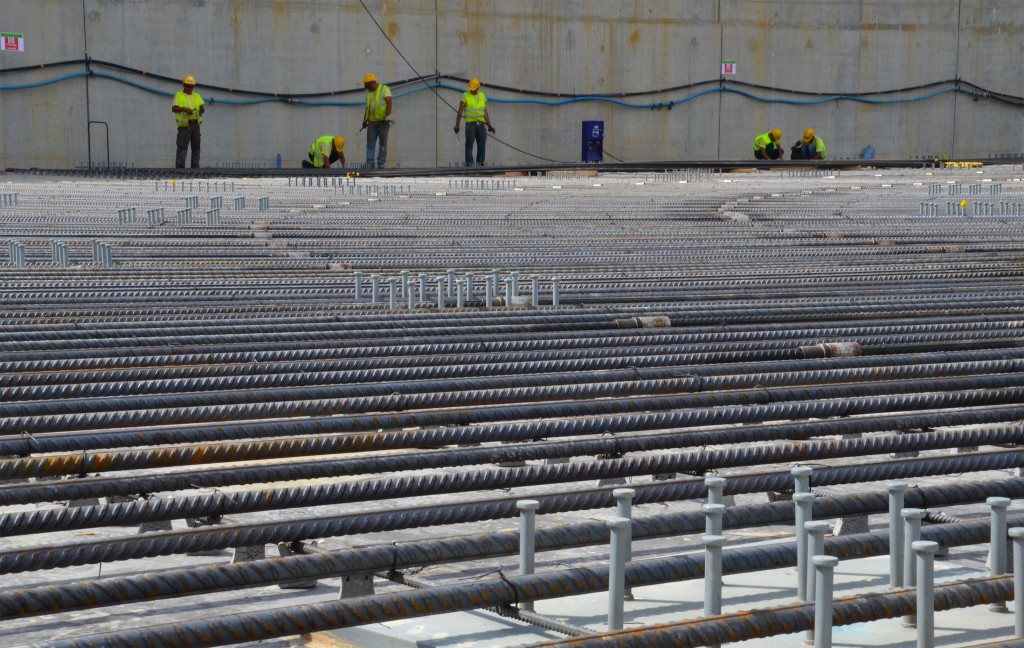
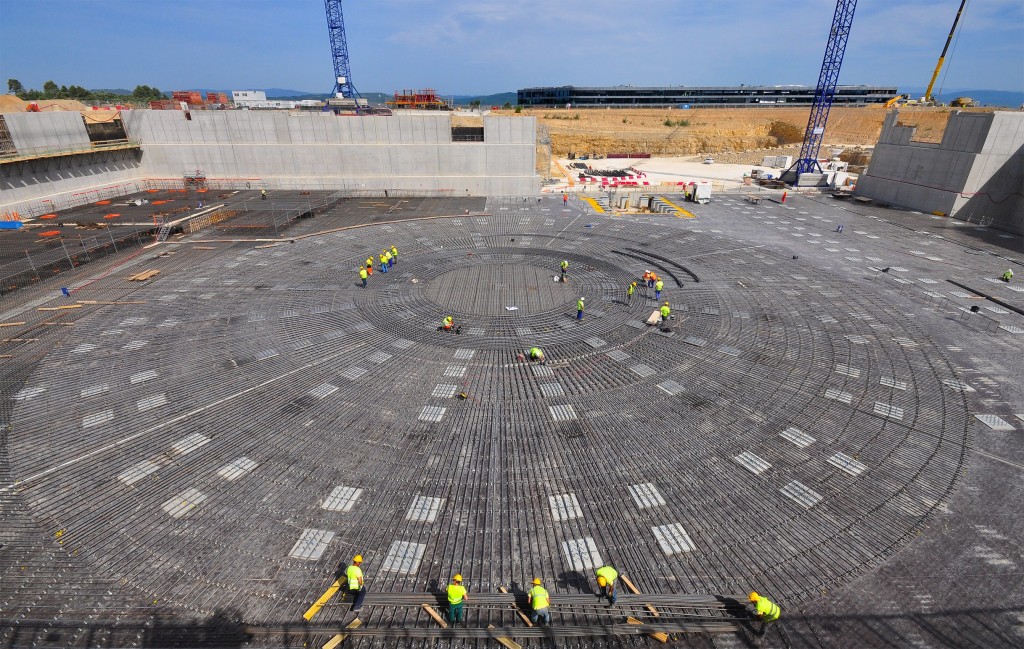
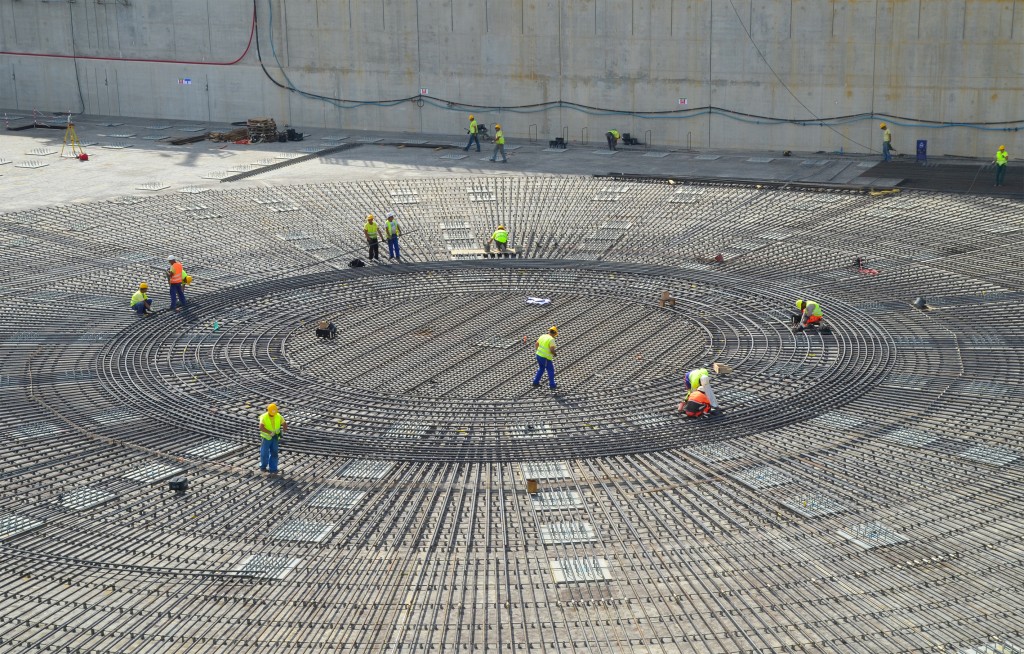
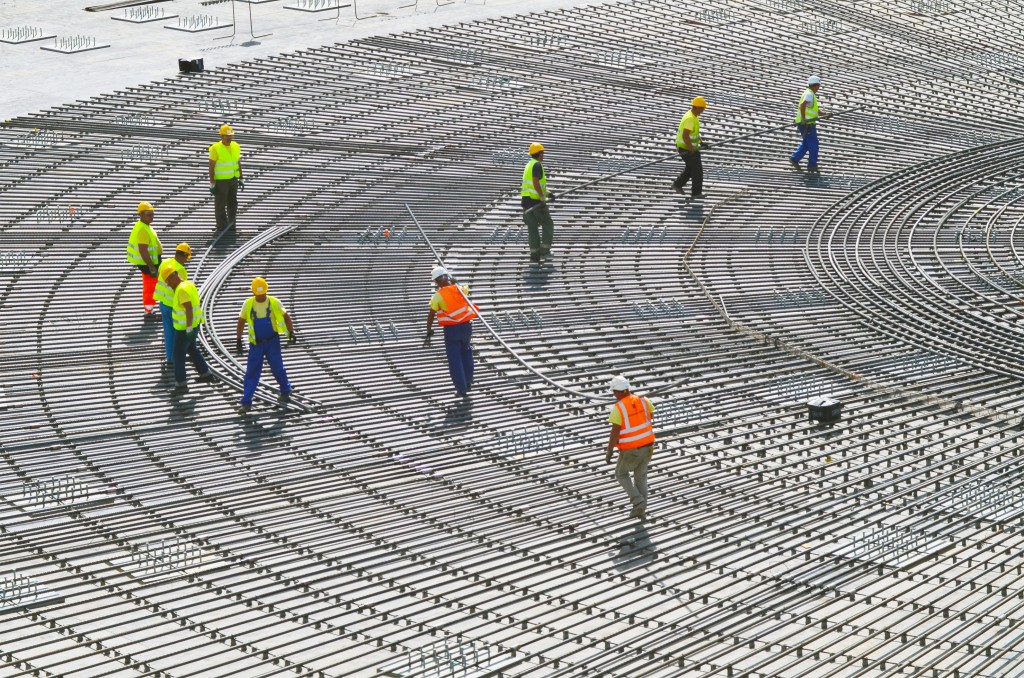

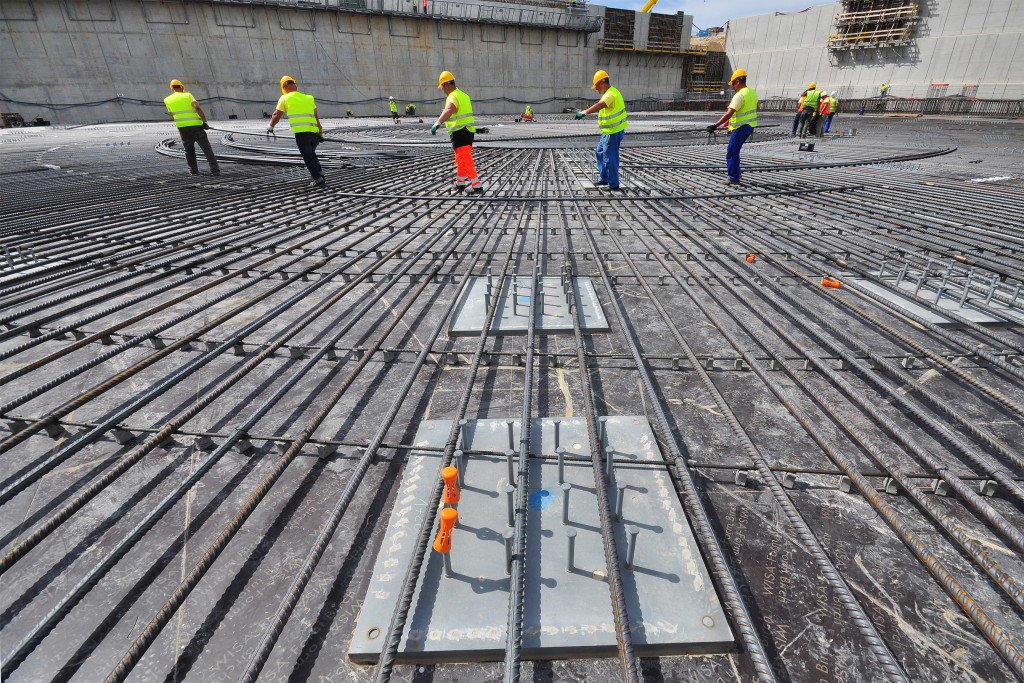
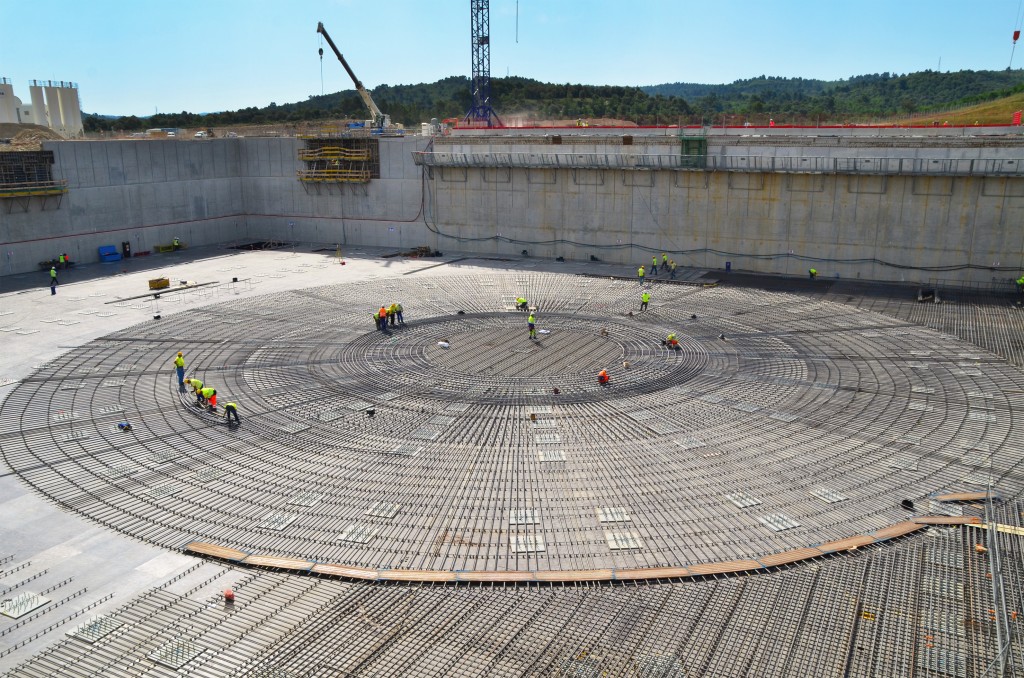
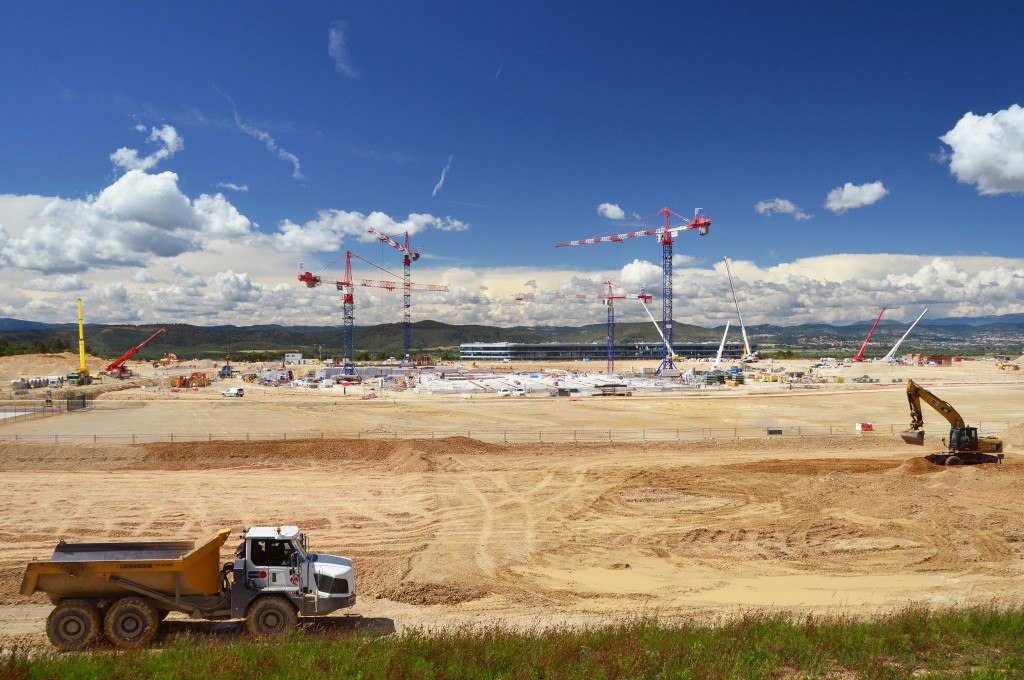
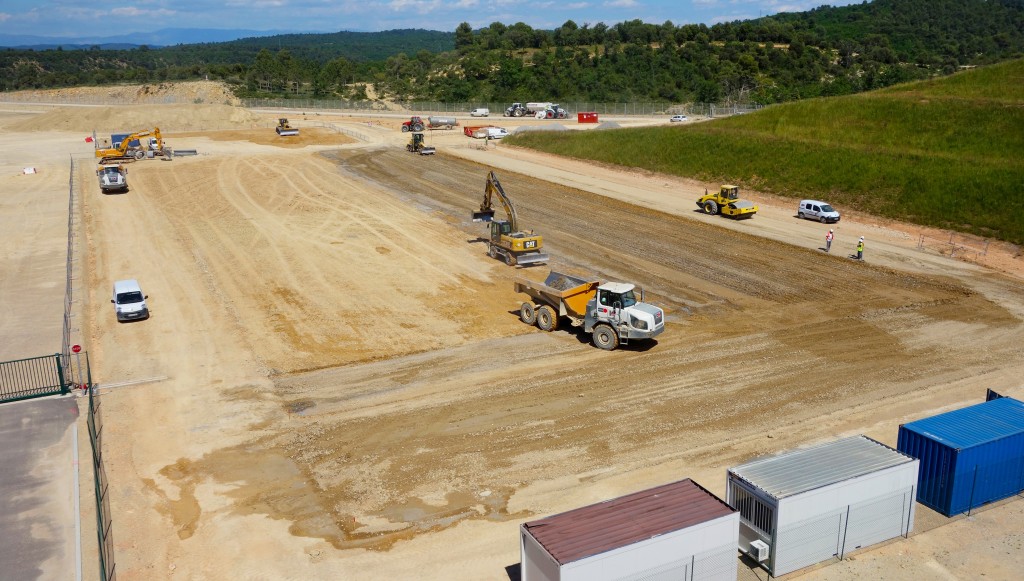


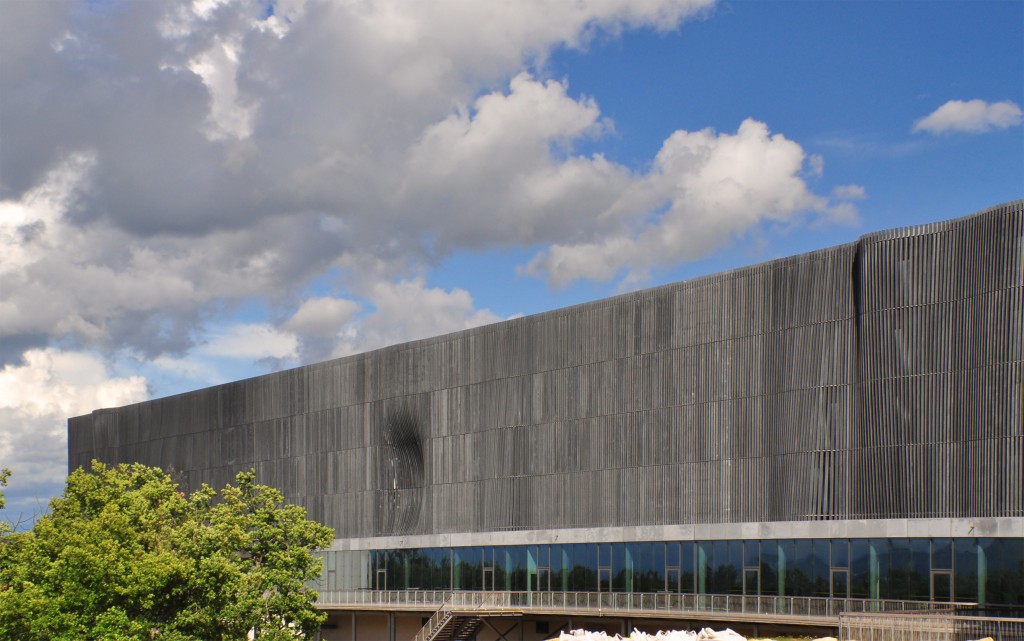
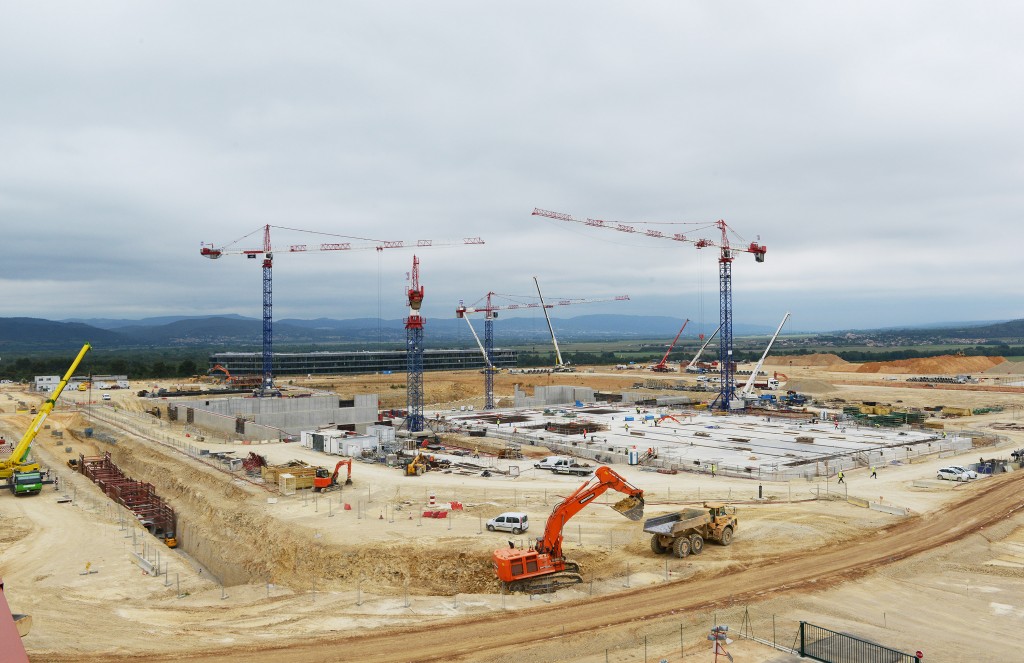
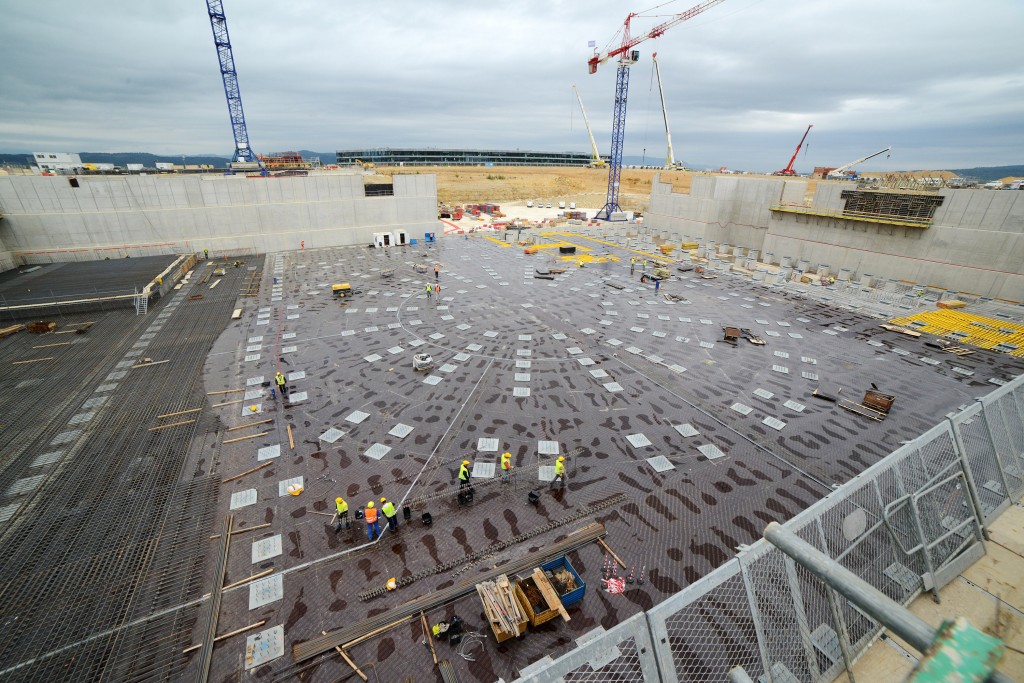
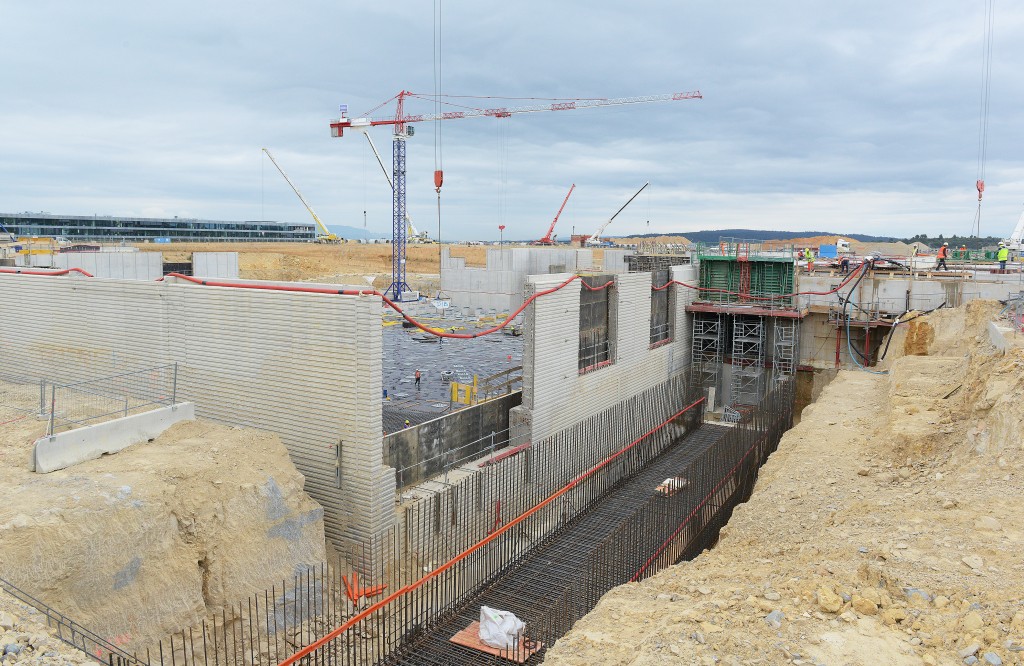

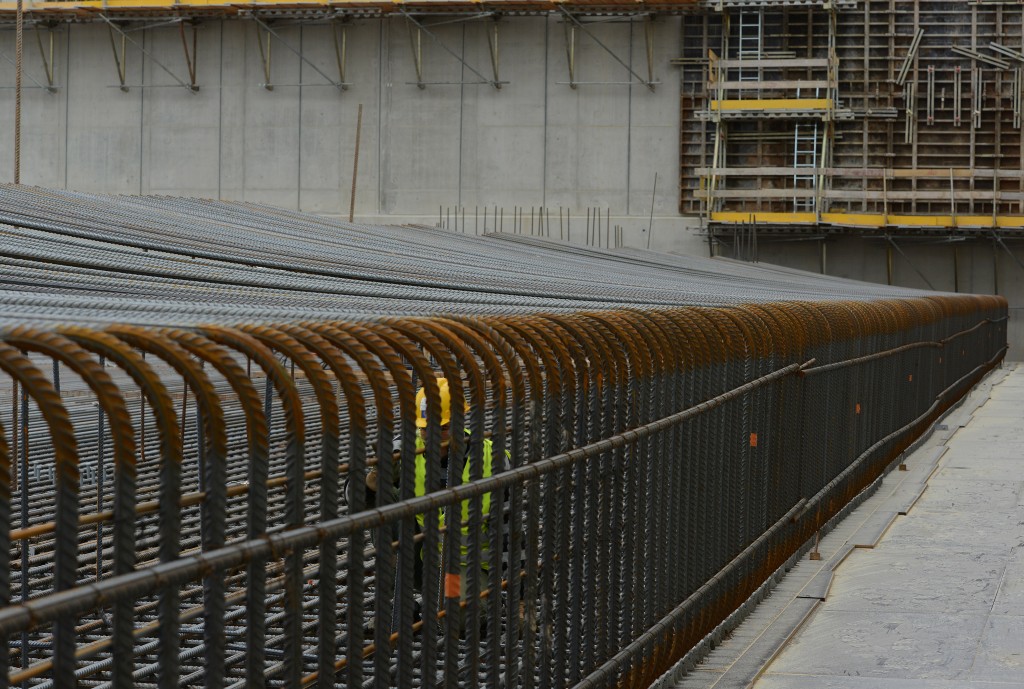
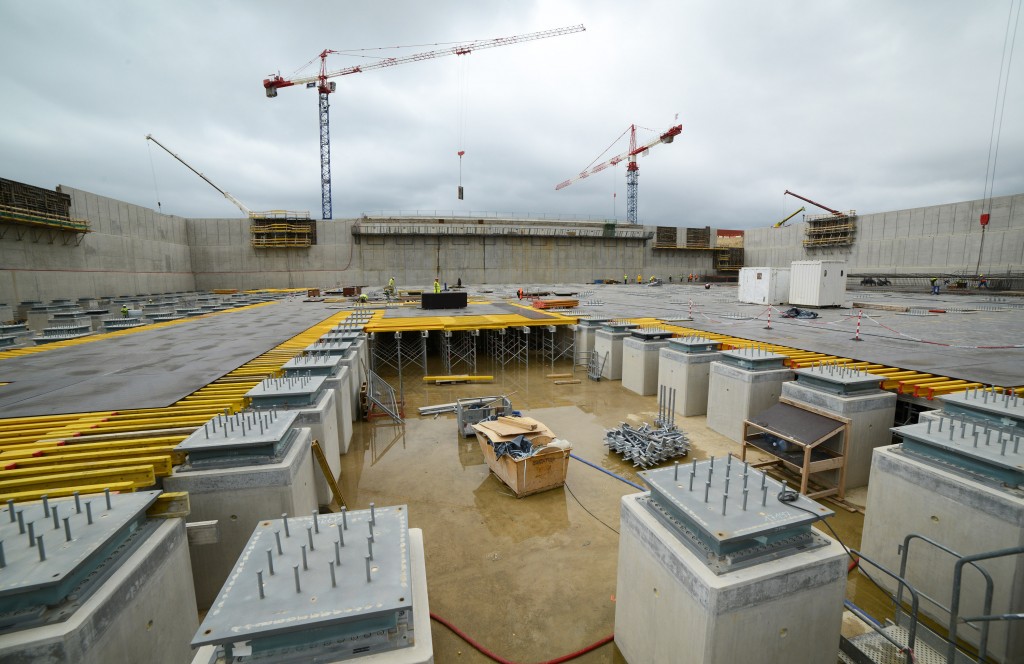
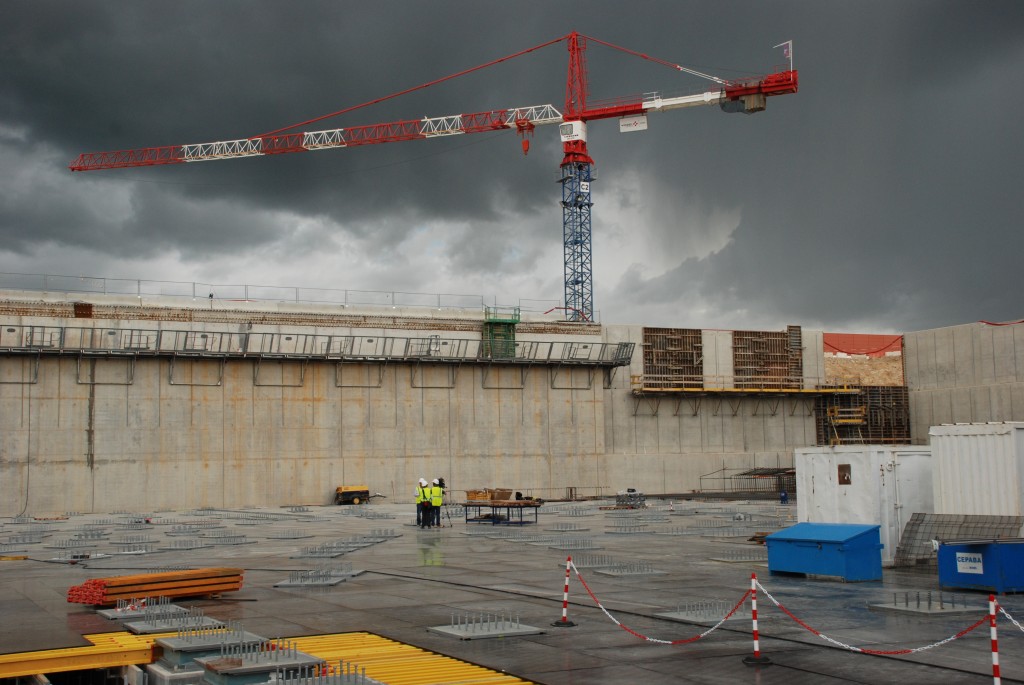

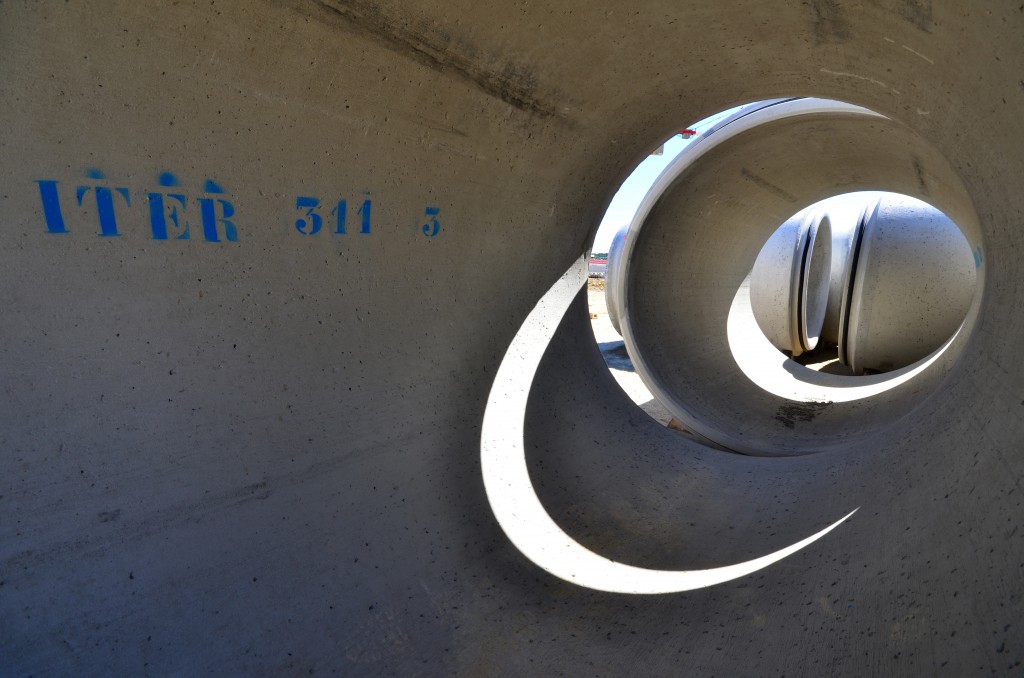
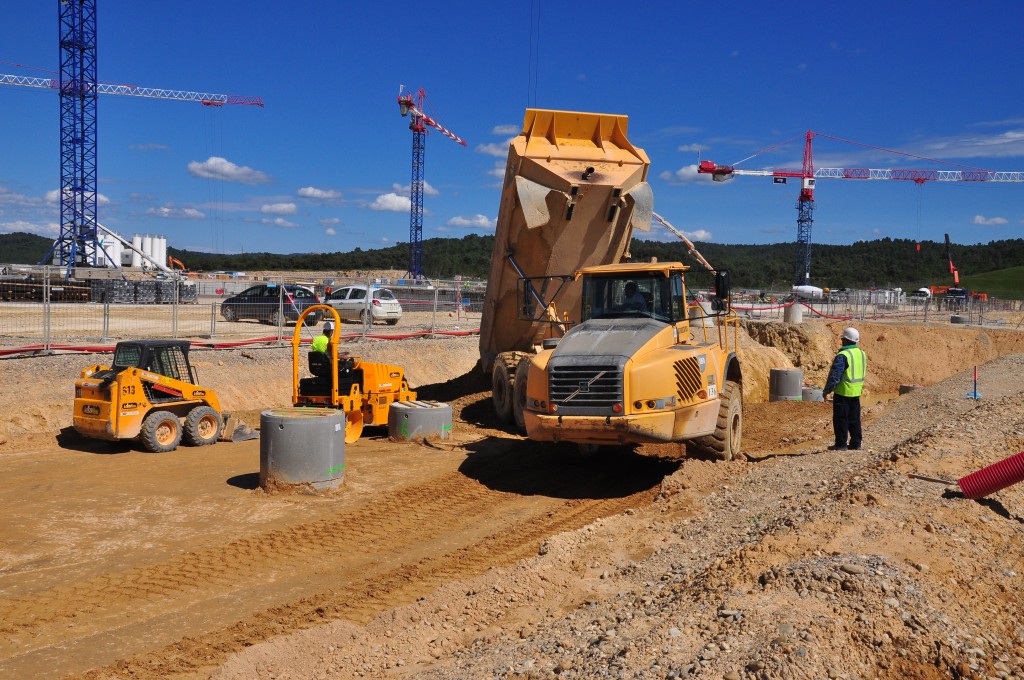
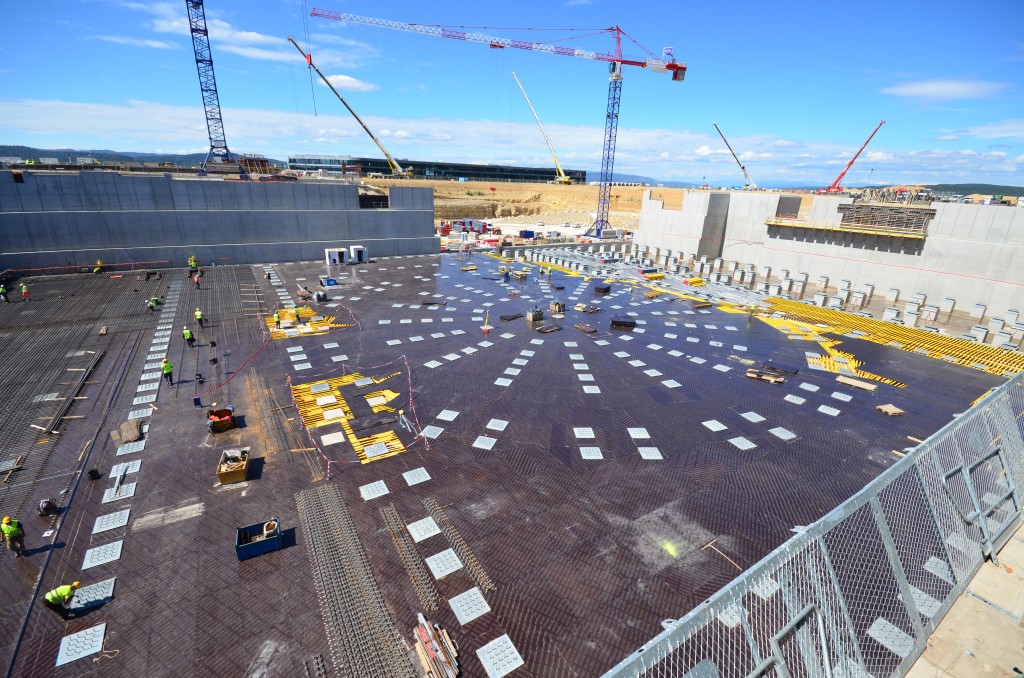
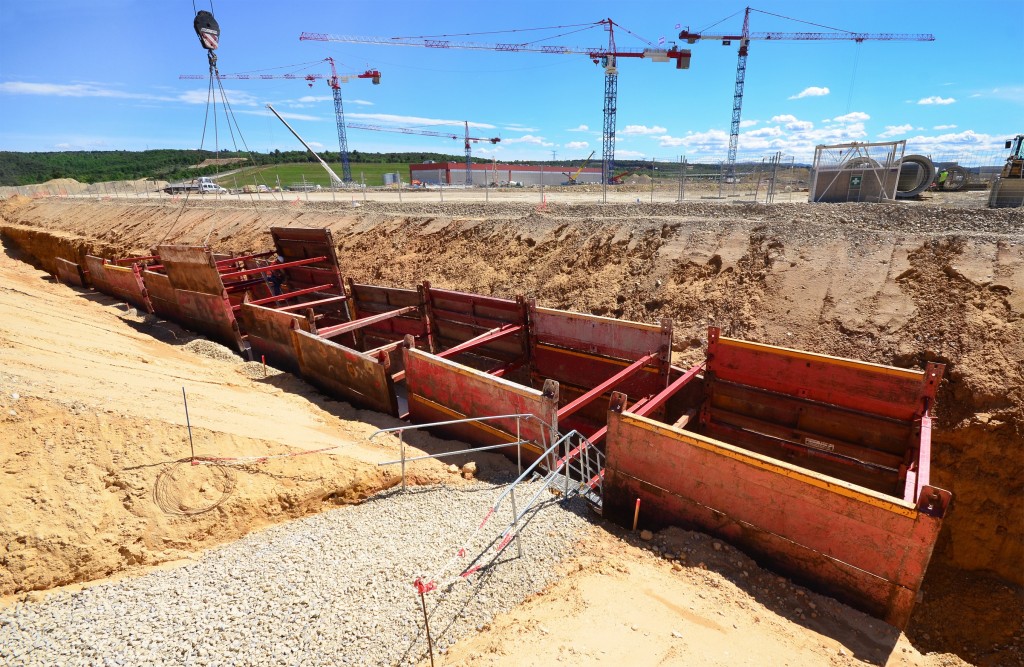

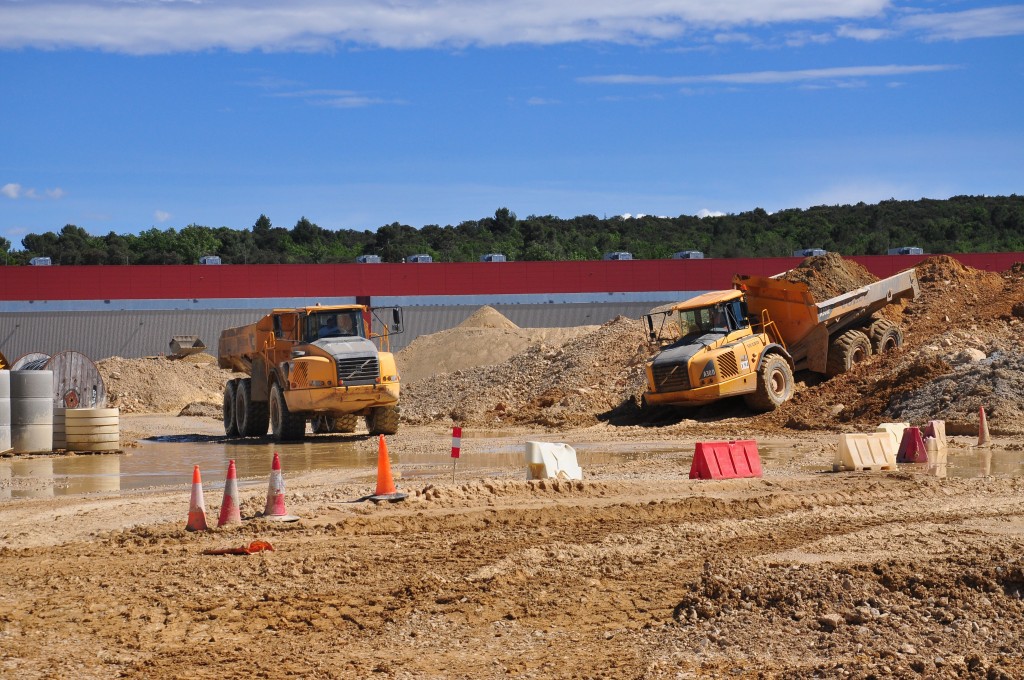
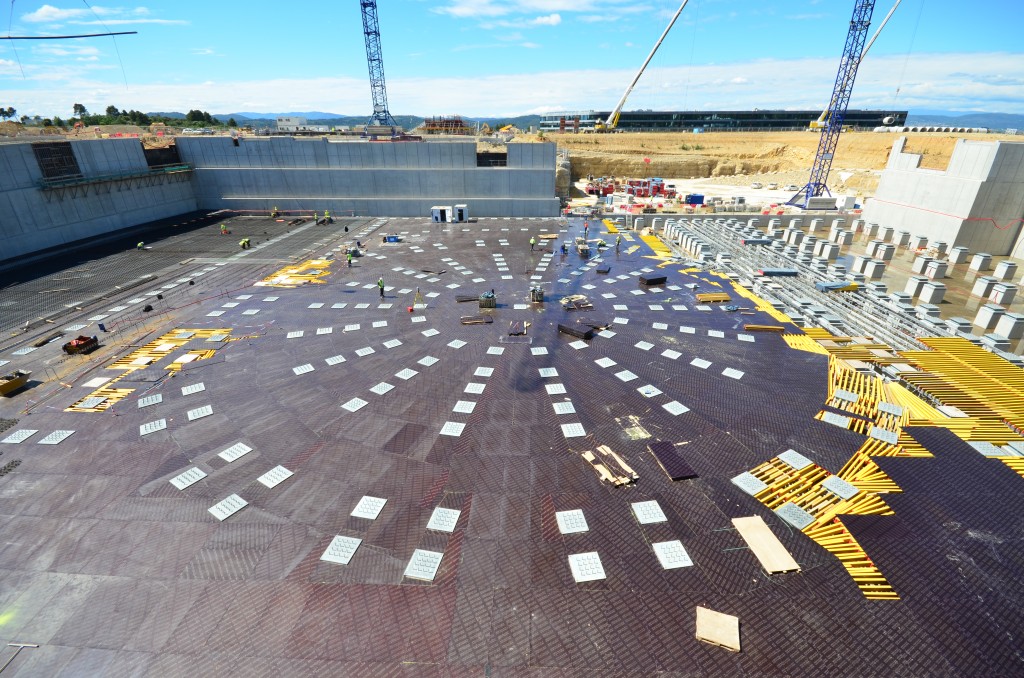
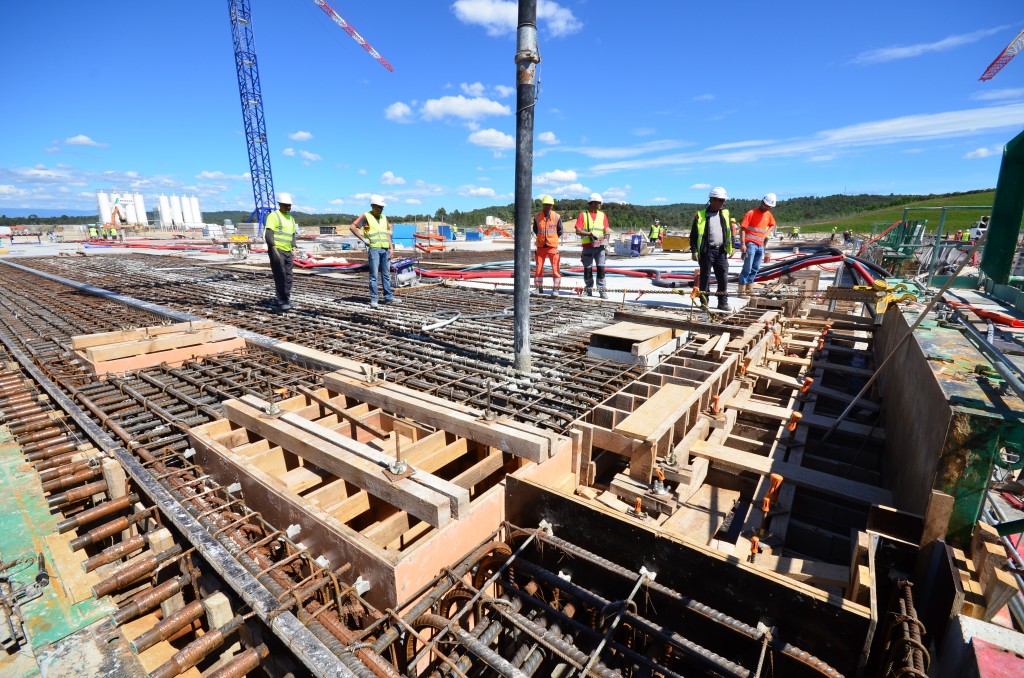

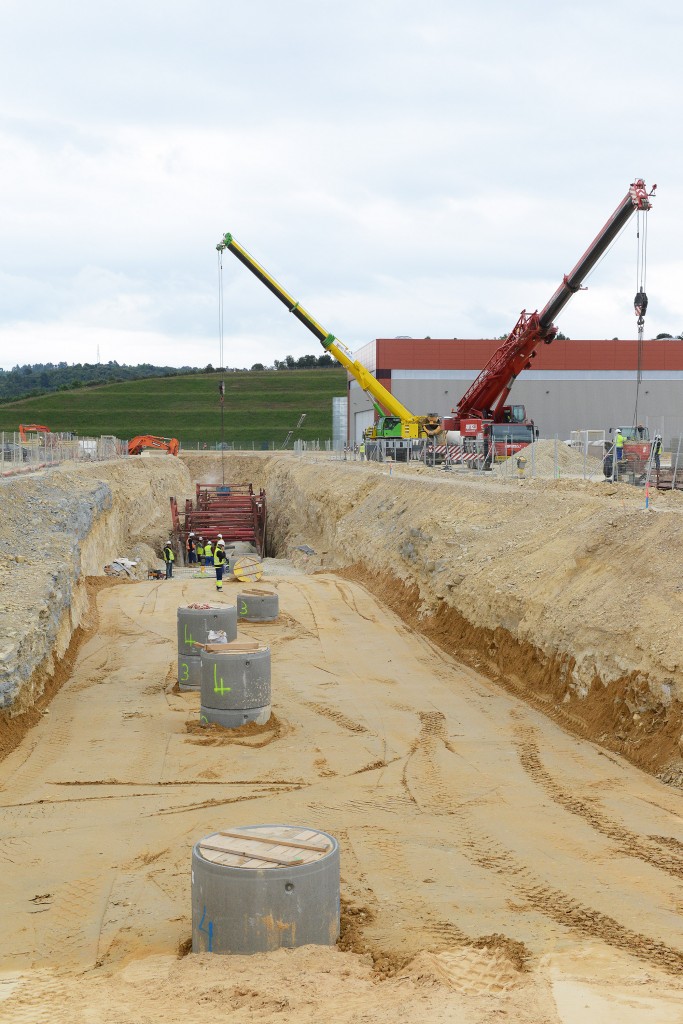
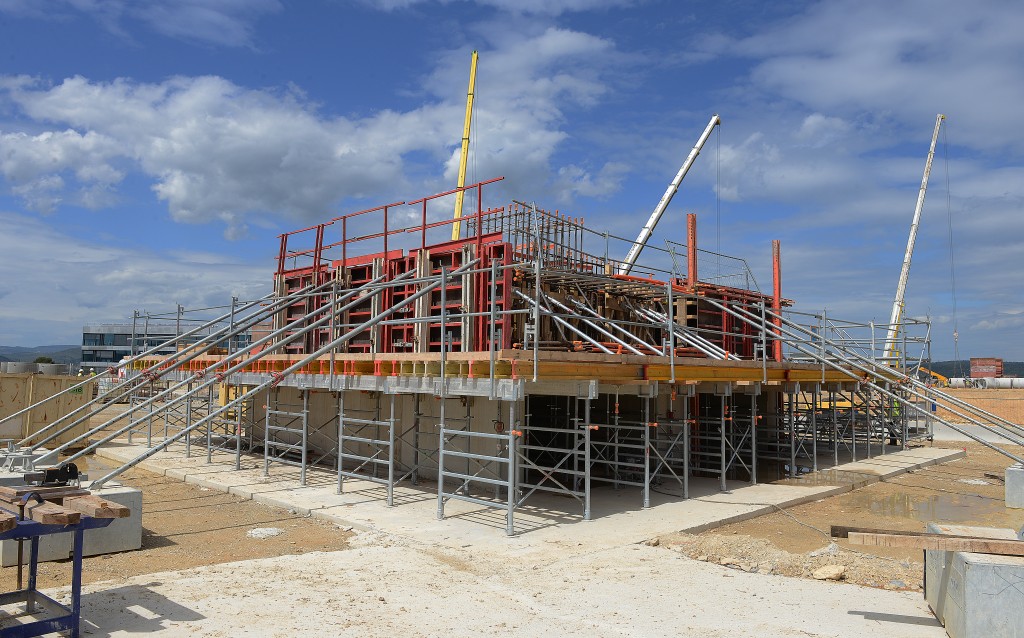
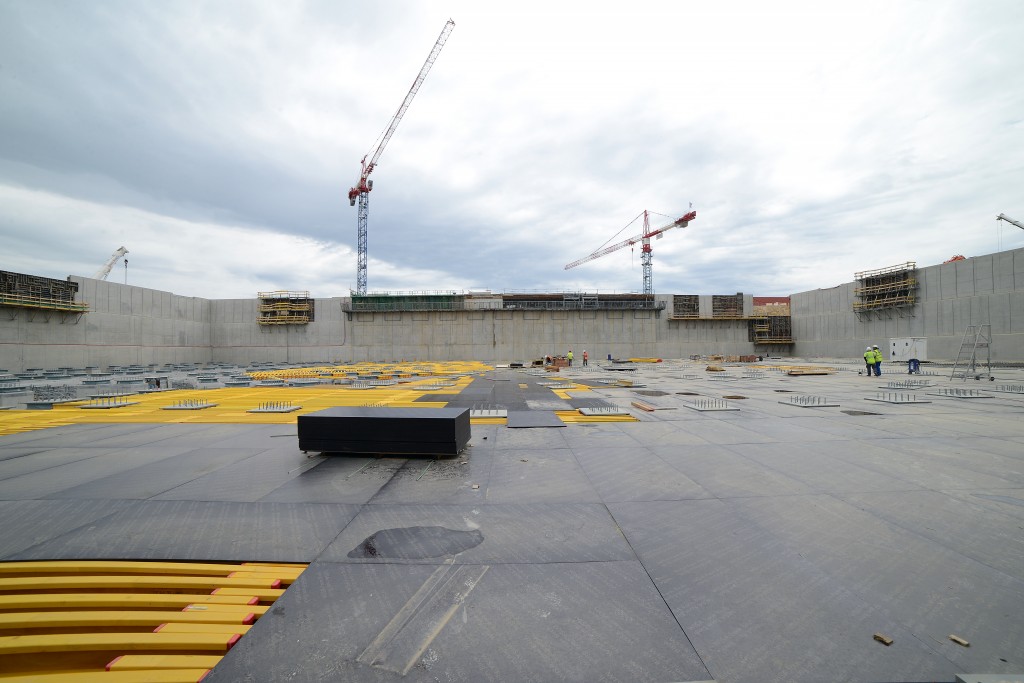
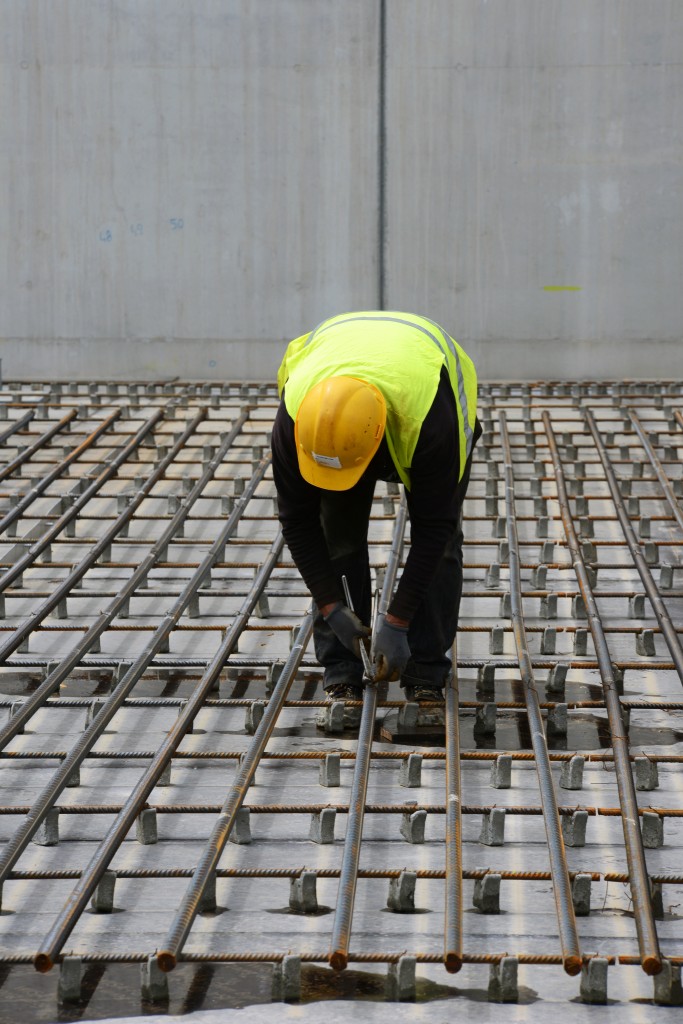
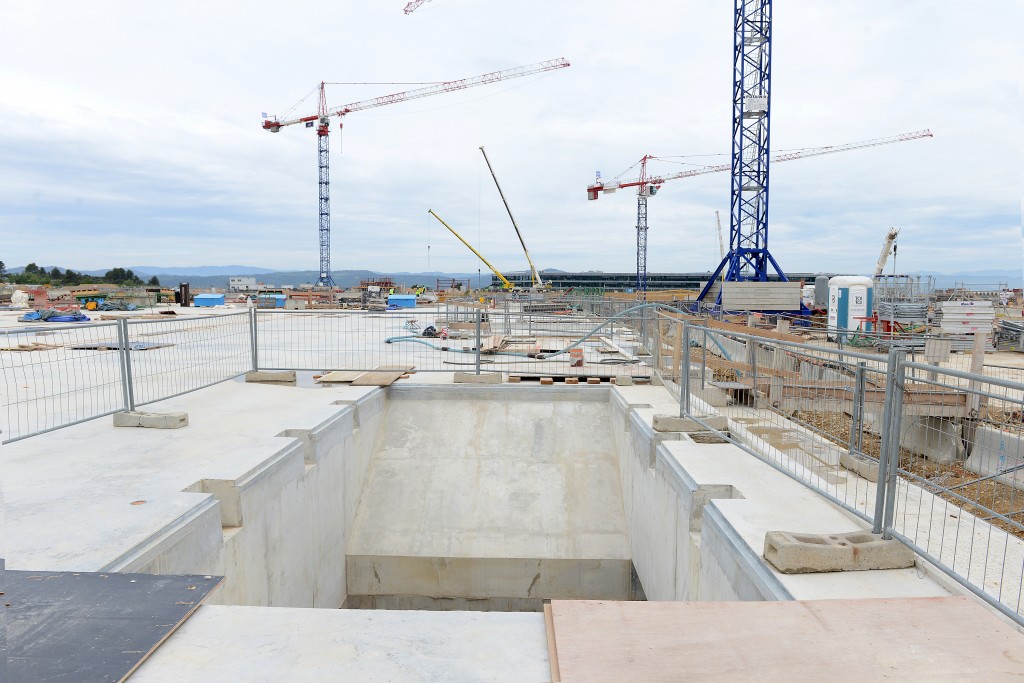
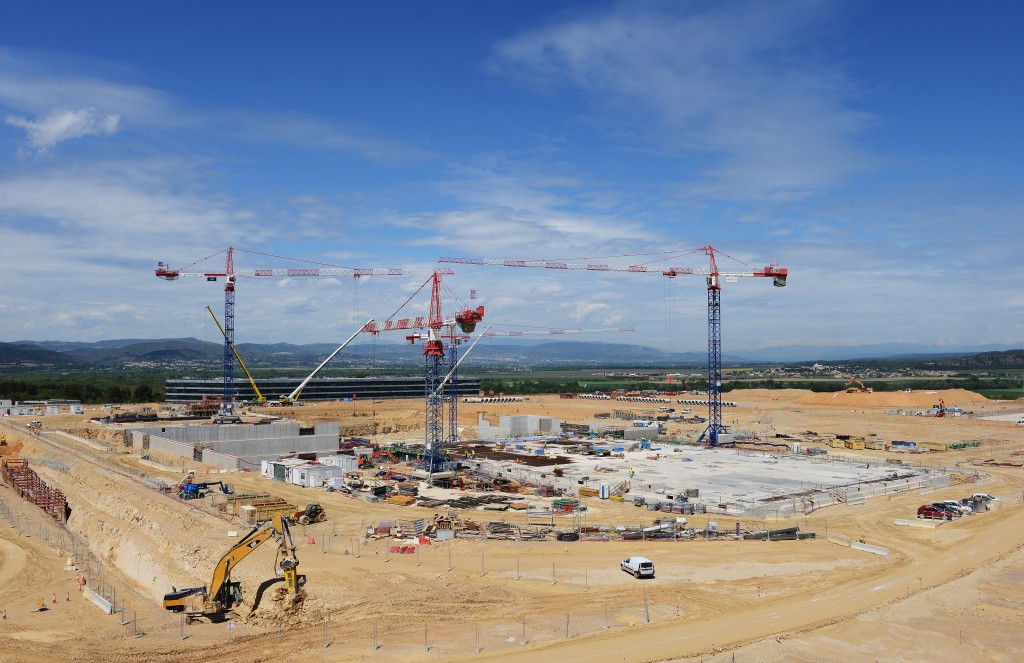

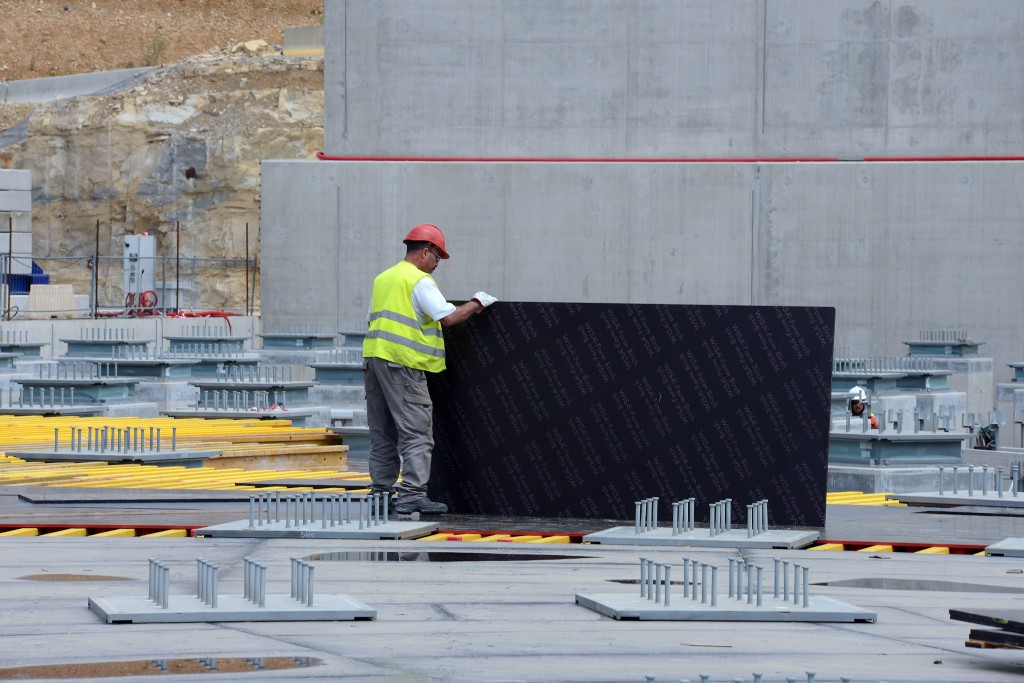
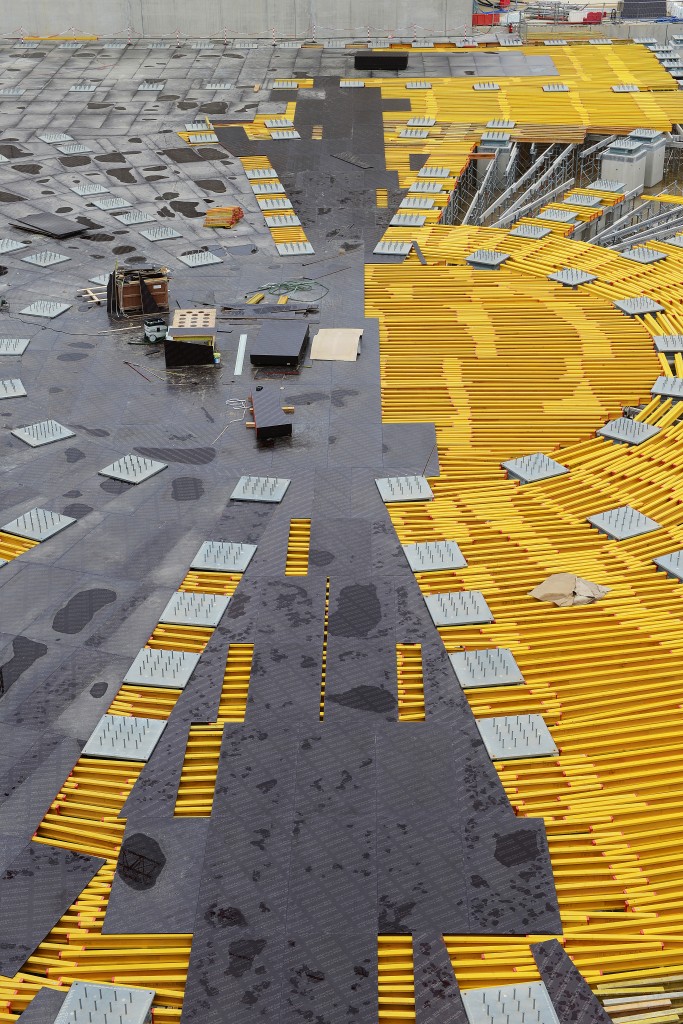
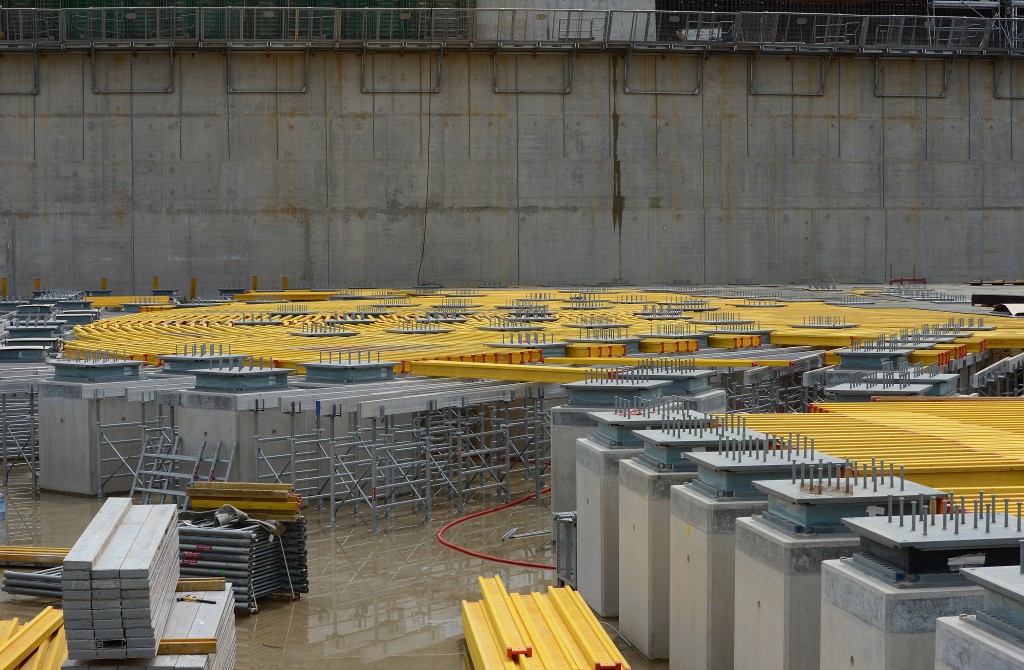

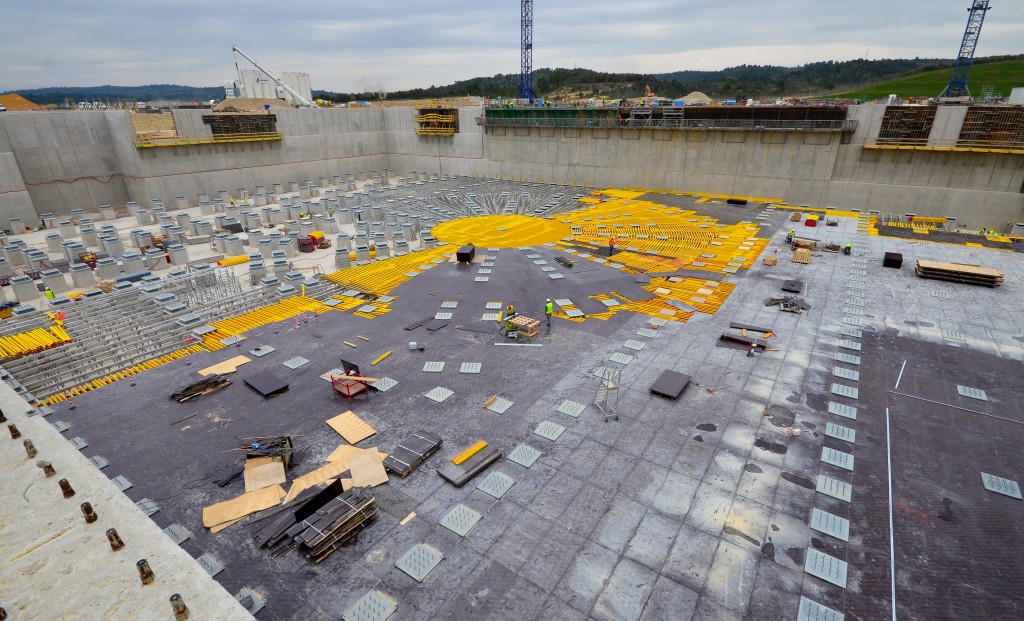
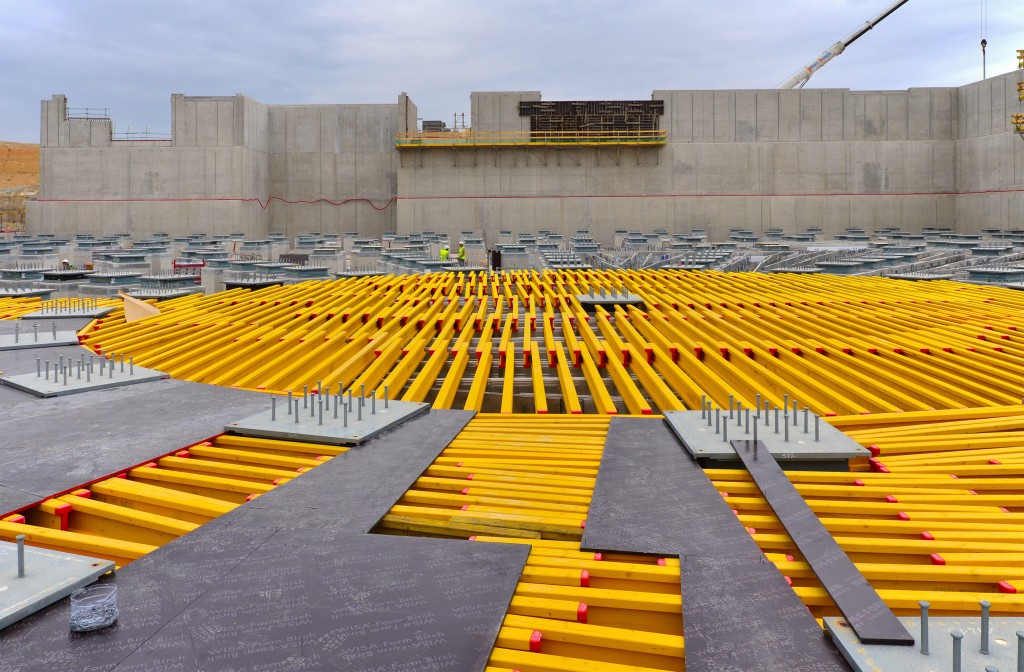
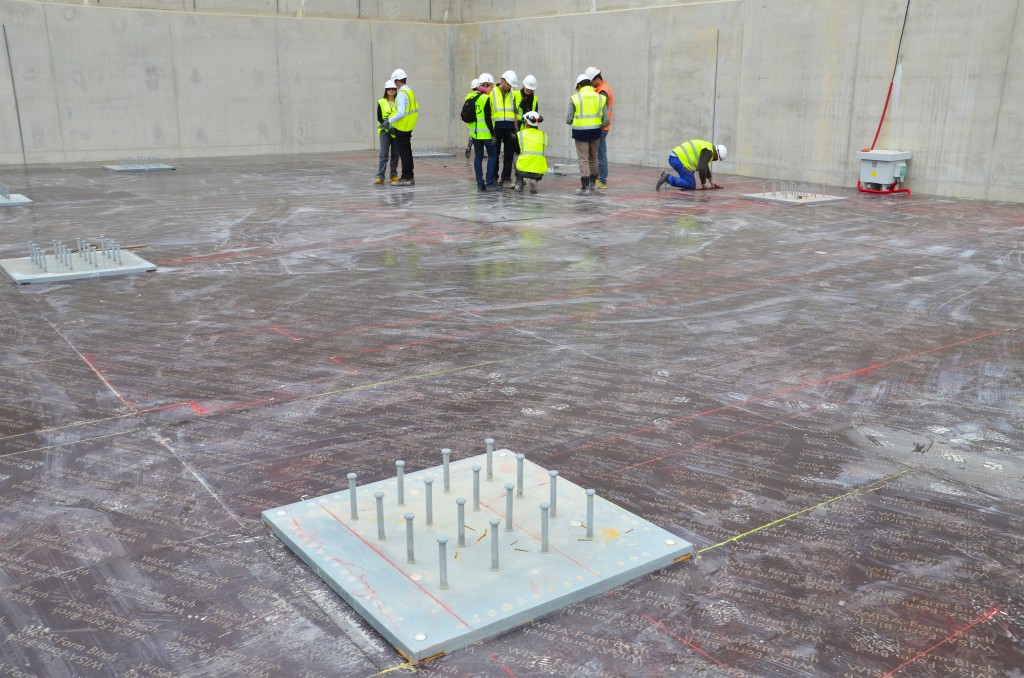
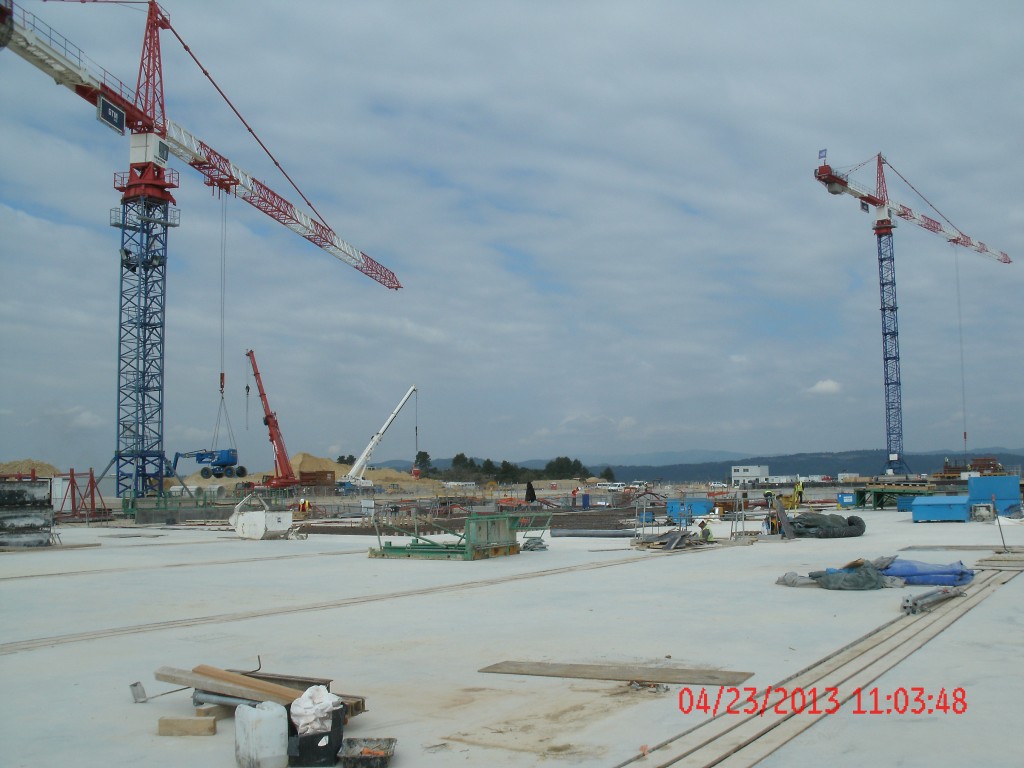
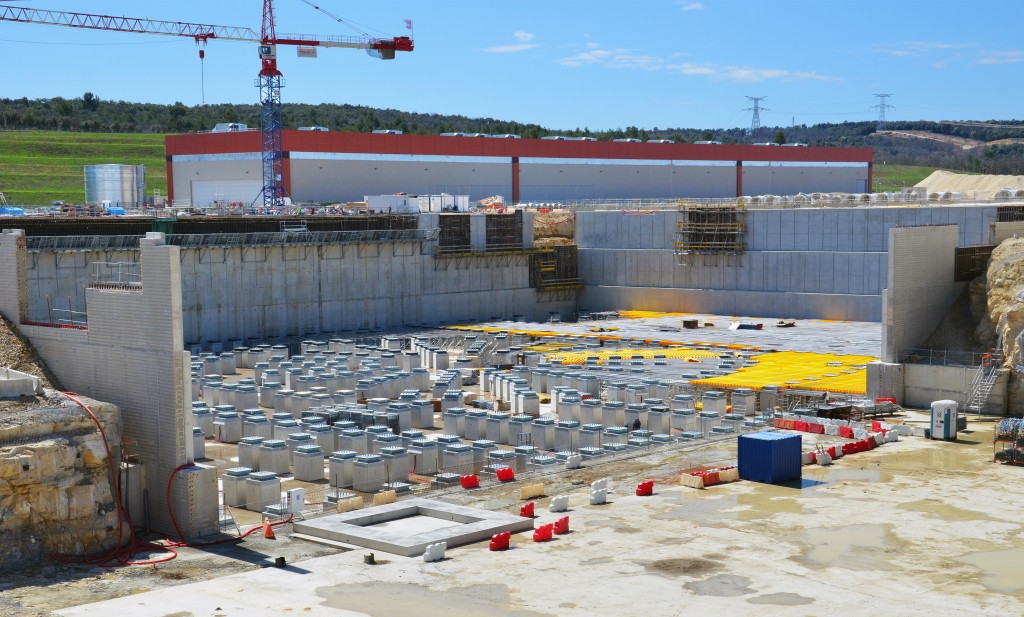
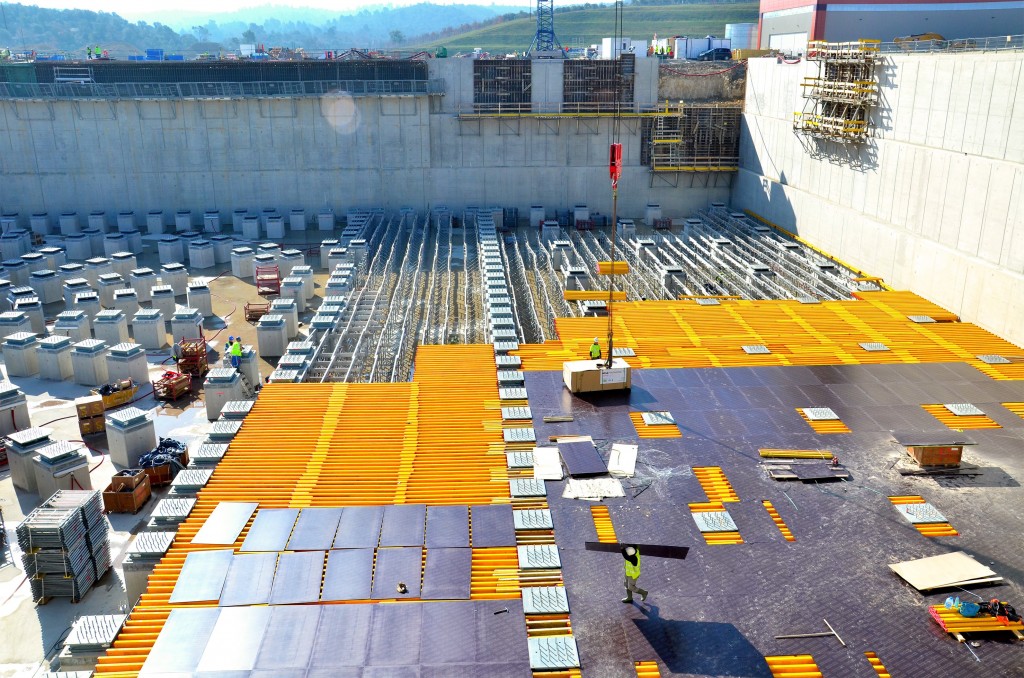
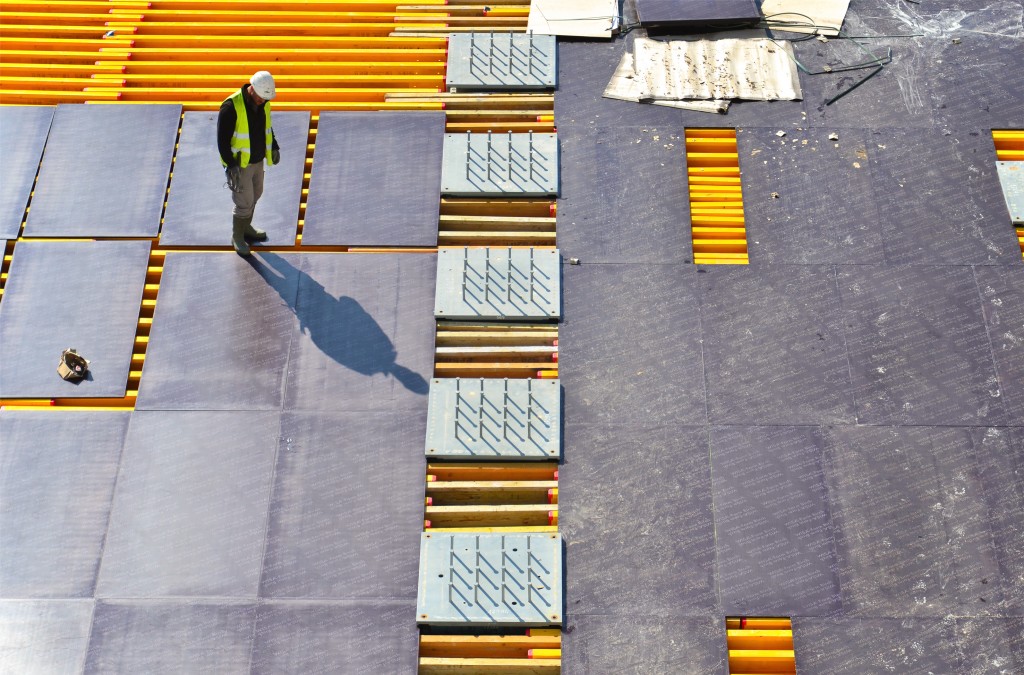
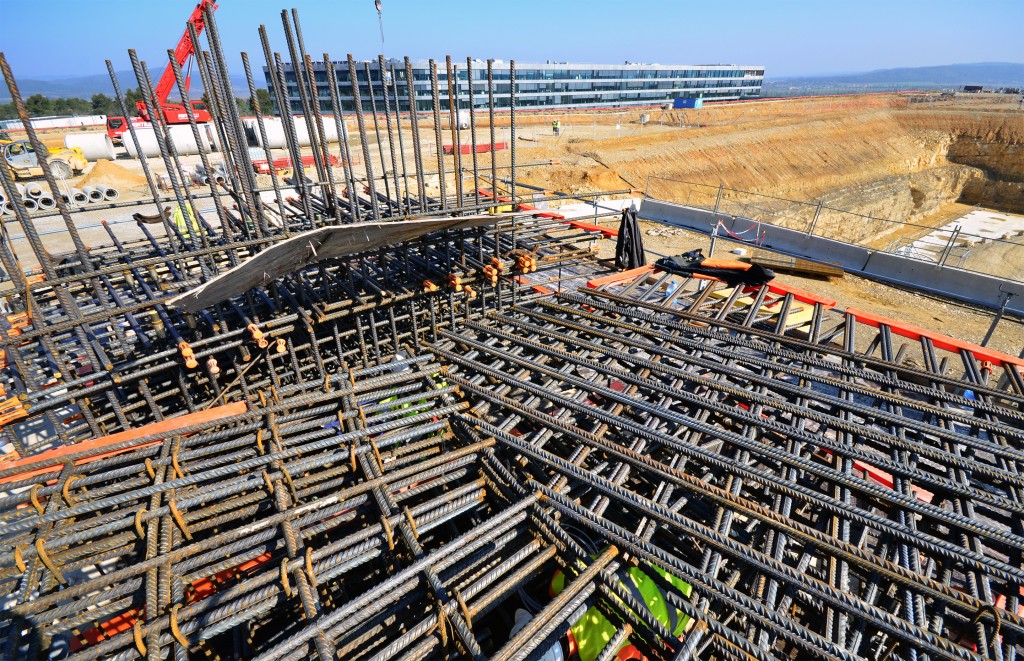
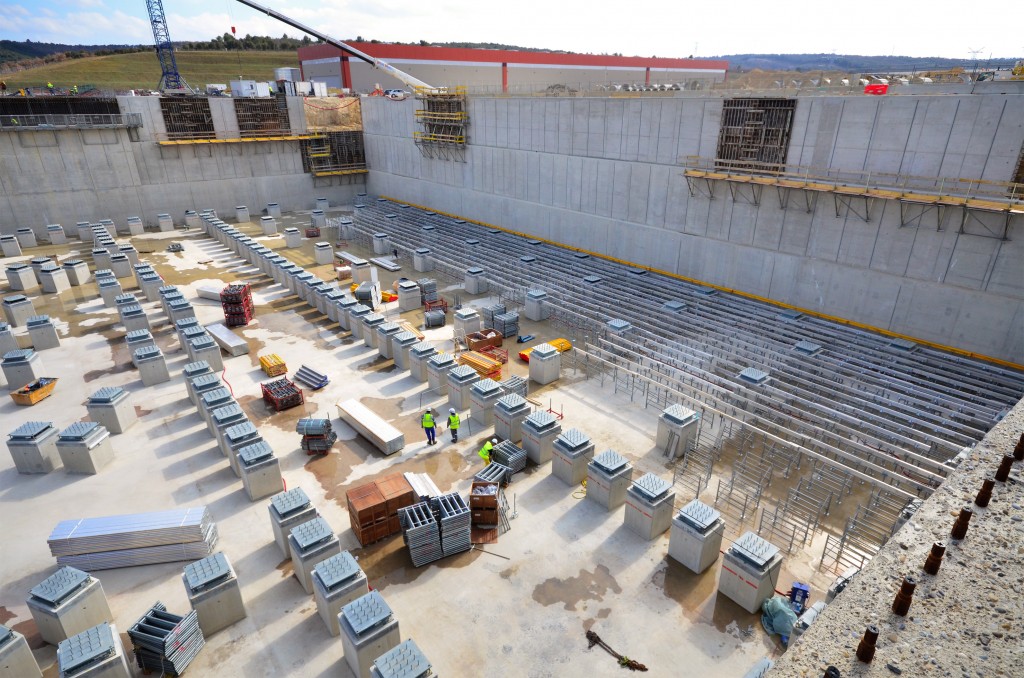
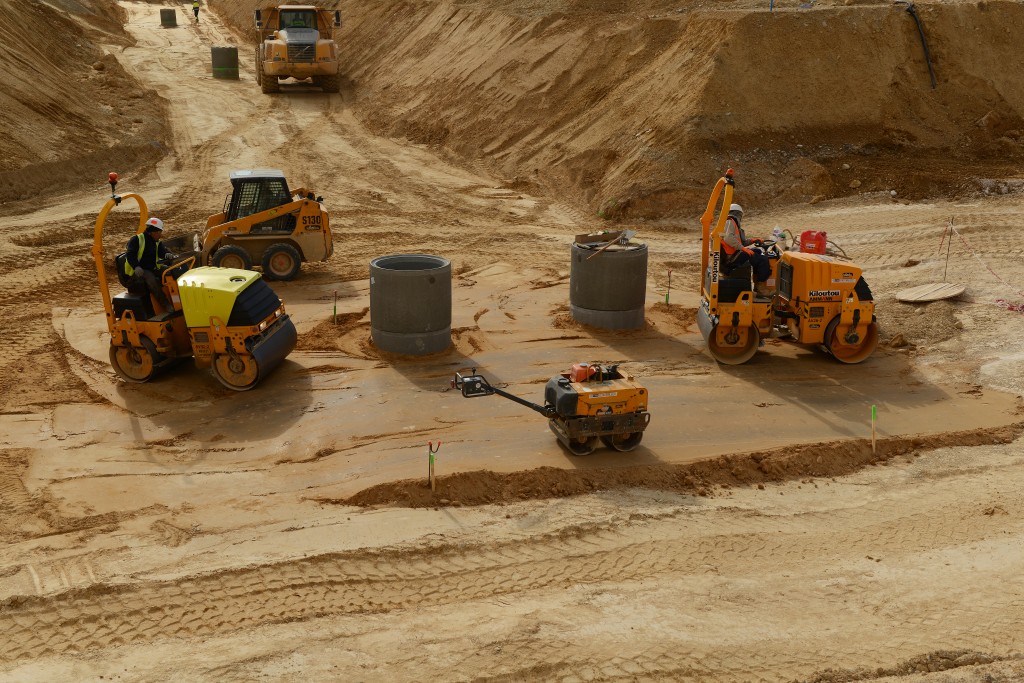
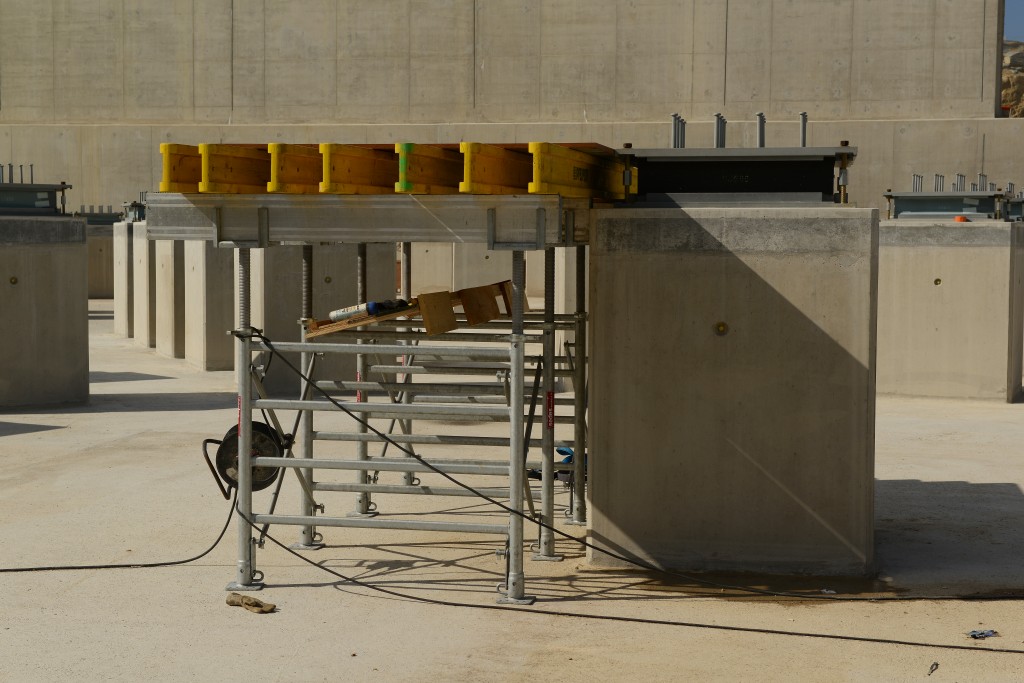
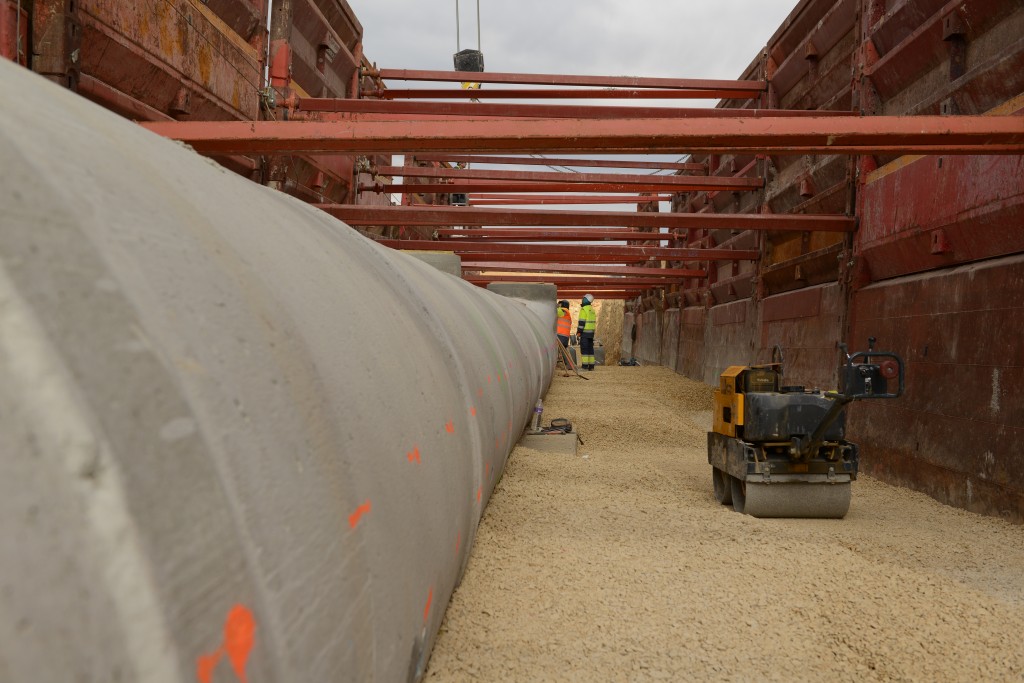
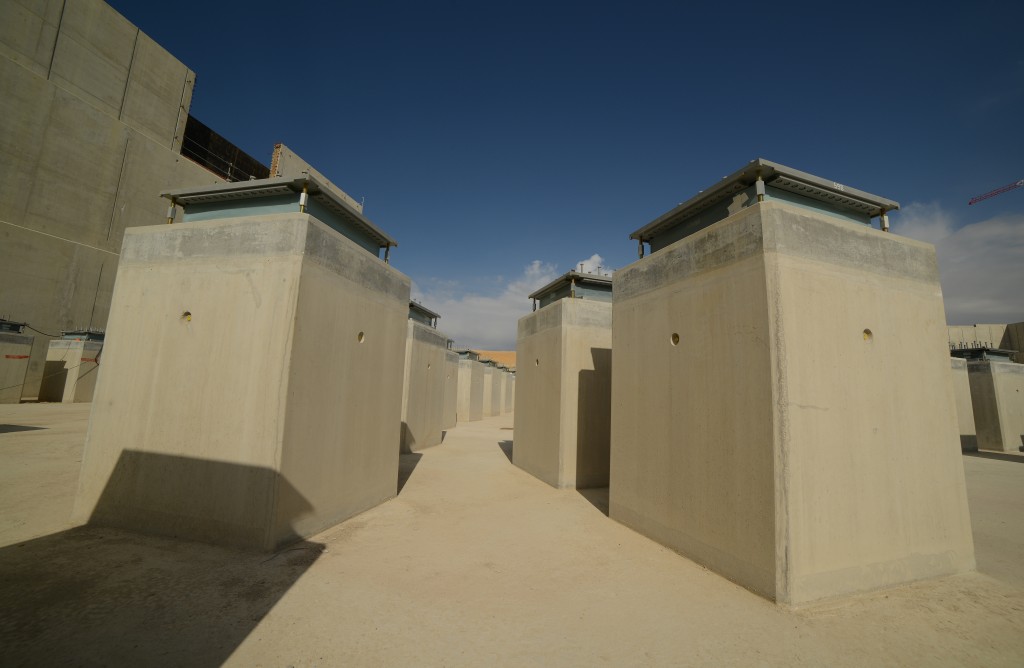
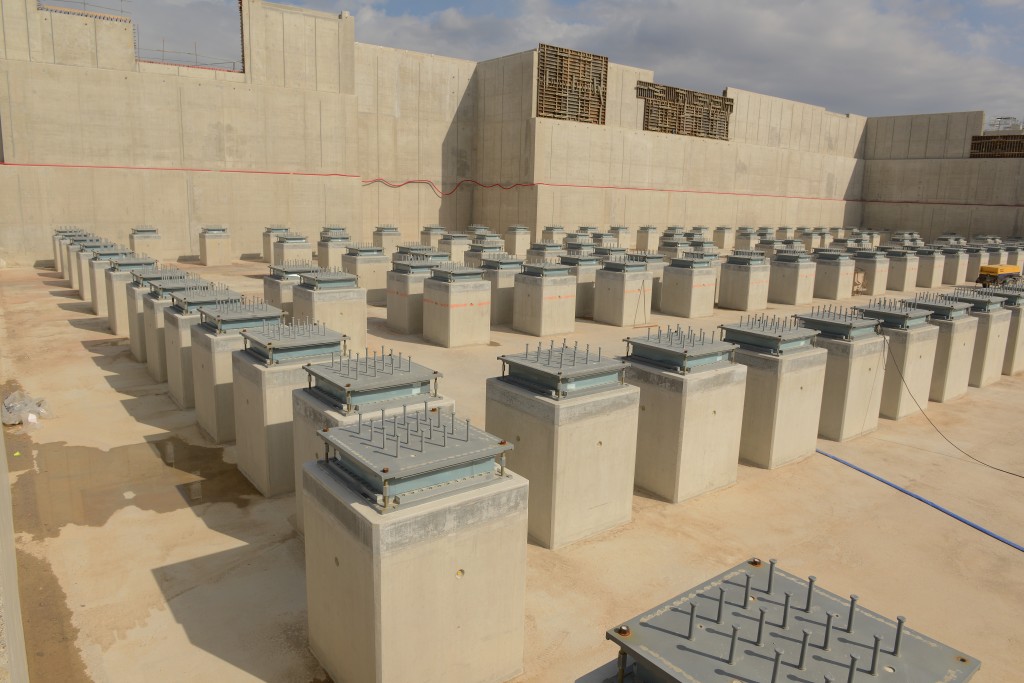
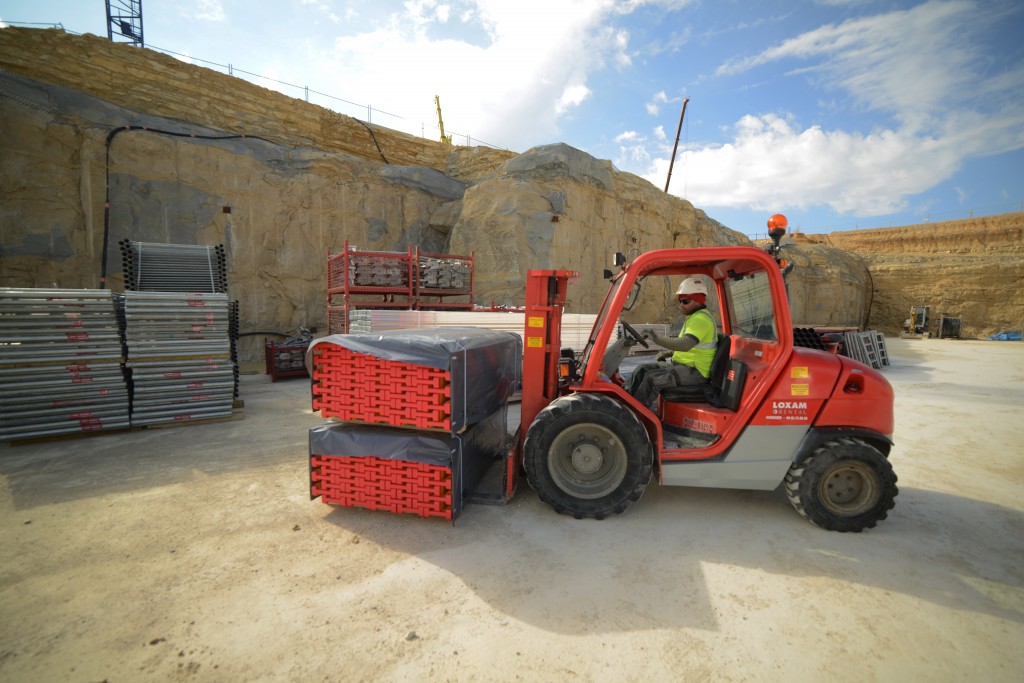
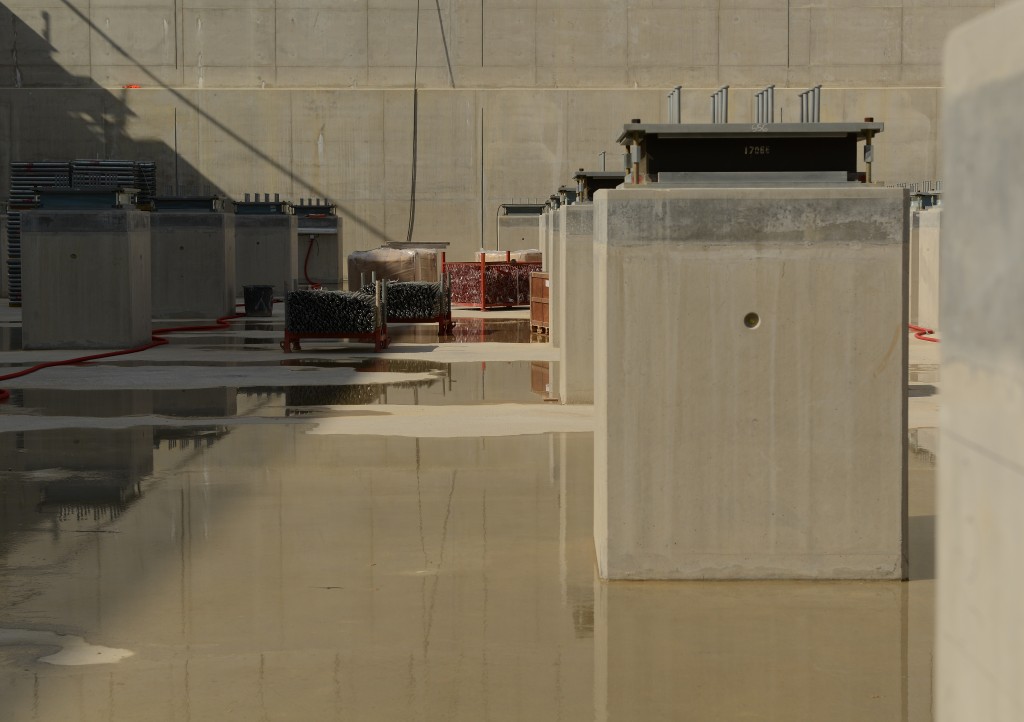
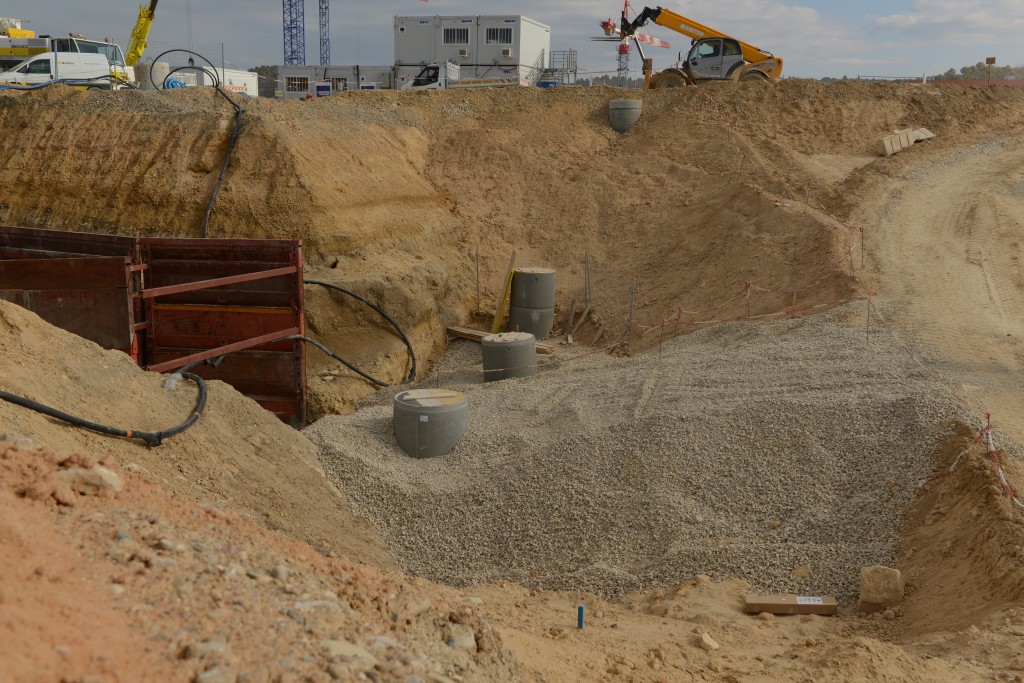
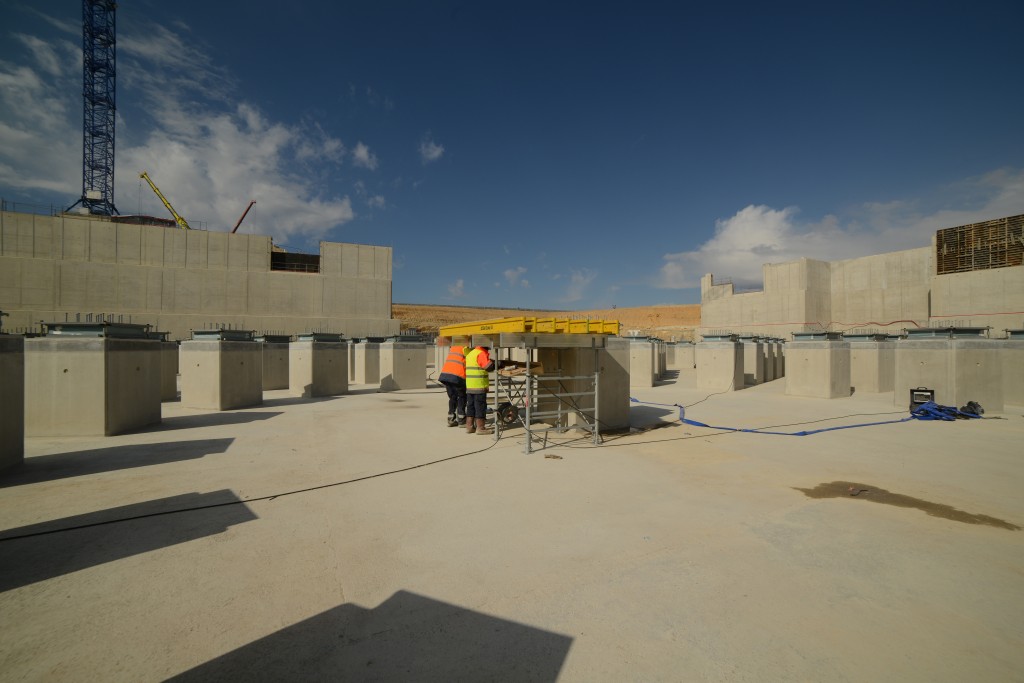
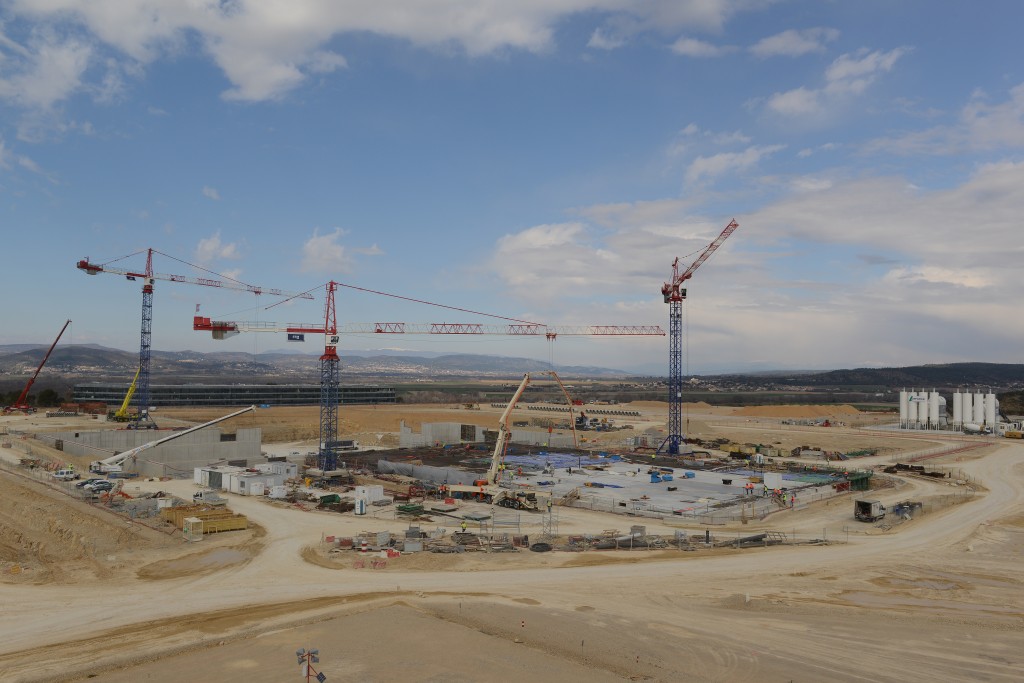
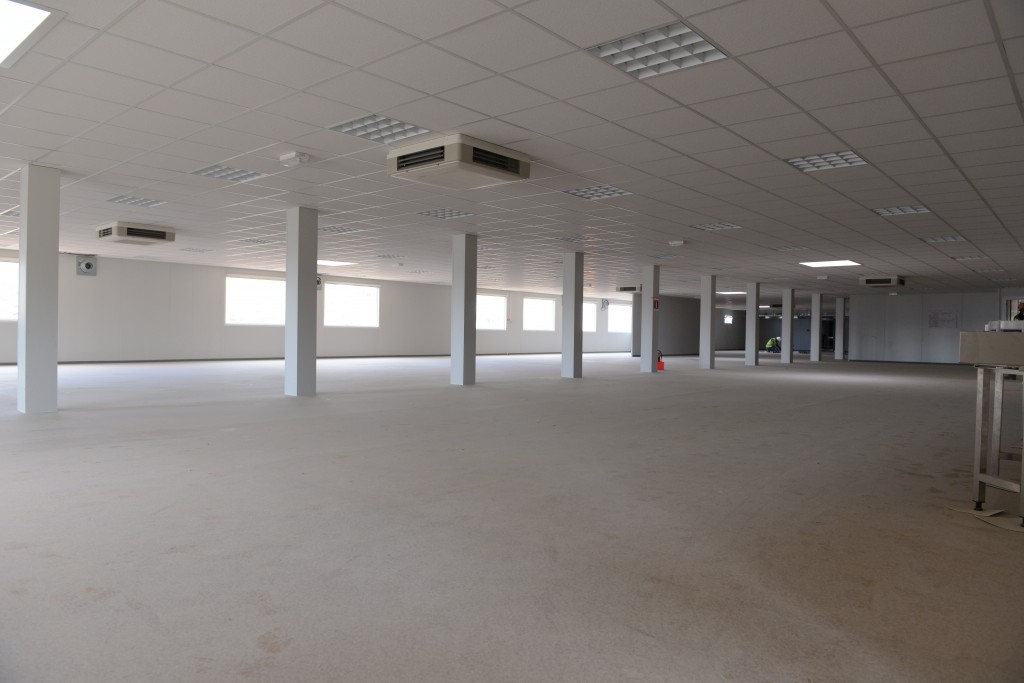
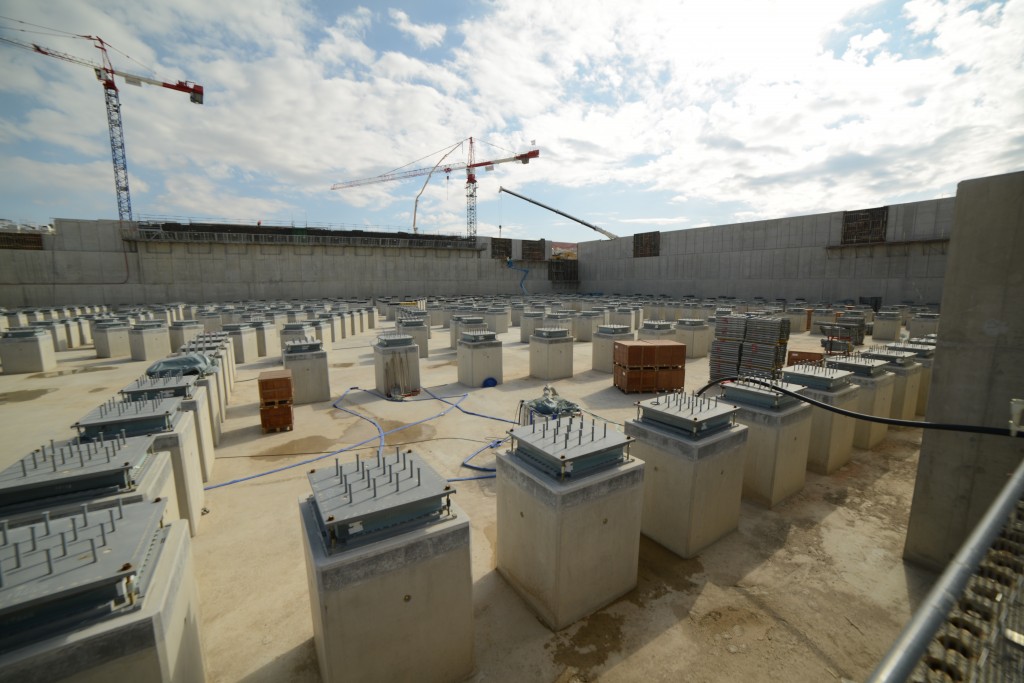
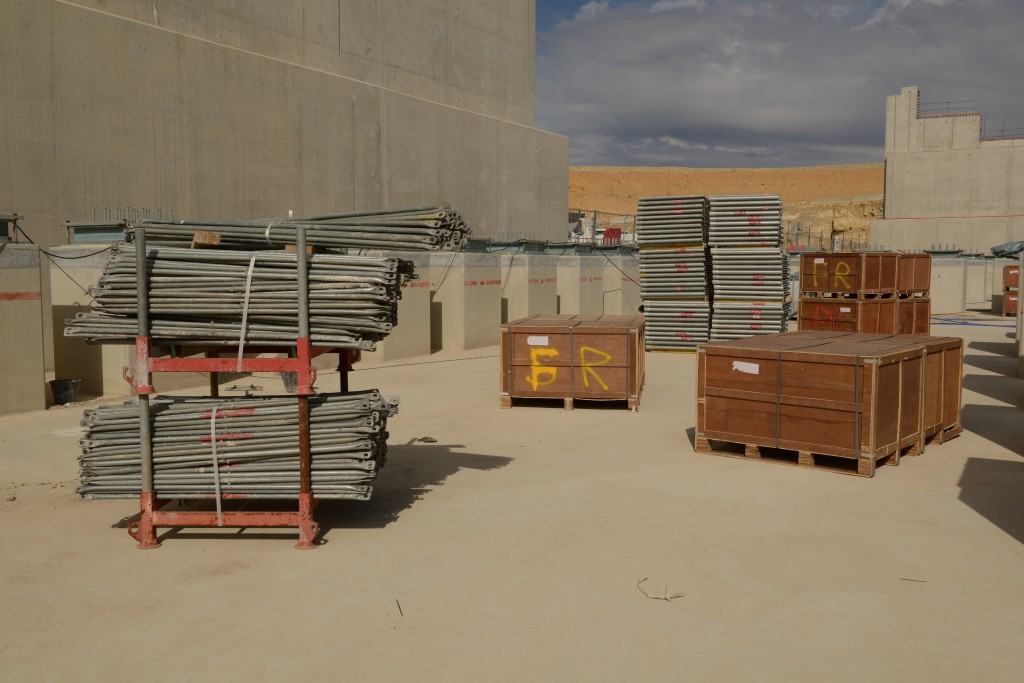
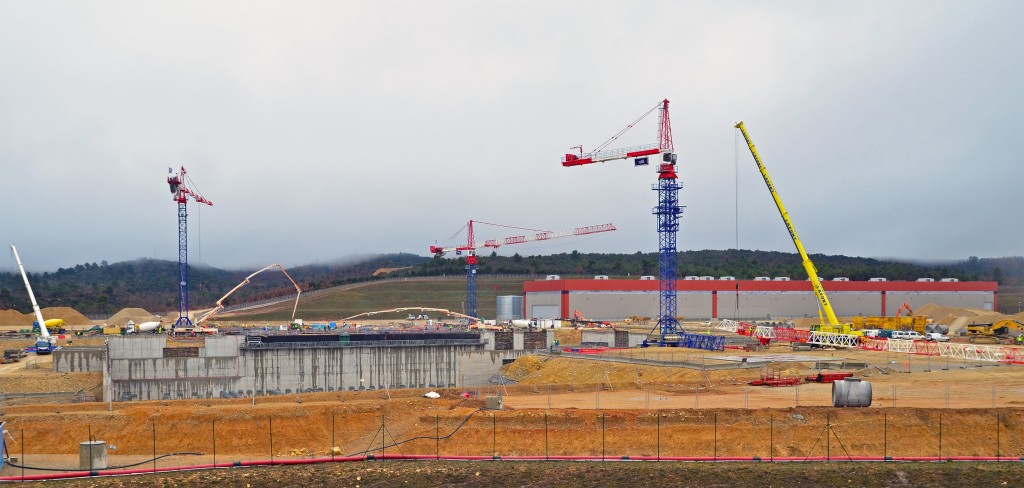
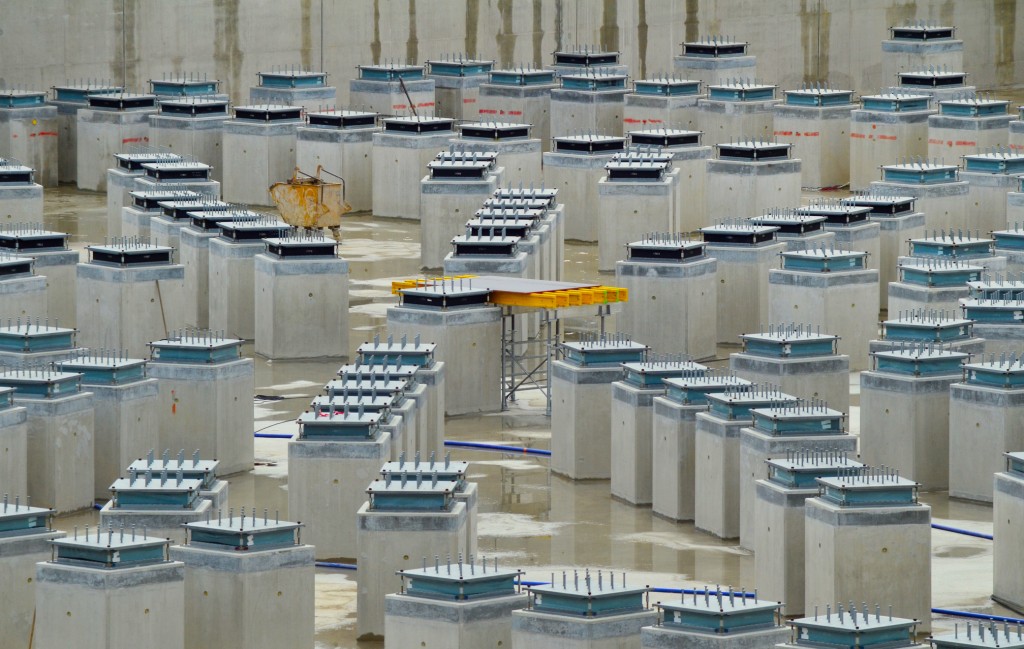
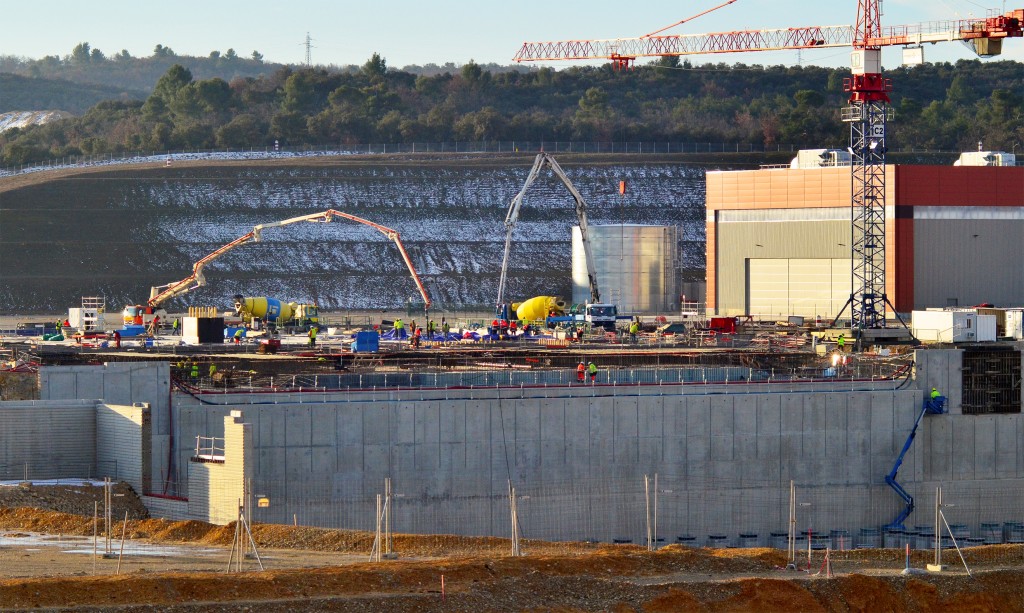
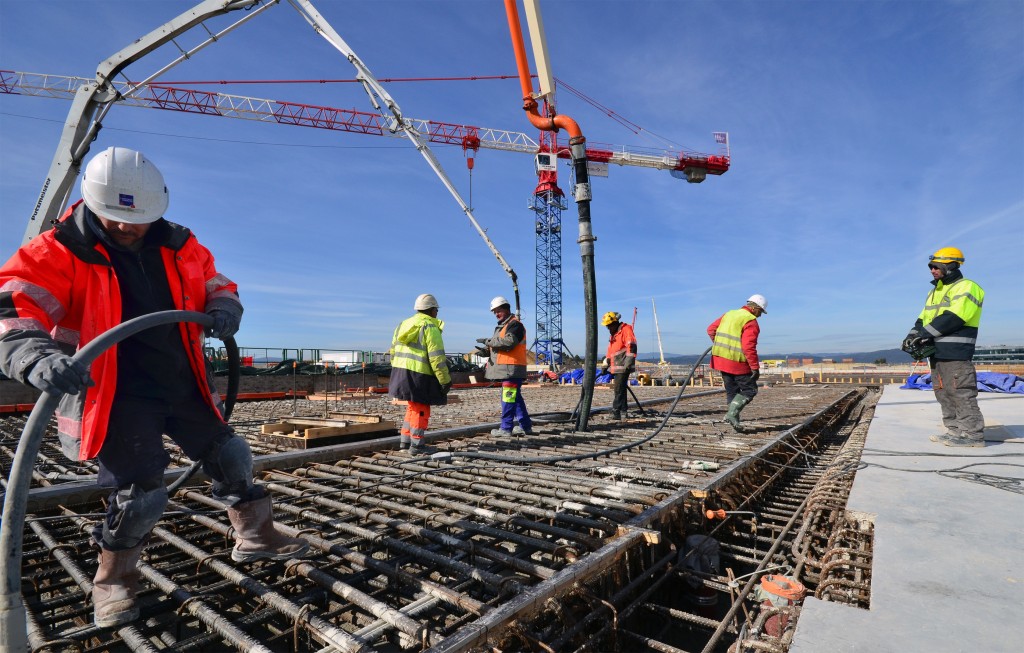
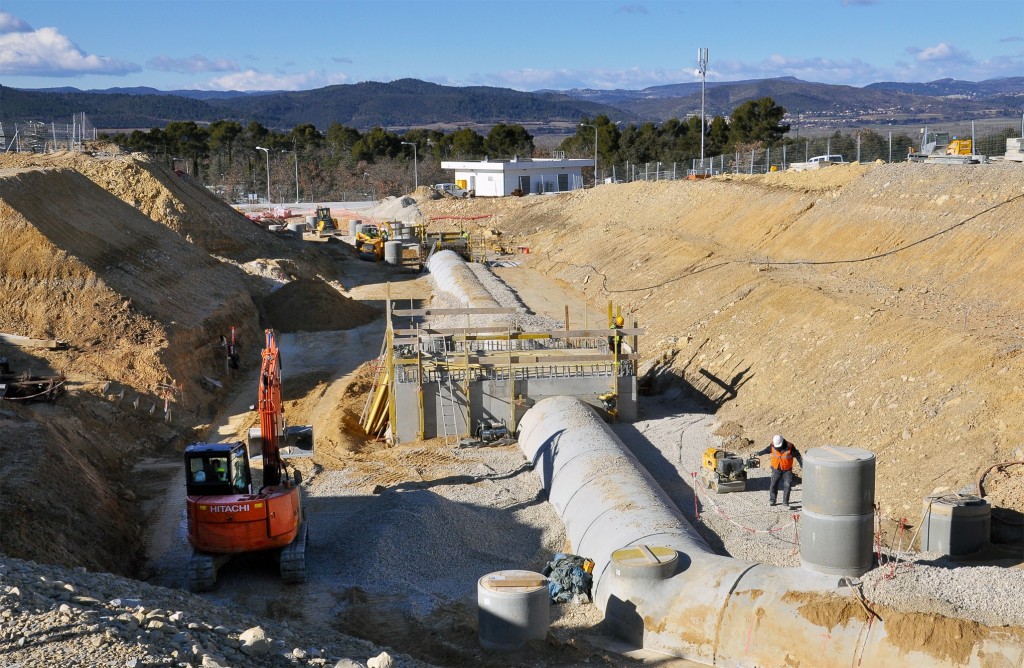
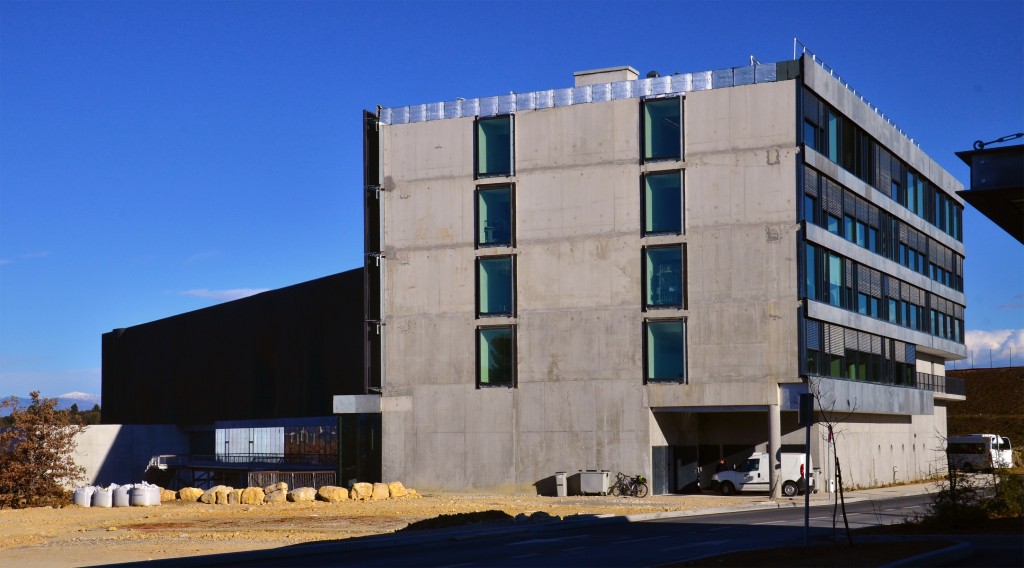
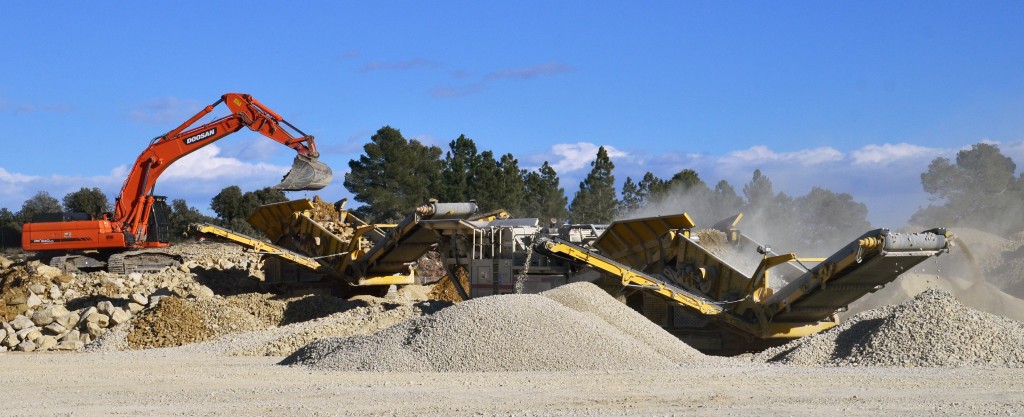
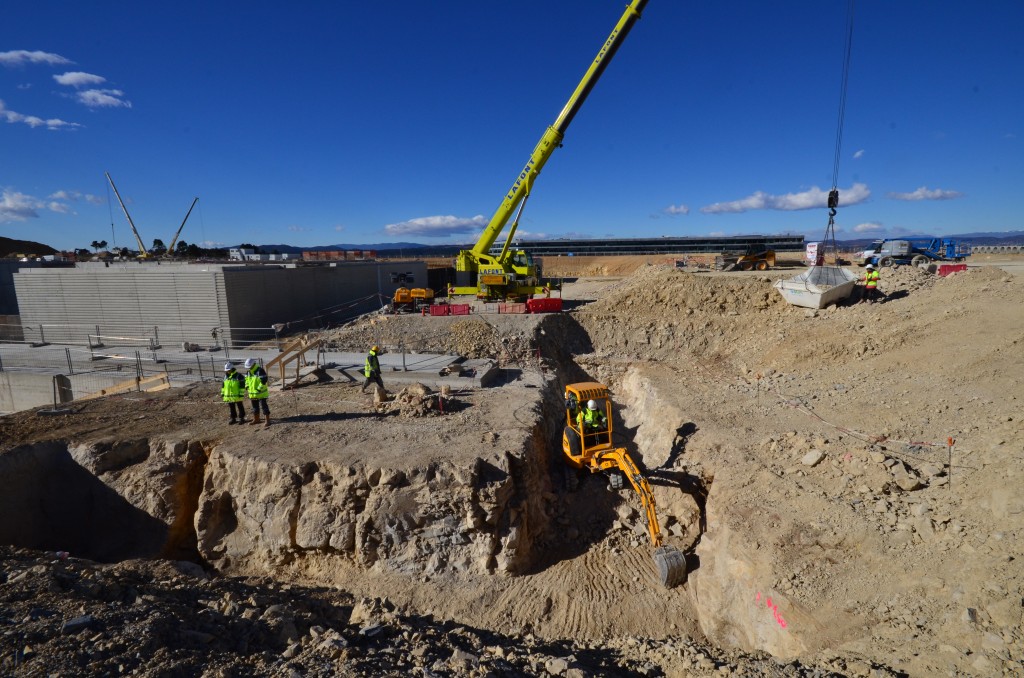
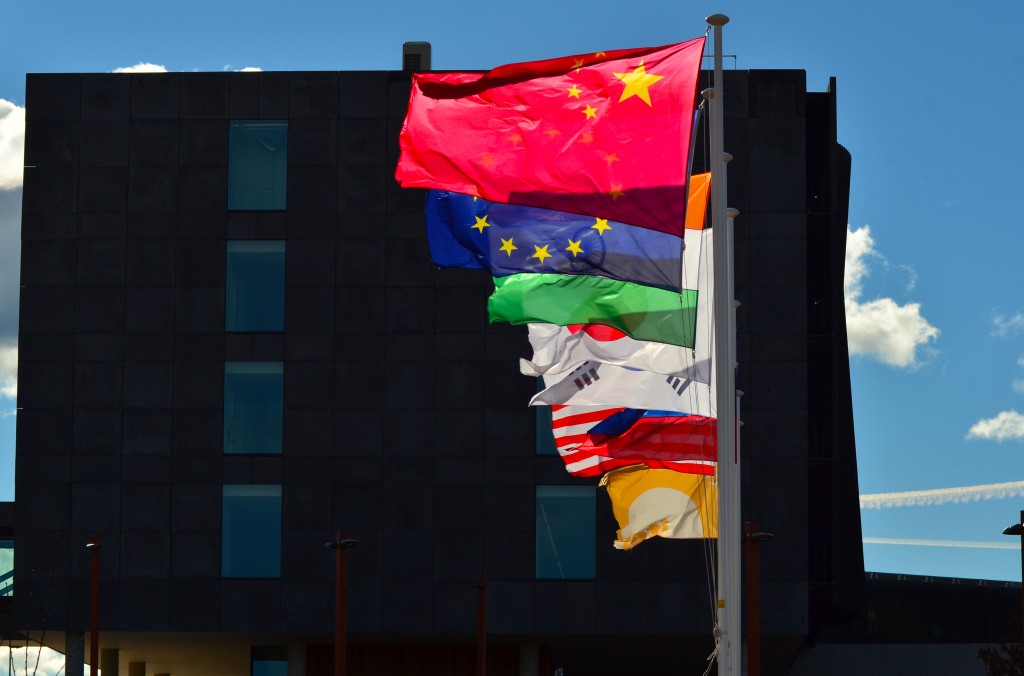
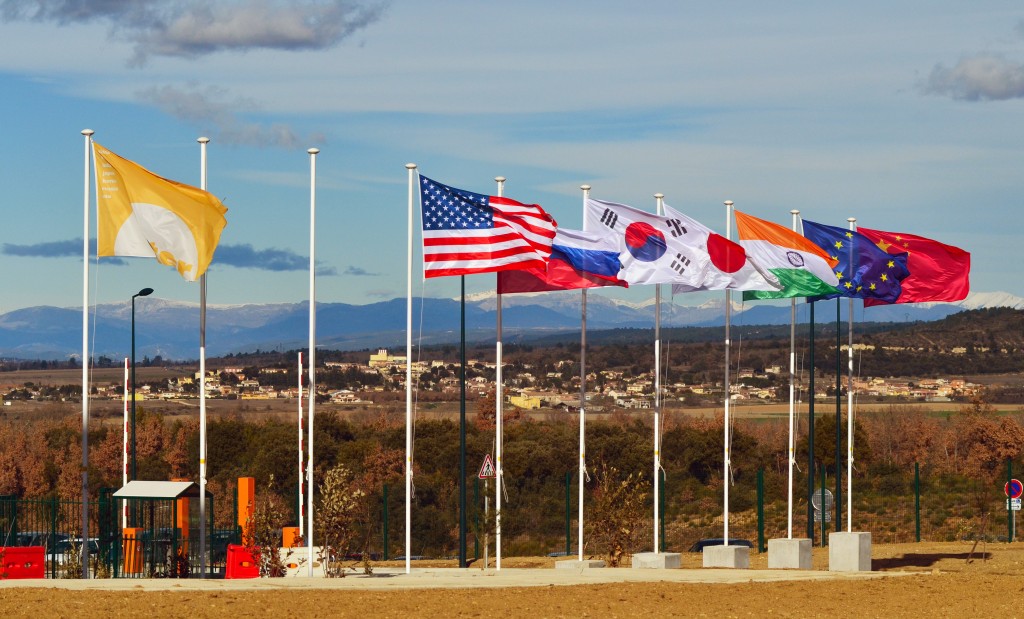
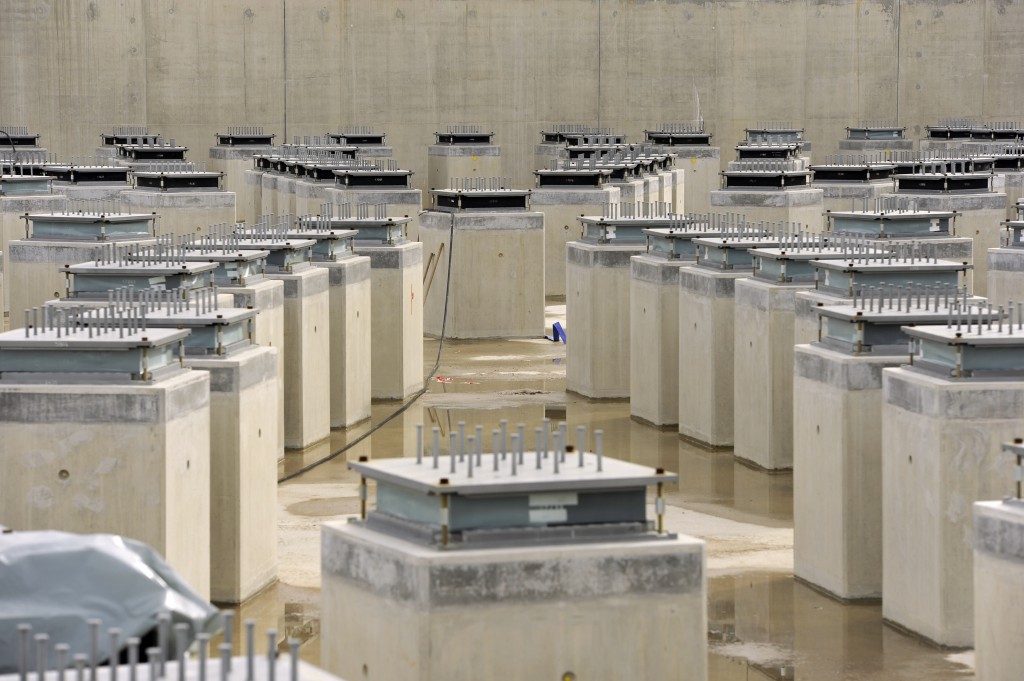
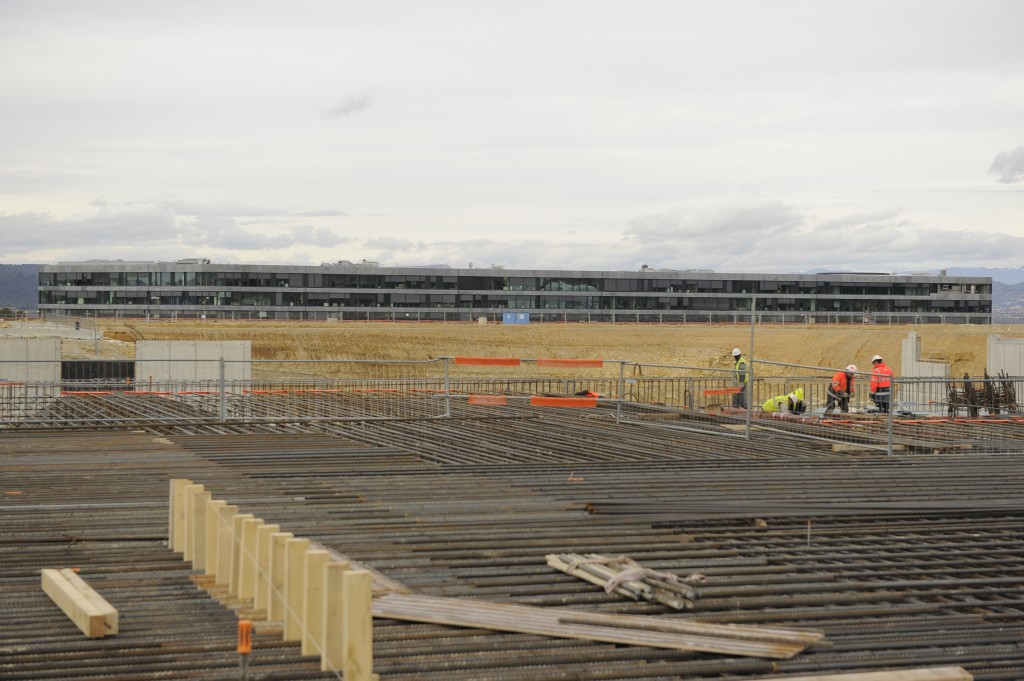
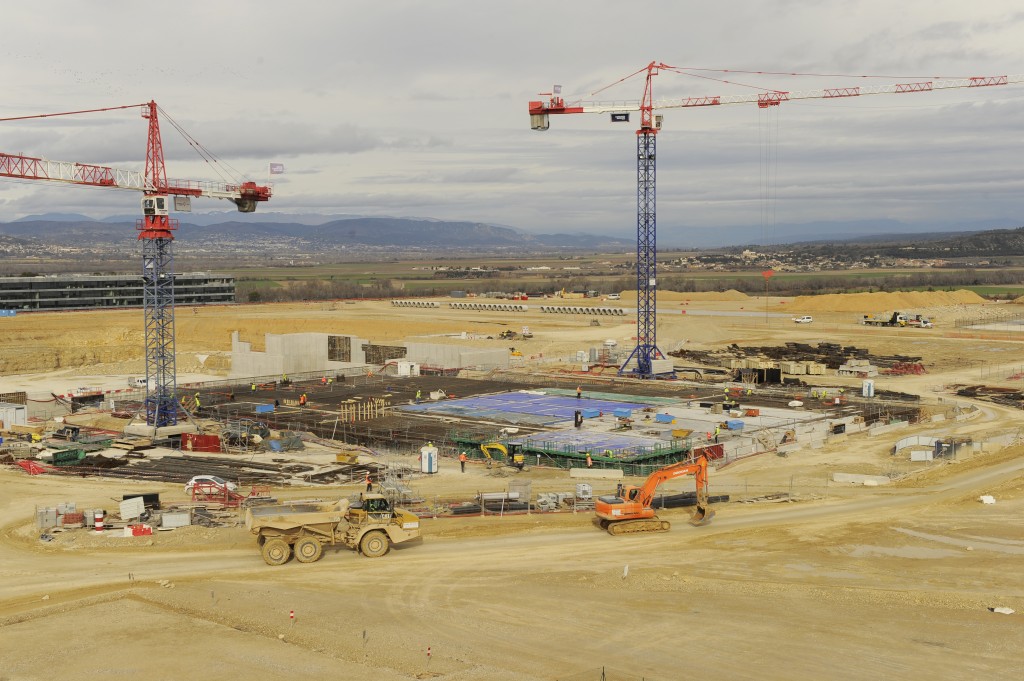
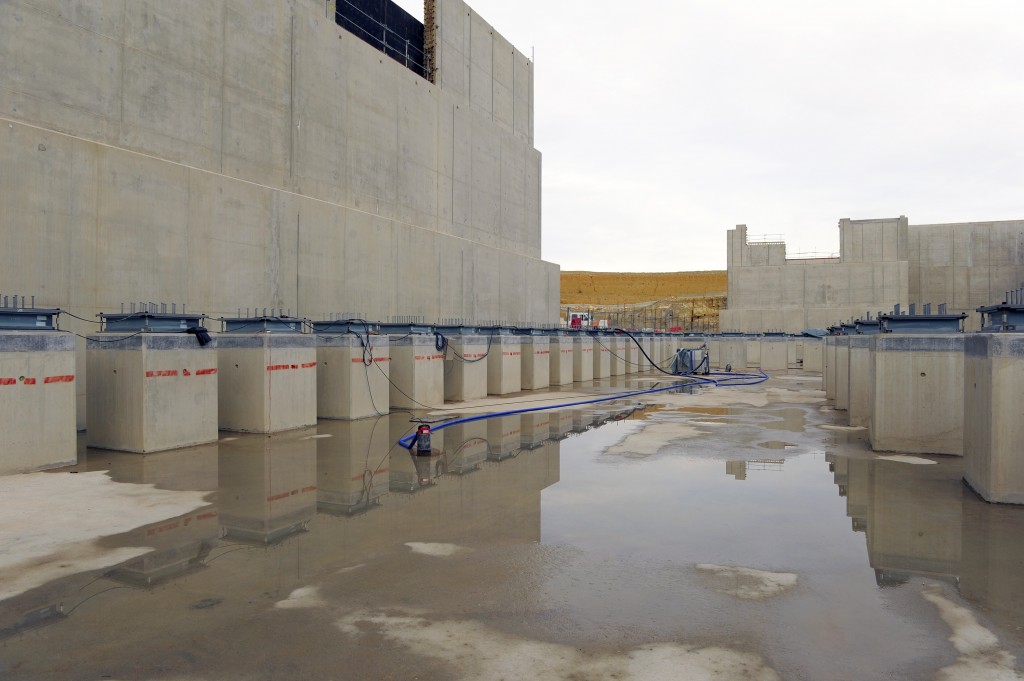
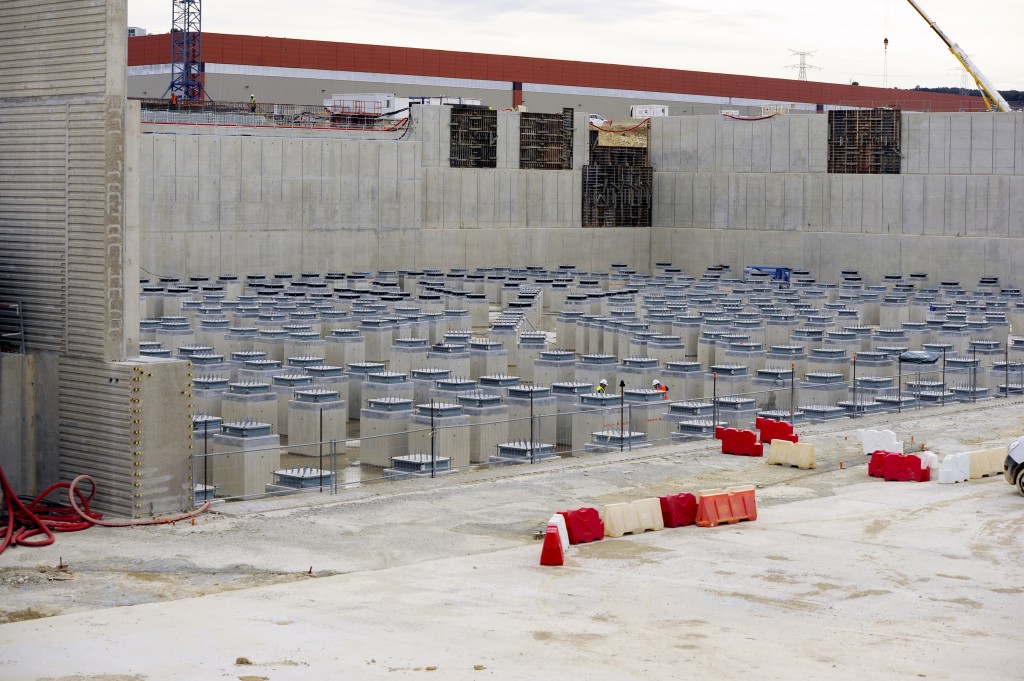
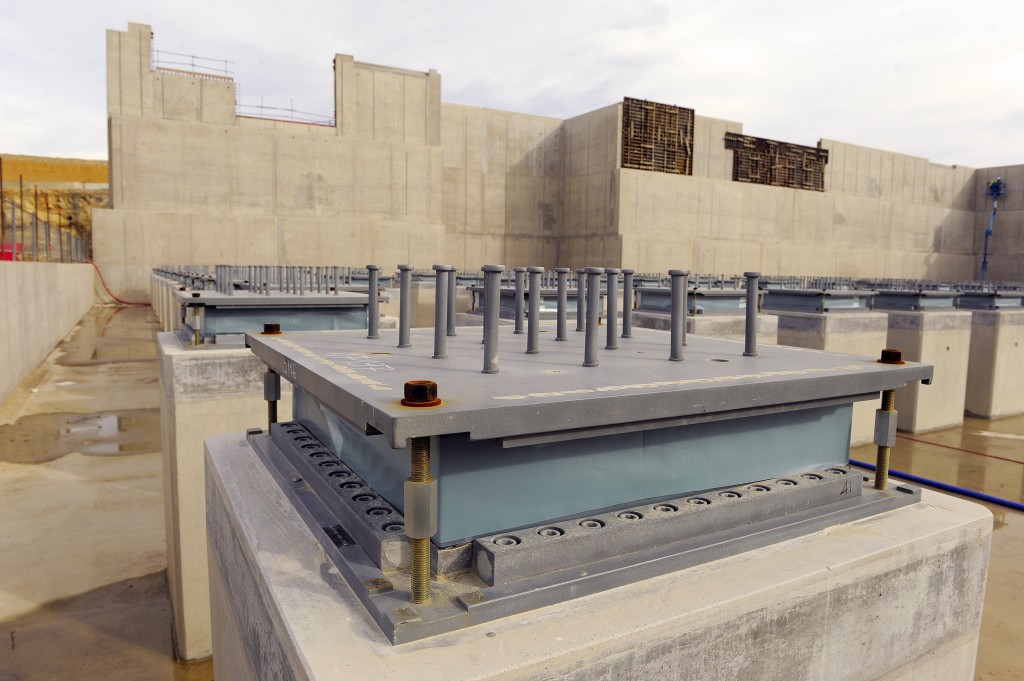
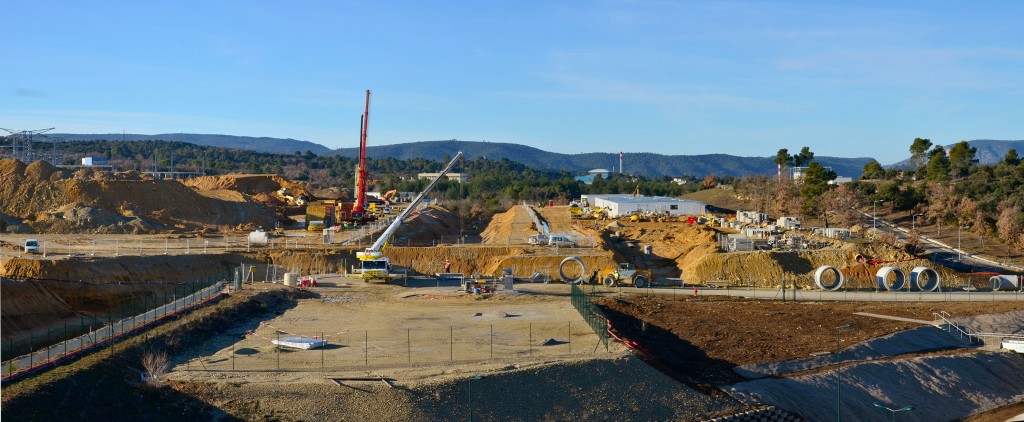
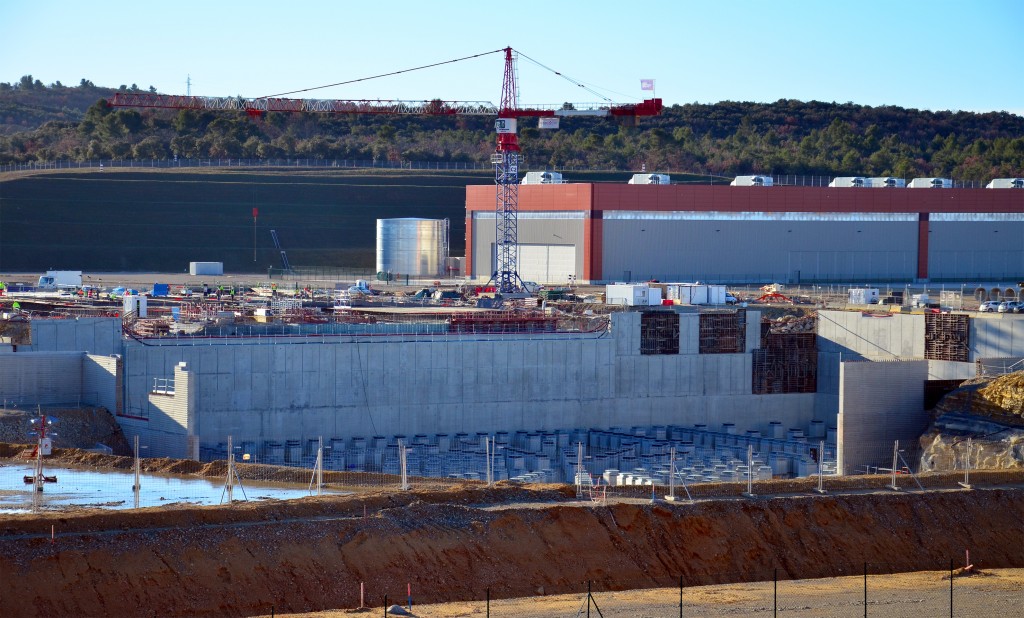
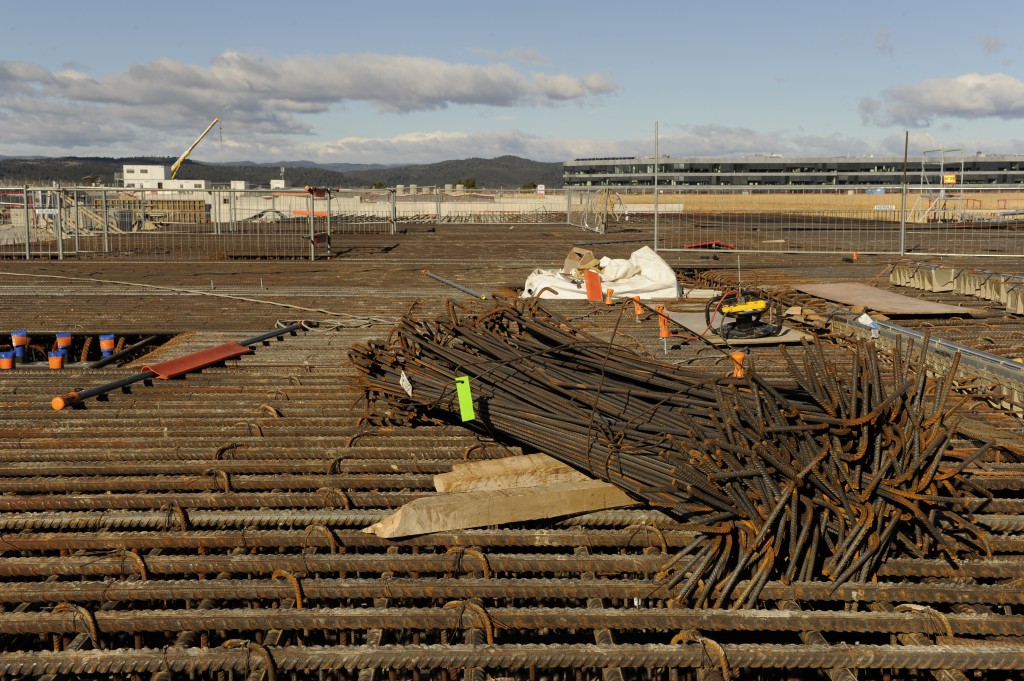

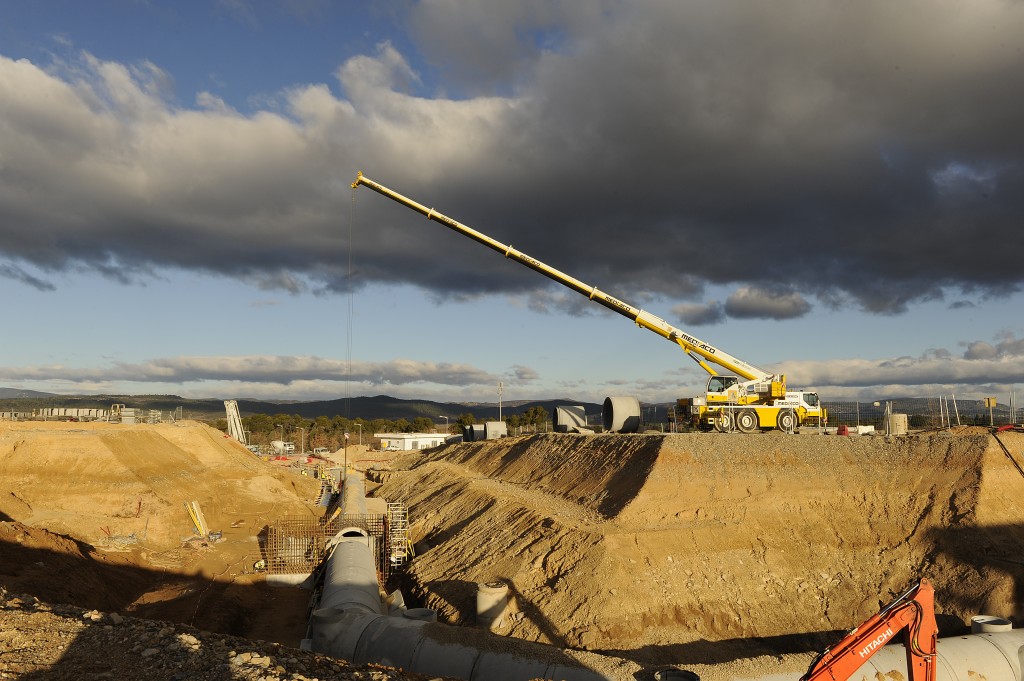

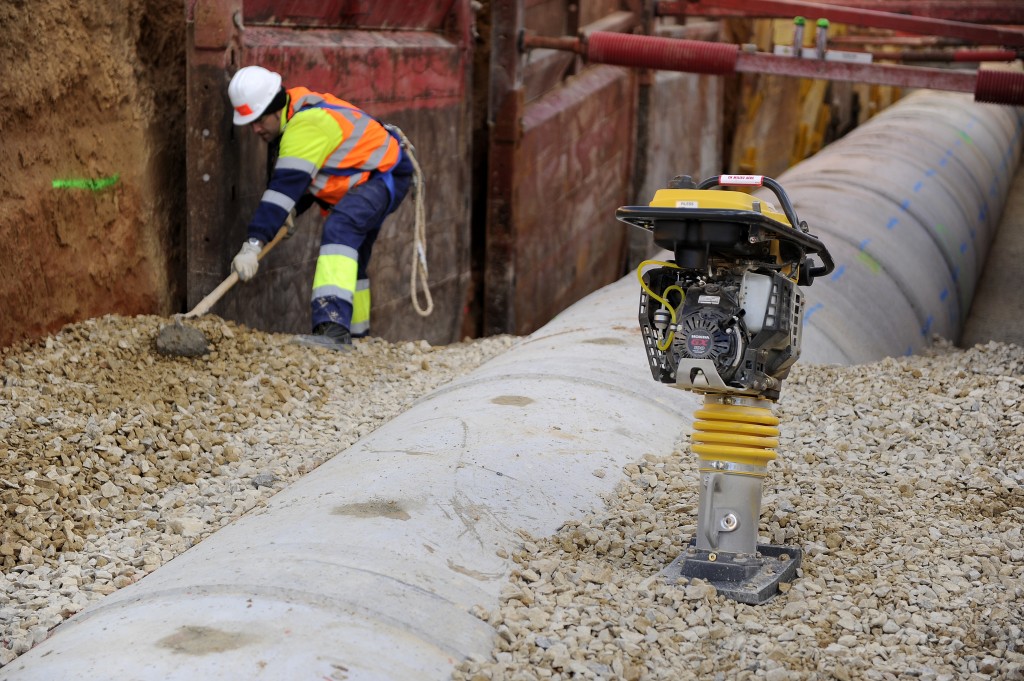
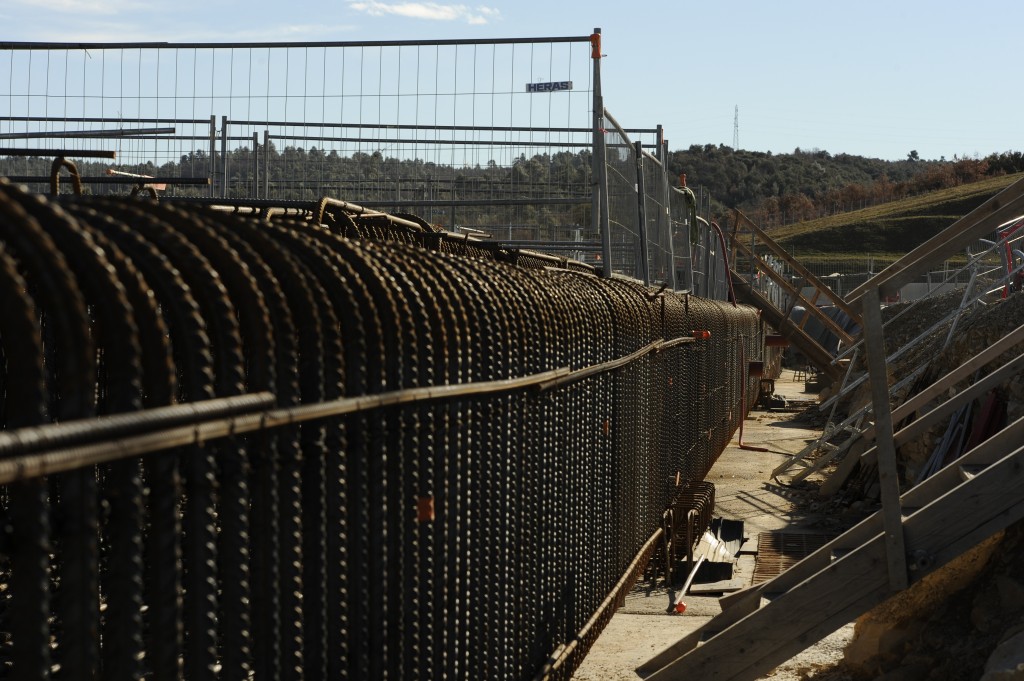
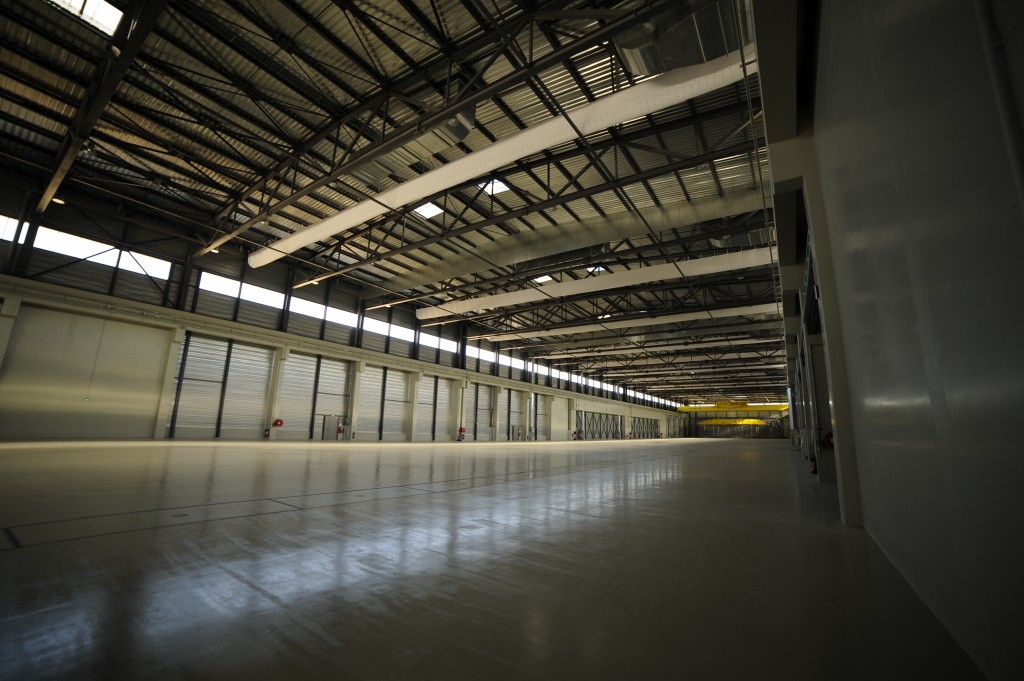
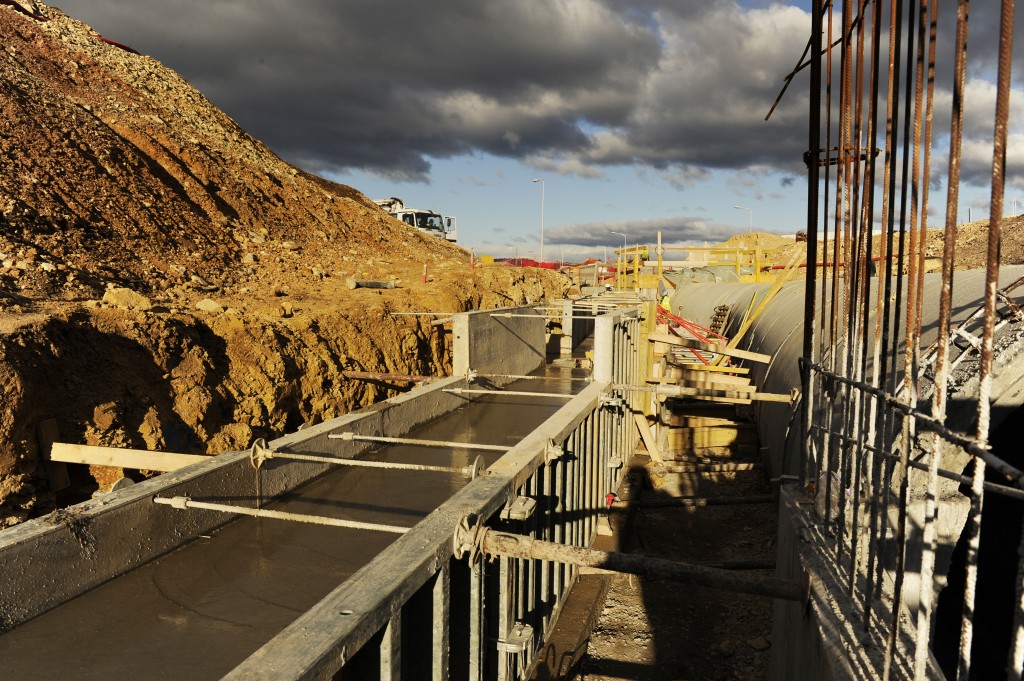
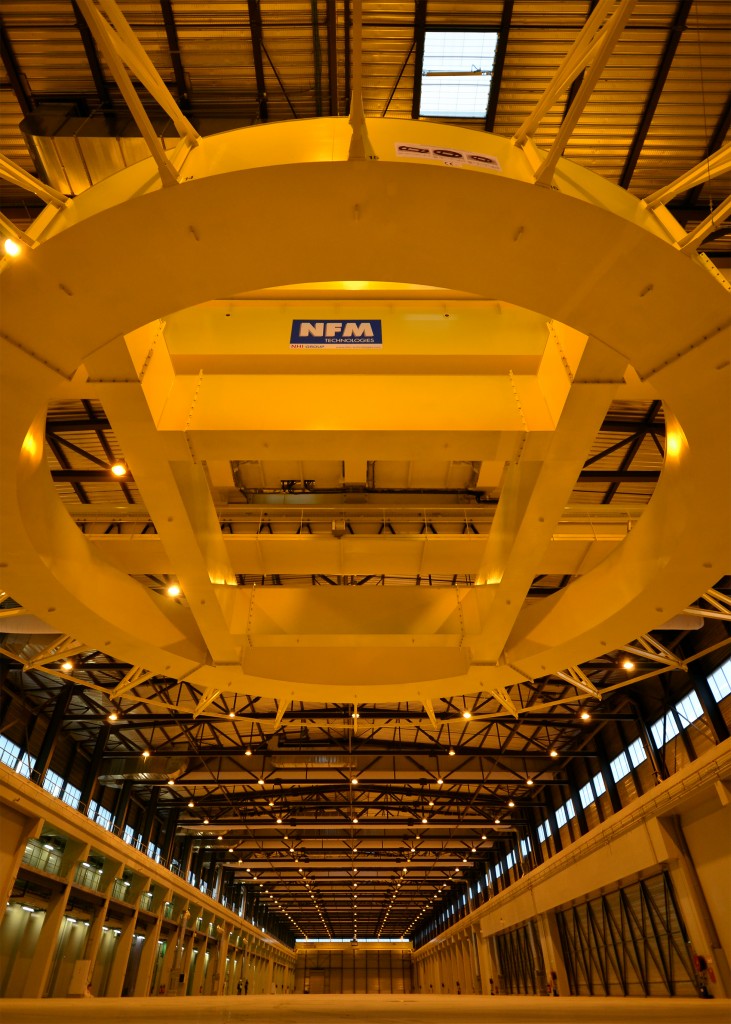
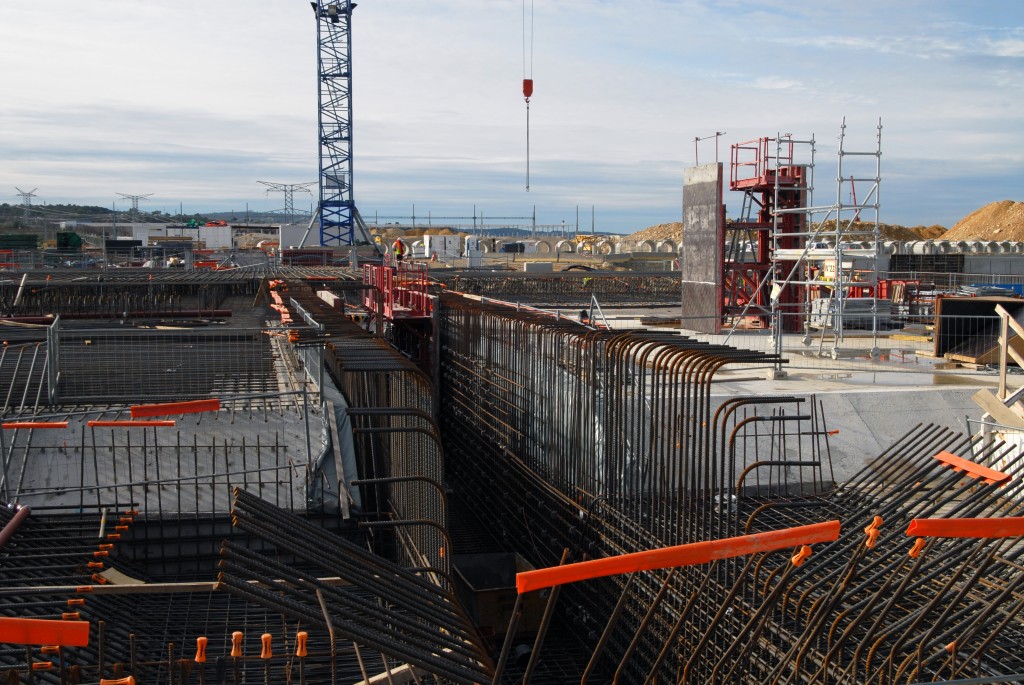
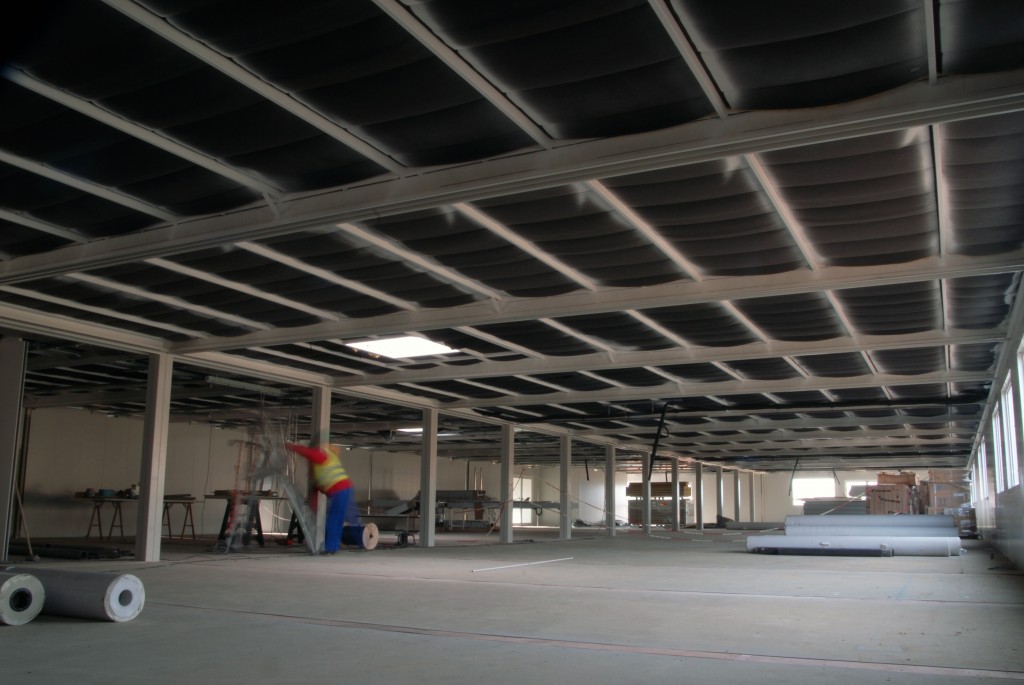
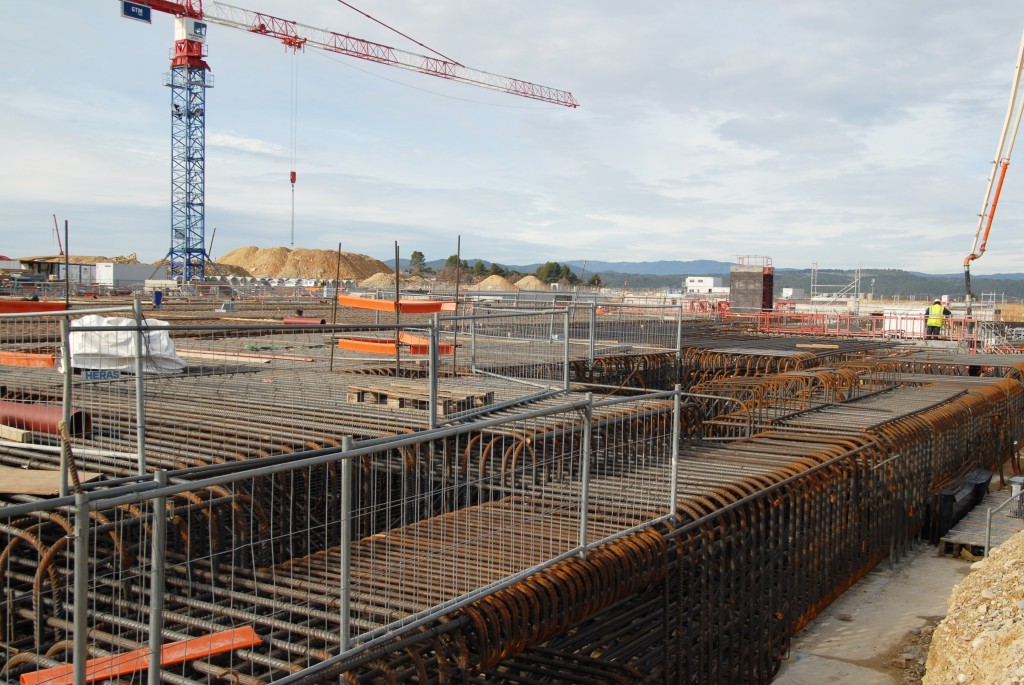
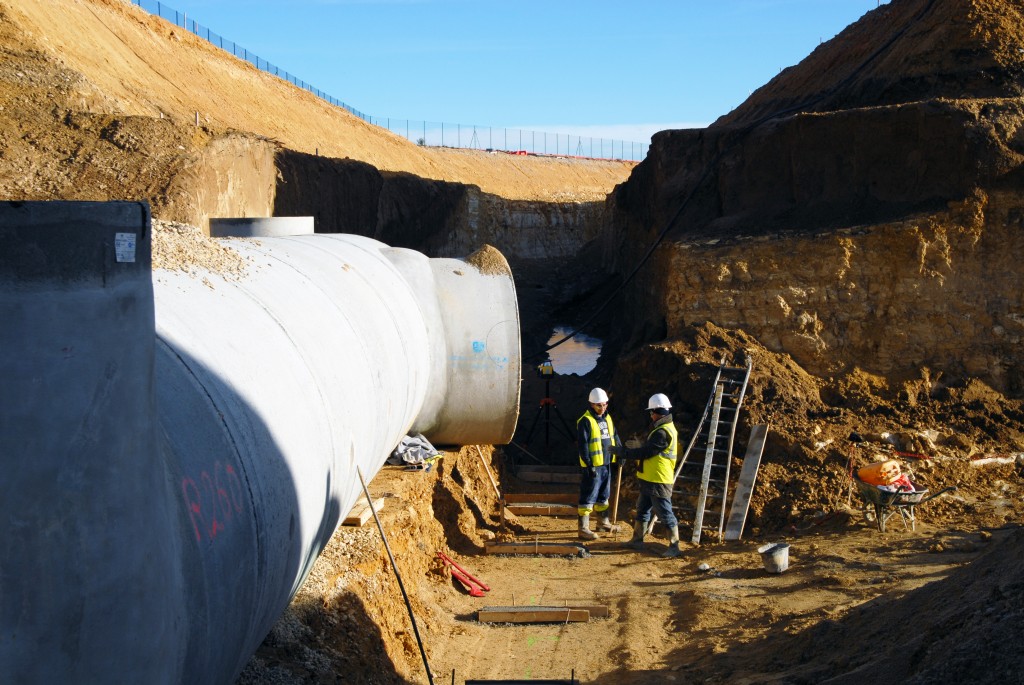
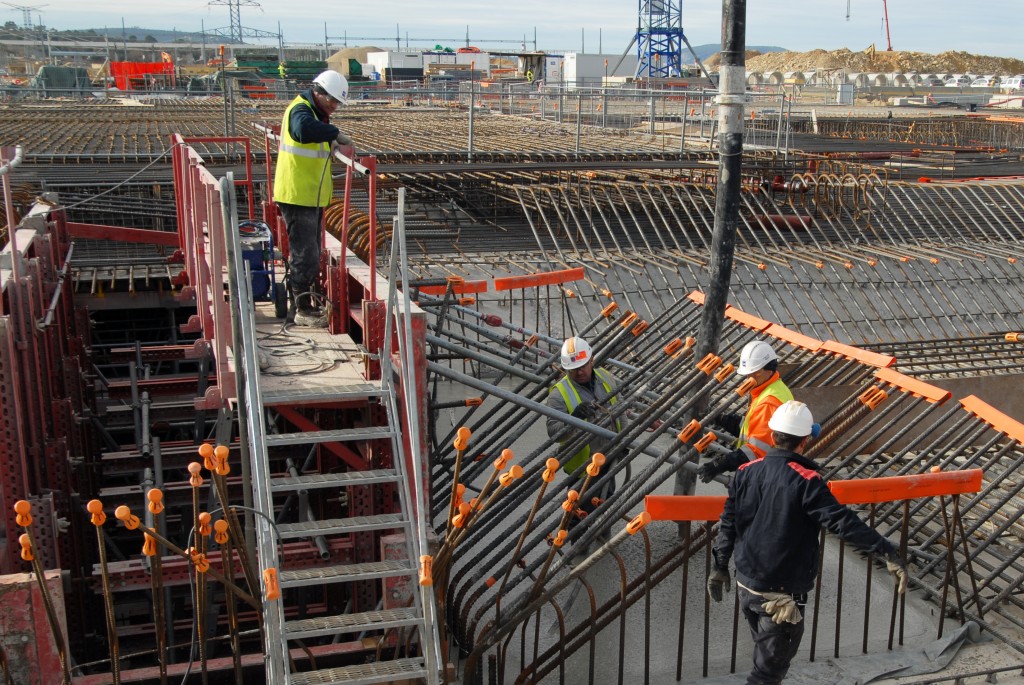
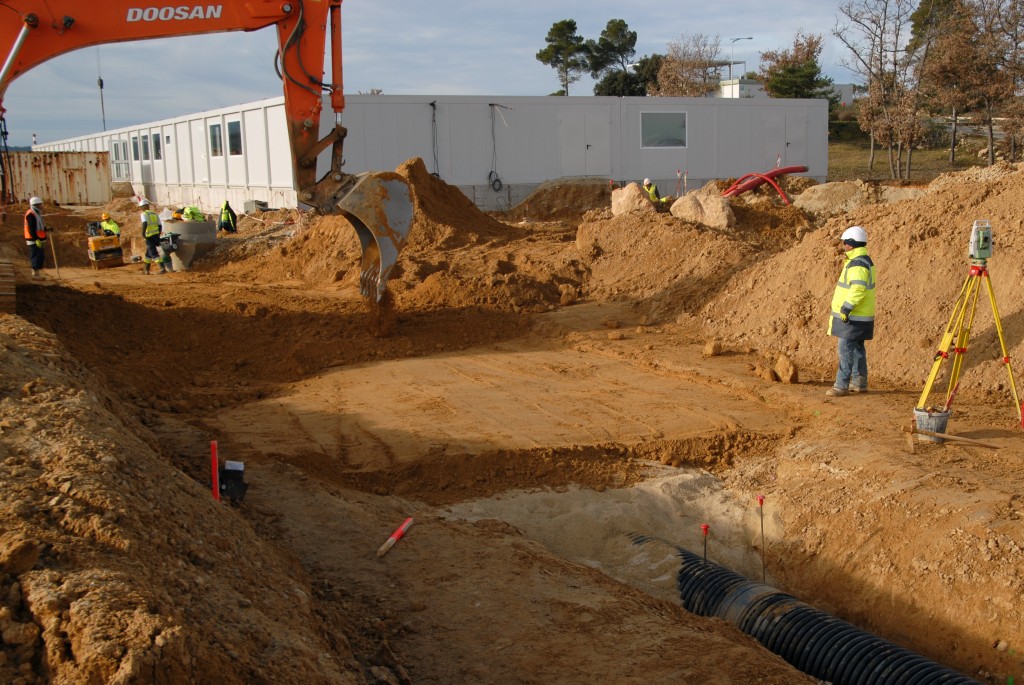

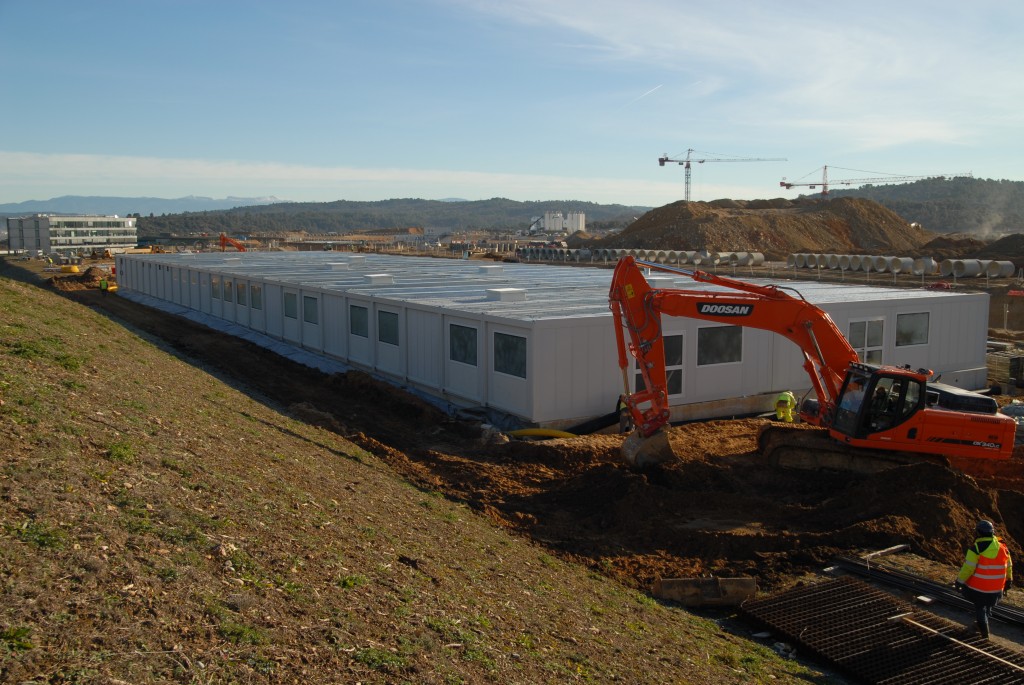
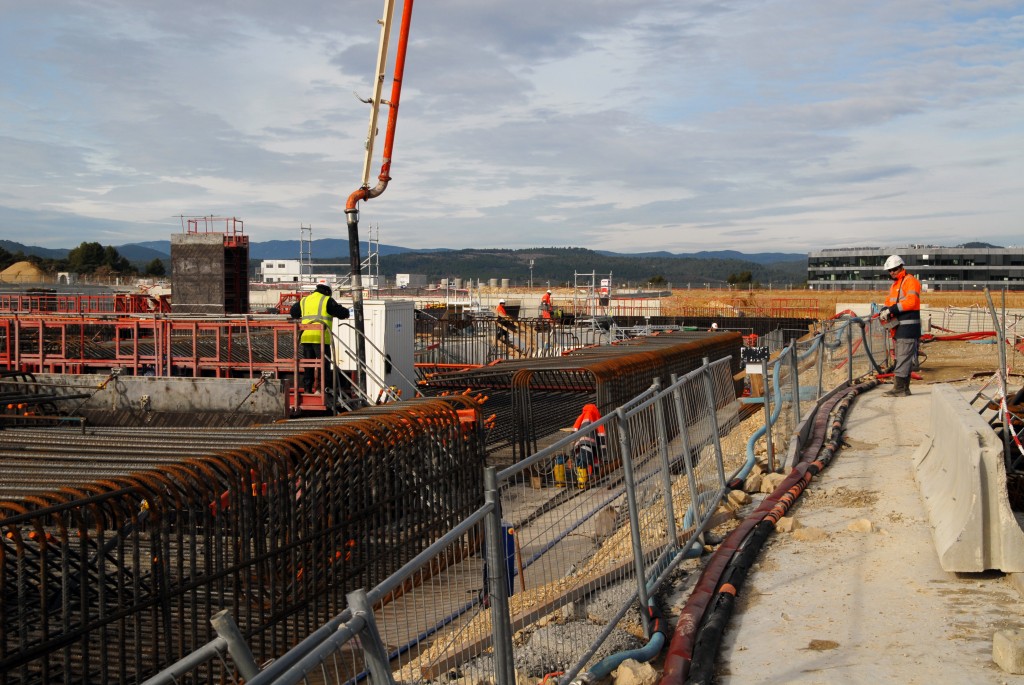
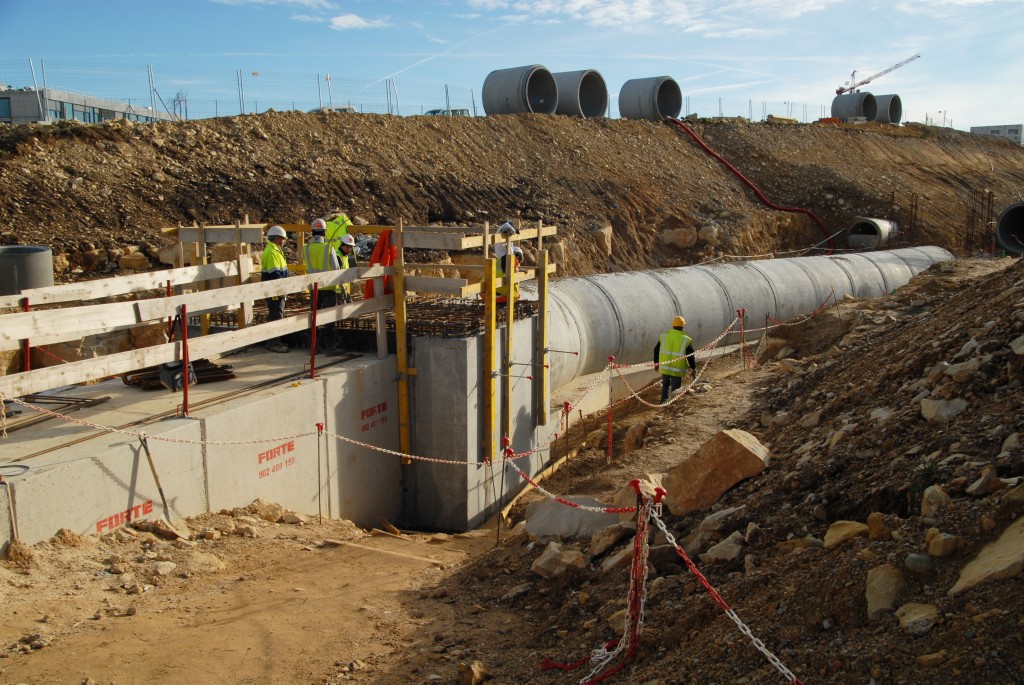
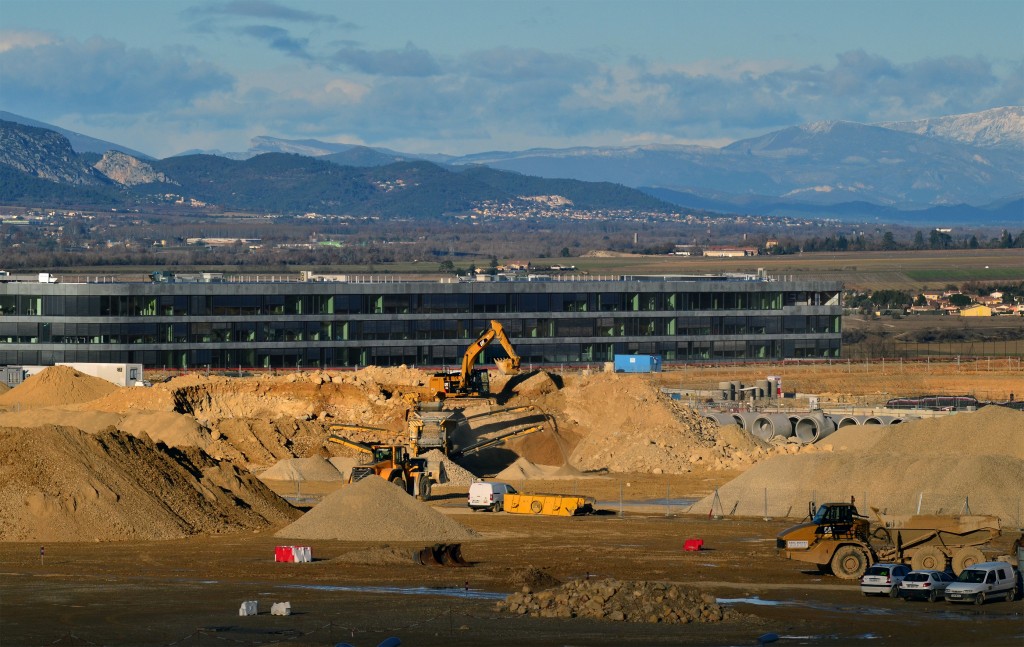
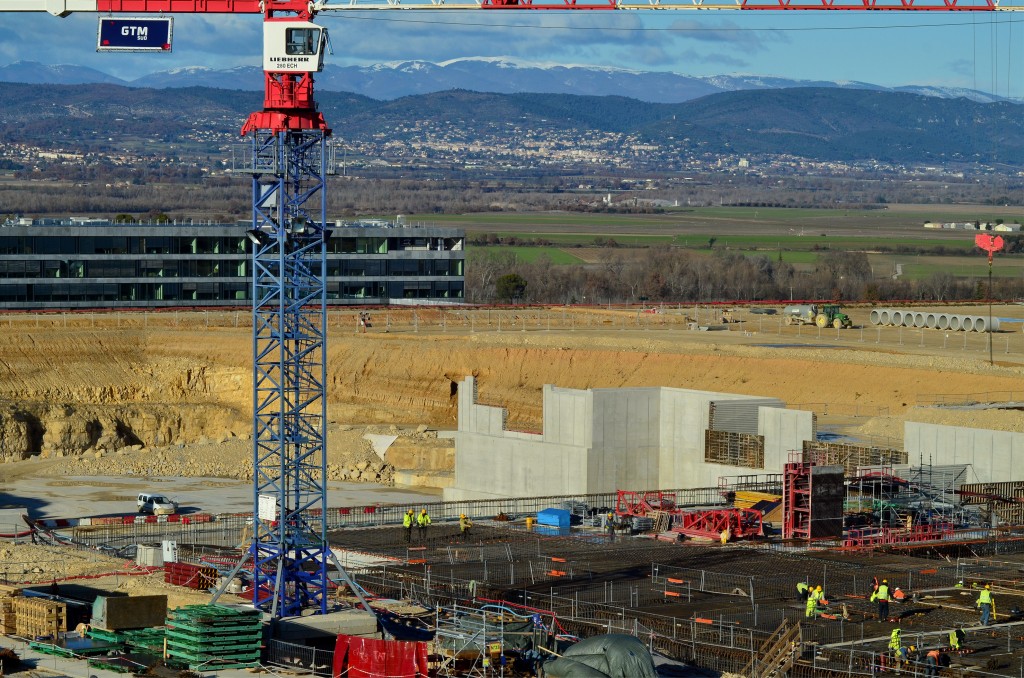


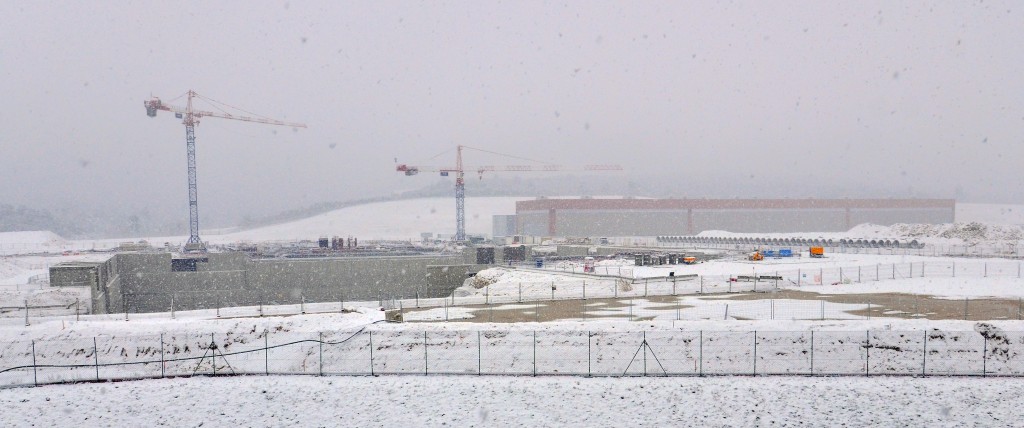
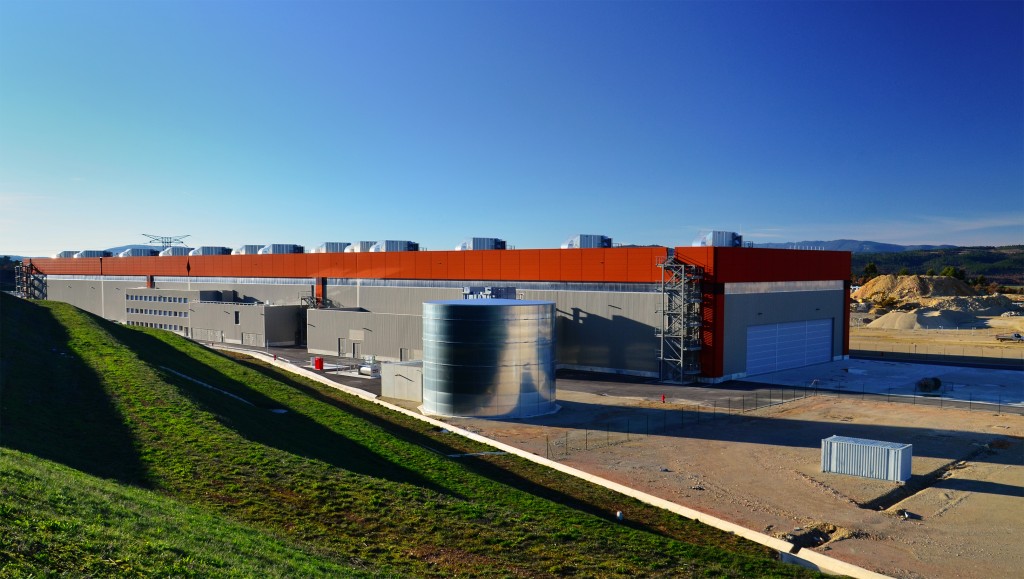
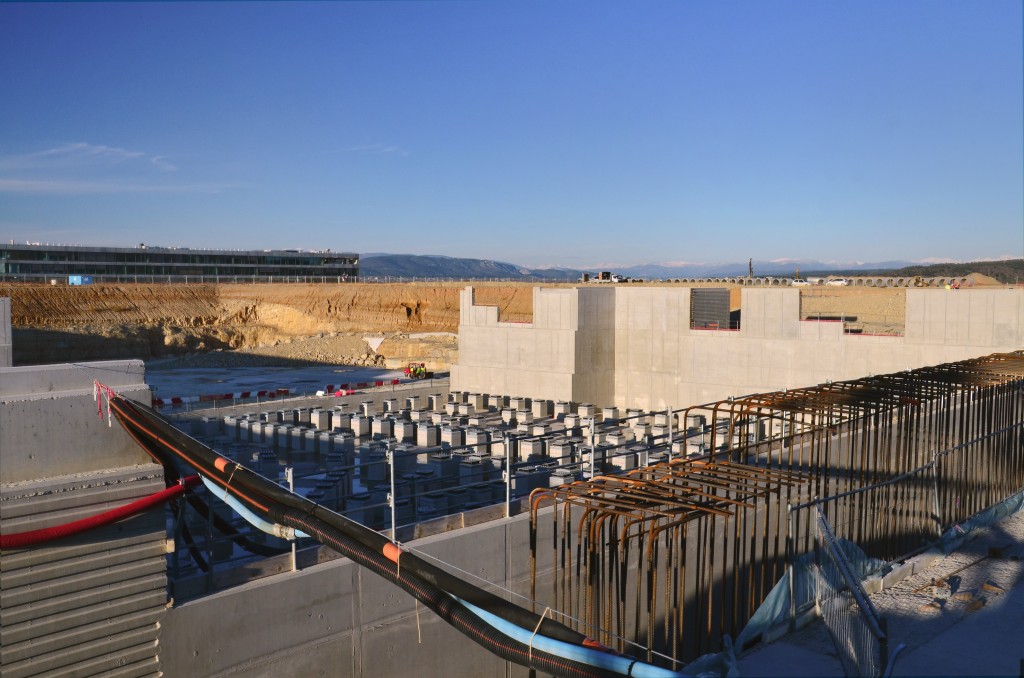
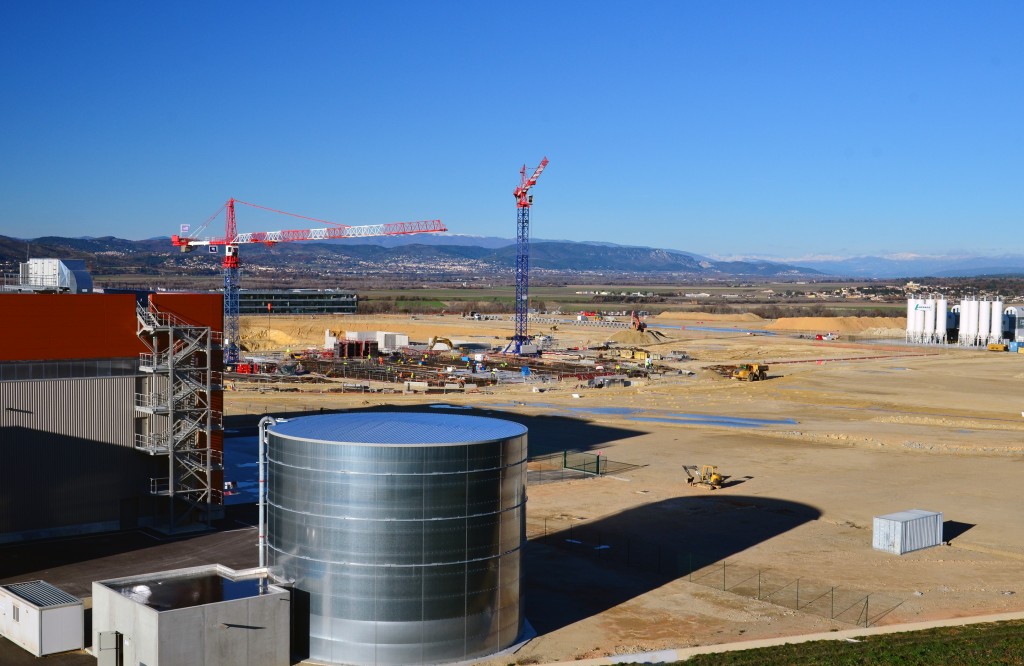
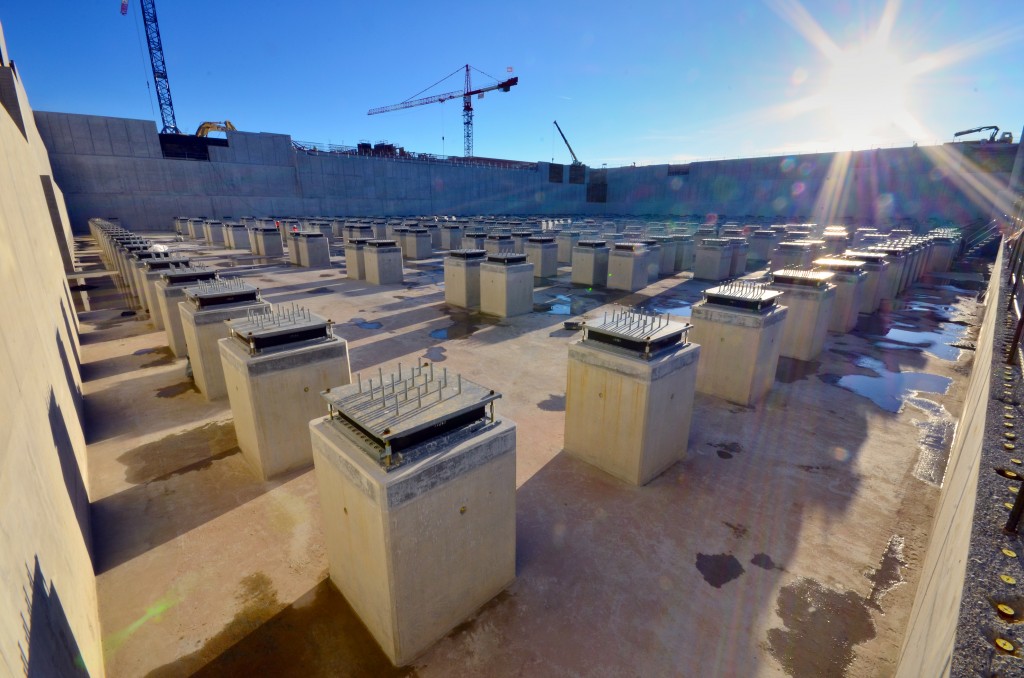
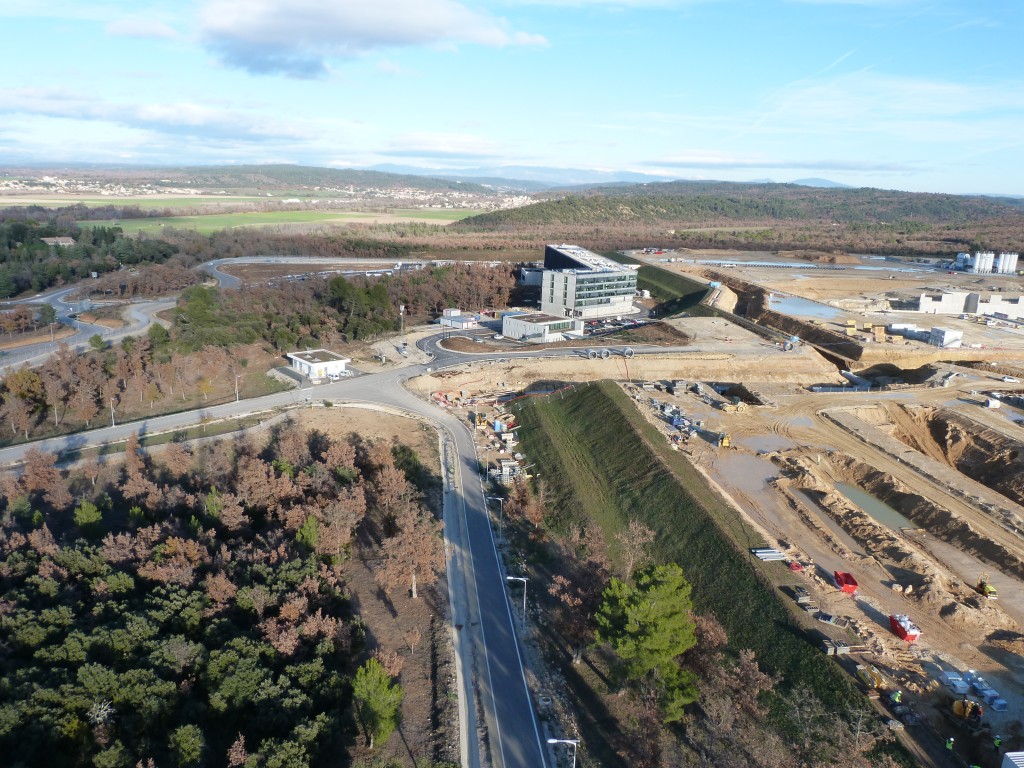
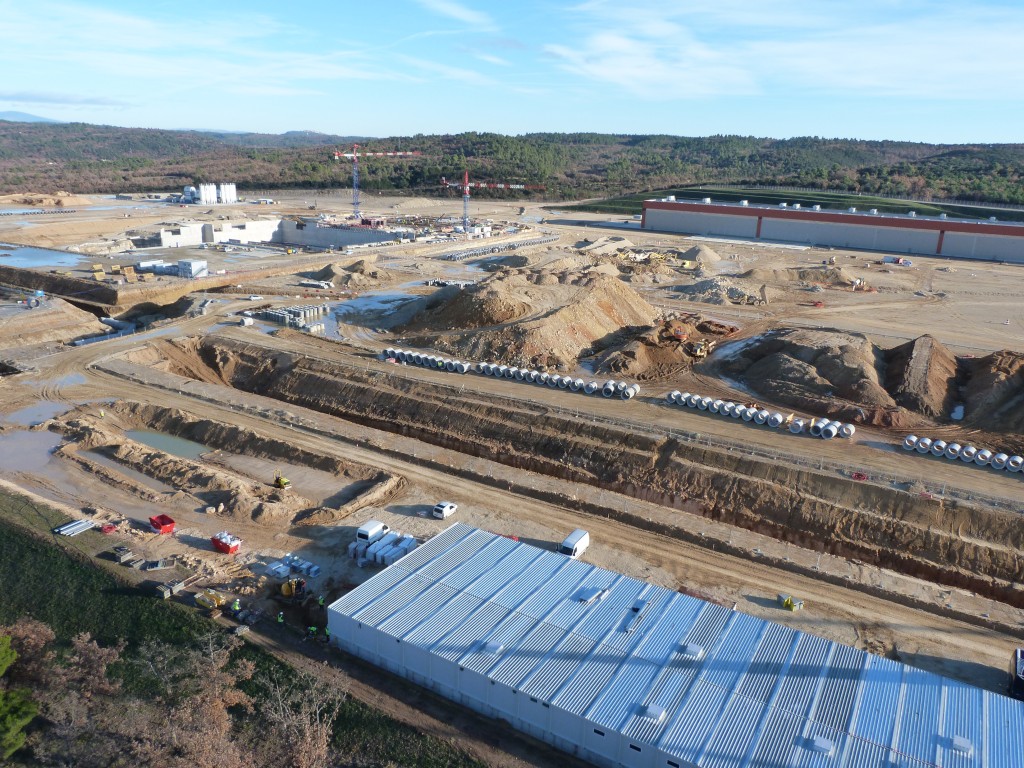
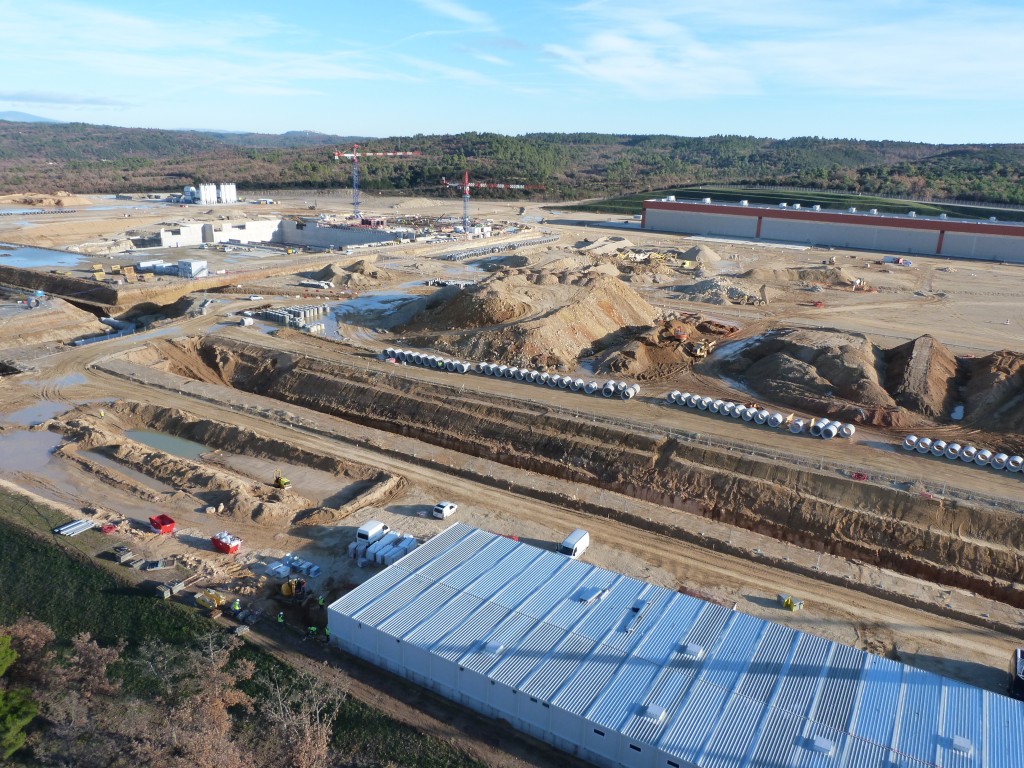
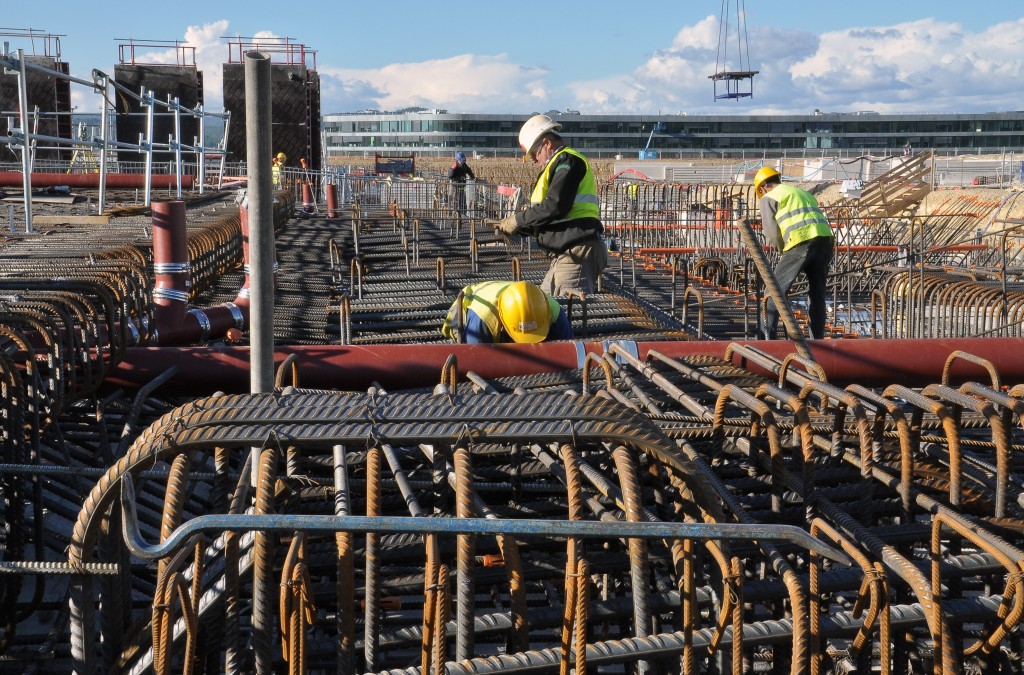
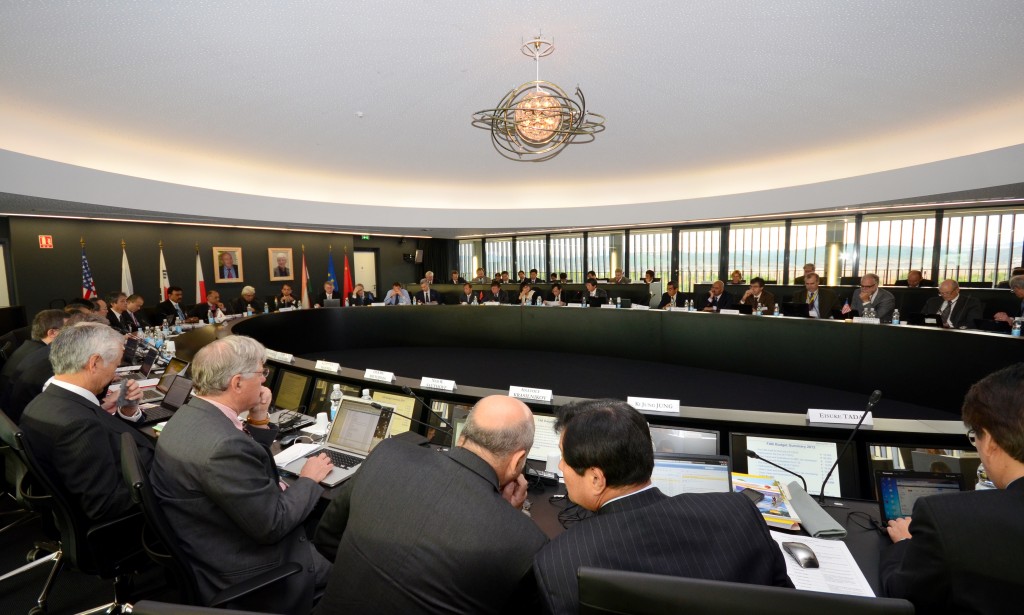
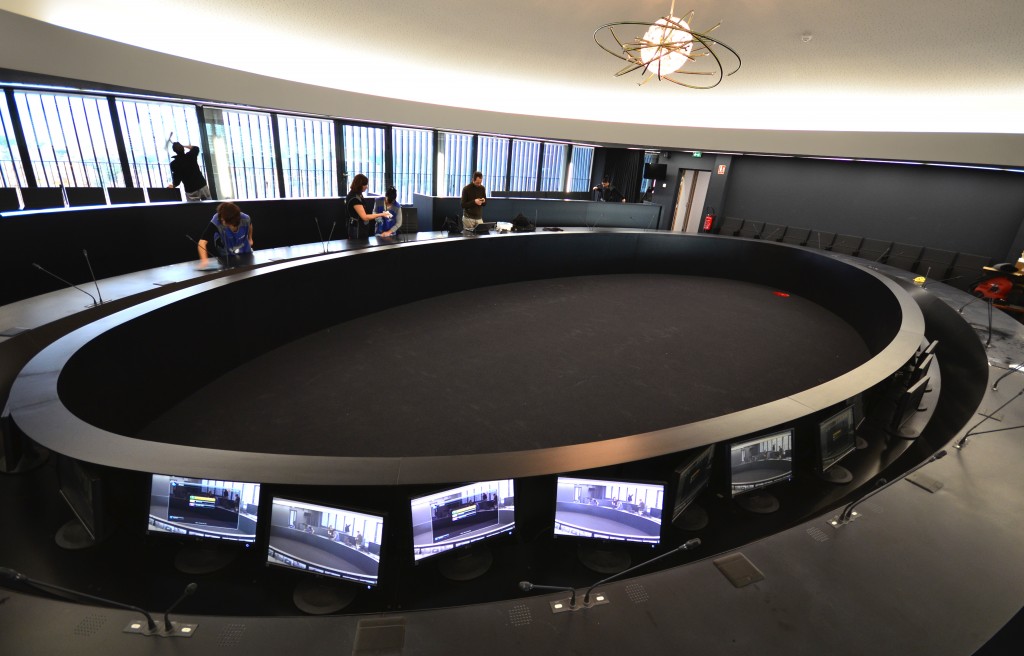
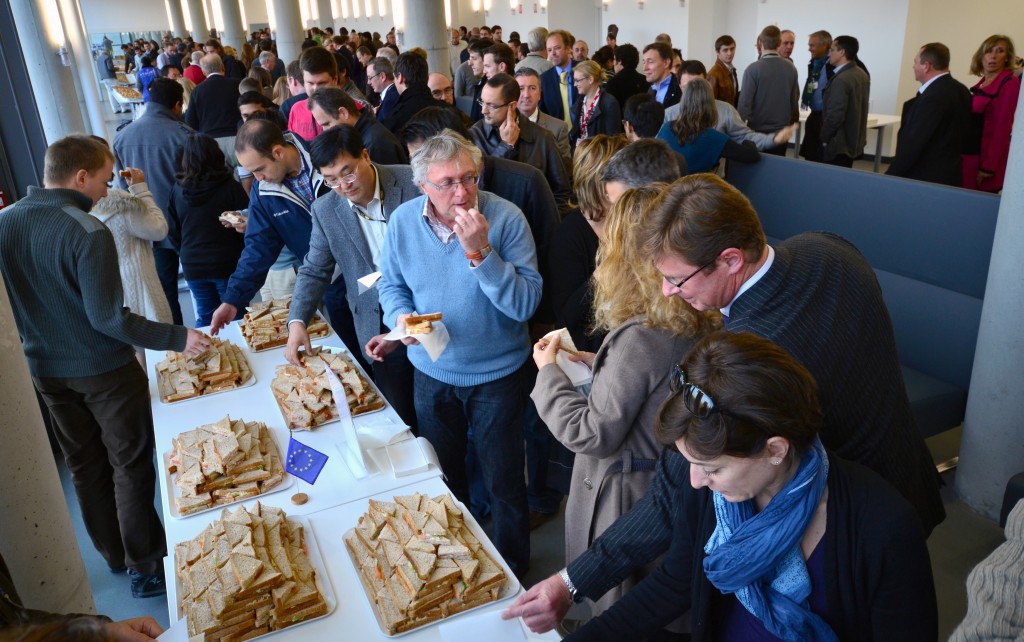
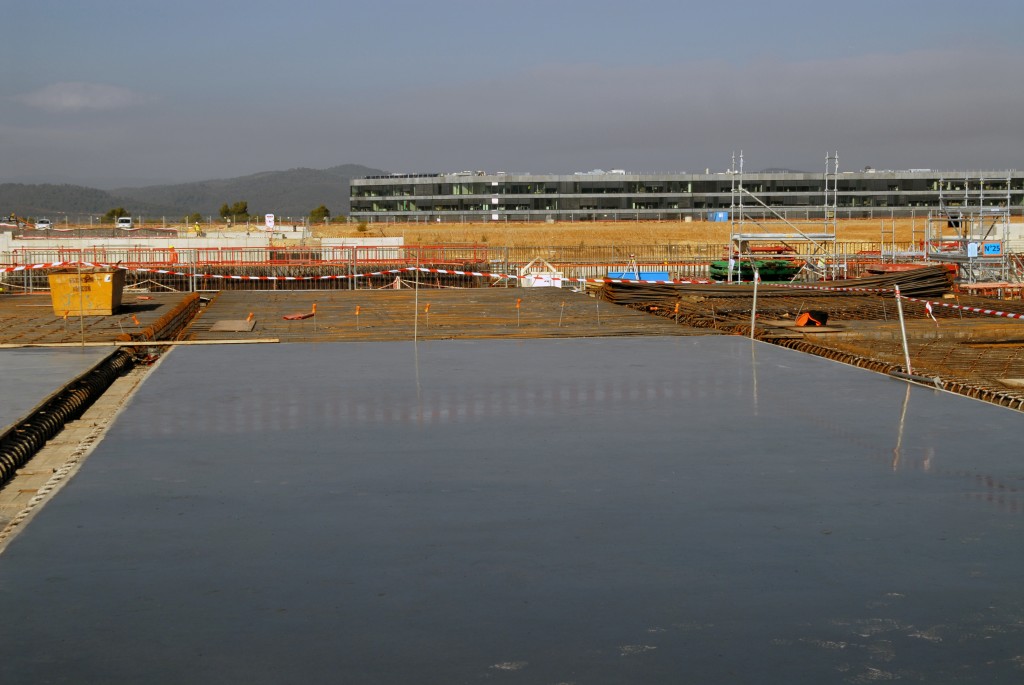

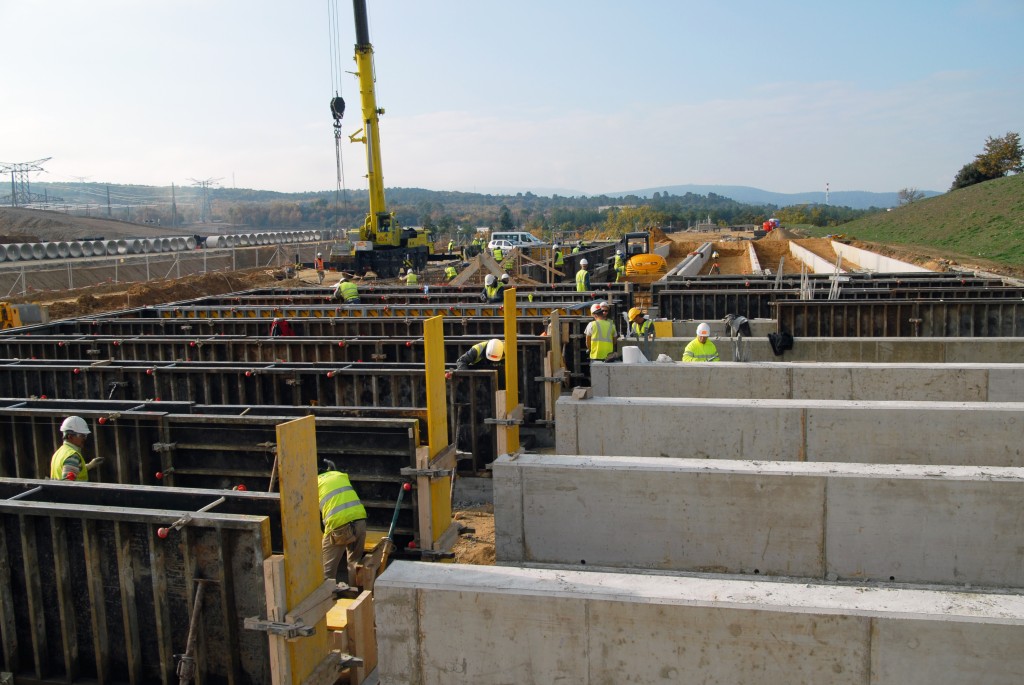
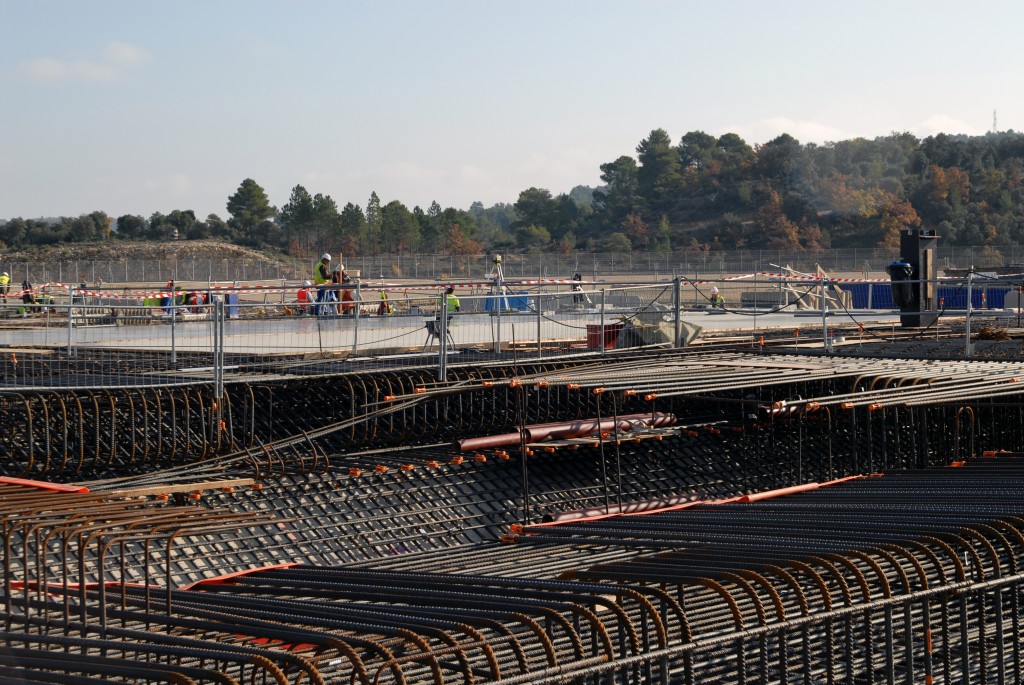
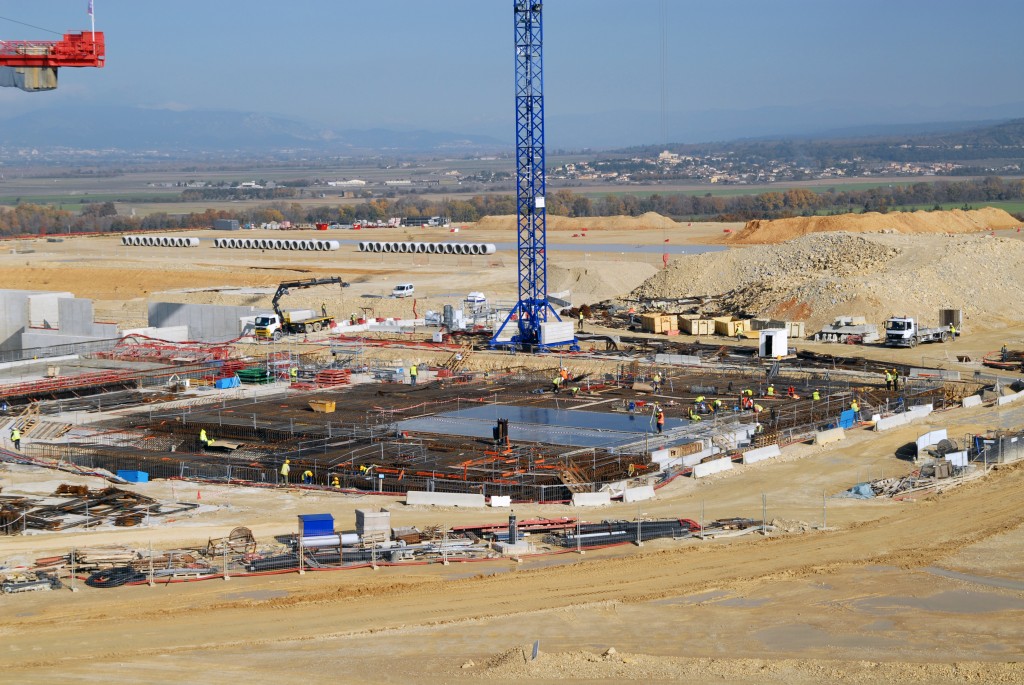
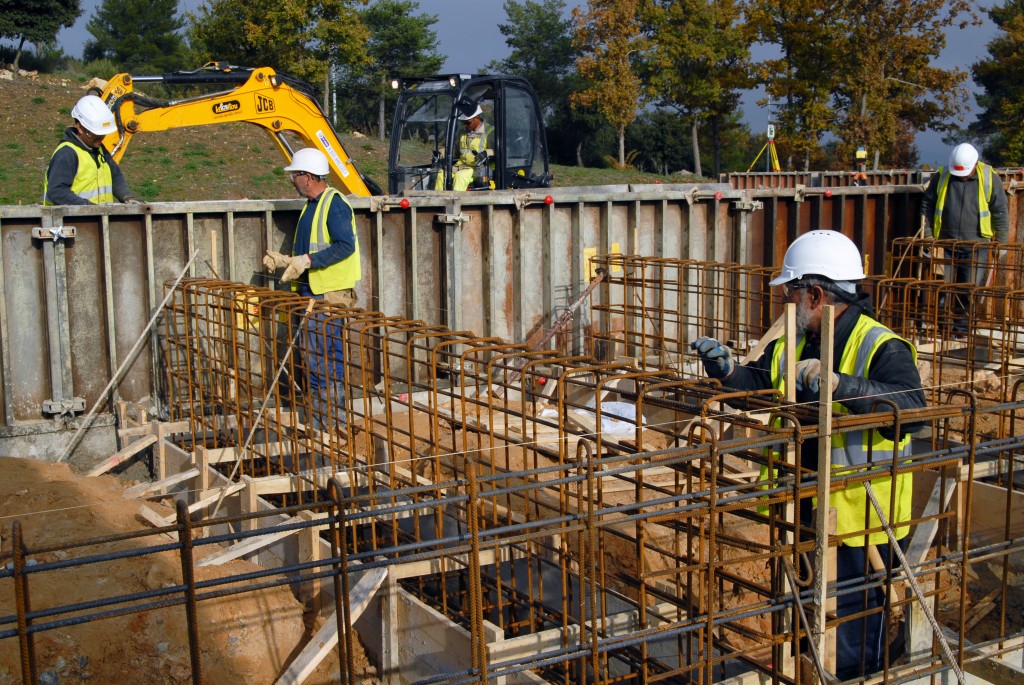
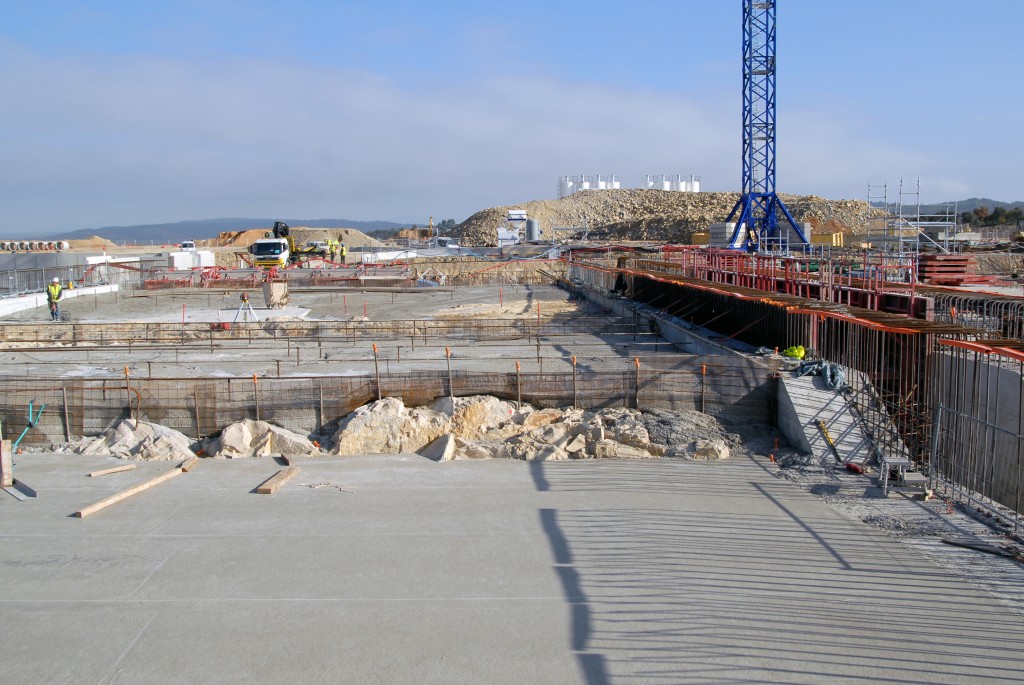
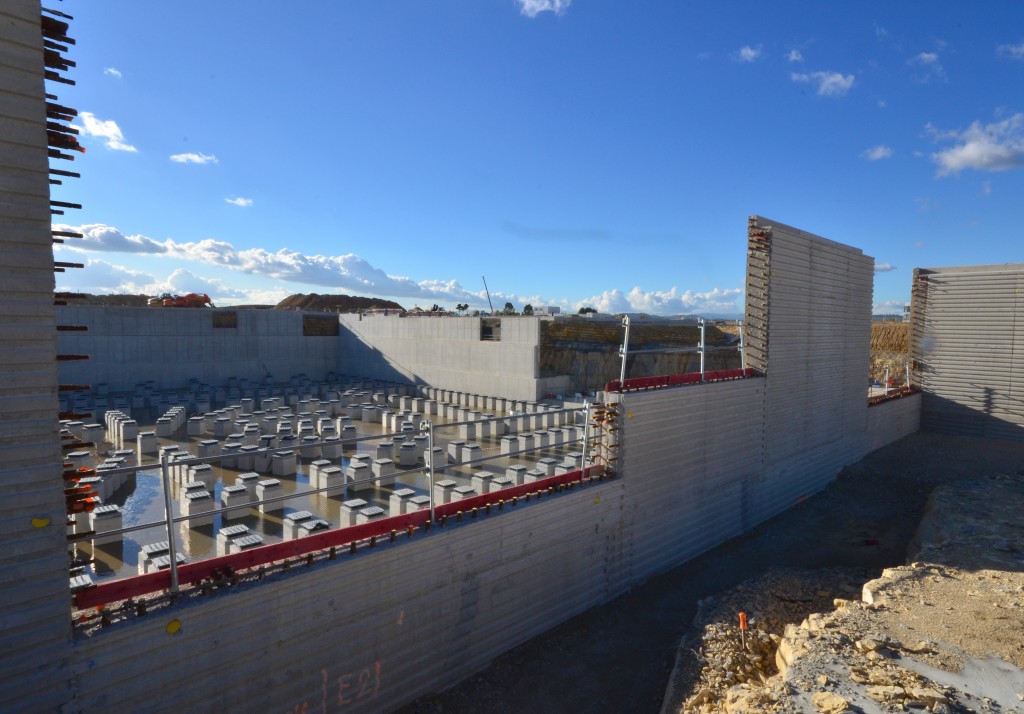
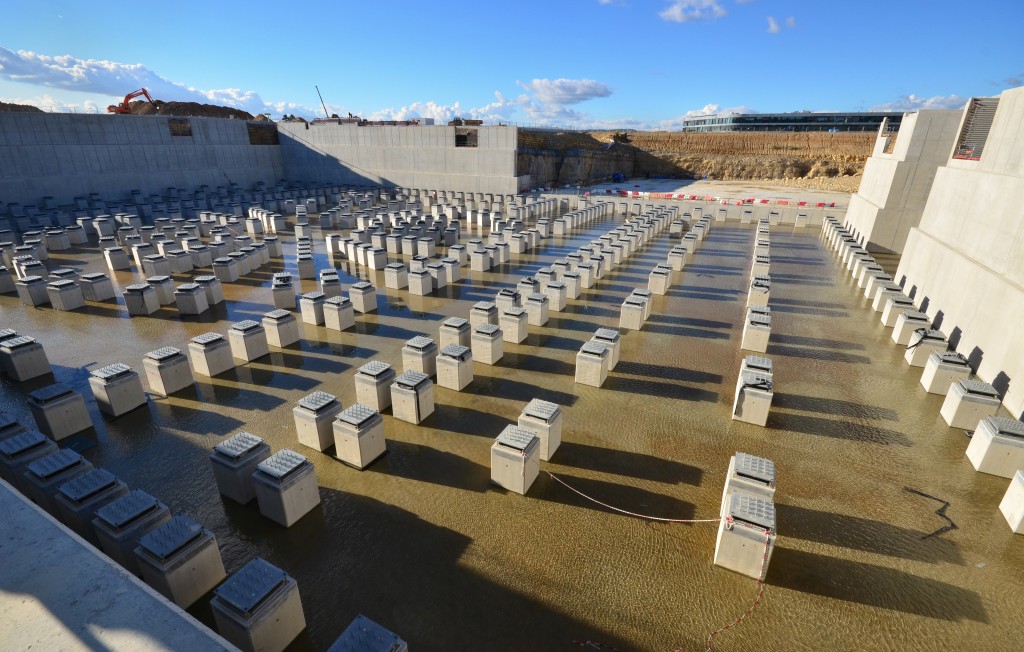
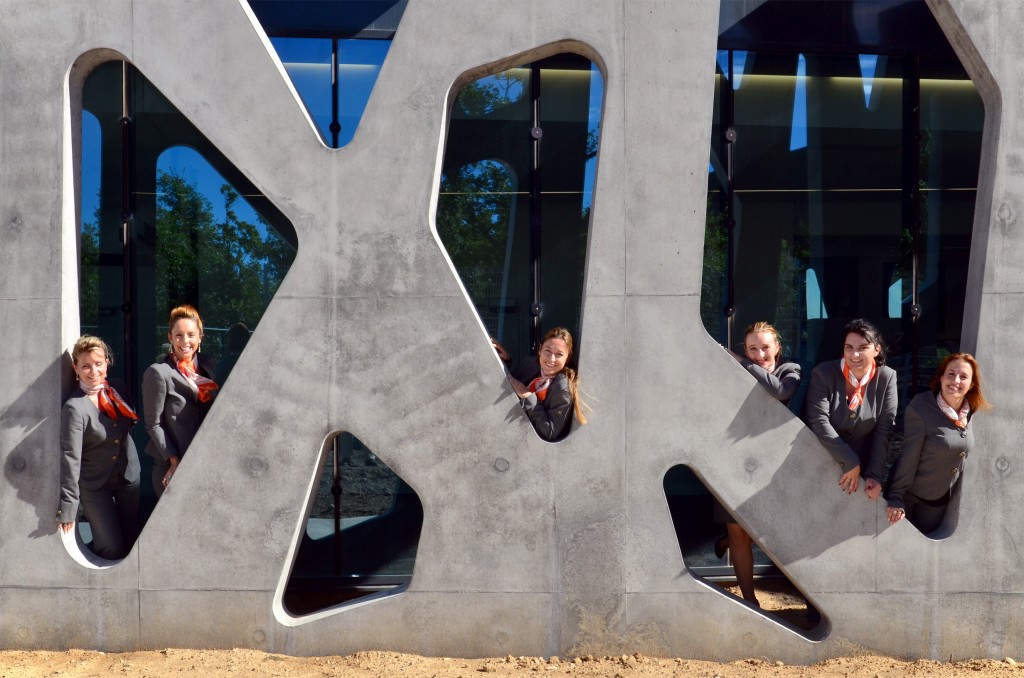
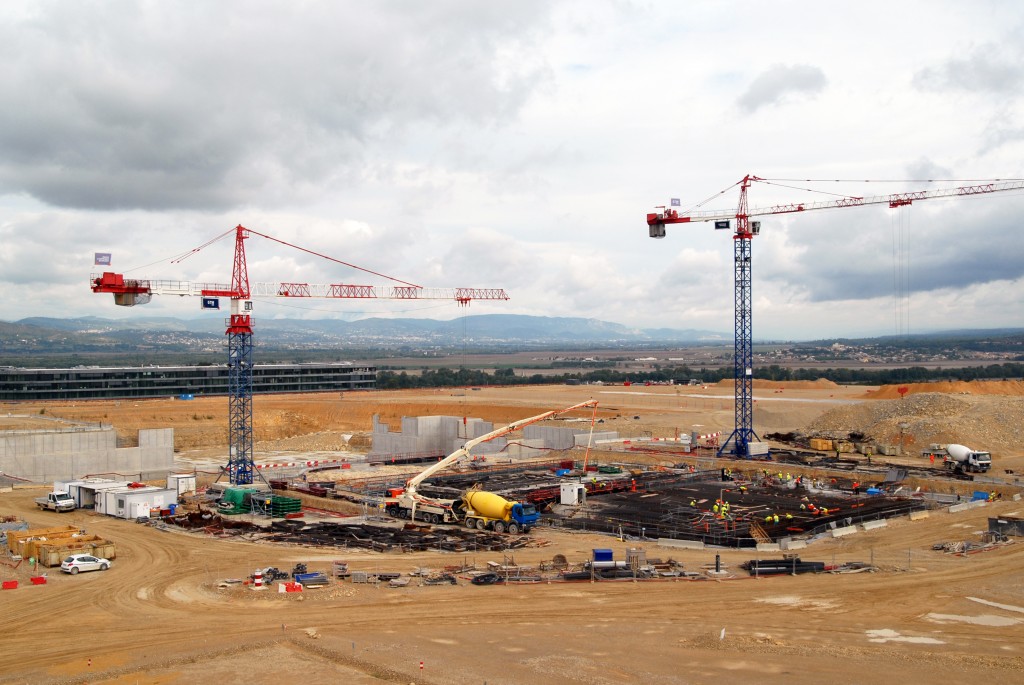
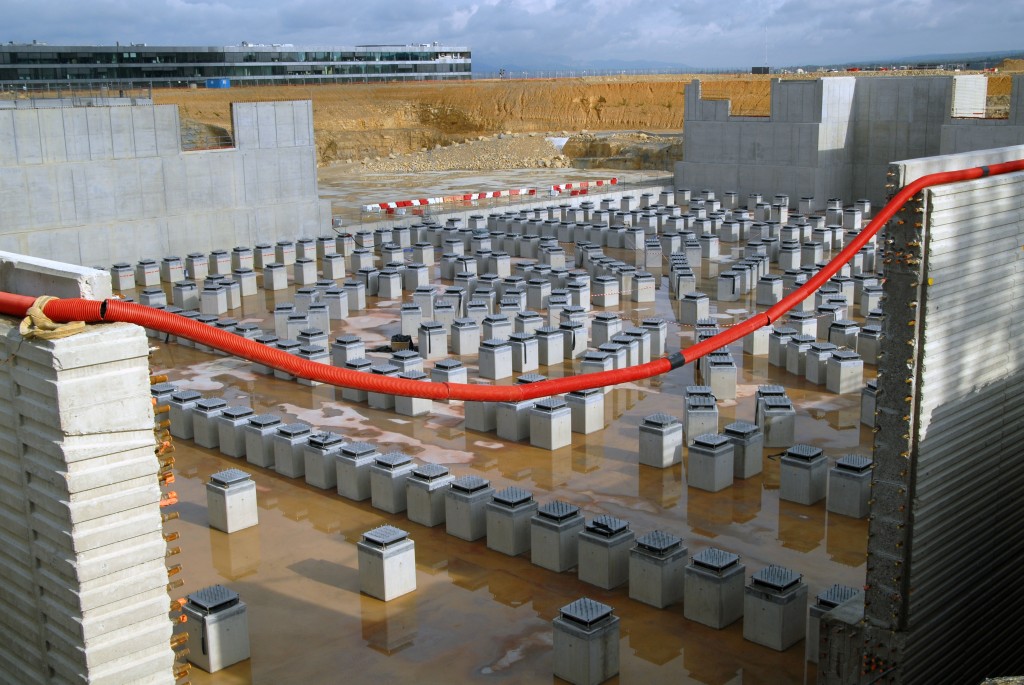
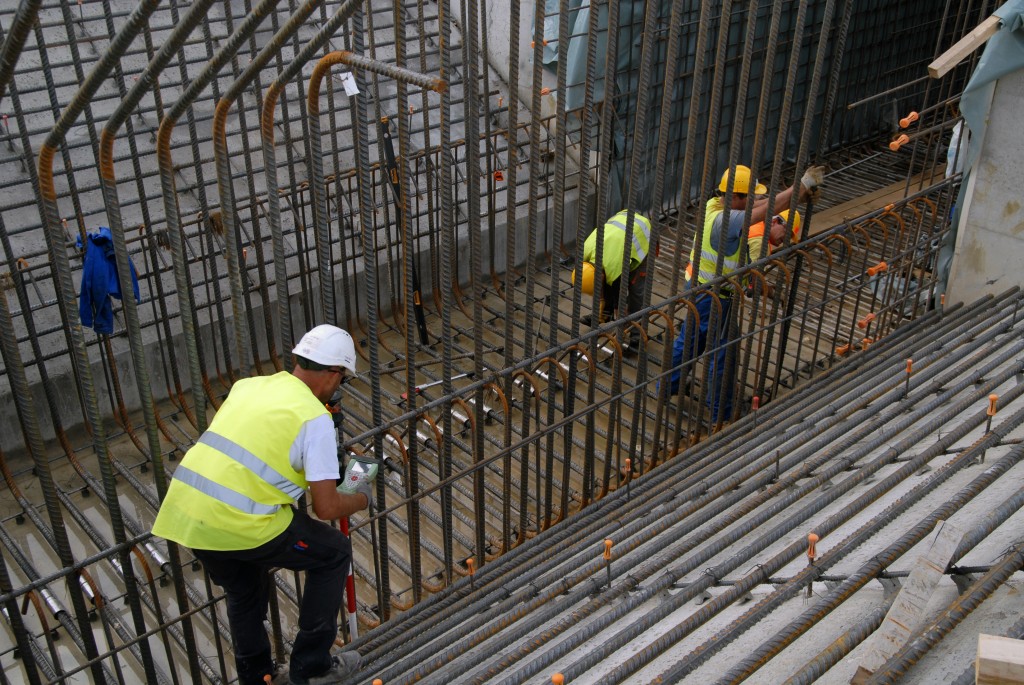
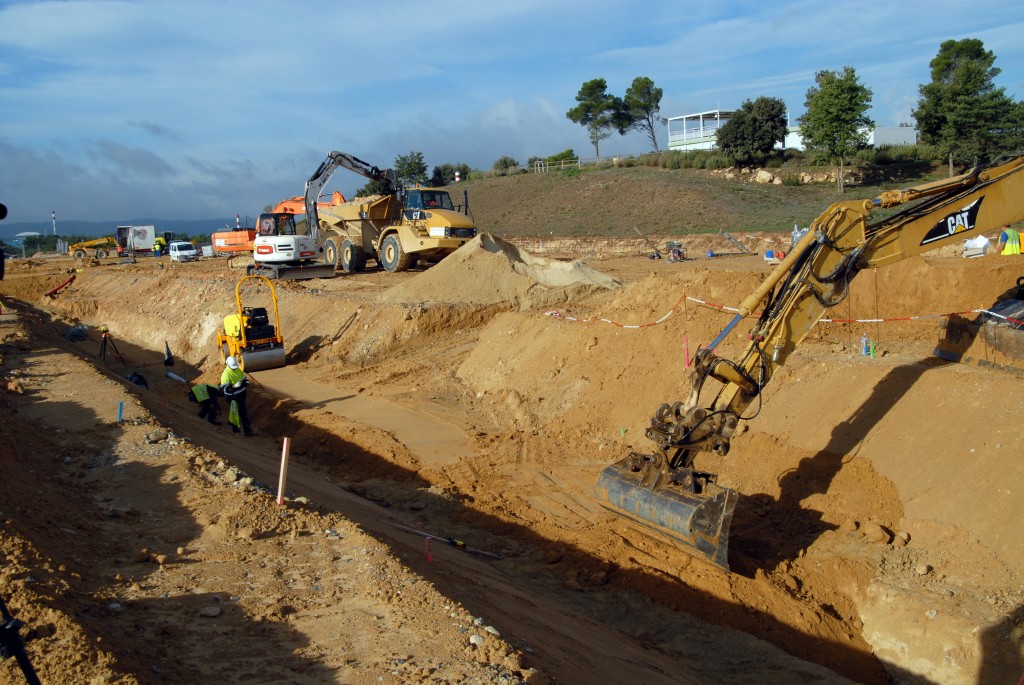
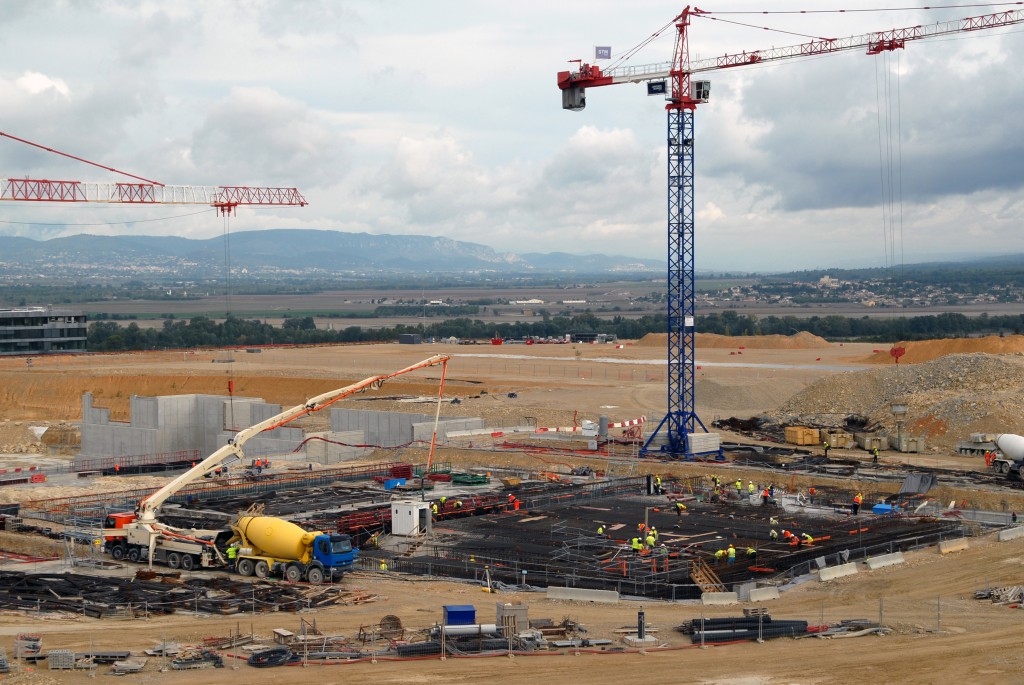
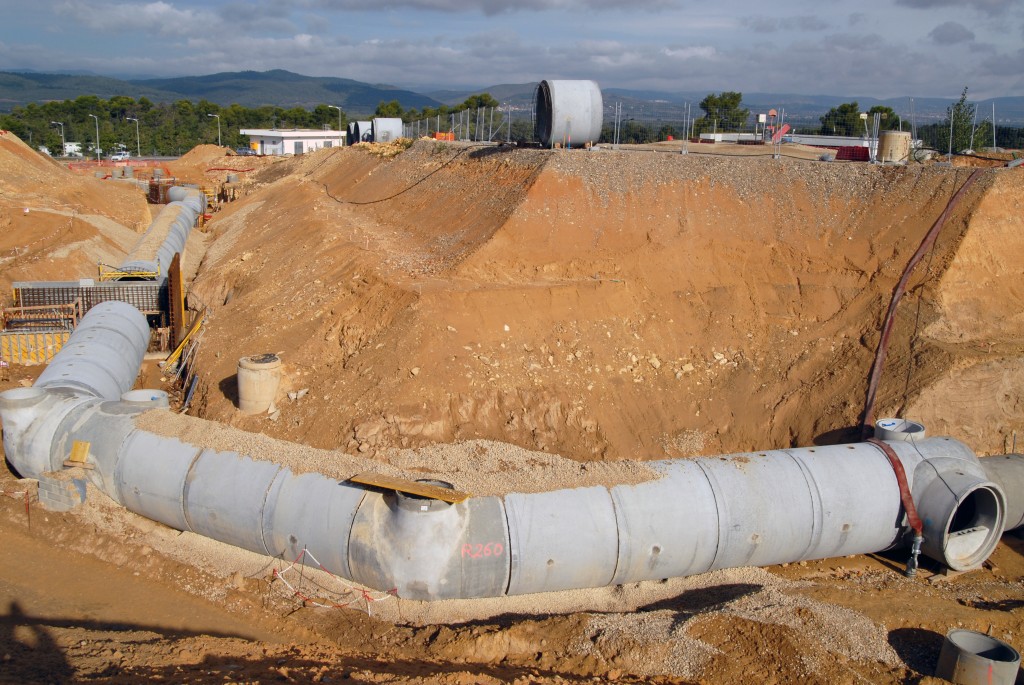

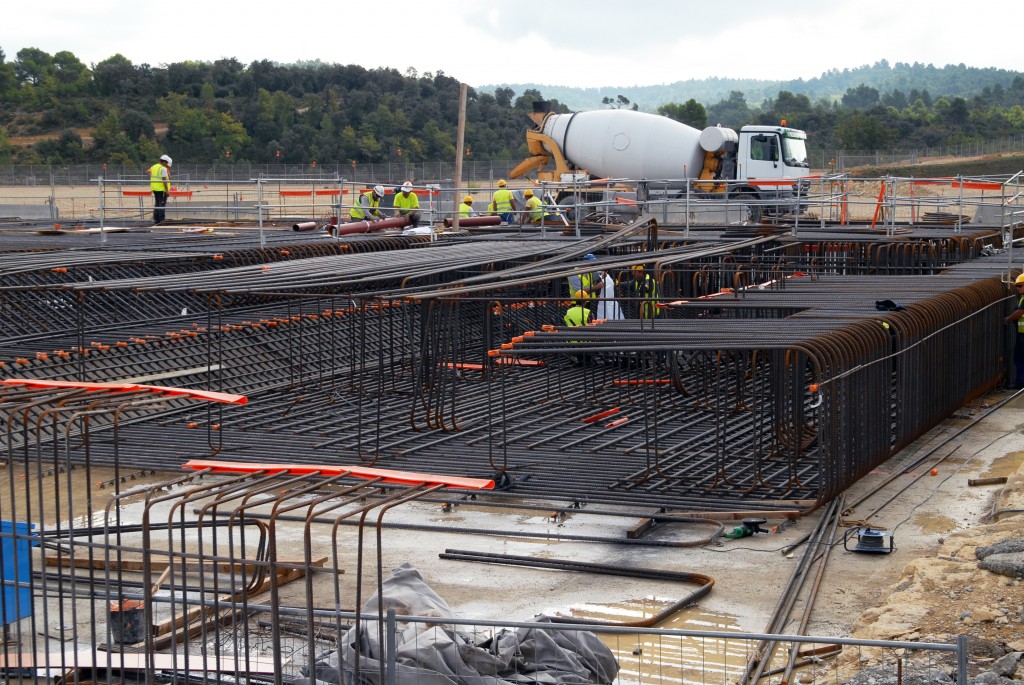
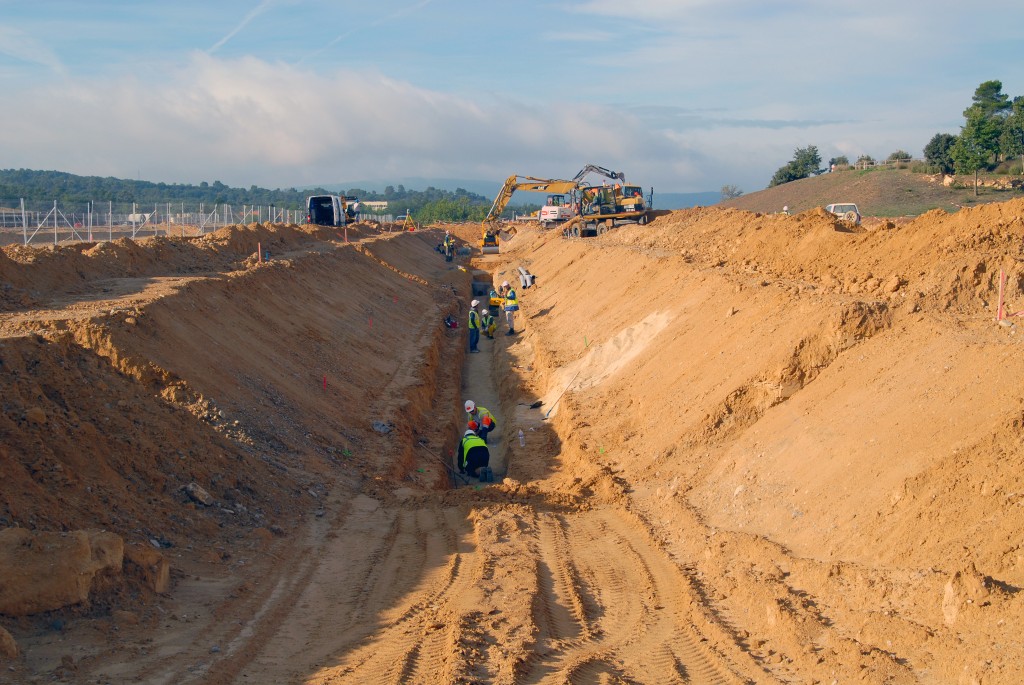
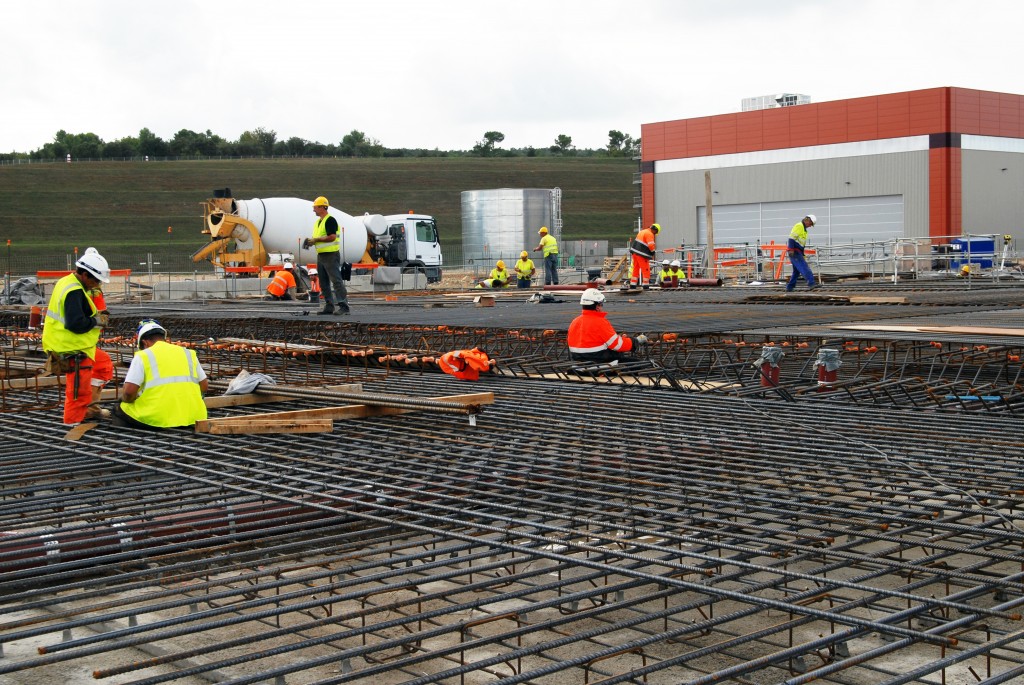
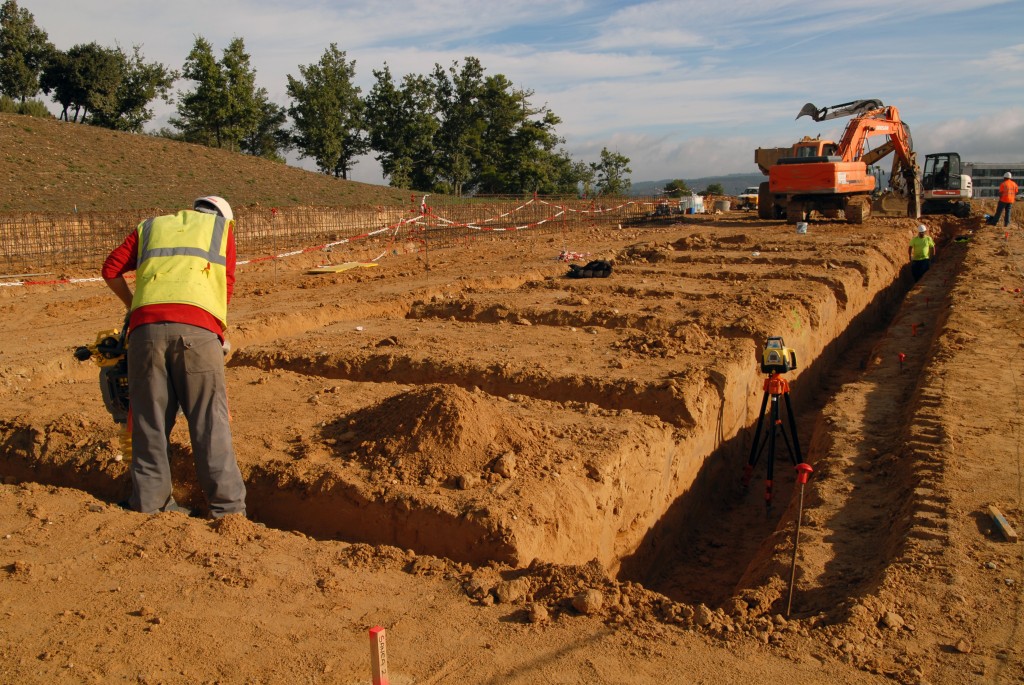
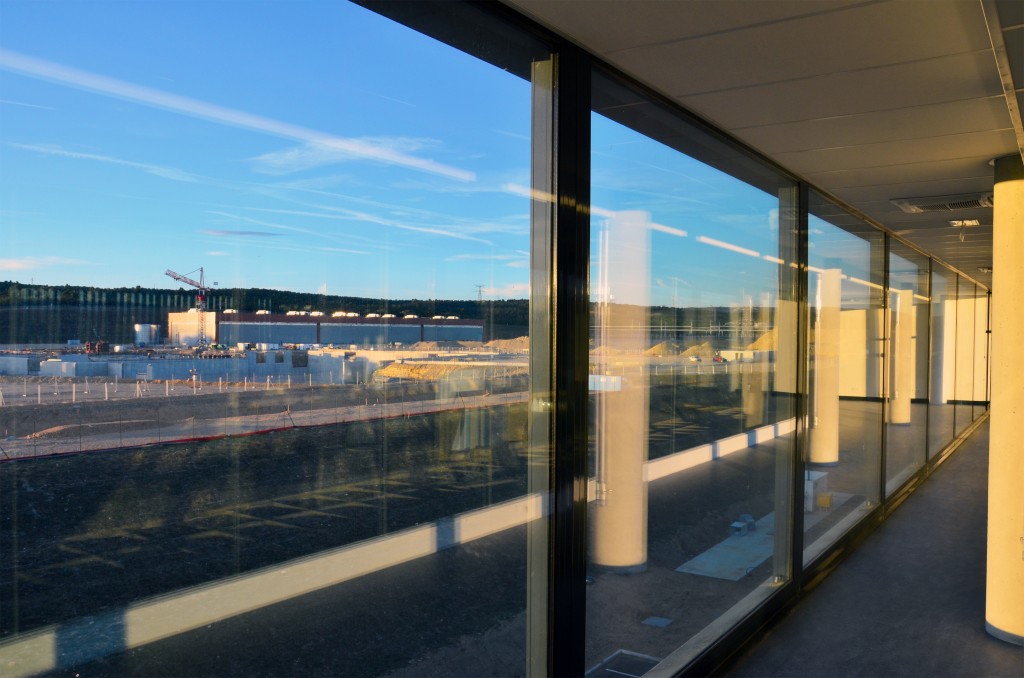
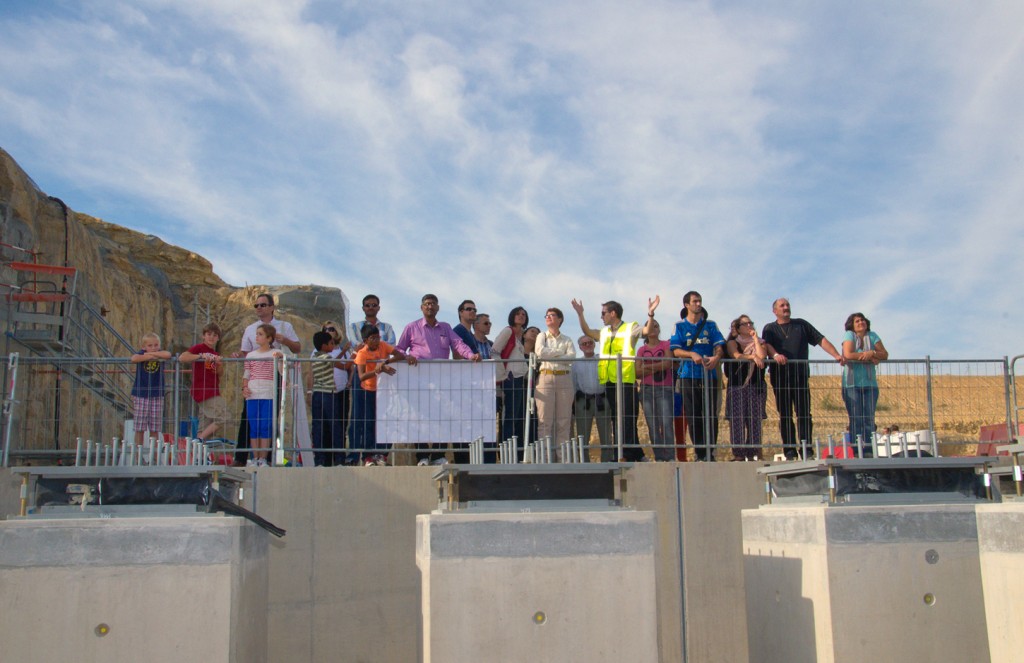
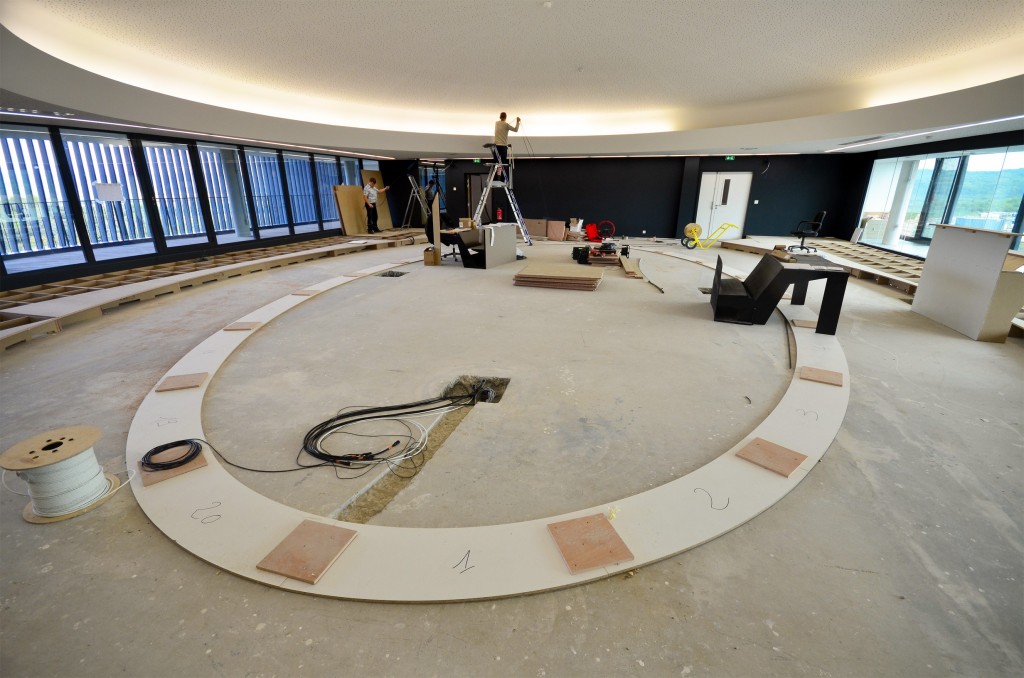
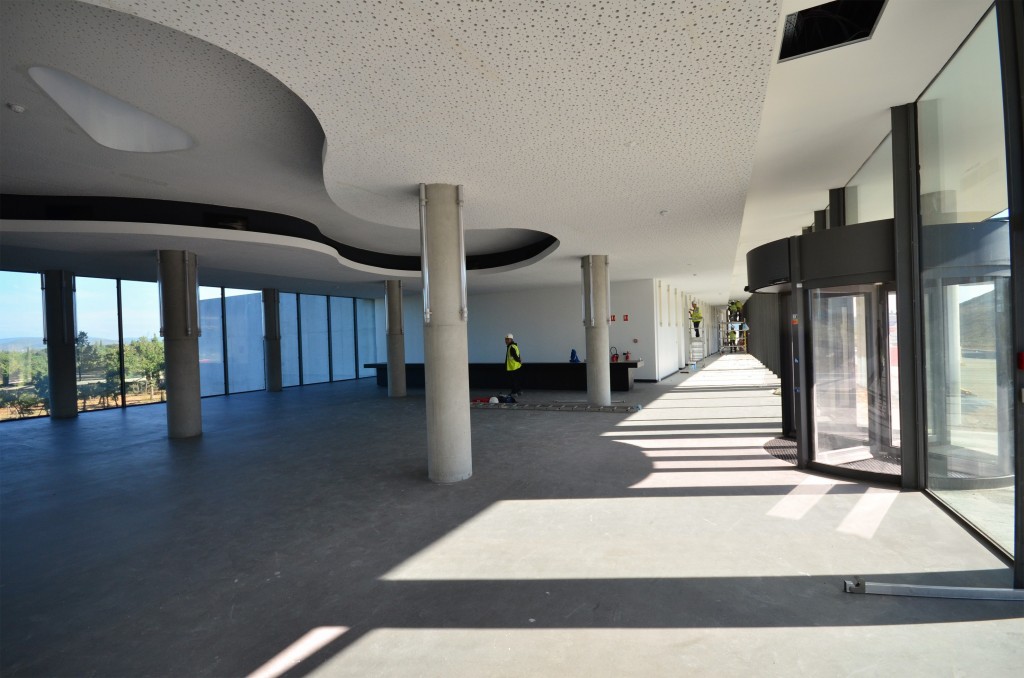
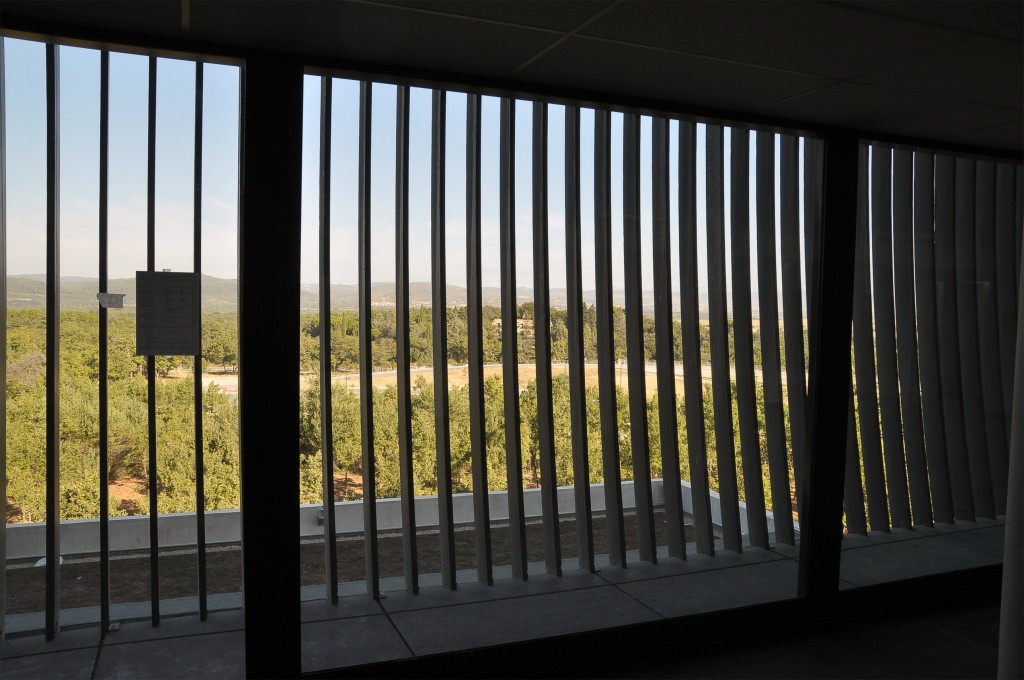
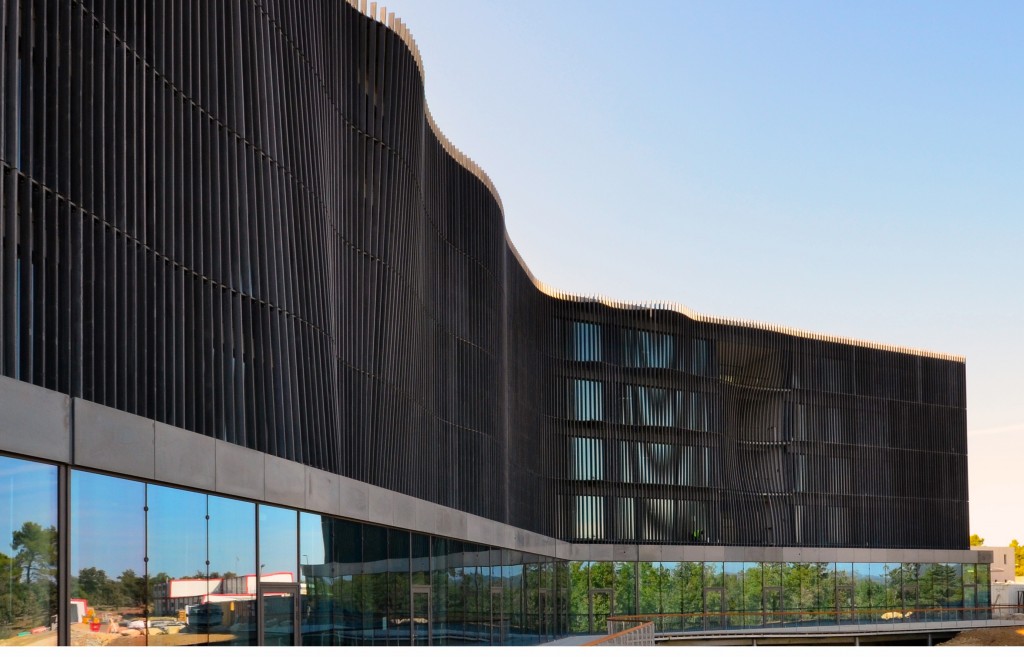

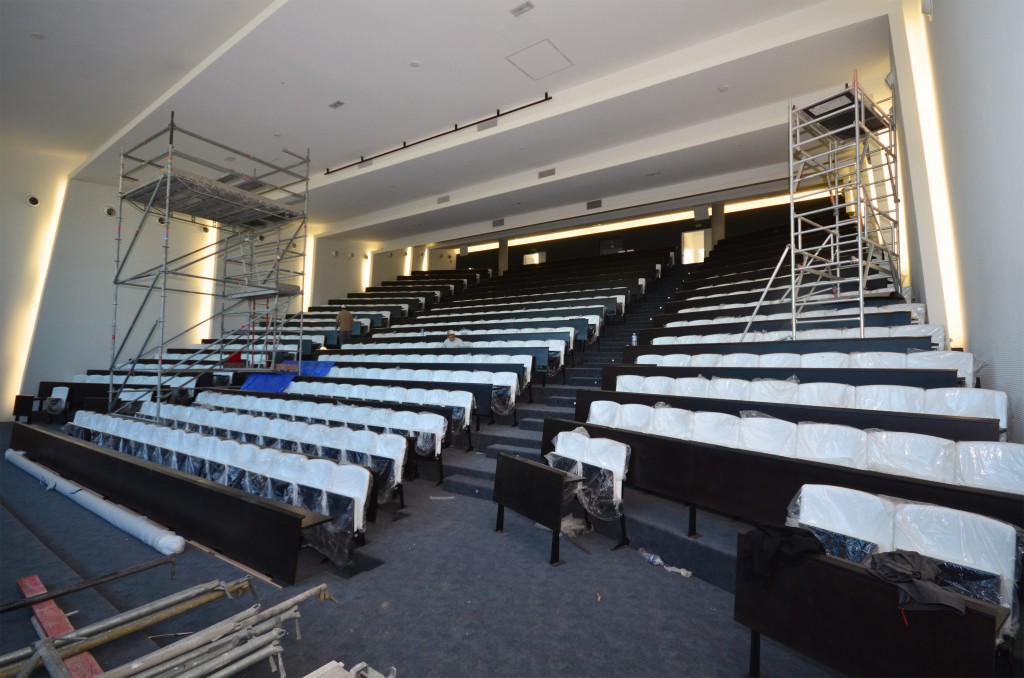
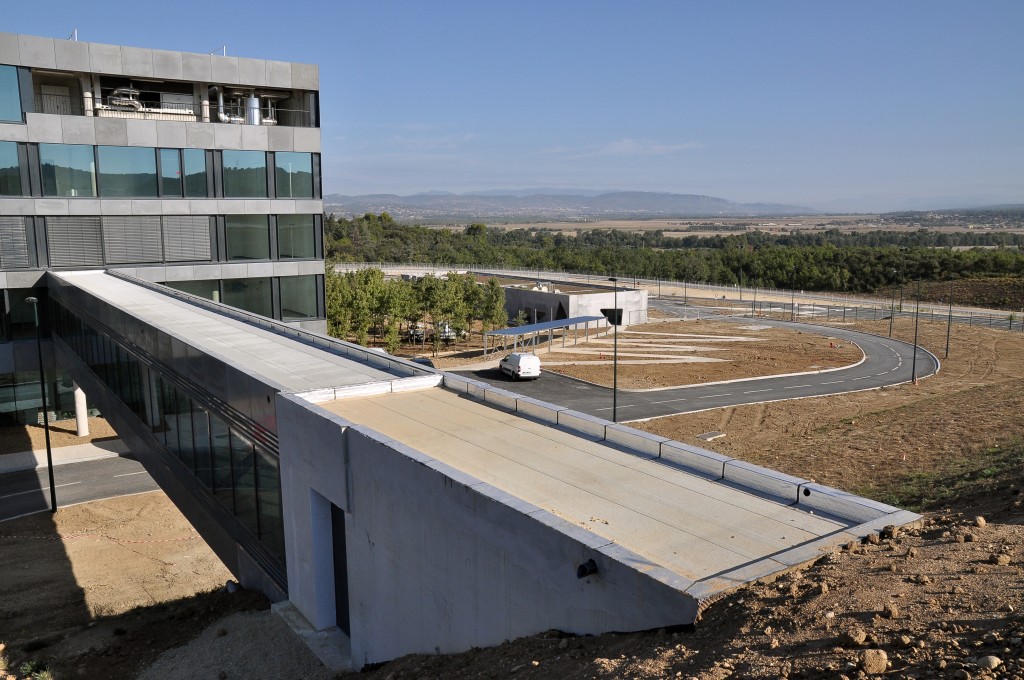
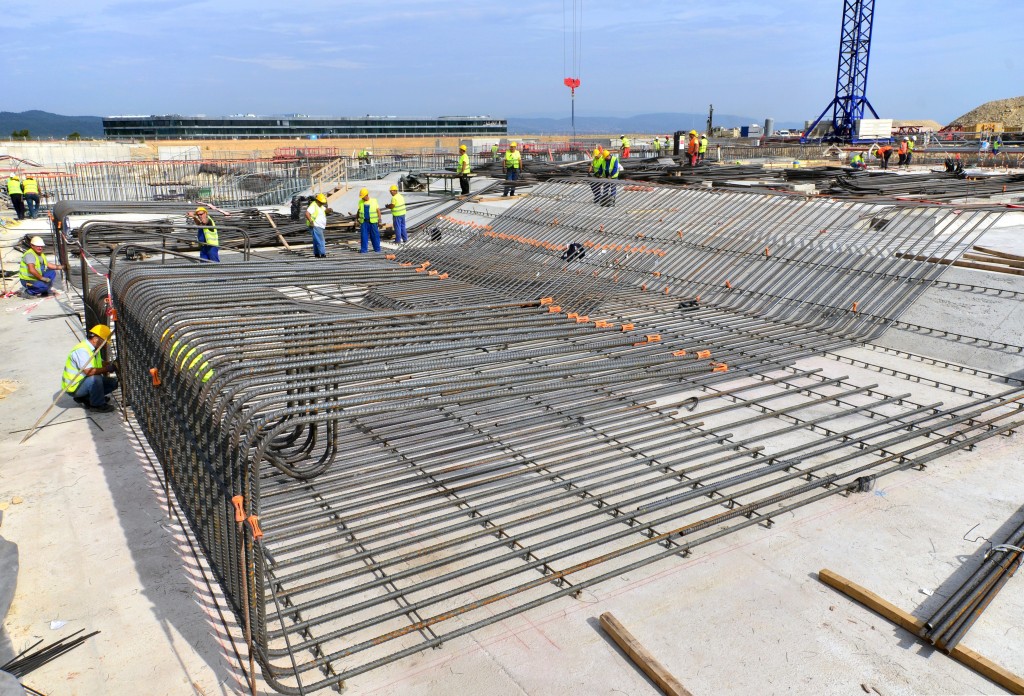
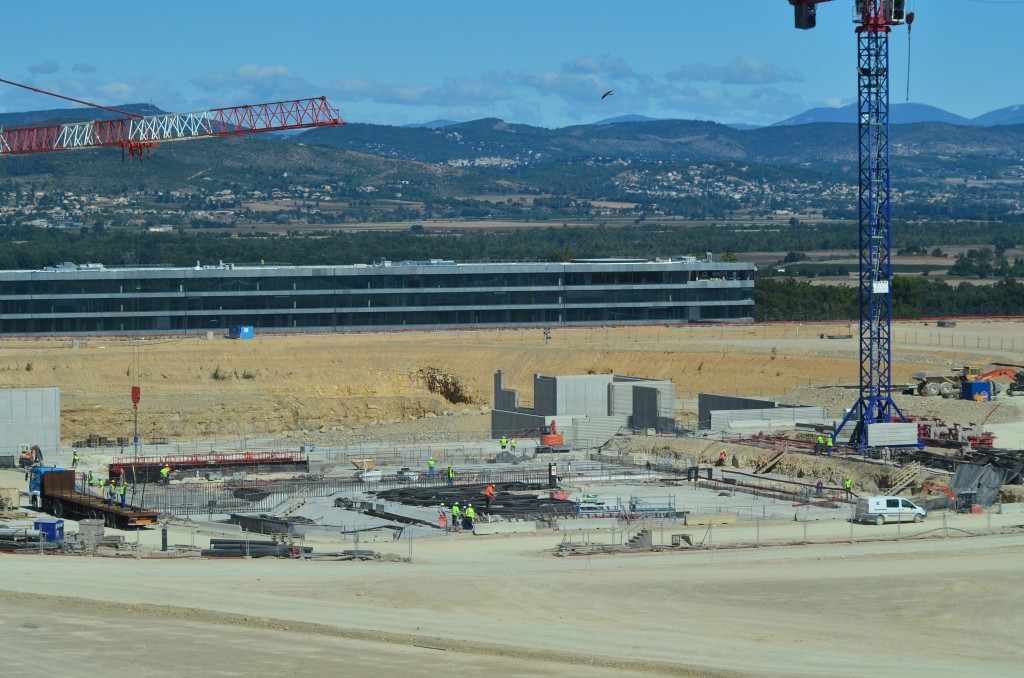
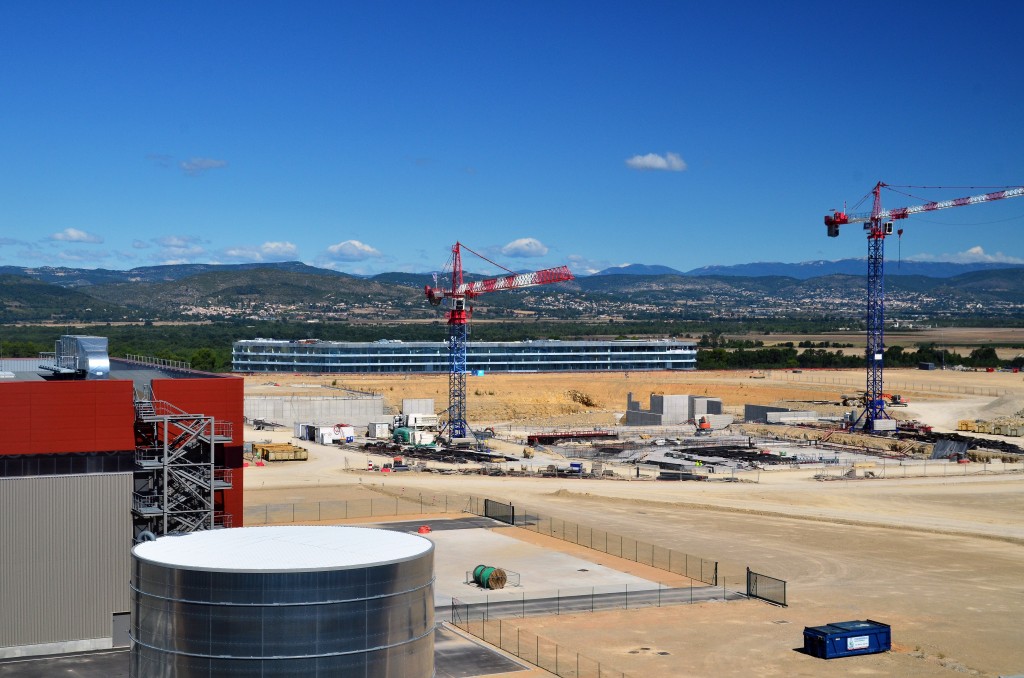
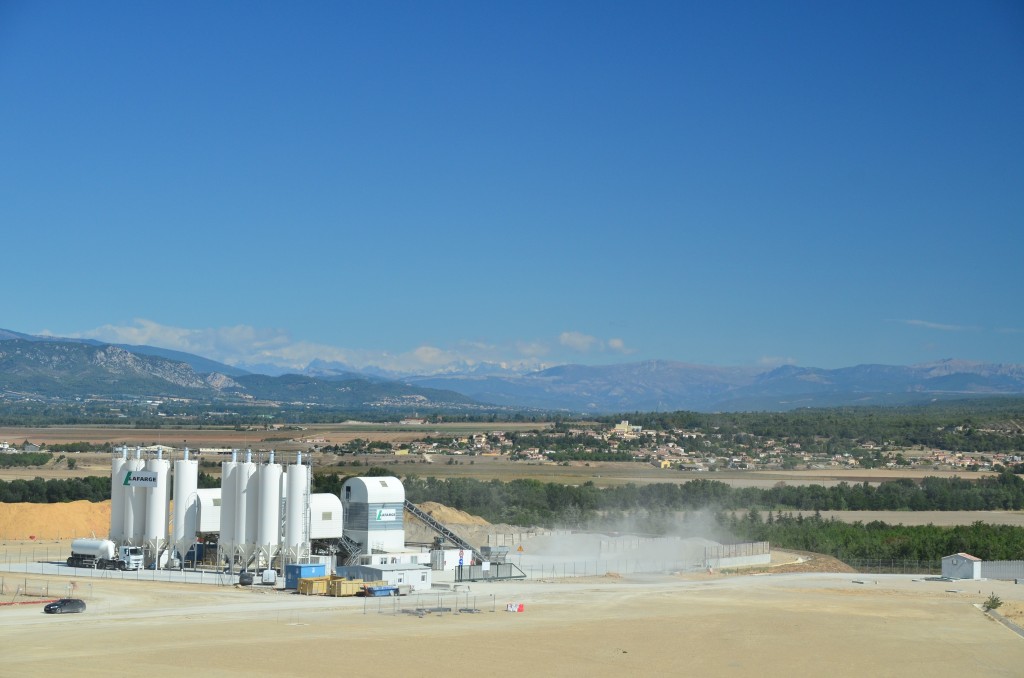
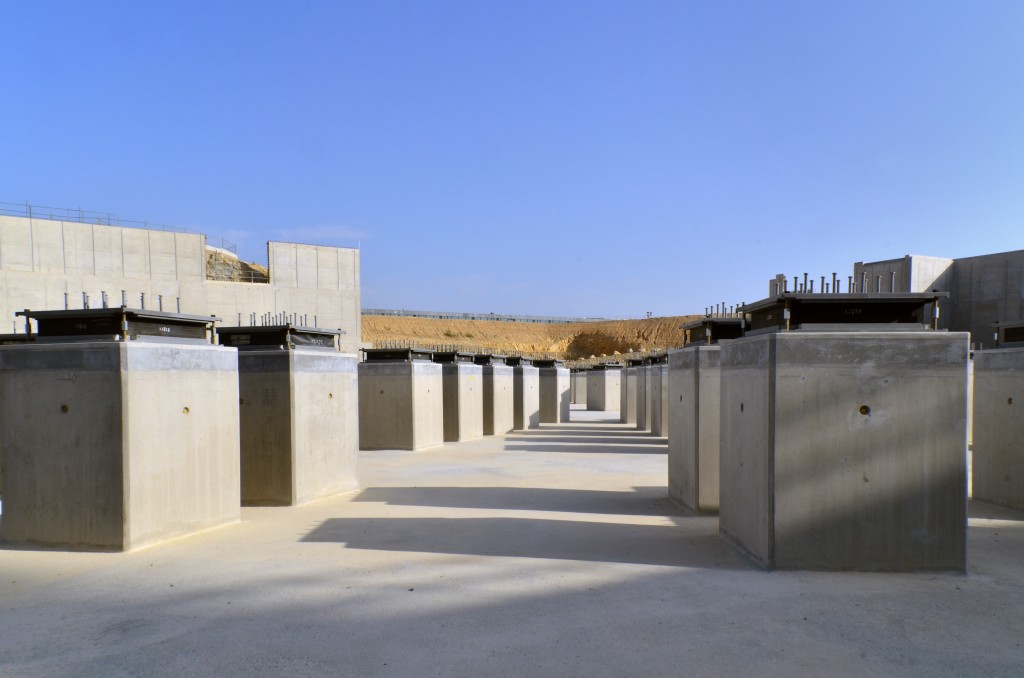
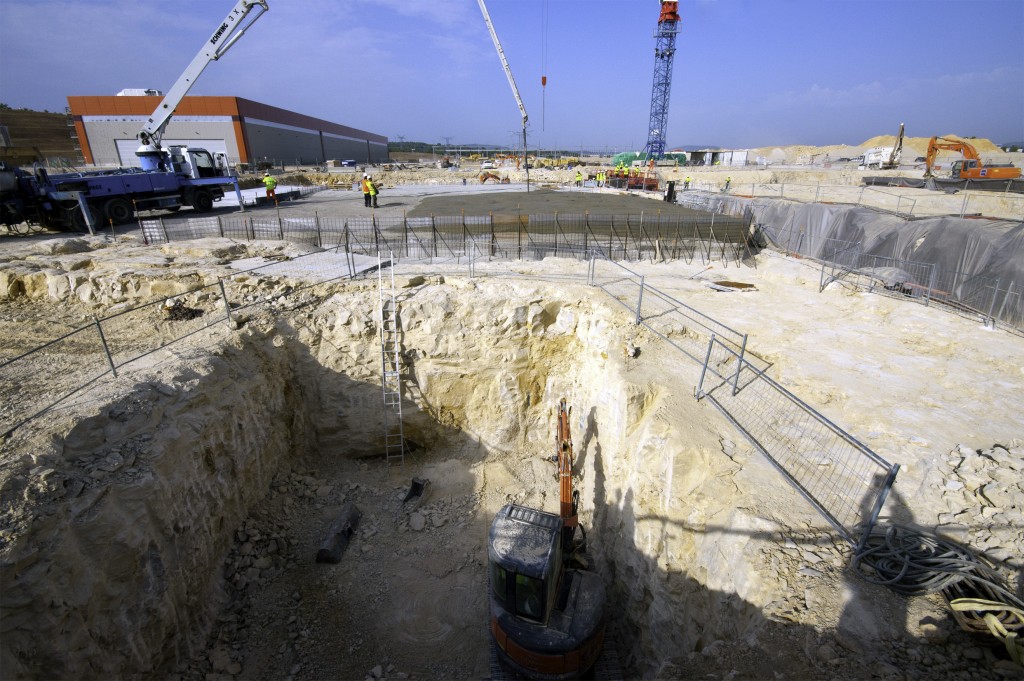
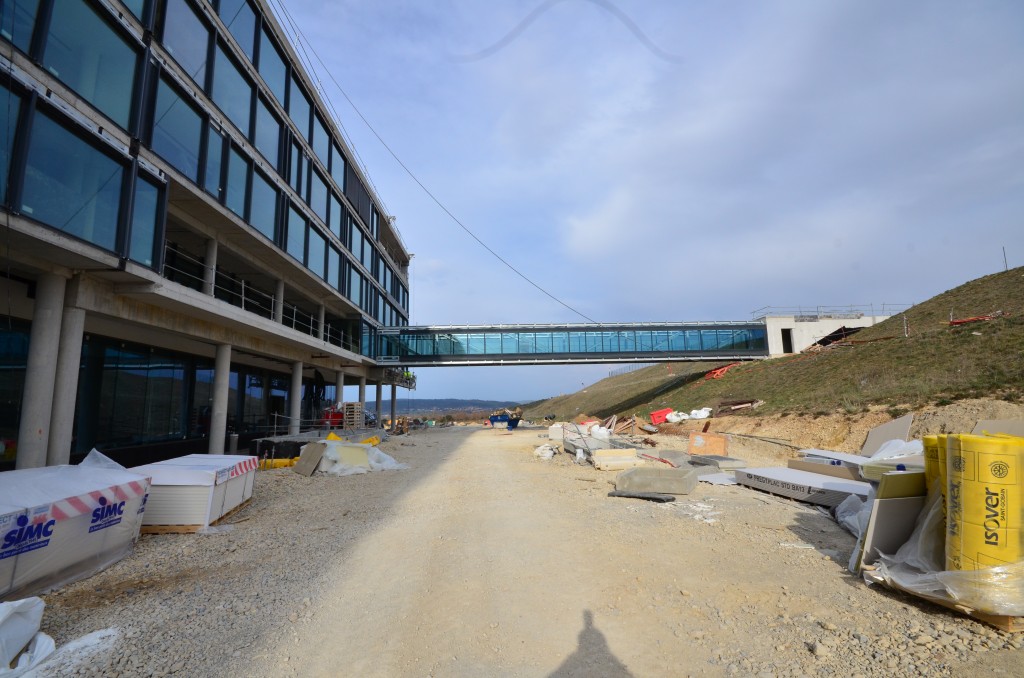
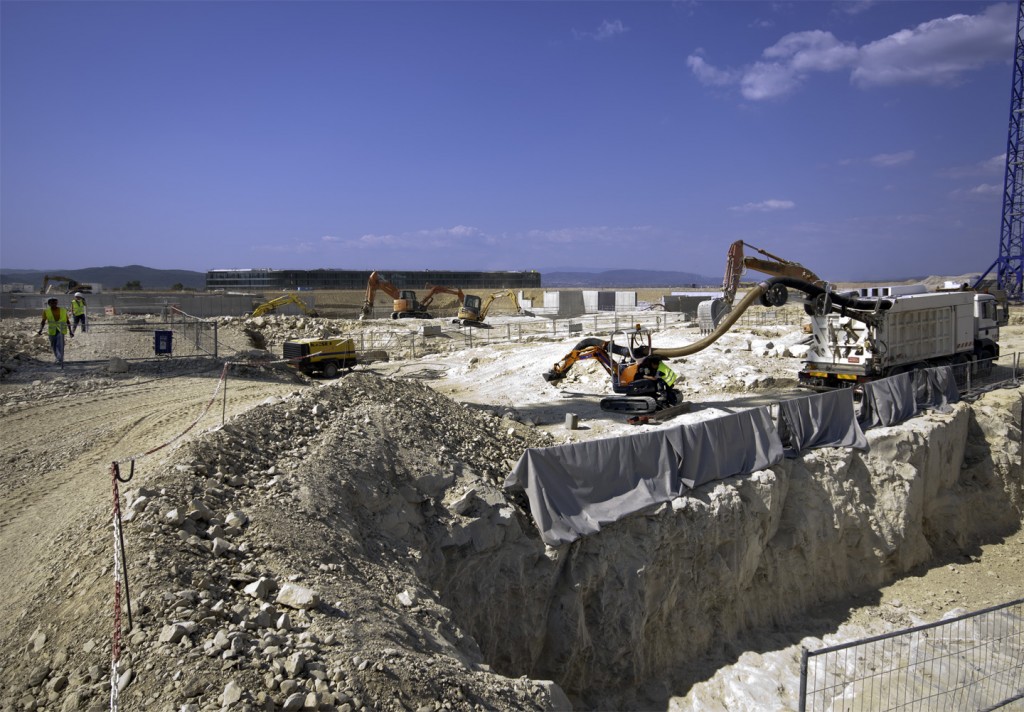
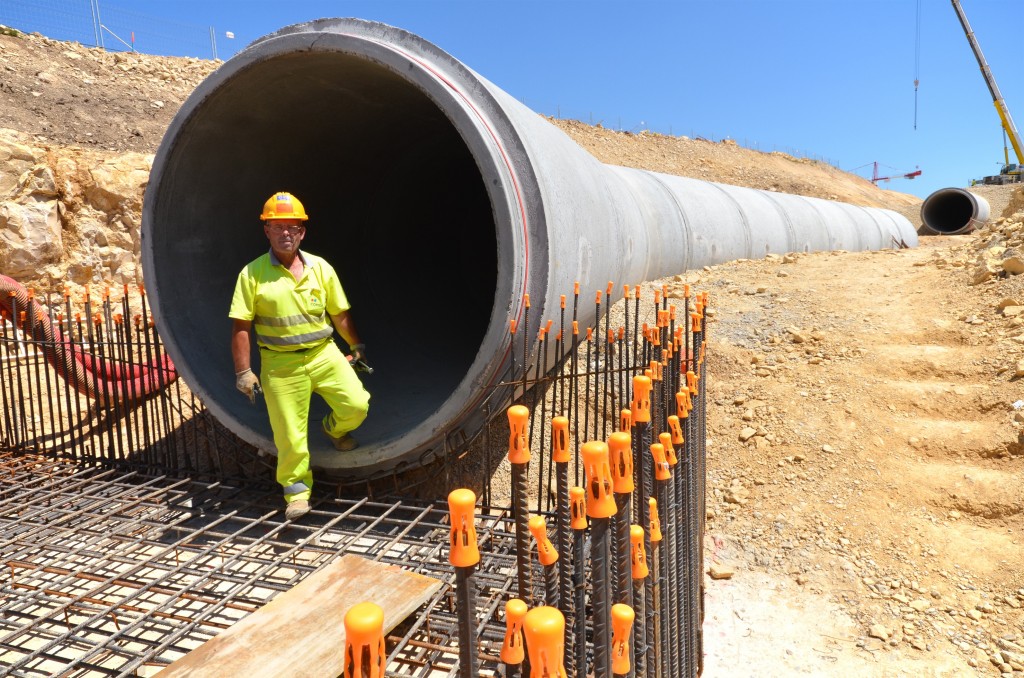
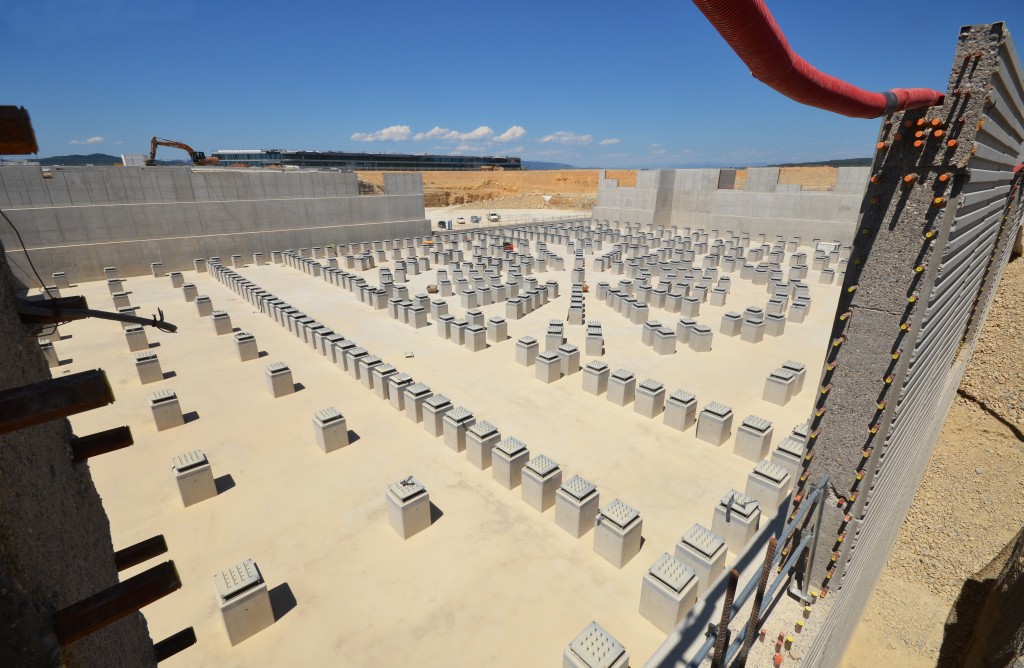
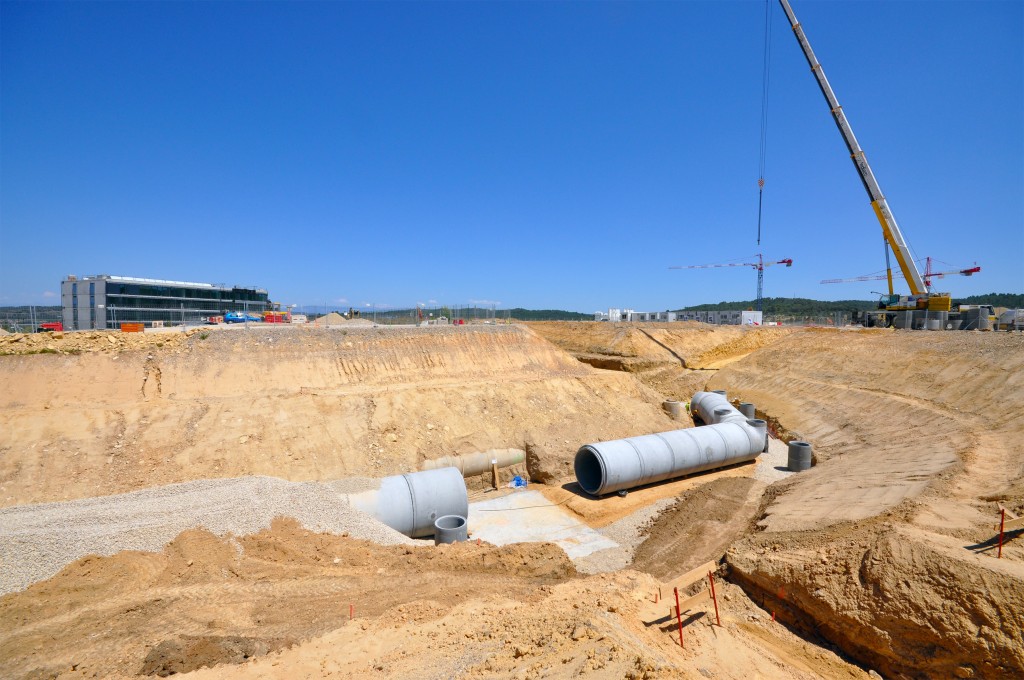
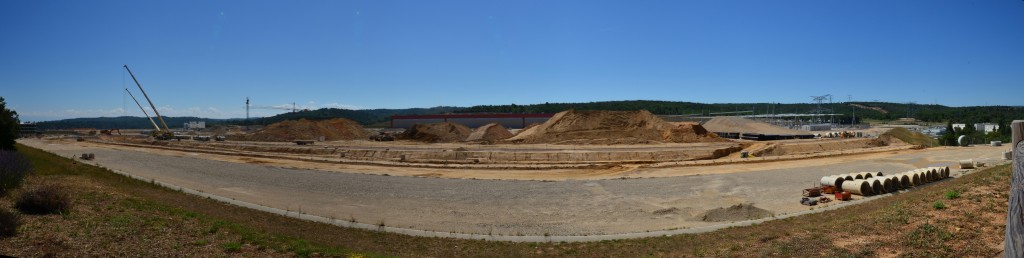
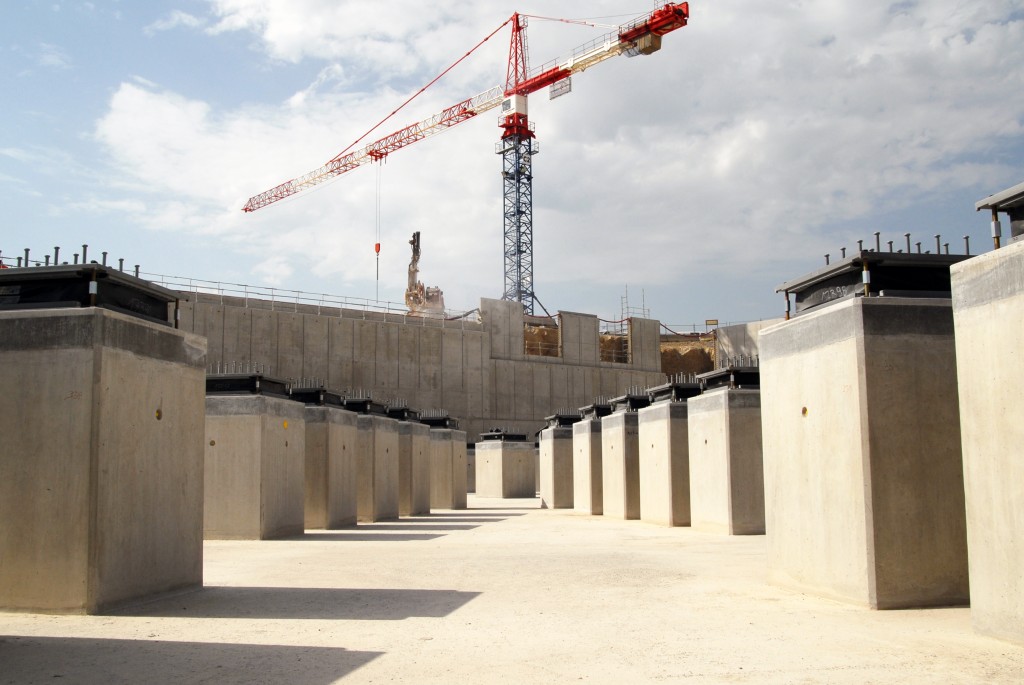
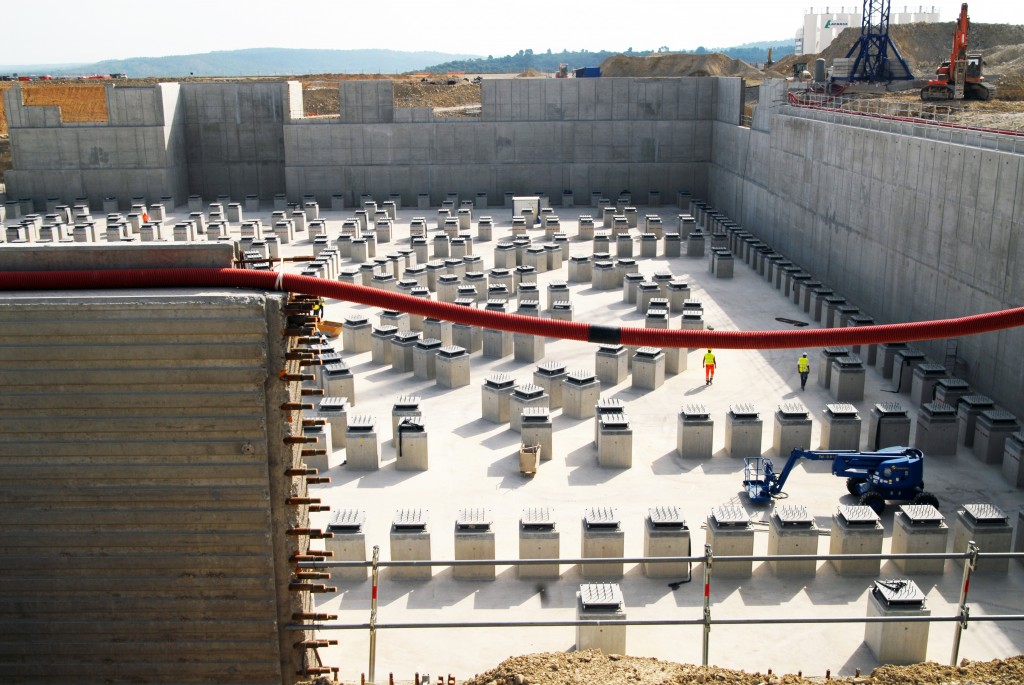
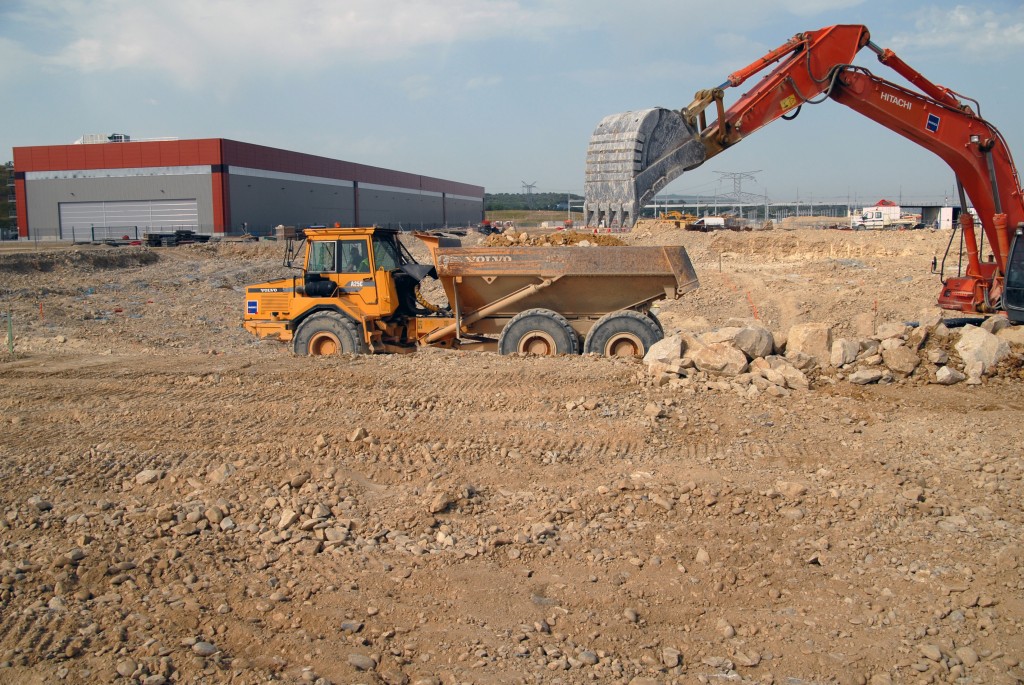
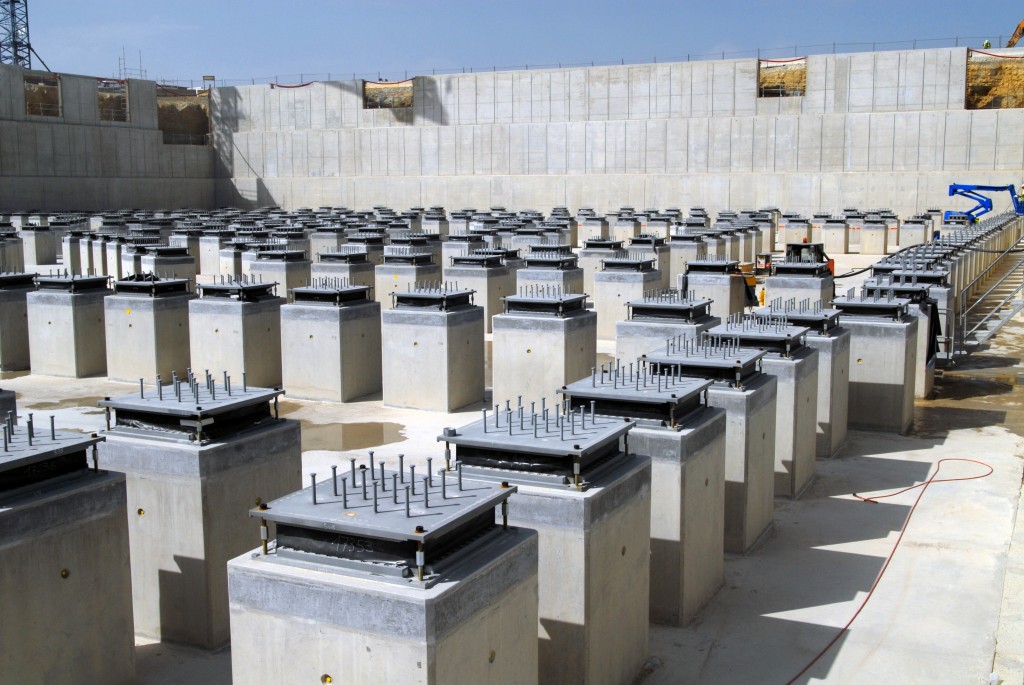
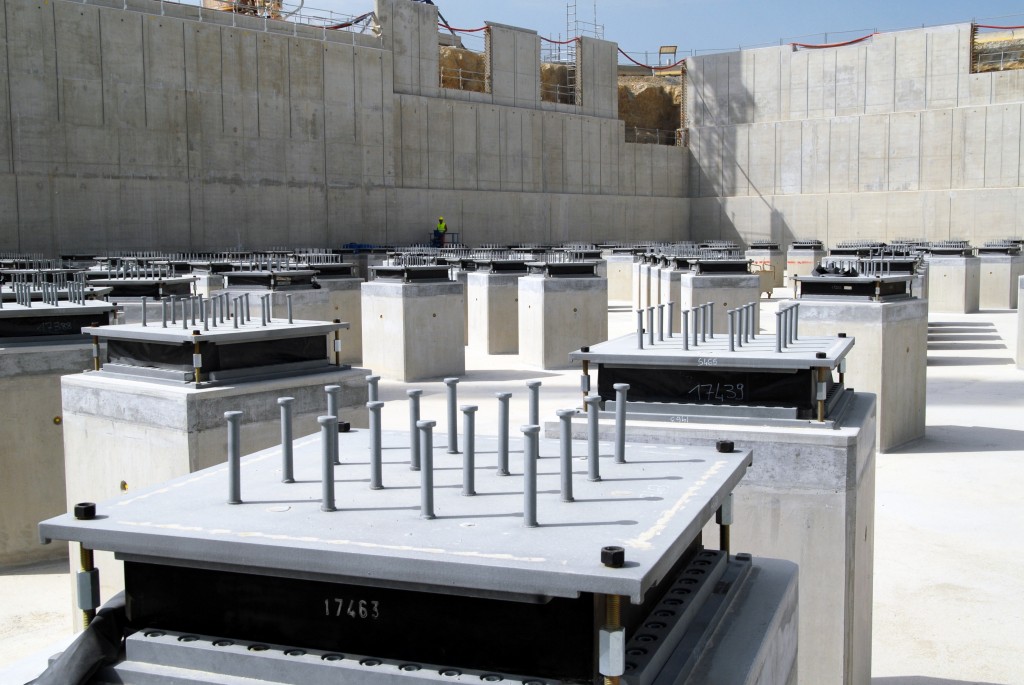
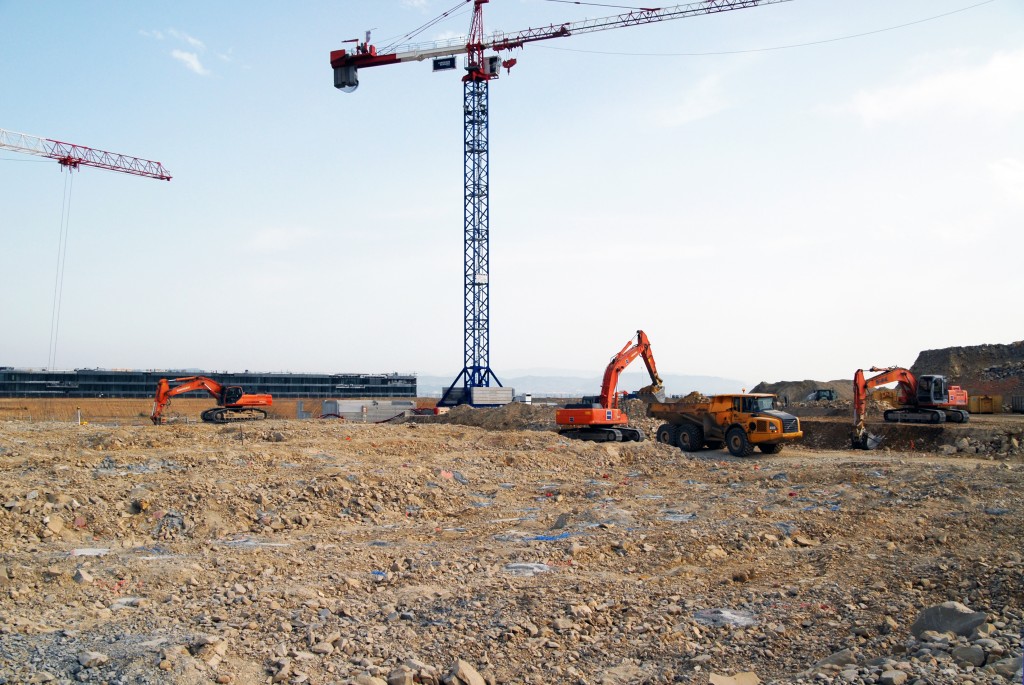
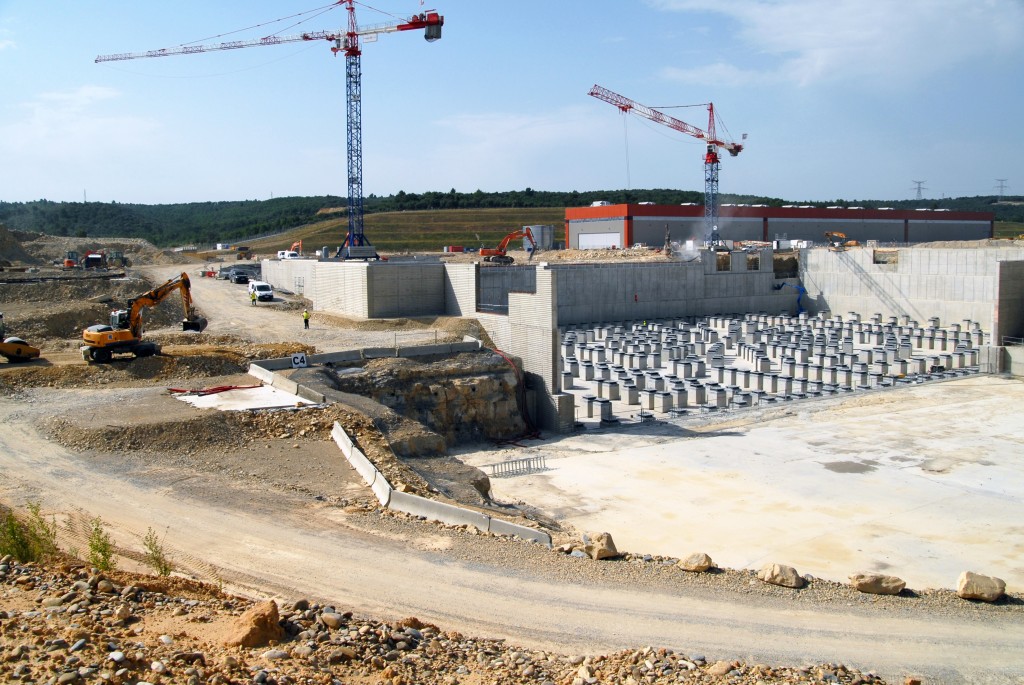
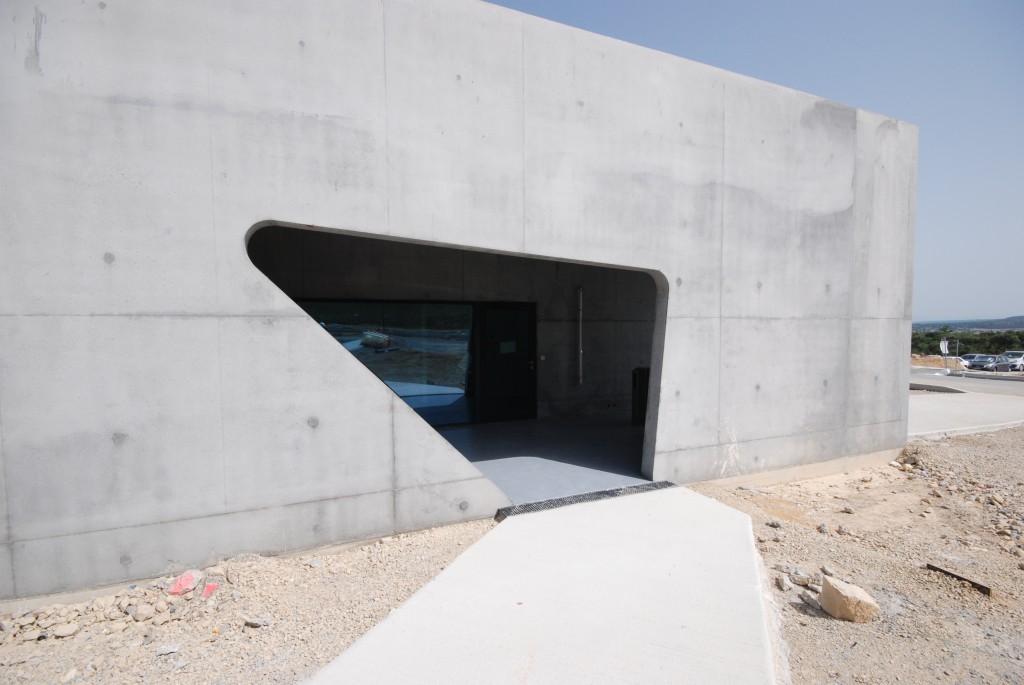
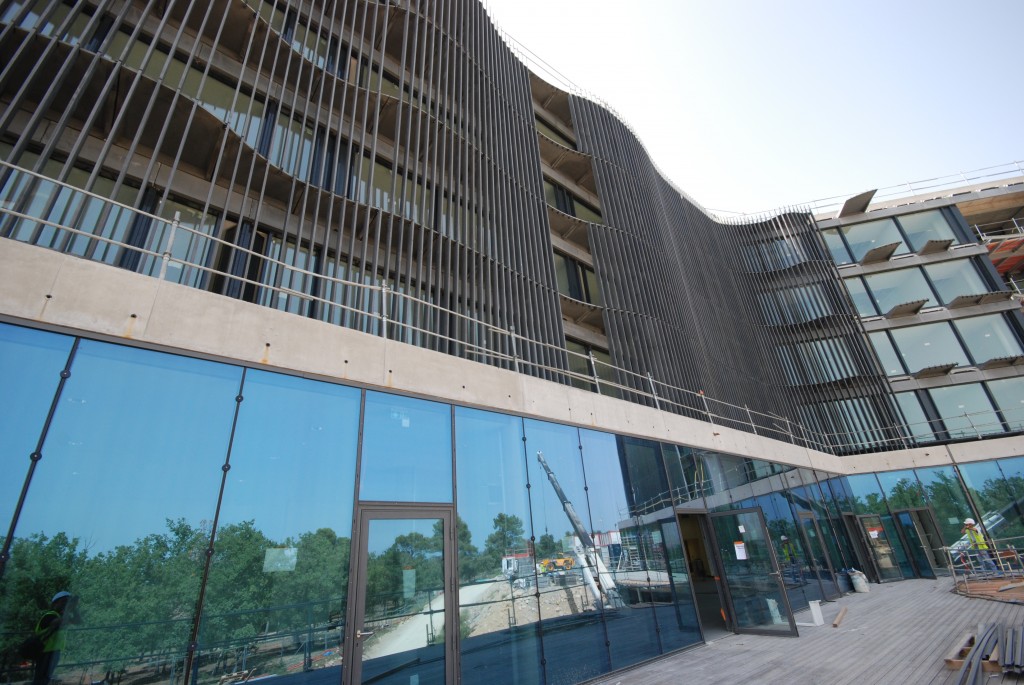
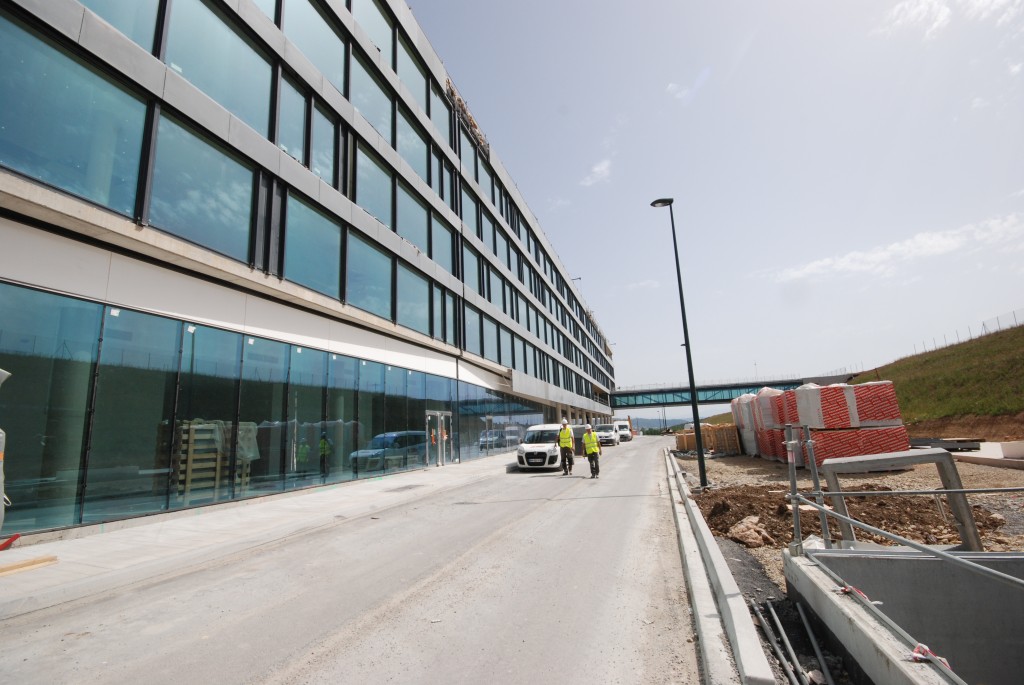
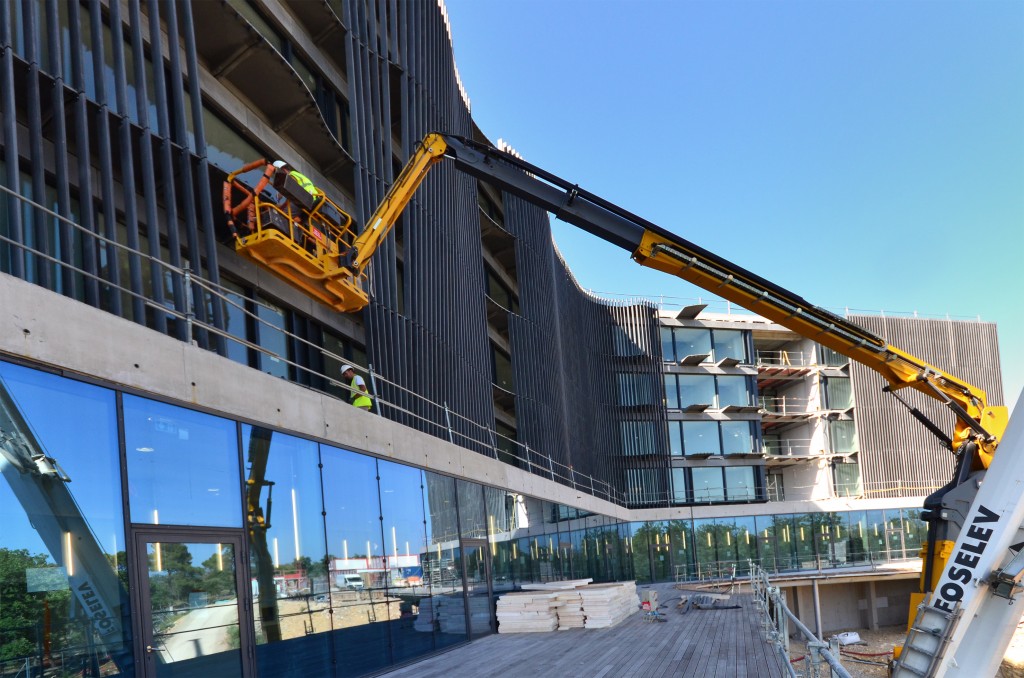
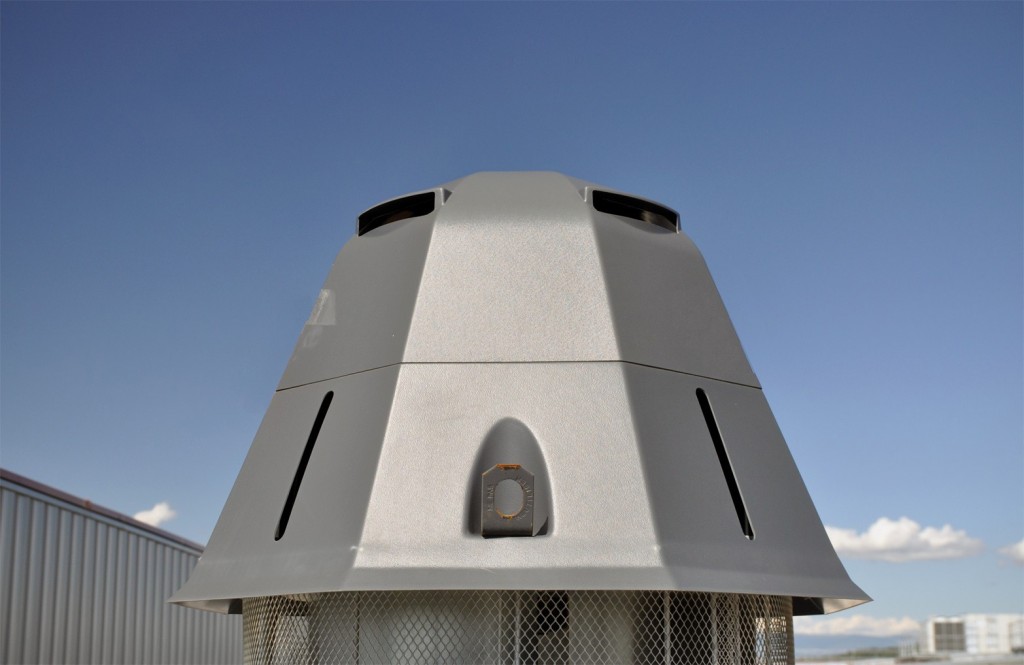
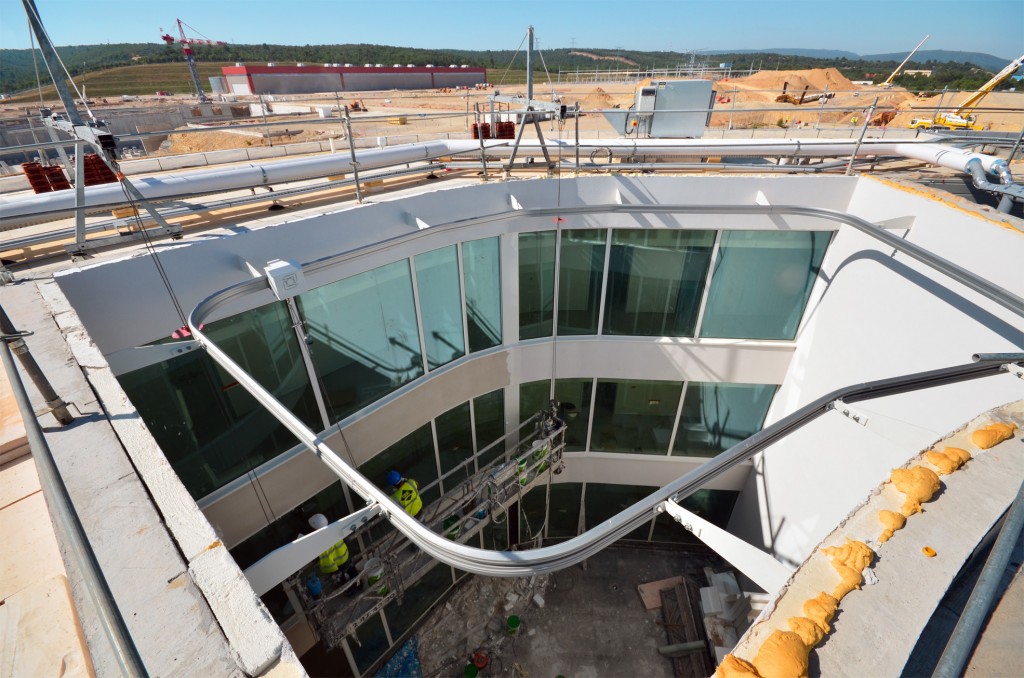
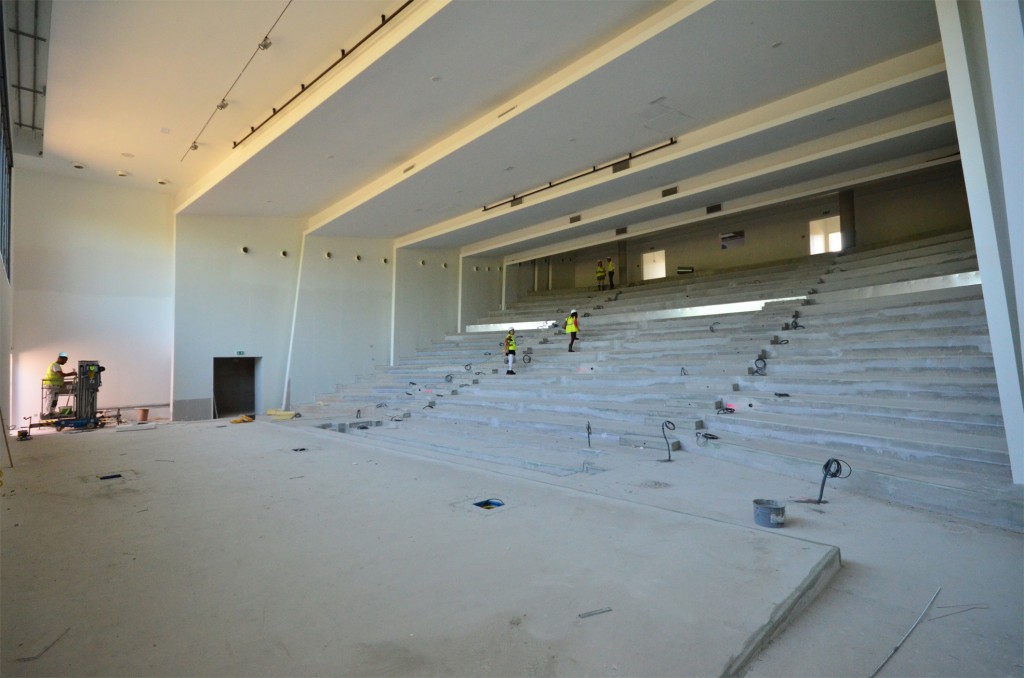
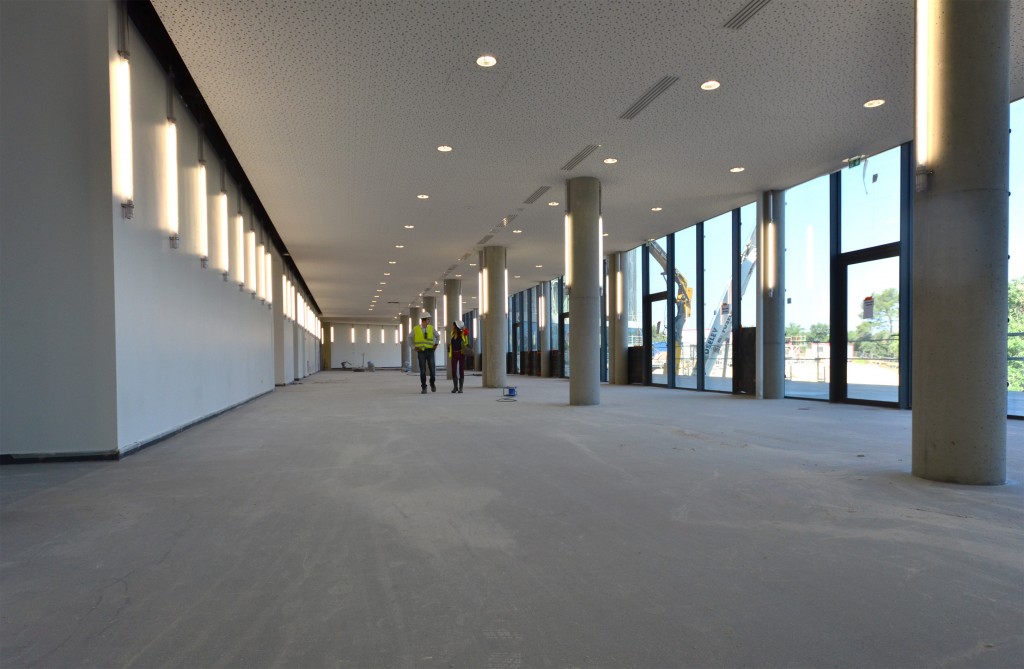
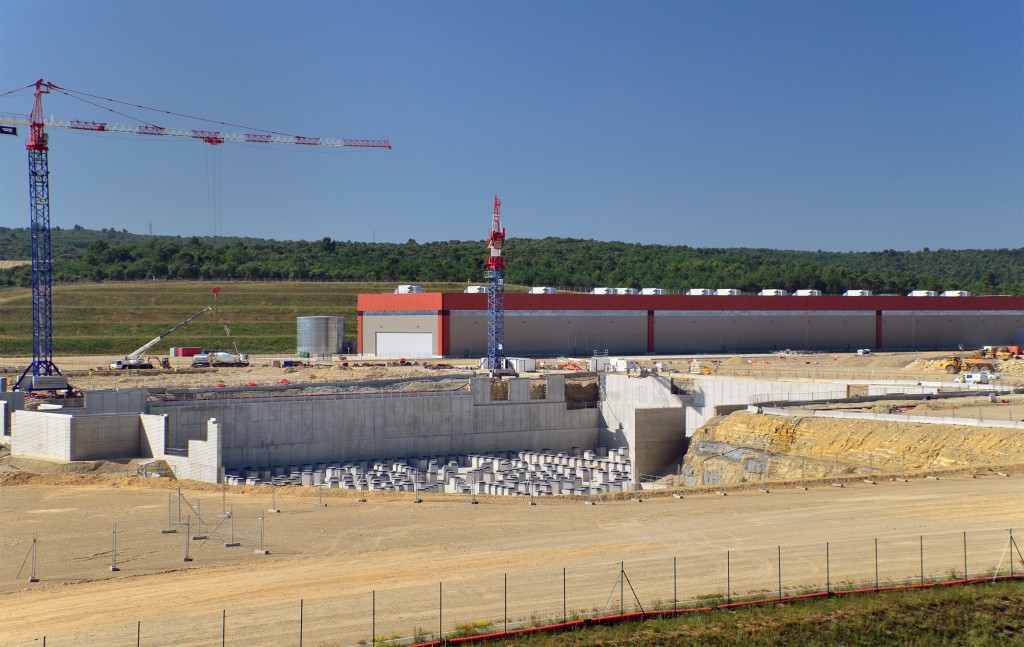
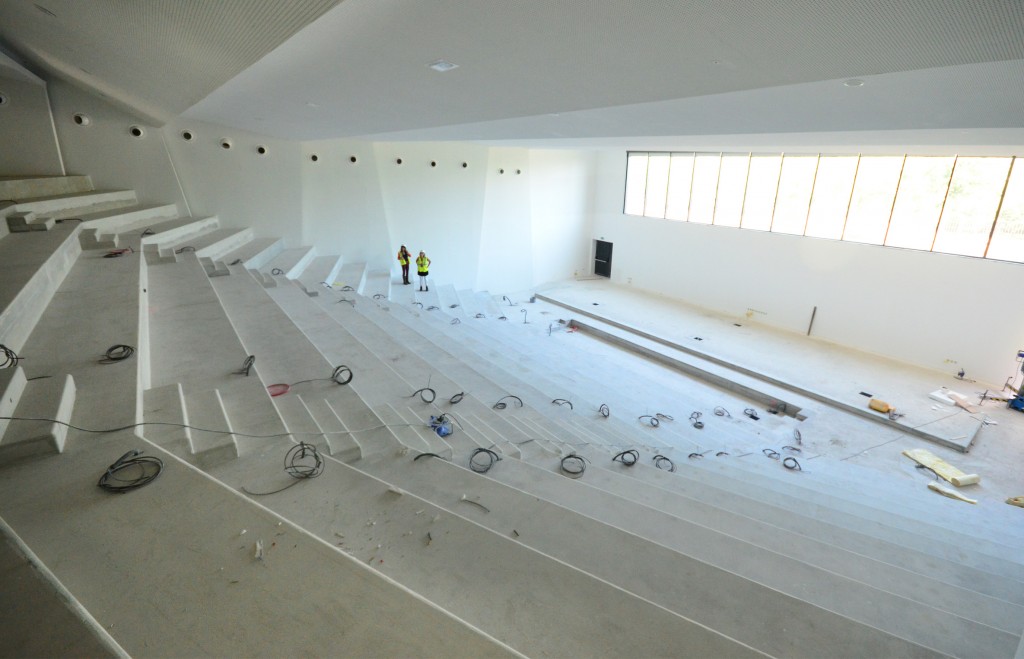
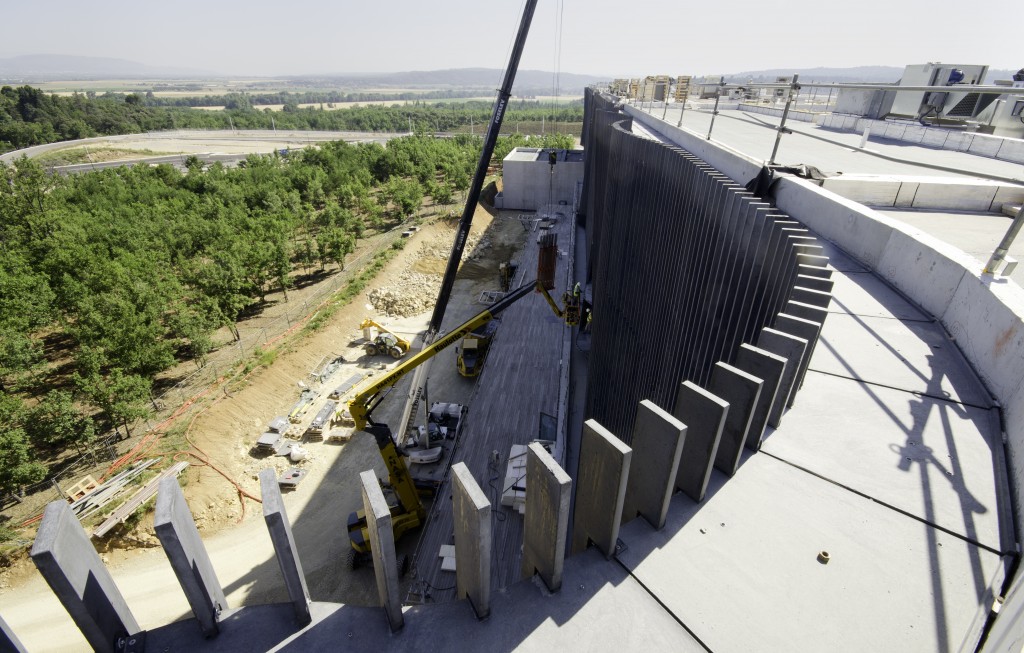
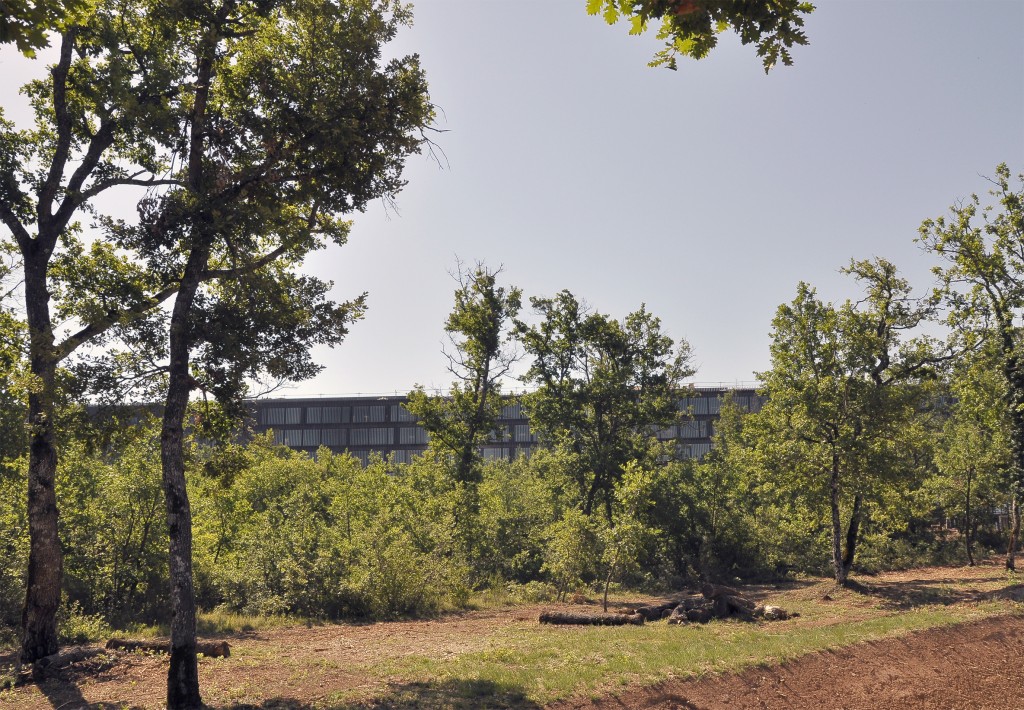
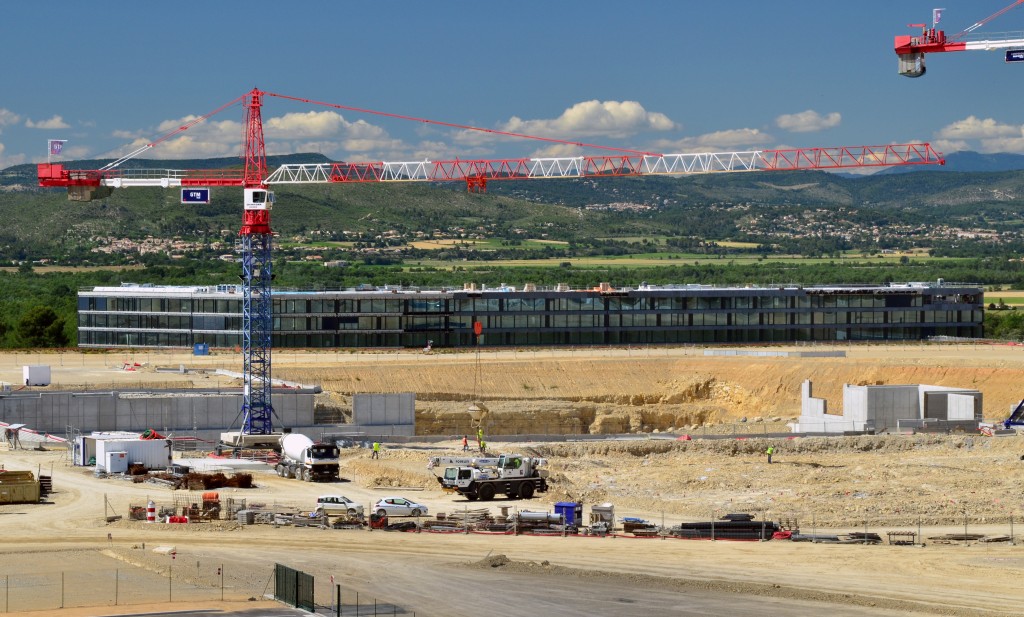
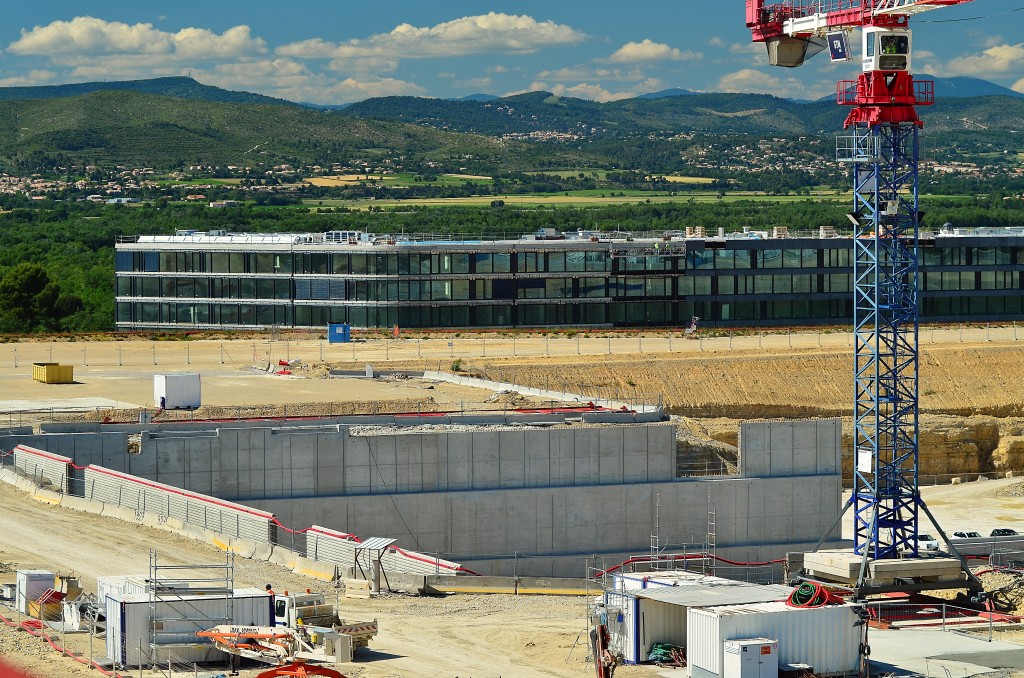
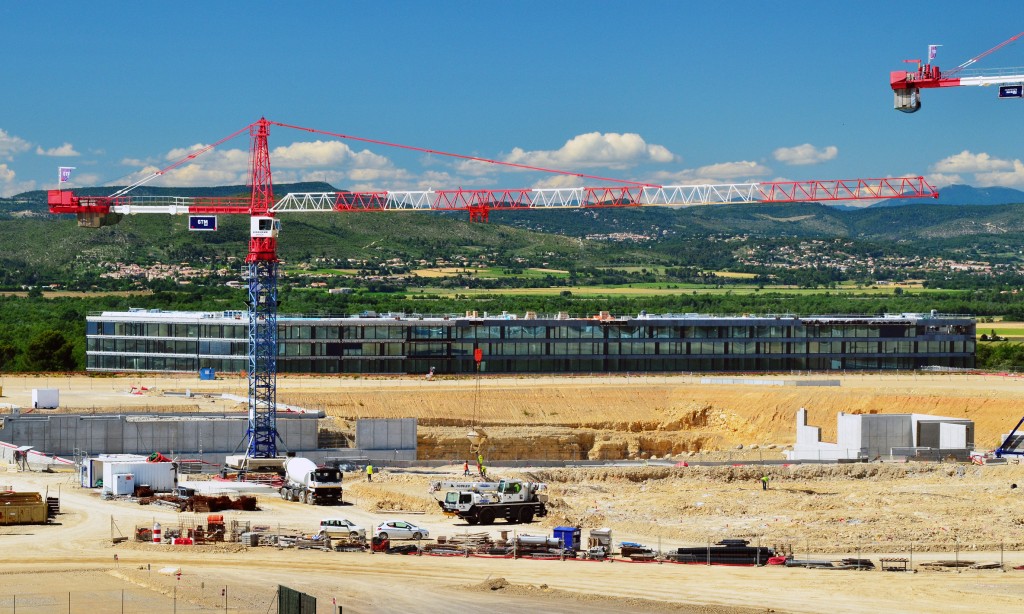
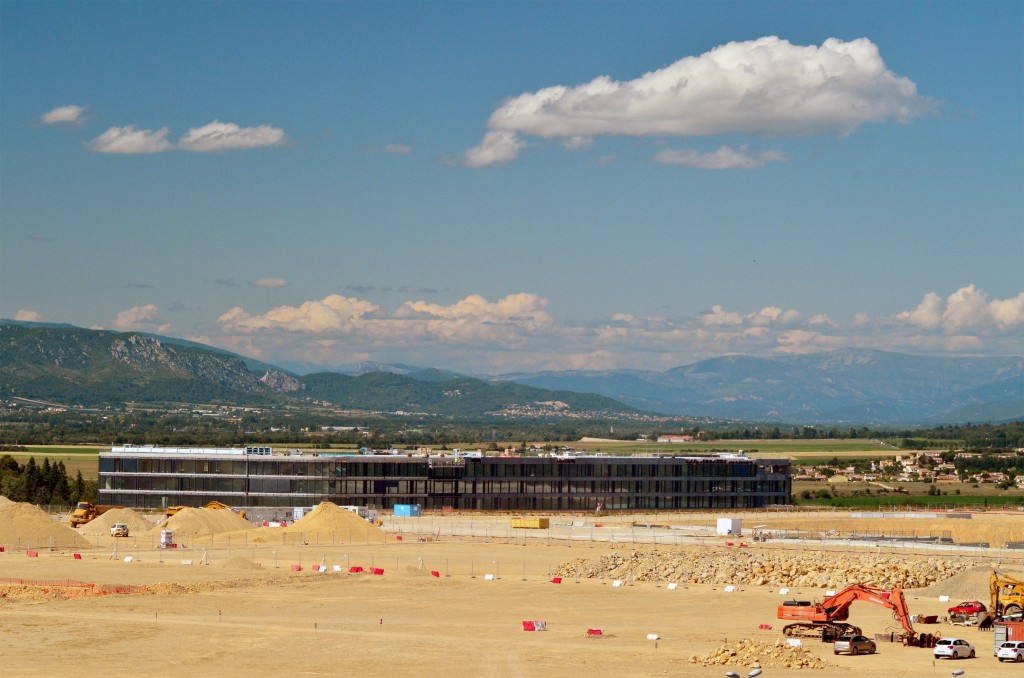
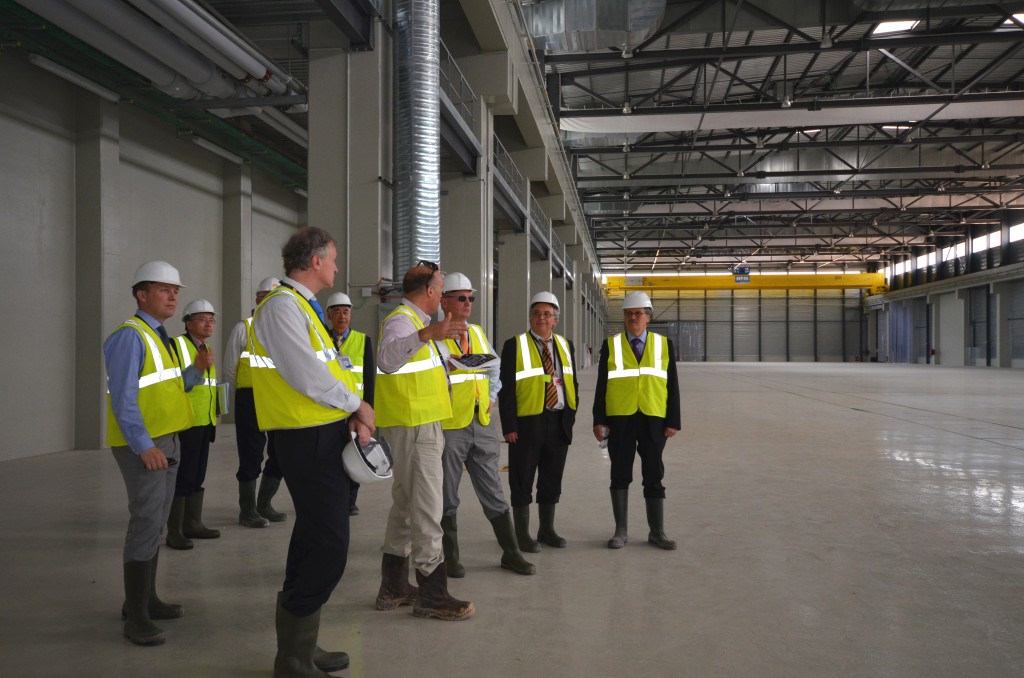
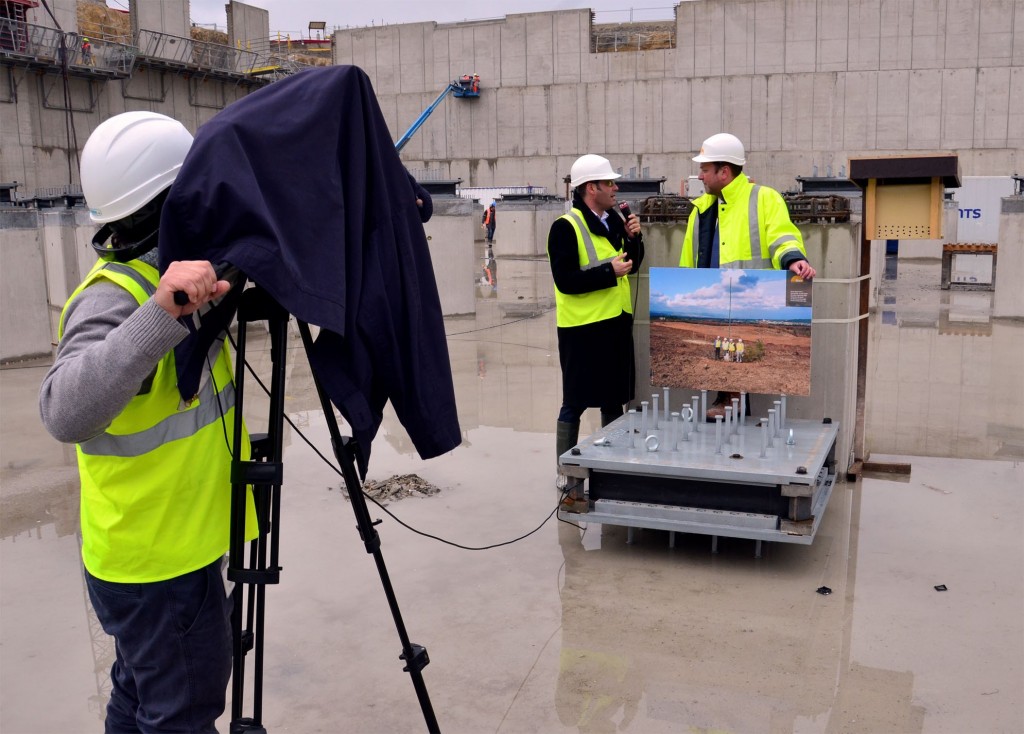
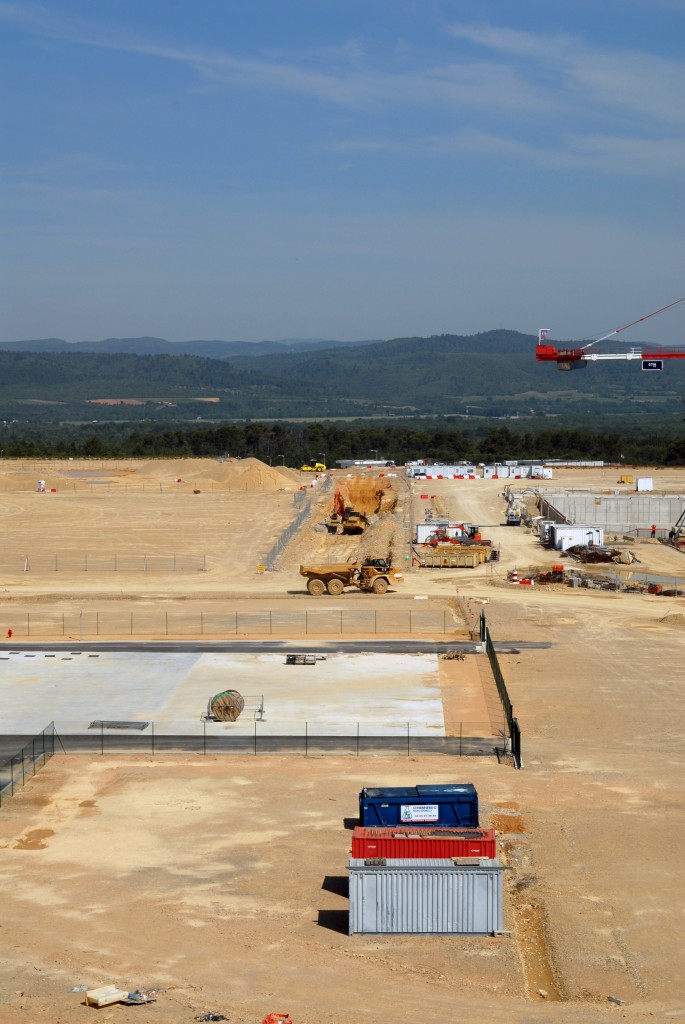
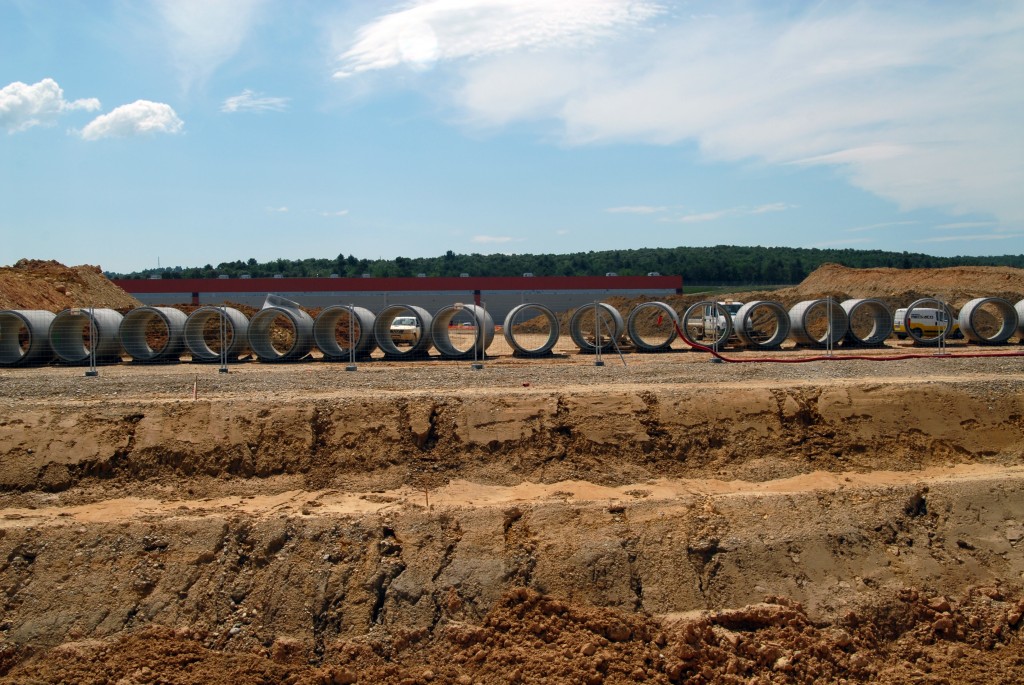
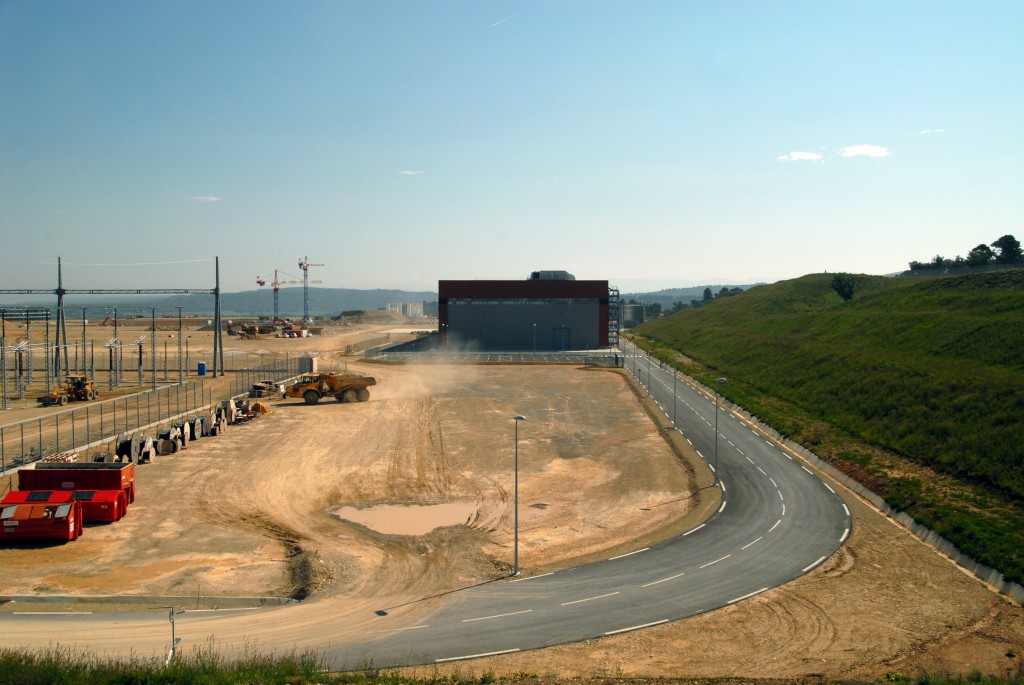
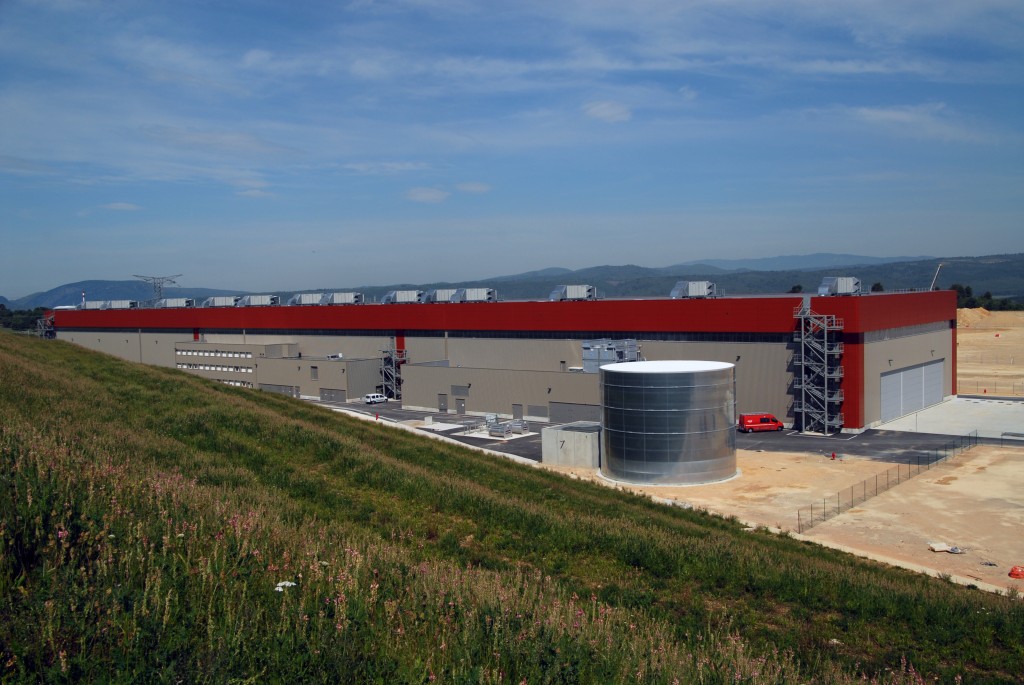
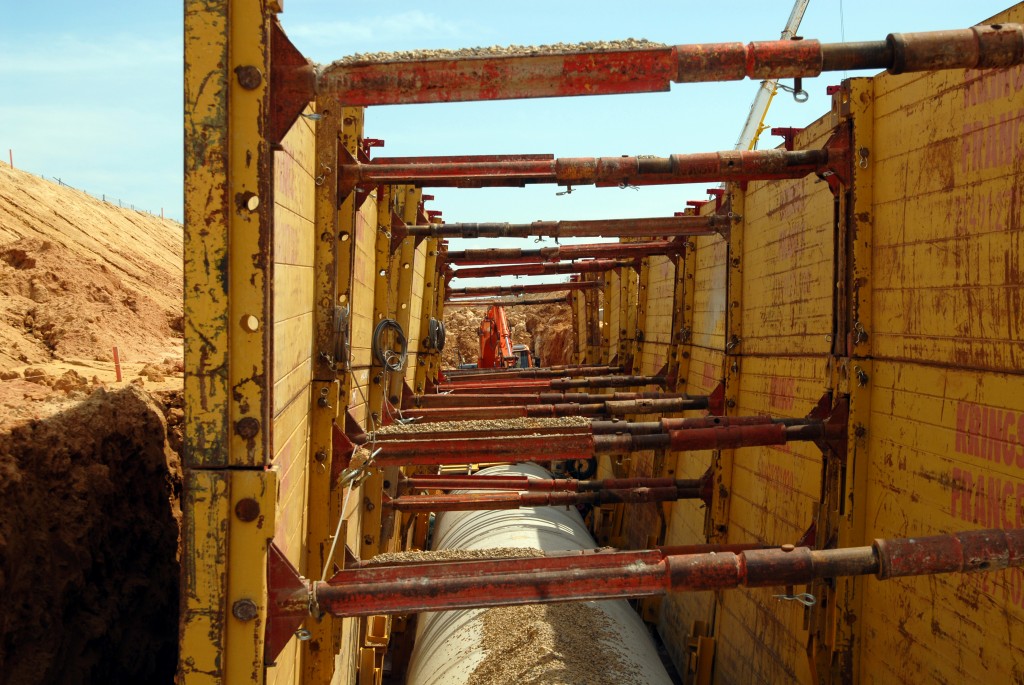
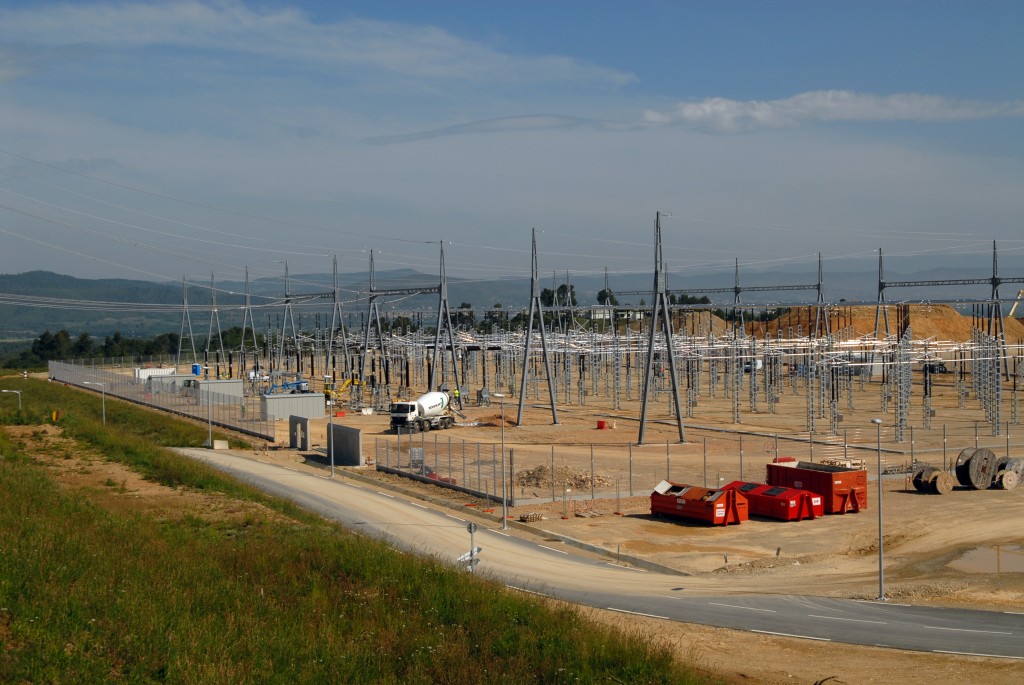
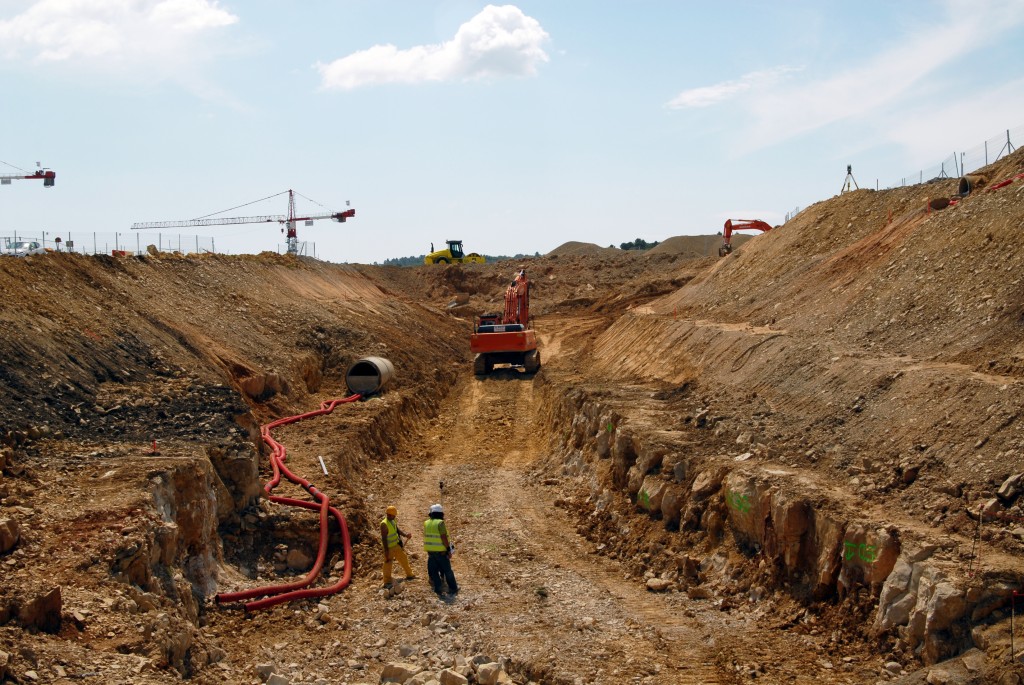
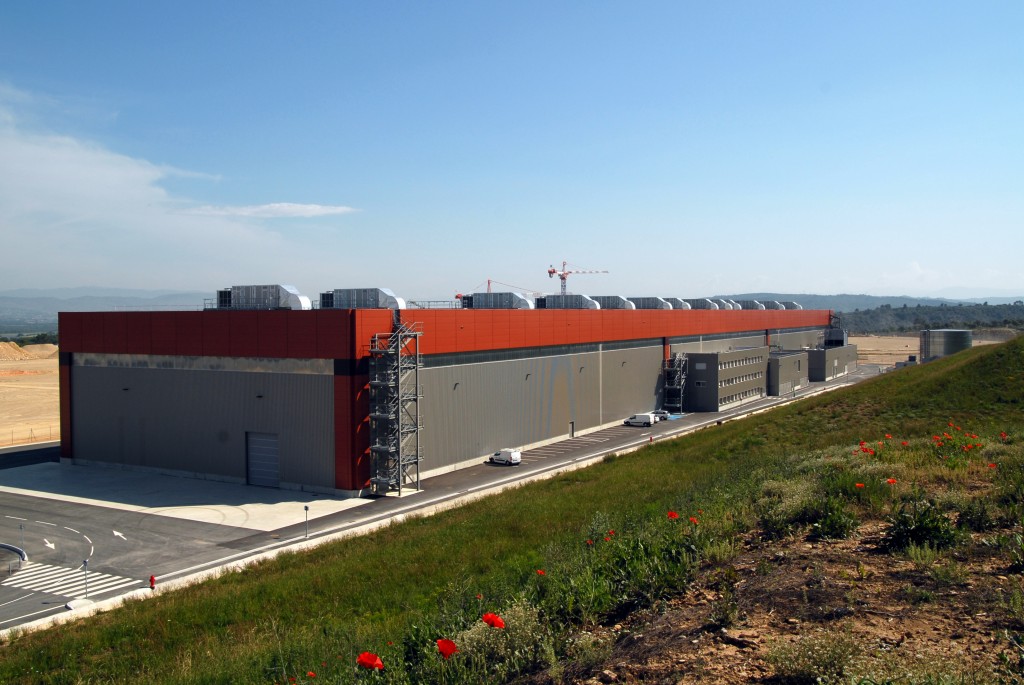
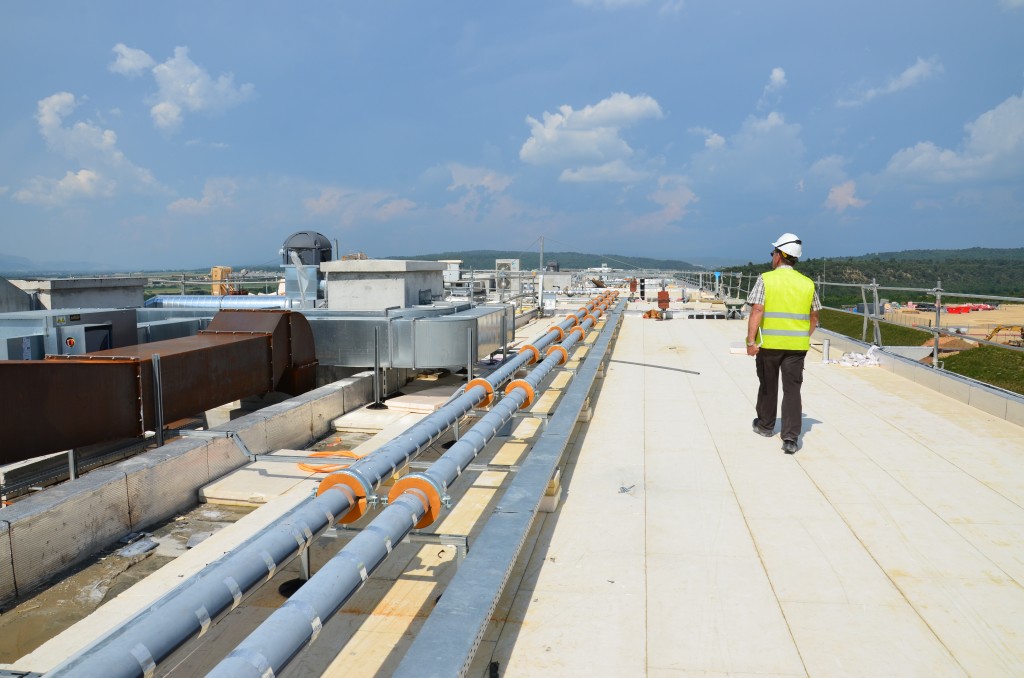
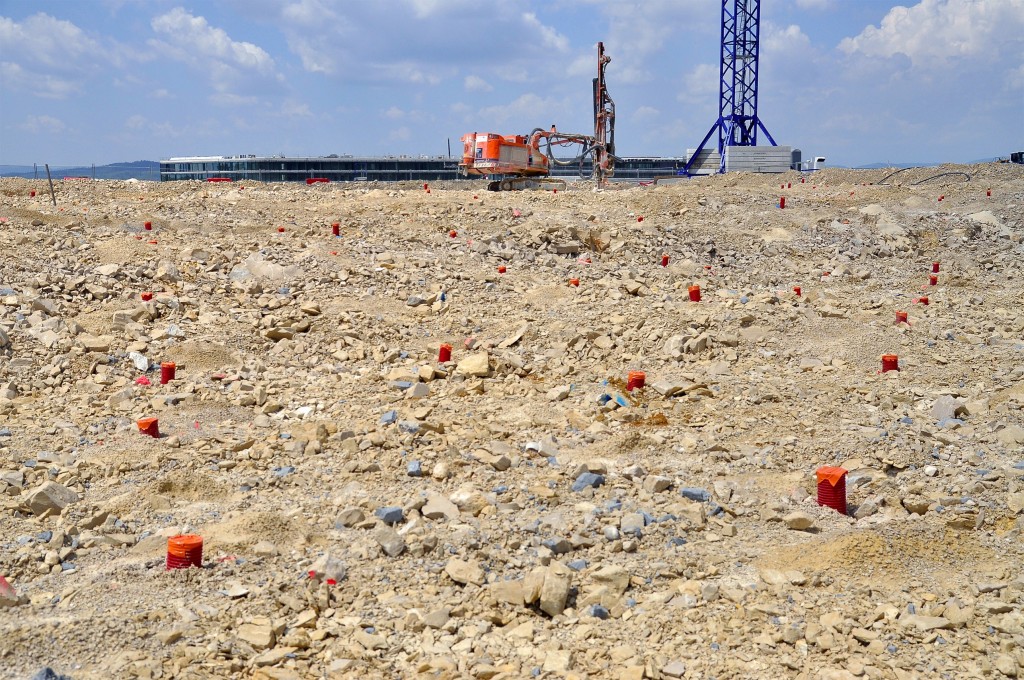
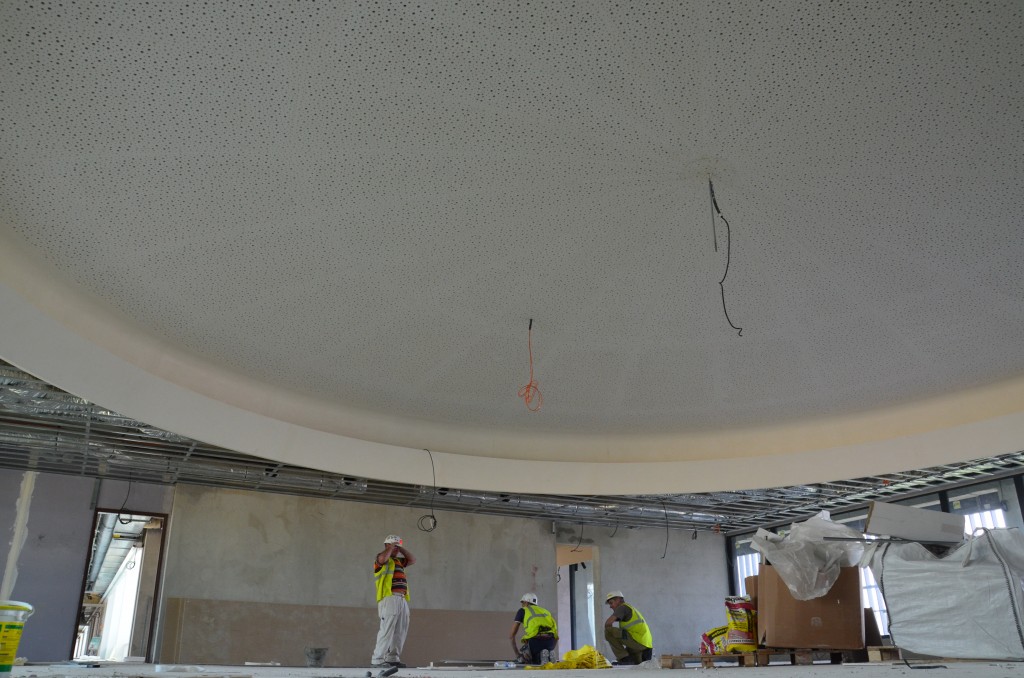
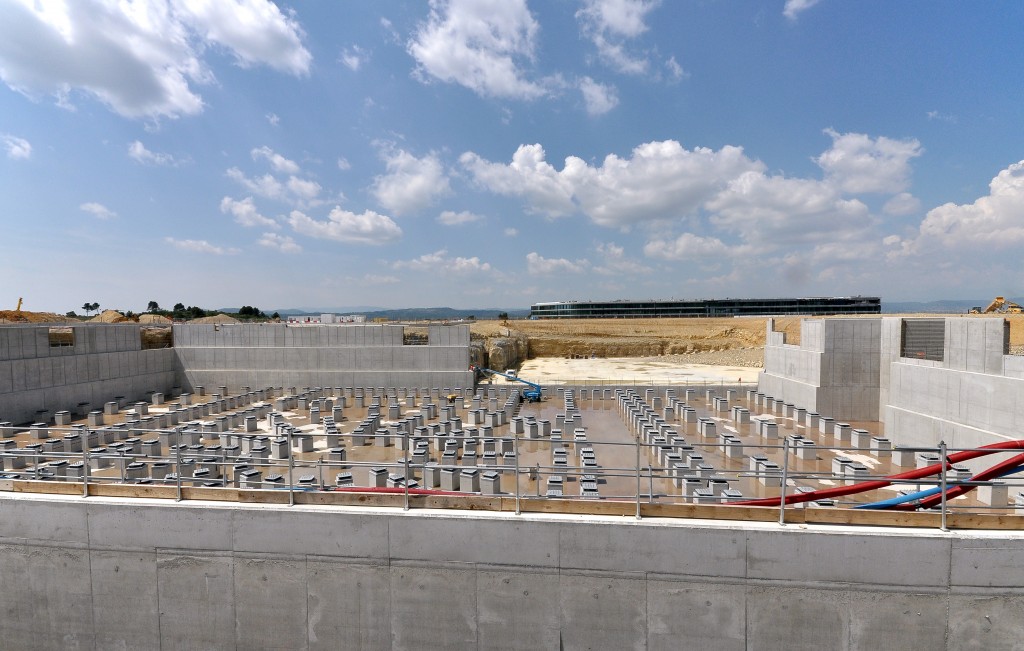
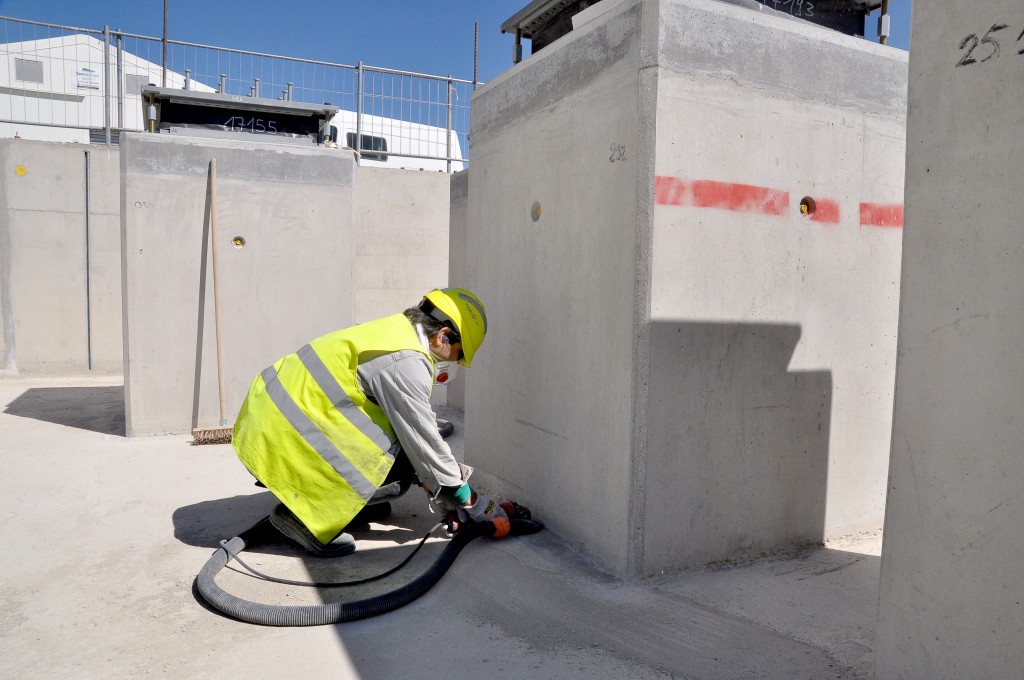
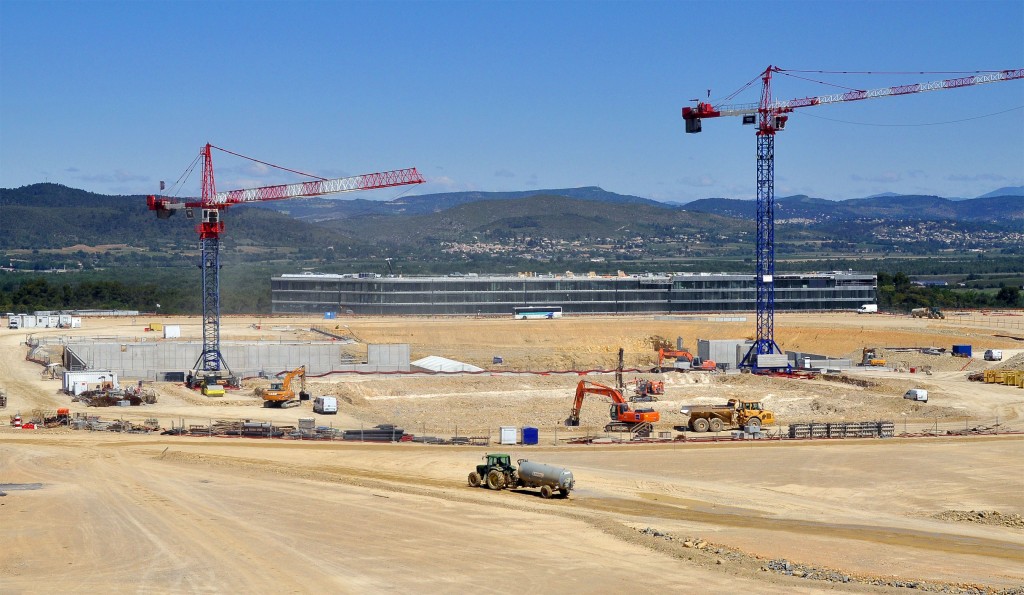
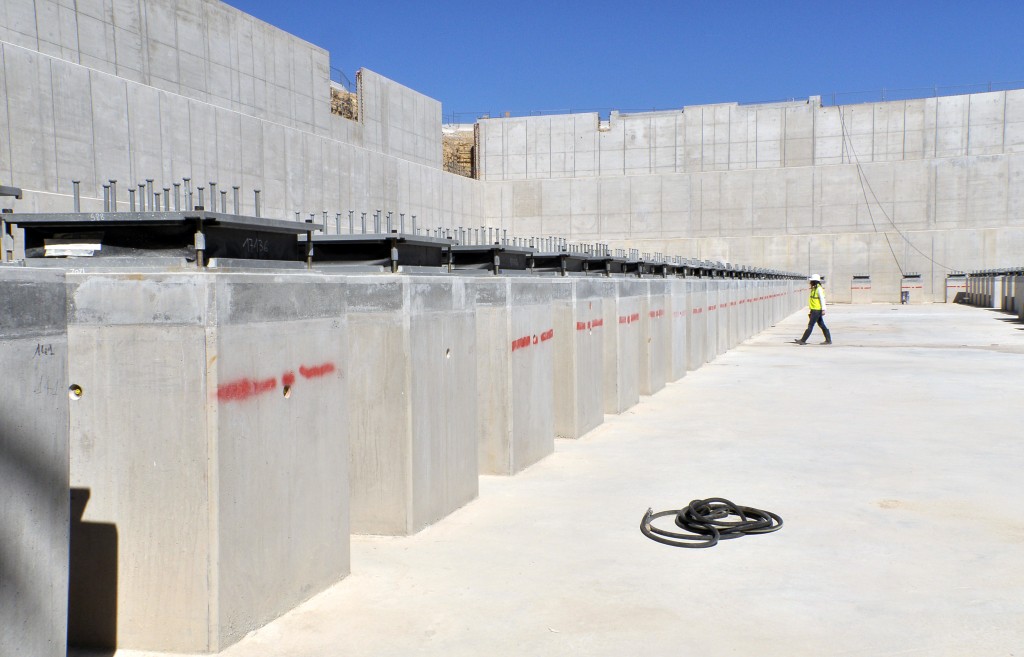
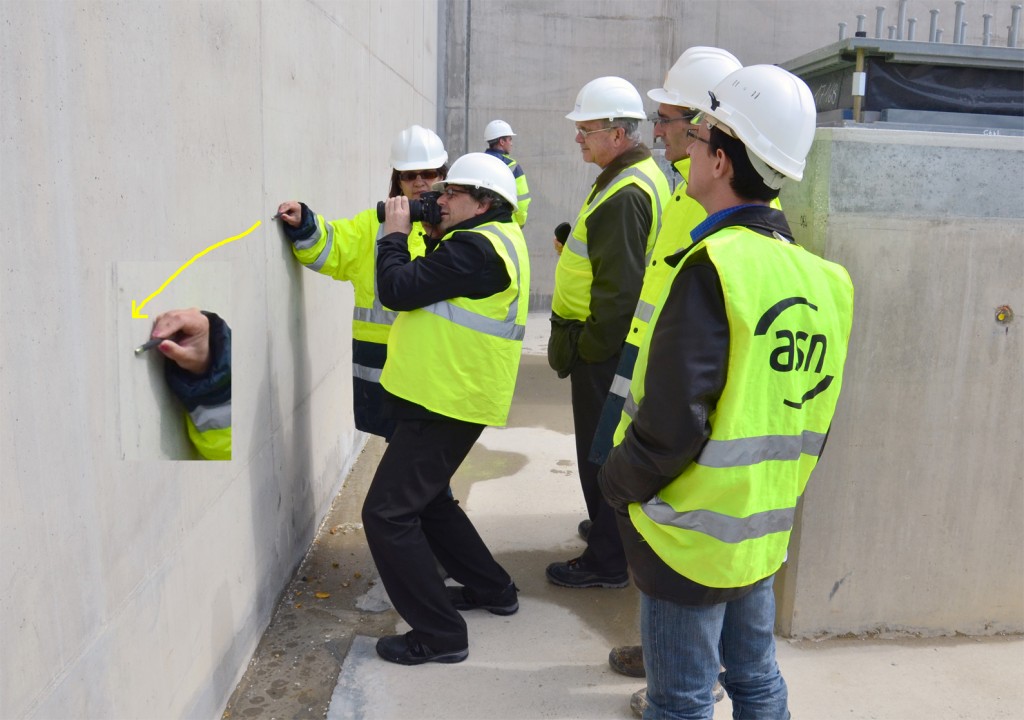
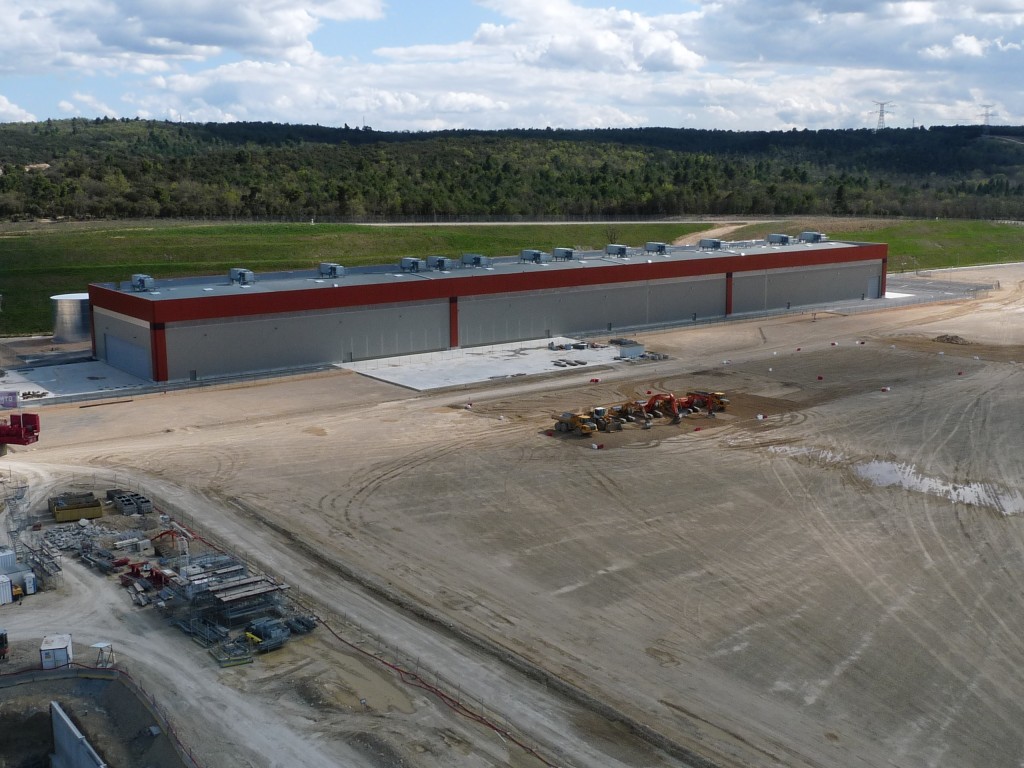
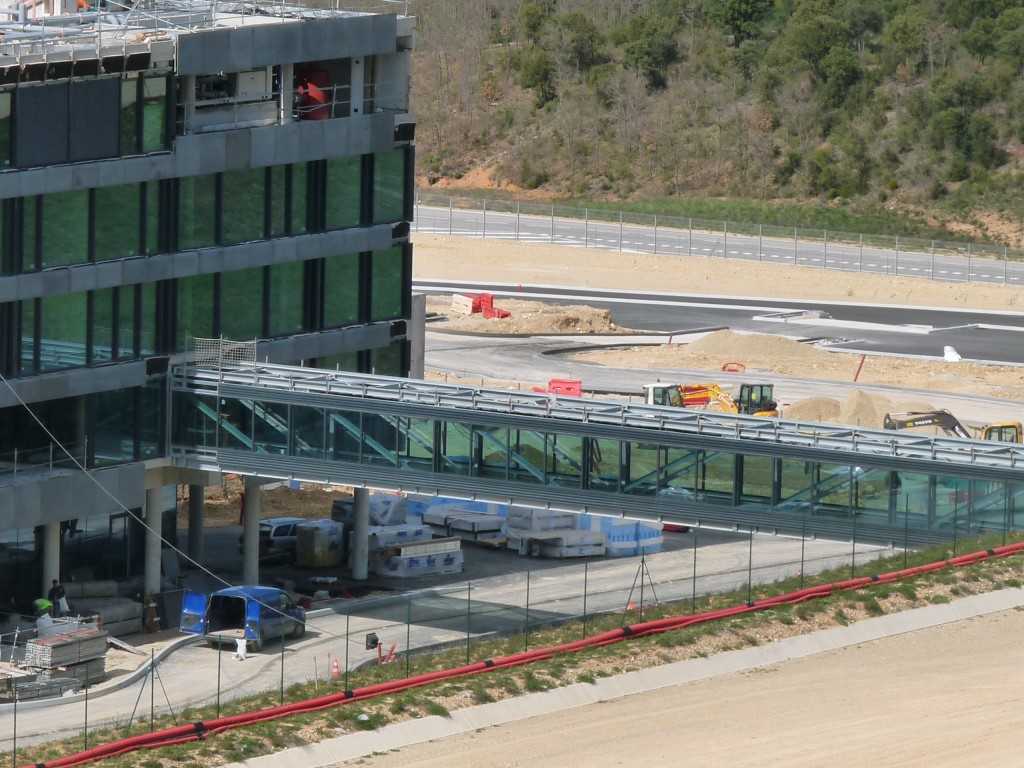
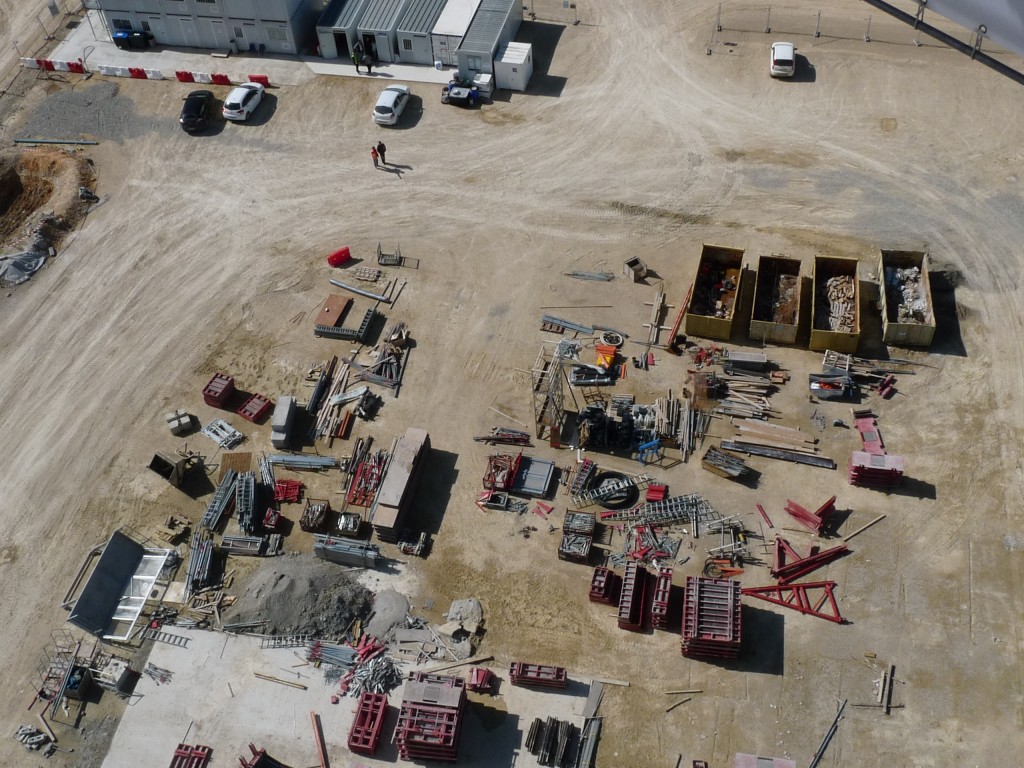
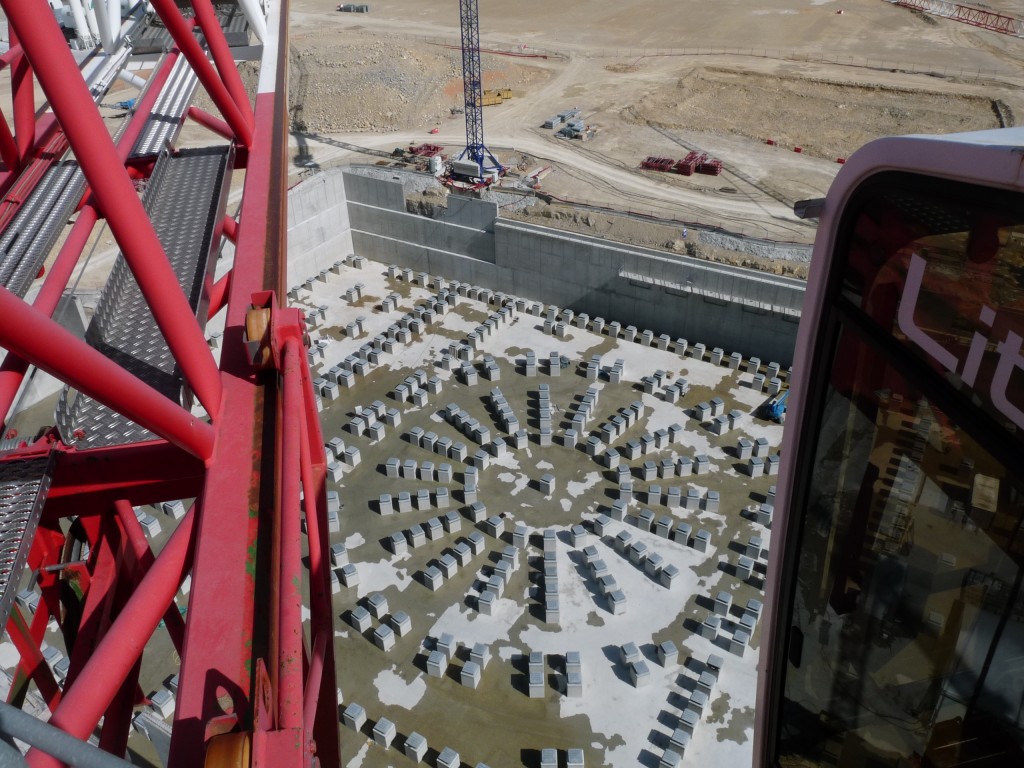
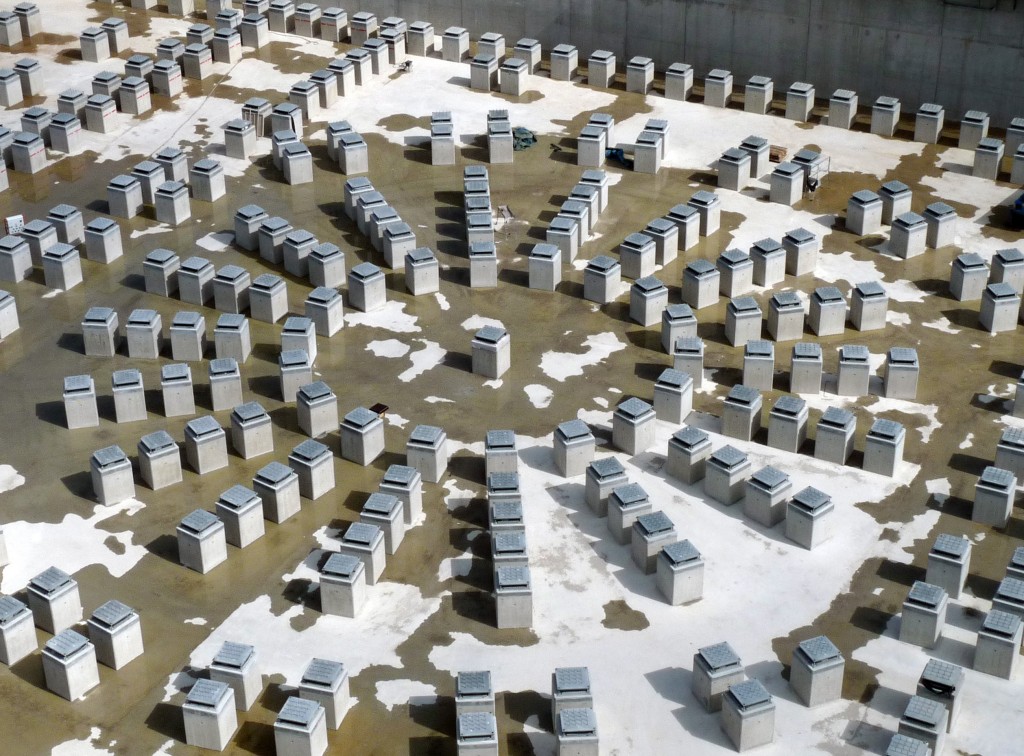

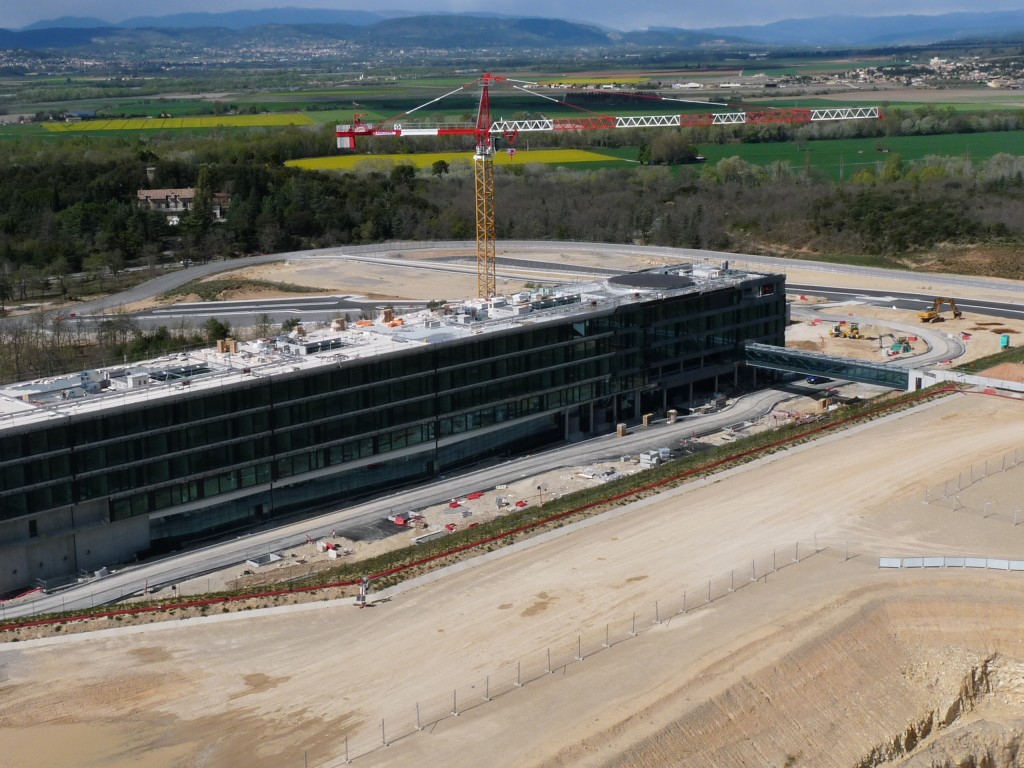
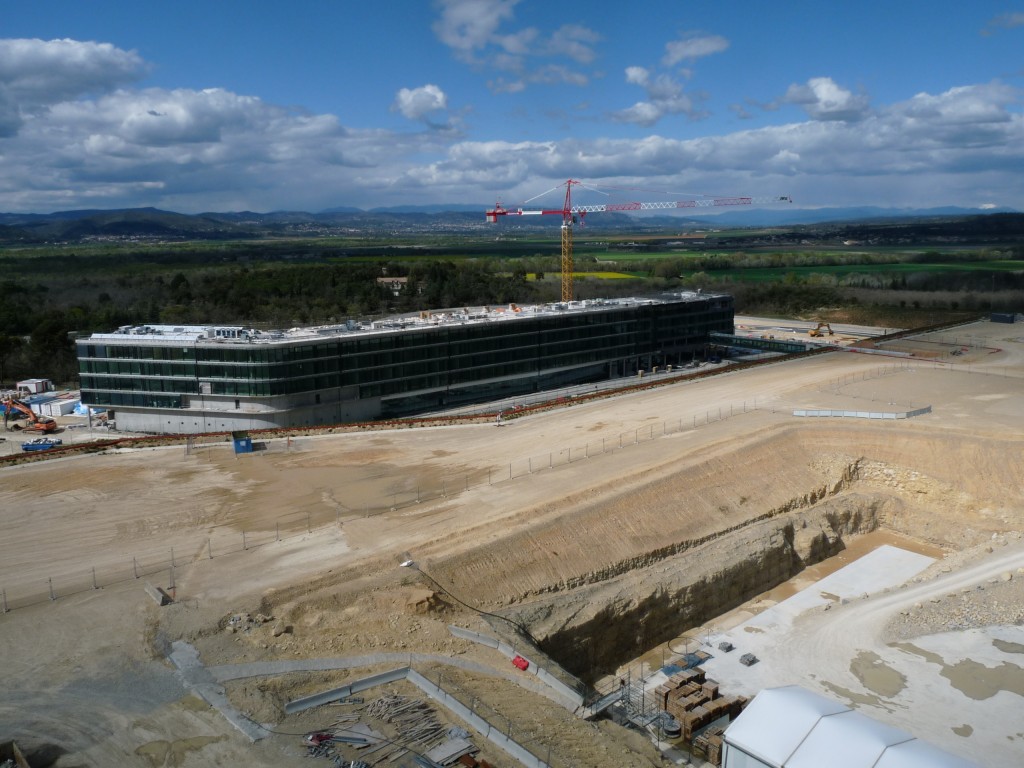
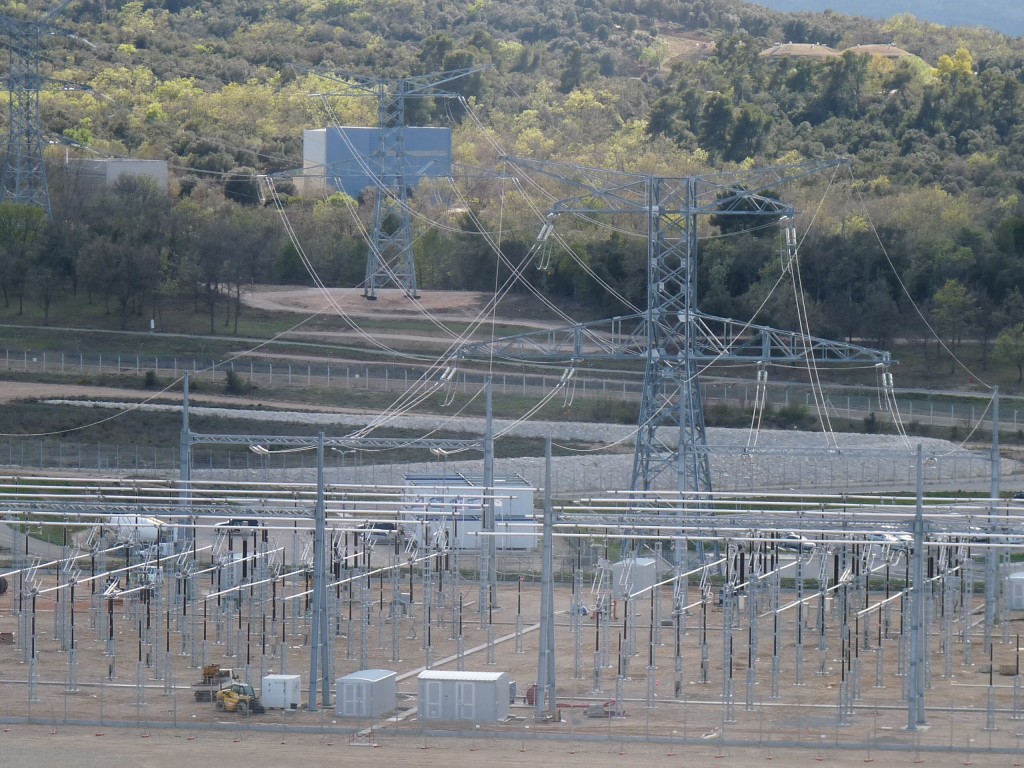
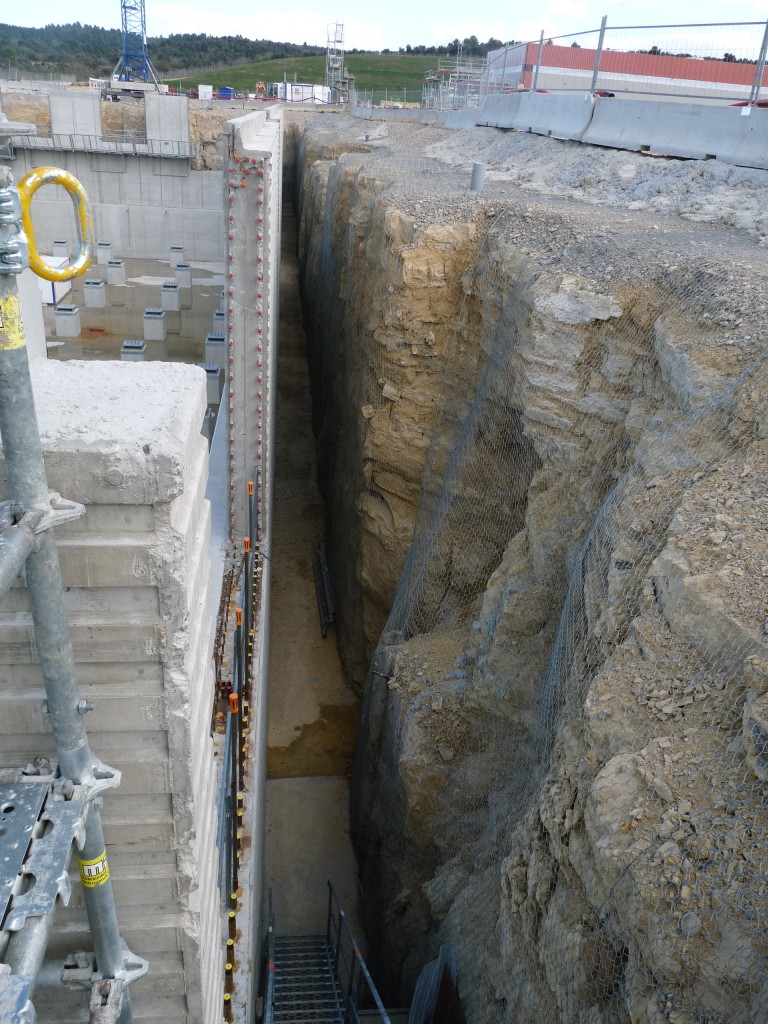
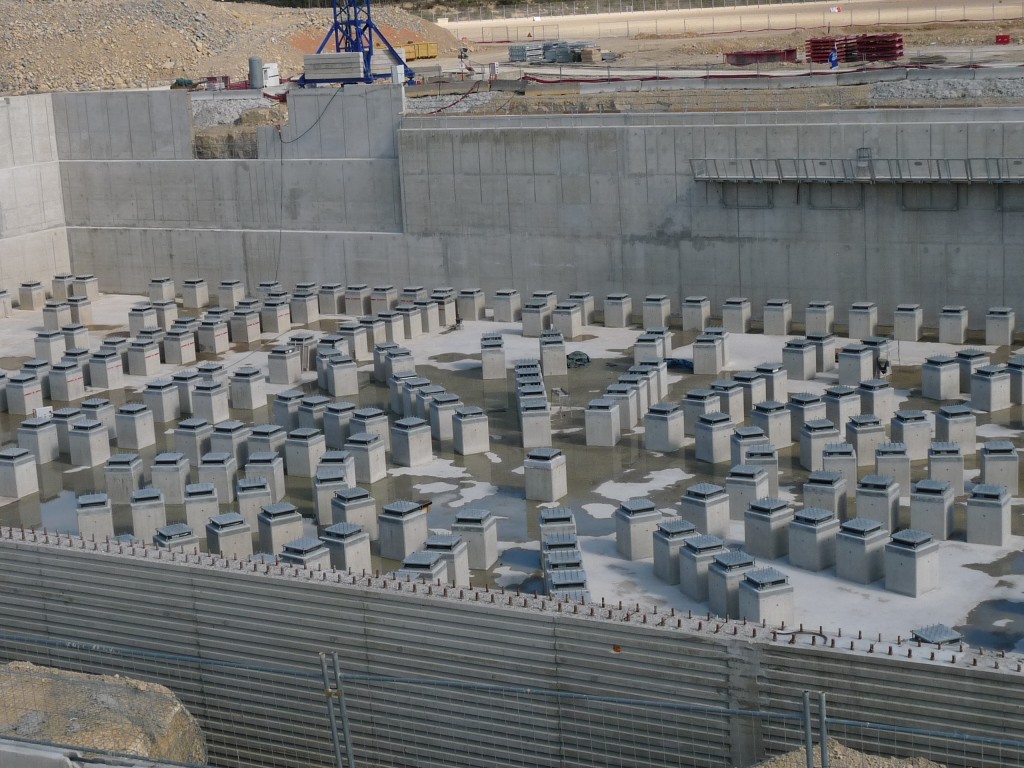
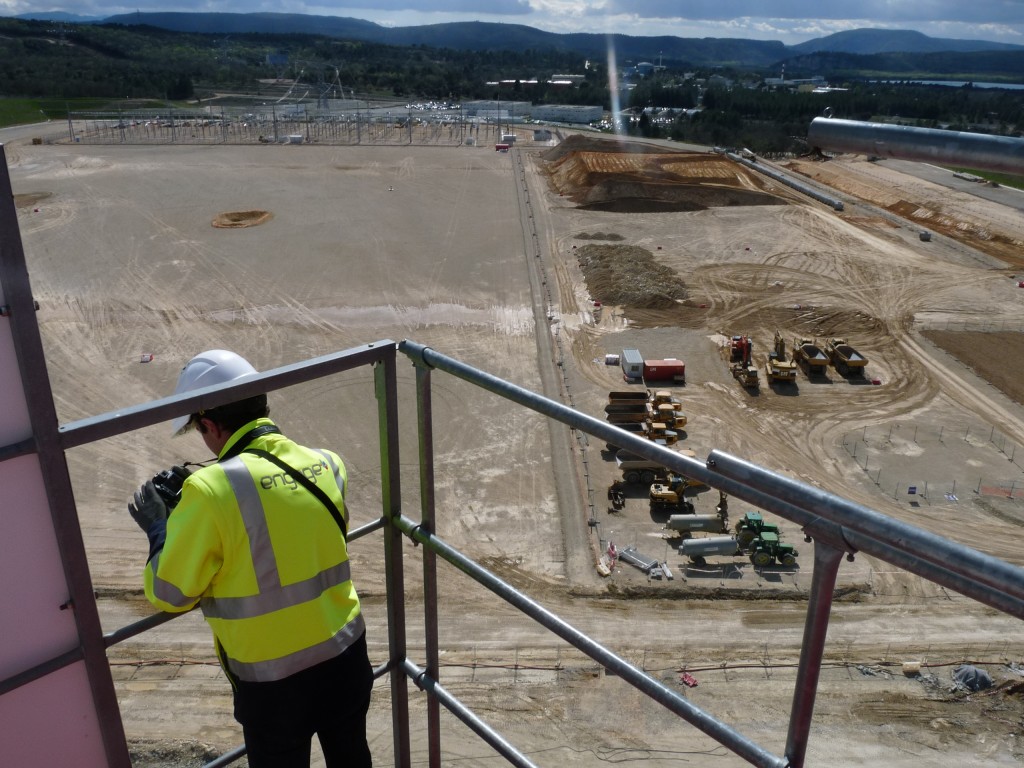
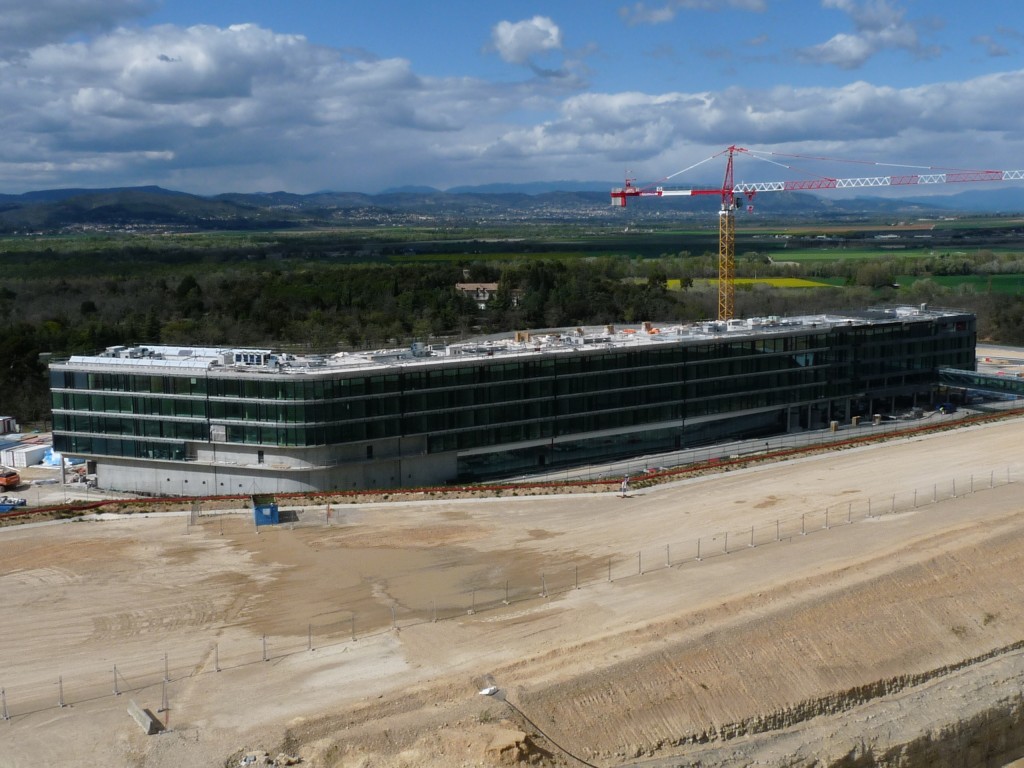
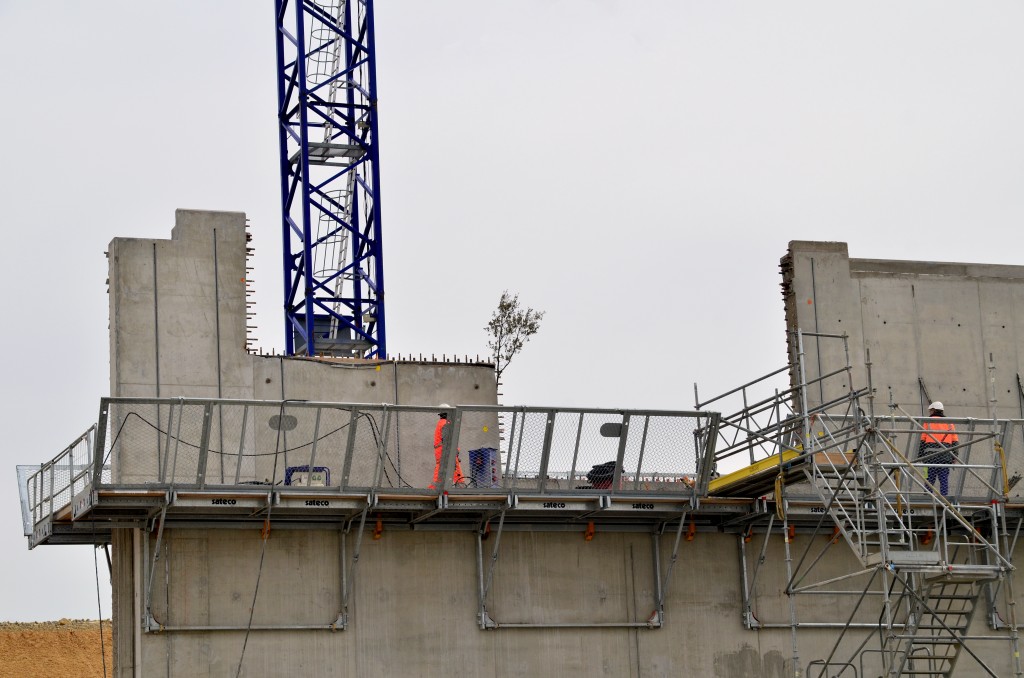

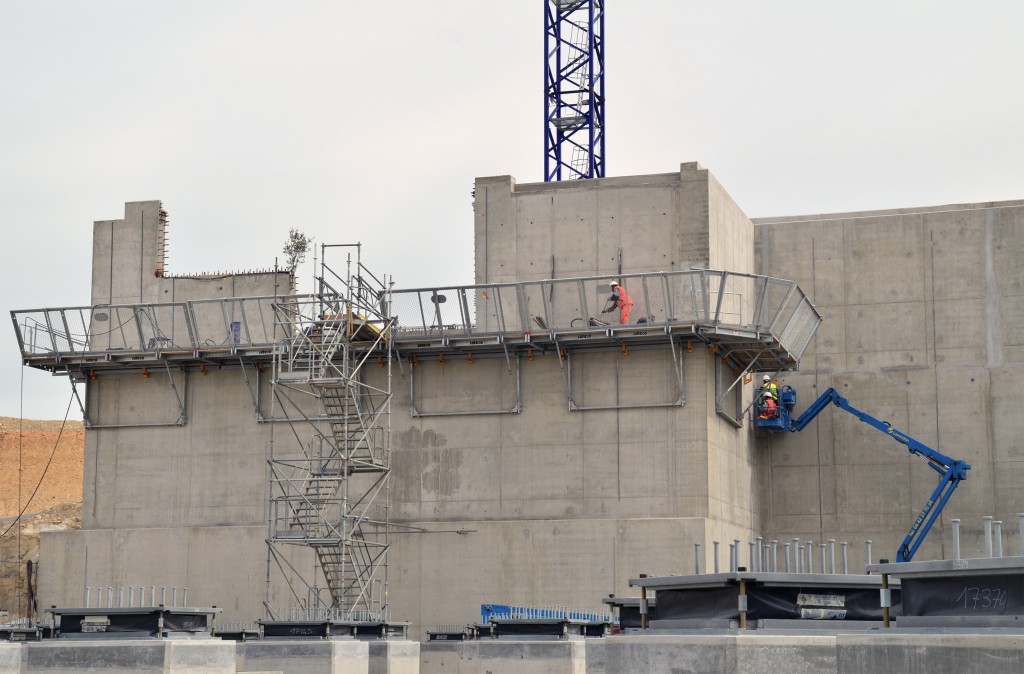
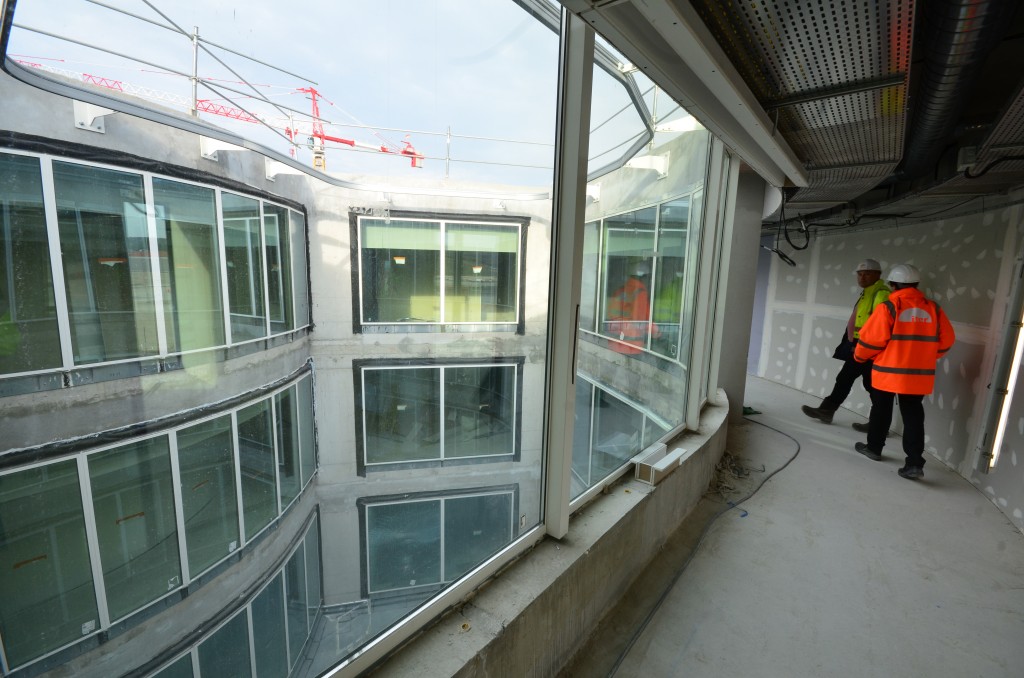
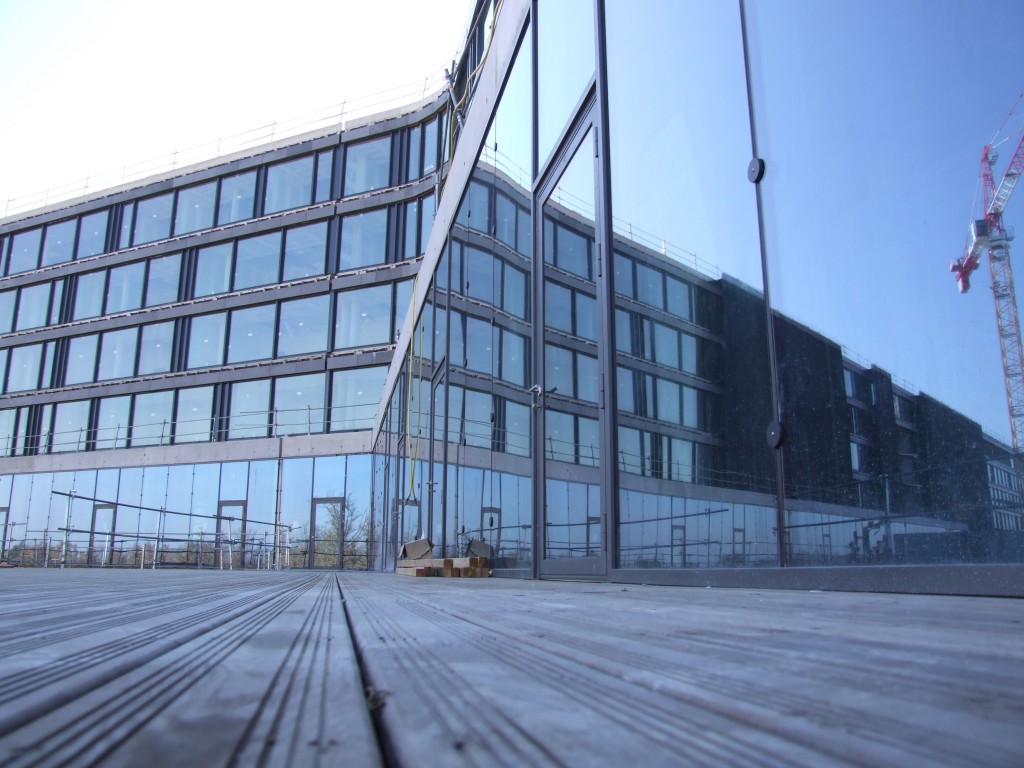
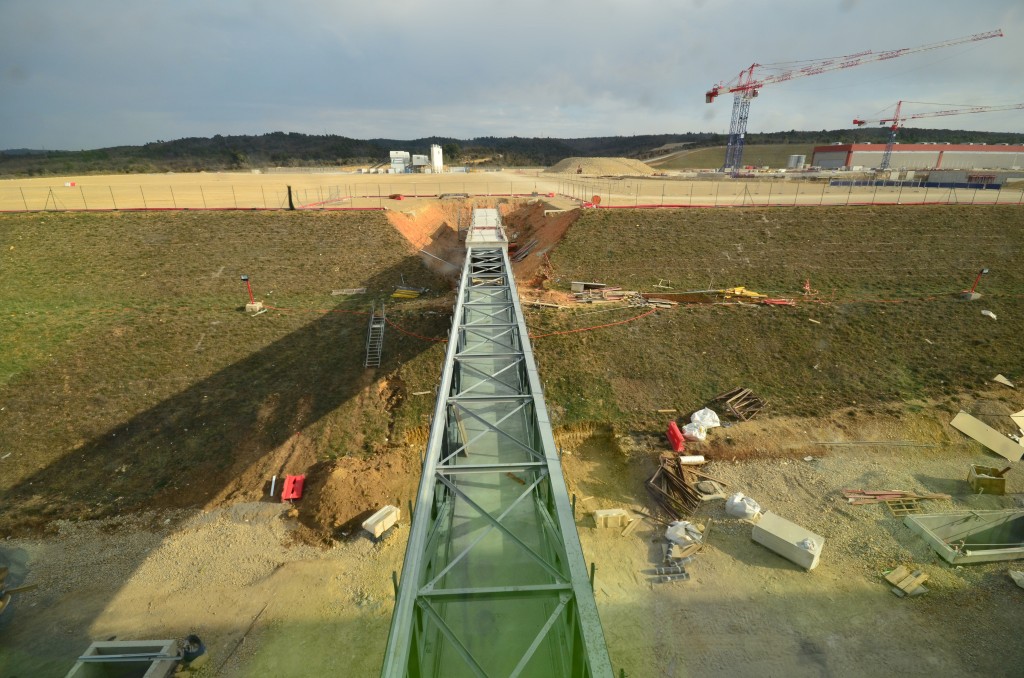
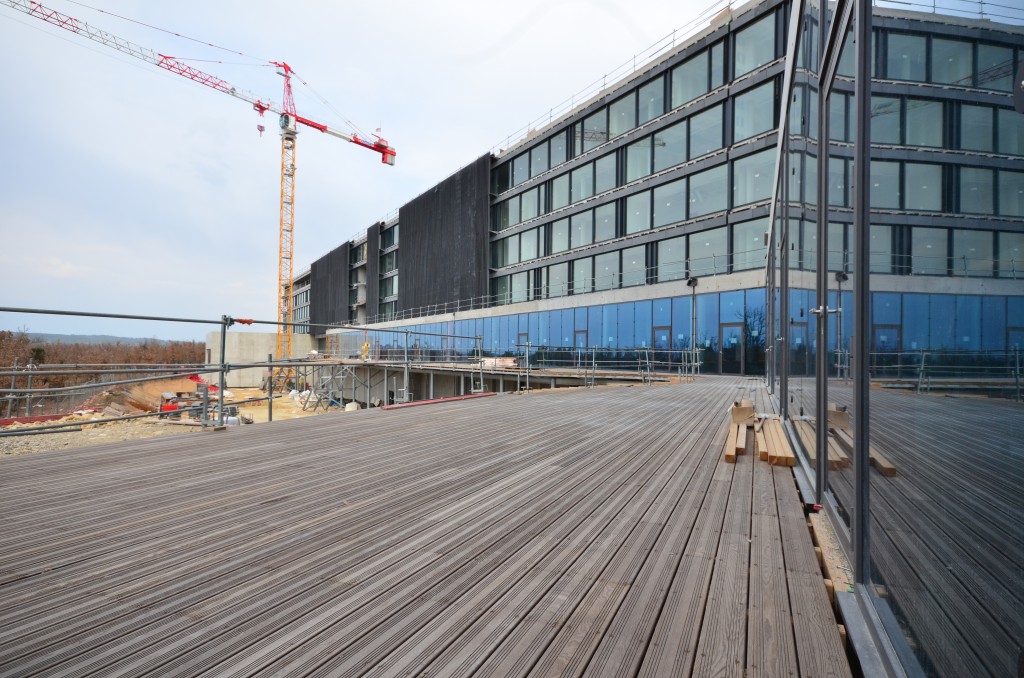
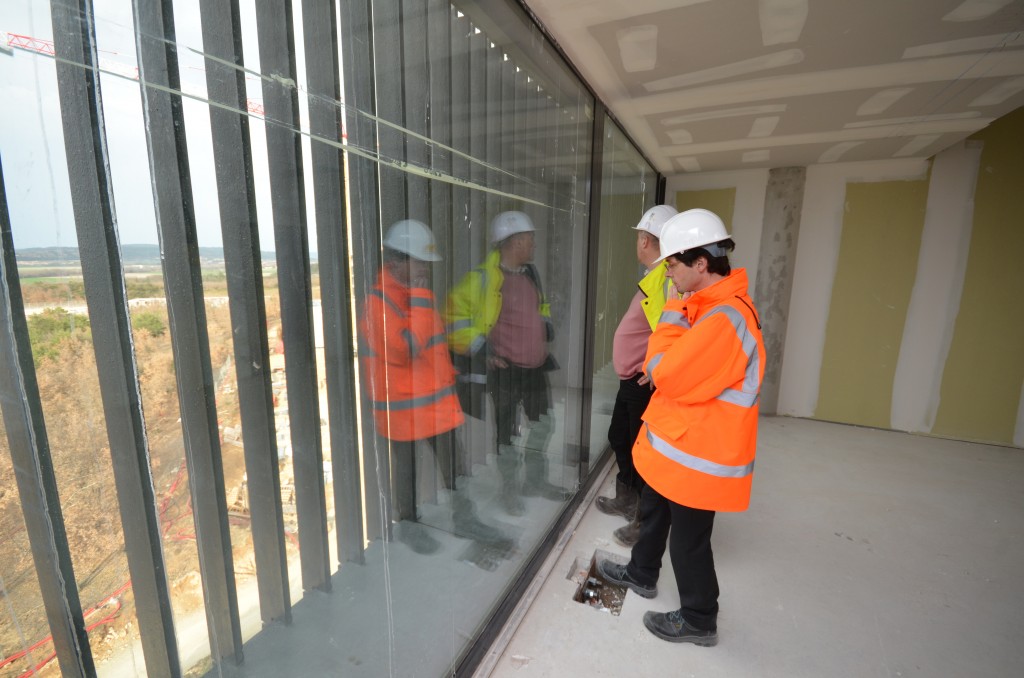
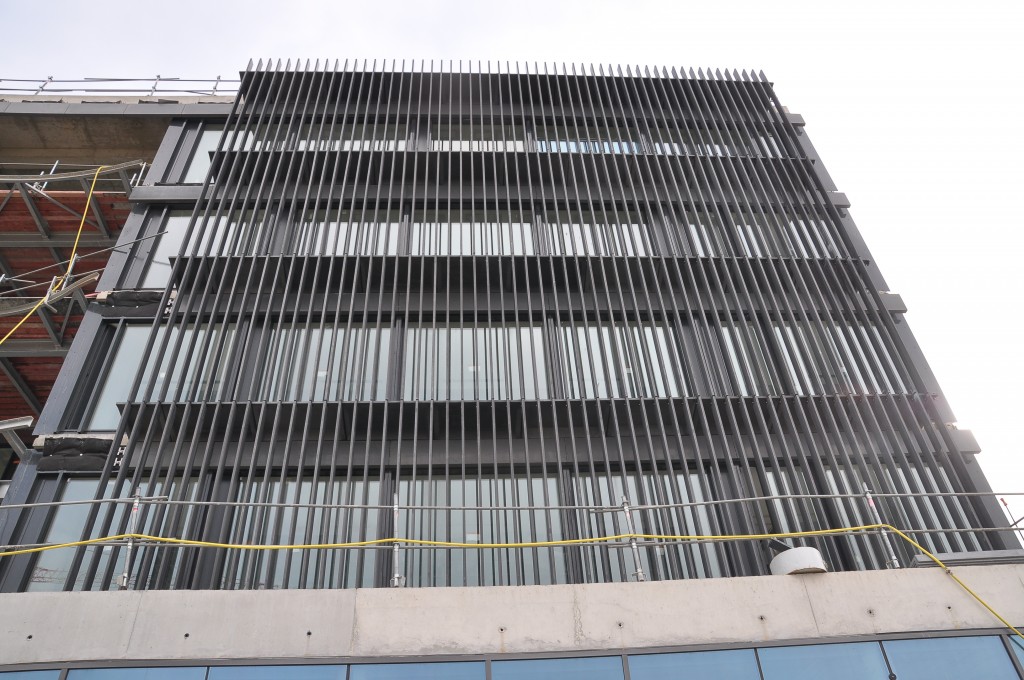
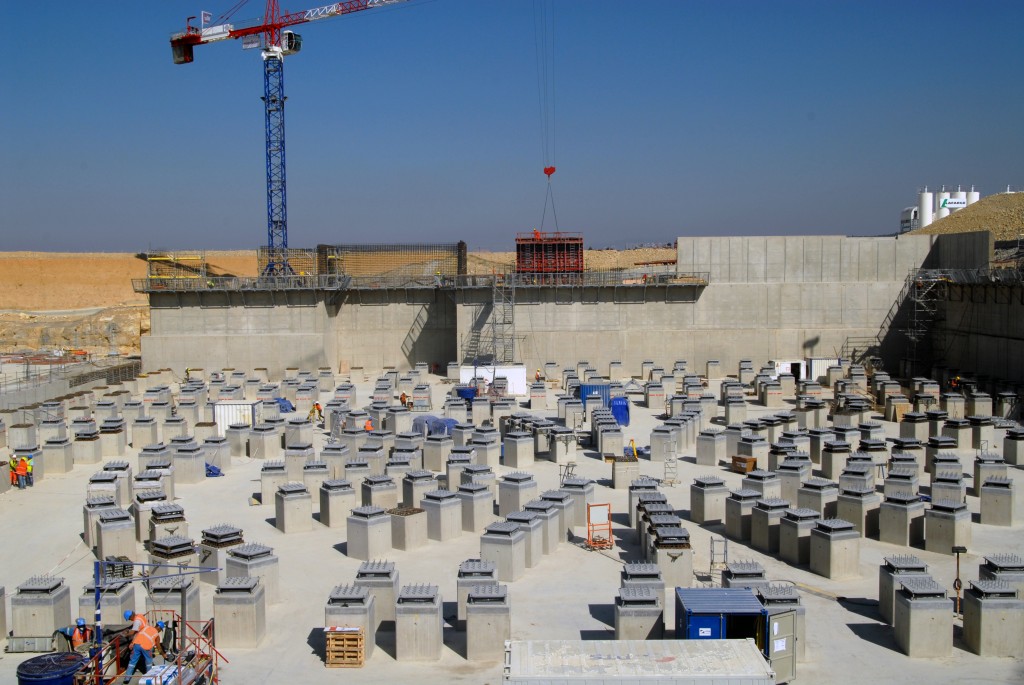
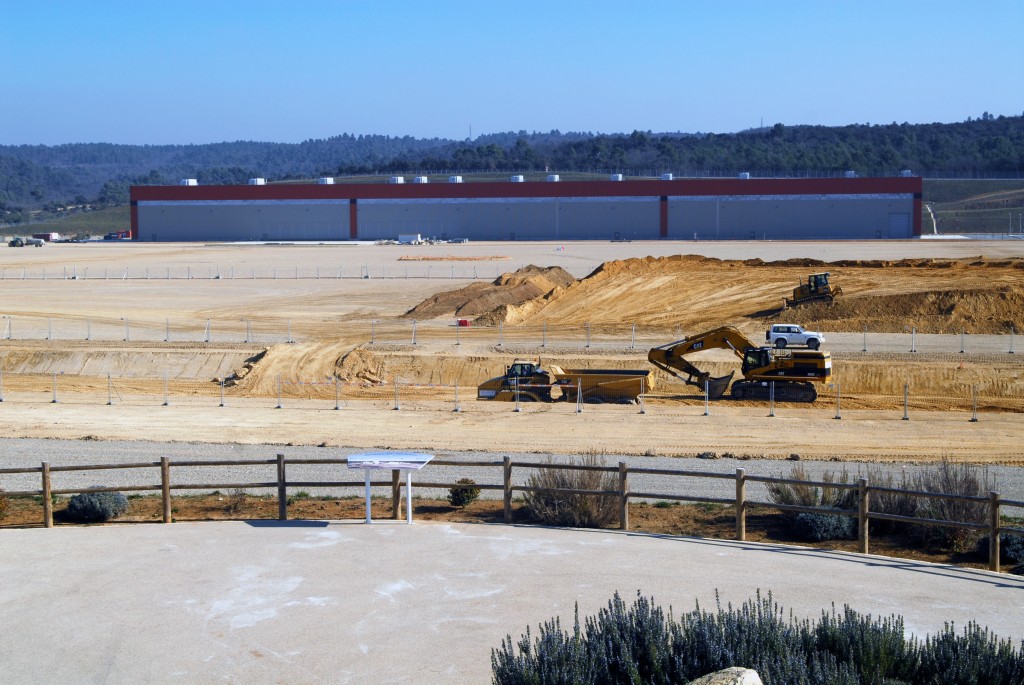
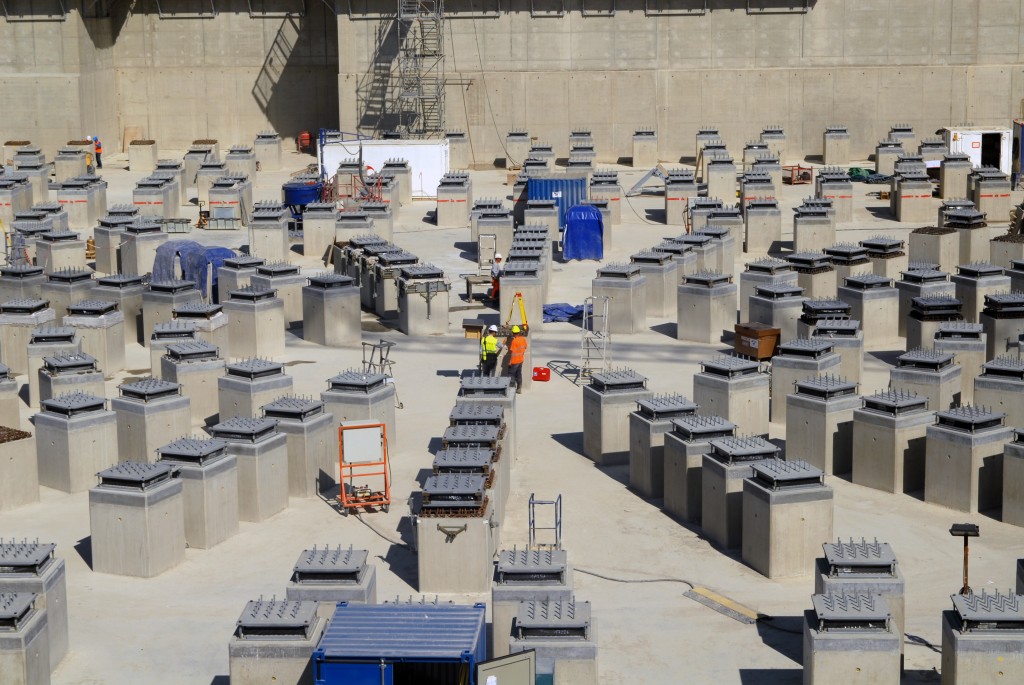
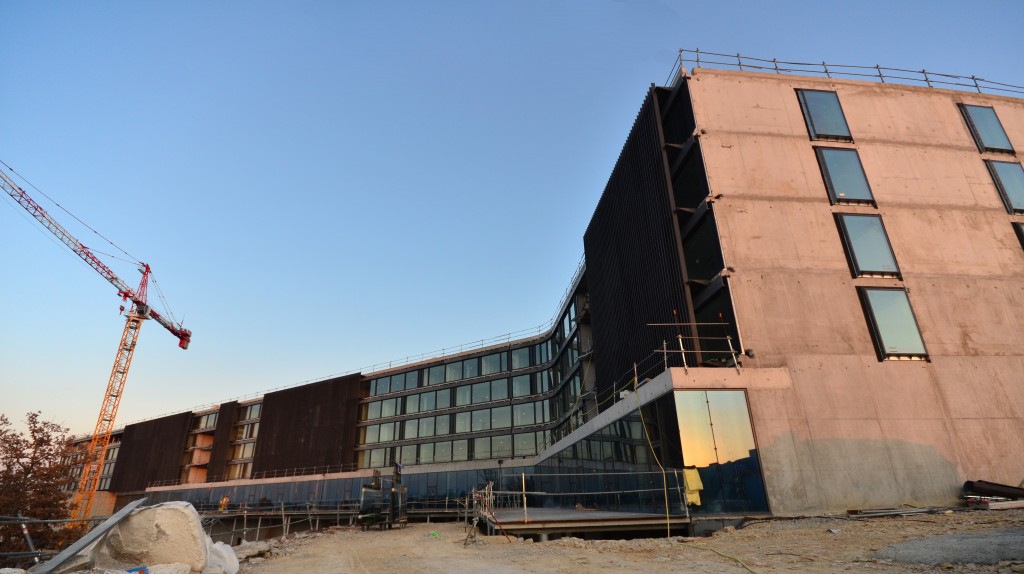
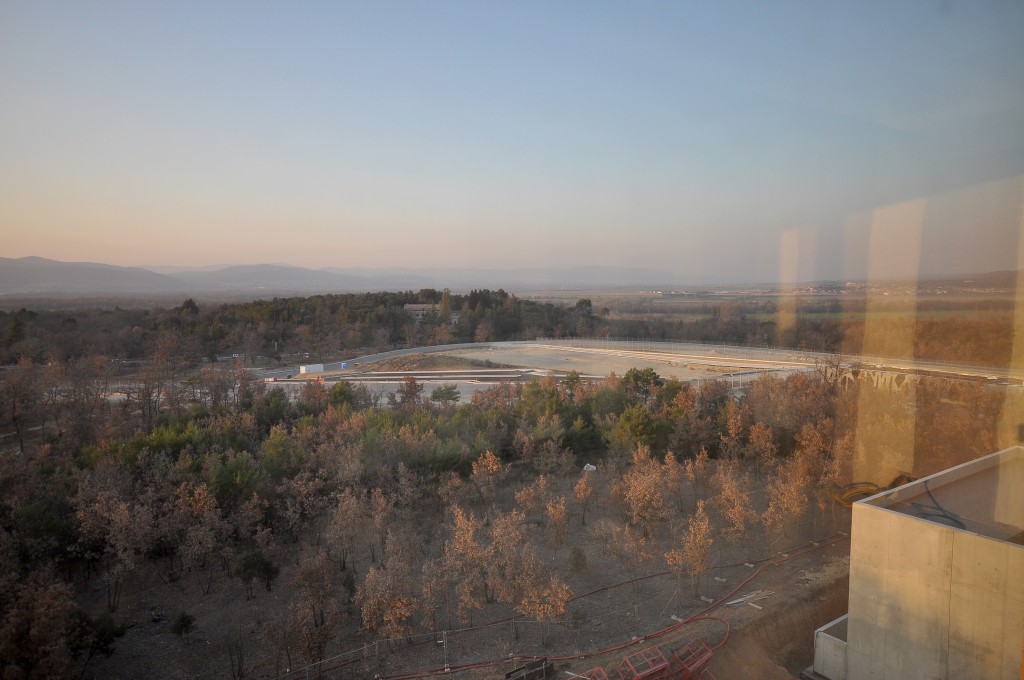
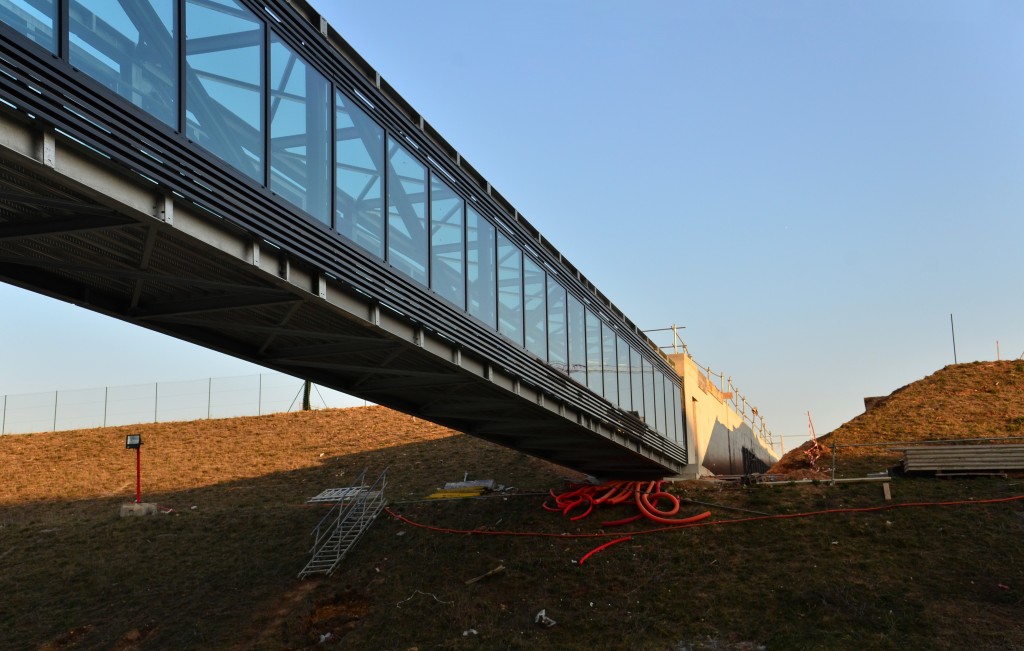
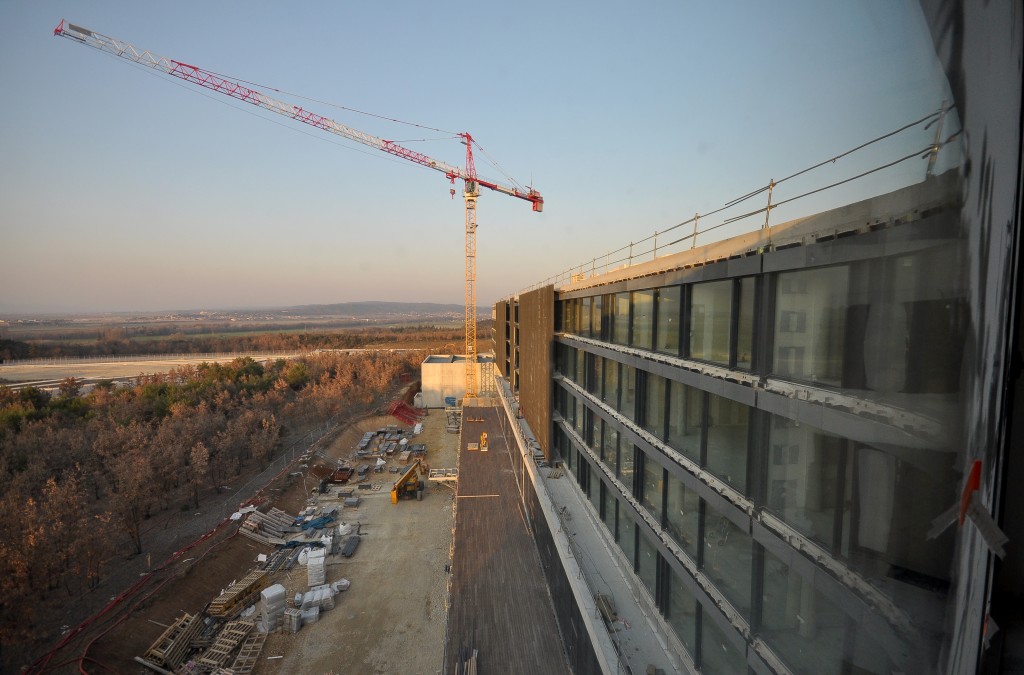
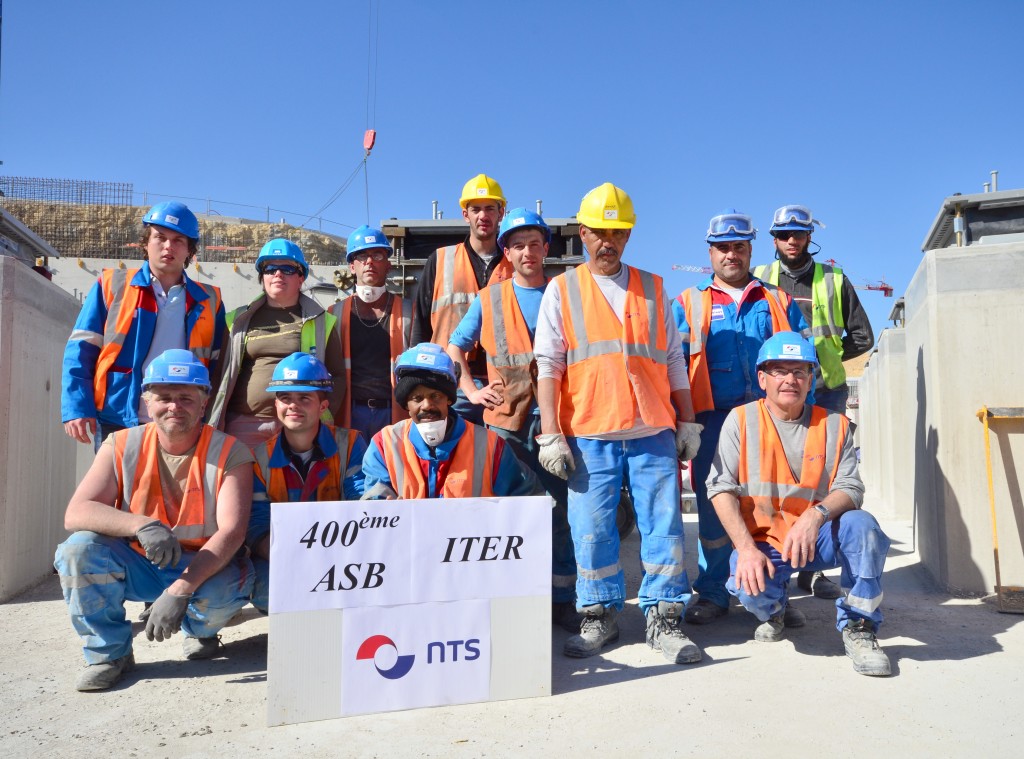
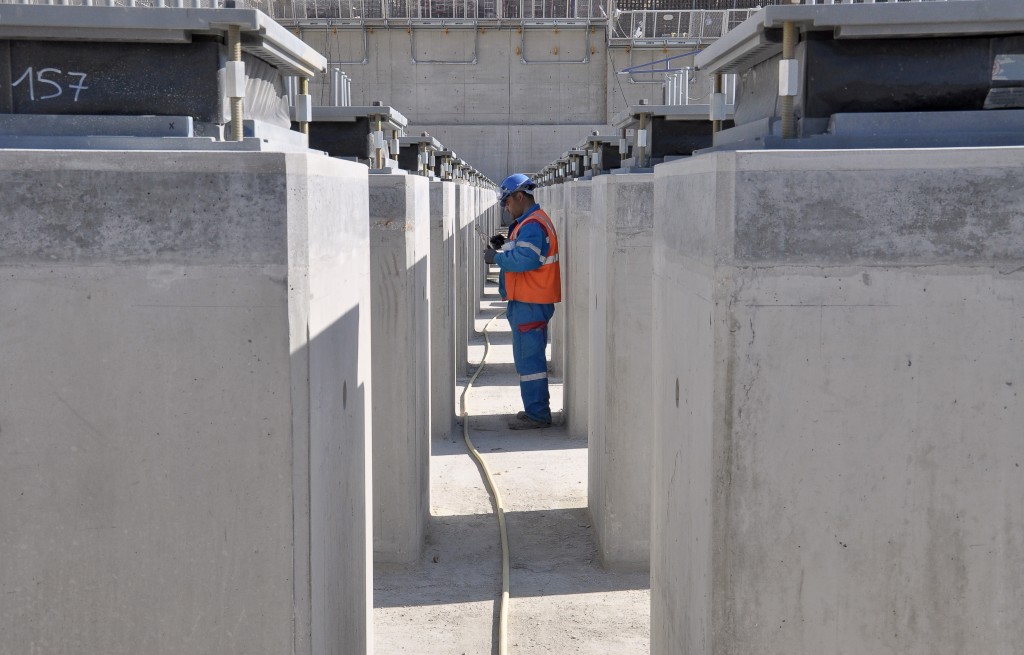
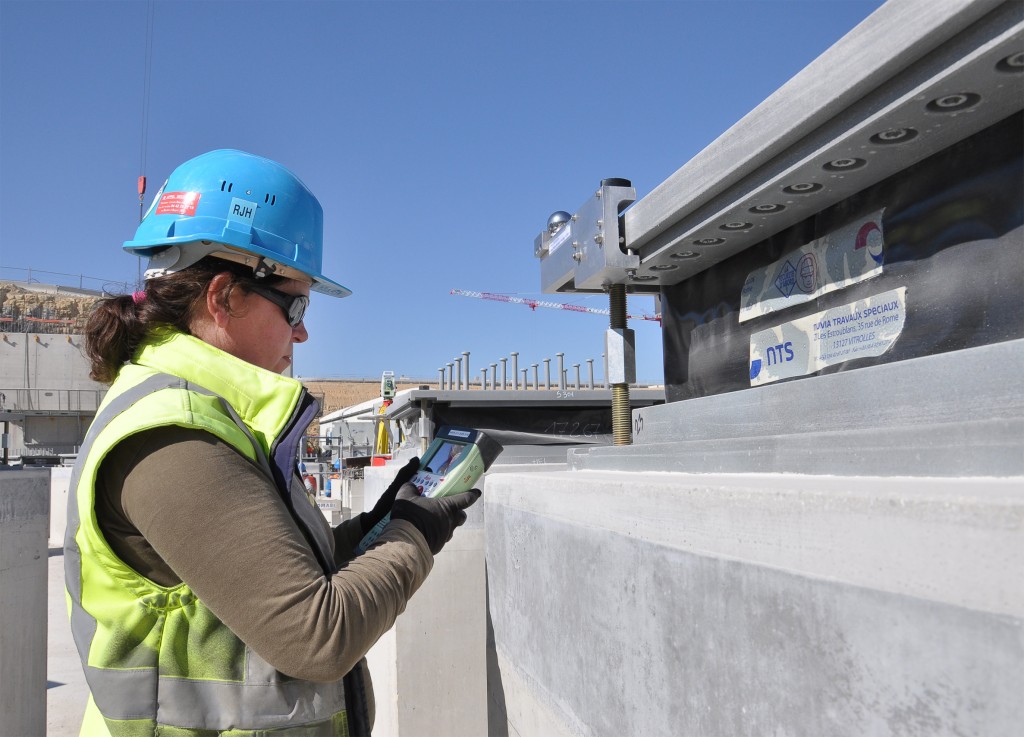

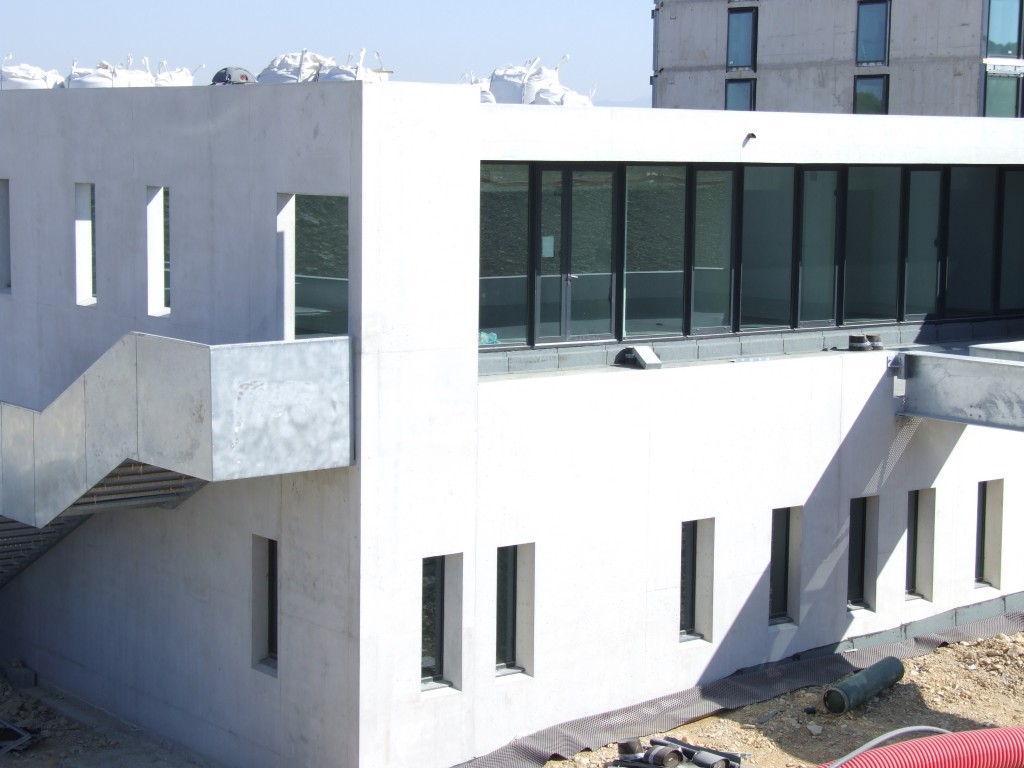
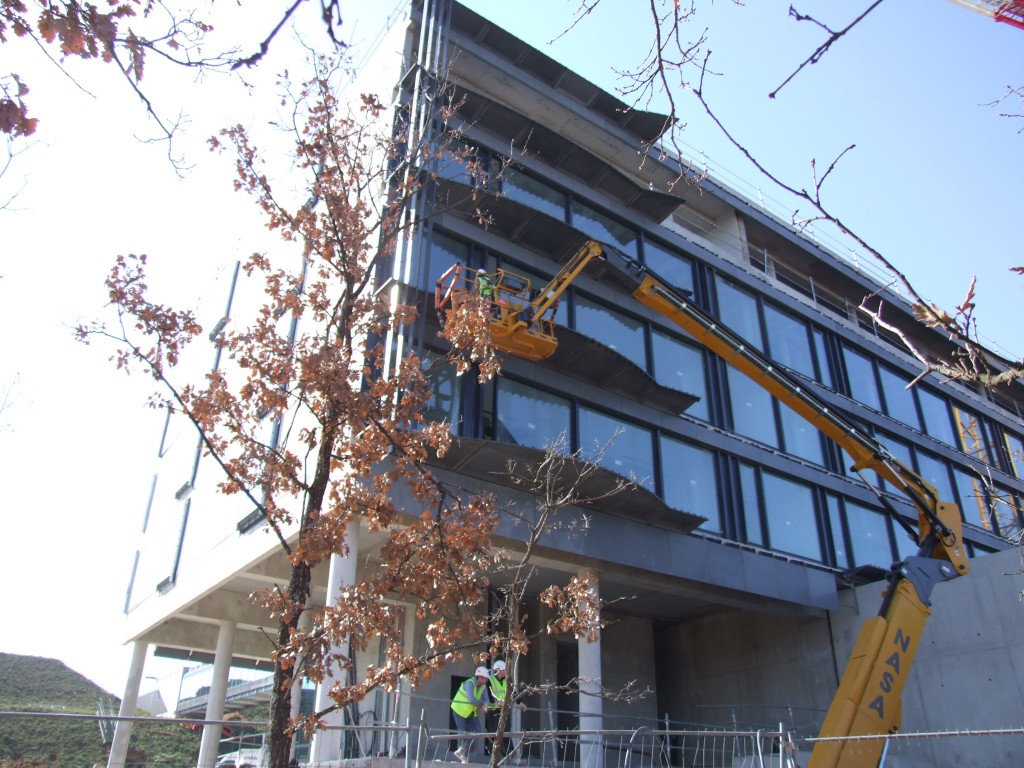
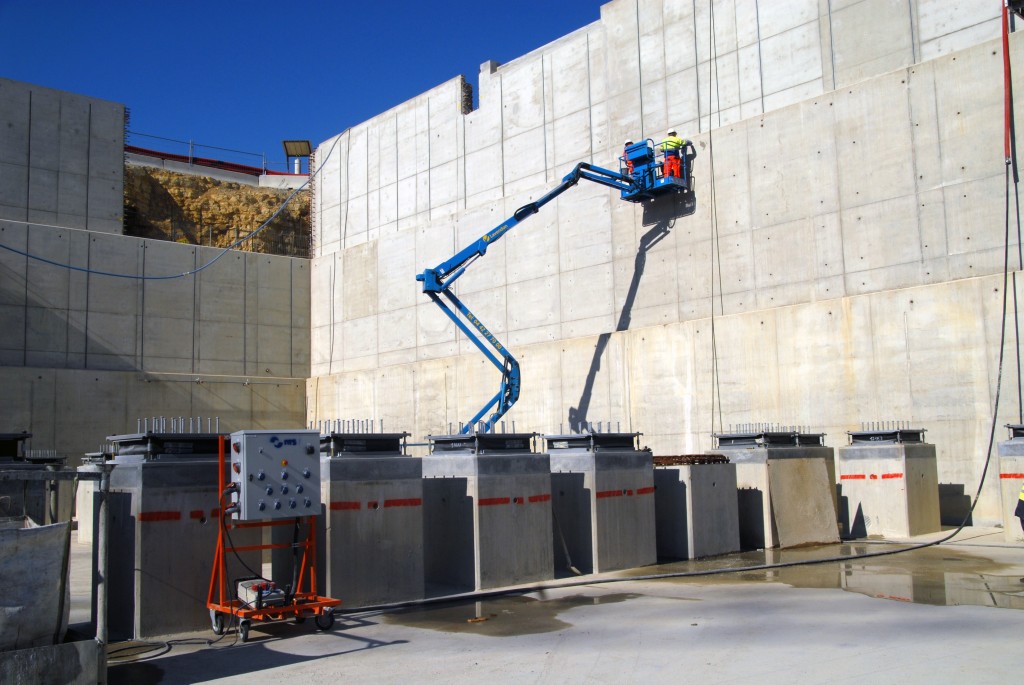
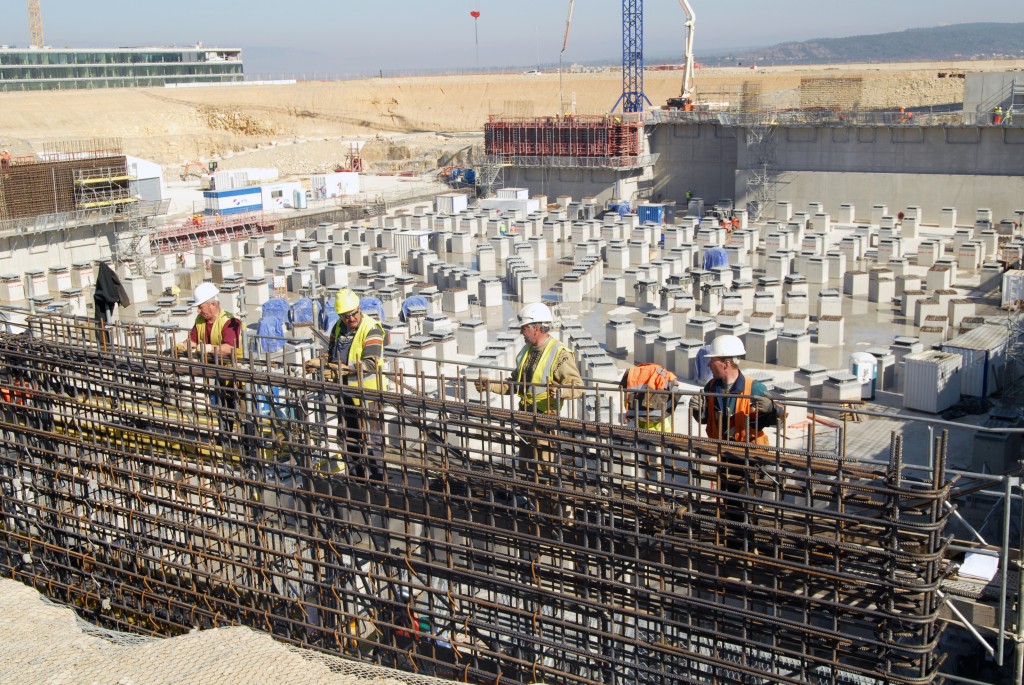
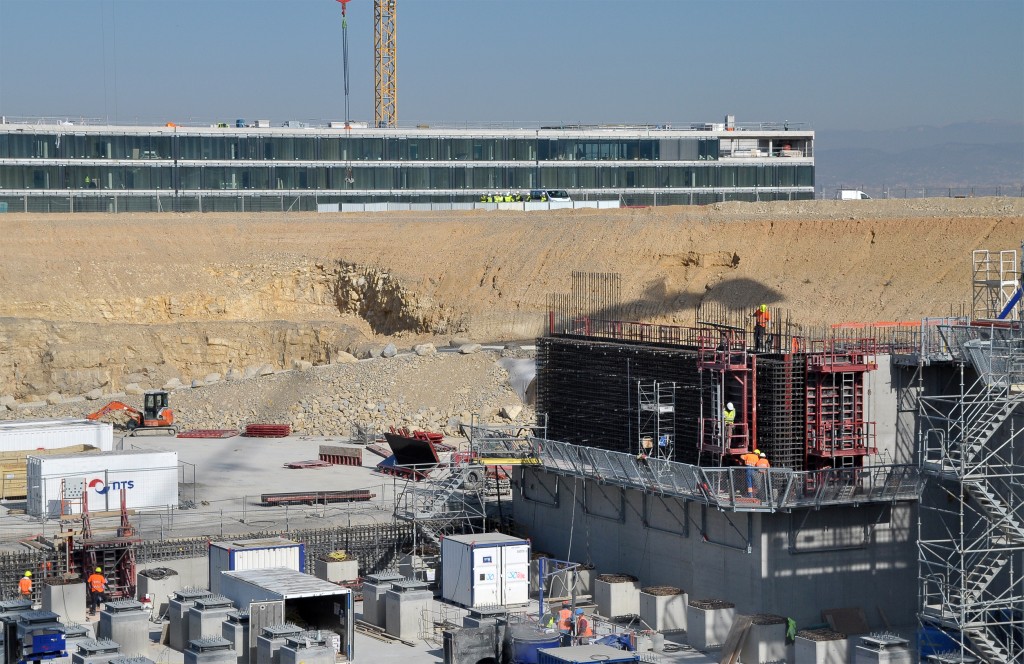
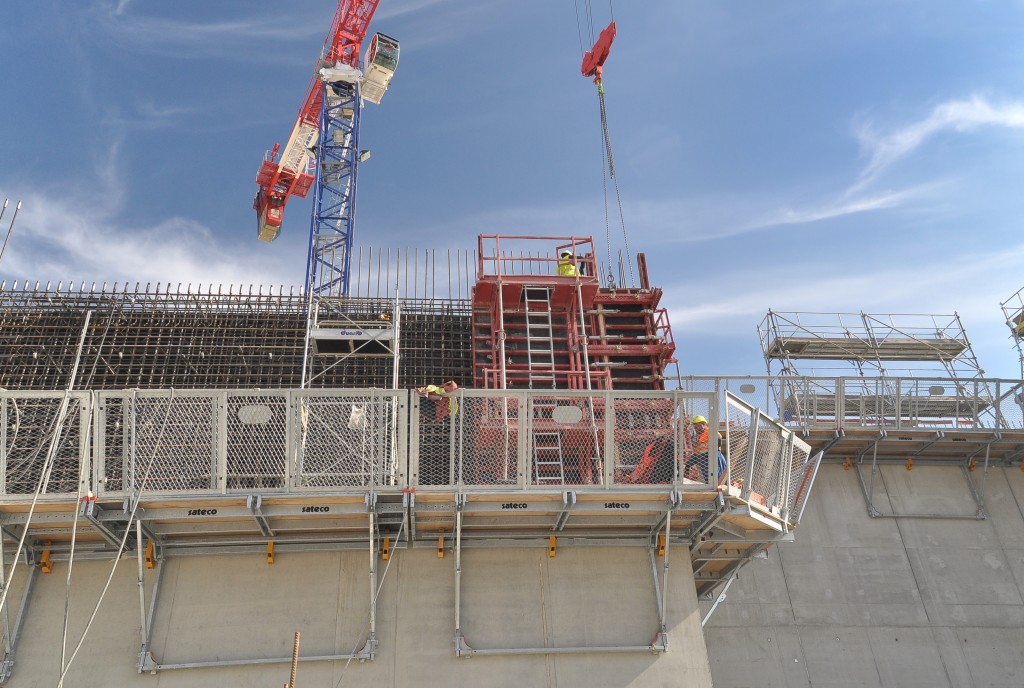
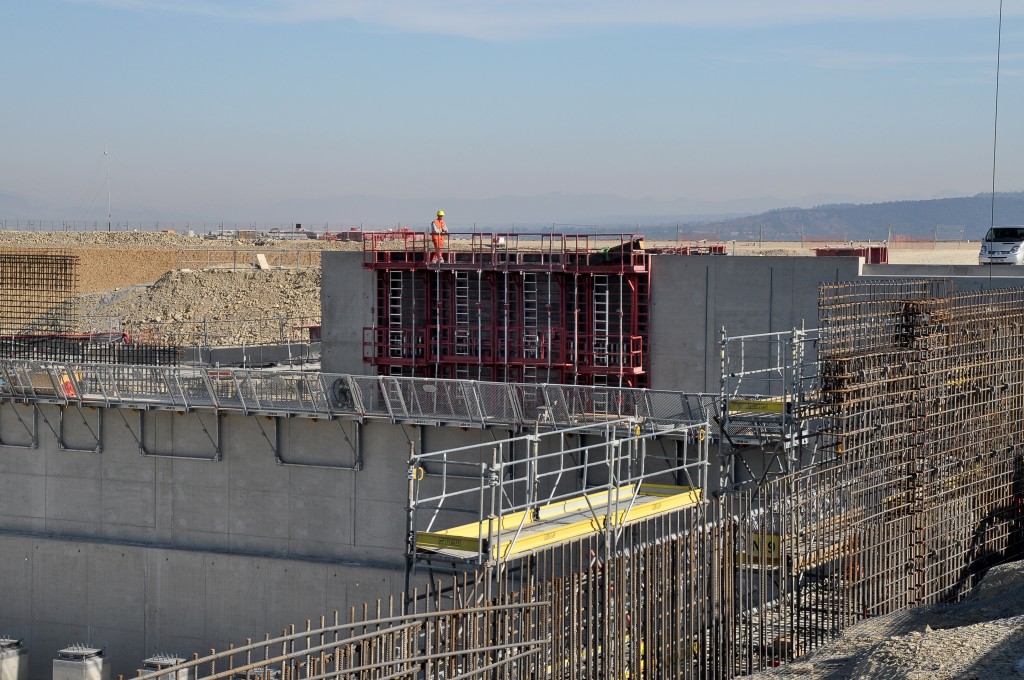
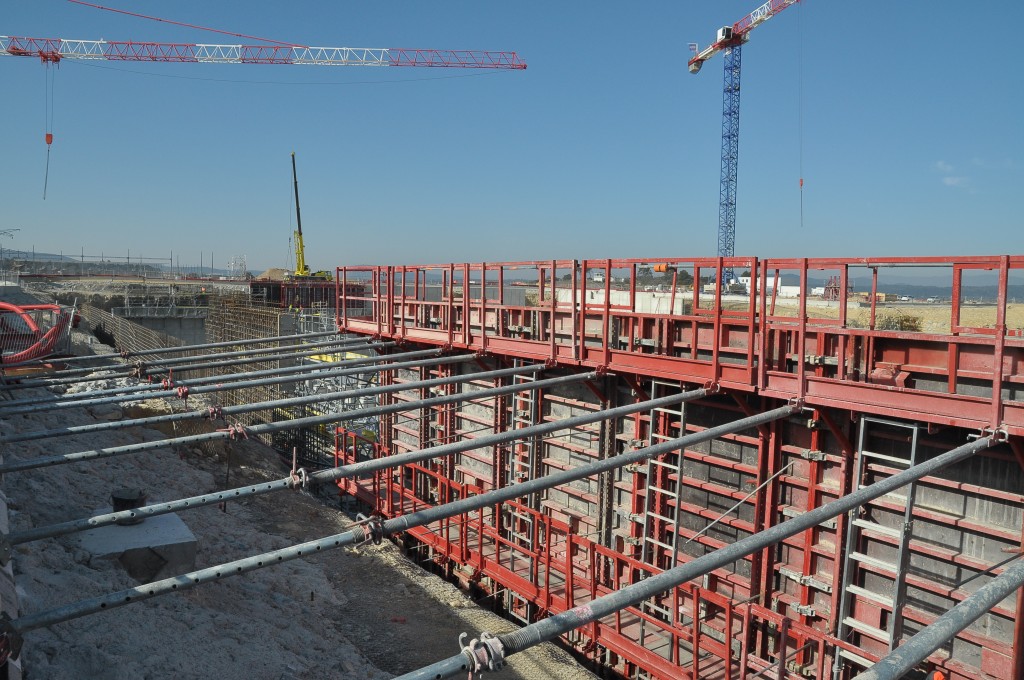
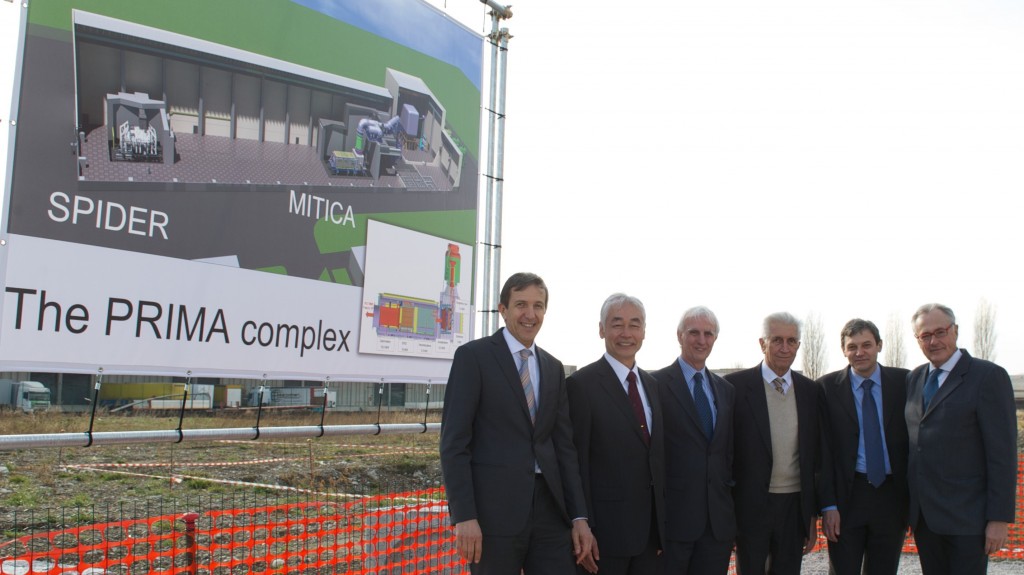
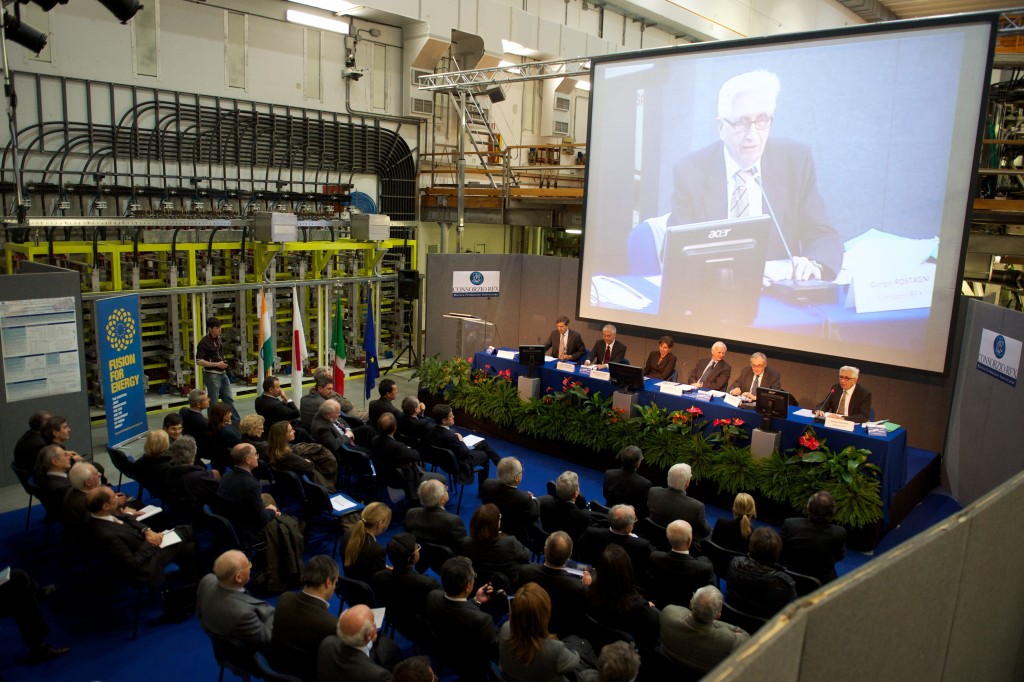
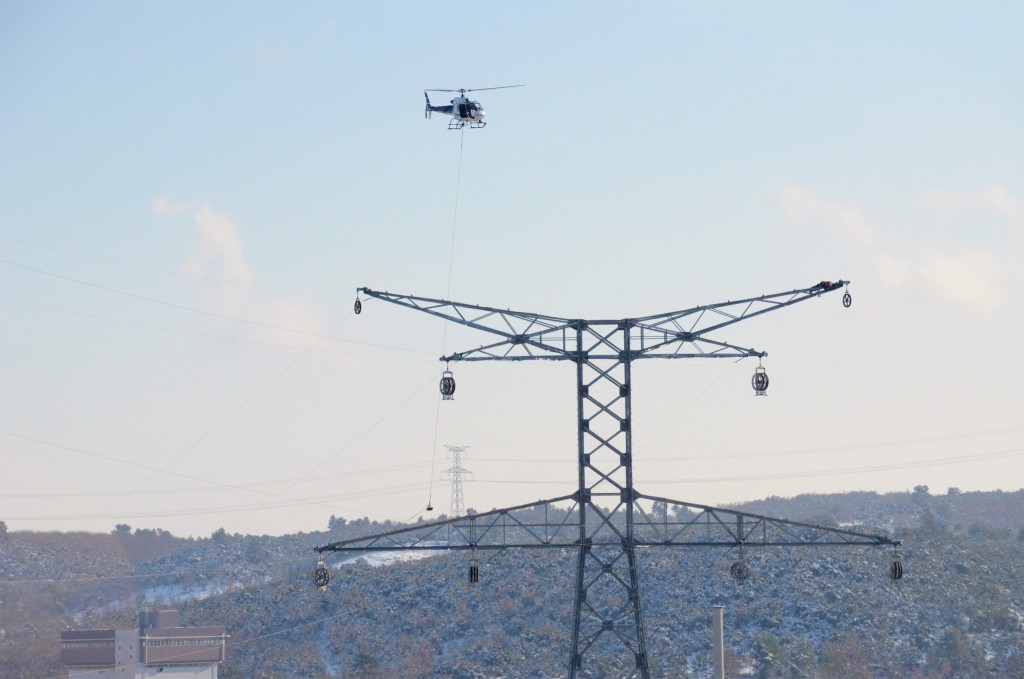
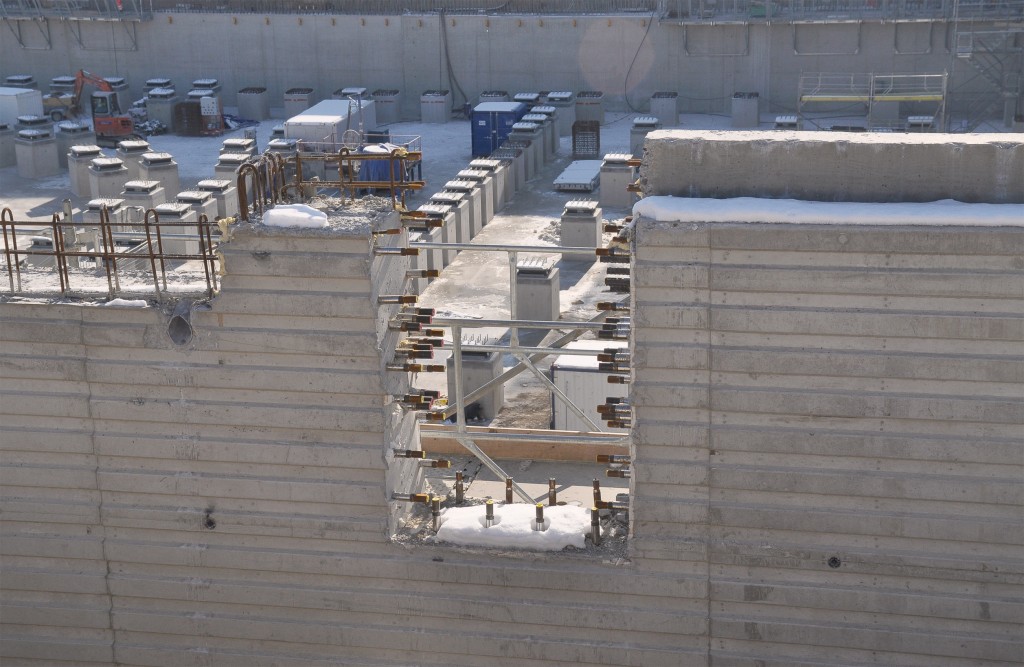

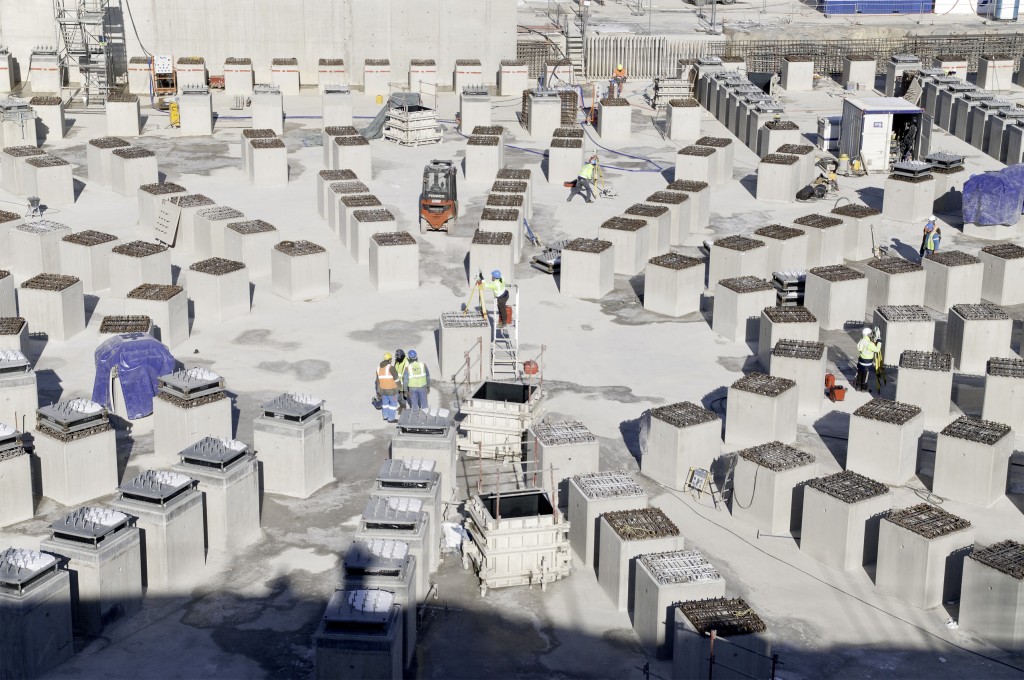
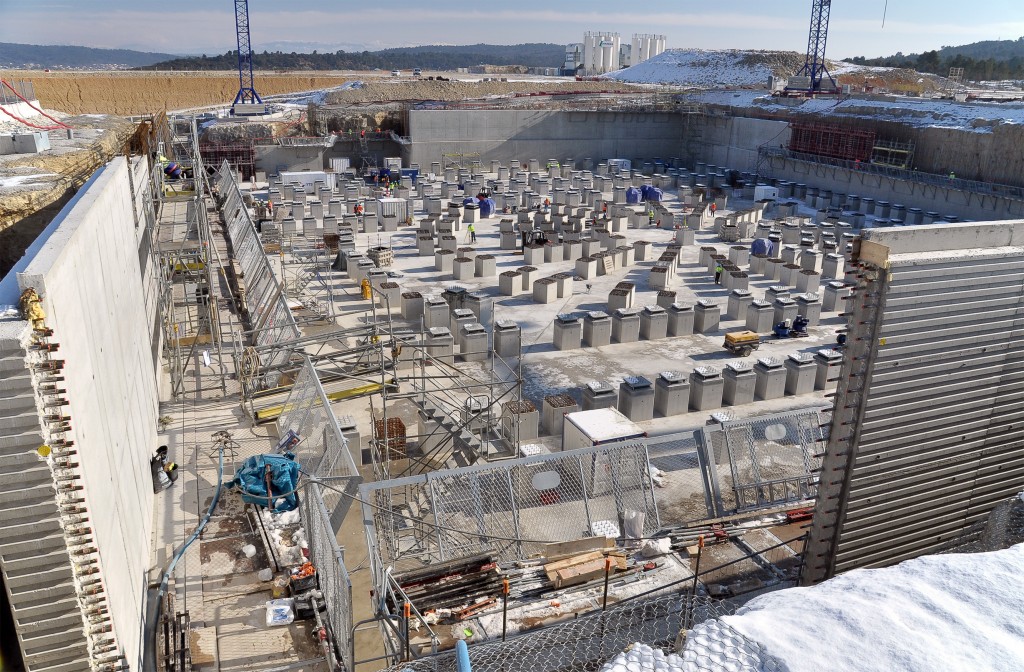
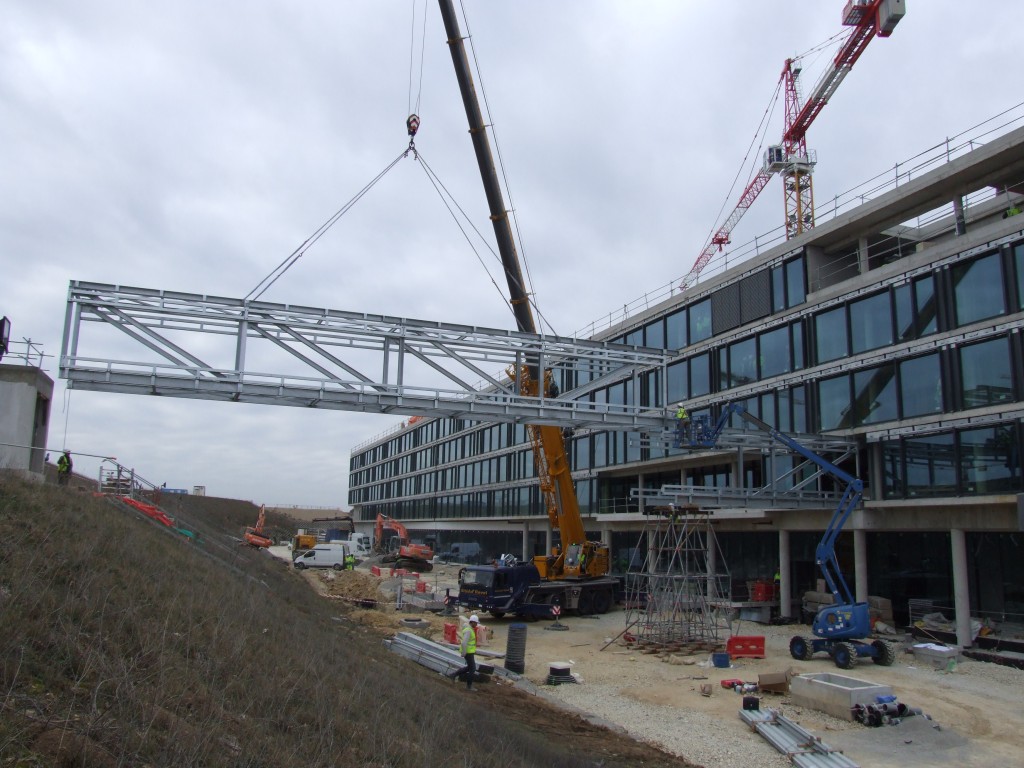


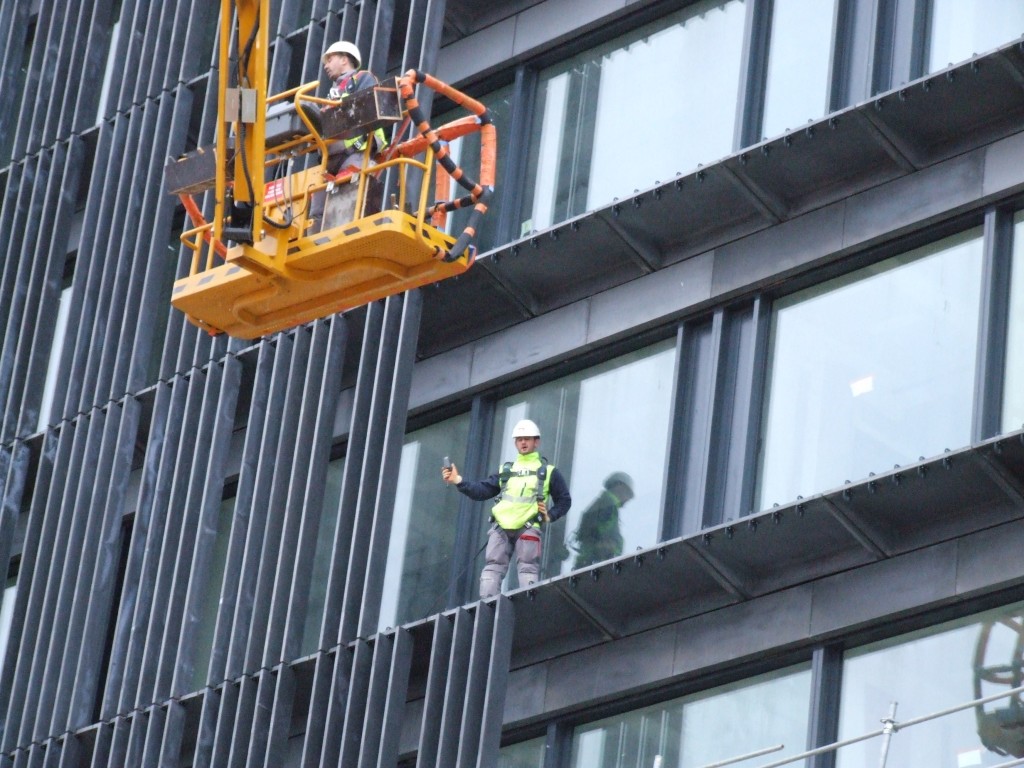
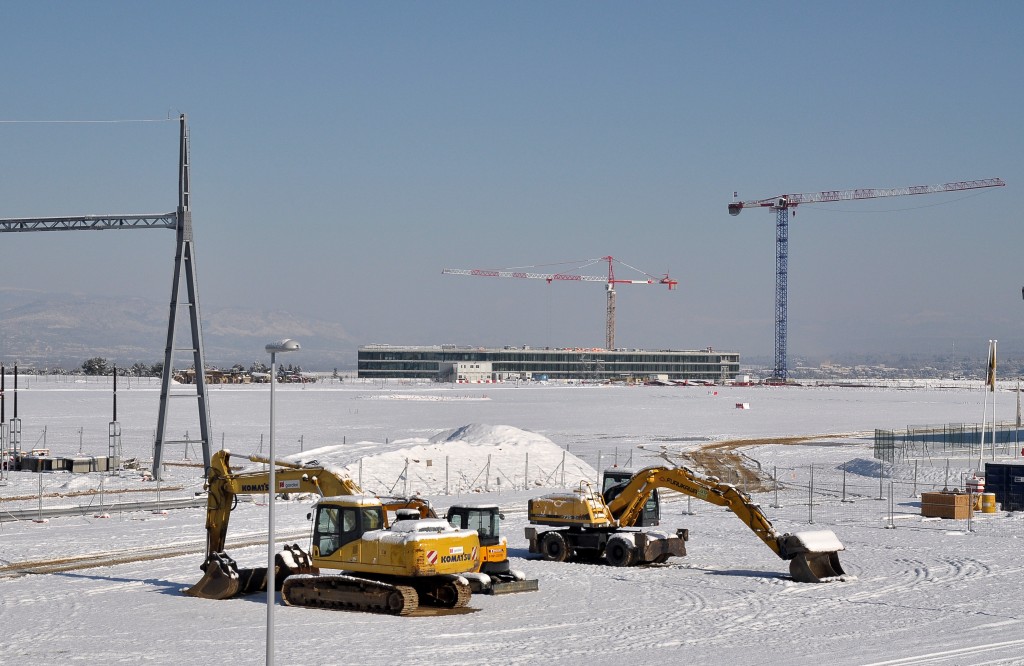
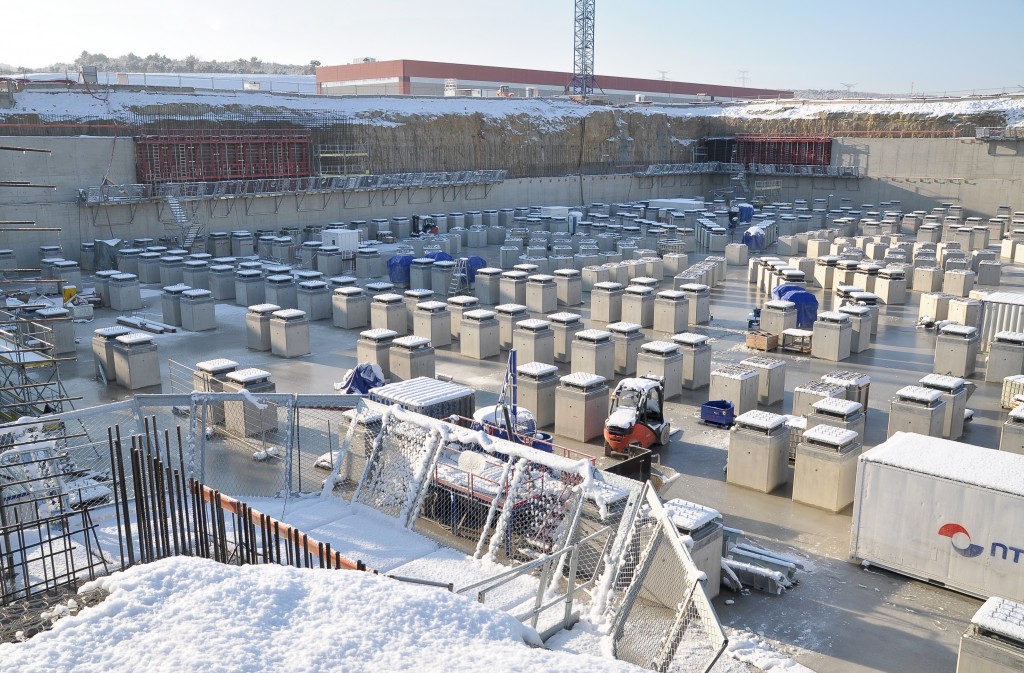
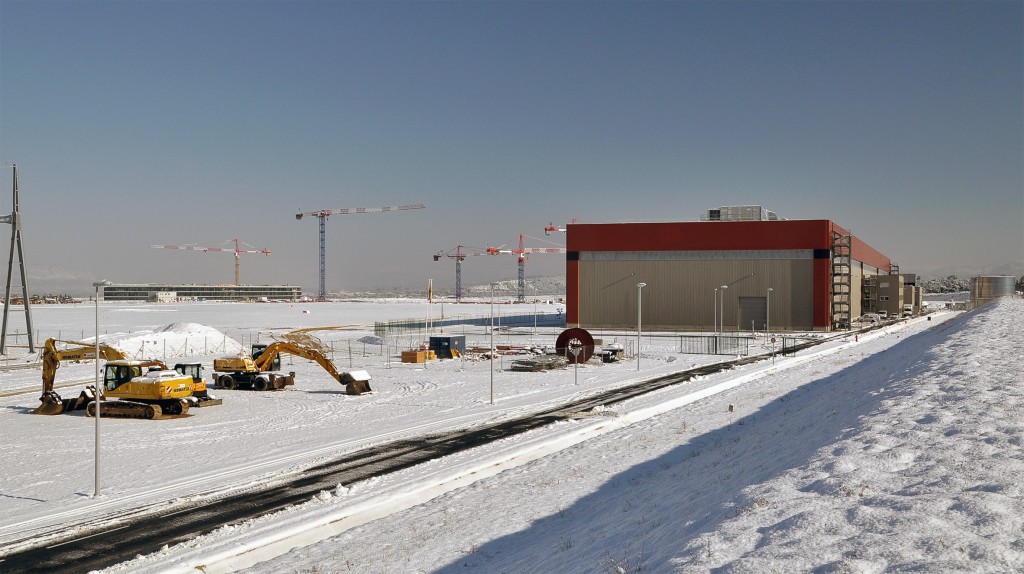


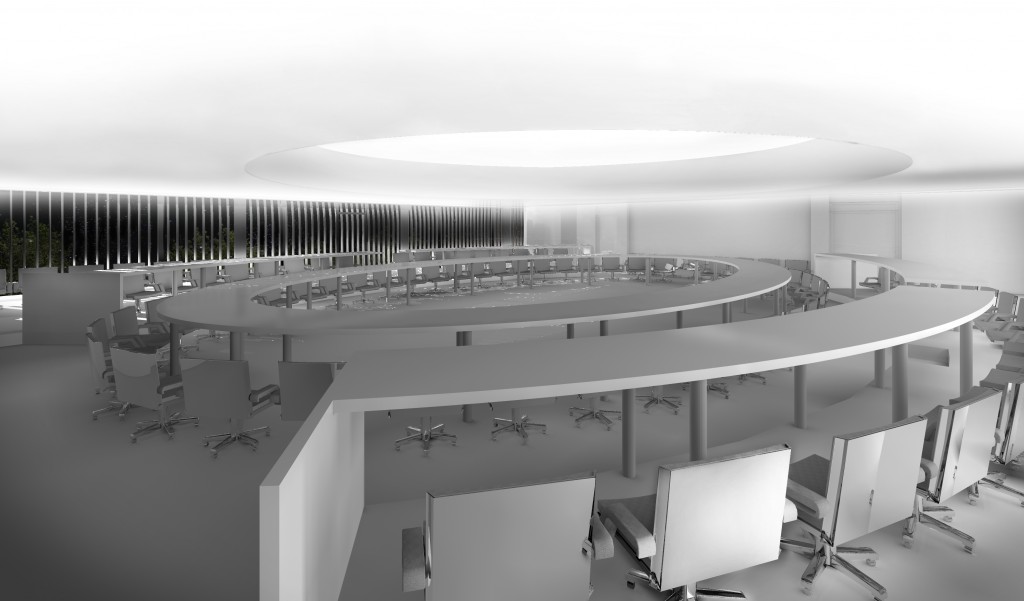
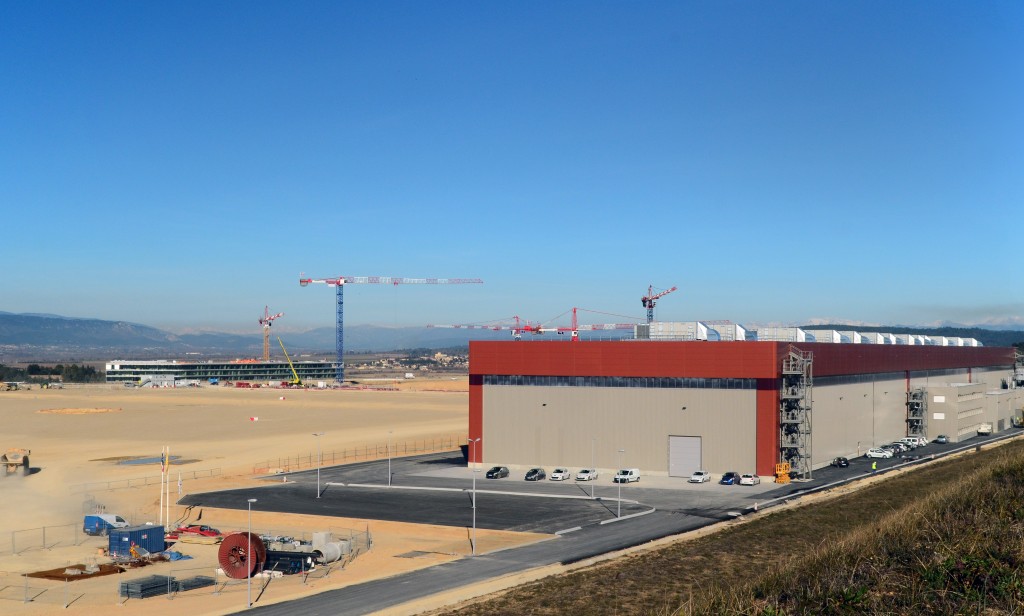
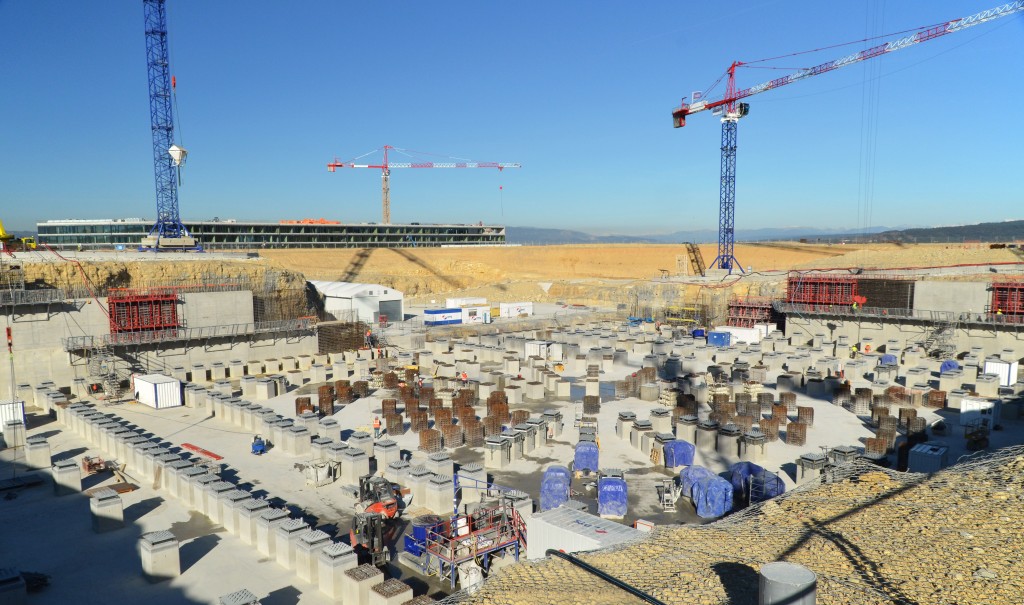

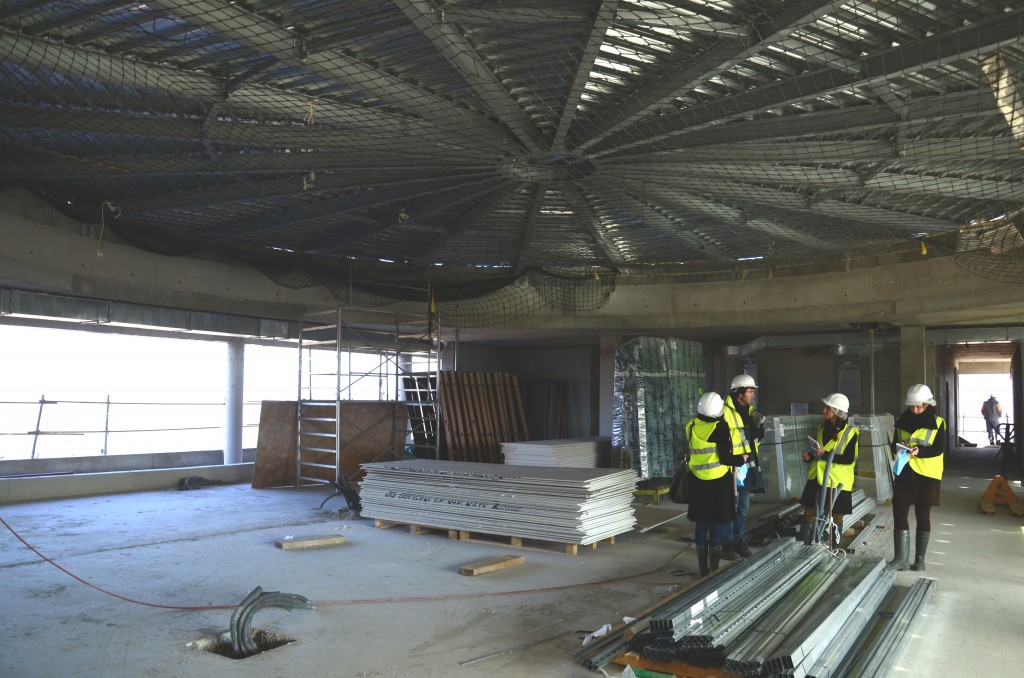
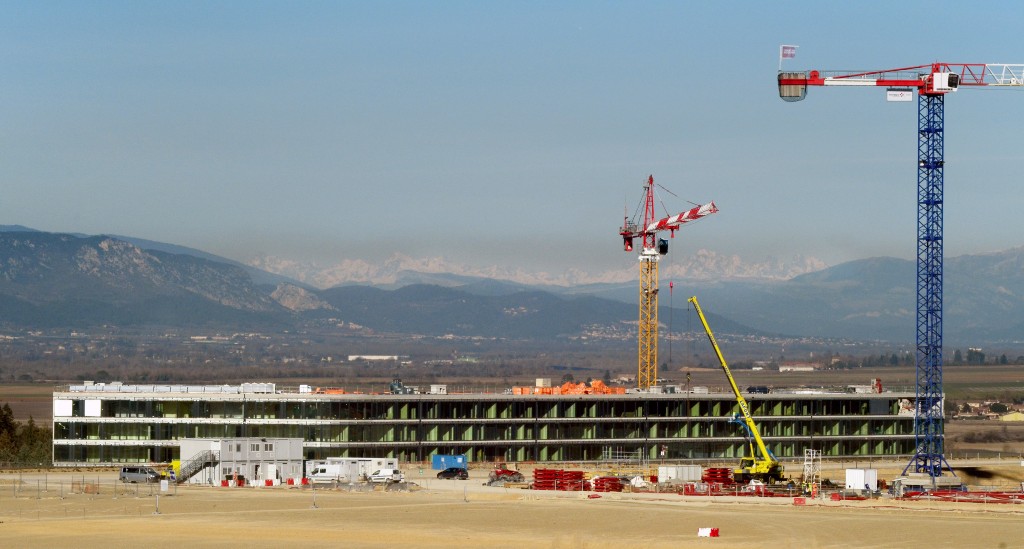
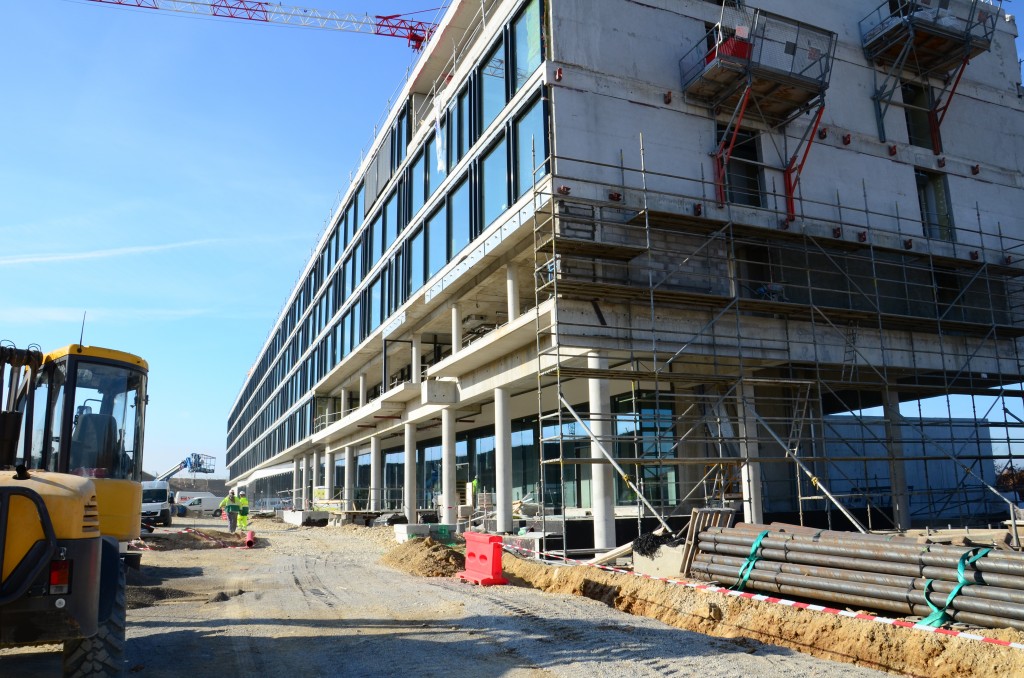
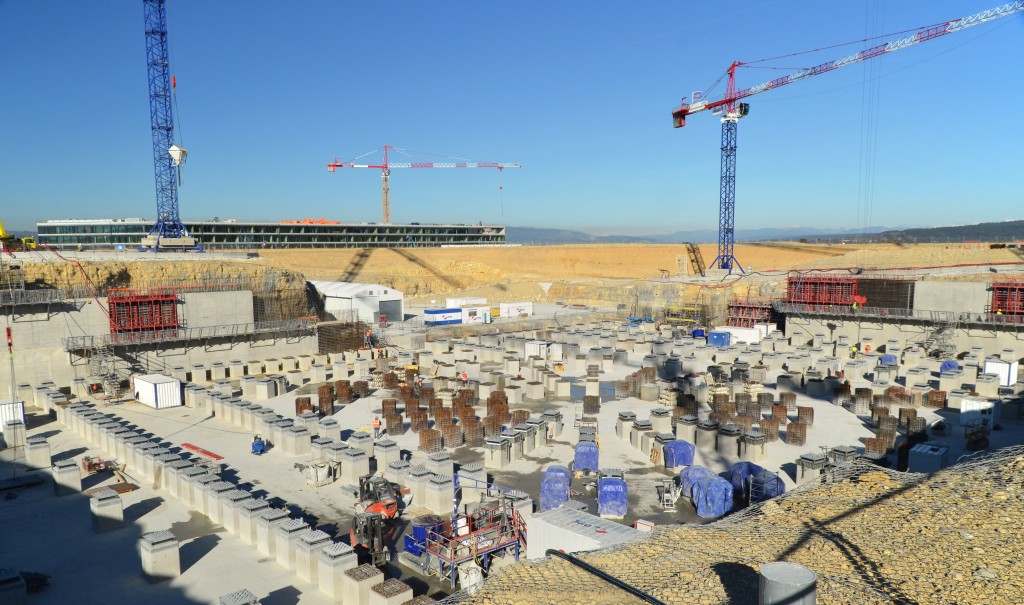
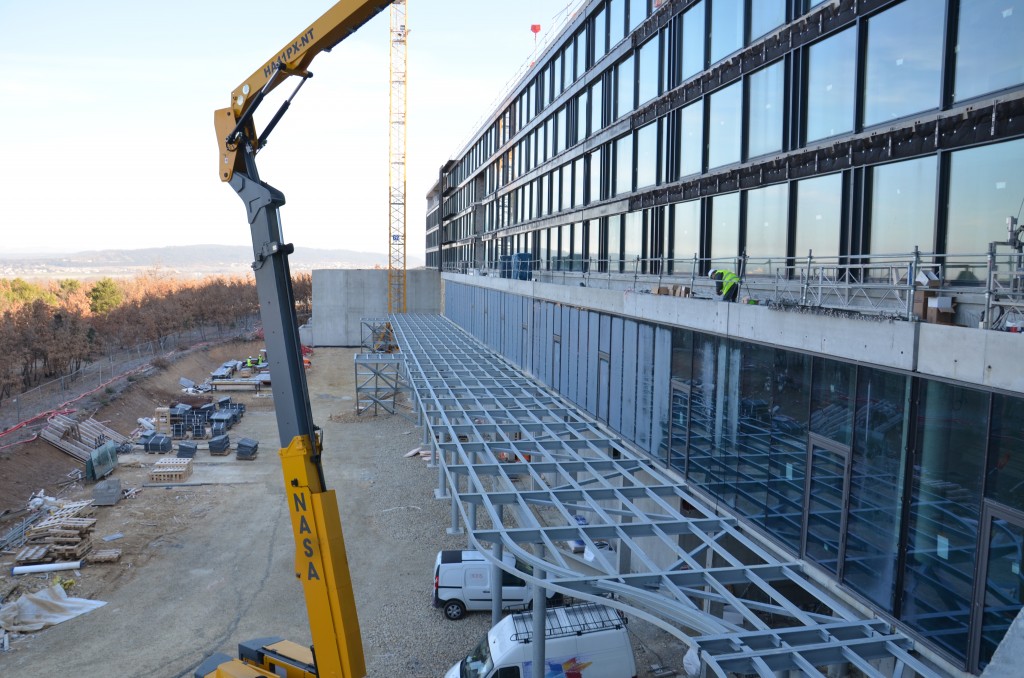

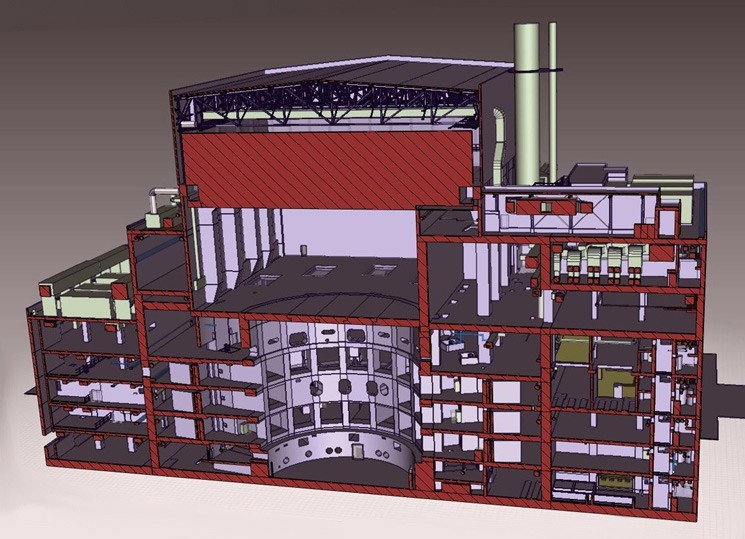
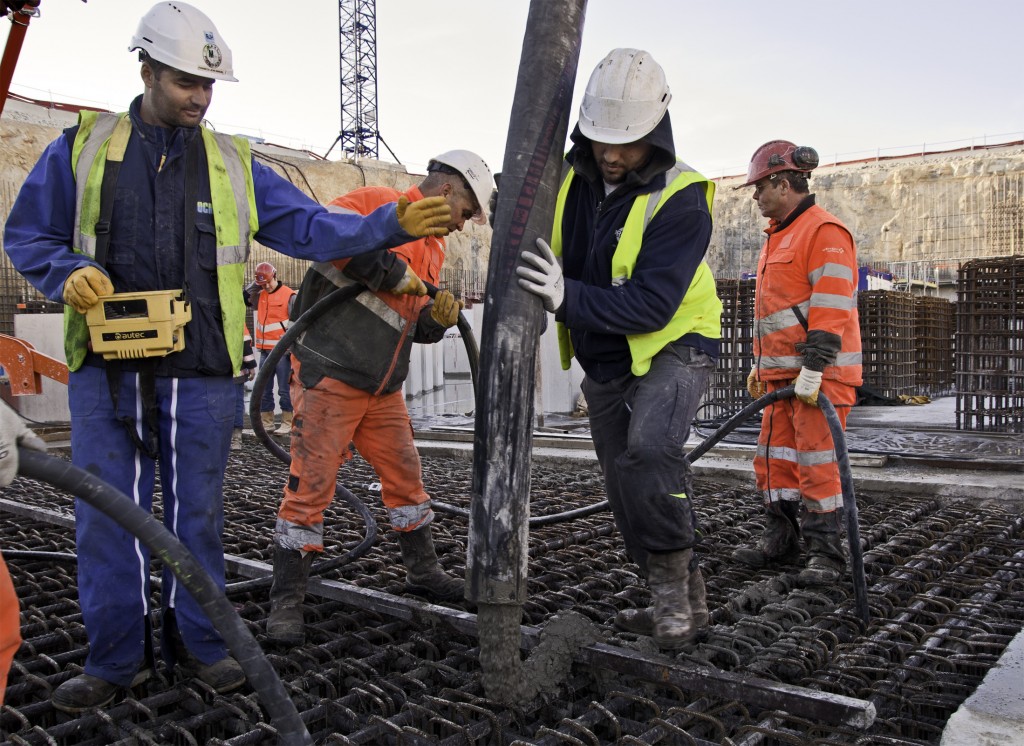
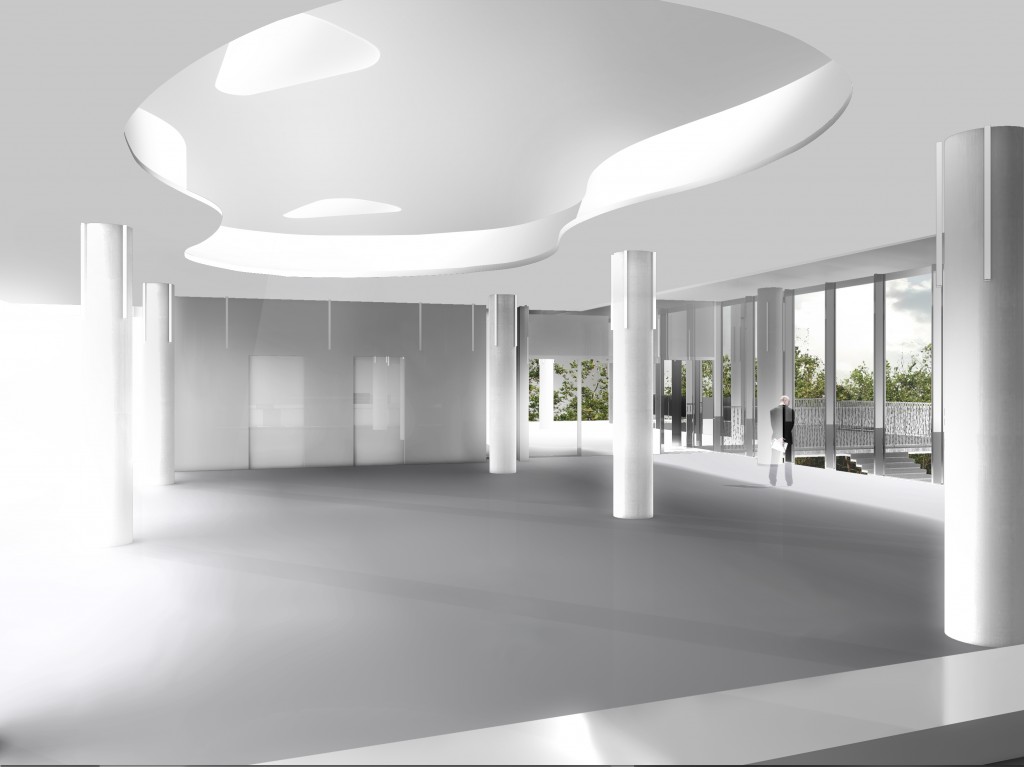
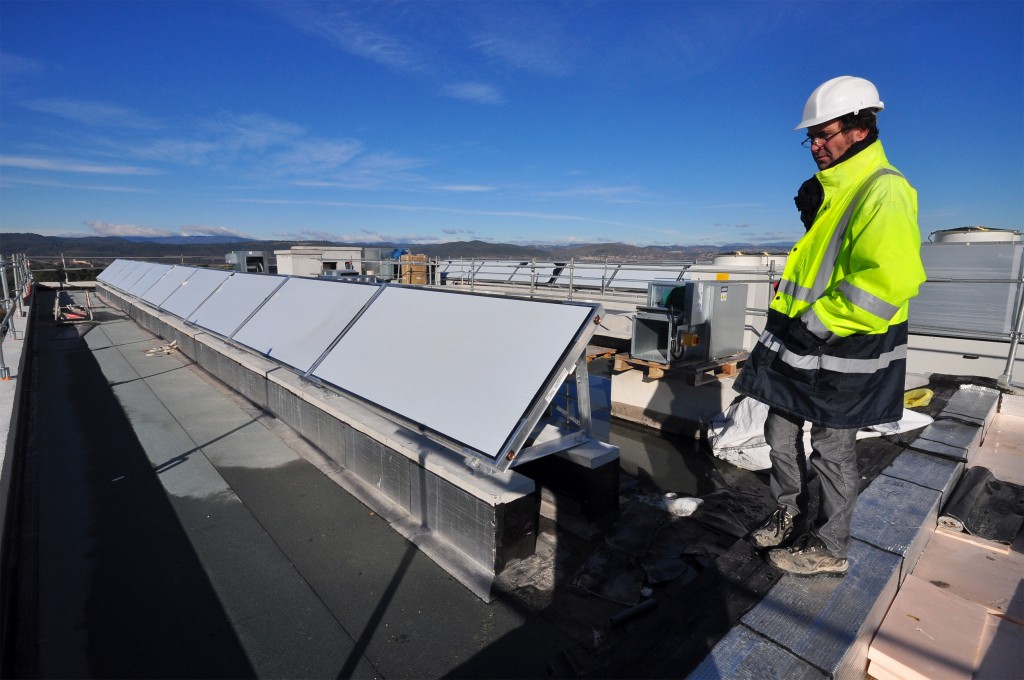
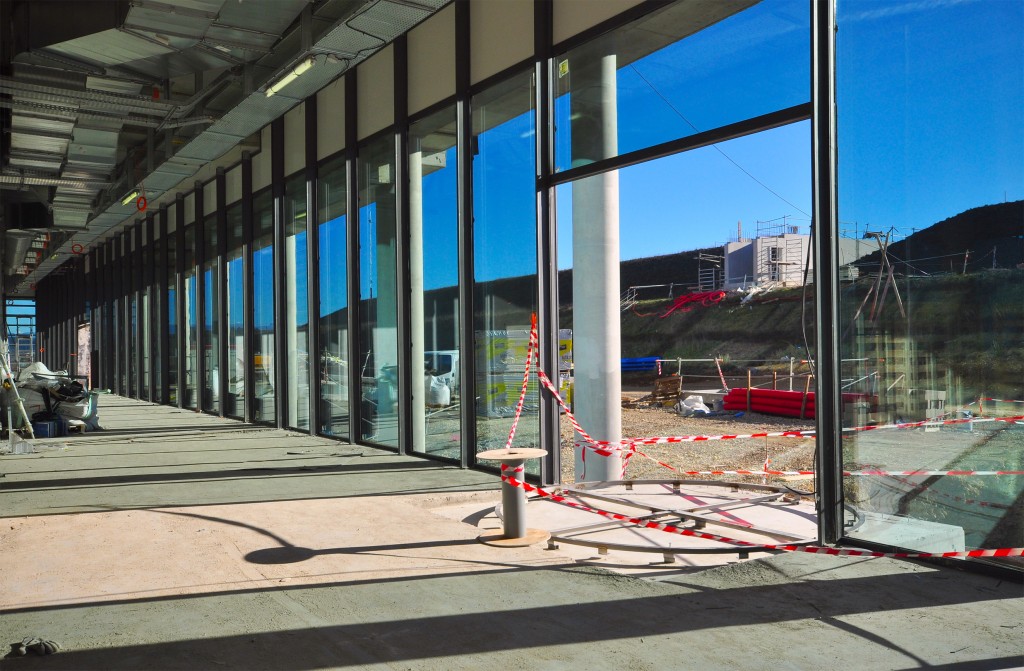
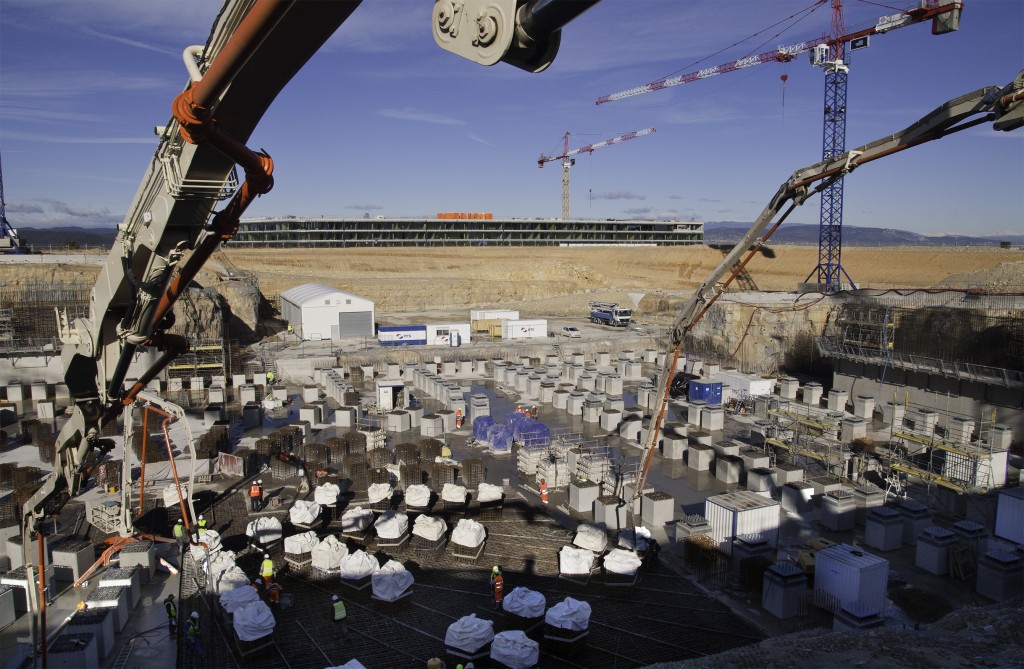
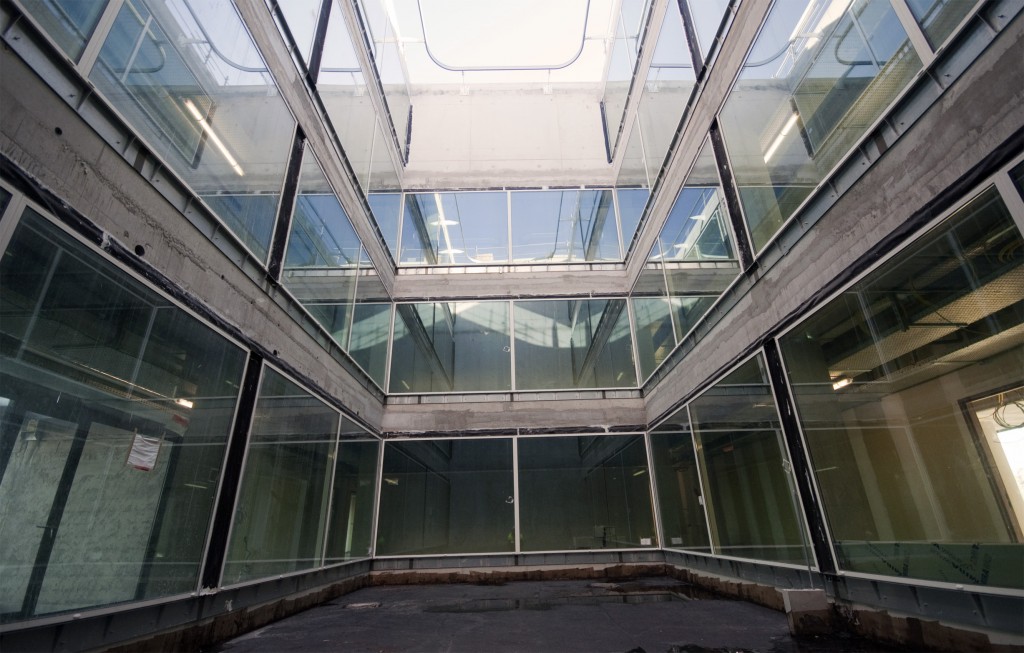
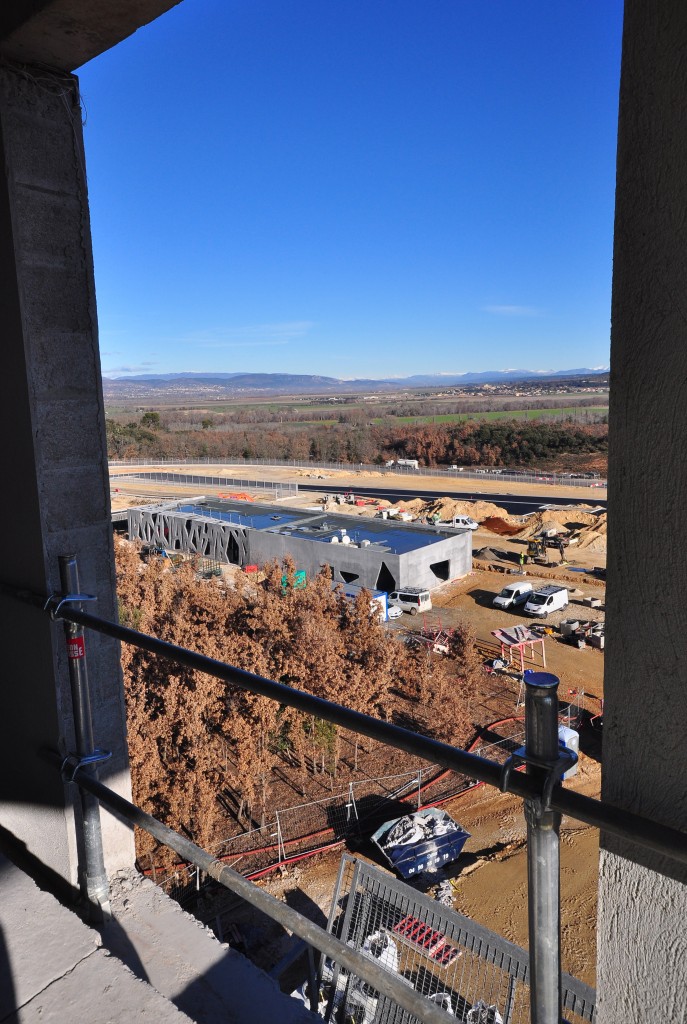
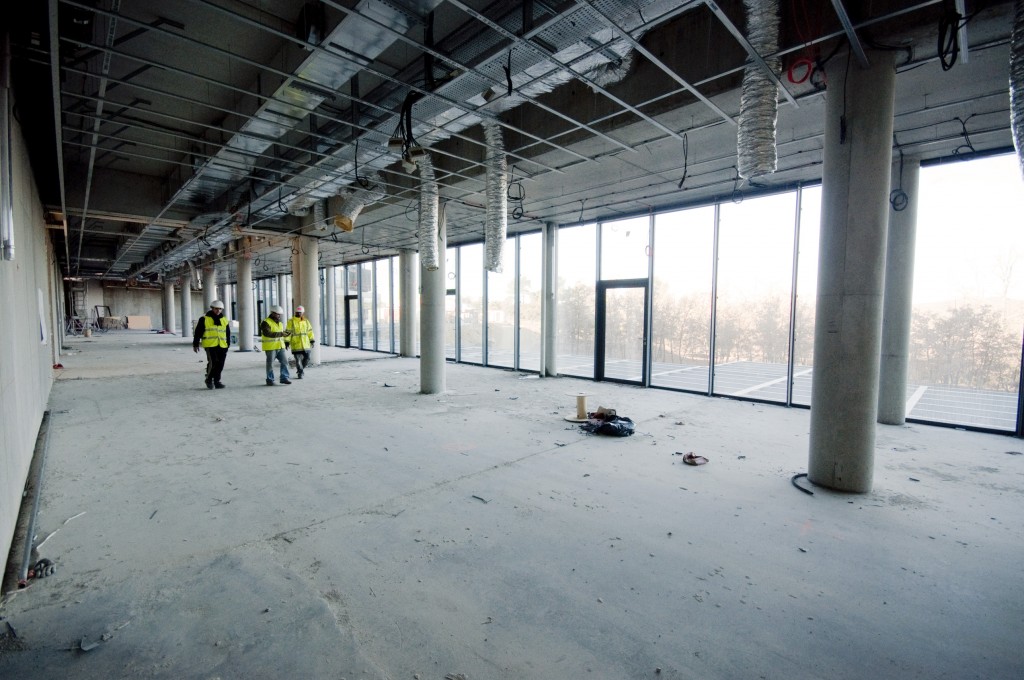
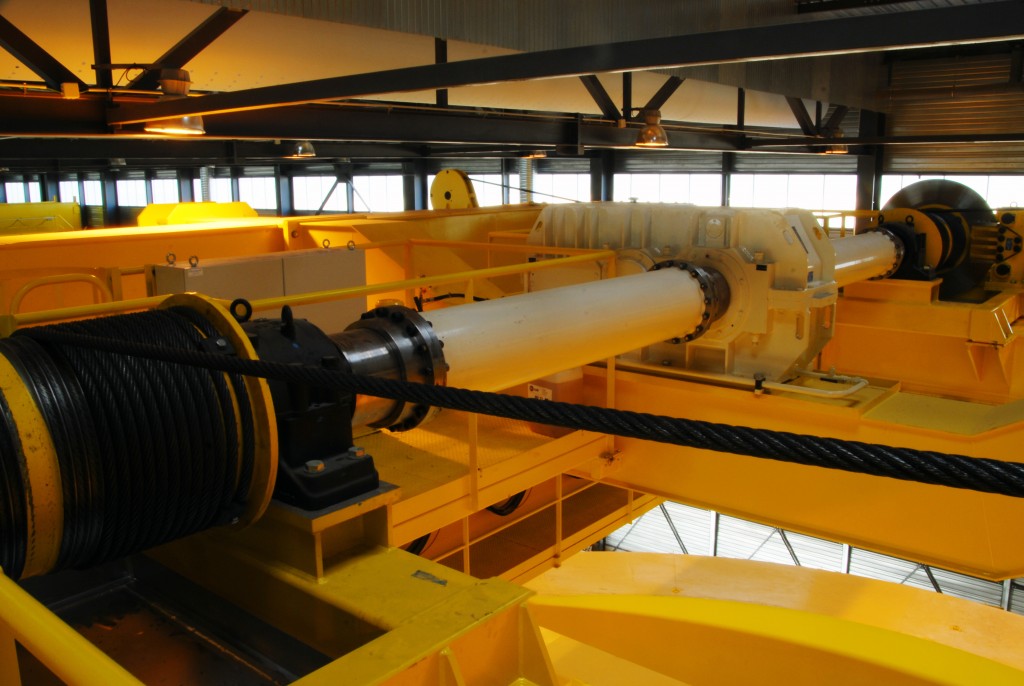
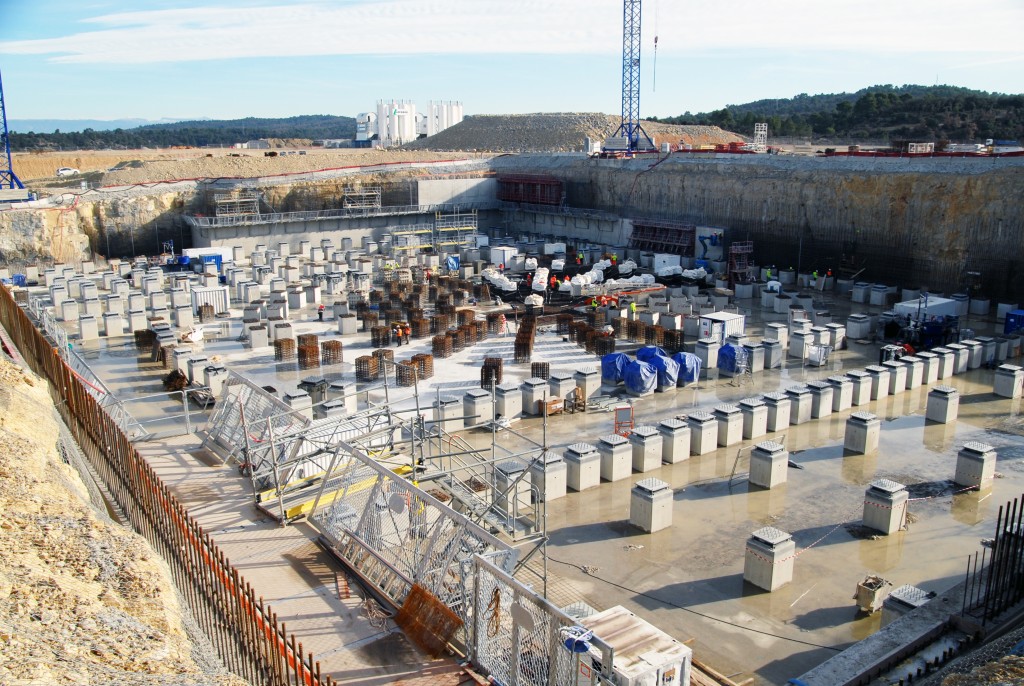

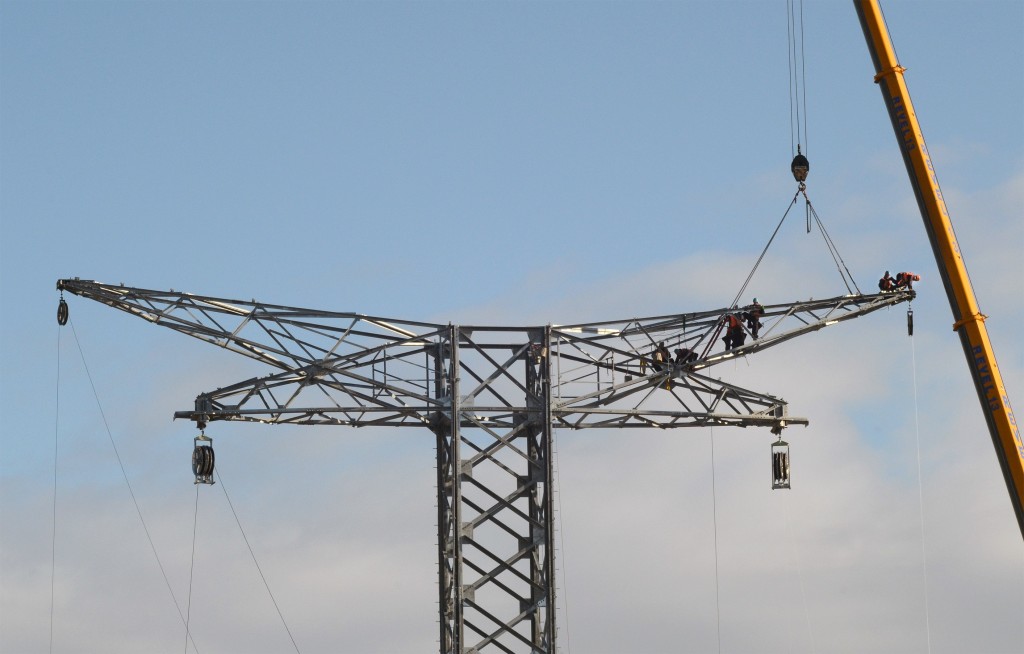

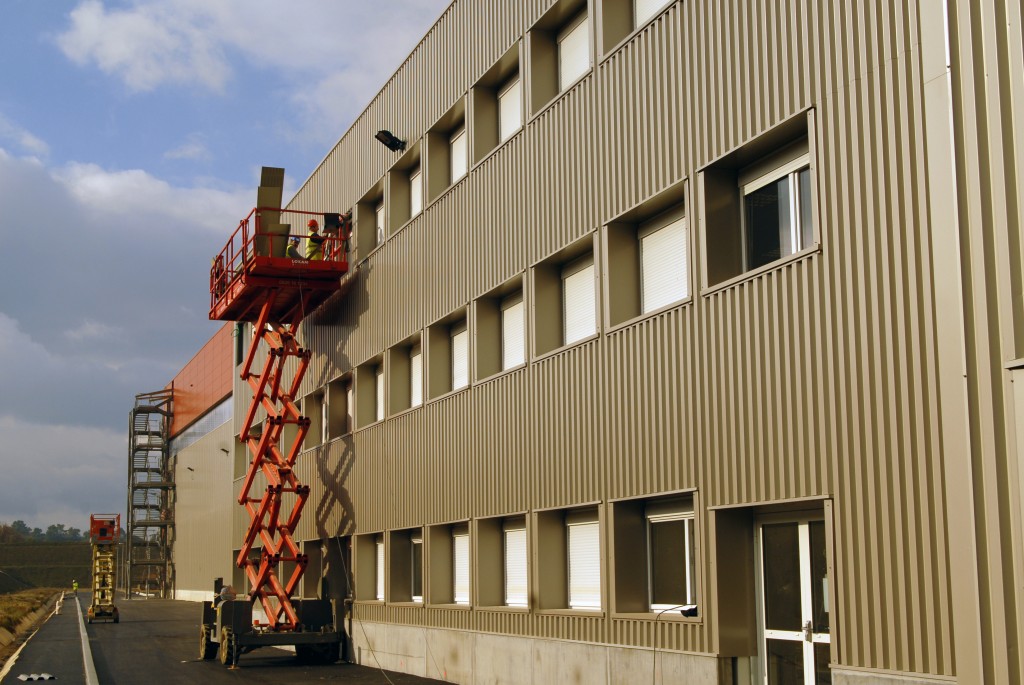

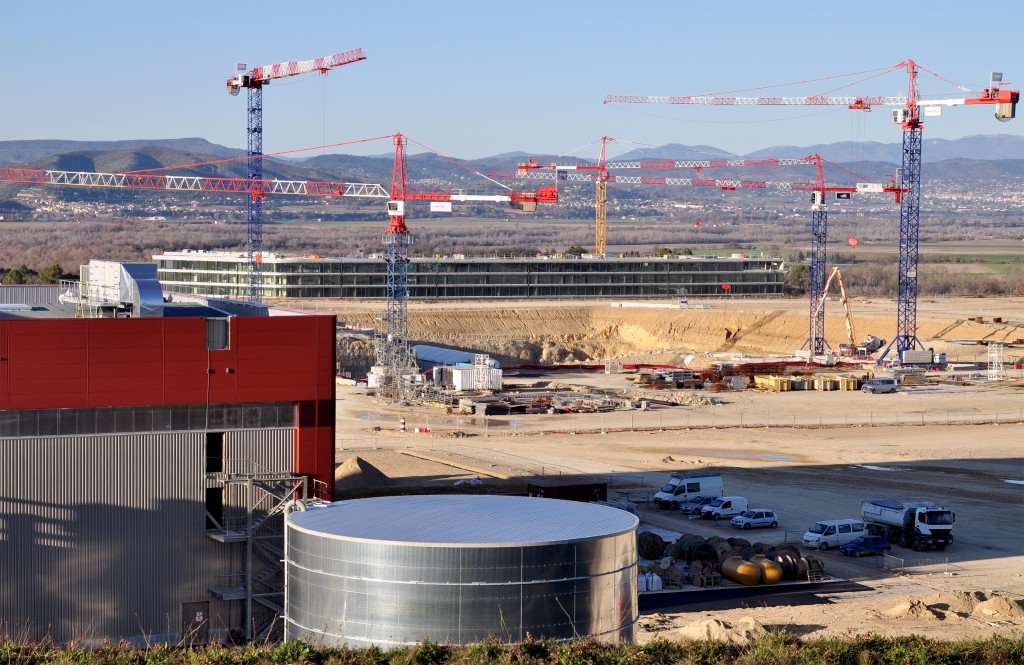
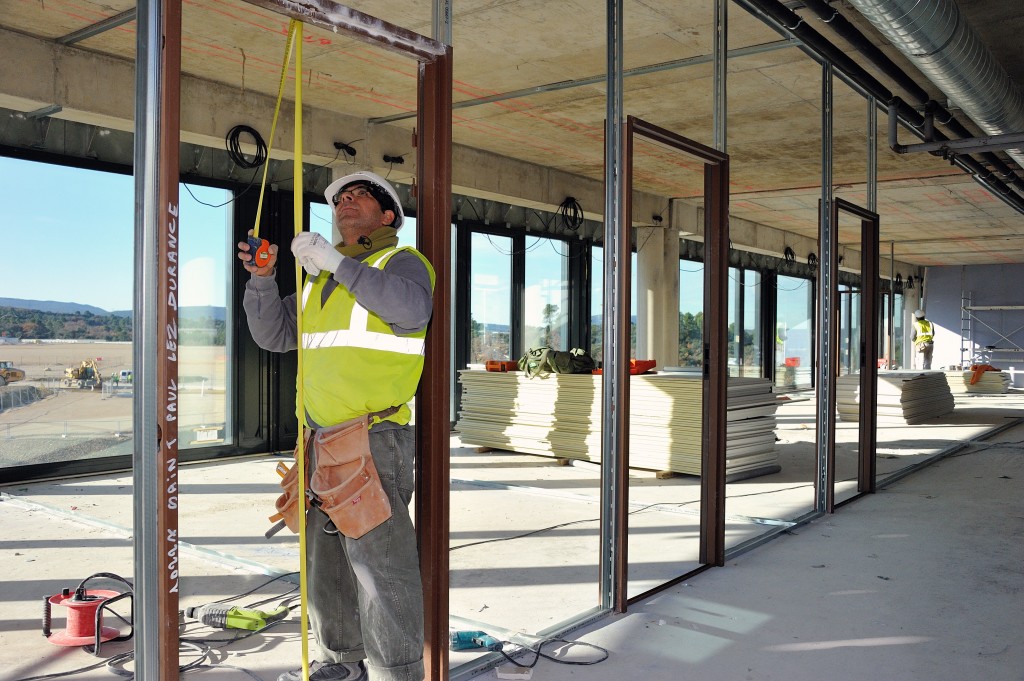
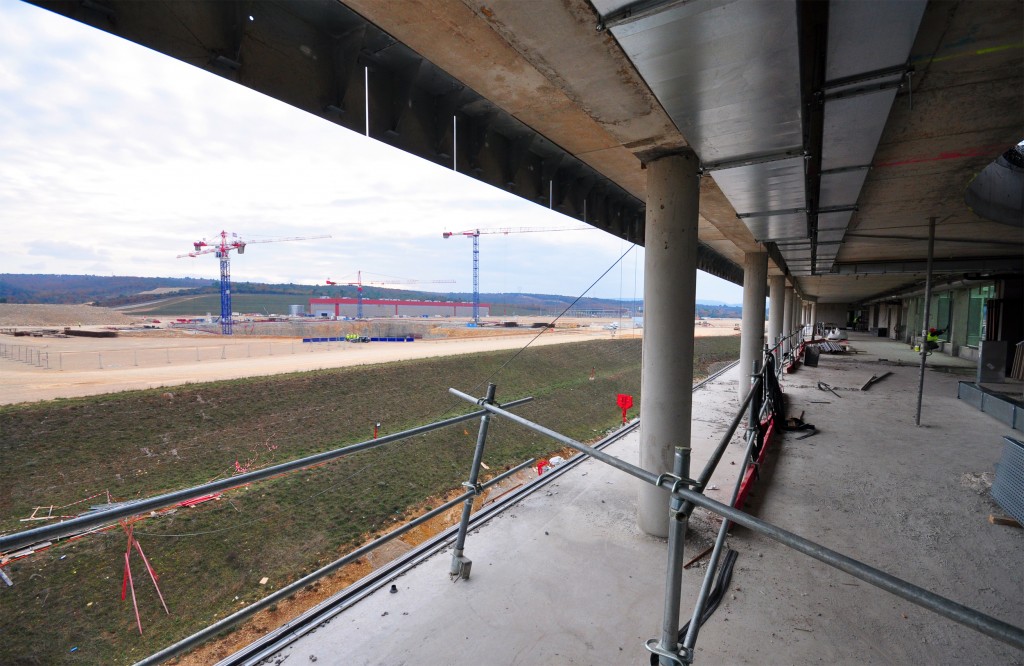
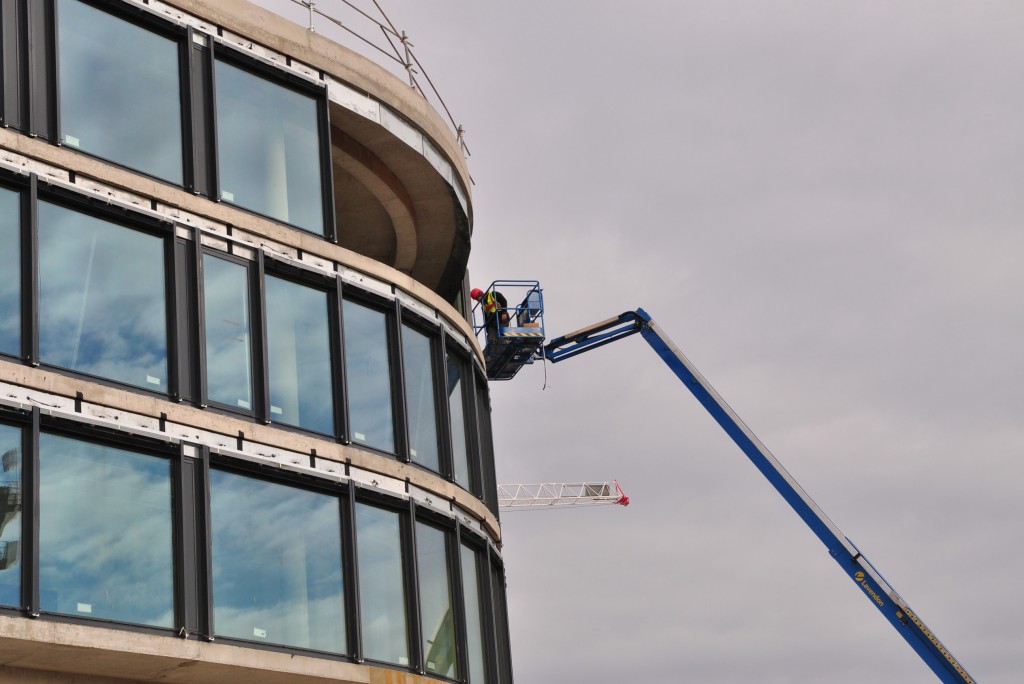
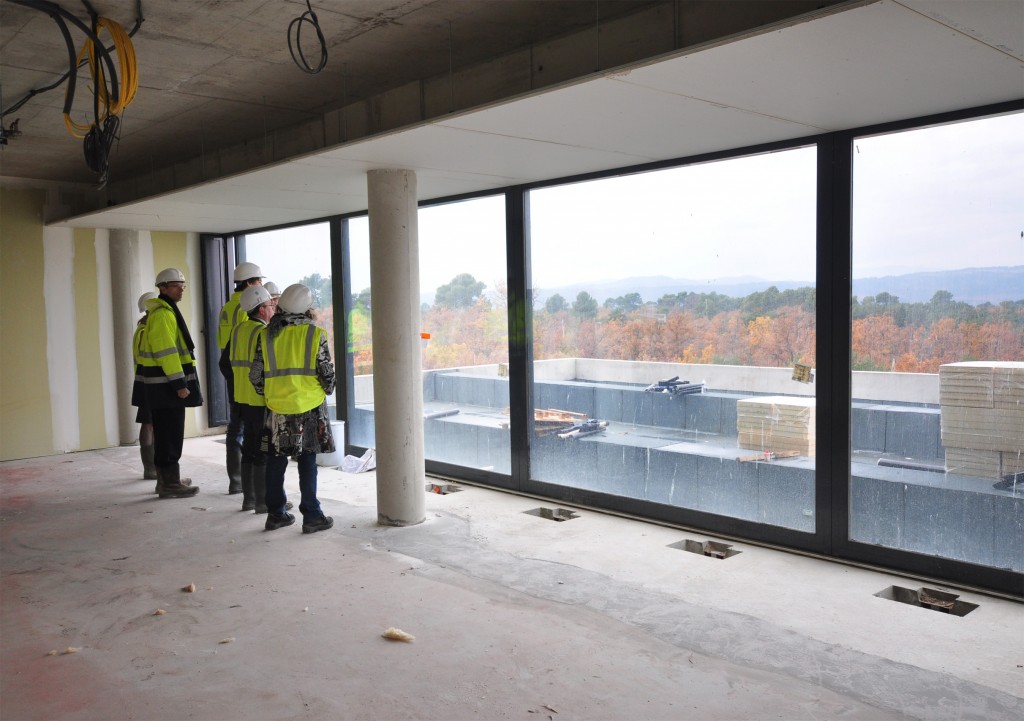
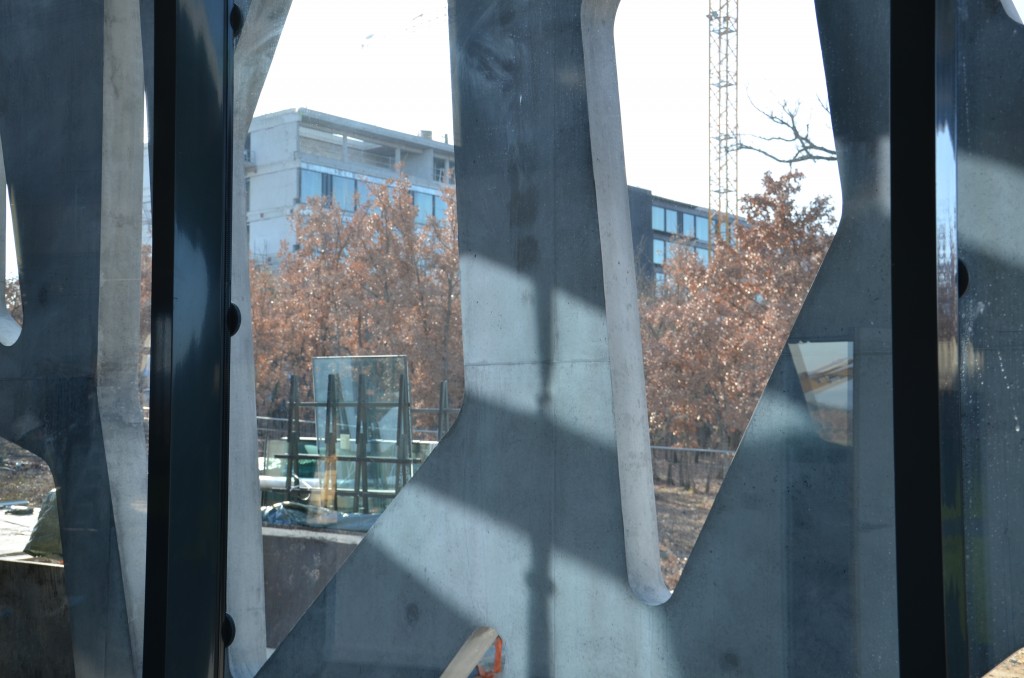
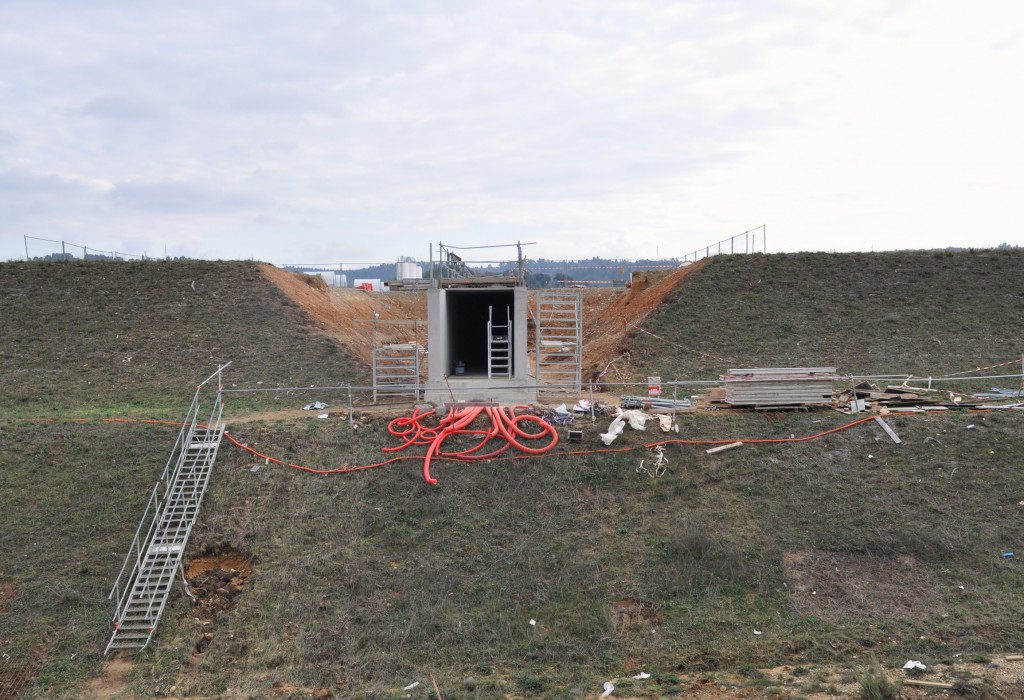
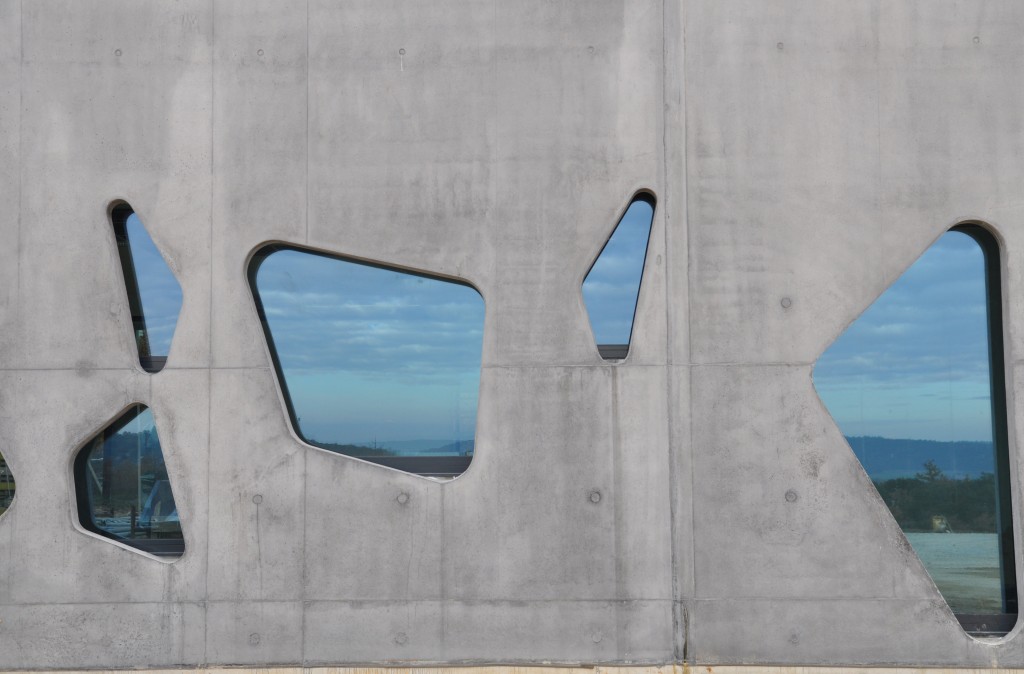
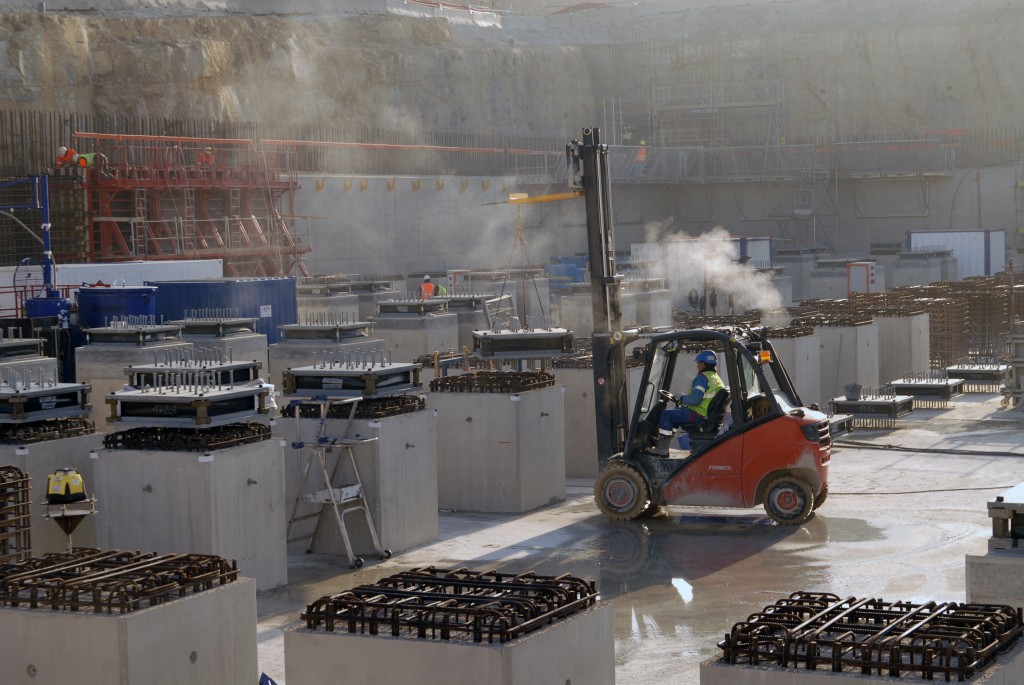
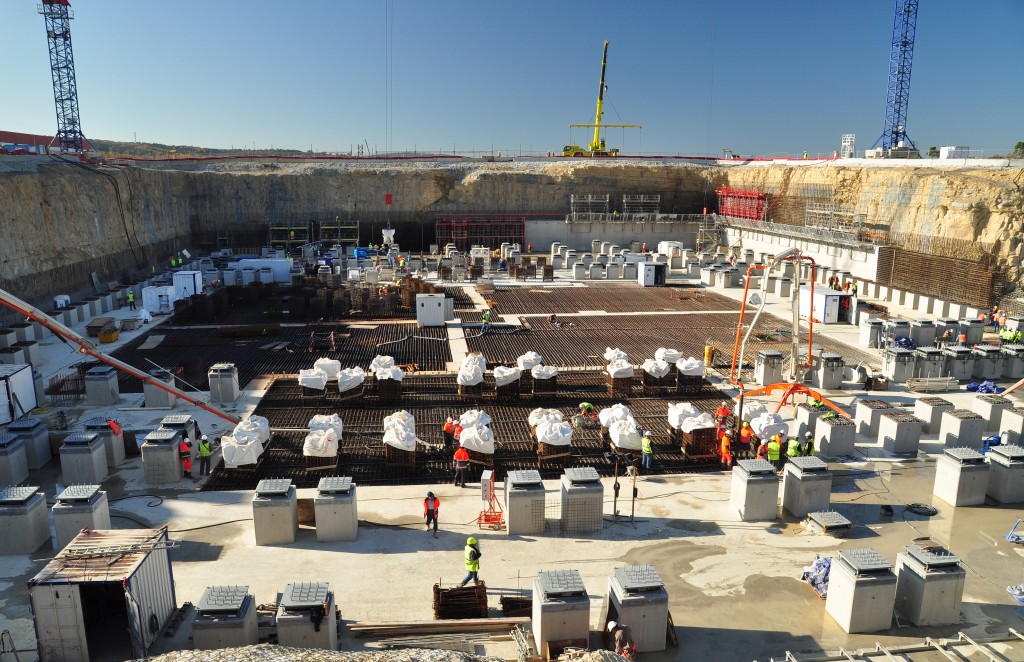
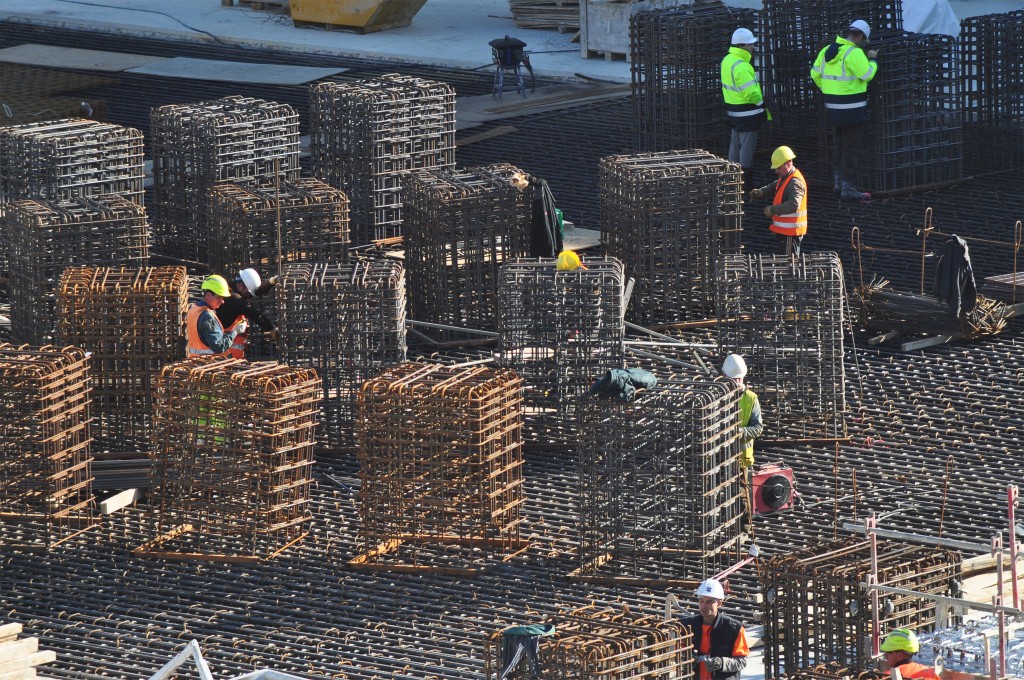
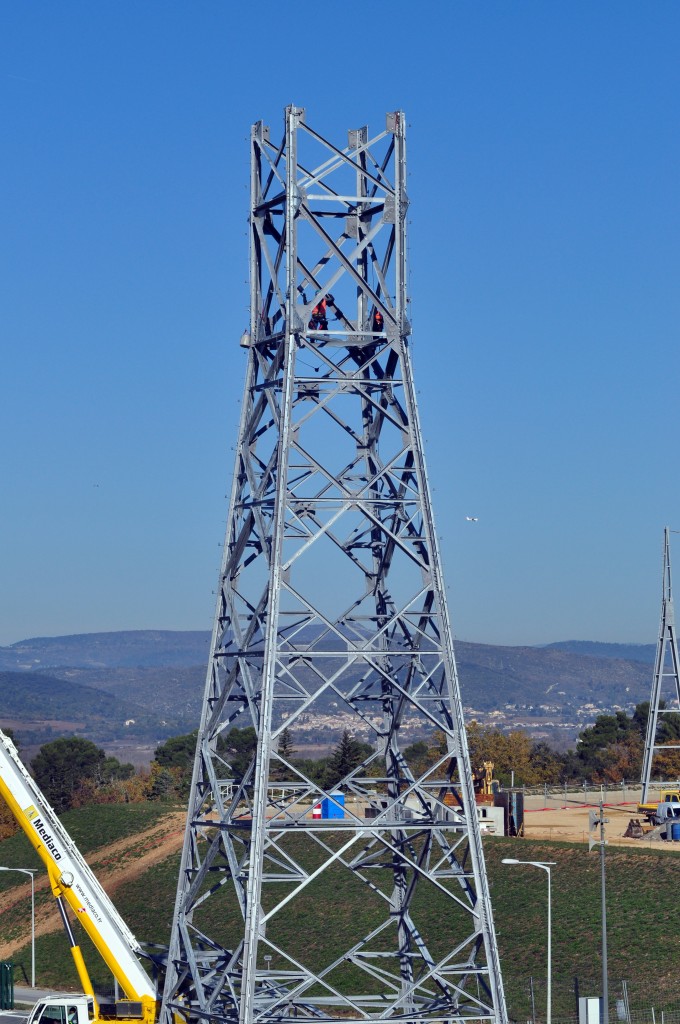
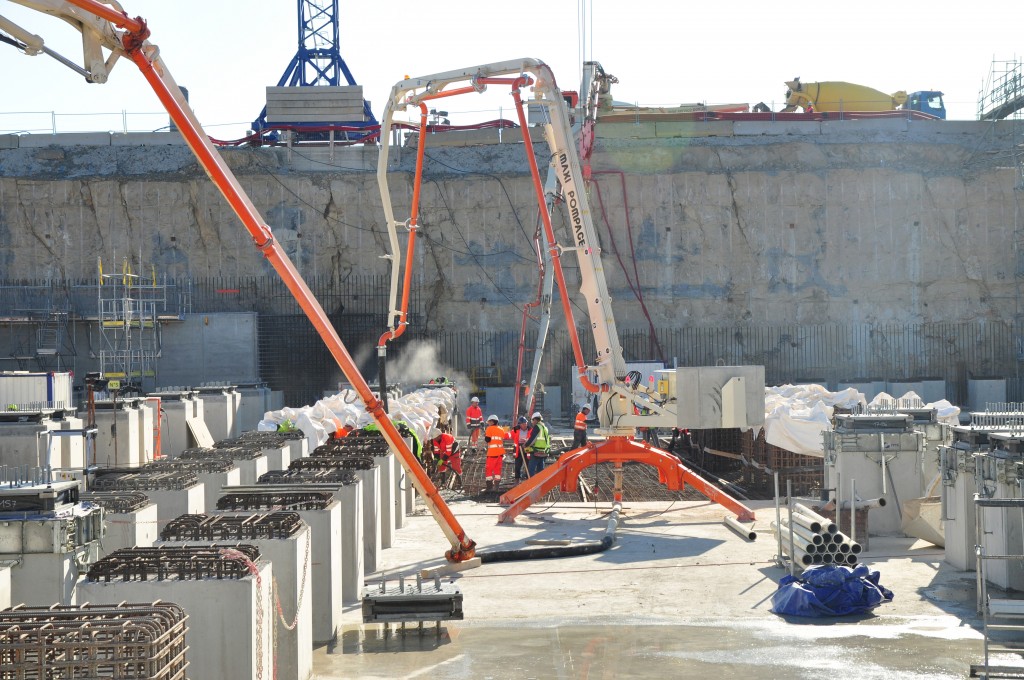
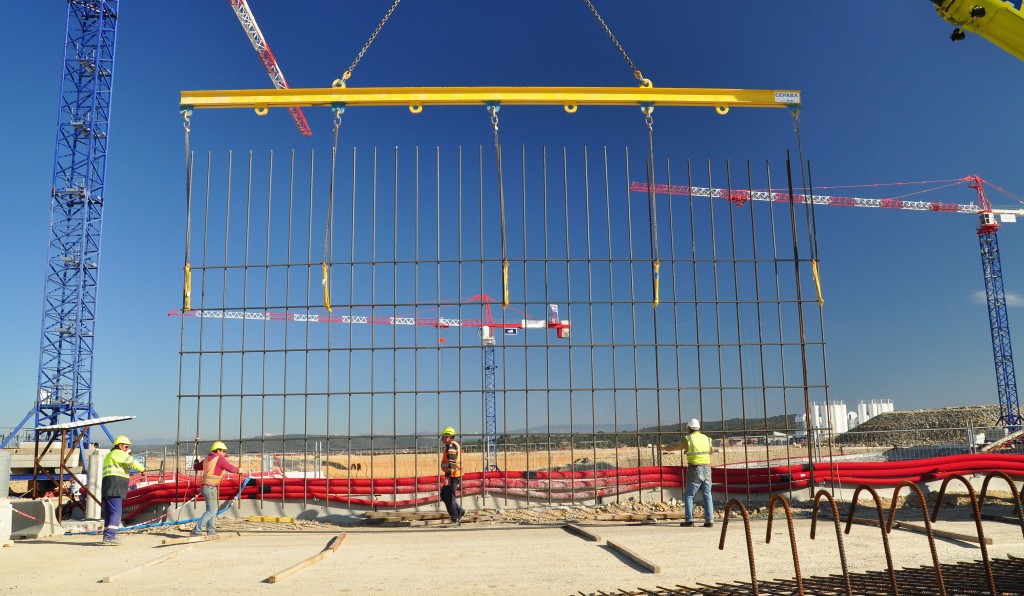
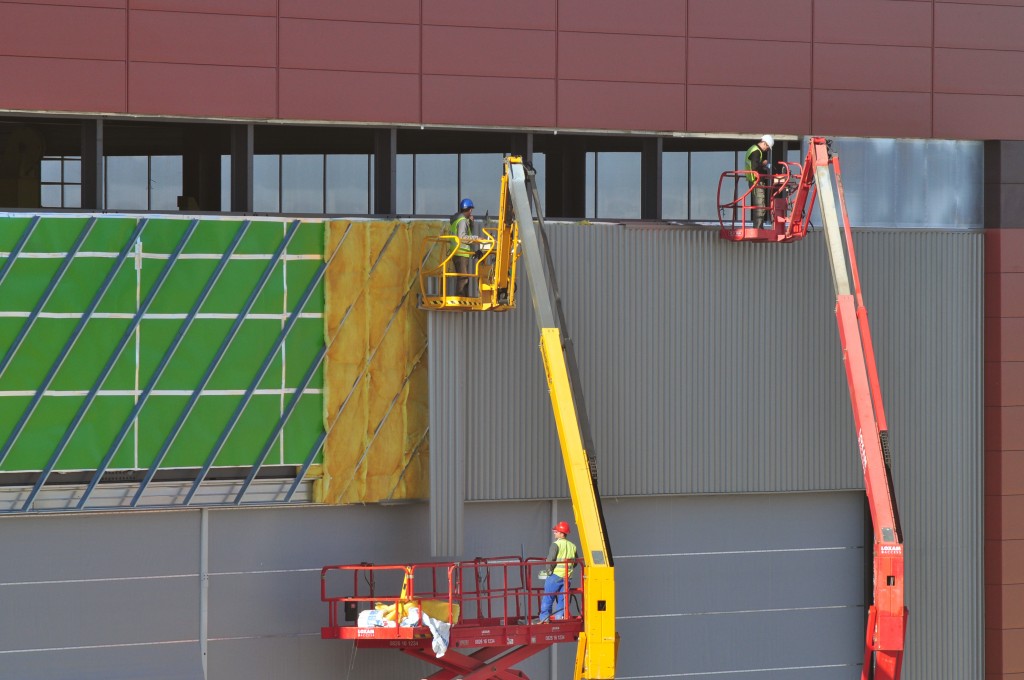
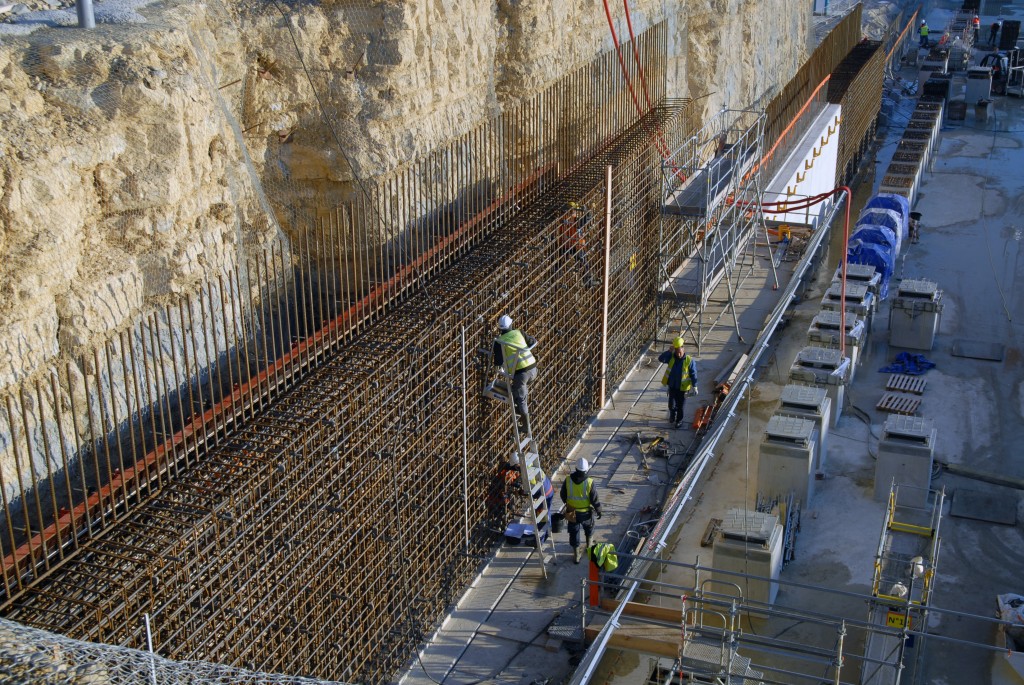
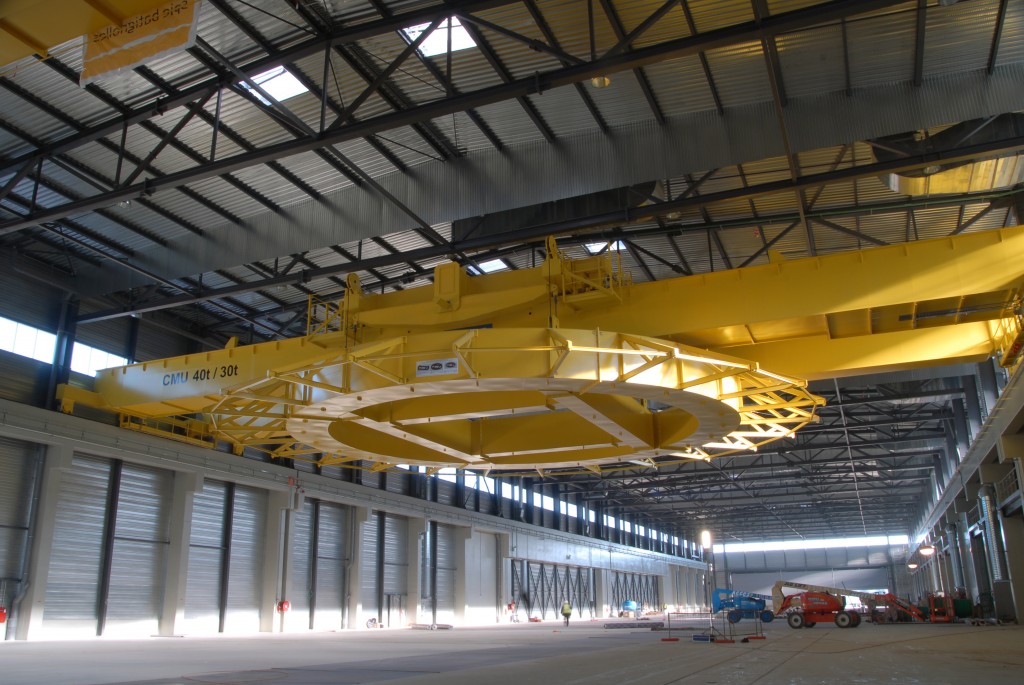
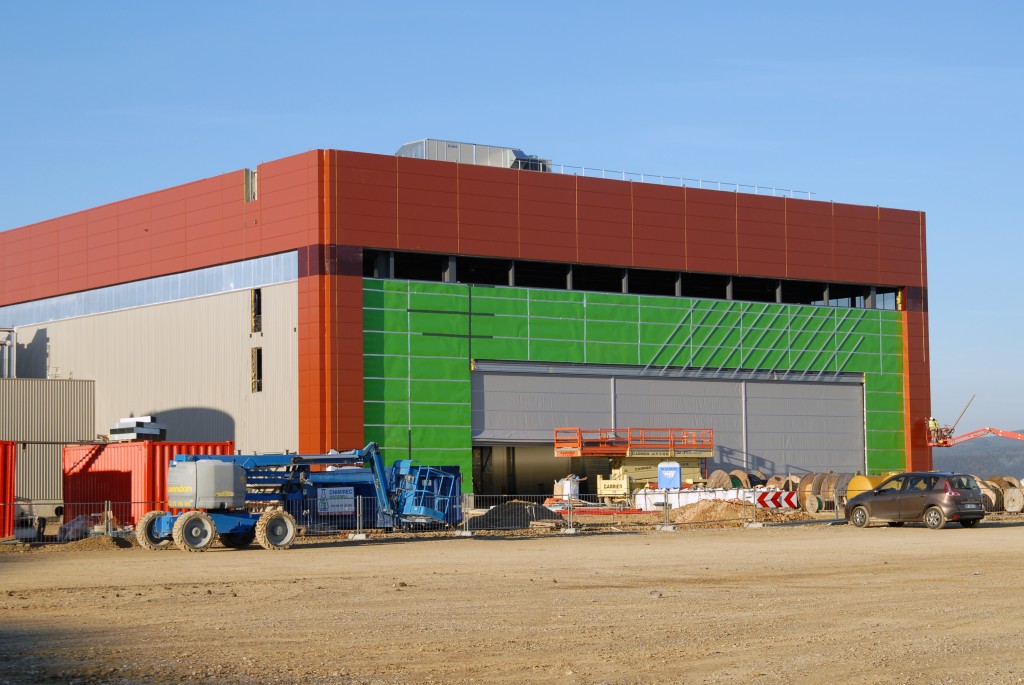
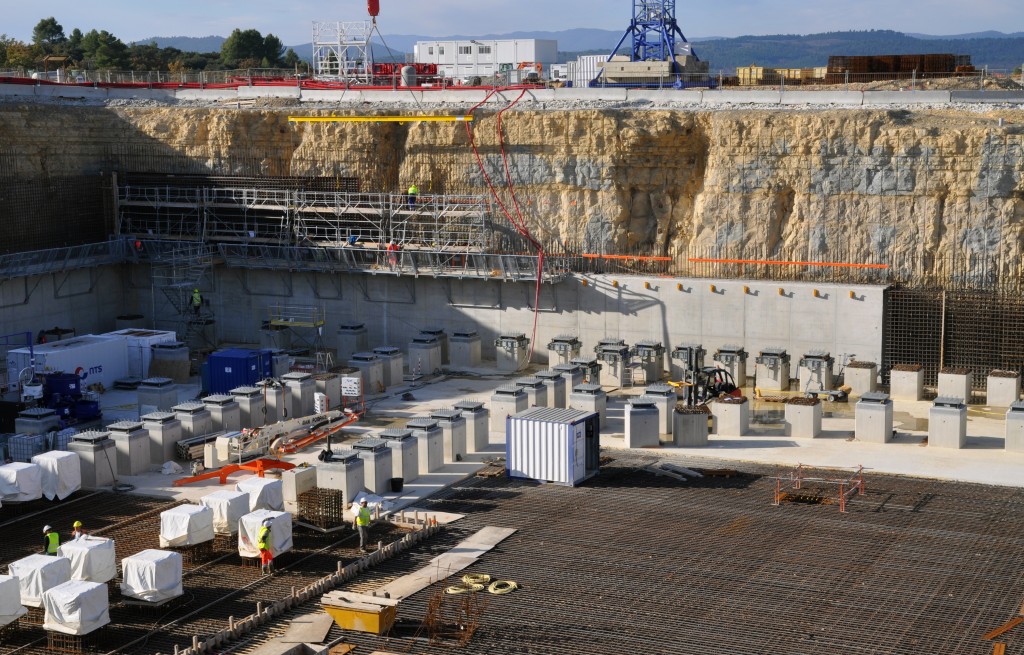
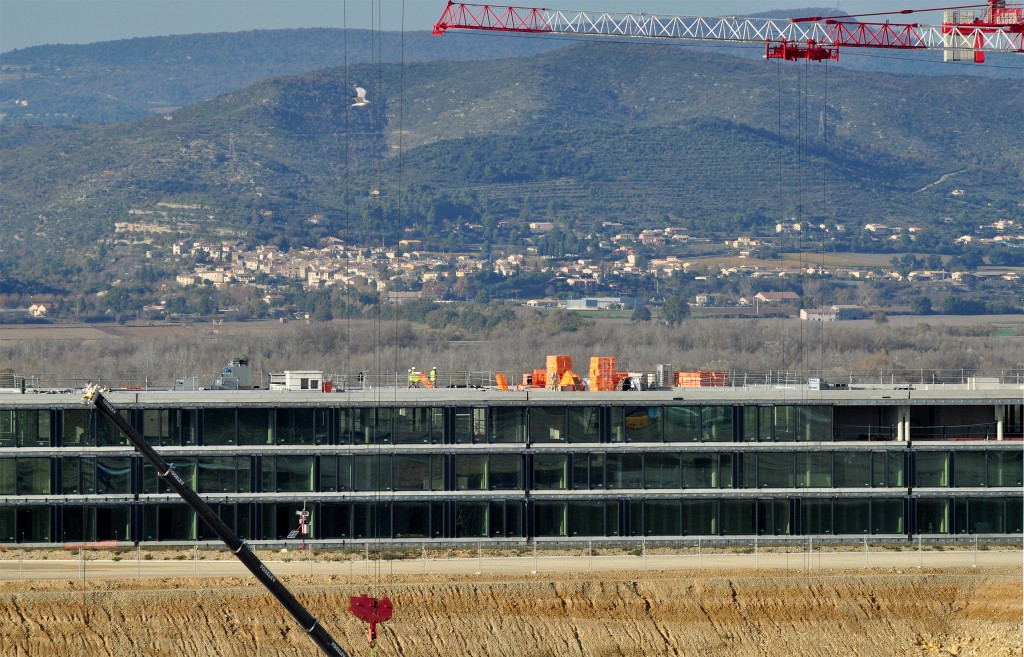
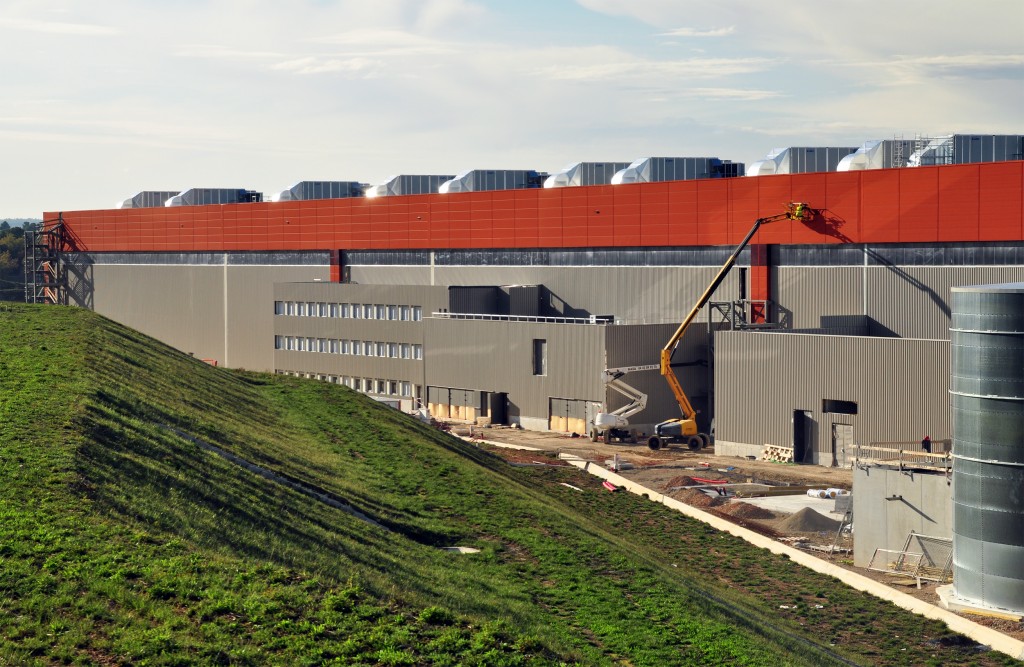
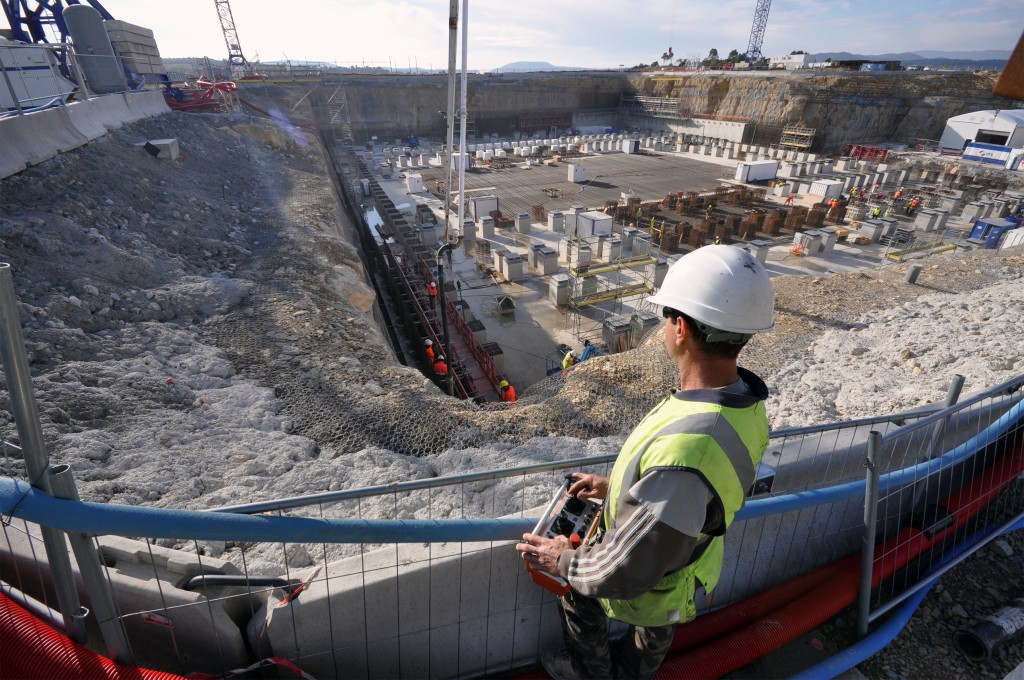
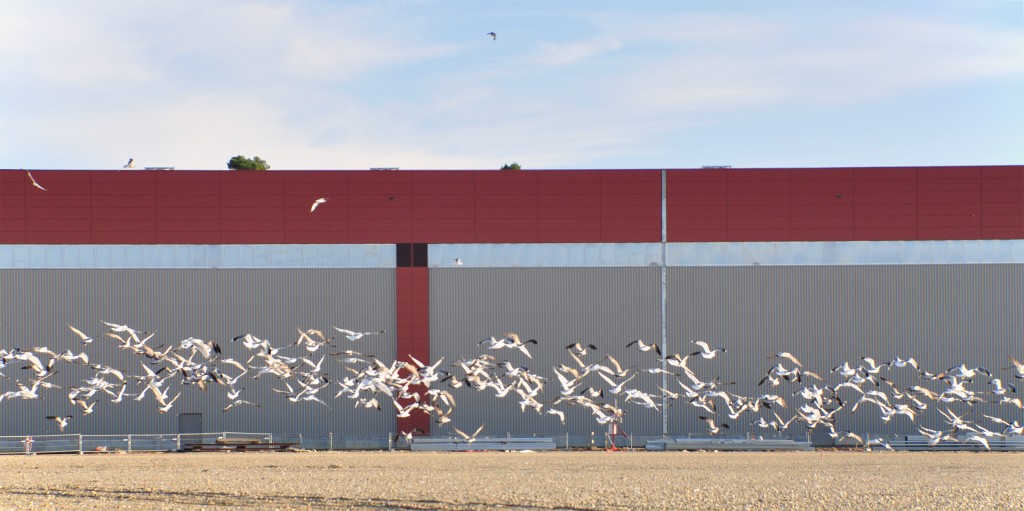
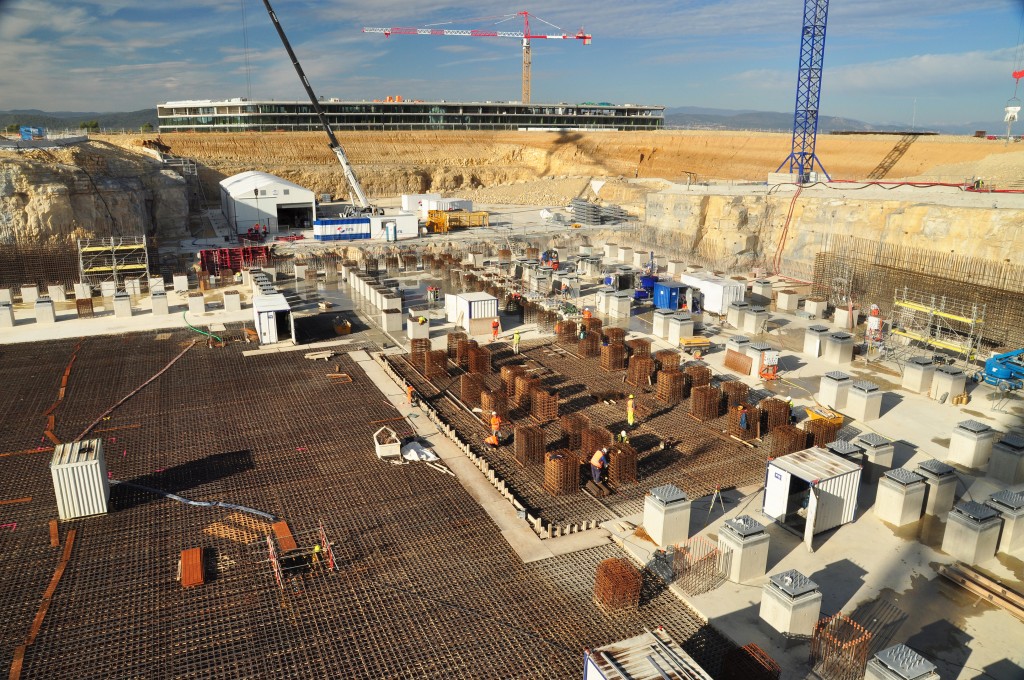
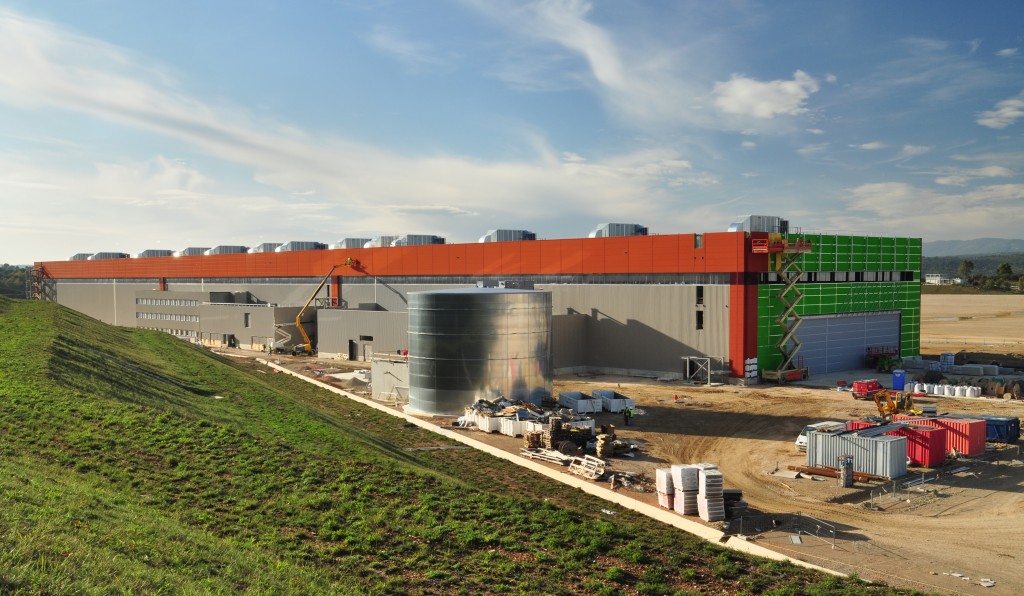
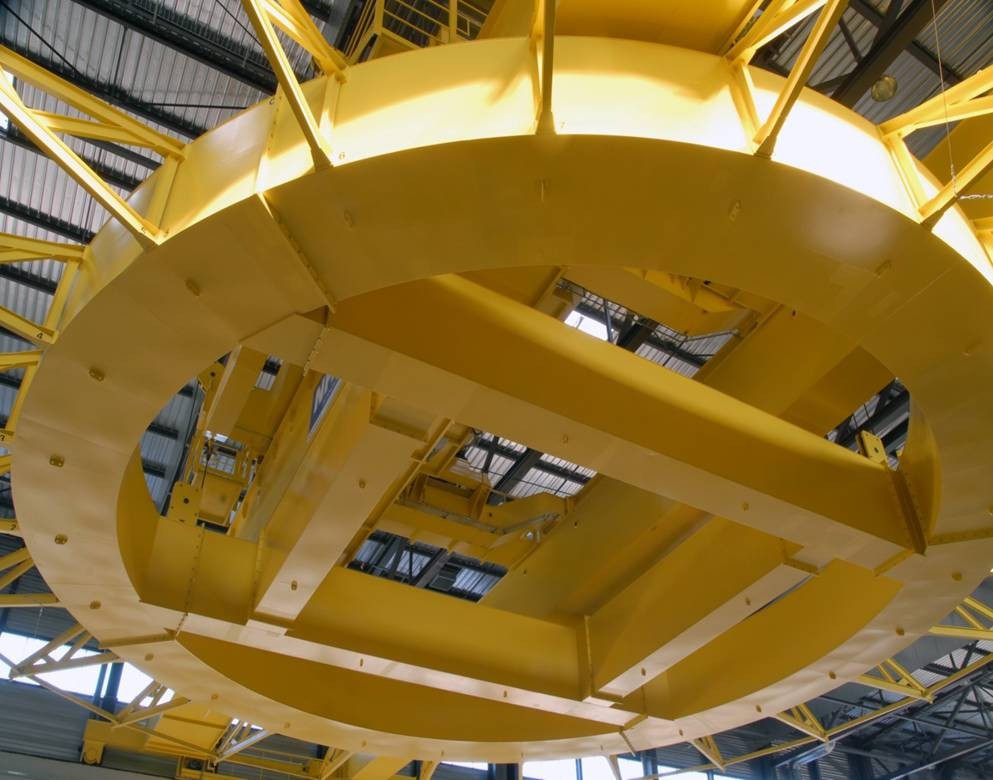
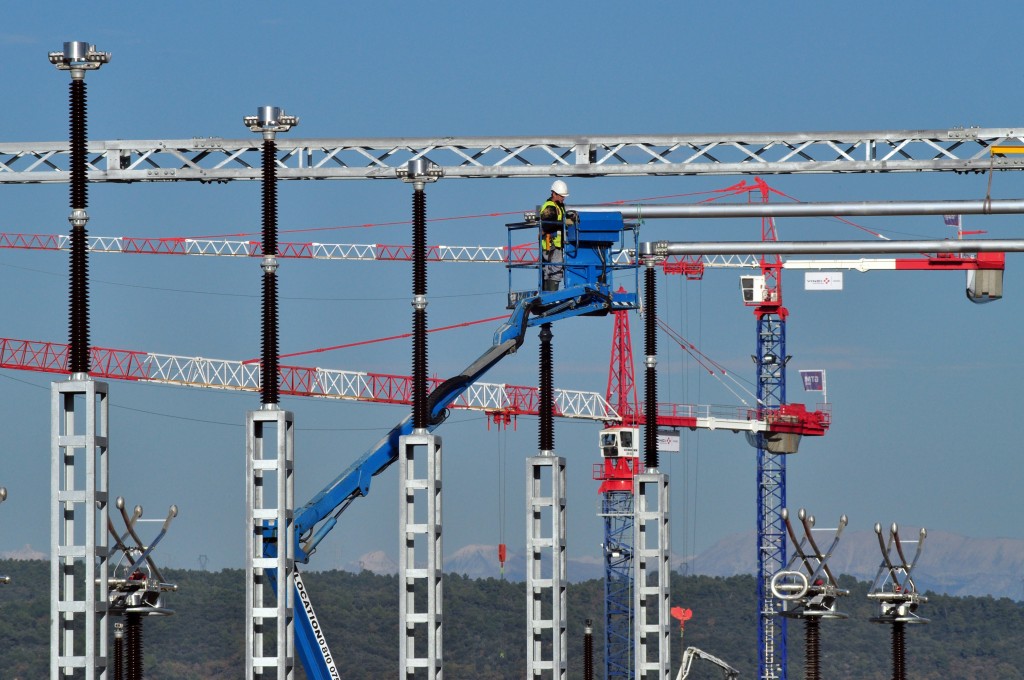
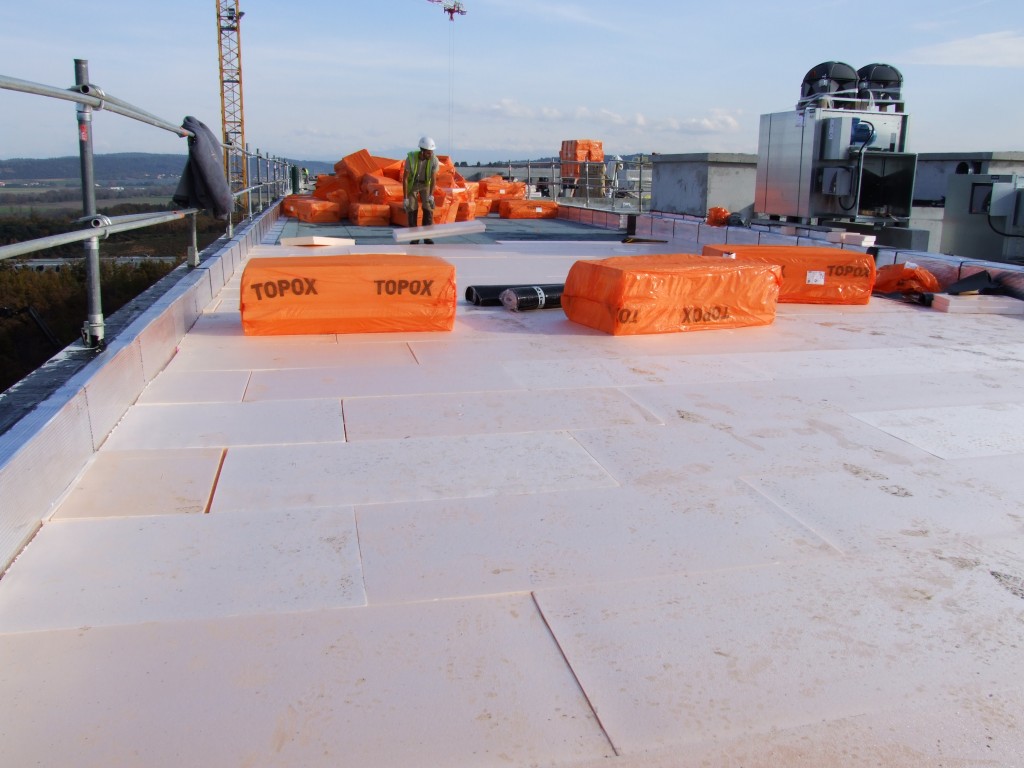
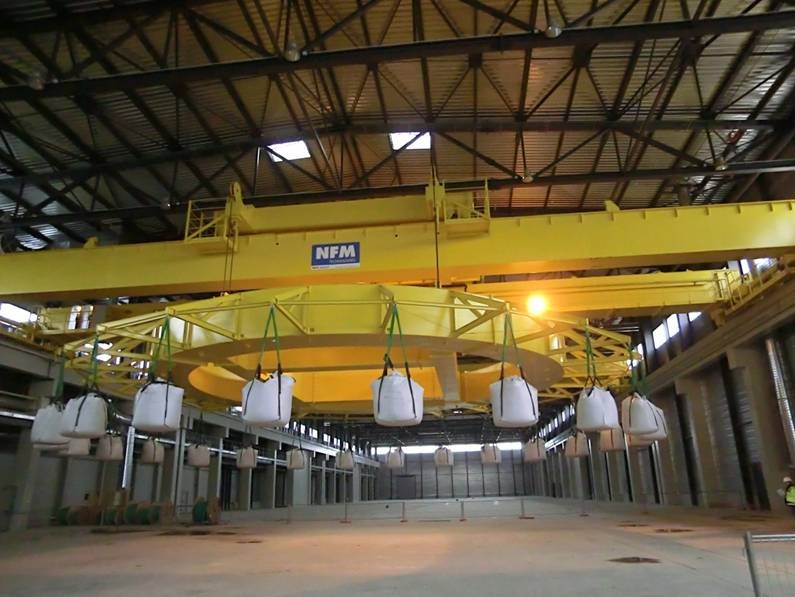
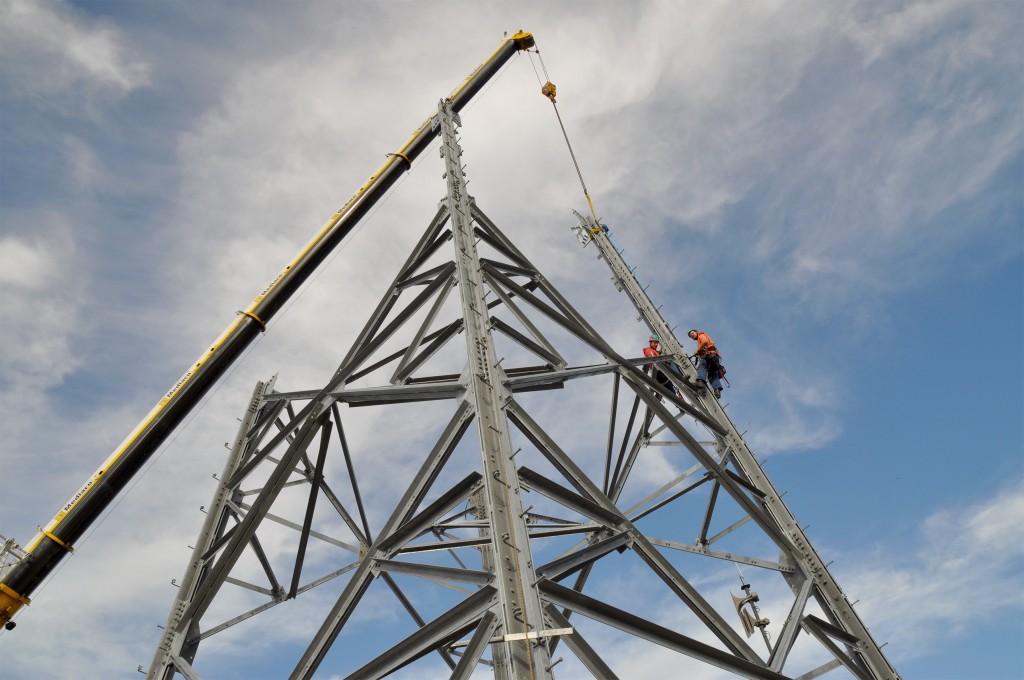
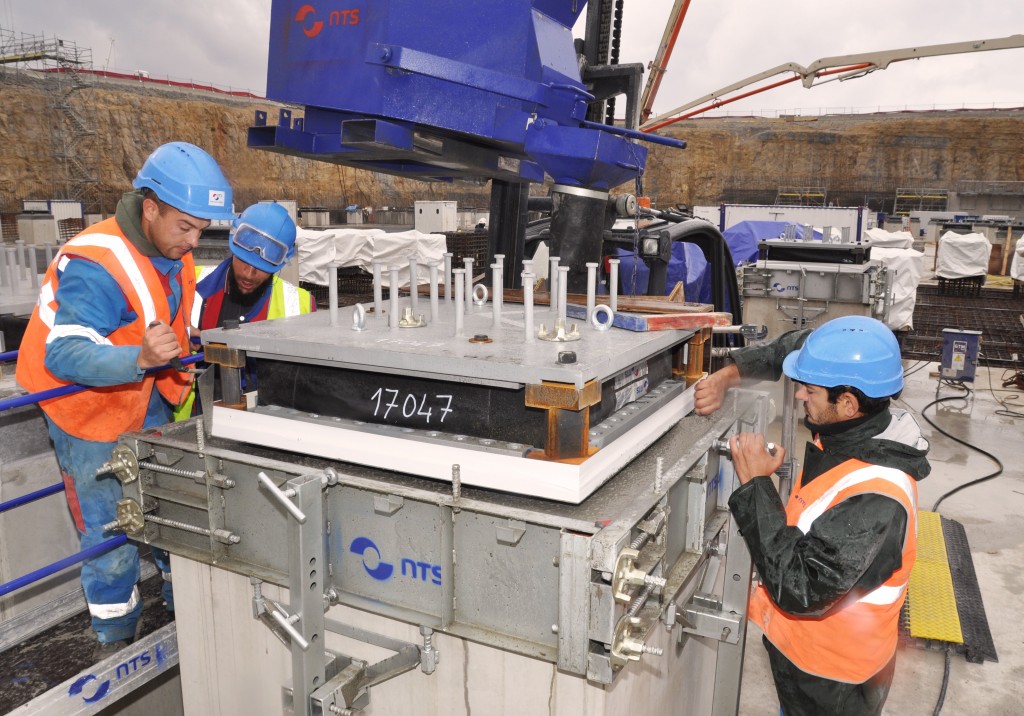
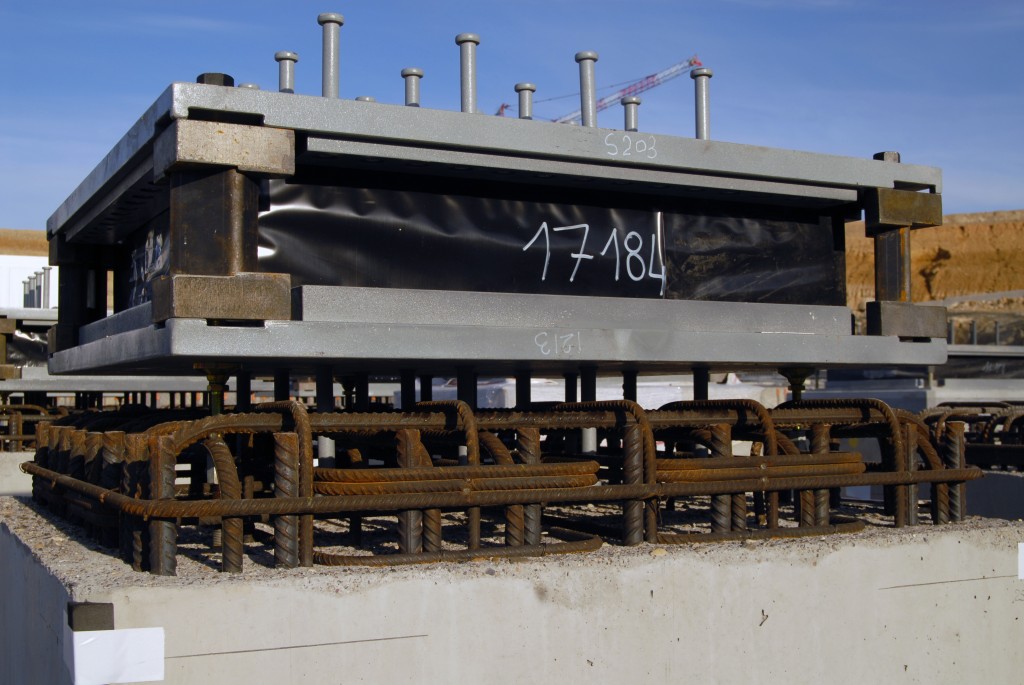
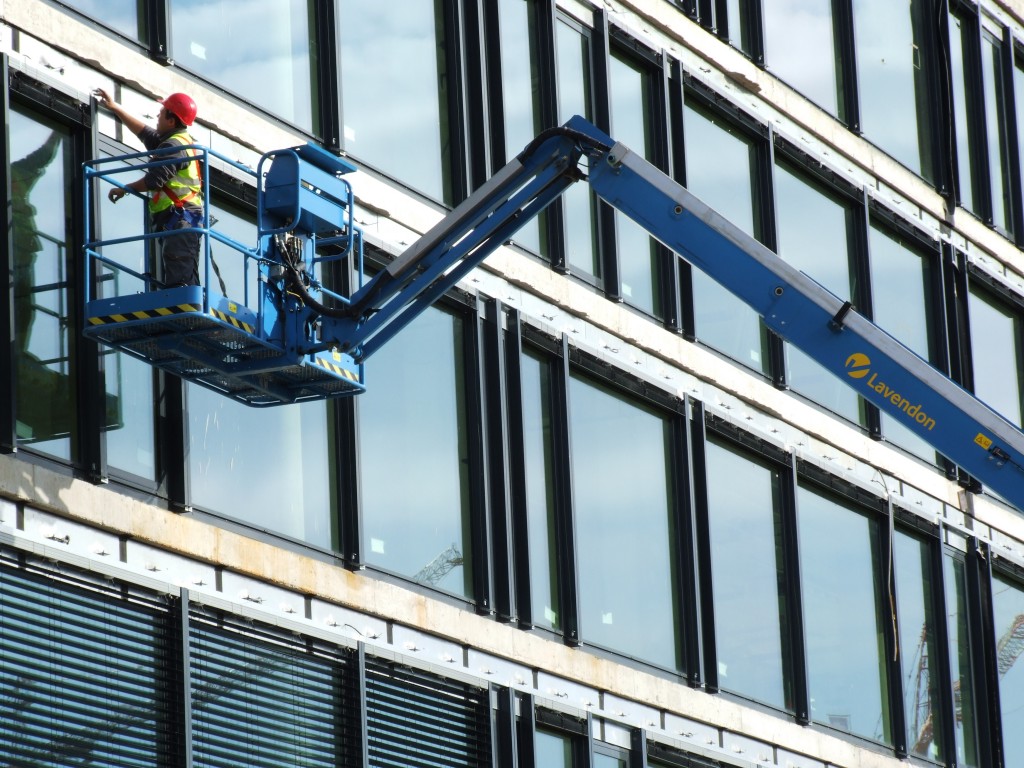
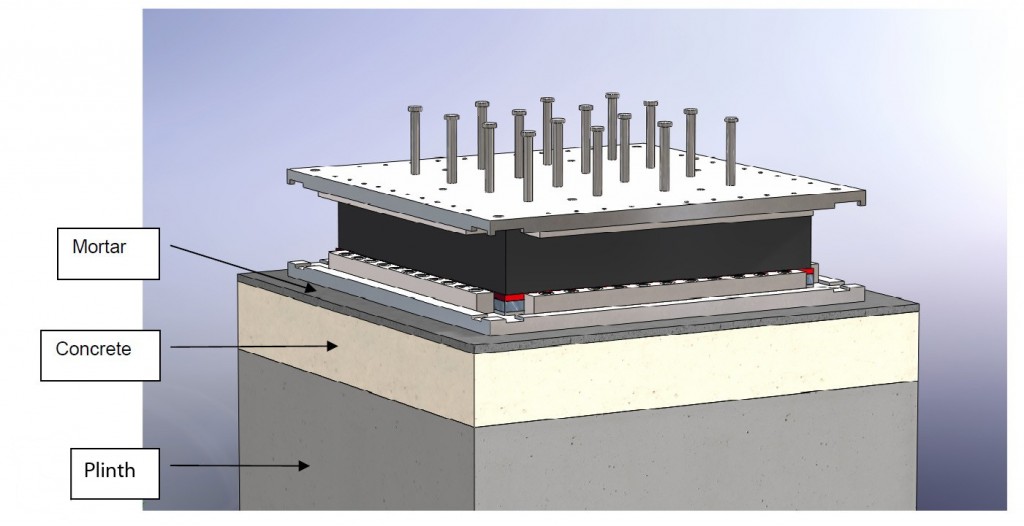
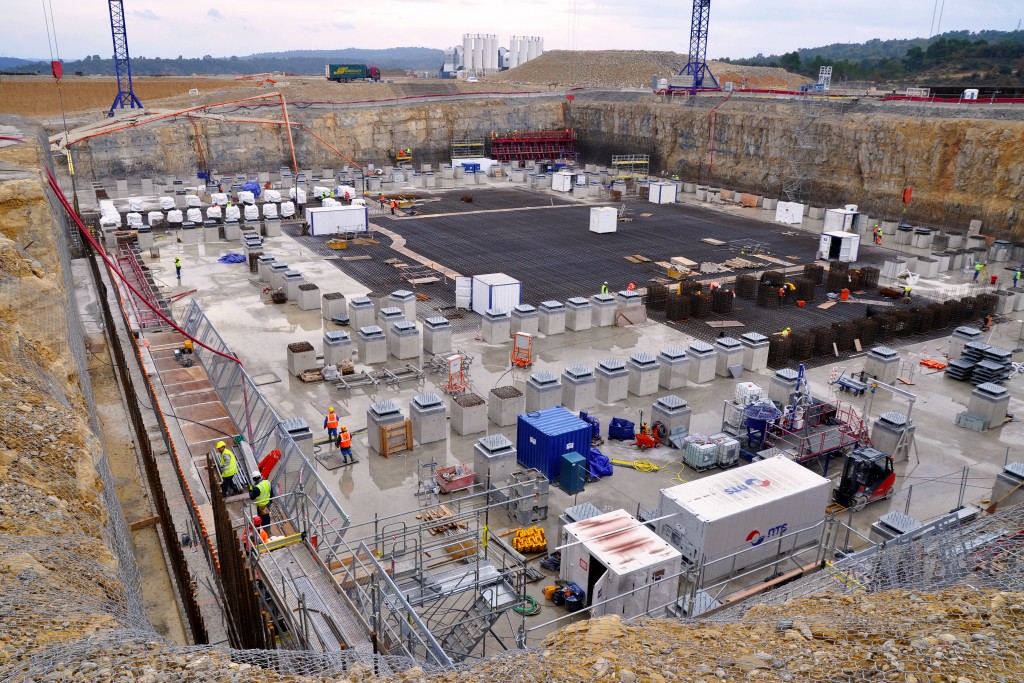
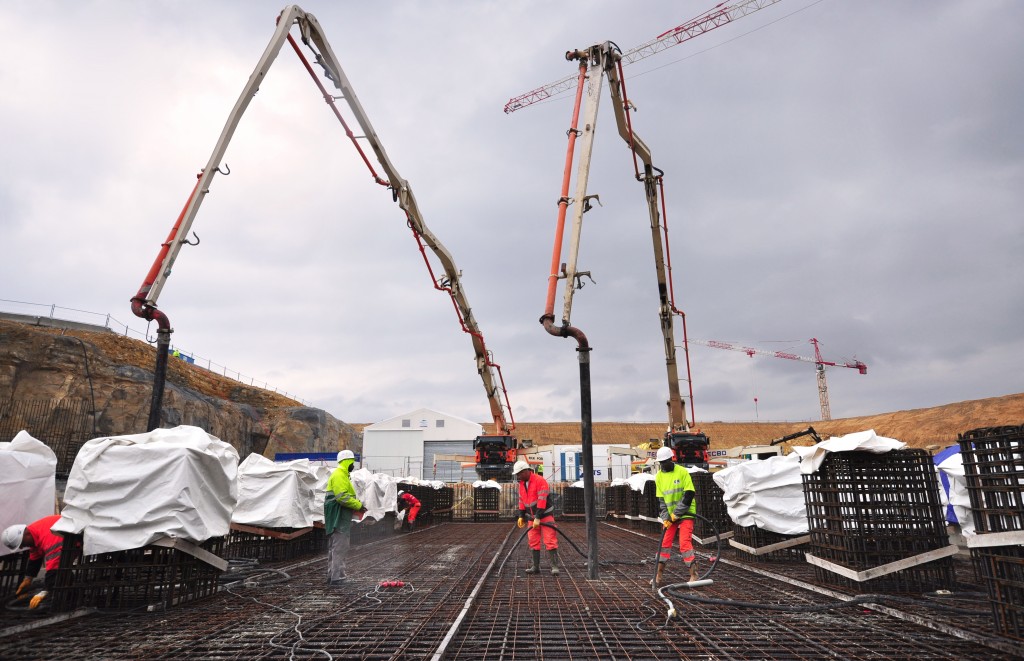
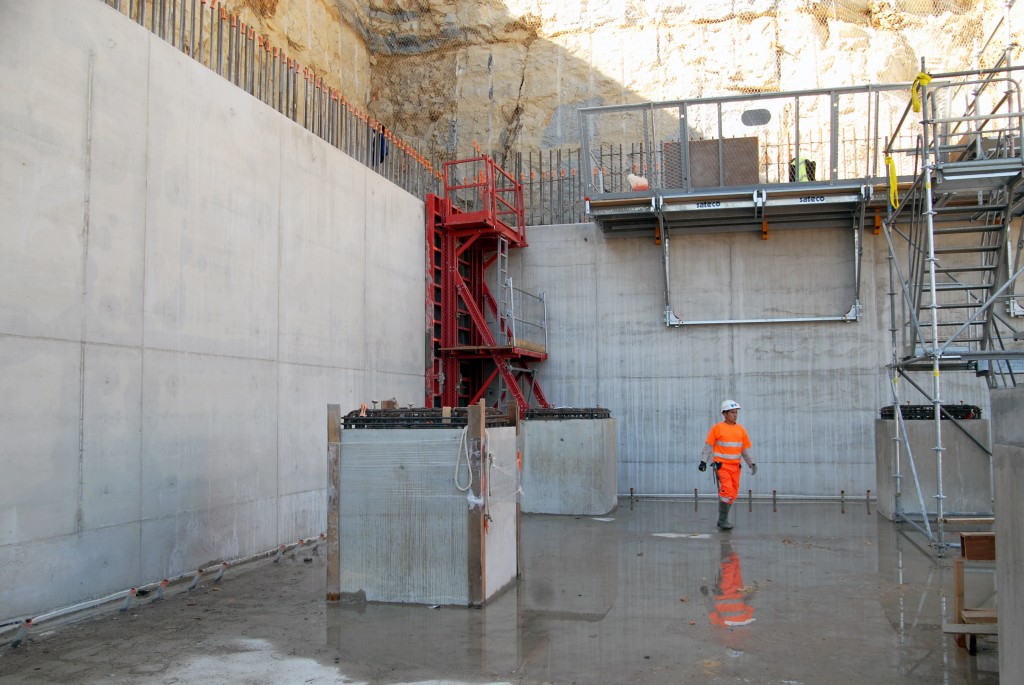
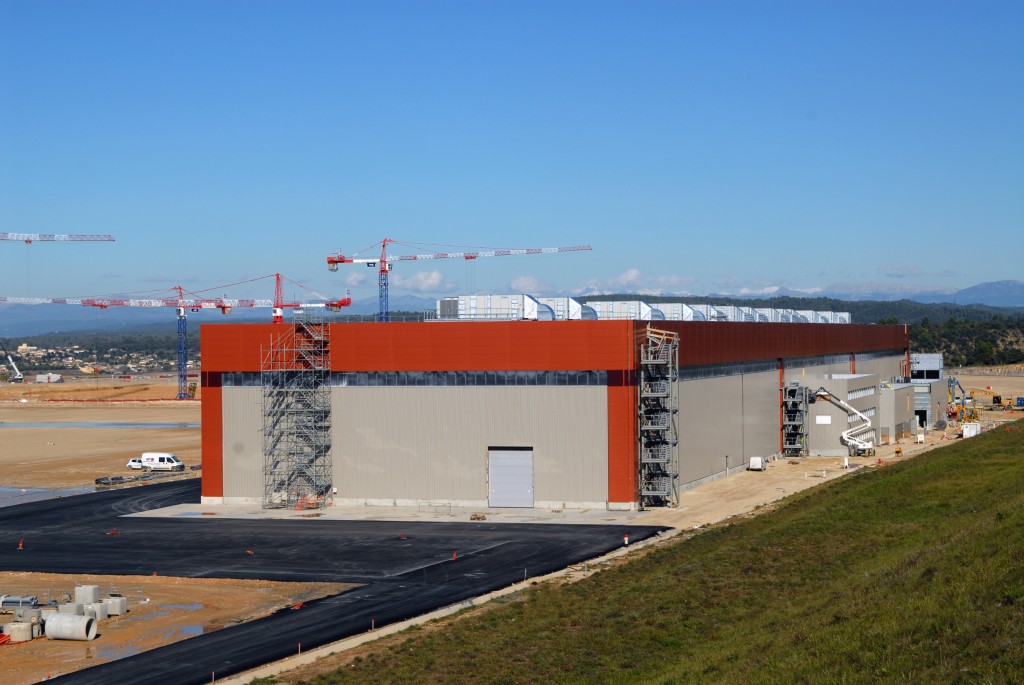
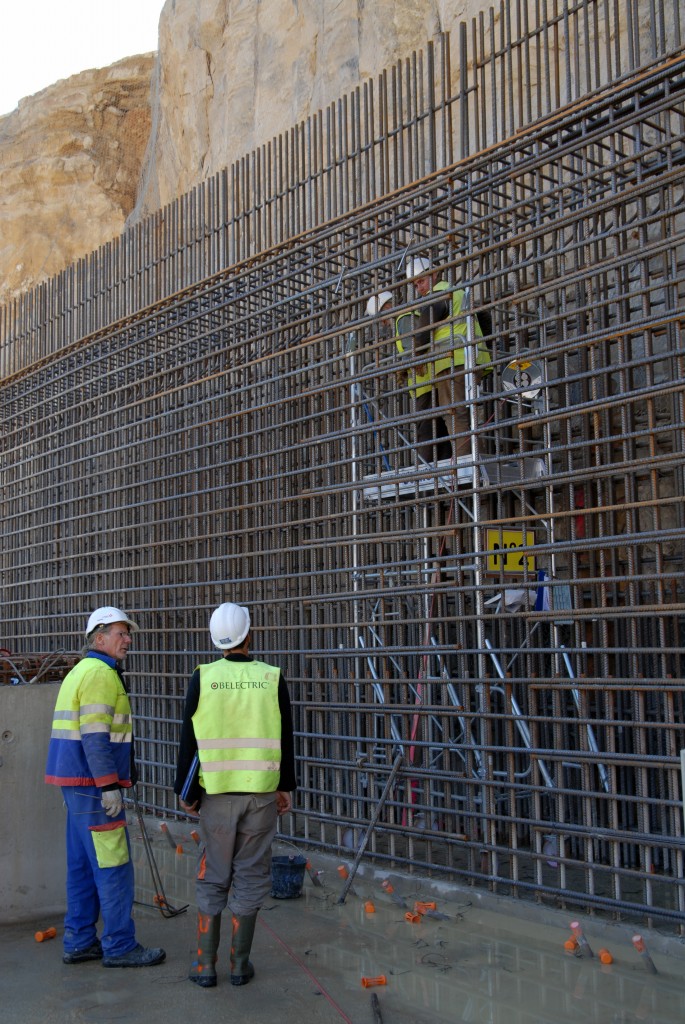
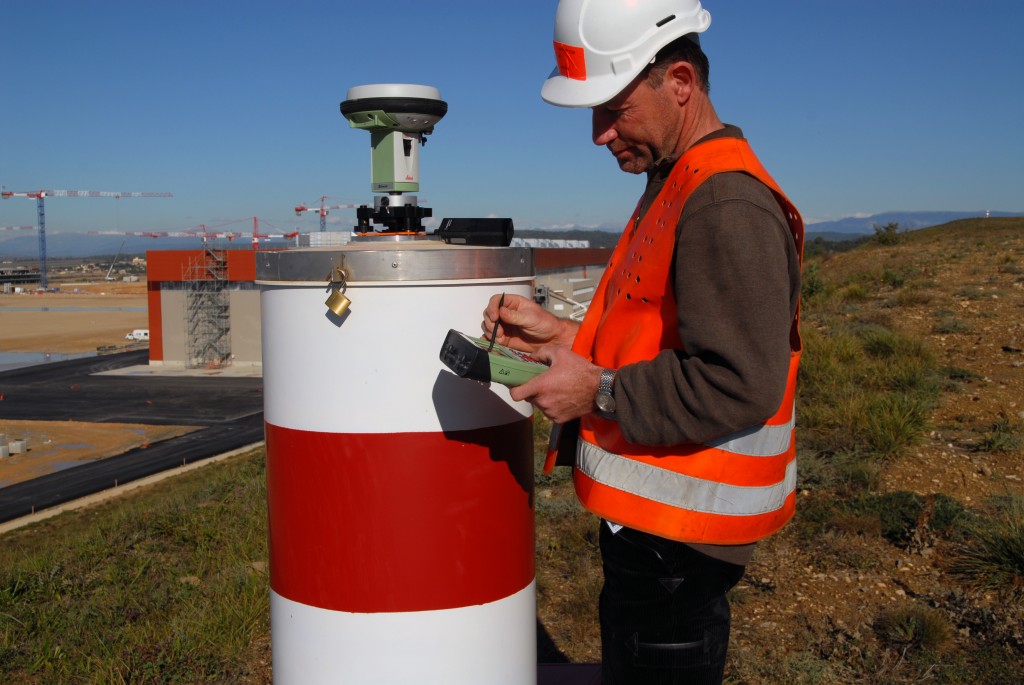
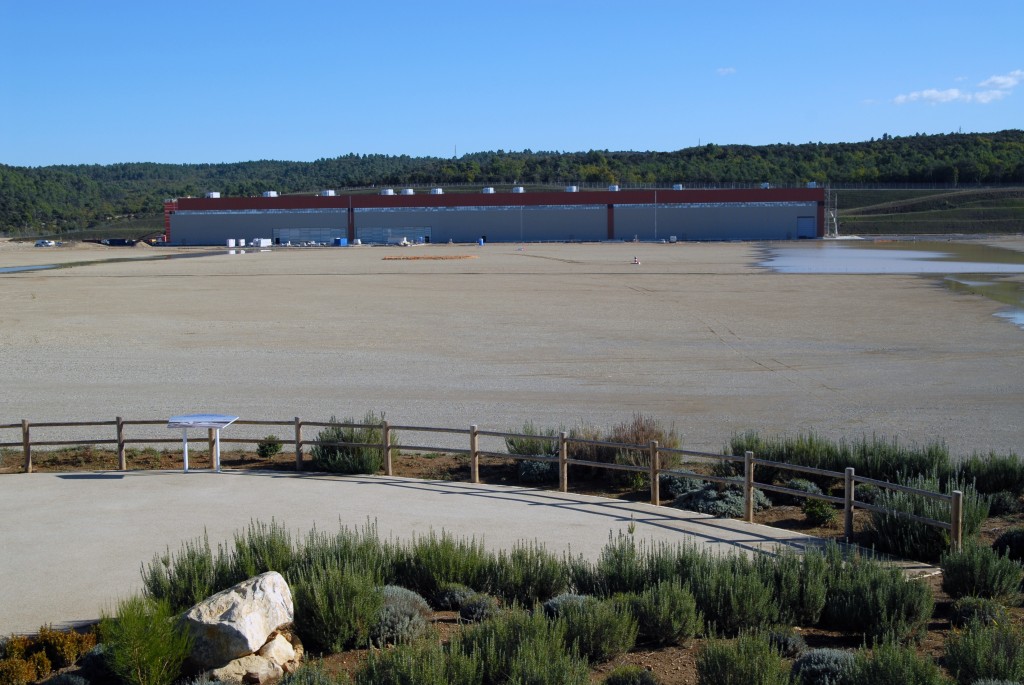
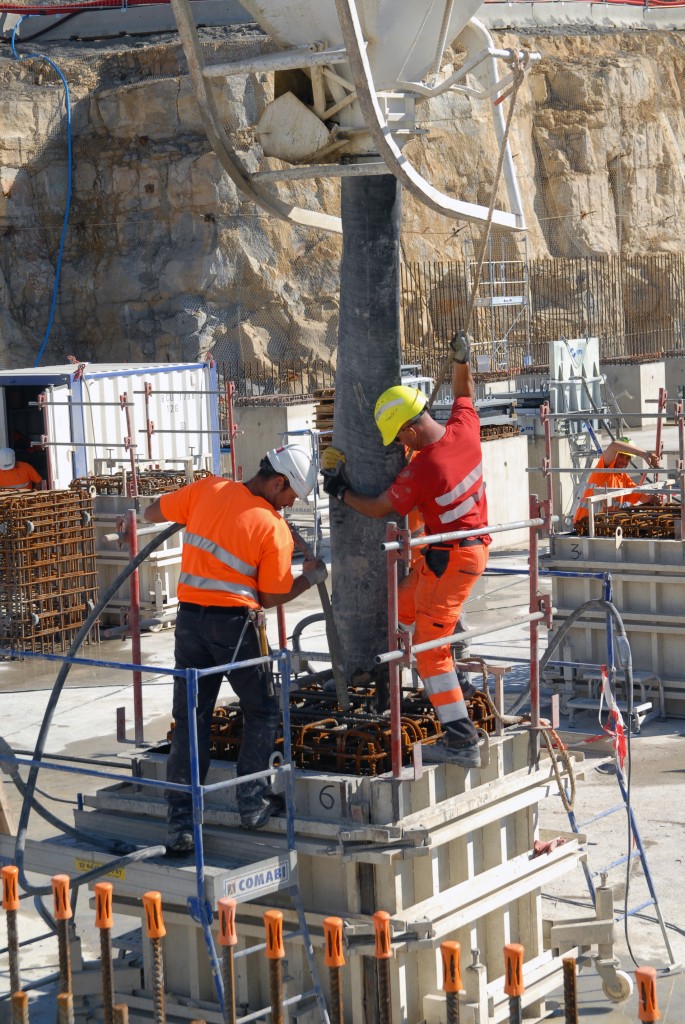
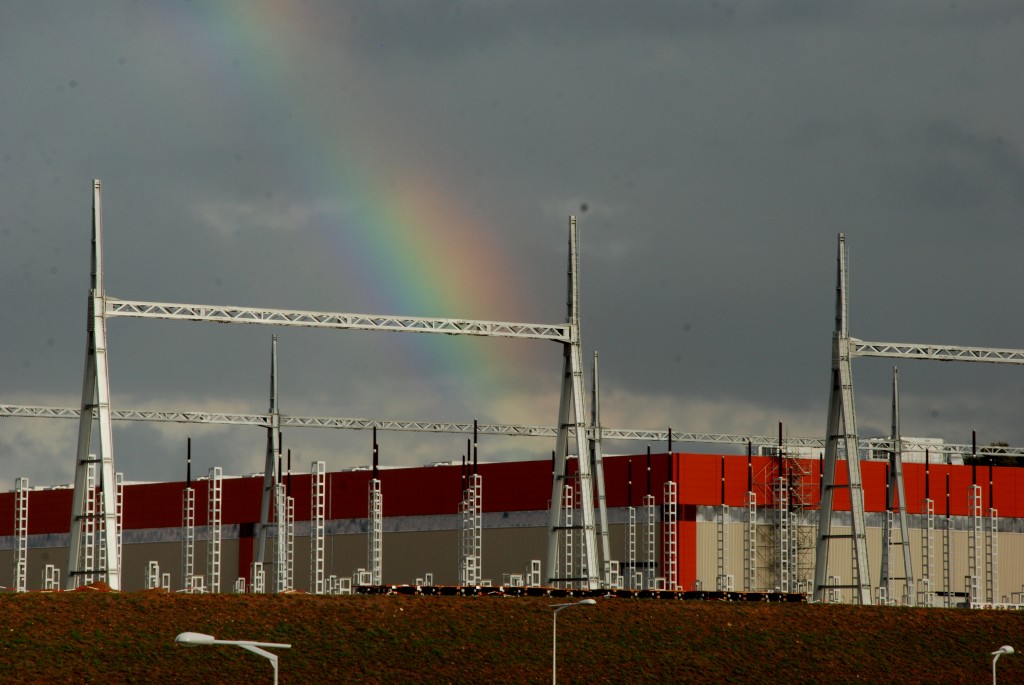
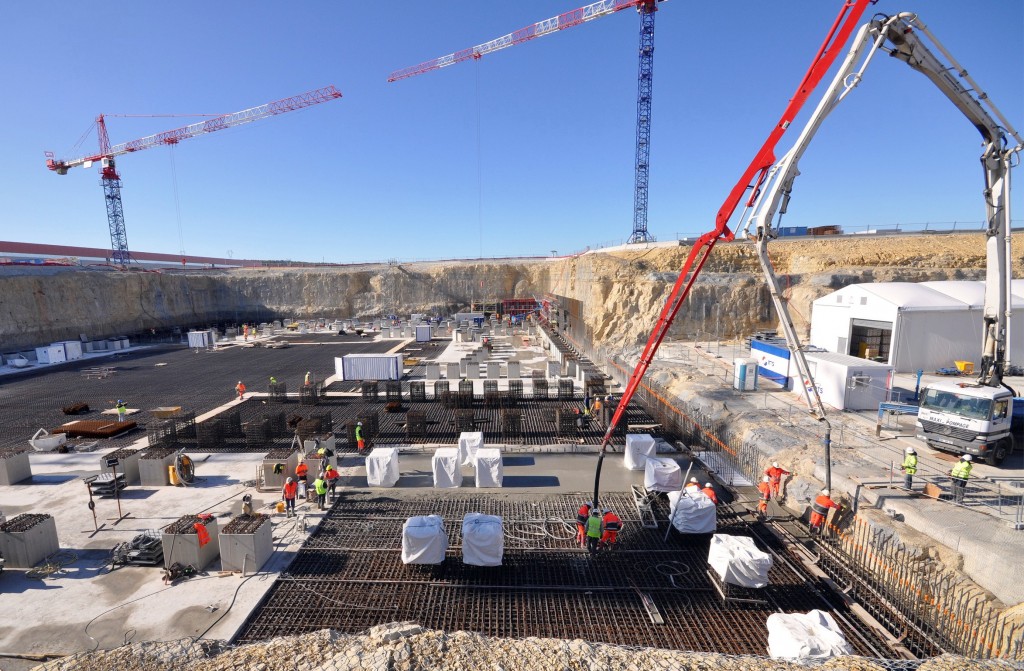
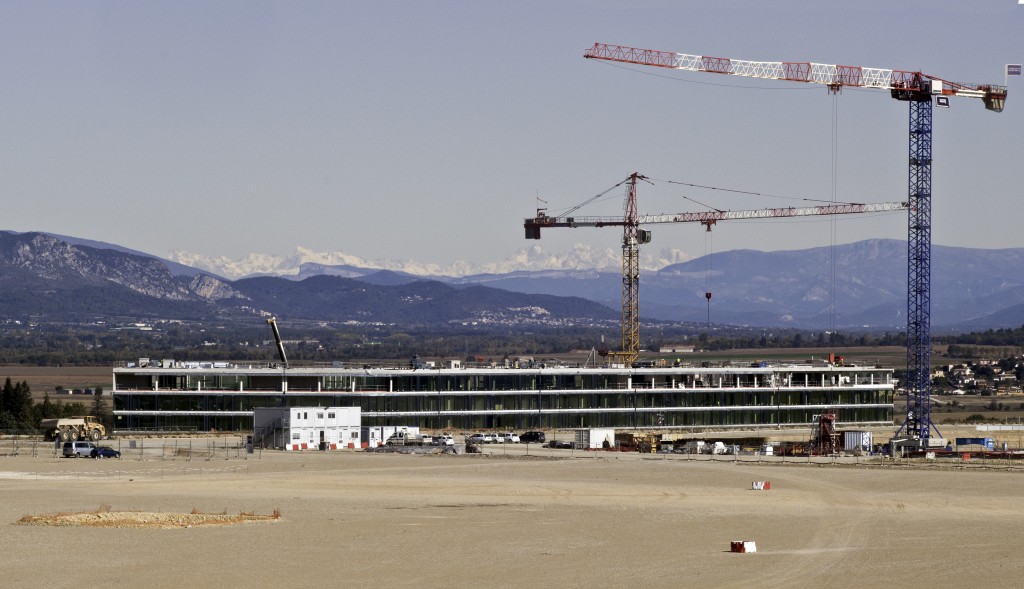
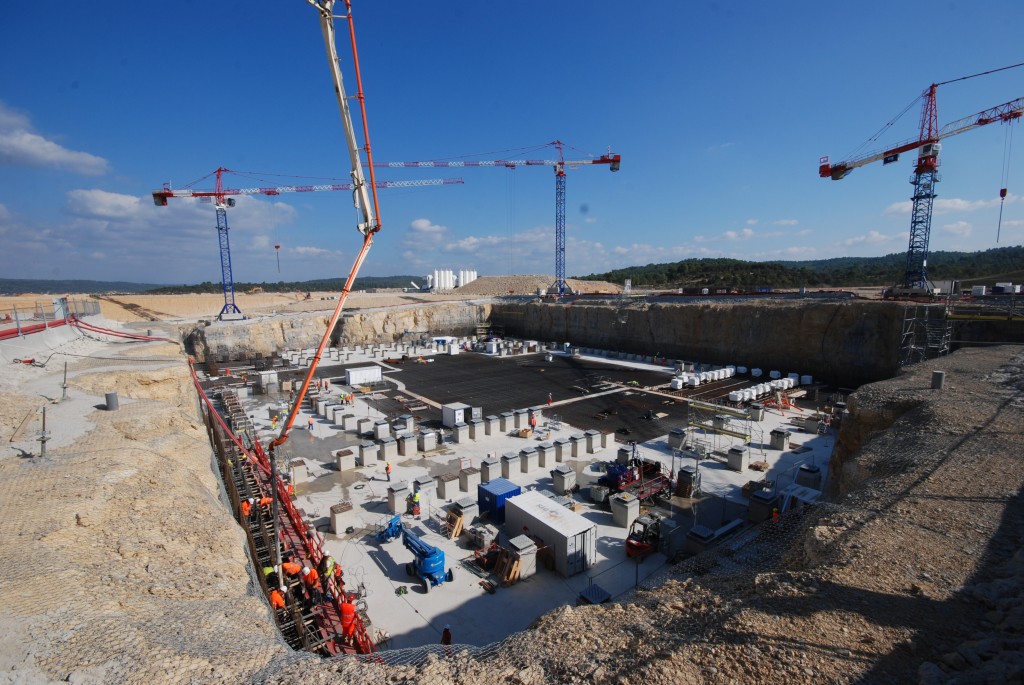
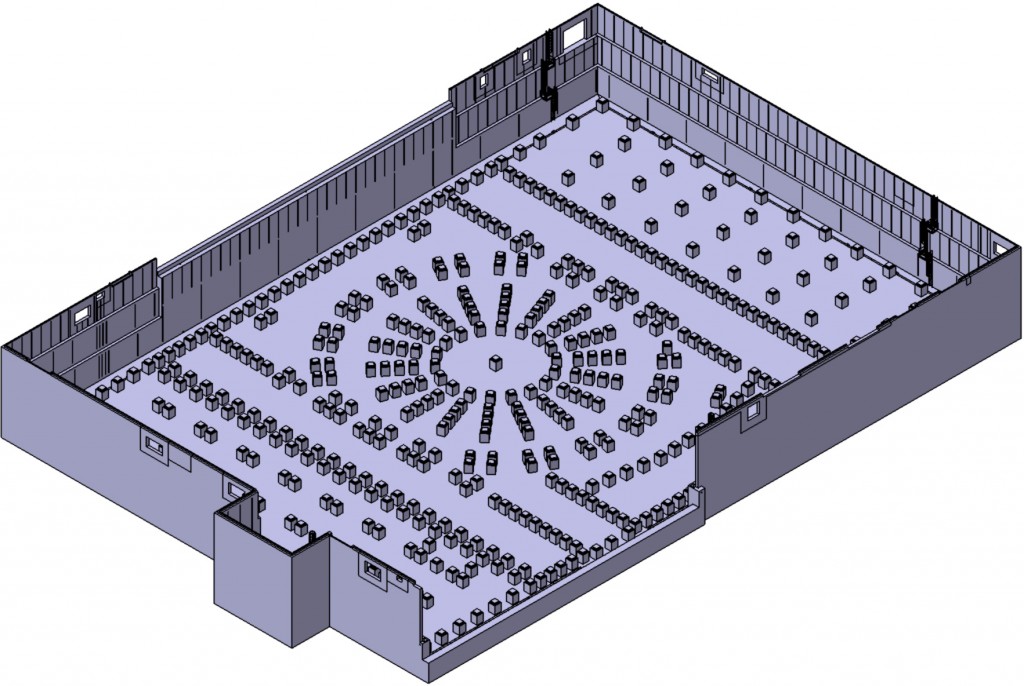
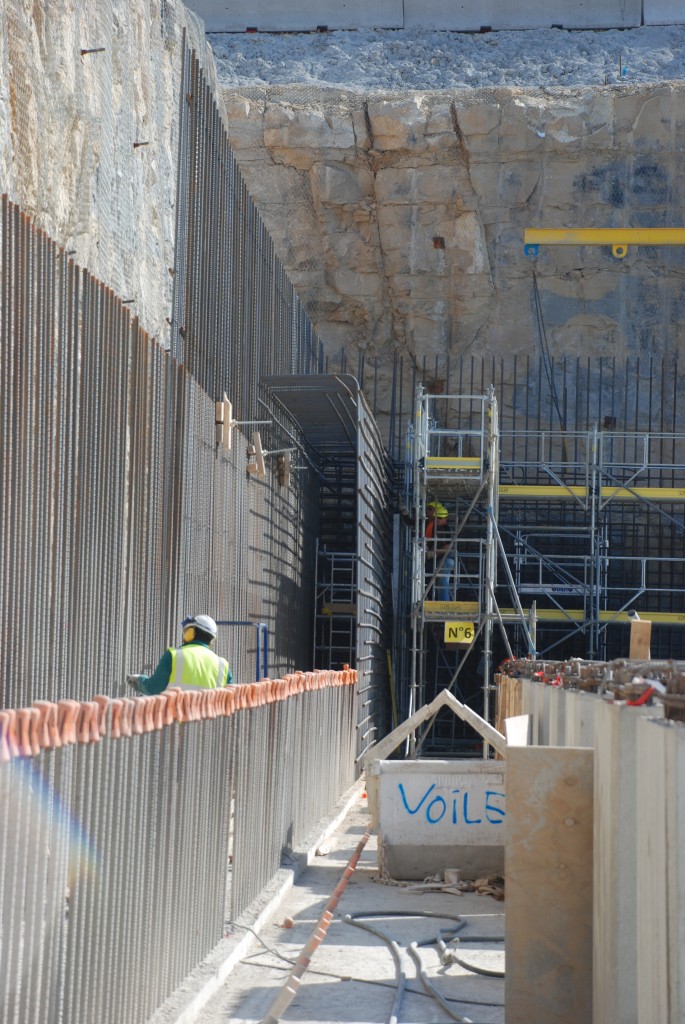
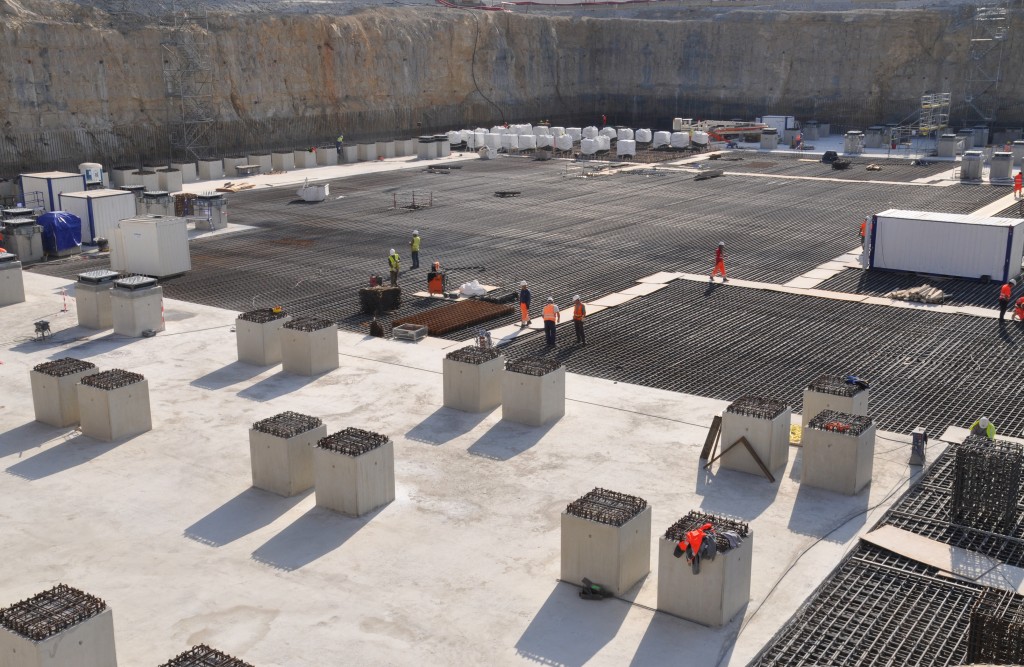
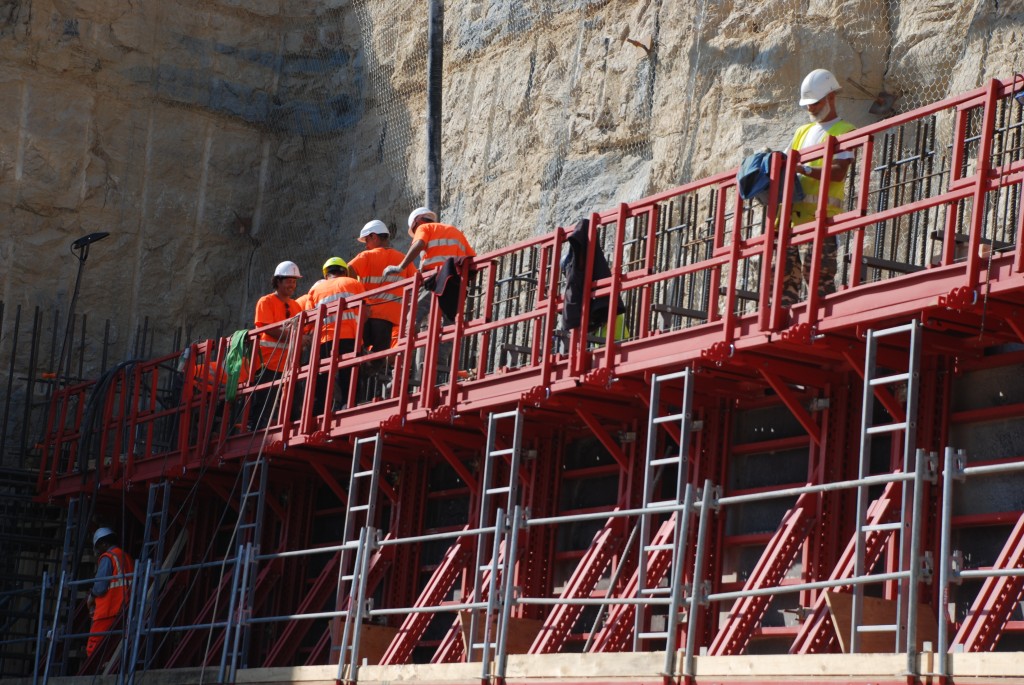
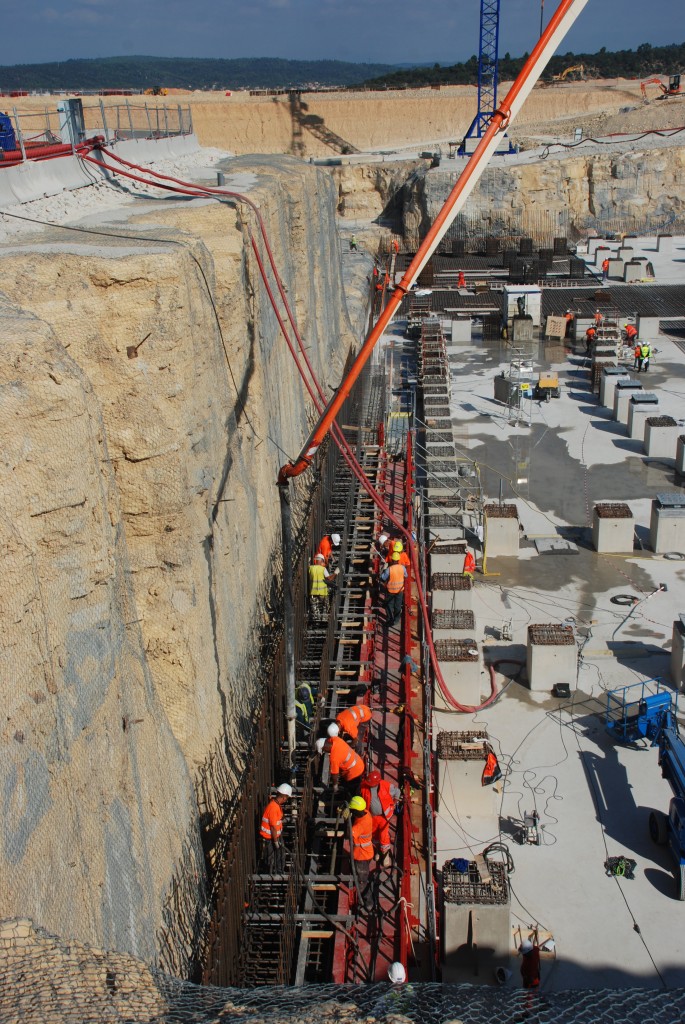
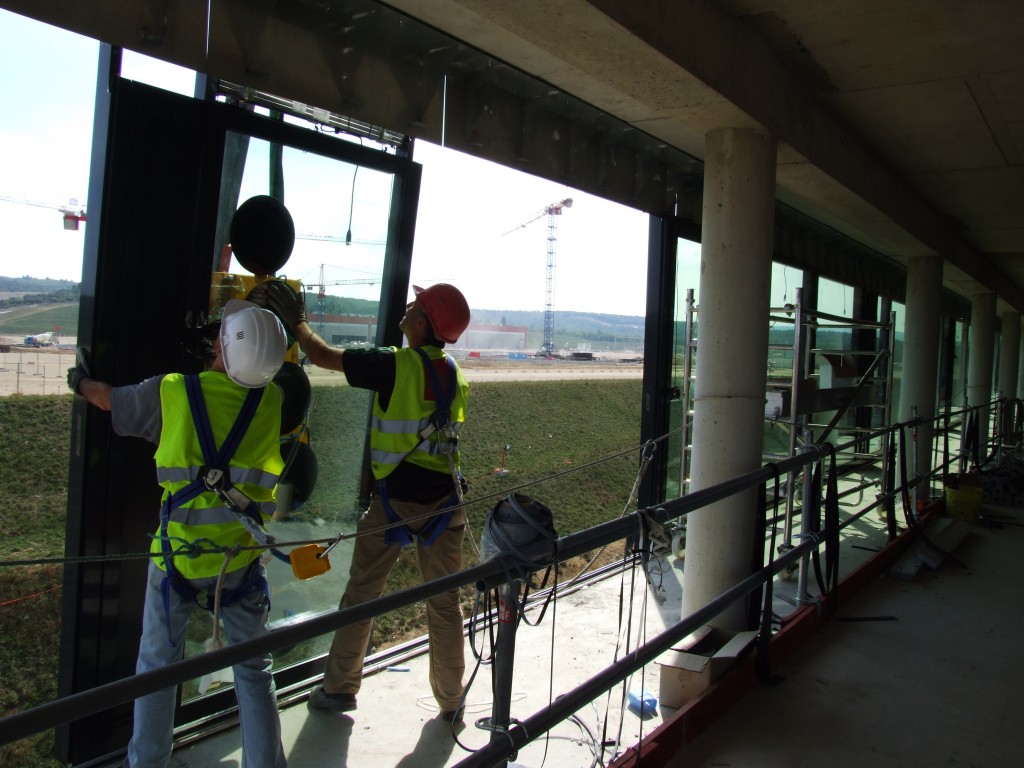
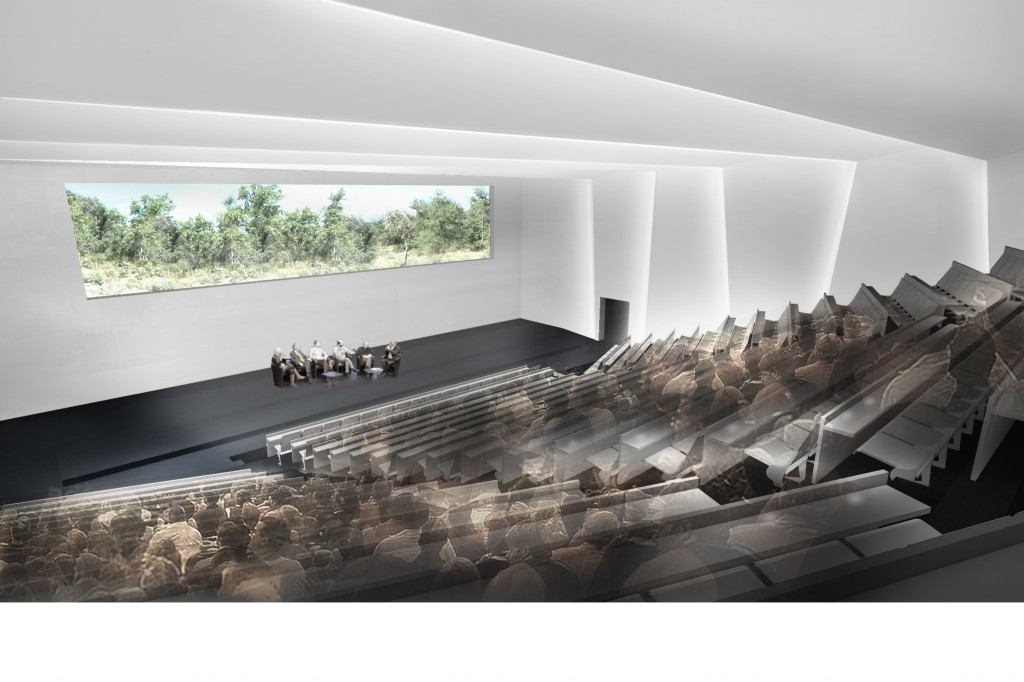

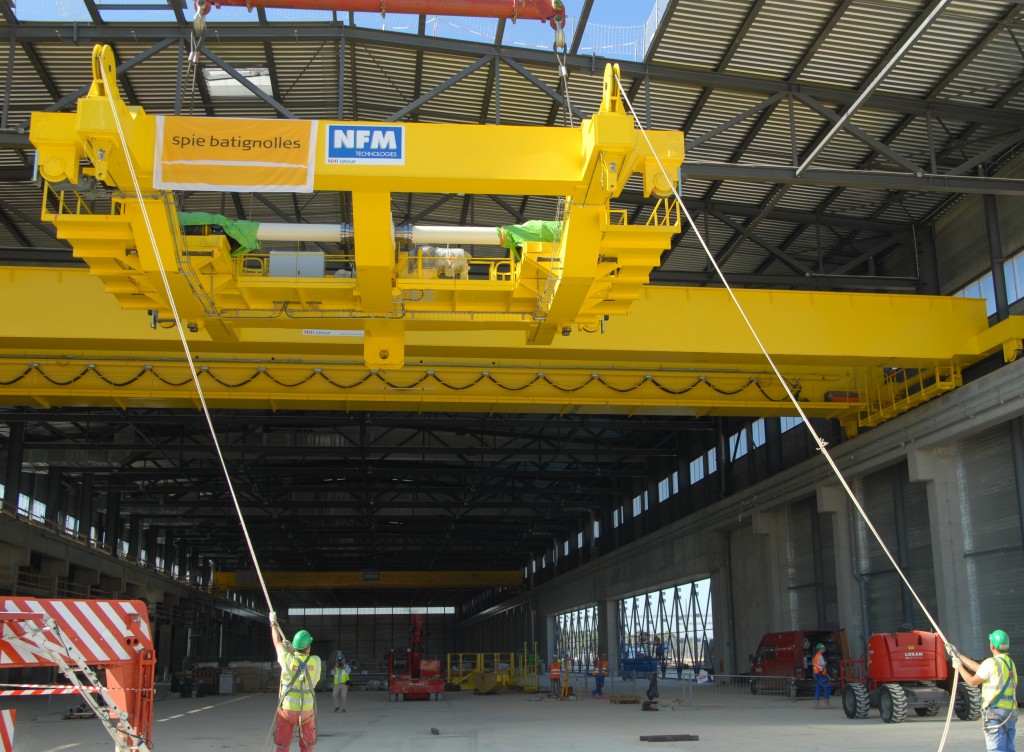
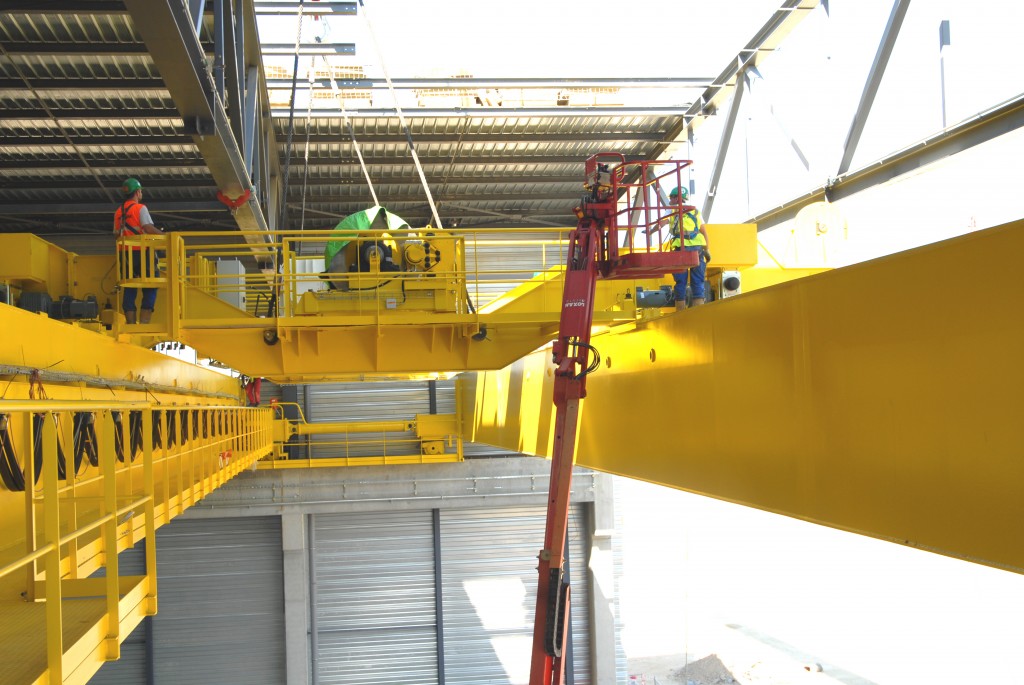
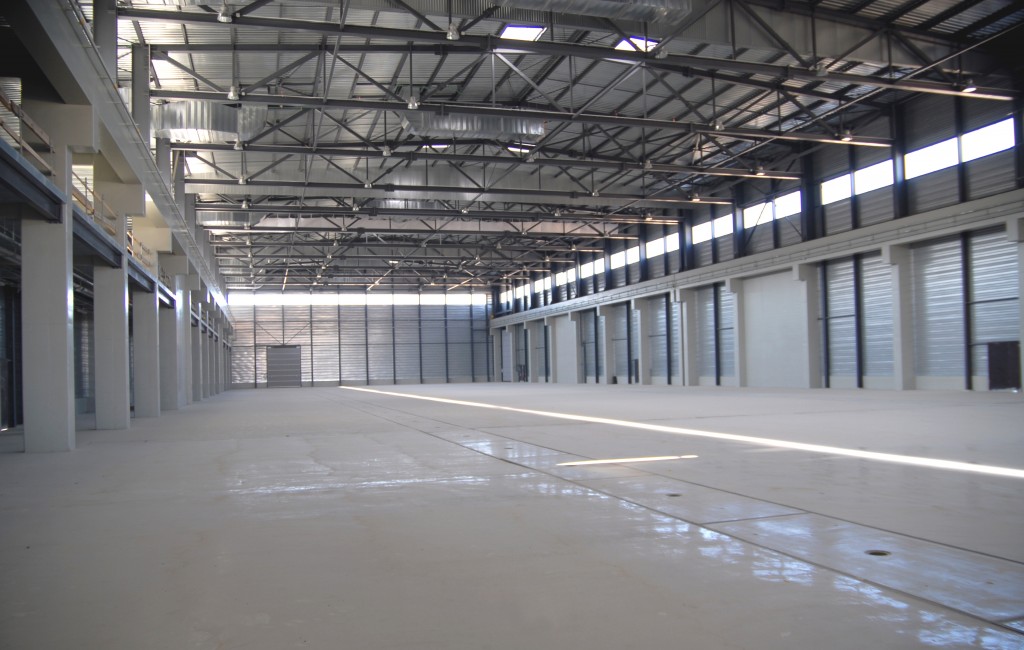
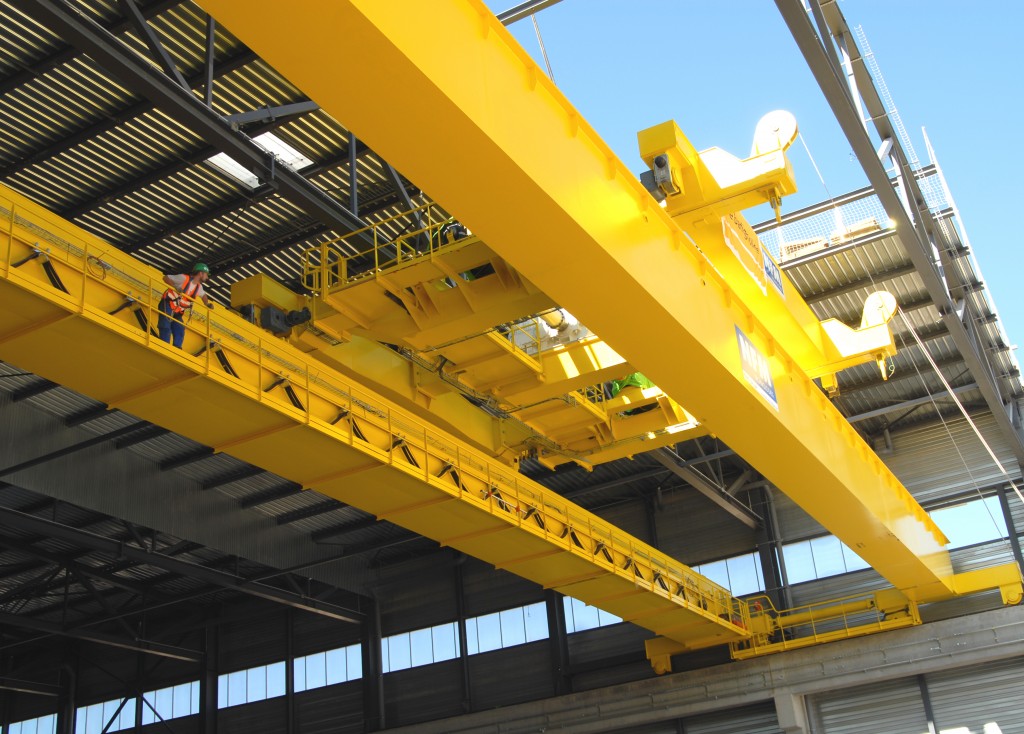
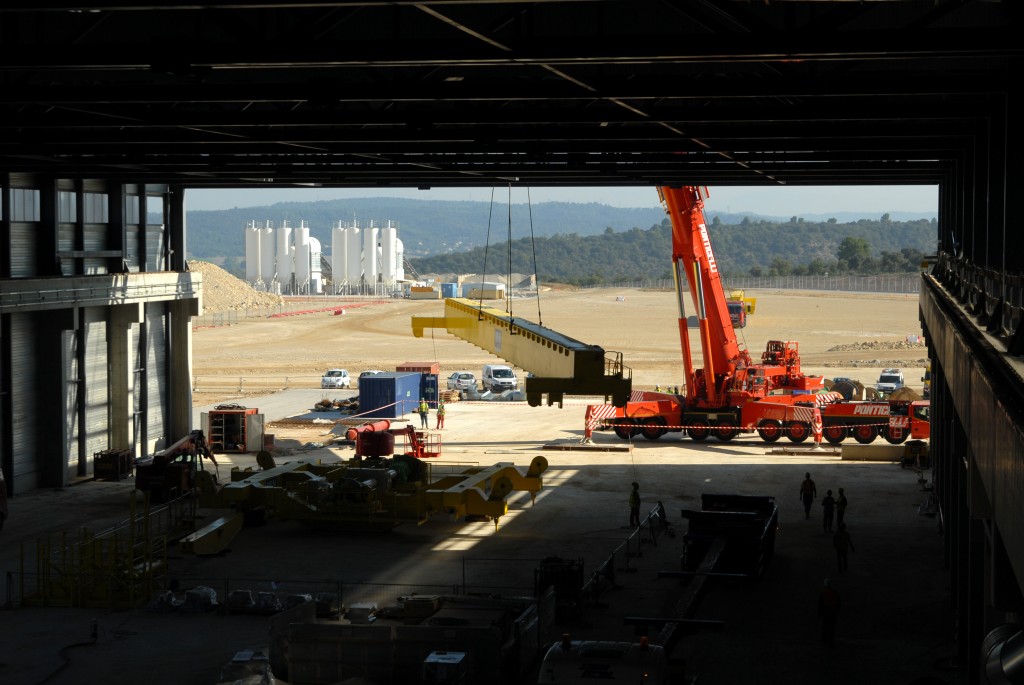
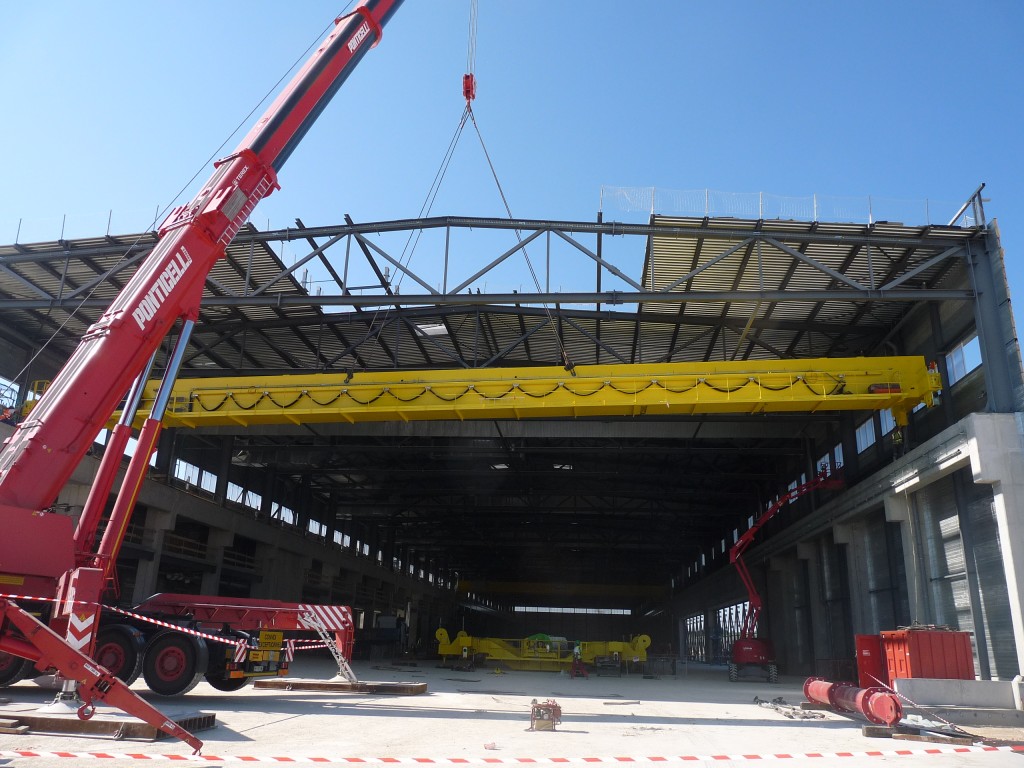

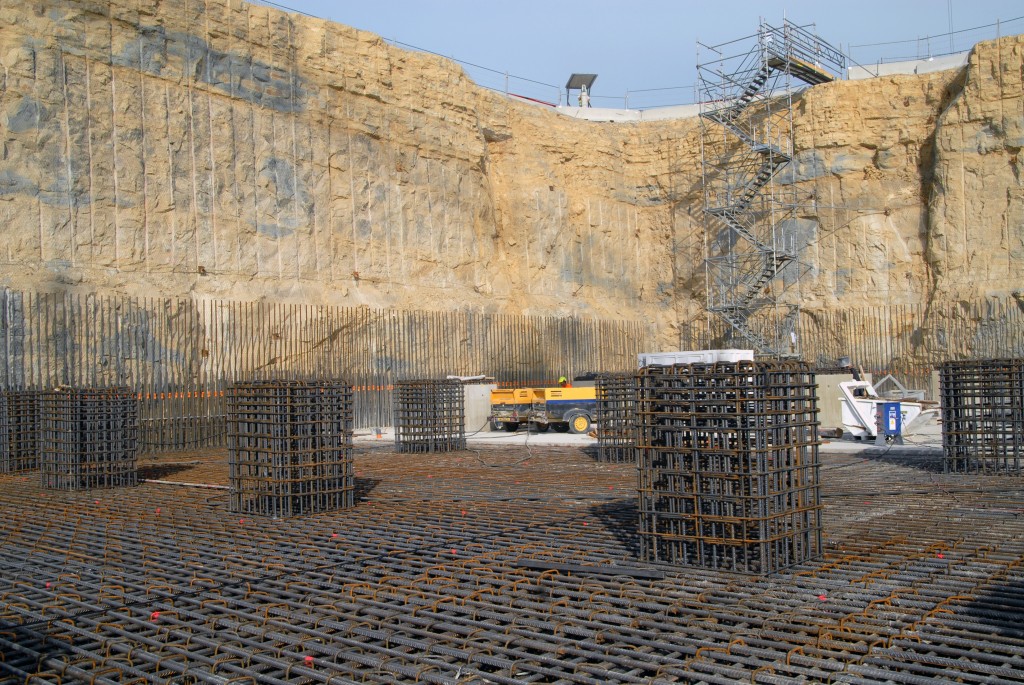
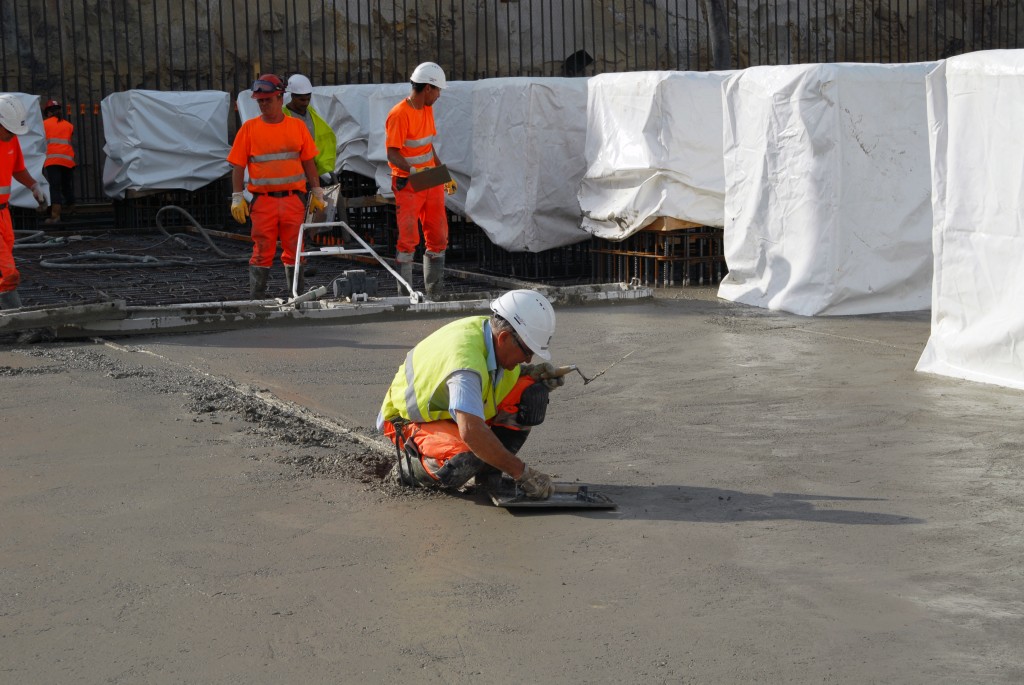
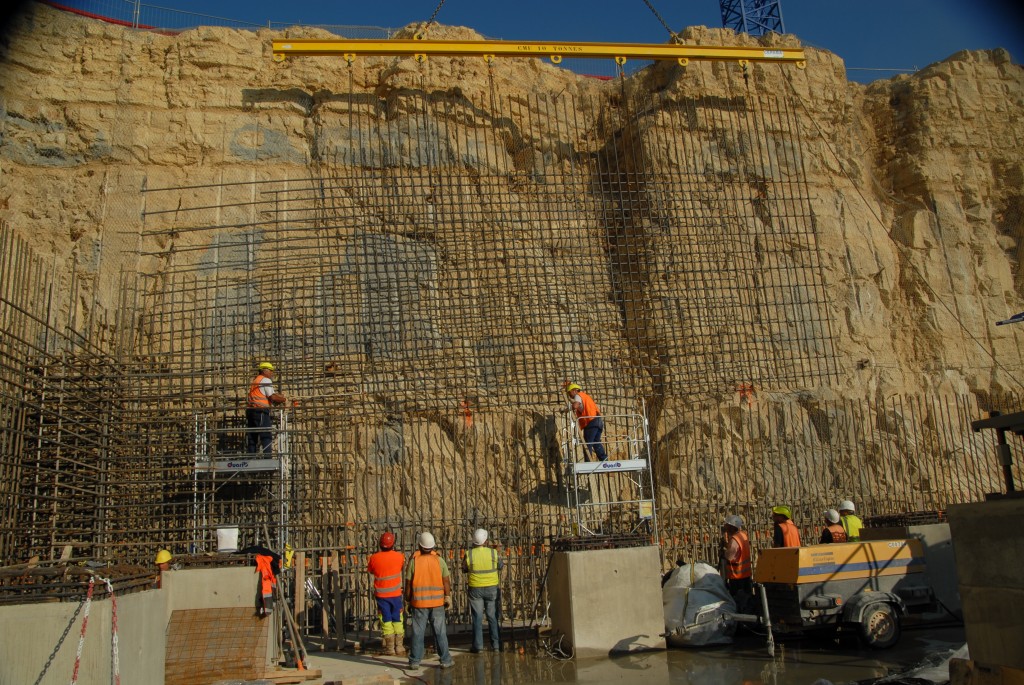

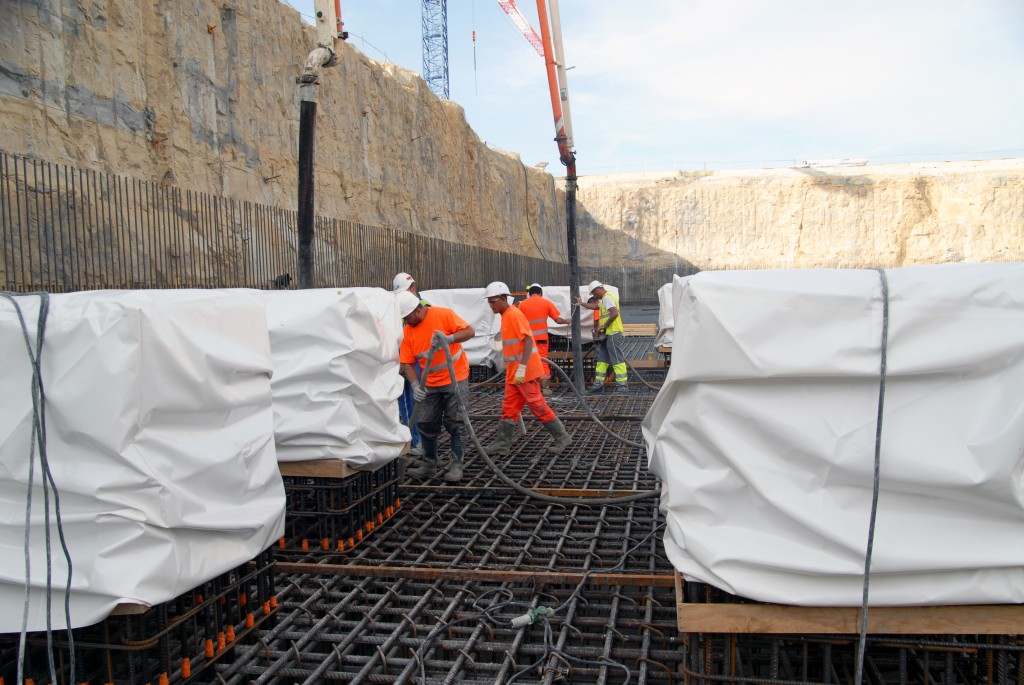
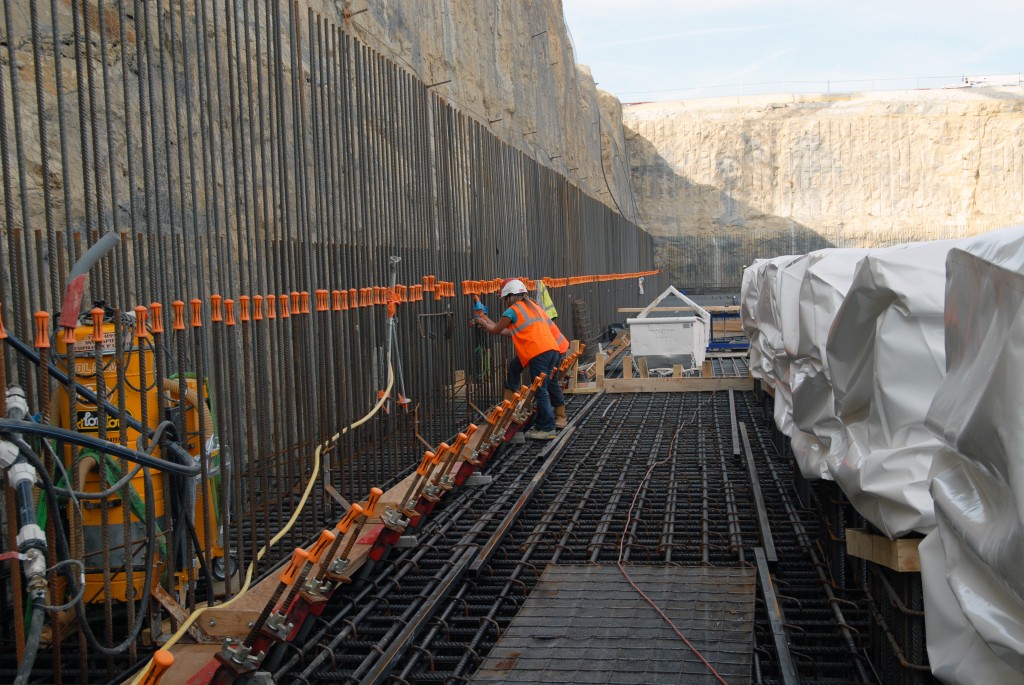
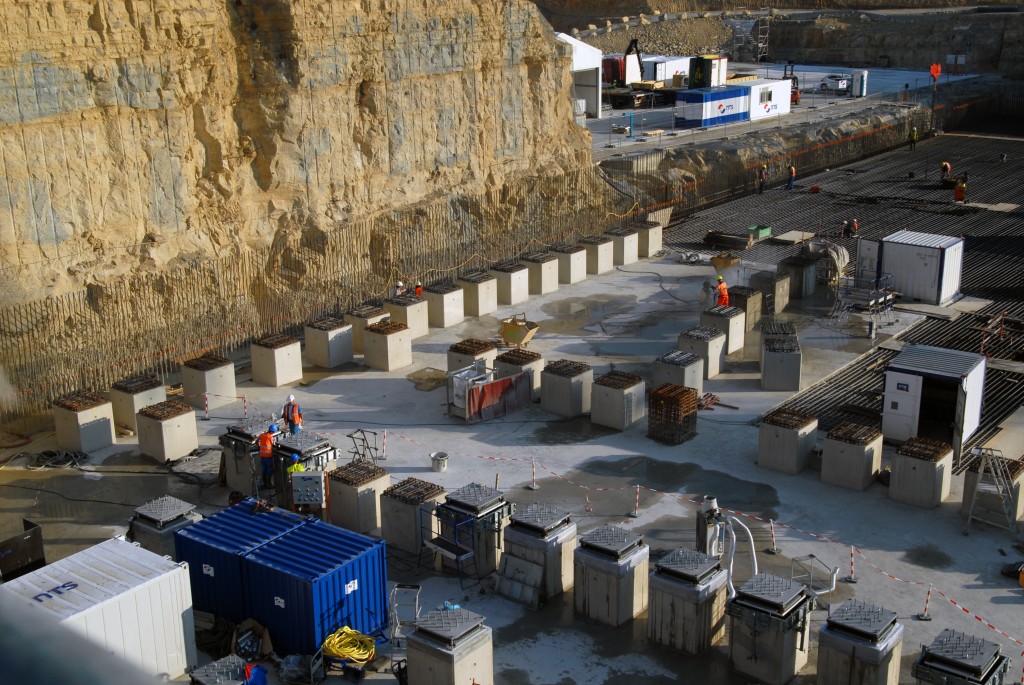
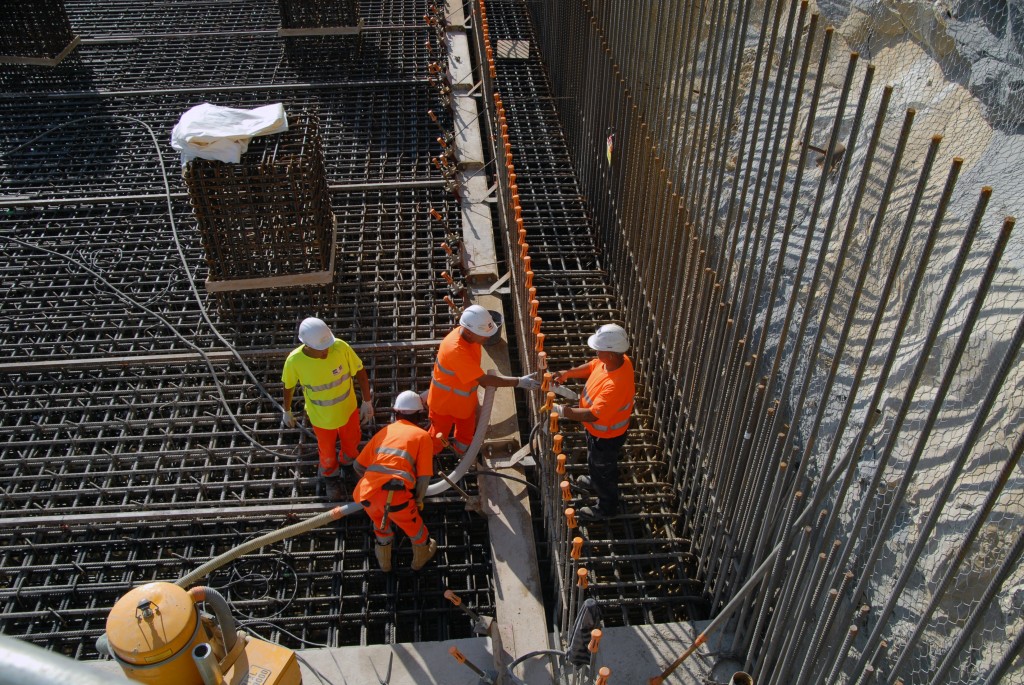
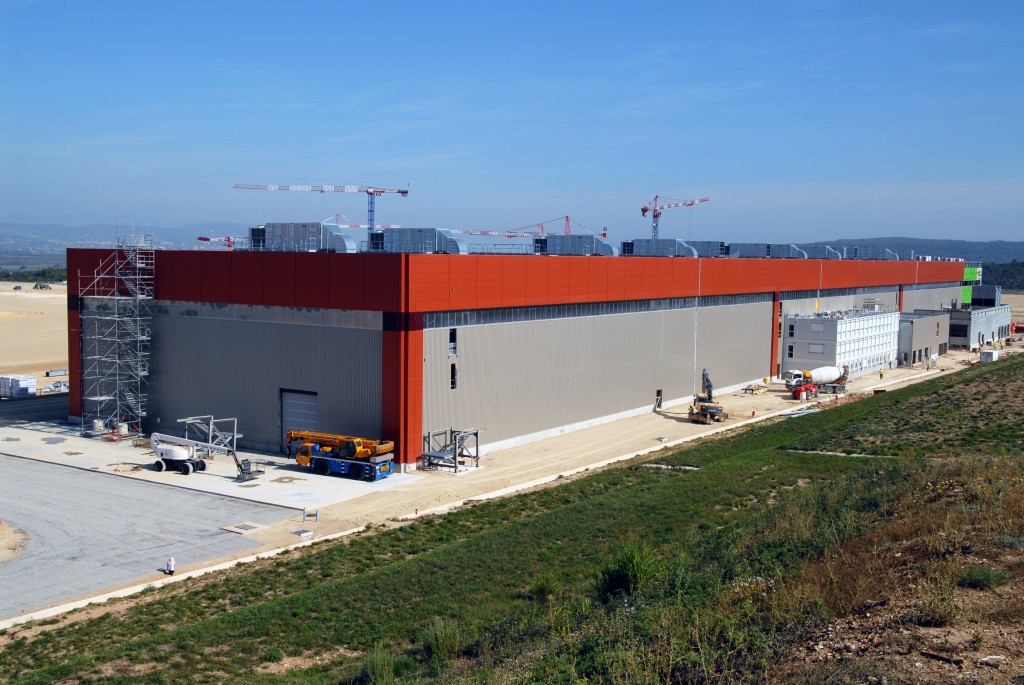
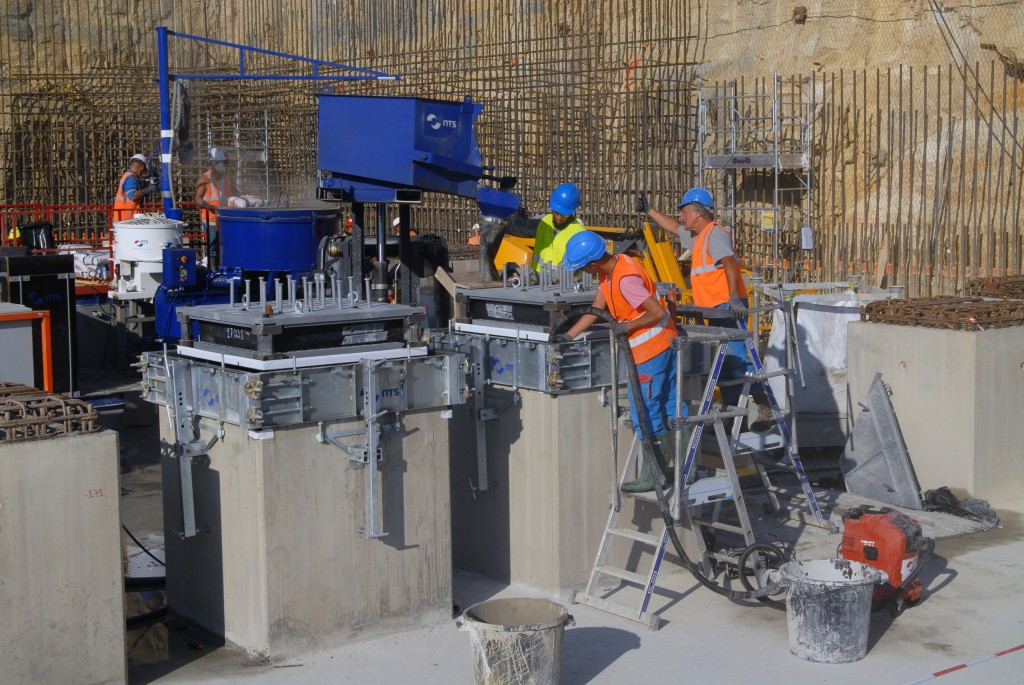
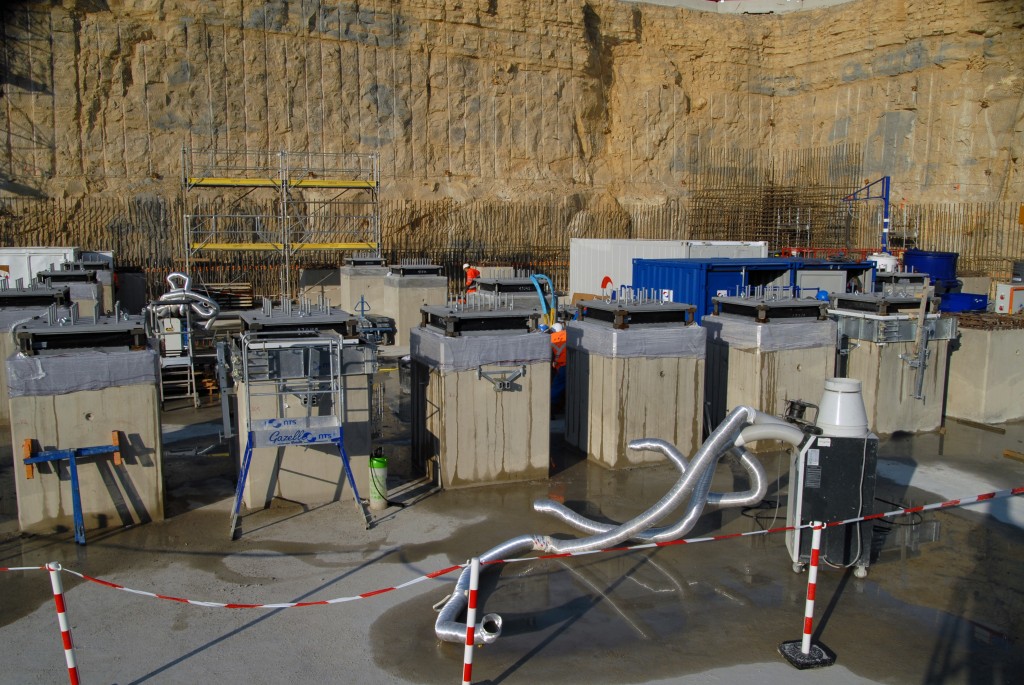
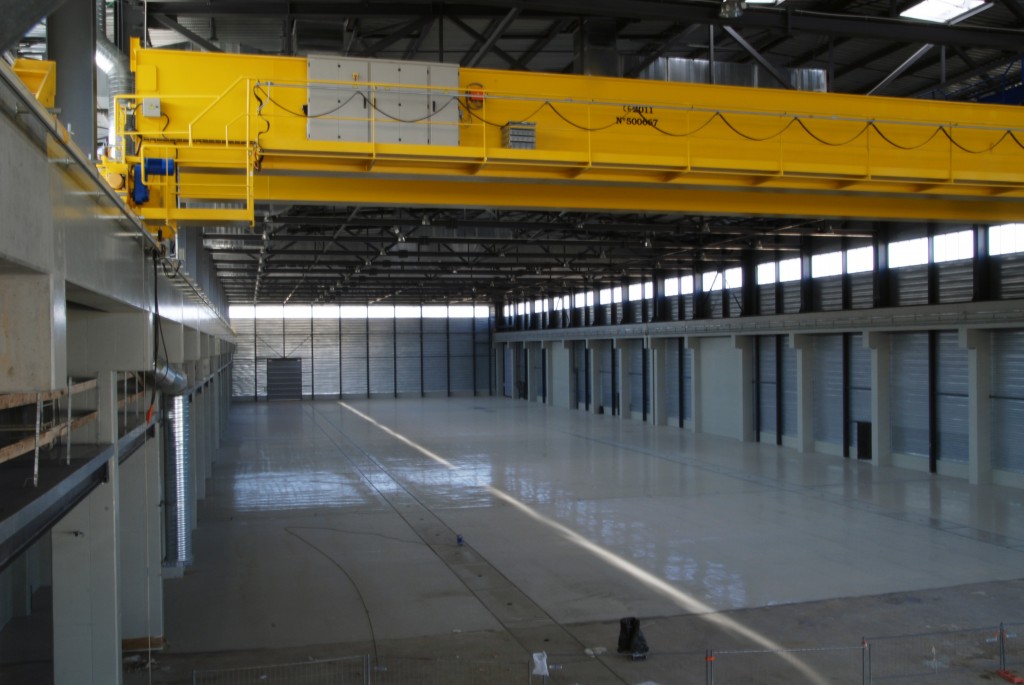
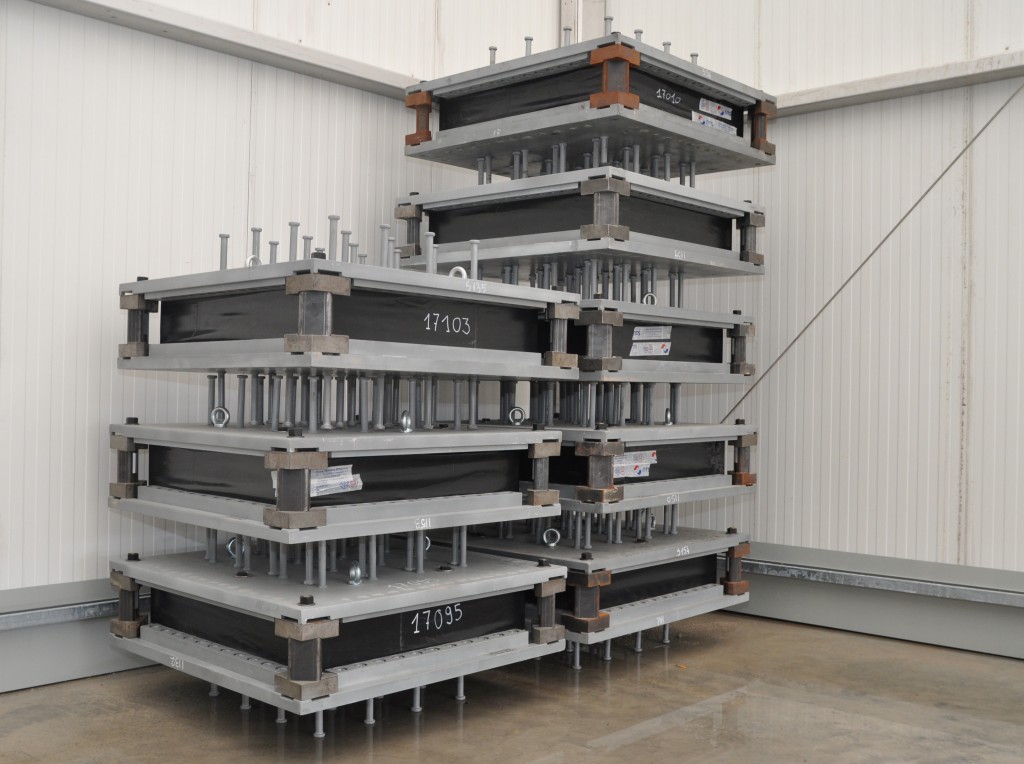
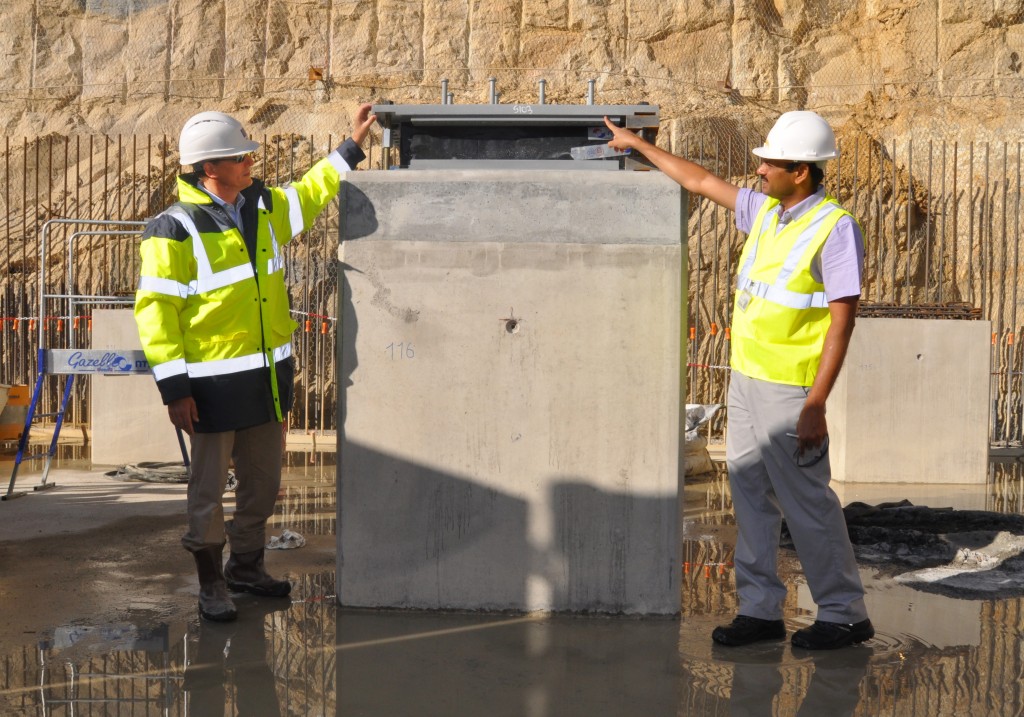
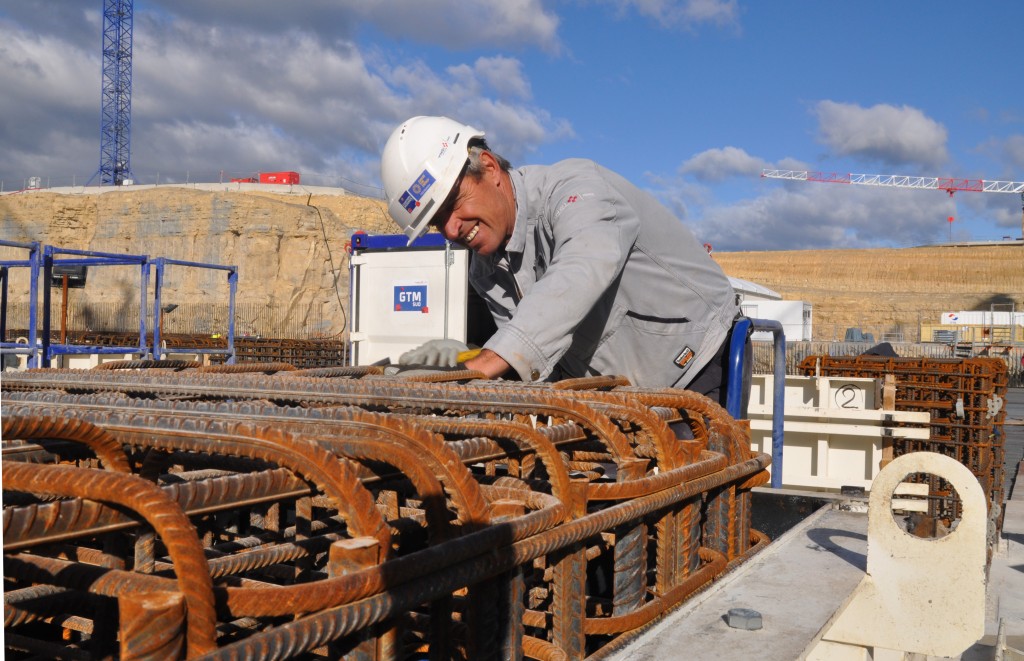
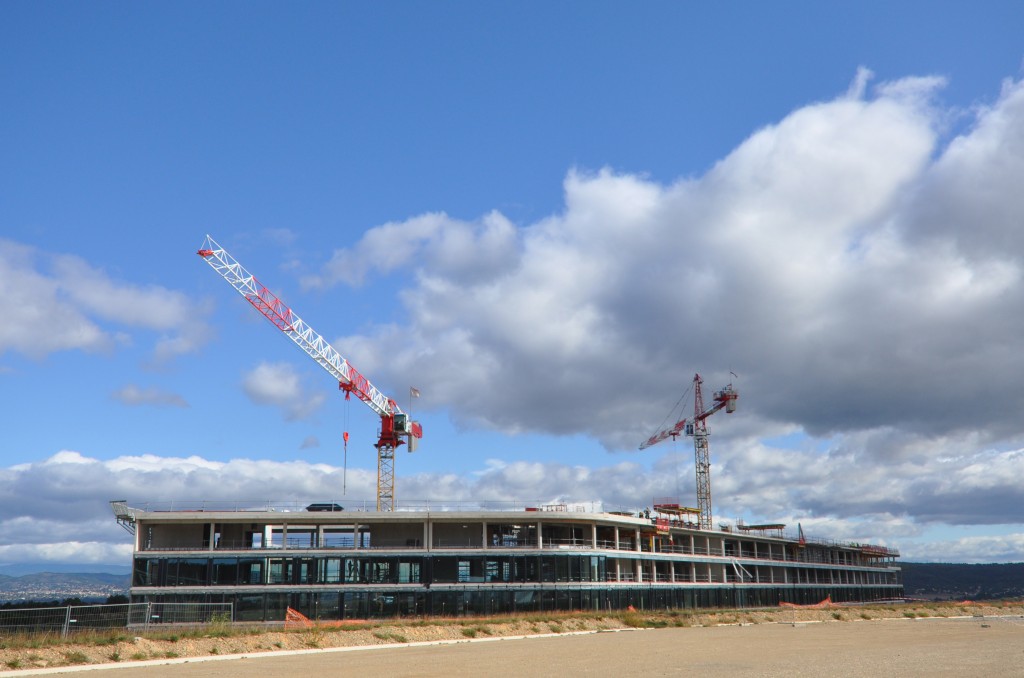
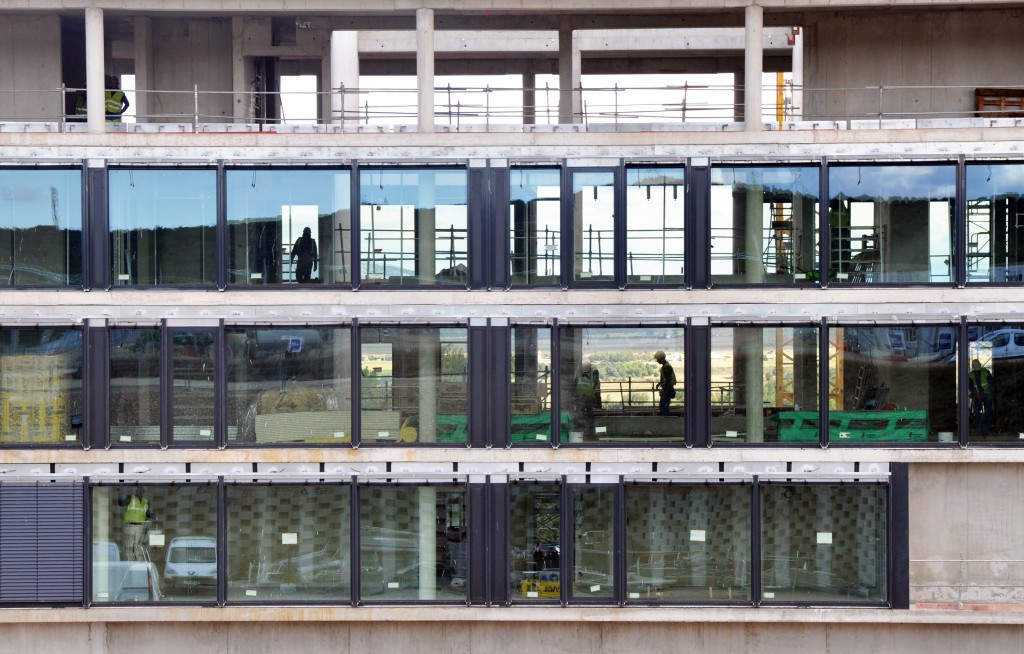

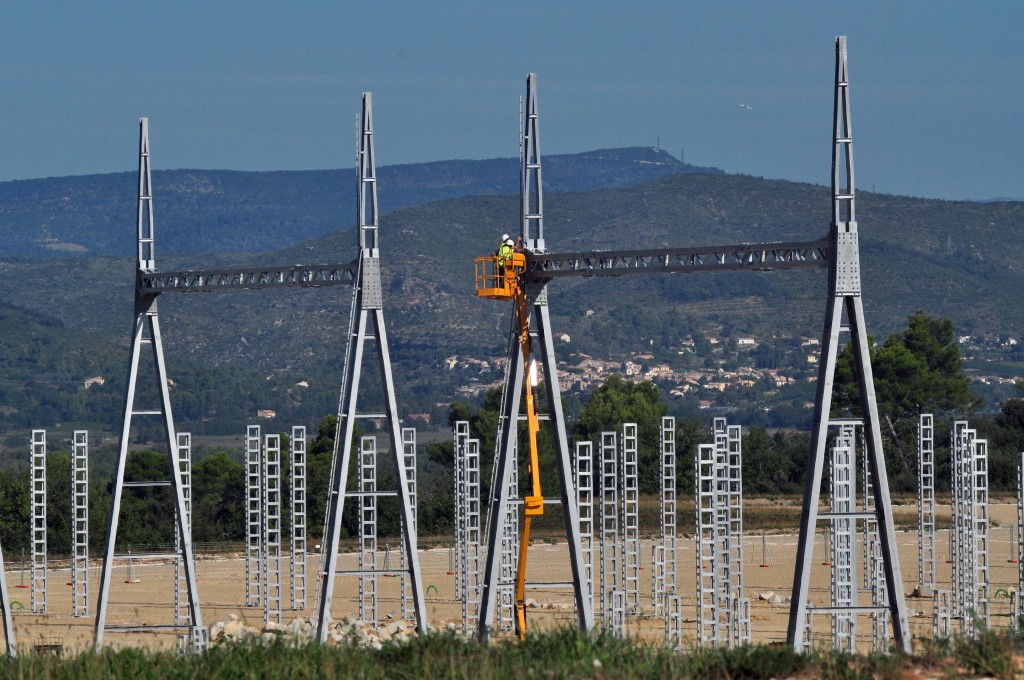
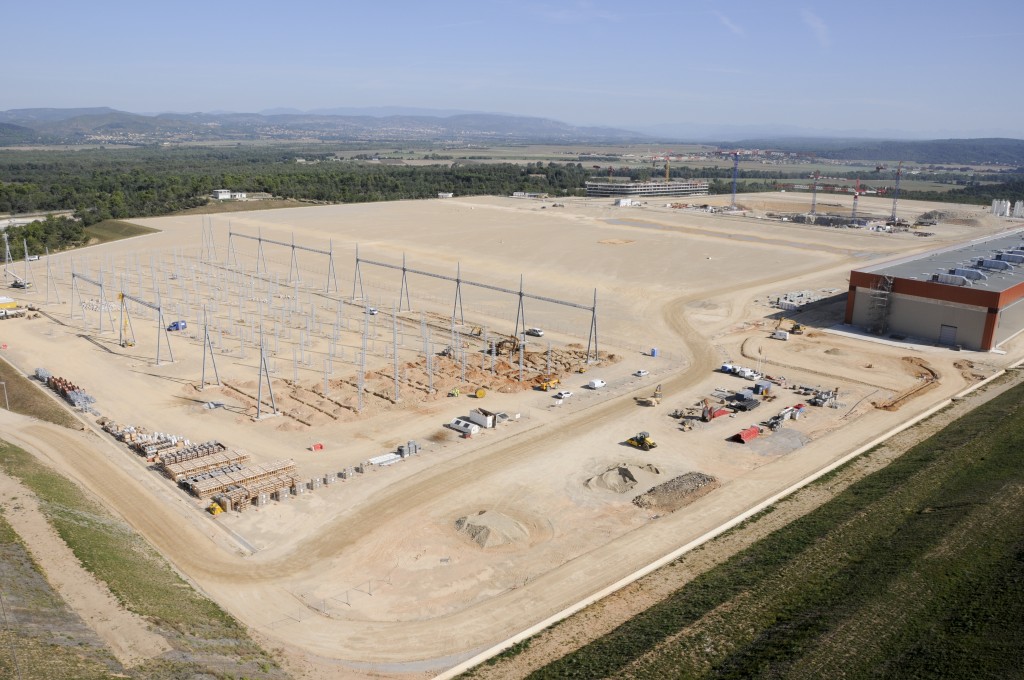
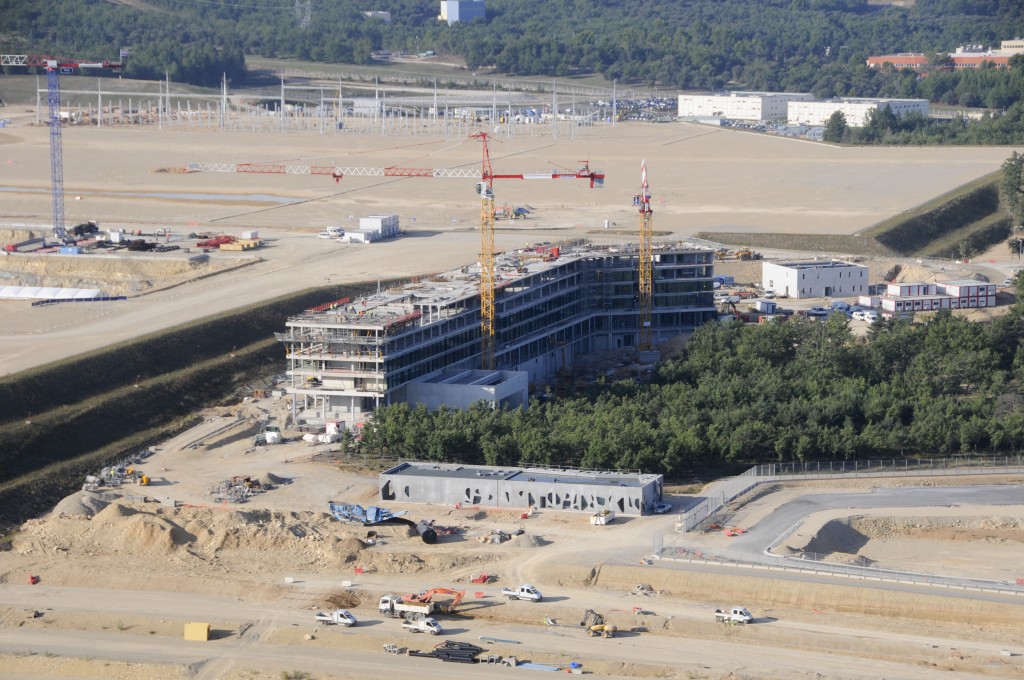
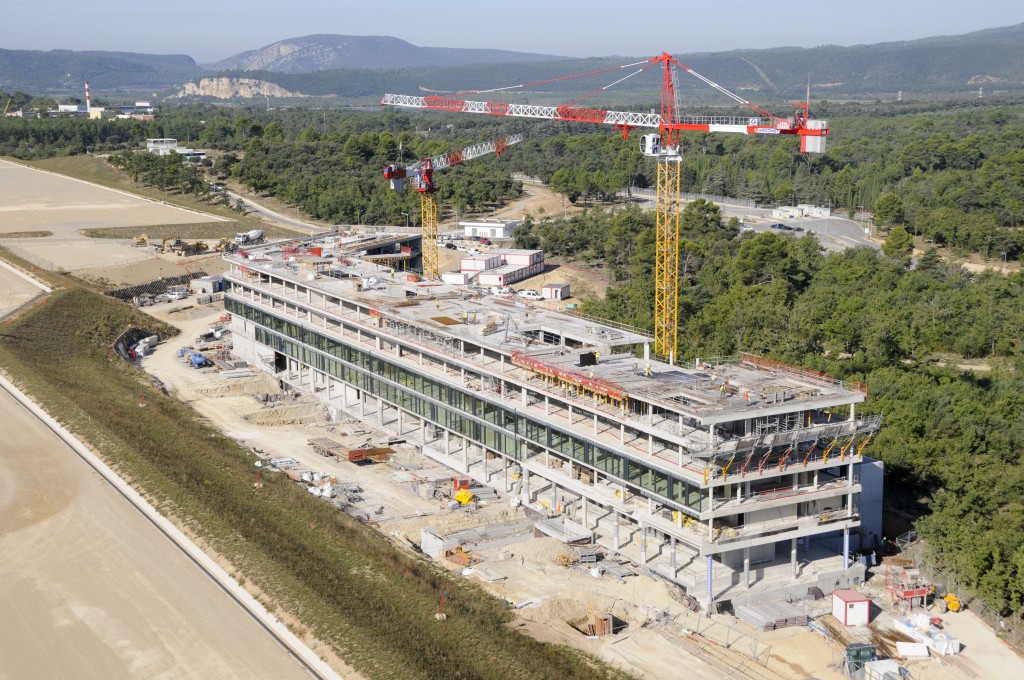
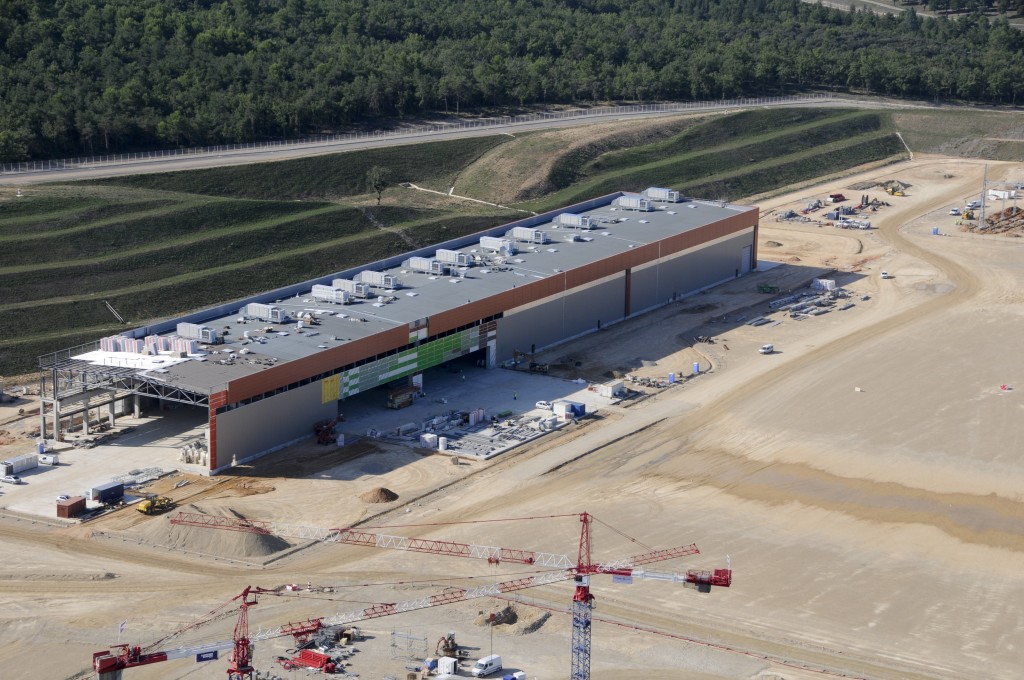
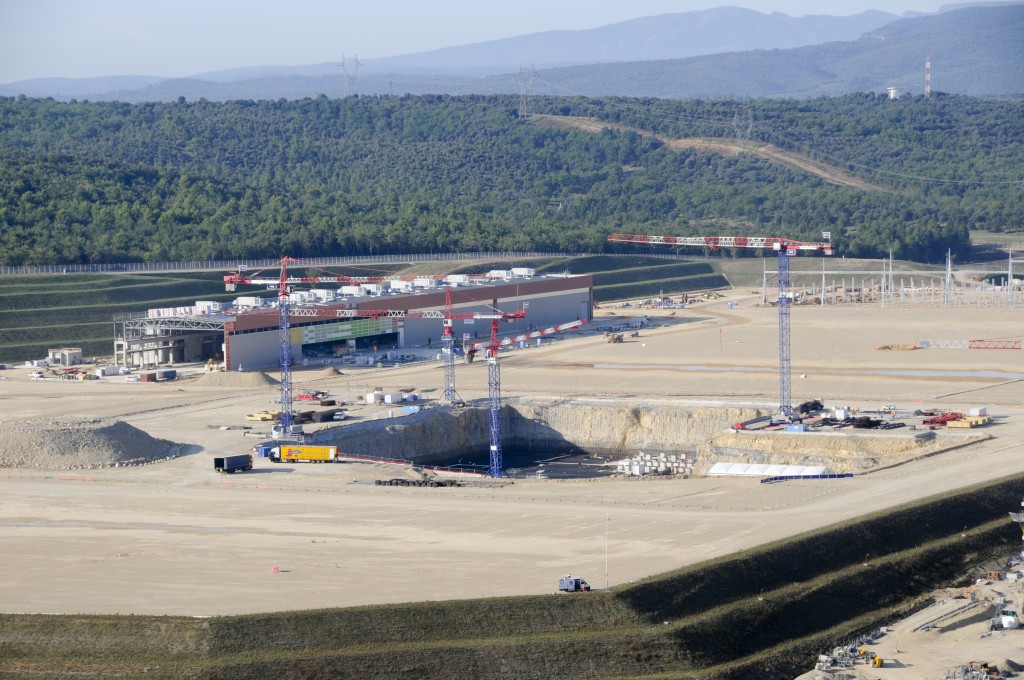
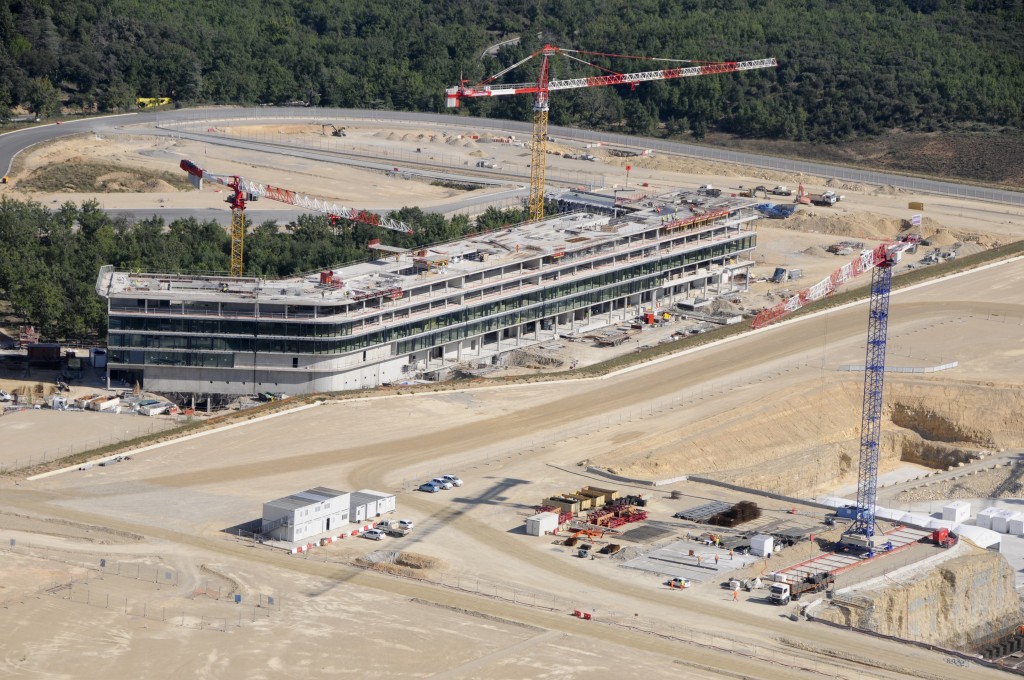
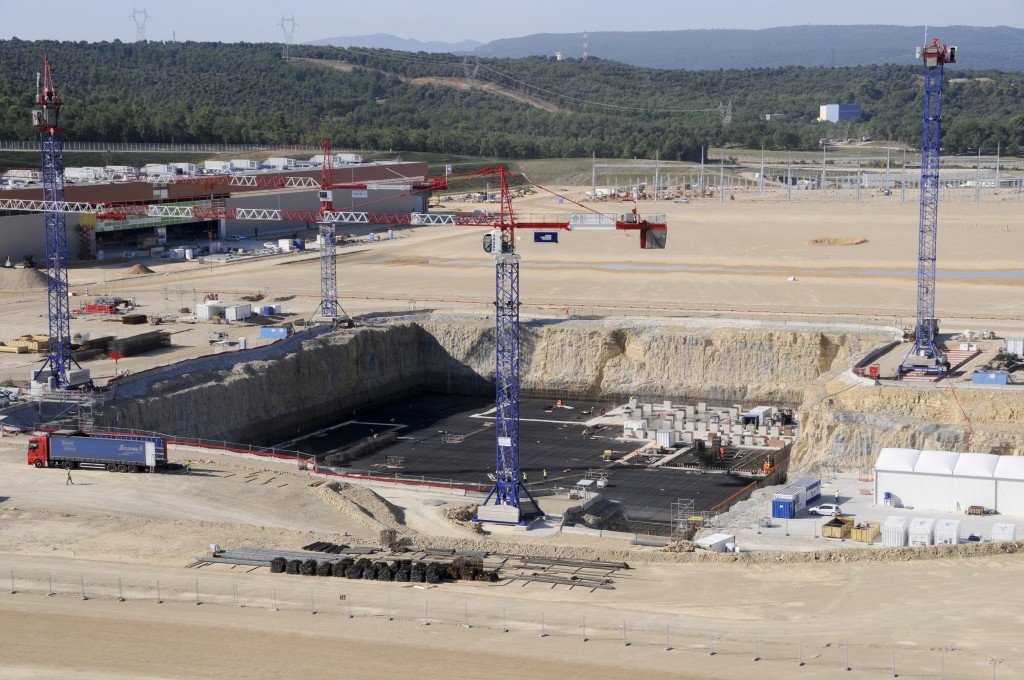
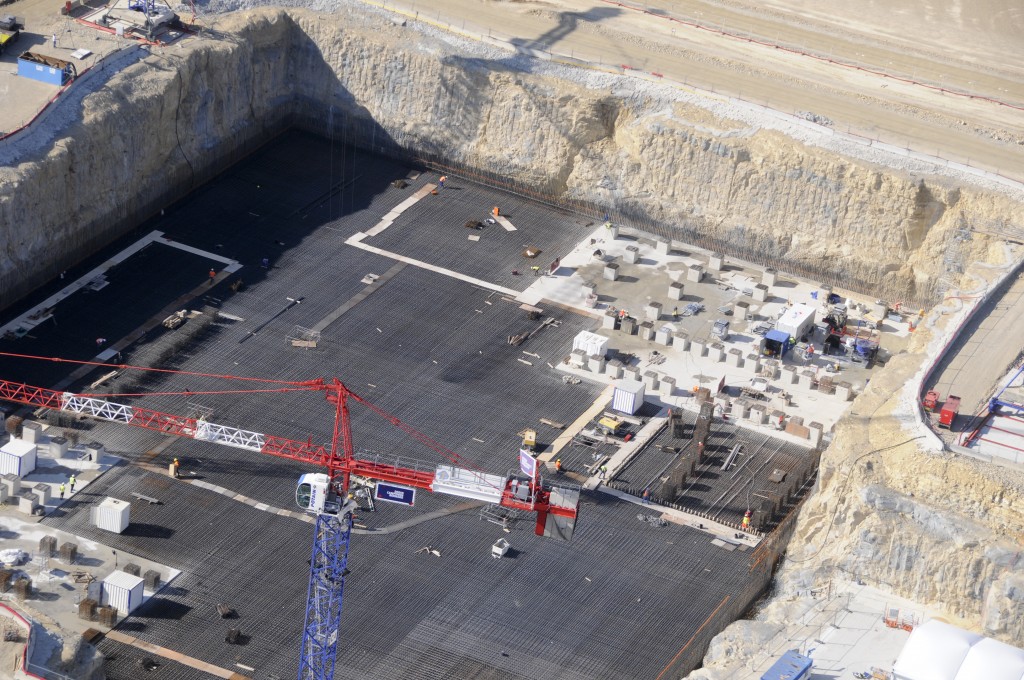
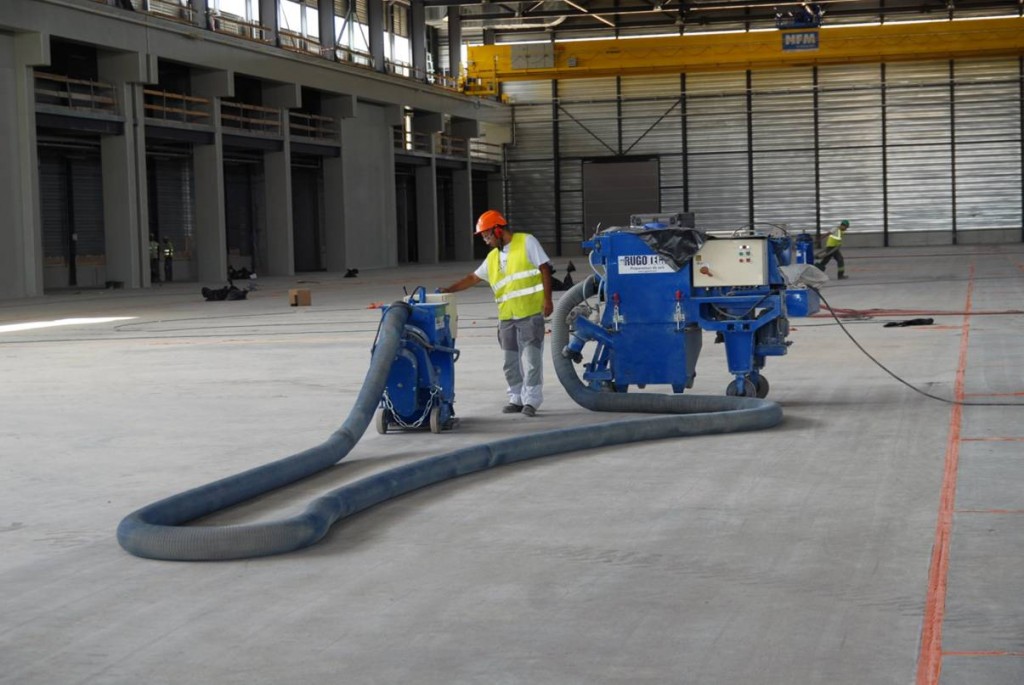
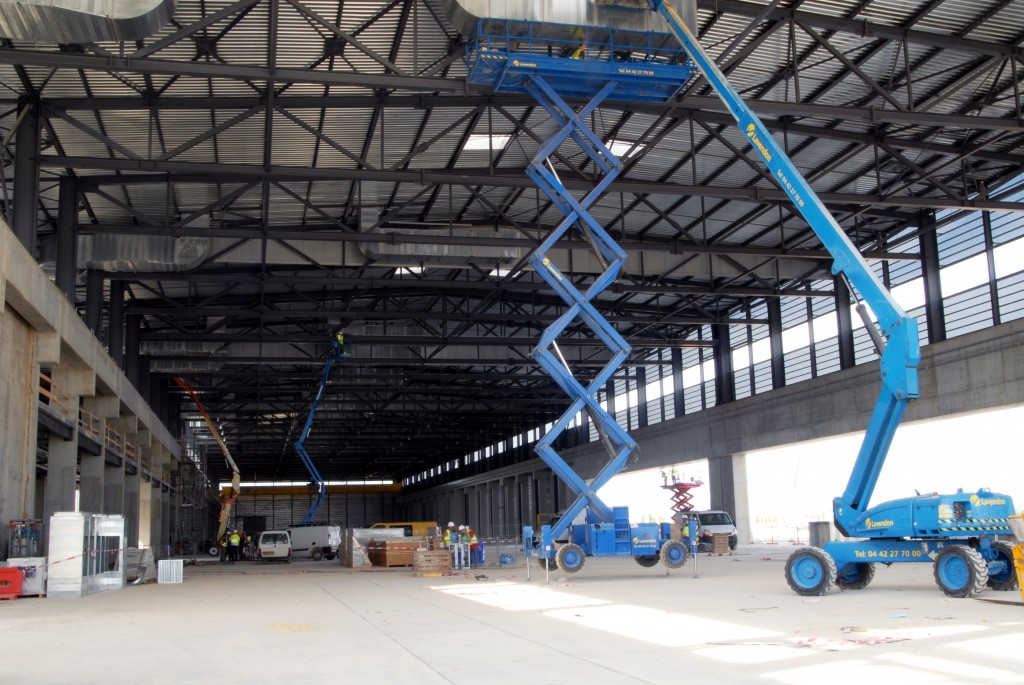
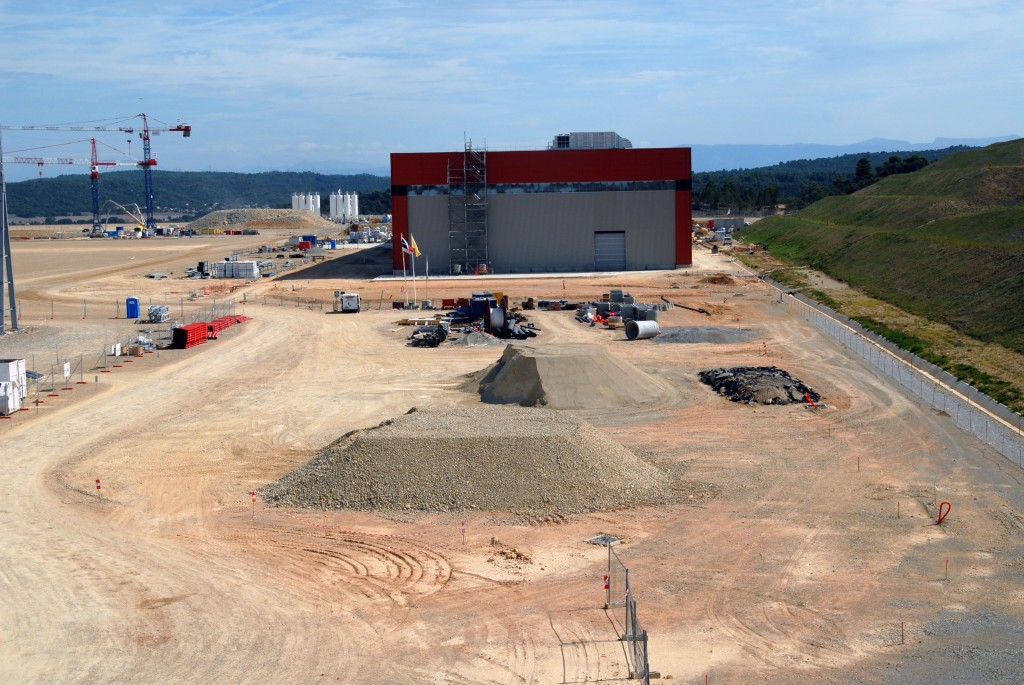
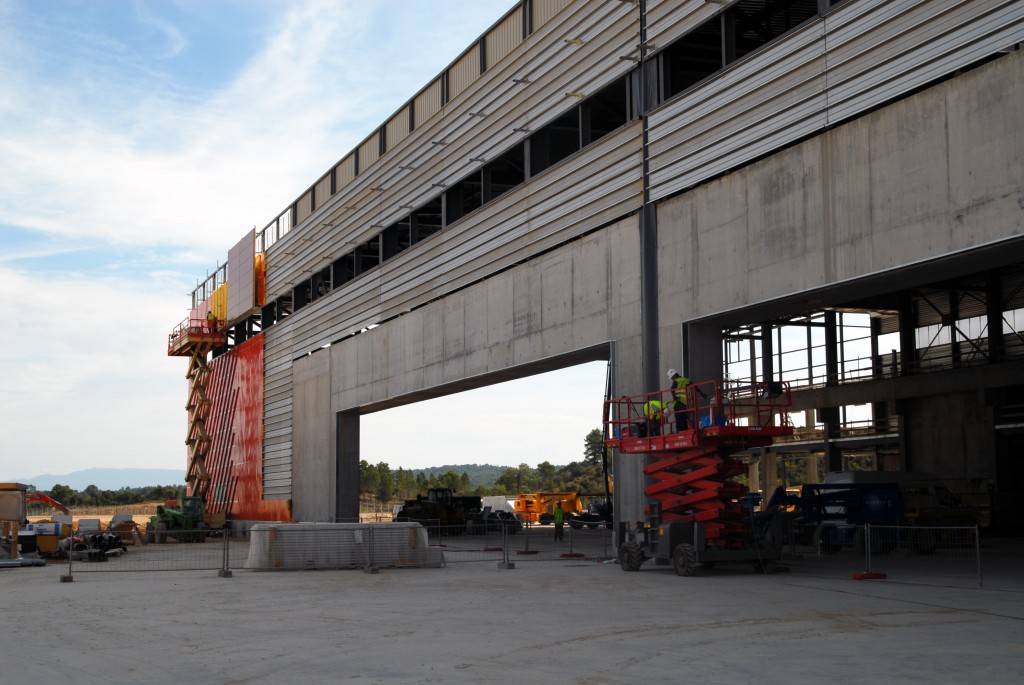
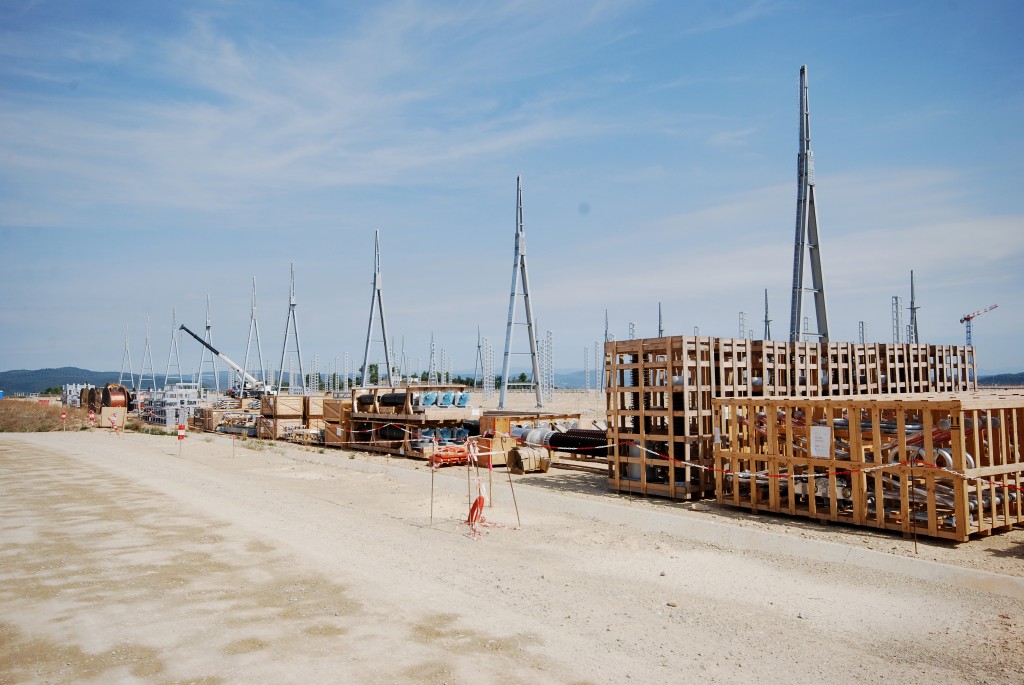
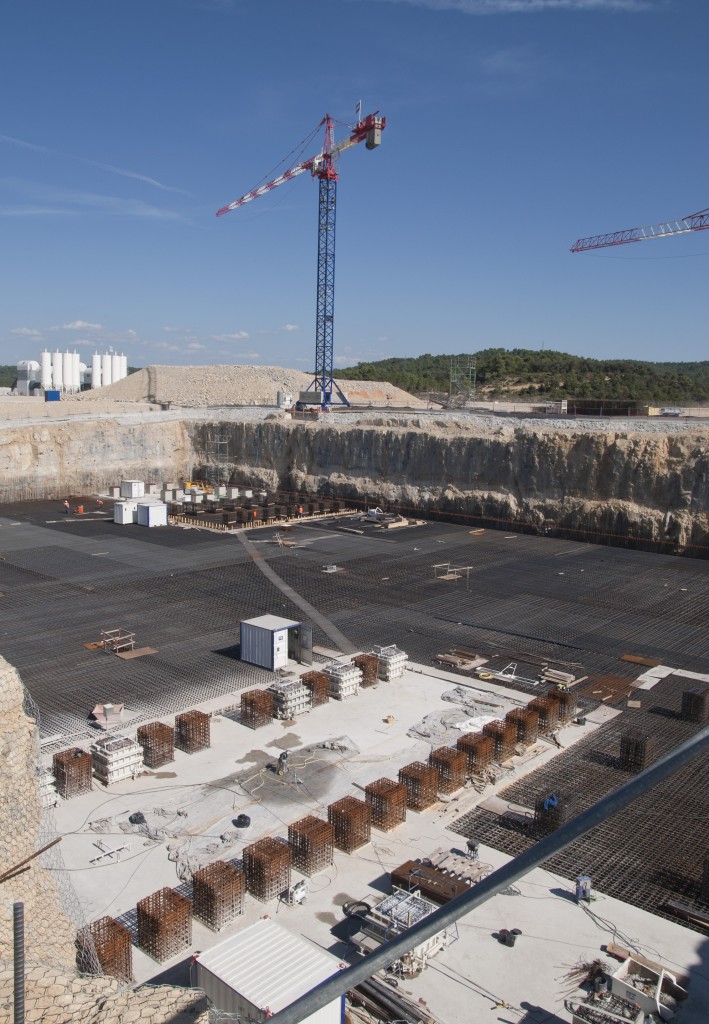
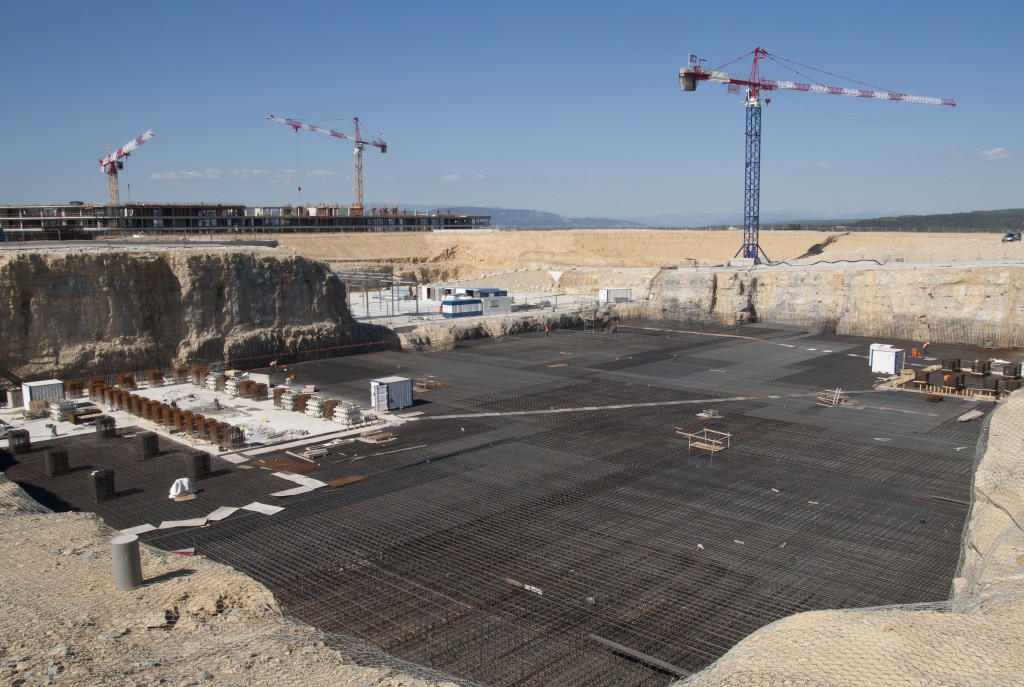
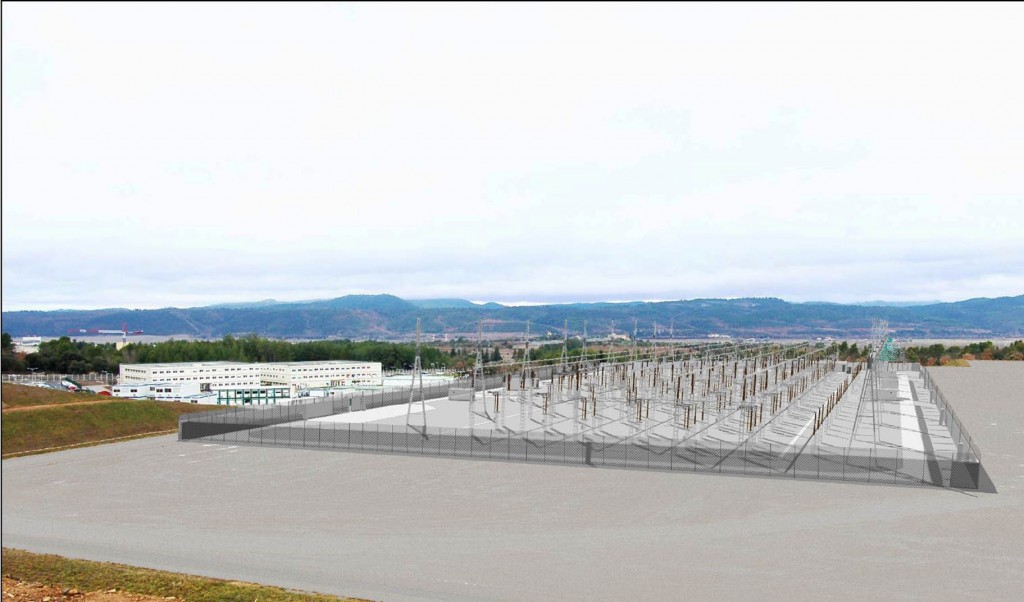
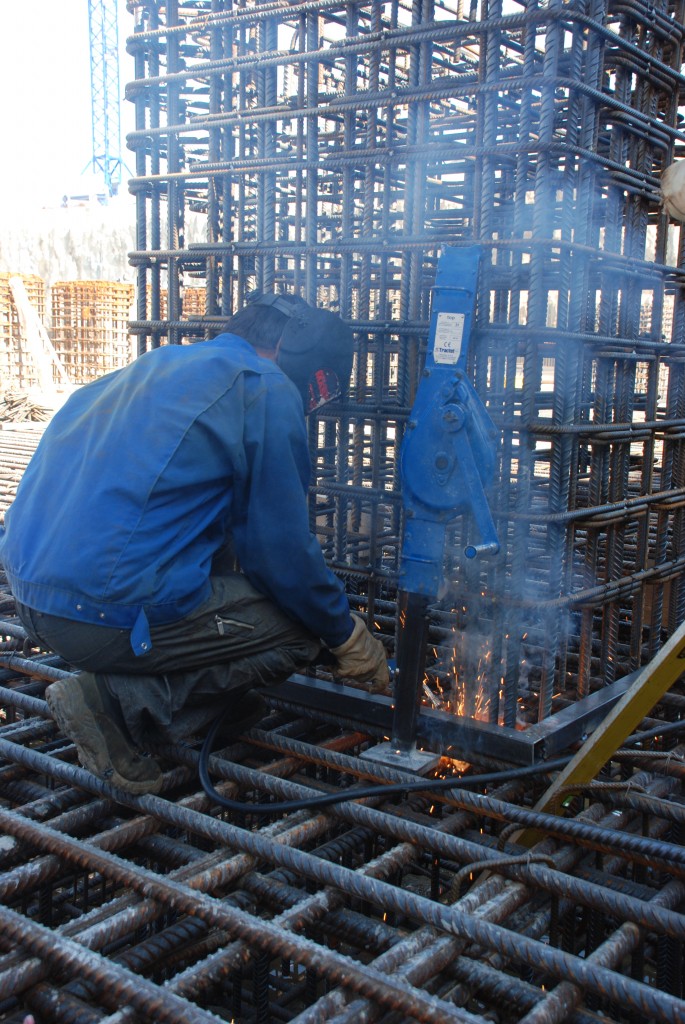
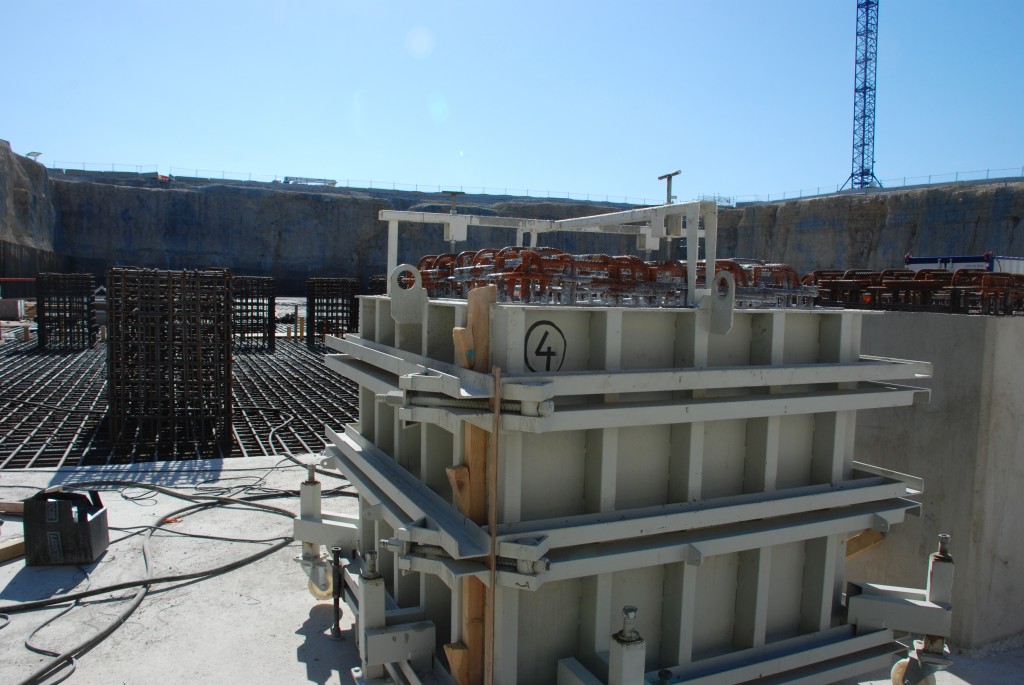
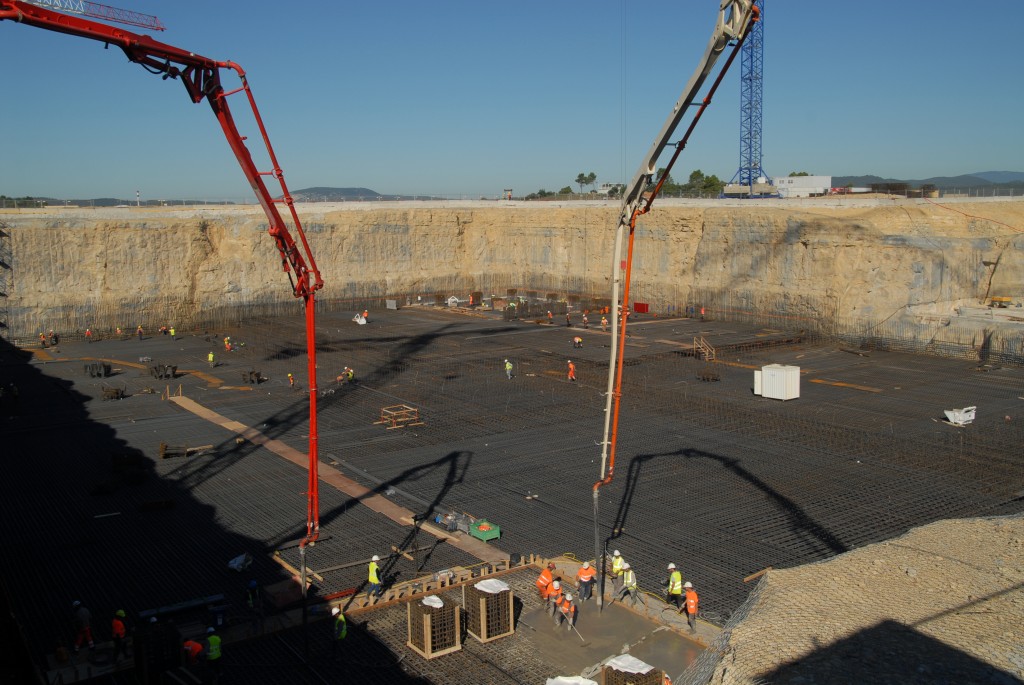
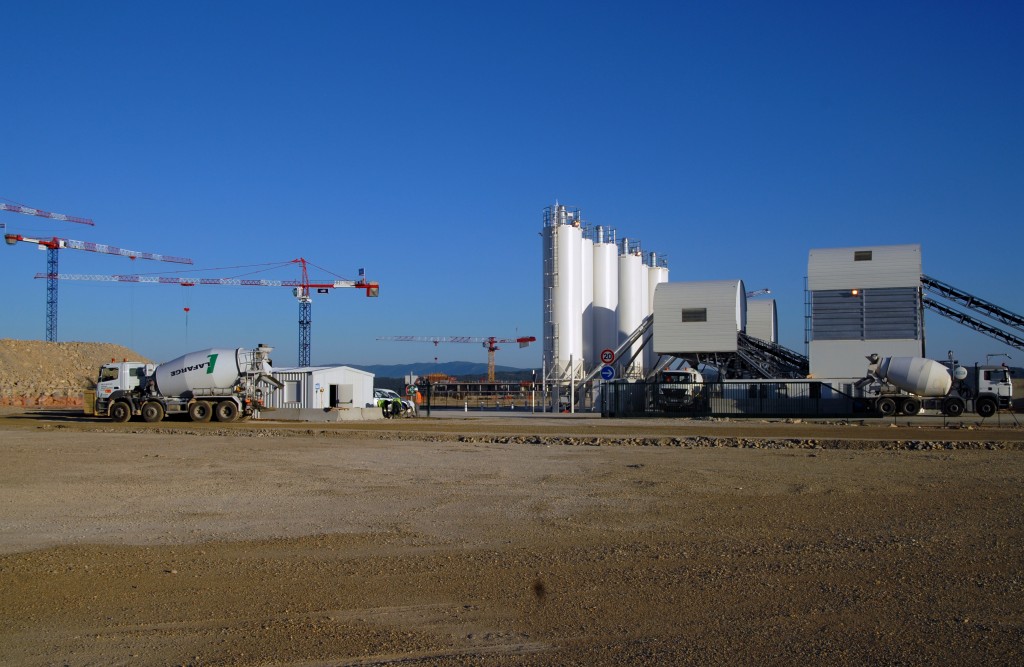
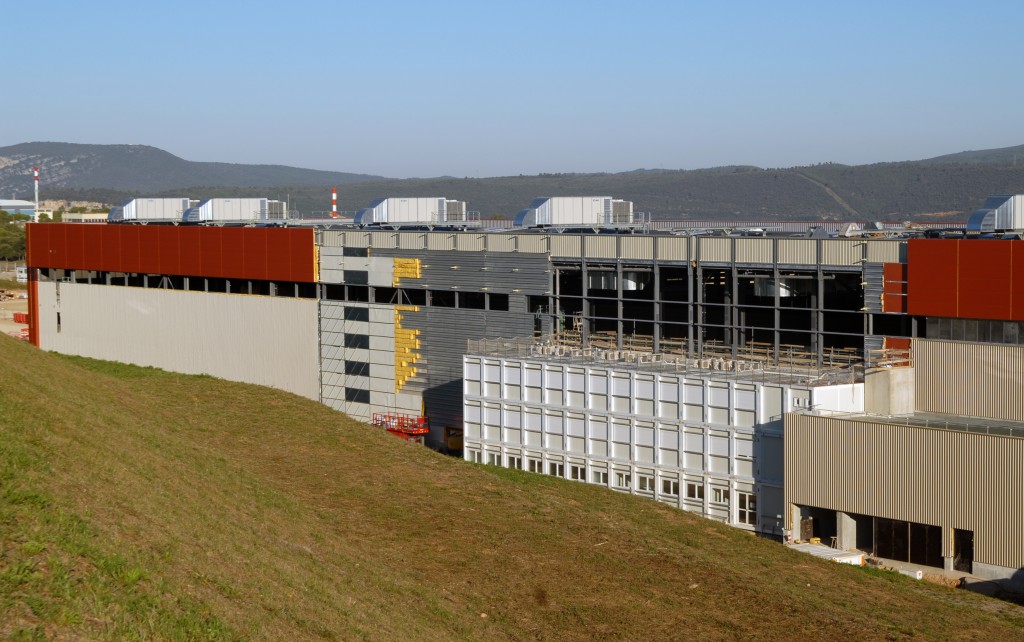
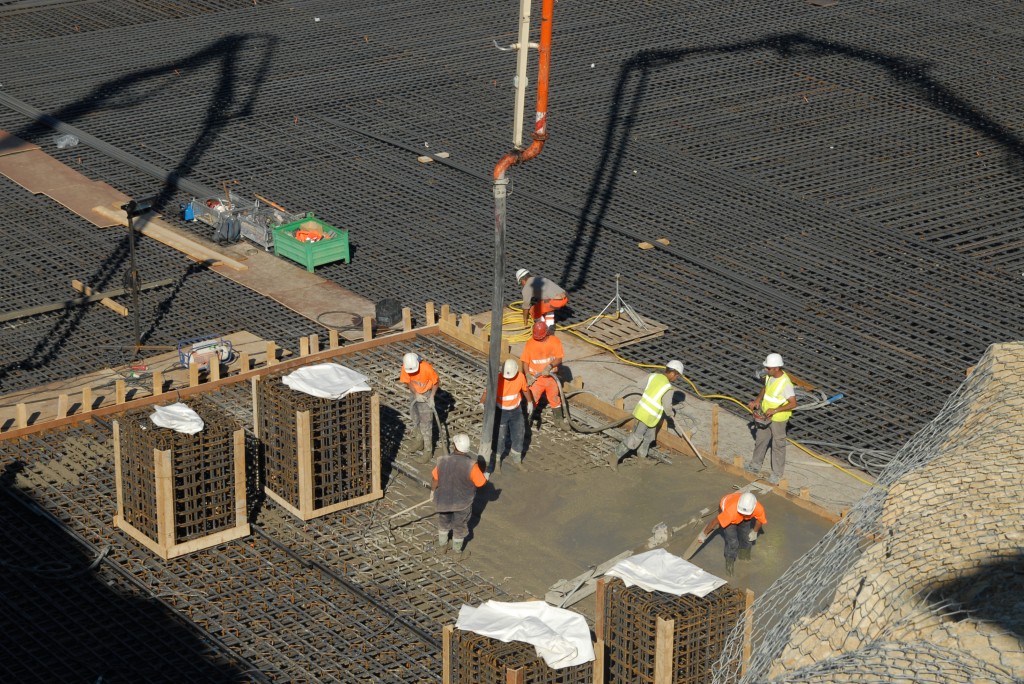
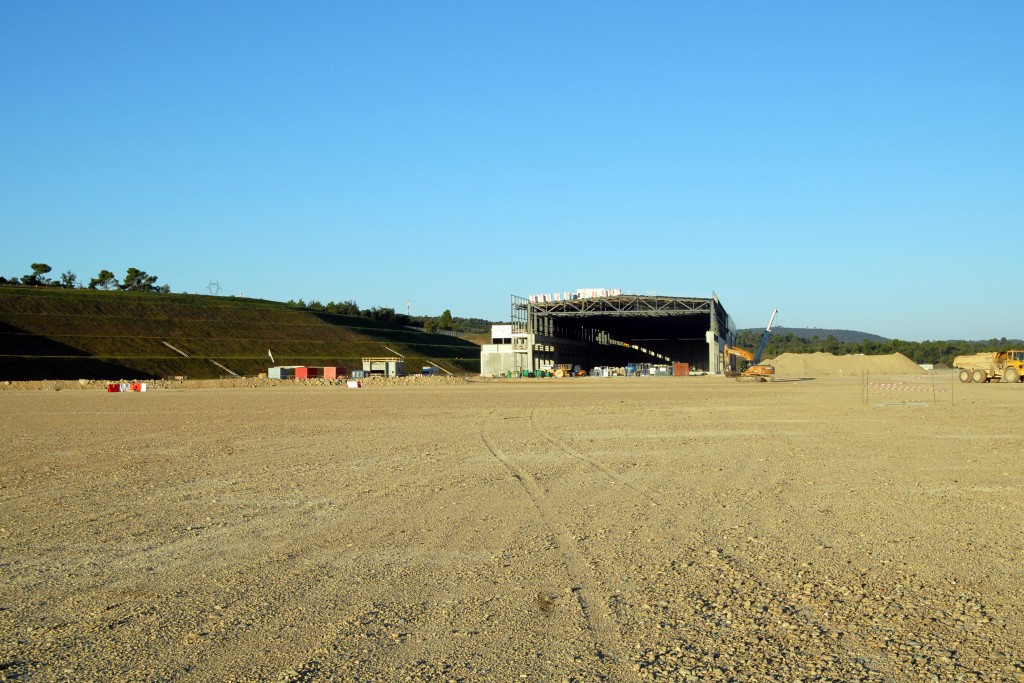
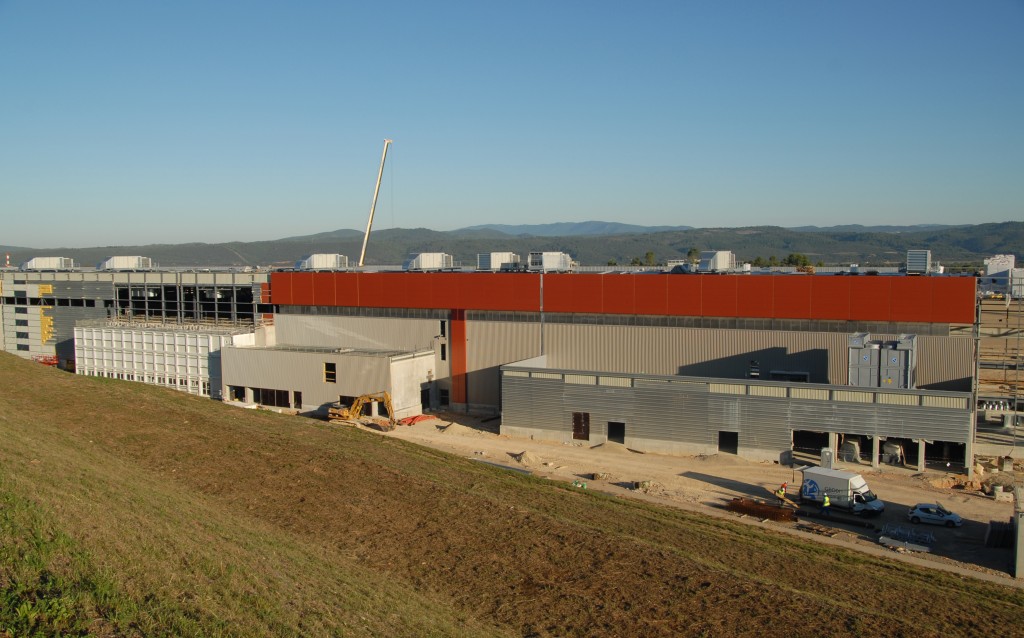
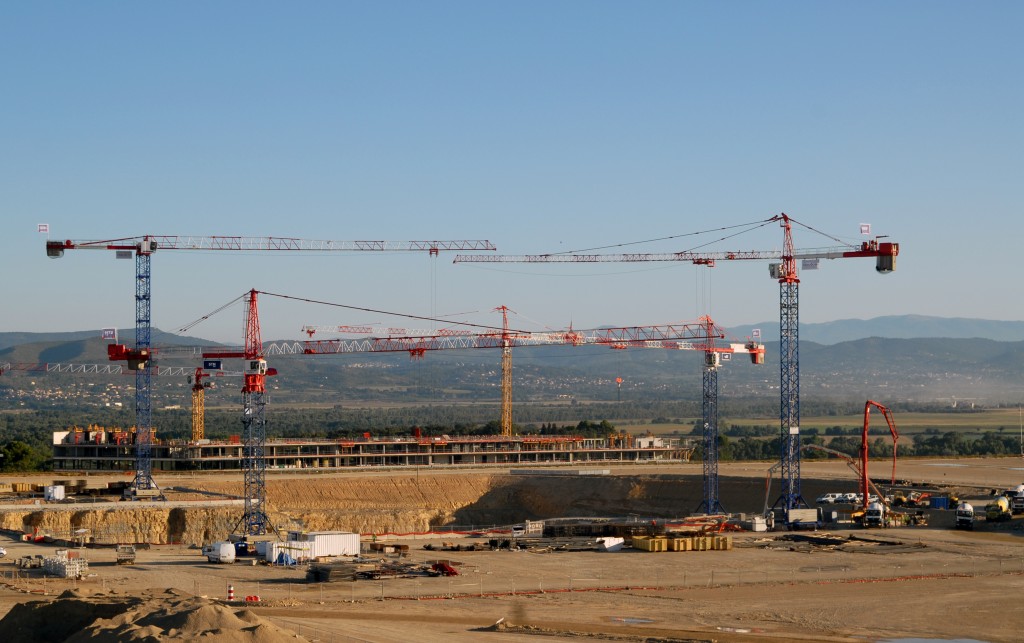
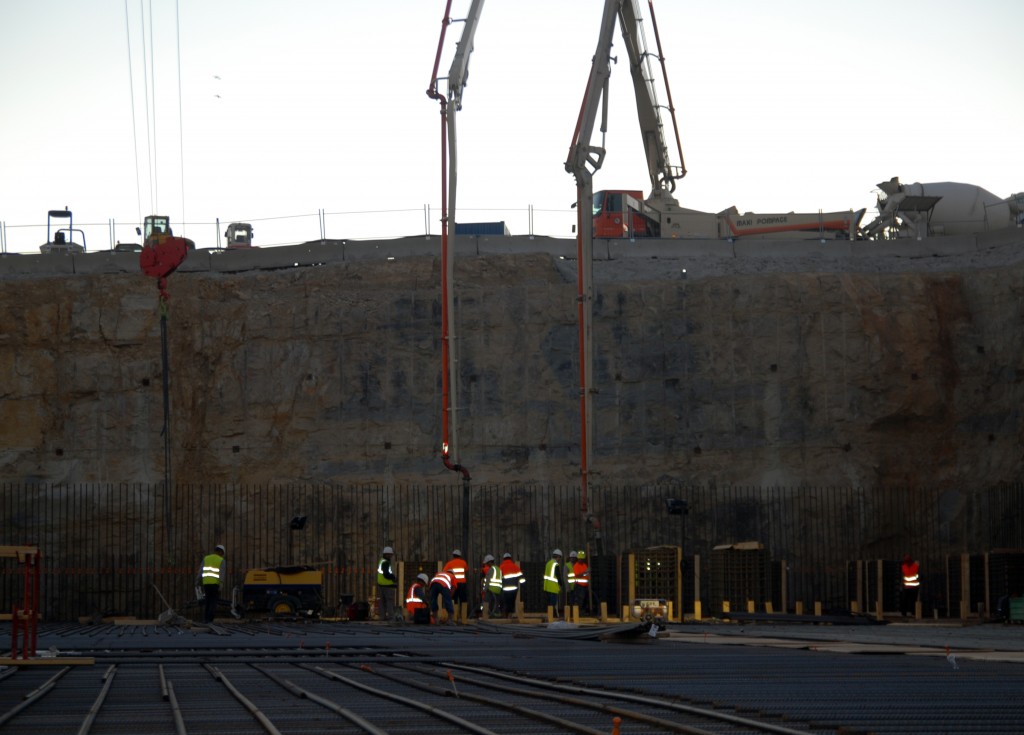
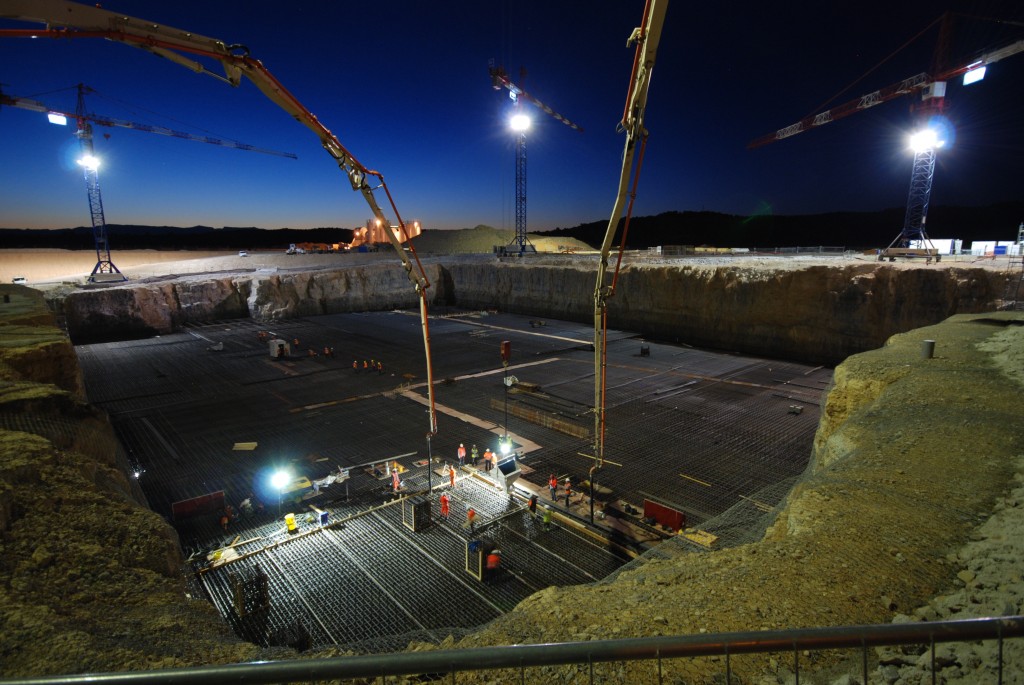
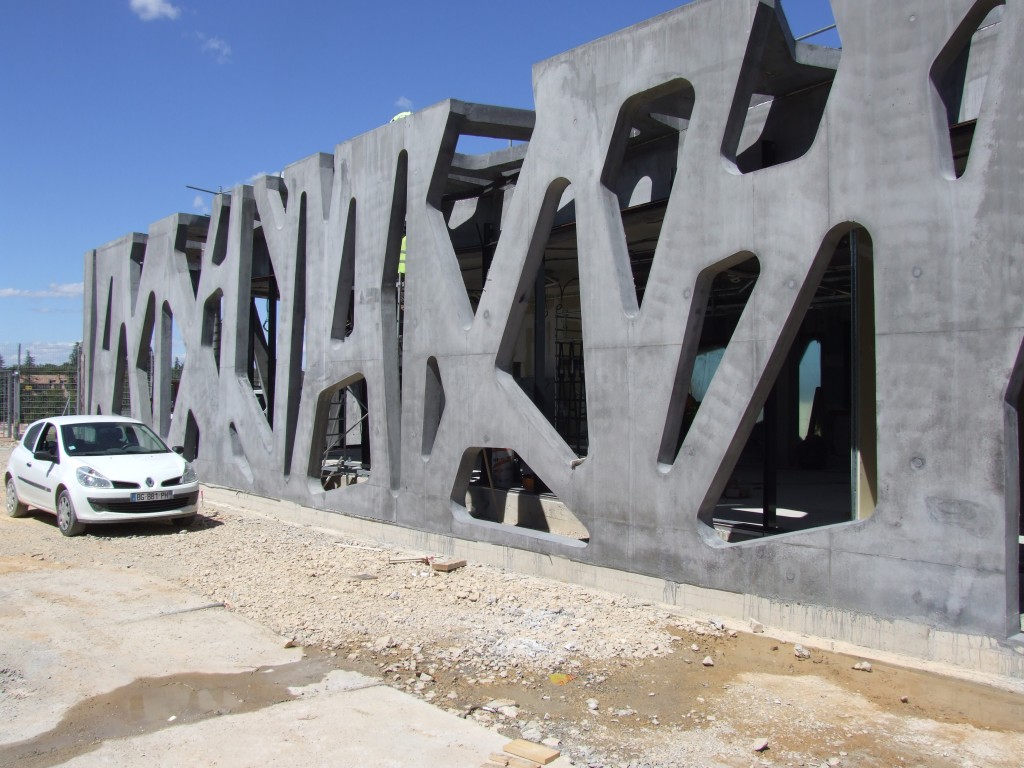
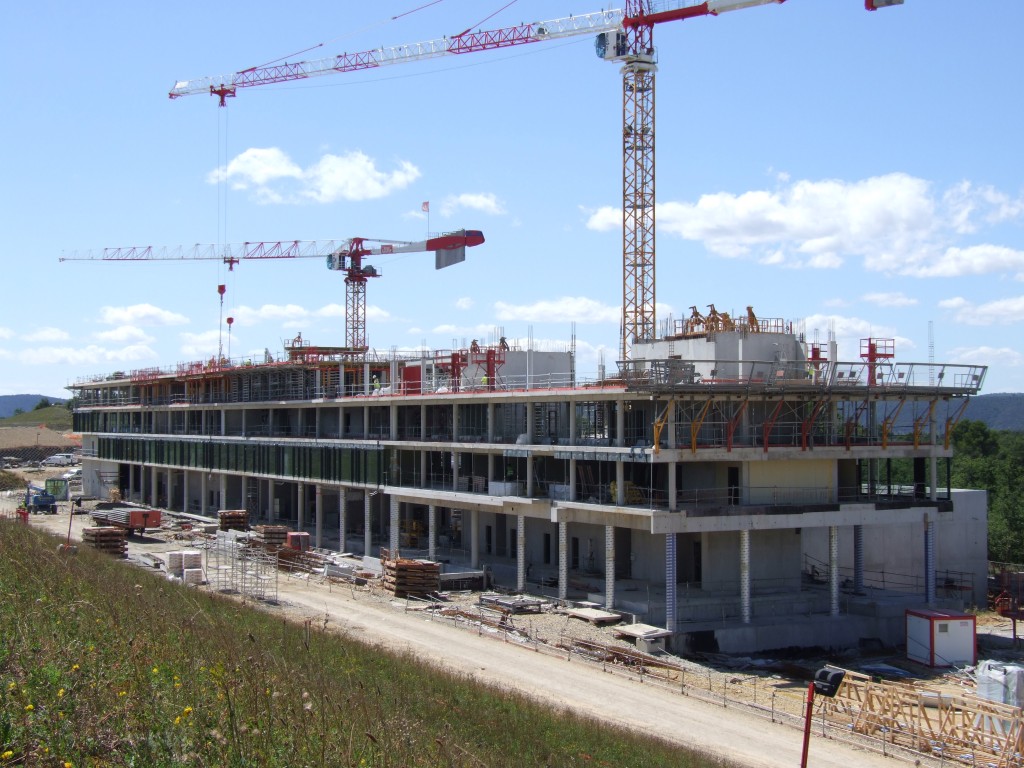
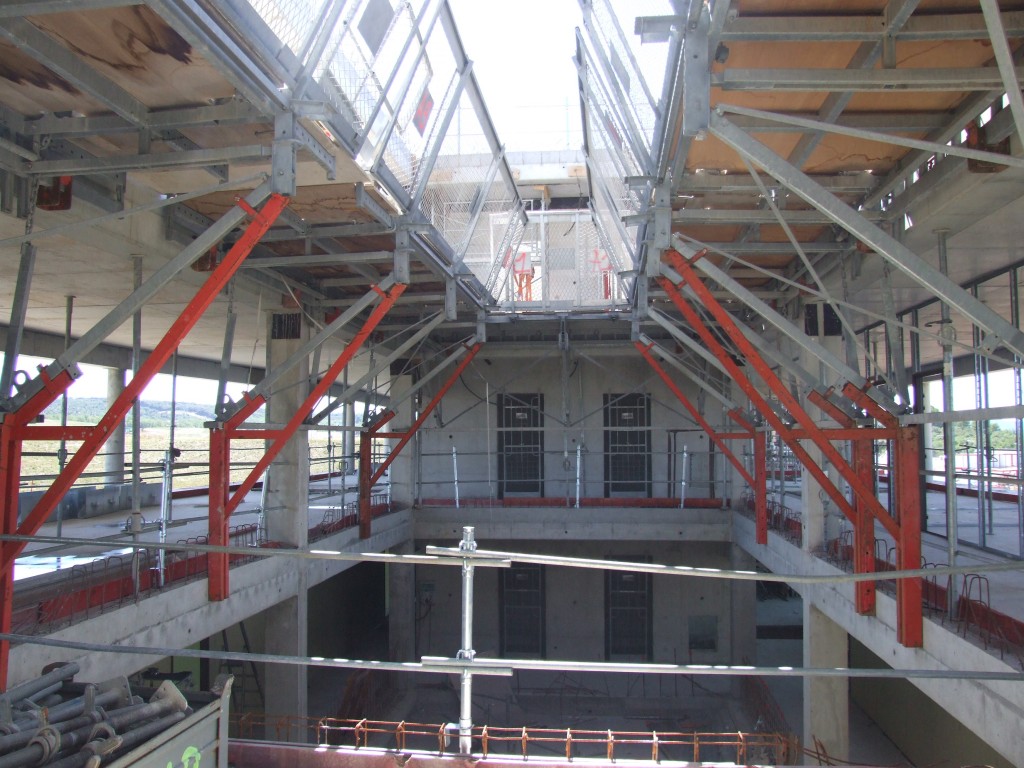
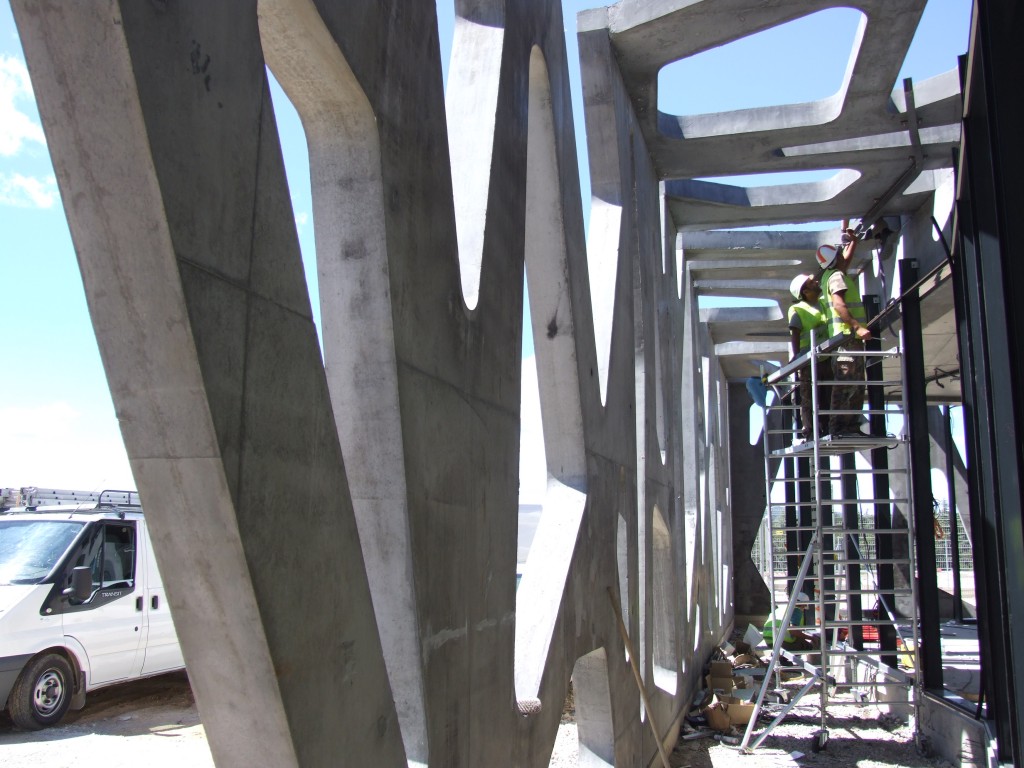
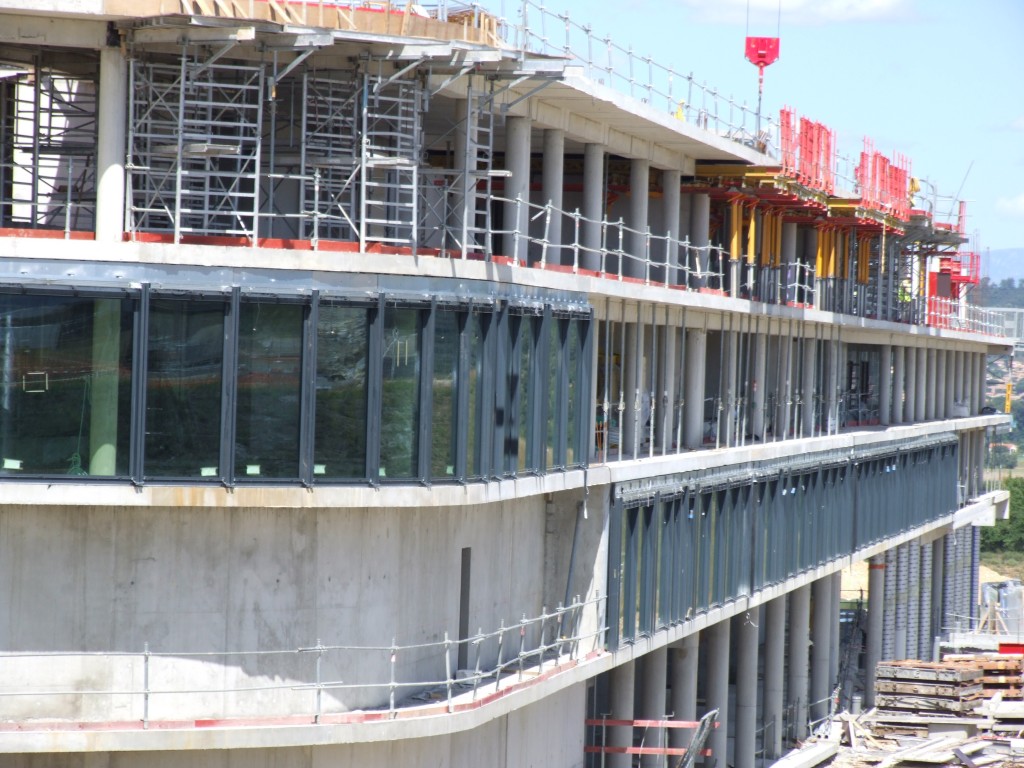
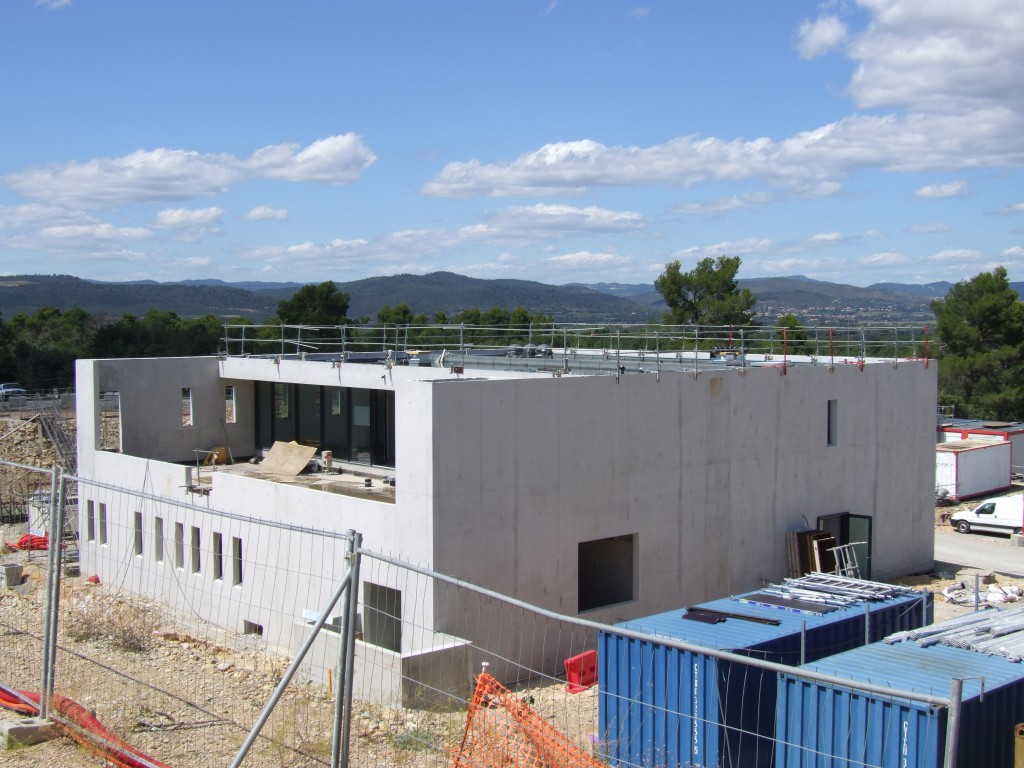
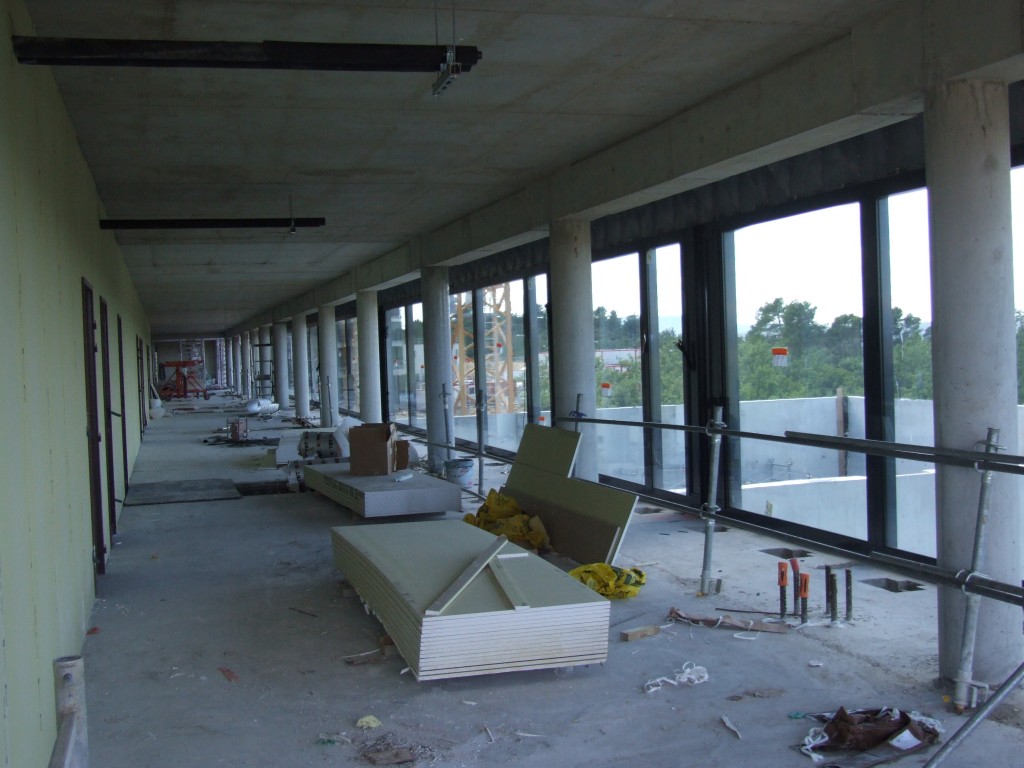
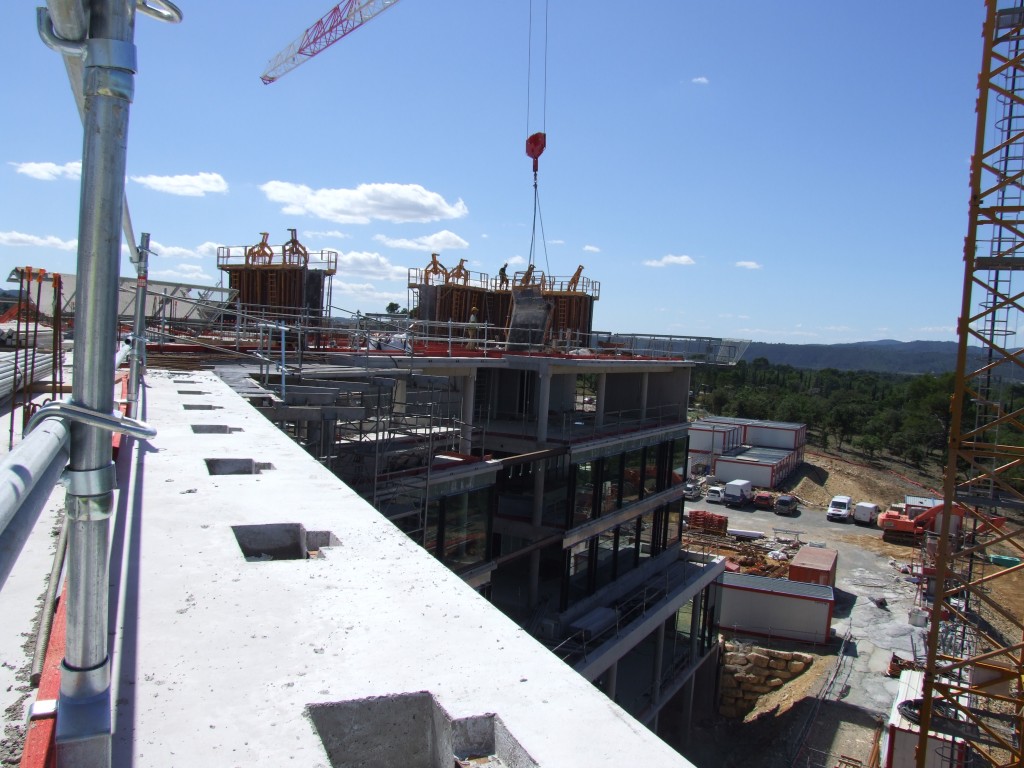
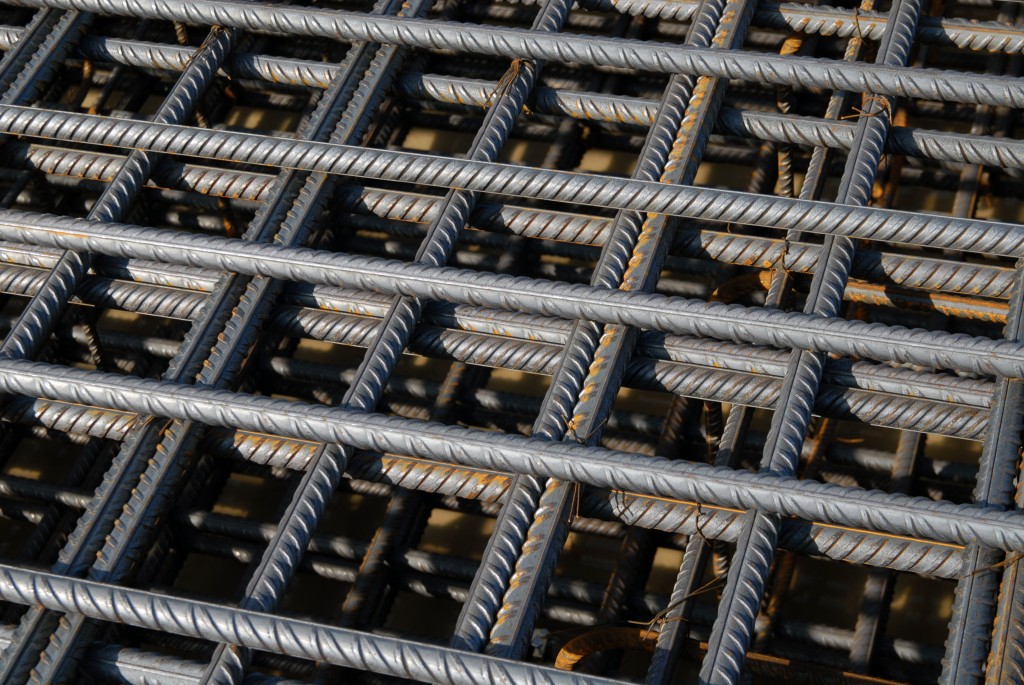
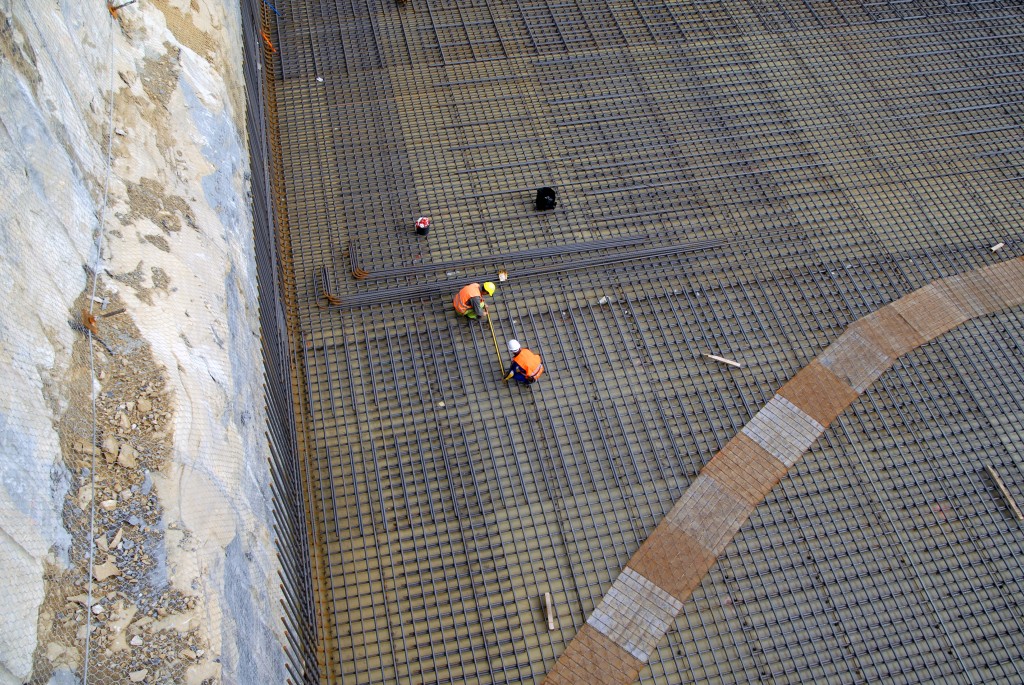
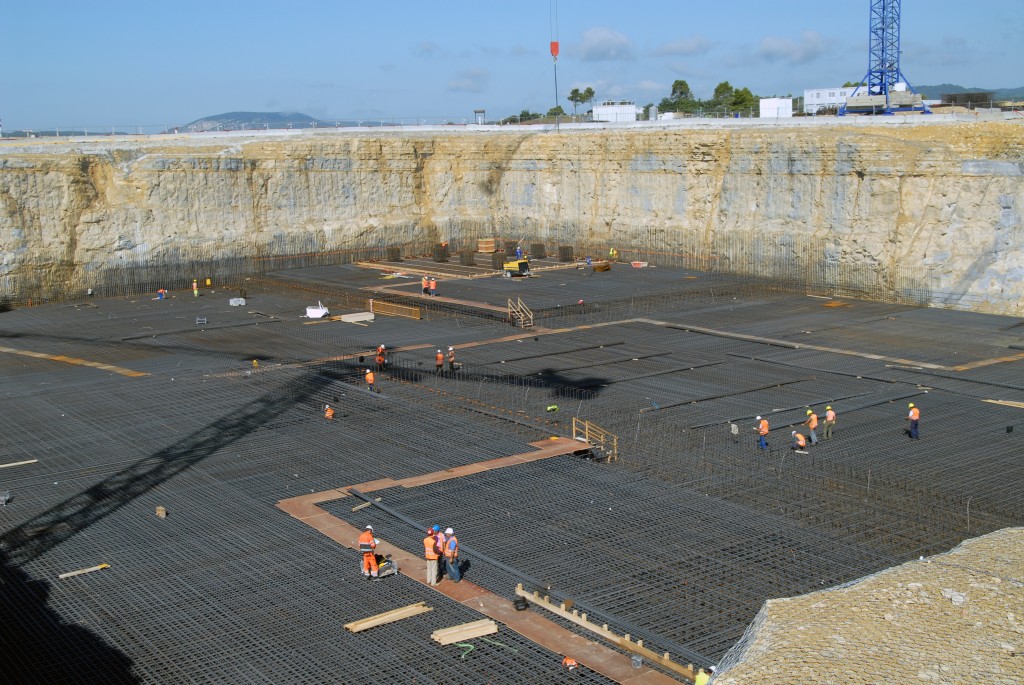
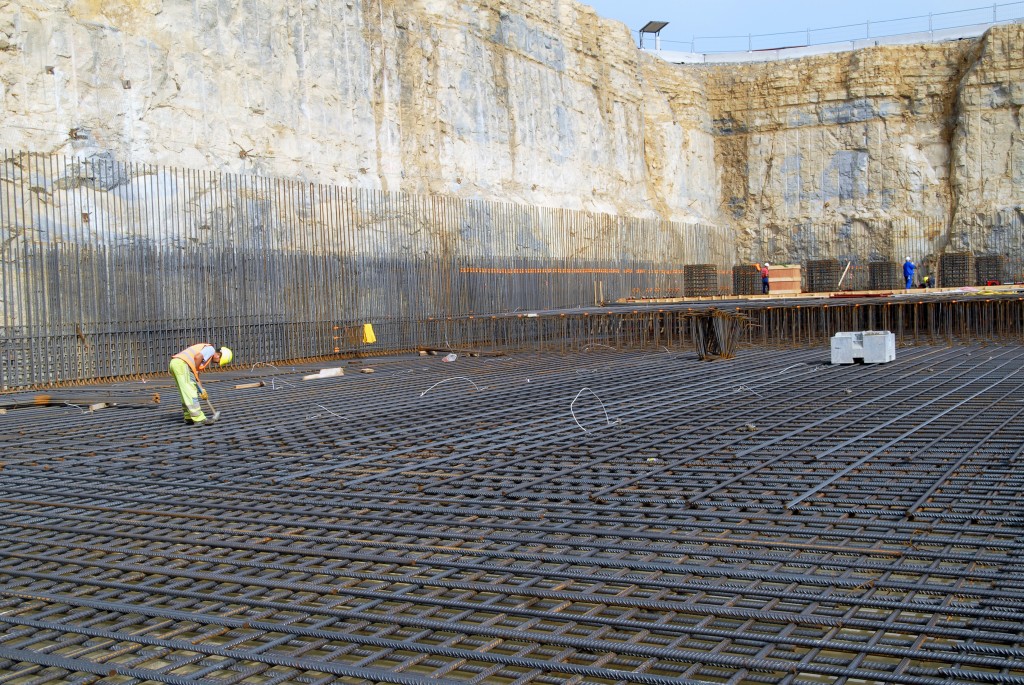
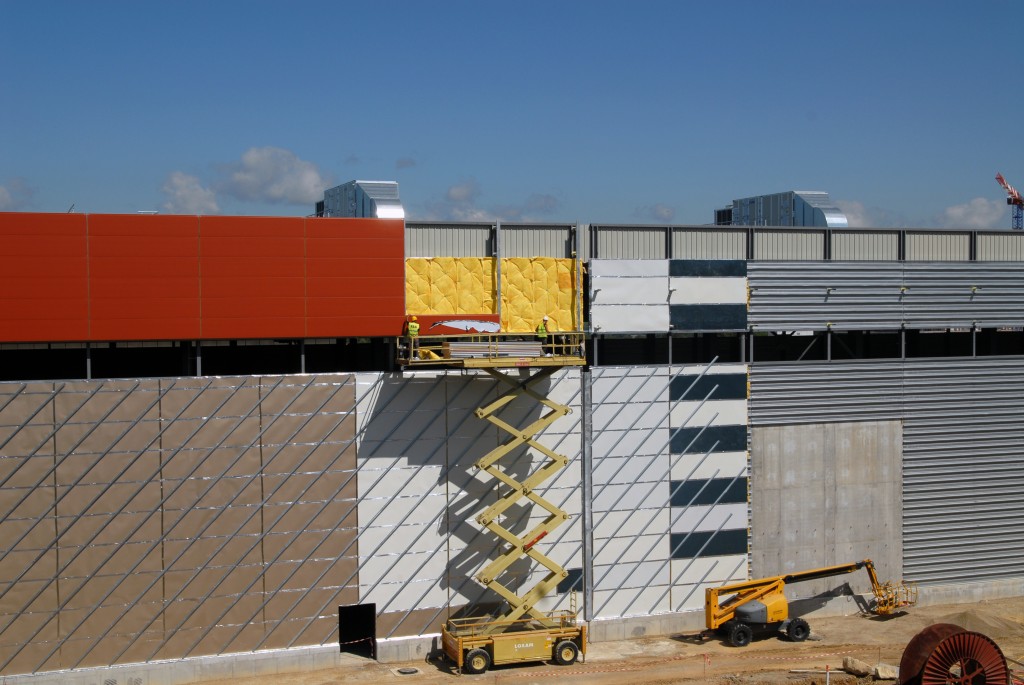
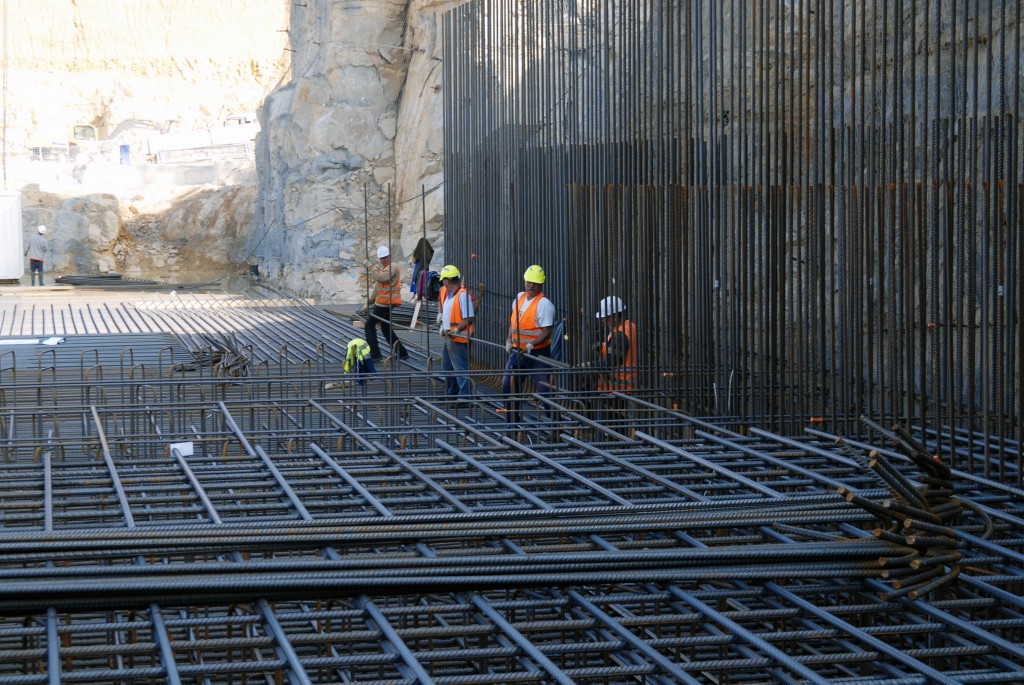
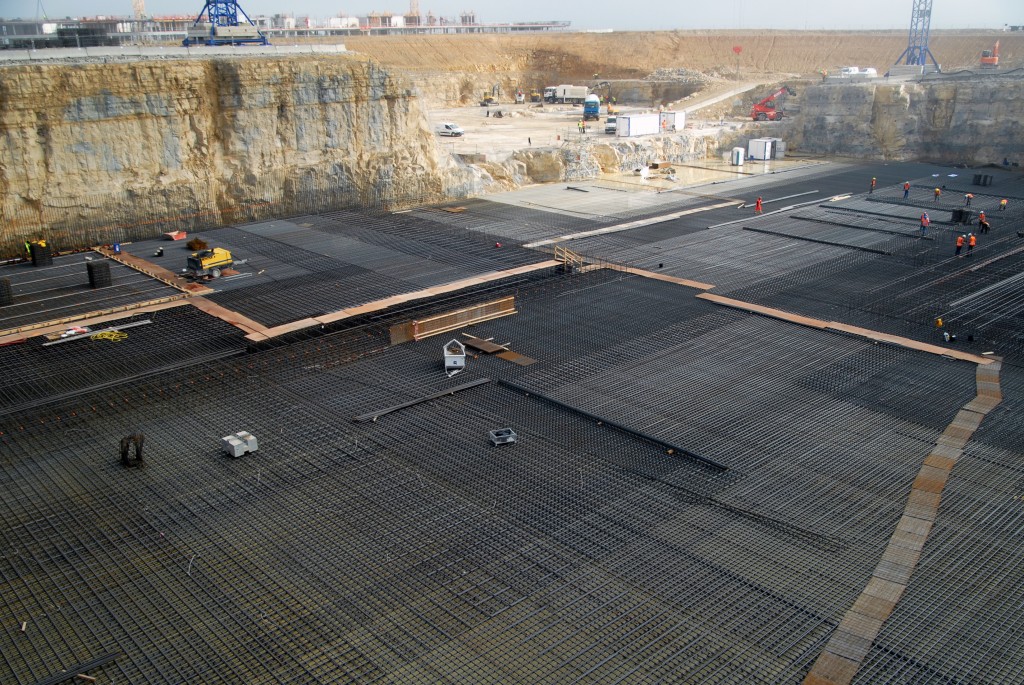
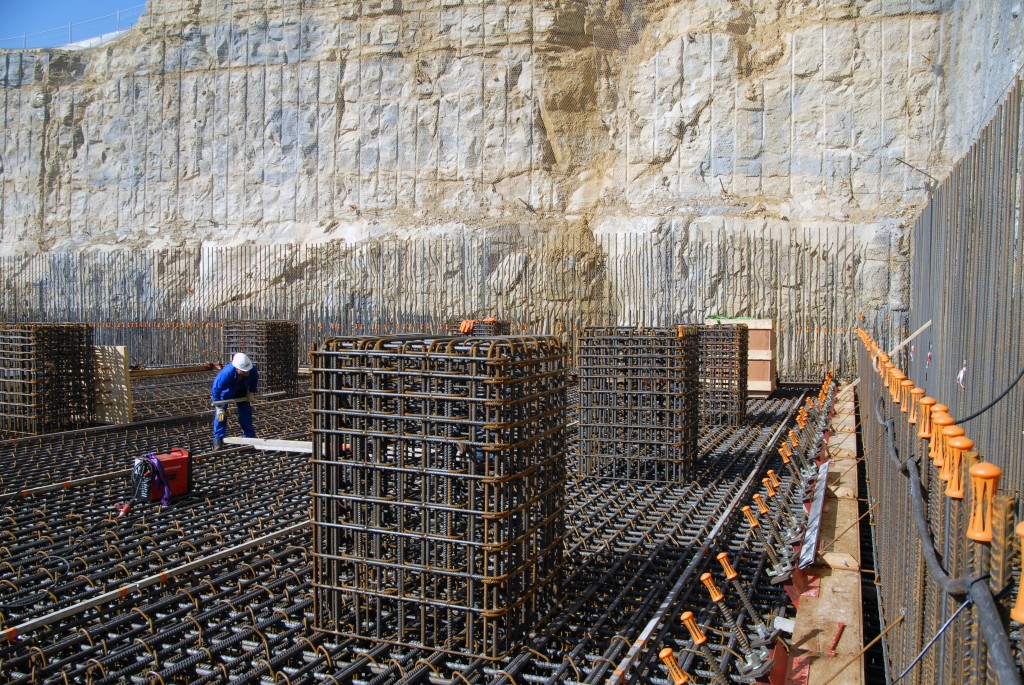
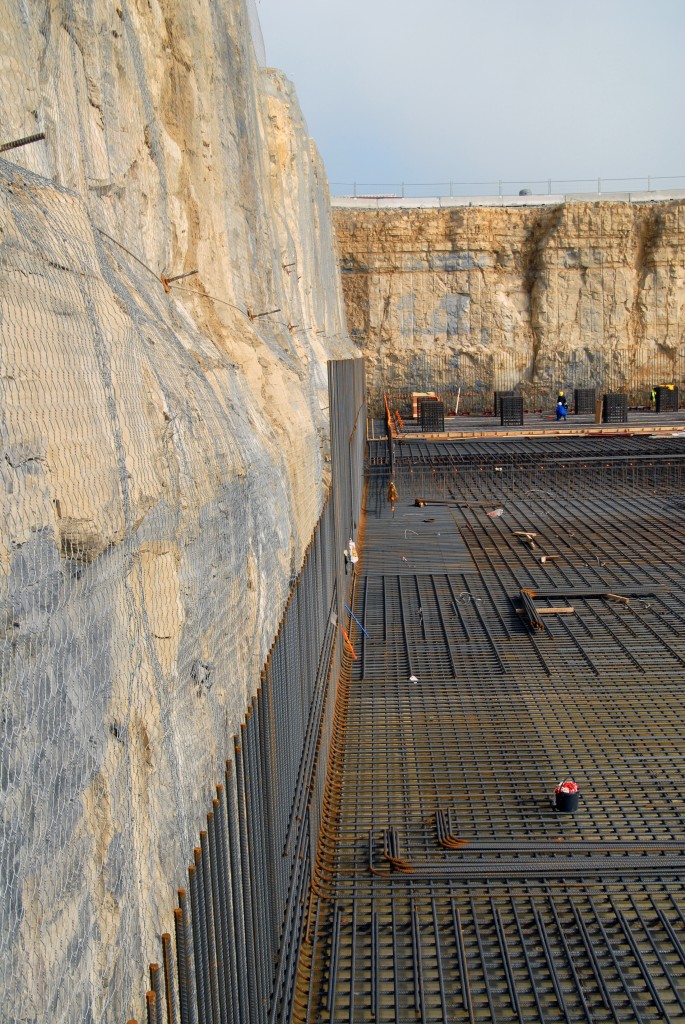
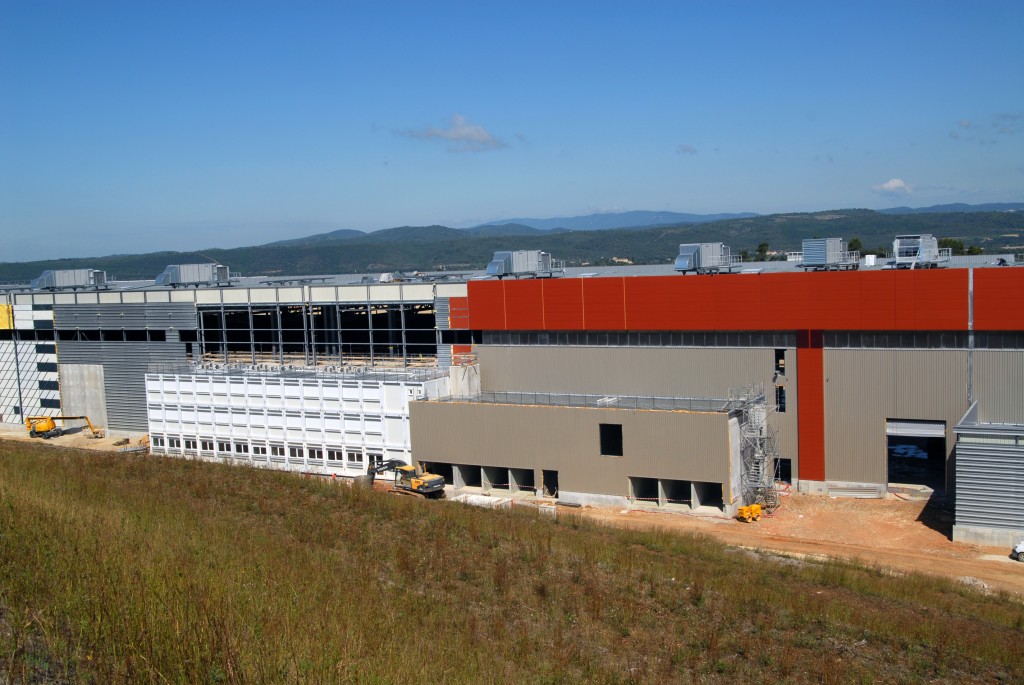
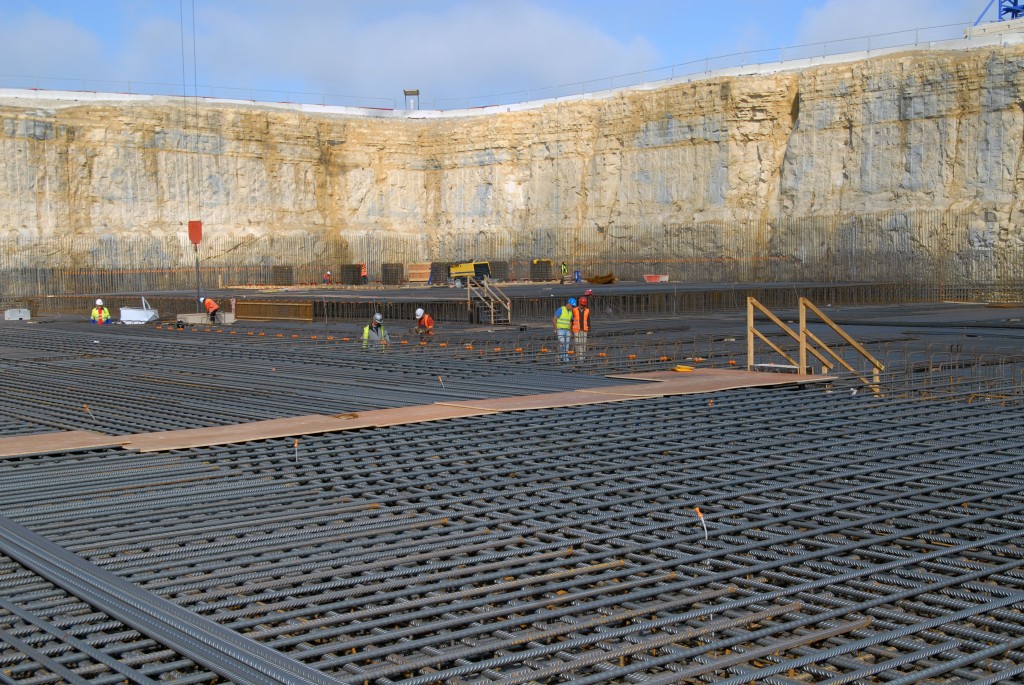


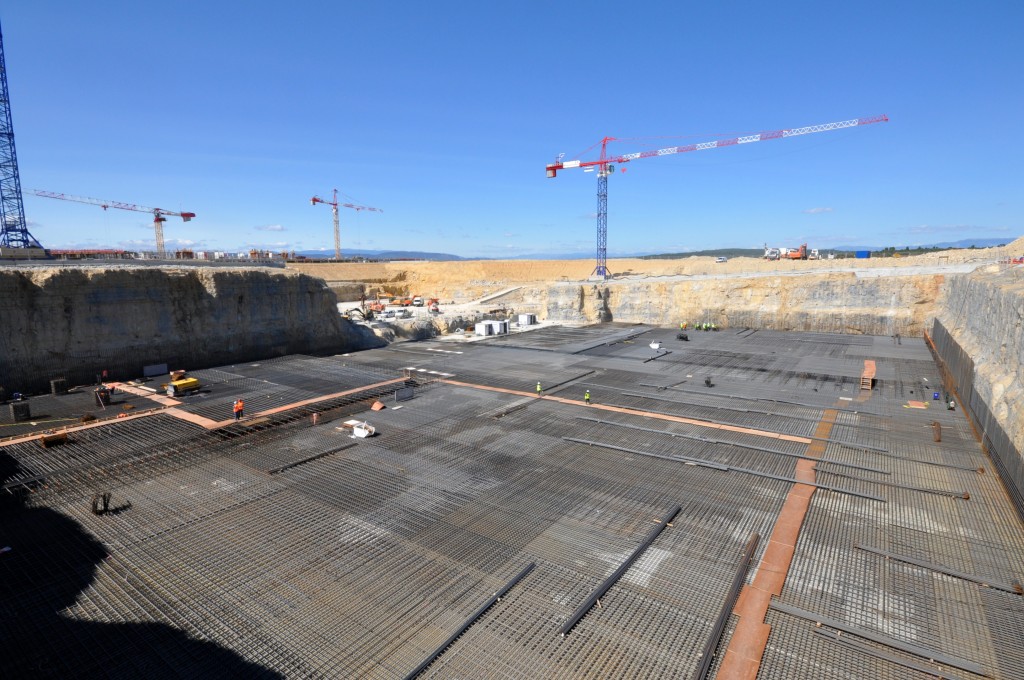

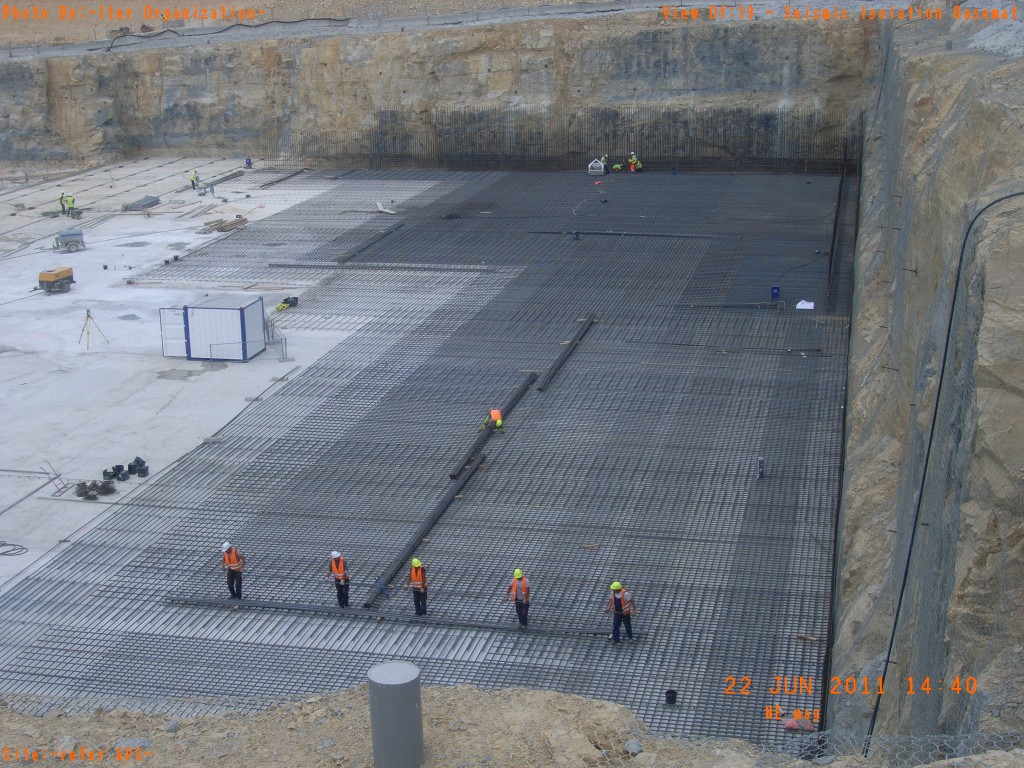
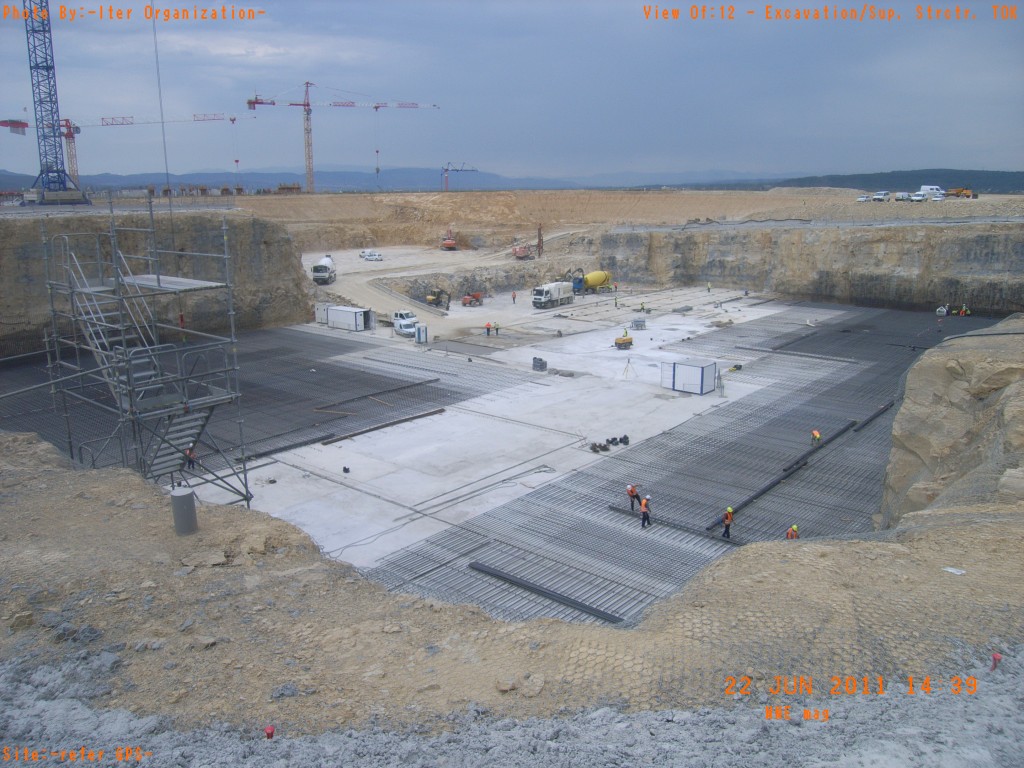


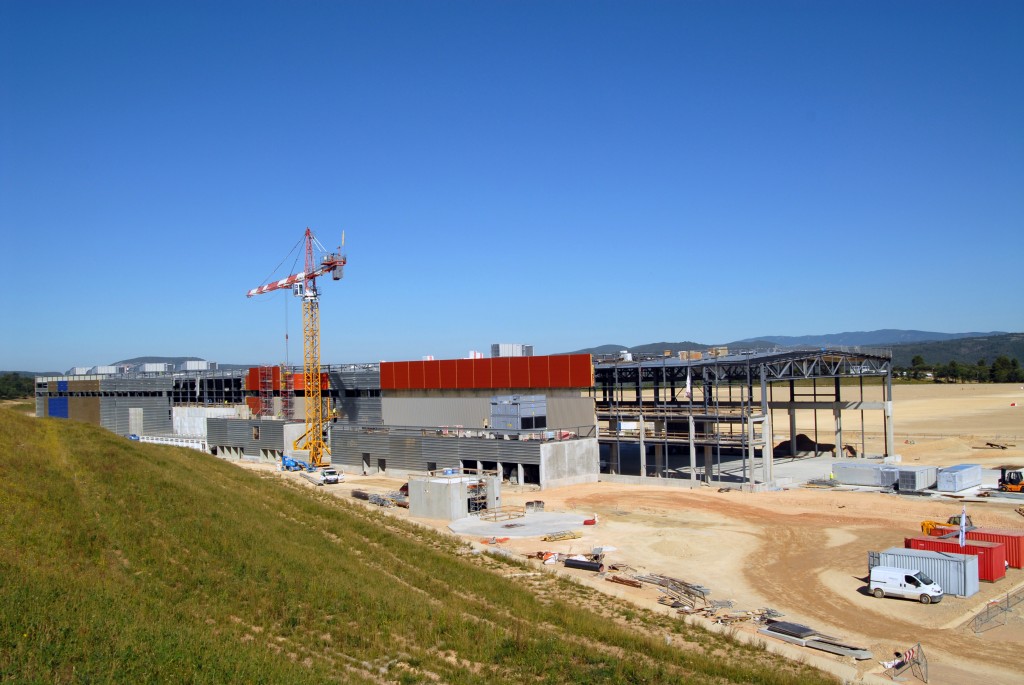
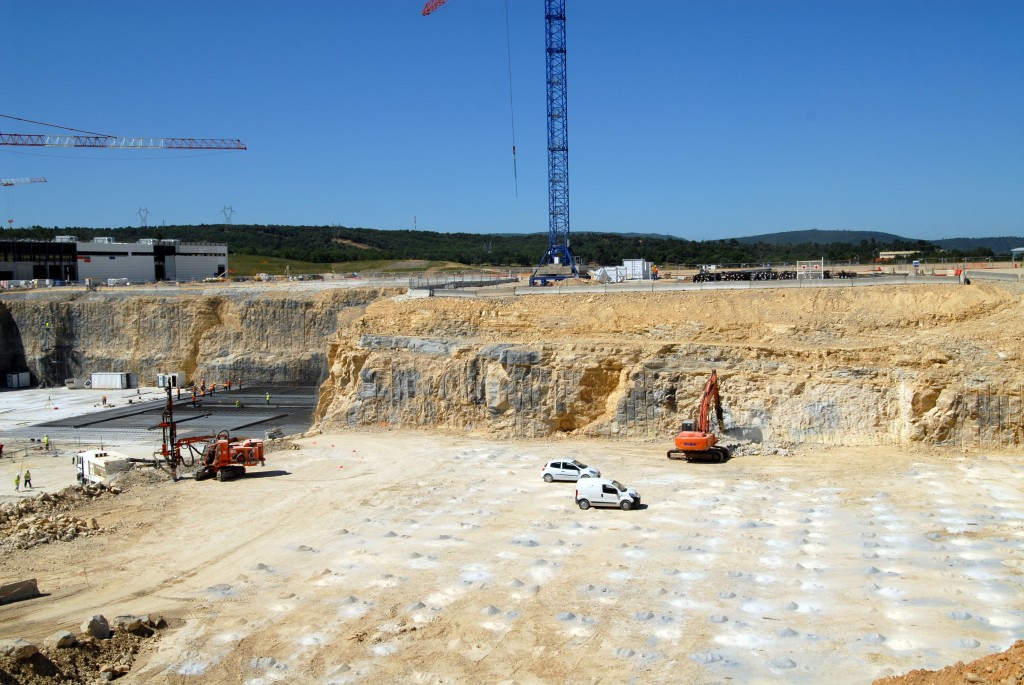
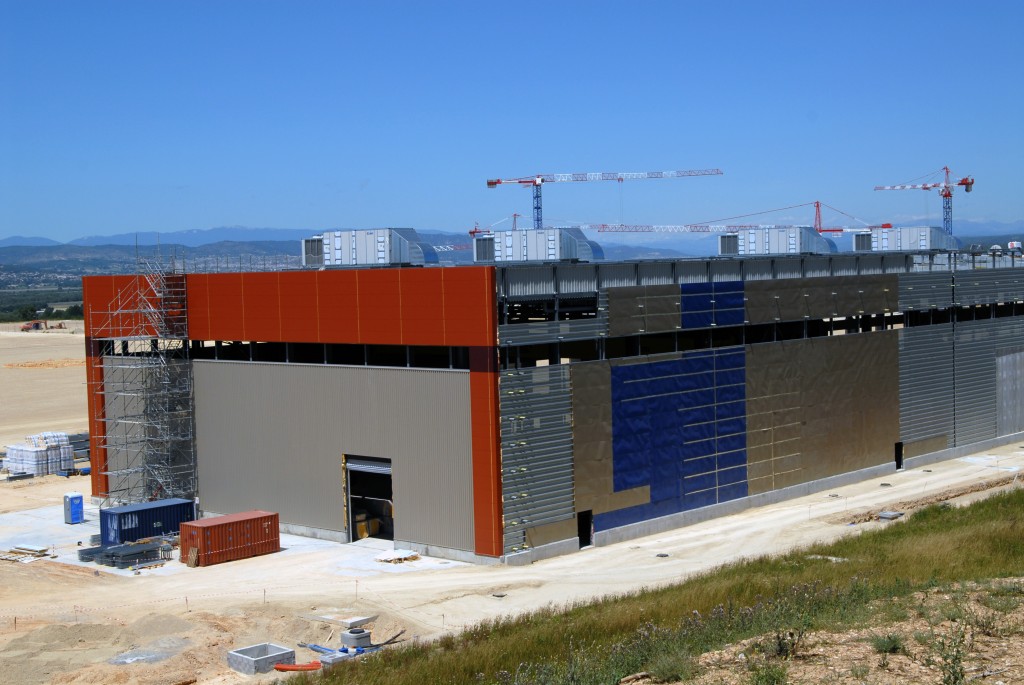
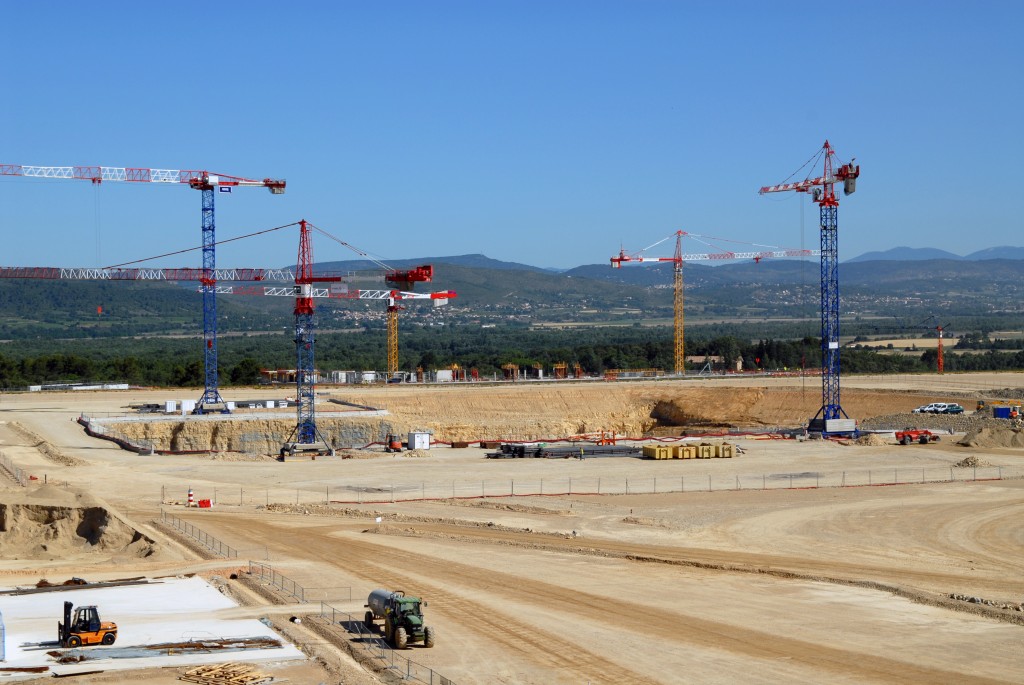

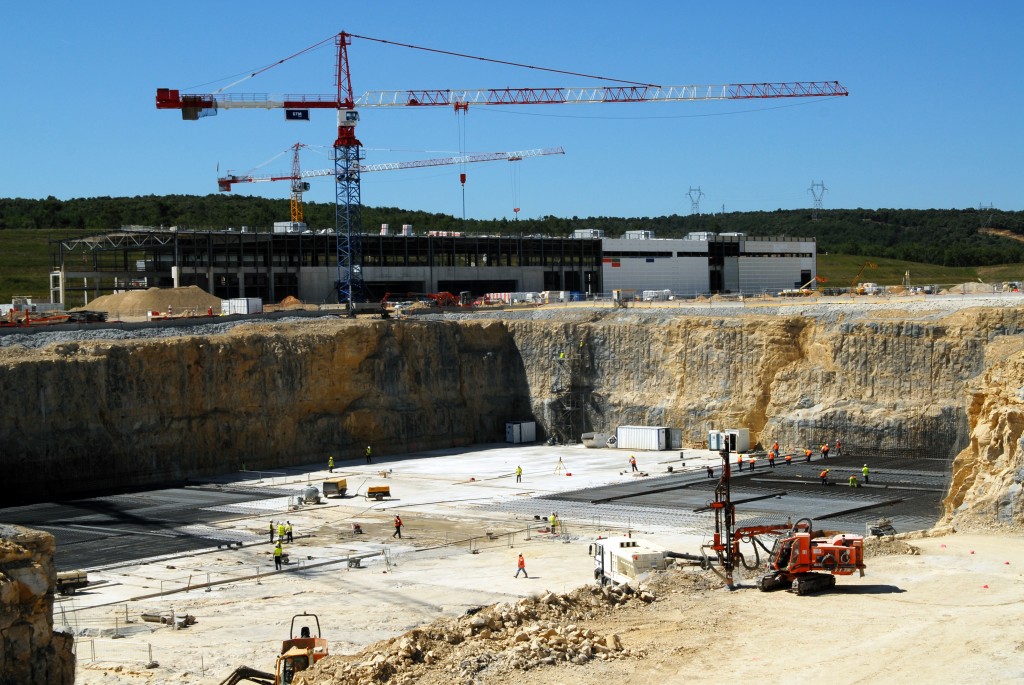
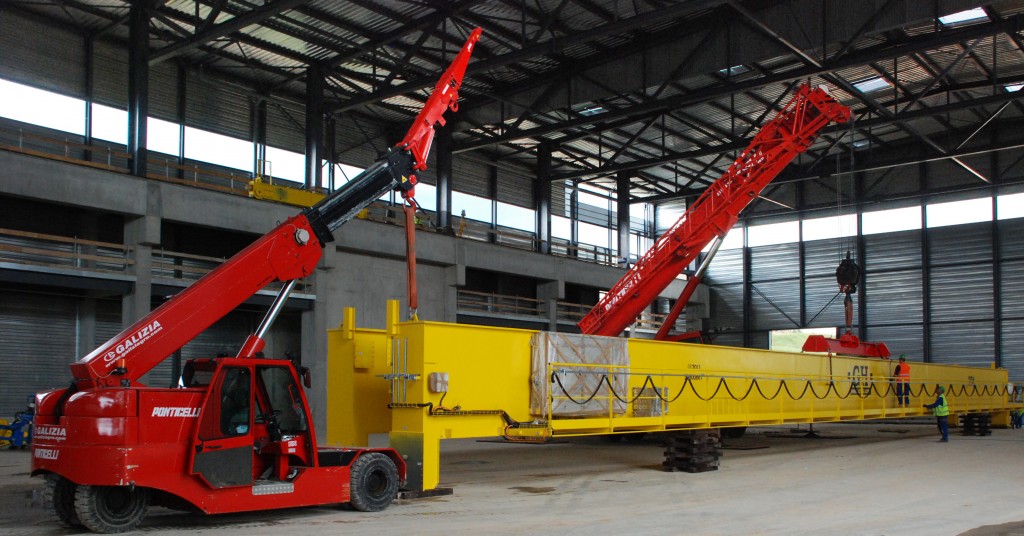
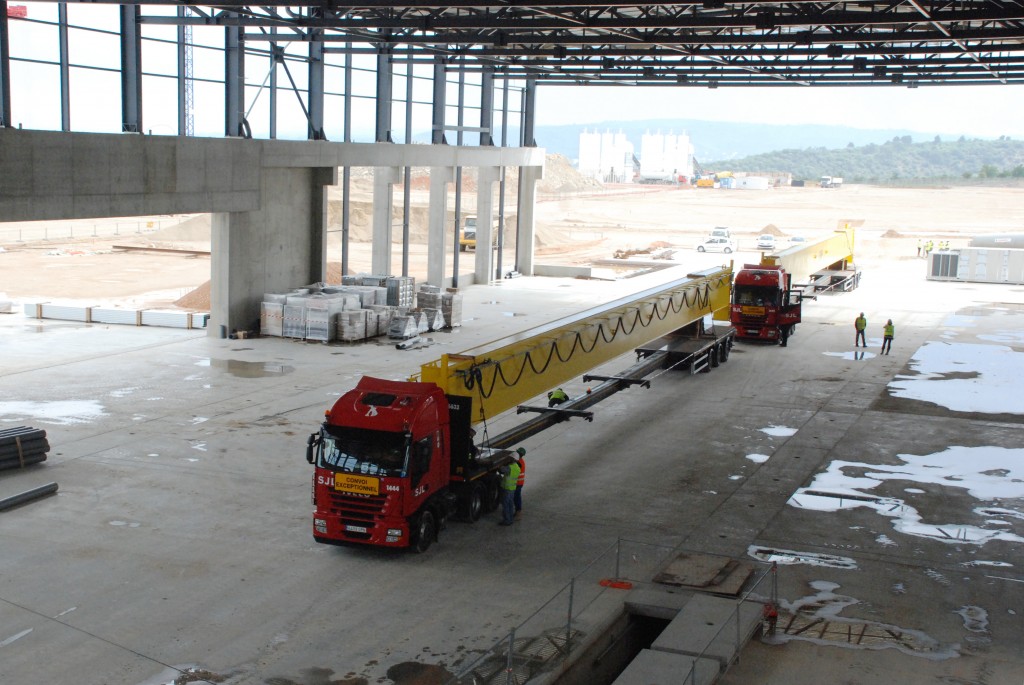
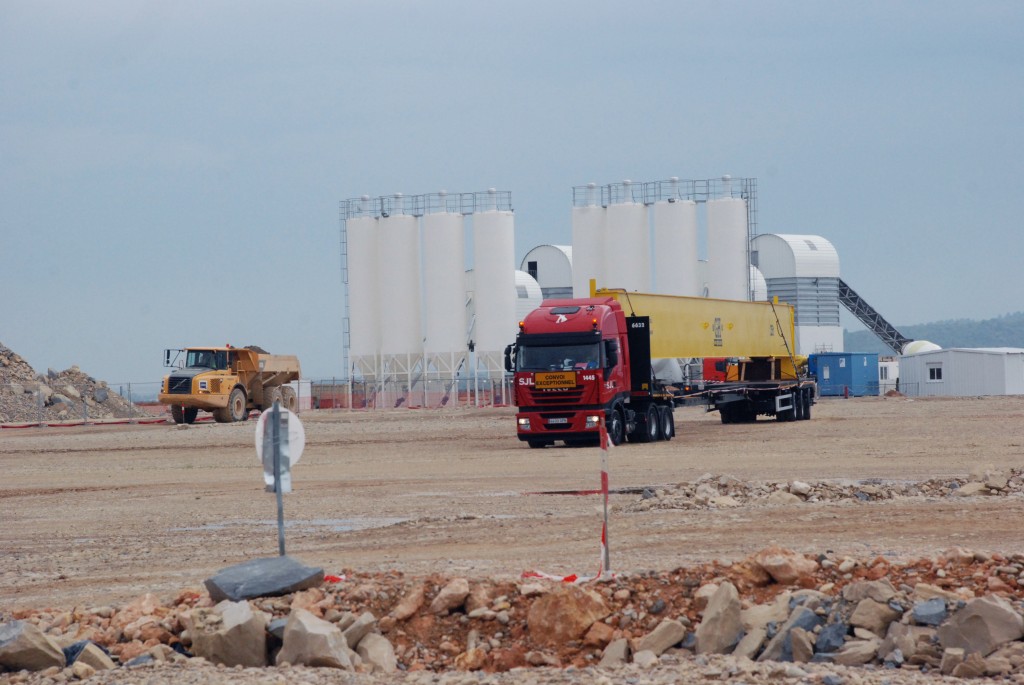
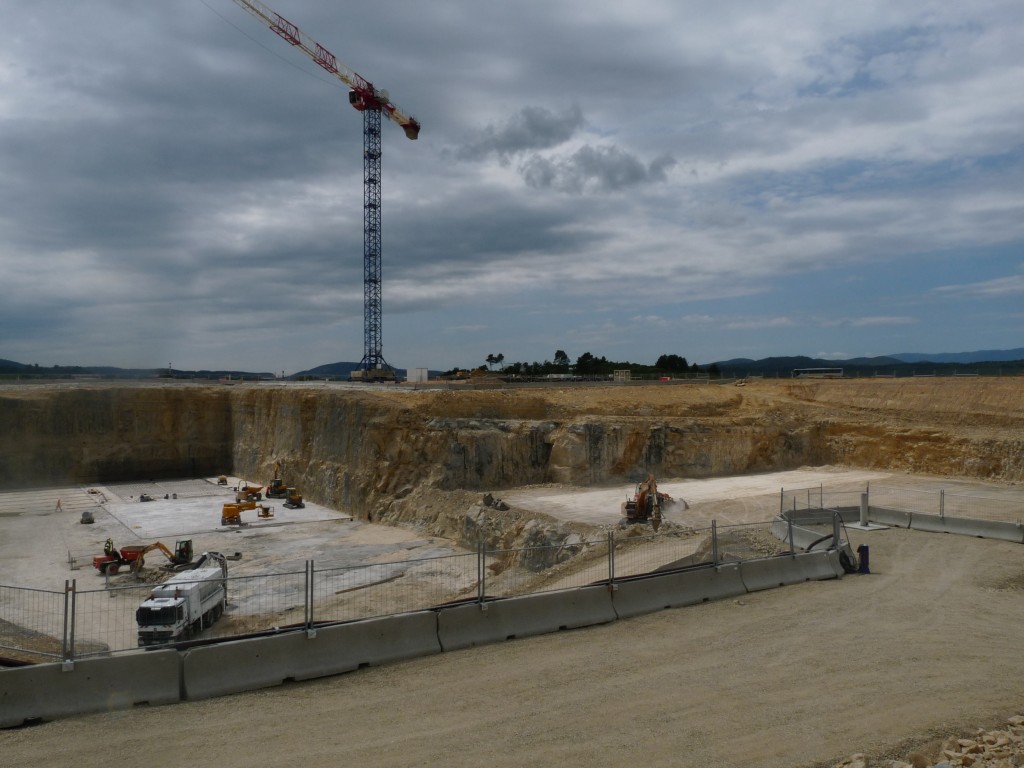
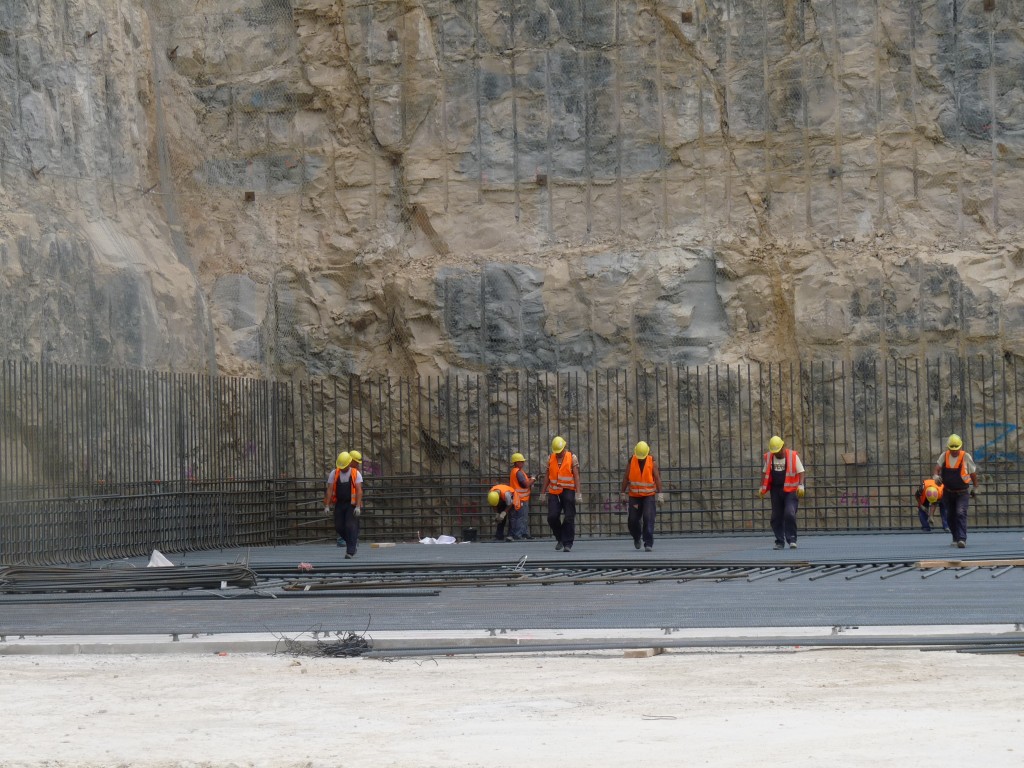

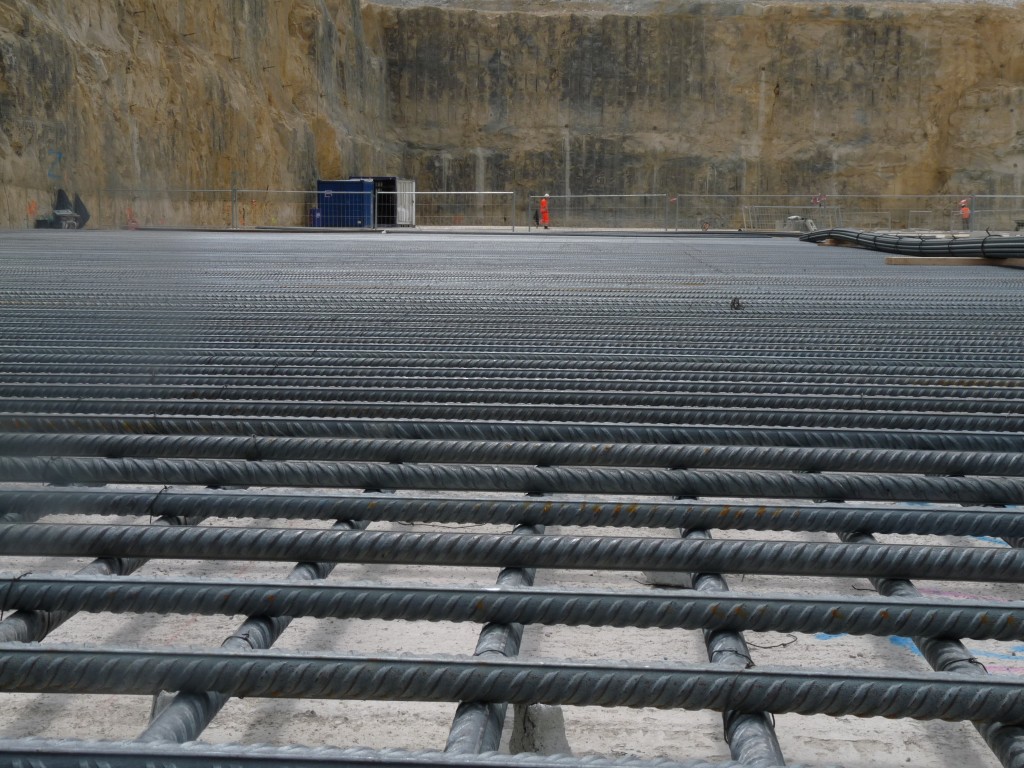
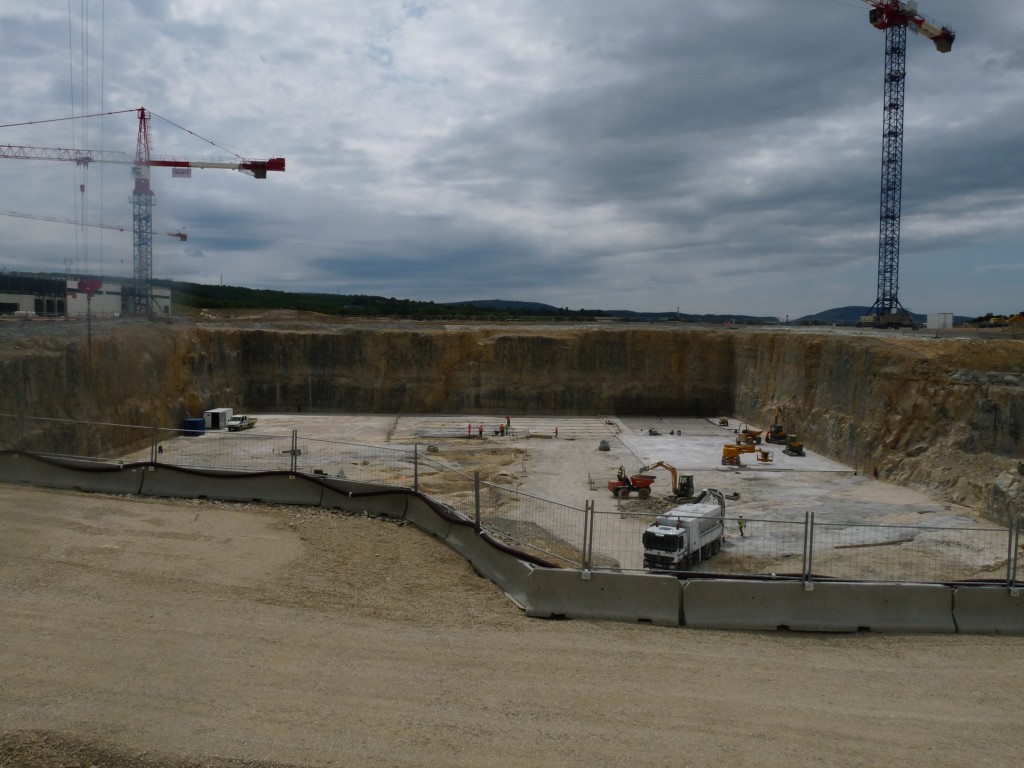
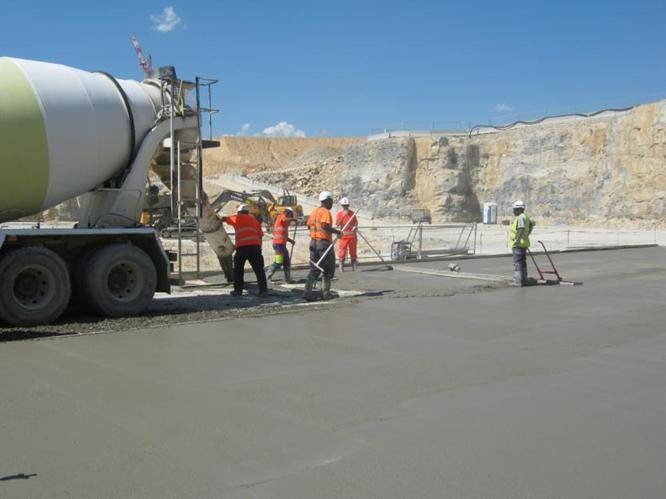
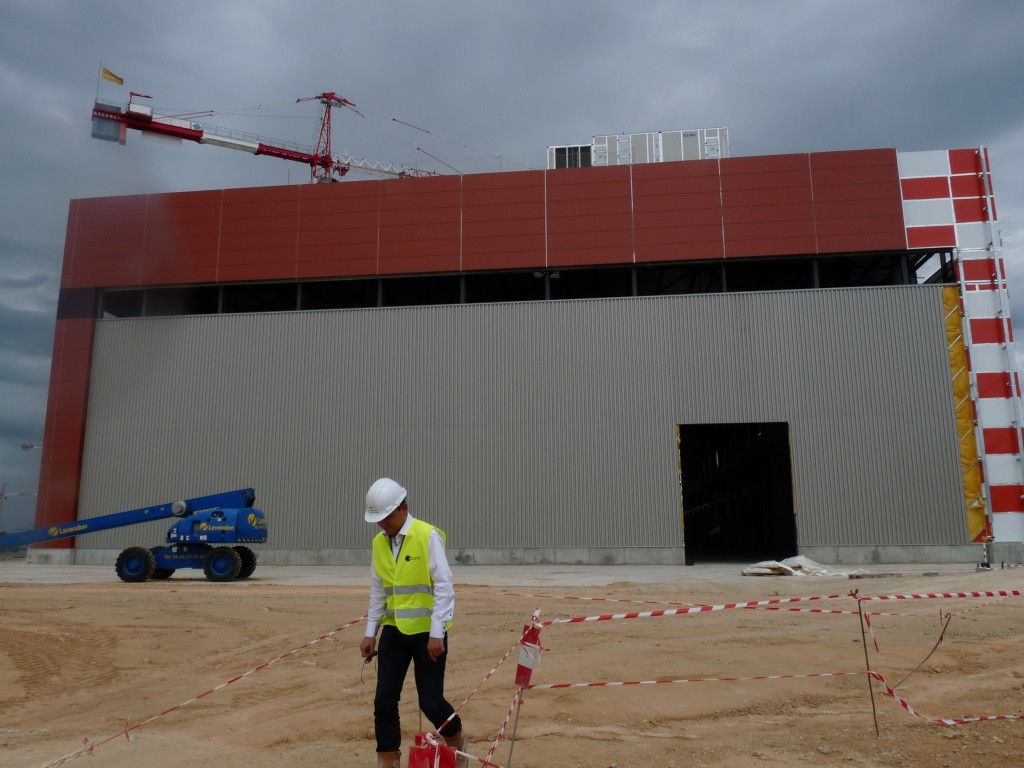
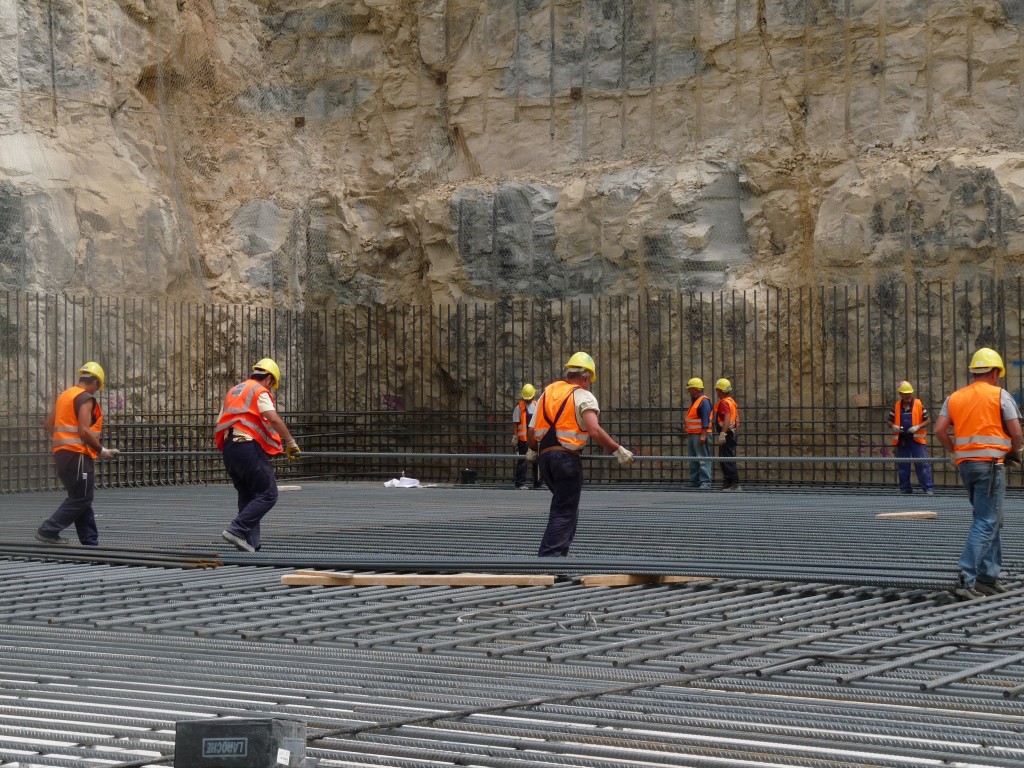
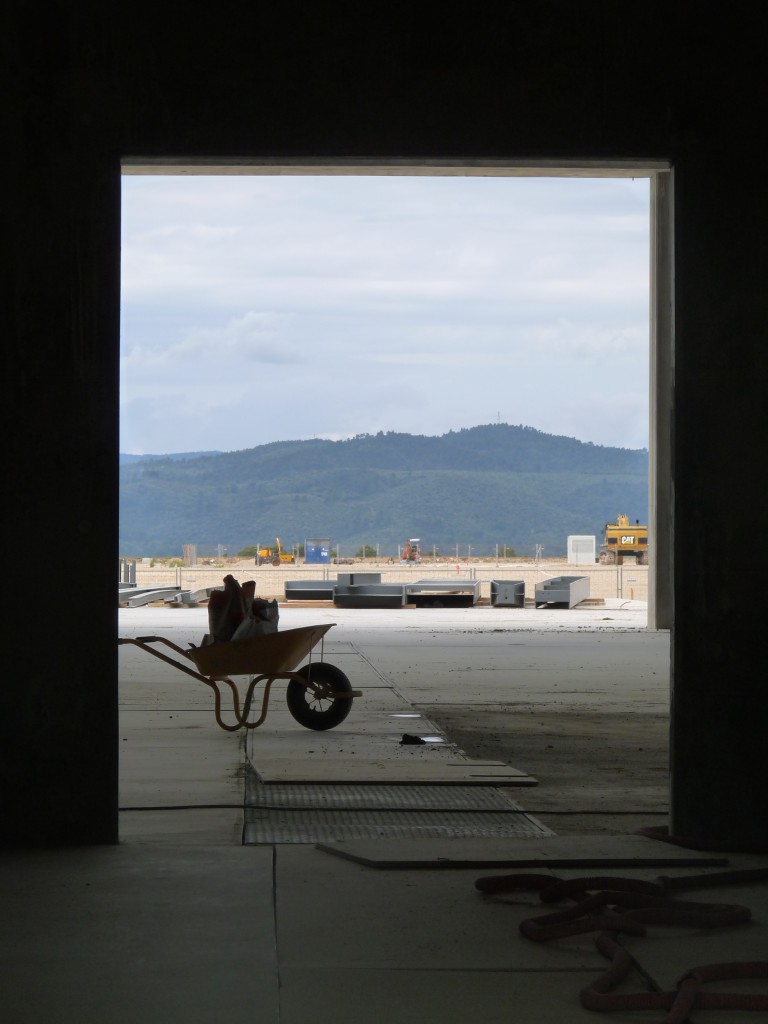
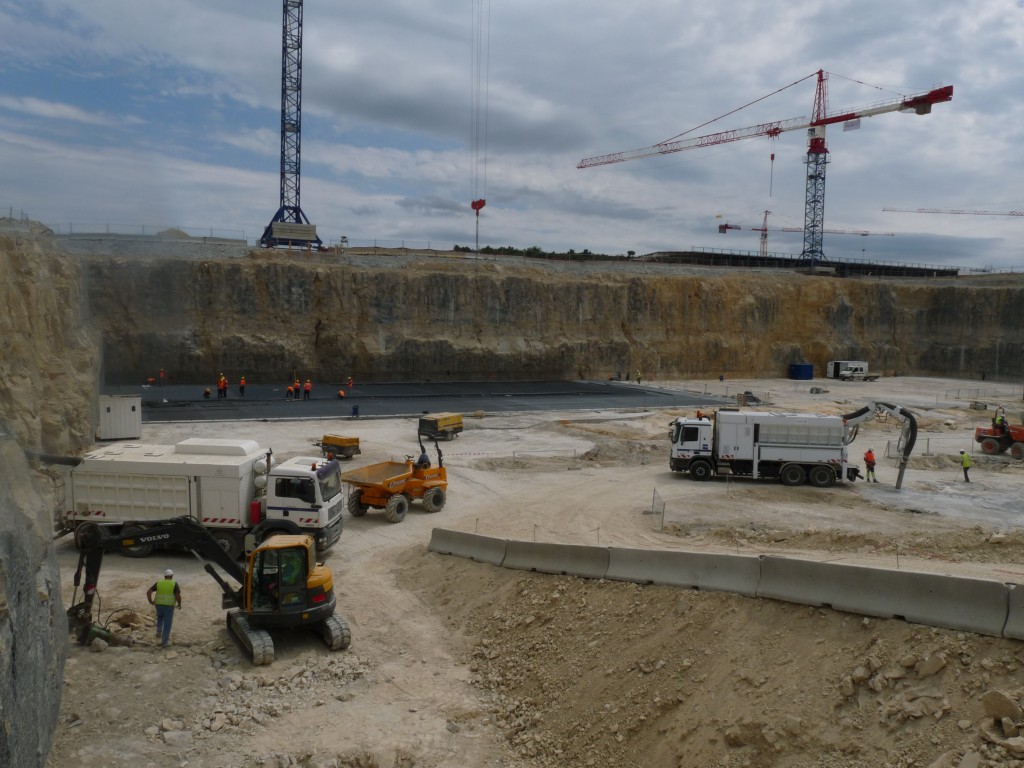
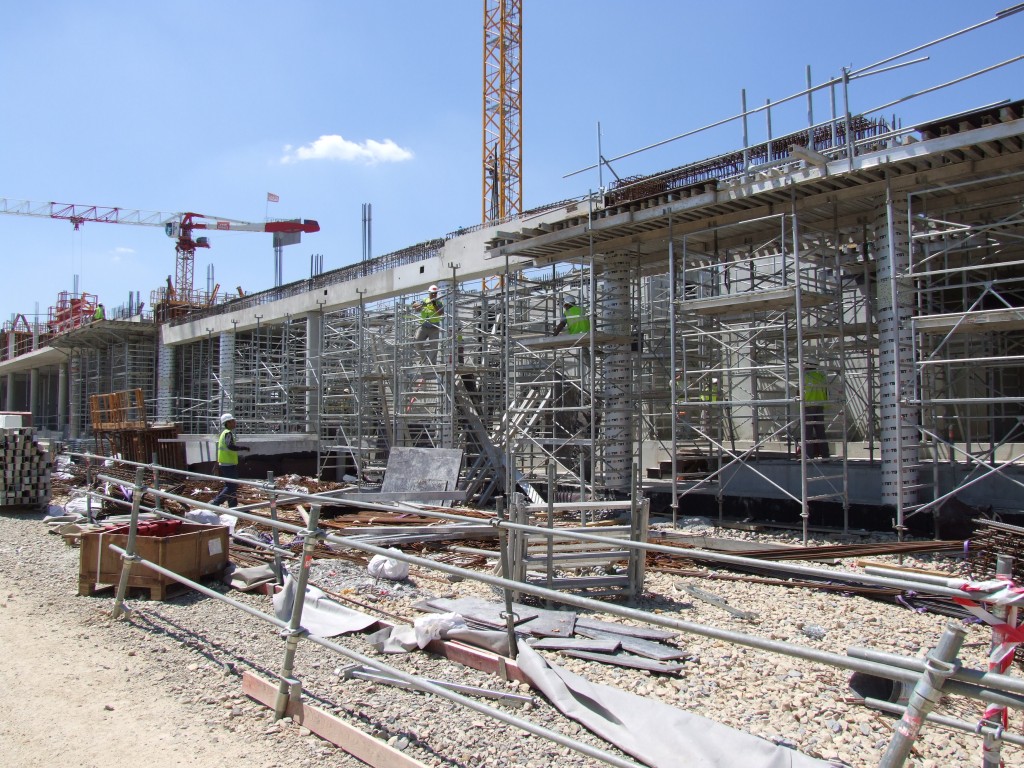
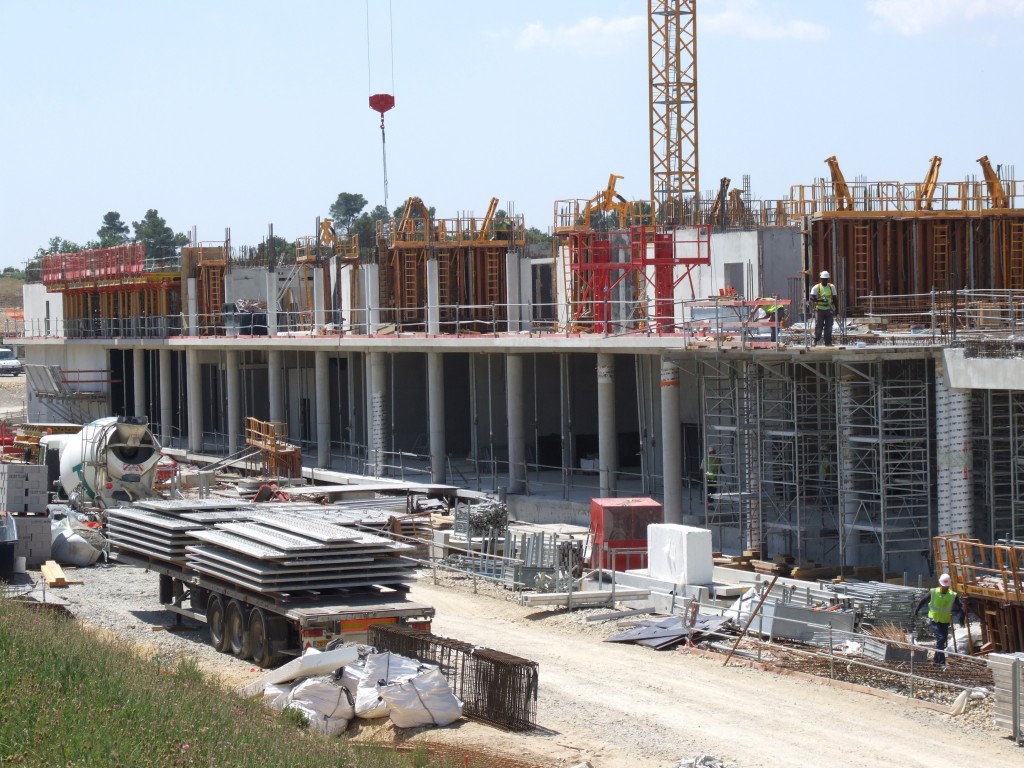
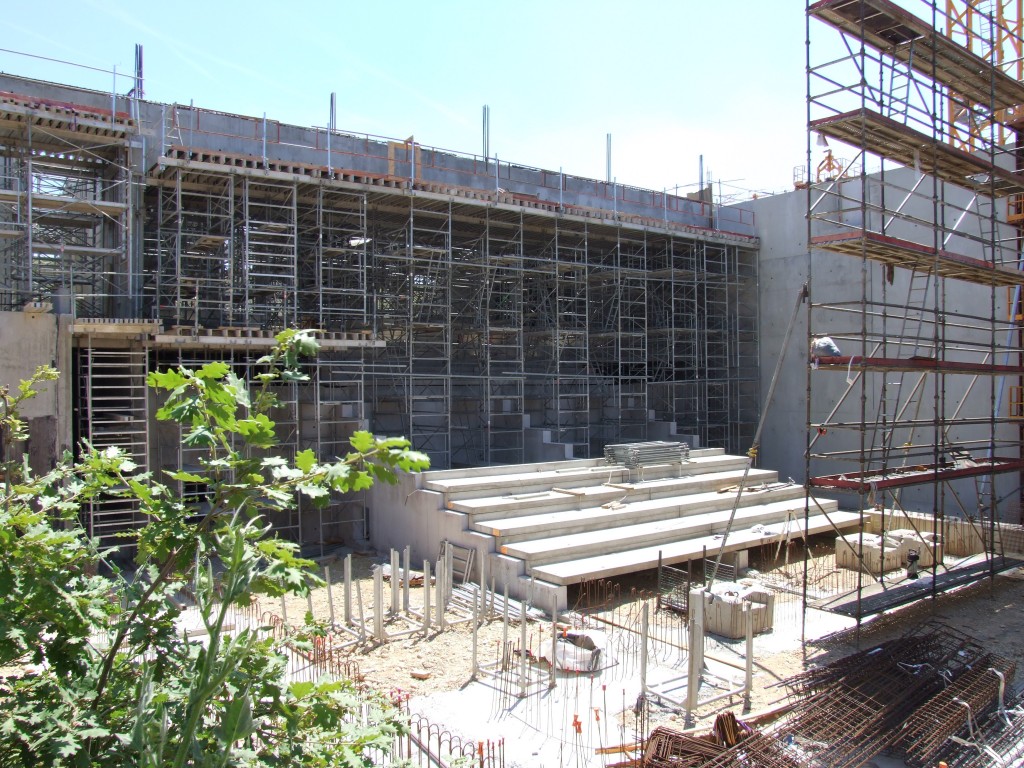
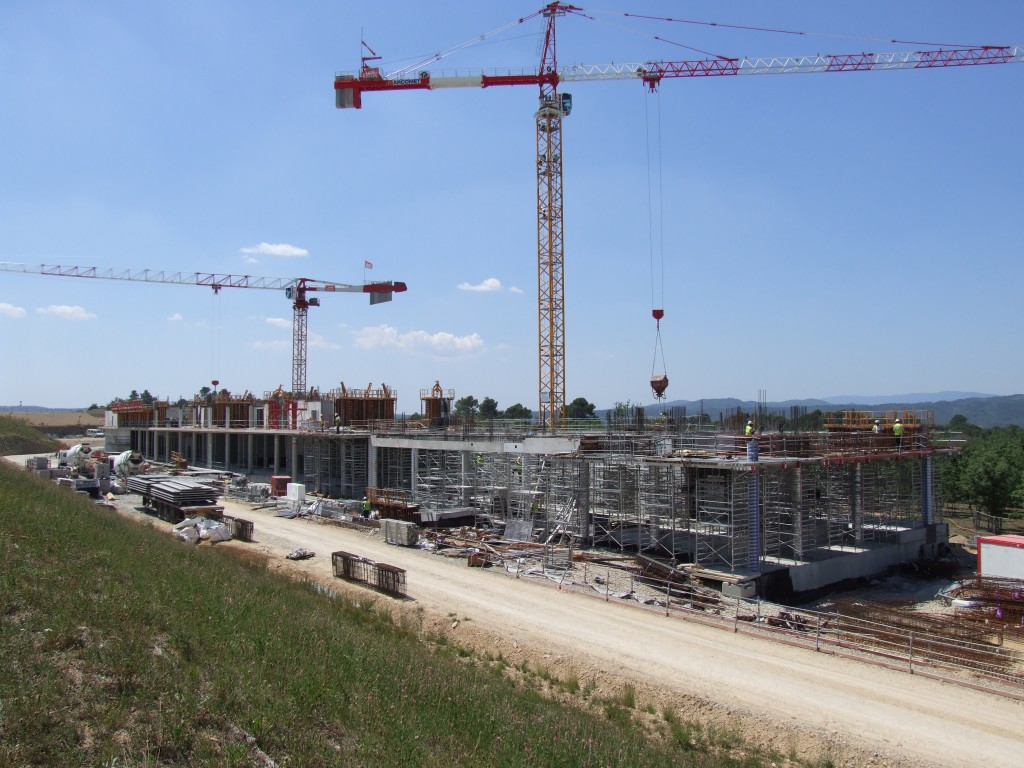
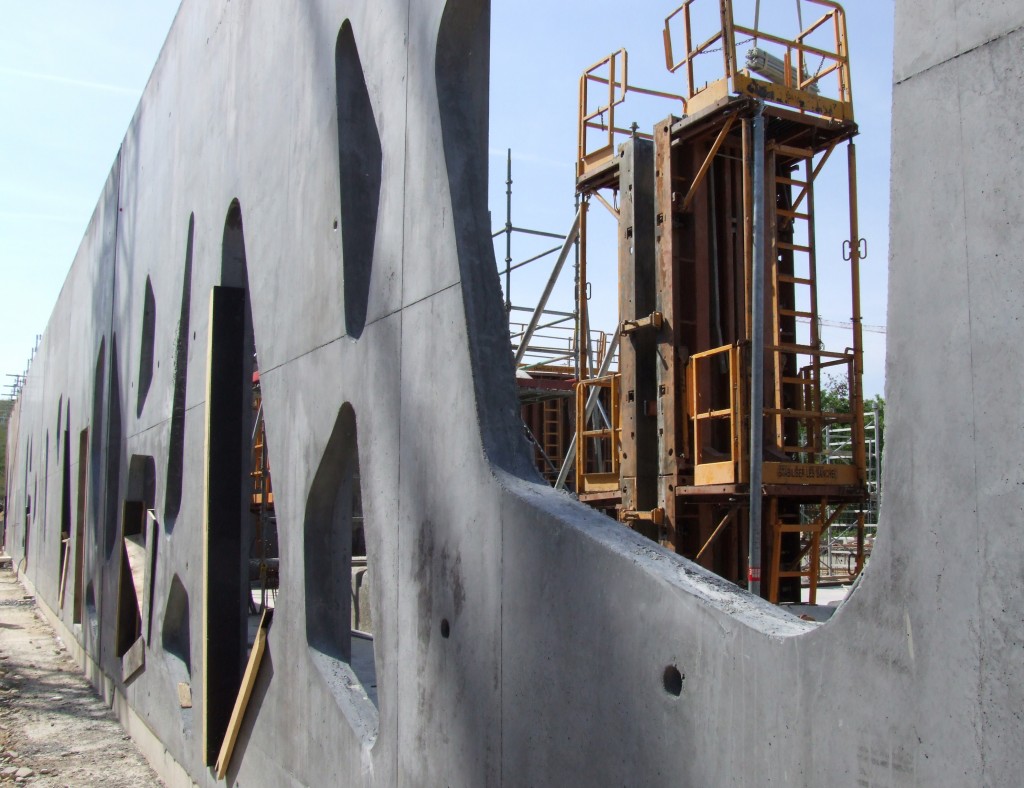
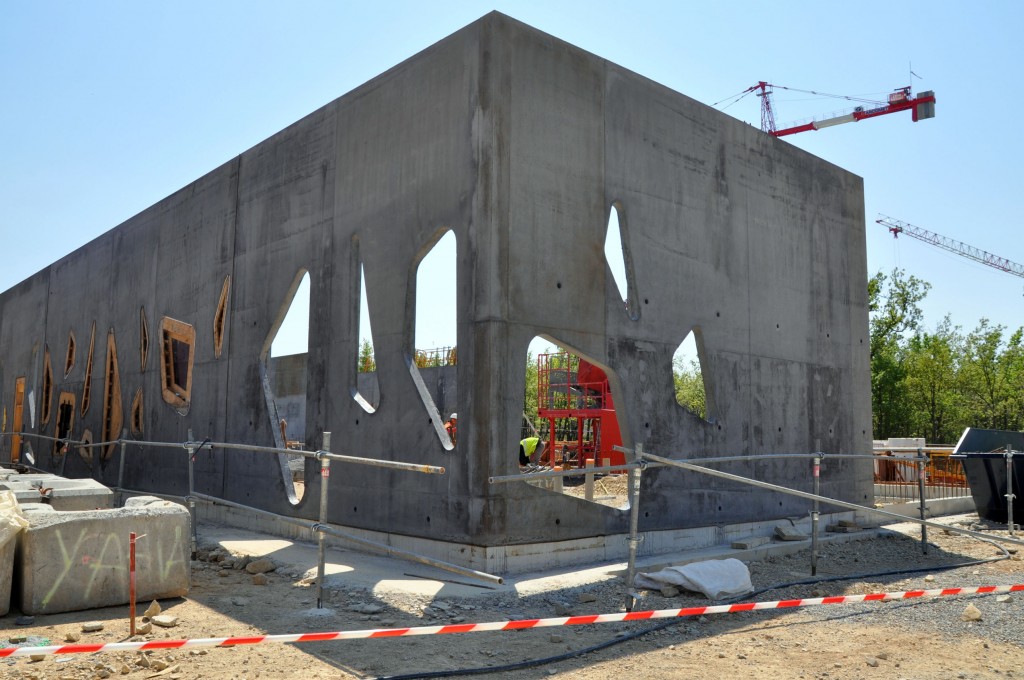
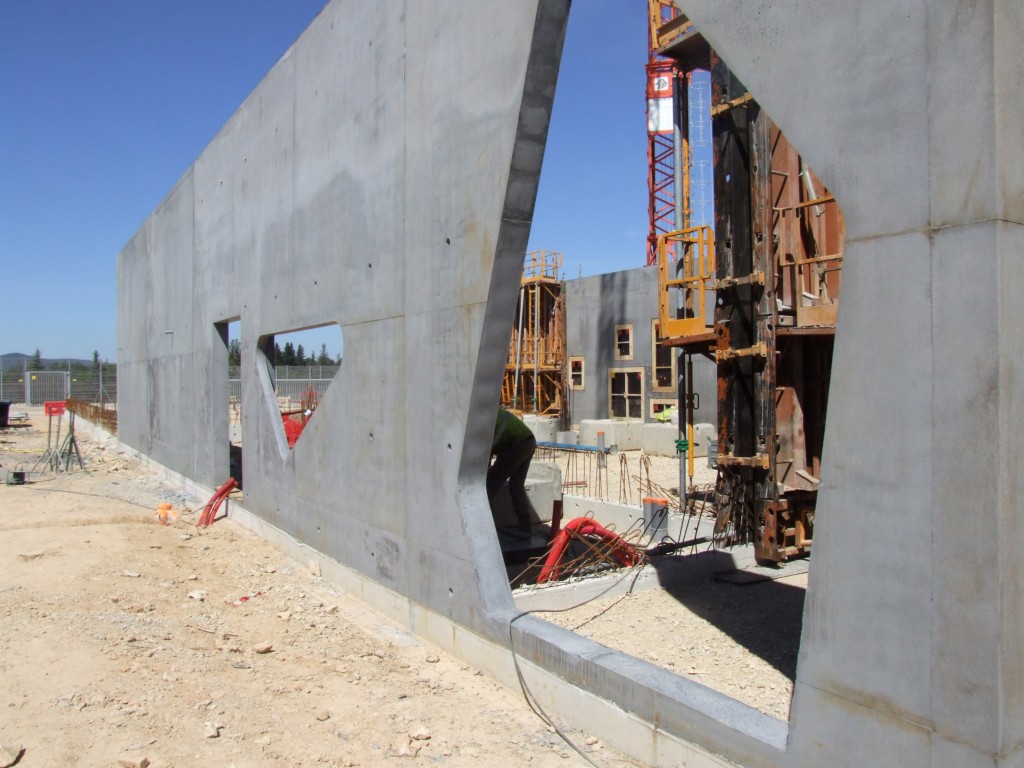
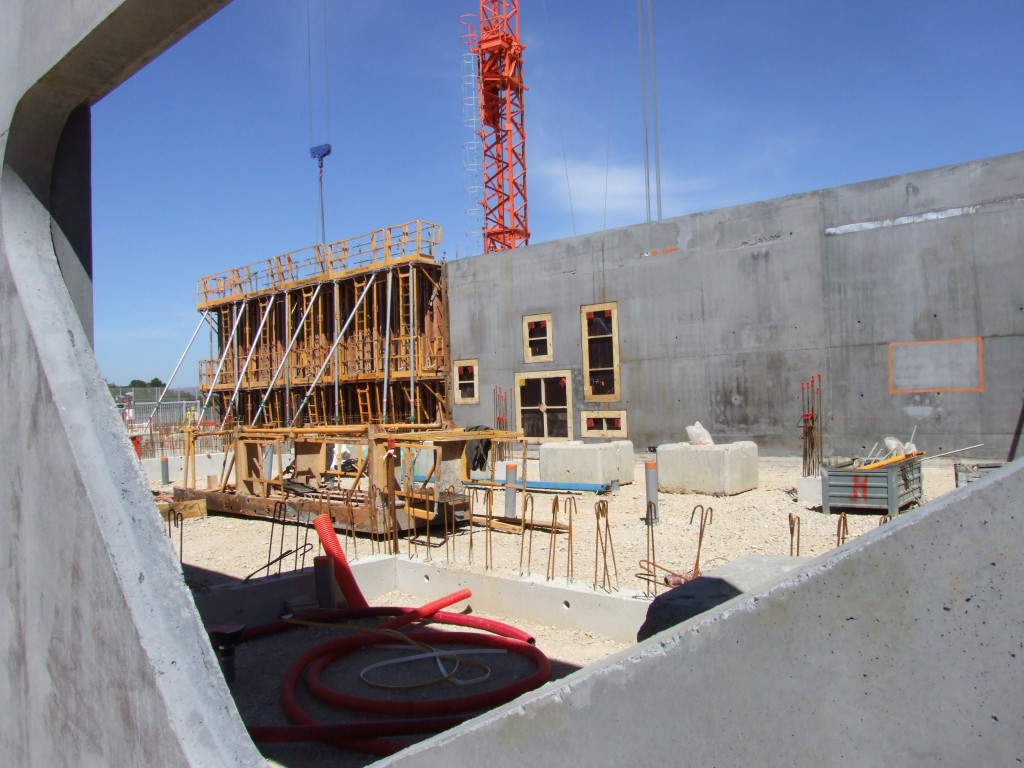
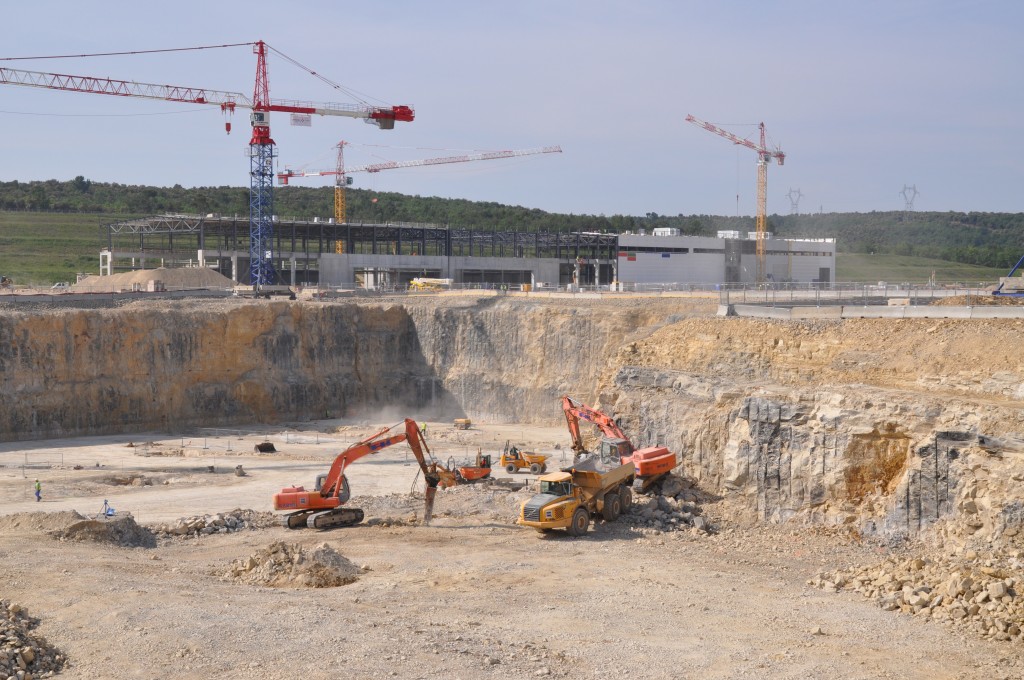
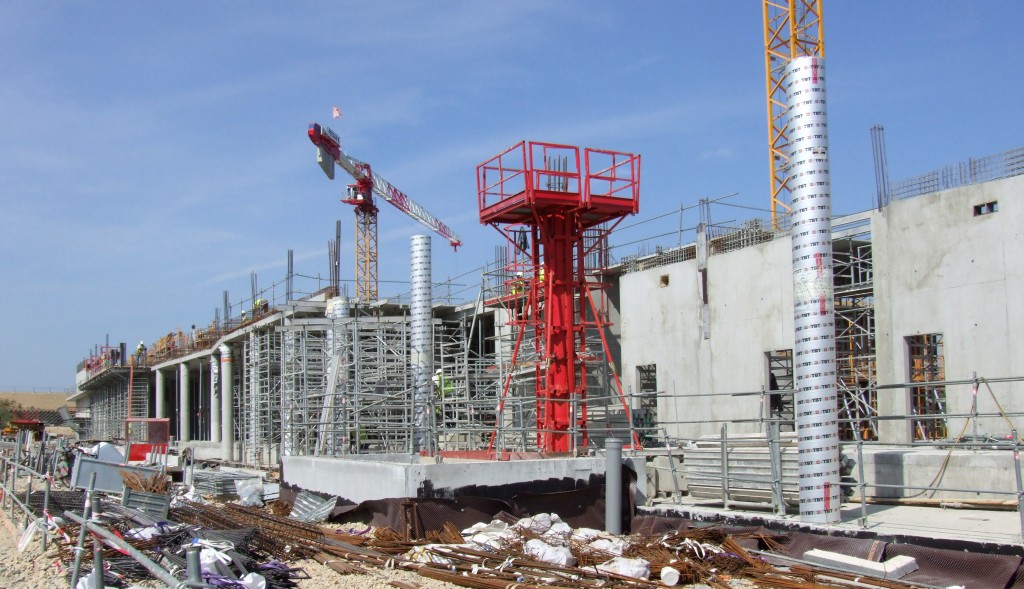
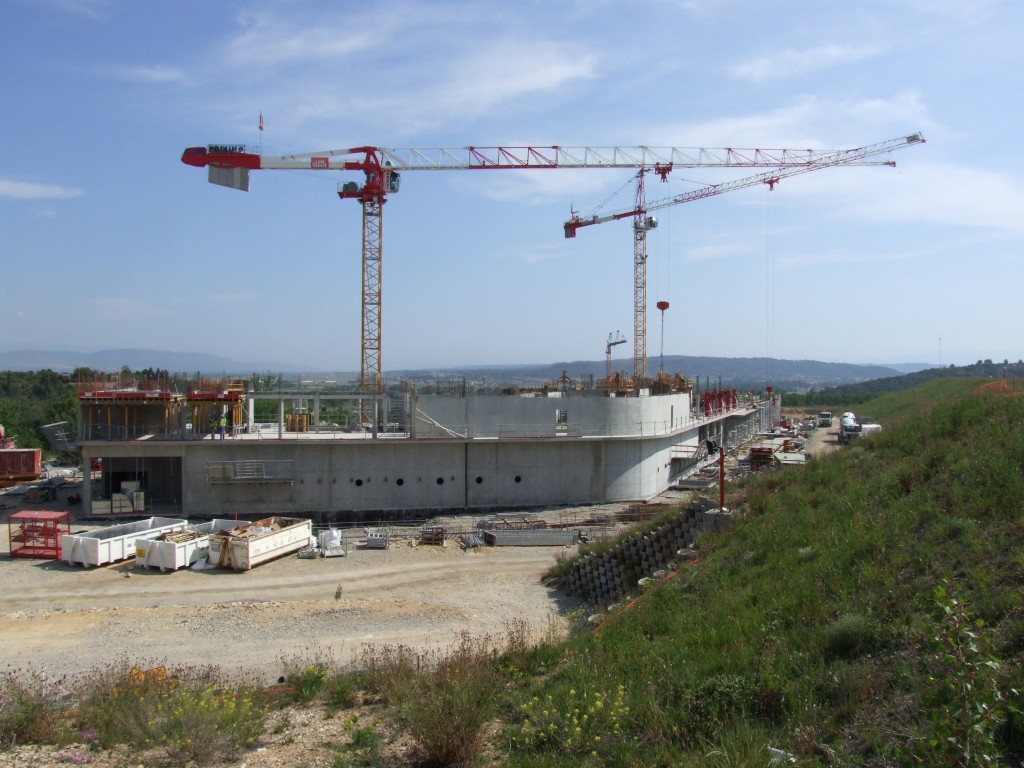
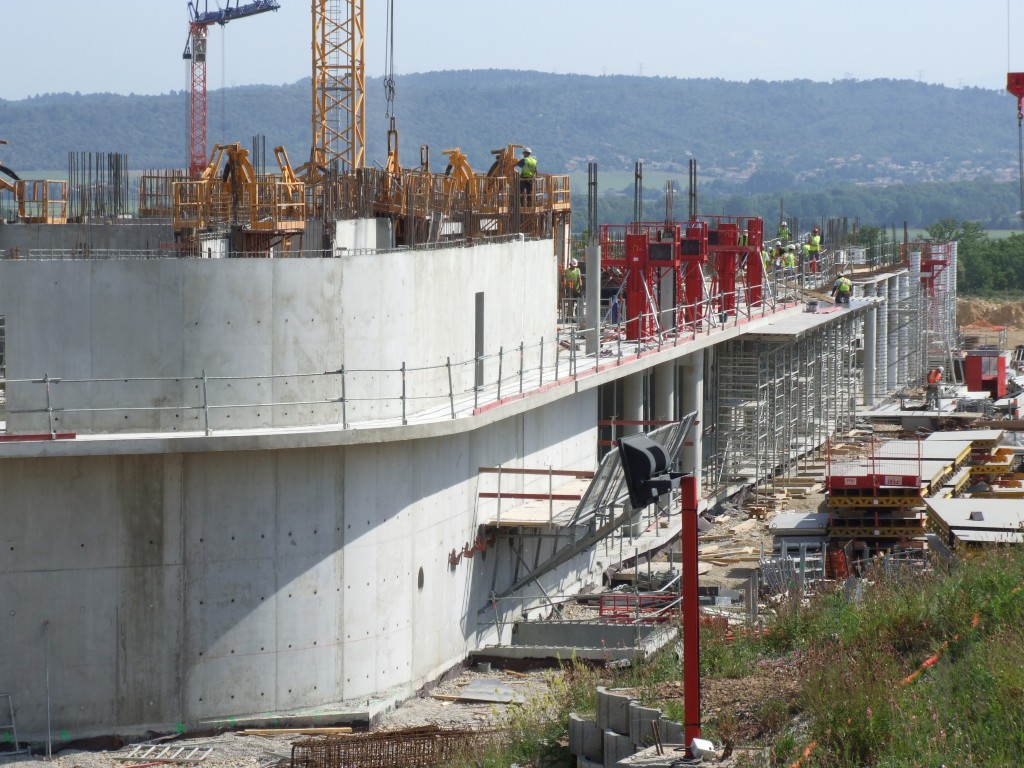
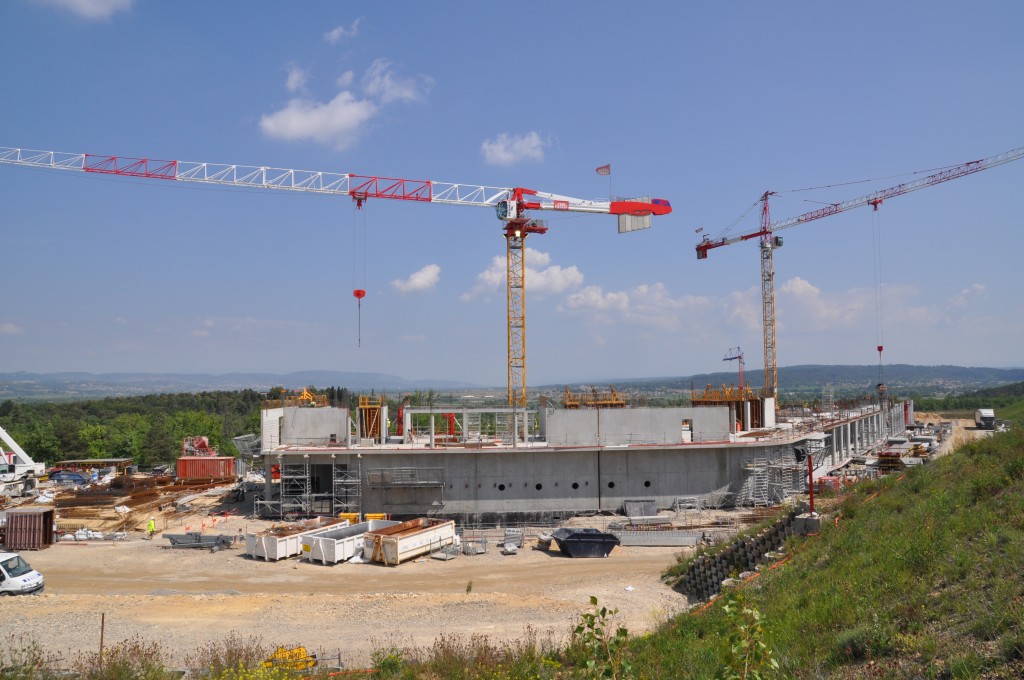
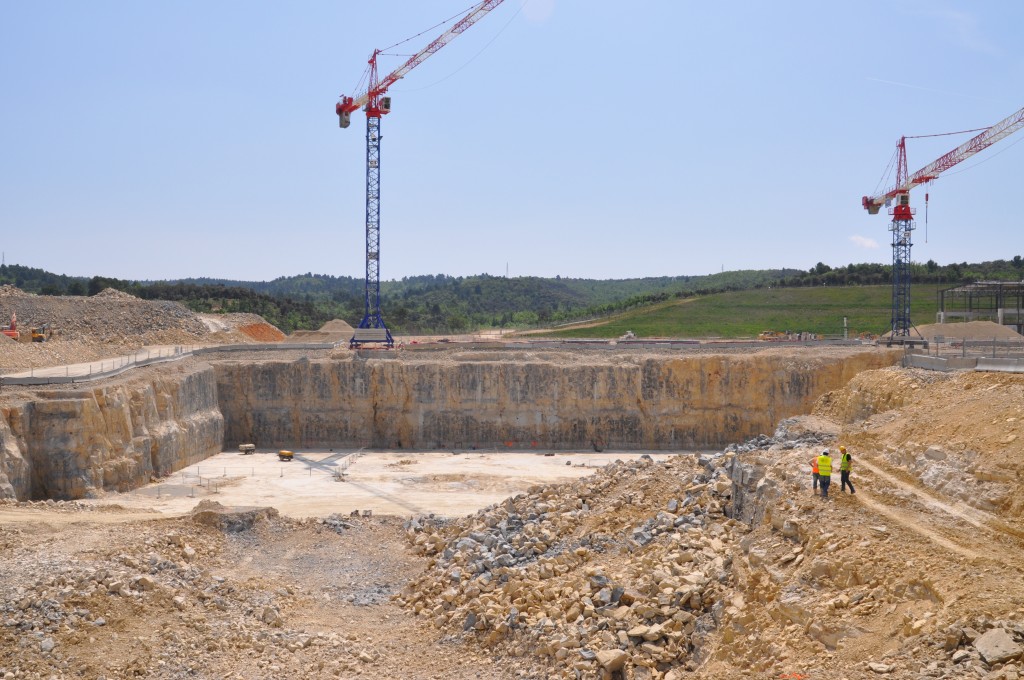
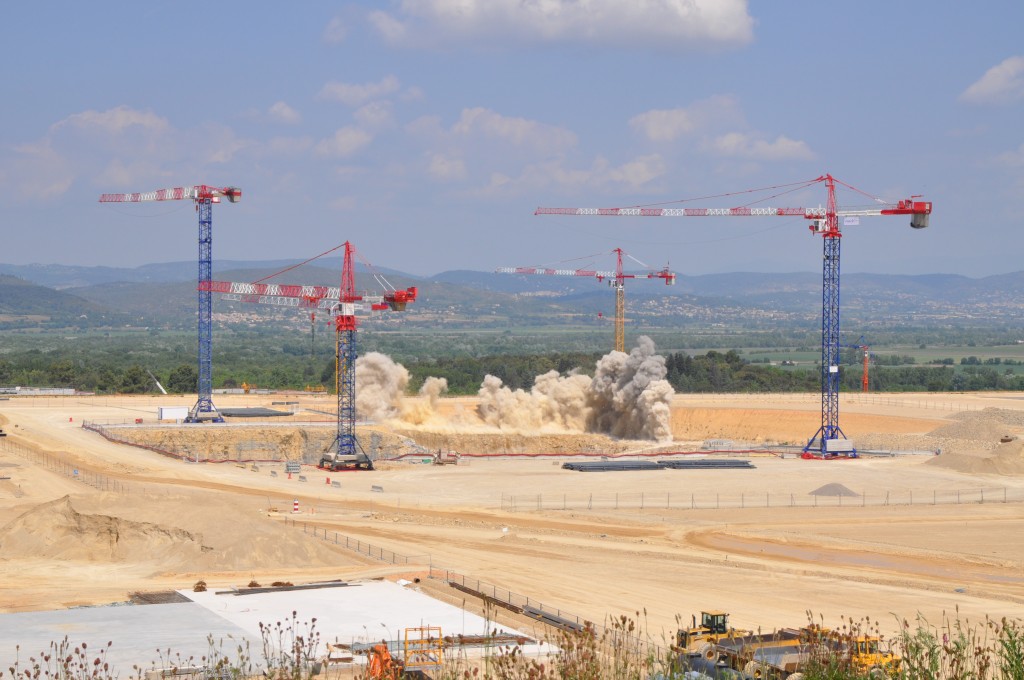


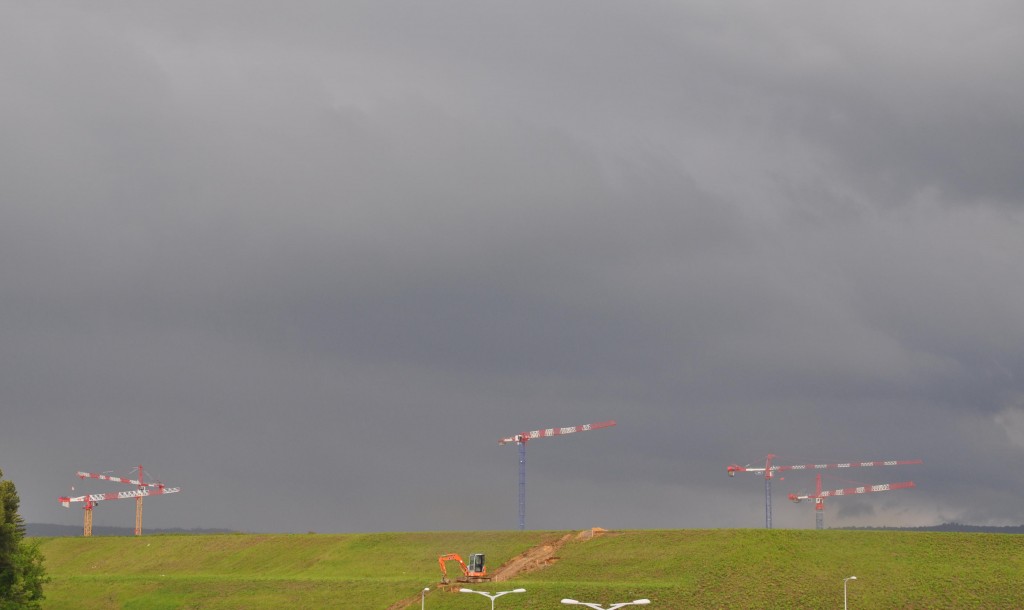
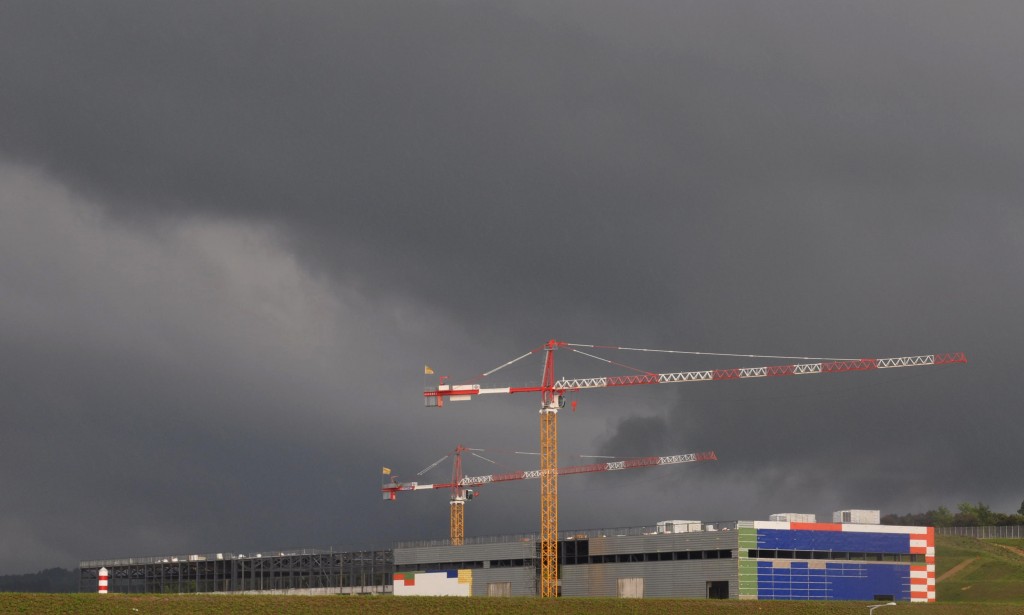
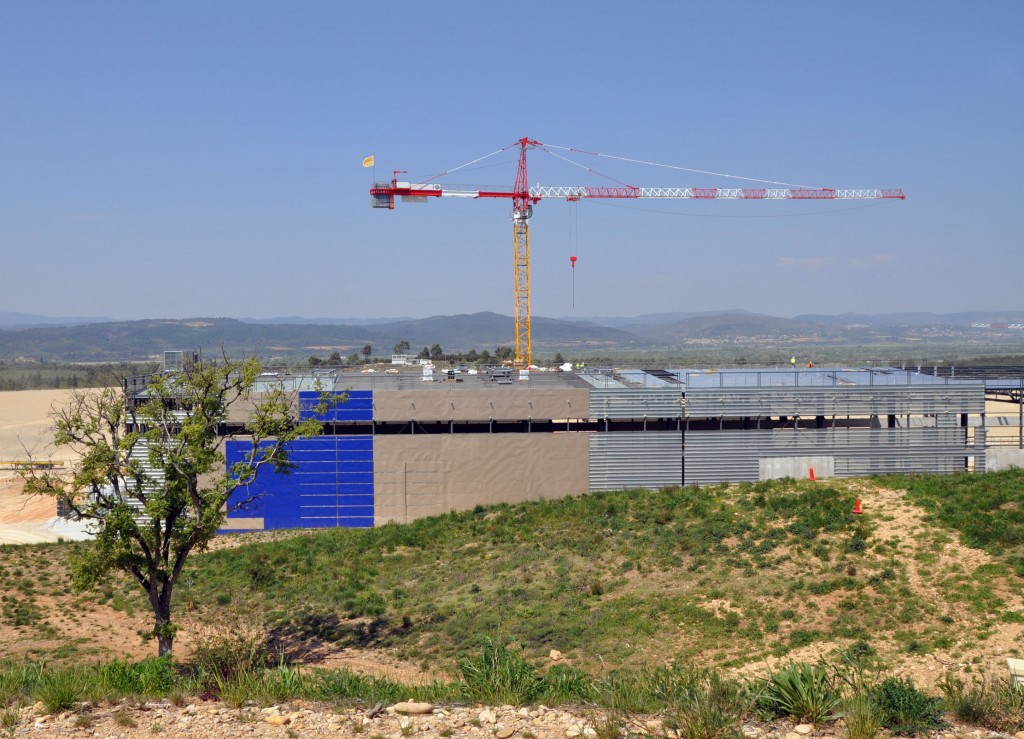
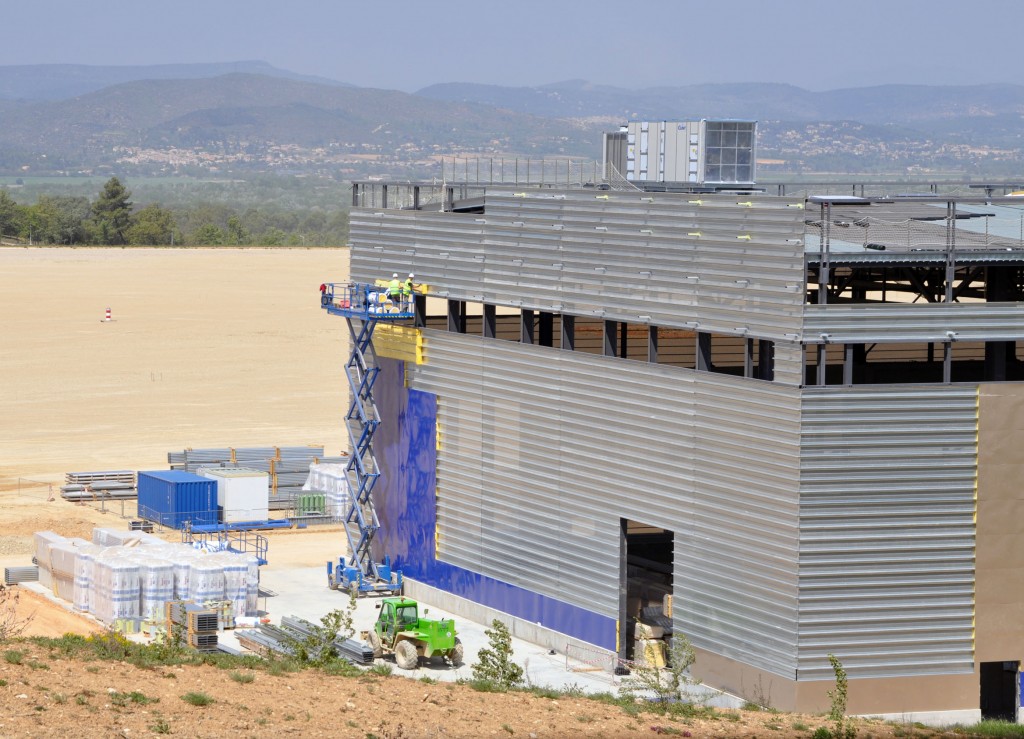
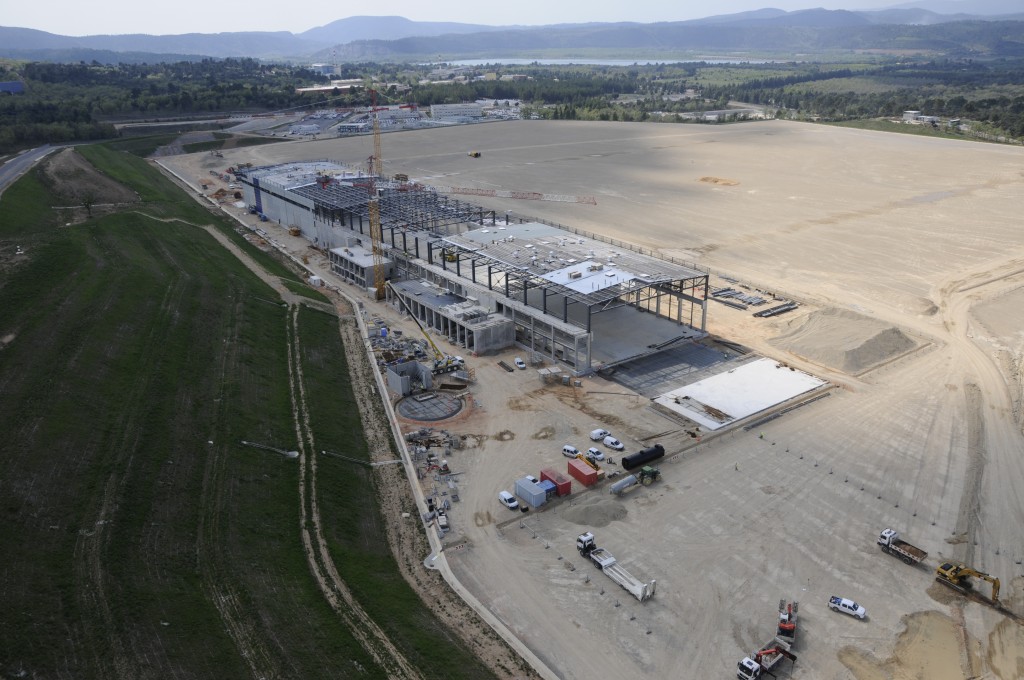
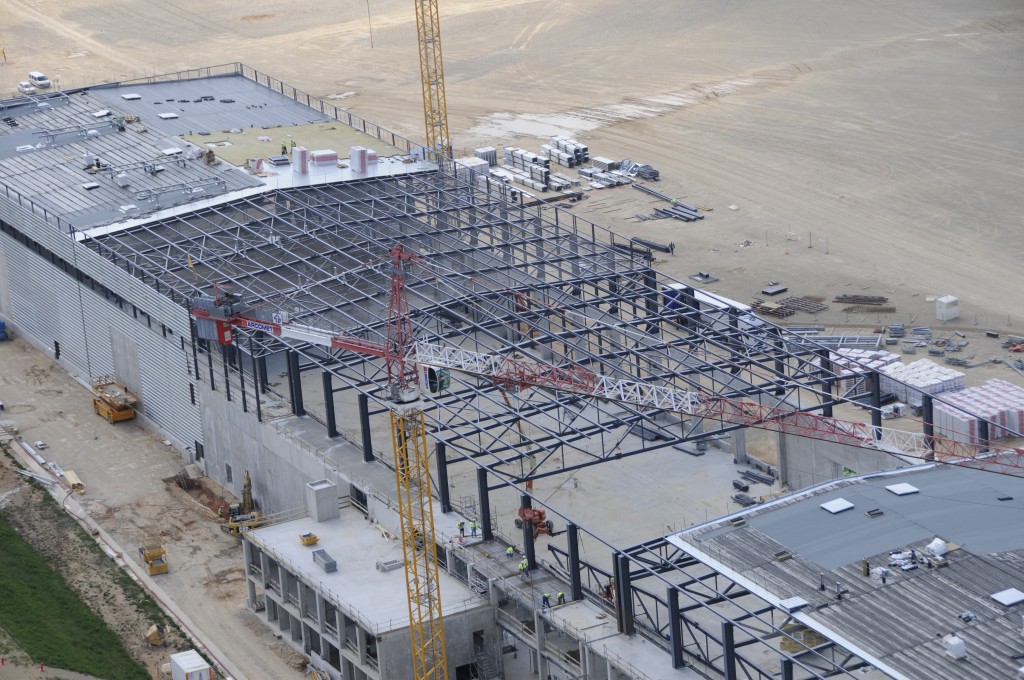
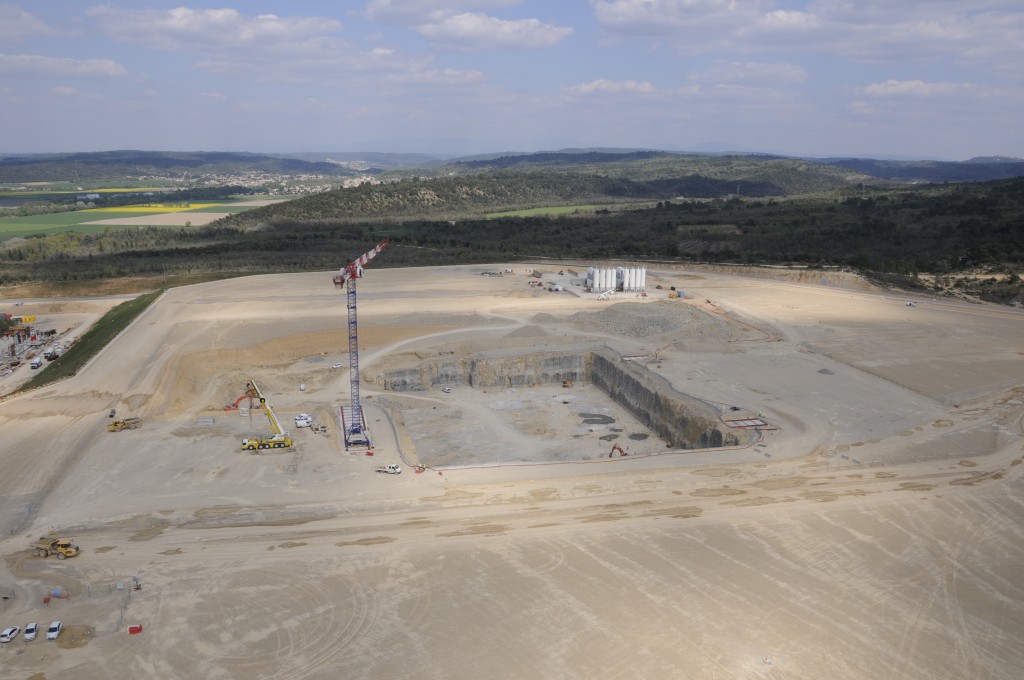
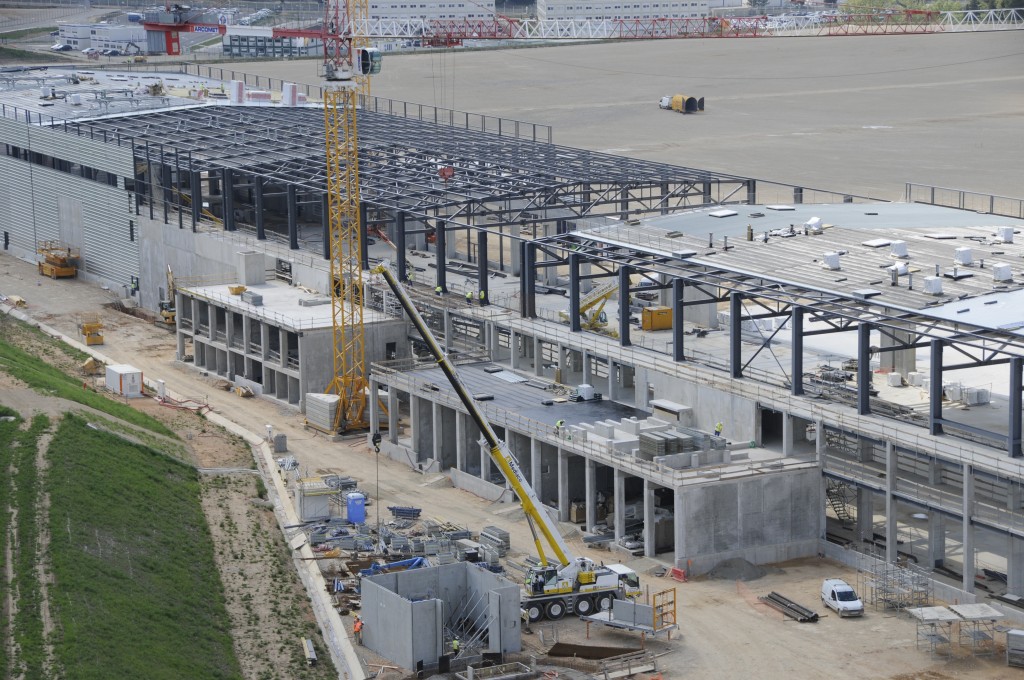

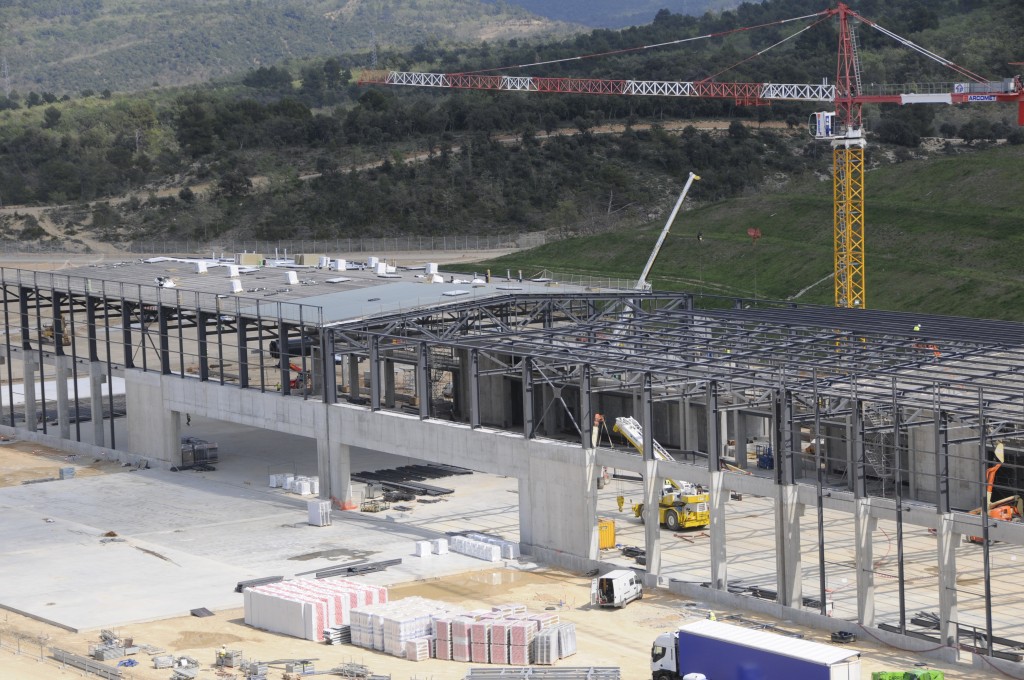
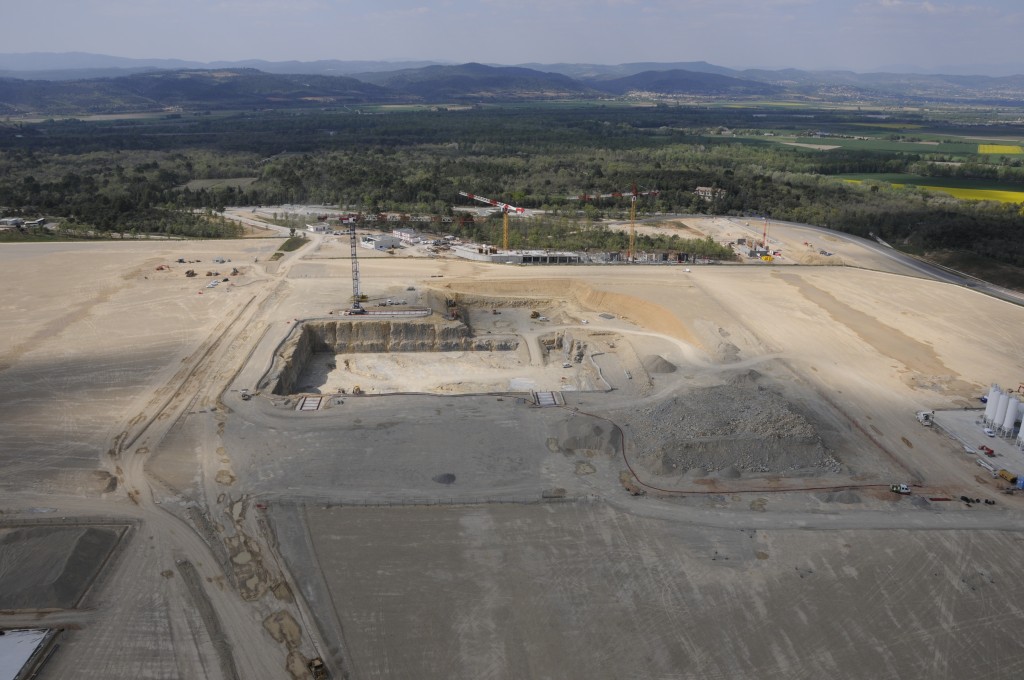
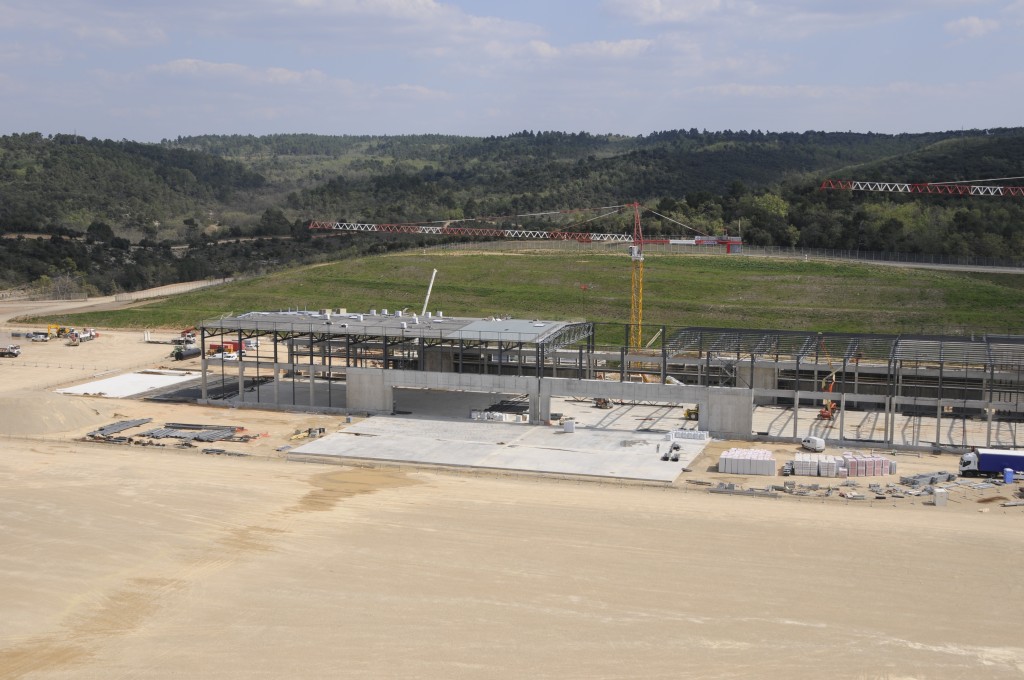
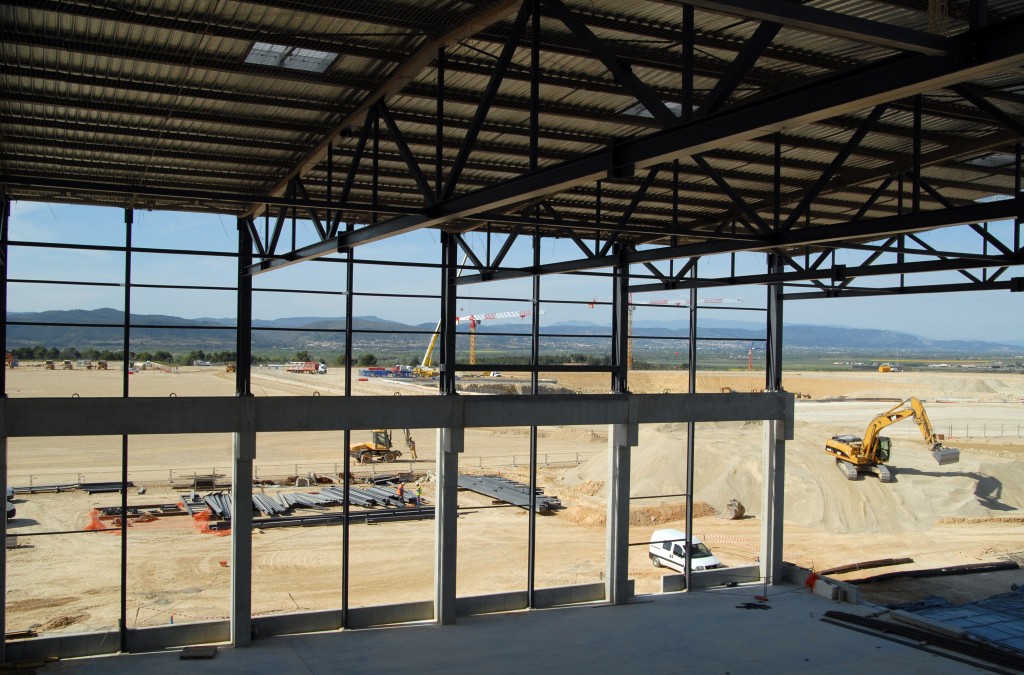
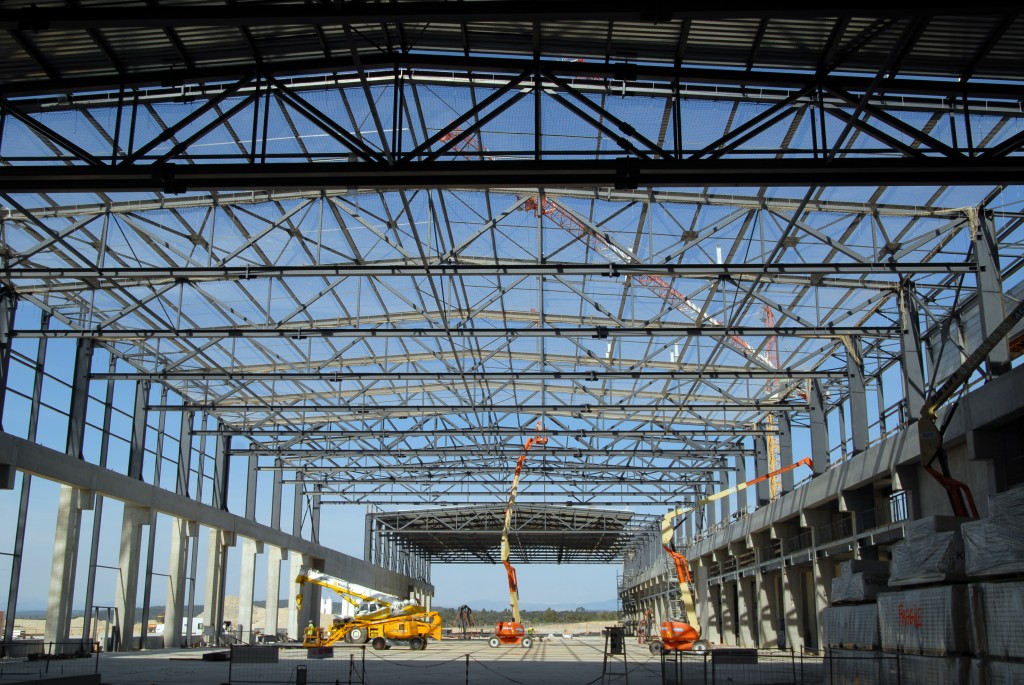
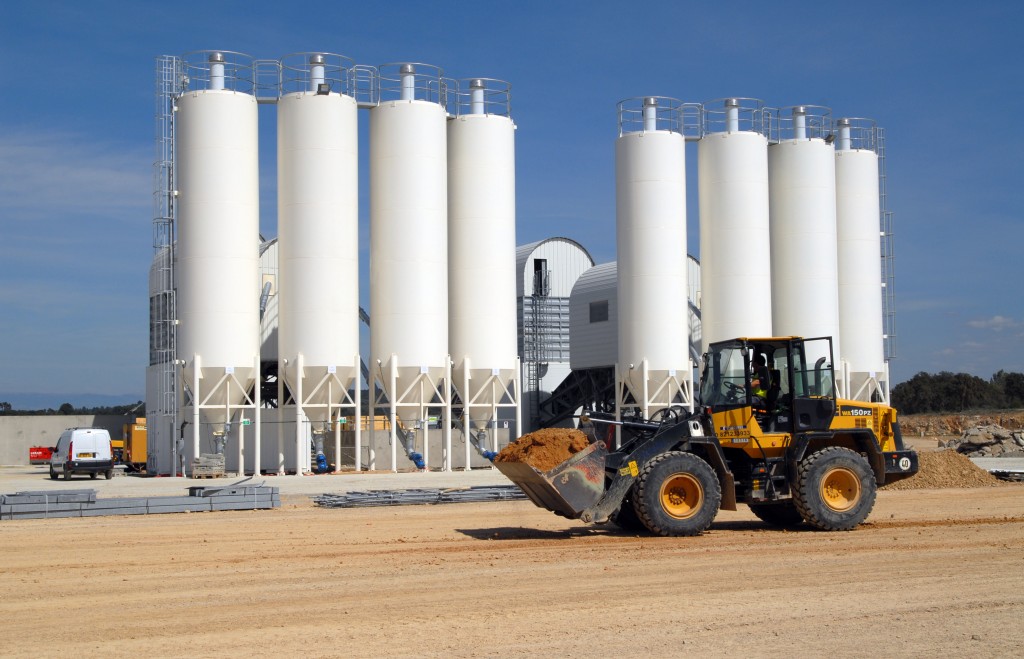
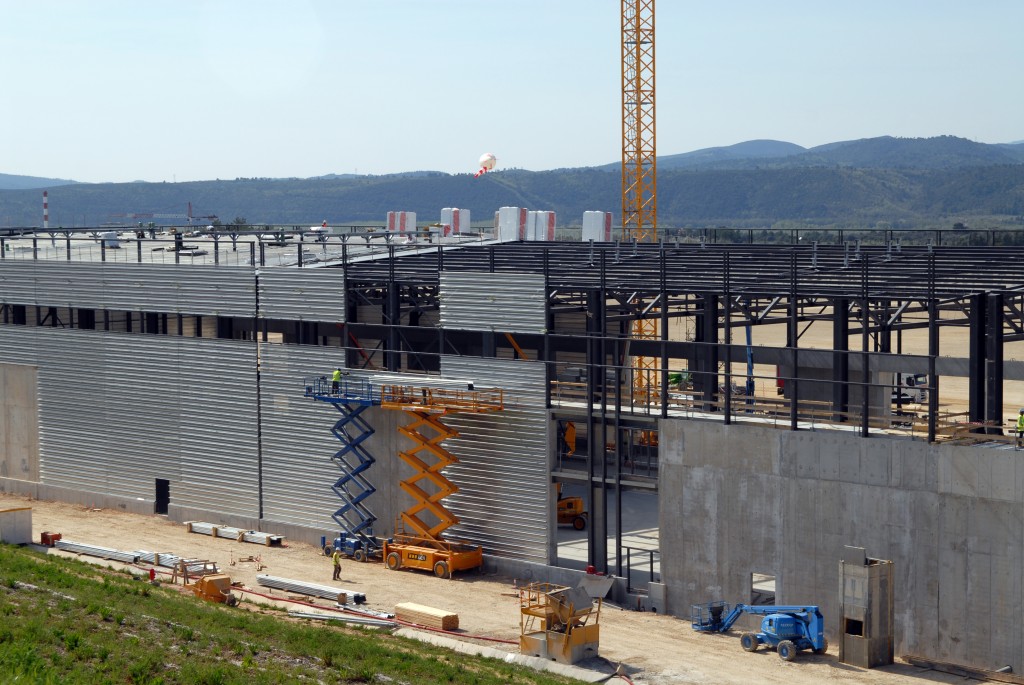
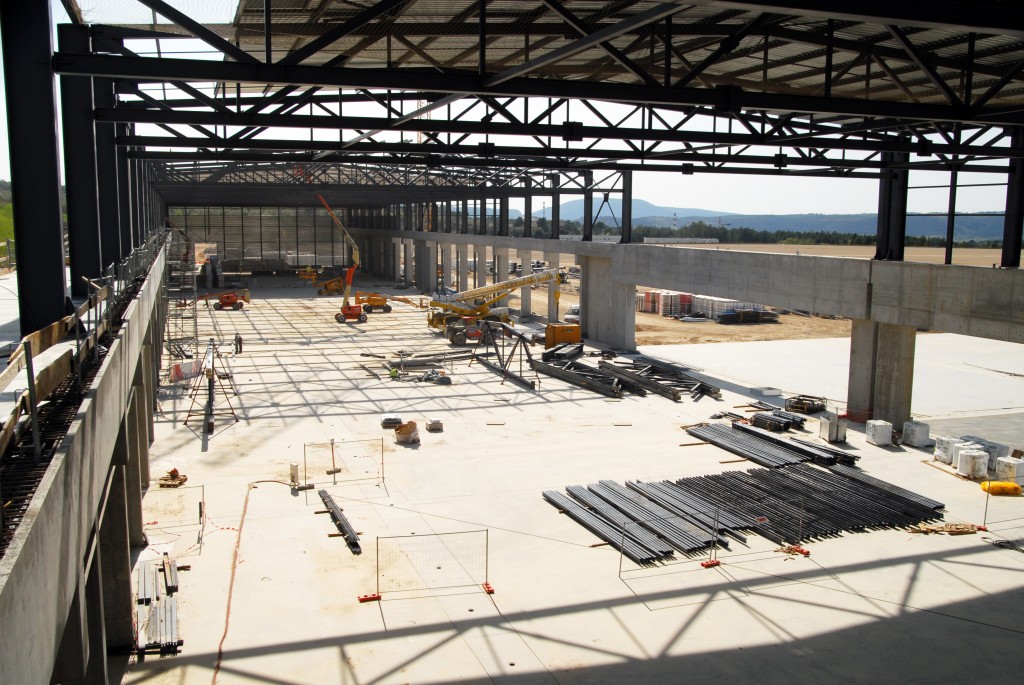
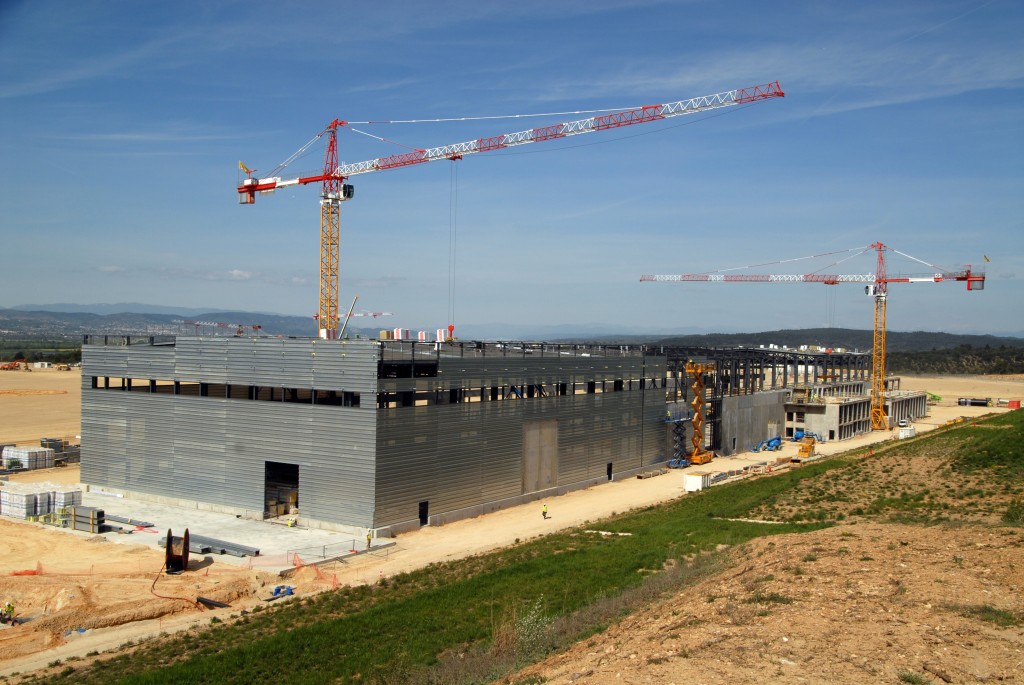
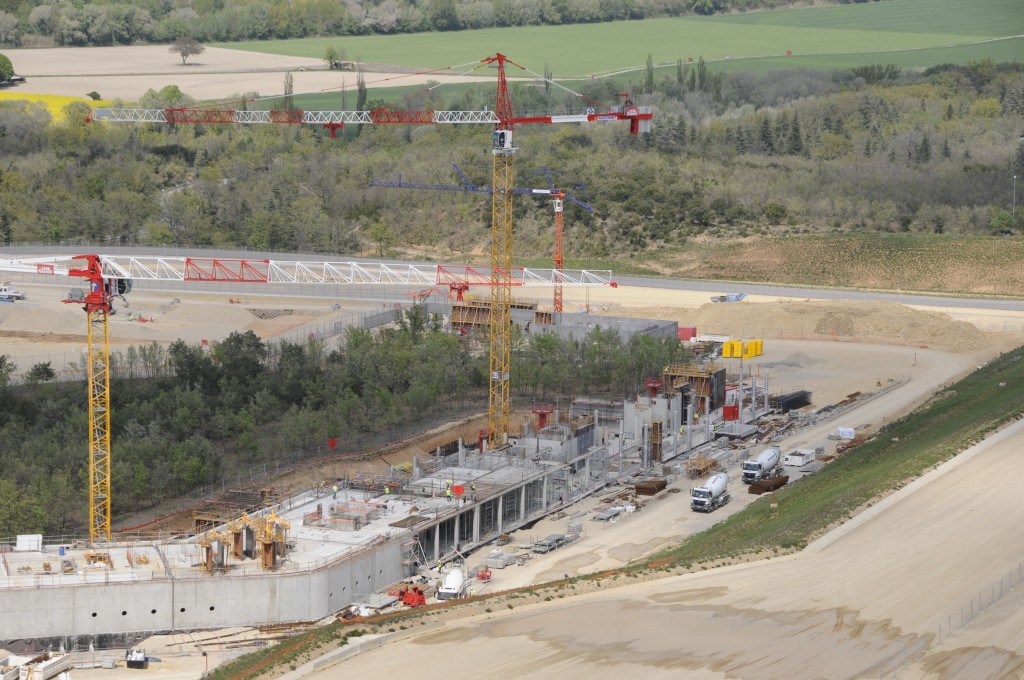
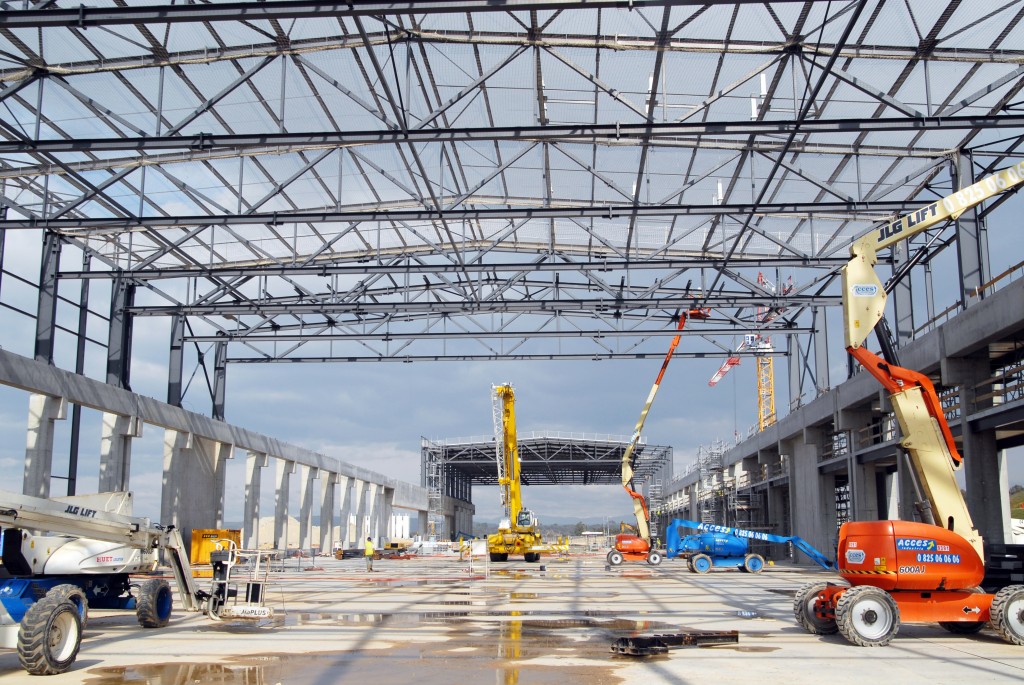

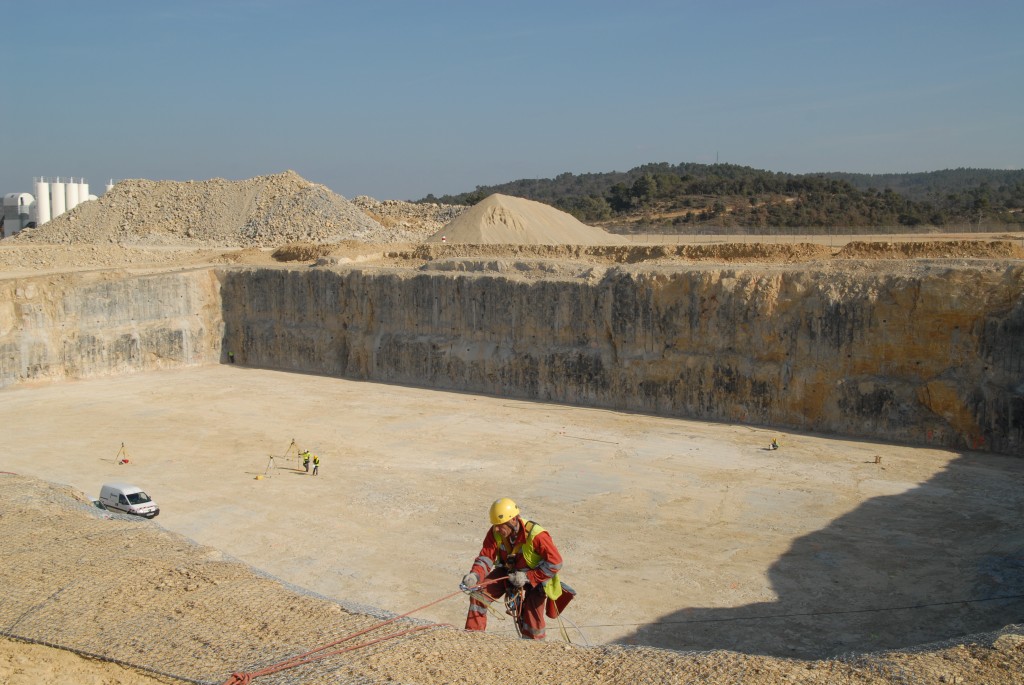
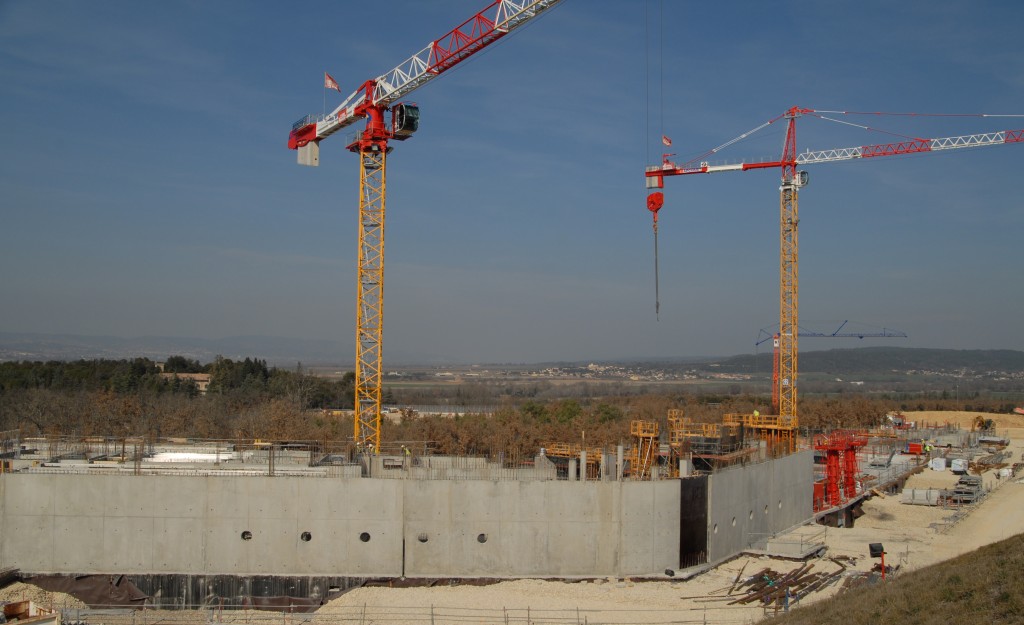
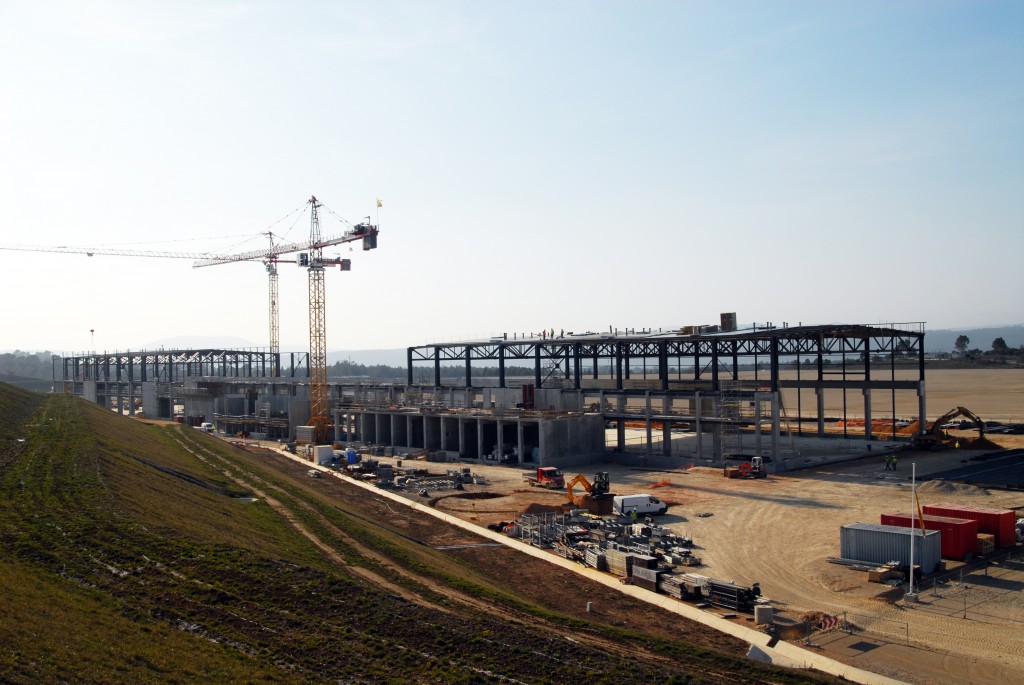
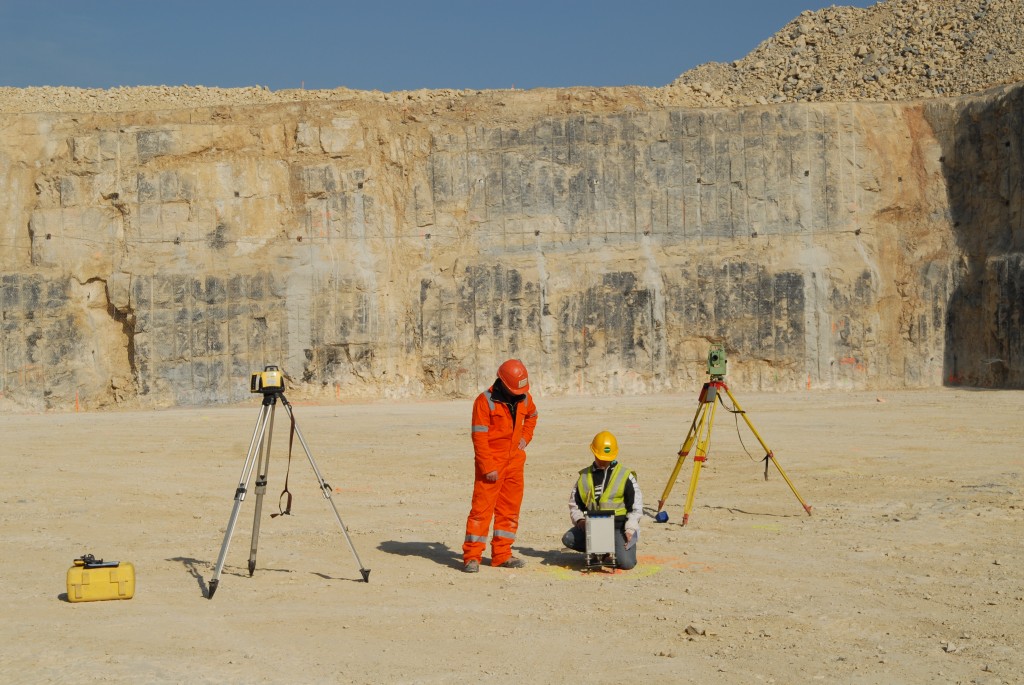
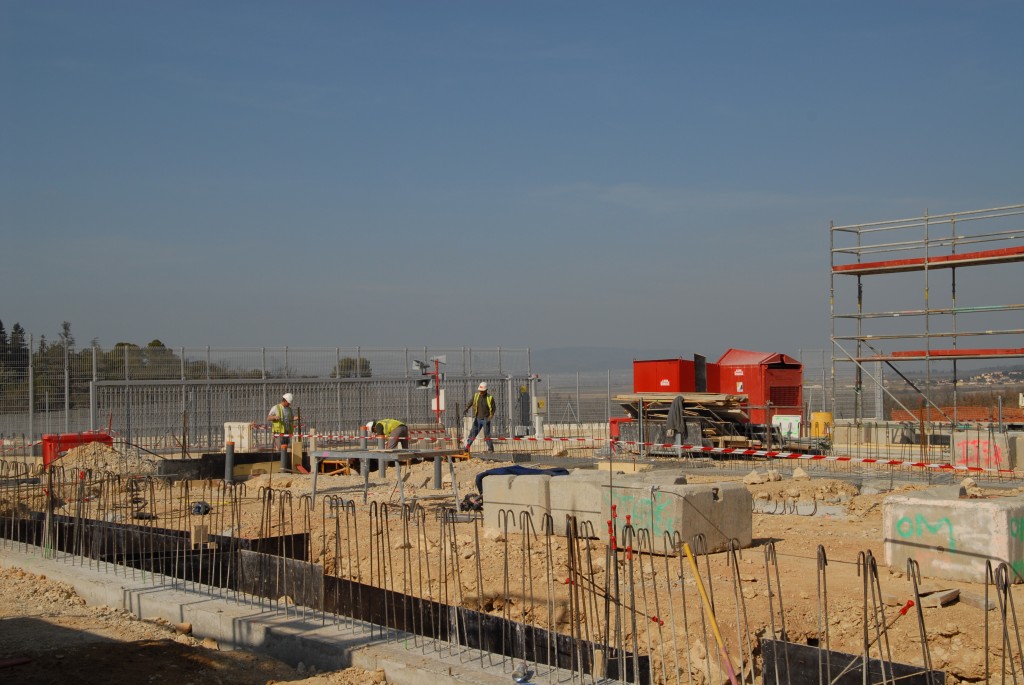
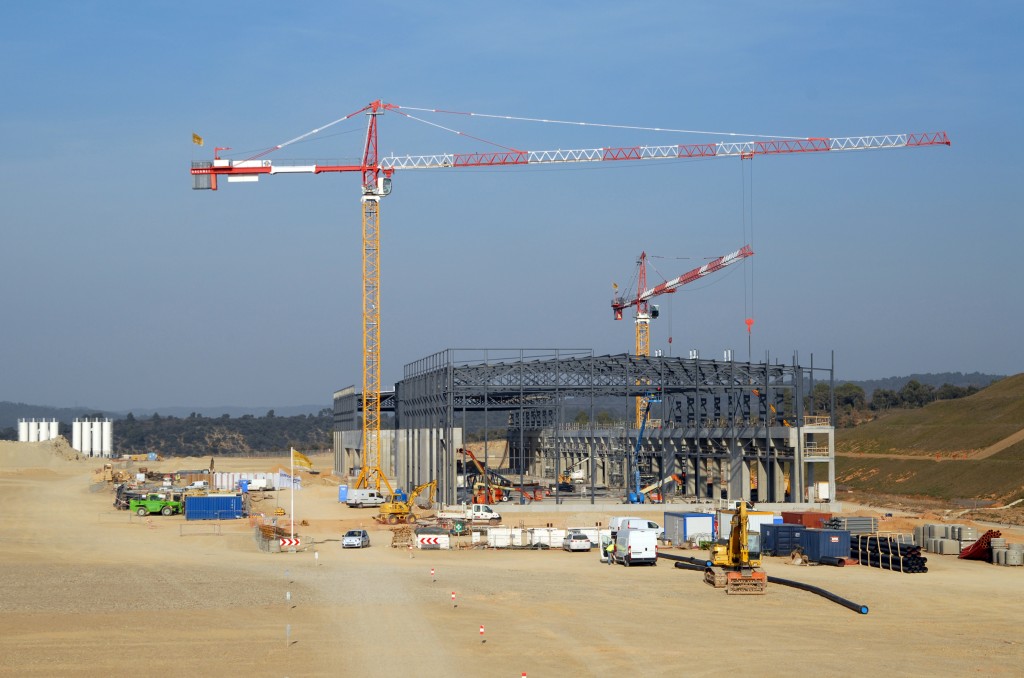
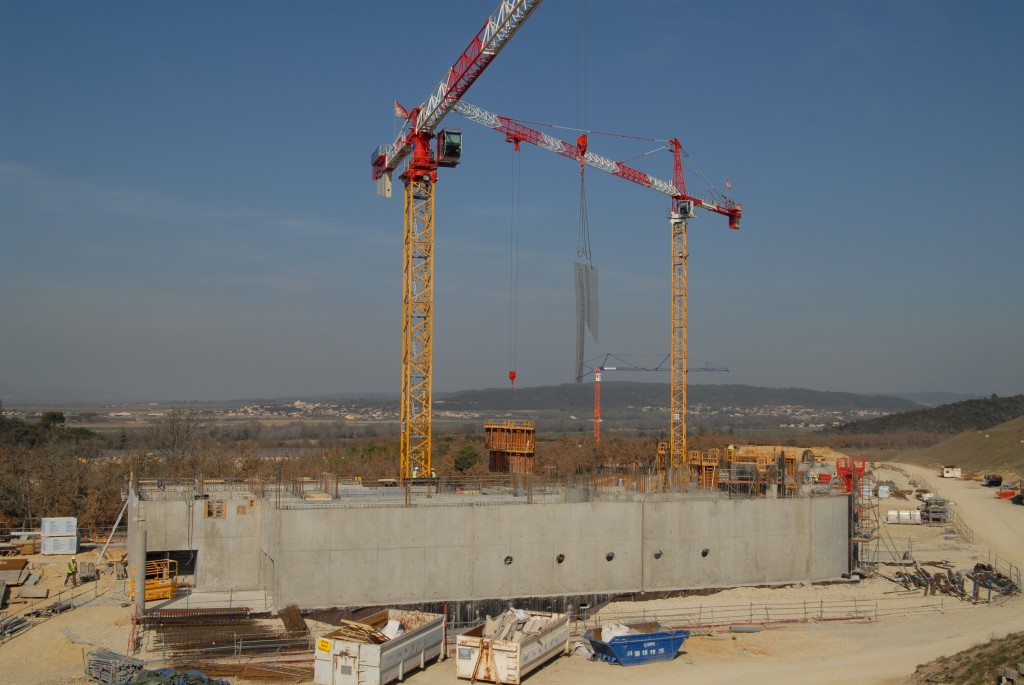
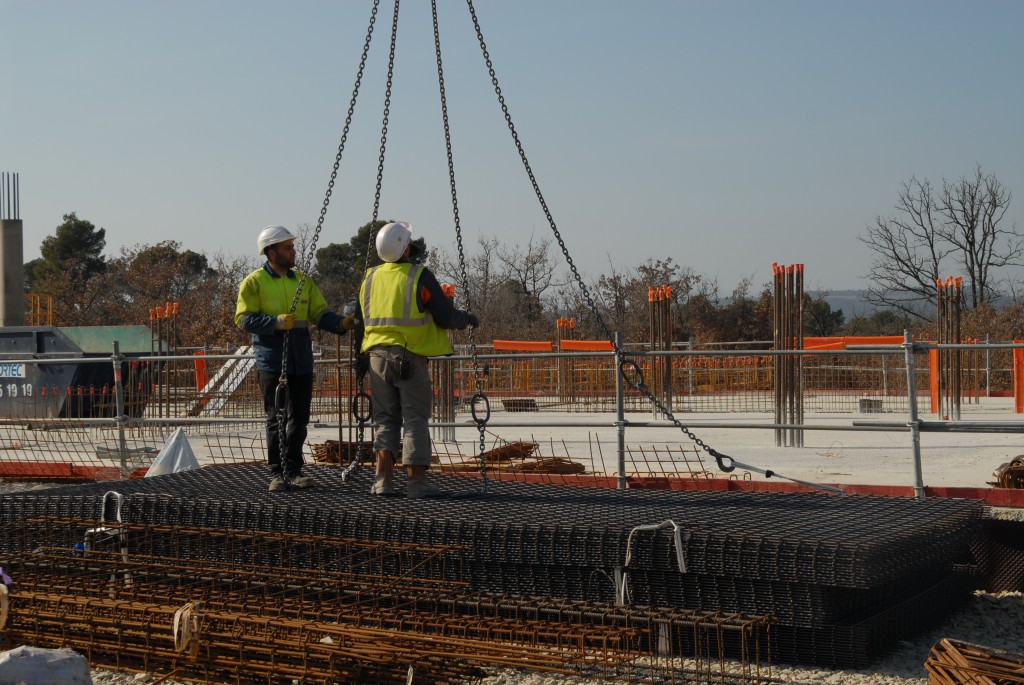
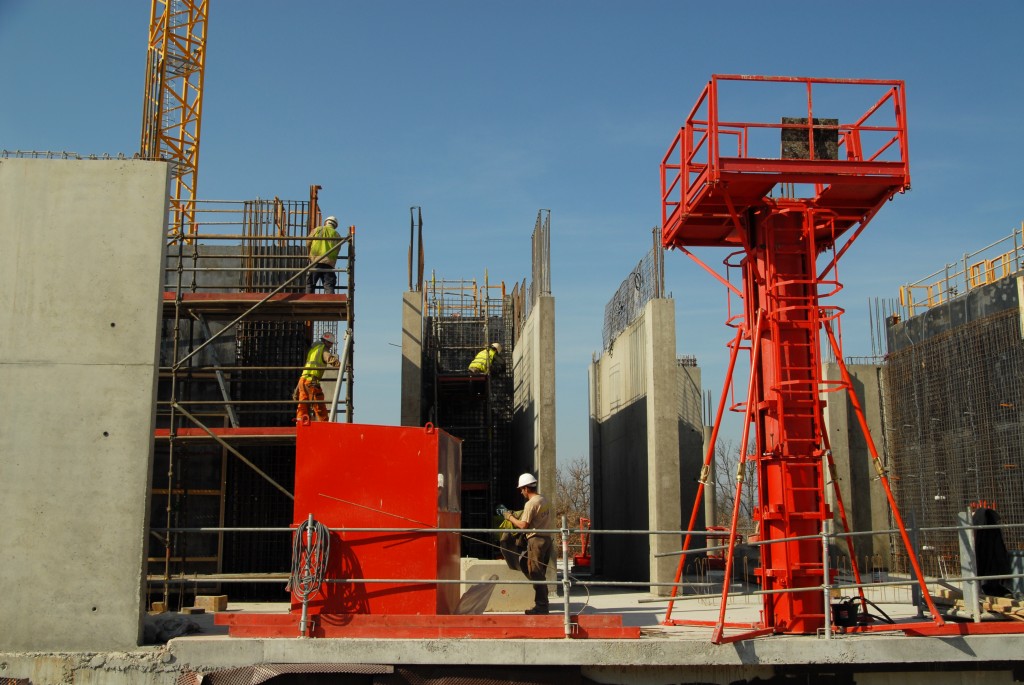
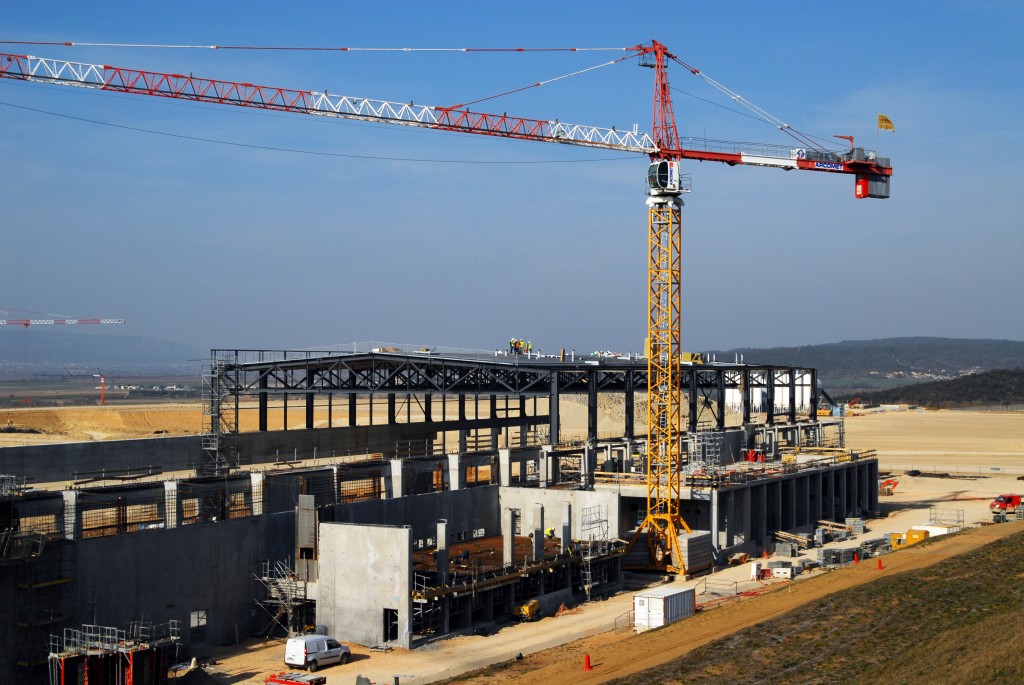
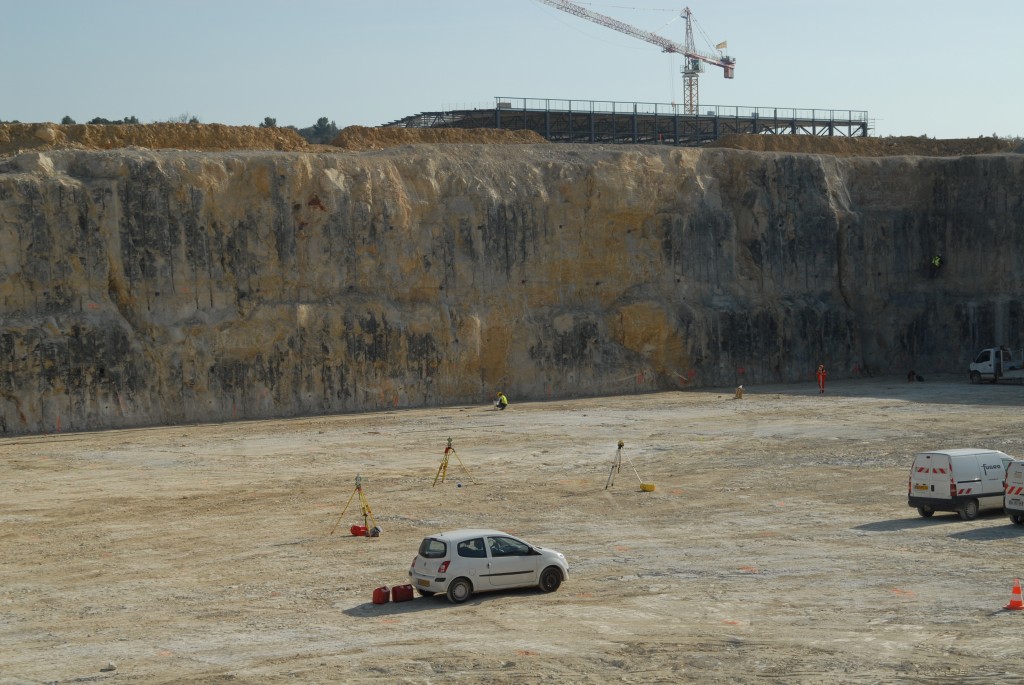
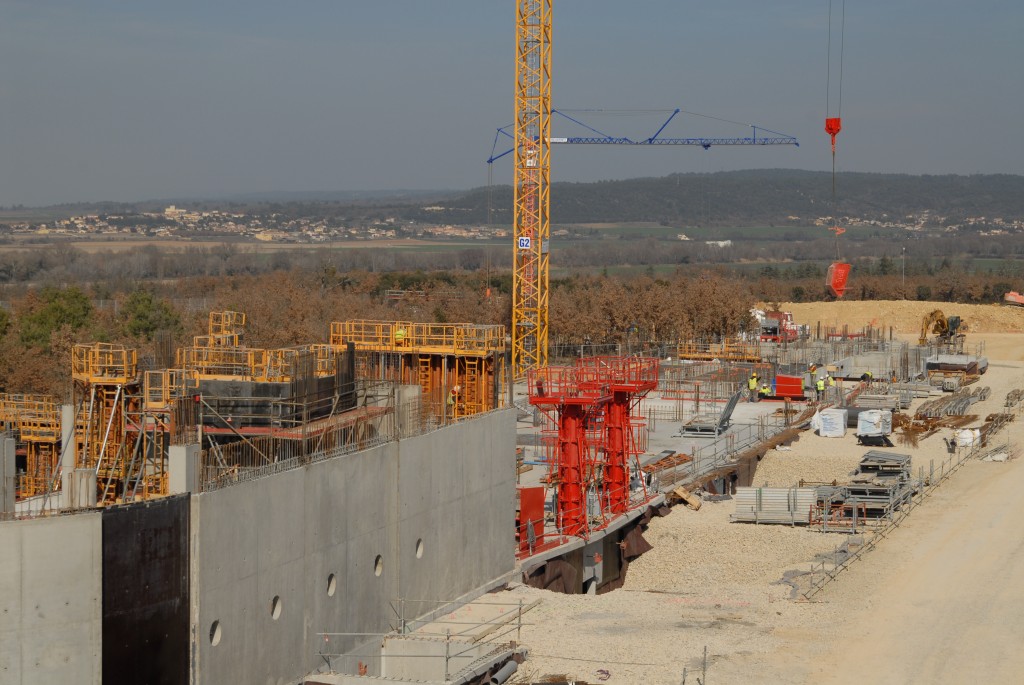
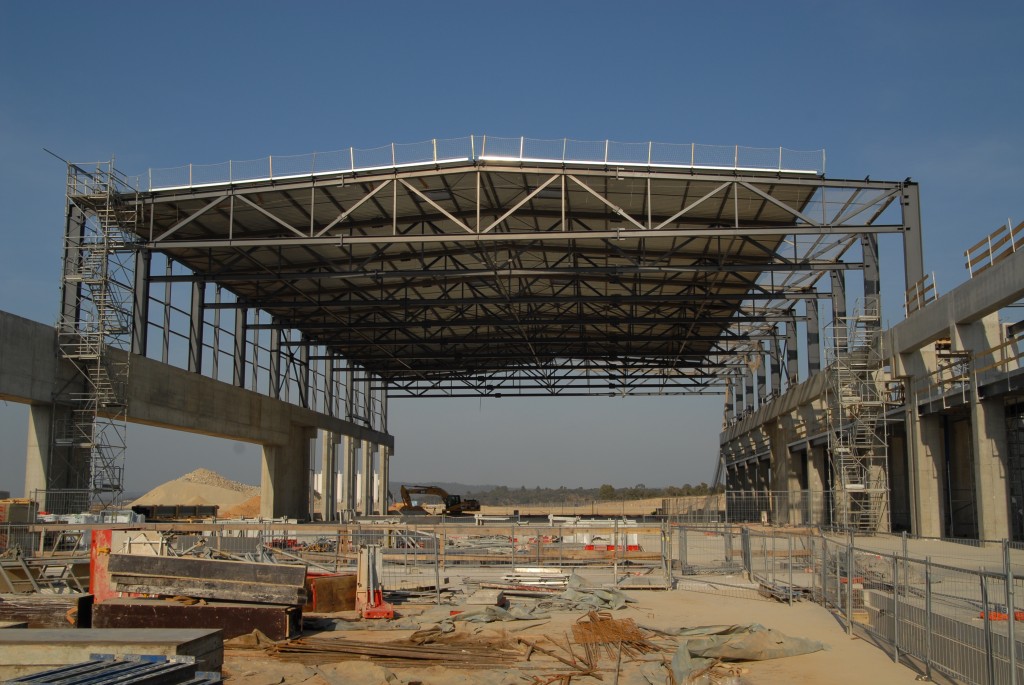
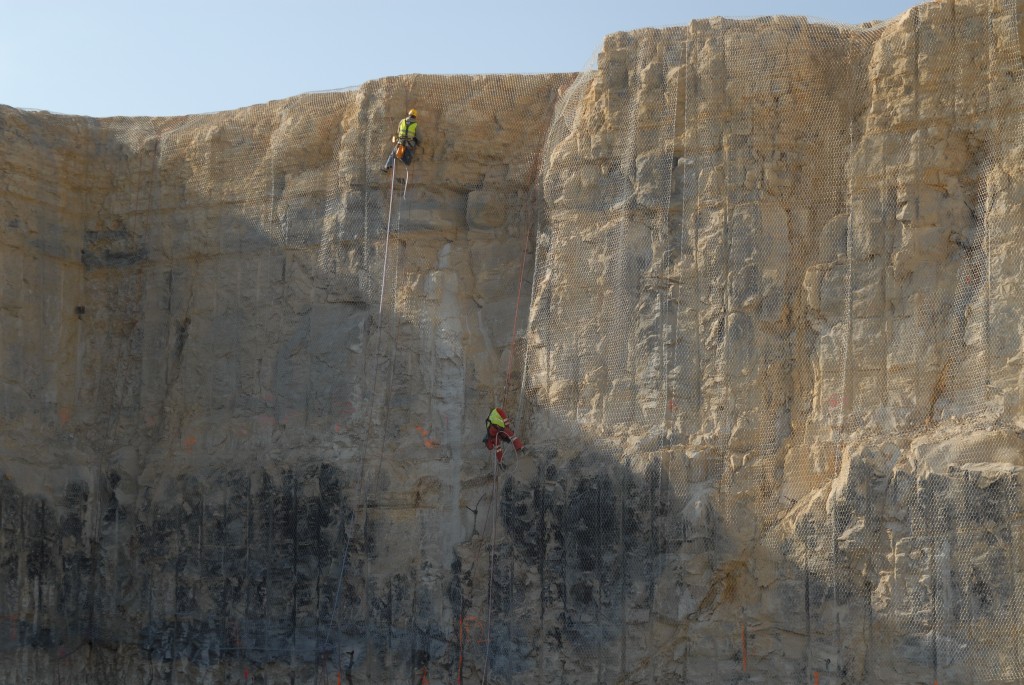
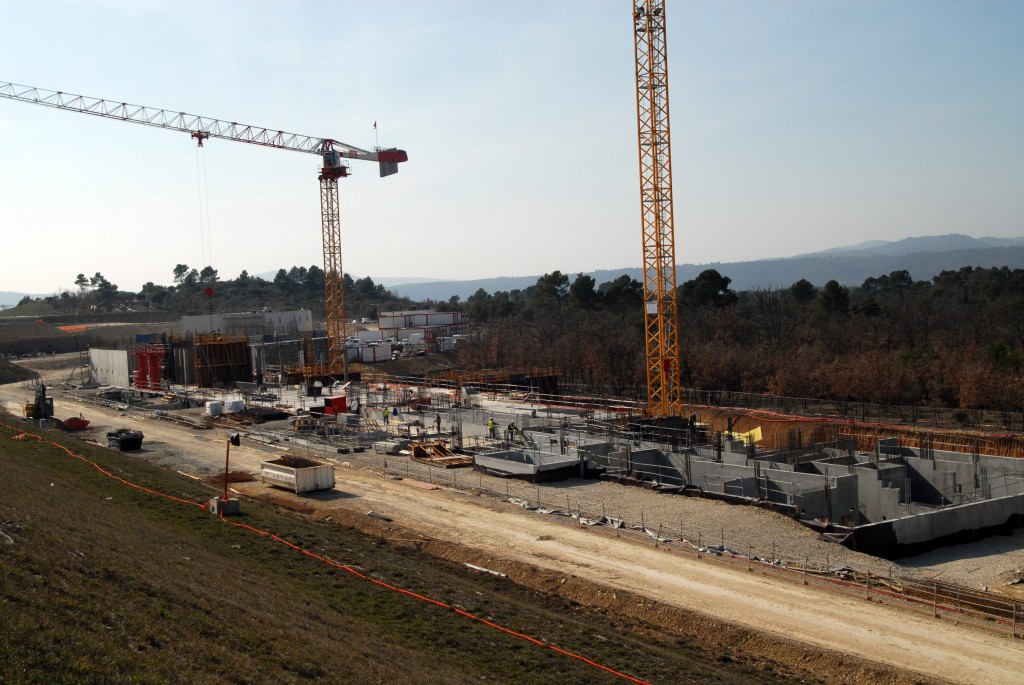
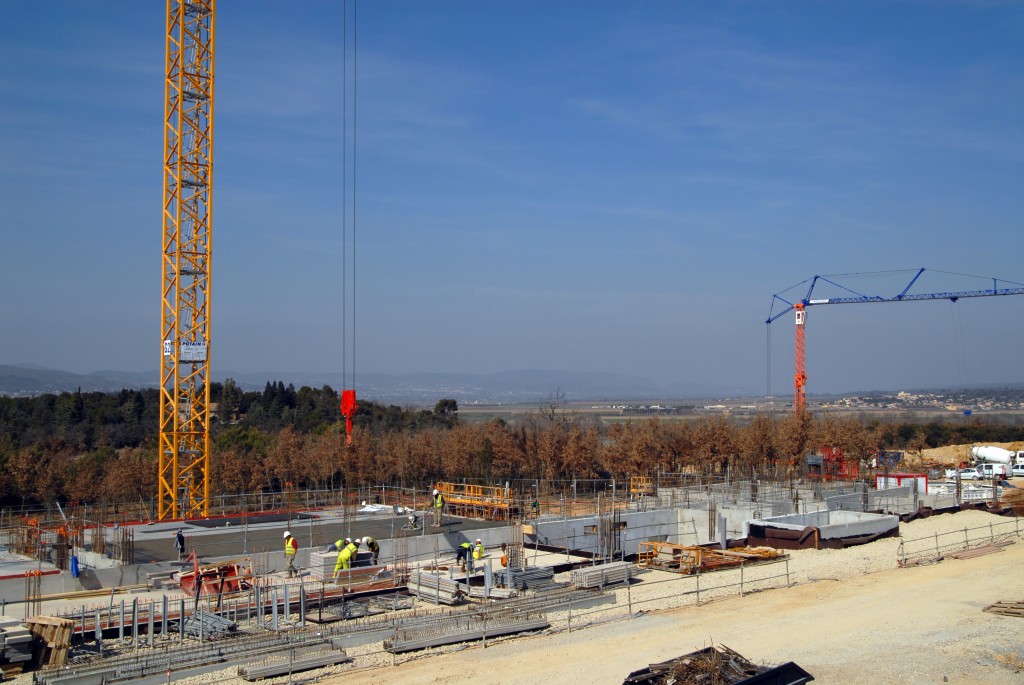
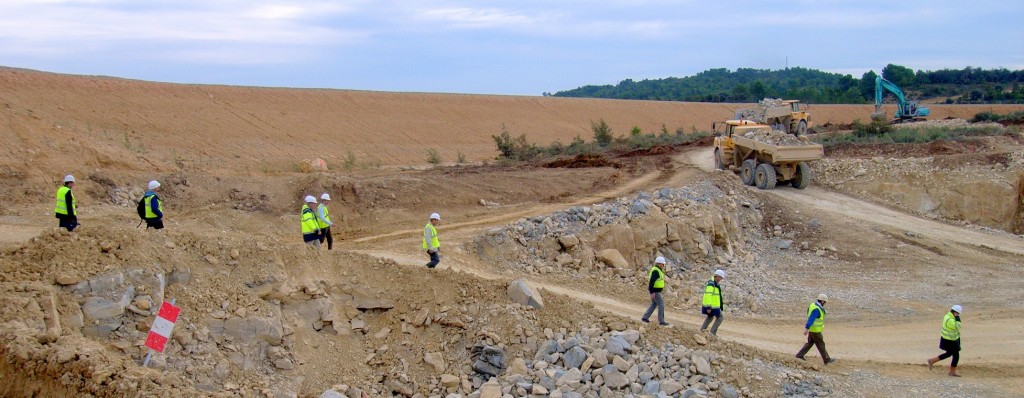
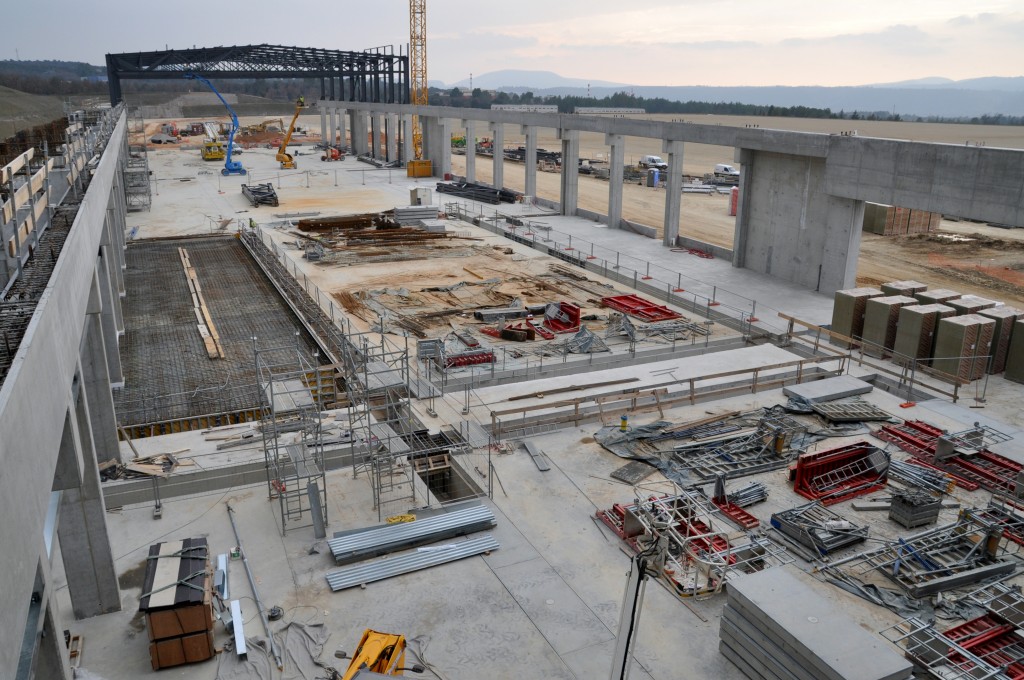
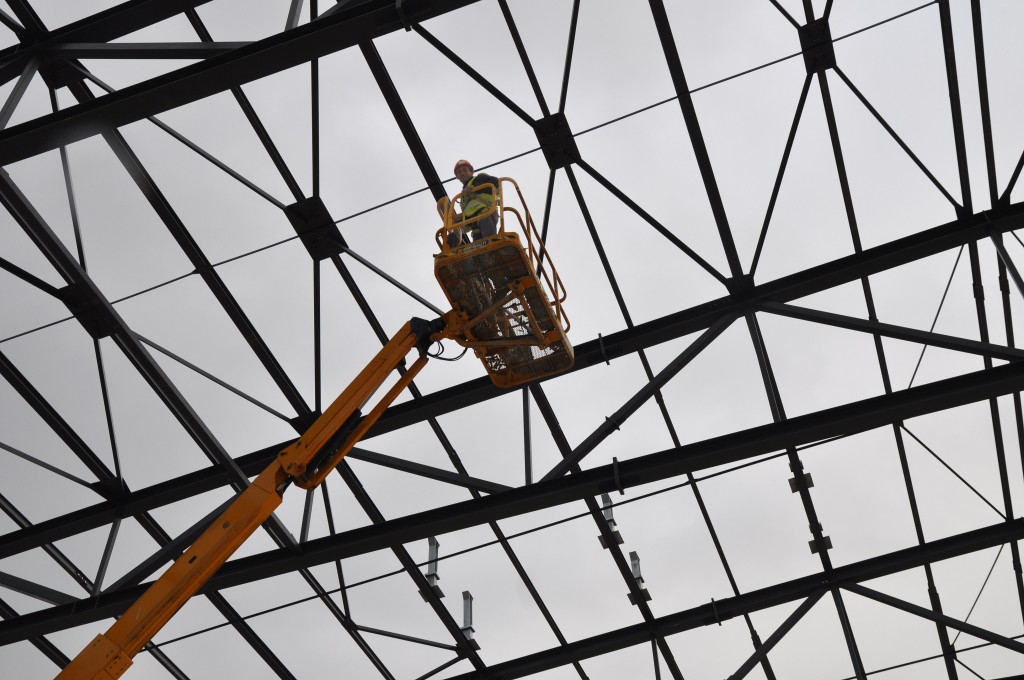
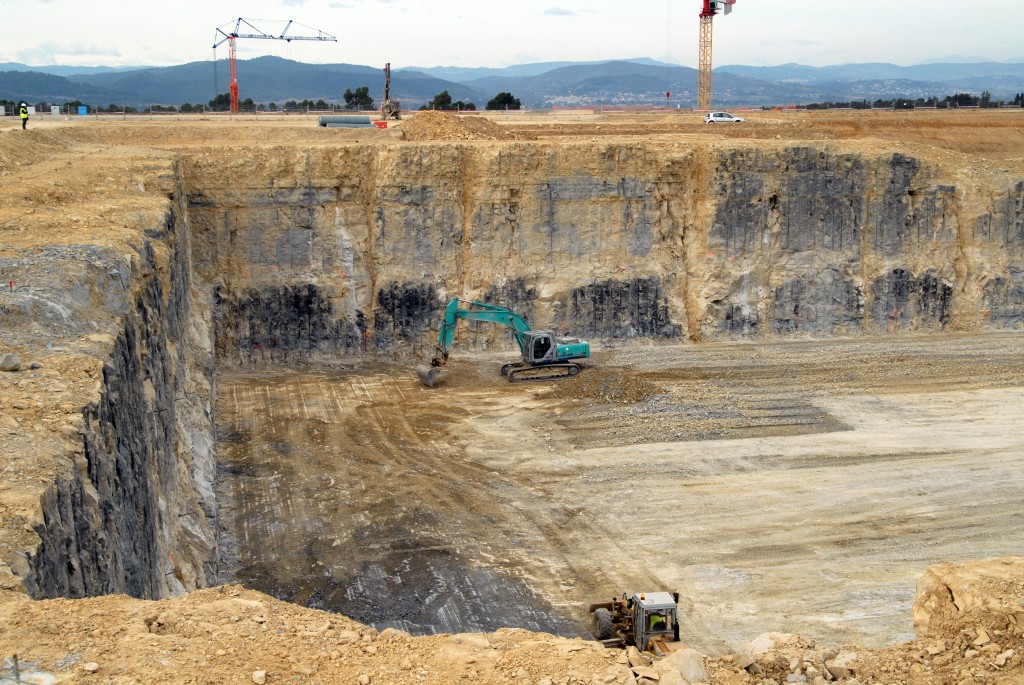


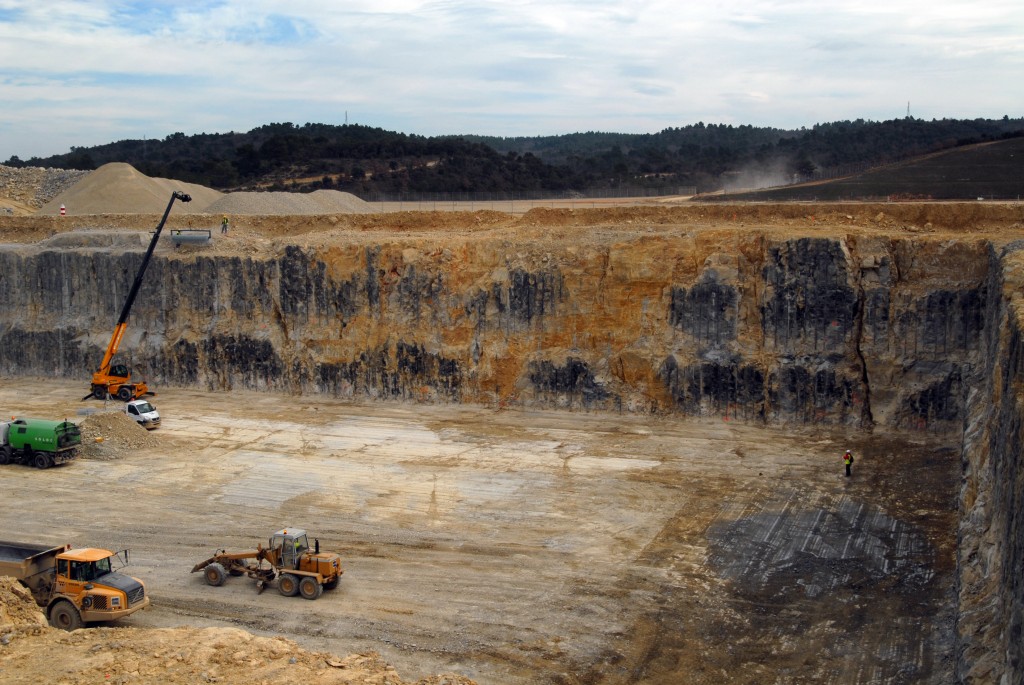
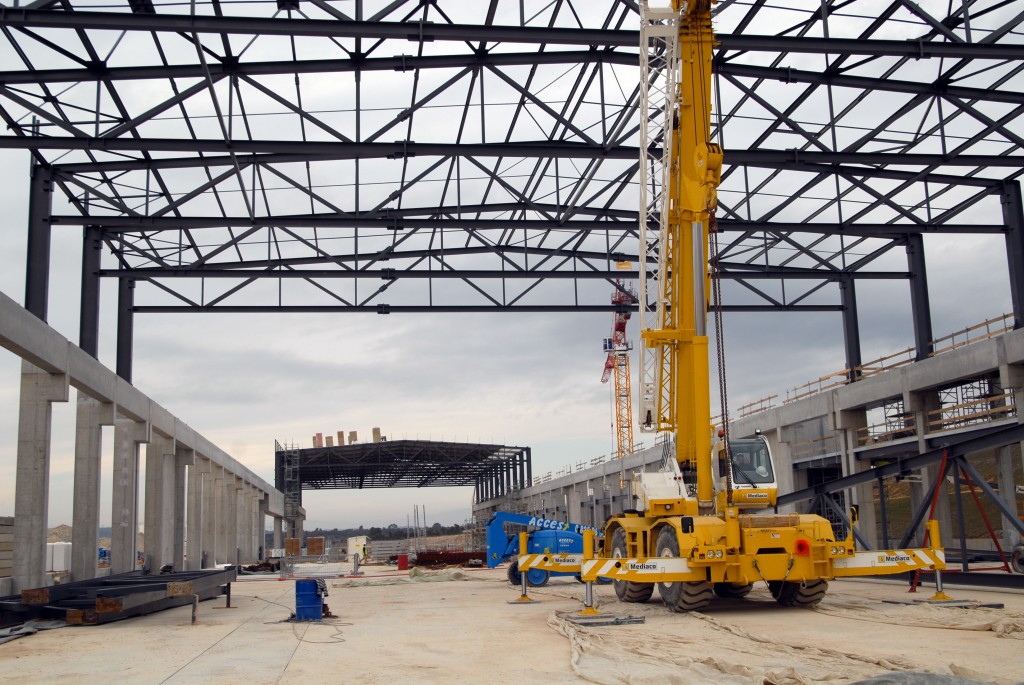
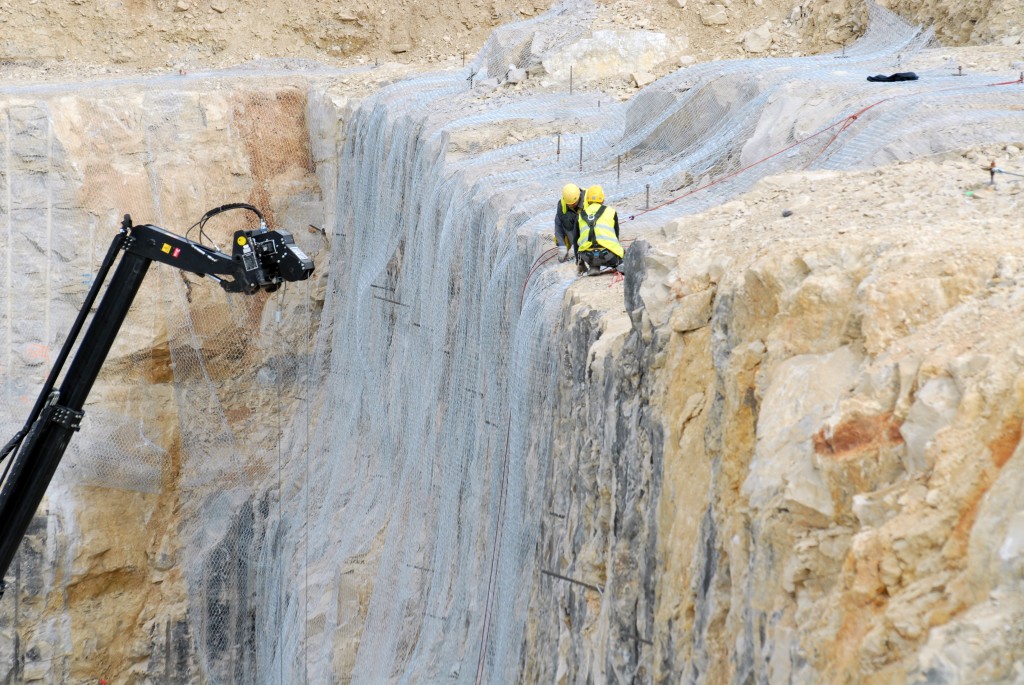
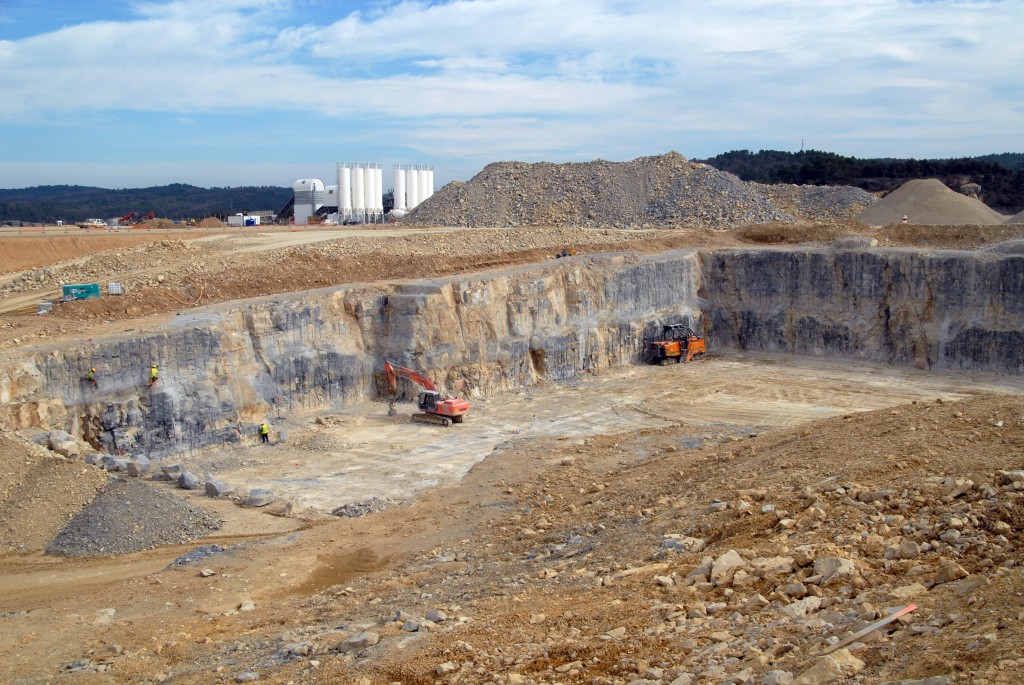
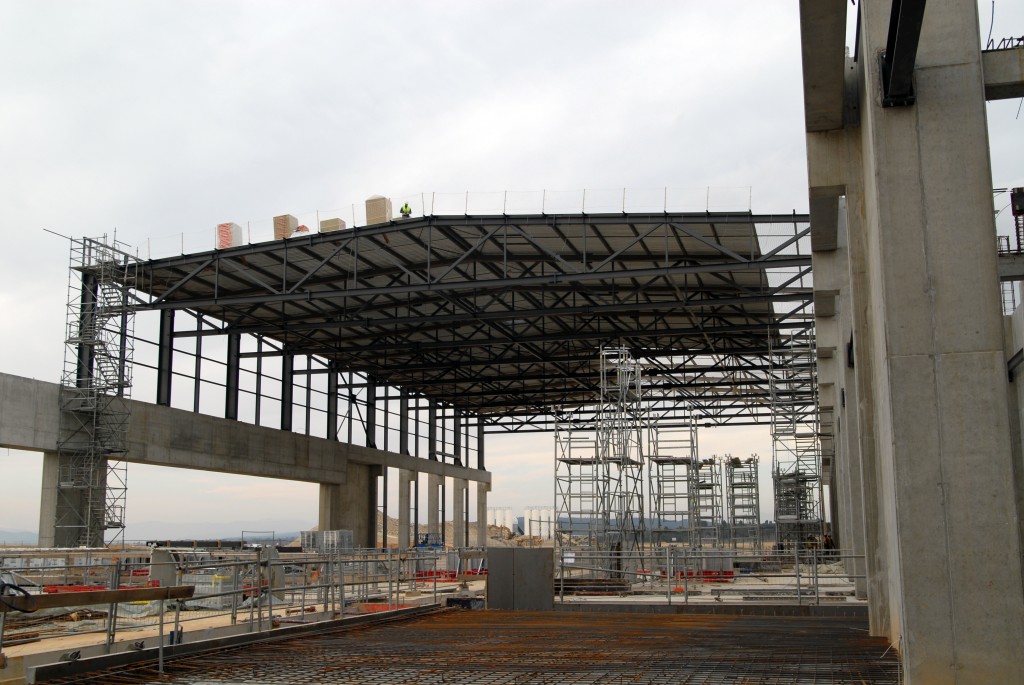
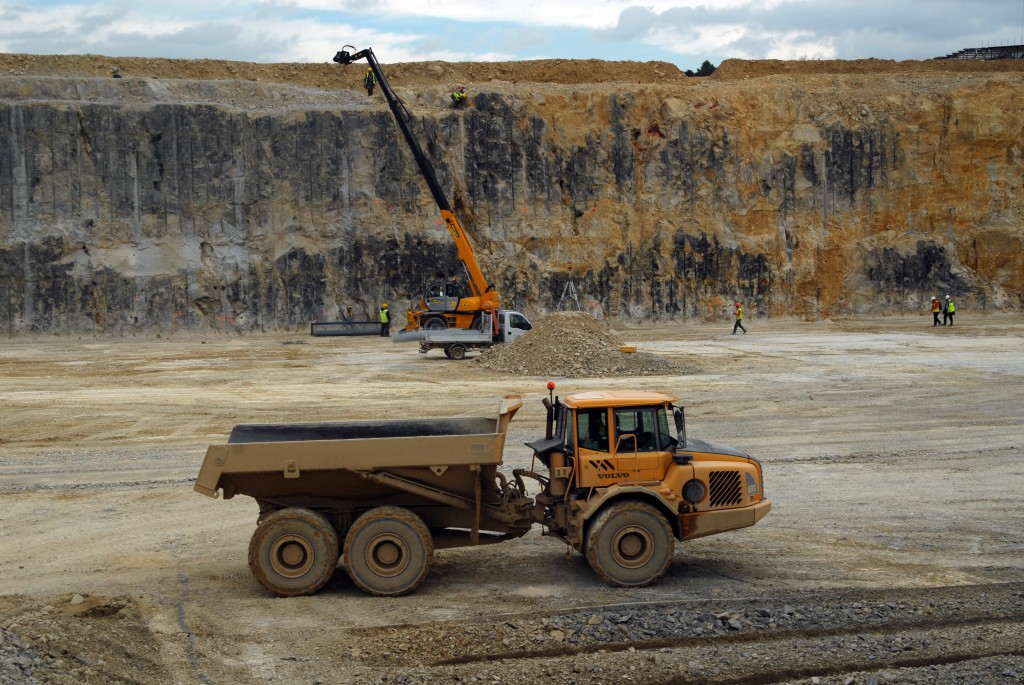
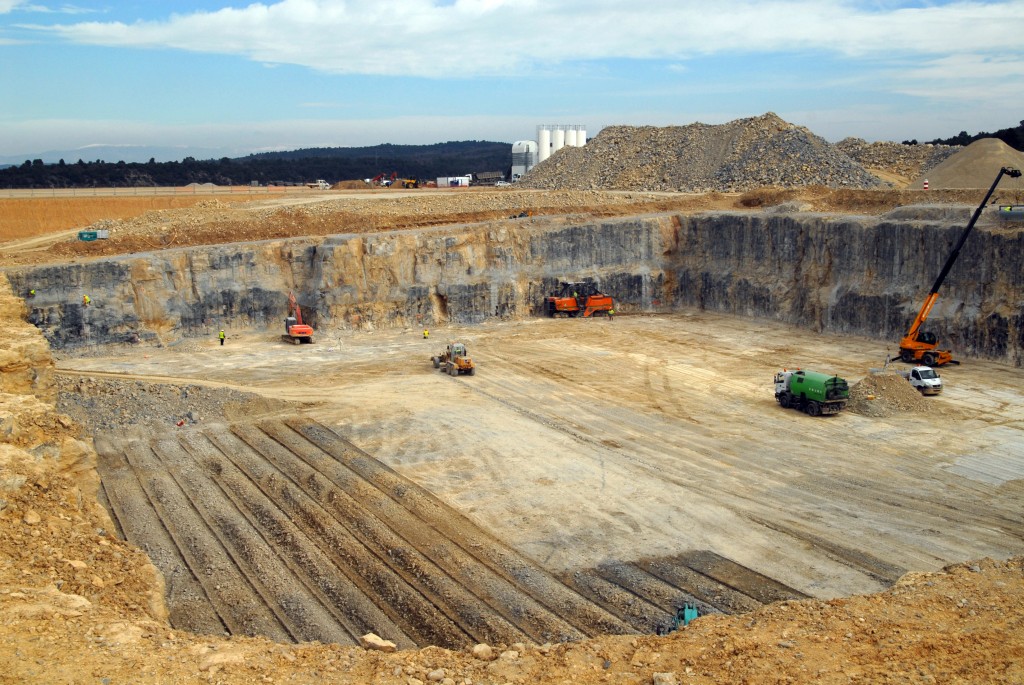
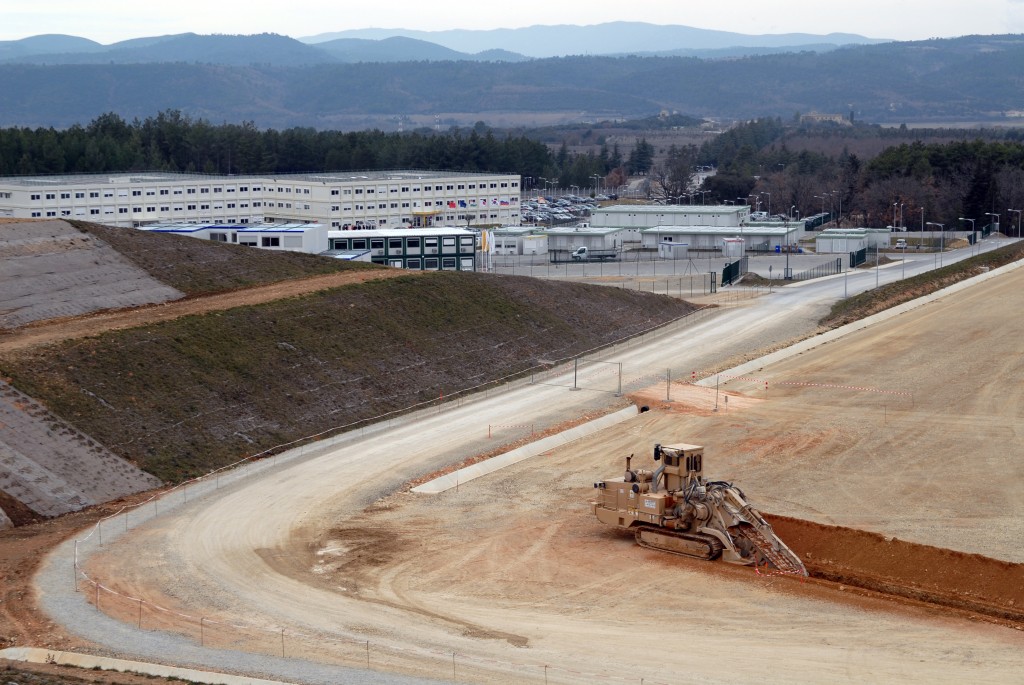
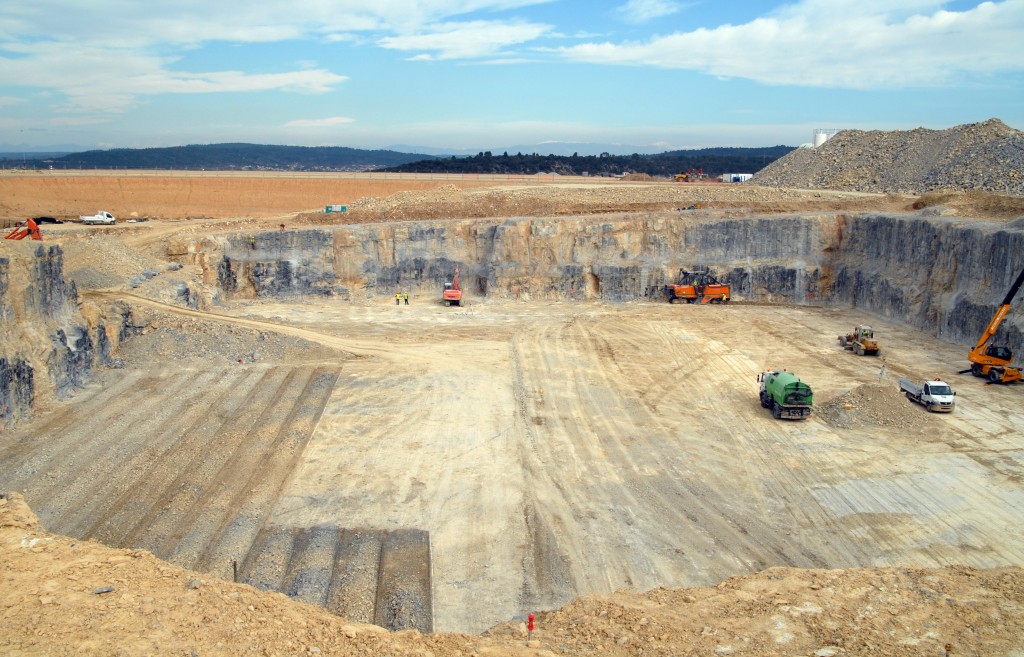
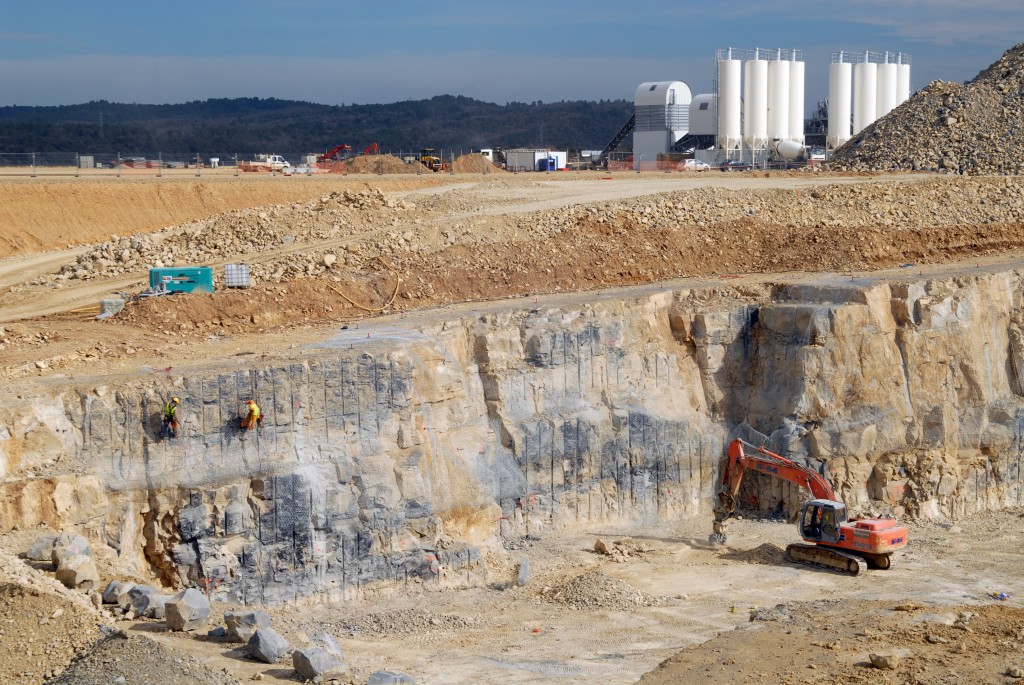
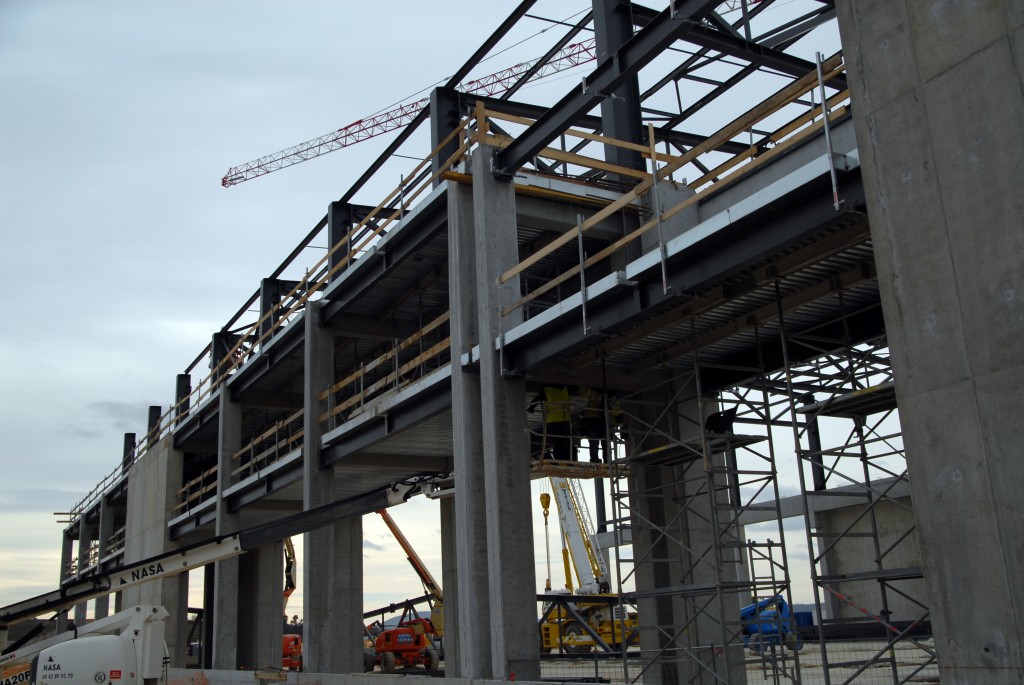
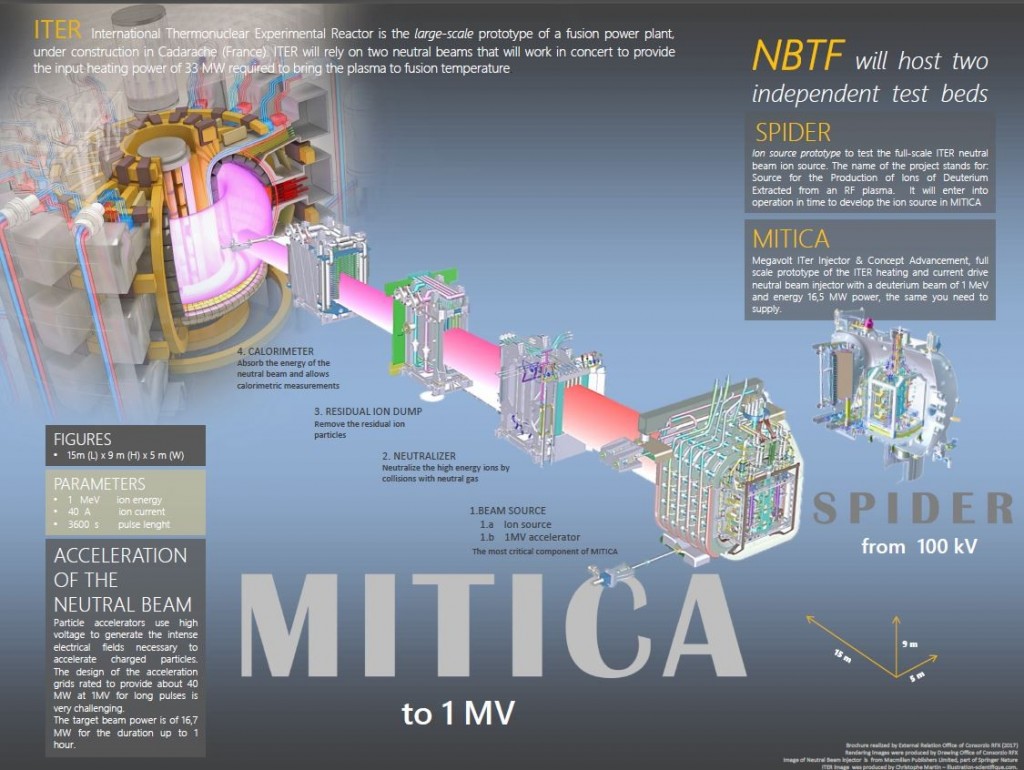
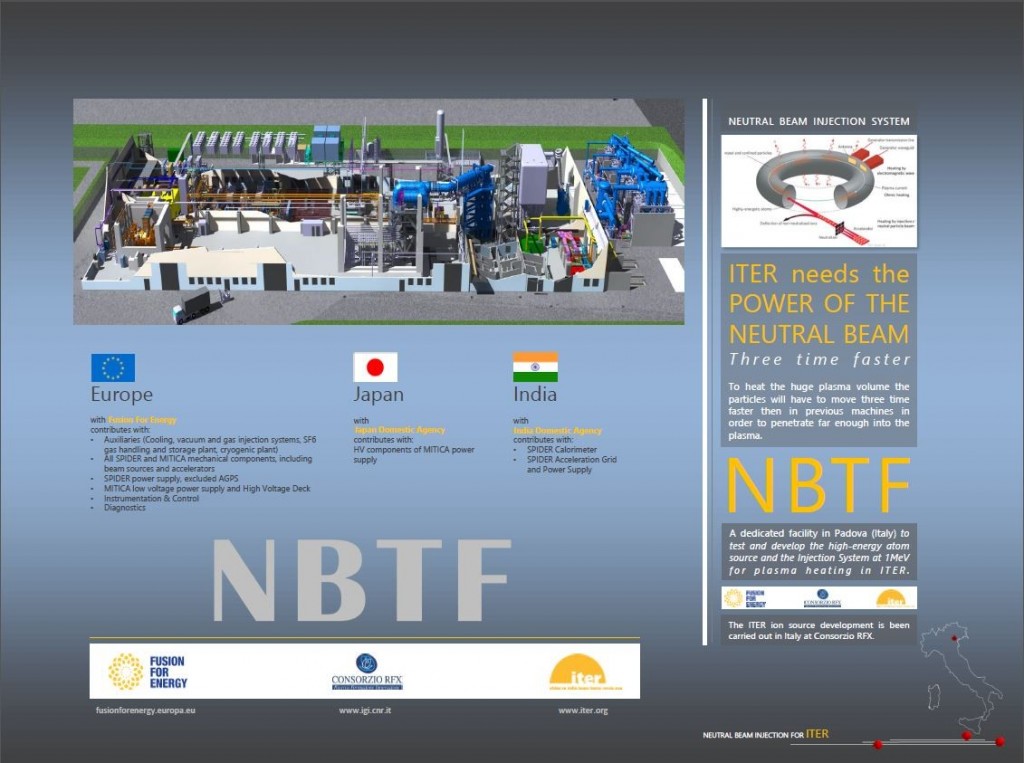

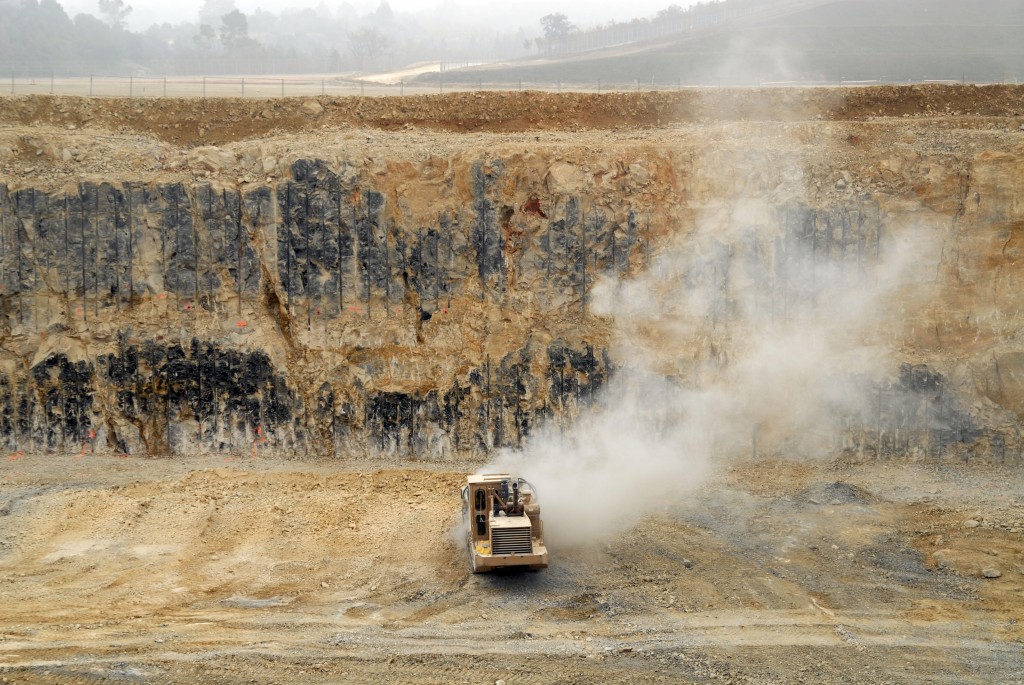
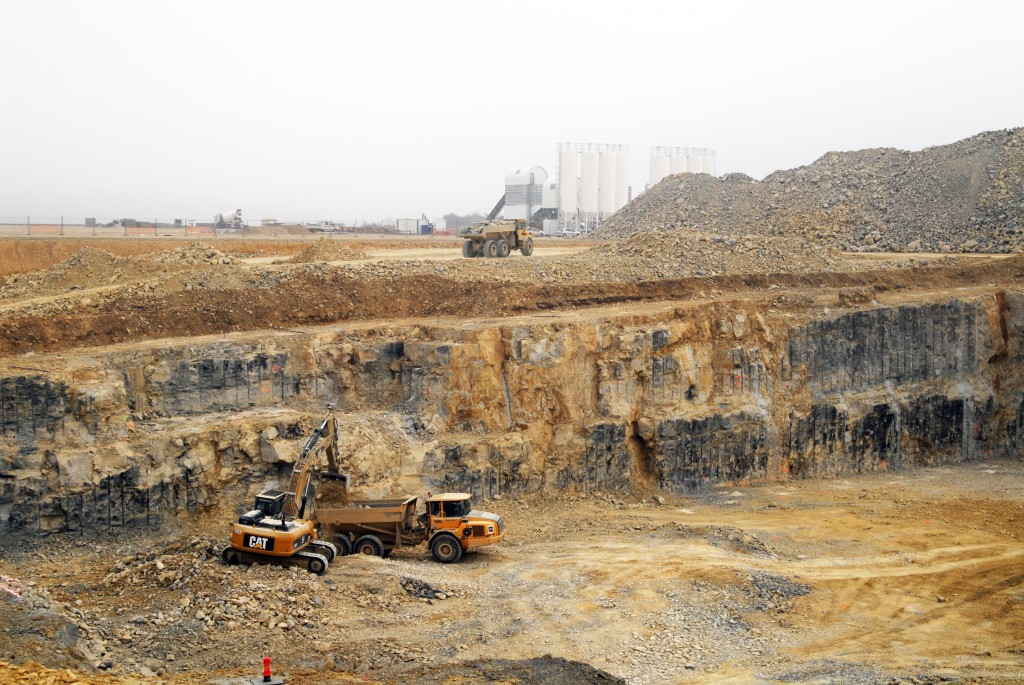

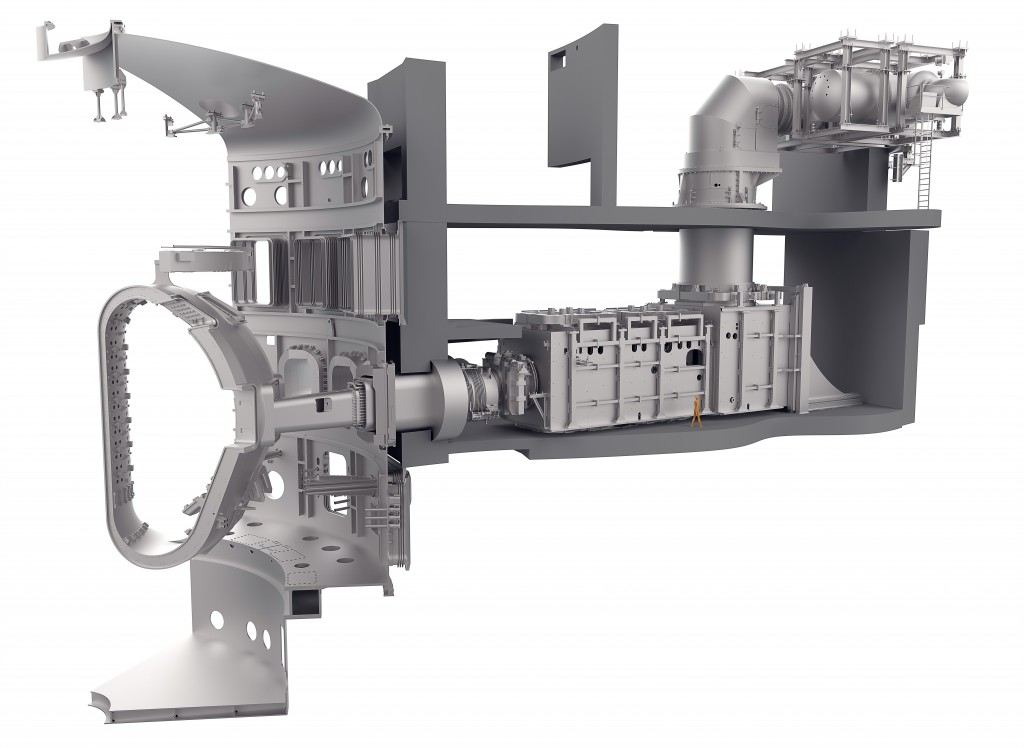

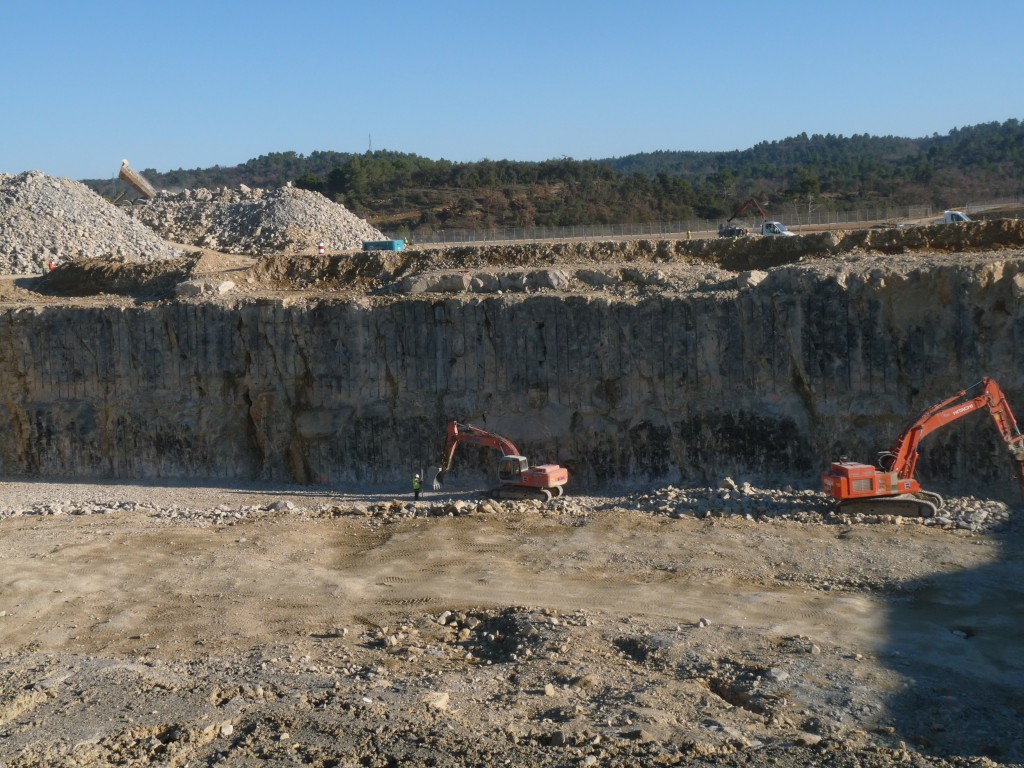
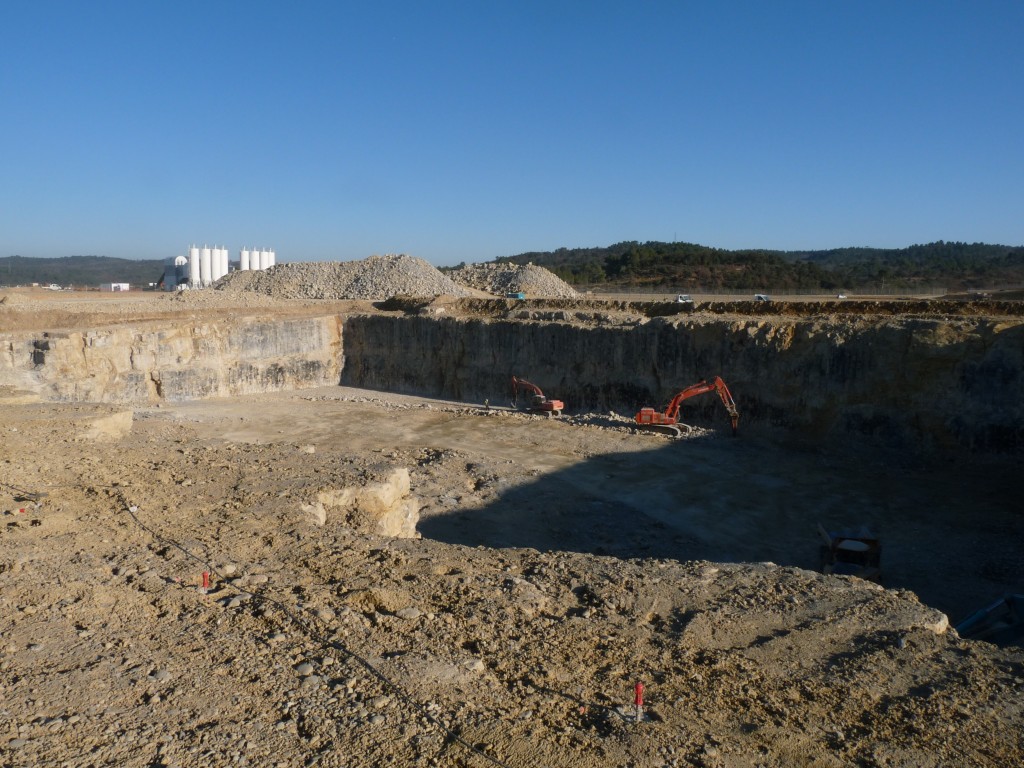

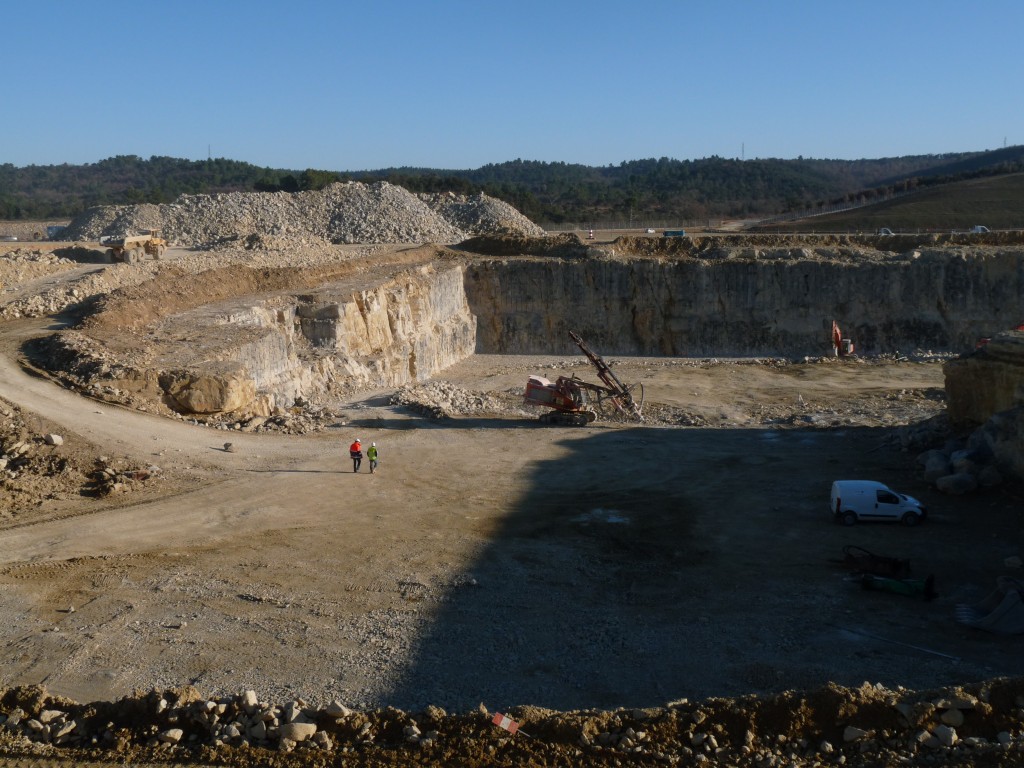
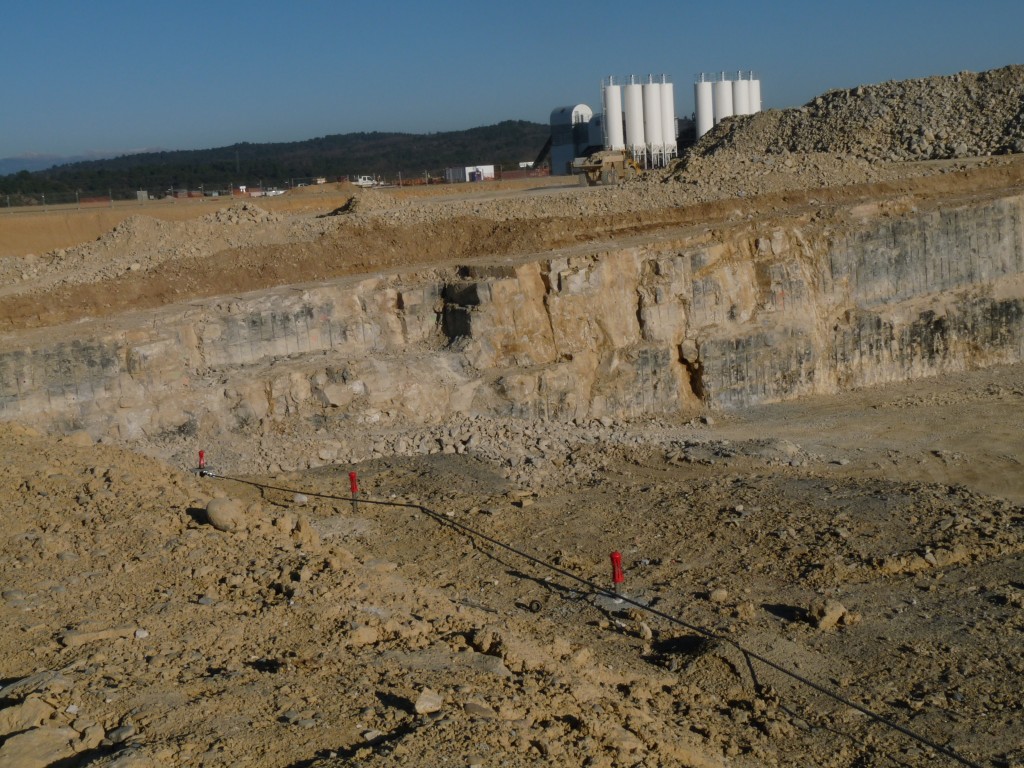
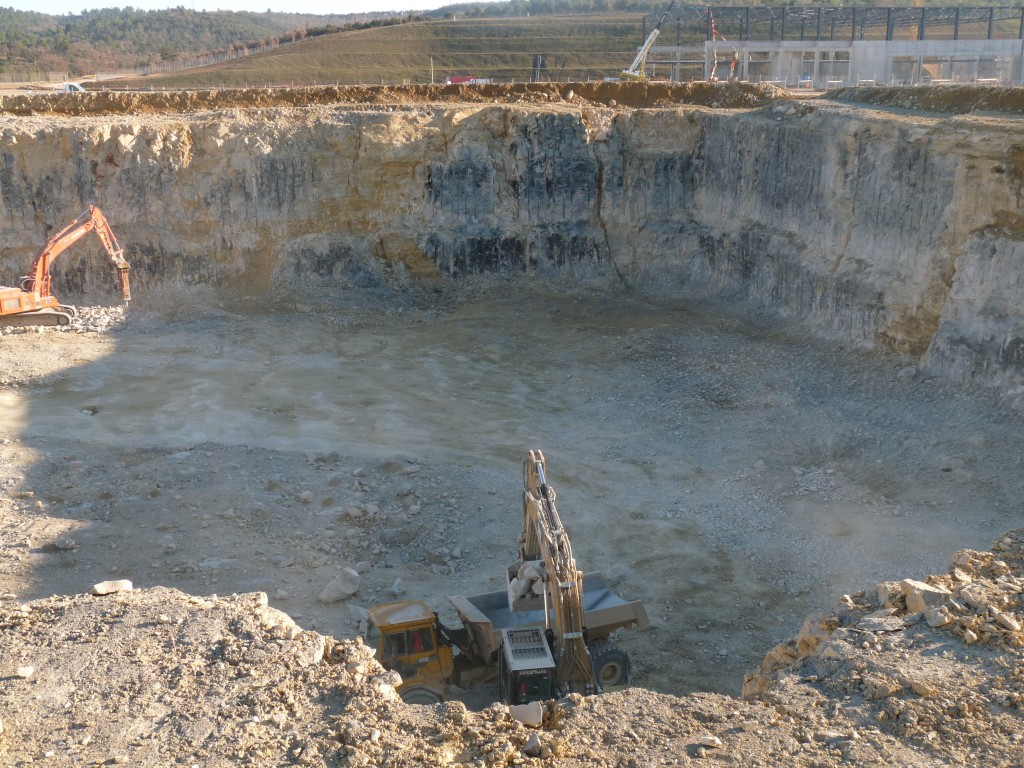
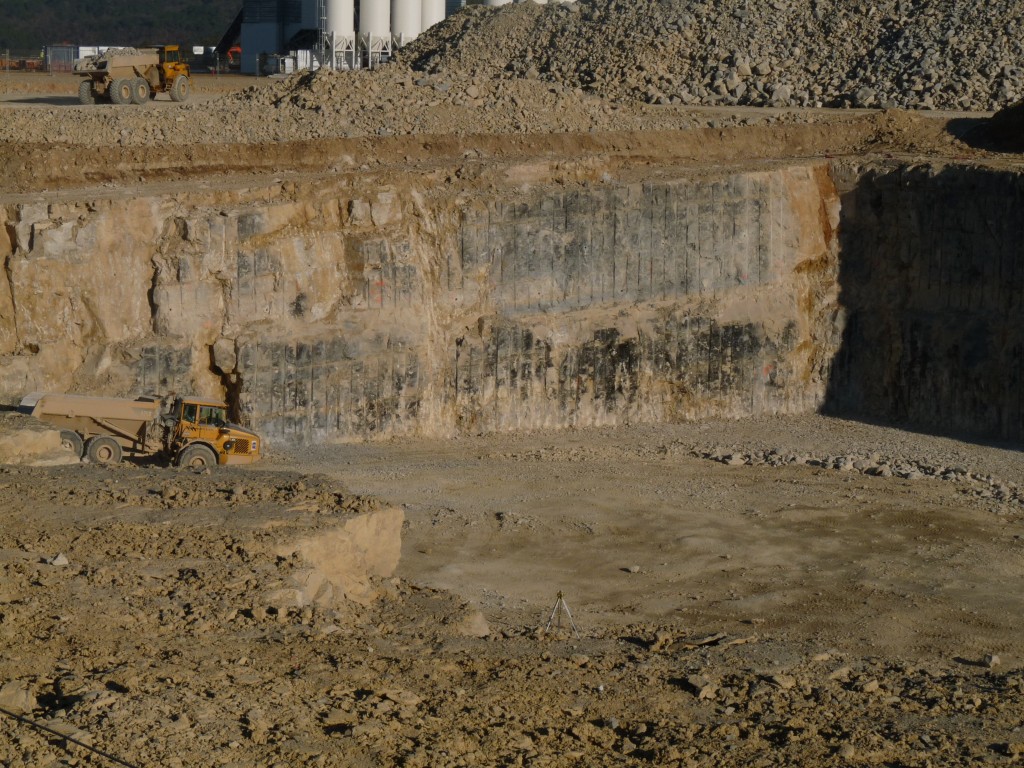
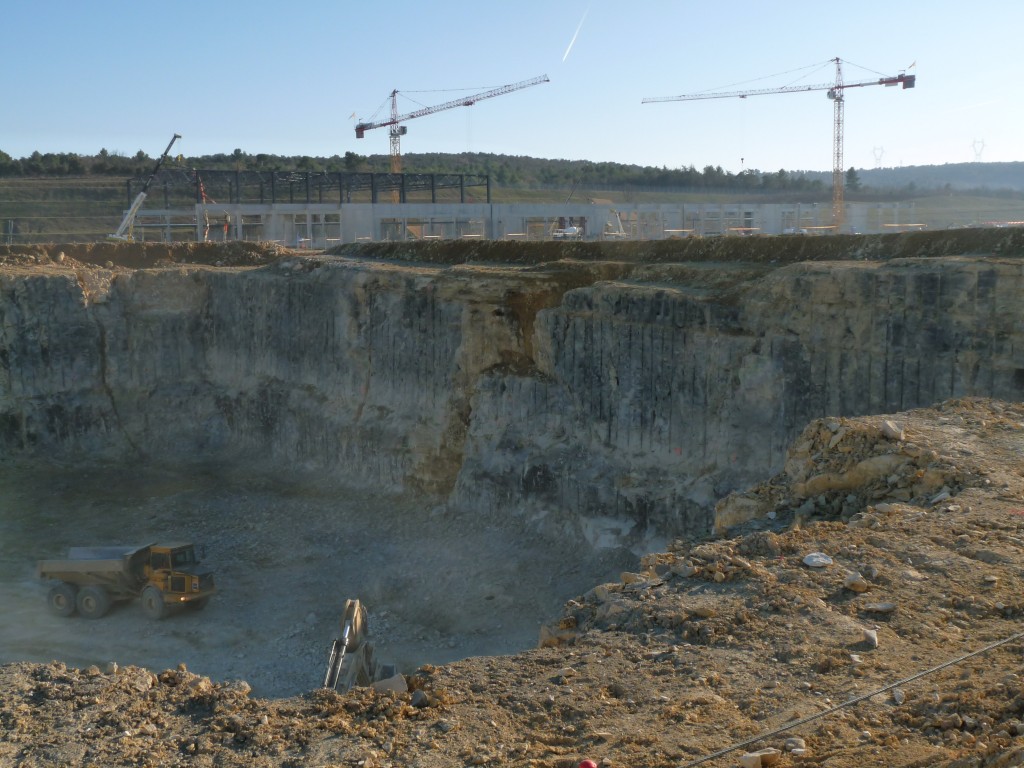

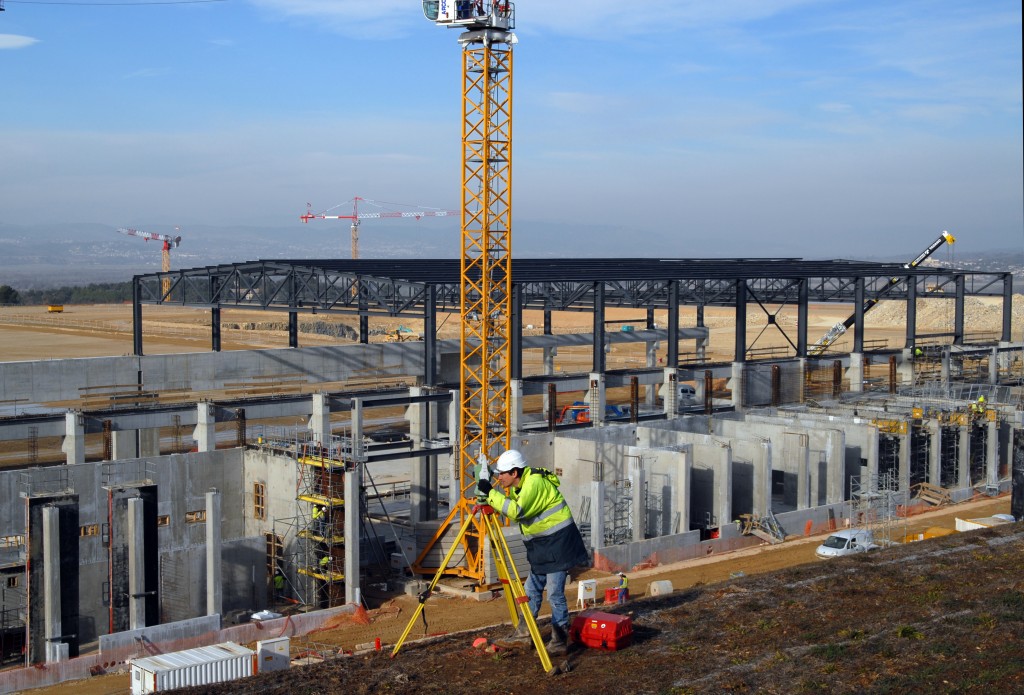
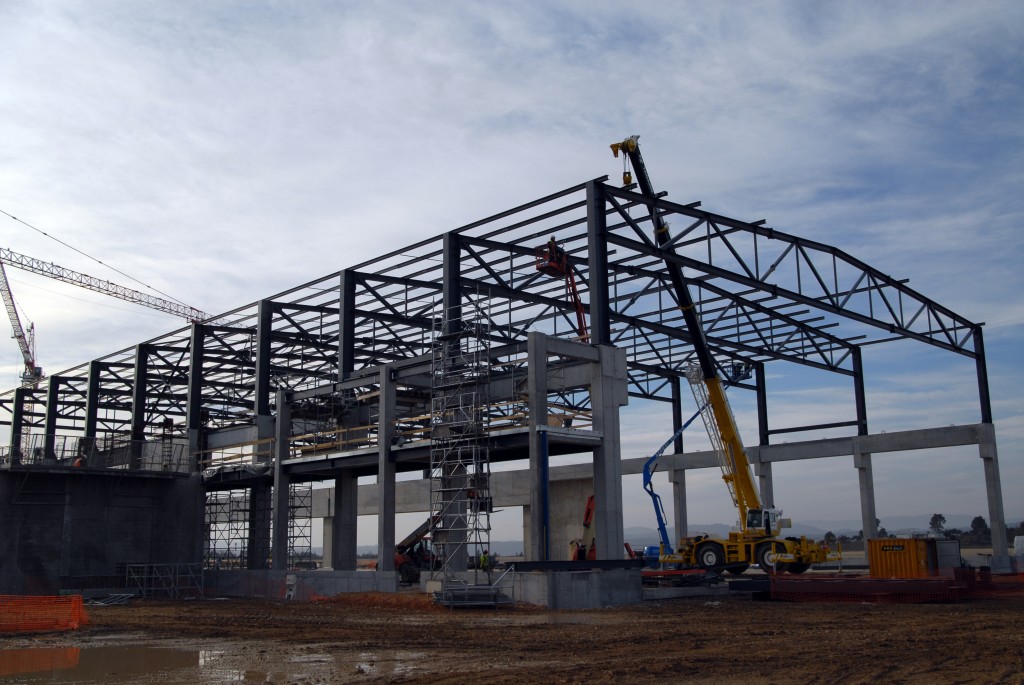
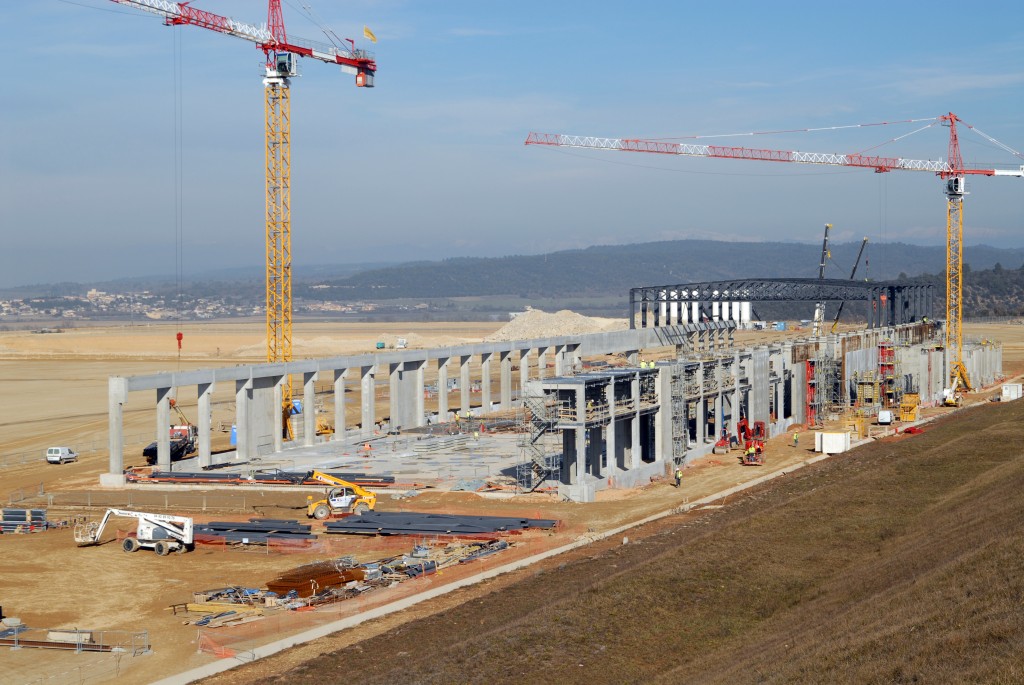
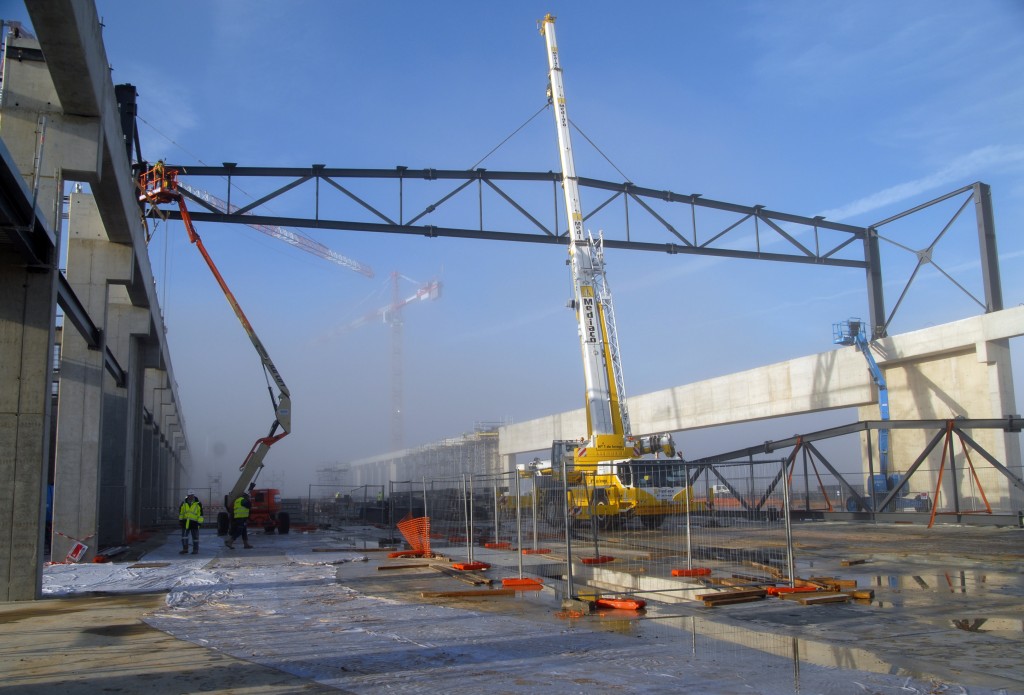
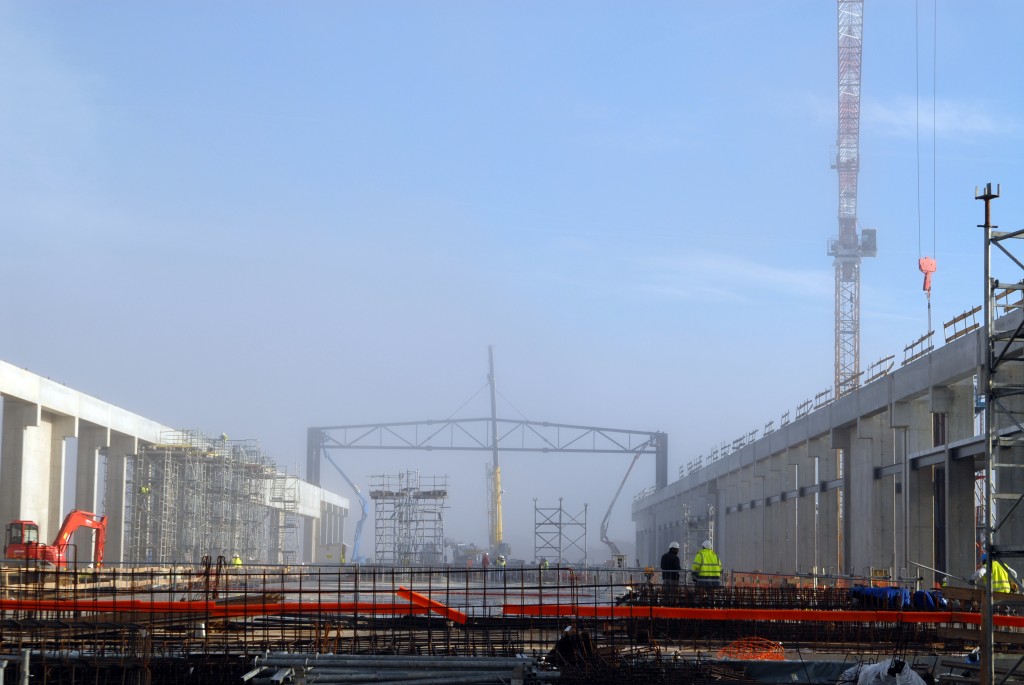
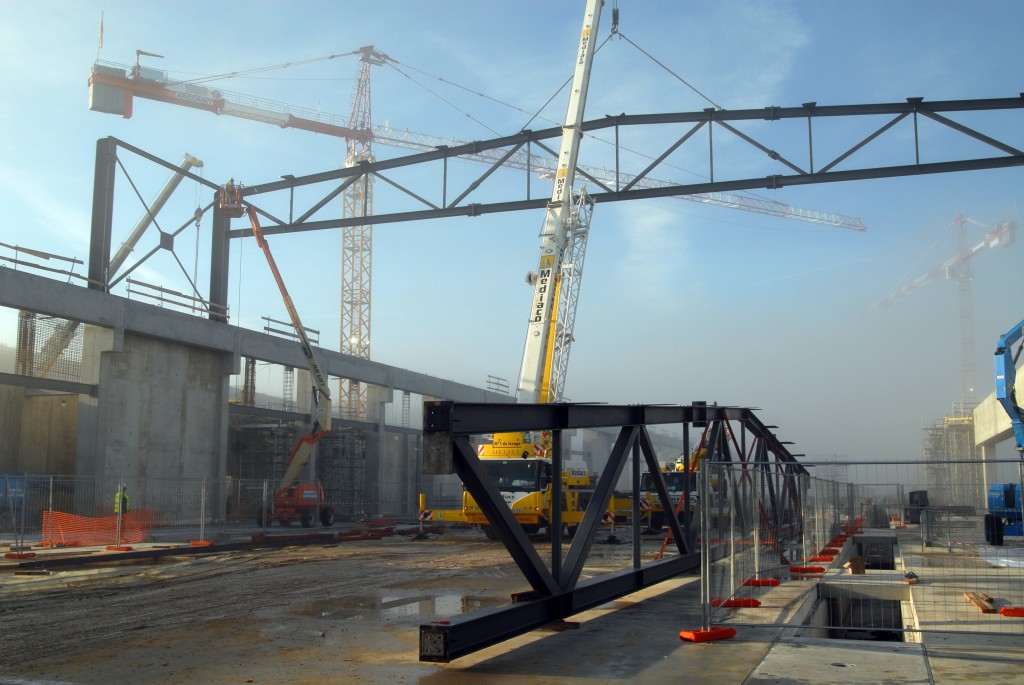

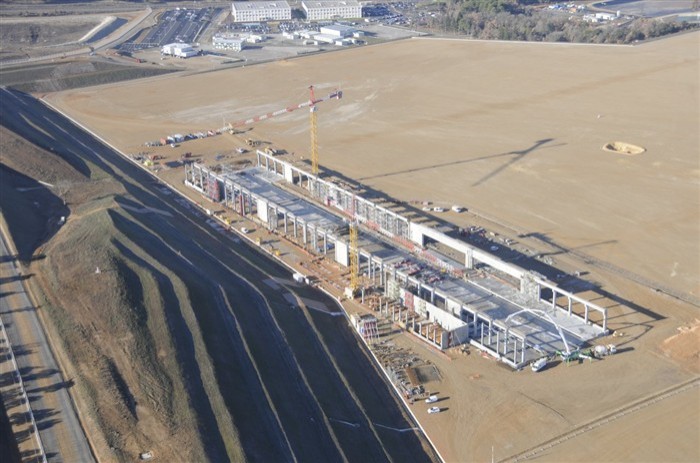
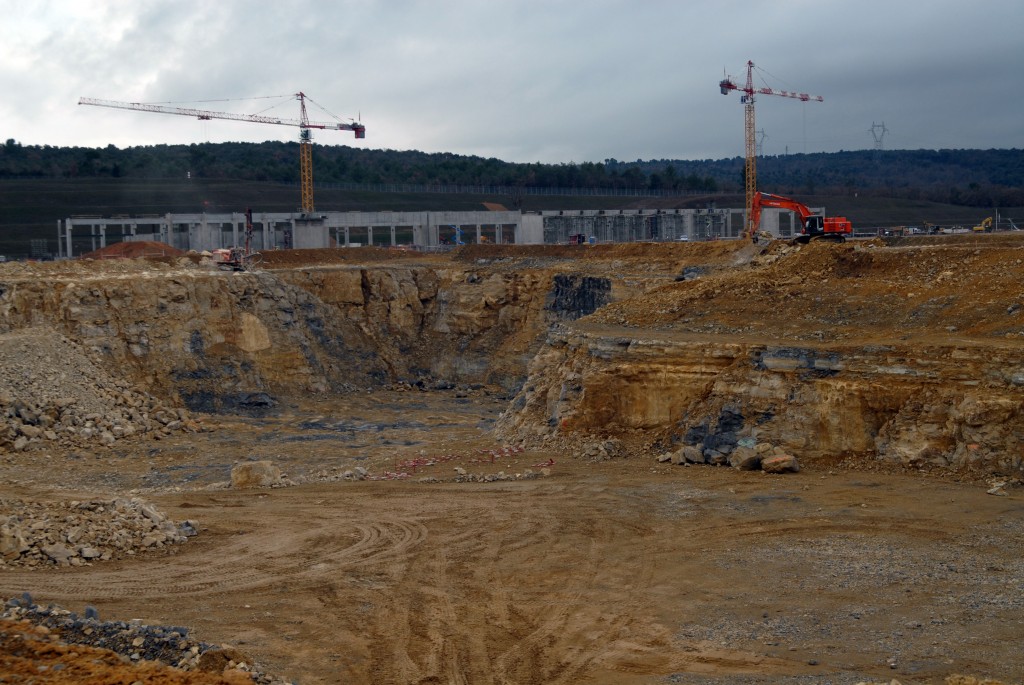
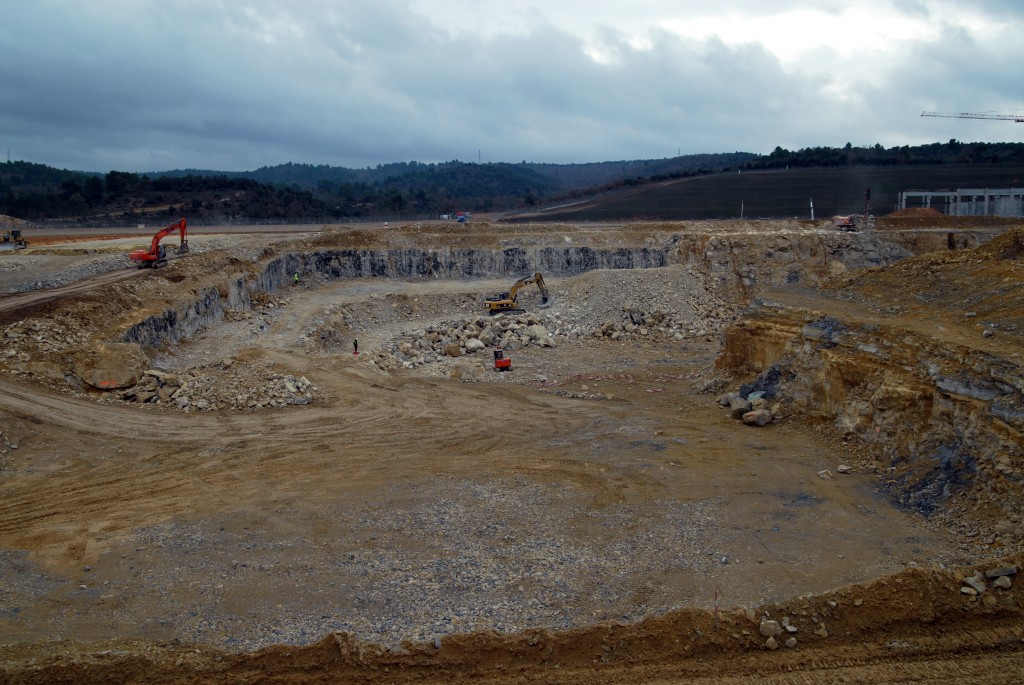

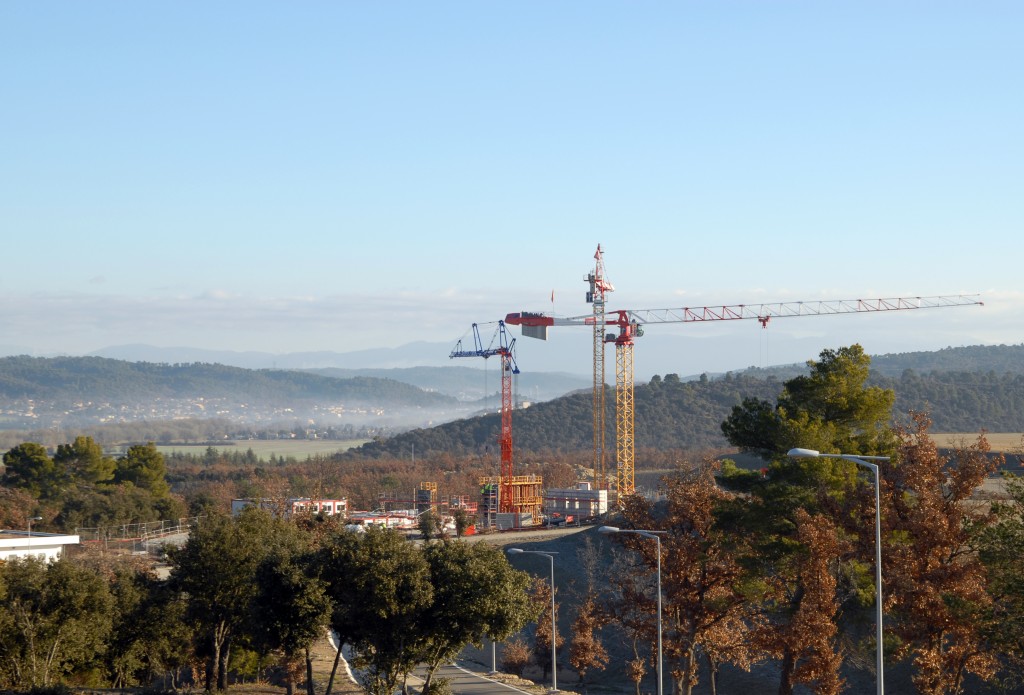

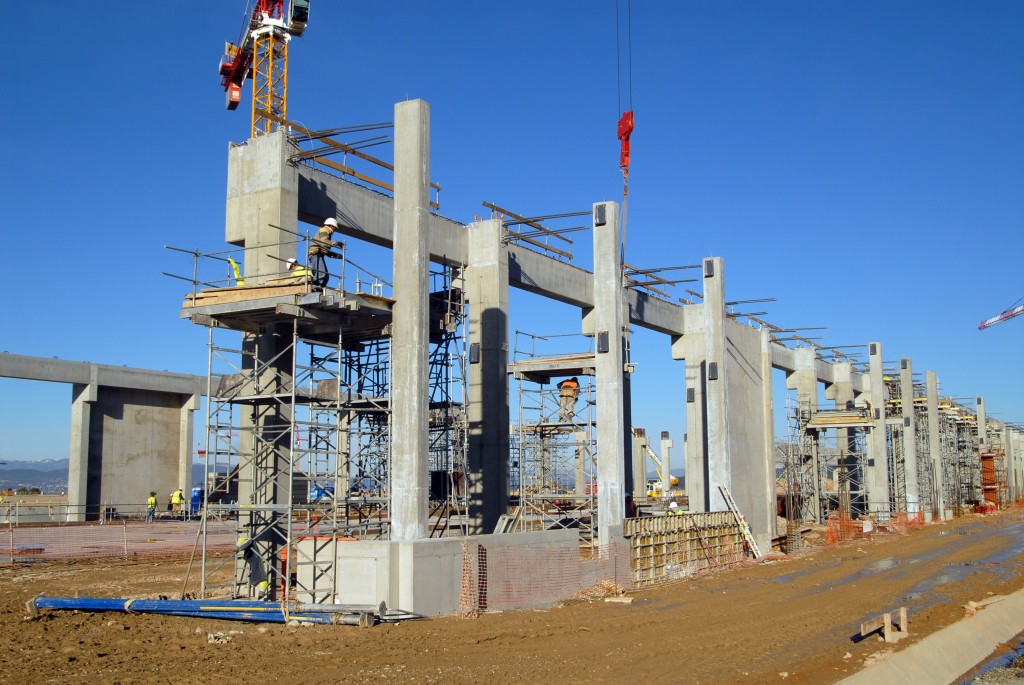
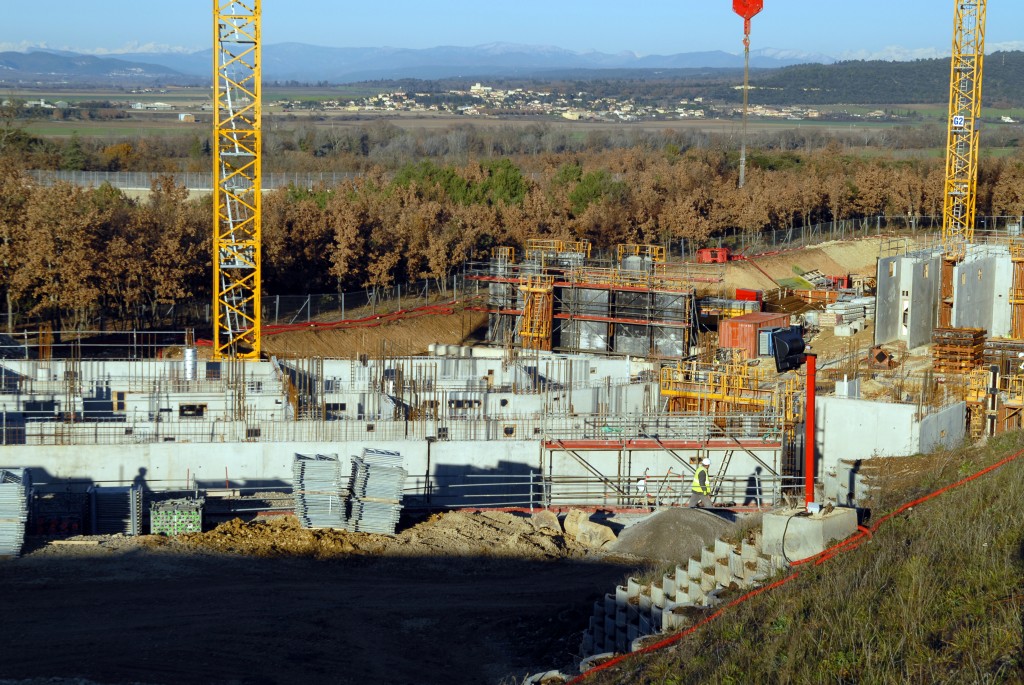
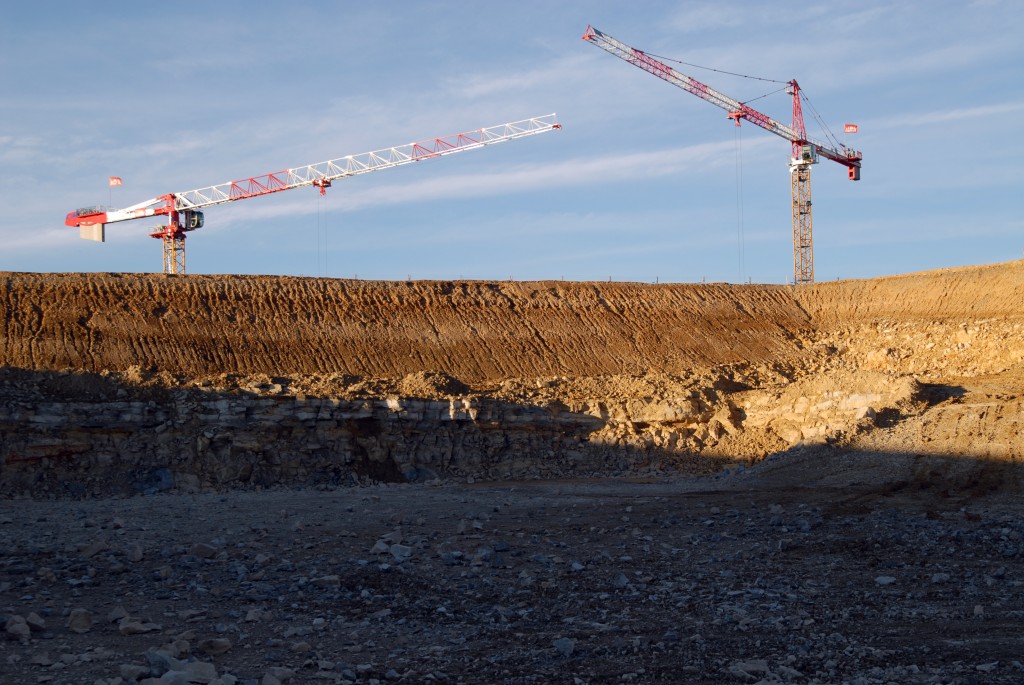
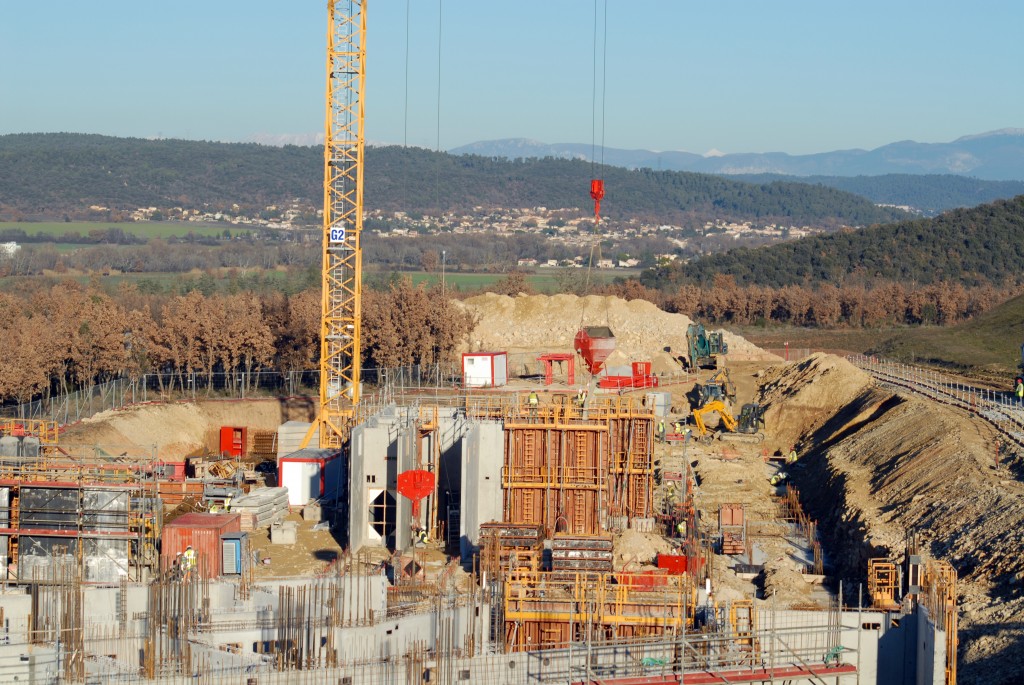
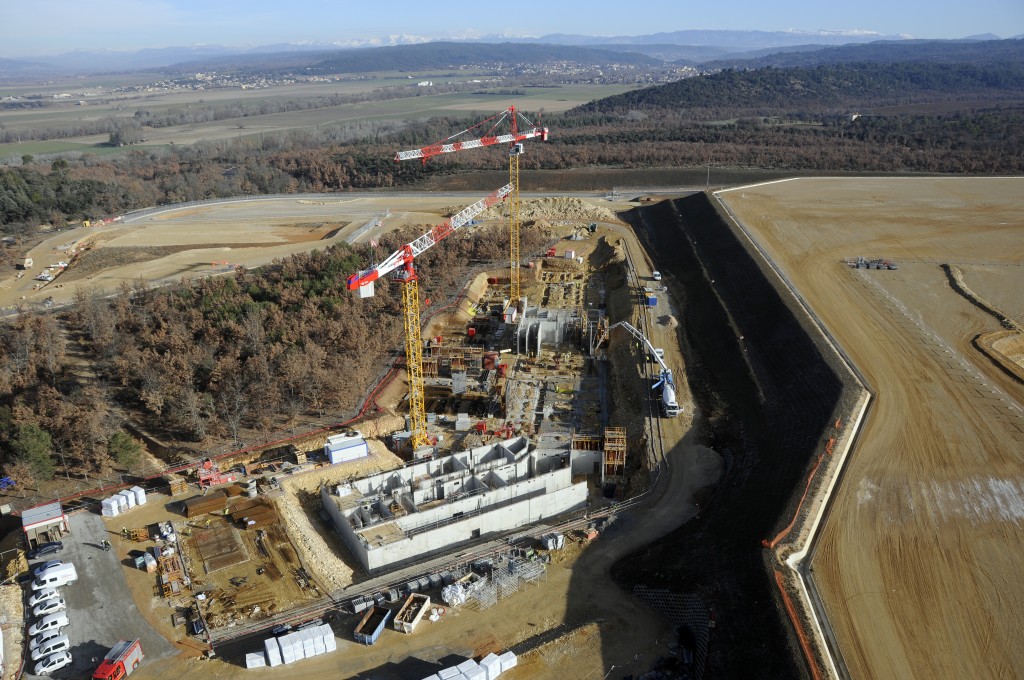
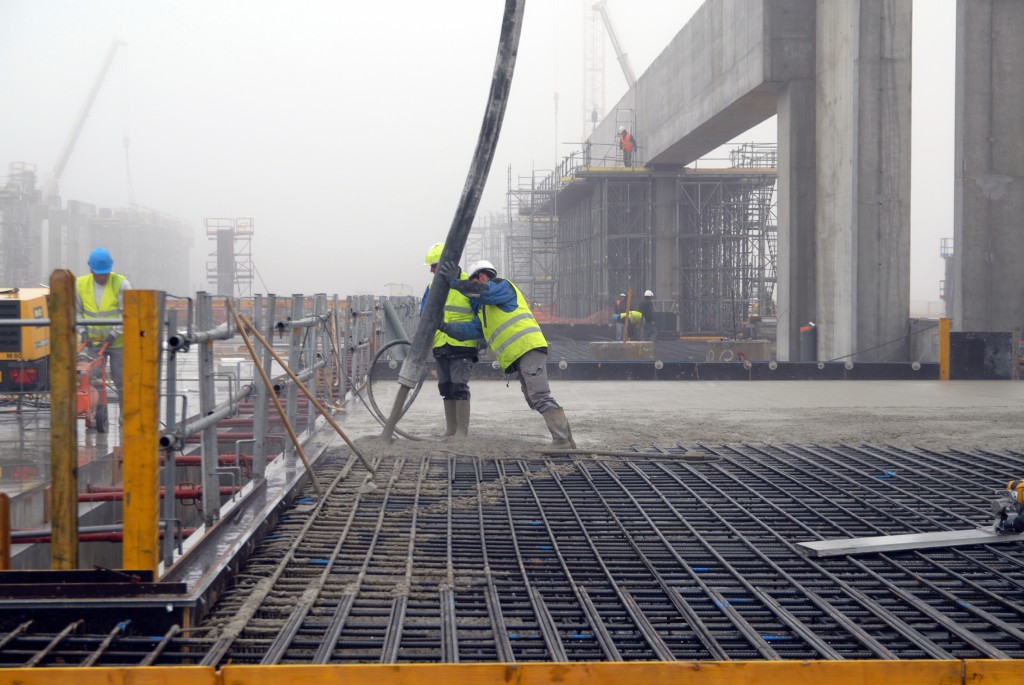
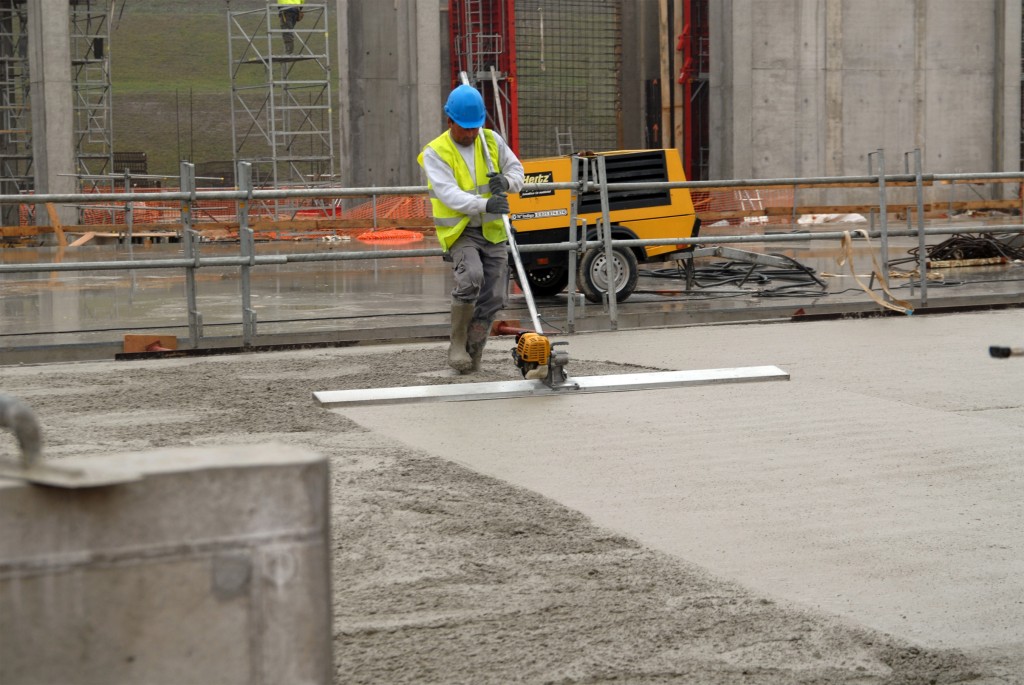
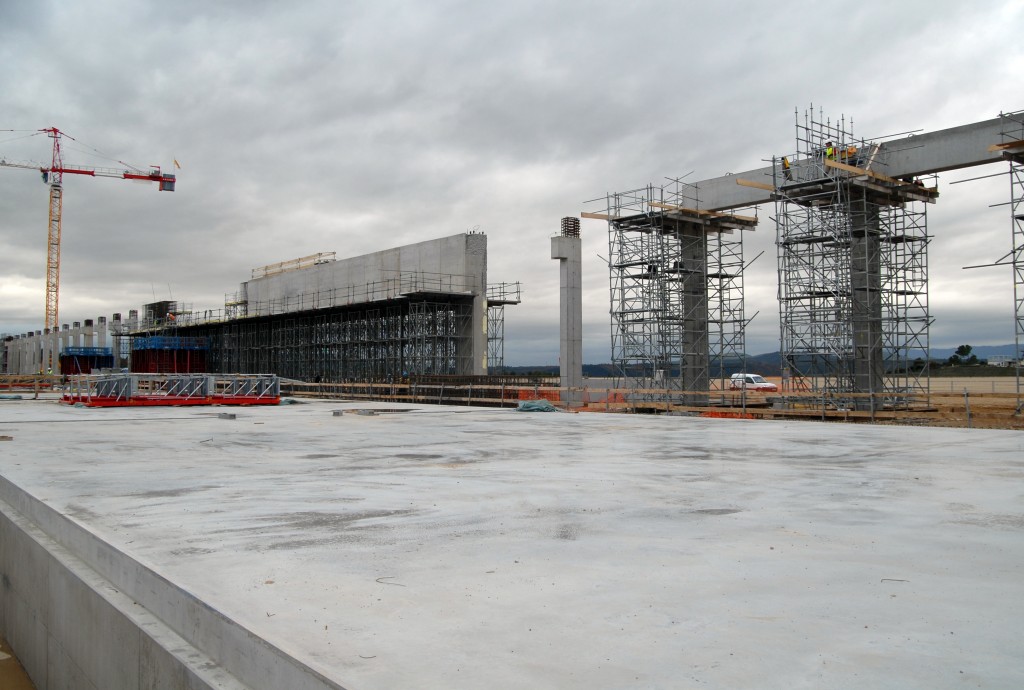

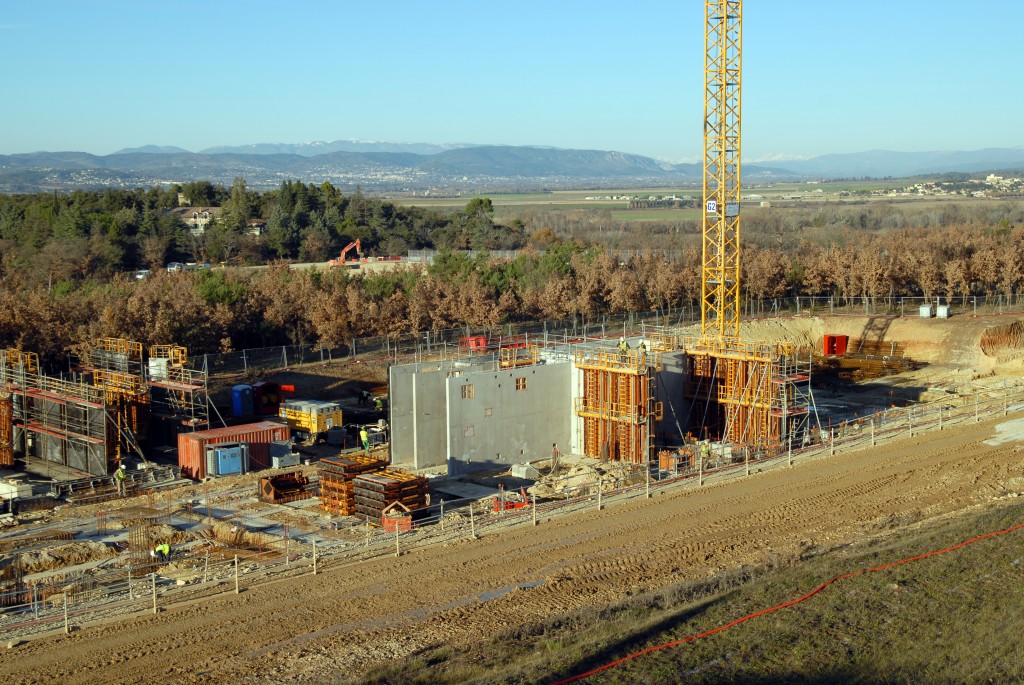
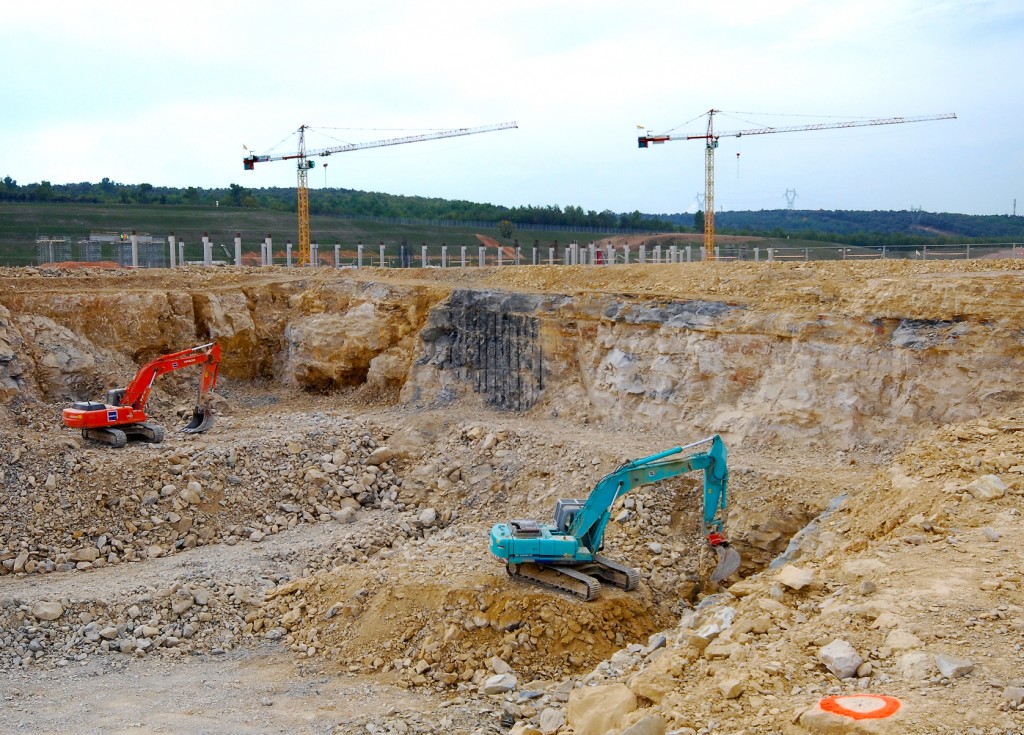
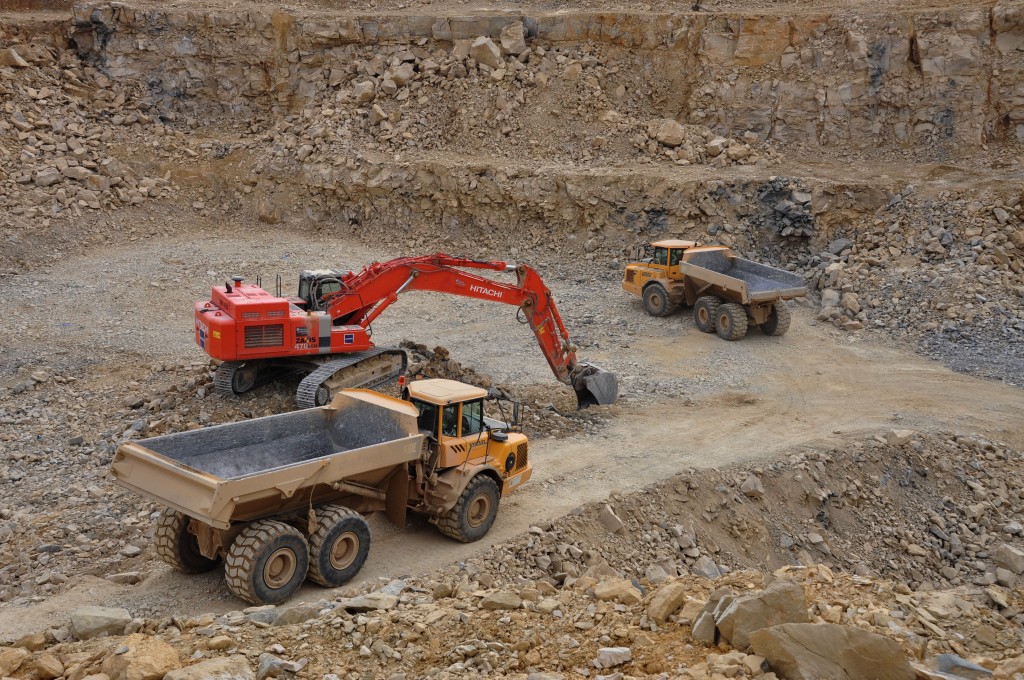
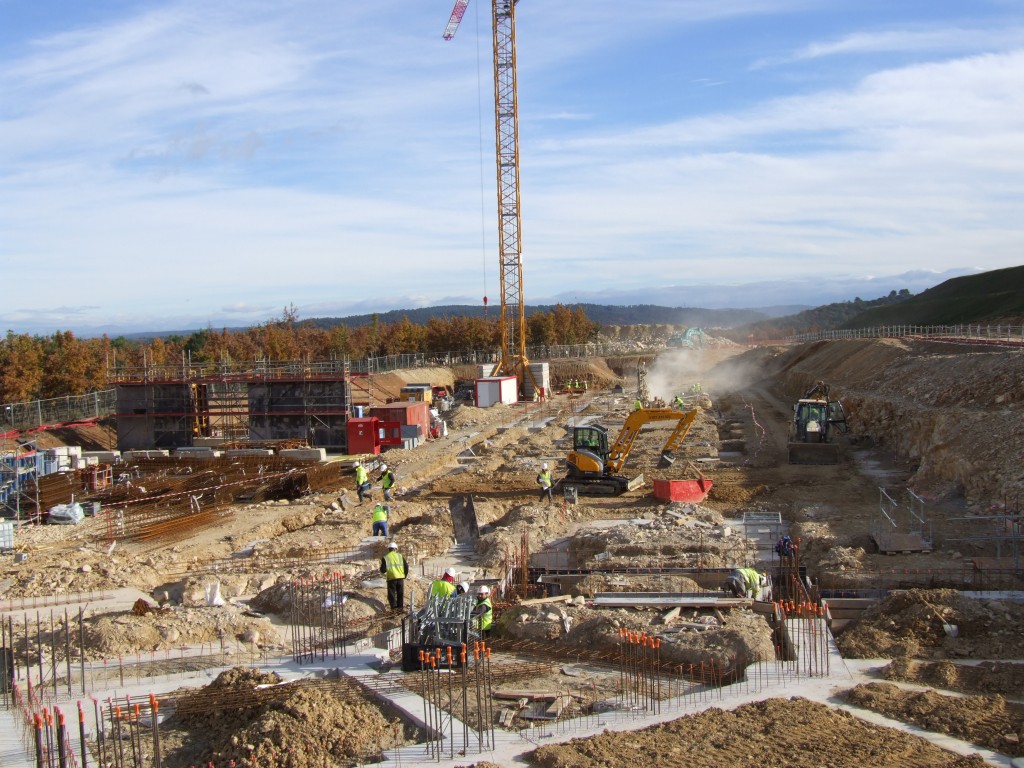
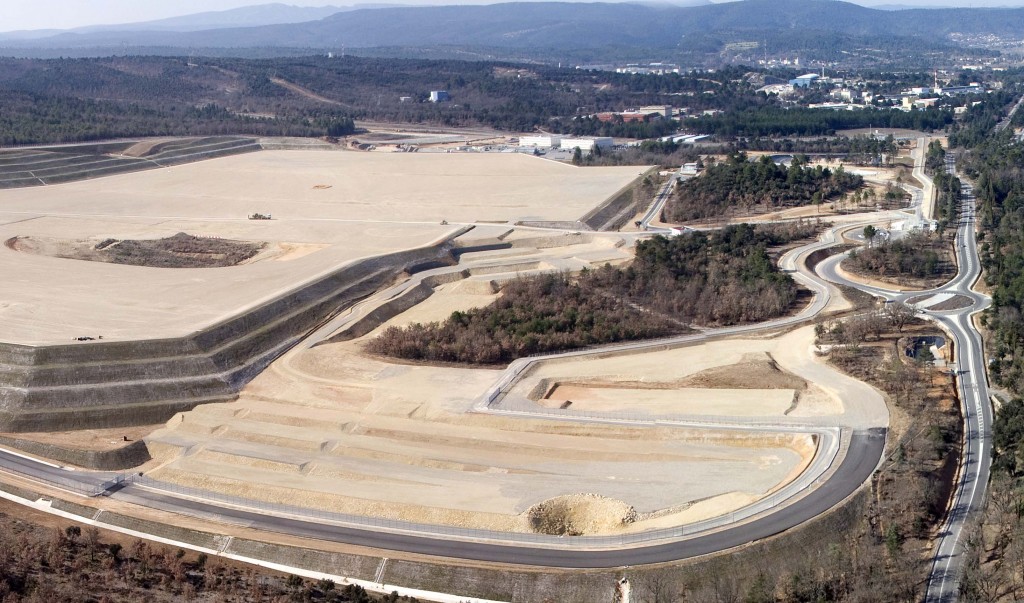
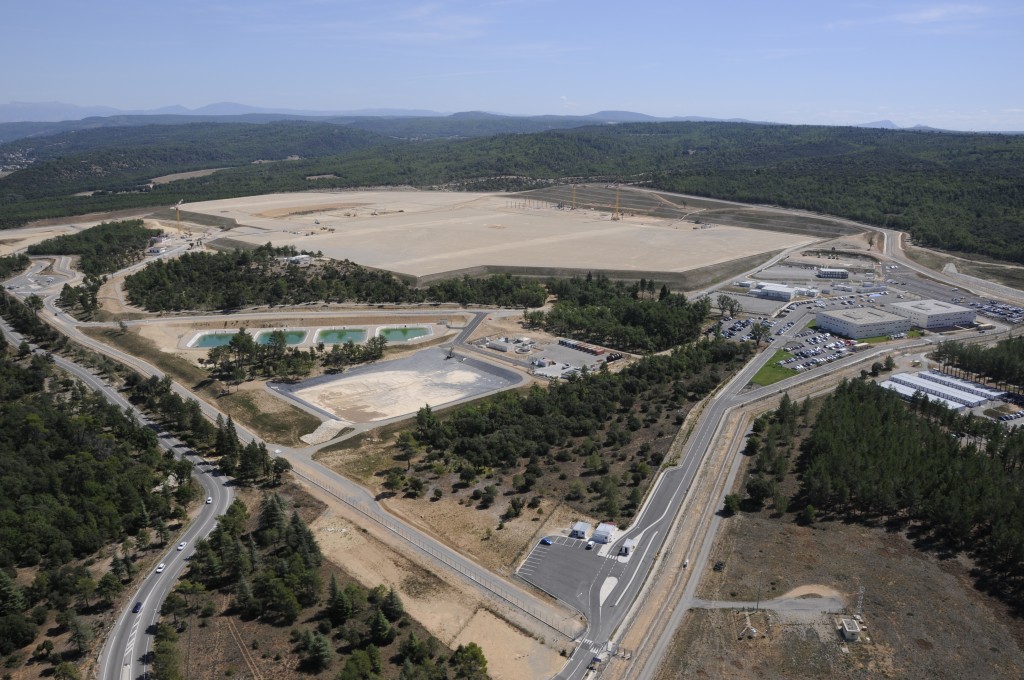
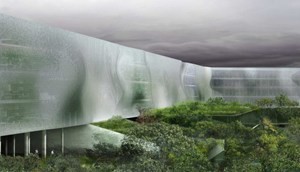
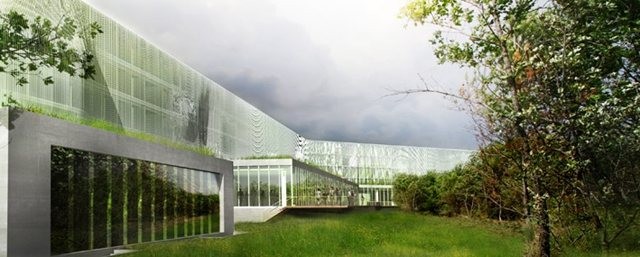
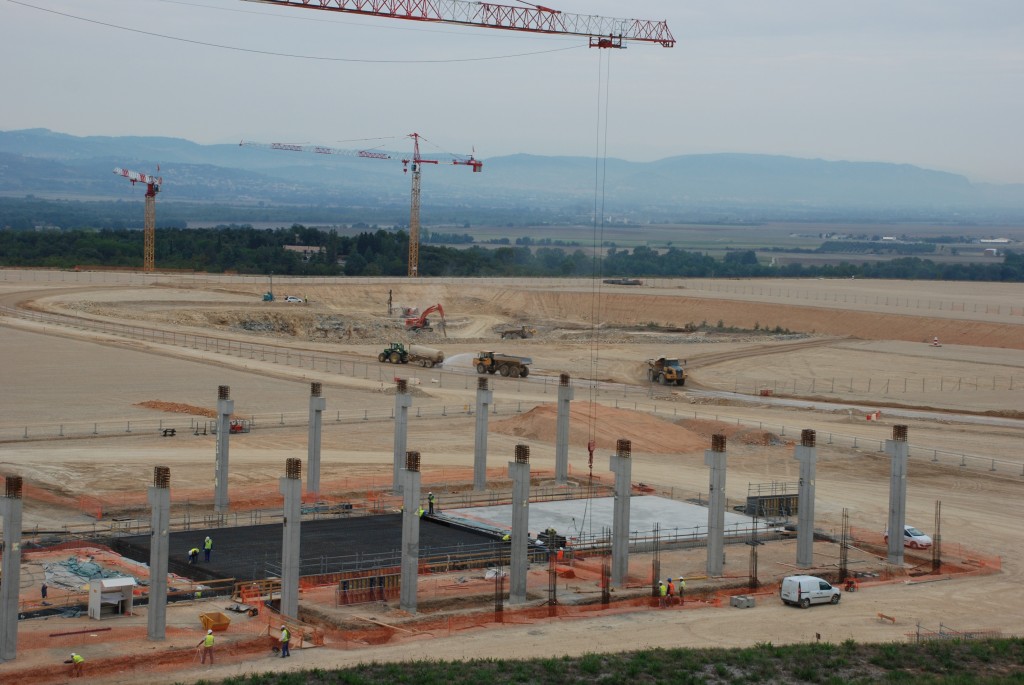
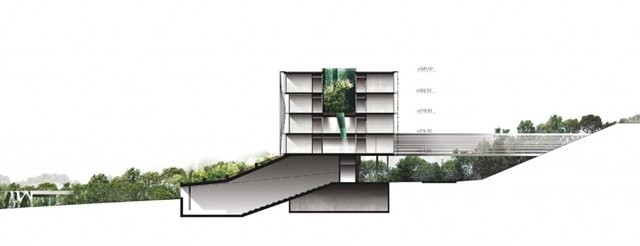
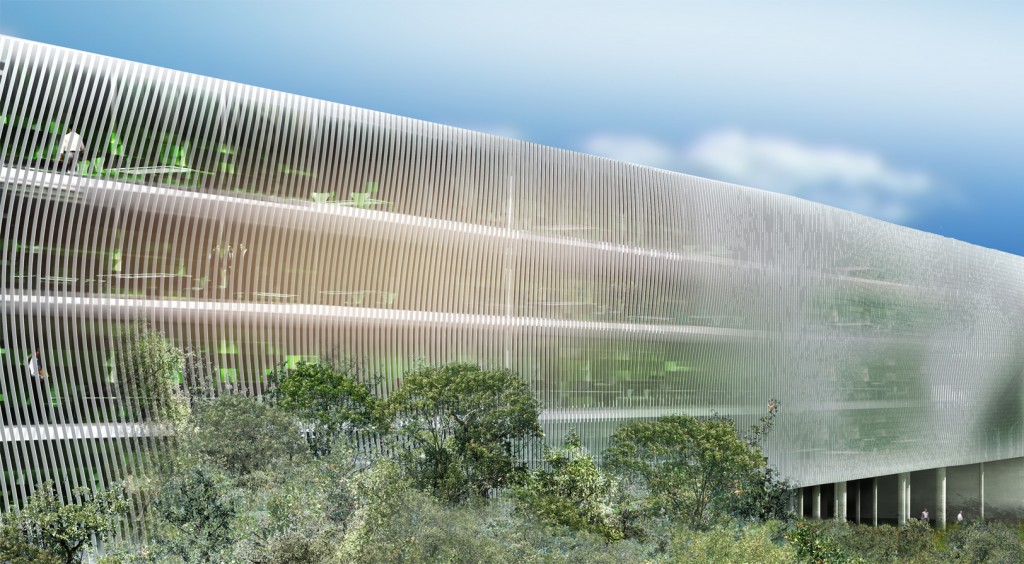
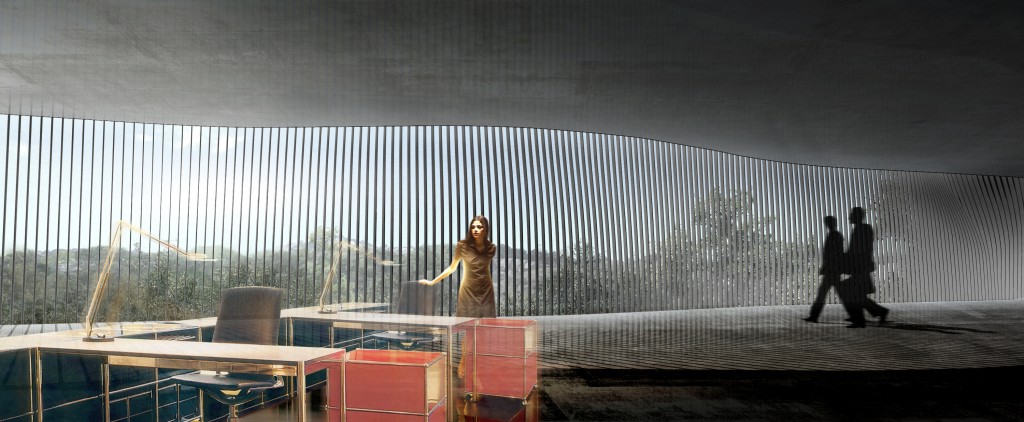
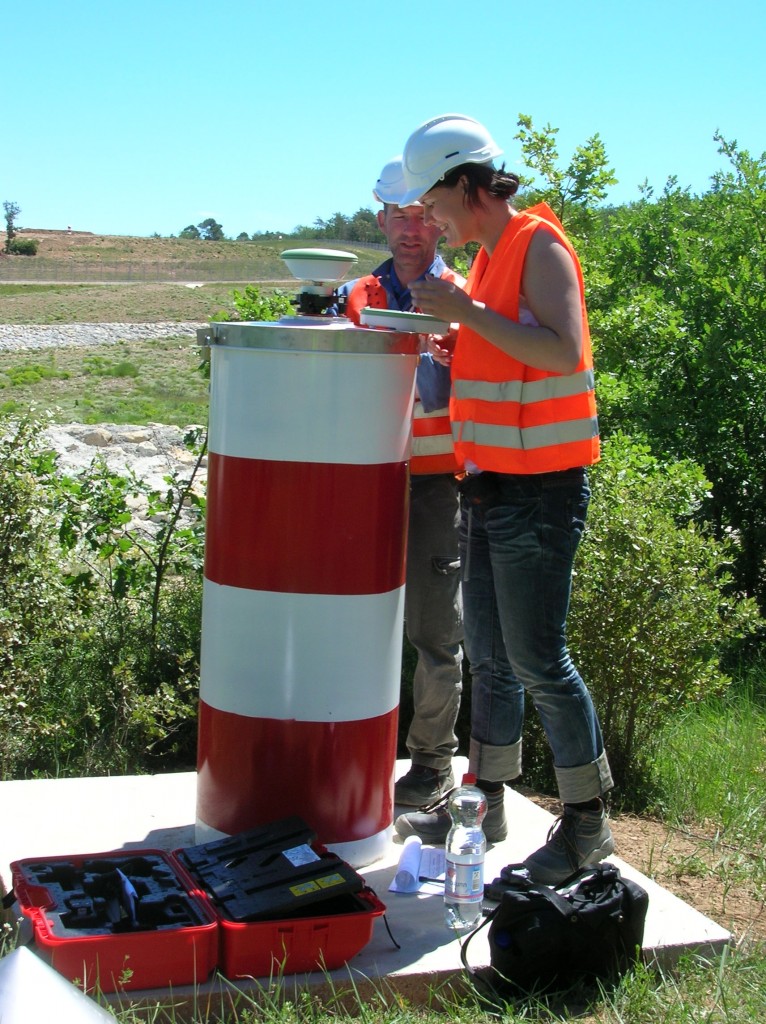
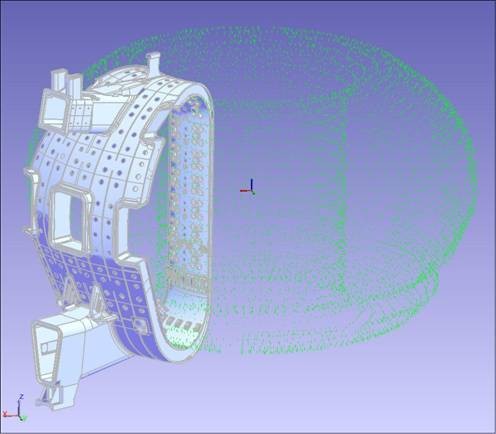

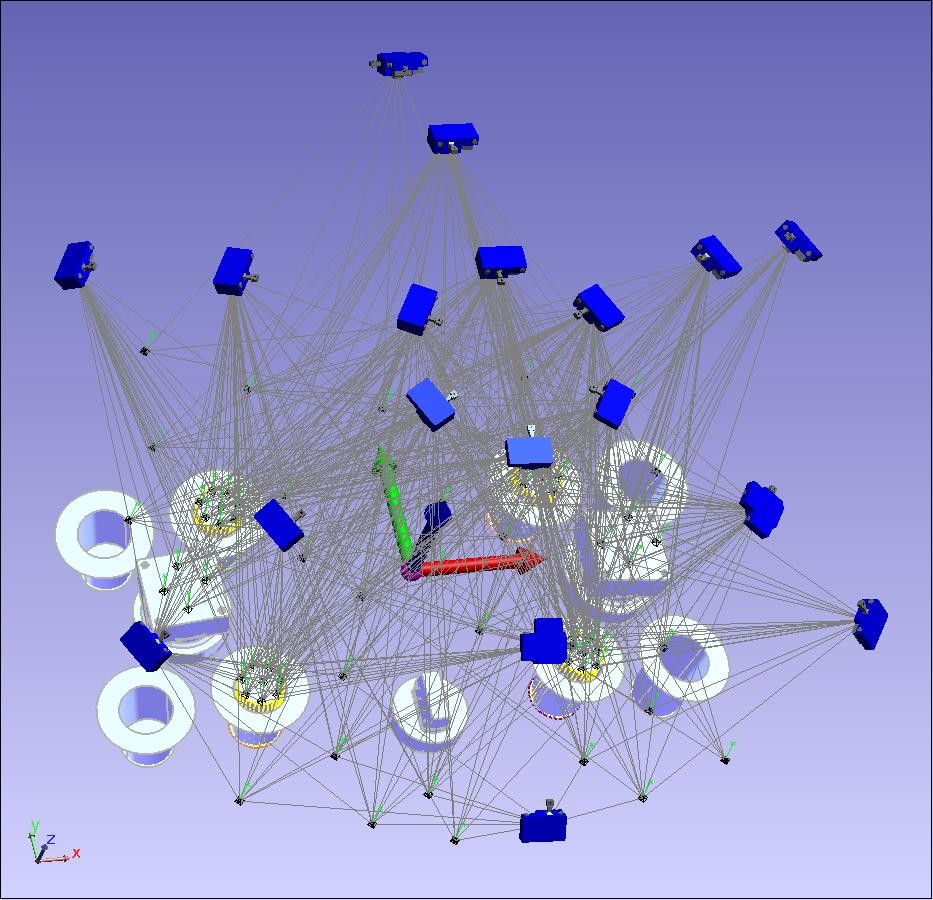
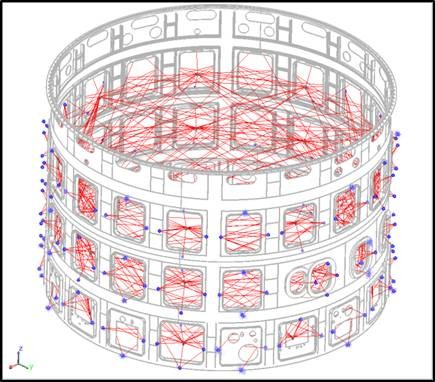
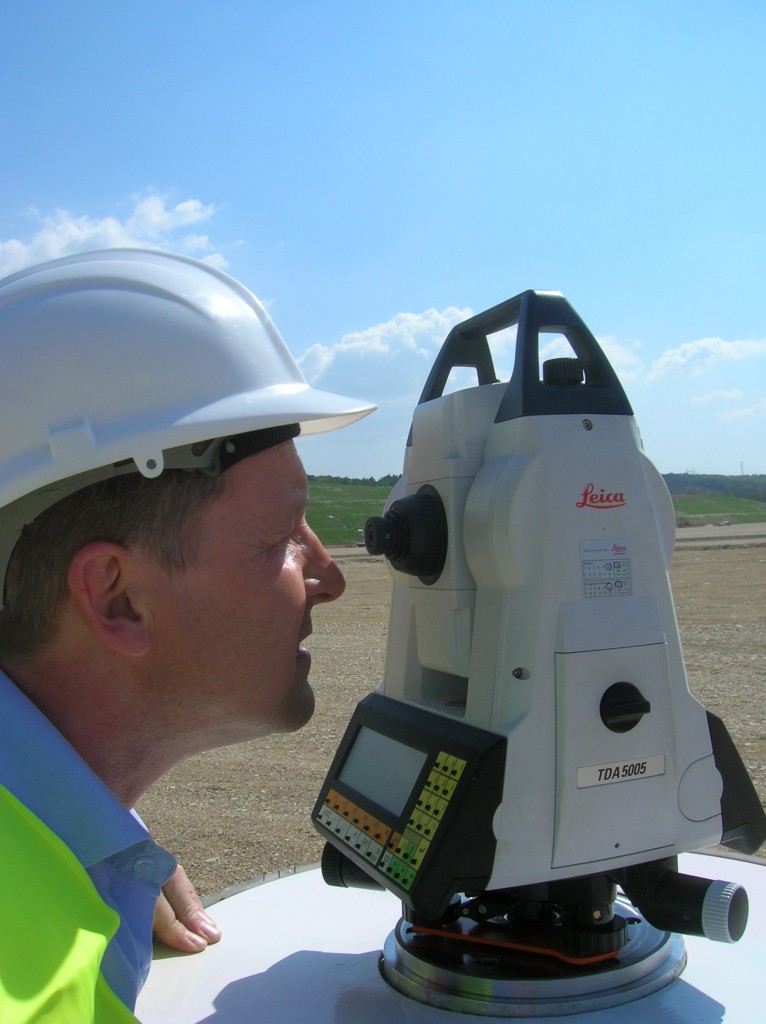
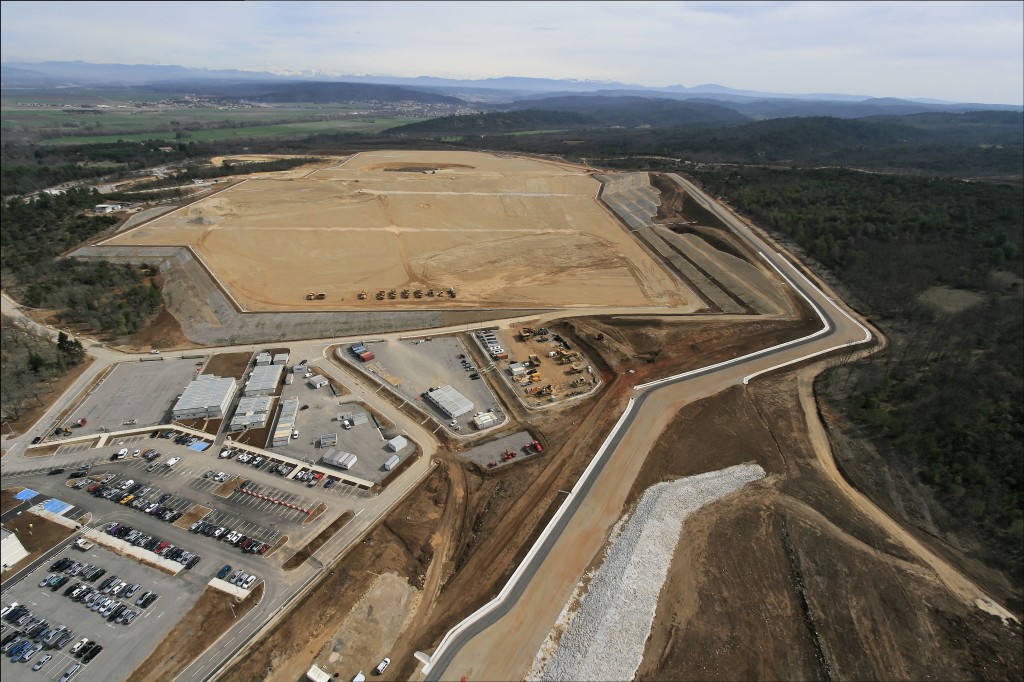
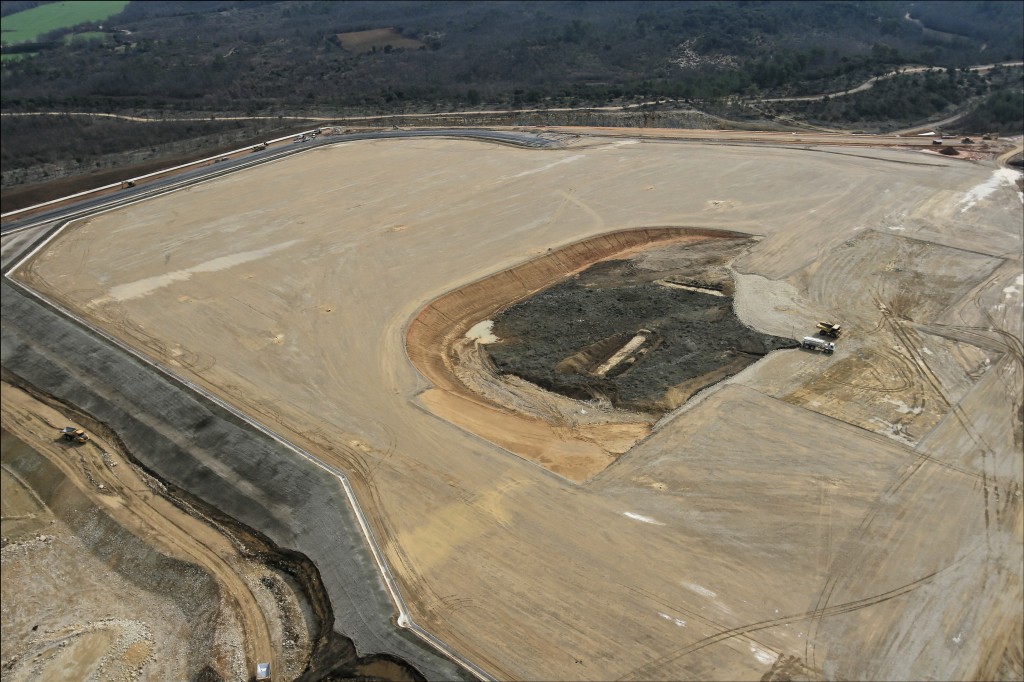


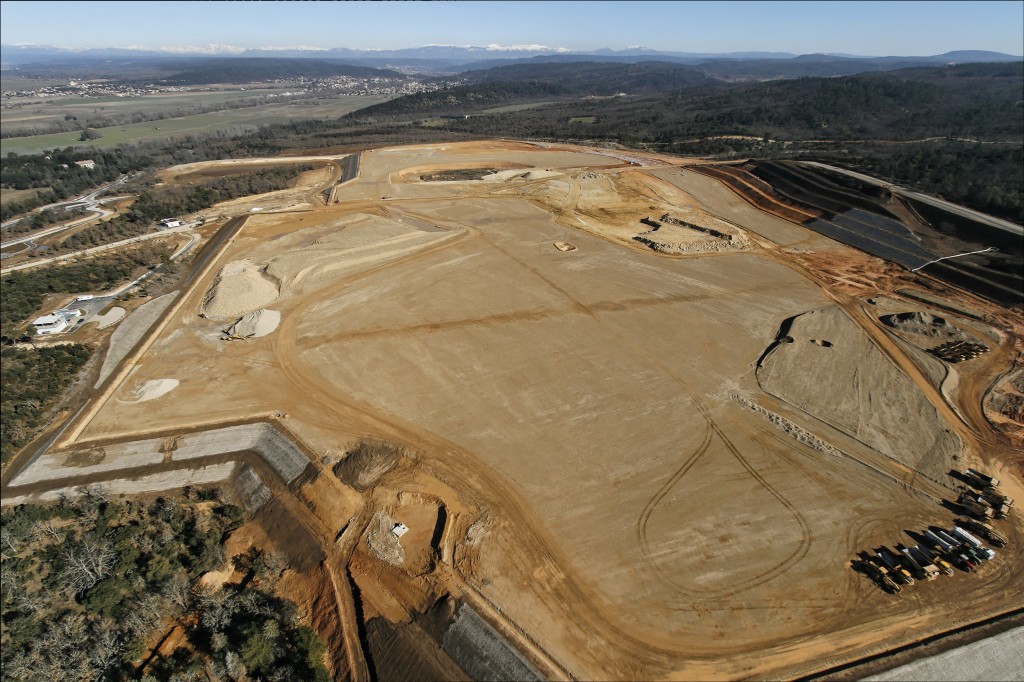
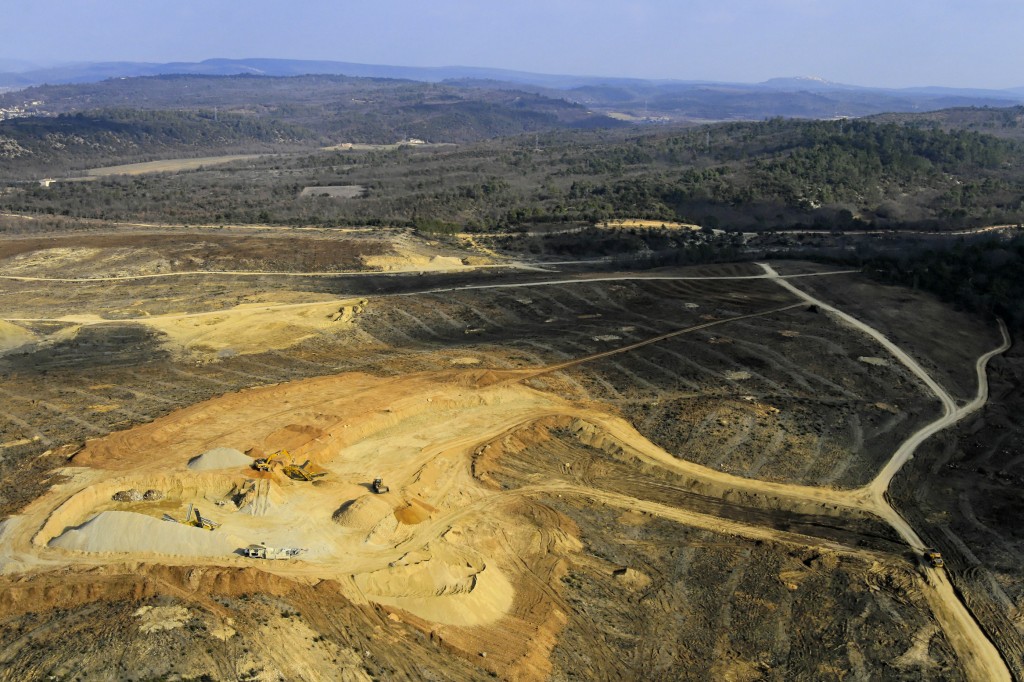
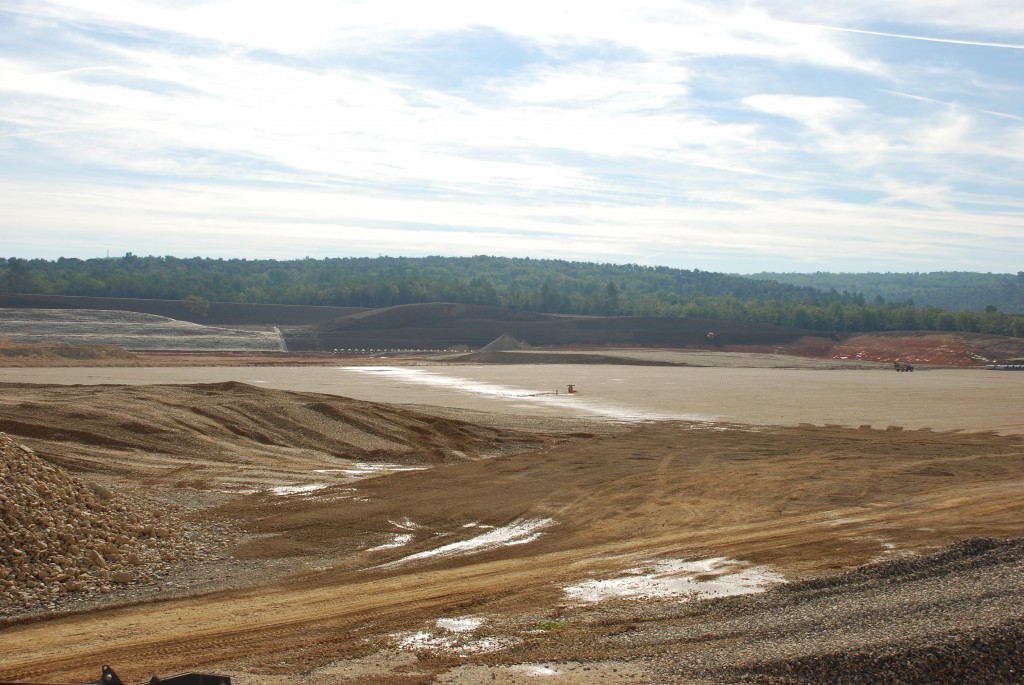






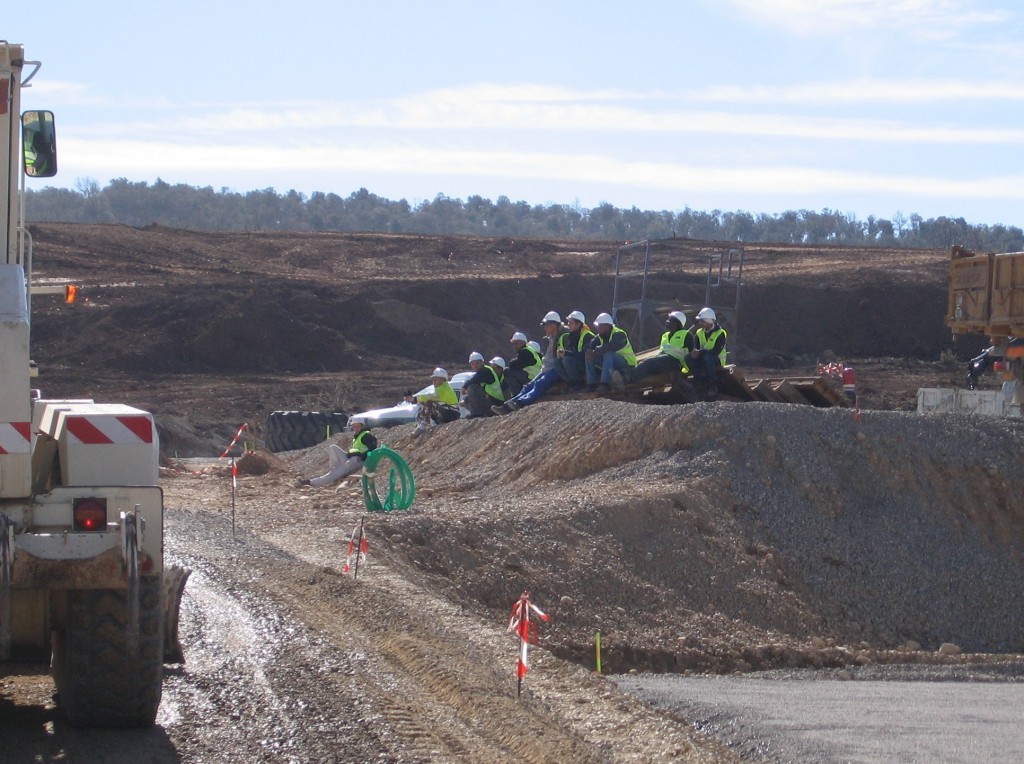



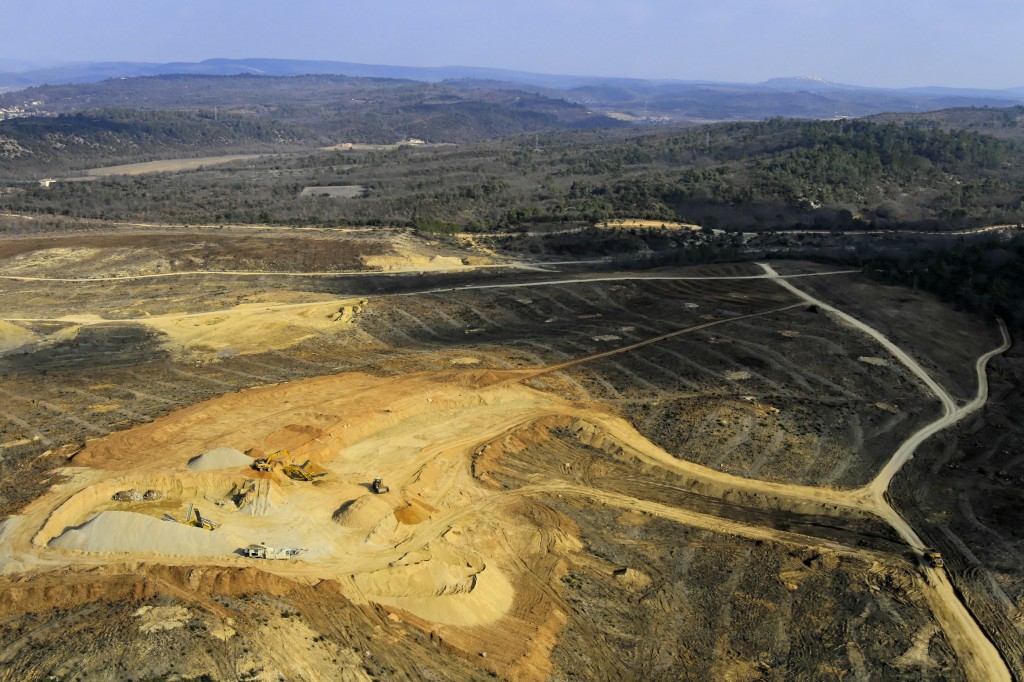
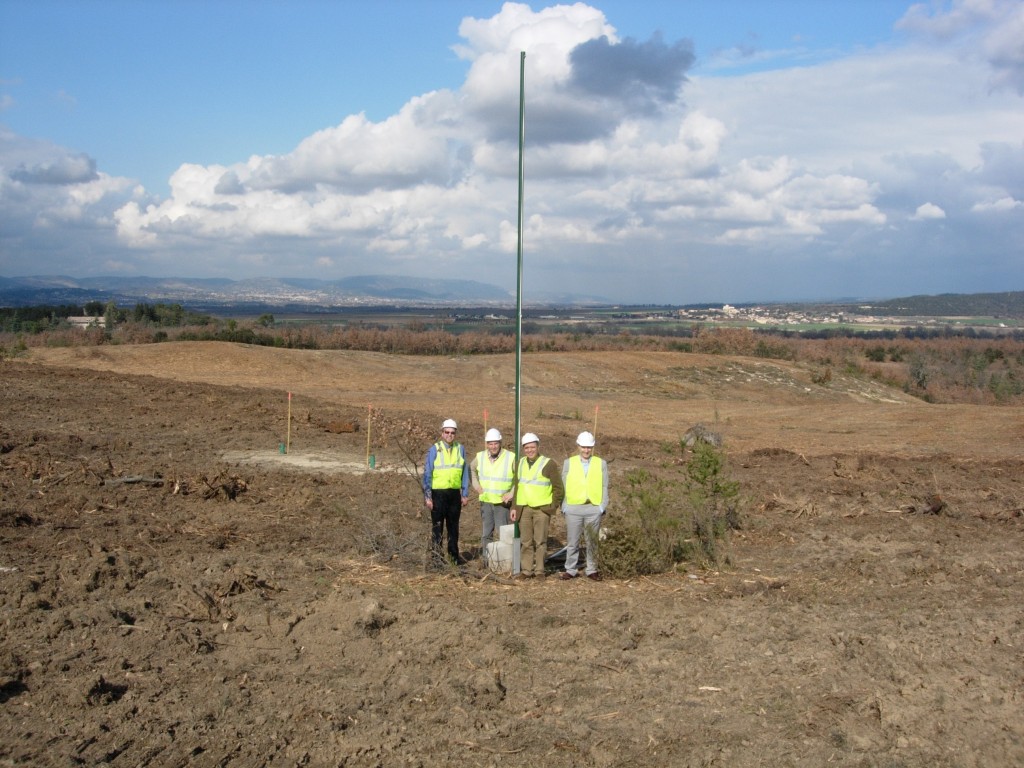
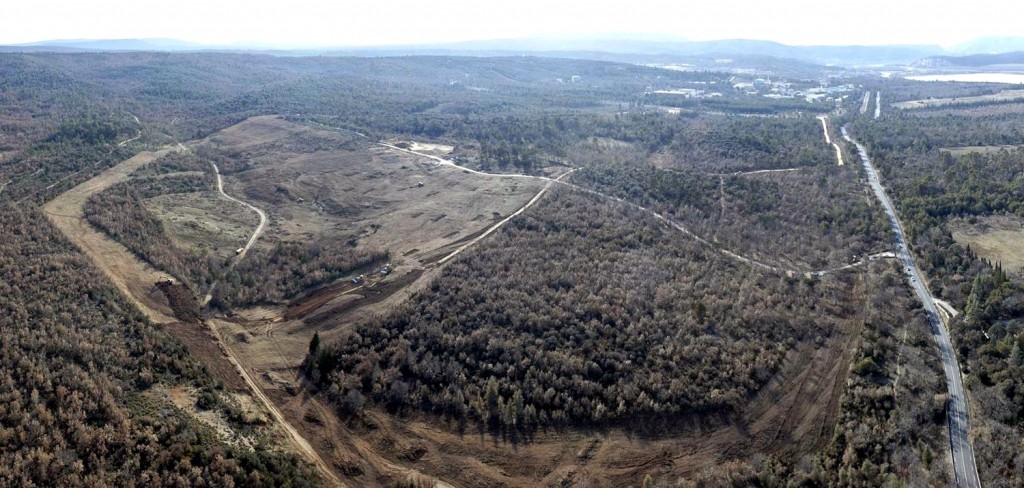
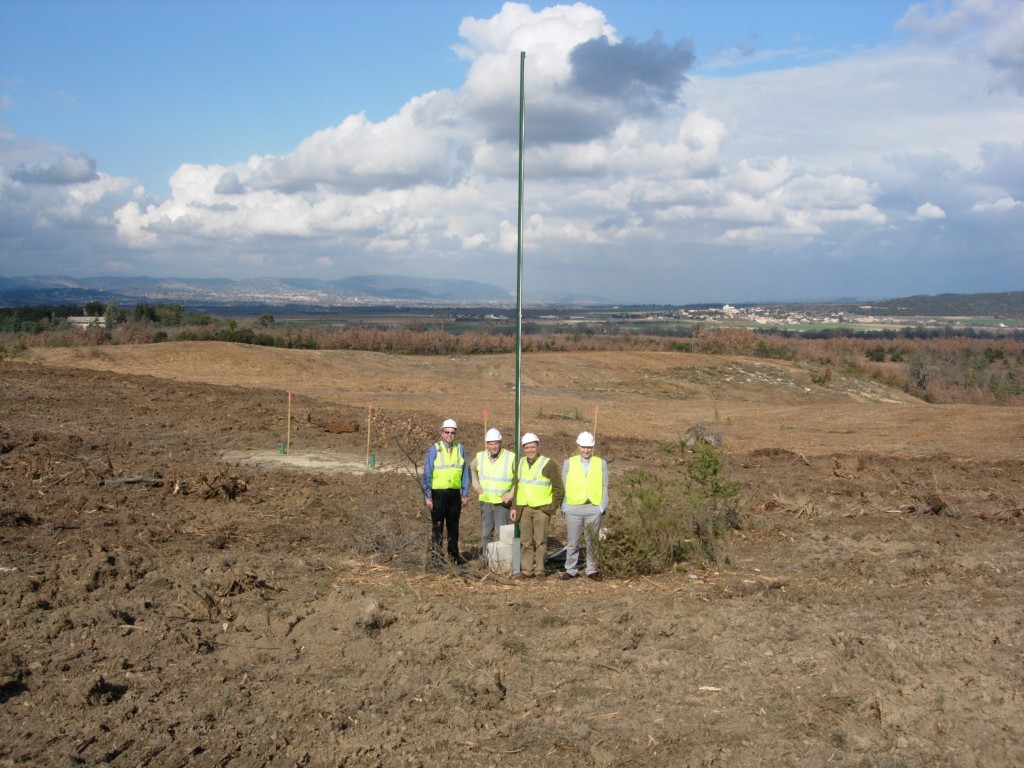