Tokamak assembly

The size and weight of the major components, the tiny tolerances and careful handling required for the assembly of huge and unique systems, the diversity of manufacturers, the tight schedule, complex interfaces ... all of these elements combine to make the assembly of the ITER tokamak an engineering and logistics challenge of enormous proportions.
Core machine assembly is proceeding from bottom to top. Beginning with the heaviest single component—the 1,250-tonne cryostat base, installed in May 2020—assembly contractors are executing the sequence as planned: lower poloidal field coils, cryostat lower cylinder and thermal shield and, over the next years, the nine vacuum vessel modules, subsequent ring coils, components at the top of the machine, central solenoid and, finally, the cryostat lid.
1
Components enter the Assembly Hall through the Cleaning Facility, where they are unpacked and cleaned with compressed air, pressurized demineralized water, or specialty detergents. The Cleaning Facility operates as an airlock between the Hall and the outside environment.
2
The overhead crane system transfers the newly arrived loads to temporary laydown areas, or zones reserved for sub-assembly activities. Then, in the order determined by assembly sequences, the components or assemblies are transported to the Tokamak pit, a 30-metre-deep concrete cylinder in the centre of the Tokamak Building.
3
The ITER Organization is using a number of other warehouse spaces on site to receive, inspect and prepare the largest components for handling in the Assembly Hall. Each ITER component is absolutely unique—and in many cases has required ten years to design, prototype and manufacture. Every possible precaution is taken in their unloading and transport.
4
Contractors working under the supervision of the ITER Organization are carrying out the thousands of complex lifting, positioning, joining, and inspection activities of ITER machine assembly.
These contractors are carrying out the day-to-day work of machine assembly under the oversight of the ITER Organization:
Tokamak in-cryostat assembly
The CNPE Consortium (China Nuclear Power Engineering; China Nuclear Industry 23 Construction Company Ltd.; Southwestern Institute of Physics; Institute of Plasma Physics, Chinese Academy of Sciences ASIPP; and Framatome) is responsible for tokamak machine assembly (assembly of the cryostat and cryostat thermal shield; magnet feeders; the central solenoid, poloidal field and correction coil magnets; and cooling structures and instrumentation).
Vacuum vessel assembly
The CNPE Consortium is responsible for Sector Module Sub-Assembly, SMSA (assembly of the vacuum vessel sectors with toroidal field coils and vacuum vessel thermal shielding). In partnership with SIMIC S.p.A., the CNPE Consortium will also execute the contract for Sector Module Assembly in Pit, SMPA (bringing all toroidal field coils onto their gravity supports and performing the interconnection between all 18 coils, including through the pre-compression rings) and the contract for Welding Positioning and Preparation, WPP (preparations for sector welding to start including landing the sectors on their in-pit gravity supports and installing special clamps). The Indian firm Larsen & Toubro has been awarded a contract for Port Position Assembly and Welding, PPAW (engineering, qualification and tools and in-pit welding of vacuum vessel ports and bellows).
Vacuum vessel welding
The ITER Organization is working with the multinational company Westinghouse for vacuum vessel welding (production phase in the tokamak pit). In the meantime, in order to develop and finalize the correct technologies and processes to be used, a contract covering welding process qualification (engineering and qualification of all processes and new tools required for nine-sector simultaneous welding) has also been placed with the company.
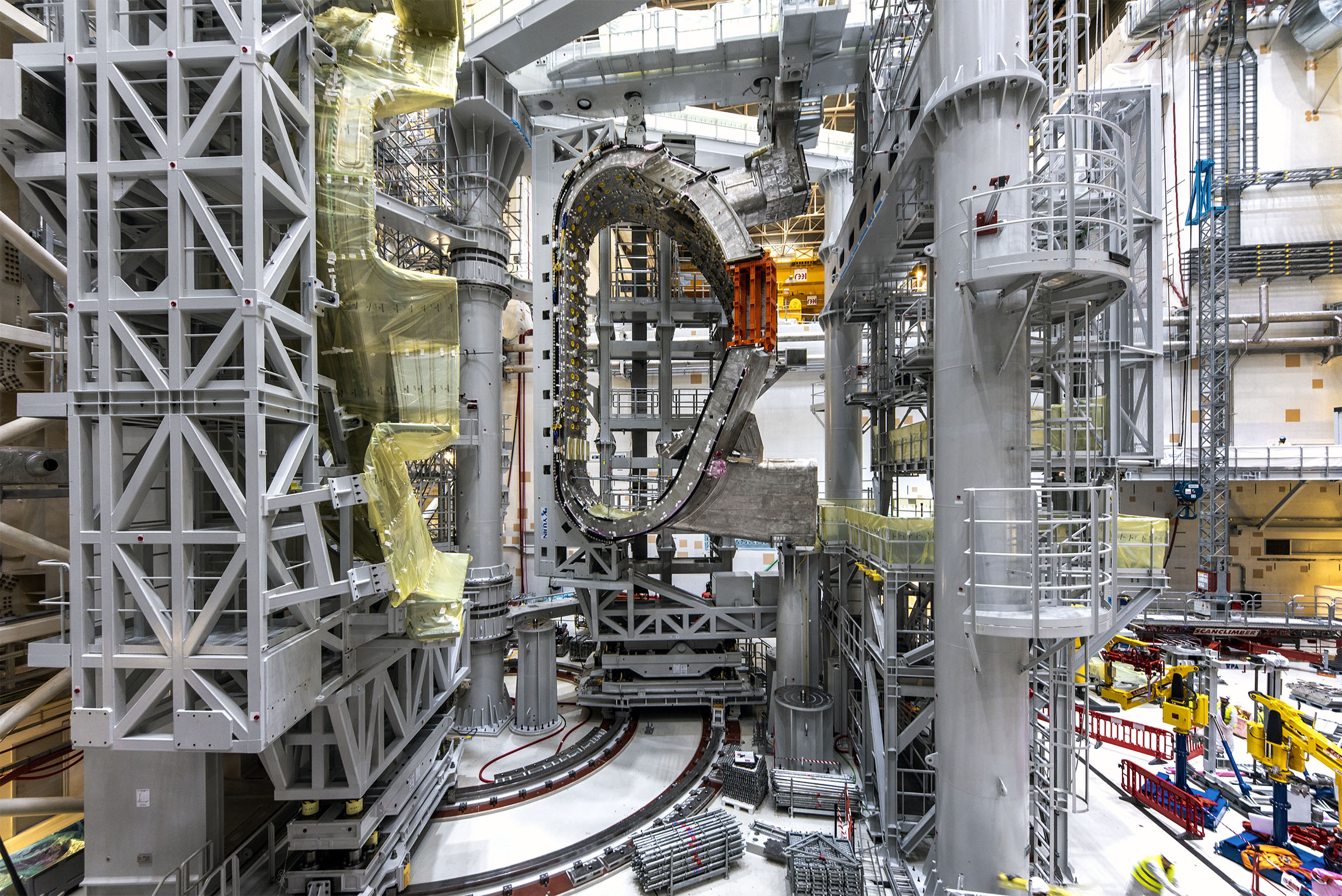
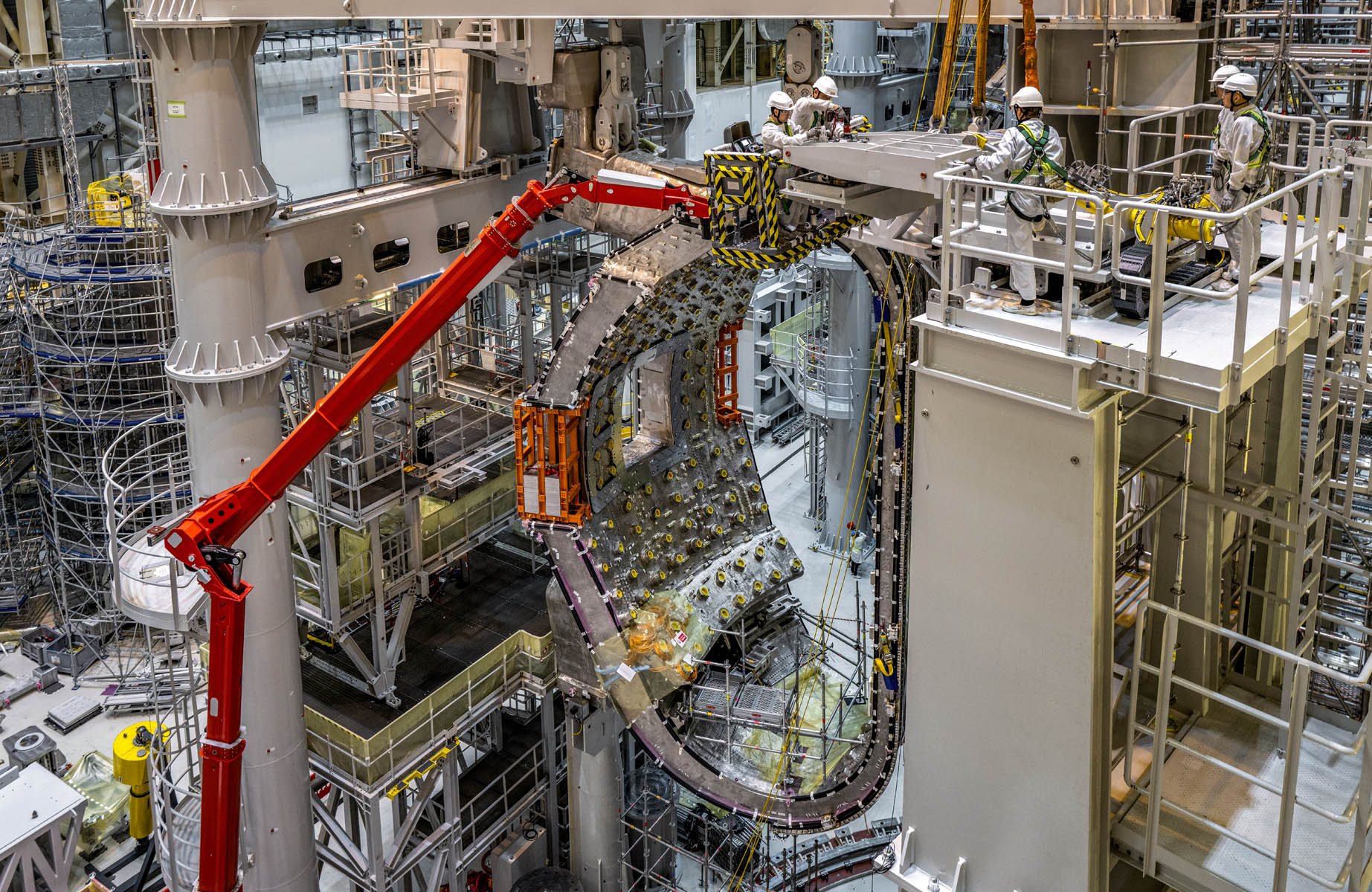
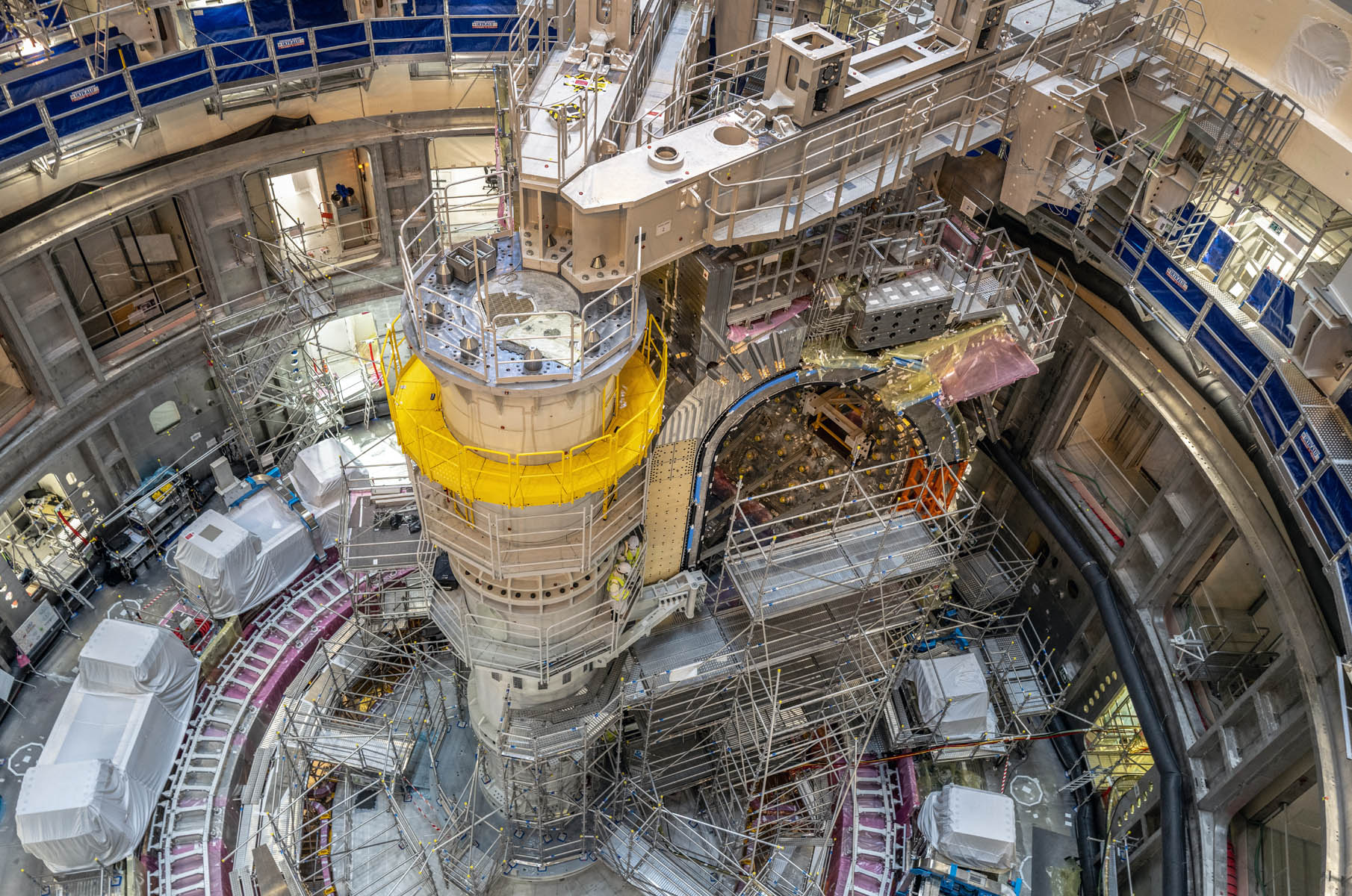
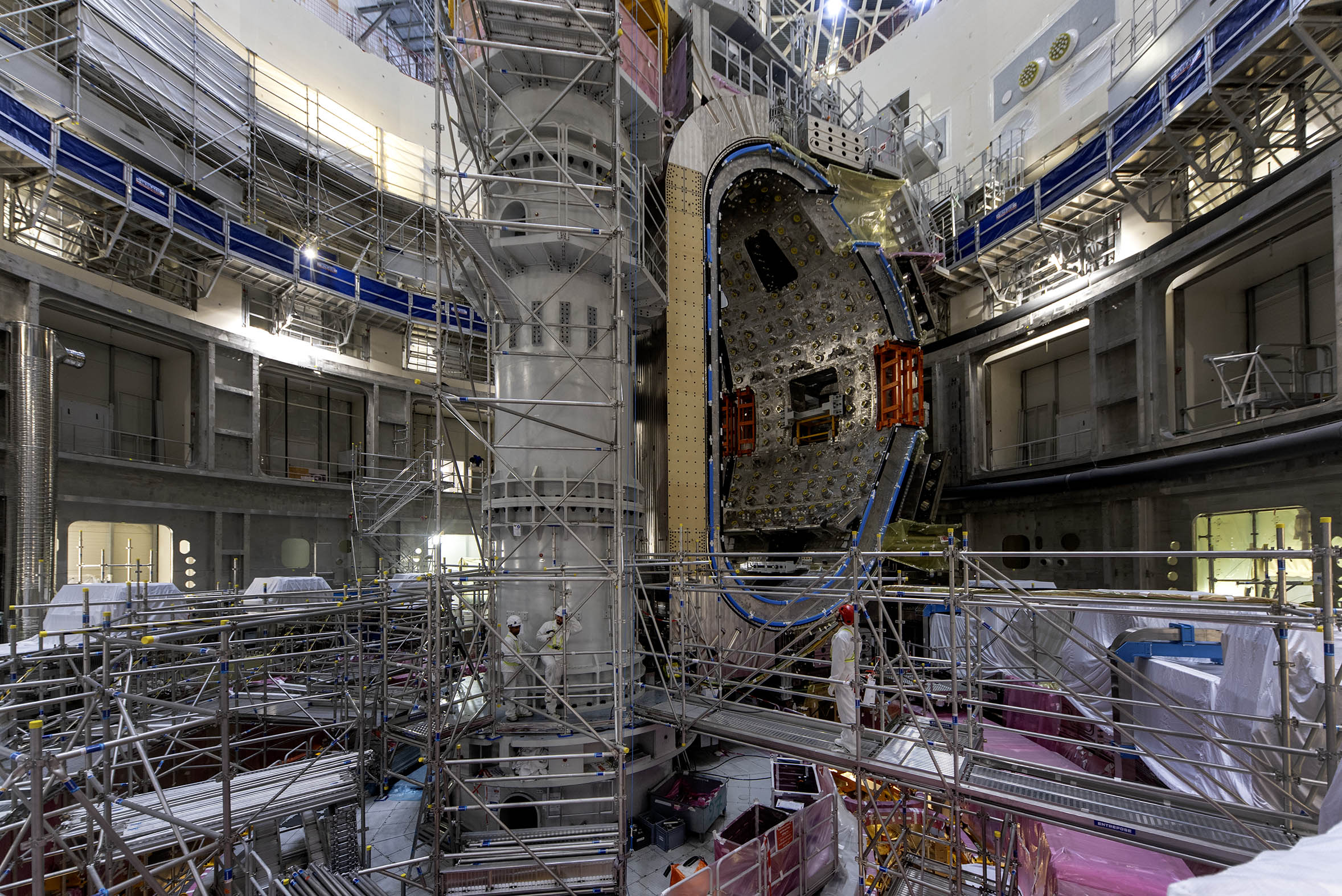
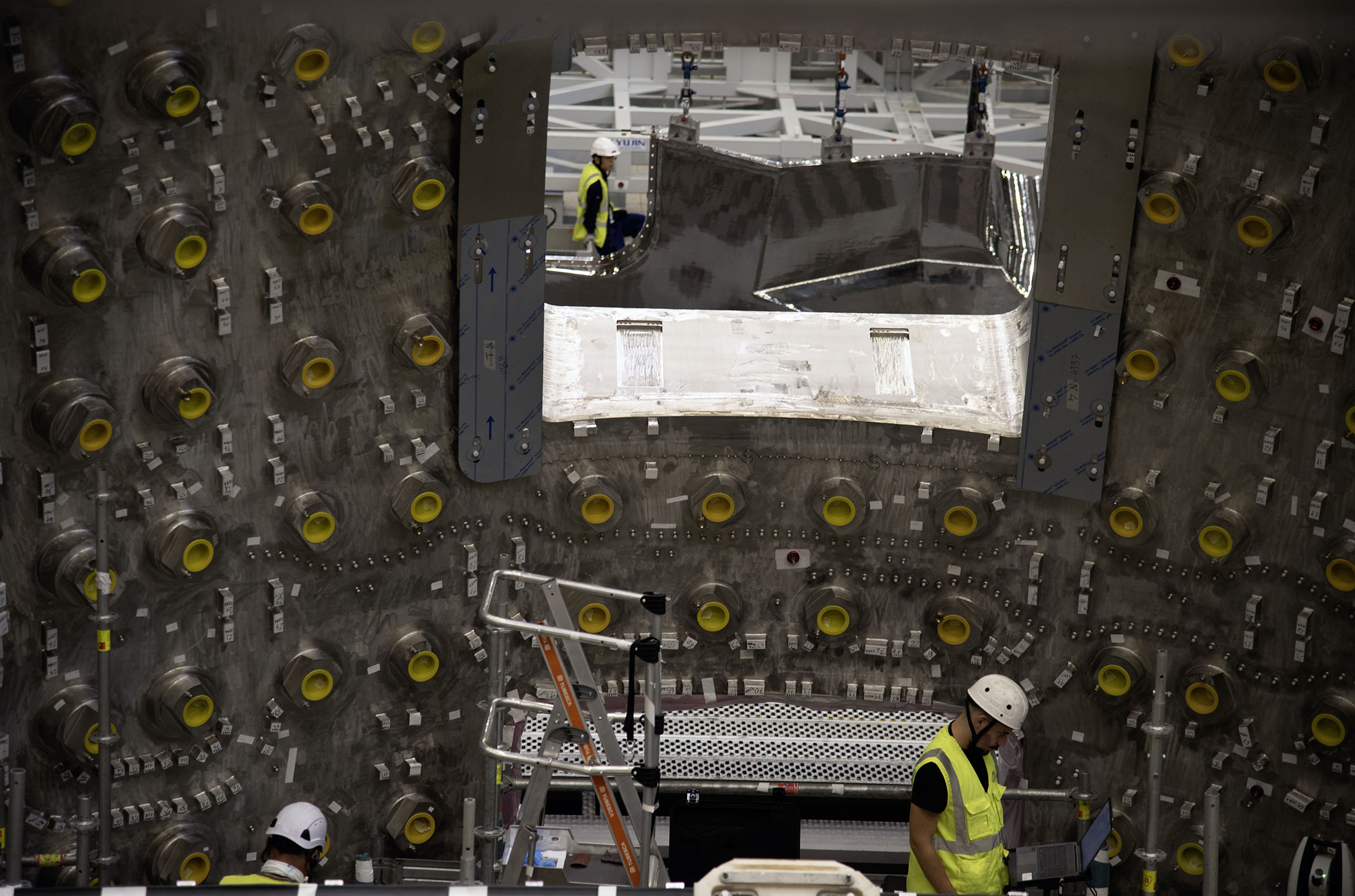
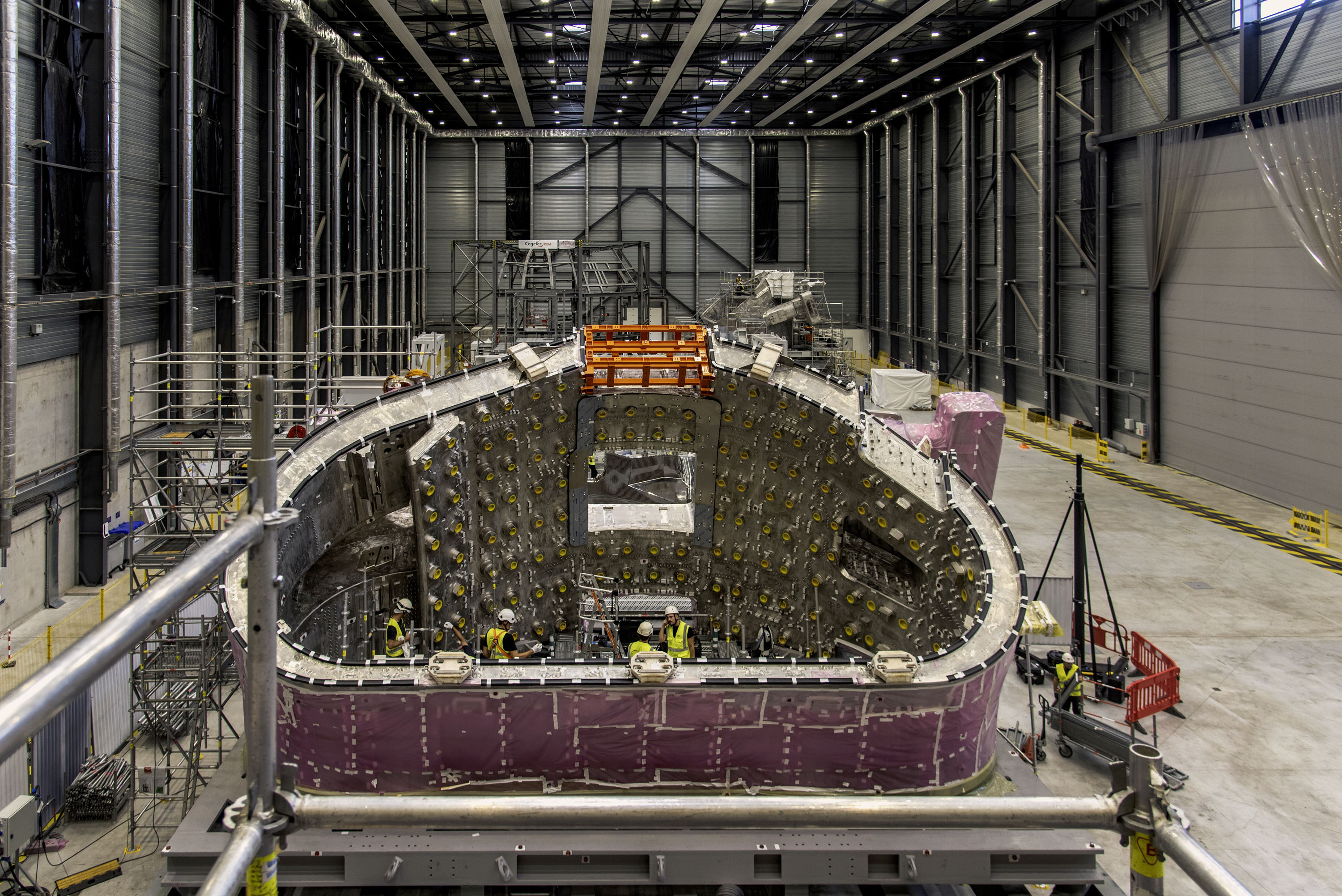
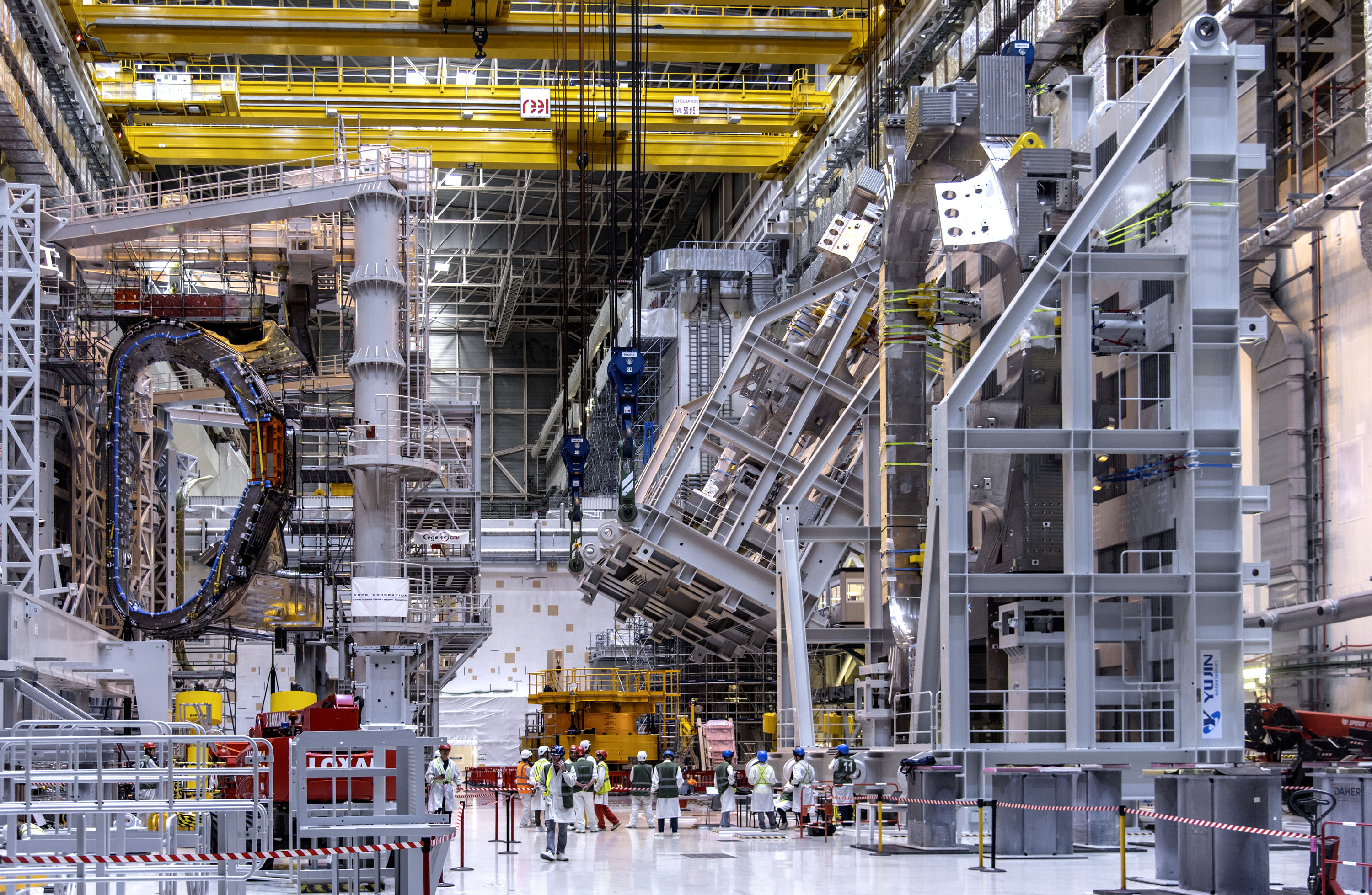
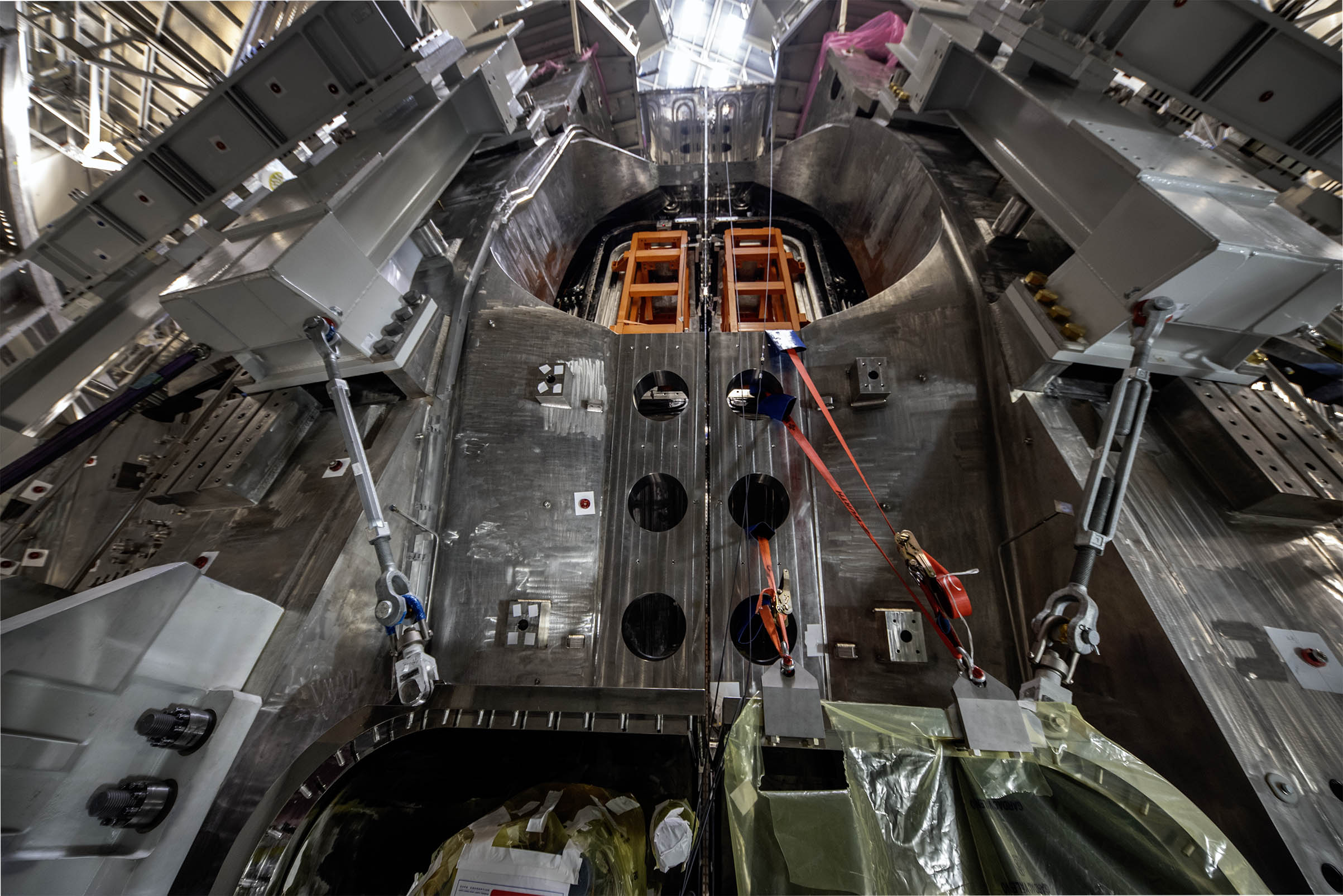
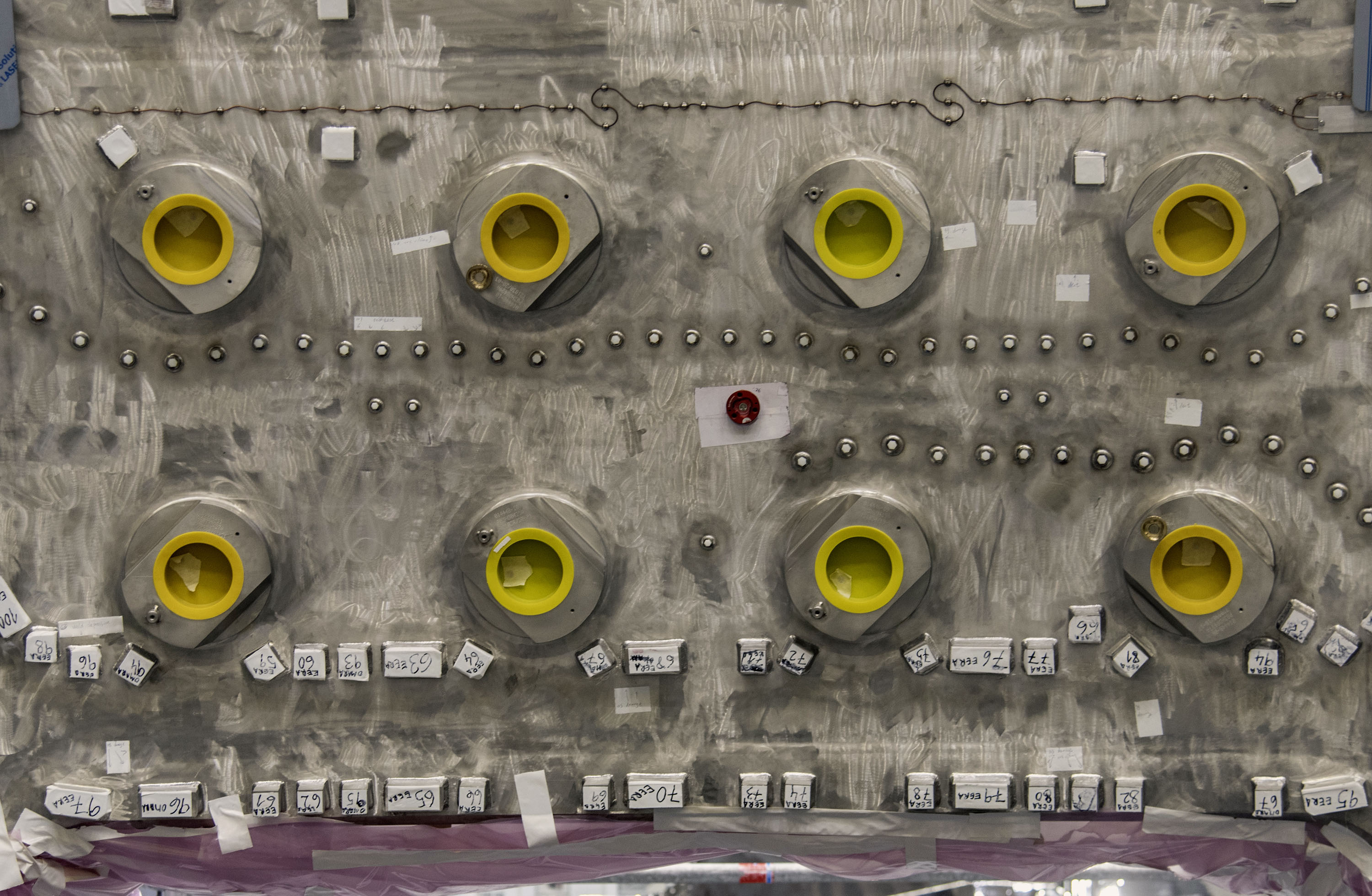
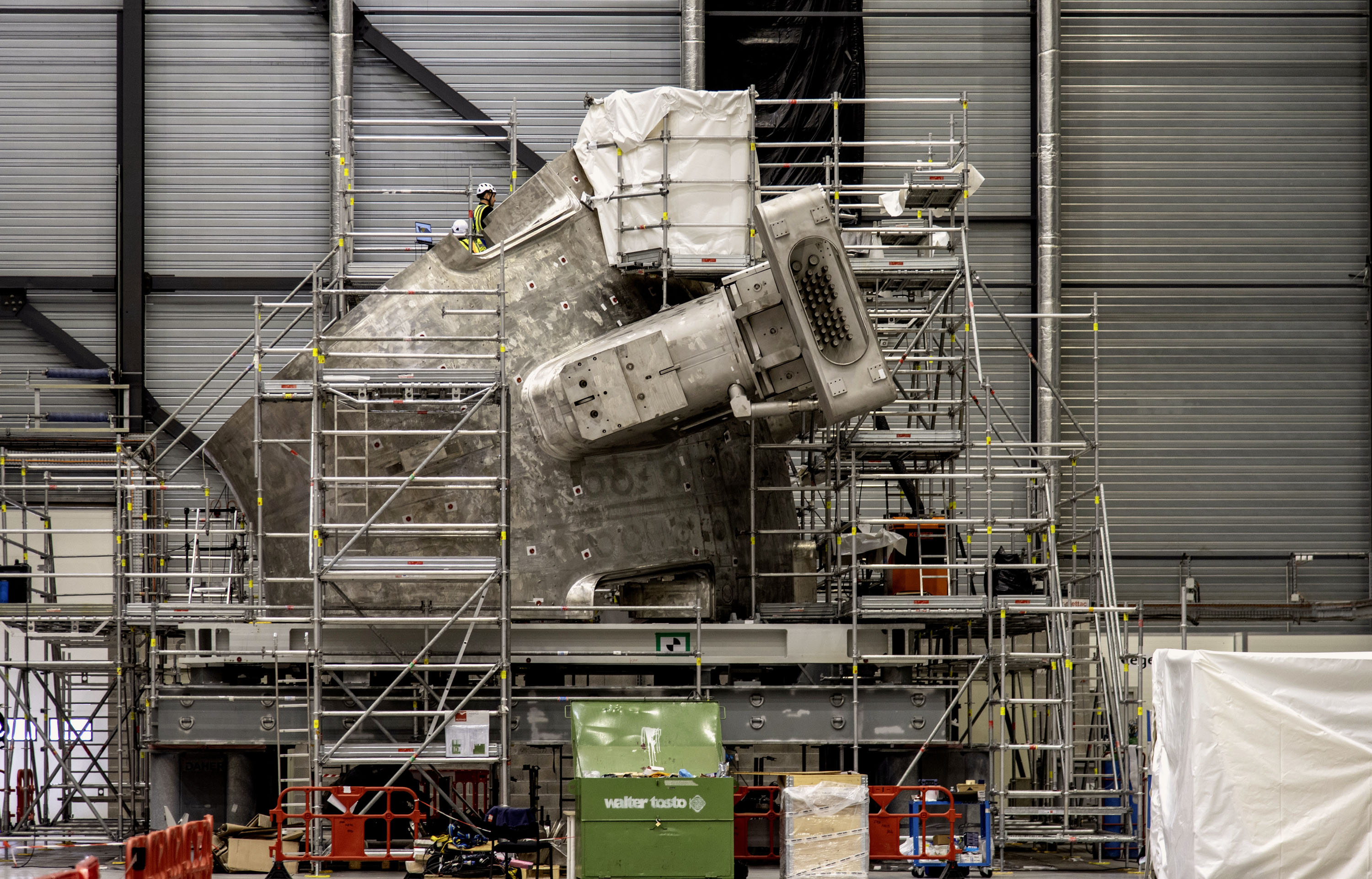
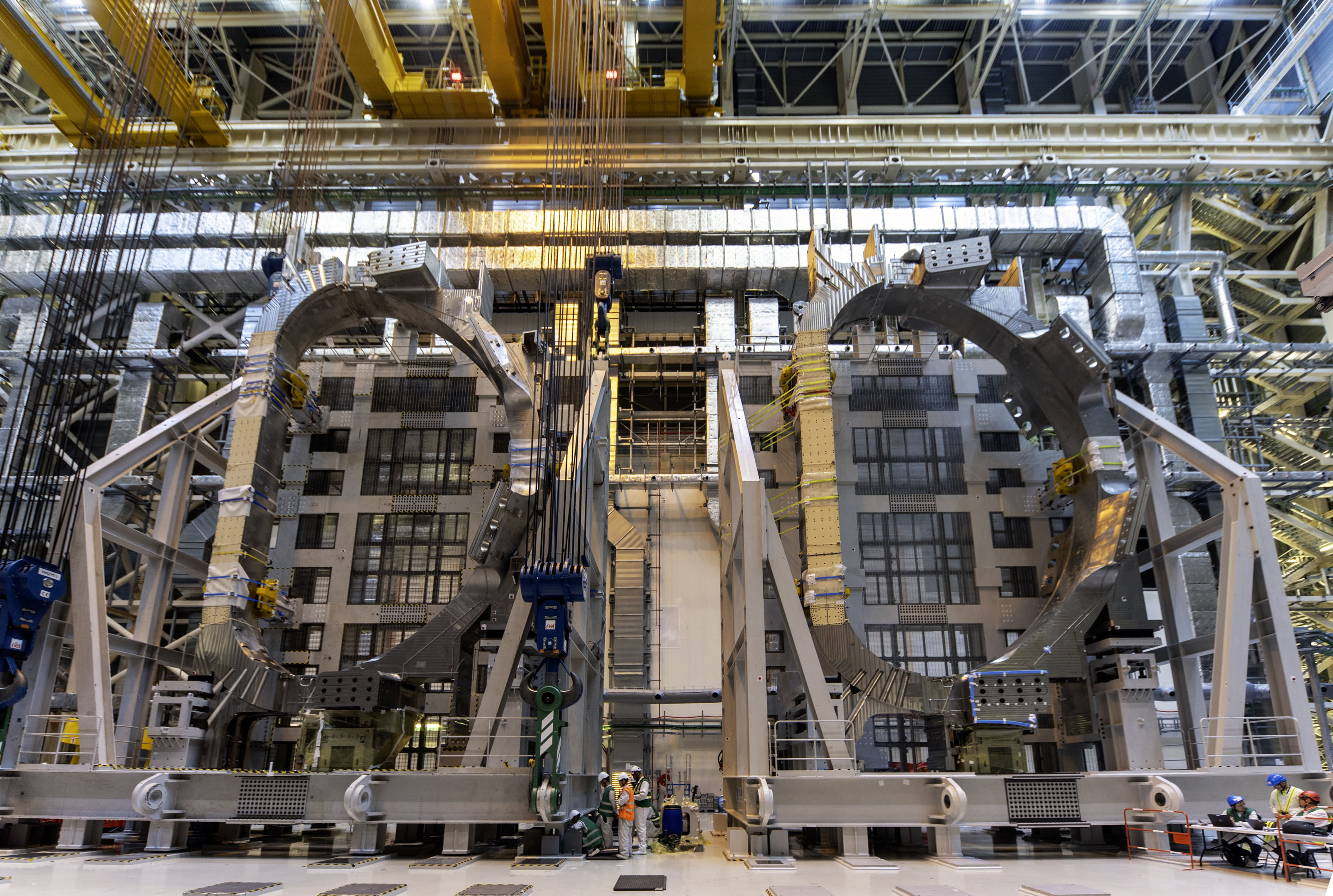
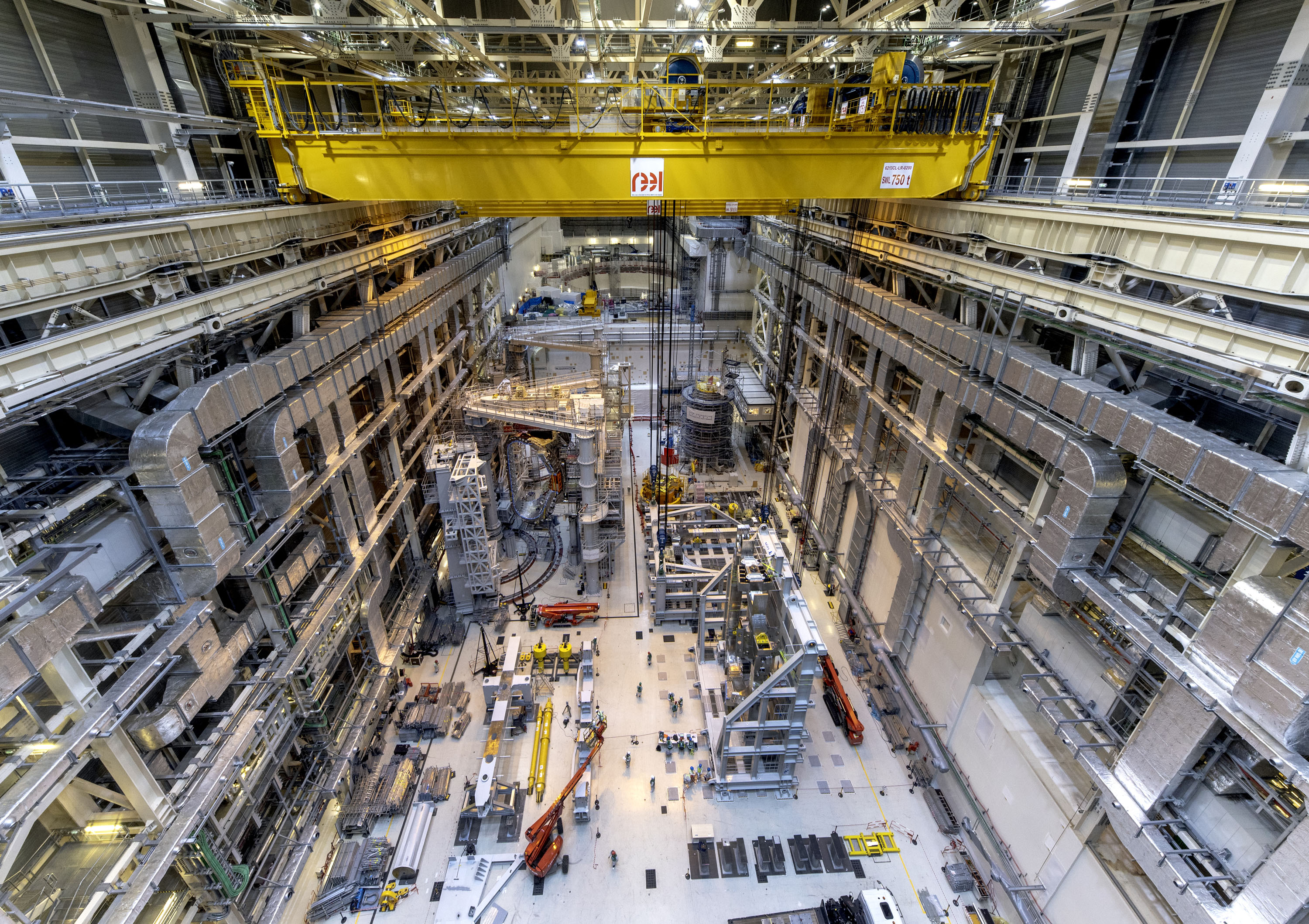
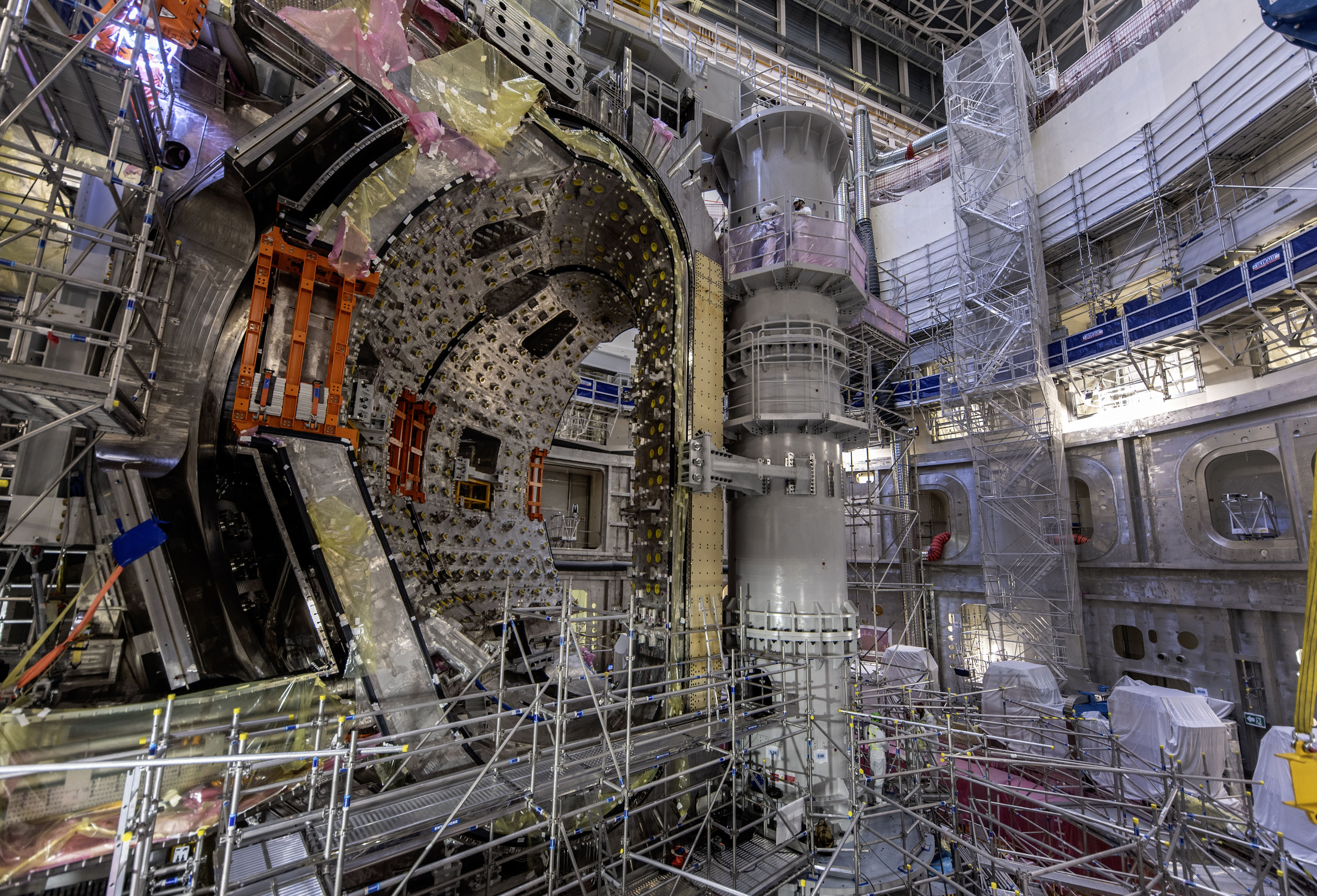
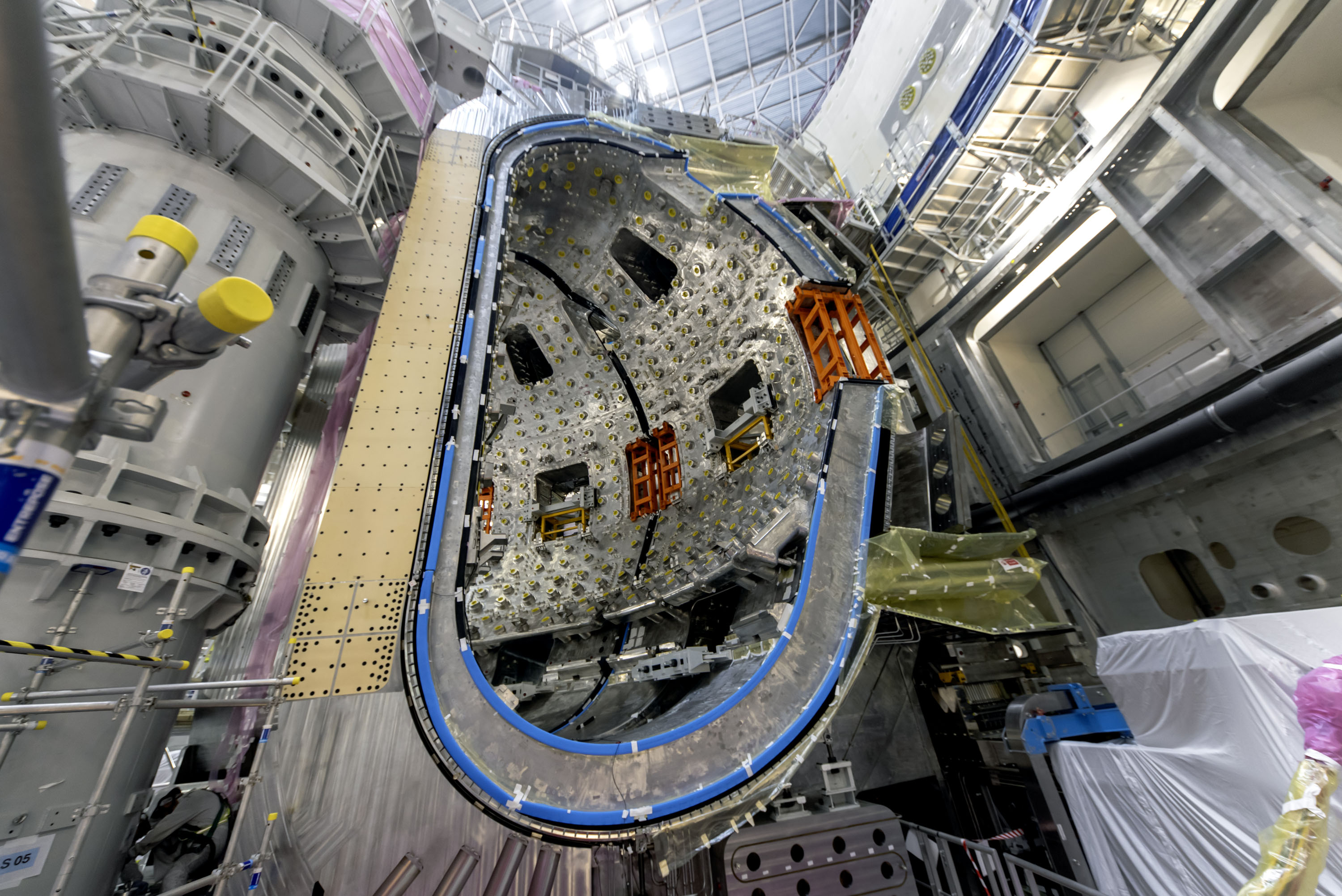
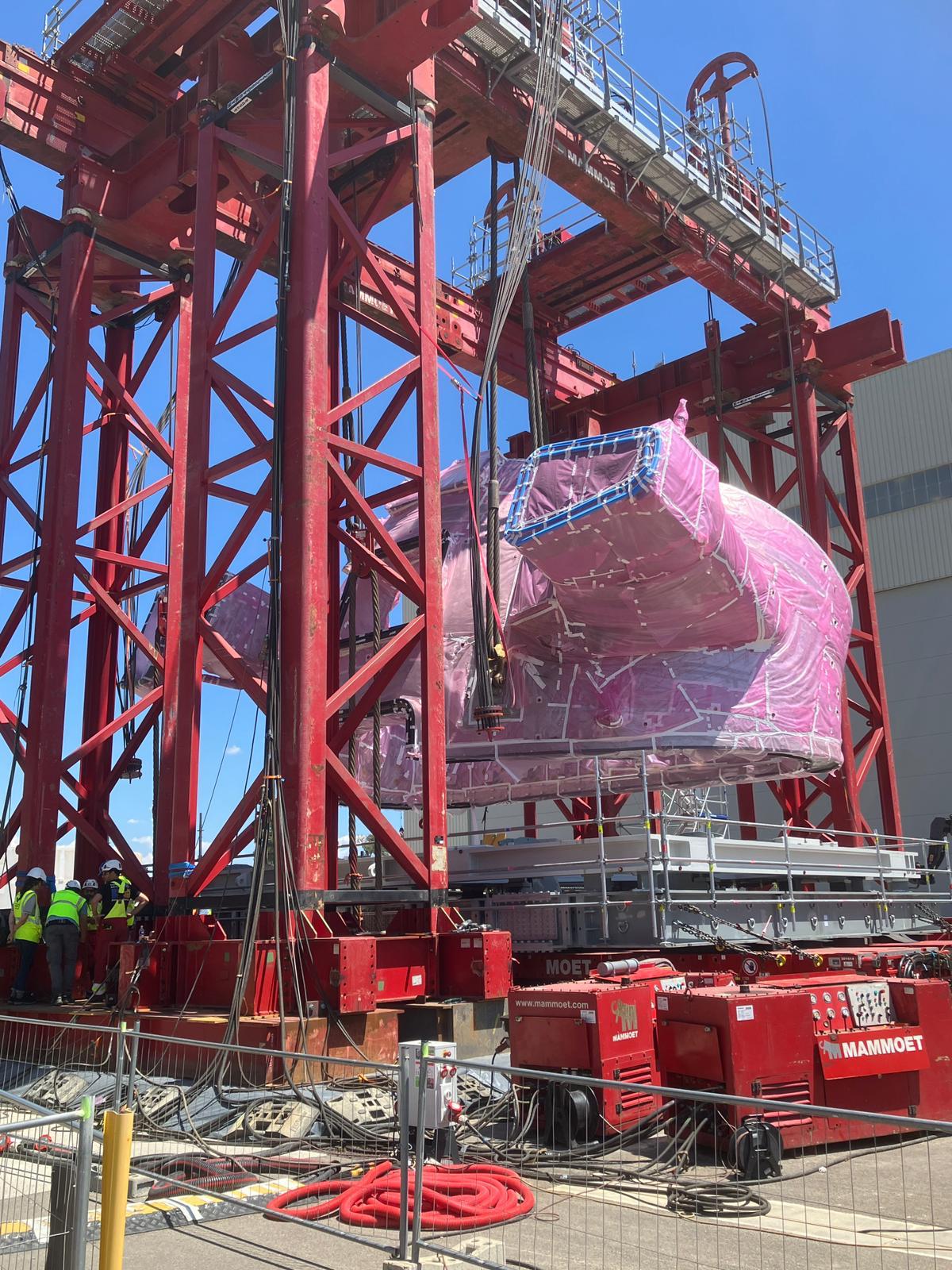
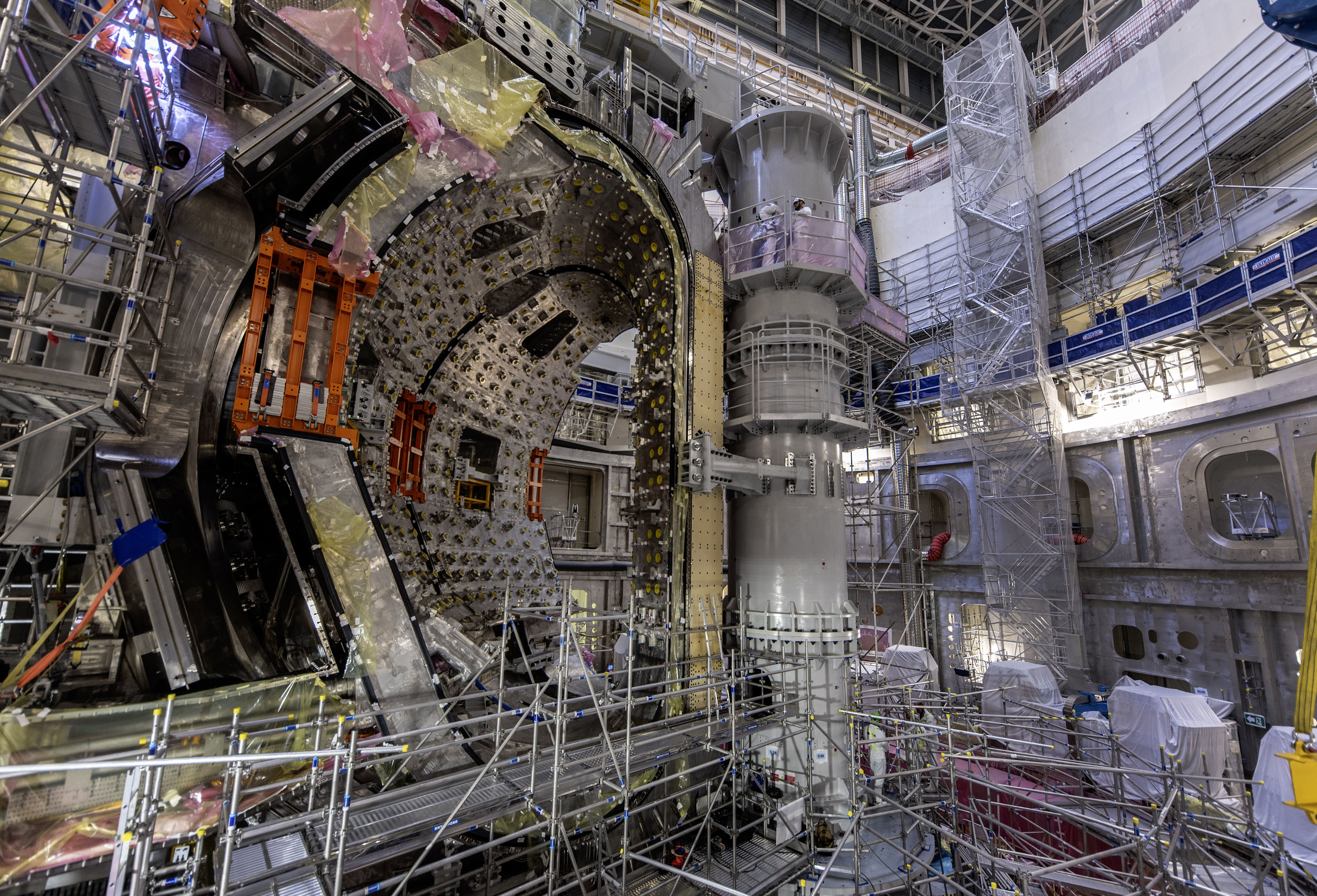
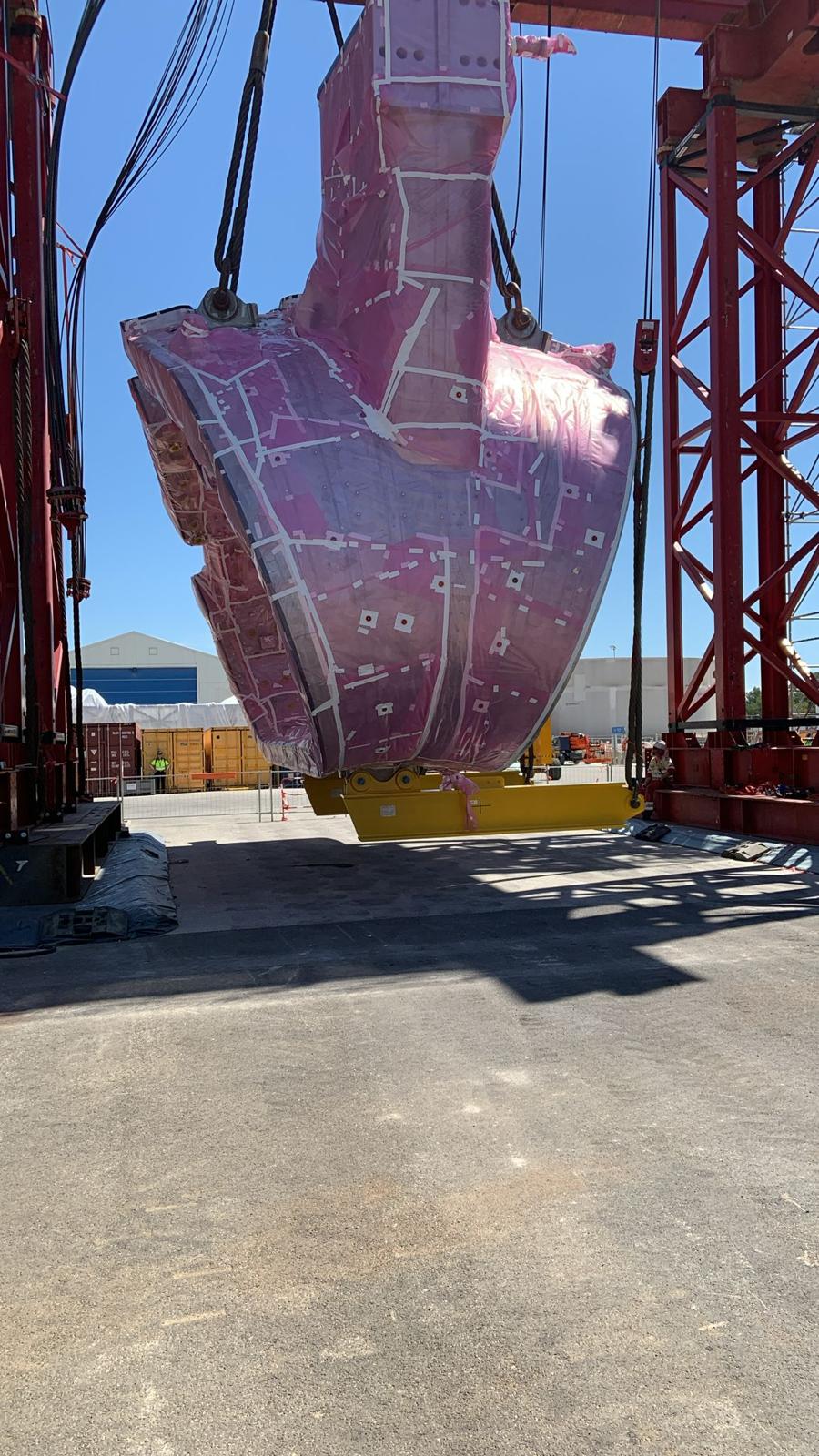
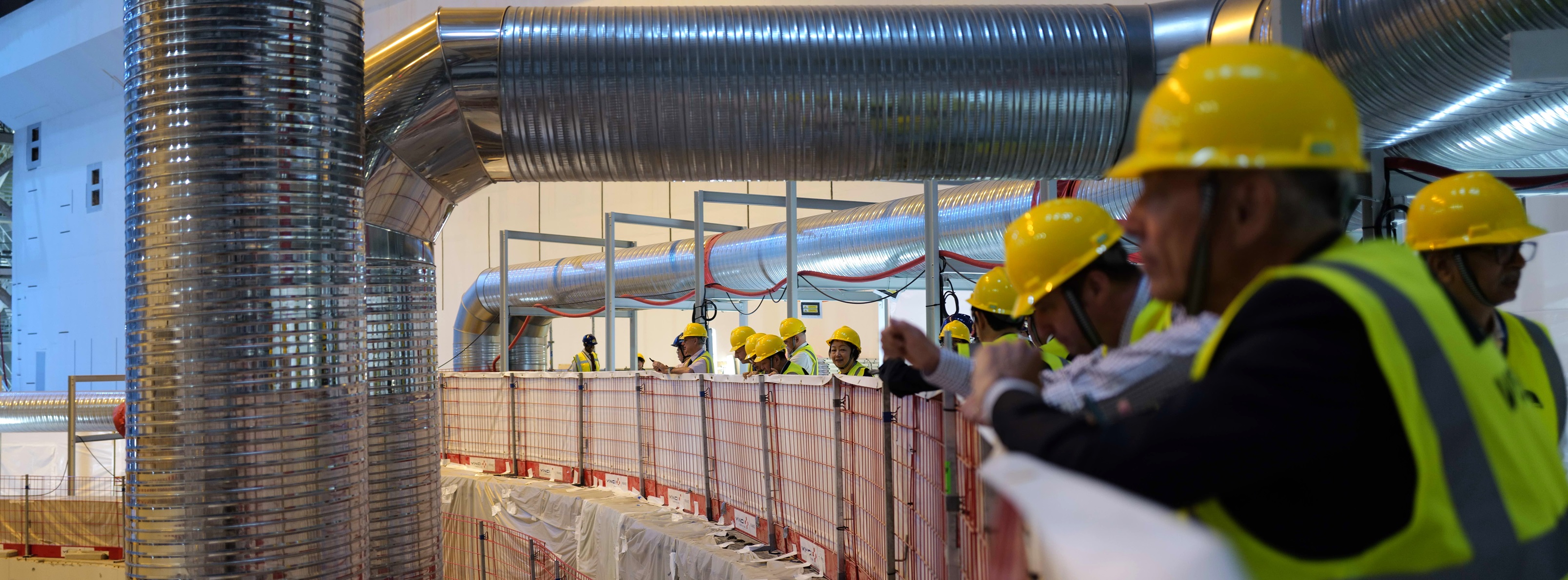
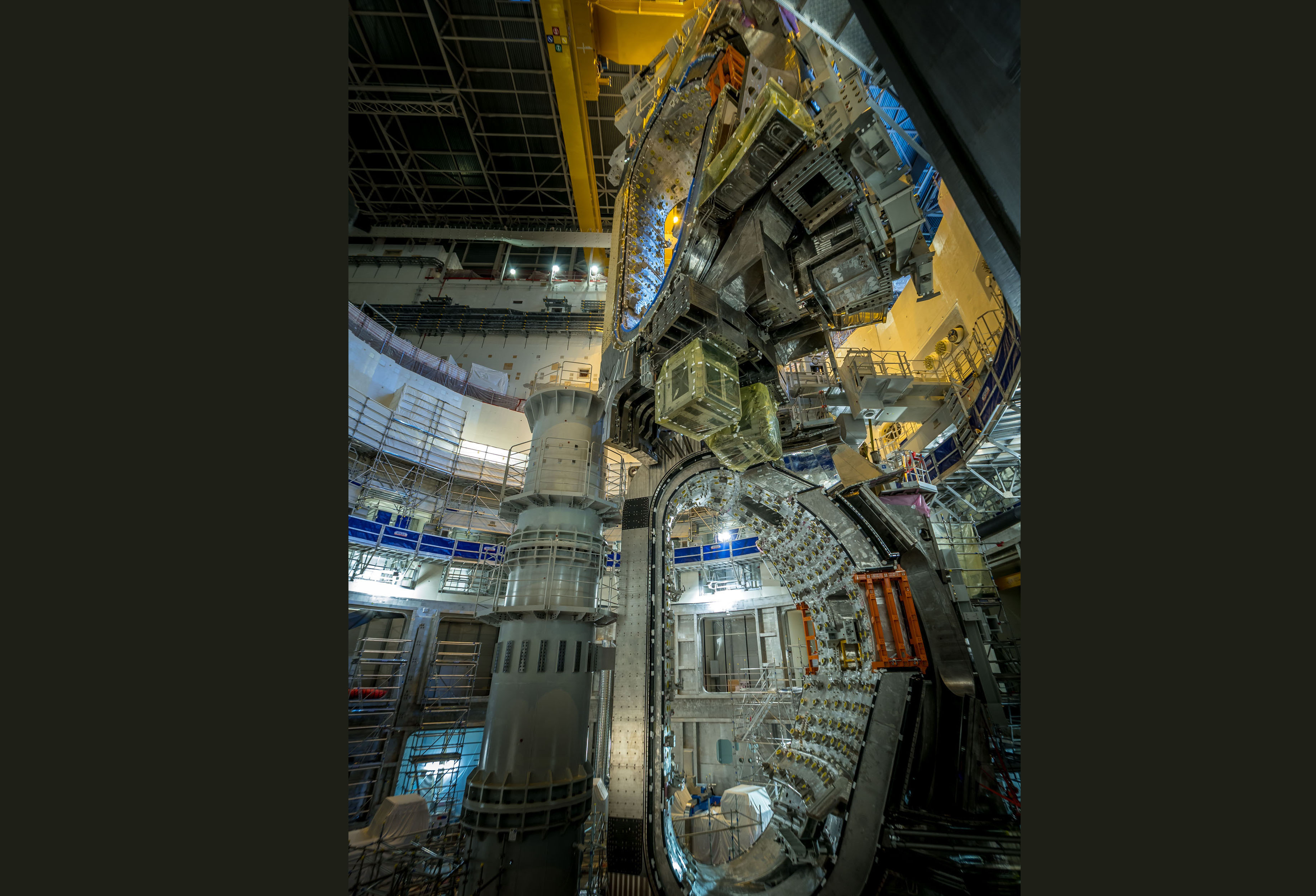
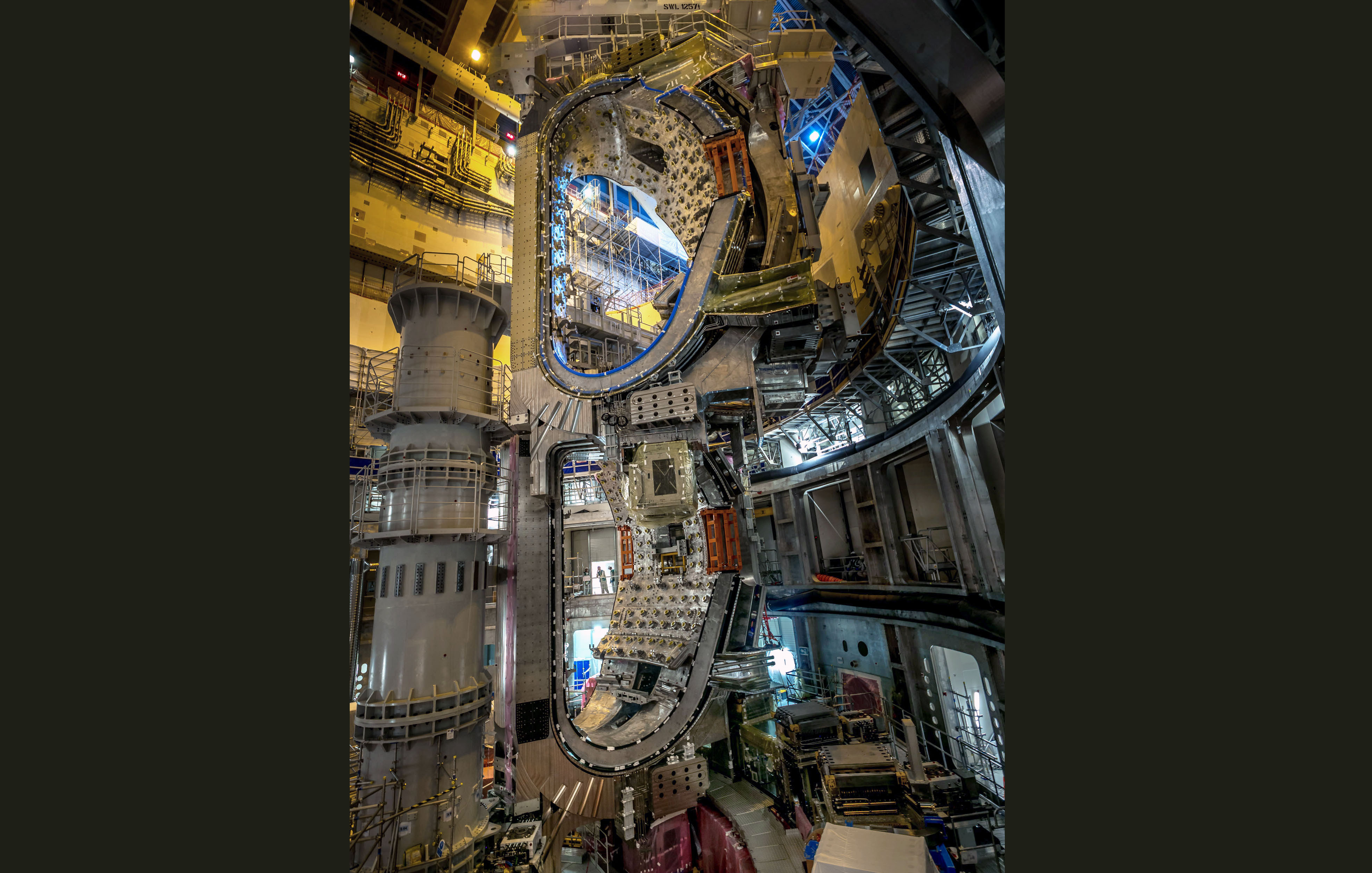
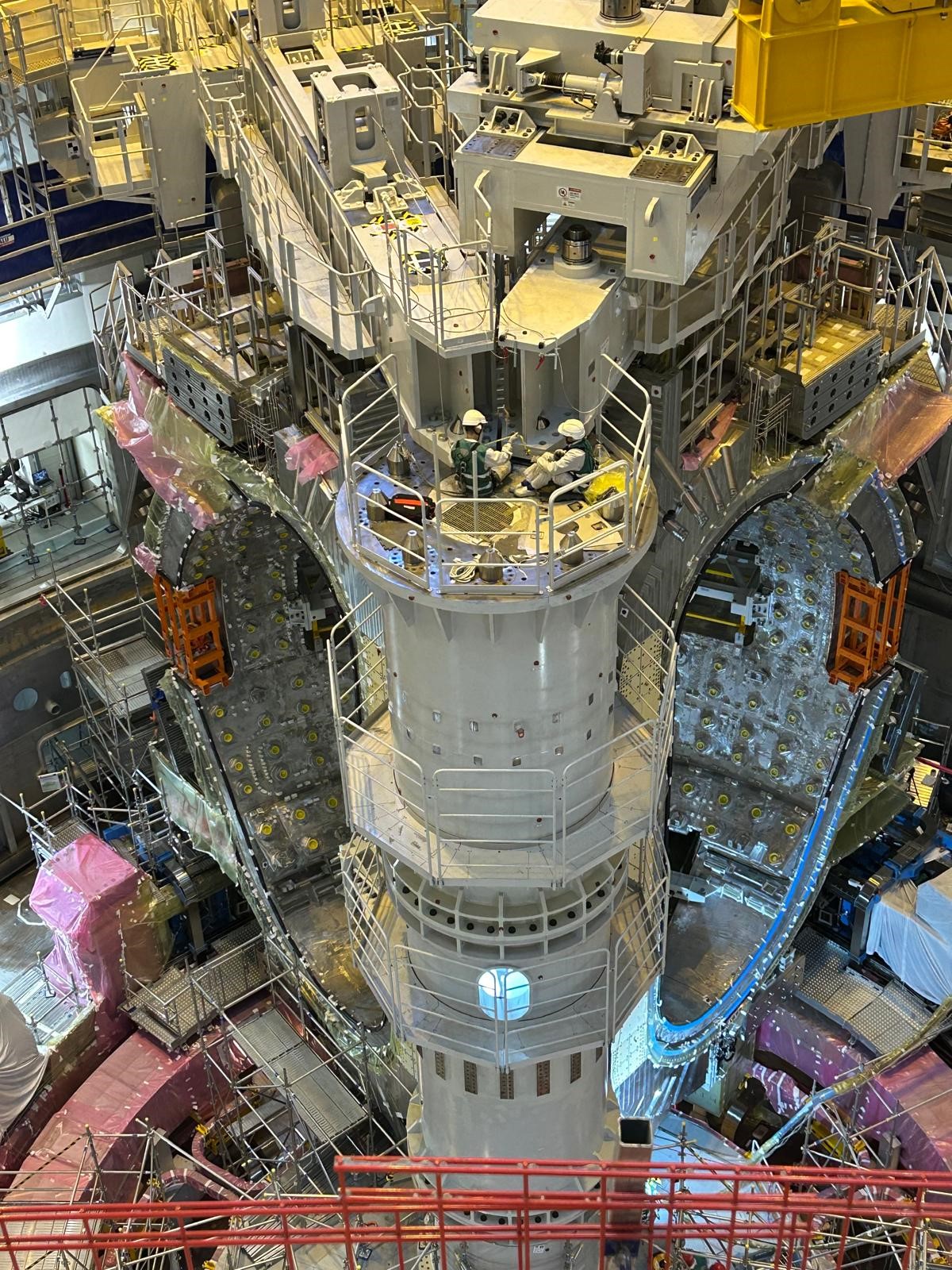
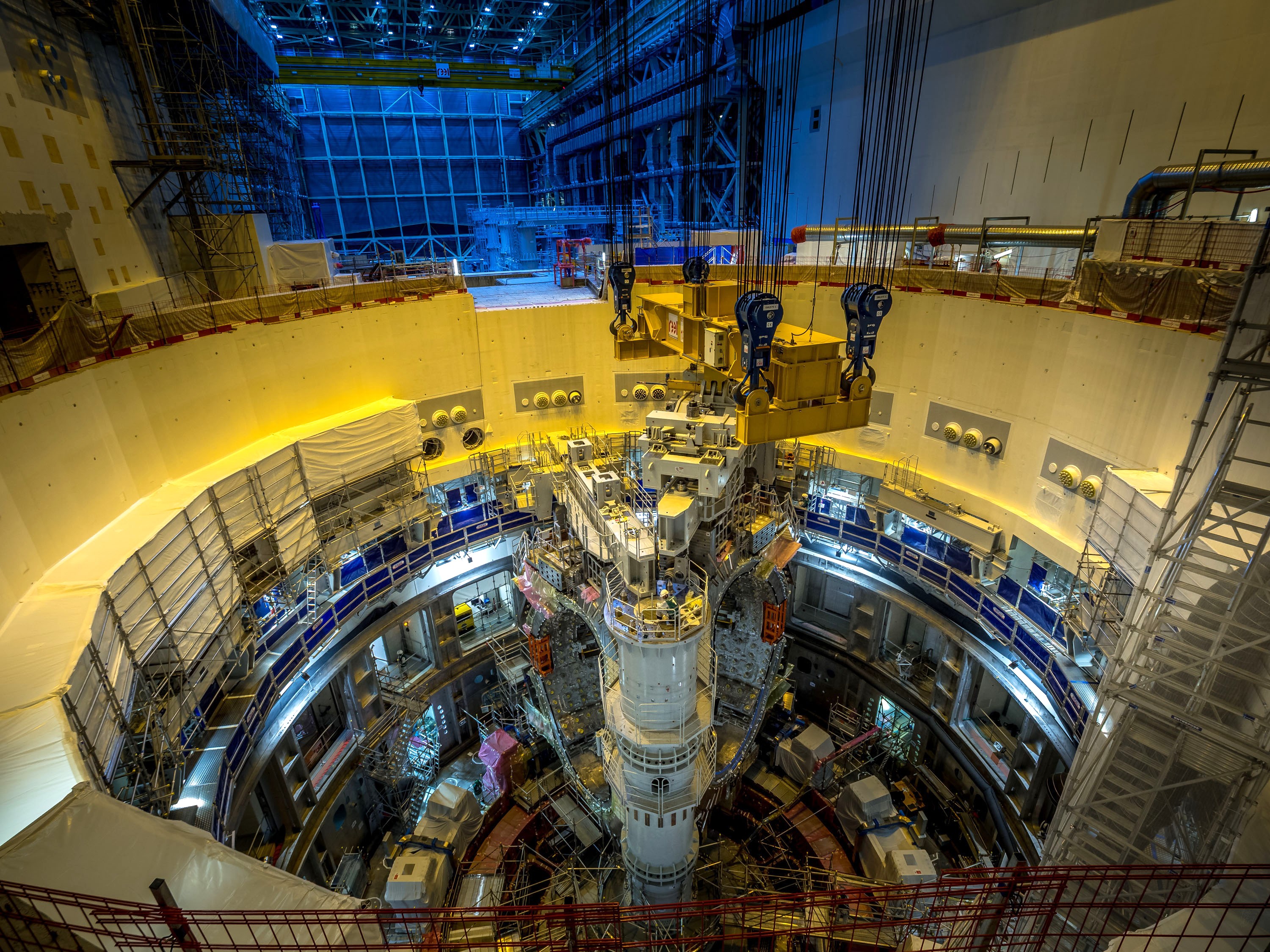
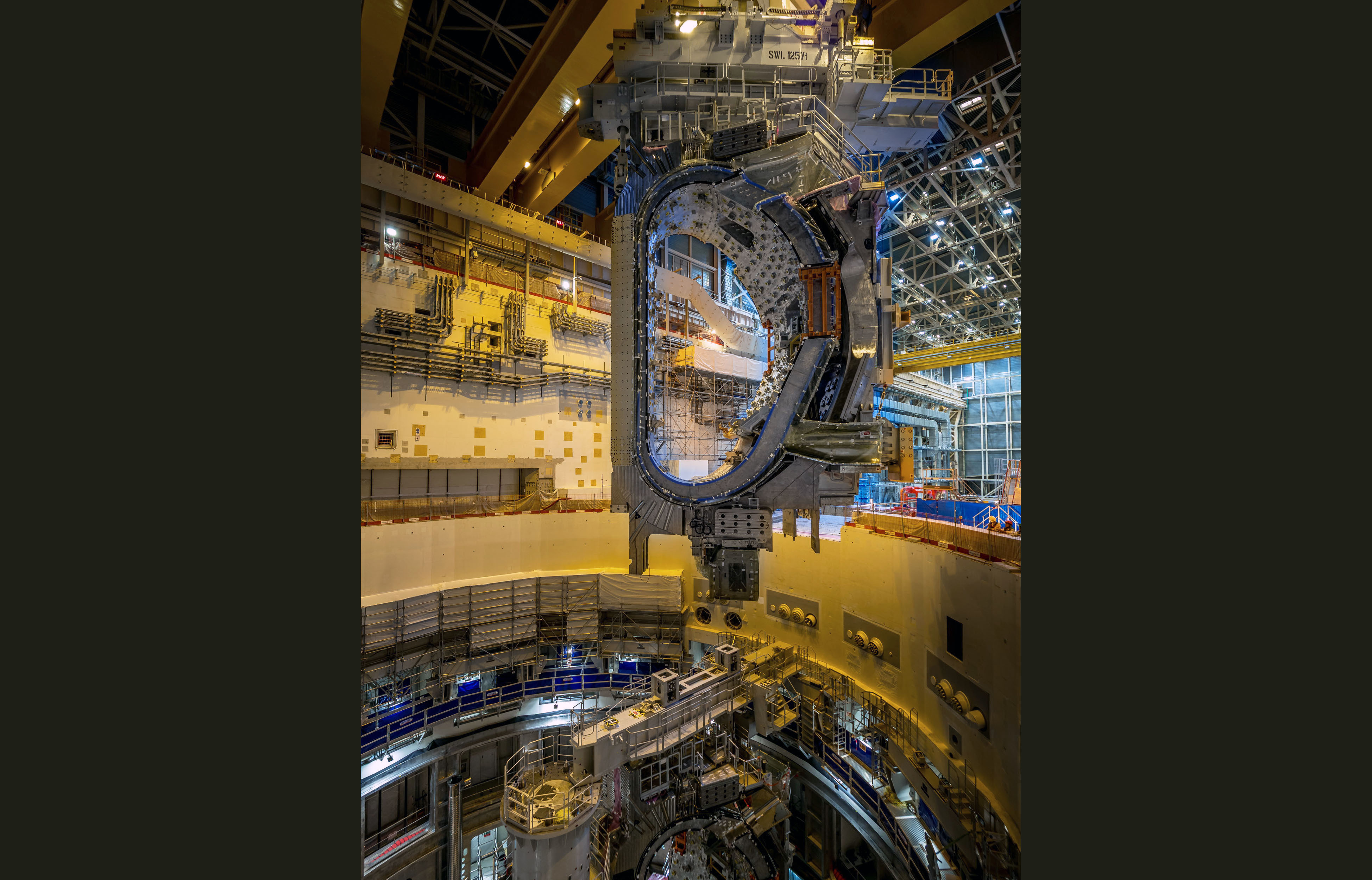
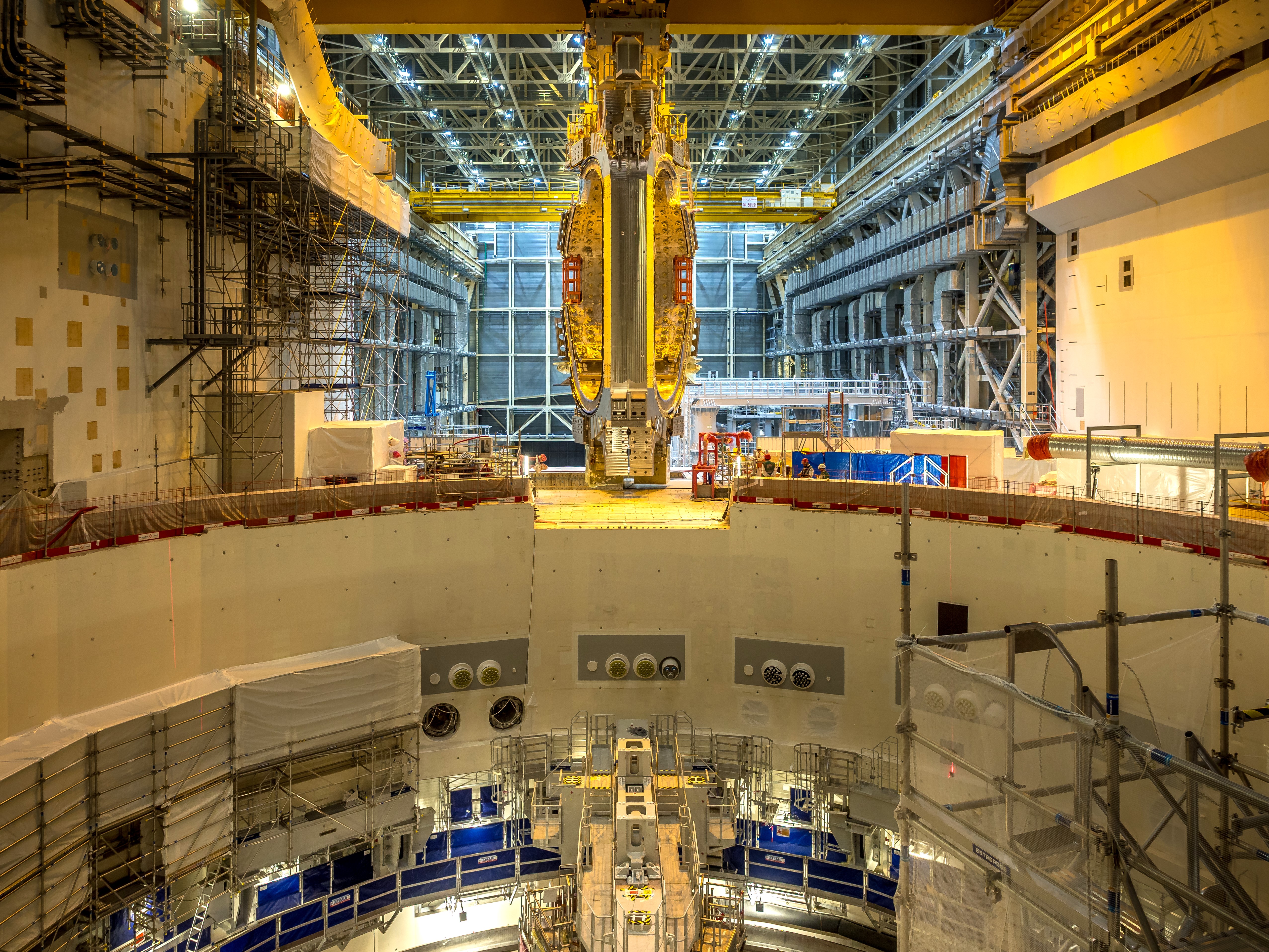
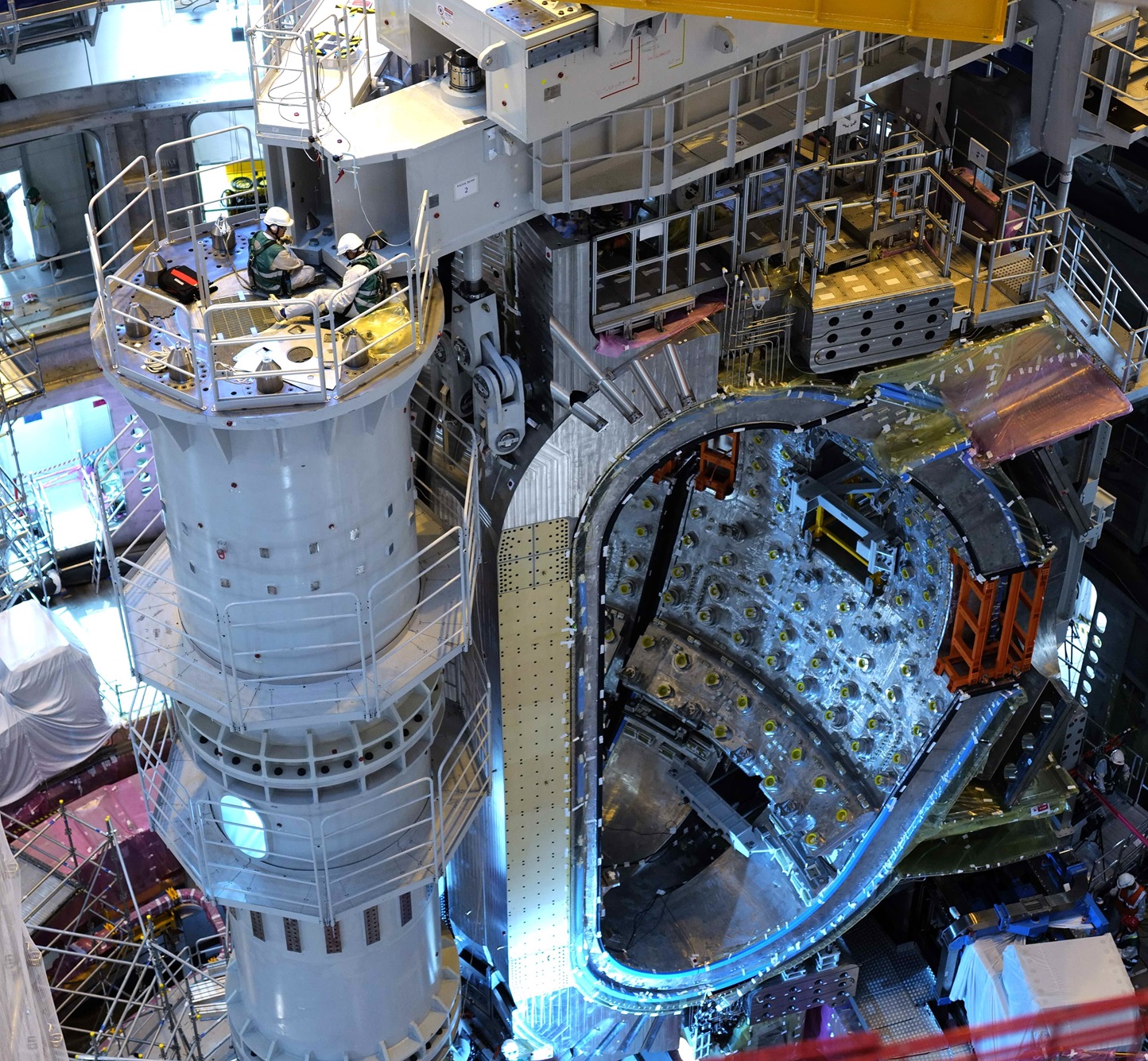
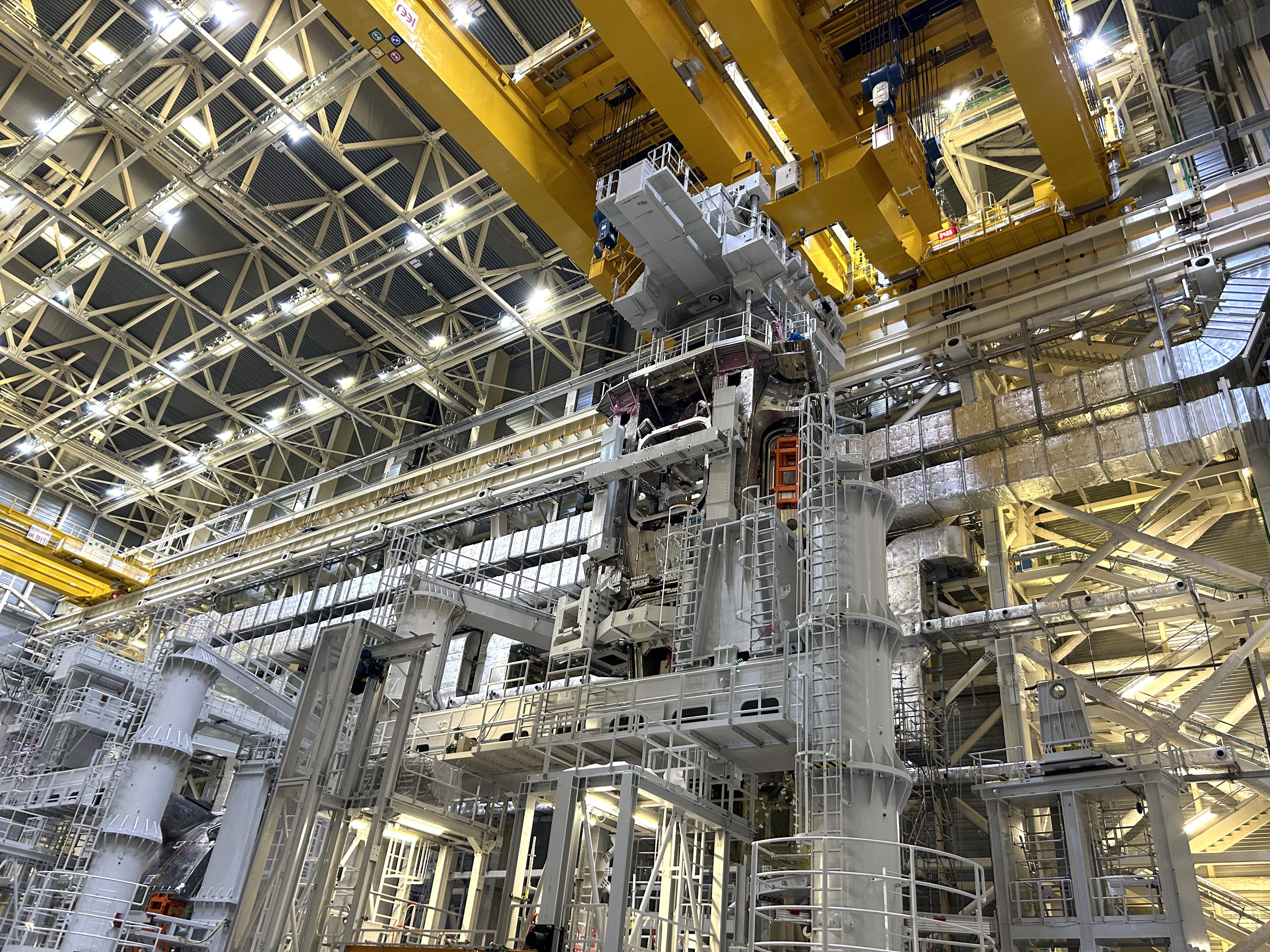
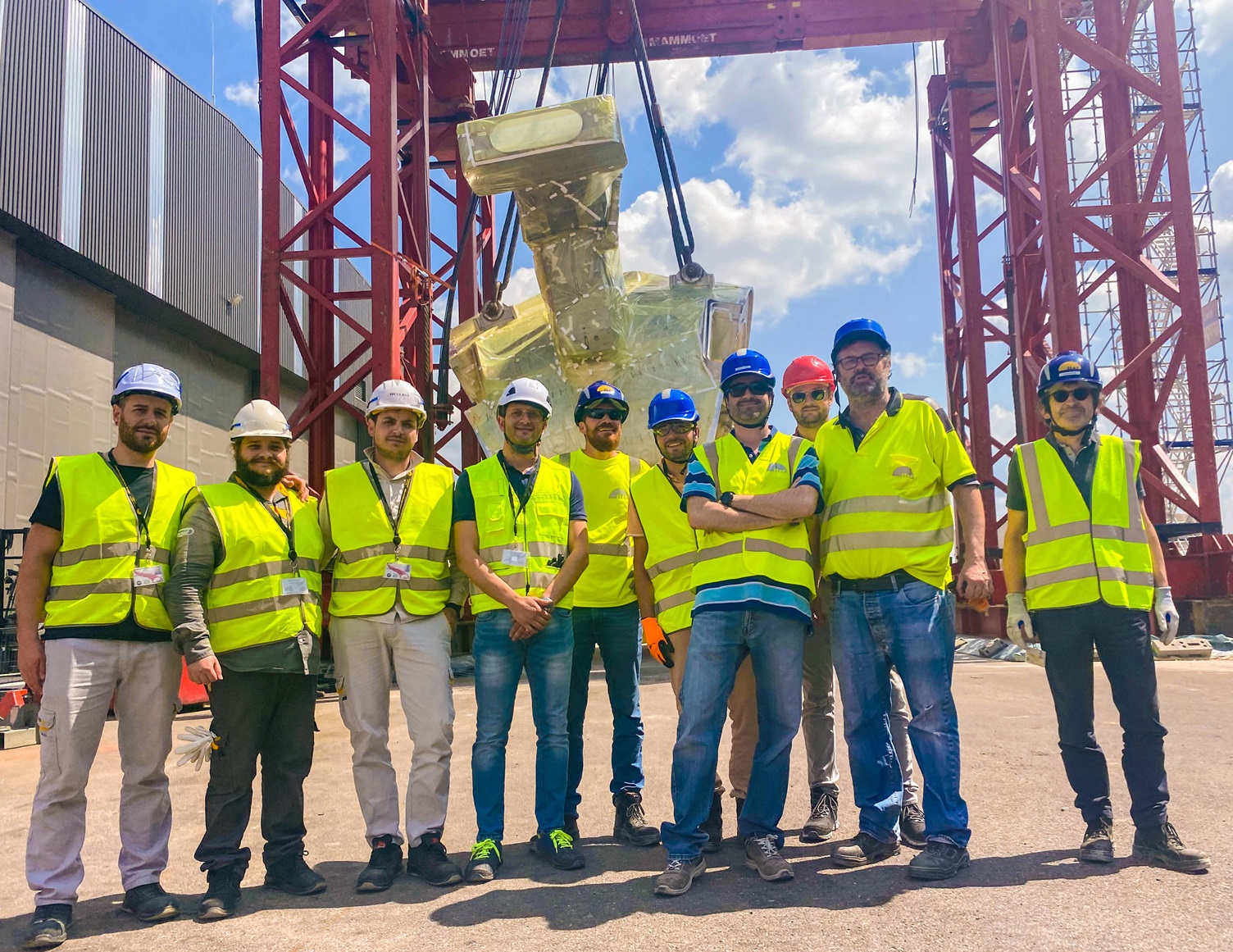
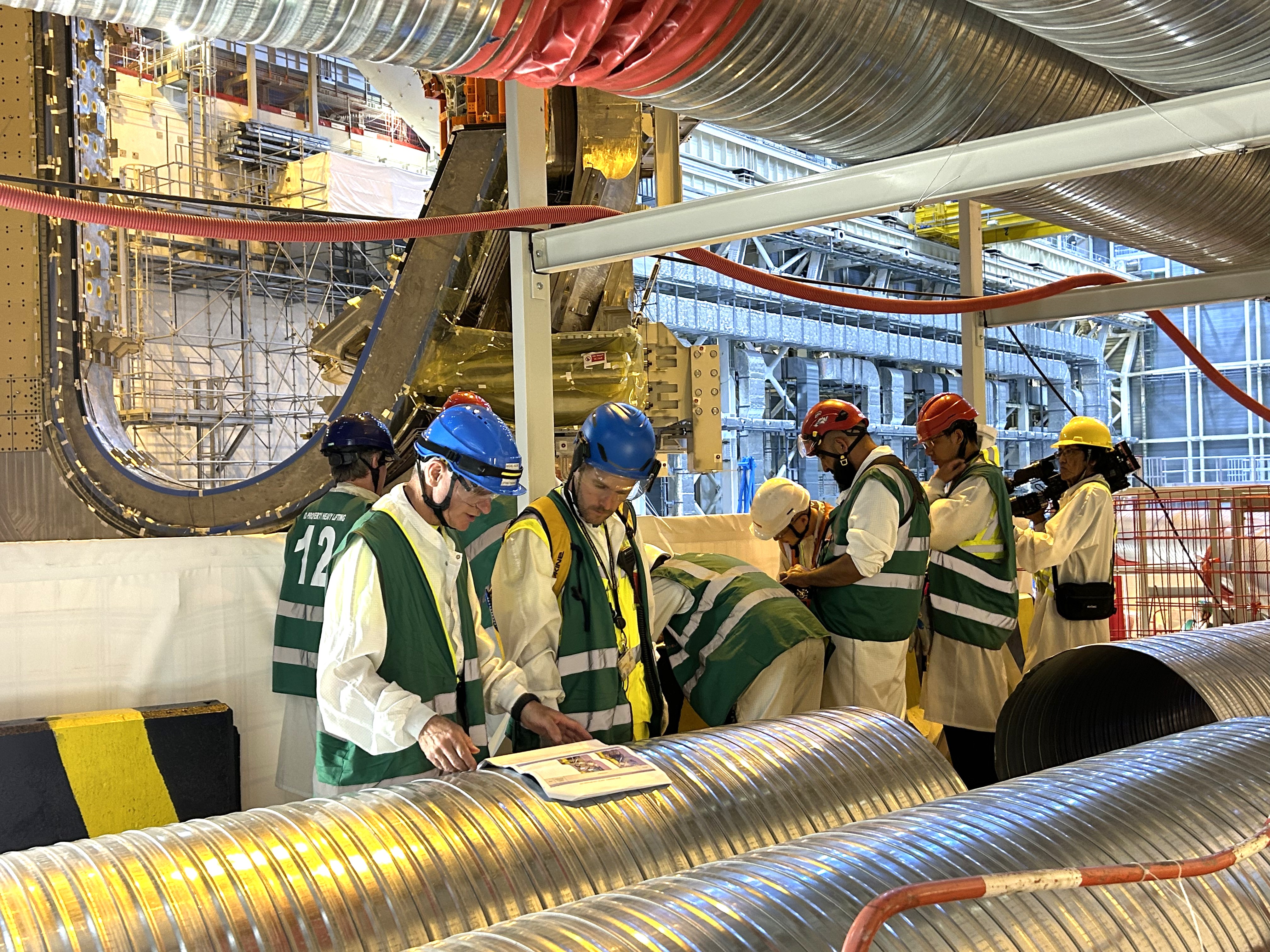
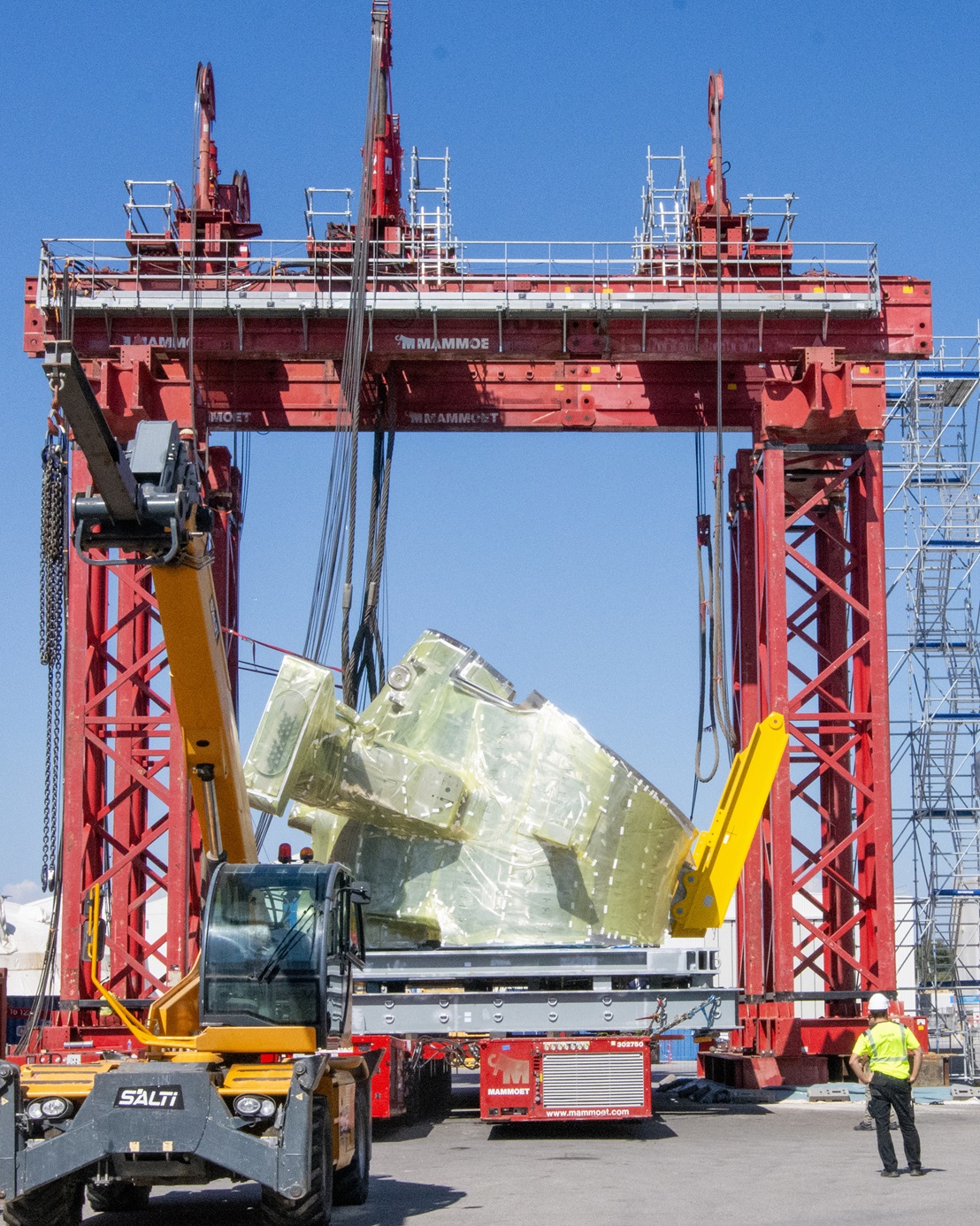
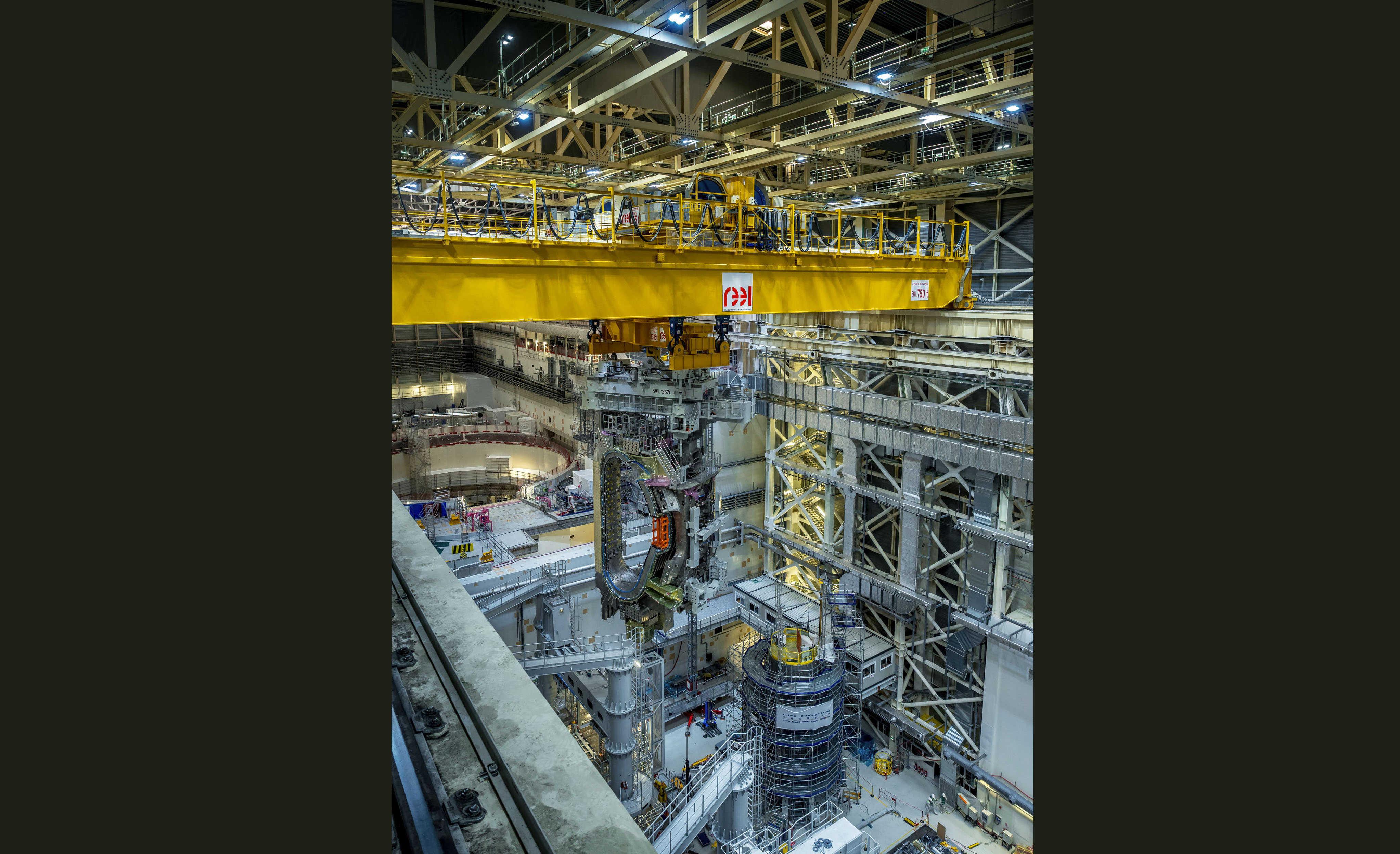
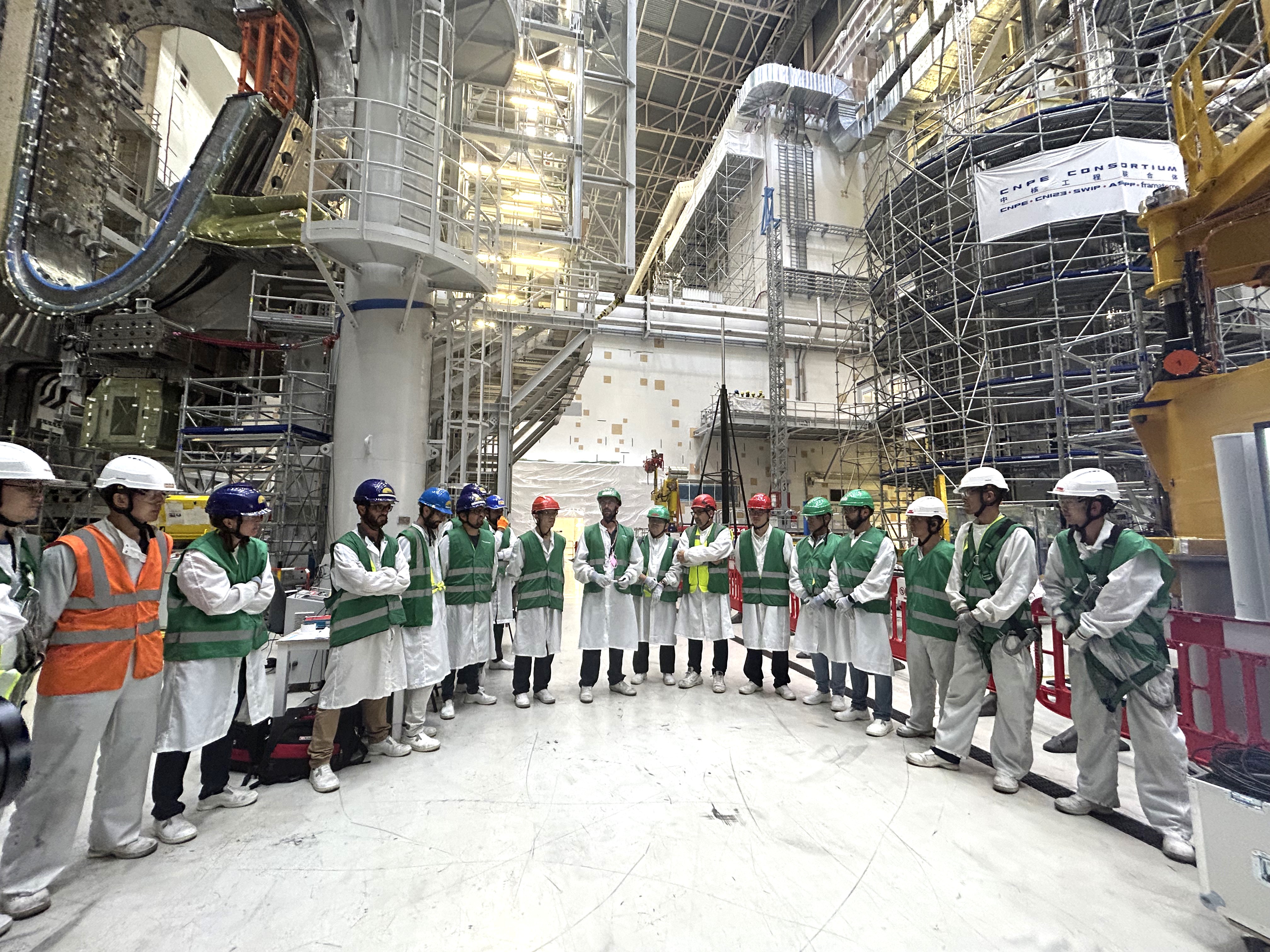
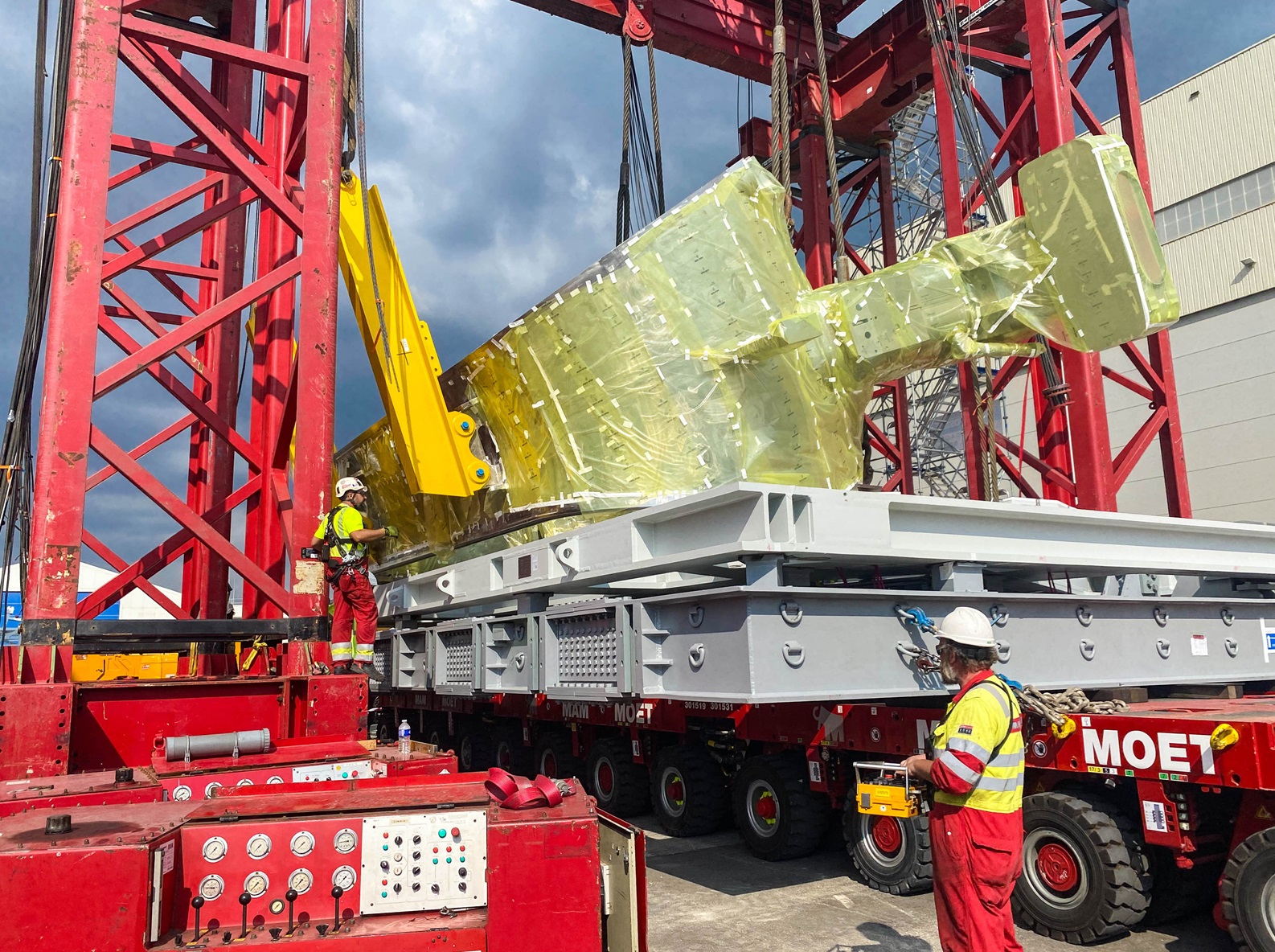
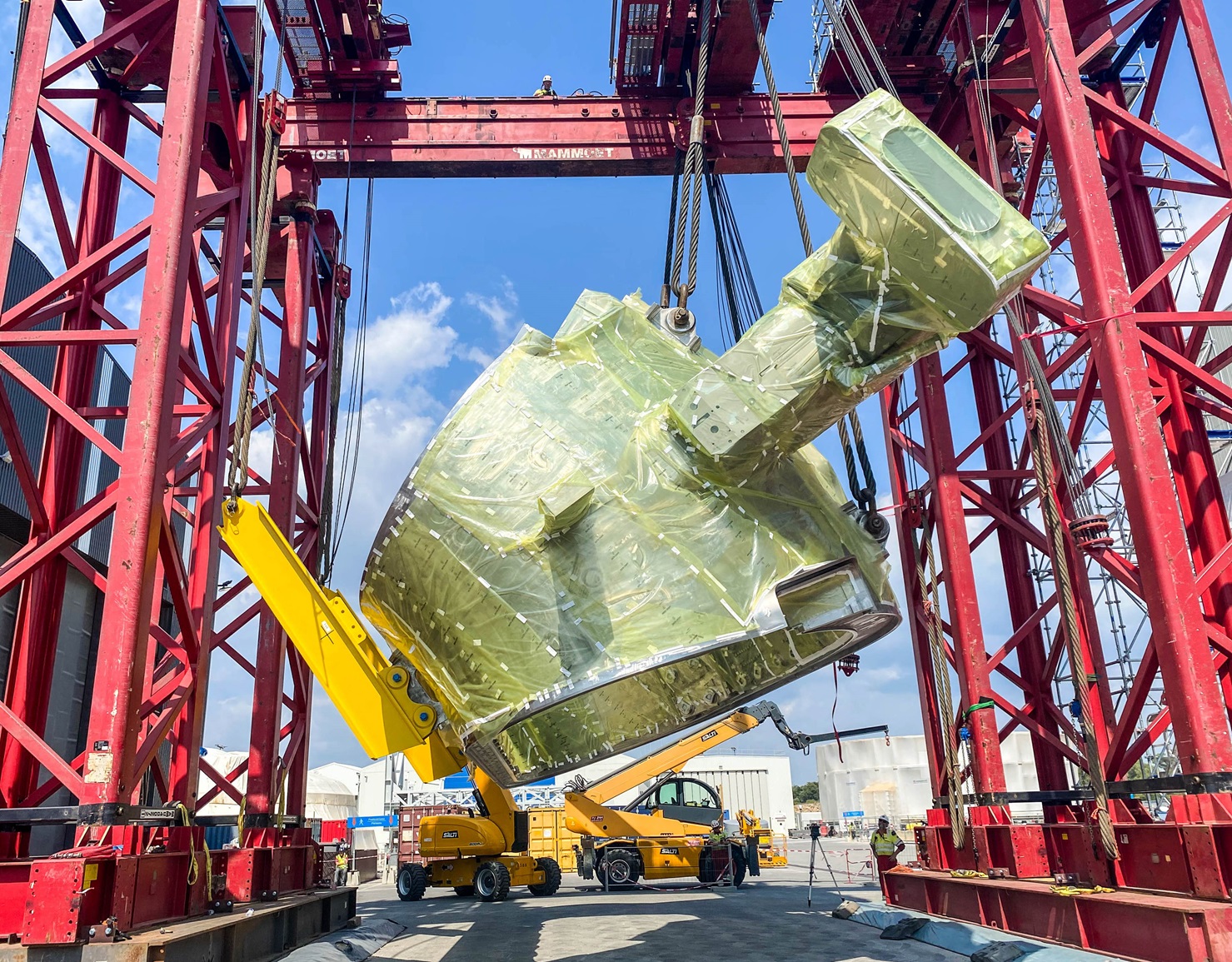
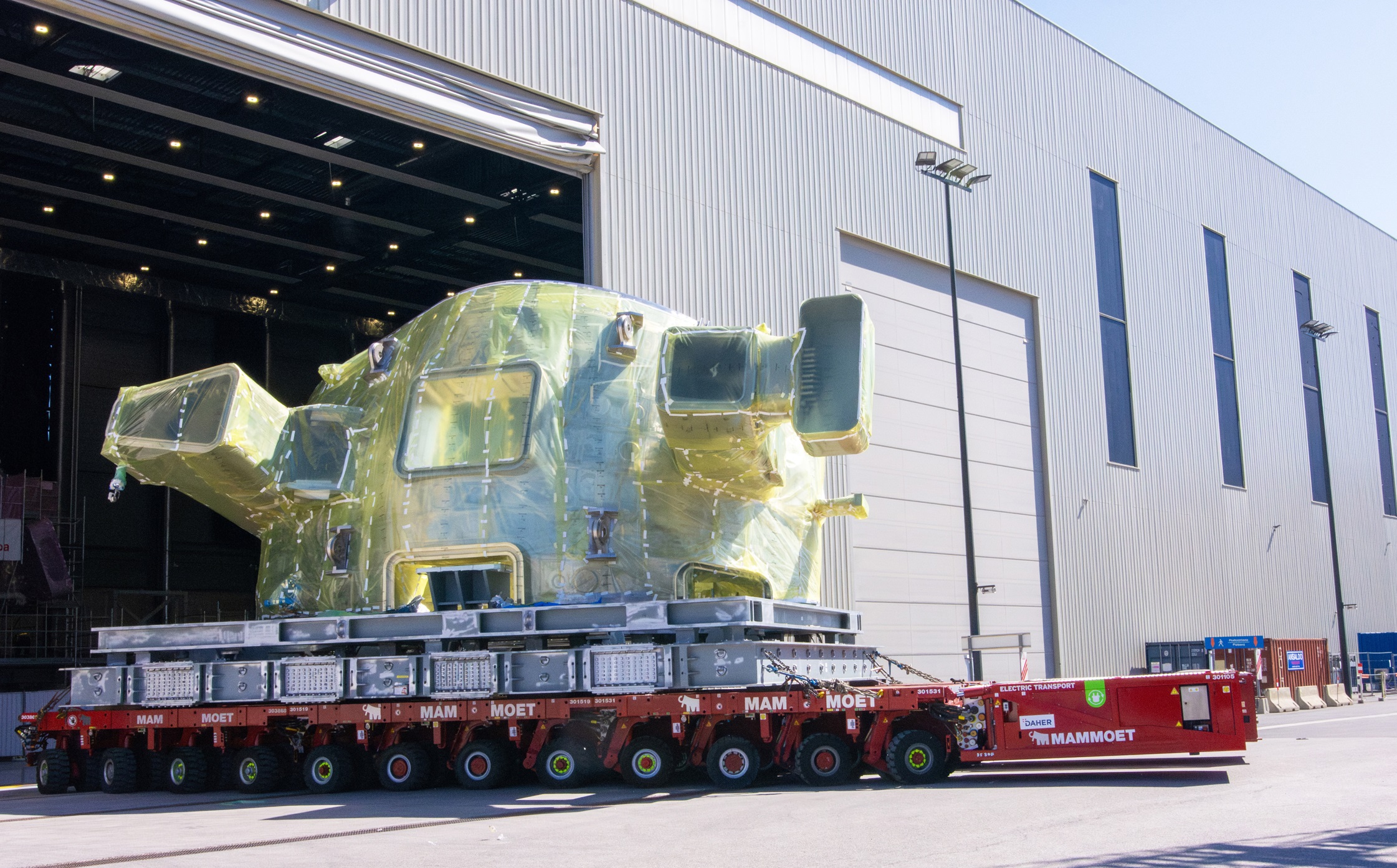
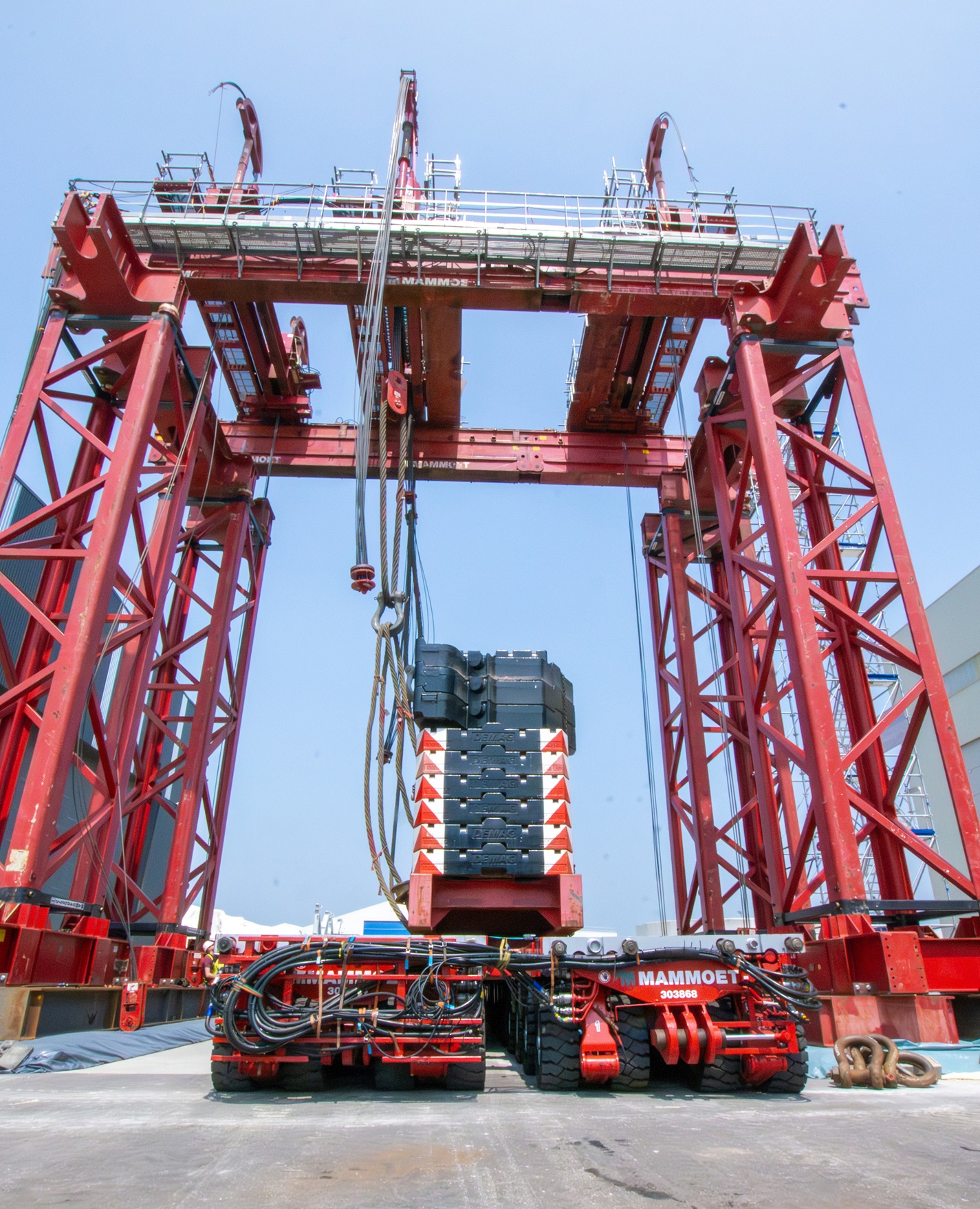
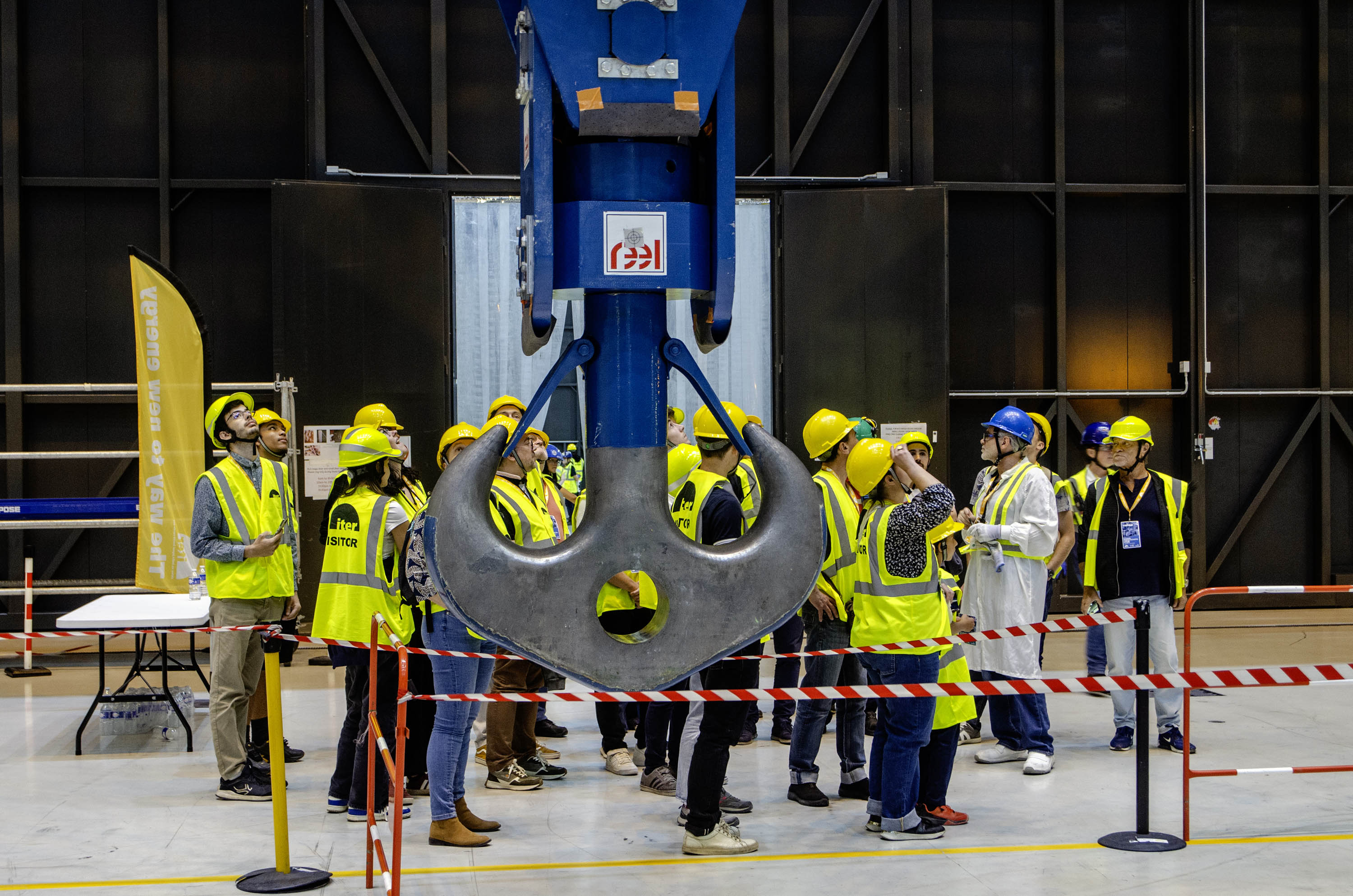
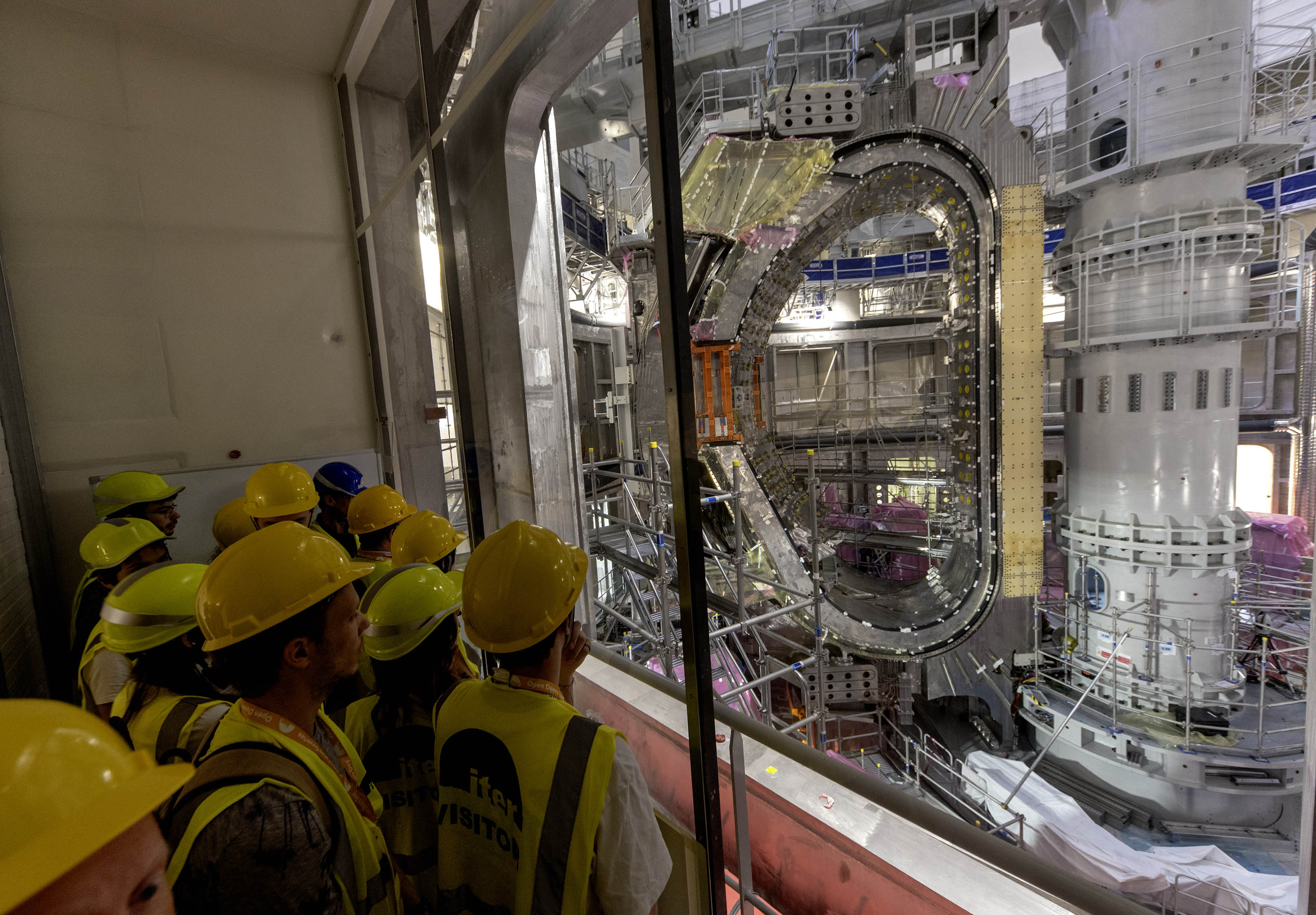

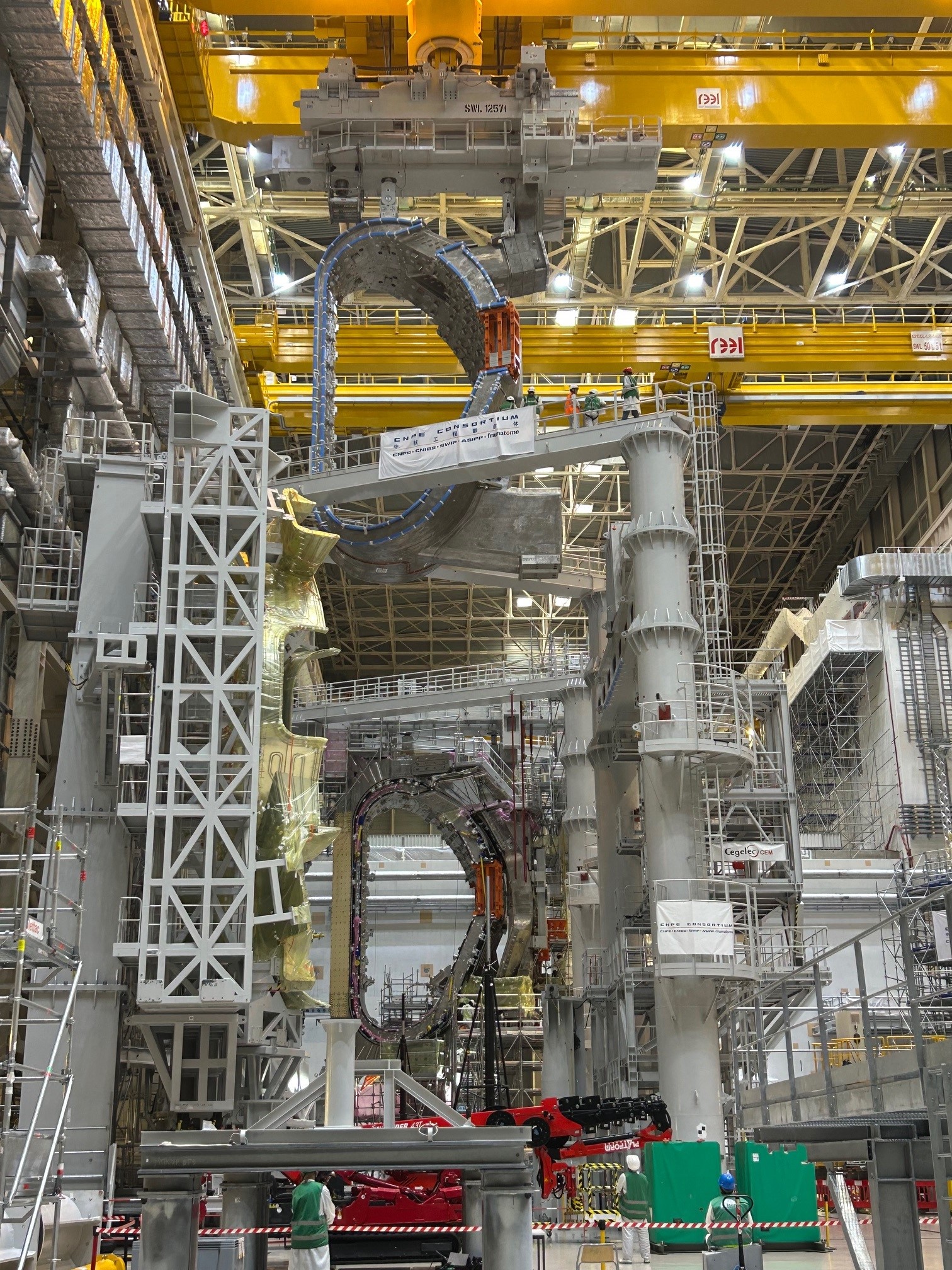
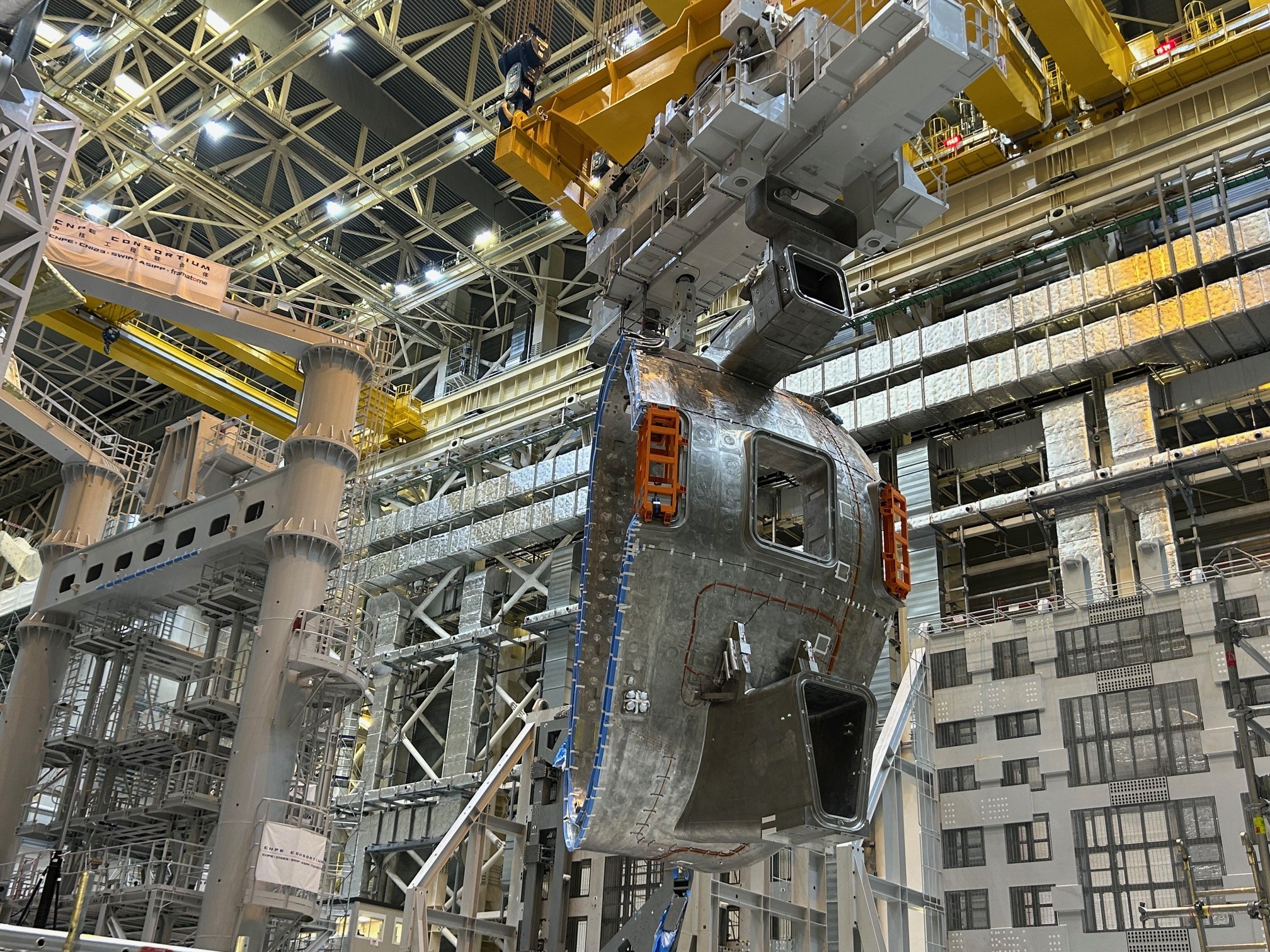
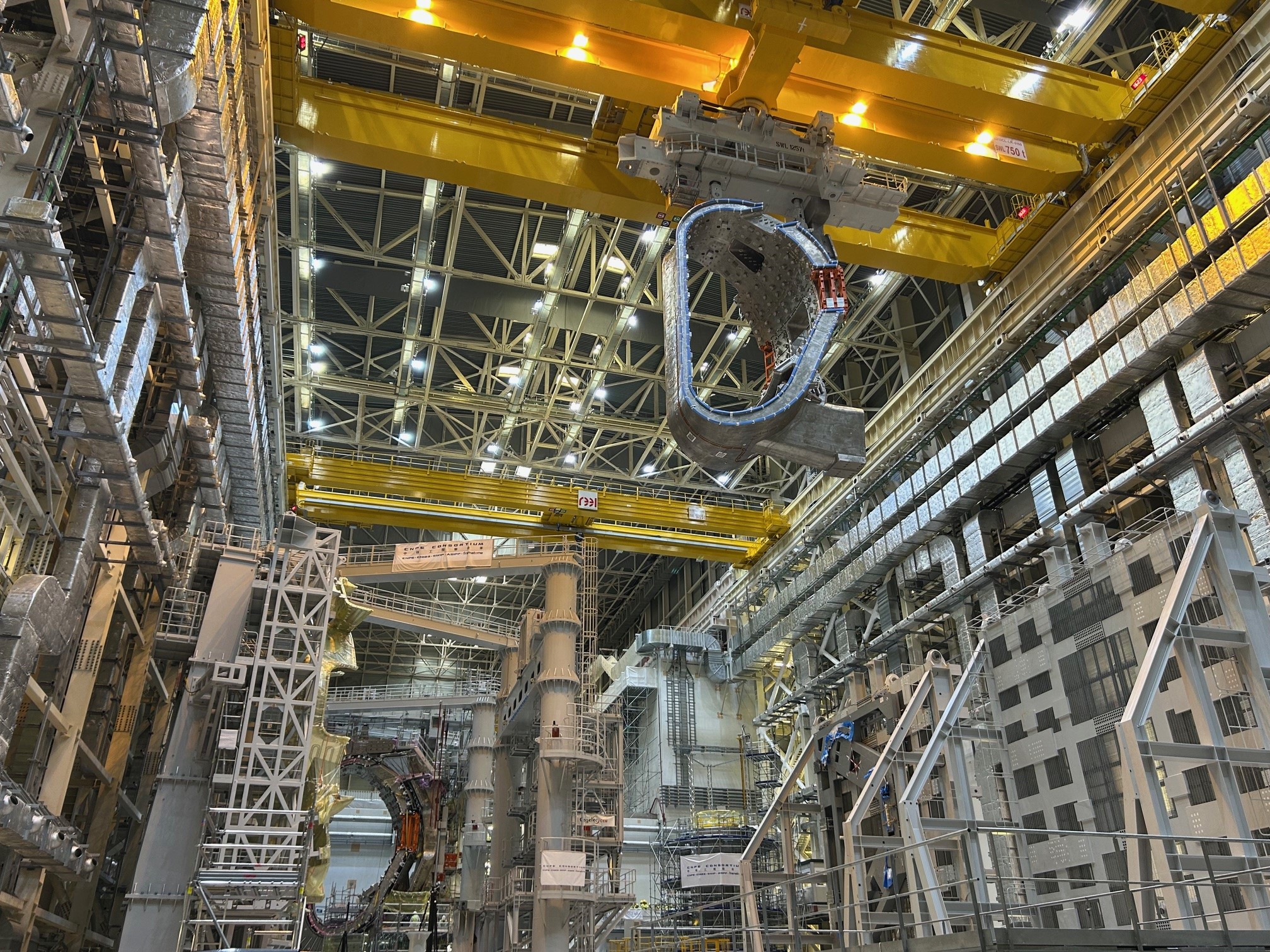
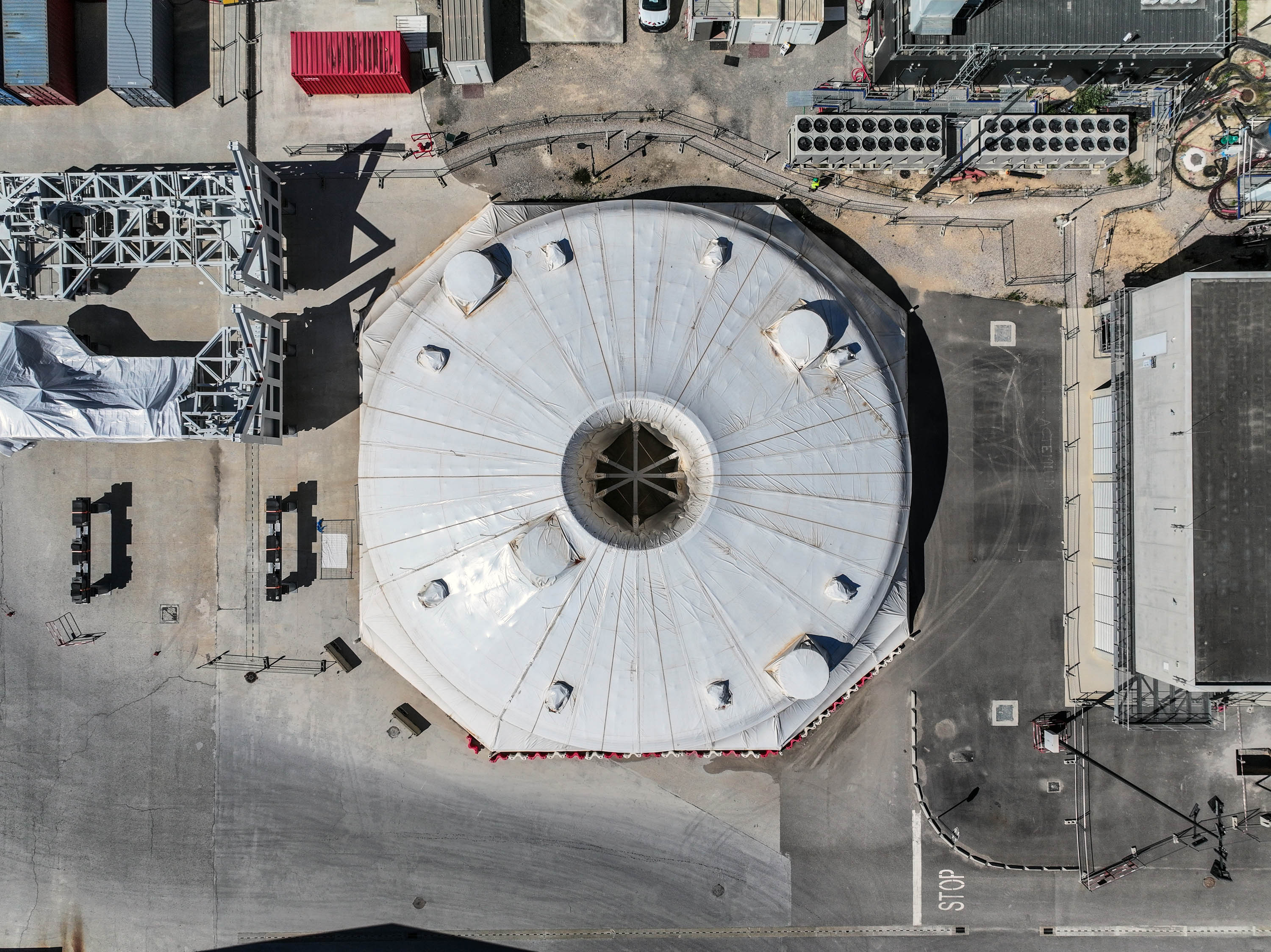
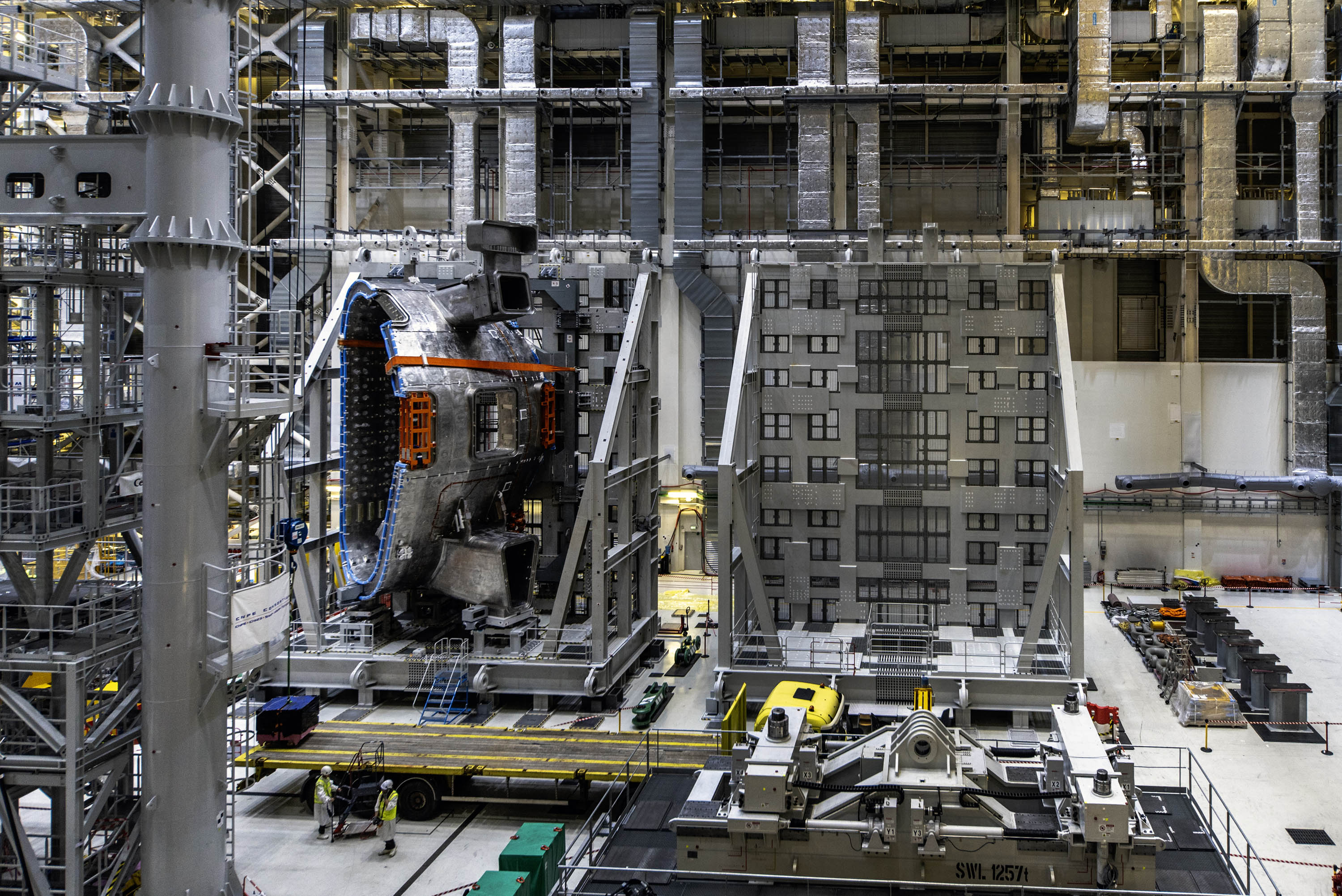
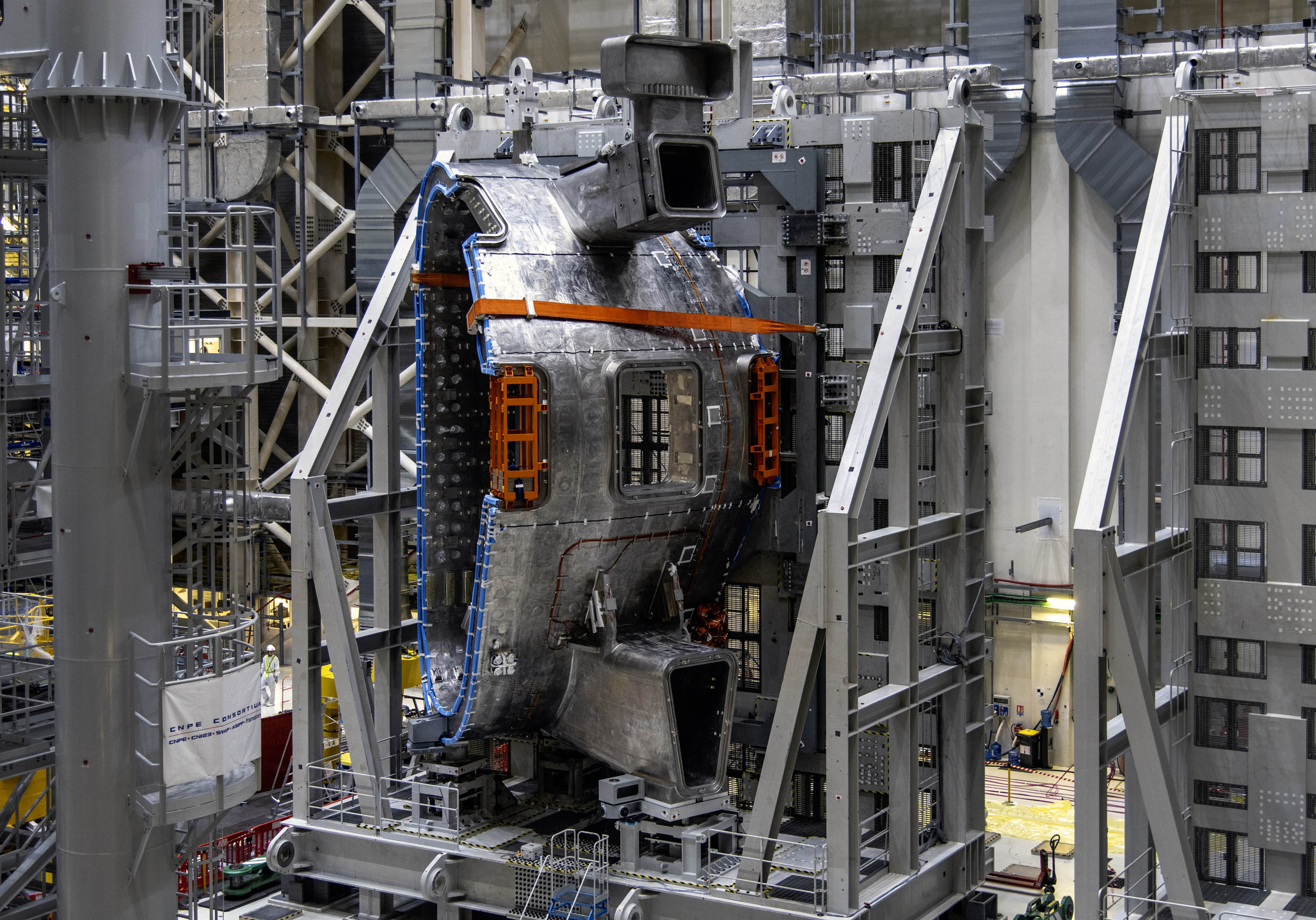
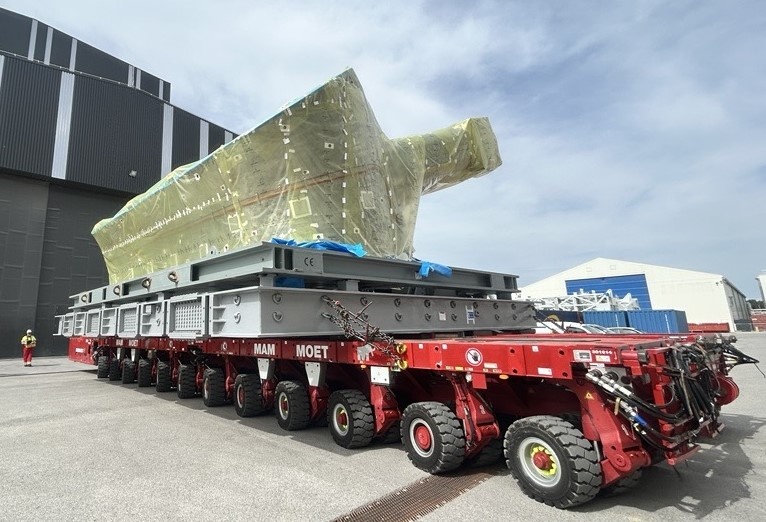
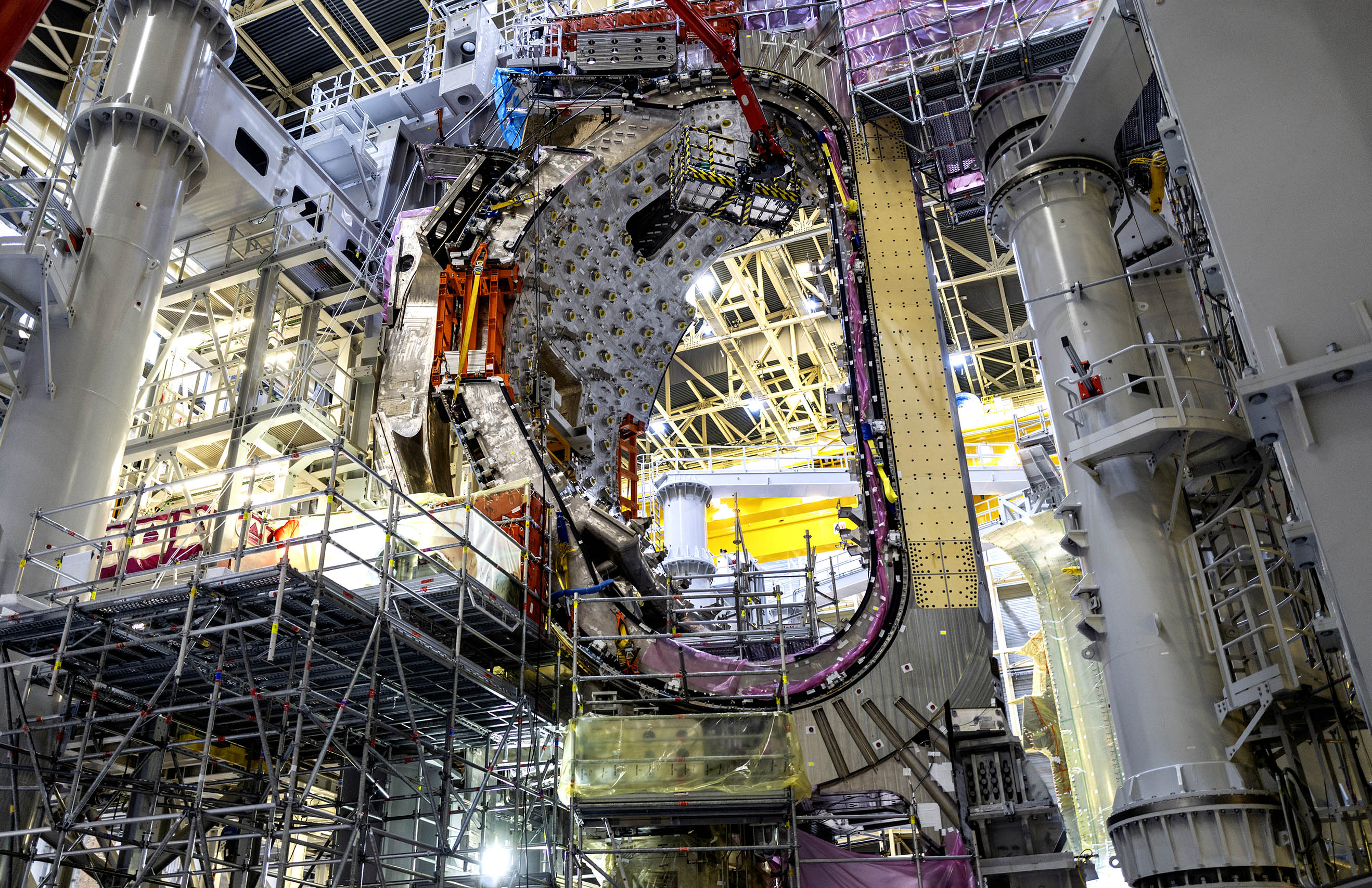
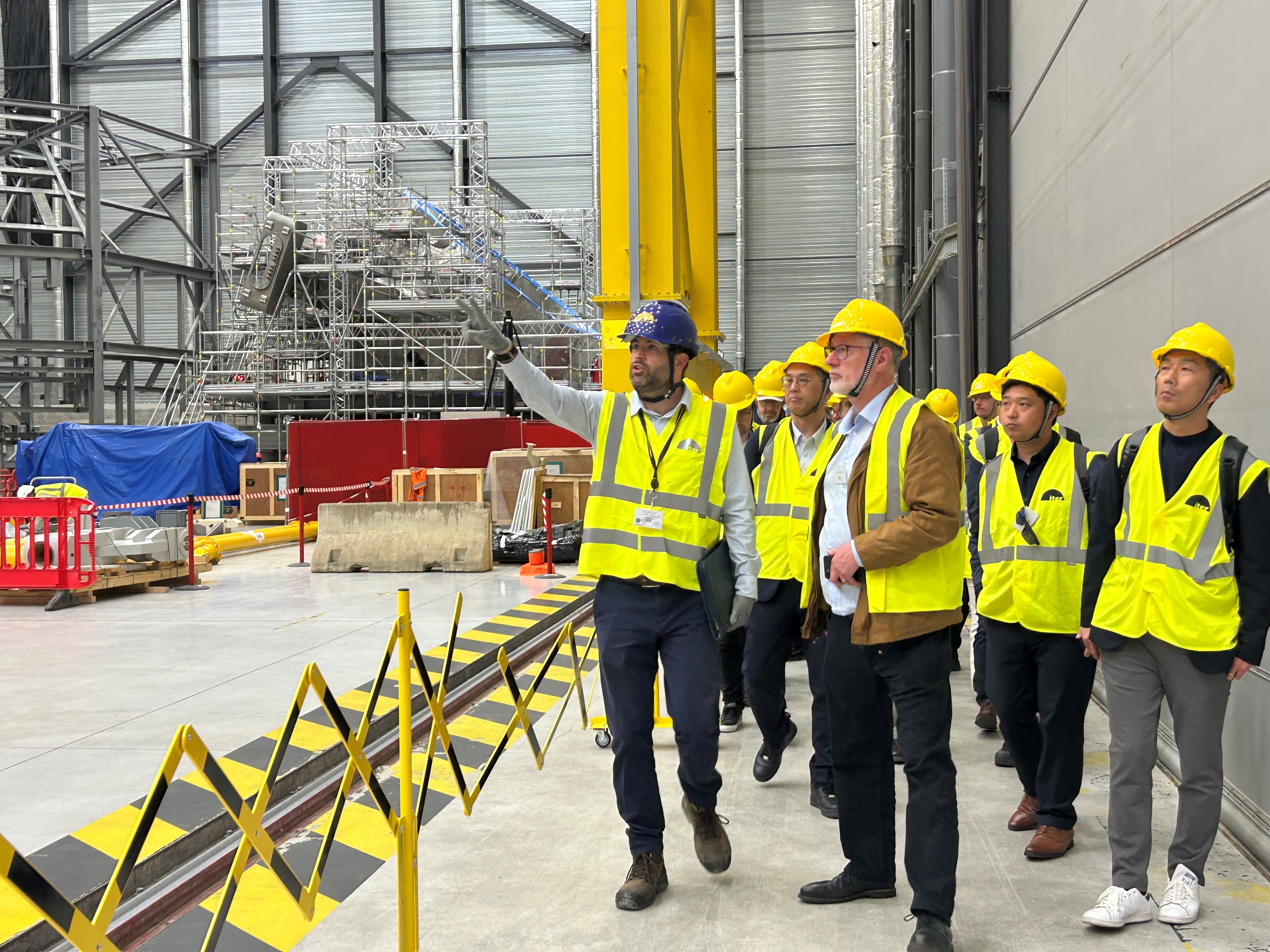
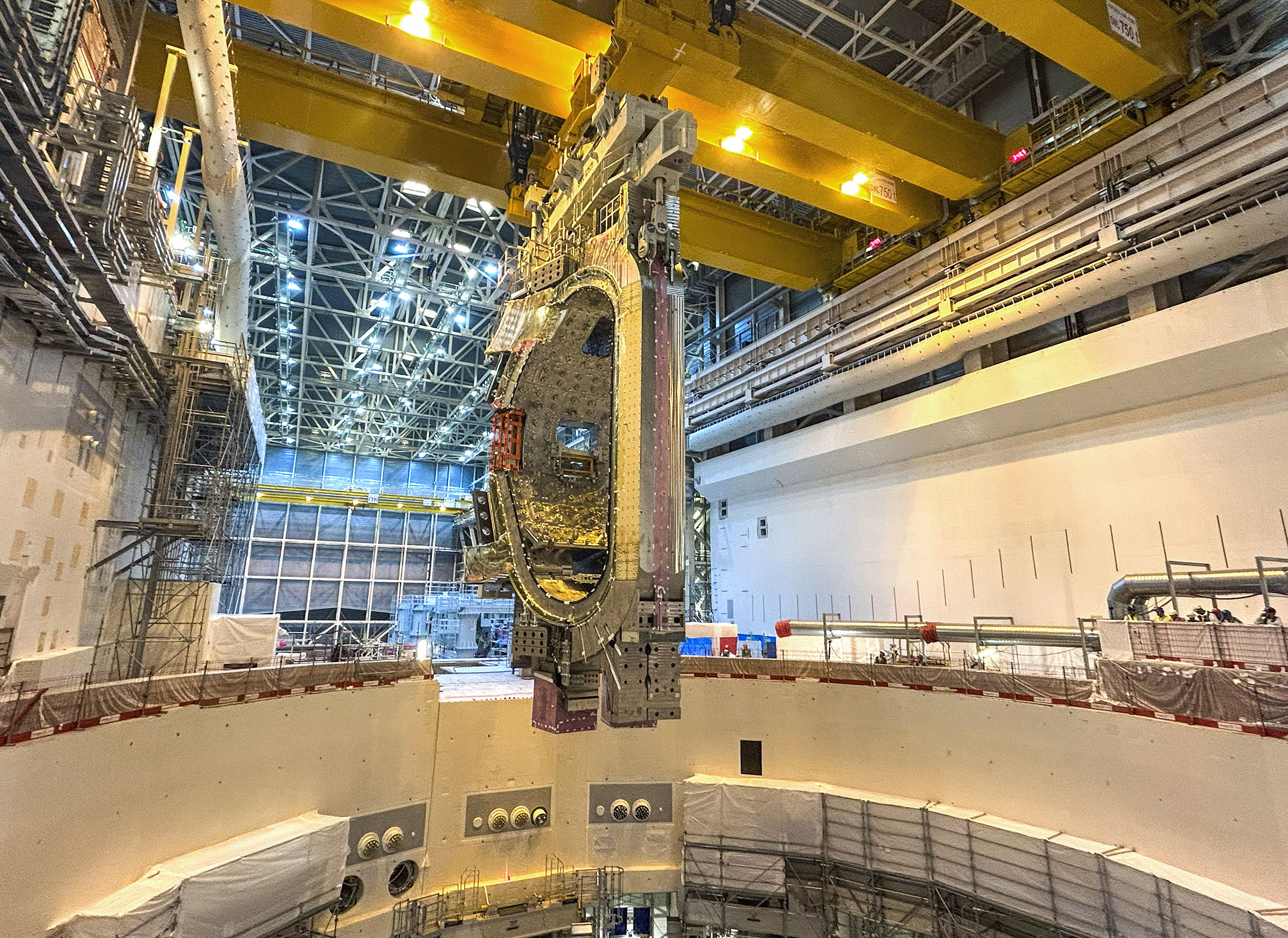
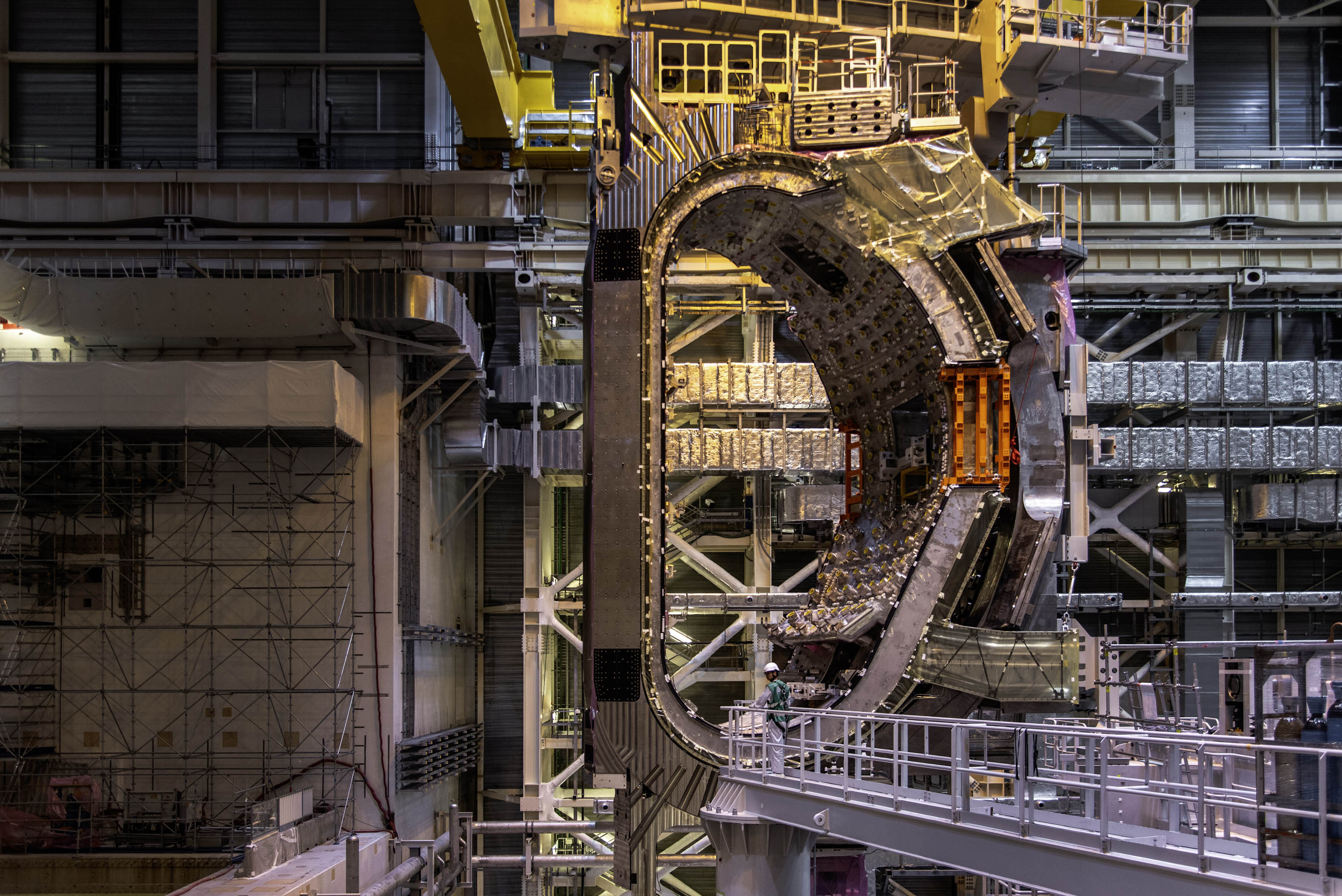
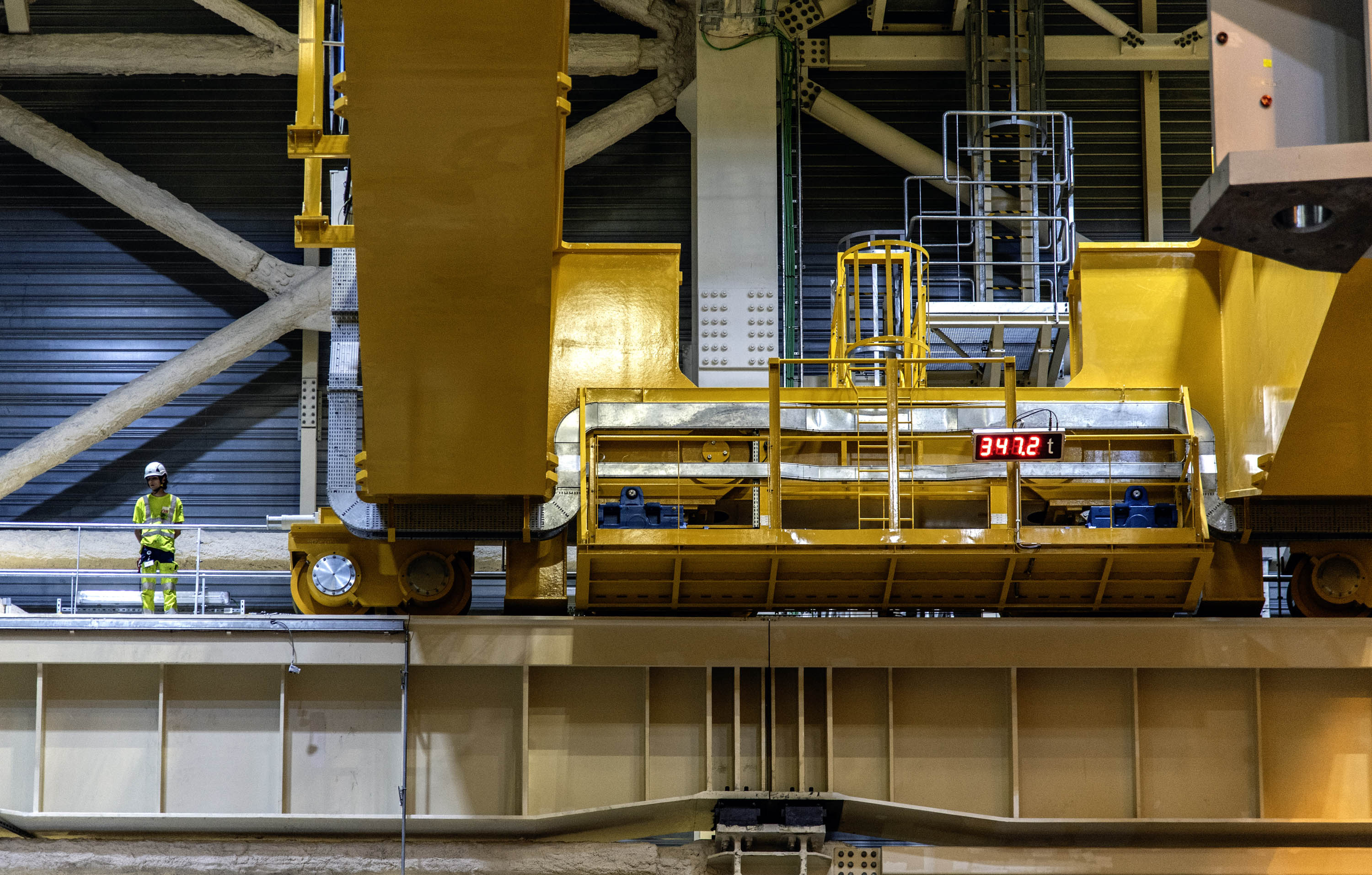
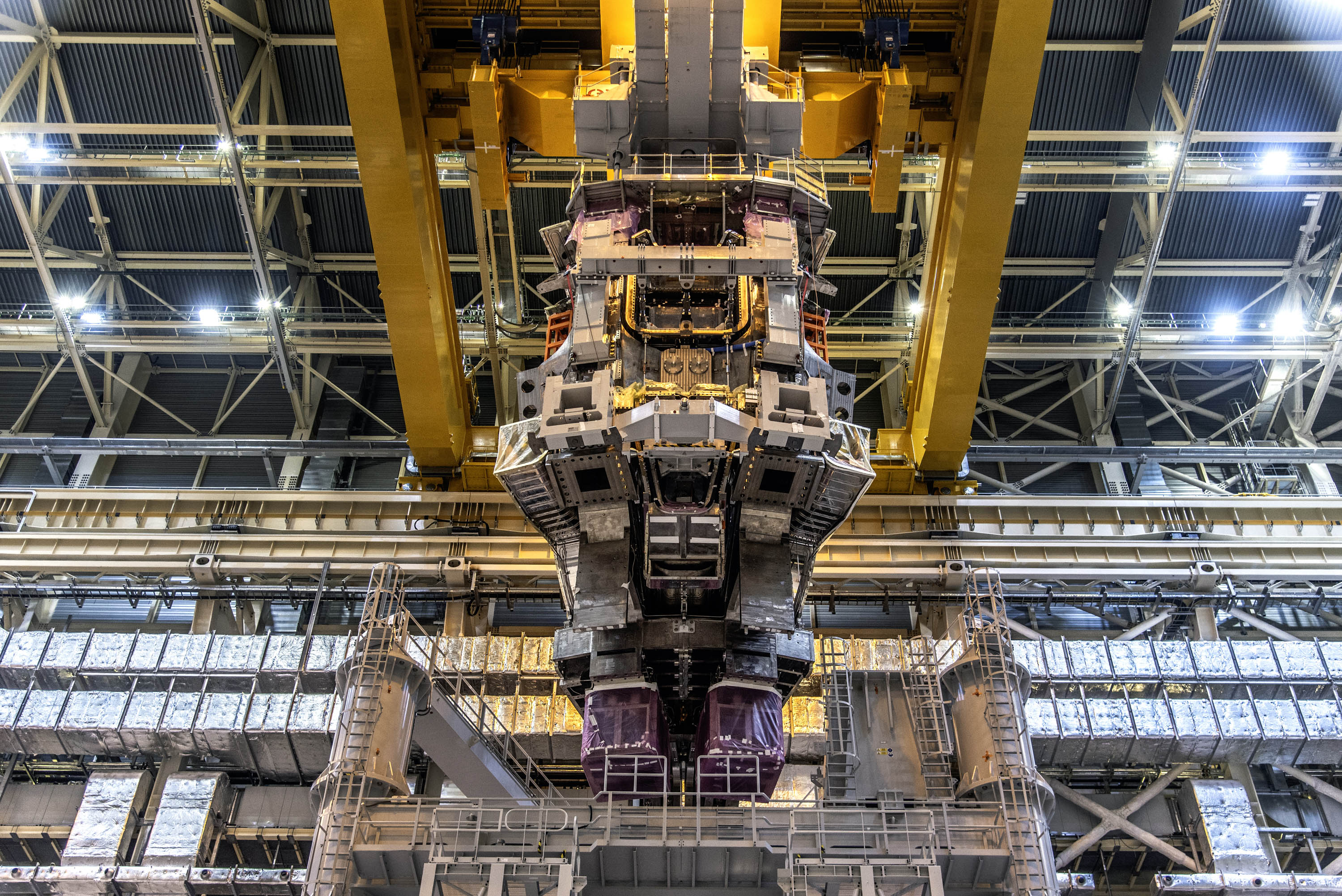
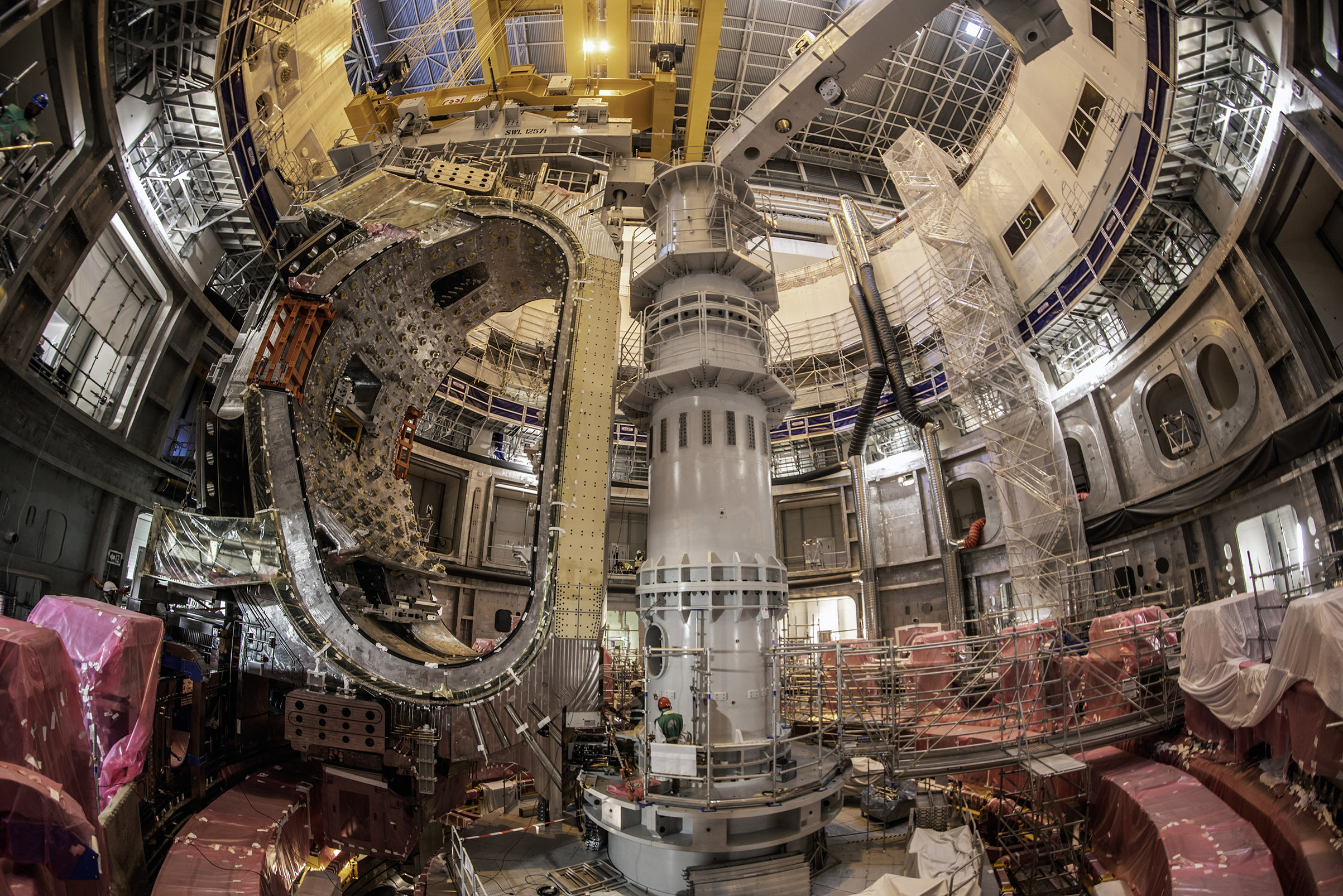

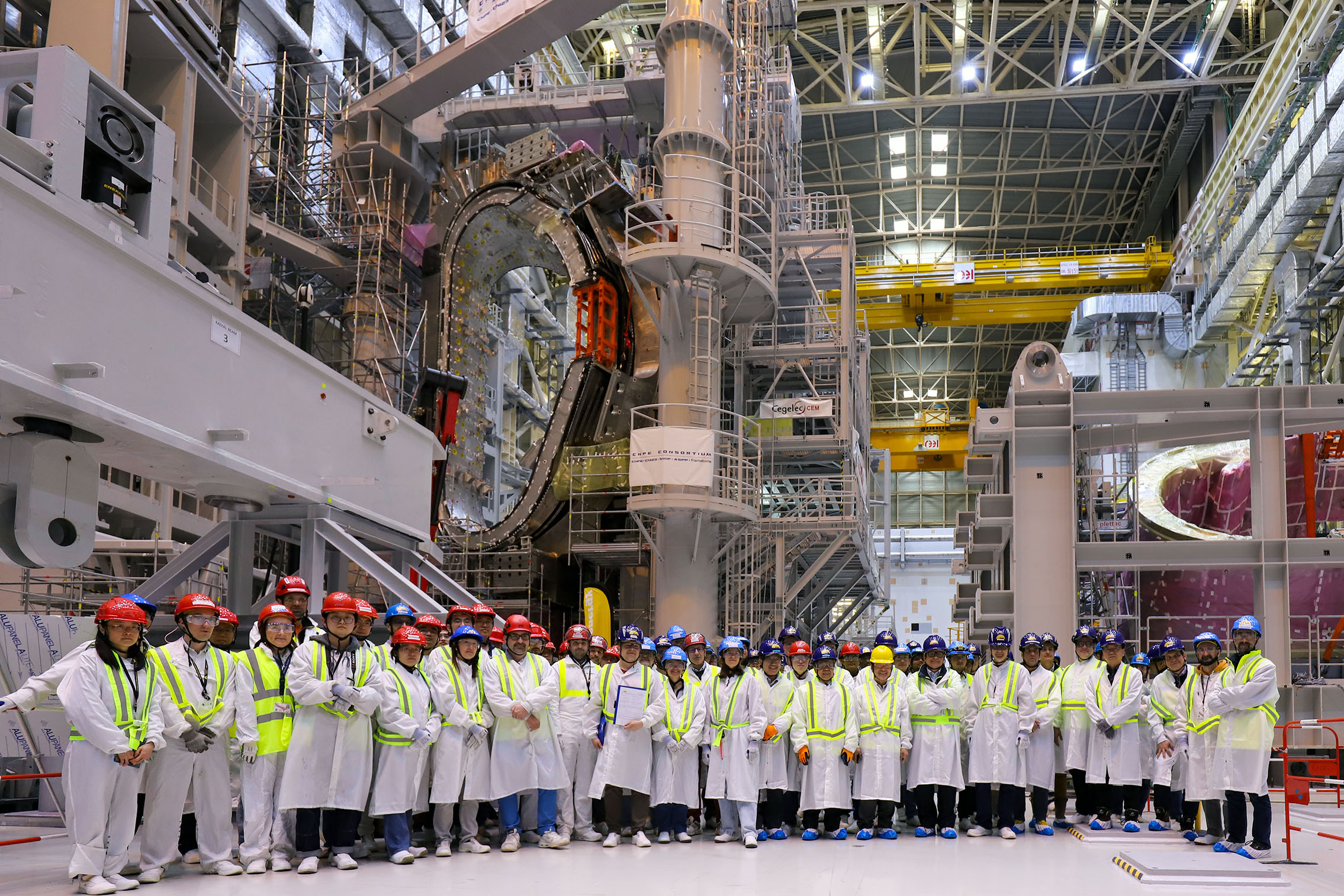

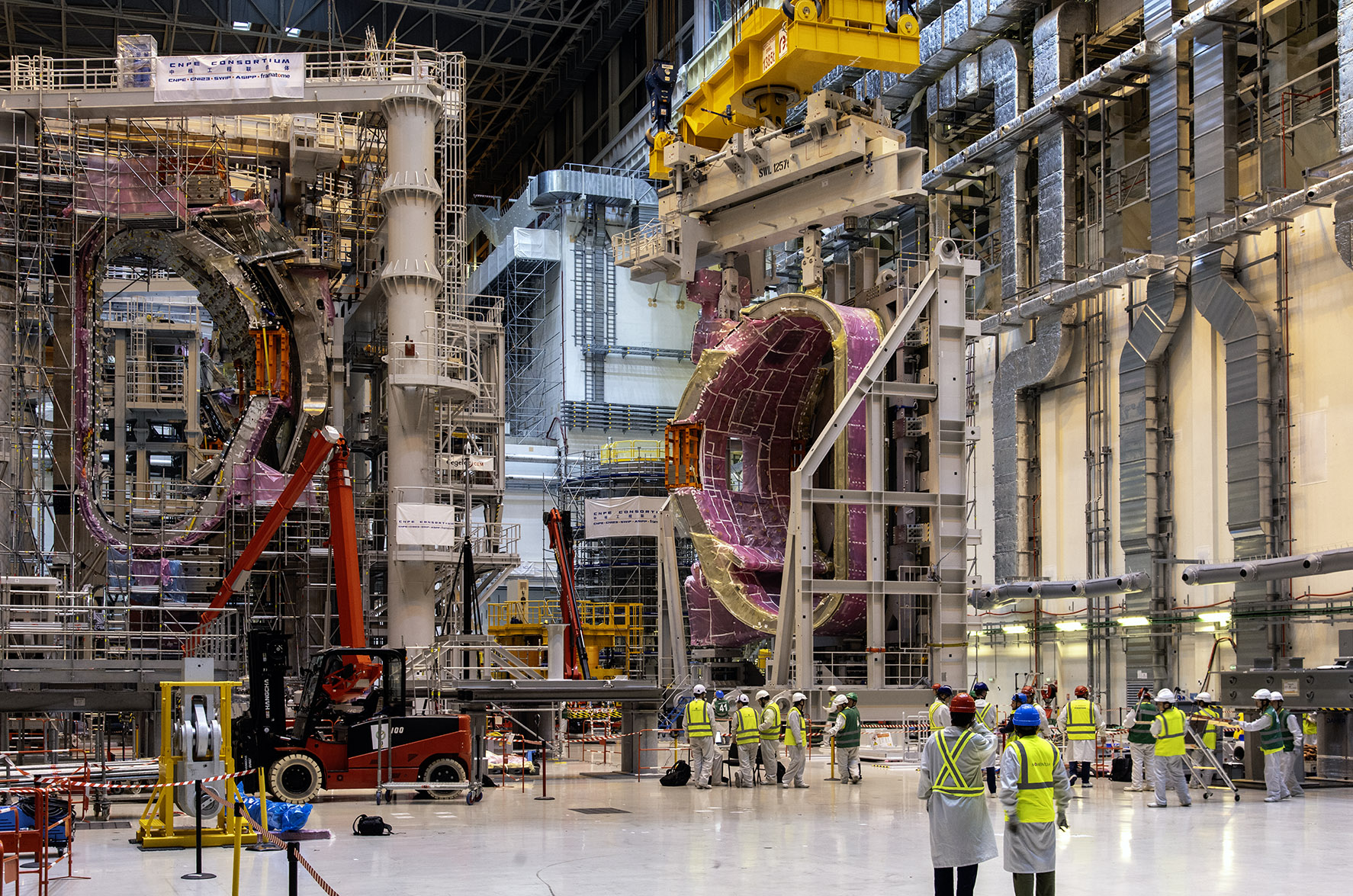
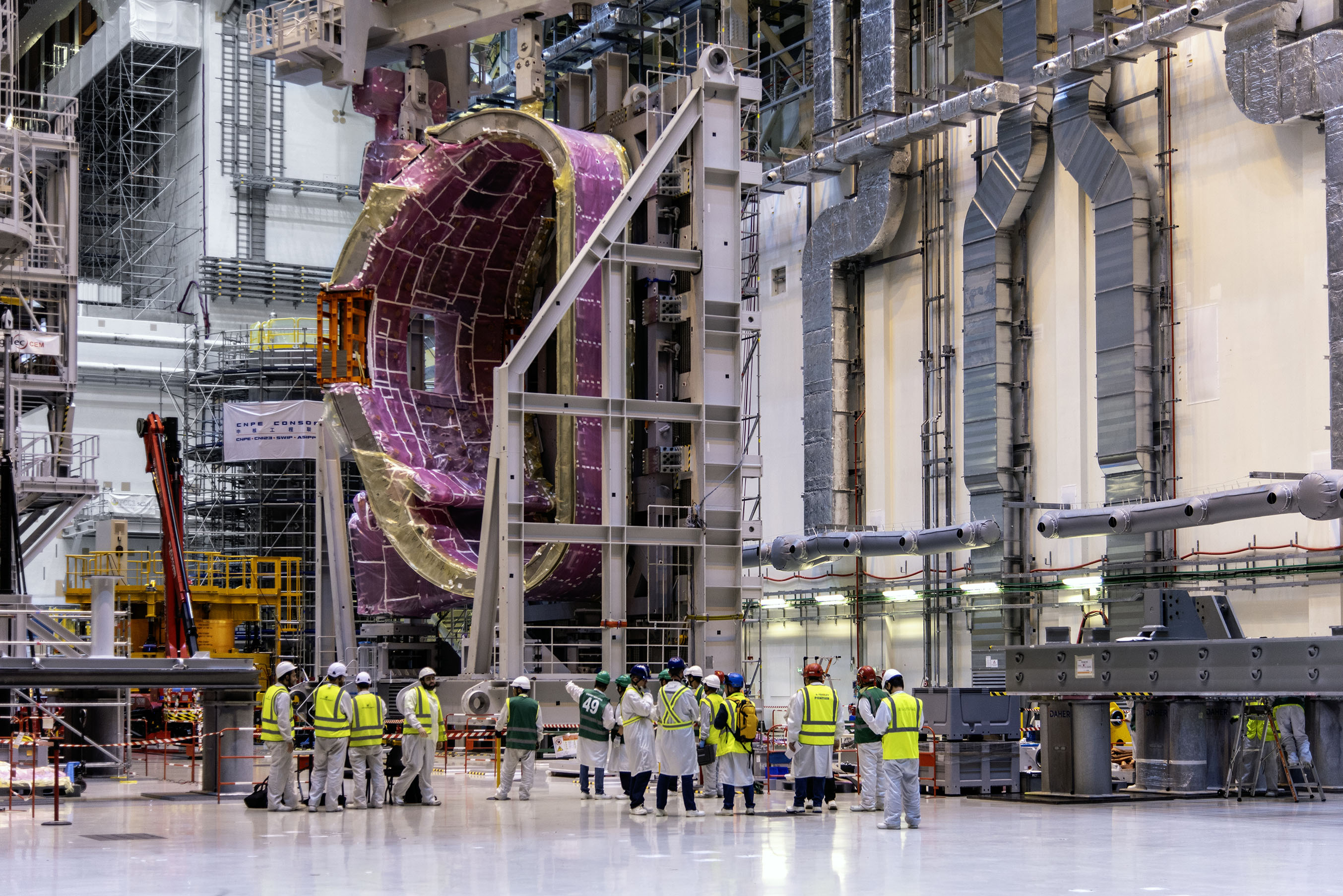
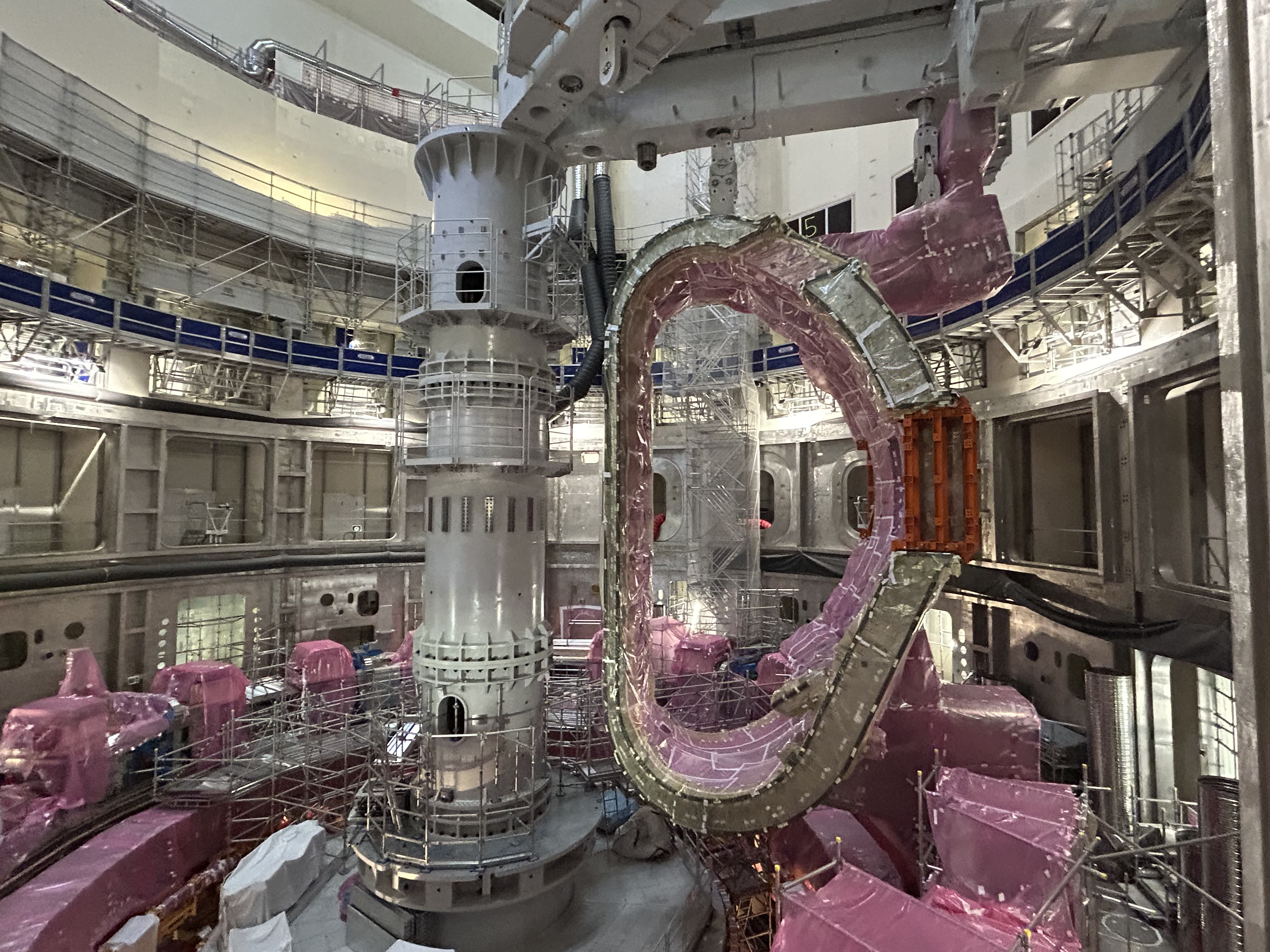
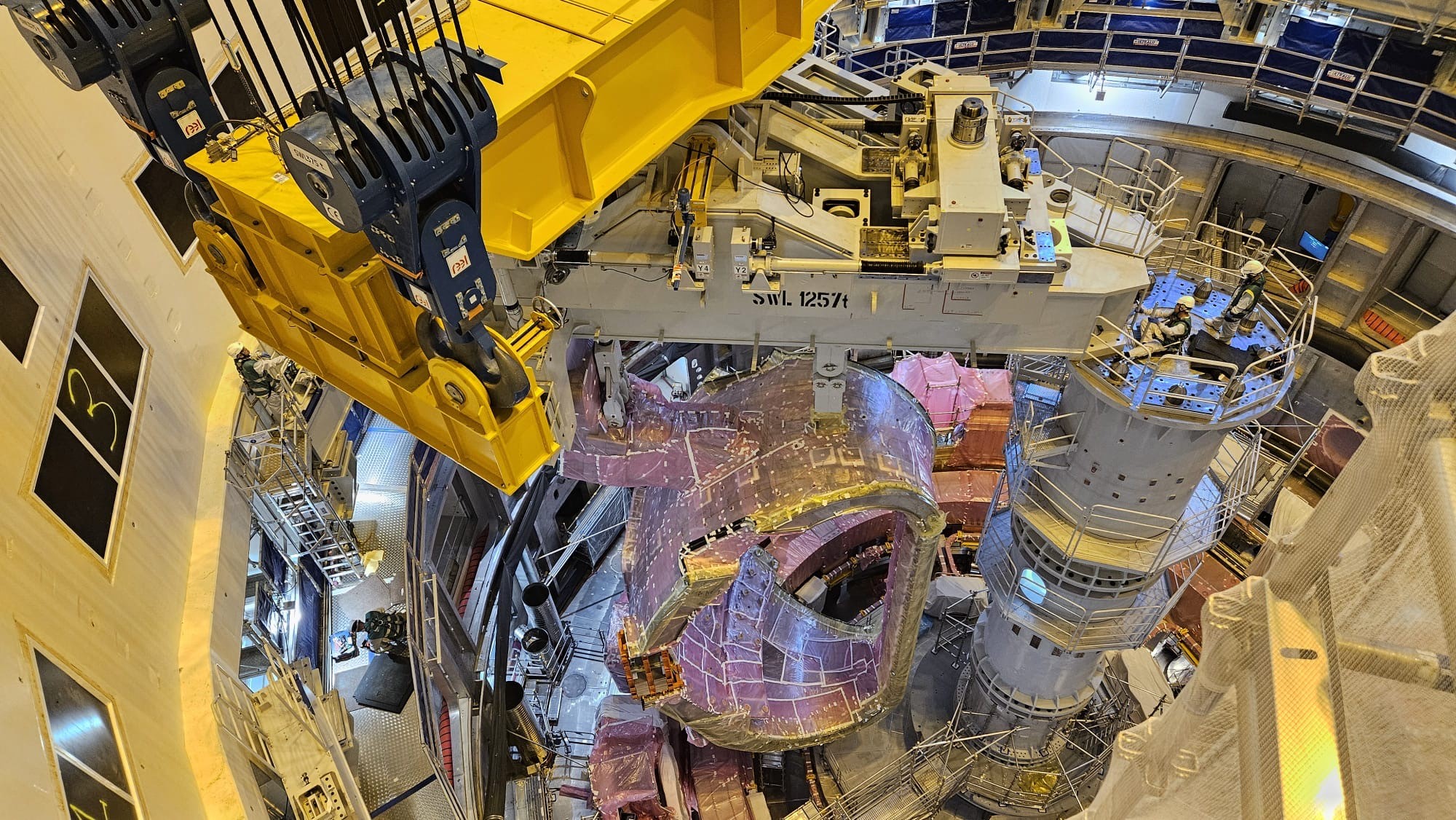
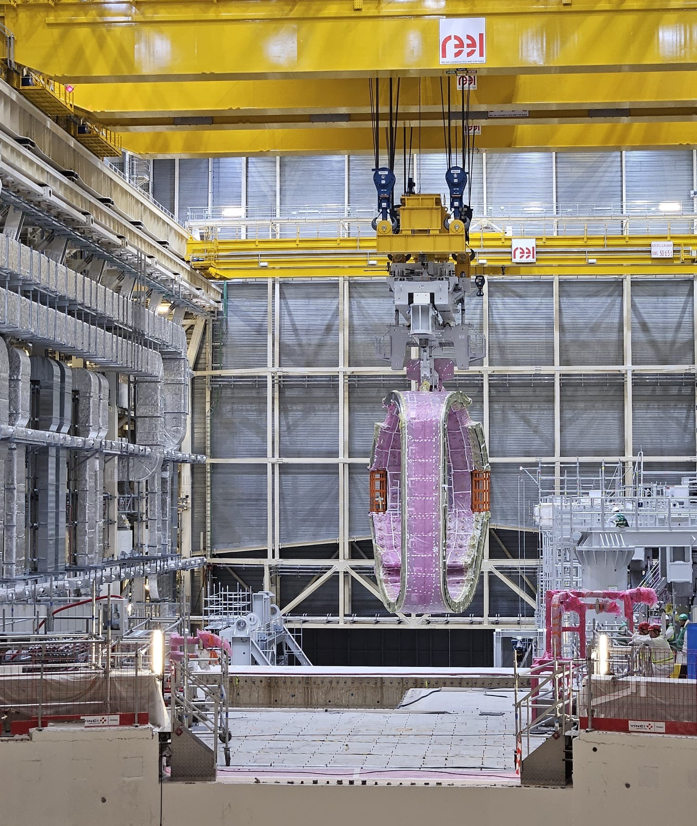
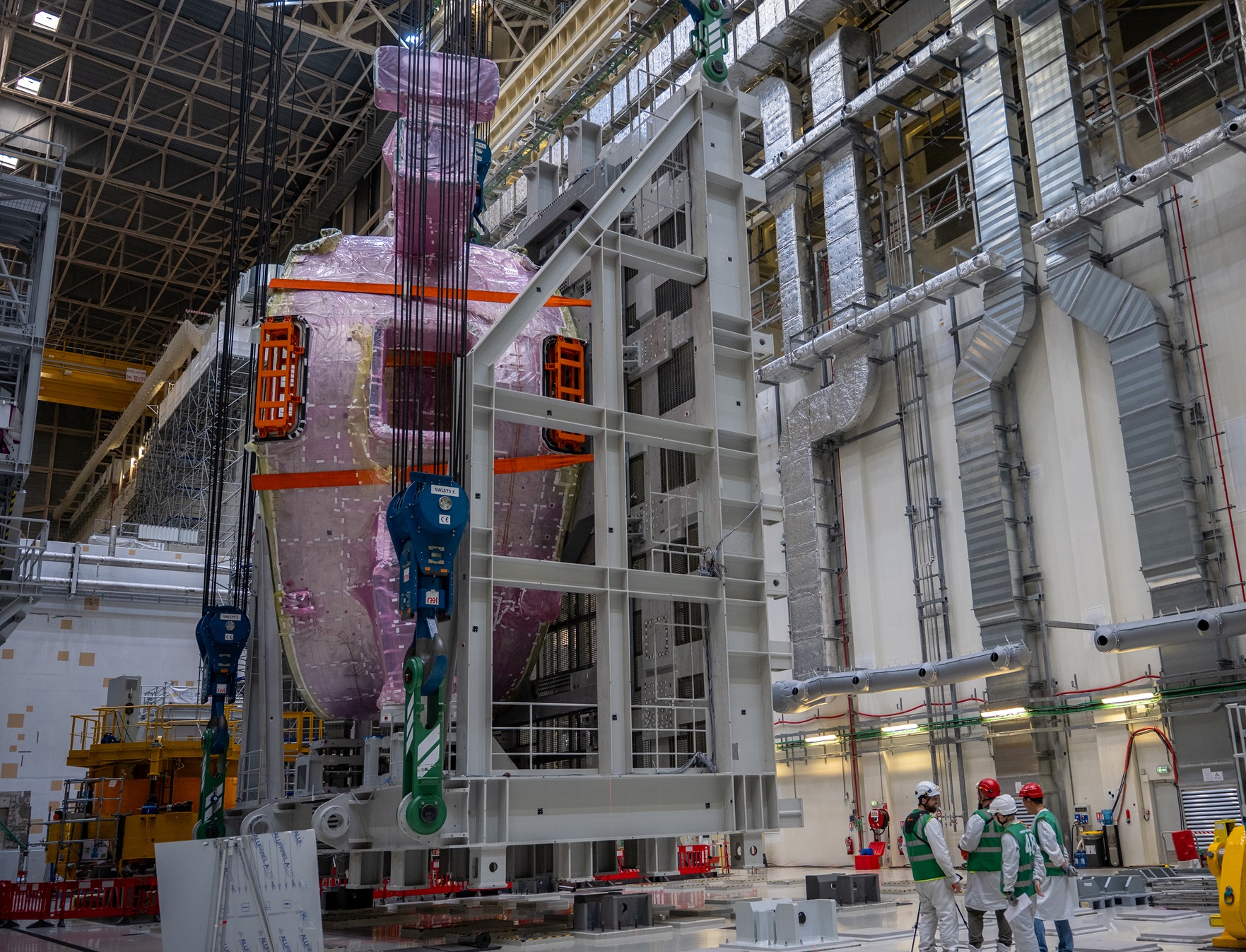
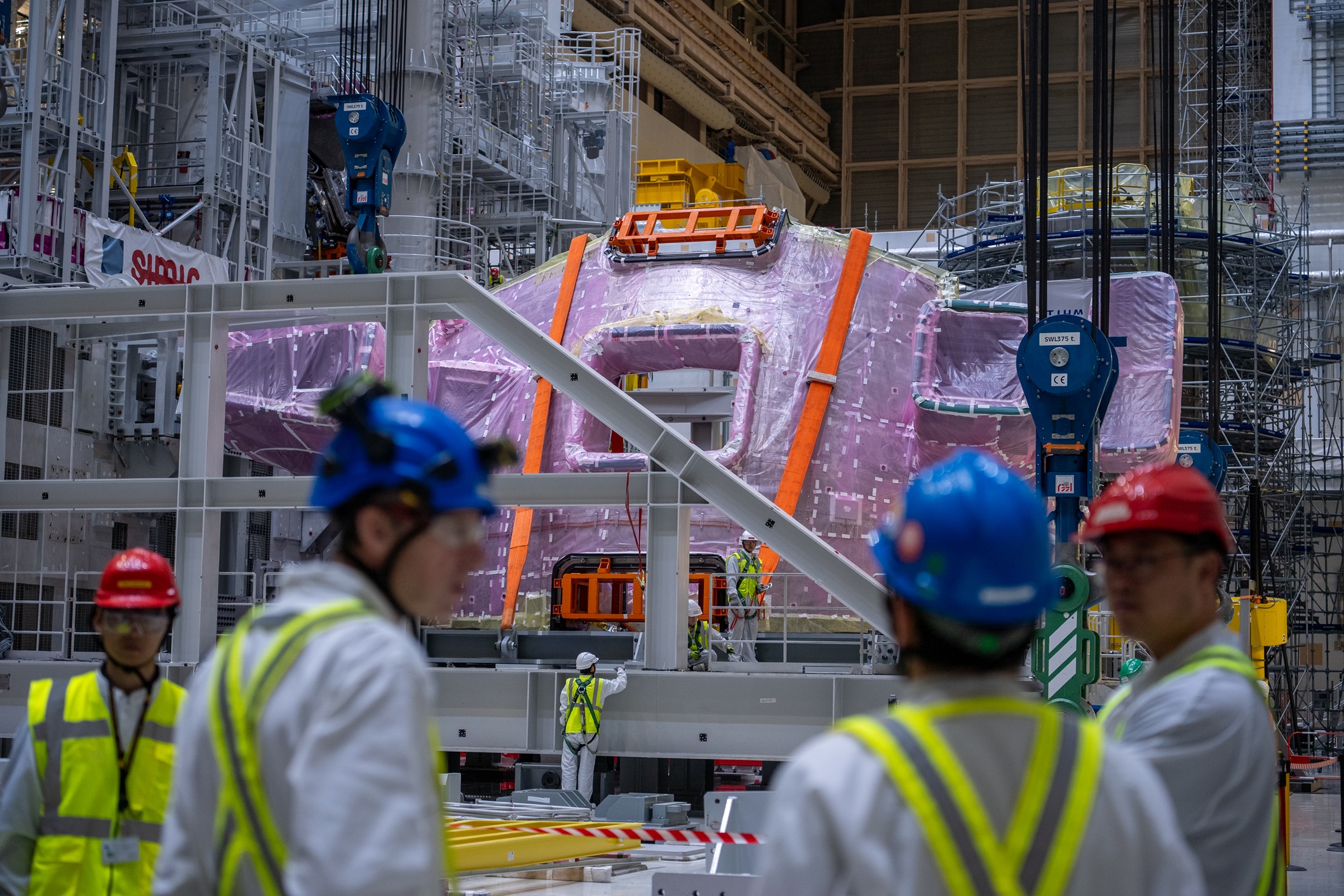
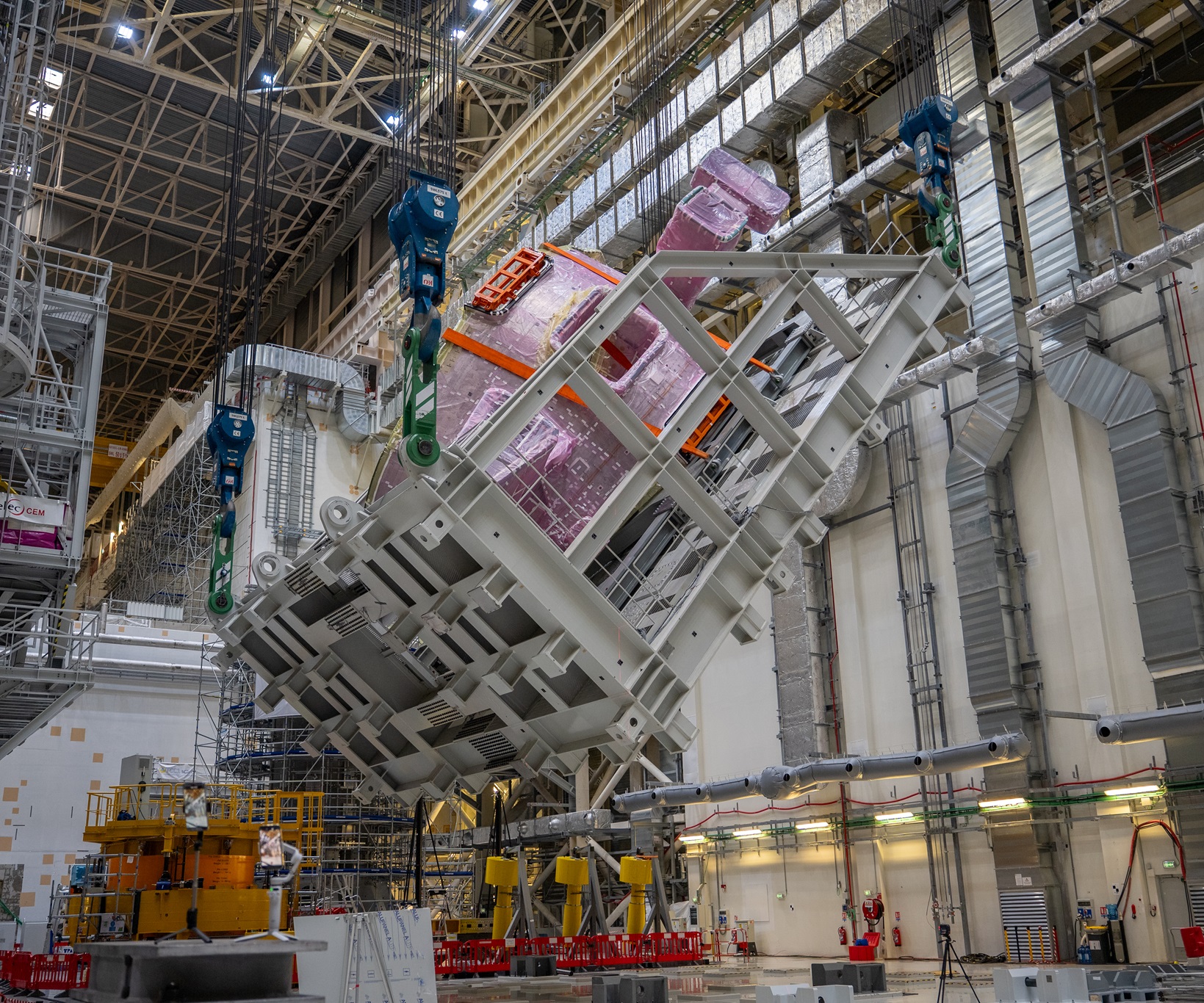

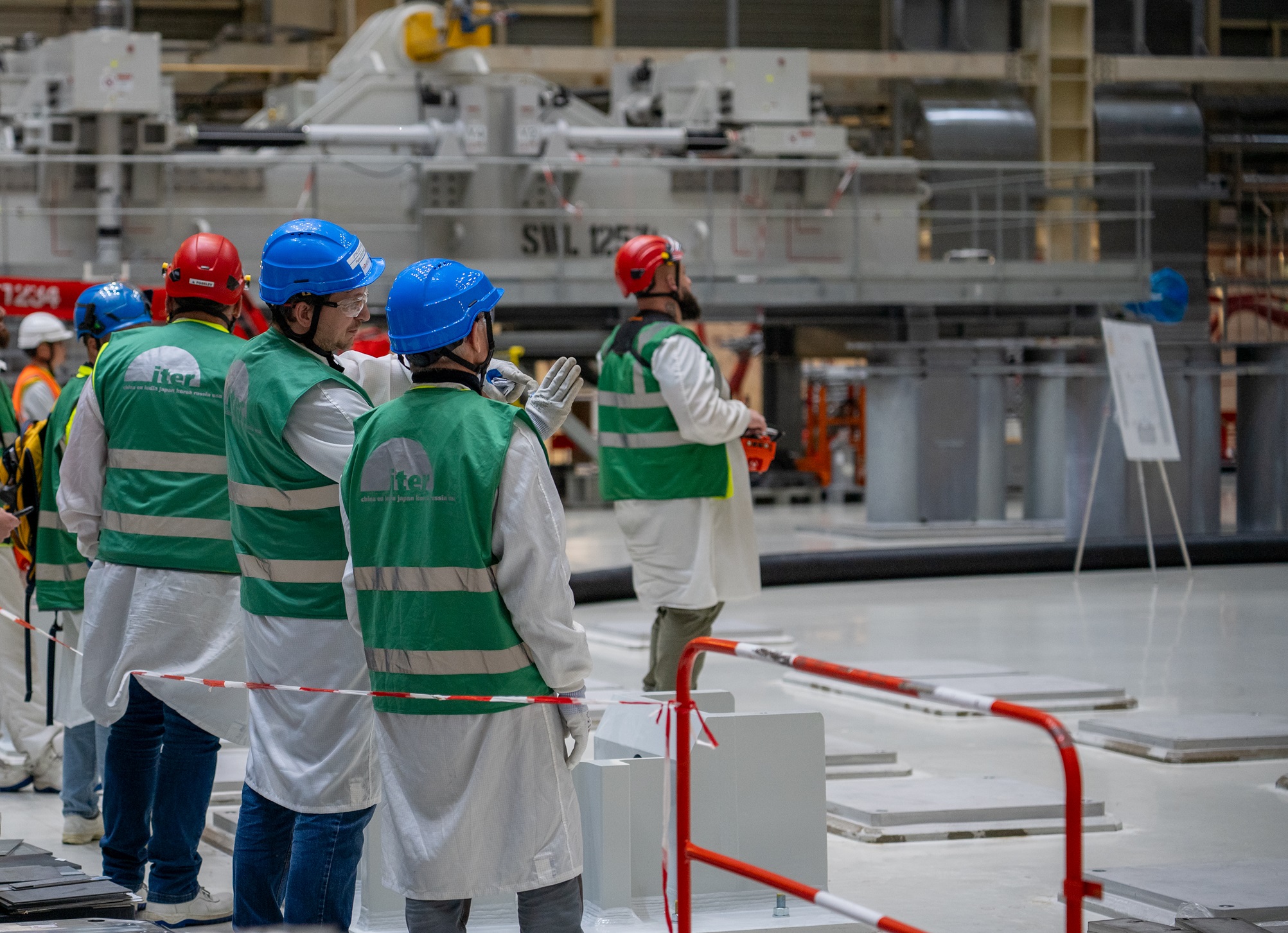
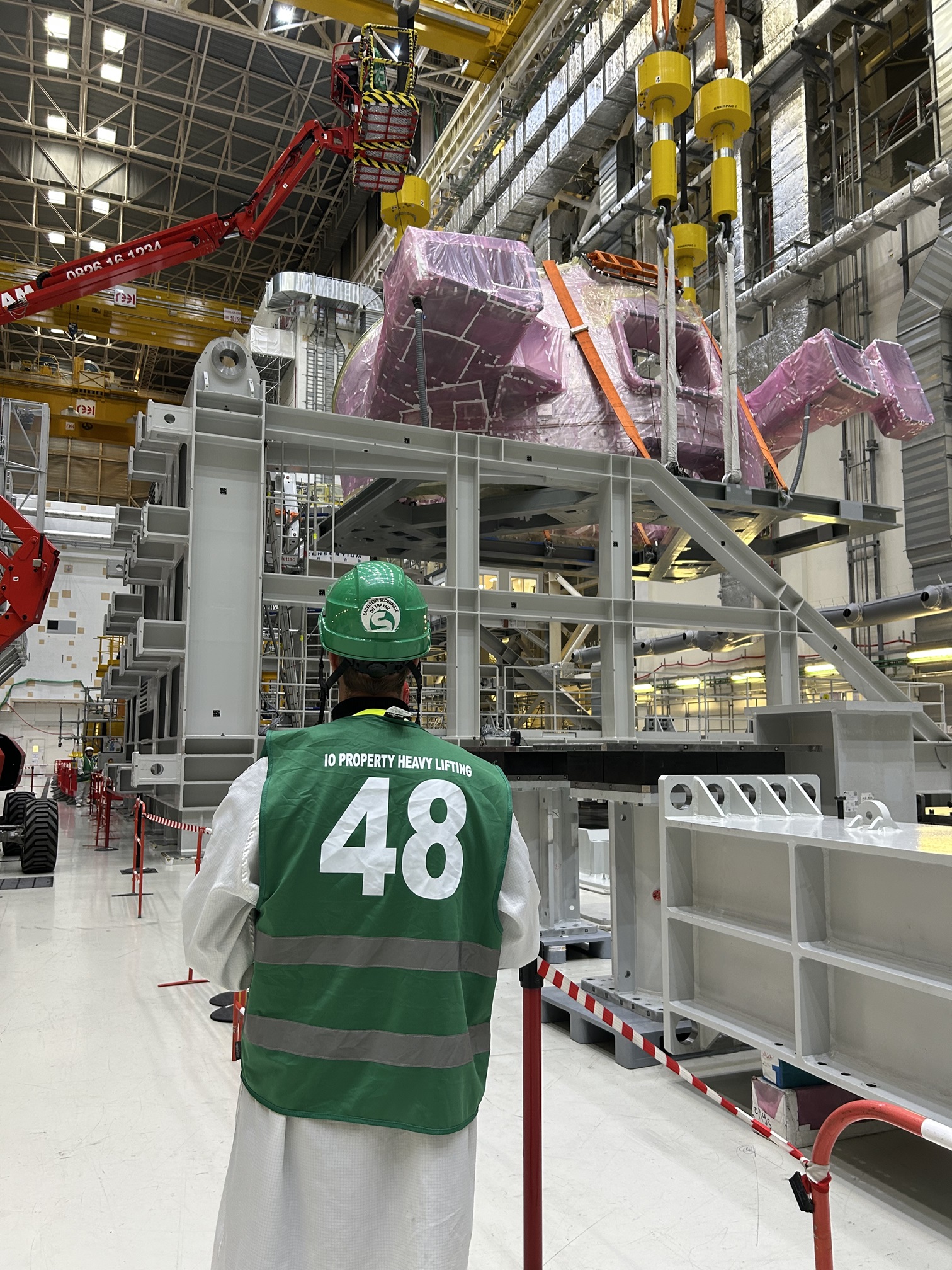
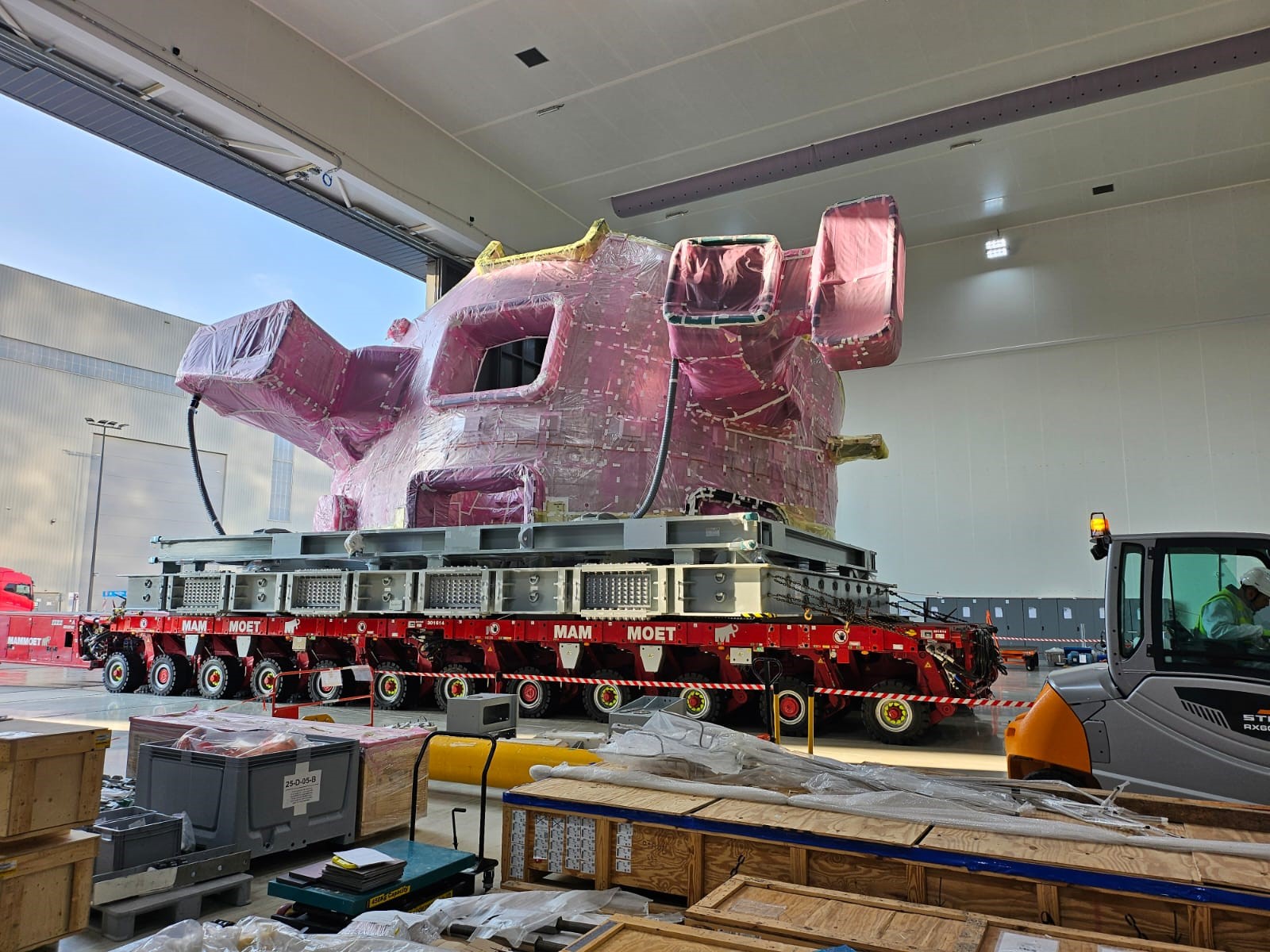
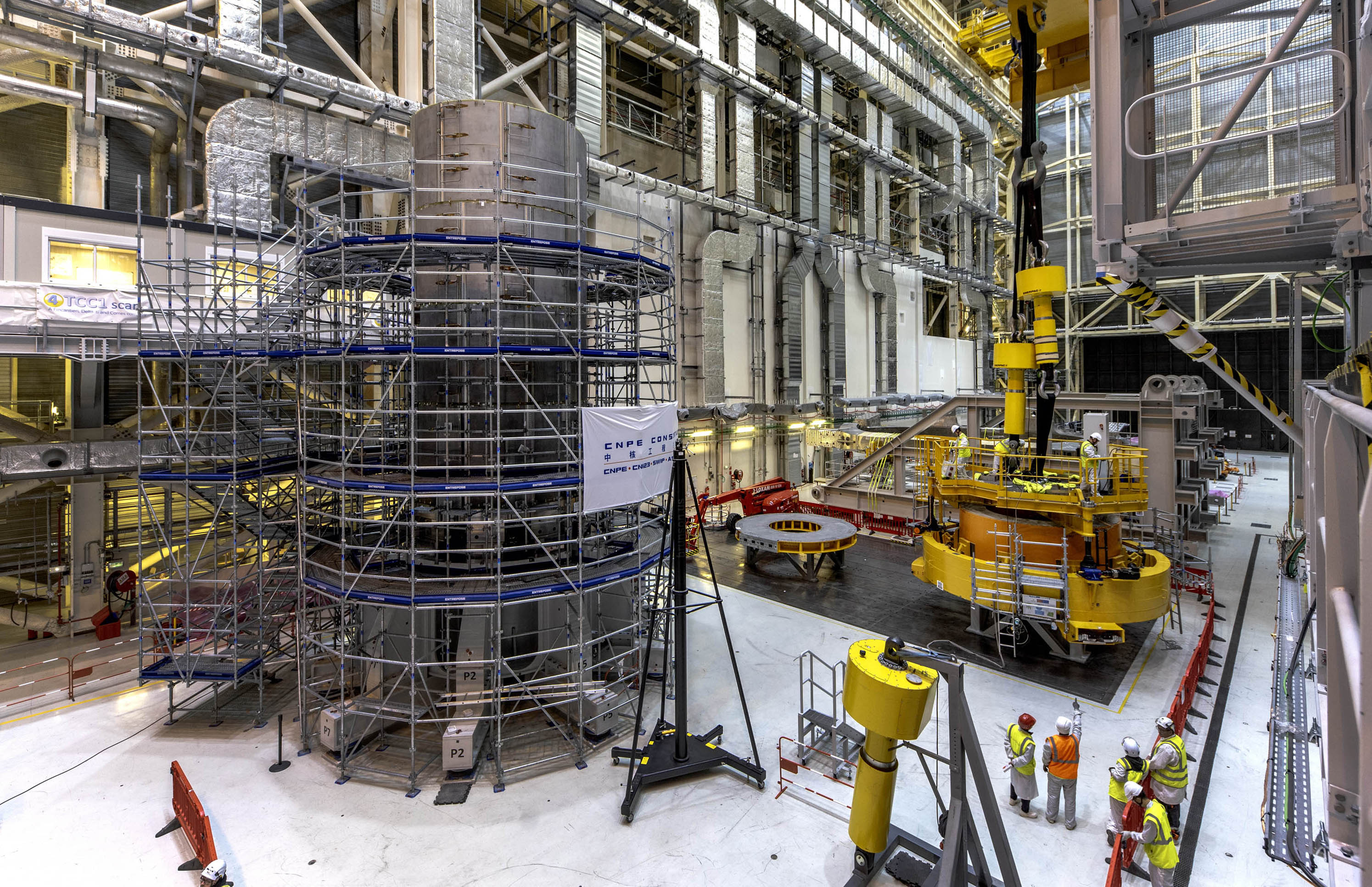
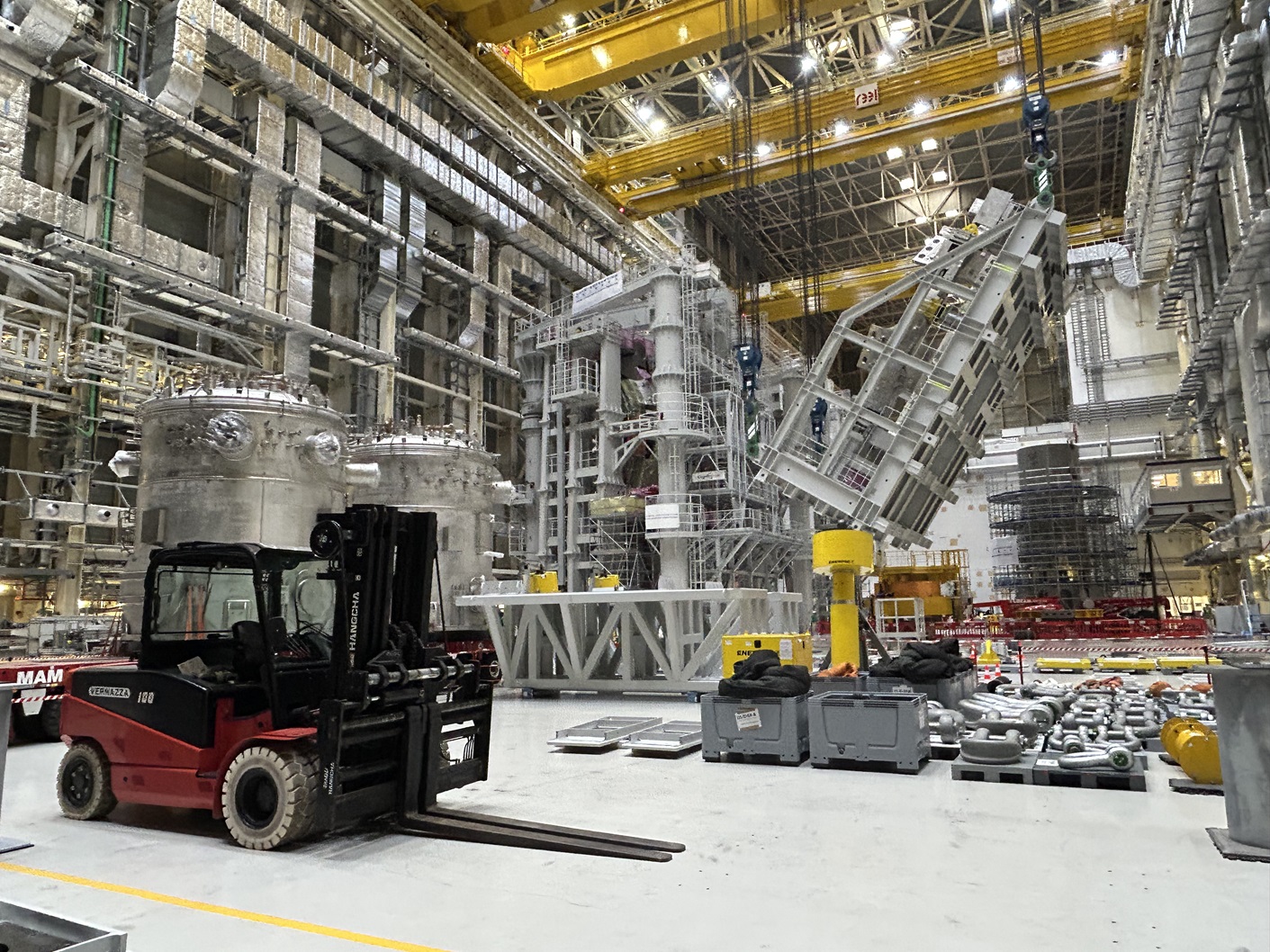
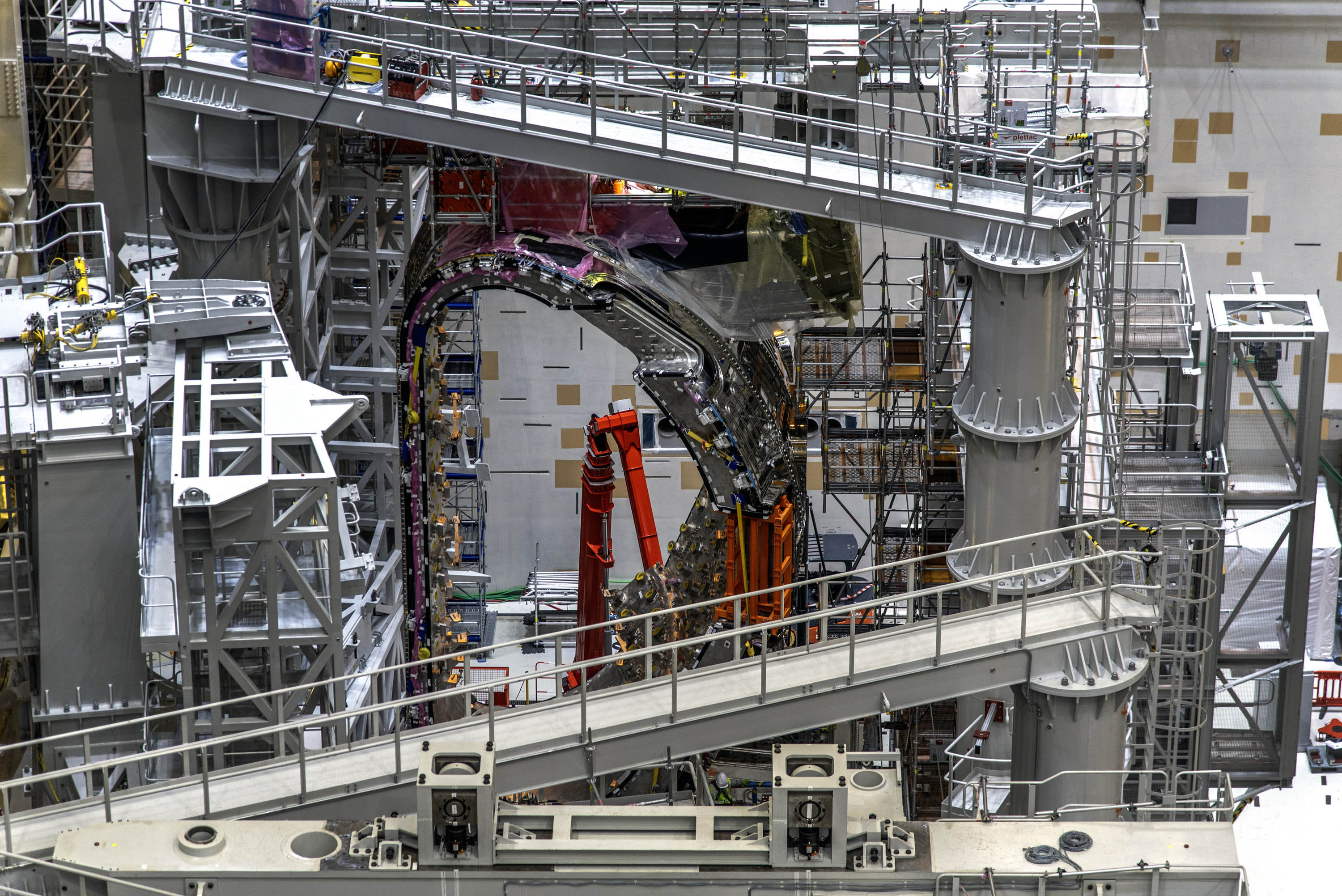
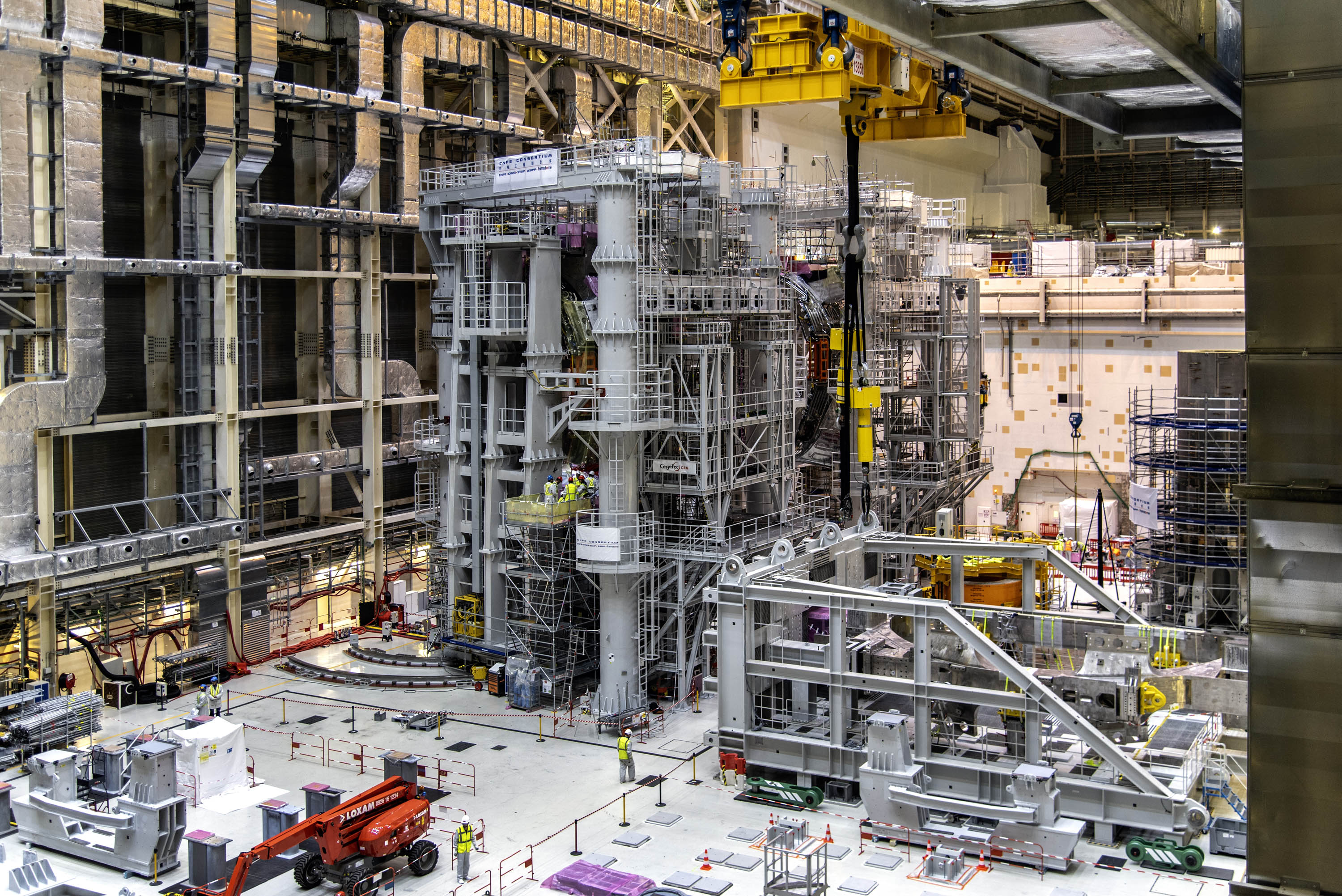
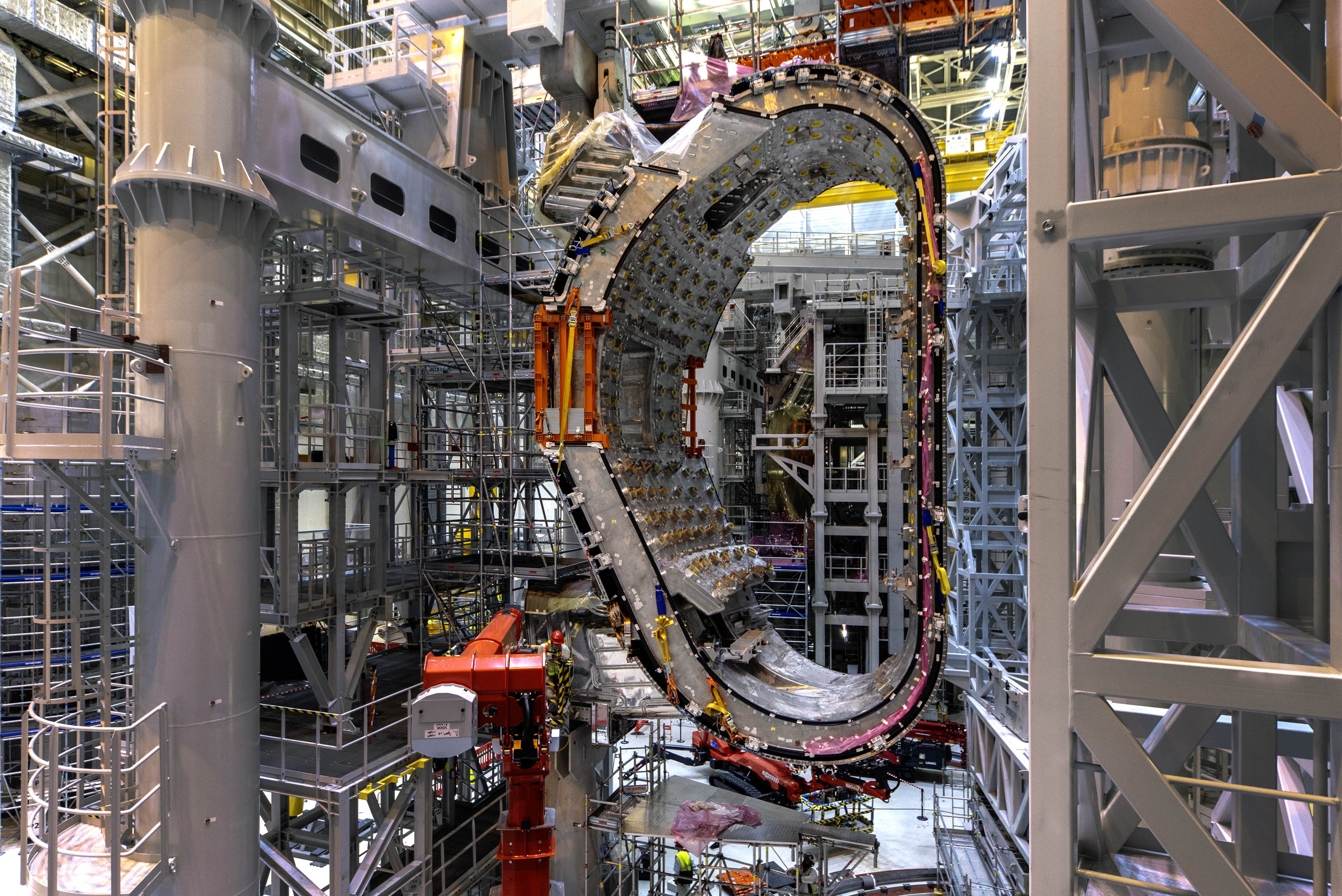
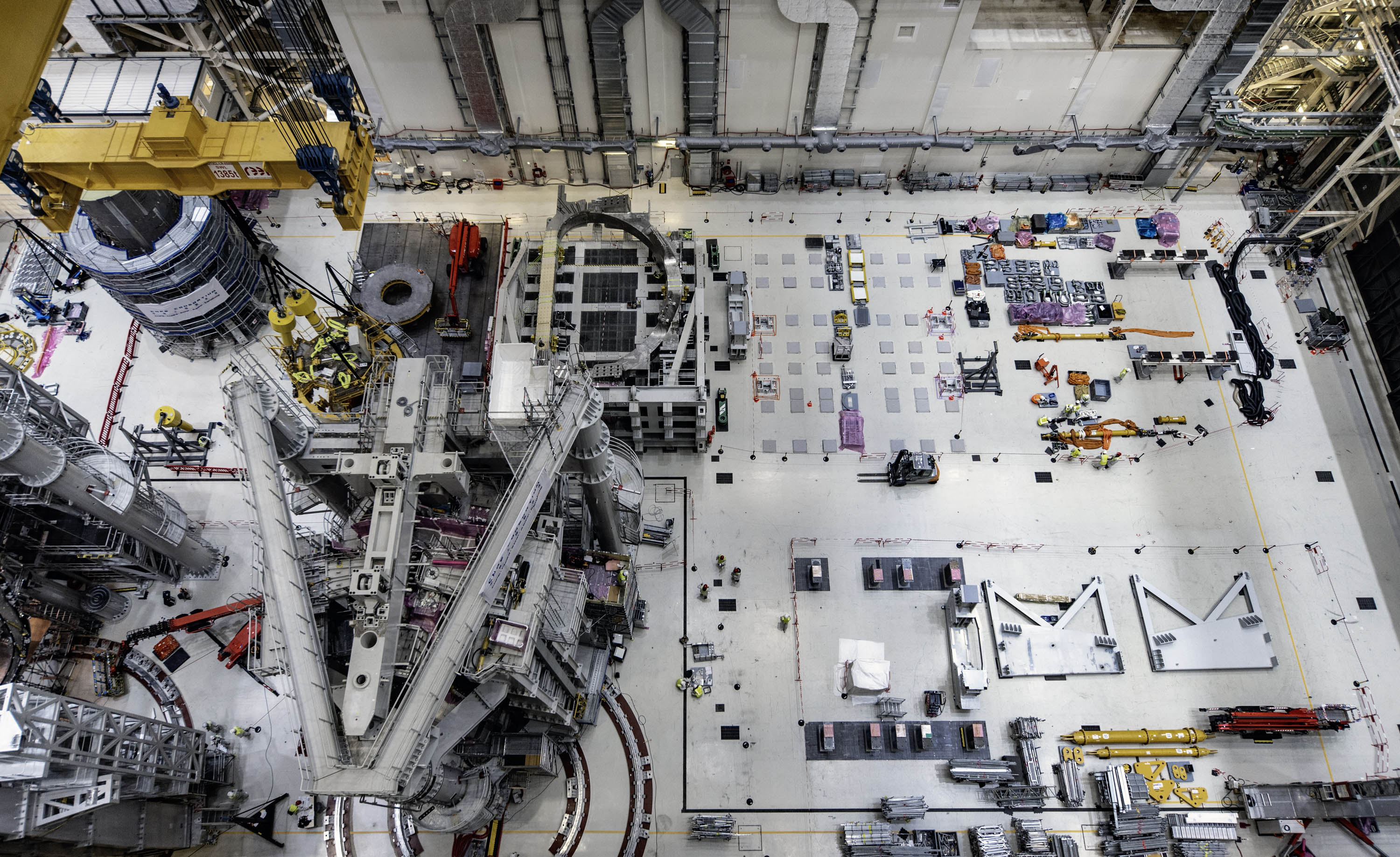
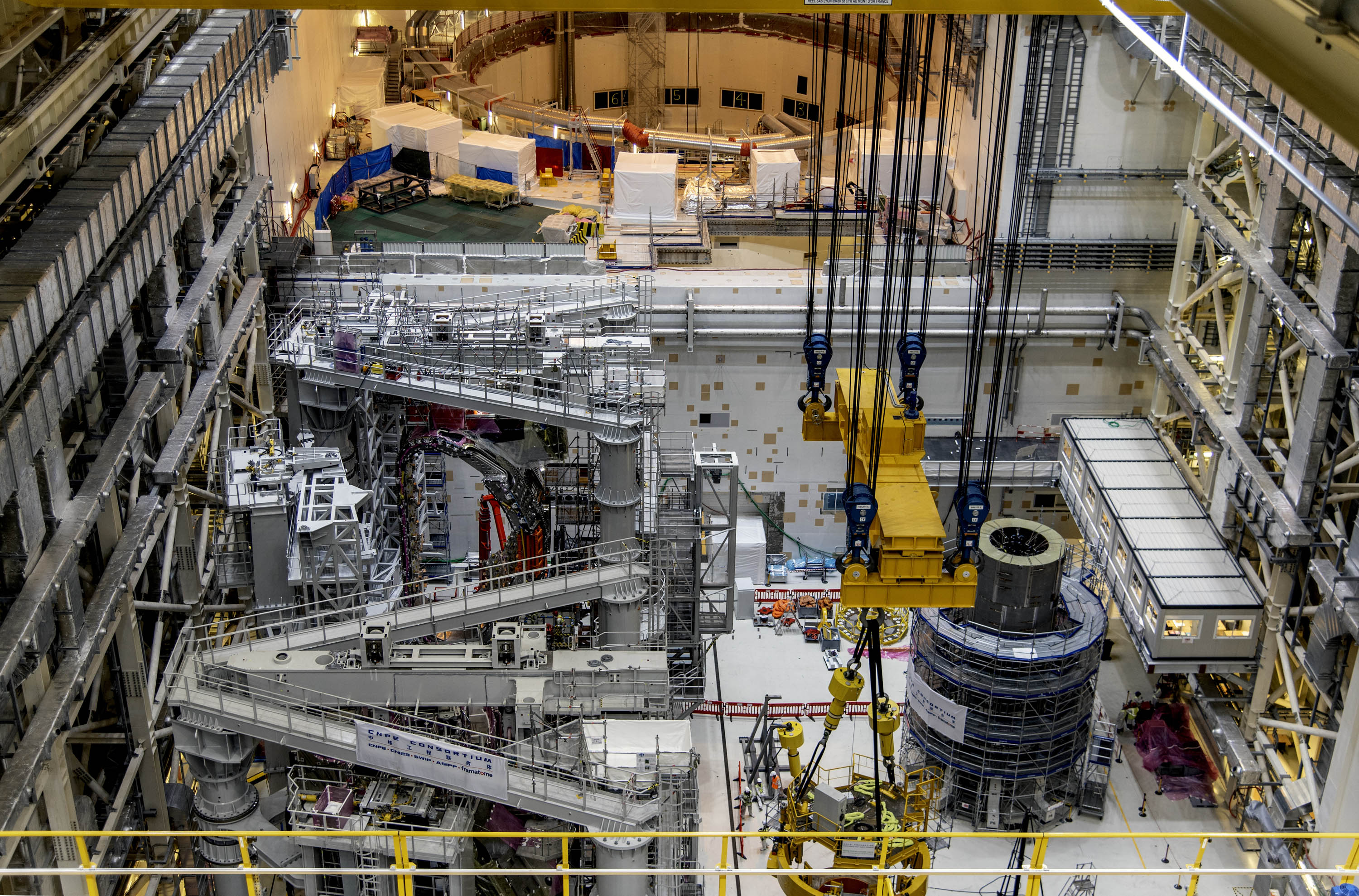
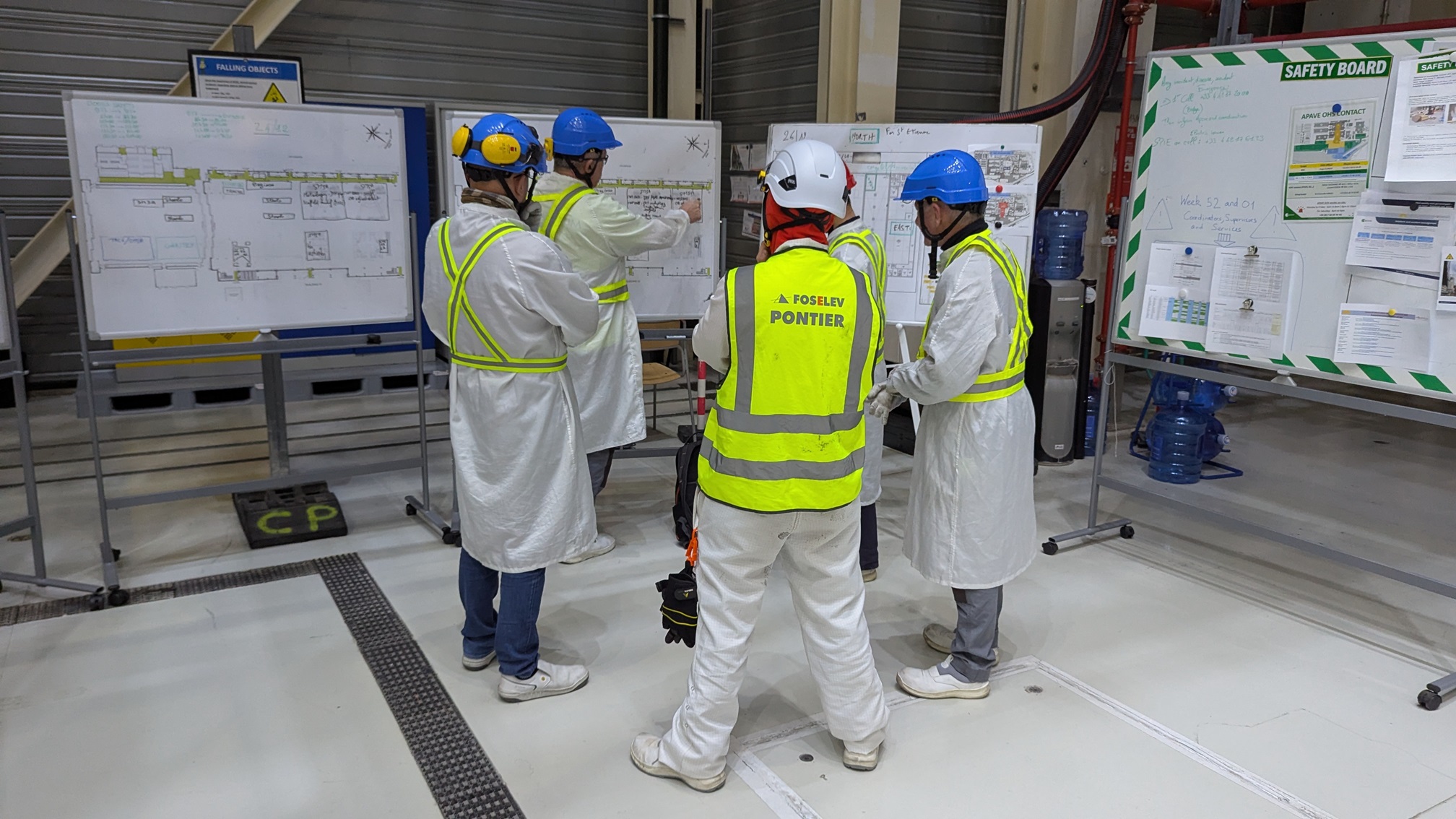
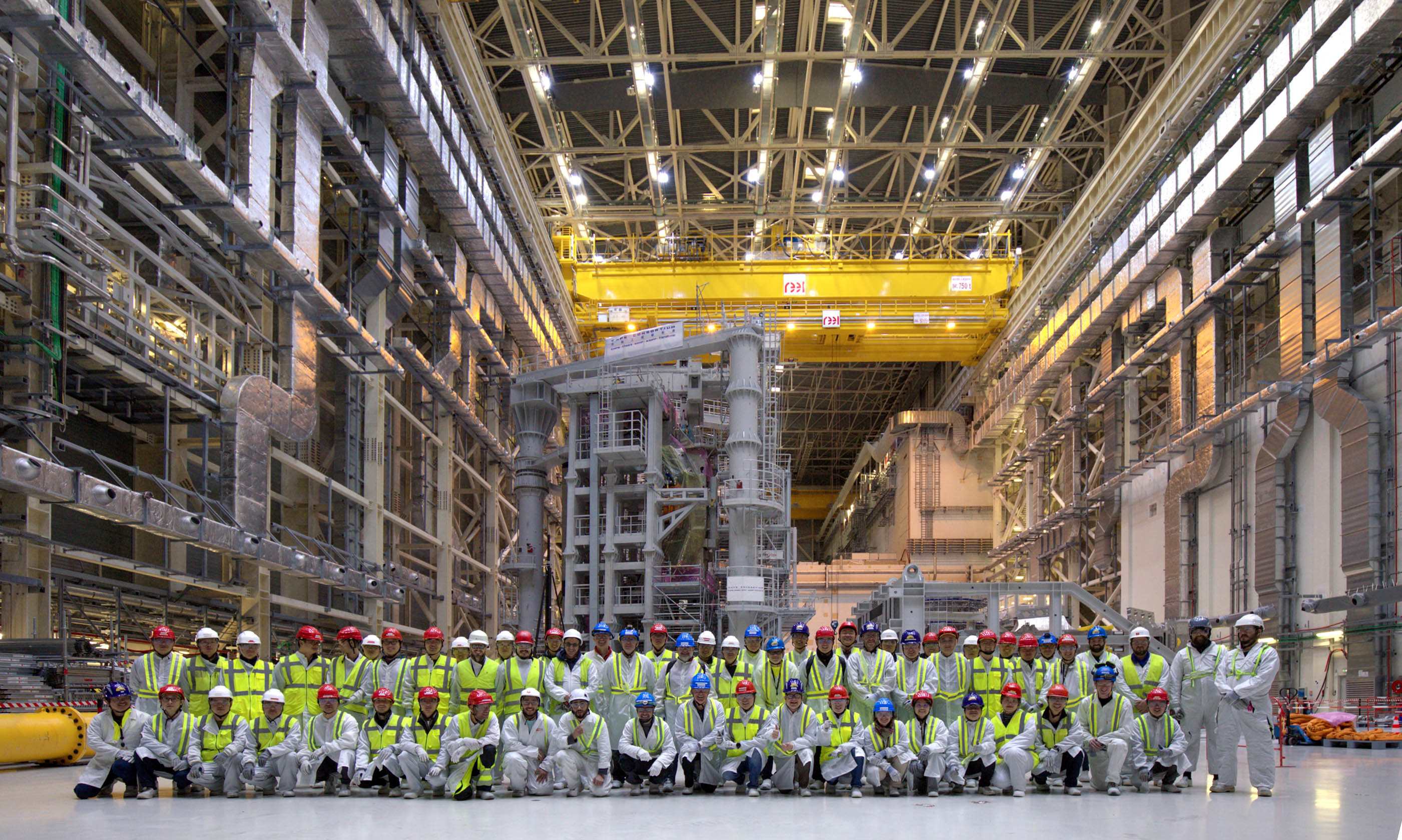
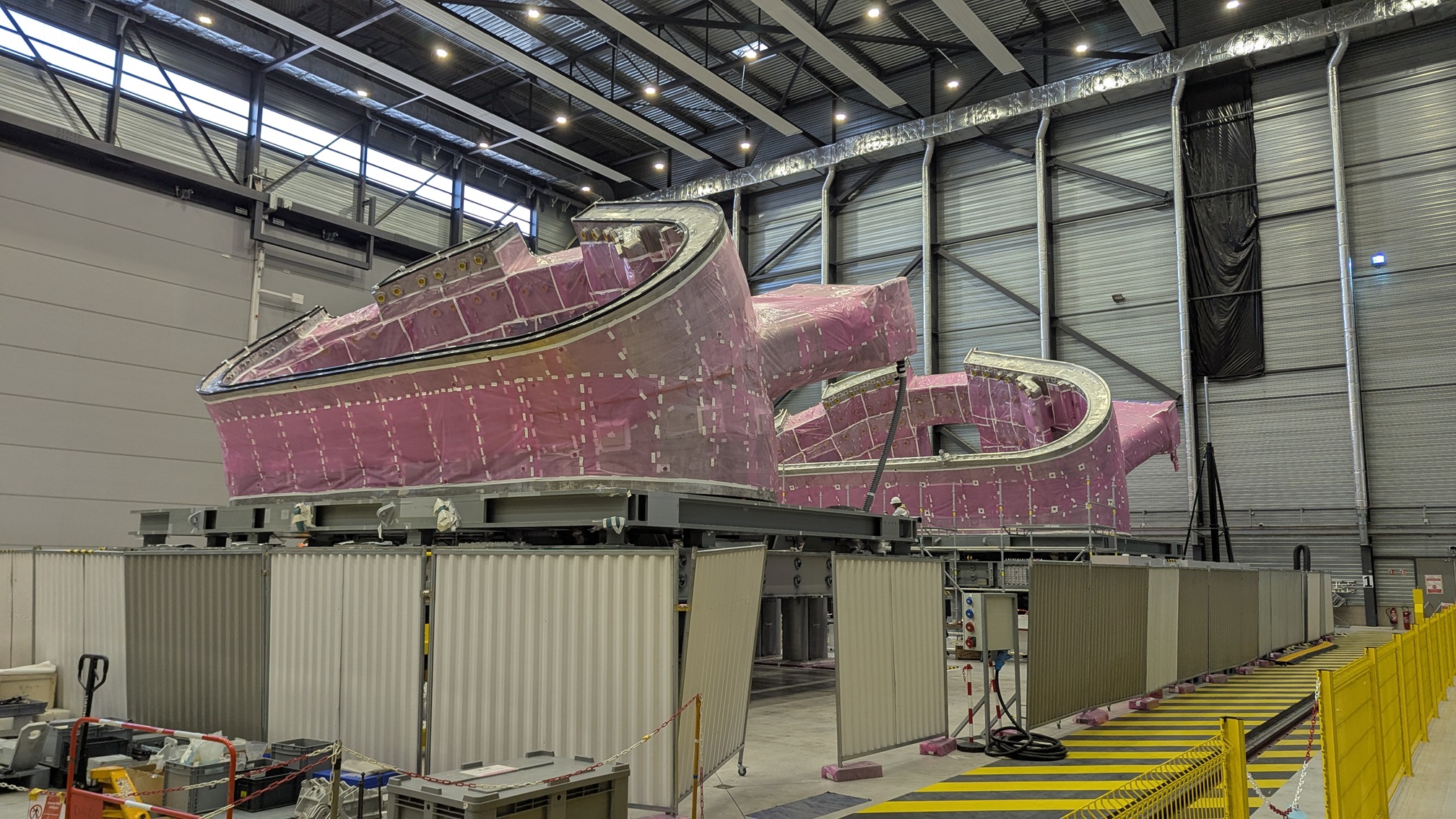
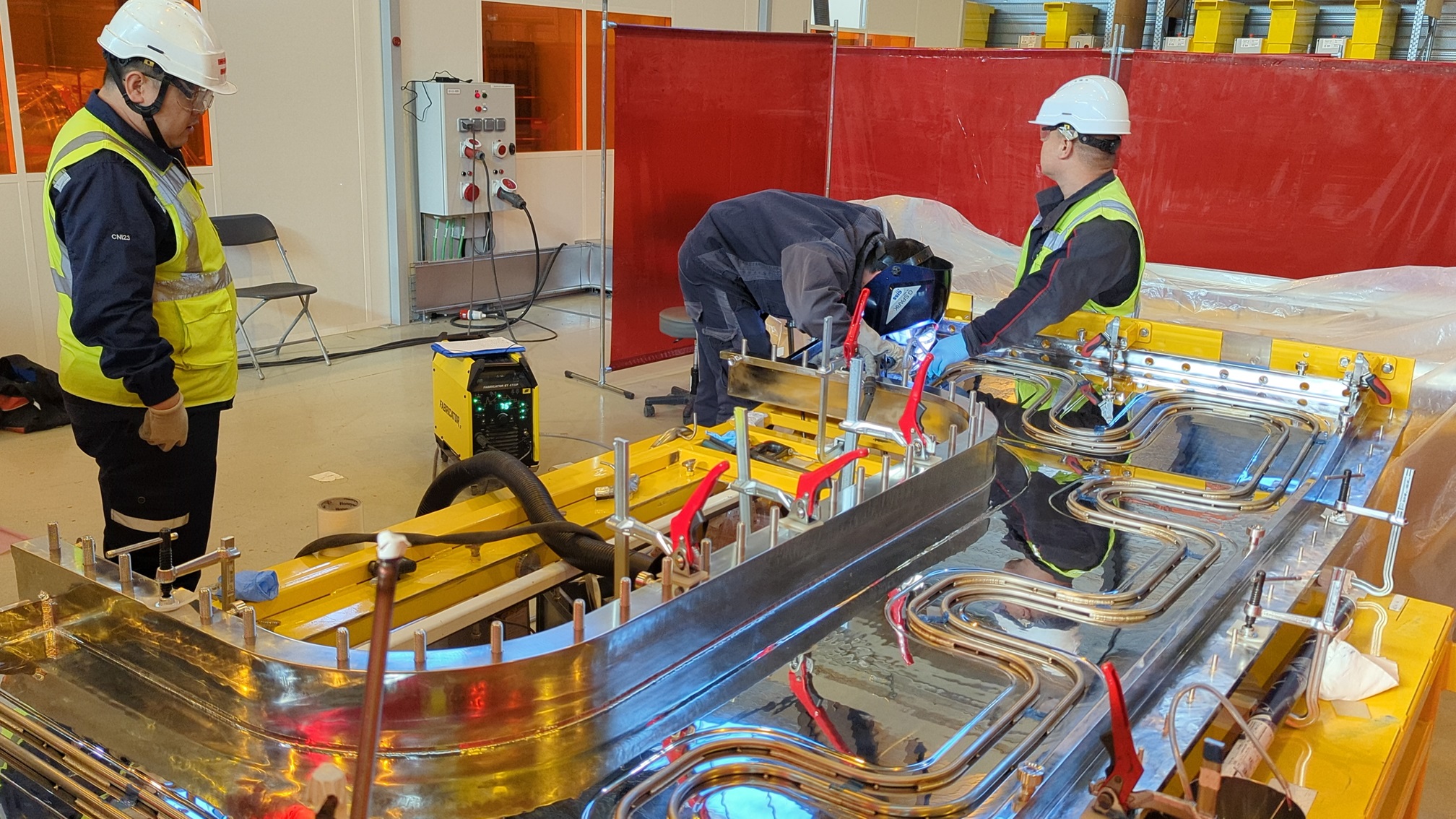

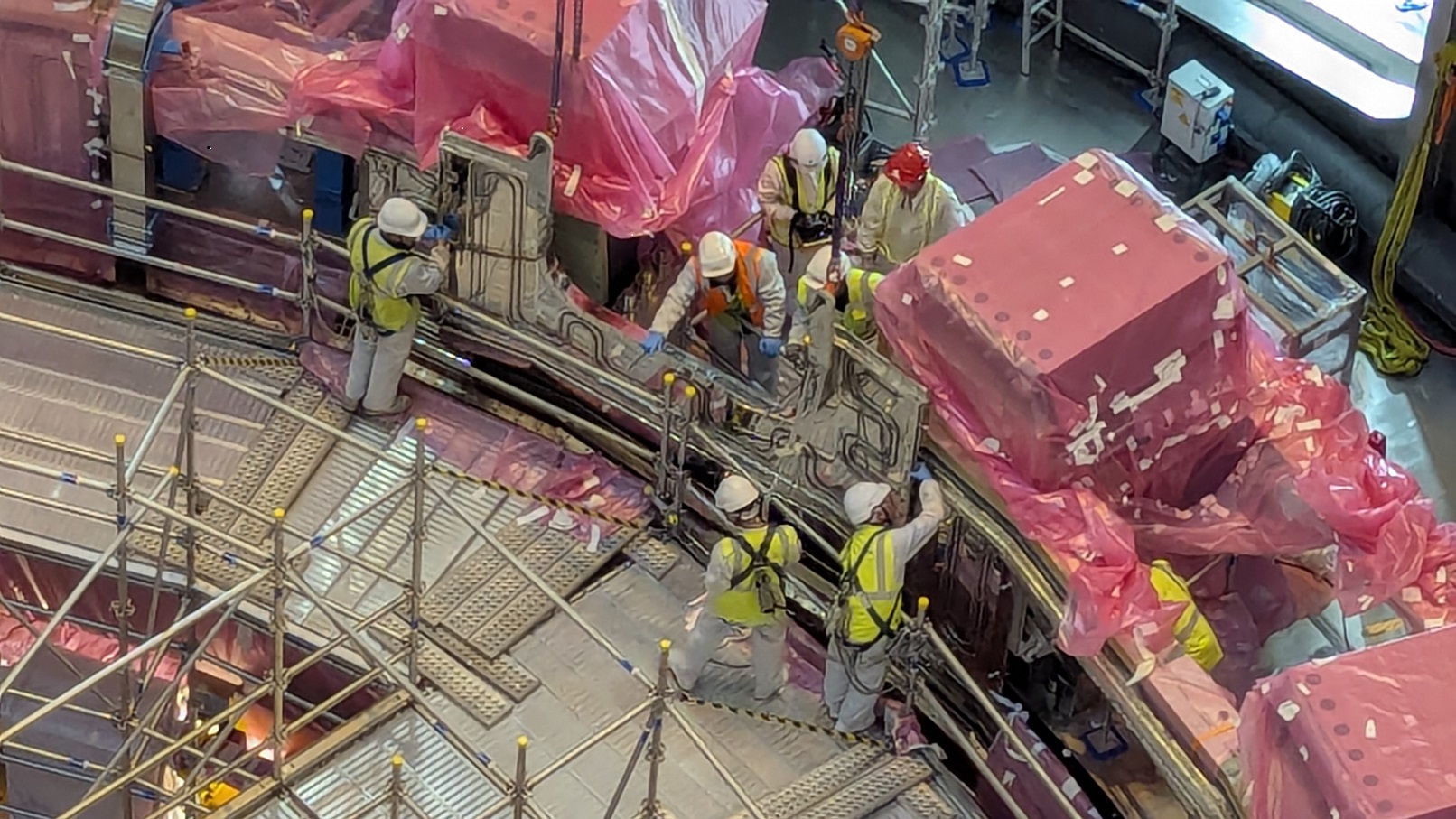
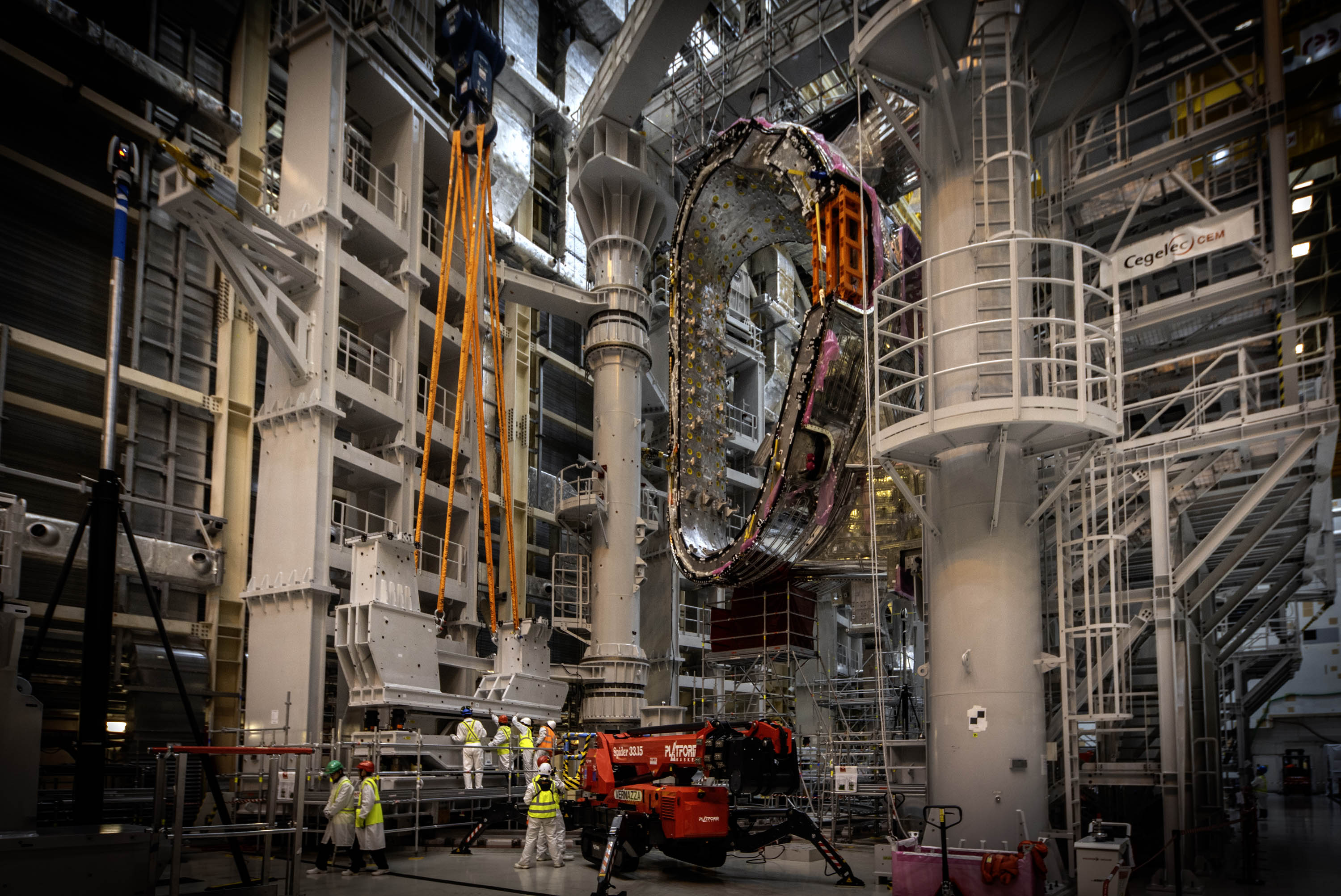
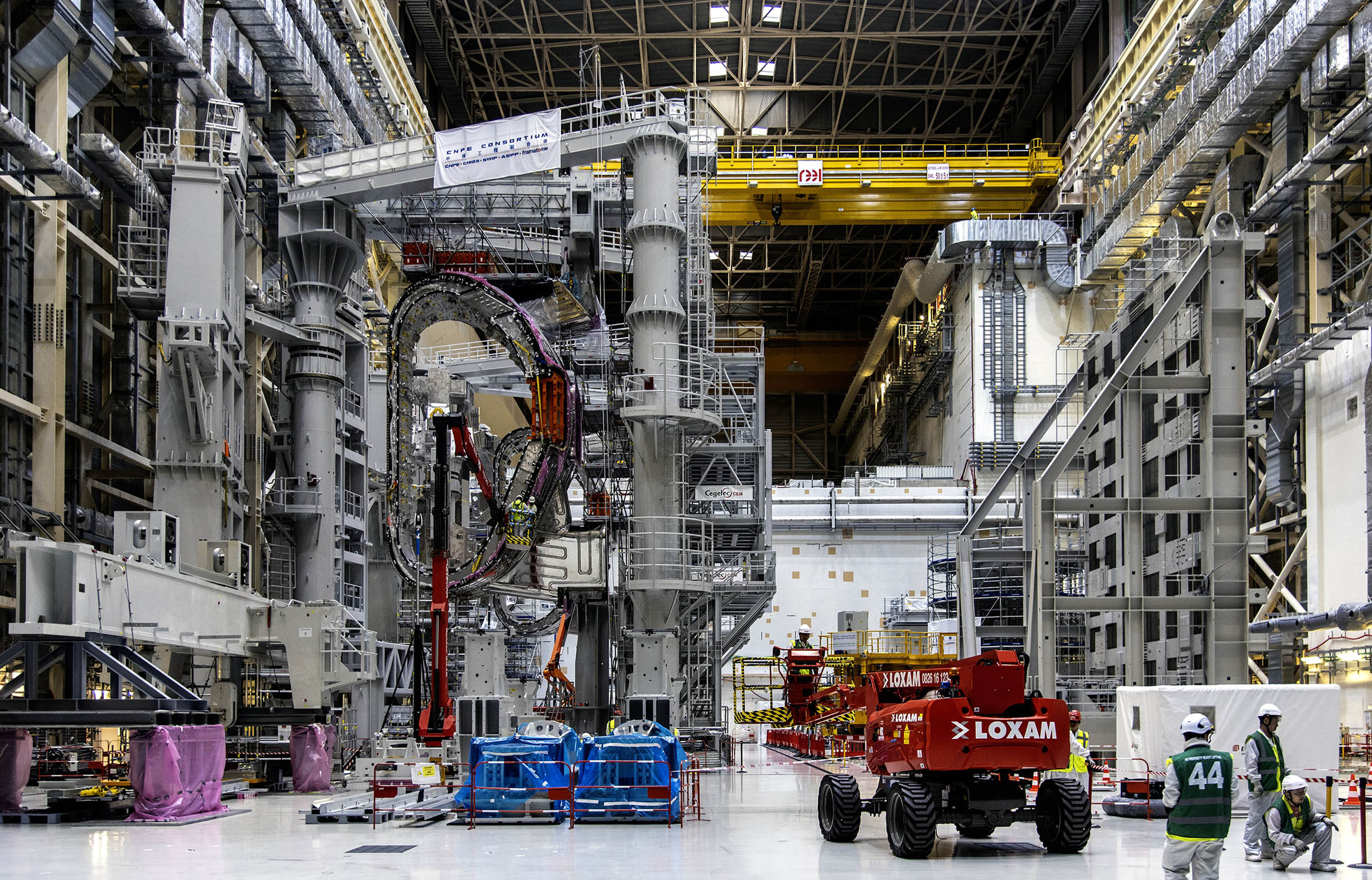
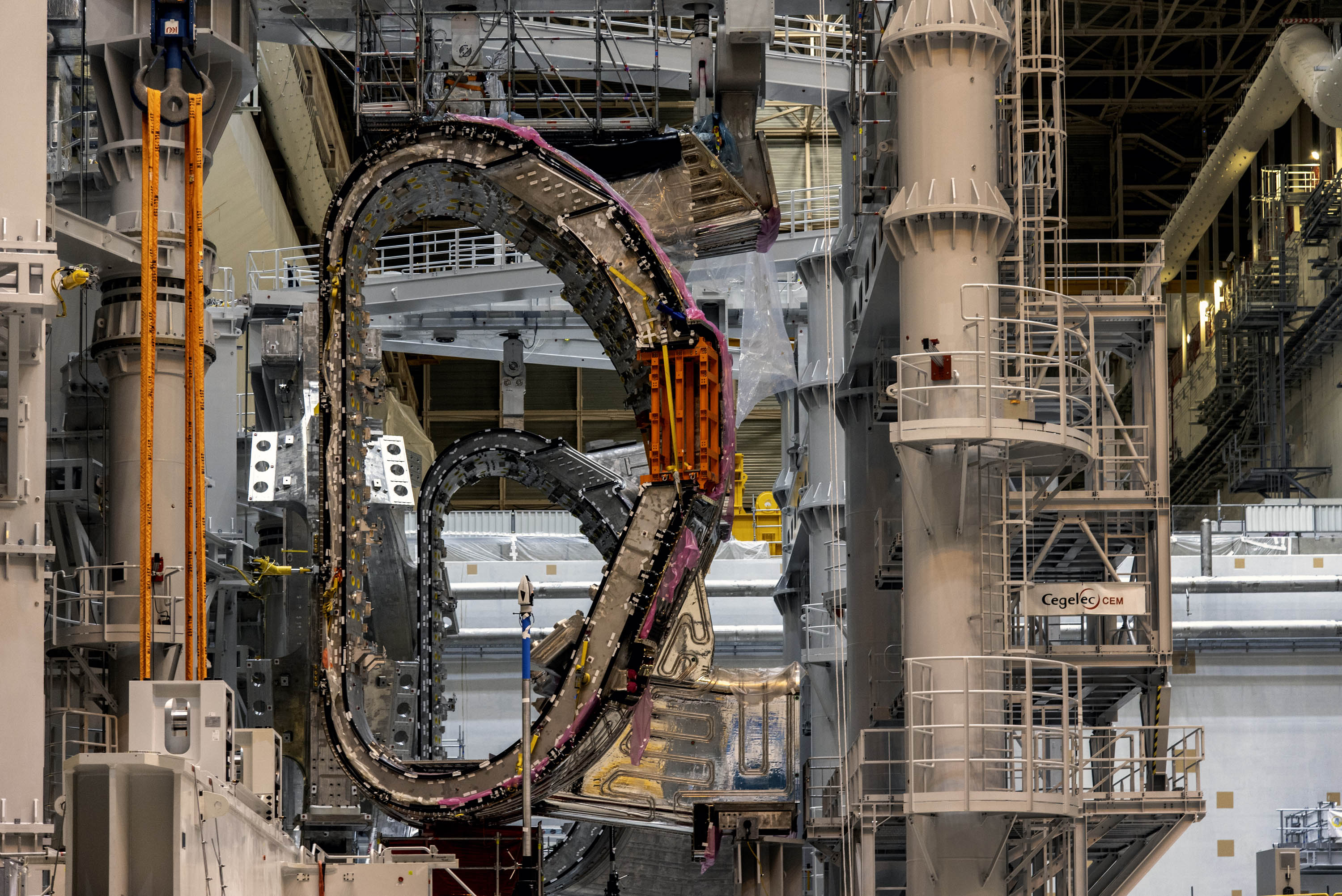

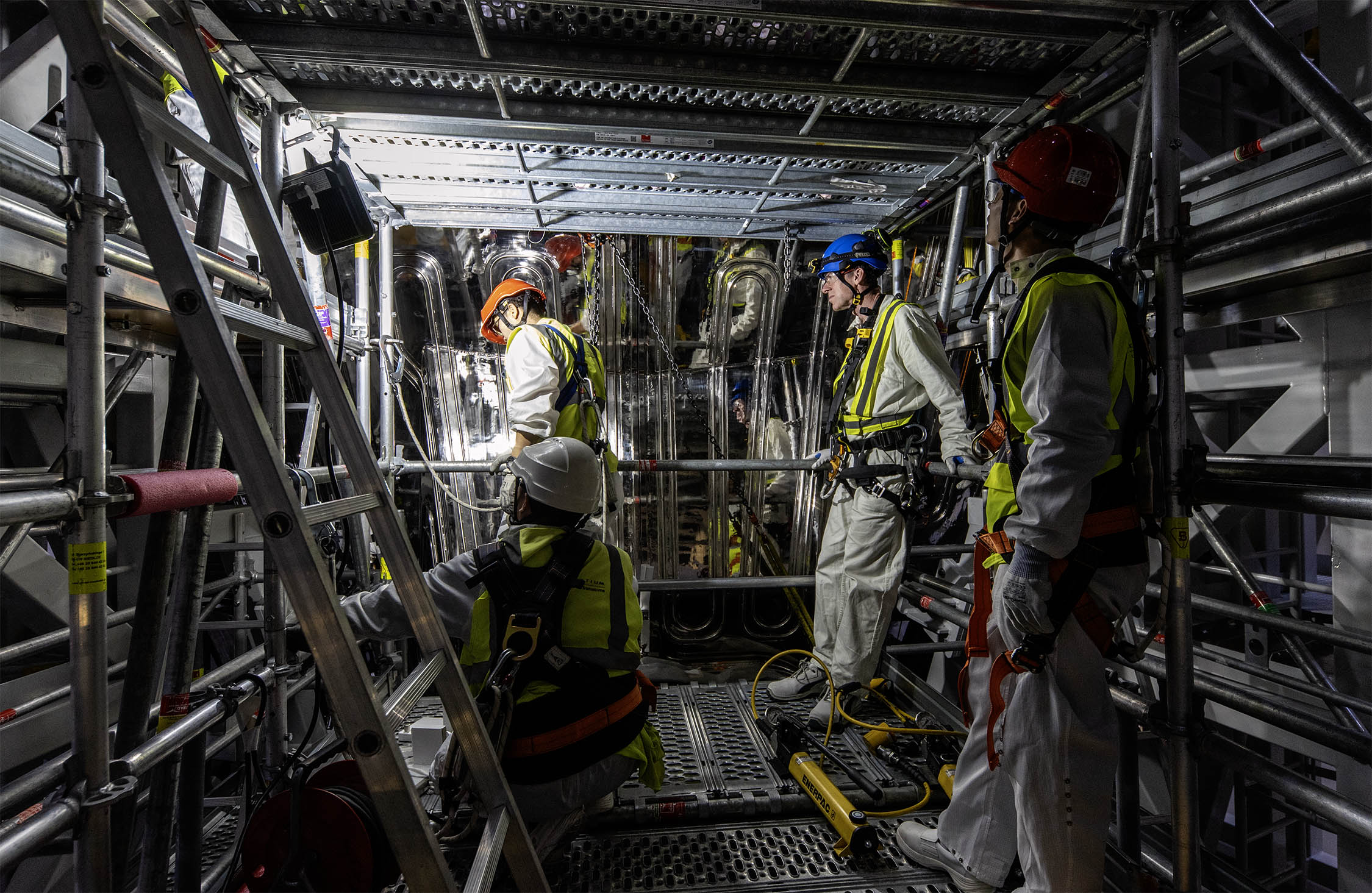
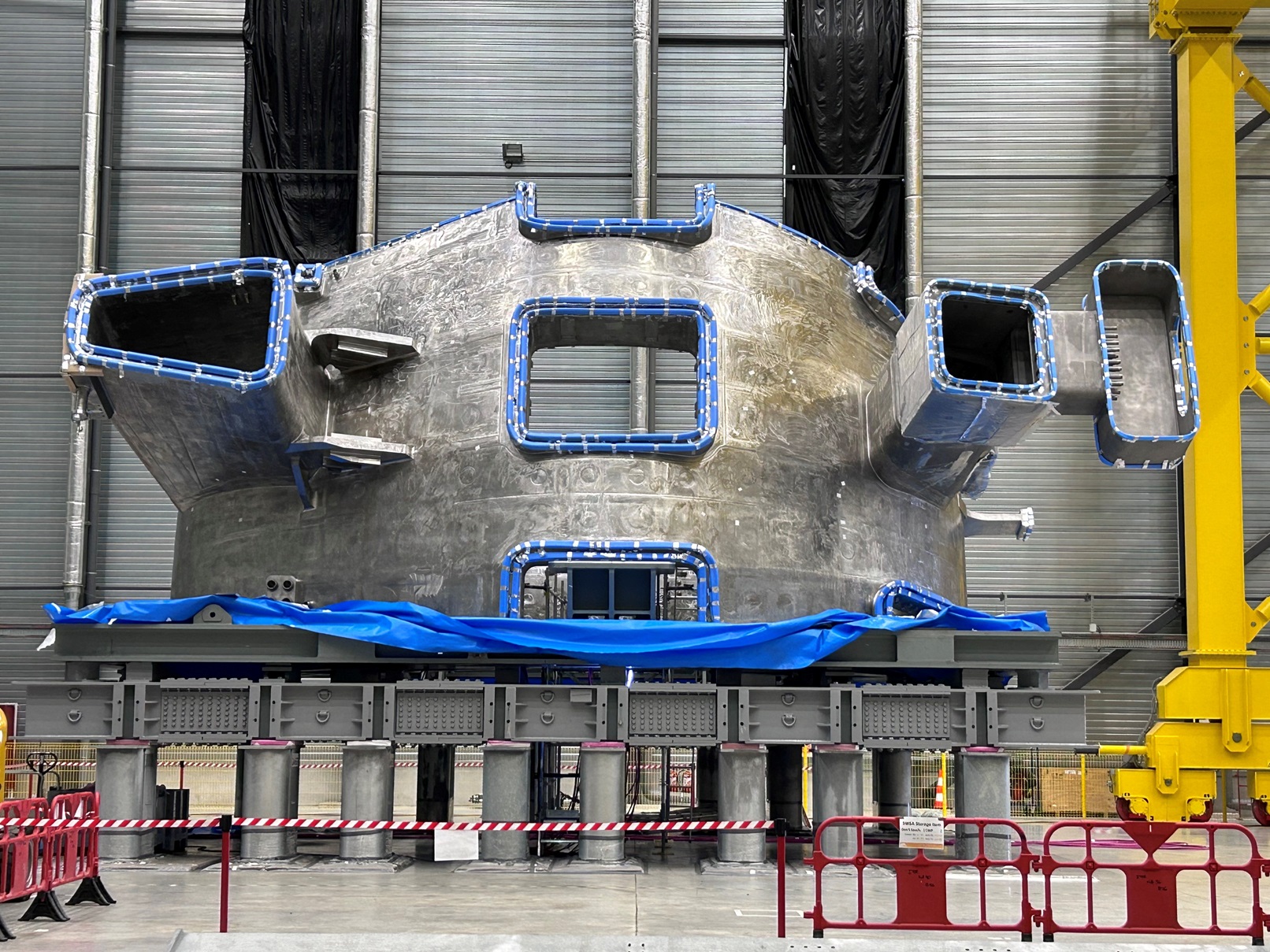
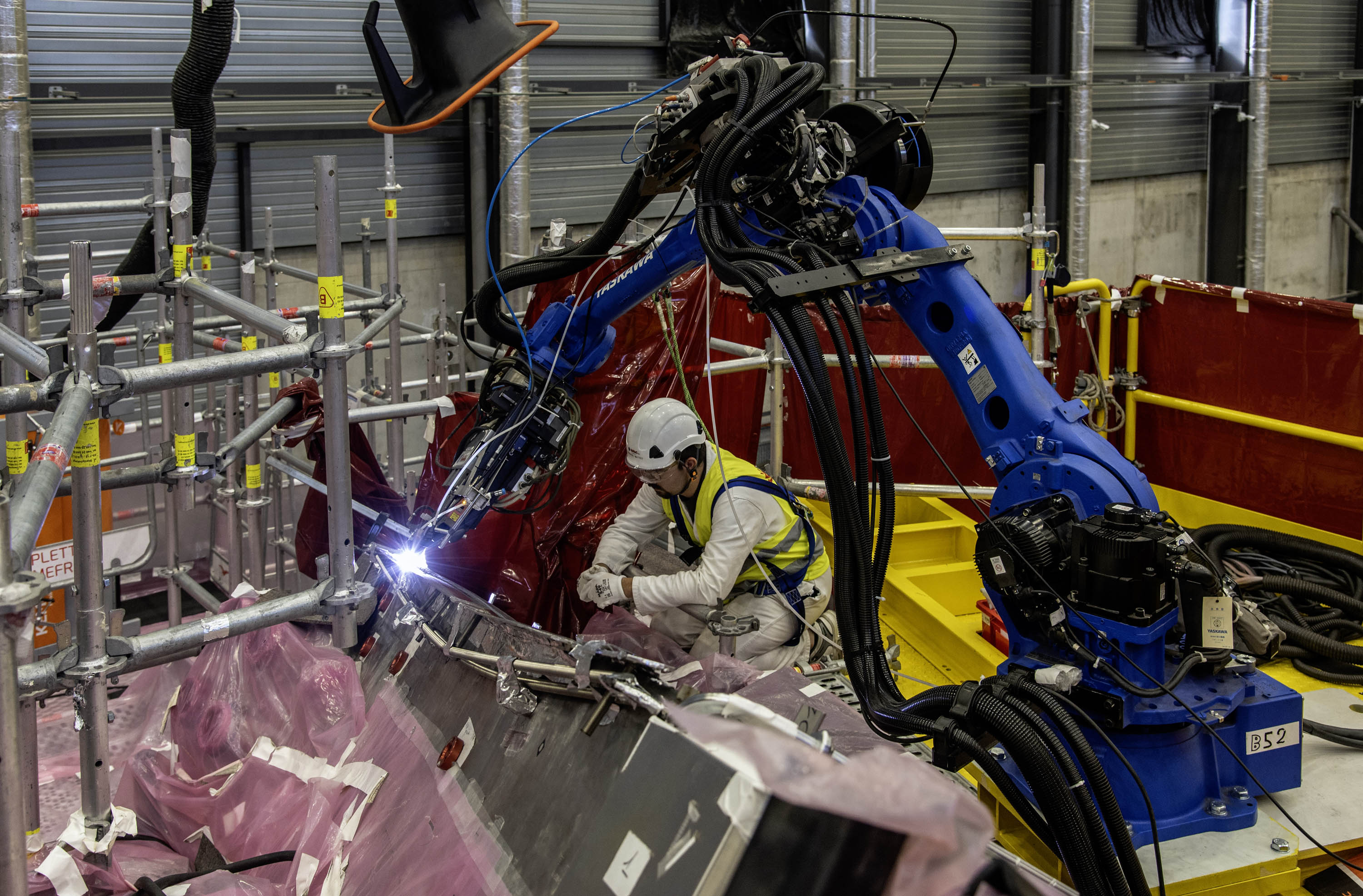
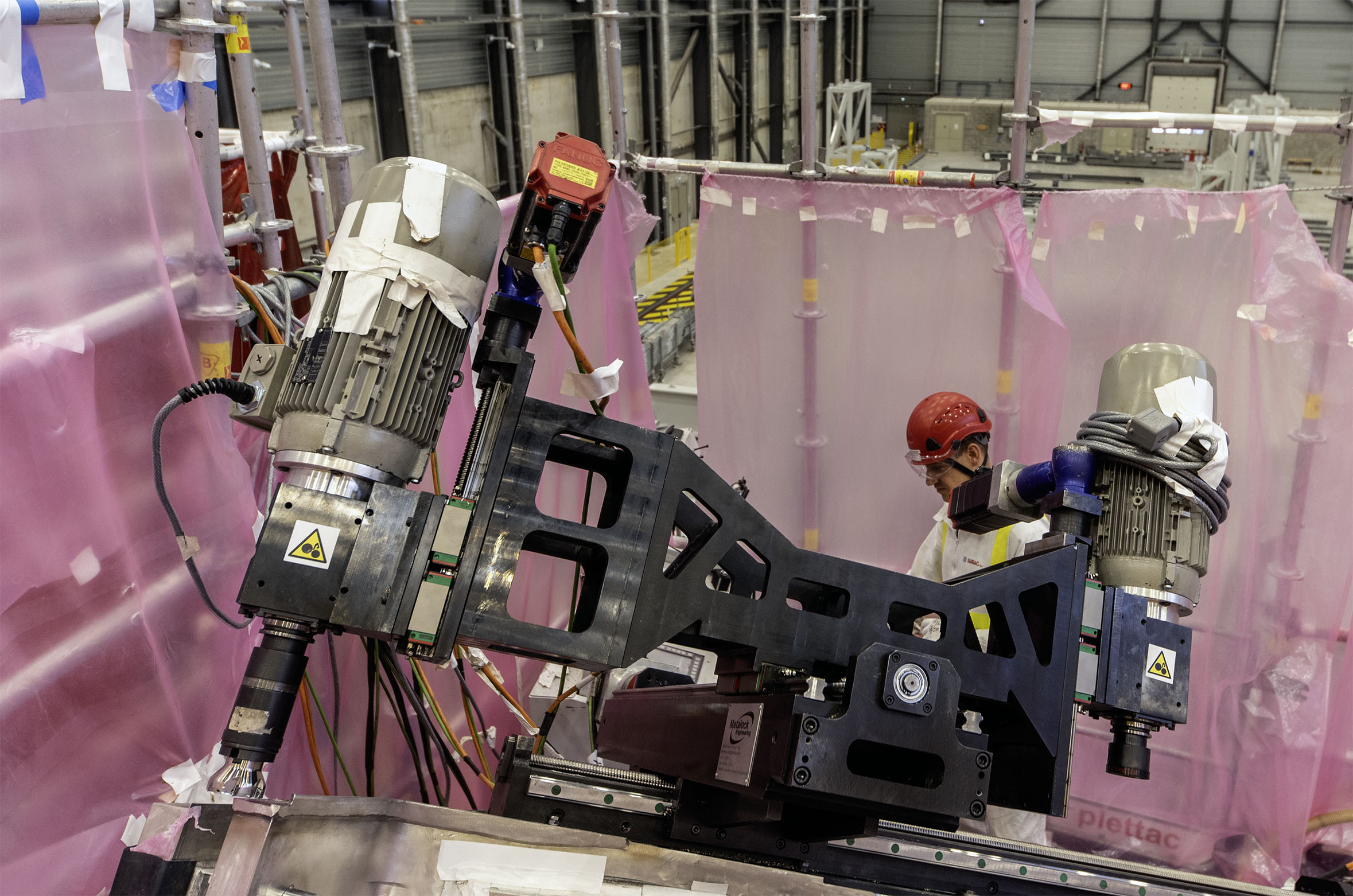
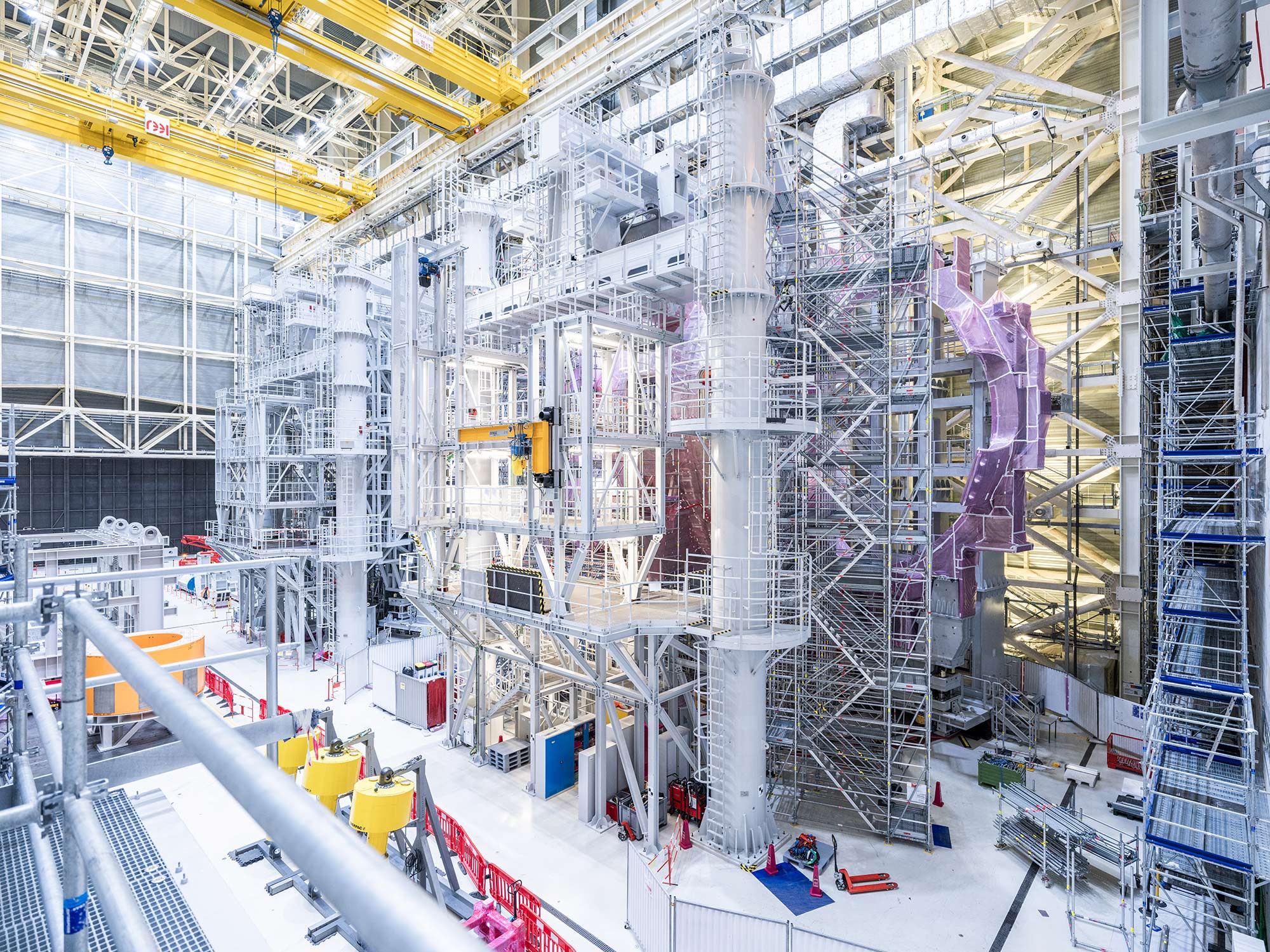
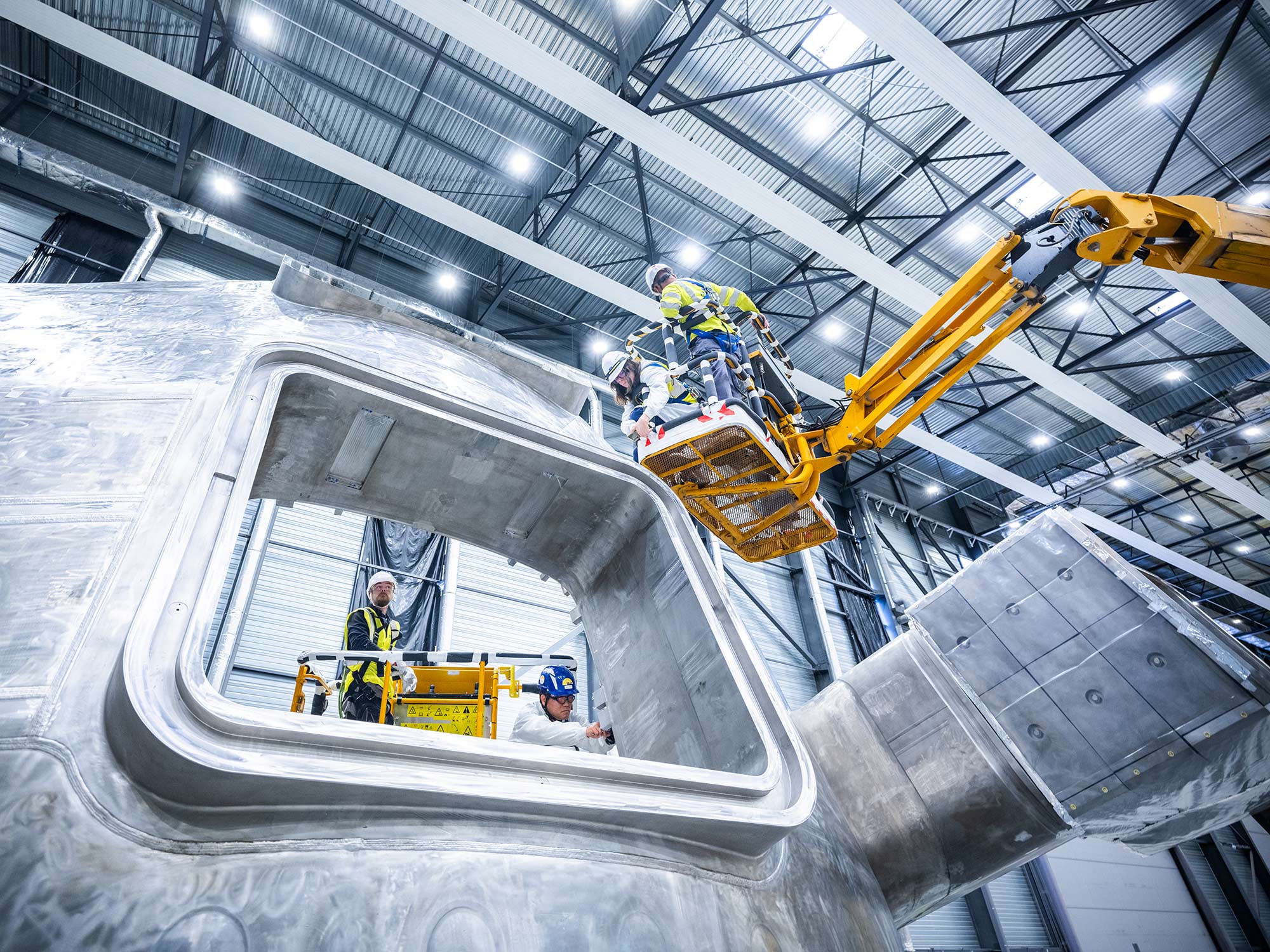
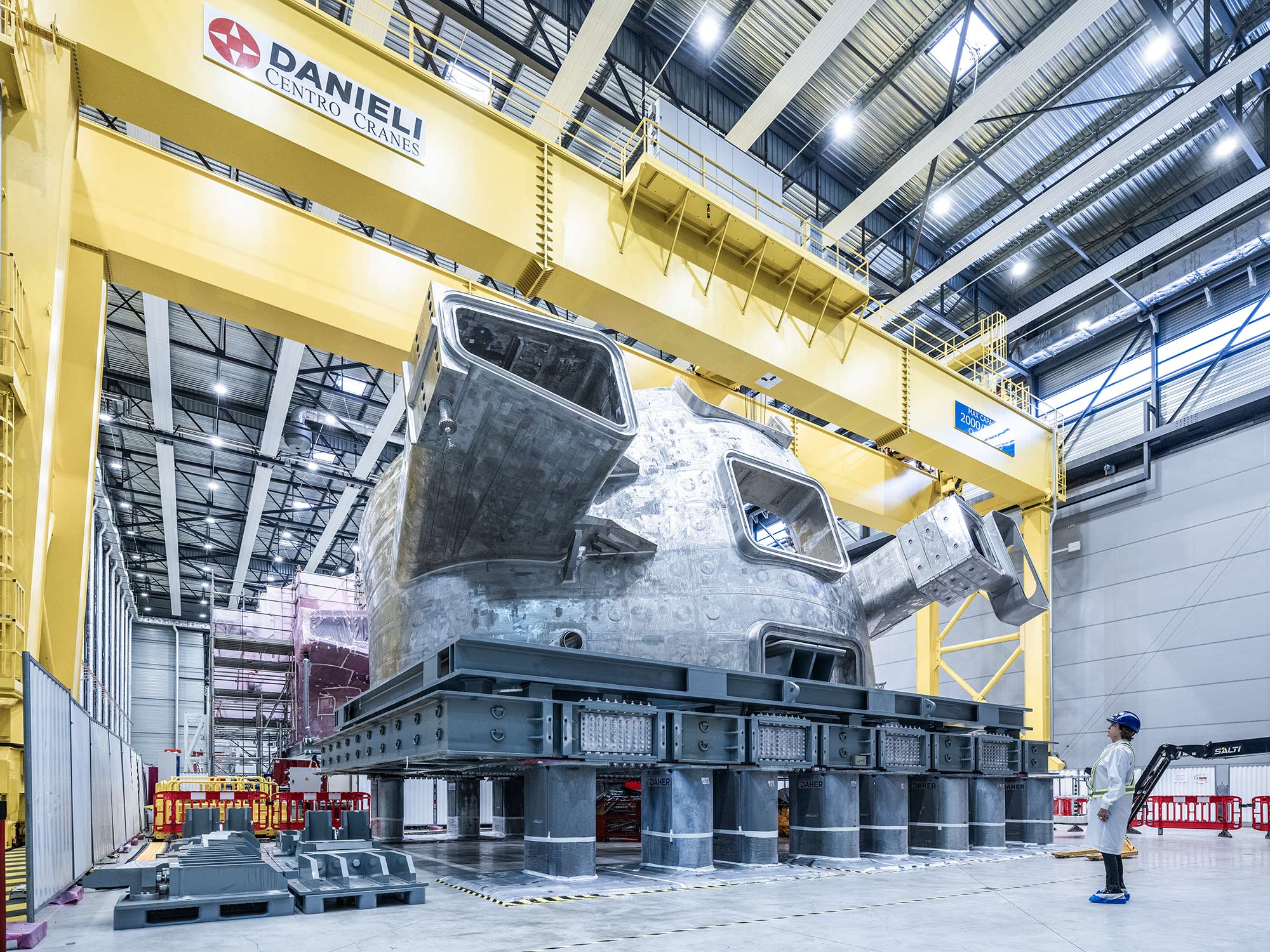
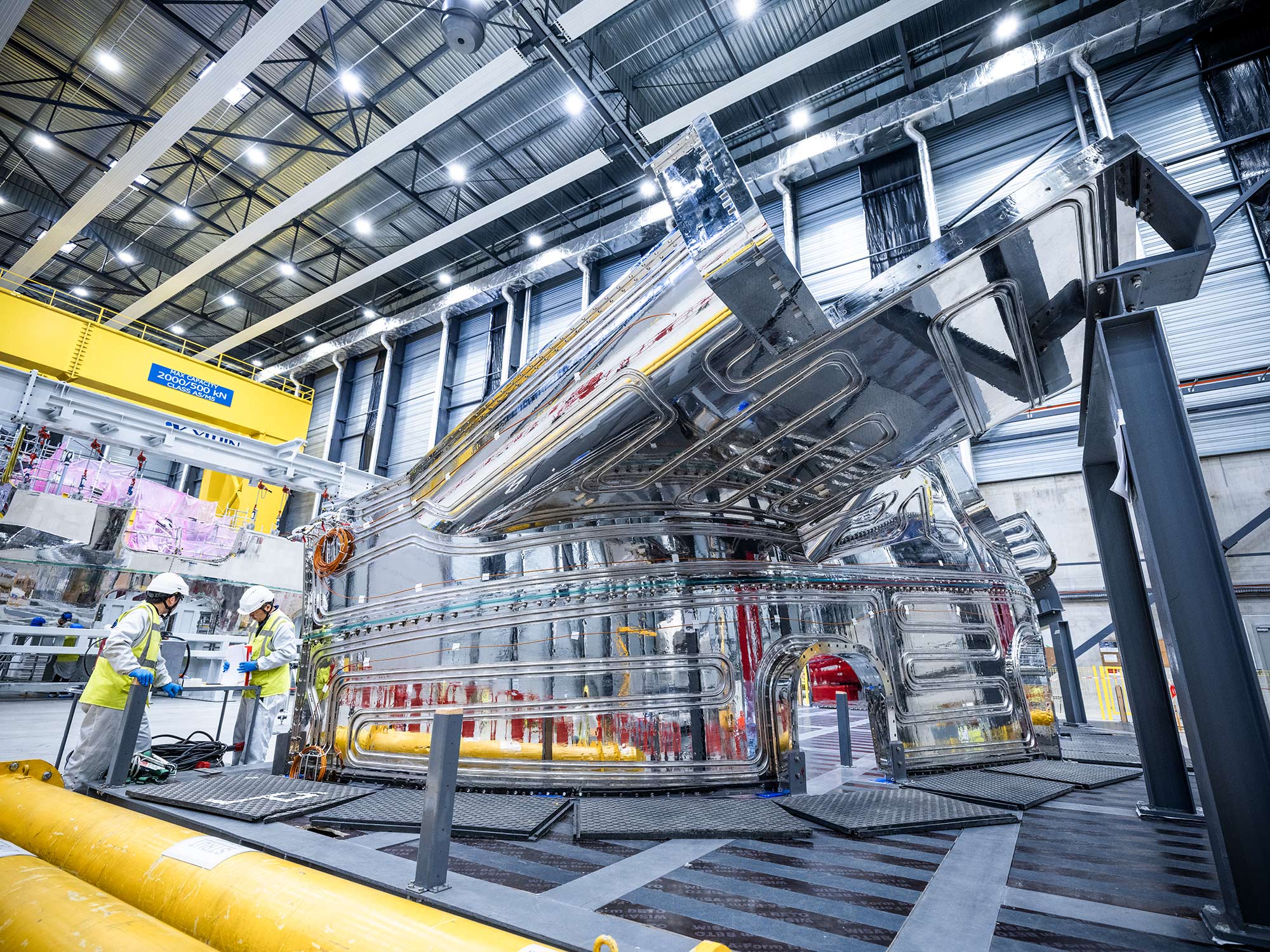
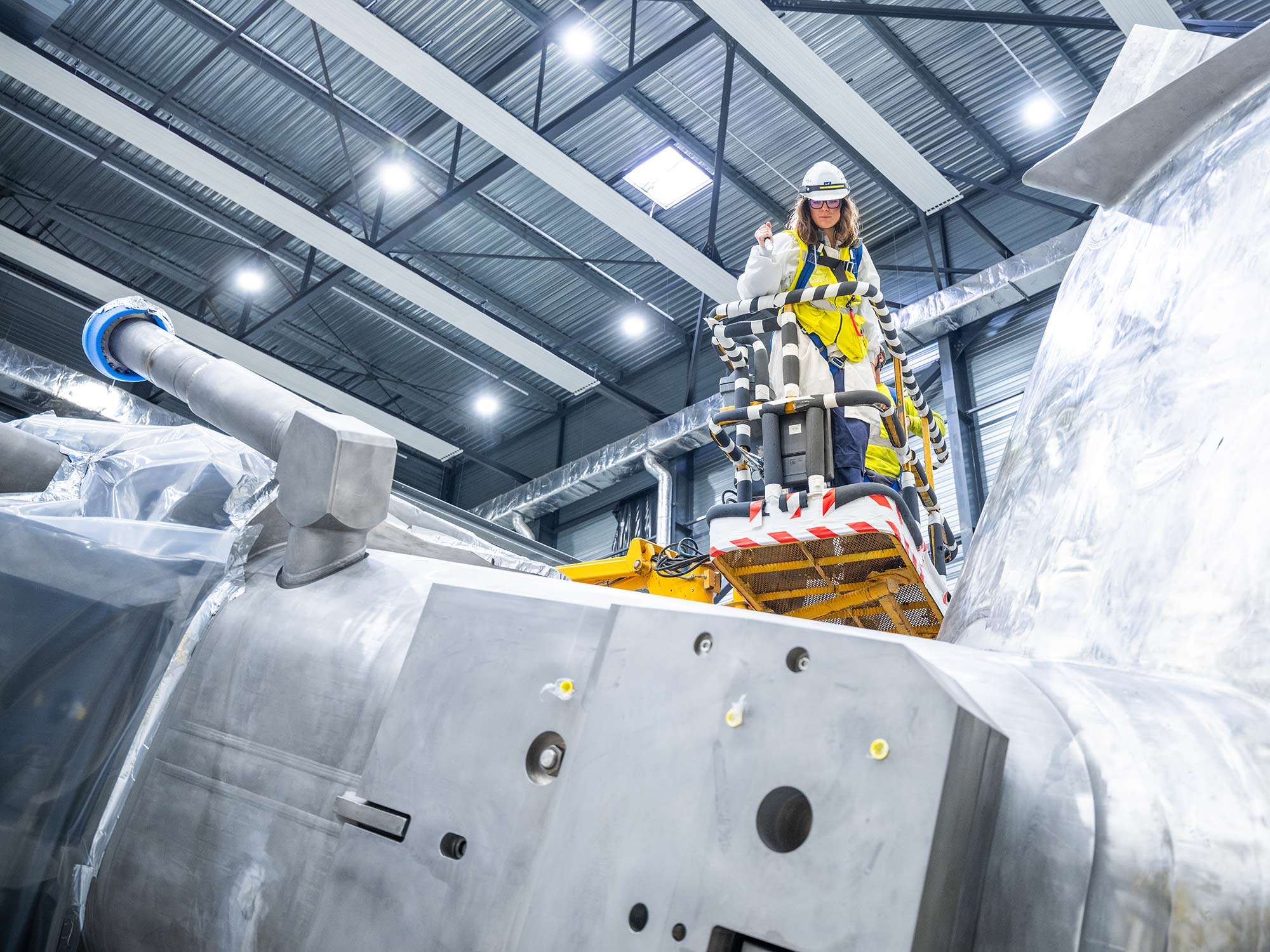
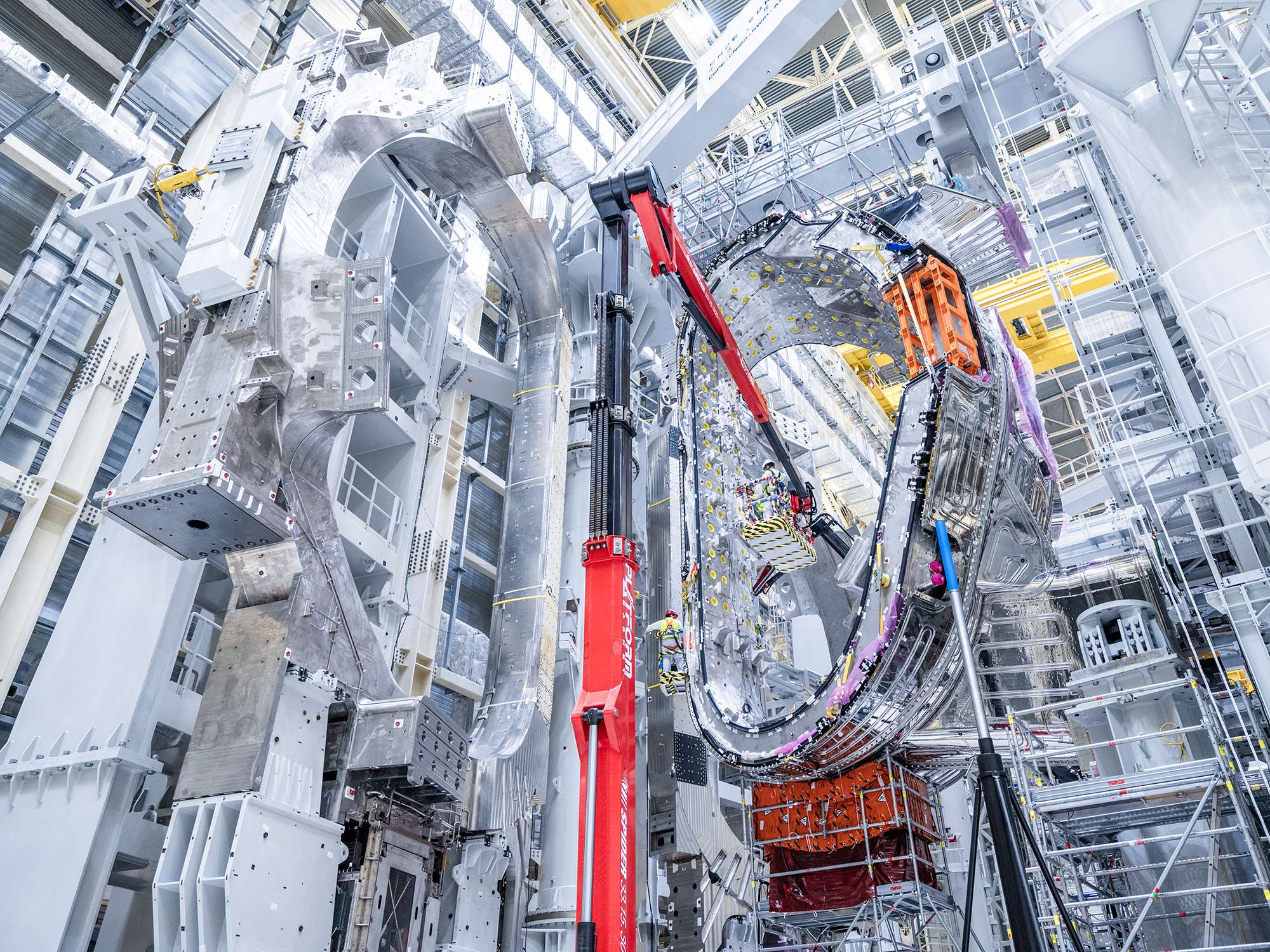
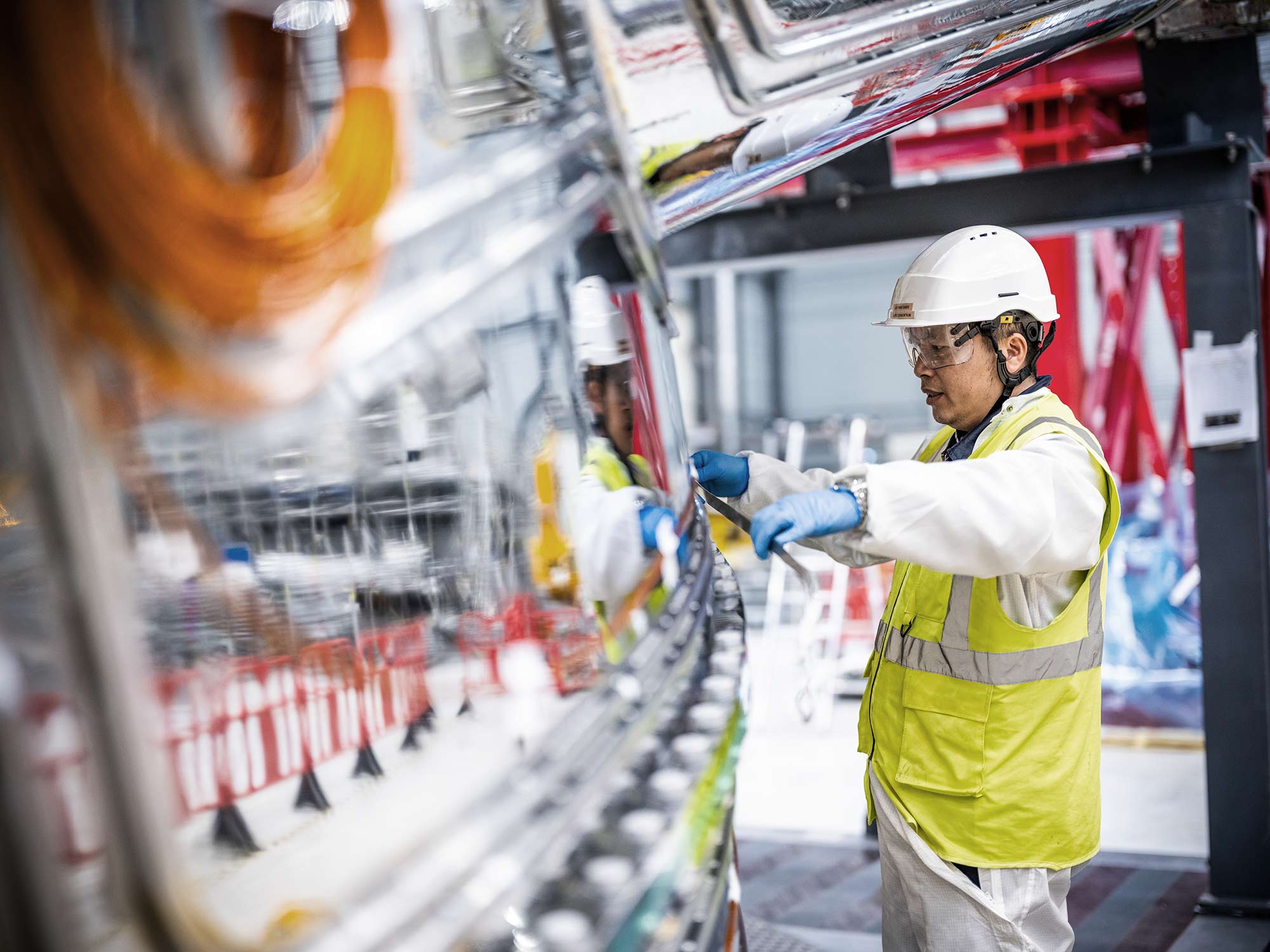
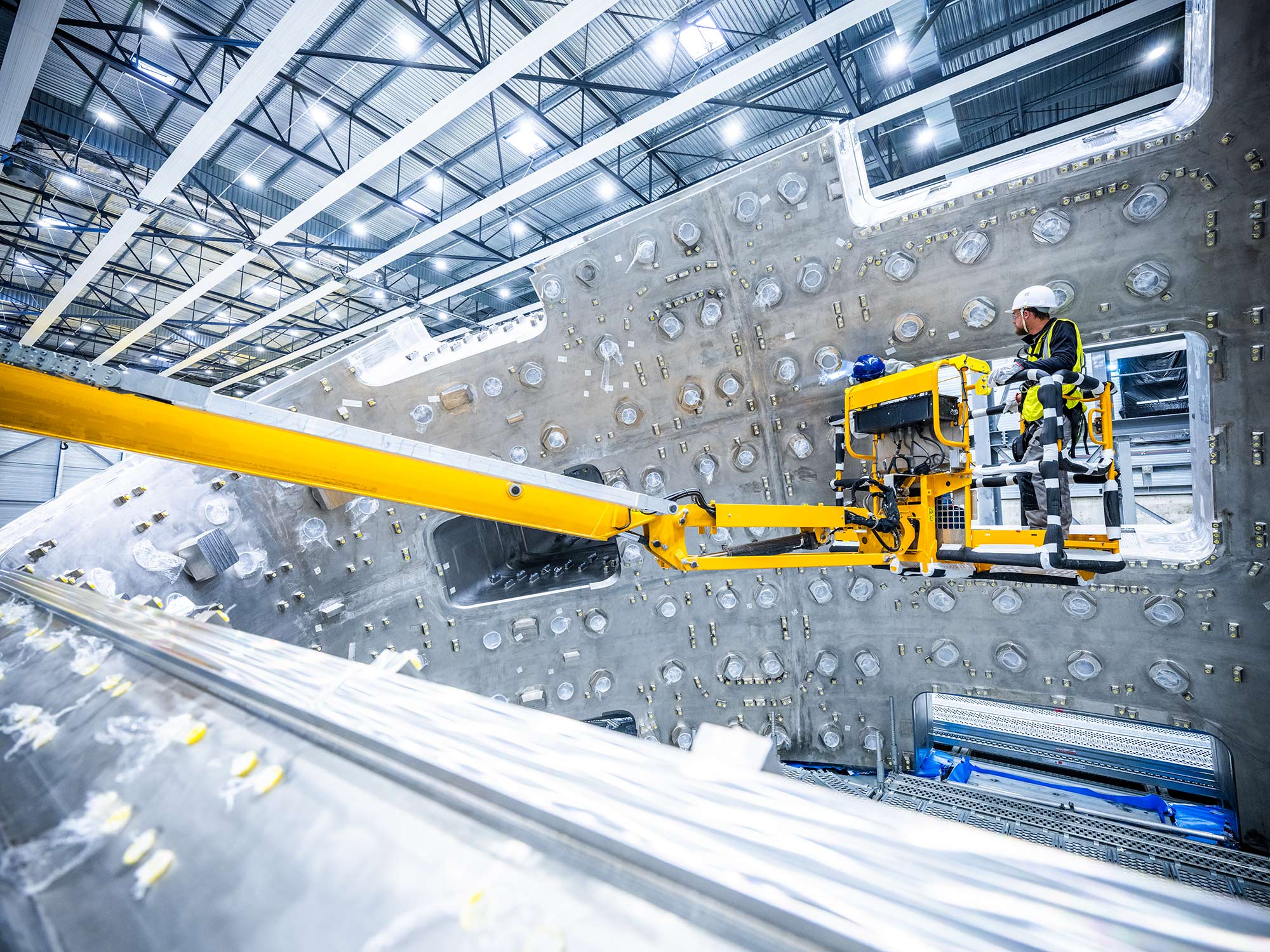


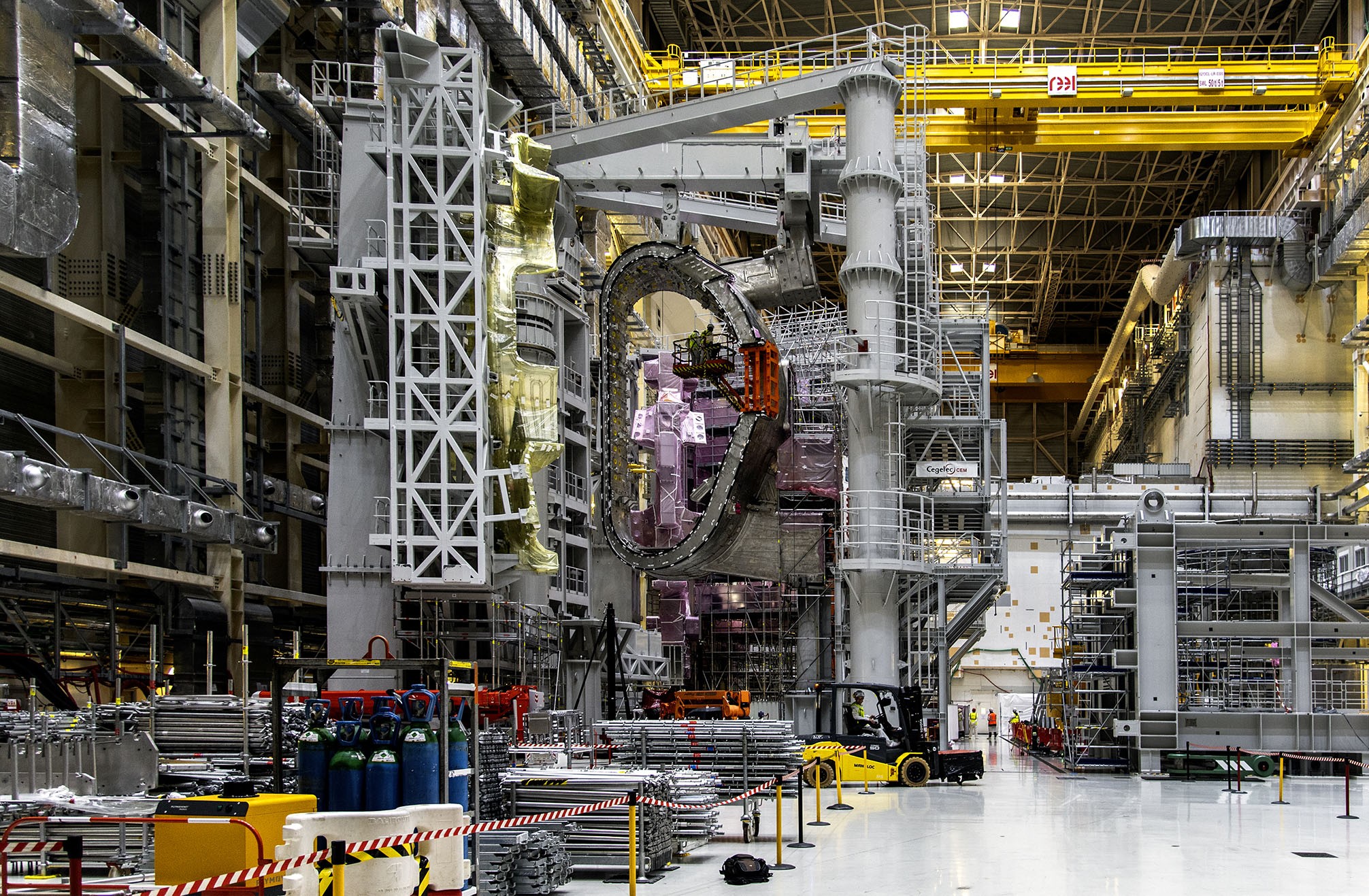

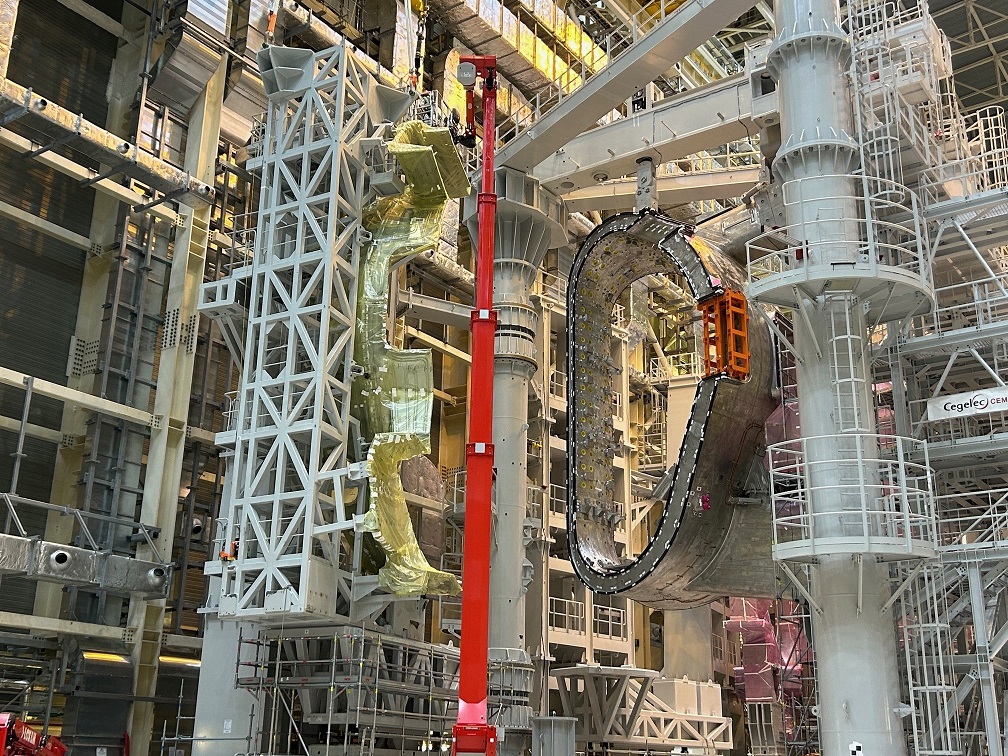
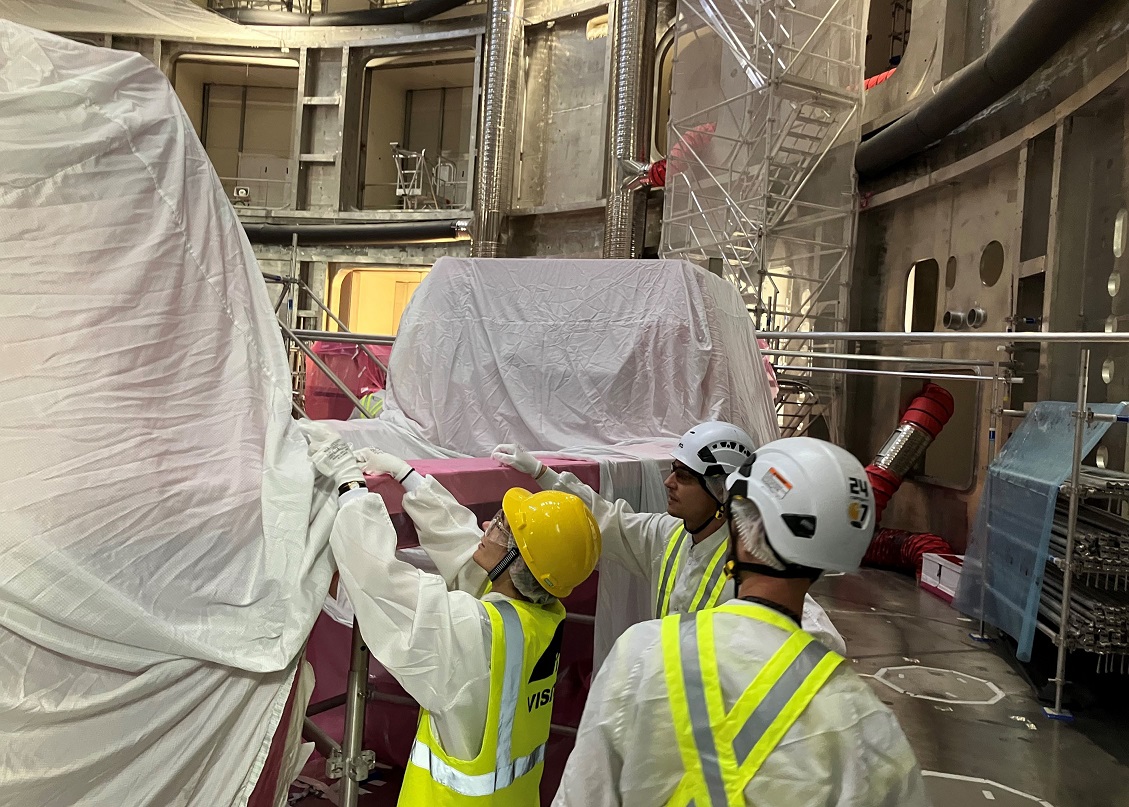

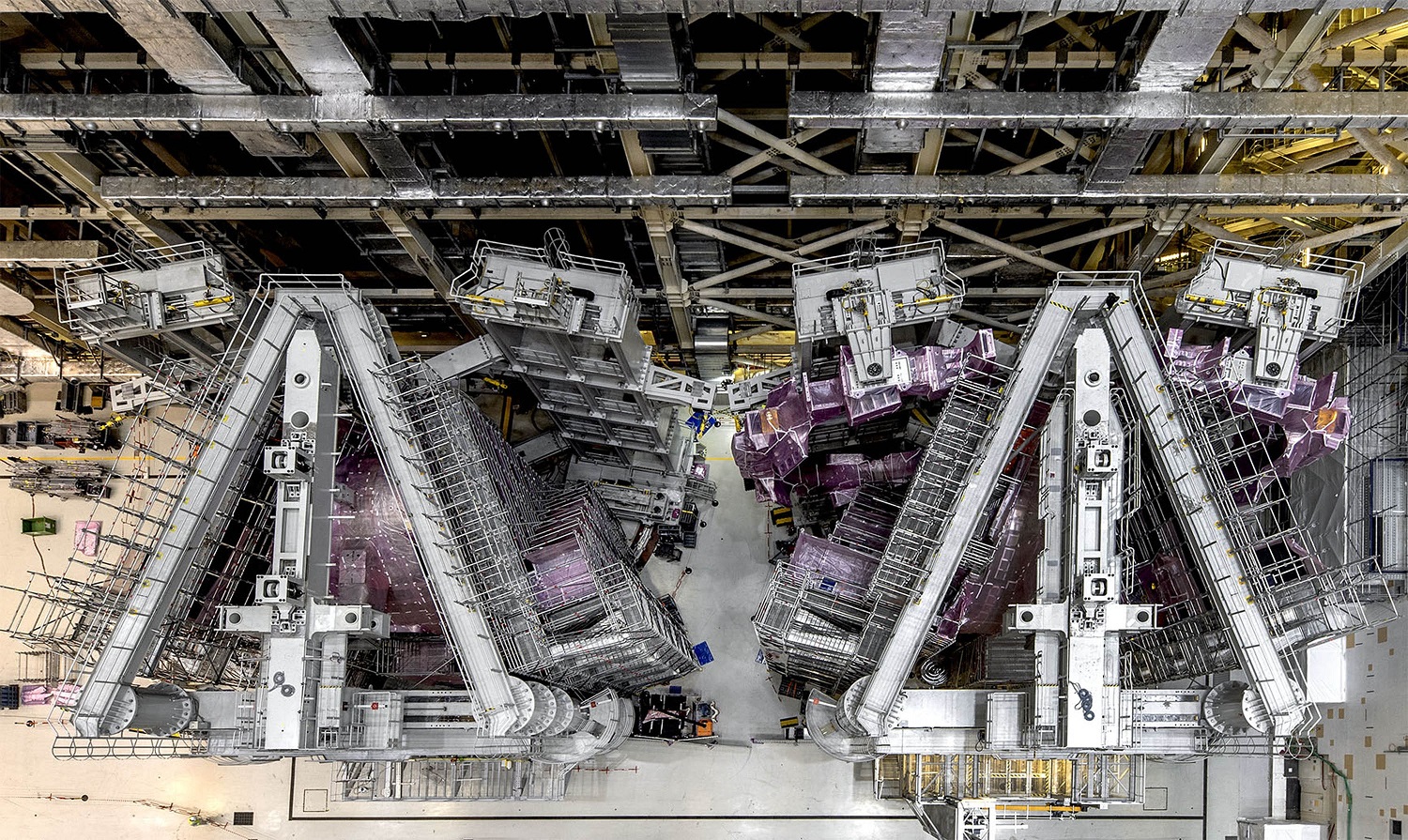

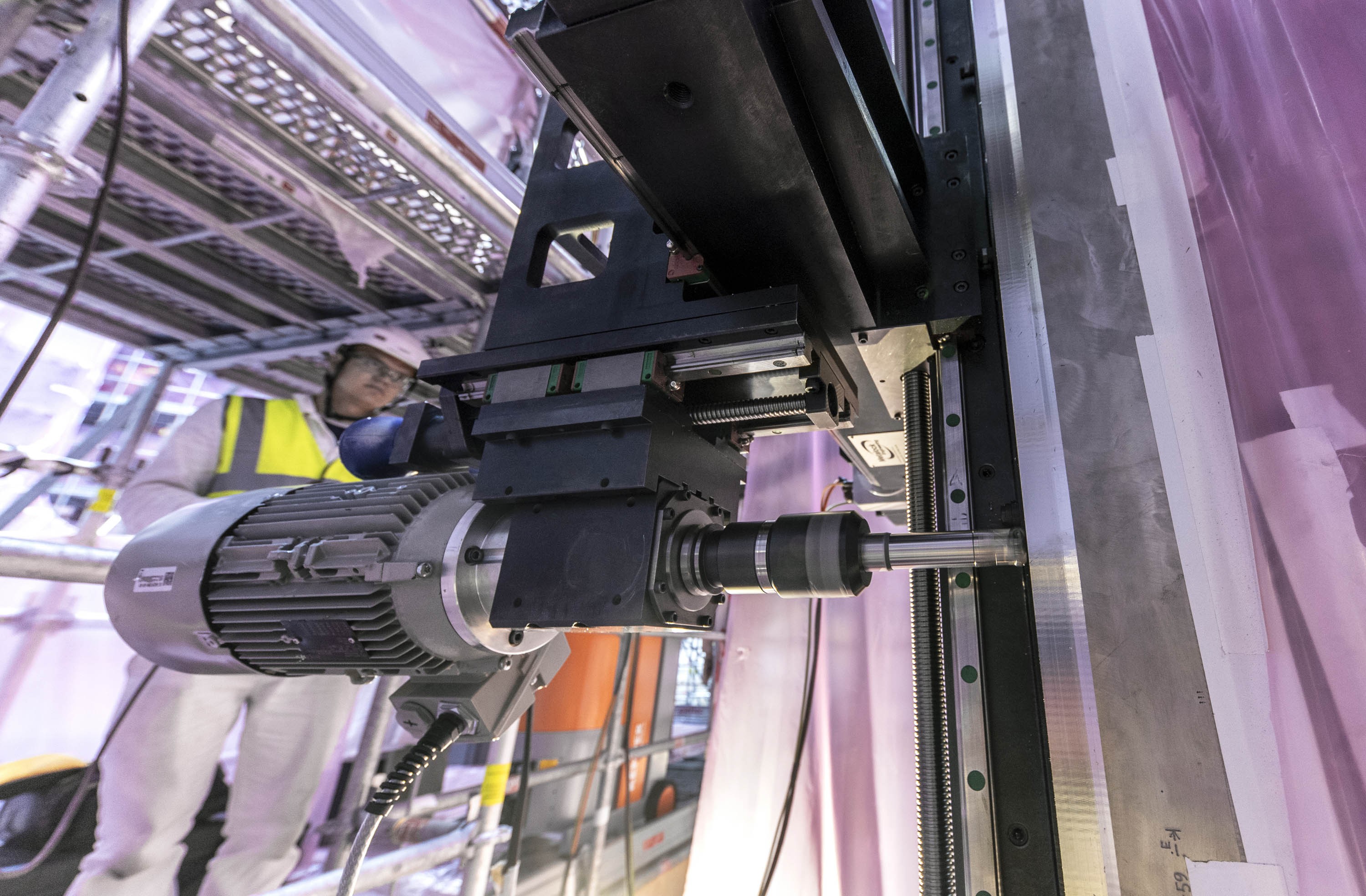

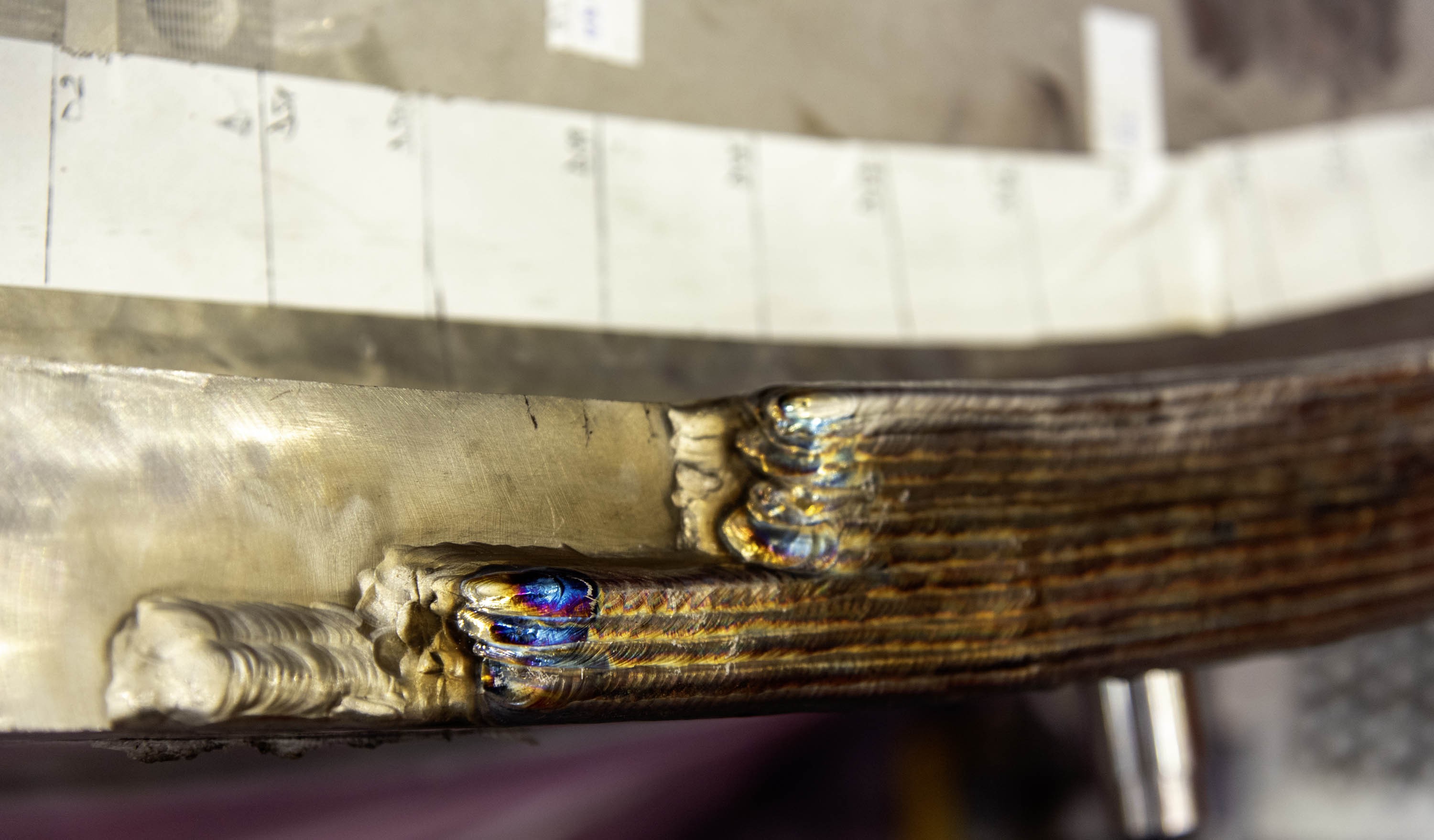


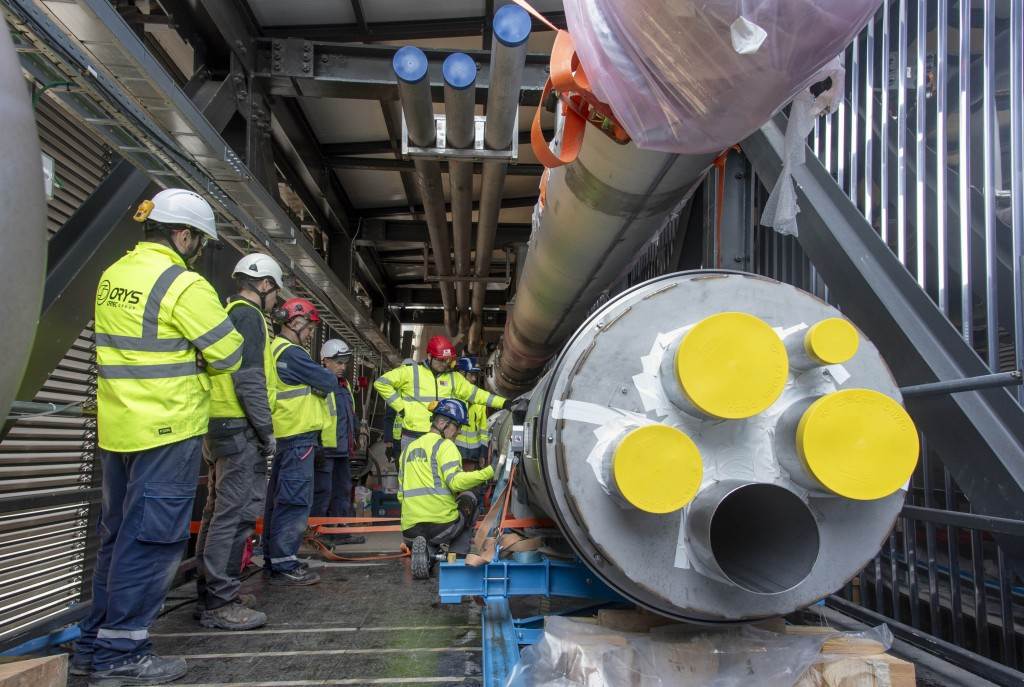






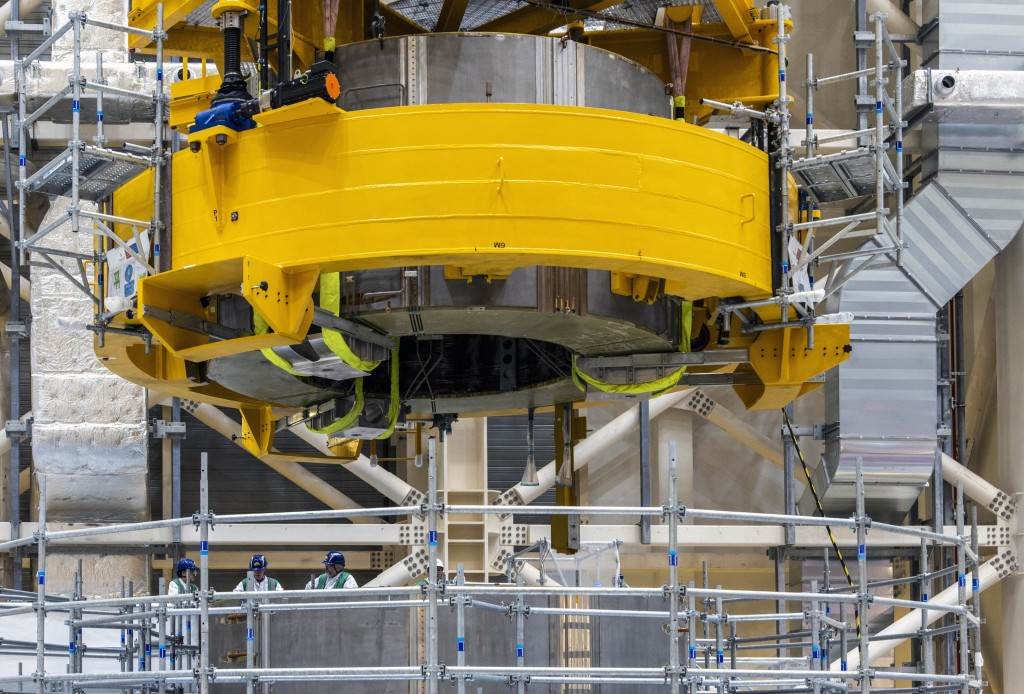
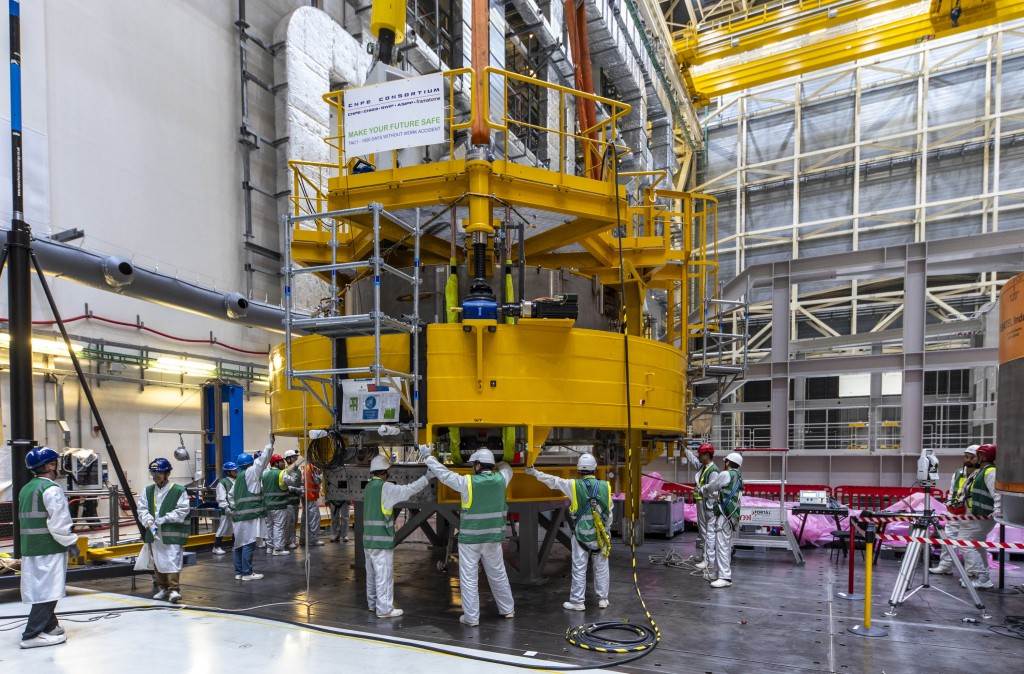
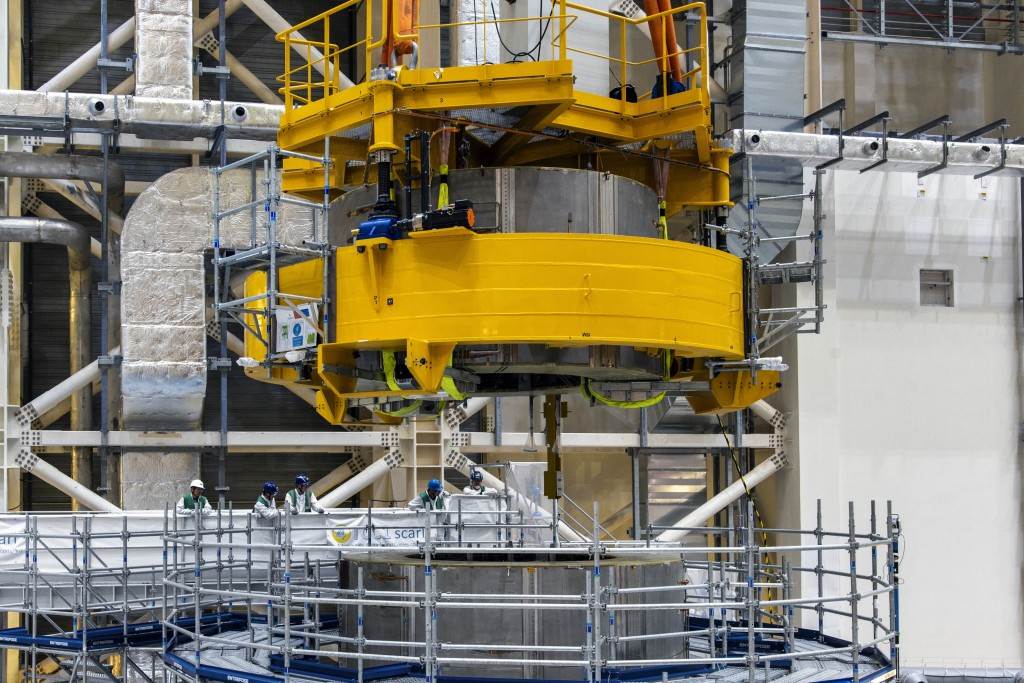
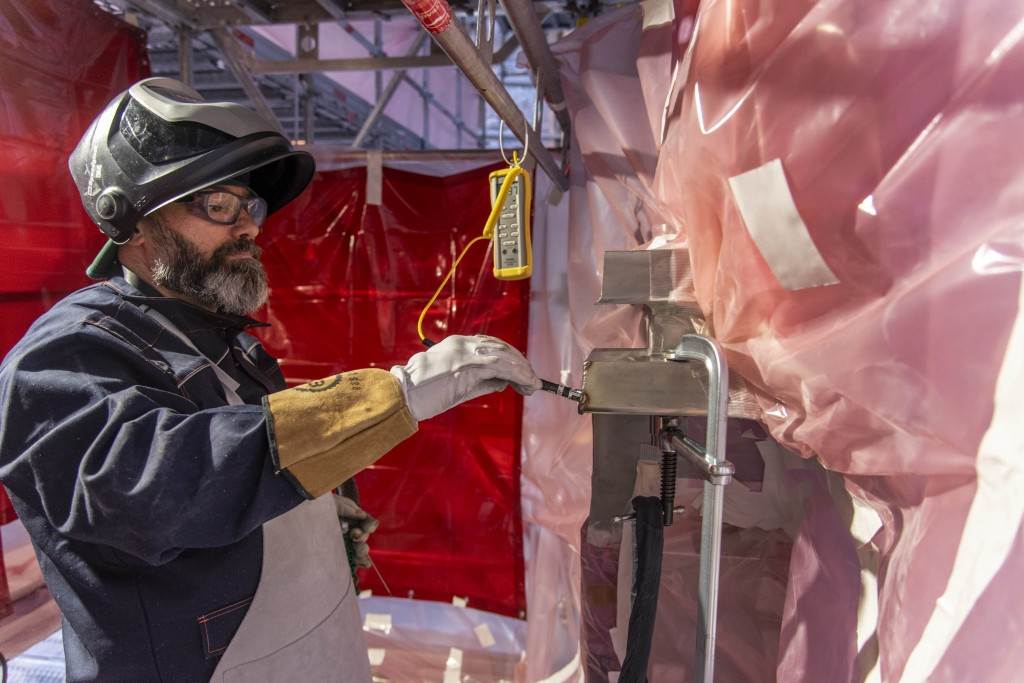


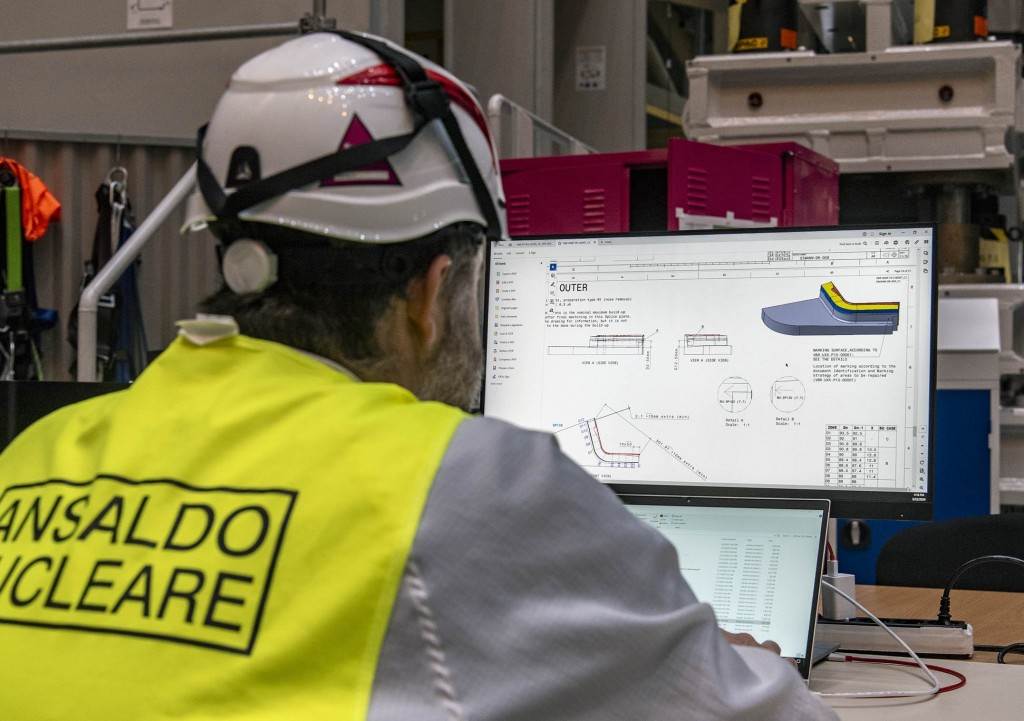
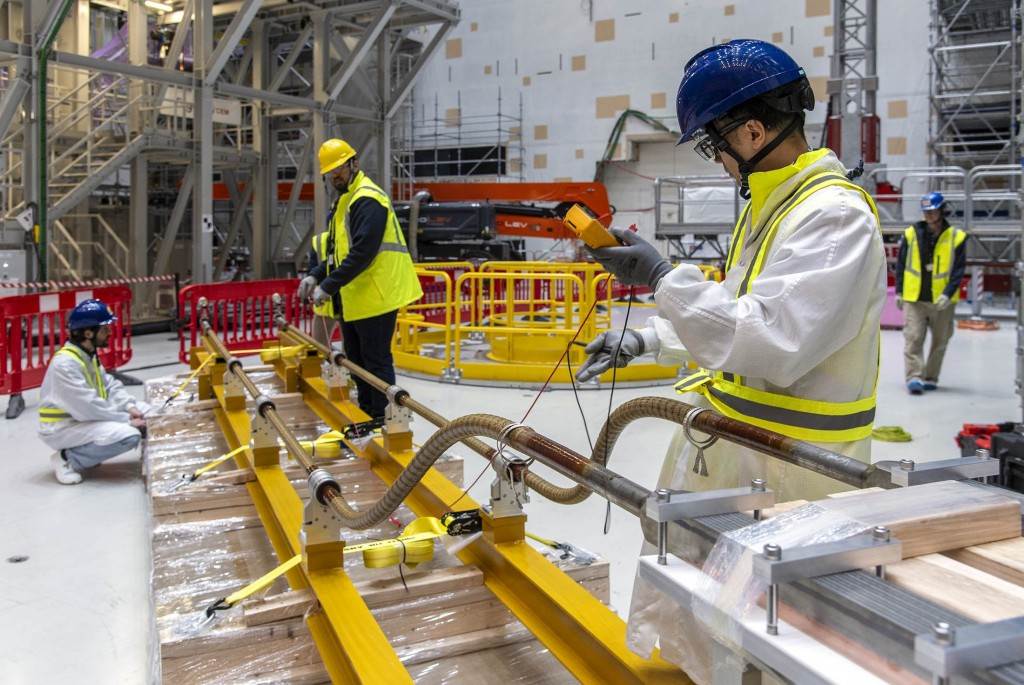

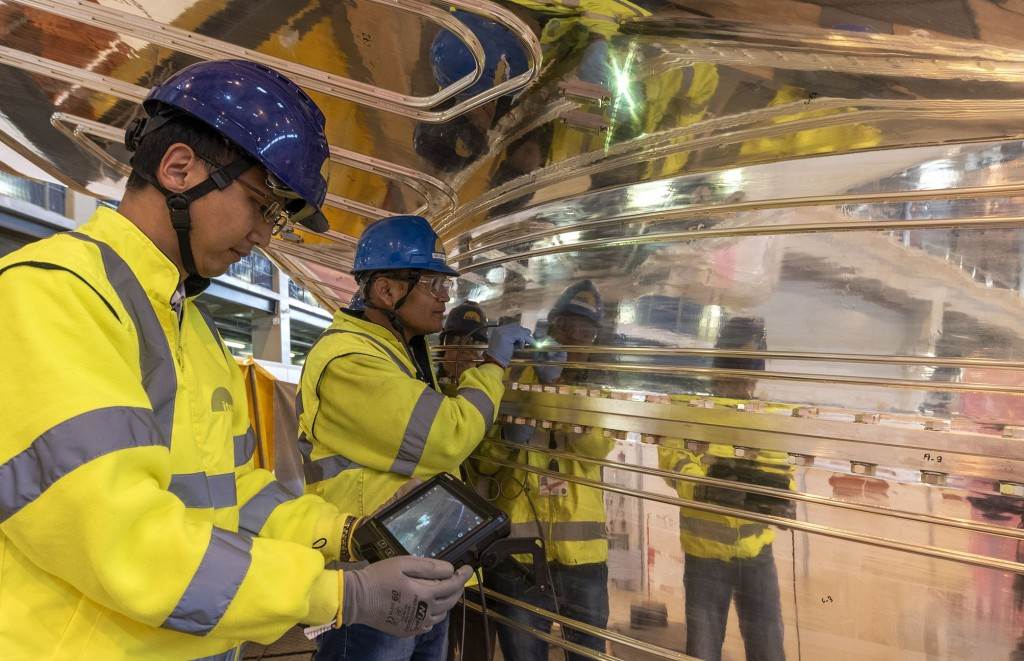
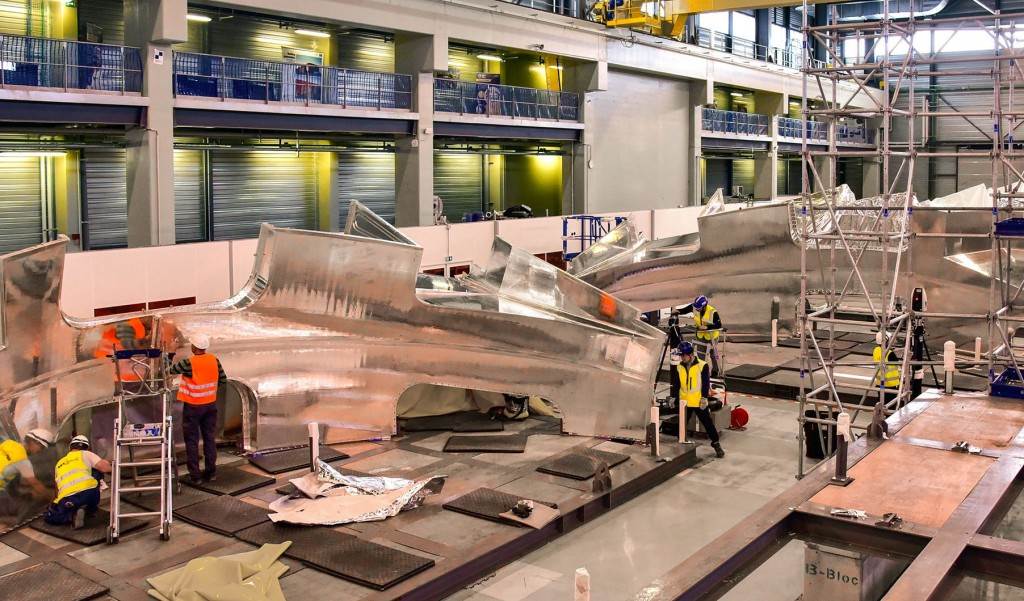



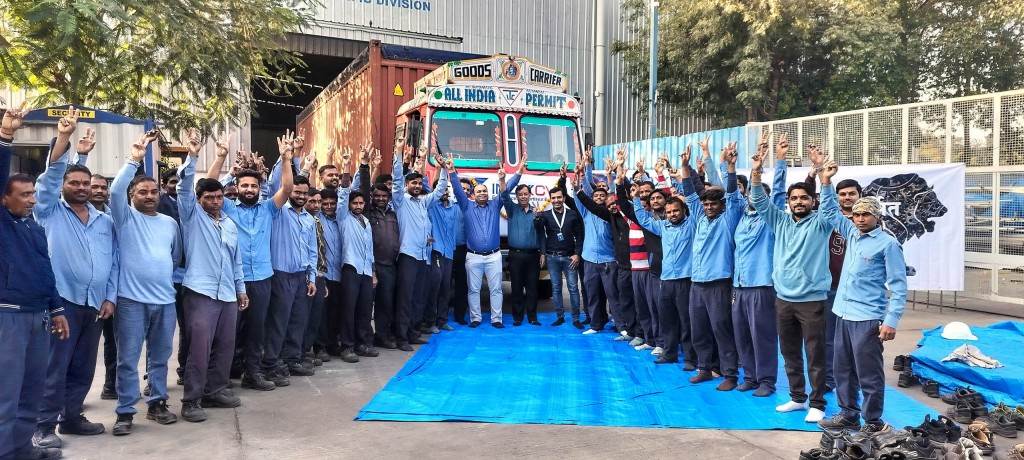


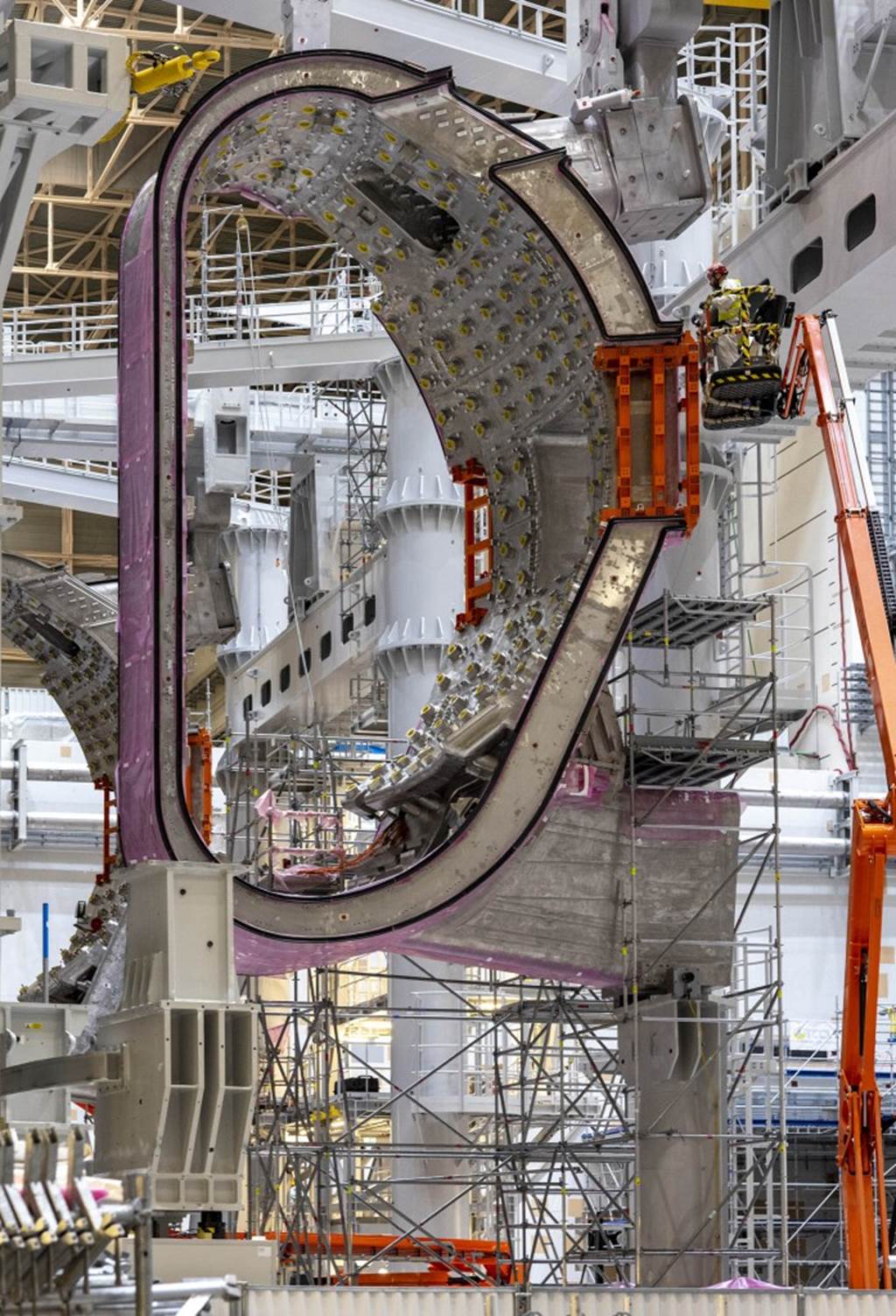


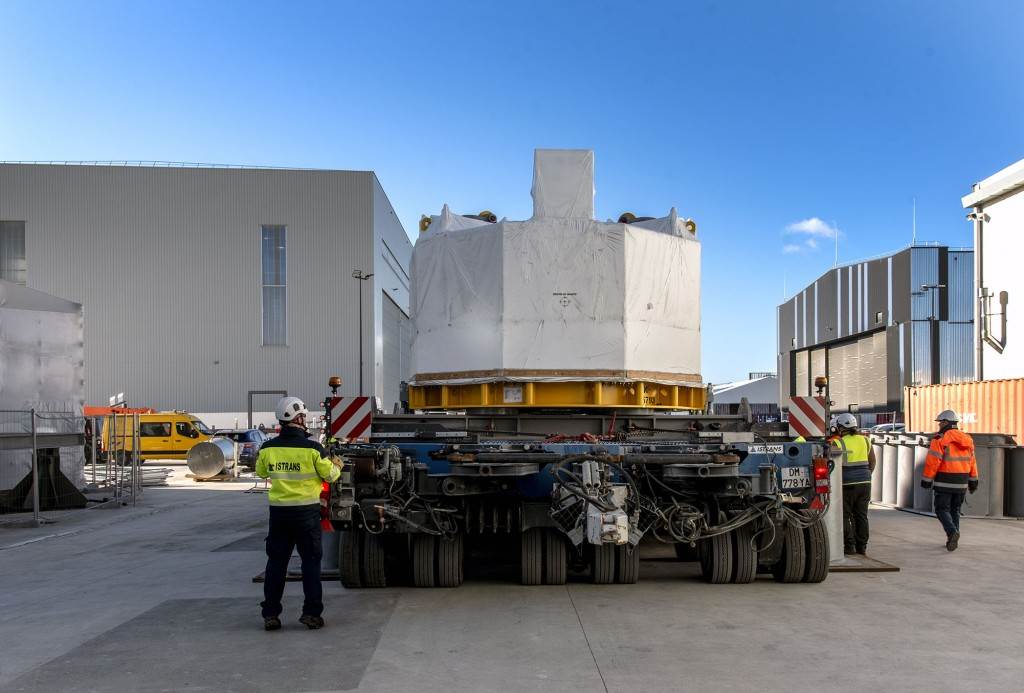

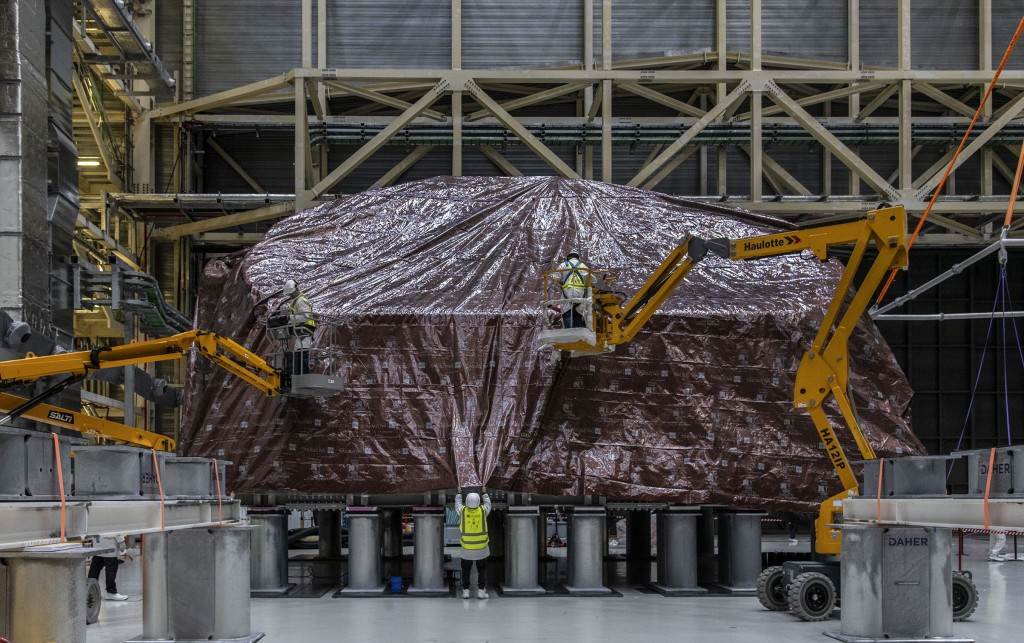



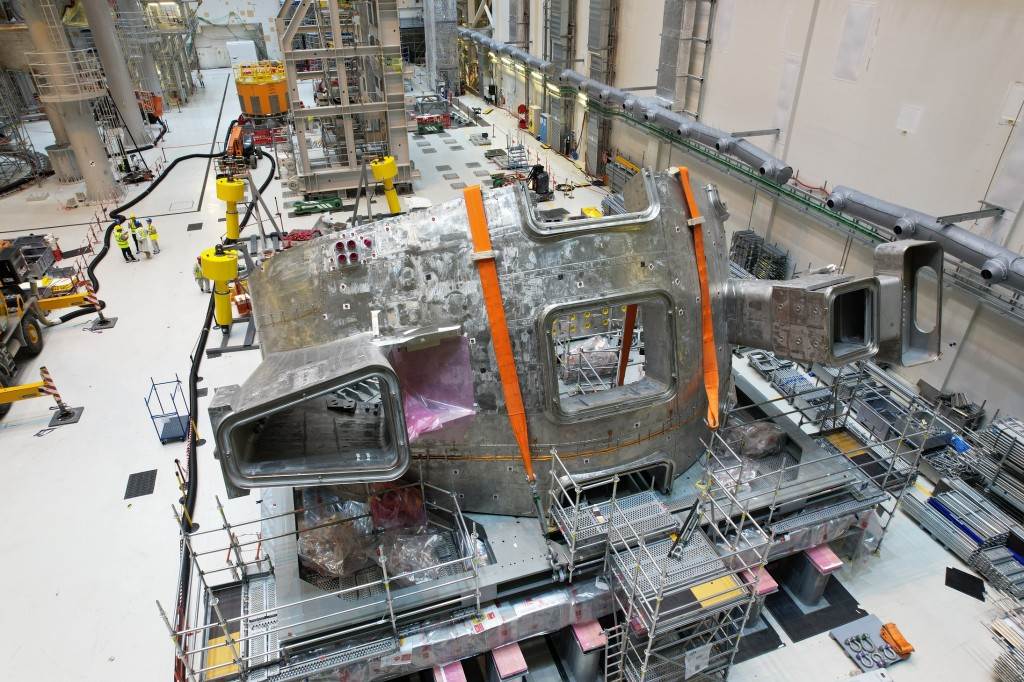

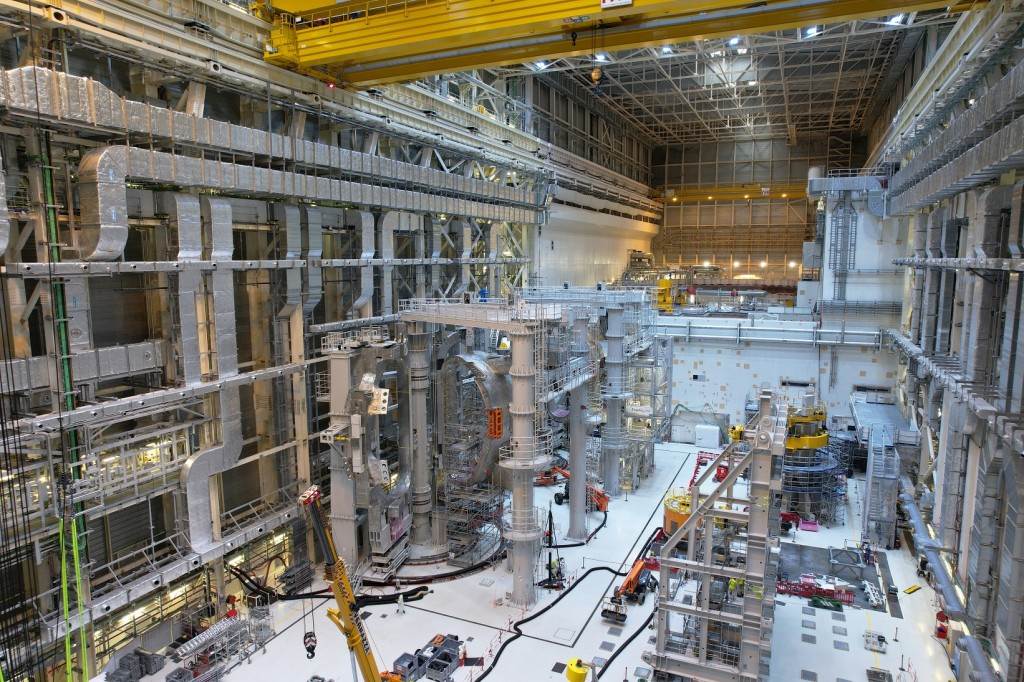

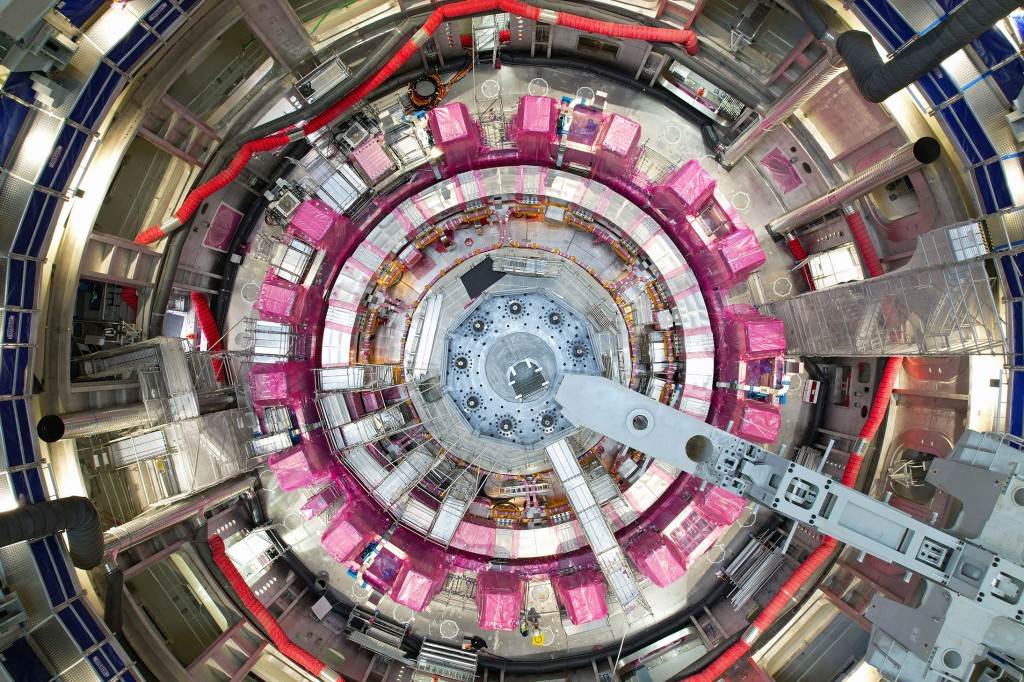




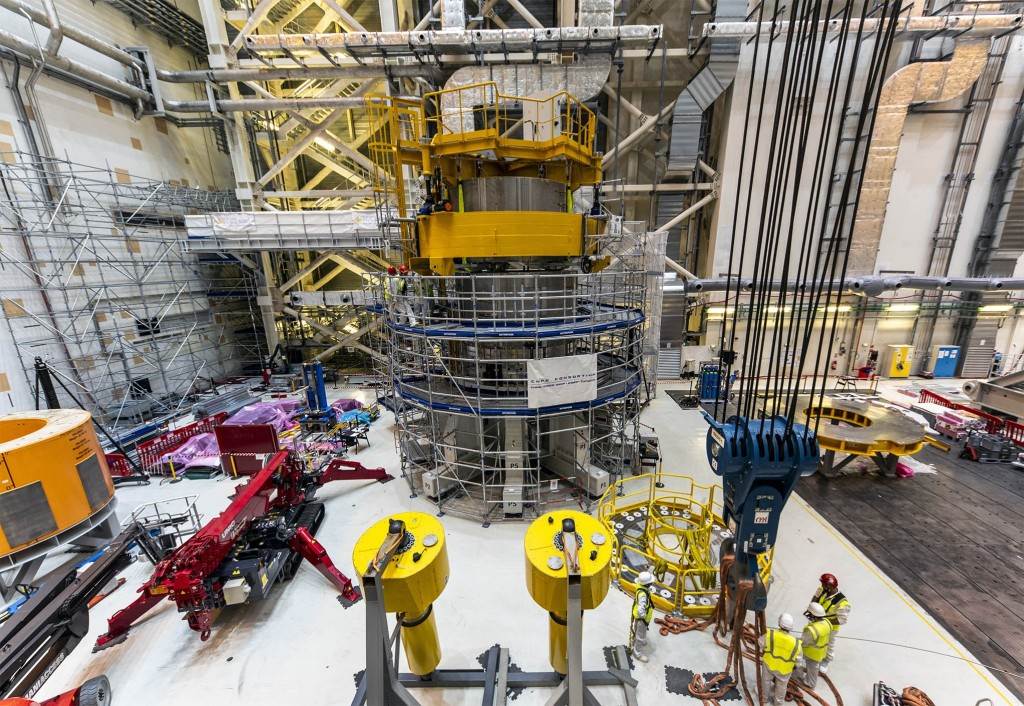

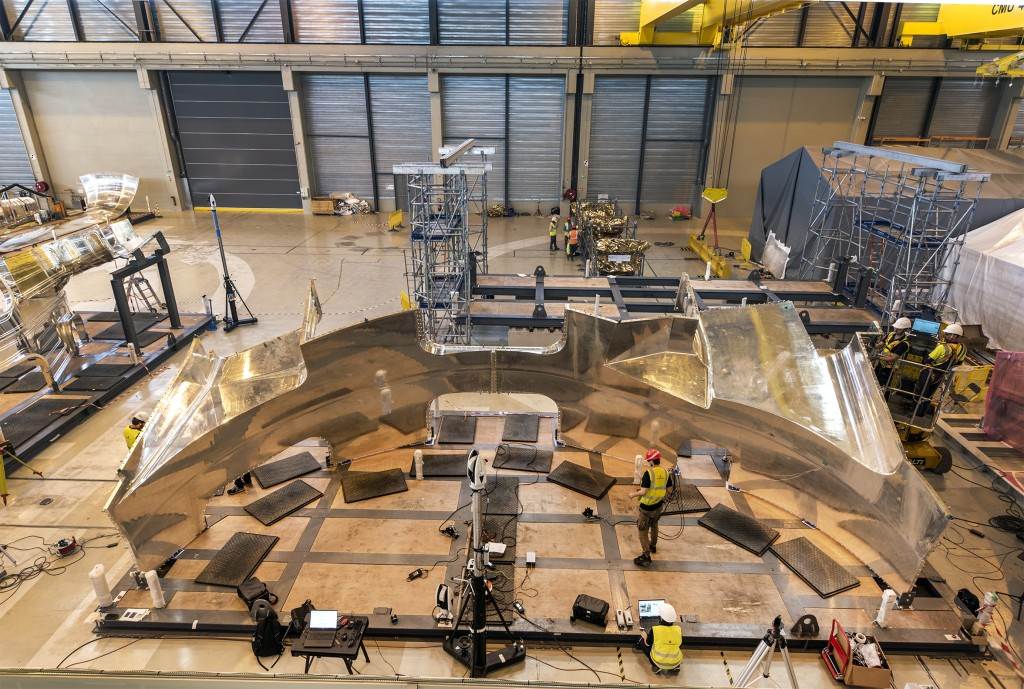



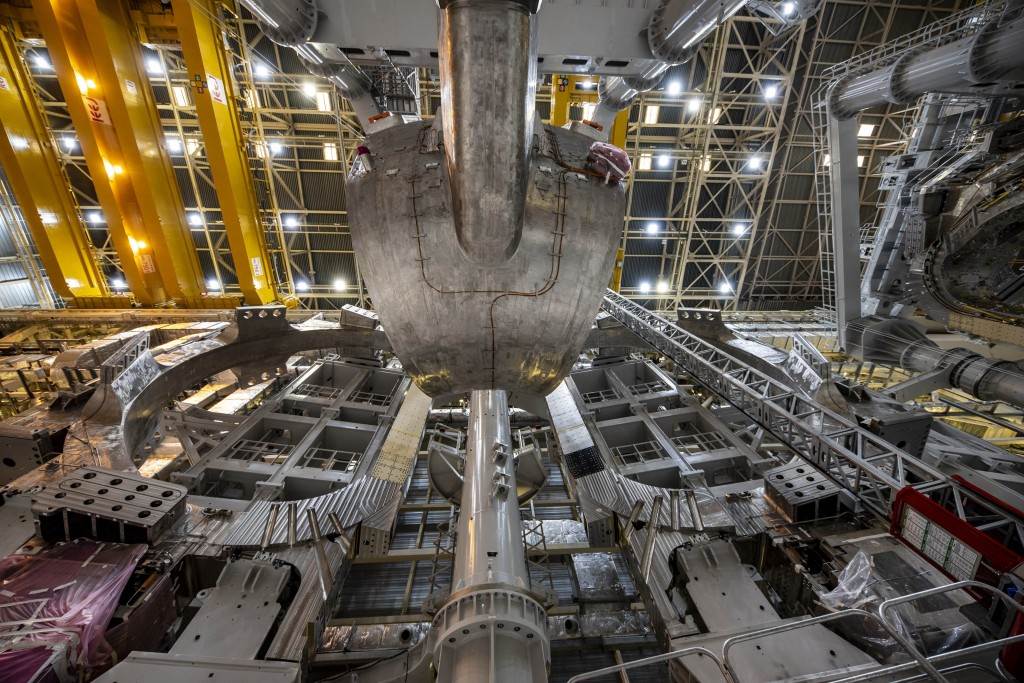


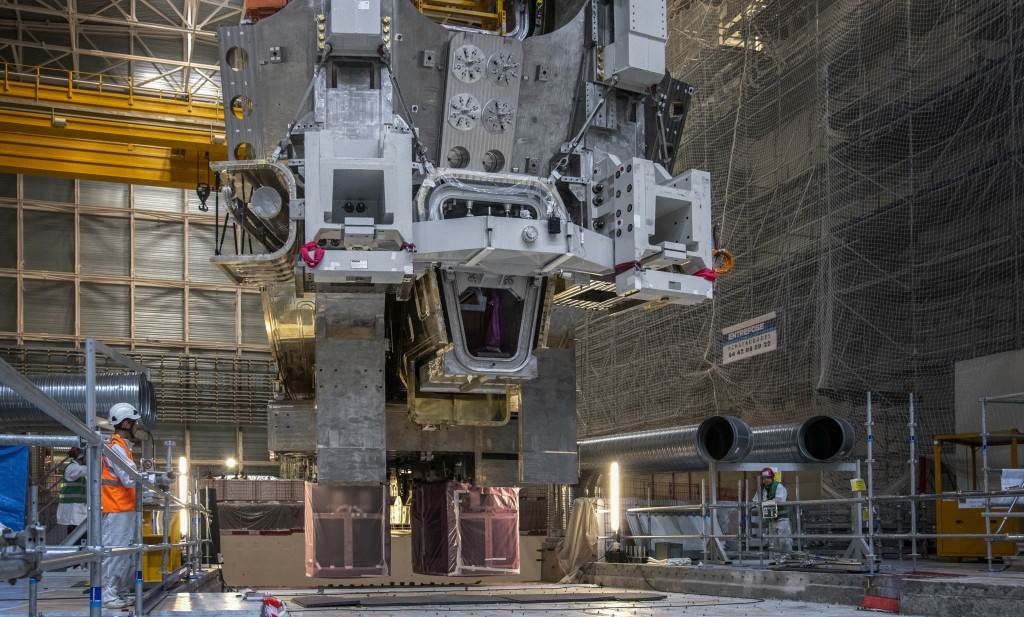

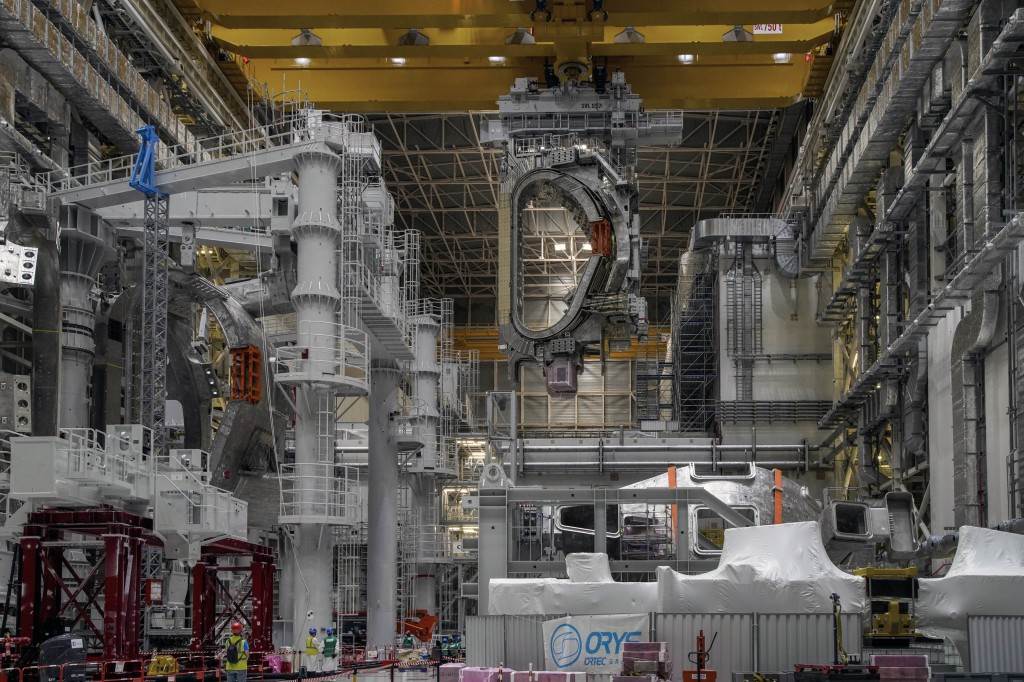





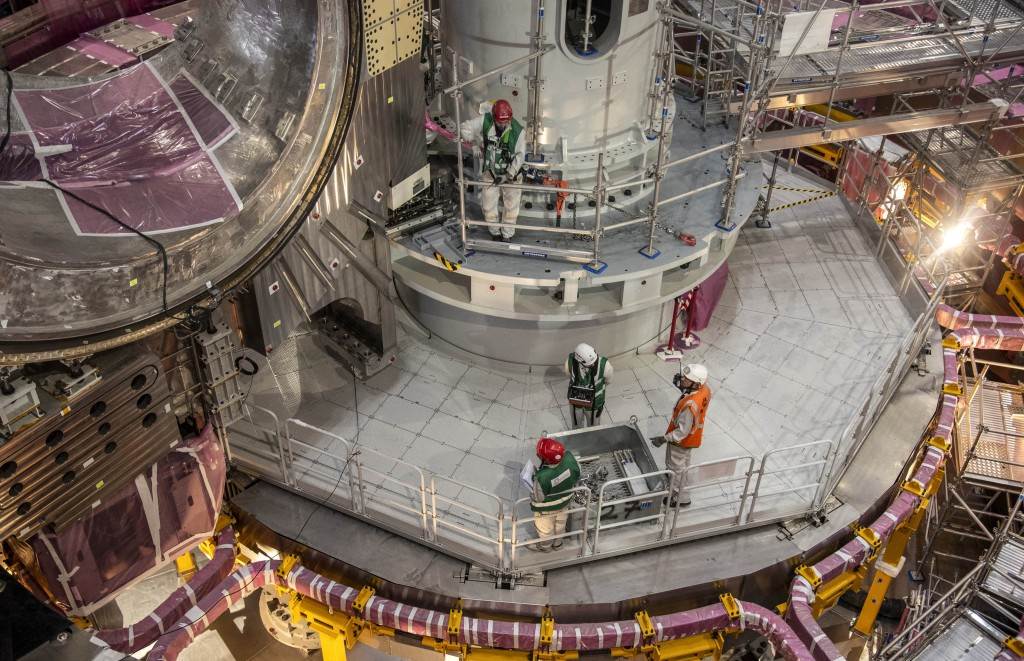
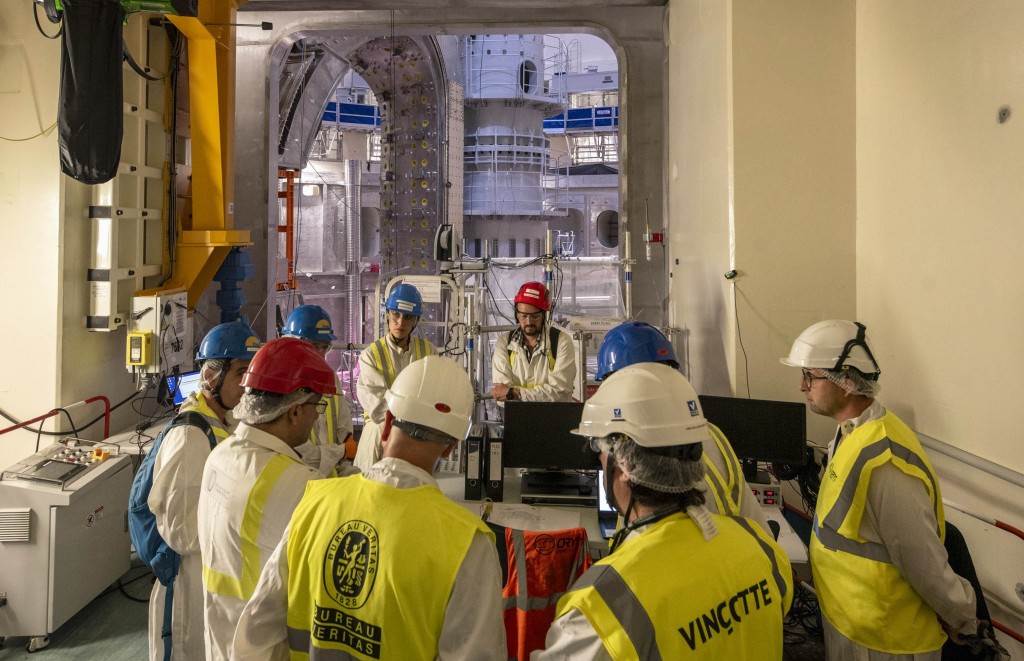
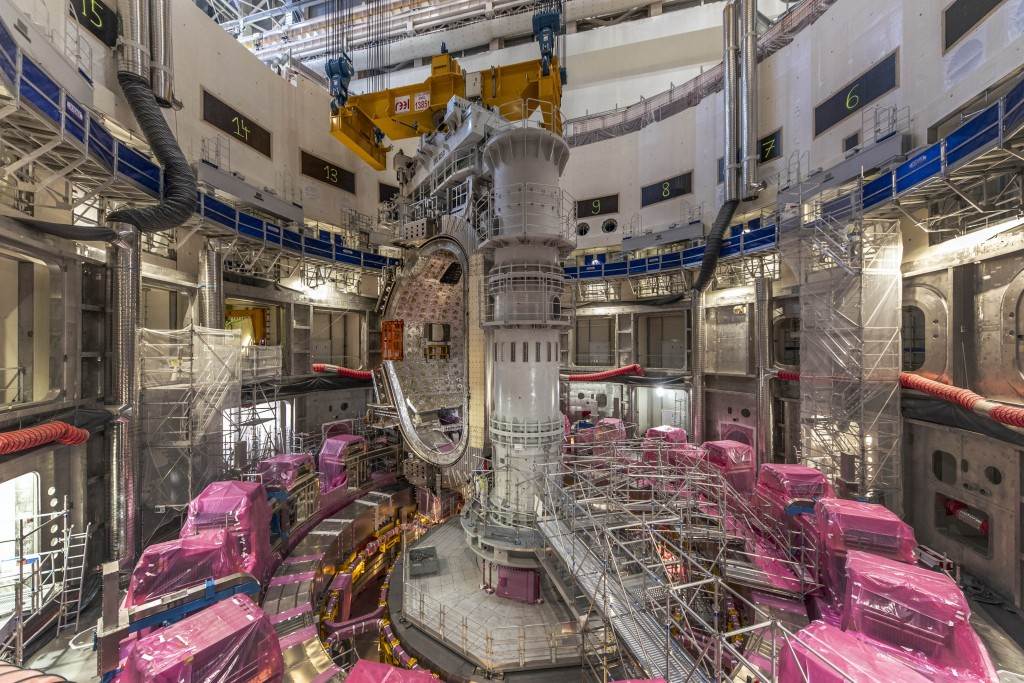
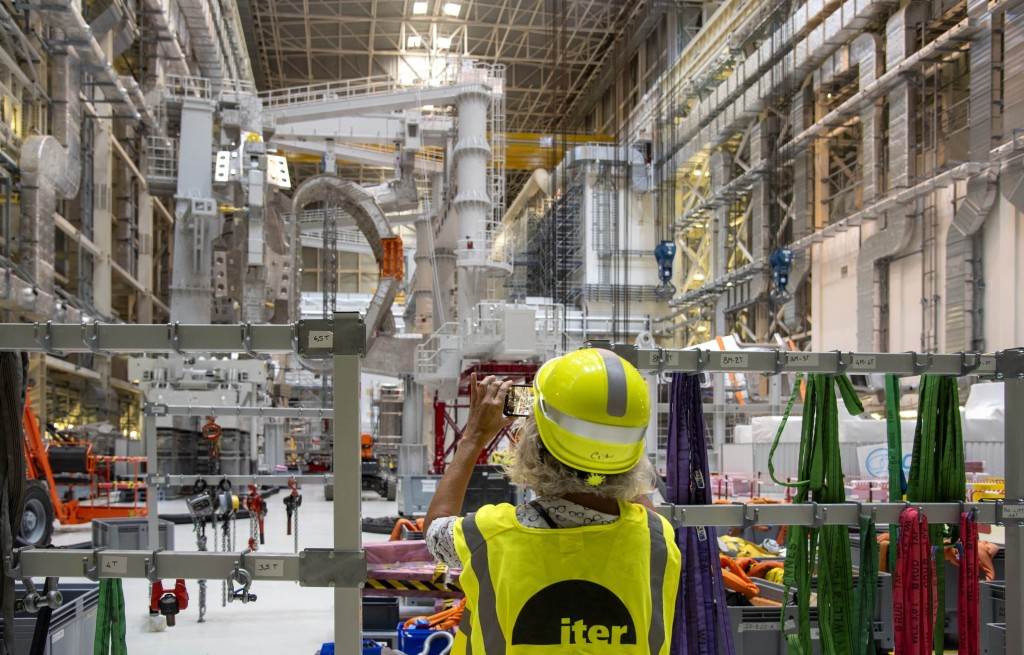

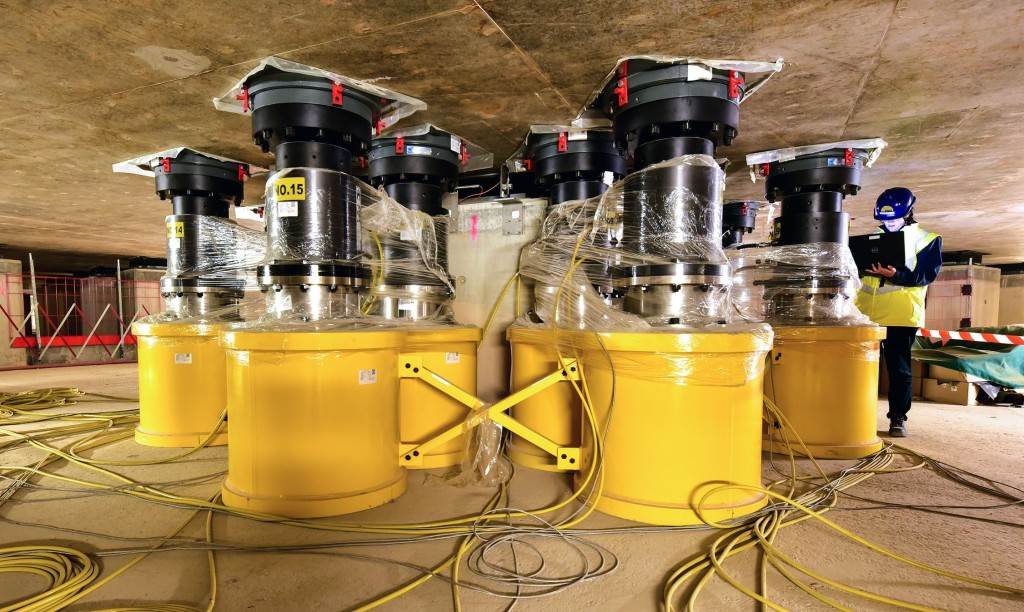
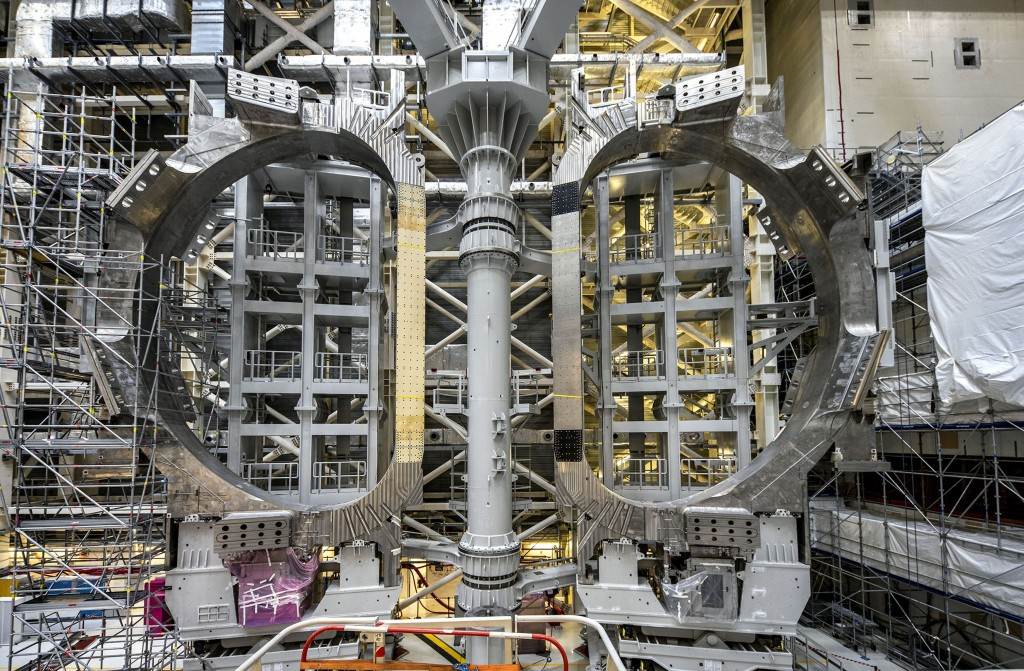



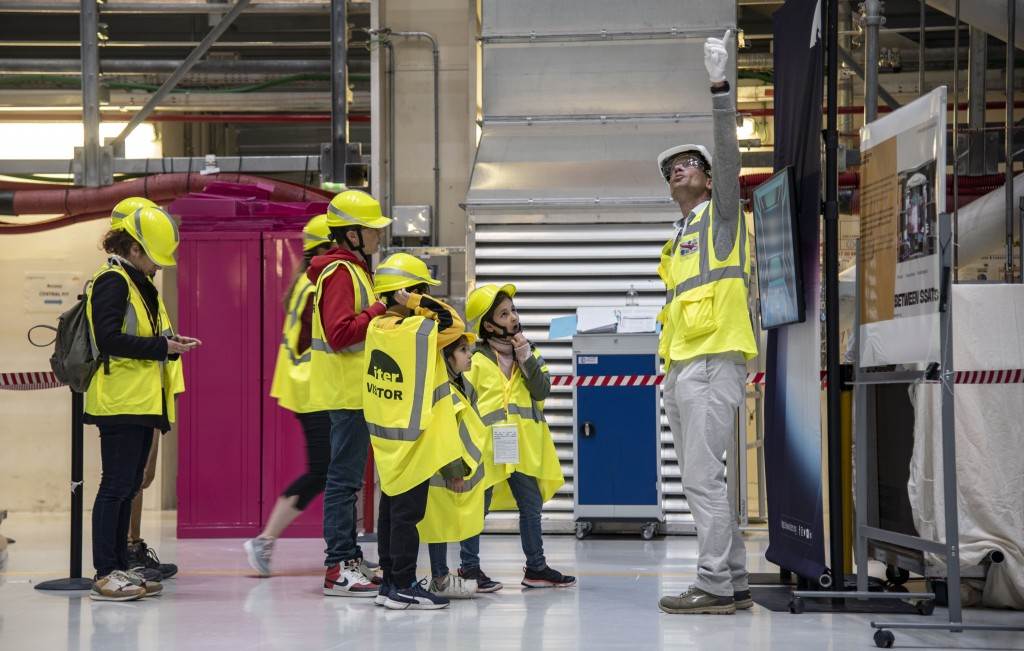
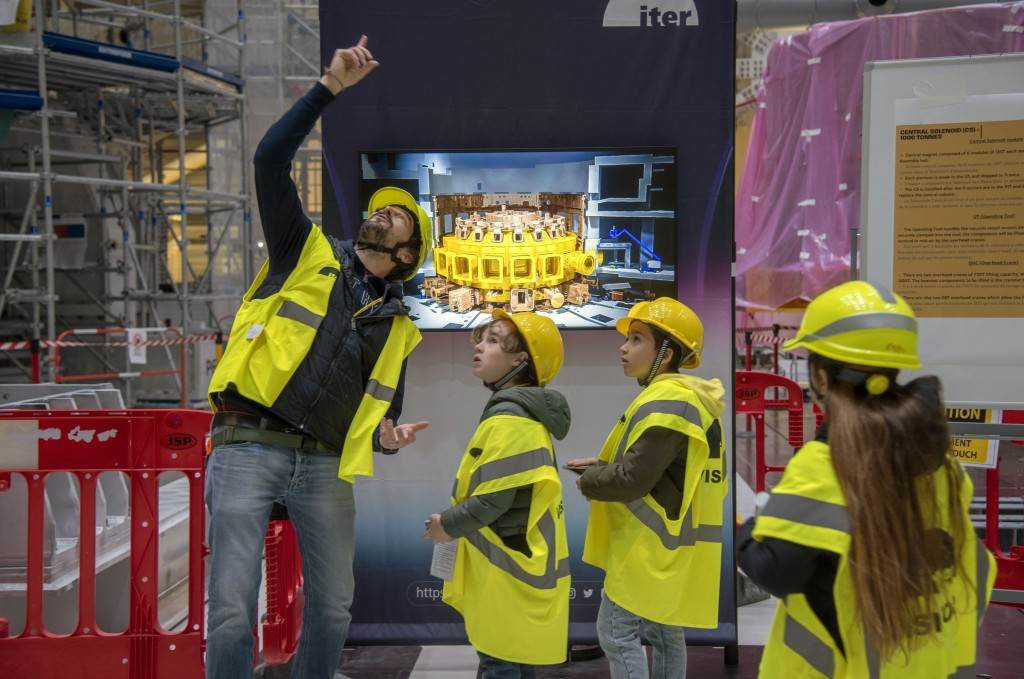
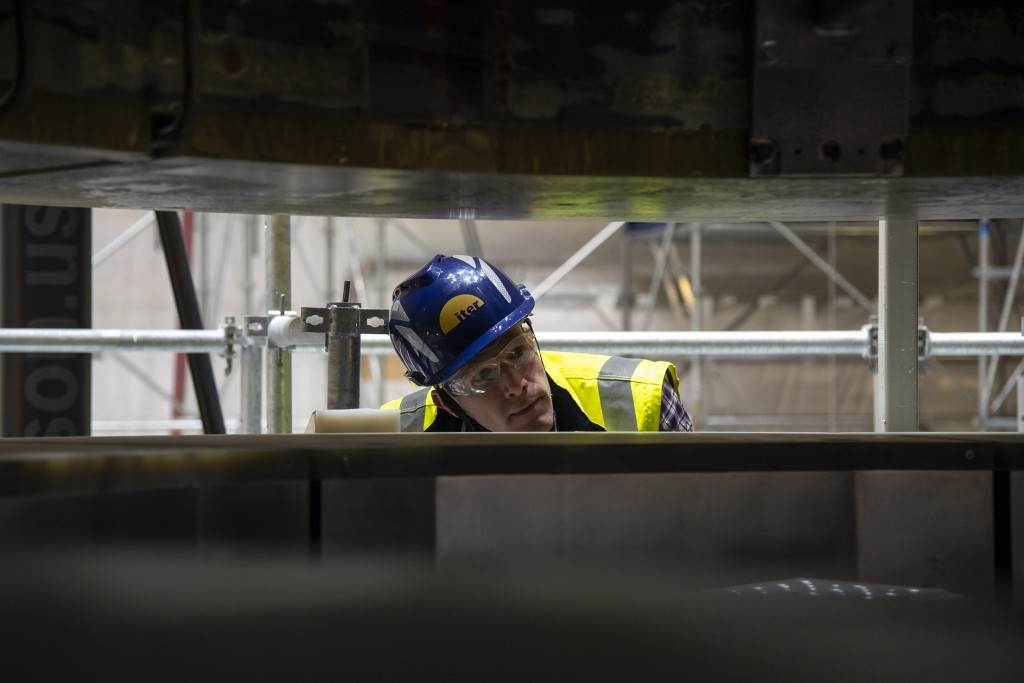











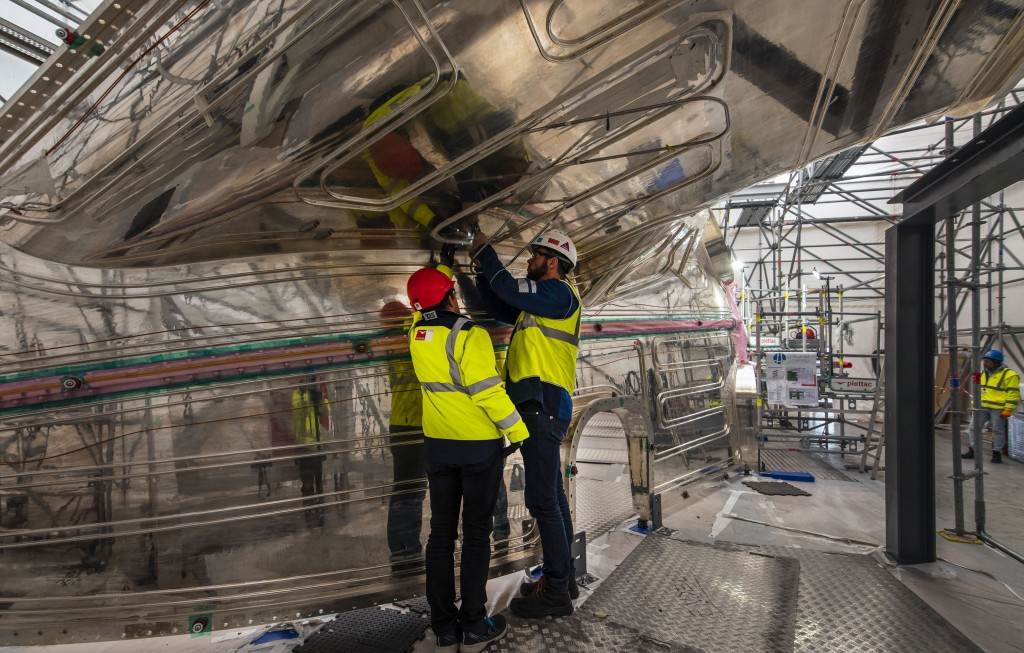

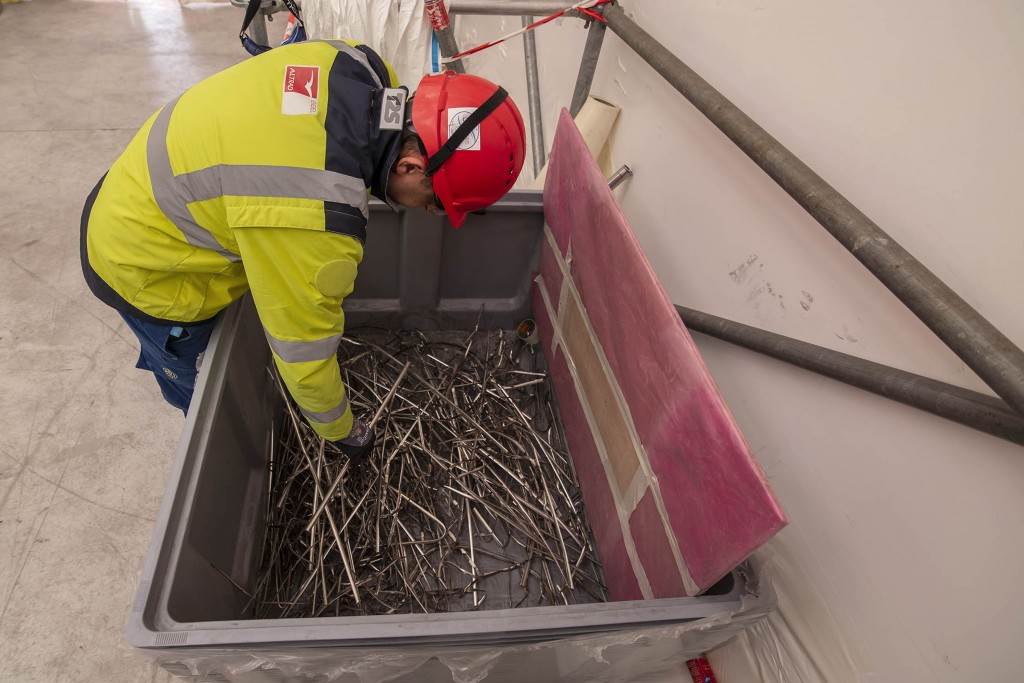






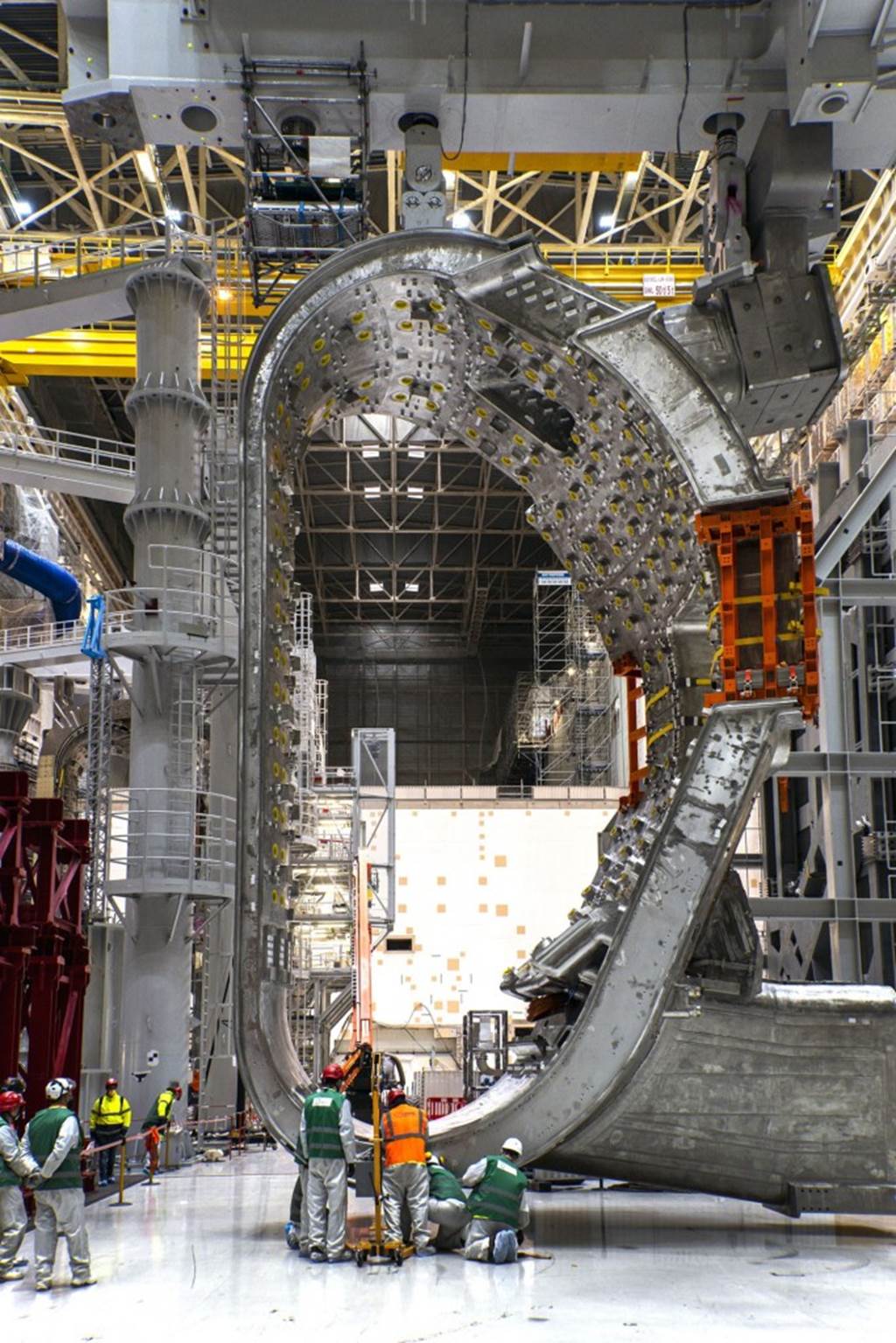





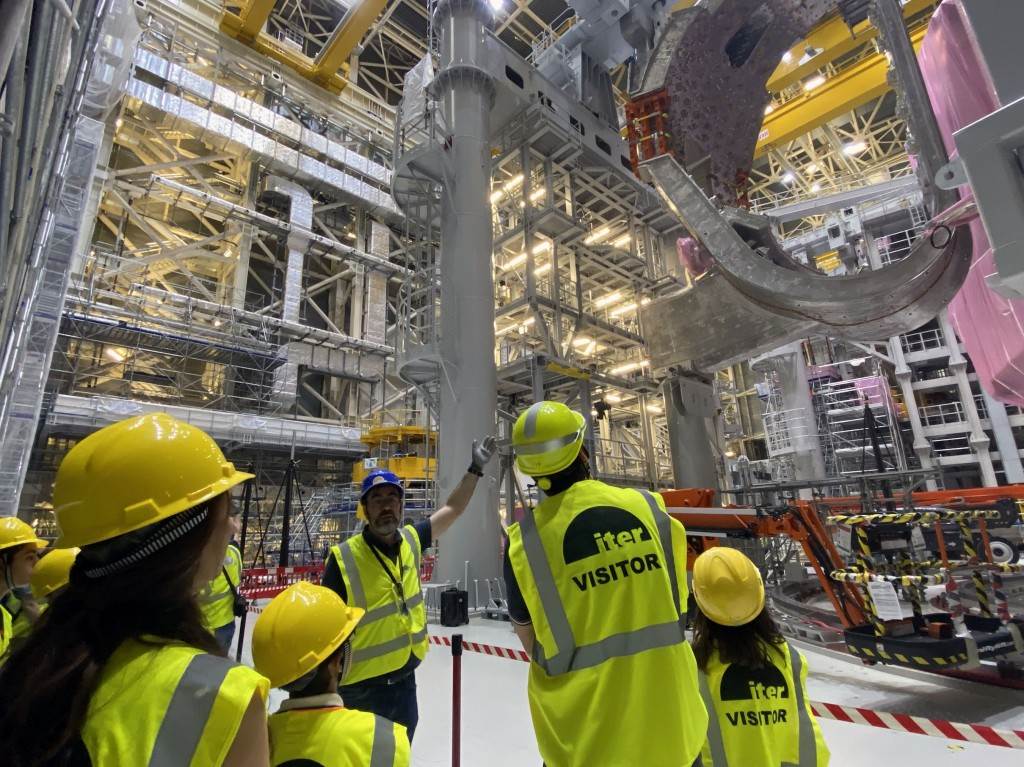


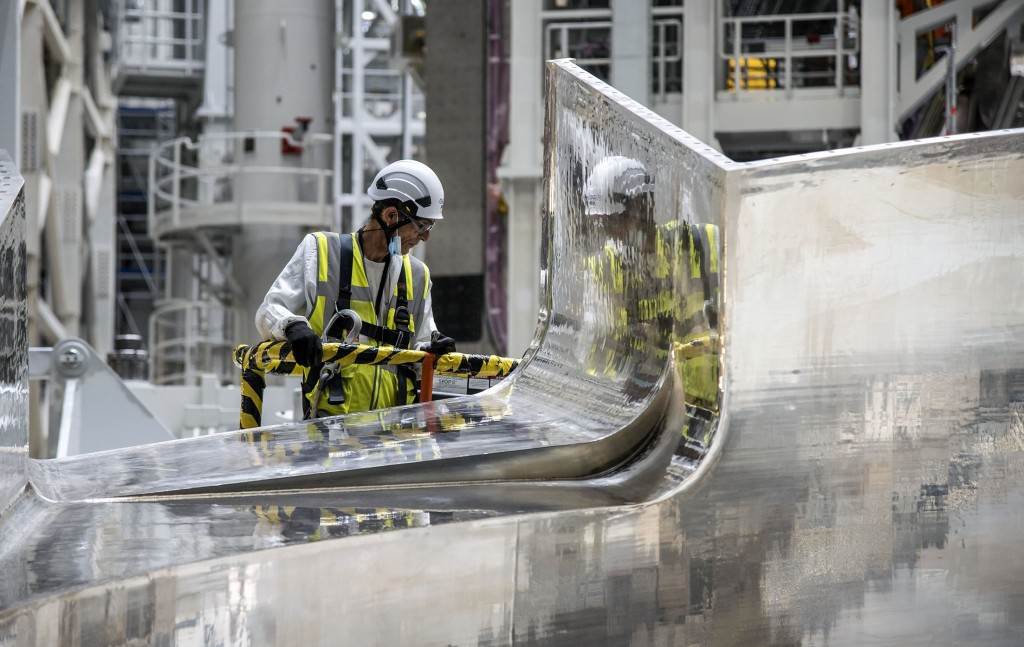

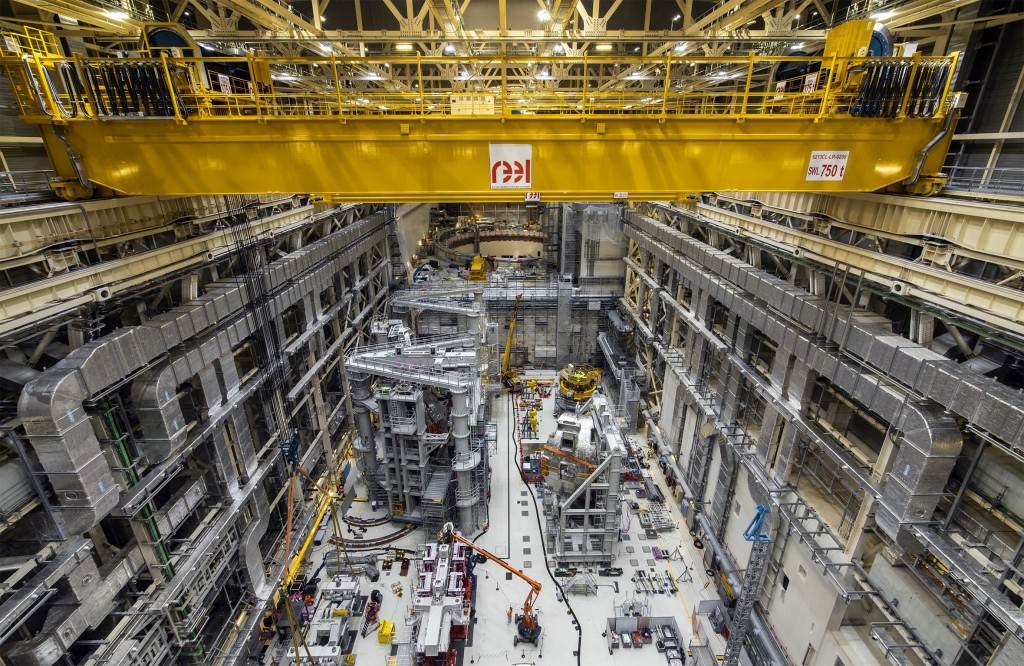
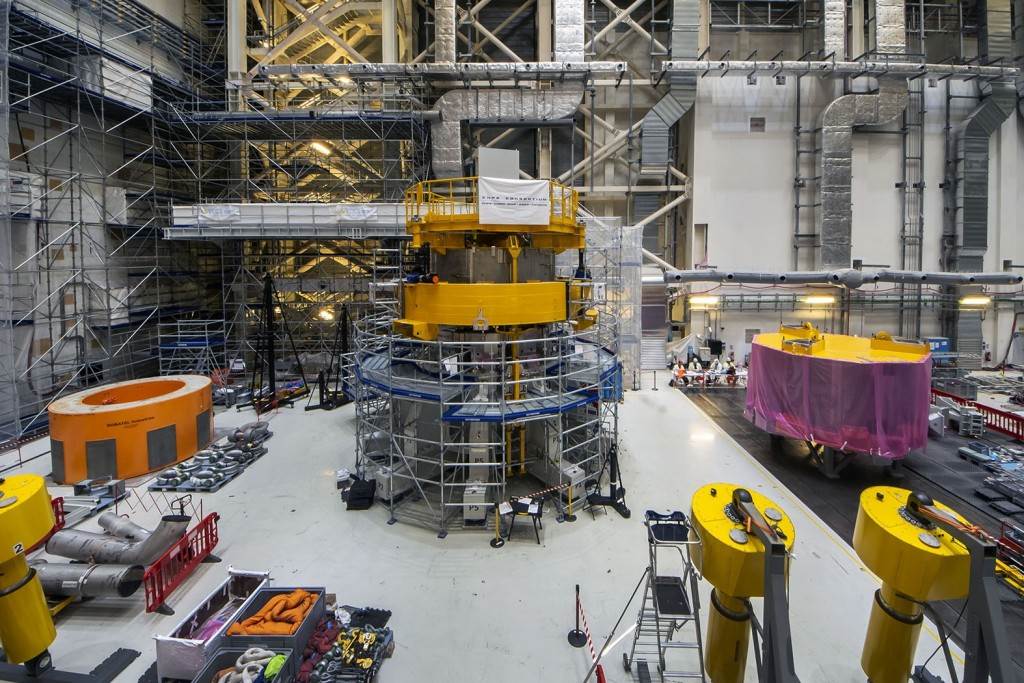
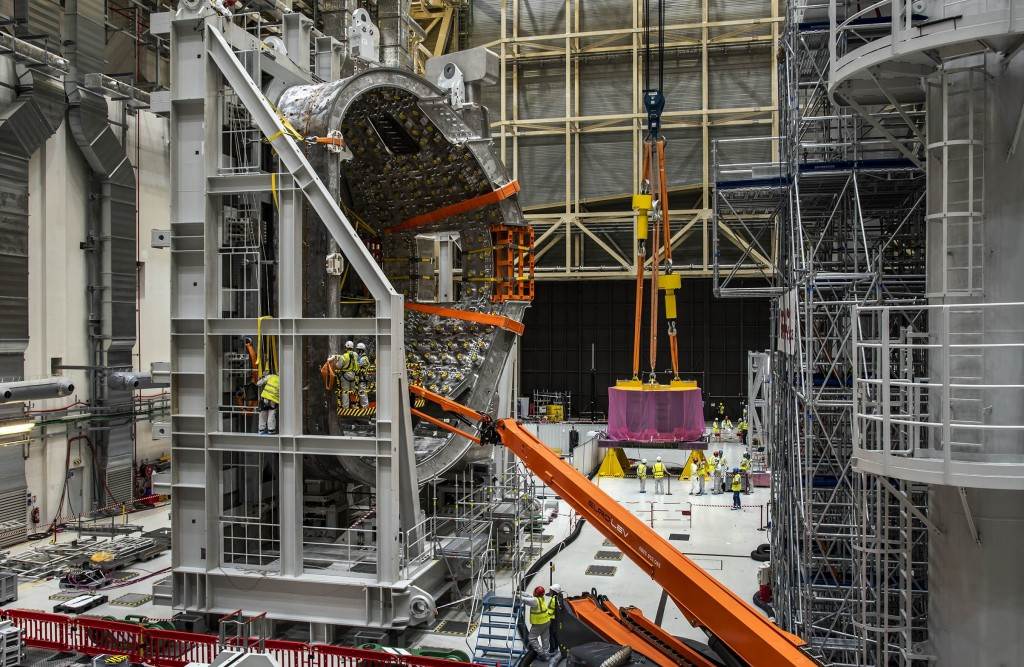
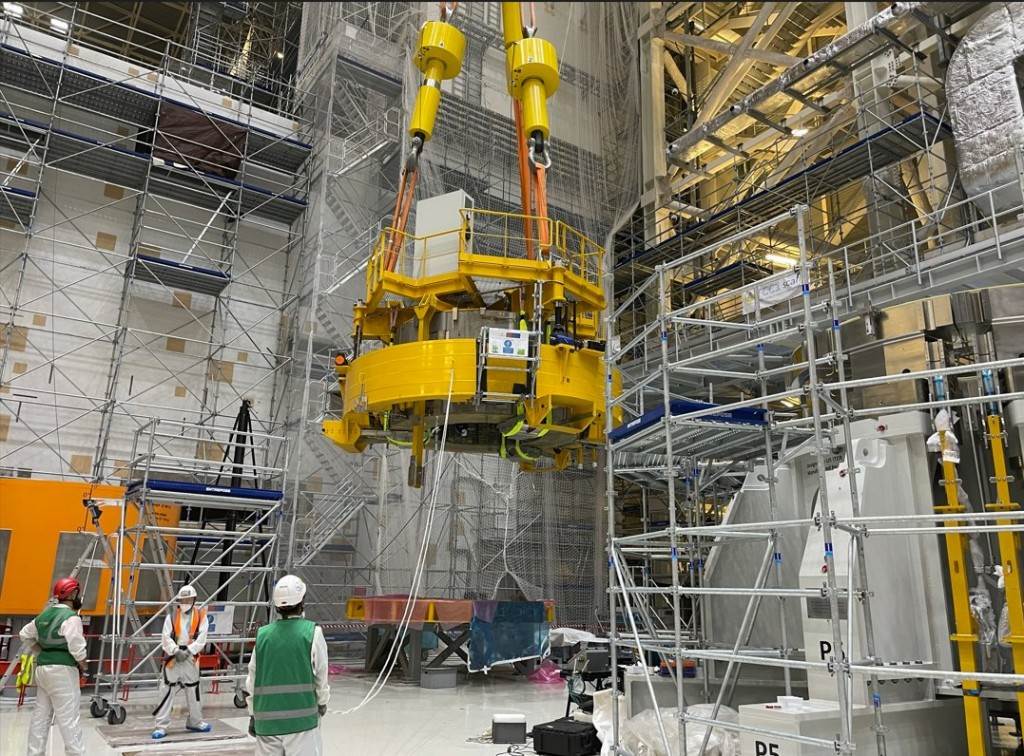







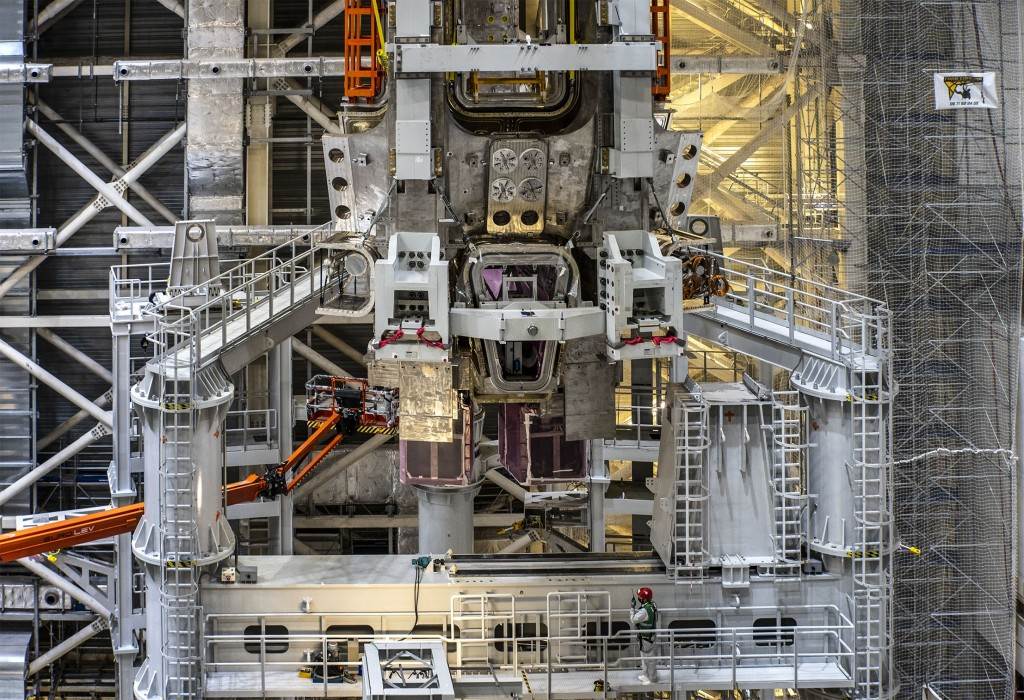







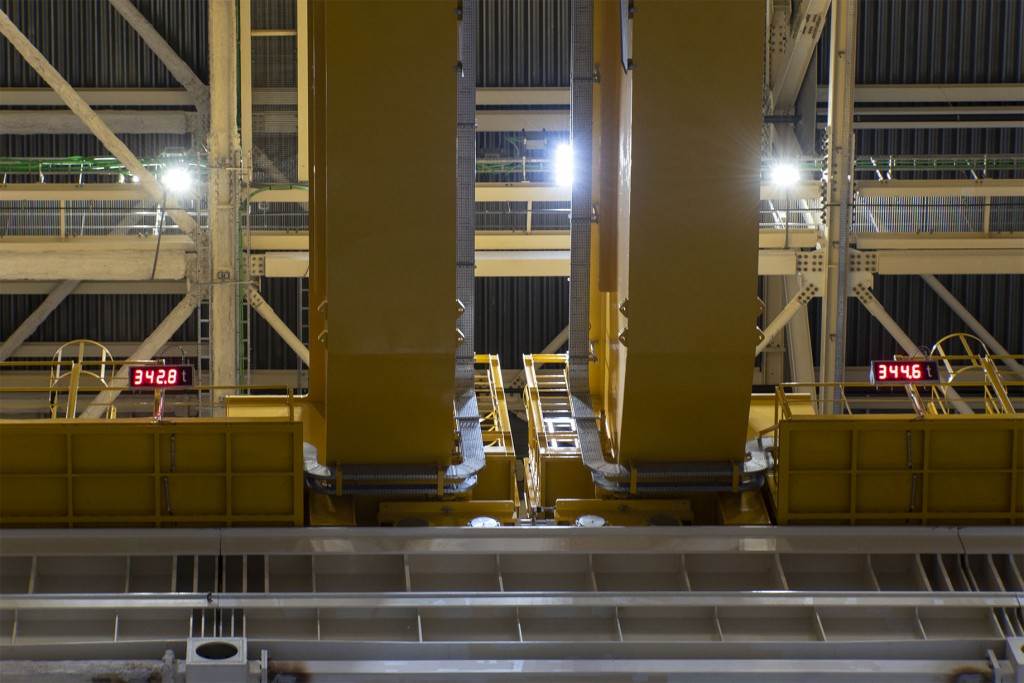

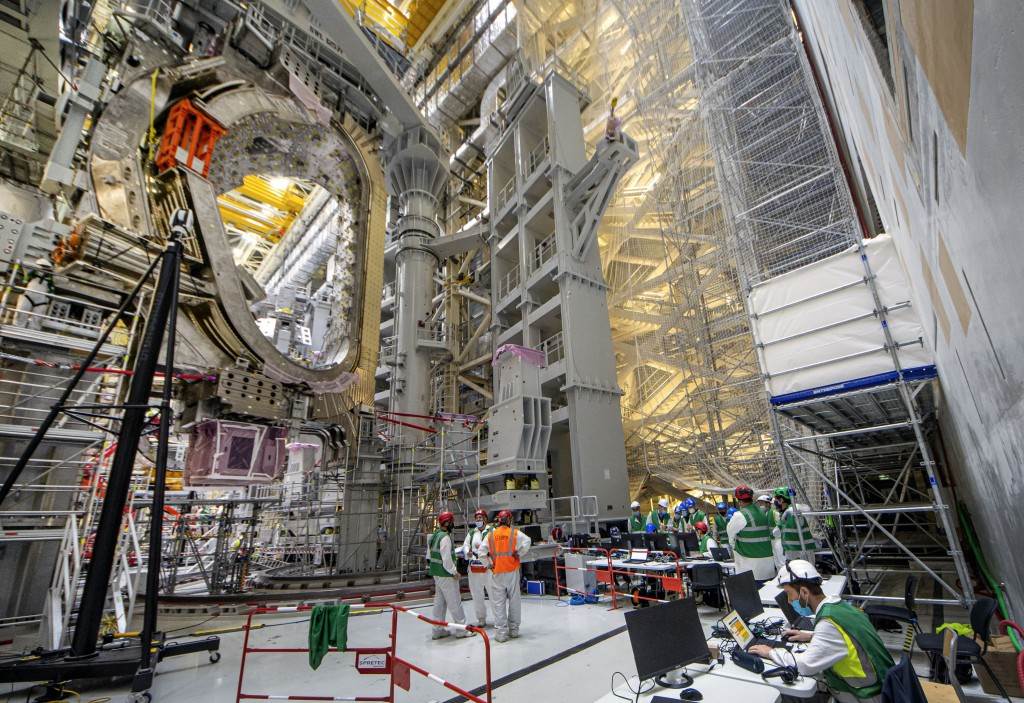



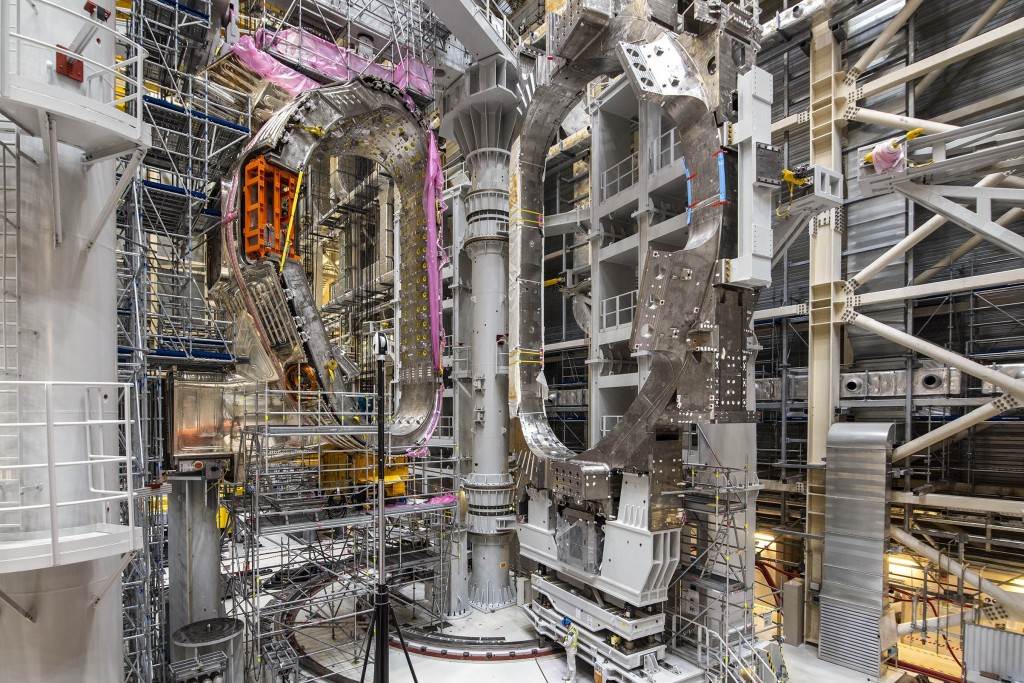


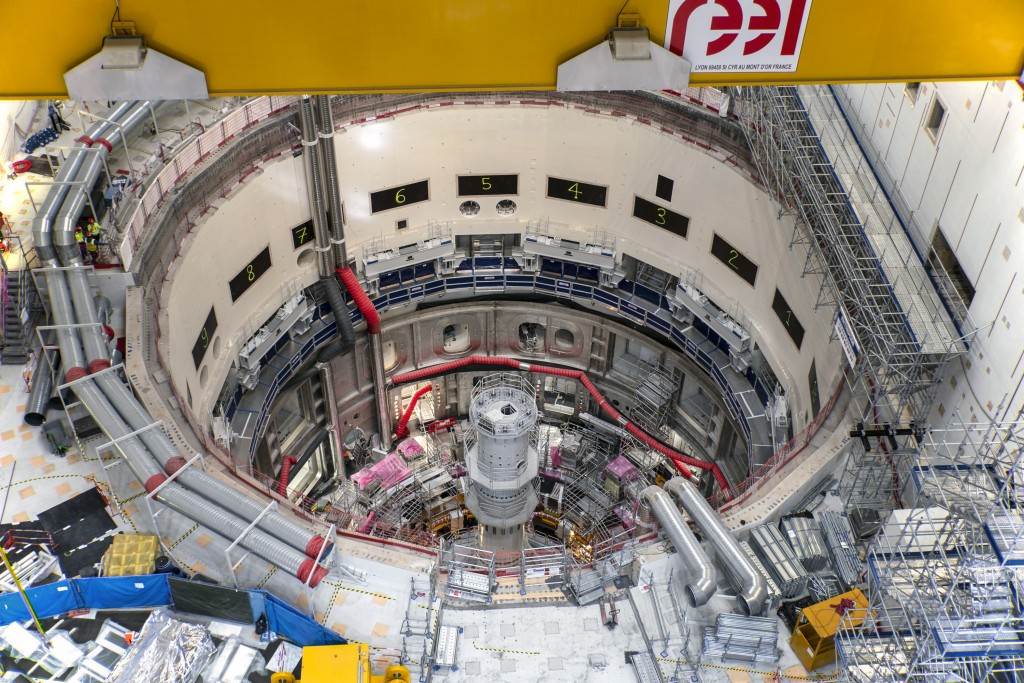



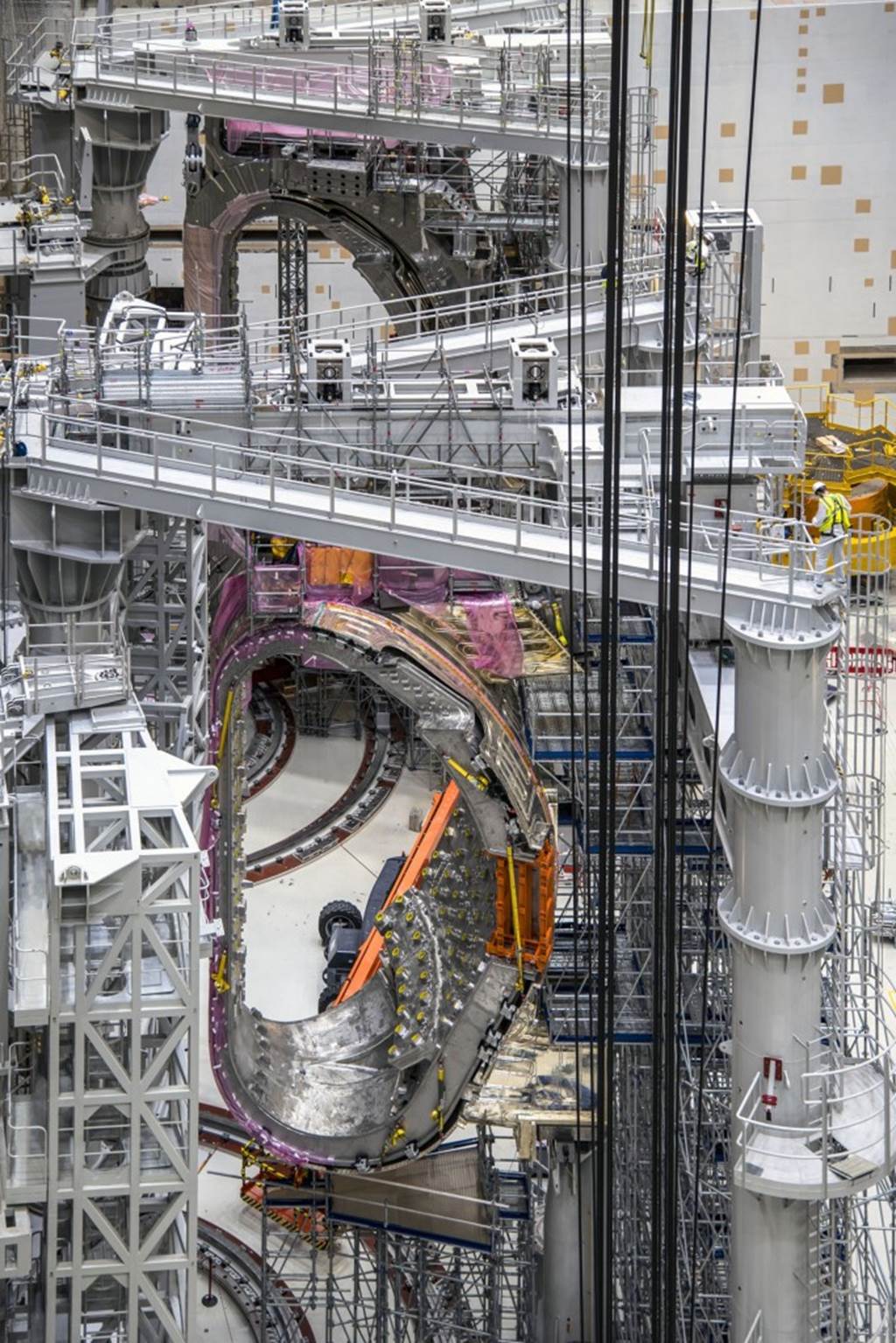



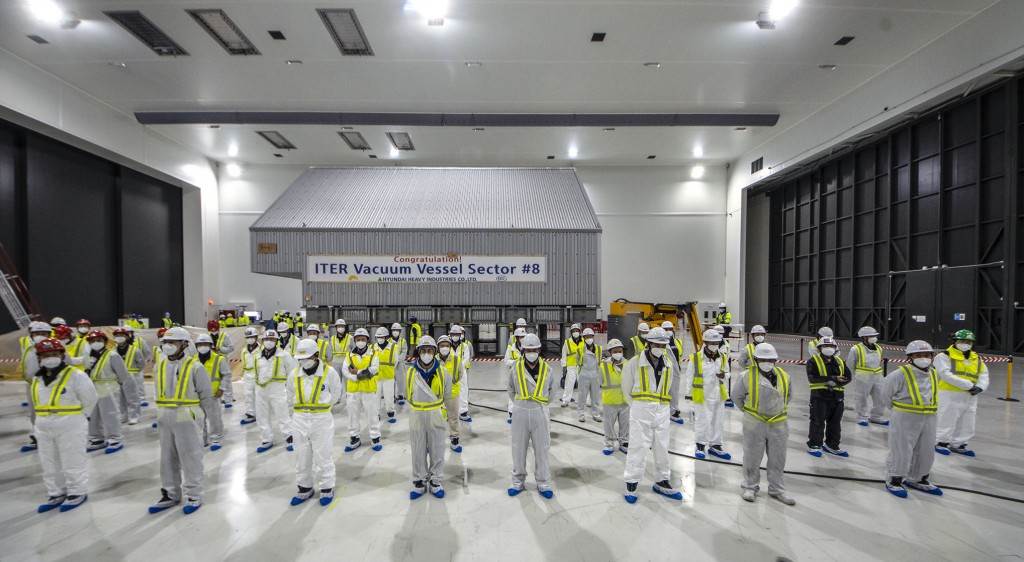

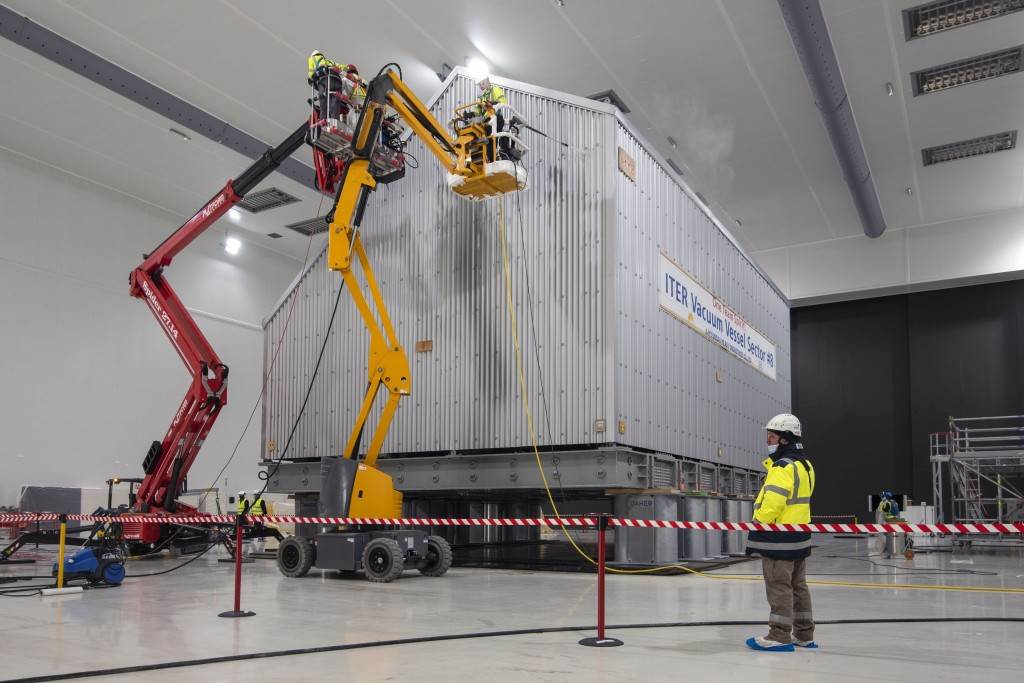

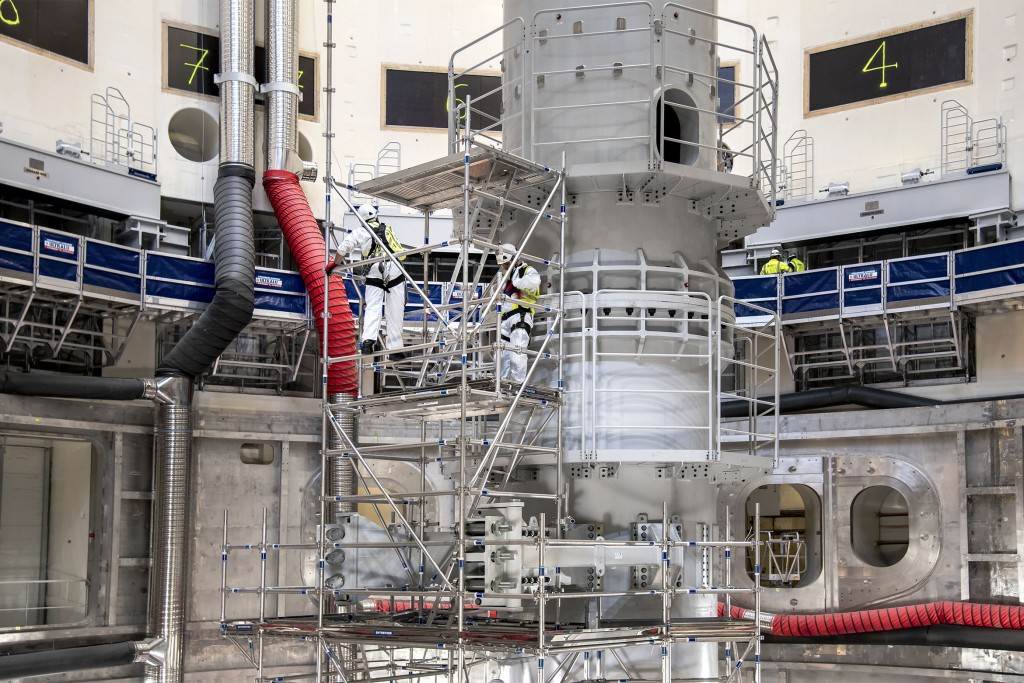
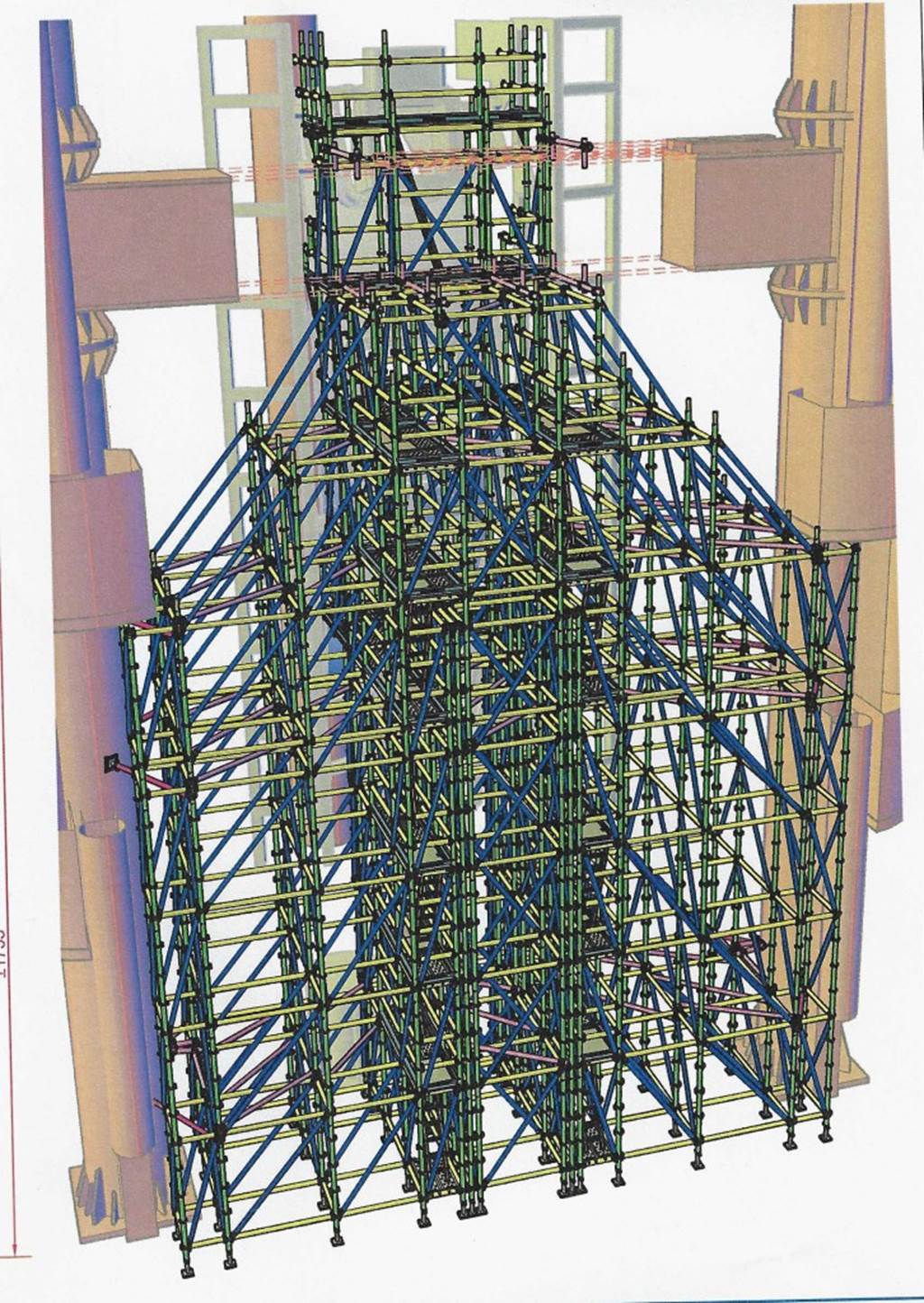
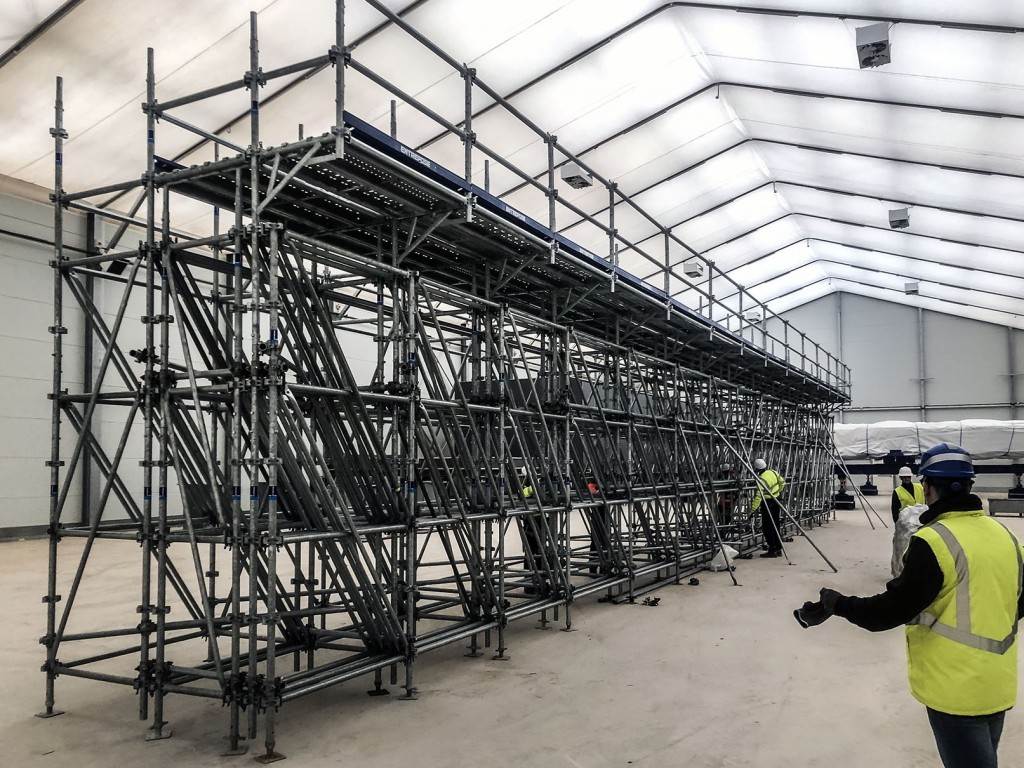

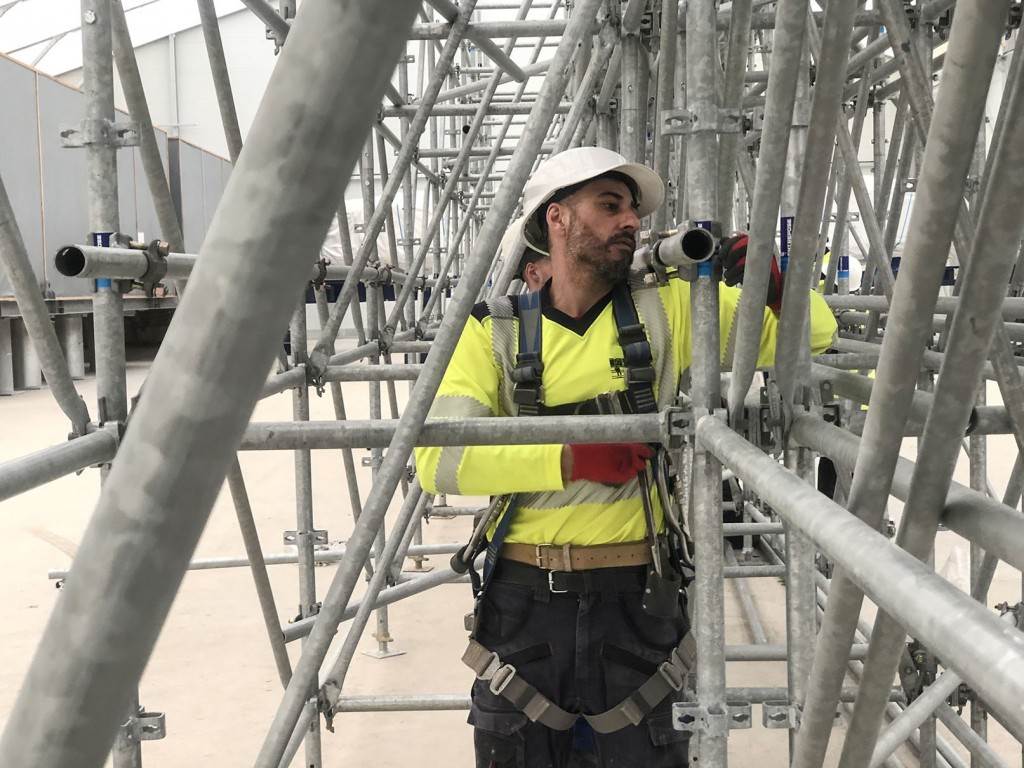


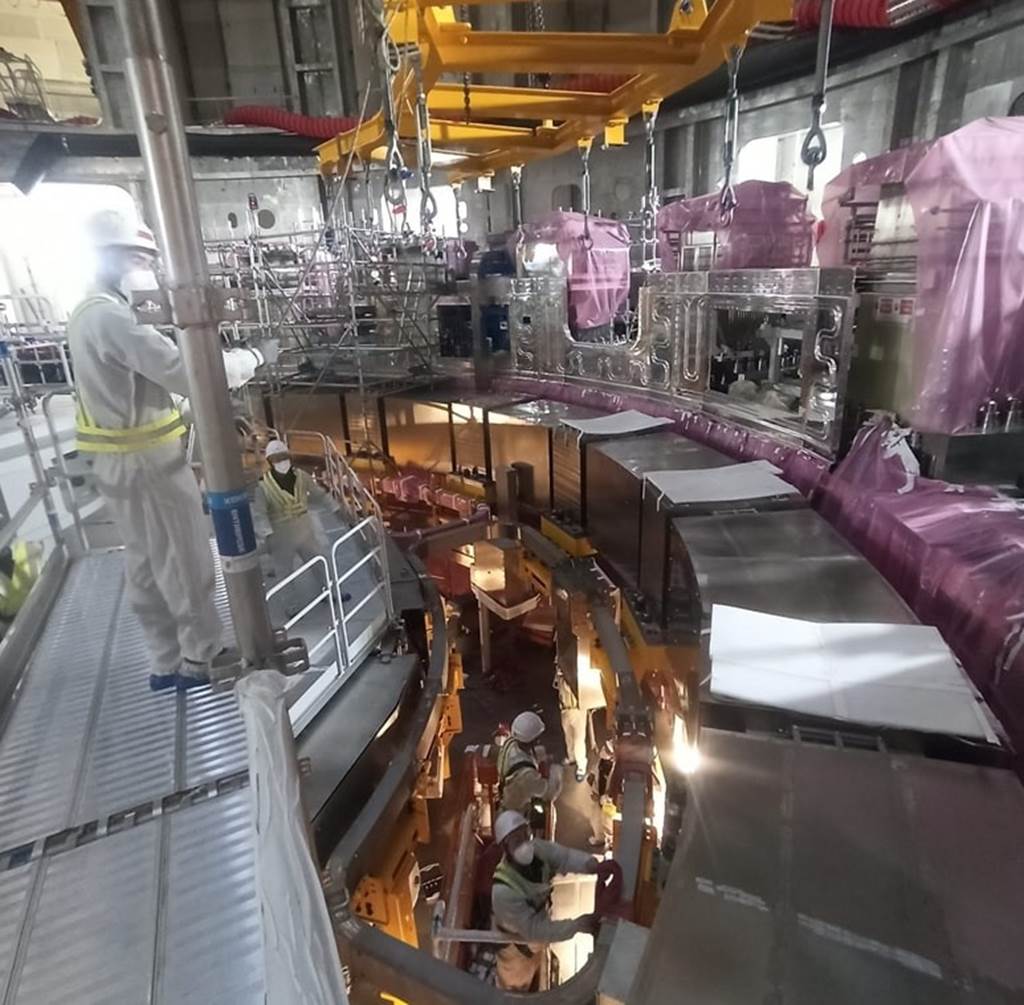



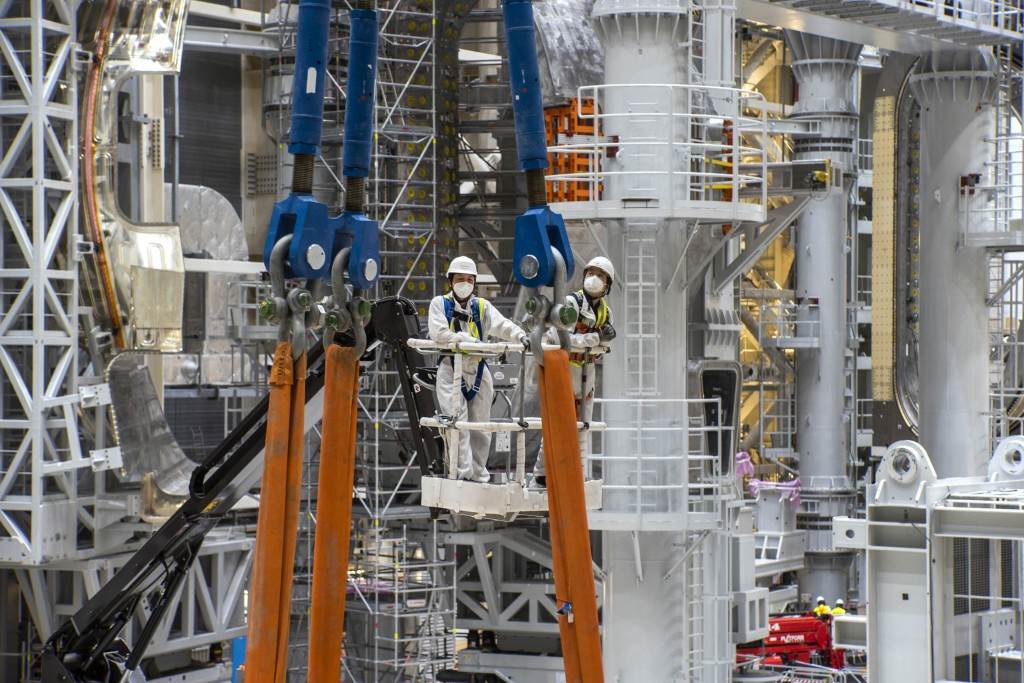
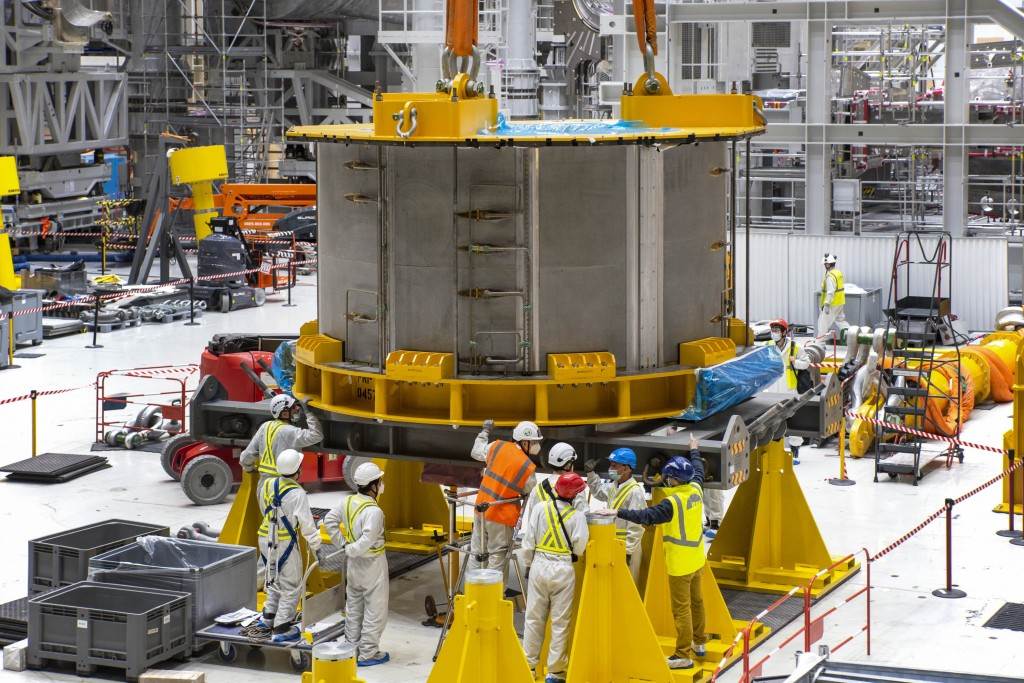



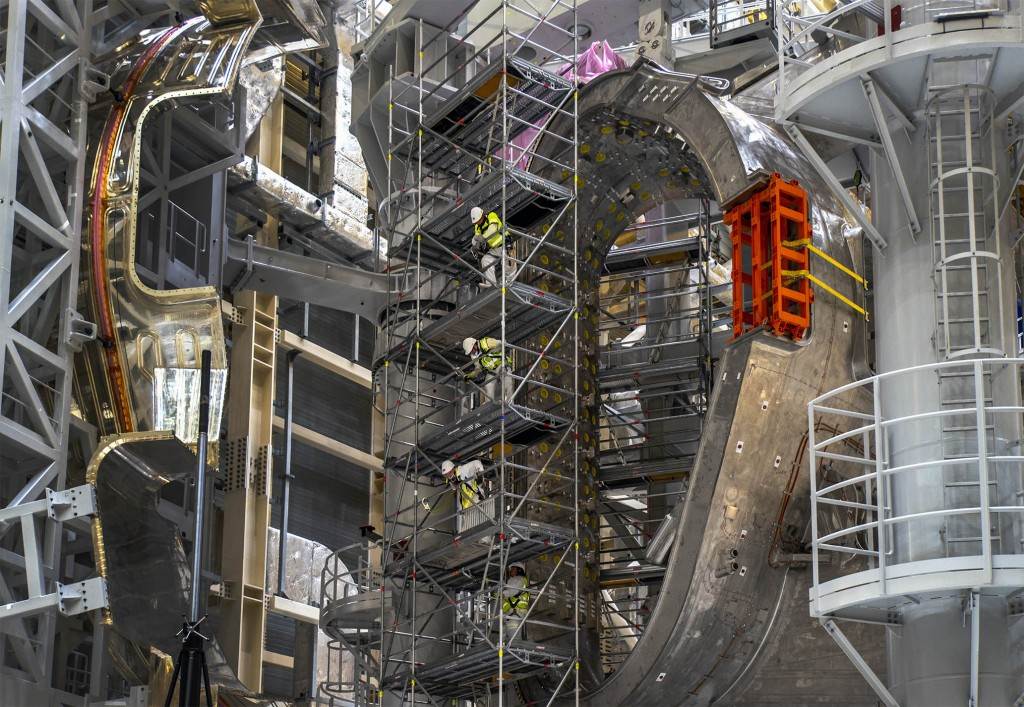


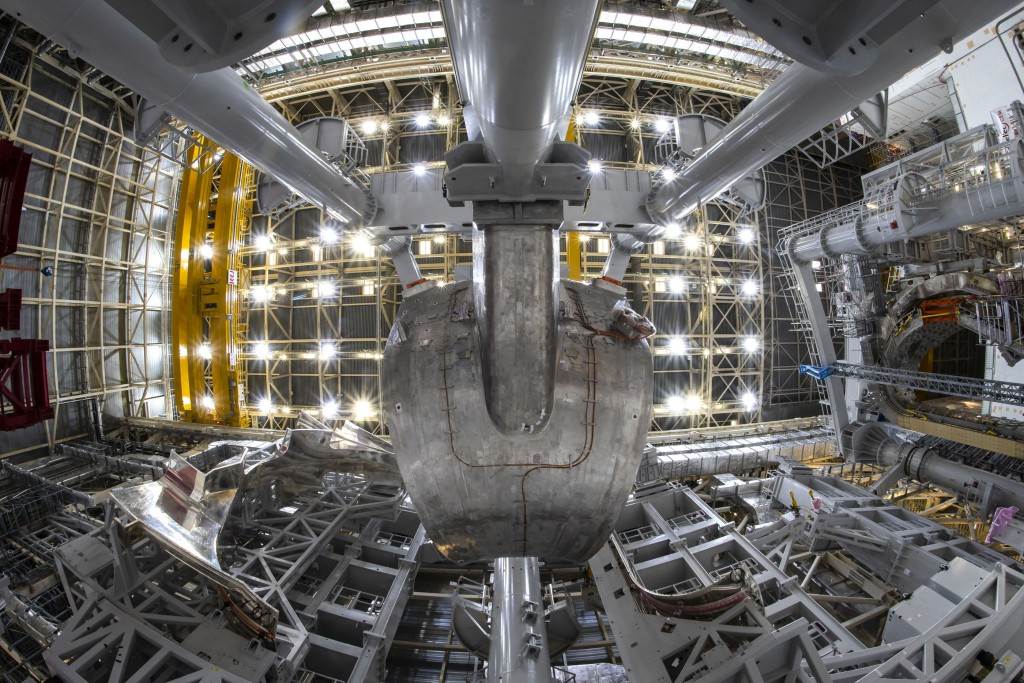


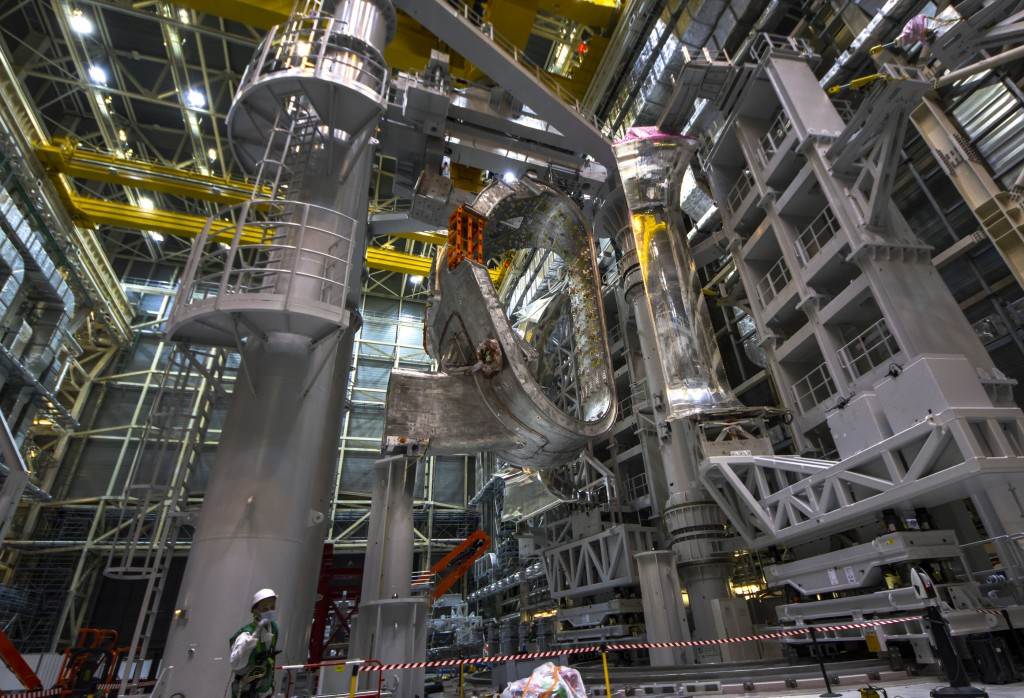





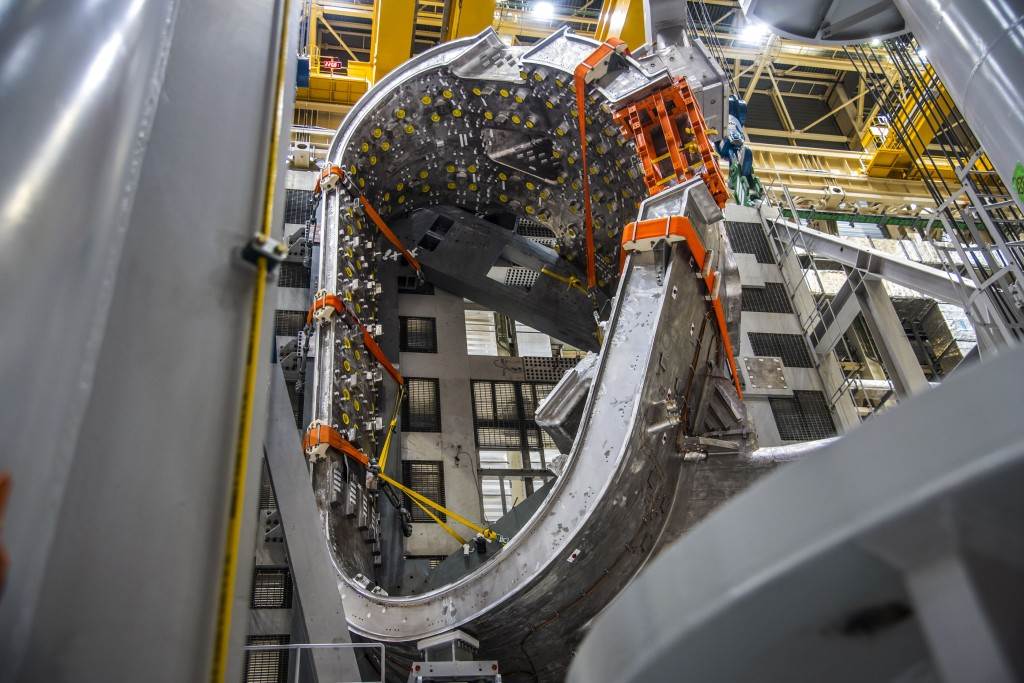
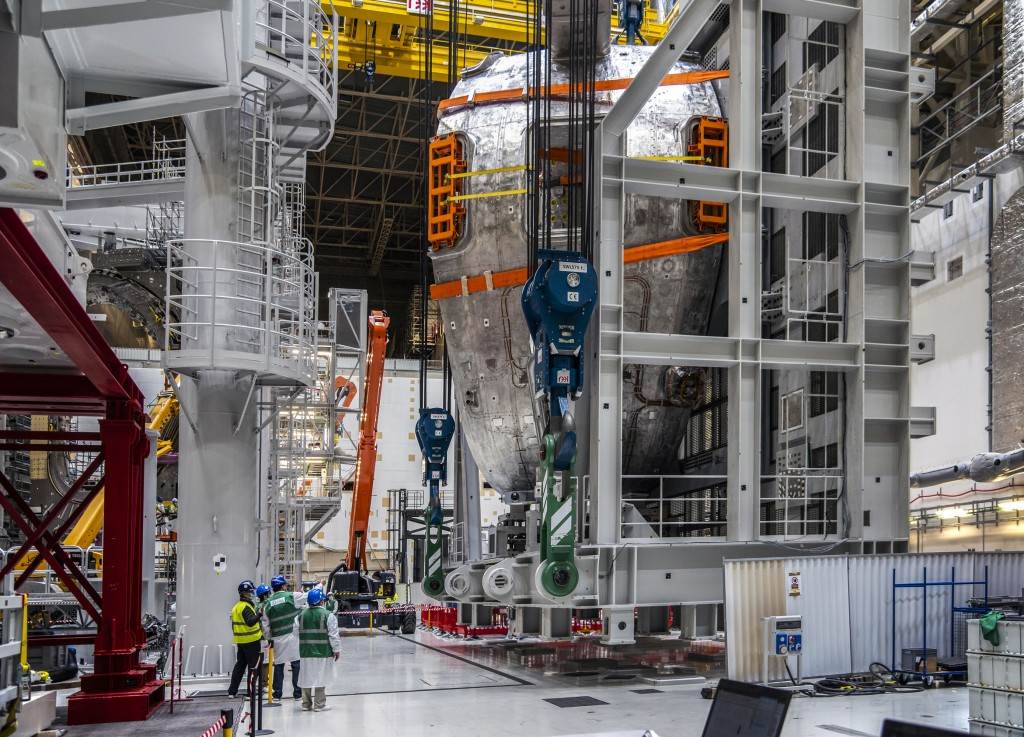

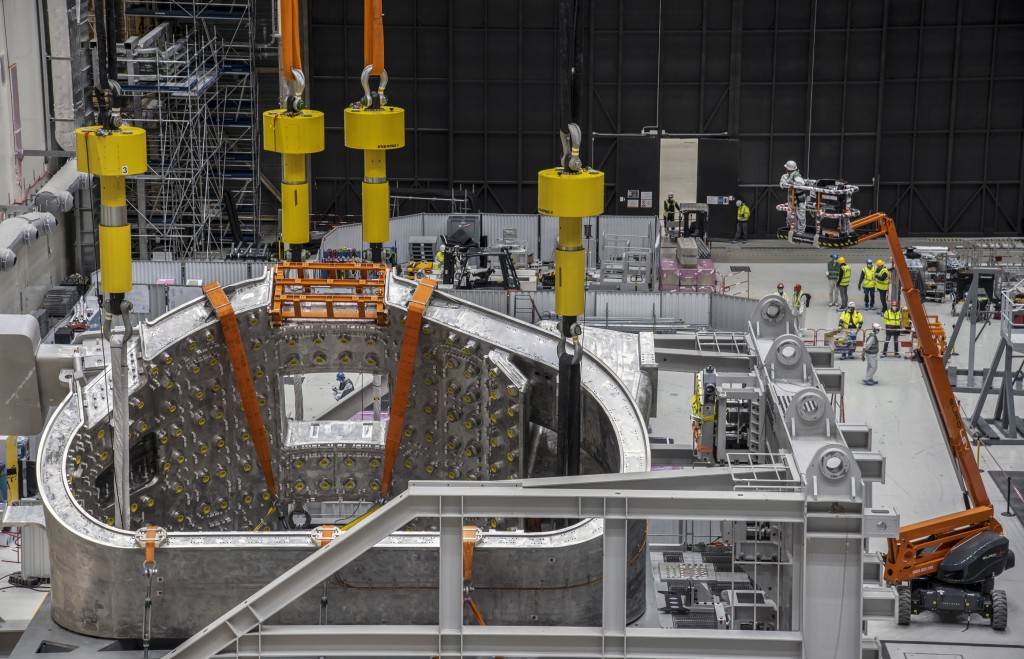

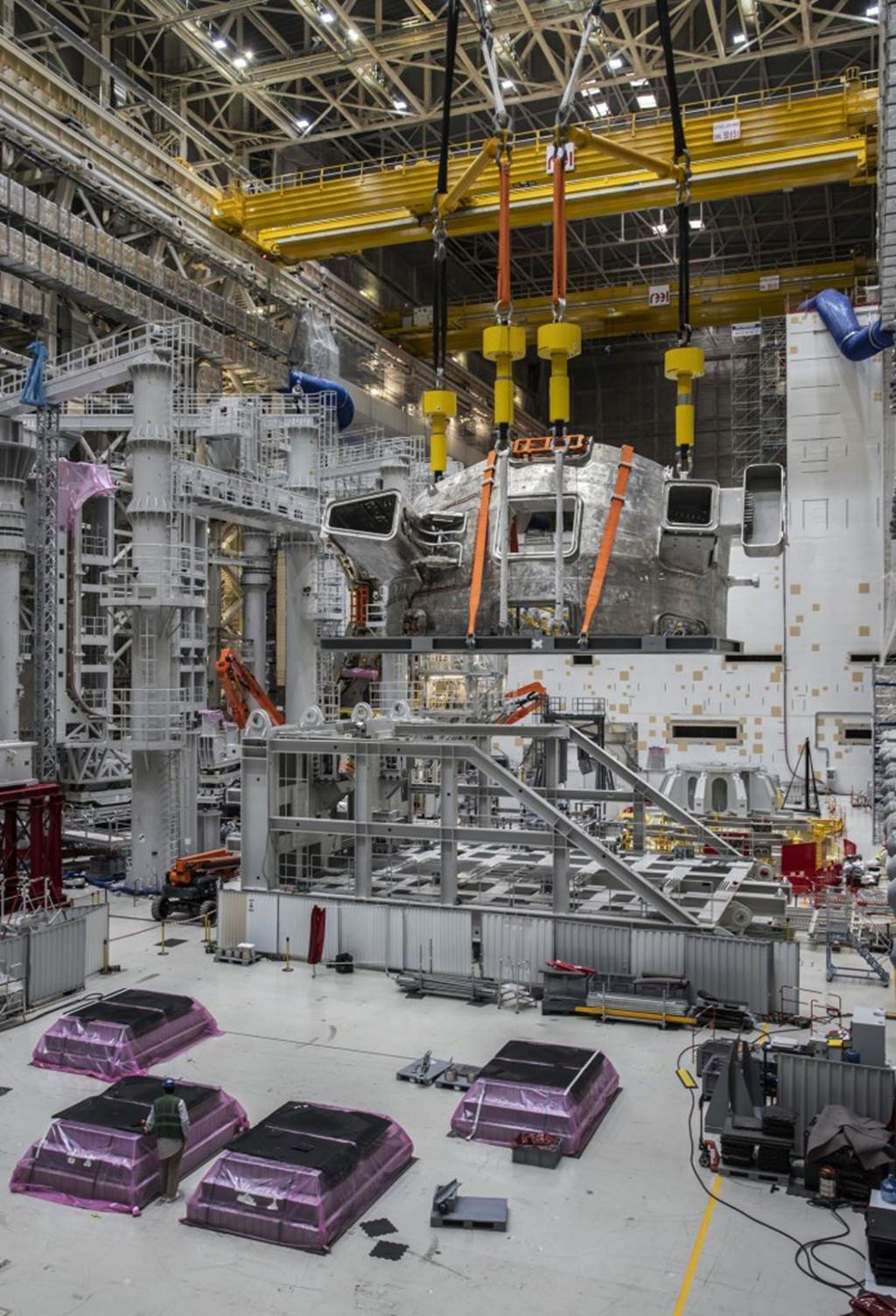




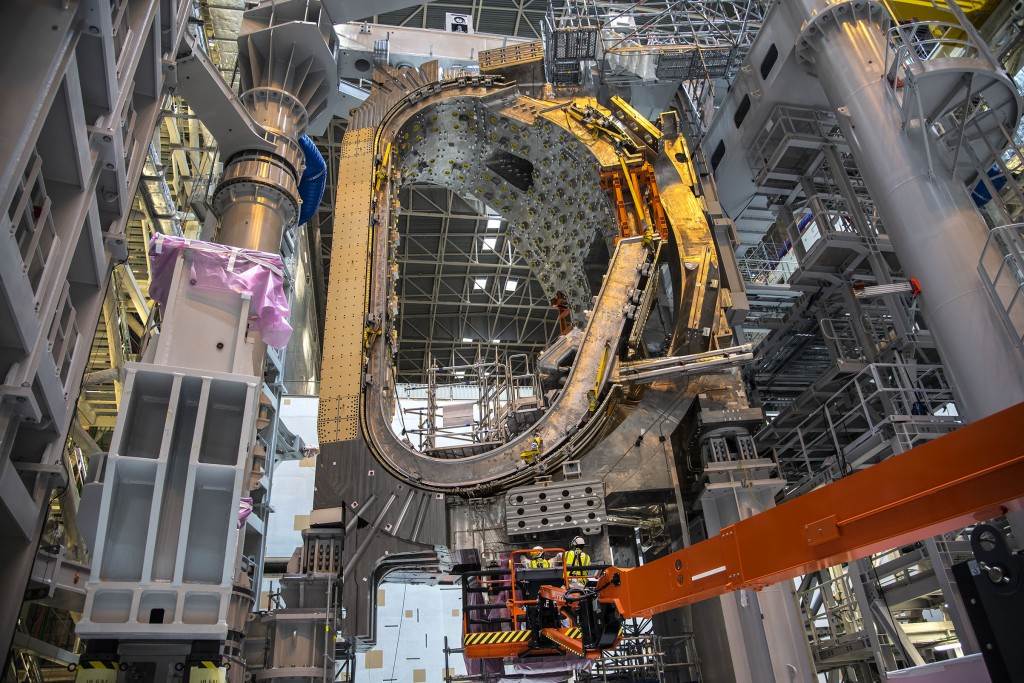



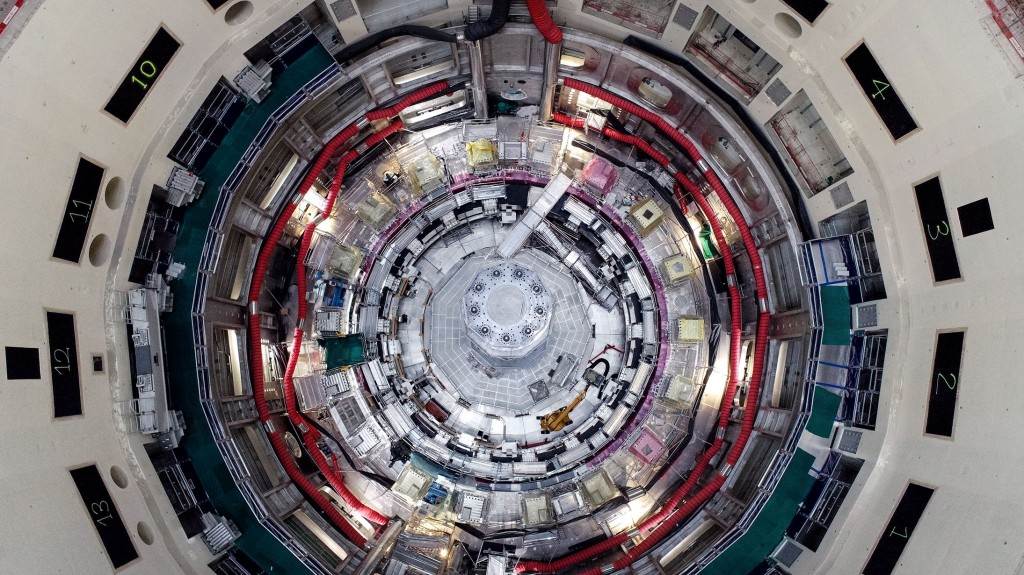

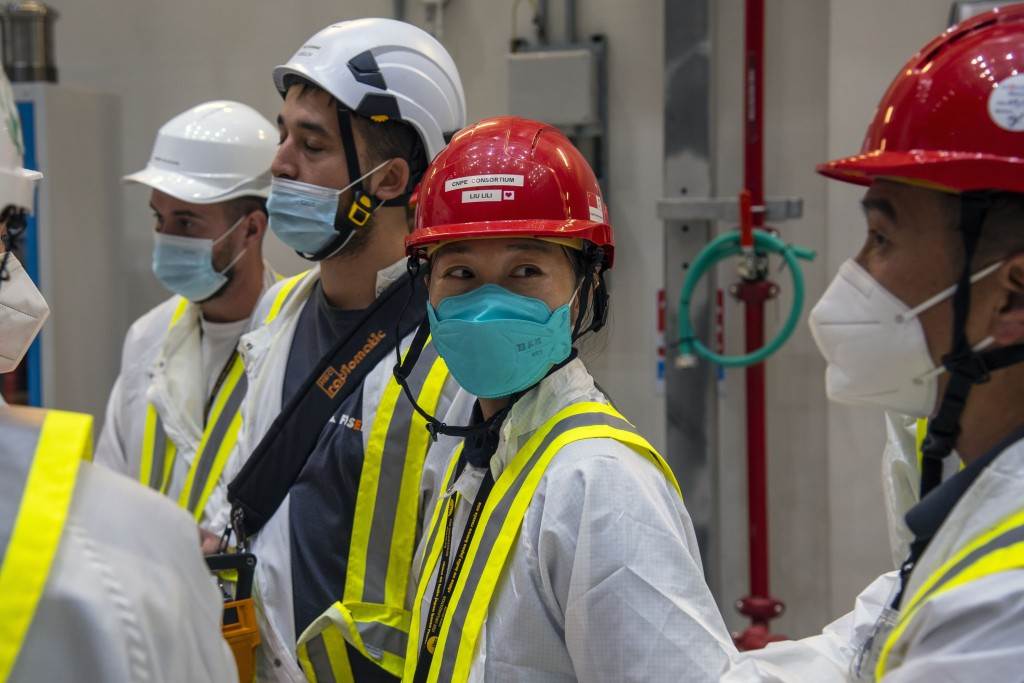
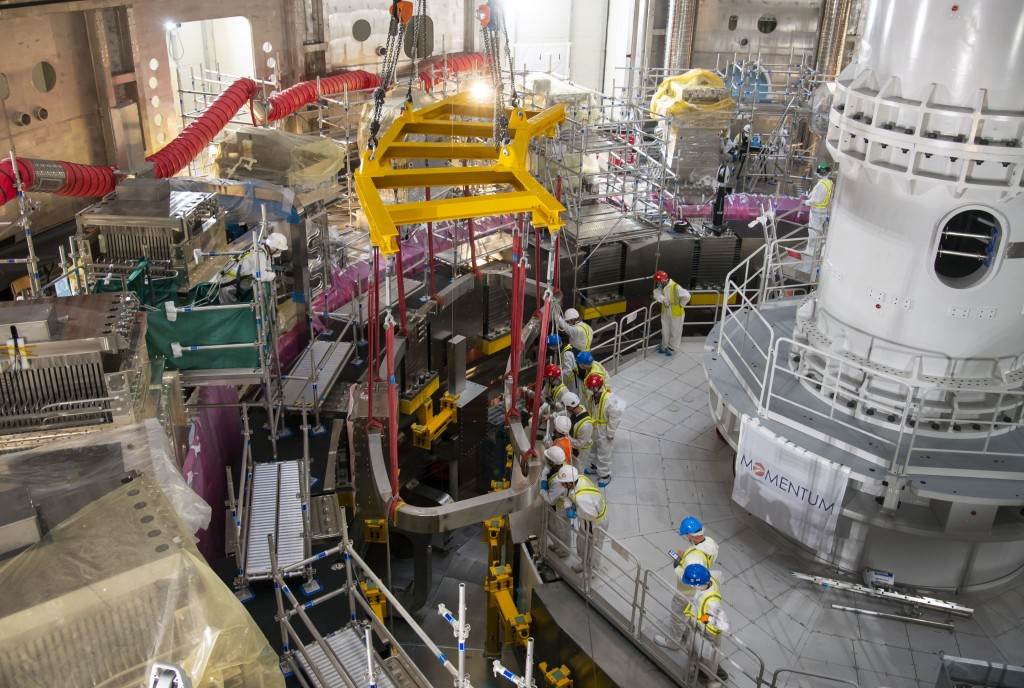

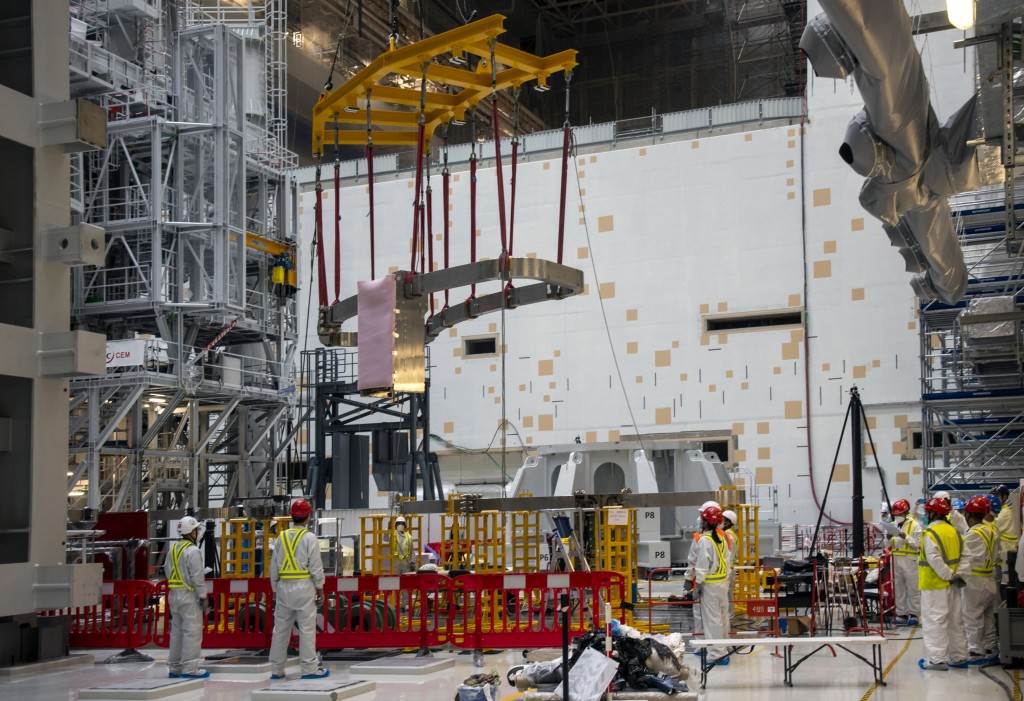
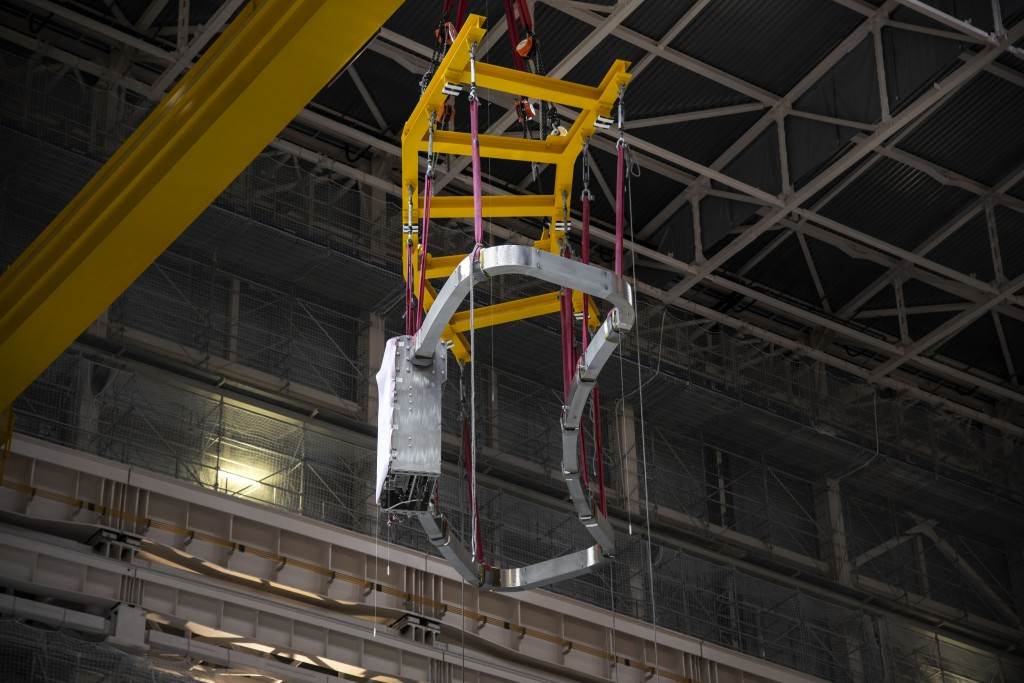



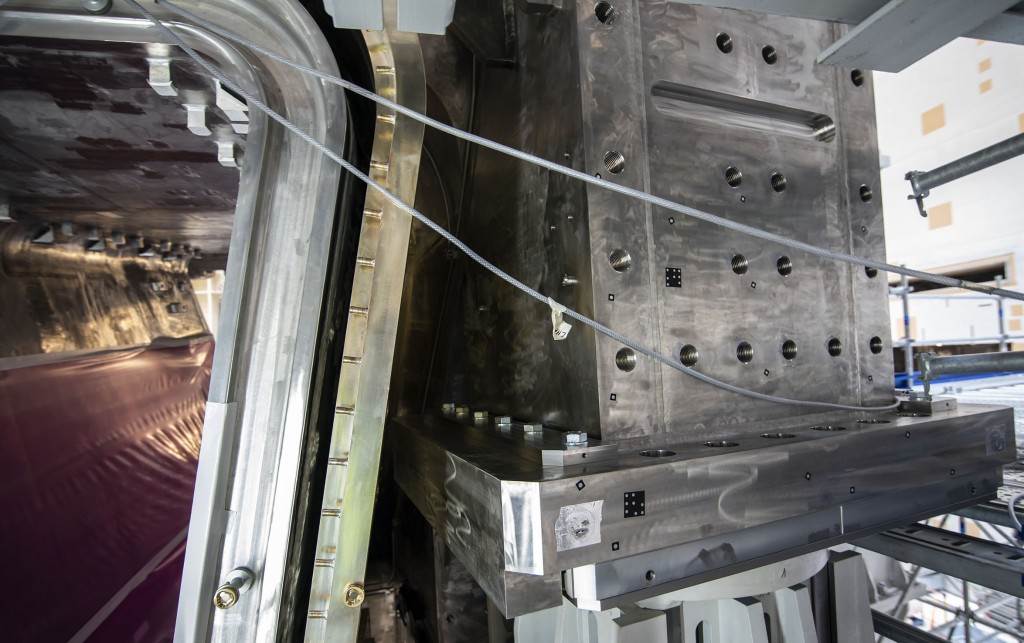


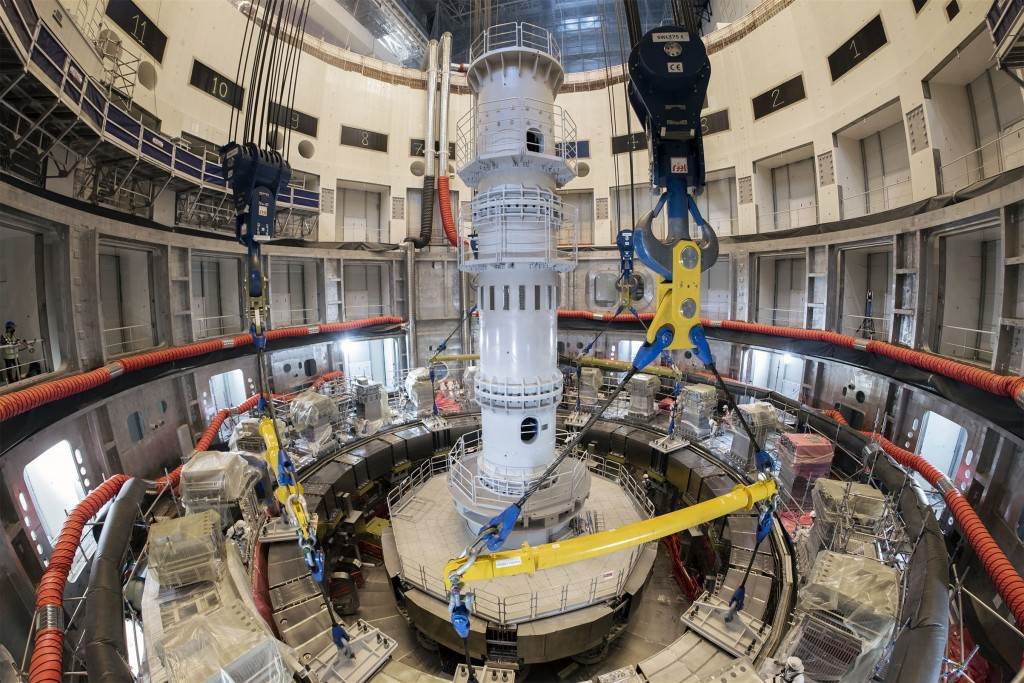




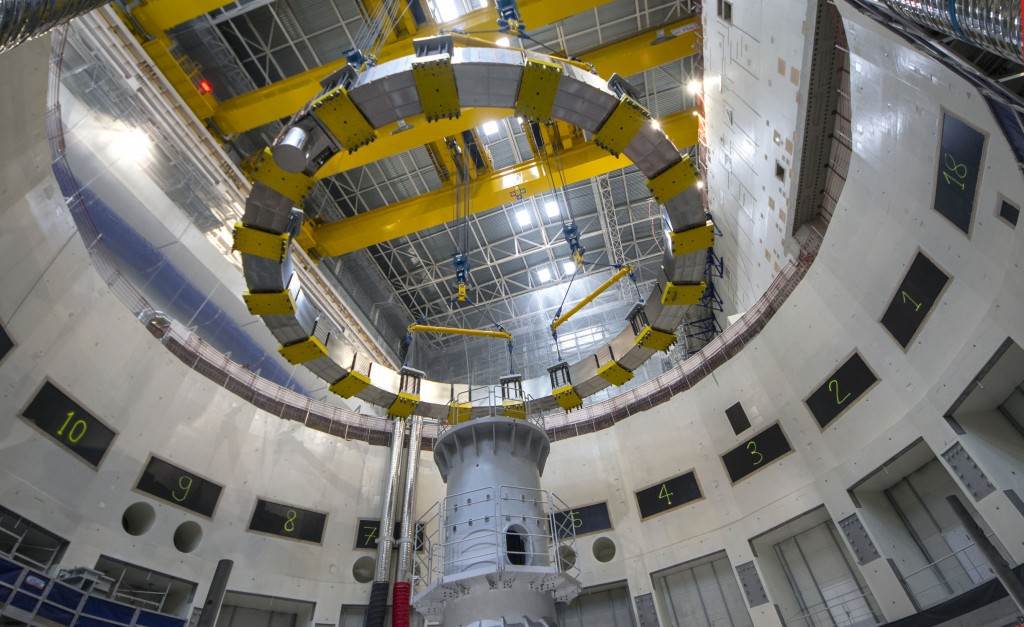



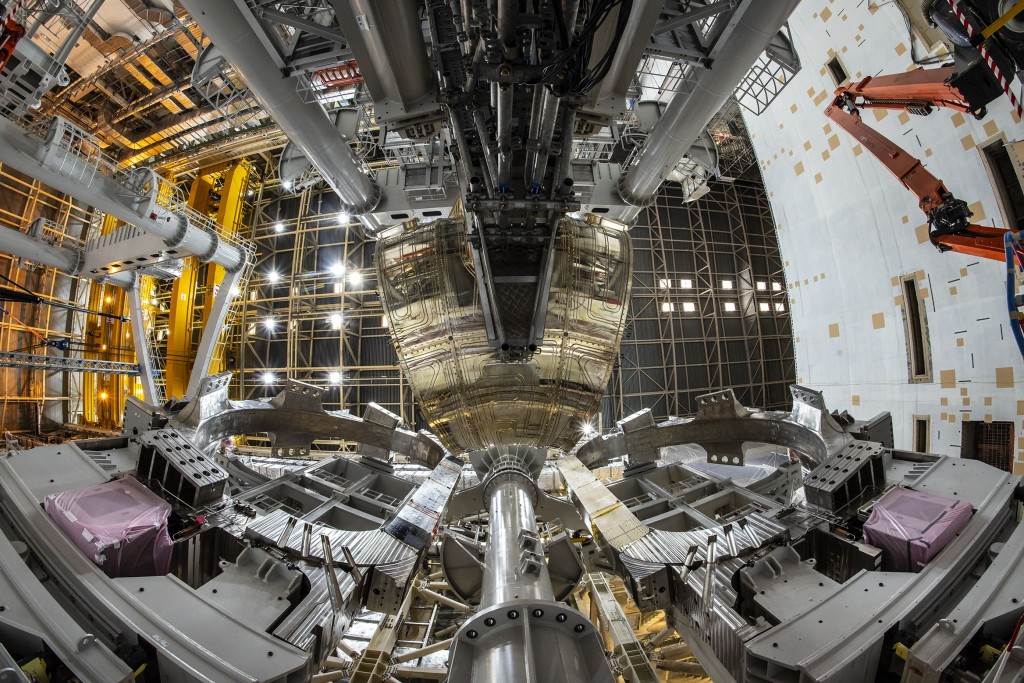
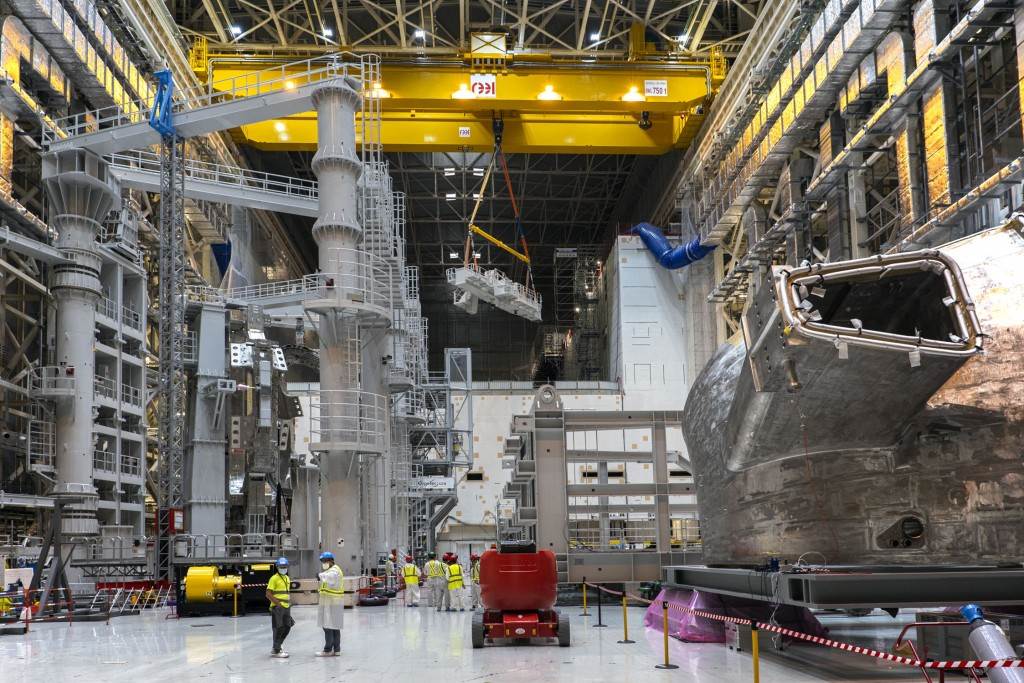
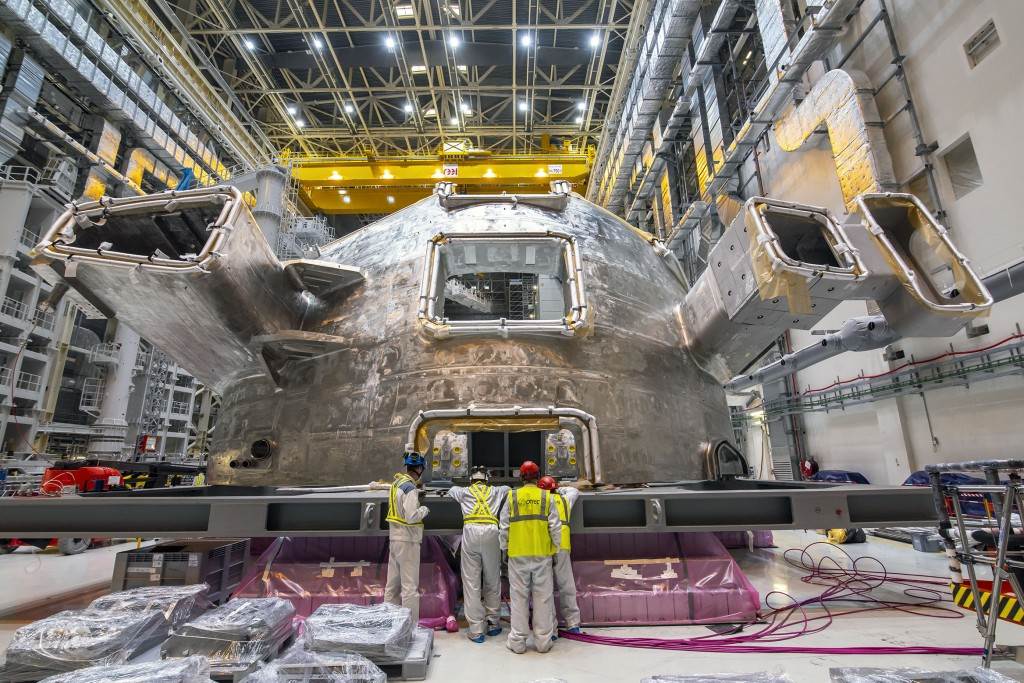



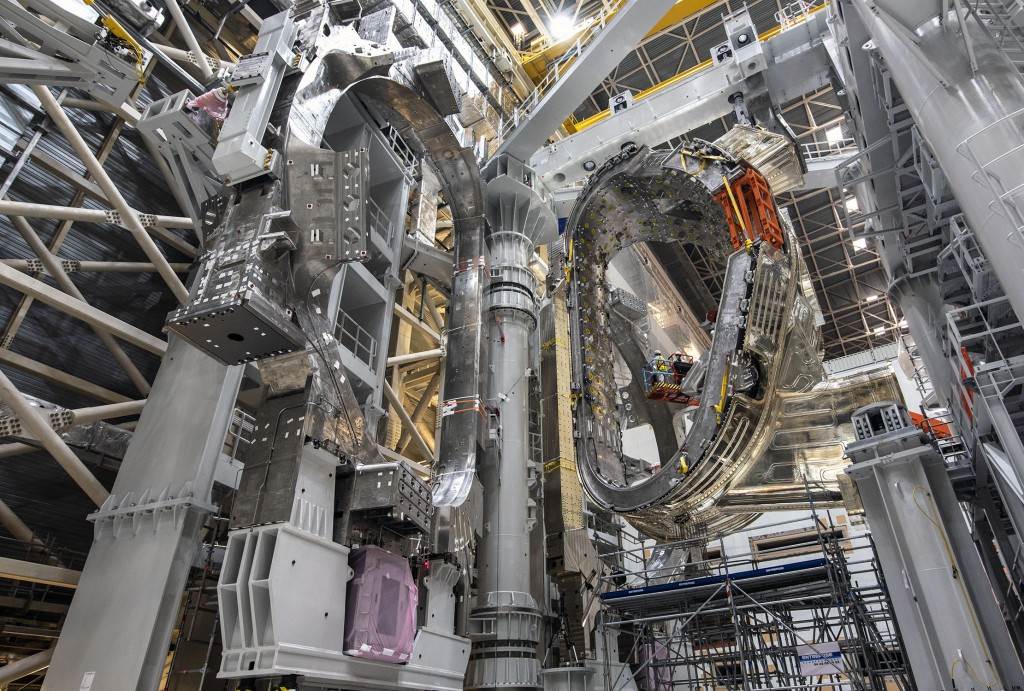
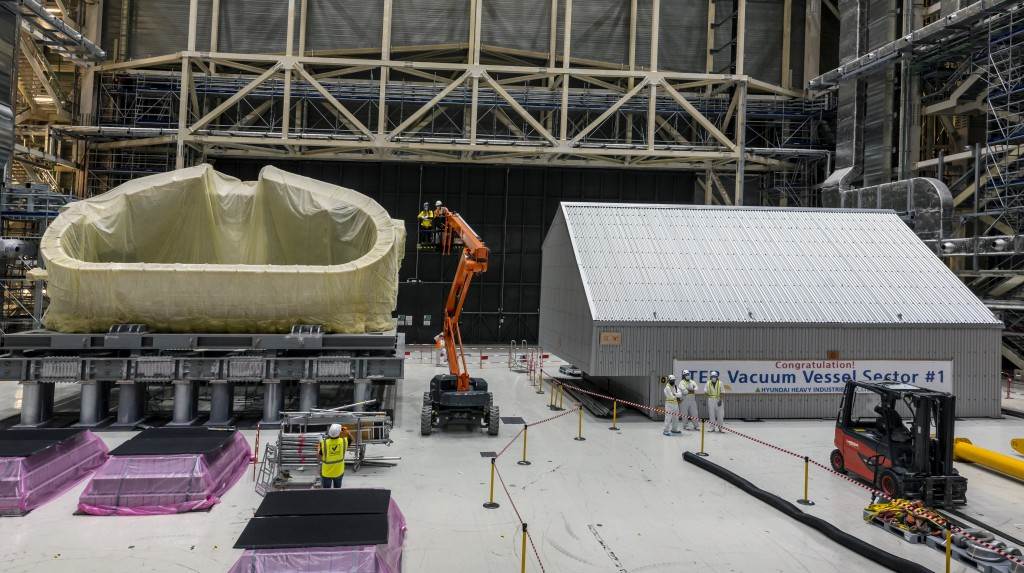
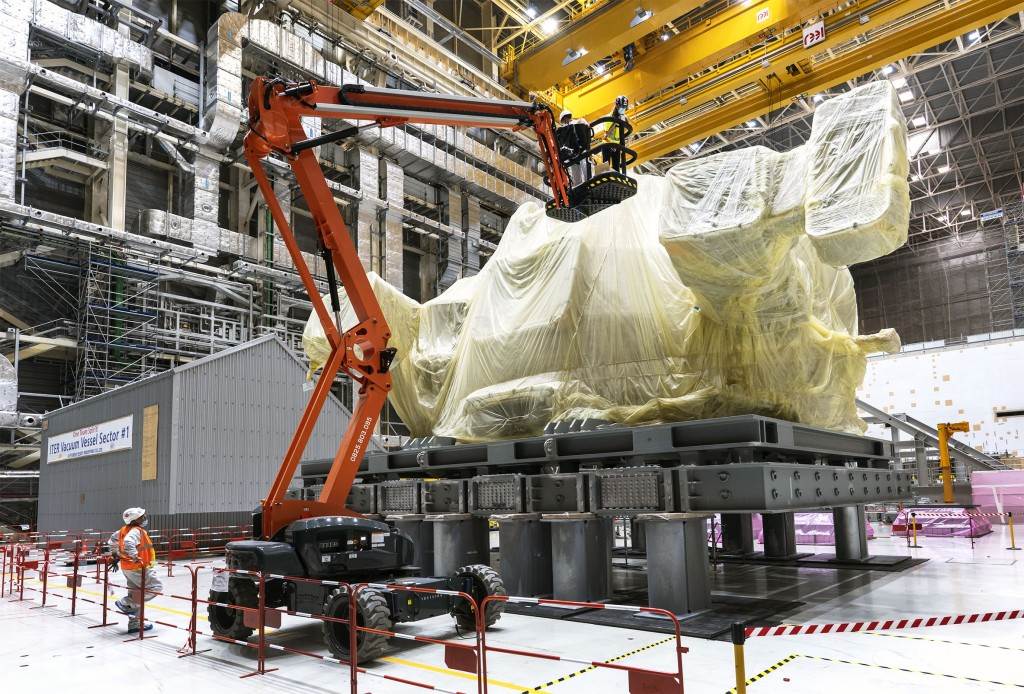



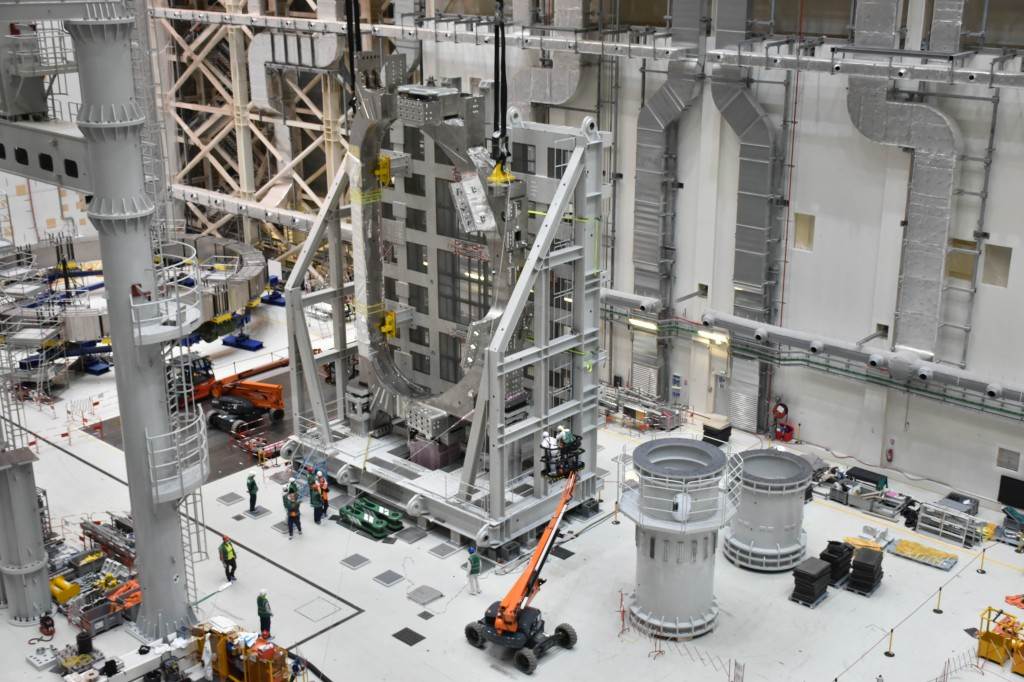












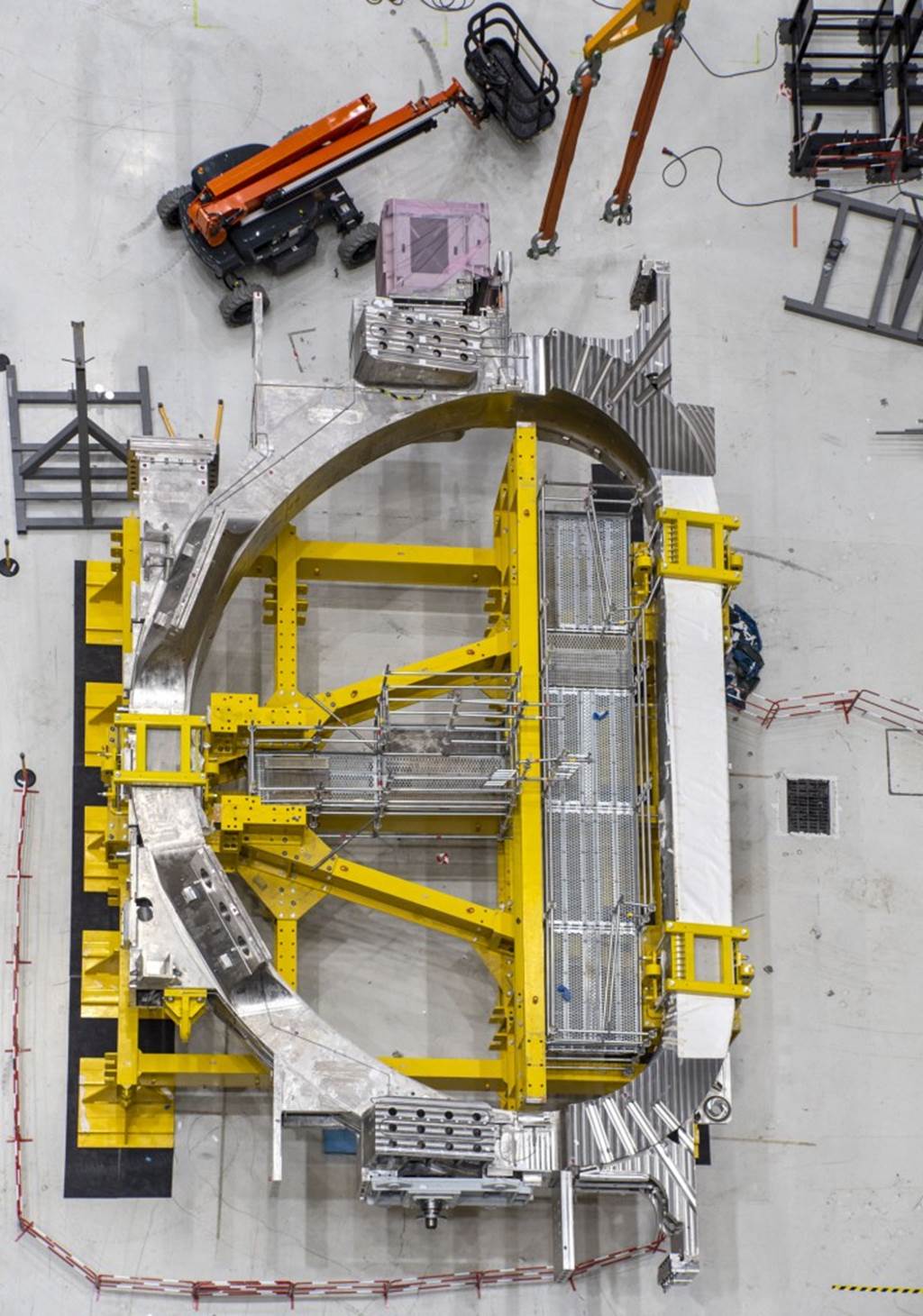

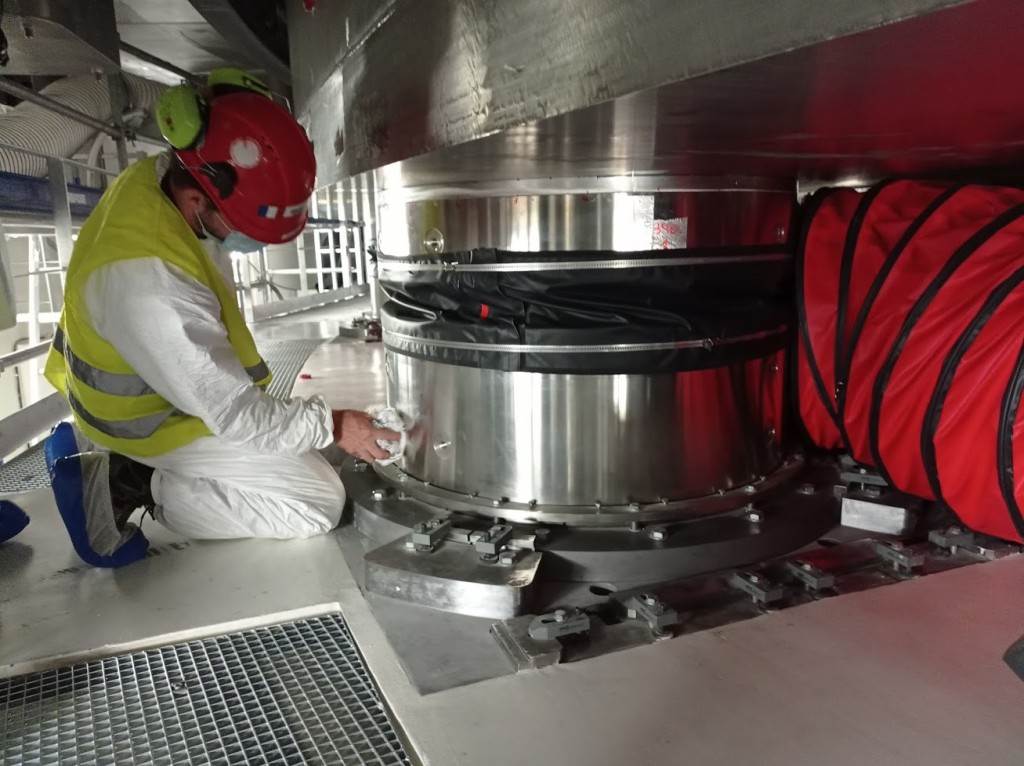
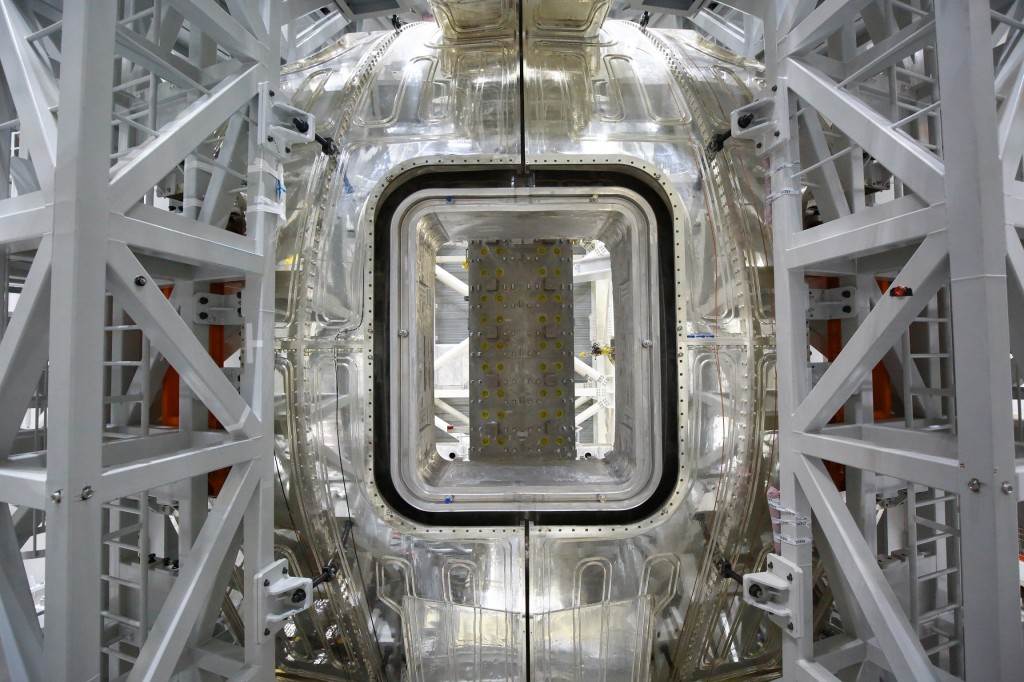
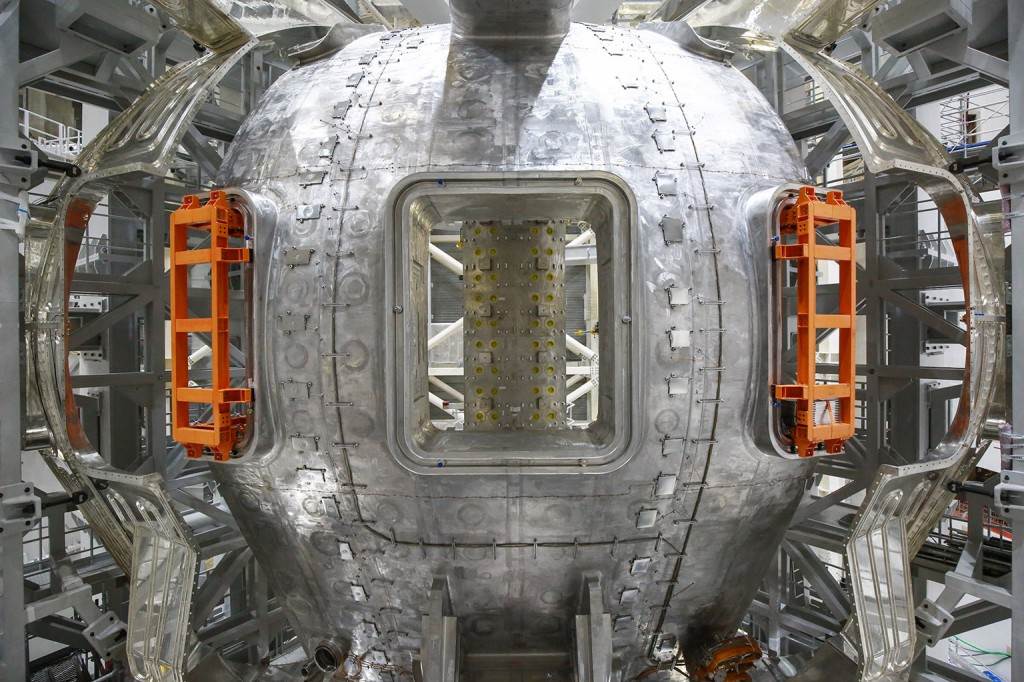




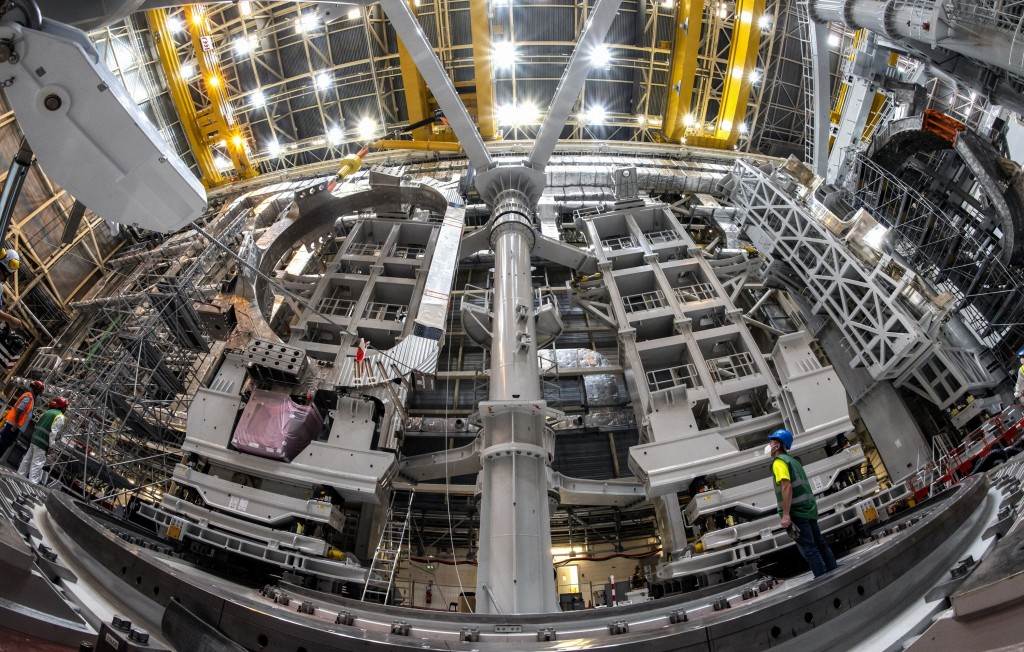





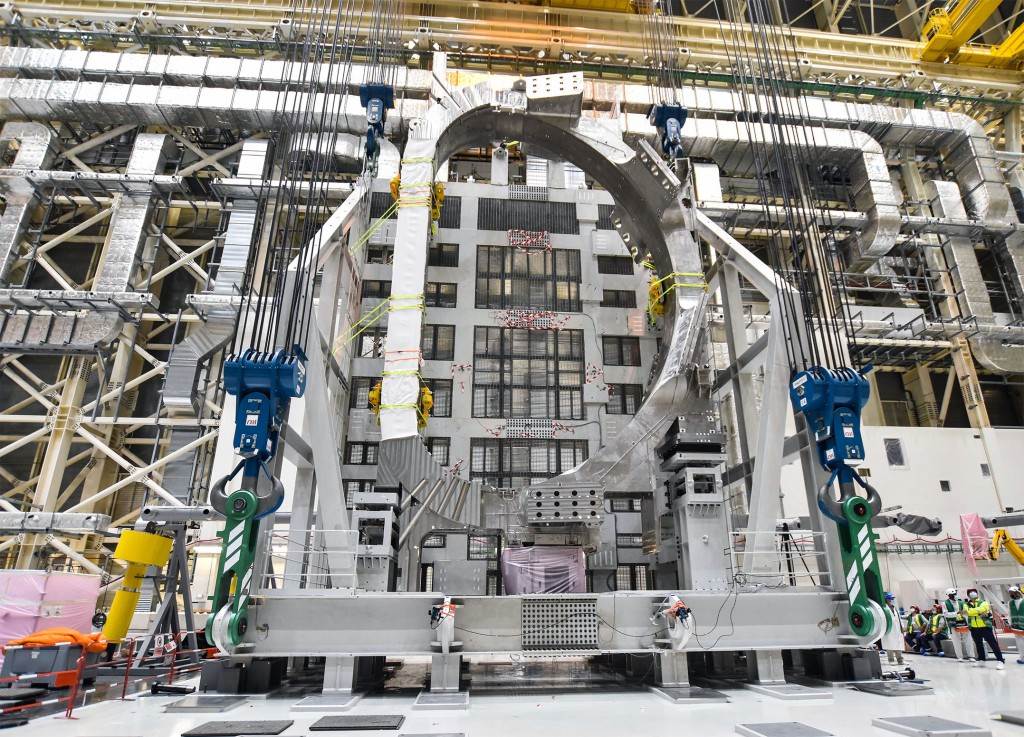





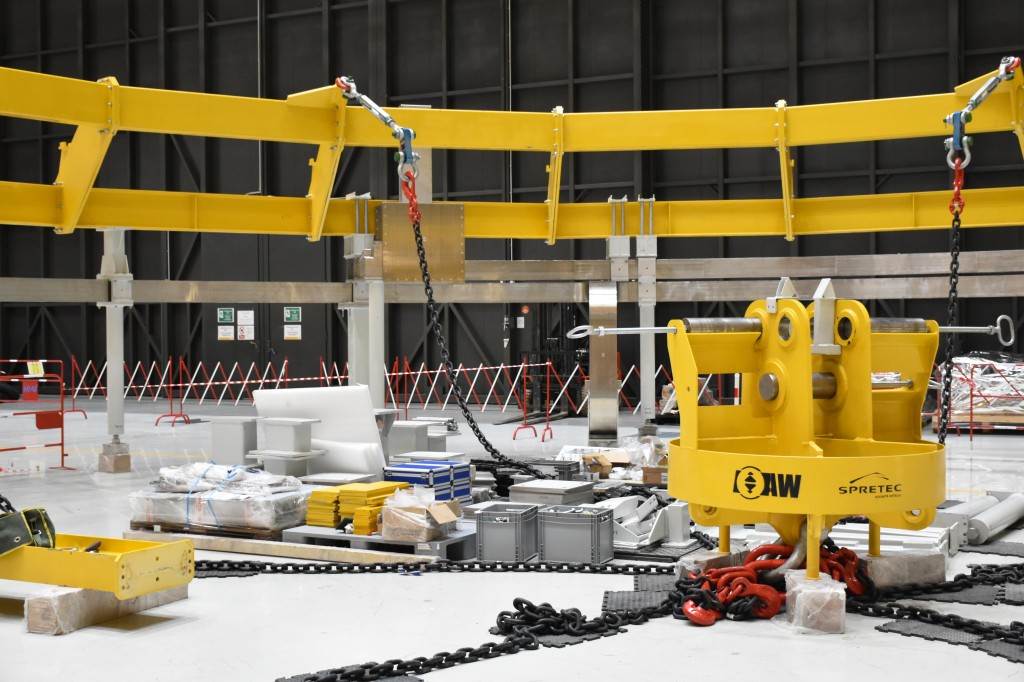




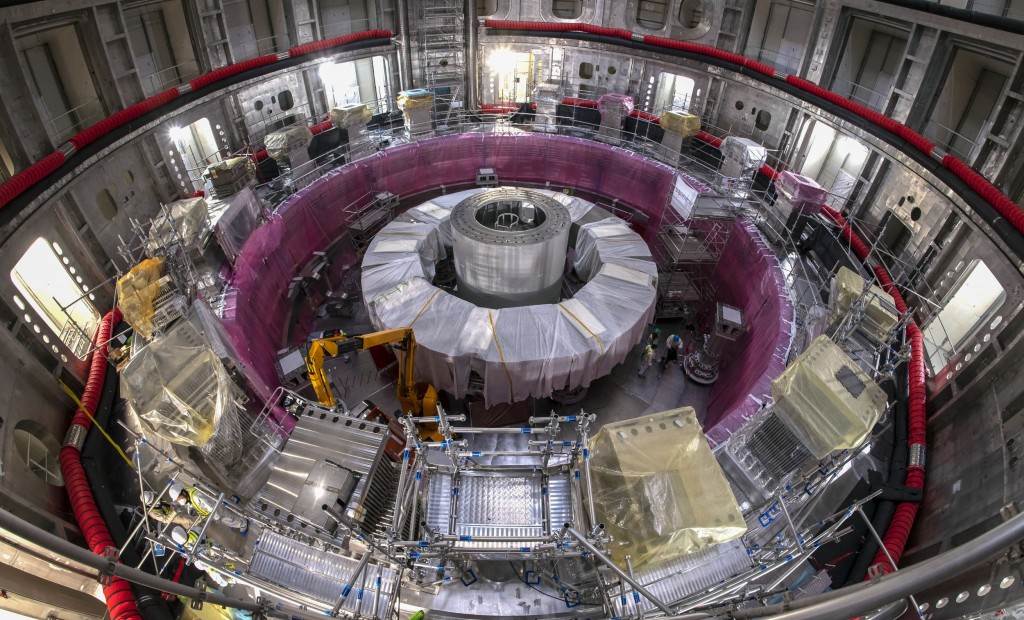
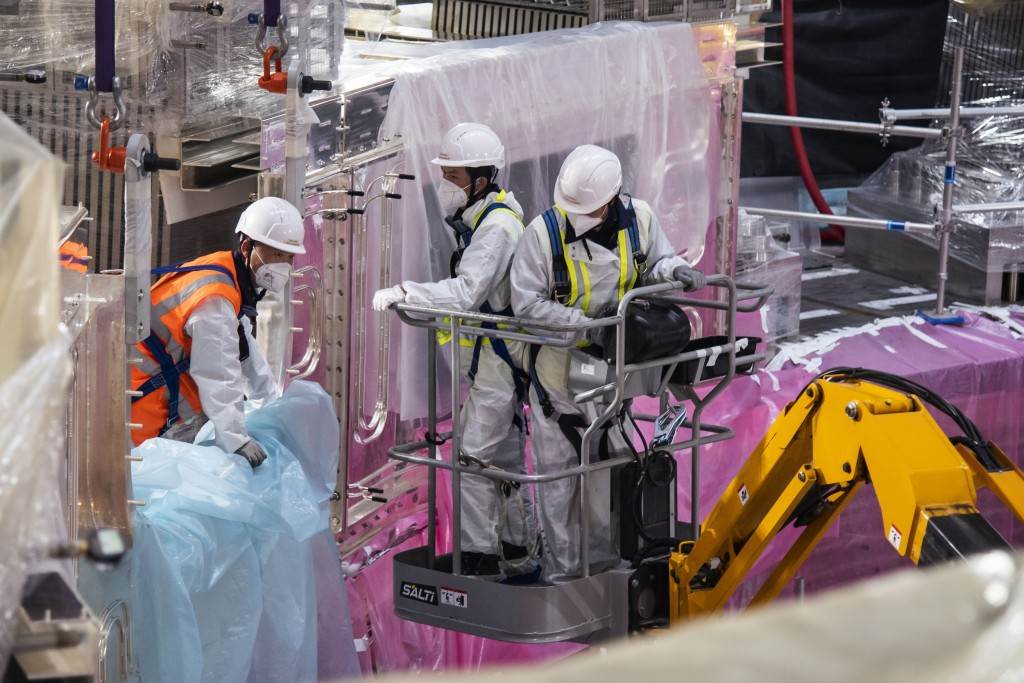
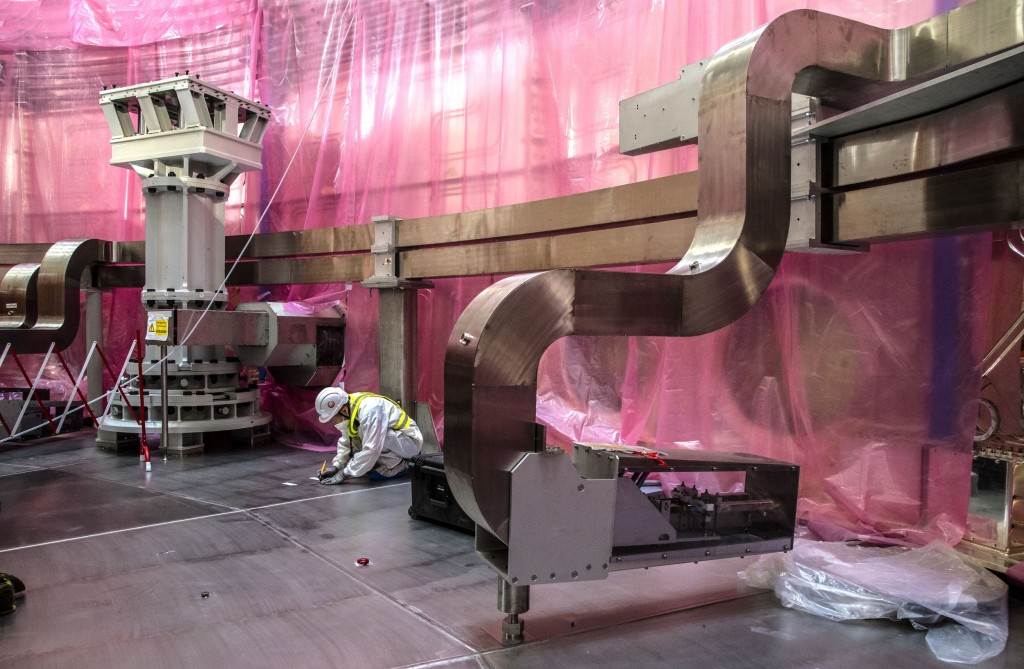
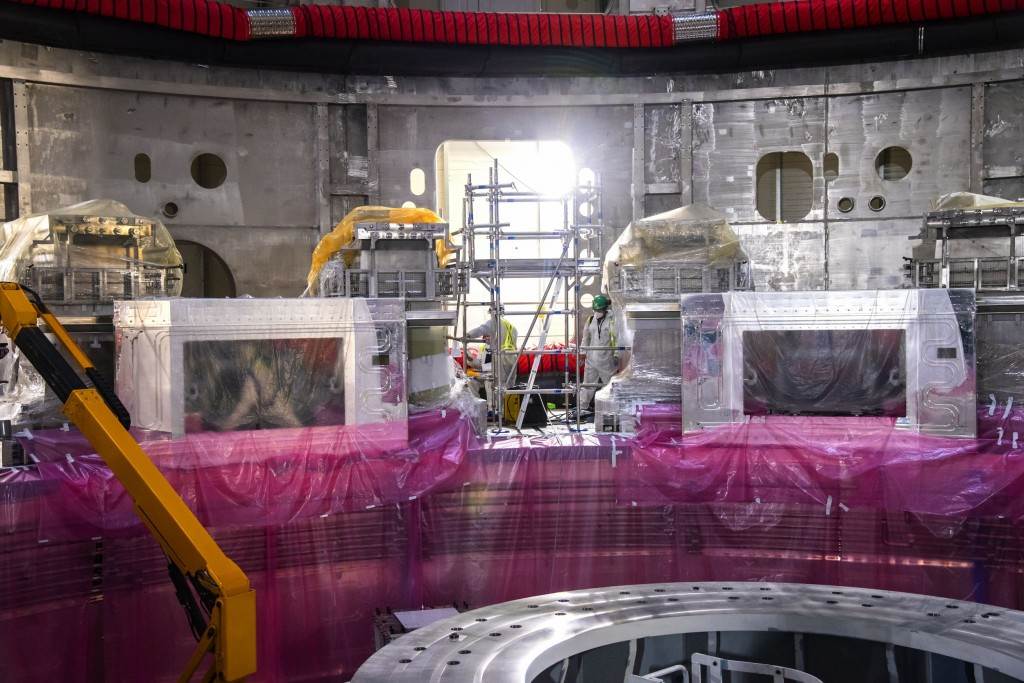





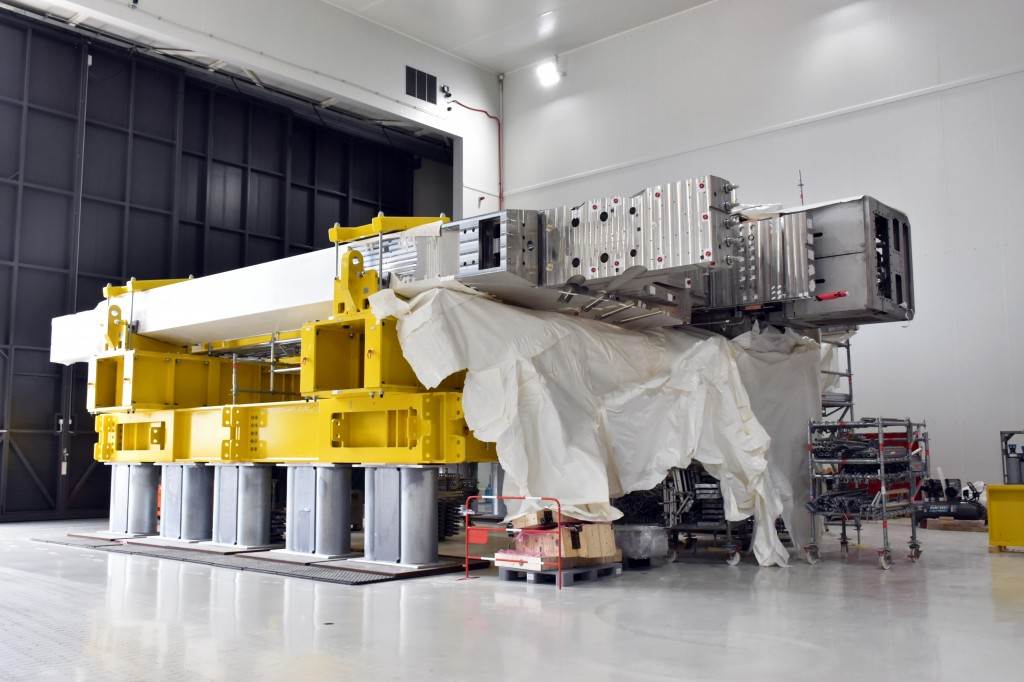

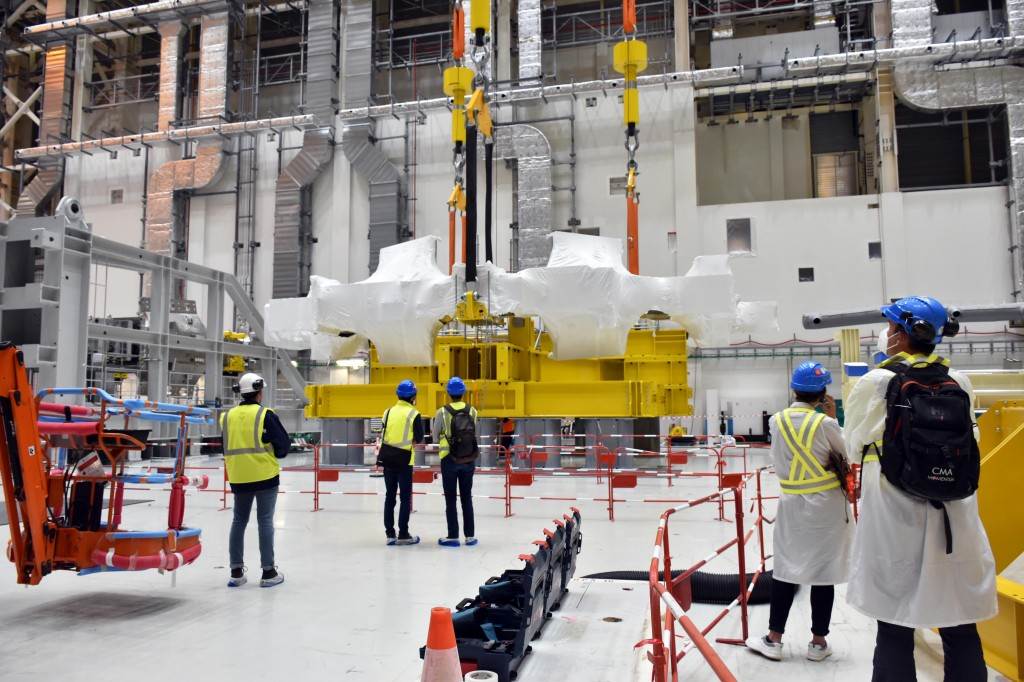




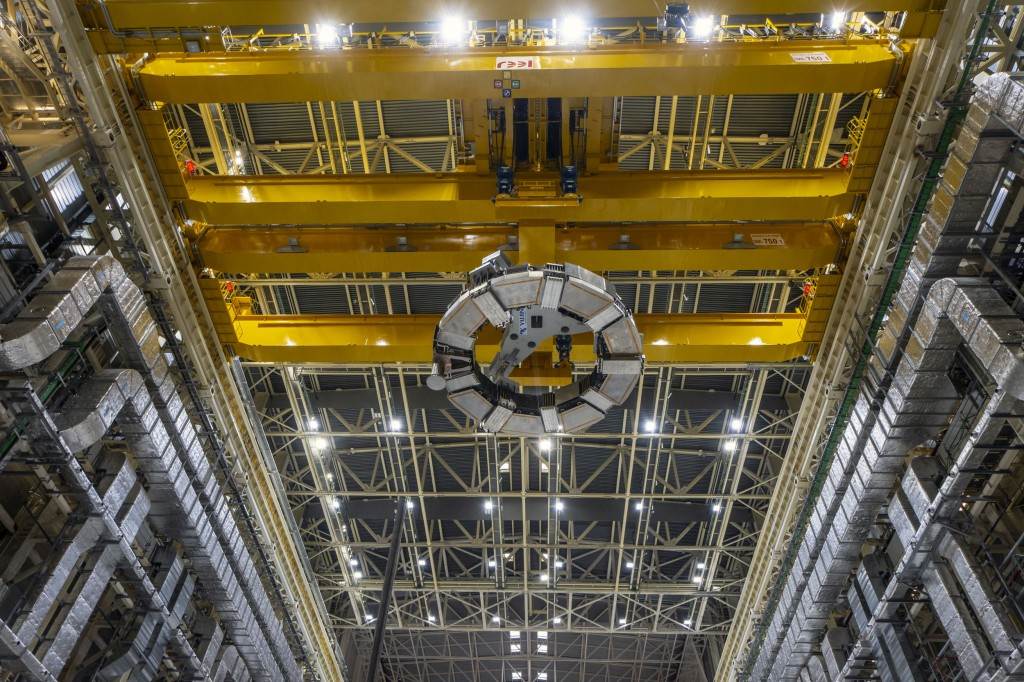

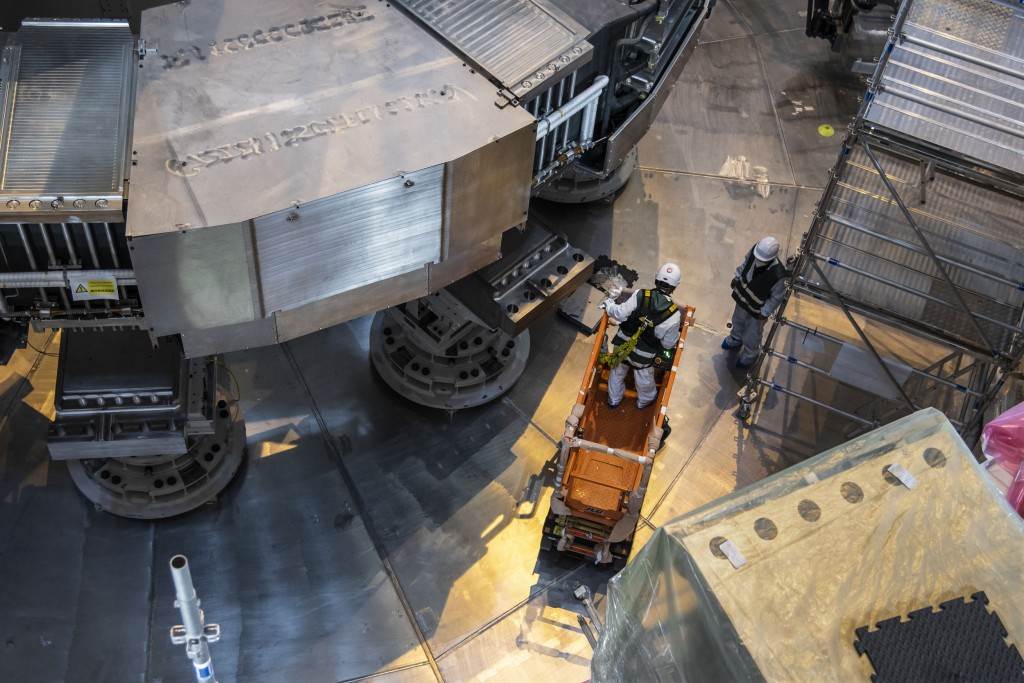





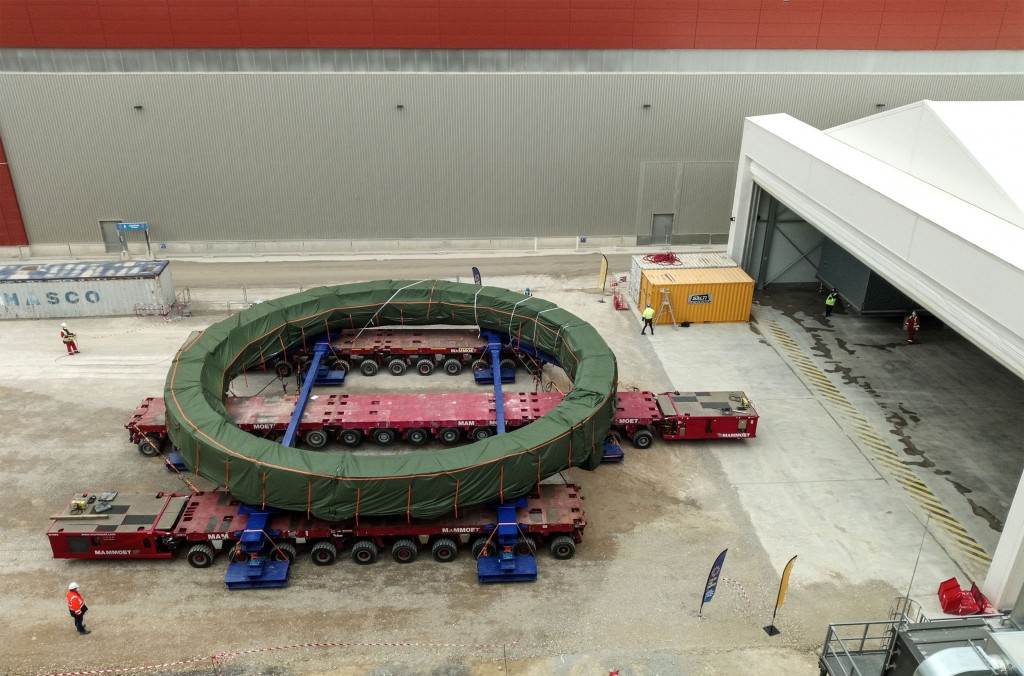
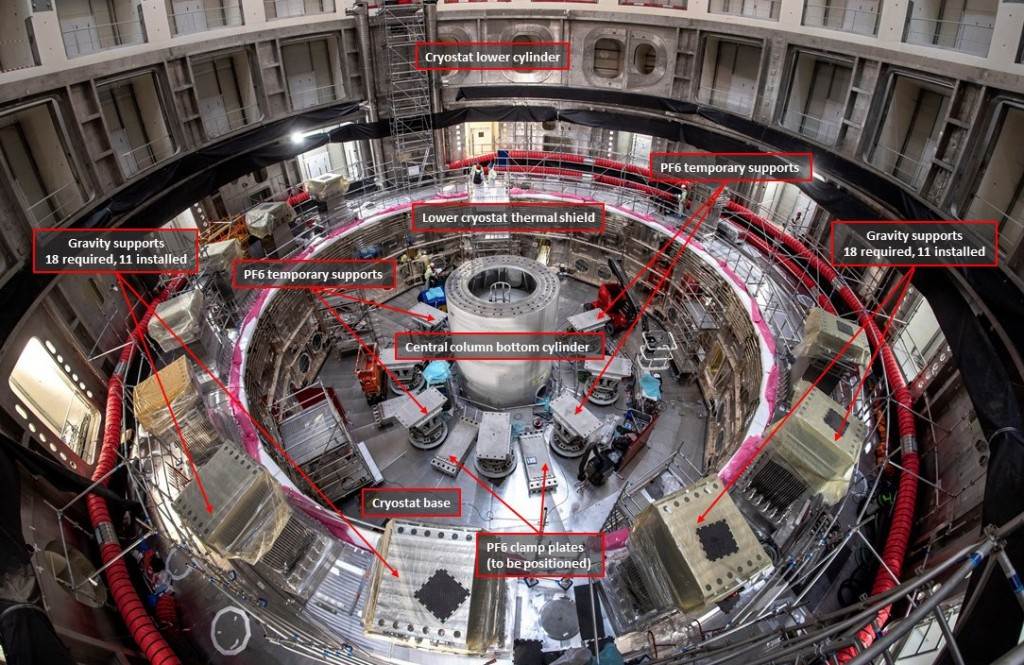
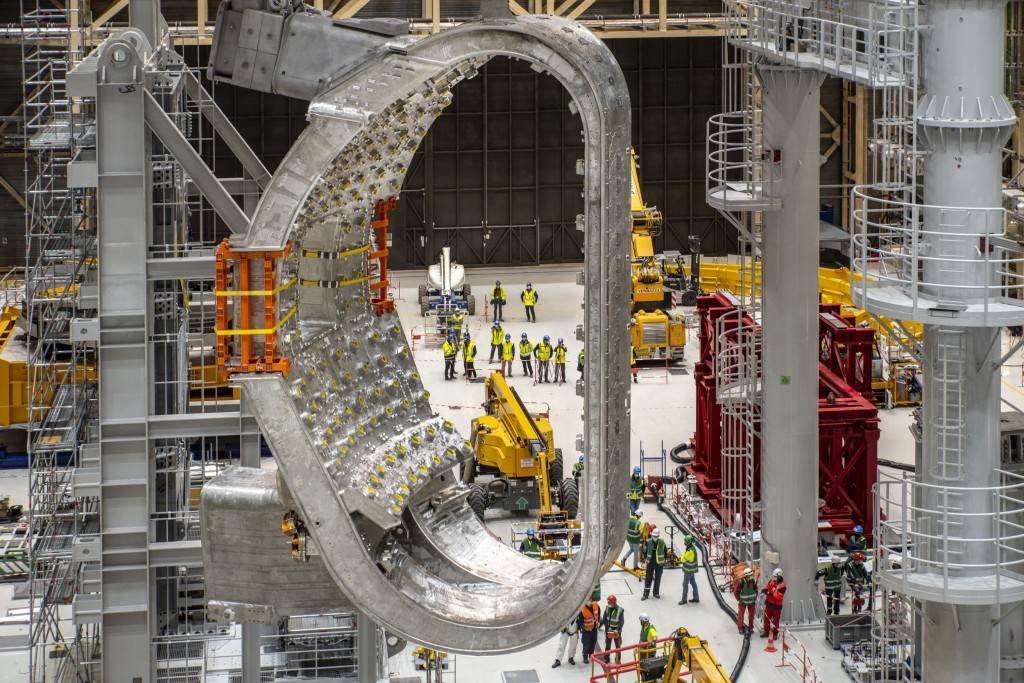
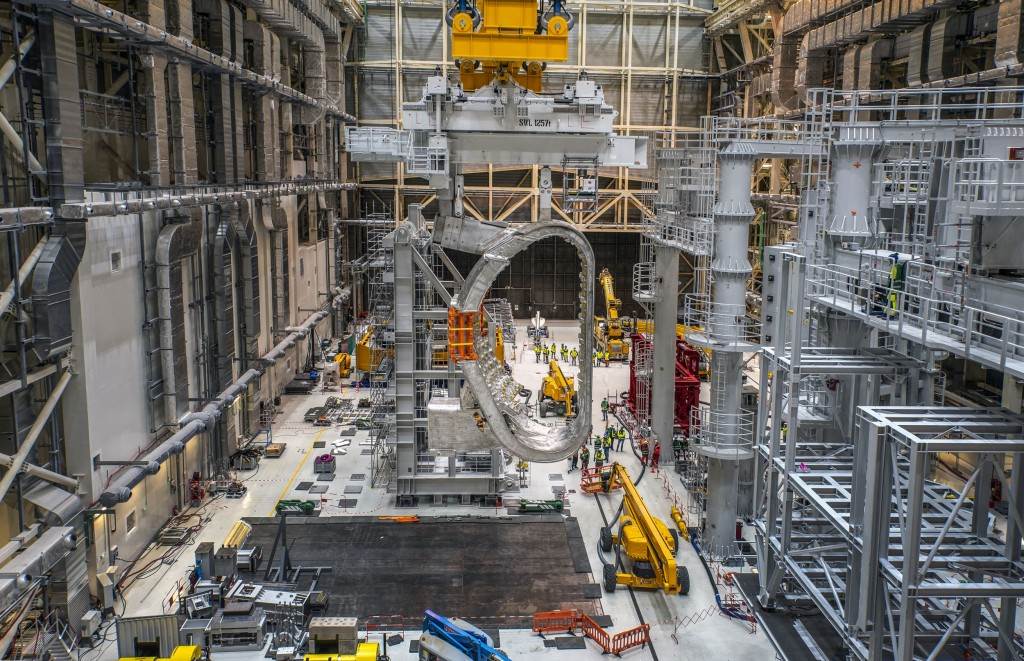

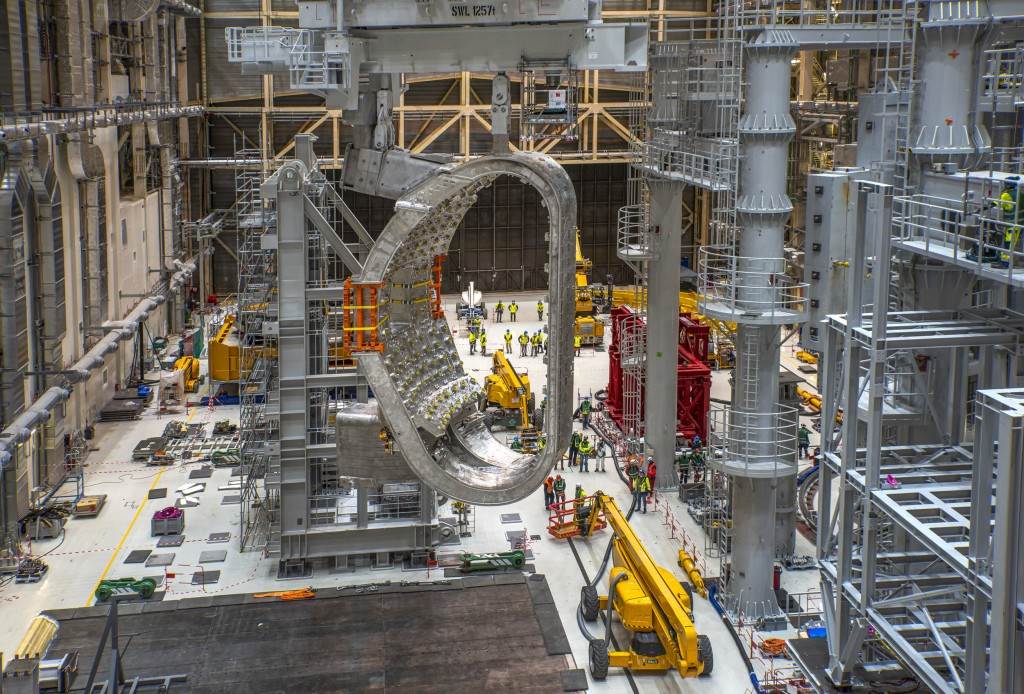

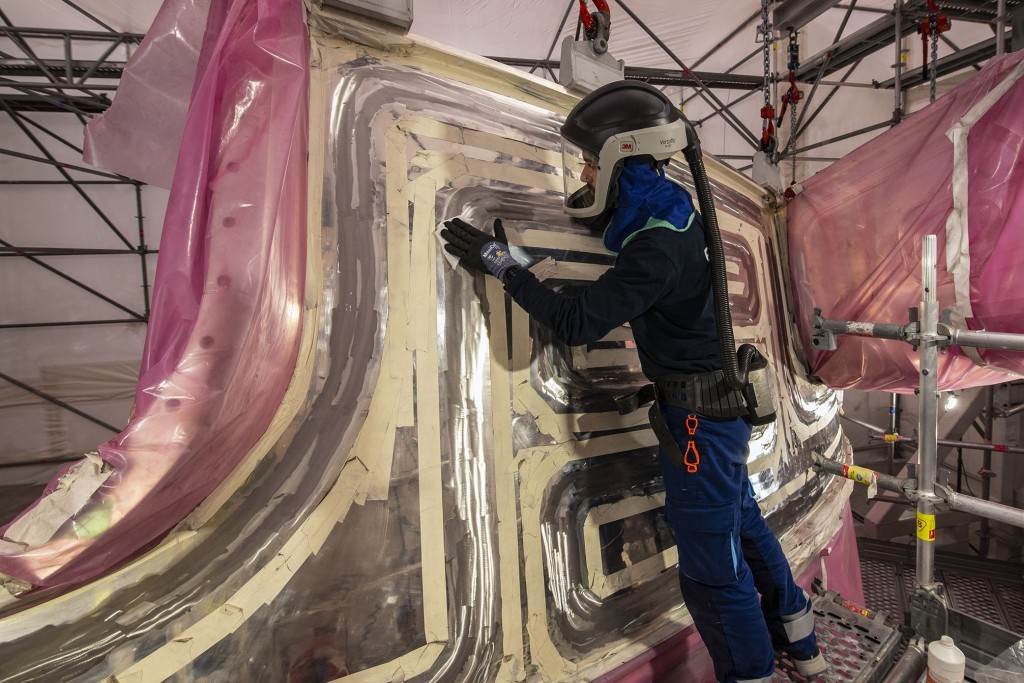
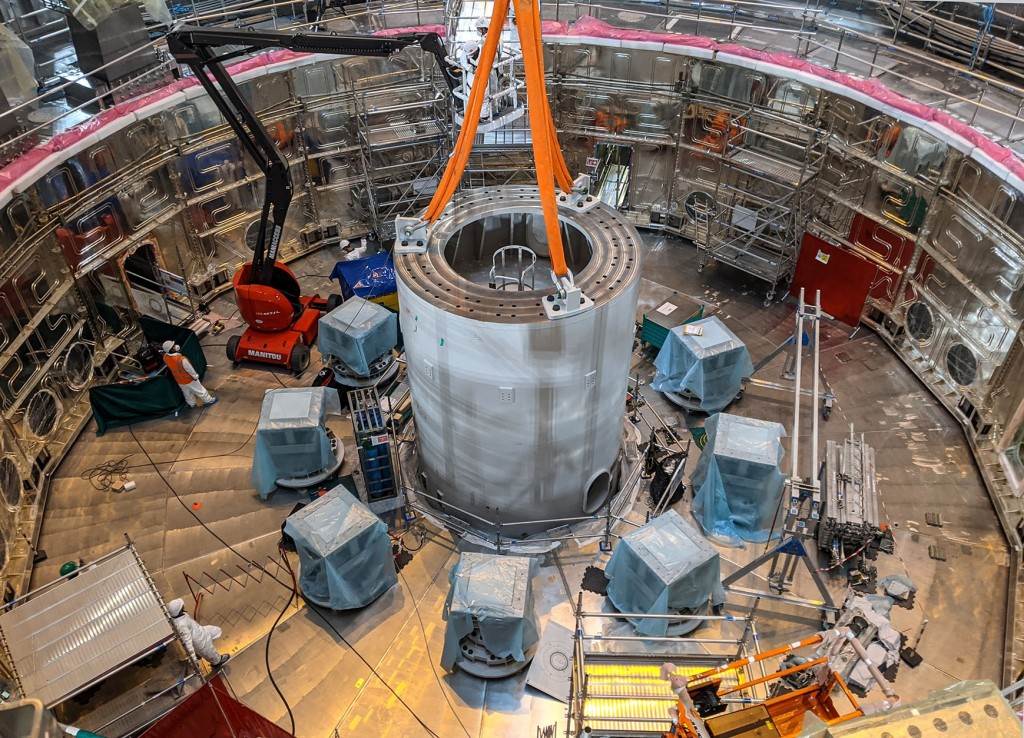

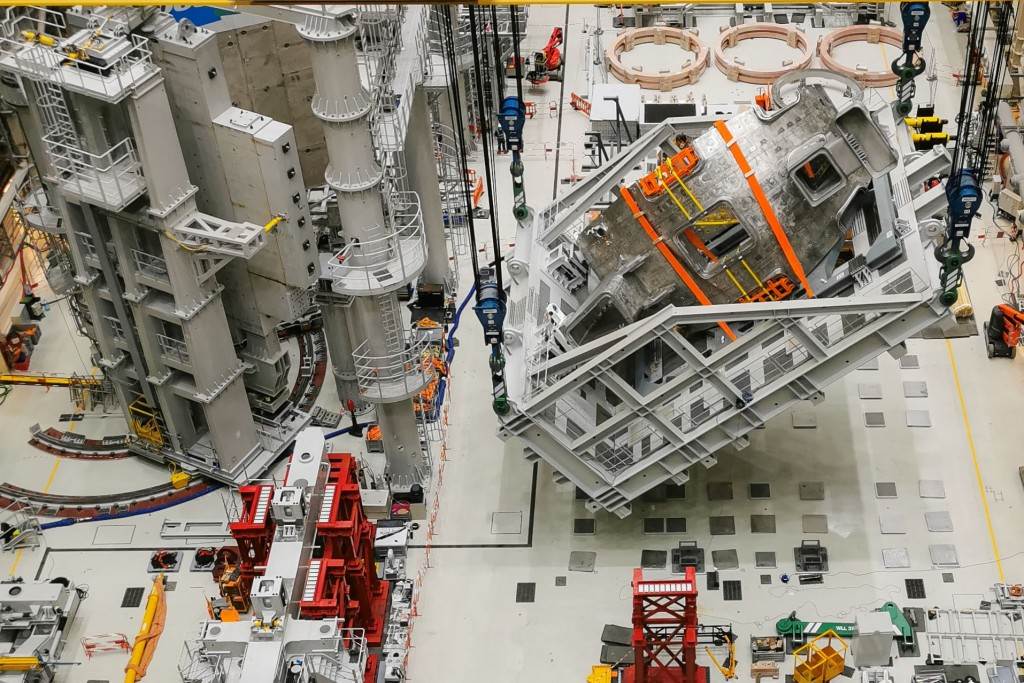
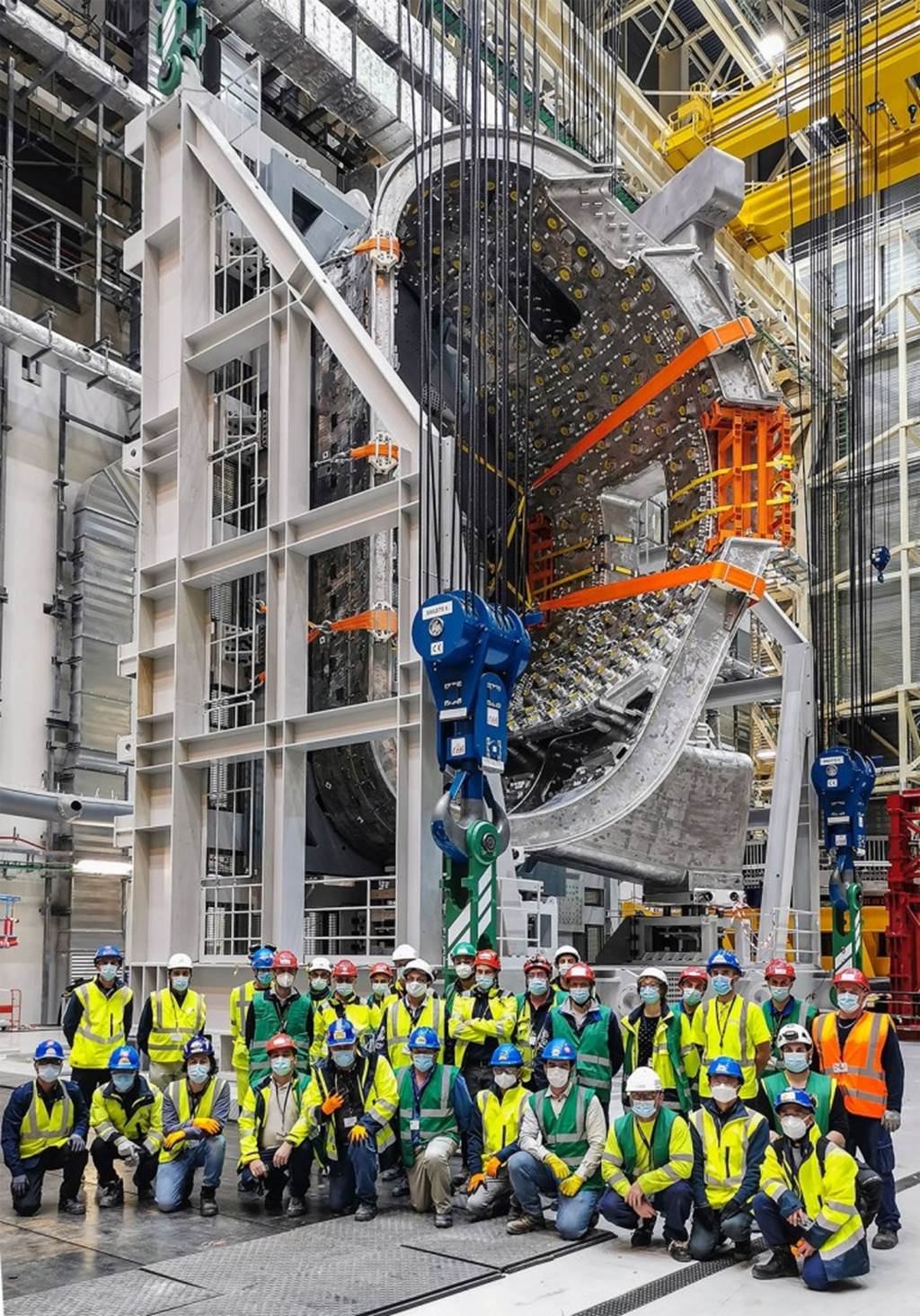





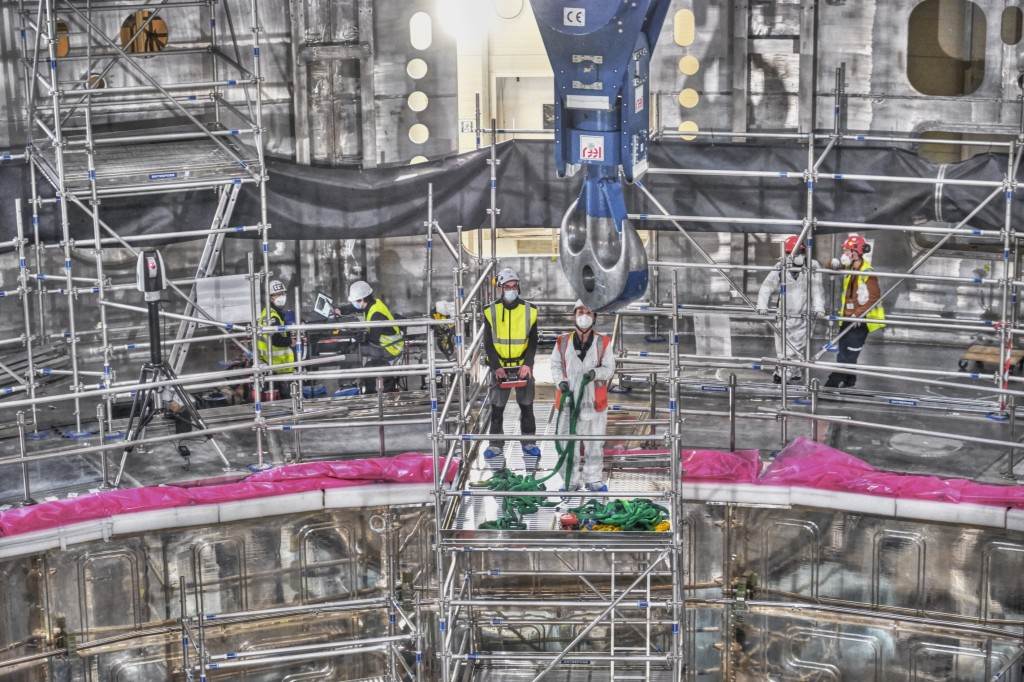



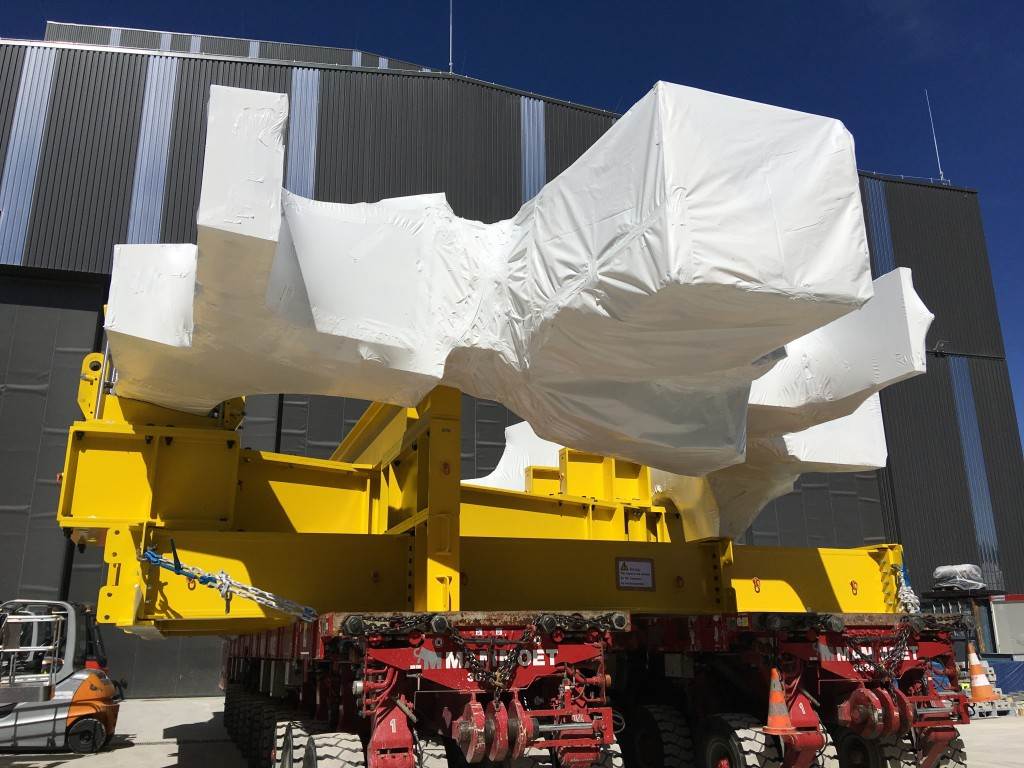





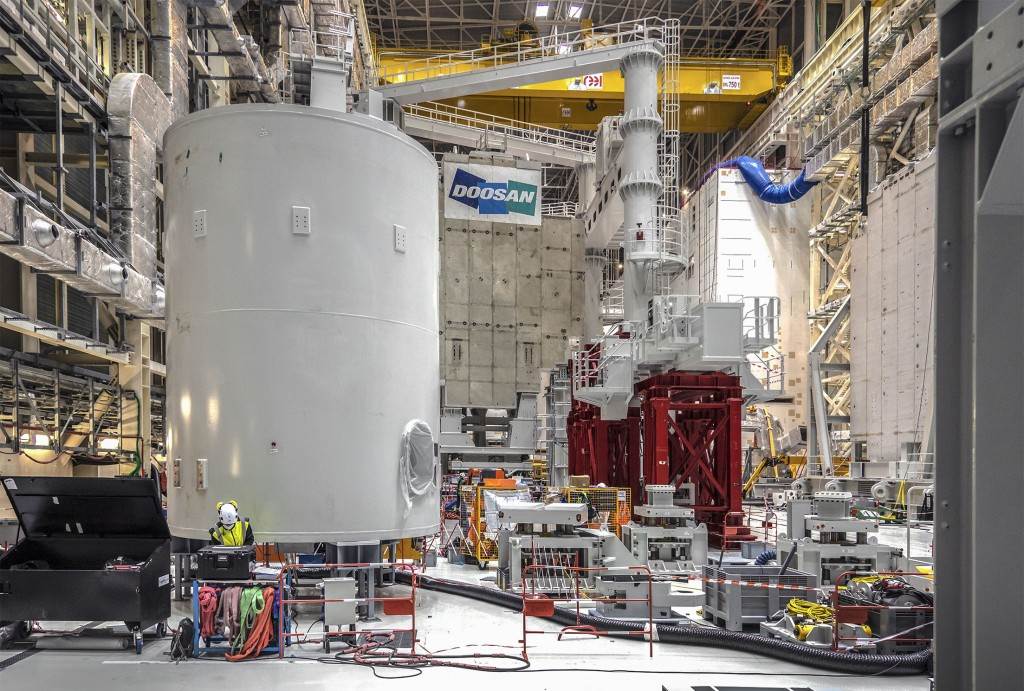
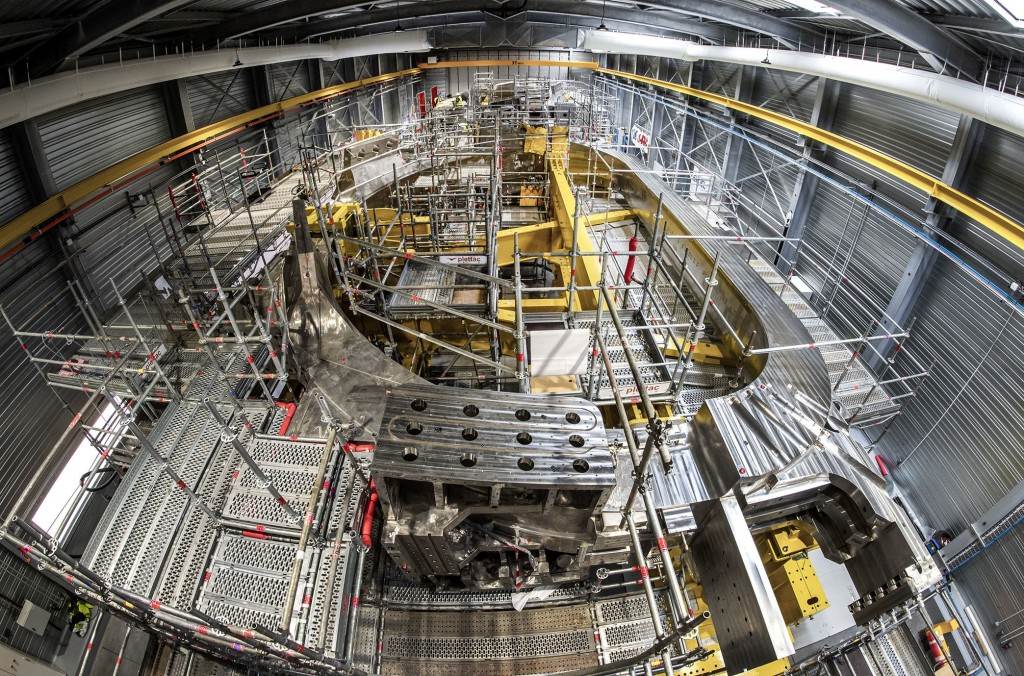



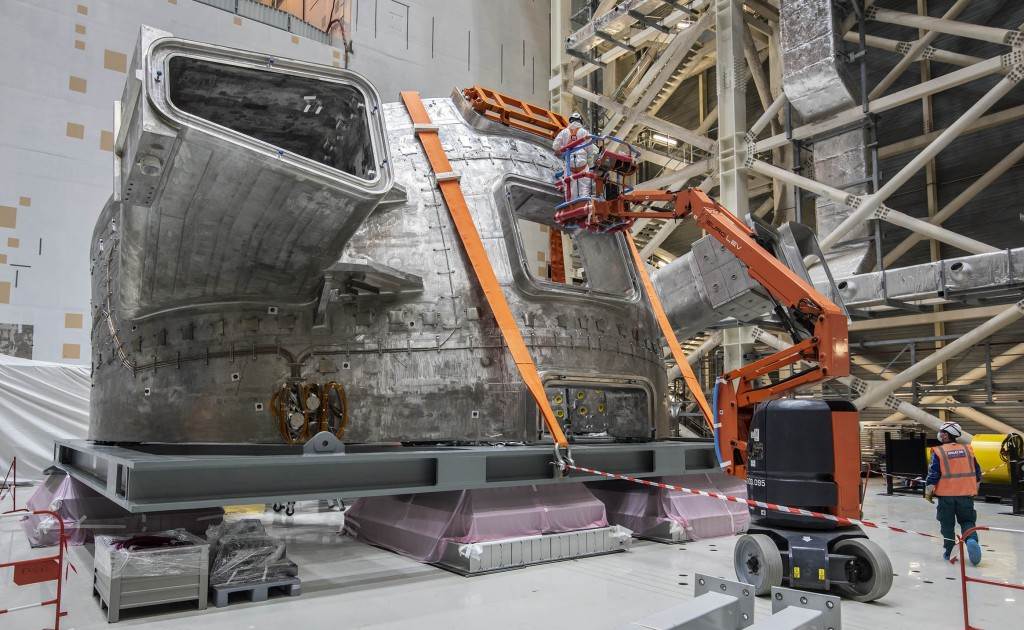
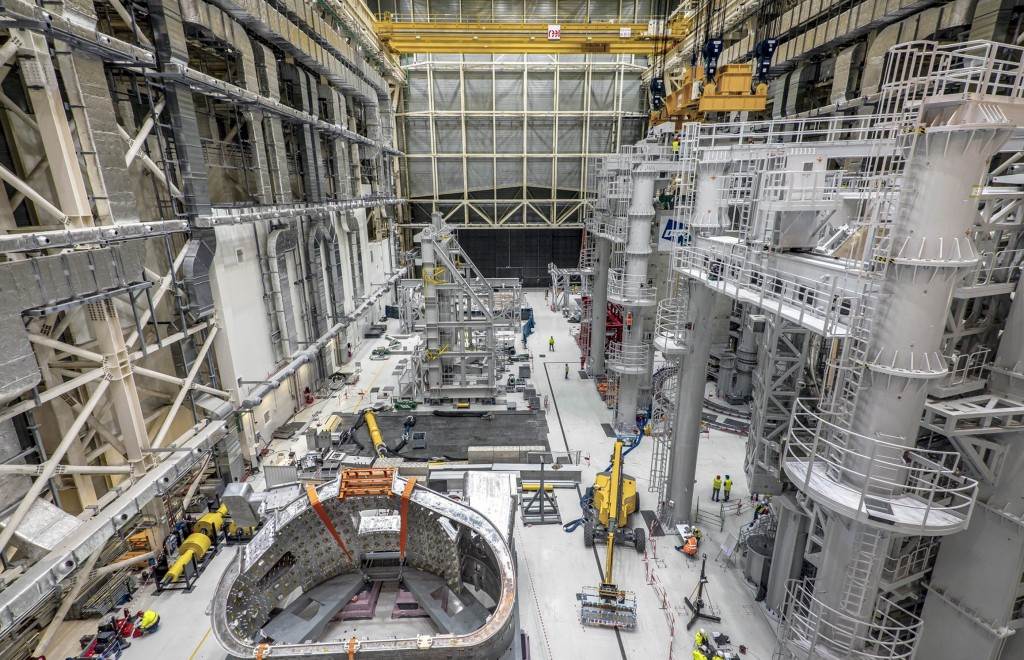

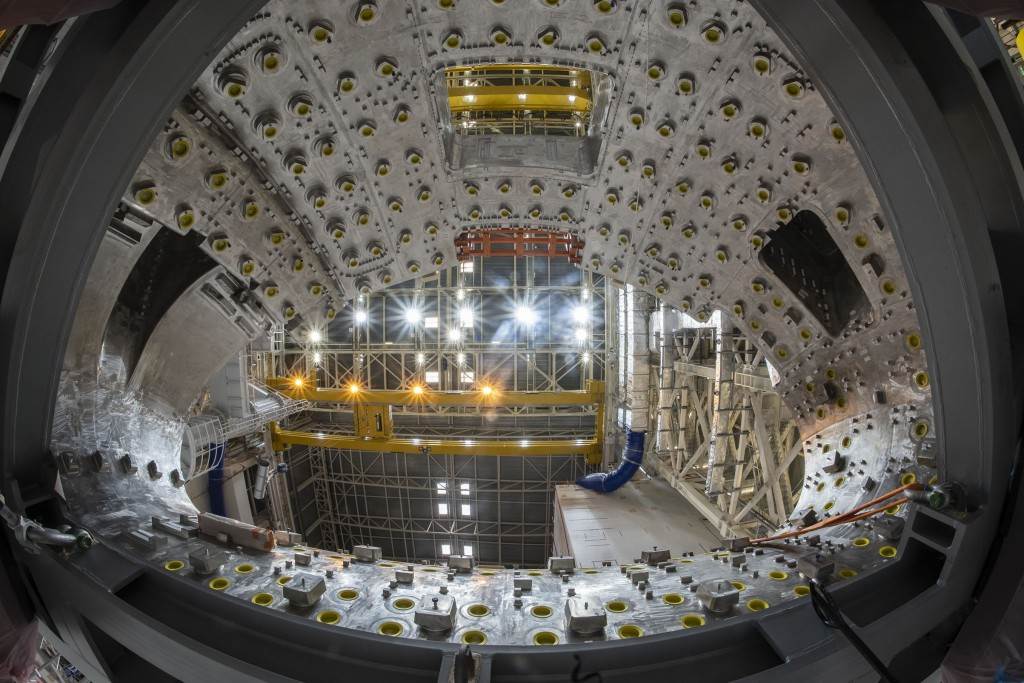
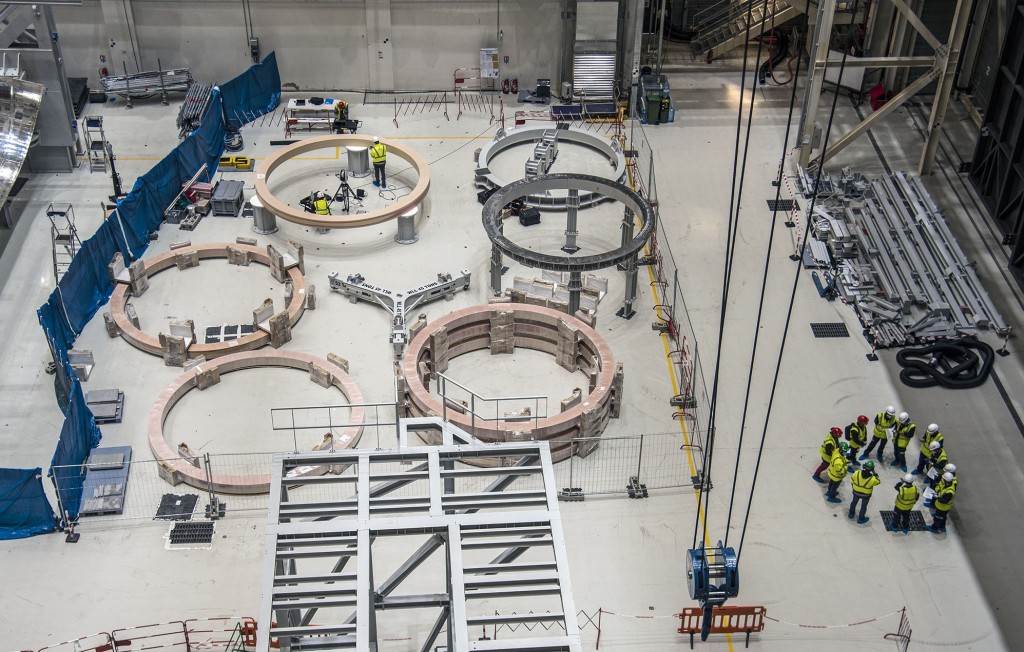





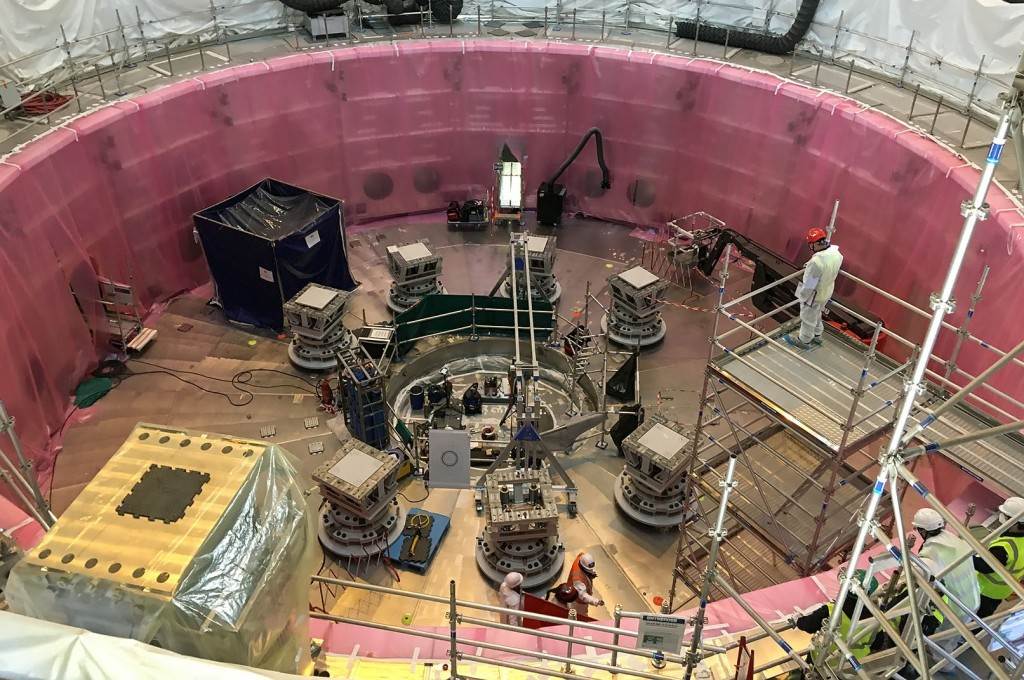
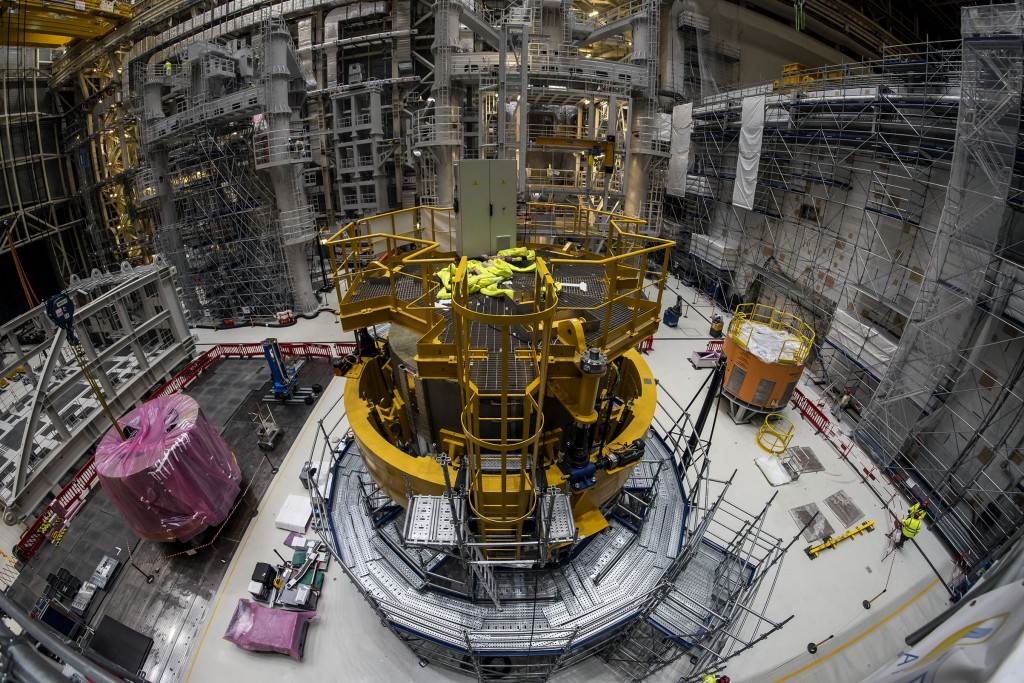
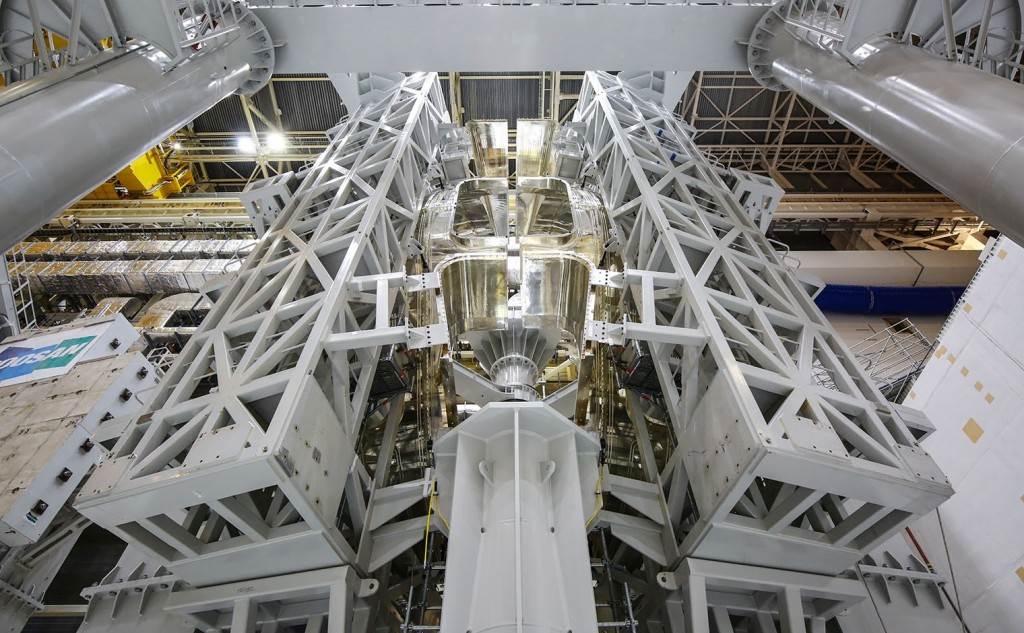

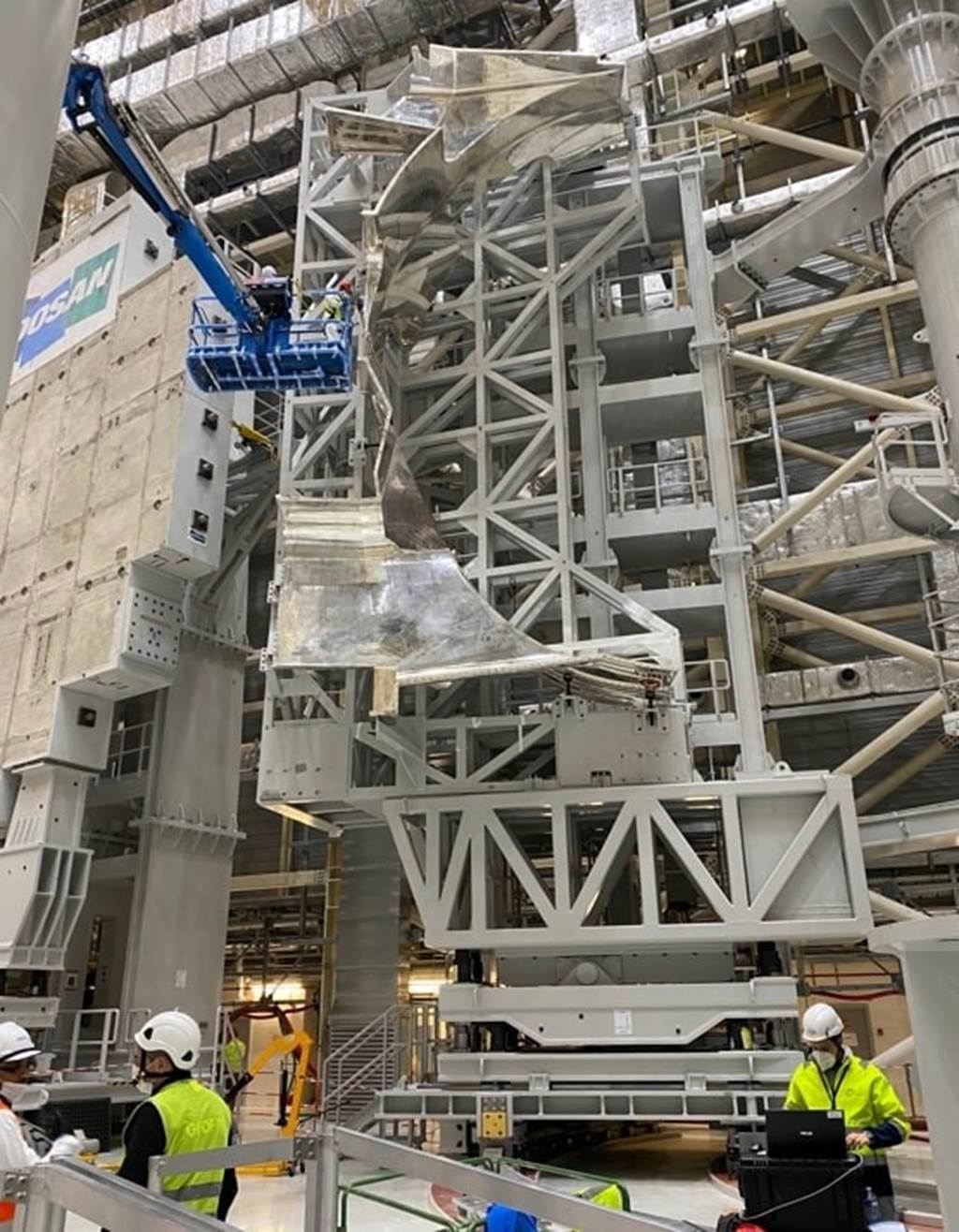
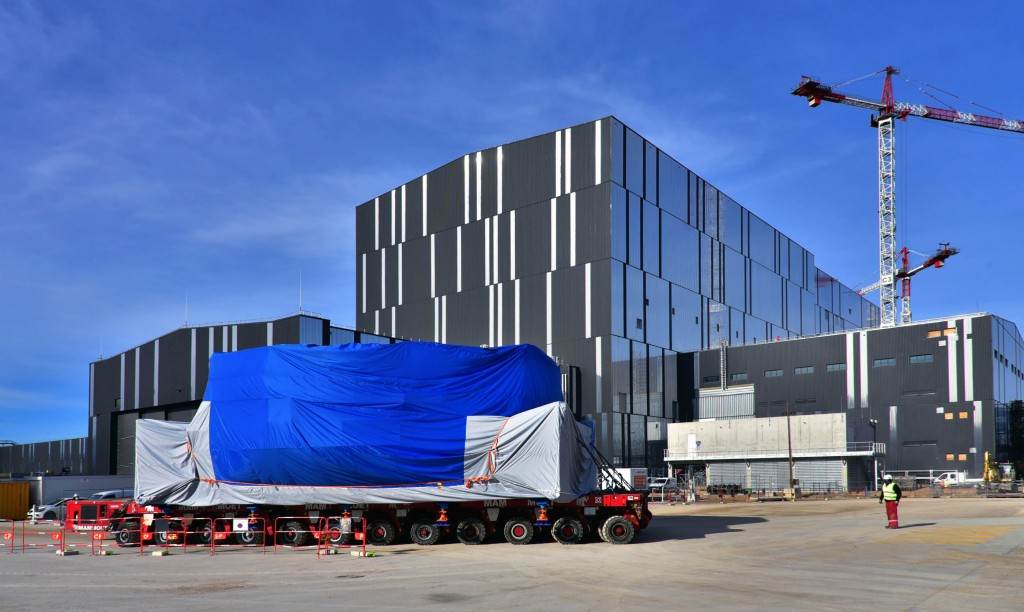



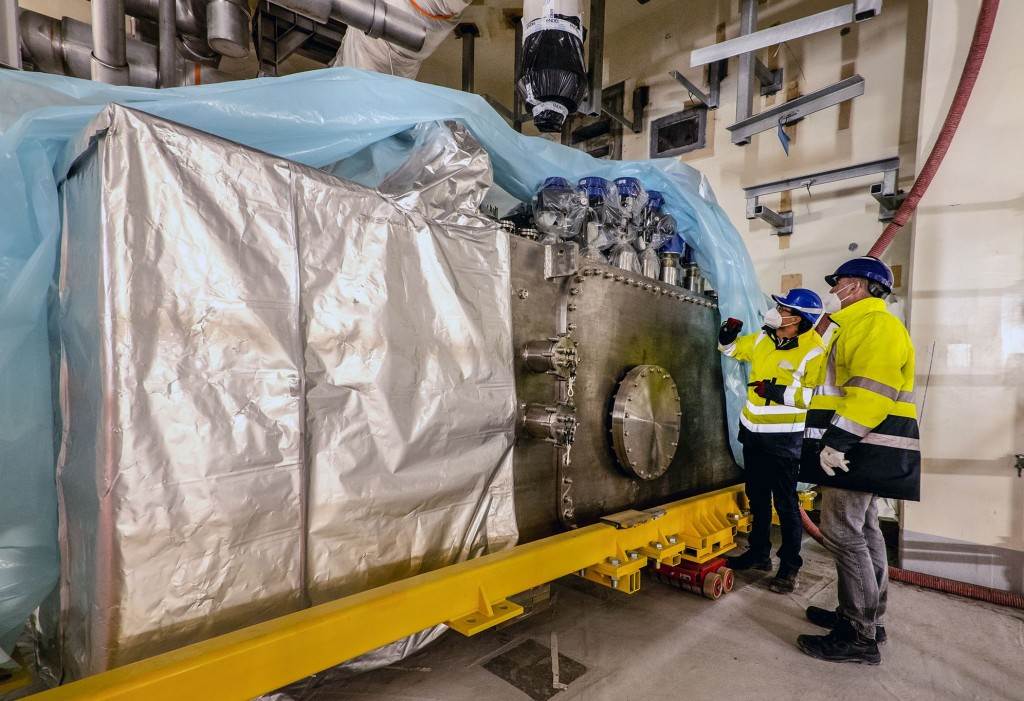

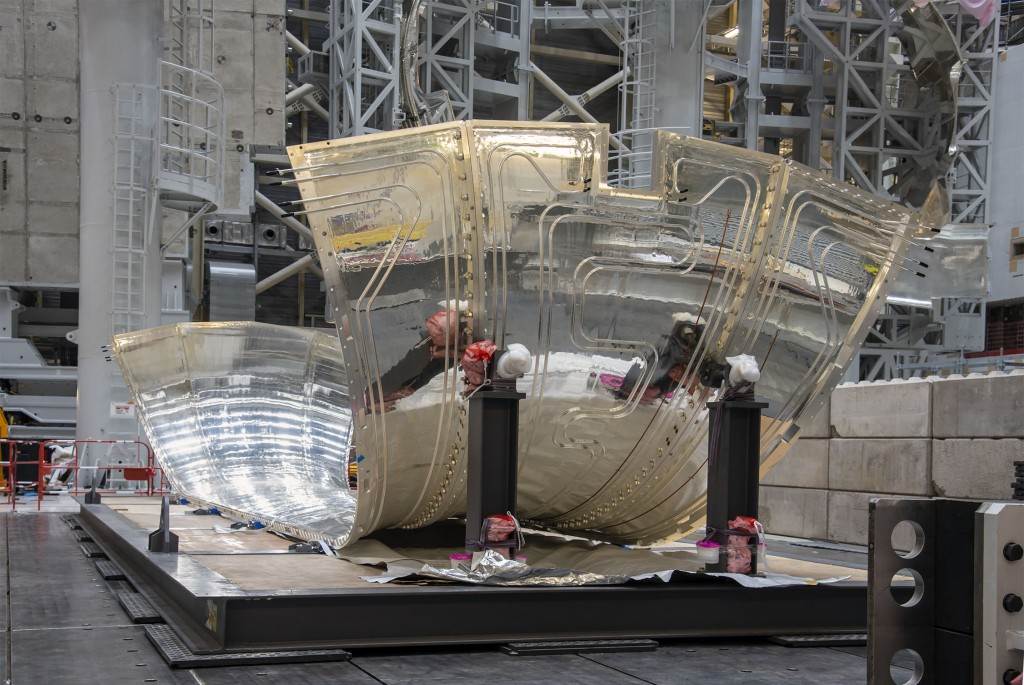






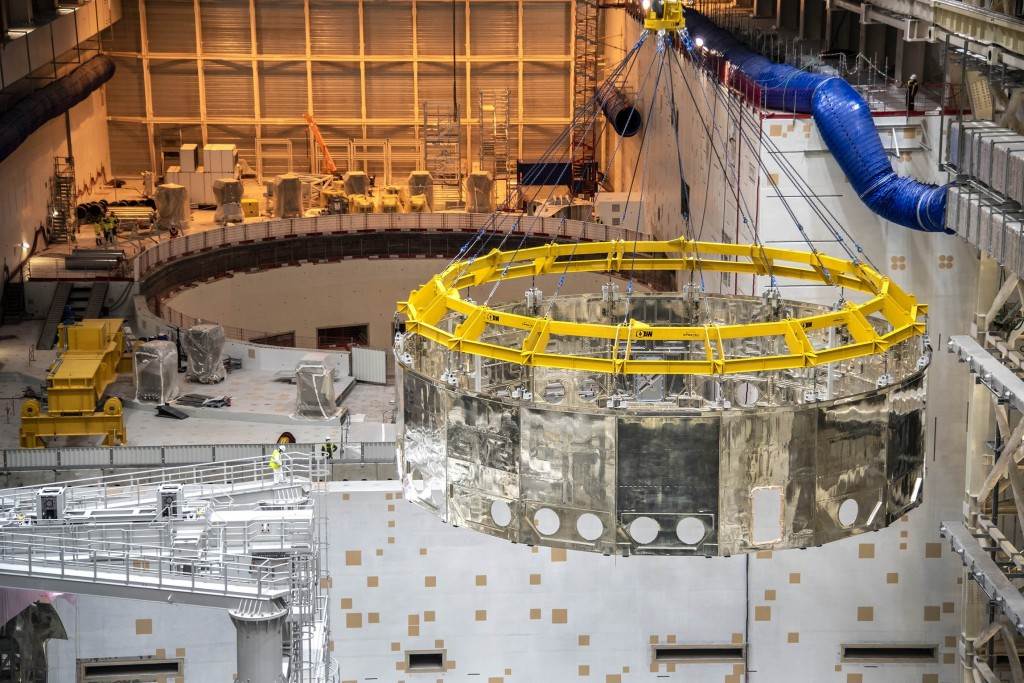
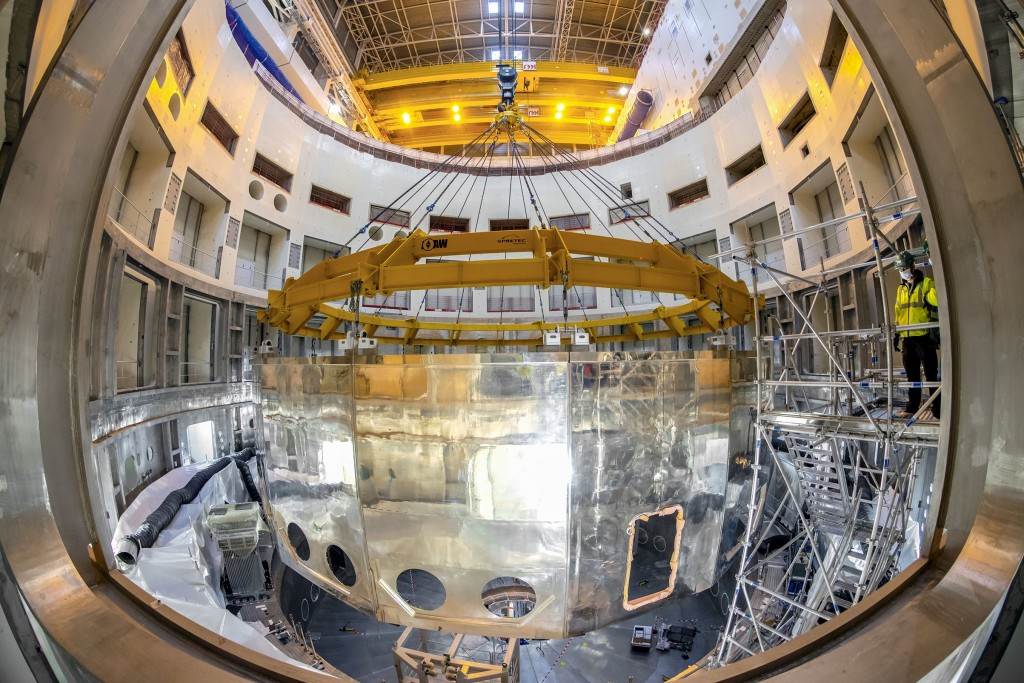
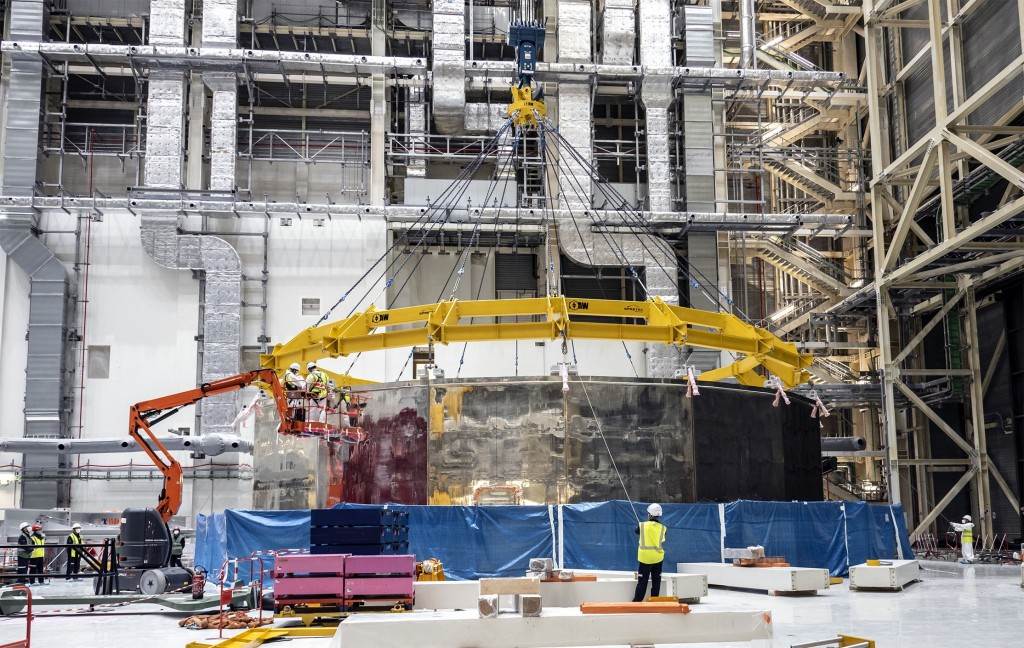

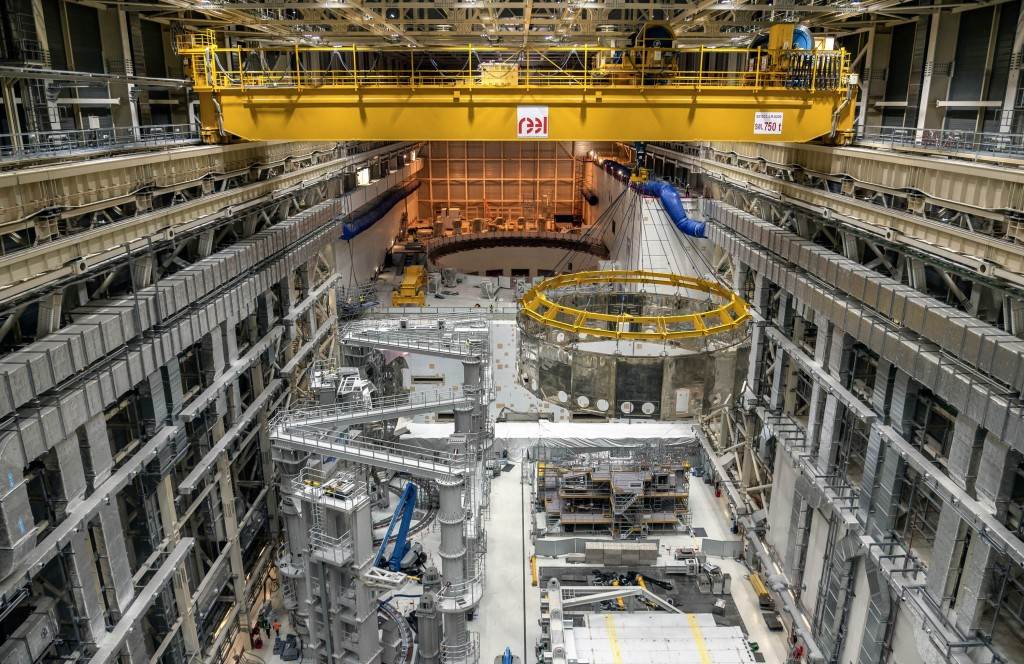
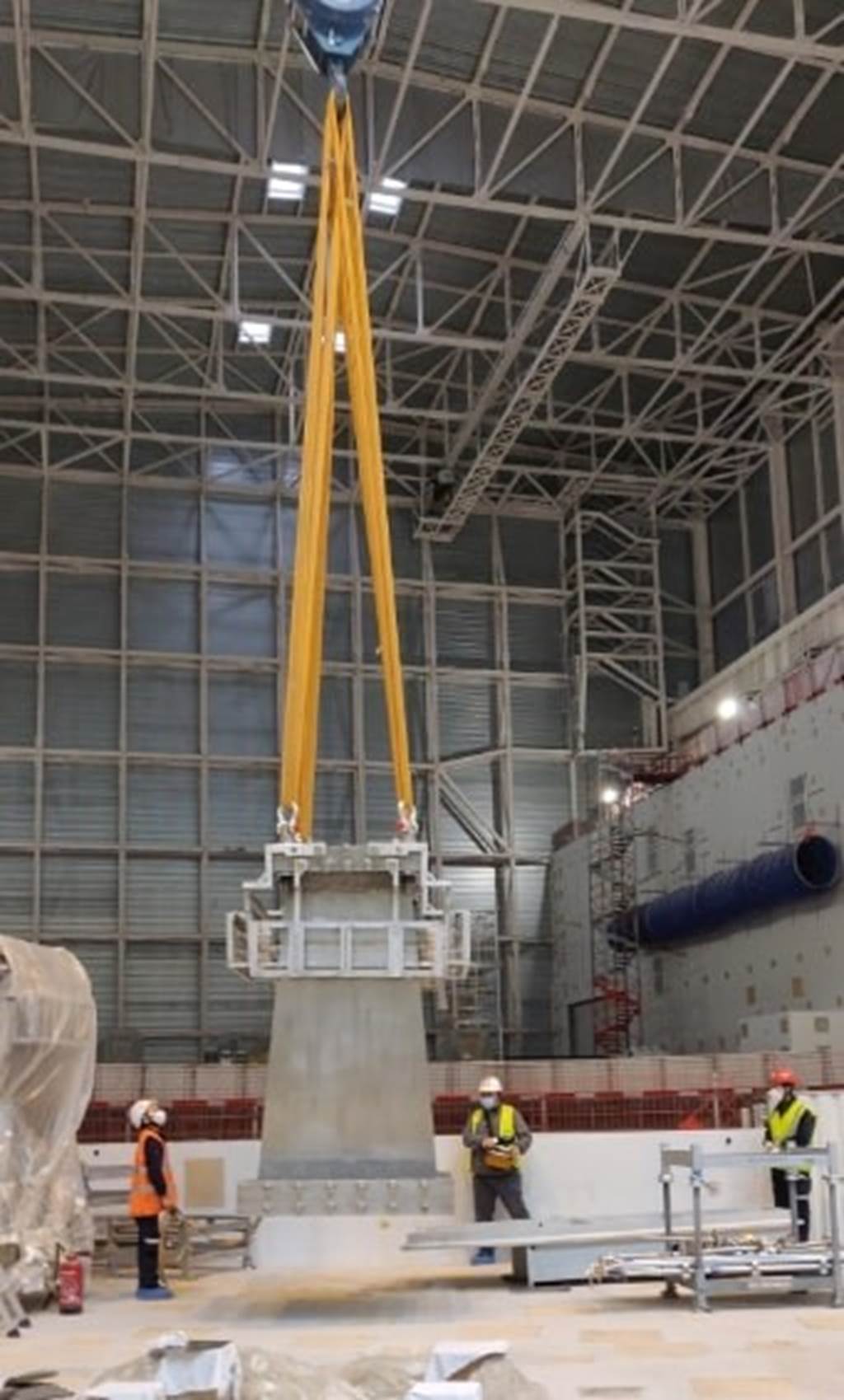




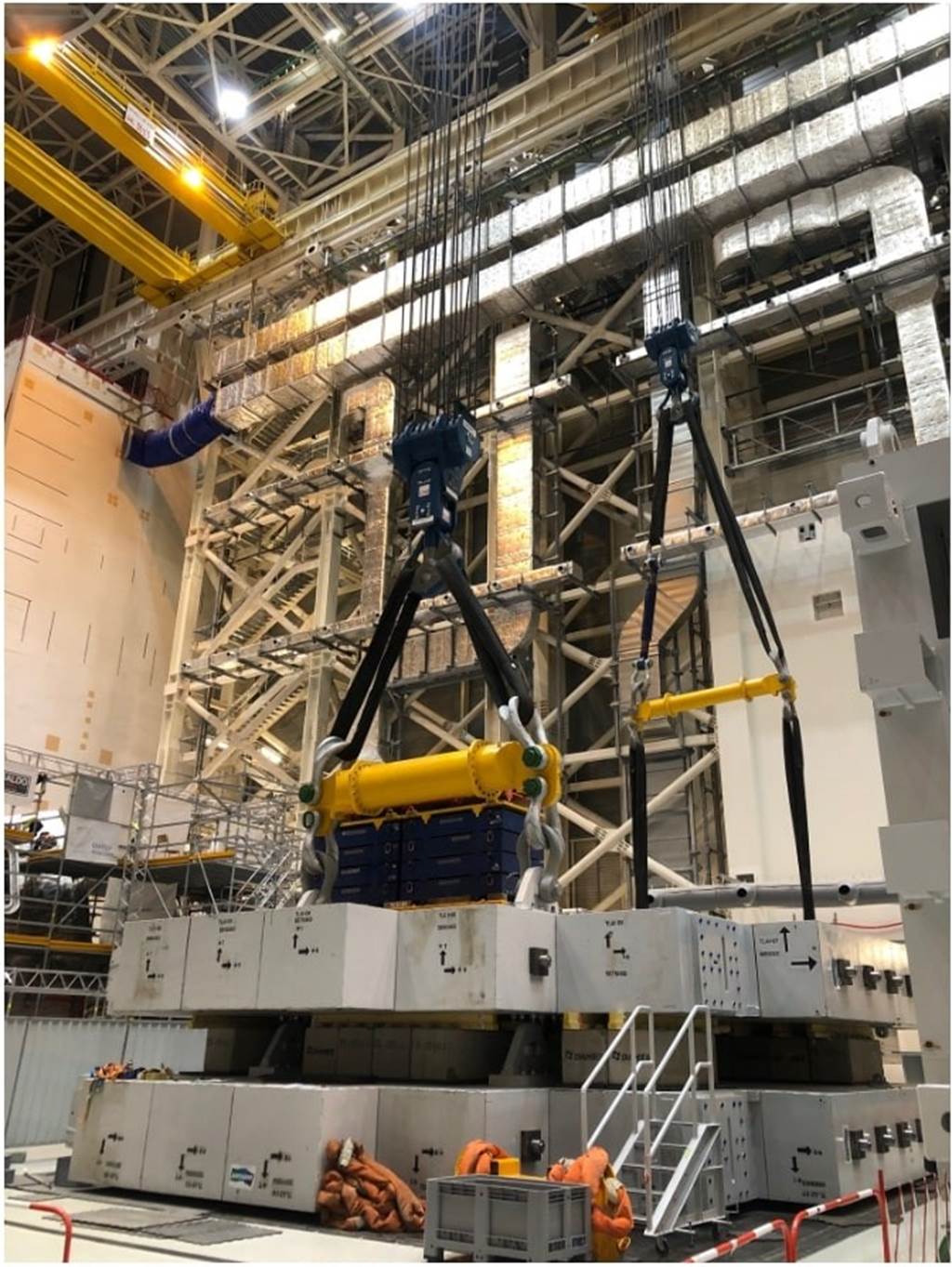
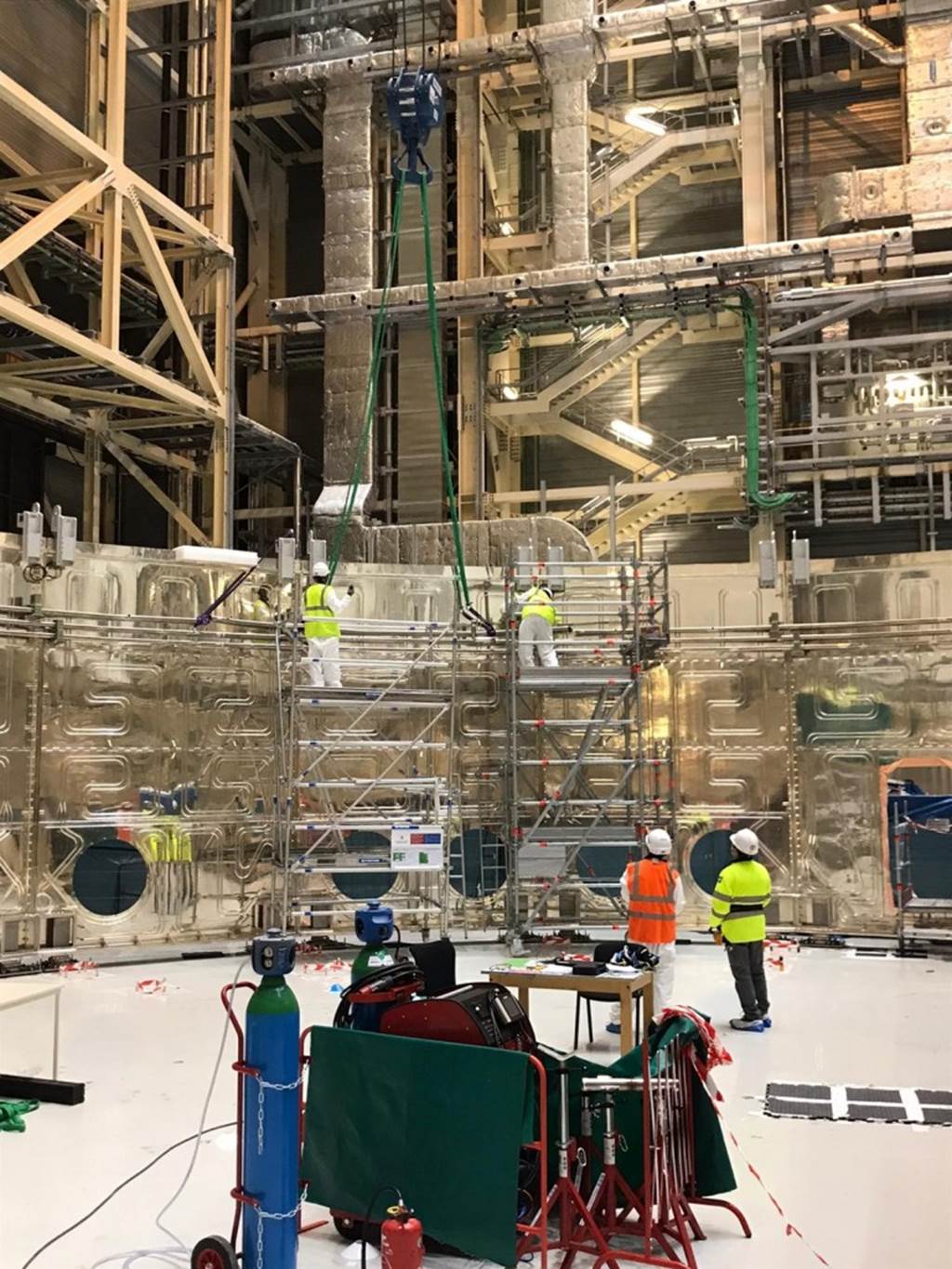



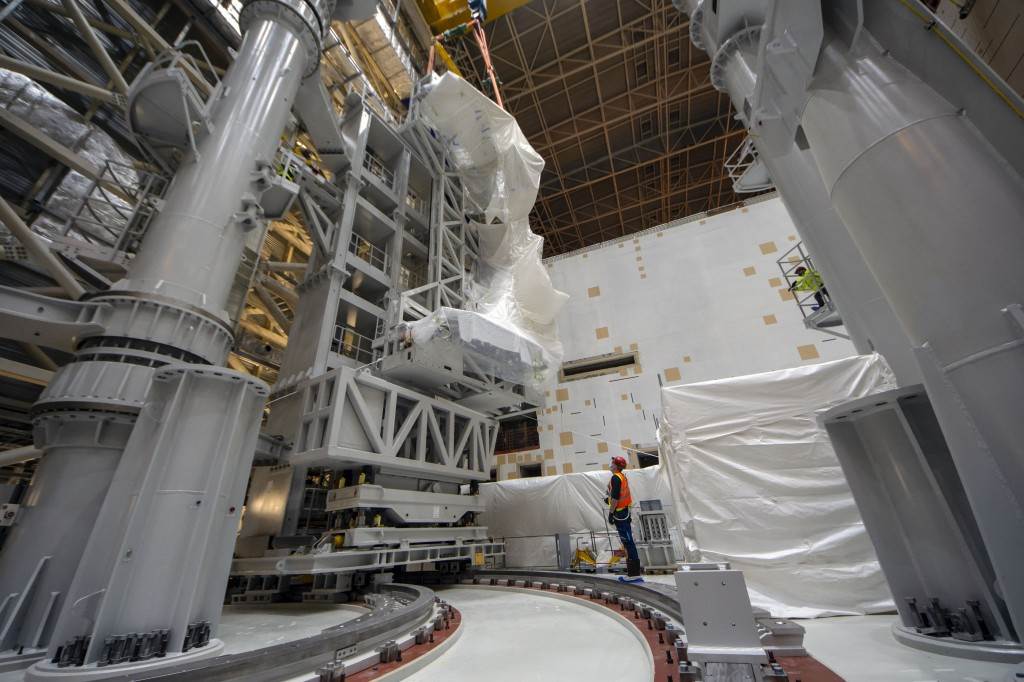

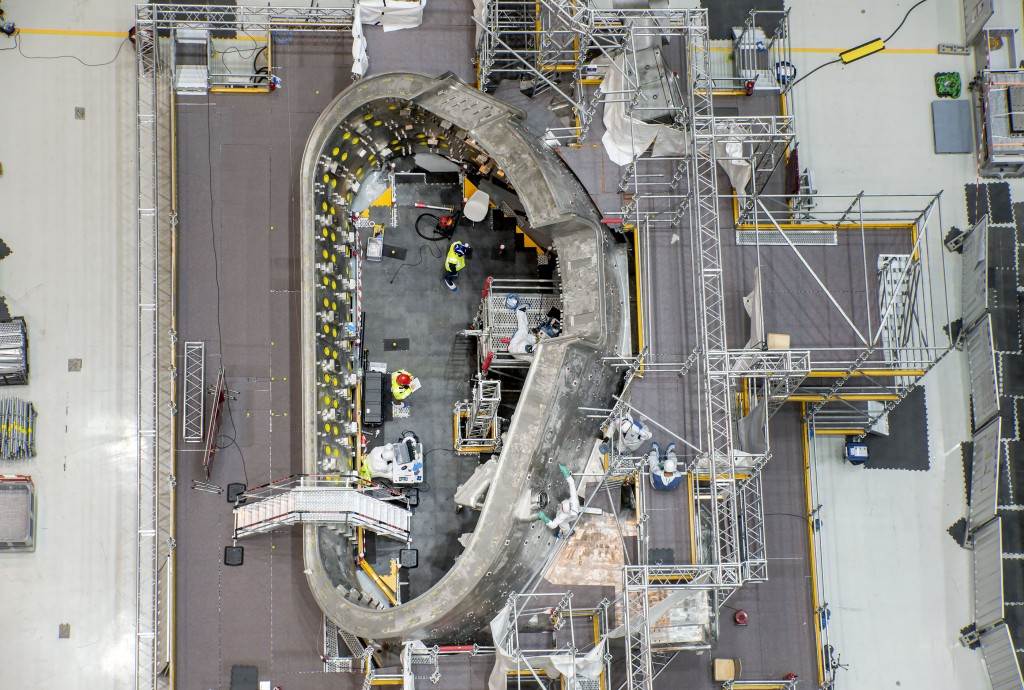







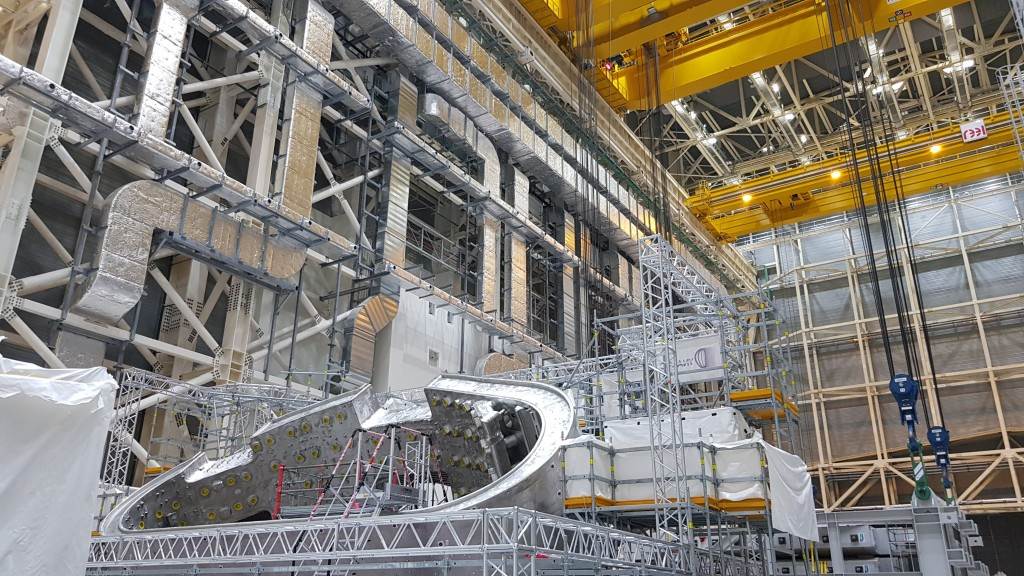


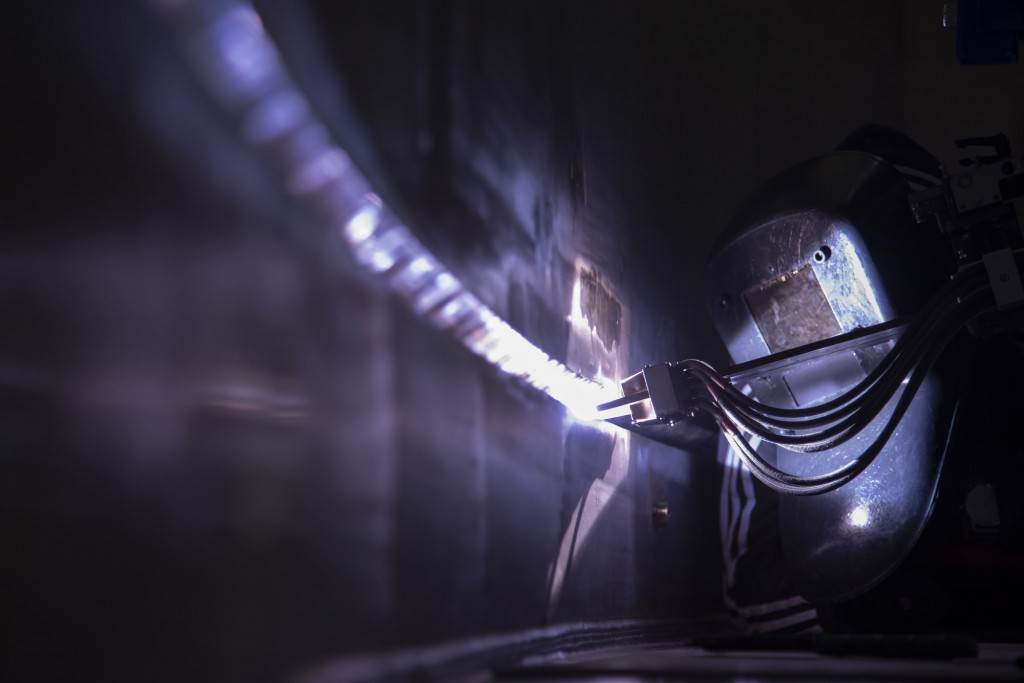

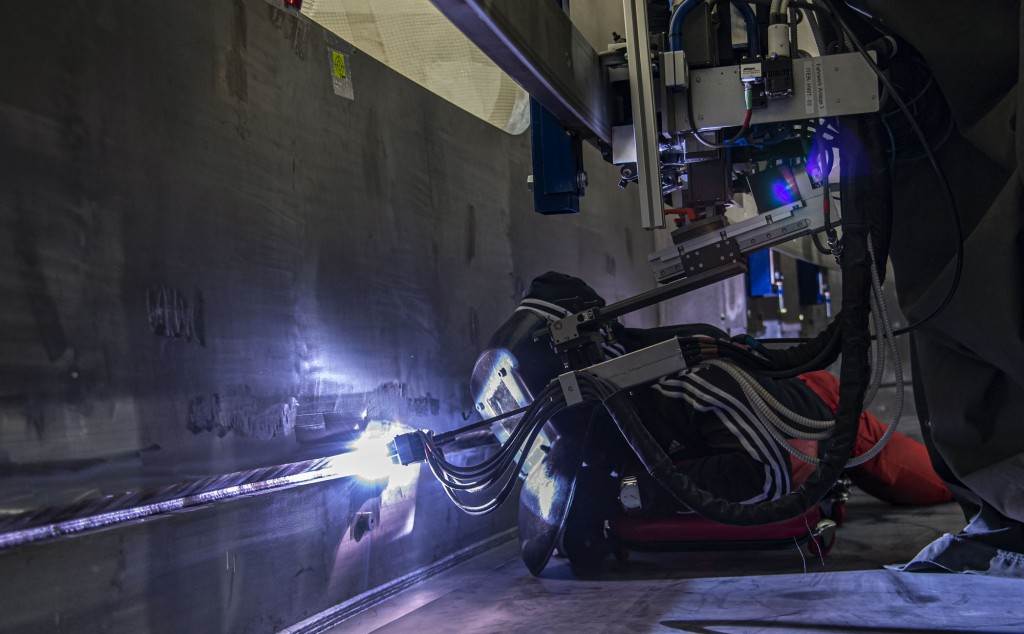
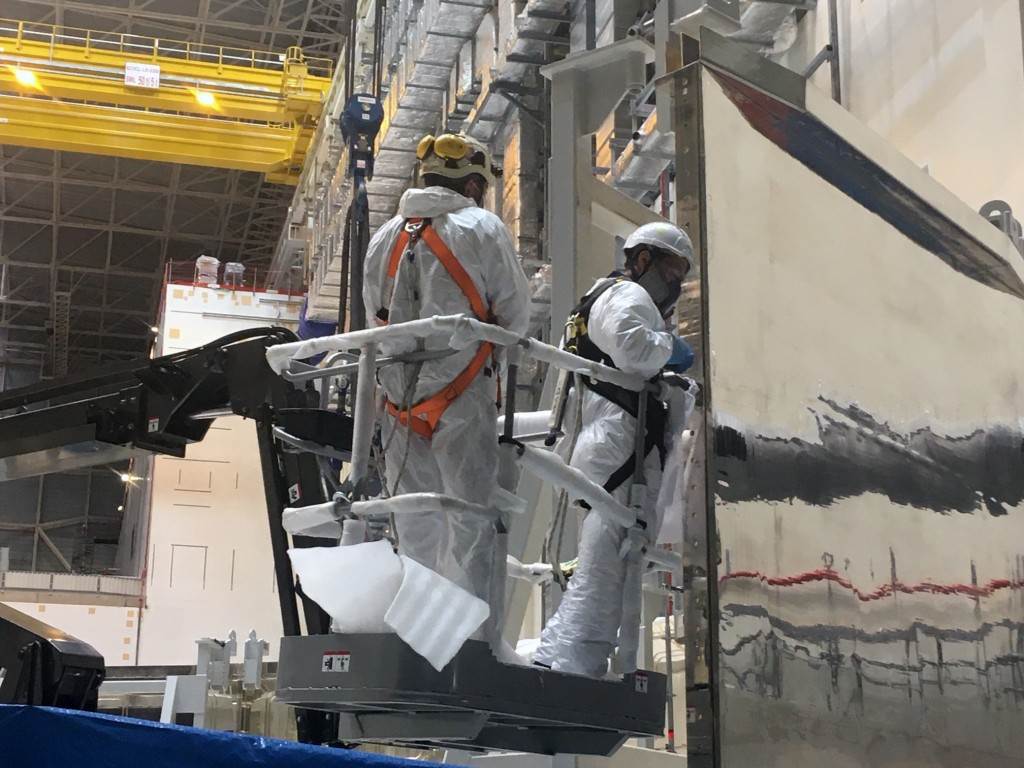
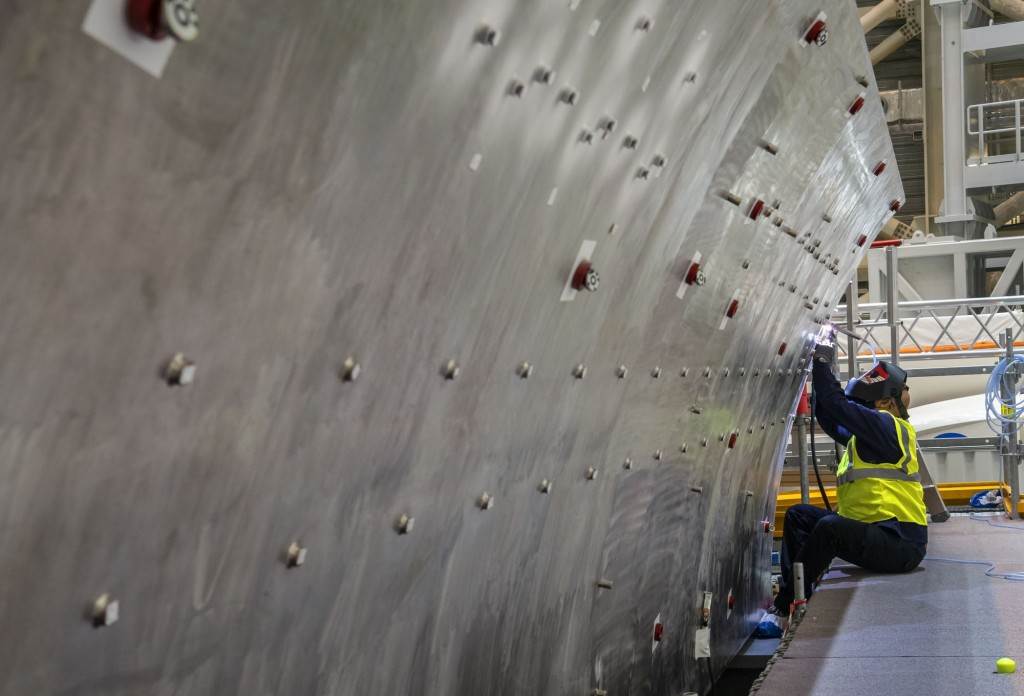
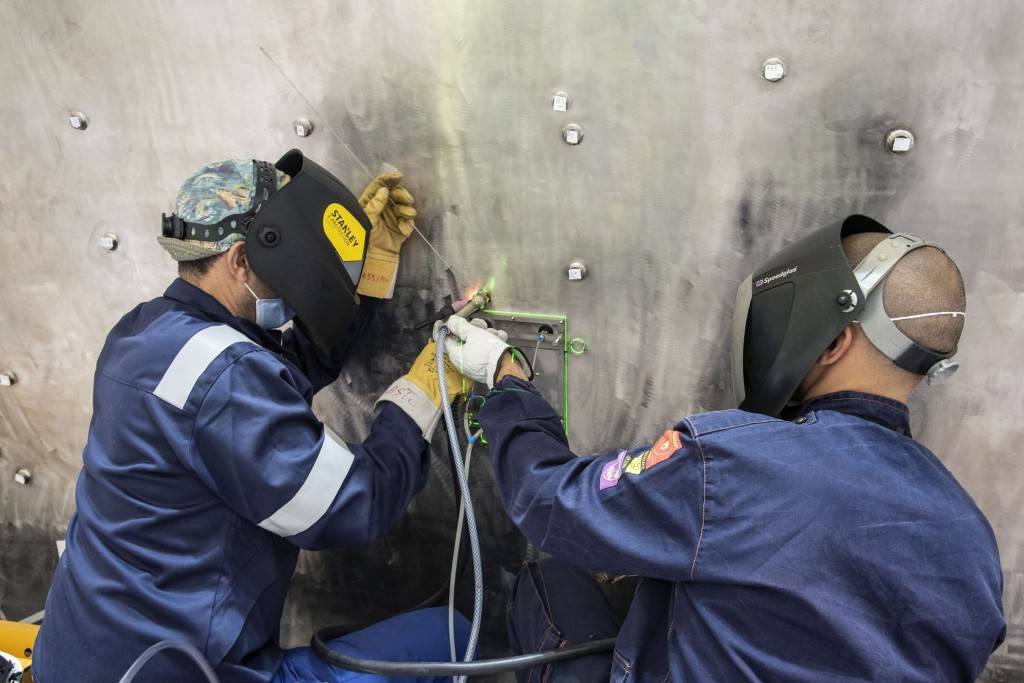



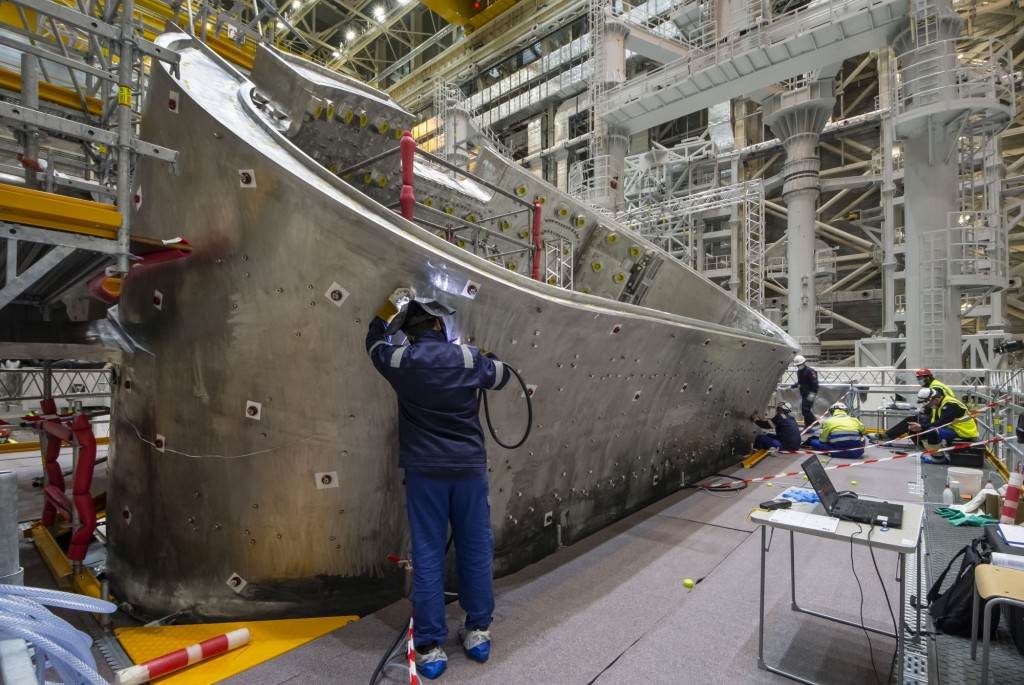
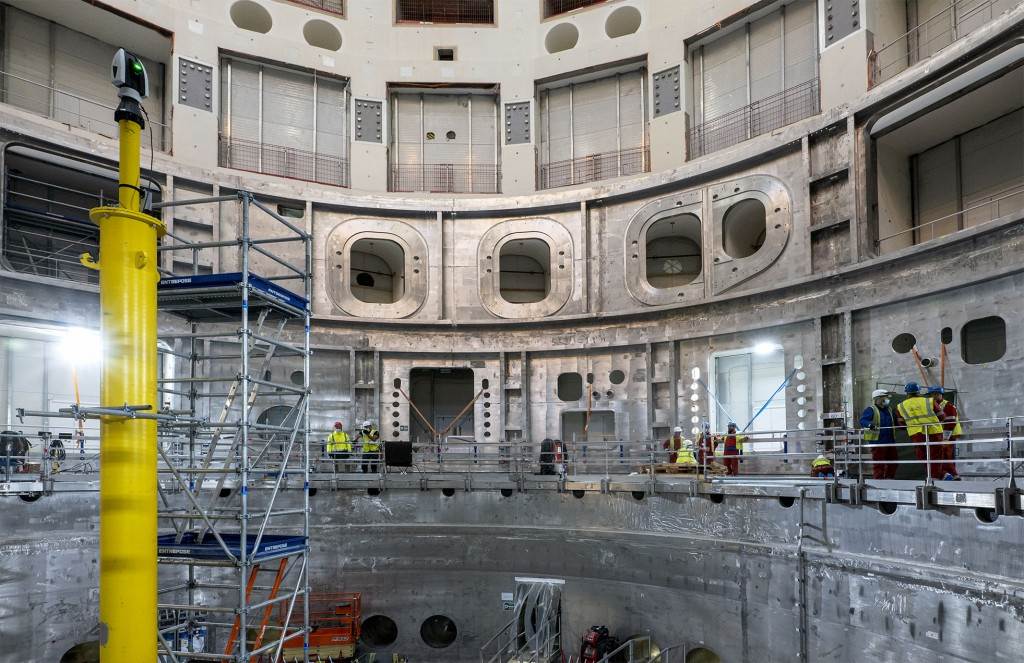







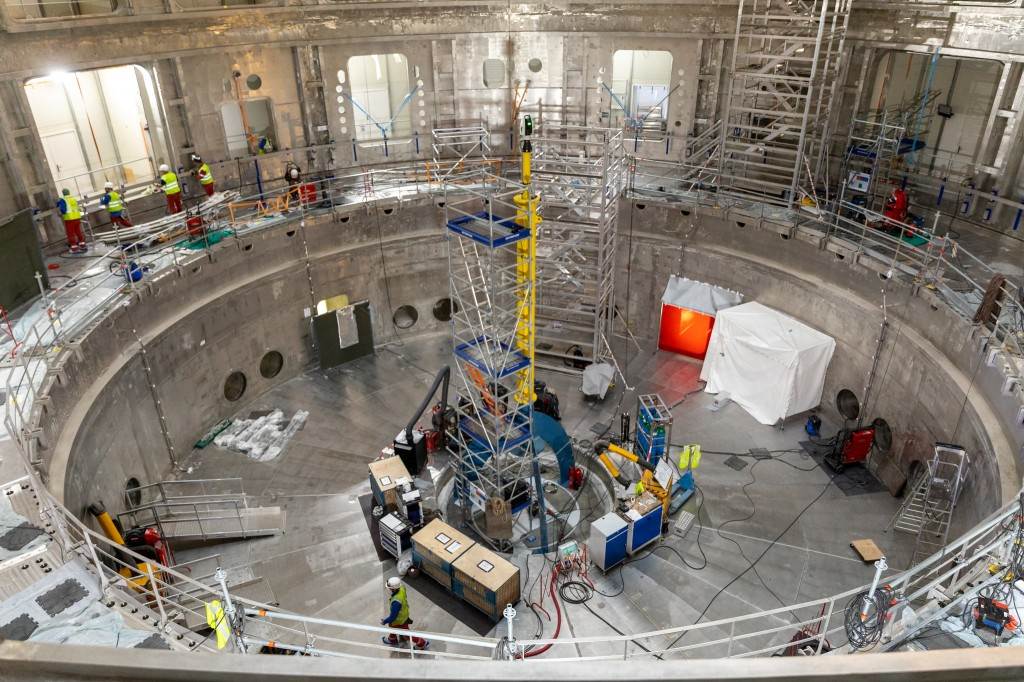




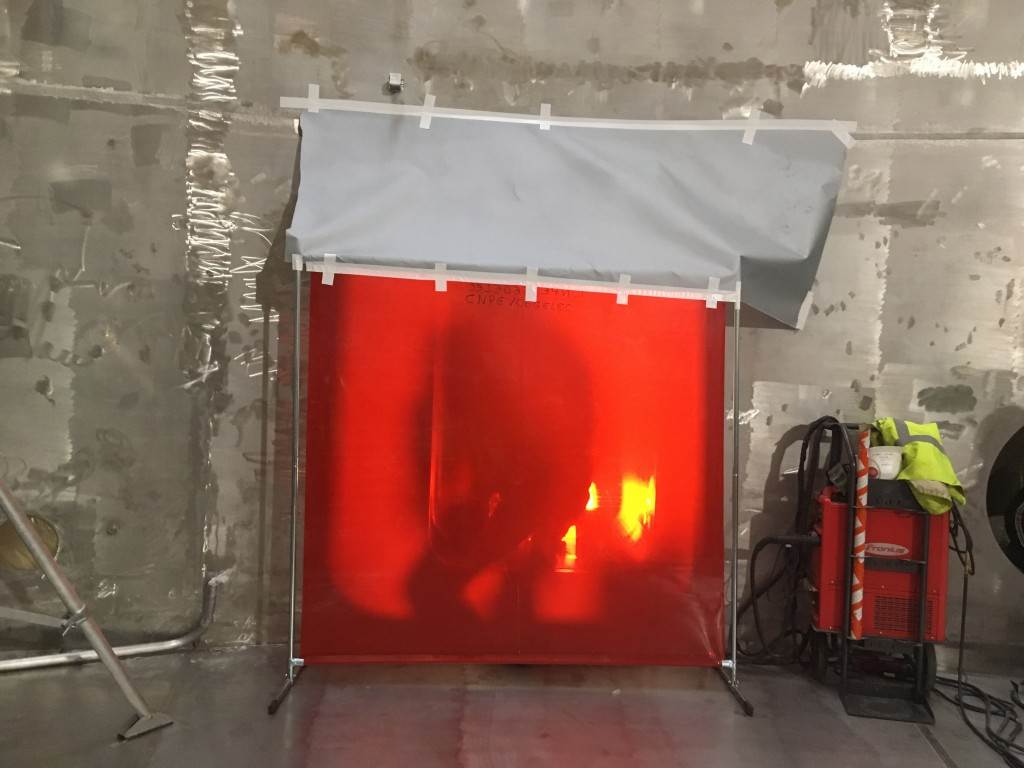

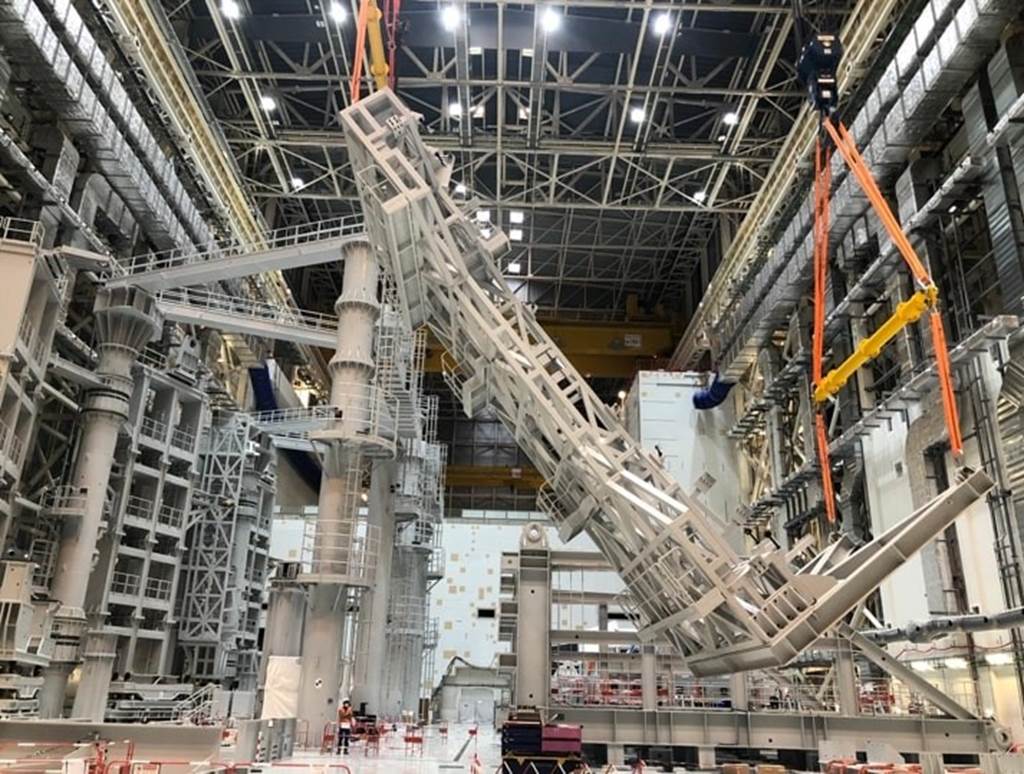



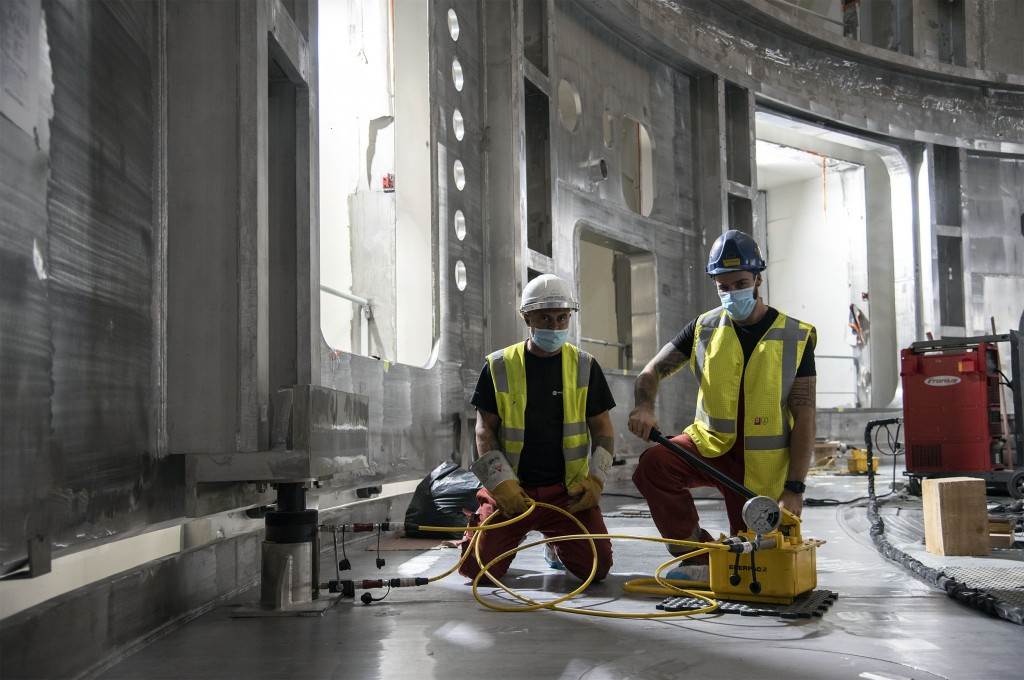

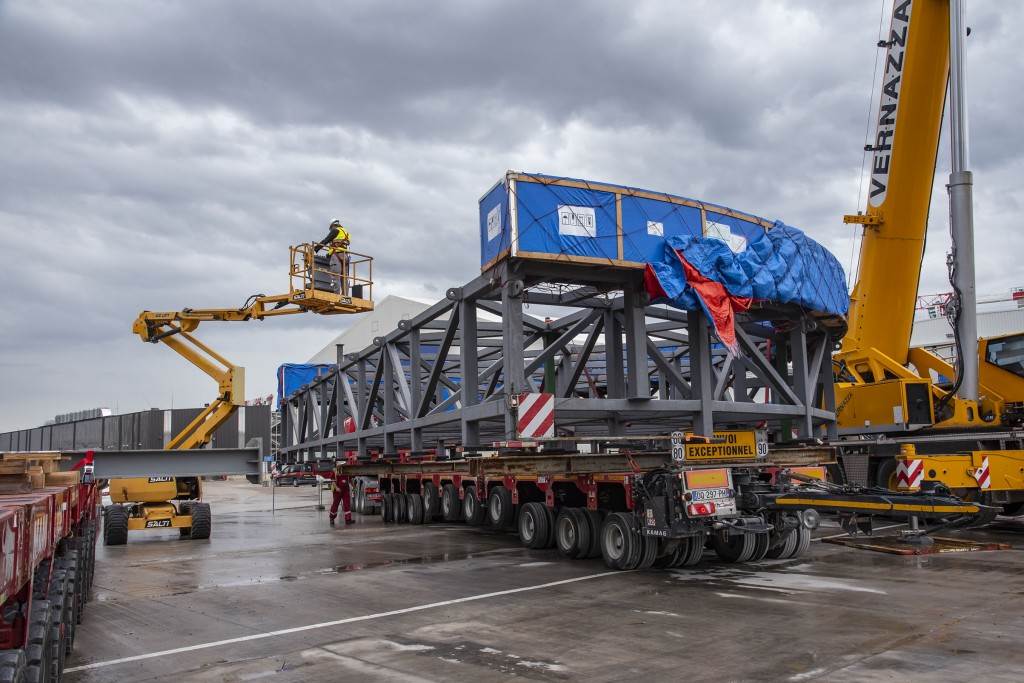





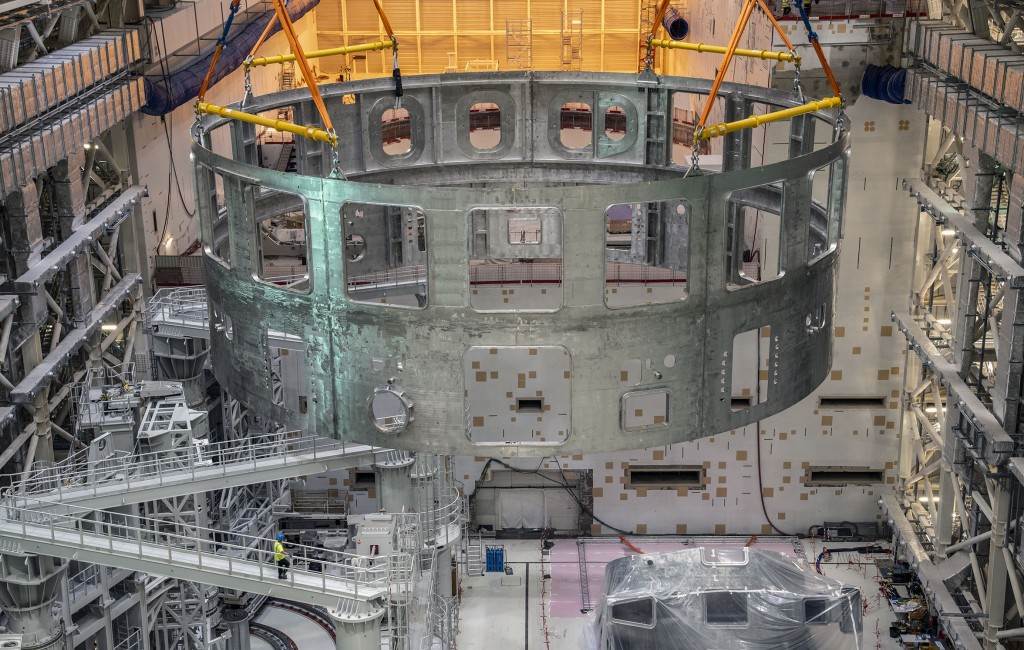






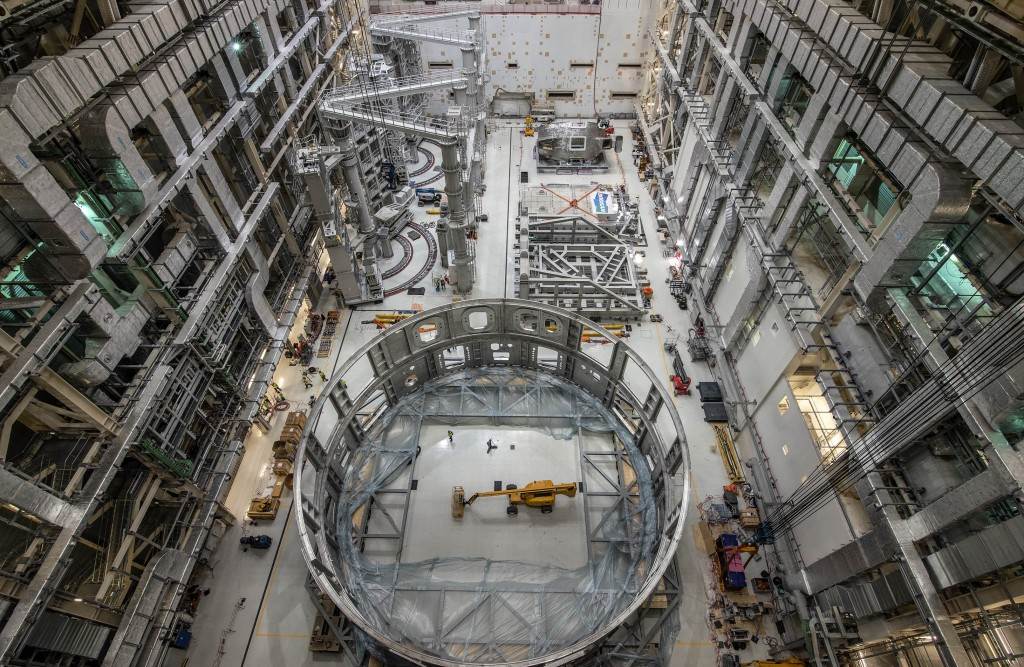
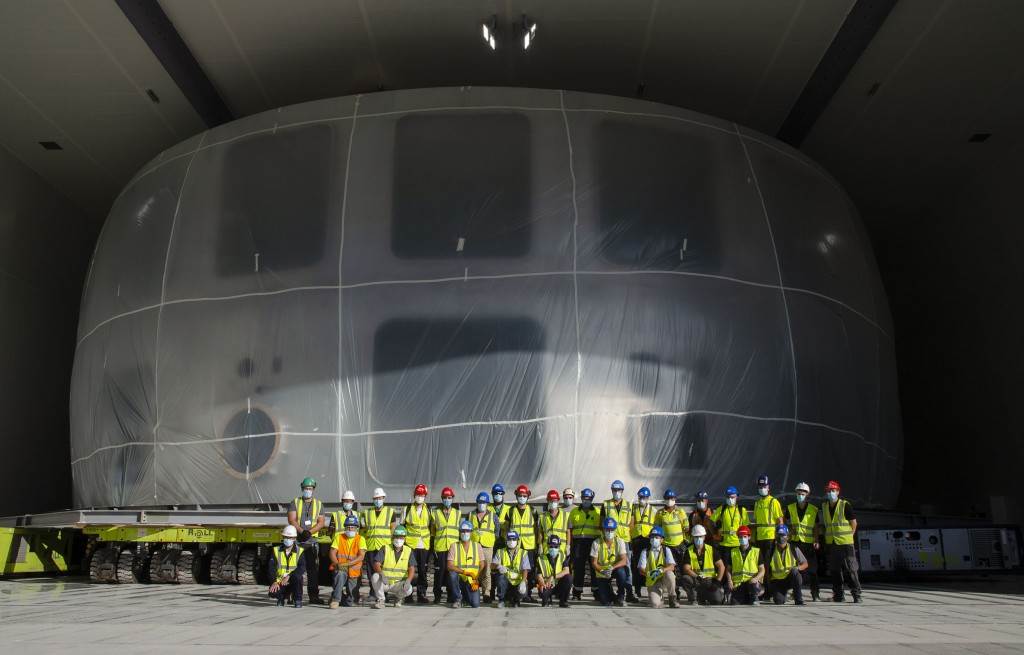


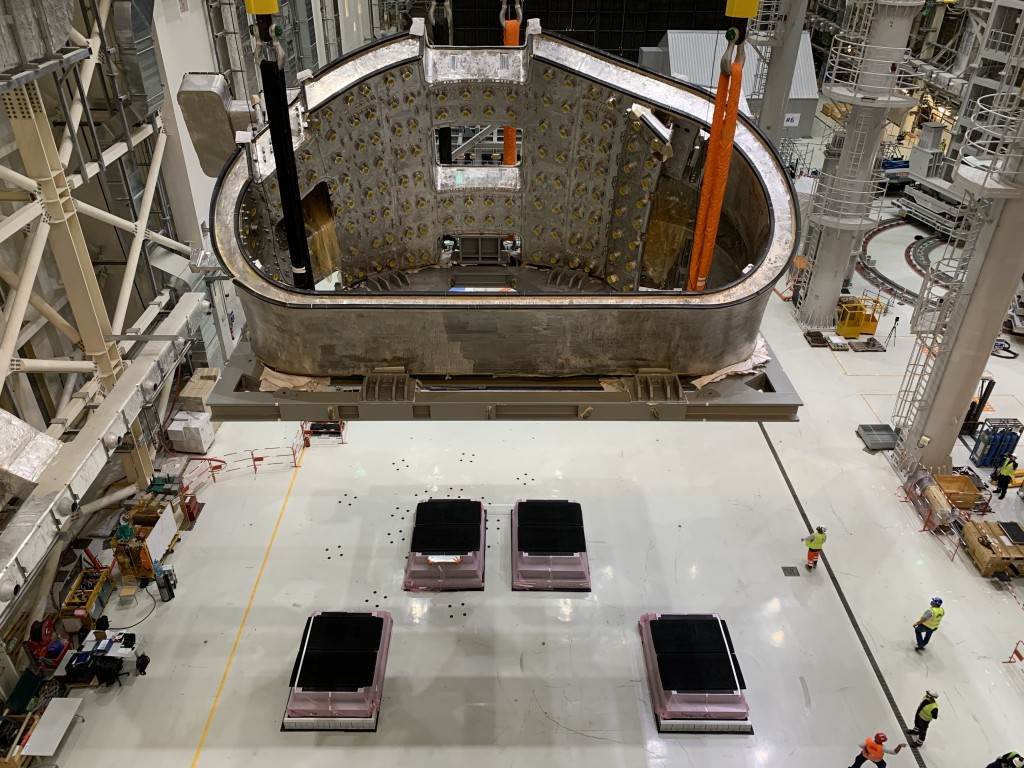








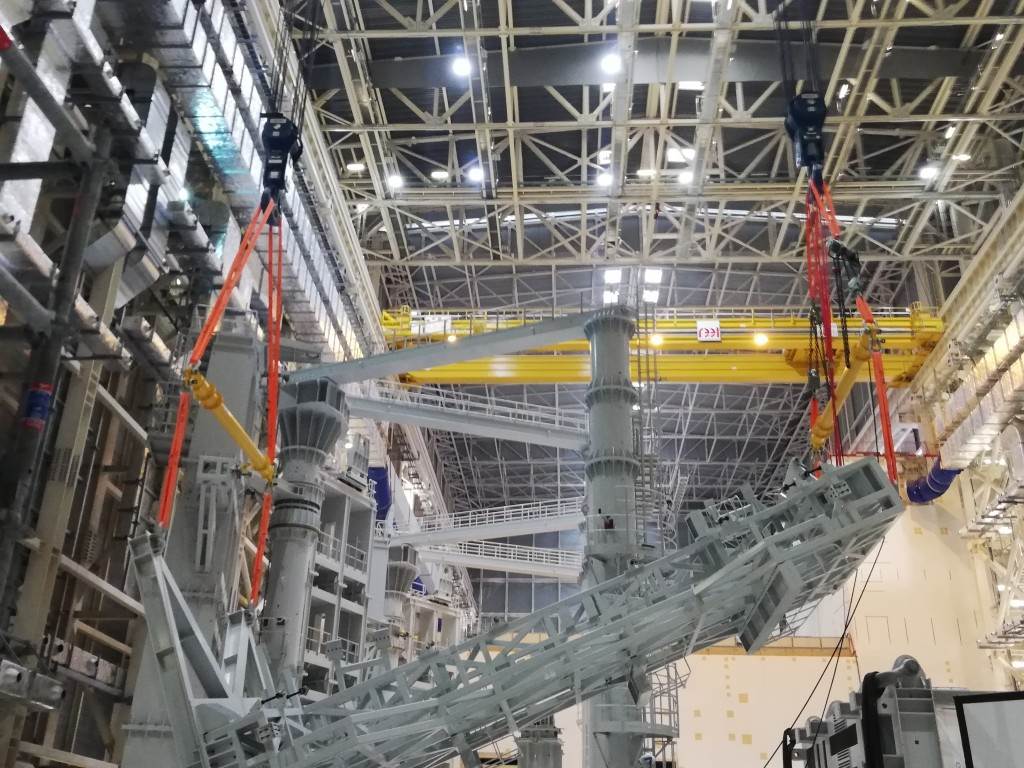
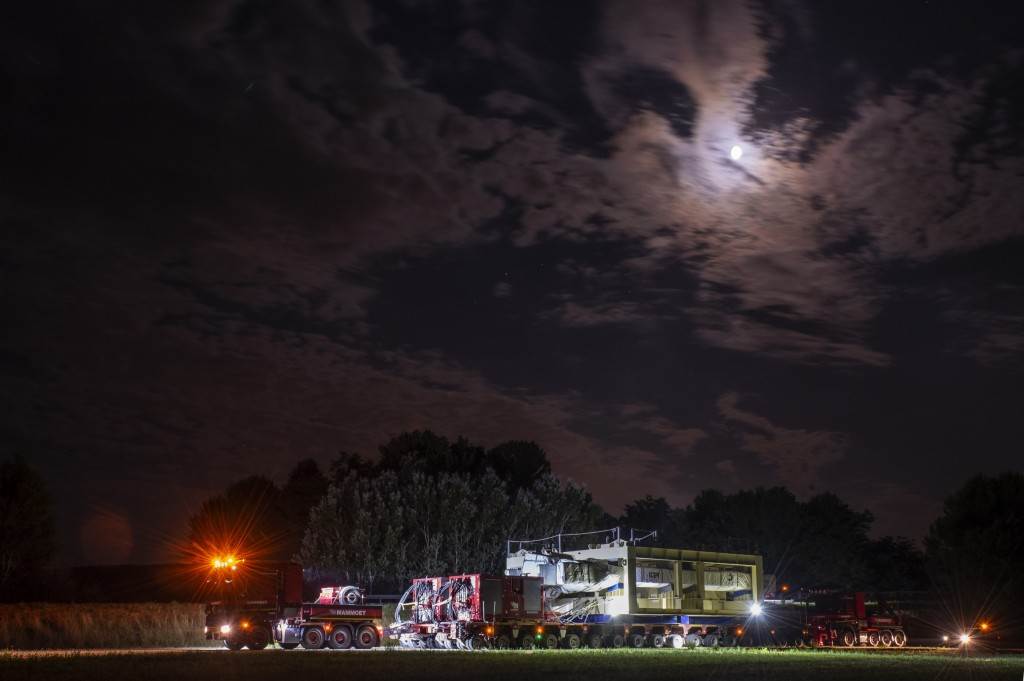






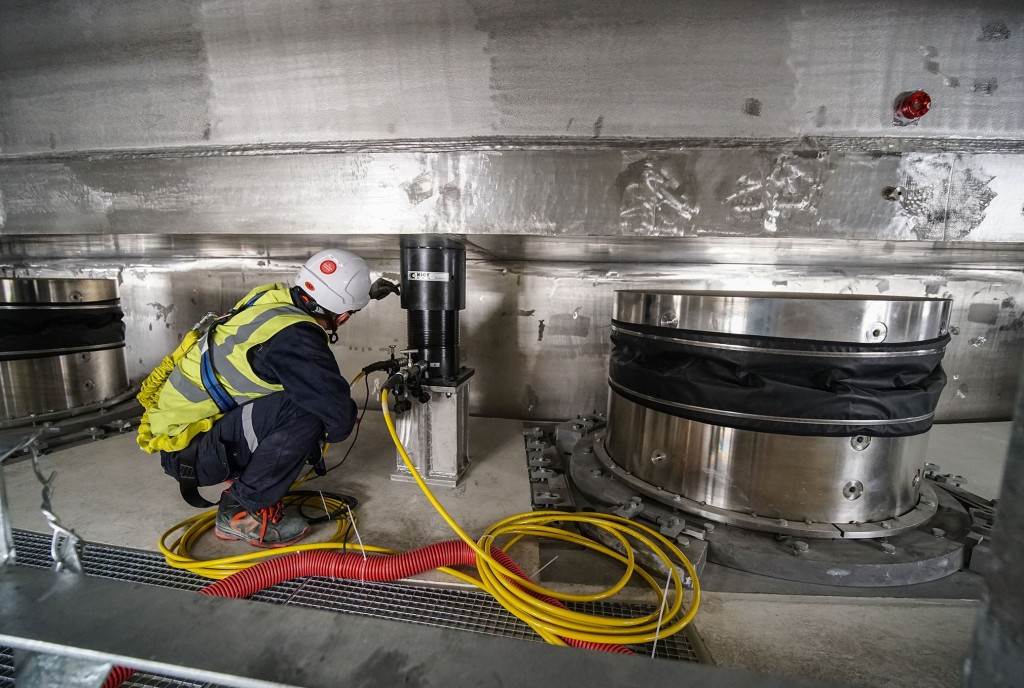
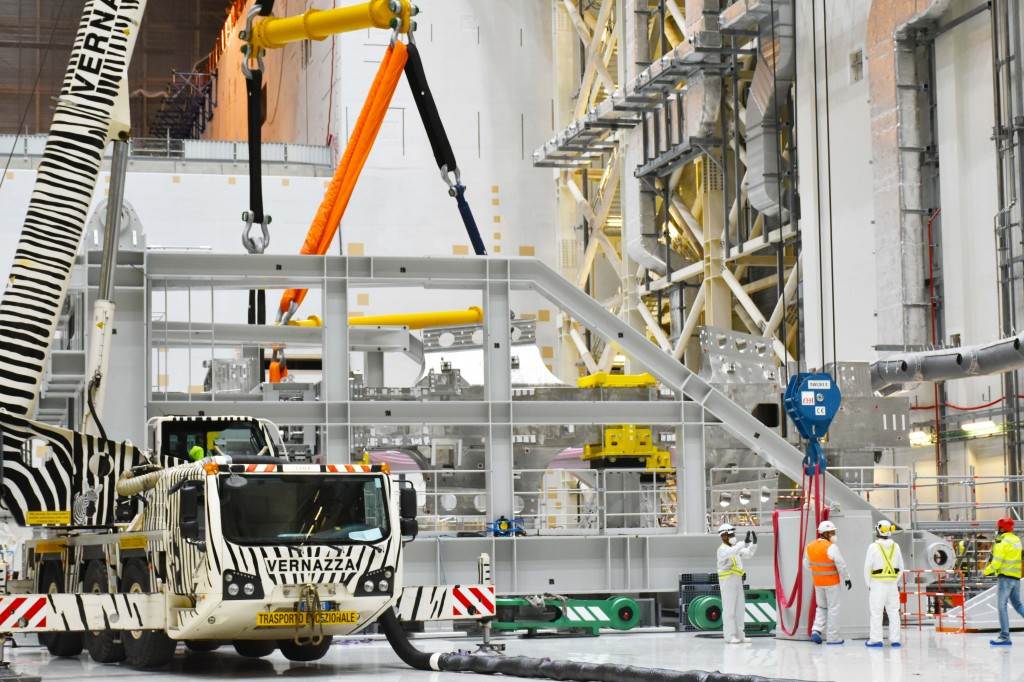





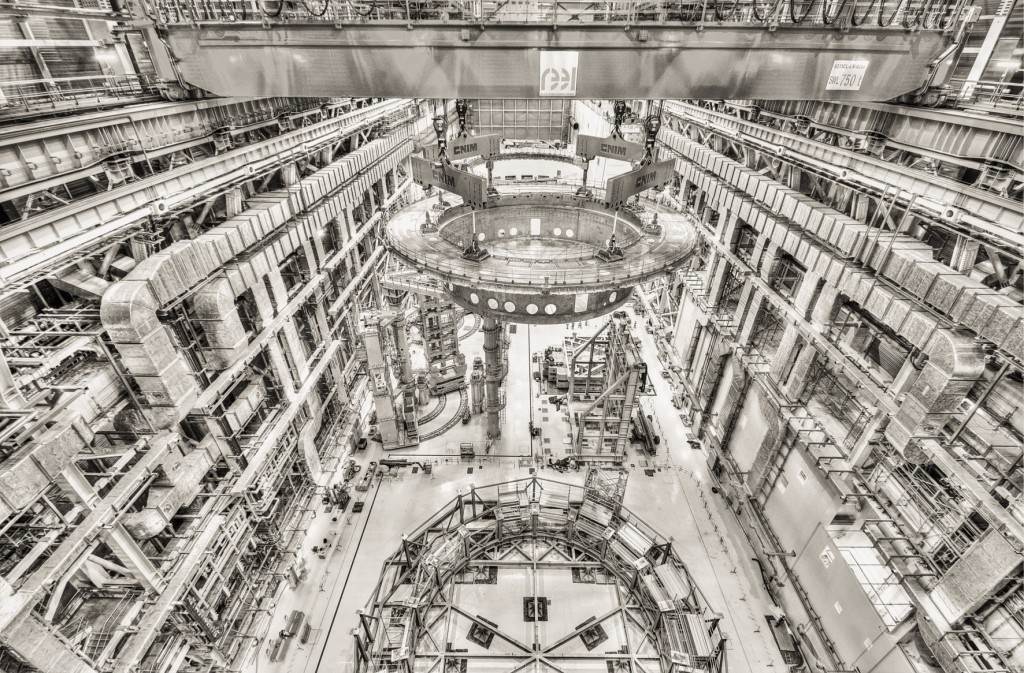



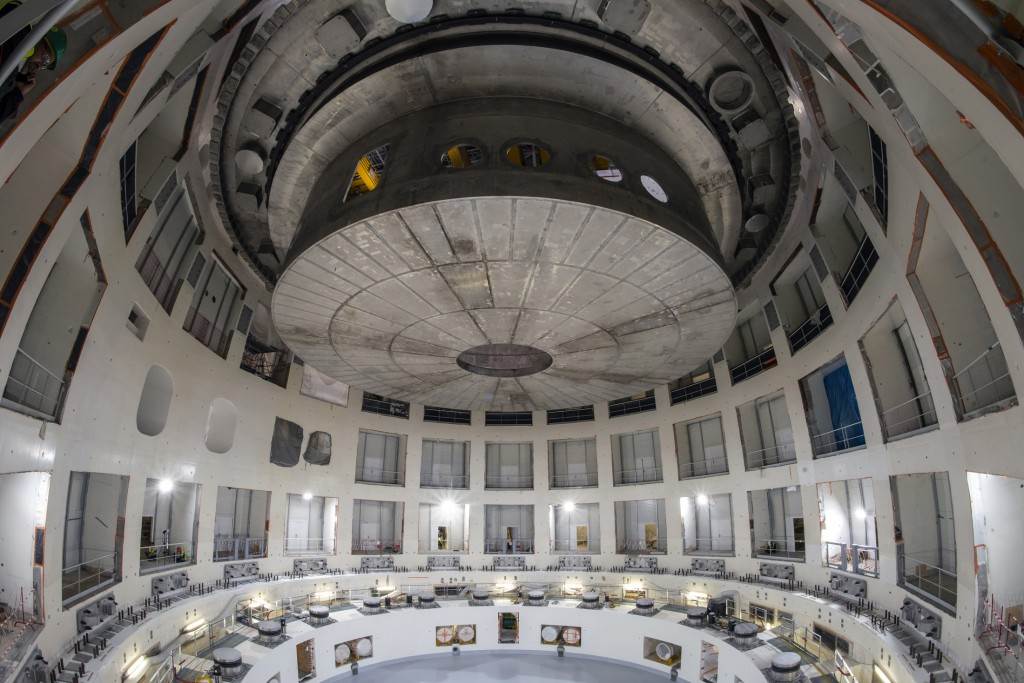
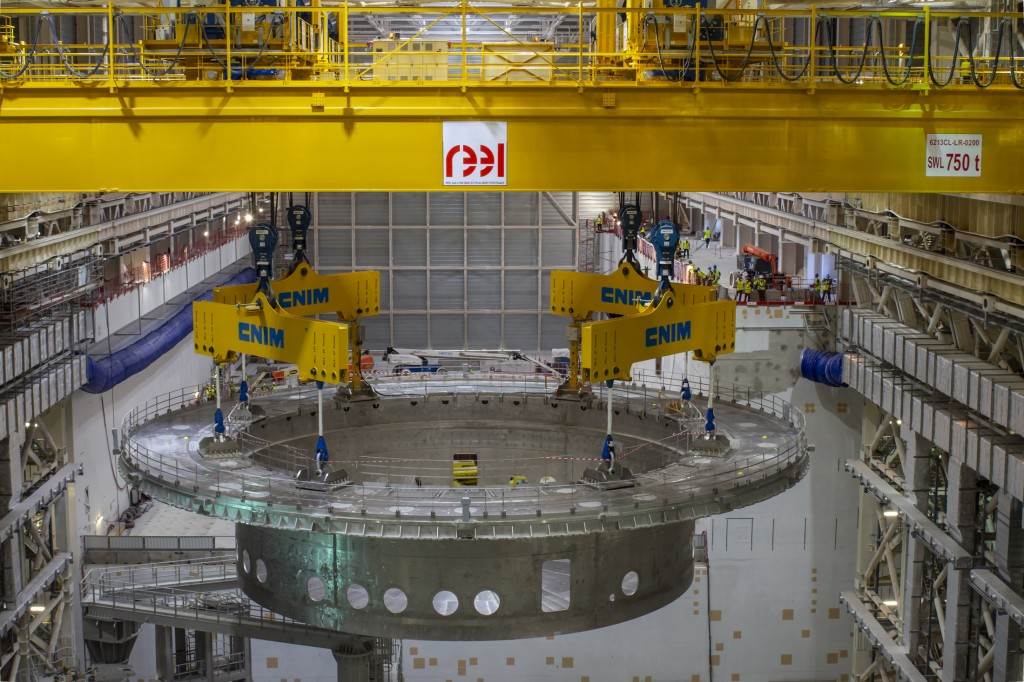





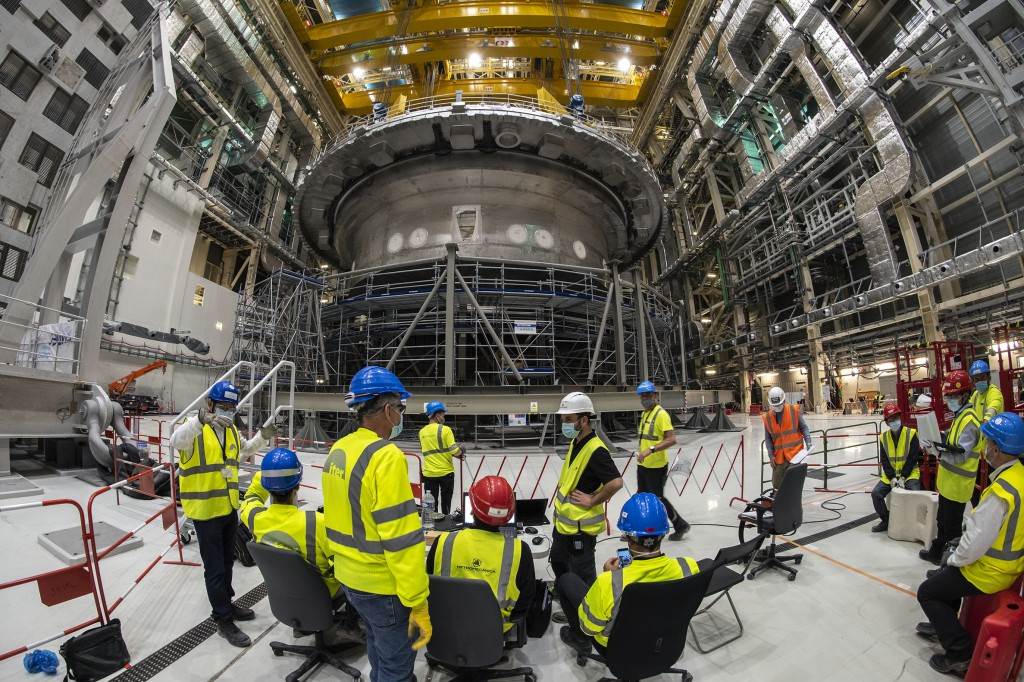

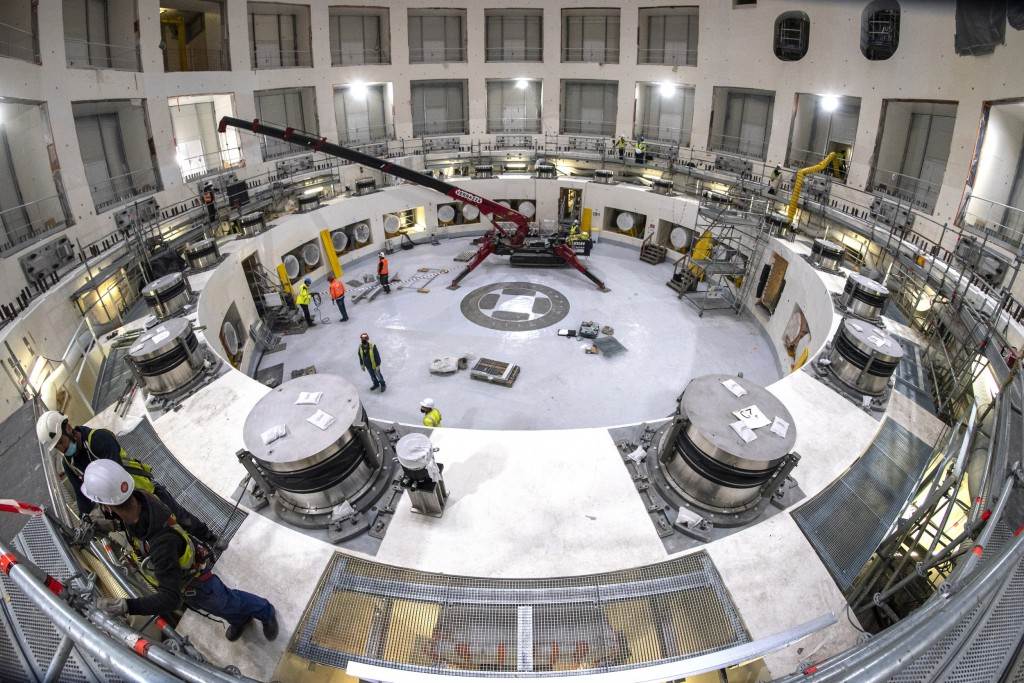

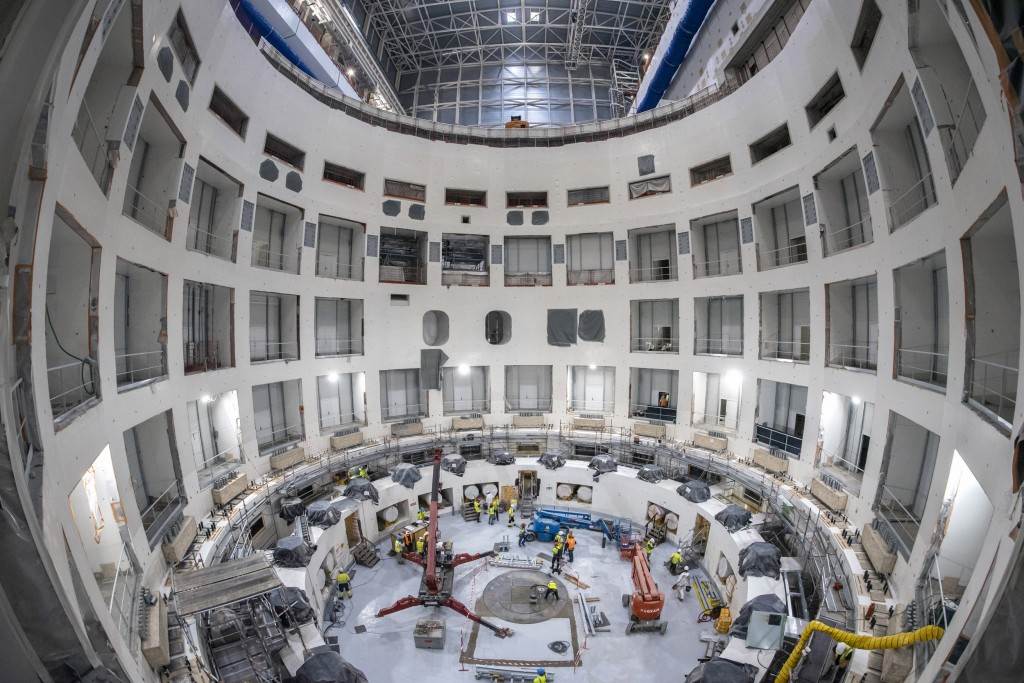

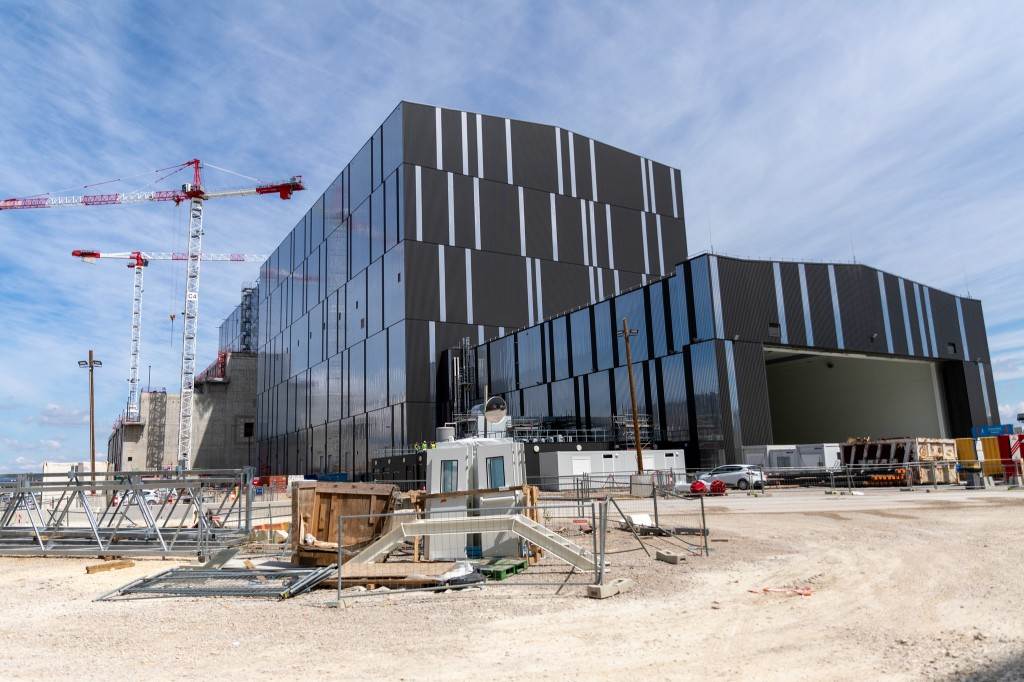
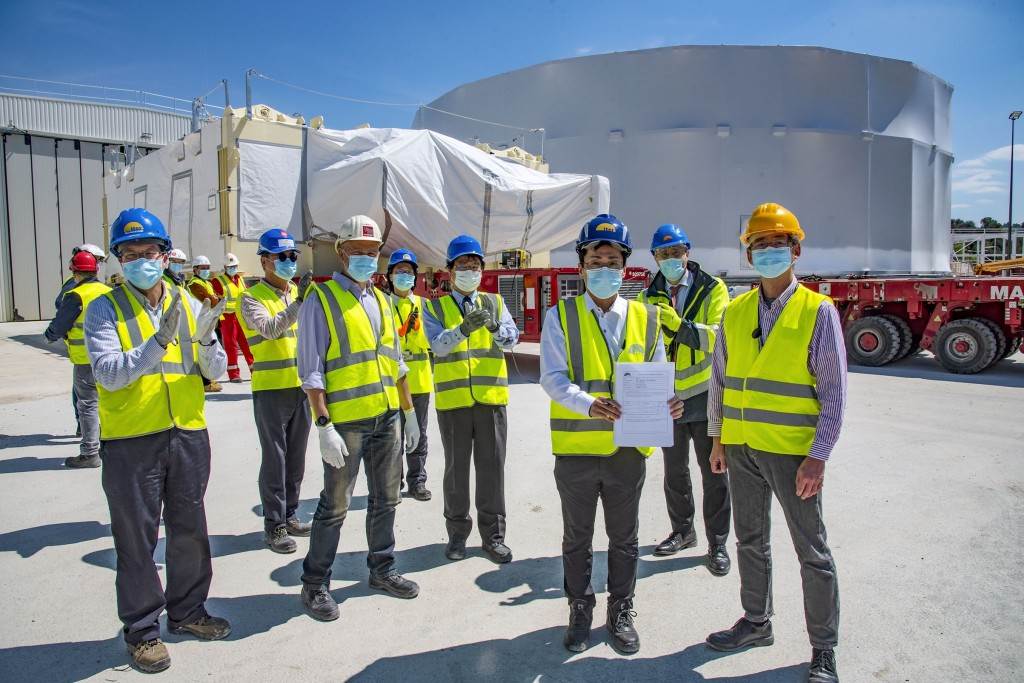
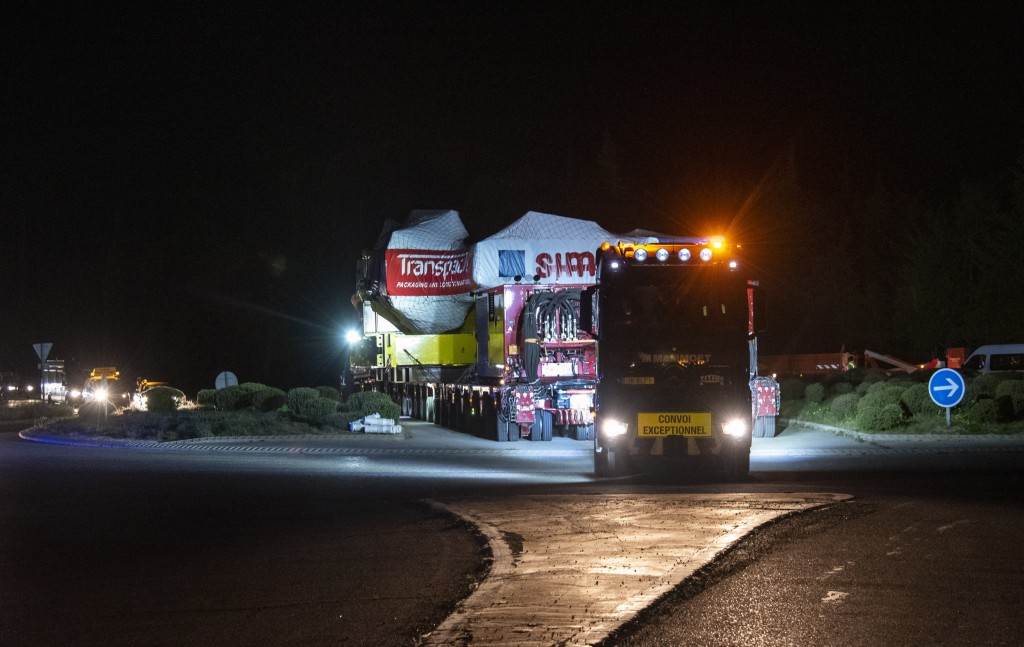





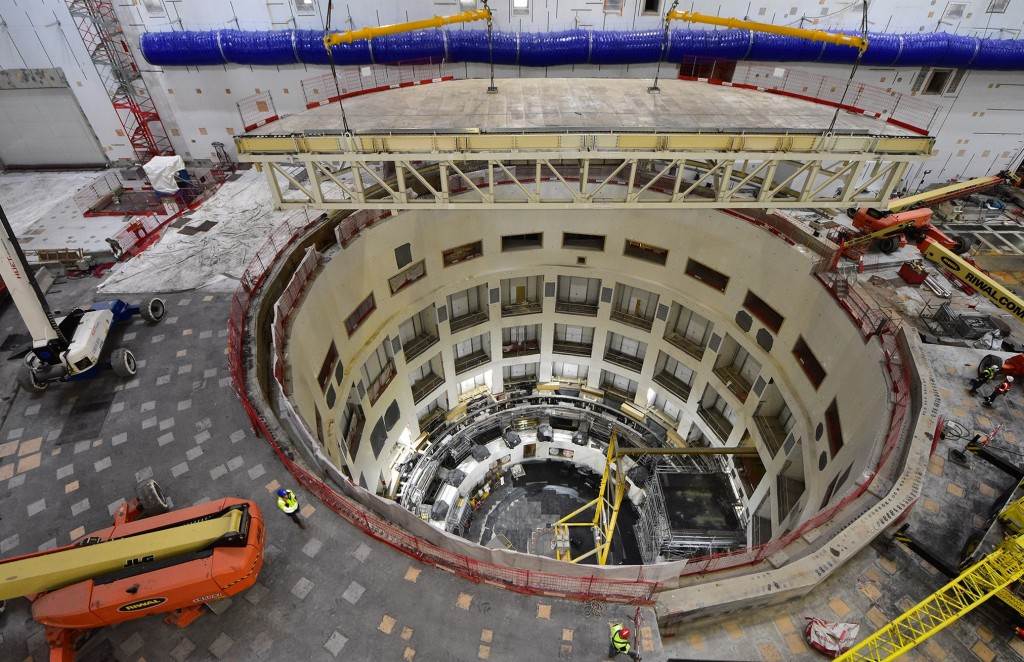







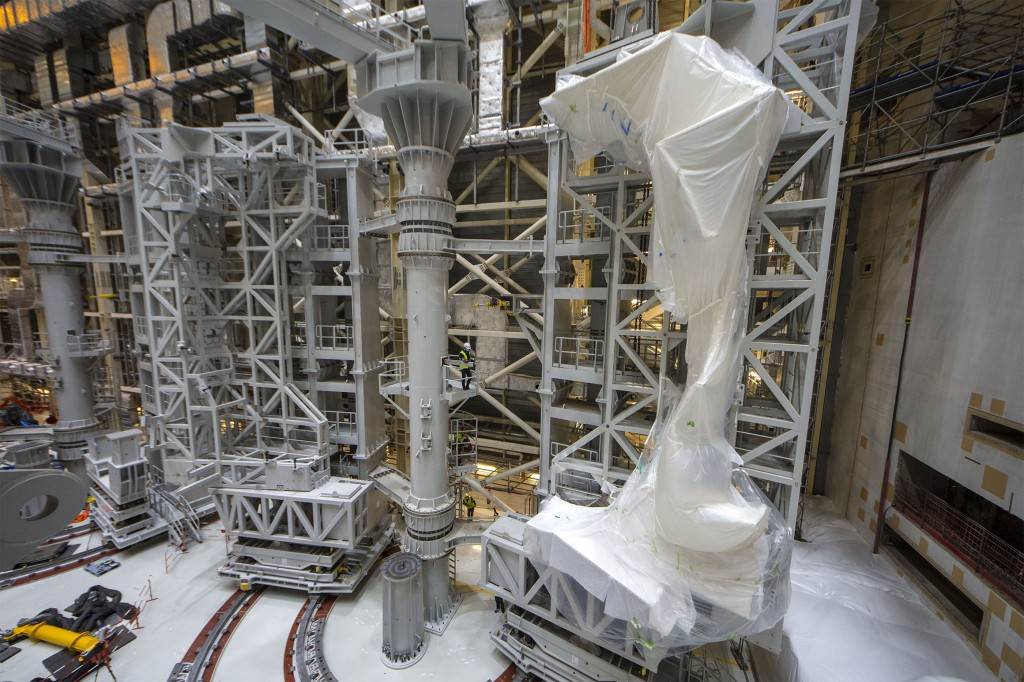

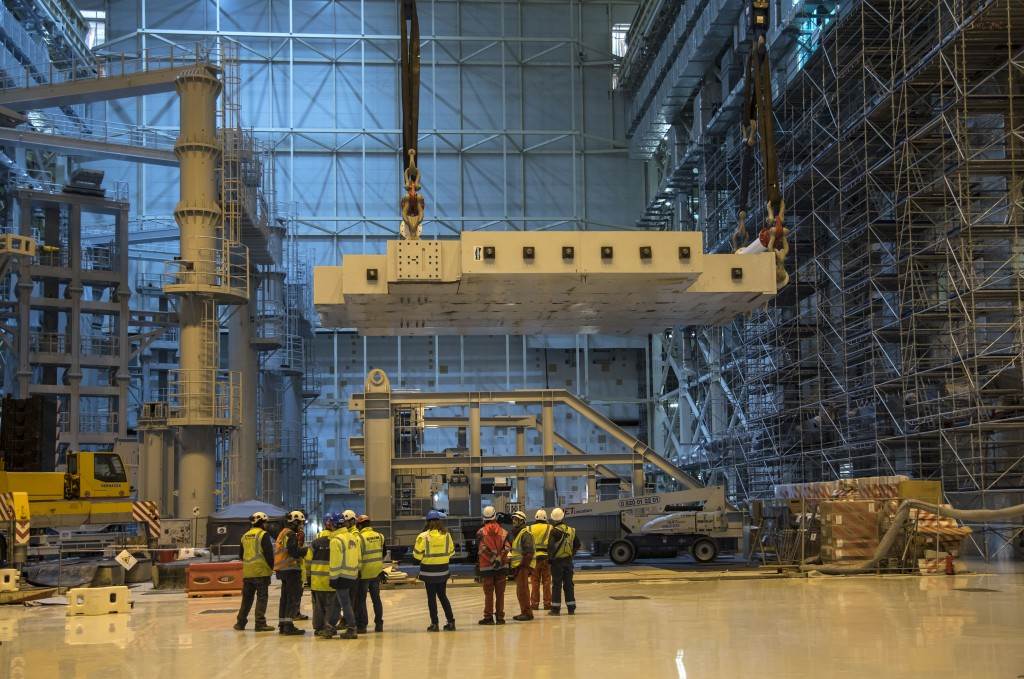
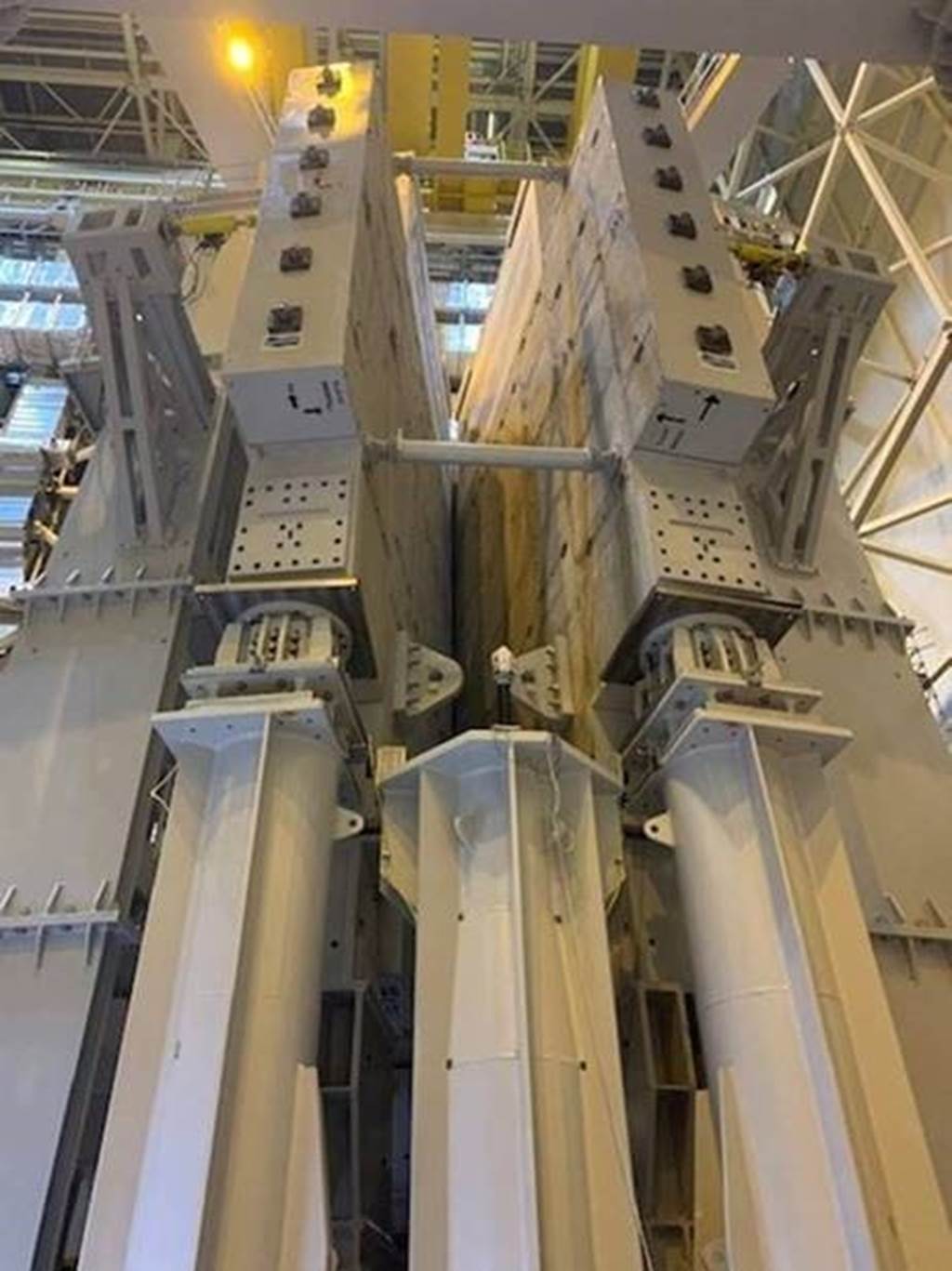








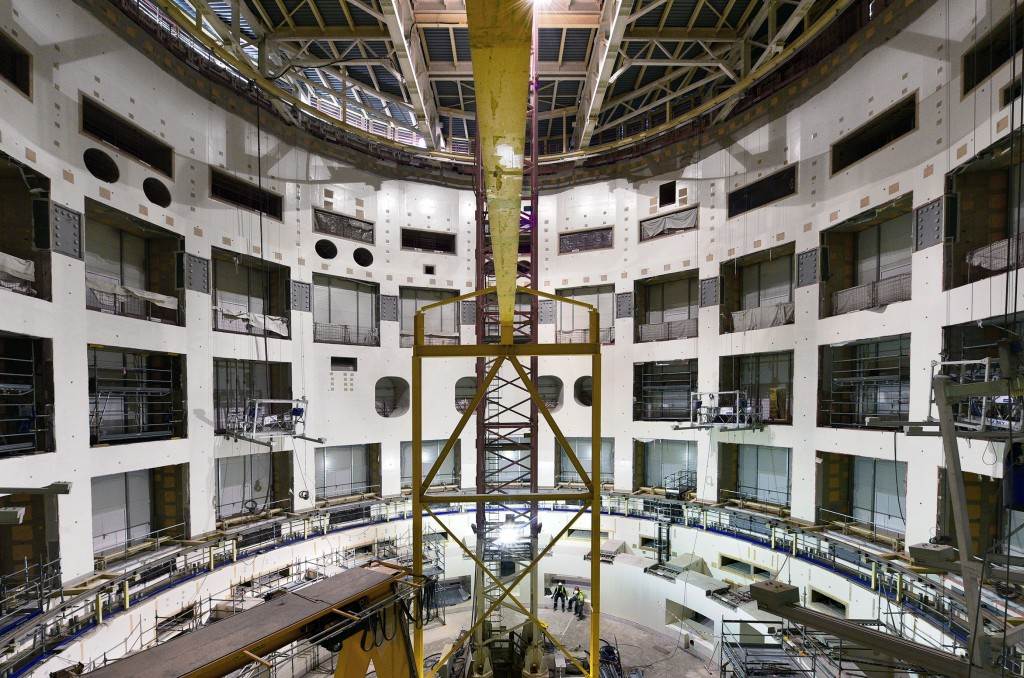
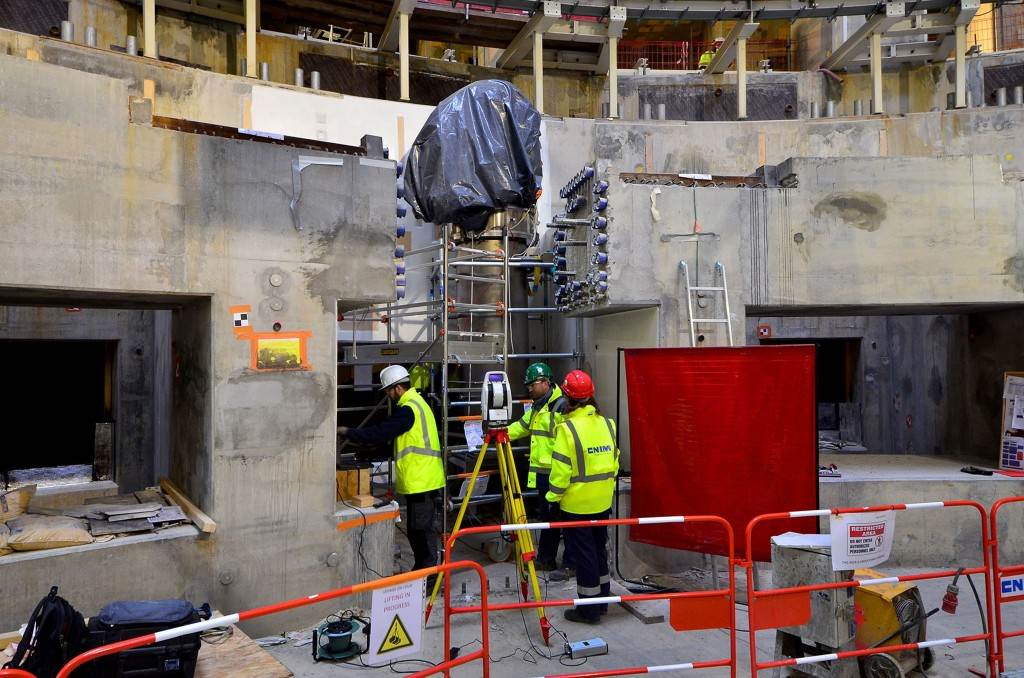
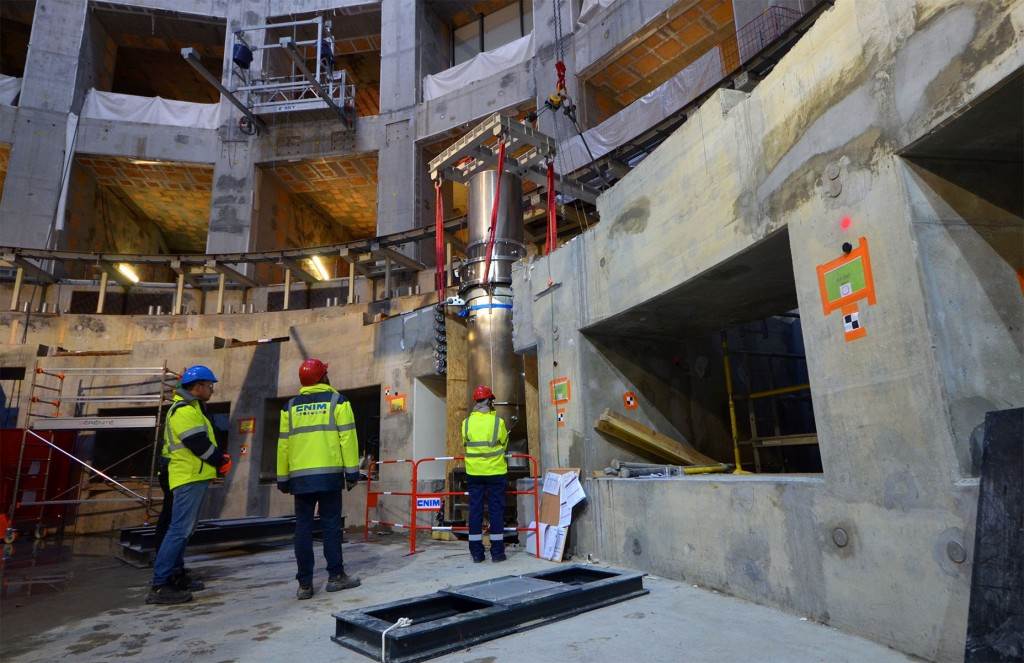
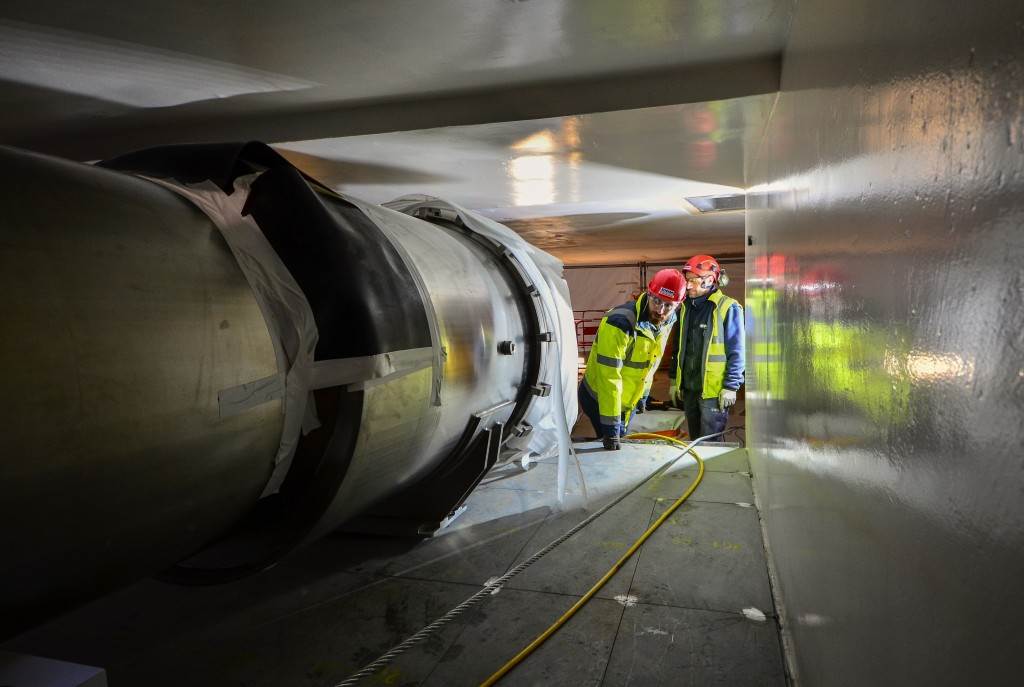

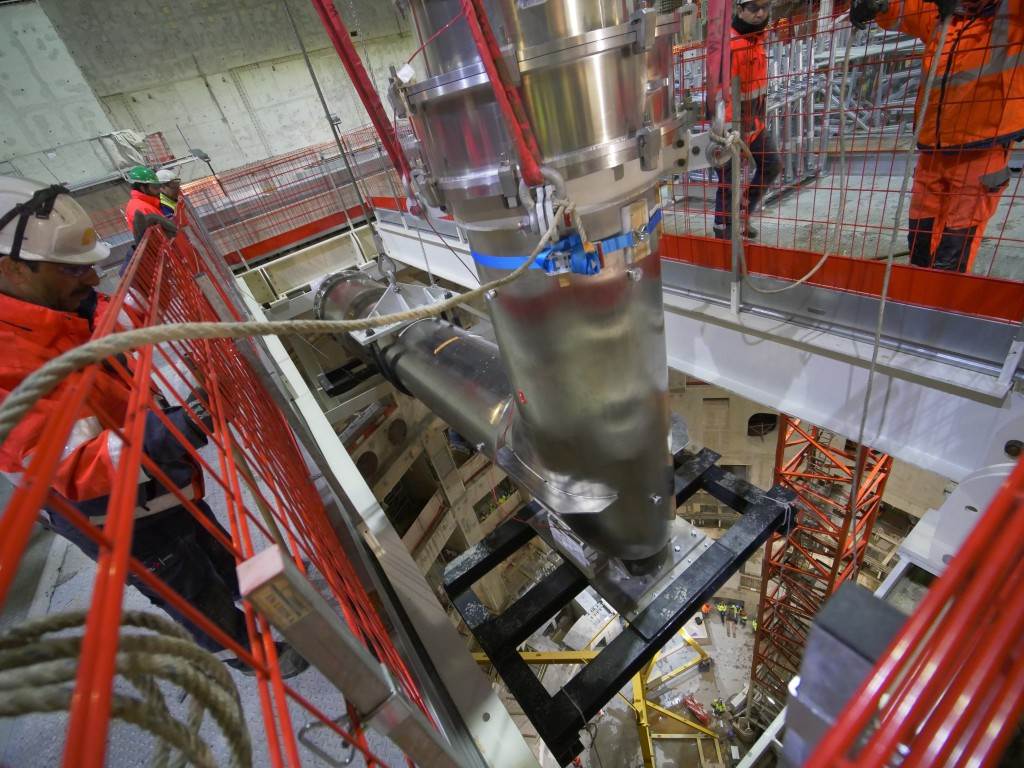





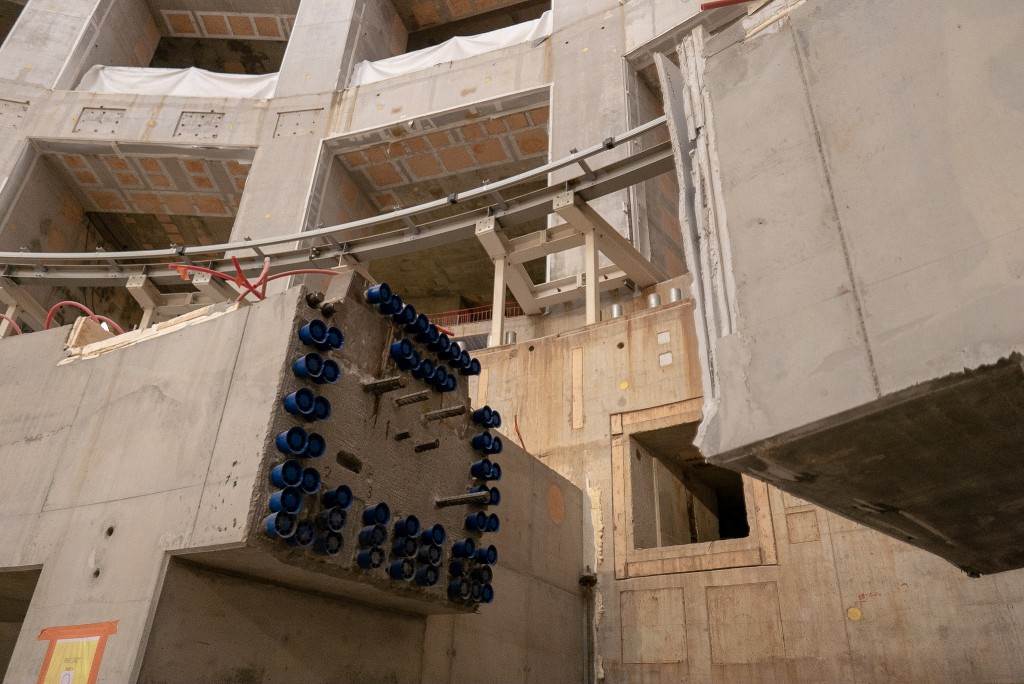

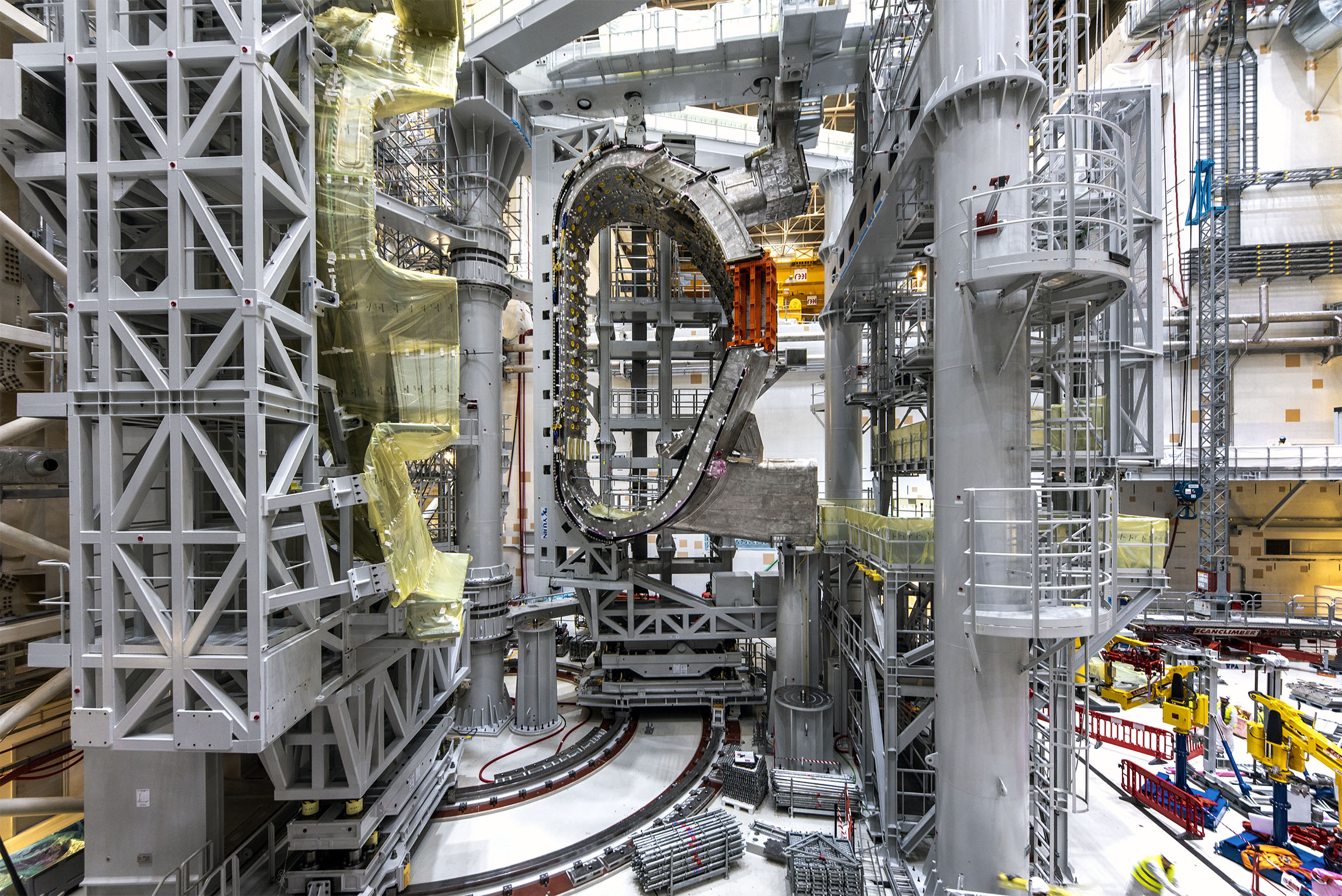
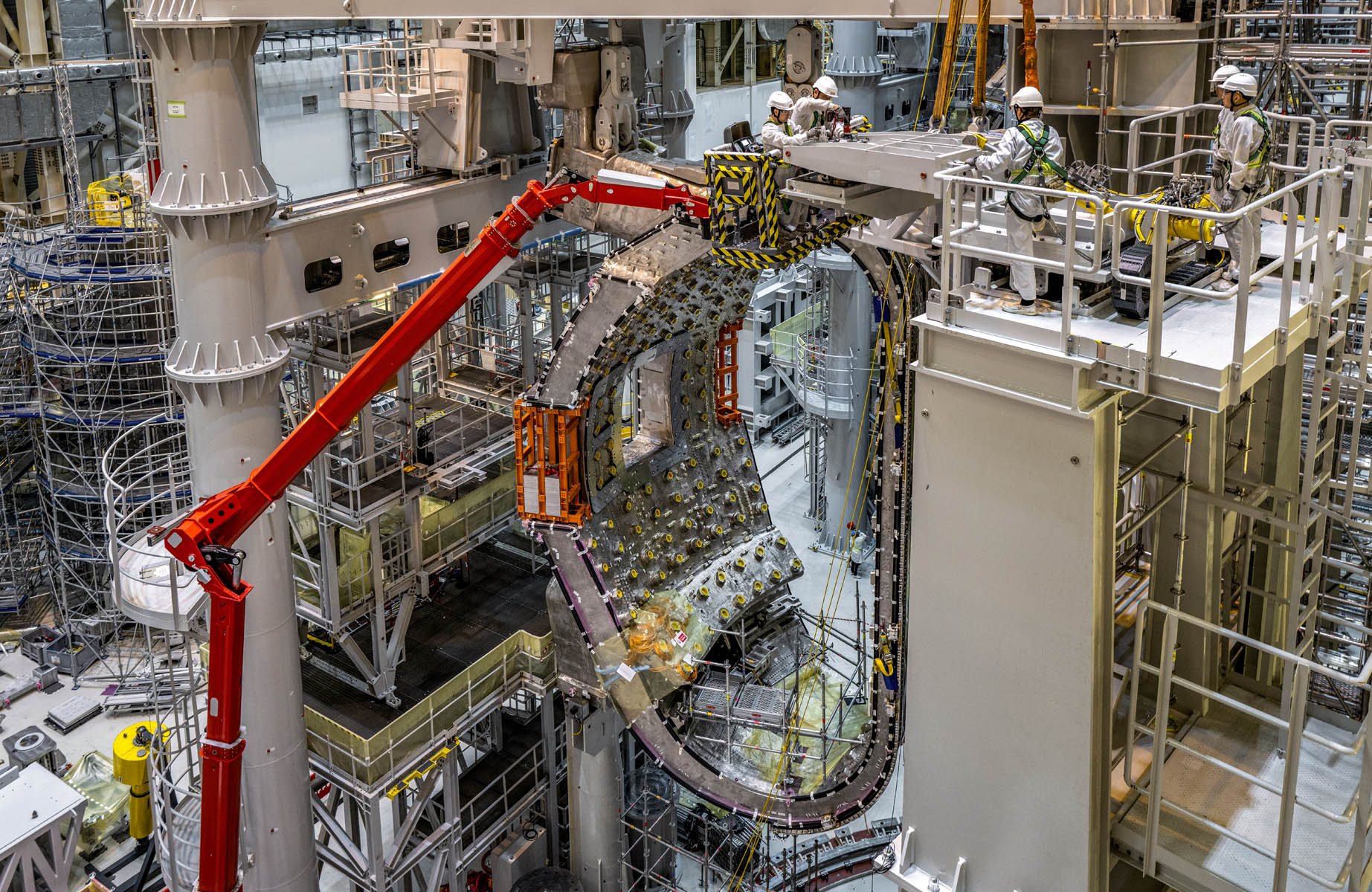
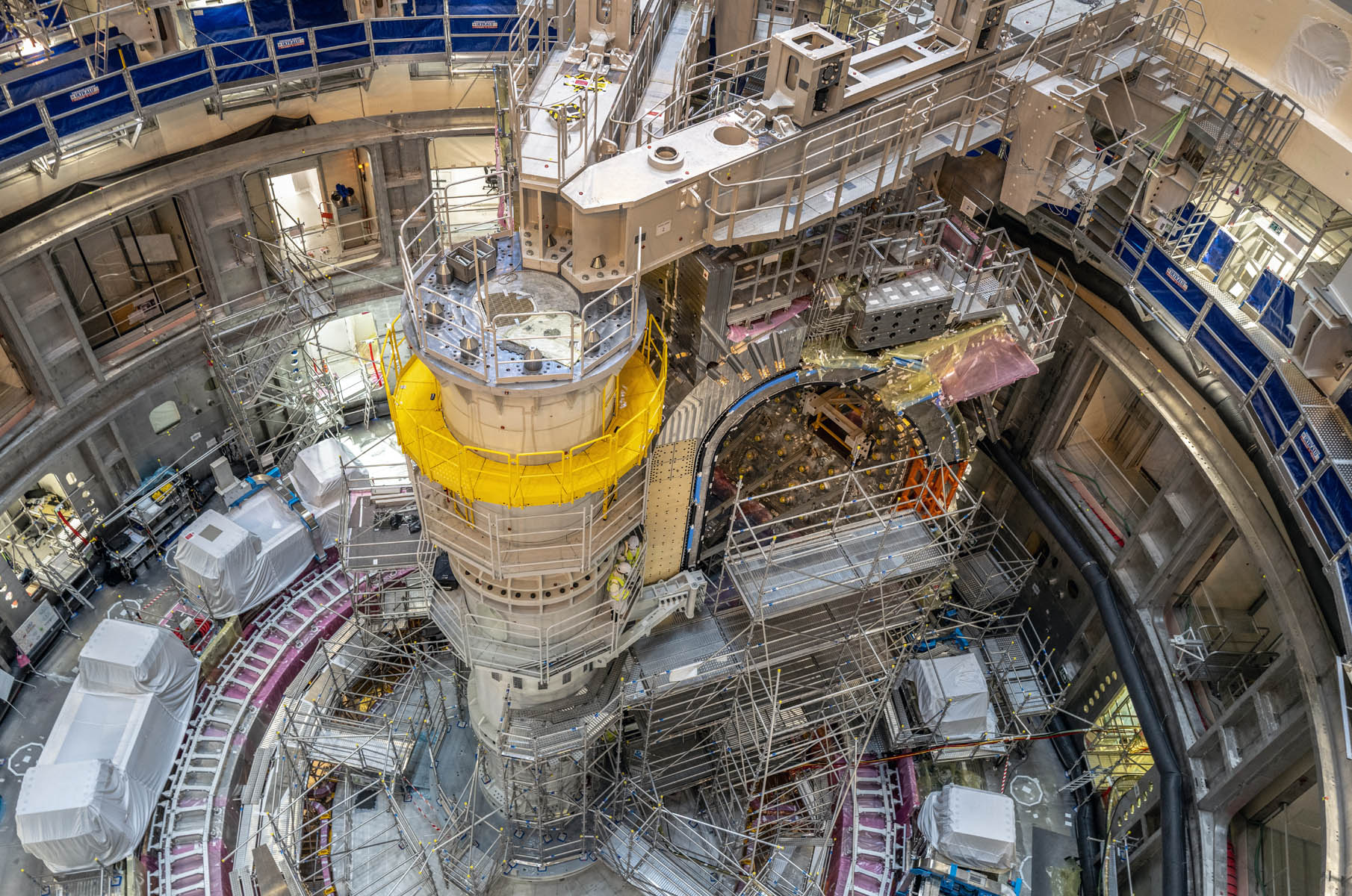
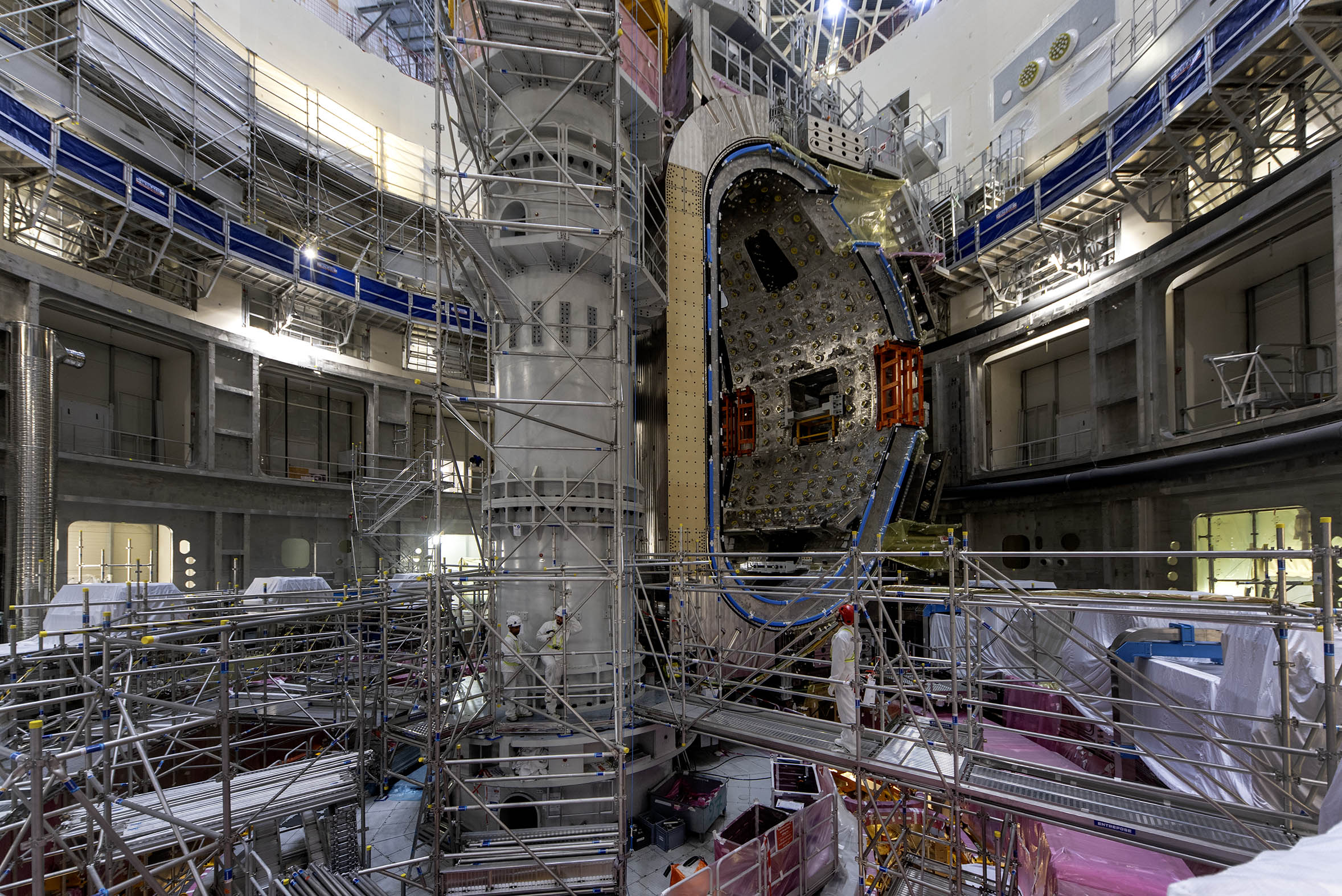
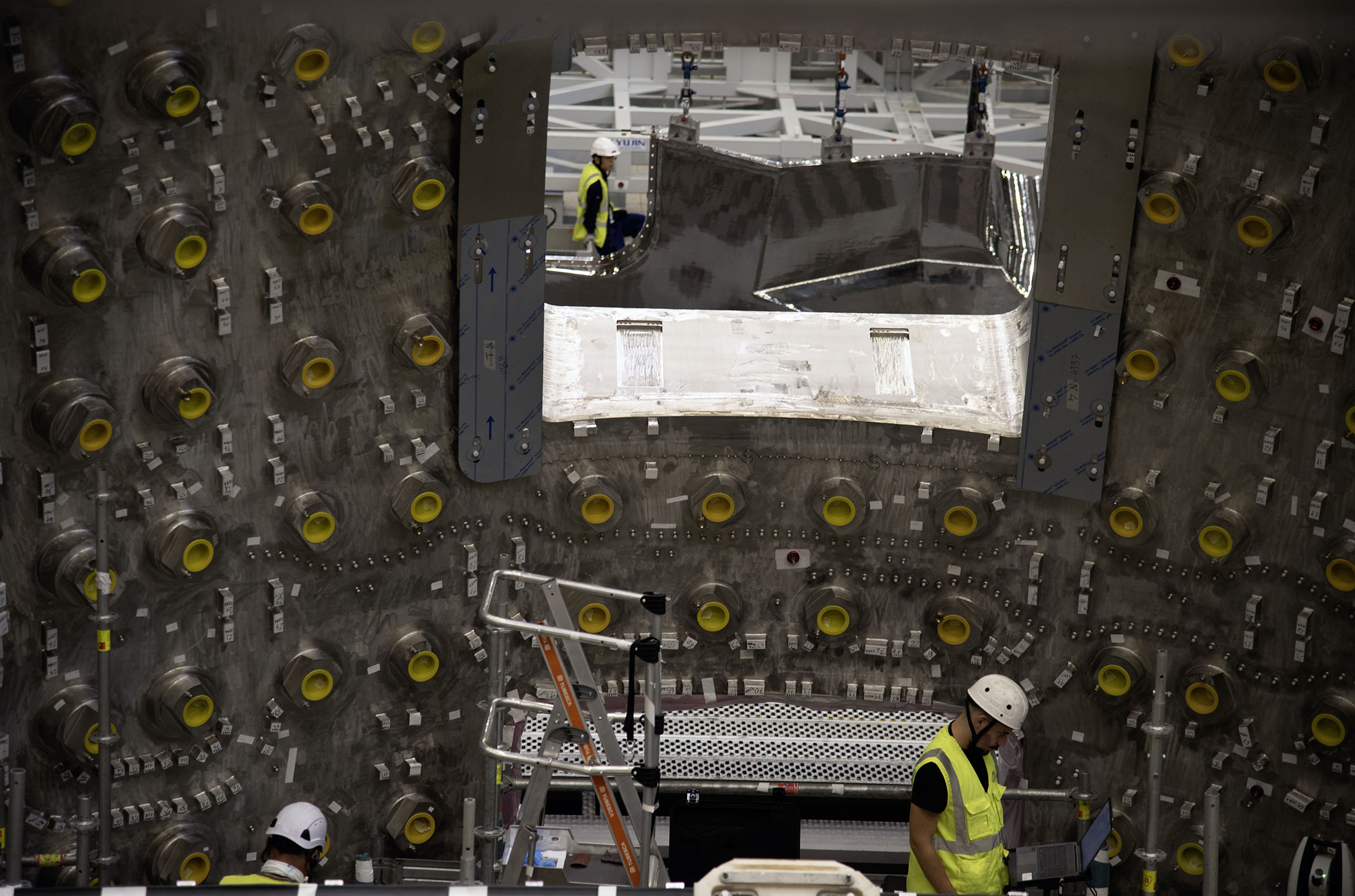
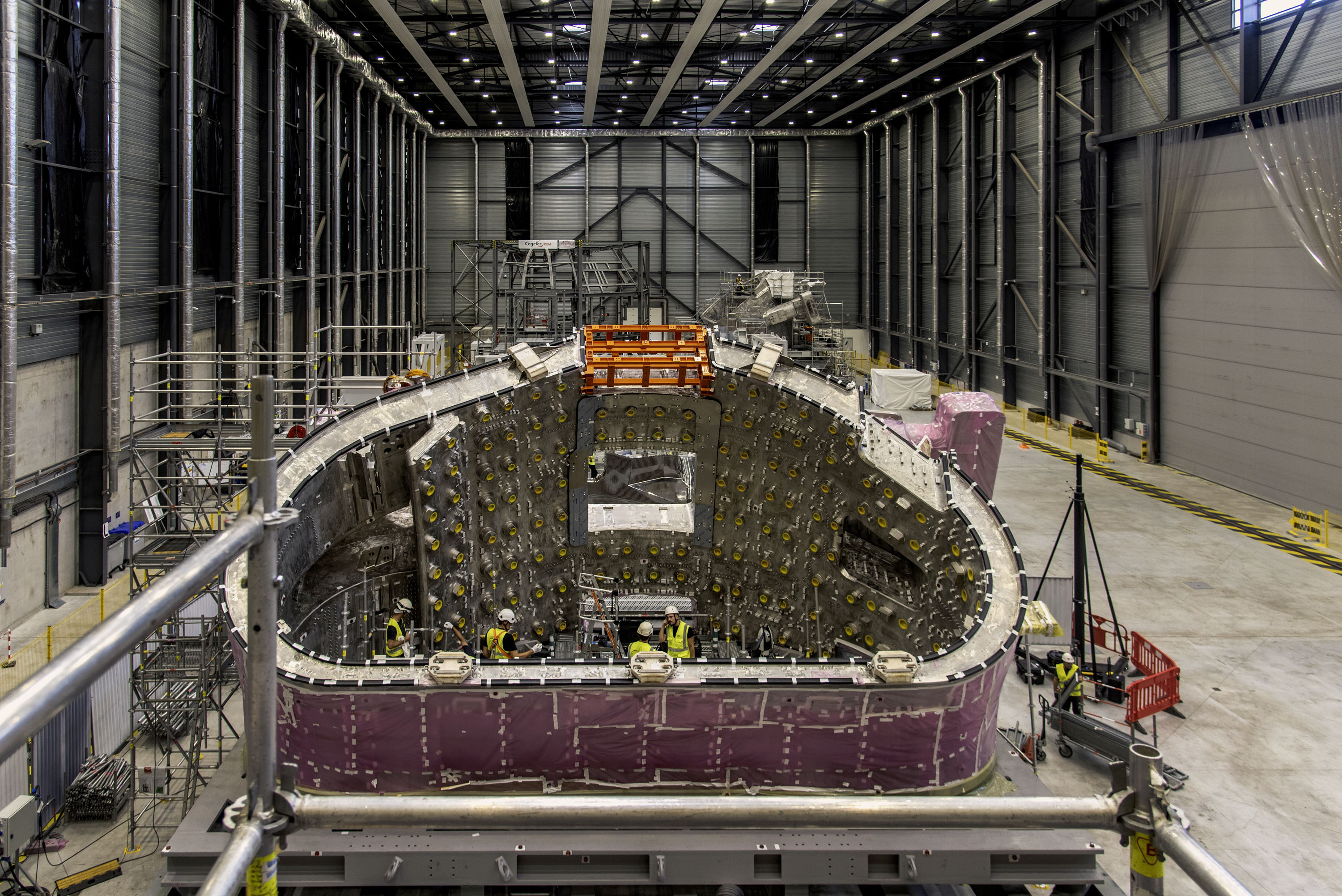
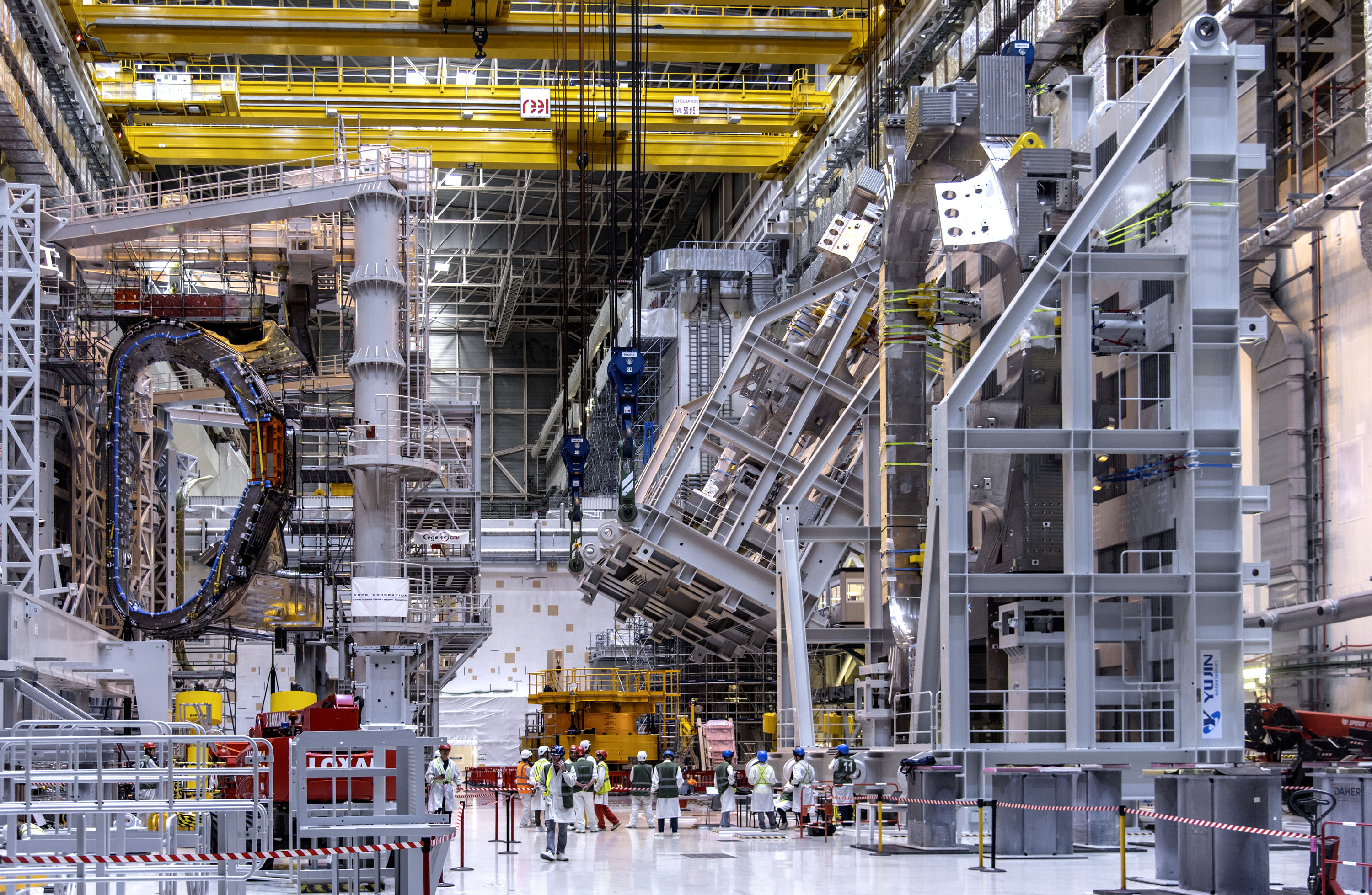
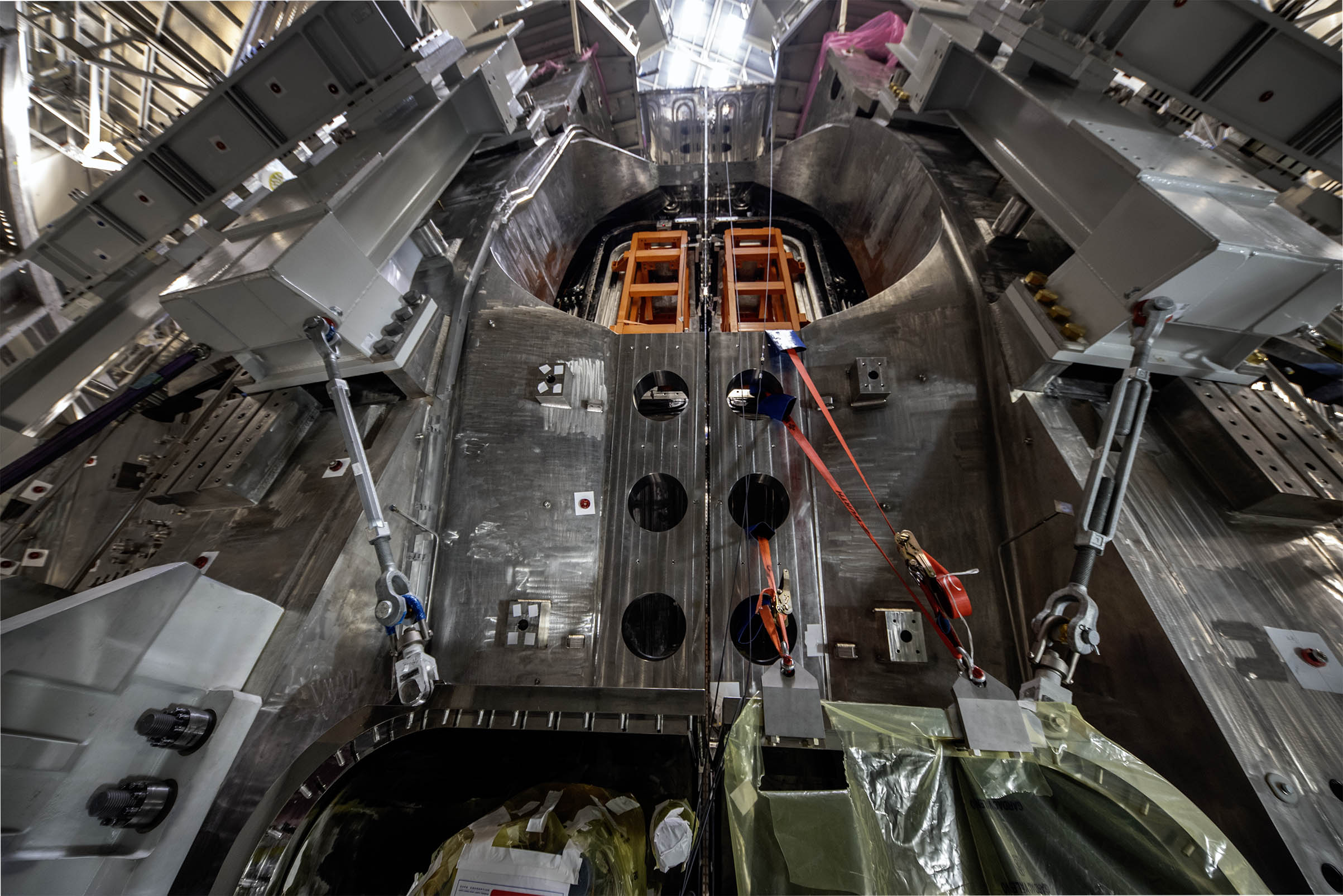
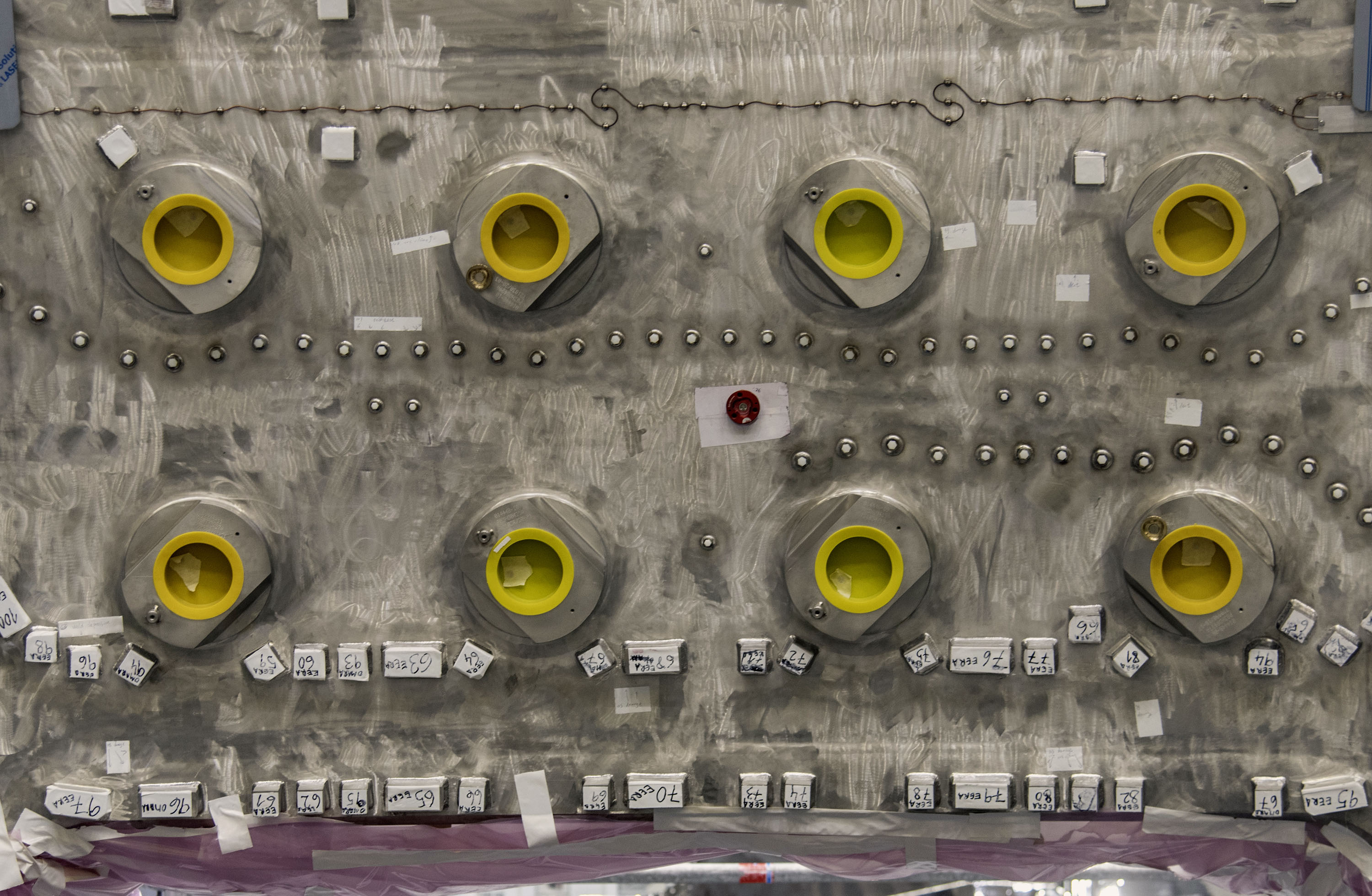
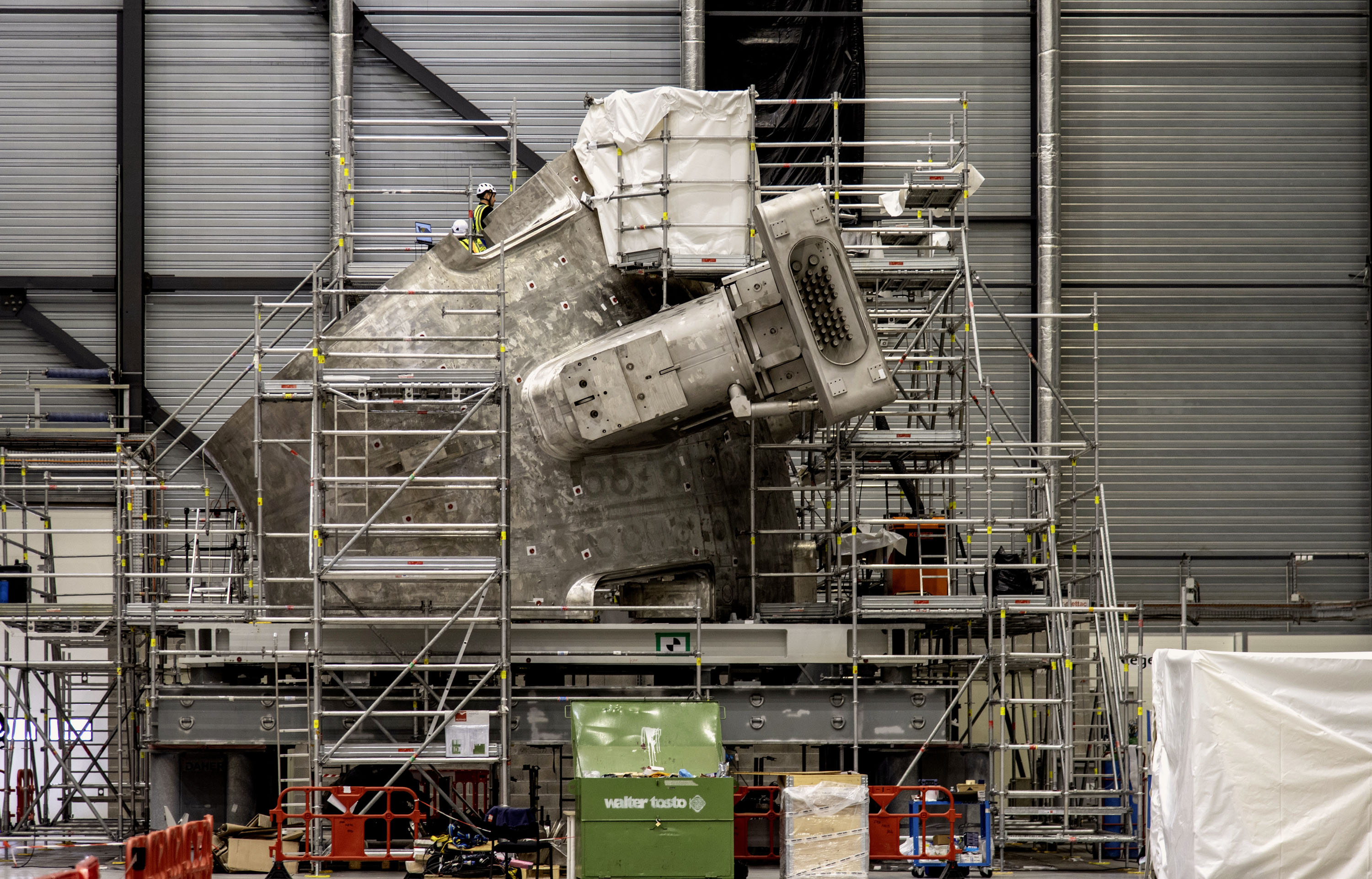
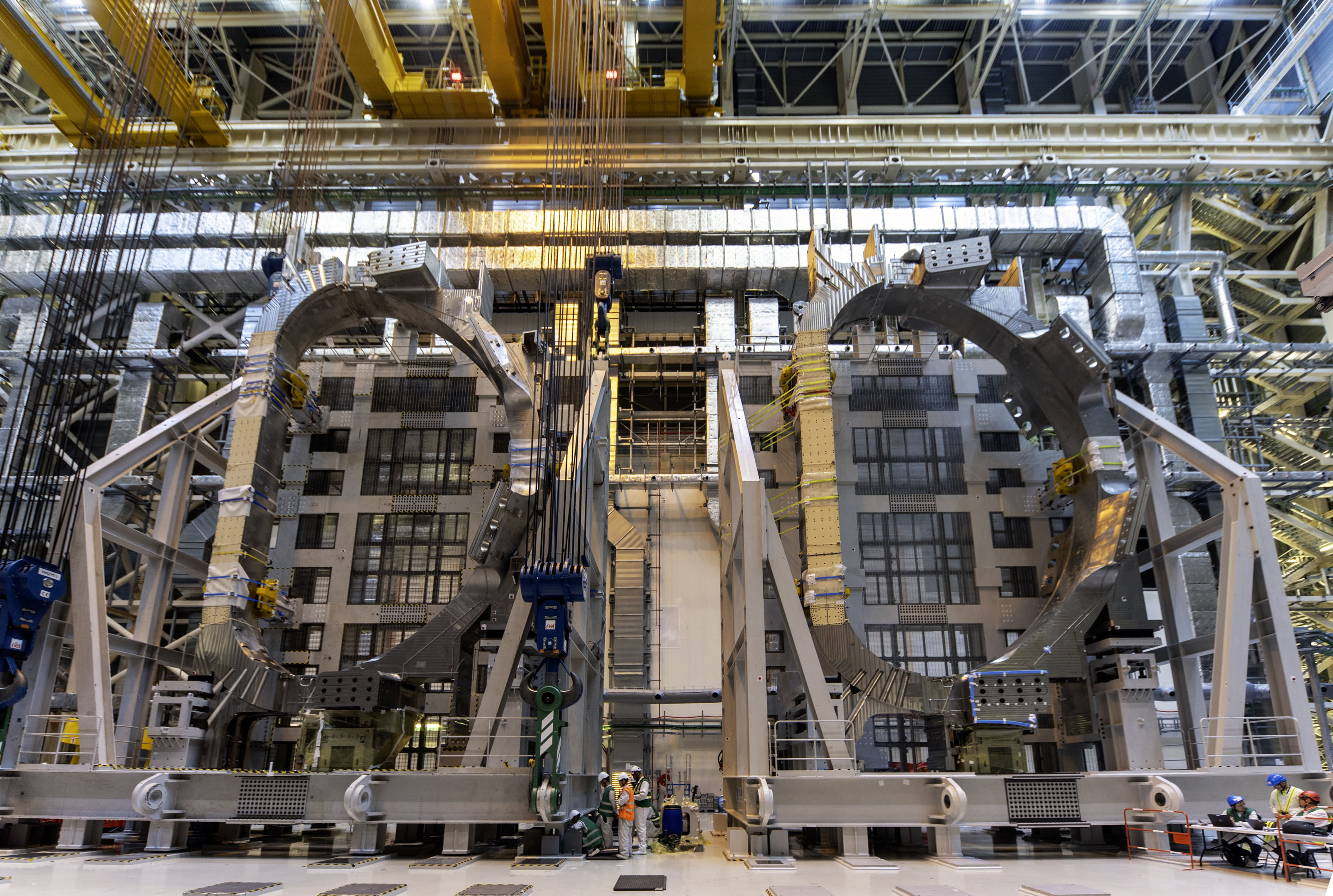
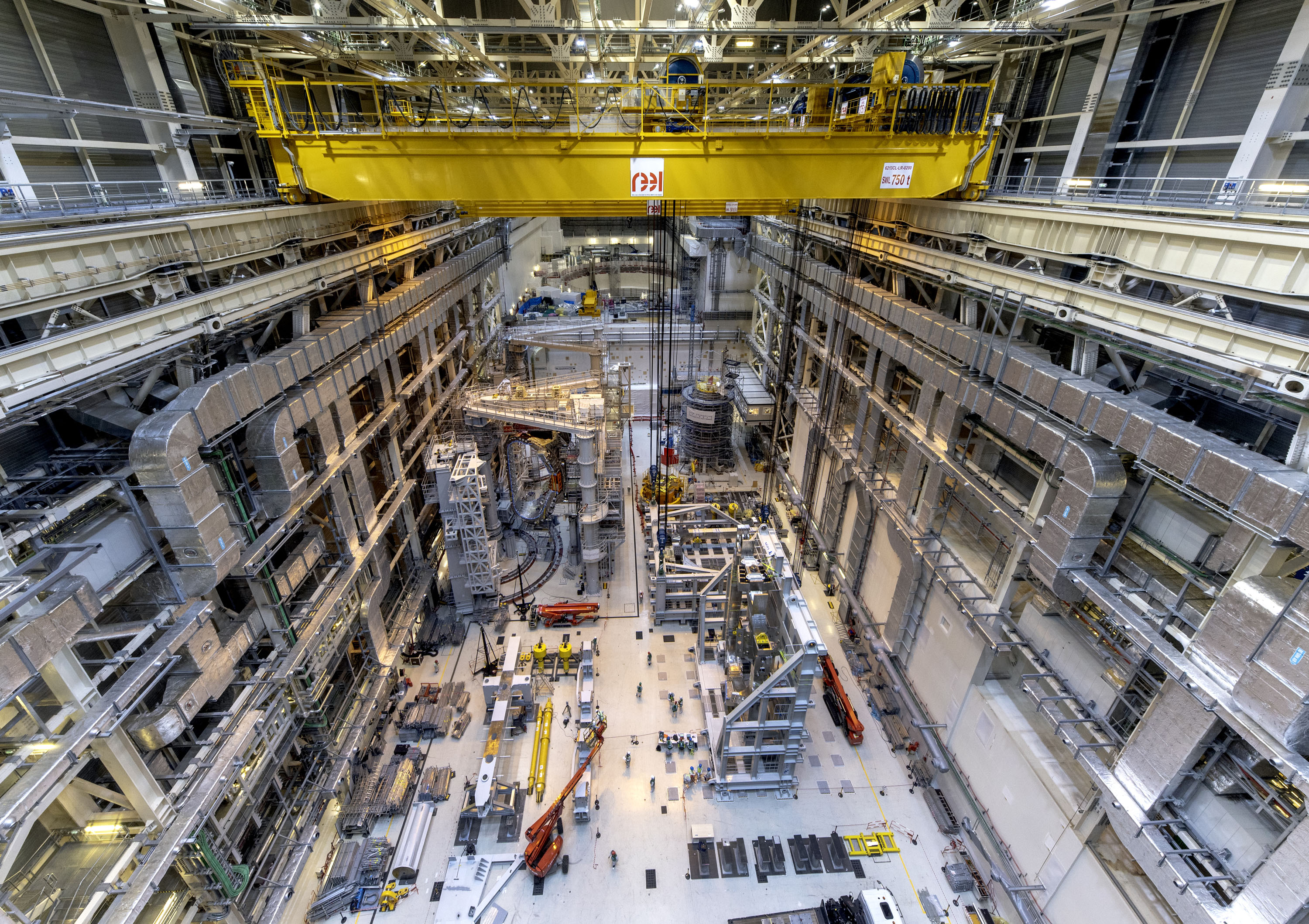
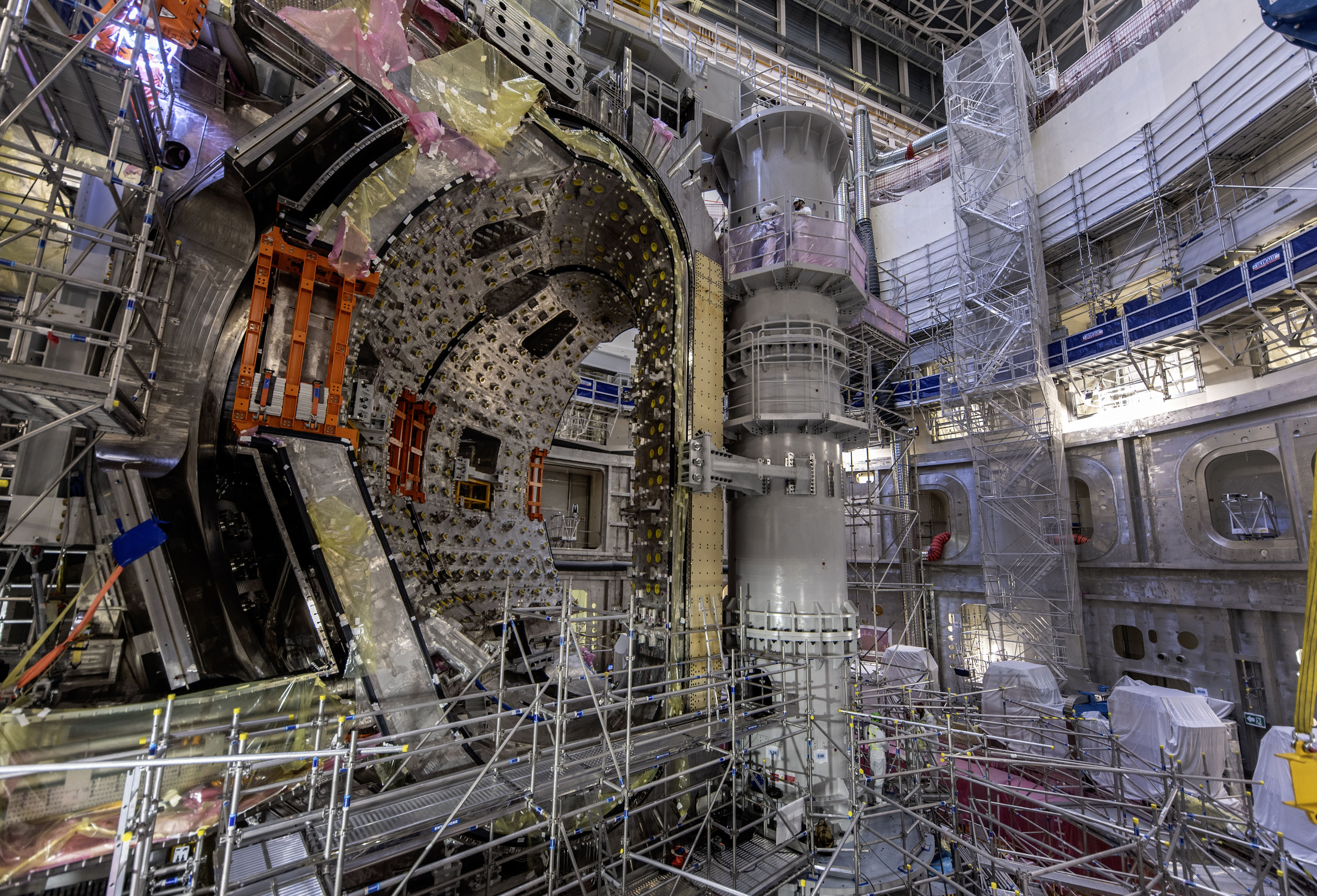
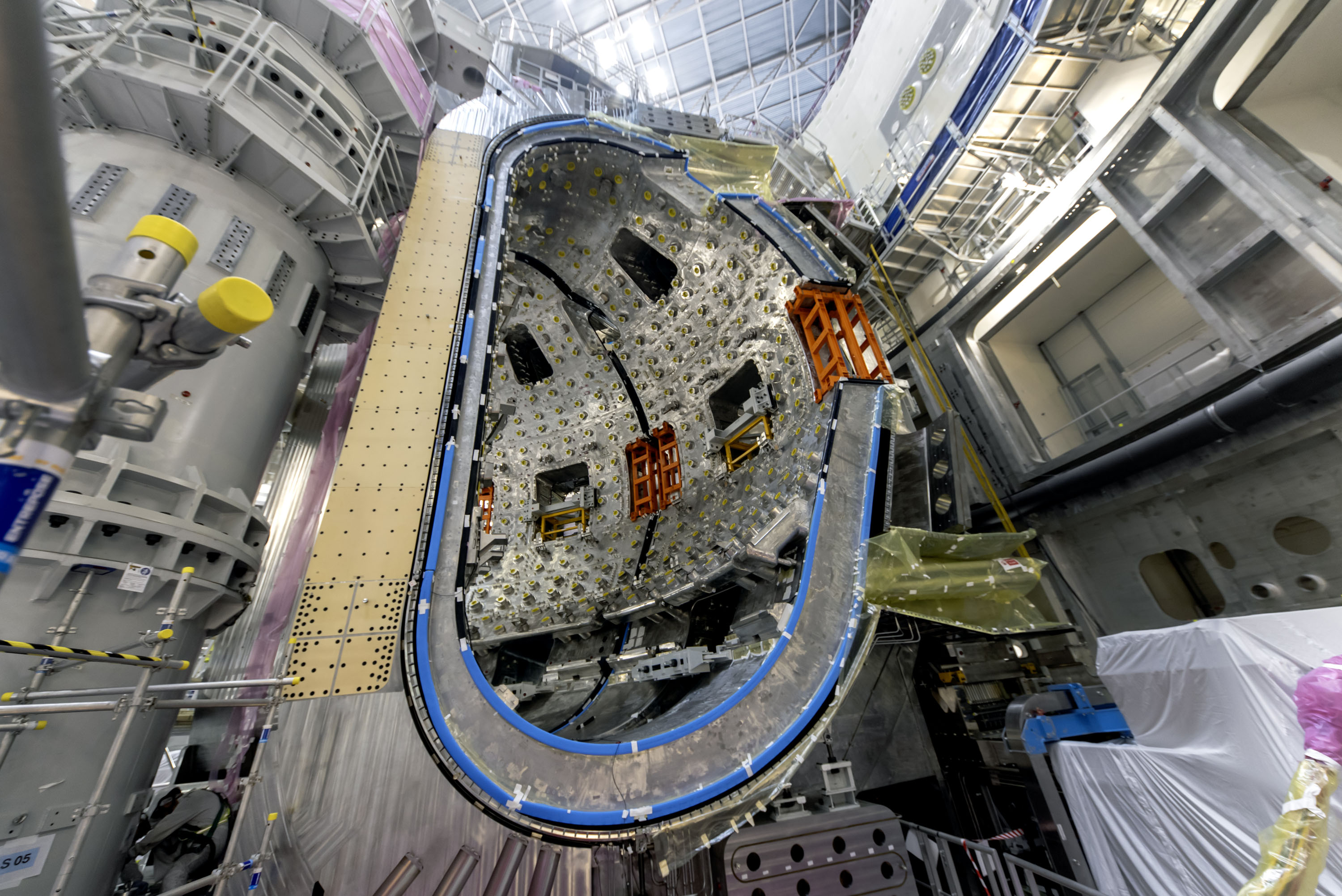
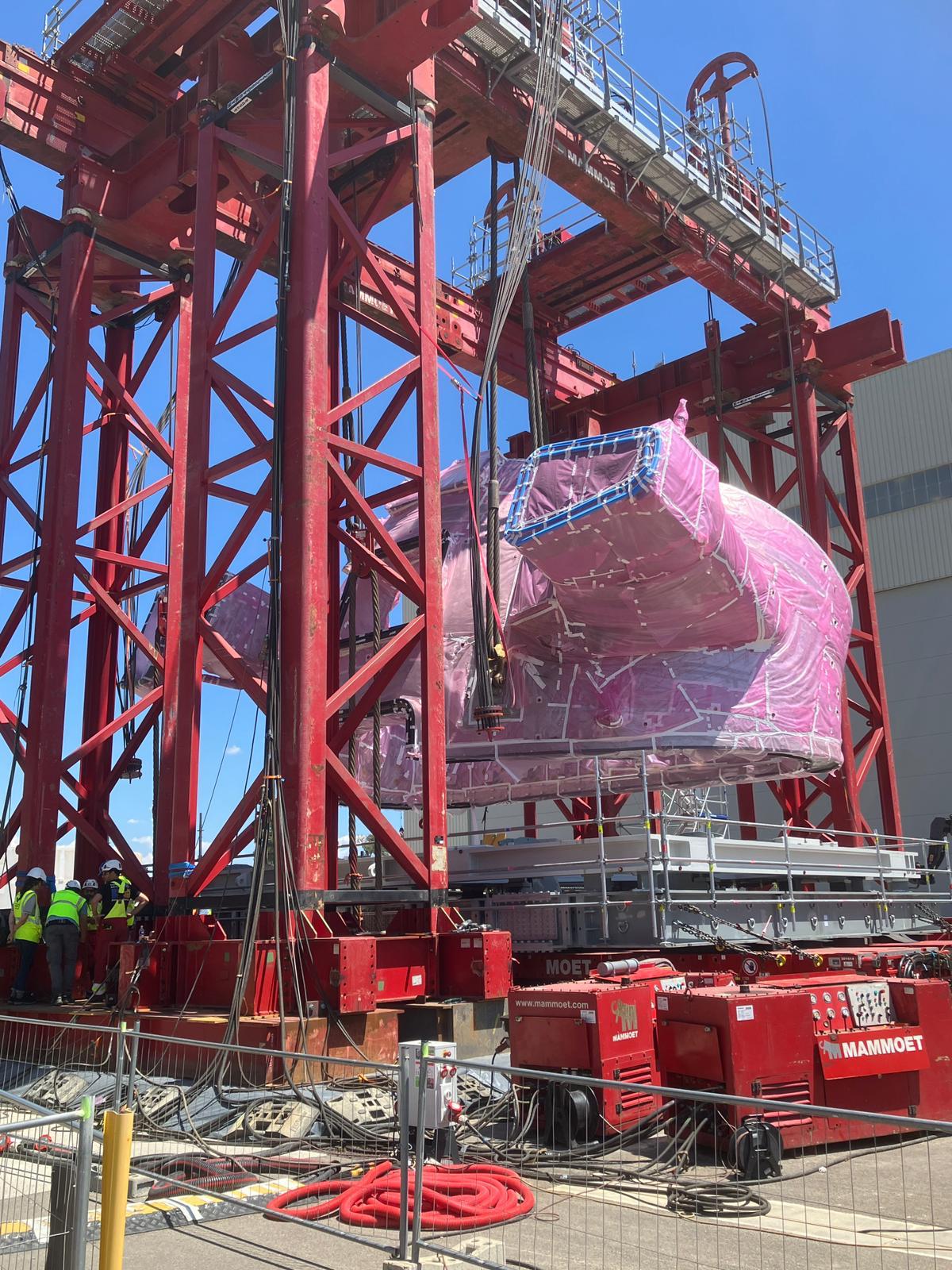
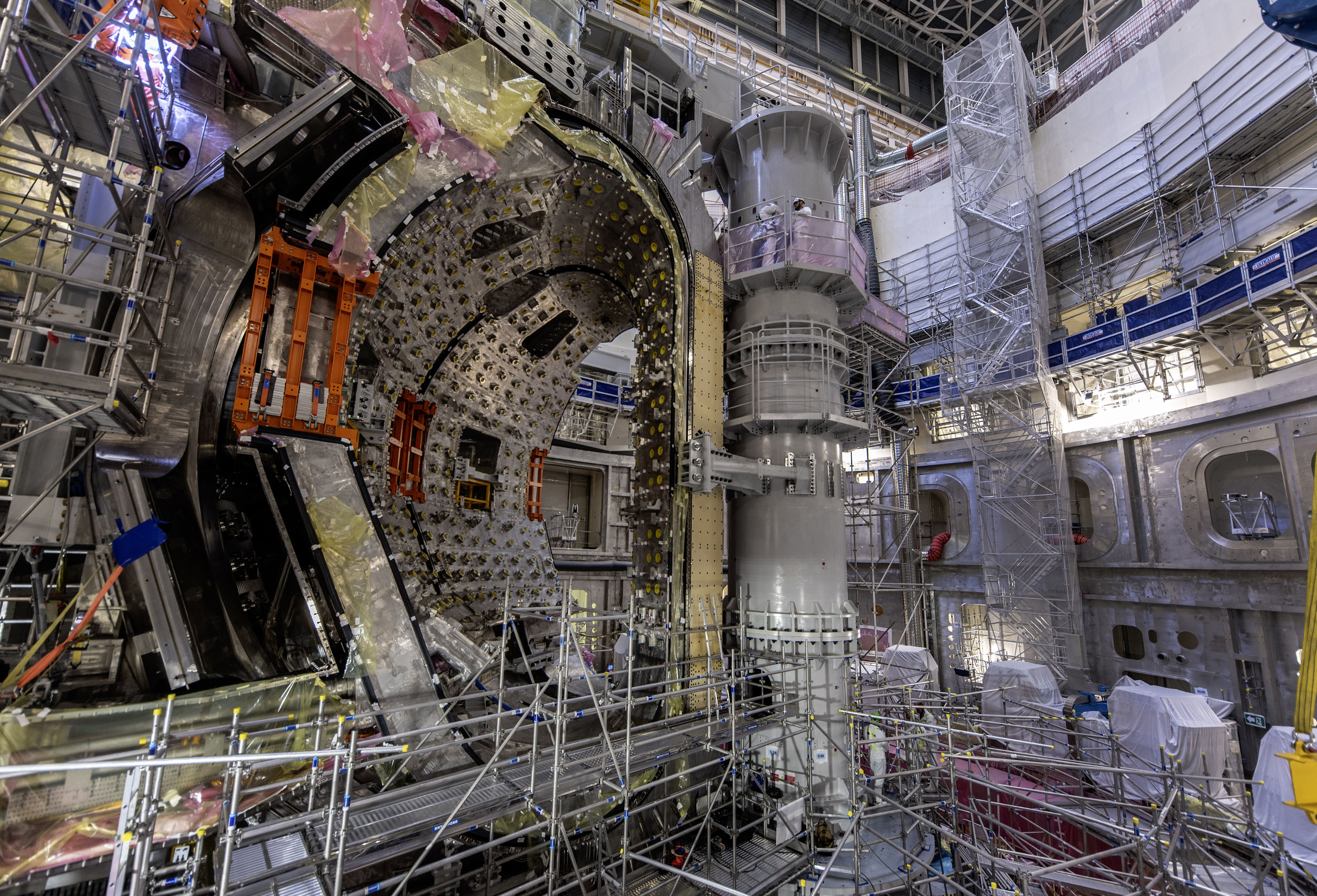
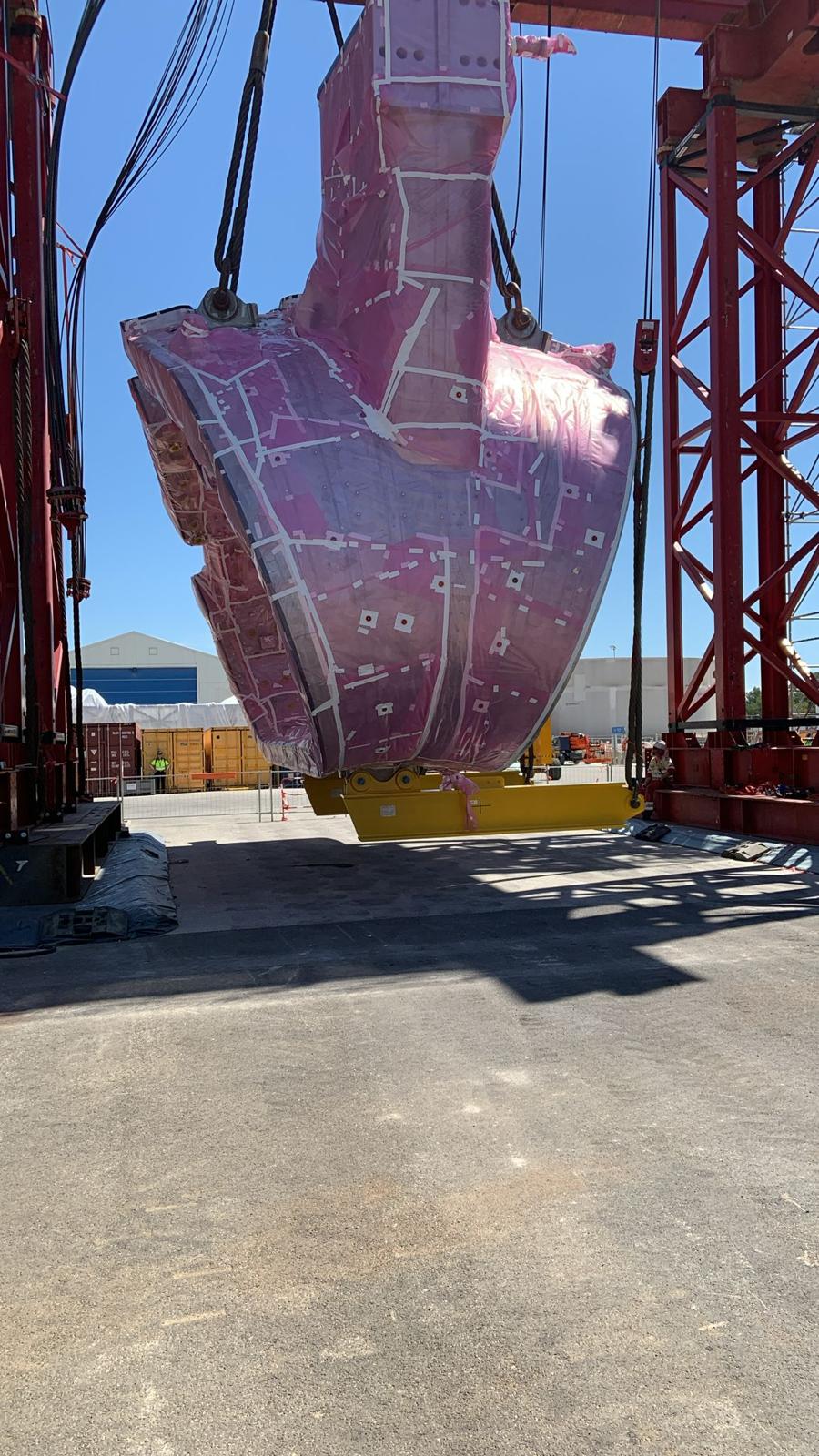
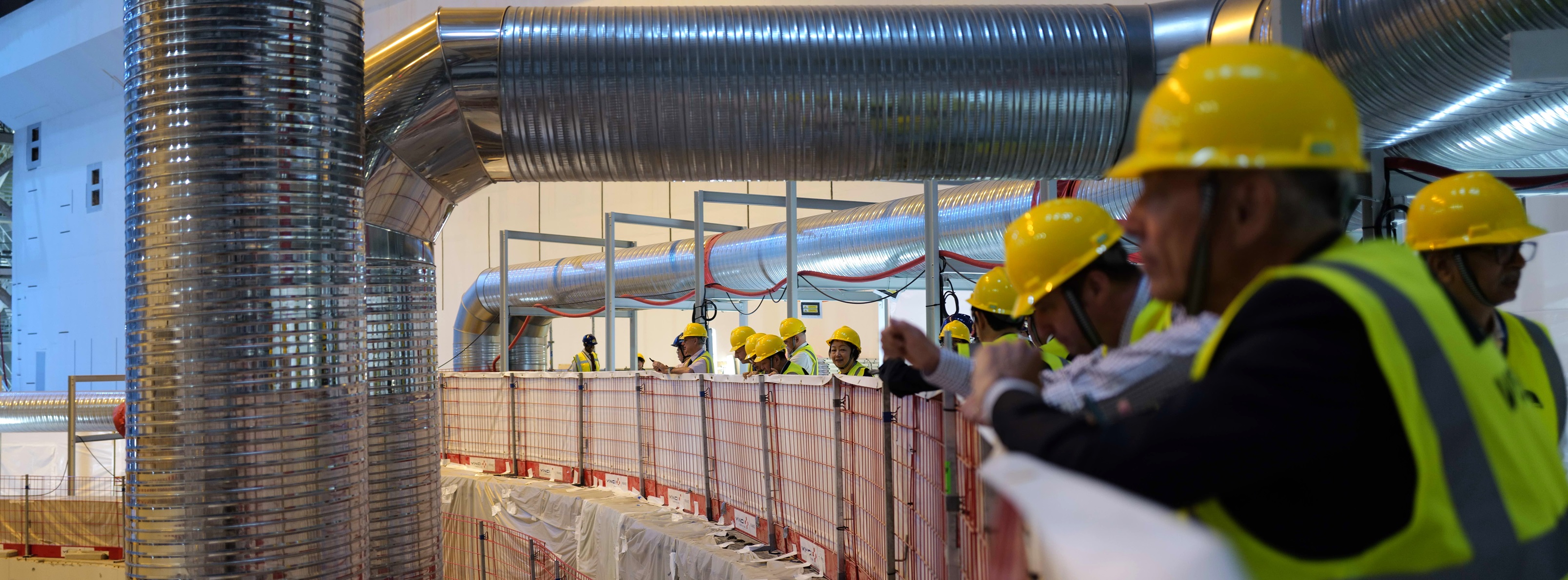
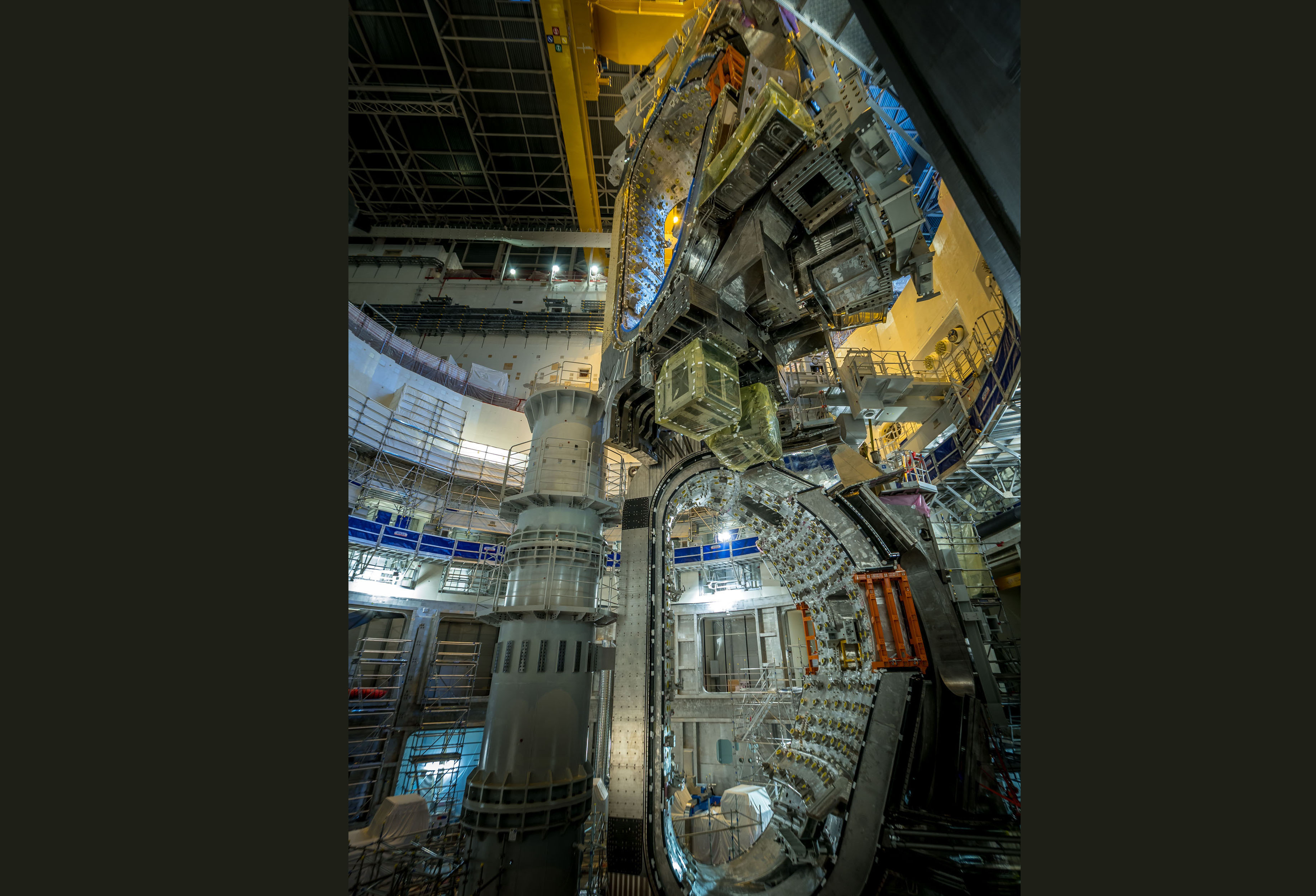
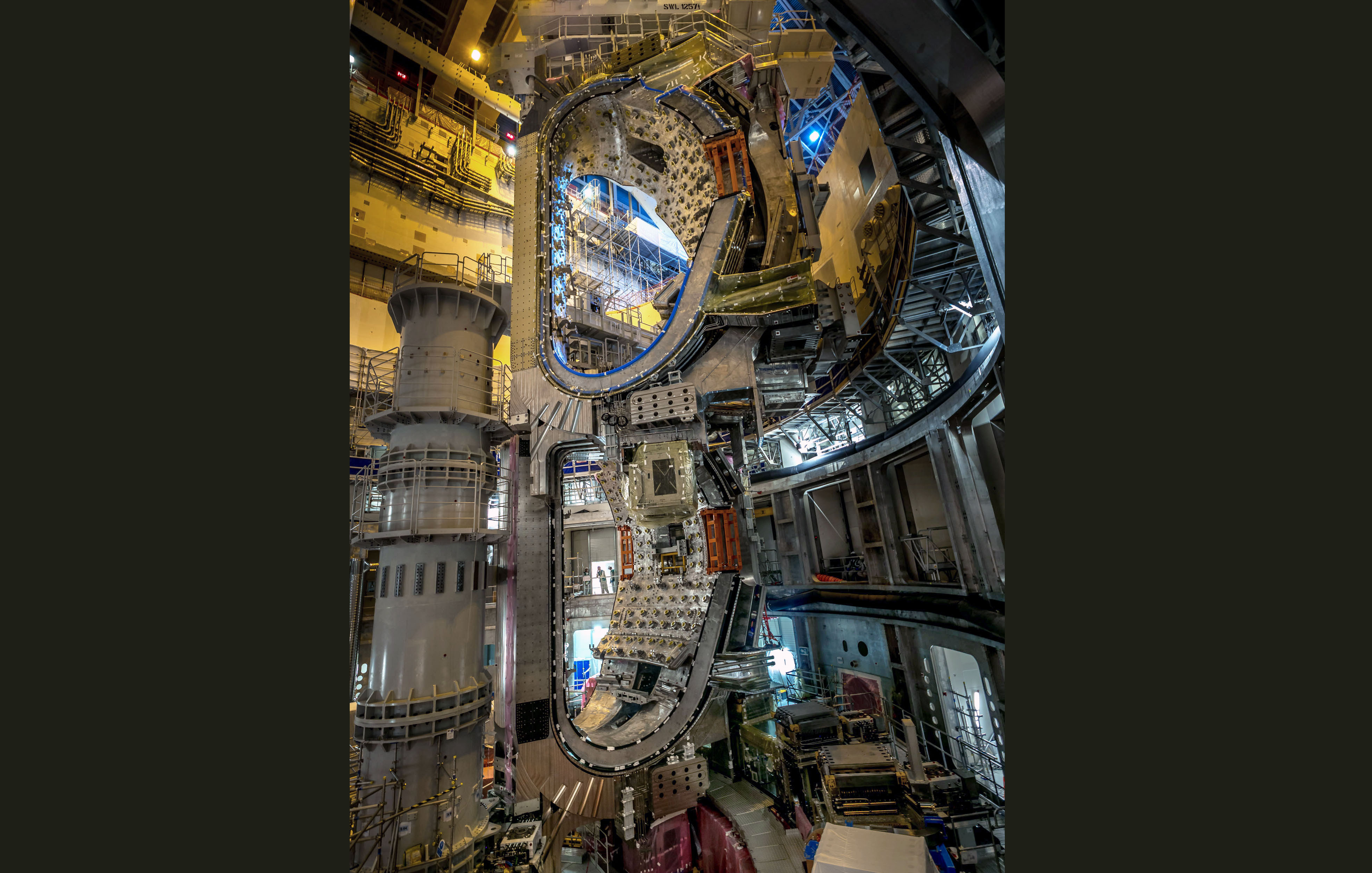
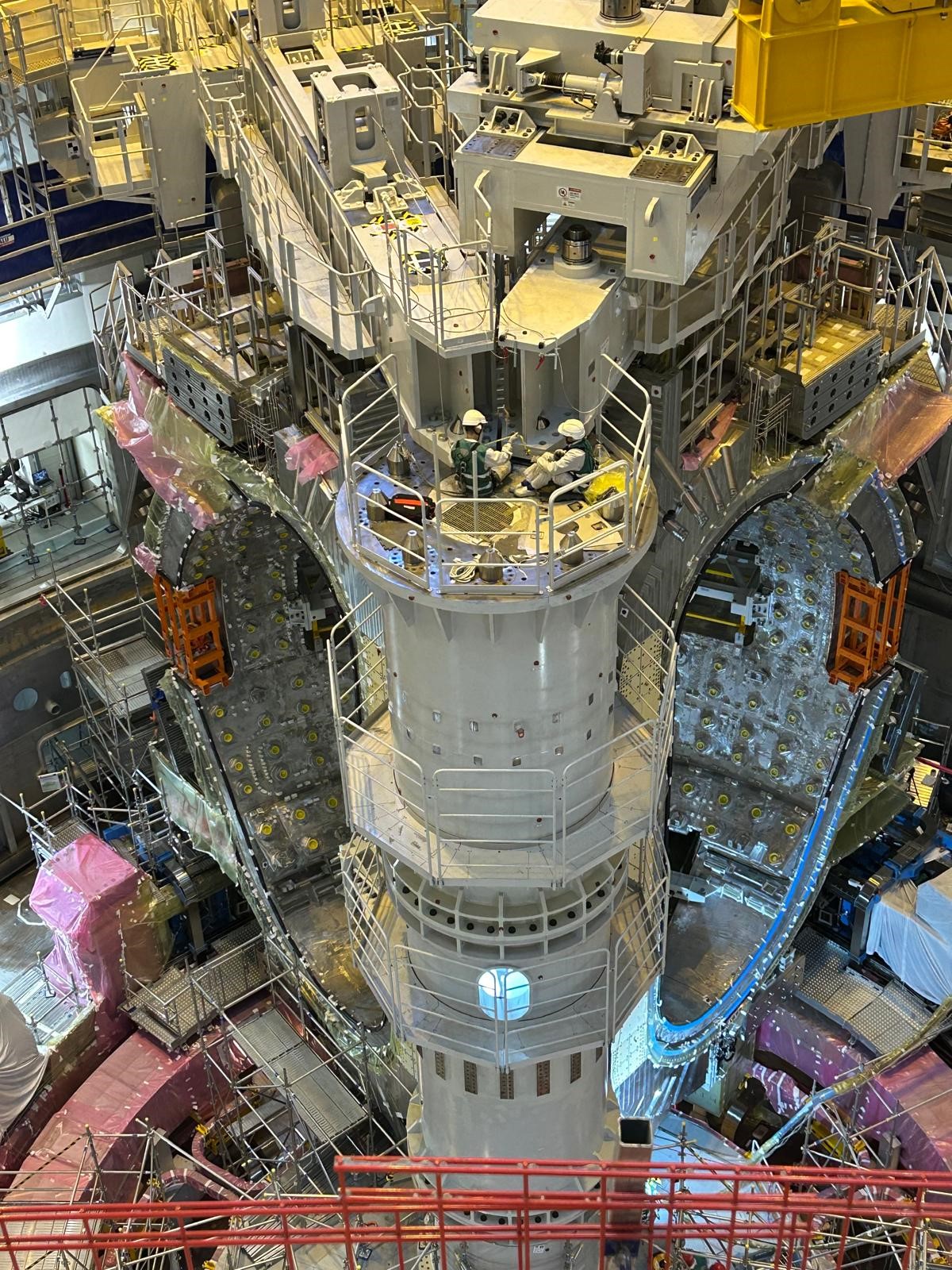
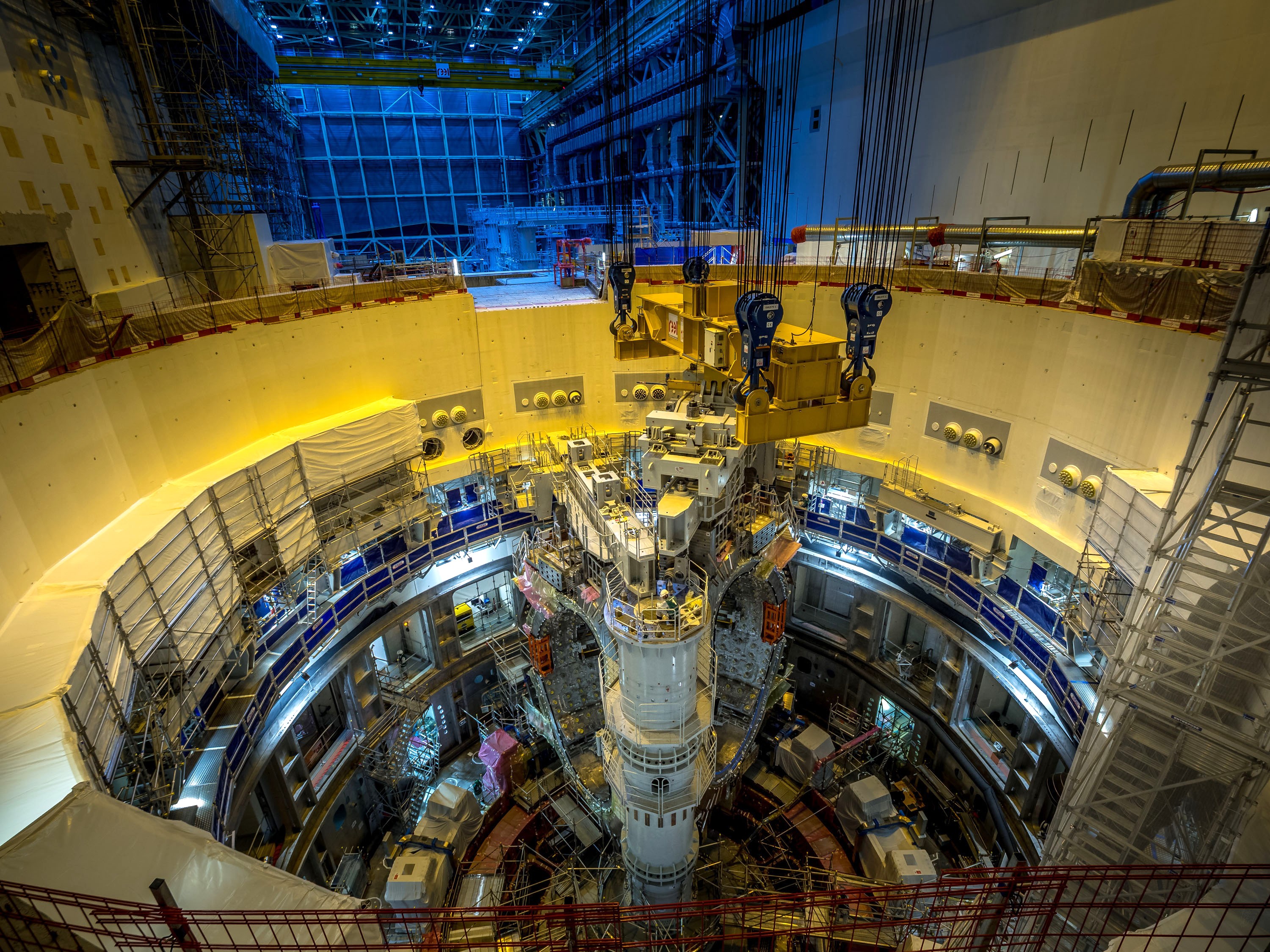
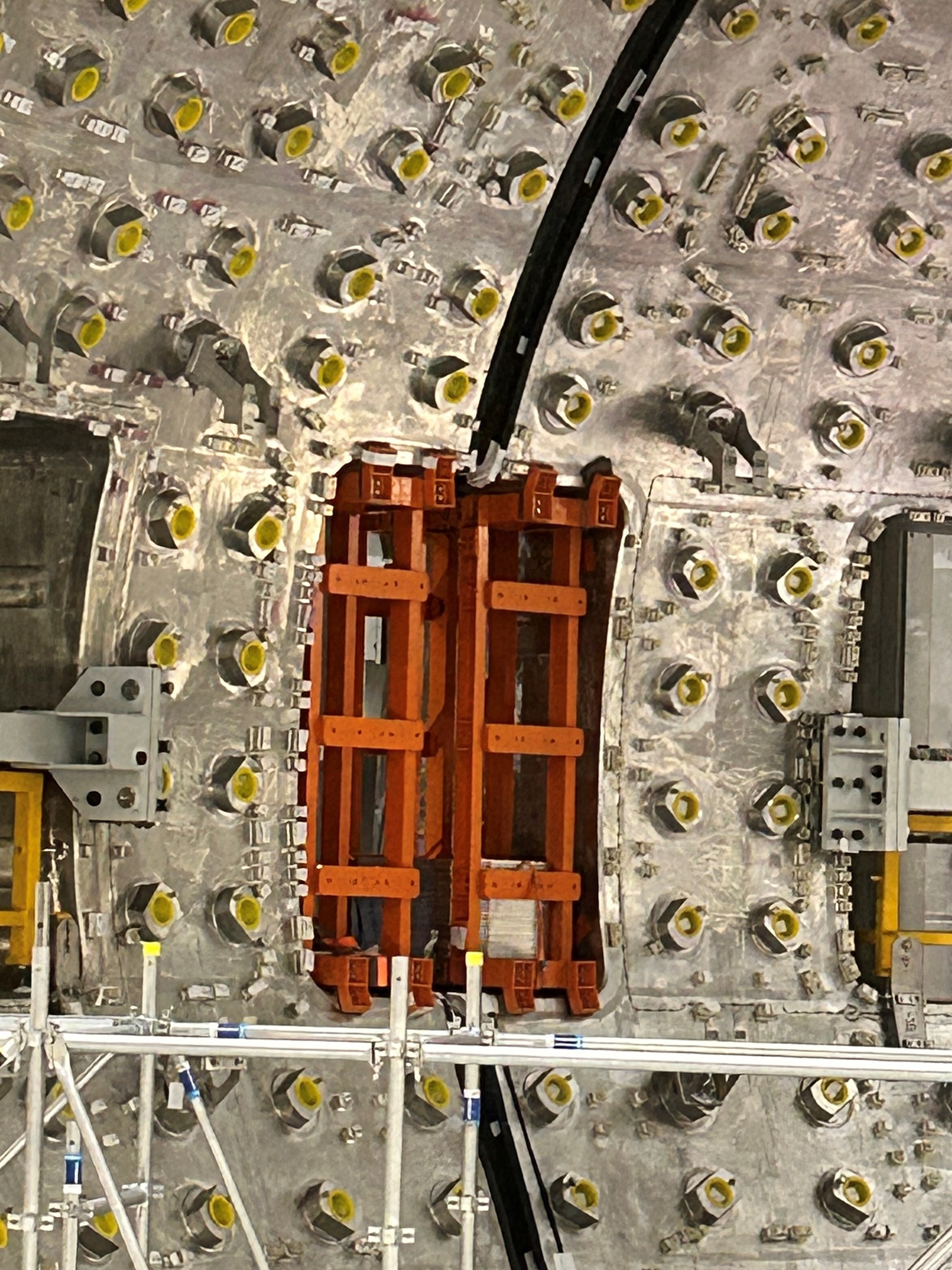
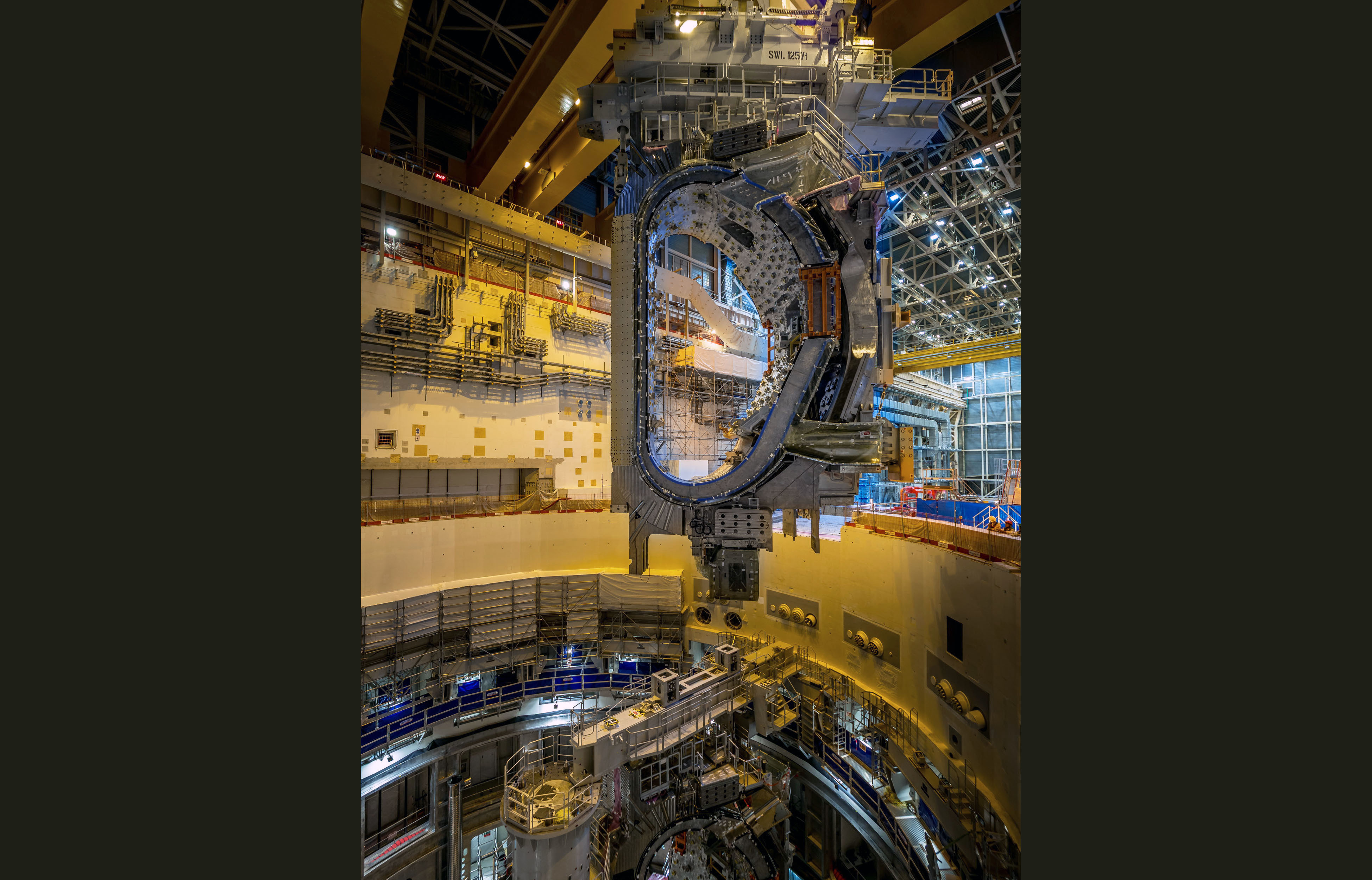
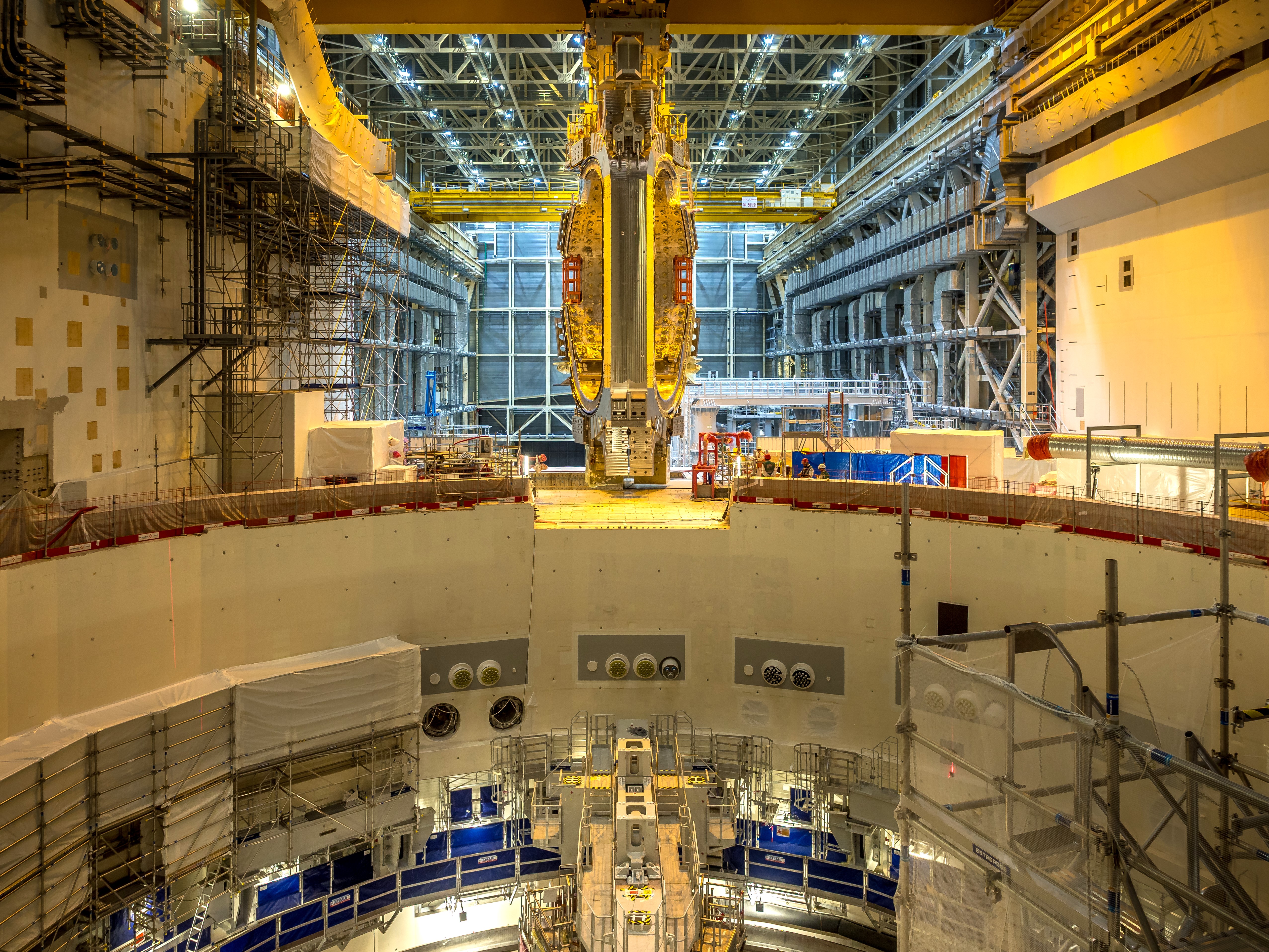
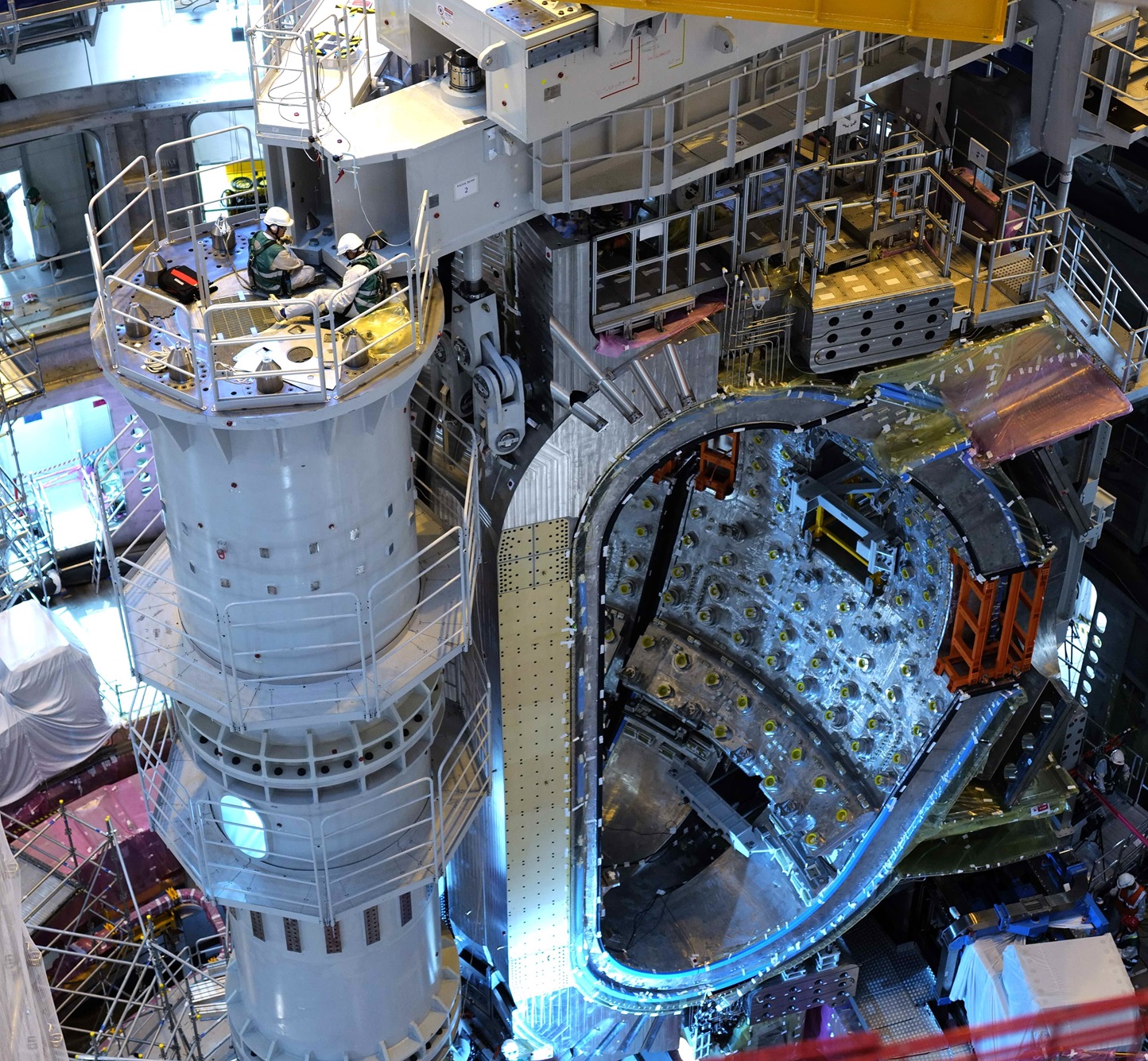
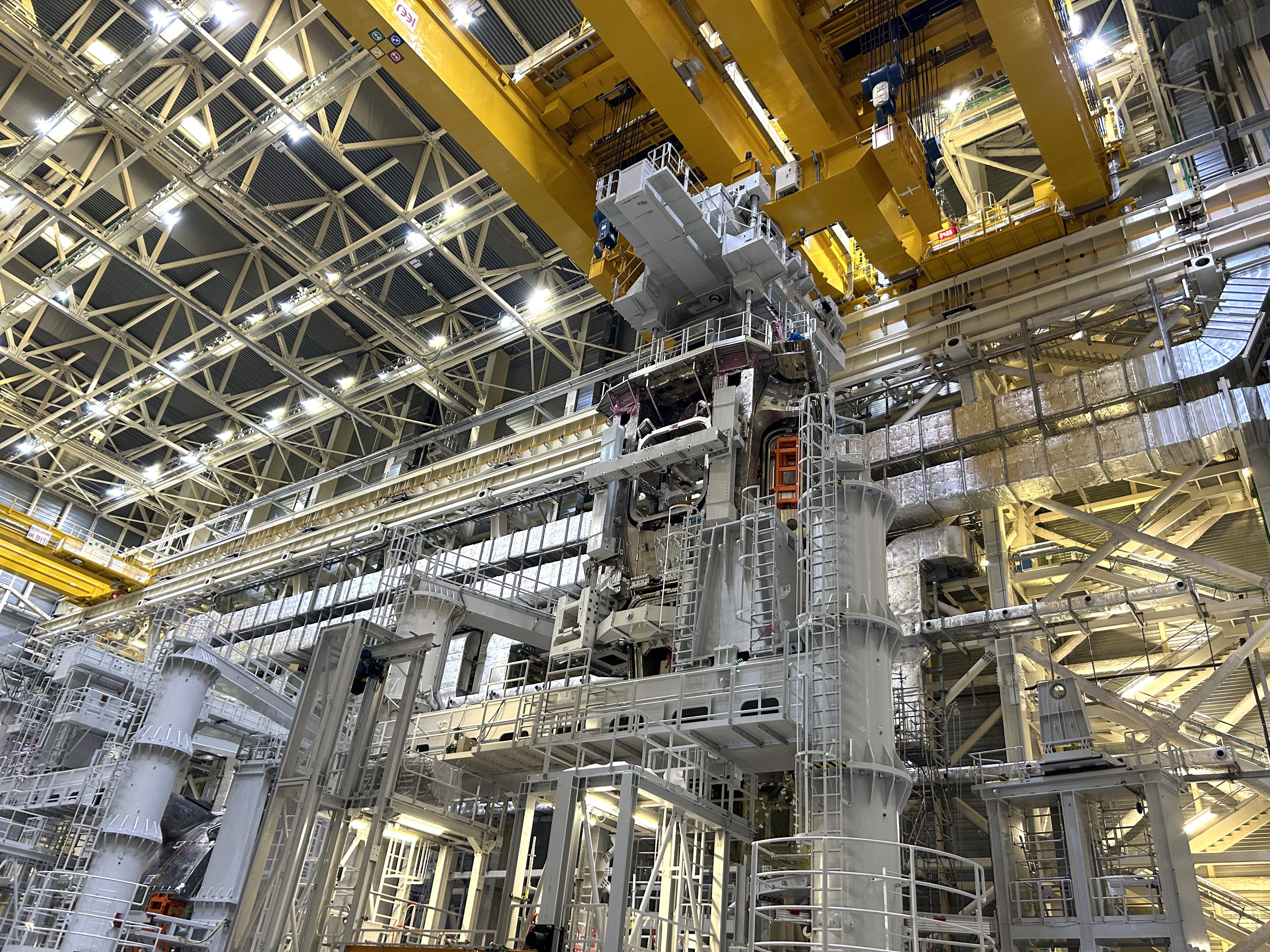
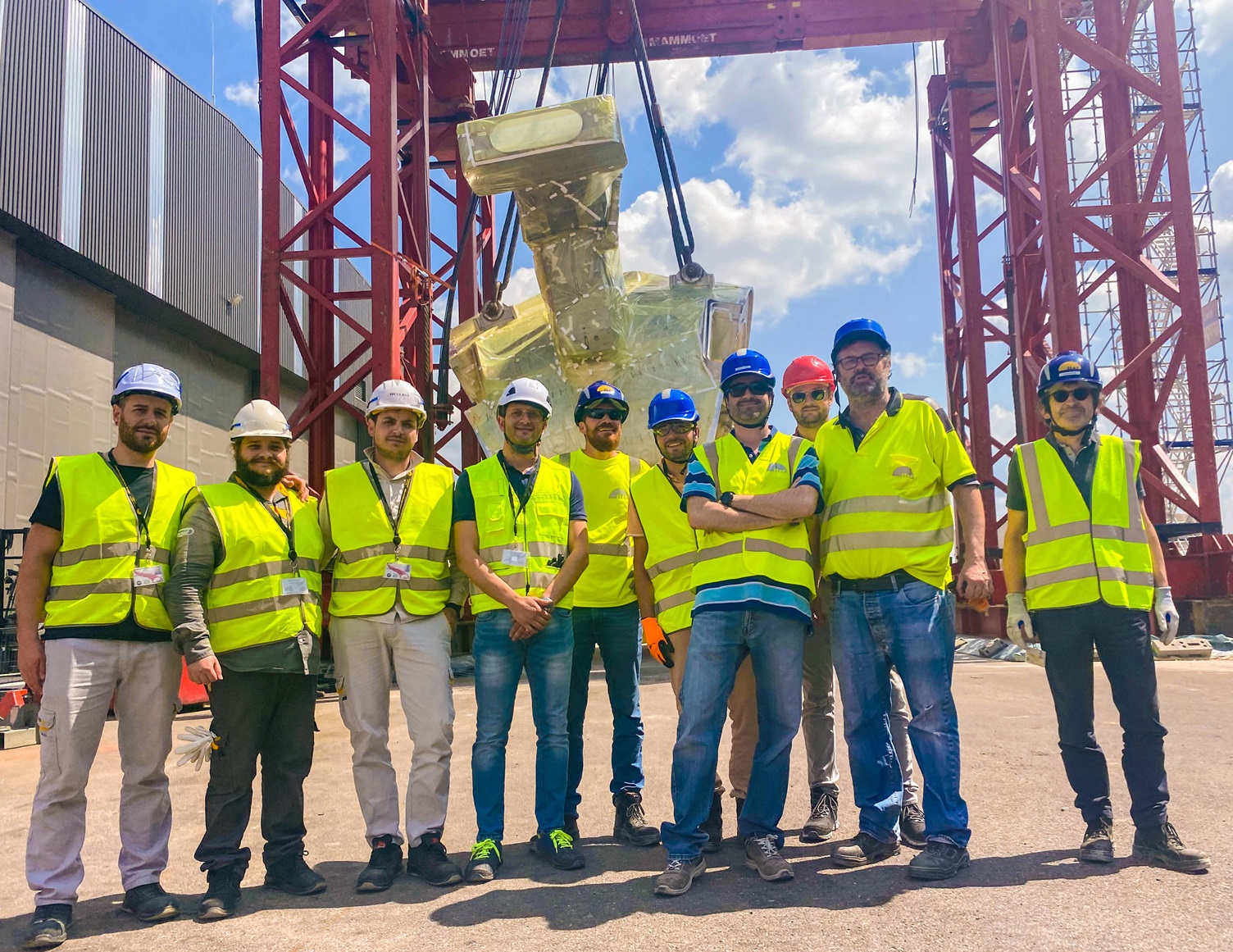
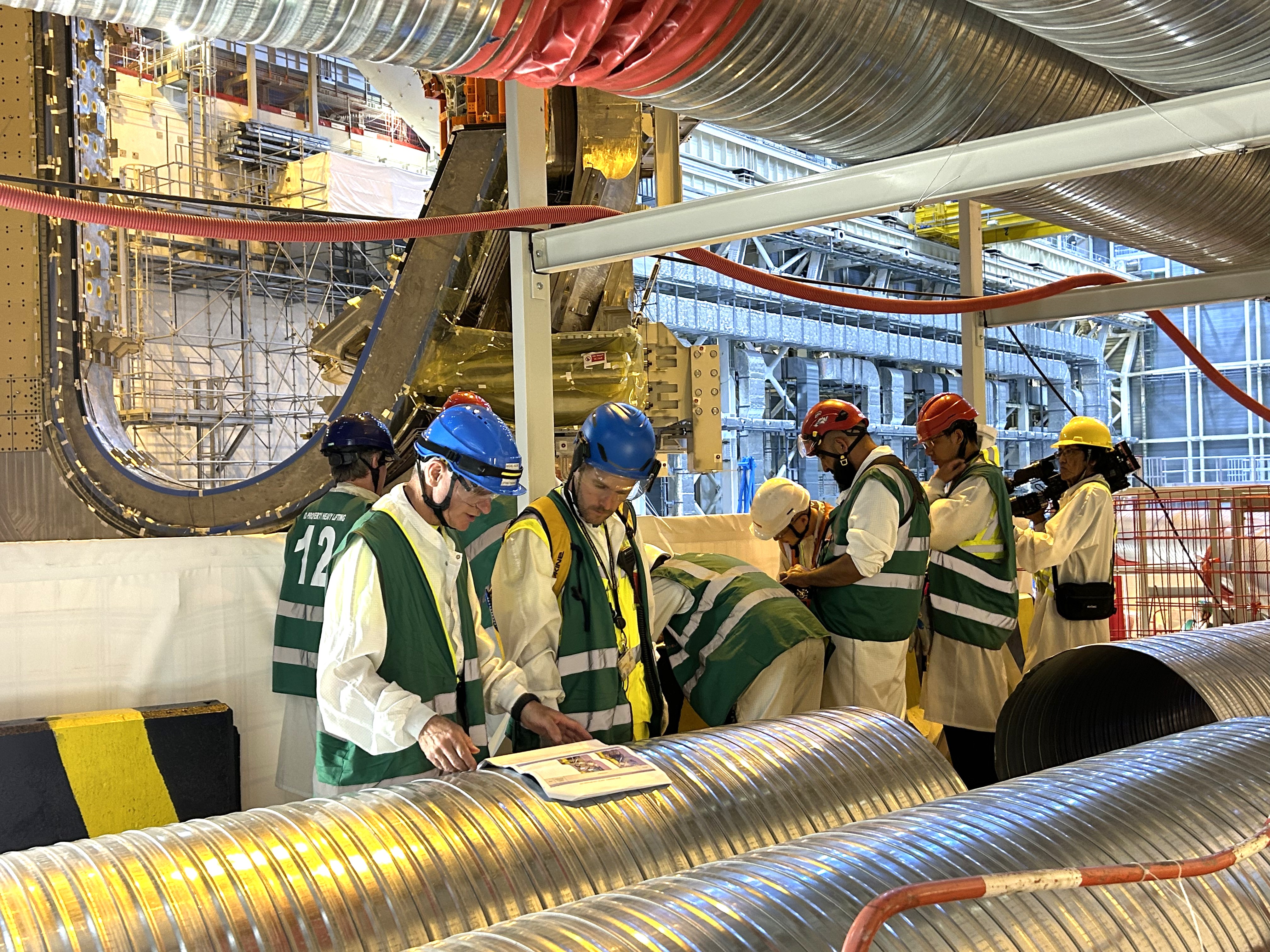
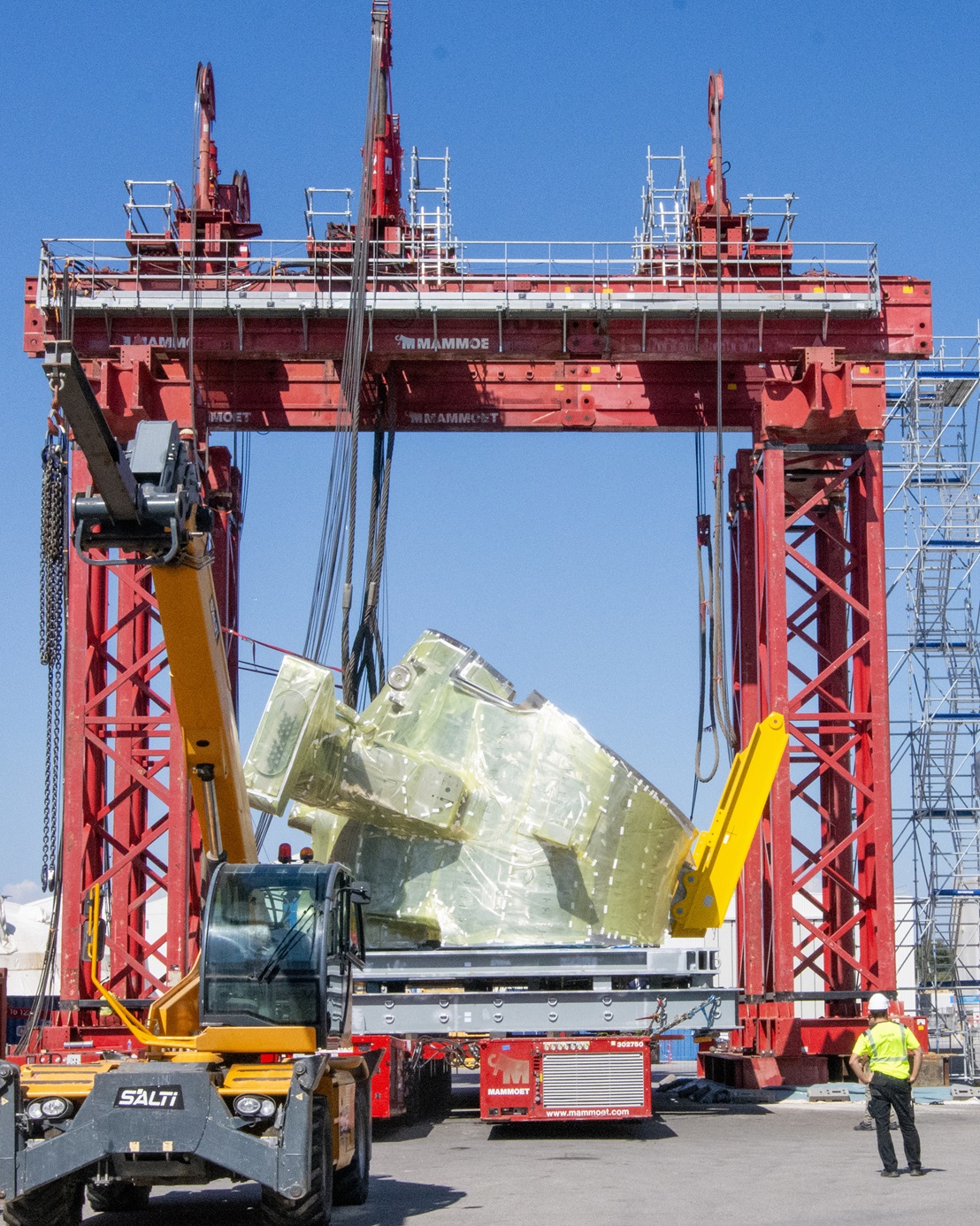
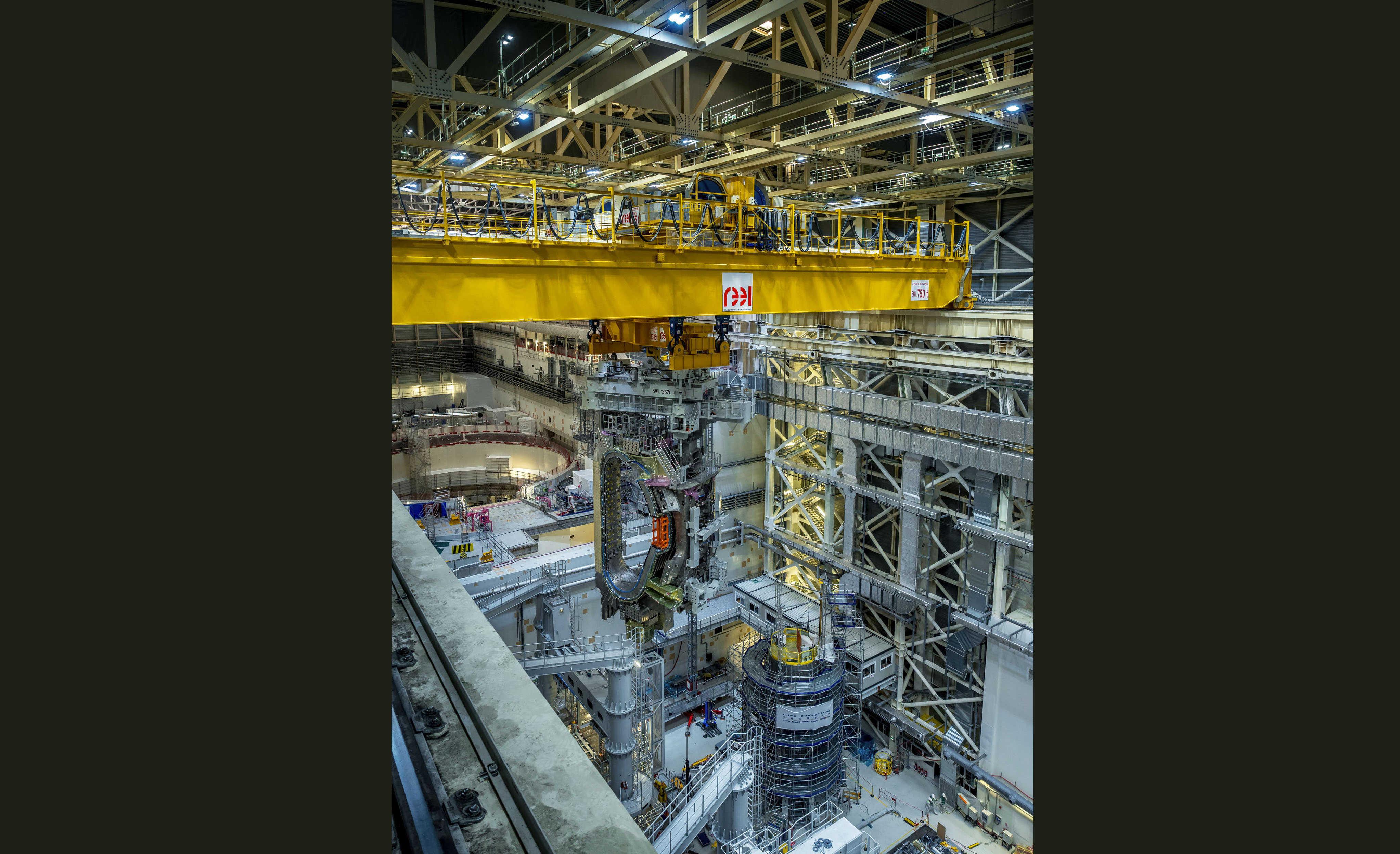
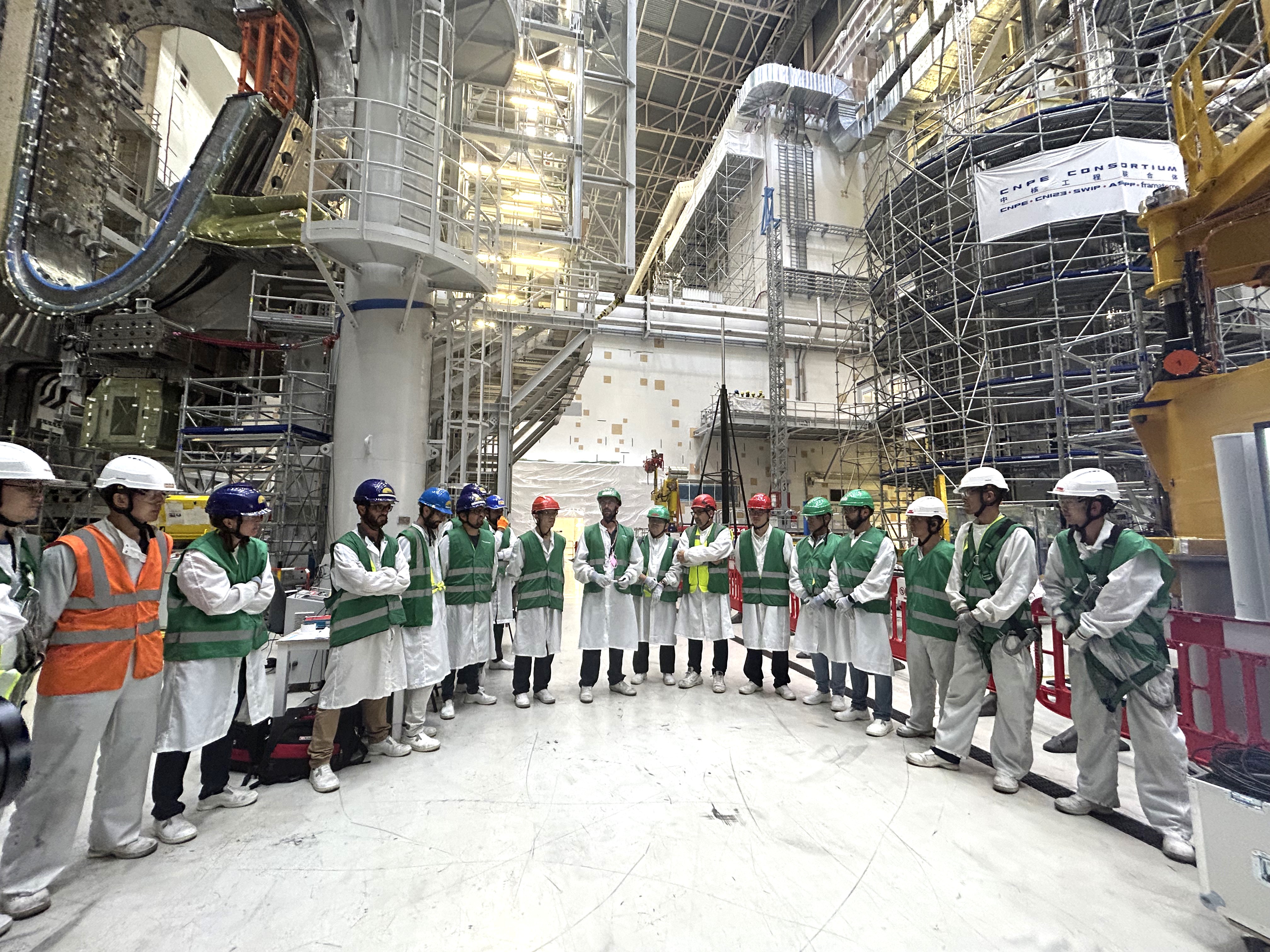
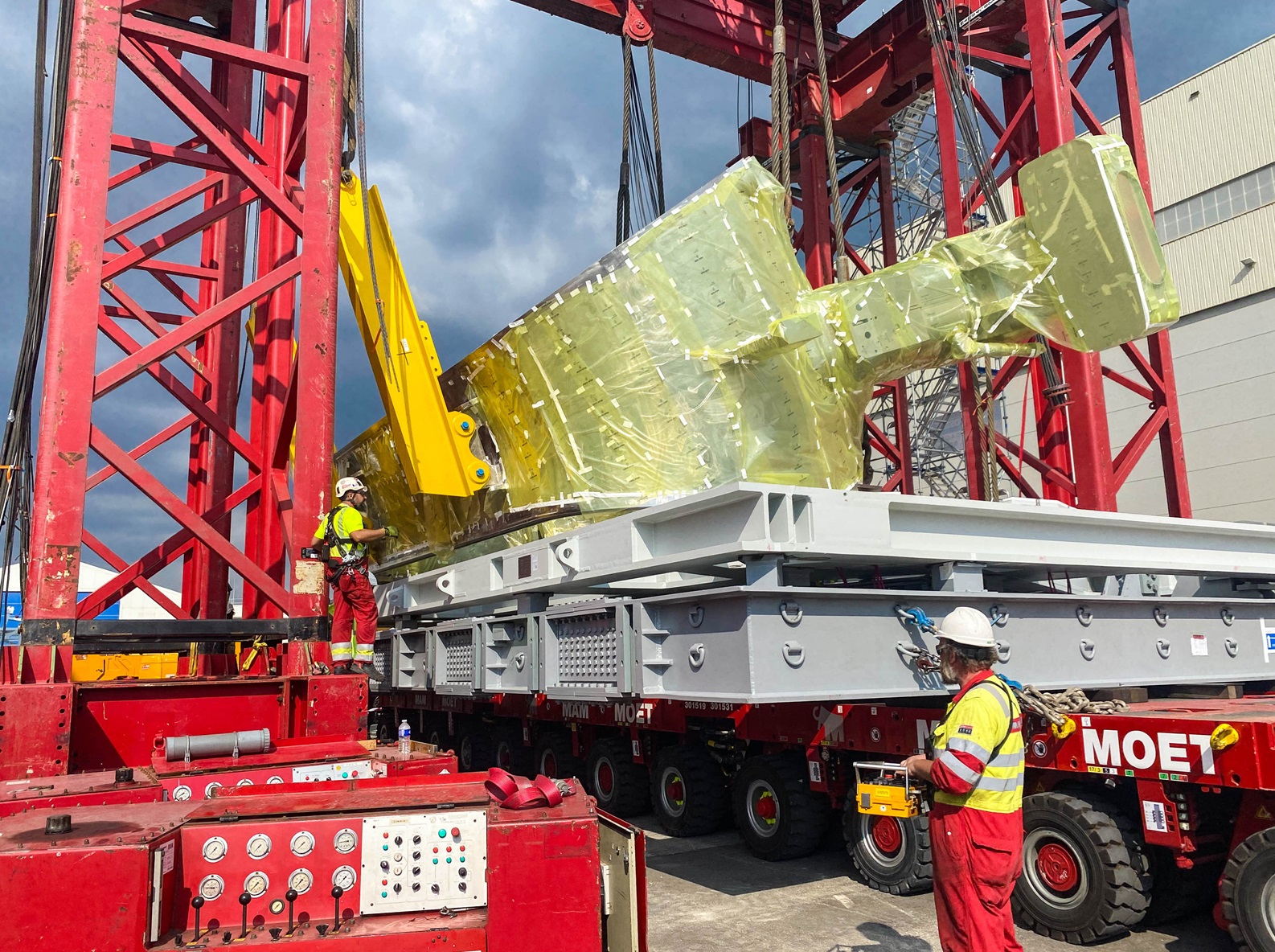
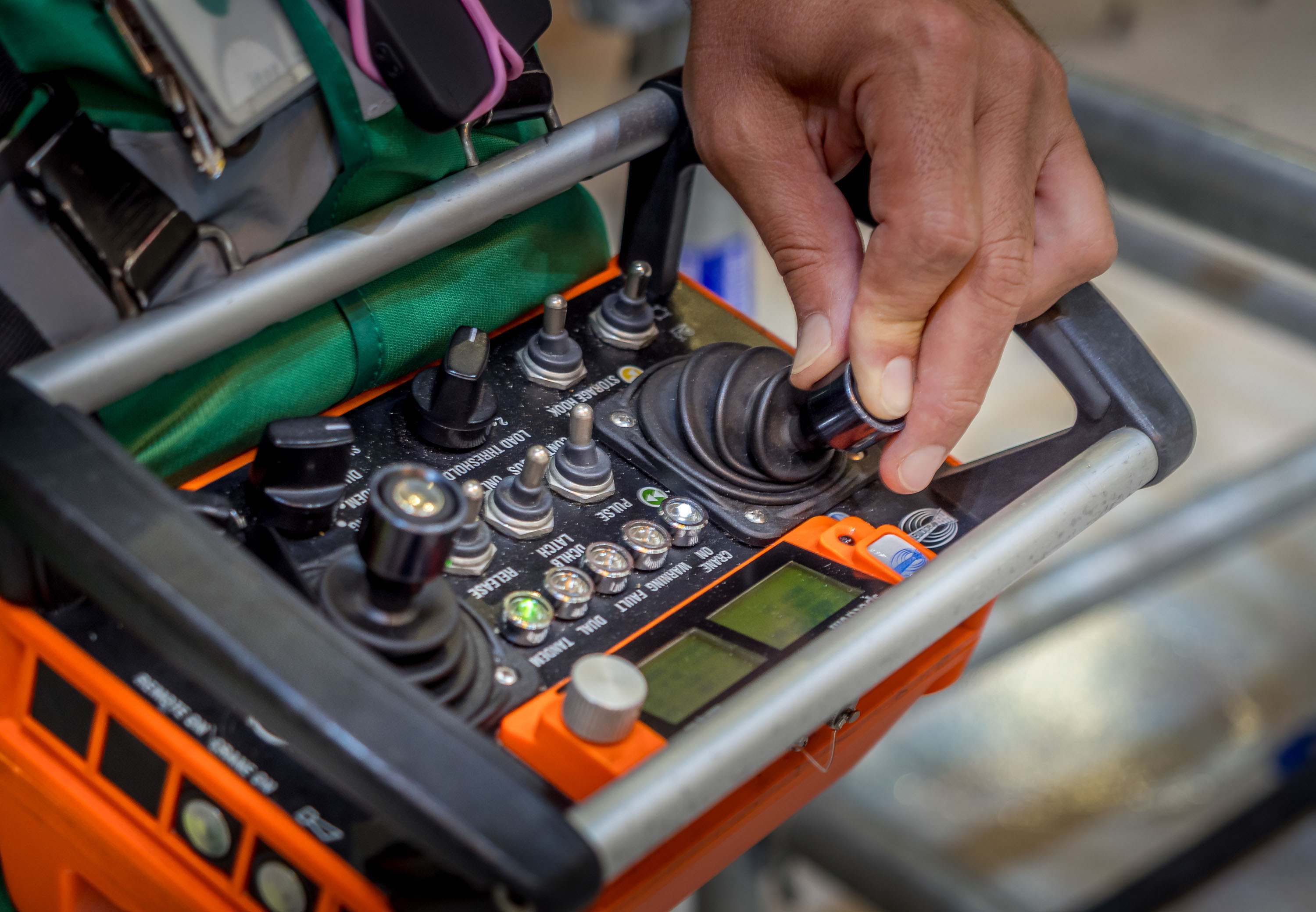
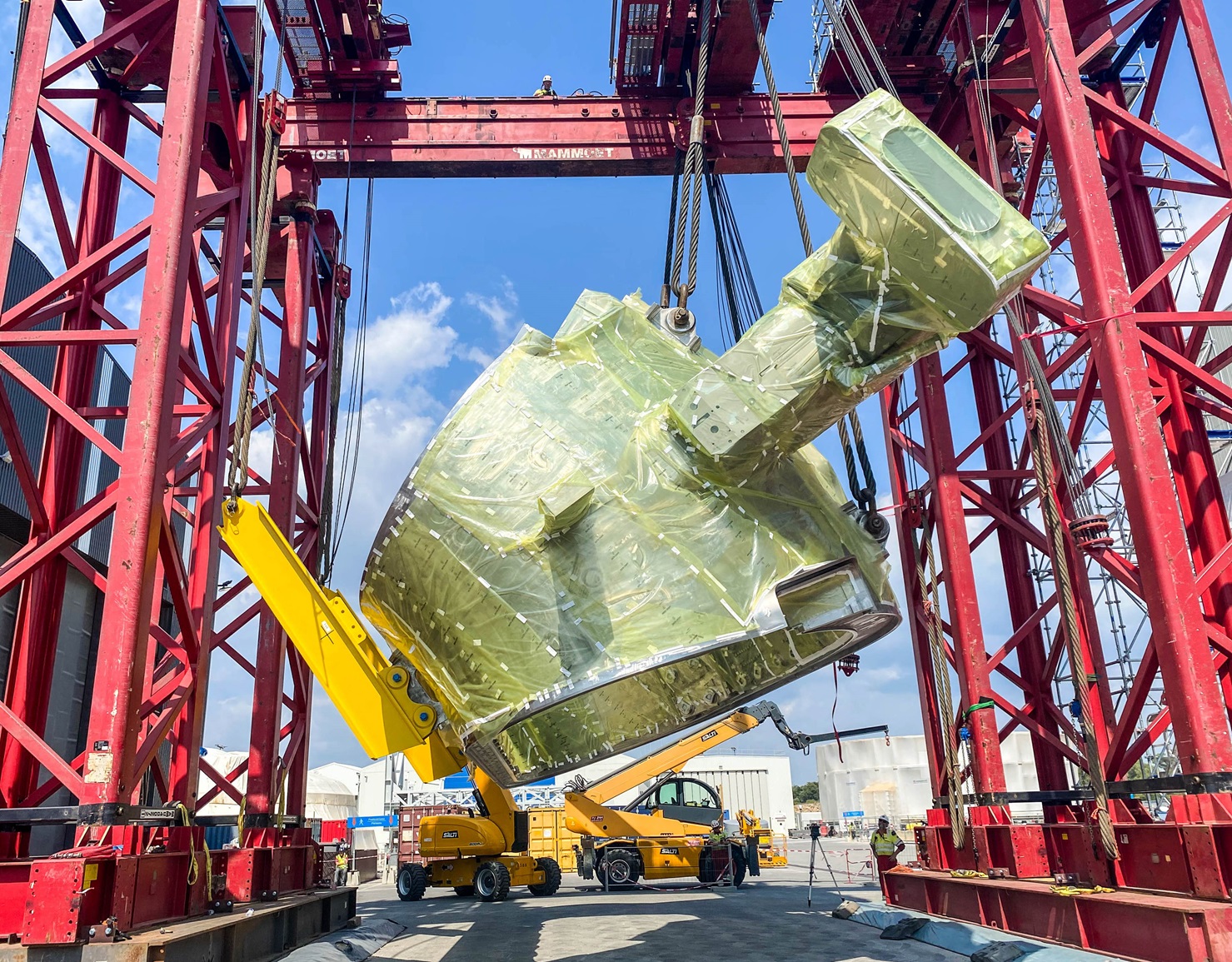
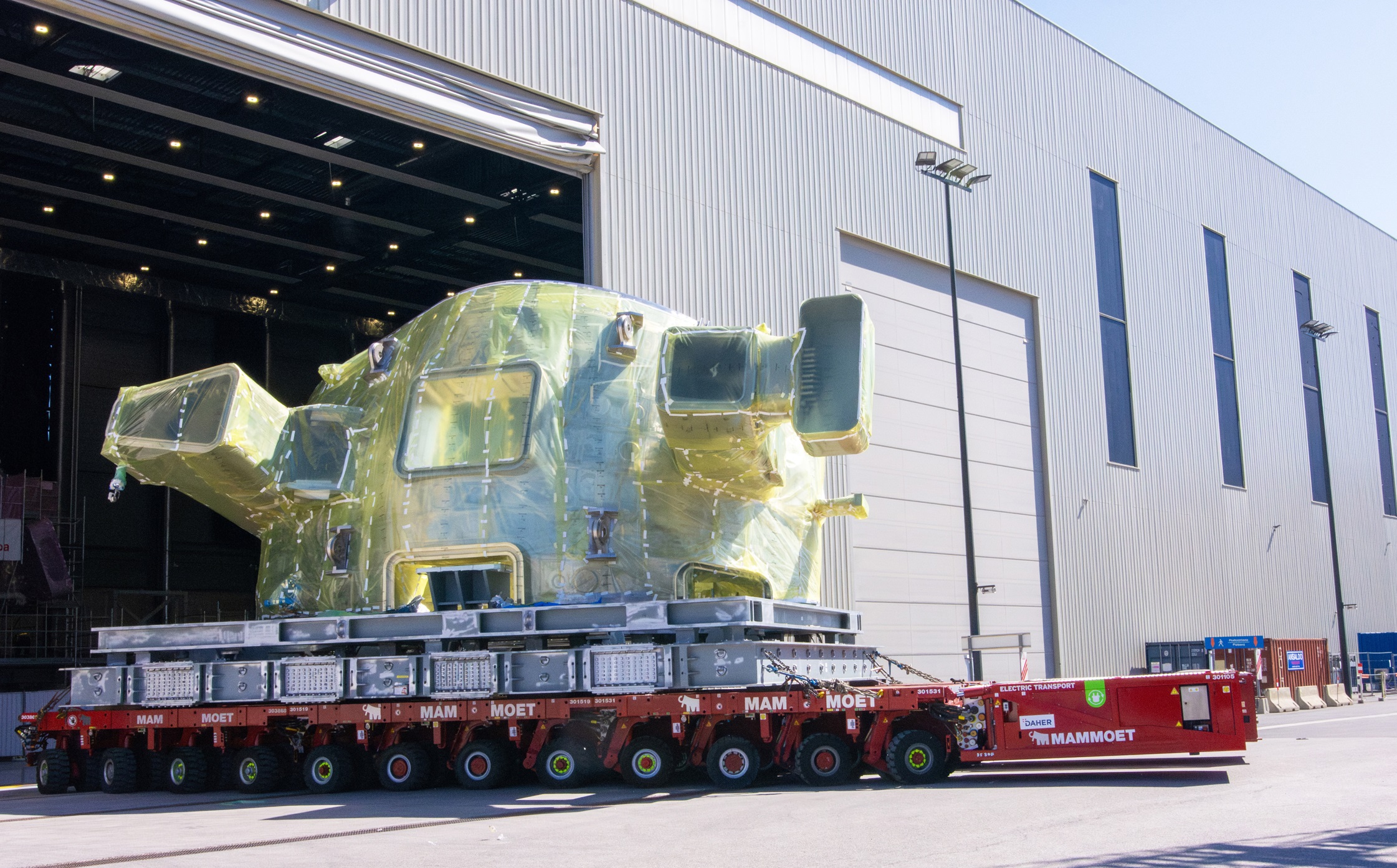
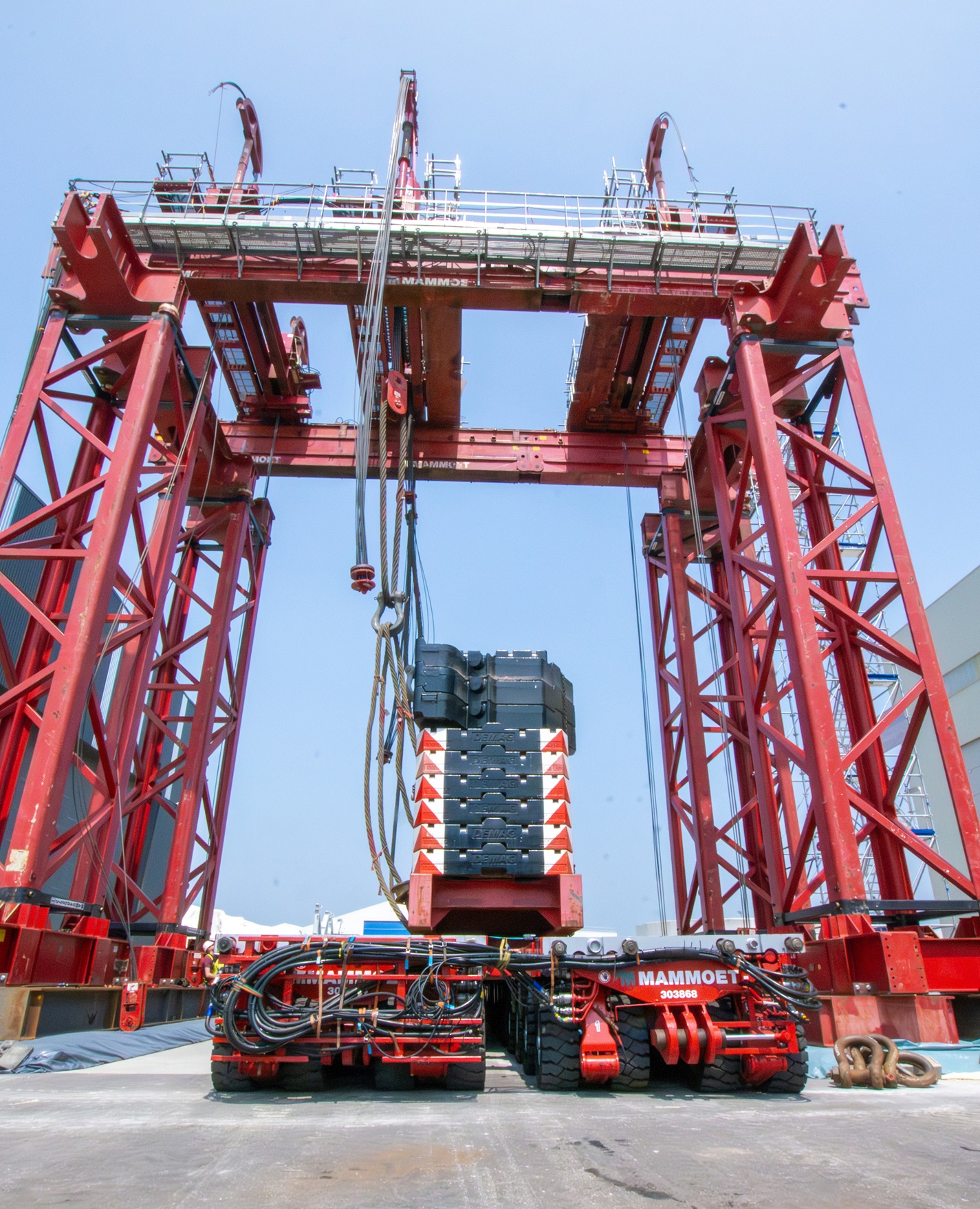
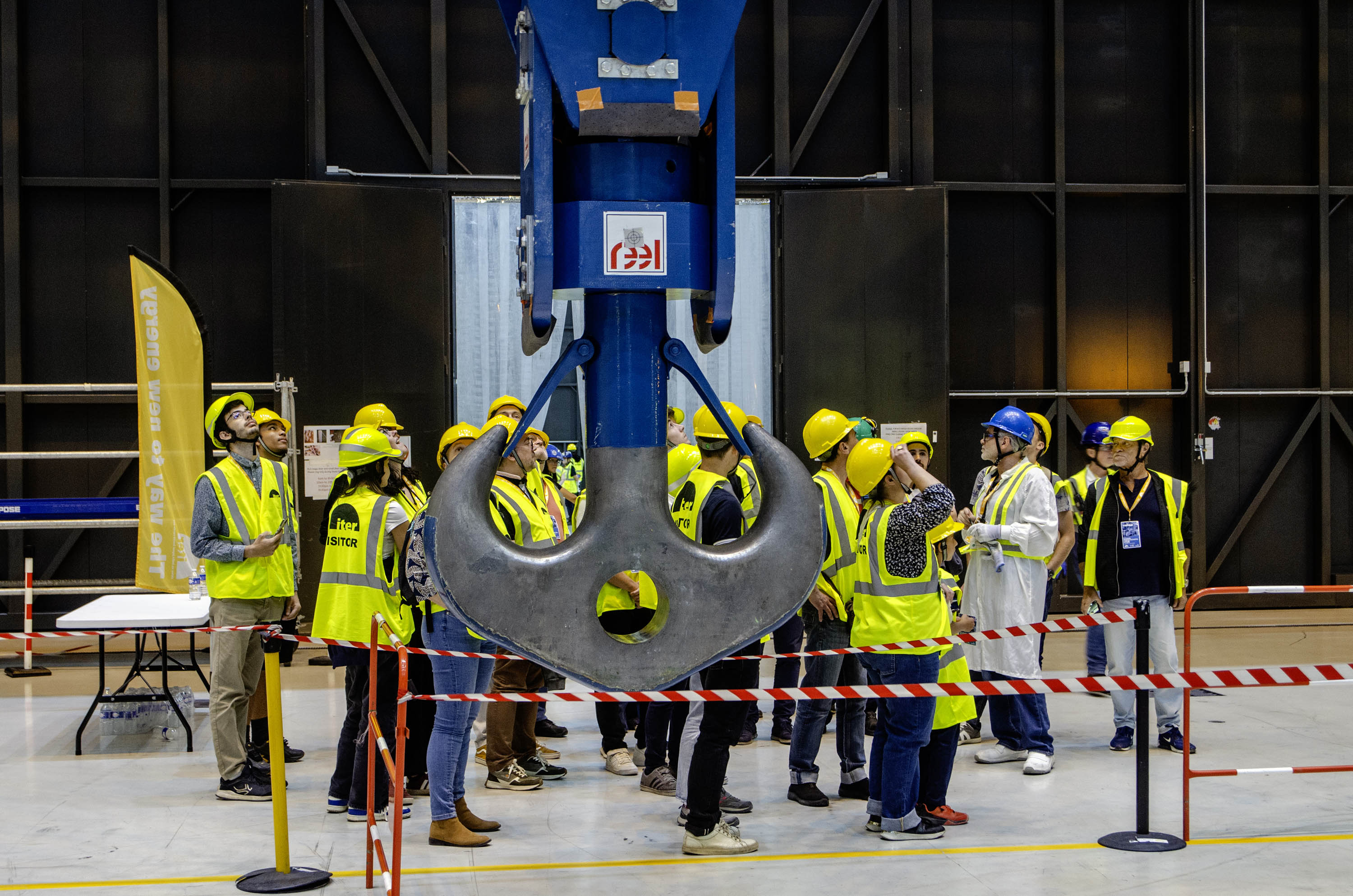
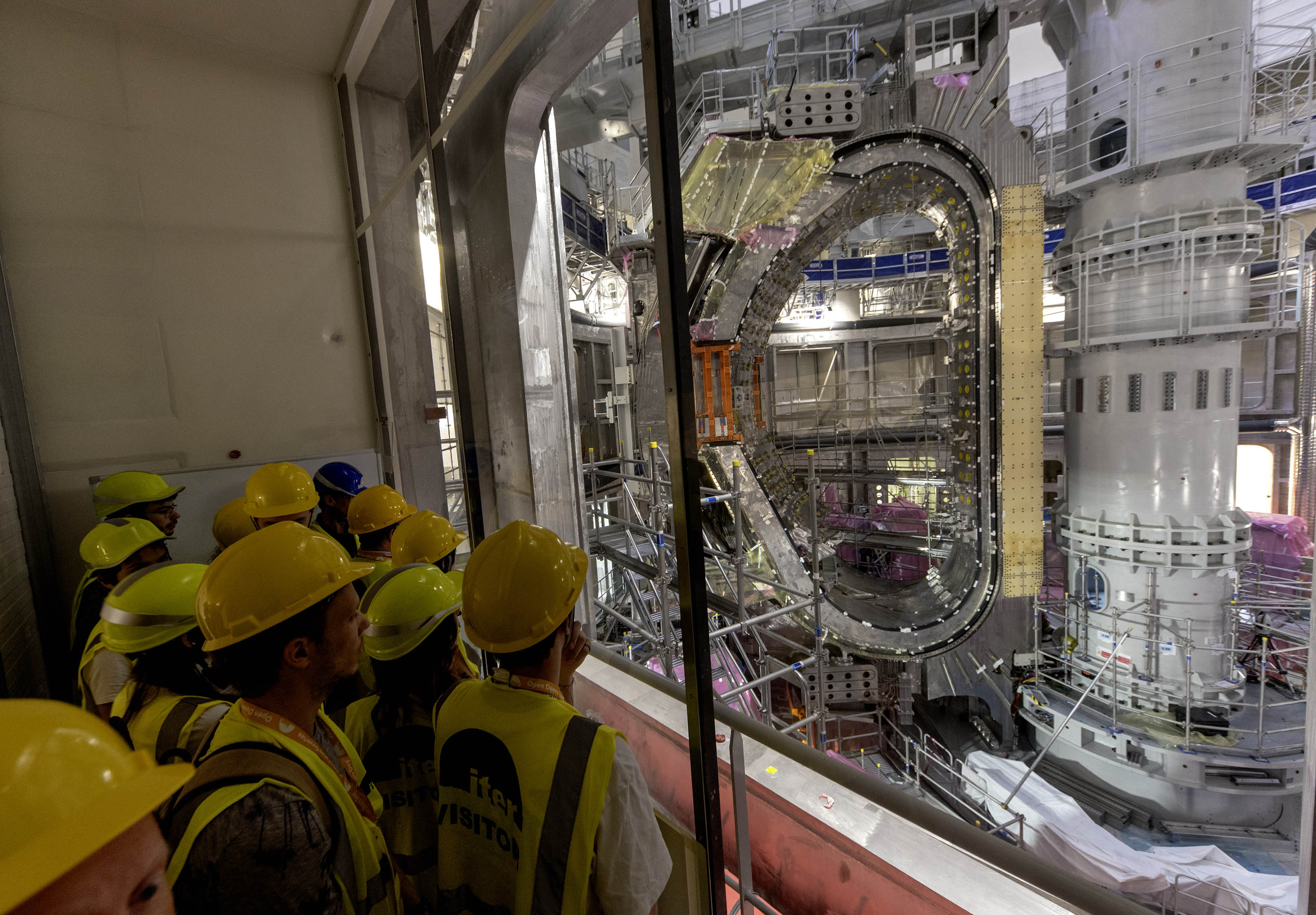

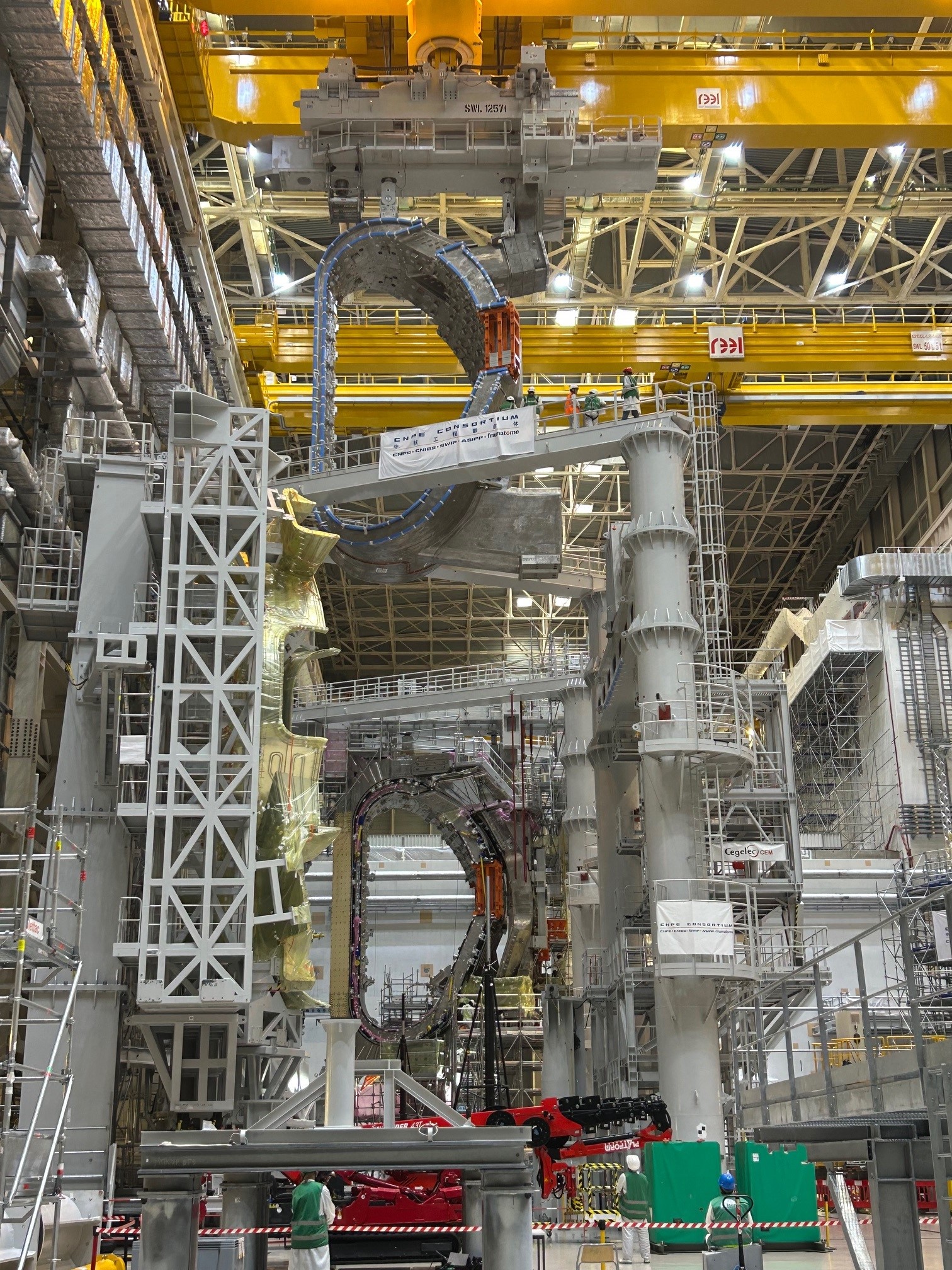
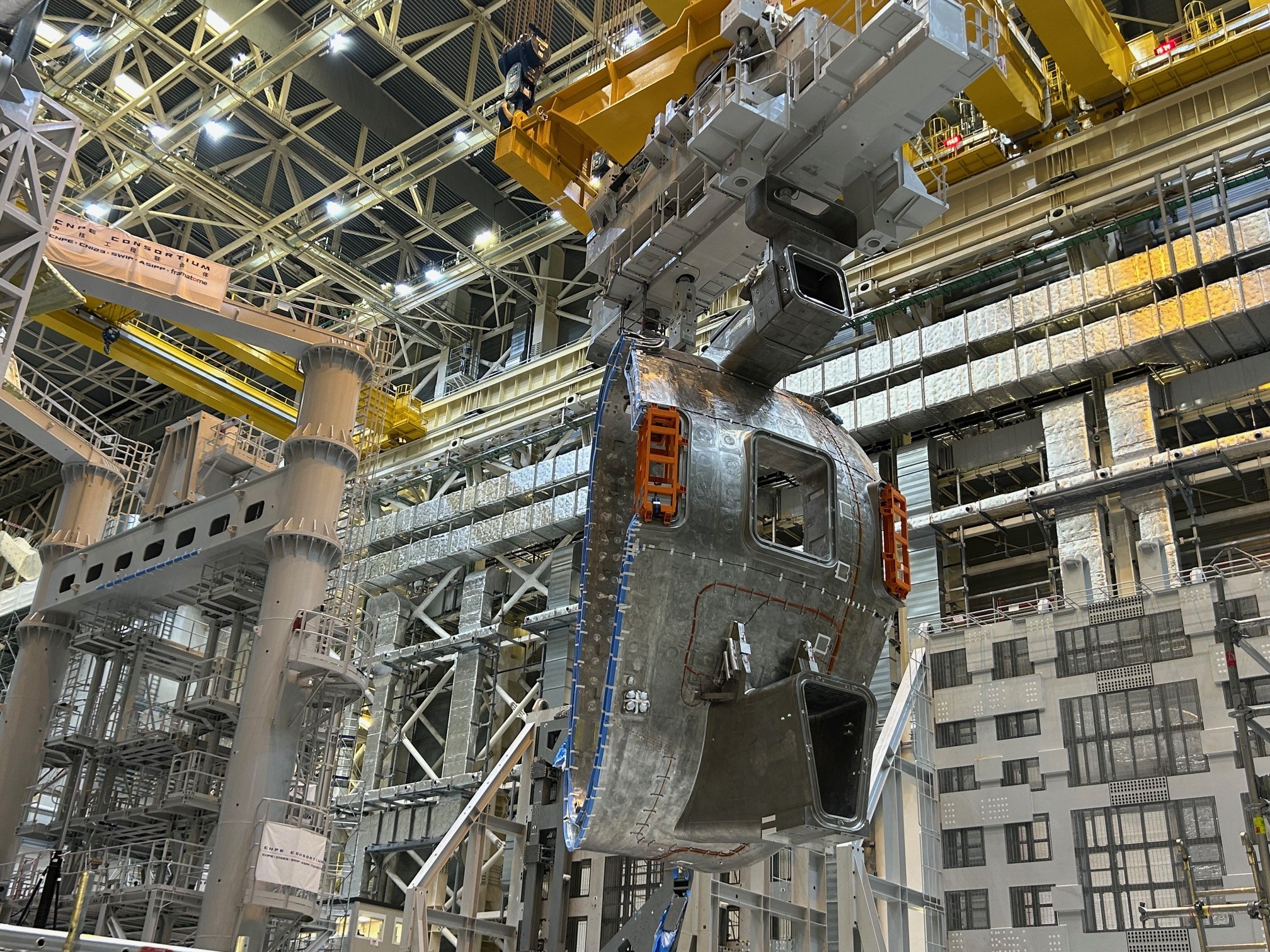
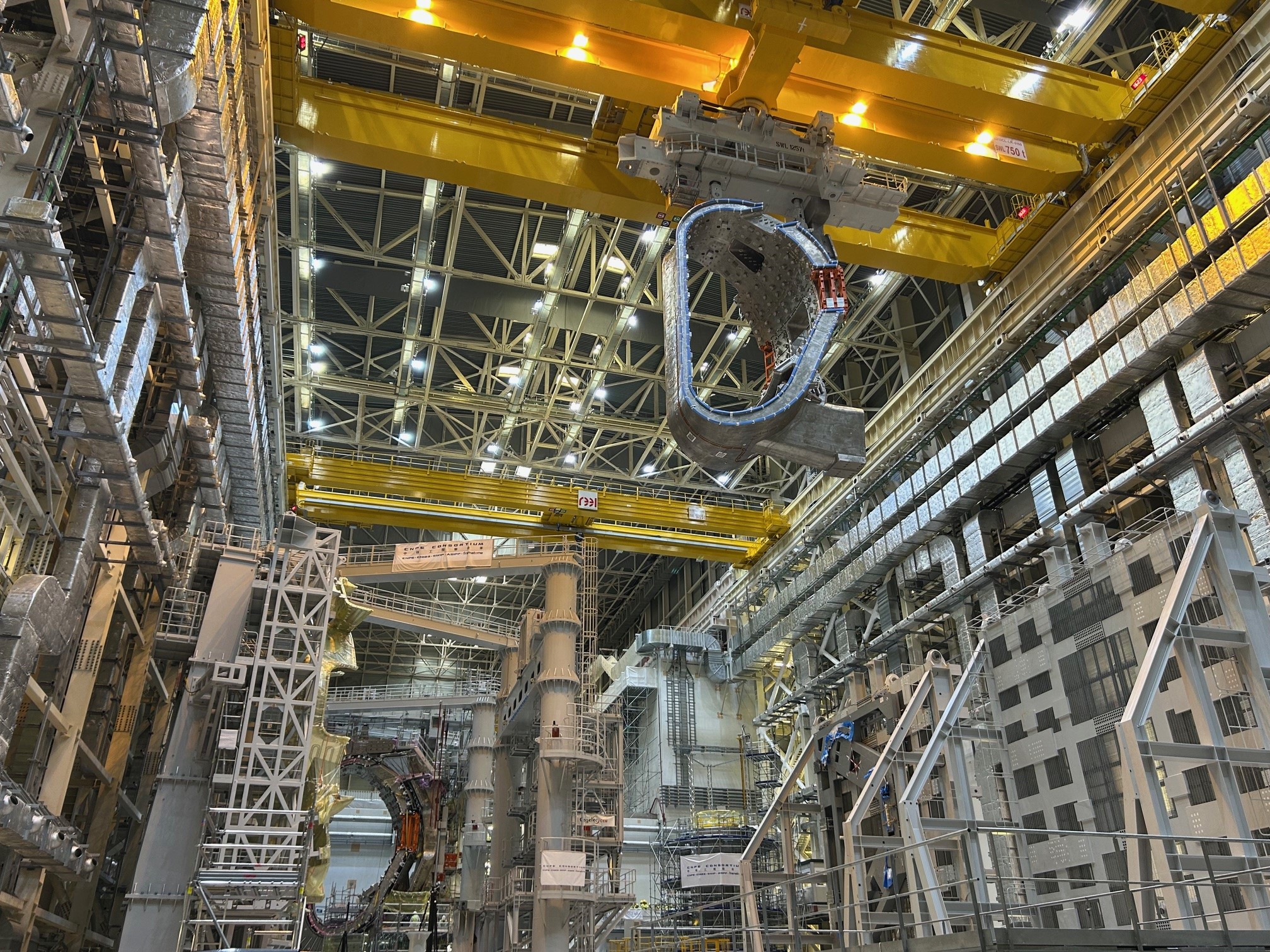
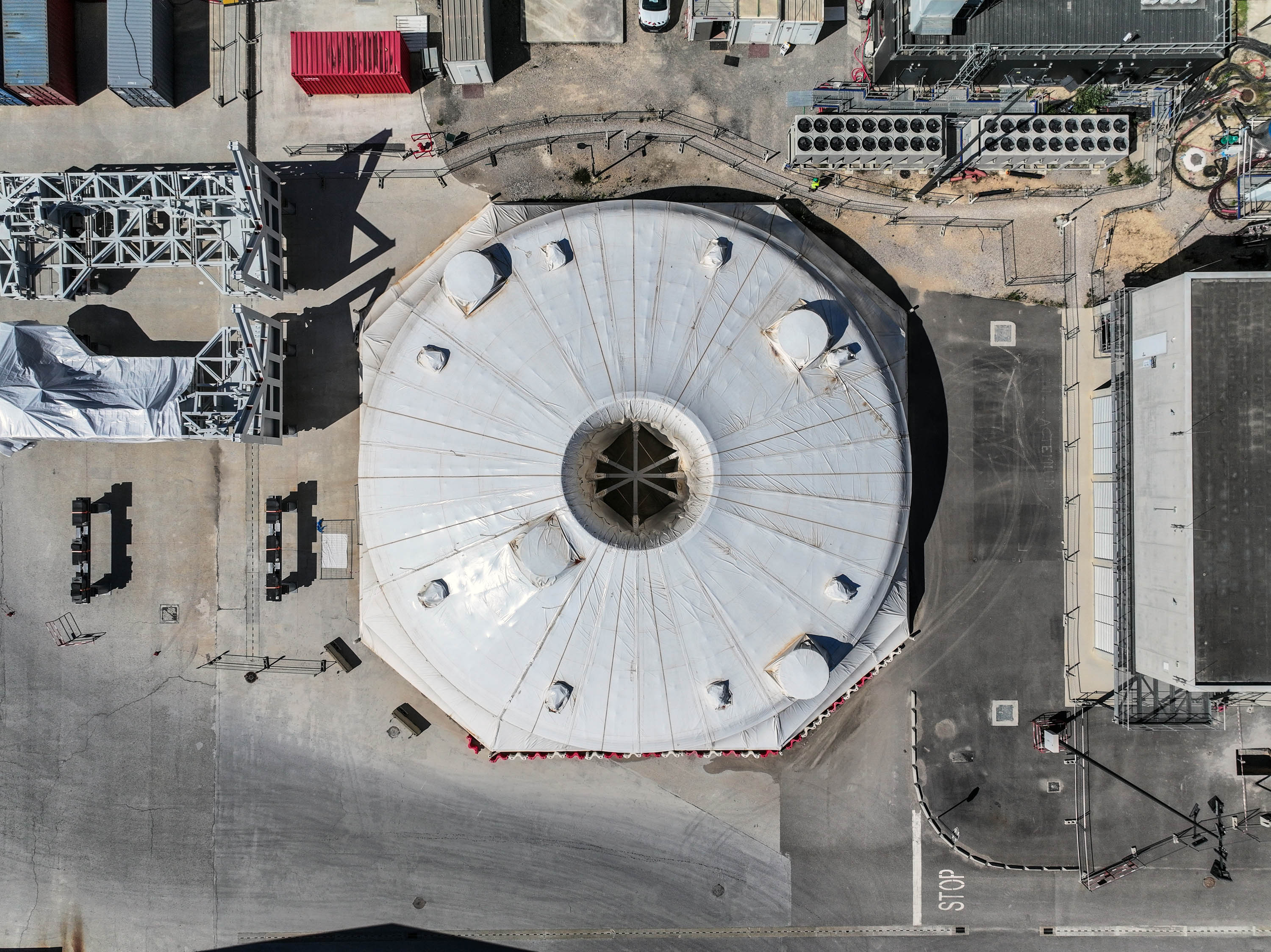
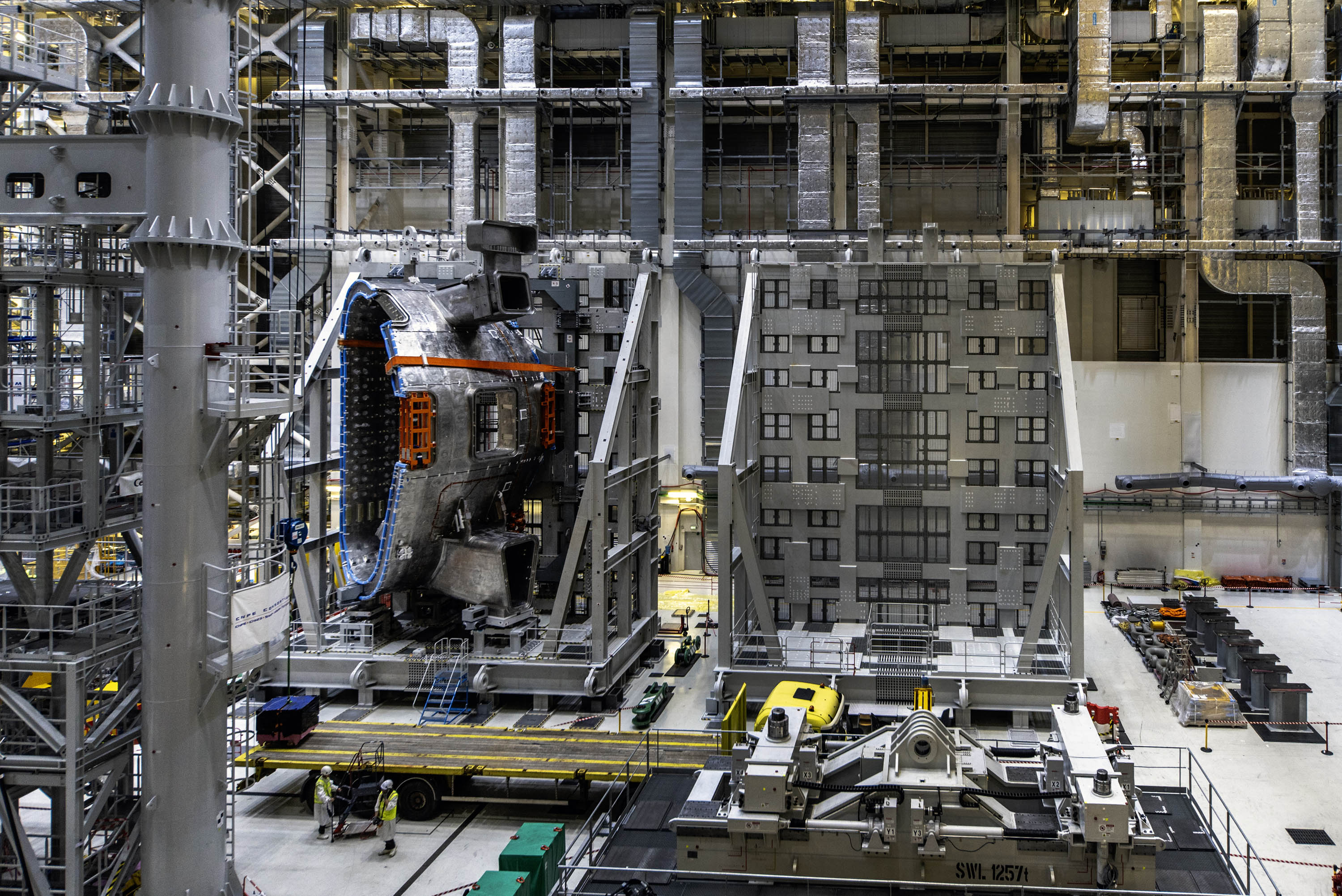
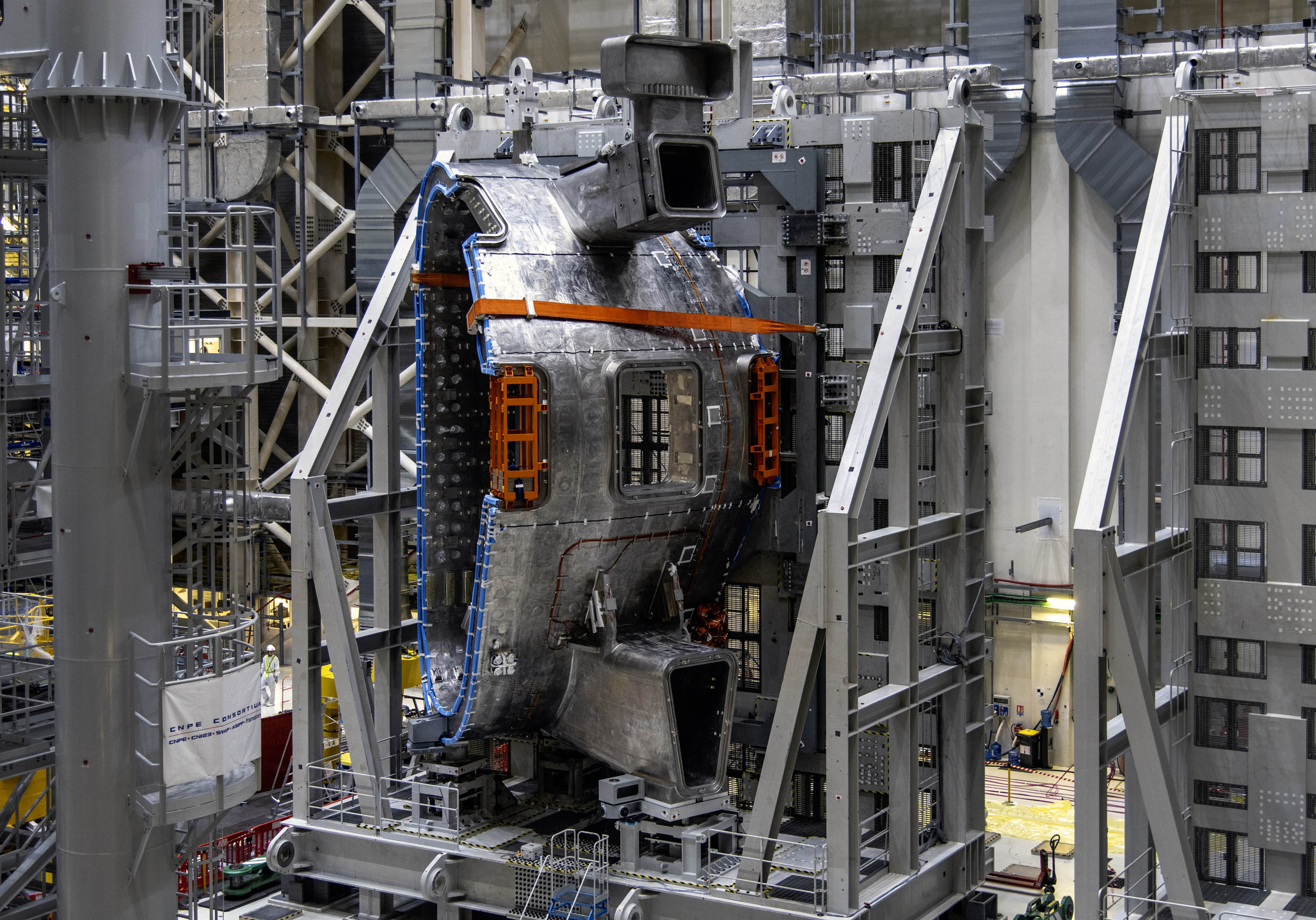
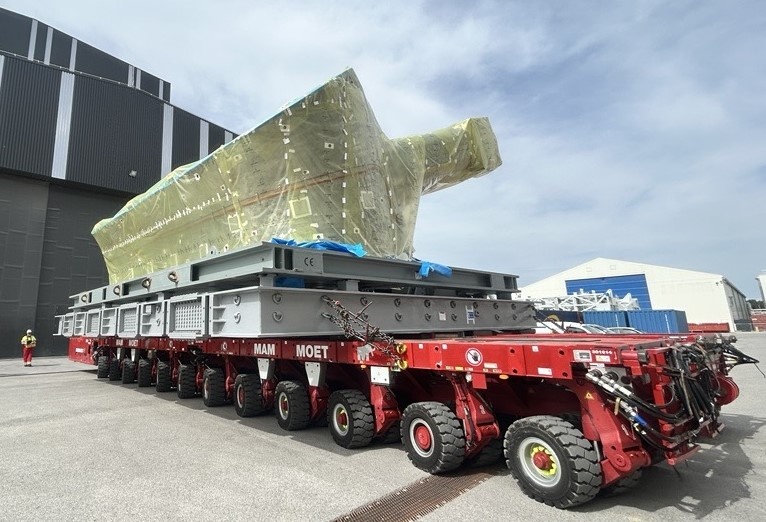
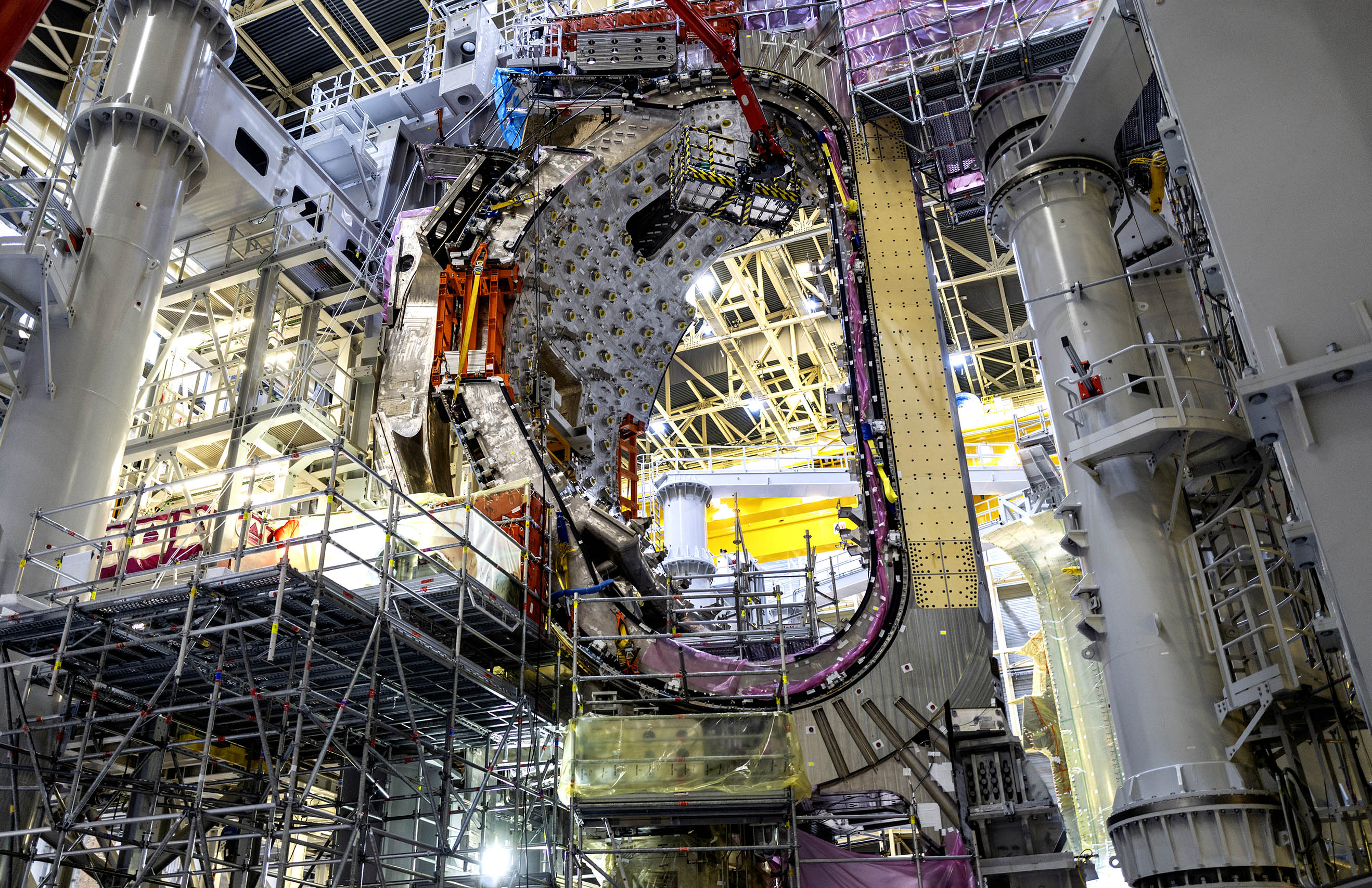
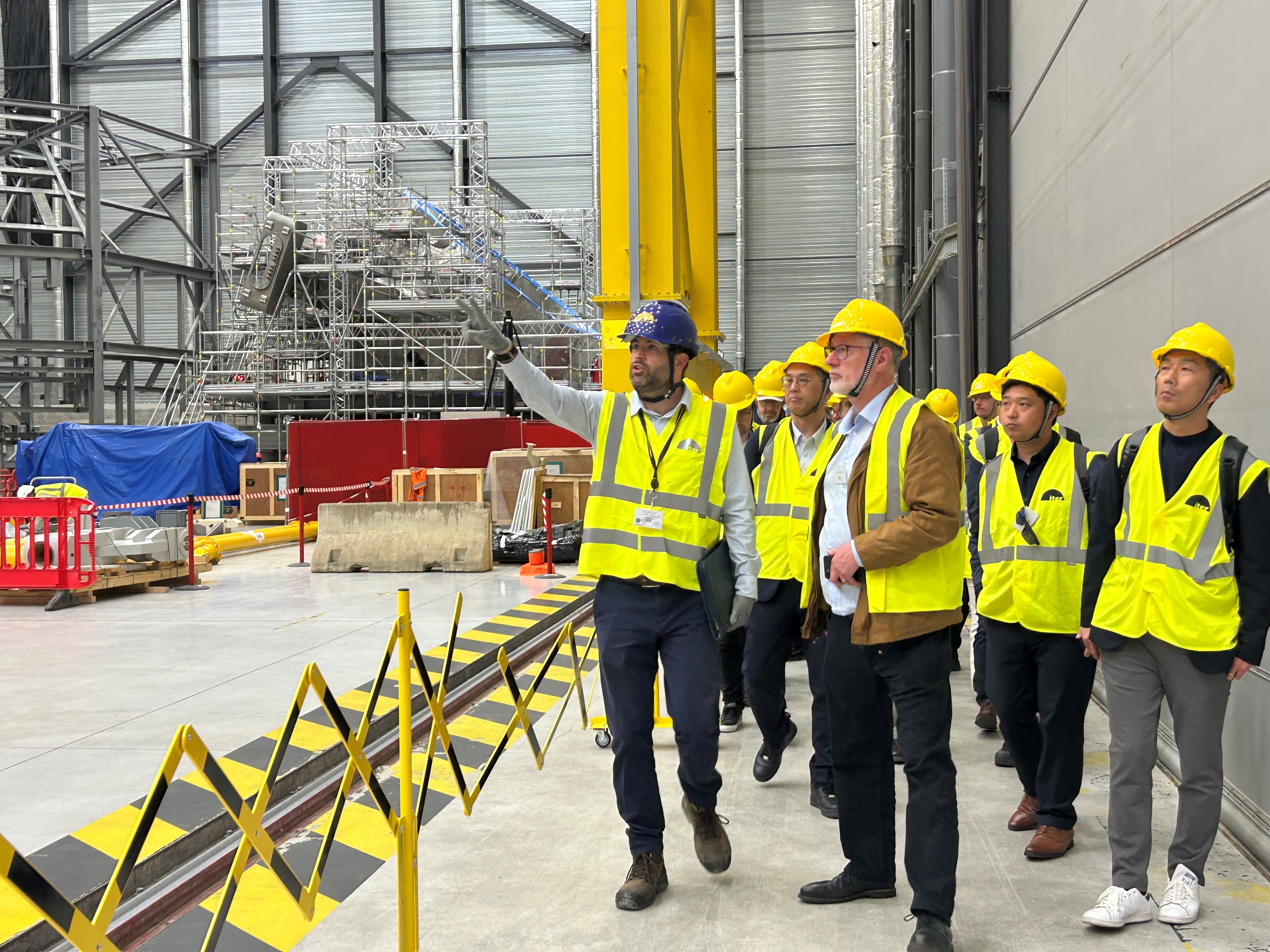
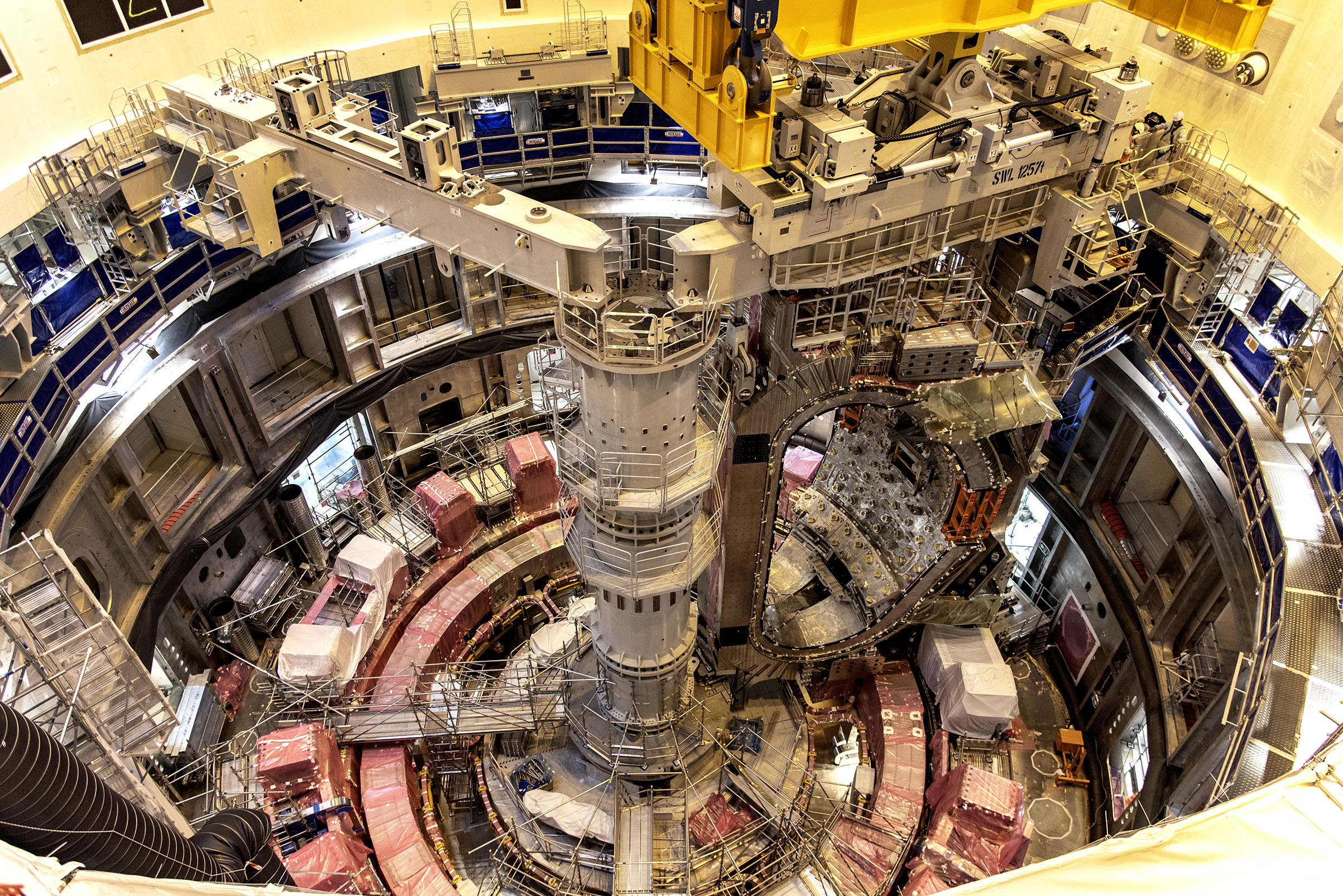
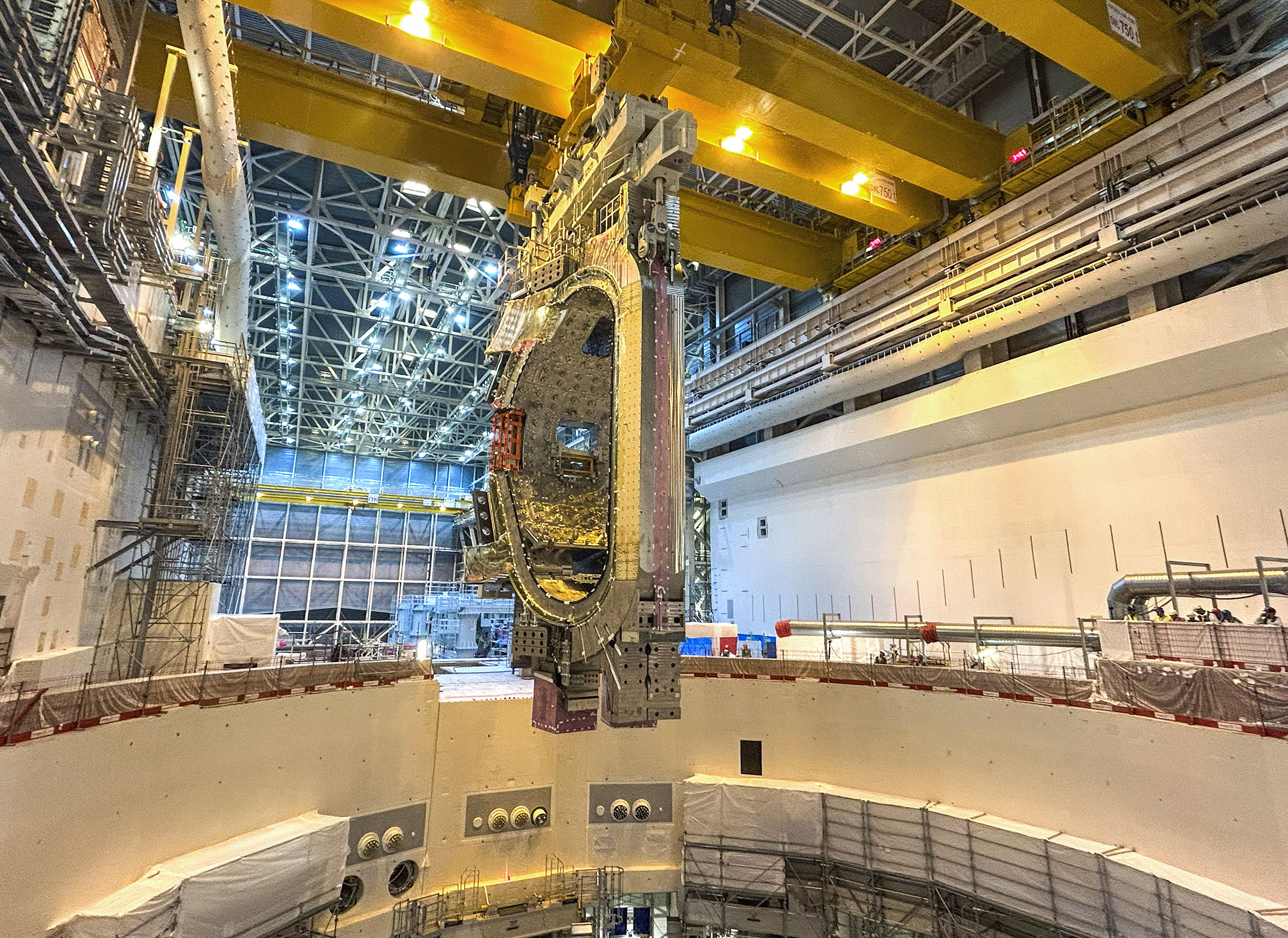
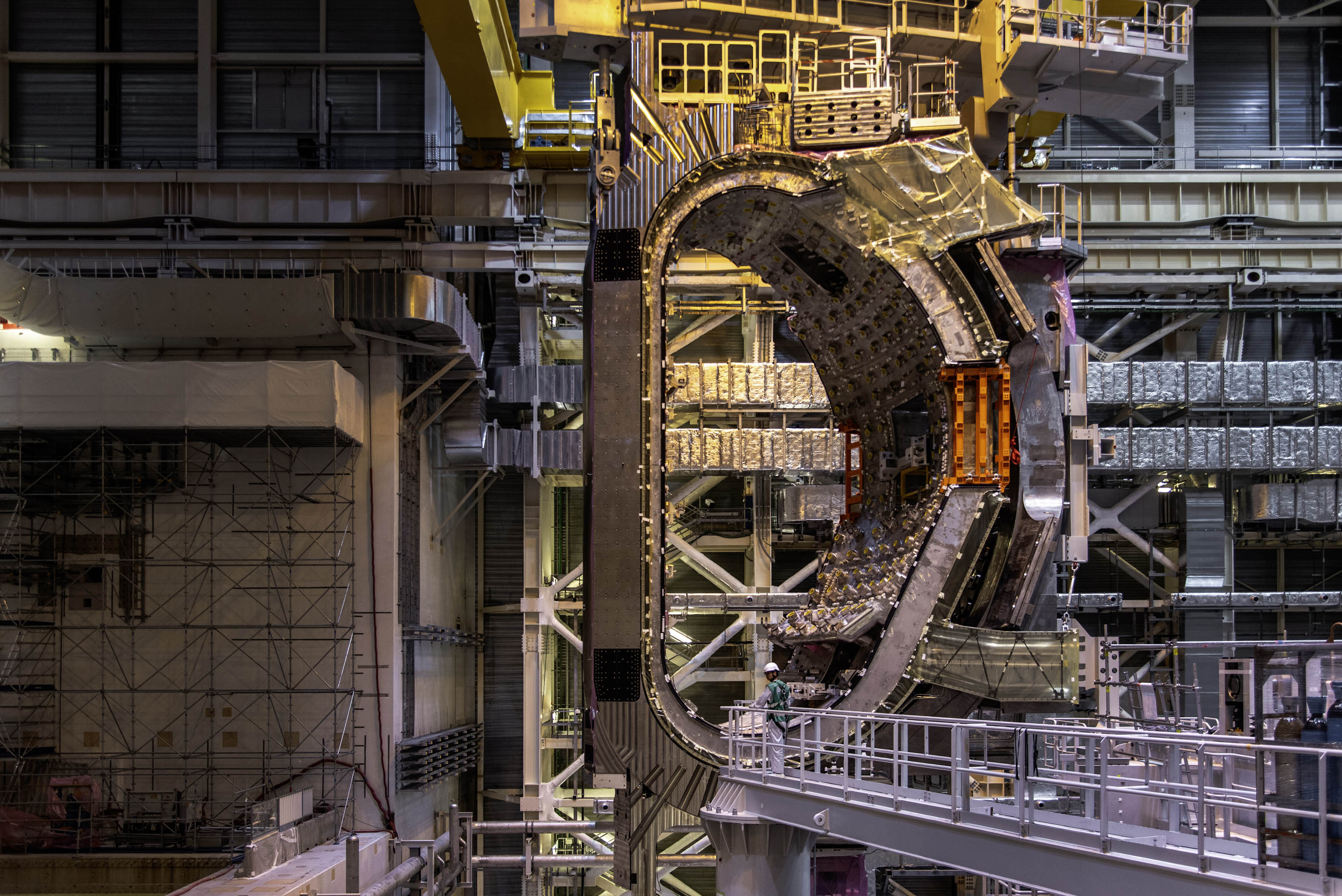
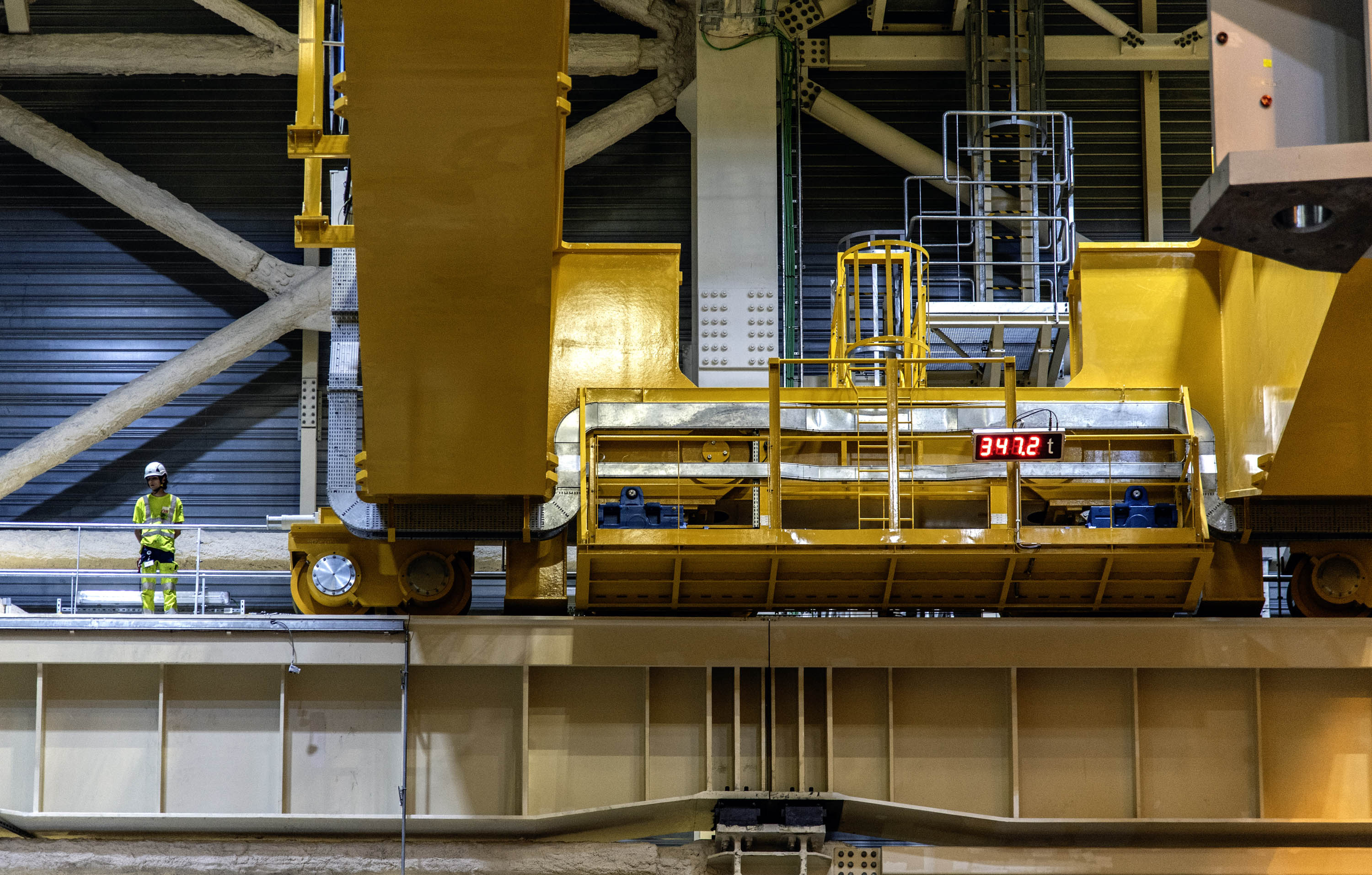
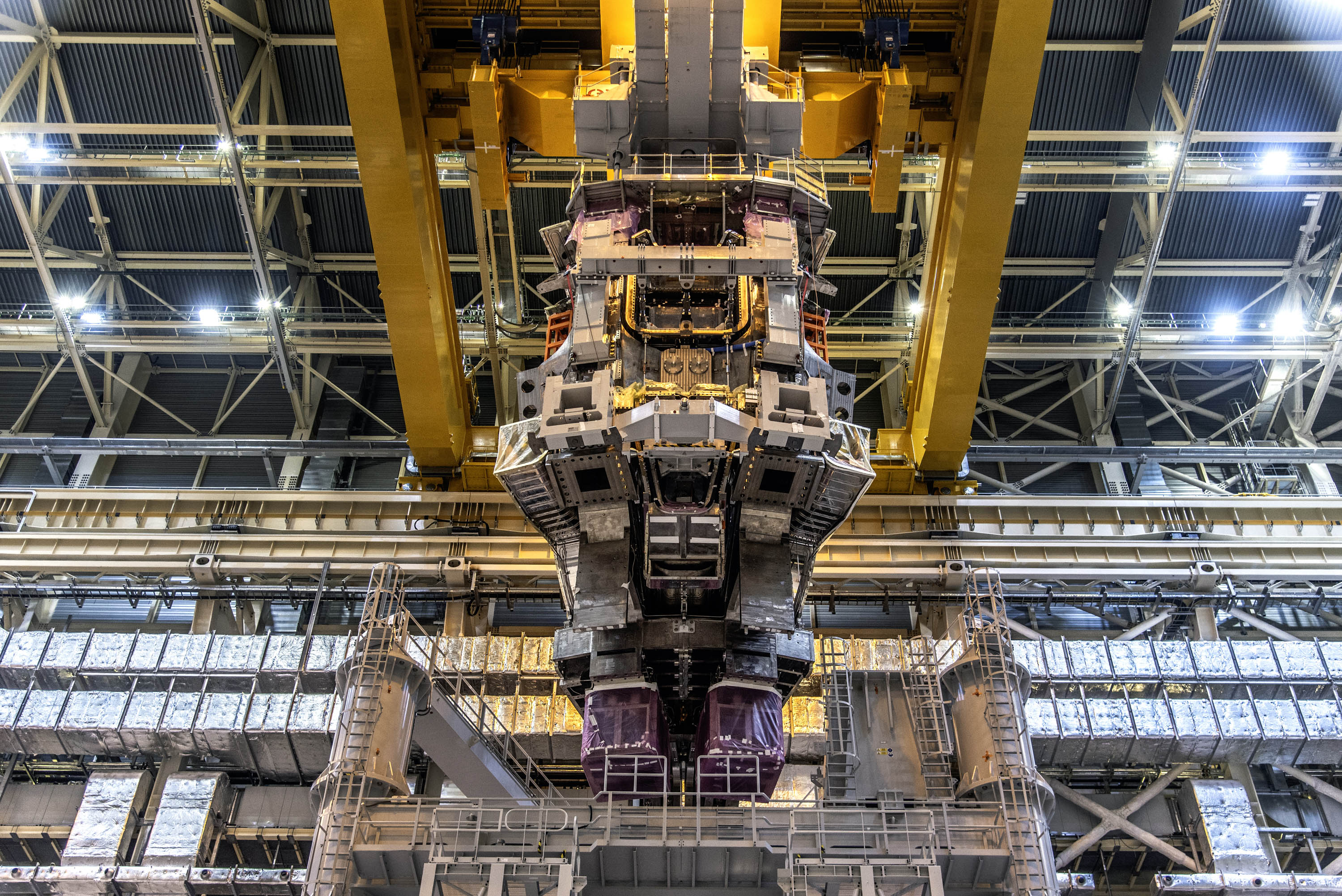
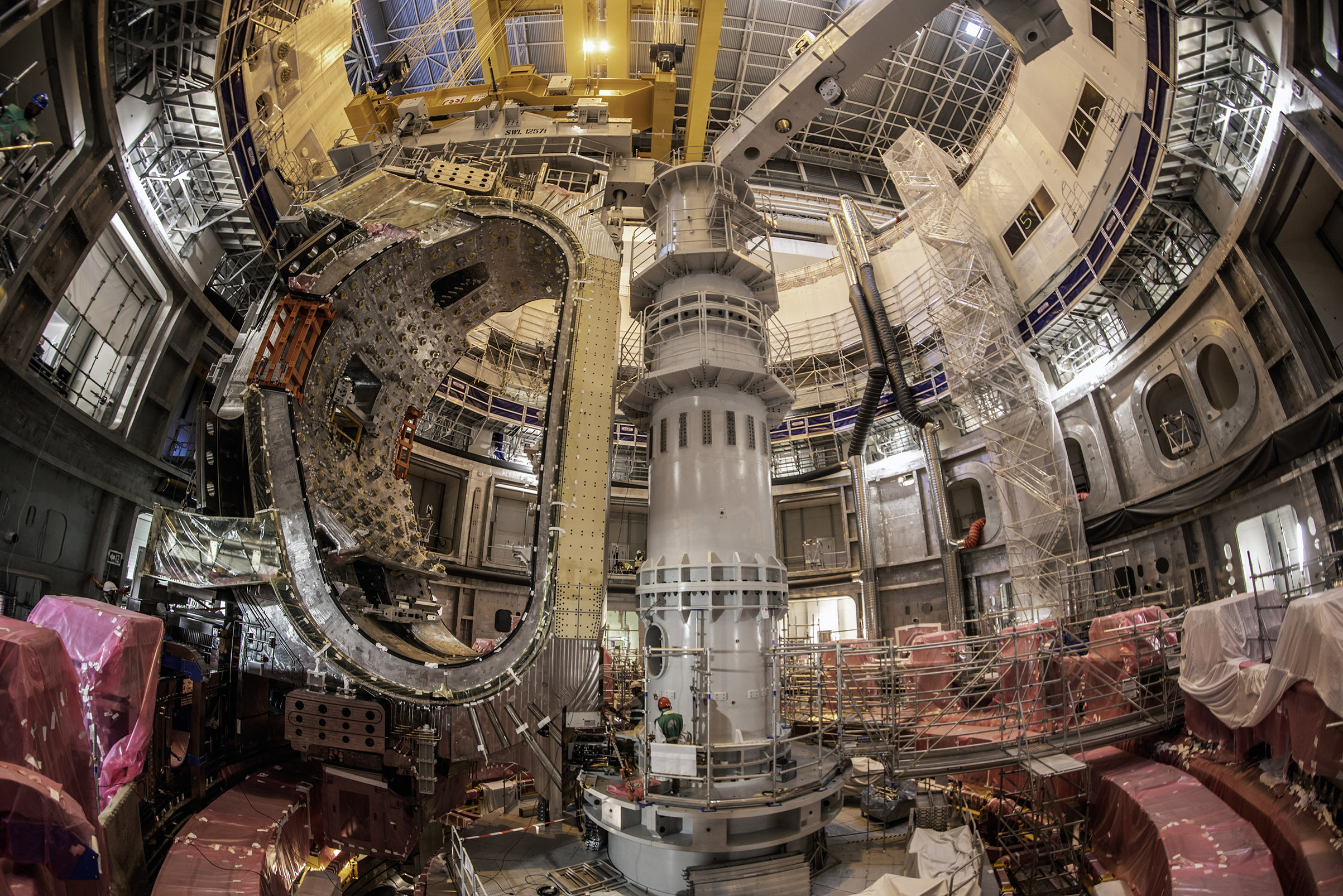

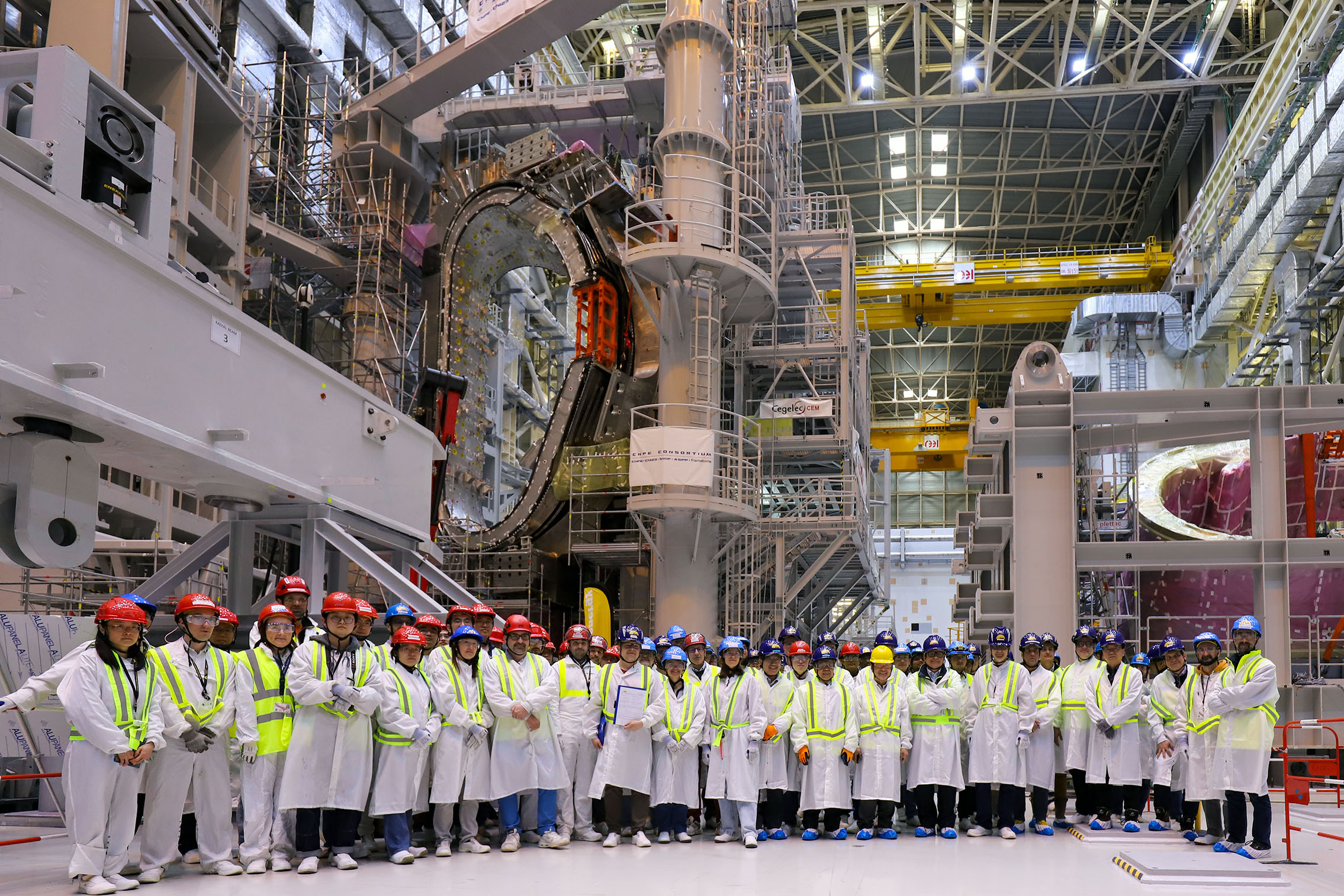

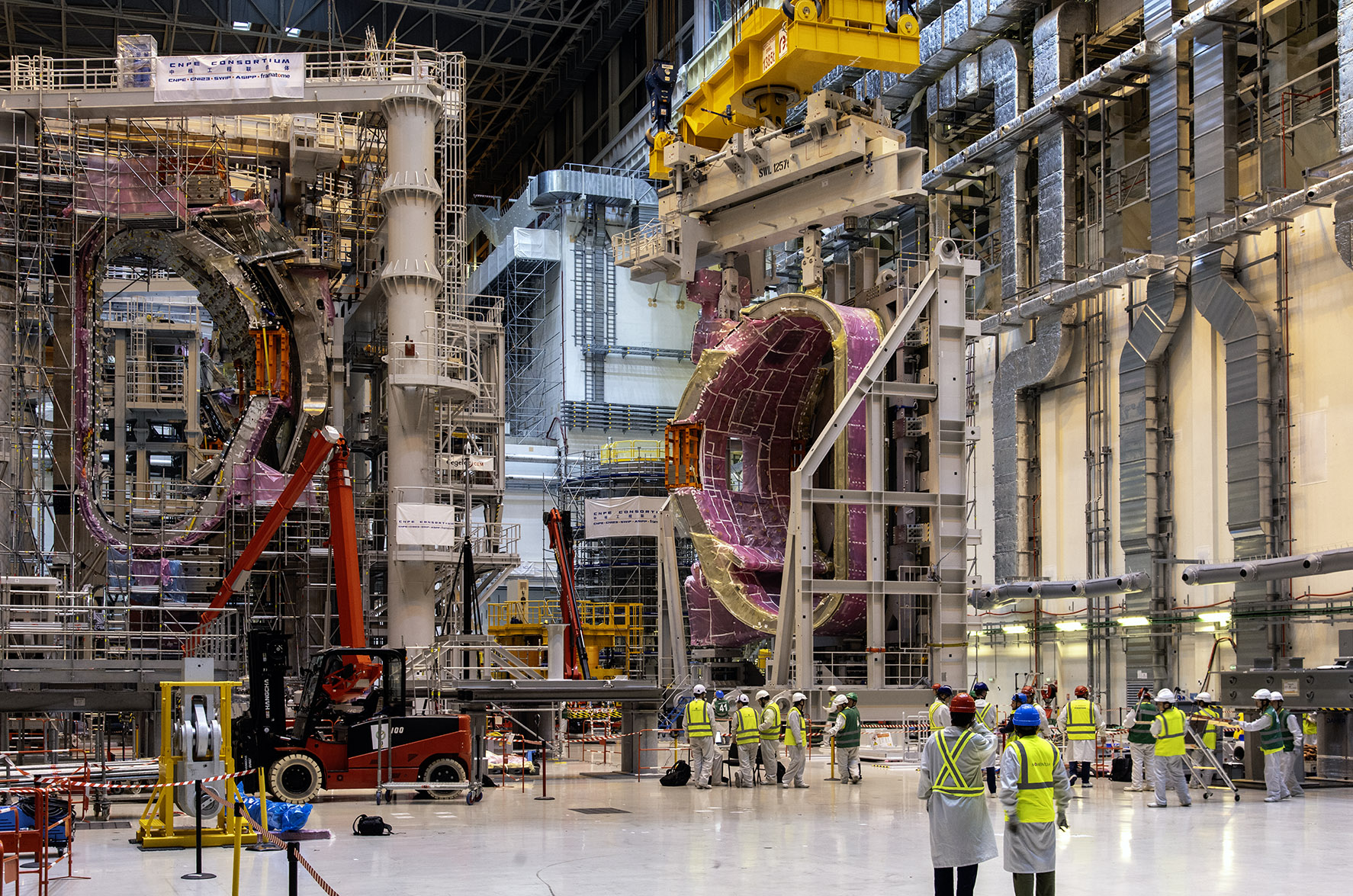
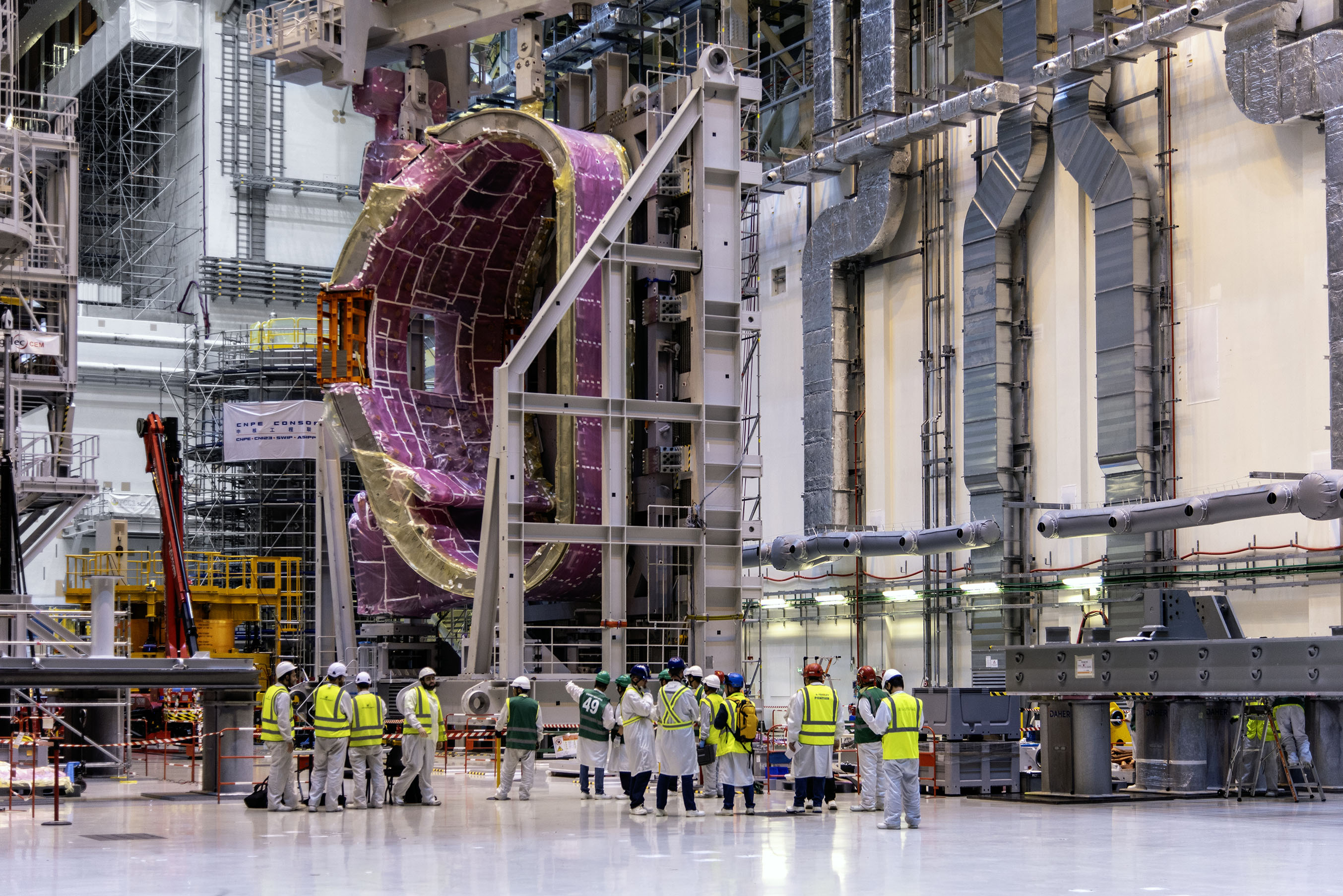
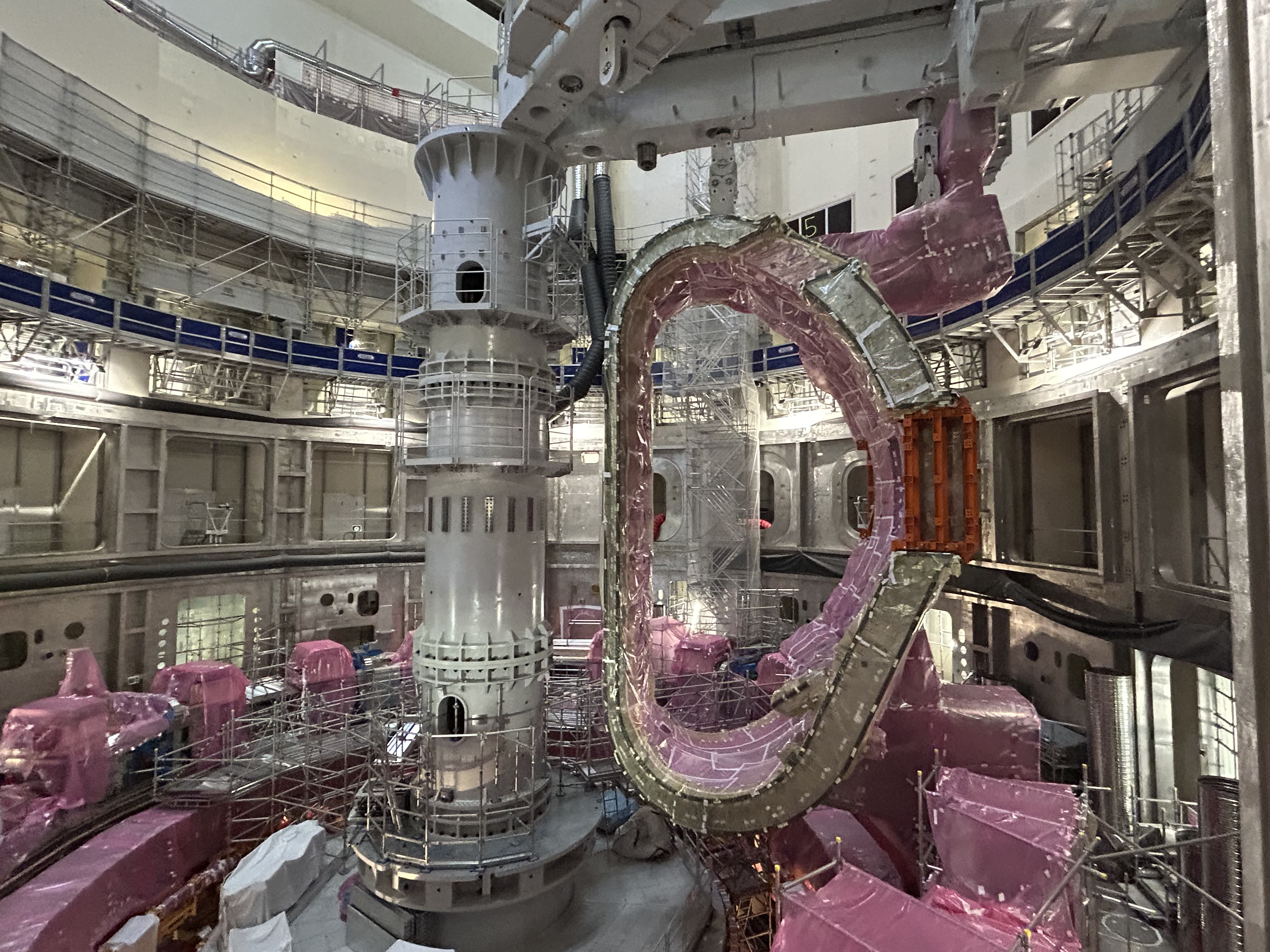
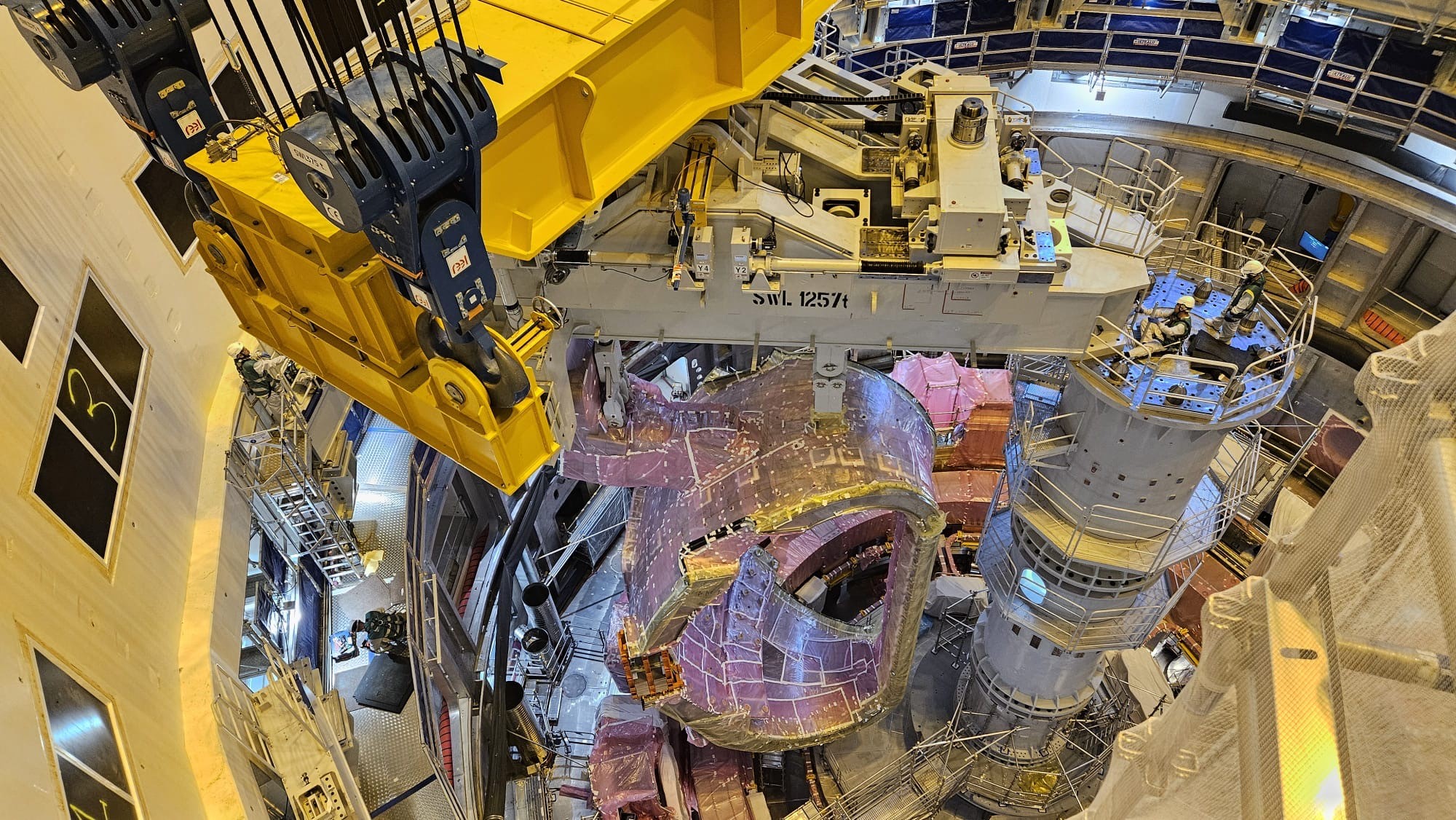
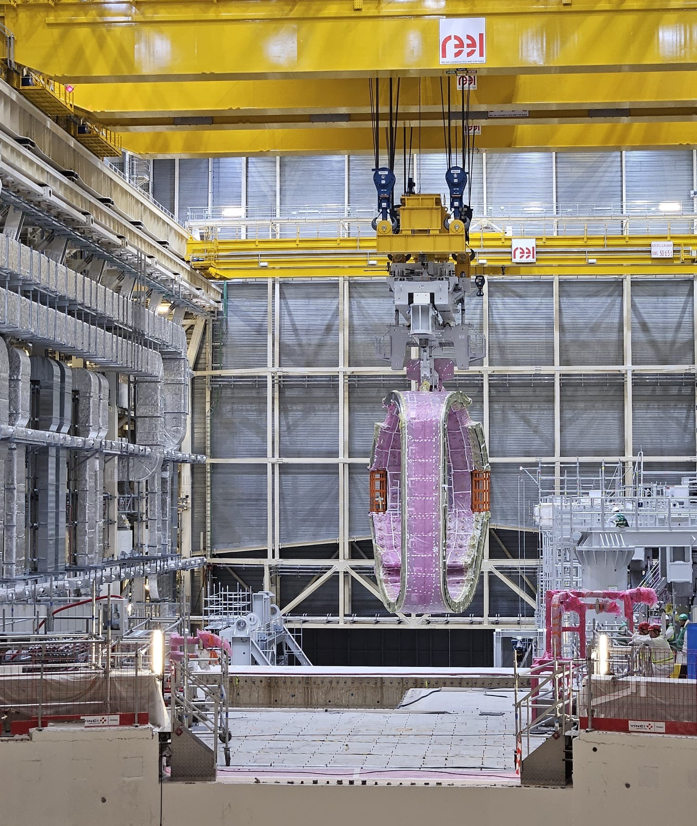
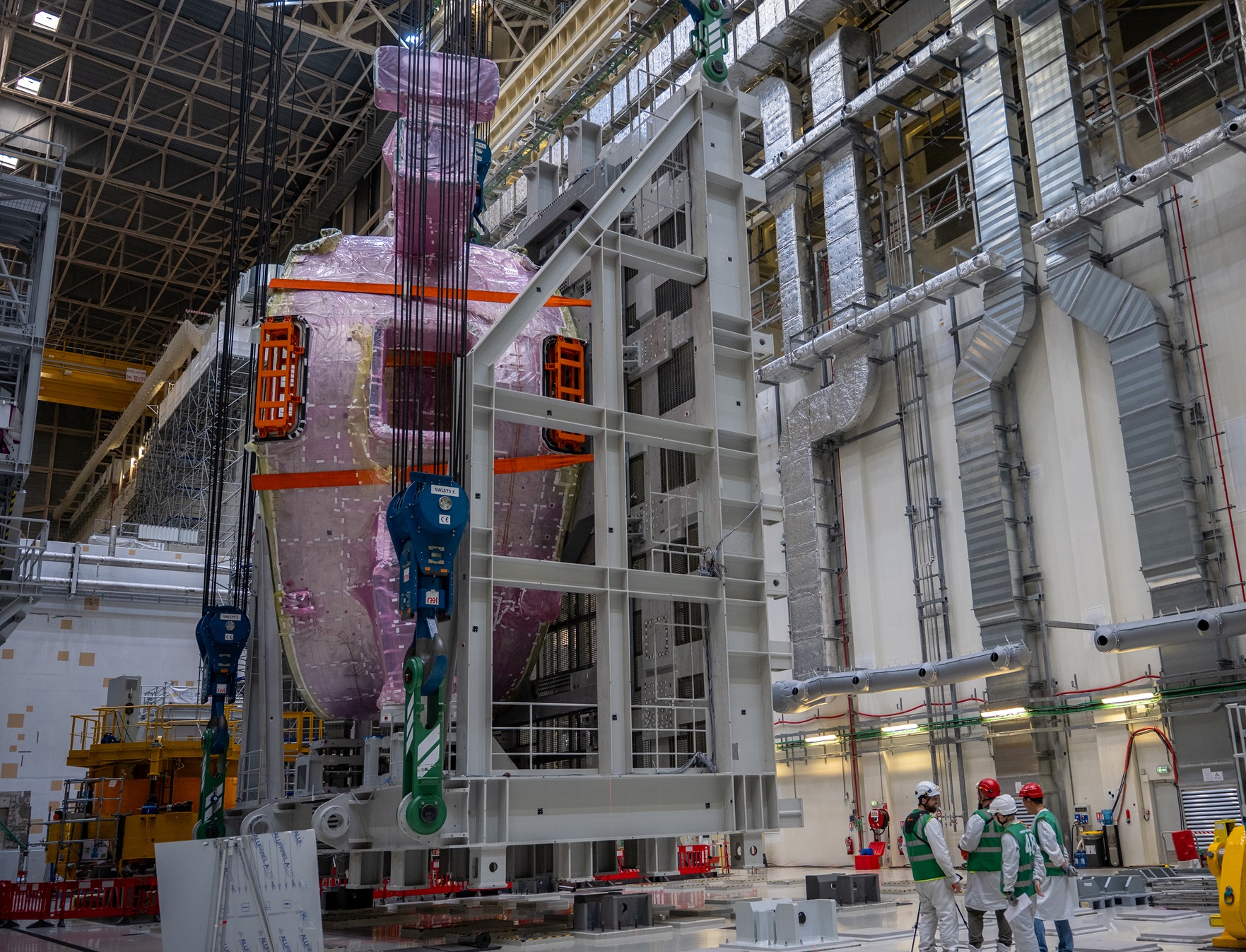
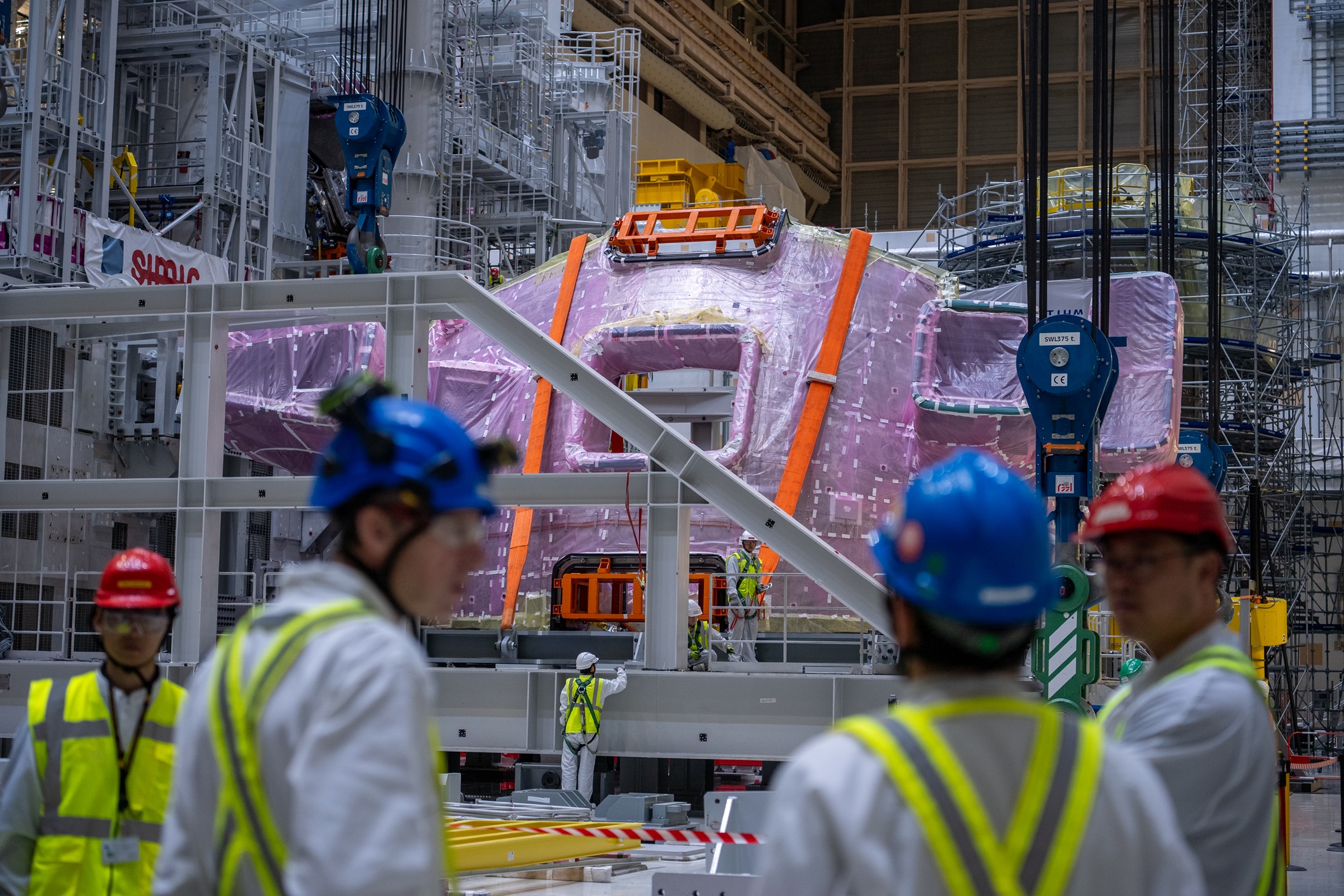
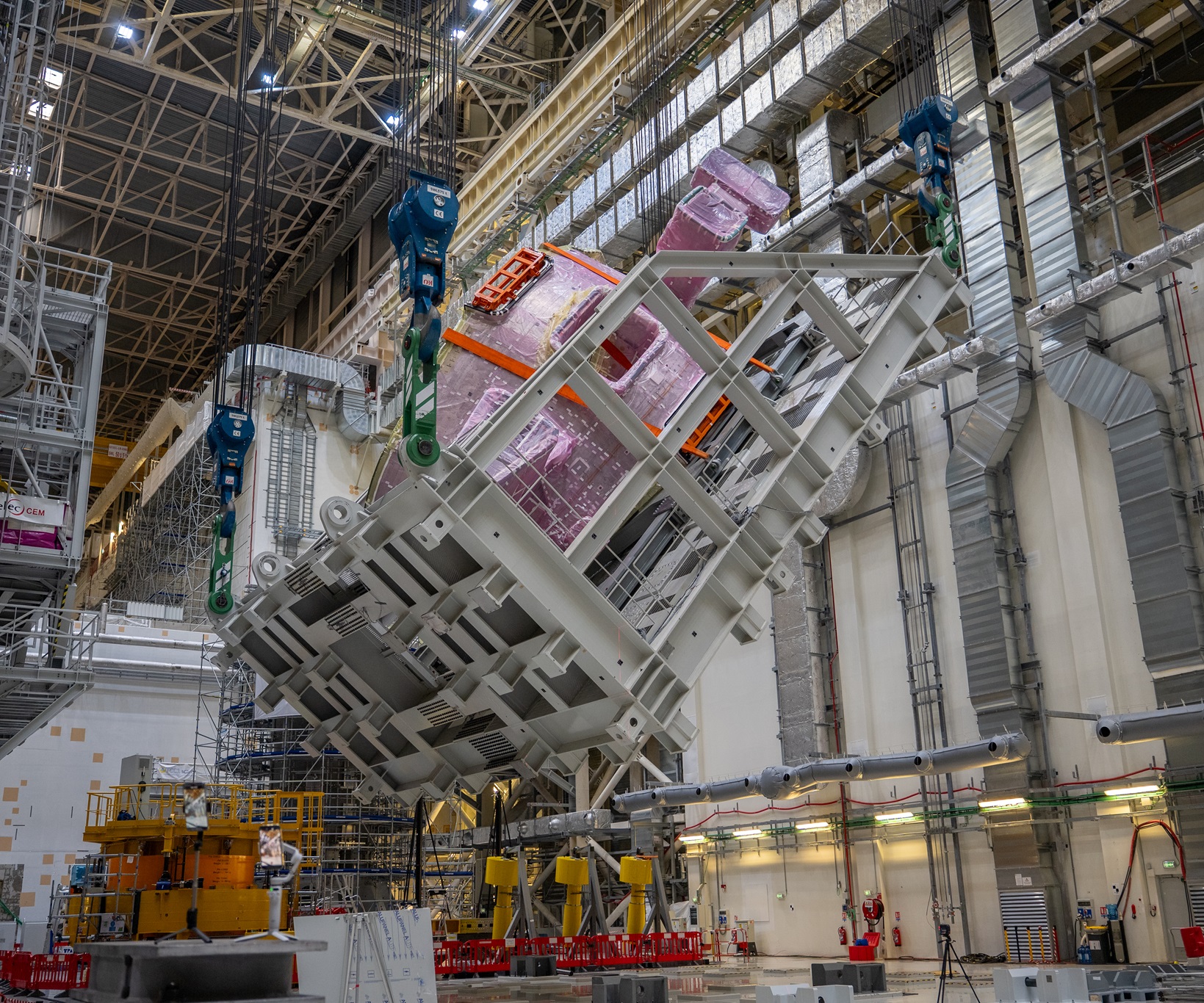

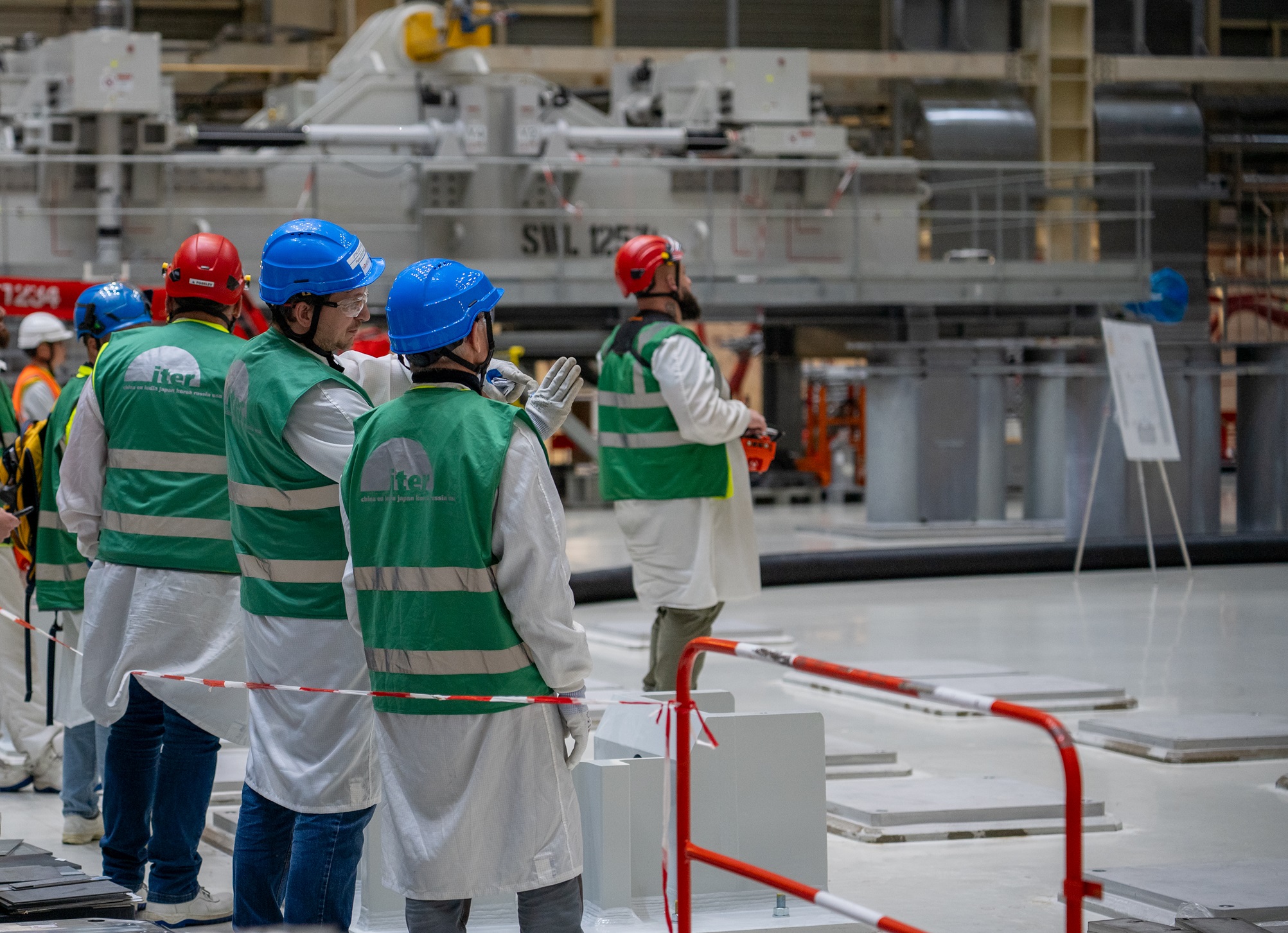
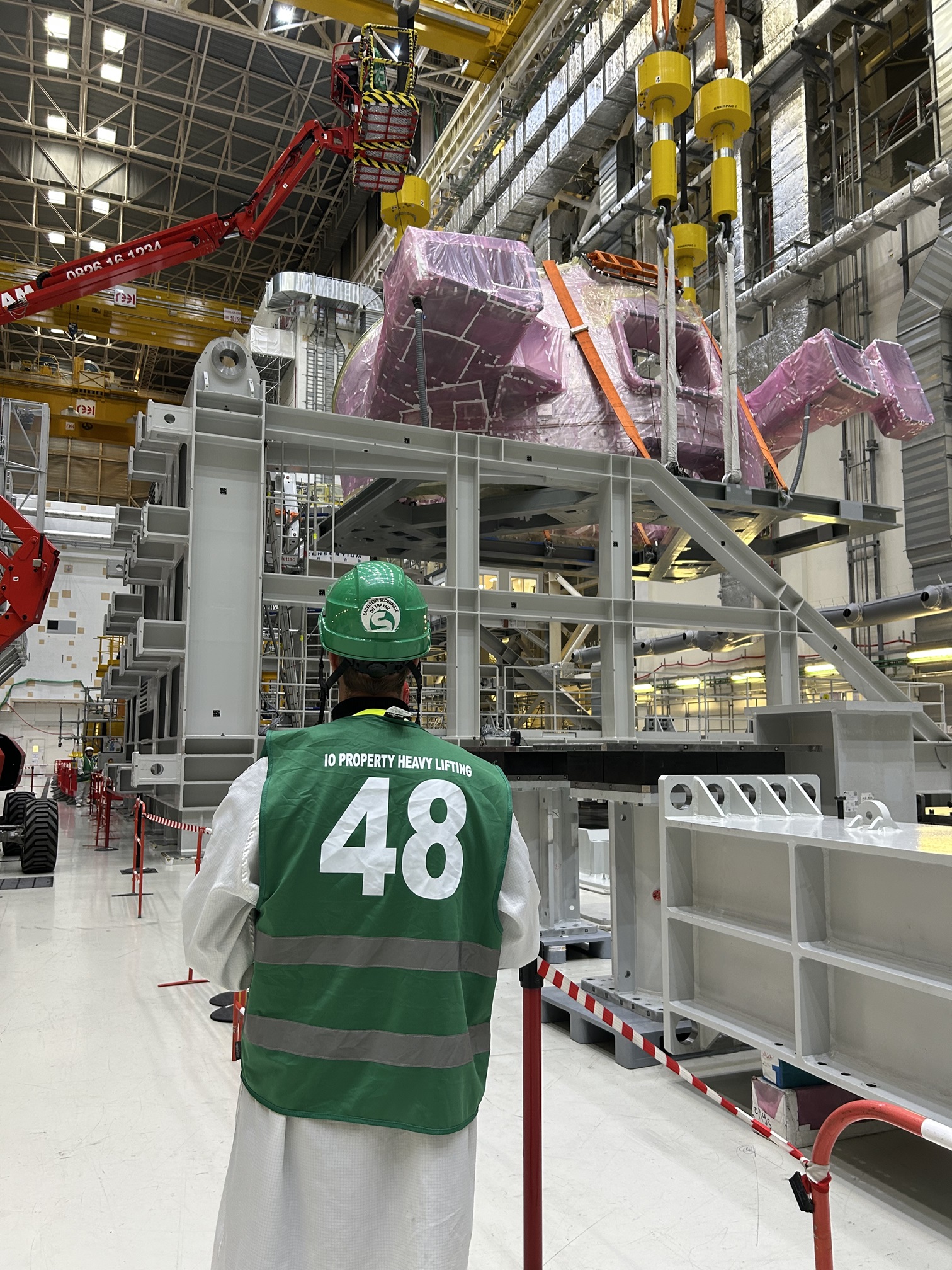
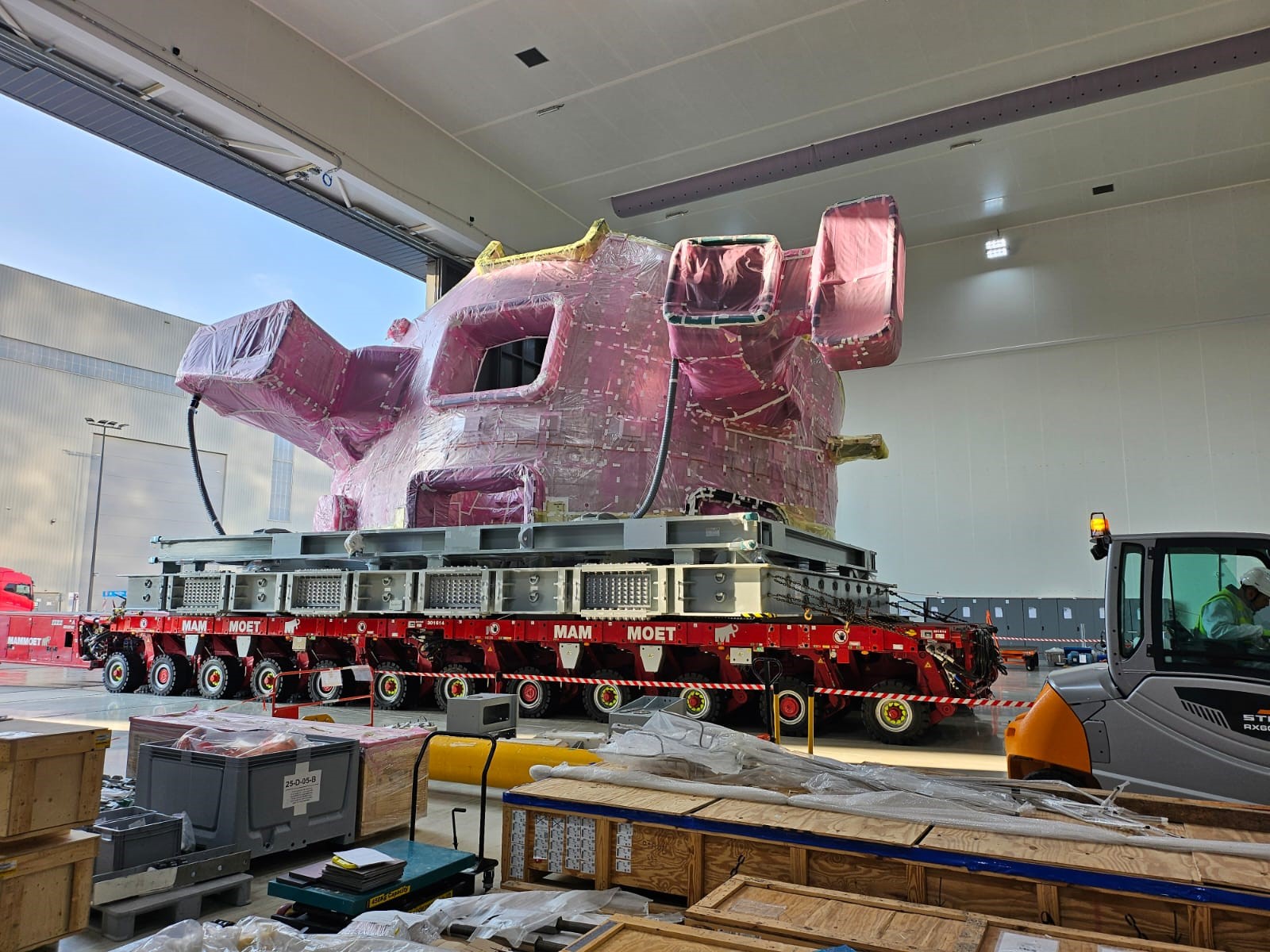
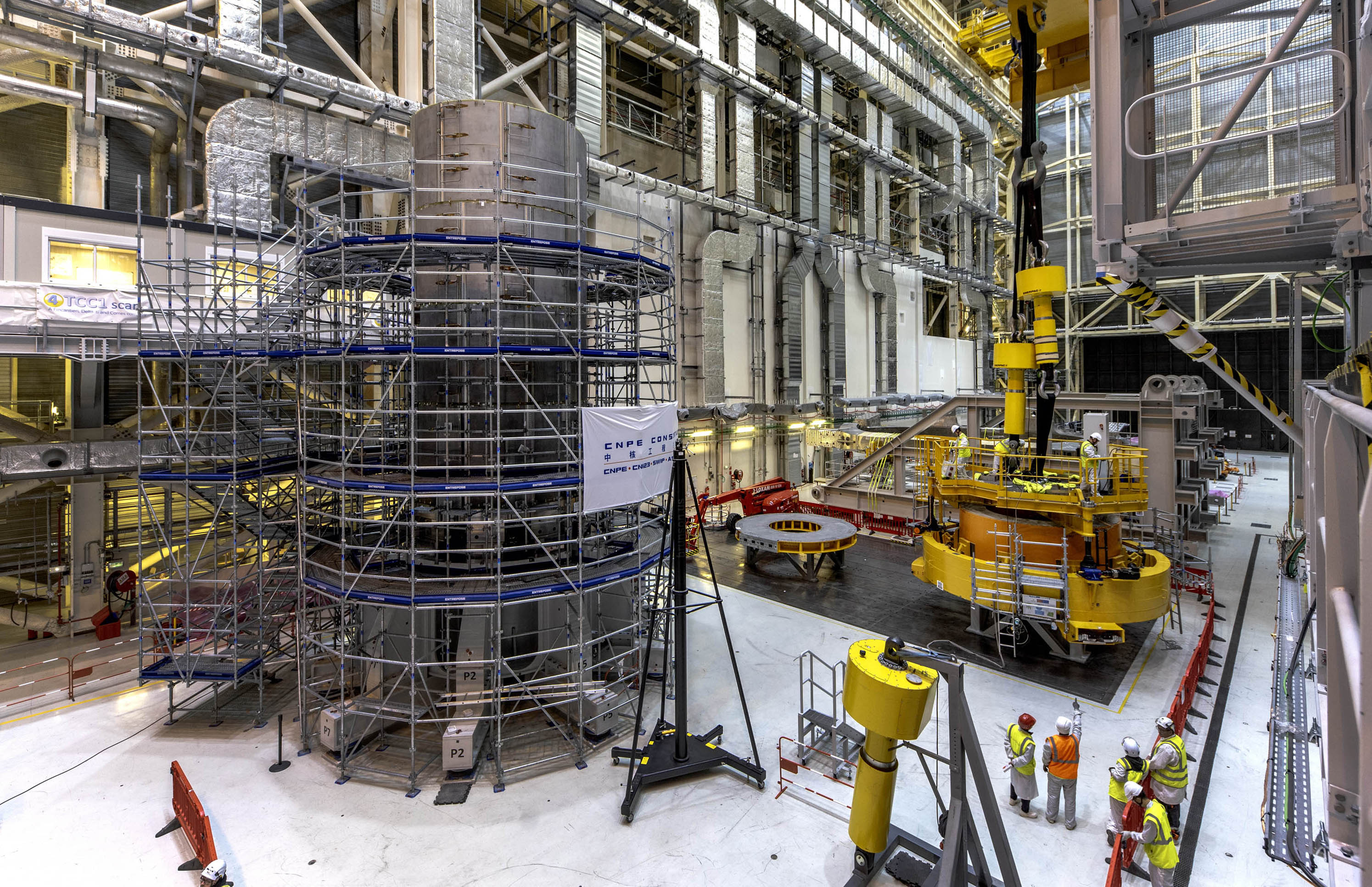
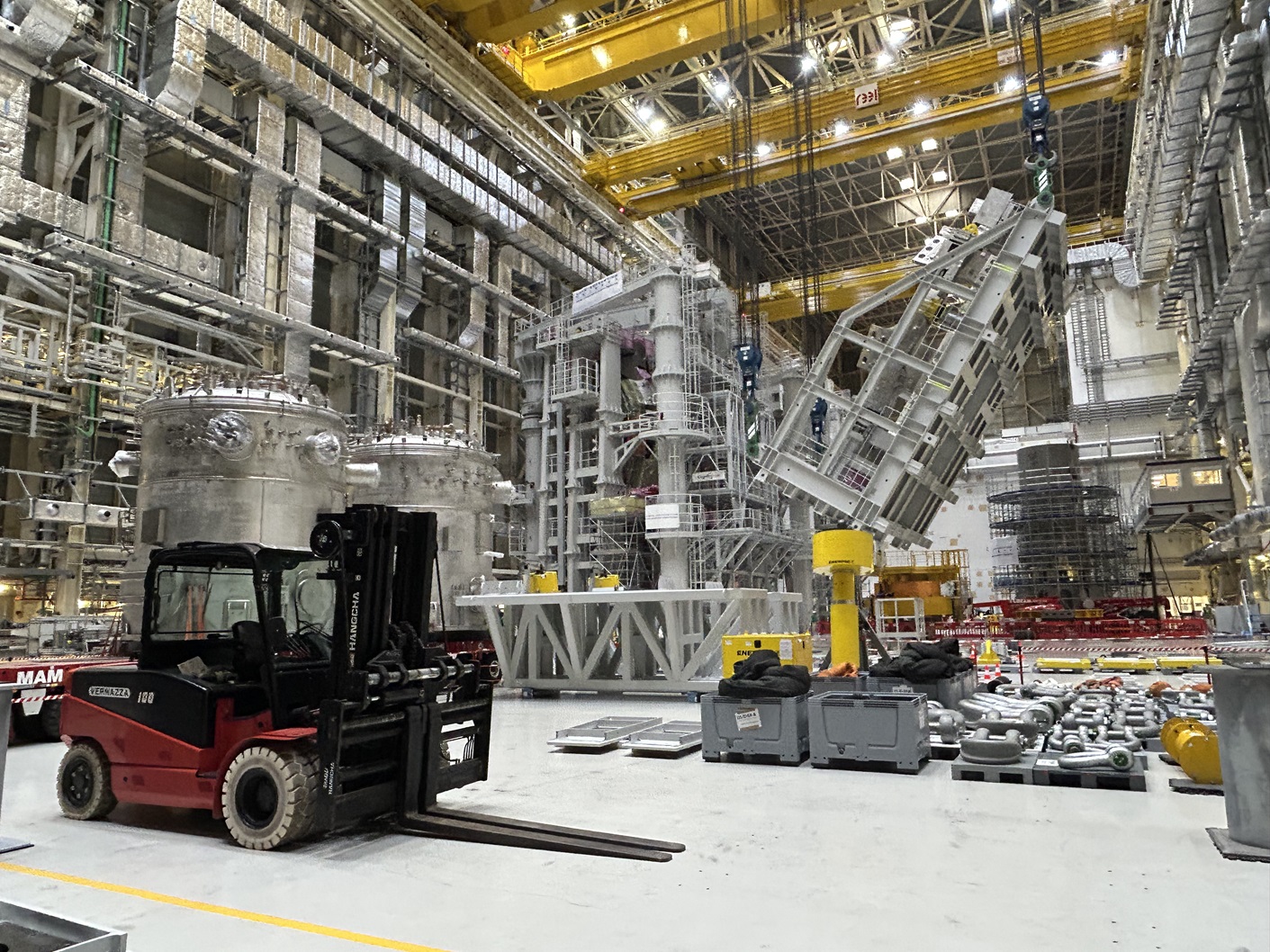
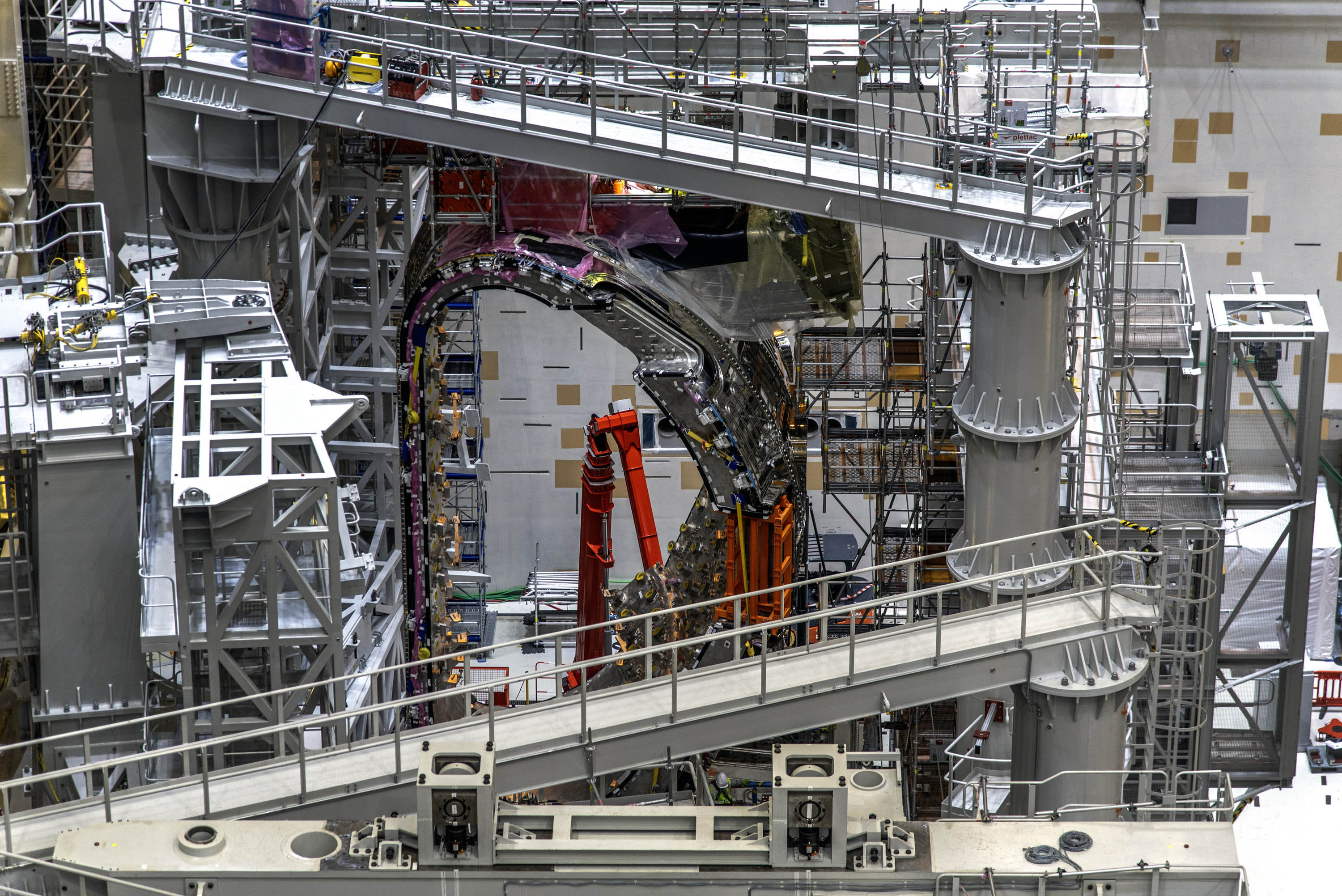
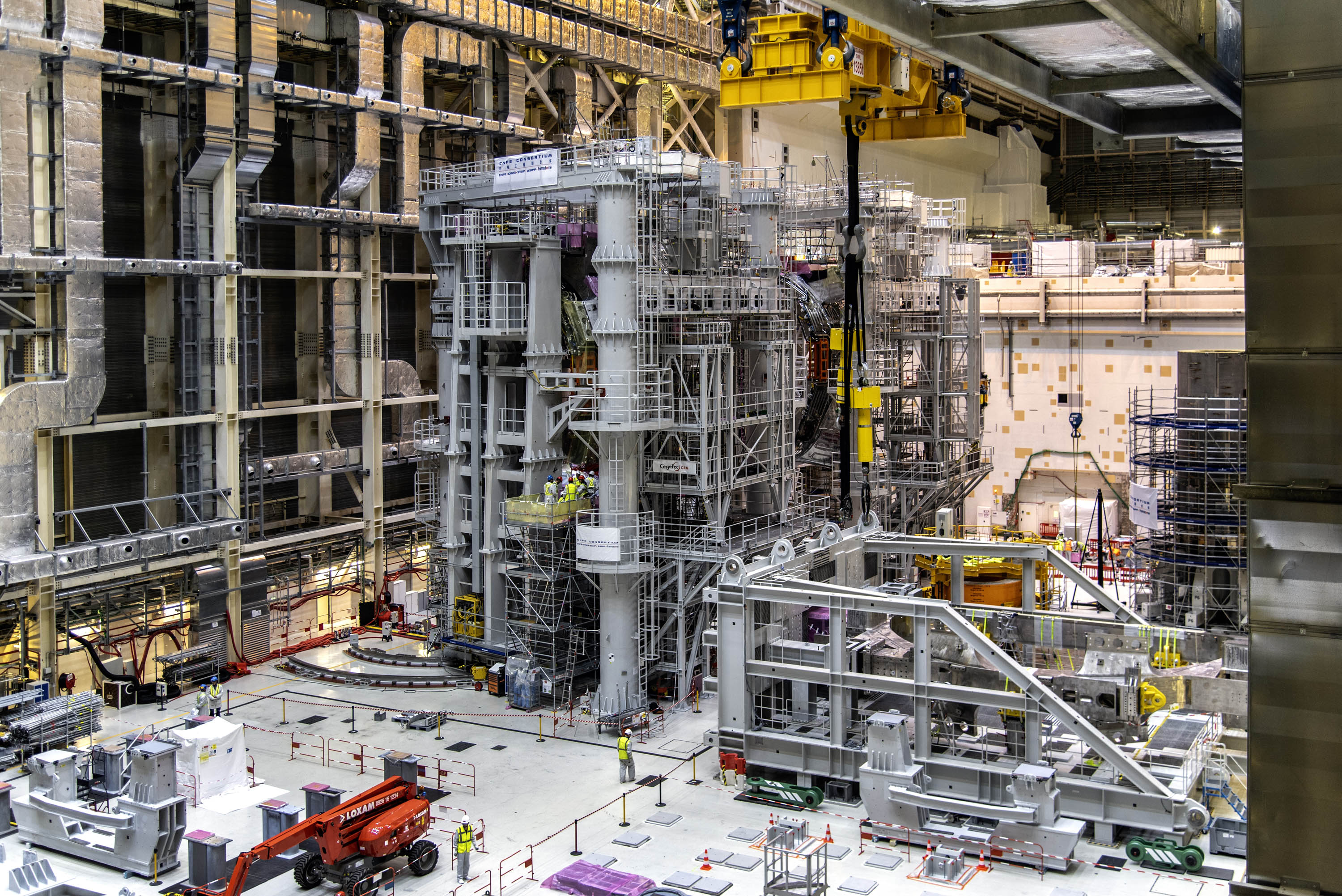
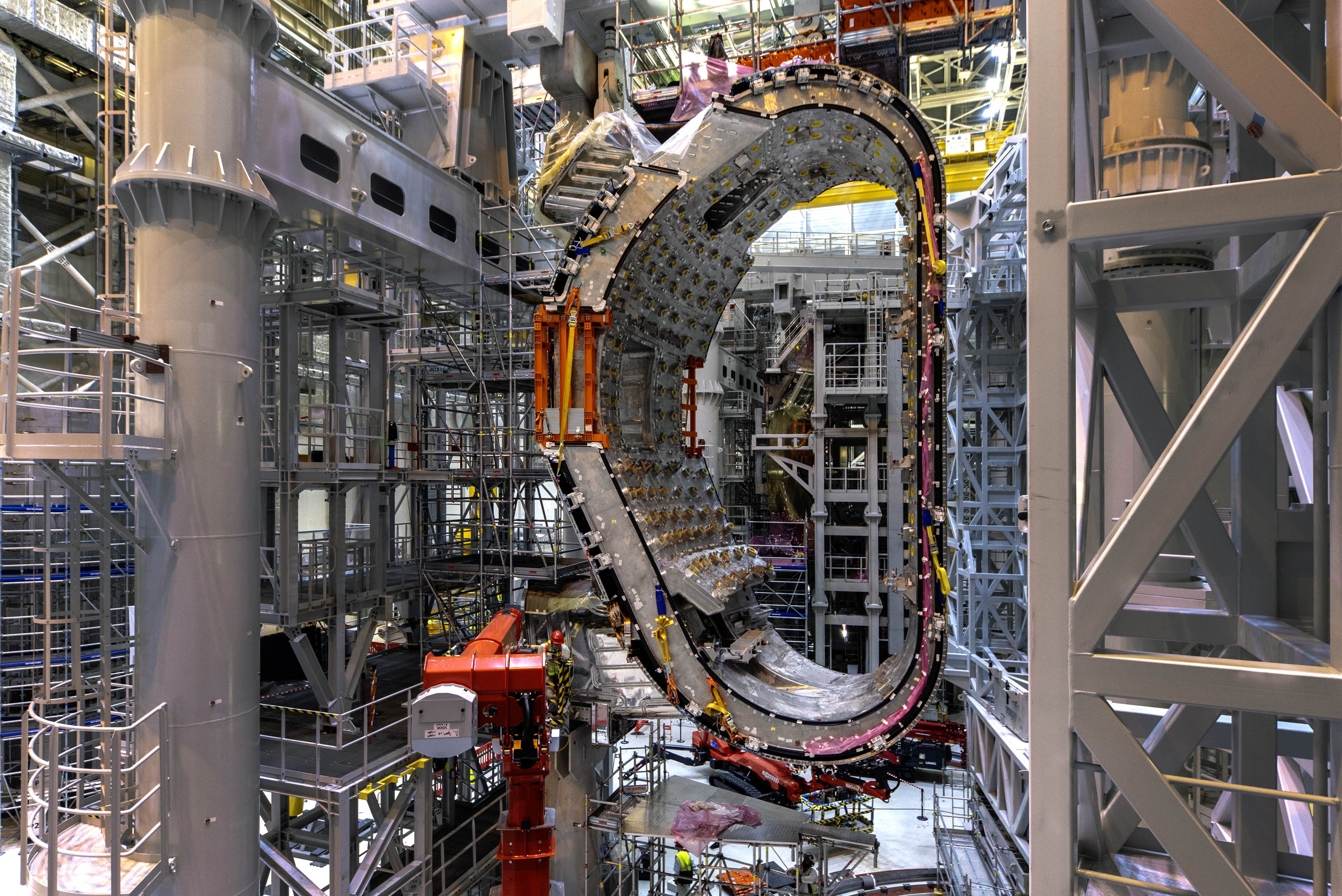
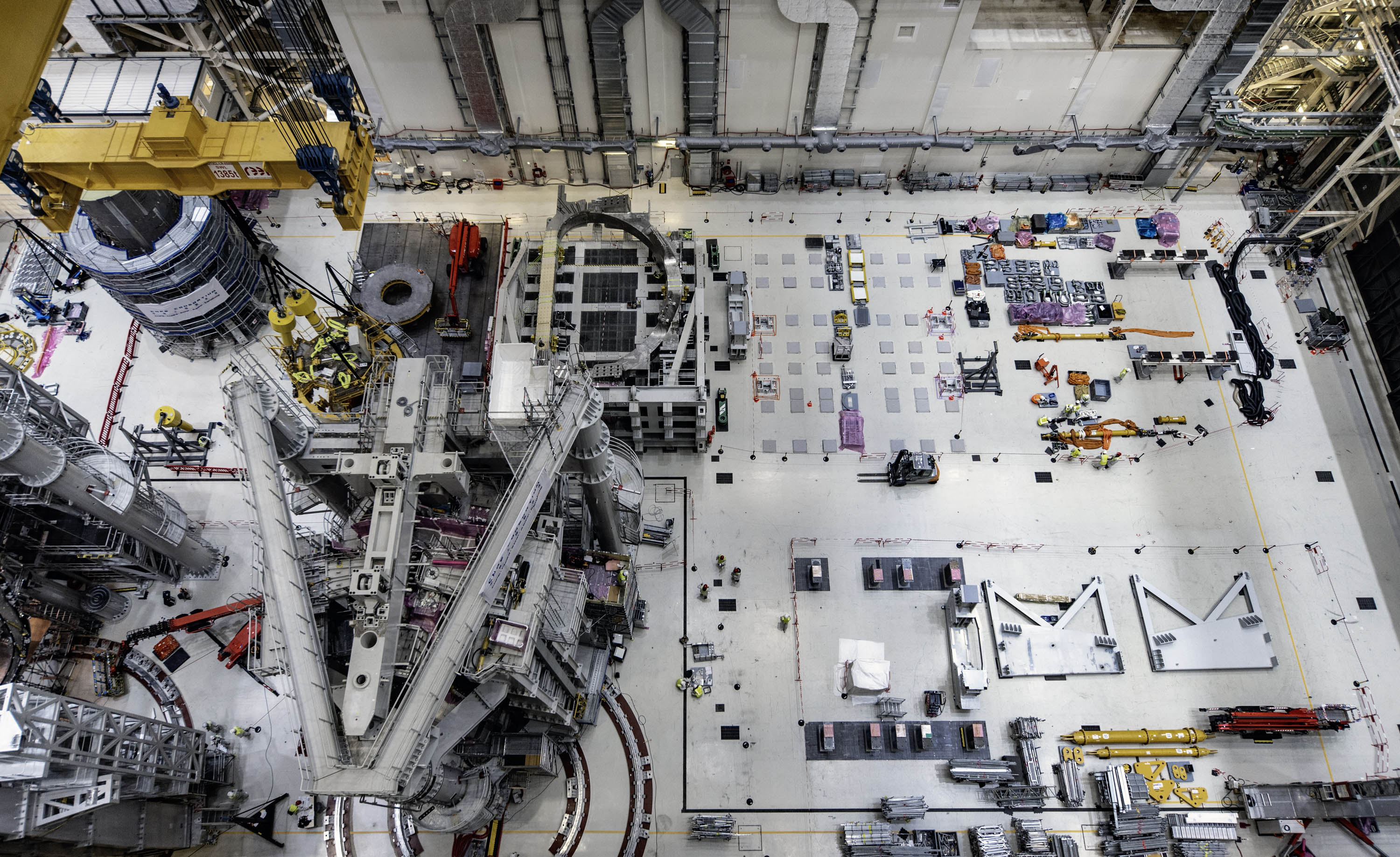
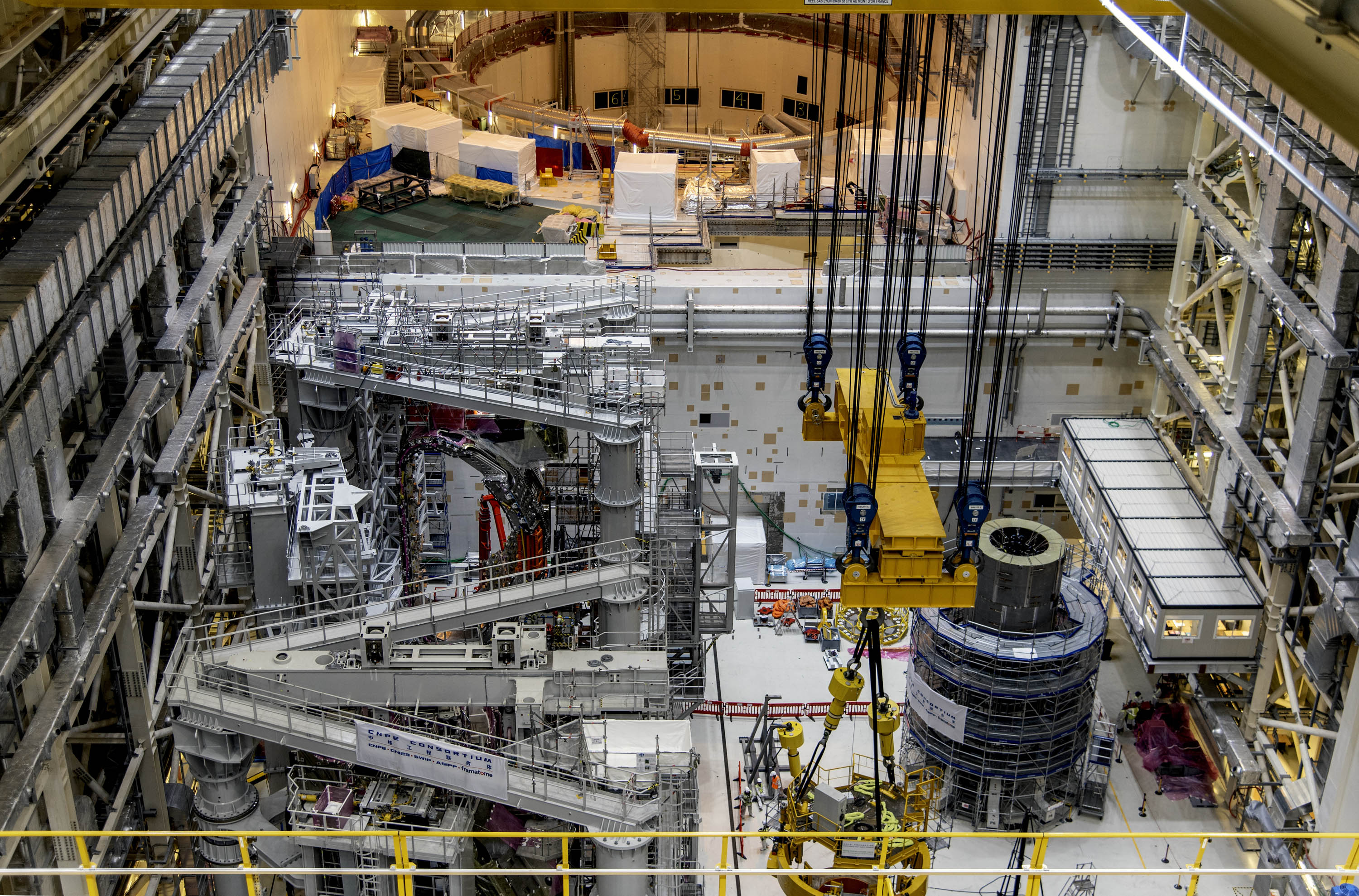
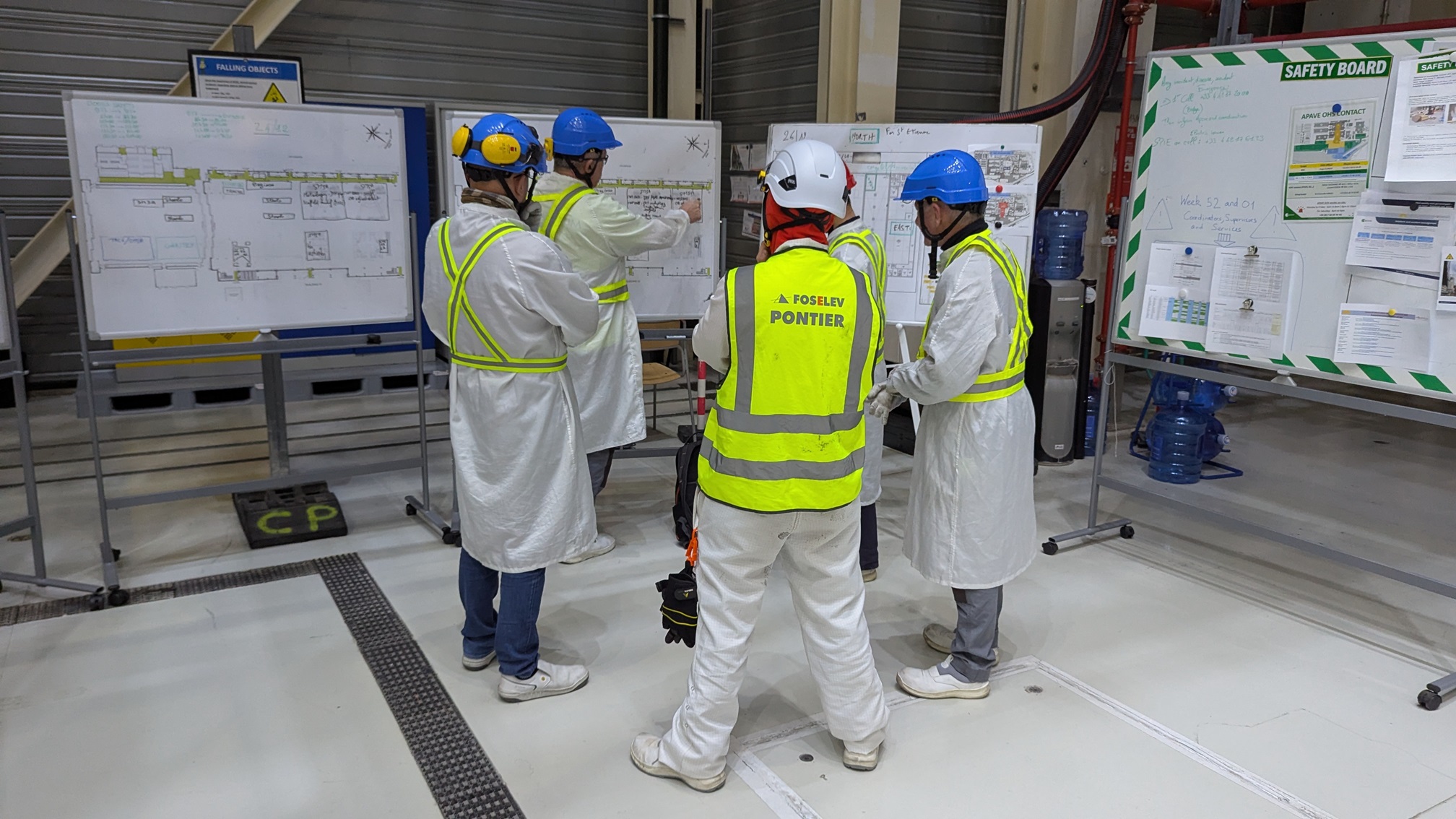
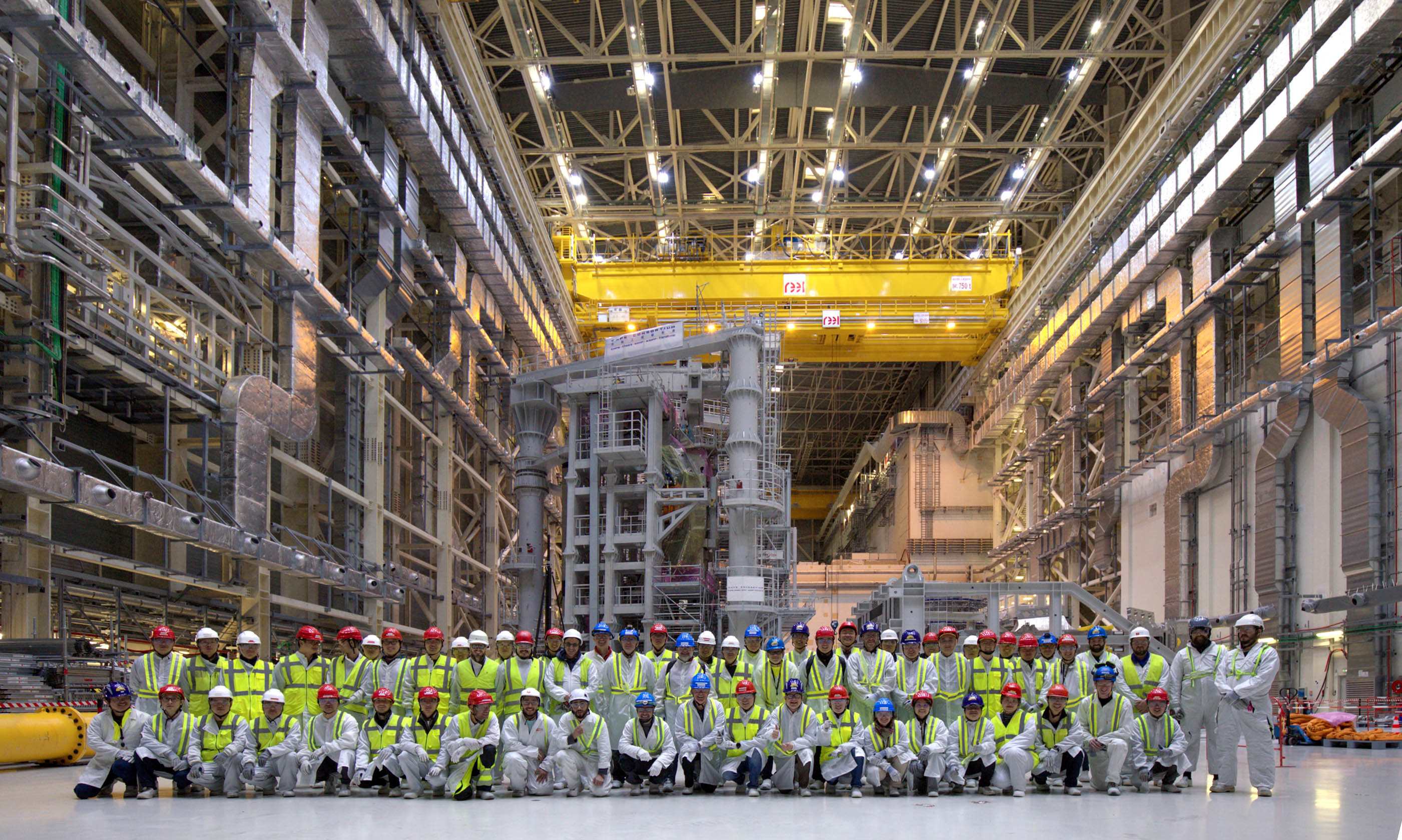
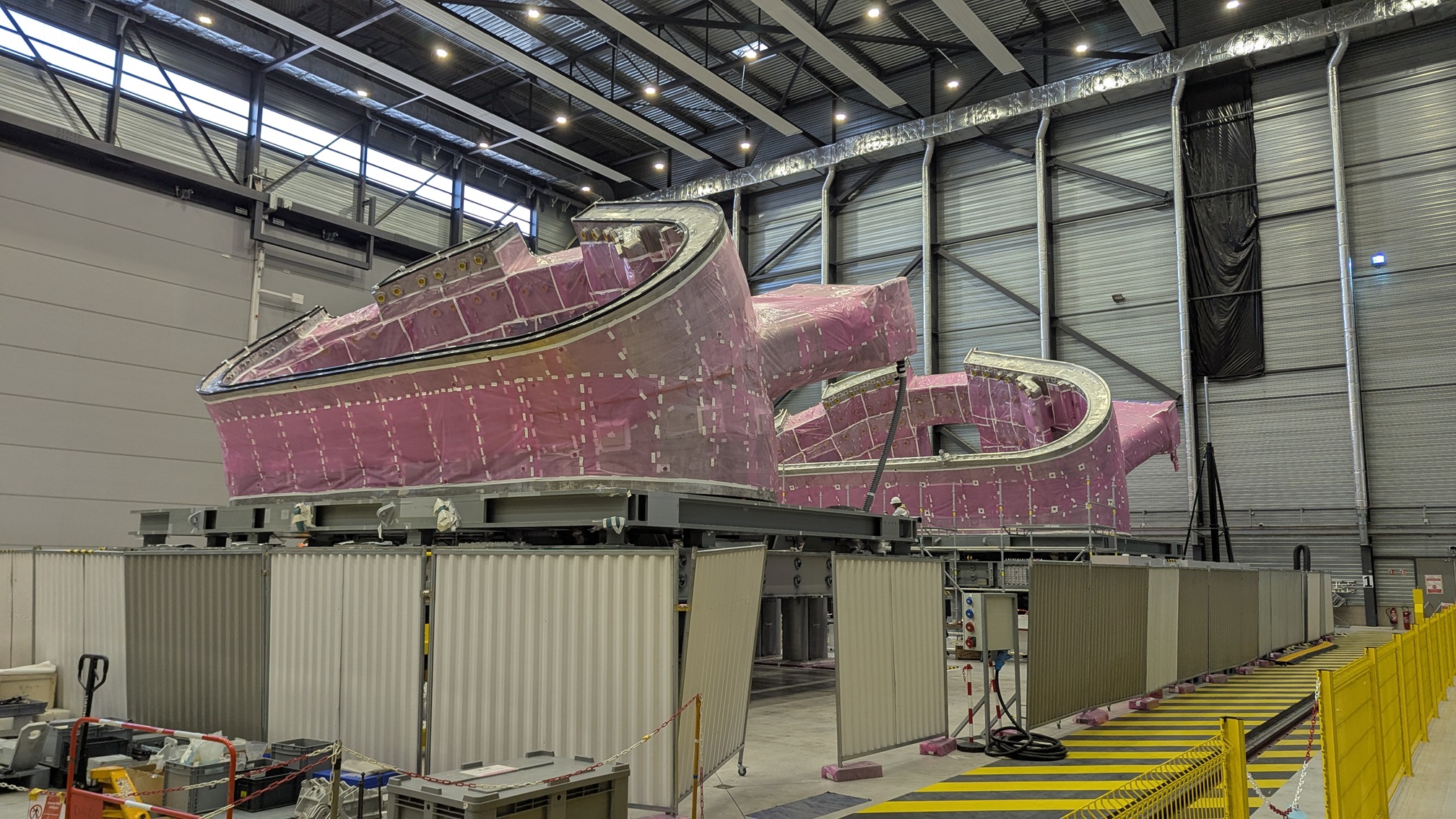
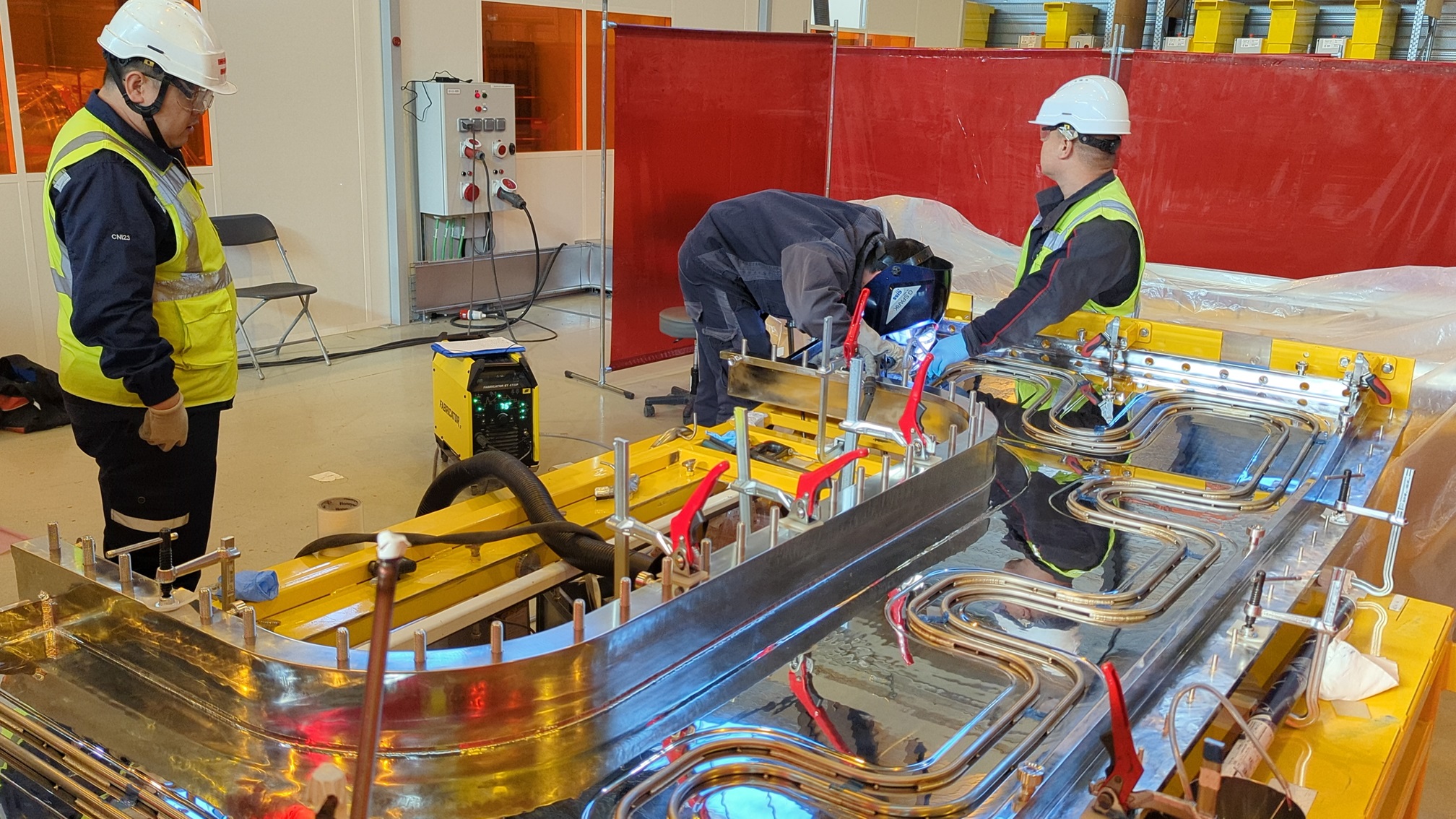

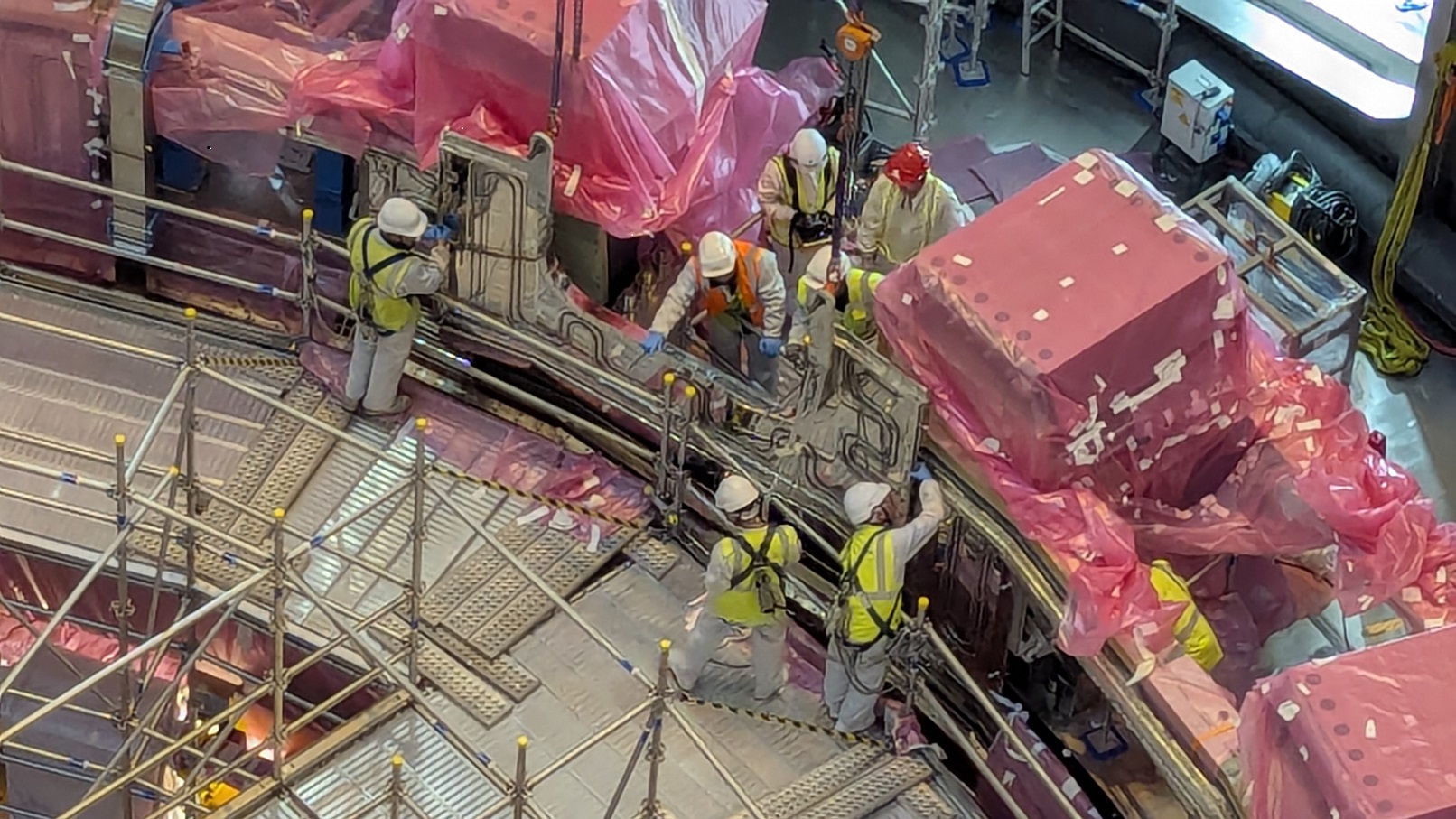
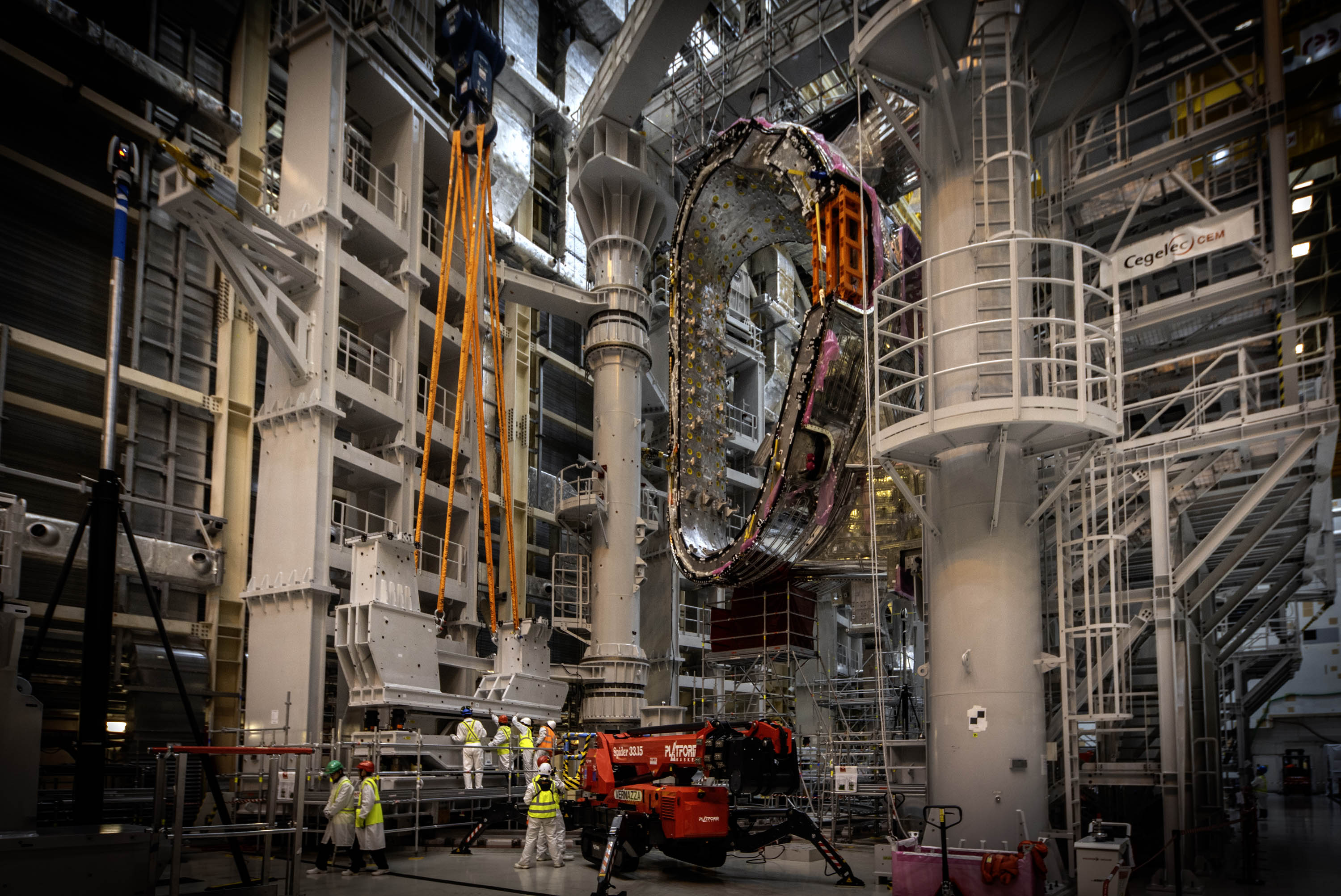
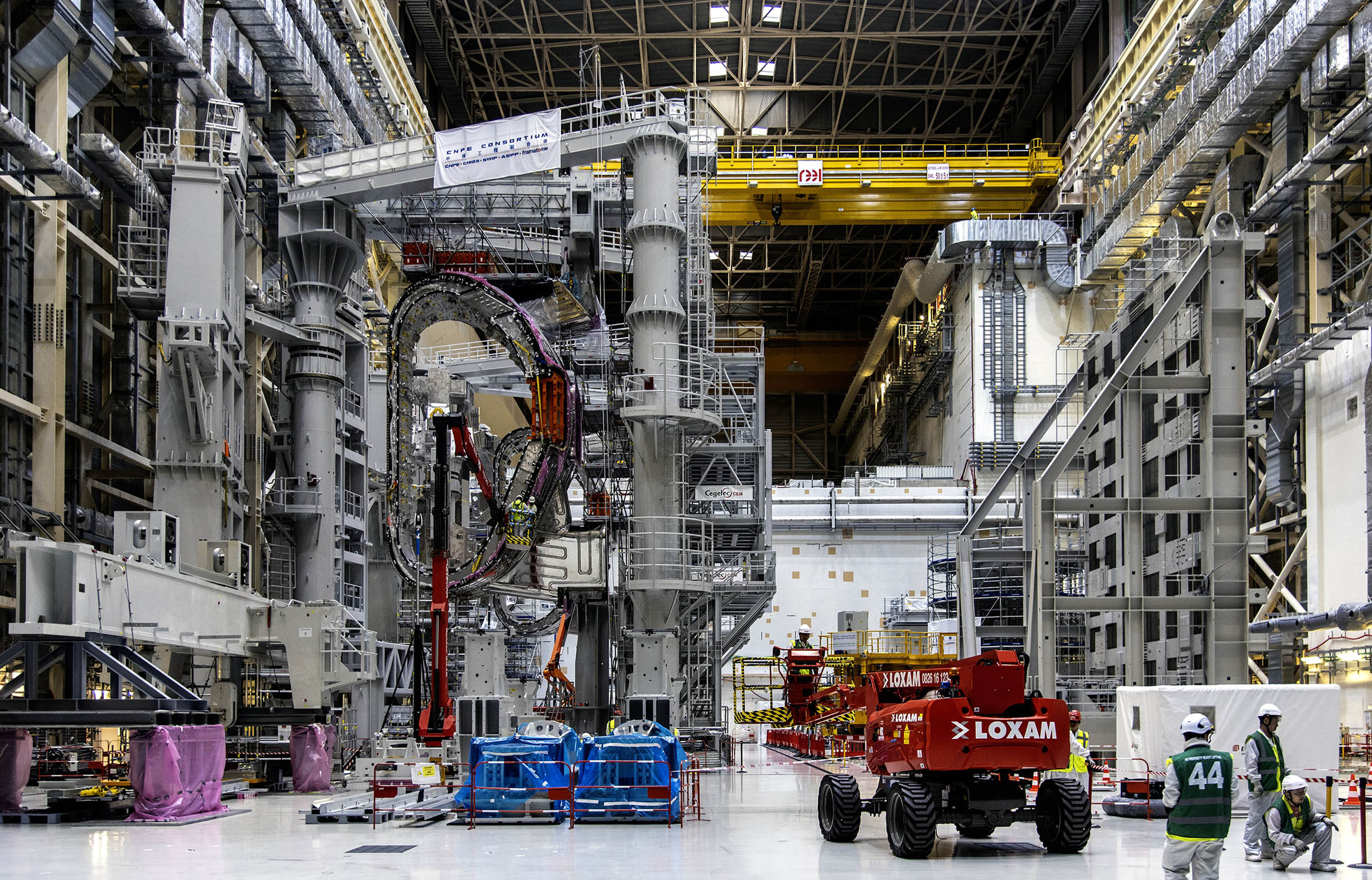
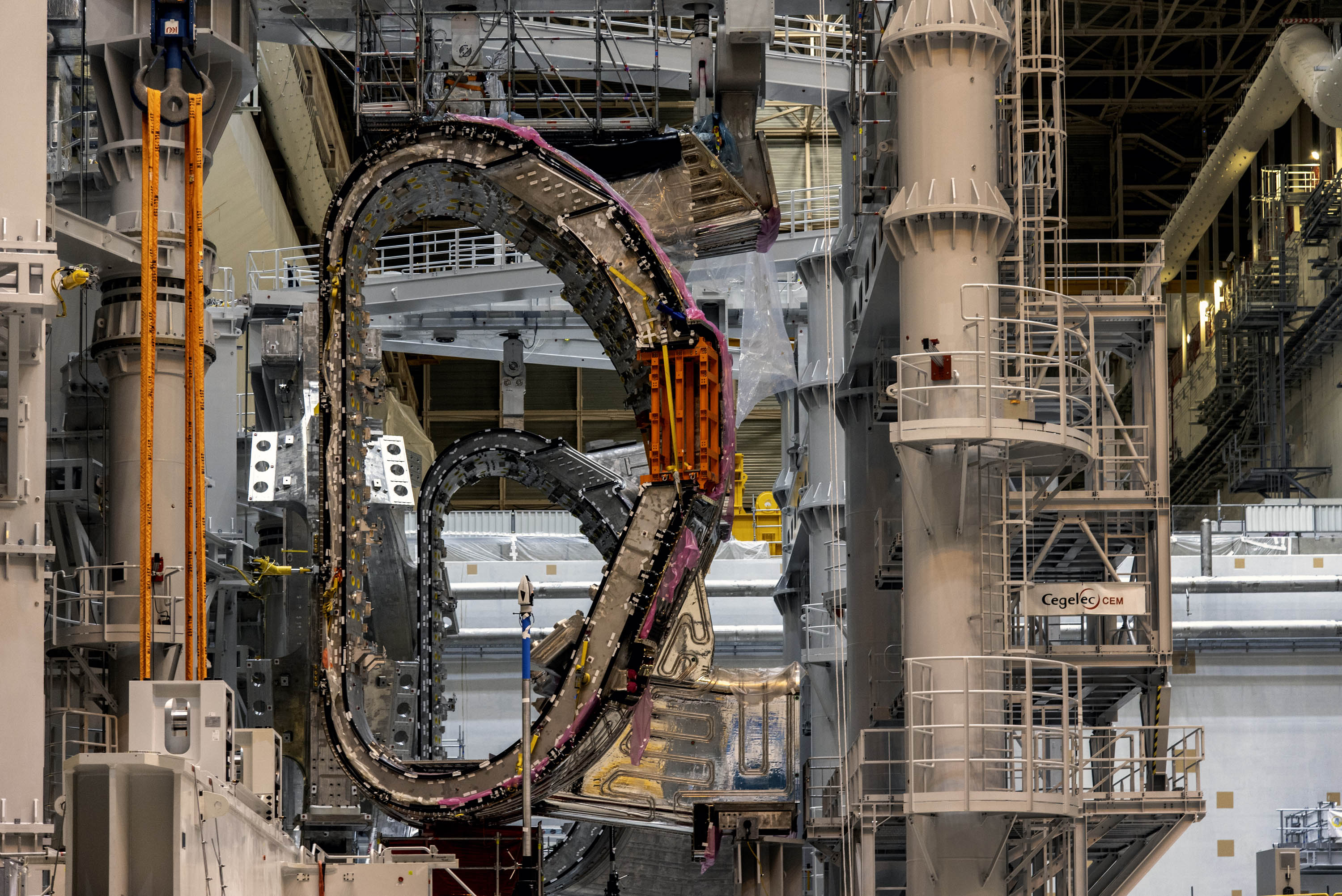

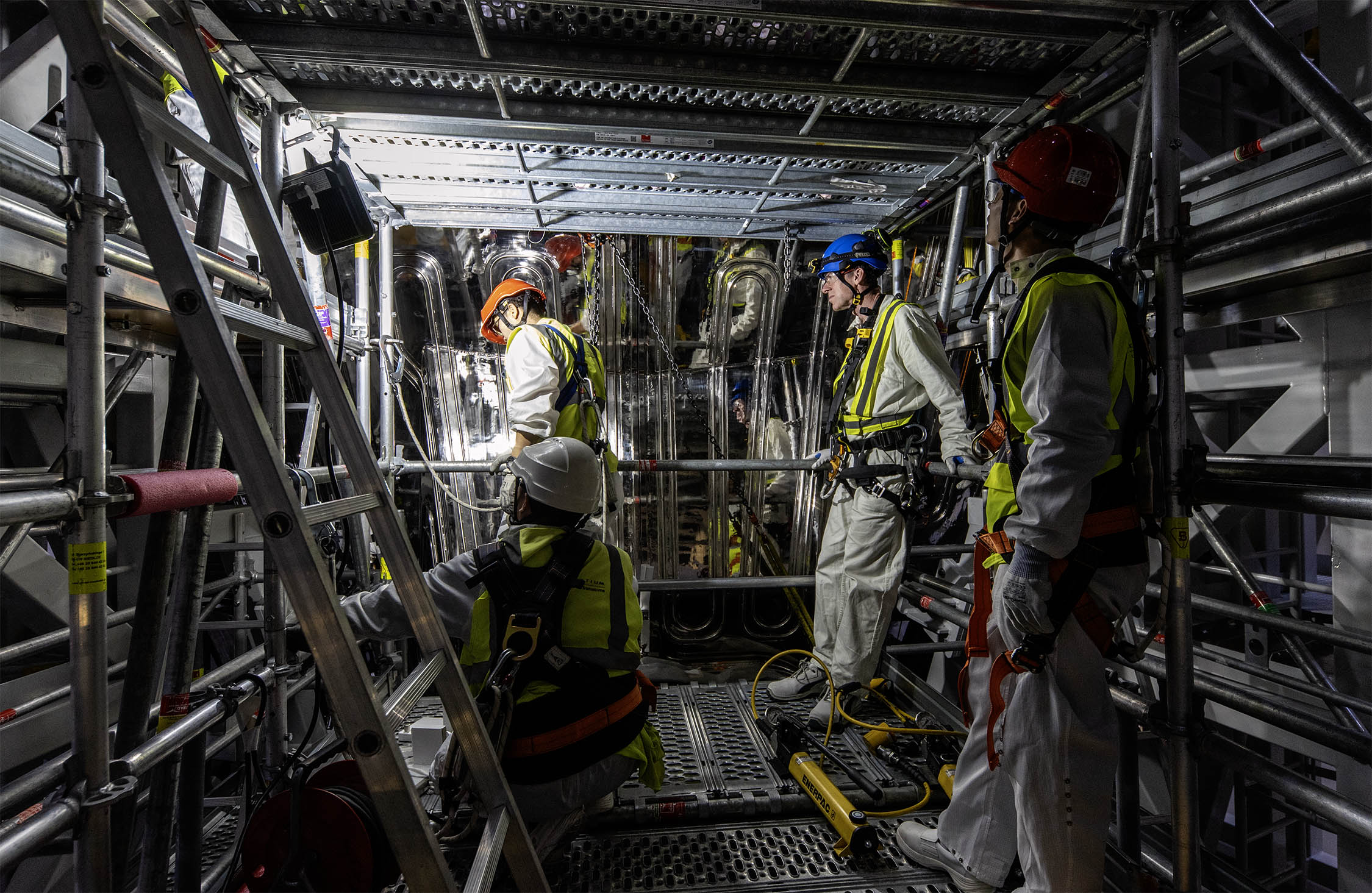
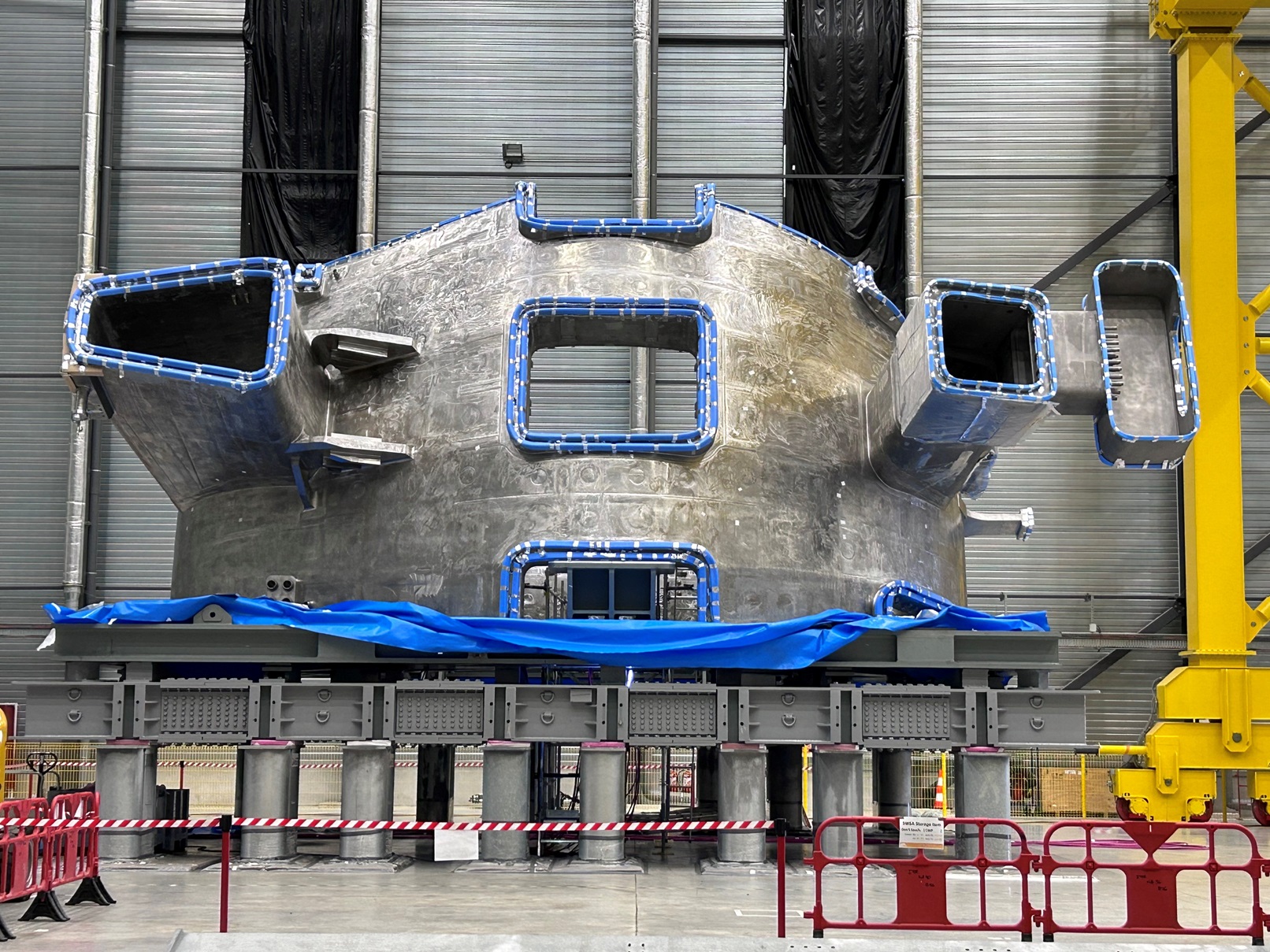
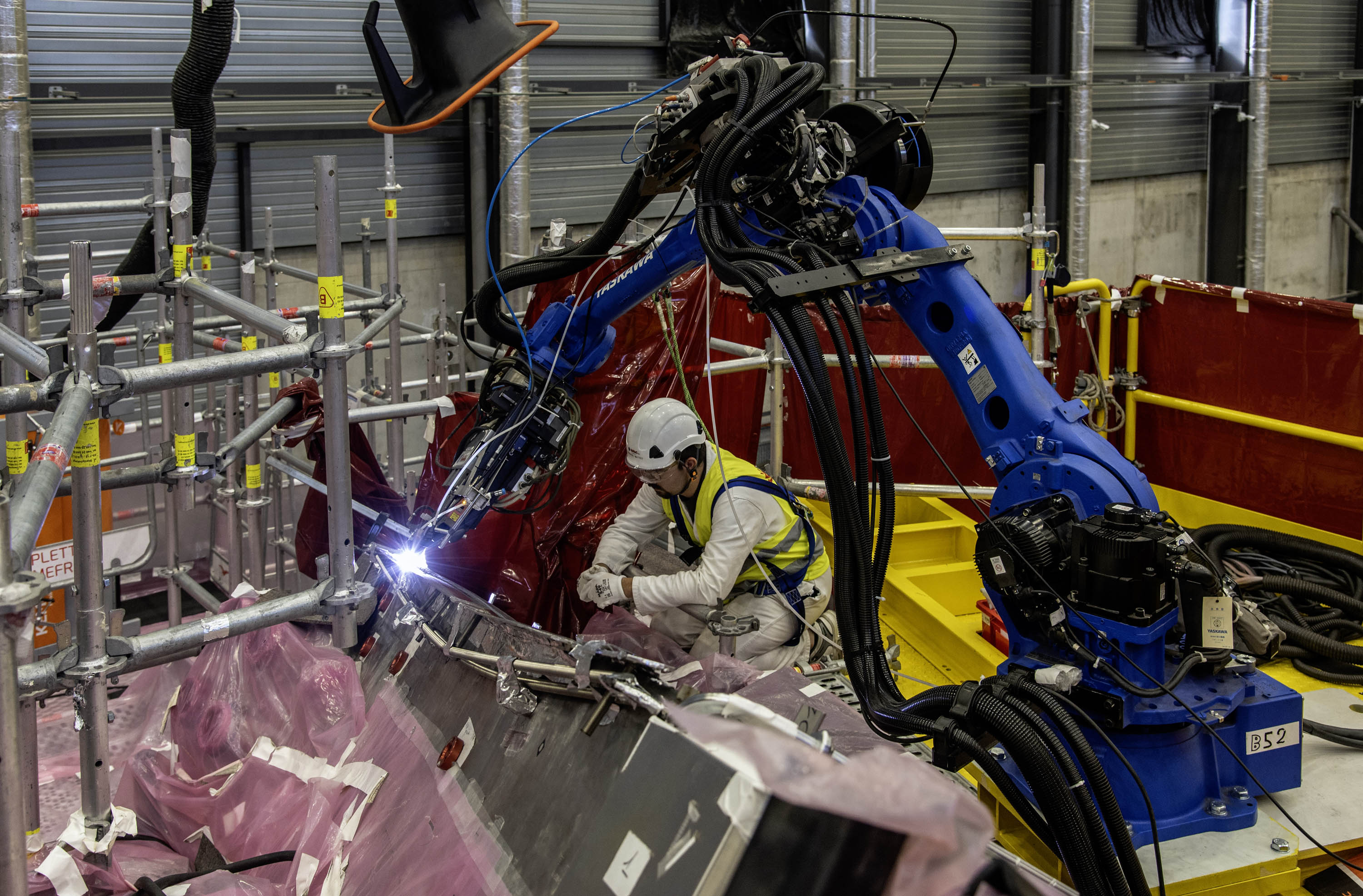
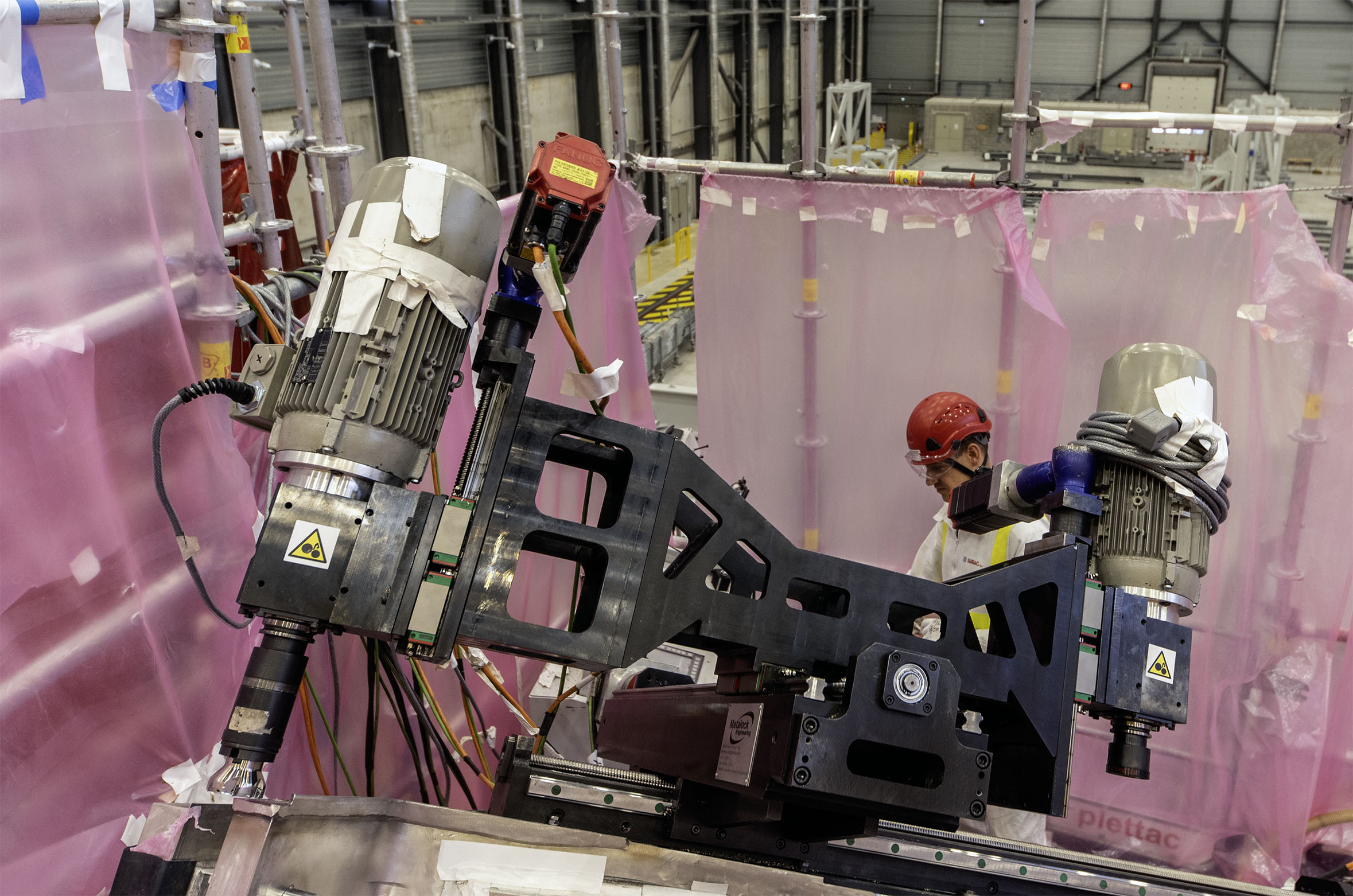
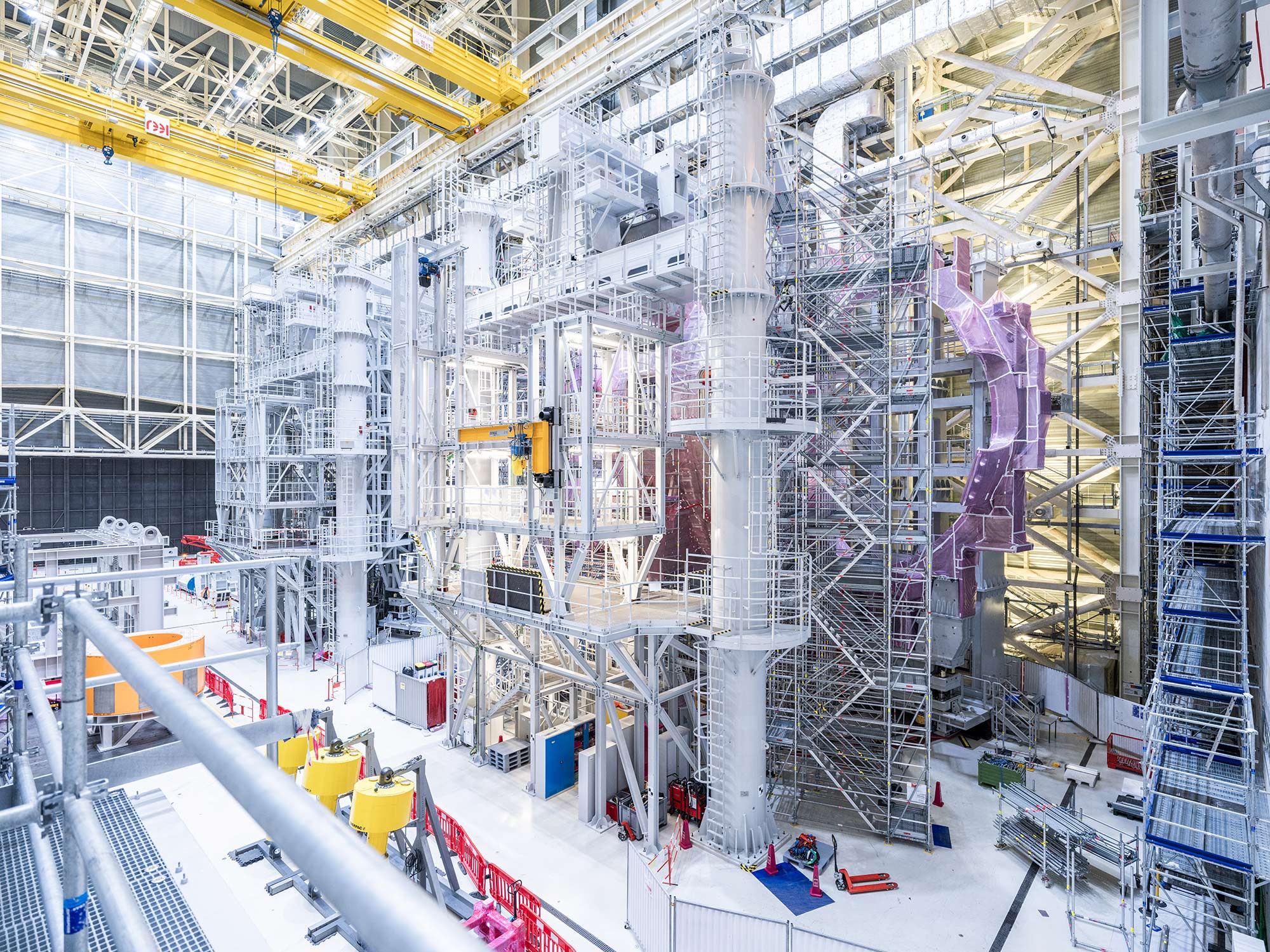
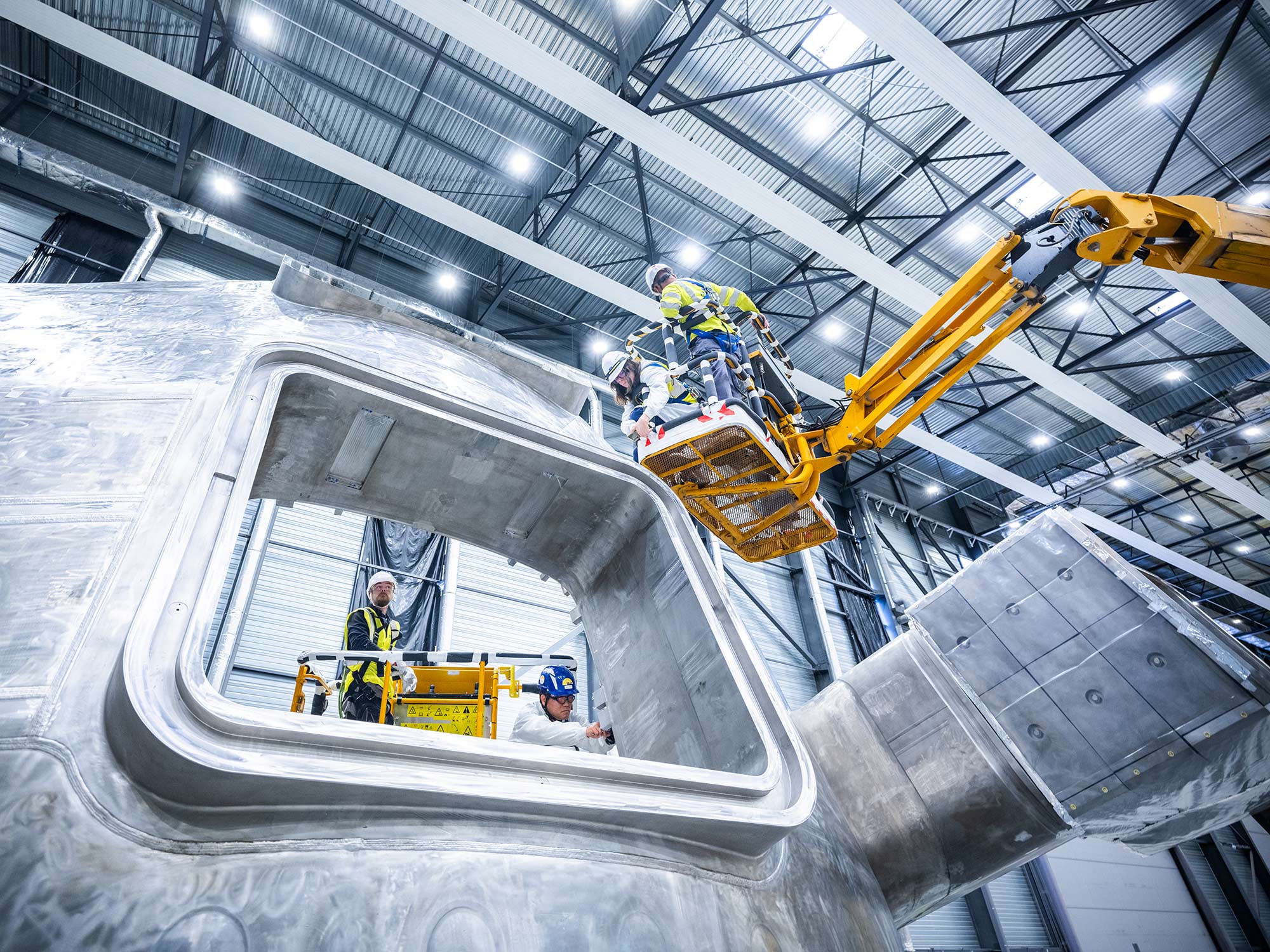
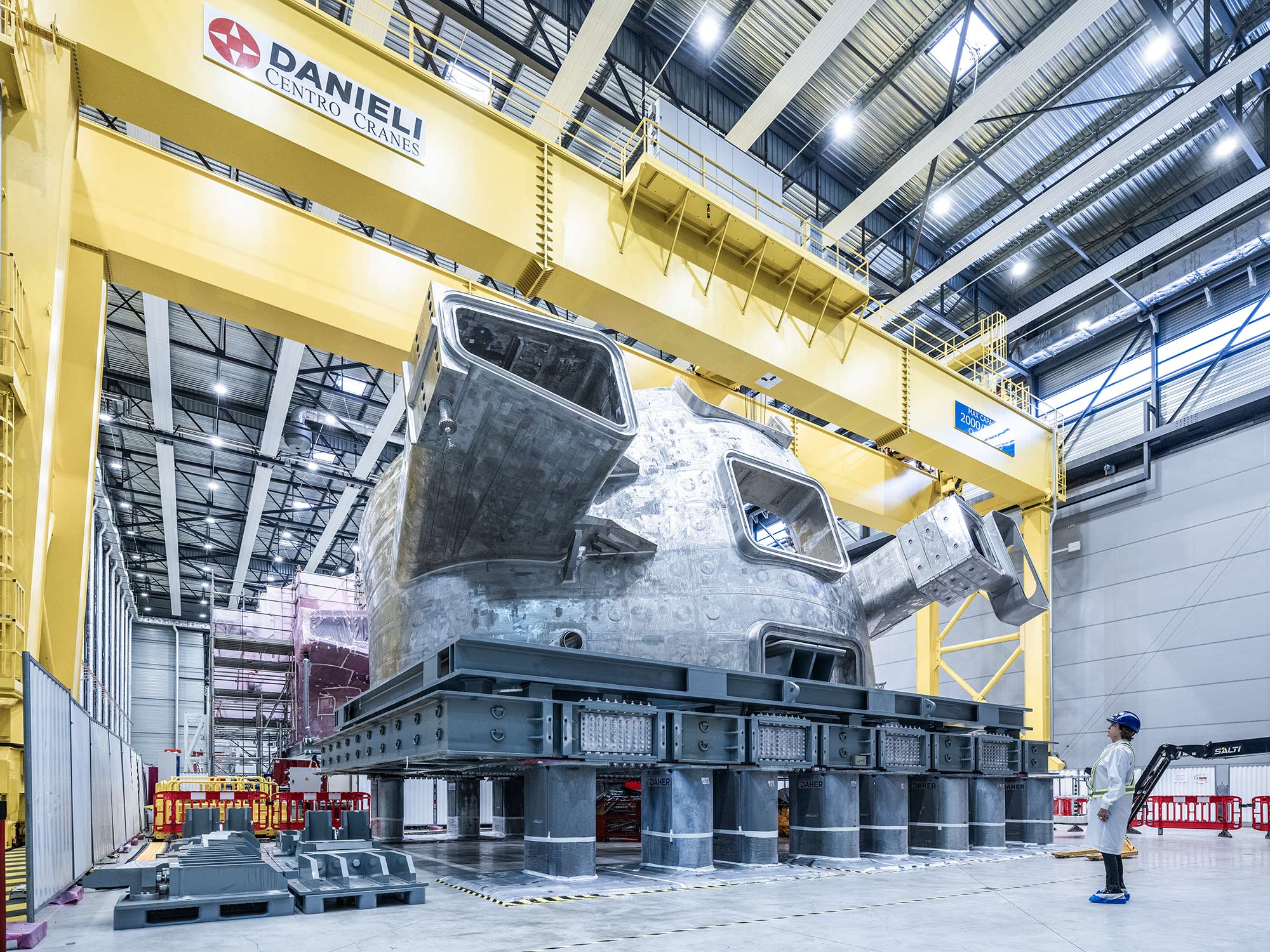
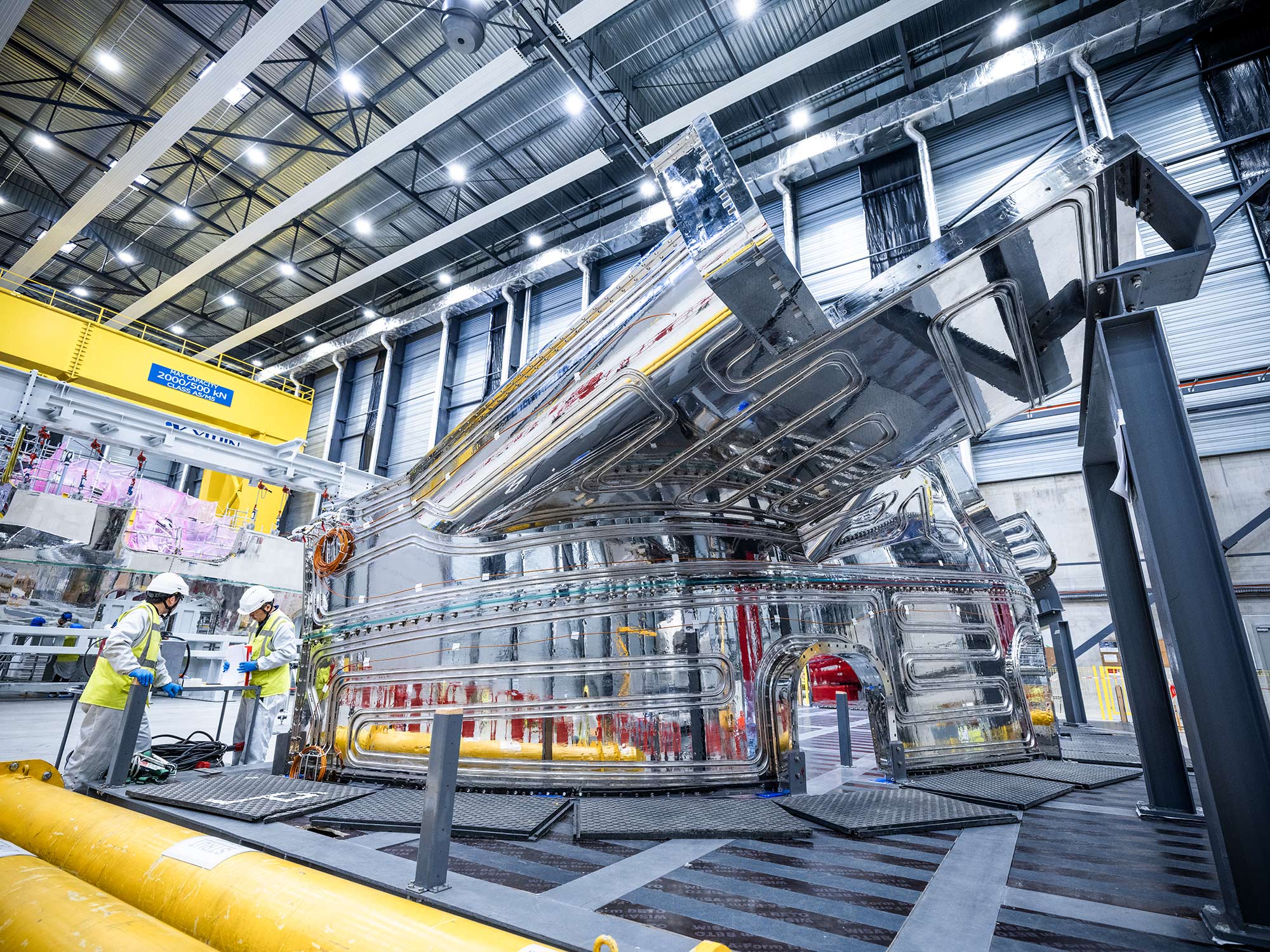
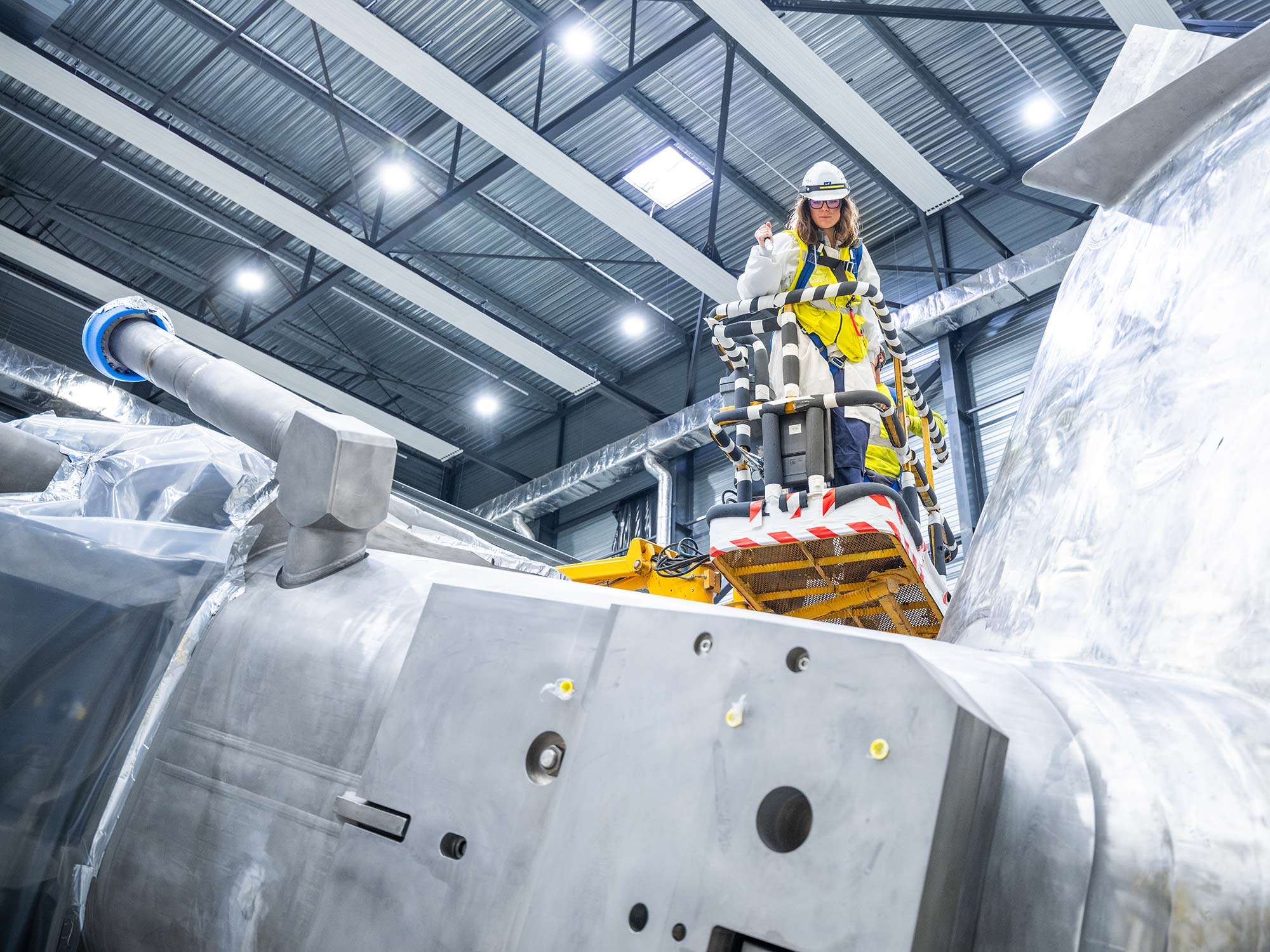
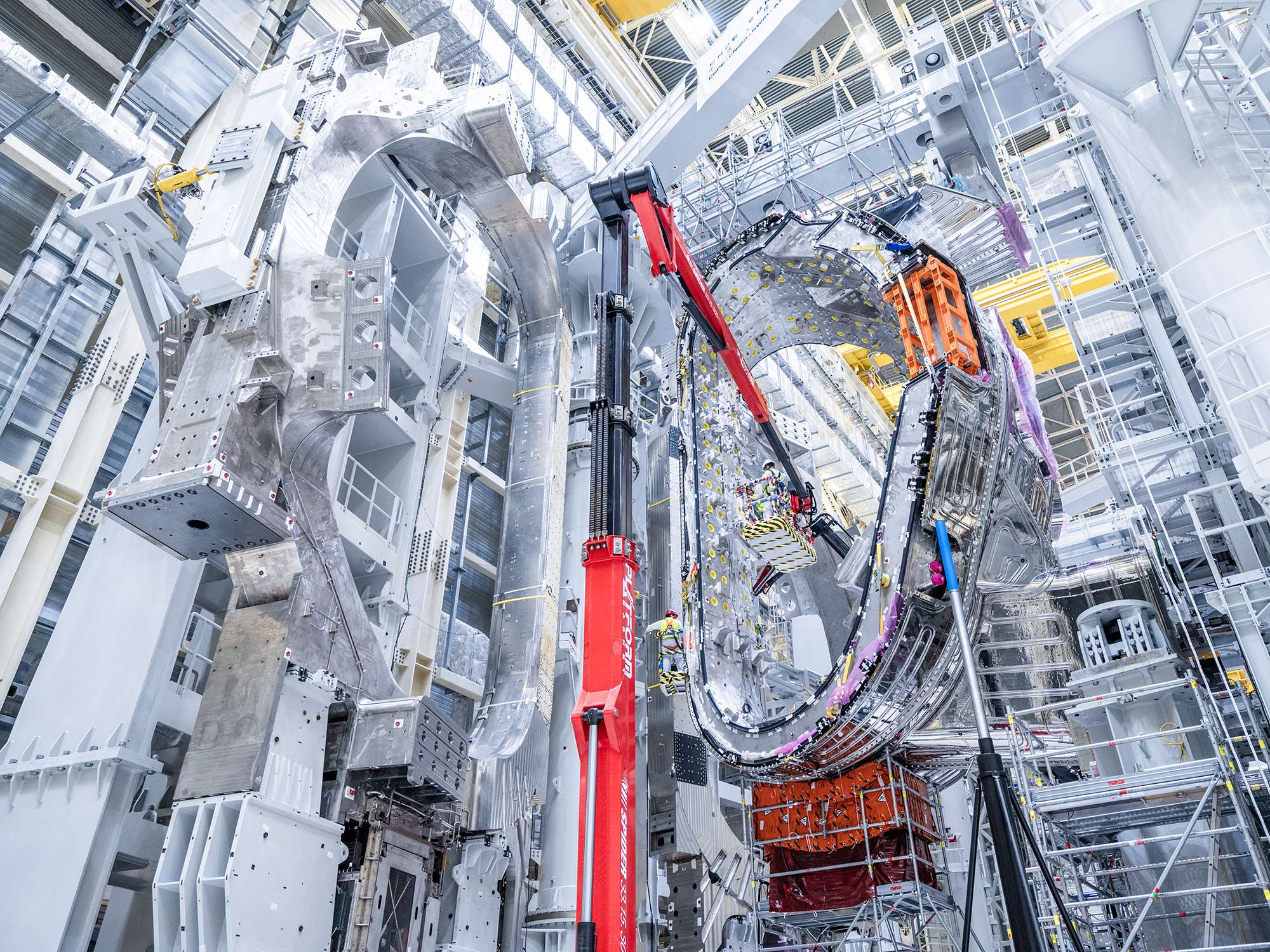
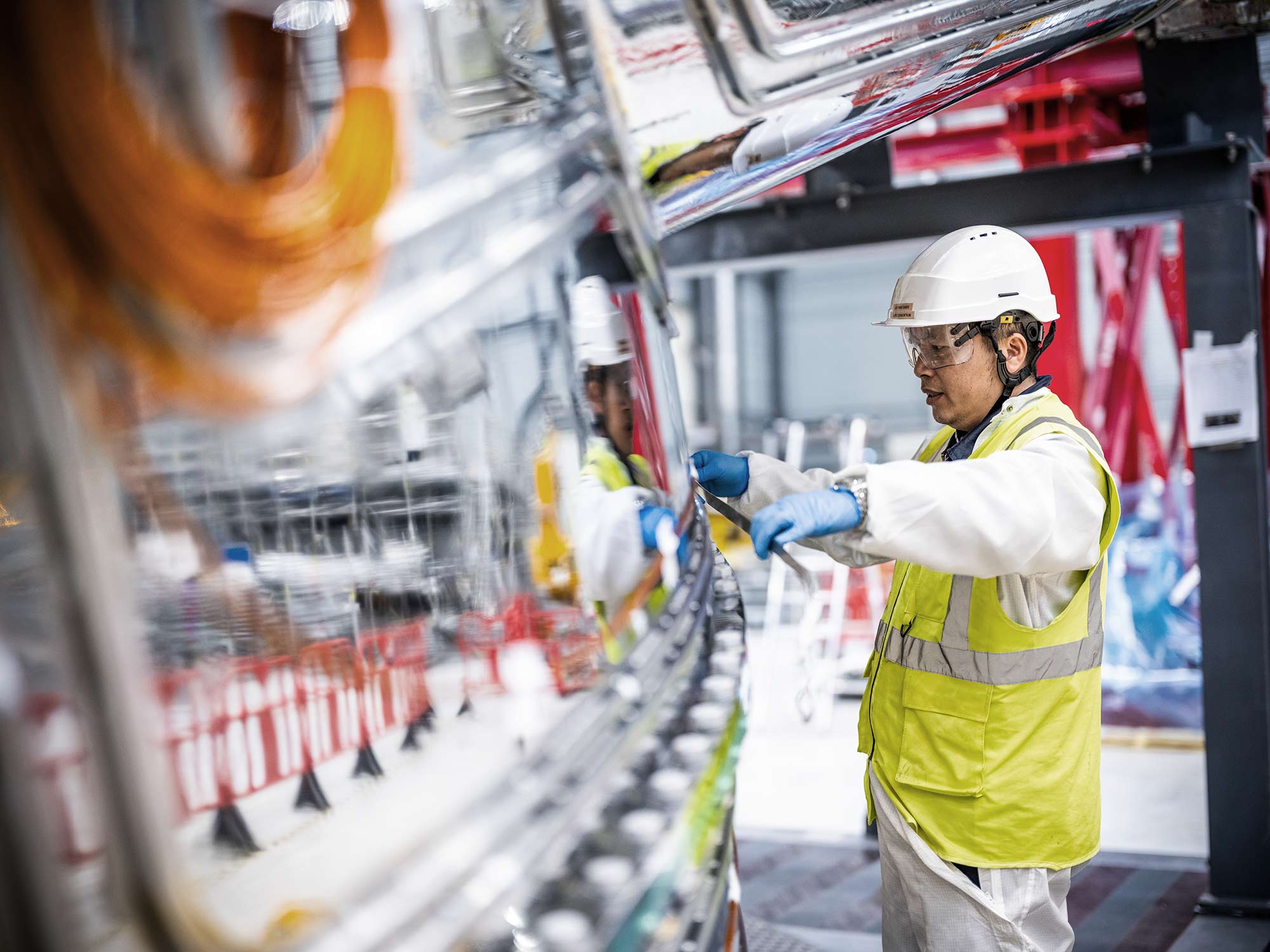
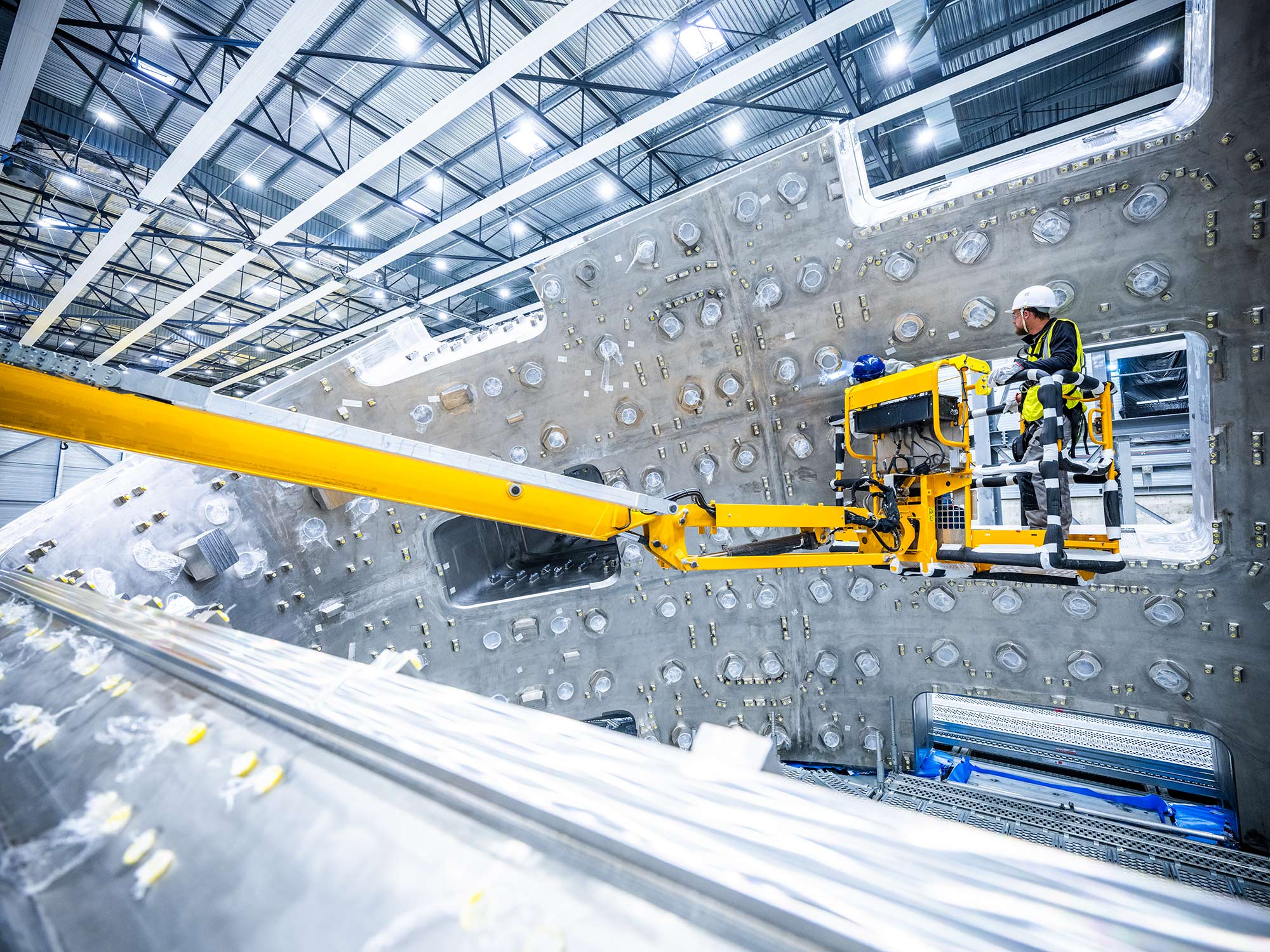


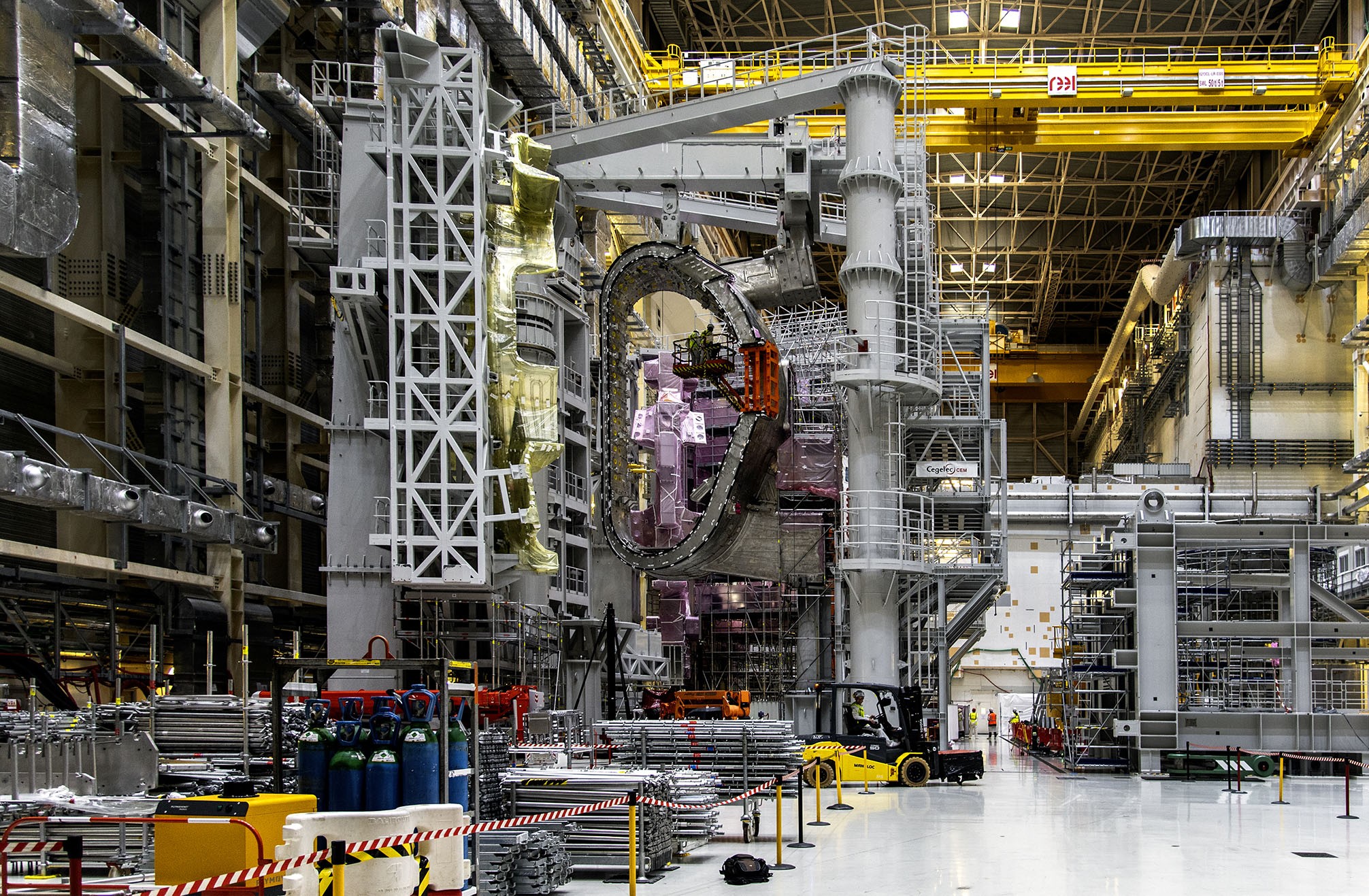

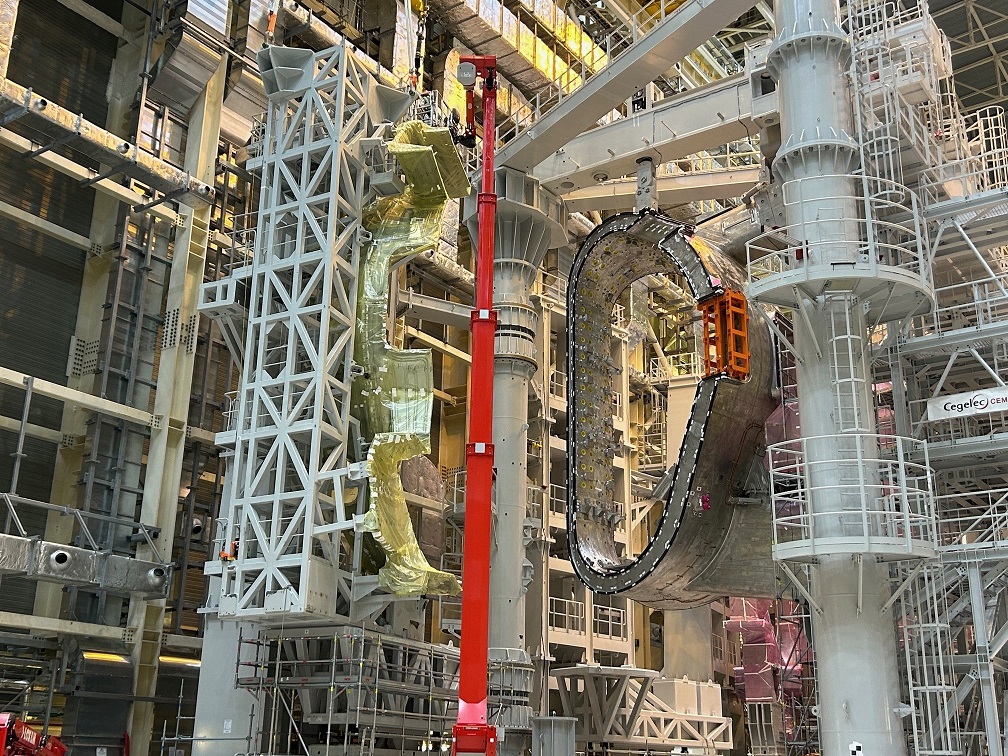
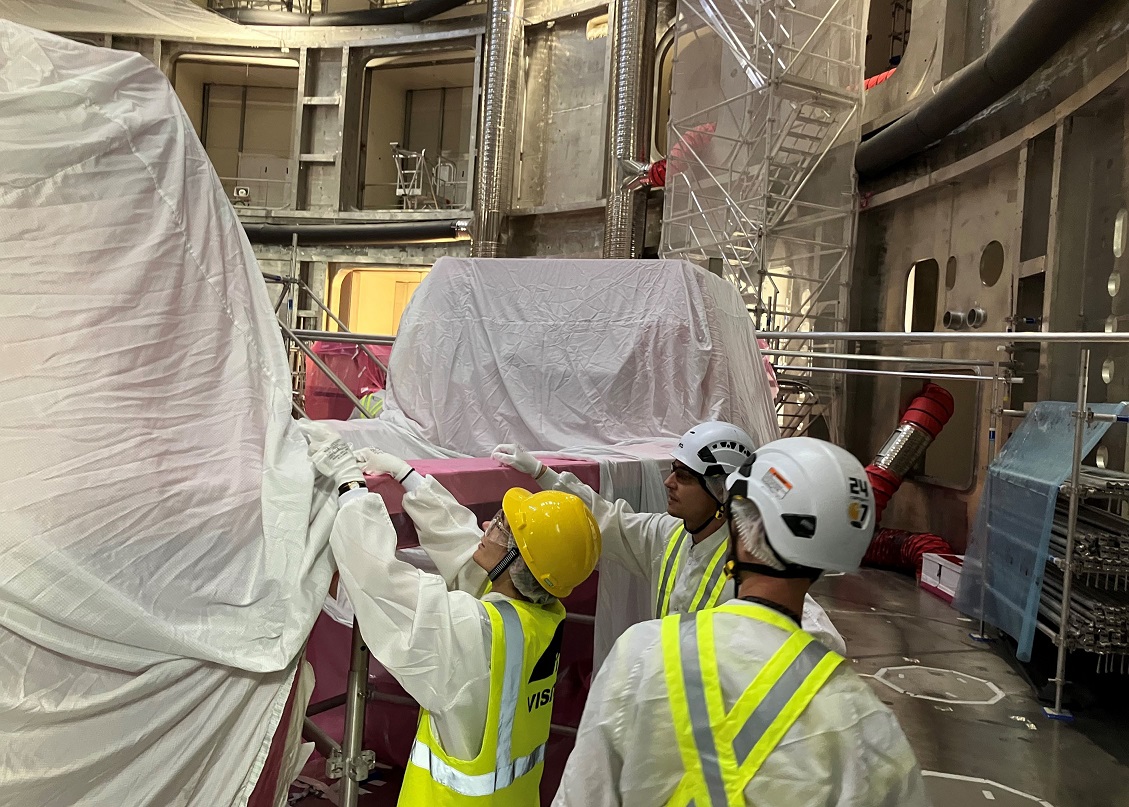

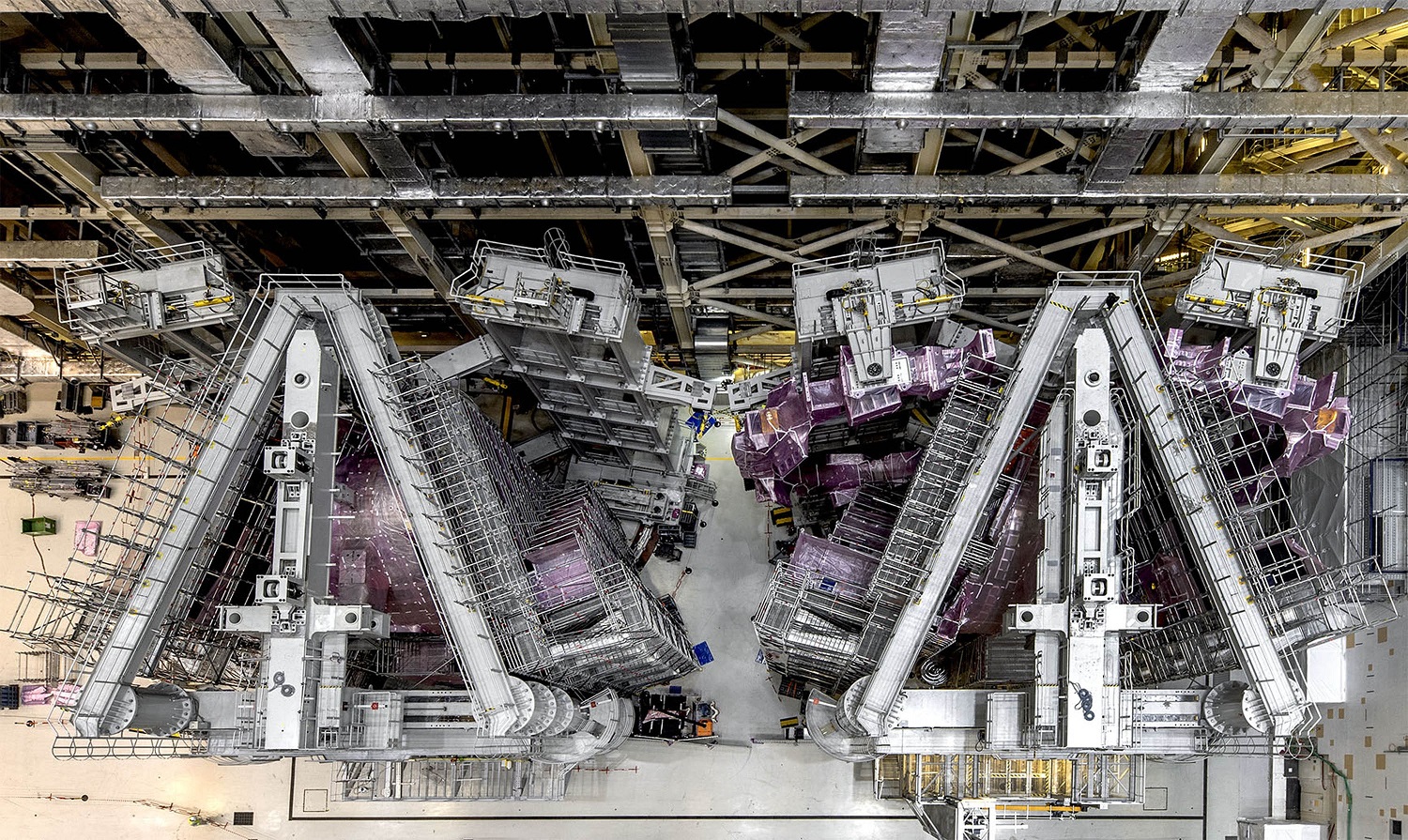

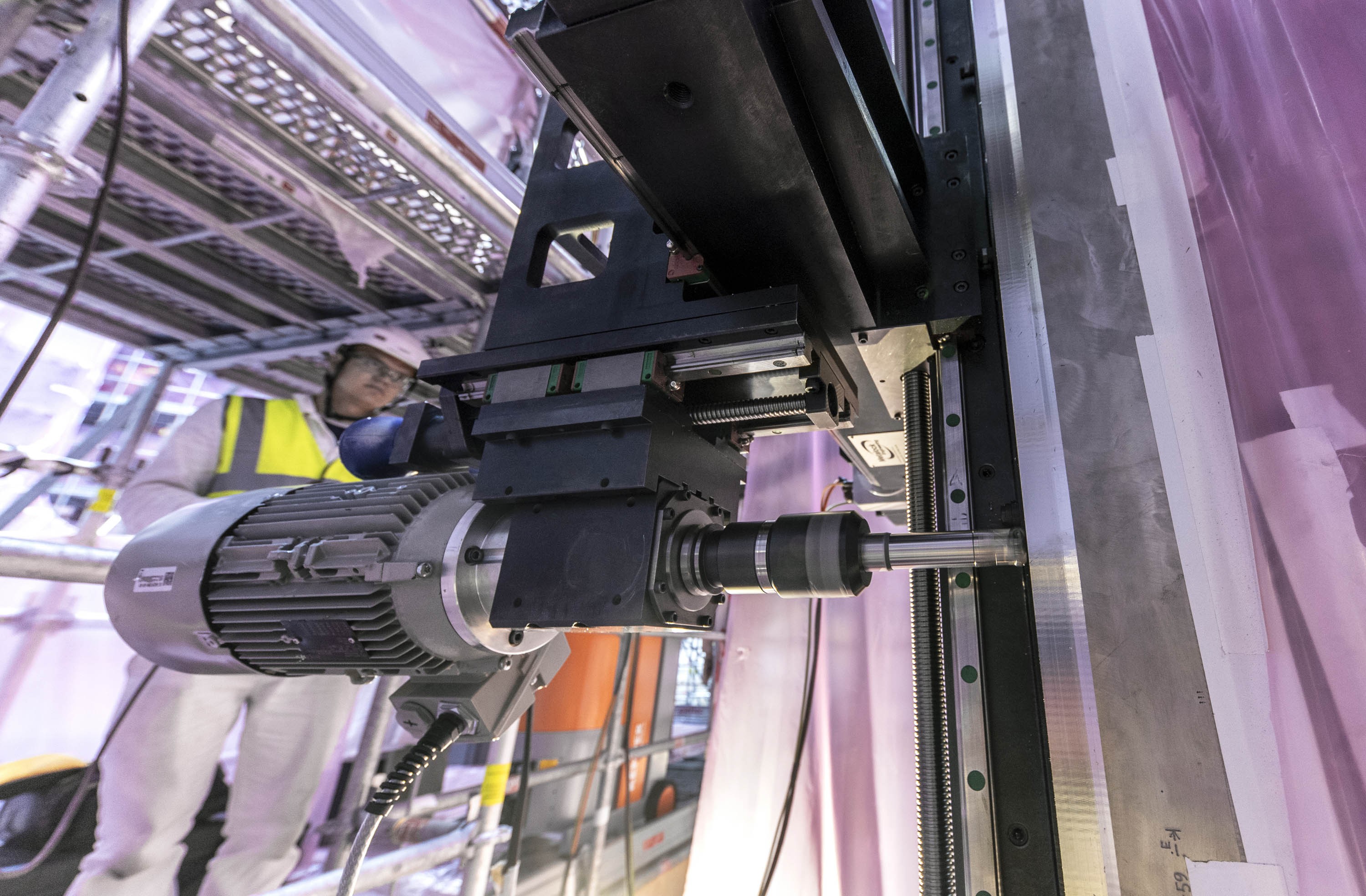

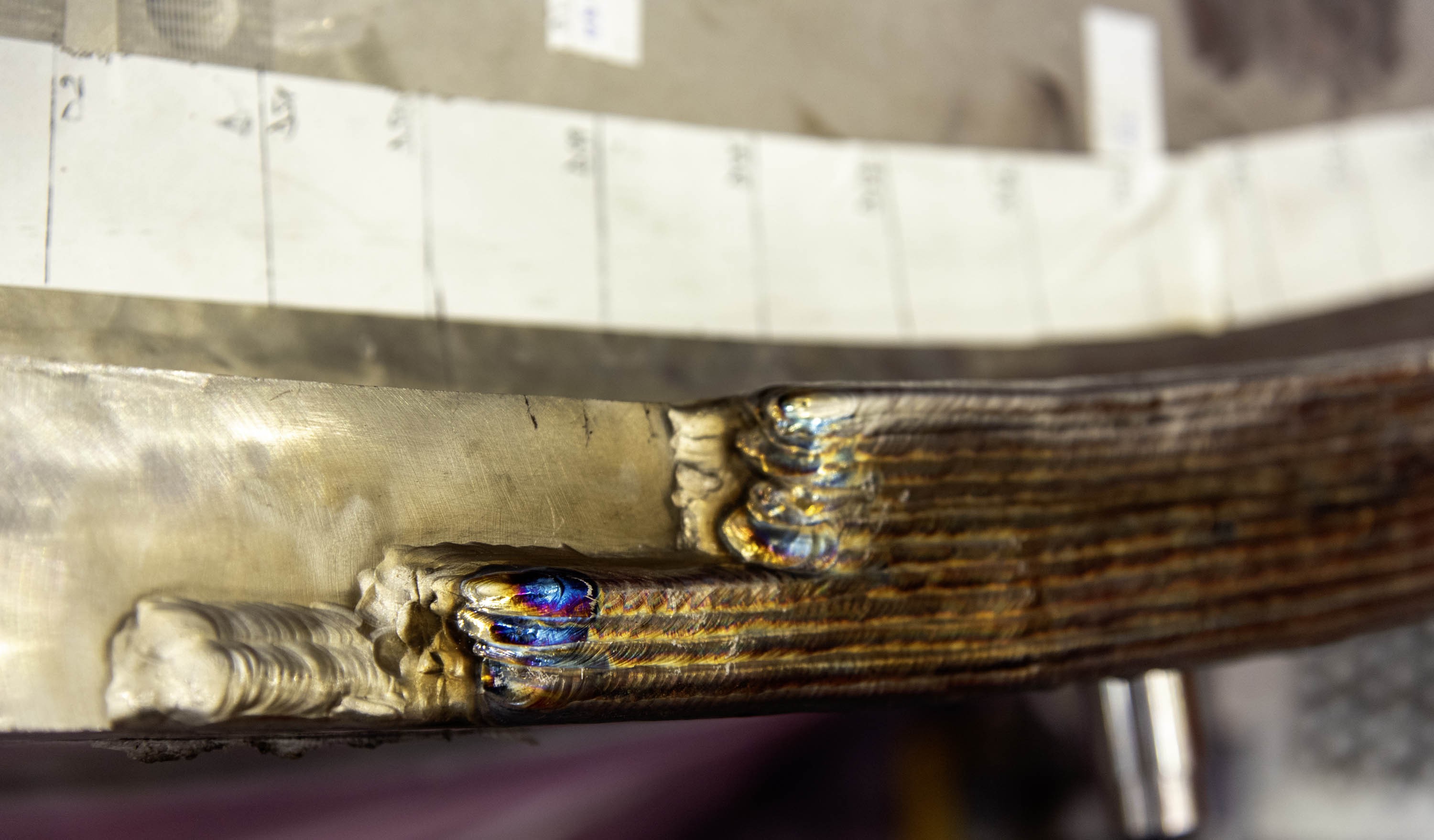


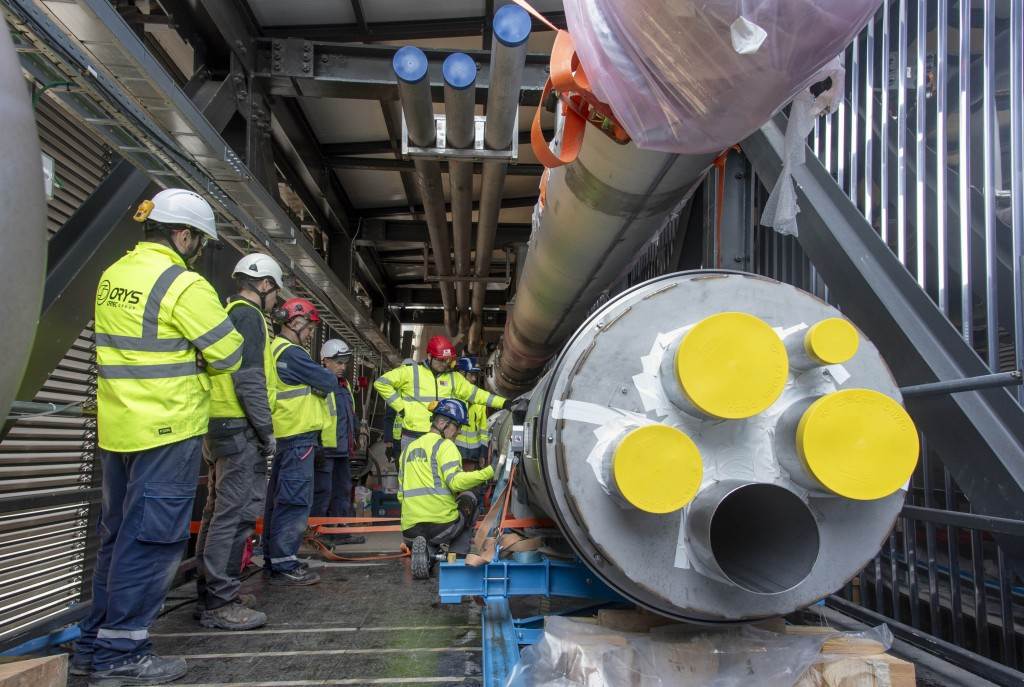






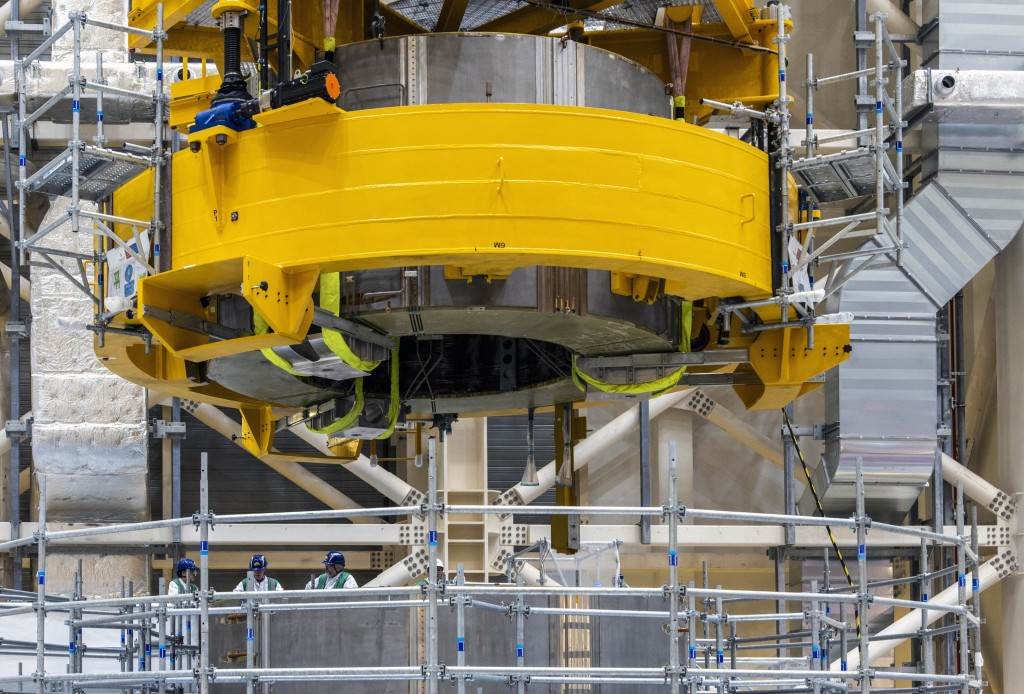
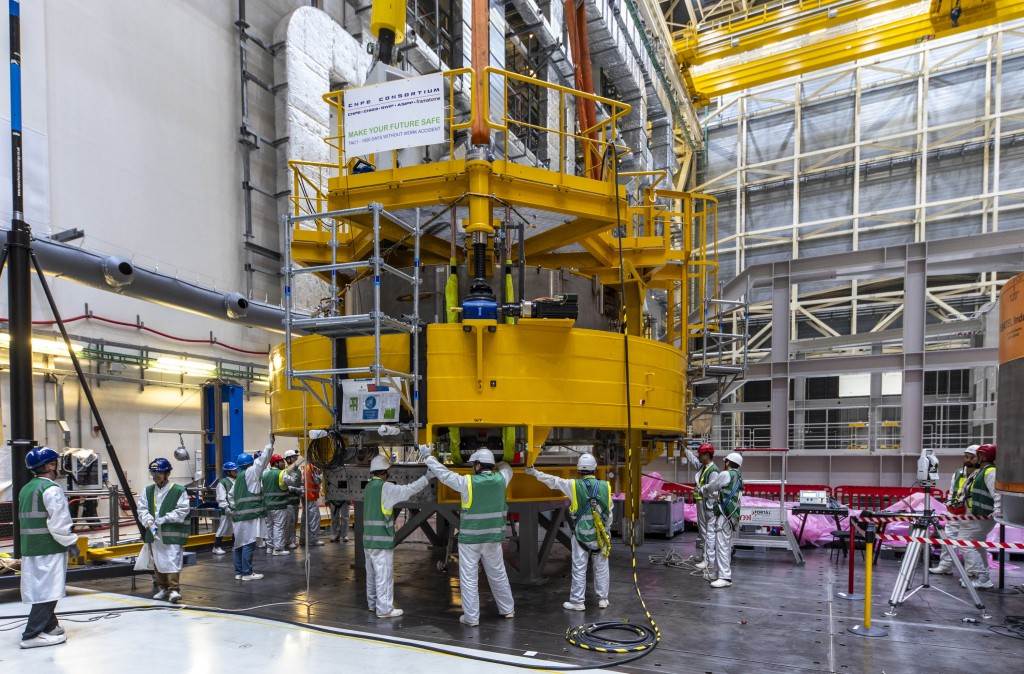
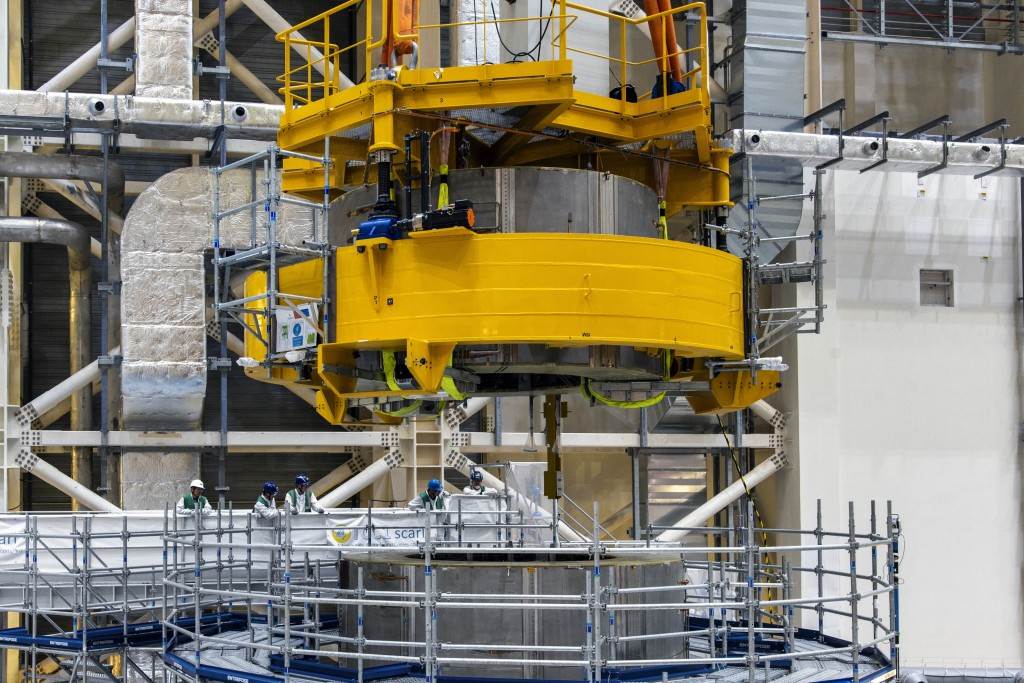
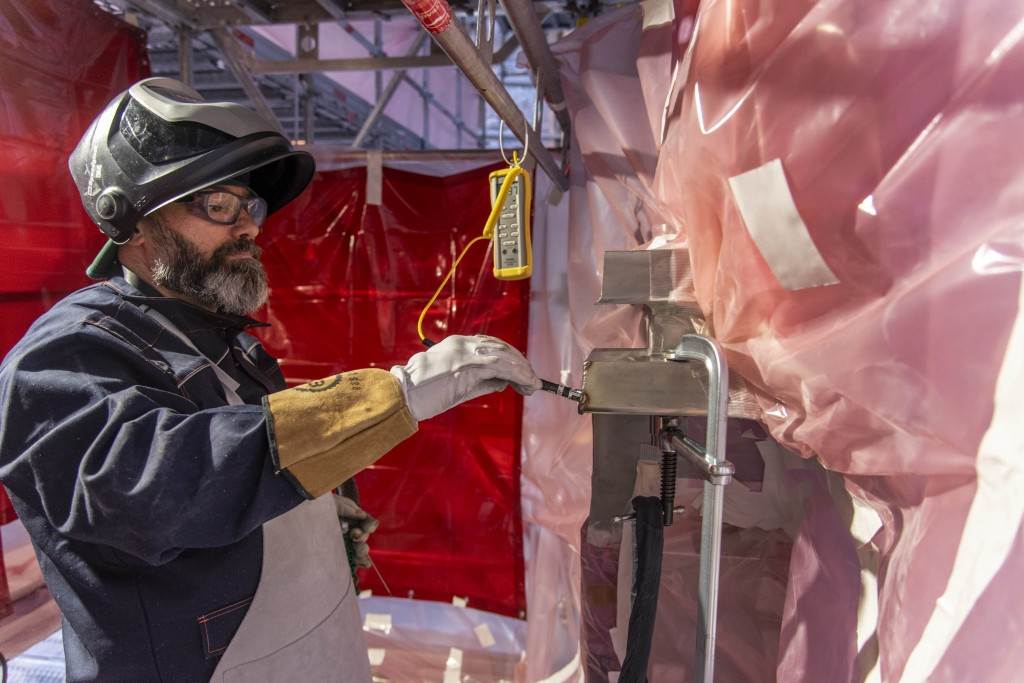


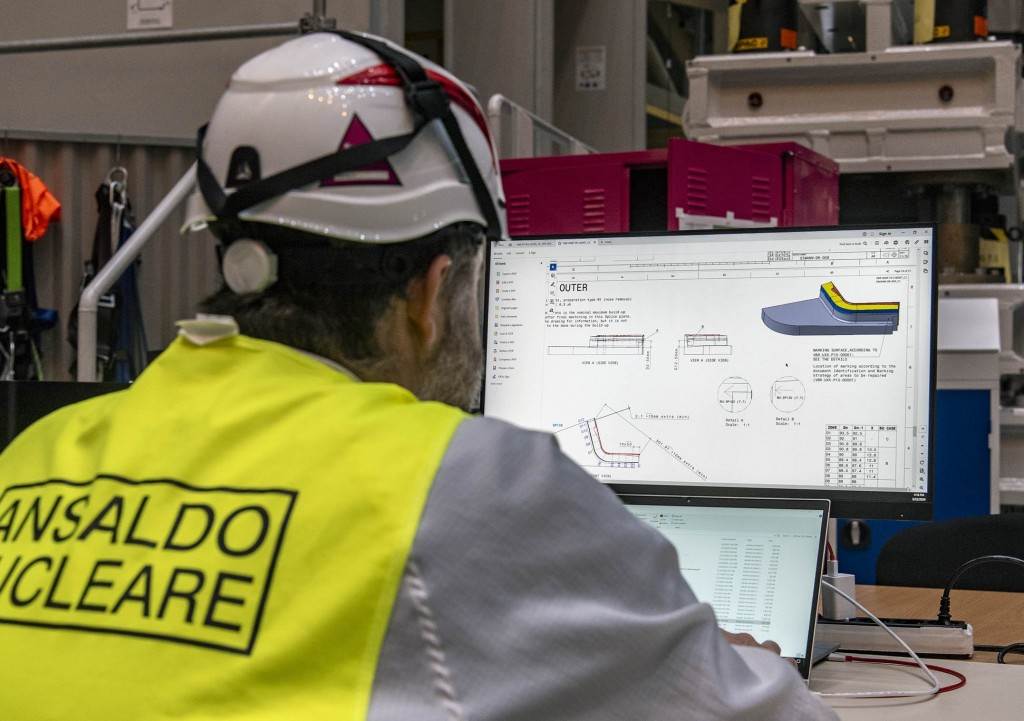
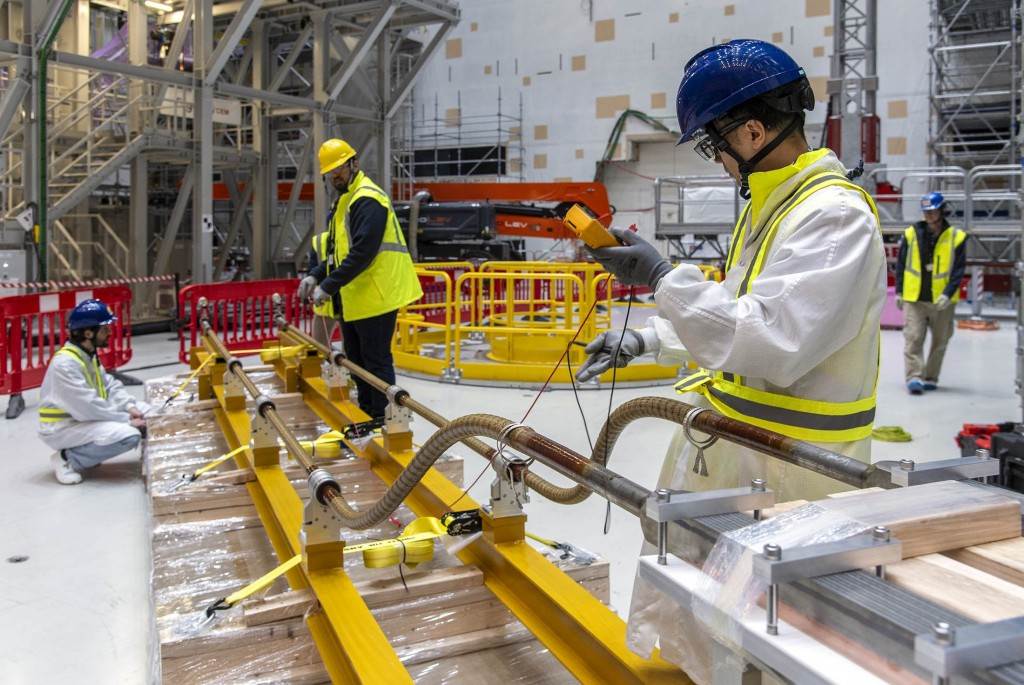

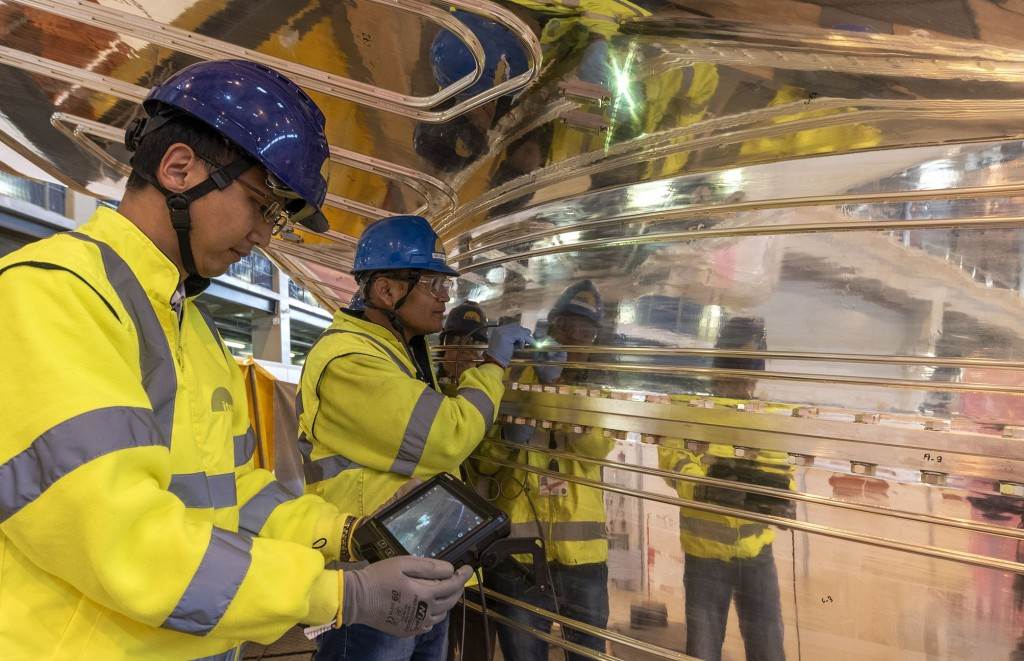
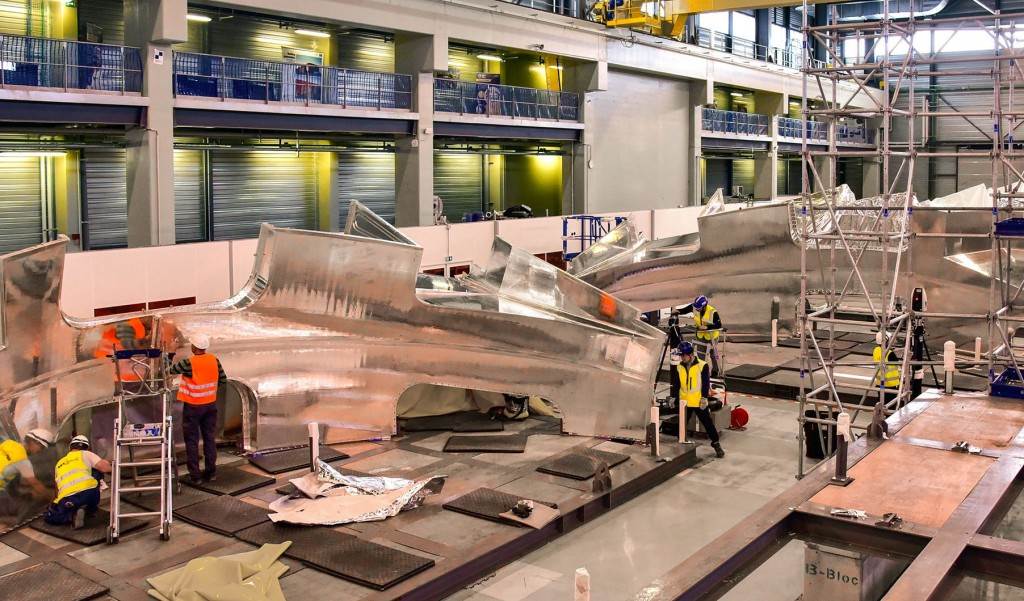



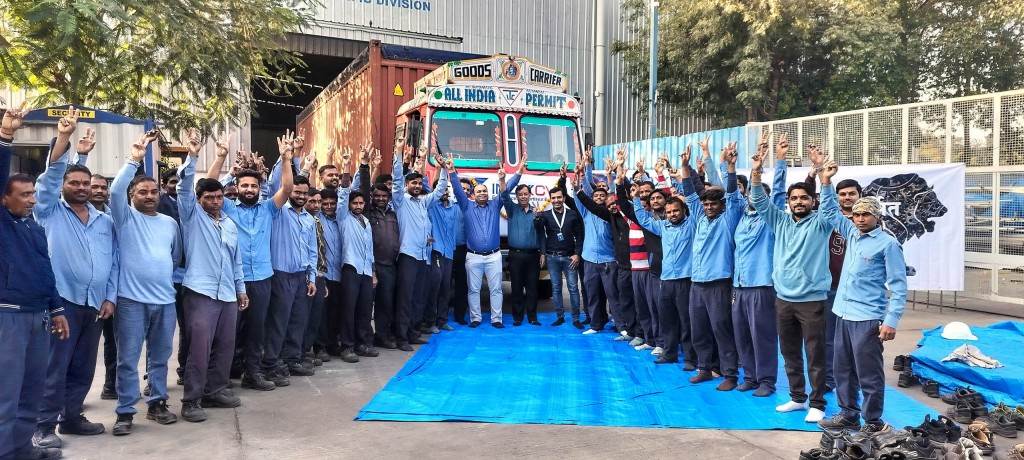


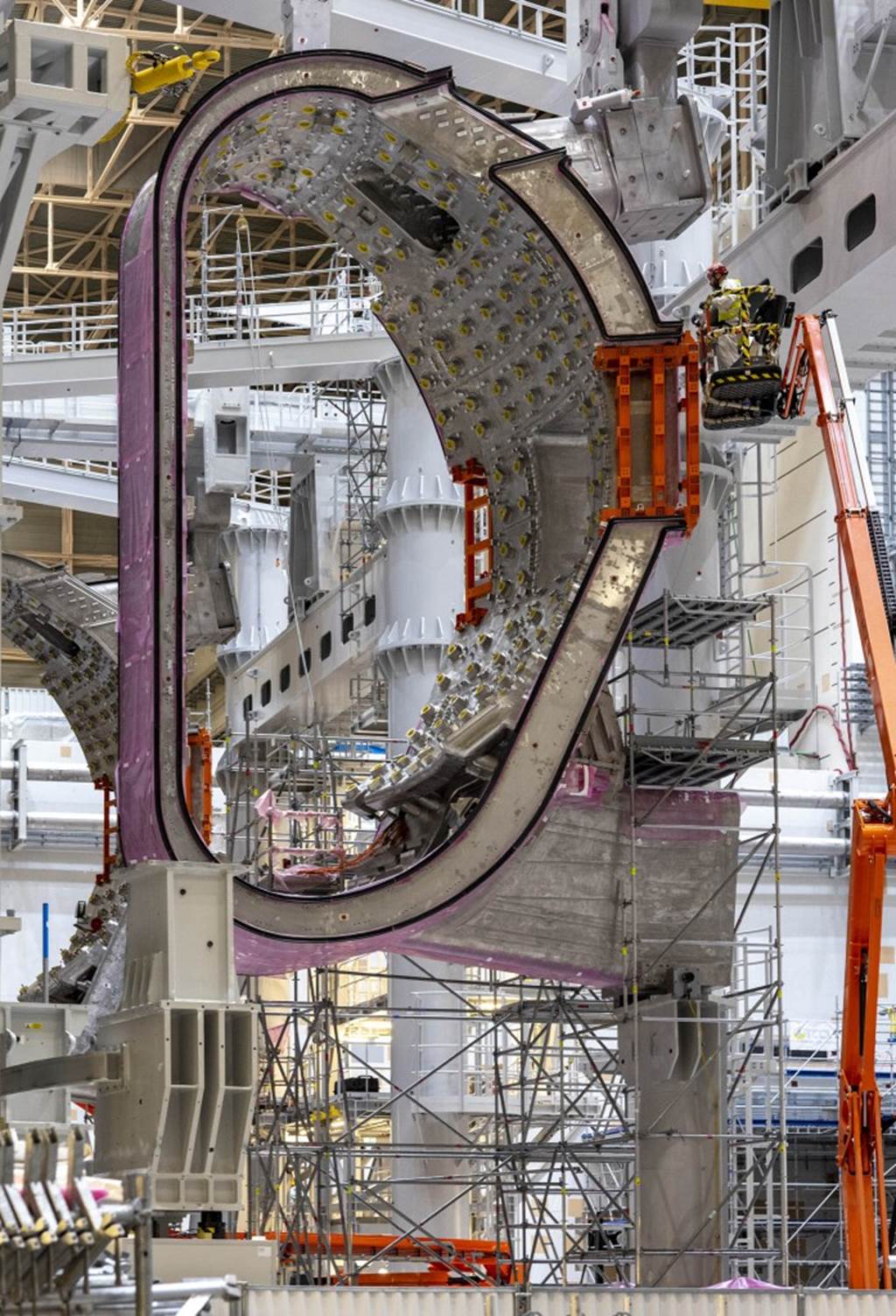


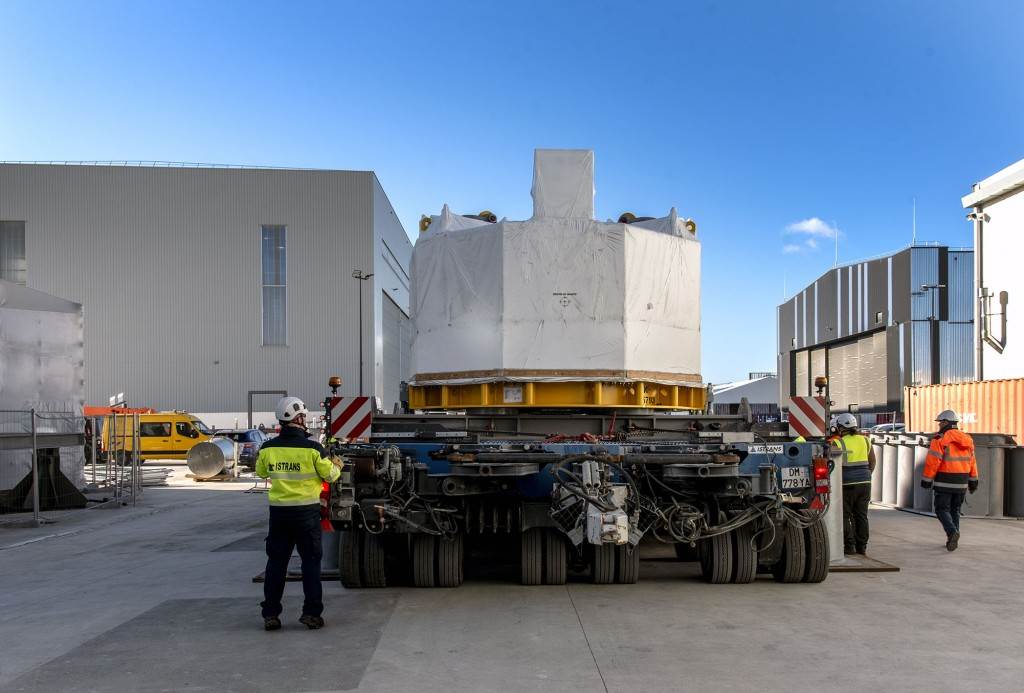

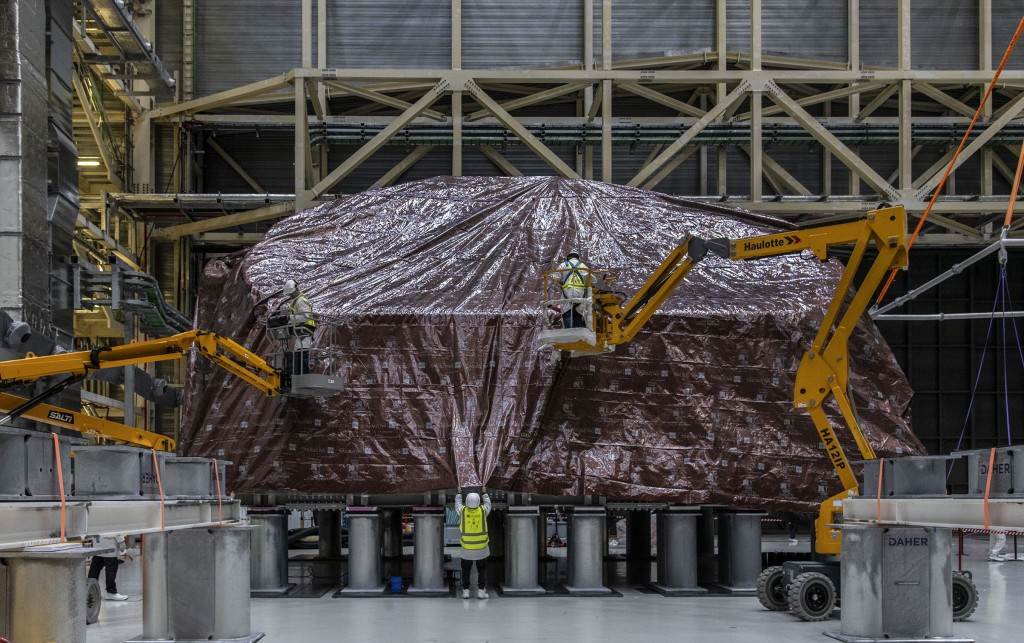



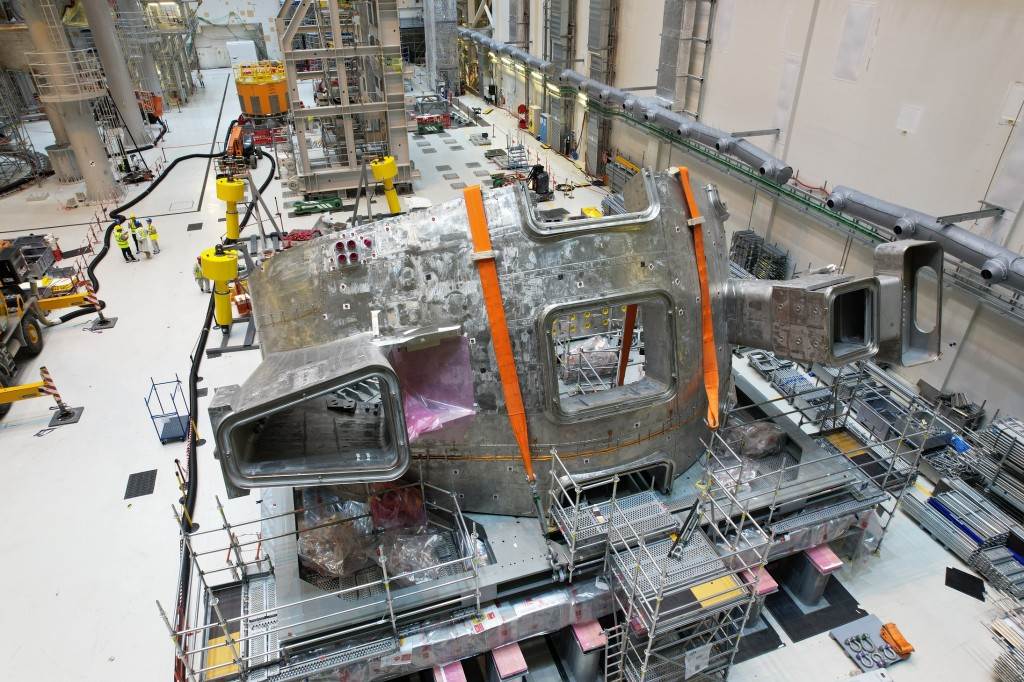

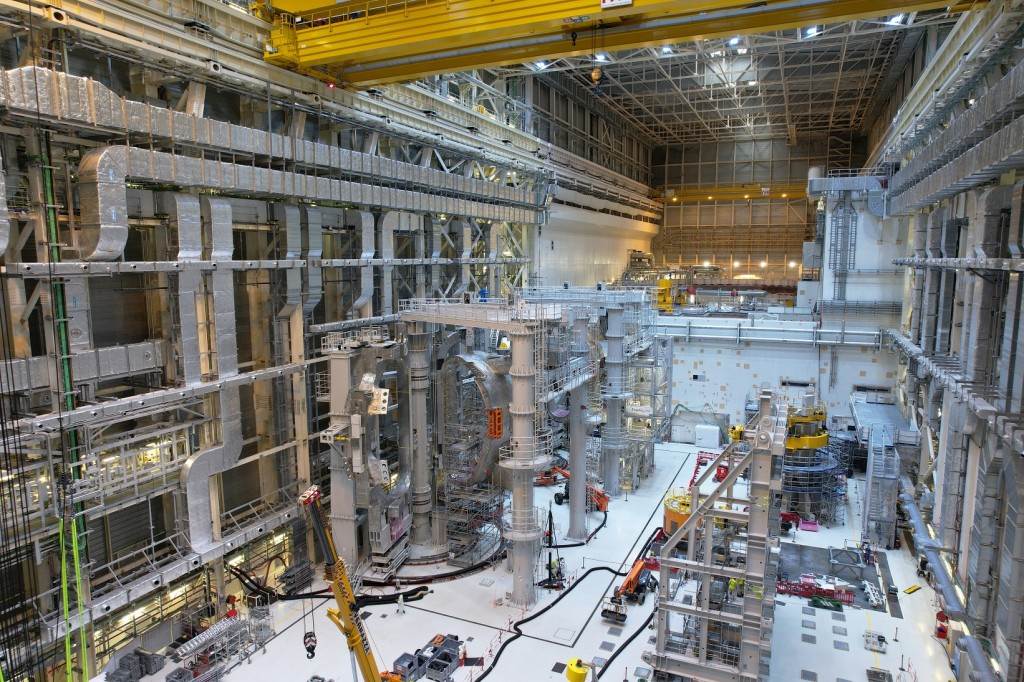

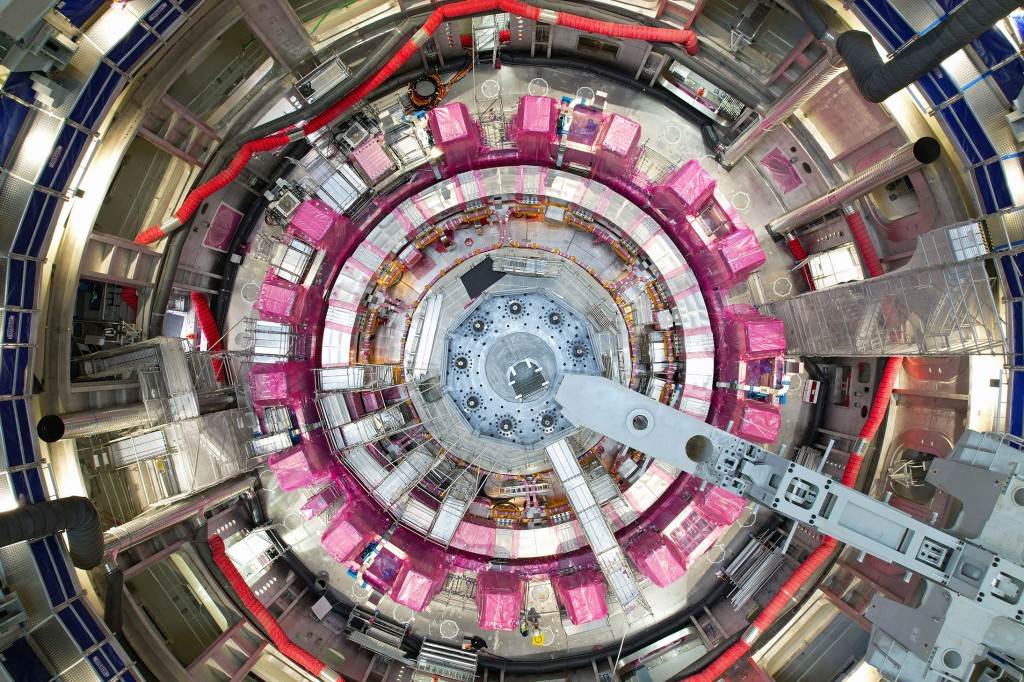




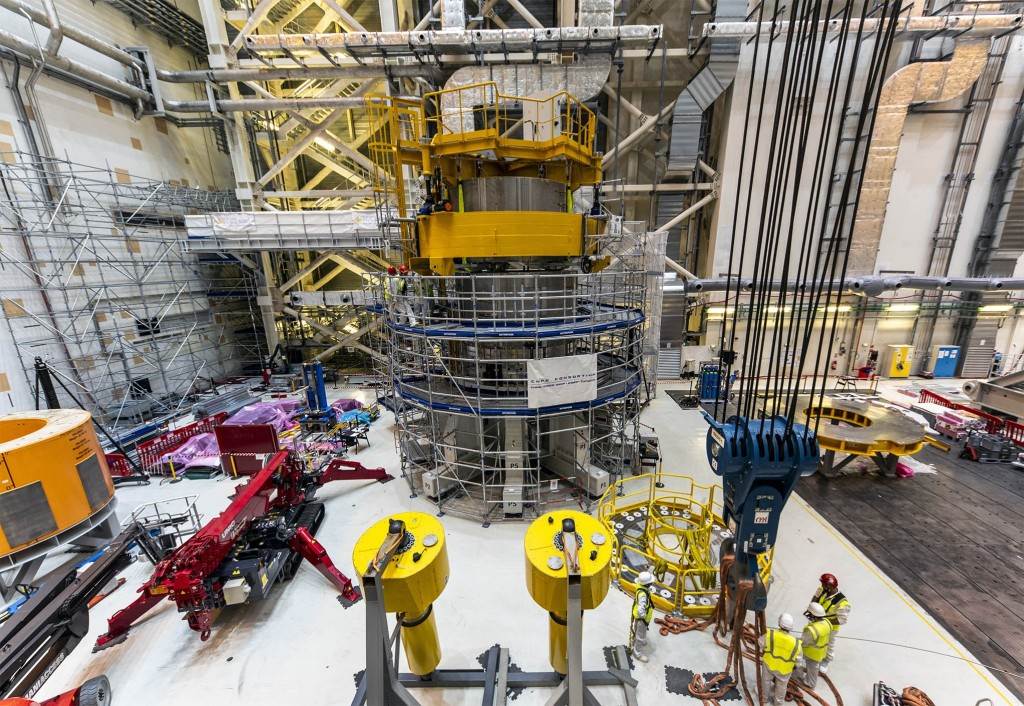

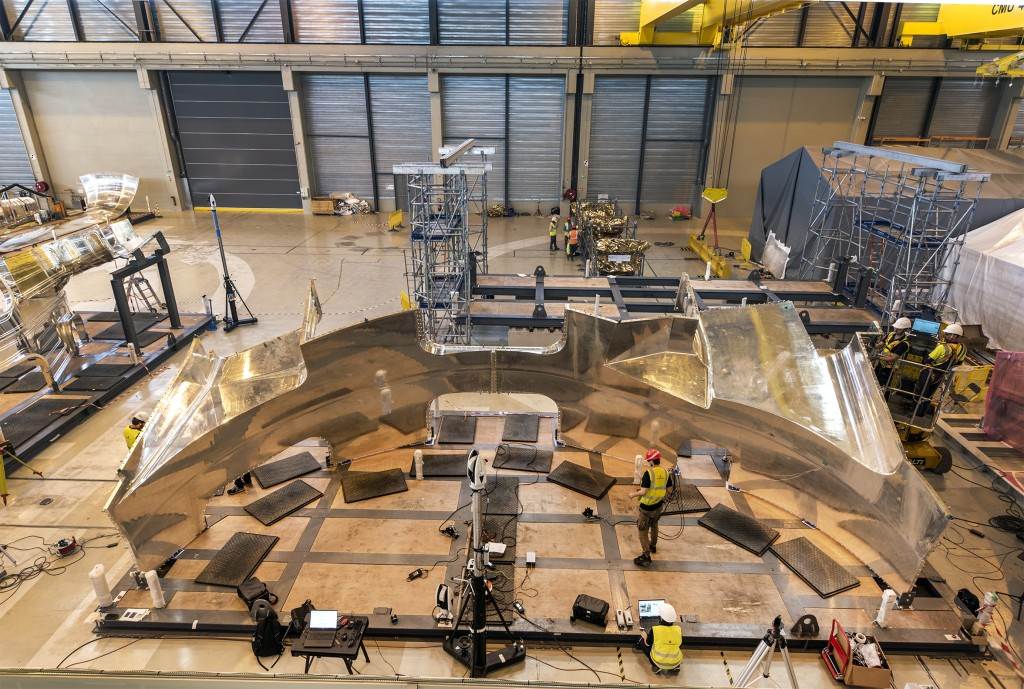



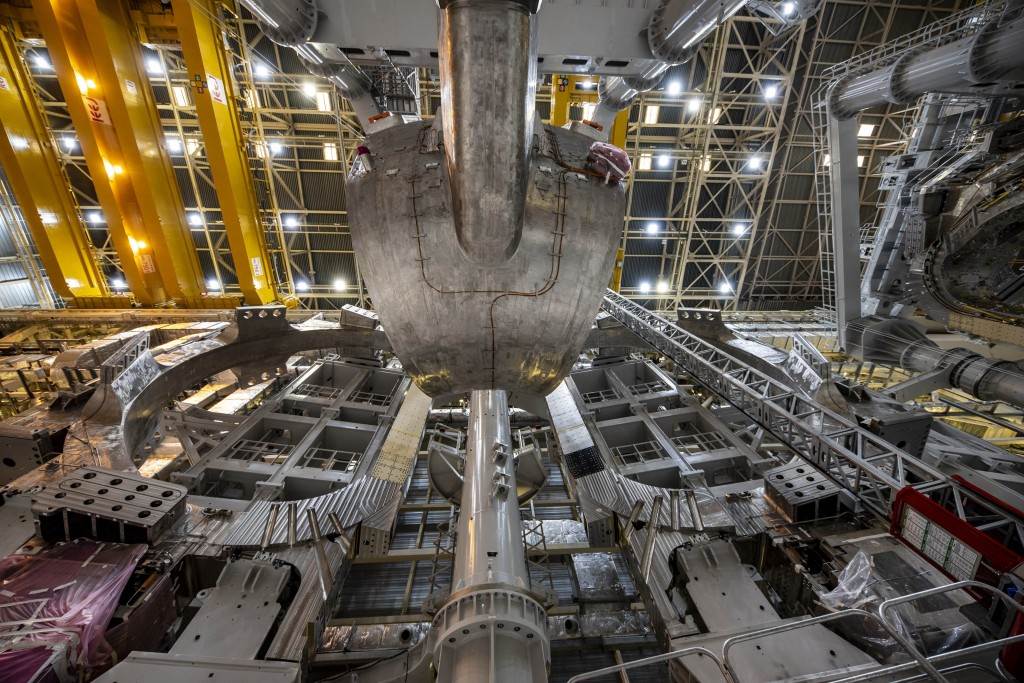


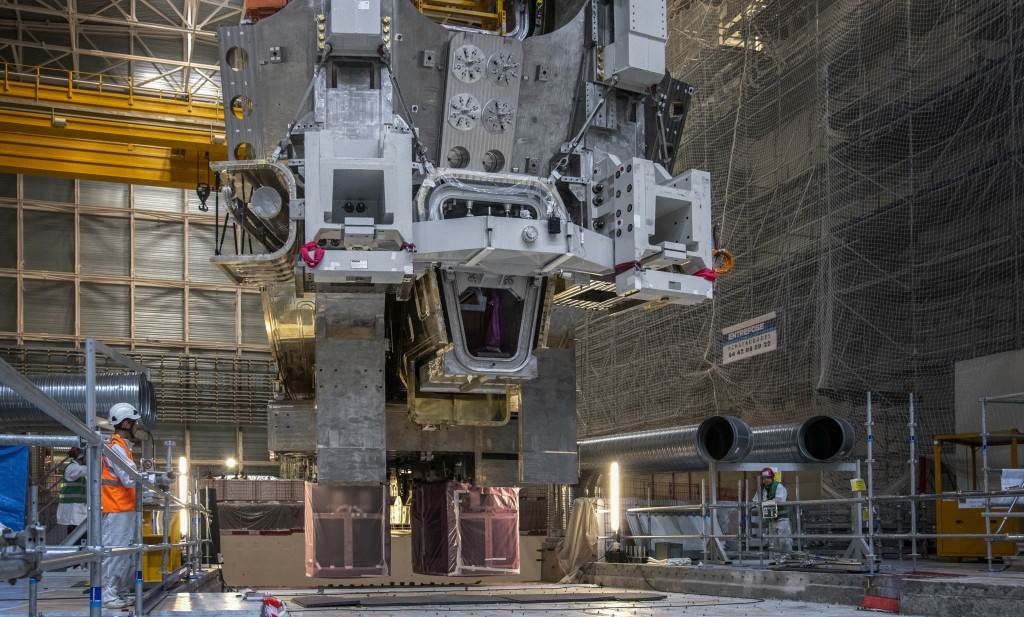

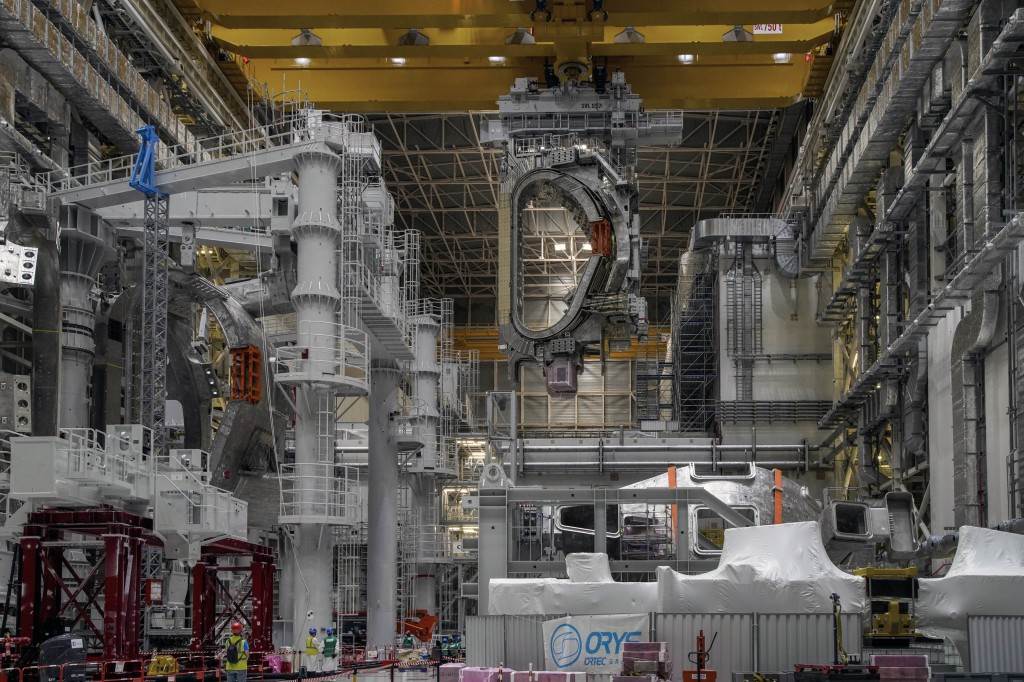





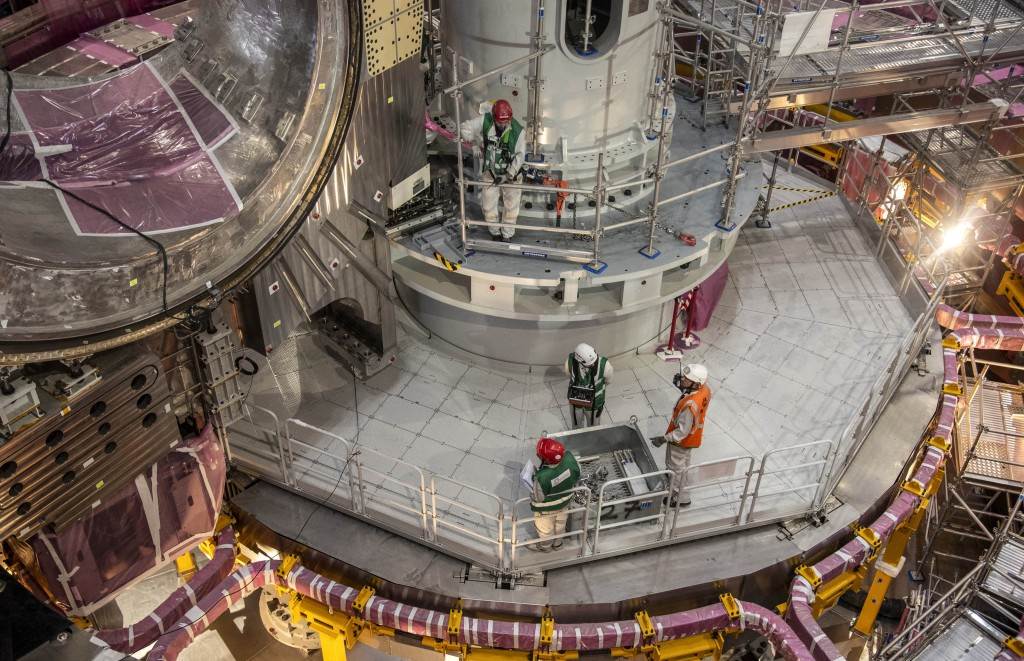
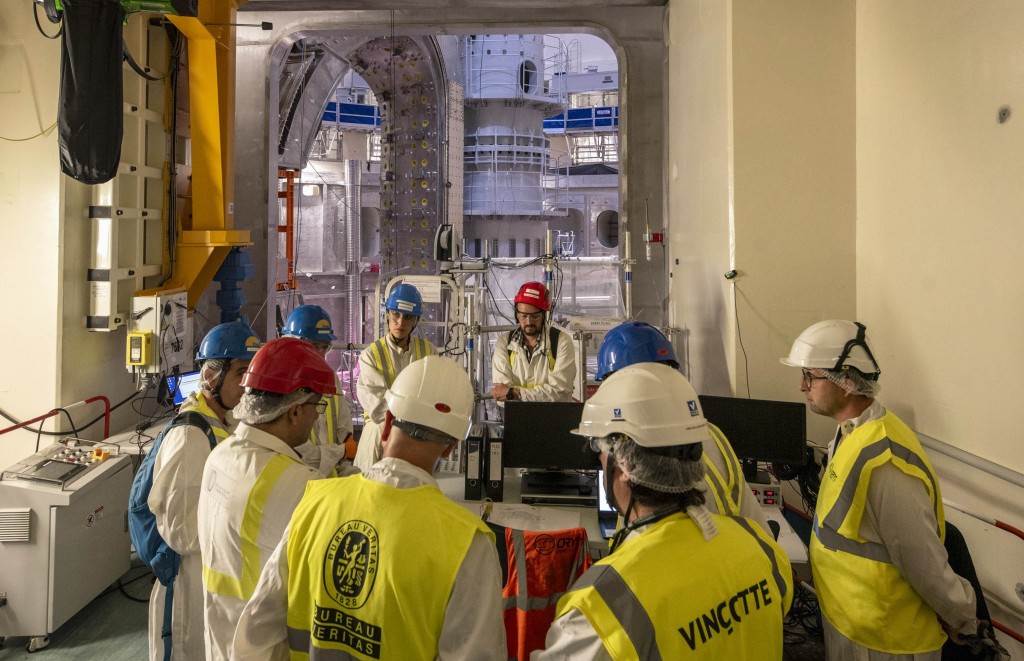
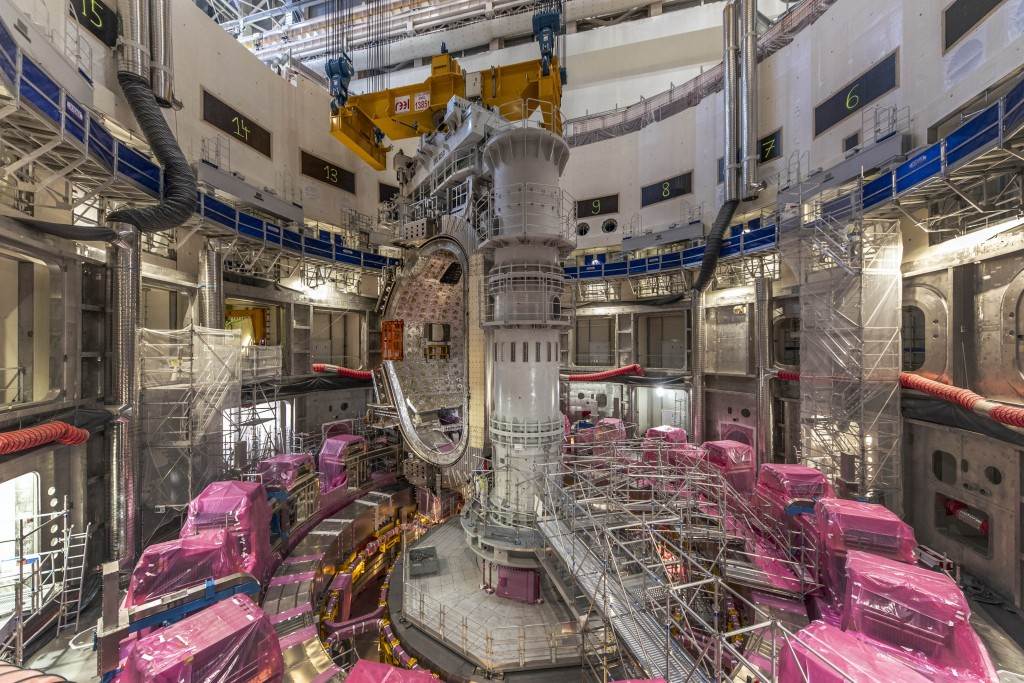
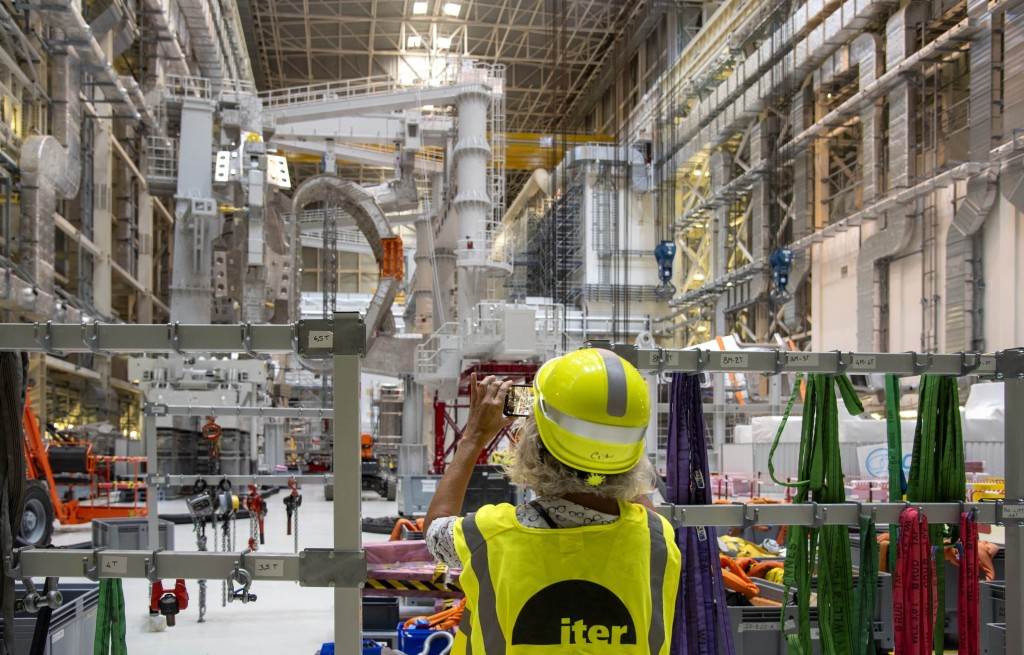

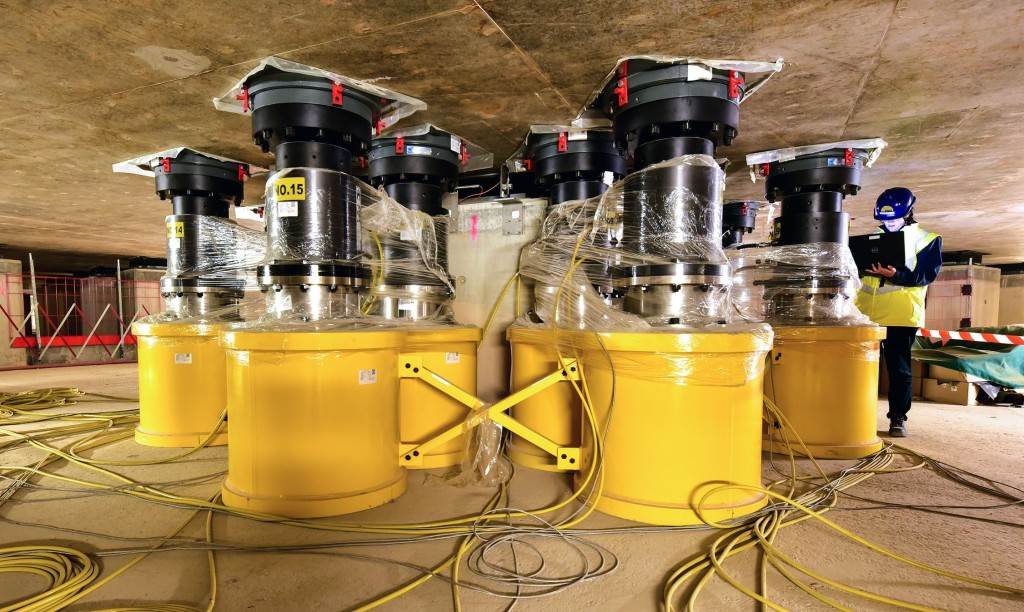
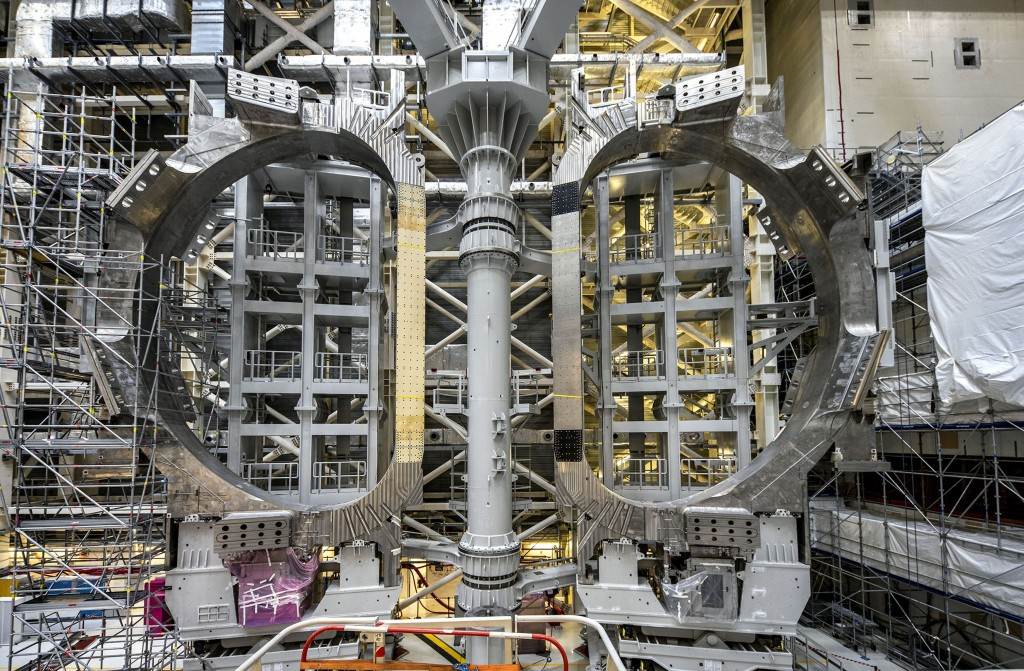



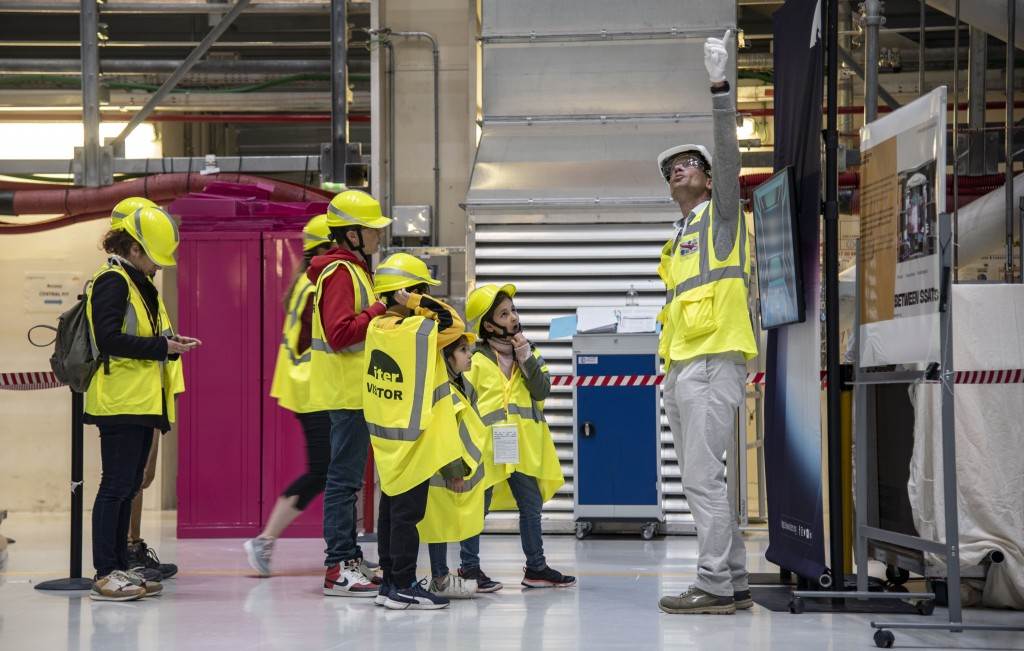
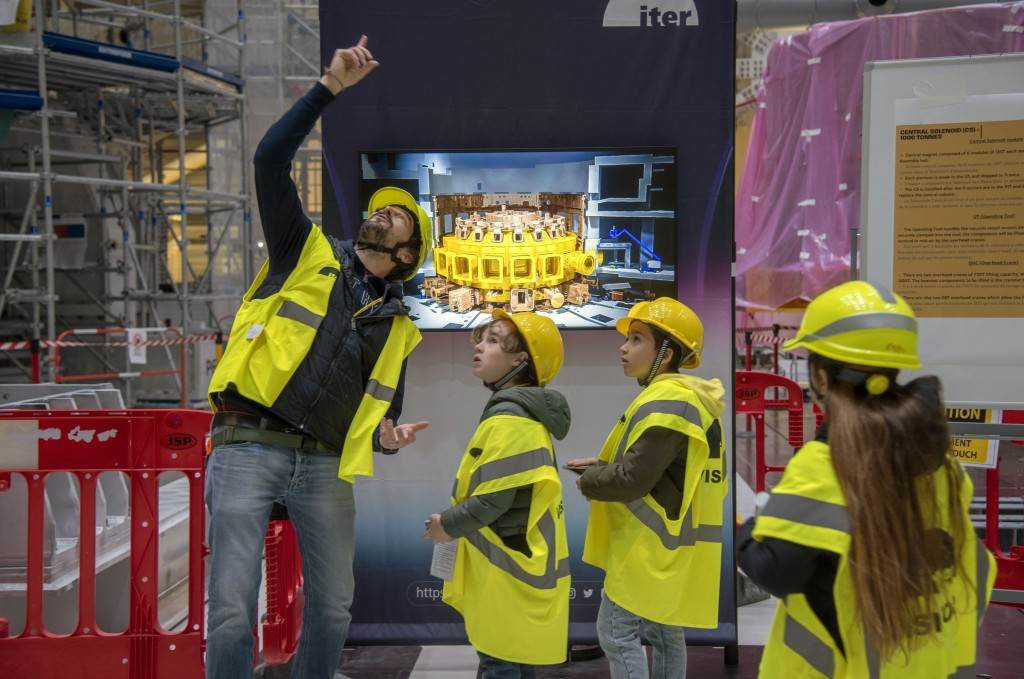
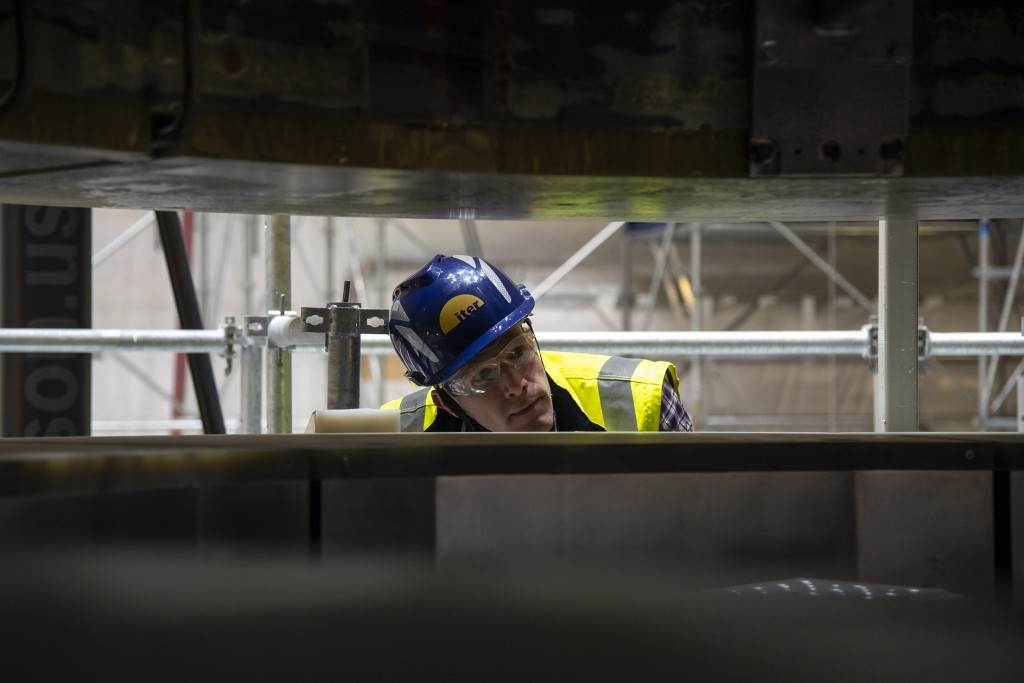












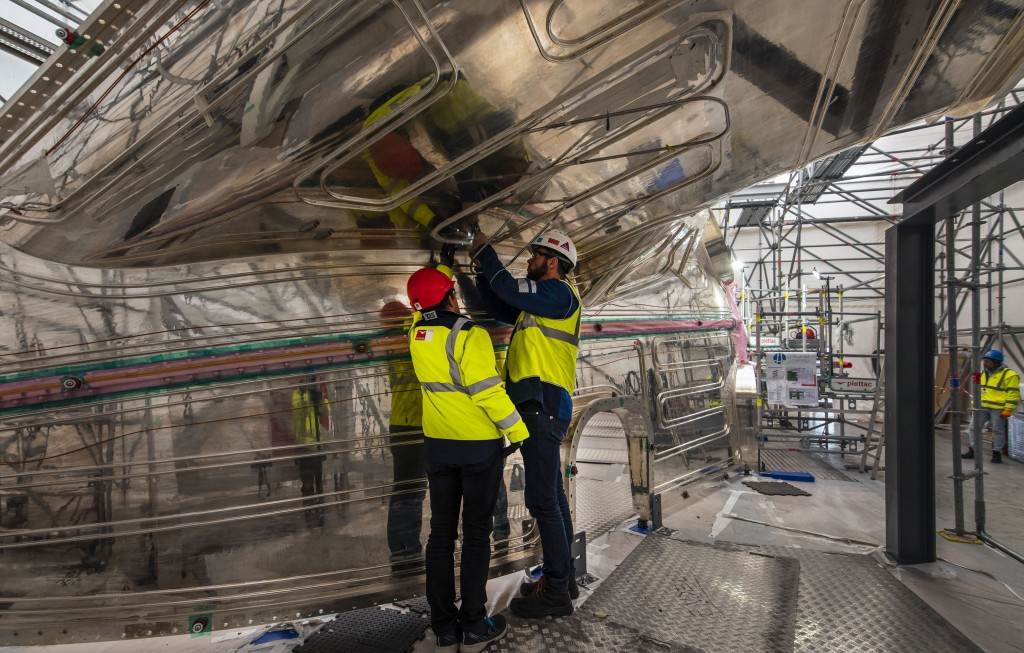

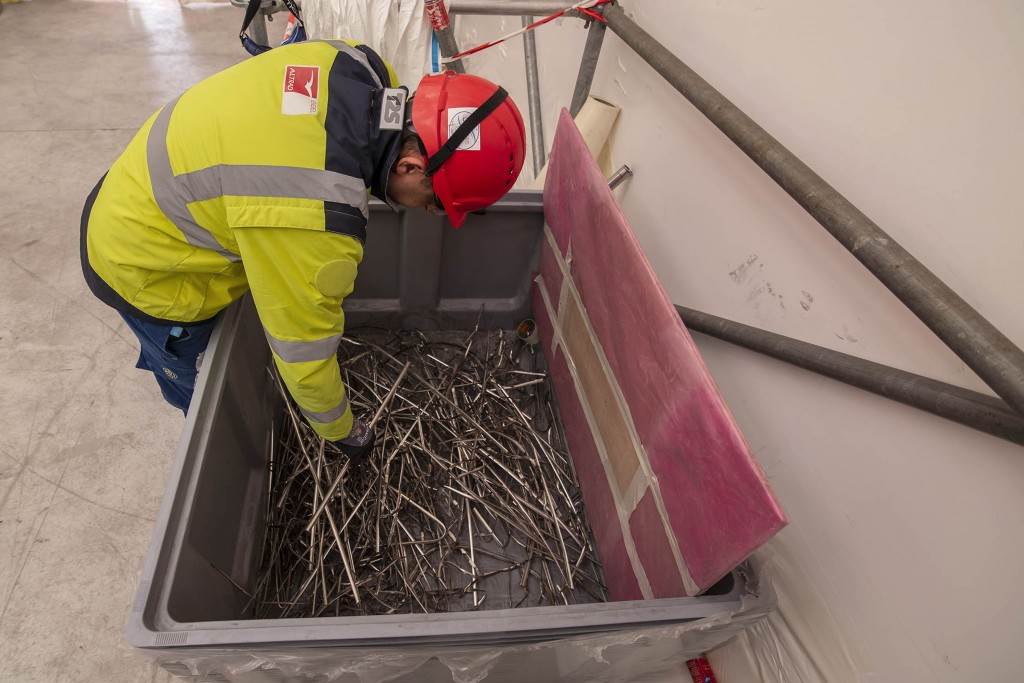






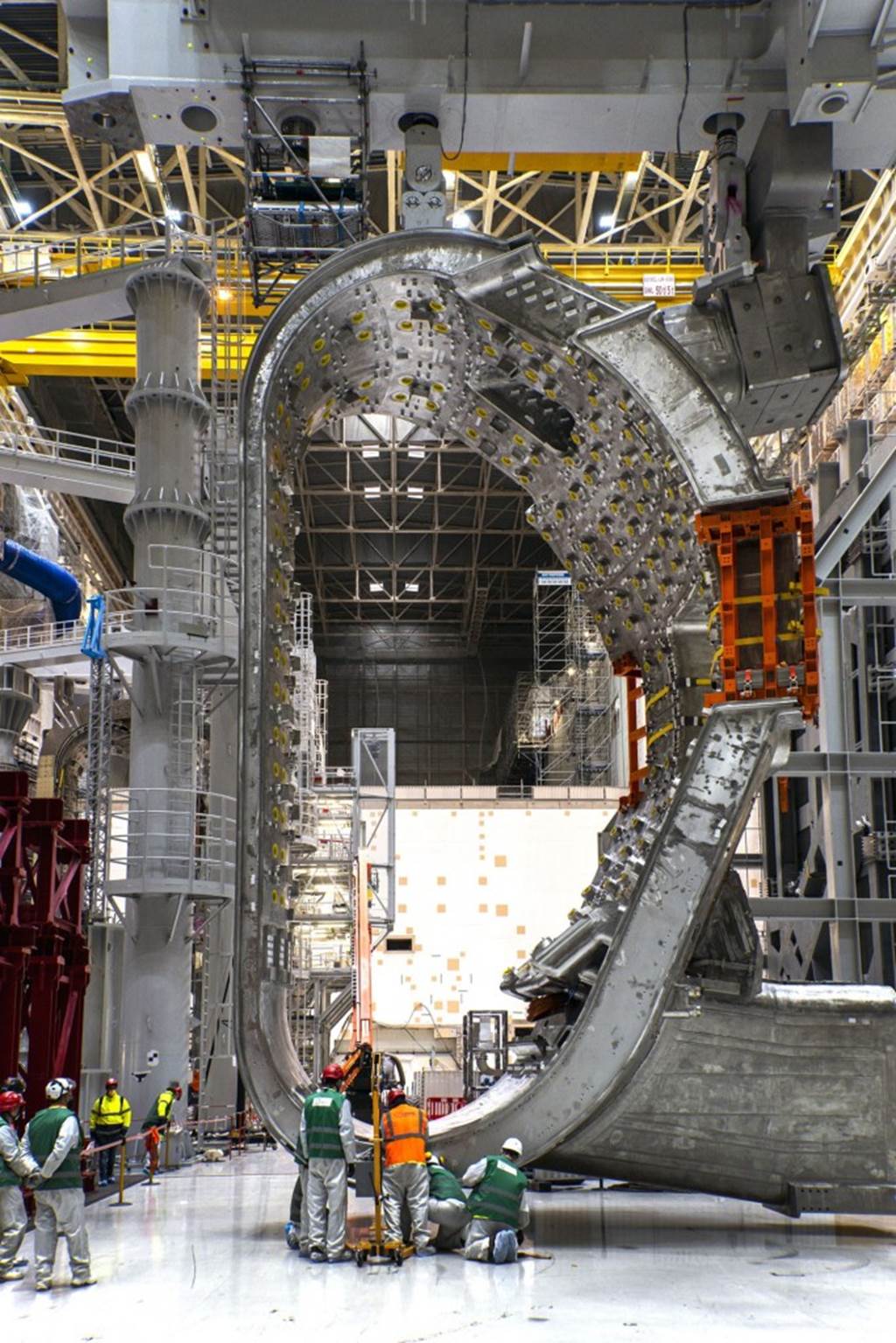





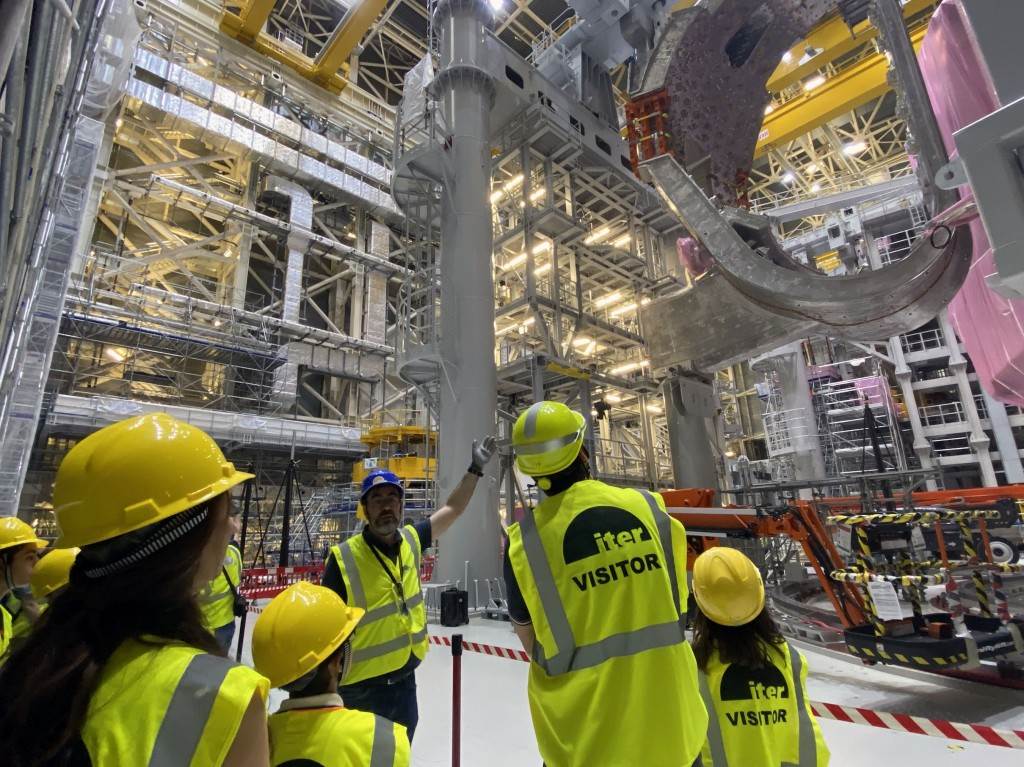


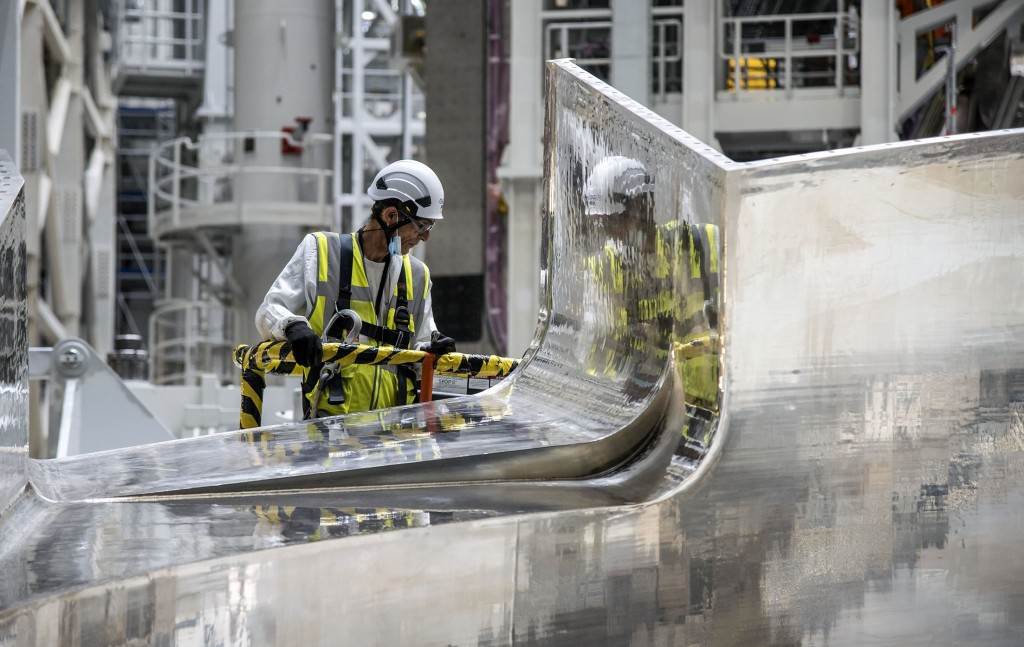

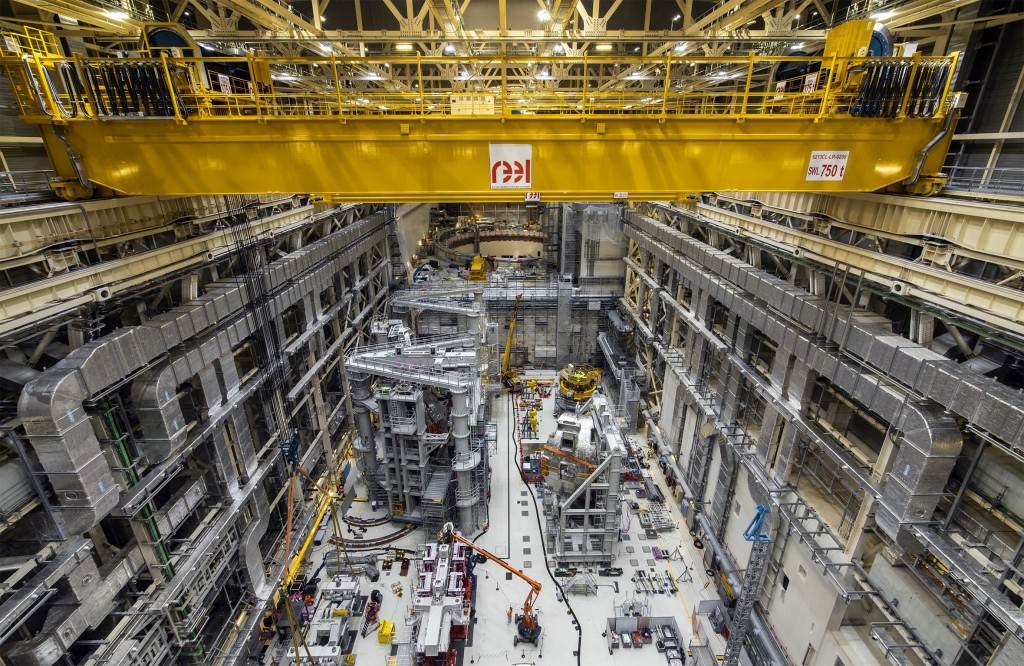
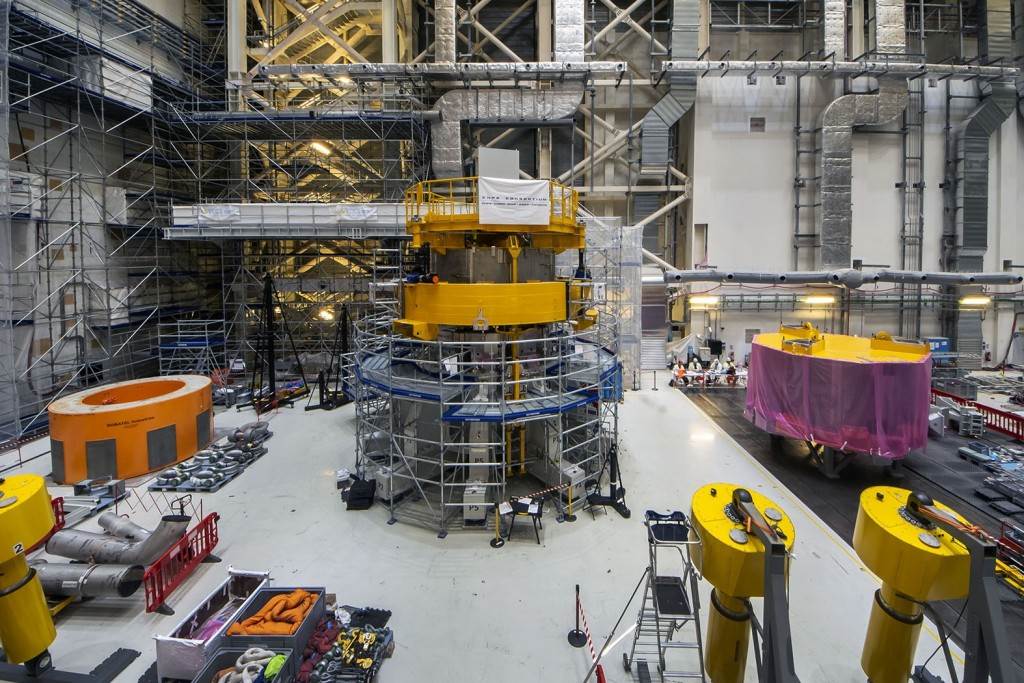
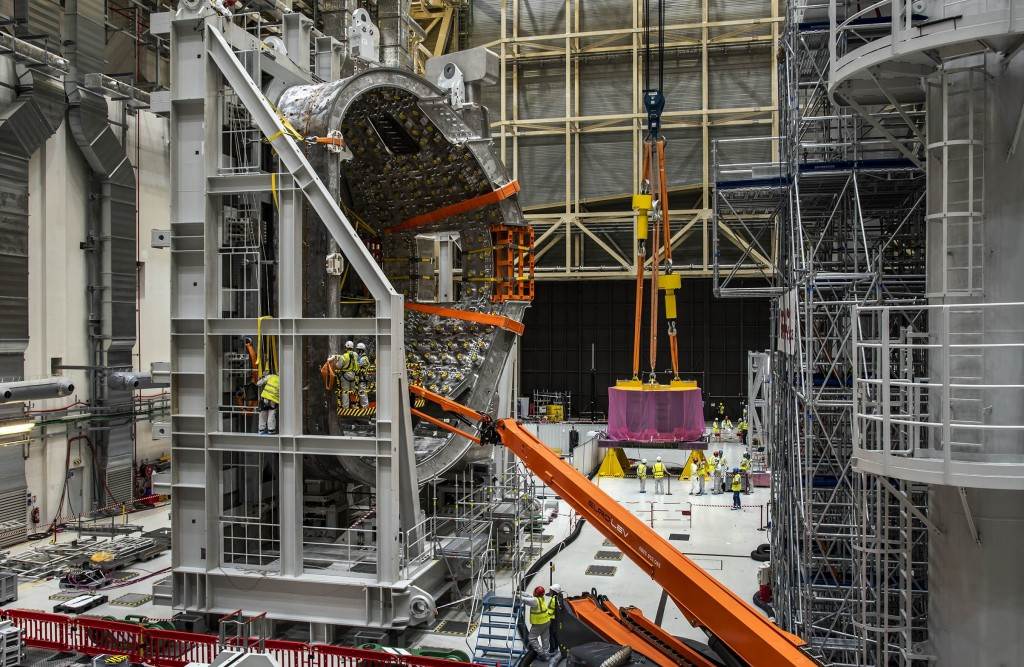
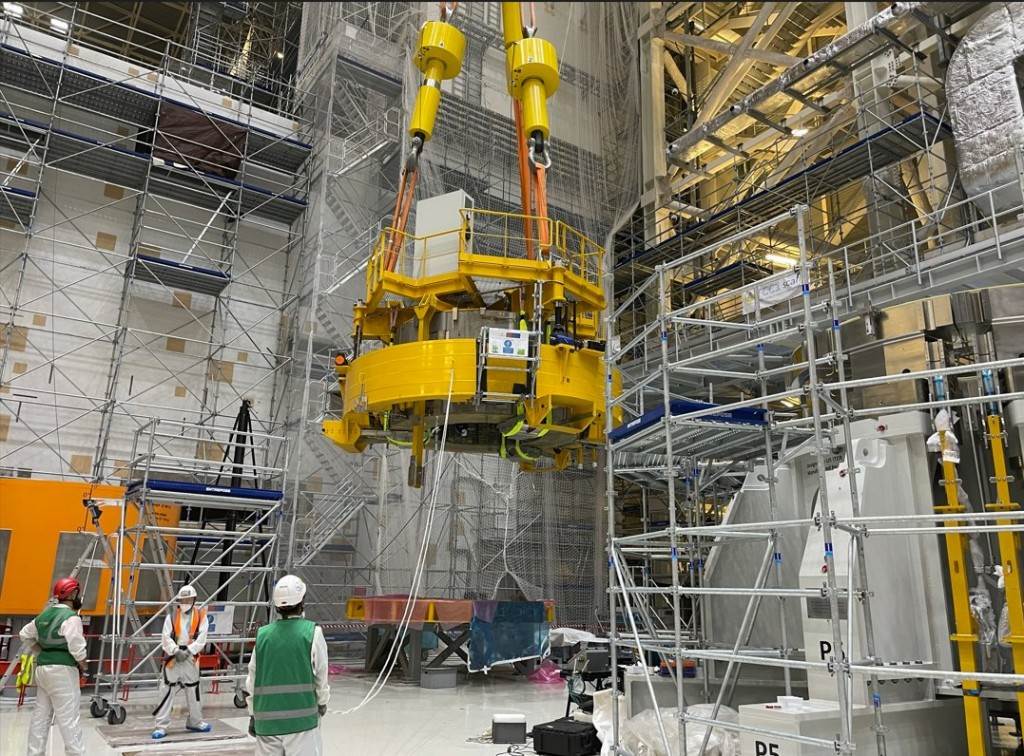

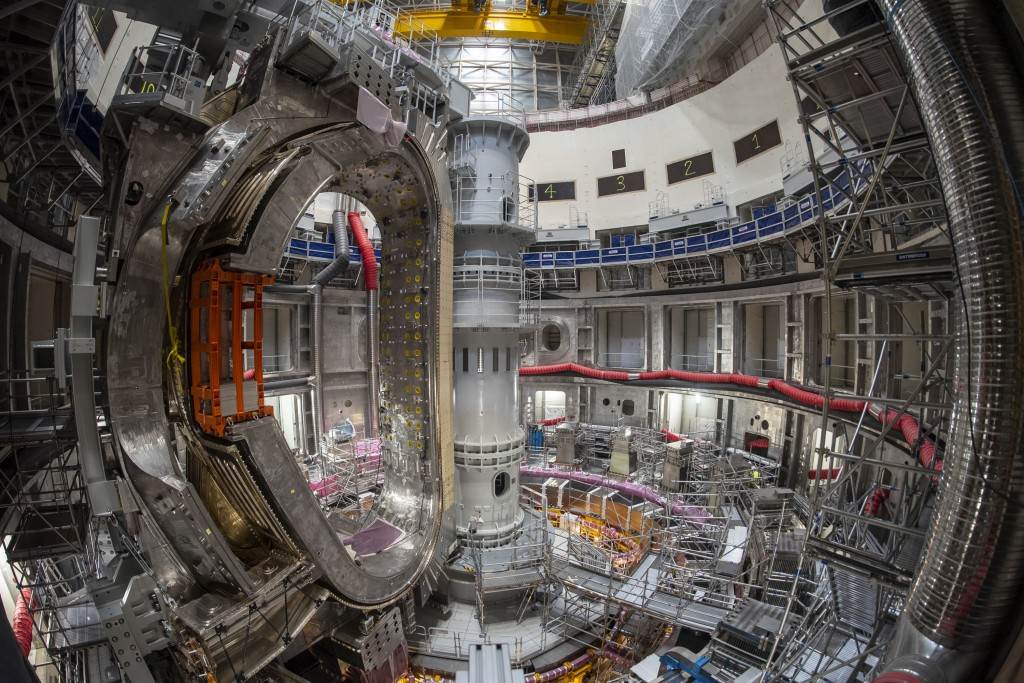






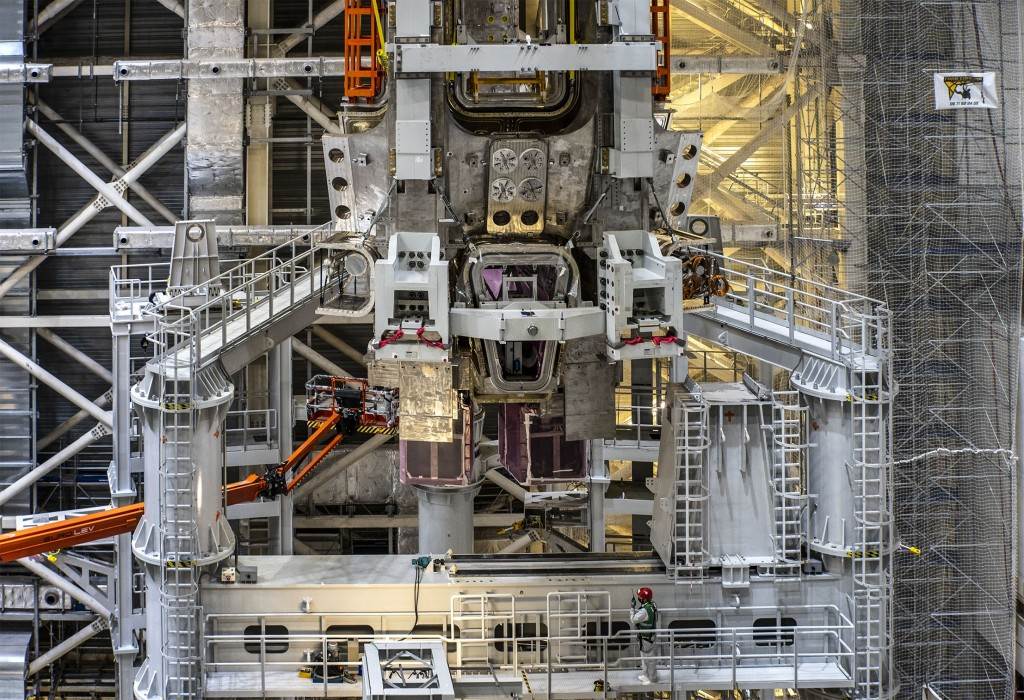







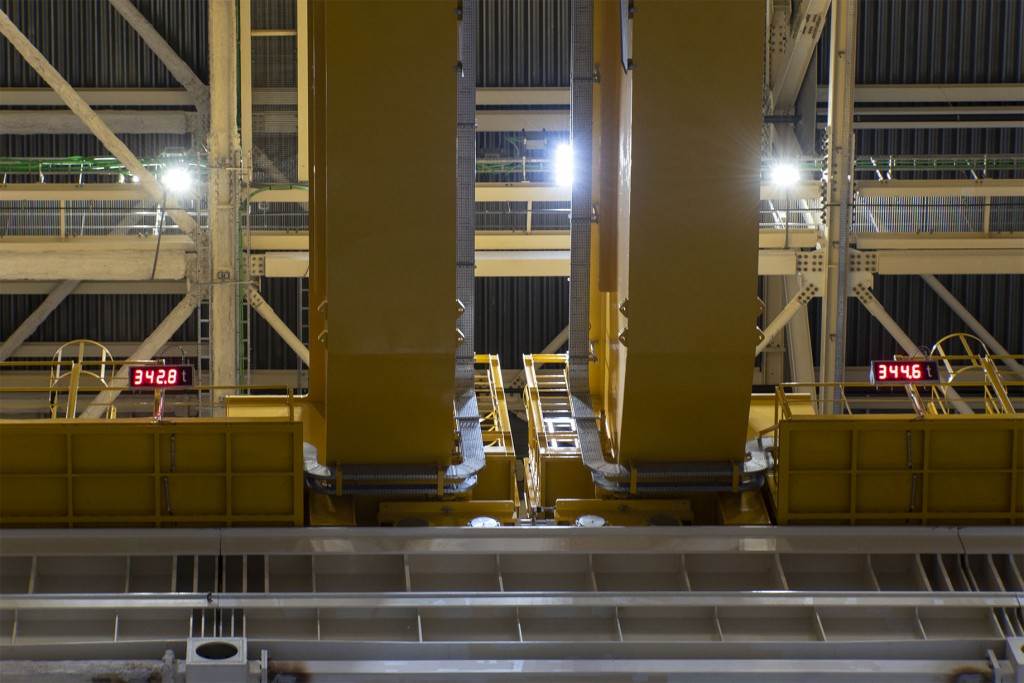

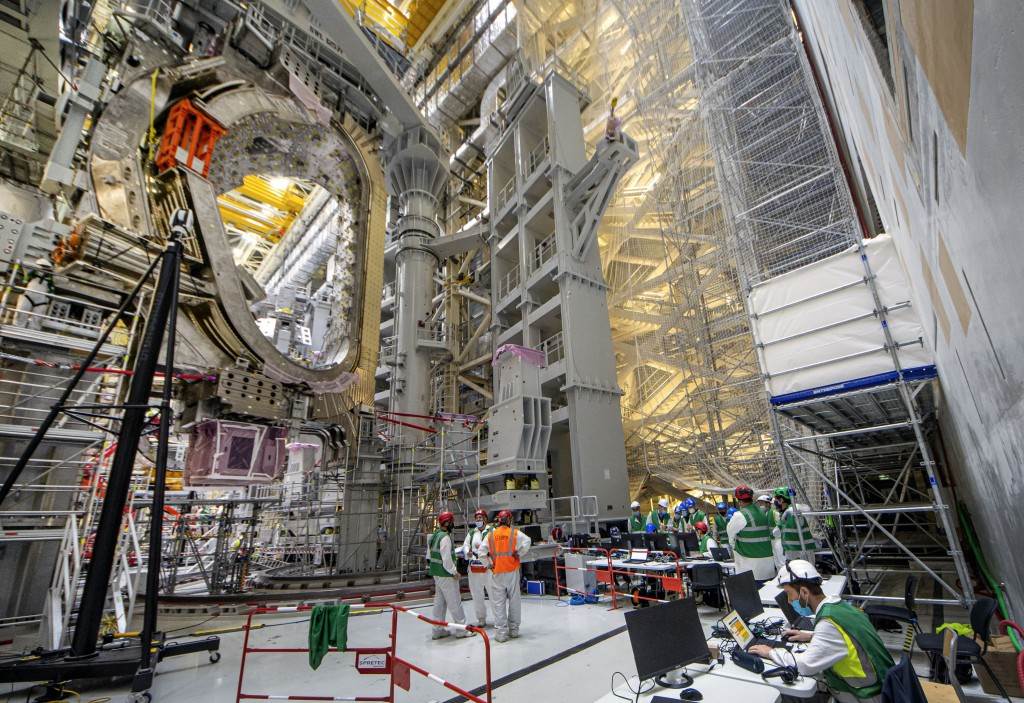



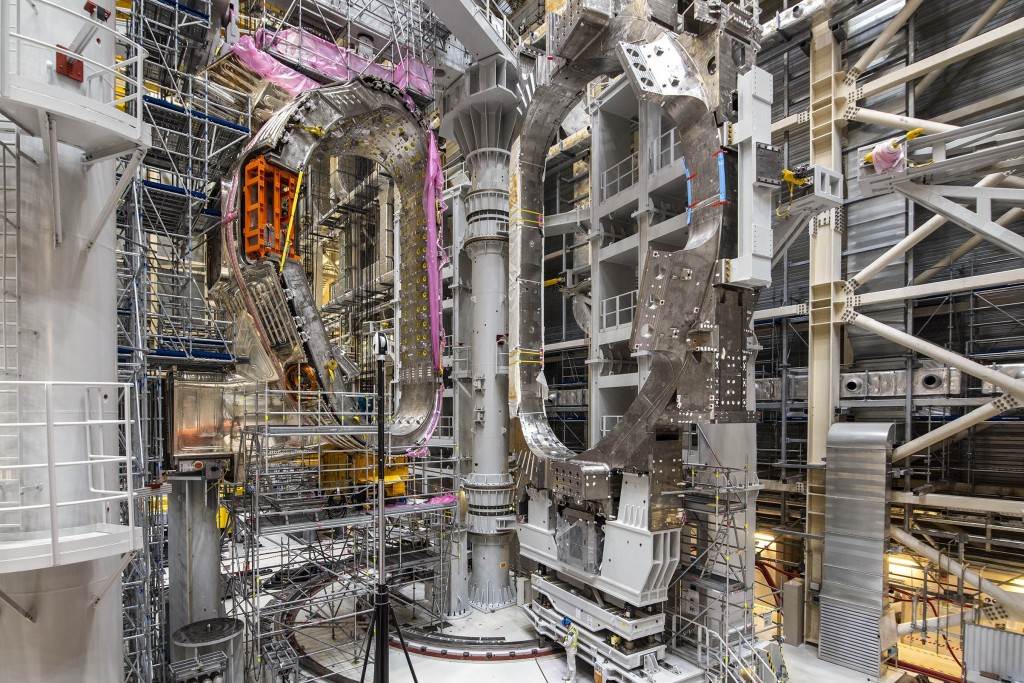


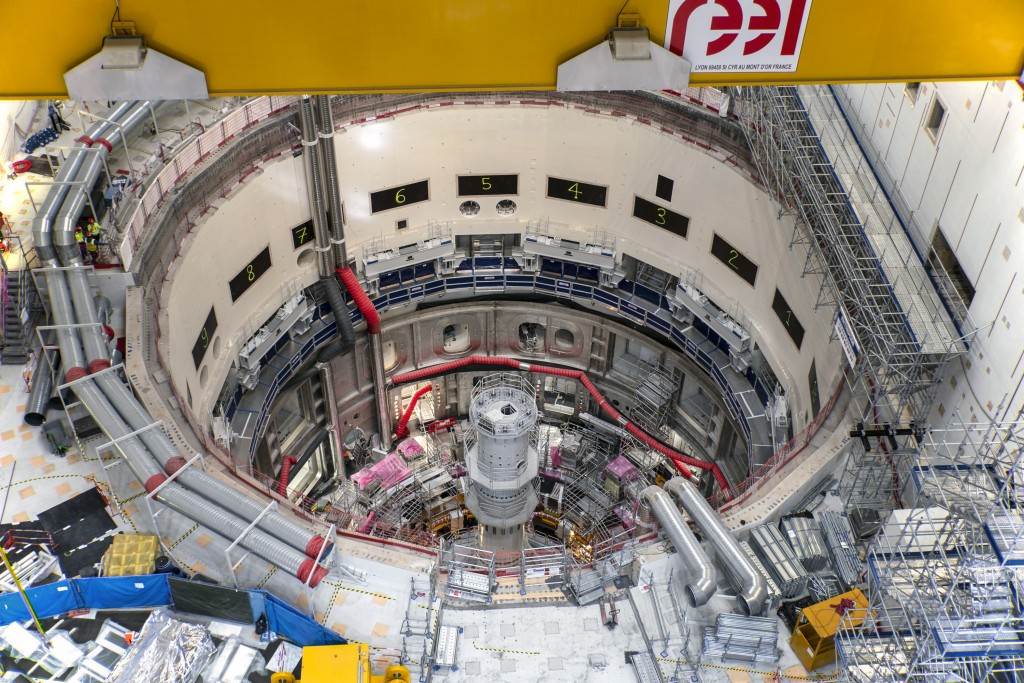



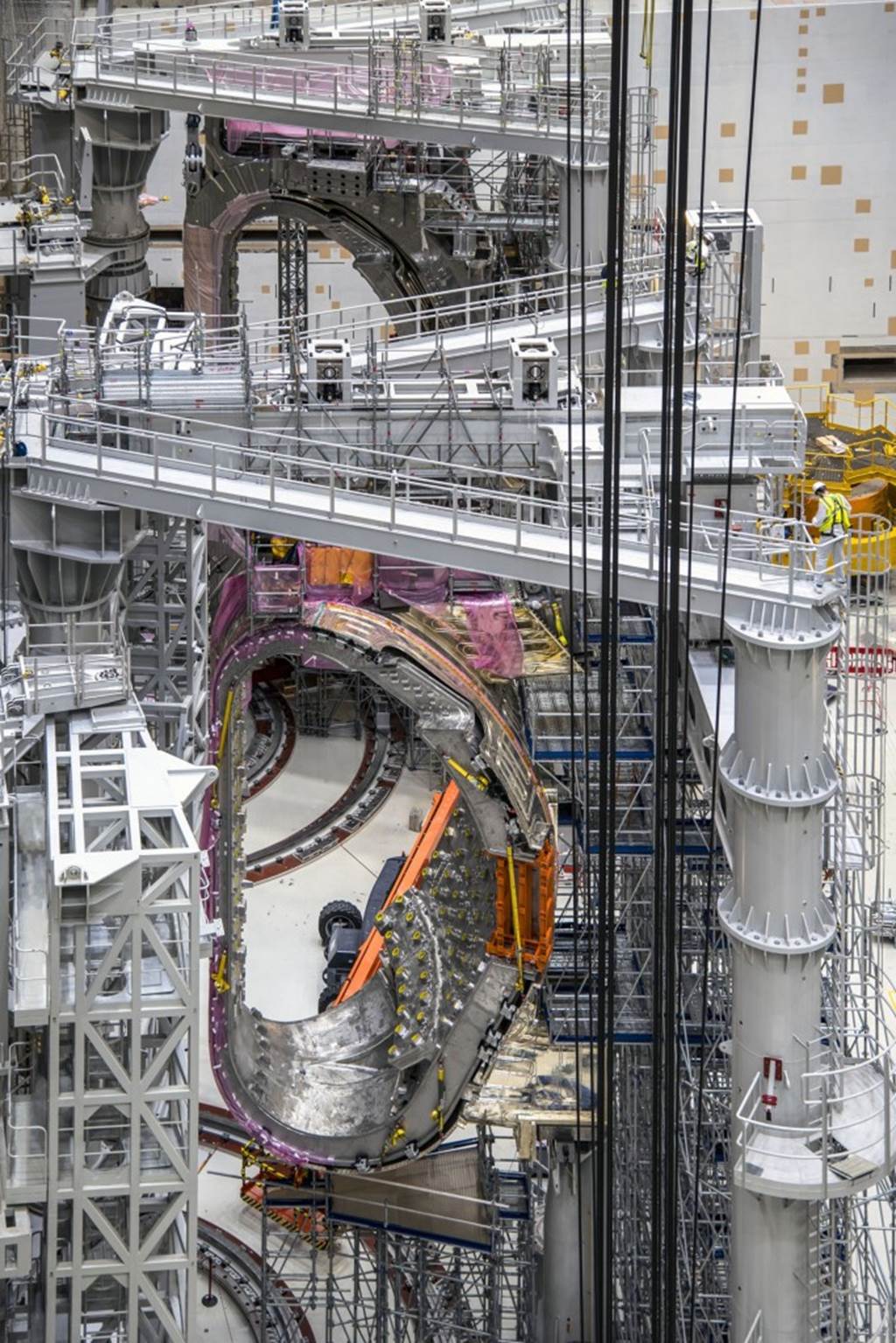



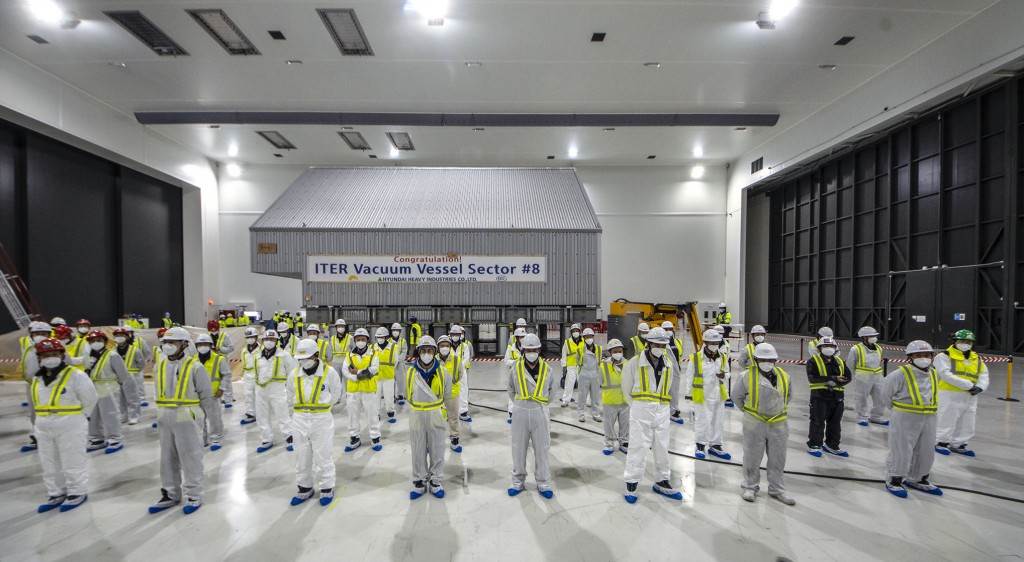

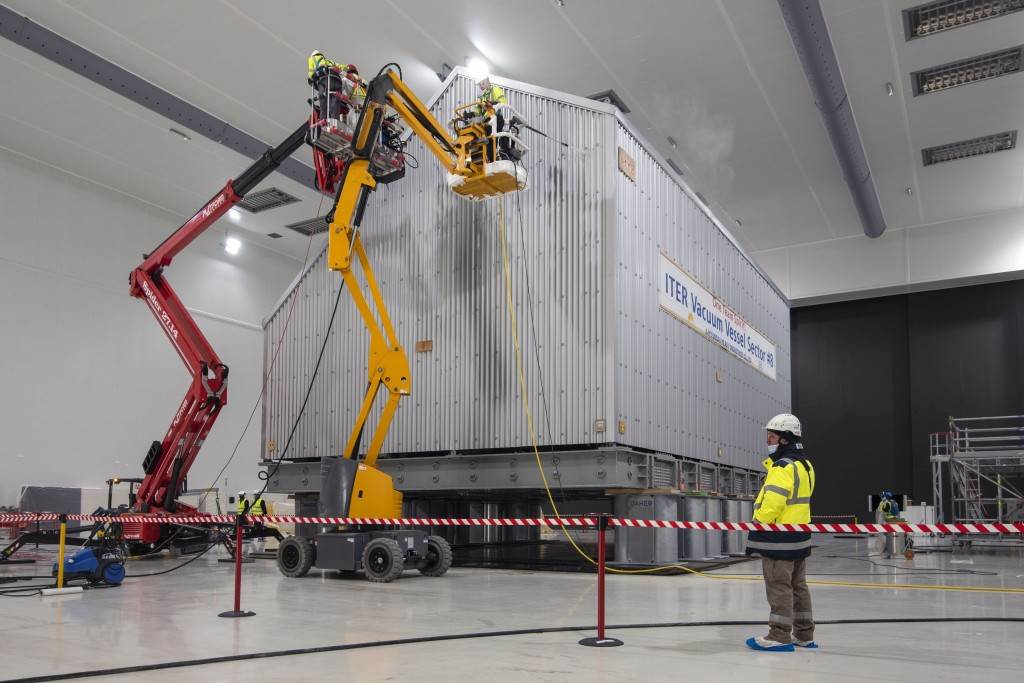

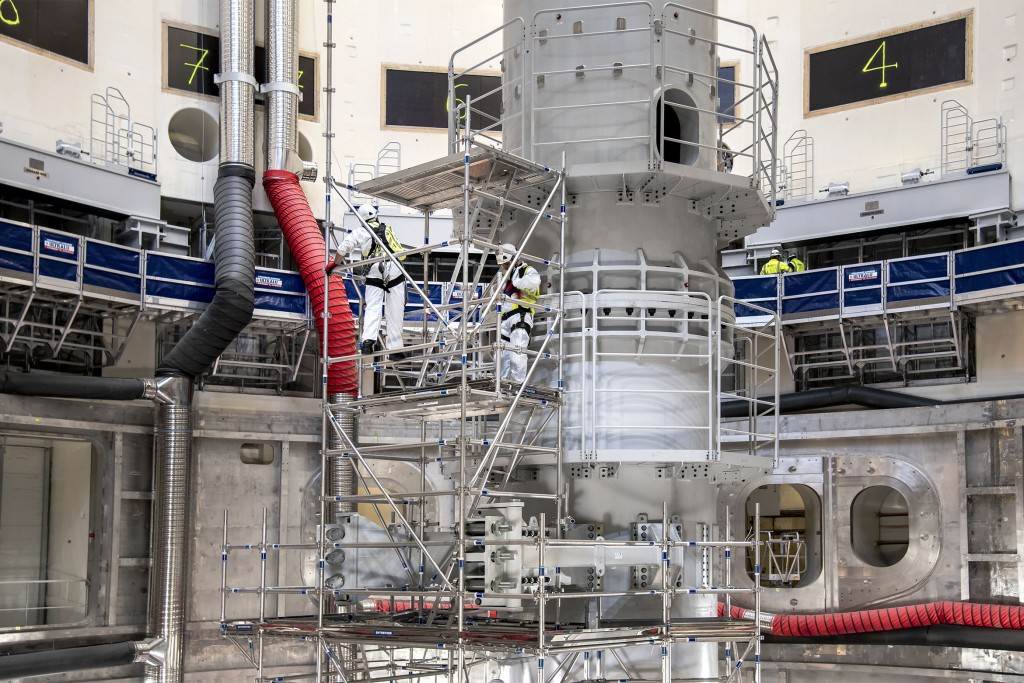
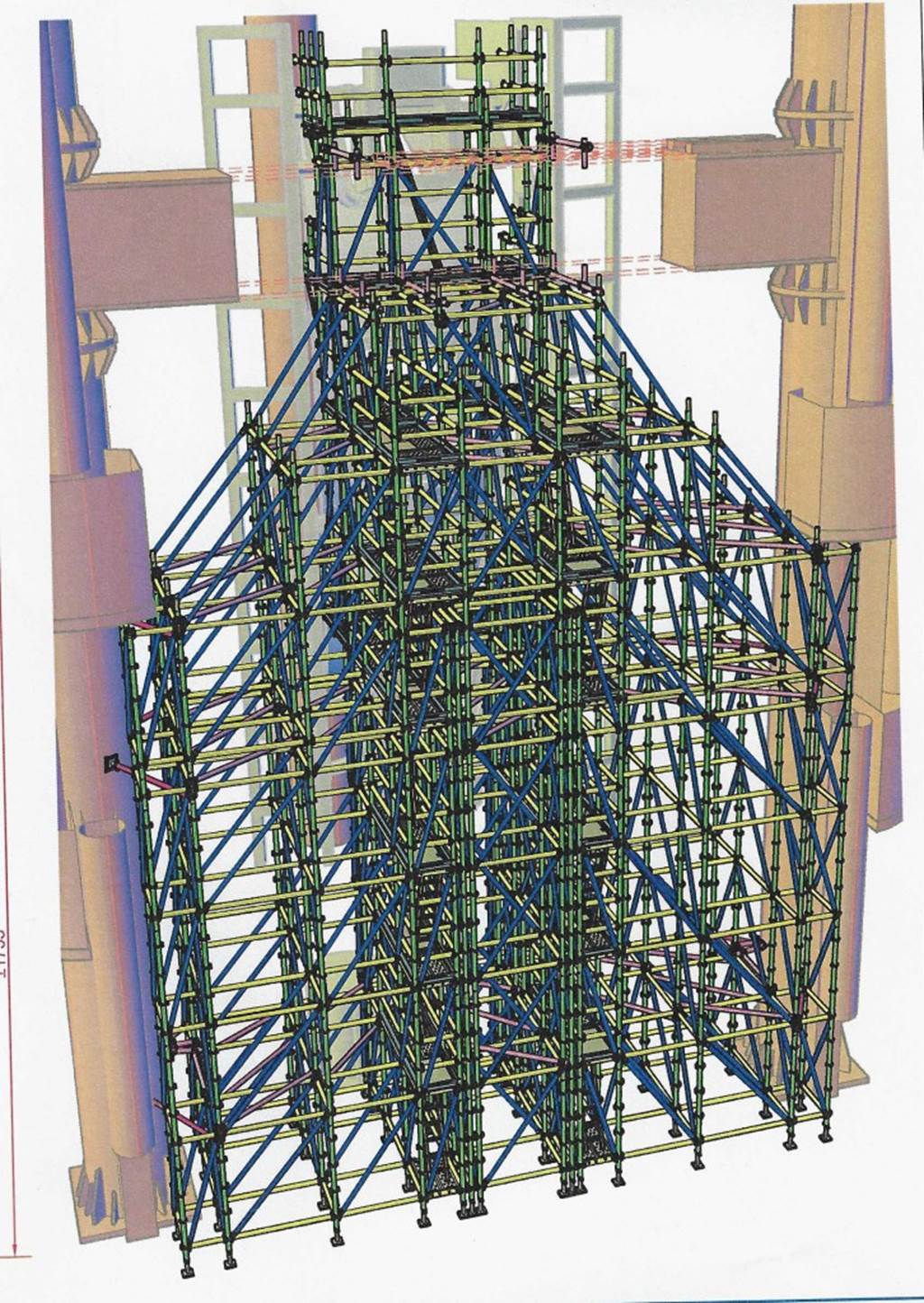
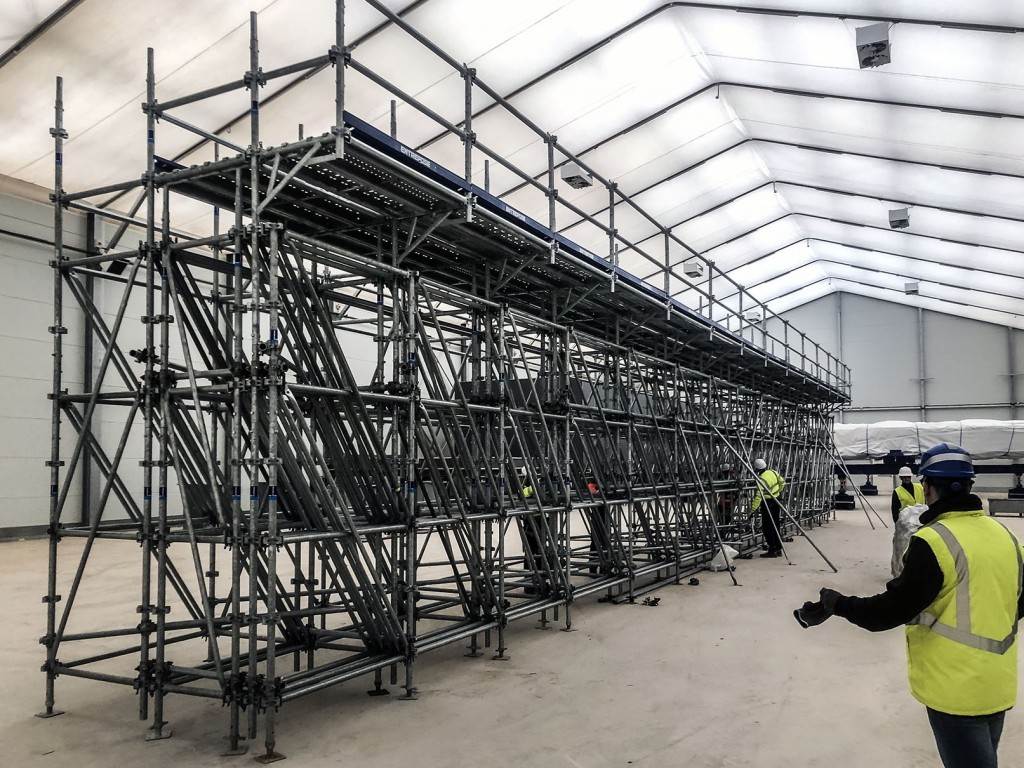

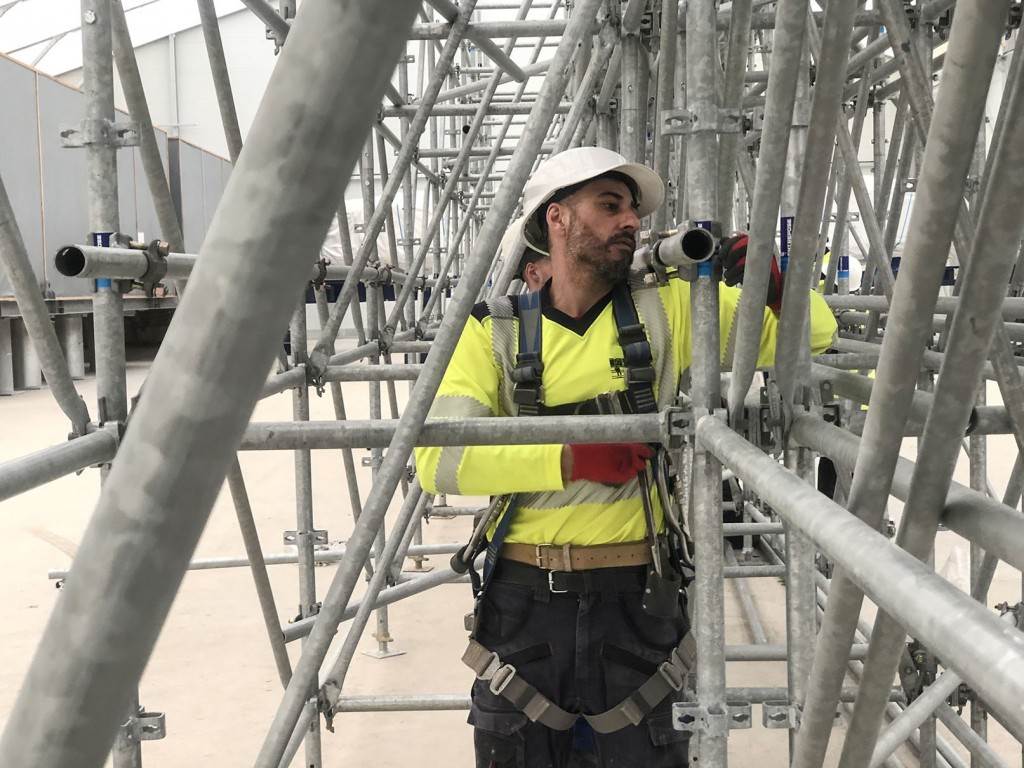


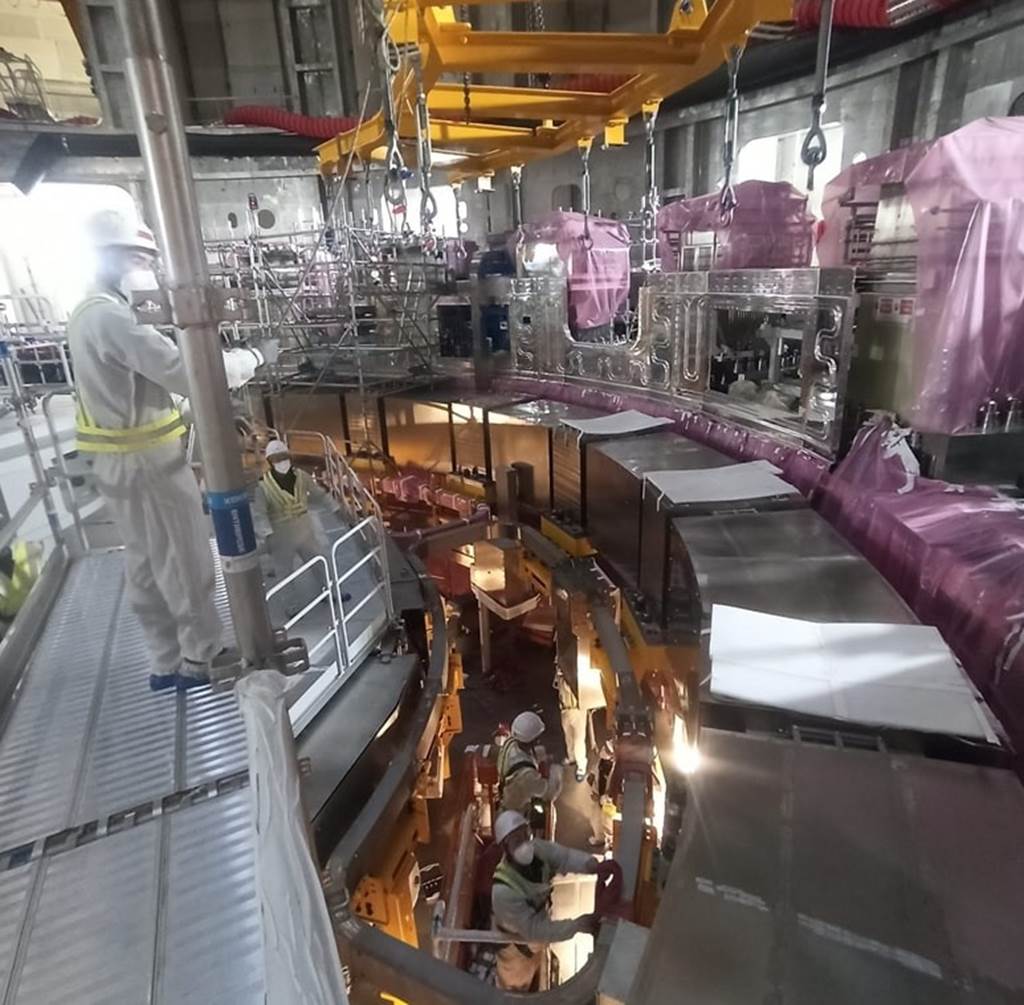



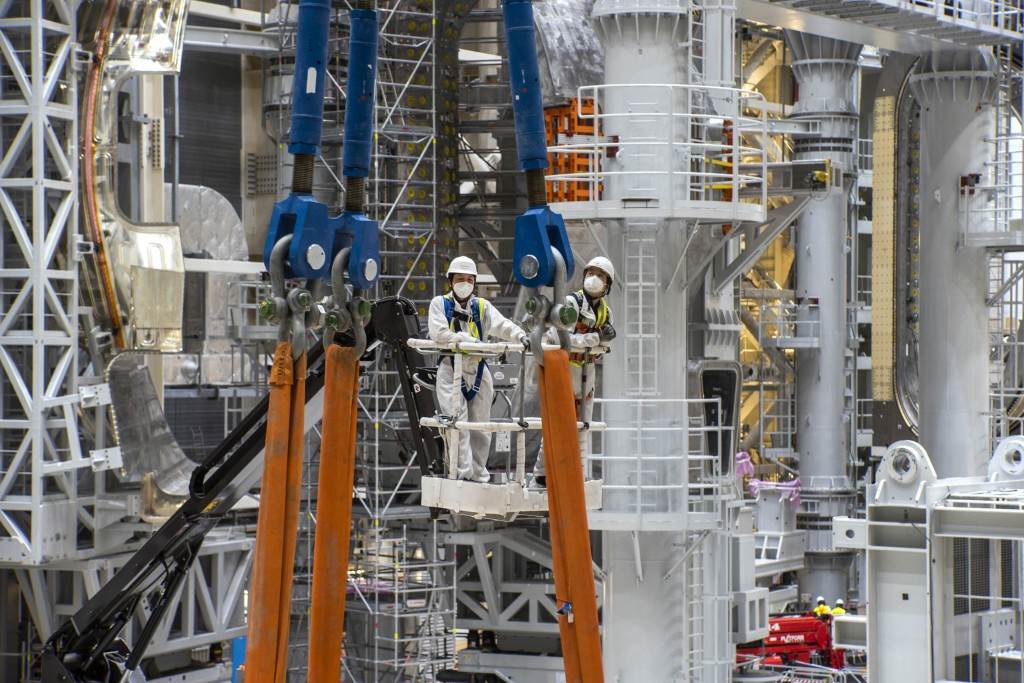
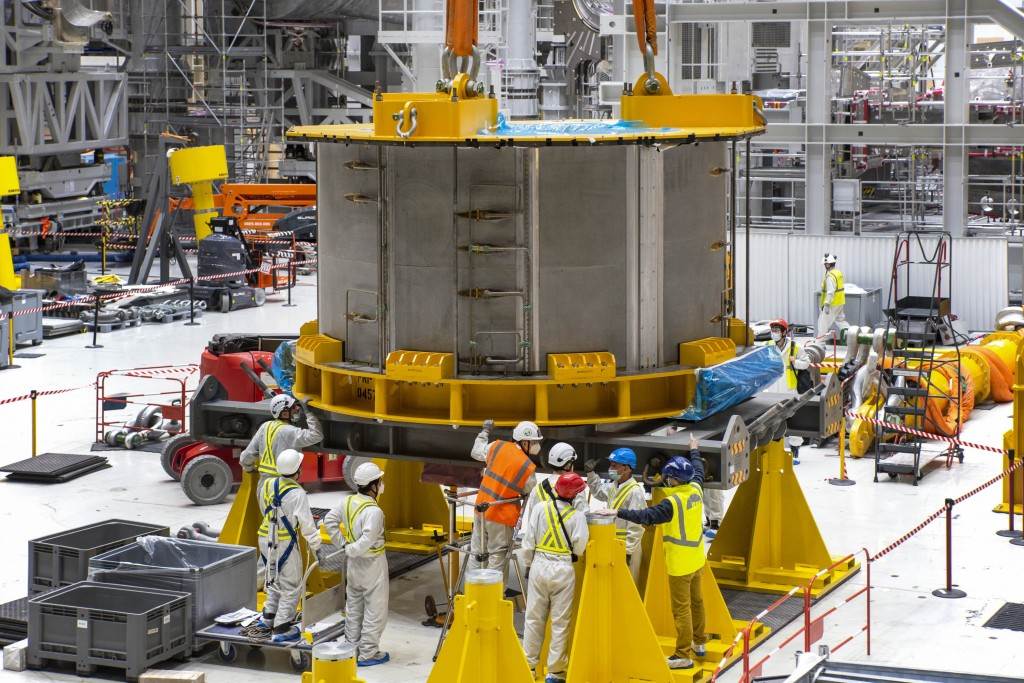



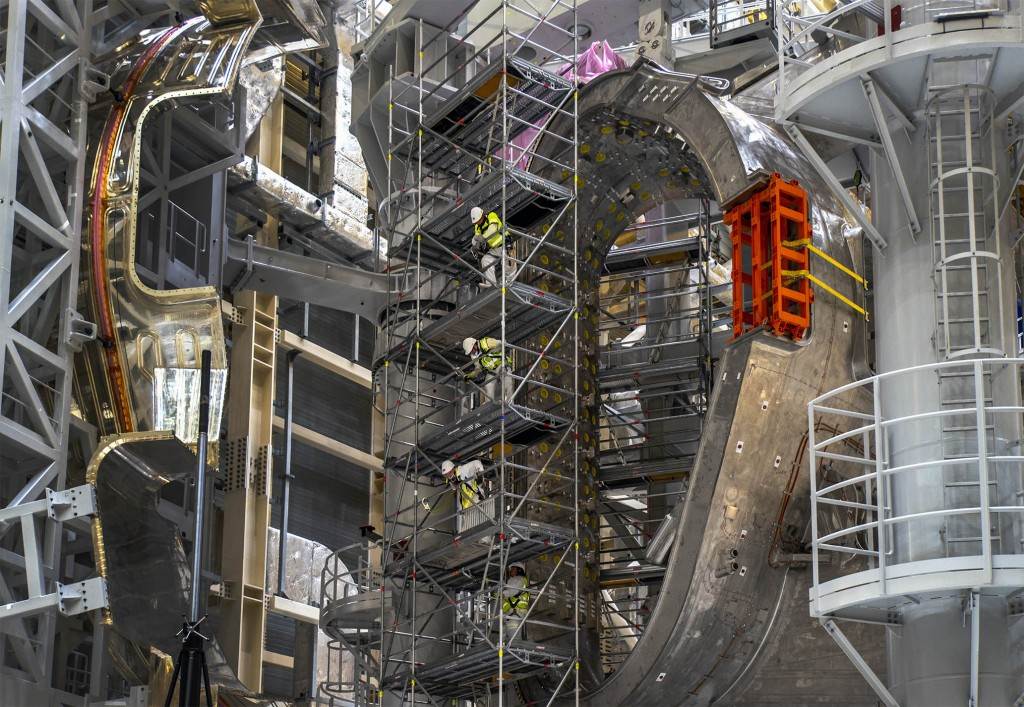


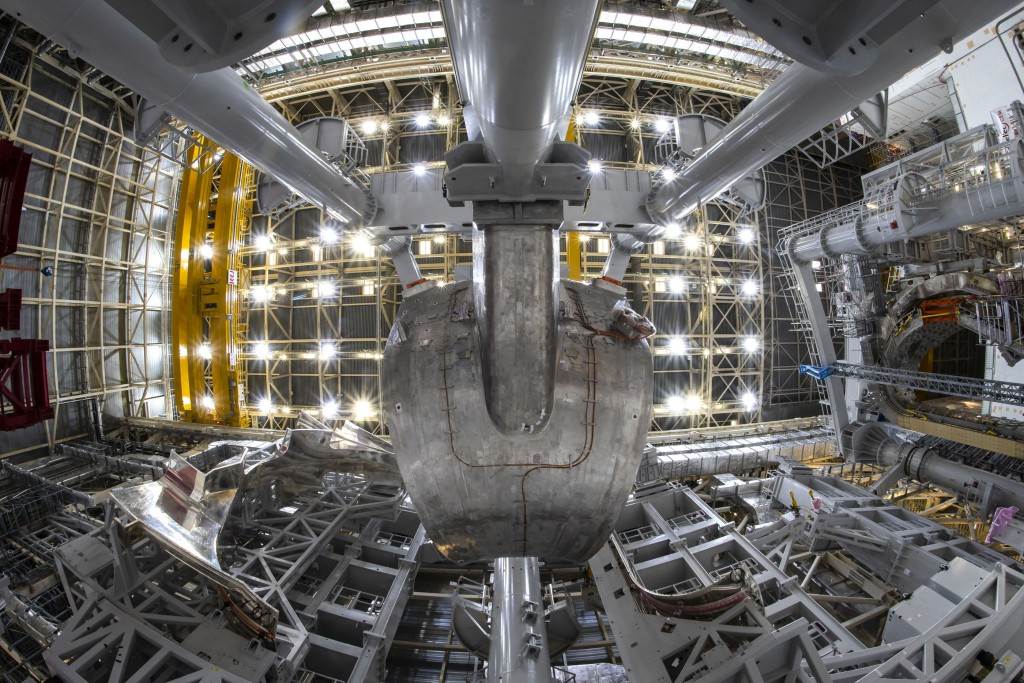


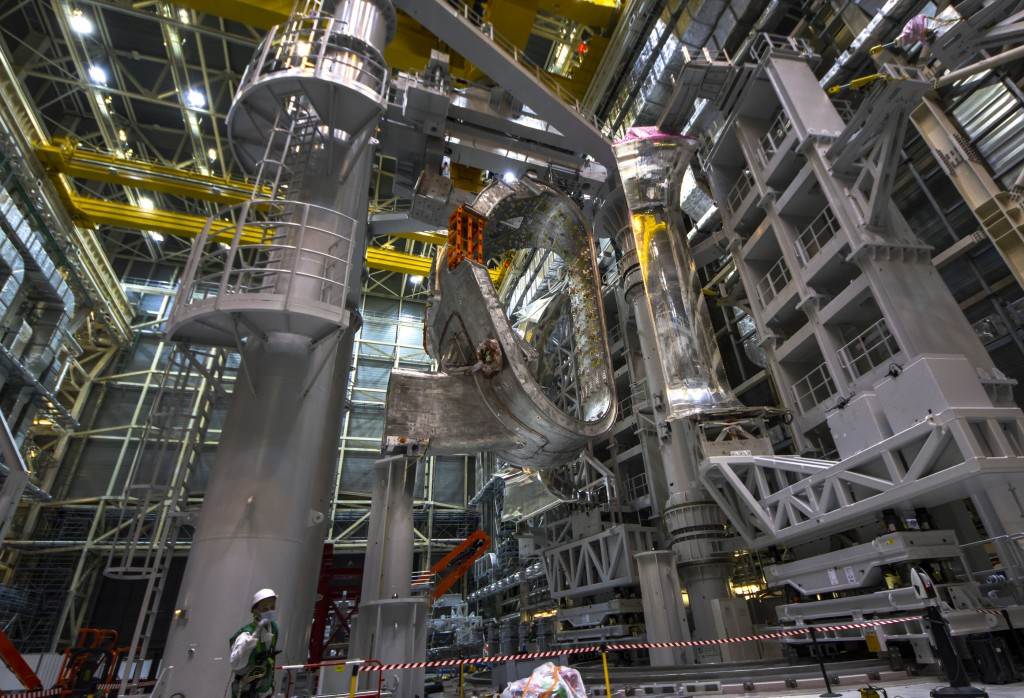






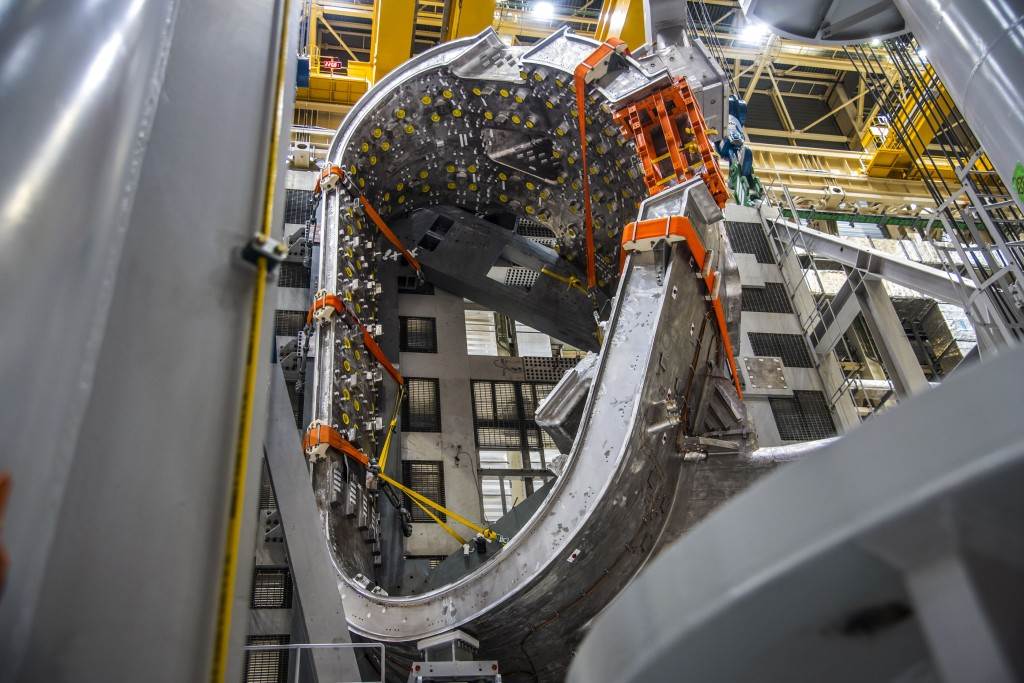
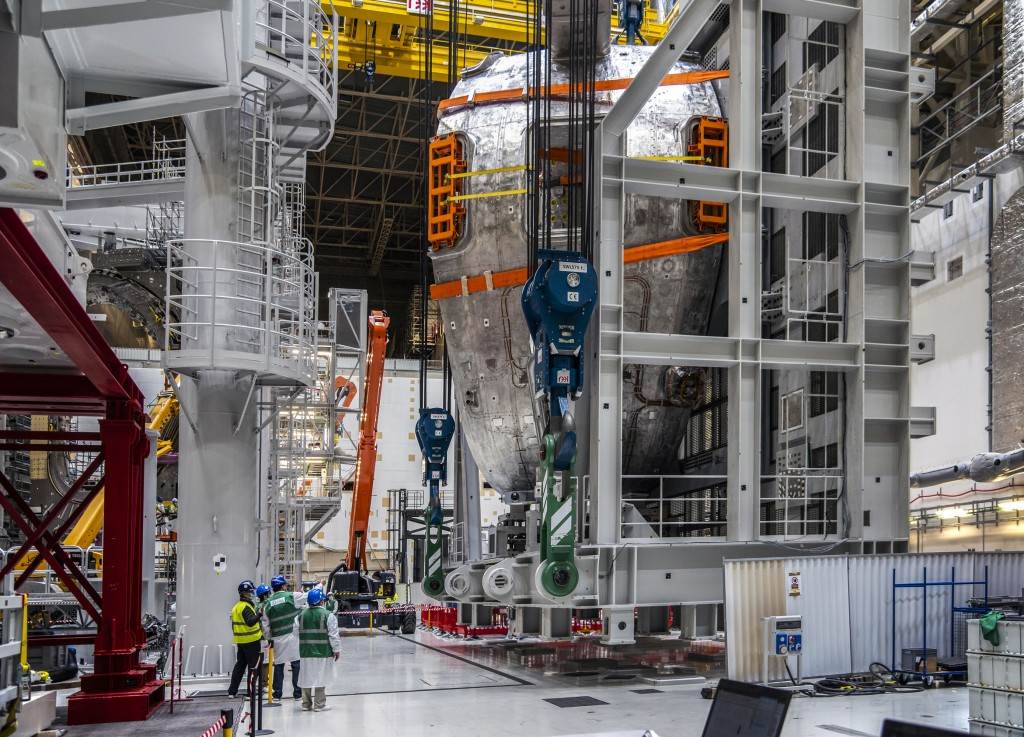


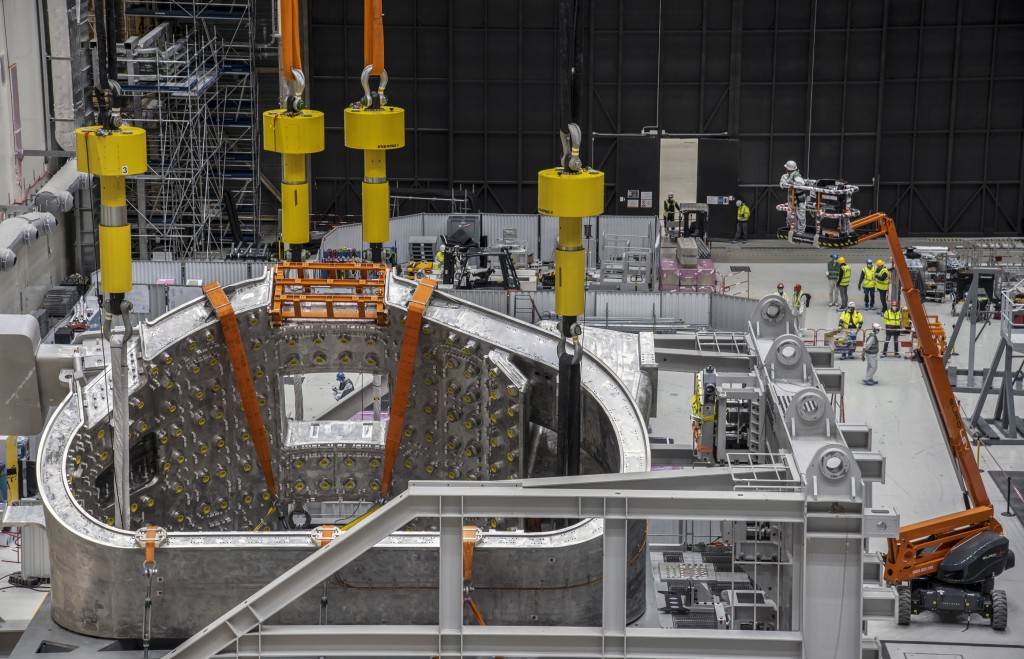

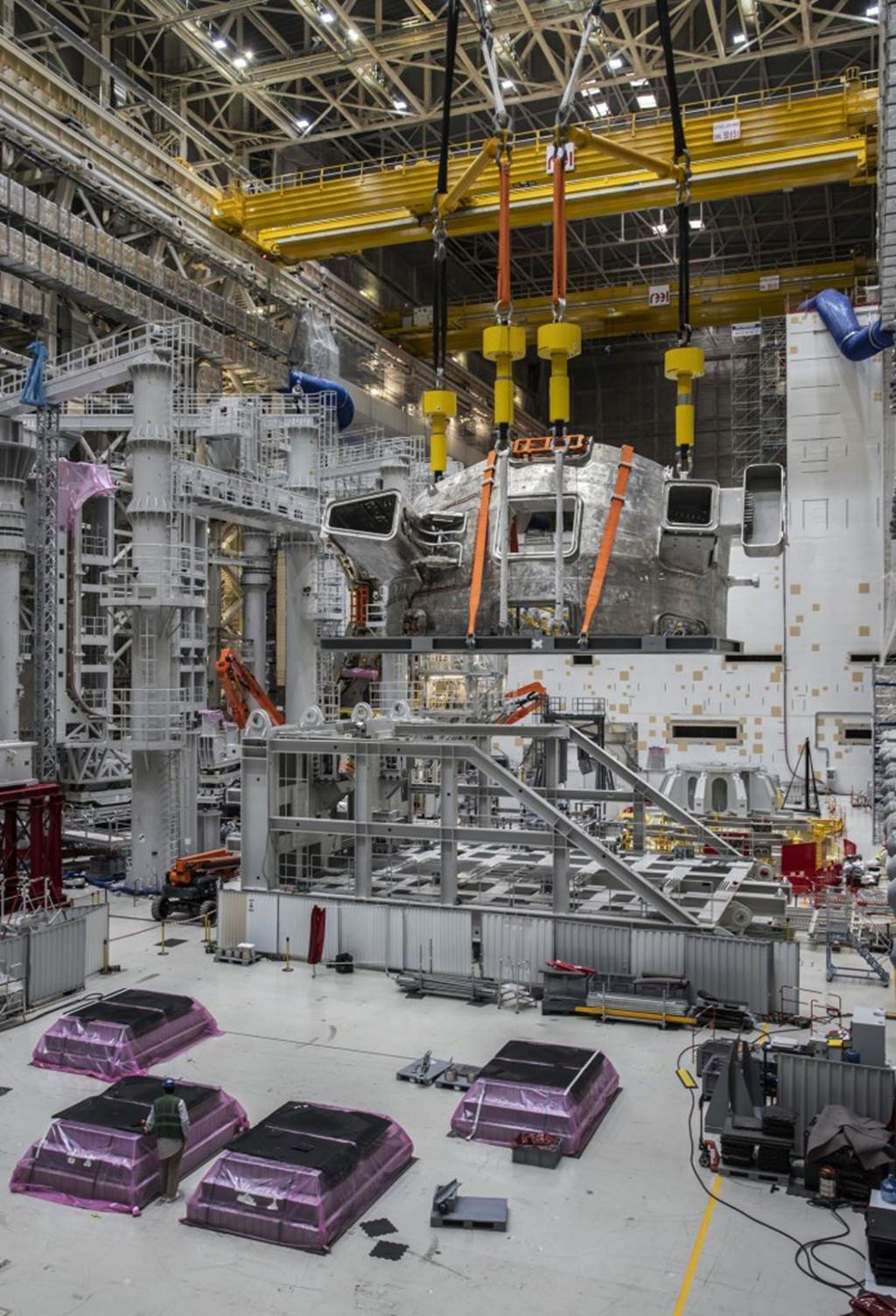




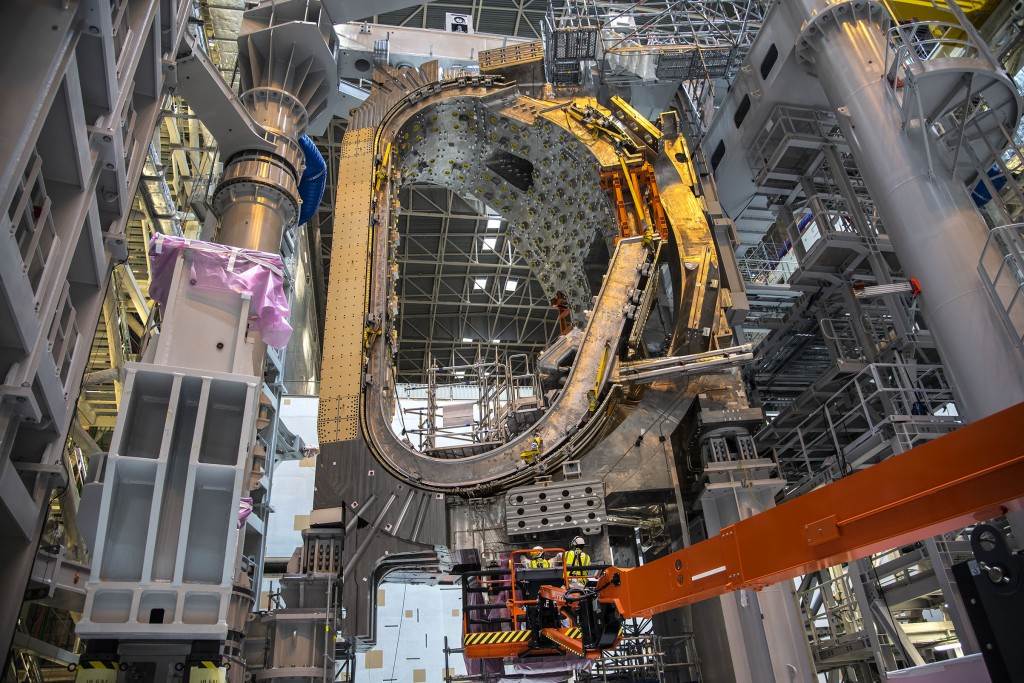



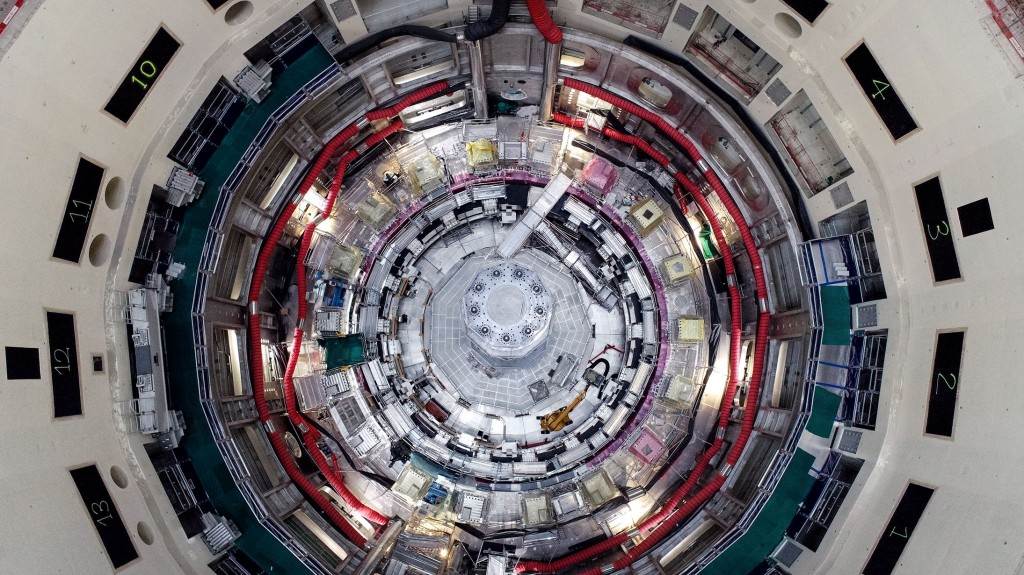

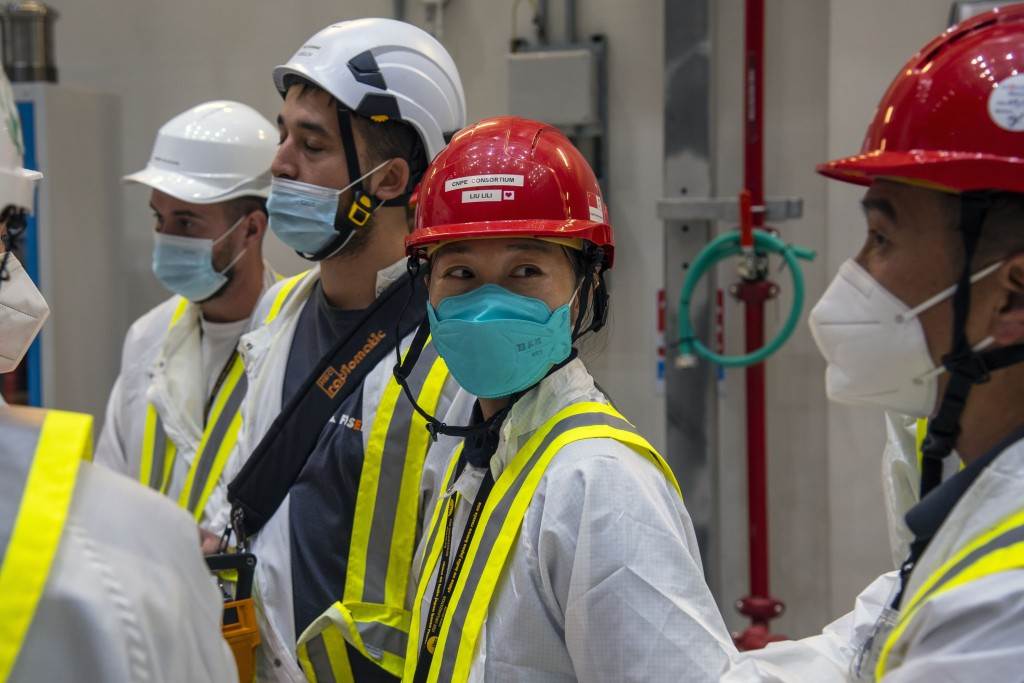
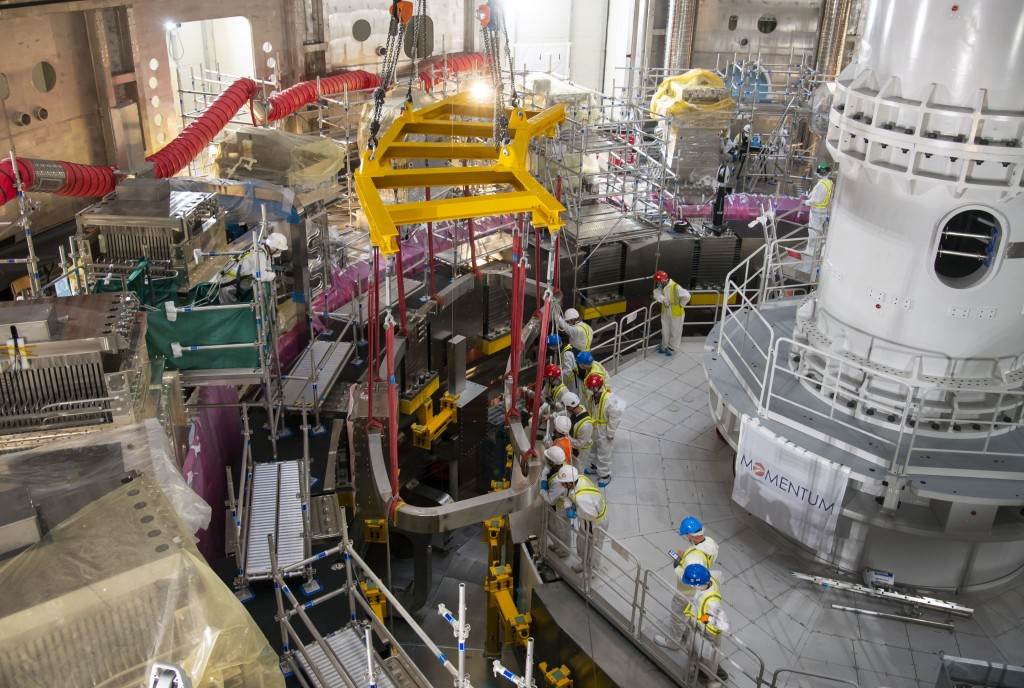

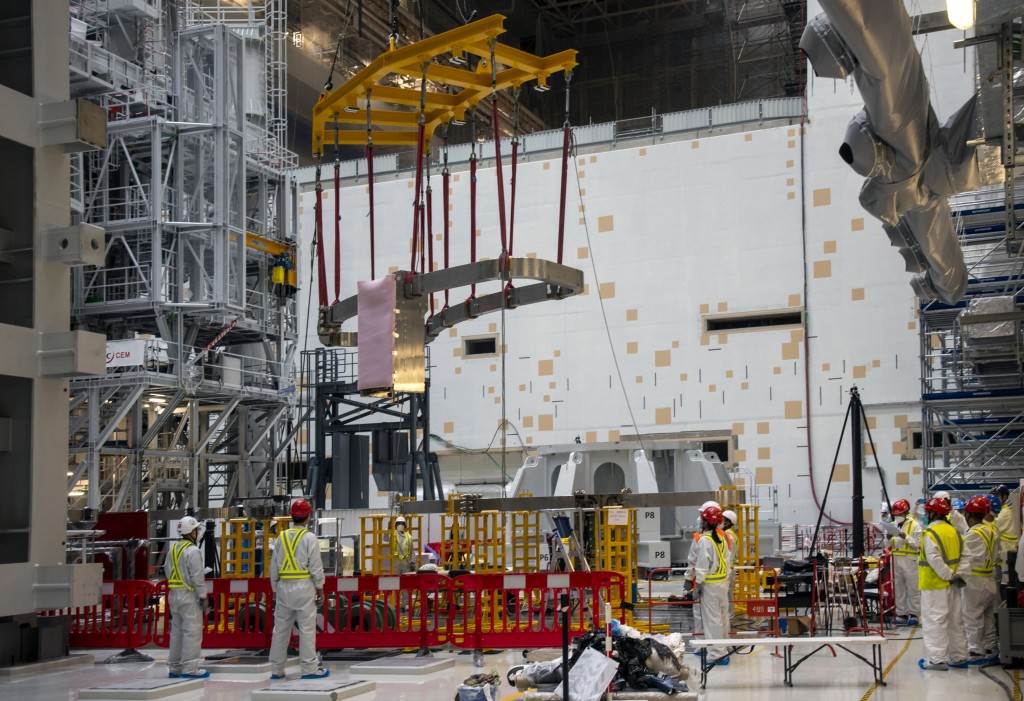
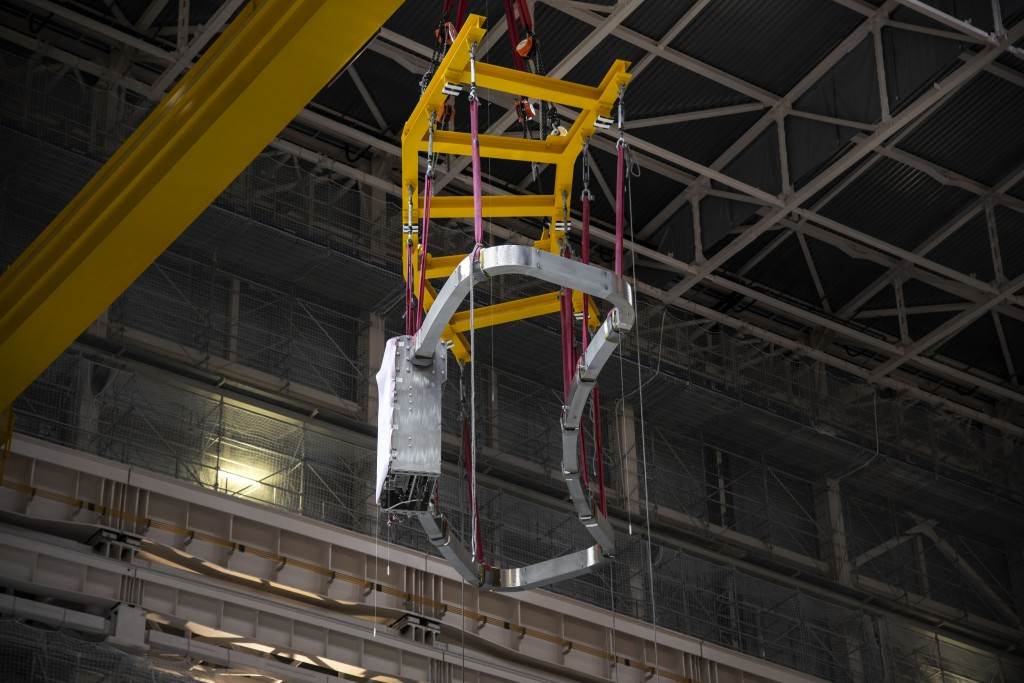



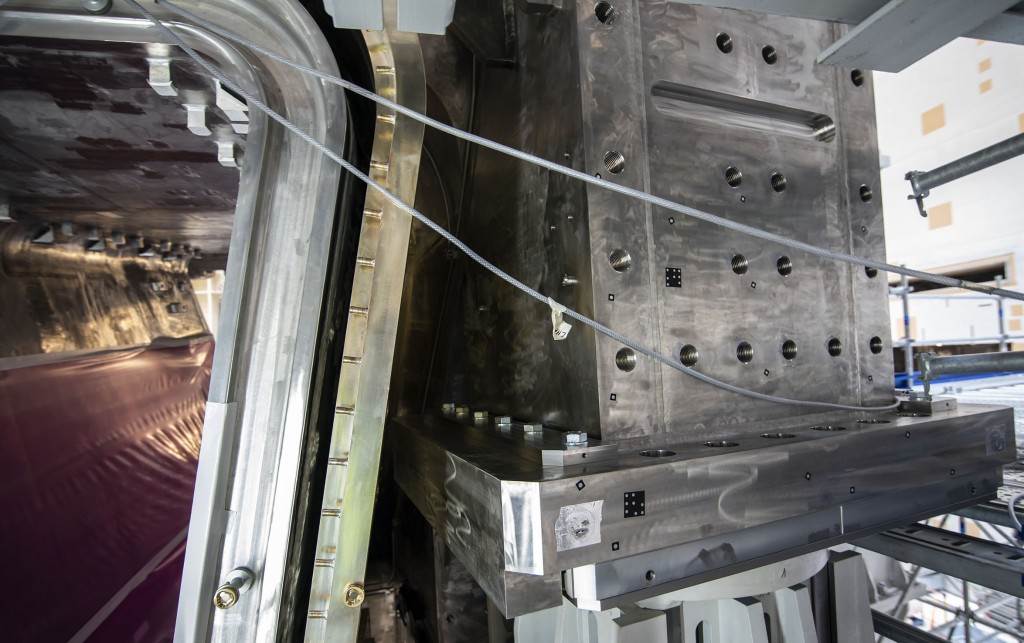


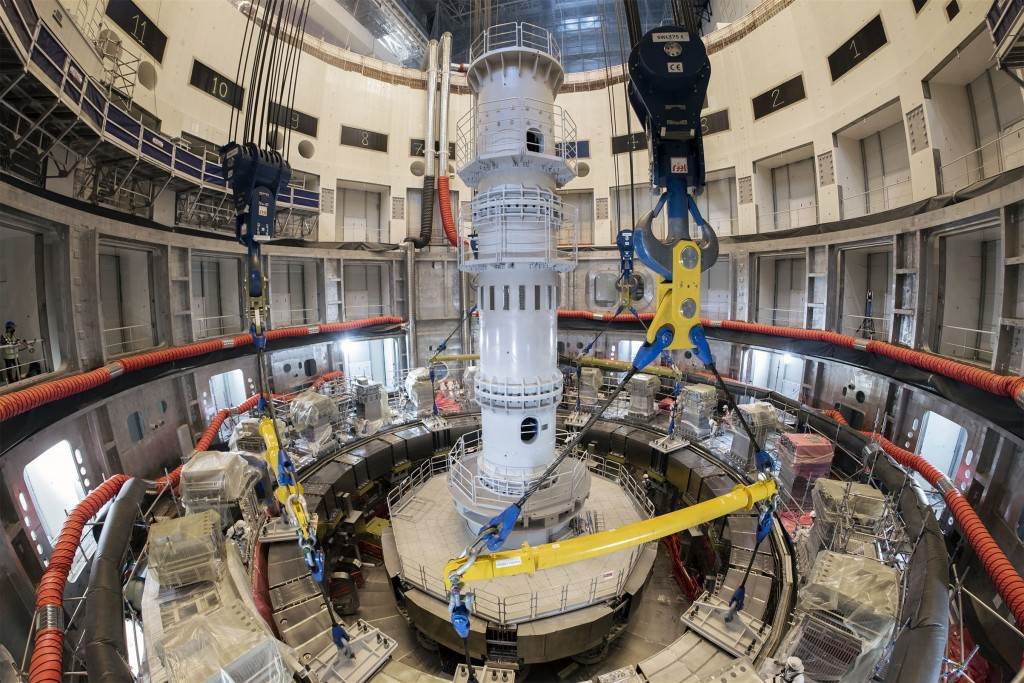




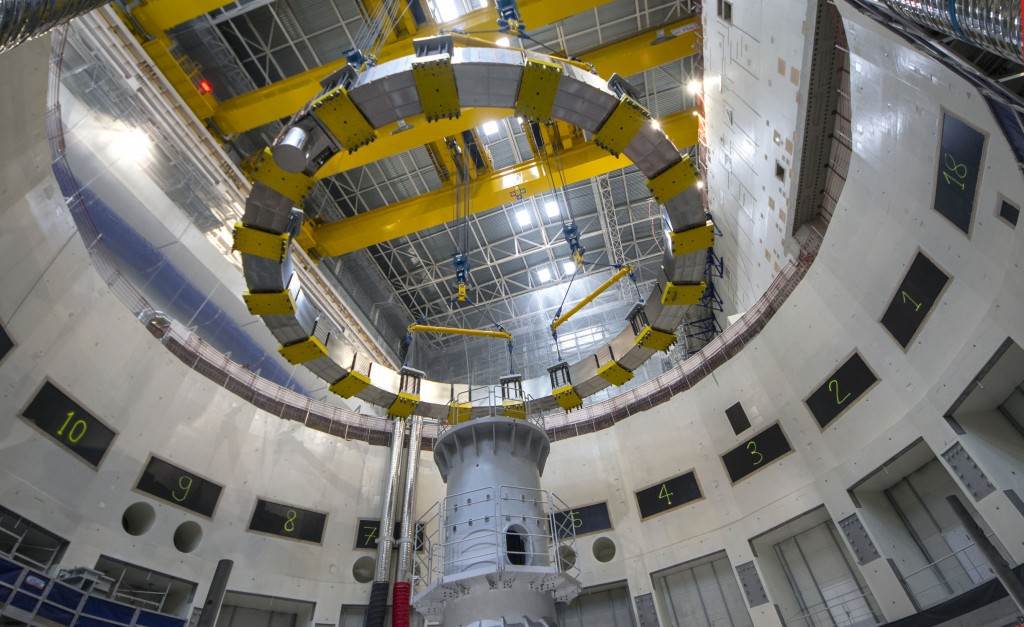



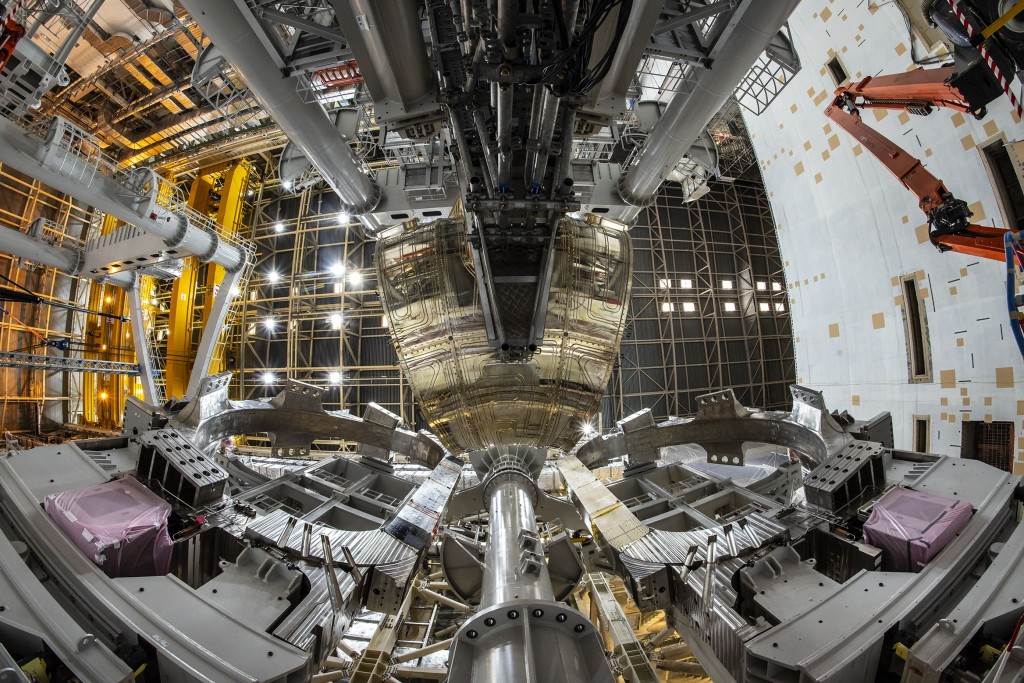
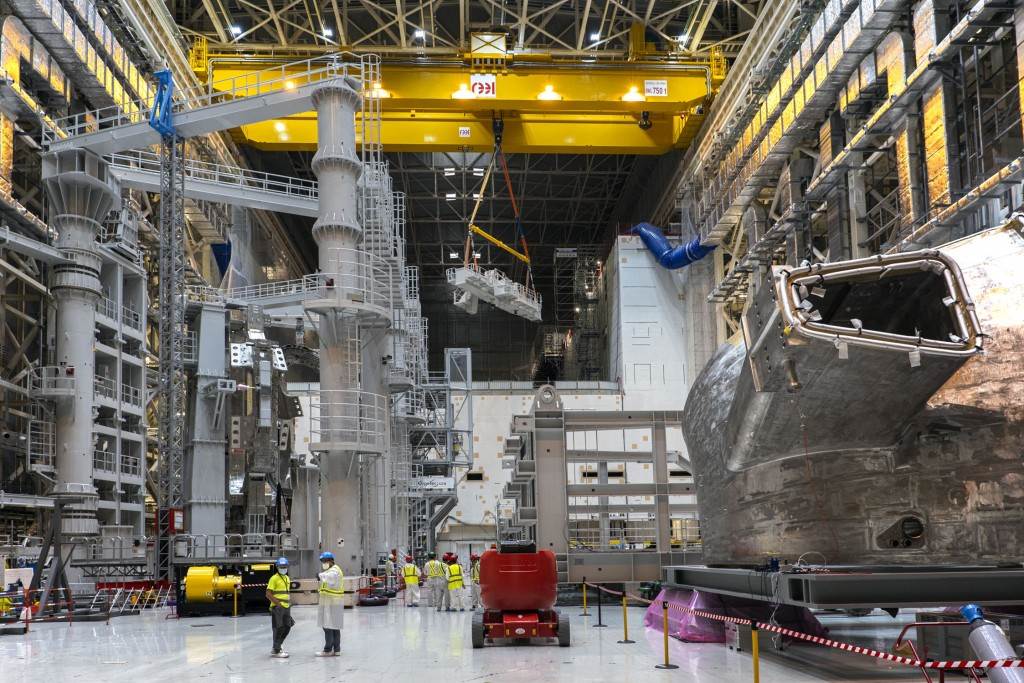
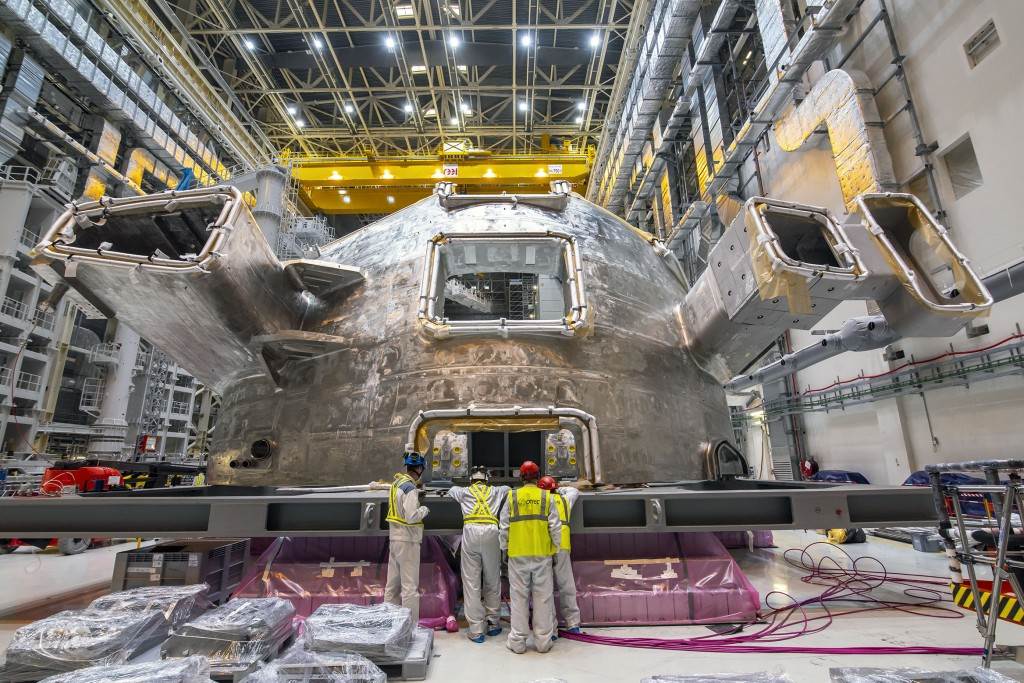



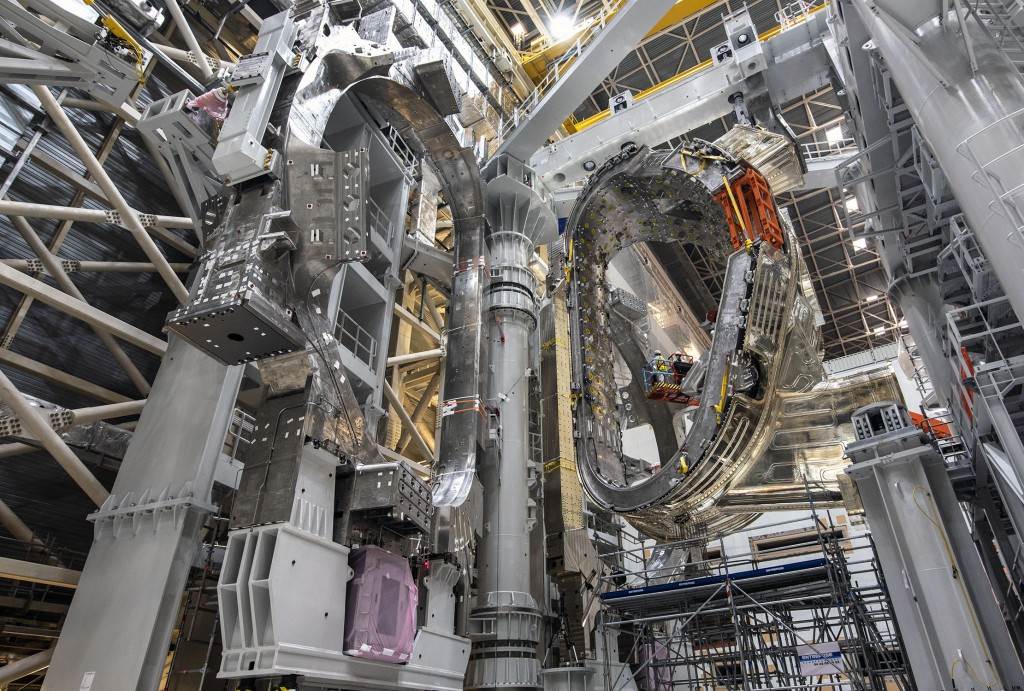
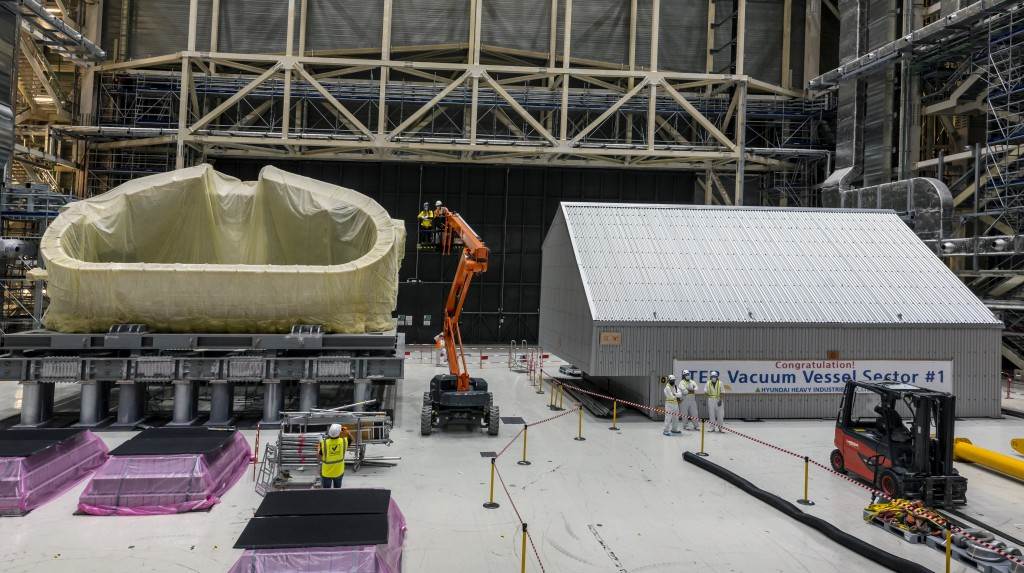
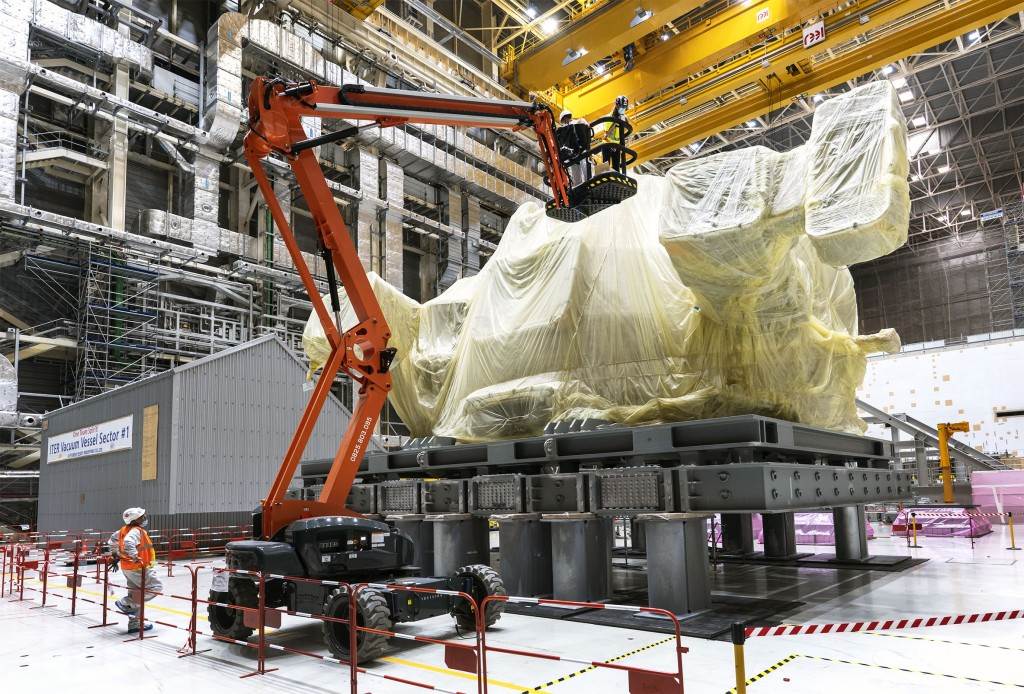



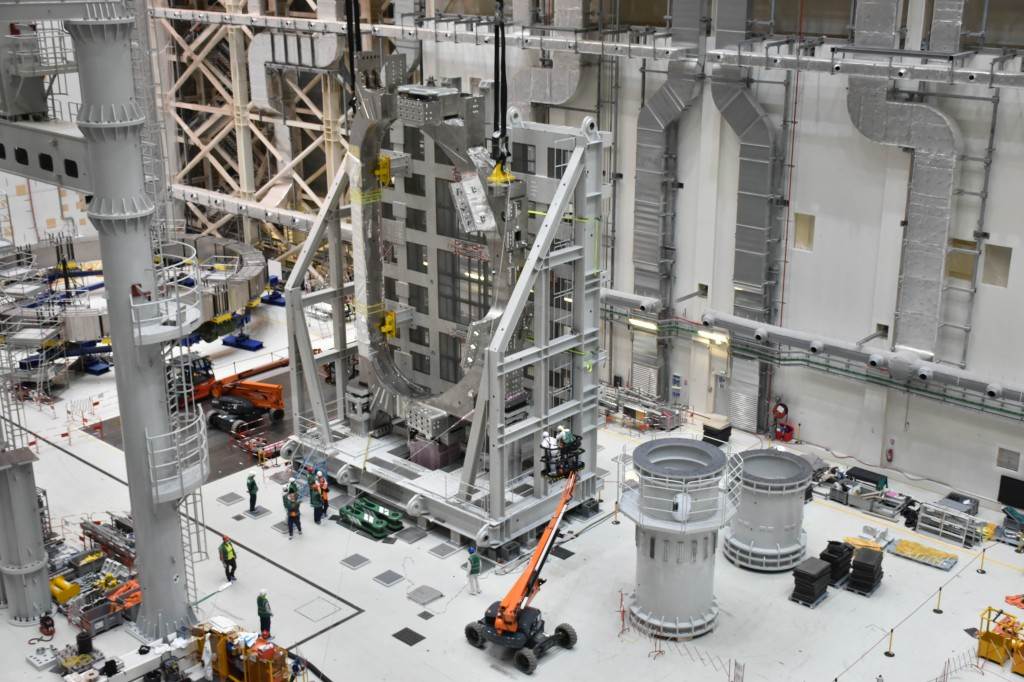












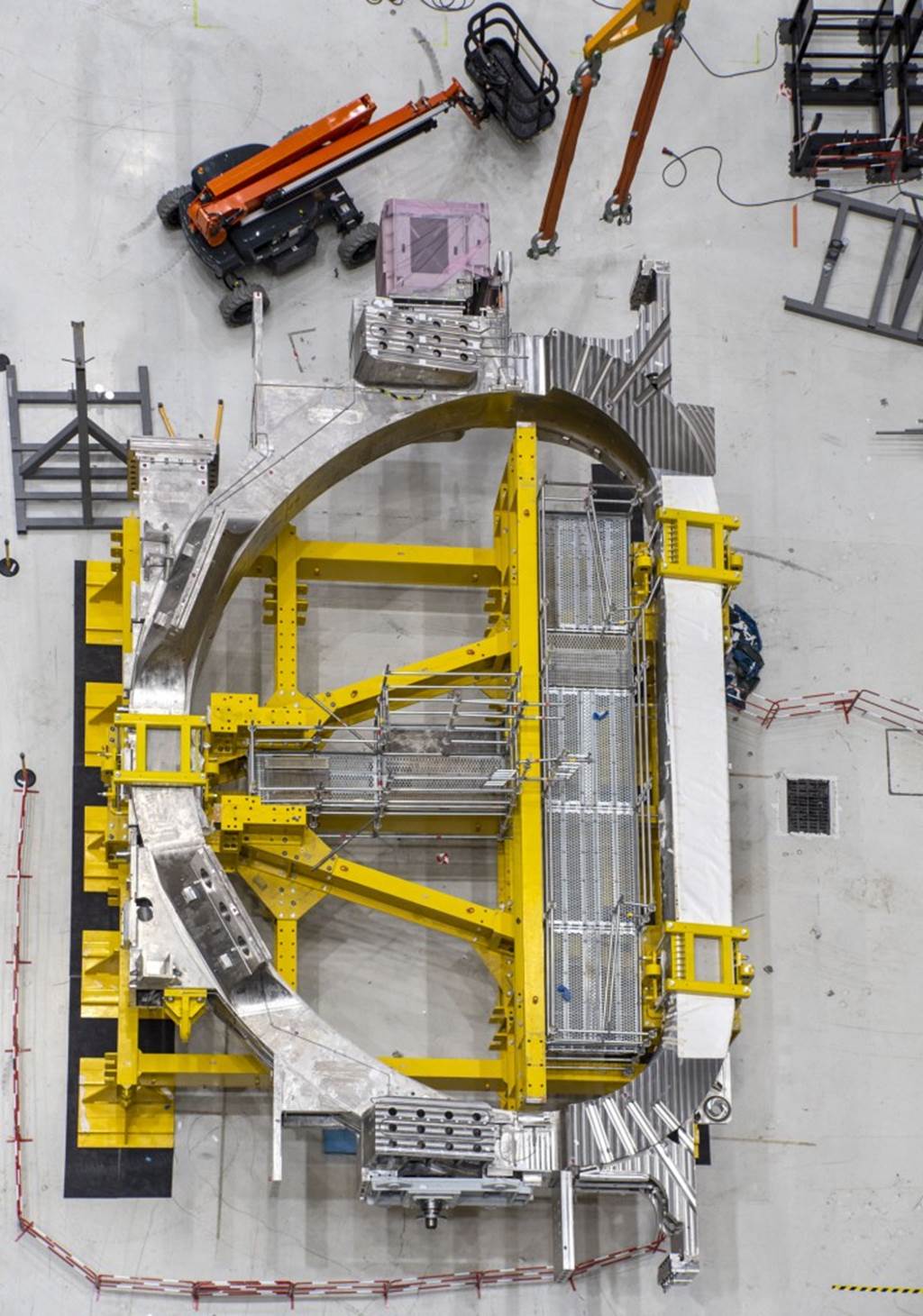

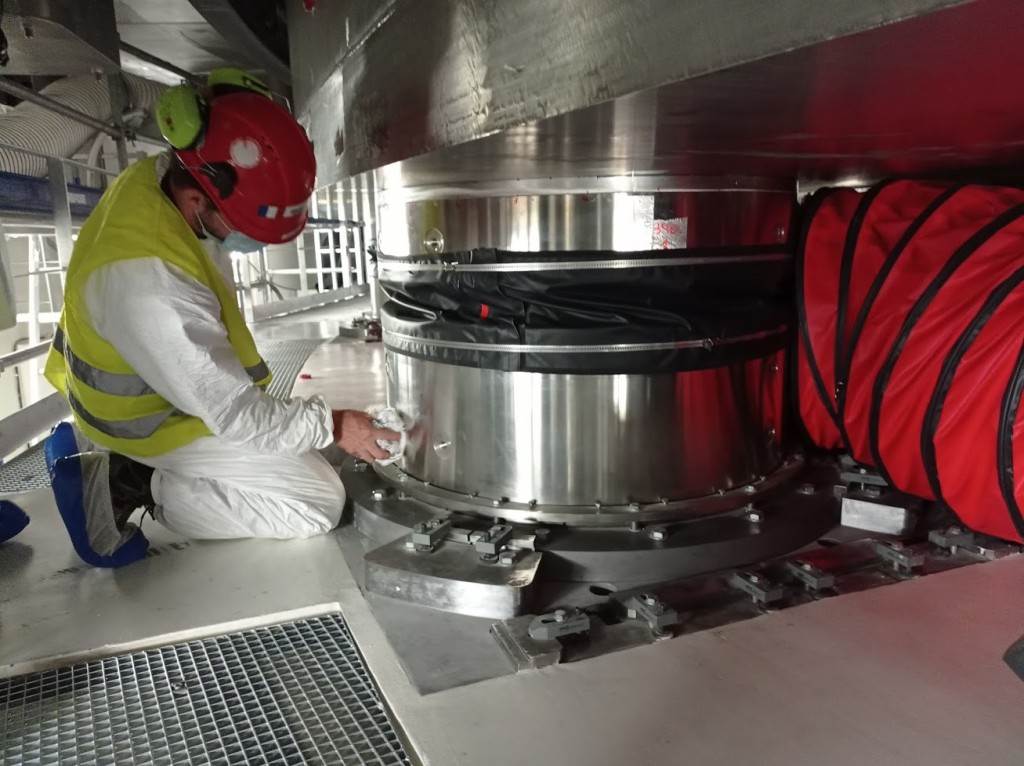
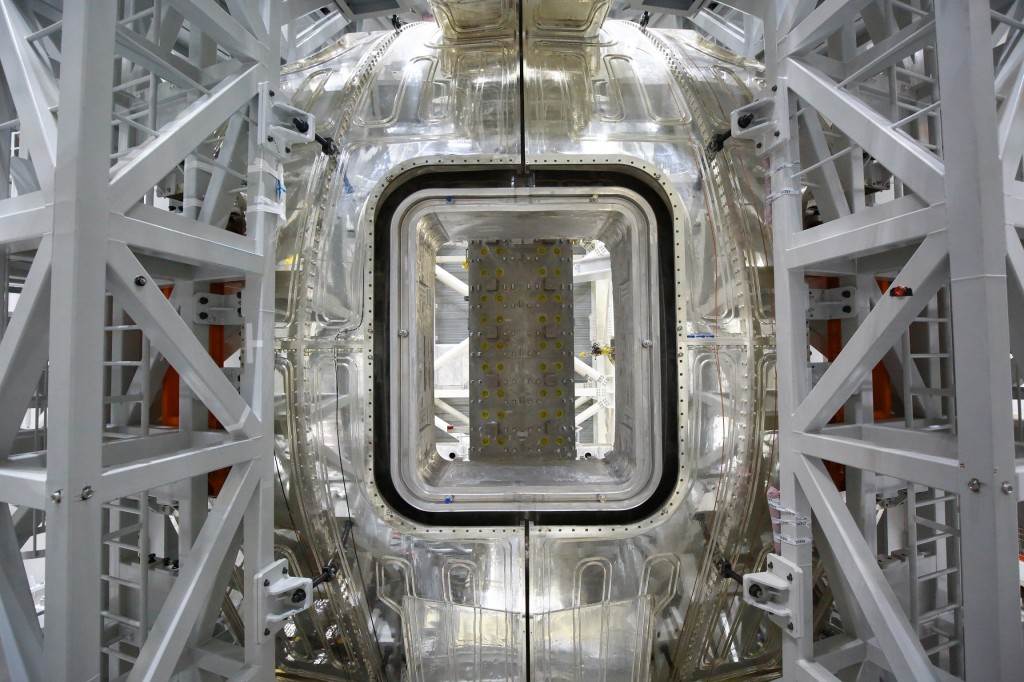
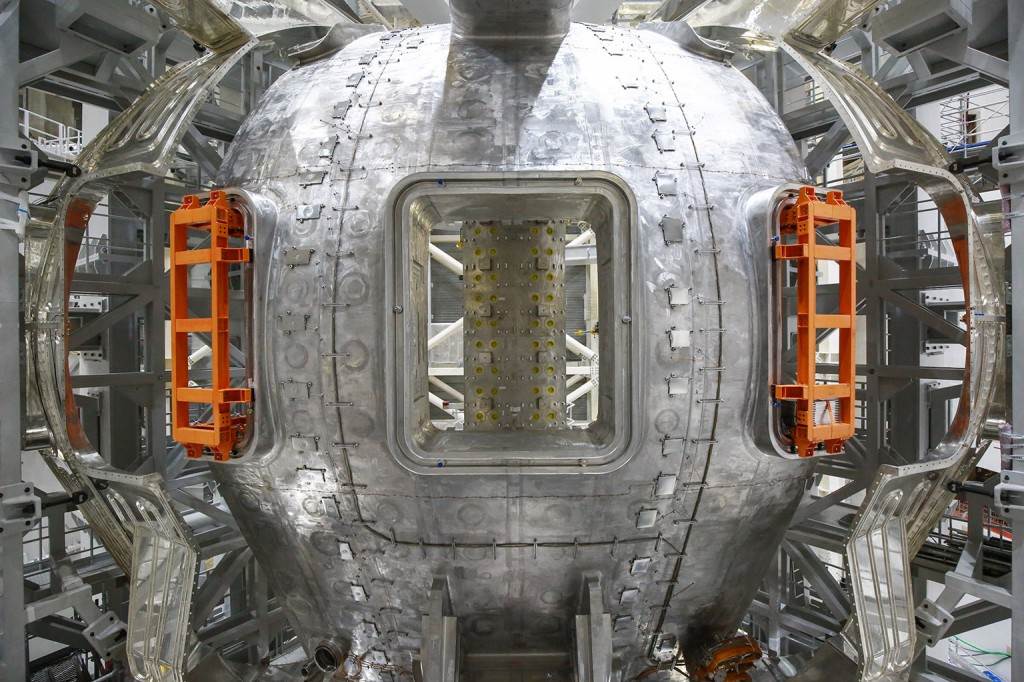




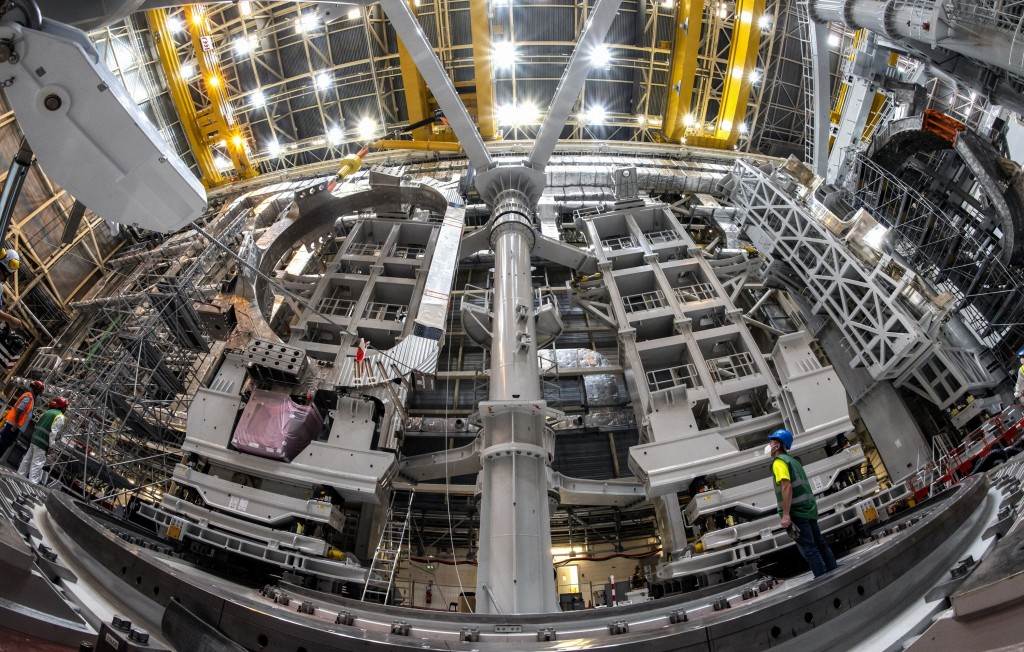





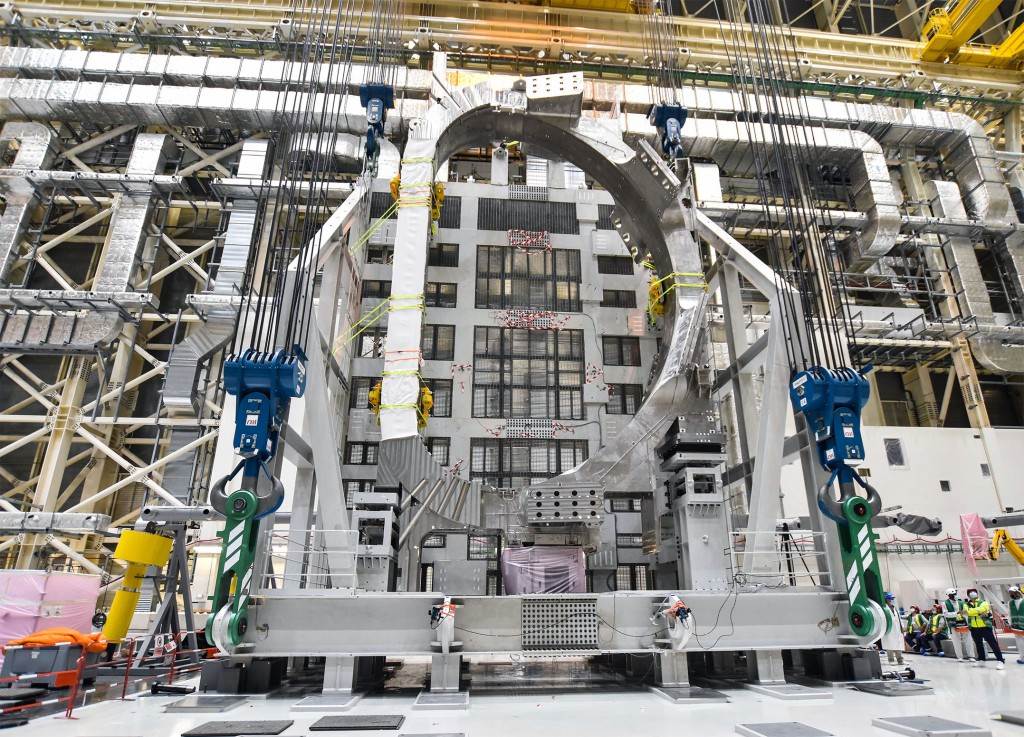





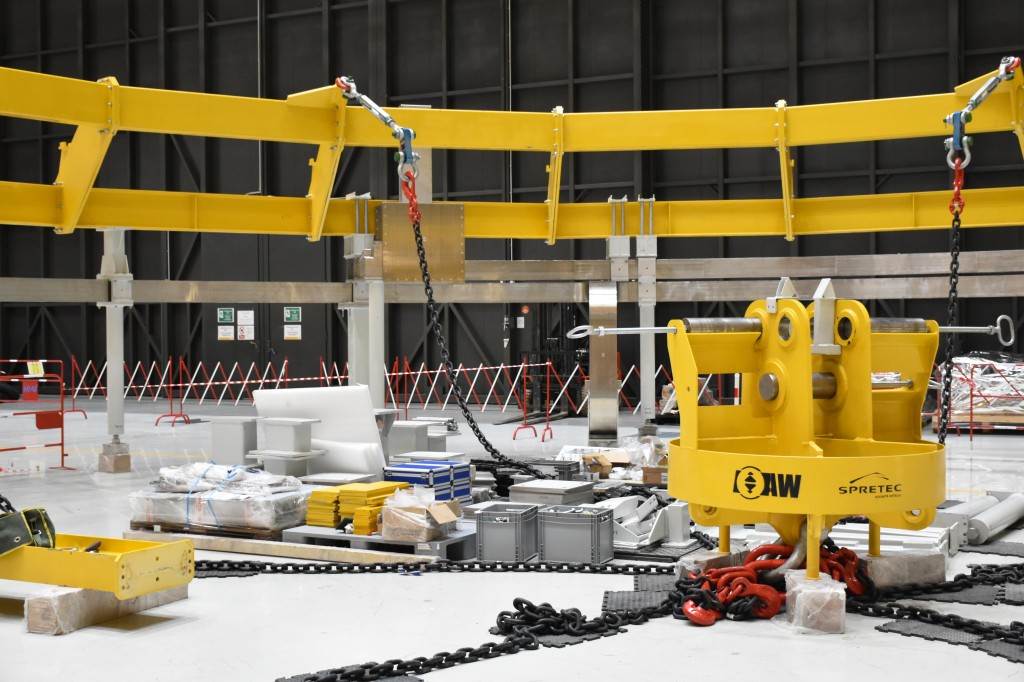




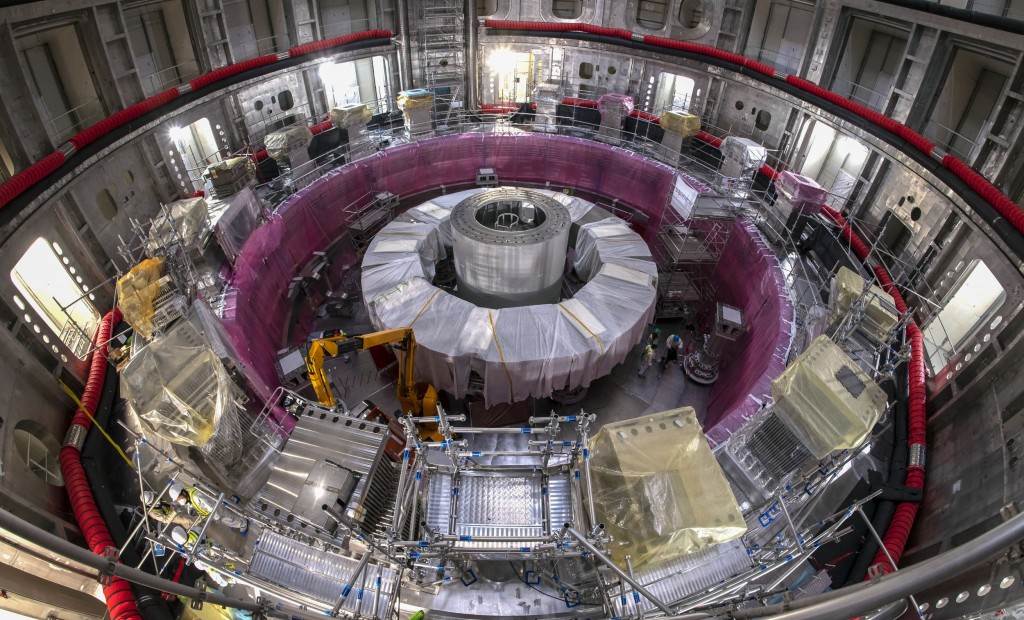
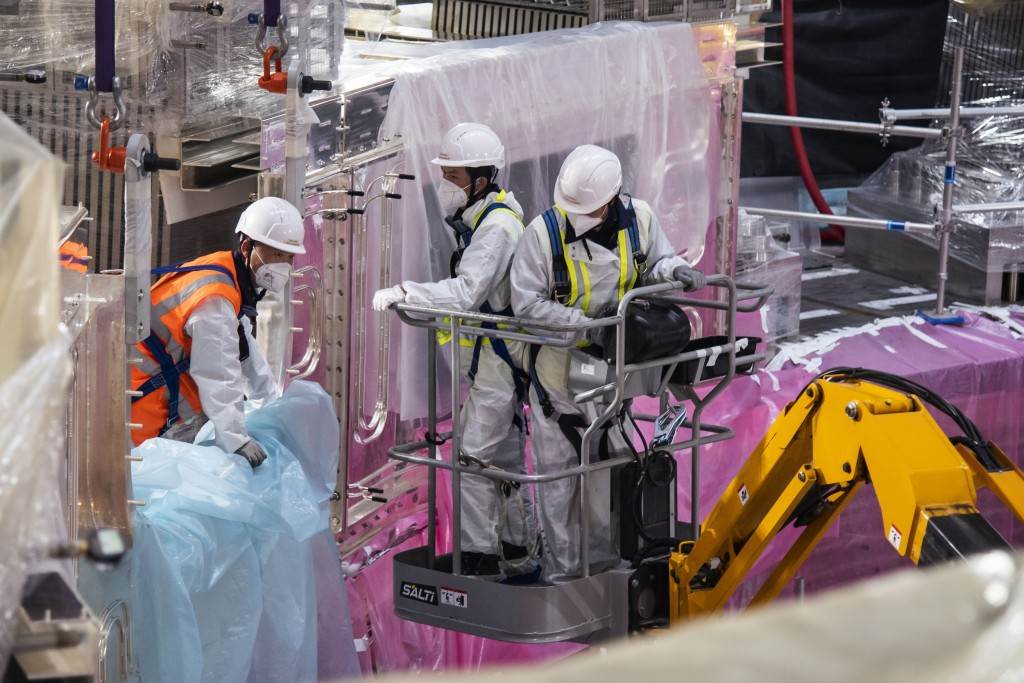
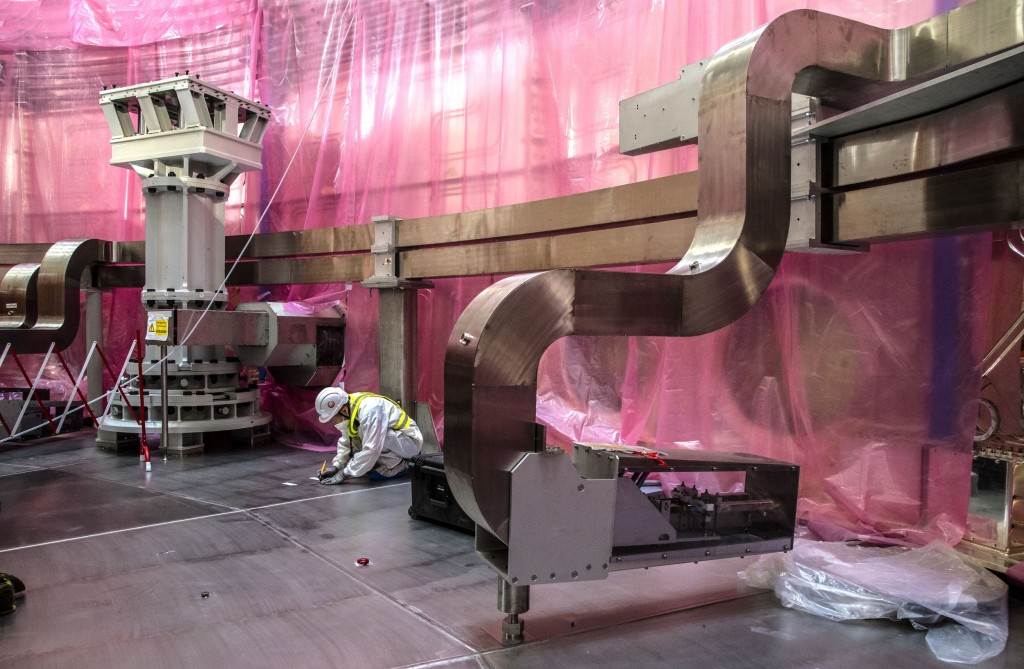
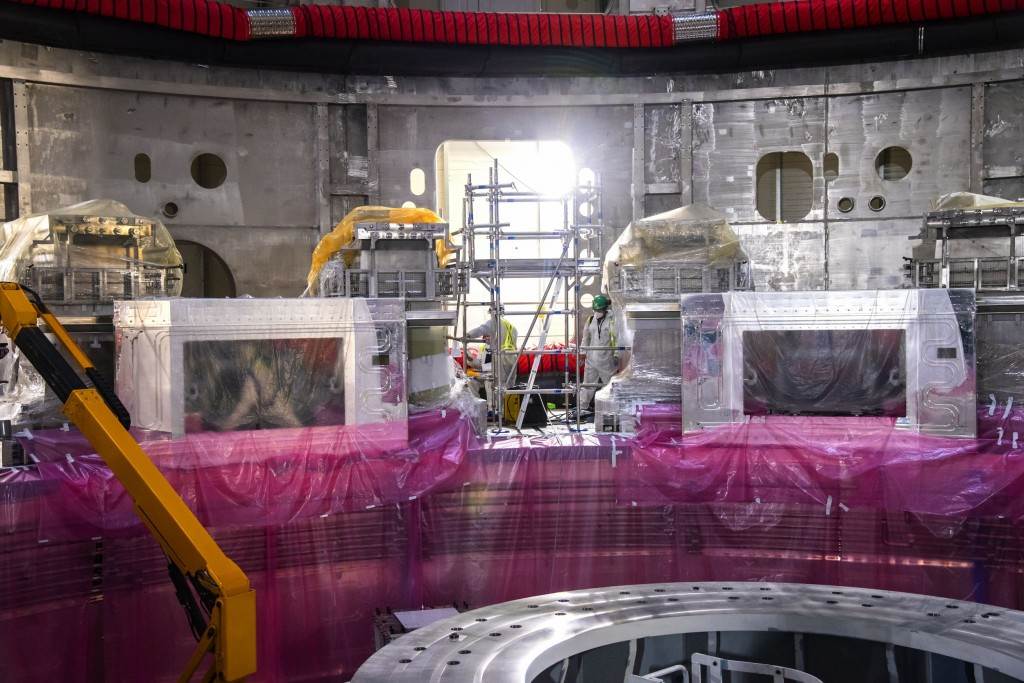





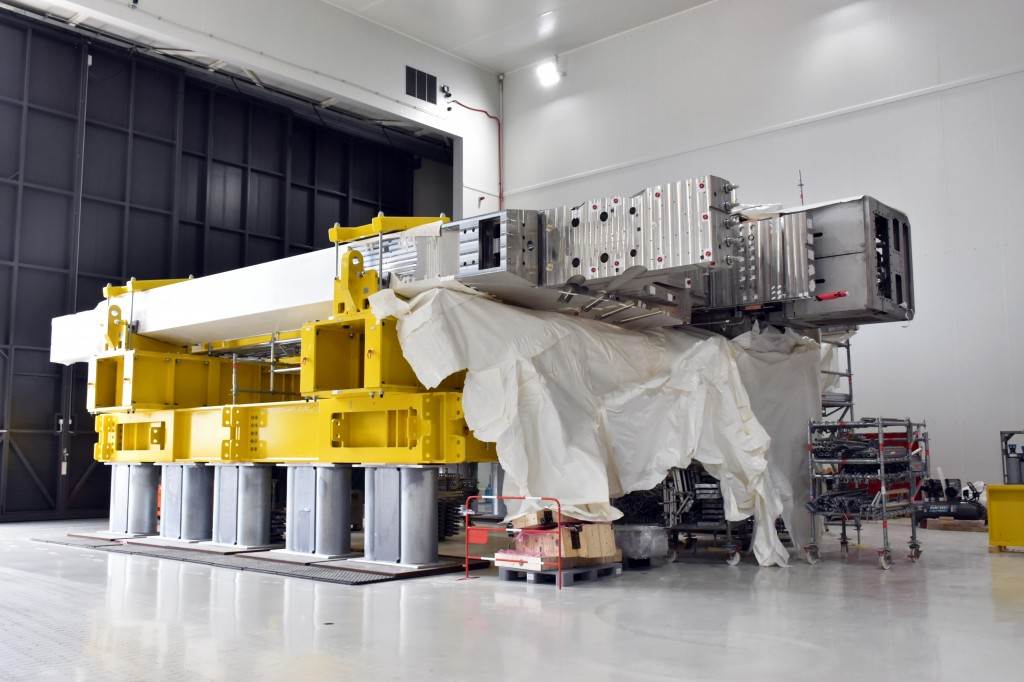

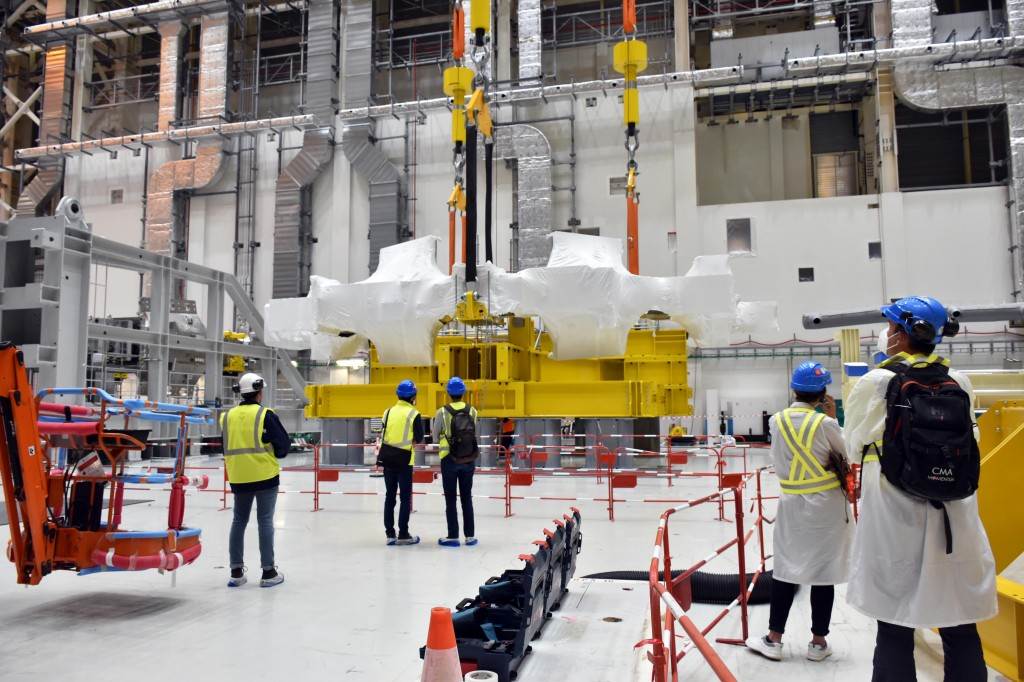




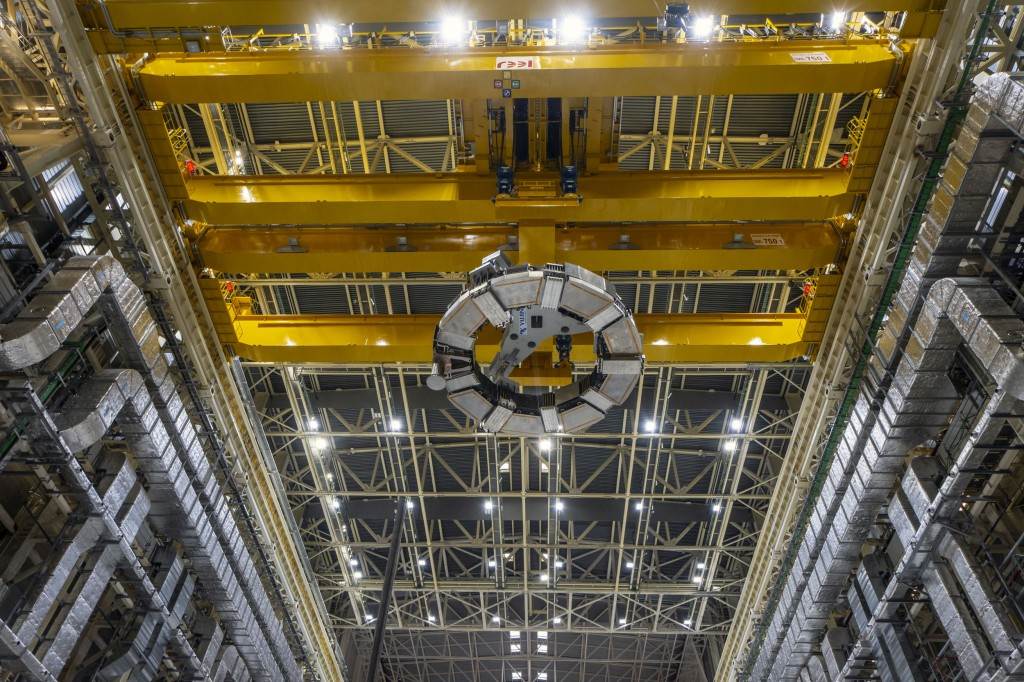

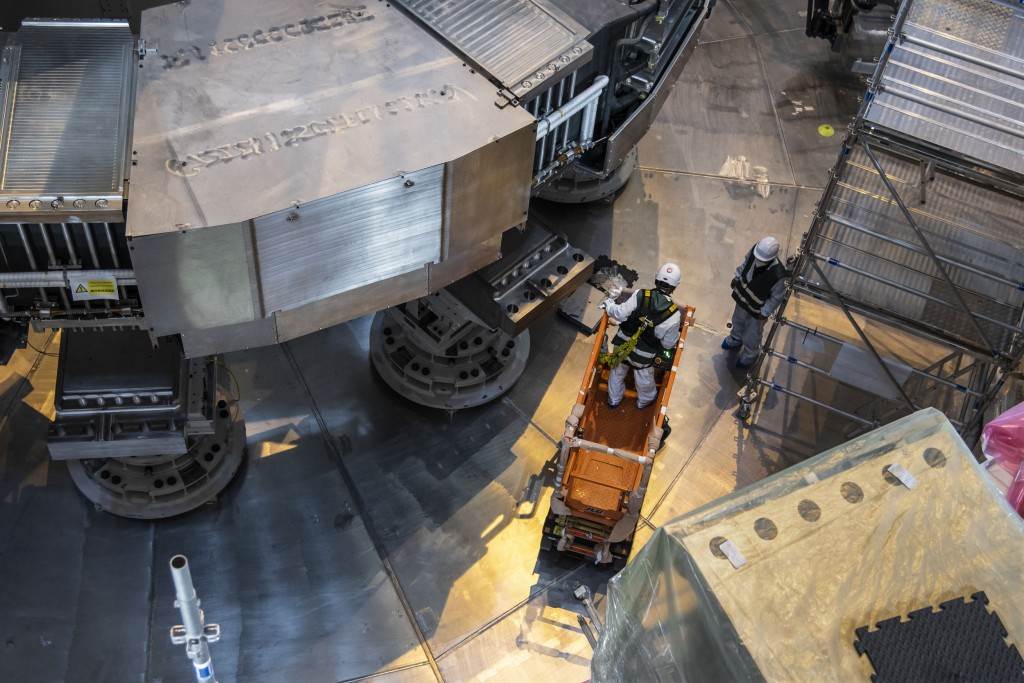





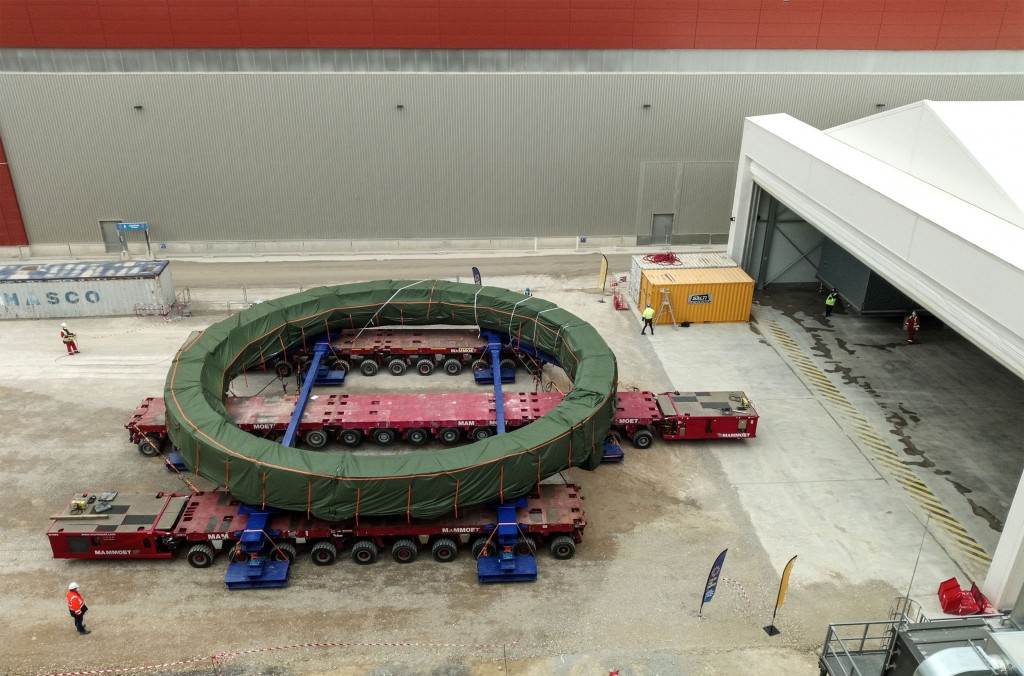
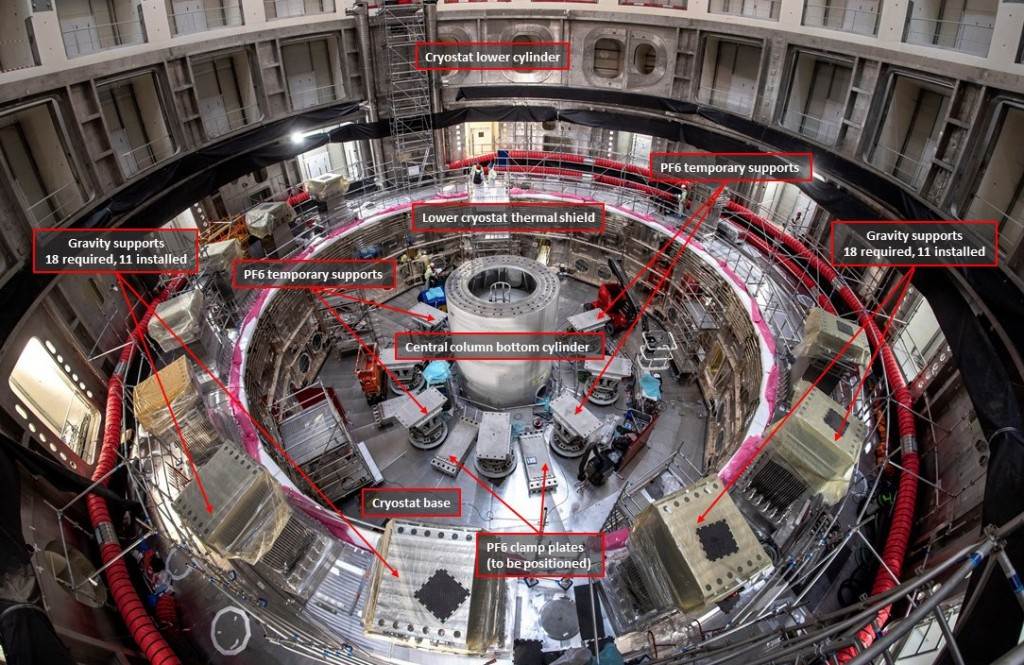
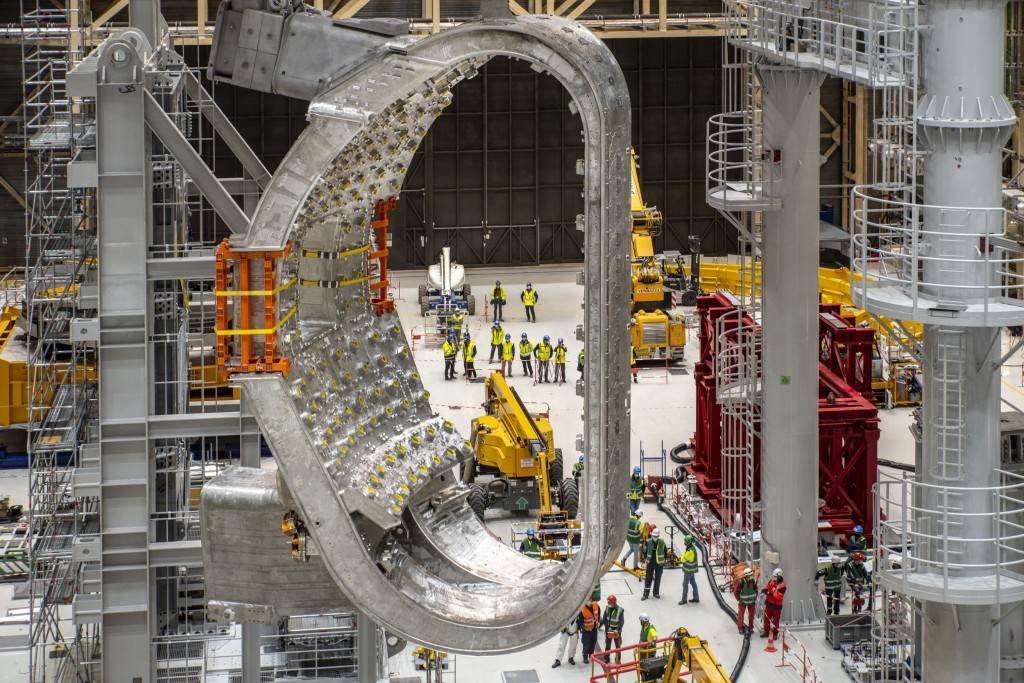
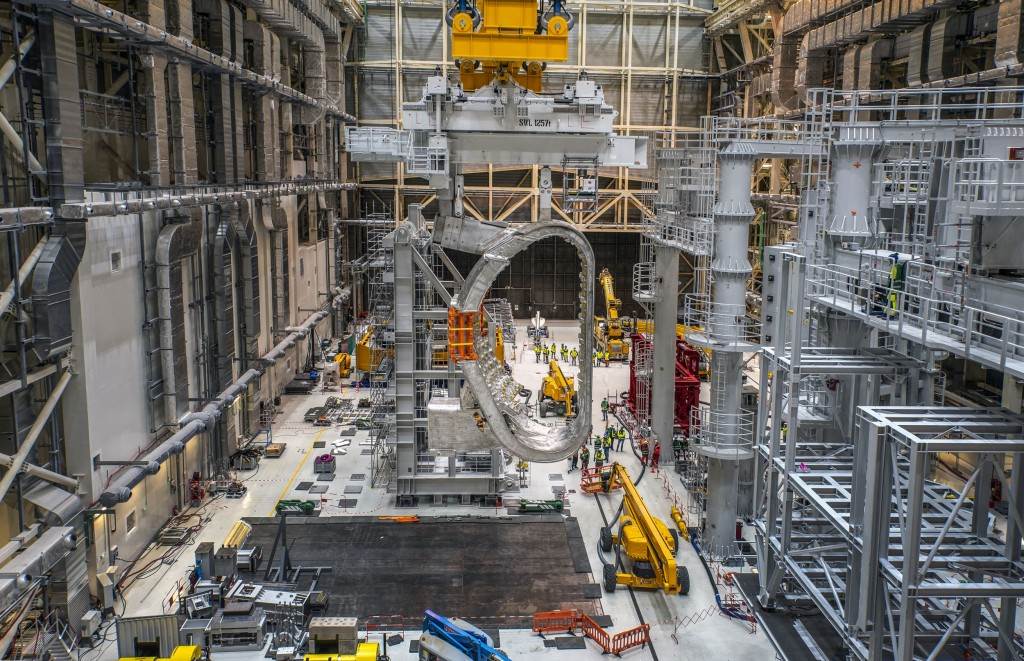

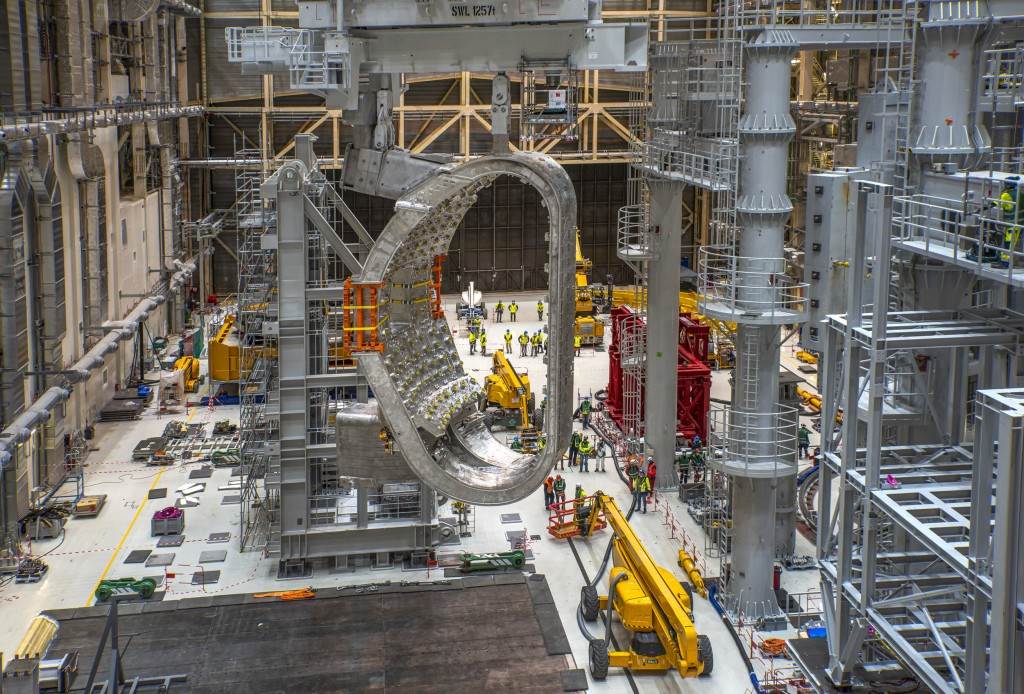

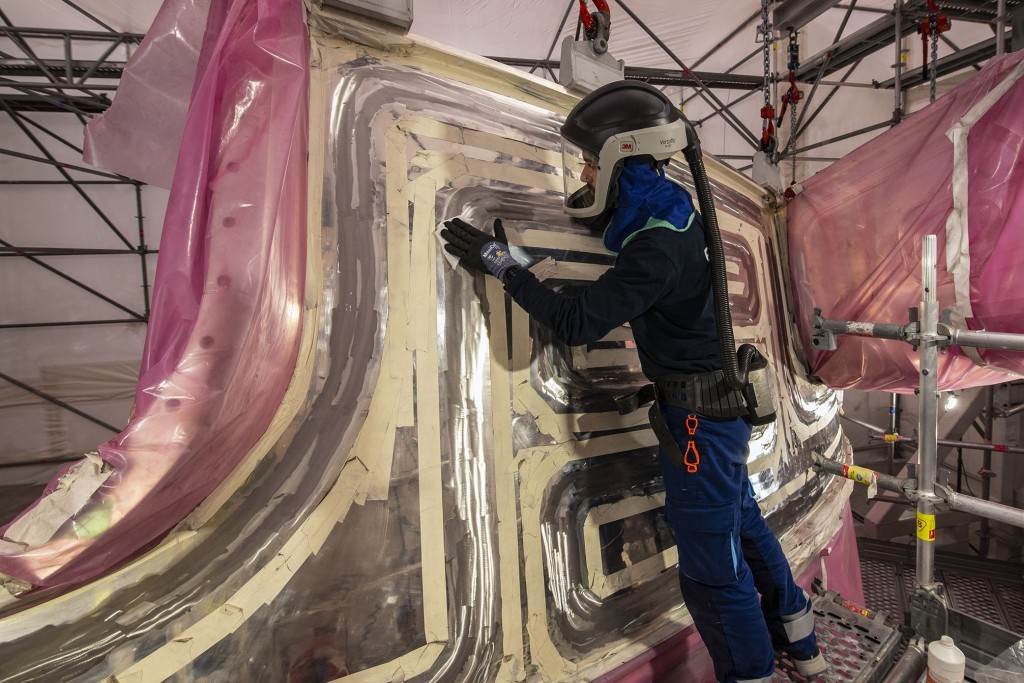
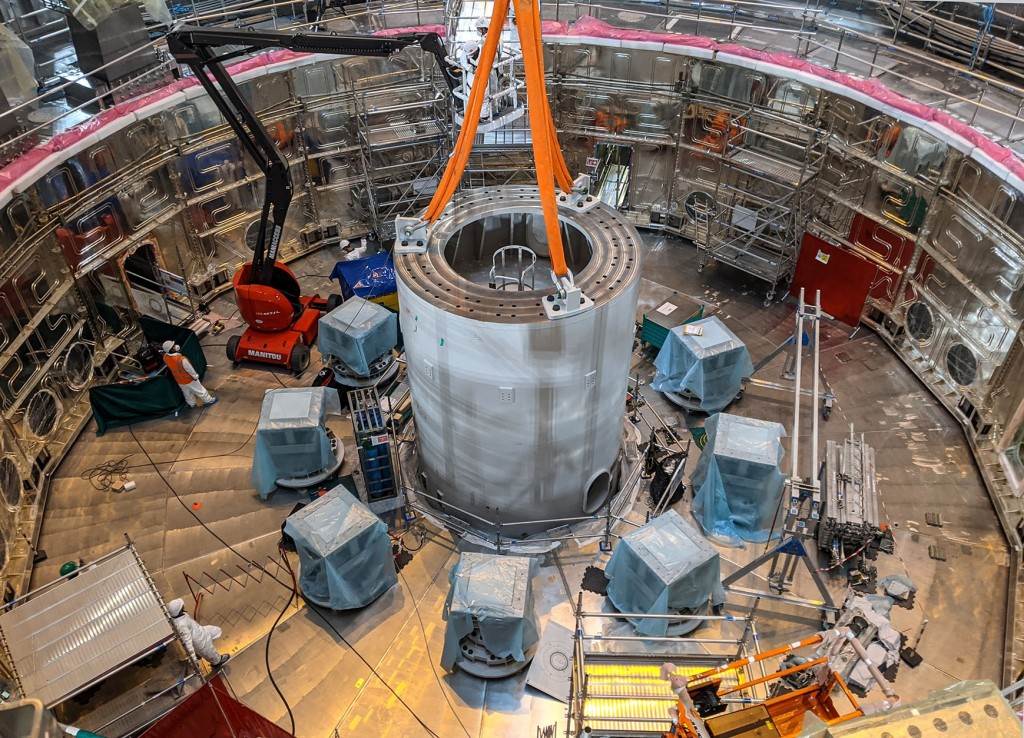

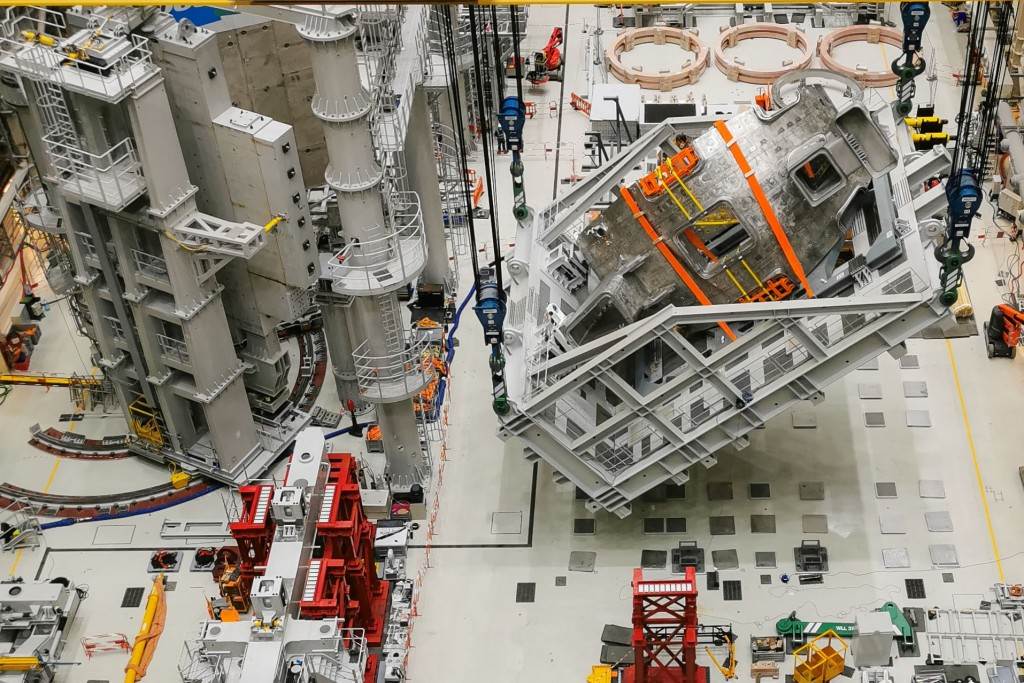
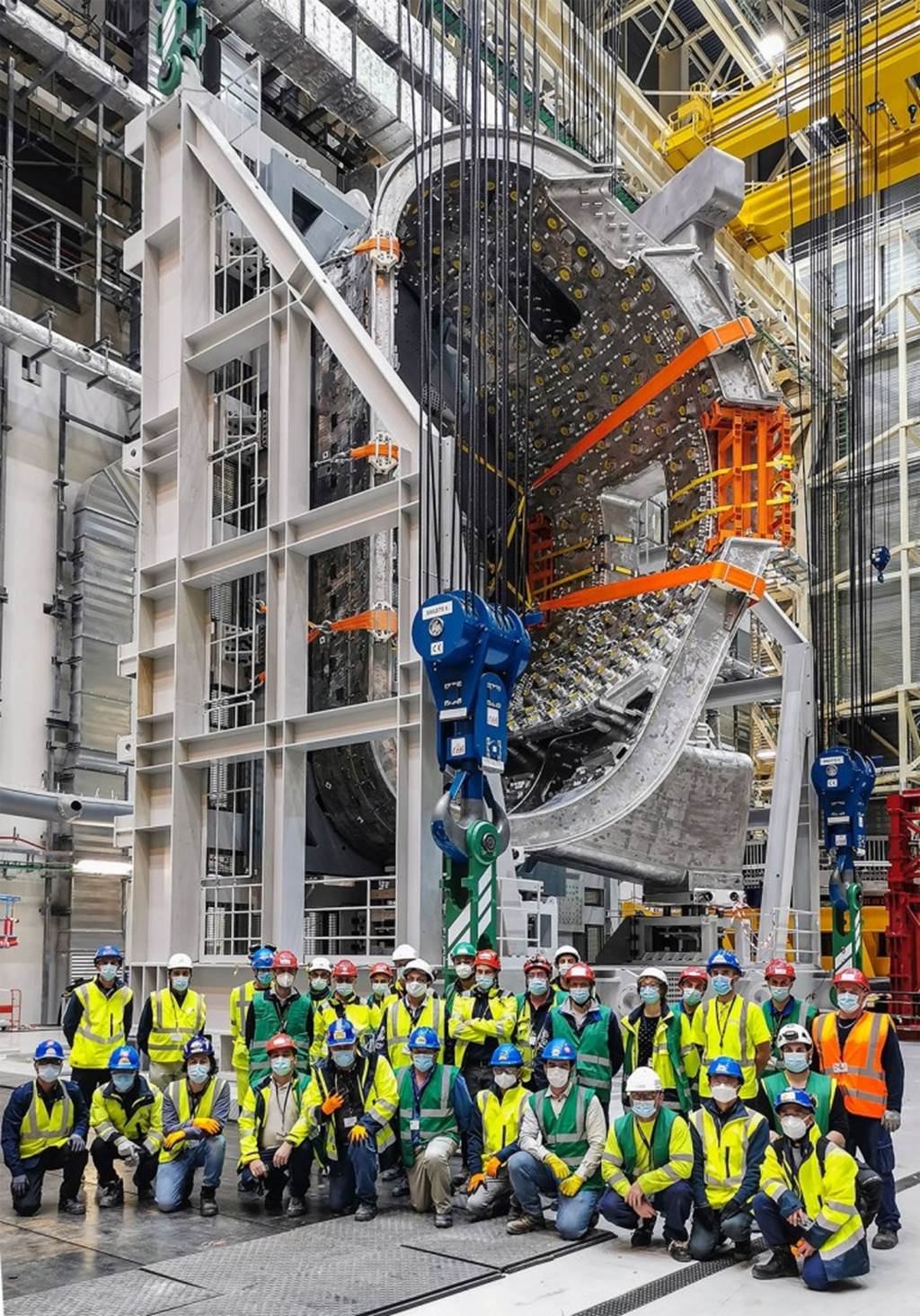





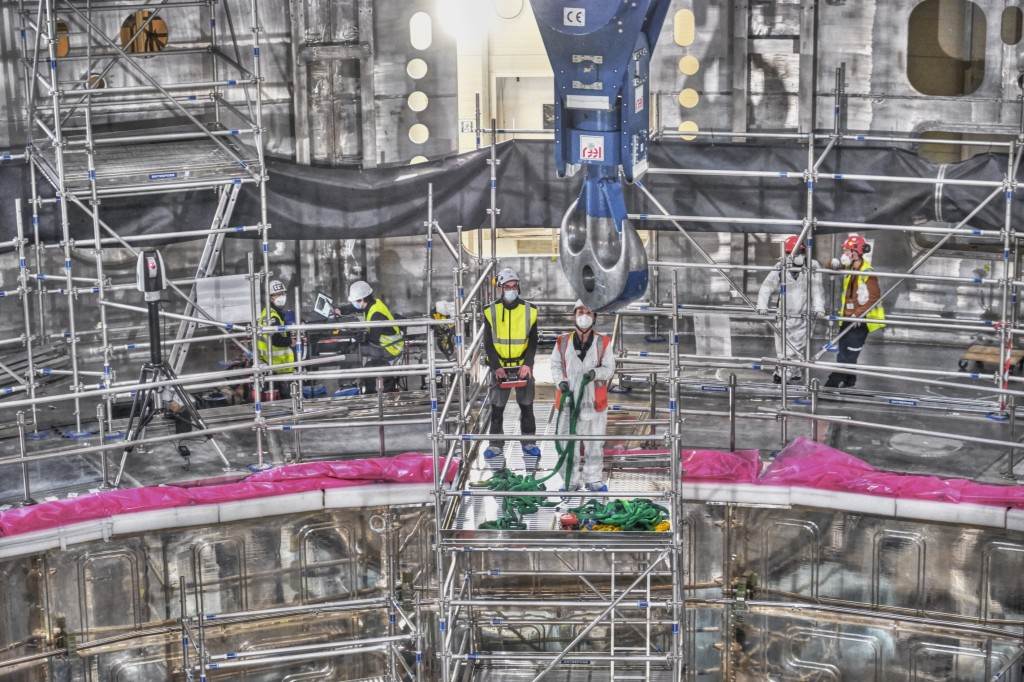



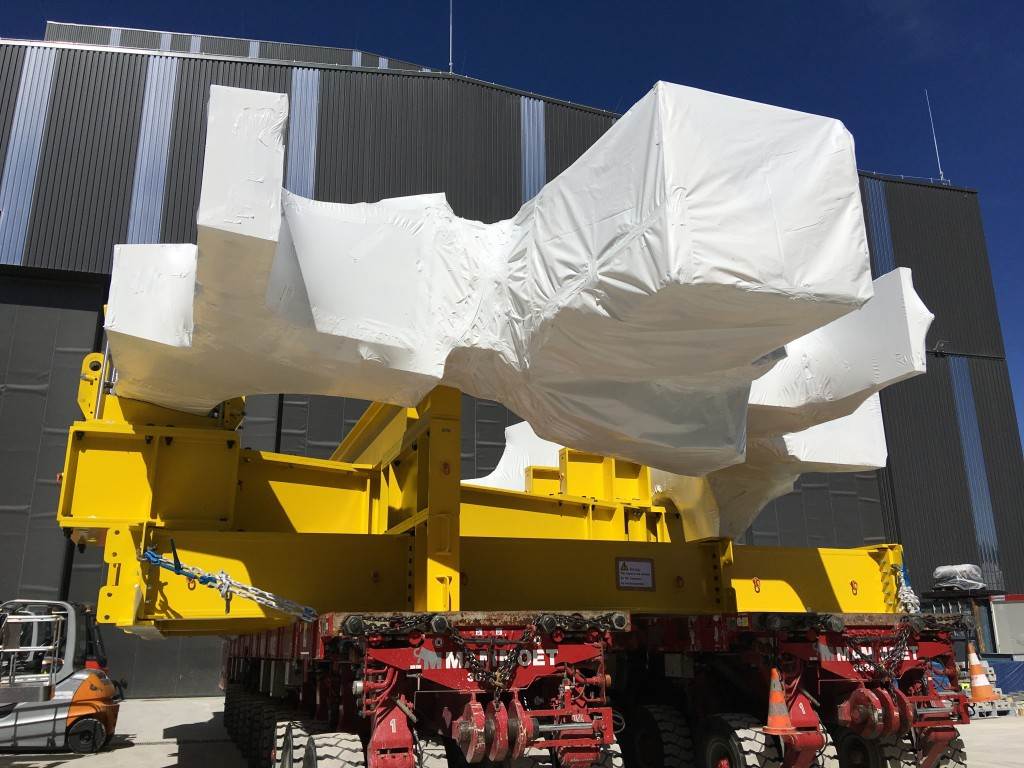





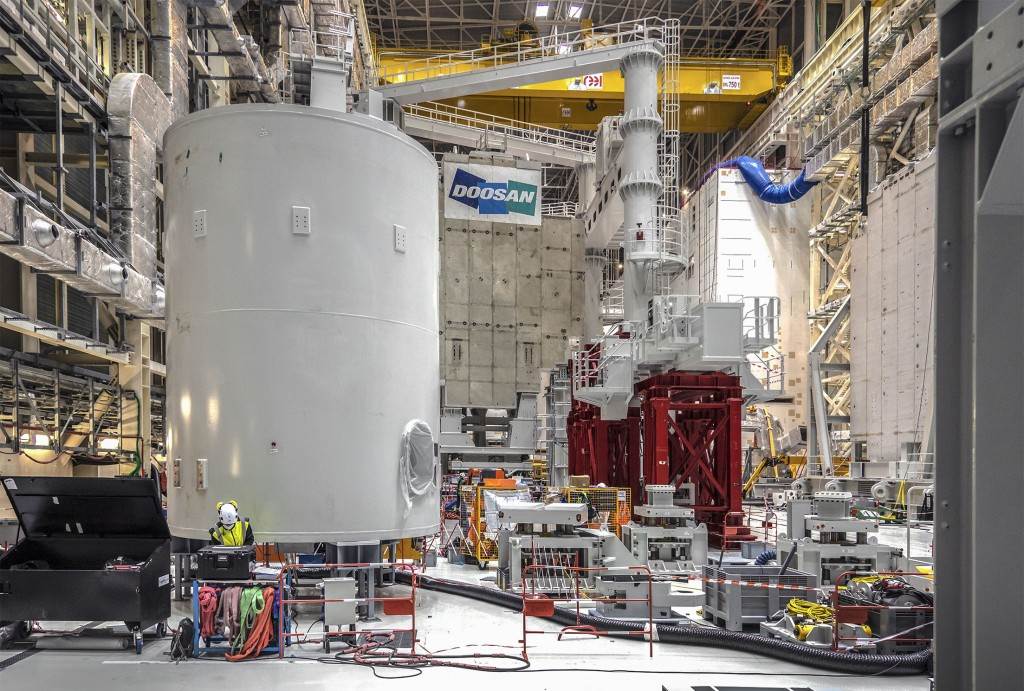
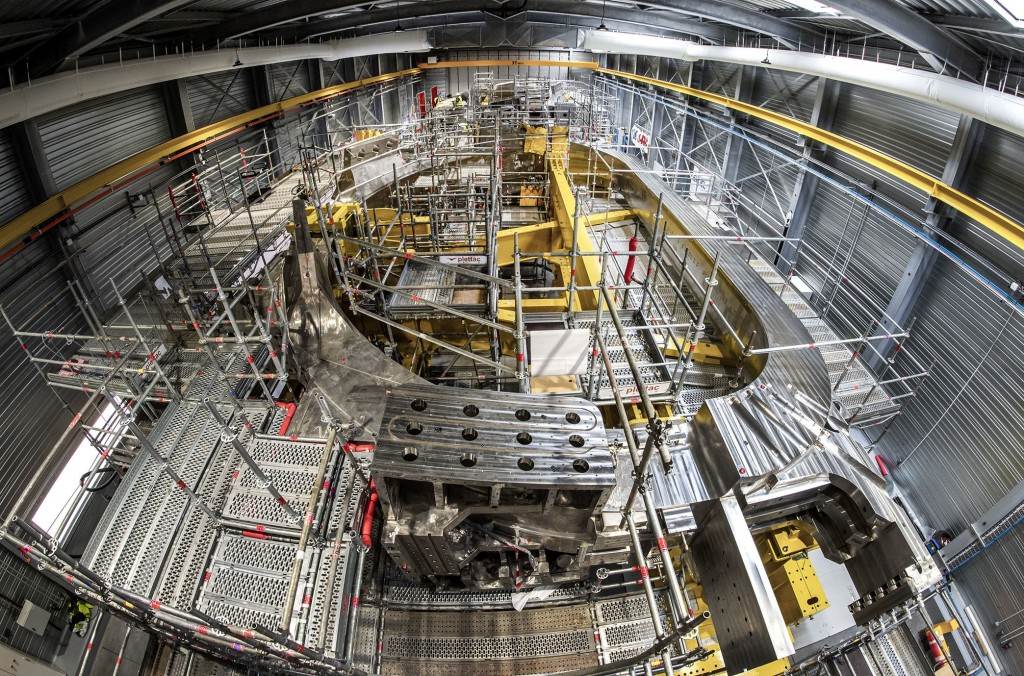



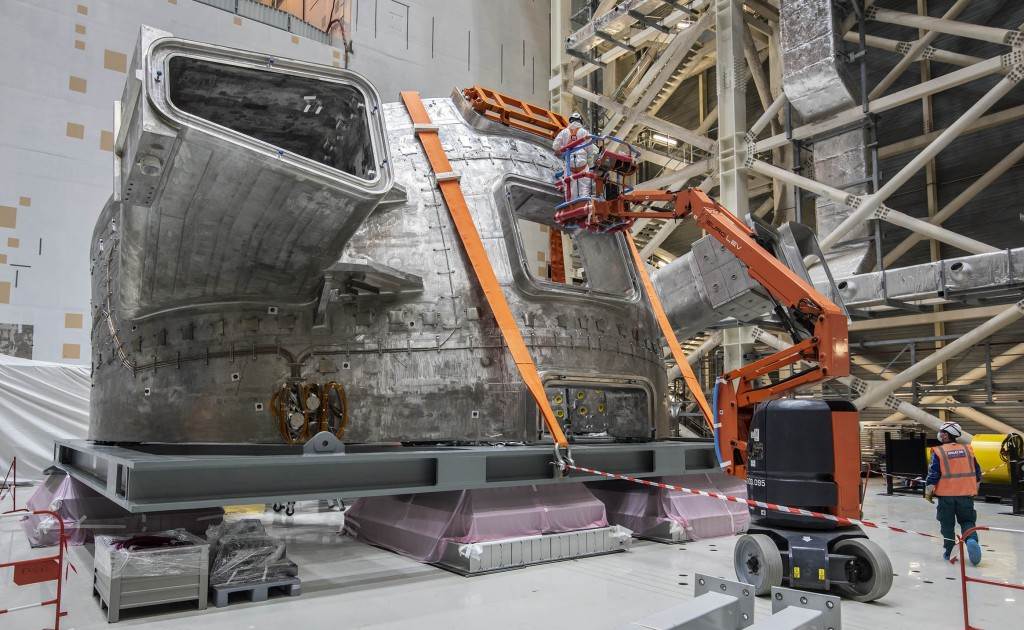
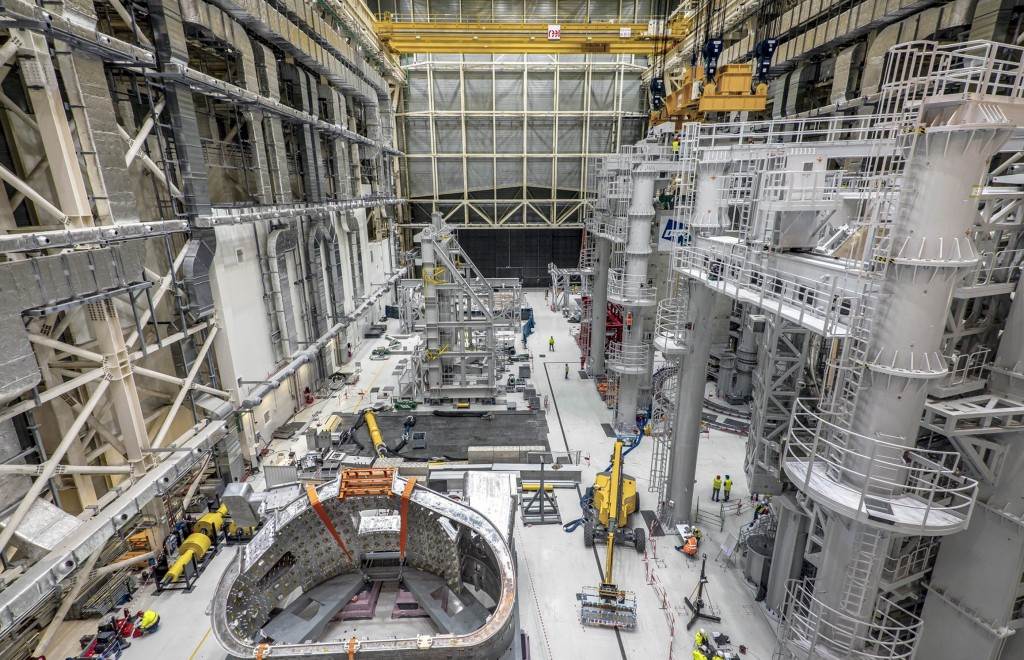

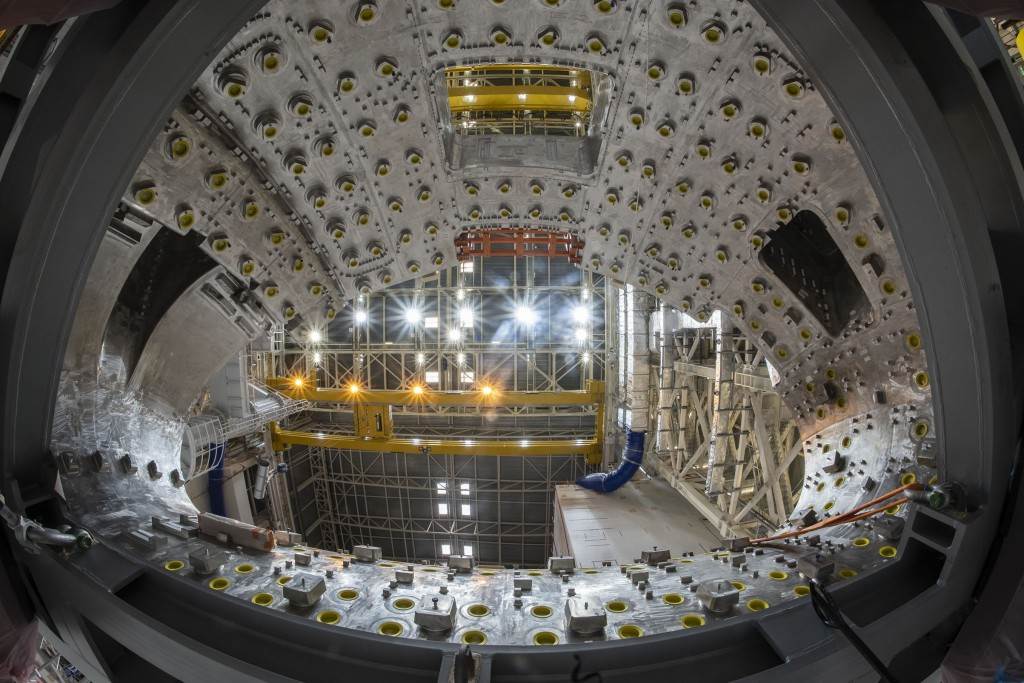
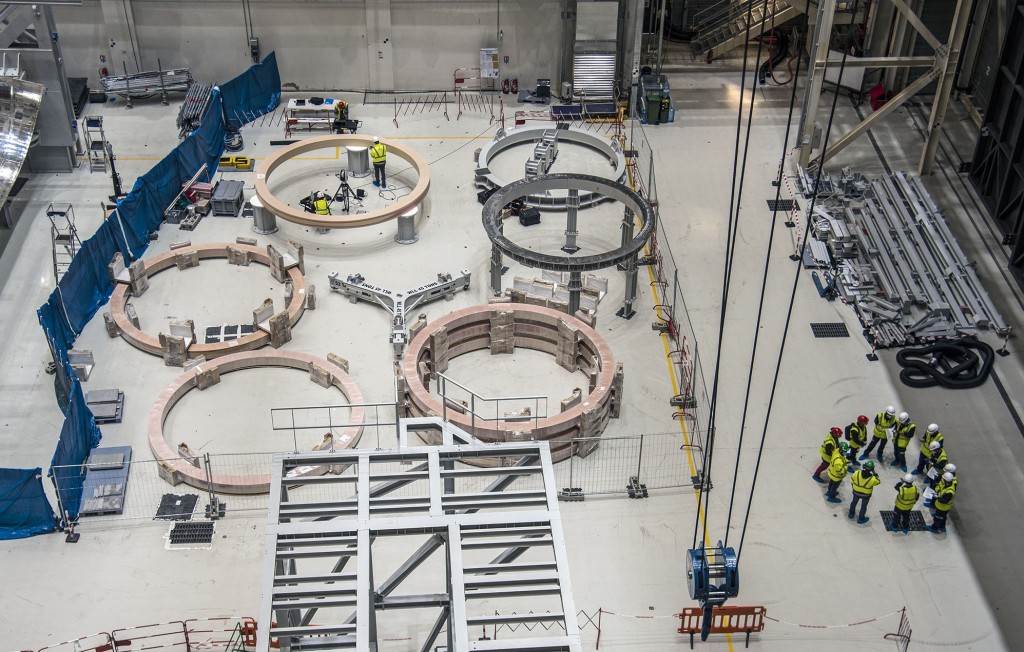





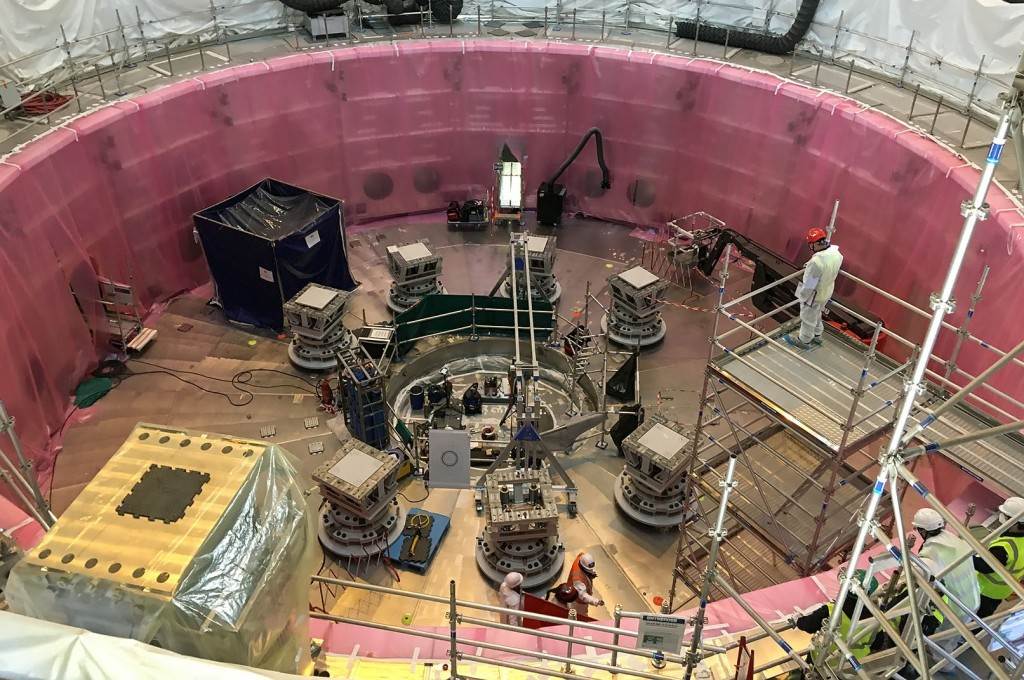
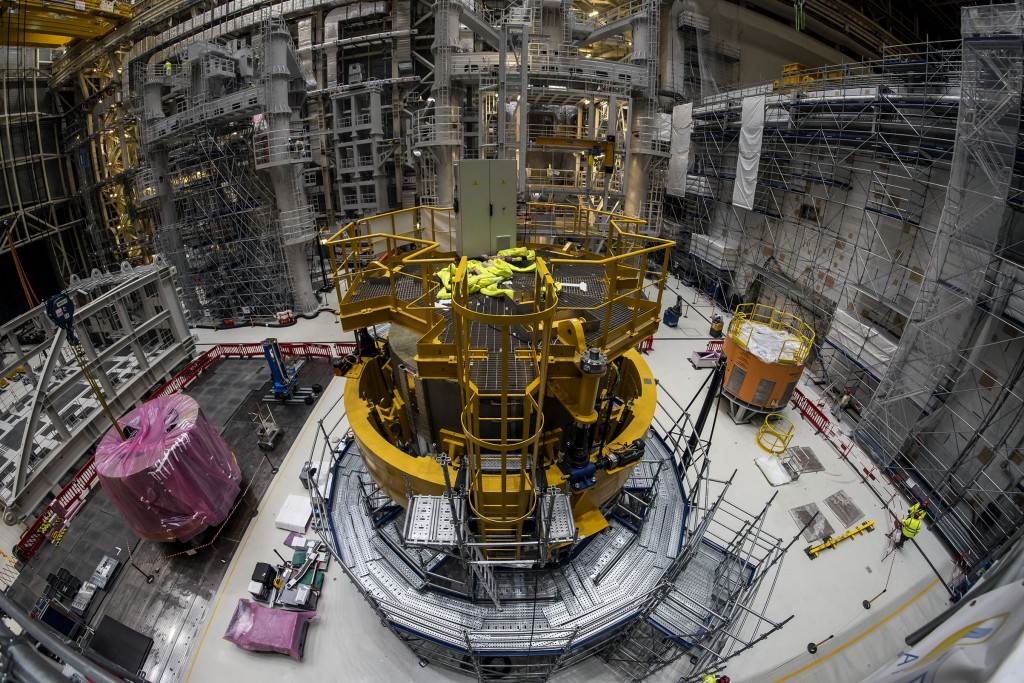
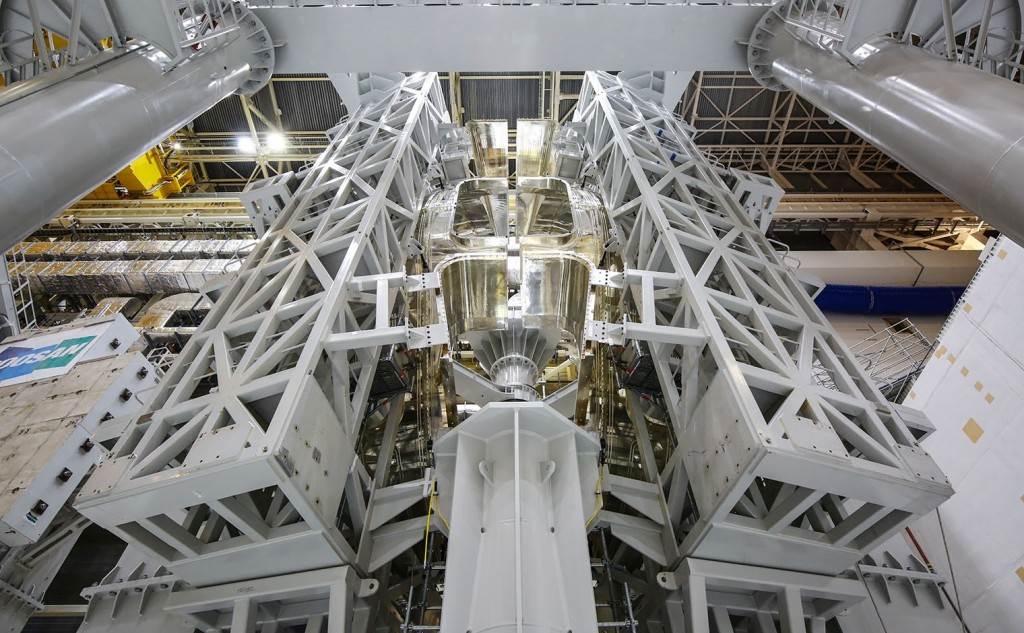

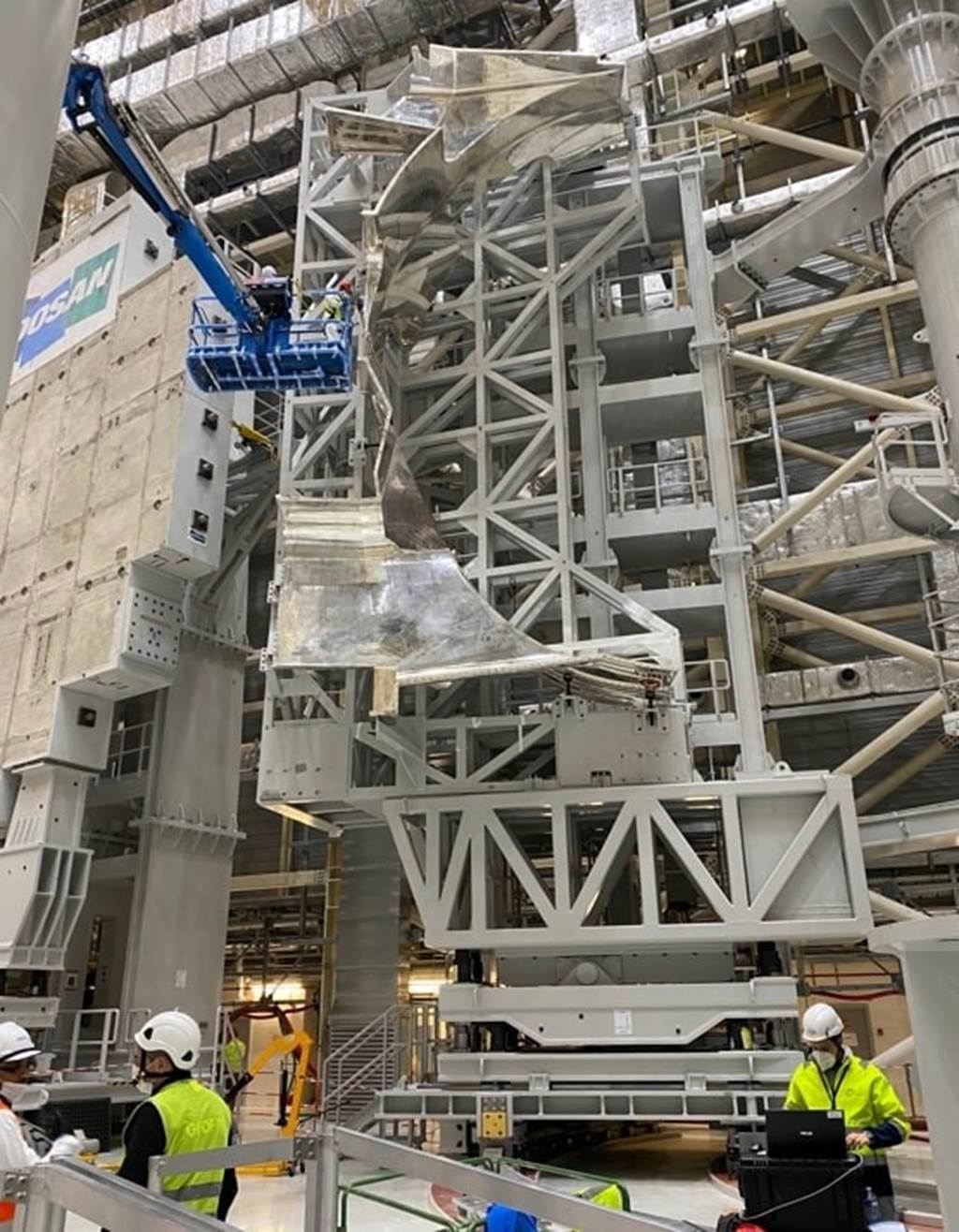
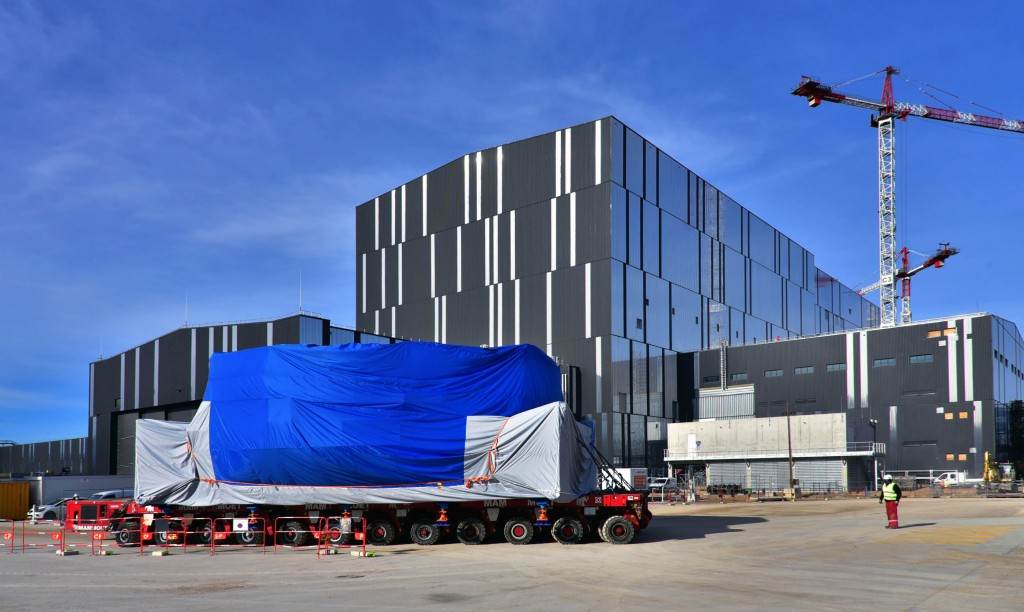



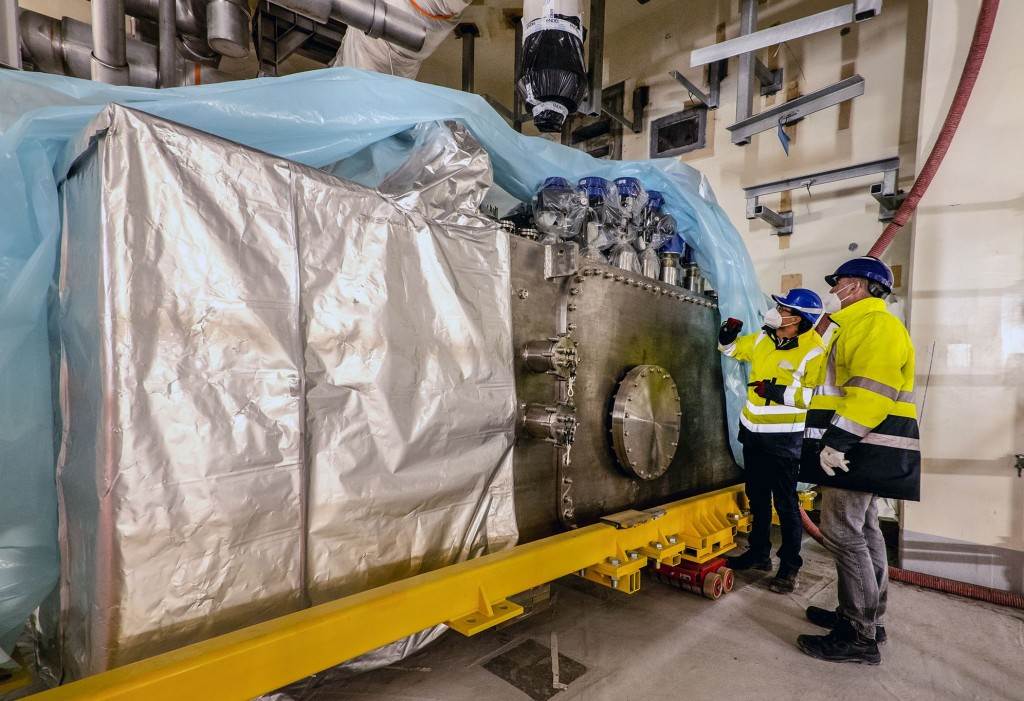

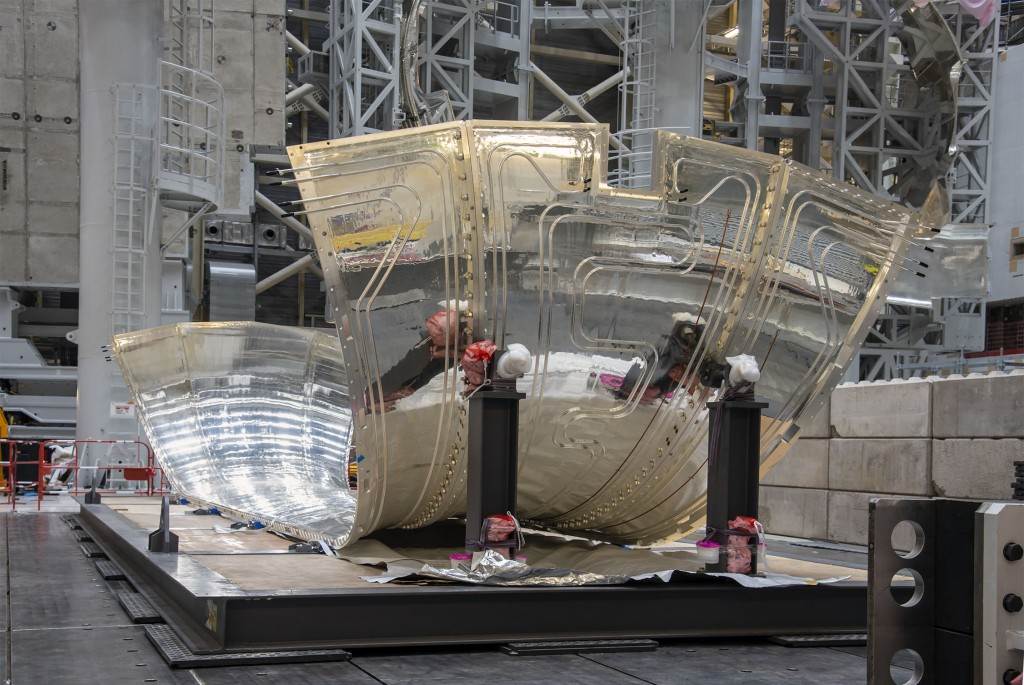






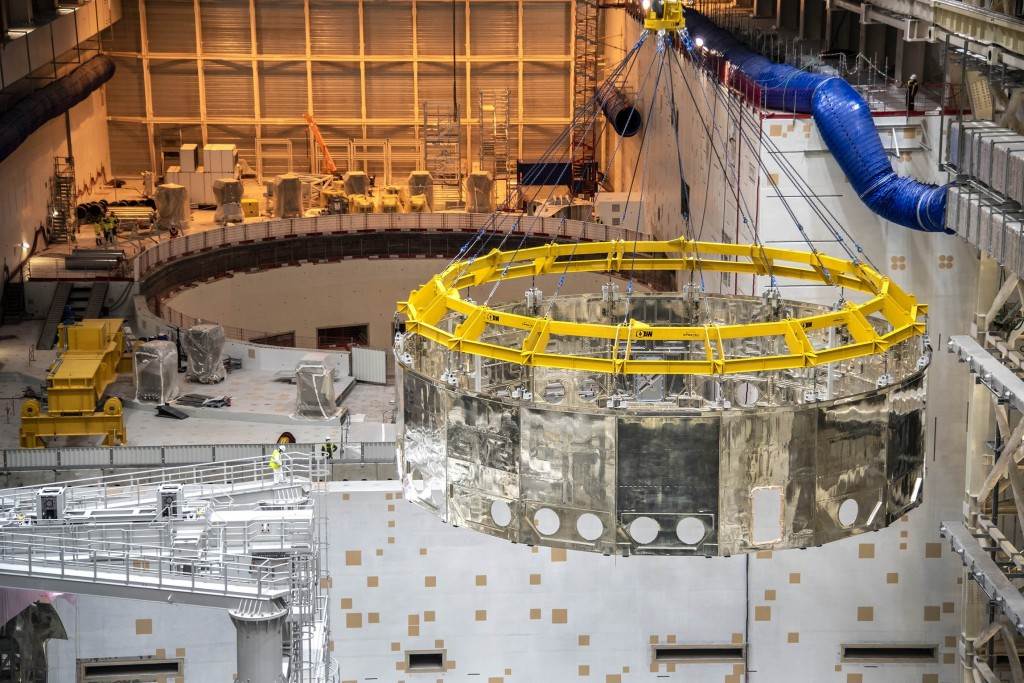
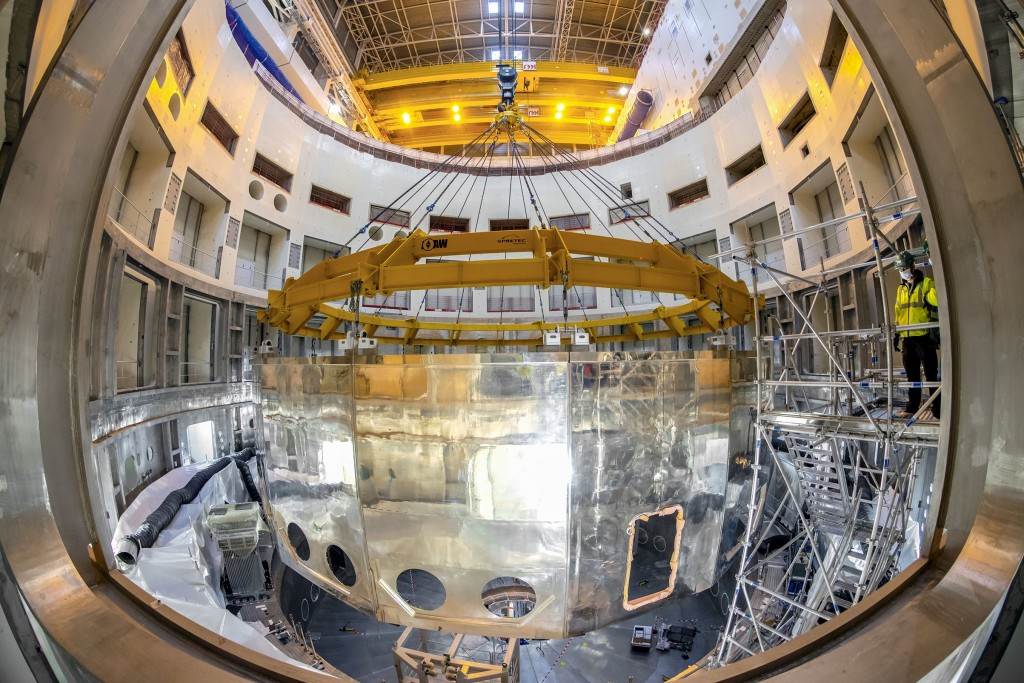
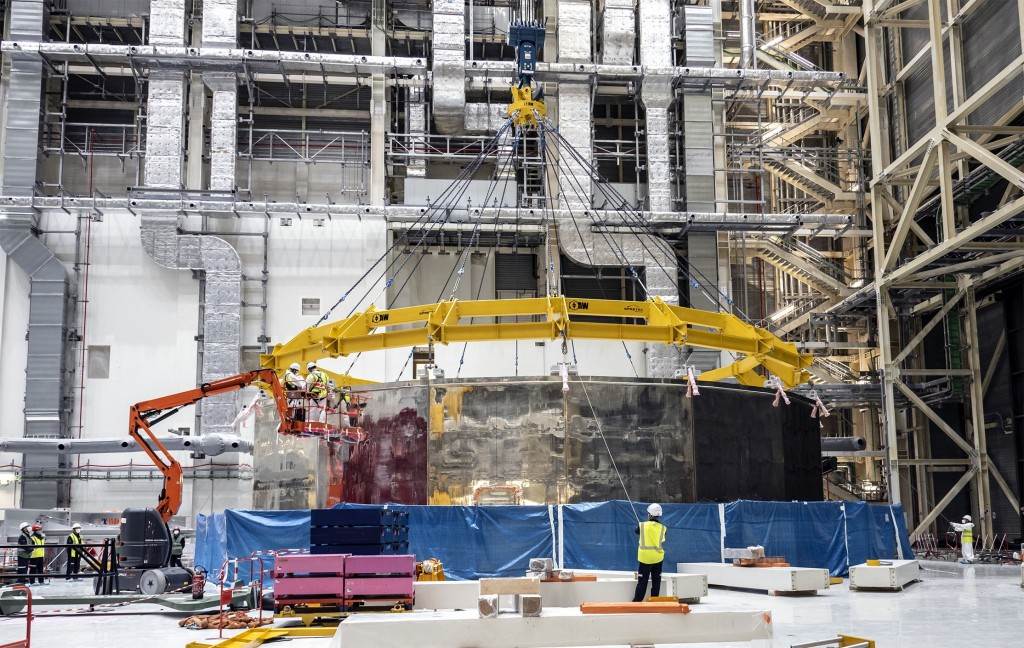

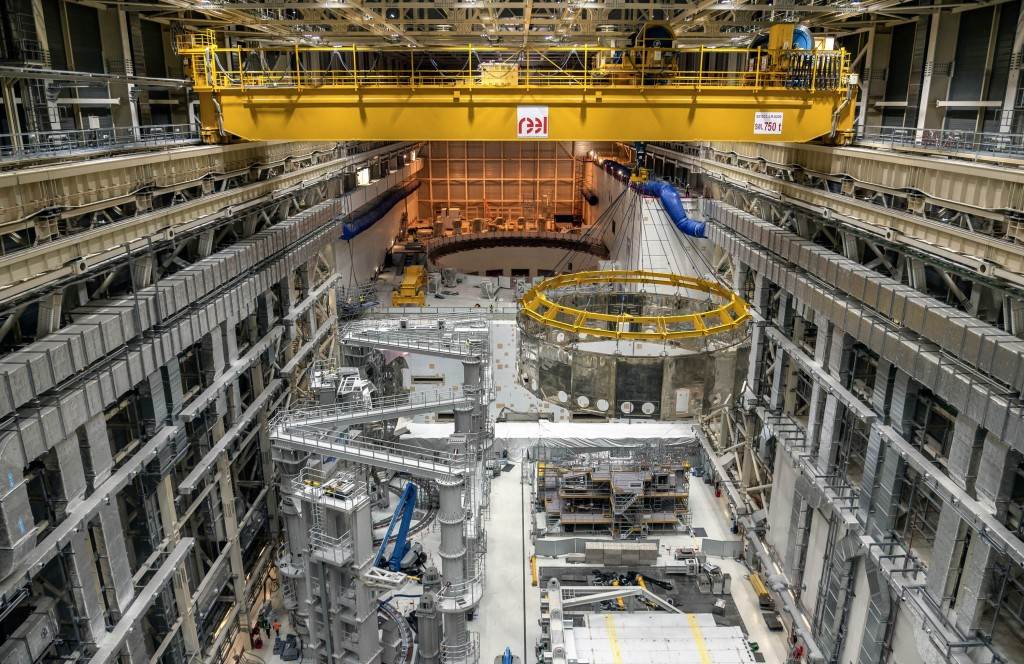

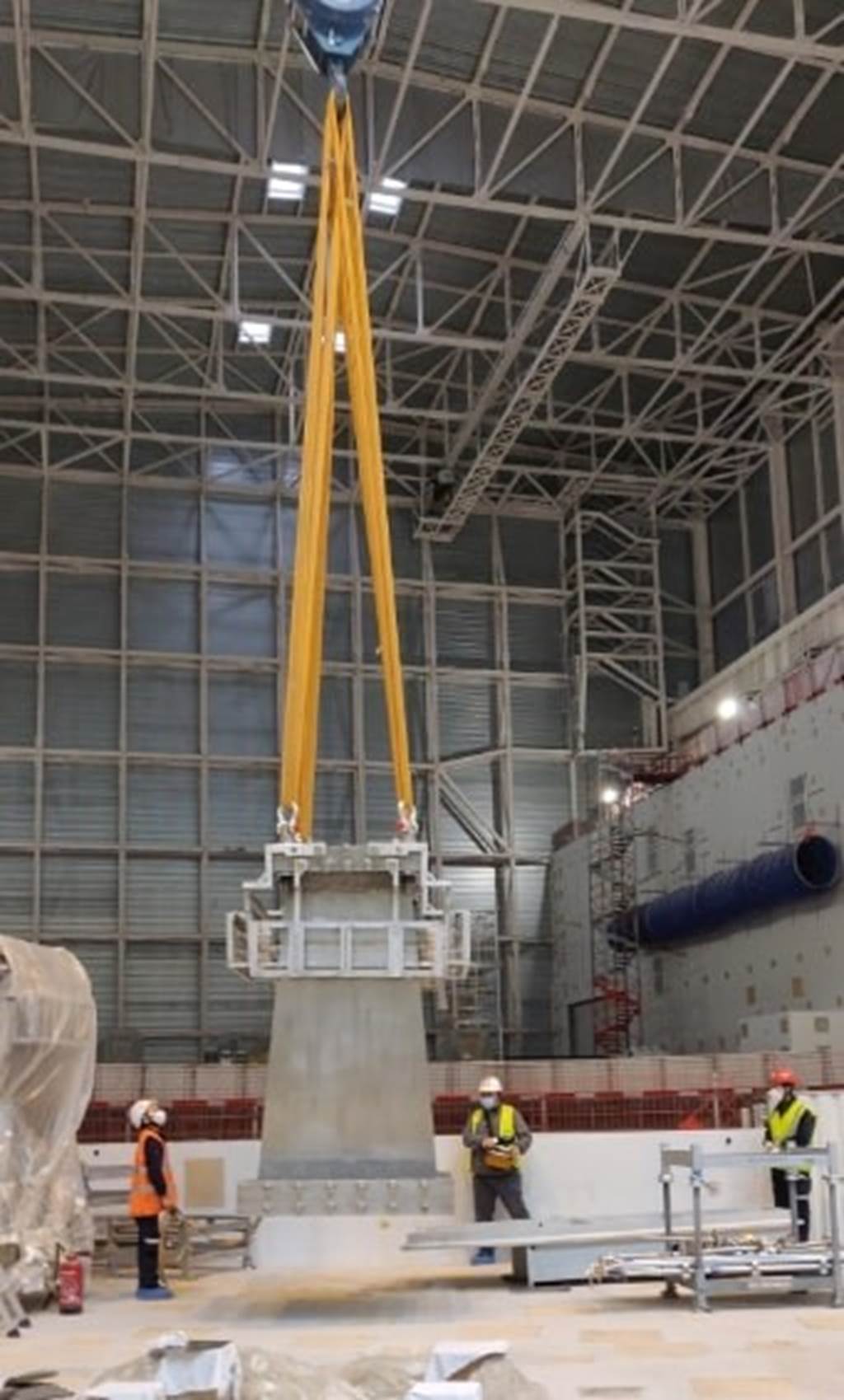


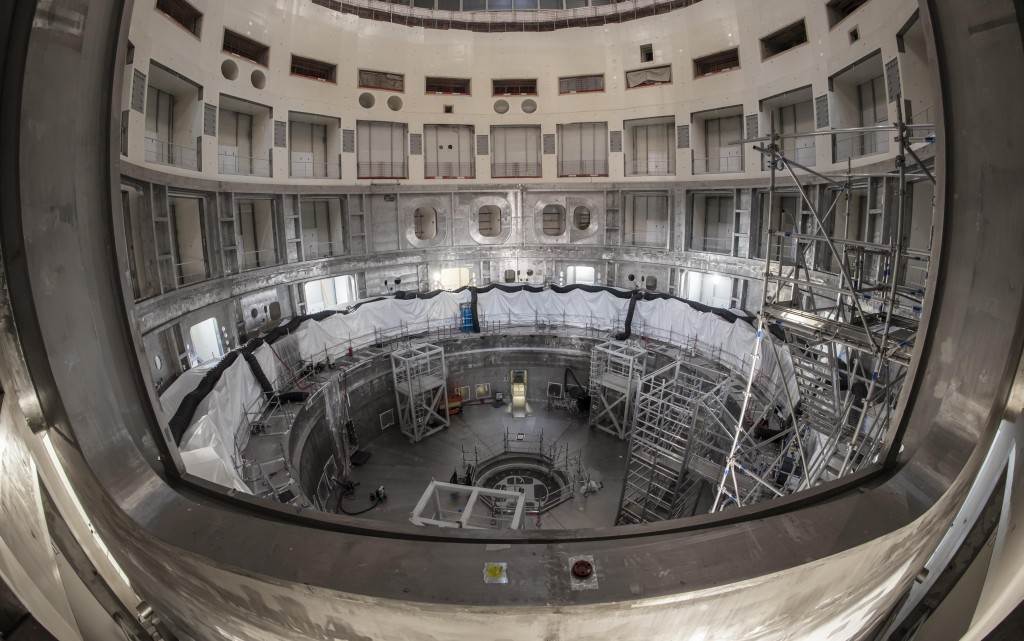


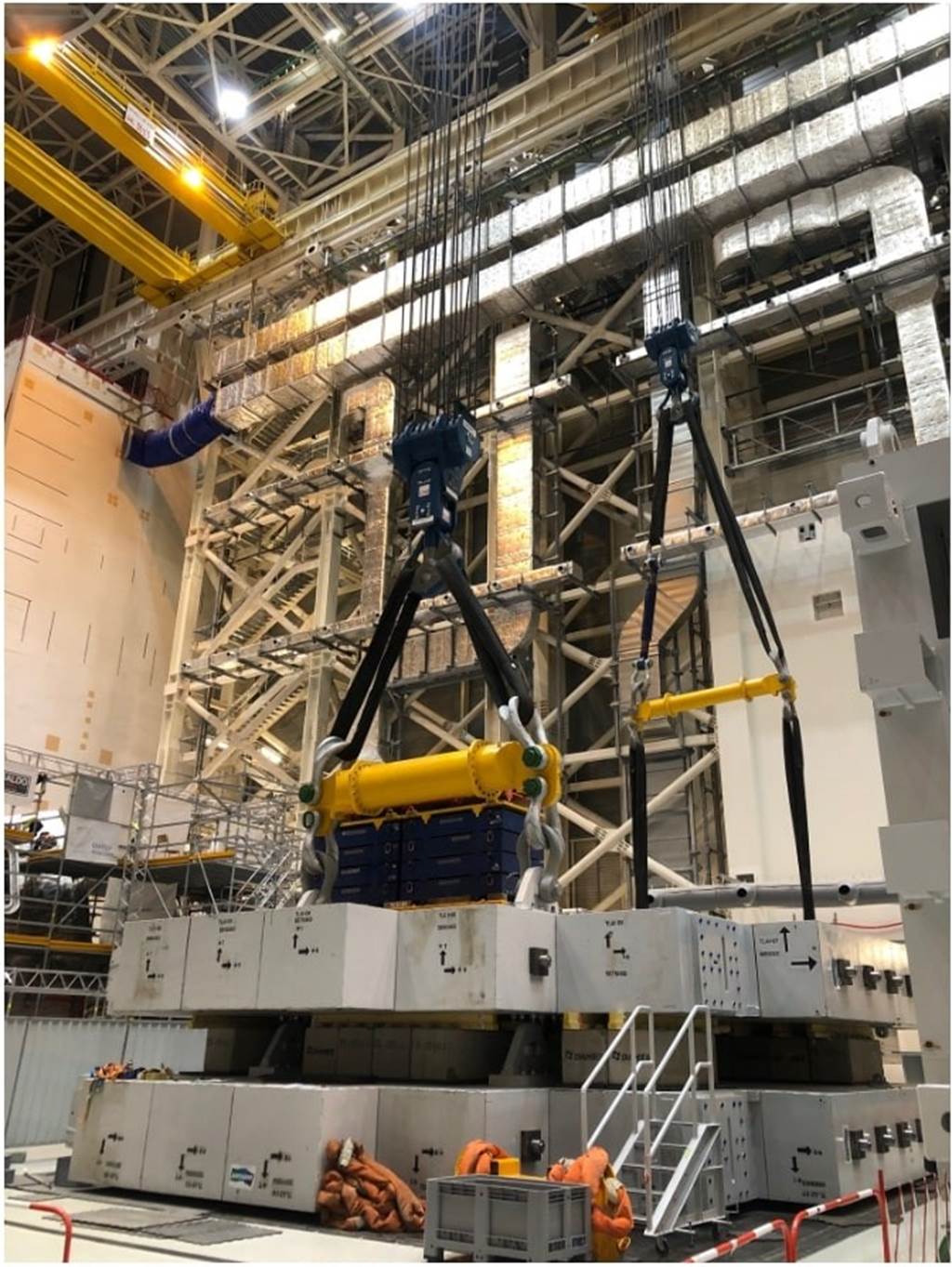
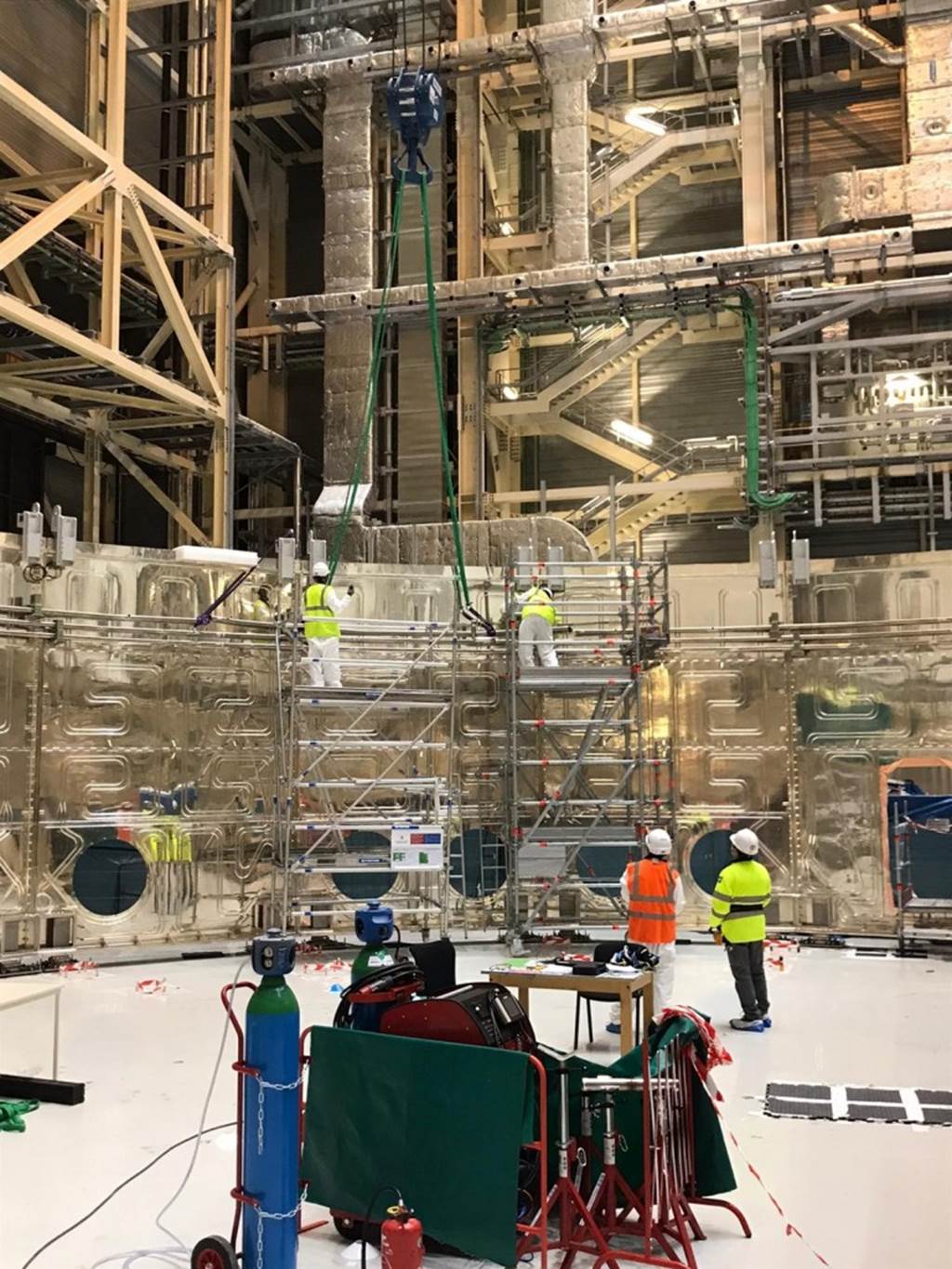



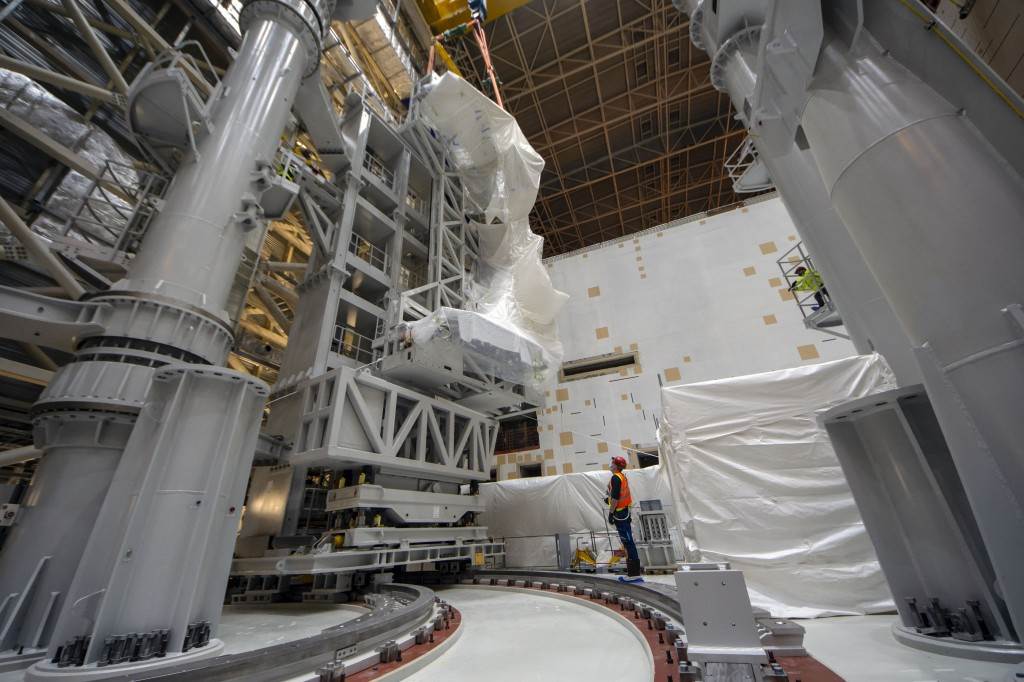

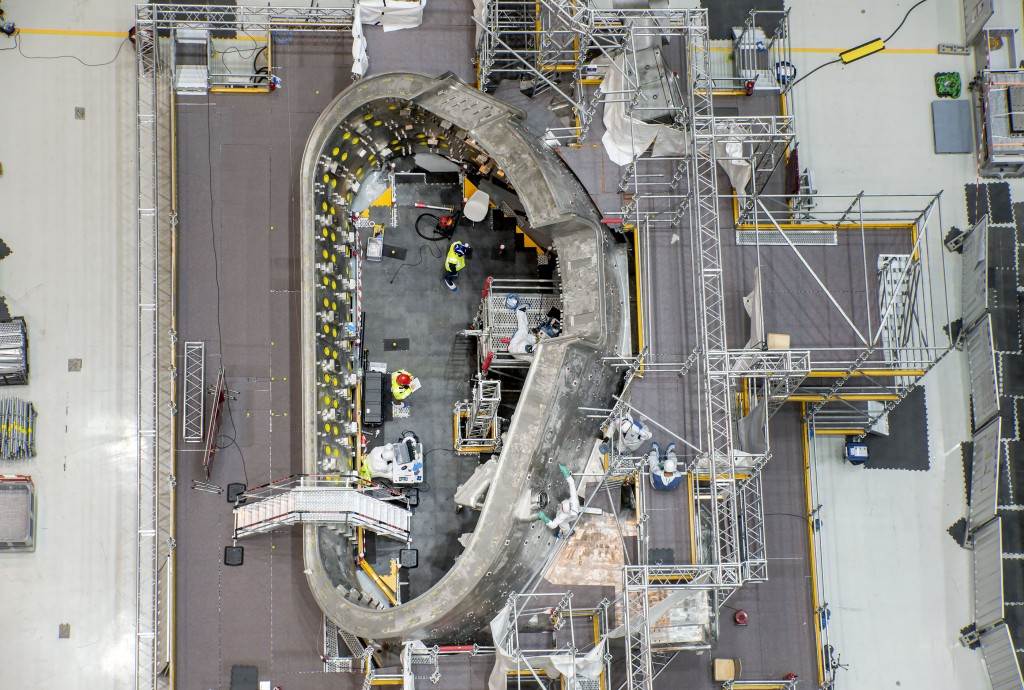







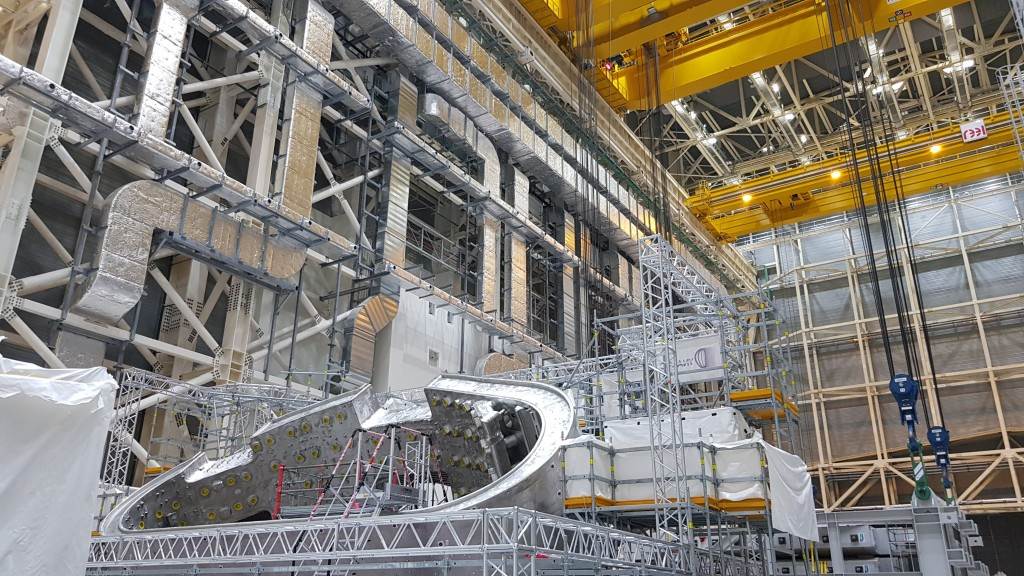


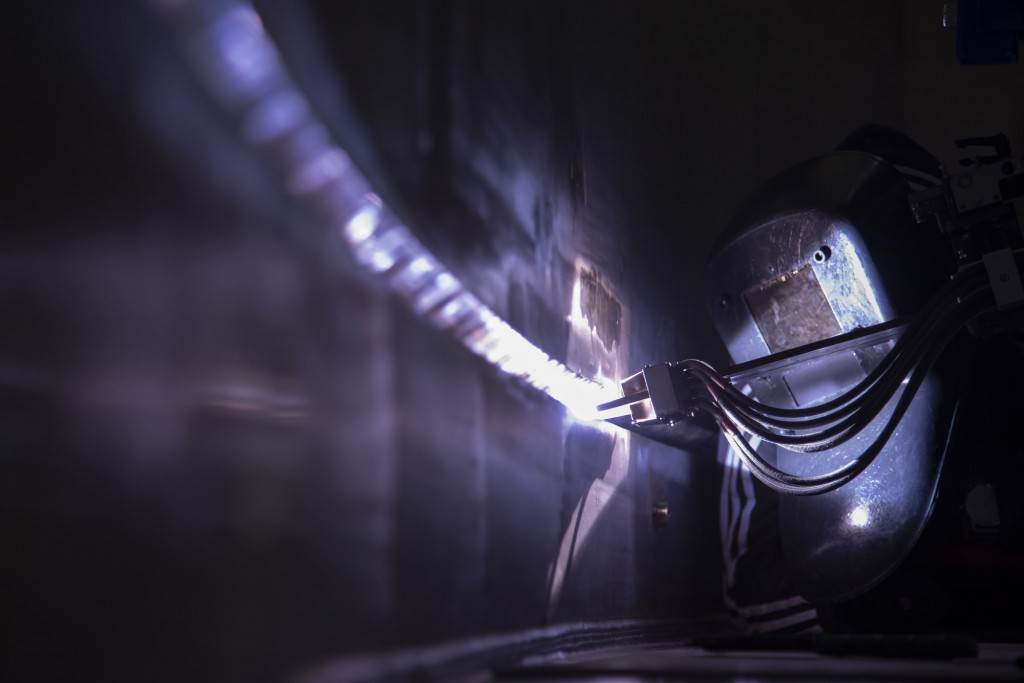

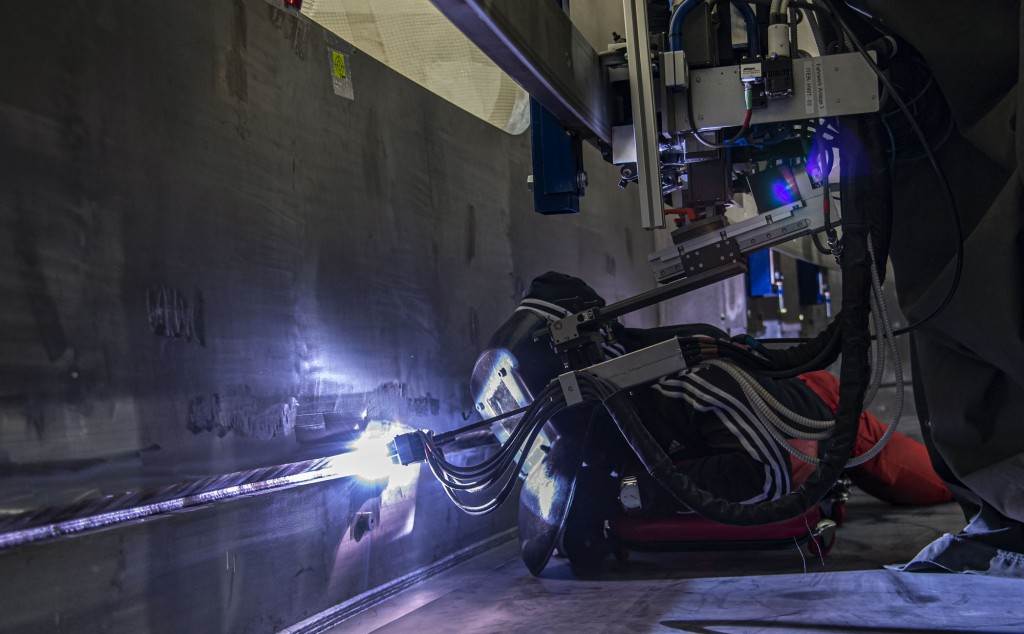
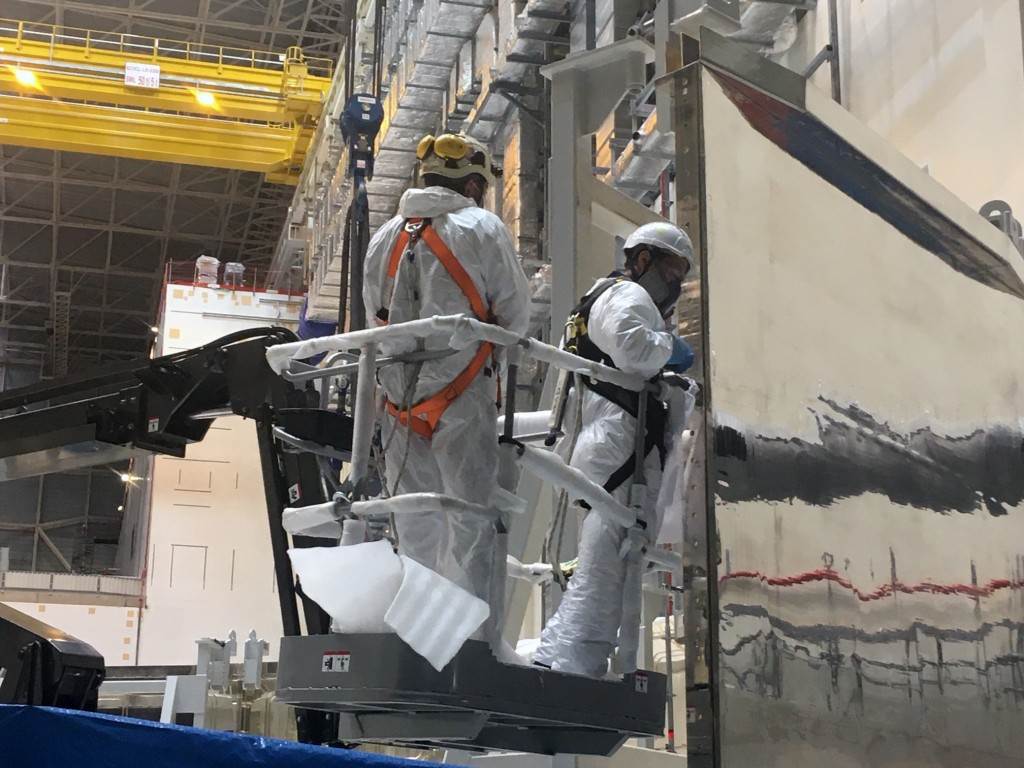
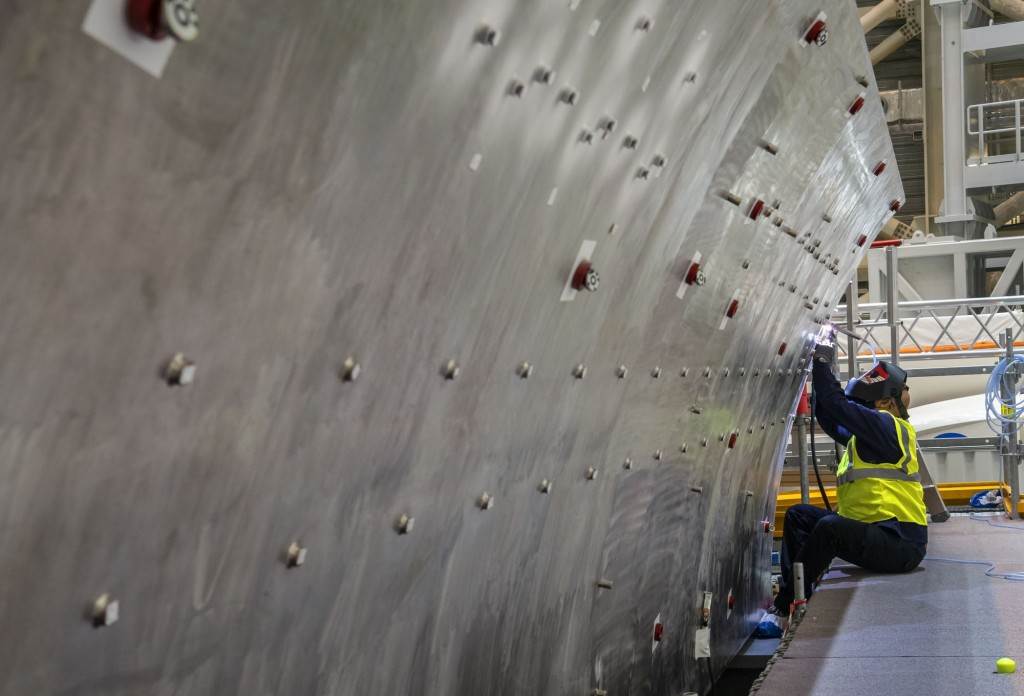
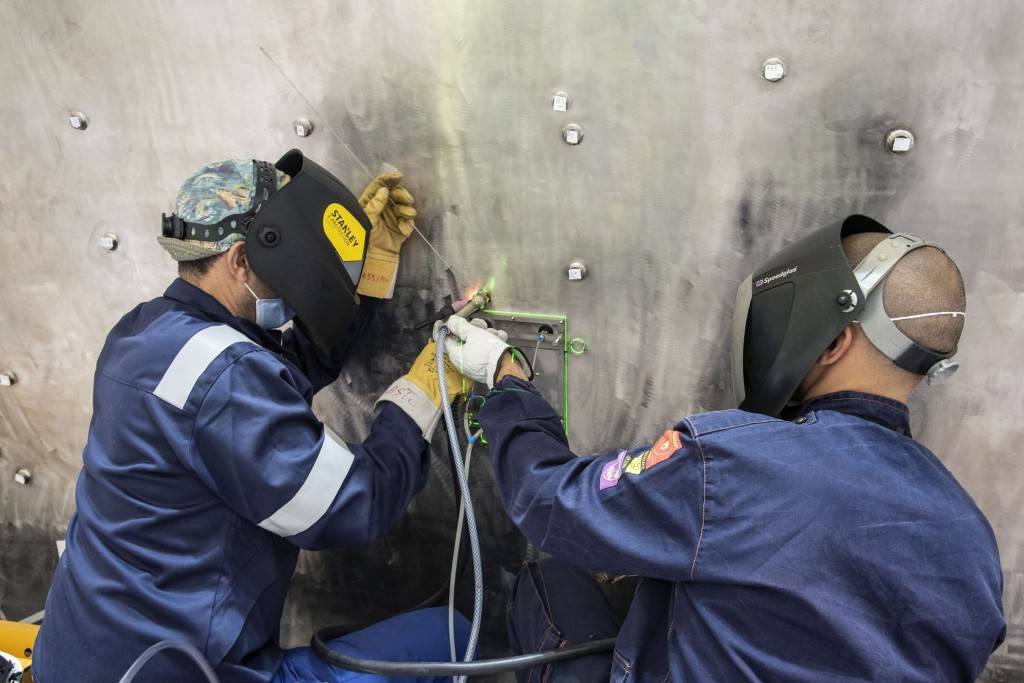



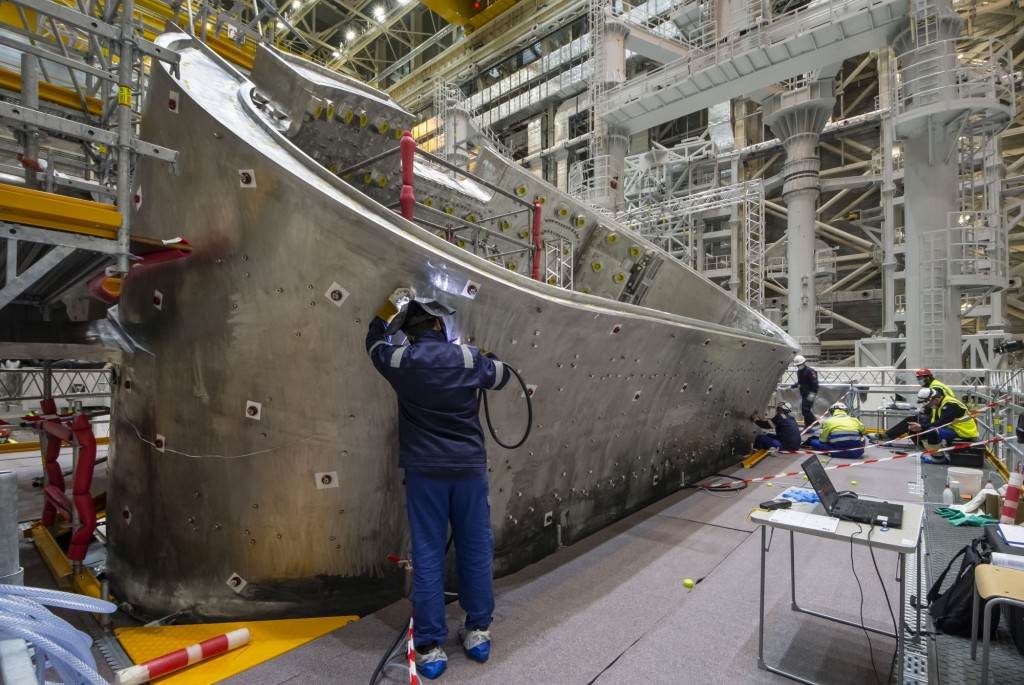
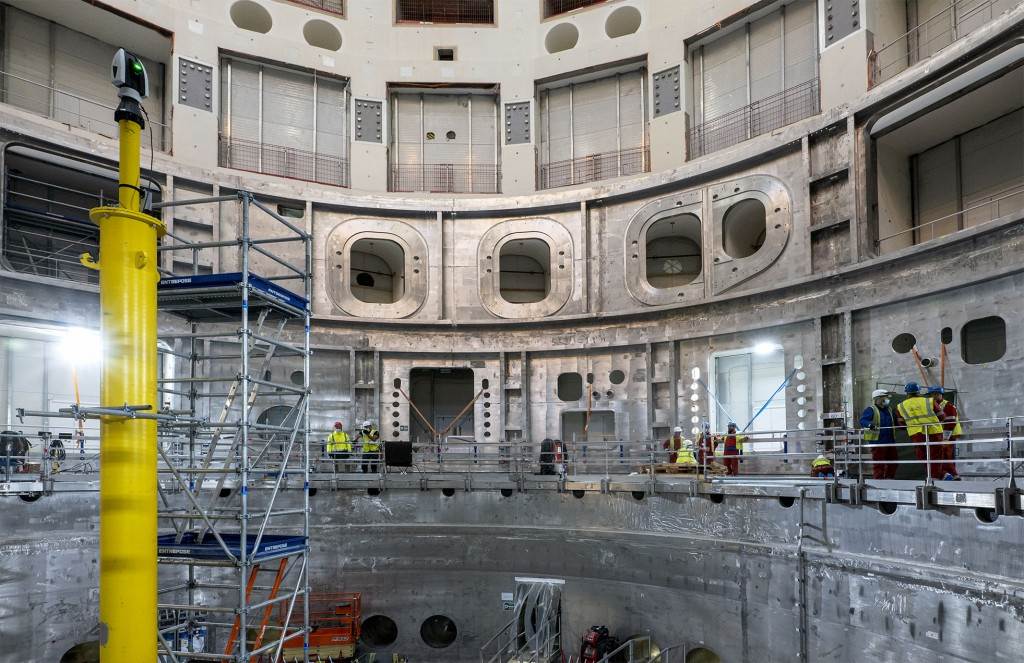







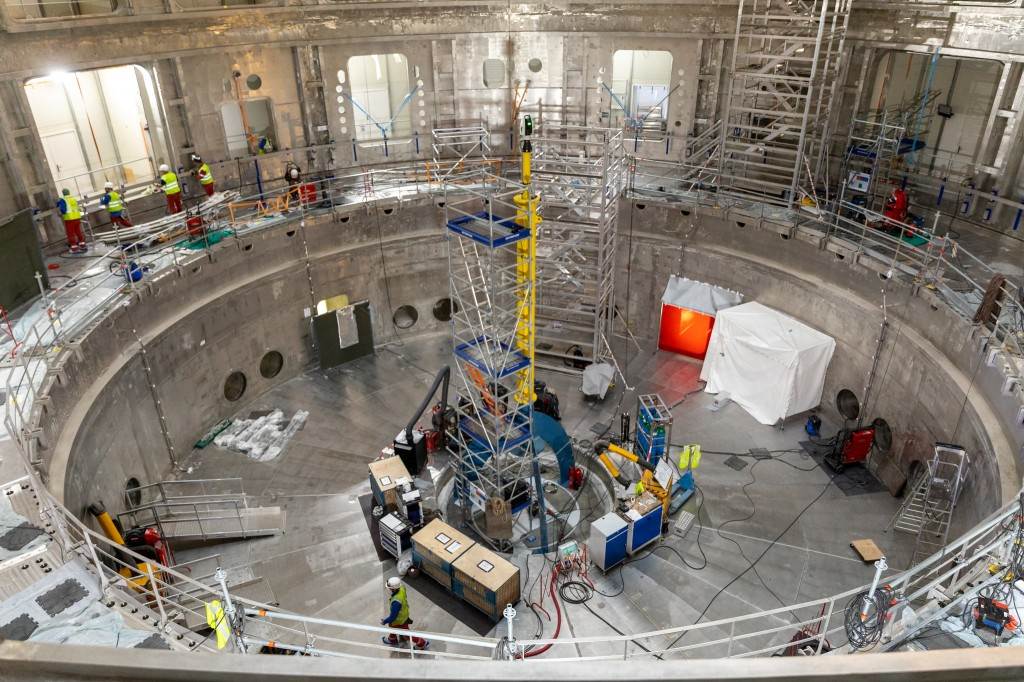




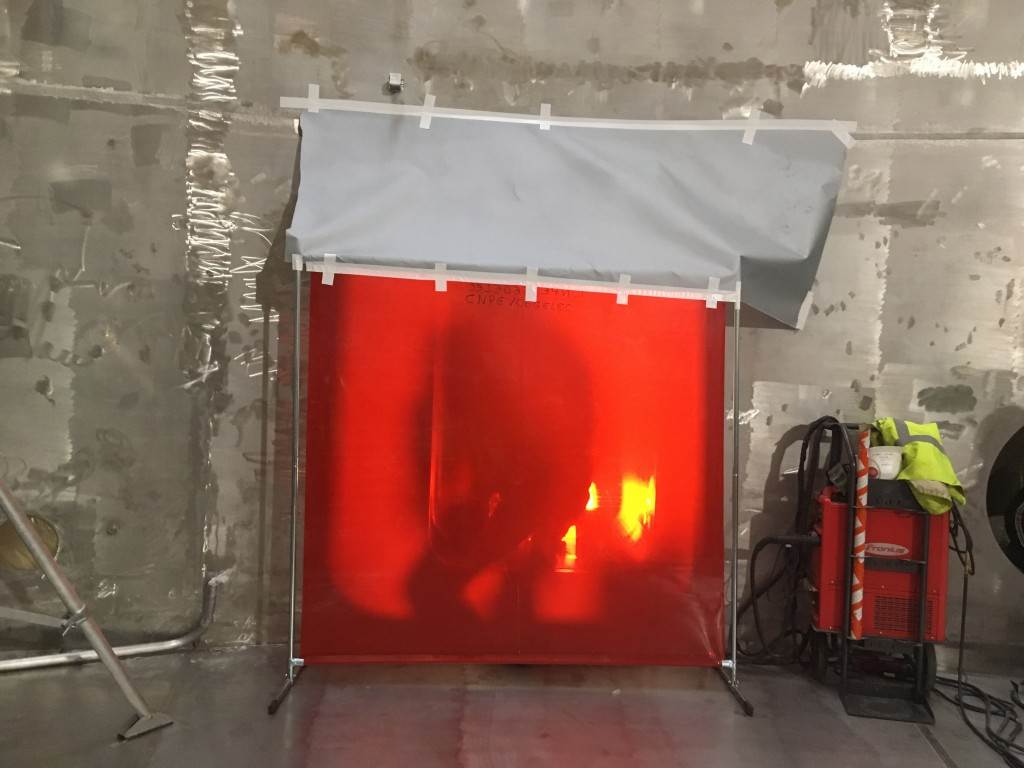

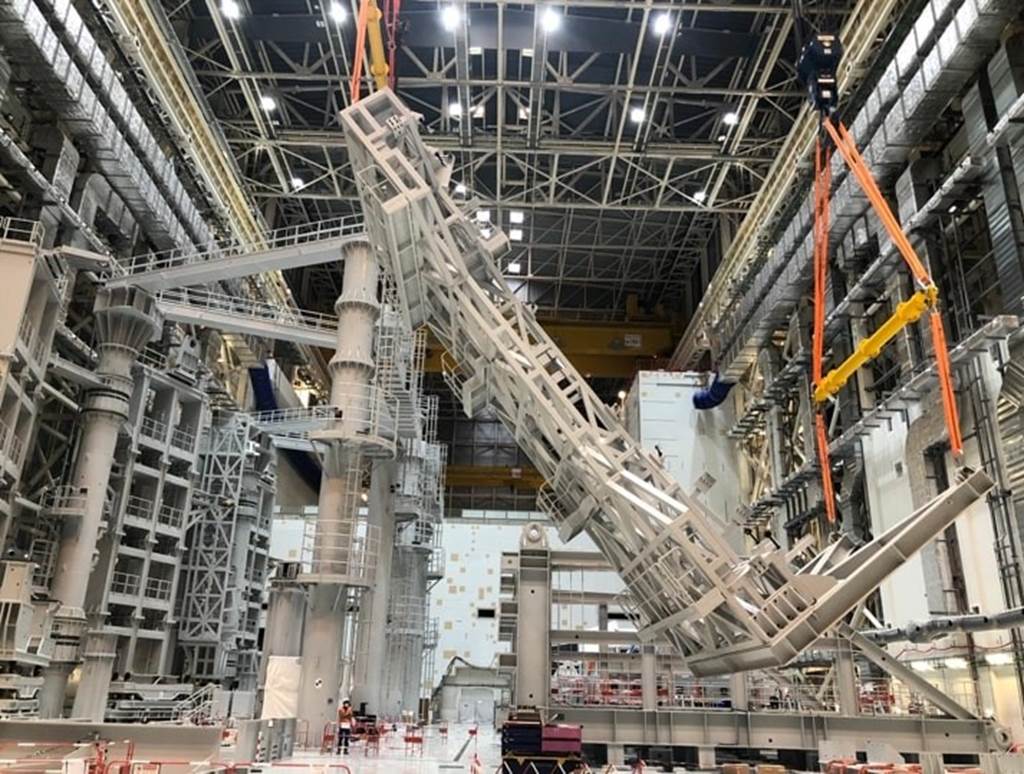



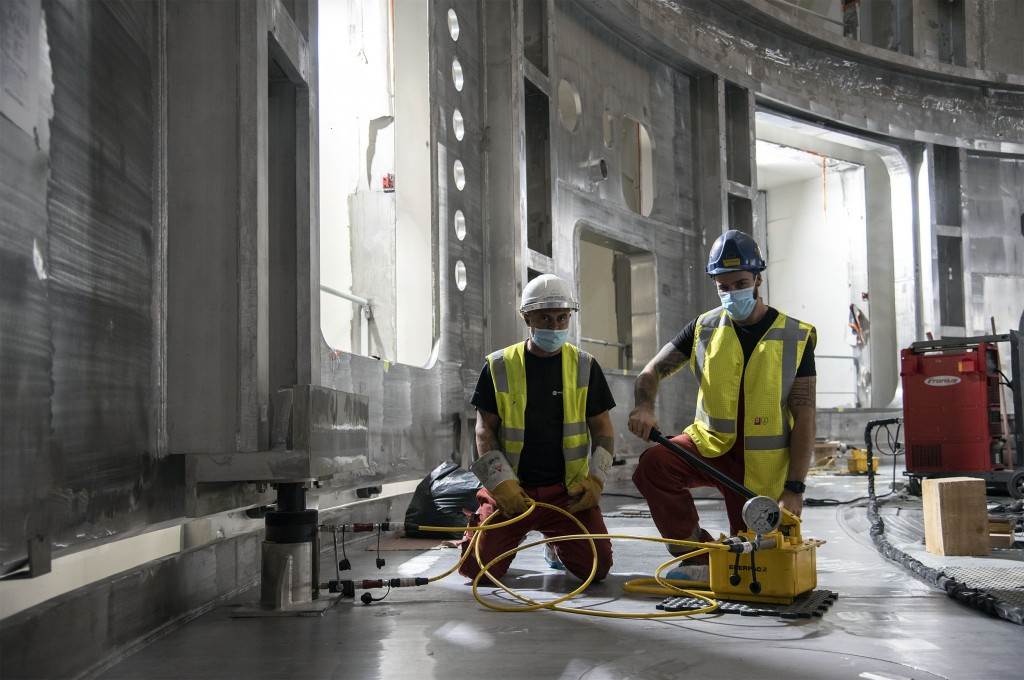

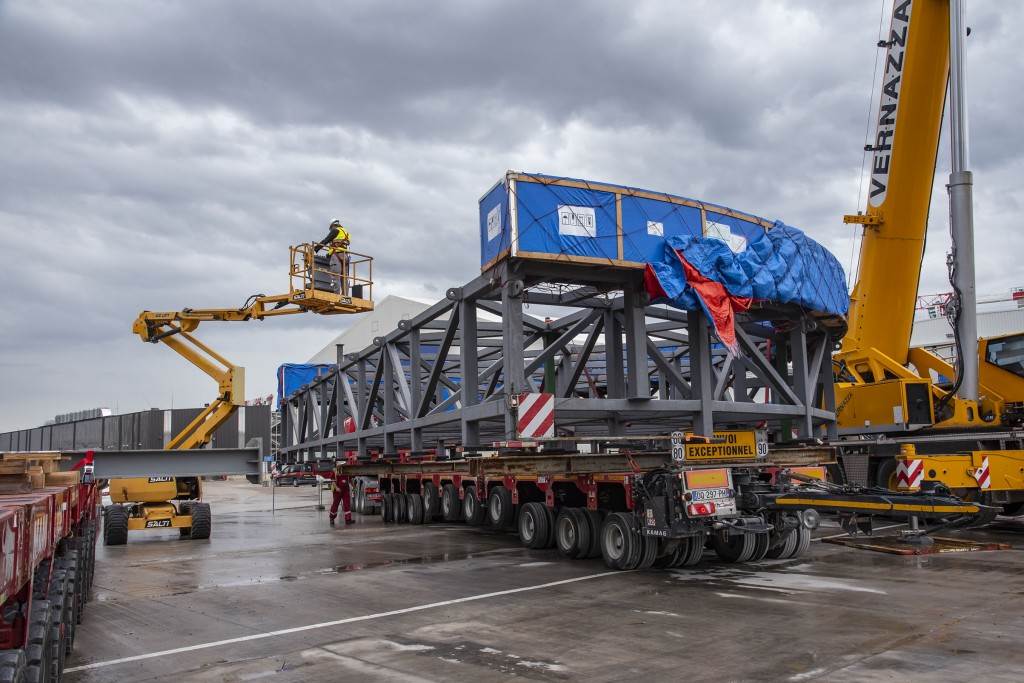





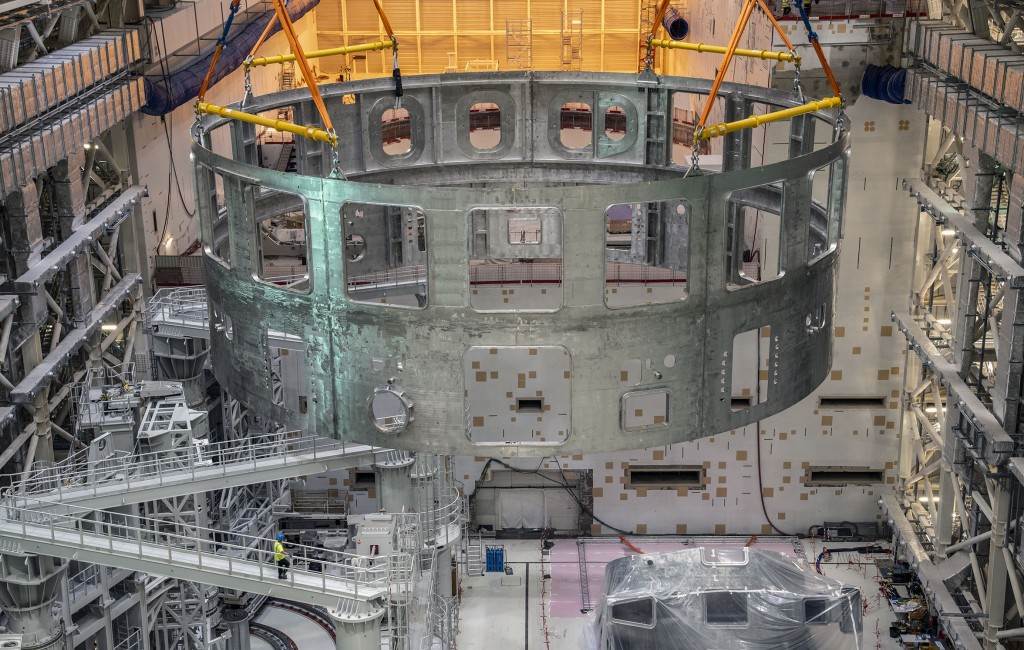






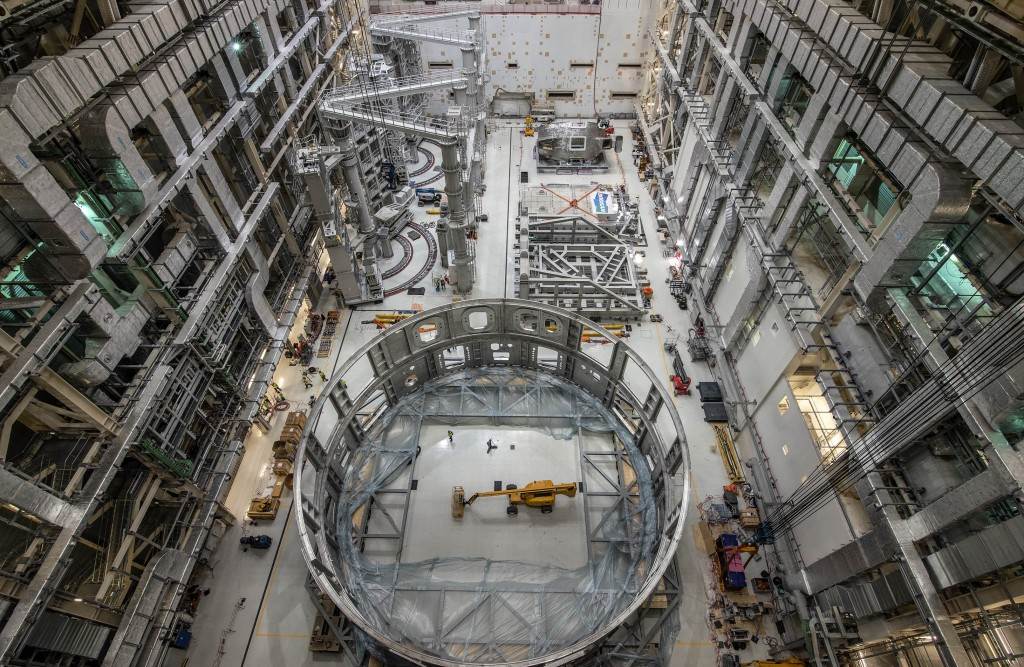
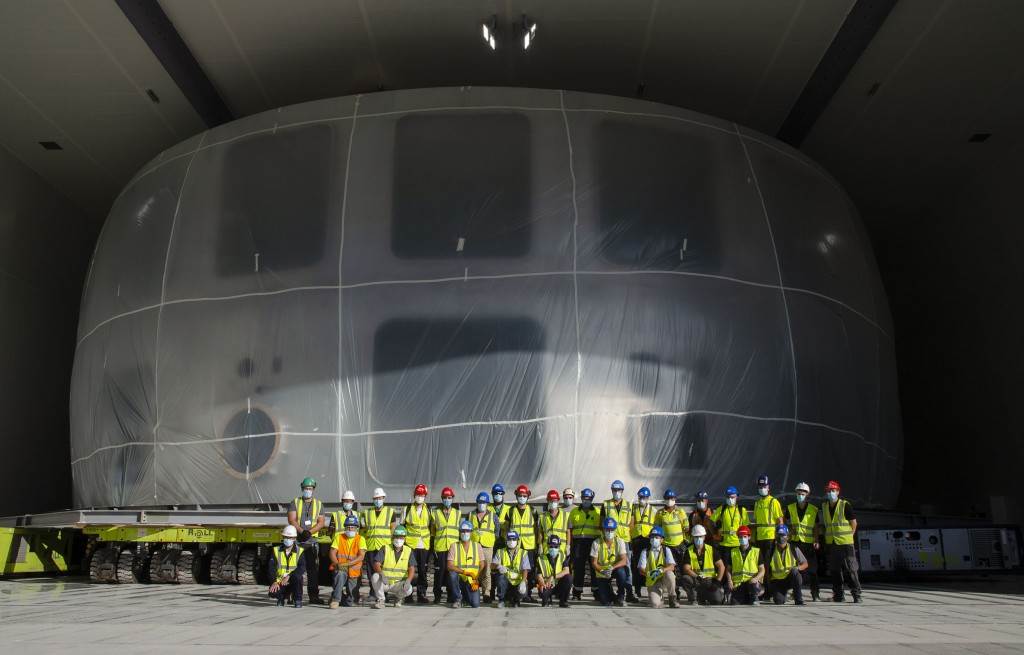


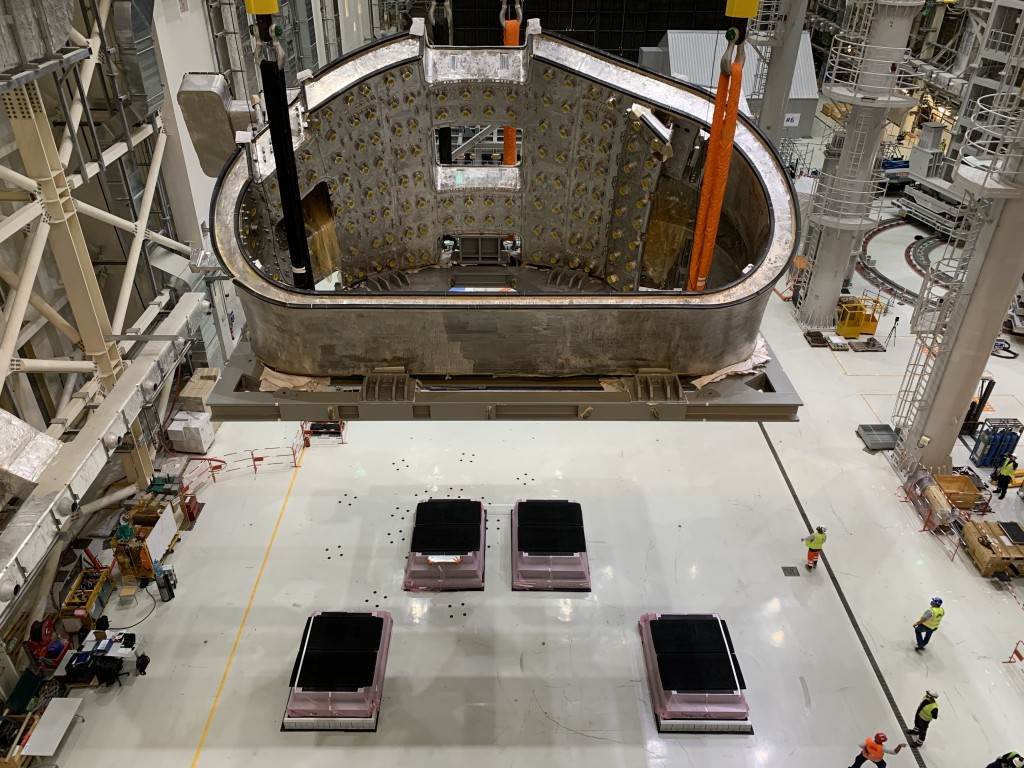








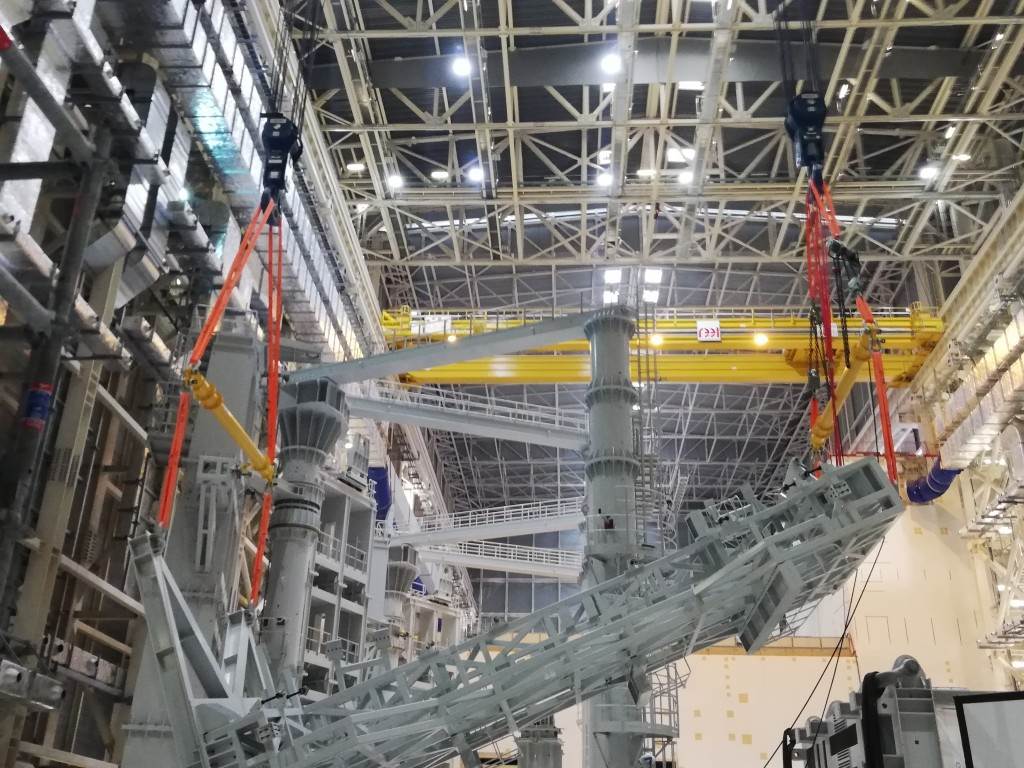
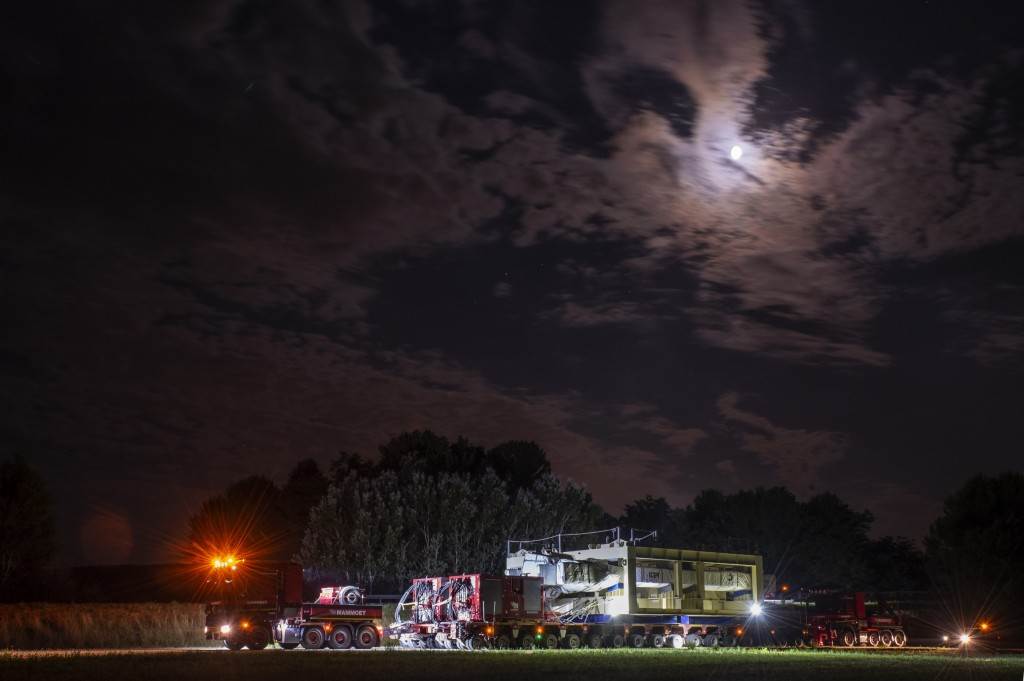






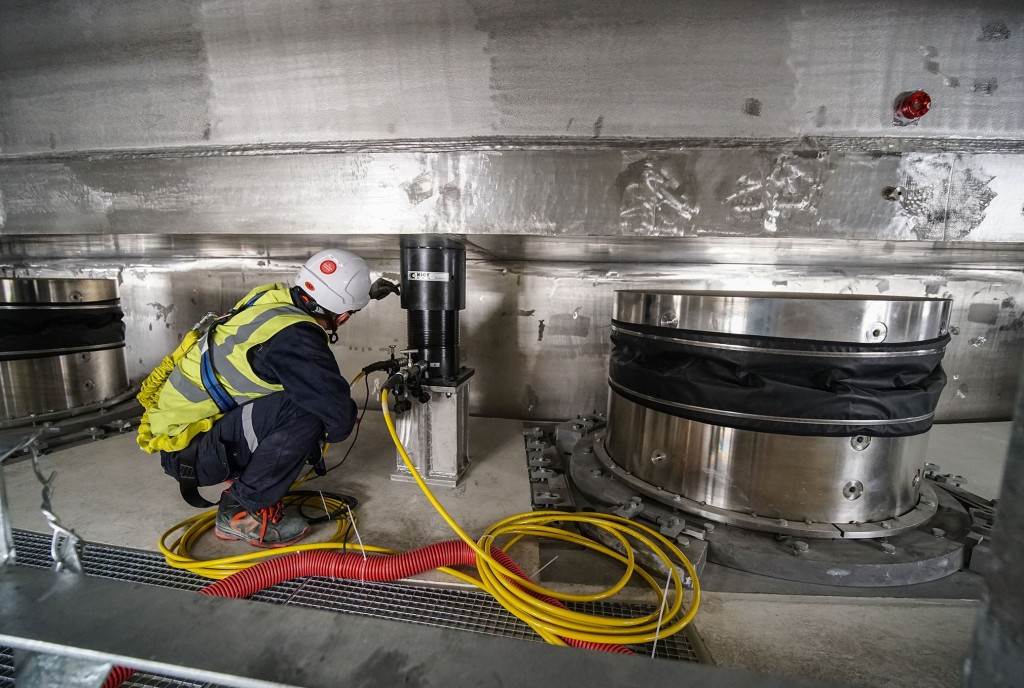
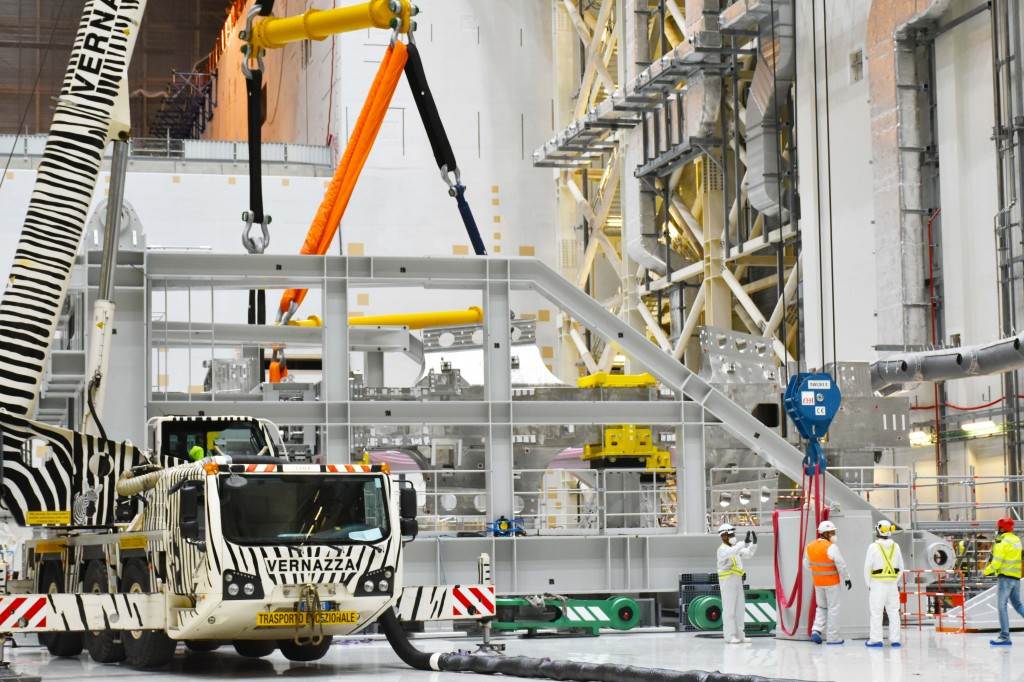





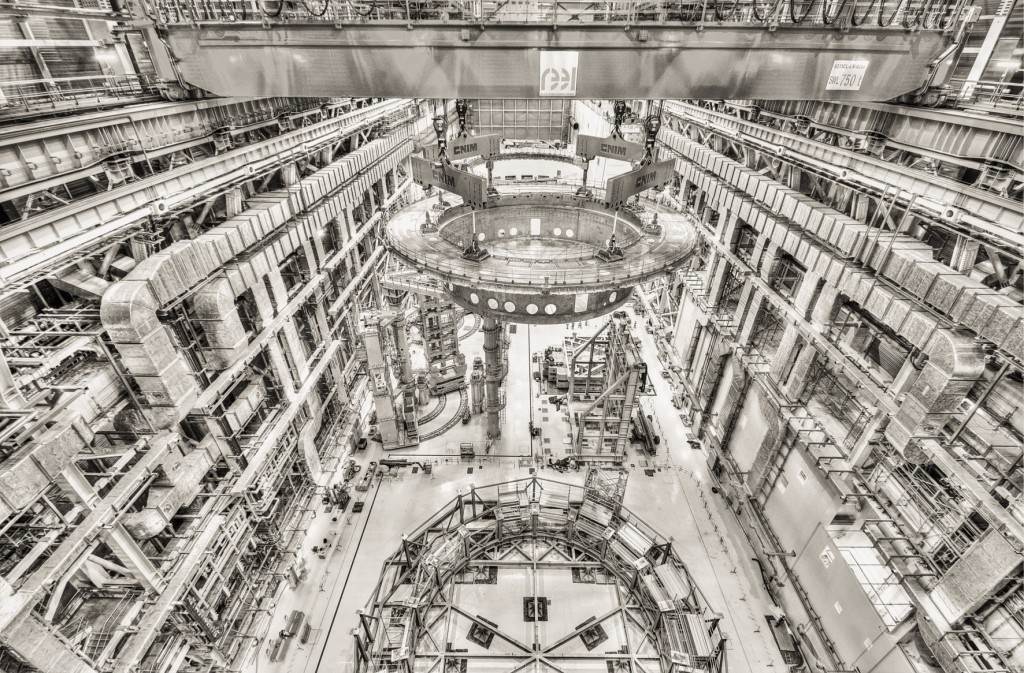



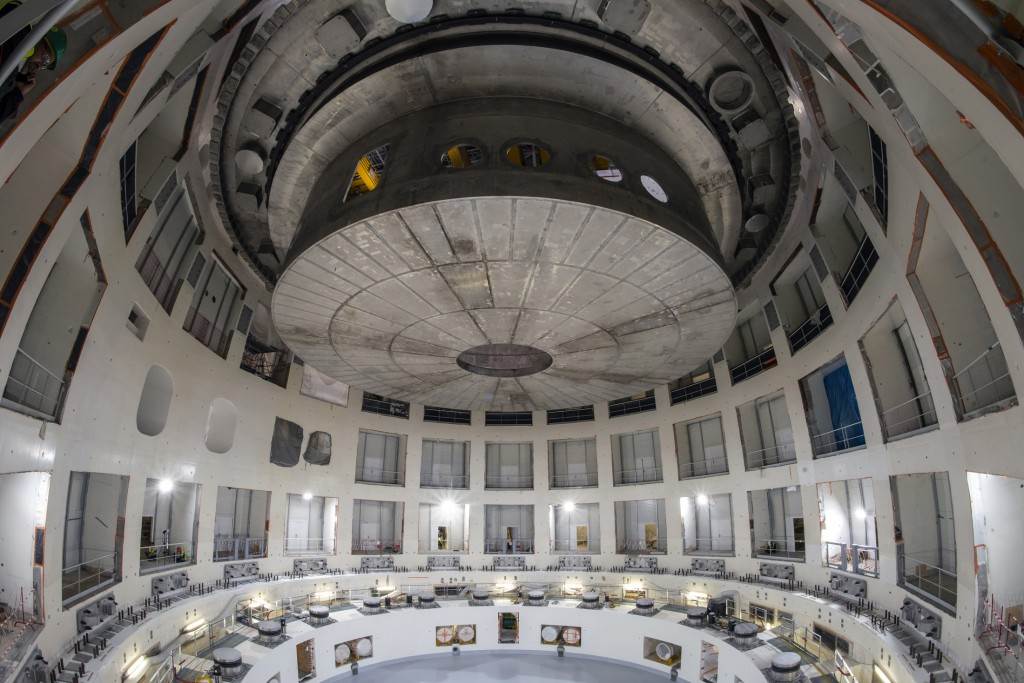
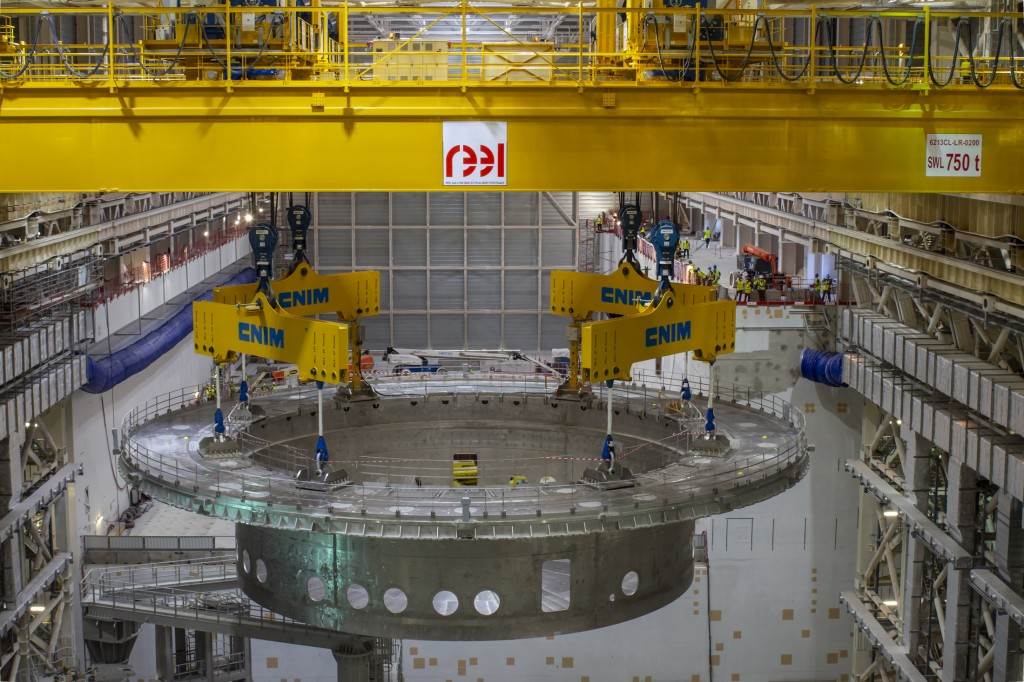





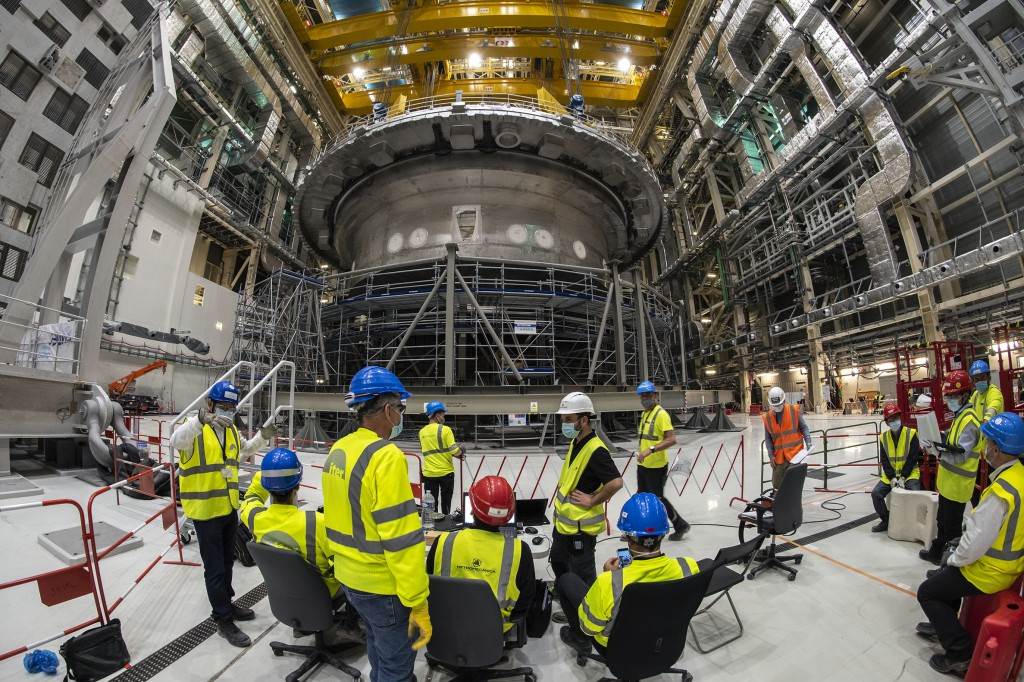

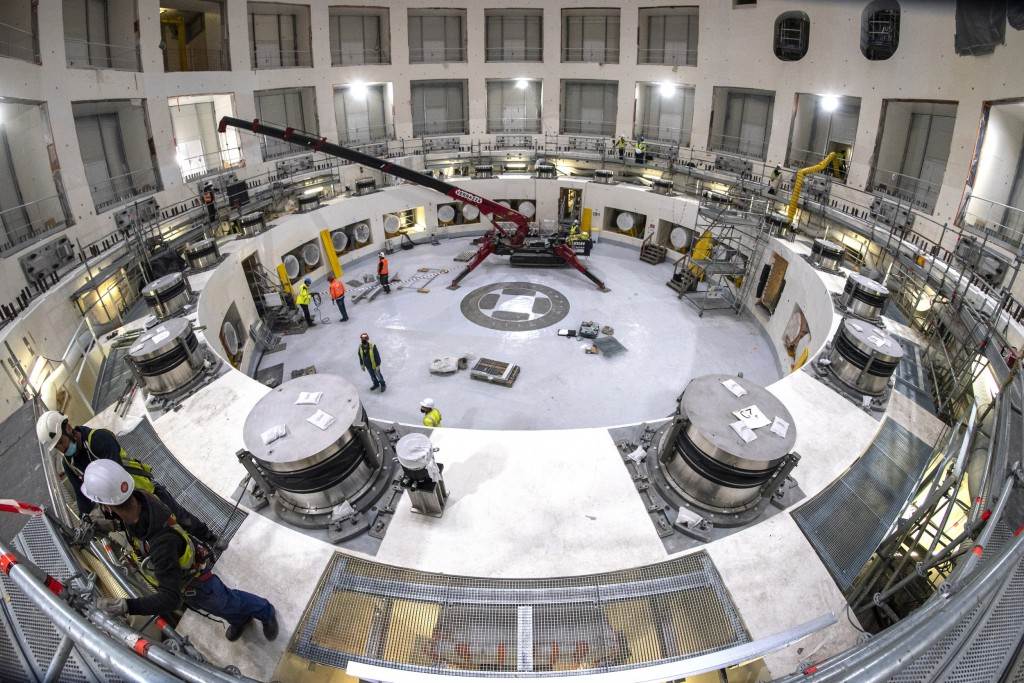

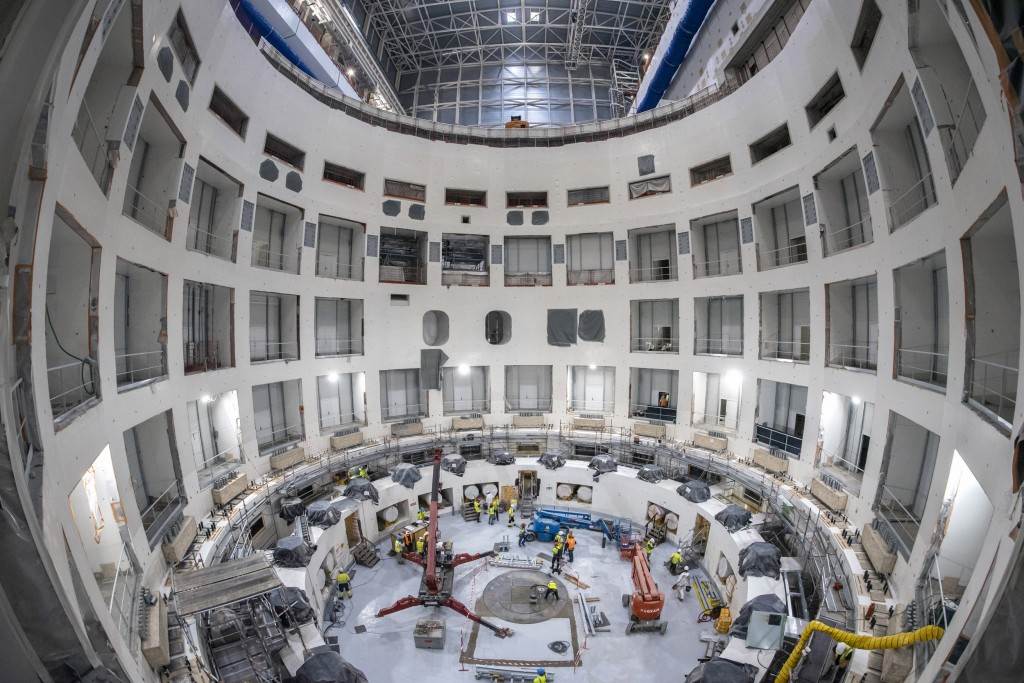

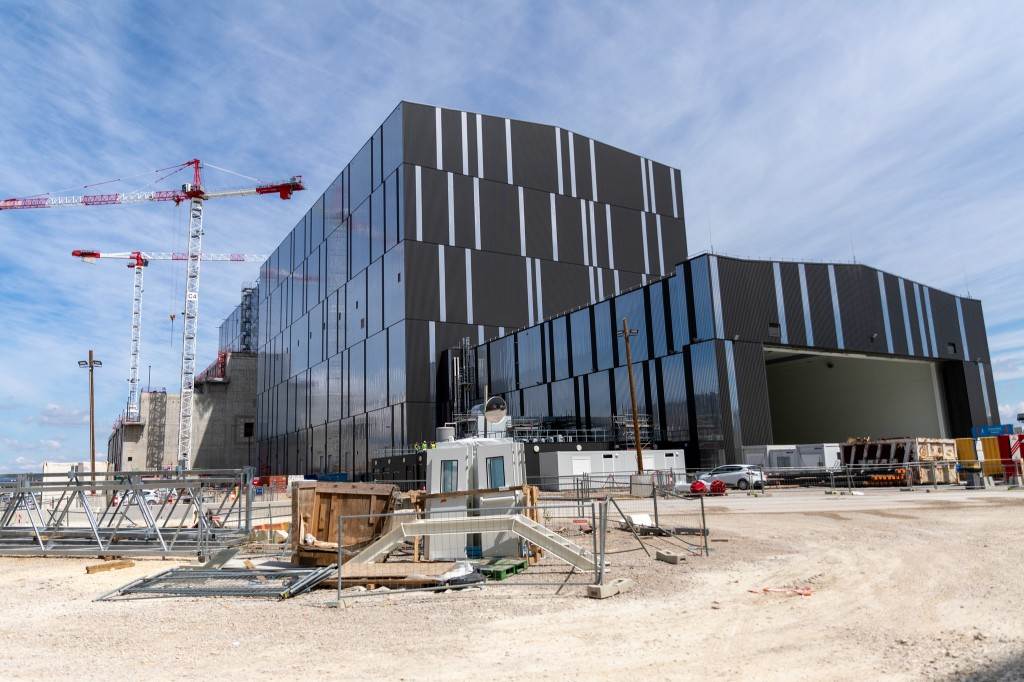
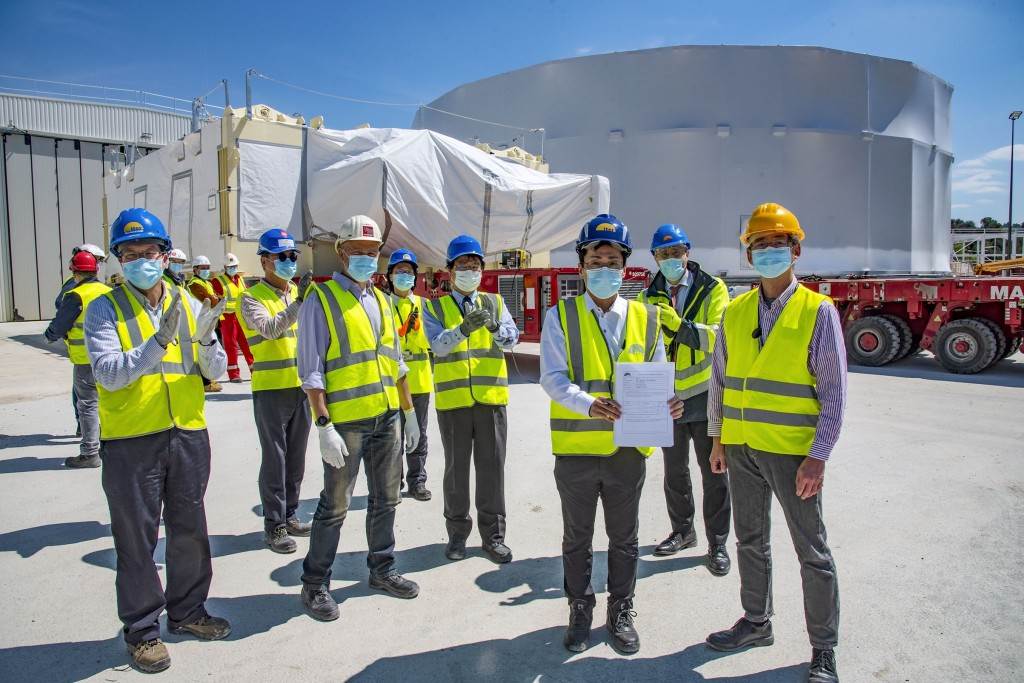
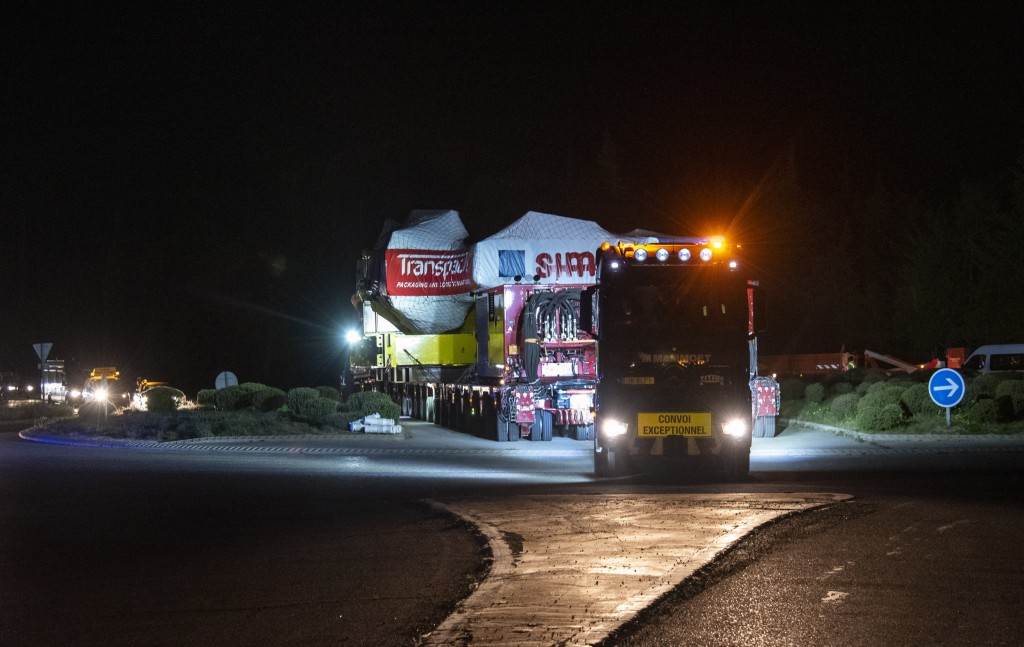





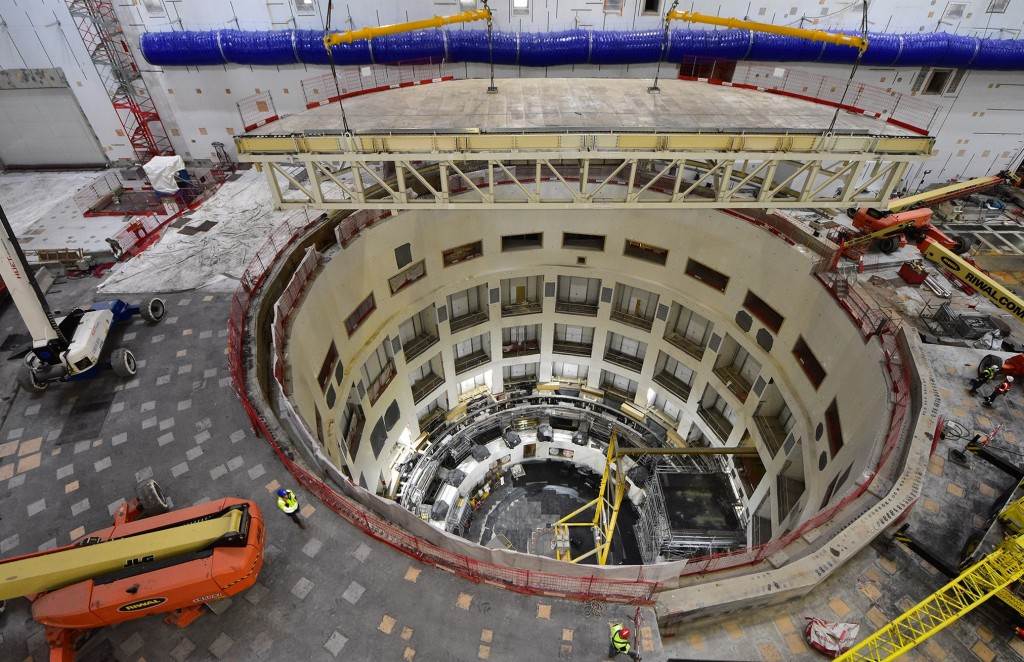







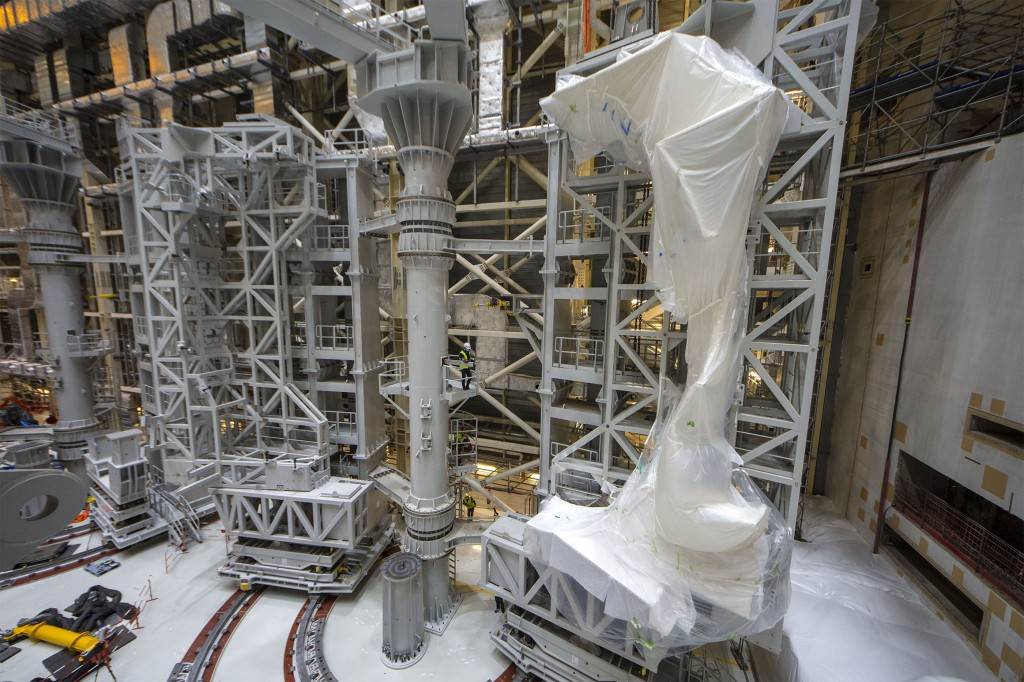

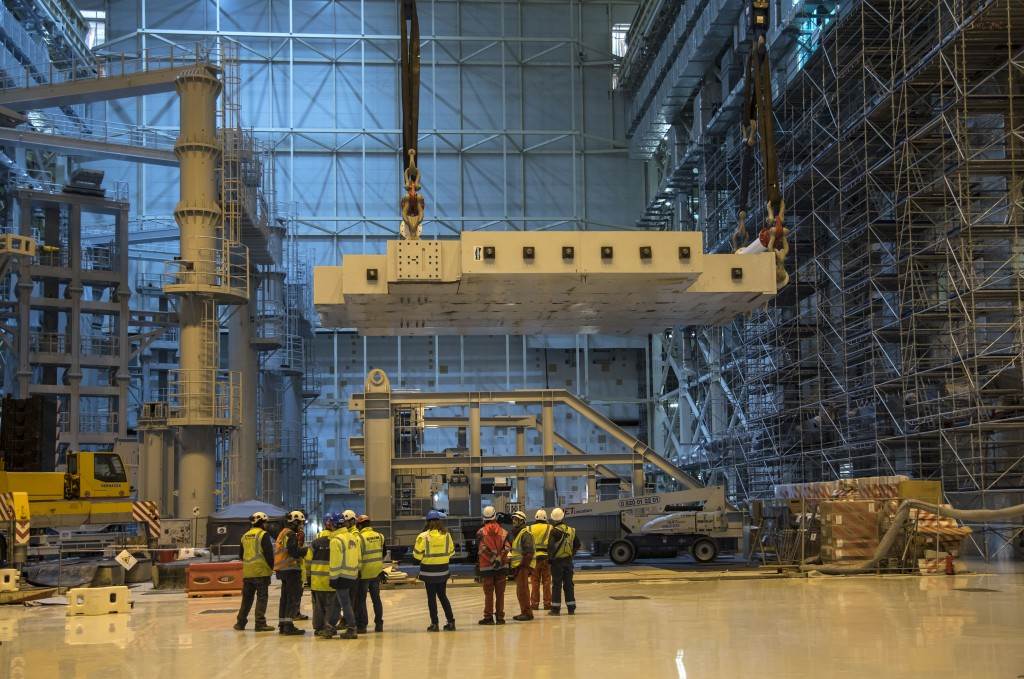
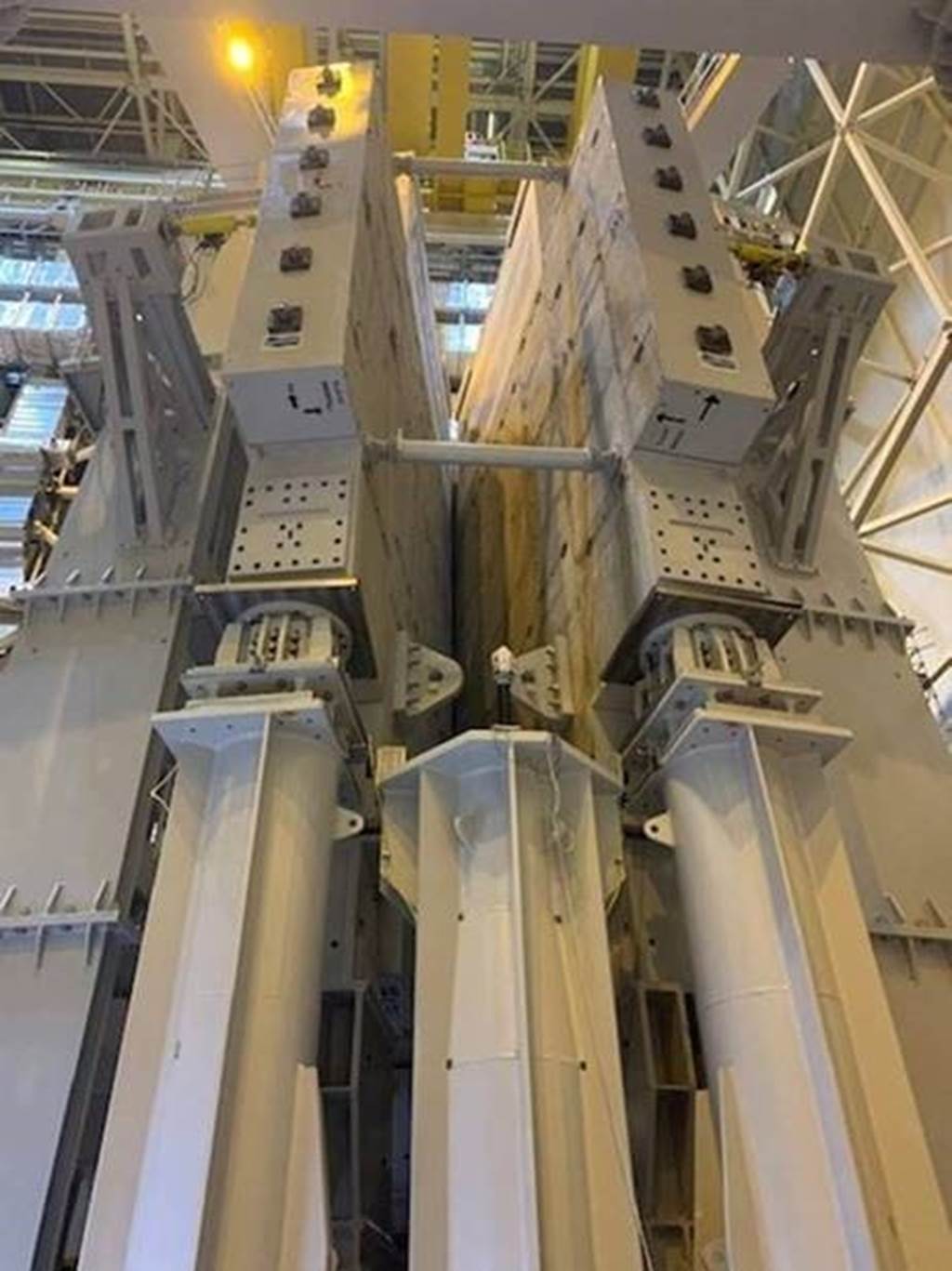








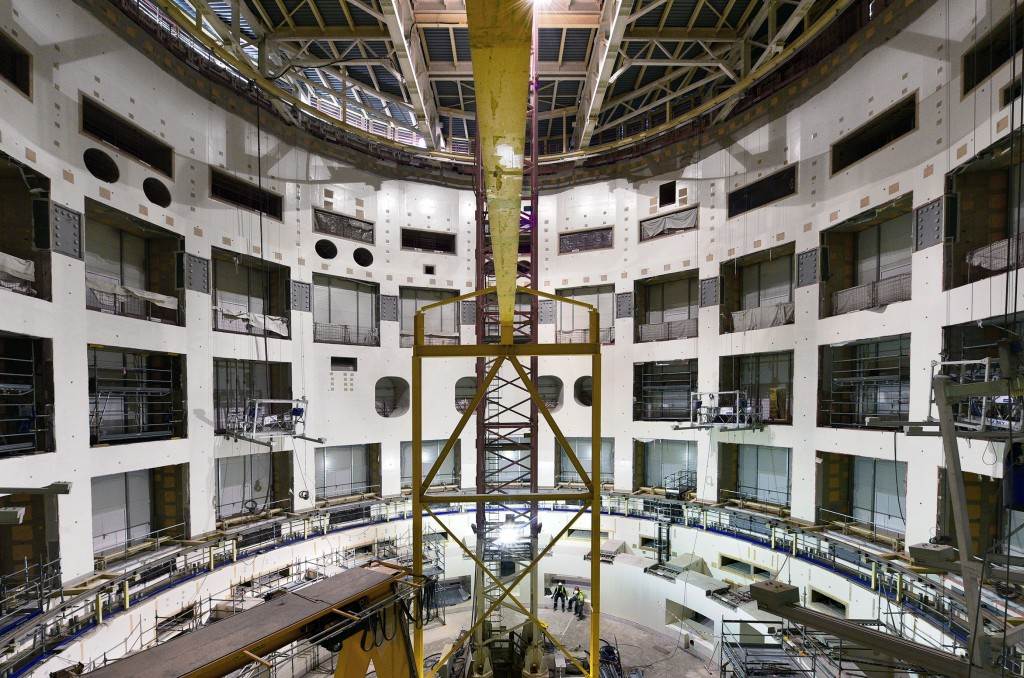
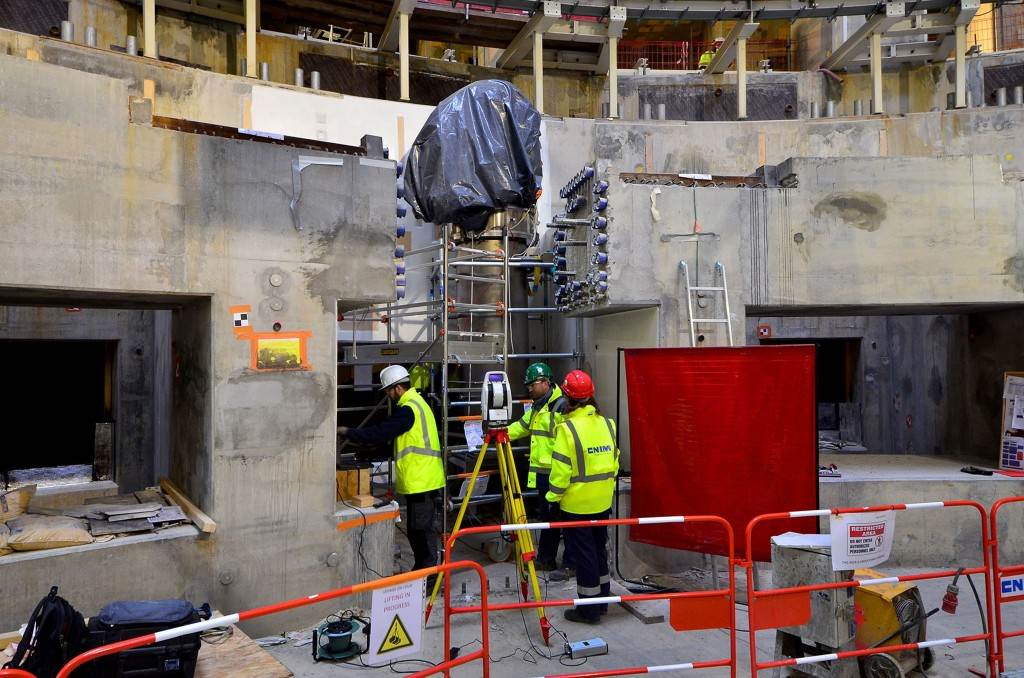
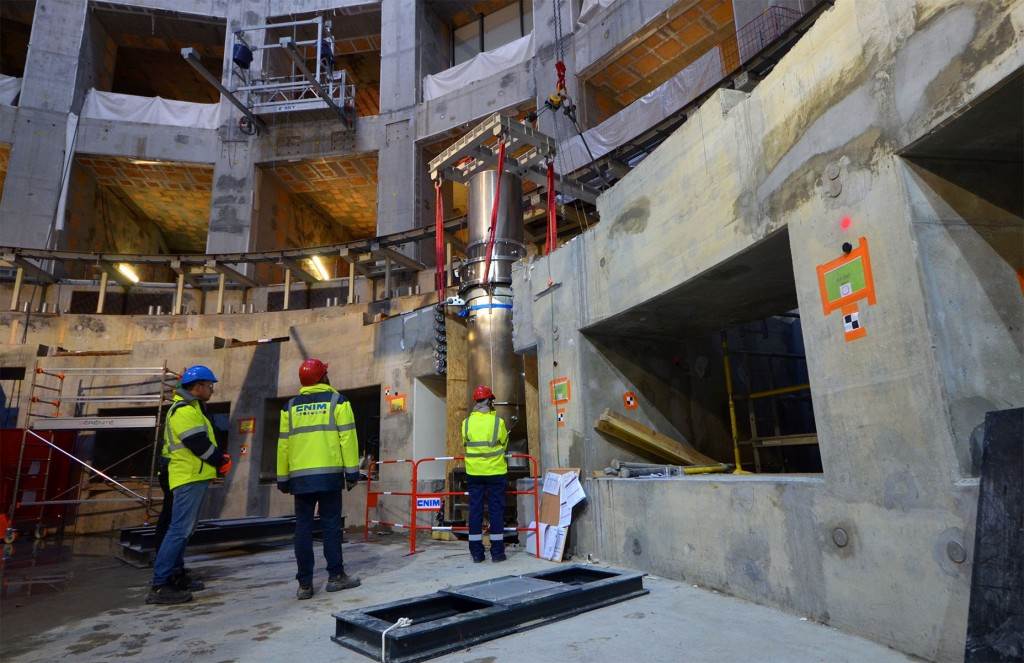
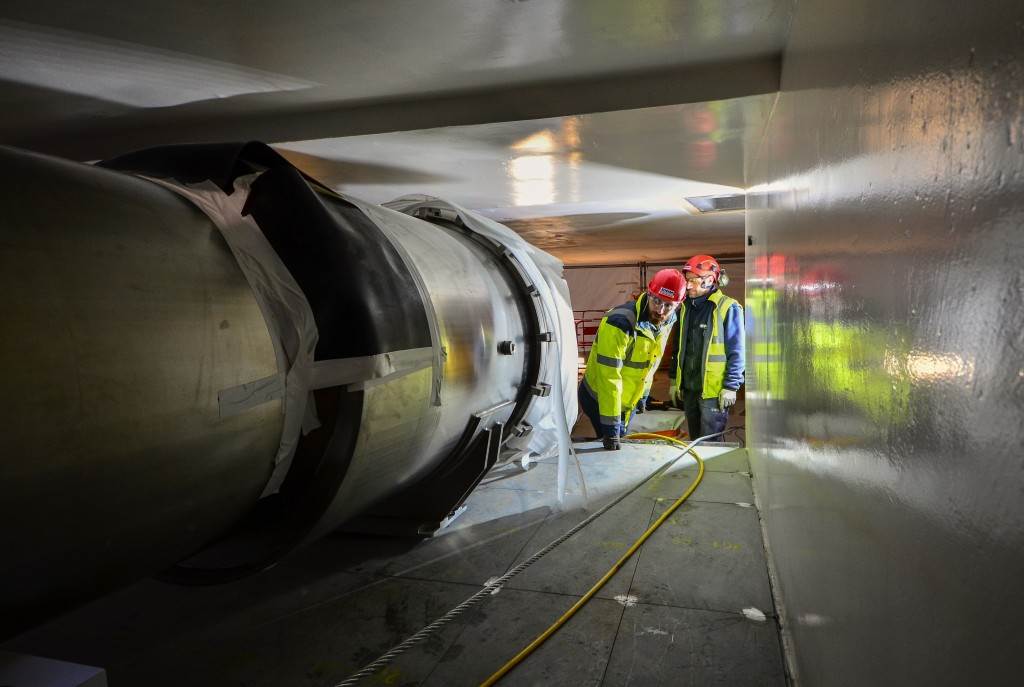

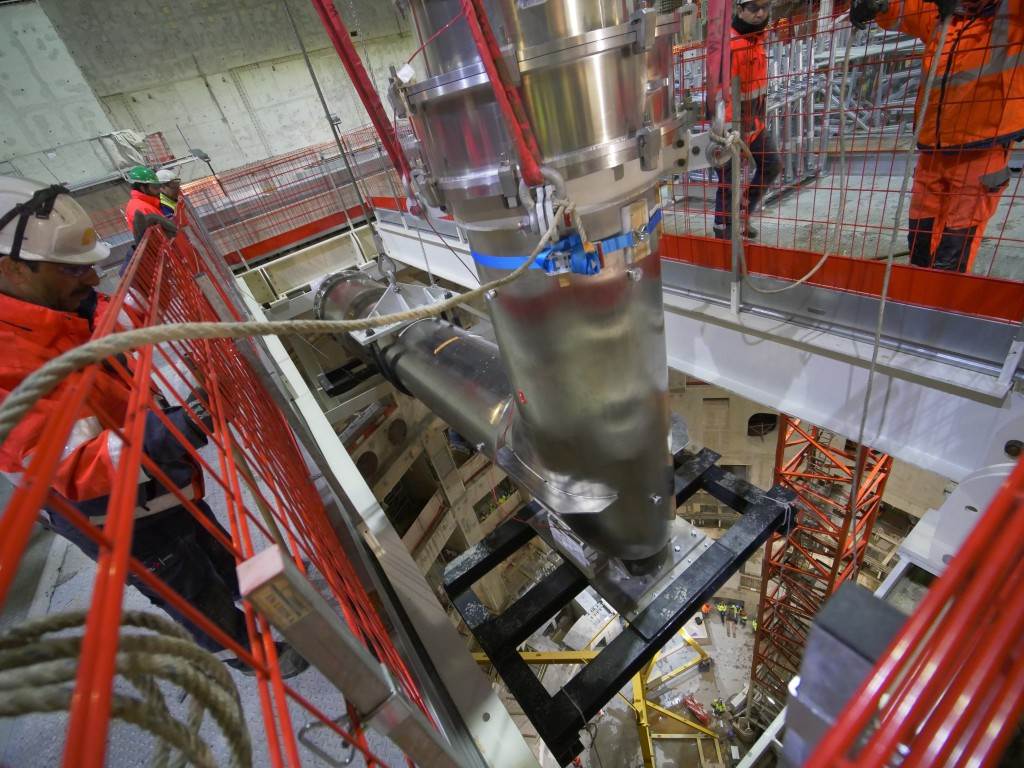





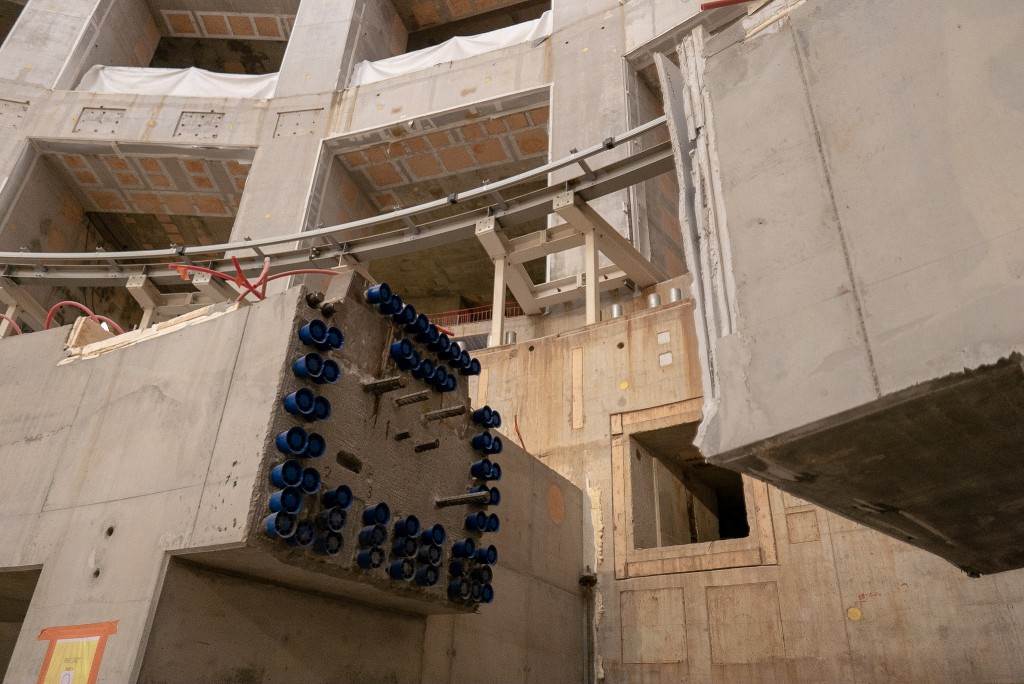

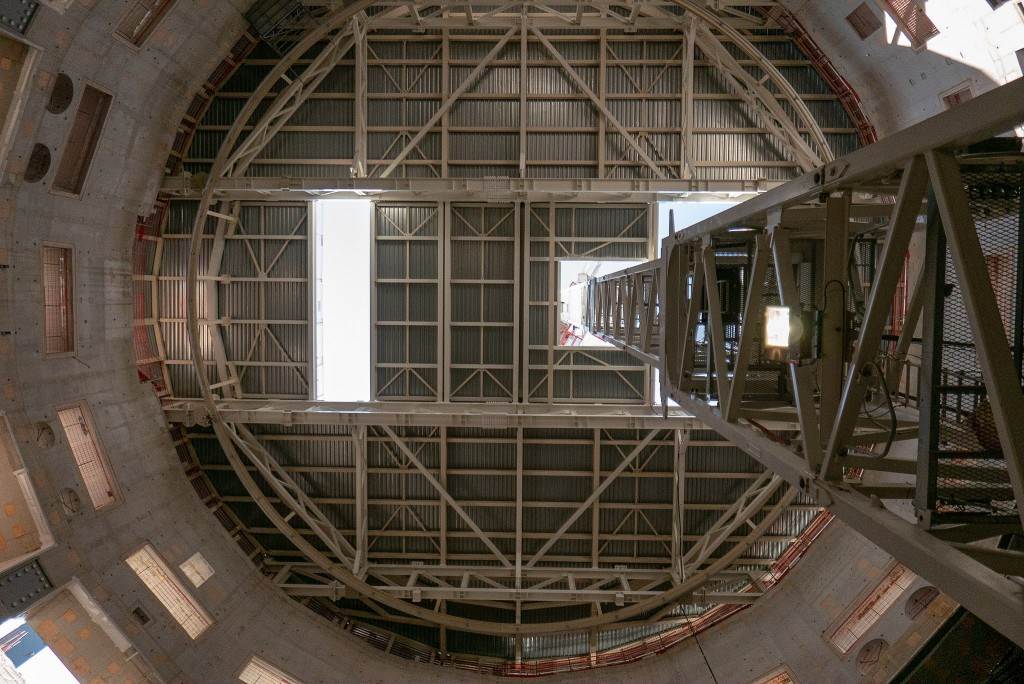
23,000
tonnes
1,000,000
components
1,200
engineering packages
10
years
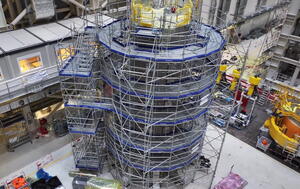
ITER by drone - May 2025 (subtitle version)
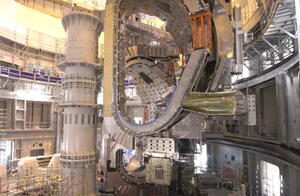
2d sector successfully installed
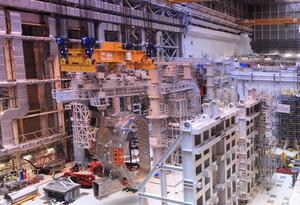
First European sector docked in tooling

A consequential lift, told by the teams

Take-off and landing of sector module #7
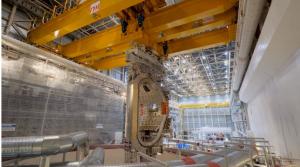
A four-day "reverse lift"
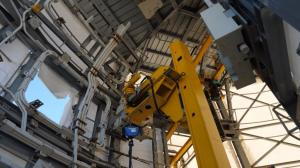
Manipulator arms: super strong and ultra precise

Tokamak assembly: The module has landed
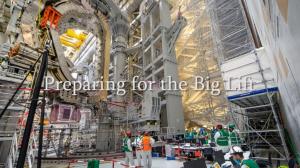
Preparing for the Big Lift
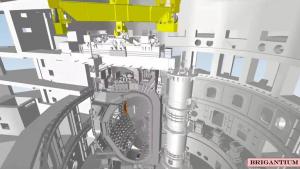
Installing a 40° section of the ITER vacuum vessel (Brigantium Engineering)
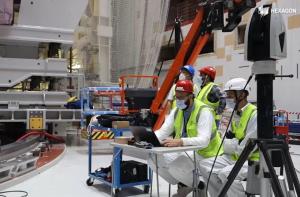
Metrology-assisted assembly at the ITER nuclear fusion project (Hexagon)

Machine Assembly
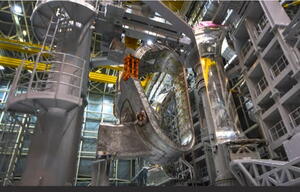
Bringing a vacuum vessel sector into tooling
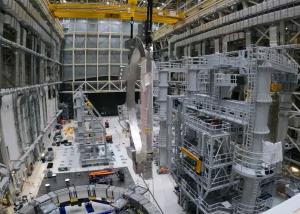
Major lift to assembly tooling (Ortec)
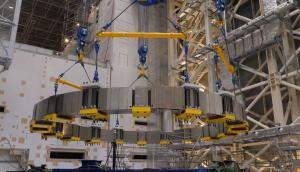
First ring-shaped coil produced on site is positioned in assembly pit
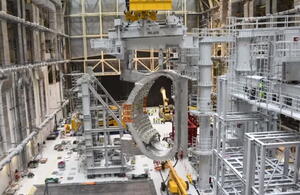
First vacuum vessel sector safely docked
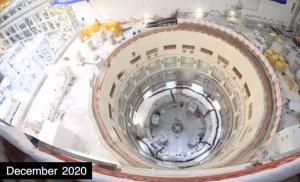
Time-lapsing through machine assembly (May 2020-March 2021)

Largest tokamak component installed
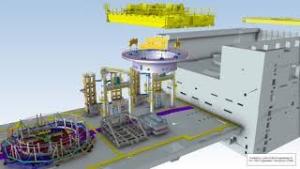
4D: Cryostat base lift
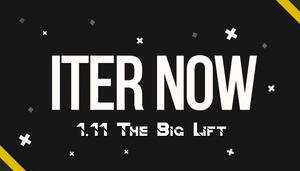
ITER NOW 1.11: The Big Lift
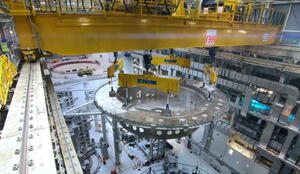
First machine component installed
Assembly challenges
Alignment
Accurate alignment, particularly of the magnet system and in-vessel components, is essential to the successful operation of the machine. Dimensional control is critical to ensuring that tolerances are respected, and to recording the "as-built" status of the machine, which will be directly compared against ITER's Computer-Aided-Design (CAD) models in order to correct eventual deviations in alignment before they accumulate. Positional tolerances for the largest components, including the magnet coils and the vacuum vessel, are as low as 2 mm. (For more information, see Metrology.)
Ultra-high and high vacuum
ITER will host one of the largest and the most complex high vacuum systems ever built. To ensure correct machine performance, all connections associated with ultra-high vacuum or high vacuum components must be 100 percent leak-tight. Vacuum lines, helium lines, pipes, valves, seals, joints, and/or flanges have all gone through pre-qualification, while some of the largest vacuum components—for example, the seals manufactured for the vacuum vessel‘s 50+ large ports—are being tested on dedicated test rigs. For in-pit assembly, only qualified welding procedures, carried out by certified professionals, are employed, and the quality of all vacuum-related welds is verified by surface and volumetric non-destructive examination. Full-scale leak testing is planned during the integrated commissioning period before the Start of Research Operations, in which the large vacuum chambers—the vacuum vessel and the cryostat—are evacuated and leak tested. In parallel, the ITER Organization is developing a set of specialized tools and technologies for the localization and detection of leaks smaller than the width of a human hair divided by one million.
Logistics
The ITER Organization and its assembly partners are managing a large volume of assembly activities—such as major lifting operations, handling/positioning, mechanical fixation, welding, cabling, pipe work, metrology, non-destructive examination, and leak testing—all in the extremely crowded environment of the Tokamak pit and the Tokamak Complex. Close coordination between assembly contractors and supervision teams is crucial.
Vacuum vessel welding
Welding the ITER vacuum vessel and ports inside of the assembly pit will require several years, a large skilled team, and a host of customized techniques and tools. The welding tools will have to manoeuvre the complex geometry of the sectors and ports and reach areas that are not directly accessible to operators and where visibility is restricted. The robots will also be confined to welding from inside the vessel and ports, as the pre-installed vacuum vessel thermal shield makes access to the exterior surfaces impossible. Extensive trials on mockups have been performed to quantify and plan for shrinkage and deformation, and to qualify tools, processes, and inspection techniques.
French nuclear regulations
As the nuclear operator of the ITER installation, the ITER Organization has an obligation to ensure that safety and security standards are implemented and enforced throughout construction, manufacturing, assembly, and operation in compliance with the Host country's safety and security regulations. All activities related to a safety-important or protection-important component or system (for example ITER's first confinement barrier, the vacuum vessel) must be performed correctly and documented as verified through regular surveillance and inspection.
Interfaces
Once delivered to the site, the interfacing elements for a number of large components such as the ITER blanket and the divertor have to be customized to comply with precise alignment requirements. Assembly contractors will have to use dimensional control and reverse engineering to plot out this customization, and must provide the workshop space, tooling and expertise to carry out the work on short timescales.
Schedule
Throughout Assembly Phase I, the ITER Organization will rely heavily on the on-time delivery of components and systems from the seven Domestic Agencies. Any delay related to fabrication or transport risks disrupting the carefully planned assembly sequences, especially for time-critical components such as the magnets or the vacuum vessel sectors.