Seeing ITER at millimetre-level resolution
Since last year, anyone at ITER can have access to an integrated 3D model that takes them from the highest-level view of the entire site, all the way down to a millimetre-level view of any component of the machine or plant.
The new solution was developed by the ITER Design Office in collaboration with ITER IT. Every week, output is extracted from all CAD tools—around 20 terabytes of data in over 100,000 files—and converted to a common format on a high-performance server. The resulting integrated model is only a few gigabytes that can be downloaded to a standard laptop or workstation, where it can be viewed through Navisworks 3D Viewer, a software package used in many other large projects.
One of the reasons the integrated model can be made so much smaller is that it only needs to be viewable, not editable. But according to Mickael Chabre, a design office infrastructure engineer, the model can also be enriched with the engineering properties of components. “For example, you can look for a specific valve and visualize it in its environment,” he says. “If you want to see the properties of the valve, meaning its nominal size, its safety class, and so on, that is possible thanks to the connection between Navisworks and the engineering database.”
Prior to June 2024, it was possible to view a design model in the context of its environment through a software package called 3DLive. “But that required an advanced level of CAD knowledge and could not be connected to an external engineering database to enrich the model,” says Jean-Daniel Delaplagne, group leader in IT in charge of support of the CAD infrastructure and construction tools.
Designers primarily use one of two CAD software platforms to develop 3D models—Dassault System’s Catia V5 for mechanical design, and Aveva’s E3D for plant design, which includes studies like piping, HVAC systems, structural supports and electrical components. Because each platform uses proprietary formats, before last June anybody wanting to view a model with its engineering attributes had to use the CAD system the model was developed on, which requires a license. That gets costly as the number of people viewing a design increases. And people who just want to view a model generally need training to use the complex tools intended for advanced design.
The new platform is user-friendly and provides a view of the entire site (see the short video clip below). License costs for the Navisworks 3D Viewer are low and there is a free version for “basic users.” The desktop version is already available as a download, but IT now plans to integrate it within the ITER Collaboration Platform (ICP), as a web version that requires no additional software. This will make it easier to access.
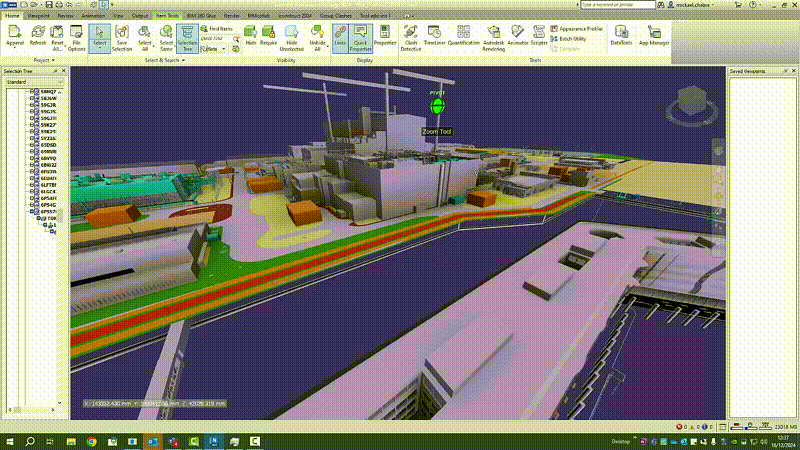
The technology made available in June meets a need that the project and the design offices identified a long time ago: a view of any part of the plant, available to everybody. The new tool allows engineers to see everything located around a system they are designing to make sure there are no clashes. It also provides construction teams with a 3D model of what they have to install and everything around it. Finally, the model can be used to prepare a site visit, allowing hosts to see where they will be taking visitors.
These use cases are just the beginning. According to Delaplagne, a new solution is now being piloted to enhance design reviews using mixed reality. Engineers and project managers can wear Meta Quest headsets to view the 3D model remotely as if they were standing in the room, which will hopefully improve productivity.
“The Design Office manages the 3D CAD software,” says Chabre. “But without help from IT, we could not have automated the extraction of the data coming from CAD software and merge it into a single platform.” While Navisworks is being used now, Chabre says that if a decision is made in the future to replace it with another solution, the input data is already available and can be pushed to the new platform.
The integrated model, which currently provides an as-designed view of ITER, will be updated with as-built information to enable a whole new set of use cases. Scanning is already underway in some of the buildings to collect and catalog what has already been installed. “We use a laser scanning solution, Cintoo, to manage scans of the buildings, creating billions of points down to millimetre-level precision,” says Delaplagne. “This will allow people to compare as-designed and as-built. One can be superposed on the other to reveal the delta.”