Magnets

The ITER magnet system will be the largest and most integrated superconducting magnet system ever built.
Ten thousand tonnes of magnets, with a combined stored magnetic energy of 51 Gigajoules (GJ), will produce the magnetic fields that will initiate, confine, shape and control the ITER plasma. Manufactured from niobium-tin (Nb3Sn) or niobium-titanium (Nb-Ti), the magnets become superconducting when cooled with supercritical helium in the range of 4 Kelvin (-269 °C).
Superconducting magnets are able to carry higher current and produce stronger magnetic field than conventional counterparts. They also consume less power and are cheaper to operate ... making superconducting magnet technology the only option for ITER's huge magnet systems.
ITER uses high-performance, internally cooled superconductors called "cable-in-conduit conductors," in which bundled superconducting strands—mixed with copper—are cabled together and contained in a structural steel jacket.
For the most technically challenging raw material—the niobium-tin (Nb3Sn) superconducting strands used in ITER's toroidal field and central solenoid magnet systems—500 metric tons of strand (more than 100,000 km) were produced by nine suppliers in a procurement effort that lasted from 2008 to 2015. This large-scale industrial effort demanded a ramp-up of global production capacity from 15 metric tons/year to 100 metric tons/year, as well as the introduction of three new strand suppliers.
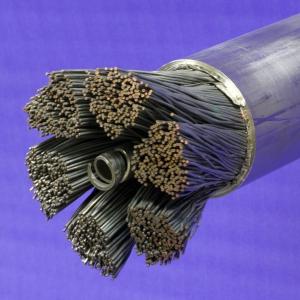
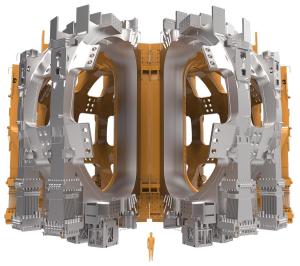
Toroidal Field System
Eighteen "D"-shaped toroidal field magnets placed around the vacuum vessel produce a magnetic field whose primary function is to confine the plasma particles. The toroidal field coils are designed to produce a total magnetic energy of 41 gigajoules and a maximum magnetic field of 11.8 tesla. Weighing 330 tonnes each, and measuring 9 x 17 m, they are among the largest components of the ITER machine.
Toroidal field coils are wound in "double pancakes"—layers of spiralled conductor embedded in radial plates and encased in large stainless steel structures. With a total weight of 3,400 tonnes, the "superstructure" of toroidal field coils pushes the limits of manufacturability. Because the precision of coil geometry is critical to creating the magnetic field required for plasma confinement, any non-conformity of fabrication tolerances or assembly misalignments can result in errors in magnetic configuration. As a result, particular attention has been paid to dimensional control throughout the fabrication process—from the manufacturing of the core winding pack and case structures, to the insertion of the winding pack inside of the case, and finally closure welding and final machining.
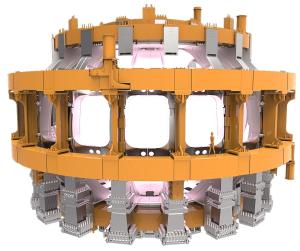
Poloidal Field System
Six ring-shaped poloidal field coils are situated outside of the toroidal field magnet structure to shape the plasma and contribute to its stability by "pinching" it away from the walls. The largest coil has a diameter of 24 metres; the heaviest is 400 tonnes. The poloidal field coils are designed to produce a total magnetic energy of 4 gigajoules and a maximum magnetic field of 6 tesla.
The four largest poloidal field coils were produced from niobium-titanium superconductor in an on-site winding facility between 2016 and 2024 (see more on on-site fabrication here).
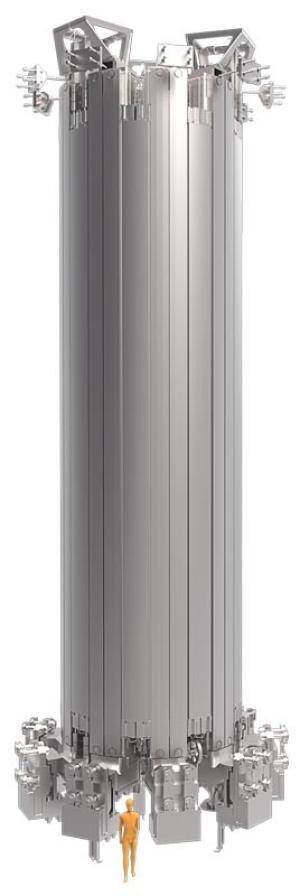
Central Solenoid
The central solenoid is the "backbone" of ITER's magnet system, allowing a powerful current to be induced in the ITER plasma and maintained during long plasma pulses. Thirteen metres tall (18 metres, with structure), four metres wide and one thousand tonnes, the central solenoid is made of six independent coil packs wound from niobium-tin superconducting cable.
Stored magnetic energy of 6.4 GJ in the central solenoid will initiate and sustain a plasma current of 15 MA for durations of 300-500 seconds. Maximum field of 13 tesla will be reached in the centre of the stacked modules, making the central solenoid the most powerful of all ITER magnet systems.
The independently operating coil packs will create large electromagnetic forces that pull in different directions. In order to maintain the structural integrity of the central solenoid assembly, a special support structure has been designed. The support structure will have to withstand forces in the range of 60 meganewtons, or over 6,000 tonnes of force. (In comparison, the force behind the thrust of a Space Shuttle lift off is about 30 meganewtons.)

Correction Coils
Eighteen superconducting correction coils inserted between the toroidal and poloidal field coils will compensate for field errors caused by geometrical deviations due to manufacturing and assembly tolerances. Although much lighter and thinner than the toroidal and poloidal field coils—and running a smaller current (10 kA)—the correction coils measure up to 8 metres in width and present particular challenges for assembly and installation.
The correction coils will be arranged in groups of six around the toroidal circumference above, at and below the mid-plane of the vacuum vessel.

Magnet Feeders
Magnet feeders are vital for the operation of the ITER Tokamak, conveying and regulating the cryogenic liquids to cool and control the temperature of the magnets and connecting the magnets to their power supplies. In total, 31 superconducting feeders will relay electrical power and cryogens through the warm-cold barrier to the ITER magnets.
The design operating current of the feeders is 68Ka. High temperature superconductor (HTS) current leads transmit the high-power currents from the room-temperature power supplies to the low-temperature superconducting coils 4K (-269°C) with minimum heat load.
Superconducting busbars, made out of steel conduit containing niobium-titanium superconductor cable, are designed to absorb the large temperature variations during the cool-down of the machine.
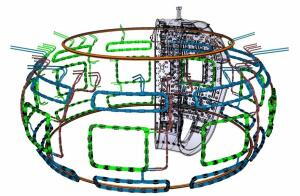
In-Vessel Coils
Two non-superconducting coil systems inside of the ITER vacuum vessel provide additional plasma control capabilities. Two vertical stability coils installed above and below the machine's mid-plane provide fast vertical stabilization of the plasma; another set of 27 coils fixed to the wall of the vessel create resonant magnetic perturbations in the plasma so that certain types of plasma instabilities, called Edge-Localized Modes (ELMs), are avoided.
The vertical stability and ELM coils are manufactured from a special type of mineral-insulated copper conductor, designed to withstand the demanding conditions inside of the machine.
Related articles
The other components
Please note that all images are for illustrative purposes only.