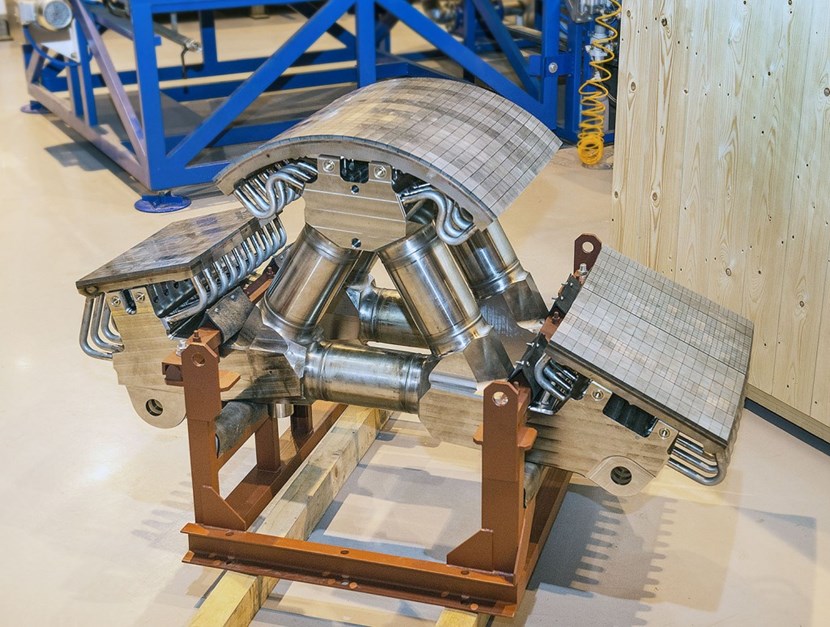
This 1-tonne divertor dome full-scale prototype passed all factory acceptance tests in Russia before shipment, including the stringent hot helium leak test (three heating/pressure cycles (250oC; 4 MPa)). The tungsten tiles developed in Russia have demonstrated thermal resistance under cycling high thermal loads, typically, thousands of cycles at 5 and 10 MW/m².
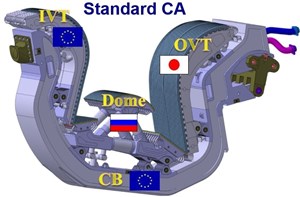
As ions and electrons in the plasma move along field lines created by the superconducting magnets of the tokamak, the impurities are pumped into the vicinity of the divertor strike points at the bottom of the vacuum vessel for evacuation and recycling. The precise tilting and shaping of the baffles and individual monoblocks (in dark blue, these are the tungsten tiles coating the plasma-facing elements) are critical to the performance of the divertor.
In a tokamak device, the divertor is the component at the base of the plasma chamber that extracts heat and ash produced by the fusion reaction, minimizes plasma contamination, and protects the surrounding walls from thermal and neutronic loads. The divertor is carefully engineered to withstand large heat and particle fluxes on its plasma-facing surfaces—the inner and outer vertical targets and the dome—while providing exhaust channels for the escaping material.