ITER NEWSLINE
-
Poloidal field coils
Winding activities end in Russia
Alexander Petrov, ITER Russia
Poloidal field coils | Winding activities end in Russia
Specialists of the Sredne-Nevsky Shipyard and the Efremov Institute in Saint Petersburg have completed the eight double pancake windings required for poloidal field coil #1. After the vacuum pressure impregnation of each double pancake, the team will start assembling the coil.
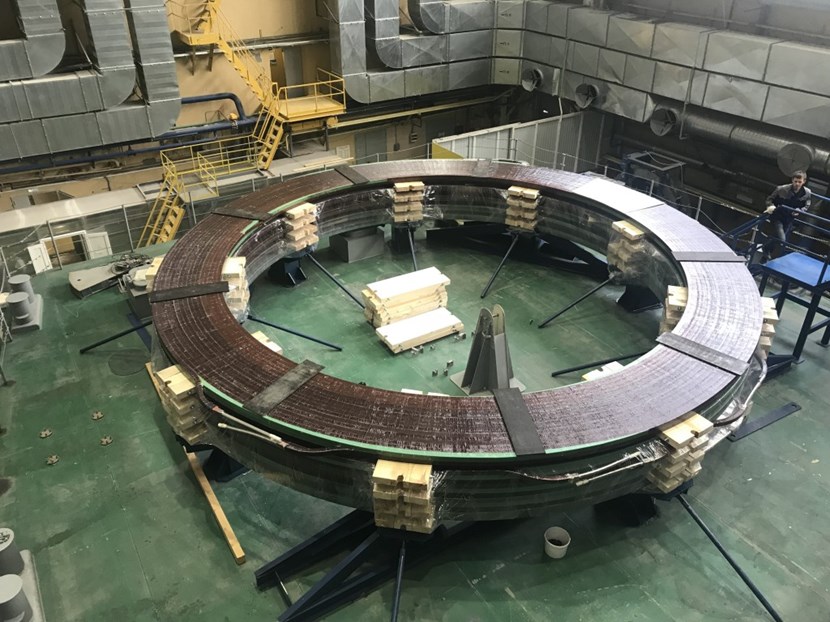
Shown stacked, the first five double pancakes have become hardened assemblies after the application of epoxy resin in a procedure known as vacuum pressure impregnation, or VPI.
Under the responsibility of the Russian Domestic Agency, the fabrication of poloidal field coil #1 (PF1)—the smallest of ITER's six poloidal field coils—is progressing. Eight double pancakes made from coiled layers of niobium-titanium conductor have come off the fabrication line and six have undergone vacuum pressure impregnation—the phase during which epoxy resin hardens the insulation materials wrapped around each conductor turn and creates a rigid assembly. The impregnated double pancakes will be stacked and joined electrically to form a final nine-metre-in diameter magnet coil weighing close to 200 tonnes.
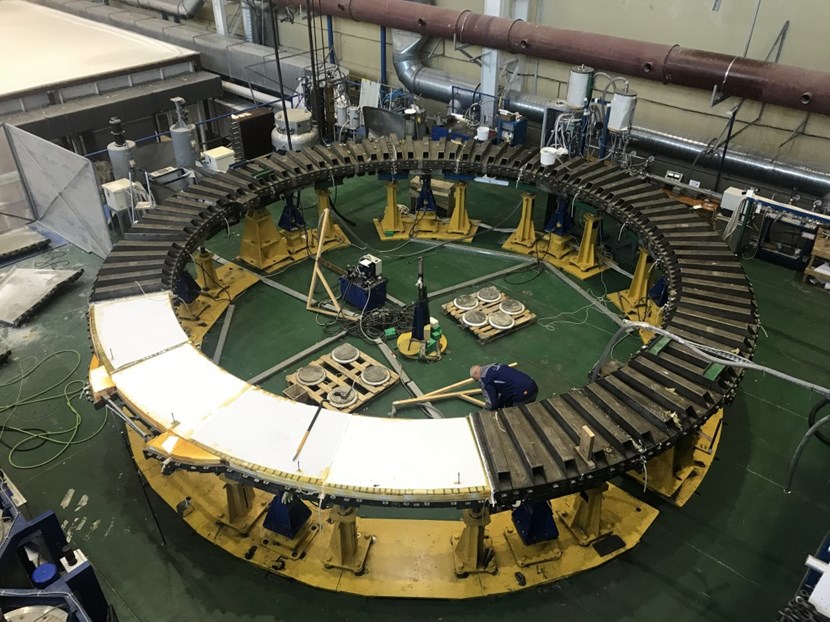
The mould is coming off the sixth double pancake after vacuum pressure impregnation. The nine-metre-in-diameter pancakes will be stacked and joined electrically.
Double pancake winding is a highly precise technical operation that has required the development of advanced technologies and processes. The most important technologies for the fabrication of PF1 were developed at the Efremov Institute (JSC "NIIEFA"), which also designed, manufactured and tested a large part of the equipment. From the signing of the
Procurement Arrangement with the ITER Organization in 2011, through the fabrication of poloidal field
conductor and the latest milestone—winding completion—development and manufacturing activities have required eight years to date.
Coil manufacture is underway at the Sredne-Nevsky Shipyard near Saint Petersburg, where the finalized coil assembly will leave the plant directly atop a barge for the nearby Neva River. (
See more on the Shipyard's barge/assembly platform here.) The completed coil is expected early in 2021.
return to the latest published articles